Moldflow 2016 Brochure
Moldflow 2016 Brochure Moldflow_2016_Brochure Moldflow_2016_Brochure products 2016 pdf ds
Moldflow 2016 Brochure moldflow_2016_brochure moldflow_2016_brochure products pdf ds
2016-06-08
: Guides Moldflow 2016 Brochure Moldflow_2016_Brochure 2016 products pdf asi
Open the PDF directly: View PDF .
Page Count: 10
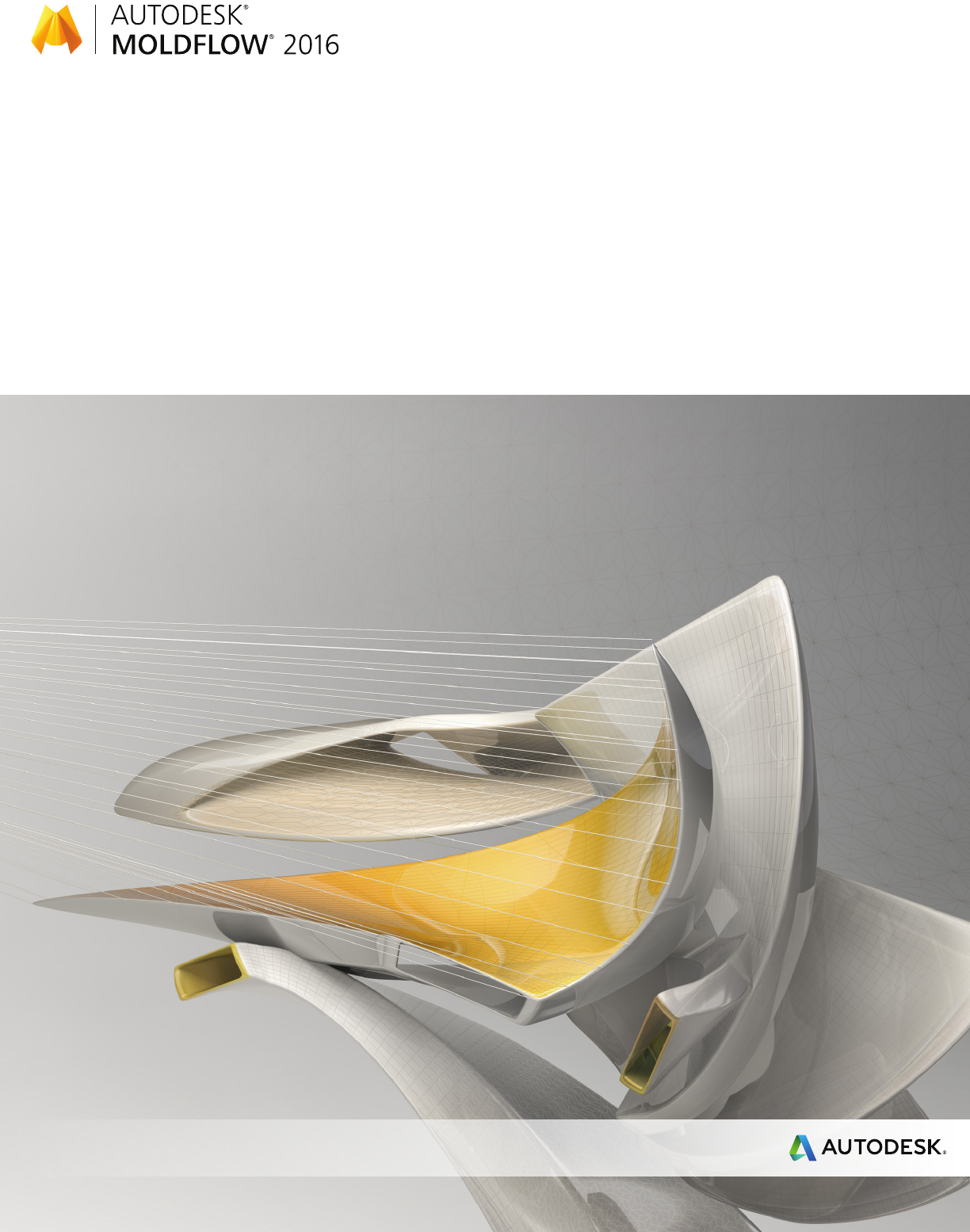
Plastics made perfect
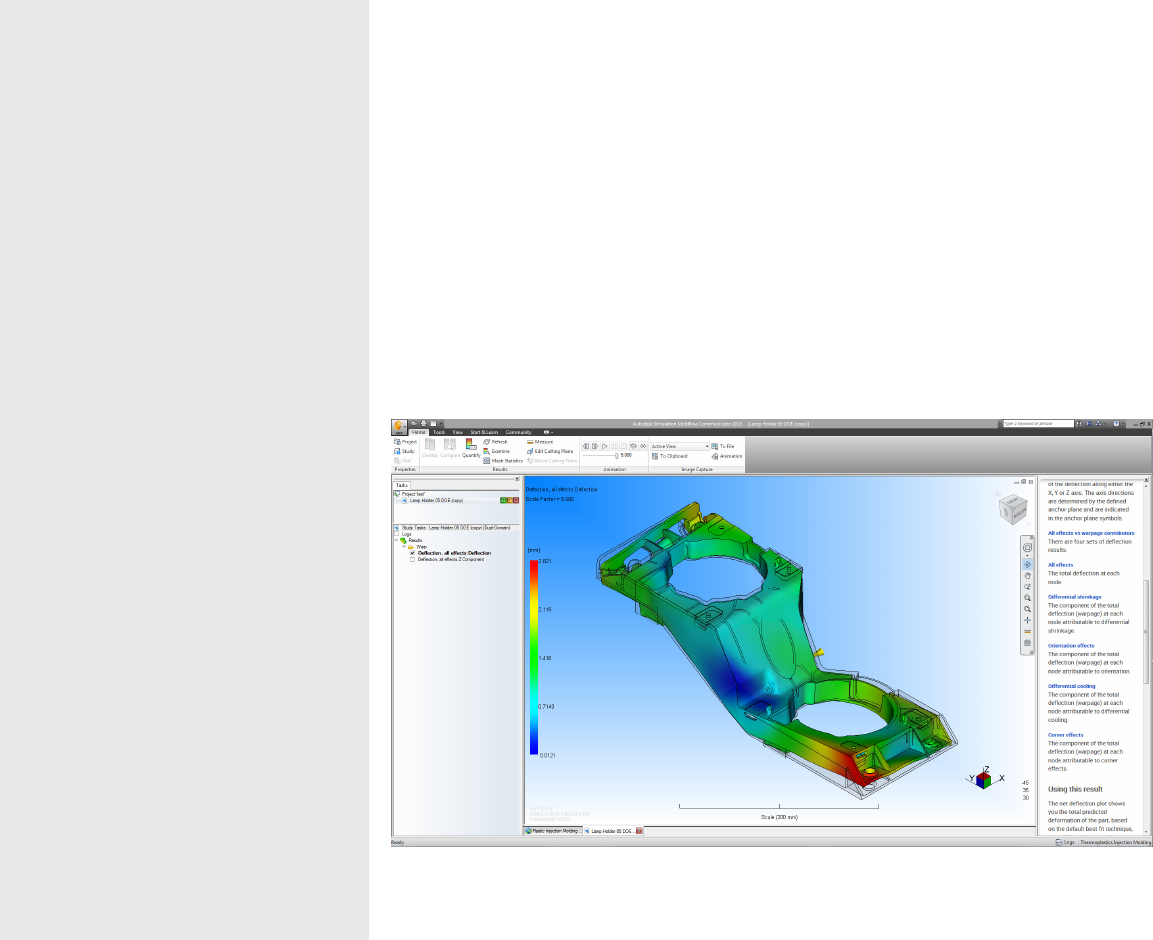
The standard for plastic mold analysis
Autodesk® Moldflow® plastic injection molding
simulation software, part of the Autodesk®
solution for Digital Prototyping, provides tools
that help manufacturers predict, optimize, and
validate the design of plastic parts, injection
molds, and molding processes. Companies
worldwide use Autodesk® Moldflow® Adviser and
Autodesk® Moldflow® Insight software to help
reduce the need for costly physical prototypes,
reduce potential manufacturing defects, and get
innovative products to market faster.
Autodesk Moldflow productline
Autodesk is dedicated to providing a wide range
of injection molding simulation tools to help CAE
analysts, designers, engineers, mold makers, and
molding professionals create more accurate digital
prototypes and bring better products to market at
less cost.
Validation and optimization of plastic parts
