Hexagon Geosystems Services QC235A safeMINE 700018 User Manual Manual
Safemine Ltd safeMINE 700018 Manual
Manual
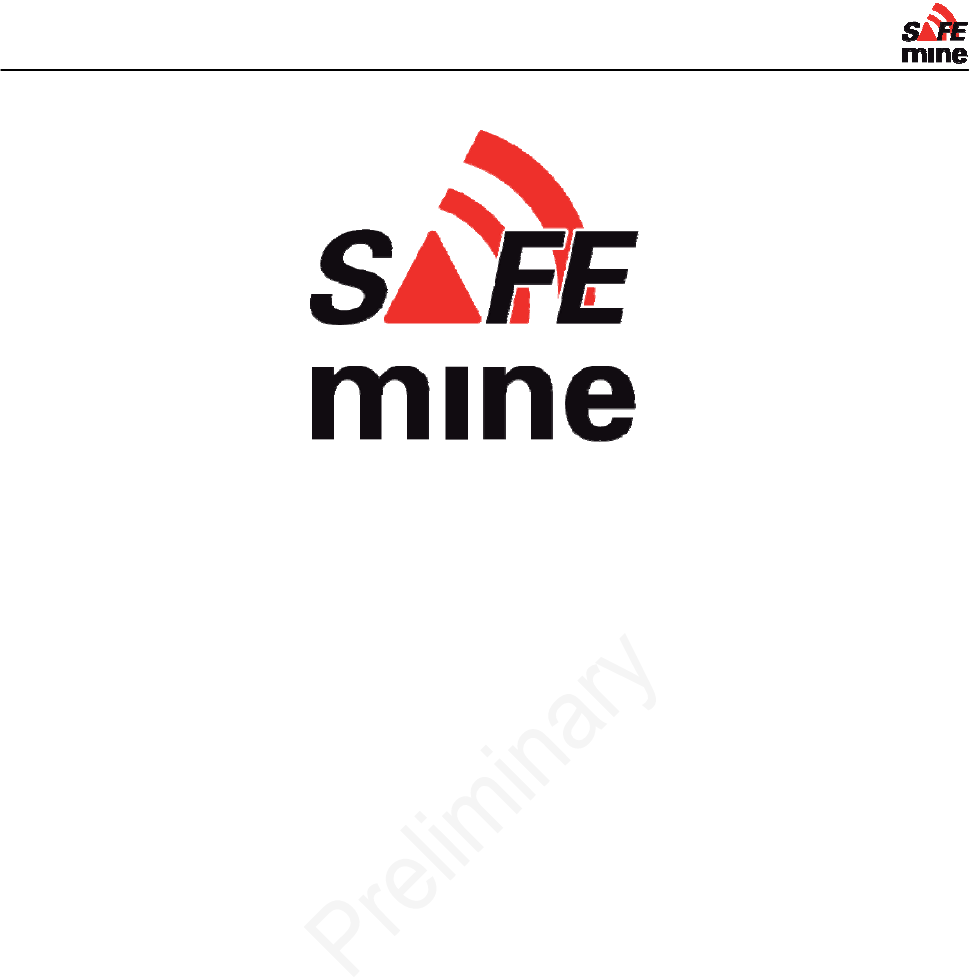
I
NSTALLATION AND
M
AINTENANCE
G
UIDE
Version 110301, Preliminary Page 1 of 56 March 2011
®
INSTALLATION AND
MAINTENANCE GUIDE
FOR
SAFEMINE COLLISION
AVOIDANCE SYSTEMS
FIRMWARE VERSION 2.20
SMTOOL VERSION 1.30
MARCH 1ST, 2011
© 2009-2011 SAFEMINE LTD.
SWITZERLAND
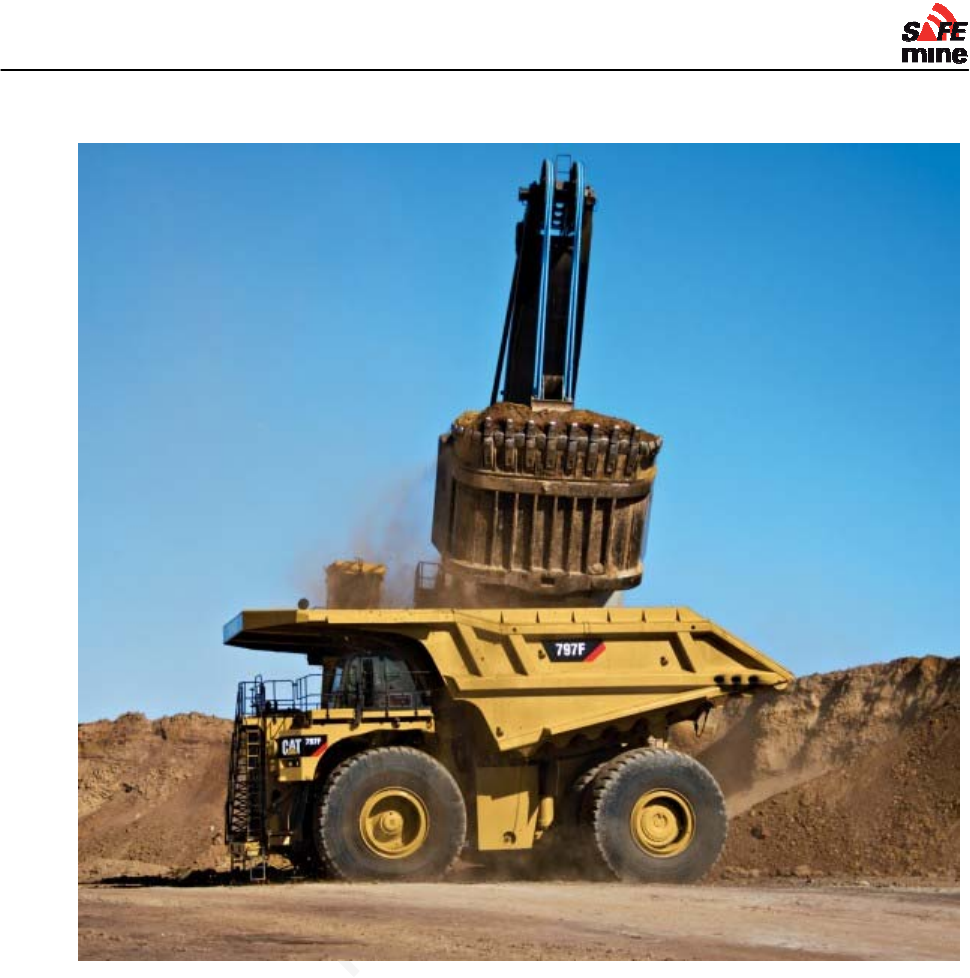
I
NSTALLATION AND
M
AINTENANCE
G
UIDE
Version 110301, Preliminary Page 2 of 56 March 2011
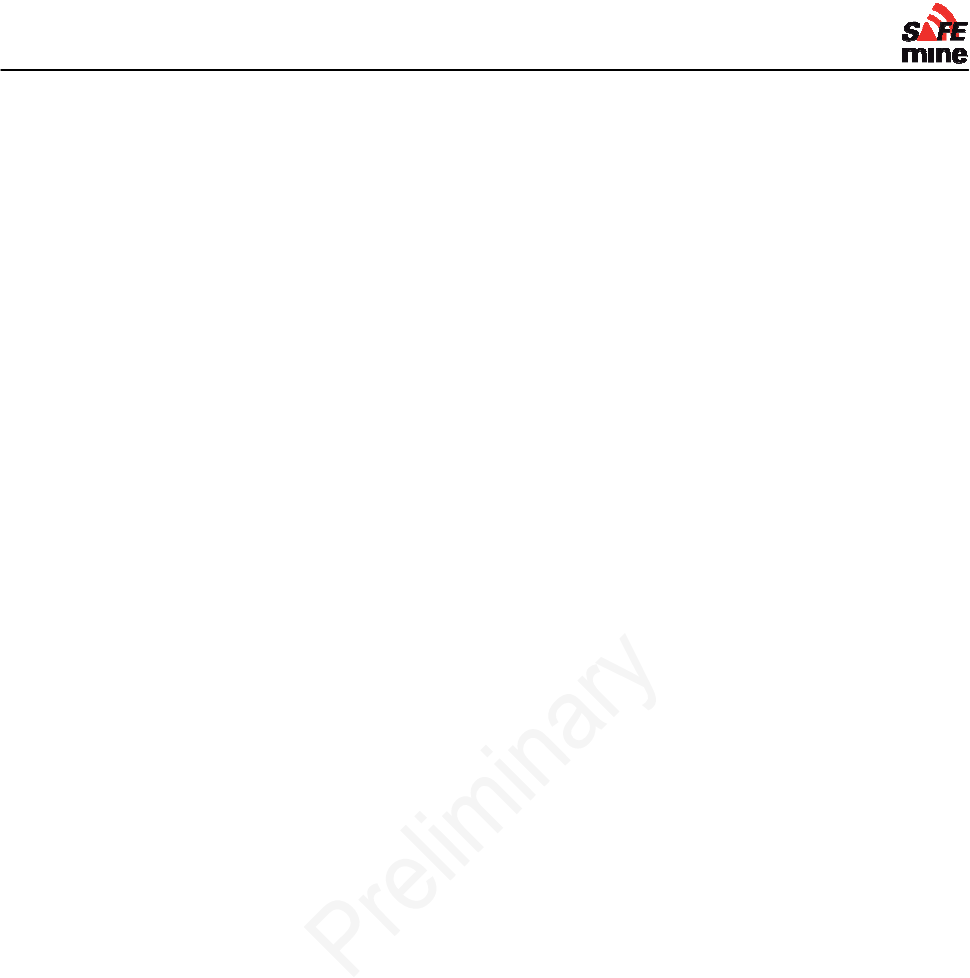
I
NSTALLATION AND
M
AINTENANCE
G
UIDE
Version 110301, Preliminary Page 3 of 56 March 2011
Section 1 – Hardware ...................................................................................................................... 6
Safety ............................................................................................................................................... 7
System .......................................................................................................................................... 7
Installation ..................................................................................................................................... 7
Introduction ..................................................................................................................................... 8
Objective ....................................................................................................................................... 8
Technology .................................................................................................................................... 8
Implementation .............................................................................................................................. 8
Limitations ..................................................................................................................................... 8
Components .................................................................................................................................. 10
Main units .................................................................................................................................... 10
GPS ......................................................................................................................................... 10
Radio Frequency (RF) communication .................................................................................... 10
Low power behavior ................................................................................................................. 10
Installing the Main Unit ................................................................................................................ 11
Connector Details – Main Unit ................................................................................................. 12
Specifications for QC230/235: ................................................................................................. 13
GPS & RF Antenna ..................................................................................................................... 15
Antenna Models ....................................................................................................................... 15
Specifications for the GPS / RF Antenna .................................................................................... 15
Remote Display unit .................................................................................................................... 17
Connections – Remote Display ............................................................................................... 17
Specification for Remote Display ............................................................................................. 17
Connectors and Cabling .............................................................................................................. 19
Antenna Cables ....................................................................................................................... 19
Section 2 – Software and Programming ..................................................................................... 20
Programs and Files ....................................................................................................................... 21
Required Components ................................................................................................................ 21
Firmware and the Configuration File ........................................................................................ 22
Remote Management .................................................................................................................. 23
File up- download over RF .......................................................................................................... 23
SAFEmine Configuration Tool (discontinued) ............................................................................. 24
Configuration file .......................................................................................................................... 25
Sample configuration file ............................................................................................................. 25
Site Specific Parameters ............................................................................................................. 26
Radio Channel ......................................................................................................................... 26
Channel Hopping ..................................................................................................................... 26
Minimum required parameters .................................................................................................... 27
Vehicle ID ................................................................................................................................ 27
Vehicle Type ............................................................................................................................ 27
Vehicle Dimensions ................................................................................................................. 28
Antenna position ...................................................................................................................... 28
Optional parameters .................................................................................................................... 28
LED Notification Distances ...................................................................................................... 28
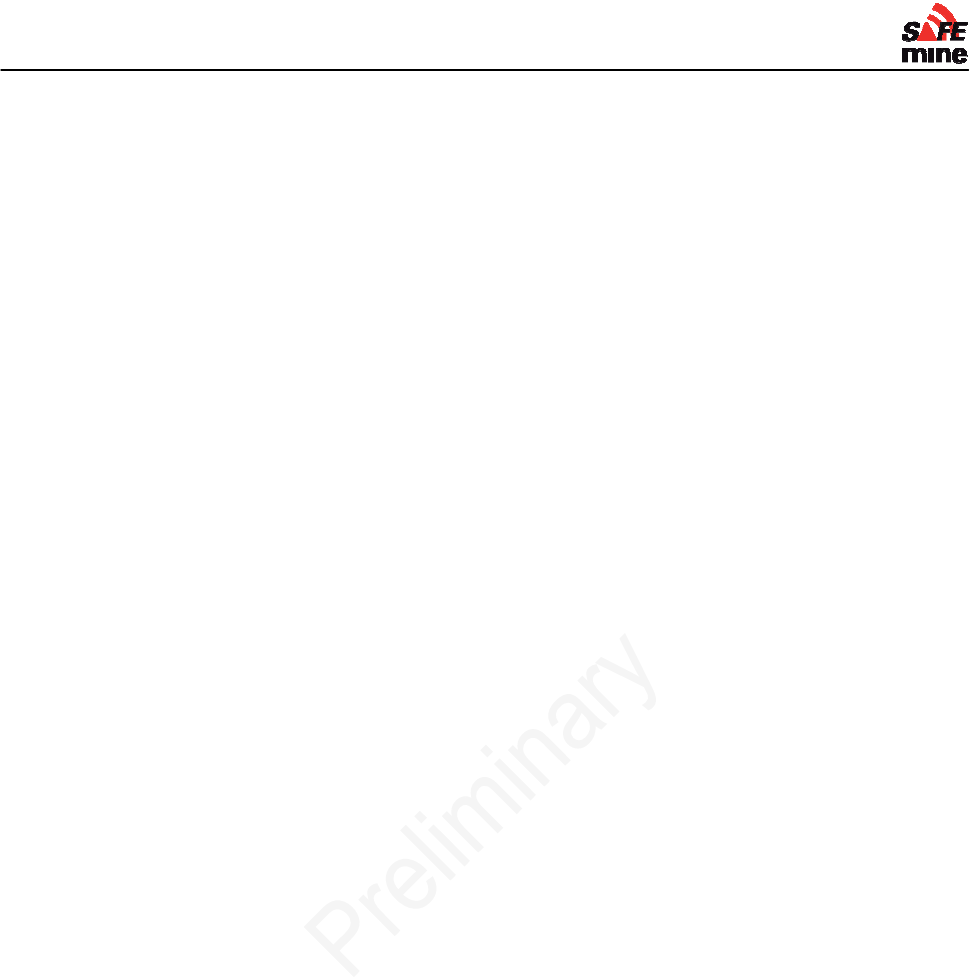
I
NSTALLATION AND
M
AINTENANCE
G
UIDE
Version 110301, Preliminary Page 4 of 56 March 2011
Safety Length ........................................................................................................................... 29
Vehicle data ............................................................................................................................. 29
Buzzer volume ......................................................................................................................... 29
User Interface Mask ................................................................................................................. 29
Reducing nuisance alarms .......................................................................................................... 29
Infobeep ...................................................................................................................................... 29
Alarm Suppressions ................................................................................................................. 30
Maximum exception speed ...................................................................................................... 32
Optional Features ......................................................................................................................... 34
Speeding Alert ......................................................................................................................... 34
Rollover alert ............................................................................................................................ 34
Voice output ................................................................................................................................ 34
Data Recording ........................................................................................................................... 34
Log interval .............................................................................................................................. 34
Obstacles .................................................................................................................................... 35
Areas ........................................................................................................................................... 36
Stockpile Collision Avoidance ..................................................................................................... 36
Special configurations ................................................................................................................. 37
Test Station ................................................................................................................................. 37
Examples ................................................................................................................................. 38
Rotating Vehicles (Patent Pending) ............................................................................................ 39
Minimum Turn Radius .............................................................................................................. 39
Usage ...................................................................................................................................... 39
Limitations ................................................................................................................................ 39
Dual Zone vehicles ...................................................................................................................... 41
Digital I/O ..................................................................................................................................... 41
Visual Displays and Alarms ......................................................................................................... 41
Alarm "Hysteresis" ....................................................................................................................... 42
Inside detection ........................................................................................................................... 42
Button press recording ................................................................................................................ 42
Error codes .................................................................................................................................... 43
Limitations ..................................................................................................................................... 44
Section 3 – Installation and Maintenance ................................................................................... 45
Installation ..................................................................................................................................... 46
General Advice ............................................................................................................................ 46
Recommended installation procedure ......................................................................................... 46
Maintaining the System ................................................................................................................ 47
DECLARATION OF CONFORMITY ............................................................................................... 47
Appendix A: Recommended parts ............................................................................................. 48
Appendix B: Additional Figures and Drawings .......................................................................... 49
Antenna Cable ............................................................................................................................. 49
Battery Cable ............................................................................................................................... 49
Appendix C: Installation Checklist .............................................................................................. 50
Appendix D: Maintenance Checklist ........................................................................................... 51
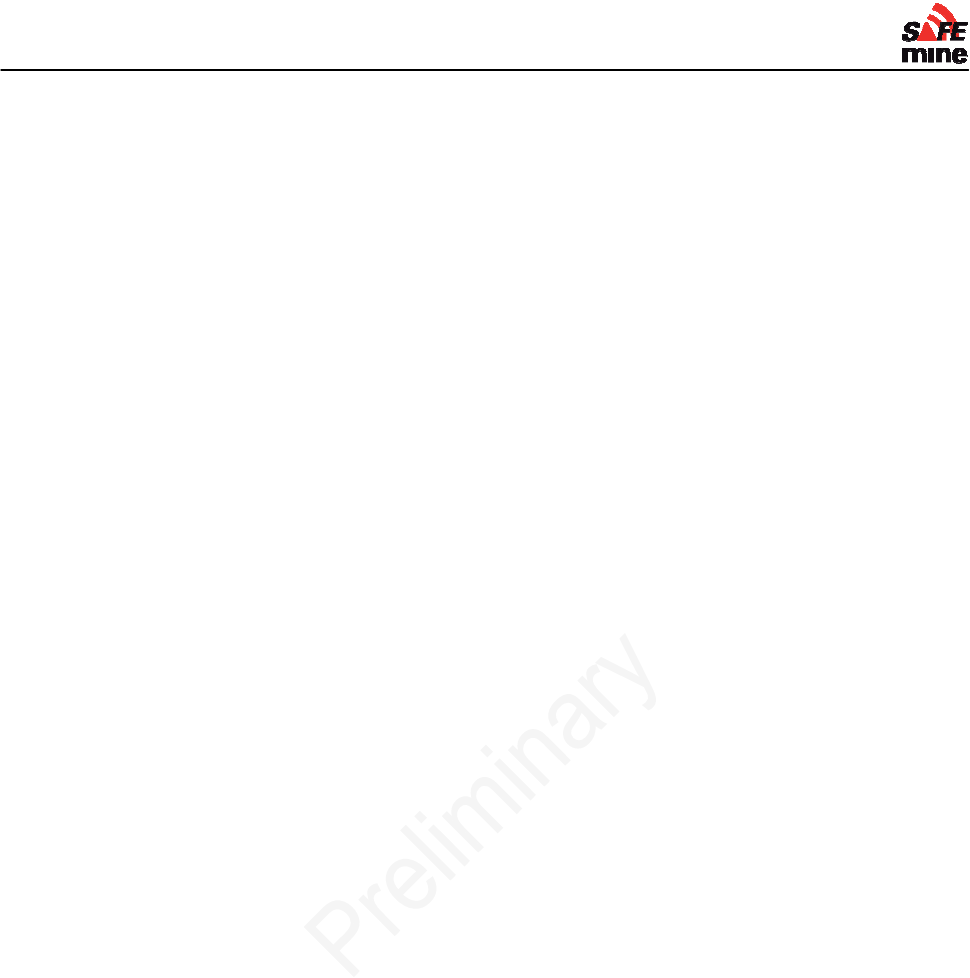
I
NSTALLATION AND
M
AINTENANCE
G
UIDE
Version 110301, Preliminary Page 5 of 56 March 2011
Appendix E: Troubleshooting guide ........................................................................................... 52
Main Unit Power .......................................................................................................................... 55
Power Cable ............................................................................................................................ 55
Fuse ......................................................................................................................................... 55
Remote Display Connection ........................................................................................................ 55
Antenna and Cable ...................................................................................................................... 56
Connection ............................................................................................................................... 56
Crimp Contacts ........................................................................................................................ 56
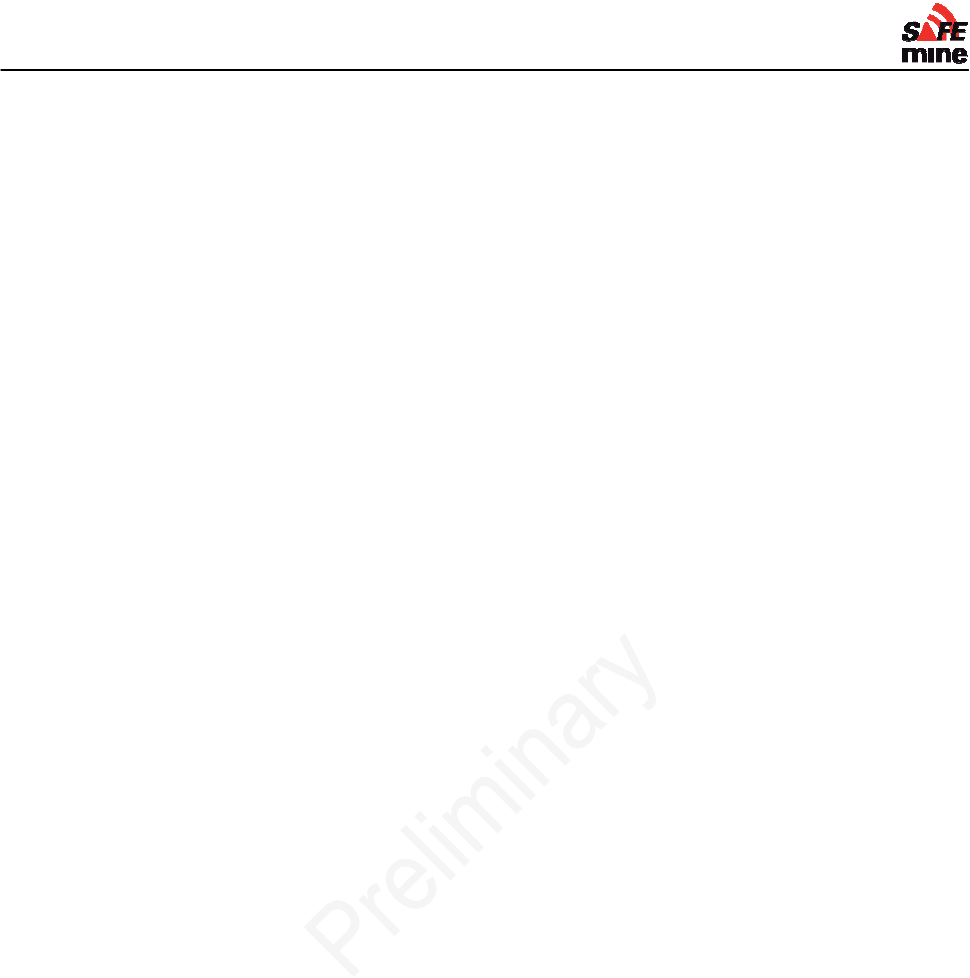
I
NSTALLATION AND
M
AINTENANCE
G
UIDE
Version 110301, Preliminary Page 6 of 56 March 2011
Section 1 – Hardware
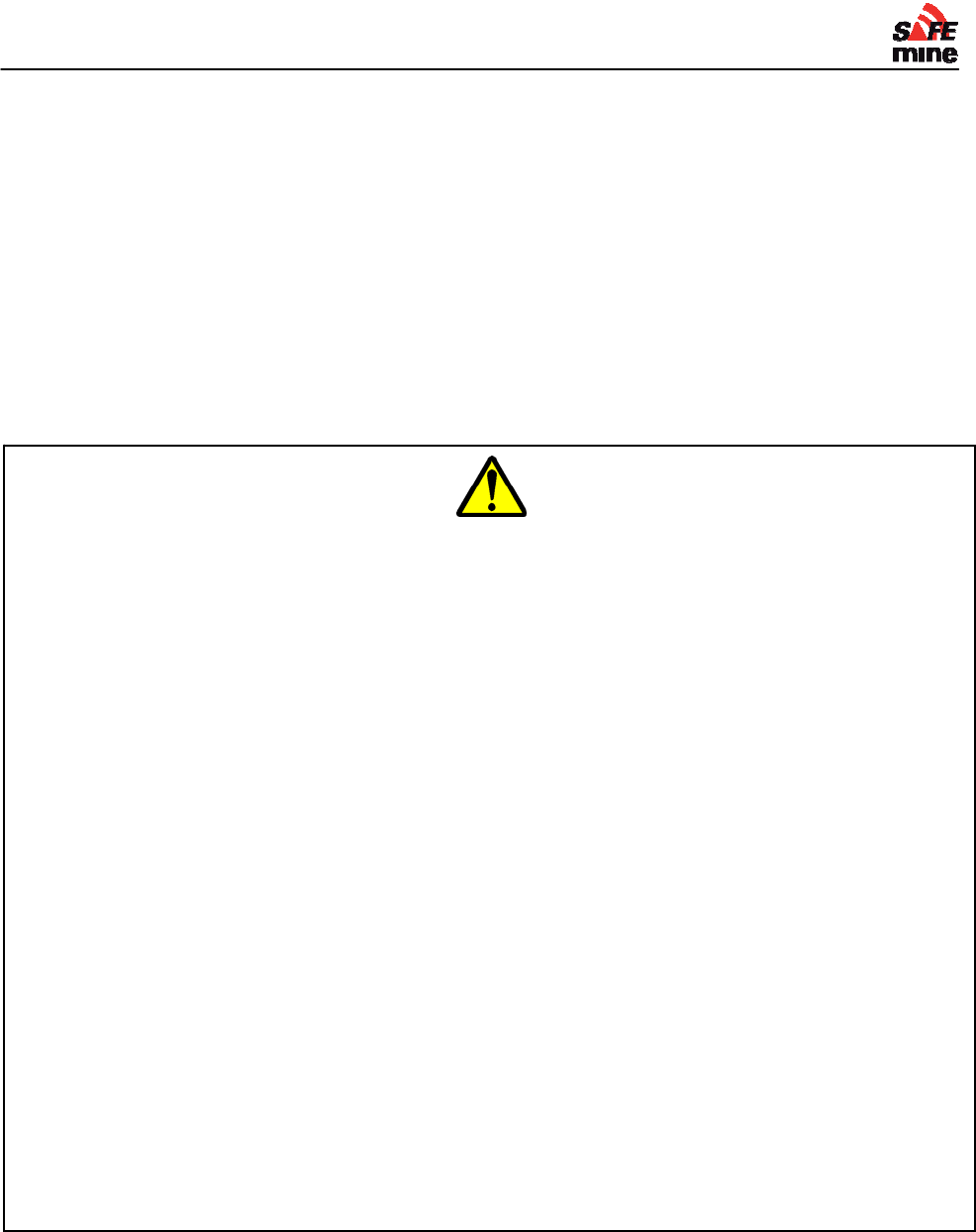
I
NSTALLATION AND
M
AINTENANCE
G
UIDE
Version 110301, Preliminary Page 7 of 56 March 2011
Safety
System
Operating any type of vehicle inside a mine at any time of the day is an inherently dangerous
activity which is associated with considerable risks for crew, passengers, third parties, pedestrians,
other vehicles and any object in its vicinity. In order to make full and safe use of SAFEmine QC200
series products, it is absolutely essential to be fully aware of the risks, operating conditions,
restrictions and limitations associated with their use, including to ensure a proper installation and to
perform regular software updates. This includes familiarity with and strict adherence to the
Operating Manual and the Installation Manual.
Installation
All work done to install the SAFEmine Collision Avoidance System shall be done in accordance
with safe work standards and shall comply with the latest Health, Safety, and Reclamation Code
for Mines in the local jurisdiction.
A vehicle equipped with the SAFEmine System must be operated in the same safe manner
as if the SAFEmine System was not installed. The system is not a substitute for normal
safe driving procedures and may never be relied upon.
The SAFEmine System will provide no warning for some hazards, such as vehicles,
obstacles, and other objects not equipped with properly operating SAFEmine devices.
SAFEmine products are intended as an additional tool in determining potential traffic threats,
supporting an alert and conscientious driver. SAFEmine products are never to be used in any
application where failure of the products could result in personal injury or material damage.
Before using, the latest versions of the respective manuals are to be consulted for familiarization
with product operation and limitations.
SAFEMINE
MAKES
NO
WARRANTIES
WITH
RESPECT
TO
THE
PRODUCT.
IN
NO
EVENT
WILL
SAFEMINE
LTD.
BE
LIABLE
FOR
LOST
USE,
PROFITS,
REVENUE,
COST
OF
PROCUREMENT
OF
SUBSTITUTE
GOODS,
OR
ANY
DAMAGES.
SAFEmine products may not be used in the USA and Canada unless the operator or customer
has been authorized to do so in writing by SAFEmine Ltd.
Customers agree to indemnify and hold harmless SAFEmine Ltd., its subsidiaries, and affiliates,
and their respective successors and assigns, from and against all third party claims, loss,
damage or expense, and any other liabilities whatsoever, which may be incurred by SAFEmine
Ltd. with respect to any of the SAFEmine products.
In addition, SAFEmine Ltd.'s current "General Terms and Conditions of Sale" apply.
