Hughes Network Systems 38SH-001 Point to multipoint - SUB User Manual
Hughes Network Systems Point to multipoint - SUB
EXB10
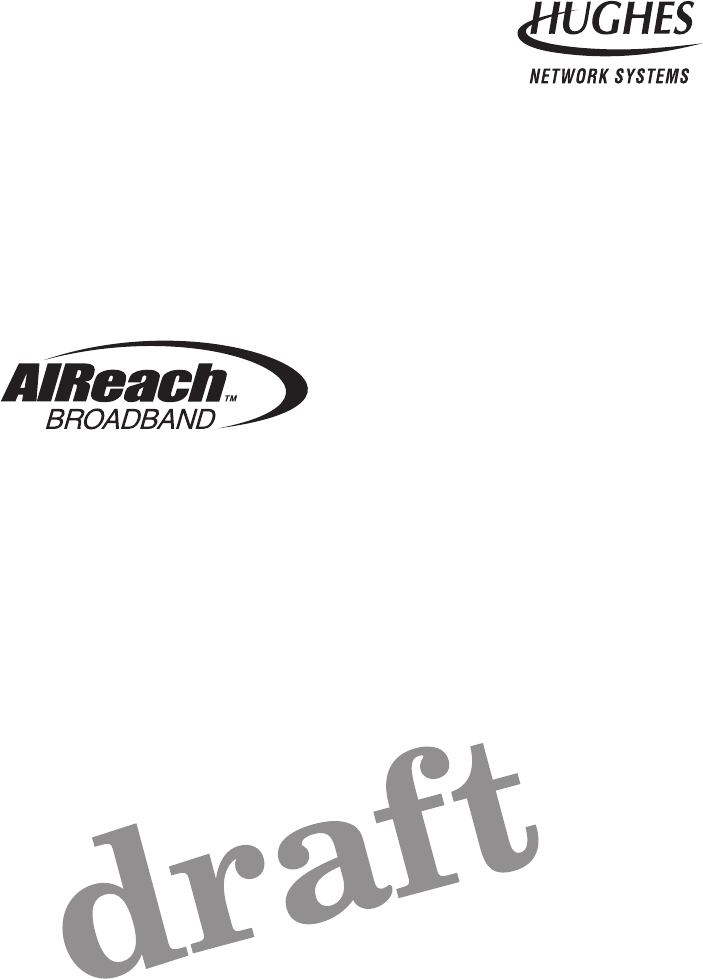
11717 Exploration Lane, Germantown, MD 20876
Tel: (301) 428–5500 Fax: (301) 428–1868/2830
1027144–0001
Draft – Revision D.01
December 17, 1999
Remote Terminal
Installation and
User Manual

1027144–0001 Draft – Revision D.01ii
For important standards compliance information, see appendix B.
Copyright 1999 Hughes Network Systems, a Hughes Electronics Corporation company
All rights reserved. This publication and its contents are proprietary to Hughes Network
Systems, a Hughes Electronics Corporation company. No part of this publication may be
reproduced in any form or by any means without the written permission of Hughes Network
Systems, 11717 Exploration Lane, Germantown, Maryland 20876.
Hughes Network Systems has made every effort to ensure the correctness and completeness
of the material in this document. Hughes Network Systems shall not be liable for errors
contained herein. The information in this document is subject to change without notice.
Hughes Network Systems makes no warranty of any kind with regard to this material,
including, but not limited to, the implied warranties of merchantability and fitness for a
particular purpose.
Trademarks
AIReach is a trademark of Hughes Network Systems. Other trademarks, marks, names, or
product names referenced in this publication are the property of their respective owners, and
Hughes Network Systems neither endorses nor otherwise sponsors any such products or
services referred to herein.

1027144–0001 Draft – Revision D.01 iii
RT installation
Contents
About this manual v. . . . . . . . . . . . . . . . . . . . . . . . . . . . . . . . . . . . . . . . . . . .
Important safety information vii. . . . . . . . . . . . . . . . . . . . . . . . . . . . . . . . . . .
