Greenheck Fan Sfd Users Manual
SFD to the manual 06b073ec-b758-4691-9075-2cf0382459c1
2015-02-09
: Greenheck-Fan Greenheck-Fan--Sfd-Users-Manual-562446 greenheck-fan--sfd-users-manual-562446 greenheck-fan pdf
Open the PDF directly: View PDF .
Page Count: 8
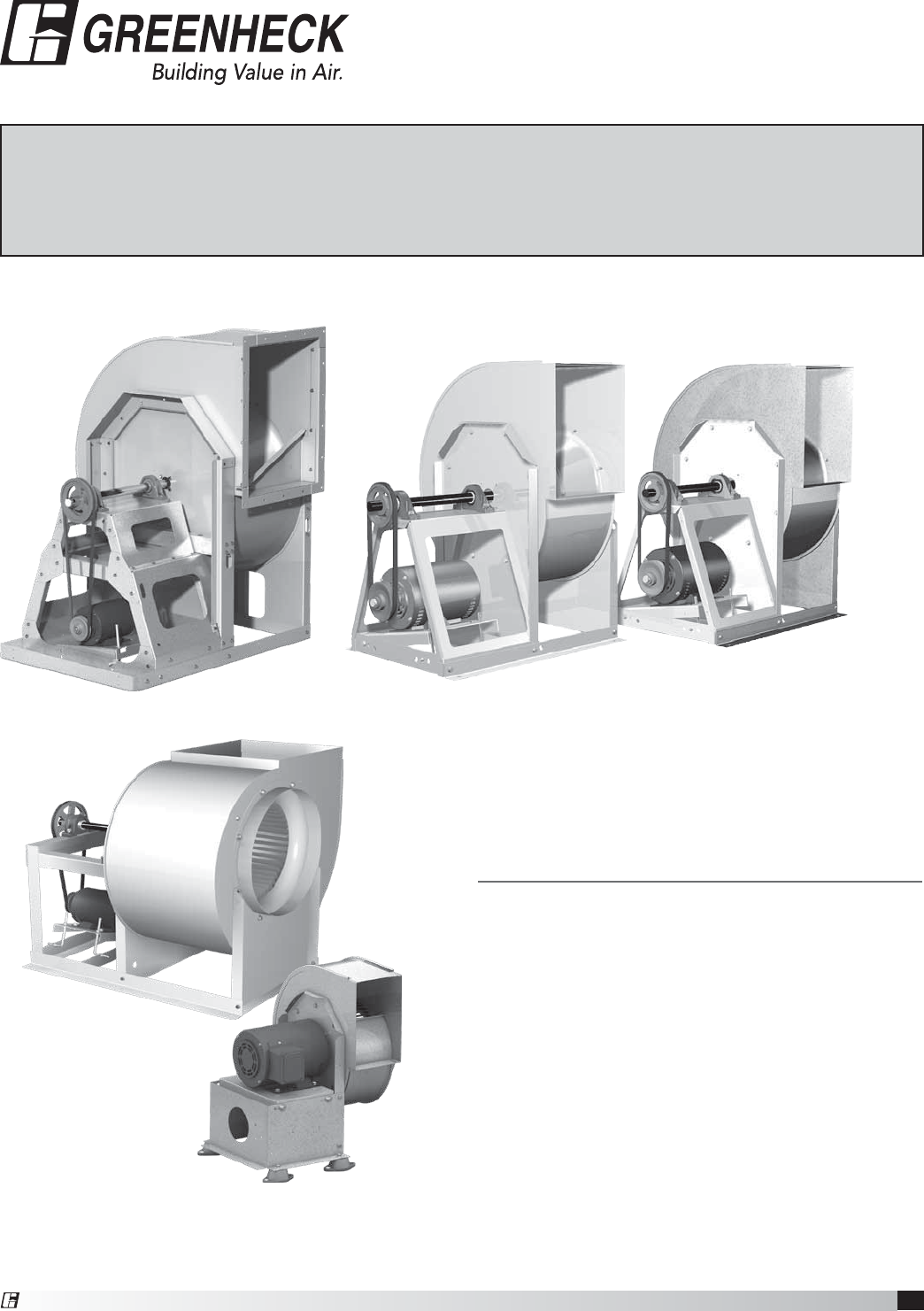
Model SWB
Series 100
Model SWB
Series 200
Model SWB
Series 300
Model SFD
Table of Contents
Motor and Drive Installation
(Units Shipped from Stock) ................ 2
Installation ............................... 3
Affect of Installation on Performance ......... 3
UL/cUL 762 - Restaurant Exhaust ............ 4
Pre-Starting Checks ......................4-5
Belt Drive Fan Maintenance ................. 6
Bearing Lubrication Schedule ............... 6
Motor Maintenance (Belt and Direct Drive) ..... 6
Parts List ................................ 7
Troubleshooting Chart ..................... 8
Model SFB
Installation, Operation and Maintenance Manual
Please read and save these instructions for future reference. Read carefully before attempting to assemble,
install, operate or maintain the product described. Protect yourself and others by observing all safety
information. Failure to comply with instructions could result in personal injury and/or property damage!