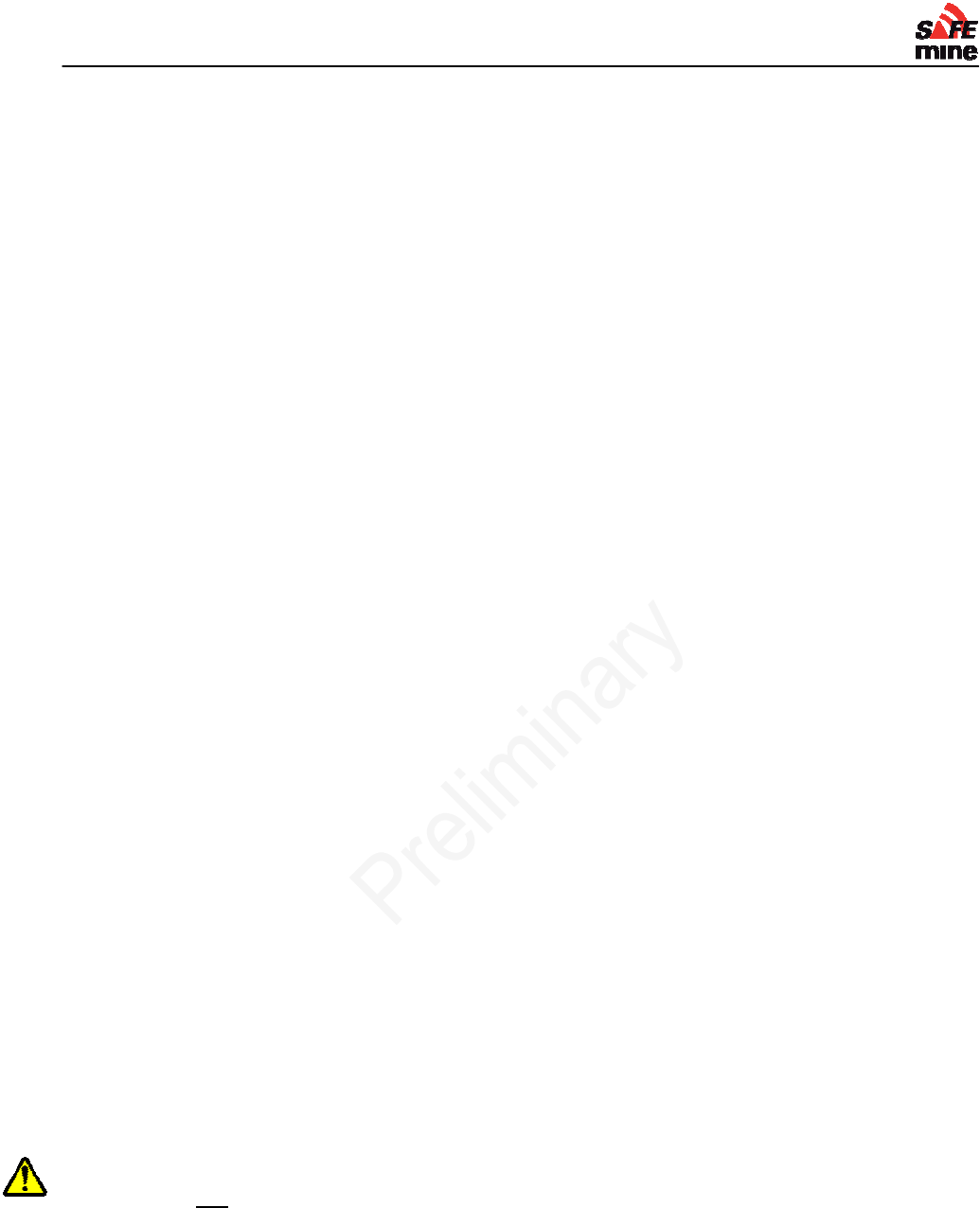
I
NSTALLATION AND
M
AINTENANCE
G
UIDE
Version 110301, Preliminary Page 8 of 56 March 2011
Introduction
Objective
The main task for SAFEmine QC200 series products is to support the operator, while he scans the
space ahead and around the vehicle with his own eyes, cameras and other aids. SAFEmine
products are simple to use and are designed not to distract the operator from operating the vehicle.
Technology
The SAFEmine system – based on technology widely used in aviation – consists of a main unit, an
operator's interface (both output and input) and a dual antenna (one for GPS, one for radio
communication). Depending on the product selected, the operator's interface is integrated into the
main unit, or mounted as a separate display unit. The main unit contains all main sensors (GPS
engine, radio transceiver, micro-controller, memory, data interfaces and a series of sensors), The
operator interface provides both a directional display of nearby traffic and danger, the
beeper/loudspeaker for acoustical warnings and one button for input.
SAFEmine QC200 series products receive position and movement information from an internal
high-sensitivity 50 channel GPS receiver with an external antenna. Additional sensors and logic
further enhances the accuracy of position measurements. The predicted driving path of the vehicle
in which a SAFEmine QC200 series product is installed, is calculated by the main unit and the
obtained information is transmitted by radio, as a low power digital burst signal at frequent
intervals. Provided they are within receiving range, these signals are received by other vehicles
also equipped with SAFEmine QC200 series products. The incoming signal is compared with the
driving path calculated and predicted for the second vehicle, taking into account configuration
parameters like maximum acceleration or vehicle dimension. At the same time, SAFEmine QC200
series products optionally compare the predicted driving path with known static obstacle data, e.g.
electric power lines.
Implementation
If a SAFEmine QC200 series product determines the risk of dangerous proximity to another vehicle
or to an obstacle equipped with a SAFEmine QC200 series product, the unit gives the operator a
warning of the greatest danger at that moment. This warning is given by a buzzing sound (beep)
and bright light emitting diodes (LED). The display also gives indication of the threat level, plus the
horizontal bearing to the threat.
The operating range is very dependent upon the antenna installation in or outside the vehicle. The
normal range is about 500m for line-of-sight operations, but up to 2 km may be achieved in
individual cases.
For their radio communication, SAFEmine QC200 series products use a proprietary patent- and
copyright-protected protocol. Any non-licensed use, dissemination, copying, implementation or
reverse engineering of the SAFEmine QC200 series radio communication protocol, their hardware
and software or parts of it is forbidden by law and will be prosecuted. SAFEmine is a registered
trademark and may not be used without license.
Limitations
SAFEmine is not designed for use
in deep or narrow open pit mines where availability of GPS satellites is not sufficient
in any other application than open pit mining
on vehicles with excessive vibration
SAFEmine units are only to be used with other SAFEmine units, otherwise inconsistent function
may occur. SAFEMINE Ltd. cannot assume any liability from correct or incorrect use of above
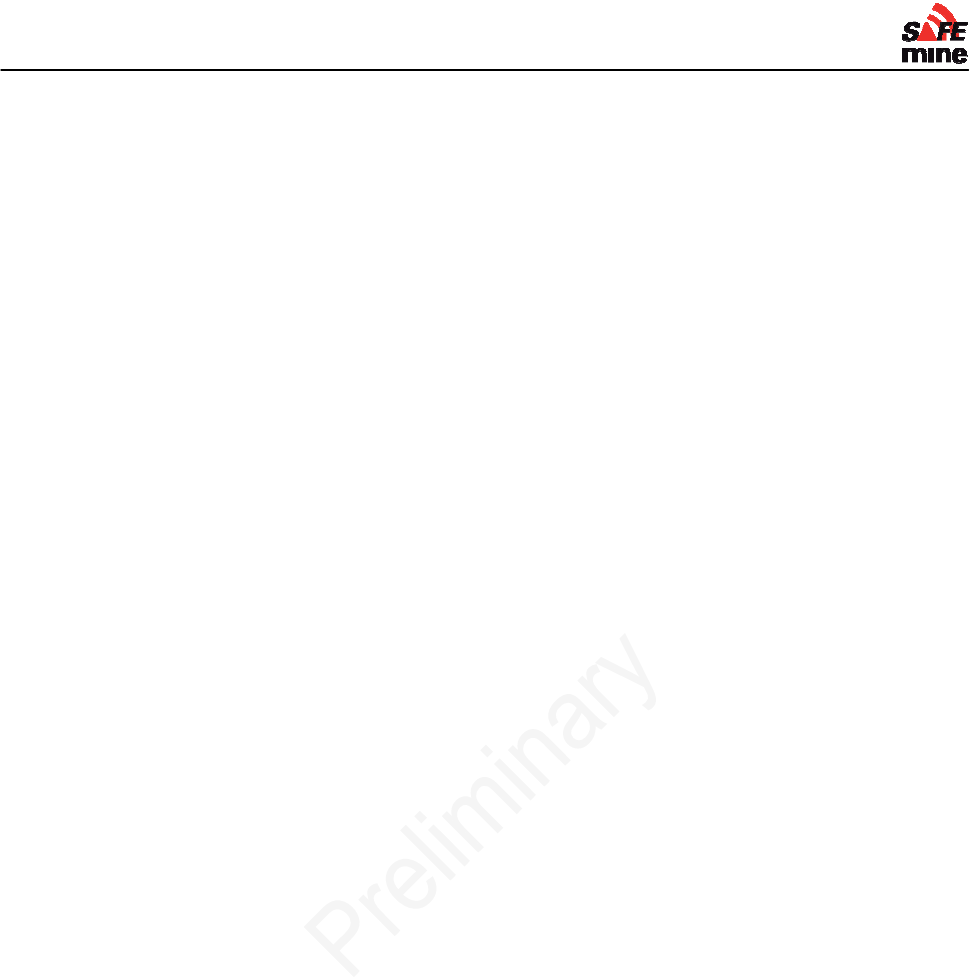
I
NSTALLATION AND
M
AINTENANCE
G
UIDE
Version 110301, Preliminary Page 9 of 56 March 2011
specified products other than regular warranty according to SAFEmine Ltd. General Terms and
Conditions.
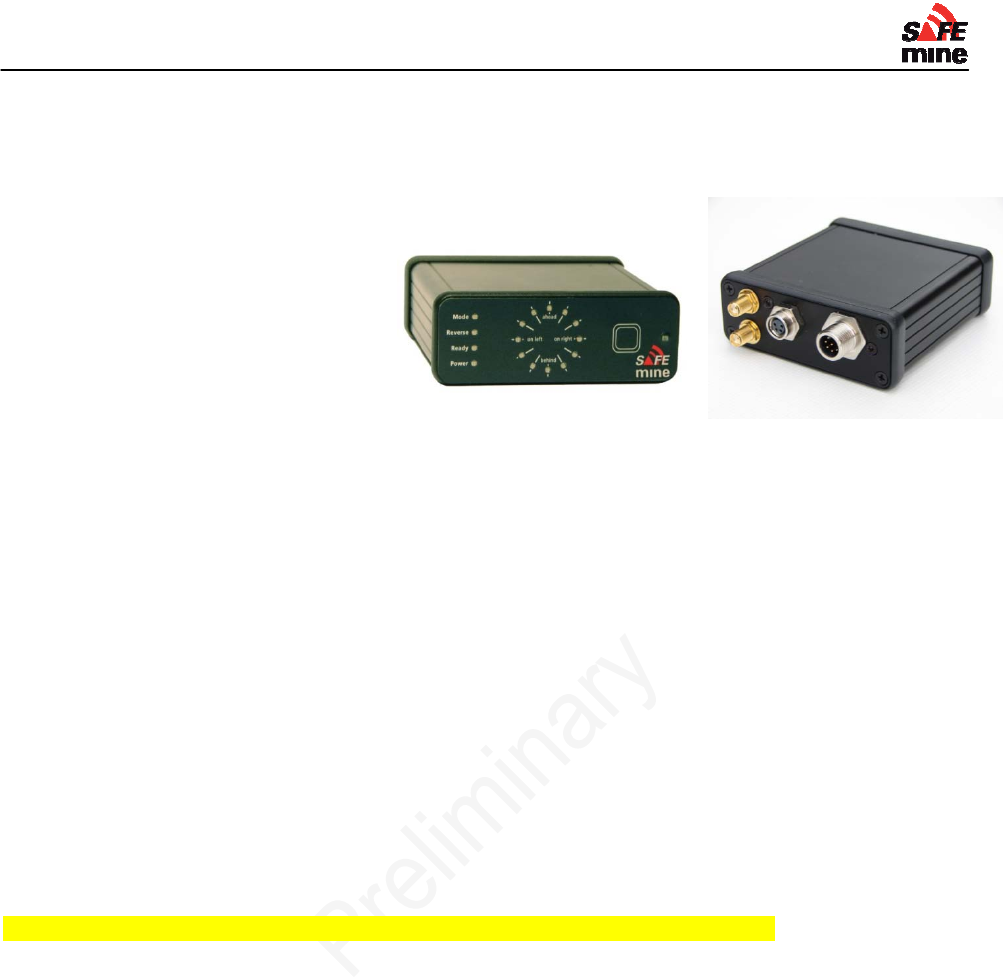
I
NSTALLATION AND
M
AINTENANCE
G
UIDE
Version 110301, Preliminary Page 10 of 56 March 2011
Components
Main units
The main unit houses the GPS
receiver, radio transceiver, processor,
interface logic and additional sensors.
The housing is made of aluminum
with plastics end-bezels. All
connectors are on the back side of the
unit.
The Main Unit is produced in two versions: Model QC235, with an integrated operator display, as
shown above, and the Model QC 230, which utilizes a separate remote display connected by
means of the Remote Display Cable, part number QD221.
GPS
50 channel GPS L1 receiver with SBAS (WAAS, EGNOS) capability, integrated RAIM (Receiver
Autonomous Integrity Monitoring) and active multipath detection and elimination algorithms;
GALILEO ready.
Radio Frequency (RF) communication
Less than 1 % Duty Cycle, Peak Pulse Power10 mW (ERP).
License free ISM / SRD bands, software selectable depending on country of use
Europe, Africa: 868.2 and 868.4 MHz, others
Australia: 921MHz
North America: around 951MHz
South America: around 951MHz
Asia: various
Country of Origin: Switzerland, Harmonized System Customs Code 852610
Low power behavior
If supply voltage is below 9.6V at startup, a ‘low supply power’ error is displayed and the device will
not power up.
If voltages below 9.6V are observed at any time during operation, the ‘Power’ LED will turn red and
‘Error Power’ is announced every 30 seconds on the voice output as long as there is sufficient
voltage to do so. At voltages below 9V the operation of the SAFEmine unit is no longer
guaranteed.
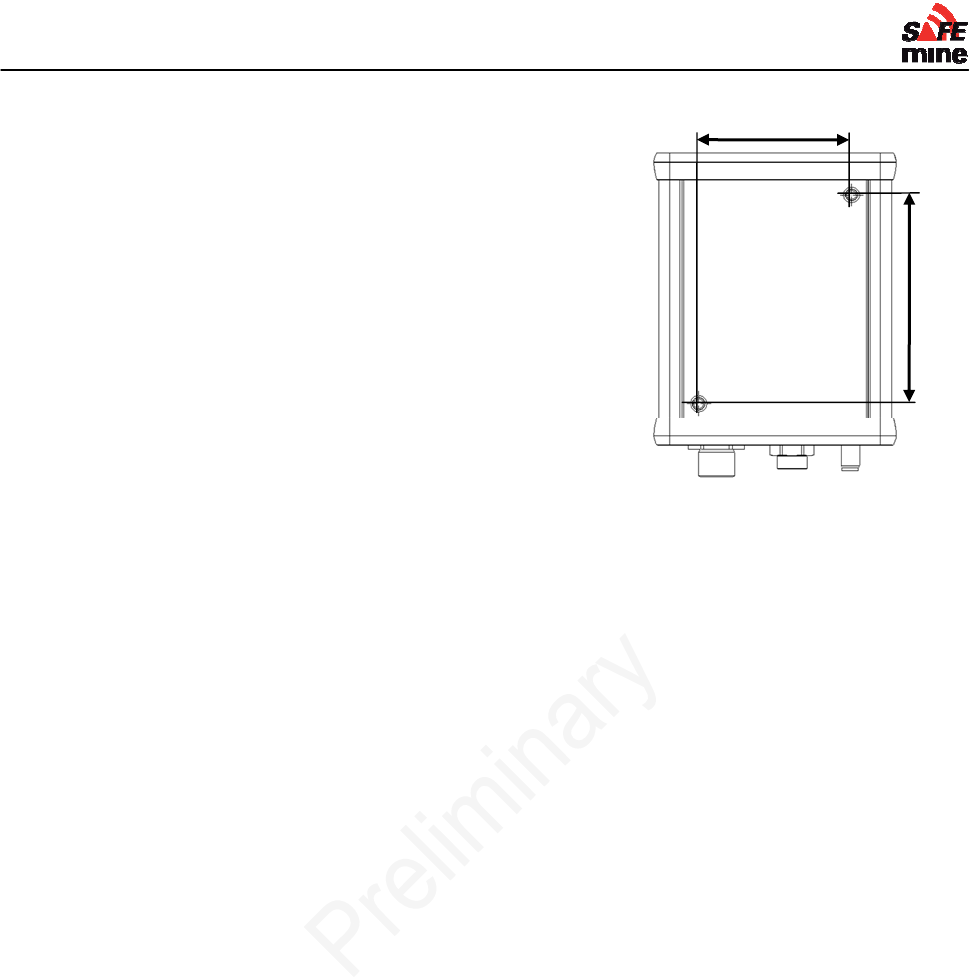
I
NSTALLATION AND
M
AINTENANCE
G
UIDE
Version 110301, Preliminary Page 11 of 56 March 2011
Installing the Main Unit
It must be assured that only one SAFEmine QC200 series
product is operated per vehicle.
The main unit must be secured in such a position that the
operator has the front panel display with the LEDs in direct view,
can hear the acoustic warning tone and can operate the control
button. The front panel display may not be obstructed at any
time.
The main unit must not impede the operation of the vehicle (incl.
emergency procedures) and in particular it must not reduce the
operators field of view.
The connectors at the back of the main unit must remain
accessible to allow the upload of firmware and maintenance
from a PC with an extension cable.
Cables must not be bent or attached under stress. The installation must allow adequate space for
cable connectors and antennae cables.
The lower face of the main units’ aluminum housing includes two blind threads, so that the housing
can easily be secured by two M4 screws. Forcing longer than 8 mm screws into the nuts may
cause damage! The unit should be installed on a flat surface so that the housing is not subject to
any mechanical stress. 3D Models (Solidworks) of the housing and all connectors are available on
request.
Care should be taken not to allow the devices to be exposed to liquids. Should the unit
become humid, it must be thoroughly dried prior to use. Wet devices can sustain permanent
damage. Sudden massive cooling should be avoided, as condensation may occur inside the unit.
The main unit should be connected directly to battery power to ensure continued operation in
case of vehicle stopping or breakdown. A 3A fuse should be installed near the vehicles battery on
both power and ground. A sealable fuse holder is highly recommended. Furthermore the fuse
should be secured with a cable tie to make any tampering obvious.
If vehicle is equipped with a "breaker" the housing should not be connected to vehicle ground as
otherwise a ground loop occurs.
The housing is black to minimize glare and is specified for temperatures from -40°C to +85°C.
It is recommended to attach the cables to the vehicle in a semi permanent way (e.g. cable ties), so
they can easily be (re)moved for service and maintenance.
51mm
70mm
Figure 3 Main unit bottom view
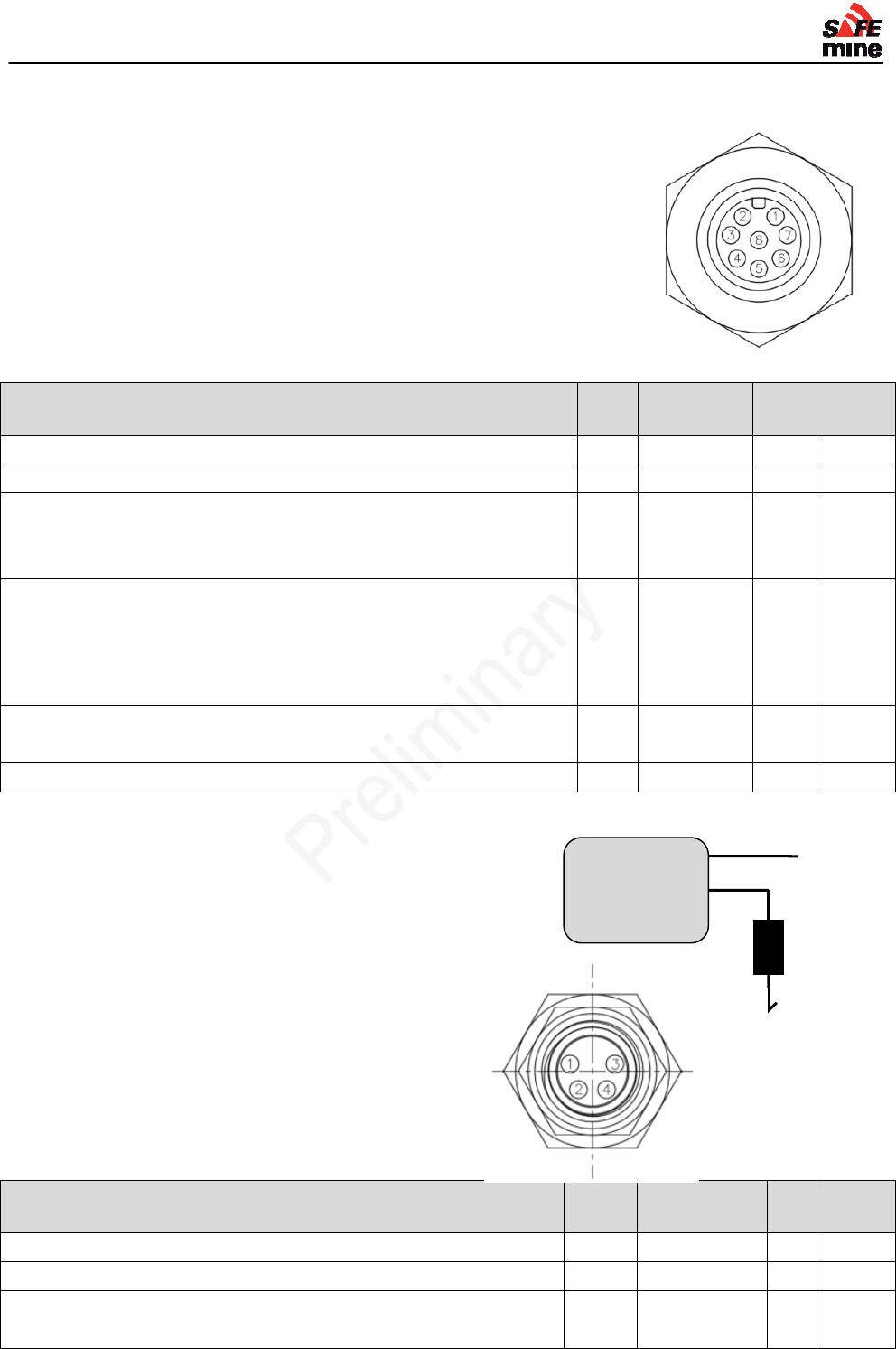
I
NSTALLATION AND
M
AINTENANCE
G
UIDE
Version 110301, Preliminary Page 12 of 56 March 2011
Connector Details – Main Unit
Power / Interface connector
To vehicle or add-on modules
Type M12 male, 8 contacts
Pin function # of
pins Pin type Pin
# Cable
color
Ground 1 Power 2 brown
Power (+9 to +28VDC) overvoltage and polarity protected 1 Power in 1 white
Digital I/O (optional)
use to control power down modes e.g. connect to ignition
May also be used to switch a load (see below) (0-28V, 0.4A)
1 Input /
Output 7 blue
RS485 (optional)
for GPS augmentation input, Modbus for IO modules
Allows interfacing to a wide range of commercially available
input / output modules, such as switches to control cameras on
haul trucks
2 Input (RX)
Output
(TX)
5
6
gray
pink
CAN listener (optional) (typically J1939, ISO 11898) 2 IO H
L 3
4
green
yellow
Audio (voice) out (optional) 1 Output 8 red
Digital Output (pin 7):
"High Side Switch"
maximum continuous load current: 0.4A
may switch capacitive, inductive and resistive loads
On-state resistance: 350mOhm
short circuit protected
ESD protection: 5kV
Pulled up with 4.7kOhm
Display / Update connector
Data and power to remote display and other peripherals
Type M8 female, 4 contacts
Pin function # of
pins Pin type Pi
n # Cable
color
Ground 1 Power 3 blue
12V out (sanitized) 1 Power 1 brown
RS 232 (data to display and for updates)
Firmware can be updated through this interface.
2 Input (RX)
Output (TX)
2
4
white
black
Load
Power
(2, white)
QC23x
Load GND
I/O
(7, blue)
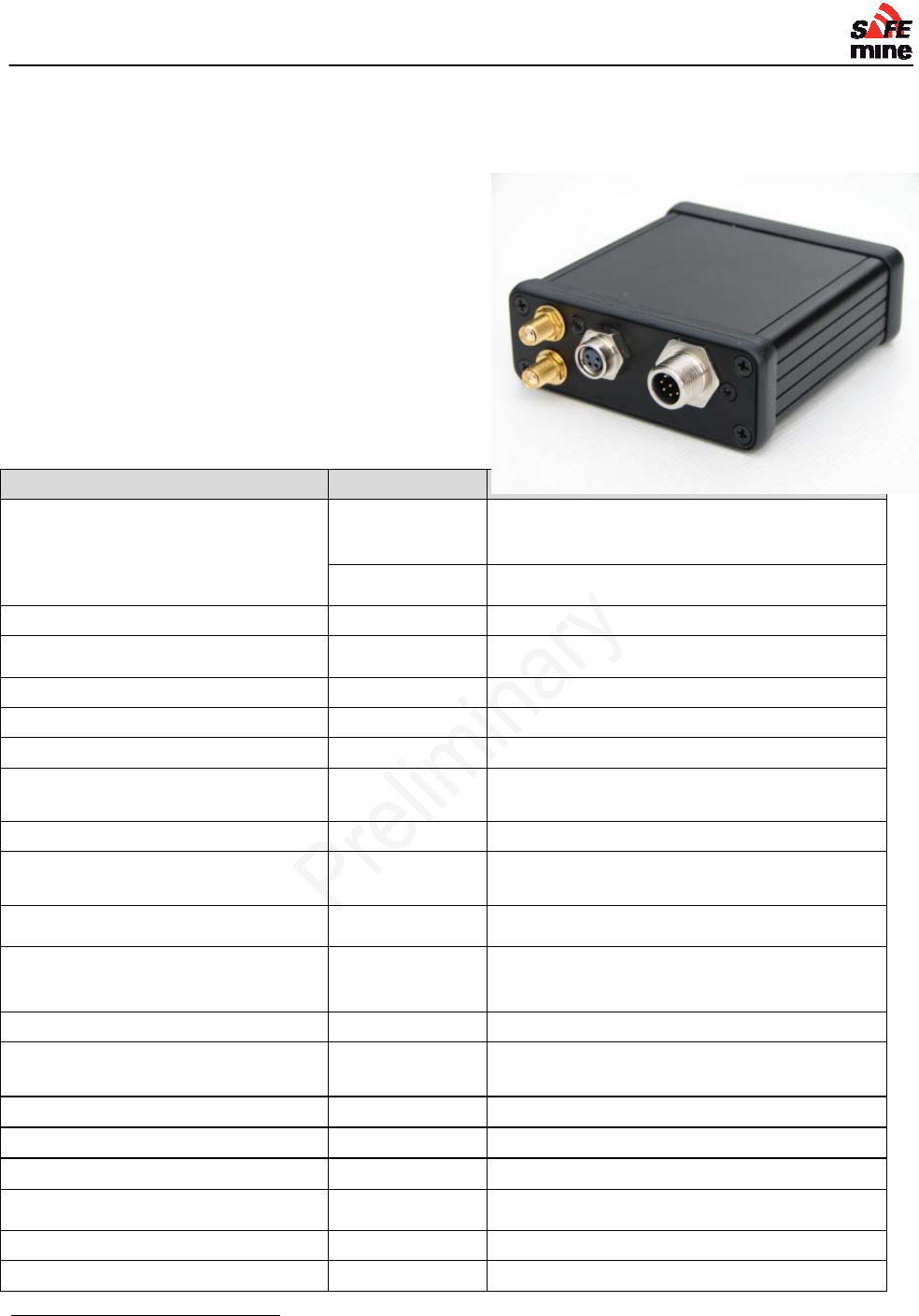
I
NSTALLATION AND
M
AINTENANCE
G
UIDE
Version 110301, Preliminary Page 13 of 56 March 2011
GPS connector
SMA female for 3.3V active GPS antenna
Only antenna supplied by SAFEmine may be used.
RF connector
SMA female for 50 Ohm RF antenna
Only antenna supplied by SAFEmine may be used.
Specifications for QC230/235:
Parameter Conditions1
Dimensions excl.
connectors 81 x 30 x 98 mm3
overall 81 x 30 x 108 mm3
Weight without cables 210 g
Power Supply nominal 12 - 28 VDC
Power Supply Range min / max 9.5 / 31 VDC
Power Consumption typical @12 V < 55 mA
peak @12 V < 180 mA
standby @12
V < 35 mA
Processor ARM7, 32bit @ 60 MHz
GPS 50 channel GPS L1, ISO/TS 16949
qualified, GALILEO ready
Time to operation after power-up typical 50 s
Time to operation from "hot"
standby max 2 s
Traffic alert range typical 500m
Maximum number of moving
units in range typical 50
Direction of Targets Updated typical 4 Hz
Average Latency typical 250 ms
Operating Conditions
.
2
Operating temperature -40°C to +85°C
Storage temperature -40°C to +85°C
Humidity 85%, non condensing
1
All specification are at an ambient temperature of 25°C.
2
Operation beyond the "Operating Conditions" is not recommended and exposure beyond the "Operating
Conditions" may affect device reliability.