Innovative plastic resins and functional plastic part designs are on
the rise in almost every industry. Plastics and fiber-filled composites
answer growing pressures to reduce costs and cut time to market.
The need for simulation tools that provide deep insight into the
plastic injection molding process has never been greater.
Contents
Validation and optimization of
plasticparts .................................................2
Part layout simulation..................................3
Injection molding process simulation ..........4
CAD interoperability and meshing...............6
Results evaluation and
productivity tools ........................................7
Feature comparison .....................................8
Autodesk Moldflow Flex
The extended solving options of Autodesk®
Moldflow® Flex software allows you to simulate
locally or in the cloud, depending on your needs.
If you are testing the setup of an analysis, use
your local machine to iterate and optimize.
When you are ready to initiate a longer, more
computationally intensive simulation, use the
power of the cloud, saving local resources for
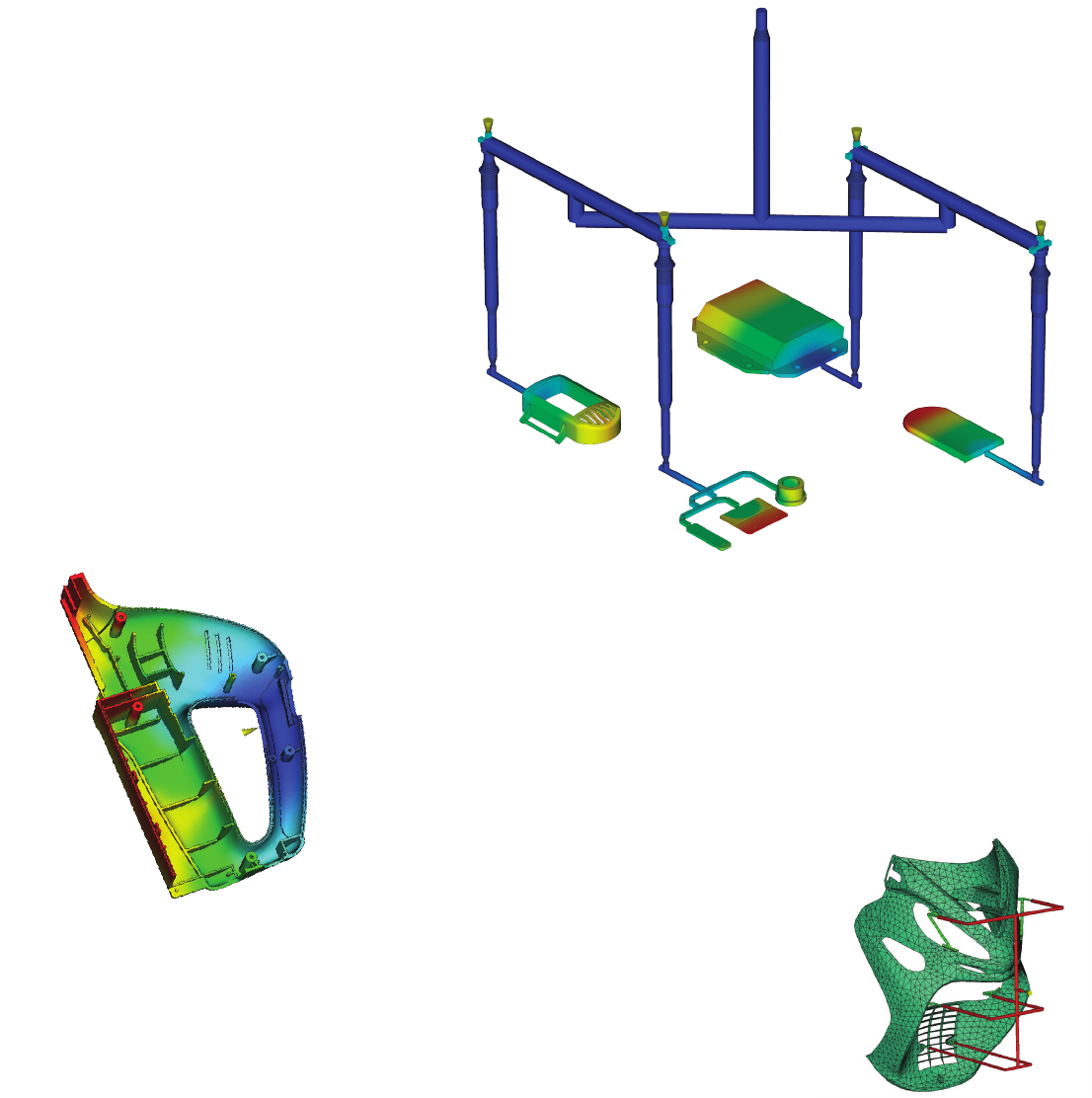
Balancing runners
Balance runner systems of single-cavity,
multicavity, and family mold layouts so parts fill
simultaneously, reducing stress levels and volume
of material.
