Friedrich Air Conditioner Mr09C1H Users Manual DSS_Manual_05 05 11
MR12C1H to the manual 5db71477-e6e6-414f-9331-8b3cbeffb404
2015-02-02
: Friedrich Friedrich-Friedrich-Air-Conditioner-Mr09C1H-Users-Manual-428260 friedrich-friedrich-air-conditioner-mr09c1h-users-manual-428260 friedrich pdf
Open the PDF directly: View PDF .
Page Count: 88
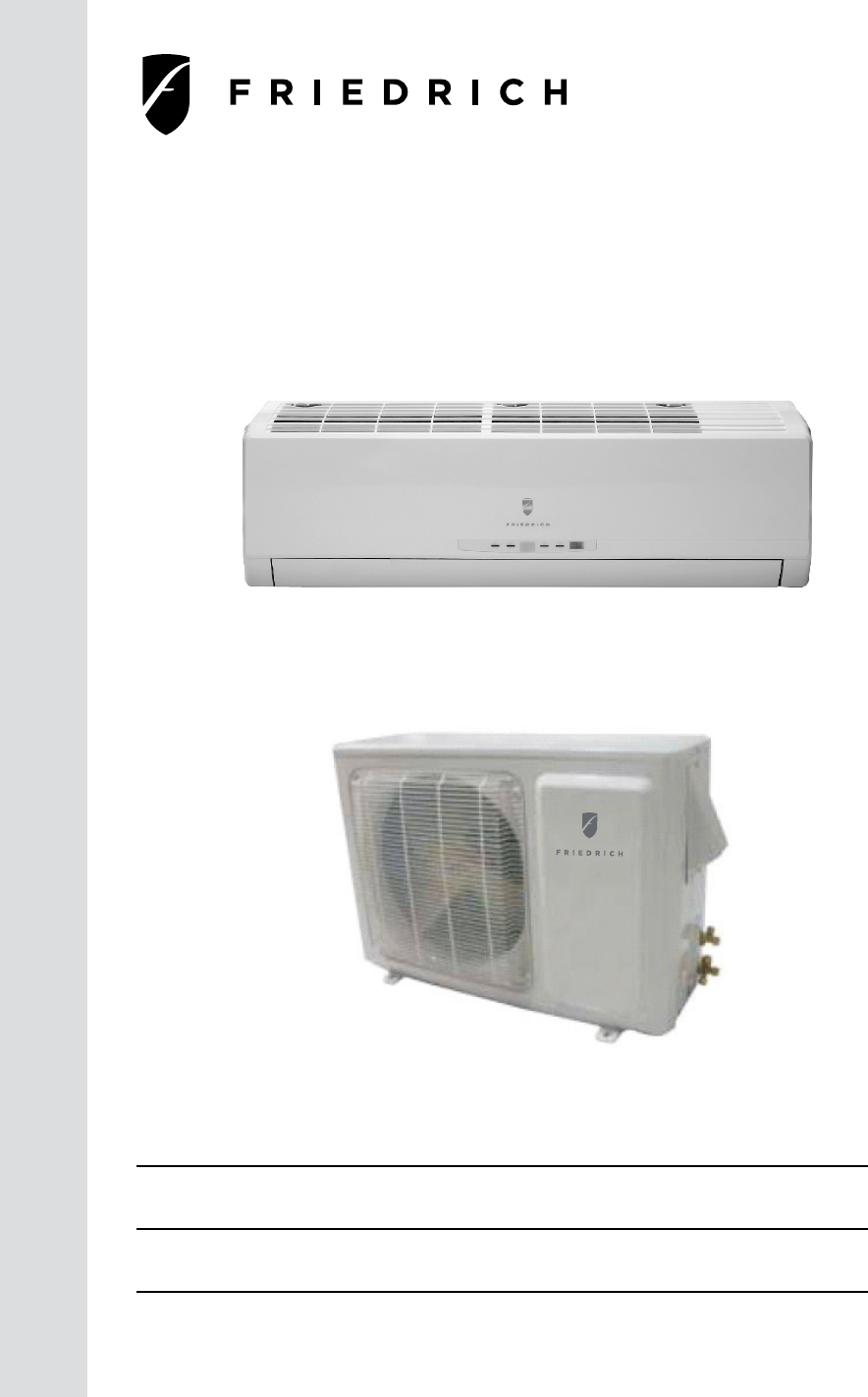
2 0 11
SPLIT TYPE ROOM AIR CONDITIONER
WALL MOUNTED TYPE
Models
Indoor Unit
Outdoor Unit
Service and Parts Manual
MW09C1H
MR09C1H
MW12C1H
MR12C1H

1. Safety Precautions ...............................................................................................................
2. Specifications ...........................................................................................................................
3. Construction Views
4. Refrigerant System Diagram .......................................................................................
5. Schematic Diagram
6. Function and Control .......................................................................................................
.....................................................................................................
...........................................................................................................
7. Installation Manual ............................................................................................................
9. Removal Procedure .......................................................................................................
10. Exploded Views and Parts List .............................................................................
2.1 Unit Specifications...........................................................................................................
2.2 Operation Date
2.3Expanded capacity data tables for both cooling and heating
3.1 Indoor Unit
3.2 Outdoor Unit
5.1 Electrical Date
8. Troubleshooting ...................................................................................................................
.................................................................................................................
9.1 Precautions before Performing Inspection or Repair ....................................................
9.2 Confirmation
Summary and features
2.4 Operation Characteristic Curven
......................................
......................................................................................
..............................................................................................................
.......................................................................................................................
....................................................................................................................
..............................................................................................................
...............................................................................................................
2.5 Noise criteria curve tables for both models....................................................................
9.3 Judgement by Flashing LED of Indoor/Outdoor Unit ...........................................................
....................................................................................
..................................................................................................
Model and product code
.........................................................................................................
9.4 How to Check simply the main part
5.2 Electrical Wiring
5.3 Printed Circuit Board
.................................................................................................................
2
3
4
5-7
16
16
16
17
18-21
22-35
20-21
18-19
18
36-43
44-72
44
44
44-51
52-62
73-78
79-85
8
8-11
12
13
14
15
Table of Contents

Model and product code
Model and product code
M09CIH115V ~ 60H W09CIH MR09CIH
M12CH115V ~ 60H W12CIH MR12CIH
Voltage range Complete unit model Indoor unit model Outdoor unit model
M
MzM
zM
3

Outdoor Unit
MR09CI H
MR012CIH
Remote control windo w
YB1FAF
Summary and features
Summary and features
4

5
IMPORTANT SAFETY INFORMATION
Th e inf or m a ti on co nt ain ed i n thi s ma nua l is inten de d fo r use by a qua l if i ed ser vi c e
technician who is familiar with the safety procedures required for installation and repair, and
who is equipped with the proper tools and test instruments required to ser vice this product.
Installation or repairs made by unqualifi ed persons can result in subjecting the unqualifi ed person making
such repairs as well as the persons being served by the equipment to hazards resulting in injury or electrical
shock which can be serious or even fatal.
Safety warnings have been placed throughout this manual to alert you to potential hazards that may be
encountered. If you install or perform service on equipment, it is your responsibility to read and obey these
warnings to guard against any bodily injury or property damage which may result to you or others.
PERSONAL INJURY OR DEATH HAZARDS
ELECTRICAL HAZARDS:
• Unplug and/or disconnect all electrical power to the unit before performing inspections, maintenance,
or service.
• Make sure to follow proper lockout/tag out procedures.
• Always work in the company of a qualifi ed assistant if possible.
• Capacitors, even when disconnected from the electrical power source, retain an electrical charge
potential capable of causing electric shock or electrocution.
• Handle, discharge, and test capacitors according to safe, established, standards, and approved
procedures.
• Extreme care, proper judgment, and safety procedures must be exercised if it becomes necessary
to test or troubleshoot equipment with the power on to the unit.
Your safety and the safety of others are very important.
We have provided many important safety messages in this manual and on your appliance. Always read, understand and obey
all safety messages.
All safety messages will tell you what the potential hazard is, tell you how to reduce the chance of injury, and tell you what will
happen if the instructions are not followed.
This is a safety Alert symbol.
This symbol alerts you to potential hazards that can kill or hurt you and others.
All safety messages will follow the safety alert symbol with the word “WARNING” or “CAUTION”.
These words mean:
You can be killed or seriously injured if you do not follow instructions.
You can receive minor or moderate injury if you do not follow instructions.
A message to alert you of potential property damage will have the word “NOTICE”.
Potential property damage can occur if instructions are not followed.
WARNING
CAUTION
NOTICE
• Do not spray or pour water on the return air grille, discharge air grille, evaporator coil, control panel,
and sleeve on the room side of the air conditioning unit while cleaning.
• Electrical component malfunction caused by water could result in electric shock or other electrically
unsafe conditions when the power is restored and the unit is turned on, even after the exterior is dry.
• Never operate the A/C unit with wet hands.
• Use air conditioner on a single dedicated circuit within the specifi ed amperage rating.
• Use on a properly grounded outlet only.
• Do not remove ground prong of plug.
• Do not cut or modify the power supply cord.
• Do not use extension cords with the unit.
• Follow all safety precautions and use proper and adequate protective safety aids such as: gloves,
goggles, clothing, adequately insulated tools, and testing equipment etc.
• Failure to follow proper safety procedures and/or these warnings can result in serious injury or death.
REFRIGERATION SYSTEM REPAIR HAZARDS:
• Use approved standard refrigerant recovering procedures and equipment to relieve pressure before
opening system for repair.
• Do not allow liquid refrigerant to contact skin. Direct contact with liquid refrigerant can result in minor
to moderate injury.
• Be extremely careful when using an oxy-acetylene torch. Direct contact with the torch’s fl ame or hot
surfaces can cause serious burns.
• Make sure to protect personal and surrounding property with fi re proof materials.
• Have a fi re extinguisher at hand while using a torch.
• Provide adequate ventilation to vent off toxic fumes, and work with a qualifi ed assistant whenever
possible.
• Always use a pressure regulator when using dry nitrogen to test the sealed refrigeration system for
leaks, fl ushing etc.
• Make sure to follow all safety precautions and to use proper protective safety aids such as: gloves,
safety glasses, clothing etc.
• Failure to follow proper safety procedures and/or these warnings can result in serious injury or death.
MECHANICAL HAZARDS:
• Extreme care, proper judgment and all safety procedures must be followed when testing,
troubleshooting, handling, or working around unit with moving and/or rotating parts.
• Be careful when, handling and working around exposed edges and corners of the sleeve, chassis,
and other unit components especially the sharp fi ns of the indoor and outdoor coils.
• Use proper and adequate protective aids such as: gloves, clothing, safety glasses etc.
• Failure to follow proper safety procedures and/or these warnings can result in serious injury or death.
6
PROPERTY DAMAGE HAZARDS
FIRE DAMAGE HAZARDS:
• Read the Installation/Operation Manual for the air conditioning unit prior to operating.
• Use air conditioner on a single dedicated circuit within the specifi ed amperage rating.
• Connect to a properly grounded outlet only.
• Do not remove ground prong of plug.
• Do not cut or modify the power supply cord.
• Do not use extension cords with the unit.
• Be extremely careful when using acetylene torch and protect surrounding property.
• Failure to follow these instructions can result in fi re and minor to serious property damage.
WATER DAMAGE HAZARDS:
• Improper installation, maintenance or servicing of the air conditioner unit can result in water damage
to personal items or property.
• Insure that the unit has a suffi cient pitch to the outside to allow water to drain from the unit.
• Do not drill holes in the bottom of the drain pan or the underside of the unit.
• Failure to follow these instructions can result in damage to the unit and/or minor to serious property
damage.
7

8
Rating conditions are:
Cooling: Indoor air temperature 80¡F D.B. / 67¡F W.B.
Outdoor air temperature 95.0¡F D.B. / 75¡F W.B.
Heating: Indoor air temperature 70¡F D.B./ 60¡F W.B.
Outdoor air temperature 47¡F D.B. / 43¡F W.B.
MW09CIH
COOLING
115V~
07zHhgiH
14zHdradnatS
51zHwoL
High W / Btu/h 3100/10600
Standard W / Btu/h 2650/9000
Low W / Btu/h 1300/4435
0501WhgiH
046WdradnatS
081WwoL
0501WhgiH
046WdradnatS
8.61AhgiH
0.7AdradnatS
SH CFM 330
HCFM 294
MCFM 253
LCFM 218
1.69pints/hour
14.0W/W
22
MW09CIH
0621nim/rHS
0501nim/rH
029nim/rM
037nim/rL
02W
0.4F
A0.38
Cross flow fan
in. 3.62 X 25.4
Aluminum fin-copper tube
in.
in.
216
0.019 - 0.055in.
25.4 X 1 X 10.5
MP24AA
4.2W
A PCB 3.15A
43)A( BdH
03)A( BdM
62)A( BdL
44)A( BdH
04)A( BdM
63)A( BdL
33.3X10.8X11
36X10X14
16X24.3X130.9lbs
in.
in.
Power Input
(Inverter different Compressor
speed)
Model
Function
Rated Voltage
Frequency
(Inverter different Compressor
speed)
Total Capacity
(Inverter different Compressor
speed)
Sound Power Level
Fuse (A)
Fan
Evaporator
Swing
Motor
width (L)
Output
Type
Model
Net Weight /Gross Weight
Output
Capacitor
RLA
Diameter-Length
Pipe Diameter
Row-Fin Gap
Sound Pressure Level
Rated Input
Rated Current
Air Flow Volume
Fan Motor
Dehumidifying Volume
STD
Indoor unit
Speed
Outdoor Unit MR09C1H
Specifi cations
Turbo
Turbo
33 1/4 X 10 7/8 X 7 1/8
22

Rating
Remarks
conditions are:
Cooling: Indoor air temperature 26.7¡C D.B. / 19.4¡C W.B.
Outdoor air temperature 35.0¡C D.B. / 23.9¡C W.B.
Heating: Indoor air temperature 21.1¡C D.B./ 15.6¡C W.B.
Outdoor air temperature 8.33¡C D.B. / 6.11¡C W.B.
MW12CIH
208-230V~
07zHhgiH
14zHdradnatS
51zHwoL
4100/14000
3520/12000
1320/4500
hgiH
dradnatS
W / Btu/h
W / Btu/h
W / Btu/h
woL
0501WhgiH
046WdradnatS
081WwoL
0501WhgiH
046WdradnatS
5.6AhgiH
2.3AdradnatS
SH CFM
CFM
CFM
CFM
300
2H 77
2M 53
2L 18
2.54pints/hour
.12.00W/W
22
0621nim/rHS
0501nim/rH
029nim/rM
037nim/rL
02W
0.1F
A0.2
Cross flow fan
in.
in.
in.
in.
3.62X25.4
25.4X1X10.5
.276
in. 33.3X10.3X7.1
in. 36X10X14
lbs .26.3/30.9
.077-.055
Aluminum fin-copper tube
MP24AA
4.2W
A PCB 3.15A
43)A( BdH
03)A( BdM
62)A( BdL
44)A( BdH
04)A( BdM
63)A( BdL
Rated Input
Rated Current
Air Flow Volume
Fan Motor
Dehumidifying Volume
EER / C.O.P
Indoor unit
Speed
SEER/HSPF
Net Weight /Gross Weight
Output
Capacitor
RLA
Diameter-Length
Pipe Diameter
Row-Fin Gap
Sound Pressure Level
Sound Power Level
Fuse (A)
Fan
Evaporator
Swing
Motor
width (L)
Output
Type
Model
Power Input
(Inverter different Compressor
speed)
Mo
12K of 115V Models
del
Function COOLING
Rated Voltage
Frequency
(Inverter different Compressor
speed)
Total Capacity
(Inverter different Compressor
speed)
Specifications
9
115
Outdoor Unit MR12CH - SYSTEM
Turbo
Turbo
33 1/4 X 10 7/8 X 7 1/8
22