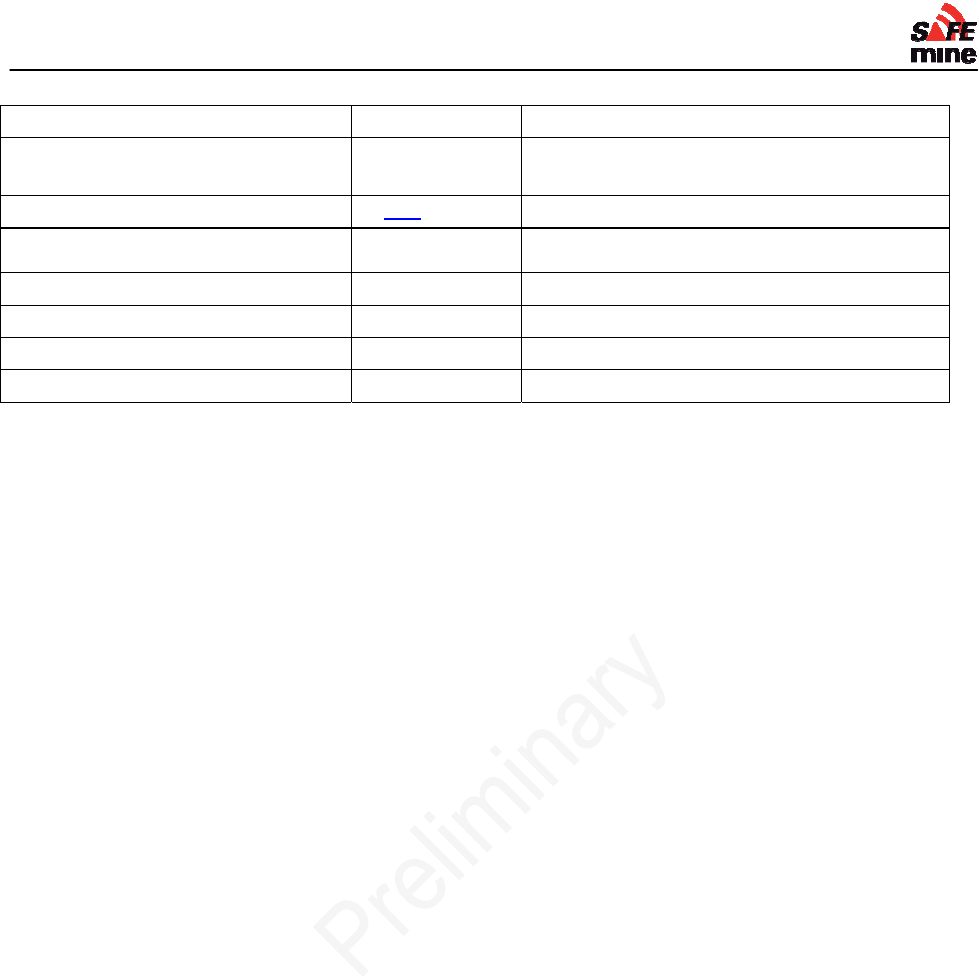
I
NSTALLATION AND
M
AINTENANCE
G
UIDE
Version 110301, Preliminary Page 14 of 56 March 2011
Vibration IEC 68-2-6 10-500 Hz; 2 hours/axis; 5g
Shock no function IEC 68-2-27 30g/11ms (halfsine); 3
Shock/axis
Protection rating IEC 60529 IP54
Connectors
Power M12, male, 8 contacts (IP67)
GPS SMA Female, color coded
RF SMA Female, color coded
Remote Display M8, female, 4 contacts (IP67)
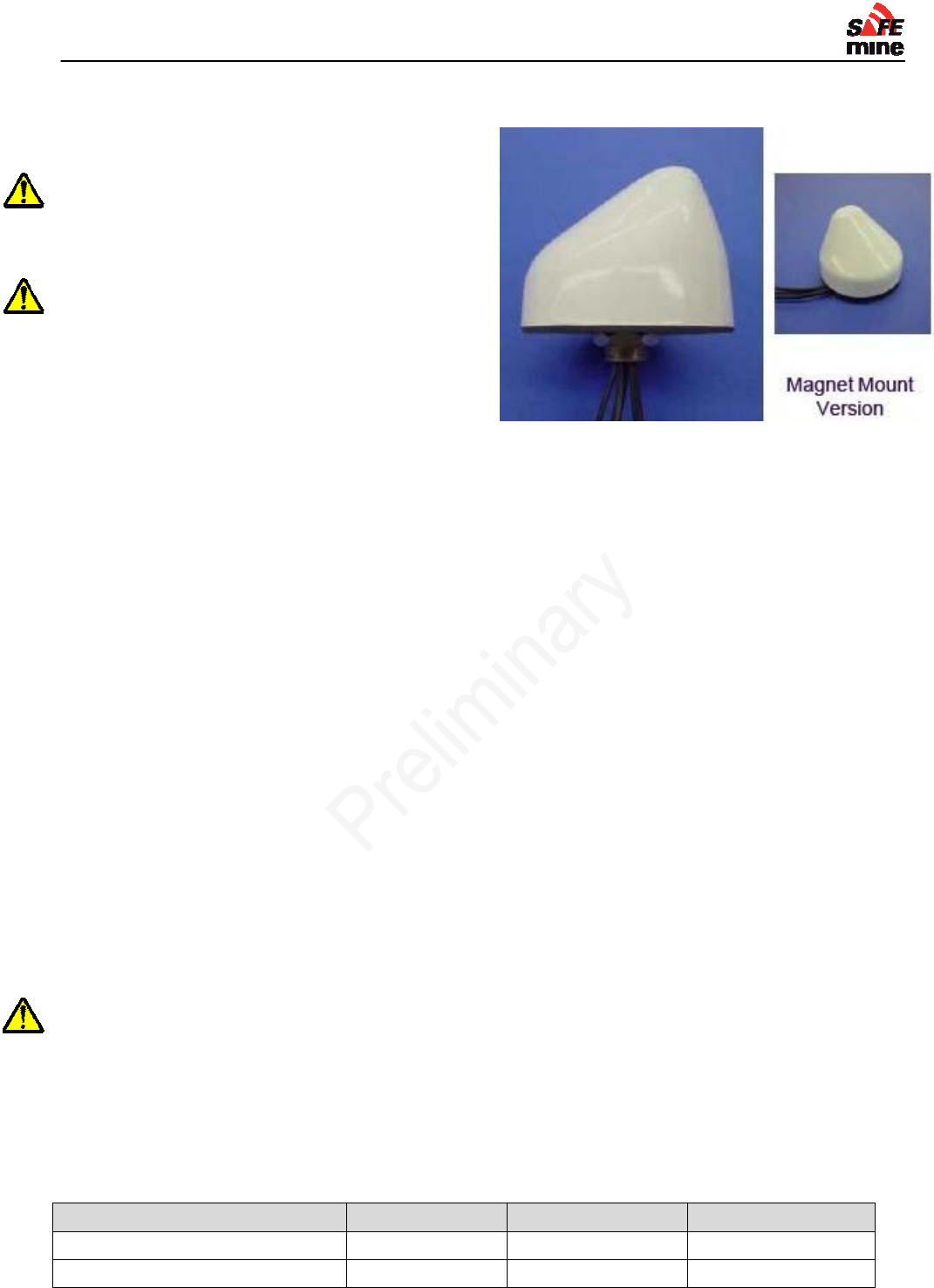
I
NSTALLATION AND
M
AINTENANCE
G
UIDE
Version 110301, Preliminary Page 15 of 56 March 2011
GPS & RF Antenna
The external combined GPS & RF antenna
supplied with the main unit must be
connected; the main unit will not operate
without the antennas.
Always verify that the antennas are
connected to the correct inputs. The
connectors are identical for both antenna
types.
Improper installation of the antenna and its
cables is the prominent cause for
malfunction.
The antenna must be professionally installed by trained personnel only and only the
antenna supplied with the equipment by SAFEmine may be used!
Antenna Models
- Through Hole Mount QF021
The screw mount antenna comes with 10/15cm of cable.
The advantage of using short cables on the antenna and then connect and run extension cables is
that in case of damage to either the antenna or the cables the defective part can be replaced
separately. Furthermore testing of the cable and antenna independently is possible with an SWR
meter (available through SAFEmine)
To mount the antenna a hole must be drilled or punched into the surface. The diameter of the hole
must be at least 19mm (3/4") the surface should also not be thicker than 12mm (1/2") In order to
secure the antenna mounting it is necessary to have access to the underside of the hole. For
optimal performance, it is recommended that the antennas be mounted on a horizontal metal
surface. This will provide the best acquisition for GPS satellites and will also optimize the RF
antenna element.
To attach the antenna, first remove the nut. The attached gasket provides a sealant to prevent
moisture from entering. Feed the cables through the hole, seat the antenna on the surface, and
then reattach the nut. The nut should be tight in order to properly seal the gasket. Tighten the nut
with a wrench. Finally, feed the cables to the receiver thru additional jumper cables.
The inside of the mounting screw of this antenna is NOT sealed. If it is exposed to the
outside additional sealing is required before installation.
The mounting screw of this antenna must be isolated from the vehicle to avoid ground
loops. Suitable insulating washers are available from SAFEmine.
- Magnetic Mount QF024
The magnetic mount antenna comes with 3.5m of cables, both GPS & RF.
Specifications for the GPS / RF Antenna
Parameter Conditions QF012 QF024
Mounting type Through Hole Magnetic
Weight 480g 620g
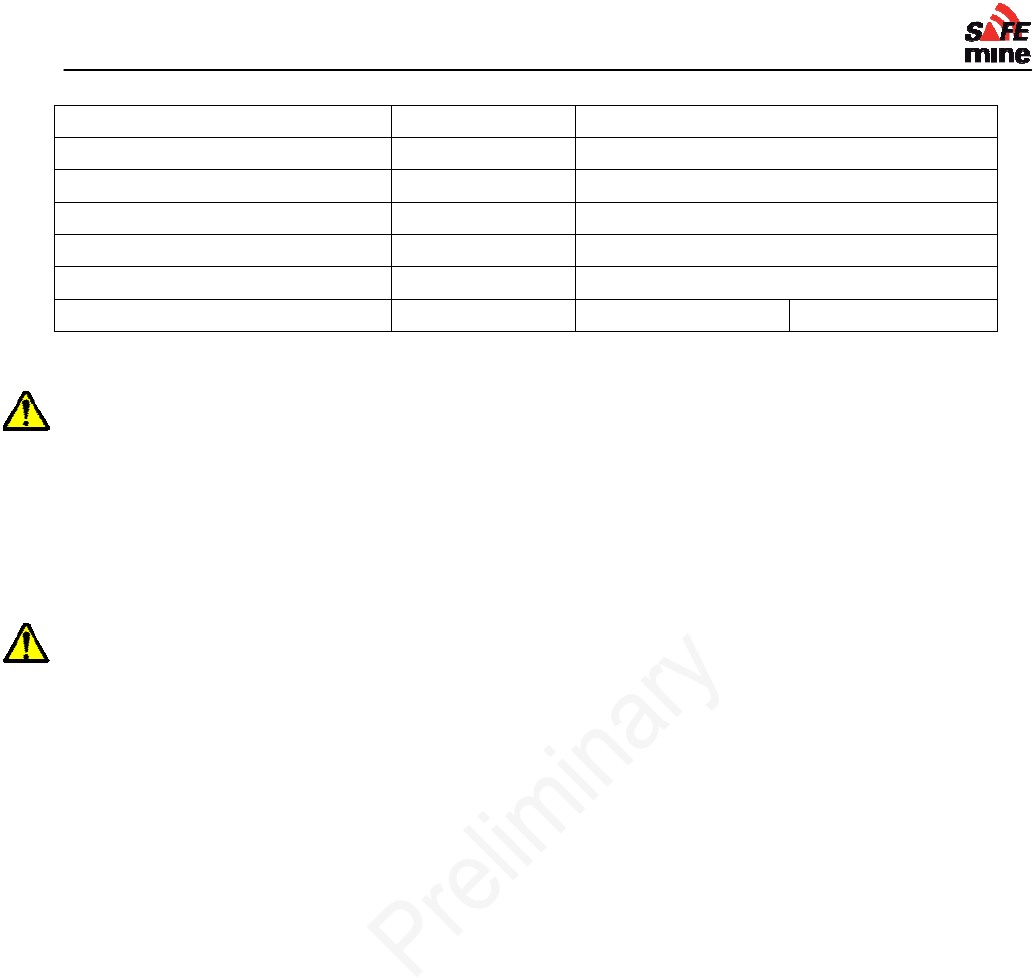
I
NSTALLATION AND
M
AINTENANCE
G
UIDE
Version 110301, Preliminary Page 16 of 56 March 2011
Dimensions ø107 x 91 mm
Power Supply from main unit
Connector 2 * SMA Male
Operating temperature -40°C to +85°C
Storage temperature -40°C to +85°C
Protection rating IP 67
Cable 2 * 20cm, coaxial 2 * 3.5m, coaxial
Installing the Antenna
The antenna must be mounted on the highest point of the vehicle, with 360° unobstructed
view of the sky and at least 50cm away from any other transmitting antenna. The antenna should
not have any electrically conducting surfaces (e.g. metal, carbon fiber) above or immediately
alongside.
If the roof is made out of non metallic material, a ground plane of minimum 18cm diameter must be
mounted underneath the antenna.
Mounting brackets for various vehicles (Haul Trucks etc.) are available from your local SAFEmine
distributor.
On tracked vehicles, the antenna must be mounted as close as possible to the axis of
rotation!
Snow and ice buildup reduces the performance of the antenna and must be removed prior
to operation.
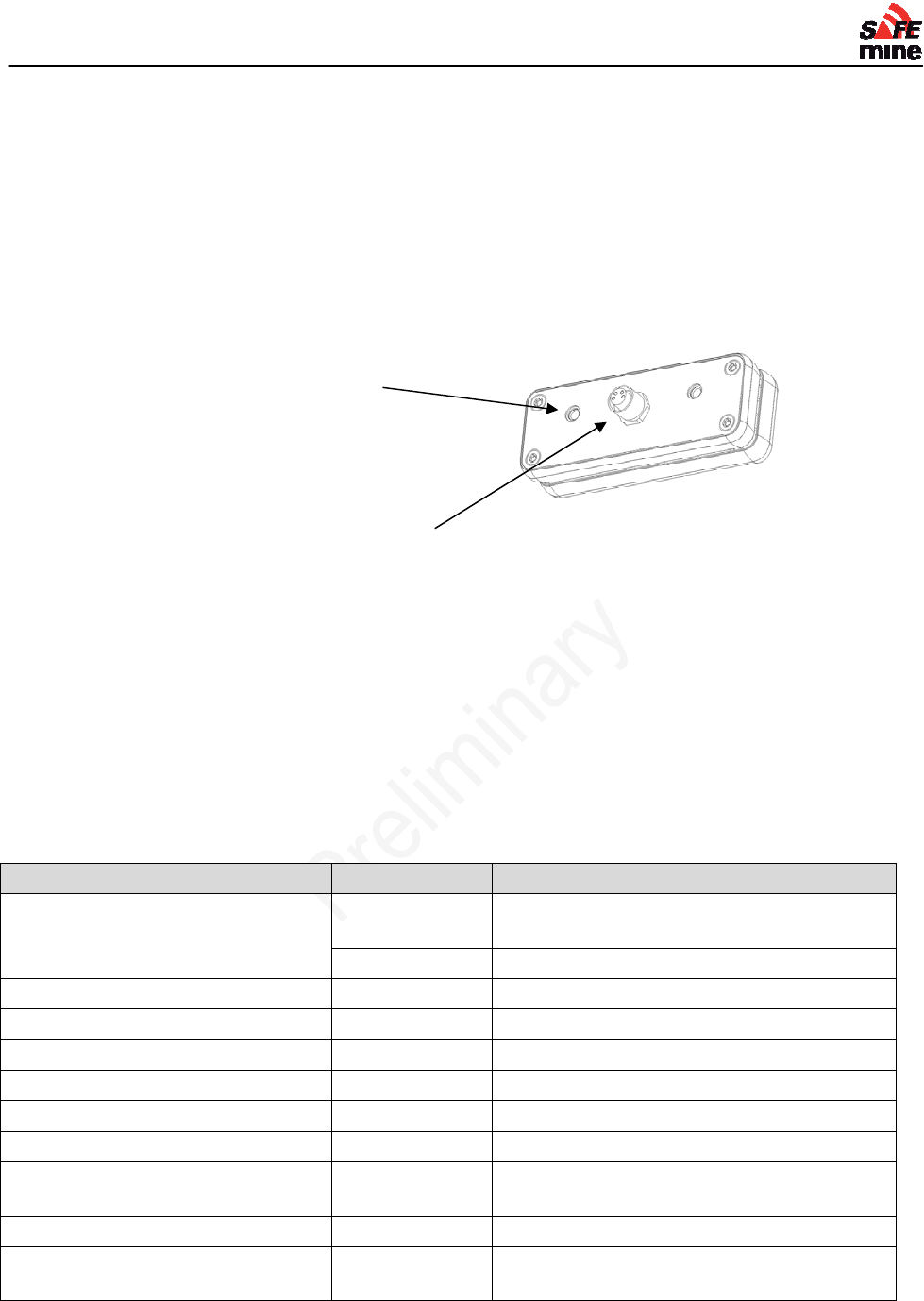
I
NSTALLATION AND
M
AINTENANCE
G
UIDE
Version 110301, Preliminary Page 17 of 56 March 2011
Remote Display unit
The back side of the aluminum housing includes two blind threads, so that the housing can easily
be secured by two M4 screws (no longer). Forcing longer than 8 mm screws into the nuts may
cause damage! 3D Models (Solidworks) of the housing and all connectors are available on
request. Alternatively the remote display can be fixed with 3M dual lock (see Appendix A:
Recommended parts), This is ideal for installation, where the owner of the vehicle does not want to
drill holes in his dashboard
Mounting Holes
Remote Cable Connector
The Remote Display QD200 can also be used with the Main Unit with internal Display QC235. This
configuration is not described in further detail here.
Connections – Remote Display
Data and power from main unit
Connector type M8 male, 4 contacts
Specification for Remote Display
Parameter Conditions
Dimensions excl.
connectors 80 x 30 x 20 mm3
overall 80 x 30 x 30 mm3
Weight without cables 60 g
Power Supply from Transceiver CG1-S
Connector M8, male, 4 contacts (IP67)
Operating temperature -40°C to +85°C
Storage temperature -40°C to +85°C
Vibration IEC 68-2-6 10-500 Hz; 2 hours/axis; 5g
Shock IEC 68-2-27 30g/11ms (halfsine)
3 Shock/axis; no function
Protection rating IP54
Construction Anodized aluminum with plastic end-
bezels, all connectors on the back side.
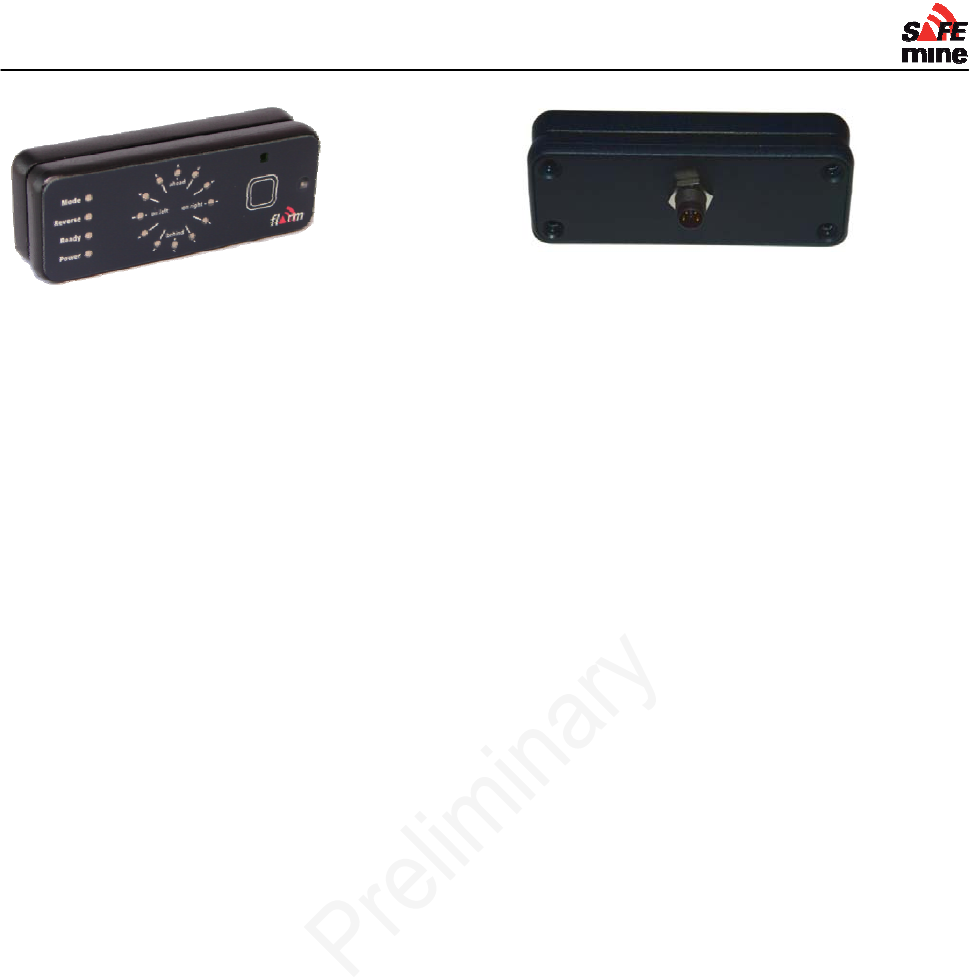
I
NSTALLATION AND
M
AINTENANCE
G
UIDE
Version 110301, Preliminary Page 18 of 56 March 2011
Figure 1 Front view of remote display
Each User Interface has
12 red / green LED in a circle, diameter 20mm
1 red / green status LED each for Mode / Reverse / Ready /Power / "Ready" / Mode
1 multifunctional button
LED brightness is automatically controlled based on ambient light, with backlight for night
operation.
Buzzer with max. 85dB sound level (@10cm) volume can be automatically controlled based on
ambient noise.
Figure 2 Rear view of remote display
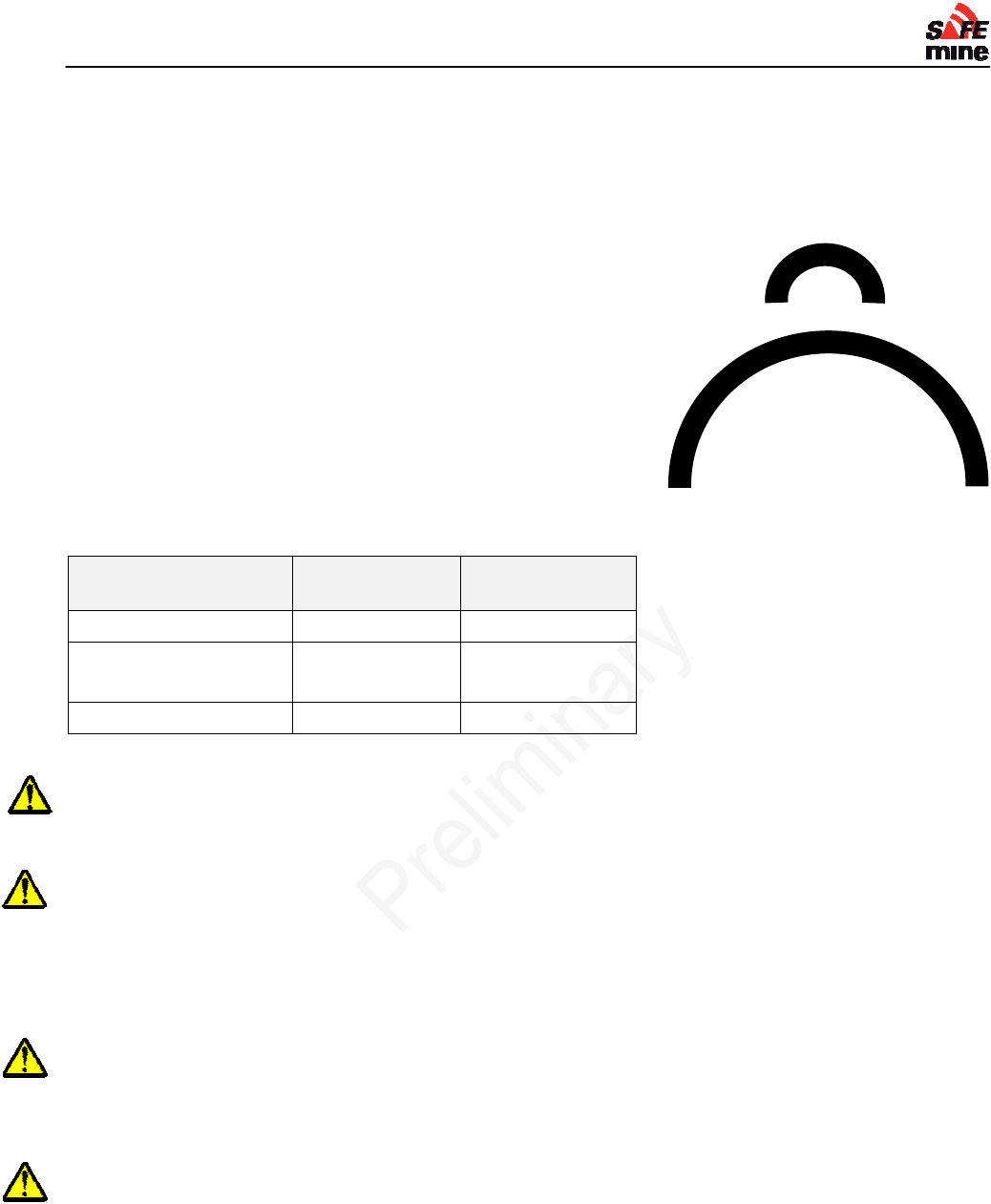
I
NSTALLATION AND
M
AINTENANCE
G
UIDE
Version 110301, Preliminary Page 19 of 56 March 2011
Figure 6 Minimum bend radius of RF19
5
coaxial cable for one-time (above) an
d
repeated bends (below).
Connectors and Cabling
Antenna Cables
It is recommended to source coaxial low loss cables
including connectors of proper length and high quality
from a professional local supplier. Any work on radio RF
cabling must be done professionally by trained
personnel according to Safemine specifications.
Manufacturing of coaxial cables to custom length on site
requires specialist tools (strip and crimp tools, soldering iron,
SWR meter) and know-how / experience and may result in
reduced reliability.
Contact SAFEmine if on site cable confectioning is
necessary.
Recommended maximum cable length between antenna
and main unit:
Coaxial cable type Max. length RF Max. length
GPS
RG174 DO NOT USE 5m
HDF-195/CFD-195
LMR -195
5m 10m
LMR 400 15m 15m
Use of other coaxial cable types must be approved in writing by SAFEmine!
The maximum acceptable attenuation rate for the RF cable is 3dB at 900MHz. The maximum
acceptable attenuation rate for the GPS cable is 10dB. To calculate the attenuation rate, sum
up the attenuation of all segments as specified by the cable manufacturer. Add 0.3dB for any
connection.
The minimum bend radius of the coaxial cables must be strictly observed!
Typical minimum bend radius for RF195 type cables is 18mm (3/4 in.) on installation, 60mm (2 1/3
in.) for repeated bending.
It is highly recommended to add a braided sleeve around the cables for further UV and abrasion
protection. Wear and damage to the RF and GPS antenna cables is not covered under warranty.
Connections in the antenna cable must be sealed over the whole assembly with heat shrink
tubing (glue type). In addition, outside connections must be sealed with silicone tape to
ensure a reliable, weatherproof operation. Never use ‘electrical tape’ or to weatherproof RF
connections!
No installation may have more than one (1) connection.
No PVC tape (black ‘electrical tape’) may be used for sealing connectors!
All antenna cables must be carefully tied to the vehicle. Loosely vibrating cable will fatigue
and the central conductor will break over time!
Make cables removable to prevent them from being cut when the vehicle is being serviced.
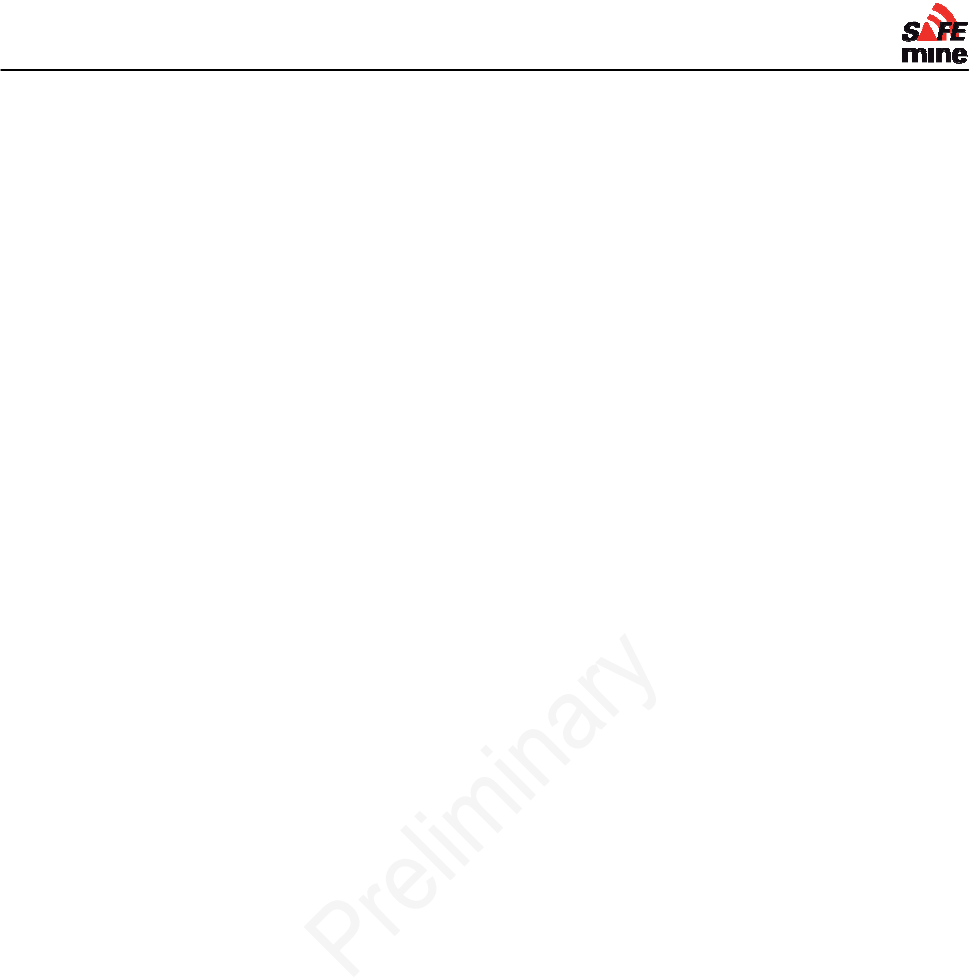
I
NSTALLATION AND
M
AINTENANCE
G
UIDE
Version 110301, Preliminary Page 20 of 56 March 2011
Section 2 – Software and
Programming
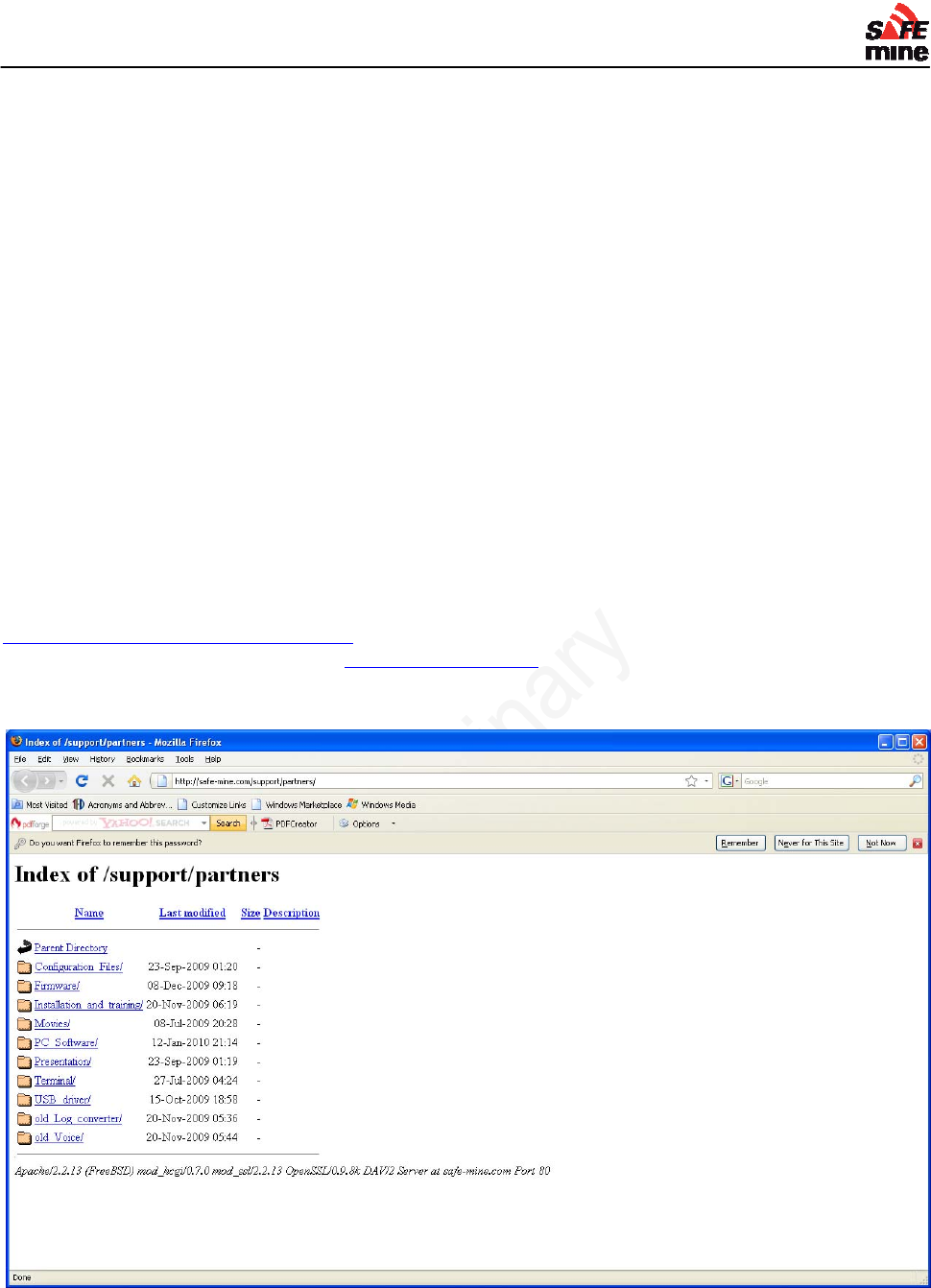
I
NSTALLATION AND
M
AINTENANCE
G
UIDE
Version 110301, Preliminary Page 21 of 56 March 2011
Programs and Files
Required Components
For the installation of the Collision Avoidance System you will need the following hardware:
PC or Laptop running Windows 2000 or later.
