Harbor Freight 8 In X 12 1 3 Hp Benchtop Wood Lathe Product Manual
2015-05-27
: Harbor-Freight Harbor-Freight-8-In-X-12-In-1-3-Hp-Benchtop-Wood-Lathe-Product-Manual-723288 harbor-freight-8-in-x-12-in-1-3-hp-benchtop-wood-lathe-product-manual-723288 harbor-freight pdf
Open the PDF directly: View PDF .
Page Count: 20
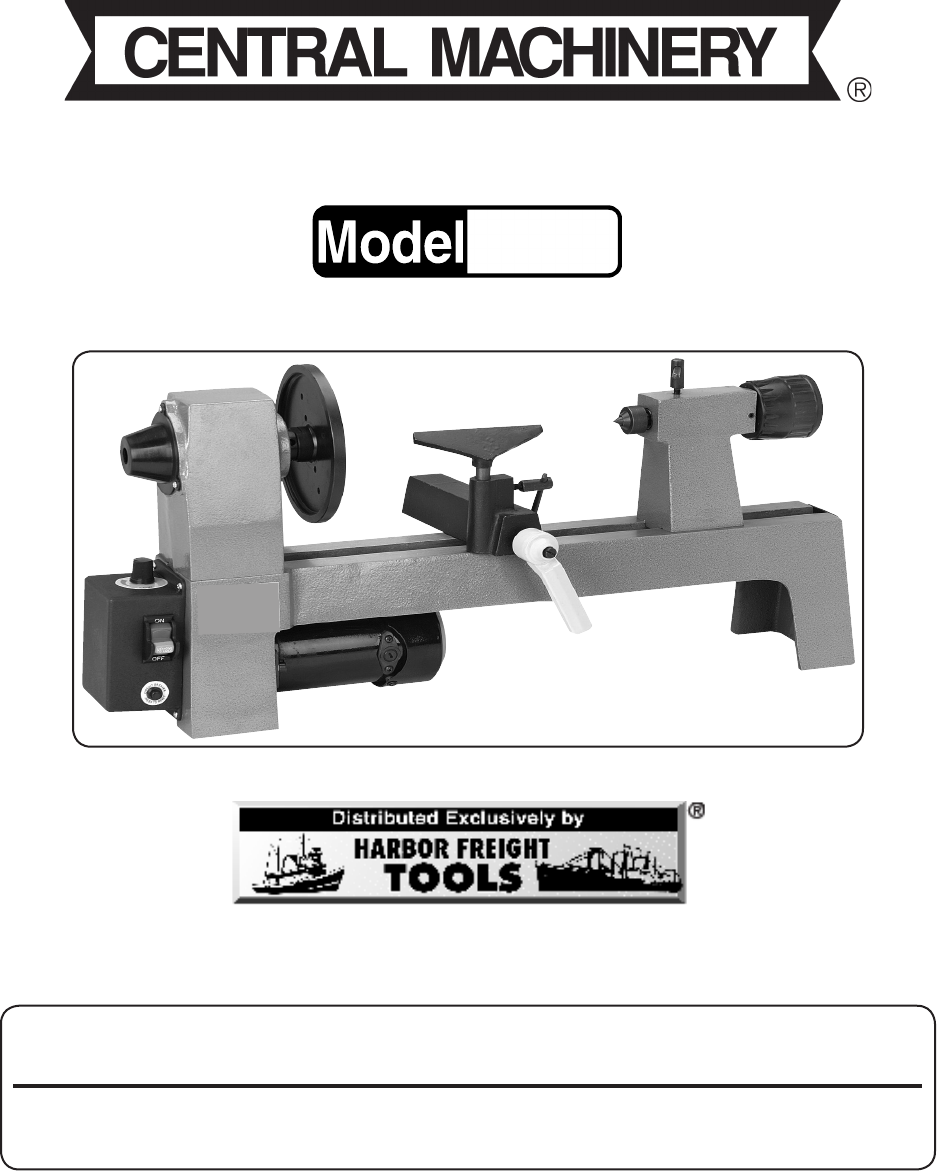
MINI WOODWORKING LATHE
95607
ASSEMBLY AND OPERATION INSTRUCTIONS
Due to continuing improvements, actual product may differ slightly from the product described herein.
3491 Mission Oaks Blvd., Camarillo, CA 93011
Visit our website at: http://www.harborfreight.com
TO PREVENT SERIOUS INJURY, READ AND UNDERSTAND ALL
WARNINGS AND INSTRUCTIONS BEFORE USE.
TO PREVENT DAMAGE TO THE LATHE, SEE STARTUP AND
SHUTDOWN PROCEDURES ON PAGE 13 BEFORE USE.
Copyright© 2006 by Harbor Freight Tools®. All rights reserved. No portion of this
manual or any artwork contained herein may be reproduced in any shape or form
without the express written consent of Harbor Freight Tools.
For technical questions or replacement parts, please call 1-800-444-3353.