Hot runner systems
Model hot runner system components and set up
sequential valve gates to help eliminate weld lines
and control the packing phase.
Plastic flow simulation
Simulate the flow of melted plastic to help
optimize plastic part and injection mold designs,
reduce potential part defects, and improve the
molding process.
Part defects
Determine potential part defects such as weld
lines, air traps, and sink marks, then rework
designs to help avoid these problems.
Thermoplastic filling
Simulate the filling phase of the thermoplastic
injection molding process to help predict the flow
of melted plastic and fill mold cavities uniformly;
avoid short shots; and eliminate, minimize, or
reposition weld lines and air traps.
Thermoplastic packing
Optimize packing profiles and visualize magnitude
and distribution of volumetric shrinkage to help
minimize plastic part warpage and reduce defects
such as sink marks.
Feed system simulation
Model and optimize hot and cold runner systems
and gating configurations. Improve part surfaces,
minimize part warpage, and reduce cycle times.
Gate location
Identify up to 10 gate locations simultaneously.
Minimize injection pressure and exclude specific
areas when determining gate location.
Runner design wizard
Create feed systems based on inputs for layout,
size, and type of components, such as sprues,
runners, and gates.
Part layout simulation
Validate and optimize plastic parts, injection molds, resin
selection, and the injection molding process
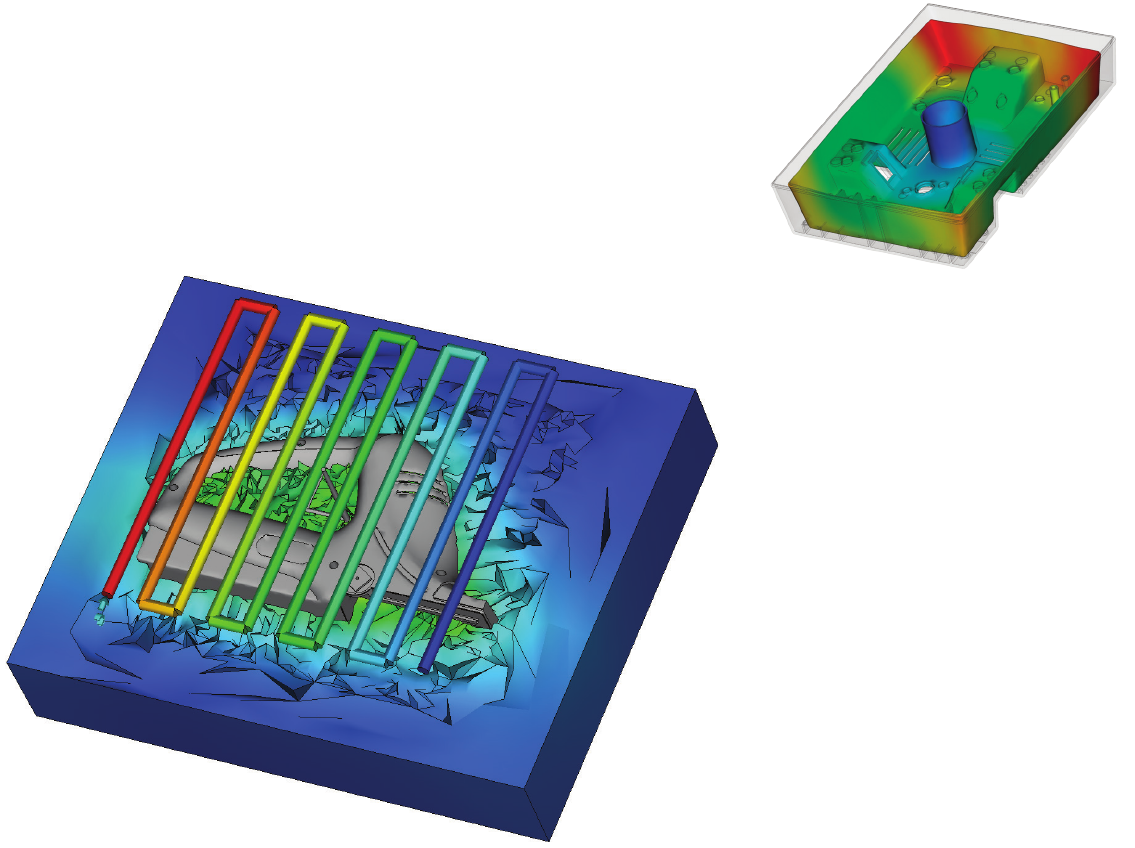
Mold cooling simulation
Improve cooling system eciency, minimize part
warpage, achieve smooth surfaces, and reduce
cycle times.
Cooling component modeling
Analyze a mold’s cooling system eciency.
Model cooling circuits, baes, bubblers, heating
elements, and moldinserts and bases.
Cooling system analysis
Optimize mold and cooling circuit designs to help
achieve uniform part cooling, minimize cycle
times, reduce part warpage, and decrease
manufacturing costs. Capture advanced cooling
techniques and layouts, such as conformal cooling,
induction heating, as well as transient heat
calculations.
Injection molding process simulation
Warpage
Predict warpage resulting from process-induced
stresses. Identify where warpage might occur
and optimize part mold design, material
choice, and processing parameters to help control
part deformation.