The above data is subject to change without notice. Please refer to the nameplate of the unit.
MR09C1H
SANYO
C-6RZ110H1A
Twin rotory
33A)A( .A.R.L
95.4A)A(ALR
Power Input(W) W 800
Int11l-3979
Electronic Expansion Valve
throttling
Transducer starting
Aluminum fin-copper tube
Pipe Diameter mm .275
2 - .005
Rows-Fin Gap in.
23.94 X 20 X 1.73
056/009mprdeepS
Output of Fan Motor W 40
71.0AALR
Capacitor μF /
CFM 1118
15.7
Axial fan - 1
Diameter in.
/
T1
I
IP24
PSI
PSI
dB (A) 53
175
552
F 41 - 115
dB (A) 63
33.4 X 12.6 X 21.3
34.6 X 14.2 X 22.3
in.
in.
lbs
lbs
ft
ft
ft
R410A
79.4/90.4
.2.65thgieW
Factory Prescharge 25
33
66
Gas additional charge 02/H .33
Liquid Pipe Diameter mm Φ6(1/4”)
Gas Pipe Diameter mm Φ9(3/8”)
Manufacturer/trademark
Starting Method
Type
Defrosting Method
Overload Protector
Air Flow Volume of Outdoor Unit
Outdoor Unit
Compressor
Fan
Fan Motor
Working Temp Range
Heat
Exchanger
Coil
Coil
Model
Coil length (l) x height (H) x coil width (L)
Throttling Method
Moisture Protection
Permissible Excessive Operating
Pressure for the Discharge Side
Permissible Excessive Operating
Pressure for the Suction Side
Type-Piece
Climate Type
Isolation
Dimension (W×H×D)
Dimension of Package (L×W×H)
Sound Pressure Level
Sound Power Level
Net Weight /Gross Weight
Connection
Pipe
Max. Interunit Piping Length
Max. Interunit Height Difference
Refrigerant Name of refrigerant
Specifications
10
33 3/8 X 23 1/2 X 12 1/2

The above data is subject to change without notice. Please refer to the nameplate of the unit.
MR12C1H
SANYO
C-6RZ110H1A
Twin rotory
33A)A( .A.R.L
95.4A)A(ALR
Power Input(W) W 800
Int11l-3979
Electronic Expansion Valve
throttling
Transducer starting
Aluminum fin-copper tube
Pipe Diameter mm .275
2 - .005
Rows-Fin Gap in.
mm 747X508X44
086/009mprdeepS
Output of Fan Motor W 40
71.0AALR
Capacitor μF /
CFM 1118
15.7
Axial fan
Diameter in.
/
T1
I
IP24
PSI
PSI
dB (A) 55
175
552
F 41 - 115
dB (A) 65
33.4 X 12.6 X 21.3
34.6 X 14.2 X 22.3
in.
in.
lbs
lbs
ft
ft
ft
R410A
79.4/90.4
.2.65thgieW
Factory Prescharge 25
33
66
Gas additional charge H 1/4 oz per ft
Liquid Pipe Diameter mm Φ6(1/4”)
Gas Pipe Diameter mmΦ9(3/8”)
Manufacturer/trademark
Starting Method
Type
Defrosting Method
Overload Protector
Air Flow Volume of Outdoor Unit
Outdoor Unit
Compressor
Fan
Fan Motor
Working Temp Range
Heat
Exchanger
Coil
Coil
Model
Coil length (l) x height (H) x coil width (L)
Throttling Method
Moisture Protection
Permissible Excessive Operating
Pressure for the Discharge Side
Permissible Excessive Operating
Pressure for the Suction Side
Type-Piece
Climate Type
Isolation
Dimension (W×H×D)
Dimension of Package (L×W×H)
Sound Pressure Level
Sound Power Level
Net Weight /Gross Weight
Connection
Pipe
Max. Interunit Piping Length
Max. Interunit Height Difference
Refrigerant Name of refrigerant
Specifications
11
33 3/8 X 23 1/2 X 12 1/2

Appending date
Standard
pressure
Indoor Outdoor P (MPa)
EVP (°F)C OD(°F)
09K 0.8 to 1.1 Turbo Rated
12K detaR 0.1 ot 8.0
(rps)
80.06/66.92
66.98/60.08
95/–
(°F) Model
name
Indoor fan
mode
COOLING:
Standard
pressure
Indoor Outdoor P (MPa)
09K 2.8 to 3.2
12K 2.8 to 3.2
Outdoor fan
mode (rps)
46.99/42.99
(°F) Model
name
Indoor fan
mode
HEATING:
Table showing operation frequency limits for cooling and heating
Performance date for both cooling and heating
NOTES :
(1) Measure surface temperature of heat exchanger pipe around center of heat exchanger path
U bent. (Thermistor themometer)
(2) Connecting piping condition : 7.6 m
Compressor Frequency(Hz)
Indoor Wet Bulb
Temperature( )
20
40
60
80
100
120
140
110
130
15 35 55 75 95
59°F
68°F
77°F
Compressor Frequency(Hz)
Capacity Change Ratio (%)
Capacity Change Ratio (%)
Indoor Wet Bulb
Temperature( )
20
40
60
80
100
120
140
110
130
15 35 55 75 95
59°F
60.8°F
62.6°F
Rated
Rated
EVP (°F) COD(°C)
Turbo
Turbo
Turbo
High
High
High
High
Specifications
0 to 3
Outdoor Relative Humidity 40% Outdoor Relative Humidity 72%
Heat exchanger pipe
temp.
Heat exchanger pipe
temp.
Temperature Condition
Temperature Condition
Outdoor fan
mode
Compressor
revolution
Compressor
revolution
105 to 10453 to 57
99 to 100
109 to 113
2 to 4
50 to 54
108 to 111
12
80/67
67/60 47/43

Expanded c apacity data tables for both cooling and heating
Capacity Variation Ratio According to Pipe Length
gnilooC
90
80
• Conditions
Indoor: DB80.06˚F/WB66.92˚F
Indoor air flow : TURBO
Pipe length : 7.6m
110
100
Outdoor temp. (˚F)
Capacity Ratio (%)
70
30252005
110
105
100
95
90
85
80
Maximum pipe length 20m
Standard pipe length 7.6m
Total pipe length (m)
01 .5
110
105
100
95
90
85
80
Total Elevation (m)
Maximum Elevation 7.6m
• Conditions
Indoor air fl
ow: TURBO
• Conditions
Indoor air flow: TURBO
10 15 3.04 .5 6.07 .5 9.0
Specifications
90
97
93
100
108
104
113
102
111
106
115
91
99
95
Indoor: DB80°F/WB67°F
Outdoor: DB95°F/WB75°FIndoor: DB80°F/WB67°F
Outdoor: DB95°F/WB75°F
13
DB80°F/WB67°F

Operation Characteristic Curve
gnilooC
01 02 03 04 05 06 07 09 0
80
25.0
22.5
20.0
17.5
15.0
12.5
10.0
7.5
5.0
2.5
0
Compressor speed (rps)
Current (A)
Current (A)
• Conditions
Indoor air flow : TURBO
Pipe lengt: 7.6m
115V
gnilooC
01 02 03 04 05 06 07 09 0
80
25.0
22.5
20.0
17.5
15.0
12.5
10.0
7.5
5.0
2.5
0
Compressor speed (rps)
:
115V
• Conditions
Indoor air flow : TURBO
Pipe length: 7.6m
Specifications
Indoor: DB80°F/WB67°F
Outdoor: DB95°F/WB75°F
Indoor: DB80°F/WB67°F
Outdoor: DB95°F/WB75°F
14
12 btu unit
9 btu unit

40
30
20
Indoor side noise when blowing Outdoor side noise
Indoor fan motor rotating speed
Low MiddleH igh
Compressor frequency/Hz
35
25
Turbo
40
30
20
Indoor side noise when blowing Outdoor side noise
Indoor fan motor rotating speed
Low MiddleH igh
Compressor frequency/Hz
35
25
Turbo
Noise/dB(A)
Noise/dB(A) Noise/dB(A)
Noise/dB(A)
80 1006040200
70
60
50
40
30
20
70
60
50
40
30
80 1006040200
Specifications
2.5 Noise criteria curve tables for both models
15
09 btu units
12 btu unit

3. Construction Views
3.1 Indoor Unit
3.2 Outdoor Unit
Constrction views
W
H
D
W2
D3
W3
D4
W4
D2
H2
961245531
Unit:m m
Additional DimensionsCabinetCabinet
W H D W2 D4H2 D2 D3 W4W3
33 1/4 10 7/8 7 1/8 30 3/4 10 7/823 1/2 12 1/2 11 21 1/233 3/8
System
Model
Number
Outdoor Unit (mm)Indoor Unit (mm)
5 1/4 6 3/421
16
09K
12K

4. Refrigerant System Diagram
Cooling Models
Refrigerant System Diagram
TINU ROODTUOTINU ROODNI
HEAT
EXCHANGE
(EVAPORATOR)
HEAT
EXCHANGE
(CONDENSER)
COMPRESSOR
GAS SIDE
3-WAY VALVE
LIQUID SIDE
2-WAY VALVE
COOLING
Accumlator
Discharge
Suction
Muffler
reniartSreniartS
Electric Expansion
Valve
17

5. Schematic Diagram
5.1 Electrical Date
5.2 Electrical wiring
Outdoor Unit
These circuit diagrams are subject to change without notice, please refer to the one supplied with the unit.
Symbol Color symbol Symbol Color symbol
WH WHITE BN BROWN
YE YELLOW BU BLUE
RD RED BK BLACK
YEGN YELLOW GREEN PROTECTIVE EARTH
Indoor Unit
Indoor Unit
Schematic Diagram
L-OUT
L1
L1
0 0
RT1 RT2
M2
JUMP
CAP
TEM.SENSOR
ROOM TUBE
TEM.SENSOR
FAN MOTOR SWING MOTOR(U.D)
AP2
SWING-UD
K4
TUBEROOM
AC-L
PG
PGF TR_OUT TR_IN
TC
TRANSFORMER
13
DISPLAY
AP1
CN1 CN2
DISP-2DISP-1
M1
GG
XT1
W4 BU
W3 BN
N(1)
OUTDOOR UNIT
2
3
COM-OUT
W1 YEGN
W2 YEGN
N
W5 BK
I
II
ELECTRIC BOX
EVAPORATOR
Symbol Parts name Symbol Color symbol
L1 REACROR WH WHITE
PCB1~PCB2 PRINTED CIRCUIT BOARD YE YELLOW
S10/S11S40/S70/S80/S90 CONNECTOR RD RED
SAT OVERLOAD BN SAT OVERLOAD BN BROWN
COMP COMPRESSOR BU BLUE
PROTECTIVE EARTH BK BLACK
YEGN YELLOW GREEN
21
18

Outdoor Unit
Schematic Diagram
COMP
M
RT5
0
0
RT4
0
RT3
OUTROOM EXHAUST
OUTTUBE
OFAN
EOVERHEAT
RE
C
S
UVW
CT1,2
AP1
W3YEGN W10 RD
COMP
W8 YEGN
FAN MOTOR
W5 BU W6 YE W7 BK
AC-N1
AC-L1
COMU
EKV
CN1
TEM.SENSOR
OUTROOM EXHUAST
TEM.SENSOR
TEM.SENSOR
TUBE
W2 BU
W1 BN
W4 BK
G
G
I
N
D
O
O
R
U
N
I
TW13 YEGN
POWER
N
L
L
N
N(1)
3
2
L2L2L2
L1
L1
G
G
G
W15 BU
W14 BN
W16 WH
W17 RD
G
L4
L4
W23 OGW20 BU
W22 WH
W21 BN
AC-L2 AC-L4AC-N5AC-N3AC-N4 AC-L2AC-L3
W19 BU W24 RD
W18 YEGN
XT2
3
4
E
2
1
FILTER
C4
C3
2
1
2
1
Cooling Models of 115V
19

5.3 Printed Circuit Board
TOP VIEW
BOTTOM VIEW
Schematic Diagram
123
4
56
7
8
9
10
11
12
1 Interface of neutral wire
2 Transformer input
3 Interface of PG motor
4 Auto button
5 Feedback from PG motor
6 Up&Down swing
7 Jumper cap
8 Indoor temperature sensor
9 Pipe temperature sensor
10 DISP-1, DISP-2 display interface
11 Protective tube
12 Communication interface
20

TOP VIEW
BOTTOM VIEW
Schematic Diagram
Terminal of
jump wire,
live wire and
neutral wire,
AC-N4 joint
AC-N3,
AC-L2 joint
AC-L3
External connect high-
capacity positive terminal
Protective
tube
External connect high-
capacity negative
terminal Terminal of DC fan
Live wire terminal of 4-way
valve
Terminal of jumper
wire, neutral wire
Neutral wire terminal
of 4-way valve
Main relay Terminal of
ground wire
Slug of on-off
power
High frequency
transformer
Stabilized voltage
block 7805
IPM module
Terminal of
compressor
overload
protector
Discharge
terminal of
compressor
Outdoor
ambient
temperature
sensor
Terminal of
outdoor pipe
temperature
Terminal of power
lead-in wire and
live wire
Protective
tube
Terminal of
communication wire
Terminal of
power lead-in
wire and
neutral wire
21

6. Function and Control
6.1 Remote Control Operations
Function and Control
2
8
9
10
3
4
11
12
7
6
13 14
5
1
Press it to start or stop operation
ON/OFF
MODE
Press it to select operation mode
(AUTO/COOL/DRY/FAN/HEAT)
+
: Press it to increase temperature
setting
-
: Press it to decrease temperature
setting
FAN
Press it to set swing angle
TIMER ON
TIMER OFF
CLOCK
X-FAN (page 31)
TEMP (page 31)
TURBO(page 32)
SLEEP(page 32)
Press it to turn on/off the light.
LIGHT
Press it to set fan speed
Press it to set auto-on timer
Press it to set auto-off timer
Press it to set clock
Note: Only name different between X-FAN and BLOW,
but the function is the same.
?
?
?
?
*Remote control works with cool and Heat Pump Models
22
MODE
(AUTO/COOL/DRY/FAN/HEAT).
setting.
: P ress to decrease temperature
setting.
FA N
Press it set swing angle.
TIMER ON
TIMER OFF
CLOCK
TEMP
TURBO
SLEEP
LIGHT
Press it to set auto-on timer.
Press it to set auto-o timer
Press it set clock.
1
6
7
5
3
2
4
11
10
14
9
12
13
15
3
9
10
13
12
5
4
11
8
7
21
6
8
Press it to turn on/o the light.
P ress to s tart or s top operation.
: P ress to increase temperature
P ress to set fan speed.
P ress to select operation mode
SENSOR
AIR SWEEP
EXTEND
AUTO
17
15
14
START / STOP
Note: Only name different between X-Fan
and Blow, but the function is the same.