1
Centrifugal Utility Fans
Part #455308
Centrifugal Utility Fans
Model SWB - Series 100, 200 and 300
Models SFB and SFD
®
®
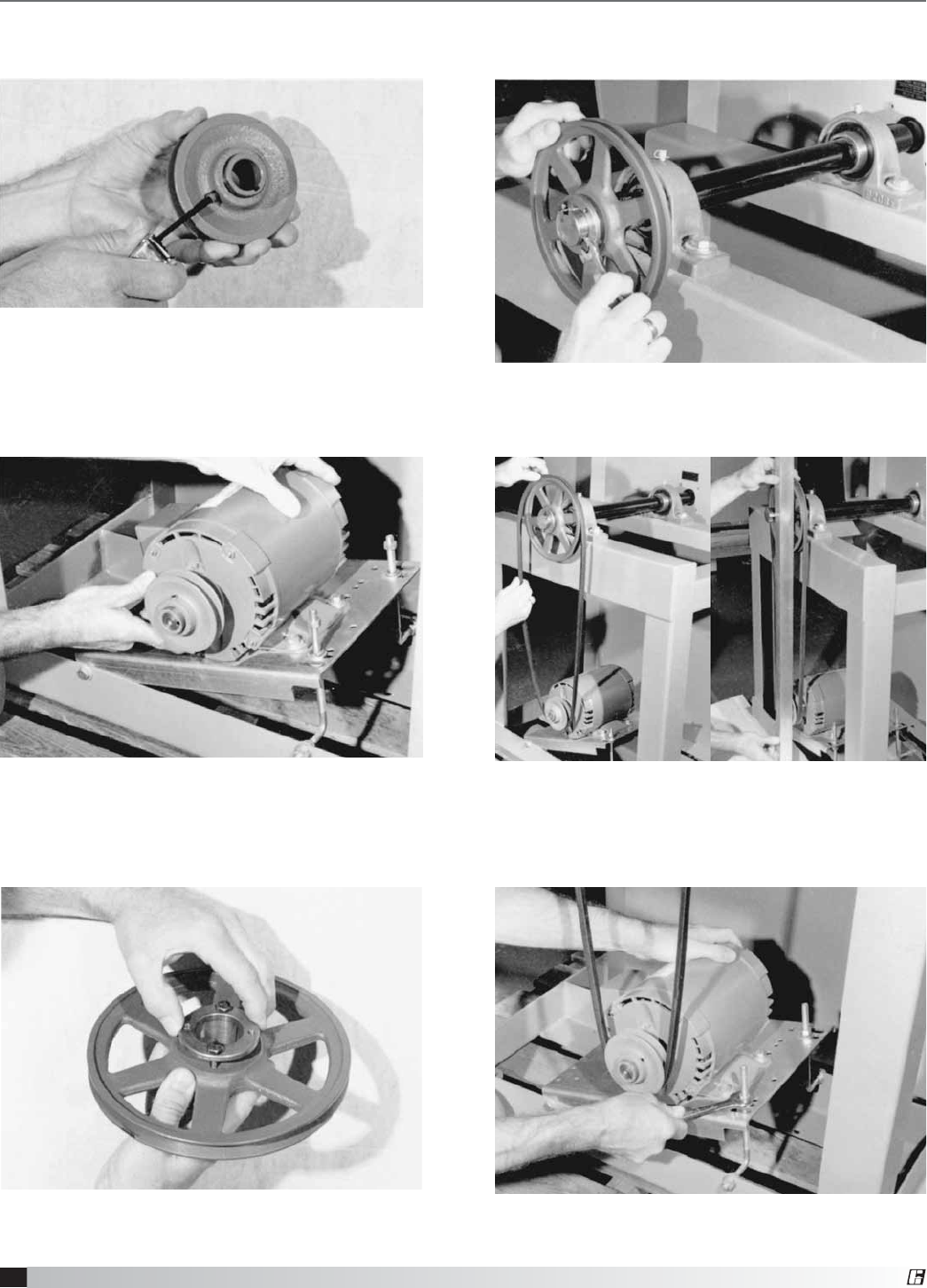
Motor and Drive Installation Instructions
Model SWB units are shipped from stock without motors or drives.
1. Adjust motor pulley to its closed position for
maximum fan speed or increments of 1/2 turn
open (maximum of 5 turns open) for reduced fan
speed. Tighten set screw on flat area only. 4. Install shaft pulley to fan shaft.
5. Install drive belt(s). Belts should not be forced
over pulleys. Align motor and shaft pulleys with a
straight edge. Tighten all set screws.
6. Adjust belt tension.
See page 6 for belt tensioning instructions.
2. Install motor pulley to the motor shaft and install
motor to the motor plate. Pre-punched holes are
provided for most common motor frame sizes.
3. If supplied, install taperlock bushing into
shaft pulley.