Page 2SKU 95607 For technical questions, please call 1-800-444-3353.
SPECIFICATIONS
Motor 110 V~ / 60 Hz / 1 Phase
Speed Range 750 - 3200 RPM
Drive Spindle Size 3/4” x 16 TPI
Swing Over Bed 8”
Distance Between Centers 13”
Spindle Bore 7/16”
Quill Travel 12”
Head Stock 4-1/8” H
Work Tolerance 0.005”
Bed Dimensions 22-3/4” L x 3” W x 5-3/4” H
Tailstock Taper MT1
V-belt size 6 x 516 mm
Net Weight 46 lb.
Save This Manual
You will need this manual for the safety warnings and precautions, assembly,
operating, inspection, maintenance and cleaning procedures, parts list and assembly
diagram. Keep your invoice with this manual. Write the invoice number on the inside of the
front cover. Write the product’s serial number in the back of the manual near the assembly
diagram, or write month and year of purchase if product has no number. Keep this manual
and invoice in a safe and dry place for future reference.
GENERAL SAFETY RULES
WARNING!
READ AND UNDERSTAND ALL INSTRUCTIONS
Failure to follow all instructions listed below may result in
electric shock, fire, and/or serious injury.
SAVE THESE INSTRUCTIONS
WORK AREA
Keep work area clean and well lit. Cluttered benches and invite accidents.
Do not operate power tools in explosive atmospheres, such as in the presence
of flammable liquids, gases, or dust. Power tools create sparks which may ignite
the dust or fumes.
1.
2.

Page 3SKU 95607 For technical questions, please call 1-800-444-3353.
Keep bystanders, children, and visitors away while operating a power tool.
Distractions can cause you to lose control. Protect others in the work area from
debris such as chips and sparks. Provide barriers or shields as needed.
ELECTRICAL SAFETY
Grounded tools must be plugged into an outlet properly installed and grounded
in accordance with all codes and ordinances. Never remove the grounding
prong or modify the plug in any way. Do not use any adapter plugs. Check with
a qualified electrician if you are in doubt as to whether the outlet is properly
grounded. If the tools should electrically malfunction or break down, grounding
provides a low resistance path to carry electricity away from the user.
Double insulated tools are equipped with a polarized plug (one blade is wider
than the other). This plug will fit in a polarized outlet only one way. If the plug
does not fit fully in the outlet, reverse the plug. If it still does not fit, contact
a qualified electrician to install a polarized outlet. Do not change the plug
in any way. Double insulation eliminates the need for the three wire grounded
power cord and grounded power supply system.
Do not expose power tools to rain or wet conditions. Water entering a power
tool will increase the risk of electric shock.
Do not abuse the Power Cord. Keep the Power Cord away from heat, oil,
sharp edges, or moving parts. Replace damaged Power Cords immediately.
Damaged Power Cords increase the risk of electric shock.
PERSONAL SAFETY
Stay alert. Watch what you are doing, and use common sense when operating
a power tool. Do not use a power tool while tired or under the influence of
drugs, alcohol, or medication. A moment of inattention while operating power
tools may result in serious personal injury.
Dress properly. Do not wear loose clothing or jewelry. Contain long hair.
Keep your hair, clothing, and gloves away from moving parts. Loose clothes,
jewelry, or long hair can be caught in moving parts.
Avoid accidental starting. Be sure the Power Switch is off before plugging in.
Plugging in power tools with the Power Switch on invites accidents.
Keep Guards in place and in working order.
Remove adjusting keys or wrenches before turning the power tool on. A
wrench or a key that is left attached to a rotating part of the power tool may result
in personal injury.
3.
1.
2.
3.
4.
1.
2.
3.
4.
5.

