Contents
- 1. User Manual 1
- 2. User Manual 2
User Manual 2
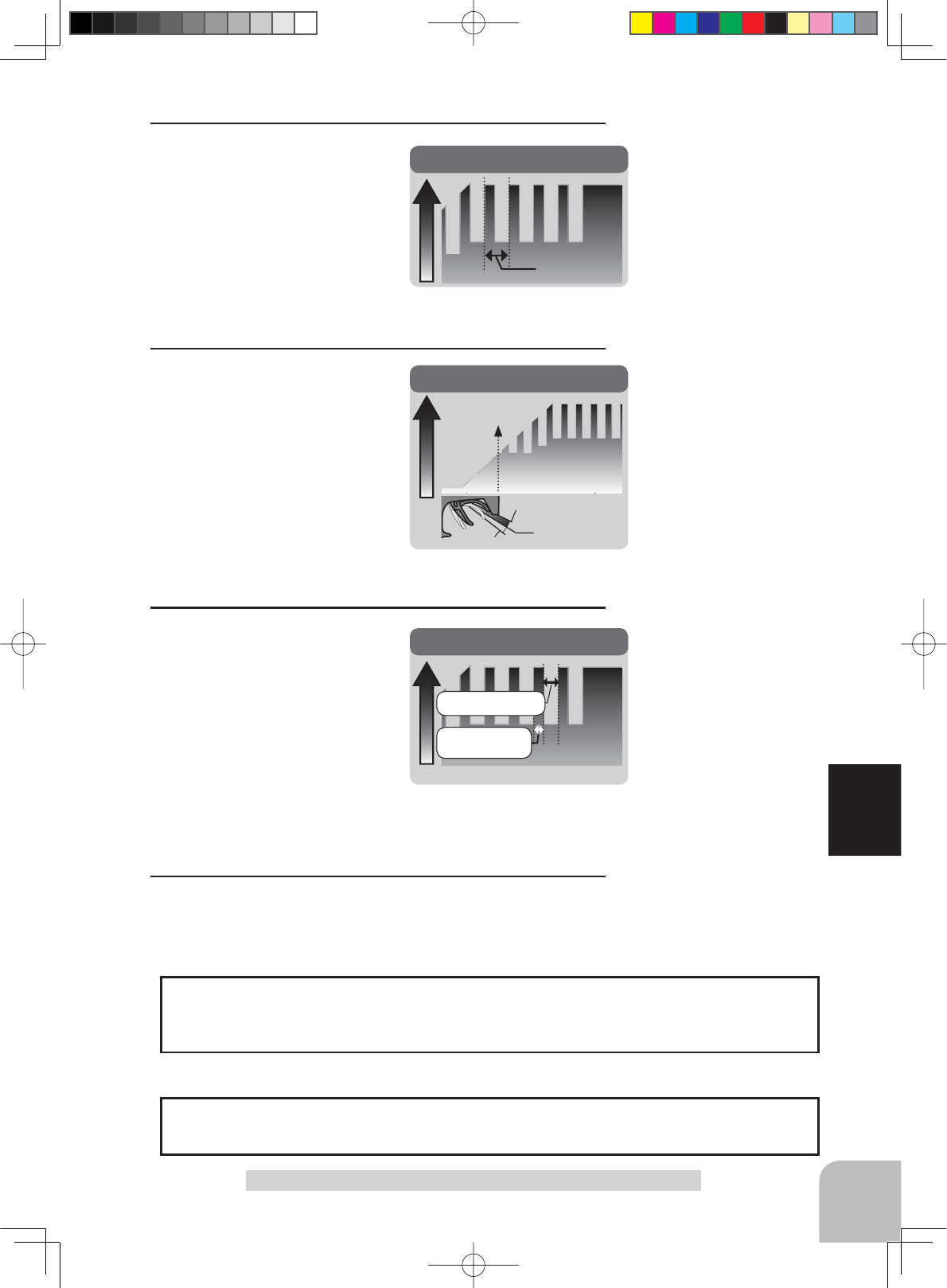
CYCL
Servo travel
CYCL (Cycle)
Cycle speed (CYCL)
1 ~ 30
Initial value: 10
DUTY
Servo travel
DUTY (duty): X and Y ratio
X: (Brake
application time)
Y: (Brake return time)
Duty ratio (DUTY)
LOW - MID - HIGH
Initial value: MID
Adjustment buttons
- Use the (+) and (-) buttons to
make adjustments.
- Return to the initial value by
pressing the (+) and (-) but-
tons simultaneously (approx.
1 sec).
TG.P
Servo travel
TG.P
(Trigger point)
TGP
Brake side
Neutral
Trigger point (TG.P)
10 ~ 100
Initial value: 30
Adjustment buttons
- Use the (+) and (-) buttons to
make adjustments.
- Return to the initial value by
pressing the (+) and (-) but-
tons simultaneously (approx.
1 sec).
61
Function
Adjustment buttons
- Use the (+) and (-) buttons to
make adjustments.
- Return to the initial value by
pressing the (+) and (-) but-
tons simultaneously (approx.
1 sec).
A.B.S. Function "TH A.B.S"
Use SW1or SW2 to switch the A.B.S. function ON/OFF.
See the function select
switch dial
function (See page 65).
Switch setting
The brake return amount (AB.P), delay amount (DELY) and cycle (CYCL) can be con-
trolled with digital dial or digital trim, with the function
switch dial
function. (See
page 65)
Dial / Trim Setting
4(Cycle speed adjustment)
Select setting item "CYCL" by
the (JOG) button up or down
operation. Use the (+) or (-)
button to adjust the pulse
speed (cycle).
- The smaller the set value, the faster the pulse speed.
5(Trigger point setup)
Select setting item "TG.P" by
the (JOG) button up or down
operation. Use the (+) or (-) but-
ton to adjust the operation point.
- Sets the throttle trigger position at which the A.B.S. function is performed.
The number is the % display with the full brake position made 100.
6(Cycle duty ratio setup)
Select setting item "DUTY" bby
the (JOG) button up or down
operation. Use the (+) or (-)
button to adjust the duty ratio.
"LOW" :Brake application time becomes shortest. (Brakes lock with difficulty)
"HIGH" :Brake application time becomes longest (Brakes lock easily)
(Remark) For low grip, set at the LOW side and for high grip, set at the
HIGH side.
7When ending, return to the MENU1 screen by pressing the
(JOG) button.
4PLS-Eng-08-1-Function-P39-64.indd 61 2013/04/07 12:41:03
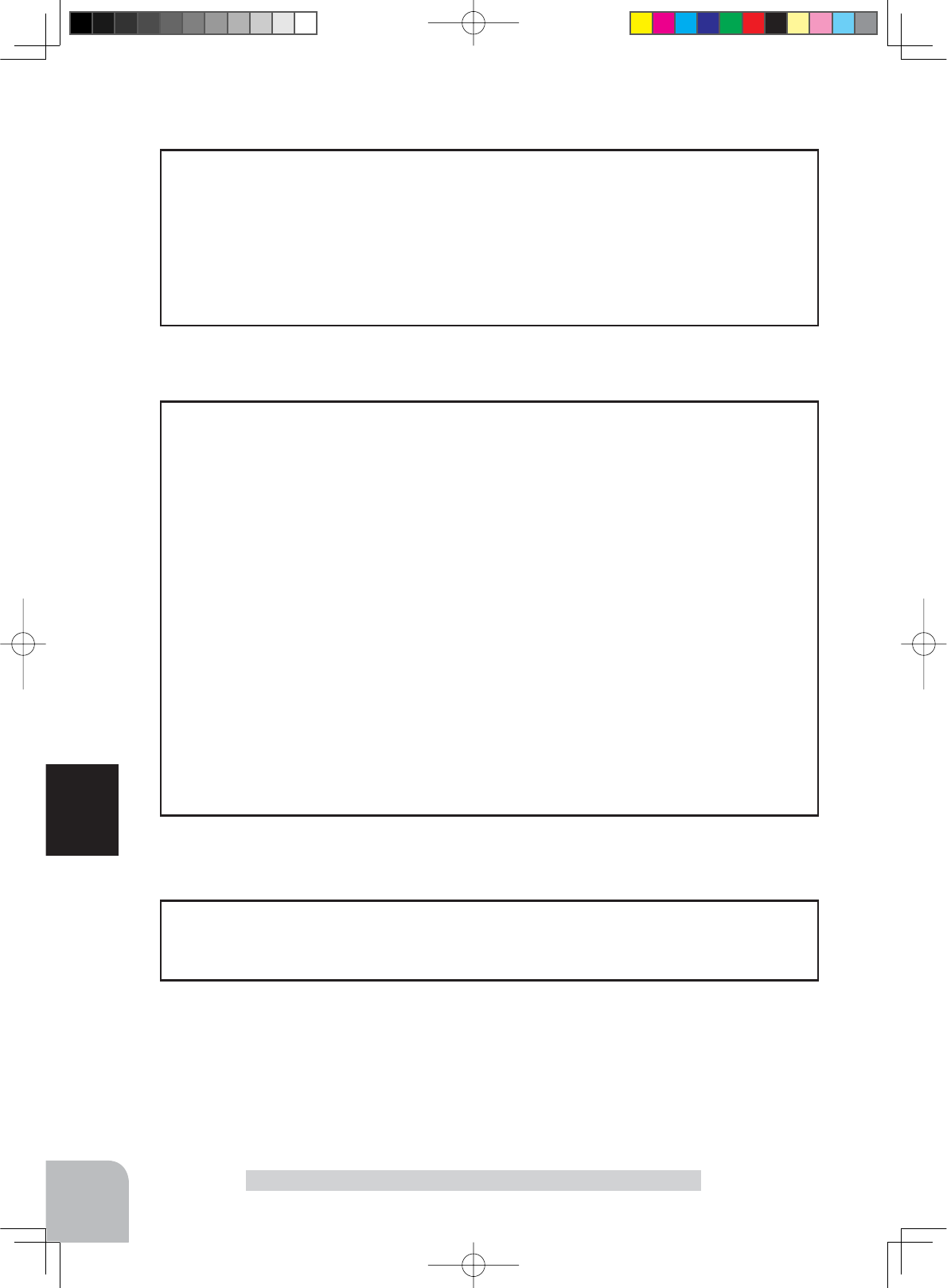
62
Function
A.B.S. Function "TH A.B.S"
When the T4PLS is used with the Futaba fail safe unit (FSU), it will operate as de-
scribed below. However, FSU-1 cannot be used at the high speed mode.
- When the FSU is connected to the throttle channel, and the A.B.S. function has been
DFWLYDWHGWKH)68/('ZLOOÀDVKHDFKWLPHWKHVHUYRRSHUDWHV7KHUHDVRQIRUWKLVLV
that the FSU responds to sudden data changes caused by A.B.S. function pumping op-
eration. It does not mean that the fail safe function is activated. The servo will not be
affected.
Fail Safe Unit
- Basic setting
AB.P: Approx. 30% (If this value is too high, the braking distance will increase.)
CYCL: 5~7
DUTY: (When grip is low: LOW side, when grip is high: HIGH side)
DELY: 10~15%
TG.P: Approx. 70%
- When the wheels lock, or the car spins, when the brakes are applied fully
AB.P: Increase from 30%
DUTY: Shift to "LOW" side
DELY: Reduce the delay
- When the braking effect is poor and the braking distance is long when the brakes are
applied fully
AB.P: Decrease from 30%
DUTY: Shift to "HIGH" side
DELY: Increase the delay
Example of A.B.S. function setting when BLS351 / BLS352 used
(There will be a slight difference depending on the state of the linkage.)
ABS can be independently set for the brakes which are controlled by the 3rd CH and
4th CH by using the brake mixing (BRAKE MIX) function described on page 68. For
more information, read the brake mixing (BRAKE MIX) item.
1/5 scale car and other independent brakes and ABS
4PLS-Eng-08-1-Function-P39-64.indd 62 2013/04/07 12:41:03
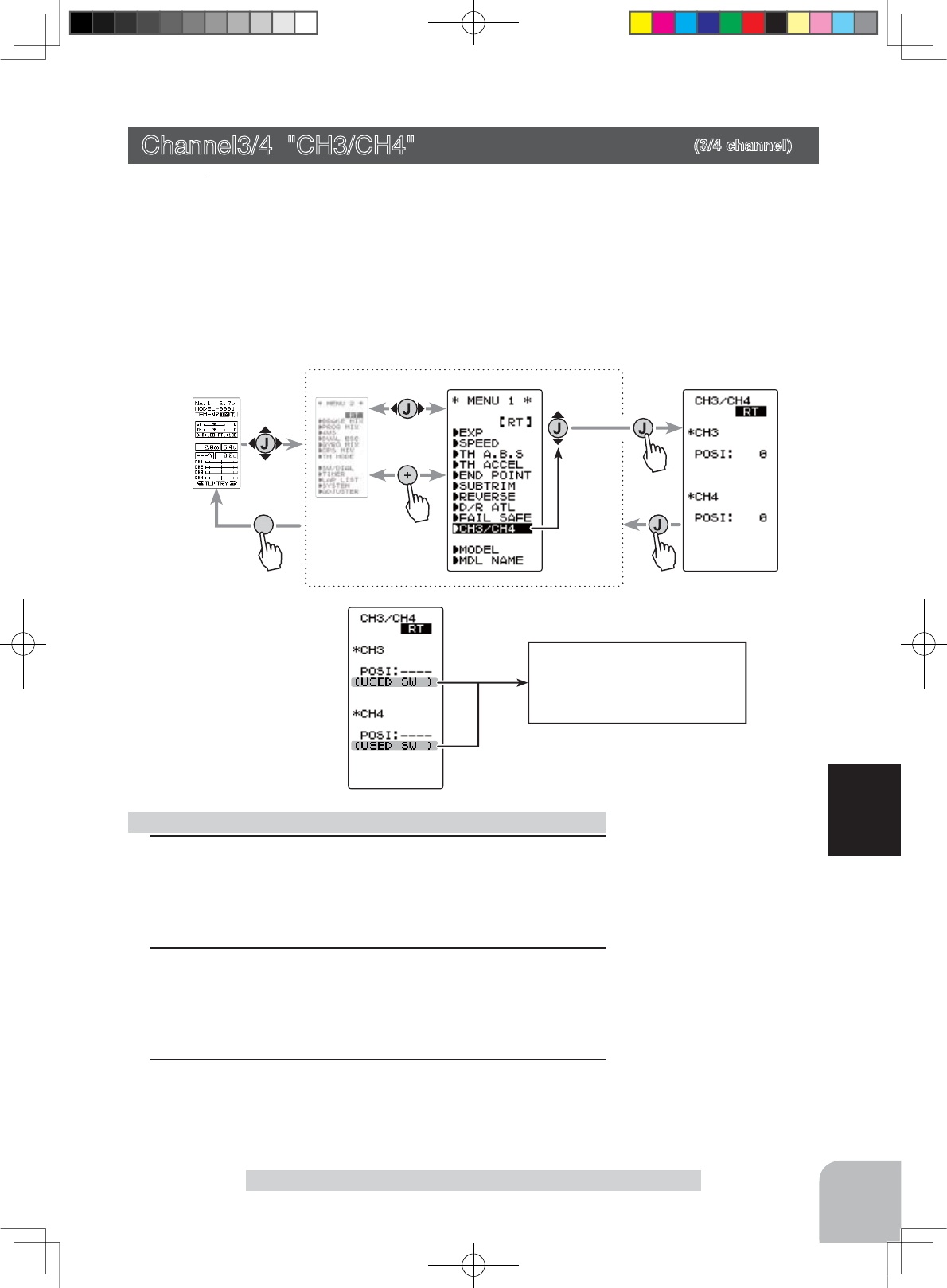
Press
Press
(HOME screen) (MENU 2 screen) (CH3/CH4 screen)
Press
(MENU 1 screen)
Press
Select
"
CH3/CH4
"
Display when CH3/4 is as-
signed to a switch by the switch
dial functiondialt.Cannot adjust
the CH3/4 via the screen.
63
Function
Channel3/4 "CH3/CH4"
Channel3/4 "CH3/CH4" (3/4 channel)
The channel 3/4 servo position can be set from the transmitter. When CH3 is as-
signed to a dial by the switch dial function (p.65), this setting is linked to that dial.
When CH3/4 is not assigned to a dial, it can be set with this screen.
When CH3/4 is assigned to a switch by the switch dial function (p.65), you cannot
adjust the CH3/4 via the screen.
Display "CH3/CH4" screen by the following method:
1 (Function selection)
On each CH3/CH4 screen select CH3 "POSI" or CH4 "POSI"
by the (JOG) button up or down operation.
2 (Position setting/rate adjustment)
Use the (+) and (-) buttons to adjust the channel 3 or chan-
nel 4 position.
3When ending, return to the MENU1 screen by pressing the
(JOG) button.
Rate/position adjustment on channel menu screen
Adjust button
- Adjust with the (+) and (-) but-
tons.
- Return to the initial value
"100" by pressing the (+) and
(-) buttons simultaneously for
about 1 second.
Channel 3 position (POSI)
Channel 4 position (POSI)
0~100%
Initial value: 0
4PLS-Eng-08-1-Function-P39-64.indd 63 2013/04/07 12:41:04
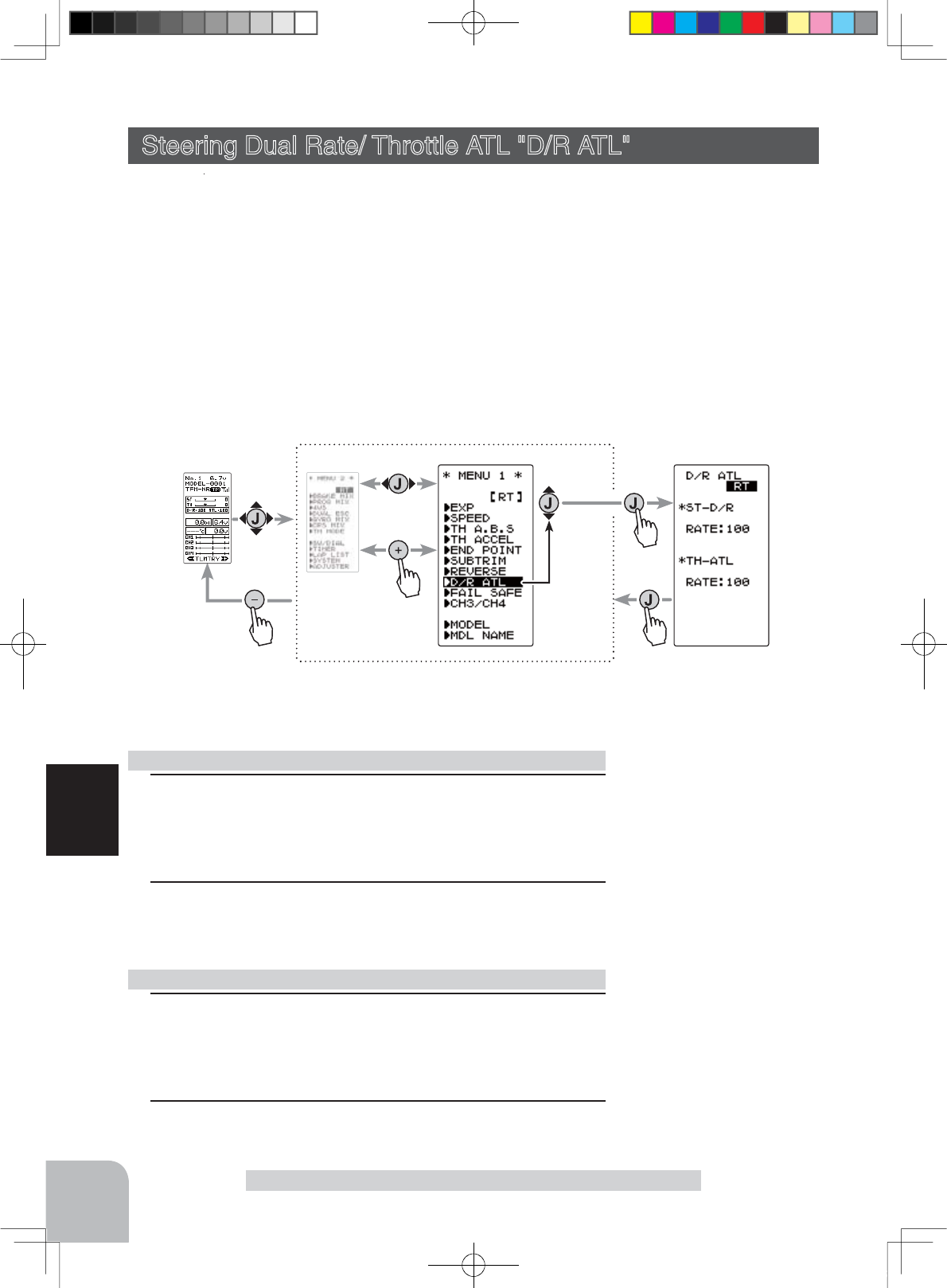
Press
Press
(HOME screen) (MENU 2 screen) (D/R ATL screen)
Press
(MENU 1 screen)
Press
Select
"
D/R ATL
"
64
Function
Steering Dual Rate/ Throttle ATL "D/R ATL"
Steering Dual Rate/ Throttle ATL "D/R ATL"
D/R (Steering dual rate)
The steering left and right servo travels are adjusted simultaneously. This setting is
linked to transmitter grip dial DT3. When DT3 is assigned another function, dual
rate can be adjusted with this screen.
ATL (Throttle ATL)
This function decreases the set value when the braking effect is strong and increas-
es the set value when the braking effect is weak. This function is linked to transmit-
ter grip dial DT4. When DT4 is assigned nother function, this function can be set
with this screen.
Display "D/R ATL" screen by the following method:
1(Dual rate adjustment)
Select the setting item ST-D/R "RATE" by (JOG) button up or
down operation. Adjust the servo travel with the (+) and (-)
buttons.
2When ending, return to the MENU1 screen by pressing the
(JOG) button.
1(Brake amount adjustment)
Select the setting item TH-ATL "RATE" by (JOG) button up
or down operation. Adjust the servo travel with the (+) and (-)
buttons.
2When ending, return to the MENU1 screen by pressing the
(JOG) button.
Dual rate adjustment
ATL function adjustment
Adjust button
- Adjust with the (+) and (-) but-
tons.
- Return to the initial value "100"
by pressing the (+) and (-) but-
tons simultaneously for about 1
second.
Adjust button
- Adjust with the (+) and (-) but-
tons.
- Return to the initial value "100"
by pressing the (+) and (-) but-
tons simultaneously for about 1
second.
D/R rate (RATE)
0~100%
Initial value: 100
ATL rate (RATE)
0~100%
Initial value: 100
4PLS-Eng-08-1-Function-P39-64.indd 64 2013/04/07 12:41:05
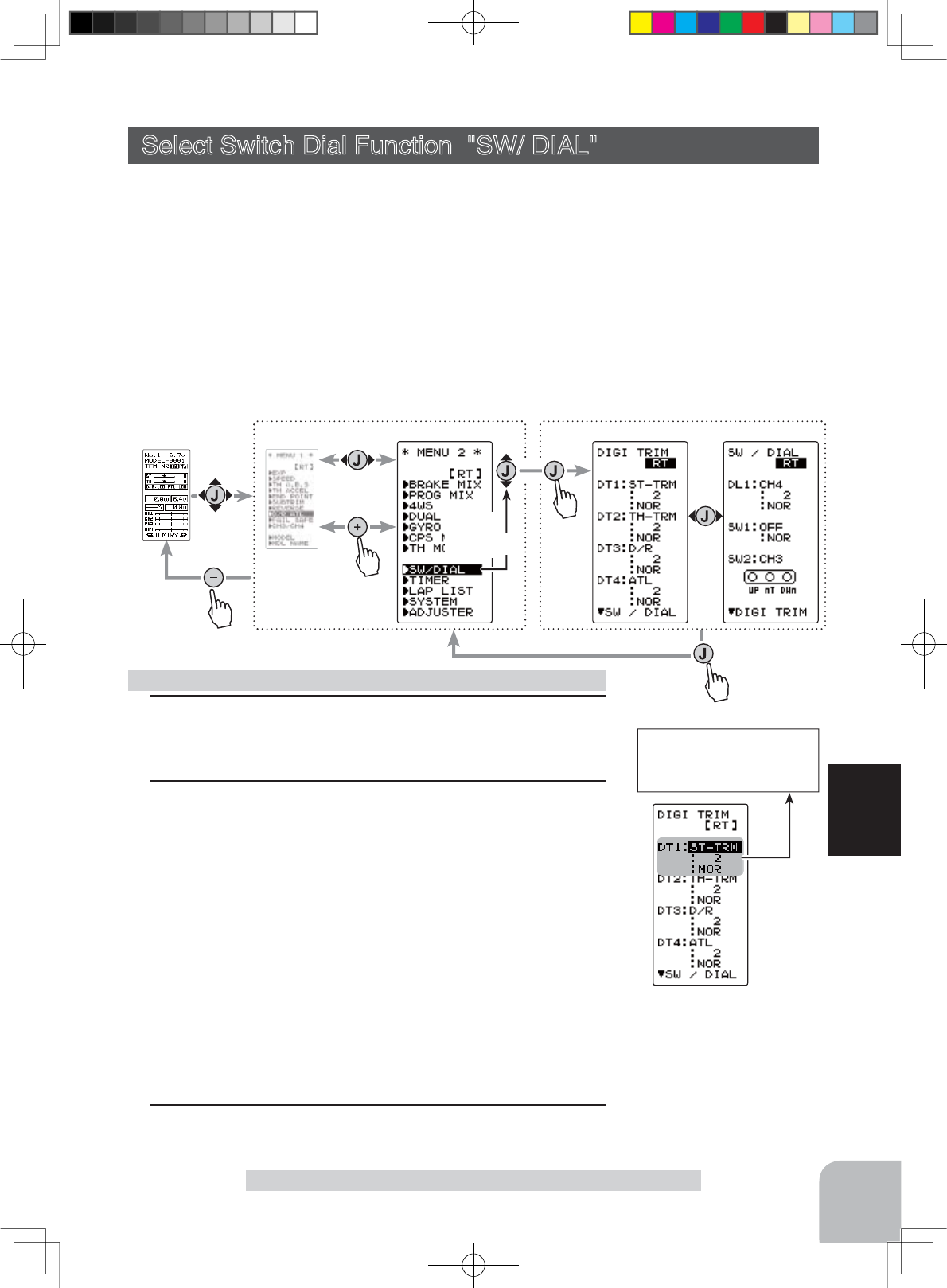
Press
Press
Press
Press
Select
"
SW/DIAL"
(HOME screen) (MENU 1 screen) (SW/DIAL screen)
(MENU 2 screen)
65
Function
Function Select Trim Dial “TRIM DIAL”
*Function selection
*Step amount setting
*Direction of operation setting
Select Switch Dial Function "SW/ DIAL"
Selection of the function to be performed by digital trim (DT1, DT2, DT3, DT4) di-
al (DL1) and switch (SW1, SW2).
-
The functions that can be assigned to dial, digital trim and switch are listed on the next page.
- The
dial and digital trim are
step amount can be adjusted. (The relationship between set
value and step amount is shown in the table on the next page.)
- The direction of operation of the servos can be reversed. (NOR/REV)
- SW1 alternate operation (operation which switches between ON and OFF each time the
switch is pressed) is possible.
NOR (Normal) -ON only while pressed, OFF when released.
ALT (Alternate) -Switched between ON and OFF each time pressed.
Display "SW/DIAL" screen by the following method:
1 (Setting dial/trim selection)
Select the dial or trim you want to set by the (JOG) button up
or down operation.
2 (Function setting)
Select the function with the (+) or (-) button.
- Refer to the list on the next page for the abbreviations of the functions.
(Step amount setting)
Select the step amount you want to set by the (JOG) button
up or down operation. Use the (+) or (-) button to set the step
amount.
- Refer to the next page for the relationship between set value and step amount.
(Changing the direction of operation)
Select the Direction of operation you want to set by the (JOG)
button up or down operation. Use the (+) or (-) button to trim/
dial the direction.
3When ending, return to the MENU1 screen by pressing the
(JOG) button.
Function select dial/trim setting
Adjust button
Adjust with the (+) and (-)
buttons.
- Return to the initial value "2"
by pressing the (+) and (-)
buttons simultaneously for
about 1 second.
4PLS-Eng-08-2-Function-P65-83.indd 65 2013/04/07 12:48:09
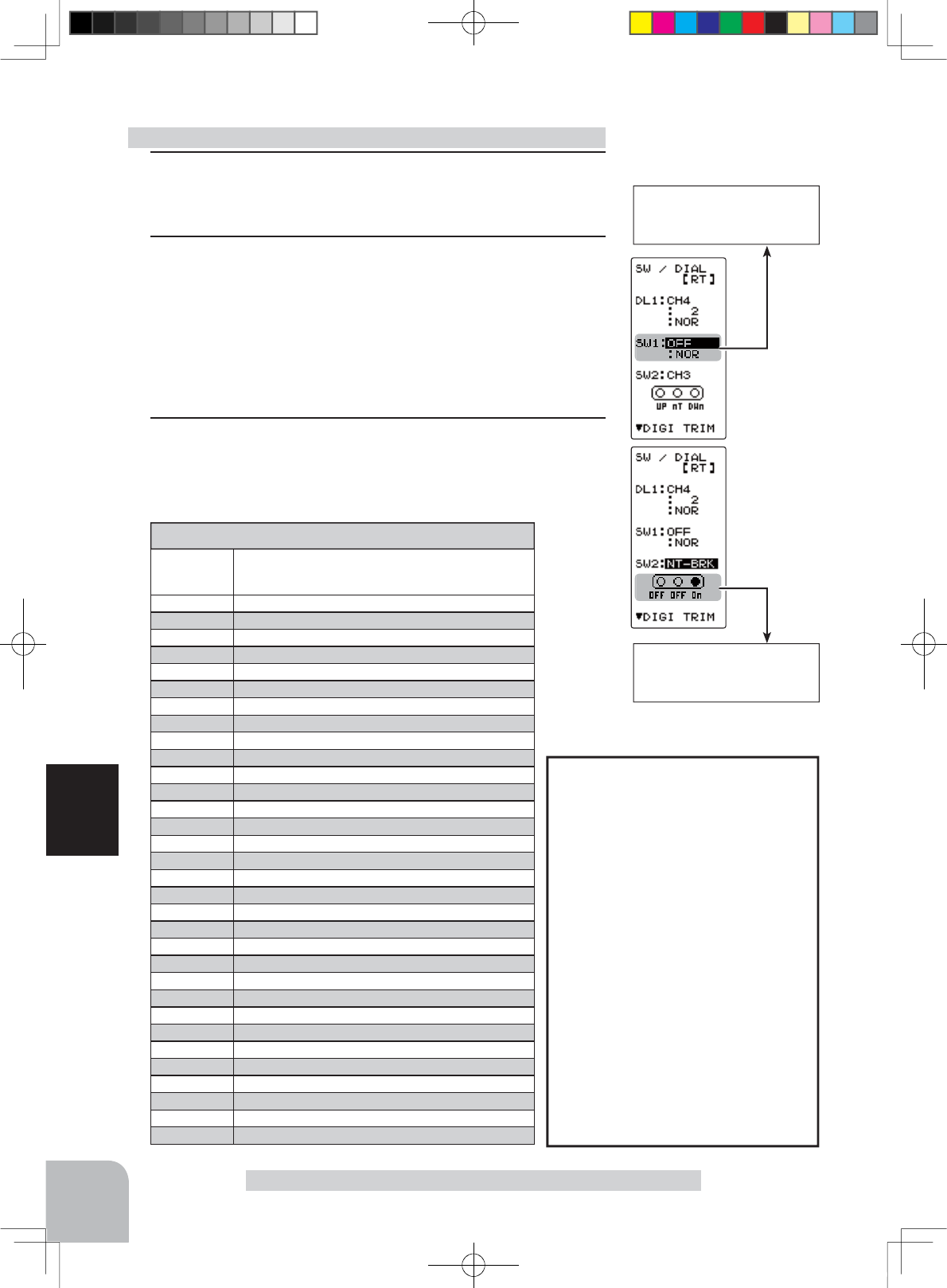
Adjust button
Adjust with the (+) and (-) but-
tons.
SW1 function selection
Direction of operation set-
ting
SW2 function selection
ON/OFF position is dis-
played.
66
Function
Abbreviation
used on setup
screen
Function name, etc
D/R Dual rate function
ATL ATL function
EXP-ST Steering EXP
EXP-FW Throttle EXP (Forward side)
EXP-BK Throttle EXP (Brake side)
SPD-TN Steering speed (Turn side)
SPD-RN Steering speed (Return side)
ABS.PS A.B.S. function (Return amount)
ABS.DL A.B.S. function (Delay)
CYCLE A.B.S. function (cycle speed)
ACC-FW Throttle acceleration (Forward side)
ACC-BK Throttle acceleration (Brake side)
TH-SPD Throttle speed
ST-TRM Steering trim
TH-TRM Throttle trim
CH3 Channel 3
CH4 Channel 4
SUBTR1 Sub trim (CH1)
SUBTR2 Sub trim (CH2)
SUBTR3 Sub trim (CH3)
SUBTR4 Sub trim (CH4)
IDLE Idle up function
ESC-RT Dual ESC mixing (4ch ESC rate)
TH-OFF Throttle off (engine cut)
PMX-A Program mixing (RGHT/BRAK/DOWN sides)
PMX-B Program mixing (LEFT/FWRD/UP sides)
BK3-RT Brake mixing (3ch brake rate)
BK4-RT Brake mixing (4th brake rate)
4WS-RT 4WS mixing (3ch steering rate)
ESC-MD Dual ESC mixing (Drive mode select)
GYRO Gyro mixing (Gain rate)
OFF Not used
Set table functions (DL1, DT1/DT2/DT3)
(Setting range: 1~10, 20, 30, 40, 50,
100, 2P)
-Steering trim/throttle trim
When set to the minimum "1", the total
trim operating width is 200 clicks. For
"100", the total operating width is 2 clicks
and for 2P, the total operating width is 1
click.
-Rate, etc. setting
This is the % value which is operated by
1 click relative to the set value of each
rate. Since the total operating width of
functions having a rate of -100~0~+100
is 200%, when set to "100", the total op-
erating width is 2 clicks. Since the total
operating width of functions with a 0~100
rate is 100%, "100" and 2P are operated
by 1 click.
-Channel 3/4
When set to the minimum "1", the to-
tal operating width of channel 3 is 200
clicks. For "100", the total operating with
is 2 clicks and 2P is operated by 1 click.
Relationship between set value
and step amount
Function Select Trim Dial "TRIM DIAL"
1 (Setting SW selection)
Select the SW you want to set by the (JOG) button up or
down operation.
2 (Function setting)
Select the function with the (+) or (-) button.
-Refer to the list for the abbreviations of the functions.
(Changing the SW1operation system)
Select DIR of <SW1> by the (JOG) button up or down opera-
tion. Select ALT or NOR with the (+) or (-) button.
3When ending, return to the MENU2 screen by pressing the
(JOG) button.
Function select switch setting
4PLS-Eng-08-2-Function-P65-83.indd 66 2013/04/07 12:48:09
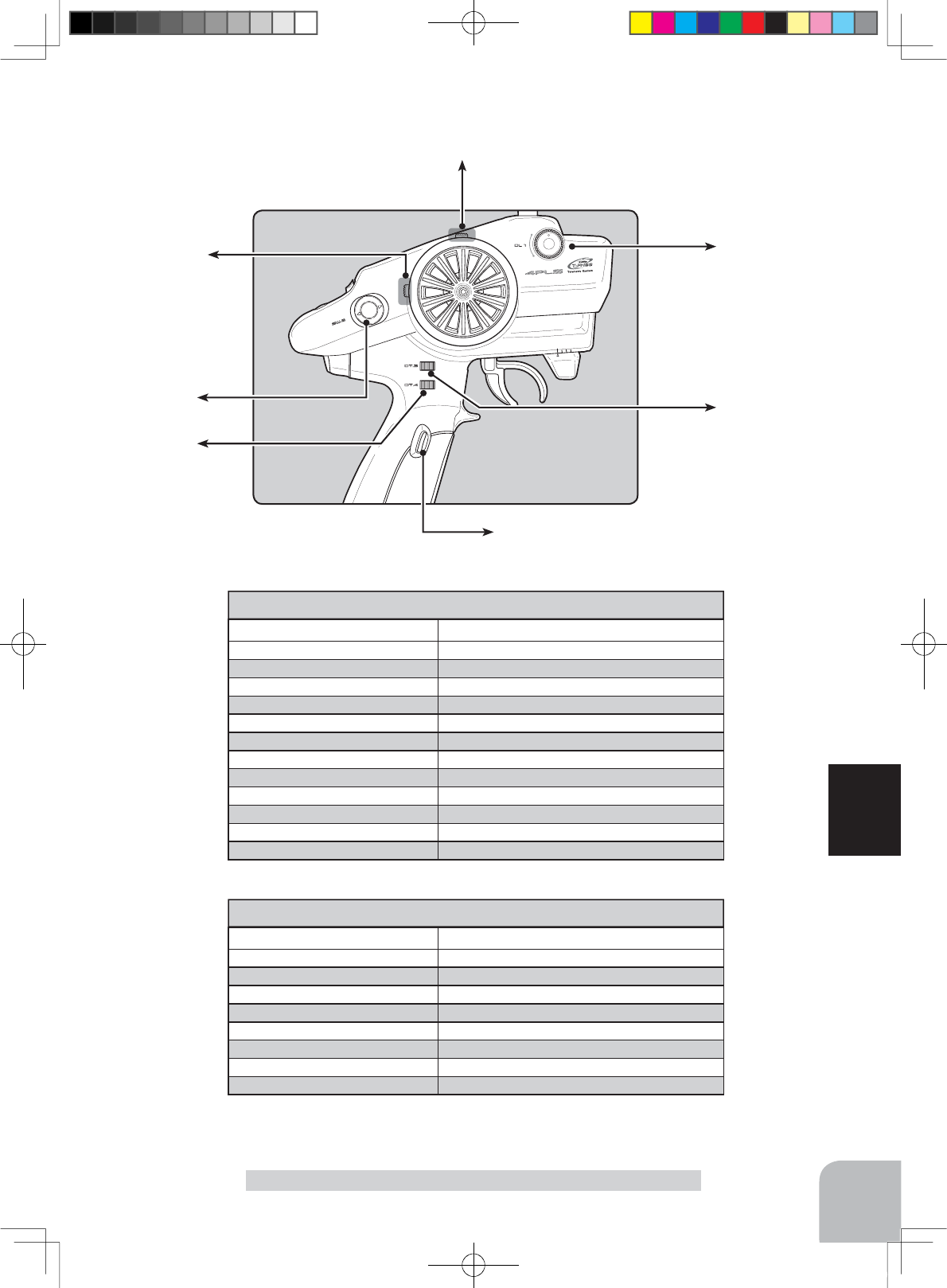
67
Function
Function Select Trim Dial "TRIM DIAL"
SW1
SW2
DT2
DT1
DT3
DT4
DL1
Abbreviation used on setup screen
Function name, etc
NT-BRK Neutral brake function ON/OFF
ABS A.B.S function ON/OFF
IDLE Idle up function ON/OFF
PRGMIX Program mixing function ON/OFF
TH-OFF Throttle off (engine cut) function ON/OFF
CH3 channel 3
CH4 channel 4
4WS MIX 4WS mixing type select
TIMER Timer function start/stop
LOGGER Telemetry log start/stop
GYRO Switching GYRO mode
OFF Not used
Set table functions (SW1)
Abbreviation used on setup screen
Function name, etc
NT-BRK Neutral brake function ON/OFF
ABS A.B.S function ON/OFF
IDLE Idle up function ON/OFF
PRGMIX Program mixing function ON/OFF
TH-OFF Throttle off (engine cut) function ON/OFF
CH3 channel 3
CH4 channel 4
OFF Not used
Set table functions (SW2)
4PLS-Eng-08-2-Function-P65-83.indd 67 2013/04/07 12:48:10
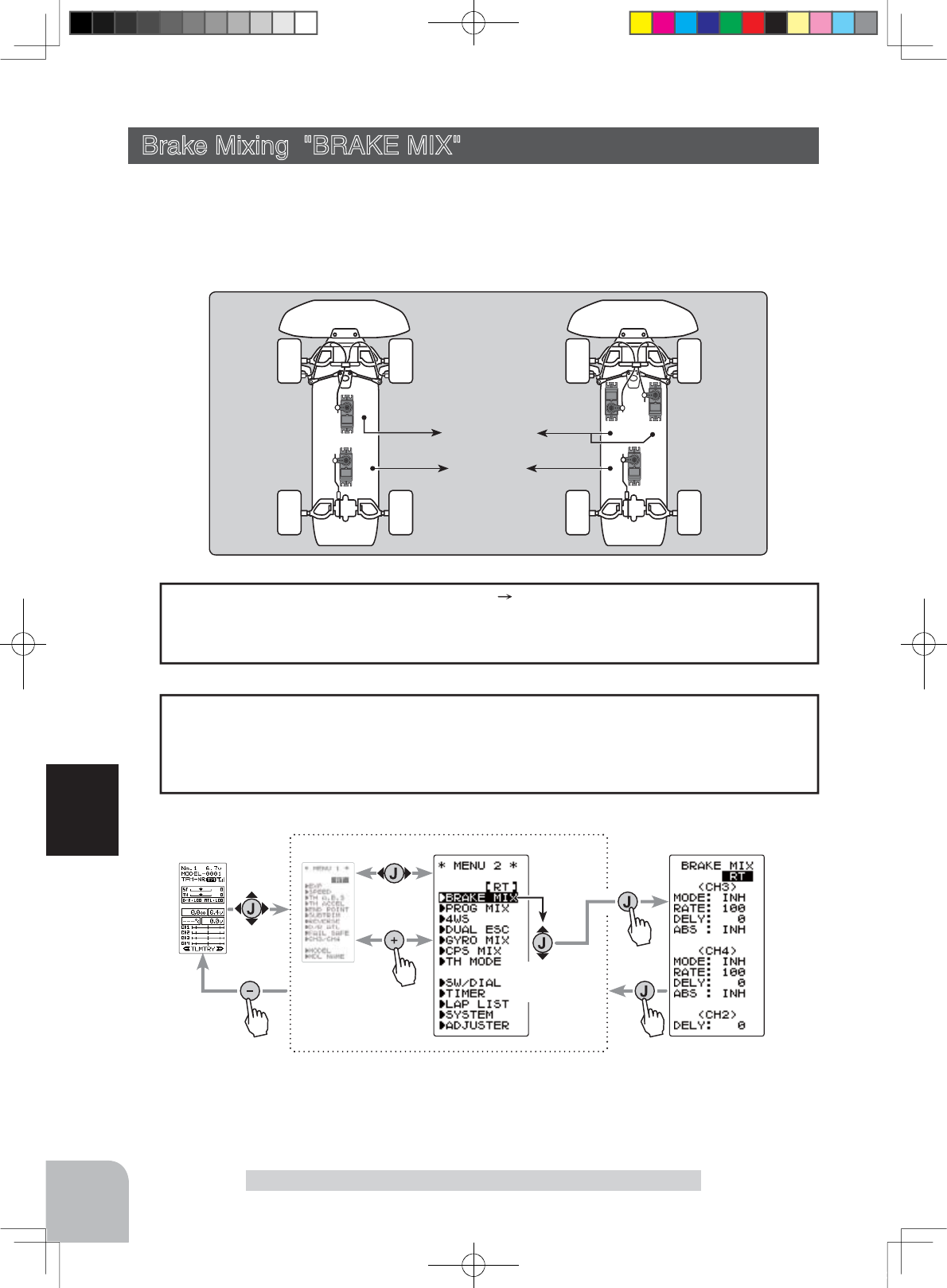
Press
Press
Press
Press
Select
"BRAKE MIX"
(HOME screen) (MENU 1 screen) (
BRAKE MIX
screen)
(MENU 2 screen)
Setup item
<CH3>
MODE : Brake function ON/OFF
RATE : Brake rate
DELY : Delay amount
ABS : ABS. function ON/OFF
<CH4>
MODE : Brake function ON/OFF
RATE : Brake rate
DELY : Delay amount
ABS : ABS. function ON/OFF
<CH2>
DELY : Delay amount
68
Function
Brake Mixing "BRAKE MIX" (Throttle, 3rd /4th channel system)
This function is used when the front and rear brakes must be adjusted independently
such as a 1/5 scale GP car. This mixing uses the 2nd CH for the rear brakes and the 3rd
or 4th CH for the front brakes, or controls the front brakes with the 3rd CH and 4th CH
servos, or controls the 2nd CH by independent throttle and controls the rear and front
brakes with the 3rd CH and 4th CH.