2Centrifugal Utility Fans ®
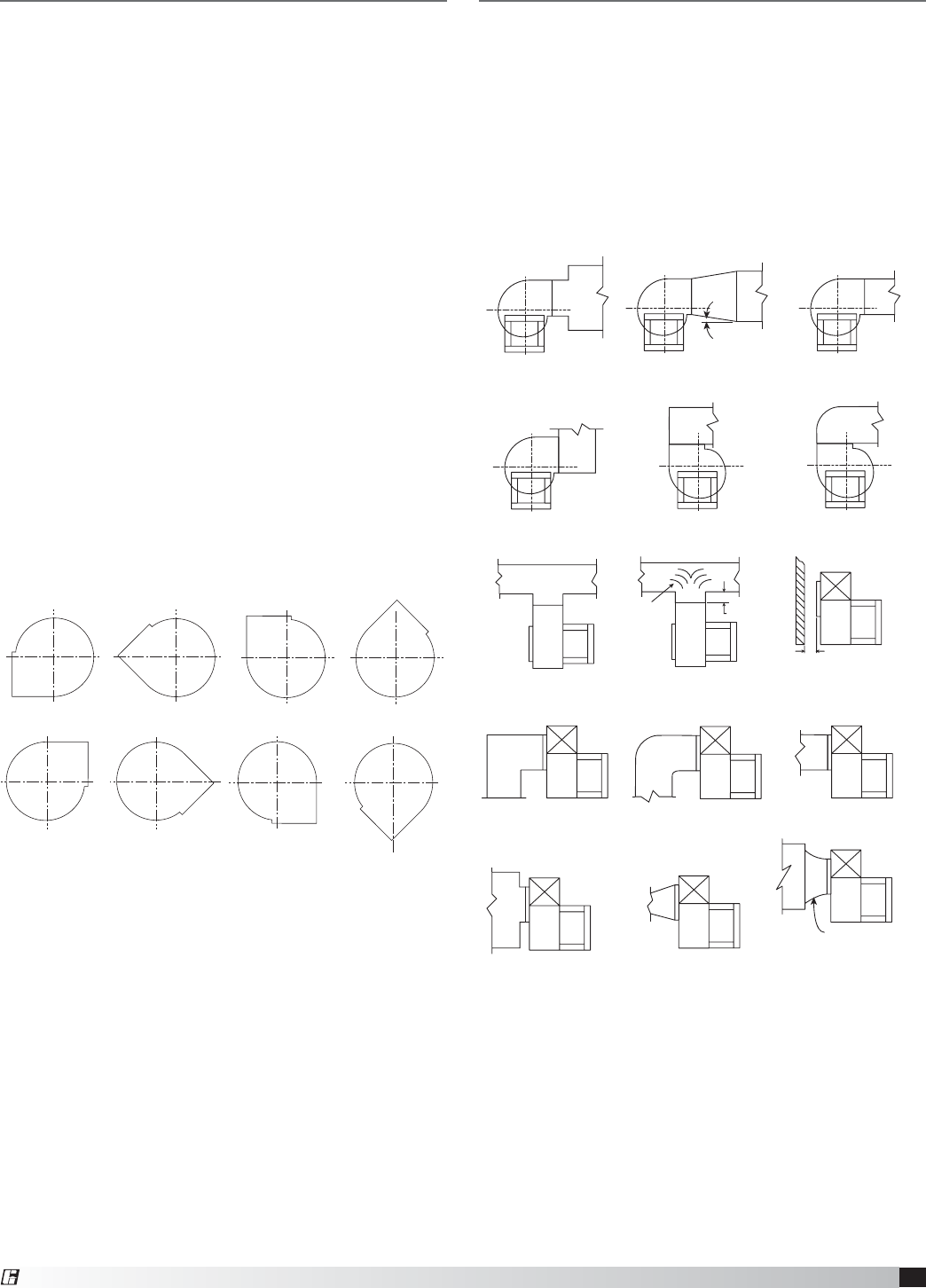
3
Installation
Inspect the unit for any damage and report it to
the shipper immediately. Also, check to see that all
accessory items are accounted for.
Move the fan to the desired location and fasten
securely through mounting holes provided in the base
angles. The unit must be set level (shimming may be
necessary). Flexible duct connections and vibration
isolators should be used where noise is a factor.
The motor voltage and ampere rating must be
checked for compatibility with the electrical supply
prior to final electrical connection. Supply wiring to the
fan must be properly fused, and conform to local and
national electrical codes.
The discharge is factory set as specified by customer
order, however, it can be rotated to other discharge
positions in the field if necessary. Removal of the
housing bolts allows the discharge to be rotated to
the clockwise positions below. For TAD, BD and BAD
discharge positions, a portion of the frame angle must
be removed.
Clockwise rotation shown. Counterclockwise
discharge positions are a mirror image of those
shown. Fan rotation is always specified from the
drive side of the housing.
Affect of Installation on Performance
Restricted or unstable flow at the fan inlet can cause
pre-rotation of incoming air or uneven loading of the
fan wheel, yielding large system losses, increased
sound levels and structural failure of the fan wheel.
Free discharge or turbulent flow in the discharge
ductwork will also result in system effect losses.
The examples below show the system layout and
inlet and discharge configurations which can affect
fan performance.
GOOD
POOR
POOR
FAIR
7o MAX.
POOR FAIR
POOR FAIR
One
Impeller
Dia.
GOOD
Should be at least
1/2 Impeller Dia.
FAIR
Not Greater than
60o Including Angle
POOR
POOR FAIR GOOD
POOR
Turning
Varies
CW BH CW BAU CW TAUCW UB
CW TH CW TAD
CW BAD
CW DB
Discharge Positions
Discharge Configurations
3
Centrifugal Utility Fans
®

Pre-Starting Checks
Wheels
Wheels must rotate freely and not rub on the inlet
venturi. Model SWB wheels overlap the inlet venturi as
shown in Figure 1. Refer to the SWB fan wheel overlap
and radial gap chart for proper dimensions.
Models SFD and SFB wheels do not overlap the
venturi, but have a gap between the inlet venturi
and the wheel (Fig. 2). Wheel position is preset at
the factory and the unit is test run. Wheel movement
may occur during shipment or installation and wheel
alignment may be necessary.
Model SWB
Fig. 1
Gap
Wheel
Radial
Gap
Overlap
Wheel
Installation of UL/cUL 762 Listed
Fans for Restaurant Exhaust
The UL/cUL 762 listing for restaurant exhaust is
available on Series 200 and 300 SWB fan model
sizes 206 - 224 and 327 - 349 with a weatherhood.