1 Installation summary 1–1. . . . . . . . . . . . . . . . . . . . . . . . . . . . . . . . . . . .
1.1 Remote terminal (RT) reference drawing 1–2. . . . . . . . . . . . . . . . . . . . .
1.2 Installation summary and checklist 1–3. . . . . . . . . . . . . . . . . . . . . . . . . .
2 Prerequisites 2–1. . . . . . . . . . . . . . . . . . . . . . . . . . . . . . . . . . . . . . . . . . .
2.1 Review site data and plans 2–1. . . . . . . . . . . . . . . . . . . . . . . . . . . . . . . .
2.2 Plan ahead for building access 2–2. . . . . . . . . . . . . . . . . . . . . . . . . . . . .
2.3 Tools needed for installation 2–3. . . . . . . . . . . . . . . . . . . . . . . . . . . . . . .
2.4 Prerequisites for commissioning 2–7. . . . . . . . . . . . . . . . . . . . . . . . . . . .
3 Installing indoor RT equipment 3–1. . . . . . . . . . . . . . . . . . . . . . . . . . .
3.1 Rack grounding 3–2. . . . . . . . . . . . . . . . . . . . . . . . . . . . . . . . . . . . . . . . .
3.2 Installing IDUs 3–3. . . . . . . . . . . . . . . . . . . . . . . . . . . . . . . . . . . . . . . . .
3.3 Power supplies 3–8. . . . . . . . . . . . . . . . . . . . . . . . . . . . . . . . . . . . . . . . . .
3.4 Installing the CCM 3–24. . . . . . . . . . . . . . . . . . . . . . . . . . . . . . . . . . . . . .
3.5 SSIs 3–28. . . . . . . . . . . . . . . . . . . . . . . . . . . . . . . . . . . . . . . . . . . . . . . . . .
3.6 Installing expansion IDUs (EIDUs) 3–34. . . . . . . . . . . . . . . . . . . . . . . . .
4 Installing IFL cables 4–1. . . . . . . . . . . . . . . . . . . . . . . . . . . . . . . . . . . .
4.1 Roof and ladder safety 4–2. . . . . . . . . . . . . . . . . . . . . . . . . . . . . . . . . . . .
4.2 Handling materials 4–3. . . . . . . . . . . . . . . . . . . . . . . . . . . . . . . . . . . . . .
4.3 IFL cable specifications 4–4. . . . . . . . . . . . . . . . . . . . . . . . . . . . . . . . . . .
4.4 Overview: IFL plan 4–5. . . . . . . . . . . . . . . . . . . . . . . . . . . . . . . . . . . . . .
4.5 Determining the IFL cable route 4–6. . . . . . . . . . . . . . . . . . . . . . . . . . . .
4.6 Penetrating the roof 4–7. . . . . . . . . . . . . . . . . . . . . . . . . . . . . . . . . . . . . .
4.7 Installing the penetration sleeve 4–8. . . . . . . . . . . . . . . . . . . . . . . . . . . .
4.8 Installing the IFL cable inside the building 4–9. . . . . . . . . . . . . . . . . . . .
4.9 Installing the remote lightning arrestor 4–10. . . . . . . . . . . . . . . . . . . . . . .
4.10 Installing the IFL cable on the roof 4–14. . . . . . . . . . . . . . . . . . . . . . . . . .
4.11 Multiple IFL cables 4–17. . . . . . . . . . . . . . . . . . . . . . . . . . . . . . . . . . . . . .
5 Installing mast mounts 5–1. . . . . . . . . . . . . . . . . . . . . . . . . . . . . . . . . .
5.1 Overview 5–2. . . . . . . . . . . . . . . . . . . . . . . . . . . . . . . . . . . . . . . . . . . . . .
5.2 ODU location 5–3. . . . . . . . . . . . . . . . . . . . . . . . . . . . . . . . . . . . . . . . . .
5.3 Roof types 5–3. . . . . . . . . . . . . . . . . . . . . . . . . . . . . . . . . . . . . . . . . . . . .
5.4 Mast mount types 5–3. . . . . . . . . . . . . . . . . . . . . . . . . . . . . . . . . . . . . . .
5.5 Standard nonpenetrating mount 5–4. . . . . . . . . . . . . . . . . . . . . . . . . . . . .
5.6 Using existing structures as ODU mounts 5–11. . . . . . . . . . . . . . . . . . . .
1027144–0001 Draft – Revision D.01iv RT installation
6 Installing ODUs 6–1. . . . . . . . . . . . . . . . . . . . . . . . . . . . . . . . . . . . . . . .