Core shift control
Minimize the movement of mold cores by
deter-mining ideal processing conditions for
injection pressure, packing profile, and gate
locations.
Fiber orientation and breakage
Control fiber orientation within plastics to help
reduce part shrinkage and warpage across the
molded part.
CAE data exchange
Validate and optimize plastic part designs using
tools to exchange data with mechanical simulation
software. CAE data exchange is available with
Autodesk® Simulation Mechanical and Autodesk®
Nastran® software, as well as ANSYS®, and
Abaqus® software to predict the real-life behavior
of plastic parts by using as-manufactured material
properties.
Rapid heat cycle molding
Set up variable mold surface temperature profiles
to maintain warmer temperatures during filling
to achieve smooth surfaces; reduce temperatures
in the packing and cooling phases to help freeze
parts and decrease cycle times.
Shrinkage and warpage simulation
Evaluate plastic part and injection mold designs to
help control shrinkage and warpage.
Shrinkage
Meet part tolerances by predicting part shrinkage
based on processing parameters and grade-
specific material data.
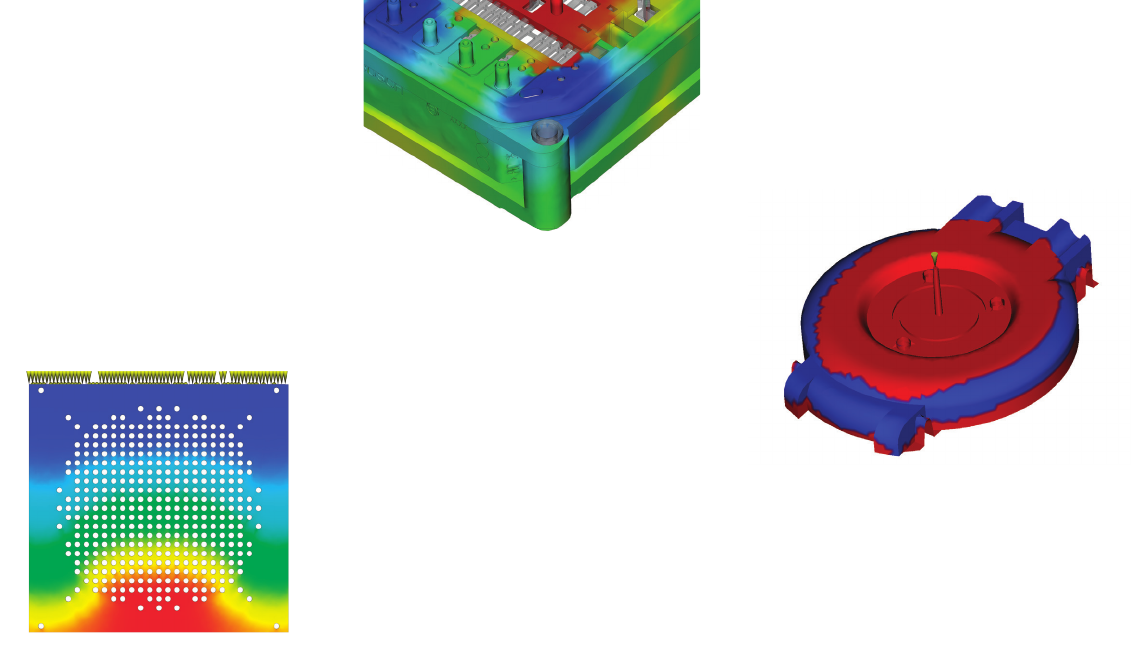
Thermoset flow simulation
Simulate thermoset injection molding, RIM/SRIM,
resin transfer molding, and rubber compound
injection molding.
Reactive injection molding
Predict how molds will fill with or without fiber-
reinforced preforms. Help avoid short shots due
to pregelation of resin, and identify air traps and
problematic weld lines. Balance runner systems,
select molding machine size, and evaluate
thermoset materials.
Microchip encapsulation
Simulate encapsulation of semiconductor chips
with reactive resins and the interconnectivity of
electrical chips. Predict bonding wire deformation
within the cavity and shifting of the lead frame
due to pressure imbalances.
Underfill encapsulation
Simulate flip-chip encapsulation to predict
material flow in the cavity between the chip and
the substrate.
Specialized simulation tools
Solve design challenges with simulation.
Insert overmolding
Run an insert overmolding simulation to help
determine the impact of mold inserts on melt flow,
cooling rate, and part warpage.
Two-shot sequential overmolding
Simulate the two-shot sequential overmolding
process: one part is filled; the tool opens and
indexes to a new position; and a second part is
molded over the first.
Birefringence
Predict optical performance of an injection-
molded plastic part by evaluating refractive index
changes that result from process-induced stresses.
Evaluate multiple materials, processing conditions,
and gate and runner designs to help control
birefringence in the part.
MuCell®
MuCell® (from Trexel, Inc.) simulation results
include filling pattern, injection pressure, and cell
size. These are all critical factors in optimizing a
given part for the process, as well as the
process itself.
Specialized molding processes
Simulate a wide range of plastic injection molding
processes and specialized process applications.
Gas-assisted injection molding
Determine where to position polymer and gas
entrances, how much plastic to inject prior to gas
injection, and how to optimize size and placement
of gas channels.
Co-injection molding
Visualize the advancement of skin and core
materials in the cavity and view the dynamic
relationship between the two materials as filling
progresses. Optimize material combinations while
maximizing the product's cost-performance ratio.
Injection-compression molding
Simulate simultaneous or sequential polymer
injection and mold compression. Evaluate
material candidates, part and mold design,
and processing conditions.