M8 to USB Cable (QLxxx)
or M8 to serial port cable (QL014) and RS232 to USB converter if PC has no serial port.
Power Supply or Battery (12 or 24 volts)
and the following software:
SM Tool (SAFEmine Software Utility)
H-Term
Latest Firmware (v.2.24)
Configuration File (see configtemplate.ini)
USB Driver (for use with cables above that connect to USB port on computer)
Note: All necessary programs and files referred to above can be obtained on-line through
www.safe-mine.com/support/partners. Enter your user name and password and then select the
corresponding directory. Contact info@safe-mine.com if you don’t have a username and
password.
Figure 1 SAFEmine support file repository
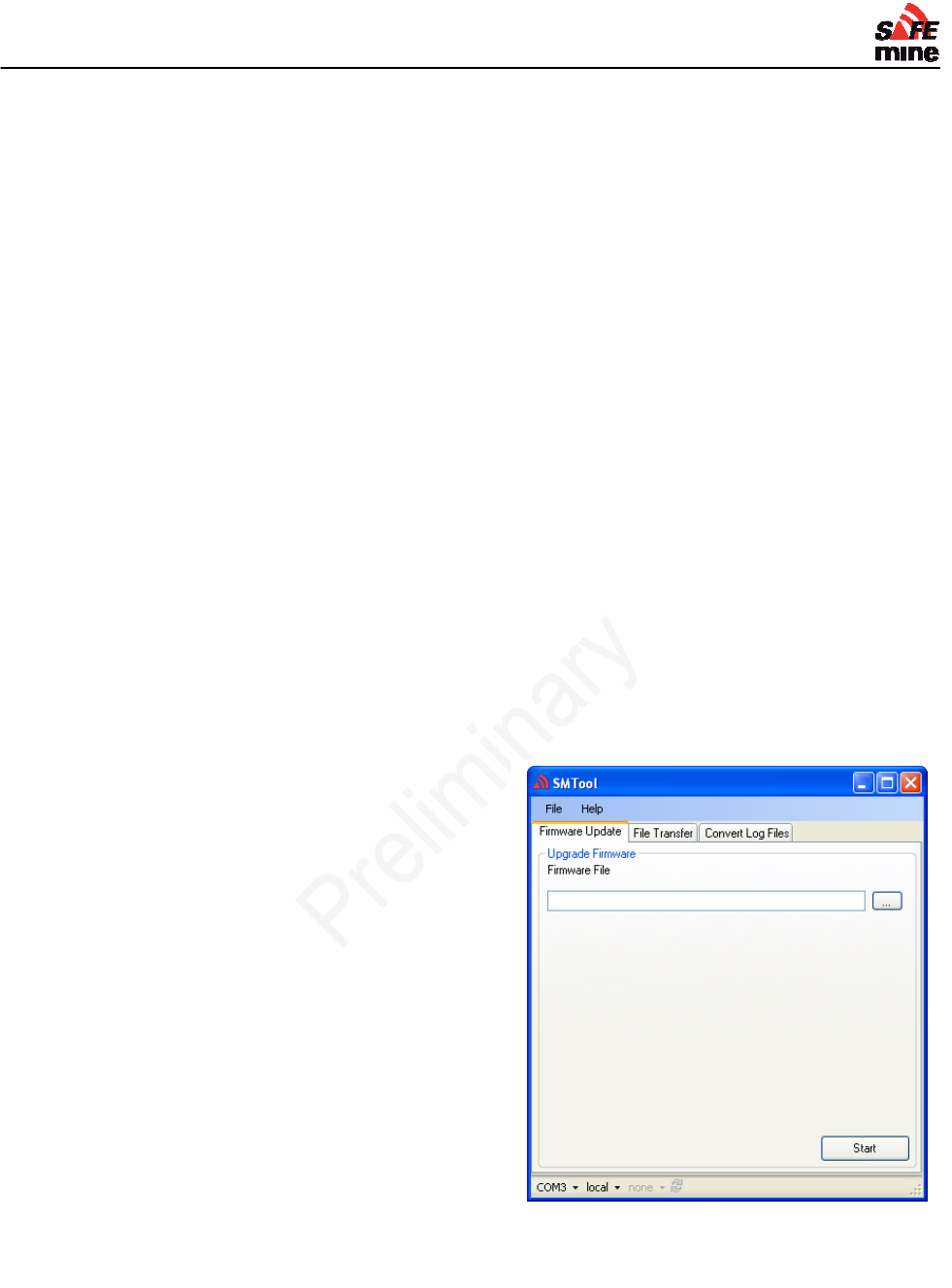
I
NSTALLATION AND
M
AINTENANCE
G
UIDE
Version 110301, Preliminary Page 22 of 56 March 2011
Firmware and the Configuration File
The QC230/235 is controlled by firmware, basically a small, embedded program that is stored
permanently in read-only memory. The firmware reads a unique configuration file (refer to
“Configuration file” for programming details) that is created and/or modified by the installer which
customizes the behavior of the device for the particular vehicle on which it is installed.
Both the firmware and configuration file need to be uploaded to the QC230/235 for the
system to function properly.
Firmware is periodically updated by SAFEmine software engineers. Many features and
improvements are available by uploading the latest released version. As a helpful feature, the
firmware version is display during start-up. Three green LEDs are lit sequentially for one second,
according to the firmware revision (“2”, “0”, “0”), where “0” is 12 o’clock, and numbers increment
clockwise.
Setting up the SM Tool File Utility -
1. If not already done, obtain and install a copy of SM Tools on your PC or Laptop.
2. Connect power (12 volts to 28 volts) to the SAFEmine QC230/235.
3. Connect either the QLxxx or QL014 to the M8 connector of the QC230/235, depending on
the type of port you have available.
4. Click on the SM Tools icon and start the program.
5. The window as shown in Figure x below appears.
6. Choose the correct COM port at the lower left-hand corner.
Uploading Firmware
1. Choose the correct firmware file
2. Disconnect power from the unit
3. Press "Start Update"
4. Apply power. Four red status LED should
stay lit after 5 seconds. If device powers up
normally, retry, select different serial port.
5. Wait 45 seconds, or until the message box
appears
6. Do not cut power until SAFEmine device
has restarted completely (another 20
seconds)!
7. Watch for Errors on restart on the
SAFEmine device display
8. In case you have a SAFEmine unit with
remote display, you must check for Errors
on the PC screen (not yet implemented) or
by connecting the display after the update.
Uploading a configuration file
1. Browse using the button to the right […] and choose the desired configuration file. Please
refer to page X for details on modifying a configuration file.
2. Click the [Upload] button.
Figure 2 The first tab of SM Tool permits the
uploading of a new version of firmware to the
QC230/235.
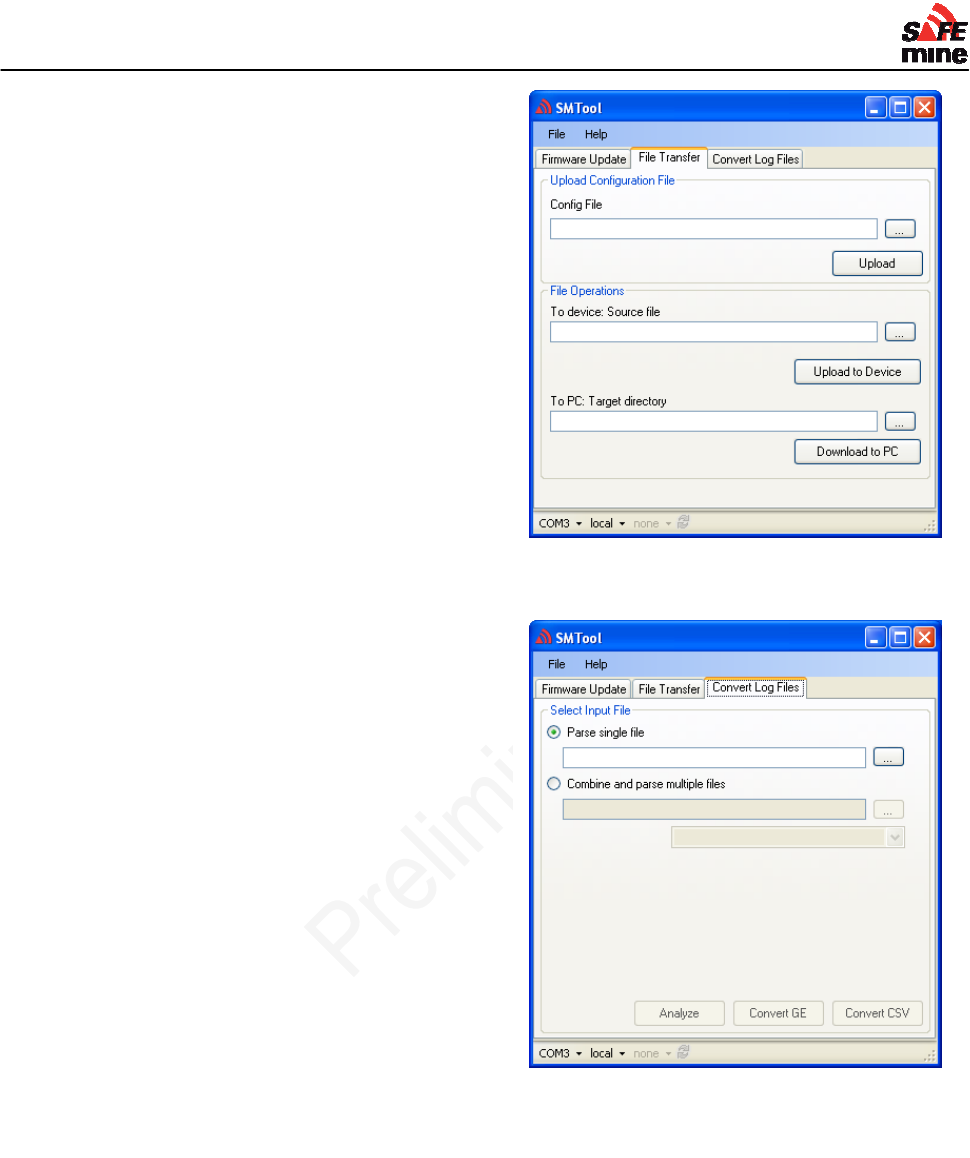
I
NSTALLATION AND
M
AINTENANCE
G
UIDE
Version 110301, Preliminary Page 23 of 56 March 2011
3. Wait 15 seconds, or until a message box
appears.
4. Disconnect and reconnect power to the
SAFEmine QC230/235.
5. Watch for Errors on startup on the
SAFEmine QC230/235.
6. In the case where you are using a QC230
(the unit without an integrated display),
check for errors by connecting the display
after the update.
Converting a raw log file
1. Choose the file to convert.
2. Press the button corresponding to the type
of desired output file
3. Find the converted file in the same directory
as the original file.
“Analyze” will analyze the recorded file and print
the results into a text file.
“Convert GE’ will convert the log file into a Google
Earth compatible .kml format file.
“Convert CSV” will convert the raw data into CSV
(Comma Seperated Value) format for further
analysis.
Remote Management
Most operations can be performed on nearby
devices using the RF link. Note that the remote
device has to be operational and GPS has been
locked.
File up- download over RF
Certain maintenance operations can be performed over the air.
Requirements:
PC with latest SM Tools installed, .NET > 3.0 recommended
Local device connected to PC and powered up. Preferably, the device also has GPS
reception. This will add direction and distance information in the host selection dialogue.
Peer device with firmware >= 2.00
Figure 3 The File Transfer Tab permits up- and
downloading of files to and from the unit
Figure 4 The File Conversion Tab permits the
conversion of raw log files to other formats
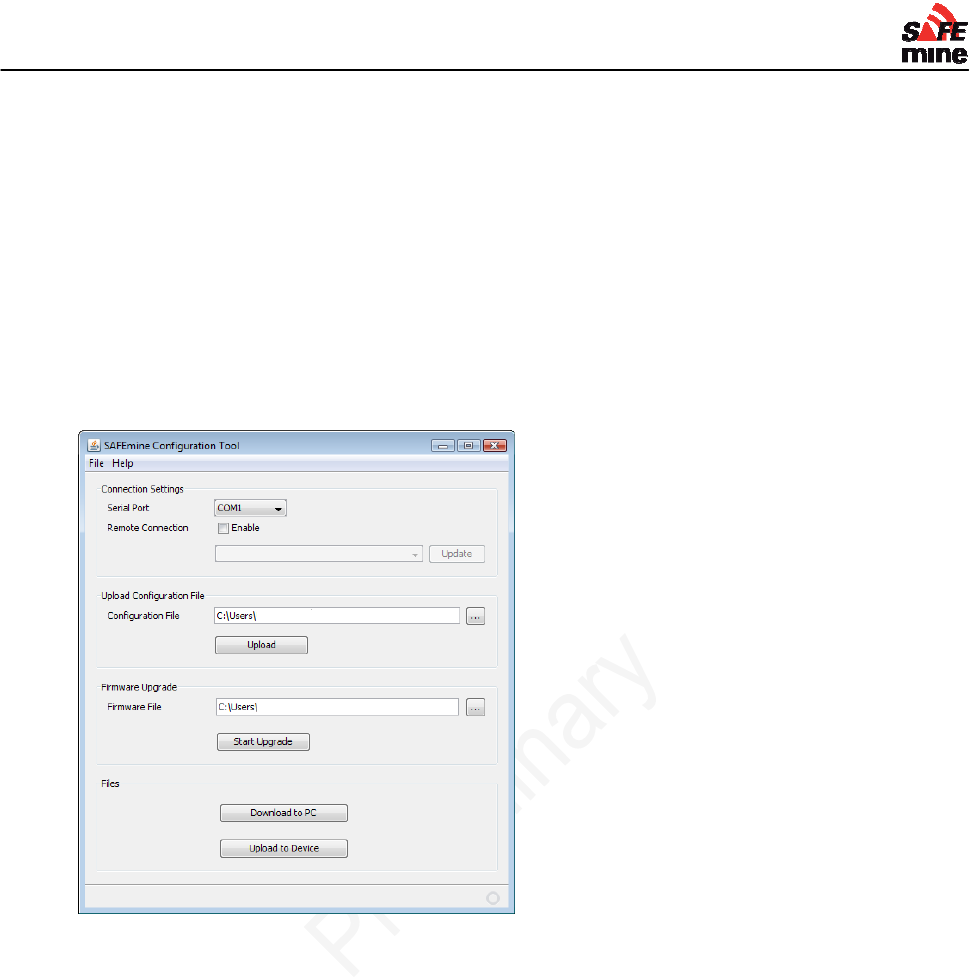
I
NSTALLATION AND
M
AINTENANCE
G
UIDE
Version 110301, Preliminary Page 24 of 56 March 2011
In SM Tools select “Remote Connection”, “Enable”. The list of available peer devices will be
populated automatically. Select a device, proceed as usual to download/upload files, and
configuration file.
Very carefully check that you are connected to the unit you want to program on!
Limitations:
The peer device must have GPS reception; otherwise it will not show up in the list.
Transmit speed is about 1500 bytes per second in good conditions, but will degrade with
increasing data traffic (i.e. other nearby vehicles).
SAFEmine Configuration Tool (discontinued)
Figure 5 Discontinued SAFEmine Configuration Tool (do not use)
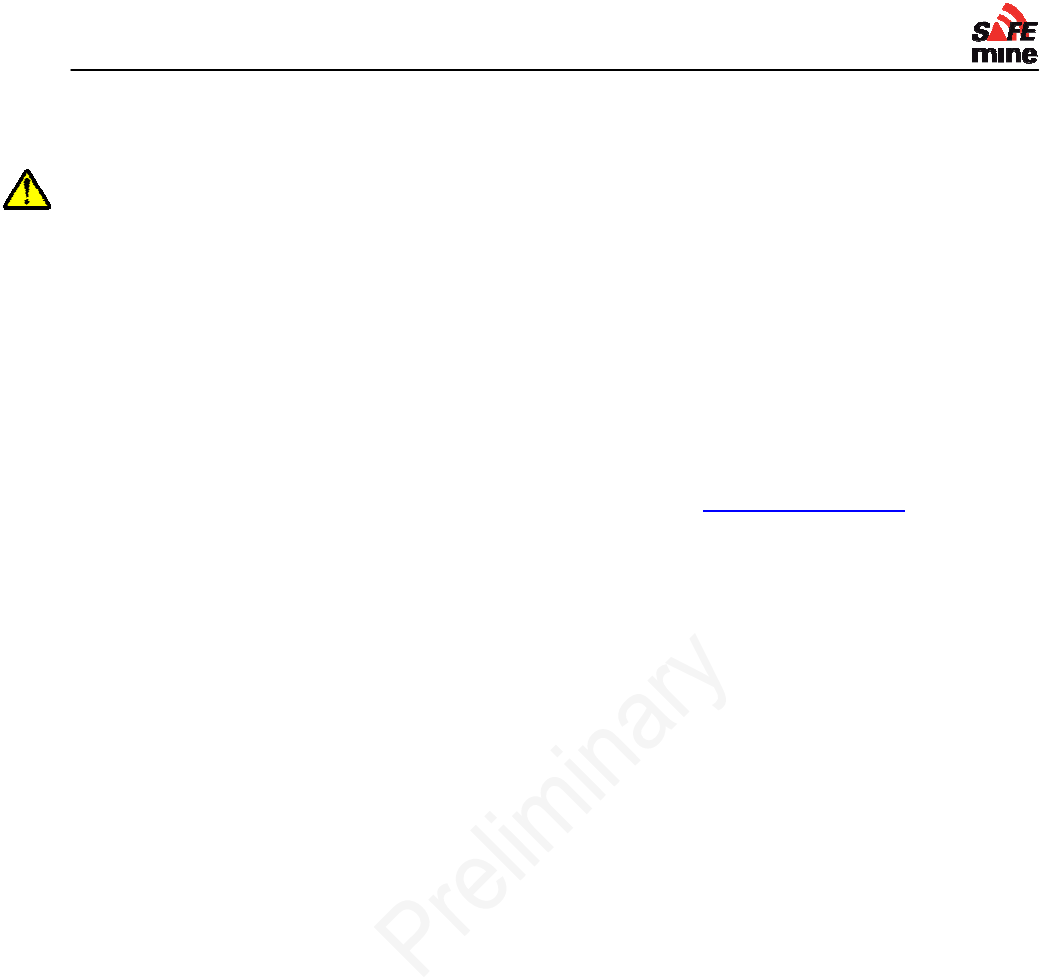
I
NSTALLATION AND
M
AINTENANCE
G
UIDE
Version 110301, Preliminary Page 25 of 56 March 2011
Configuration file
A unique configuration file must be compiled and uploaded for each vehicle.
The file name should consist of the individual "Plant Number" of the vehicle and end with .cfg
Example: HT10.cfg
Maintaining a repository of all files allows for easy configuration of replacement units.
Syntax:
Parameter = value
The "#" character at the beginning of a line indicates a comment. Comments are ignored
and have no effect on the function of the configuration file.
Sample configuration files for various vehicles are available from SAFEmine. We strongly
recommend that you submit your configuration files for review to info@safe-mine.com.
NOTE: Values not set in a configuration file are automatically treated as default value. For
instance, if there is no “volume = xxx” entry in the configuration file, it will be set to “100”.
Mandatory parameters which must be present in every configuration file are marked in red.
Sample configuration file
# Sample SAFEmine configuration for Loader
#########################################
# do not modify!
#########################################
channel = 287
hopping = 1
# site specific configurations
#########################################
# all alarm exceptions activated
alarmexceptions = 0xffffffff
# vehicle specific configuration below, please adapt
#########################################
# speaker volume
volume = 20
distfar = 80
distnear = 40
distclose = 10
vehtype = 52
vehmanu = CAT
vehmod = 988H Loader
vehid = 741
vehlength = 6
safetylength = 0
vehwidth = 3
safetywidth = 0
vehheight = 4
antennaaft = 3
antennaright = 1
antennaup = 3.3
minturnrad = 0
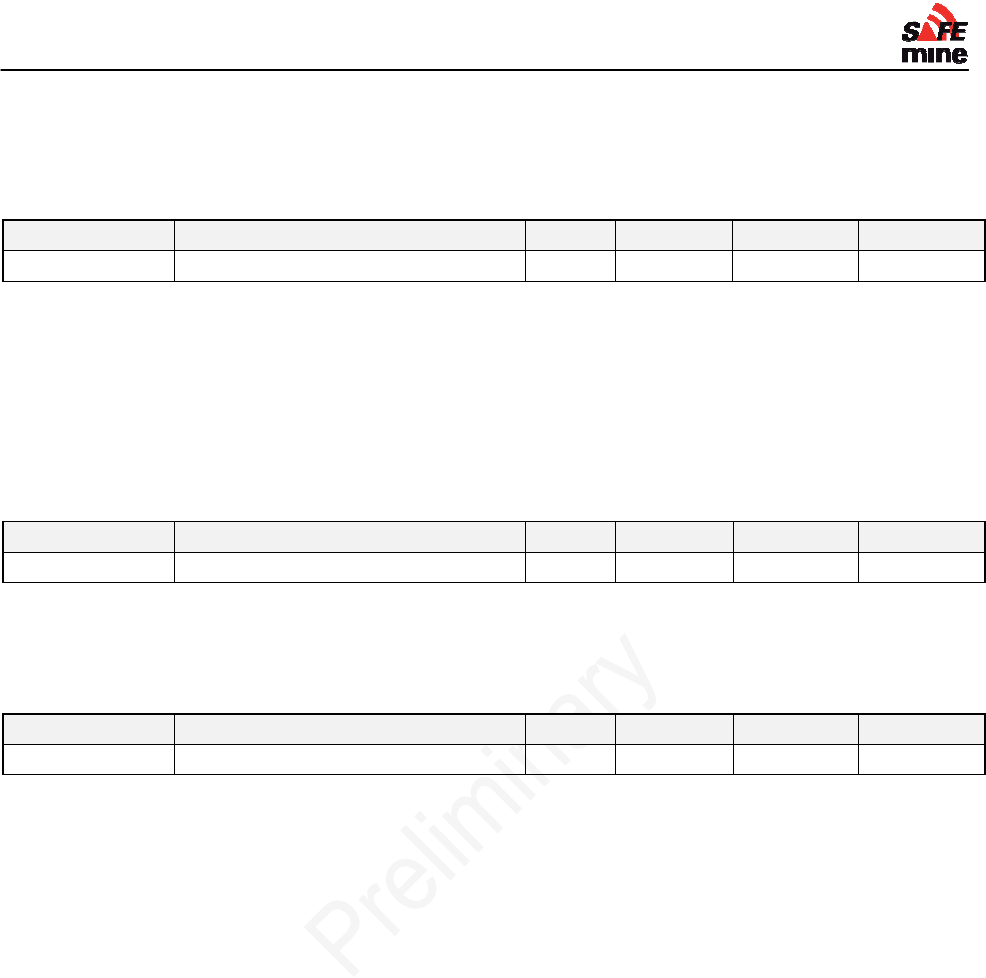
I
NSTALLATION AND
M
AINTENANCE
G
UIDE
Version 110301, Preliminary Page 26 of 56 March 2011
Site Specific Parameters
Site specific parameters are the same and must be set on all units.
Radio Channel
Keyword Description Unit Range Default Example
CHANNEL RF Radio Channel - 117 - 381 - 117
Sets the frequency of the radio transmission
117: for Europe / Africa
287: North / South America
301: North America countries under FCC regulation
122: New Zealand
381: Australia
357: Israel
Channel Hopping
Keyword Description Unit Range Default Example
HOPPING Number of channels to use for hopping - 1 - 50 1 1
50: North America countries under FCC regulation
1: All other areas
Transmit Power
Keyword Description Unit Range Default Example
RFPOWER Transmit Power Setting. - 0 - 3 3 3
Sets the transmit power of the radio. A setting of 3 results in maximum power and range of the radio
2: North America countries under FCC regulation (lower power setting required to comply with FCC)
3: All other areas
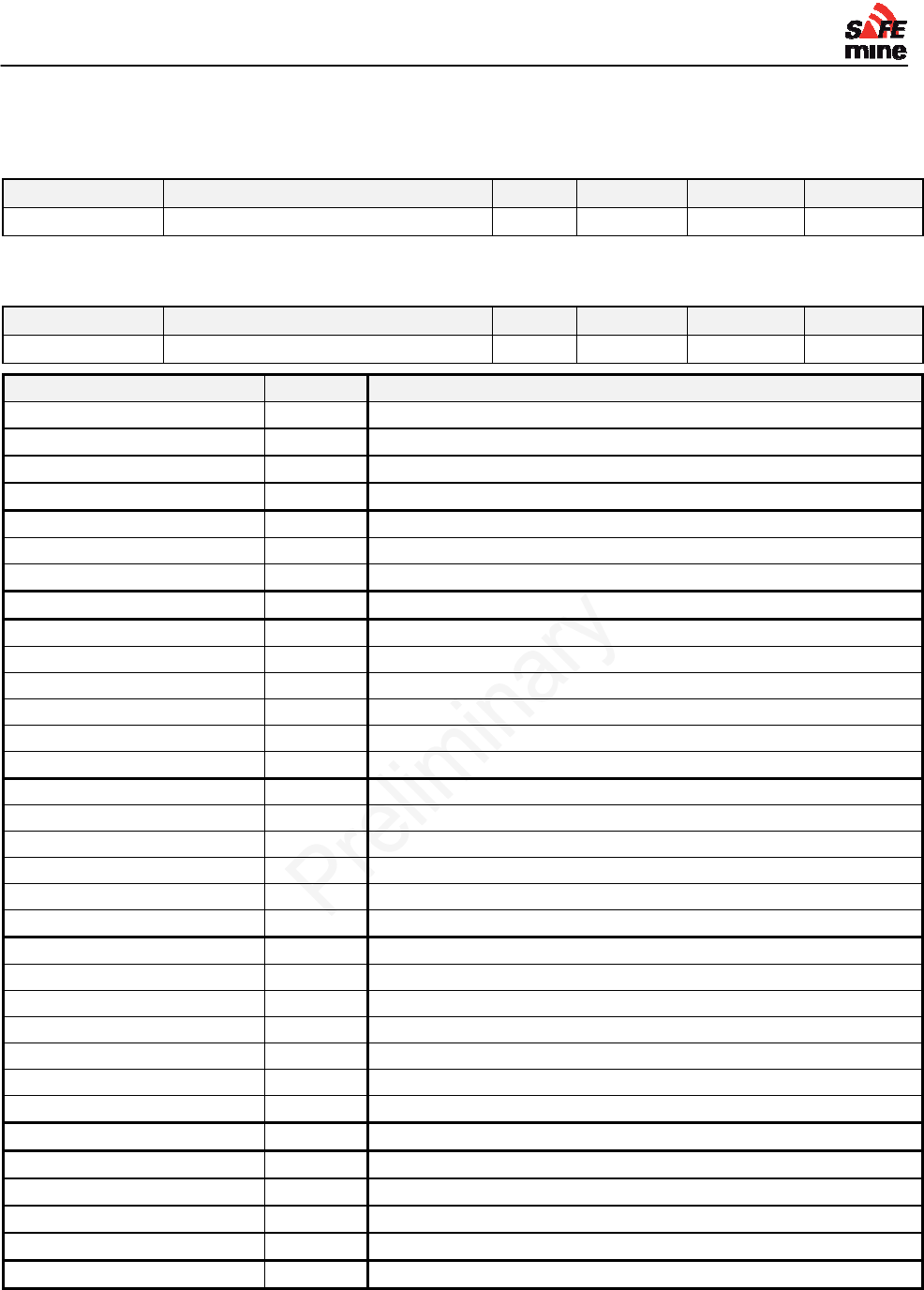
I
NSTALLATION AND
M
AINTENANCE
G
UIDE
Version 110301, Preliminary Page 27 of 56 March 2011
Minimum required parameters
Vehicle ID
Keyword Description Unit Range Default Example
VEHID Vehicle ID, e.g. mine plant number - max 6 char - LV007
Must be unique within the site
Vehicle Type
Keyword Description Unit Range Default Example
VEHTYPE Vehicle Type - 10 - 100 - 31
Vehicle Type VEHTYPE Examples
Light Vehicle 10 Fort F150,F250
Small Tractor 11
Small Service Truck 13 Ford 750
Bus 15
Haul Truck 21 Komatsu 730E,
Dump Truck 22
Water Tanker 23 CAT 777
Lomak Trucks 24 Lomak, Freightliner
ADT 31
Fuel Bowser 32
Service Truck 33
Low Bed Truck 35
Mobile Crane 34
Rear Tip Truck 36
Excavator 41 CAT 385C, PC4000
Shovel 42
PC 43
Dozer 44
Dragline 45
Drill 46 Atlas Copco PV271
Large Front End Loader 51
Small Front End Loader 52 CAT 988H
Tire Handler 53
Cable Handler 54
Grader 55
TLB, JCB 56
Large Tractor 57
Train 61
Stockpile Stacker 71
Test Station 72
Stockpile Dozer 73
Lighting Plant 74
Beacon 100
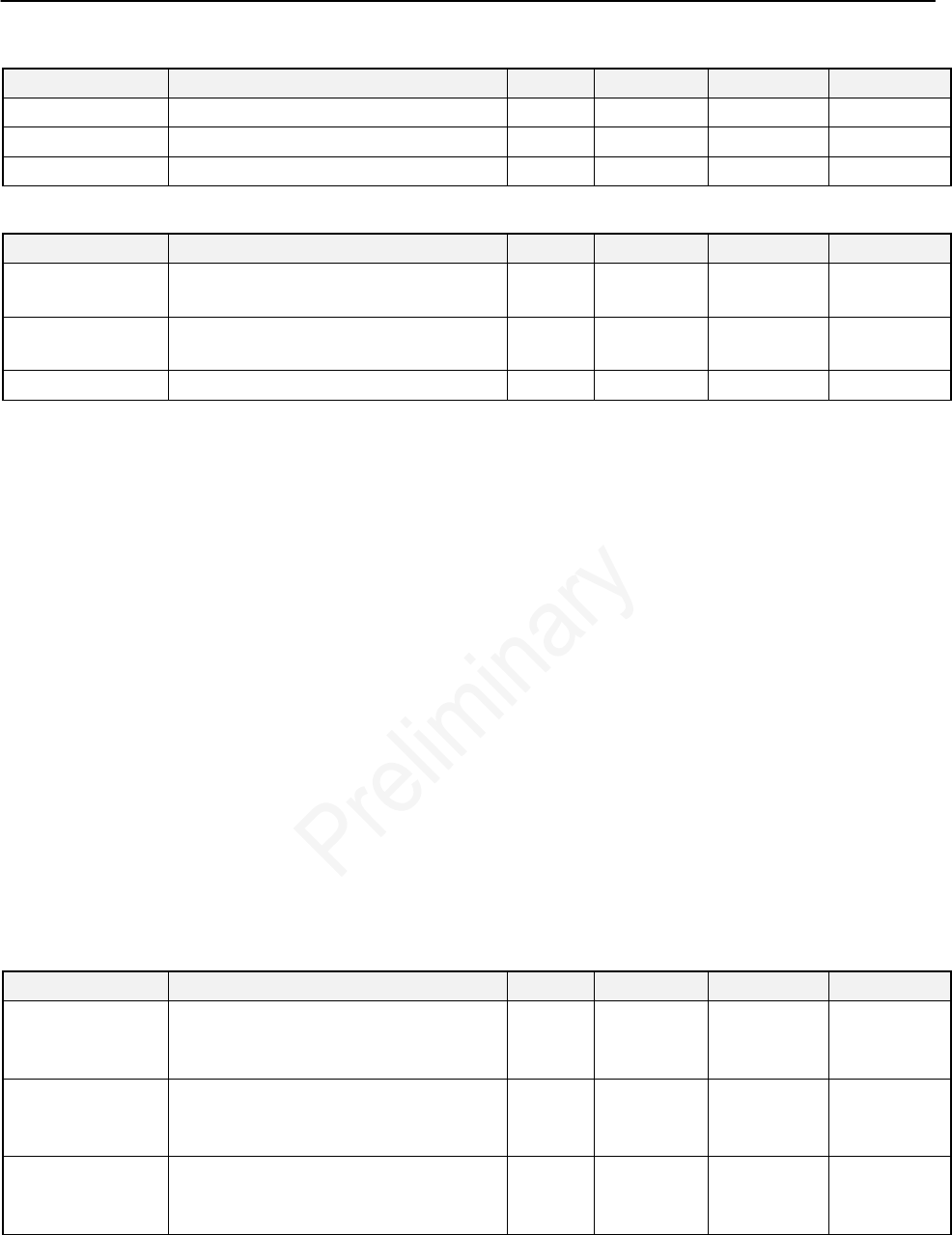
INSTALLATION AND MAINTENANCE GUIDE
Version 110301, Preliminary Page 28 of 56 March 2011
Vehicle Dimensions
Keyword Description Unit Range Default Example
VEHLENGTH Vehicle length, overall meter 1 - 655 - 12.8
VEHWIDTH Vehicle width, overall meter 1 - 655 - 3.4
VEHHIGHT meter 0 -
Antenna position
Keyword Description Unit Range Default Example
ANTENNAAFT Distance between front of vehicle and
antenna. meter 0 - 655 - 3.4
ANTENNARIGH
T Distance between left side of vehicle and
antenna. meter 0 - 655 1.2
ANTENNAUP Elevation of antenna above ground meter 0 - 2.1
Figure 6 Vehicle dimension and antenna position parameter
Optional parameters
LED Notification Distances
Keyword Description Unit Range Default Example
DISTFAR Green LED indicates vehicle closer than
disfar meters; taken from outer boundary
of “alarm area”
meter 1 - 500 150 180
DISTNEAR Steady Red LED indicates vehicle closer
than disnear meters; taken from outer
boundary of “alarm area”
meter 1 - 250 40 40
DISCLOSE Flashing Red LED indicates vehicle
closer than disclose meters; taken from
outer boundary of “alarm area”
meter 1 - 250 5 5
For best situation awareness it is recommended to keep the DISTFAR value larger than the
maximum breaking distance of any vehicle in the mine, typically about 110m.