-When braking, mixing is applied to 2nd CH 3rd CH, 4th CH.
-3rd CH and 4th CH brake amount, 2nd CH, 3rd CH, and 4th CH brake delay, and 3rd
CH and 4th CH brake ABS can be set.
Operation
The ABS function can be used independently at the CH3 and CH4 sides even when
the CH2 side ABS function is OFF. The amount of pumping speed (CYCL), operation
point (TG.P), and duty ratio (DUTY) can be set in common with the CH2 side ABS
IXQFWLRQ&+DQG&+EUDNHUHWXUQ$%3LV¿[HGDW
CH3/4 brake ABS function
3CH
3CH 4CH
2CH
2CH
or
4CH
Front Brake
Rear Brake
Brake Mixing "BRAKE"
Display "SW/DIAL" screen by the following method:
4PLS-Eng-08-2-Function-P65-83.indd 68 2013/04/07 12:48:12
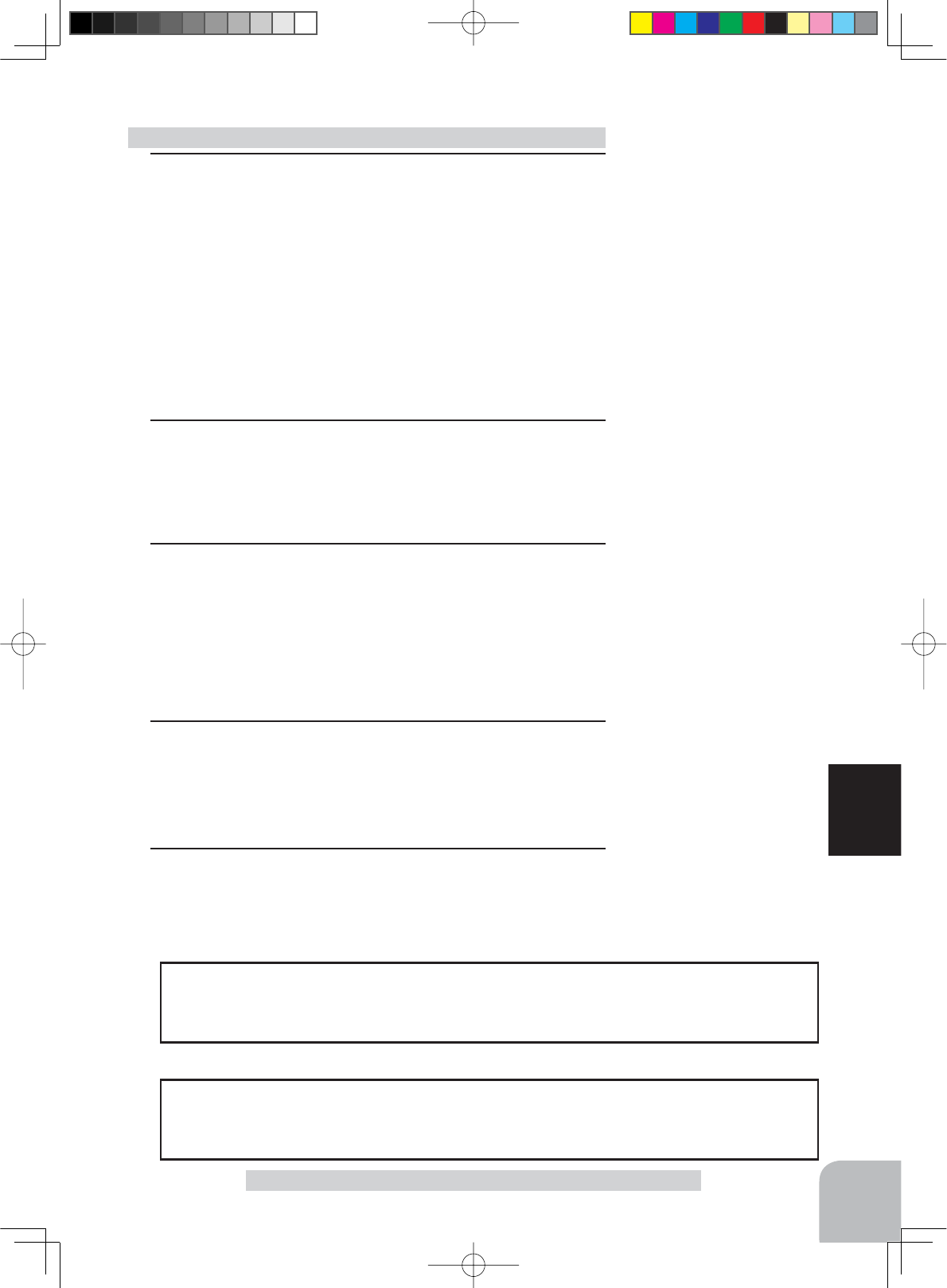
69
Function
Brake Mixing "BRAKE"
1 (Brake mixing function ON/OFF)
Using the (JOG) button, select "MODE" of <CH3> for CH3
brake and "MODE" of <CH4> for CH 4 brake.
Use the (+) or (-) key and set the function to the "ACT" state.
"INH" : Function OFF
"ACT" : Function ON
- When "(4WS>OFF)" is displayed below <CH3>ABS, the CH3 brake cannot
be used if the 4WS function is not set to "ACT".
- When "(ESC>INH)" is displayed under <CH4>ABS, the CH4 brake cannot
be used if the dual ESC function is not set to "INH".
2(Brake rate)
Using the (JOG) button, select "RATE" of <CH3> for CH3
brake and "RATE" of <CH4> for CH 4 brake , and use the (+)
and (-) buttons to adjust the Brake rate amount.
3(Delay amount setup)
Using the (JOG) button, select "DELY" of <CH3> for CH3
brake, "DELY" of <CH4> for CH 4 brake and "DELY" of
<CH2> for CH 2 brake. Use the (+) and (-) buttons to adjust
the delay amount.
"0" : No delay
"100" : Maximum delay amount
4(3rd & 4th channels brake-A.B.S ON/OFF)
Using the (JOG) button, select "ABS" of <CH3> for CH3
brake and "ABS" of <CH4> for CH 4 brake.
Use the (+) or (-) key and set the function to the "ACT" state.
5When ending, return to the MENU2 screen by pressing the
(JOG) button.
Brake mixing adjustment
Adjustment buttons
- Use the (+) and (-) buttons to
make adjustments.
- Return to the initial value by
pressing the (+) and (-) but-
tons simultaneously for about
1 second.
Brake rate (RATE)
0 ~ 100
Initial value:100
Delay amount (DELY)
(CH3) 0 ~ 100
(CH4) 0 ~ 100
(CH2) 0 ~ 100
Initial value:0
Function ON/OFF (MODE)
INH, ACT
Function ON/OFF (ABS)
INH, ACT
The function select
switch dial
function can control the 3rd/4th channels. Brake rate
(RATE) can be controlled with digital dial or digital trim, using the function select di-
al function. (See page 65)
Dial / Trim Setting
To use CH3 of the brake mixing function, 4WS mixing (p.72) must be set to "INH".
To use CH4 of the dual ESC function (p.74) and CPS mixing (p.78) must be set to
"INH".
Setting the 4WS mixing/dual ESC function
Select button
- Select with the (+) or (-) but-
tons.
Select button
- Select with the (+) or (-) but-
tons.
4PLS-Eng-08-2-Function-P65-83.indd 69 2013/04/07 12:48:12
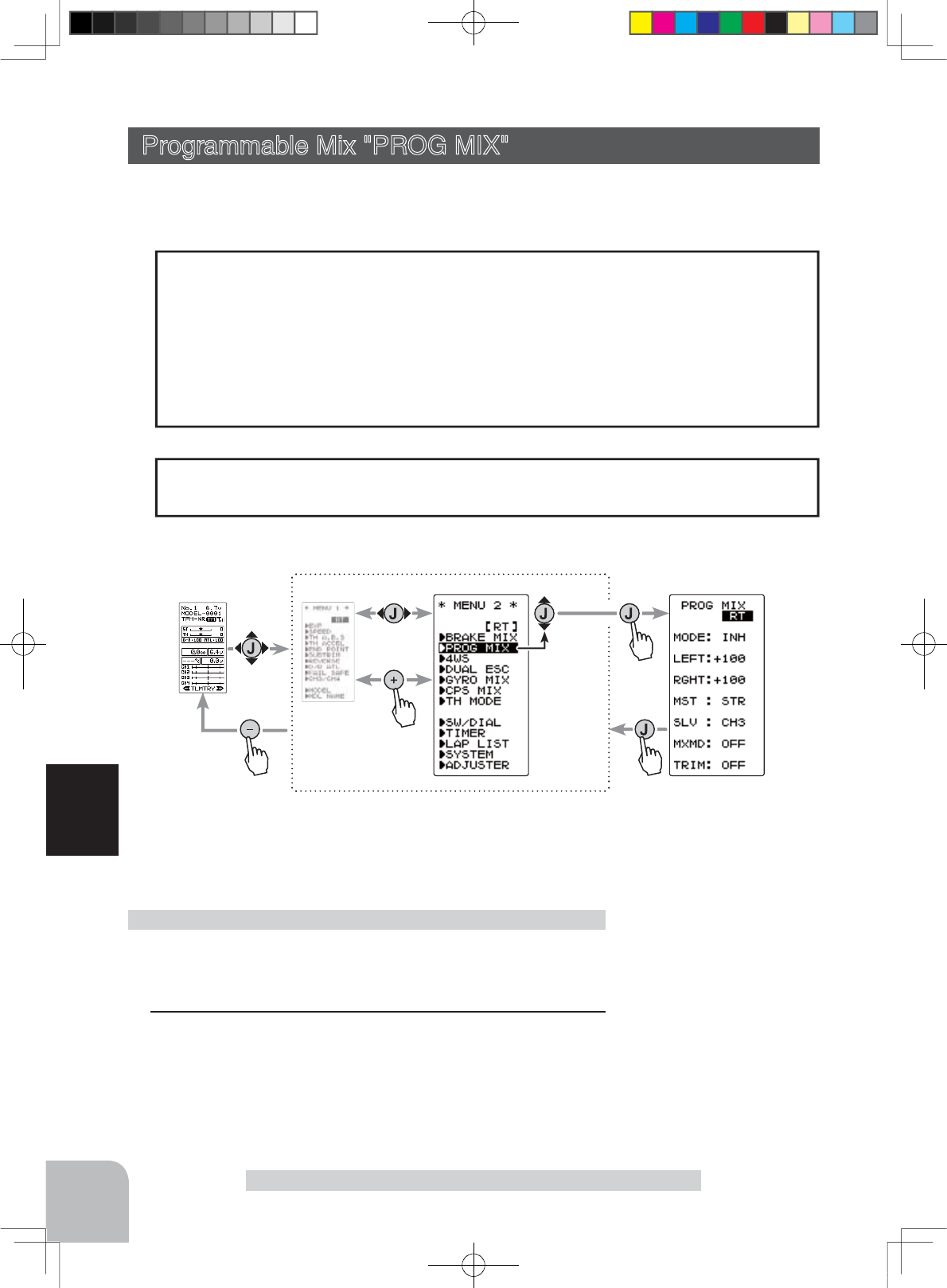
Press
Press
Press
(HOME screen) (MENU 1 screen) (PROG MIX screen)
(MENU 2 screen)
Press
Select
"
PROG MIX
"
70
Function
Programmable Mix "PROG MIX"
This function allows you to apply mixing between the steering, throttle, channel 3 and
channel 4.
-When the steering or throttle channel is the master channel (channel that applies mix-
ing), trim data can be added. (Trim mode)
- The mixing mode selection. (Master mixing mode)
Relating function
steering :EPA, STR EXP, D/R, SPEED, 4WS
throttle :EPA, THR EXP, ATL, ABS, SPEED, BRAKE MIX, NT-BRK, ESC MIX, TH ACCEL
CH3 :EPA,BRAKE MIX,4WS
CH4 :EPA,BRAKE MIX,ESC MIX
Additional Functions
The movement of the master channel side will be added to the movement of the slave
channel side.
Movement of the slave channel side
Programmable Mix "PROG MIX" (All channels)
Function SW
PROGMIX
Program mixing adjustment
(Preparation)
- When "PROG MIX" is turned ON and OFF by switch, set
the switch by select switch dial function (p.65).
1 (Mixing function ON/OFF)
Select the setting item "MODE" by the (JOG) button up or
down operation. Use the (+) or (-) and set the function to the
"ON" or "OFF" state.
“INH” : Function OFF
“ON” : Function ON. When the switch is OFF, “OFF” is displayed.
Display "PROG MIX" screen by the following method:
Function ON/OFF (MODE)
INH,ON(OFF)
Setup items
MODE : Function ON/OFF
LEFT :
Mixing rate (Left side)
RGHT :
Mixing rate (Right side)
MST : Master channel
SLV : Slave channel
MXMD : Mix mode
TRIM : Trim mode
Select button
- Select with the (+) or (-) but-
tons.
4PLS-Eng-08-2-Function-P65-83.indd 70 2013/04/07 12:48:12
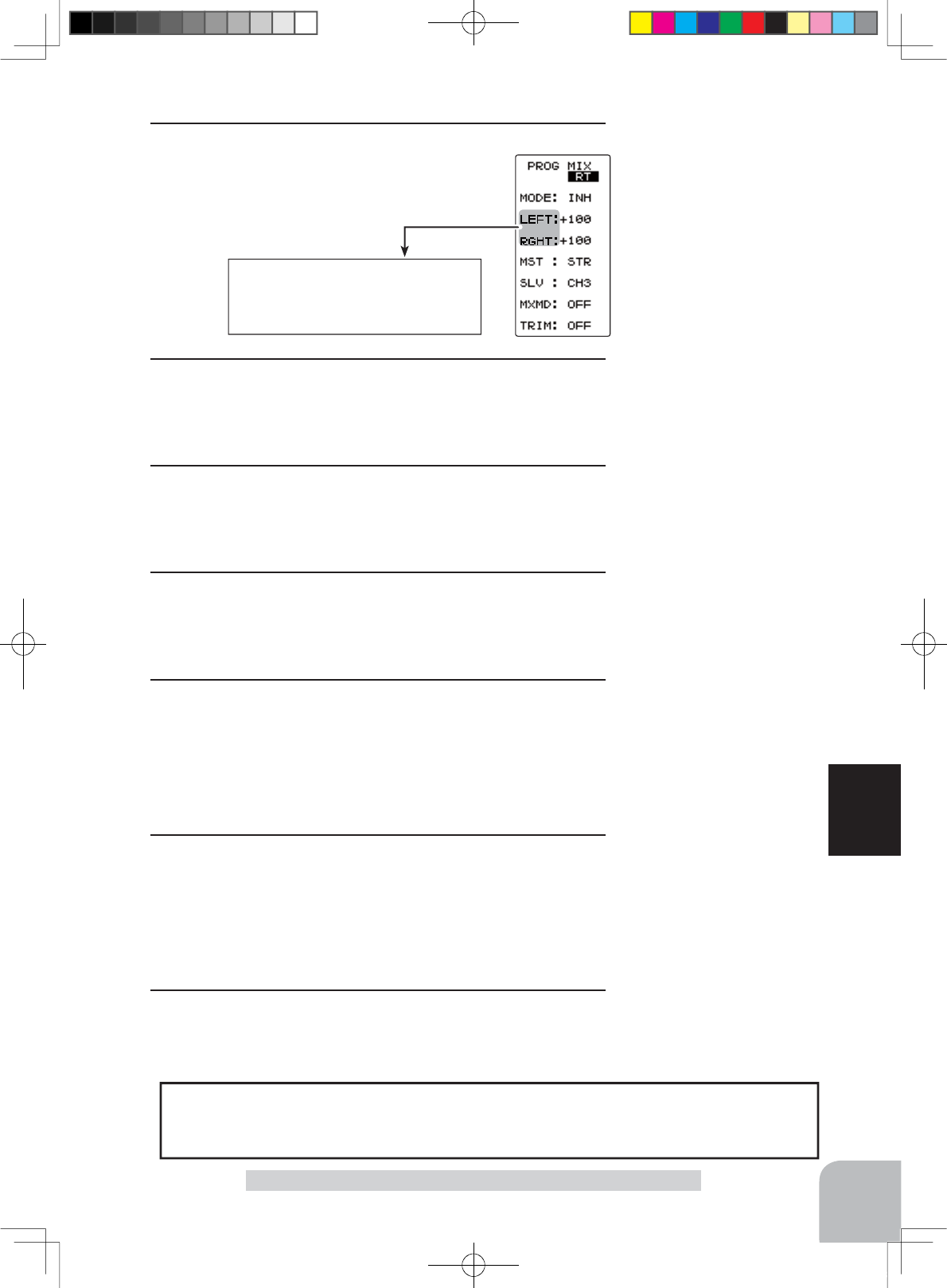
These setup items are different de-
pending on the master channel.
Upper side : LEFT/FWRD/UP
Lower side : RGHT/BRAK/DOWN
Program mixing function
71
Function
Programmable Mix "PROG MIX"
Mixing amount
-120~0~+120
Initial value: +100
Channel selection (MST)
STR, THR, CH3, CH4
Initial value :STR
Channel selection (SLV)
STR, THR, CH3, CH4
Initial value :CH3
Mixing mode (MXD)
OFF, ON
Initial value: OFF
Mixing amount
-120~0~+120
Initial value: +100
Trim mode (TRIM)
OFF, ON
Initial value: OFF
2(Master channel)
Select setup item "MST" y the (JOG) button
up or down operation, and select the master
channel by pressing the (+) or (-) button.
Select the program mixing function ON/OFF switch with the function select switch di-
al function. Mixing rate (RATE) can be controlled with digital dial or digital trim, us-
ing the function select switch dial function. (See page 65)
Switch / Dial / Trim Setting
3(Slave channel)
Select setup item "SLV" by the (JOG) button up or down op-
eration, and select the slave channel by pressing the (+) or (-)
button.
4 (Left, forward or up side mixing amount adjustment)
Select the setting item "LEFT", "FWRD", or "UP" by the (JOG)
button up or down operation. Use the (+) or (-) button and
adjust the left, forward, or up side mixing amount.
5 (Right, brake or down side mixing amount adjustment)
Select the setting item "RGHT", "BRAK", or "DOWN" by the
(JOG) button up or down operation. Use the (+) or (-) button
and adjust the right, brake, or down side mixing amount.
6(Mixing mode setup)
Select setup item "MXMD" by the (JOG) button up or down
operation, and use the (+) or (-) button to select the mixing
mode.
"OFF" :Mixing proportional to master channel operation.
"MIX" :Mixing by master channel another function considered.
7(Trim mode setup)
Select setup item "TRIM" by the (JOG) button up or down
operation, and use the (+) or (-) button to select the mixing
mode.
"OFF" :Trim is removed.
"ON" :Trim is added.
8When ending, return to the MENU2 screen by pressing the
(JOG) button.
Adjust button
- Use the (+) and (-) buttons to
make adjustments.
- Return to the initial value
"100" by pressing the (+) and
(-) buttons simultaneously for
about 1 second.
Select button
- Select with the (+) or (-) but-
tons.
Select button
- Select with the (+) or (-) but-
tons.
Select button
- Select with the (+) or (-) but-
tons.
Select button
- Select with the (+) or (-) but-
tons.
4PLS-Eng-08-2-Function-P65-83.indd 71 2013/04/07 12:48:13
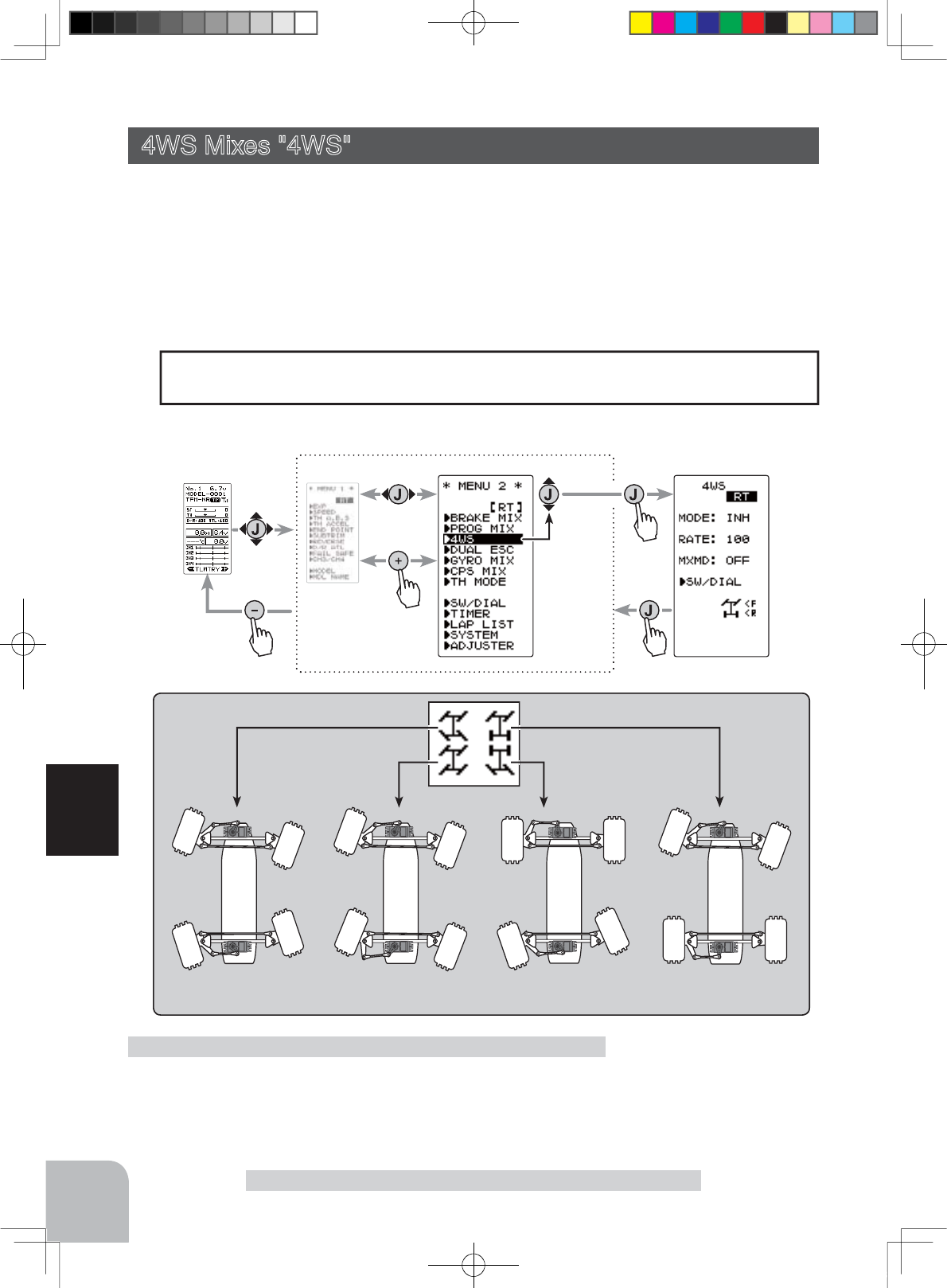
Front side only
(4WS OFF)
Same phase Reverse phase Rear side only
Press
Press
Press
(HOME screen) (MENU 1 screen) (4WS screen)
(MENU 2 screen)
Press
Select
"
4WS
"
72
Function
This function can be used with crawlers and other 4WS type vehicles. It is mixing which
uses the 1st CH to control the front side steering and the 3rd CH to control the rear side
steering.
OFF (front side only), reverse phase, same phase, rear side only and other 4WS type
switching is used by selecting SW1 with the function select switch function (p.65). If
not selected, <NO SW> is displayed. Therefore, select SW1.
4WS Mixes "4WS" (Steering, 3rd channel system)
Setup items
MODE :4WS Type
RATE :
3ch rate (Rear side)
MXMD :Mix mode
4WS Mixes “4WS”
(Preparation)
Since this function is used by switching the type of 4WS with
a switch, the switch used by the function select switch dial
function (page 65) is set.
4WS mixing adjustment
When the 3rd CH was set to ACT at Brake Mixing (p.68) or when Gyro Mixing (p.76)
is used, 4WS mixing cannot be used.
Setting Special mixings
Display "4WS" screen by the following method:
Function SW
4WS
4PLS-Eng-08-2-Function-P65-83.indd 72 2013/04/07 12:48:13
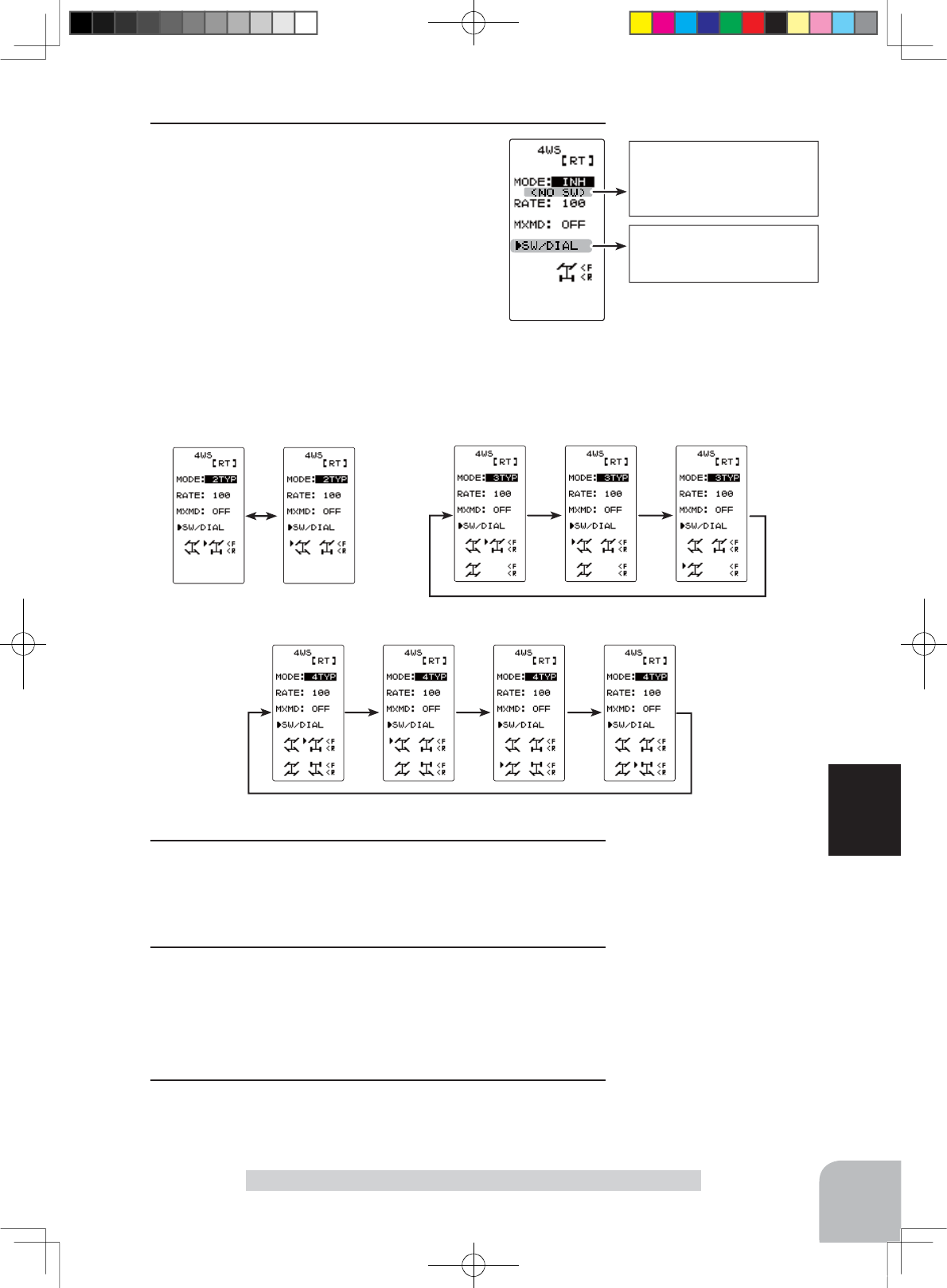
The function select switch
screen (P65) can be dis-
played from this screen.
< NO SW >
If function’s ON/OFF
switch is not selected,
<NO SW> is displayed.
73
Function
4WS Mixes “4WS”
1(4WS type selection)
Select the setting item "MODE" by the (JOG)
button up or down operation. Use the (+) or
(-) and set the function to the "ON" or "OFF"
state.
"INH" :Function OFF (front only)
"2TYP" :Front side only, reverse phase switching
"3TYP" :Front side only, reverse phase and same phase switching
"4TYP" :Front side only, reverse phase, same phase, and rear side only switching
Switched in the order shown in the figure below by set SW
Function ON/OFF (MODE)
OFF, 2TYP, 3TYP, 4TYP
Mixing mode (MXMD)
OFF, ON
Initial value: OFF
Rear rate (RATE)
0 ~ 100
Initial value:100
"2TYP":Front side only and reverse
phase switching "3TYP":Front side only, reverse phase, and same phase switching
"4TYP":Front side only, reverse phase, same phase, and rear side only switching
Adjustment buttons
- Use the (+) and (-) buttons to
make adjustments.
- Return to the initial value by
pressing the (+) and (-) but-
tons simultaneously (approx.
1 sec).
2(Rear side travel adjustment)
Select setting item "RATE" by the (JOG) button up or down
operation. Adjust the rear side travel with the (+) or (-) but-
ton.
3(Mix mode setting)
Select setting item "MXMD" by the (JOG) button up or down
operation. Set the mix mode with the (+) or (-) button.
"OFF" :The EXP function of the 1st CH and other settings are not mixed.
"ON" :The EXP function o the 1st CH and other settings are mixed.
4When ending, return to the MENU screen by moving the cur-
sor to the positions other than SW/DIAL and pressing the
(JOG) button.
Select button
- Select with the (+) or (-) but-
tons.
Select button
- Select with the (+) or (-) but-
tons.
4PLS-Eng-08-2-Function-P65-83.indd 73 2013/04/07 12:48:14
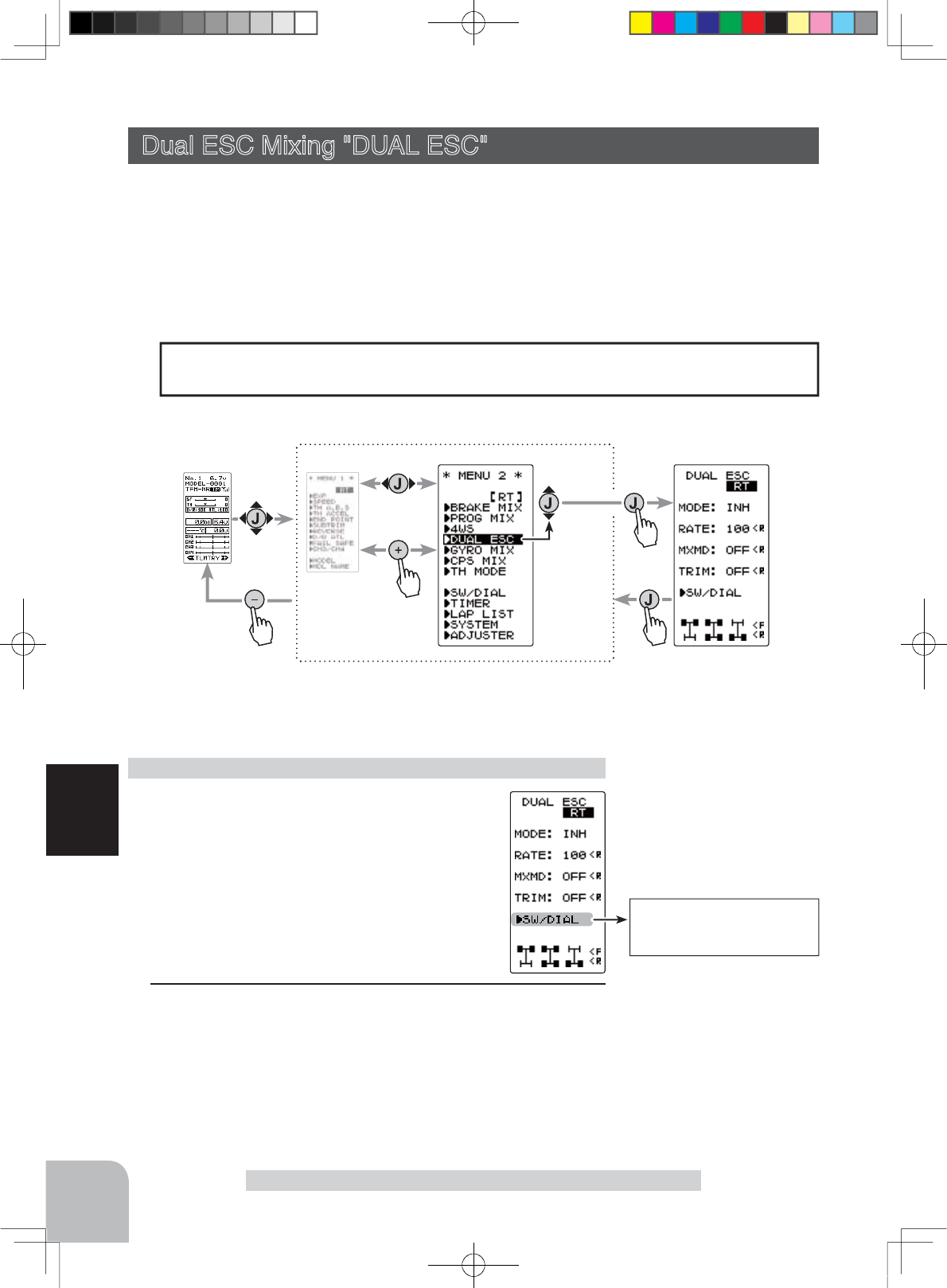
Press
Press
Press
(HOME screen) (MENU 1 screen) (DUAL ESC screen)
(MENU 2 screen)
Press
Select
"
DUAL ESC
"
The function select switch
screen (P65) can be dis-
played from this screen.
74
Function
Dual ESC mixing "DUAL ESC"
This function is mixing used with crawlers and other 4WD type vehicles and uses the
2nd CH to control the front motor controller and the 4th CH to control the rear motor
controller.
Front drive only, rear drive only, or both front and rear drive can be selected using any
programmed DT (digital trim) button.
Dual ESC Mixing "DUAL ESC" (Throttle system)
(Preparation)
- This function is used to switch between front
drive/4WD/rear drive using one of the dial
(trim). Set the desired dial (trim) for this func-
tion using the SW/DIAL screen (p.65).
1 (Dual ESC setting)
Select the setting item "MODE" by the (JOG) button up or
down operation. Set the function by pressing the (+) or (-)
button.
"INH" : Function OFF
"ACT" : Function ON
Dual ESC mixing adjustment
Function ON/OFF (MODE)
INH, ACT
Display "DUAL ESC" function screen by the following method:.
When the 4th CH was set to ACT at Brake Mixing (p.68) or when CPS Mixing (p.78)
is used, Dual ESC mixing cannot be used.
Setting Special mixings
Setup items
MODE : Function ON/OFF
RATE :
4ch rate (Rear side)
MXMD : Mix mode
TRIM : Trim mode
Function SW
ESC-MD
Select button
- Select with the (+) or (-) but-
tons.
4PLS-Eng-08-2-Function-P65-83.indd 74 2013/04/07 12:48:14
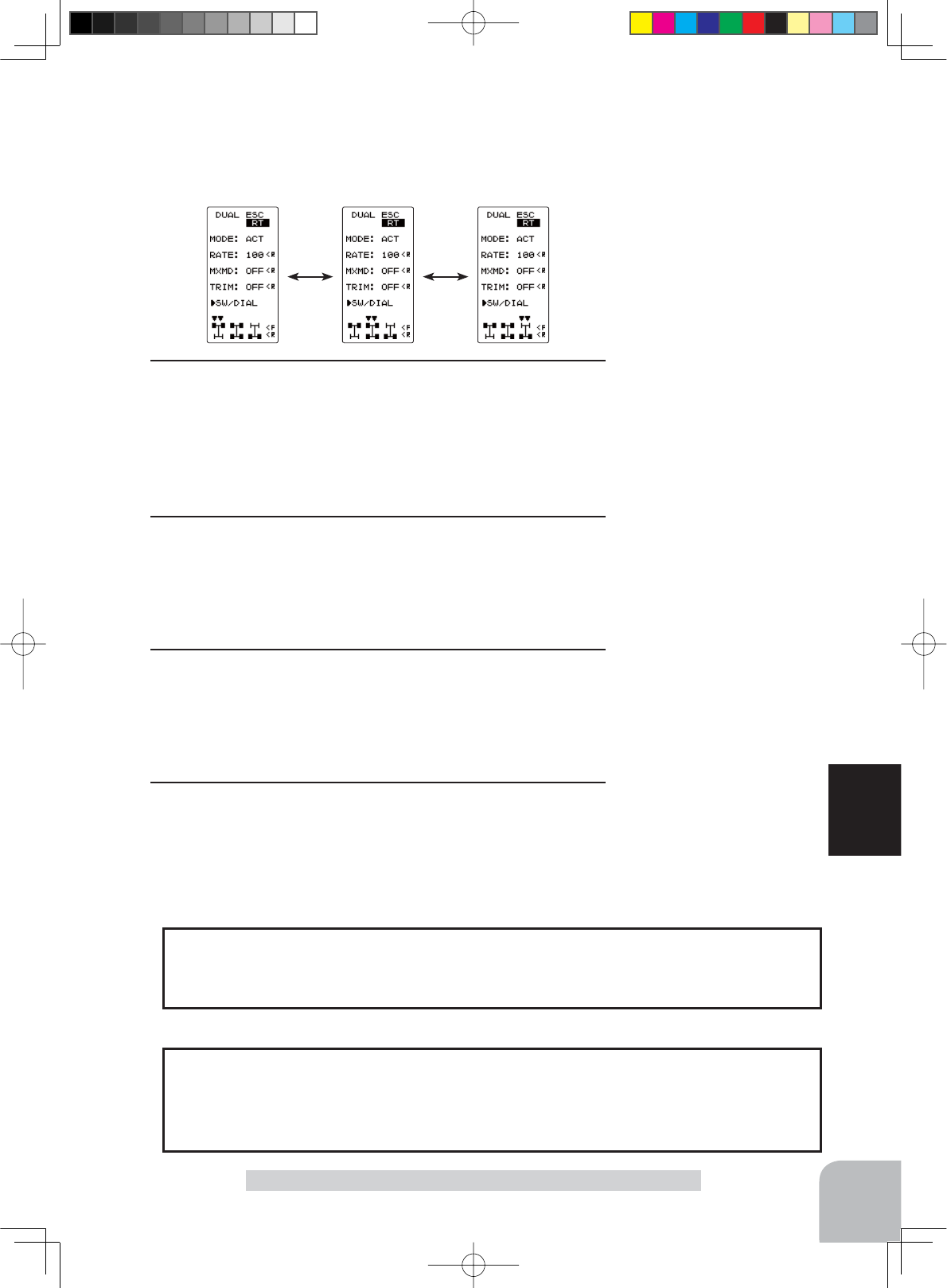
75
Function
Dual ESC mixing "DUAL ESC"
The programmed DT button is used to select the drive type
as shown in the figure below.
The function select dial function can control the 4th channel’s ESC (Rear side) rate
(RATE) with digital dial or digital trim, using the function select switch dial function.
(See page 65)
Dial / Trim Setting
As this function drives 2 separate motor controllers simultaneously, a mutual load is
applied. Use this function carefully so that the motor controllers are not damaged. Fut-
aba will not be responsible for motor controller, motor, and other vehicle trouble due to
use of this function.