Page 4SKU 95607 For technical questions, please call 1-800-444-3353.
Do not overreach. Keep proper footing and balance at all times. Proper footing
and balance enables better control of the power tool in unexpected situations.
Use safety equipment. Always wear eye protection. Dust mask, nonskid safety
shoes, hard hat, or hearing protection must be used for appropriate conditions.
Always wear ANSI-approved safety goggles, heavy-duty work gloves, and a dust
mask/respirator when using or performing maintenance on this tool.
TOOL USE AND CARE
Secure and support the working tools to a stable platform. Holding the tool by
hand or against your body is unstable and may lead to loss of control.
Do not force the tool. Use the correct tool for your application. The correct
tool will do the job better and safer at the rate for which it is designed. Do not force
the tool and do not use the tool for a purpose for which it is not intended.
Do not use the power tool if the Power Switch does not turn it on or off. Any
tool that cannot be controlled with the Power Switch is dangerous and must be
replaced.
Disconnect the Power Cord Plug from the power source and remove key before
making any adjustments, changing accessories, or storing the tool. Such
preventive safety measures reduce the risk of starting the tool accidentally. Always
unplug the tool from its electrical outlet and remove key before performing
any inspection, maintenance, or cleaning procedures.
Keep out of reach of children and other untrained persons. Tools are dangerous
in the hands of untrained users.
Maintain tools with care. Keep cutting tools sharp and clean. Properly maintained
tools with a sharp cutting edge are less likely to bind and are easier to control. Do
not use a damaged tool. Tag damaged tools “Do not use” until repaired.
Check for misalignment or binding of moving parts, breakage of parts, and any
other condition that may affect the tool’s operation. If damaged, have the tool
serviced before using. Many accidents are caused by poorly maintained tools.
Use only accessories that are recommended by the manufacturer for your
model. Accessories that may be suitable for one tool may become hazardous
when used on another tool.
SERVICE
Tool service must be performed only by qualified repair personnel. Service or
maintenance performed by unqualified personnel could result in a risk of injury.
When servicing a tool, use only identical replacement parts. Follow instructions
in the “Inspection, Maintenance, And Cleaning” section of this manual. Use
6.
7.
1.
2.
3.
4.
5.
6.
7.
8.
1.
2.

Page 5SKU 95607 For technical questions, please call 1-800-444-3353.
of unauthorized parts or failure to follow maintenance instructions may create a risk
of electric shock or injury.
SPECIFIC SAFETY RULES
Maintain labels and nameplates on the Mini Lathe. These carry important
information. If unreadable or missing, contact Harbor Freight Tools for a
replacement.
Direction of feed. Feed tool into workpiece against the direction of the workpiece
only.
Avoid unintentional starting. Make sure you are prepared to begin work before
turning on the Mini Lathe.
Never leave the Mini Lathe unattended when it is plugged into an electrical
outlet. Turn off the tool, and unplug it from its electrical outlet before leaving.
Never stand on tool. Serious injury could occur if the tool is tipped or if the cutting
tool is unintentionally contacted.
WARNING! People with pacemakers should consult their physician(s) before using
this product. Electromagnetic fields in close proximity to a heart pacemaker could
cause interference to or failure of the pacemaker.
WARNING! Some dust created by power sanding, sawing, grinding, drilling, and
other construction activities, contain chemicals known (to the State of California)
to cause cancer, birth defects or other reproductive harm.
Some examples of these chemicals are:
Lead from lead-based paints.
Crystalline silica from bricks and cement or other masonry products.
Arsenic and chromium from chemically treated lumber.
Your risk from these exposures varies, depending on how often you do this type of
work. To reduce your exposure to these chemicals: work in a well-ventilated area,
and work with approved safety equipment, such as those dust masks that are
specially designed to filter out microscopic particles.
(California Health & Safety Code § 25249.5, et seq.)
1.
2.
3.
4.
5.
6.
7.
•
•
•

Page 6SKU 95607 For technical questions, please call 1-800-444-3353.
GROUNDING
WARNING!
Improperly connecting the grounding wire can result in the risk of electric shock.
Check with a qualified electrician if you are in doubt as to whether the outlet is
properly grounded. Do not modify the power cord plug provided with the tool.
Never remove the grounding prong from the plug. Do not use the tool if the
power cord or plug is damaged. If damaged, have it repaired by a service facility
before use. If the plug will not fit the outlet, have a proper outlet installed by a
qualified electrician.
GROUNDED TOOLS: TOOLS WITH THREE PRONG PLUGS
Tools marked with “Grounding Required” have a three wire cord and three prong
grounding plug. The plug must be connected to a properly grounded outlet. If
the tool should electrically malfunction or break down, grounding provides a low
resistance path to carry electricity away from the user, reducing the risk of electric
shock. (See Figure A.)
The grounding prong in the plug is connected through the green wire inside the
cord to the grounding system in the tool. The green wire in the cord must be the
only wire connected to the tool’s grounding system and must never be attached to
an electrically “live” terminal. (See Figure A.)
Your tool must be plugged into an appropriate outlet, properly installed and grounded
in accordance with all codes and ordinances. The plug and outlet should look like
those in the following illustration. (See Figure A.)
FIGURE A FIGURE B
DOUBLE INSULATED TOOLS: TOOLS WITH TWO PRONG PLUGS
Tools marked “Double Insulated” do not require grounding. They have a special
double insulation system which satisfies OSHA requirements and complies with
the applicable standards of Underwriters Laboratories, Inc., the Canadian Standard
Association, and the National Electrical Code. (See Figure B.)
1.
2.
3.
1.