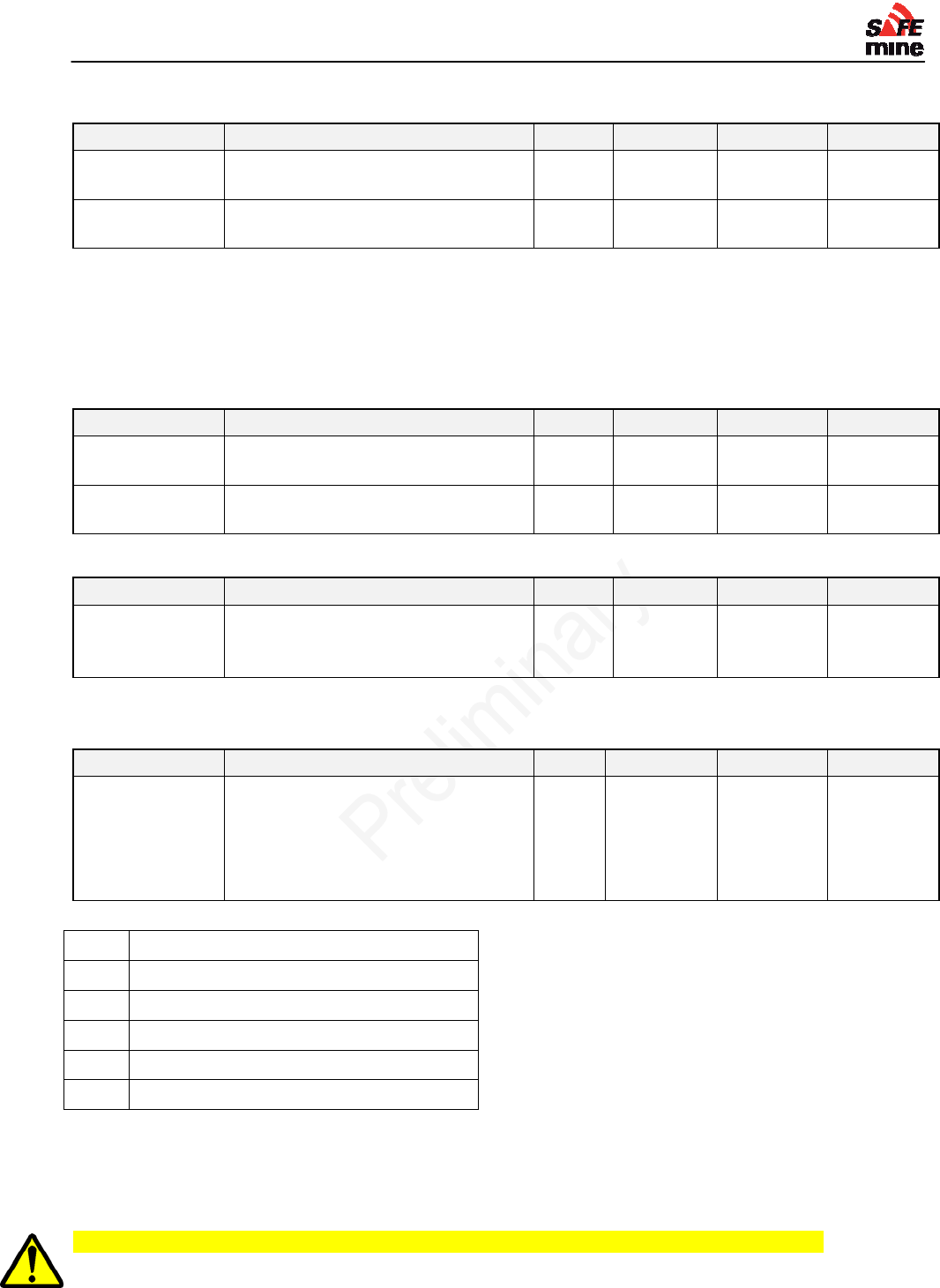
I
NSTALLATION AND
M
AINTENANCE
G
UIDE
Version 110301, Preliminary Page 29 of 56 March 2011
Safety Length
Keyword Description Unit Range Default Example
SAFETYLENGT
H Extends the alarm region in percent of
vehicle dimension. % of
length 0 - 100 0 20
SAFETYWIDTH % of
width 1 - 100 0 5
Example: A vehicle with length 5m sets SAFETYLENGTH = 30 thus will have an additional safety
area of 1.5m ahead AND behind the vehicle.
Setting above values too high (typically > 30) may result in unwanted "nuisance alarms" as alerts
will sound even though there is no danger of collision. Recommended values are 30 for haul trucks
and 10 for light vehicles
Vehicle data
Keyword Description Unit Range Default Example
VEHMANU Vehicle Manufacturer - max. 31
characters - KOMATSU
VEHMOD Manufacturers model name - max. 31
characters - 785
Buzzer volume
Keyword Description Unit Range Default Example
VOLUME Volume of the buzzer of the display in
percent of full volume
-1: automatic (not yet implemented)
% 0 - 100 100 60
User Interface Mask
Individual user interface components can be deactivated (e.g. buzzer, LED circle)
Keyword Description Unit Range Default Example
UIMASK Deactivatesselecteduserinterface
components,e.g.buzzer,LEDcircle.
Individualuserinterface
componentscanbedeactivated
(e.g.buzzer,LEDcircle).
Flags 0 – 0xFF 0xFF 0xE2
RefertotheUIMASKUtilityinordertoenterthecorrectparameter.
0x01Buzzer
0x02WarningLED(Compassrose)
0x04Voice
0x08GPSstatus(buzzerandvoiceonly)
0x10Infobeep(invertedlogic,cleartoenable)
0x20AllLED
Reducing nuisance alarms
Infobeep
All Infobeep functions are still in a ‘BETA’ state and may only be used for testing!
“Infobeep” instead of DM Alarm on passing vehicles
To enable the new “Infobeep”, clear UIMASK bit number 5 e.g. with UIMASK = 0xEF
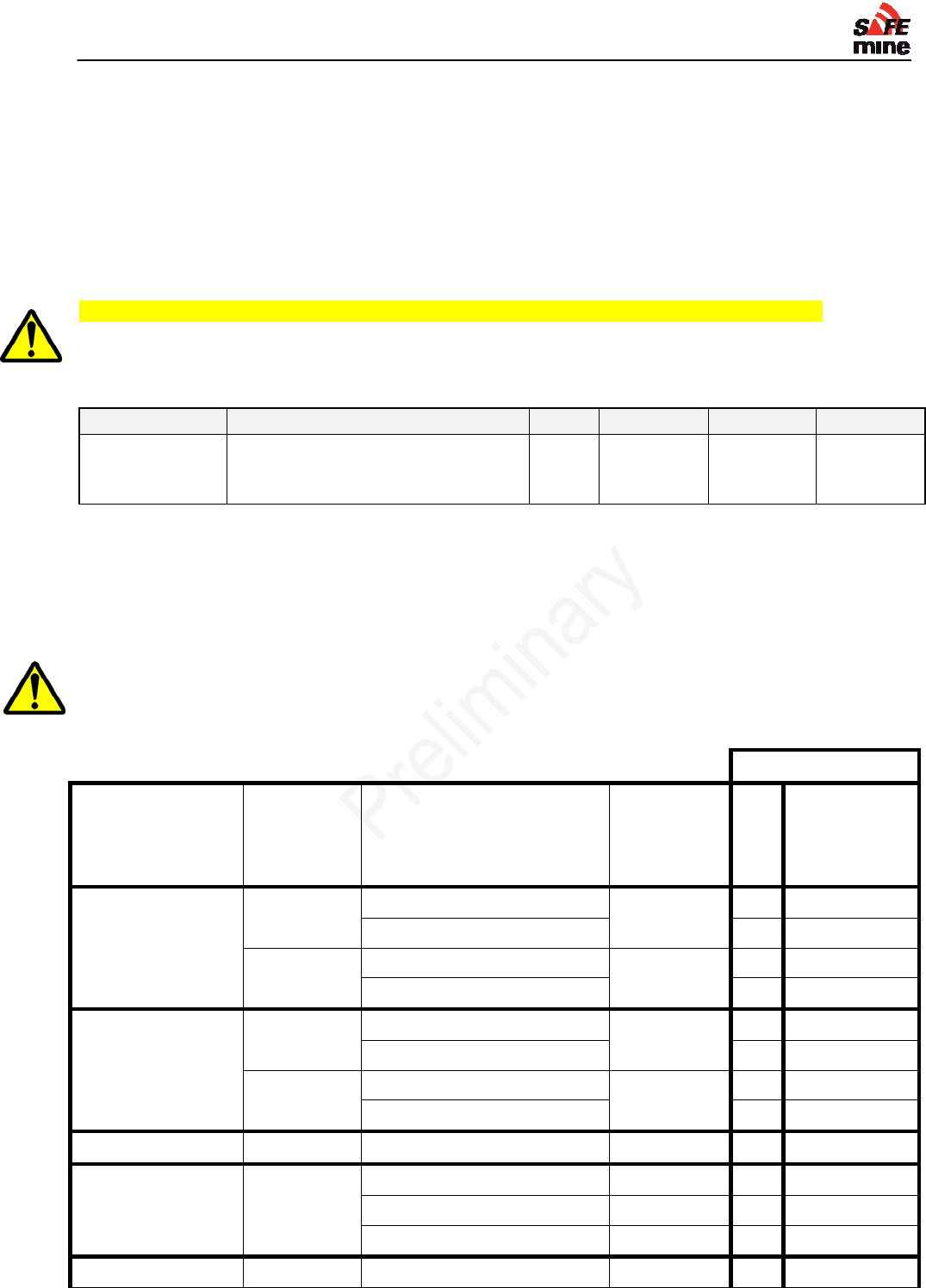
I
NSTALLATION AND
M
AINTENANCE
G
UIDE
Version 110301, Preliminary Page 30 of 56 March 2011
Conditions for triggering an Infobeep:
- The other vehicle could .
- I can see the other vehicle at +- 30 degrees from my direction of travel
- The other vehicle has a heading that is opposed to mine with a max deviation of +- 30 degrees
- The other vehicle is within DISTFAR (otherwise it is not shown on the display and should not be
announced)
A vehicle that has been announced through “Infobeep” will never generate a DM alarm (beeping)
on approaching, as it is assumed that the operator is aware of the approaching vehicle and will
avoid it.
Alarm Suppressions
Keyword Description Unit Range Default Example
ALARMSUPPRE
SSION -
0-
0xFFFFFFF
F
0 0FFFFFFFF
To avoid unnecessary ‘nuisance alarms’ several alarm exceptions detailed below have been
implemented which suppress alerting for certain DM (dangerous movement) alarms. To allow
flexibility, they can be switched on or off by setting ALARMSUPPRESSIONS in the configuration file
accordingly. If ALARMSUPPRESSIONS is not set, by default all suppressions are switched off
(there will be an alarm in the described situations). To edit the settings, sum up the listed codes
(hex) and set ALARMSUPPRESSIONS (hex) to the total result.
Use of this parameter will permanently disable some alarms when vehicles approach each
other.
code
My vehicle My
vehicle is
moving
Type of other vehicle I
am approaching Direction
where I
come
from
off on
Light Vehicle forward Light Vehicle anywhere 0 0x1
Small Tractor 0 0x2
backwards Light Vehicle anywhere
0 0x4
Small Tractor 0 0x8
Small Tractor forward Light Vehicle anywhere 0 0x10
Small Tractor 0 0x20
backwards Light Vehicle anywhere
0 0x40
Small Tractor 0 0x80
ADT forward PC anywhere
0 0x100
Small Front End
Loader forward ADT side 0 0x200
Dump Truck side 0 0x400
Rear Tip Truck side 0 0x800
Large Front End forward Haul Truck side 0 0x1000
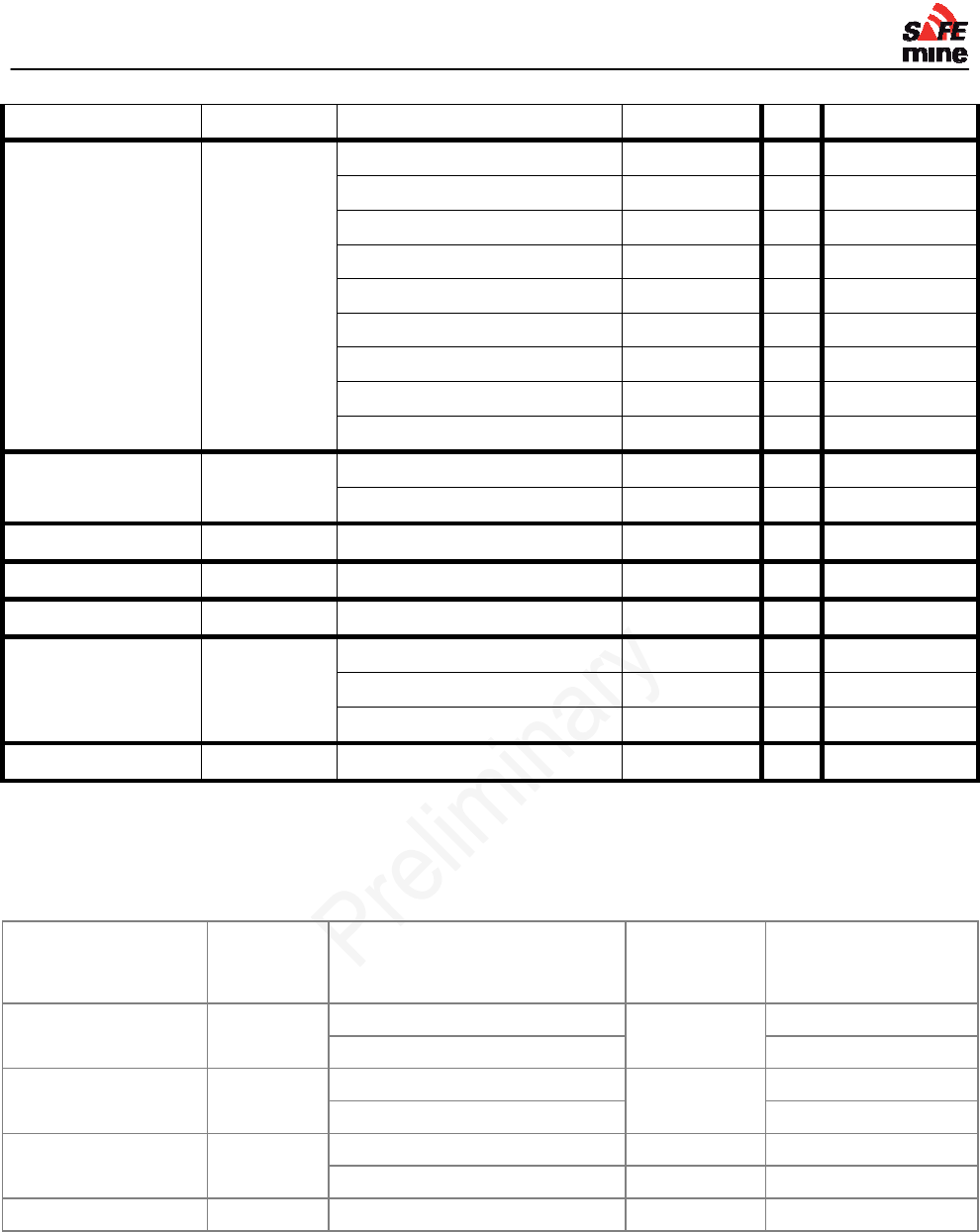
I
NSTALLATION AND
M
AINTENANCE
G
UIDE
Version 110301, Preliminary Page 31 of 56 March 2011
Loader Dump Truck side
0 0x2000
Tire Handler forward Grader side 0 0x4000
Service Truck side 0 0x8000
Fuel Bowser side 0 0x10000
Small Front End Loader side 0 0x20000
Large Front End Loader side 0 0x40000
Tyre Handler side 0 0x80000
Haul Truck side 0 0x100000
Water Tanker side 0 0x200000
Dump Truck side 0 0x400000
Haul Truck all Excavator anywhere 0 0x800000
PC side
0 0x1000000
Dump Truck all PC anywhere 0 0x2000000
Rear Tip Truck all PC anywhere 0 0x4000000
Excavator all Haul Truck anywhere
0 0x8000000
PC all ADT anywhere
0 0x10000000
Dump Truck anywhere 0 0x20000000
Rear Tip Truck anywhere 0 0x40000000
Dozer all Dozer anywhere
0 0x80000000
Example:
Following suppressions turned on:
My vehicle I am
moving Other vehicle I am
approaching Direction
where I
come from
code for switching
on:
Light Vehicle forward Light Vehicle anywhere
0x1
Small Tractor 0x2
Small Tractor forward Light Vehicle anywhere
0x10
Small Tractor 0x20
Large Front End
Loader forward Haul Truck side 0x1000
Dump Truck side 0x2000
Tyre Handler forward Service Truck side 0x8000
All other exceptions turned off
sum of all codes = 0x4 + 0x8 + 0x40 + 0x80 + 0x1000 + 0x2000 + 0x8000 = 0xB033
the following line has to be added into the configuration file:
ALARMSUPPRESSIONS = 0xB033
Note that the number entered for the parameter ALARMSUPPRESSIONS is hexadecimal. A single
digital hex number can range from 0 to 15, so letters are used to represent numbers greater than
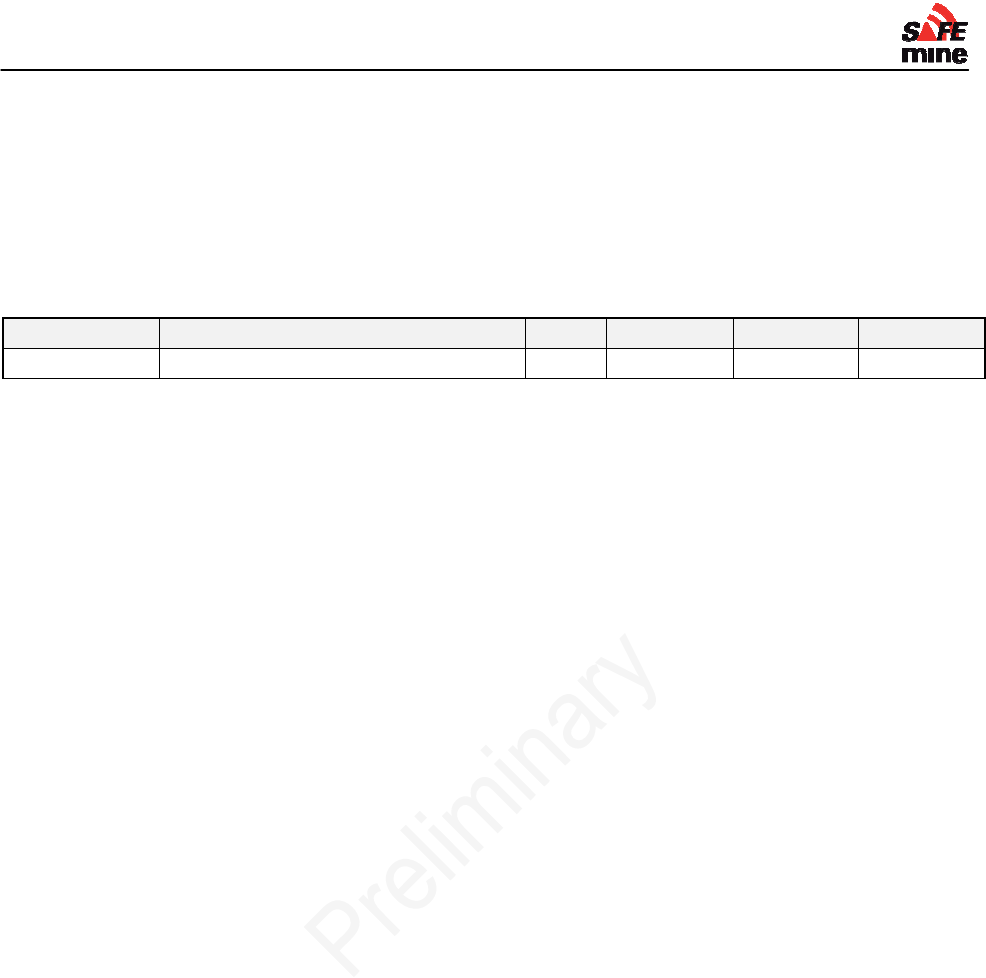
I
NSTALLATION AND
M
AINTENANCE
G
UIDE
Version 110301, Preliminary Page 32 of 56 March 2011
9, i.e., 10=A, 11=B, 12=C, 13=D, 14=E, and 15=F. Hence when numbers are added they are done
one column at a time. If the total for a column is greater than 9 letters between A and F are used to
represent the hex number.
To eliminate some of the work, if only some few exceptions have to be turned off, the associated
on-codes can be subtracted from the value 0xFFFFFFFF.
Maximum exception speed
Keyword Description Unit Range Default Example
MAXEXSPEED Limit of alarm suppression km/h 0 - xx 0 10
If MAXEXSPEED [km/h] is set in the configuration file, all active suppressions are only suppressing
beeping if my vehicle is moving below that speed. If MAXEXSPEED is not set, there will be no
limiting speed for alarm suppressions.
Use 0 to disable this feature (default).
Put another way, Suppressions only have an effect when vehicle speed > MAXEXPTSPEED.
Example:
On a Large Front End Loader, MAXEXSPEED = 5 and ALARMEXCEPTIONS = 0xB033 are set in
the configuration file. Therefore there will be no DM (beeping) alarms if the Large Front End Loader
approaches a Dump- or Haultruck from the side, except if the Large Front End Loader is going
faster than 5km/h.
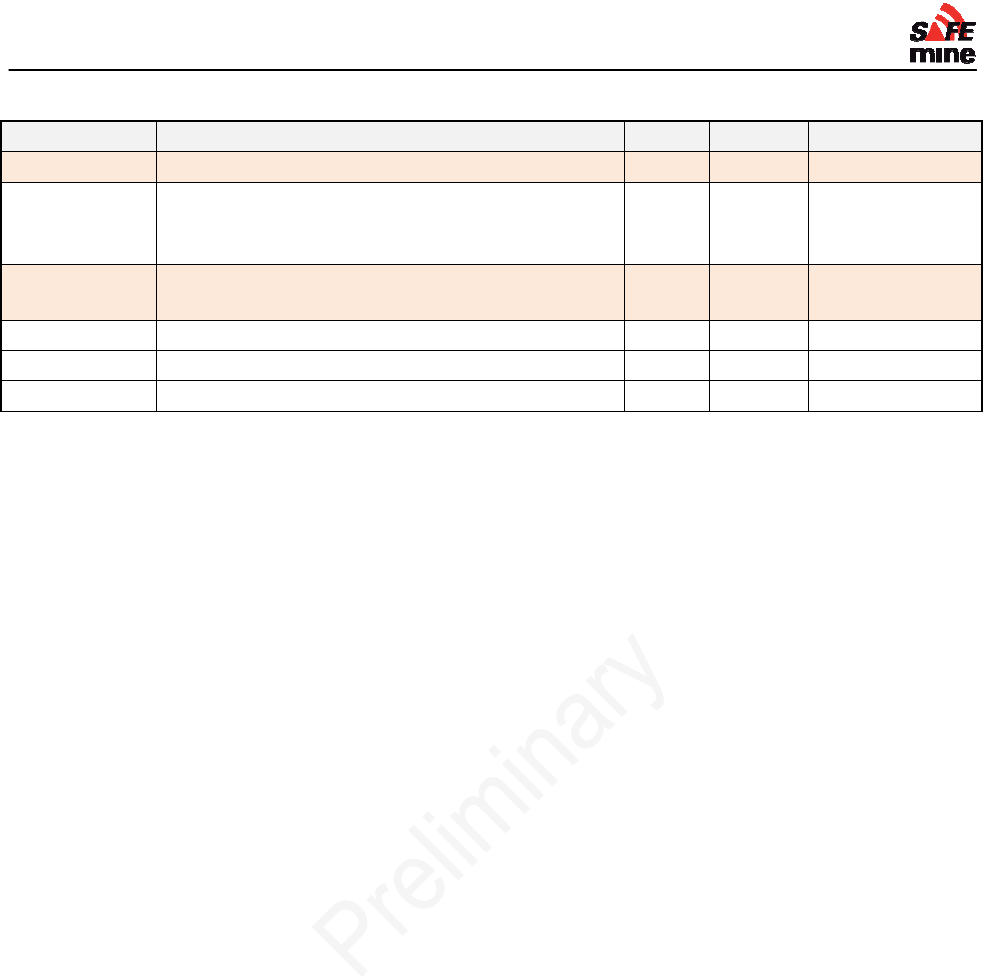
I
NSTALLATION AND
M
AINTENANCE
G
UIDE
Version 110301, Preliminary Page 33 of 56 March 2011
Parameter Description Unit Example Keyword
Weight Maximum vehicle weight (including load) Ton 350 VEHWEIGHT
Max Speed Rev Maximum speed in reverse. Alarm will sound on
speeding (optional. Requires Option QP117)
0: disabled
km / h 5 MAXSPEEDREV
Turning radius Turning radius SAE (set to 0 for rotating, e.g. tracked
vehicles). See additional instructions below Meter 28 MINTURNRAD
Driver Pos Aft Distance between front of vehicle and driver Meter 1.5 DRIVERAFT
Driver Pos Right Distance between left side of vehicle and driver Meter 1.5 DRIVERRIGHT
Driver Pos Up Elevation of driver above ground Meter 4 DRIVERUP
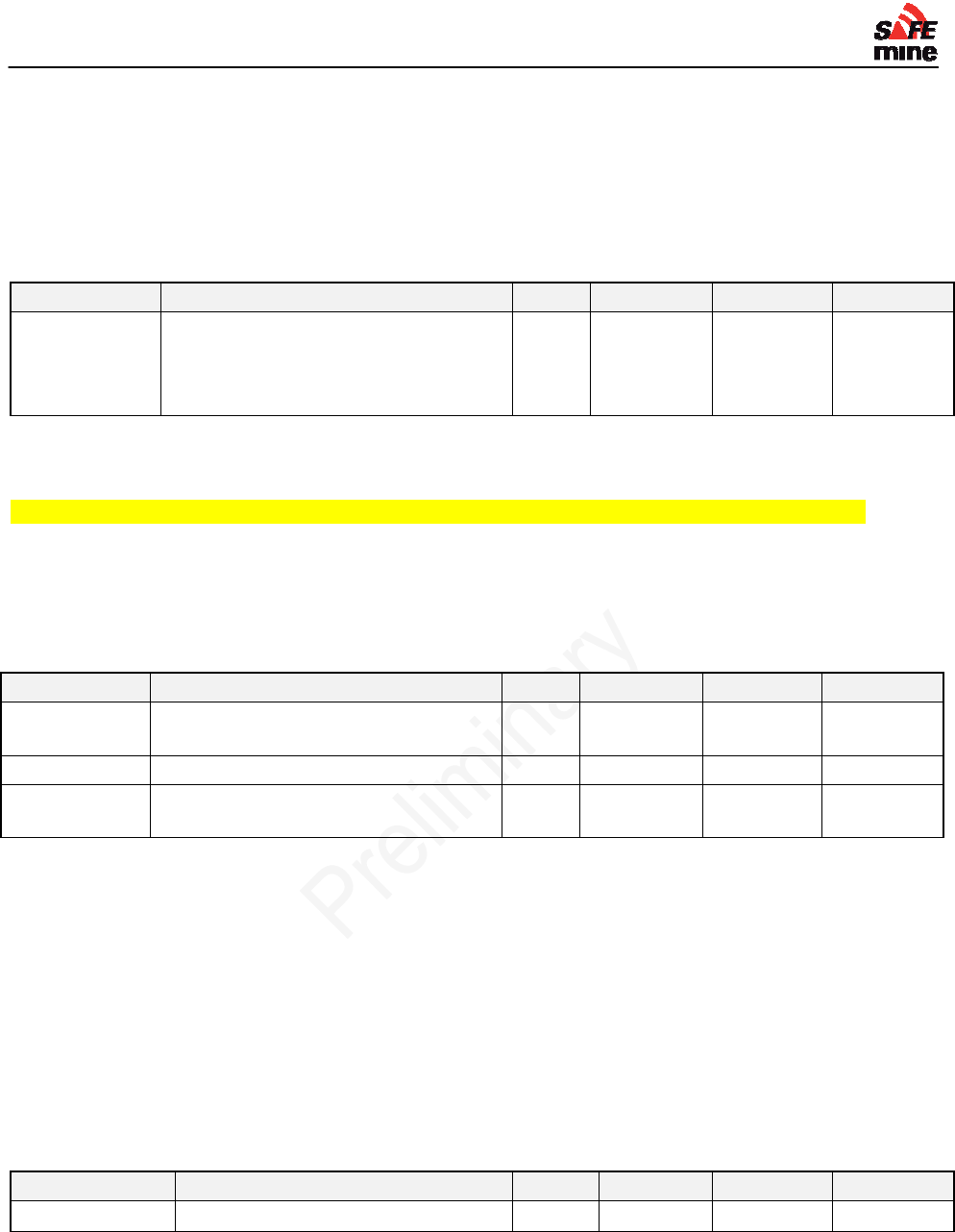
I
NSTALLATION AND
M
AINTENANCE
G
UIDE
Version 110301, Preliminary Page 34 of 56 March 2011
Optional Features
Speeding Alert
Alerts are issued through the LED display and the voice output if the vehicle goes faster than
MAXSPEED.