Function and Control
Press this button to start the unit operation .Press this button again to stop the unit operation.
ON/OFF :
MODE :
Each time you press this button,a mode is selected in a sequence that goes from AUTO,
COOL,DRY, FAN,and HEAT *, as the following:
AUTO COOL DRY FAN HEAT *
*Note:Only for models with heating function.
+ :
Press this button to increase set temperature.Holding down button above 2 seconds rapidly
Press this button to decrease set temperature.Holding down button above 2 seconds rapidly
.
FAN :
Auto
Low speed Medium speed High speed
:
OFF
1
2
3
4
5
6
After energization, AUTO mode is defaulted. In AUTO mode, the set temperature will not
be displayed on the LCD, and the unit will automatically select the suitable operation
mode in accordance with the room temperature to make indoor room comfortable.
increases set temperature. In AUTO mode, set temperature is not adjustable.
decreases set temperature. In AUTO mode, set temperature is not adjustable.
This remote controller is universal . If any command , or is sent out,
the unit will carry out the command as
indicates the guide louver swings as:
Every press of FAN button changes the fan speed in the following order:
Every press of the button changes the swing angle in the follow order:
23

Function and Control
Pressing X-FAN button in COOL or DRY mode,the icon is displayed and the indoor
fan will continue operation for 10 minutes in order to dry the indoor unit even though you
X-FAN:
have turned off the unit.
After energization, X-FAN OFF is defaulted. X-FAN is not available in AUTO,FAN or
HEAT mode.
10
11 TEMP:
9
8
TIMER ON:
7
Press TIMER ON button, "ON" blinks and disappears. Within 5 seconds, every press of + or -
button increases or decreases the ON time setting by 1 minutes. Holding down either buton
above 2.5 seconds rapidly changes the time setting by 1 minute and then by 10 minutes.
Within 5 seconds after setting, press TIMER ON to confirm. To cancel the TIMER ON
operation, press TIMER ON button.
TIMER OFF :
Press TIMER OFF button to set TIMER OFF. The setting method is the same as TIMER
ON.
Press CLOCK button, the icon blinks. During 5 seconds blinking, pressing + or - button adjusts
CLOCK :
preset time. Holding down either button above 2 seconds increases or decreases the time by
1 minute every 0.5 second. If you are still pressing the button after 10 minutes increased or
decreased, the time will be changed by 10 minutes every 0.5 second. During blinking, press
the CLOCK button again, the icon will be constantly displayed and it indicates that setting
has been finished.
Press TEMP button, (set temperature), (indoor ambient temperature) and
(outdoor ambient temperatur) is displayed circularly. Not displaying icon is defaulted.
During operation of TEMP button, the set temperature is always displayed.
Note: Outdoor ambient temperature is only displayed for some models.
24

Function and Control
Press "+
" and "-" buttons simultaneously to lock or unlock the keypad. If the remote
controller is locked, is displayed. In this case, pressing any button, blinks
three times.
At unit OFF, press
"
MODE
"
and
" - "
buttons simultaneously to switch between and .
ḉ
About switch between fahrenheit and cenrigrade
34
and About lock
24
and
LIGHT:
14
TURBO:
SLEEP:
12
13
Press this button in COOL or HEAT mode turns on/off Turbo function. After TURBO
function is set, its icon is displayed. When switching operation mode or changing
fan speed, this function will be canceled automatically.
at super high fan speed. (This function is not applicable for some models).
Press SLEEP button into SLEEP operation. Press SLEEP button again to cancel SLEEP.
This function only can be used in COOL, HEAT (applicable to heat pump unit) or DRY
mode, to maintain the most comfortable temperature for you.
Press LIGHT button turns on/off the display's light.If the light is tunrned on , is
displayed. If the light is tunrned off disappears.
25

Function and Control
ƾ
●
●
●
●
●
Sketch map for
replacing batteries
Replacement of Batteries
When the wireless remote controller is lost
o r damaged, please use the manual switch
on the main unit. Operation will be in AUTO
mode and the temperature setting or fan
speed can not be changed.
The manual switch can be operated as follow:
To operate: Pressing the AUTO/STOP button,
the unit enters into AUTO mode.
The microcomputer will monitor the room
temperature to select the (COOL, HEAT, FAN)
mode automatically,to abtain the comfortable
effect.
To turn off: Press the AUTO/STOP button to
switch the unit off.
Emergency Operation
ƽ
ƽ
Manual switch
Fig.3
1.Remove the battery cover plate from the rear of the remote controller.
(As shown in the figure)
2.Take out the old batteries.
3.Insert two new AAA1.5V dry batteries, and pay attention to the polarity.
4. Replace the battery cover plate.
Notes:
When changing the batteries, do not use old or different batteries,
otherwise, it may cause malfunction of the wireless remote control.
If the wireless remote controller will not be used for a long time, please
remove batteries to prevent damage from leaking batteries.
The operation should be performed in its receiving range.
It should be kept 1m away from the TV set or stereo sound sets.
If the wireless remote controller does not operate normally, please take
the batteries out and replace them after 30 s. If still not operating properly,
replace the batteries.
26

27
6.2 Description of Each Control Operation
Function and Control
1. Temperature Parameters
Indoor preset temperature (T
preset
)
Indoor ambient temperature (T
amb.
2. Basic Functions
Once energized, in no case should the compressor be restarted within less than 3 minutes. In the situation that memory
function is available, for the first energization, if the compressor is at stop before de-energization, the compressor will be
started without a 3-minute lag; if the compressor is in operation before de-energization, the compressor will be started with
a 3-minute lag; and once started, the compressor will not be stopped within 6 minutes regardless of changes in room
temperature;
(1) Cooling Mode
Working conditions and process of cooling
When T
amb
.≥T
preset
, the unit will enter cooling operation, in which case the indoor fan, the outdoor fan and the compressor
will work and the indoor fan will run at preset speed.
When T
amb
.≤T
preset
-28 , the compressor will stop, the outdoor fan will stop with a time lag of 30s, and the indoor fan will
run at preset speed.
When T
preset
-28 <T
amb
.< T
preset
+34 F
FF
F
F
, the unit will remain at its previous state.
Under this mode, the four-way valve will be de-energized and temperature can be set within a range from 61 to 86
If the compressor is shut down for some reasons, the indoor fan and the swing device will operate at original state.
Protection
Antifreeze protection
Under cooling and dry mode, 6 minutes after the compressor is started:
If T
evap
.≤36 , the compressor will operate at reduced frequency.
If T
evap
.≤-30 is detected for durative 3 minutes, the compressor will stop, and after 30 seconds, the outdoor fan will stop;
and under cooling mode, the indoor fan and the swing motor will remain at the original state.
If T
evap
.≥42 and the compressor has remained at OFF for at least 3 minutes, the compressor will resume its original
operation state.
Total current up and frequency down protection
If I
total
≤A, frequency rise will be allowed; if I
total
≥B, frequency rise will not be allowed; ifI
total
≥C, the compressor will
run at reduced frequency; and if I
total
≥D, the compressor will stop and the outdoor fan will stop with a time lag of 30s.
(2) Dry Mode
Working conditions and process of dry
If T
amb
. T
preset
, the unit will enter cooling and dry mode, in which case the compressor and the outdoor fan will
operate and the indoor fan will run at low speed.
If T
preset
-28 T
amb
.≤T
preset
, the compressor remains at its original operation state.
If T
amb
.< T
preset
-28 , the compressor will stop, the outdoor fan will stop with a time lag of 30s, and the indoor fan will
operate at low speed.
Start cooling
Stop cooling
Compressor
Original working state
Run Stop
Outdoor fan
Indoor fan
Tpreset
Tpreset
-28
Tamb
Preset fan Speed
6 minutes 6 minutes
3 minutes
)
F
F
F
F
F
F

28
≤108°F, the indoor fan will run at low speed, and after one minute, the indoor fan
: if T tube ≤104°F and the indoor fan is at stop state, the indoor fan will begin to run at low
b. A°F≤T
c. B°F≤T
<C°F, T
<C°F, T
<B°F, T
≥A°F, T
+36°F<T +41°F, the unit will maintain its
+41°F, the compressor will stop, the outdoor fan will stop with a time lag of 30s, and the indoor fan will stop
+36°F, the unit enters heating mode, in which case the four-way valve, the compressor and the outdoor fan
Function and Control
Protection
Protection is the same as that under the cooling mode.
(3) Heating Mode
Working conditions and process of heating
If Tamb
.≤Tpreset
will operate simultaneously, and the indoor fan will run at preset speed in the condition of preset
cold air prevention.
If T amb.
≥Tpreset
after 60-second blow at low speed
If Tpreset amb.
< Tpreset original operating status.
Under this mode, the four-way valve is energized and temperature can be set within a range of 61 - 86°F . The
operating symbol, the heating symbol and preset temperature are revealed on the display.
Condition and process of defrost
When duration of successive heating operation is more than 45 minutes, or accumulated heating time more than 90 minutes,
and one of the following conditions is reached, the unit will enter the defrost mode after 3 minutes.
a. T
outdoor amb. outdoor tube ≤W°F;
outdoor amb. outdoor tube ≤X°F;
outdoor amb. outdoor tube ≤Y°F;
d. Touter amb. outer tube ≤Z°F
At that time, the indoor fan stops and the compressor stops, and after 30 seconds the outdoor fan will stop, and then after 30
seconds, the four-way valve will stop. After 30 seconds, the
compressor is initiated for raising the frequency to defrost
frequency.
When the compressor has operated under defrost mode for 7.5 minutes, or Touter tube ≥E°F, the compressor will be converted
to 53Hz operation. After 30 seconds, the compressor will stop
. And after another 30 seconds, the four-way valve will be
opened, and after 60 seconds, the compressor and the outdoor fan will be started, the in door fan will run under preset cold air
prevention conditions, and H1 will be displayed at temperat ure display area on the display panel. Defrost frequency is
70Hz.
3.Protection
Cold air prevention
The unit is started under heating mode (the compressor is ON):
In the case of T
indoor amb.
<75°F
speed with a time lag of 2 minutes. Within 2 minutes, if T
tube >40 , the indoor fan also will run at low speed; and after
1-minute operation at low speed, the indoor fan will be converted to operation at preset speed. Within 1-minute low speed
operation or 2-minute non-operation, if T
tube >108°F , the fan will run at present speed.
In the case of T
indoor amb.
≥75°F : if T
tube
will be converted to preset speed. With in one-minute low speed operation, if T
tube , the indoor fan will be converted
to preset speed.
Note: T
indoor amb. 12 refers to, under initially heating mode, the indoor ambient temperature before the
command to start the compressor is performed according to the program, or after the unit is withdrawn from defrost, the
indoor ambient temperature before the defrost symbol is cleared.
Total current up and frequency down protection
If the total current Itotal ≤W, frequency rise will be allowed; if Itotal ≥X, frequency rise will not be allowed; if Itotal ≥Y, the
compressor will run at reduced frequency; and if Itotal ≥Z, the compressor will stop and the outdoor fan will stop with a time
lag of 30s.
(4) Fan Mode
Under the mode, the indoor fan will run at preset speed and the compressor, the outdoor fan, the four-way valve and the
electric heater will stop.
Under the mode, temperature can be set within a range of 61°F - 86°F.
(5) AUTO Mode
Working conditions and process of AUTO mode
Under AUTO mode, standard cooling temperature T
preset
is 77°F
and standard heating temperature T
preset is 64.4°F.
a. Once energized, if T
amb.≤68°F
, the unit will be started under heating mode; if 68°F < T
amb.< 77°F, the unit will run
under fan mode and the operation indicator lamp will be bright; and if T
amb
.≥77°F, the unit will be started under cooling mode.
>108°F

29
–(28°F
Function and Control
a. Under AUTO mode, if Tamb
.≥Tpreset is detected, the unit will select to run under cooling mode, in which case implicit
preset temperature is 77°F; if Tamb
.≤Tpreset 28°F, the compressor will stop, the outdoor fan will stop with a time lag of 1
minute, and the indoor fan will run at preset speed; and if T
preset )< Tamb
.< Tpreset , the unit will remain at its original
state.
b. Under AUTO mode, if T
amb
.≤Tpreset +36°F is detected, the unit will select to run under heating mode, in which case
implicit preset temperature is 64°F; if T
amb.≥Tpreset 41°F
, the compressor will stop, the outdoor fan will stop with a time lag
of 1 minute, and the indoor fan will run under the mode of residue heat blowing; and if T
preset +36°F < Tamb
.< Tpreset +41°F, the
unit will remain at its original state. The cooling-only unit will run under fan mode.
c. Under AUTO mode, if 68°F< T
amb.< 77°F, the unit will remain at its original state.
2.Protection
a. In cooling operation, protection is the same as that under the cooling mode;
b. In heating operation, protection is the same as that under the heating mode;
c. When ambient temperature changes, operation mode will be converted preferentially. Once started, the compressor will
remain unchanged for at least 6 minutes.
(6) Common Protection Functions and Fault Display under COOL, HEAT, DRY and AUTO Modes
Overload protection
T
tube : measured temperature of outdoor heat exchanger under cooling mode; and measured temperature of indoor heat
exchanger under heating mode.
1) Cooling overload
a. If T tube ≤106°F, the unit will return to its original operation state.
b. If T tube ≥131°F, frequency rise is not allowed.
c. If T tube ≥136°F, the compressor will r un at reduced frequency.
d. If T tube ≥144°F , the compressor will stop and the indoor fan will run at preset speed.
2) Heating overload
a. If T tube ≤106°F, the unit will return to its original operation state.
b. If T tube ≥131°F, frequency rise is not allowed.
c. If T tube ≥136°F, the compressor will run at reduced frequency.
d. If T tube≥144°F , the compressor will stop and the indoor fan will blow residue heat and then stop.
Exhaust temperature protection of compressor
If exhaust temperature
≥208°F, frequency is not allowed to rise.
If exhaust temperature
≥217°F, the compressor will run at reduced frequency.
If exhaust temperature
≥230°F, the compressor will stop.
If exhaust temperature ≤194°F and the compressor has stayed at stop for at least 3 minutes, the compressor will resume its
operation.
Communication fault
If the unit fails to receive correct signals for durative 3 minutes, communication fault can be justified and the whole system
will stop.
Module protection
Under module protection mode, the compressor will stop. When the compressor remains at stop for at least 3 minutes, the
compressor will resume its operation. If module protection occurs six times in succession, the compressor will not be started
again.
Overload protection
If temperature sensed by the overload sensor is over 239°F, the compressor will stop and the outdoor fan will stop with a
time lag of 30 seconds. If temperature is below 203°F, the overload protection will be relieved.
If voltage on the DC bus is below 150V or over 420V, the compressor will stop and the outdoor fan will stop with a time
lag of 30 seconds. When voltage on the DC bus returns to its normal value and the compressor has stayed at stop for at least
3 minutes, the compressor will resume its operation.
Faults of temperature sensors