Injection molding process simulation
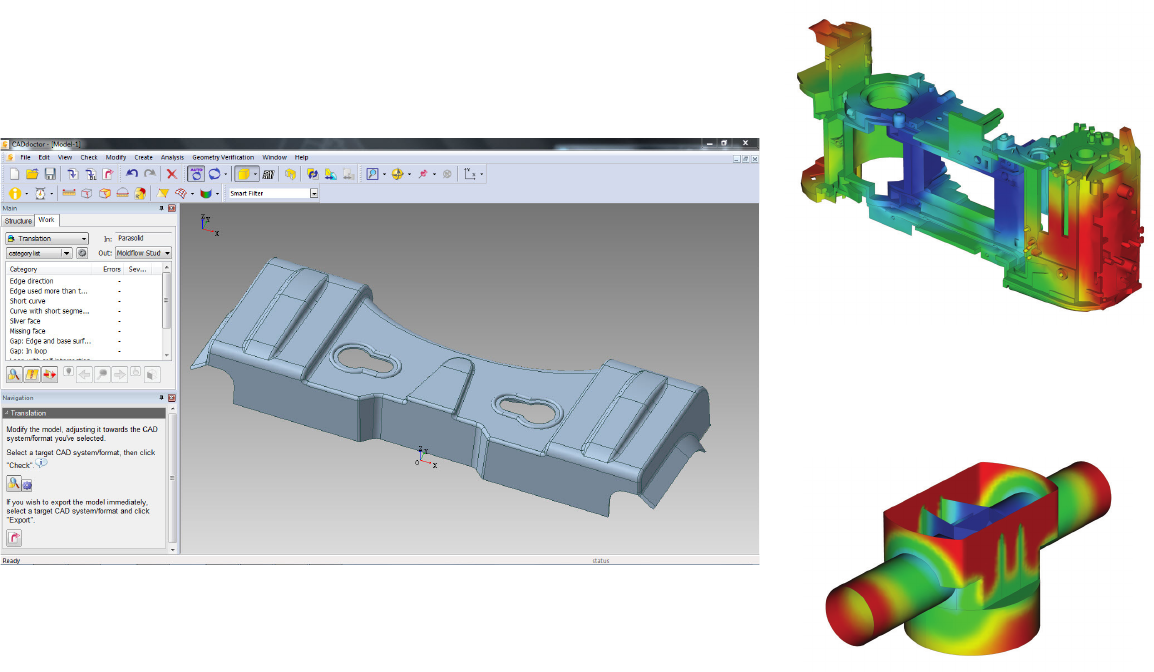
CAD interoperability and meshing
Use tools for native CAD model translation and optimization.
Autodesk Moldflow provides geometry support for thin-walled
parts and thick and solid applications. Select mesh type based on
desired simulation accuracy and solution time.
CAD solid models
Import and mesh solid geometry from Parasolid®-
based CAD systems, Autodesk® Inventor® and
Autodesk® Alias® software, CATIA® V5, Creo®
Parametric, Pro/ENGINEER®, Siemens® NX®, Rhino®,
and SolidWorks® software, as well as ACIS®, IGES,
and STEP universal files.
Autodesk SimStudio Tools
Quickly simplify and edit your geometry for
simulation in Moldflow. SimStudio Tools reads
in multiple CAD file formats and enables you to
quickly simplify models, eliminate unnecessary
detail, perform basic repair, or easily make design
changes so you can explore various design ideas
faster.
Error checking and repair
Scan imported geometry and automatically fix
defects that can occur when translating a model
from CAD software.
Centerline import/export
Import and export feed system and cooling
channel centerlines from and to CAD software, to
help decrease modeling time and avoid runner
and cooling channel modeling errors.
CADdoctor for Autodesk Simulation
Check, correct, heal, and simplify solid models
imported from 3D CAD systems to prepare
for simulation.
3D simulations
Perform 3D simulations on complex geometry
using a solid, tetrahedral, finite element mesh
technique. This approach is ideal for electrical
connectors, thick structural components, and
geometries with thickness variations.
Dual domain technology
Simulate solid models of thin-walled parts using
Dual Domain™ technology. Work directly from 3D
solid CAD models, leading to easier simulation of
design iterations.
Midplane meshes
Generate 2D planar surface meshes with assigned
thicknesses for thin-walled parts.
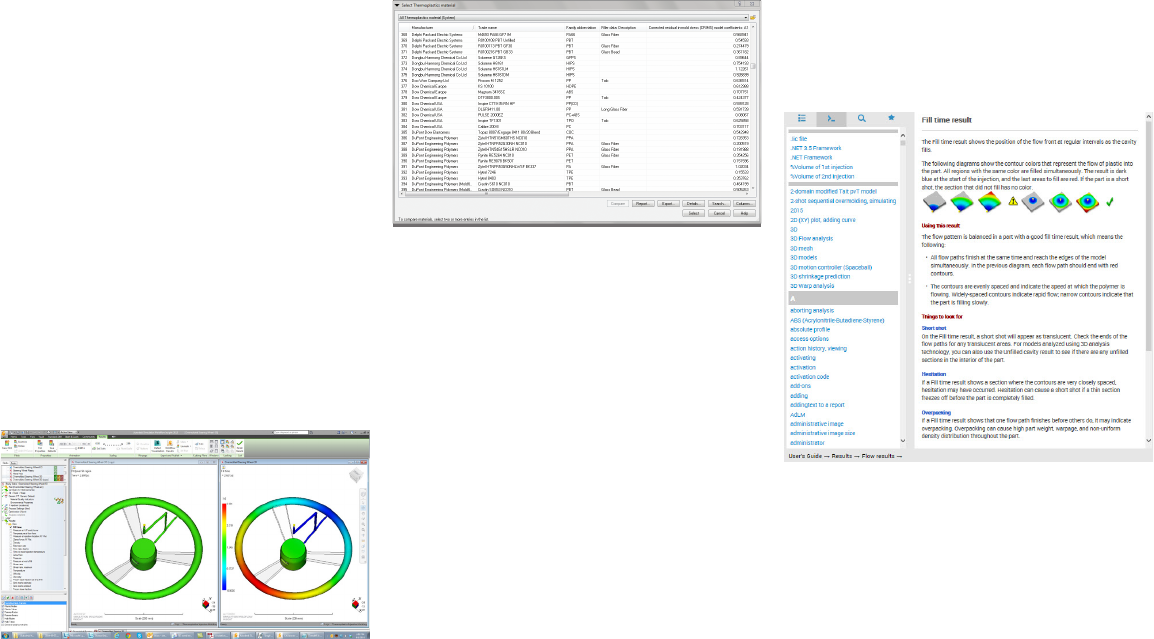
Results interpretation and presentation
Use a wide range of tools for model visualization,
results evaluation, and presentation.
Results adviser
Query regions of a model to identify primary
causes of short shots and poor part or cooling
quality. Get suggestions on how to correct the
part, mold, or process.