Note:
Rear rate (RATE)
0 ~ 120
Initial value:100
Adjustment buttons
- Use the (+) and (-) buttons to
make adjustments.
- Return to the initial value by
pressing the (+) and (-) but-
tons simultaneously (approx.
1 sec).
Mixing mode (MXMD)
OFF, ON
Initial value: OFF
Trim mode (TRIM)
OFF, ON
Initial value: OFF
2 (Rear side travel adjustment)
Select the setting item "RATE" the (JOG) button up or down
operation. Use when applying a rotation difference to the
front and rear wheels by adjusting the rear (CH4) motor con-
troller travel with the (+) or (-) button.
3 (Mix mode setting)
Select the setting item "MXMD" the (JOG) button up or down
operation. Set the mix mode with the (+) or (-) button.
"OFF" : CH2 EXP function and other settings are not mixed.
"ON" : CH2 EXP function and other settings are mixed.
4 (Trim mode setting)
Select the setting item "TRIM" the (JOG) button up or down
operation. Set the trim mode with the (+) or (-) button.
"OFF" : Front side (CH2) trim data is not included.
"ON" : Front side (CH2) trim data is included.
5When ending, return to the MENU screen by moving the cur-
sor to the positions other than SW/DIAL and pressing the
(JOG) button.
Select button
- Select with the (+) or (-) but-
tons.
Select button
- Select with the (+) or (-) but-
tons.
4PLS-Eng-08-2-Function-P65-83.indd 75 2013/04/07 12:48:15
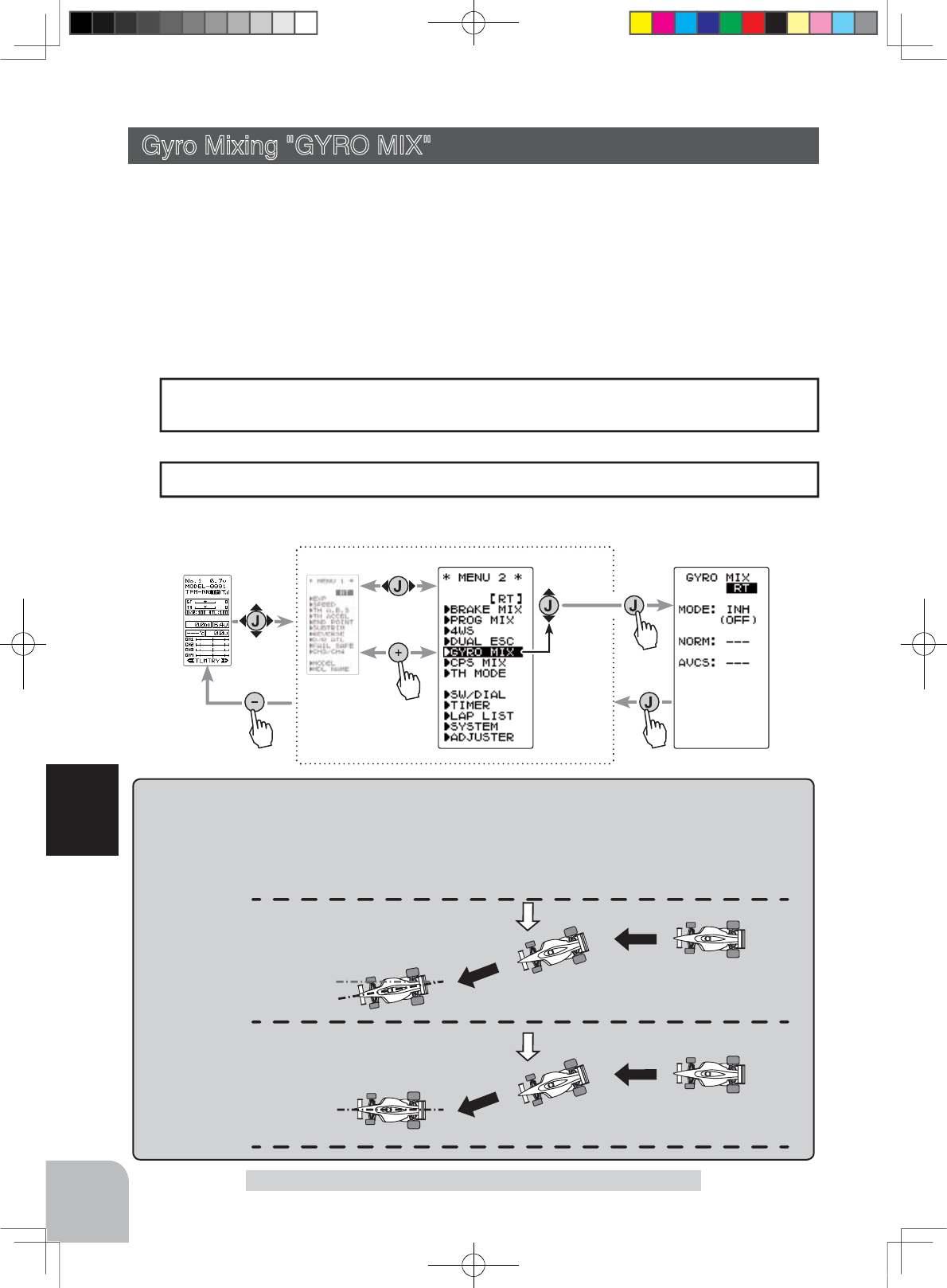
AVCS / NORMAL Modes
The gyro has 2 operating modes: NORMAL mode and AVCS mode. In the AVCS mode, the angle is con-
trolled simultaneously with NORMAL mode rate control (swing speed). The AVCS mode increases straight
running stability more than that of the NORMAL mode. Because the feel of operation is different, choose your
favorite mode.
NORMAL
Countersteers against out-
side force, but cannot cor-
rect the skid direction.
AVCS
Corrects the skidding direc-
tion and forcefully main-
tains the heading.
Outside
force
Outside
force
Press
Press
Press
(HOME screen) (MENU 1 screen) (GYRO MIX screen)
(MENU 2 screen)
Press
Select
"
GYRO MIX
"
76
Function
This function is a remote gain function which adjusts the sensitivity of the Futaba car
rate gyro at the T4PLS side, and is mixing that uses the 3rd CH to adjust the gyro sensi-
tivity.
When using the T4PLS by switching the AVCS and normal modes use SW1 with the
function select switch function (p.65).
For a description of the car rate gyro mounting method and handling, refer to the rate
gyro instruction manual.
Gyro Mixing "GYRO MIX" (Steering system)
When the 3rd CH was set to ACT at Brake Mixing (p.68) or when 4WS Mixing (p.72)
is used, Gyro mixing cannot be used.
Setting Special mixings
The gain amount can be adjusted by using the function switch dial function (p.65).
Dial / Trim Setting
Display "GYRO MIX" screen by the following method:
Gyro mixing "GYRO MIX"
4PLS-Eng-08-2-Function-P65-83.indd 76 2013/04/07 12:48:16
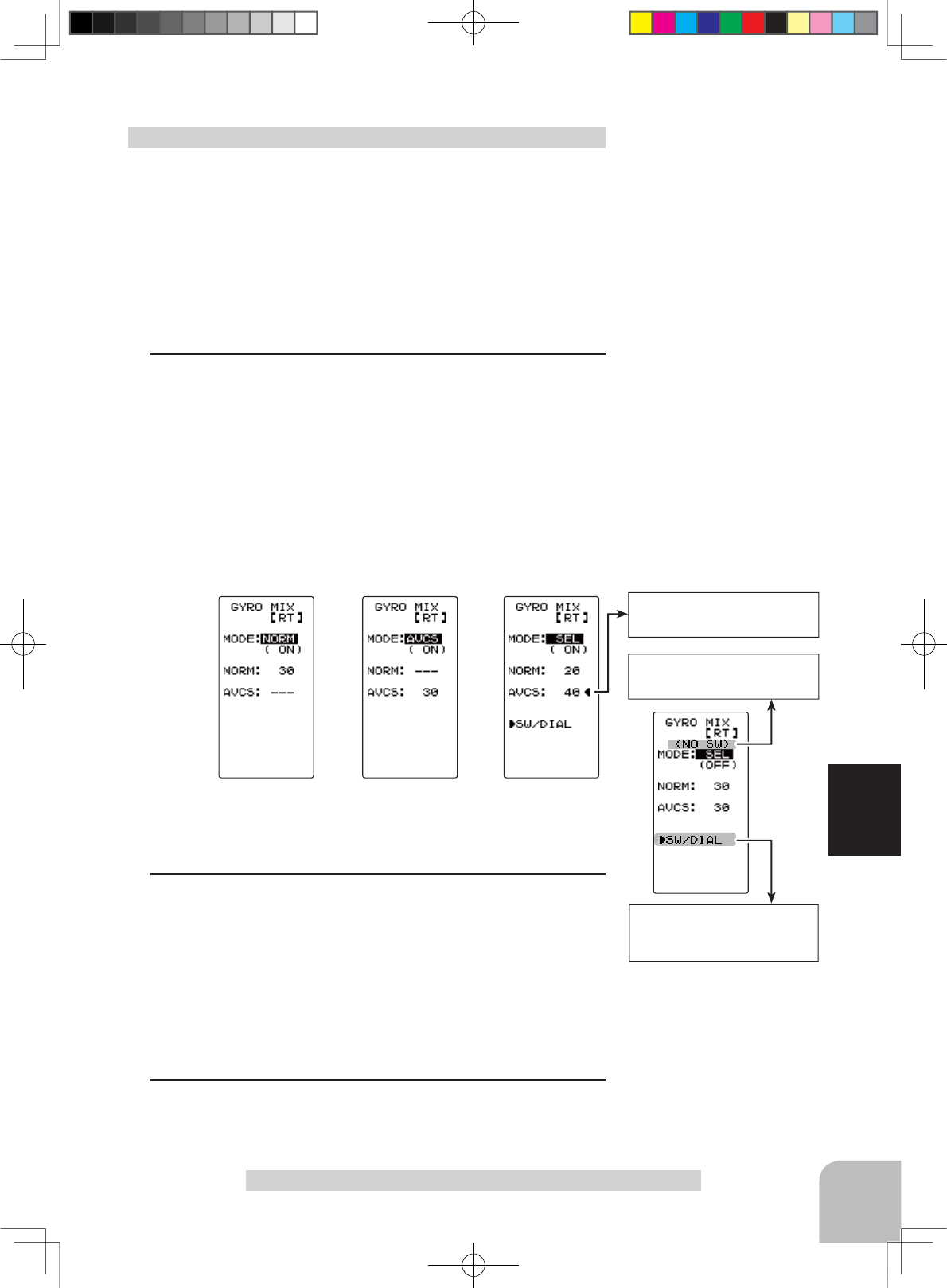
The function select switch
screen (P65) can be dis-
played from this screen.
77
Function
Gyro mixing "GYRO MIX"
(Preparation)
- Refer to the gyro instruction manual and connect the gyro
to the receiver. When using remote gain, connect gyro sensi-
tivity adjustment to the 3rd CH of the receiver.
- When using gyro mixing by switching between the NORM
(normal) and AVCS modes, use the function select switch di-
al function (p.65) to set the switch to be used.
1 (Gyro mixing setting)
Select the setting item "MODE" by the (JOG) button up or
down operation. Set the function by pressing the (+) or (-)
button.
"INH" : Function OFF
"NORM" :NORMAL mode gain
"AVCS" :AVCS mode gain
"SEL" :Switching Normal mode and AVCS mode
(Displayed <NO SW> when the Gyro Mode SW is not used.)
Gyro mixing adjustment
2(NORMAL side gain adjustment)
Select the setting item "NORM" by the (JOG) button up or
down operation. Adjust the NORMAL side gain with the (+)
or (-) button.
(AVCS side gain adjustment)
Select the setting item "AVCS" by the (JOG) button up or
down operation. Adjust the AVCS side gain with the (+) or (-)
button.
3When ending, return to the MENU screen by moving the cur-
sor to the positions other than SW/DIAL and pressing the
(JOG) button.
Function selection (MODE)
INH, NORM, AVCS, SEL
NORMAL / AVCS gain
(NORM / AVCS)
0 ~ 120
Initial value:30
Displayed when the Gyro
Mode SW is not used.
"NORM" mode "AVCS" mode
Shows the gyro mode se-
lect switch mode.
"SELE" mode
Function SW
GYRO
SW type
ALT
Adjustment buttons
- Use the (+) and (-) buttons to
make adjustments.
- Return to the initial value by
pressing the (+) and (-) but-
tons simultaneously for about
1 second.
Select button
- Select with the (+) or (-) but-
tons.
Setup items
MODE : Gyro mode
NORM :
Normal mode gain
AVCS :
AVCS mode gain
4PLS-Eng-08-2-Function-P65-83.indd 77 2013/04/07 12:48:16
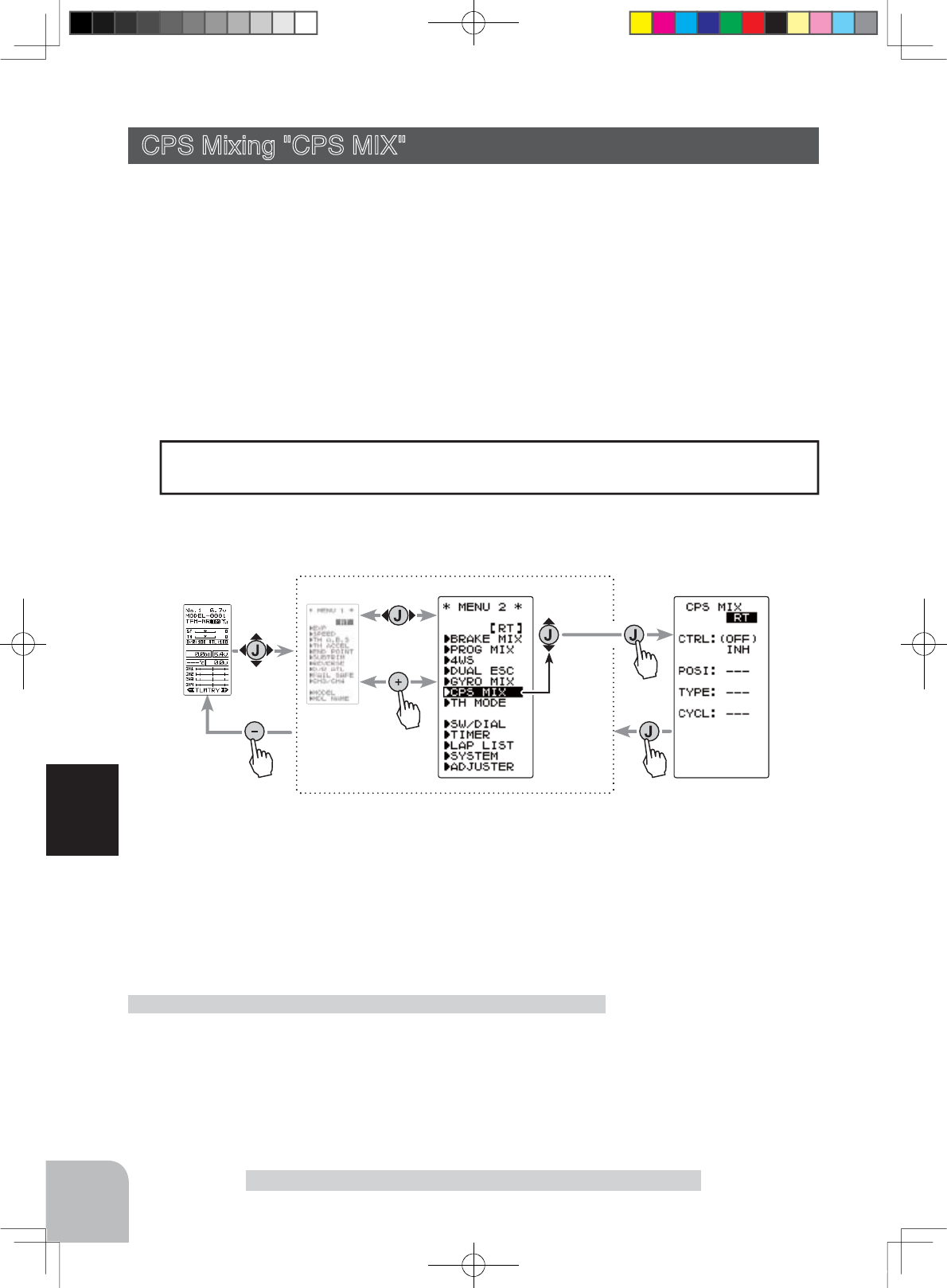
Press
Press
Press
(HOME screen) (MENU 1 screen) (CPS MIX screen)
(MENU 2 screen)
Press
Select
"
CPS MIX
"
78
Function
Gyro mixing "CPS MIX"
Display "CPS MIX" screen by the following method:
This function controls the Futaba CPS-1 channel power switch.
Normally, when using the CPS-1 unit to light the vehicle dress-up and other illumina-
tion (LED) the CPS-1 unit with LED connected is connected to a vacant switch channel
and the LEDs are turned on and off by switch while the vehicle is running. However,
when the CPS-1 mixing (CPS MIX) function is used, the LED can be turned on and off
DQGÀDVKHGLQVWHSZLWKVWHHULQJDQGWKURWWOHRSHUDWLRQDVZHOODVEHLQJWXUQHGRQDQG
RIIE\VZLWFK7KHÀDVKLQJVSHHGF\FOHFDQDOVREHVHW
)RULQVWDQFHWKH/('FDQEHÀDVKHGDVDEUDNHOLJKWE\WKURWWOHEUDNHVLGHRSHUDWLRQ
CPS Mixing "CPS MIX"
When the 4th CH was set to ACT at Brake Mixing (p.68) or when Dual ESC Mixing
(p.78) is used, CPS mixing cannot be used.
Setting Special mixings
(Preparation)
- Connect the CPS-1 to the 4th CH of the receiver.
- When the LEDs are turned on and off by switch, use the
function select switch dial function (p.65) to set the switch to
be used.
CPS mixing adjustment
Function SW
CH4
Setup items
MODE : Function ON/OFF, control mode
POSI :
ON/OFF position
TYPE :
ON/OFF type
TCYCL : Flashing speed
4PLS-Eng-08-2-Function-P65-83.indd 78 2013/04/07 12:48:17

ON/OFF Position (POSI)
5 ~ 95
Initial value: 50
Shows the ON/OFF state
79
Function
Gyro mixing "CPS MIX"
1 (Control system setup)
Operate the (JOG) button up and down and select the setting
item "CTRL". Use the (+) or (-) button and select the function.
"INH" : Function OFF
"CH4 FUNC" : ON/OFF by switch set at the 4th CH
"STR NT" : ON at steering neutral
"STR END" : ON at both sides of steering
"THR NT" : ON at throttle neutral
"THR FWD" : ON at throttle forward side
"THR BRK" : ON at throttle back (brake) side
"TH NT+BK" : ON at throttle neutral and back (brake) sides
2 (ON/OFF switching position selection)
Select the setting item "POSI" by the (JOG)
button up or down operation. Use the (+) or (-)
button and select the ON/OFF position. Since
the ON/OFF state is displayed at the right
side of the setting item "CTRL", setting can be
confirmed while operating the function to be
controlled (for example, throttle).
3 (ON/OFF type setup)
Select the setting item "TYPE" by the (JOG) button up or
down operation. Use the (+) or (-) button and select the type
of LED lighting. Normal ON/Off type or flashing can be se-
lected.
"NORMAL" : Normal ON/OFF type
"FLASH" : Flashing display
4 (Flashing cycle setting)
When flashing type "FLASH" was selected at the setting item
"TYPE" the flashing speed (cycle) can be set.
Select the setting item "CYCL" by the (JOG) button up or
down operation. Use the (+) or (-) button and select the flash-
ing speed (cycle).
5When ending, return to the MENU2 screen by pressing the
(JOG) button.
Select button
- Select with the (+) or (-) but-
tons.
Adjust button
- Use the (+) and (-) buttons to
make adjustments.
- Return to the initial value by
pressing the (+) and (-) but-
tons simultaneously for about
1 second.
Select button
- Select with the (+) or (-) but-
tons.
Function selection (MODE)
INH, CH4 FUNC, STR NTR,
STR END, THR NT, THR FWD,
THR BRK, TH NT+BK
Function selection (TYPE)
NORMAL, FLASH
Flashing cycle (CYCL)
1 ~ 100
Initial value:50
4PLS-Eng-08-2-Function-P65-83.indd 79 2013/04/07 12:48:17
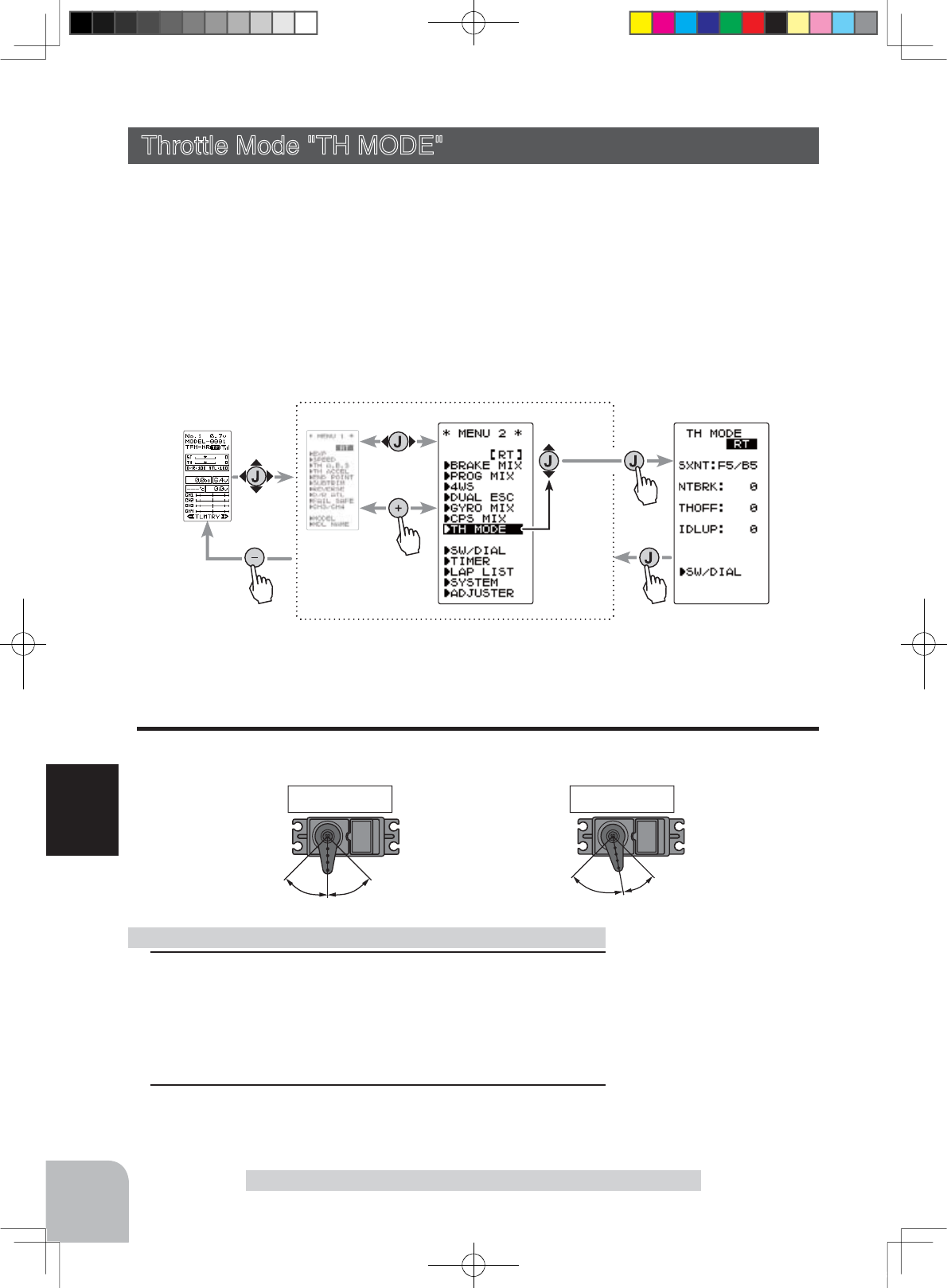
5:5 7:3
F5/B5 F7/B3
Forward side Brake side Forward side Brake side
Press
Press
Press
(HOME screen) (MENU 1 screen) (TH MODE screen)
(MENU 2 screen)
Press
Select
"
TH MODE
"
80
Function
Throttle Mode "TH MODE"
This menu has the following 4 functions:
- Servo neutral mode, which sets the throttle neutral ratio to 7:3 or 5:5
- Idle up, which raises the idling speed when starting the engine to improve engine start-
ing performance of a gasoline car (boat)
- Neutral brake, which applies the brakes at the neutral position of the throttle trigger
- Throttle off (engine cut), which stops the engine of a boat, etc. by operating the throttle
servo to the low side regardless of the position of the throttle trigger.
Throttle servo neutral position "SXNT"
-This function allows selection of the forward side and brake (reverse) side operation ra-
tio from 7:3 or 5:5 by changing the neutral position of the throttle servo.
Throttle Mode "TH MODE" (Throttle system)
1 (Mode selection)
Select the setting item "SXNT" by (JOG) button. Select "F5/
B5" or "F7/B3" by (+) or (-) button.
"F5/B5" =Forward 50% : Back50%
"F7/B3" =Forward 70% : Back30%
2When ending, return to the MENU screen by moving the cur-
sor to the positions other than SW/DIAL and pressing the
(JOG) button
Selecting the throttle servo neutral position
Mode selection (SXNT)
F5/B5, F7/B3
Display "TH MODE" screen by the following method:
Select button
- Select with the (+) or (-) but-
tons.
Setup items
SXNT :Throttle servo neutral position
IDLUP :Idle-Up rate
NTBRK :Neutral brake rate
THOFF :Throttle off (engine cut) position
4PLS-Eng-08-2-Function-P65-83.indd 80 2013/04/07 12:48:18

Warning display
The function select switch
dial screen (p.65) can be
displayed from this screen.
< NO SW >
If function’s ON/OFF switch
is not selected, <NO SW>
is displayed.
81
Function
Throttle Mode "TH MODE"
Idle-Up "IDLUP"
This is a function select switch dial function. The idle up ON/OFF switch must be set.
(P65)
This function is used to improve engine starting performance by raising the idling speed
when starting the engine of a gasoline car (boat). It is also effective when you want to
prevent the braking when the power was turned off during running, due to the effect
of your gear ratio setting and choice of motor when operating an electric car. However,
considering safety, and to prevent the motor from rotating instantly when the power was
WXUQHGRQWKH0&&50&&0&&0&&5DQGRWKHU)XWDED0&0RWRU
&RQWUROOHUVZLOOQRWHQWHUWKHRSHUDWLRQPRGHLIWKHQHXWUDOSRVLWLRQLVQRWFRQ¿UPHG
:KHQXVLQJWKH0&&50&&0&&0&&5RURWKHU)XWDED0&FRQ-
¿UPWKDWWKH0&LVLQWKHQHXWUDOSRVLWLRQDQGWKHVHWLVLQWKHRSHUDWLRQPRGHEHIRUH
setting the idle up function switch to ON.
The throttle neutral position is offset to the forward side or brake side. There is no link-
age locking, etc. because there is no change near the maximum operation angle even
when the neutral position is offset by this function.
Operation
(Preparation)
- Use the function select switch dial to select the switch. (p.65)
1(Idle-Up rate)
Select the setting item "IDLUP" by the (JOG) button. Use the
(+) and (-) buttons to set the Idle-Up rate.
2When ending, return to the MENU screen by moving the cur-
sor to the positions other than SW/DIAL and pressing the
(JOG) button
Idle-Up function adjustment Adjust button
- Adjust with the (+) and (-) but-
tons.
- Return to the initial value "0" by
pressing the (+) and (-) buttons
simultaneously for about 1 sec-
ond.
Idle-Up rate (IDLUP)
D50 ~ D1, 0, U1 ~ U50
Initial value: 0
"D": Brake side
"U": Forward side
If the power switch is
turned on while the
idle-up switch is on, an
audible alarm will be
heard. Immediately set
the Idle-Up switch to
OFF.
While this function is ON, the LED blinks.
Operation Display
The function select dial function can control the Idle-up rate with digital dial or digital
trim. (See page 65)
Dial / Trim Setting
4PLS-Eng-08-2-Function-P65-83.indd 81 2013/04/07 12:48:18
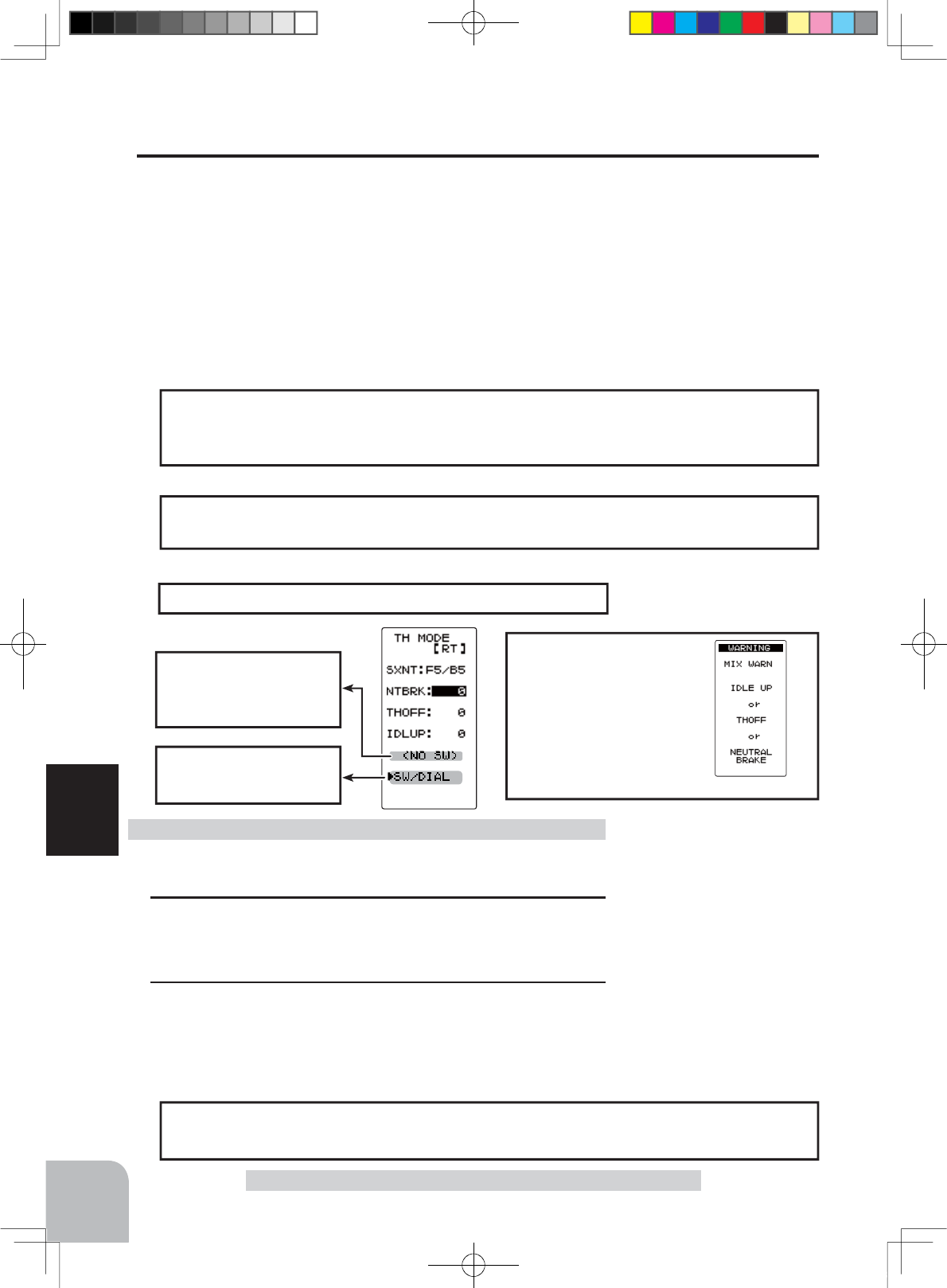
Warning display
The function select switch
screen (p.65) can be dis-
played from this screen.
< NO SW >
If function’s ON/OFF
switch is not selected,
<NO SW> is displayed.
82
Function
(Preparation)
- Use the function select switch dial to select the switch. (p.65)
1(Neutral brake rate)
Select the setting item "NTBRK" by the (JOG) button. Use
the (+) and (-) buttons to set the neutral brake rate.
2When ending, return to the MENU screen by moving the cur-
sor to the positions other than SW/DIAL and pressing the
(JOG) button
Neutral Brake function adjustment
The ESC neutral brake function and T4PLS neutral brake function can be used simul-
WDQHRXVO\+RZHYHUZKHQVHWWLQJLVGLI¿FXOWWRXQGHUVWDQGZHUHFRPPHQGWKDWRQO\
one neutral brake function be used.
Reference
Throttle Mode "TH MODE"
When the neutral brake function is
"
ON
"
, the
neutral
brake rate adjustment is auto-
matically assigned to the throttle trim (DT1/2/3/4 or DL1).
Dial / Trim Setting
Throttle side EPA function, or ATL function setting, also affects neutral brake side
operation.
Effect of set value of other functions on neutral brake
Neutral Brake "NTBRK"
This is a function select switch dial function. The neutral brake function ON/OFF
switch must be set. (P65)
The neutral brake, which applies the brakes at the neutral position of the throttle trigger,
FDQEHVHW+RZHYHUZKHQXVLQJWKH0&&50&&0&&0&&5RURWK-
HU)XWDED0&0RWRU&RQWUROOHUFRQ¿UPWKDWWKH0&LVLQWKHQHXWUDOSRVLWLRQDQGWKH
set is in the operation mode before setting the neutral brake function switch to ON, the
same as the idle up function (P81). In addition, when the idle up function or throttle off
function (P83) is set, this function has a higher priority than the neutral brake function.
An LED blinks while the neutral brake function is active.
Operation display
If the power switch is
turned on while the neu-
tral brake switch is on,
an audible alarm will be
heard. Immediately set
the neutral brake switch
to OFF.
Adjust button
- Adjust with the (+) and (-) but-
tons.
- Return to the initial value "0" by
pressing the (+) and (-) buttons
simultaneously for about 1 sec-
ond.
Brake rate (NTBRK)
0 ~ B100
Initial value: 0
4PLS-Eng-08-2-Function-P65-83.indd 82 2013/04/07 12:48:18
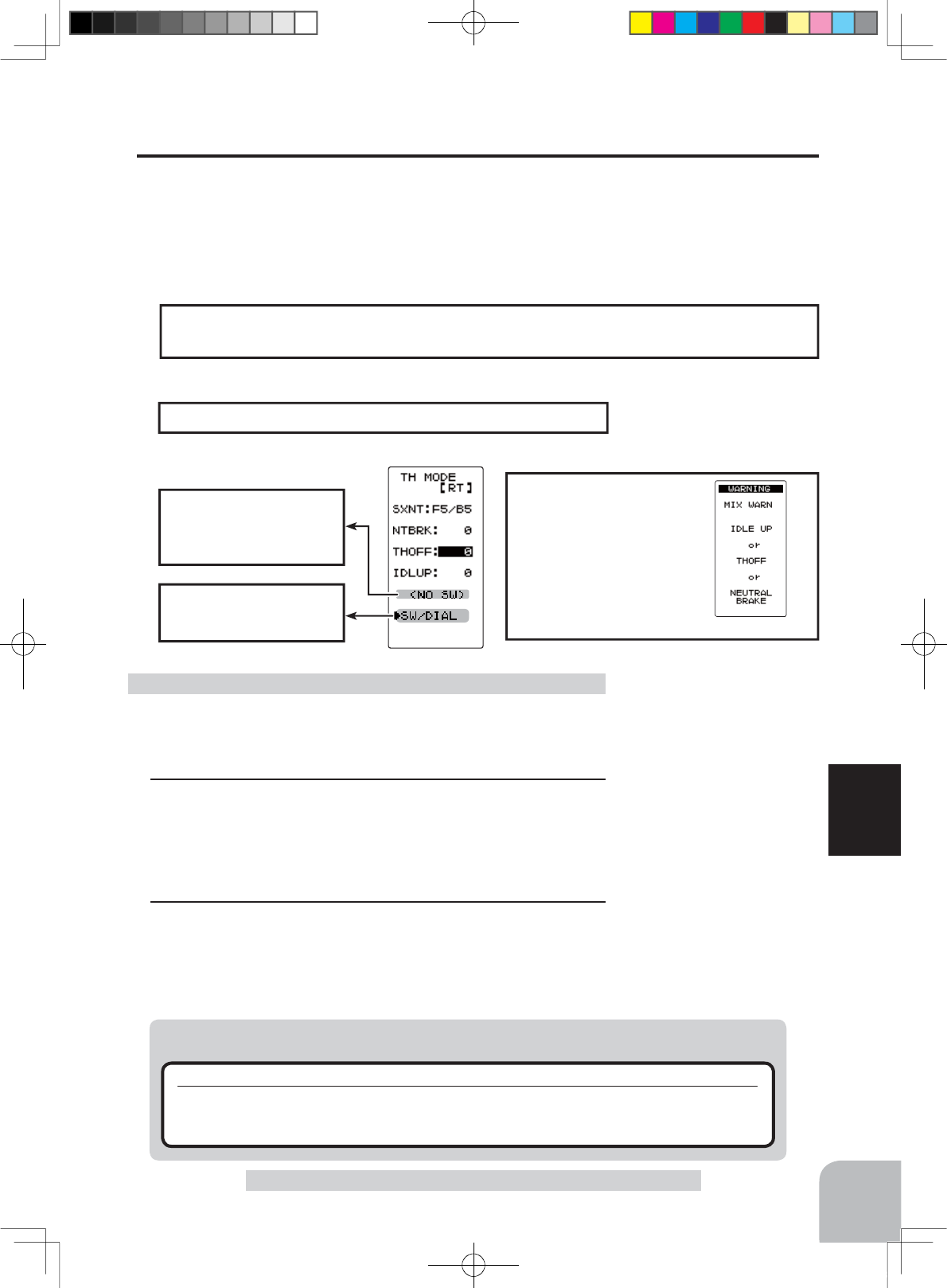
Warning display
The function select switch
screen (p.65) can be dis-
played from this screen.
< NO SW >
If function’s ON/OFF
switch is not selected,
<NO SW> is displayed.
83
Function
Throttle Mode "TH MODE"
(Preparation)
- Use the function select switch dial to select the switch. (p.65)
1(Preset position setup)
- Select the setting item "THOFF" by the (JOG) button. Use
the (+) and (-) buttons to set the preset position of the throt-
tlle servo.
2When ending, return to the MENU screen by moving the cur-
sor to the positions other than SW/DIAL and pressing the
(JOG) button
Engine Cut function adjustment
Caution
Always operate carefully before using this function.
While switch with preset function set is in the ON state, the servo (motor controller) is locked in the preset posi-
tion and does not operate even if the throttle trigger is operated. If the servo was operated at the wrong setting,
you may lose control of the car (boat).
Adjust button
- Adjust with the (+) and (-) but-
tons.
- Return to the initial value by
pressing the (+) and (-) buttons
simultaneously (approx. 1 sec).
Preset position (THOFF)
0 ~ B100
Initial value: 0
Throttle Off (engine cut) "THOFF"
This is a function select switch dial function. The throttle off function ON/OFF switch
must be set. The engine cut function stops the engine of a boat, etc. by operating the
throttle servo to the slow side by switch regardless of the position of the throttle trigger
and the setting of other functions (reverse function setting is effective).
An LED blinks while the neutral brake function is active.
Operation display
If the power switch is
turned on while the
throttle-off switch is on,
an audible alarm will be
heard. Immediately set
the neutral brake switch
to OFF.
The function select dial function can control the throttle-off position can be controlled
with digital dial or digital trim. (See page 65)
Dial / Trim Setting
4PLS-Eng-08-2-Function-P65-83.indd 83 2013/04/07 12:48:18
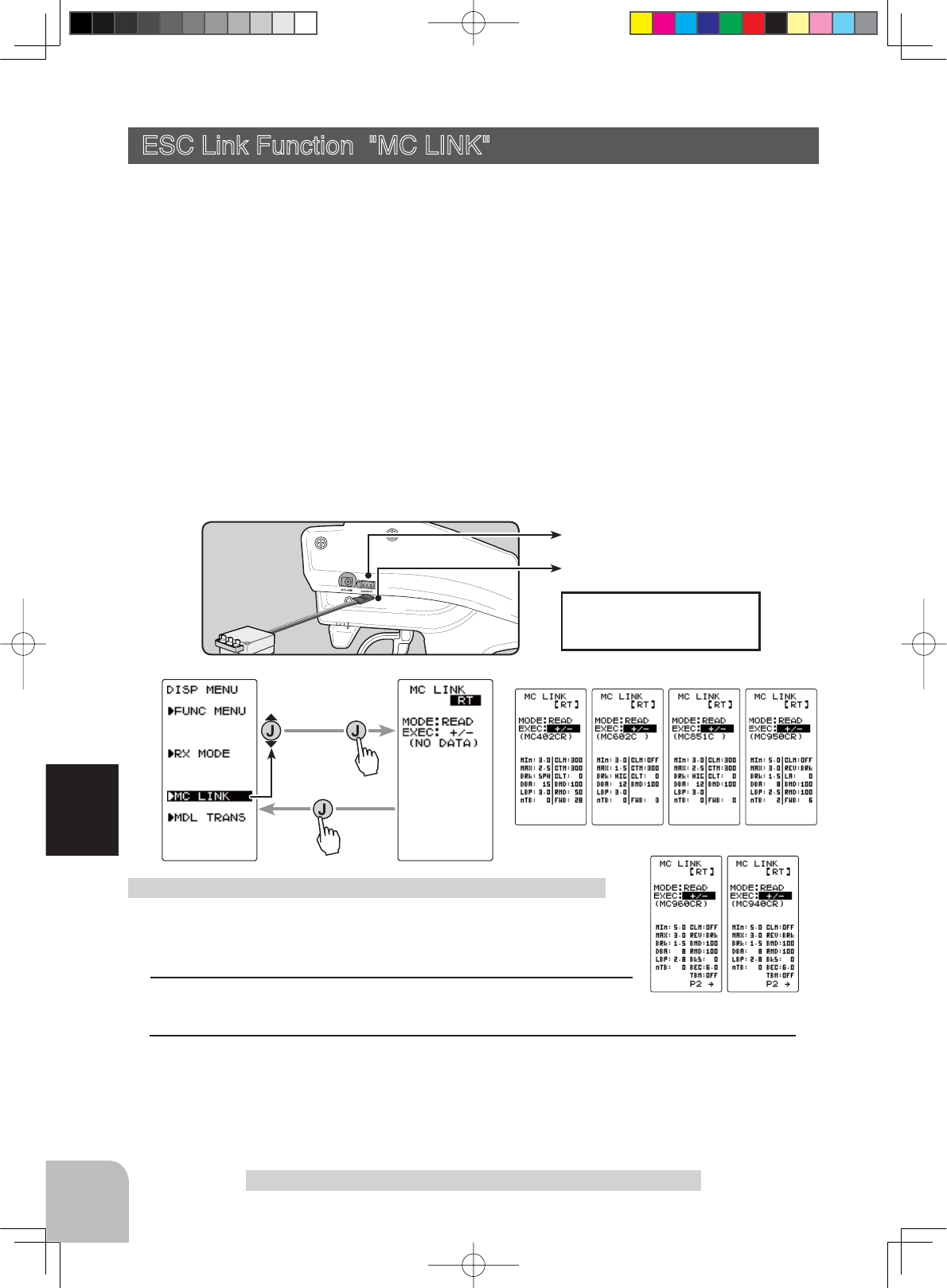
Communication port
ESC receiver connector
Connecting ESC receiver
connector to the transmitter
Communication port
Connection diagram
84
Function
(Preparation)
-Connect the T4PLS and ESC in accordance with the connection
diagram, and connect the battery to ESC.