30
Designation of sensors Faults
Indoor ambient temperature The sensor is detected to be open-circuited or short-circuited for successive 30
seconds
Indoor tube temperature The sensor is detected to be open-circuited or short-circuited for successive 30
seconds
Outdoor ambient temperature The sensor is detected to be open-circuited or short-circuited for successive 30
seconds
Outdoor tube temperature The sensor is detected to be open-circuited or short-circuited for successive 30
seconds, and no detection is performed within 10 minutes after defrost begins.
Exhaust After the compressor has operated for 3 minutes, the sensor is detected to be
open-circuited or short-circuited for successive 30 seconds.
Overload After the compressor has operated for 3 minutes, the sensor is detected to be
open-circuited or short-circuited for successive 30 seconds.
3. Other Controls
(1) ON/OFF
Press the remote button ON/OFF: the on-off state will be changed once each time you press the button.
(2) Mode Selection:
Press the remote button MODE, then select and show in the following ways: AUTO, COOL, DRY, FAN, HEAT, AUTO.
(3) Temperature Setting Option Button
Each time you press the remote button TEMP+ or TEMP-, the setting temperature will be up or down by 34°F. Regulating
Range: 61°F~86°F, the button is useless under the AUTO mode.
(4) Time Switch
You should start and stop the machine according to the setting time by remote controller.
(5) SLEEP State Control
a. When the air conditioner is under the mode of COOL, DRY, and the SLEEP mode has been set well, after the SLEEP
state keeps about 1 hour, the pre-setting T will raise 34°F, and it will raise 34°F again after 2 hours, so it raise 36°F in
2 hours, then it will run on at the setting temperature and fan speed.
b. When the air conditioner is under the mode of HEAT, and the Timer has been set well, after the SLEEP state keeps about
1 hour, the pre-setting T will reduce 34°F, and it will reduce 34°F again after 2 hours, so it reduce 36°F in 2 hours, then
it will run on at the setting temperature and wind speed.
c. The setting temperature keeps the same under the FAN mode and AUTO mode.
(6) Indoor Fan Control
The Indoor Fan can be set as HIGH, MED, LOW by remote controller, and the Indoor Fan will be respectively run at high,
medium, low speed. It will also be set as AUTO, and the Indoor Fan is as the following at the automatic fan speed.
Cooling mode: T
ring
≥ T
setting
+ 2, high speed; T
setting
- 2 T
ring
T
setting
+ 2, medium speed; T
ring
≤ T
setting
– 2, low speed.
Sending fan mode: : T
ring
T
setting
+ 4, high speed; T
setting
+2≤T
ring
≤T
setting
+ 4, medium speed; T
ring
T
setting
+2, low
speed.
Moisture removal mode: force to be set as the low speed
Heating mode: T
ring
≤ T
setting
+ 1 high speed; T
setting
+1 T
ring
T
setting
+ 5, medium speed; T
ring
≥T
setting
+ 2, low speed.
(7) Buzzer Control
The buzzer will send a sound when the air conditioner is powered up or received the information sent by the remote
control or there is a button input, the single tube cooler doesn’t receive the remote control ON signal under the mode of
heating mode.
(8) Auto button
If the controller is on, it will stop by pressing the button, and if the controller is off, it will be automatic running state
by
pressing the button, swing on and light on, and the main unit will run based on the remote control if there is remote control
order.
(9) Up-and-Down Swinging Control
When power on, the up-and-down motor will firstly move the air deflector to o counter-clockwise, close the air outlet.
After starting the machine, if you don’t set the swinging function, heating mode and auto-heating mode, the up-and-down
air deflector will move to D clockwise; under other modes, the up-and-down air deflector will move to L1. If you set the
swing function when you start the machine, then the wind blade will swing between L and D. The air deflector has 7
swing states: Location L, Location A, Location B, Location C, Location D, Location L to Location D, stop at any
location between L-D (the included angle between L~D is the same). The air deflector will be closed at 0 location, and the
swing is effectual only on condition that setting the swing order and the inner fan is running. The indoor fan and
compressor may get the power when air deflector is on the default location.
Function and Control

31
(10) Display
Operation pattern and mode pattern display
All the display patterns will display for a time when the unit is power de on, the operation indication icon will display in red under
standby status. When the machine is start by remote controller, the indication icon will light and display the current
operation mode (the mode light includes: Cooling, heating and dry). If you close the light key, all the display icons
will close.
Double-8 display
According to the different setting of remote control, the nixie lamp may display the current temperature (the temperature
scope is from 61°F to 86°F ) and indoor ambient temperature. The heating and air supply temperature will display 77°F
under auto-mode, the temperature will display 64 under the heating mF ode, and the temperature will display H1 under the
defrosting mode.(If you set the fahrenheit temperature display, the nixie lamp will display according to fahrenheit
temperature)
(11) Protection function and failure display
E2: Freeze-proofing protection E4: Exhausting protection E5: Overcurrent protection
E6: Communication failure E8: Overload protection
F1: Indoor ambient sensor start and short circuit (continuously measured failure in 30S)
F2: Indoor evaporator sensor start and short circuit (continuously measured failure in 30S)
F3: Outdoor ambient sensor start and short circuit (continuously measured failure in 30S)
F2: Outdoor condenser sensor start and short circuit (continuously measured failure in 30S, and don’t measure within 10
minutes after defrosted)
F5: Outdoor exhausting sensor start and short circuit (continuously measured failure in 30S after the compressor operated 3
minutes)
H3: Overload protection of compressor H5: Module protection
PH: High-voltage protection PL: Low-voltage protection
P1: Nominal cooling and heating P2: Maximum cooling and heating
P3: Medium cooling and heating P0: Minimum cooling and heating
(12) Drying Function
You may start or stop the dry function under the modes of cooling and dry at the starting status (The modes of
automatism, heating and air supply do not have dry function). When you start the dry function, after stop the
machine by pressing the switch button, you should keep running the infoor fans for 10 minutes under low air damper (The
swing will operate as the former status within 10 minutes, and other load is stopped), then stop the entire machine; When
you stop the dry function, press the switch button will stop the machine directly.
When you start the drying function, operating the drying button will stop the inner fans and close the guide louver.
(13) Memory function when interrupting the power supply
Memory content: mode, swing function, light, set temperature and wind speed.
After interrupted the power supply, the machine will start when recovering the power according to the memory content
automatically. If the last remote control command has not set the timed function, the system will remember the last remote
control command and operate according it. If the last remote control command has set timed function and the power supply
is interrupted before the timed time, the system will remember the timed function of the last remote control command, the
timed time will recounted form power on. If the last remote control command has set timed function, the time is out and the
system is start or stop according to the set time when the power supply is interrupted, the system will remember the
operation status before the power supply was interrupted, and do not carry out timed action; The timed clock will not be
remembered.
Heating angle Cooling angle
Function and Control

Function and Control
Detect malfunctions of temperature sensor any time.
In defrosting period, the temperature sensor malfunction will not be detected. 5 min after finishing defrosting, the system begins to
detect the temperature sensor malfunction. In other times, the temperature sensor malfunction will be detected.
1. When short-circuit occurs to the temperature sensor for 30s:
The temperature sensor overheats. In this case, the complete unit will stop for protection. At the same time, the temperature protection
and temperature sensor malfunction will be shown.
2. When break-circuit occurs to the temperature sensor for 30s:
The unit will stop and the temperature sensor malfunction will be displayed
6.4 Frequency Control
<Outline>
When starting the compressor, or when conditions are varied due to the change of the room, the frequency must be initialized according
to the D value of the indoor unit and the Q value of the indoor unit.
Q value: Indoor unit output determined from indoor unit volume, air flow rate and other factors.
1. Pcontrol
Calculate D value in each sampling time (20 seconds), and adjust the frequency according to its difference from the frequency
previously calculated.
2. Icontrol
If the operating frequency is not change more than a certain fixed time, adjust the frequency up and down according to the D value,
obtaining the fixed D value.
When the D value is small...lower the frequency.
When the D value is large...increase the frequency.
3. Frequency management when other controls are functioning
When frequency is drooping;
Frequency management is carried out only when the frequency droops.
For limiting lower limit
Frequency management is carried out only when the frequency rises.
4. Upper and lower limit of frequency by PI control
The frequency upper and lower limits are set depending on indoor unit.
When low noise commands come from the indoor unit or when outdoor unit low noise or quiet commands come from indoor unit, the
upper limit frequency must be lowered than the usual setting.
6.5 3-minutes Standby
Prohibit to turn ON the compressor for 3 minutes after turning it off.(except when defrosting)
6.6 Compressor Protection Function
When turning the compressor from OFF to ON, the upper limit of frequency must be set as follows. (The function must not be used when
defrosting.)
FCG 3
FCG 2
FCG 1
TCG1
TCG2
TCG3
88
64
48
240
360
180
TCG 1sec TCG 2sec TCG 3sec Time
Frequency
FCG3
FCG2
FCG1
6.3 Detection of temperature sensor malfunction
32

6.7 Discharge Pipe Control
Outline
The discharge pipe temperature is used as the compressor’s internal temperature. If the discharge pipe temperature rises above a
certain level, the operating frequency upper limit is set to keep this temperature from going up further.
Detail
6.8 Input Current Control
Outline
Detect an input current by the CT during the compressor is running, and set the frequency upper
limit from such input current.
In case of heat pump model, this control is the upper limit control function of the frequency which
takes priority of the lower limit of four way valve activating compensation.
Detail
The frequency control will be made within the following zones.
When a “stop current” continues for 2.5 seconds after rushing on the stop zone, the compressor operation stops.
If a “drooping current” is continues for 1.0 second after rushing on the drooping zone, the frequency will be 2 Hz drooping.
Repeating the above drooping continues until the current rushes on the drooping zone without change.
In the keep zone, the frequency limit will remain.
In the return / reset zone, the frequency limit will be cancelled.
Limitation of current drooping and stop value according to the outdoor air temperature
1. In case the operation mode is cooling
* The current droops when outdoor air temperature becomes higher than a certain level (model by model).
2. In case the operation mode is heating
* The current droops when outdoor air temperature becomes higher than a certain level (model by model).
6.9 Freeze-up Protection Control
Outline
Divide the Zone
Management within the Zones
stnetnoc lortnoCenoZ
Stop zone When the temperature reaches the stop zone, stop the compressor and
correct abnormality.
Drooping zone Start the timer, and the frequency will be drooping.
Keep zone Keep the upper limit of frequency.
Return / Reset zone Cancel the upper limit of frequency.
Heat exchanger
thermistor
temperature
Stop zone
Drooping zone
Keep zone
Up zone
Reset zone
2 Hz drooping
1.0second after
rushing in the
drooping zone
After 2.5 seconds
Compressor stops
Stop zone
Drooping zone
Keep zone
Reset zone
1
2
3
Function and Control
33

During cooling operation, the signals being sent from the indoor unit allow the operating frequency limitation and then prevent
freezing of the indoor heat exchanger. (The signal from the indoor unit must be divided into the zones as the followings.)
Detail
Conditions for Start Controlling
Judge the controlling start with the indoor heat exchanger temperature after 2 sec from operation start.
Control in Each Zone
A
B
C
D
E
Return/Reset zone
Up zone
Keep zone
Drooping zone
Stop zone
Heat exchanger
thermistor temperature
Function and Control
34

6.12 Fan Control
Outline
Fan control is carried out according to the following priority.
1. Fan ON control for electric component cooling fan
2. Fan control when defrosting
3. Fan OFF delay when stopped
4. ON/OFF control in cooling operation
5. Tap control when drooping function is working
6. Fan control in forced operation
7. Fan control in indoor/outdoor unit silent operation
8. Fan control in powerful mode
9. Fan control in normal operation
Detail
Fan OFF Control when Stopped
* Fan OFF delay for 60 seconds must be made when the compressor is stopped.
Tap Control in indoor/outdoor unit silent operation
1. When Cooling Operation
When the outdoor air temperature is lower than 99°F, the fan tap must be set to L.
2. When Heating Operation
When the outdoor air temperature is higher than 39°F, the fan tap must be turned to L (only for heat pump model).
Frequency
Compressor
Four way valve
Fan
Electronic expansion
valve opening
ON
OFF
ON
OFF
ON
OFF
0Hz
5sec.
350pps 450pps450pps
Initial opening
PI control
5sec.
50sec.50sec. 600sec.
60sec.
Function and Control
35

7. Installation Manual
Installation Manual
Select a position where the condensing water can be easily drained out, and the place
is easily connected for outdoor unit.
Can select the place where is strong enough to withstand the full weight and vibration of
the unit. And will not increase the noise.
Make sure that the indoor unit installation should accord with installation dimension
diagram requirements.
Select a location where the children can not reach.
The unit installation work must be done by qualified personnel according to the local
rules and this manual.
Before installating, please contact with local authorized maintenance center, if unit is
not installed by the authorized maintenance center, the malfunction may not solved,
due to discommodious contacts.
W
The appliance must be positioned so that the plug is accessible
After pull out the power plug then make the appliance operation again,to avoid the
icing of outdoor unit damage axial flow fan,should electrify the appliance but not
operation for 4 hours for warm-up purpose(only for Heat Pump models).
hen removing the unit to the other place, please firstly contact with the authorized
Maintenance Center in the local area.
Important Notices
Basic Requirements For Installation Position
Install in the following place may cause malfunction. If it is unavoidable contact with
service center please:
Place where strong heat sources, vapors, flammable gas or volatile object are emitted.
Place where high-frequency waves are generated by radio equipment, welders and
medical equipment.
Place where a lot of salinities such as coast exists.
Place where the oil (machine oil) is contained in the air.
Place where a sulfured gas such as the hot spring zones is generated.
Other place with special circumstance.
Indoor Unit Installation Position Selection
The air inlet and outlet vent should be far from the obstruction, make sure that the air
can be blown through the whole room.
Be sure to leave enough space to allow access for routine maintenance. The height of the
installed location should be 8ft or more from the floor.
Select a place about 1m or more away from TVset or any other electric appliances.
Select a place where the filter can be easily taken out.
Do not use the unit in the immediate surroundings of a laundry a bath a shower or a
swimming pool.
7.1 Notices for installation
36

Installation Manual
Make sure that the Live wire or Zero line as well as the ground wire in the family power
socket can not be wrong connected, there should be reliable and no short circuit in the
diagram.
wrong connection may cause fire.
4. The min. distance from the unit and combustive surface is 5ft.
1. The power supply should be used the rated voltage and AC exclusive circuit,
the power cable diameter should be satisfied.
2. Don't drag the power cable emphatically.
3.
1. Air conditioner is type I electric appliance, thus please do conduct reliable earthing
measure.
2. The yellow-green two-color wire in air conditioner is earthing wire and cannot be used
for other propose. It cannot be cut off and be fix it by screw, otherwise it would cause
electric shock.
3. The earth resistance should accord to the National Criterion.
4. The user power must offer the reliable grounding terminal. Please don't connect the
earthing wire with the following place:
Tap water pipe. Gas pipe. Contamination pipe.
Other places that professional personnel consider them unreliable.
5. The appliance shall be installed in accordance with national wiring regulations.
An all-pole disconnection switch having a contact separation of at least 3mm in all poles
should be connected in fixed wiring.
It should be reliably earthed, and it should be connected to the special earth device,
the installation work should be operated by the professional.
The air switch must have the functions of magnetic tripping and heat tripping, in order
to protect the short circuit and overloading.
6.
5. The model and rating values for fuses according the silk print on fuse cover or related
PCB board.
Safety Requirements For Electric Appliances
Ground requirements
Select a location from which noise and outflow air emitted by unit will not inconvenience
neighbors, animals, plants.
Select a location where there should be sufficient ventilation.
Select a location where there should be no obstructions cover the inlet and outlet vent .
The location should be able to withstand the full weight and vibration of the outdoor unit
and permit safe installation.
Select a dry place, but do not expose under the direct sunlight or strong wind.
Outdoor Unit Installation Position Selection
Make sure that the outdoor unit installation dimension should accord with installation
dimension diagram, convenient for maintenance, repair.
The height difference of connecting the tubing within 16ft, the length of connecting the
tubing within 32ft.
Select a place where it is out of reach for the children.
Select a place where will not block the passage and do not influence the city appearance.
37