Photorealistic defect visualization
Integration with Autodesk® Showcase® software
enhances quality assessments of plastic parts by
examining near-photorealistic renderings of digital
prototypes.
Automatic reporting tools
Use the Report Generation wizard to create web-
based reports. Prepare and share simulation results
more quickly and easily with customers, vendors,
and team members.
Microsoft Oce export capability
Export results and images for use in Microsoft®
Word reports and PowerPoint® presentations.
Autodesk Moldflow Communicator
Collaborate with manufacturing personnel,
procurement engineers, suppliers, and external
customers using Autodesk® Moldflow®
Communicator software. Use the Moldflow
Communicator results viewer to export results
from Autodesk Moldflow software so stakeholders
can more easily visualize, quantify, and compare
simulationresults.
Material data
Improve simulation accuracy with precise
material data.
Material database
Use the built-in material database of grade-
specific information on more than 8,500 plastic
materials characterized for use in plastic injection
molding simulation.
Autodesk Moldflow Plastics Labs
Get plastic material testing services, expert data-
fitting services, and extensive material databases
with Autodesk® Moldflow® PlasticsLabs.
Productivity tools
Use advisers and extensive help to boost
productivity.
Cost adviser
Learn what drives part costs to help minimize
those costs. Estimate product costs based
on material choice, cycle time, post-molding
operations, and fixed costs.
Design adviser
Quickly identify areas of plastic parts that
violate design guidelines related to the injection
moldingprocess.
Results evaluation and productivity tools
Visualize and evaluate simulation results, and use automatic
reporting tools to share the results with stakeholders. Take
advantage of features such as a material database and advisers to
further boost productivity.
Help
Get help on a results plot, including information
on what to look for and how to correct typical
problems. Learn more about solver theory,
interpreting simulation results, and designing
better plastic parts and injection molds.
Automation and customization
Automate common tasks and customize Autodesk
Moldflow software for your organization.
API tools
Application programming interface (API) tools
enable you to automate common tasks, customize
the user interface, work with third-party
applications, and help implement corporate
standards and best practices.
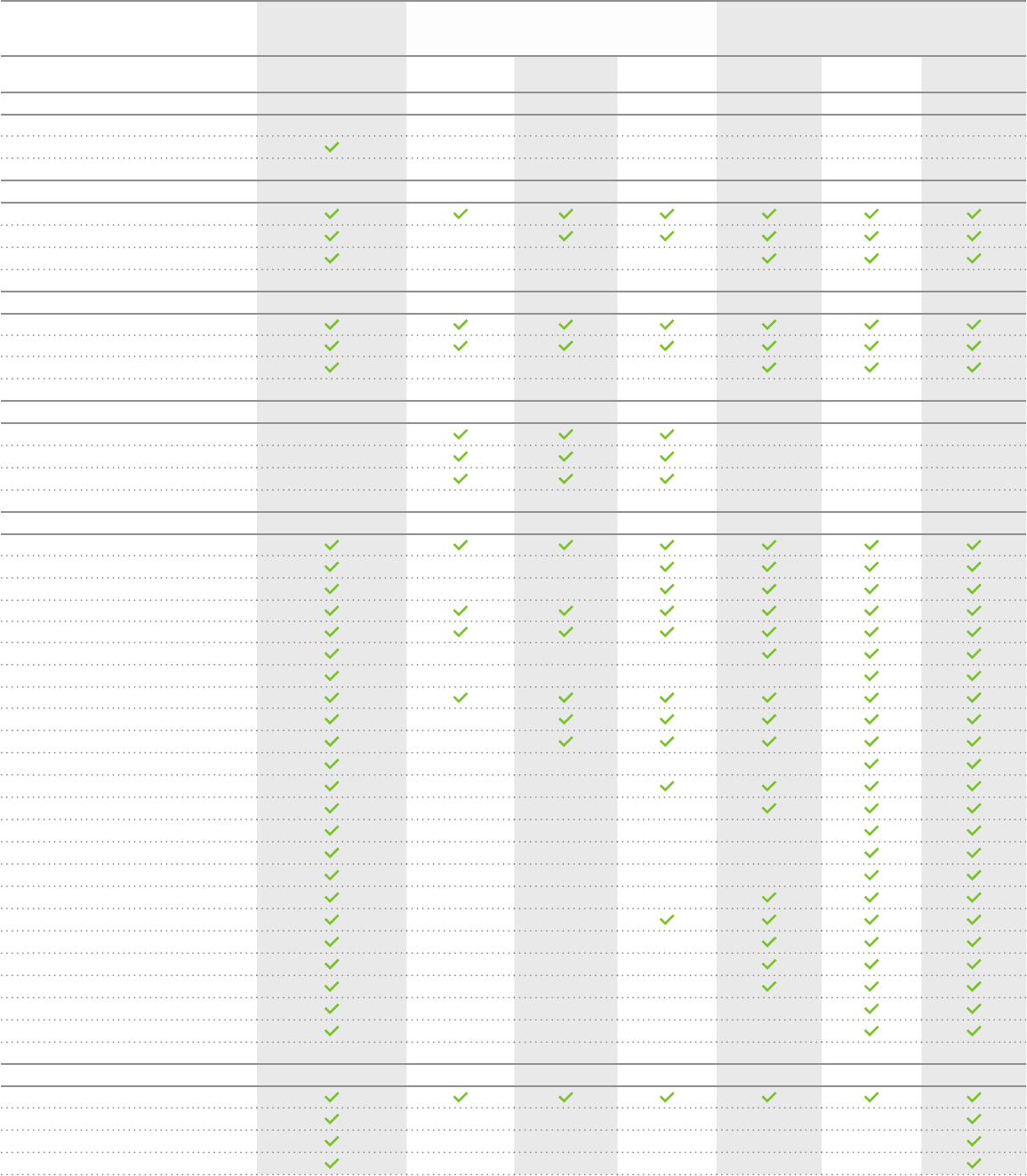
Feature comparison
Compare the features of Autodesk Moldflow products to learn how Autodesk Moldflow Adviser and Autodesk Moldflow Insight software can help meet the
needs of your organization.