Rollover alert
Keyword Description Unit Range Default Example
ROLLOVER Maximum roll angle. Alarm will sound on
higher angle
Requires Option QP
0: disabled
°
degree
s
0 - 90 0 40
Rollover alarm is currently deactivated on very bumpy roads to avoid nuisance alarms.
Voice output
All voice output functions are still in a ‘BETA’ state and may only be used for testing!
[intro]
Voice is currently available in English and Spanish. More languages can be ordered through your
SAFEmine dealer.
The 'announce all on button press' works again, however the vehicle must meet the conditions
described below to get re-announced.
Voice plays for the first time if its predicted trajectories come within DISTVOICE.
0 suppresses all vehicle alarms
The distance to the other vehicle is no longer announced, as the announcement took too long.
Conditions for Clustering:
I see the vehicles within +-40 degrees and between them there is less than DISTFAR/2 distance.
Clustered vehicles are announced as “n Vehicles”.
Data Recording
Log interval
Keyword Description Unit Range Default Example
LOGINTERVAL Log interval for track and data recording. seconds 1 - 255 1 2
The internal flash memory will overwrite the oldest logs after about 80h of vehicle movement (if 1
second interval is chosen). Log interval is multiplied by 60 when vehicle is stationary to save
memory.
Each position record also contains information on the accumulated RMS (Root Mean Square)
vibration since the last log entry.
It also contains the movement mode (for easier data analysis)
Keyword Description Unit Range Default Example
VOICEFILE File name of voice audio file 0 sm_EN_M_1
.1.voc
DISTVOICE
AUDIOVOLUM
E Controls speaker volume independent of
the buzzer volume % 0 - 100 80
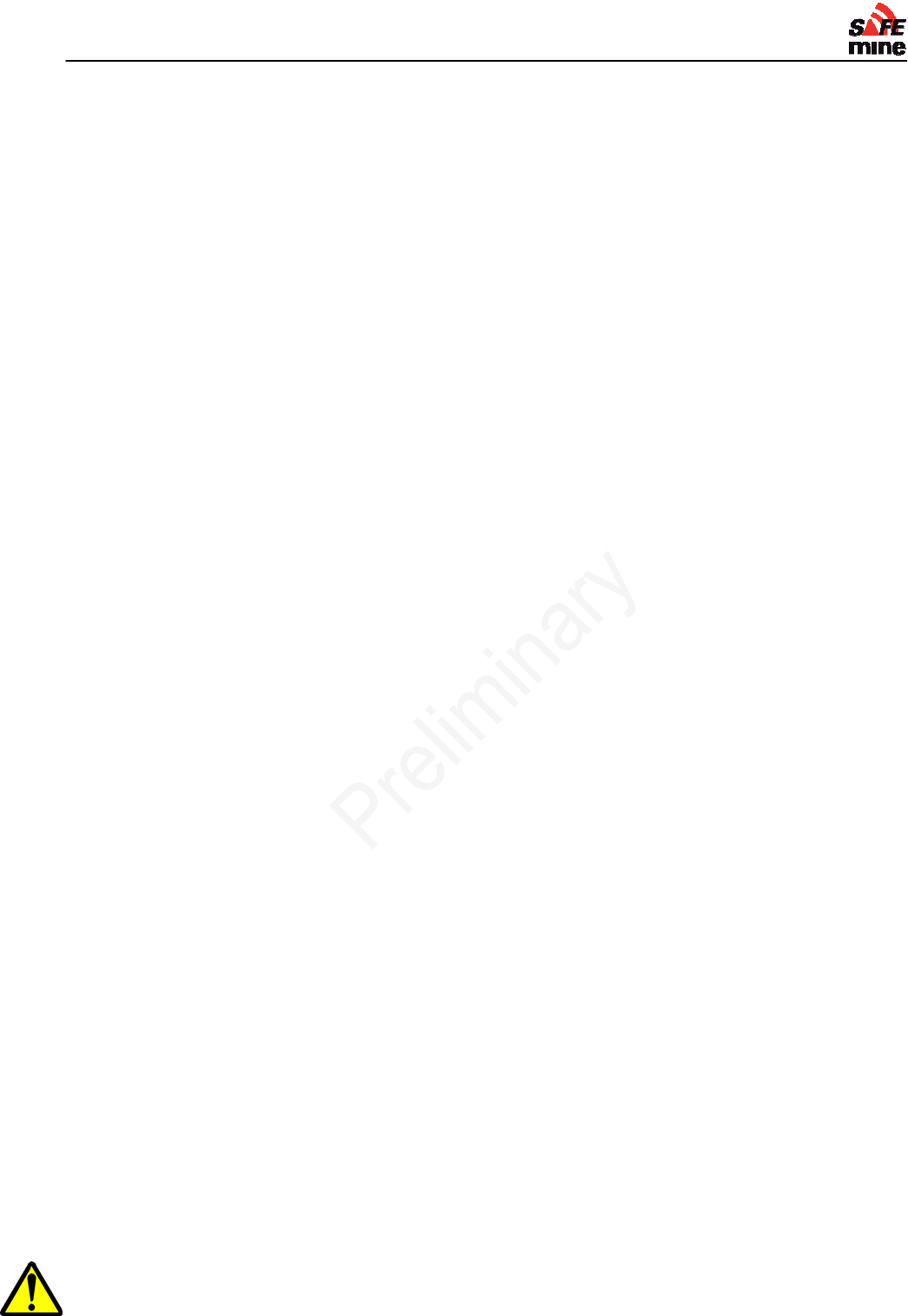
I
NSTALLATION AND
M
AINTENANCE
G
UIDE
Version 110301, Preliminary Page 35 of 56 March 2011
Note: Analysis of vibration data is not yet supported by the PC software.
Fatal errors that lead to a device reset are now recorded.
Note: Analysis of this data is not yet supported by the PC software.
Vehicles are only recorded if they trigger a sound alarm, or if a sound alarm was suppressed by an
alarm exceptions setting.
Obstacles
Fixed obstacles can be defined. If a vehicle approaches these obstacles the operator will be
warned.
Obstacle data must be placed in a separate file named “obst.ini”. It may be updated through the
Sync Station
The syntax of an obstacle entry is:
OBST = <type>,<geometry type>,<geometry>
You may also use “;” as delimiting characters. The fields are:
<type> A number, where:
0 -> Generic Obstacle (announced as ‘Obstacle’)
10 -> Building
21 -> Power line
22 -> ‘Stop’ sign
23 -> reduced speed area
71 -> Coal valve
72 -> Stockpile edge
<geometry type> one of the following
1d: circular obstacle
2d: line obstacle (i.e. conduit, cable)
<geometry> depends on geometry type.
For 1d: <lat>,<lon>,<radius>
For 2d: <lat><lon>,<lat>,<lon> (designating the start and endpoint of the
conduit)
<lat> latitude, decimal notation (decimal sign is the period “.”), followed by “N” or “S”
character. E.g.: 48.1234N (trailing zeros may be omitted)
coordinates must be in WGS84 system
<lon> same as lat, but using “E” or “W” character. E.g.: 167.987552W.
<radius> radius in meters, decimal notation.
Examples:
# This is a "line" obstacle, issuing "power line" voice alerts
OBST = 21;2d;37.845N,122.243W;37.847N,122.243W
# This is a circular obstacle, issuing "obstacle" voice alerts
OBST = 0;1d;37.841343N,122.248W;5.3
The maximum number of obstacles is 25.
The maximum numbers of characters in a line is to 80.
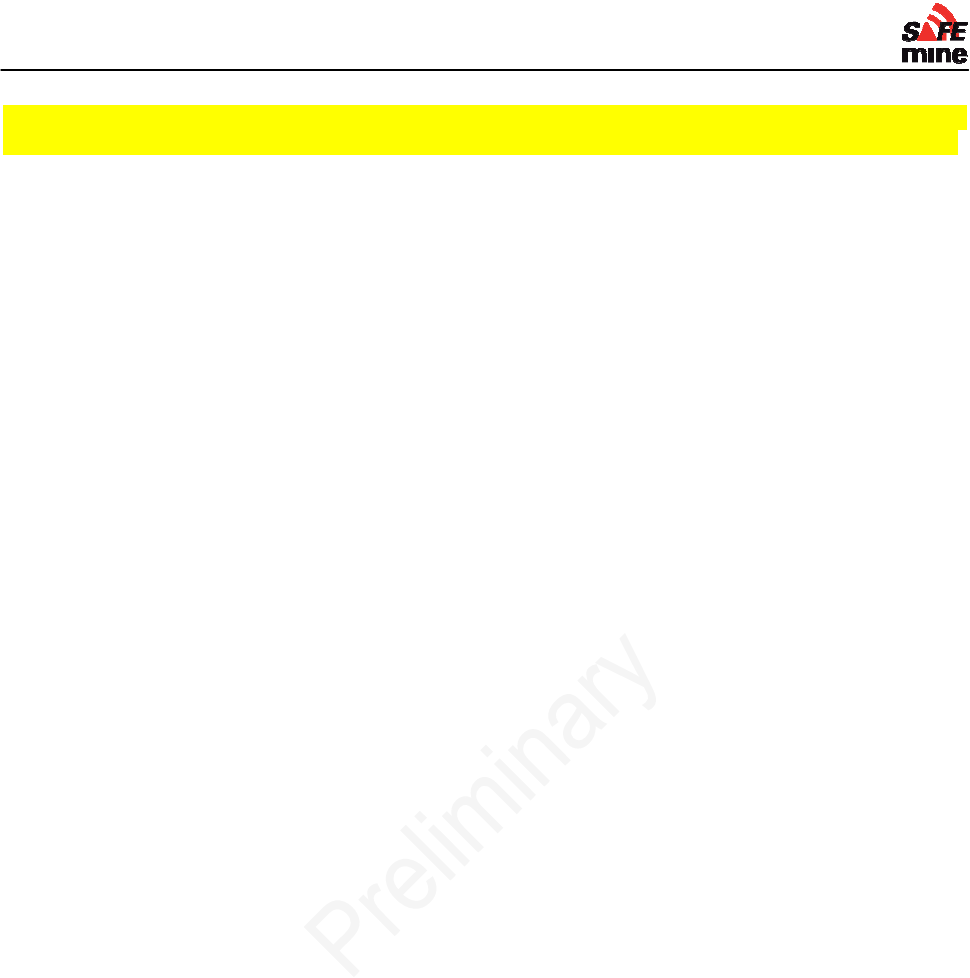
I
NSTALLATION AND
M
AINTENANCE
G
UIDE
Version 110301, Preliminary Page 36 of 56 March 2011
Distance to obstacles is calculated from the GPS antenna of the vehicle, no vehicle
dimensions and antenna locations are considered! This will be improved in future releases.
Areas
Areas allow to automatically change parameters based on the location of the vehicle, e.g. to have
different maximum speed limits on site and on the highway.
See separate documentation for details on how to program areas.
Stockpile Collision Avoidance
Special modes are available to support stockpile collision avoidance system application. This
includes warnings for stackers, reclaimers, coal valves and vehicles operating on the stockpile.
Please contact SAFEmine for additional information.
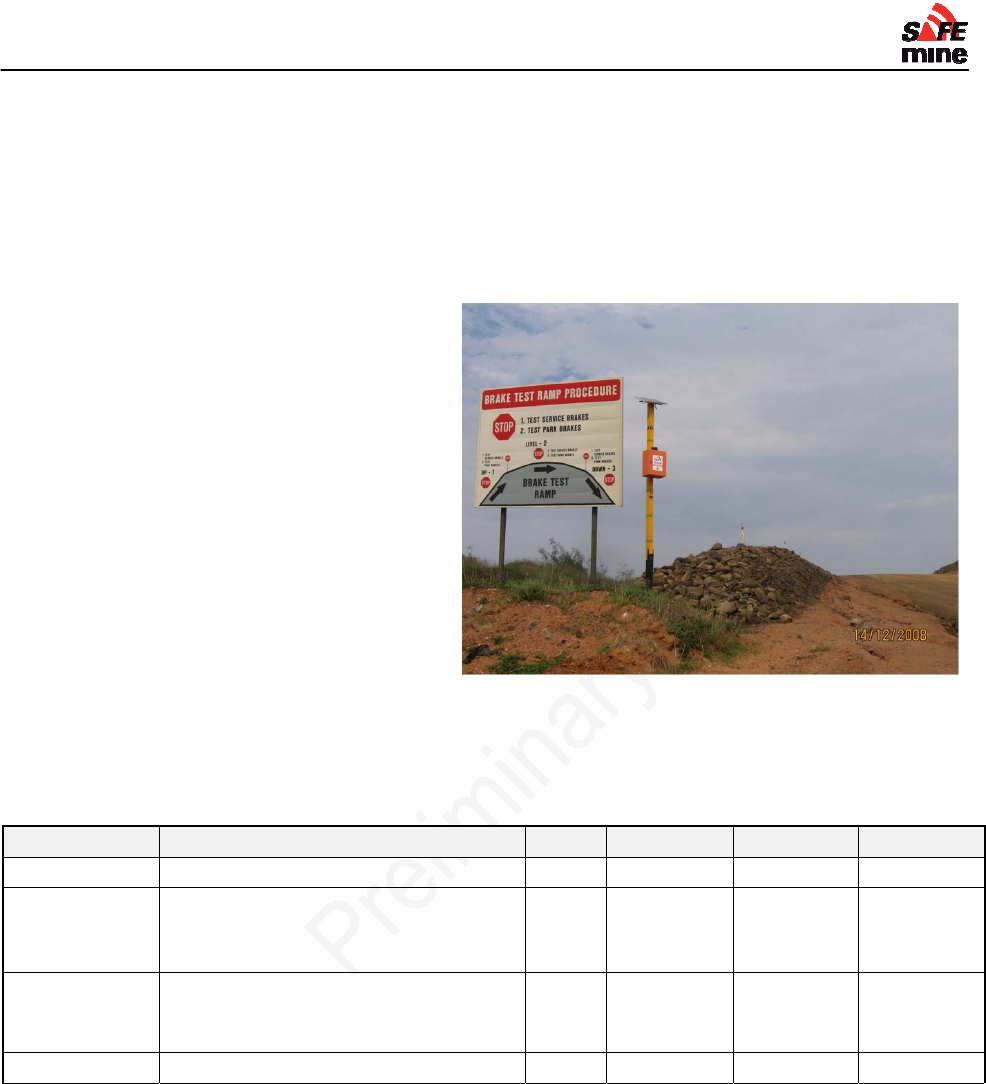
I
NSTALLATION AND
M
AINTENANCE
G
UIDE
Version 110301, Preliminary Page 37 of 56 March 2011
Special configurations
Test Station
[Intro]
A Test Station may be in command of an electric boom gate for automated access control.
Any SAFEmine equipped vehicle within the
range of the Test Station will cause the
digital output to go high. The output will
remain high until the vehicle is again out of
range. The approaching vehicle will have its
LED flash red along with a buzzer alarm
when it is within its DISTNEAR setting.
To use the Test Station mode, set vehicle
type VEHTYPE to 72 and DISTCLOSE to the
range in meters where it is desired to be
activated. The unit must be purchased as
option QP141 per price list.
Setting DISTCLOSE to 0 will make the unit behave as if it was approached by a vehicle, this is the
test mode to test the digital output.
Test stations do not trigger on any vehicle in the vicinity but look at the location and direction of
travel. Only vehicles that drive ‘IN’ will be detected and shown by the test station.
Add the keyword ‘moving’ to the VEHMOD parameter to limit detection to forward moving vehicles
Keyword Description Unit Range Default Example
VEHTYPE Set to 72 72 0 72
VEHMOD Determines behavior ‘from left’ or
‘from right’
‘moving’
- FROM LEFT
MOVING
FIXHEADING Orientation °
degree
s
0 - 360 - 53
DISTCLOSE Range m 0 - 255 5 40
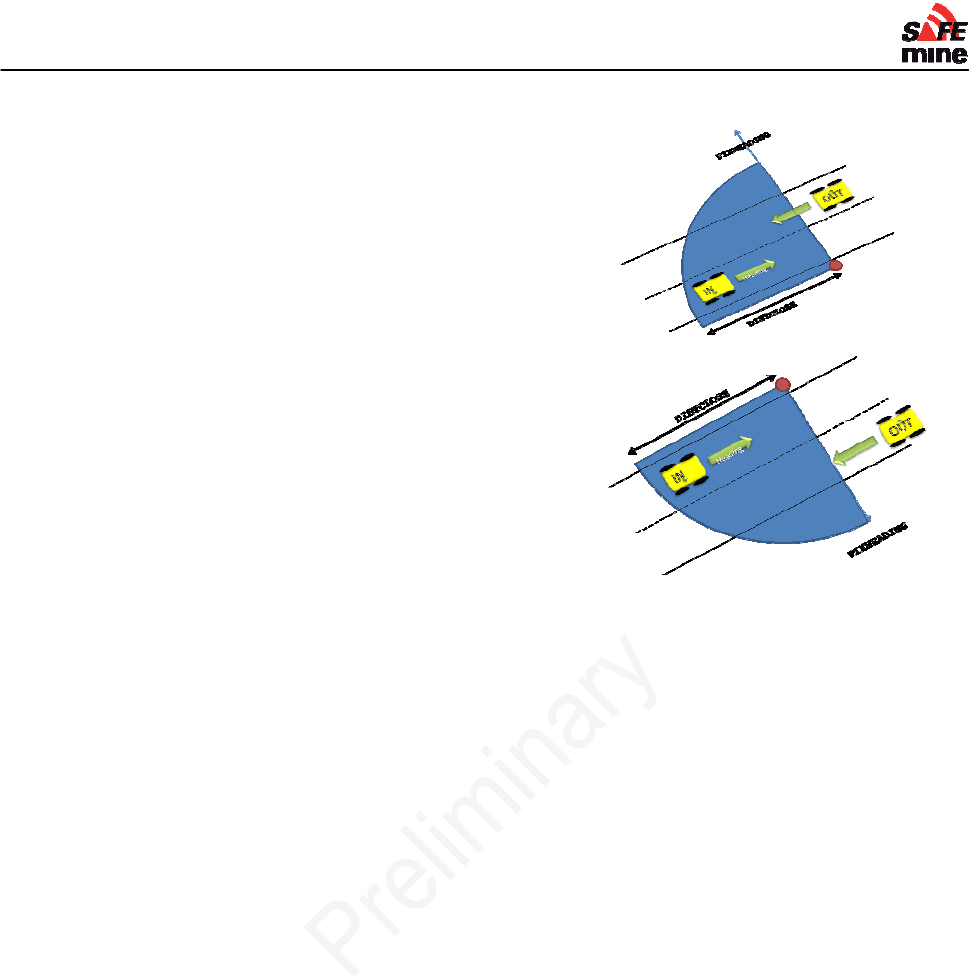
I
NSTALLATION AND
M
AINTENANCE
G
UIDE
Version 110301, Preliminary Page 38 of 56 March 2011
Examples
Right hand traffic
(traffic keeps to the right side of the road)
The example below uses the following parameters:
VEHMOD = from left
FIXHEADING = 330
DISTCLOSE = 50
Left hand traffic
(traffic keeps to the left side of the road)
The example below uses the following parameters:
VEHMOD = from right
FIXHEADING = 150
DISTCLOSE = 50
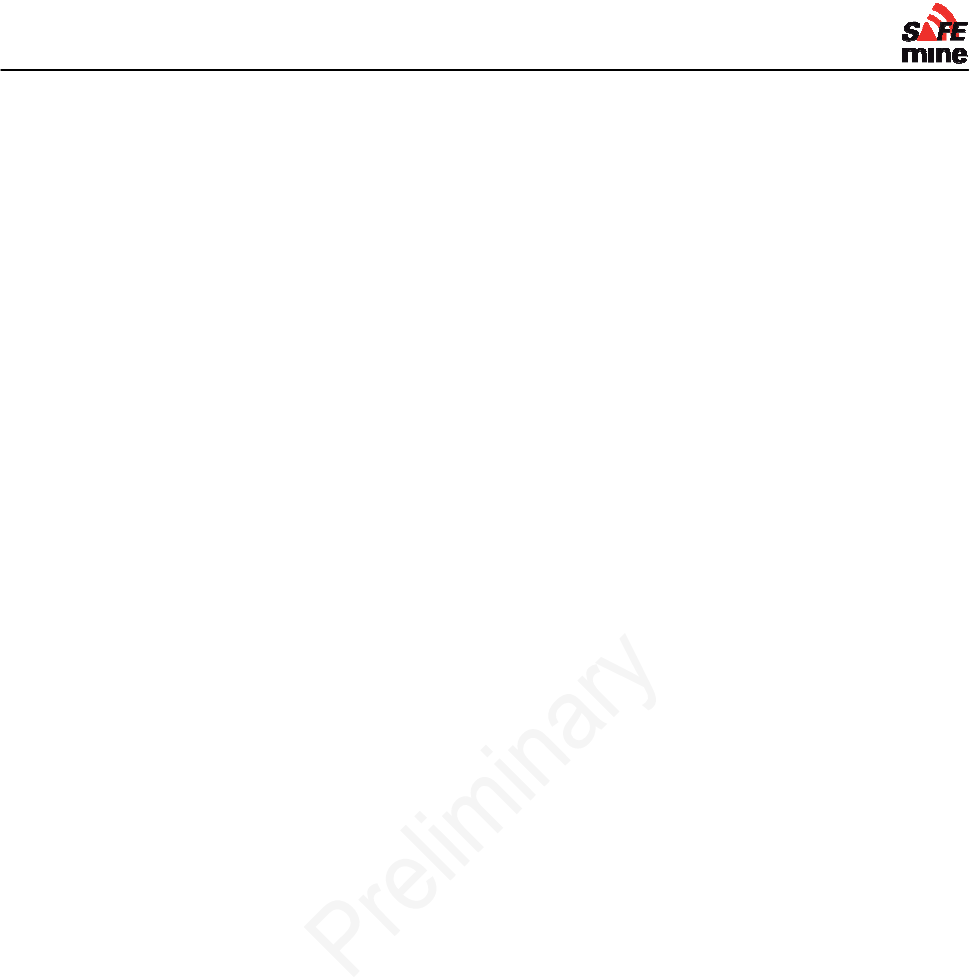
I
NSTALLATION AND
M
AINTENANCE
G
UIDE
Version 110301, Preliminary Page 39 of 56 March 2011
Rotating Vehicles (Patent Pending)
Minimum Turn Radius
Vehicles with unknown heading (e.g. non moving, tracked, rotating vehicles) are calculated as
circular objects. No threat heading can be displayed to the operator of such vehicles.
The parameter minturnrad should be set to zero for tracked vehicles and other vehicles where
the orientation of the driver may differ from the direction of travel. Setting minturnrad = 0 will
result in the motion filter discarding heading information once the vehicle enters standstill. Setting a
value greater than 0 will disable this behavior.
To determine the heading of rotating vehicles (e.g. tracked dozers etc), two units must be
mounted. The main unit can be mounted as normal, except that its antenna should be mounted
towards a corner of the vehicle.
The minimum distance between the antennas of the units is 5 meters for vehicles operating on the
surface of the mine and 15 meters for vehicles active in regions with more than 30% obstruction of
the sky. Contact SAFEmine if these restrictions cannot be met.
It is essential that both antennas are not obstructed by any part of the vehicle and have a
360° view of the horizon (except for terrain obfuscation).
Configuring the main unit
Set BEACON = XXXXXXXXXXX
Where XXXXXXXXXX is the serial number of the beacon unit, e.g. “70011855000”.
Also, accurately enter the position of the slave (beacon) antenna:
BCNANTENNAAFT = XX.X meters
BCNANTENNARIGHT = XX.X meters
BCNANTENNAAUP = X.X meters
Configuring the beacon unit
Set VEHICLETYPE = 100 (required!)
It is essential that both the main and the beacon unit have their antenna positions programmed
accurately.
Usage
The main unit's "Reverse" LED is flashing red if no valid beacon signal is received.
The LED of the beacon unit will flash green at 1Hz and 50% duty cycle and the "reverse" LED is
always off".
Limitations
The center of rotation is assumed to be in the middle of the vehicle for the rotation prediction.
Rotating vehicles
Some vehicles can turn or rotate and hence change their heading without any forward or backward
movement, such as in the case of track dozers and shovels. In effect, these vehicles have a turning
radius of zero. In such cases, it is recommended that a second antenna be added so that the direction
of movement of the vehicle is always defined.
Installing Hardware
The principal antenna should be installed as close to the center of rotation of the vehicle as possible
and the second antenna, referred to as a beacon, should be installed in a corner location such that
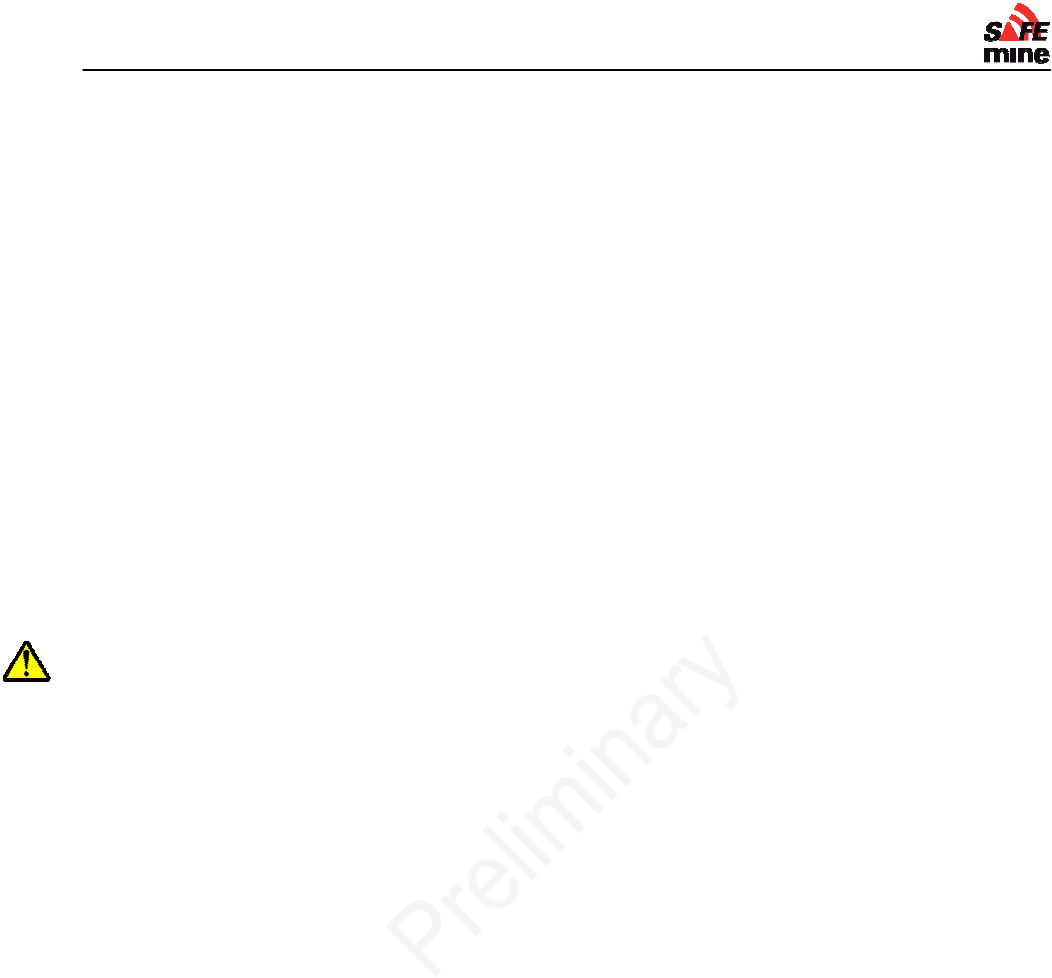
I
NSTALLATION AND
M
AINTENANCE
G
UIDE
Version 110301, Preliminary Page 40 of 56 March 2011
the distance between the principal and beacon antennas is as large as possible. Both antennas
require their own SAFEmine main unit. The principal main unit can be either a QC230 with a remote
display or a QC235; the beacon main unit does not require a display and often a QC230 without a
remote display is used here. For convenience, both main units are often mounted close together in the
cab of the vehicle, in a piggy-back or side-by-side fashion.
It is recommended that the distance between the two antennas be at least 5 meters. For vehicles that
operate in regions of the mine where more than 30% of the view of the sky is obstructed, this distance
is increased to 15 meters. Contact SAFEmine if these restrictions cannot be met.
It is essential that both antennas are not obstructed by any part of the vehicle and have a 360°
view of the horizon (except for terrain obfuscation).
Software Configuration
For the system to operate properly, the principal main unit needs to recognize the beacon main unit.
This is accomplished by means of the main unit serial number. By including the beacon main unit
serial number in the configuration file of the principal main unit, the two antennas can be linked.
It is also critical that the relative position of the two antennas be known. This is also done by means of
special parameters in the principal main unit configuration file, such that the relative position of the
beacon antenna is stored in the principal main unit. By knowing the position of the principal and
beacon antennas and the distance and angle between the two, the heading of the vehicle can easily
and accurately be determined.
To do this, add the following to the standard configuration file of the principal main unit:
Minturnrad = 1
(Rotating vehicles using only a single antenna are vehicles of unknown headings and are
calculated as circular objects. No threat heading can be displayed to the operator. In such cases of
rotating vehicles, where only a single antenna is used, minturnrad is set to 0).
BEACON = XXXXXXXXXXX
where XXXXXXXXXX is the serial number of the beacon unit, e.g. “70011855000”.
BCNANTENNAAFT = XX.X
BCNANTENNARIGHT = XX.X
BCNANTENNAAUP = XX.X
where XX.X is the distance measured in meters. These configuration file parameters are defined
as follows:
BCNANTENNAAFT - distance measured from the front of the vehicle to the beacon antenna
BCNANTENNARIGHT - distance measured from the left side of the vehicle to the beacon
antenna
BCNANTENNAAUP – distance measured from the ground level to the beacon antenna.