38
Installation Manual
Space to the wall
Space to the ceiling
Space to the wall
Space to the wall
Air outlet side
Space to the floor
Space to the obstruction
Air outlet side
Space to the wall
Air inlet side
The dimensions of the space necessary for correct
installation of the appliance including the minimum
permissible distances to adjacent structures
7.2 Installation dimension diagram
12 in. side
6 in.
side
above
6 in. to side
6 ft.
from
bottom
10 ft. from front
6 in. to side
12 in. side
12 in. back
19 in. top
7 ft. front

Installation Manual
Installing Mounting Plate
1.Make the mounting plate completely level . As the water tray's oulet of the indoor unit is two-way type, the
indoor unit during installation should slightly slant to watert tray's outlet for smooth drainage of condensing
water.
2.Fix the mounting plate on the wall with screws.(Where is pre-covered with plastic granula)
3.Be sure that the mounting plate has been fixed firmly enough to withstand the weight of an adult of 60kg;
further more, the weight should be evenly shared by each screw.
Fig.5
Wall Wall
Mark on the middle of it Gradienter
Left Right
(Rear piping hole)
(Rear piping hole)
Space
to the
wall
6 in
above
Space
to the
wall
6 in
above
Fig.6
Ø55
Boring Piping Hole
Installing Drain Hose
Wrenched Bent
Flooded
Indoor Outdoor
Wall pipe Seal pad
Connecting Indoor and Outdoor Electric Wires
1.Make the piping hole (2.5 in) in the wall at a slight downward slant to the
outdoor side.
2.Insert the piping-hole sleeve into the hole to prevent the connection piping
and wiring from being damaged when passing through the hole.
1.For proper draining, the drain hose should be placed at a downward slant.
2.Do not wrench or bend the drain hose or flood its end by water.
3.The long drain hose passing through indoor areas should
be wrapped with insulation material.
1.Open the front panel.
2.Remove the wiring cover as shown in Fig 6.
3.Make the power connection cord and signal control wire (onlyf or heat pump unit ) through the hole in the
4.Reinstall the clamp and wiring cover.
5.Recovert he front panel.
the back of indoor unit.
2.5 in2.5 in
39
(only for heat pump unit) through the hole in the

Installation Manual
Installing Indoor Unit
The piping can be output from right, right rear, left
or left rear.
When routing the piping and wiring from the left
or right side of indoor unit, cut off the tailings
from the chassis as necessary(As shown in Fig.7)
Cut off the tailings 1 when routing the wiring only;
Cut off the tailings 1 and tailings 2 when routing
both the wiring and piping.
Take out the piping from body case, wrap the piping,
power cords, drain hose with the tape and make them
through the piping hole. (As shown in Fig.8)
Hang the mounting slots of the indoor unit on the
upper hooks of the mounting plate and check if it is
firm enough.(As shown in Fig.9)
The height of the installed location should be 8ft
or more from the floor.
Installing Connection Pipe
Align the center of the piping flare with the relevant valve.
Screw in the flare nut by hand and then tighten the
nut with spanner and torque wrench referring to the
following:
NOTE: Firstly connect the connection pipe to indoor unit, then to outdoor unit; pay attention
to the piping bending, do not damage the connection pipe; ensure the joint nut is adequately
tightened, otherwise it may cause leakage.
Spanner Torque
wrench
Piping
Taper nut
Indoor unit piping
Fig.9
Mounting
plate
Fixing hook Mounting
plate
Right
Right rear Fig.8
Left rear
Left
Fig.7
Tailing 1
Tailing 2
Finally wrap it
with tape
Gas side piping
insulation
Water drainage pipe
Liquid side
Piping insulation
Gas side pipe External connection
electric wire
Liquid side piping
Hex nut diameter Tightening torque (lb ft)
11 ~ 14.7
22.8 ~ 25.8
36.9 ~ 40.6
44.3 ~ 47.9
51.6 ~ 55.3
After tightening the screws, slightly pull the wire and confirm whether it is firm or not.
Ensure all wiring connections are secure and the cover plates are reinstalled properly.Poor
NOTE:
All interconnecting wiring between indoor and outdoor unit must be performed by a
a licenced electrical contractor
The electric wiring must be correctly connected.Improper connection may cause spare parts
malfunction.
Tighten the terminal screws adequately to prevent loosening.
Ensure the electrical connections are properly earthed to prevent electrical shocks.
installations that allow dust or moisture incursion may cause fire or electrocution.
40
6ft

Ø
Condensate drainage of outdoor unit (not for cooling only)
The condensate and defrosting water formd during heating
in the outdoor unit can be properly discharged by drainage
pipe .
Installation method:set the drain connection in 25 hole of the
chassis has been installed and then connect drainage pipe
with drain nozzle,so that condensate and defrosting water can
be properly discharged Chassis
Drain
connection
Electric wiring
NOTE:
Wrong wiring may cause spare parts malfunction.
After the cable fixed, make sure there should be a free space between the connection
and connection and fixing place on the lead wire.
Cable Cross Plate sub-assy
Air purging and leakage test
Disassemble the cable cross plate sub-assy on the outdoor unit right side plate.
Take off wire clamp. Connect and fix power connect
cord (for cooling and heating unit,connect and fix power
connect cord and signal control wire)to terminal of line
Fix the power connection cable with wire clamp,
(for cooling and heating unit, use the wire clamp
to fix the power connection cable and the signal
control wire), then connect the corresponding
Ensure wire has been fixed well.
Install the cable cross plate sub-assy.
connector.
bank. Wiring should fit that of indoor unit.
5
Fig.
1. Connect charging hose of manifold valve to charge end of low pressure
valve (both high/low pressure valves must be tightly shut).
2. Connect joint of charging hose to vacuum pump.
3. Fully open handle handle of Lo manifold valve.
4. Open the vacuum pump to evacuate. At the beginning, slightly
loosen joint nut of low pressure valve to check if there
is air coming inside. (If noise of vacuum pump has
been changed, the reading of multimeter is 0) Then
tighten the nut.
5. Keep evacuating for more than 15mins and make
sure the reading of multi-meter is
6. Fully open high/low pressure valves.
7. Remove charging hose from charging end of low pressure valve.
8. Tighten bonnet of low-pressure valve. (As shown in Fig.10)
Liquid pipe
Gas pipe
Valve
cap
Vacuum
gauge
Vacuum pump
For 115V Uints
For 208~230V Uints
Power
Power
7.4 Installing Outdoor Unit
Installation Manual
41
*Note: Terminal 2 is the communication connection

Do not switch on power before installation is finished completely.
Electric wiring must be connected correctly and securely.
Cut-off valves of the connection pipes should be opened.
Switch on power and press "ON/OFF" button on the wireless remote controller to start
the operation.
Check after Installation
Items to be checked Possible malfunction
Has it been fixed firmly? The unit may drop, shake or emit noise.
Have you done the refrigerant leakage test? It may cause insufficient cooling(heating)
capacity
Is heat insulation sufficient? It may cause condensation and dripping.
Is water drainage satisfactory? It may cause condensation and dripping.
Is the voltage in accordance with the rated
voltage marked on the nameplate?
It may cause electric malfunction
or damage the product.
Is the electric wiring and piping
connection installed correctly and securely?
It may cause electric malfunction
or damage the part.
Has the unit been connected to a secure
ground connection? It may cause electrical leakage.
Is the power cord specified? It may cause electric malfunction
or damage the part.
Are the inlet and outlet openings blocked? It may cause insufficient cooling(heating)
capacity.
Is the length of connection pipes
and refrigerant capacity been recorded?
The refrigerant capacity is not accurate.
Operation Test
Before Operation Test
All the impurities such as scraps and thrums must be cleared from the unit.
Operation Test Method
Press MODE button to select the COOL, HEAT (Cooling only unit is not available),
FAN to check whether the operation is normal or not.
7.5 Check after Installation and Operation Test
Installation Manual
42

Fig. a
1.
2.
(as shown in Fig.b).
3. Mount the air filter properly along the arrow
direction in Fig.c, and then close the panel cover.
Cleaning and Maintenance
Service Life
ƽ
filter
Air filter
(as shown Fig.a)
Fig. b
Fig. c
Lift up the front panel from the two ends
of it, as the arrow direction shown. Then
pull the air filter out.
Attach the healthy filter onto the air filter,
.
Healthy
Remove the healthy filter before cleaning and re-install it after clean
according to the installation instruction, but can't with brush or hard
things. After washing, be sure to shake off remaining water and dry
in the shade.
The healthy filter commonly has its usage life time for one year under
normal condition. As for silver ion filter, it is invalid when its surface
becomes black (green).
This supplementary instruction is provided for reference to the unit with
healthy filter. If the graphics provided herein is different from the physical
goods, the latter one shall prevail. The quantity of healthy filters shall be
based on the actual delivery.
Installation of Healthy Filter
7.6 Installation and Maintenance of Healthy Filter(Optional)
Installation Manual
43

Troubleshooting
9. Troubleshooting
9.1 Precautions before Performing Inspection or Repair
Be cautious during installation and maintenance. Do operation following the regulations to avoid electric shock and casualty or even death
due to drop from high altitude.
* Static maintenance is the maintenance during de-energization of the air conditioner.
For static maintenance, make sure that the unit is de-energized and the plug is disconnected.
* Dynamic maintenance is the maintenance during energization of the unit.
Before dynamic maintenance, check the electricity and ensure that there is ground wire on the site. Check if there is electricity on the
housing and connection copper pipe of the air conditioner with voltage tester. After ensure insulation place and the safety, the mainte-
nance can be performed.
Take sufficient care to avoid directly touching any of the circuit parts without first turning off the power.
At times such as when the circuit board is to be replaced, place the circuit board assembly in a vertical position.
Normally,diagnose troubles according to the trouble diagnosis procedure as described below.(Refer to the check points in servicing
written on the wiring diagrams attached to the indoor/outdoor units.)
No. Troubleshooting procedure
1 Confirmation
2 Judgement by Flashing LED of Indoor/Outdoor Unit
3 How to Check simply the main part
Precautions when inspecting the control section of the outdoor
unit:
A large-capacity electrolytic capacitor is used in the outdoor unit controller
(inverter).Therefore,if the power supply is turned off,charge(charging volt-
age DC280V to 380V)remains and discharging takes a lot of time.. After
turning off the power source,if touching the charging section before
discharging, an electrical shock may be caused.
Please open the outdoor unit after the unit is power off for 20min.
9.2 Confirmation
(1)Confirmation of Power Supply
Confirm that the power breaker operates(ON) normally;
*Trouble shooting is for cooling and Heat Pump models.
(2)Confirmation of Power Voltage
Confirm that power voltage is AC 220-240± 10%.
If power voltage is not in this range, the unit may not operate normally.
9.3 Judgement by Flashing LED of Indoor/Outdoor Unit
115 ± 10%.
44

The breaker trips at once when it is set to
"ON".
Measure insulation resistance to grou
nd to see if there is any leakage.
Trip of breaker or blow
of fuse
The breaker trips in few
minutes
when it is set to "ON"
Check power supply circuit.
Check if the plug is properly plugged in
and make the loose contact firm.
Change controller fuse
Check remote controller
Change batteries
Power voltage is too low
Remote controller malfunction
Receiver is broken
Controller is broken
Receiver loose or poor connection
No power
Fuse of controller burnt out
Remote controller is short of power
Power plug is not well plugged in and poor
connection
Fasten the wiring; measure the output
voltage of the transformer, if it is
incorrect, change the transformer
The air conditioner
does not react after
it is powered ( after
the plug is inserted,
the buzzer does
not sound and the
remote startup has
no response)
The remote contro-
ller signals (after it is
powered, the buzzer
will sound, unless it
has malfunction)
The circuit or the part of the air conditioner has
malfunction. They heat and break the insulation
and lead to short circuit or creepage. Measure
the insulation resistance or eliminate the malfunc-
tion one by one. If the breaker itself has
malfunction, then replace the breaker.
The transformer connection is loose or has
bad contact or the transformer has
malfunction
First, press the manual switch button
AUTO,if there is no response,check
based on the above methods. If it runs
normally after pressing the button,check
again whether the installation position
and the connection wire of the reception
head is correct. If it is correct,then repla-
ce the receiver or the remote controller.
Check the voltage. If it is lower than 10% of the rated
voltage, check the
cause, improve the power supply
condition and add the stabilized voltage
power supply.
Air conditioner can not start up
Troubleshooting
45

46
Improper set of temperature Adjust set temperature
If cooling (heating) load is
proper
Check the forecasted load of cooling (heating)
The refrigerant has leakage or is
insufficient
heck and fill the leakage, then
vacuumize it and supplement the re-
frigerant as required
Leakage between the high pres-
sure and the low pressure in-
side the compressor
Replace the compressor
Malfunction of four-way valve Replace the four-way valve
Local block of capillary Replace the capillary
Blockage of cooling system
Judge whether the system is blocked by
observing the condensation of evapora-
tor and the pressure value of the high
pressure manometer and take measures
to deal with the system.
Malfunction of
refrigerant
flow
Heat insulation for the connection
pipes of the indoor unit and the out-
door unit is bad.
Make sure that heat insulation for the thick and thin pipes
is good. Heat insulation must also be provided for the
joint andthe exposed part of the copper pipe .
Block of outdoor heat ex-
changer
Clean the dust accumulated on the surface of
the heat exchanger.
Air filter were blocked Clean the filter
Fan speed was set too slow
To set the fan speed to high or
middle speed
Air circulation
is insufficient
Fan rotation speed becomes
low
Capacitor
damage
Motor damage
Replace the capaci-
tor
Replace the motor
The installation position of the
outdoor unit is not appropriate.
Good ventilation must be provided for the
installation position of the outdoor unit.
The outdoor temperature is too high. Properly install the rainproof plate or the sunproof plate. If the
maximum cool air still can not meet the requirement, it is sug-
gested to replace the air conditioner.
Keep certain air tightness indoors, try not to use
electricalappliance with large quantity of heat
The air tightness is not enough. People
come in and out too frequently. There
are heating devices indoors.
Poor COOL(HEAT) operation
Troubleshooting