Autodesk
Moldflow Flex Autodesk Moldflow Adviser Autodesk Moldflow Insight
STANDARD STANDARD PREMIUM ULTIMATE STANDARD PREMIUM ULTIMATE
SOLVER CAPACITY
Simultaneous local solving (max) 1 - - - 1 3 3
Cloud Solving
MESHING
Dual Domain
3D
Midplane
CAD INTEROPERABILITY
CAD solid models
Parts
Assemblies
SIMULATION ADVISERS
Design adviser
Results adviser
Cost adviser
SIMULATION CAPABILITIES
Filling
Packing
Fiber orientation
Surface defect prediction
Molding window
Venting analysis
Crystallization analysis
Gate location
Cold & hot runners
Runner balancing
Design of experiments (DOE)
Cooling
Transient mold cooling or heating
Conformal cooling
Rapid temperature cycling
Induction heating
Heating elements
Warpage
Insert overmolding
In-mold label
Two-shot sequential overmolding
Core shift
Wire sweep, paddle shift
MOLDING PROCESSES
Thermoplastic injection molding
Gas-assisted injection molding
Injection-compression molding
Co-injection molding
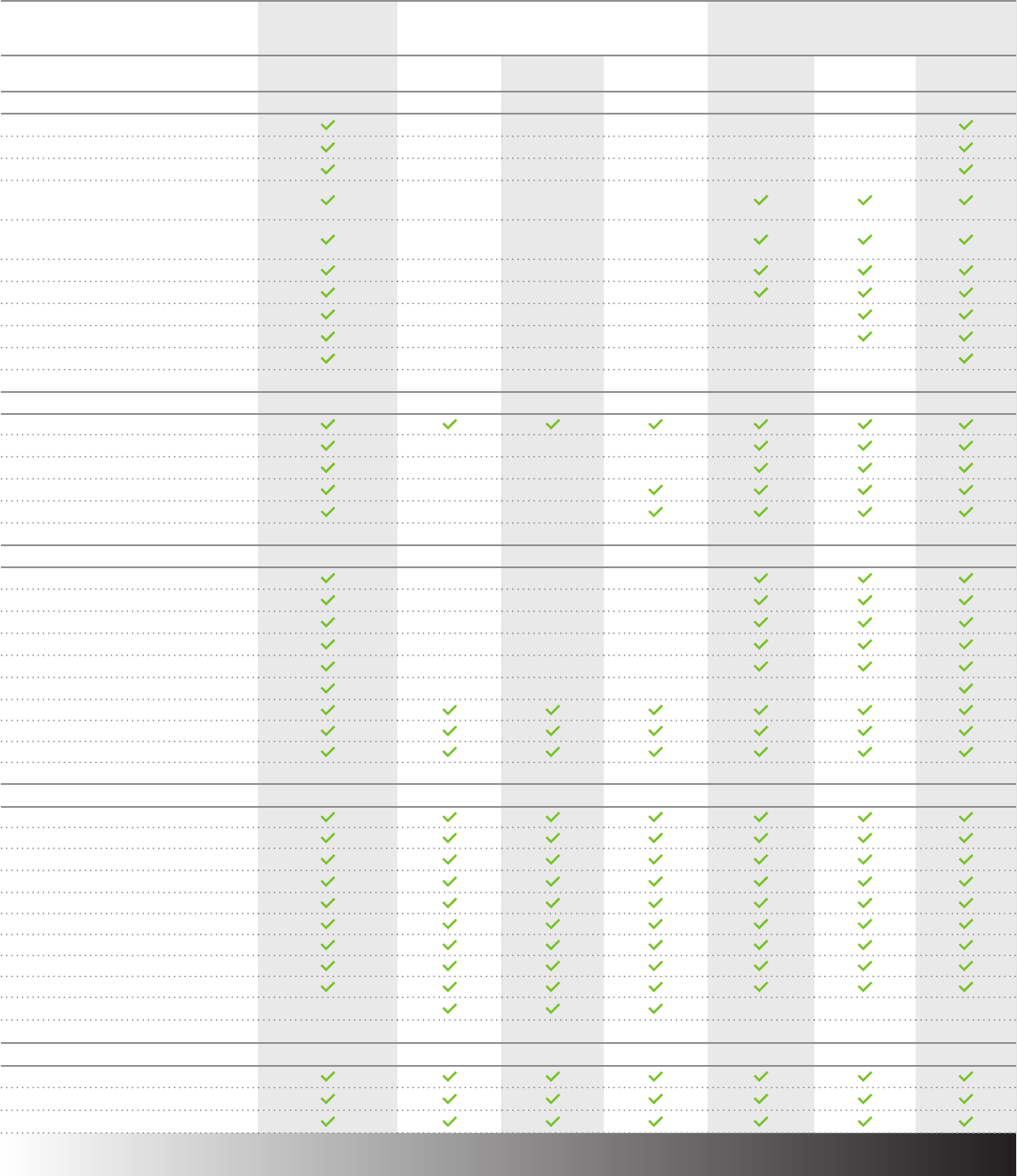
Autodesk
Moldflow Flex Autodesk Moldflow Adviser Autodesk Moldflow Insight
STANDARD STANDARD PREMIUM ULTIMATE STANDARD PREMIUM ULTIMATE
MOLDING PROCESSES (CONT)
Bi-injection molding
Microcellular injection molding
Birefringence
Resin transfer and structural reaction
injection molding
Rubber, liquid silicone injection
molding
Multiple-barrel reactive molding
Reaction injection molding
Microchip encapsulation
Underfill encapsulation
Compression molding
DATABASES
Thermoplastics materials
Thermoset materials
Molding machines
Coolant materials
Mold materials
SOFTWARE INTEROPERABILITY
Simulation Mechanical (FEA)
Autodesk Nastran (FEA)
Abaqus (FEA)
ANSYS (FEA)
LS-DYNA (FEA)
CODE V (Birefringence)
VRED (defect visualization)
Showcase (defect visualization)
CADdoctor for Autodesk Simulation
SUPPORTED LANGUAGES
English
Chinese (Simplified)
Chinese (Traditional)
French
German
Italian
Japanese
Portuguese
Spanish
Korean
Included software and services
Moldflow Communicator
SimStudio Tools
Vault
*Some process/analysis types may not support all mesh types.