UL/cUL 762 fans are listed for a maximum operating
temperature of 375°F (191°C) and includes an access
door and 1inch (25.4 mm) drain connection. An
outlet guard is strongly recommended when the fan
discharge is accessible. An upblast discharge is
recommended. The fan discharge must be a minimum
of 40 inches (1016 mm) above the roof line and the
exhaust duct must be fully welded to a distance of
18inches (457mm) above the roof surface.
This drawing is for dimensional information only. See
the latest edition of NFPA 96 Standard for Ventilation
Control and Fire Protection of Commercial Cooking
Operations for detailed installation instructions,
materials, duct connections and clearances.
Model SFD or SFB
Fig. 2
Gap
Wheel
Radial
Gap
Overlap
Wheel
Alignment of Pulleys and Belts
Check pulleys and belts for proper alignment to avoid
unnecessary belt wear, noise, vibration and power
loss. Motor and drive shafts must be parallel and
pulleys in line as shown below.
The adjustable motor pulley is set at the factory for
the fan RPM specified by the customer. Fan RPM can
be increased by closing or decreased by opening the
adjustable motor pulley. Multigroove variable pitch
pulleys must be adjusted an equal number of turns
open or closed. Any increase in fan speed represents
a substantial increase in load on the motor.
To avoid motor overheating and possible burnout,
motor load amperes should always be checked and
compared to nameplate rating when fan speed is
increased.
Series 200 & 300 SWB models
are listed for grease removal
(UL/cUL 762) File no. MH11745.
WARNING
Always disconnect power before working on or near
a fan. Lock and tag the disconnect switch or breaker
to prevent accidental power up.
CAUTION
When servicing the fan, motor may be hot enough
to cause pain or injury. Allow motor to cool before
servicing.
CAUTION
Precaution should be taken in explosive
atmospheres.
Wrong Wrong Right
40 in.**
(1016 mm)
18 in.*
(457 mm)
Duct
from
kitchen
hood
Upblast Discharge
Optional Companion
Flange
3 Wheel
Diameters
Weatherhood
**Per NFPA 96 the fan discharge must
be a minimum of 40 in. (1016 mm)
above the roof surface.
*Per NFPA 96 the duct
must be of all-welded
construction to a
minimum distance of
18 inches (457 mm)
above the roof surface.
4Centrifugal Utility Fans ®

Wheel Rotation
Rotation direction of the wheel is critical and incorrect
rotation will result in reduced air performance,
increased motor loading and possible motor burnout.
Check wheel rotation by momentarily energizing the
unit and noting if rotation is in the same direction as
the airflow at the outlet and conforms to the rotation
decal affixed to the unit.
Approximate Wheel Clearance Dimensions
Unit Size
SWB SFD SFB
SFD SFB
SWB
Series
100
SWB
Series
200
SWB
Series
300
Overlap Overlap
Tolerance
Radial
Gap Gap Gap
inches (mm)
6 106 206 — — — 3⁄8 (10) —
7.5 107 207 — — — 3⁄8 (10) —
9 9 108 208 — — — 1⁄2 (13) 1⁄2 (13)
10 10 110 210 3⁄8 (10) 1⁄4 (6) 5⁄32 (4) 1⁄2 (13) 1⁄2 (13)
12 212 3⁄8 (10) 1⁄4 (6) 5⁄32 (4) —1⁄2 (13)
113 213 7⁄16 (11) 1⁄4 (6) 5⁄32 (4) —1⁄2 (13)
15 115 215 1⁄2 (13) 1⁄4 (6) 5⁄32 (4) —1⁄2 (13)
116 216 1⁄2 (13) 1⁄4 (6) 5⁄32 (4) — —
18 118 218 5⁄8 (16) 3⁄8 (10) 5⁄32 (4) —1⁄2 (13)
20 120 220 5⁄8 (16) 3⁄8 (10) 5⁄32 (4) —5⁄8 (16)
22 222 11⁄16 (18) 3⁄8 (10) 5⁄32 (4) —5⁄8 (16)
124 224 3⁄4 (19) 3⁄8 (10) 5⁄32 (4) — —
25 — — — — 3⁄4 (19)
27 327 7⁄8 (22) 1⁄4 (6) 3⁄16 (5) —3⁄4 (19)
30 330 15⁄16 (24) 3⁄8 (10) 3⁄16 (5) —3⁄4 (19)
333 11⁄16 (27) 3⁄8 (10) 3⁄16 (5) — —
336 13⁄16 (30) 3⁄8 (10) 3⁄16 (5) — —
340 11⁄4 (32) 3⁄8 (10) 1⁄4 (6) — —
344 17⁄16 (37) 3⁄8 (10) 5⁄16 (8) — —
349 19⁄16 (40) 1⁄2 (13) 5⁄16 (8) — —
On belt drive units, centering can be accomplished
by (a) loosening the inlet cone bolts to move the inlet
cone or by (b) loosening the bearings in order to
move the shaft. Wheel and inlet cone overlap can be
adjusted by loosening the wheel hub set screws and
moving the wheel to the desired position. Tighten all
fasteners and set screws securely and realign drive
pulleys after adjustment.
NOTE
Models SFD and SFB units should be operated only
when attached to the system for which they were
designed. Without proper system static pressure,
the motor could be overloaded.