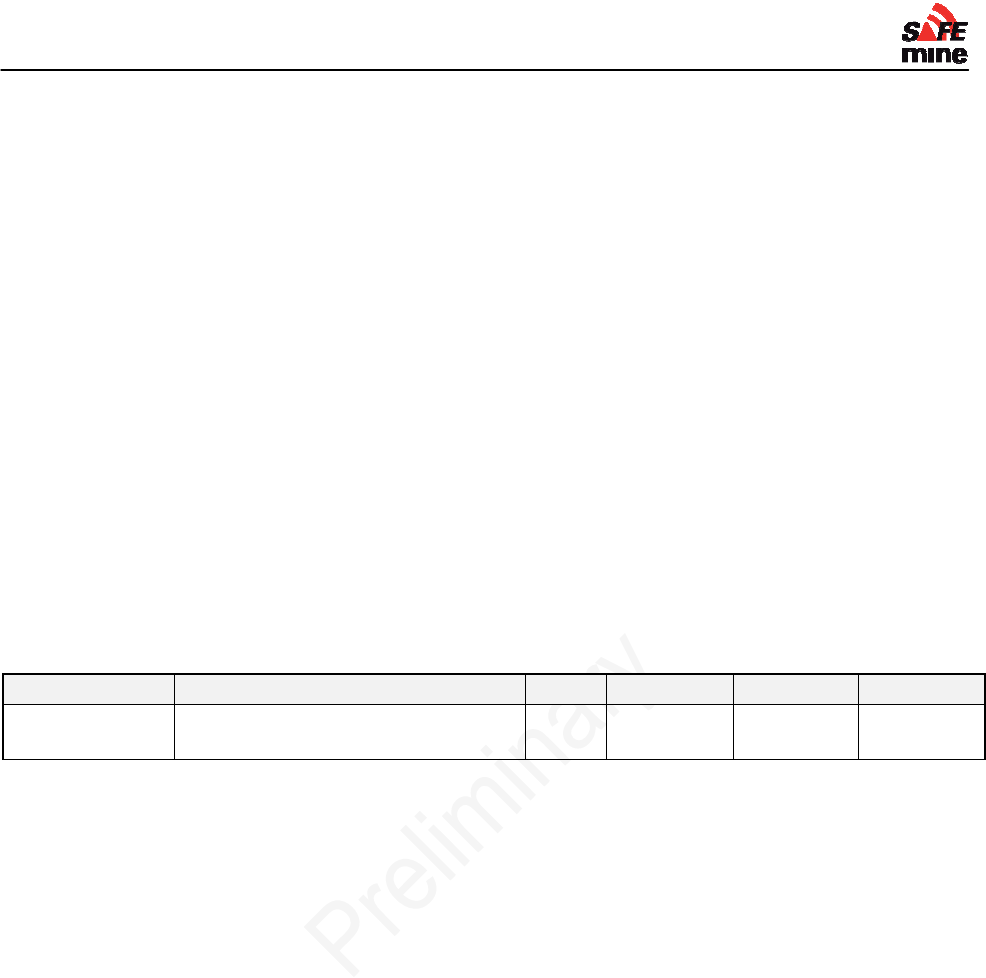
I
NSTALLATION AND
M
AINTENANCE
G
UIDE
Version 110301, Preliminary Page 41 of 56 March 2011
It is essential that both the main and the beacon unit have their antenna positions programmed
accurately for proper operation!
Now add the following to the configuration file of the beacon main unit to set its vehicle type to 100:
VEHICLETYPE = 100
Performance
The LED of the beacon unit will flash green at 1Hz, 50% duty cycle, and the "reverse" LED is always
off.
However, the main unit's "Reverse" LED will flash red if no valid beacon signal is received.
Limitations
The center of rotation is assumed to be in the middle of the vehicle for the rotation prediction. If there
is a significant difference between the true axis of rotation and the center a slight positional error will
result.
Dual Zone vehicles
Keyword Description Unit Range Default Example
VEHBASELENG
TH Length of the vehicles body m 0 - 655 0 20
Some Vehicle types can be configured to have a base-length (configuration value
“vehbaselength”). This allows Haul-Trucks and Dump-Trucks to reverse towards the loading boom
of an excavator or shovel without causing an alarm. Also no alarm will be given to the operator of
the excavator or shovel when swinging the boom over the haul truck.
This behavior only occurs in interactions between shovels/excavators (VEHTYPE = xx / xx) and
haul- and dump trucks (VEHTYPE = 21 / 22)
Vehicles with configured vehbaselength are currently exempt from collision de-escalation.
Digital I/O
The digital IO module can be used to monitor and record vehicle parameters such as: door open,
seatbelt, handbrake, etc.
Another use of this module is the switching of cameras based on movement direction or
surrounding vehicles and obstacles.
This option requires additional hardware, contact SAFEmine for evaluation.
Visual Displays and Alarms
The visualization of rollover alarm, obstacle alarm and over speed alarm are as follows:
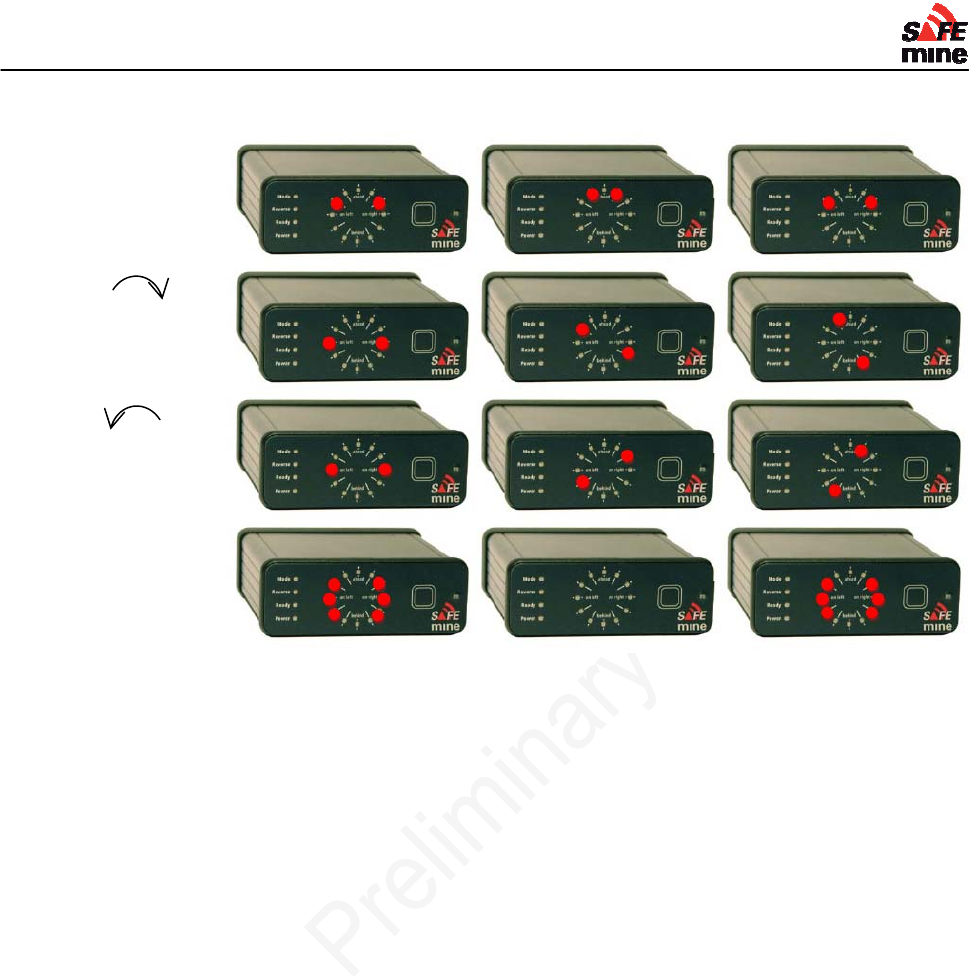
I
NSTALLATION AND
M
AINTENANCE
G
UIDE
Version 110301, Preliminary Page 42 of 56 March 2011
These special alarms are not shown with other alarms together. Therefore they only appear if no
other more important alarm was found.
Alarm "Hysteresis"
All alarms are show for a minimum of 1.5 seconds to allow the operator to see and react to it.
Changes to higher alarm levels are immediate, lower levels only after showing higher level for 1.5
seconds.
Inside detection
The unit automatically detects when the vehicle is inside (e.g. a garage) and goes into standby
mode. This prevents nuisance alarms due to bad GPS coverage and also prevents spurious GPS
ok/not ok signals while being parked inside.
When the unit detect that it is inside, the ‘Ready’ LED changes to red.
Button press recording
Short button presses are being recorded and are visible in the CSV file as ‘BUTTON’ Entry.
This can be used to flag special situations, e.g. incidents or situations where the user believes the
SAFEmine device does not perform as expected.
Obstacles, Powerlines
Rollover
Rollover
Overspeed
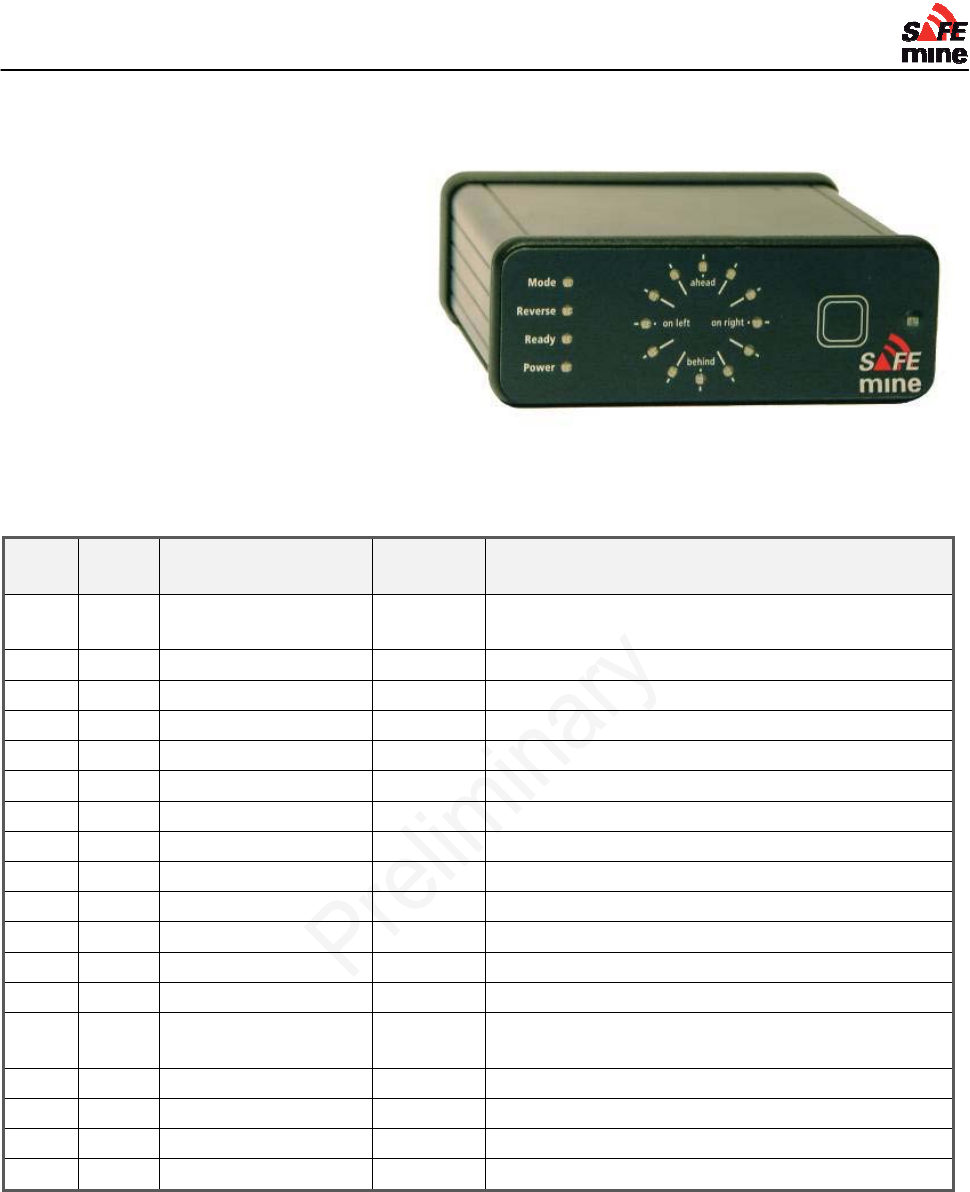
I
NSTALLATION AND
M
AINTENANCE
G
UIDE
Version 110301, Preliminary Page 43 of 56 March 2011
Error codes
The unit performs a self-test upon power
up. Errors are indicated by flashing of all
status LED in red while showing the error
code(s) on the circular display and also
sending it to the serial port.
Debugging of error codes is best done
with a PC running a terminal program
(e.g. Hyperterm) connected to the serial
port.
On first restart after updating a "non
fatal" error may be displayed for 30 seconds due to the additional configuration options (green
flashing status lights and one green light on the compass display)
Error
code LED # Subsystem Severity Cause
01 1 Flash Memory (Fatal) Flash memory failure; non-fatal if operational, but data
lost. Fatal if operation is not possible.
02 2 Serial Fatal Serial number invalid, contact support
04 3 GPS receiver Fatal
05 1 & 3 GPS Antenna Fatal GPS antenna defective or bad connection
08 3 Power Fatal Power supply defective or low/high voltage
RF transceiver Fatal
Microphone
Buzzer Fatal
Ambient Light Sensor
Acceleration Sensors Fatal
Flash Memory
Flash File System
16 4 User Interface Fatal
32 5 Config (Fatal)
Configuration file contains errors, or loading default
configuration
64 6 Firmware Fatal Firmware corrupt, upload new firmware
128 7 Generic Generic error
Speaker Only when configured for Speaker use
255 8 Unknown
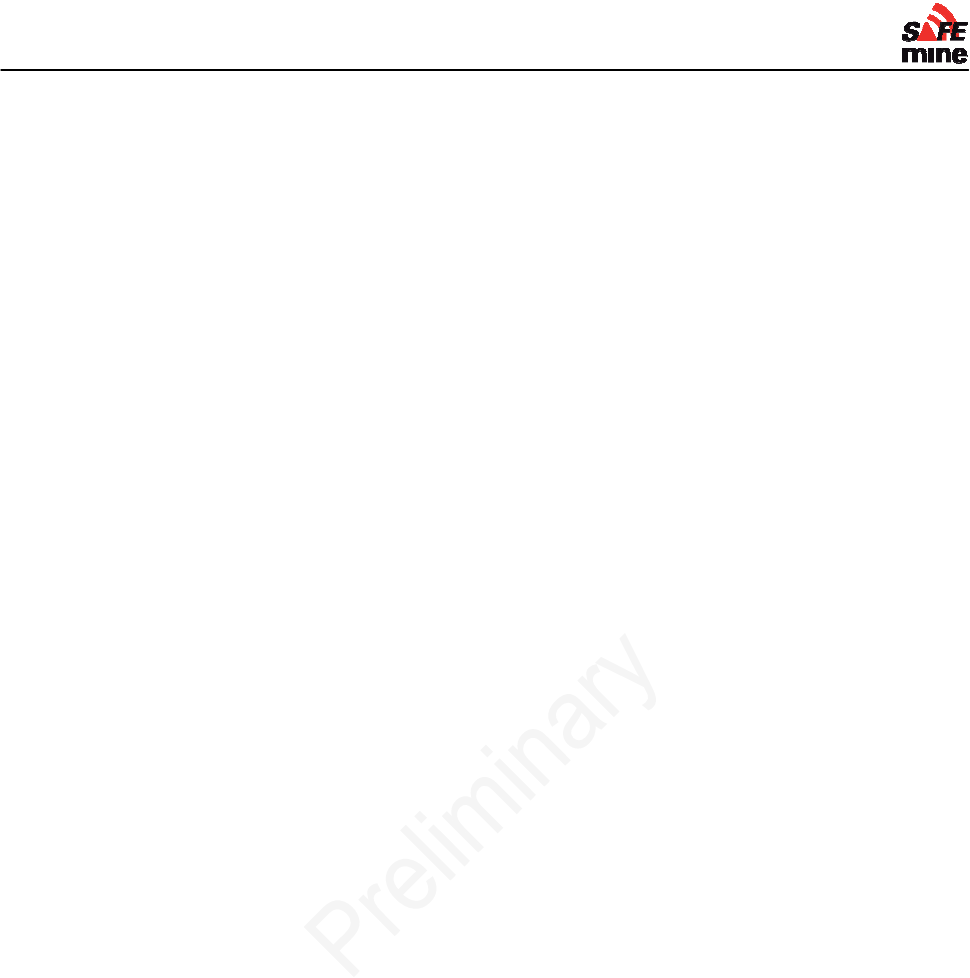
I
NSTALLATION AND
M
AINTENANCE
G
UIDE
Version 110301, Preliminary Page 44 of 56 March 2011
Limitations
Distance to obstacles is calculated from the GPS antenna of the vehicle, no vehicle dimensions
and antenna locations are considered!
Only the following obstacle types are implemented in the voice output: “Power Line”, “Obstacle”.
Vehicles with unknown heading (e.g. non-moving, tracked vehicles) are not calculated with their
exact dimensions / behavior. Will be resolved in next revision.
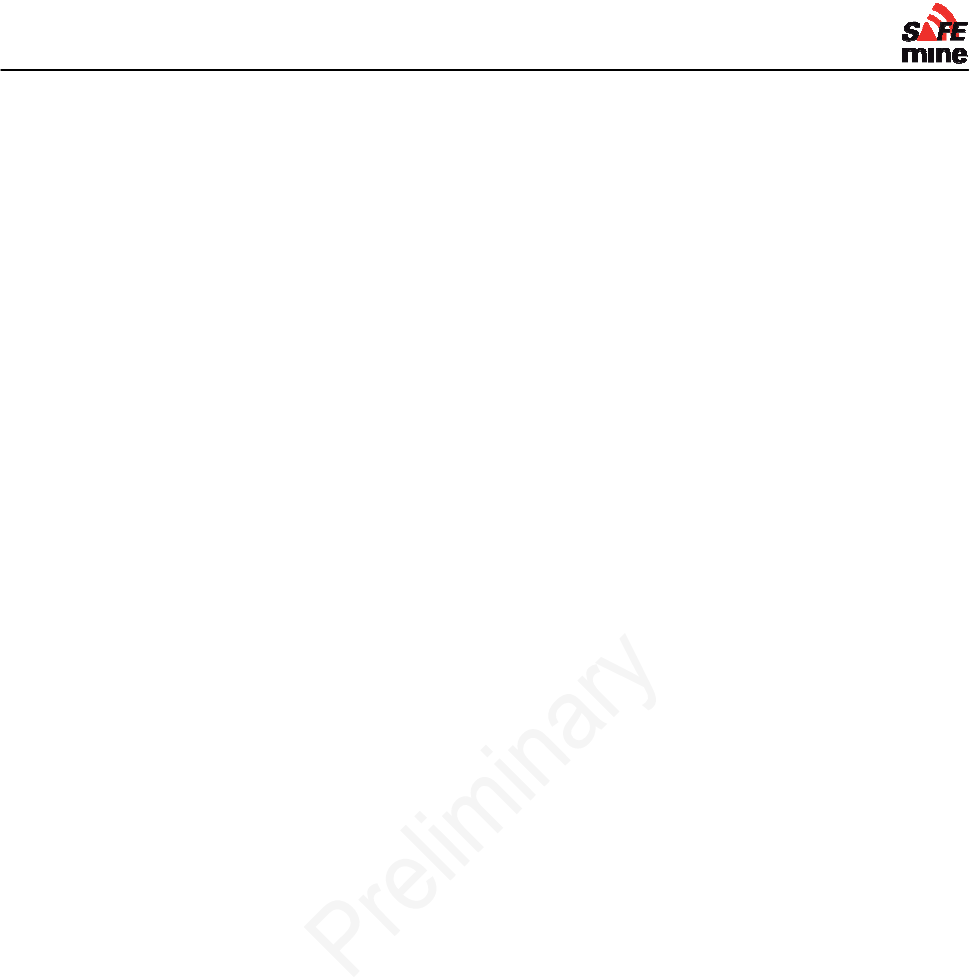
I
NSTALLATION AND
M
AINTENANCE
G
UIDE
Version 110301, Preliminary Page 45 of 56 March 2011
Section 3 – Installation and
Maintenance
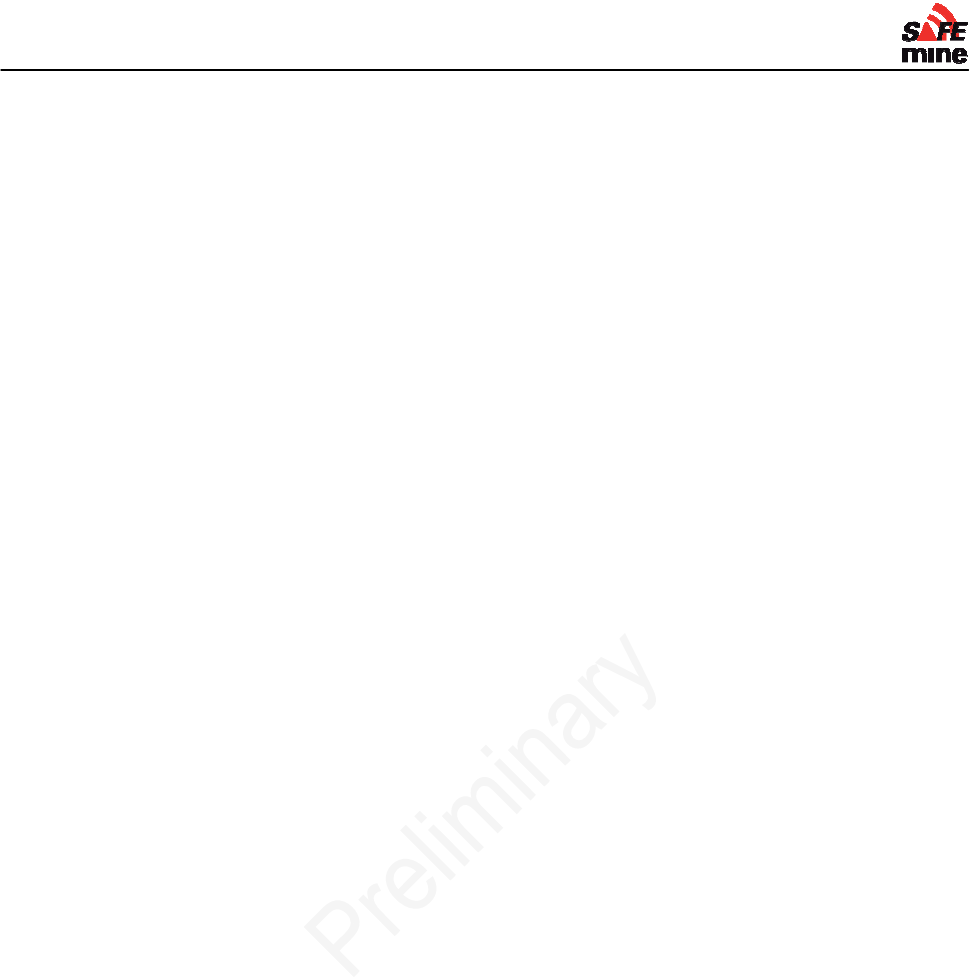
I
NSTALLATION AND
M
AINTENANCE
G
UIDE
Version 110301, Preliminary Page 46 of 56 March 2011
Installation
General Advice
Unless certified, installation and operation must be on the basis of non-interference with and no
hazard to the existing equipment installed for safe operation. When certified, installation and
operation must be done according to certification procedures in order to comply with official
regulations and requirements.
After installation, an appropriate entry should be made in the vehicle’s technical logs and a check
is to be made that the installation is in no way detrimental to the mechanical or electrical
performance of other vehicle’s systems (e.g. radio). The unit serial number and software version is
to be recorded in the vehicle’s technical log.
We highly recommend establishing a “Radio Map”, containing all intentional transmitters and their
operating frequencies. This map will help to minimize radio interference.
Recommended installation procedure
Create list of all vehicles, with properties as required, for the configuration files.
Create one configuration file for each vehicle. These files must remain readily available to
maintenance so they can be used anytime a unit needs to be replaced.
See Appendix C: Installation Checklist for mandatory installation checklist to be filled out and kept
on file for each vehicle.
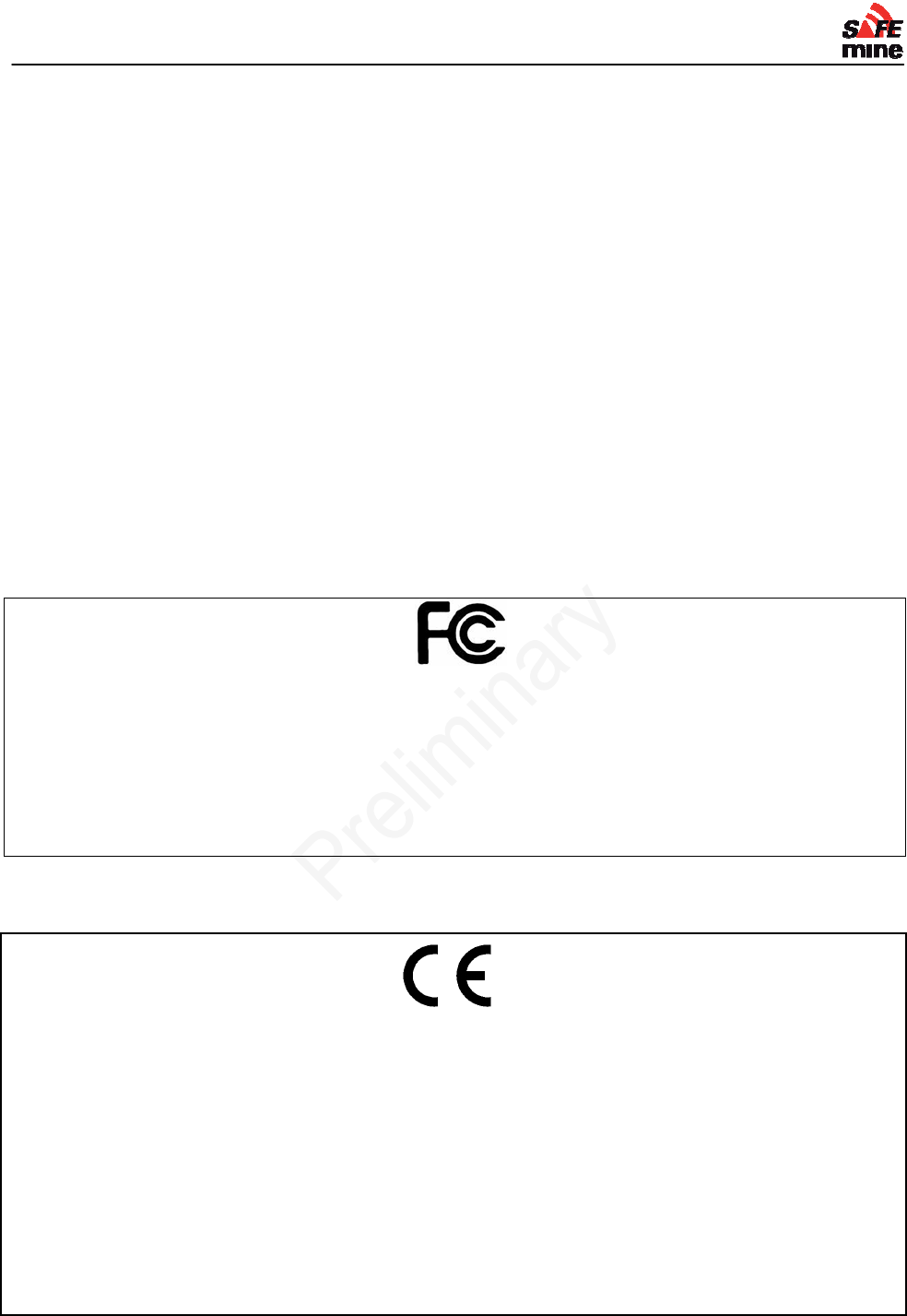
I
NSTALLATION AND
M
AINTENANCE
G
UIDE
Version 110301, Preliminary Page 47 of 56 March 2011
Maintaining the System
Contact your local dealer to find out about available maintenance services.
See Appendix D: Maintenance Checklist for a sample maintenance checklist to be filled out and
kept on file for each vehicle.
The housing should only be cleaned with a slightly moist non-abrasive cloth without any cleaning
agents. All electrical connection and cables should be controlled regularly and the GPS antenna
should not be covered by snow or a thick mud layer.
If new firmware is available, it should be uploaded to the device at earliest convenience.
It is highly recommended to install a "Test Station", available through SAFEmine on site (e.g. in the
brake test area and at site access), where all vehicles and their units can be tested for proper
operation before use.
Solar panels on Test stations must be inspected every week. Any dust, snow or ice buildup must
be removed immediately.
This device complies with Part 15 of the FCC Rules. Operation is subject to the following two
conditions: (1) this device may not cause harmful interference, and (2) this device must accept
any interference received, including interference that may cause undesired operation.
The user shall be cautioned that changes modifications not approved by the responsible party
could void the user’s authority to operate the equipment.
DECLARATION OF CONFORMITY
SAFEmine Ltd., CH-6340 Baar, Switzerland, declares that in typical configuration the Hardware
Version 1 meets the requirements of the CE Mark.
The radio conforms with the requirements of EN 300 220-3:2000 (Power Class 9). The EMC
conforms with EN 301 489-3:2002-08 for a Class 3 SRD Device (equipment type I). It is a Class 1
item of radio equipment as defined by R&TTE Directive. The necessary tests and certification were
undertaken by TRAC-KTL, Unit E, South Orbital Trading Park, Hedon Road, Hull, HU9 1NJ, UK.
These documents may be inspected at the premises of SAFEmine Ltd. by arrangement through:
info@safe-mine.com
Schwyz, September 2008
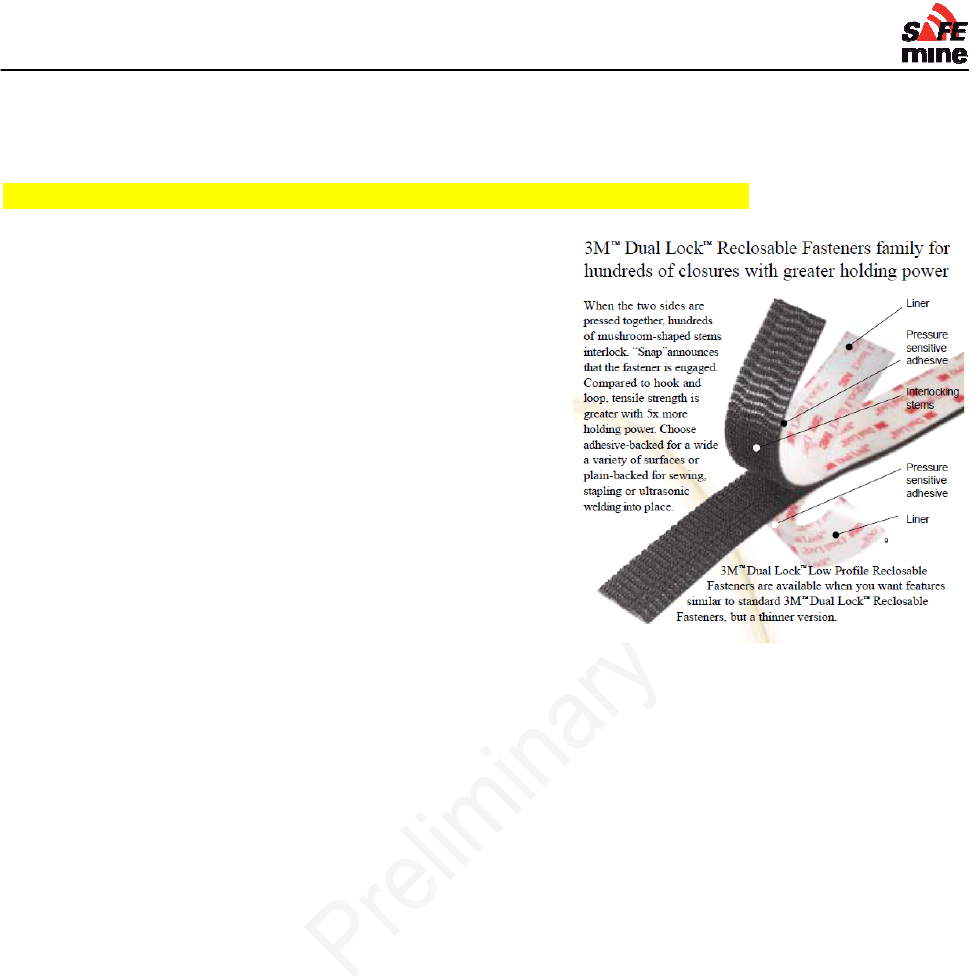
I
NSTALLATION AND
M
AINTENANCE
G
UIDE
Version 110301, Preliminary Page 48 of 56 March 2011
Appendix A: Recommended parts
These parts have been tested by SAFEmine and allow an installation with highest reliability.