1Set the transmitter power switch to the display side (DISP).
Display the MC LINK function screen in the above manner.
Using the ESC Link function
ESC Link Function "MC LINK"
This is a special function which lets you set the contents of the Link software
which performs Futaba speed controller (ESC), MC960CR, MC940CR, MC950CR,
MC851C, MC602C, MC402CR, etc. variable frequency and other data changes at
the T4PLS transmitter. However, some data changes require a PC and Link soft-
ware. This function is used by connecting ESC directly to the transmitter. The
T4PLS power switch is used at the display side. Use the various optional servo ex-
tension cords according to the distance between the transmitter and ESC. The last
data read from ESC to T4PLS or the last data written from T4PLS to ESC is saved
to the T4PLS. Since the data for each model memory can be saved, the data of up to
40 models can be saved.
-When the T4PLS battery voltage drops, the display switches to low battery display. Therefore, use this function when there
is ample battery capacity remaining.
-Also connect the battery at the ESC side.
-Note: Do not read to the T4PLS an MC940/960CR whose speed was set to over 99990rpm by Link software side Boost An-
gle rpm setting.
ESC Link Function "MC LNK"
2 (ESC read)
Execute this function to read the connected ESC type and the data currently set at the
amp. To save the ESC data to the T4PLS, rewrite the read data.
When you want to write the data saved in the T4PLS to an ESC of the same type, exe-
cute the following "WRITE"(write) without executing "READ"(read).
(MC LINK screen)
Press
(DISP MENU screen)
Press
Select
"
MC LINK
"
MC402CR MC602C MC851C MC950CR
MC960CR MC940CR
4PLS-Eng-08-3-Function-P84-114.indd 84 2013/04/08 9:10:18
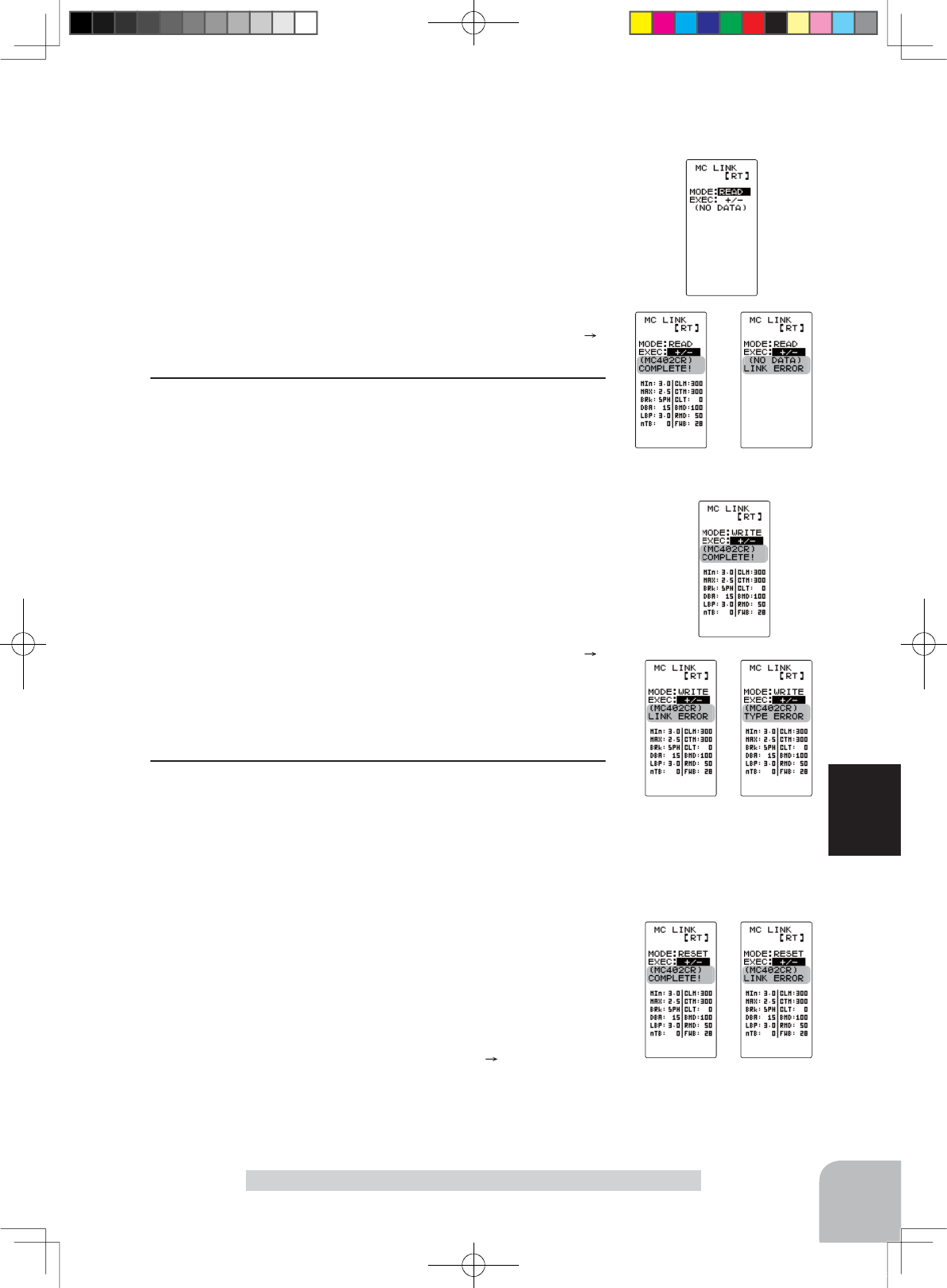
85
Function
ESC Link Function "MC LNK"
a-Select the setting item "MODE" by the (JOG) button, and
select "READ" by (+) or (-) button.
b-Select the setting item
"
EXEC:+/-
"
by the (JOG) button,
and press the (+) and (-) buttons simultaneously for 1 second
or longer.
-"COMPLETE!" blinks on the screen and the ESC type and currently set con-
tents are read.
- If "LINK ERROR" blinks on the screen, communication with the amp is not
being performed normally. Check the T4PLS and ESC connection and the
battery connection to ESC and the ESC power switch and repeat steps a b.
3 (Writing to ESC)
Execute this function to write the setting data to ESC. See
pages 84~85 for the setting data contents.
a-Select the setting item
"
MODE
"
by the (JOG) button, and
select
"
WRITE
"
by (+) or (-) button.
b-Select the setting item
"
EXEC:+/-
"
by the (JOG) button,
and press the (+) and (-) buttons simultaneously for 1 second
or longer.
-"COMPLETE!" blinks on the screen and the setting data is written to ESC.
If "LINK ERROR" blinks on the screen, communication with the amp is not
being performed normally. Check the T4PLS and ESC connection and the
battery connection to ESC and the ESC power switch and repeat steps a b.
In addition, if (NO DATA) is displayed on the T4PLS screen, "WRITE" cannot
be selected because there is no setting data to be written.
- Different type ESC data cannot be written. If writing is attempted, "TYPE
ERROR" will link on the screen to show that the ESC type is wrong.
4 (Initialization)
This function writes the MC setting data set at the factory to
the connected MC and T4PLS. Perform "READ" before per-
forming initialization.
a-Select the setting item "MODE" by the (JOG) button, and
select "RESET" with the (+) or (-) button.
b-Select the setting item "EXEC:+/-" by the (JOG) button,
and press the (+) and (-) buttons simultaneously for approxi-
mately 1 second
- "COMPLETE!" blinks on the screen and the initial data is written to the ESC.
If "LINK ERROR" blinks, communication with the amp was not performed
normally. Check the T4PLS and ESC connection and the battery connection
to ESC and the ESC power switch, and repeat steps a b. In addition, when
(NO DATA) is displayed on the T4PLS screen "RESET" cannot be selected
because there is no write initial data.
4PLS-Eng-08-3-Function-P84-114.indd 85 2013/04/08 9:10:18
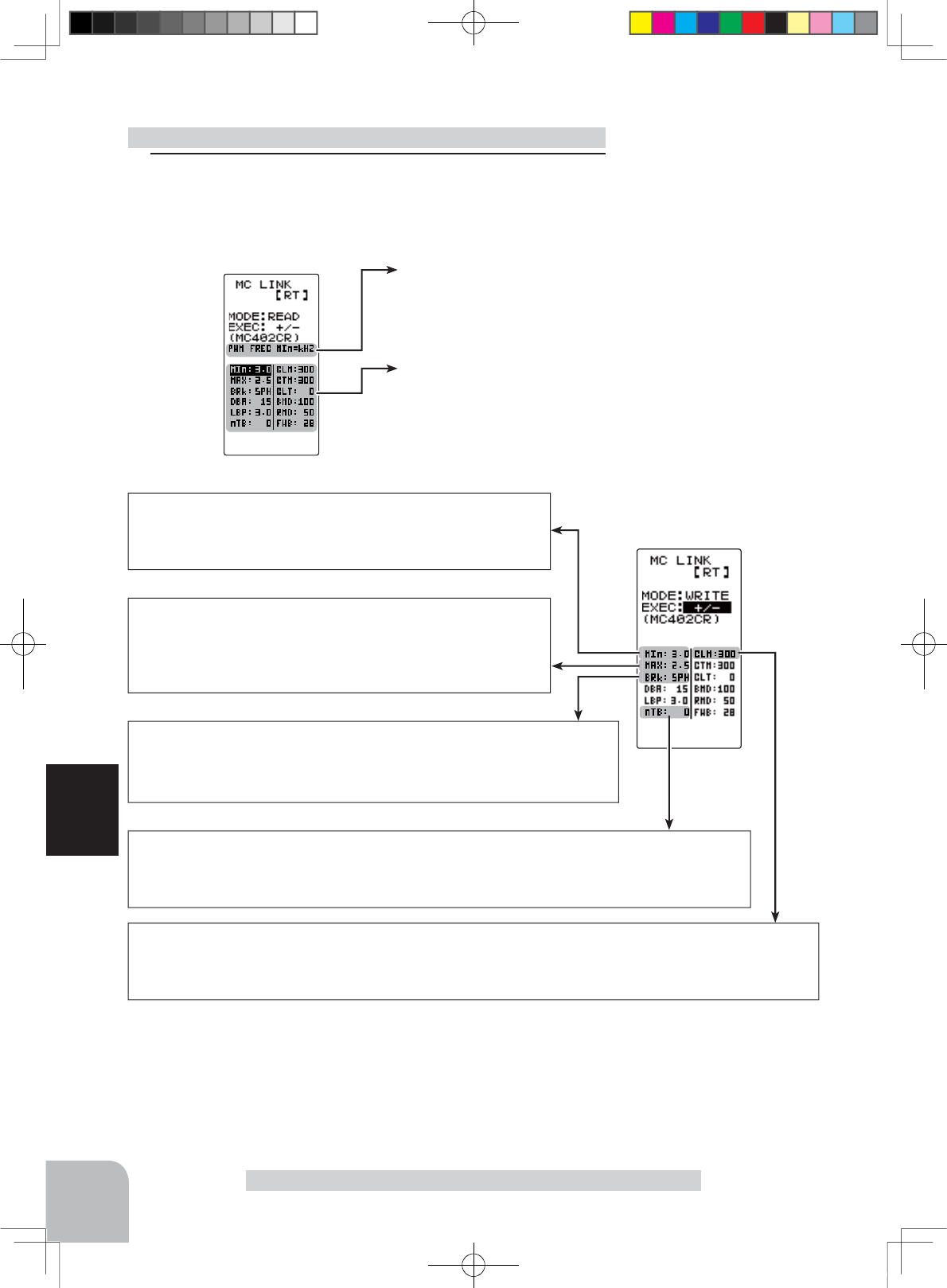
The currently set item is
displayed here.
The item indicated by the
reverse displayed cursor
is selected.
Adjustment buttons
- Use the (+) and (-) buttons to
make adjustments.
- Return to the initial value by
pressing the (+) and (-) buttons
simultaneously (approx. 1 sec).
Setup item selection
- Select by the (JOG) button.
86
Function
MIn-(PWM FREC MIN LD) 100Hz~10000Hz (10kHz)
MC950CR:500Hz~30000Hz (30kHz)
Same as Link software PWM frequency (at Min. load),
MIn sets the "0"A PWM frequency at minimum load.
MAX-(PWM FREC MAX LD) 100Hz~10000Hz (10kHz)
MC950CR:500Hz~30000Hz (30kHz)
Same as Link software PWM frequency (at Max. load).
MAX sets the PWM frequency at maximum load at the output cur-
rent limit value set by Current Limiter.
CLM-(CURRENT LIMIT) 50A~300A (MC950CR:50A~300A), OFF Same as Link software Current Limiter.
Current Limiter sets the current value at maximum load here.
Since setting of the MAX is based on the output current limit value set by Current Limiter, Current Limiter does not
have to be turned OFF except when a current exceeding 300A is generated.
BRK-(PWM FREC BRK LD) nOR(2000Hz)/ HIG(1000Hz)/ SPH(500Hz)
MC950CR:500Hz~30000Hz (30kHz)
Same as Link software Brake PWM at frequency.
This setting can set the brake PWM frequency.
"MIn" which sets the frequency when the load is small, is set to the high frequency side (large value) when extension is desired after straight-
aways and curves.
"MAX" which sets the frequency when the load is large, is set to the high frequency side (large value) when you want to suppress the rise
from low speed and when motor heating and commutator roughness are sensed.
When the rise from low speed is poor, and becomes bad even when "MAX" is set to the low frequency side, use the log data to check if there
was a momentary voltage drop. When you want to suppress the overall power, lengthen the run time, and otherwise improve efficiency, set
both "MAX" and "MIn" to the high frequency side. When you want to set a fixed PWM frequency at full range regardless of the load current,
set PWM frequency (at Max. load) and PWM frequency (at Min. load) to the same value.
nTB-(NEUTRAL BRAKE) 0%(OFF)~100%
Same as Link software Neutral Brake.
Make this setting when you want to use the brakes at the neutral throttle (OFF) position by throttle operation. The
larger this value, the greater the braking force. When you want to use the neutral brake, set this value to "0%".
ESC function setup (MC601/602/850/851C, 401/402/950CR)
Setup item
ESC Link Function "MC LNK"
1Select the setting item by the (JOG) button.
Set the value by (+) and (-) button.
4PLS-Eng-08-3-Function-P84-114.indd 86 2013/04/08 9:10:19
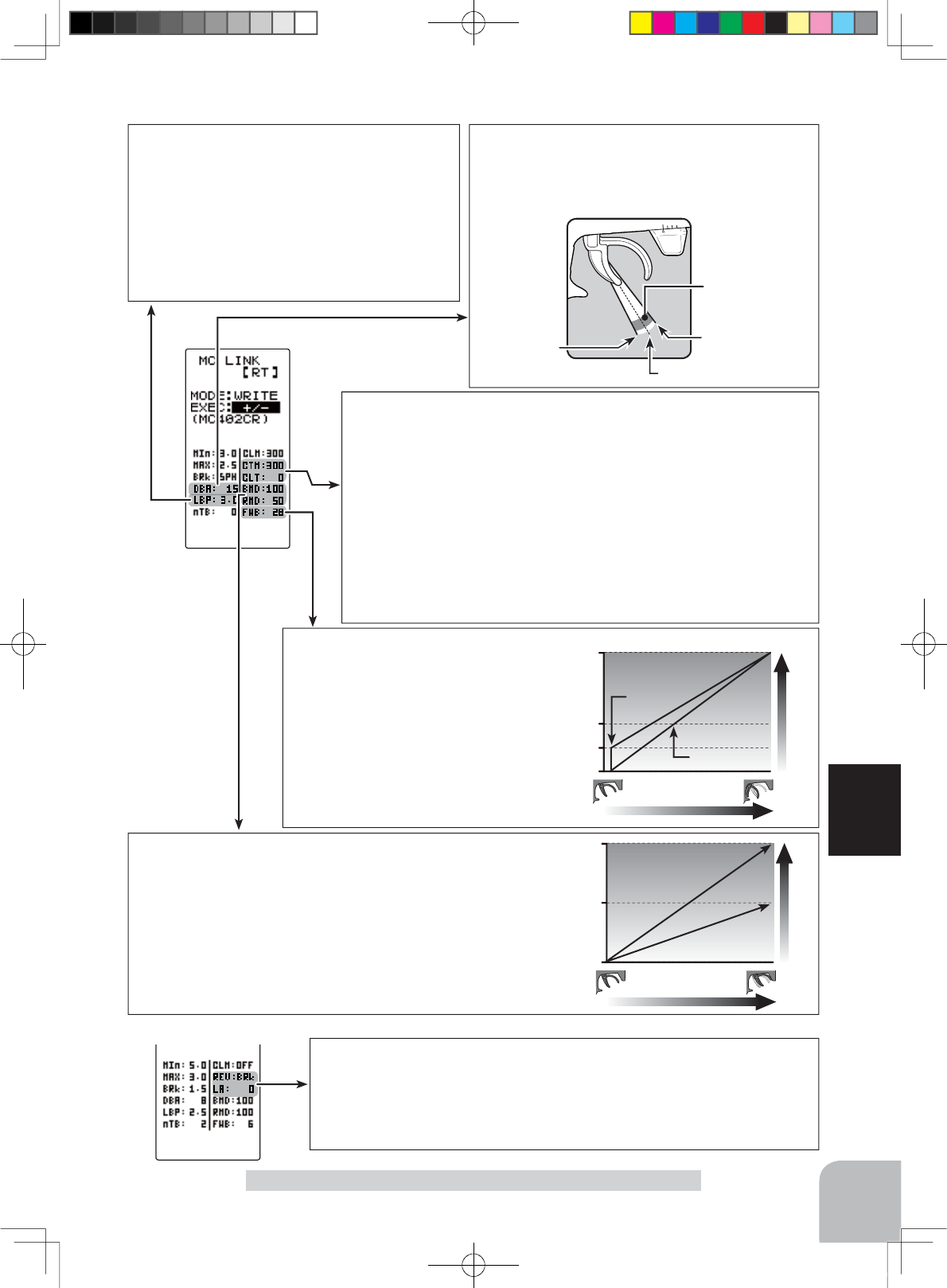
87
Function
LBP-(LOW BATTERY VOLT) 2.5V~6V
2.5V~7.5V for MC950CR
Same as Link software Low Bat Protection
This setting cuts off the output to the motor when
the running battery voltage drops to the set volt-
age to prevent the receiver from stopping operation
when the supply of voltage to the receiver becomes
in sufficient while running due to a drop in the pow-
er supply voltage. When the power supply voltage
recovers, power is supplied to the motor once more.
CTM-(C.L. TIME LIMIT) 50A~300A /CLT-(C.L. TIMER) 0sec(OFF)~240sec
(except MC950CR)
Same as Link software Current Limiter (Time Limit)/Current Limit timer.
The output current can be limited up to the set time lapse from the start of run-
ning. This is effective in preventing the motor from outputting wasted energy
when the voltage is high immediately after the power battery was recharged.
- "CTM" (Time Limit) sets the maximum output current within the time the out-
put current is limited.
- "CLT" sets the time the output current is limited. This function is disabled
when set to "0" sec.
Since the Current Limit Timer starts when the throttle is operated to the for-
ward side and current is output to the motor, this function begins to operate
when the motor is run during trim adjustment, etc.
100
50
0
%
Brake (Reverse) operation
Braking force
Reverse Power
BMD-(BRAKE MAX DUTY) 0%~100%
Same as Link software Brake Max. Duty.
This setting can set the braking force between the neutral point and Max
brake point. The larger this value, the greater the braking force. When set
to "0%", the brakes are not effective.
RMD-(REVERSE MAX DUTY) w/back only 0%~100%
Same as Link software Reverse Max. Duty
This setting can set the reverse power between the neutral point and Max
reverse point. The larger this value, the greater the reverse power. When
set to "0%", the reverses are not effective.
100
50
0
Forward operation
Throttle response
FWB "50"
FWB "0"
FWB-(FORWARD BOOST) 0~100 (except MC850C)
Same as Link software Forward Boost
Operation near the throttle trigger (stick) neu-
tral position becomes a sharp rise.
MC950CR only setup item
REV-(REV CANCEL) BRk /REV Same as Link software Reverse Cancel.
When set to BRk, reverse operation is not performed.
LA-(LEAD ANGLE) 0~1500 Same as Link software Lead Angle.
The lead angle of the motor can be set at the MC950CR side. However, we recommend that it
normally be set to "0". Since this setting is premised on setting by referring to the speed log by
the Link software, independent use of the MC LINK function of the T4PLS is recommended.
ESC Link Function "MC LNK"
Throttle neutral position
Dead Band
Point at which brakes
start taking effect
Position at which
motor starts to
run
DBA-(DEAD BAND) ±2μs~±50μs
Same as Link software Dead Band.
This sets the range (neutral point range) over which the
ESC does not respond to transmitter throttle operation.
The larger the set value, the wider this range.
4PLS-Eng-08-3-Function-P84-114.indd 87 2013/04/08 9:10:20
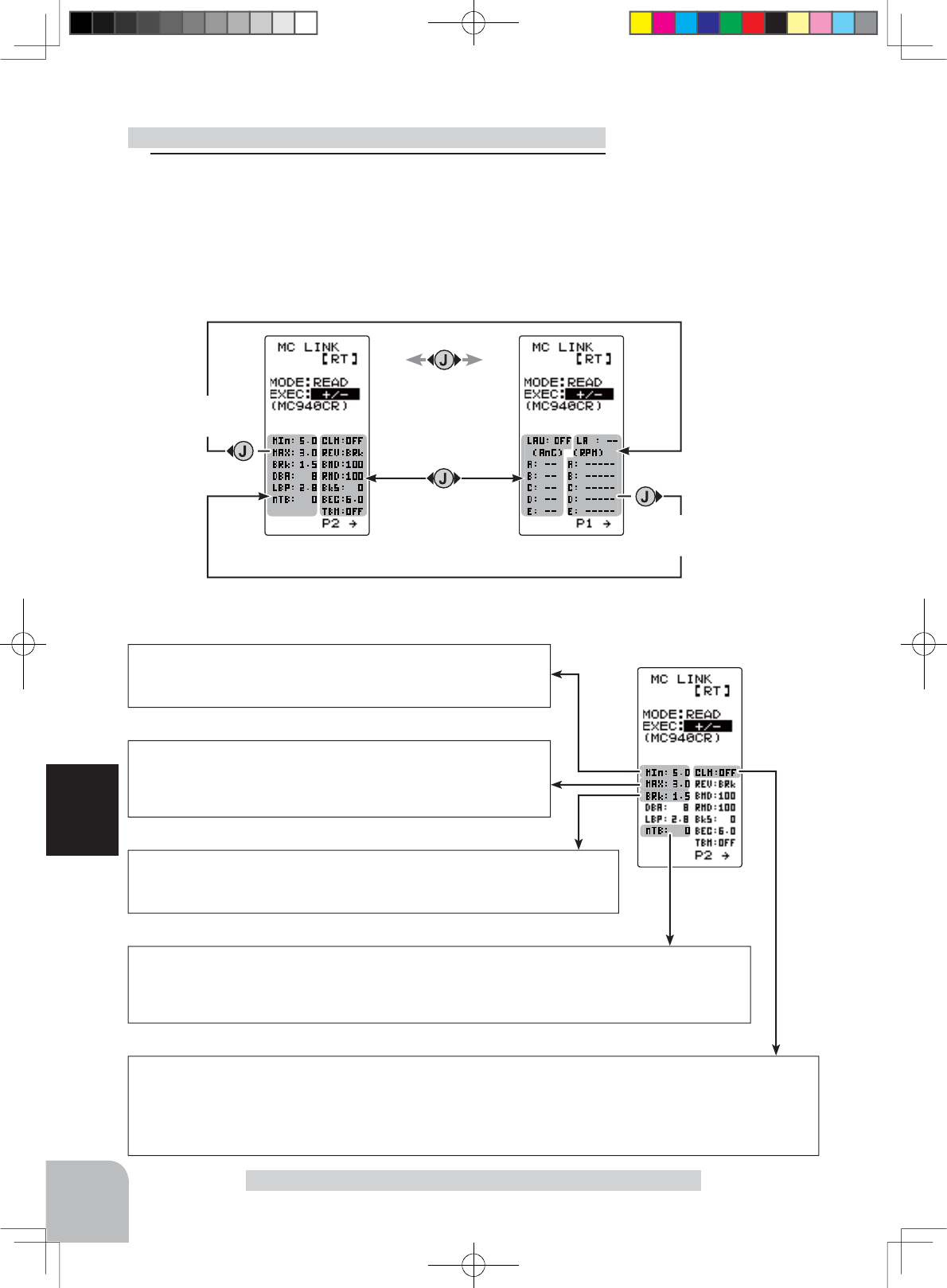
Adjustment buttons
- Use the (+) and (-) buttons to
make adjustments.
- Return to the initial value by
pressing the (+) and (-) buttons
simultaneously (approx. 1 sec).
Setup item selection
- Select by the (JOG) button.
Page1 Page2
To right side
on Page2
To left side
on Page1
88
Function
ESC Link Function "MC LNK"
ESC function setup (MC940CR, MC960CR)
1Select the setting item by the (JOG) button.
Set the value by (+) and (-) button.
Operate the following (JOG) button and switch between
Page1 and Page2 of the setup screen.
The cursor positions
"EXEC +/-"
Page1
Setup item
MIn-(PWM FREC MIN LD) 1kHz(1000Hz)~30kHz (30000Hz)
Same as Link software PWM frequency (at Min. load),
MIn sets the "0"A PWM frequency at minimum load.
MAX-(PWM FREC MAX LD) 1kHz(1000Hz)~30kHz (30000Hz)
Same as Link software PWM frequency (at Max. load).
MAX sets the PWM frequency at maximum load at the output cur-
rent limit value set by Current Limiter.
CLM-(CURRENT LIMIT) 50A~500A
Same as Link software Current Limiter.
Current Limiter sets the current value at maximum load here.
Since setting of the MAX is based on the output current limit value set by Current Limiter, Current Limiter does not
have to be turned OFF except when a current exceeding 300A is generated.
BRK-(PWM FREC BRK LD) 1kHz(1000Hz)~30kHz (30000Hz)
Same as Link software Brake PWM at frequency.
This setting can set the brake PWM frequency.
nTB-(NEUTRAL BRAKE) 0%(OFF)~100%
Same as Link software Neutral Brake.
Make this setting when you want to use the brakes at the neutral throttle (OFF) position by throttle operation. The
larger this value, the greater the braking force. When you want to use the neutral brake, set this value to "0%".
4PLS-Eng-08-3-Function-P84-114.indd 88 2013/04/08 9:10:21
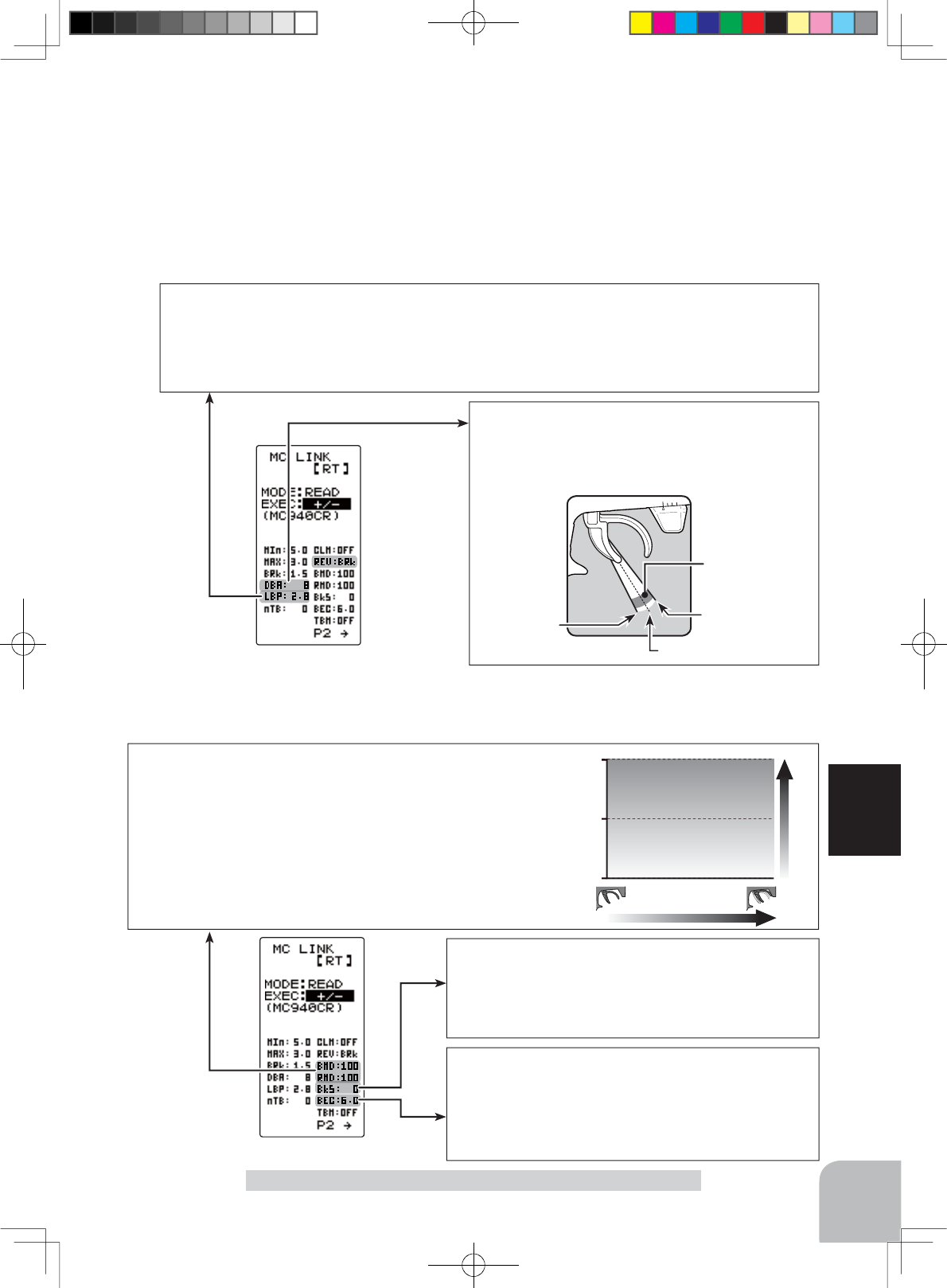
89
Function
ESC Link Function "MC LNK"
"MIn" which sets the frequency when the load is small, is set to the high frequency side (large value) when extension is desired after straight-
aways and curves.
"MAX" which sets the frequency when the load is large, is set to the high frequency side (large value) when you want to suppress the rise
from low speed and when motor heating and commutator roughness are sensed.
When the rise from low speed is poor, and becomes bad even when "MAX" is set to the low frequency side, use the log data to check if there
was a momentary voltage drop. When you want to suppress the overall power, lengthen the run time, and otherwise improve efficiency, set
both "MAX" and "MIn" to the high frequency side. When you want to set a fixed PWM frequency at full range regardless of the load current,
set PWM frequency (at Max. load) and PWM frequency (at Min. load) to the same value.
LBP-(LOW BATTERY VOLT) 2.5V~7.5V
Same as Link software Low Bat Protection
This setting cuts off the output to the motor when the running battery voltage drops to the set voltage to pre-
vent the receiver from stopping operation when the supply of voltage to the receiver becomes in sufficient
while running due to a drop in the power supply voltage. When the power supply voltage recovers, power is
supplied to the motor once more.
REV-(REV CANCEL) BRk /REV
Same as Link software Reverse Cancel.
When set to BRk, reverse operation is not performed.
Throttle neutral position
Dead Band
Point at which brakes
start taking effect
Position at which
motor starts to
run
DBA-(DEAD BAND) ±2μs~±50μs
Same as Link software Dead Band.
This sets the range (neutral point range) over which the
ESC does not respond to transmitter throttle operation.
The larger the set value, the wider this range.
Page1
Page1
100
50
0
%
Brake (Reverse) operation
Braking force
Reverse Power
BMD-(BRAKE MAX DUTY) 0%~100%
Same as Link software Brake Max. Duty.
This setting can set the braking force between the neutral point and Max
brake point. The larger this value, the greater the braking force. When set
to "0%", the brakes are not effective.
RMD-(REVERSE MAX DUTY) w/back only 0%~100%
Same as Link software Reverse Max. Duty
This setting can set the reverse power between the neutral point and Max
reverse point. The larger this value, the greater the reverse power. When
set to "0%", the reverses are not effective.
BKS-(BRAKE SLOPE) 0~300 (Only when used TBM-LEV2)
Same as Link software Brake Slope.
This function adjusts the braking effect when the throttle
was returned (throttle off). It cancels operation like that
called engine brake of actual vehicles.
BEC-(BEC VOLT)
6.0V /7.4V
Same as Link software BEC Volt.
The receiver BEC voltage can be selected from 60V and
74V. Match the voltage to the rating of the servo connected
to the same receiver. This BEC voltage cannot output a
voltage higher than the input voltage.
4PLS-Eng-08-3-Function-P84-114.indd 89 2013/04/08 9:10:21
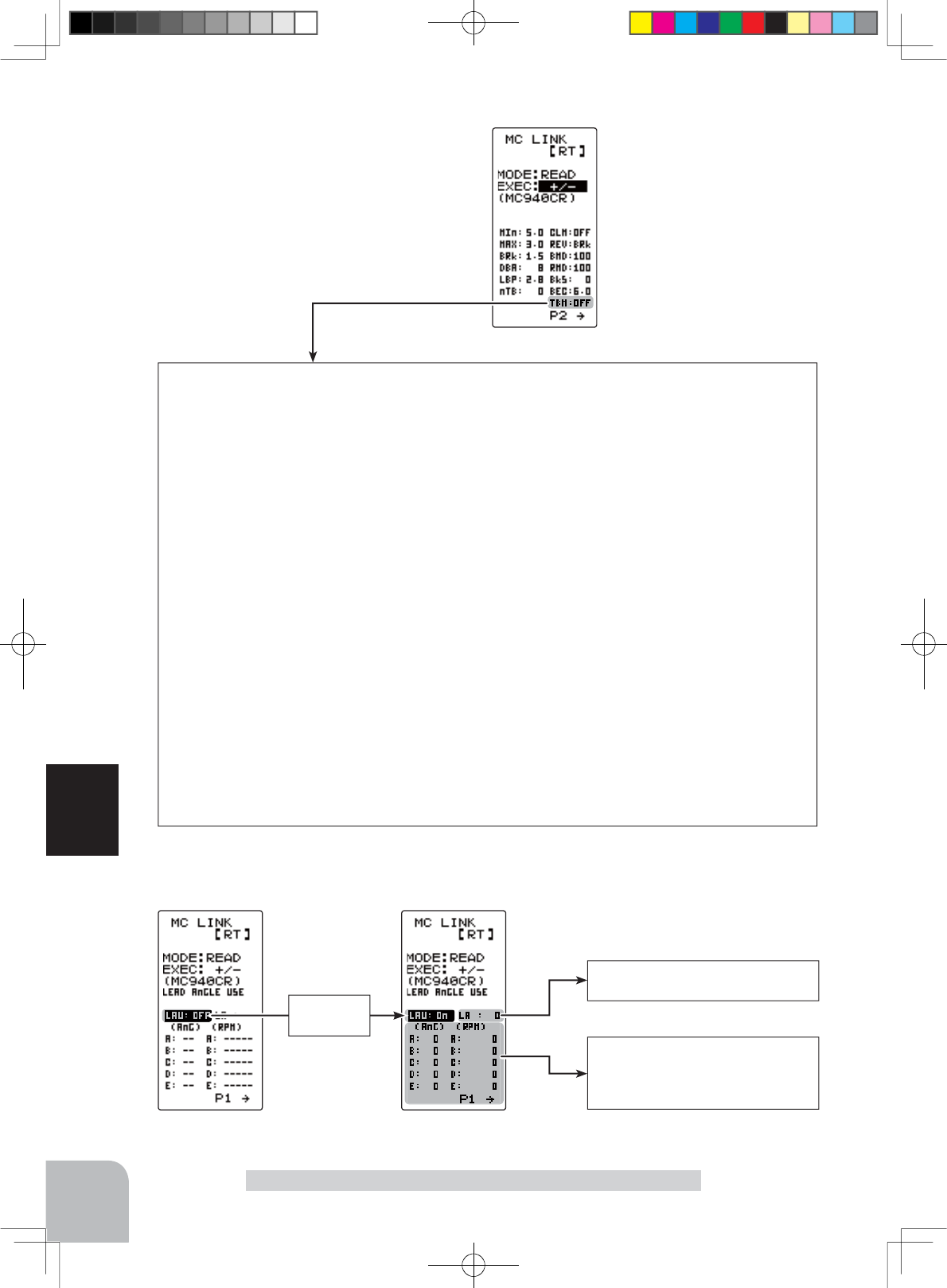
90
Function
Page1
TBM-(TURBO MODE)
OFF /LV1 /LV2
Same as Link software Turbo Mode
This function sets the turbo mode. More power can be displayed by using the turbo mode. Depending on the
setting, the motor and ESC may be damaged so make this setting carefully.
(Note) When LAU (LEAD ANGLE USE) is off, lead angle setting will not operate even if set to LEV1 or LEV2.
(Turbo mode disabled, TBM=OFF)
OFF mode: (No Lead Angle mode) Lead angle - No
When used in races in which the lead angle setting function is inhibited by ESC, set to this mode. The lead
angle function is disabled the same as if LAU (LEAD ANGLE USE) was turned off.
When the lead angle function was disabled by the method described above, the MC960CR shows that the
lead angle function is off by blinking a blue LED at an ON 0.1 second, OFF 0.9 second cycle at the neutral
point.
LV1 turbo mode: (Lead Angle mode) Lead angle – Yes
The output can be increased by setting a lead angle.
Depending on the set value, the motor may be damaged so increase the lead angle value in steps from a
small value while observing the conditions.
Turn on LAU (Lead Angle Use) and adjust the lead angle by LA-(LEAD ANGLE) and A, B, C, D, E BA-(A, B,
C, D, E BOOST ANGLE) value.
LV2 power mode: (Power Mode) Lead angle – Yes
Displays still more power than a turbo.
However, since even a motor applies a large load on the ESC, make the lead angle larger in steps from a
small value while observing the conditions.
Turn on LAU (LEAD ANGLE USE) and adjust the lead angle by LA-(LEAD ANGLE) and A, B, C, D, E BA-(A, B,
C, D, E BOOST ANGLE) value.
The BOOST ANGLE and BOOST
ANGLE RPM which can set the
lead angle of 5 points relative to
the speed.
Page2 Page2
"LAU"
turned on
"LA" (LEAD ANGLE) is displayed
and the lead angle can be set.
When "LAU" (LEAD ANGLE USE) is turned on "LA" (LEAD ANGLE) is the lead angle can be set. In addition, the "BOOST
ANGLE" and "BOOST ANGLE RPM" can be set.