6.1 Introduction 6–2. . . . . . . . . . . . . . . . . . . . . . . . . . . . . . . . . . . . . . . . . . . .
6.2 Transporting the ODU to the roof 6–4. . . . . . . . . . . . . . . . . . . . . . . . . . .
6.3 ODU installation and alignment tools 6–5. . . . . . . . . . . . . . . . . . . . . . . .
6.4 Installing the temporary collar 6–6. . . . . . . . . . . . . . . . . . . . . . . . . . . . .
6.5 Installing the antenna mount 6–10. . . . . . . . . . . . . . . . . . . . . . . . . . . . . . .
6.6 Attaching the antenna to the mount 6–12. . . . . . . . . . . . . . . . . . . . . . . . . .
6.7 Initial (coarse) antenna azimuth adjustment 6–15. . . . . . . . . . . . . . . . . . .
6.8 Adjusting the antenna elevation 6–17. . . . . . . . . . . . . . . . . . . . . . . . . . . .
6.9 Checking the radome drain position 6–18. . . . . . . . . . . . . . . . . . . . . . . . .
6.10 Installing the mechanical attenuator 6–19. . . . . . . . . . . . . . . . . . . . . . . . .
6.11 Attaching the transceiver to the antenna 6–21. . . . . . . . . . . . . . . . . . . . . .
6.12 Grounding the ODU 6–23. . . . . . . . . . . . . . . . . . . . . . . . . . . . . . . . . . . . .
6.13 Connecting the IFL to the ODU 6–25. . . . . . . . . . . . . . . . . . . . . . . . . . . .
6.14 Finer antenna azimuth adjustment 6–26. . . . . . . . . . . . . . . . . . . . . . . . . . .
6.15 Finer antenna elevation adjustment 6–28. . . . . . . . . . . . . . . . . . . . . . . . . .
7 Commissioning the RT 7–1. . . . . . . . . . . . . . . . . . . . . . . . . . . . . . . . . .
7.1 Prerequisites for commissioning 7–2. . . . . . . . . . . . . . . . . . . . . . . . . . . .
7.2 Connecting the IFL to the CCM (IDU) 7–3. . . . . . . . . . . . . . . . . . . . . . .
7.3 Front panel LCD operation 7–4. . . . . . . . . . . . . . . . . . . . . . . . . . . . . . . .
7.4 Pointing the antenna 7–8. . . . . . . . . . . . . . . . . . . . . . . . . . . . . . . . . . . . .
7.5 Removing the installation tools 7–13. . . . . . . . . . . . . . . . . . . . . . . . . . . . .
7.6 Verifying HT acquisition 7–14. . . . . . . . . . . . . . . . . . . . . . . . . . . . . . . . . .
7.7 Checking component status 7–14. . . . . . . . . . . . . . . . . . . . . . . . . . . . . . . .
7.8 RT to HT connection tests 7–19. . . . . . . . . . . . . . . . . . . . . . . . . . . . . . . . .
8 Final steps 8–1. . . . . . . . . . . . . . . . . . . . . . . . . . . . . . . . . . . . . . . . . . . . .
8.1 Weatherproofing 8–2. . . . . . . . . . . . . . . . . . . . . . . . . . . . . . . . . . . . . . . .
8.2 Inspection, cleanup, and sign–off 8–3. . . . . . . . . . . . . . . . . . . . . . . . . . .
8.3 Connecting customer equipment 8–3. . . . . . . . . . . . . . . . . . . . . . . . . . . .
9 Troubleshooting 9–1. . . . . . . . . . . . . . . . . . . . . . . . . . . . . . . . . . . . . . . .
9.1 Troubleshooting flow charts 9–1. . . . . . . . . . . . . . . . . . . . . . . . . . . . . . .
9.2 Additional troubleshooting information 9–6. . . . . . . . . . . . . . . . . . . . . .
9.3 Repair or replacement service 9–6. . . . . . . . . . . . . . . . . . . . . . . . . . . . . .
10 Maintenance 10–1. . . . . . . . . . . . . . . . . . . . . . . . . . . . . . . . . . . . . . . . . . .
10.1 Adding or moving SSIs 10–2. . . . . . . . . . . . . . . . . . . . . . . . . . . . . . . . . . .
10.2 Replacing components 10–3. . . . . . . . . . . . . . . . . . . . . . . . . . . . . . . . . . .
10.3 Replacing the ODU 10–3. . . . . . . . . . . . . . . . . . . . . . . . . . . . . . . . . . . . . .
