Graco Resin Transfer Molding Systems Users Manual
2015-04-02
: Graco Graco-Resin-Transfer-Molding-Systems-Users-Manual-685892 graco-resin-transfer-molding-systems-users-manual-685892 graco pdf
Open the PDF directly: View PDF .
Page Count: 4
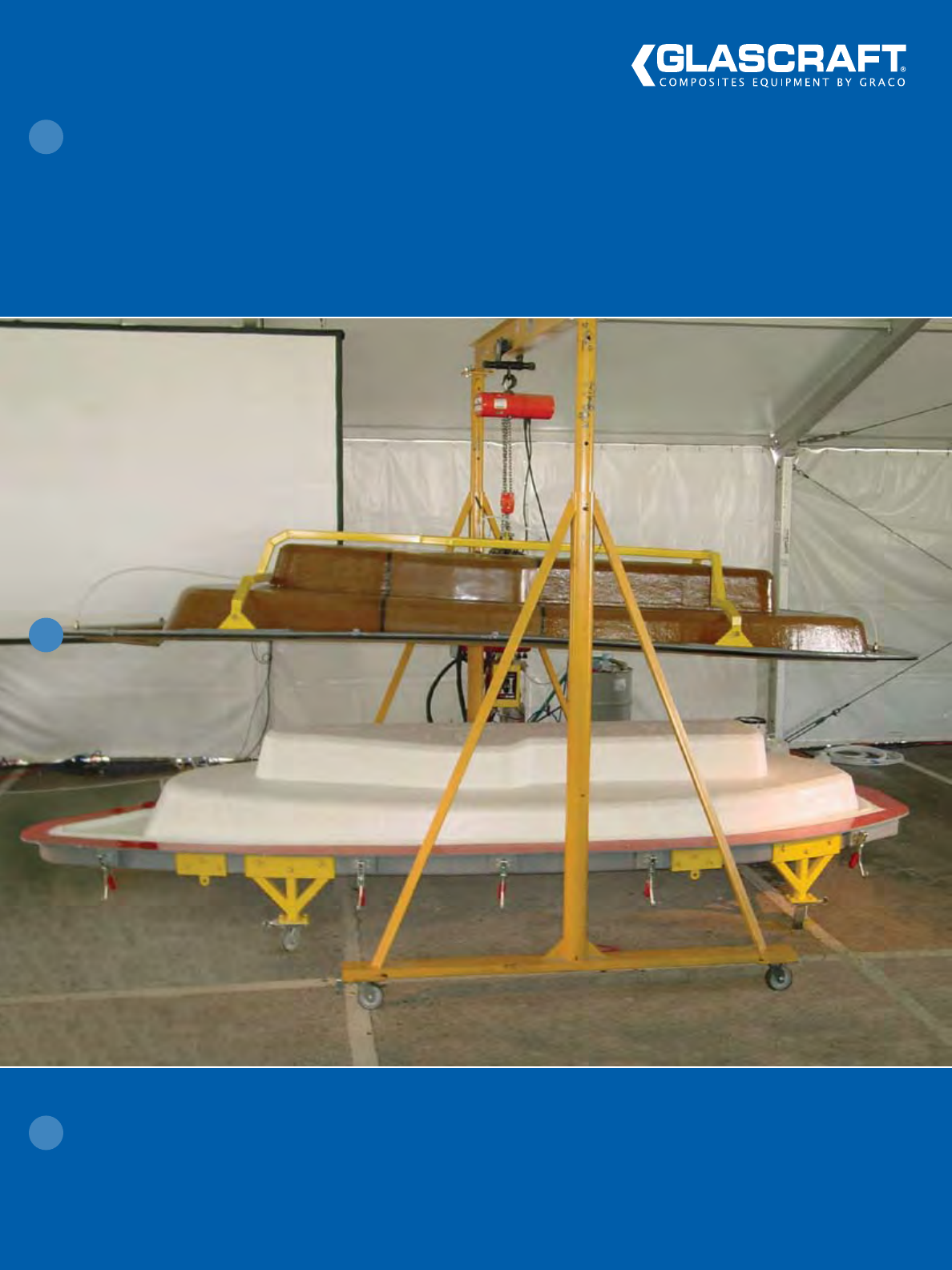
Resin Transfer Molding Systems
Dispensing Equipment for RTM and Light RTM Applications
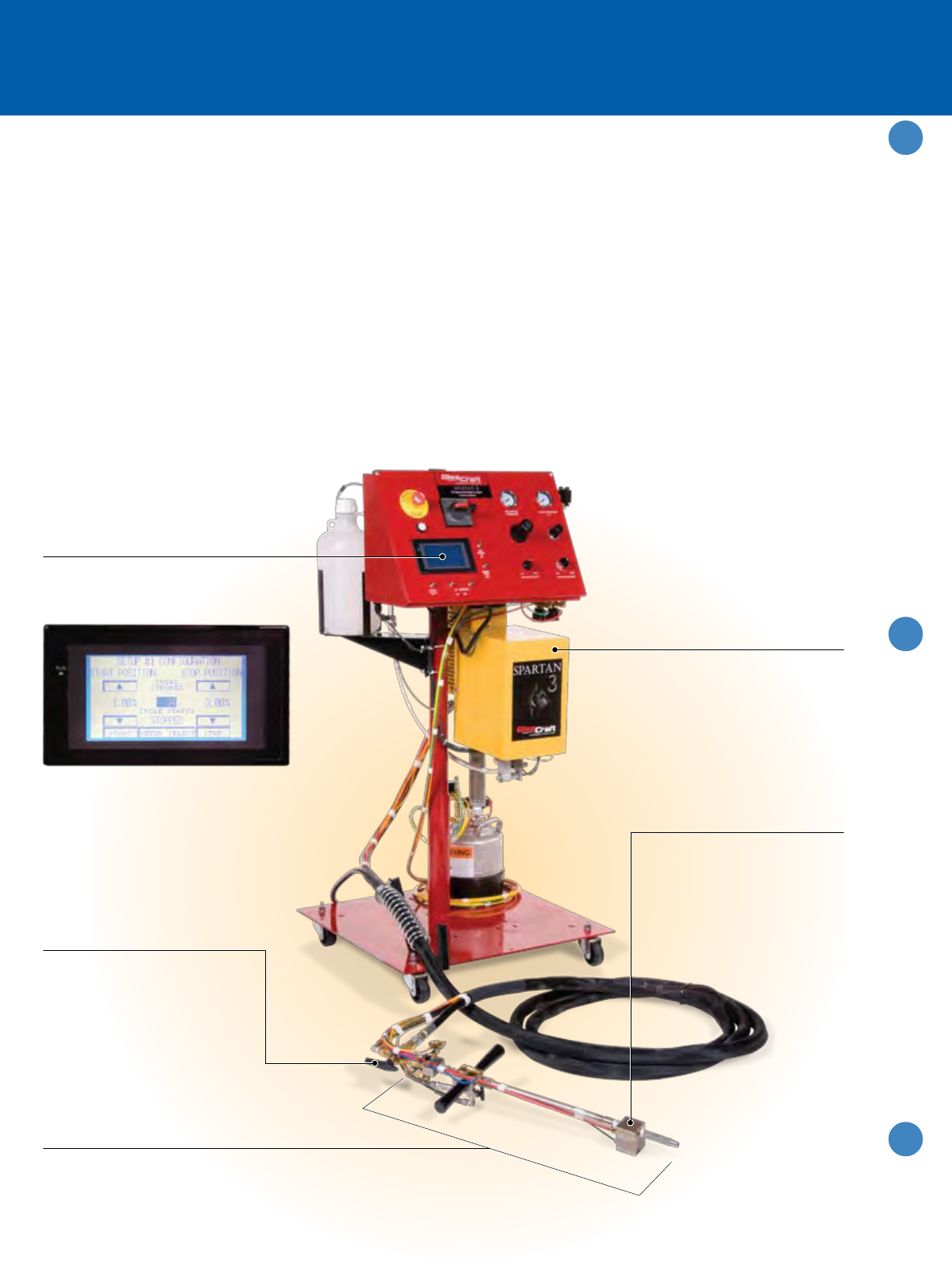
GlasCraft® RTM Systems
A full line of solutions for resin transfer molding
Resin transfer molding (RTM) is a closed
mold manufacturing process. Finished
parts are made by introducing polyester
or vinyl ester resins into closed molds
containing fiberglass, carbon or other
reinforcements.
Whether your process is traditional RTM,
Light RTM, Vacuum Infusion Process (VIP),
Closed Cavity Bag Molding (CCBM), or
other similar process, GlasCraft offers a
complete line of RTM systems to fit your
application.