ESC Link Function "MC LNK"
4PLS-Eng-08-3-Function-P84-114.indd 90 2013/04/08 9:10:21
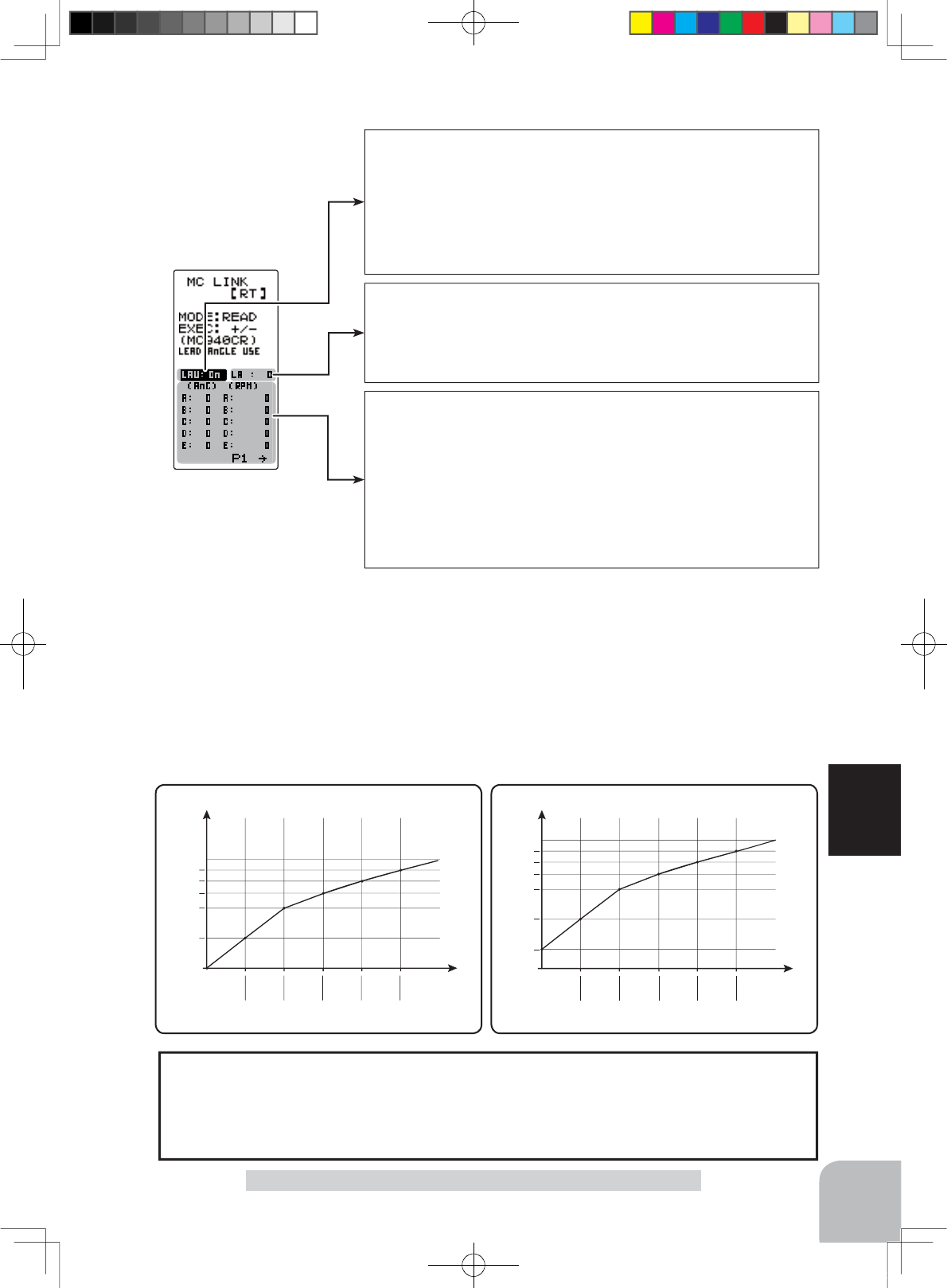
91
Function
LAU-(LEAD ANGLE USE)
ON /OFF
Same as Link software Lead Angle Use
This function is effective when TBM (Turbo Mode) is LEV1 or LEV2 and
sets whether or not lead angle is used. This setting has priority over the
TURBO MODE setting. When using in races in which the lead angle func-
tion is inhibited by the ESC set this function to OFF.
OFF : Lead angle function not used.
ON : Lead angle used
LA-(LEAD ANGLE) 0~59deg
Same as Link software Lead Angle
When LAU (LEAD ANGLE USE) is turned on the motor lead angle can
be set at the MC960CR. The lead angle can be set up to 59 degrees in 1
degree increments.
A,B,C,D,E BA-(A,B,C,D,E BOOST ANGLE) 0~59deg
Same as Link software Boost Angle
A
,B,C,D,E
RPM-(A
,B,C,D,E
BOOST ANGLE RPM) 0~
99990rpm
Same as Link software Boost Angle rpm
When LAU (LEAD ANGLE USE) is turned on the lead angle versus motor
speed of the 5 points A to E can be set. The lead angle can be set up to
59 degrees in 1 degree increments.
Note: Do not read to the T4PLS an MC940/960CR whose speed was set
to over 99990rpm by Link software side Boost Angle rpm setting.
Page2
When using in races in which the lead angle setting function is inhibited by the ESC, set LAU (LEAD
ANGLE USE) to OFF. The LAU setting has priority over TBM-(TURBO MODE). If LAU is set to
"OFF", the lead angle setting function can be turned off even if TBM is set to "LV1" or "LV2".
The MC940,960CR shows that the lead angle setting function is OFF ("0" timing) by blinking a LED.
The LA-(LEAD ANGLE) and A, B, C, D, E BA- (A, B, C, D, E BOOST ANGLE) relationship is shown on
the graphs below. Graph [A] shows the relationship when the same value is set at points A, B, C, D, E BA-
(A, B, C, D, E BOOST ANGLE) of [A] and [B] and the LA-(LEAD ANGLE) was set to "0" and graph [B]
shows the relationship when a value other than "0" was set at LA-(LEAD ANGLE).
As shown in the graphs, [B] is added to the A, B, C, D, E BA-(A, B, C, D, E BOOST ANGLE) set lead an-
gle and [A] is added to the LA-(LEAD ANGLE) set lead angle. For example, if "3" is set at ABA and LA of [B]
is set to "2", the actual ABA becomes 3+2=5 (deg). Since LA of [A] is "0", the actual ABA also becomes
3+0=3 (deg).
RPM(A) RPM(B) RPM(C) RPM(D) RPM(E)
AnG(A)
AnG(B)
AnG(C)
AnG(D)
AnG(E)
RPM(A) RPM(B) RPM(C) RPM(D) RPM(E)
AnG(A)
LA
AnG(B)
AnG(C)
AnG(D)
AnG(E)
B (LA >"0")A (LA ="0") Lead Angle(deg) Lead Angle(deg)
rpmrpm
ESC Link Function "MC LNK"
4PLS-Eng-08-3-Function-P84-114.indd 91 2013/04/08 9:10:22
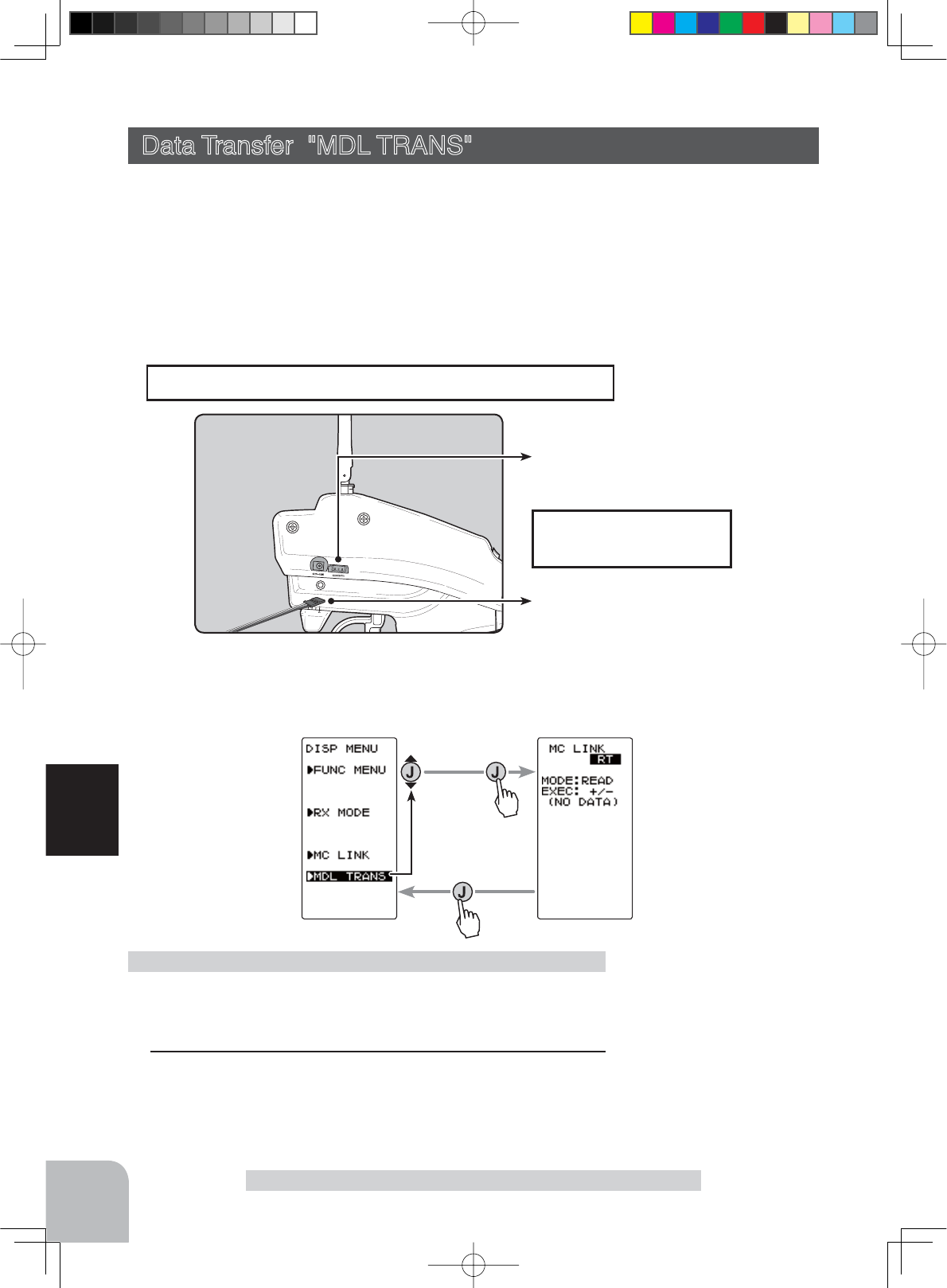
Connect the communication
port of both T4PLS with the
optional DSC cord.
Communication port
DSC cord for T4PK (option)
(MDL TRANS screen)
Press
(DISP MENU screen)
Press
Select
"
MDL TRANS
"
92
Function
Data Transfer "MDL TRANS"
This function copies the model memory data of one T4PLS to another T4PLS. Connect
the communication port of both T4PLS with the optional DSC cord for T4PK. Use with
this function with the T4PLS power switch at the display side.
Note: If the T4PLS battery voltage drops, the display switches to low battery display.
Therefore, use this function when there is ample battery capacity remaining.
Note: Since the receiving side writes the new contents of the currently selected model
memory, always check the model number before executing this function.
Data is not interchangeable with another type of transmitter.
Display "MDL TRANS" screen by with the T4PLS power switch at the display side and
following method:
(Preparation)
- Connect the communication port of both transmitters with the
optional DSC cord for T4PK.
1Set the power switch of both transmitters to the display (DISP)
side.
Use the (JOG) button and (+) button to display the
"M
DL-
TRN
"
at both transmitter.
Using the Data Transfer function
Data Transfer "MDL TRANS"
4PLS-Eng-08-3-Function-P84-114.indd 92 2013/04/08 9:10:23
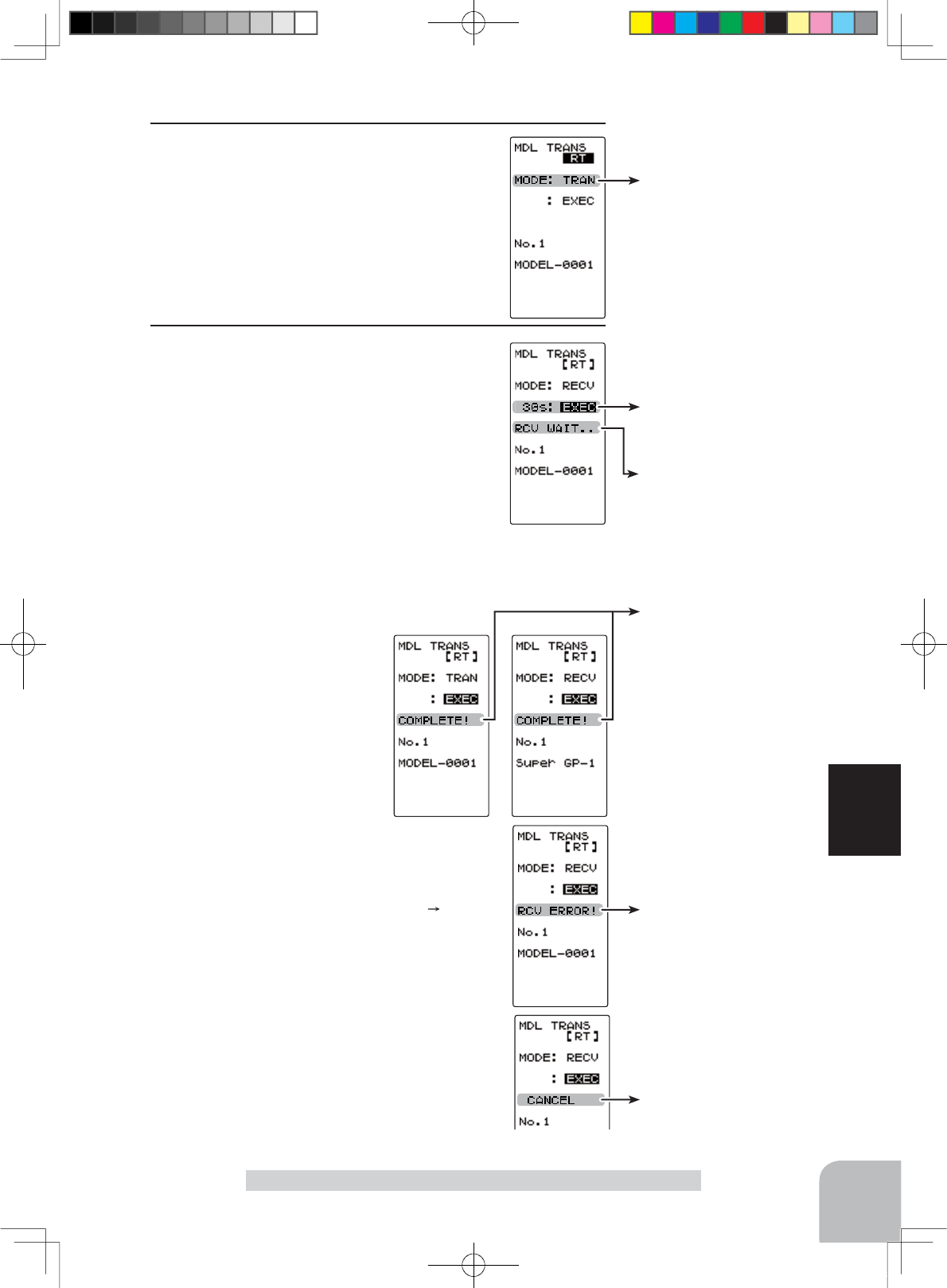
30 seconds wait is displayed
on the receive side screen.
Transfer execution button
- (+) and (-) buttons pressed
simultaneously for about 1
second.
Mode selection
"TRANSFER" "RECEIVE"
Setup item selection
- Select by (JOG) button up or
down operation.
Mode change button
- Use the (+) and (-) buttons to
make adjustments.
"COMPLELE!" is displayed.
"RCV ERROR!" is displayed.
"CANCEL" is displayed.
93
Function
2 (Select the setting item )
"MODE" by the (JOG) button up or down op-
eration, and select the transfer side and re-
ceive side by (+) or (-) button.
"TRAN":Data transfer side
"RECV":Data receive side
3 (Data transfer execution)
Select the setting item
"
EXEC
"
by (JOG) but-
ton up or down operation of both transmitter.
First, press the receive side
"
RECV
"
trans-
mitter (+) and (-) buttons simultaneously. The
message
"
RCV WAIT..
"
appears and count
down begins.
Within 30 seconds, press the transfer side
"
TRANS
"
trans-
mitter (+) and (-) buttons simultaneously. (If data transfer is
not executed within 30 seconds, an error will be displayed at
the receive side
"
RECV
"
transmitter.)
-"COMPLETE!" is displayed
on the screen of the receive
side "RECV" transmitter and
data transfer is ended.
-If "RCV ERROR!" is displayed on the screen
of the receive side "RECEIVE" transmitter, da-
ta transfer was not performed normally. Check
the connection and repeat steps 1 3. Since
the transfer side "TRANS" transmitter only
sends, "COMPLETE!" is displayed even when
data transfer was not performed normally.
Data transfer can also be canceled before the
end of transfer by operating the (JOG) button
at a T4PLS that is waiting to receive data.
When ending, return to the DISP MENU
screen by pressing the (JOG) button.
Data Transfer "MDL TRANS"
4PLS-Eng-08-3-Function-P84-114.indd 93 2013/04/08 9:10:23
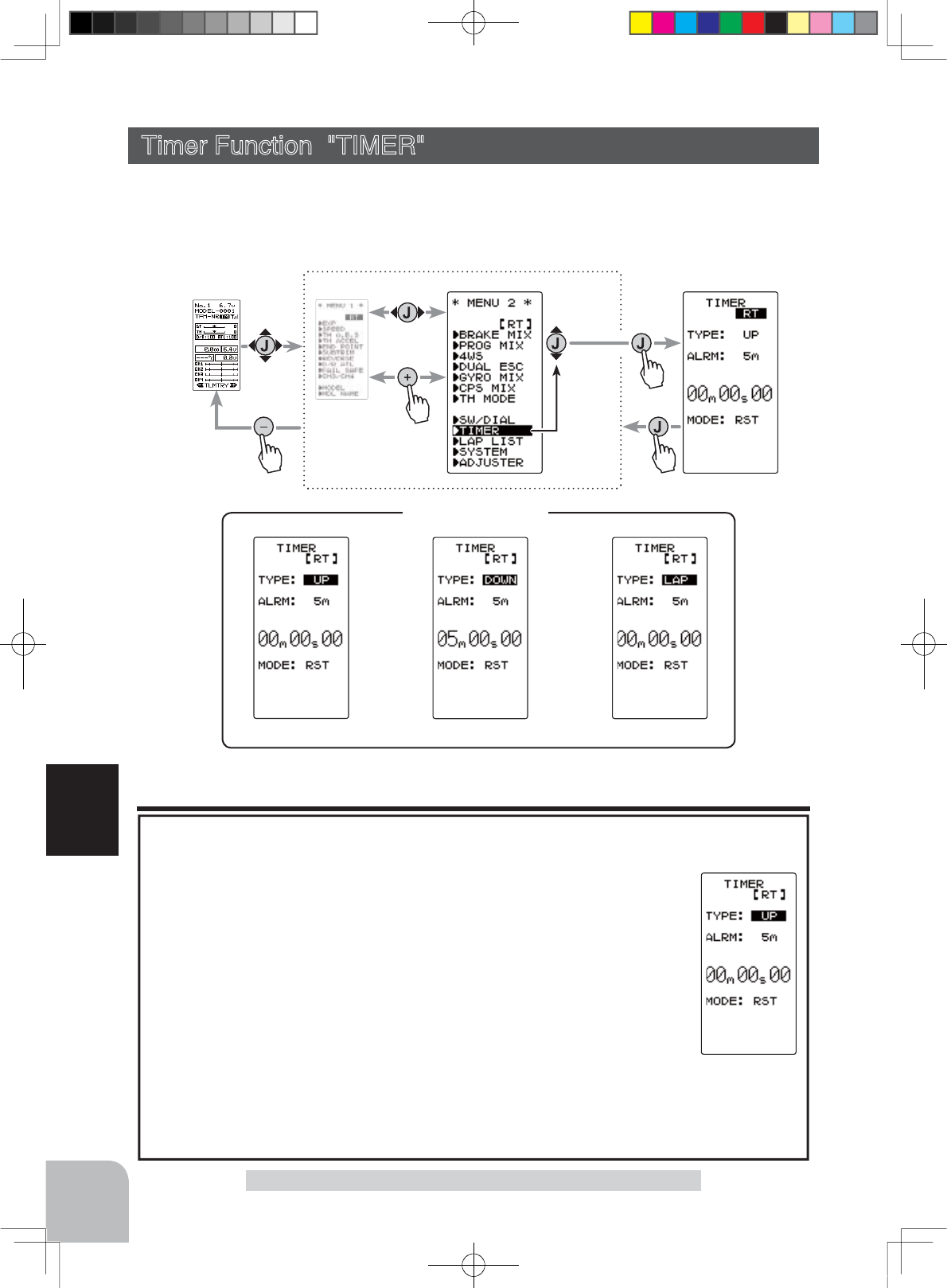
UP TIMER FUEL DOWN TIMER LAP TIMER
TIMER Disply
Press
Press
Press
Press
Select
"
TIMER
"
(HOME screen) (MENU 1 screen) (TIMER screen)
(MENU 2 screen)
94
Function
Timer Function "TIMER"
Use the timer by selecting one of the three timers UP TIMER, DOWN TIMER, and
LAP TIMER.
Display "PTIMER" screen by the following method:
UP TIMER function
Up timer function
- This function can be used to count the time between start and stop, etc.
- The timer repeatedly starts and stops each time the switch is pressed and
accumulates the time between each start and stop. When the count reach-
es 99 minutes 99 seconds, the count returns to 00 minutes 00 seconds and
is repeated.
7KH¿UVWVWDUWRSHUDWLRQFDQEHOLQNHGWRWKHWKURWWOHWULJJHU
- The passage of time is announced by sounding of a buzzer (beep) each
minute after starting.
- Alarm :Beep sounds at the set time (minute).
- Prealarm :Alarm advance announcement sound. Beeping begins 5 seconds before the alarm.(beeps)
- After starting, the timer continues to count and can be stopped by switch even when
the LCD switches to another screen.
Timer Function "TIMER"
4PLS-Eng-08-3-Function-P84-114.indd 94 2013/04/08 9:10:24
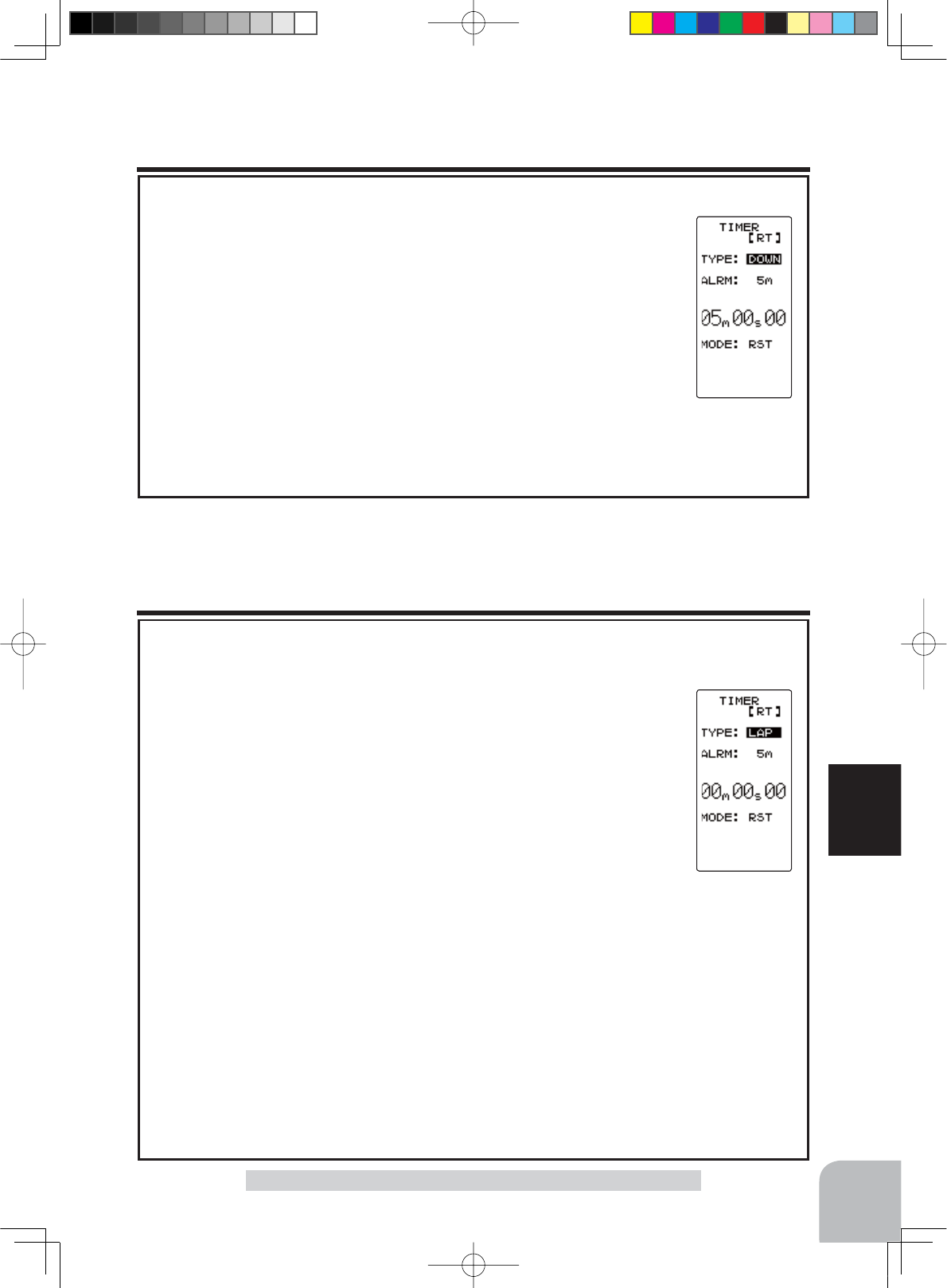
95
Function
FUEL DOWN TIMER function
Fuel down timer function
- This function is primarily used to check the refueling time of a gasoline
car. (The remaining time is displayed.)
- Each time the switch is pressed, the timer is restarted and the set time is
reset. The start time becomes the alarm set time. (When counted down to
00 minute 00 second, the down timer becomes an up timer.)
- The down timer can be initially started by throttle trigger.
- The passing of time is indicated by sounding of a buzzer (beep) each
minute after starting.
- Alarm :A beep sounds at the set time (minute).
- Prealarm :Alarm advance announcement sound. Beeping begins 5 seconds before the alarm.(beeps)
- After starting, the timer continues to count even if the LCD switches to another screen.
Timer Function "TIMER"
LAP TIMER
Lap timer function
- Each lap time can be memorized by switch operation. (100 laps)
- The race time can be set. Switch operation after the time set by alarm
has elapsed automatically stops the timer. The passing of time is indicat-
ed by sounding of a buzzer (beep) each minute after starting.
-Alarm :Beep sounds at the set time.
Prealarm :Alarm advance announcement sound. Sounding begins 5 seconds before
the alarm. (beeps)
- The lap timer can be initially started by throttle trigger.
(LAP TIMER operation)
- The lap timer is started by switch or throttle trigger.
- Number of laps (LAP): After starting, the timer is counted up and the lap time blinks for 3 seconds
each time the switch is pressed. To prevent erroneous counting, switch operation is not accepted
during this period. When 1 lap exceeds 10 minutes, counting is repeated from 0.
- Lap list: Up to 10 lap times are memorized beginning from lap list 1. After lap memory "No.100", op-
eration returns to lap memory "No.1" and the lap memories are overwritten.
- The lap time data memorized in the lap memories can be checked with the lap list screen (p.92). The
entire lap list data is cleared the next time the lap timer is started.
- TIME: For the first 3 seconds, the preceding lap time is displayed. After that the current lap time is
displayed.
4PLS-Eng-08-3-Function-P84-114.indd 95 2013/04/08 9:10:24
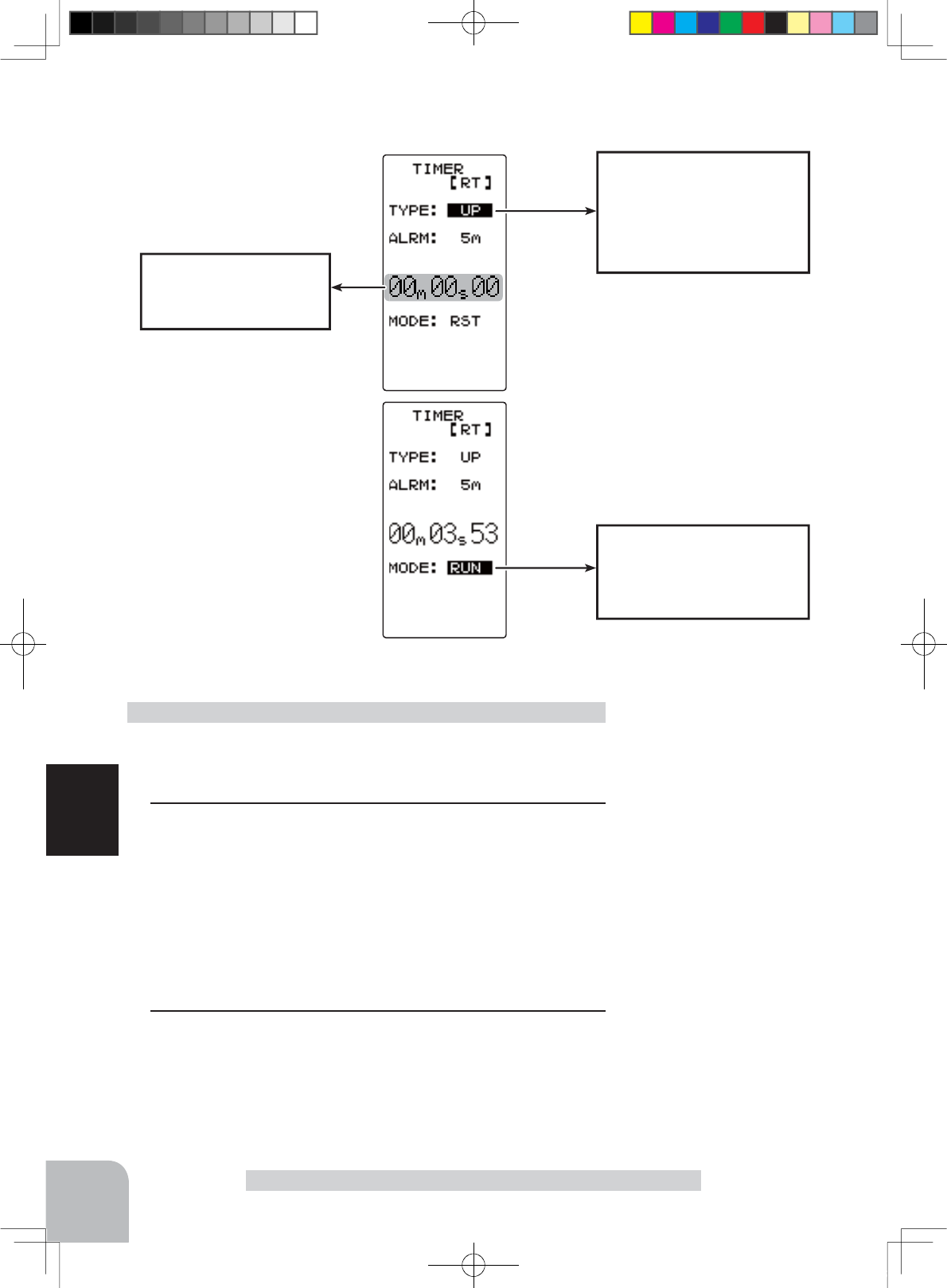
Status display
RST :Reset state
RDY :
Throttle trigger operation wait
RUN :Timer running
STP : Timer stopped
96
Function
Timer selection
First, select the type of timer
at the "TYPE" item. The setup
screen varies depending on the
type of timer. This figure shows
the UP TIMER setup screen.
Timer Function "TIMER"
(Preparation)
Assign the "TIMER" switch using the function select switch
(p.65).
1 (Racing timer type selection)
Select the setting item "TYPE" by the (JOG) button. Use the
(+) or (-) button and set the racing timer type.
Timer selection (TYPE)
UP : Up timer
DOWN : Down timer
LAP : Lap timer
2When ending, return to the MENU2 screen by pressing the
(JOG) button.
Racing timer type selection
Time display
Minute display (m)
Second display (s)
1/100 second display
Setup item selection
- Select by the (JOG) button.
Adjustment buttons
- Use the (+) and (-) buttons to
make adjustments.
Timer screen
4PLS-Eng-08-3-Function-P84-114.indd 96 2013/04/08 9:10:25
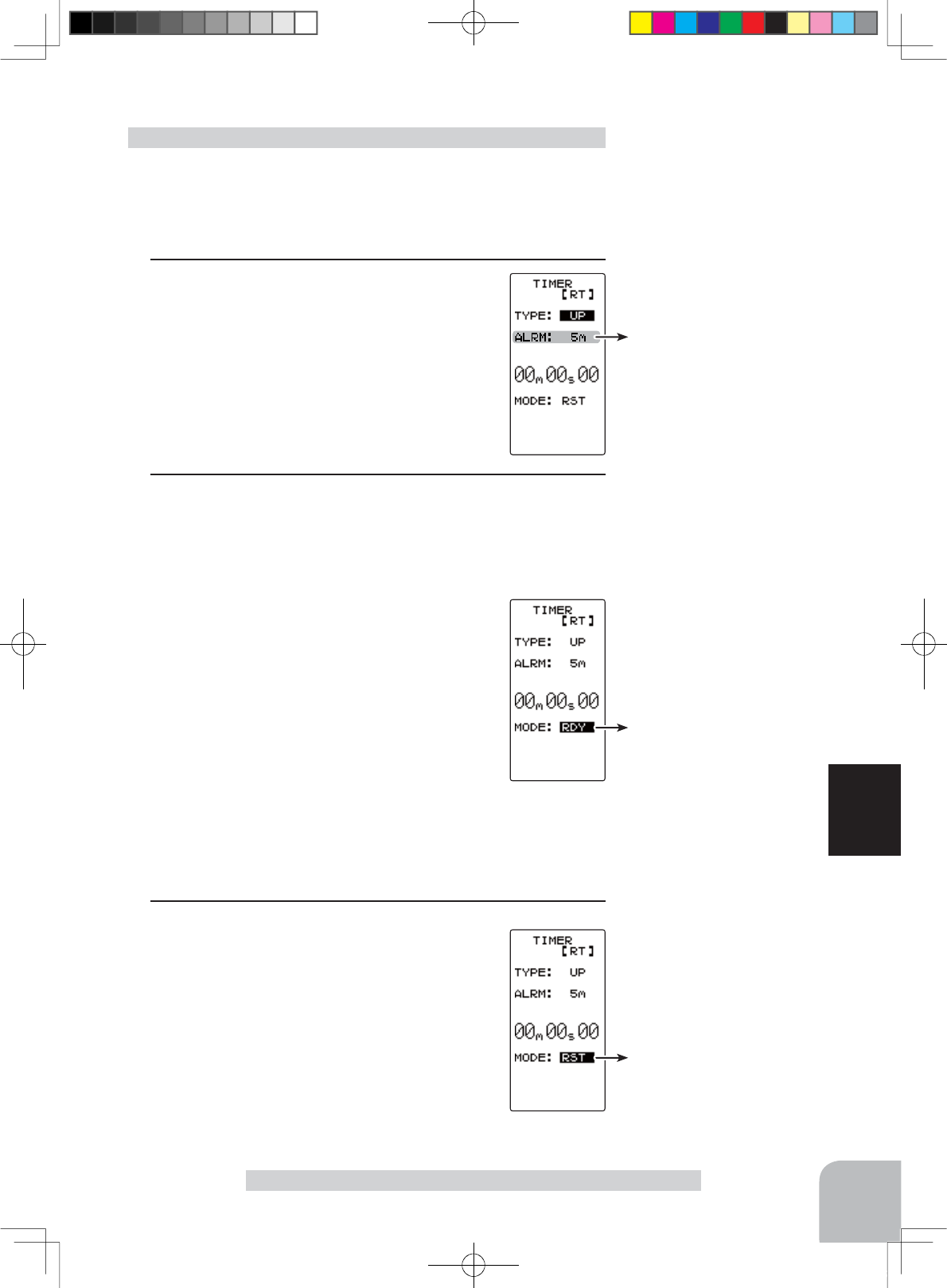
Alarm time (ALRM)
OFF, 1 ~ 99 m
Initial value: 5 m
Status display
RST :Reset state
RDY :
Throttle trigger operation wait
RUN :Timer running
STP : Timer stopped
Status display
RST :Reset state
RDY:
Throttle trigger operation wait
RUN :Timer running
STP : Timer stopped
Switches
Time start / stop
97
Function
Timer Function "TIMER"
(Preparation)
Select the setting item "TYPE" by the (JOG) button.
Press the (+) or (-) button and select "UP".
1 (Alarm time setting)
Select the setting item "ALRM" by the (JOG)
button and set the alarm time with the (+) or (-)
button.
2 (Timer start/stop operation)
Start the timer by pressing the switch ("TIMER") set by func-
tion select switch function.
Stop the timer with the same switch ("TIMER") as start.
- Linking only start to the throttle trigger
Select the setting item "RST" by the (JOG)
button and press the (+) and (-) buttons simul-
taneously for approximately 1 second. When
the set beeps and the status display switches
from "RST" to blinking "RDY", the system en-
ters the trigger operation ready state. When
the trigger is operated at the forward side, the
timer starts. (Status display "RUN")
If the (JOG) button is pressed while the timer is operating,
the LCD returns to MENU2 screen.
3 (Timer reset operation)
Select a status display ("RUN", "STP", or
"RDY") by the (JOG) button and press the (+)
and (-) buttons simultaneously for approxi-
mately 1 second. A beep is generated and
"RST" appears on the status display and the
timer resets.
Using the up timer
Adjustment buttons
- Use the (+) and (-) buttons to
make adjustments.
- Press the (+) and (-) buttons si-
multaneously (approx. 1 sec) to
return to the HOME screen.
4PLS-Eng-08-3-Function-P84-114.indd 97 2013/04/08 9:10:25
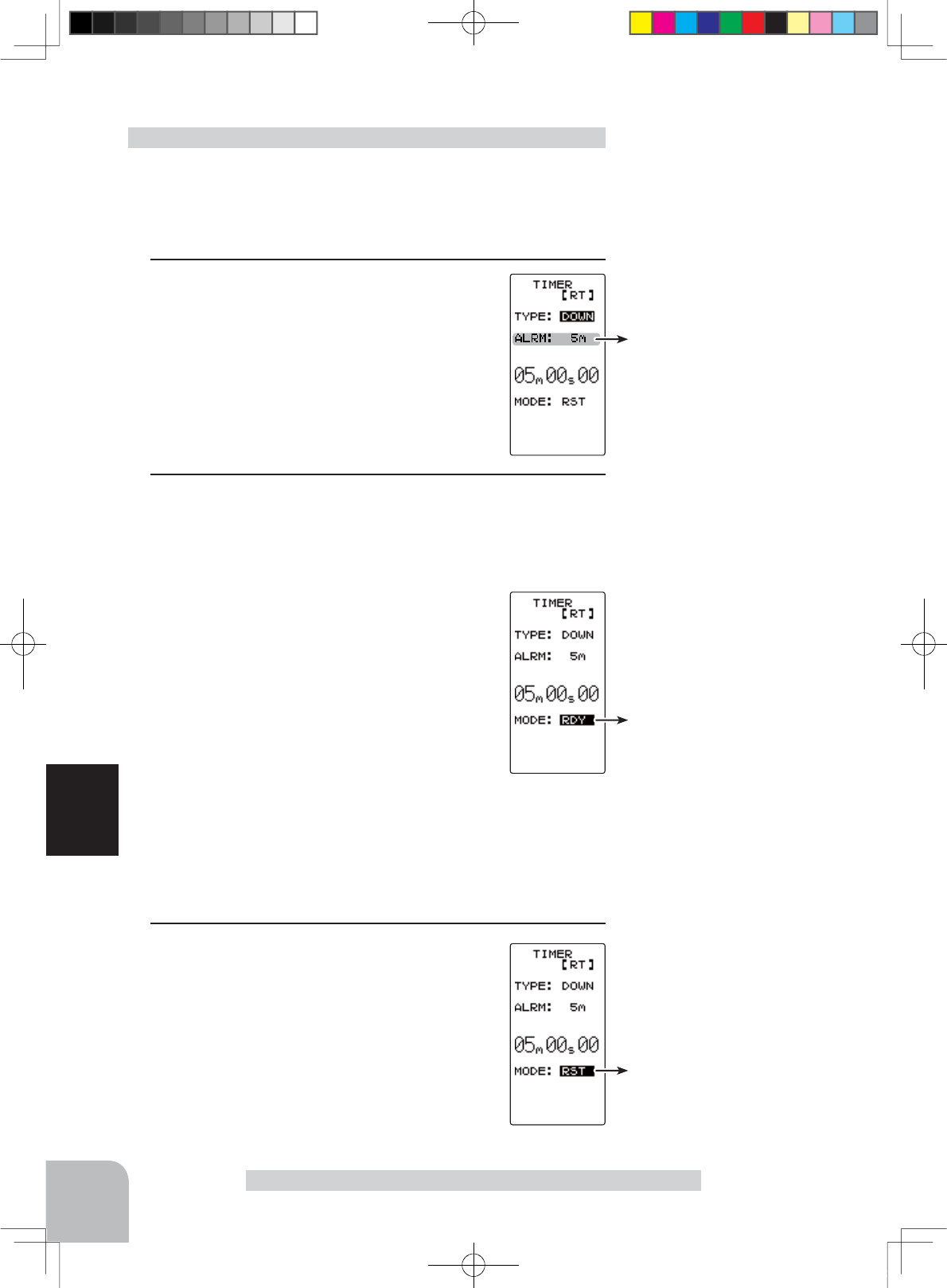
Alarm time (ALRM)
OFF, 1 ~ 99 m
Initial value: 5 m
Status display
RST :Reset state
RDY :
Throttle trigger operation wait
RUN :Timer running
STP : Timer stopped
Status display
RST :Reset state
RDY :
Throttle trigger operation wait
RUN :Timer running
STP : Timer stopped
98
Function
Timer Function "TIMER"
(Preparation)
Select the setting item "TYPE" by the (JOG) button.
Press the (+) or (-) button and select "DOWN".
1 (Alarm time setting)
Select the setting item "ALRM" by the (JOG)
button and set the alarm time with the (+) or (-)
button.
2 (Alarm start/restart operation)
When the switch ("TIMER") set by function select switch
function is pressed, the timer starts. When the same switch
("TIMER") is pressed while the timer is operating, the timer is
reset and simultaneously restarted. (Restart)
- Linking only start to the throttle trigger
Select the setting item "RST" by the (JOG)
button and press the (+) and (-) buttons simul-
taneously for about 1 second. When the set
beeps and the status display switches from
"RST" to blinking "RDY", the system enters
the trigger operation ready state.