Wheels as viewed from the drive side:
Airfoil
Forward Curved
Backward Inclined
R
o
t
a
t
i
o
n
R
o
t
a
t
i
o
n
R
o
ta
t
io
n
R
o
ta
t
io
n
Backward Inclined
Forward Curved
Airflow
Airflow
Backward Inclined Forward Curved
Airflow
Airflow
These are the original drawings on the Illustrator file
when I opened it. The IOM had the wheel layered on
top of the scroll.
I will incorporate the
wheel on the scroll
without creating
an additional
layer in the
InDesign file.
April 19, 2011
I positioned the wheels onto the scroll outline. The forward curved wheel was mirrored and
positioned on the scroll above. This is how was done in the InDesign Utility Fans IOM file.
The wheel was laid on top of the scroll within the InDesign file. Better to do this within Illustrator.
barb w
R
o
t
a
t
i
o
n
R
o
t
a
t
i
o
n
Airflow
Airfoil
R
o
t
a
t
i
o
n
R
o
t
a
t
i
o
n
R
o
ta
t
io
n
R
o
ta
t
io
n
Backward Inclined
Forward Curved
Airflow
Airflow
Backward Inclined Forward Curved
Airflow
Airflow
These are the original drawings on the Illustrator file
when I opened it. The IOM had the wheel layered on
top of the scroll.
I will incorporate the
wheel on the scroll
without creating
an additional
layer in the
InDesign file.
April 19, 2011
I positioned the wheels onto the scroll outline. The forward curved wheel was mirrored and
positioned on the scroll above. This is how was done in the InDesign Utility Fans IOM file.
The wheel was laid on top of the scroll within the InDesign file. Better to do this within Illustrator.
barb w
R
o
t
a
t
i
o
n
R
o
t
a
t
i
o
n
Airflow
Airfoil
R
o
t
a
t
i
o
n
R
o
t
a
t
i
o
n
R
o
ta
t
io
n
R
o
ta
t
io
n
Backward Inclined
Forward Curved
Airflow
Airflow
Backward Inclined Forward Curved
Airflow
Airflow
These are the original drawings on the Illustrator file
when I opened it. The IOM had the wheel layered on
top of the scroll.
I will incorporate the
wheel on the scroll
without creating
an additional
layer in the
InDesign file.
April 19, 2011
I positioned the wheels onto the scroll outline. The forward curved wheel was mirrored and
positioned on the scroll above. This is how was done in the InDesign Utility Fans IOM file.
The wheel was laid on top of the scroll within the InDesign file. Better to do this within Illustrator.
barb w
R
o
t
a
t
i
o
n
R
o
t
a
t
i
o
n
Airflow
Airfoil
5
Centrifugal Utility Fans
®
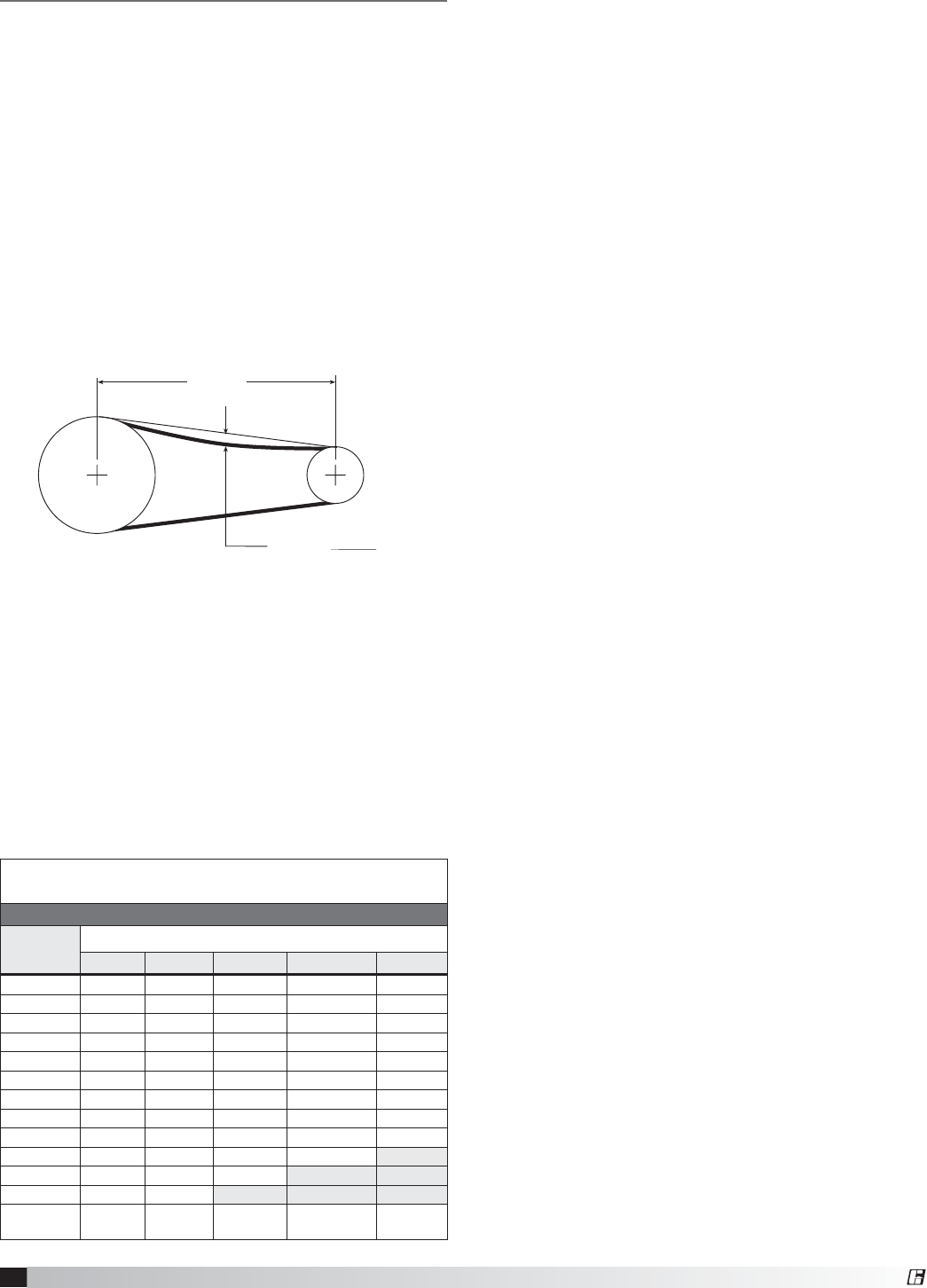
Blower Maintenance (Belt Drive)
Belts tend to stretch after a period of time. They
should be periodically checked for tension and wear.