The indoor fan motor is burned or bre-
aks or has the heat protector malfun-
ction.
Replace the fan motor or the defective part.
The built-in heat protector of the motor
breaks frequently because the motor is
abnormal.
Replace the fan motor
Wrong connection Make the correction connection based on the circuit
drawing.
The fan does not
run when it is set
to supply air.
The fan capacitor has open circuit or
is damaged Replace the fan capacitor of the same type and same
specification.
The outdoor fan motor is damaged. Replace the fan motor
Wrong connection Make the correct connection based on the circuit
drawing.
In the cooling and
heating mode, the
compressor runs,
but the outdoor
fan does not run.
The outdoor fan capacitor is damaged. Replace the fan capacitor
Malfunction of compressor Replace the compressor
Breakage of running capacitor of
compressor Replace the capacitor
The voltage is too low or too high. Manostat is recommended.
Wrong wire connection Connect the circuit diagram correctly
When cooling or
heating, outdoor
fan runs,compr-
essor
doesn't run.
The protector itself has malfunction. Use the multimeter to check whether the contact of
the compressor is on when it is not overheated. If it
is not on, then replace the protector
The refrigerant is not enough or is too
much. Adjust the volume of the refrigerant
The capillary is blocked and the temp-
erature rises. Replace the capillary
The compressor does not run smoothly
or is stuck. The air discharge valve is
damaged
Replace the compressor
The compressor is
too hot and leads to
the action of the
protector.
The protector itself has malfunction. Replace the protector
The torque of the swing motor is not
enough
wrong connection
The swing fan
does not run.
The controller is damagedIC2003 is
damaged, the swing relay can not close,
etc
First, check whether the connection is wrong. If no,
replace the parts
Troubleshooting
47

Water leakage
Abnormal sound
and shake
Drainage pipe blocked or broken Change drainage pipe
Wrap of refrigerant pipe joint is not close
enough. Re-wrap and make it tight.
Fan of indoor unit contacts other parts. Adjust fan location.
Foreign object in indoor unit Take out the foreign object.
Compressor shakes too much.
Adjust support washer of compressor, and
tighten loosen screws.
Touch of pipeline of outdoor unit Separate the touching pipeline.
Touch of inner plates
Louver of outdoor unit touched outer
case.
Abnormal sound inside compressor Change compressor
Adjust location of louver.
1. Tighten connect screw.
2. Stick absorbing clay between plates.
In cool, heat mode,
the outdoor unit and
compressor will not
run.
C o n t r o l l e r m a l f u n c t i o n ( I C 2 0 -
0 3 b r o k e n , creepage of parallel
capacitor of relay loop,relay is bro-
ken etc.)
Wire loose or wrong connection
Improper setting of temperature
Change controller
Correctly wire according to the drawing
Adjust setting temp.
Troubleshooting
48

IPM protection
Overcurrent protection
Overload protection
Exhaust protection
Overlod protection of compresoor
r
Outdoor condenser temp. sensor mal.
Outdoor exhaust temp. sensor mal.
Starting at temp. does not reach
Communication is abnormal
Indicator display
of outdoor unit
If malfunction occurs,corresponding code will display and the unit will resume normal until protection or
malfunction disappears.
Compressor stars (normal)Yellow indicator blinks for once
Yellow indicator blinks for 3 times
Defrosting (normal display of indoor unit)
Yellow indicator blinks for twice
Yellow indicator blinks for 4 times
Yellow indicator blinks for 5 times
Yellow indicator blinks for 6 times
Yellow indicator blinks for 7 times
Yellow indicator blinks for 8 times
Red indicator blinks for once
Red indicator blinks for twice
Red indicator blinksfor 3 times
Red indicator blinks for 4 times
Red indicator blinks for 5 times
Red indicator for 6 times
Red indicator blinks for 7 times
Red indicator blinks for 8 times
Green indicator does not blink
Anti-freezing protection (normal
display of indoor unit)
Cooling (dehumidify) or heating current
Exhaust temp. dropped frequency temp.
dropped frequency current.
temp. dropped frequency temp.
T
tube-in
dropped frequency temp.
Outdoor ambient temp. sensor mal.
Tube
Troubleshooting
49

Troubleshooting
YELLOW-LED4 GREEN-LED2 RED-LED3
Name of running status Yellow light Red light Green light Indoor unit display
1 Compressor start Blink once
2 Defrosting Blink twice H1
3 Anti-freezing protection Blink three times E2
4 IPM protection Blink four times H5
5 Overcurrent protection Blink five times E5
6 Overload protection Blink six times H4
7 Air exhaust protection Blink seven times E4
8 Overload protection Blink eight times H3
9 Limited frequency (current) Blink once
10 Limited frequency (Air exhaust) Blink twice
11 Limited frequency (overload) Blink three times
12 Limited frequency (anti-freezing) Blink four times
13 Outdoor unit ambient sensor malfunction Blink five times F3
14 Outdoor unit tube temp. sensor malfunction Blink six times F4
15 Outdoor air exhaust sensor malfunction Blink seven times F5
16 Achieve the temperature of unitstartsup Blink eight times
17 Communication is normal Blink continuously
18 Communication malfunction OFF E6
19 Overload sensor malfunction Blink nine times H3
20 Low voltage protection Blink twelve times PL
21 High voltage protection Blink thirteen times PH
22 Indoor ambient sensor malfunction F1
23 Indoor tube temperature sensormalfunction F2
24 Normal cooling or norminal heating P1
25 Max. cooling or max. heating P2
26 Interim cooling or interim heating P3
27 Min. cooling or Min. heating P0
50

2. Low voltage over current protection
Possible reason: Sudden drop of supply voltage.
3. Communication malfunction
Processing method:Check if communica tion signal cable is connected reliably.
4. Sensor openo rs hort circuit
Processing method: Check whether sensor is normal, connected with the corresponding position on the
controller and if damage lf lead wire is found.
5. Compressor overload protection
Possible reasons: insufficient or too much refrigrant; blockage of capillary and increase of suction temp.;
improper running of compressor, burning in or stuck of bearing, damage of discharge valve;
malfunctioning of protector.
Processing method: adjust refrigerant amount; replace the capillary; replace the compressor; use
universal meter to check if the contactor of compressor is fine when it is not overheated, if not replace
the protector.
6. System malfunction
i.e.overload protection.When tube temperature (Check the temperature of outdoor heat exchanger
when cooling and check the temperature of indoor heat exchanger when heating) is too high,
protection will be activated.
Possible reasons: Outdoor temperature is too high when cooling; insufficient outdoor air circulation;
refrigerant flow malfunction.
please refer to the malfunction analysis in the previous section for handling method .
7. IPM module protection
Processing method:Once the module malfunction happens,if it persists for a long time and can not be self- canceled,
cut off the power and turn off the unit,and then re-energize the unit again after about 10 min. After repeating the
procedure for sever times, if the malfunction still exists, replace the module.
Analysis or processing of some of the malfunction display:
1. Compressor discharge protection
Possible reasons: shortage of refrigerant; blockage of air filter; poor ventilation or air flow short pass for condenser;
the system has noncondensing gas (such as air, water etc.); blockage of capillary assy (including filter); leakage
inside four-way valve causes incorrect operation; malfunction of compressor; malfunction of protection relay;
malfunction of discharge sensor; outdoor temperature too high.
Processing method: refer to the malfunction analysis in the above section.
Troubleshooting
51

9.4 How to Check simply the main part
Troubleshooting
N
Y
N
Y
N
Y
N
Y
N
Y
Switch on the unit
and wait 1 minute
Use DC voltmeter
to measure the
voltage on the two
ends of electrolytic
capacitor (test3)
Fault with the
voltage testing
circuit on contr-
ol panel AP1
Replace the
control panel
AP1
Measure the AC voltage between
terminal L and N on wiring board
XT
Switch off the
power and repair
the supply power
to restore the volt-
age to 103.5~126.5
VVAC For 115V
Units
Re-energize
and switch
on the unit
If the fault is
eliminated?
Switch off the power and wait 20 minutes;
or use DC voltmeter to measure the volt-
age on the use DC voltmeter to measure
the voltage on the two ends of capacitor
(test3), until the voltage is lower than 20V
Check the
connection of reactor
(L in the Electrical
Wiring Diagram)
If the wiring of
reactor L is normal?
Connect the rea-
ctor L according to
Electrical Wiring
Diagram
Re-energize
and switch on
the unit
If the fault
is eliminated?
End
Replace the control
panel AP1
Voltage within 103.5~126.5V?
For 115V Units
Voltage higher than 103.5V?
For 115V Units
Voltage higher than 187V?
For 208~230V Units
Main Check Points:
Units of 115V: Use AC voltmeter to check wether the voltage between terminal L and N on the wiring board is 115V AC
Units of 115V: Whether the reactor (L) is correctly connected? Whether the connection is loose or fallen? Whether the reactor
(L) is damaged ?
Fault diagnosis process:
52

53
Troubleshooting
Mainly detect:
Whether the connection between control panel AP1 and compressor COMP is secure? Whether loose? Whether the connection
is in correct order?
Whether the voltage input of the machine is within normal range? (Use AC voltmeter to measure the voltage
between terminal L and N on the wiring board XT)
Whether the compressor coil resistance is normal? Whether the insulation of compressor coil against the copper tube
is in good condition?
Whether the working loads of the machine are too high? Whether the radiation is good?
Whether the charge volume of refrigerant is correct?

Troubleshooting
Energize and
switch on
IPM protection
occurs after the
machine has run for
a
p
eriod of time?
Use AC voltmeter
to measure the
voltage between
terminal L and N
on the wiring
board XT)
If the voltage
between terminal L
and N on wiring
board XT is within
210VAC~250VAC?
Check the supply
voltage and
restore it to
210VAC~250VAC
Voltage between
the two ends of
electrolytic
capacitor (test3) is
hi
g
her than 250V
Start and run the
unit. Before
protection occurs,
use DC voltmeter to
measure the voltage
between the two
ends of electrolytic
capacitor on control
p
anel AP1
(
test3
)
If the unit can
work
normally?
Please confirm:
1. If the indoor and
outdoor heat
exchangers are
dirty? If they are
obstructed by other
objects which affect
the heat exchange
of indoor and
outdoor unit.
2. If the indoor and
outdoor fans are
working normally?
3. If the environment
temperature is too
high, resulting in
that the system
pressure is too high
and exceeds the
permissible range?
4. If the charge
volume of
refrigerant is too
much, resulting in
that the system
pressure is too
high?
5. Other conditions
resulting in that the
system pressure
becomes too high.
The connection
of capacitor C2
is loose.
Stop the unit and
disconnect the powe
r
supply. Then, check
the connection o
f
capacitor C2
according to Electrical
Wiring Diagram.
Reconnect the
capacitor C2 according
to Electrical Wiring
Diagram. Then,
energize and start the
unit.
Remove the wires
on the two ends o
f
capacitor C2. Then,
use capacitance
meter to measure
the capacitor C2.
Verify as per the
Parameters Sheet.
Stop the unit and
disconnect the power
supply. Wait 20 minutes,
or use DC voltmeter to
measure the voltage
between the two ends of
capacitor C2, until the
voltage is lower than 20V
If capacito
r
C2 is failed?
Replace the capacitor
C2. Then, energize
and start the unit.
Replace the
control panel AP1
Take corrective actions
according to Technical
Service Manual, and
then energize and start
the unit.
If there is any
abnormality
described above?
Refer to the
Electrical Wiring
Diagram and check
if the connection
between AP1 and
COMP is loose and i
f
the connection order
is correct.
Replace the
control panel AP1
If the connection
between AP1 and
COMP is unsecure
or the connection
order is wrong?
Connect the control panel
A
P1 and compressor
COMP correctly according
to the Electrical Wiring
Diagram. Then, energize
and start the unit.
Use ohmmeter to
measure the resistance
between the three
terminals on compressor
COMP, and compare the
measurements with the
compressor resistance on
Service Manual.
If the
resistance is
normal?
Use ohmmeter to
measure the resistance
between the two
terminals of compressor
COMP and copper tube.
Replace the
compressor
COMP
Resistance higher
than 500MΩ?
Replace the
control panel
AP1
END
Y N
Y
N
Y
N
Y
If the unit can
work
normall
y
?
Y
If the unit can
work
normally? Y
N
N
Y
N
If the unit can
work
normally? Y
Y
NN
If the unit can
work
normally? Y
Y
N
N
N
N
Y
Fault diagnosis process:
54

55

Troubleshooting
AP1
End
Y
N
Y
N
Y
N
Overheat and high
temperature protection
Is outdoor ambient temperature higher than 53?
20 minutes after the complete
unit is powered off.
Is heat dissipation of the indoor unit
and outdoor unit abnormal?
Normal protection, please operate it after the
outdoor ambient temperature is normalized.
Improve the heat
dissipation environment
of the unit
Does the outdoor fan work normally?
1. Check if the fan terminal O FAN
is connected correctly
2. Resistance between any two
terminals is measure by an ohm
gauge and should be less than 1K
Ohm.
Replace the control panel
Replace the fan
capacitor C1
Replace the
outdoor fan
Mainly detect:
Is outdoor ambient temperature in normal range?
Are the outdoor and indoor fans operating normally?
Is the heat dissipation environment inside and outside the unit is good?
56

Troubleshooting
Y
N
Y
N
N
Y
Y
N
Power on the unit
Is stop time of the compressor
longer than 3 minutes? Restart it up after 3 minutes
Does startup fail?
Are the wires for the compressor connected
correctly? Is connection sequence right?
Connect the wires as per the
connection diagram
Replace the control panel AP1
If the fault is eliminated?
Replace the
compressor
End
Mainly detect:
Whether the compressor wiring is connected correct?
Is time for compressor stopping enough?
Is compressor broken?
57

Out of step occurs once the
unit is powered on.
Is stop time of the
compressor longer than
3 minutes?
Are the wires for the compressor connected
correctly? Is connection sequence right?
Is the connection made in clockwise
direction?
Connect the
wires correctly
Replace the control
panel AP1
If the fault is eliminated?
Replace the
compressor
End
Out of step occurs in
operation
Is the outdoor fan working
normally?
Is the outdoor unit blocked
by foreign objects?
Replace the
control panel AP1
If the fault is eliminated?
Replace the
compressor
End
Check if the fan terminal
O FAN is connected correctly
Remove foreign objects
Replace the fan
capacitor C1
Replace the
outdoor fan
Troubleshooting
Mainly detect:
Whether the unit voltage is too high?
Whether the work voltage is too low?
58

20 minutes after the
complete unit is
powered off
Is the terminal FA for the
electronic expansion valve
connected correctly?
Connect the
wires correctly
Resistances between the first four pins
close to the terminal hole and the fifth
pin are almost the same, less than 100
ohm.
Replace the electronic
expansion valve
If the fault is eliminated?
If the fault is eliminated?
Replace the
control panel
AP1
Coolant leakage, refilling
the coolant
End
Troubleshooting
Mainly detect:
Whether the electronic expansion valve is connected well or not? Is electronic expansion valve damaged?
Is refrigerant leaked?
59