When the trigger is operated at the forward side, the timer
starts. (Status display "RUN")
If the (JOG) button is pressed while the timer is operating,
the LCD returns to MENU2 screen.
3 (Timer reset operation)
Select a status display ("RUN") by the (JOG)
button and press the (+) and (-) buttons simul-
taneously for approximately 1 second. A beep-
ing sound is generated and "RST" appears on
the status display and the timer resets.
Using the fuel down timer
Adjustment buttons
- Use the (+) and (-) buttons to
make adjustments.
- Press the (+) and (-) buttons si-
multaneously (approx. 1 sec) to
return to the HOME screen.
Switches
Timer start / restart
4PLS-Eng-08-3-Function-P84-114.indd 98 2013/04/08 9:10:25
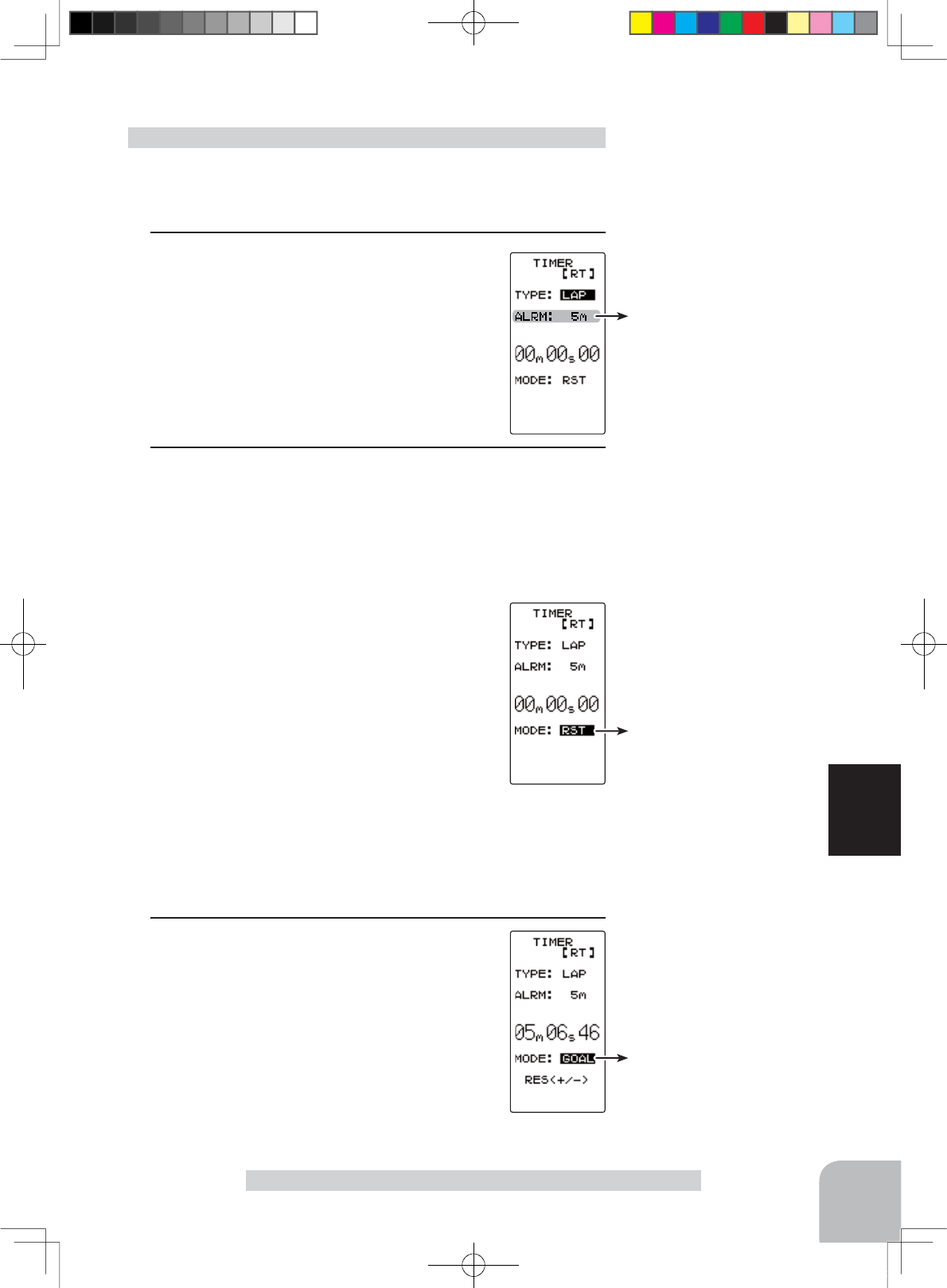
Status display
RST :Reset state
RDY :
Throttle trigger operation wait
RUN :Timer running
GOAL: Timer stopped
Status display
RST :Reset state
RDY :
Throttle trigger operation wait
RUN :Timer running
GOAL: Timer stopped
Alarm time (ALRM)
OFF, 1 ~ 99 m
Initial value: 5 m
99
Function
Timer Function "TIMER"
(Preparation)
Select the setting item "TYPE" by the (JOG) button.
Press the (+) or (-) button and select "LAP".
1(Alarm time setting)
Select the setting item "ALRM" by the (JOG)
button and set the alarm time with the (+) and
(-) buttons.
2(Timer start/ lap count/ stop operation)
When the switch (TIMER) set by function select switch func-
tion is pressed, the timer starts. At timer operation, the same
switch becomes the lap switch and when the set time elaps-
es, the timer is stopped by the same switch (TIMER)
- Linking only start to the throttle trigger
Select the setting item "RST" by the (JOG)
button and press the (+) and (-) buttons simul-
taneously for about 1 second. When the set
beeps and the status display switches from
"RST" to blinking "RDY", the system enters
the trigger operation ready state. When the
trigger is operated at the forward side, the tim-
er starts. (Status display "RUN")
When the switch (TIMER) is pressed after the time set by
alarm has elapsed, the timer stops and the lap time and total
time are memorized. The status display becomes "GOAL".
If the (JOG) button is pressed while the timer is operating,
the LCD returns to MENU2 screen.
3(Timer reset operation)
Select a status display ("GOAL") by the (JOG)
button and press the (+) and (-) buttons simul-
taneously for approximately 1 second. A beep-
ing sound is generated and "RST" appears on
the status display and the timer resets.
- When reset operation was performed before the "ALRM"
set time had elapsed, the total time is not memorized.
- The lap memory data can be checked with the lap list
(P98) screen.
Using the Lap timer Adjustment buttons
- Use the (+) and (-) buttons to
make adjustments.
- Press the (+) and (-) buttons si-
multaneously (approx. 1 sec) to
return to the HOME screen.
Switches
Timer start / Lap count
4PLS-Eng-08-3-Function-P84-114.indd 99 2013/04/08 9:10:25
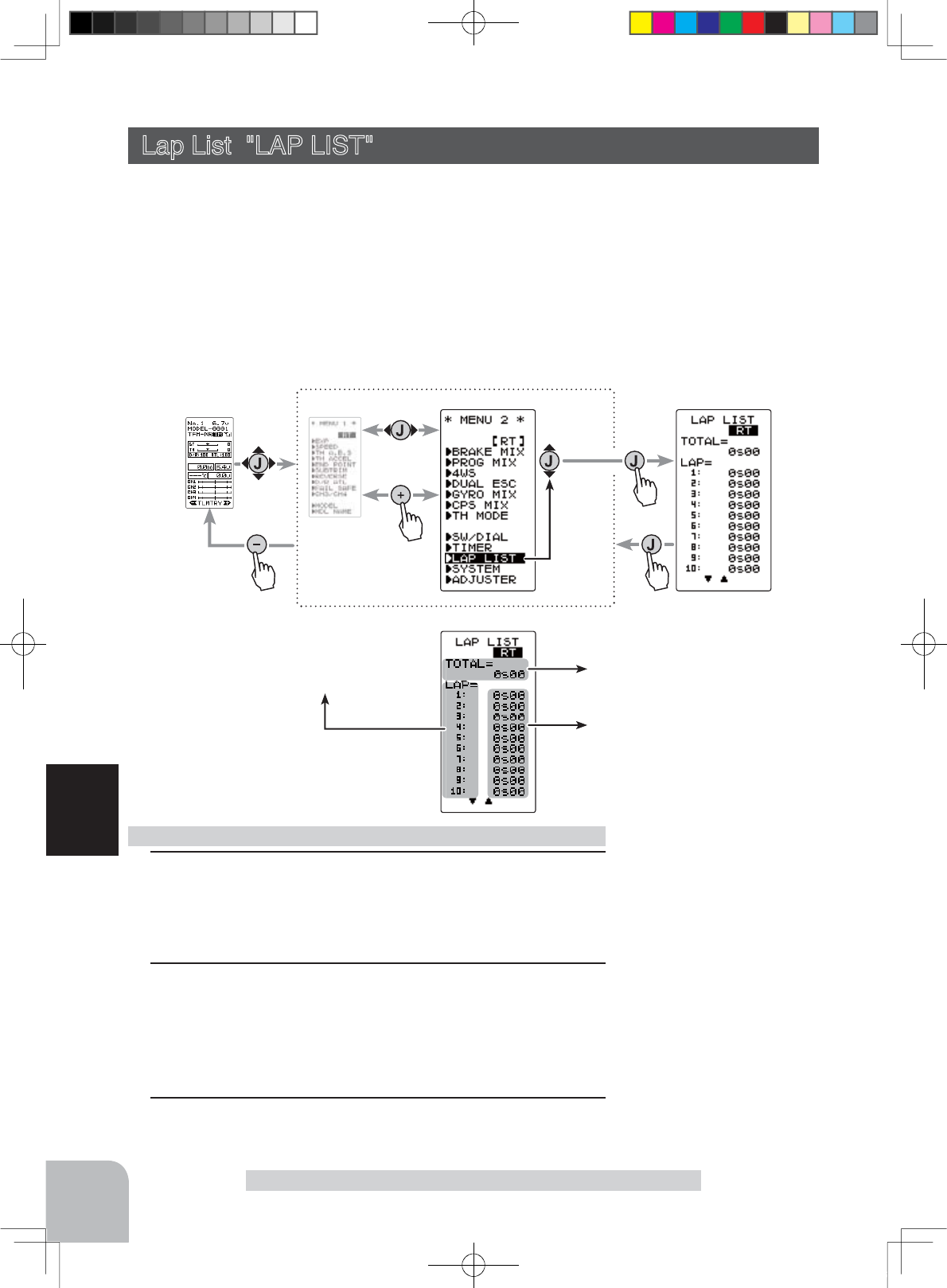
Reset button
- Reset by pressing the (+) and
(-) buttons simultaneously for
about 1 second.
Lap memory No. display
Total time display
Lap time display
Press
Press
Press
Press
Select
"
LAP LIST
"
(HOME screen) (MENU 1 screen) (LAP LIST screen)
(MENU 2 screen)
100
Function
Lap List "LAP LIST"
Lap List "LAP LIST"
The lap list is displayed when checking the lap memory data (lap times) memorized by
lap timer (P99) operation.
- After the lap timer starts, the lap times are memorized sequentially each time the
switch is operated.
,IWKHWLPHULVVWRSSHGDIWHUWKHVHW$/50WLPHKDVHODSVHGWKH¿QDOODSWLPHLVPHP-
orized and the total time after the last lap is automatically written.
- When the timer was stopped before the set ALRM time has elapsed, the total time is not memorized.
Display "LAP LIST" screen by the following method:
1 (Lap memory check)
When the (JOG) button is pressed, the list is scrolled every
10 laps and each lap time can be checked.
2 (Lap memory total data reset)
Press the (+) and (-) buttons simultaneously for approximate-
ly 1 second. A beeping sound is generated and all the data is
reset.
3When ending, return to the MENU2 screen by pressing the
(JOG) button.
Using the lap memory
4PLS-Eng-08-3-Function-P84-114.indd 100 2013/04/08 9:10:26
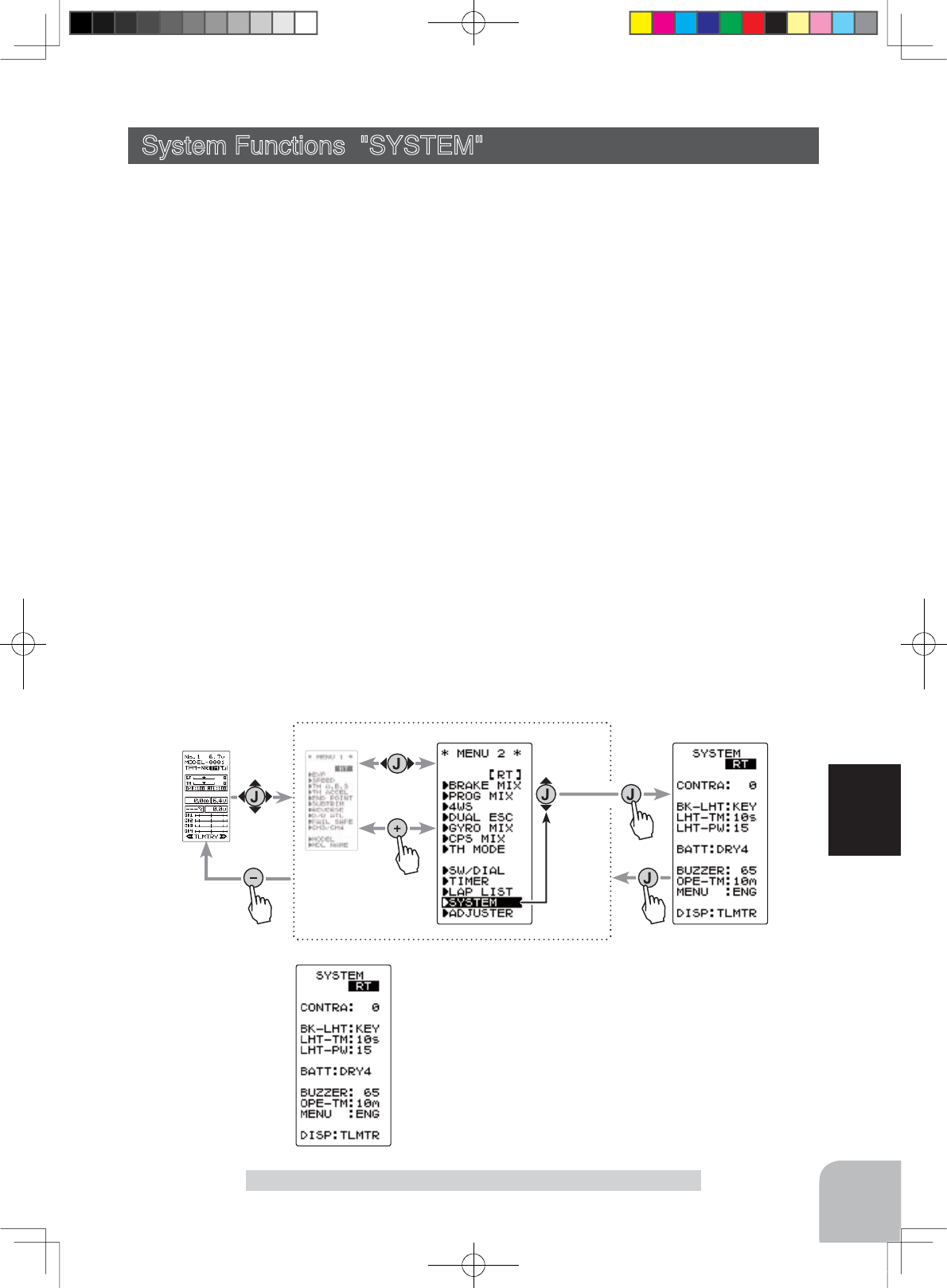
Display "SYSTEM" screen by the following method:
Press
Press
Press
Press
Select
"
SYSTEM
"
(HOME screen) (MENU 1 screen) (SYSTEM screen)
(MENU 2 screen)
101
Function
System Functions "SYSTEM"
System Functions "SYSTEM"
The graphic liquid crystal screen display mode, buzzer sound and menu character mode,
etc can be set.
- "CONTRA"---Liquid crystal screen contrast adjustment (20 steps)
- "BK-LHT"---Liquid crystal screen backlighting display mode setup
(OFF, ON at button operation, normally ON)
- "LHT-TM"---Setting of ON time (1~30 secs) when [ON at button operation] was selected above.
- "LHT-PM"---Liquid crystal screen backlighting brghtness adjustment (30 steps)
- "BATT"---Battery type setting (LiFe2/NiMH5/DRY4)
The T4PLS can use an optional rechargeable battery. However, the battery alarm setting is dif-
ferent from that of the dry cell battery (alkaline battery recommended). Therefore, always set the
battery type to match the power source used.
If used with the incorrect setting, the normal low battery alarm function will not work and the sys-
tem may stop before a battery alarm is generated. The usage time may also become extremely
short.
- "BUZZER"---Buzzer sound tone adjustment (OFF, 100 steps)
- "OPE-TM"---The power off forgotten alarm setting (OFF, 10 m)
- "MENU"---Item which displays the basic menu screen in katakana characters for Japanese use.
- "DISP"---HOME screen display mode setting (Telemetry data, Timer, Users name)
Setup items
CONTRA :Contrast
BK-LHT :Backlighting mode
LHT-TM :Backlighting time
LHT-PW :Backlighting brightness
BATT :Battery type
BUZZER :Buzzer tone
OPE-TM :Power off forgotten alarm
MENU :Menu screen character
DISP :HOME screen display mode
4PLS-Eng-08-3-Function-P84-114.indd 101 2013/04/08 9:10:27
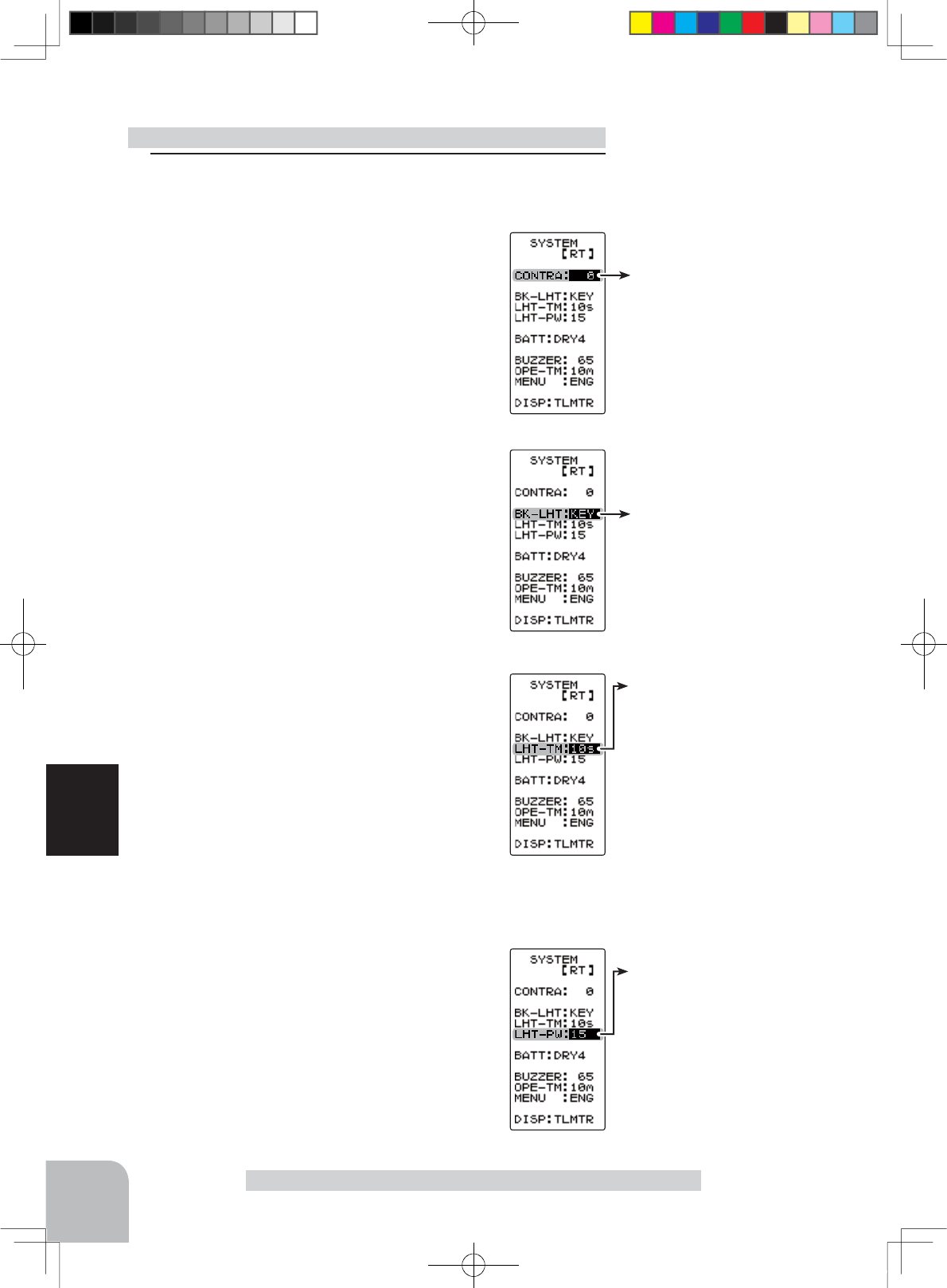
Contrast (CONTRA)
-10~0~+10
Initial value: 0
Backlight mode (BK-LHT)
KEY, ALL, OFF
Backlighting time (LHT-TM)
1~30
Initial value: 10
Backlighting brightness
(LHT-PW)
1~30
Initial value: 15
102
Function
1(Setting of each item)
(Adjusting the liquid crystal contrast)
Select the setting item "CONTRA"
by the (JOG)
button
, and use the (+) and (-) buttons to adjust
the screen contrast.
- Adjust to an easy-to-see contrast.
When ending, return to the MENU2 screen by
pressing the (JOG) button.
(Setting the liquid crystal backlighting mode)
Select the setting item "BK-LHT"
by the (JOG)
button
, and select the mode by pressing the (+)
or (-) button.
"KEY" :Fixed time backlighting ON after button operated.
"ALL" :Backlighting always ON
"OFF" :Backlighting OFF
When ending, return to the MENU2 screen by
pressing the (JOG) button.
(Setting liquid crystal backlighting time)
Select the setting item "LHT-TM"
by the (JOG)
button
, and use the (+) and (-) buttons to set the
ON time.
- When "KEY" is set at the preceding item, this ON time be-
comes effective
.
When ending, return to the MENU2 screen by
pressing the (JOG) button.
(Setting liquid crystal backlighting brightness)
Select the setting item "LHT-PW"
by the (JOG)
button
, and use the (+) and (-) buttons to set the
ON time.
-If too bright, the battery will be consumed.
When ending, return to the MENU2 screen by
pressing the (JOG) button.
System function setup Adjustment buttons
- Use the (+) and (-) buttons to
make adjustments.
- Press the (+) and (-) buttons si-
multaneously (approx. 1 sec) to
return to the initial value.
System Functions "SYSTEM"
4PLS-Eng-08-3-Function-P84-114.indd 102 2013/04/08 9:10:27
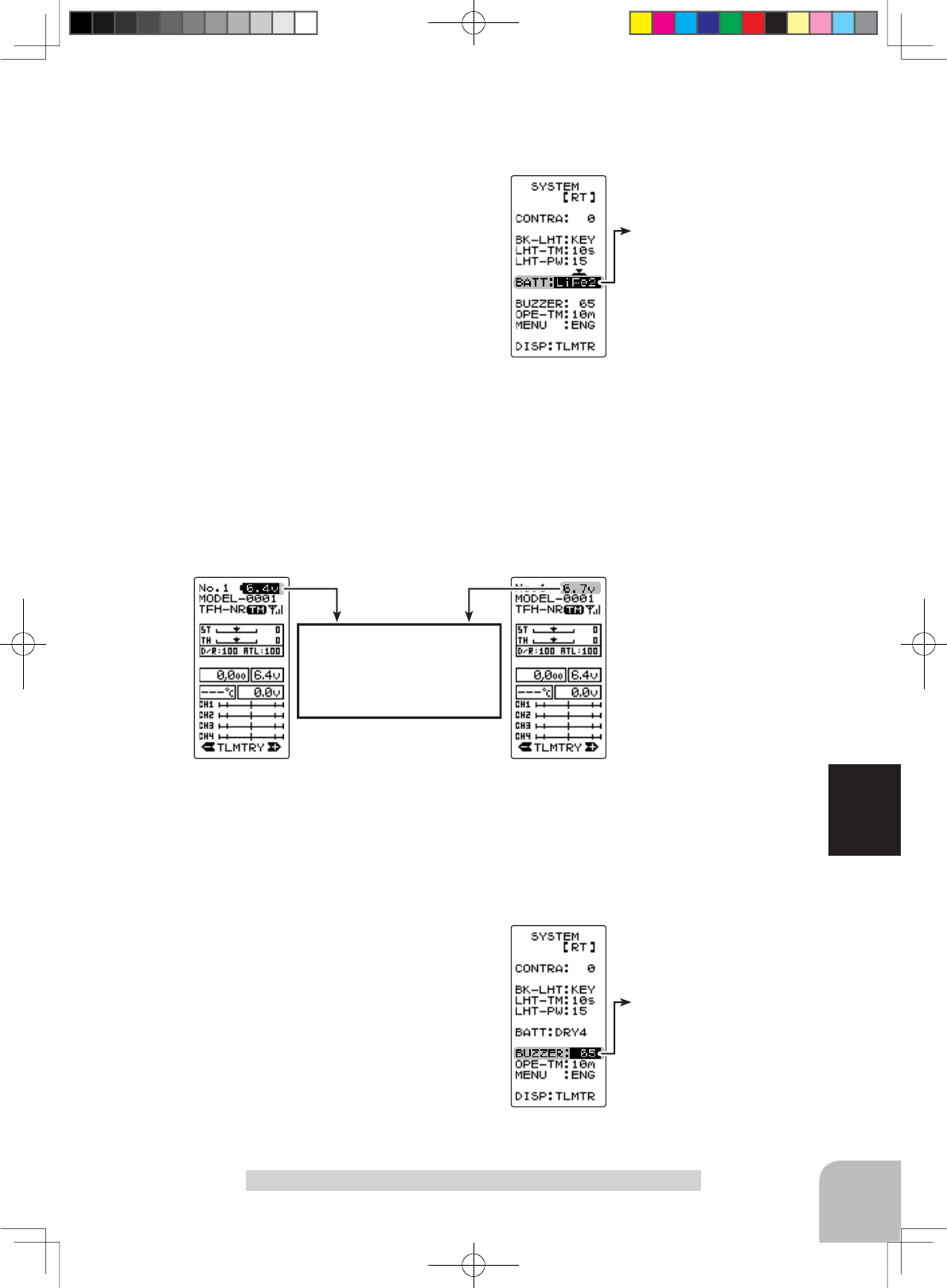
Battery Type (BATT)
DRY4, N5/L2
Buzzer tone (BUZZER)
OFF, 1~100
Initial value: 85
Voltage display
When BATT is set to dry cell
use DRY4 or LiFe2/NiMH5,
the voltage display of the
HOME screen changes.
DRY4 LiFe2, NiMH5
103
Function
(Setting the battery type)
Select the setting item "BATT" by the (JOG)
button, and select the mode by pressing the
(+) or (-) button. When changing the battery
type, press the (JOG) button after thorough-
ly checking whether or not the mistake was
made again. An electronic beeping sound is
generated and the setting is changed.
Note: If the battery type is changed to the wrong setting, the
low battery alarm will be generated immediately after the
change and operation will become impossible.
When the low battery alarm was generated, turn off the power and replace the bat-
tery with a fully charged battery or a new dry cell battery and then reset the battery
type.
Note: If used with the incorrect setting, a normal low battery alarm will not be gen-
erated and the system may stop before the battery alarm is generated. The usage
time may also become extremely short.
"N5/L2" :Futaba LiFe type battery (FT2F1700B/2100B)
"N5/L2" :Futaba MiMH type battery (HT5F1800B)
"DRY4" :Dry cell battery (alkaline battery recommended) 4 batteries
System Functions "SYSTEM"
When ending, return to the menu screen by
pressing the (JOG) button.
(Adjusting the buzzer tone)
Select the setting item "BUZZER"
by the (JOG)
button
, and use the (+) and (-) buttons to adjust
the tone.
- Decide by referring to the tone at adjustment.
When ending, return to the menu screen by
pressing the (JOG) button.
4PLS-Eng-08-3-Function-P84-114.indd 103 2013/04/08 9:10:27
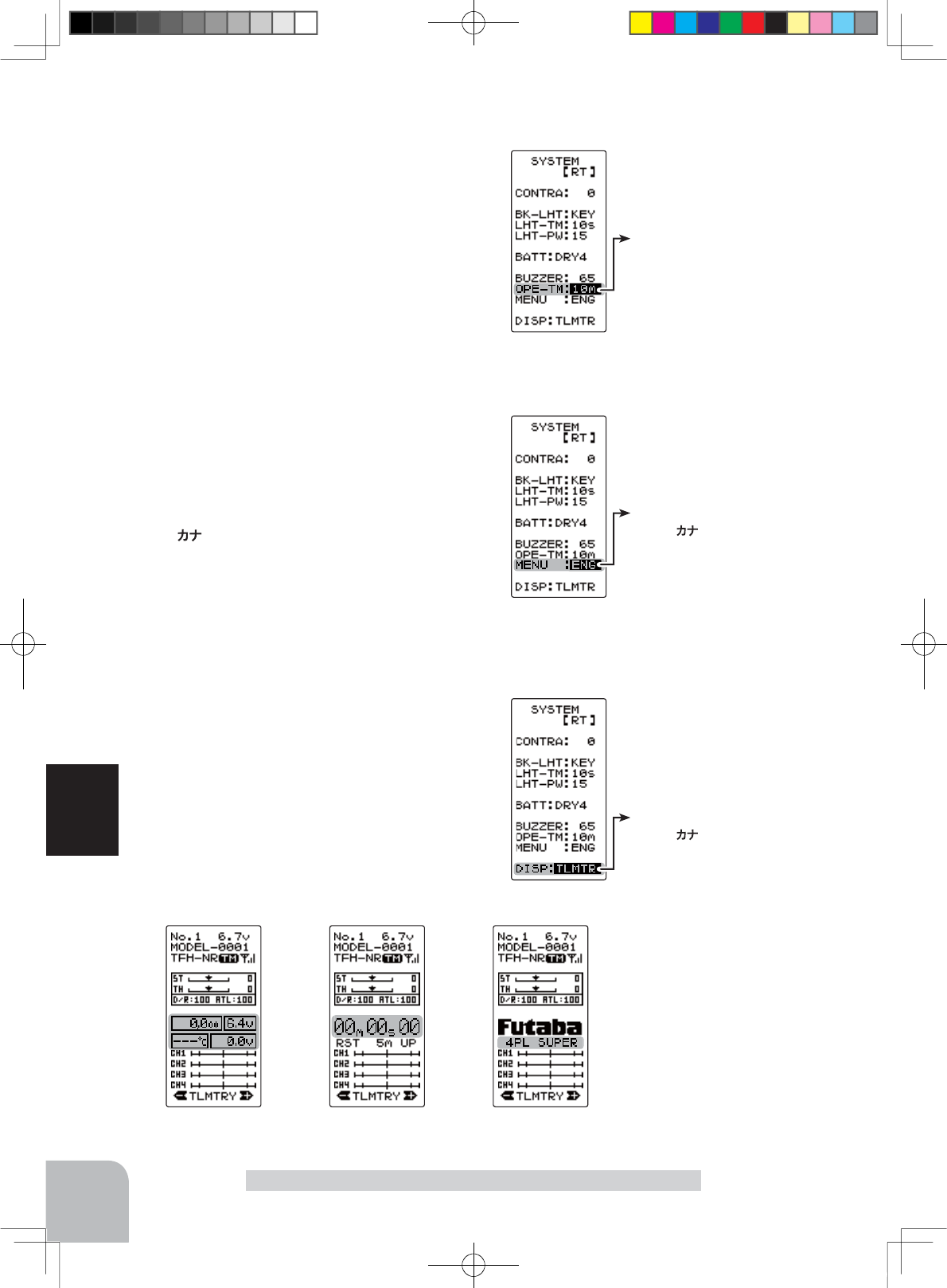
USERTIMERTLMTR
The power off forgotten alarm
(OPE-TM)
10m, OFF
Menu charactre (MENU)
ENG,
HOME screen mode (DISP)
ENG,
104
Function
System Functions "SYSTEM"
(Changing the power off forgotten alarm setting)
Select the setting item "OPE-TM"
by the (JOG)
button
, and use the (+) and (-) buttons to select
the power off forgotten alarm mode.
"10m" :If an operation is not performed within 10 min-
utes while the power is on, an audible alarm
sounds.
"OFF" :Power off forgotten alarm setting OFF
When ending, return to the menu screen by pressing the
(JOG) button.
(Changing the menu character display)
Select the setting item "MENU" by the (JOG)
button, and set the basic menu character dis-
play with the (+) or (-) button. (See page 37)
"ENG" : Basic menu displayed in Alphabetic character.
" " : Basic menu displayed in katakana character.
When ending, return to the menu screen by pressing the
(JOG) button.
(Changing the HOME screen display mode)
Select the setting item "DISP" by the (JOG)
button, and set the HOME screen display
mode with the (+) or (-) button.
"TLMTR" :Telemetry data is displayed
"TIMER" :Timer is displayed
"USER" :User name is displayed
Only the T-FHSS system can display telemetry data.
Nothing is displayed with an S-FHSS/FHSS system.
4PLS-Eng-08-3-Function-P84-114.indd 104 2013/04/08 9:10:29
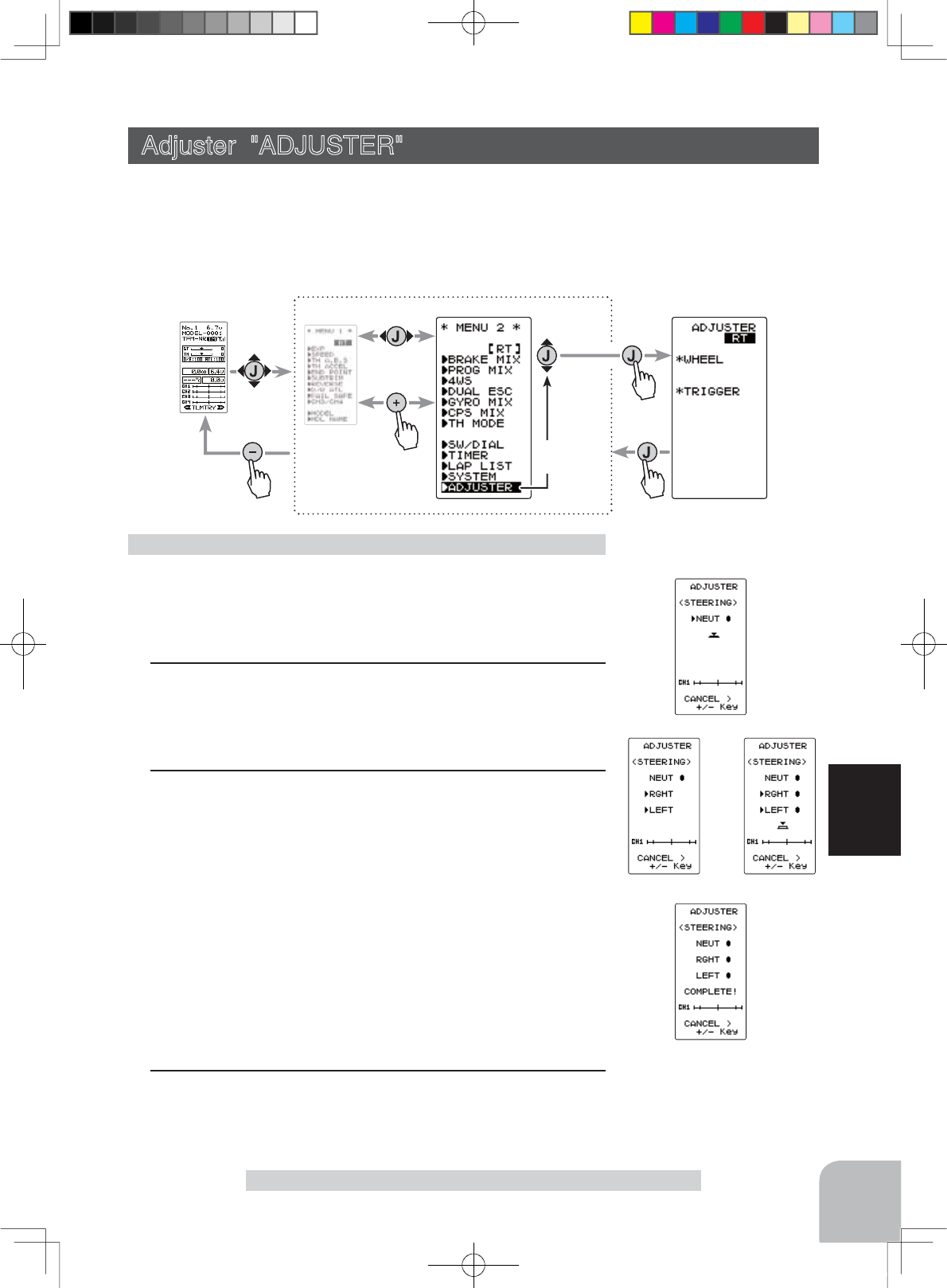
fig-1
fig-4
fig-2 fig-3
Press
Press
Press
Press
Select
"
ADJUSTER
"
105
Function
Adjuster "ADJUSTER"
(Preparation)
On the ADJUSTER screen, select the setting item "WHEEL"
by the (JOG) button, and pressing the (JOG) button.
1 (Steering neutral adjustment)
In the neutral setup screen (fig-1) state, lightly pull the steer-
ing wheel and then press the (JOG) button in the state in
which the wheel is not being touched.
2 (Steering throw adjustment)
In the throw setup screen state (fig-2), lightly turn the wheel
fully to the left or right and when button mark (fig-3) is dis-
played, pressing the (JOG) button.
Internal check is performed automatically. When each adjust-
ment point is within a fixed range, correction is performed
and "COMPLETE" (fig-4) is displayed.
If an adjustment point is not within a fixed range, correction
is not performed and the correction data is not updated.
When button mark is not displayed even though correction
was performed again, please contact a Futaba Radio Control
Customer Center.
3When ending, return to the MENU2 screen by pressing the
(JOG) button.
Steering adjustment
Adjuster "ADJUSTER"
Steering wheel and throttle trigger neutral position and servo operating angle correction
can be applied. This is used when a mechanical offset has occurred for some reason.
*
However, when correction was applied, the set value of all the setting functions
must be rechecked.
Display the adjuster screen from the system menu.
(HOME screen) (MENU 1 screen) (ADJUSTER screen)
(MENU 2 screen)
4PLS-Eng-08-3-Function-P84-114.indd 105 2013/04/08 9:10:29
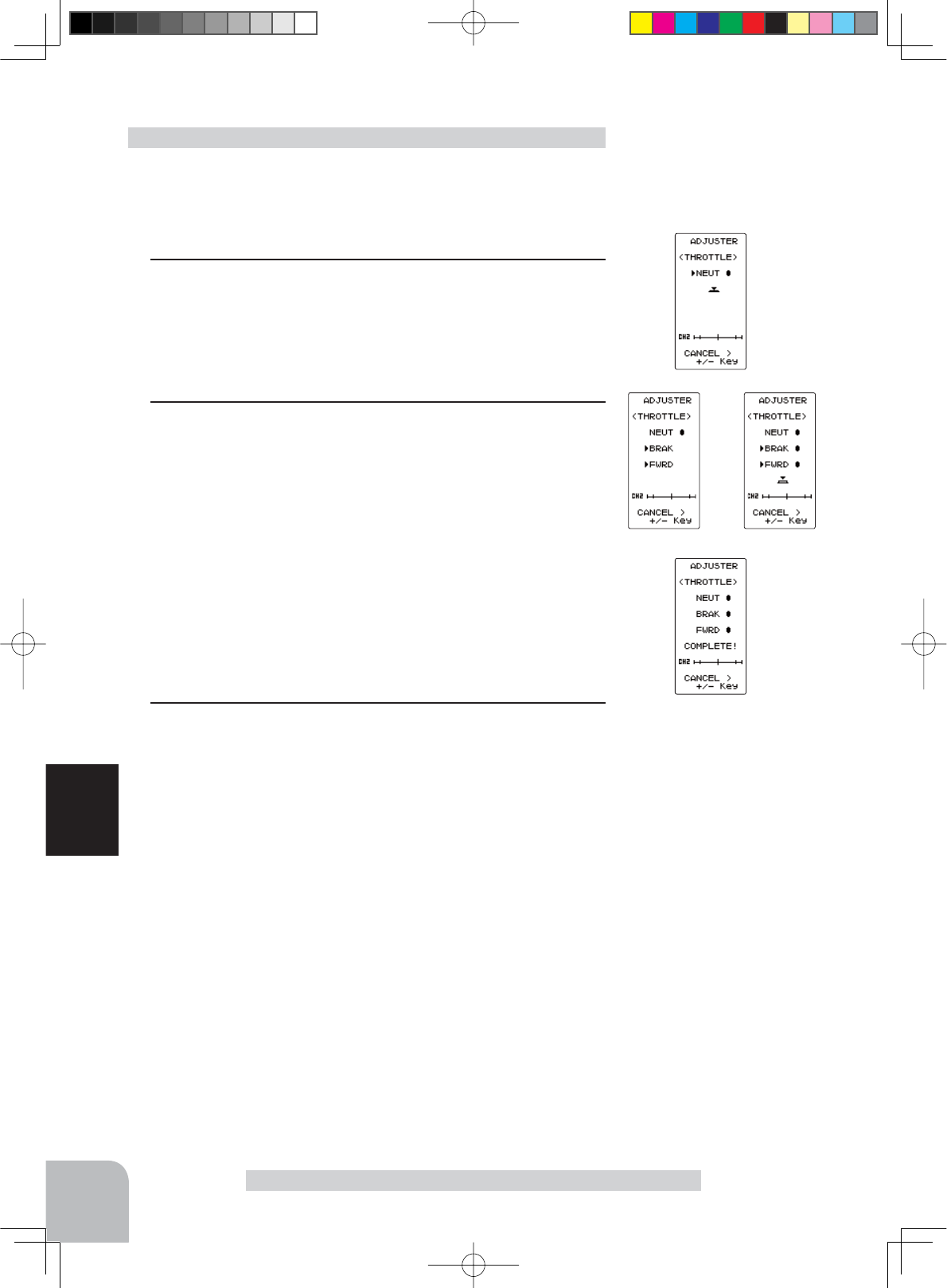
fig-1
fig-2 fig-3
fig-4
106
Function
Adjuster "ADJUSTER"
(Preparation)
On the ADJUSTER screen, select the setting item "THROT-
TLE" by the (JOG) button, and pressing the (JOG) button.