When replacing belts, use the same type as supplied
with the unit. Replacement of belts should
be accomplished by loosening the tensioning
“L-Bolts” so the belts may be removed by hand. Do
not force belts on or off as this may cause breakage
of cords and lead to premature belt failure.
Belt tension should be adjusted to allow 1/64 in. of
belt deflection per 1 in. of belt span. For example,
a 16 in. belt span should have 16/64 in. or 1/4 in. of
deflection with moderate thumb pressure at mid-point
between the pulleys. (Fig. 3). Refer to Greenheck’s
Product Application Guide, “Measuring Belt Tension”
for additional information—FA/127-11 found online at
www.greenheck.com under the library section.
Shaft bearings are the most critical moving part of a
fan. Therefore, special attention should be given to
keeping the bearings clean and well lubricated. Proper
lubrication provides for reduction in friction and
wear, transmission and dissipation of heat, extended
bearing life and prevention of rust.
In order for a lubricant to fulfill these tasks, the proper
grease applied at regular intervals is required. See the
recommended bearing lubrication schedule below.
If unusual conditions exist - temperatures below 32°F
or above 200°F, moisture or contaminants - more
frequent lubrication is required.
Deflection = Belt Span
64
Belt Span
Fig. 3
• Lubrication interval is based on 12 hour per
day operation and maximum 160°F housing
temperature. For 24 hour per day operation, the
interval should be cut in half.
• Lubricant should be added with the shaft rotating
and until clean grease is seen purging from the
bearing. The lubrication interval may be modified
based on the condition of the purged grease. If
bearing is not visible to observe purged grease,
lubricate with number of shots indicated in chart
for bore size.
• For conditions including high temperatures,
moisture, dirt or excessive vibration, consult the
factory for a specific lubrication interval for your
application.
• Lubricant should be a high quality lithium complex
grease conforming to NLGI Grade 2. Factory
recommends Mobilux EP-2.
• The use of synthetic lubricants will increase
lubrication intervals by approximately 3 times.
In addition to lubricating the bearings at specified
intervals, set screws in the bearing collars should be
checked for tightness. A bearing collar which has
loosened will cause premature failure of the fan shaft.
Fasteners attaching the bearings to the drive frame
should also be checked.
Motor Maintenance (Belt & Direct Drive)
Motor maintenance is generally limited to cleaning
and lubrication (where applicable). Cleaning should be
limited to exterior surfaces only. Removing dust and
grease buildup on the motor housing assures proper
motor cooling. Use caution and do not allow water
or solvents to enter the motor or bearings. Under no
circumstances should motors or bearings be sprayed
with steam, water or solvents.
Many fractional horsepower motors are permanently
lubricated for life and require no further lubrication.
Motors supplied with grease fittings should be
greased in accordance with the manufacturer’s
recommendations.
Wheel and Fastener Maintenance
Wheels require very little attention when exhausting
clean air, however, air heavily laden with grease or
dirt will tend to accumulate on the wheel causing
unbalance. Wheels exhausting dirty or grease-laden
air require frequent cleaning to assure smooth and
safe operation.
All fasteners, including set screws in the bearing
collars, should be checked for tightness each time
maintenance checks are performed.
A proper maintenance program will help preserve the
performance and reliability designed into the fan.