Page 7SKU 95607 For technical questions, please call 1-800-444-3353.
Double insulated tools may be used in either of the 120 volt outlets shown in the
preceding illustration. (See Figure B.)
EXTENSION CORDS
Grounded tools require a three wire extension cord. Double Insulated tools can
use either a two or three wire extension cord.
As the distance from the supply outlet increases, you must use a heavier gauge
extension cord. Using extension cords with inadequately sized wire causes a serious
drop in voltage, resulting in loss of power and possible tool damage.
(See Figure C, next page.)
The smaller the gauge number of the wire, the greater the capacity of the cord. For
example, a 14 gauge cord can carry a higher current than a 16 gauge cord.
(See Figure C.)
When using more than one extension cord to make up the total length, make sure
each cord contains at least the minimum wire size required. (See Figure C.)
If you are using one extension cord for more than one tool, add the nameplate
amperes and use the sum to determine the required minimum cord size.
(See Figure C.)
If you are using an extension cord outdoors, make sure it is marked with the suffix
“W-A” (“W” in Canada) to indicate it is acceptable for outdoor use.
Make sure your extension cord is properly wired and in good electrical condition.
Always replace a damaged extension cord or have it repaired by a qualified electrician
before using it.
Protect your extension cords from sharp objects, excessive heat, and damp or wet
areas.
2.
1.
2.
3.
4.
5.
6.
7.
8.