1 (Throttle neutral adjustment)
In the neutral setup screen (fig-1) state, lightly
pull the throttle trigger and then press the (JOG) button in
the state in which the trigger is not being touched.
2 (Throttle throw adjustment)
In the throw setup screen state (fig-2), lightly operate the
trigger fully to the brake side and the forward side and when
button mark (fig-3) is displayed, pressing the (JOG) button.
Internal check is performed automatically. When each adjust-
ment point is within a fixed range, correction is performed
and "COMPLETE!" (fig-4) is displayed.
If an adjustment point is not within a fixed range, correction
is not performed and the correction data is not updated.
When button mark is not displayed even though correction
was performed again, please contact a Futaba Radio Control
Customer Center.
3When ending, return to the MENU2 screen by pressing the
(JOG) button.
Throttle adjustment
4PLS-Eng-08-3-Function-P84-114.indd 106 2013/04/08 9:10:29
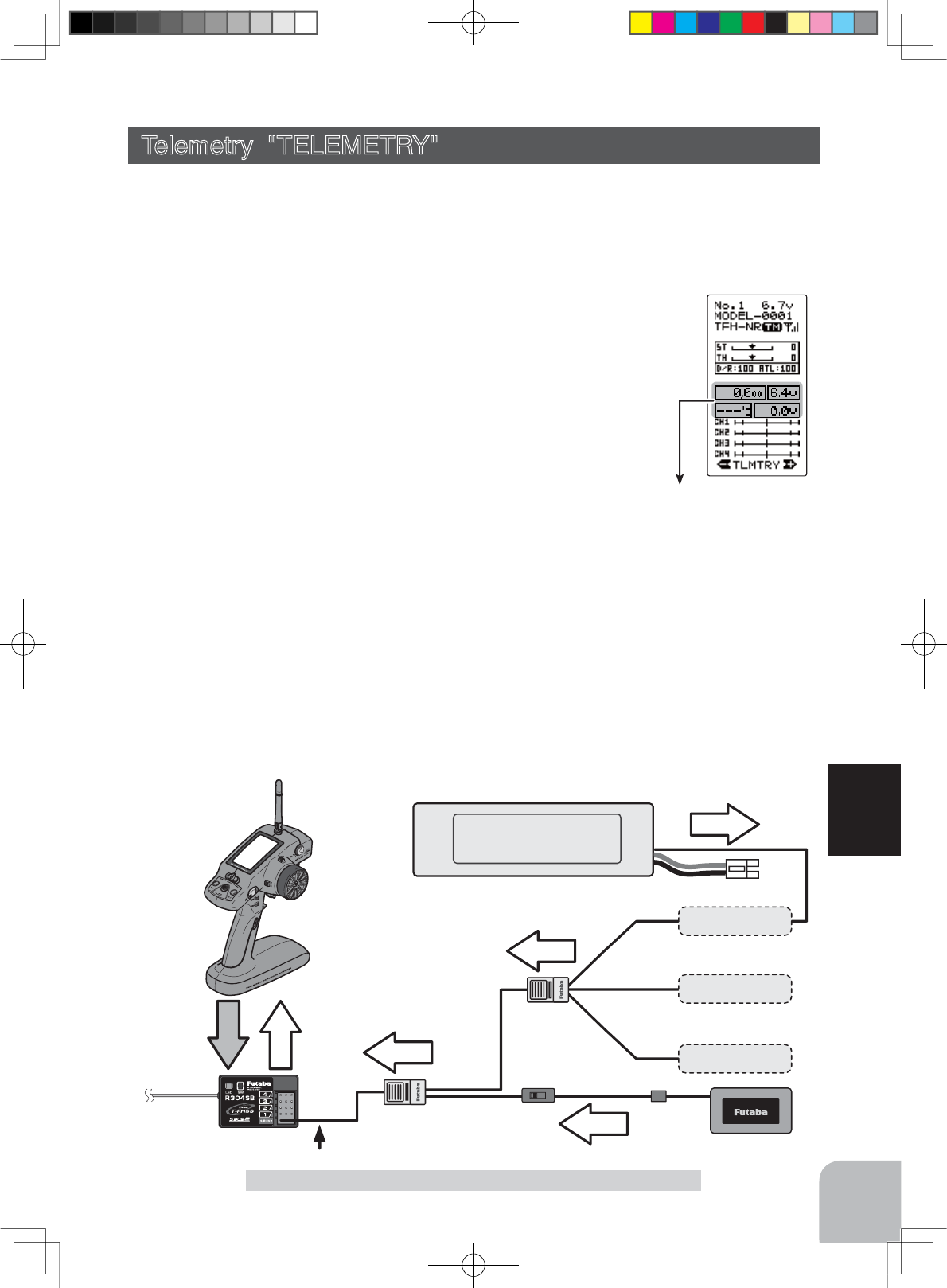
Telemetry info
(HOME screen)
107
Function
Info
Info
Info
Info
Signal
Info
Temperature
Sensor
RPM Sensor
Voltage Sensor
Battery voltage is displayed
at the transmitter.
Power battery voltage is
displayed at the transmitter.
voltage
T-FHSS Receiver
Transmitter
Switch
Connect to S.BUS2 Connector
HUB
HUB
Temperature Sensor (SBS-01T)
RPM Sensor (SBS-01RM)
Voltage Sensor (SBS-01V)
Telemetry "TELEMETRY"
Telemetry "TELEMETRY"
With the telemetry system, the running status can be displayed at the transmitter and al-
so recorded as a data log by mounting various sensor units to the chassis.
The telemetry related screens are only displayed when the T4PLS power switch is in the
PWR ON position. When the power switch is in the DISP position, the telemetry related
screens are not displayed.
The T4PLS displays four kinds of information on the HOME screen; re-
ceiver power source (battery) voltage, external power supply (drive bat-
tery) voltage, speed, and temperature.
*The telemetry function is compatible with only the T-FHSS system.
*The telemetry function requires a corresponding receiver (R304SB).
*Only T4PLS with R304SB ID registered have a telemetry display.
*Multiple sensors of the same type cannot be used.
The sensor data can be checked at the transmitter by connecting
the telemetry sensor sold separately to the S.BUS2 connector of
the R304SB receiver.
7KH¿JXUHLVDQH[DPSOHRIFRQQHFWLRQRIDWHOHPHWU\VHQVRU7KHGDWDRIXSWRWKHIRO-
lowing 3 types of sensors and the receiver power supply voltage can be transmitted by
using the 3-way extension cord or double extension cord sold separately.
The receiver power supply can also be connected to the S-BUS2 connector or each of
CH1-4. A receiver power supply voltage sensor is unnecessary.
*The S-BUS2 system exerts control by connecting multiple gyros, servos and other devices corresponding to one S-BUS2
connector. Each device is separately controlled by setting the channel No. or slot No. individually for each device.
A slot No. is also set for telemetry sensors. With the T4PLS system, each slot No. of a telemetry sensor must be set to its ini-
tial value. Since the slot No. can be changed for other aircraft type transmitters (T18MZ, etc.), sensors with changed slot No.
will not operate if not returned to their initial slot No. When using a sensor that is used with transmitters other than a T4PL,
whether or not the slot No. is set to the initial value given in the sensor instruction manual must be checked at the changed
transmitter (T18MZ, etc.). With the T4PLS, the set slot No. cannot be checked or changed.
Connection
diagram
4PLS-Eng-08-3-Function-P84-114.indd 107 2013/04/08 9:10:30
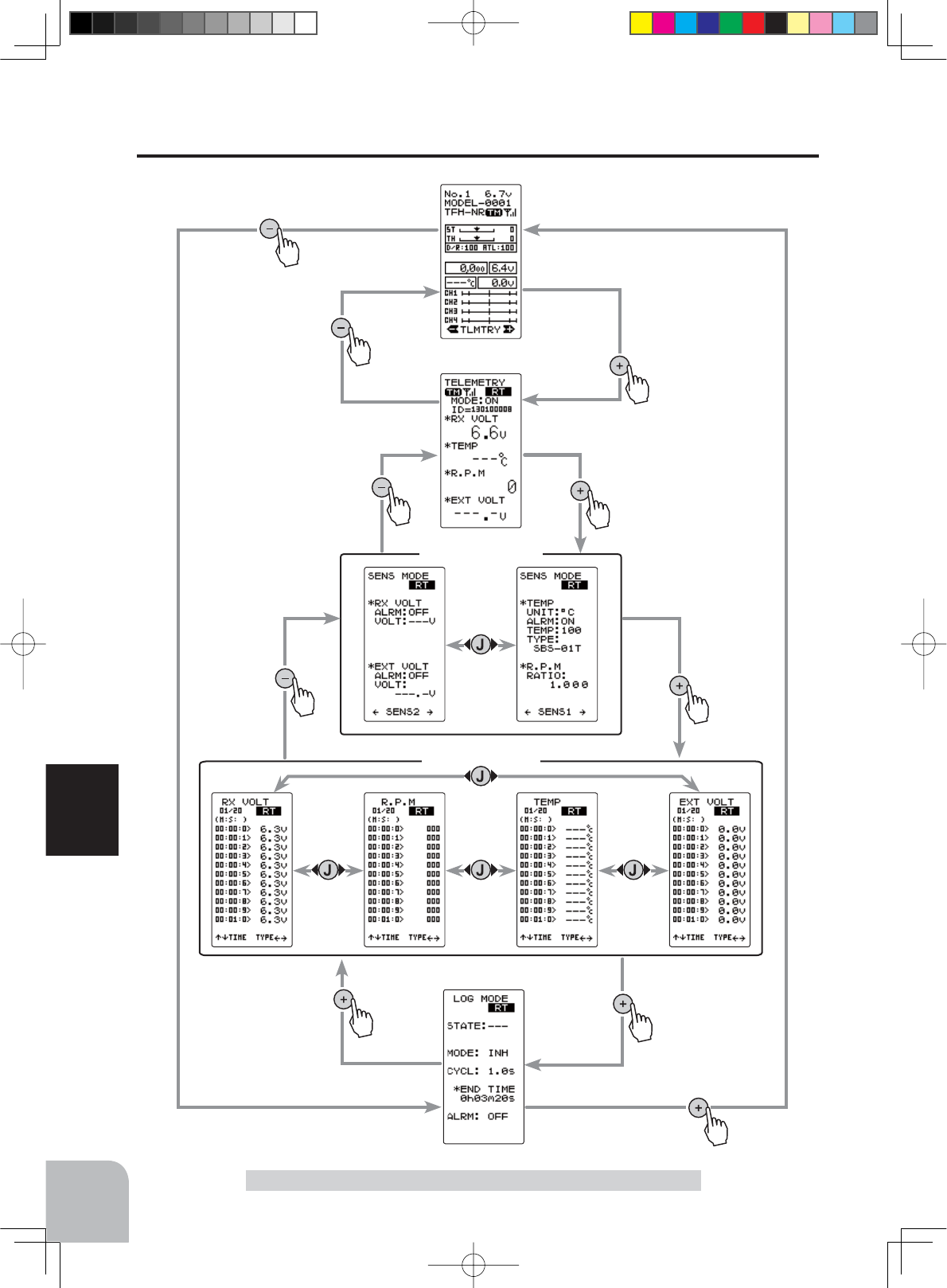
(Sensor Set Screen)
(Log Set Screen)
(Telemetry Function ON/OFF Screen)
(HOME screen)
Press
Press
Press
Press
Press
Press
Press
Press
Press
Press
p.109
p.112
p.110
The cursor on [RT]
The cursor on [RT]
(Log Data Screen)
108
Function
Telemetry "TELEMETRY"
Telemetry/Log Screen Map
4PLS-Eng-08-3-Function-P84-114.indd 108 2013/04/08 9:10:32
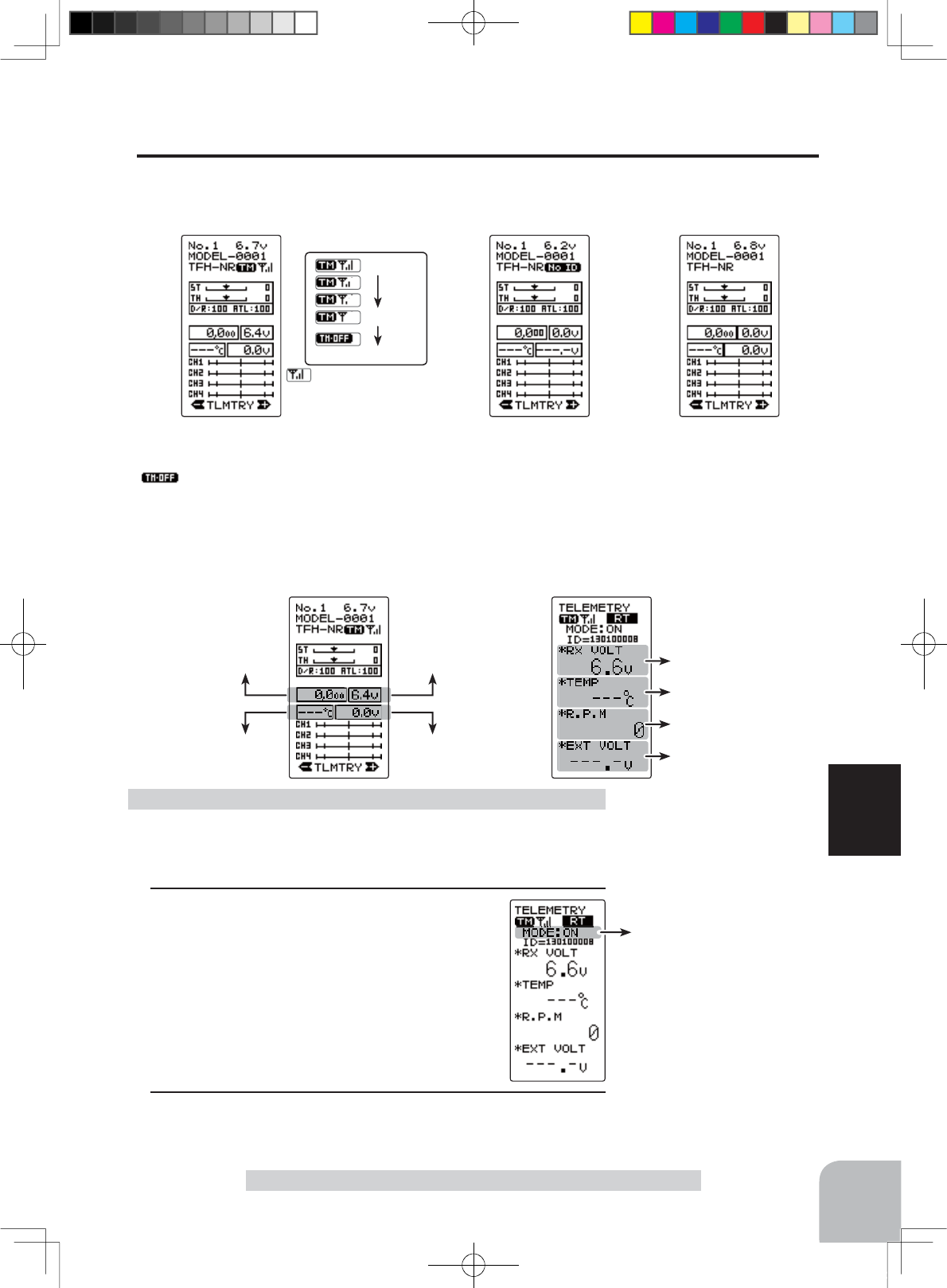
Function ON/OFF (MODE)
INH, ACT
Select button
- Select with the (+) or (-) but-
tons.
Telemetry function :OFF- Telemetry function :ON
- Receiver ID before setting or ID mis-
match.
- When the receiver ID is set, before
ID check in the receiver power OFF
stat.
- Telemetry function :ON
- Receiver ID setting complete.
- Data receiving sensitivity display.
-shows that data cannot be received be-
cause it is outside the data receiving range or
because of the effects of an obstruction or the
receiver power is OFF after receiver ID check.
Receiver -> Transmitter:
The reception strength is shown.
The reception strength
No signal reception
High
Low
109
Function
Telemetry "TELEMETRY"
(HOME screen)
Temperature Sensor info
RPM Sensor info Receiver voltage info
Voltage Sensor info
(TELEMETRY ON/OFF screen)
Temperature Sensor info
RPM Sensor info
Receiver voltage info
Voltage Sensor info
Telemetry Function ON/OFF
The telemetry data can be viewed at the HOME screen and telemetry ON/OFF screen.
The telemetry function can also be turned on and off at the telemetry ON/OFF screen.
The telemetry ON/OFF and communication status can be checked at the HOME screen.
Refer to the map on page 108 for the telemetry ON/OFF (telemetry) screen display.
(Preparation)
- On the HOME screen, open the TELEMETRY ON/OFF
screen by pressing the (+) button.
1Select the setting item "MODE" by the (JOG)
button up or down operation. Set the function
by pressing the (+) or (-) button.
"OFF" : Function OFF
"ON" : Function ON
2When ending, move the cursor to [RT] by the (JOG) button,
and return to the HOME screen by pressing the (JOG) but-
ton.
Telemetry function ON/OFF
4PLS-Eng-08-3-Function-P84-114.indd 109 2013/04/08 9:10:32
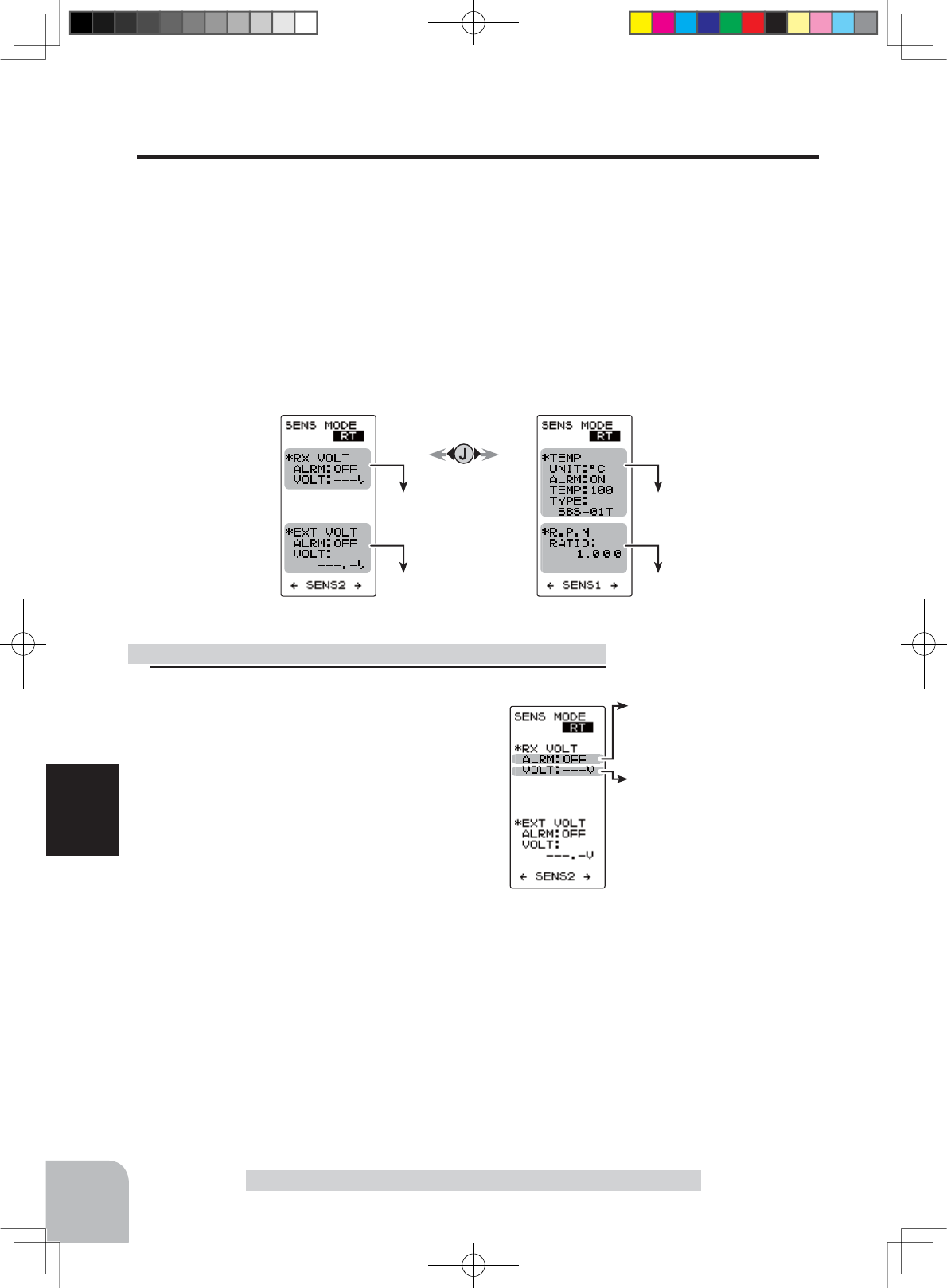
Alarm
ON/OFF
ON, OFF
- Select with the (+) or (-) but-
tons.
Voltage alarm
3.8V~8.0V
Initial value: 5V
Adjust button
- Adjust with the (+) and (-) but-
tons.
- Return to the initial value “0” by
pressing the (+) and (-) buttons
simultaneously for about 1 sec-
ond.
110
Function
Telemetry "TELEMETRY"
Receiver power sup-
ply voltage setting
External power
supply Voltage
sensor setting
Page1
Temperature sensor
setting
RPM sensor setting
Page2
Telemetry Sensor Setting
An audible alarm can be generated by the T4PLS from the data from a telemetry sensor.
This setting sets alarm ON/OFF and the alarm conditions.
Refer to the map on page 108 for the sensor setting (SENS MODE) screen display.
There are receiver power source (battery) voltage and external power source (drive bat-
tery) voltage settings on page 1 of the sensor setting screen and temperature and speed
settings on page 2. Pages 1 and 2 are switched by (JOG) button left or right operation.
(Setting of each item)
Setting the receiver power supply voltage alarm
Display page 1 by (JOG) button left or right
operation.
Select "ALRM" of the "*RX VOLT" setting
items by (JOG) button up or down operation,
and set alarm ON/OFF with the (+) button or (-)
button.
"OFF" : Alarm OFF
"ON" : Alarm ON by a voltage drop below the specified voltage
Select "VOLT" of the "*RX VOLT" setting items by (JOG) but-
ton up or down operation, and set the voltage at which the
alarm begins to sound with the (+) button or (-) button. The
number of digits can be shifted by (JOG) button left or right
operation.
When ending, move the cursor to [RT] by the (JOG) button,
and return to the HOME screen by pressing the (JOG) but-
ton twice.
Setting method
4PLS-Eng-08-3-Function-P84-114.indd 110 2013/04/08 9:10:32
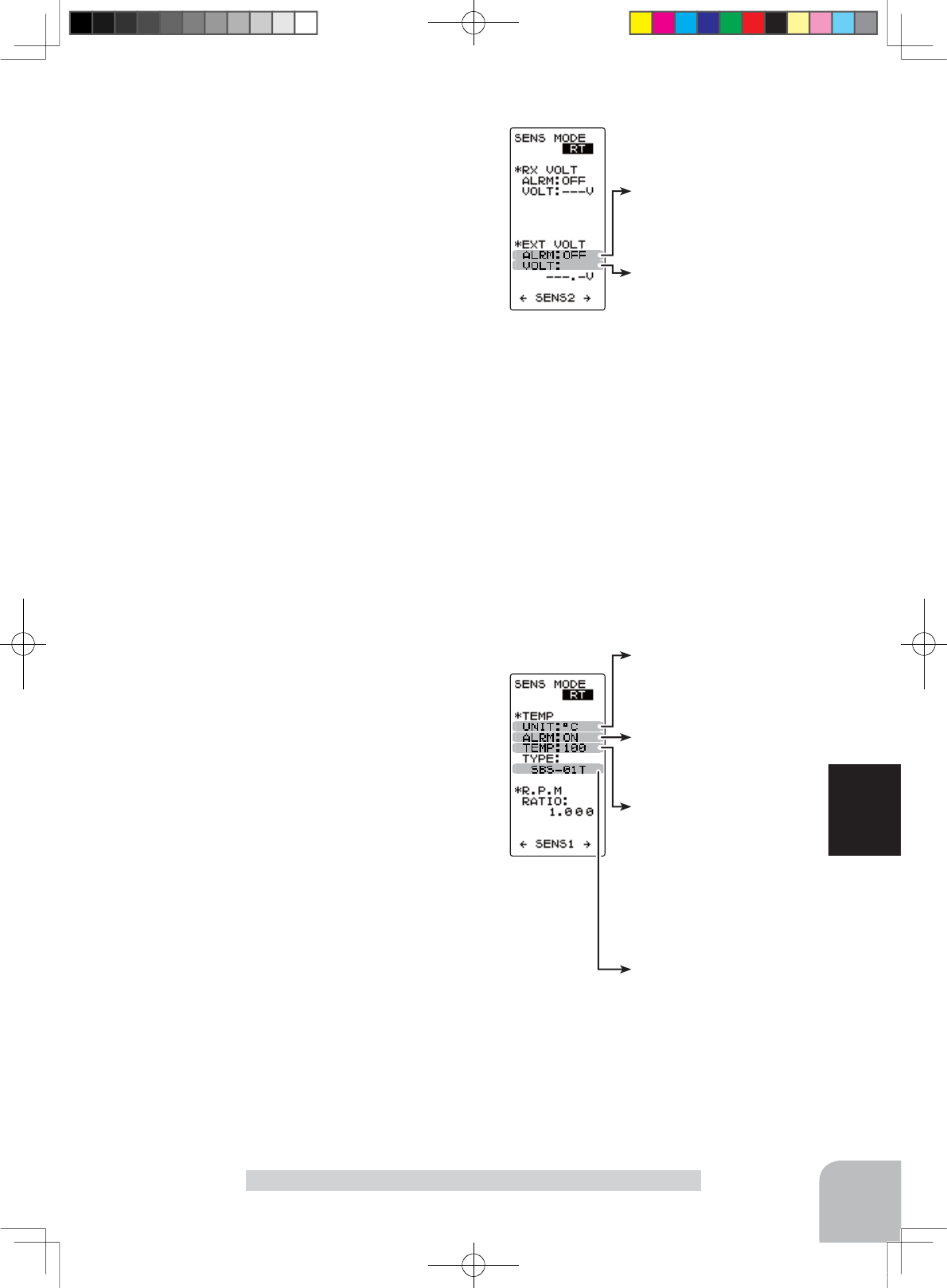
Alarm
ON/OFF
ON, OFF
- Select with the (+) or (-) but-
tons.
Voltage alarm
0.0V~90.0V
Initial value: 5V
Adjust button
- Adjust with the (+) and (-) but-
tons.
- Return to the initial value “0” by
pressing the (+) and (-) buttons
simultaneously for about 1 sec-
ond.
Sensor type
SBS-01T, Temp 125
Select button
- Select with the (+) or (-) but-
tons.
Display type
°C, °F
- Select with the (+) or (-) but-
tons.
Alarm
ON/OFF
ON, OFF
- Select with the (+) or (-) but-
tons.
Temperature alarm
-20~200°C/ -4~392°F
Initial value: 200°C/ 212°F
Adjust button
- Adjust with the (+) and (-) but-
tons.
- Return to the initial value "0" by
pressing the (+) and (-) buttons
simultaneously for about 1 sec-
ond.
111
Function
Telemetry "TELEMETRY"
Setting external power supply voltage alarm
Display page 1 by (JOG) button left or right
operation.
Select "ALRM" of the "EXT VOLT" setting
items by (JOG) button up or down operation,
and set alarm ON/OFF with the (+) button or (-)
button.
"OFF" : Alarm OFF
"ON" : Alarm ON by a voltage drop below the specified voltage
Select "VOLT" of the "*EXT VOLT" setting items by (JOG)
button up or down operation, and set the voltage at which the
alarm begins to sound with the (+) button or (-) button. The
number of digits can be shifted by (JOG) button left or right
operation.
When ending, move the cursor to [RT] by the (JOG) button,
and return to the HOME screen by pressing the (JOG) but-
ton twice.
Setting the temperature alarm
Display page 2 by (JOG) button left or right operation.
Select "UNIT" of the "*TEMP" setting items by (JOG) button
up or down operation, and select Celsius or Fahrenheit tem-
perature display with the (+) button or (-) button.
"°C" : Celsius display
"°F" : Fahrenheit
Select "ALRM" of the "*TEMP" setting items
by (JOG) button up or down operation, and
set alarm ON/OFF with the (+) button or (-)
button.
"OFF" : Alarm OFF
"ON" : Alarm ON at the specified temperature
Select "TEMP" of the "*TEMP" setting items by (JOG)
button up or down operation, and set the temperature at
which the alarm begins to sound with the (+) button or
(-) button. Select "TYPE" of the "*TEMP" setting items by
(JOG) button up or down operation, and set the type of
sensor with the (+) button or (-) button
"SBS-01T" : Option sensor
"Temp 125" : Option sensor for Europ
When ending, move the cursor to [RT] by the (JOG) button,
and return to the HOME screen by pressing the (JOG) but-
ton twice.
4PLS-Eng-08-3-Function-P84-114.indd 111 2013/04/08 9:10:32
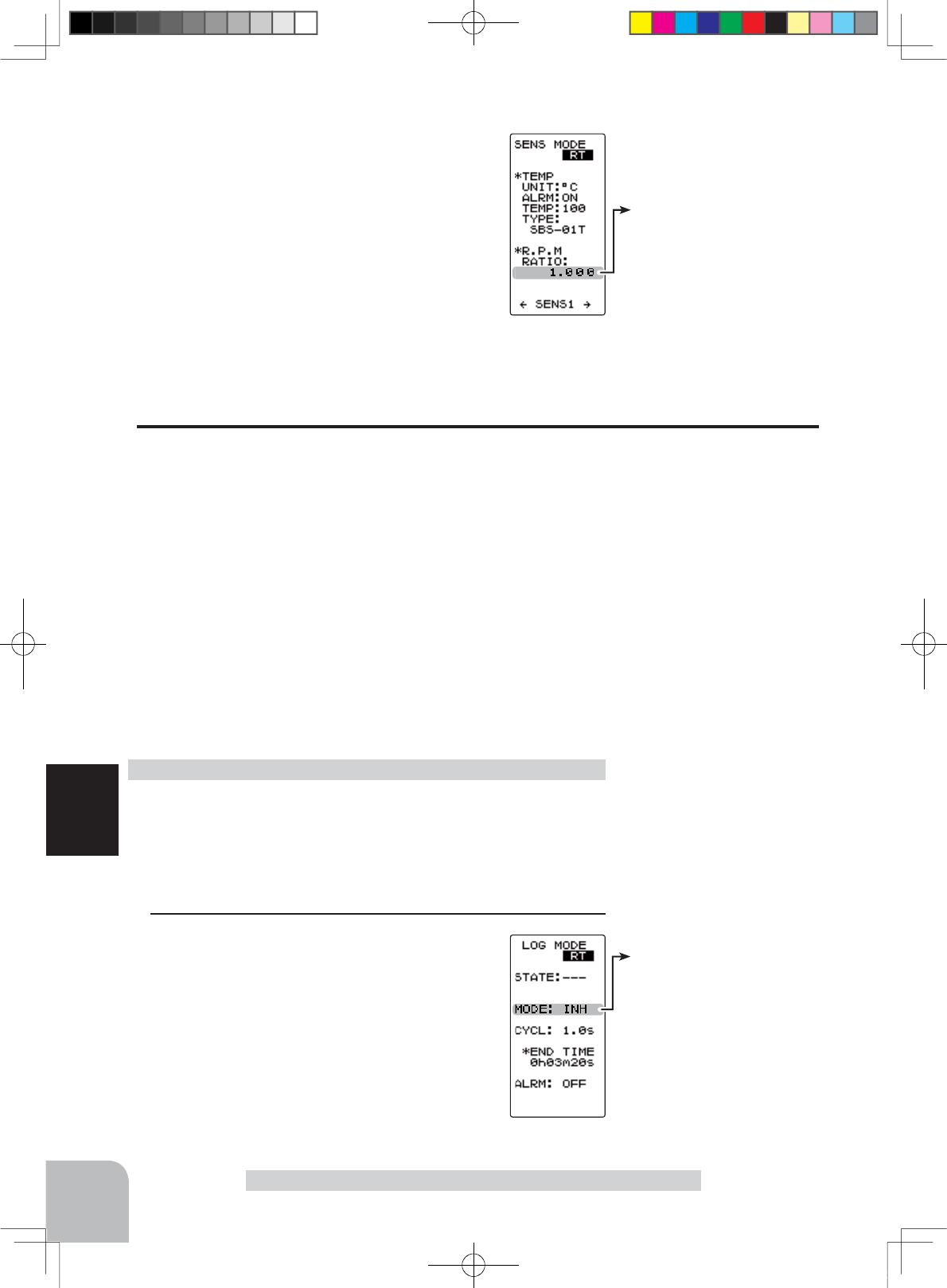
Function ON/OFF (MODE)
INH, ACT
- Select with the (+) or (-) but-
tons.
Gear ratio (moderating ratio)
0.001~64
Initial value: 1
Adjust button
- Adjust with the (+) and (-) but-
tons.
- Return to the initial value “0” by
pressing the (+) and (-) buttons
simultaneously for about 1 sec-
ond.
112
Function
Telemetry "TELEMETRY"
Setting the gear ratio
Display page 2 by (JOG) button left or right
operation. Select "RATIO" of the "R.P.M" set-
ting items by (JOG) button up or down opera-
tion, and set the location the sensor is to actu-
ally measure and the gear ratio of the motor
and engine with the (+) button or (-) button.
There is no alarm function.
When ending, move the cursor to [RT] by the (JOG) button,
and return to the HOME screen by pressing the (JOG) but-
ton twice.
Log Setting Start/Stop
The data from a telemetry sensor can be saved to the T4PLS as a data log. Since the data
is sequentially updated, when data logging is performed, the old data is erased. Only 1
data is saved.
The interval at which the data is acquired can be selected from a minimum 0.1 second
to a maximum 60 seconds. Because the maximum count is 200, if the count is made 200
counts at 0.1 second intervals, 20 seconds worth of data is acquired, and if the count is
made 200 counts at 60 second intervals, 3 hours 20 minutes worth of data is acquired.
Data logging is started and stopped by setting SW1 set by SW/Dial function (p.65) to
"LOGGER" and by switch (SW1). If the switch (SW1) is not set, data logging is started
by throttle trigger from the log setting screen.
Data logging can also be started by throttle trigger from this screen and stopped by
switch (SW1) set by SW/dial function (p.65).
Refer to the map on page 108 for the log setting (LOG MODE) screen display.
(Preparation)
When using a switch (SW1) to start and stop data logging,
set SW1 to "LOGGER" by SW/dial function (p.65)
- On the HOME screen, open the LOG MODE screen by
pressing the (-) button.
1 (Log function ON/OFF)
Move the cursor to the "MODE" setting item
by (JOG) button up or down operation, and
turn on the log function by setting "MODE" to
"ACT" by pressing the (+) button or (-) button.
If "MODE" is not set to "ACT", the log function
will not be performed even is the switch, etc. is
operated.
"INH" : Function OFF
"ACT" : Function ON
Log setting method
4PLS-Eng-08-3-Function-P84-114.indd 112 2013/04/08 9:10:32
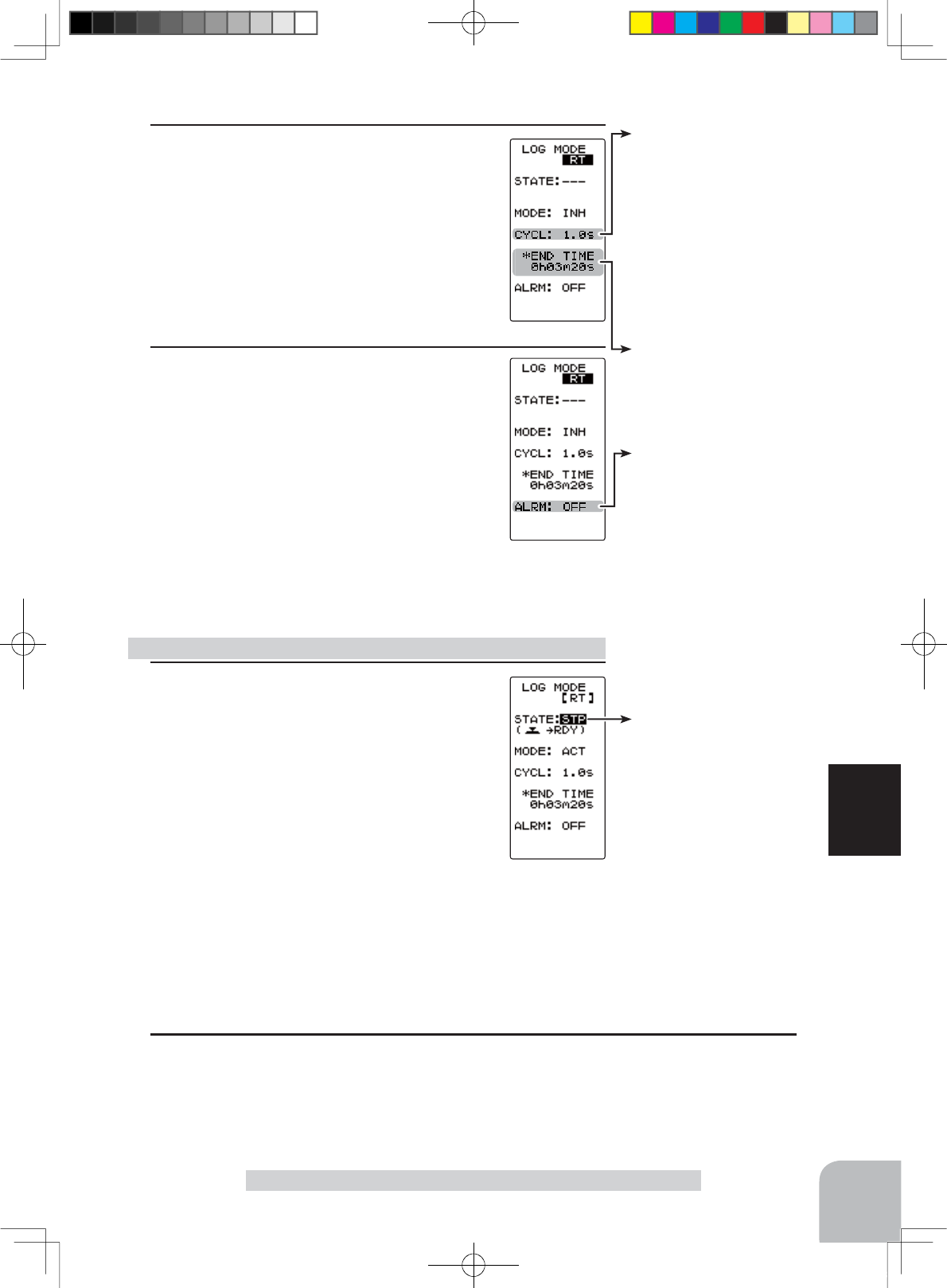
Log recording cycle
0.1~60s(sec)
0.1~10s(sec)0.1s step
10s~60s(sec)1s step
Initial value: 1.0sec
Adjust button
- Adjust with the (+) and (-) but-
tons.
- Return to the initial value “0” by
pressing the (+) and (-) buttons
simultaneously for about 1 sec-
ond.
Log recording time
20s (seconds) 3h 20m (3 hours
20 minutes)
The maximum recordable time
set by CYCL is displayed auto-
matically.
Status display
RDY :
Throttle trigger operation wait
STA :Logger running
STP : Logger stopped
Alarm
ON/OFF
ON, OFF
- Select with the (+) or (-) but-
tons.
113
Function
Telemetry "TELEMETRY"
1 (Log start operation)
-Start by switch (SW1)
When the switch (SW1) set by SW/dial func-
tion (p.65) is pressed, data logging starts.
-Starting by throttle trigger
Display the log setting (LOG MODE) screen
and select the "STATE" setting item by (JOG)
button up or down operation, and press the
(JOG) button for approximately 1 second.
Log function start/stop operation
2 (Recording cycle setting)
Select the "CYCL" setting item by (JOG) but-
ton up or down operation, and set the data ac-
quisition interval from a minimum 0.1 second
to a maximum 60 seconds with the (+) button
or (-) button.
The maximum recordable time set by CYCL is
displayed at END TIME shown below.
3 (Count alarm ON/OFF)
Select the "ALRM" setting item by (JOG)
button up or down operation. To sound an
electronic beep at each log count, set "ALRM"
to ON with the (+) button or (-) button.
"OFF" : Alarm OFF
"ON" : Alarm ON at each log count
When ending, move the cursor to [RT] by the (JOG) button,
and return to the HOME screen by pressing the (JOG) but-
ton twice.
An electronic beeping sound is generated and the "STATE" display switches from "RST"
to blinking "RDY", and the logger enters the trigger operation wait state. When the trig-
ger is operated in the forward direction, data logging begins. (STATE display "STA")
When the end time arrives, an electronic beep sounds and data logging stops. To return
to the HOME screen during data logging, move the cursor to [RT] by (JOG) button up or
down operation, and press the (JOG) button or (+) button.