Troubleshooting
Y
Y
N
N
N
N
N
N
Y
Y
Y
Start
Check wiring of the
reactor (L) of the
outdoor unit and the
PFC capacitor
Whether there is any
damage or
short-circuit?
Replace it as per the
wiring diagram and
reconnect the wires If the fault is eliminated?
Remove the PFC capacitor
and measure resistance
between the two terminals.
Is the resistance around zero?
The capacitor is
short circuited and
the capacitor
should be repla-
ced
Restart the unit If the fault is eliminated?
Disconnect the terminals for the
reactor and measure the resistance
between the two terminals of the
reactor by an ohm gauge
Whether there is any damage
or short-circuit? Replace the reactor Restart the unit If the fault is eliminated?
Replace the control
panel AP1
End
Y
Mainly detect:
Check if the reactor (L) of the outdoor unit and the PFC capacitor are broken
The failure diagnosis process is as follows:
60

Y
N
Y
N
N
Y
N
N
Y
N
Y
N
Y
Y
Start
Did the equipment operate
normally before the failure
occurs?
The AP1 voltage
detection circuit
is at fault
Check wiring inside of
the indoor and outdoor
units
Are wires broken?
Check the communication
circuit of the outdoor unit
If the fault is eliminated?
The communication
circuit is abnormal
Replace the main board
of the indoor unit
End
If the fault is eliminated?
Replace the main board
˄AP1˅of the outdoor unit
If the fault is eliminated?
Is the connection right?
Check the wiring of the indoor and
outdoor units with reference to the
wiring diagram
Correctly connect the
corresponding wires for
the indoor and outdoor
units with reference to
the wiring diagram
Troubleshooting
Mainly detect:
Detect the indoor and outdoor units connection wire and indoor and outdoor units inside wiring is connect
well or not, if is there any damage?
Is there any damage for the indoor unit mainboard communication circuit? Is communication circuit damaged?
The flow chart for malfunction detect:
61

Y
Y
Y
Y
Y
N
N
N
N
Start
Measure voltage at the
Test 10 position as
shown in the diagram
with a voltmeter
Value jumping
Measure voltage at the
Test 15 position as
shown in the diagram
with a voltmeter
Value jumping
Measure voltage at the
Test 11 position as
shown in the diagram
with a voltmeter
Value jumping
Measure voltage at the
Test 12 position as
shown in the diagram
with a voltmeter
Value jumping
The communication
circuit of the outdoor
unit is normal
End
Fault with
outdoor unit
Troubleshooting
62

Troubleshooting
(9) Flow chart for outdoor communitcation circuit detecting:
7HVWWKHYROWDJHEHWZHHQ1SRLQWRIZLULQJERDUGDQGFRPPXQLFDWLRQFDEOHZLWKXQLYHUVDOPHWHU7KHYROWDJHVKDOOEH
YDULDEOH2WKHUZLVHLWPLJKWEHPDOIXQFWLRQRIPDLQERDUGRILQGRRUXQLWRUPDOIXQFWLRQRIPDLQERDUGRIRXWGRRUXQLWRU
ZURQJZLUHFRQQHFWLRQRILQGRRUDQGRXWGRRUXQLW3OHDVHHQVXUHWKDWWKHUHLVQRPDOIXQFWLRQRIPDLQERDUGRILQGRRUXQLWRU
ZURQJZLUHFRQQHFWLRQRILQGRRUDQGRXWGRRUXQLW$IWHUUHPRYLQJWKHPDOIXQFWLRQRILQGRRUXQLWUHPRYHWKHPDOIXQFWLRQRI
RXWGRRUXQLW
7HVWWKHYROWDJHRISLQDQGSLQRI8ZLWKXQLYHUVDOPHWHUYROWDJHRIERWKVLGHVRI57KHYROWDJHVKRXOGEH
YDULDEOH7HVW7HVWWKHYROWDJHRISLQDQGSLQRI8ZLWKXQLYHUVDOPHWHUYROWDJHRIERWKVLGHVRI57KH
YROWDJHVKRXOGEHYDULDEOH7HVW2WKHUZLVHWKHUHLVPDOIXQFWLRQRIPDLQERDUGRIRXWGRRUXQLW
7HVWWKHYROWDJHRISLQDQGSLQRI8ZLWKXQLYHUVDOPHWHUYROWDJHRIERWKVLGHVRI57KHYROWDJHVKRXOG
EHYDULDEOHWHVW7HVWWKHYROWDJHRISLQDQGSLQRI8ZLWKXQLYHUVDOPHWHUYROWDJHRIERWKVLGHVRI&7KH
YROWDJHVKRXOGEHYDULDEOHWHVW2WKHUZLVHWKHUHLVPDOIXQFWLRQRIPDLQERDUGRIRXWGRRUXQLW
7HVWWKHYROWDJHEHWZHHQSLQRI5ZKLWHDQGSLQRI87KHYROWDJHVKRXOGEHYDULDEOH7HVWYROWDJHEHWZHHQ
SLQRI5ZKLWHDQGSLQRI8ZLWKXQLYHUVDOPHWHU7KHYROWDJHVKRXOGEHYDULDEOH2WKHUZLVHWKHUHLVPDOIXQFWLRQRI
PDLQERDUGRIRXWGRRUXQLW
63

Troubleshooting Guide
Temp.Resistance Temp. Temp. Resistance Temp. Resistance
Resistance
Appendix 1: form for indoor/outdoor unit's ambient sensor numerical value of resistance
Troubleshooting
-2
0
1
3
5
7
9
10
12
14
16
18
19
21
23
25
27
28
30
32
34
36
37
39
41
43
45
46
48
50
52
54
55
57
59
61
63
64
66
68
70
72
73
75
77
79
81
82
84
86
88
90
91
93
95
97
99
100
102
104
106
108
109
111
113
115
117
118
120
122
124
126
127
130
131
133
135
136
138
140
142
144
145
147
149
151
153
154
156
158
160
162
163
165
167
169
171
172
174
176
178
180
181
183
185
187
189
190
192
194
196
198
199
202
203
205
207
208
210
212
214
216
217
219
221
223
225
226
228
230
232
234
235
237
239
241
243
244
246
248
250
252
253
255
257
259
261
262
264
266
268
270
271
273
275
277
(°F) (°F) (°F) (°F)
64
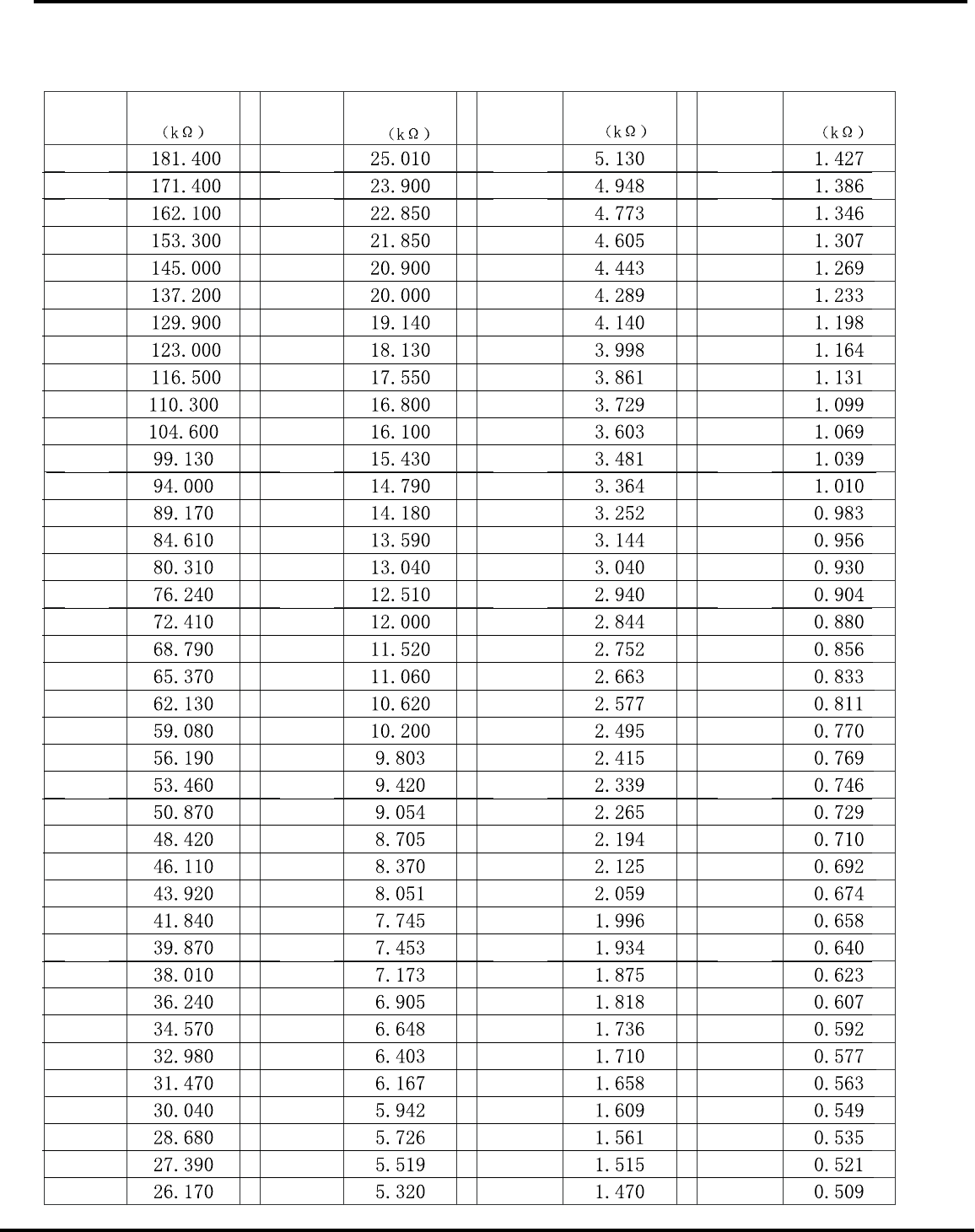
Troubleshooting Guide
Temp.
Resistance
Temp. Temp. Temp.
Resistance
Resistance
Resistance
Appendix 2: form for indoor/outdoor unit's tube temperature sensor numerical value of resistance
Troubleshooting
-2
0
1
3
5
7
9
10
12
14
16
18
19
21
23
25
27
28
30
32
34
36
37
39
41
43
45
46
48
50
52
54
55
57
59
61
63
64
66
68
70
72
73
75
77
79
81
82
84
86
88
90
91
93
95
97
99
100
102
104
106
108
109
111
113
115
117
118
120
122
124
126
127
130
131
133
135
136
138
140
142
144
145
147
149
151
153
154
156
158
160
162
163
165
167
169
171
172
174
176
178
180
181
183
185
187
189
190
192
194
196
198
199
202
203
205
207
208
210
212
214
216
217
219
221
223
225
226
228
230
232
234
235
237
239
241
243
244
246
248
250
252
253
255
257
259
261
262
264
266
268
270
271
273
275
277
(°F) (°F) (°F) (°F)
65

Troubleshooting Guide
Temp. Resistance Temp. Temp. Temp. Resistance
Resistance Resistance
Appendix 3: form for indoor/outdoor unit's air exhaust temperature sensor numerical value of resistance
Troubleshooting
-2
0
1
3
5
7
9
10
12
14
16
18
19
21
23
25
27
28
30
32
34
36
37
39
41
43
45
46
48
50
52
54
55
57
59
61
63
64
66
68
70
72
73
75
77
79
81
82
84
86
88
90
91
93
95
97
99
100
102
104
106
108
109
111
113
115
117
118
120
122
124
126
127
130
131
133
135
136
138
140
142
144
145
147
149
151
153
154
156
158
160
162
163
165
167
169
171
172
174
176
178
180
181
183
185
187
189
190
192
194
196
198
199
202
203
205
207
208
210
212
214
216
217
219
221
223
225
226
228
230
232
234
235
237
239
241
243
244
246
248
250
252
253
255
257
259
261
262
264
266
268
270
271
273
275
277
(°F) (°F) (°F) (°F)
66

9.5 2-way, 3-way Valve Appearance
2-way Valve (Liquid Side) 3-way Valve (Gas Side)
Shaft position Shaft position Service port
desolCdesolCdesolC
desolC
(with valve cap) (with valve cap) (with cap)
nepOdesolC
(clockwise)
desolCnepOnepO
(with valve cap) (with valve cap) (with cap)
nepOnepOdesolC
(clockwise) (counter-clockwise) (connected manifold
gauge)
nepOnepOnepO
(with charging
cylinder)
nepOnepOnepO
(with charging
cylinder)
nepO
nepO
nepOnepO
Works
Shipping
Air purging
(Installation)
Operation
Pumping down
(Transfering)
Evacuation
(Servicing)
Gas charging
(Servicing)
Pressure check
(Servicing)
Gas releasing
(Servicing)
1.
2.
3.
4.
5.
6.
Valve cap
Open position
Closed position
Pin
Service
port
Service
port cap
To outdoor unit
Flare nut
To
piping
connection
To outdoor unit
Hexagonal wrench (4mm)
Open position
Closed position
To
piping
connection
Flare nut
Open
(with charging cylinder)
Open
(with charging cylinder)
(with vacumm pump)
(clockwise)
Troubleshooting
67

Liquid side
Outdoor unit
3-way
valve
Gas side
Indoor unit
2-way
valve
Clsed
Clsed
Lo
Vacuum pump
CLOSE
OPEN
* Procedure
(1)Connect the charge hose from the manifold valve to the ser-
vice port of the gas side packed valve.
(2)Connect the charge hose to the port of the vacuum pump.
(3) Open fully the low pressure side handle of the gauge mani-
fold valve.
(4)Operate the vacuum pump to begin evacuating. Perform
evacuating for about 15 minutes if the piping length is 20 meters
(15 minutes for 20 meters) (assuming a pump capacity of 27
liters per minute). Confirm that the compound pressure gauge
reading is –101 kPa (–76 cmHg).
(5)Close the low pressure valve handle of gauge manifold.
– Check the flare connections for gas leakage.
(6)Use torque wrench to tighten the service port nut to a torque
of 1.8kg.cm.
(7)Set the 3-way valve to the back seat.
(8)Mount the valve stem nuts to the 2-way and 3-way valves.
(9)Check for gas leakage.
– At this time, especially check for gas leakage from the 2-way
and 3-way valve’s stem nuts, and from the service port nut.
CAUTION:
If gas leakage are discovered in step 5 above, take the
following mesures :
If the gas leaks stop when the piping connections are
tightened further, continue working from step 6. If the
gas leaks do not stop when the connections are
retightened, repair the location of the leak, discharge
all of the gas through the service port, and then recharge
with the specified amount of gas from a gas cylinder.
Troubleshooting
68

Lo
Closed
Purge the air
Outdoor unit
Indoor unit Liquid side
Gas side
CLOSE
Open
2-Way
valve
3-Way
valve
CLOSE
• Procedure
(1) Confirm that both the 2-way and 3-way valves are set to
the open position.
– Remove the valve stem caps and confirm that the valve stems
are in the raised position.
– Be sure to use a hexagonal wrench to operate the valve stems.
(2) Operate the unit for 10 to 15 minutes.
(3) Stop operation and wait for 3 minutes, then connect the
charge set to the service port of the 3-way valve.
– Connect the charge hose with the push pin to the service port.
(4) Air purging of the charge hose.
– Open the low-pressure valve on the charge set slightly to air
purge from the charge hose.
(5) Set the 2-way valve to the closed position.
(6) Operate the air conditioner at the cooling cycle and stop it
when the gauge indicates 1kg/cm2g.
(7) Immediately set the 3-way valve to the closed position.
– Do this quickly so that the gauge ends up indicating 3 to 5kg/
cm2g.
(8) Disconnect the charge set, and mount the 2-way and 3-
way valve’s stem nuts and the service port nut.
– Use torque wrench to tighten the service port nut to a torque of
1.8 kg.m.
– Be sure to check for gas leakage.
Troubleshooting
69