Page 8SKU 95607 For technical questions, please call 1-800-444-3353.
RECOMMENDED MINIMUM WIRE GAUGE FOR EXTENSION CORDS*
(120 OR 240 VOLT)
NAMEPLATE
AMPERES
(at full load)
EXTENSION CORD LENGTH
25 Feet 50 Feet 75 Feet 100 Feet 150 Feet
0 – 2.0 18 18 18 18 16
2.1 – 3.4 18 18 18 16 14
3.5 – 5.0 18 18 16 14 12
5.1 – 7.0 18 16 14 12 12
7.1 – 12.0 18 14 12 10 -
12.1 – 16.0 14 12 10 - -
16.1 – 20.0 12 10 - - -
FIGURE C * Based on limiting the line voltage drop to five volts at 150% of the rated amperes.
SYMBOLOGY
Double Insulated
Canadian Standards Association
Underwriters Laboratories, Inc.
V~ Volts Alternating Current
AAmperes
n0 xxxx/min. No Load Revolutions per Minute (RPM)
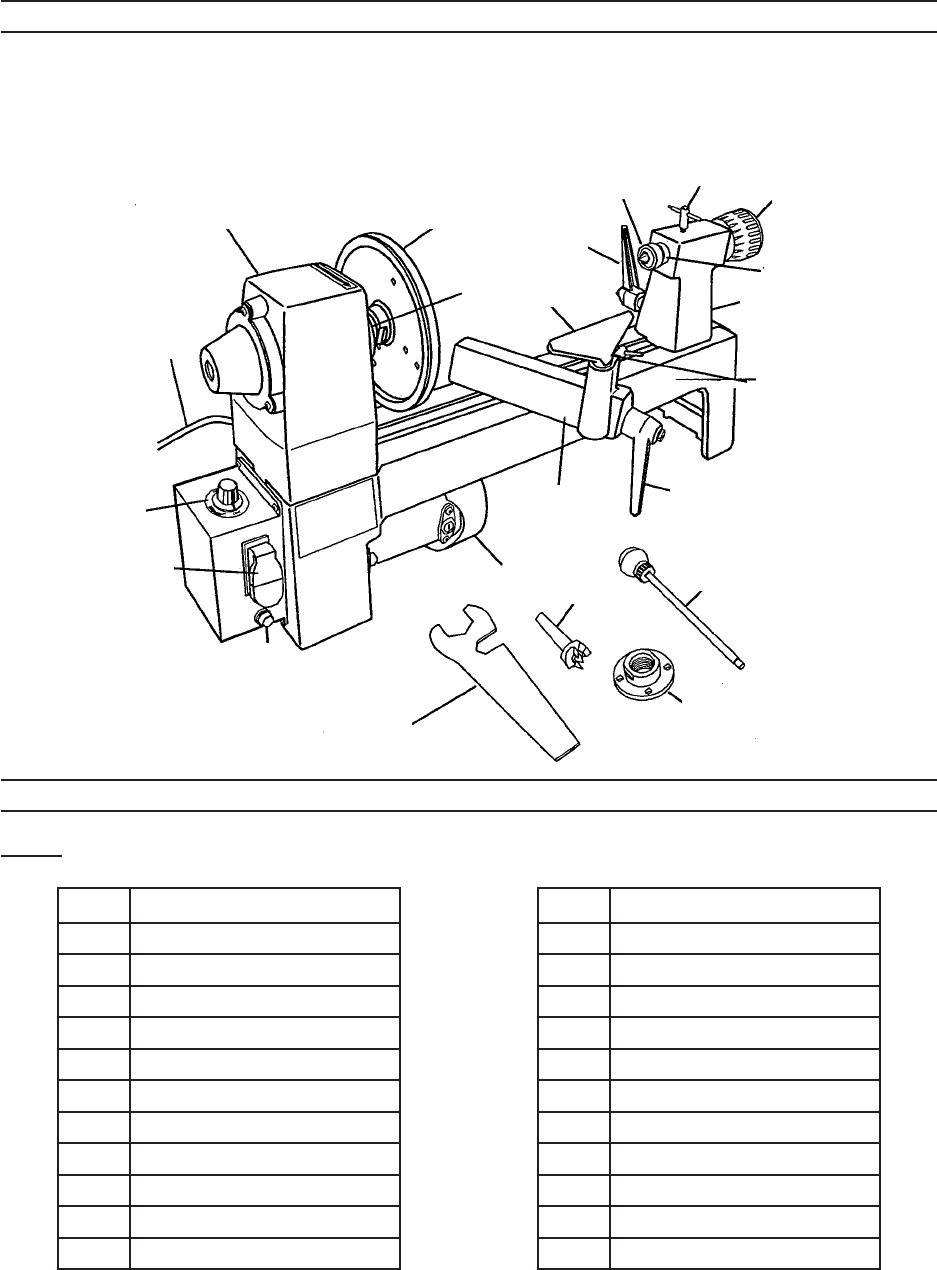
Page 9SKU 95607 For technical questions, please call 1-800-444-3353.
UNPACKING
When unpacking, make sure the item and its accessories and components are
intact and undamaged. If any parts are missing or broken, call Harbor Freight Tools at the
number shown on the cover of this manual as soon as possible. See packing list below.
GENERAL MINI LATHE COMPONENTS
Note: Refer to the parts list and diagram at the end of this manual for complete part number
listings and locations.
Part Description
A Large faceplate
B Headstock spindle
C Headstock
D Power cord
E ON/OFF switch with key
F Speed control knob
G Circuit breaker reset button
H Motor
I Tool rest base
J Base lock lever
K Tool rest lock lever
Part Description
L Tool rest
M Tailstock
N Tailstock spindle
O Hand wheel
P Spindle lock lever
Q Tailstock cup center
R Tailstock lock lever
S Flat wrench
T Headstock spur center
U Small faceplate
V Push-out rod
H
E
A
B
C
D
F
G
IJ
K
LM
N
O
P
Q
R
S
T
U
V

Page 10SKU 95607 For technical questions, please call 1-800-444-3353.
ASSEMBLY INSTRUCTIONS
Note: For additional information regarding the parts listed in the following pages, refer to
the Assembly Diagram near the end of this manual.
WARNING! Make sure the Power Switch of the Lathe is in its “OFF” position and
that the Lathe is unplugged from its electrical outlet before making any adjustments
to the Lathe.
Mount the Lathe on a benchtop by first measuring and marking three hole centers.
See Figure 1.
Drill holes through the marked locations. Be sure there are no hidden wires.
Install the bolts and washers (not included) from under the benchtop and
into the holes in the bottom of the Lathe frame. Please note: To hold
the Lathe securely, the bolts must be a minimum of 1” into the frame.
5. The spring-loaded lock levers for the Tailstock
Spindle (N) and the Tool Rest (L) are made of
separate parts. If either lock lever has come
loose during shipping, they must be reassembled.
6. To reassemble a lock lever, the shoulder screw
passes through the spring and the handle lever and
then into the Tailstock Spindle and Tool Rest, as
shown in Figure 2.
1.
2.
3.
4.
Figure 1
Figure 2
Shoulder
Screw
Spring
Handle
Lever
REV 07l