2 (Log forced end)
To abort logging, press the switch (SW1), the same as starting, or display the log setting
(LOG MODE) screen and select the "STATE" setting item by (JOG) button up or down
operation and press the (JOG) button for approximately 1 second. An electronic beeping
sound is generated and logging is stopped.
4PLS-Eng-08-3-Function-P84-114.indd 113 2013/04/08 9:10:33
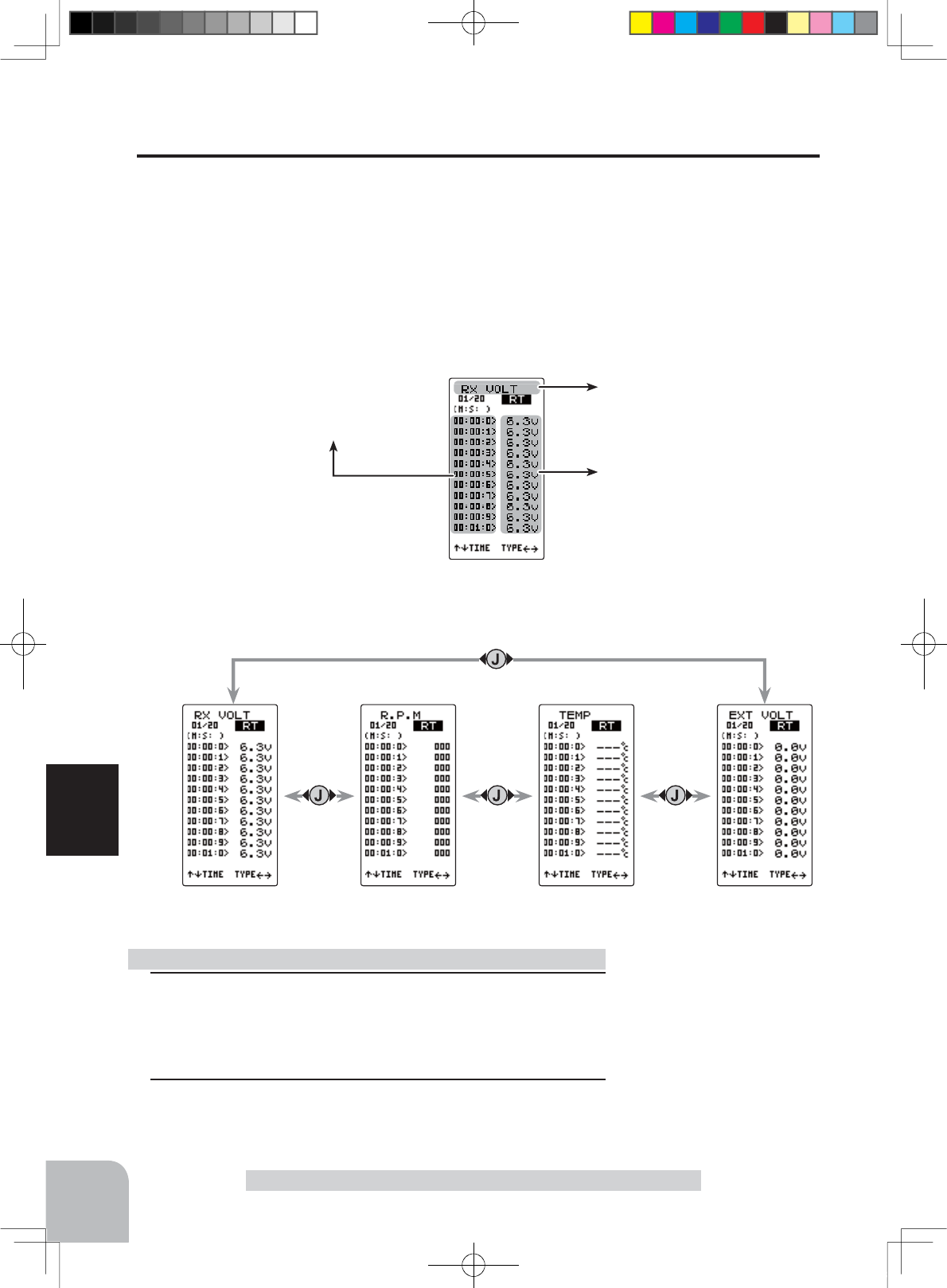
114
Function
Telemetry "TELEMETRY"
Displays the log data elapsed time.
Displays the type of log data.
Displays the data
Receiver power supply voltage.
Receiver power supply voltage log.
Receiver power supply
voltage log
External power
supply voltag log
Temperature sensor log RPM sensor log
1(Log memory check)
Each time the (JOG) button is operated up or down the list is
scrolled 10 counts and each log data can be checked up to
200 counts.
2 When ending, return to the HOME screen by pressing the
(JOG) button.
Log list check method
Log Data List
The log data list can be called when checking the log data memorized by logging opera-
tion (P112).
The maximum log data is up to 200 counts.
Refer to the map on page 108 for the log list screen.
Example: Receiver power supply voltage log list screen.
Refer to the below map for the display method of each log list screen.
4PLS-Eng-08-3-Function-P84-114.indd 114 2013/04/08 9:10:33
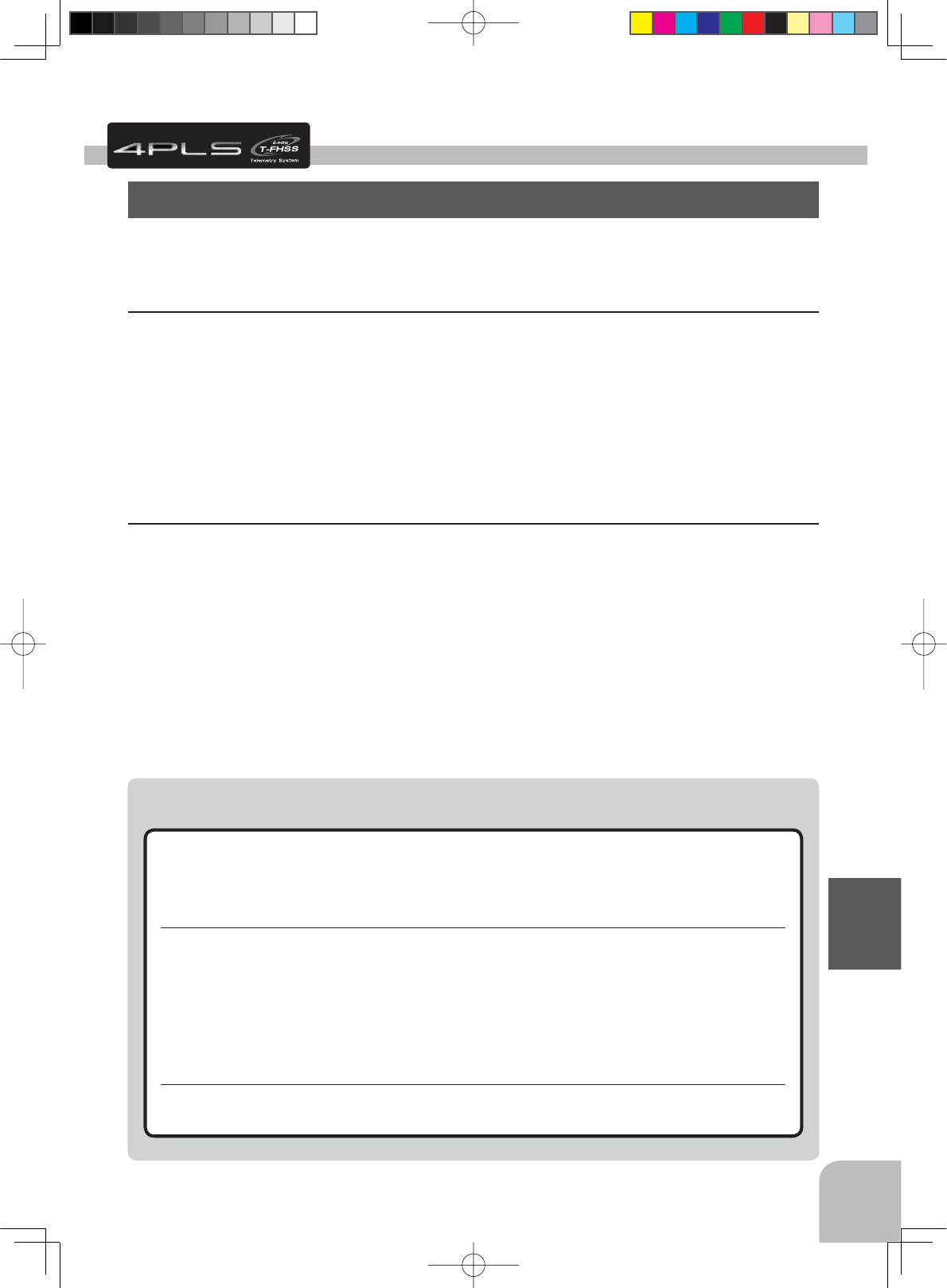
115
Reference
Reference
Ratings
6SHFL¿FDWLRQVDQGUDWLQJVDUHVXEMHFWWRFKDQJHZLWKRXWSULRUQRWLFH
Caution
Communication method:2QHZD\RSHUDWLRQV\VWHP
Maximum operating range:P2SWLPXPFRQGLWLRQ
For safety: )6%)6,'
Transmitter T4PLS-2.4G
7)+666)+66)+66V\VWHPZKHHOW\SHFKDQQHOV
Transmitting frequency:
*+]EDQG
Power requirement:
'U\FHOOEDWWHU\3HQOLJKW[9
Current drain:
P$RUOHVV
Transmission antenna:
ȜGLSROH
Receiver R304SB: 7)+66V\VWHPFKDQQHOV
Power requirement:
9a9EDWWHU\a9XVHDEOH
'U\FHOOEDWWHU\FDQQRWEHXVHG
Receiving frequency:
*+]EDQG
System:
7)+66V\VWHPDXWRGHWHFWLRQ
Size:
[[[[PPH[FOXGLQJDSURMHFWLRQSDUW
Weight: R]J
When using the T4PLS in the T-FHSS (HIGH) and S-FHSS (HIGH) mode, always use it under the
following conditions:
Servos :
Futaba digital servo (including BLS Series brushless servos)
Receiver’s battery :Matched to the ratings of the receiver and connected digital servo (dry cell battery cannot be used).
Transmitter mode :
RX MODE (See p.29 for setting method.)
Under other conditions, the set will not operate, or the specified performance will not be displayed even if it operates.
In addition, it may cause servo trouble. Futaba will not be responsible for damage, etc. caused by combination with the
products of other companies.
In addition, the FSU Fail Safe Unit cannot be used because the system is different. Use the fail safe function of the trans-
mitter.
When using analog servos, always switch the T4PLS servo response to the "NORM" mode.
Transmitter mode
:"
T-FHSS(NORM)", "T-FHSS(NORM)"and FHSS mode (See p.29 for setting method.)
Receiver’s battery :Matched to the ratings of the receiver and connected servo (dry cell battery cannot be used).
The set cannot operate in the "HIGH" mode. Operation in this mode will cause trouble with the servo and other equipment.
Digital servos (including BLS Series brushless servos) can also be used in the "NORM" mode.
4PLS-Eng-09-Reference-115-120.indd 115 2013/04/08 8:36:48
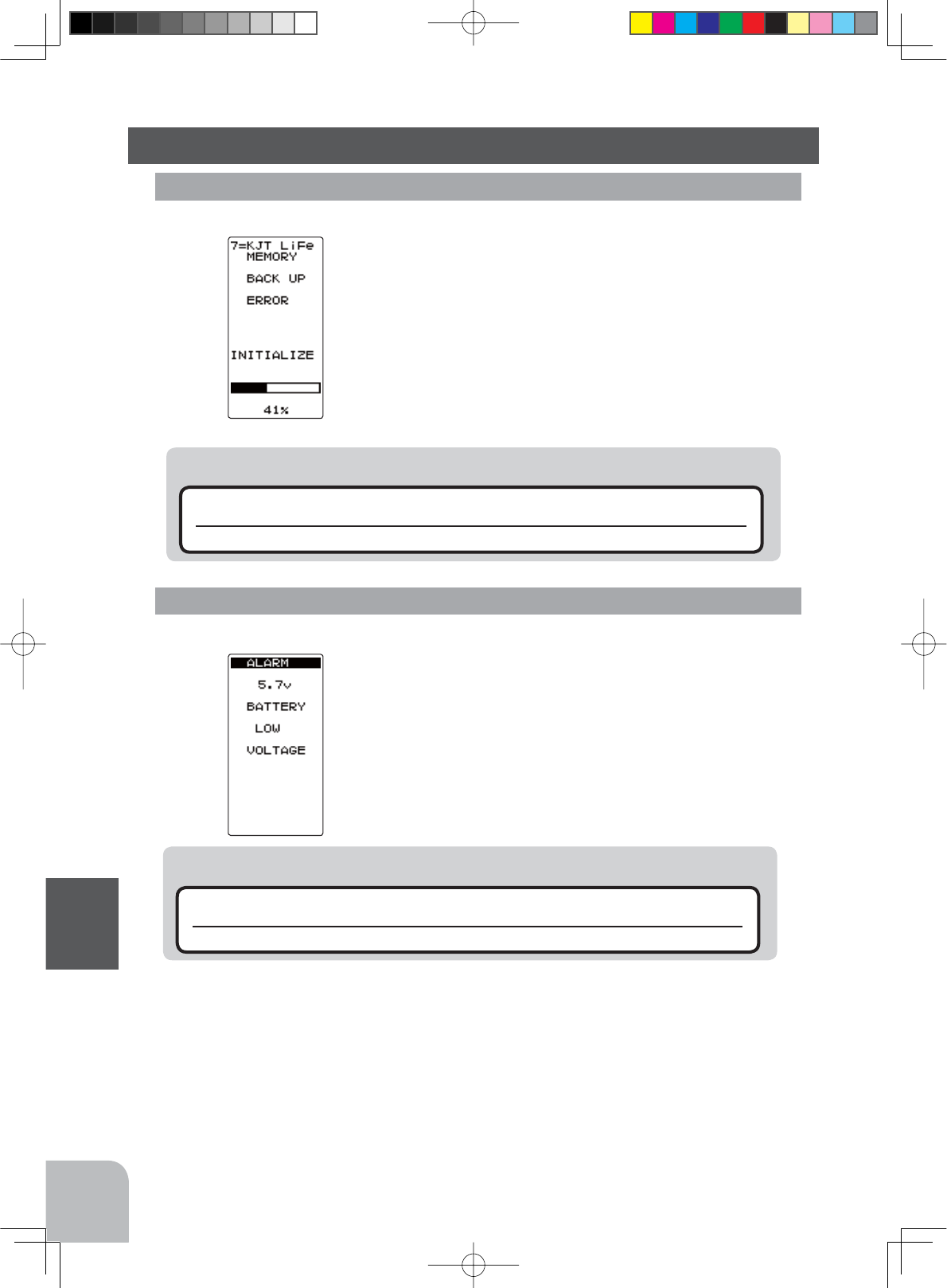
116
Reference
Warning Displays
Low Battery Alarm
,IWKHWUDQVPLWWHUEDWWHU\YROWDJHGURSVWR9ZKHQXV
LQJ)XWDEDUHFKDUJHDEOHW\SHEDWWHU\9RUOHVVDQ
DXGLEOHDODUPZLOOVRXQGDQG%$77(5</2:92/7
$*(ZLOOEHGLVSOD\HGRQWKH/&'VFUHHQ
LCD screen:
Audible alarm:
Continuous tone.
Warning
When a low battery alarm is generated, cease operation immediately and retrieve the
model.
If the battery goes dead while in operation, you will lose control.
Power supply and low battery alarm
7KH73/6FDQXVHDQRSWLRQDOUHFKDUJHDEOHEDWWHU\+RZHYHUWKHEDWWHU\DODUPVHWWLQJ
LVGLIIHUHQWIURPWKDWRIWKHGU\FHOOEDWWHU\DONDOLQHEDWWHU\UHFRPPHQGHG7KHUHIRUH
DOZD\VVHWWKHEDWWHU\W\SHWRPDWFKWKHSRZHUVRXUFHXVHG$OZD\VVHWWKHEDWWHU\W\SH
WR1/HVSHFLDOO\ZKHQXVLQJD)XWDEDUHFKDUJHDEOHW\SHEDWWHU\,IWKHVHWLVXVHG
DW'5<VHWWLQJWKHWLPHIURPORZEDWWHU\DODUPWRV\VWHPVWRSSLQJZLOOEHFRPHH[
WUHPHO\VKRUW6HHSDJHIRUDGHWDLOHGGHVFULSWLRQRIWKHEDWWHU\W\SHV
Backup Error
,IWKHGDWDLVORVWIRUDQXQNQRZQUHDVRQDQDXGLEOH
DODUPZLOOVRXQGDQG0(025<%$&.83(5525
ZLOOEHGLVSOD\HGRQWKH/&'VFUHHQ
LCD screen:
Audible alarm:
Tone will sound (9 times), then repeat.
Warning
When a backup error is generated, immediately stop using the system and request
repair from the Futaba Service Center.
If you continue to use the system, the transmitter may malfunction and cause loss of control
4PLS-Eng-09-Reference-115-120.indd 116 2013/04/08 8:36:48
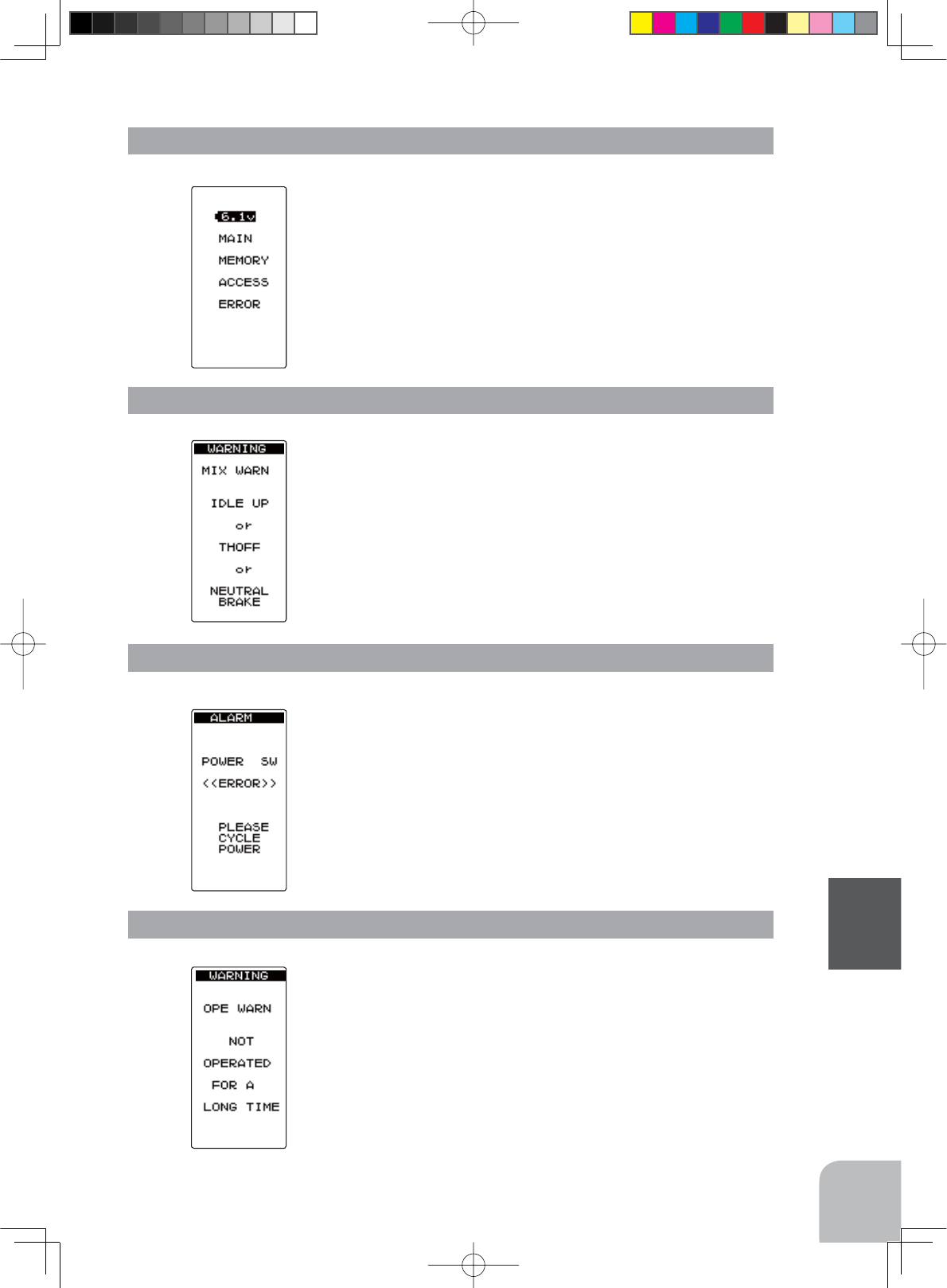
,IWKHSRZHUVZLWFKLVTXLFNO\VZLWFKHGIURPWKH',63
PRGHWRWKH3:21PRGHRUYLFHYHUVDWKHVZLWFKHU
URUVKRZQDW WKHOHIW PD\EH JHQHUDWHG ,I WKLV RFFXUV
F\FOHWKHSRZHU
LCD screen:
117
Reference
Power off forgotten warning
,IWKH73/LVQRWRSHUDWHGIRUPLQXWHVDQDXGLEOH
DODUPLVVRXQGHGDQG23(:$51LVGLVSOD\HGRQ
WKH VFUHHQ 7KH DXGLEOH DODUP VWRSV ZKHQ WKH VWHHULQJ
ZKHHOWKURWWOHWULJJHUDQGDQ\GLDOVZLWFKRUHGLWEXW
WRQ LV RSHUDWHG ,I \RX DUH QRW JRLQJ WR XVH WKH WUDQV
PLWWHUWXUQWKHSRZHURII6HWWLQJFDQEHUHVHWDWWKH
V\VWHPPHQXRQSDJH
Audible alarm:
Tone sounds (7 times) and stops (repeated)
LCD screen:
MIX Warning
MIX Warning
:KHQWKHSRZHUVZLWFKLVWXUQHGRQZKLOHWKHLGOHXS
SUHVHWHQJLQHFXWRUQHXWUDOEUDNHIXQFWLRQVZLWFKLVRQ
DQDXGLEOHDODUPZLOOVRXQGDQG0,;:$51ZLOOEH
GLVSOD\HGRQWKH/&':KHQWKDWIXQFWLRQVZLWFKLVWXUQHG
RIIWKHDODUPZLOOVWRS
LCD screen:
Audible alarm:
Tone sounds (7 times) and stops (repeated)
Audible alarm:
Tone sounds (7 times) and stops (repeated)
Memory Error
,IWKHGDWDLQWKHWUDQVPLWWHULVQRWWUDQVIHUUHGQRUPDOO\
ZKHQWKHSRZHULVWXUQHGRQDQDXGLEOHDODUPZLOO
VRXQGDQG0$,10(025<$&&(66 (5525ZLOO
EHGLVSOD\HGRQWKH/&'
- To stop the alarm, turn off the power.
- Turn the power back on. If the alarm is not generated again, there
is no problem.
LCD screen:
Audible alarm:
Tone sounds (7 times) and stops (repeated)
4PLS-Eng-09-Reference-115-120.indd 117 2013/04/08 8:36:48
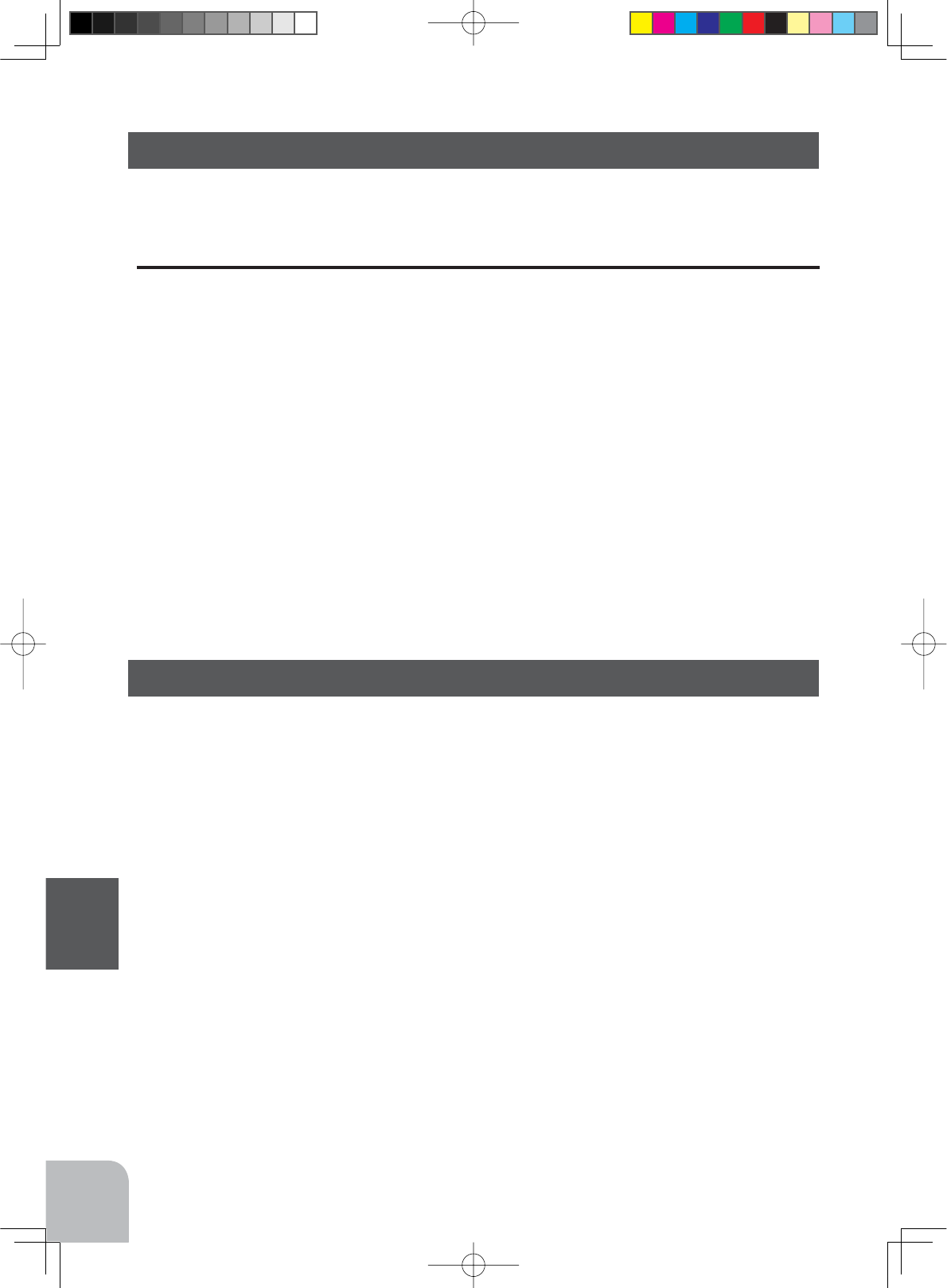
Optional Parts
118
Reference
7KHIROORZLQJSDUWVDUHDYDLODEOHDV3/6RSWLRQV3XUFKDVHWKHPWRPDWFK\RXUDSSOL
FDWLRQ)RURWKHURSWLRQDOSDUWVUHIHUWRRXUFDWDORJ
Transmitter Battery
:KHQSXUFKDVLQJDWUDQVPLWWHUEDWWHU\XVHWKHIROORZLQJ
Part name
+7)%9P$K1L0+EDWWHU\
)7)9P$K%9P$K/L)HEDWWHU\
3OHDVHGRQRWXVHWKHWUDQVPLWWHUEDWWHULHV+7)%DQG
)7)%
DVWKHUHFHLY
HUVEDWWHU\
6LQFHWKHWUDQVPLWWHUVEDWWHU\KDVDQRYHUORDGSURWHFWLRQFLUFXLWWKHRXWSXWSRZHUZLOOEH
VKXWGRZQZKHQWKHKLJKFXUUHQWORDGLVDSSOLHG7KLVPD\UHVXOWLQUXQDZD\RUIDWDOFUDVK
7HPSHUDWXUH6HQVRU6%67
5306HQVRU6%650
9ROWDJH6HQVRU6%69
When requesting repair
%HIRUH UHTXHVWLQJ UHSDLU UHDG WKLV LQVWUXFWLRQ DJDLQ DQG UHFKHFN \RXU V\VWHP 6KRXOG
WKHSUREOHPVFRQWLQXHUHTXHVWDVIROORZV
(Information needed for repair)
'HVFULEHWKHSUREOHP LQ DVPXFKGHWDLO DVSRVVLEOHDQGVHQGWKHOHWWHUDORQJZLWKWKH
V\VWHPLQTXHVWLRQ
6\PSWRP,QFOXGLQJWKHFRQGLWLRQVDQGZKHQWKHSUREOHPRFFXUUHG
5&6\VWHP6HQGWUDQVPLWWHUUHFHLYHUDQGVHUYRV
0RGHO7\SHRIPRGHOEUDQGQDPHDQGPRGHOQXPEHURUNLWQDPH
'HWDLOHGSDFNLQJOLVW0DNHDOLVWRIDOOLWHPVVHQWLQIRUUHSDLU
<RXUQDPHDGGUHVVDQGWHOHSKRQHQXPEHU
(Warranty)
5HDGWKH:DUUDQW\FDUG
:KHQUHTXHVWLQJZDUUDQW\VHUYLFHVHQGWKHFDUGRUVRPHW\SHRIGDWHGSURRISXU
FKDVH
4PLS-Eng-09-Reference-115-120.indd 118 2013/04/08 8:36:48
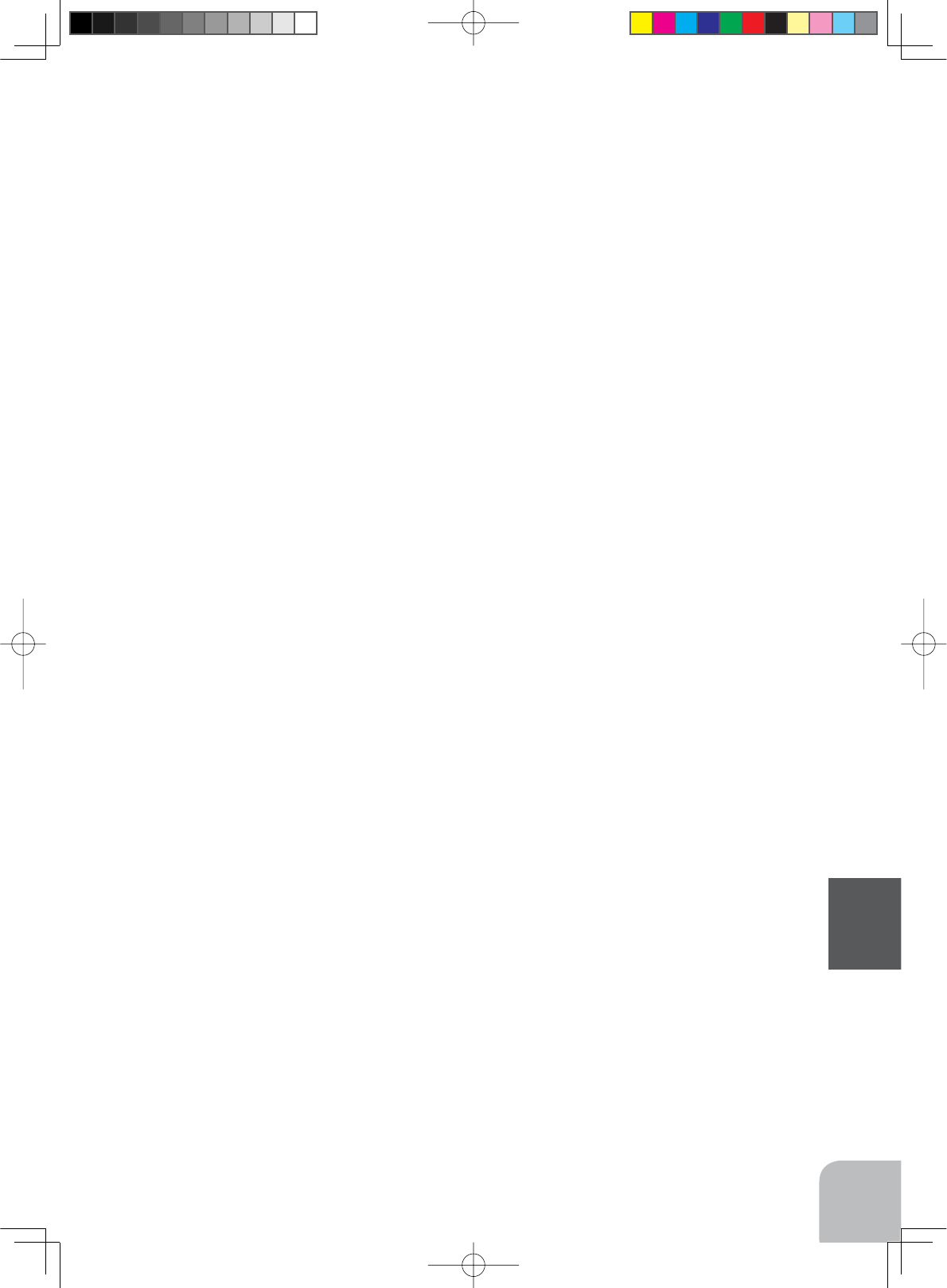
119
Reference
Federal Communications Commission Interference Statement (for U.S.A.)
7KLVHTXLSPHQWKDVEHHQWHVWHGDQGIRXQGWRFRPSO\ZLWKWKHOLPLWVIRUD&ODVV%GLJLWDO
GHYLFHSXUVXDQWWR3DUWRIWKH)&&5XOHV7KHVHOLPLWVDUHGHVLJQHGWRSURYLGHUHD
VRQDEOHSURWHFWLRQDJDLQVWKDUPIXOLQWHUIHUHQFHLQDUHVLGHQWLDOLQVWDOODWLRQ
7KLVHTXLSPHQWJHQHUDWHVXVHVDQGFDQUDGLDWHUDGLRIUHTXHQF\HQHUJ\DQGLIQRWLQ
VWDOOHGDQGXVHGLQDFFRUGDQFHZLWKWKHLQVWUXFWLRQVPD\FDXVHKDUPIXOLQWHUIHUHQFHWR
UDGLRFRPPXQLFDWLRQV+RZHYHUWKHUHLVQRJXDUDQWHHWKDWLQWHUIHUHQFHZLOOQRWRFFXU
LQDSDUWLFXODULQVWDOODWLRQ,IWKLVHTXLSPHQWGRHVFDXVHKDUPIXOLQWHUIHUHQFHWRUDGLR
RUWHOHYLVLRQUHFHSWLRQZKLFKFDQEHGHWHUPLQHGE\WXUQLQJWKHHTXLSPHQWRIIDQGRQ
WKHXVHULVHQFRXUDJHGWRWU\WRFRUUHFWWKHLQWHUIHUHQFHE\RQHRUPRUHRIWKHIROORZLQJ
PHDVXUHV
5HRULHQWRUUHORFDWHWKHUHFHLYLQJDQWHQQD
,QFUHDVHWKHVHSDUDWLRQEHWZHHQWKHHTXLSPHQWDQGUHFHLYHU
&RQQHFWWKHHTXLSPHQWLQWRDQRXWOHWRQDFLUFXLWGLIIHUHQWIURPWKDWWRZKLFKWKHUH
FHLYHULVFRQQHFWHG
&RQVXOWWKHGHDOHURUDQH[SHULHQFHGUDGLR79WHFKQLFLDQIRUKHOS
Compliance Information Statement (for U.S.A.)
7KLVGHYLFHWUDGHQDPH)XWDED&RUSRUDWLRQRI$PHULFDPRGHOQXPEHUT4PLSFRP
SOLHVZLWK SDUW RI WKH)&&5XOHV 2SHUDWLRQLV VXEMHFWWRWKHIROORZLQJWZRFRQGL
WLRQV
7KLVGHYLFHPD\QRWFDXVHKDUPIXOLQWHUIHUHQFHDQG7KLVGHYLFHPXVWDFFHSWDQ\
LQWHUIHUHQFHUHFHLYHGLQFOXGLQJLQWHUIHUHQFHWKDWPD\FDXVHXQGHVLUHGRSHUDWLRQ
7KHUHVSRQVLEOHSDUW\IRUWKHFRPSOLDQFHRIWKLVGHYLFHLV
)XWDED6HUYLFH&HQWHU
1$SROOR'ULYH6XLWH&KDPSDLJQ,/86$
7(/RU(PDLOVXSSRUW#IXWDEDUFFRP6XSSRUW
7(/RU(PDLOVHUYLFH#IXWDEDUFFRP6HUYLFH
CAUTION:
7RDVVXUHFRQWLQXHG)&&FRPSOLDQFH
$Q\FKDQJHVRUPRGL¿FDWLRQVQRWH[SUHVVO\DSSURYHGE\WKHJUDQWHHRIWKLVGHYLFHFRXOG
YRLGWKHXVHU¶VDXWKRULW\WRRSHUDWHWKHHTXLSPHQW
Exposure to Radio Frequency Radiation
7RFRPSO\ZLWK)&&5)H[SRVXUHFRPSOLDQFHUHTXLUHPHQWVDVHSDUDWLRQGLVWDQFHRIDW
OHDVWFPPXVWEHPDLQWDLQHGEHWZHHQWKHDQWHQQDRIWKLVGHYLFHDQGDOOSHUVRQV7KLV
GHYLFHPXVWQRWEHORFDWHGRURSHUDWLQJLQFRQMXQFWLRQZLWKDQ\RWKHUDQWHQQDRUWUDQV
PLWWHU
4PLS-Eng-09-Reference-115-120.indd 119 2013/04/08 8:36:49
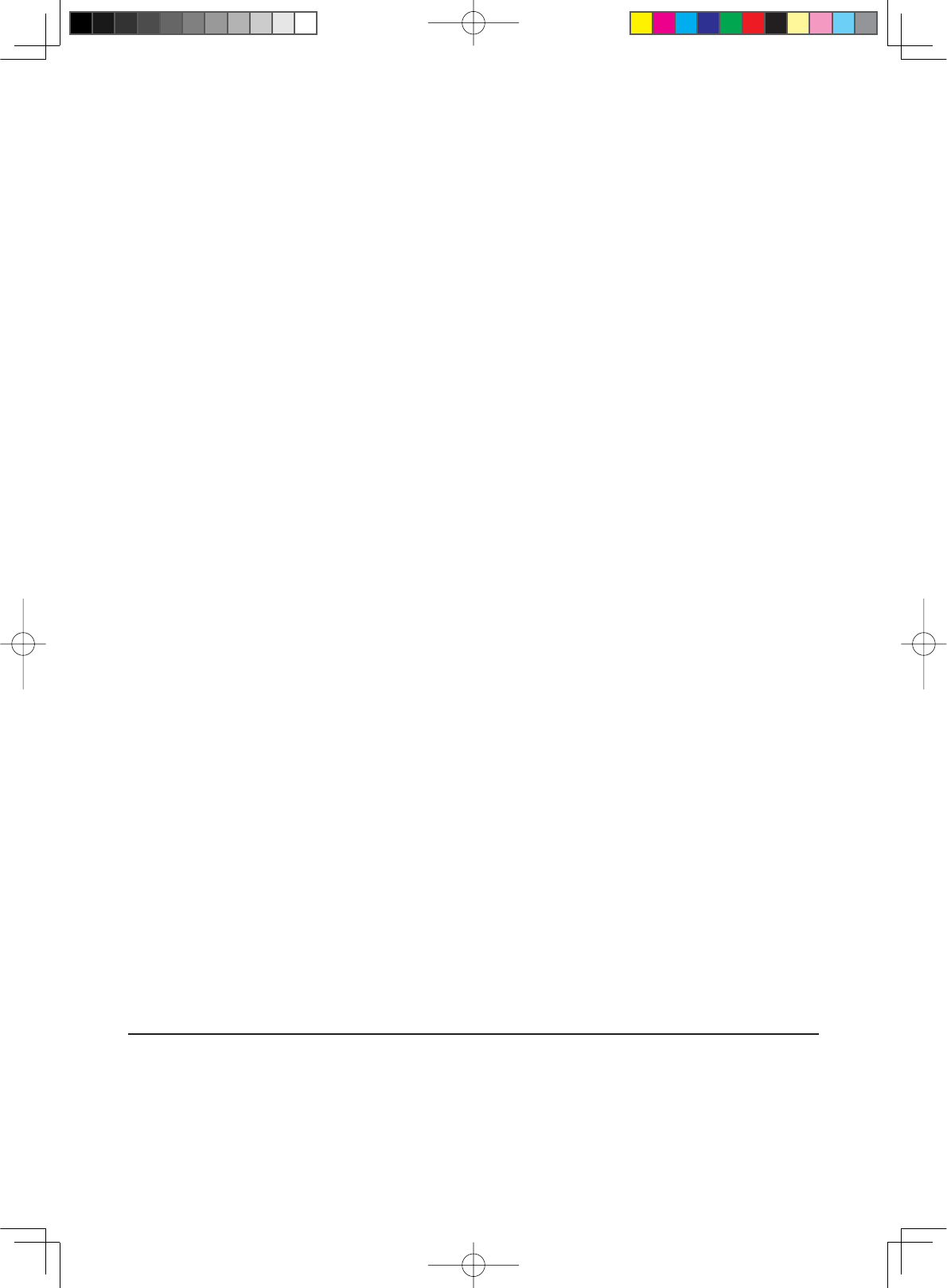
©Copyright 2010. No part of this manual may be reproduced in any form without prior permission. The contents of this manual are subject
to change without prior notice. While this manual has been carefully written, there may be inadvertent errors or omissions. Please contact
our service center if you feel that any corrections or clarifications should be made.
)87$%$&25325$7,213KRQH)DFVLPLOH
<DEXWVXND&KRVHLPXUD&KRVHLJXQ&KLED-DSDQ
1M23N28302 ©FUTABA CORPORATION 2013, 04 (1)
4PLS-Eng-09-Reference-115-120.indd 120 2013/04/08 8:36:49