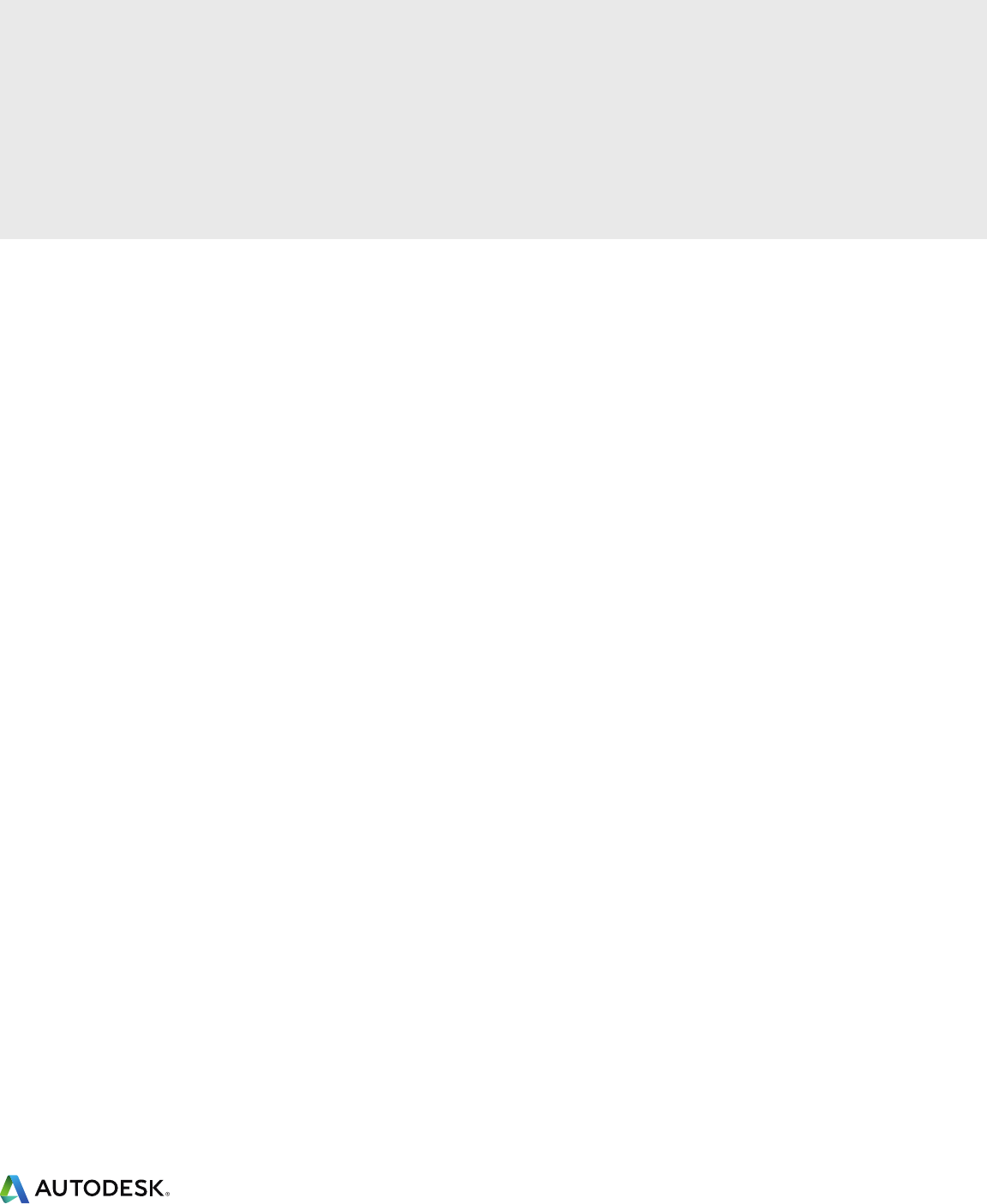
Learn more or purchase
Access specialists worldwide who can provide product expertise, a deep
understanding of your industry, and value that extends beyond your software
purchase. To purchase Autodesk Moldflow software, contact an Autodesk Premier
Solutions Provider or Autodesk Authorized Reseller. Locate a reseller near you at
www.autodesk.com/reseller.
Autodesk Education
Autodesk offers students and educators a variety of resources to help ensure students
are prepared for successful design careers, including access to free* software,
curricula, training materials, and other resources. Anyone can get expert guidance at
an Autodesk Authorized Training Center (ATC®) site, and validate skills with Autodesk
Certification. Learn more at www.autodesk.com/education.
Autodesk Subscription
Autodesk® Subscription for Autodesk Moldflow gives you a greater advantage with
powerful cloud-based services, access to the latest software, online technical support,
and flexible licensing privileges.** Learn more at www.autodesk.com/subscription.
Autodesk 360
The Autodesk® 360 cloud-based framework provides tools and services to extend
design beyond the desktop. Streamline your workflows, effectively collaborate, and
quickly access and share your work anytime, from anywhere. Learn more at
www.autodesk.com/autodesk360.
*Free products are subject to the terms and conditions of the end-user license agreement that accompanies download of
this software.
**All Subscription benefits are not available for all products in all languages and/or regions. Flexible licensing terms,
including previous version rights and home use, are subject to certain conditions.
Autodesk, the Autodesk logo, Alias, ATC, Autodesk Inventor, Inventor, Moldflow, Showcase, VRED, and 3ds Max
are registered trademarks or trademarks of Autodesk, Inc., and/or its subsidiaries and/or aliates in the USA and/or
other countries. Nastran is a registered trademark of the National Aeronautics and Space Administration. SolidWorks
is a registered trademark of Dassault Systèmes SolidWorks Corporation. All other brand names, product names, or
trademarks belong to their respective holders. Autodesk reserves the right to alter product offerings and specifications
at any time without notice, and is not responsible for typographical or graphical errors that may appear in this document.
© 2015 Autodesk, Inc. All rights reserved.
Autodesk Digital Prototyping is an innovative way for you to explore your
ideas before they’re even built. It’s a way for team members to collaborate
across disciplines. And it’s a way for individuals and companies of all sizes to
get great products into market faster than ever before. From concept through
design, manufacturing, marketing, and beyond, Autodesk Digital Prototyping
streamlines the product development process from start tofinish.