Page 11SKU 95607 For technical questions, please call 1-800-444-3353.
ASSEMBLY INSTRUCTIONS (CONTINUED)
The Mini Lathe comes with two different sized Faceplates (A). Use the one best
suited to size of the workpiece. Mount the workpiece onto the Faceplate with wood
screws (not provided). Make sure the screws are not so long that they enter the
workspace of where the material is being removed.
Please note: Both Faceplates (A) have an open center. When cutting through
a workpiece from the Tailstock (M), the drill bit can go completely through the
workpiece.
Installing or removing a faceplate:
Make sure the ON/OFF Switch (E) of the tool is in its “OFF” position, the key
removed and the tool is unplugged from its electrical outlet before making
adjustments to the tool. Thread the Faceplate (A) onto the end the Headstock
Spindle (B) and hand tighten.
Place the Wrench (S) over the flats on the Faceplate (A). See Figure 2. Please
note: Since the Headstock Spindle (B) is belt driven, it will turn freely if not held
stationary while the Faceplate (A) is tightened or loosened.
Insert the tip of the Push-out Rod (V) into one of the slots in the side of the
Headstock Spindle (B).
Grip the Push-out Rod (V) firmly while turning the Wrench (S) to either tighten or
loosen the Faceplate (A).
Remove the Push-out Rod (V) and Wrench (S). If the Faceplate (A) is being
removed, continue turning it until it comes off of the spindle threads.
1.
2.
3.
4.
5.
Figure 2
A
S
V

Page 12SKU 95607 For technical questions, please call 1-800-444-3353.
ASSEMBLY INSTRUCTIONS (CONTINUED)
Installing a spur and center:
First, insert the shaft of the Headstock Spur Center (T) into the hollow center of
the Headstock Spindle (B). Please see Figure 3.
Then, insert the shaft of the Tailstock Cup Center (Q) into the hollow center of the
Tailstock Spindle (N). Please see Figure 4.
Removing a spur and center:
Insert the Push-out Rod (V) into the far end of the Headstock Spindle (B) or the
Tailstock Spindle (N) until it comes into contact with the shaft of the Spur Center
(T). See Figure 5.
Tap end of Push-out Rod (V) until the Headstock Spur Center (T) comes loose.
1.
2.
3.
4.
Figure 3
T
Figure 4
Q
Figure 5
V

Page 13SKU 95607 For technical questions, please call 1-800-444-3353.
SPEED CONTROL OPERATION
The variable speed control contains the electrical connections to the motor and
has three external controls - ON/OFF switch (E), Speed Control Knob (F), and
the Circuit Breaker reset button (G). See Figure 6, below.
ON/OFF Switch (controls electrical power to the Lathe’s motor)
WARNING! Always set the Speed Control Knob (F) to its lowest
(counterclockwise) setting before starting the Lathe. Never start a workpiece
at maximum speed. There is a 1 to 3 second delay in motor activation when
starting.
Move the Switch (E) to the ON position to start the motor. The Lathe will begin
turning and driving the Headstock Spindle (B). Please note: A special “soft start”
safety feature does not allow the Lathe to reach full speed until 1 to 3 seconds
after activation. The time it takes the motor to reach the speed set by the Speed
Control Knob (F) depends on the size and weight of the workpiece.
Move the Switch (E) to the OFF position to stop the Lathe. Please note:
The Spindle and workpiece will continue to spin until the motor stops.
CAUTION: Never leave the Lathe unattended until it has come to a complete
stop.
The Switch Key can be pulled out of the Power Switch (E) when it is in the OFF
position. With the Key removed, the Switch (E) is locked in that position and
Lathe cannot be started. Always store the Key in a safe place whenever the
Lathe is left idle.
1.
2.
3.
Figure 6 E
F
G
Key

Page 14SKU 95607 For technical questions, please call 1-800-444-3353.
The Speed Control Knob (F) sets the speed of the Lathe to suit the weight of the
workpiece or the type of tool being used. After the Lathe is started, turn the Knob
(F) clockwise to increase the Spindle speed (up to maximum of 3200 RPM). See
Figure 8.
Turn the Knob (F) counterclockwise to decrease the Spindle speed (down to a
minimum of 750 RPM).
Adjust the Knob (F) until the desired workpiece rotation speed is reached.
1.
2.
3.
SPEED CONTROL OPERATION
Speed Control Knob
The Circuit Breaker Reset Button (G) will reset the Motor (H) after it shuts off
during operation due to overloading or low voltage. See Figure 8.
Turn the ON/OFF Switch (E) to the OFF position.
Wait about 5 minutes for the Motor (H) to cool.
Push the Reset Button (G).
Turn the ON/OFF Switch (E) to the ON position.
1.
2.
3.
4.
5.
Circuit Breaker Reset Button
Figure 8
F
G
E
WARNING! To prevent accidental start-up if Reset Button (G) is
pushed, the ON/OFF Switch (E) should be in OFF position and plug should
be removed from the outlet as the Motor (H) cools. Overheating may be
caused by misaligned parts or dull chisel. Inspect Lathe for proper setup
before using again.