GlasCraft RTM Systems provide control
at low pressure – the key to successful
Light RTM injection
• Engineered for low-pressure injection
of polyester and vinyl ester resins
• Accu-Pressure sensor monitors and
controls pressure
• Entry-level to automated, high-volume
production models are available
Typical applications:
• Marine and watercraft
• Pool and spa
• Bathware
• Consumer products
• Automotive panels and parts
• Aircraft components
2
Touch-screen PLC
Programmable machine functions –
from injection volume to catalyst ratio
(depending on options)
Superior recirculation
• Allows resin and catalyst to cycle to
the dispense head and back to the
containers, unmixed
• Keeps pigments and llers suspended
in the resin
• Allows line to be de-gassed without
wasting material
Spartan Dispense Head
Provides excellent mix of resin and
catalyst, and trouble-free injection as well
Positive Feed Catalyst pump
Allows for innite adjustment of catalyst
percentage – no tools required
Air Purge/Solvent Flush
For quick, efficient maintenance cleaning
Accu-Pressure Sensor
• Regulates, monitors and controls
injection pressure
• Stops material from dispensing if
injection pressures go above the user
set point
• Prevents molds from becoming
over-pressured
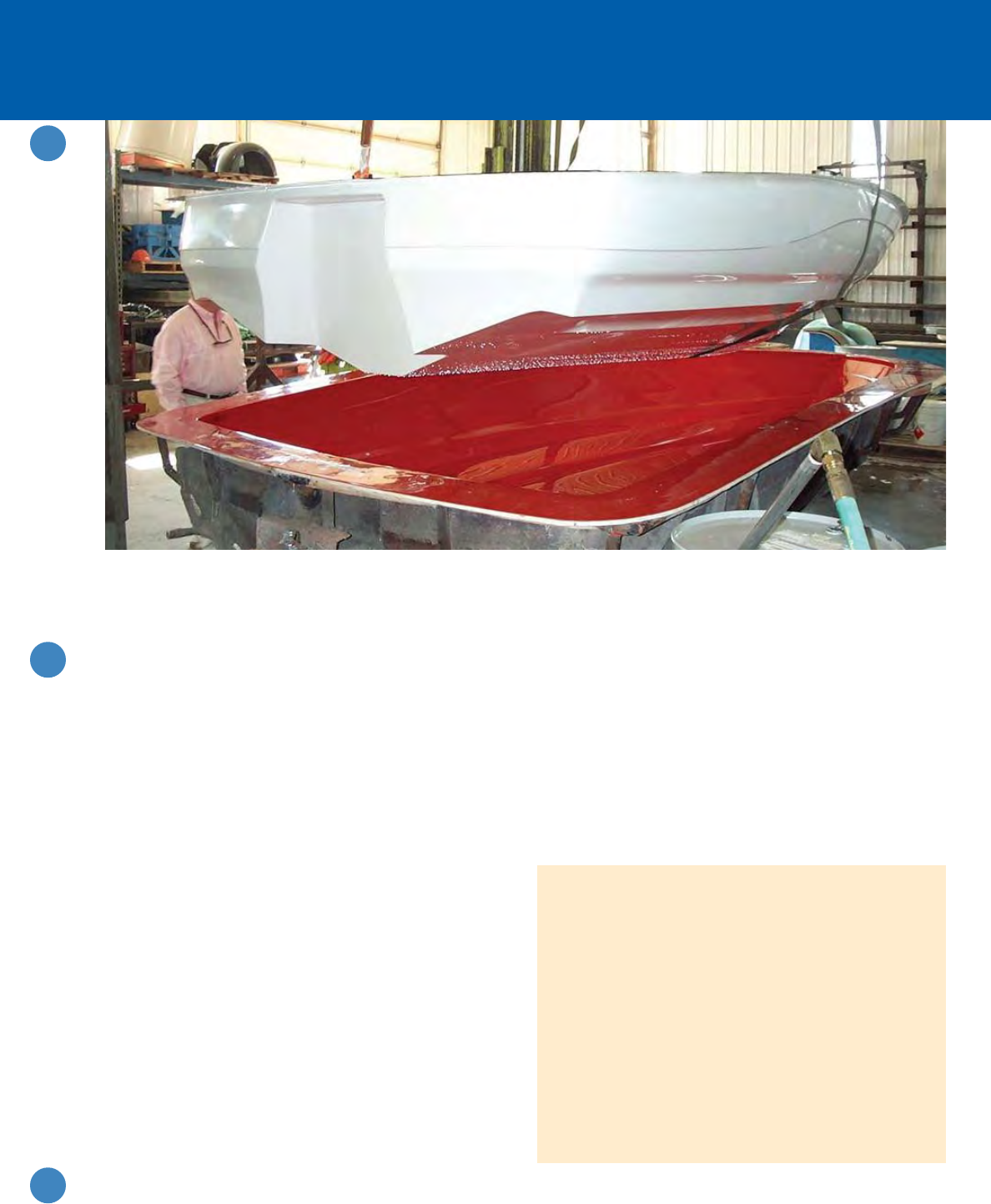
Advanced features for automated, high-volume RTM production
Advanced GlasCraft models are available with the following:
Touch screen PLC
Programmable logic controller allows you to program injection volume
and catalyst ratio settings. Reduces operator error. Results in less
wasted material and improved productivity.