Lo
Closed
OPEN
Closed
Gas cylinder
R410A
Outdoor unit
Indoor unit Liquid side
Gas side
CLOSE
3-Way
valve
3-Way
valve
• Procedure
(1) Confirm that both the liquid side valve and the gas side
valve are set to the closed position.
(2) Connect the charge set and a gas cylinder to the service
port of the Gas side valve.
– Leave the valve on the gas cylinder closed.
(3) Air purging.
– Open the valves on the gas cylinder and the charge set. Purge
the air by loosening the flare nut on the liquid side valve ap-
proximately 45o or 3 seconds then closing it for 1 minute;repeat
3 times.
– After purging the air, use a torque wrench to tighten the flare
nut on liquid side valve.
(4) Check for gas leakage.
– Check the flare connections for gas leakage.
(5) Discharge the refrigerant.
– Close the valve on the gas cylinder and discharge the refriger-
ant until the gauge indicates 3 to 5 kg/cm2g.
(6) Disconnect the charge set and the gas cylinder, and set
the Liquid side and Gas side valves to the open position.
– Be sure to use a hexagonal wrench to operate the valve stems.
(8) Mount the valve stem nuts and the service port nut.
– Use torque wrench to tighten the service port nut to a torque of
1.8 kg.m.
– Be sure to check for gas leakage.
CAUTION: Do not leak the gas in the air during Air Purging.
Troubleshooting
70

Troubleshooting
Balance Refrigerant of the 3-way Valve
(Gas leakage)
• Procedure
(1) Confirm that both the 2-way and 3-way valves
are set to the back seat.
(2) Connect the charge set to the 3-way valve’s
port.
– Leave the valve on the charge set closed.
– Connect the charge hose to the service port.
(3) Open the valve (Lo side) on the charge set and
discharge the refrigerant until the gauge indi-
cates 0 kg/cm
2
G.
– If there is no air in the refrigerant cycle (the
pressure when the air conditioner is not running
is higher than 1 kg/cm
2
G), discharge the refrig-
erant until the gauge indicates 0.5 to 1
kg/cm
2
G. if this is the case, it will not be neces-
sary to apply a evacuatin.
– Discharge the refrigerant gradually; if it is dis-
charged too suddenly, the refrigeration oil will
also be discharged.
Lo
Open
Open
3-Way
valve
3-Way
valve
Gas side
CLOSEOPEN
Outdoor unit
Liquid side
Indoor unit
71

Troubleshooting
Evacuation
(All amount of refrigerant leaked)
• Procedure
(1) Connect the vacuum pump to the center hose
of charge set center hose
(2) Evacuation for approximately one hour.
– Confirm that the gauge needle has moved
toward -76 cmHg (vacuum of 4 mmHg or less).
(3) Close the valve (Lo side) on the charge set,
turn off the vacuum pump, and confirm that
the gauge needle does not move (approxima-
tely 5 minutes after turning off the vacuum
pump).
(4) Disconnect the charge hose from the vacuum
pump.
– Vacuum pump oil.
If the vacuum pump oil becomes dirty or
depleted, replenish as needed.
Lo
Open
Open
Vacuum pump
3-Way
valve
Outdoor unit
Liquid side
Indoor unit
Gas side
3-Way
valve
CLOSE
OPEN
72

Troubleshooting
Gas Charging
(After Evacuation)
• Procedure
(1) Connect the charge hose to the charging
cylinder.
– Connect the charge hose which you dis-con-
nected from the vacuum pump to the valve at
the bottom of the cylinder.
– If you are using a gas cylinder, also use a
scale and reverse the cylinder so that the sys-
tem can be charged with liquid.
(2) Purge the air from the charge hose.
– Open the valve at the bottom of the cylinder
and press the check valve on the charge set to
purge the air. (Be careful of the liquid refriger-
ant). The procedure is the same if using a gas
cylinder.
(3) Open the valve (Lo side on the charge set and
charge the system with liquid refrigerant.
– If the system can not be charged with the spec-
ified amount of refrigerant, it can be charged
with a little at a time (approximately 150g each
time) while operating the air conditioner in the
cooling cycle; however, one time is not suffi-
cient, wait approximately 1 minute and then
repeat the procedure (pumping down-pin).
(4) Immediately disconnect the charge hose from
the 3-way valve’s service port.
– Stopping partway will allow the gas to be dis-
charged.
– If the system has been charged with liquid
refrigerant while operating the air conditioner
turn off the air conditioner before disconnecting
the hose.
(5) Mount the valve stem nuts and the service
port nut.
– Use torque wrench to tighten the service port
nut to a torque of 1.8 kg.m.
– Be sure to check for gas leakage.
\
This is different from previous procedures.
Because you are charging with liquid refrigerant
from the gas side, absolutely do not attempt to
charge with larger amounts of liquid refrigerant
while operating the air conditioner.
Lo
Charging
cylinder
Outdoor unit
Indoor unit Liquid side
Gas side
CLOSE
Open
3-Way
valve
3-Way
valve
OPEN
Open
Check valve
(1)
73

3. Remove electirc box cover
Unscrew the screw fixing the electric box cover to
remove it.
10. Removal Procedure
10.1 Removal Procedure of Indoor Unit
Warning Be sure to wait 10 minutes or more after turning
off all power supplies before disassembling work.
Removal Procedure
1. Remove front panel
Open the front panel and slightly pull it to remove it.
2. Remove guide louver
Push out the shaft sleeve and slightly bend the
guide louver to remove it.
filter
screw
front panel
guide louver
Image shown here is indicative only. Actual product
you receive may differ.
74

4. Remove front case
Unscrew the 6 tapping screws fixng the front panel
and turn the front case backward to remove it.
Removal Procedure
5. Remove electric box
Unscrew the 2 screws fixing the electric box
Pull out the wiring terminal of motor and then un-
screw the 3 screws fixing electric box.Lift the ele-
ctric box to remove it.
6. Remove evaporator
Unscrew the screws on the rear pipe cardplate
and then remove the cardplate.
temp. sensor
clasps
screw
clasp
screw
clasps
screws
75

Removal Procedure
7. Remove motor and cross flow fan
Unscrew the screws fixing the motor press plate
of motor and then the screws connecting the mo-
tor and cross flow fan to separate and remove
them.
screws
screw
screws
76

Removal Procedure
top cover
Cable Cross Plate sub-assy
cabinet
screws
front panel
screws
screws
1. Remove top cover and the Cable Cross Plate sub-
assy Unscrew the screw on the handle and pull the
Cable Cross Plate sub-assy forcibly downwards to re-
move it. Unscrew the 3 screws fixing the top cover to
remove it.
2. Remove cabinet
Unscrew the 4 screws fixing the cabinet to remove it.
3. Remove front panel
Unscrew the 5 screws fixing the front panel and
pull out the front panel to remove it.
10.2 Removal Procedure of Outdoor Unit
(If it's 108-230V, there are 6 screws need to be unscrewed
because there are one more power transformer.)
77

Removal Procedure
4. Remove electric box cover
Unscrew the 2 screws fixing the electiric box. Pull
theelectric box upwards and unplug the plug-in
line to remove the electric box.
5. Remove axial flow fan
Unscrew the nut and remove the washer fixing the
axial flow fan and then pull it out.
nut and washer
screws
axial flow fan
6.Remove 4-way valve
Wrap the 4-way valve with wet cloth and unsolder
the 4 weld spots of the 4-way valve to remove it.
weld spots
4-way valve
78

Removal Procedure
7. Remove electronic expannsion valve
Unsolder the weld spots of eletronic expansion
valve connecting with other pipelines to remove it.
8. Remove gas valve and liquid valve
Unscrew the 2 screws fixing the gas valve and
unsolder the weld spots of gas valve and suction
pipe to remove the gas valve.
Unscrew the 2 screws fixing the liquid valve and
unsolder the weld spots of liquid valve and suc-
tion pipe to remove the liquid valve.
screws
gas valve
electronic expannsion valve
liquid valve
9 . Remove compressor
Unsolder the 2 weld spots of the compressor and
unscrew the 3 feet nuts and remove the was-
heres fixing the compressor to remove it.
compressor foot
79

13
14
15
16
17
18
19
20
21
22
23
24
11
25
26
27
28
30
31
32
33
34
29
35
36
37
38
40
39
41
1
2
3
5
4
6
8
910
12
7
MW09C1H / MW12C1H Exploded Diagram
SPLIT TYPE ROOM AIR CONDITIONER - WALL MOUNTED
SYSTEM COMPONENTS
80

NO. FPN Part Description
1 69700100 Filter Sub-Assy
2 69700101 Front Case Sub-Assy
3 69700102 Front Case
4 69700103 Evaporator Assy
5 69700104 Evaporator Support
6 69700105 Guide Louver
7 69700106 Axile Bush (guide louver)
8 69700107 Rear Grill
9 69700108 Helicoid tongue
10 69700109 Air Louver 2
11 69700110 Air Louver 1
12 69700111 Left Axile Bush
13 69700112 Bearing cushion rubber base
14 69700113 O-Gasket sub-assy of Bearing
15 69700114 Cross Flow Fan
16 69700115 Water Tray Glue Plug
17 69700116 Wall Mounting Frame
18 69700117 MotorPressPlate
19 69700118 Pipe Clamp
20 69700119 Drainage Pipe
21 69700120 Cable Cross Plate
22 69700121 Rear Case assy
23 69700122 Fan Motor
24 69700123 Motor MP24AA
25 69700124 Crank
26 69700125 Display Board
27 69700126 Ambient Temperature Sensor
28 69700127 Transformer
29 69700128 Electric Box Assy
30 69700129 Electric Box
31 69700130 4-bit Terminal Board
32 69700131 Main Board
33 69700132 Jumping Connector
34 69700133 Tube Sensor (20K black)
35 69700134 Electric Box Cover1
36 69700135 Shield cover of Electric Box sub-assy
37 69700136 Remote Control
38 69700137 Electric Box Cover2
39 69700138 Screw Cover
40 69700139 Front panel D1
41 69700140 Front Panel Sub-Assy
MW09C1H Parts List
81

NO. FPN Part Description
1 69700100 Filter Sub-Assy
2 69700141 Front Case Sub-Assy
3 69700142 Front Case
4 69700103 Evaporator Assy
5 69700104 Evaporator Support
6 69700105 Guide Louver
7 69700106 Axile Bush (guide louver)
9 69700108 Helicoid tongue
10 69700109 Air Louver 2
11 69700110 Air Louver 1
12 69700111 Left Axile Bush
13 69700112 Bearing cushion rubber base
14 69700113 O-Gasket sub-assy of Bearing
15 69700114 Cross Flow Fan
16 69700115 Water Tray Glue Plug
17 69700116 Wall Mounting Frame
18 69700117 MotorPressPlate
19 69700118 Pipe Clamp
20 69700119 Drainage Pipe
21 69700120 Cable Cross Plate
22 69700121 Rear Case assy
23 69700122 Fan Motor
24 69700123 Motor MP24AA
25 69700124 Crank
26 69700125 Display Board
27 69700126 Ambient Temperature Sensor
28 69700127 Transformer
29 69700143 Electric Box Assy
30 69700129 Electric Box
31 69700130 4-bit Terminal Board
32 69700131 Main Board
33 69700144 Jumping Connector
34 69700133 Tube Sensor (20K black)
35 69700134 Electric Box Cover1
36 69700135 Shield cover of Electric Box sub-assy
37 69700145 Remote Controller
38 69700137 Electric Box Cover2
39 69700138 Screw Cover
40 69700139 Front panel D1
41 69700140 Front Panel Sub-Assy
MW12C1H Parts List
82

27
26
24
22
23
18
17
16 15
14
13
12
11
10
6
5
7
9
25
8
19
20
21
4
3
2
1
31
29
28
30
MR09C1H Exploded Diagram
SPLIT TYPE ROOM AIR CONDITIONER - WALL MOUNTED
SYSTEM COMPONENTS
83

NO. FPN Part Description
1 69700000 Mesh Enclosure
2 69700001 Cabinet
3 69700002 Axial-flow Fan
4 69700003 Motor FW30G-ZL
5 69700004 Reactor Support Assy
6 69700005 Choke Plug
7 69700006 Compressor Gasket
8 69700007 Compressor C-6RZ110H1A
9 69700008 Electric Expansion Valve Sub-Assy
10 69700009 Cut-off Valve (1/4)
11 69700010 Cut-off Valve (3/8)
12 69700011 Valve Support
13 69700012 Cable Cross Plate Assy
14 69700013 Right Side Plate Assy
15 69700014 Wire cover
16 69700015 Magnet Coil
17 69700016 Temperature Sensor for Discharge Gas
18 69700017 Tube Sensor (20K black)
19 69700018 Discharge Tube
20 69700019 Inhalation Tube
21 69700020 Overload Protector
22 69700021 Sensor
23 69700022 Rear Grill
24 69700023 Condenser Assy
25 69700024 Clapboard Sub-Assy
26 69700025 Top Cover Plate
27 69700026 Motor suport spot welding sub-assy
28 69700027 Electric box cover sub-assy
29 69700028 Main Board
30 69700029 Electric Box Assy
31 69700030 Terminal Board
MR09C1H Parts List
84

17
18
27
19
20
21
26
23
22
16
12
14
11
9
810
13
15
25
24
2
1
3
5
4
6
7
MR12C1H Exploded View
SPLIT TYPE ROOM AIR CONDITIONER - WALL MOUNTED
SYSTEM COMPONENTS
85

NO. FPN Part Description
1 69700000 Mesh Enclosure
2 69700031 Front Panel
3 69700002 Axial-flow Fan
4 69700003 Motor FW30G-ZL
5 69700017 Tube Sensor (20K black)
6 69700016 Temperature Sensor for Discharge Gas
7 69700021 Sensor
8 69700032 Motor suport spot welding sub-assy
9 69700033 Condenser Assy
10 69700019 Inhalation Tube
11 69700025 Top Cover Plate
12 69700034 Rear Grill
13 69700035 Discharge Tube
14 69700015 Magnet Coil
15 69700036 Right Side Plate
16 69700011 Valve Support
17 69700027 Electric box cover sub-assy
18 69700029 Electric Box Assy
19 69700020 Overload Protector
20 69700006 Compressor Gasket
21 69700037 Drainage Plug
22 69700010 Cut-off Valve (3/8)
23 69700009 Cut-off Valve (1/4)
24 69700007 Compressor C-6RZ110H1A
25 69700038 Clapboard Sub-Assy
26 69700039 Chassis Sub-assy
27 69700028 Main Board
MR12C1H Parts List
86


FRIEDRICH AIR CONDITIONING CO.
10001 Reunion Place, Ste. 500, San Antonio, TX 78216
(210) 546-0500 877-599-5665 x 261 FAX (210) 546-0630
Email: tac@friedrich.com
www.friedrich.com
Printed in the U.S.A.