Page 15SKU 95607 For technical questions, please call 1-800-444-3353.
OPERATION INSTRUCTIONS
Move the Tailstock (M) by loosening the
Lock Lever (R) and pushing the Tailstock
to the desired position on the bed. Lock in
place by tightening the Lock Lever (R). See
Figure 9.
The spindle extends up to 2-1/2” from the
Tailstock (M) housing. Move the Tailstock
Spindle (N) by loosening the Spindle Lock
Lever (R) and the Hand Wheel (O).
Turn the Hand Wheel (O) clockwise to
extend the spindle. Turn the Hand Wheel
(O) counterclockwise to retract the spindle.
Then tighten the Spindle Lock Lever (P).
Caution: Always lock the Levers (P) and
(R) before operating the Lathe.
The Tailstock Spindle (N) is hollow and
can be accessed from the Hand Wheel (O)
end. Use the Push-out Rod (V) to remove
the Cup Center (Q), which will then allow
you to drill holes through the center of a
workpiece on a faceplate.
Loosen Base Lock Lever (J) to allow Tool
Rest Base (I) to move to the right or left
and back or front. Tighten Lever (J) when
the Tool Rest Base (I) is in the desired
position on the Lathe bed. See Figure 10.
To adjust the Tool Rest (L), loosen the
Tool Rest Lock Lever (K) to move the Tool
Rest (L) to the center line of the workpiece.
Then tighten the Lock Lever (K).
To change the Tool Rest (L), loosen the
Lock Lever (K) and pull the Tool Rest (L)
out of the Tool Rest Base (I). Insert the
other Tool Rest, adjust to the desired
position, and tighten the Lock Lever (K).
Caution: Make sure the Tool Rest (L) is
adjusted to be as close to the workpiece
as possible. Rotate workpiece by hand to
check clearance before turning on Lathe.
1.
2.
3.
4.
5.
6.
7.
8.
9.
Figure 9
R
P
M
N
O
Figure 10
I
L
J
K

Page 16SKU 95607 For technical questions, please call 1-800-444-3353.
INSPECTION, MAINTENANCE, AND CLEANING
WARNING! Make sure the Power Switch (E) of the Lathe is in its “OFF” position
and that the Lathe is unplugged from its electrical outlet before performing any
inspection, maintenance, or cleaning procedures.
BEFORE EACH USE, inspect the general condition of the Lathe. Check for
loose screws, misalignment or binding of moving parts, cracked or broken
parts, damaged electrical wiring, and any other condition that may affect its safe
operation. If abnormal noise or vibration occurs, have the problem corrected
before further use. Do not use damaged equipment.
Using compressed air, blow out the dust that has accumulated inside the motor,
housing and bed assembly after each use. After using the Tailstock (13) as a
guide for drilling, blow any sawdust or shavings out of the center of both spindles.
Apply a coat of wax to the bed after cleaning. This will keep the surface clean
and the Tool Rest (12) and Tailstock (13) moving smoothly.
Periodically lubricate spring levers and other threaded parts for easier operation.
MAINTENANCE CHART
Maintenance Type Before
Use
After
Use Weekly Monthly Every 6
Months Yearly
Inspect tool for damage
(see #2, above) X
Blow off dust and wipe with
dry cloth XXXXX
Apply coat of wax to bed and
lubricate spring levers XXXXX
1.
2.
3.
4.
5.