Recommended Bearing Lubrication Schedule
Relubrication Schedule in Months
Standard Grease
Fan
RPM
Bearing Bore, inches
1⁄2
-1 1
1⁄8
- 1
1⁄2
1
5⁄8
- 1
7⁄8
1
15⁄16
- 2
3⁄16
2
7⁄16
- 3
To 250 12 12 12 12 12
500 12 12 11 10 8
750 12 9 8 7 6
1000 12 7 6 5 4
1250 12 6 5 4 3
1500 12 5 4 3 2
2000 12 3 3 2 1
2500 12 2 2 1 0.5
3000 12 2 1 0.5 0.25
3500 12 1 0.5 0.25 x
4000 12 0.5 0.25 x x
5000 12 0.25 x x x
Number
of Shots 4 8 8 10 16
6Centrifugal Utility Fans ®
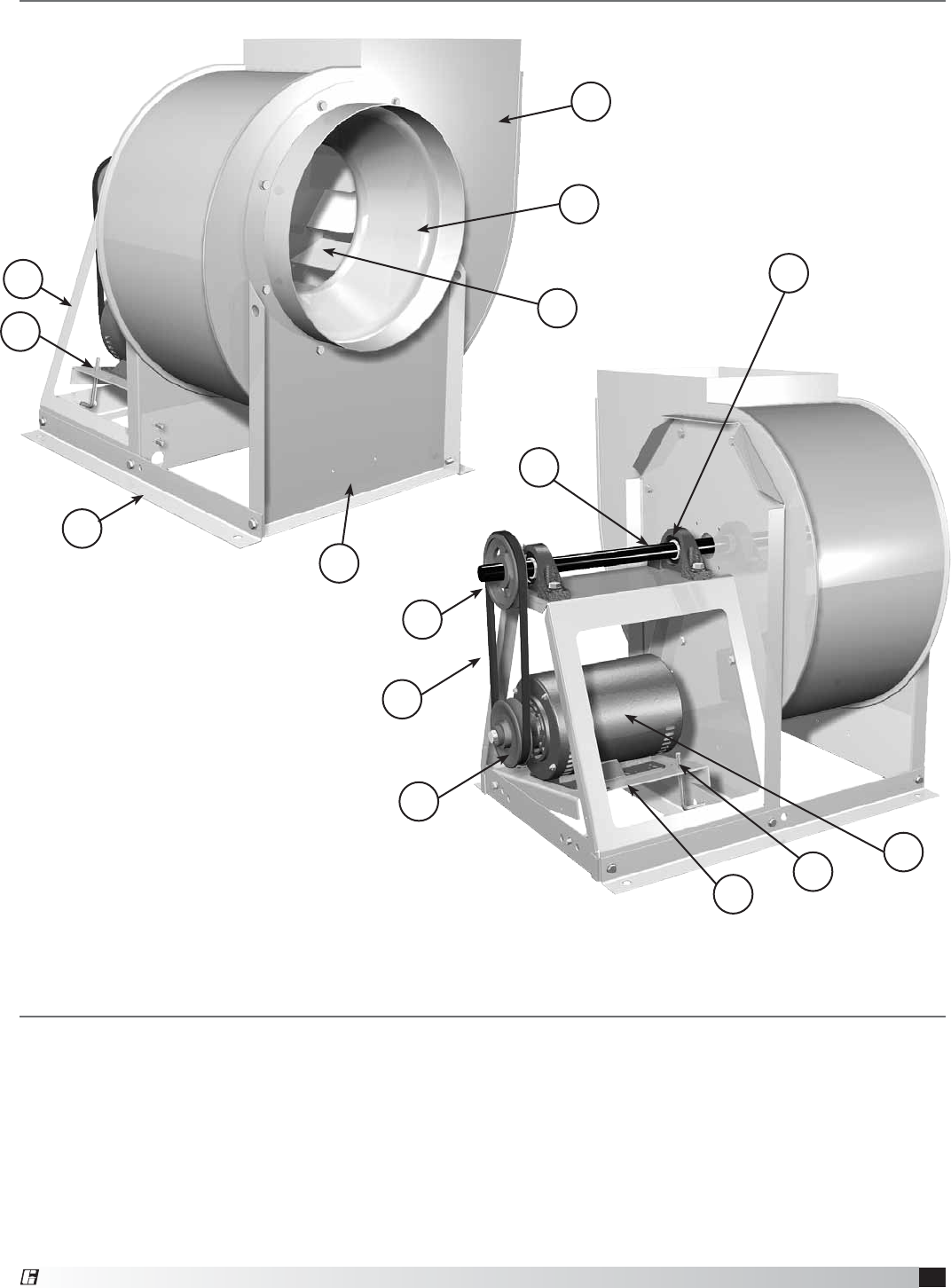
Parts List
1
2
3
4
5
7
8
9
10
6
11
12
13
14
Always provide the unit model and serial number when requesting parts or information.
Replacement Parts
1. Scroll housing
2. Drive frame - base angle
3. Intake support panel
4. Inlet ring and cone
5. Wheel (specify rotation)
6. Drive frame assembly
7. Pillow block bearings
8. Fan shaft
9. Shaft pulley
10. Belt
11. Motor pulley
12. Belt tensioning bolts
13. Motor plate
14. Motor
12
7
Centrifugal Utility Fans
®
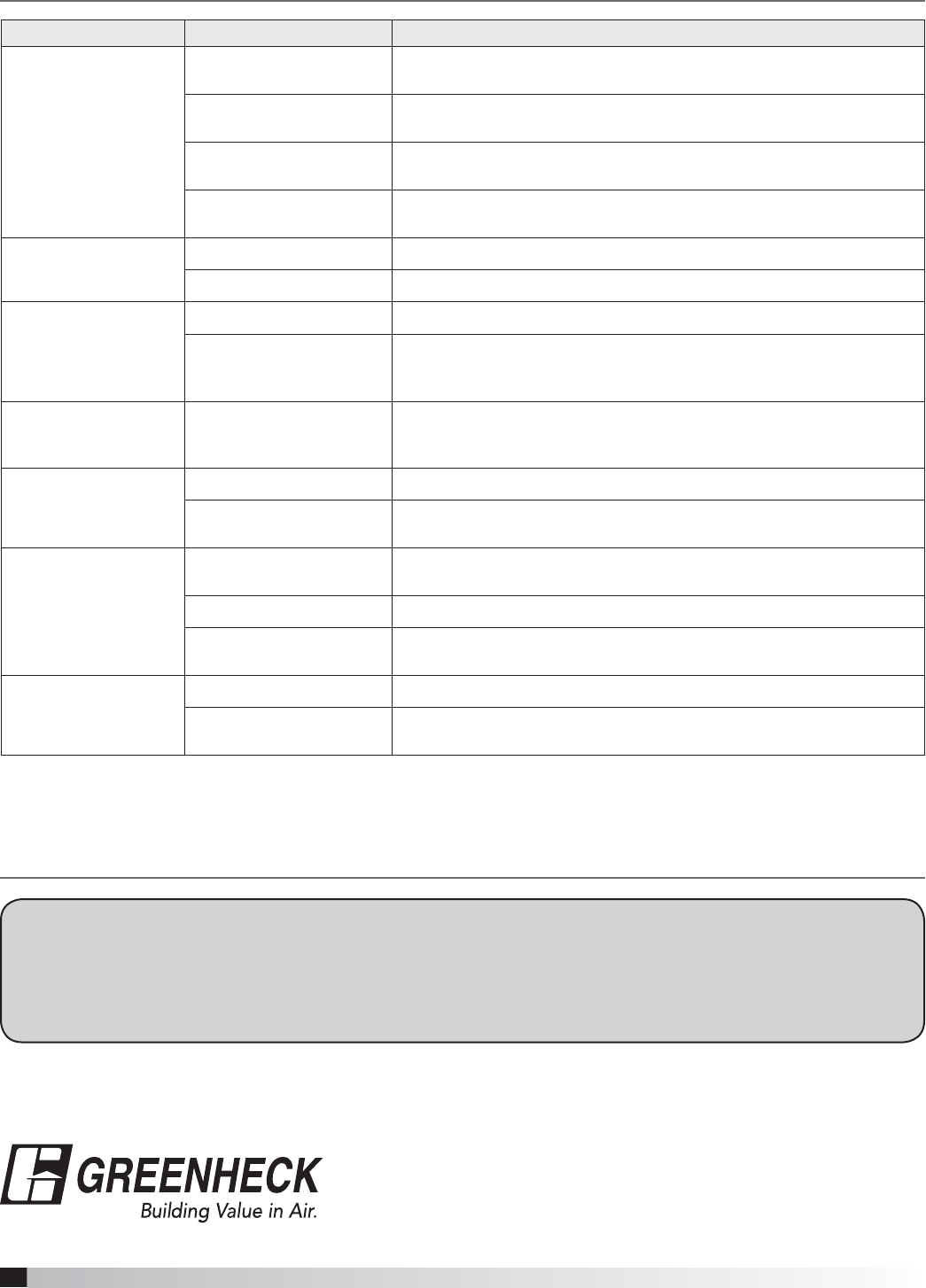
Problem Cause Corrective Action
Excessive Noise
Wheel Rubbing Inlet Adjust wheel and/or inlet cone. Tighten wheel hub or bearing
collars on shaft.
V-Belt Drive Tighten sheaves on motor/fan shaft. Adjust belt tension. Align
sheaves properly (see page 4). Replace worn belts or sheaves.
Bearings Replace defective bearing(s). Lubricate bearings. Tighten
collars & fasteners.
Wheel Unbalance Clean all dirt off wheel. Check wheel balance, rebalance in
place if necessary.
Low CFM Fan Check wheel for correct rotation. Increase fan speed.*
Duct System See page 4.
High CFM
Fan Resize ductwork. Access door, filters, grills not installed.
Duct System
Change obstructions in system. Use correction factor to adjust
for temperature/altitude. Resize ductwork. Clean filters/coils.
Change fan speed.*
Static Pressure
Wrong
Duct system has more
or less restriction than
anticipated
Check rotation of wheel. Adjust fan speed.
High Horsepower
Fan Check rotation of wheel. Reduce fan speed.
Duct System Resize ductwork. Check proper operation of face and bypass