Please consult with SAFEmine before substituting with non listed parts
3M "Dual Lock"
Type 3550 / 51 / 52
Heat shrink tubing
HellermannTyton HISA-9/3-PEX-BK
Self-Fusing Silicone Rubber Electrical Tape
3M Scotch® 70
Braided Sleeving
Polyamide
HellermannTyton TMEGA10MM
Clean Cut PET Expandable Sleeving
Techflex CCP0.50
Low loss 50Ohm coaxial cable
RF-195 / LMR-195 / HDF195 / LMR 400
SMA connectors
SMA connectors, crimp and strip tools are specific to the cable type. Information below is for the
HDF195 cable.
Male: Wellshow P/N C01AA31058A04A
Female: Wellshow P/N C02AA31058A12
Crimp tool: .213 Hex
Strip tool: Paladin CST Vario 3-Stage Coax Cable Stripper
Solder - .5mm or 23 gauge 60/40 Rosin Core
Small Torch
for shrink tubing
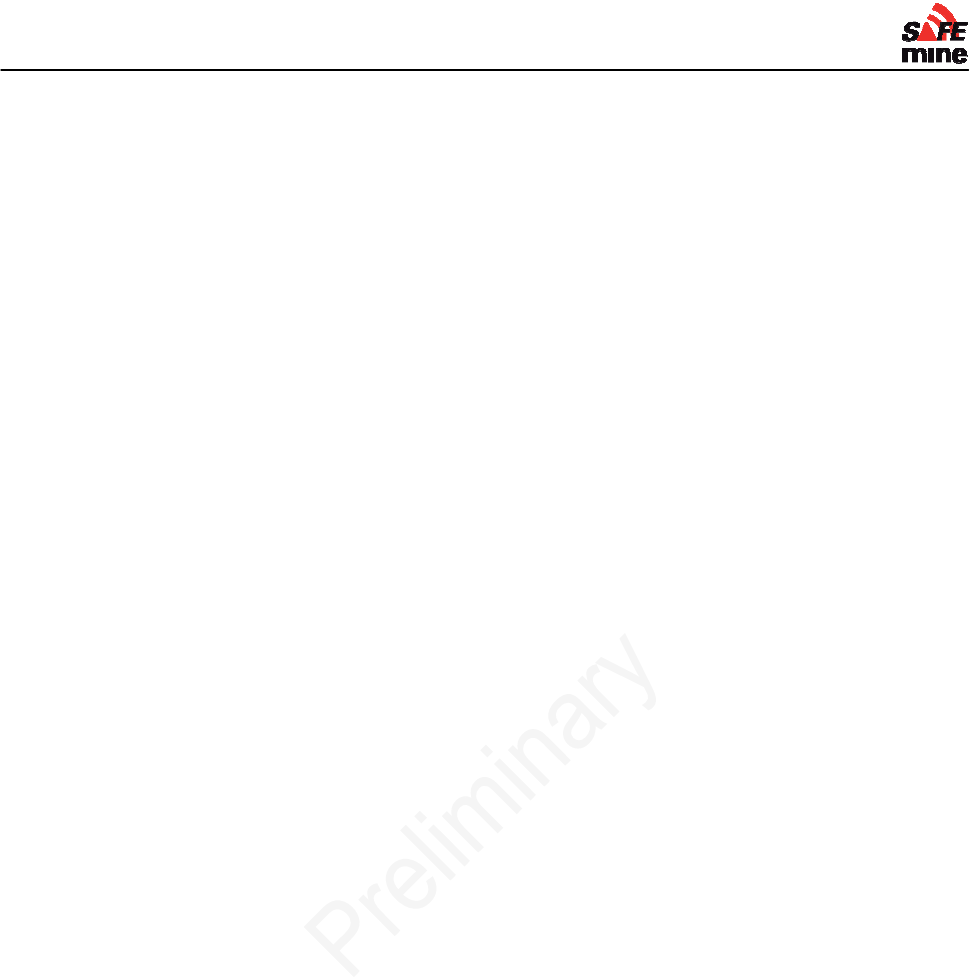
I
NSTALLATION AND
M
AINTENANCE
G
UIDE
Version 110301, Preliminary Page 49 of 56 March 2011
Appendix B: Additional Figures and Drawings
Antenna Cable
TBA
Battery Cable
TBA
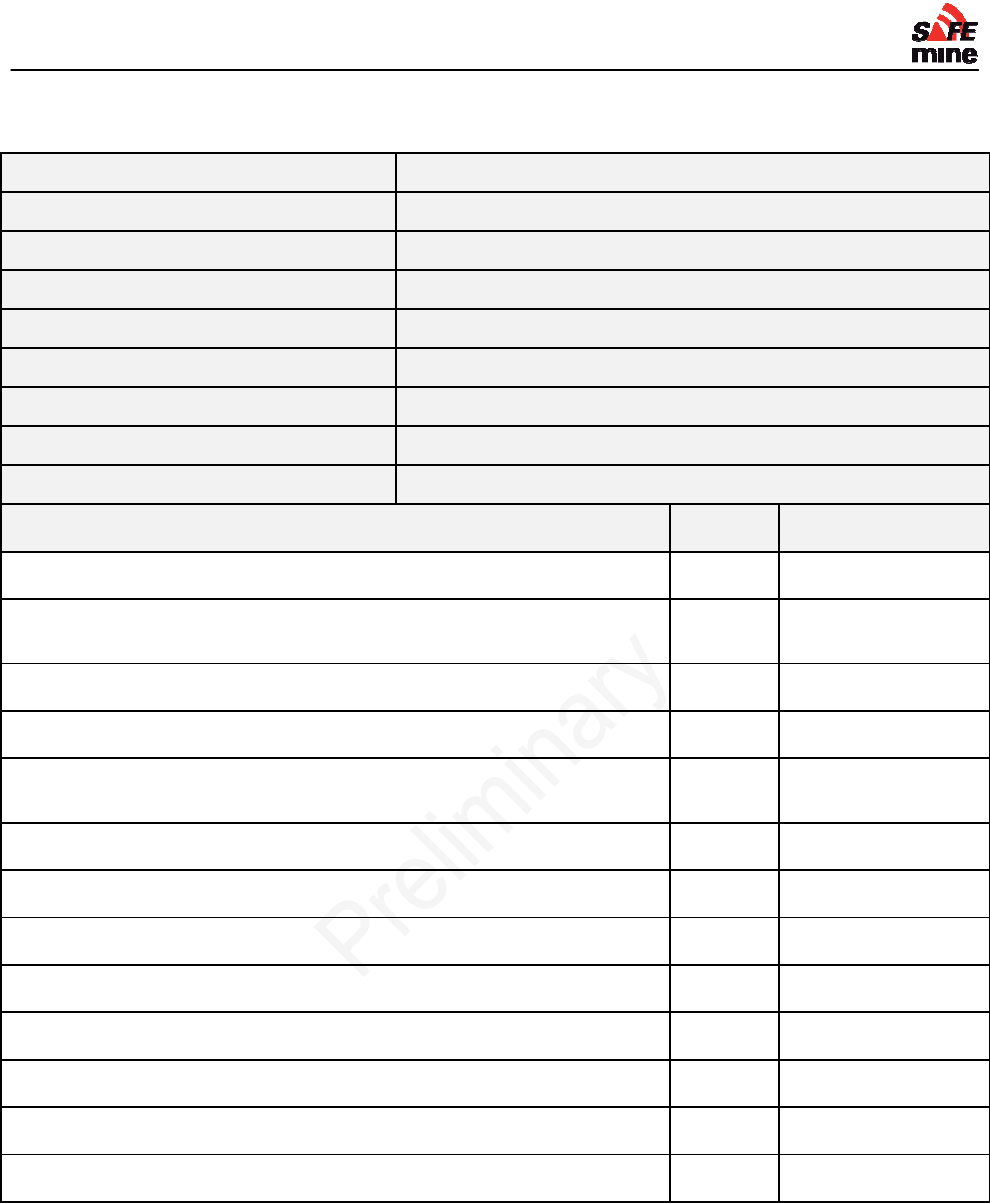
I
NSTALLATION AND
M
AINTENANCE
G
UIDE
Version 110301, Preliminary Page 50 of 56 March 2011
Appendix C: Installation Checklist
Item
Date installed
Installation technician
Configuration technician
SAFEmine serial number
Firmware version loaded
Configuration file loaded
Vehicle ID (Plant number)
Vehicle type
Initial Comment
GPS antenna is at highest point of vehicle
Antenna bolt and main housing are insulated from vehicle
frame
Main unit secured to vehicle
Maximum one connection in RF cable
All coaxial (RF/GPS) cable connections well covered by
adhesive lined heat shrink or silicone tape
Maximum total RF cable lengths 8m
RF cables sleeved if outside or where chafing is possible
Unit powered up with no error messages after installation
Ready LED green after <3 minutes (if vehicle is outside)
3A fuse on Power and GND if it is not connected to chassis
Buzzer (speaker if installed) unobstructed
Driven by test station
Signoff vehicle owner
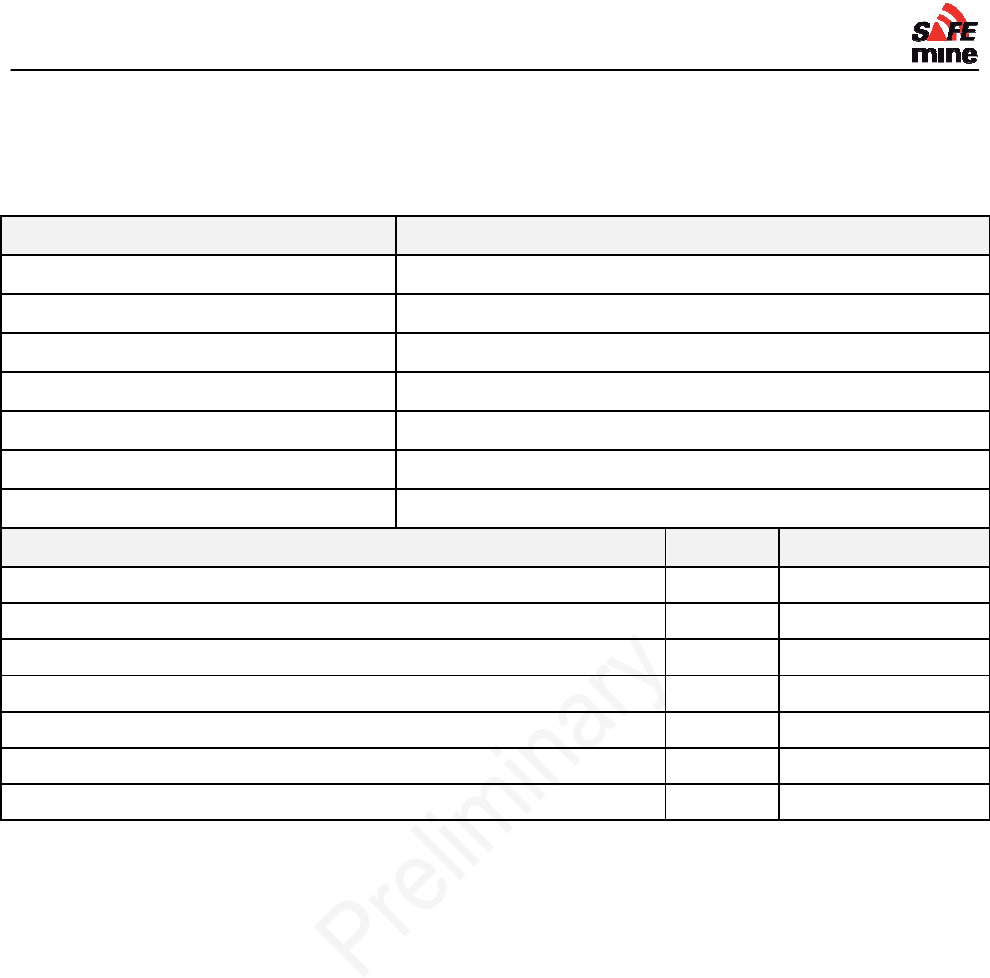
I
NSTALLATION AND
M
AINTENANCE
G
UIDE
Version 110301, Preliminary Page 51 of 56 March 2011
Appendix D: Maintenance Checklist
To be performed before vehicle is released after a regular PM
Item
Date checked
Responsible
Configuration technician
SAFEmine serial number
Firmware version loaded
Configuration file loaded
Vehicle Plant number
Initial Comment
Check cables, abrasion, UV damage
Visual inspection of housing for damage
Firmware updated to latest version
Buzzer (speaker if installed) unobstructed and working
Ready LED green after <3 minutes (if vehicle is outside)
Press button (> 5 seconds) for reset -> light, beep, self test
Driven by test station
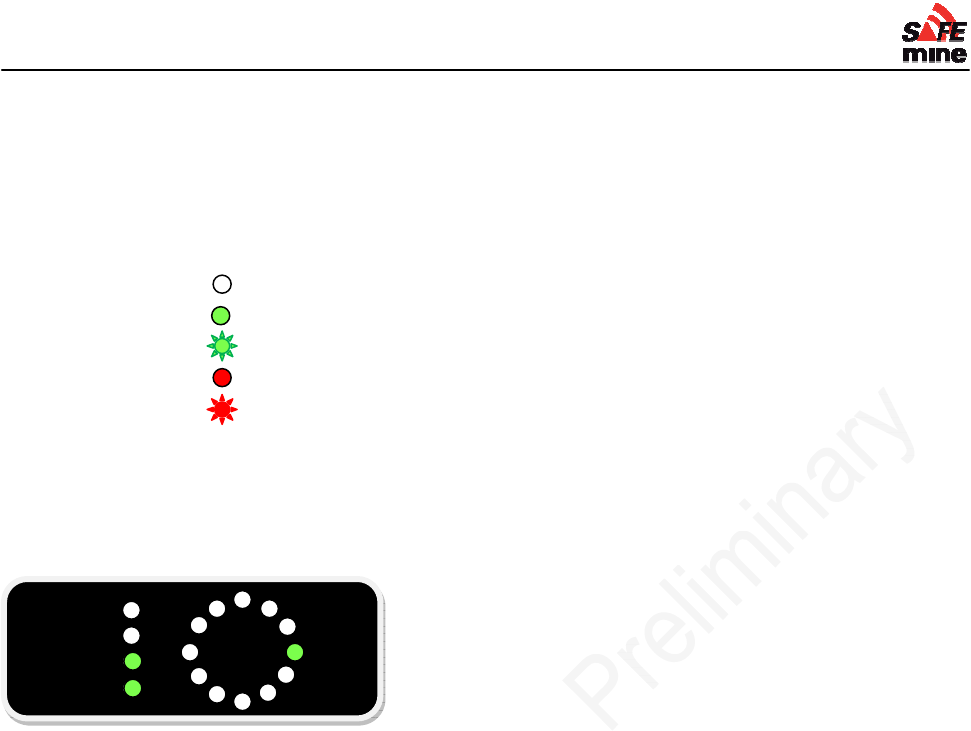
I
NSTALLATION AND
M
AINTENANCE
G
UIDE
Version 110301, Preliminary Page 52 of 56 March 2011
Appendix E: Troubleshooting guide
Find the failure case in the table below. Click on the links in the “Troubleshooting Instructions” column for more detailed instructions on how to resolve
failure. Consult Installation Manual for further information.
LED OFF
LED ON green
LED flashing green
LED ON red
LED flashing red
Normal working system moving forward reporting one distant vehicle to the right:
Mode
Reverse
Ready
Power
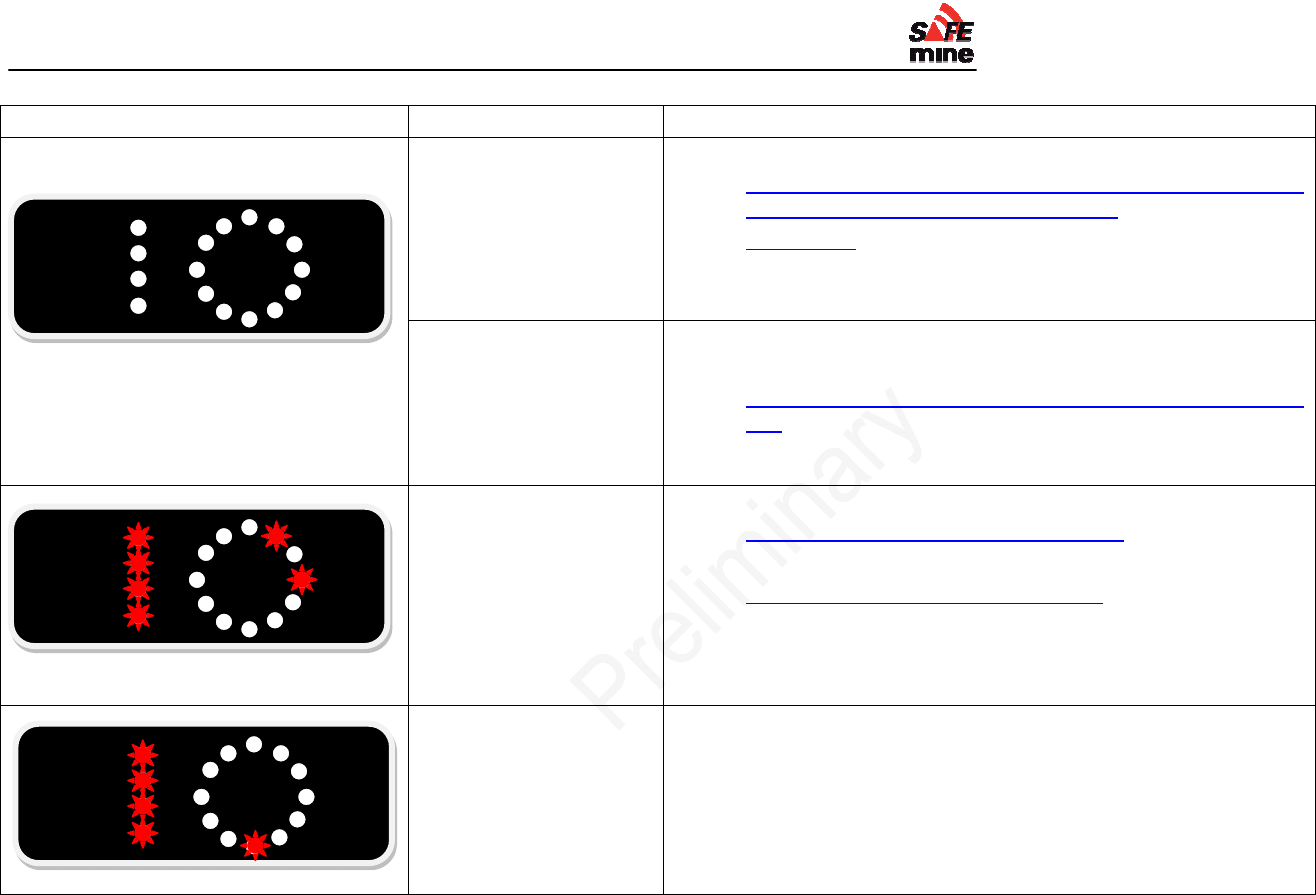
I
NSTALLATION AND
M
AINTENANCE
G
UIDE
Version 110301, Preliminary Page 53 of 56 March 2011
Symptom Failure Description Troubleshooting Instructions
All LED OFF
No power indication
main unit - Check vehicle has power
- Ensure main unit is connected to power cable, power
connector fully engaged, no bent pins.
- Check fuse
- Check power cable properly attached to battery
- Replace main unit with known good unit
No power indication
remote display Check all items above. If problem persists:
- Check main unit is connected to remote display by cable
- Check for bent pins on remote display, cable, and main
unit
- Replace remote display with known good unit
No GPS - Ensure Antenna has unobstructed view of sky
- Check Antenna connected to main unit
- Check Antenna cable intact
- Check Antenna cable crimp contacts
- Check Antenna for damage
- Replace Antenna with known good unit
- Replace main unit with known good unit
Bad configuration file - Check configuration file for errors
- Upload known good configuration file
Mode
Reverse
Ready
Power
Mode
Reverse
Ready
Power
Mode
Reverse
Ready
Power
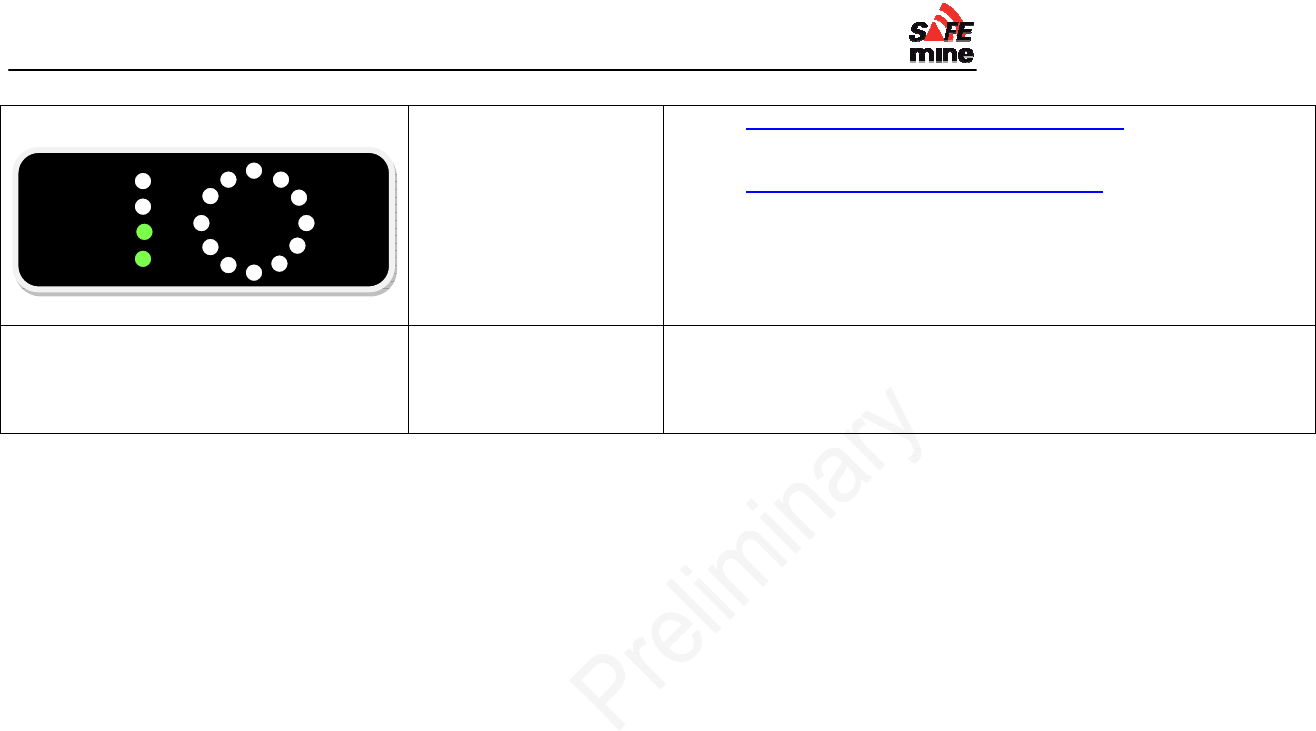
I
NSTALLATION AND
M
AINTENANCE
G
UIDE
Version 110301, Preliminary Page 54 of 56 March 2011
No indication of nearby vehicles
No radio
communication - Check Antenna connected to main unit
- Check Antenna cable intact
- Check Antenna cable crimp contacts
- Replace Antenna with known good unit
- Replace main unit with known good unit
Indication of vehicles where no
vehicles are Bad GPS - Vehicles inside buildings or next to walls may obtain an
inaccurate GPS position. If such an inaccurate position is
reported to another vehicle it may indicate a vehicle
where none is.
Mode
Reverse
Ready
Power
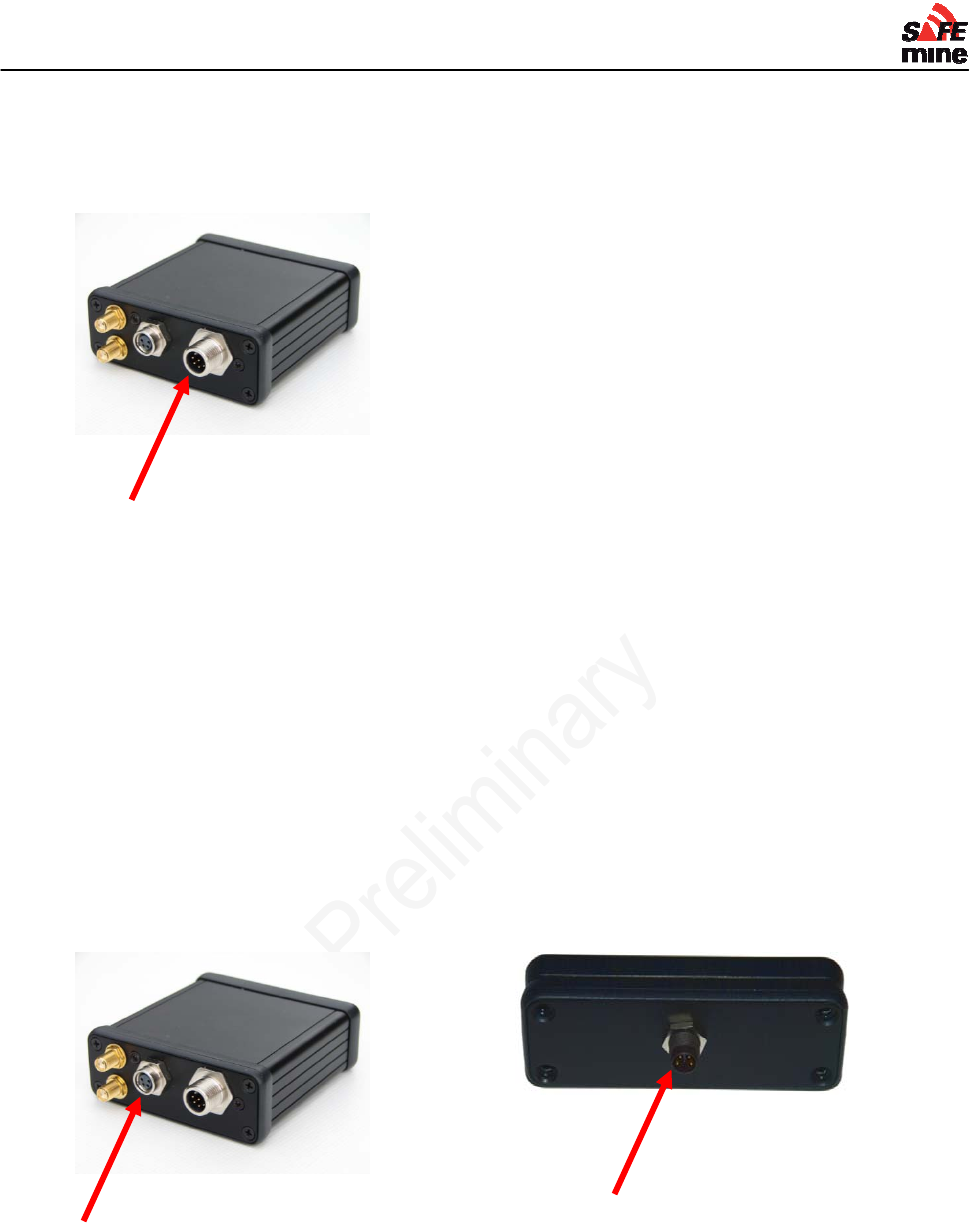
I
NSTALLATION AND
M
AINTENANCE
G
UIDE
Version 110301, Preliminary Page 55 of 56 March 2011
Main Unit Power
Power Cable
Check for bent pins on the main unit power connector. Screw power cable onto connector until fully
engaged.
Fuse
Fuse holder is usually placed in line with the power cable close where power cable is attached to
vehicle power (i.e. battery).
Open fuse holder. Remove fuse and check if intact.
Remote Display Connection
Check for bent pins on the main unit remote display connector and on the remote display as well
as the cable. Carefully connect remote display cable. Note that there are no locking pins. The
contacts prevent the connector from rotating when it is screwed on and can bend.
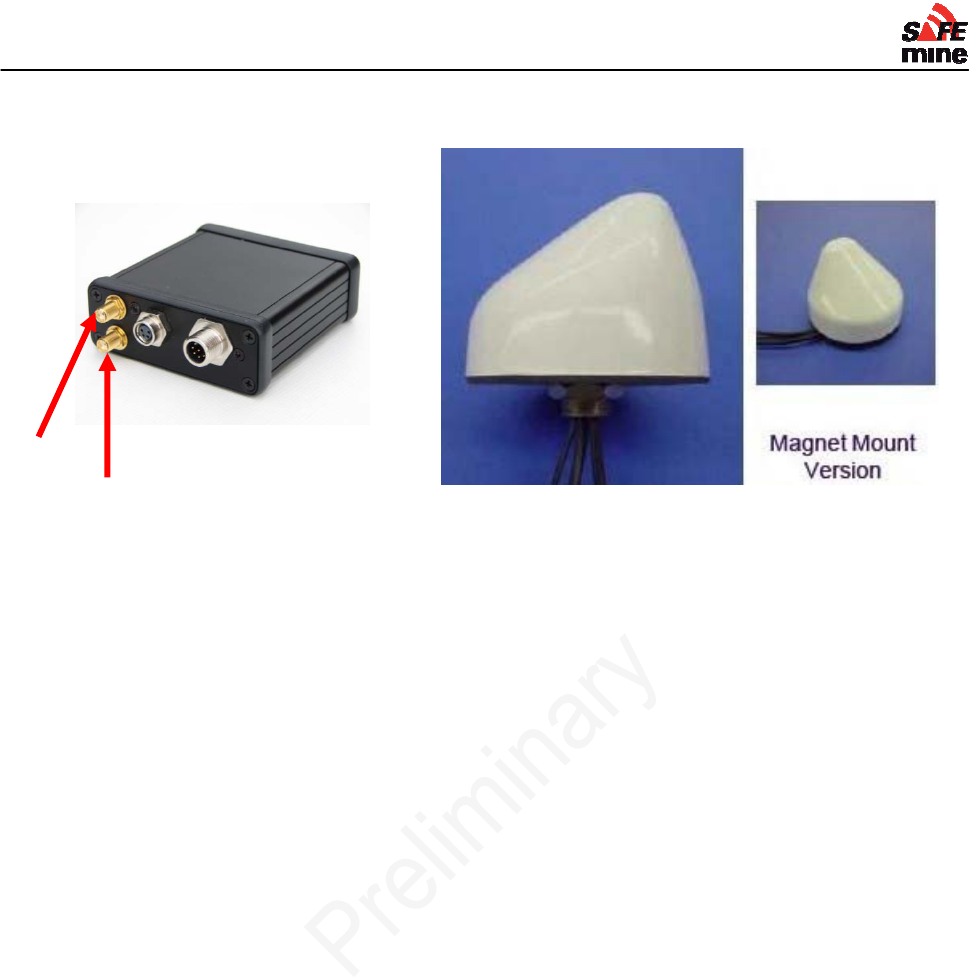
I
NSTALLATION AND
M
AINTENANCE
G
UIDE
Version 110301, Preliminary Page 56 of 56 March 2011
Antenna and Cable
Connection
Ensure antenna cable is connected to main unit and antenna. Two cables exit the antenna, one
carrying the GPS signal, the other carrying the RF signal. Both cables need to be connected and
fully engaged.
The main unit has a port labeled GPS and a port labeled RF. If not sure which cable connects to
which port try both combinations until main unit lights ready LED.
Crimp Contacts
Check the crimp contacts of the RF and GPS cable for any damage. Re-crimp if needed or use
new cable.