Page 17SKU 95607 For technical questions, please call 1-800-444-3353.
PARTS LIST
Part Description Q’ty
1 Bed 1
2 Retaining plate 1
3 PHLP HD screw M5x8 2
4 Special set screw M6x8 1
5 Hand wheel 1
6 Tailstock 1
7 T-lock knob bolt for tailstock 1
8 Cap screw M8x40 2
9 Sleeve 1
10 Eccentric axis 1
11 Tailstock spindle 1
12 Lock Washer 8MM 3
13 Paddle switch 1
14 Live center assembly 1
15 Headstock spur center 1
16 Tailstock lock handle 1
17a Face plate-6” 1
17b Face plate-2” 1
18 Headstock spindle 1
19 Ball bearing 6004ZZ 1
20 Ext. Retaining ring C40 1
21 Retaining ring C40 1
22 Ball bearing 6004ZZ 1
23 Headstock 1
24 Speed dial switch 1
25 Speed dial label 1
26 Headstock spindle nut 1
27 Outboard spindel cover 1
28 PHLP HD screw M4x8 3
Part Description Q’ty
29 Spec label 1
30 Set screw M6x10 1
31 Drive pulley 1
32 Belt K-516 1
33 Set screw M6x10 1
34 Motor pulley 1
35 Power cord 1
36 Variable speed box 1
37 PHLP HD screw M4x8 4
38 Cap screw M8x25 1
39 Cap screw M6x18 1
40 Motor plate 1
41 Motor 1
42 Warning label 1
43 Ext retaining ring 8MM 1
44 Tool rest base 1
45 Special bolt M8x32 1
46 Plate 1
47 Lock nut M8x25 3
48 Sleeve 1
49 Eccentric rod 1
50A Large Tool rest 1
50B Small Tool rest 1
51 Special bolt M8x32 1
52 Plate 1
53 T-lock knob bolt for tool rest 1
54 Tool holder lock handle 1
55 Fuse (not shown) 1
PLEASE READ THE FOLLOWING CAREFULLY
THE MANUFACTURER AND/OR DISTRIBUTOR HAS PROVIDED THE PARTS LIST AND ASSEMBLY
DIAGRAM IN THIS MANUAL AS A REFERENCE TOOL ONLY. NEITHER THE MANUFACTURER OR
DISTRIBUTOR MAKES ANY REPRESENTATION OR WARRANTY OF ANY KIND TO THE BUYER
THAT HE OR SHE IS QUALIFIED TO MAKE ANY REPAIRS TO THE PRODUCT, OR THAT HE OR
SHE IS QUALIFIED TO REPLACE ANY PARTS OF THE PRODUCT. IN FACT, THE MANUFACTURER
AND/OR DISTRIBUTOR EXPRESSLY STATES THAT ALL REPAIRS AND PARTS REPLACEMENTS
SHOULD BE UNDERTAKEN BY CERTIFIED AND LICENSED TECHNICIANS, AND NOT BY THE
BUYER. THE BUYER ASSUMES ALL RISK AND LIABILITY ARISING OUT OF HIS OR HER REPAIRS
TO THE ORIGINAL PRODUCT OR REPLACEMENT PARTS THERETO, OR ARISING OUT OF HIS
OR HER INSTALLATION OF REPLACEMENT PARTS THERETO.

Page 18SKU 95607 For technical questions, please call 1-800-444-3353.
ASSEMBLY DIAGRAM

Page 19SKU 95607 For technical questions, please call 1-800-444-3353.
WIRING DIAGRAM

Page 20SKU 95607 For technical questions, please call 1-800-444-3353.
LIMITED 90 DAY WARRANTY
Harbor Freight Tools Co. makes every effort to assure that its products meet high
quality and durability standards, and warrants to the original purchaser that this product
is free from defects in materials and workmanship for the period of 90 days from the date
of purchase. This warranty does not apply to damage due directly or indirectly, to misuse,
abuse, negligence or accidents, repairs or alterations outside our facilities, criminal activity,
improper installation, normal wear and tear, or to lack of maintenance. We shall in no event
be liable for death, injuries to persons or property, or for incidental, contingent, special
or consequential damages arising from the use of our product. Some states do not allow
the exclusion or limitation of incidental or consequential damages, so the above limitation
of exclusion may not apply to you. THIS WARRANTY IS EXPRESSLY IN LIEU OF ALL
OTHER WARRANTIES, EXPRESS OR IMPLIED, INCLUDING THE WARRANTIES OF
MERCHANTABILITY AND FITNESS.
To take advantage of this warranty, the product or part must be returned to us with
transportation charges prepaid. Proof of purchase date and an explanation of the complaint
must accompany the merchandise. If our inspection verifies the defect, we will either
repair or replace the product at our election or we may elect to refund the purchase price
if we cannot readily and quickly provide you with a replacement. We will return repaired
products at our expense, but if we determine there is no defect, or that the defect resulted
from causes not within the scope of our warranty, then you must bear the cost of returning
the product.
This warranty gives you specific legal rights and you may also have other rights
which vary from state to state.
3491 Mission Oaks Blvd. • PO Box 6009 • Camarillo, CA 93011 • (800) 444-3353