dampers. Check filters and access doors.
Fan Doesn’t Operate
Electrical Supply Check fuses/circuit breakers. Check for switches off. Check for
correct supply voltage.
Drive Check for broken belts. Tighten loose pulleys.
Motor Assure motor is correct horsepower and not tripping overload
protector.
Overheated Bearing
Lubrication Check for excessive or insufficient grease in the bearing.
Mechanical Replace damaged bearing. Relieve excessive belt tension.
Align bearings. Check for bent shaft.
NOTE: Always provide the unit model and serial numbers when requesting parts or service information.
* Always check motor amps and compare to nameplate rating. Excessive fan speed may overload the motor
and result in burnout.
Troubleshooting
8455308 • SWB / SFB / SFD, Rev. 6, June 2011 Copyright 2011 © Greenheck Fan Corporation
Greenheck warrants this equipment to be free from defects in material and workmanship for a period of one year from the
shipment date. Any units or parts which prove to be defective during the warranty period will be replaced at our option
when returned to our factory, transportation prepaid. Motors are warranted by the motor manufacturer for a period of one
year. Should motors furnished by Greenheck prove defective during this period, they should be returned to the nearest
authorized motor service station. Greenheck will not be responsible for any removal or installation costs.
As a result of our commitment to continuous improvement, Greenheck reserves the right to change specifications without notice.
Greenheck Centrifugal Utility Fan catalog provides additional
information describing the equipment, fan performance,
available accessories, and specification data.
®
Phone:(715)359-6171•Fax:(715)355-2399•E-mail:gfcinfo@greenheck.com•Website: www.greenheck.com
Warranty
AMCA Publication 410-96, Safety Practices for Users and
Installers of Industrial and Commercial Fans, provides
additional safety information. This publication can be
obtained from AMCA International, Inc. at www.amca.org.