Programmable digital air/solvent flush
Flushes out the static mixer with a pre-programmed amount of
solvent. Can be used in combination with the air purge function for
extra cleaning power.
Programmable Automatic Catalyst (PAC)
Ideal for manufacturers of larger parts. PAC allows you to program
and adjust catalyst ratios for the injection cycle. By reducing the
catalyst required for the first infusion of material, and increasing the
catalyst during the last part of the infusion cycle, the part cures at a
more even rate.
Programmable Radio Frequency Identification tags (RFID)
Each mold in your plant gets a unique RFID tag that you program
with specic parameters such as amount of resin required and a
catalyst injection prole. The operator simply scans the tag and
the machine automatically loads the pre-programmed settings.
RFID tags eliminate operator error and programming errors, and
save wasted material as well.
In addition, RFID tags provide your facility with unlimited
programming potential. That’s because the system only stores the
current RFID tag’s dispense parameters. Since all molding parameters
are stored on each chip, you can have an unlimited number of RFID-
tagged molds in your production facility.
Password Protected PLC
Spartan 3 PLC with PAC and RFID systems are designed with
password protection so that operators cannot change mold settings
and parameters.
3
Advantages of RTM
A growing number of companies are moving to closed mold
processes because it offers many signicant benets:
• Less wasted material
• Faster gel and cure times
• Uniform part size and thickness
• Consistent material usage
• Finished surface on both sides
• Reduced VOC emissions – less environmental impact
• Higher glass content which results in lighter weight parts
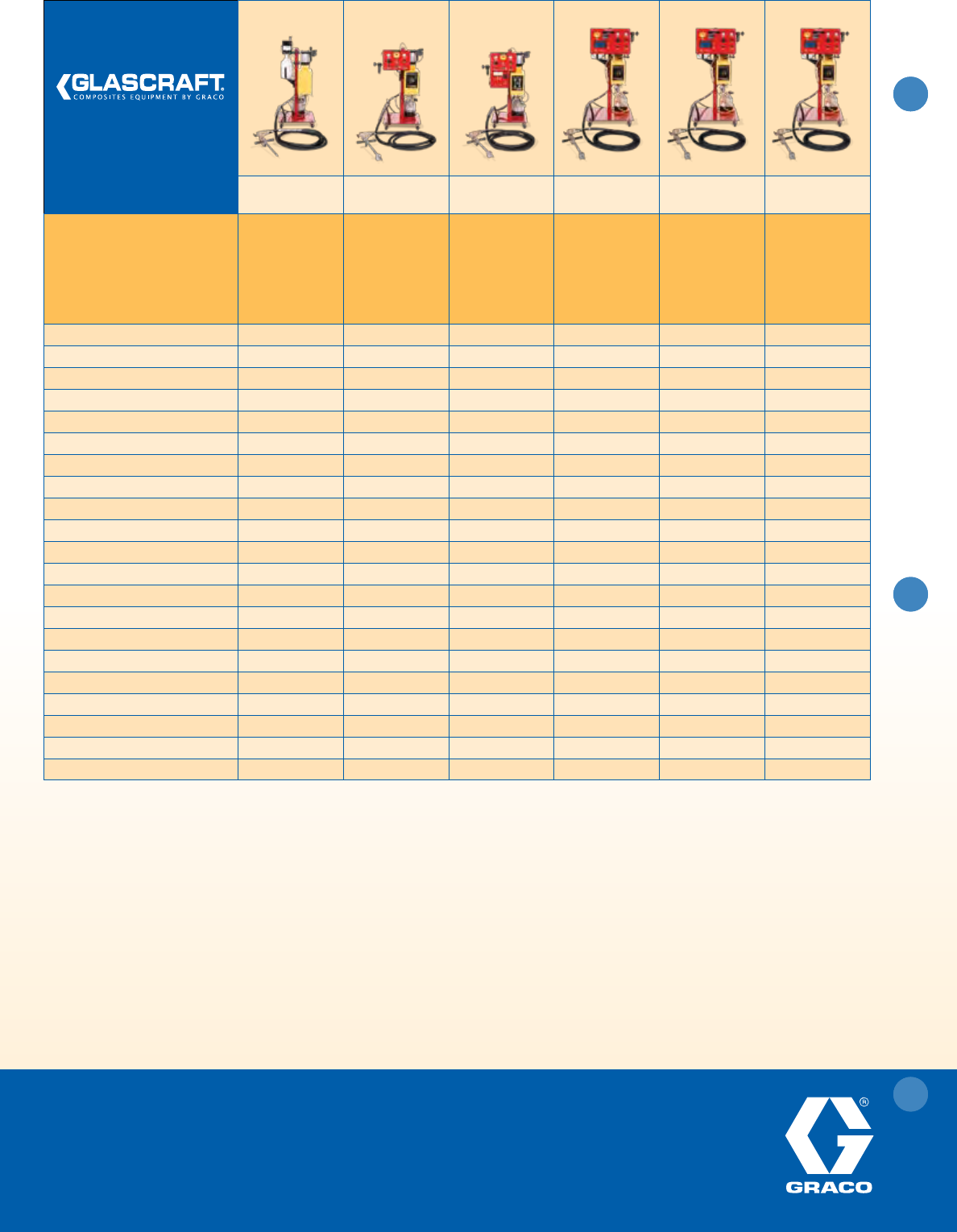
Spartan Spartan II Basic Spartan II Deluxe Spartan 3 PLC Spartan 3 PLC with PAC Spartan 3 PLC
with PAC & RFID
Feature
Entry level designed
for RTM high-
pressure injection
For all forms of
closed molding
For all forms of
automated closed
molding
For all forms of
automated closed
molding with touch-
screen programming
For all forms of high-
volume, automated
closed molding
For all forms of
closed molding;
designed to simplify
high-volume
production when
numerous mold sizes
are used
Complete recirculation ••••••
Pneumatic trigger ••••••
Air/Solvent flush ••••••
Low-pressure injection ••••••
Spartan dispense head ••••••
Positive feed SSP catalyst slave pump ••••••
Stroke counter •••••
Auto-valve ready •••••
Low-pressure injection with Accu-Pressure •••••
User-friendly control panel •••••
Dispense timer • • • •
Adjustable independent solvent flush • • • •
Independent air flush toggle switch • • • •
Adjustable gel timer •
Touch-screen programmable •••
30 programmable injection settings •••
Programmable digital air/solvent flush •••
Programmable automatic catalyst • •
Programmable radio frequency identification tags •
Unlimited programming •
Password protected •
Call today for product information or to request a demonstration.
800-746-1334 or visit us at www.graco.com.
© 2008 Graco Inc. 340040 Rev A 12/08. All other brand names or marks are used for identification purposes and are trademarks of their respective owners. All written and visual data
contained in this document are based on the latest product information available at the time of publication. Graco reserves the right to make changes at any time without notice.
Ordering Information
21650-00 Spartan
23200-00 Spartan II Basic
23240-00 Spartan II Deluxe
23280-02 Spartan 3 PLC
23280-00 Spartan 3 PLC w/PAC
23280-01 Spartan 3 PLC w/PAC & RFID
Repair Kits
Catalyst Pump
LPA-190-RK Complete rebuild kit
LPA-190-SK Seal kit
Air Motor (5-in)
20101-00 Complete service kit
20107-00 Pilot valve kit
20106-00 Main valve kit
20105-00 Gasket kit
20104-00 Stroke signal repair kit
20103-00 Rod seal kit
20102-00 Piston rod seal kit
Fluid Section
21570-00 5:1/11:1 Repair kit
Check Valves
21675-00 Resin check valve
21664-00 Solvent/air purge check valve
23547-01 Catalyst check valve
21676-00 Washer, crush, nylon, .52 ID
22904-00 Stem check valve
21044-02 Silicone o-ring
23540-00 Catalyst body check valve
22906-00 Washer, crush, nylon, ¼ ID
23524-01 Compression spring
22908-00 Round nut
Mixer
20625-00 Static mixer
Specifications
Air consumption 35 cfm @ 100 psi (991 lpm @ 6.8 bar)
at maximum pump output
Material pump capacity 2.5 gpm (9.5 lpm)
Pump output .05 gal per cycle
20 cycles = 1 gal
5 cycles = 1 liter
Max Output Pressure 1,300 psi (89 bar, 8.9MPa)
Catalyst Range 0.5% to 3.5%