10.4 Replacing the IDU chassis 10–10. . . . . . . . . . . . . . . . . . . . . . . . . . . . . . . .
10.5 Replacing the CCM 10–12. . . . . . . . . . . . . . . . . . . . . . . . . . . . . . . . . . . . . .
10.6 Replacing SSIs 10–13. . . . . . . . . . . . . . . . . . . . . . . . . . . . . . . . . . . . . . . . .
1027144–0001 Draft – Revision D.01 v
RT installation
10.7 Replacing the IFL 10–14. . . . . . . . . . . . . . . . . . . . . . . . . . . . . . . . . . . . . . .
10.8 Dismantling an RT 10–16. . . . . . . . . . . . . . . . . . . . . . . . . . . . . . . . . . . . . . .
A Acronyms and abbreviations A- 1. . . . . . . . . . . . . . . . . . . . . . . . . . . . .
B Standards compliance B–1. . . . . . . . . . . . . . . . . . . . . . . . . . . . . . . . . . .
B.1 Outdoor unit B–2. . . . . . . . . . . . . . . . . . . . . . . . . . . . . . . . . . . . . . . . . . .
B.2 Indoor unit (ac) B–3. . . . . . . . . . . . . . . . . . . . . . . . . . . . . . . . . . . . . . . . .
C Terminating the IFL cable C–1. . . . . . . . . . . . . . . . . . . . . . . . . . . . . . .
C.1 Cable parts and terminology C–2. . . . . . . . . . . . . . . . . . . . . . . . . . . . . . .
C.2 Preparing the cable end C–3. . . . . . . . . . . . . . . . . . . . . . . . . . . . . . . . . . .
C.3 Attaching the connector C–6. . . . . . . . . . . . . . . . . . . . . . . . . . . . . . . . . . .
C.4 Applying heat–shrink tubing C–11. . . . . . . . . . . . . . . . . . . . . . . . . . . . . . .
Index . . . . . . . . . . . . . . . . . . . . . . . . . . . . . . . . . . . . . . . . . . . . follows appendix C
1027144–0001 Draft – Revision D.01vi RT installation

1027144–0001 Draft – Revision D.01 About this manual vii
RT installation
About this manual
This manual provides instructions for installing and using
AIReachBroadband point–to–multipoint remote terminal (RT)
equipment.
This manual is intended for use by qualified equipment installers.
Installers must understand:
•Electronics fundamentals
•Cabling and connection practices
•Electrical circuits and grounding practices
•The importance of safety precautions
Installers must also be familiar with:
•Radio frequency (RF) fundamentals
•Applicable electrical, building, fire, and
safety codes and regulations
Note: HNS recommends a team of two installers to install the
AIReach Broadband indoor and outdoor equipment.
The instructions in this manual are organized according to tasks
and are intended to be followed in sequential order.
For site preparation instructions, see:
•Hub and Remote Terminal Site Preparation Guide,
document number 1027032–0001
For hub site installation instructions, see:
•Hub Installation and User Manual,
document number 1027145–0001
This manual primarily describes equipment manufactured and/or
provided by Hughes Network Systems (HNS), but in some cases
also refers to equipment that may be supplied by another vendor.
HNS equipment deliverables are defined in the customer
contract. Some equipment referred to in this manual may be
provided by the customer, as stated in the customer’s contract.
User qualifications
Organization
Related publications
HNS- and
customer-provided
equipment
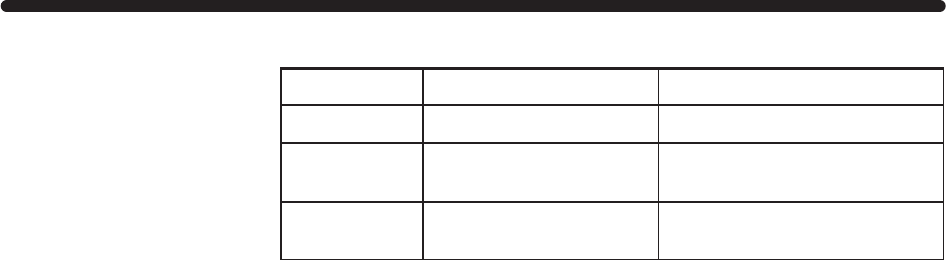
1027144–0001 Draft – Revision D.01 viii About this manual RT installation
Revision record
Revision Date of issue Scope
AApril 21, 1999 Released for UL approval.
BJune 8, 1999 Added new and updated
information.
CAugust 9, 1999 Added troubleshooting and
maintenance information.
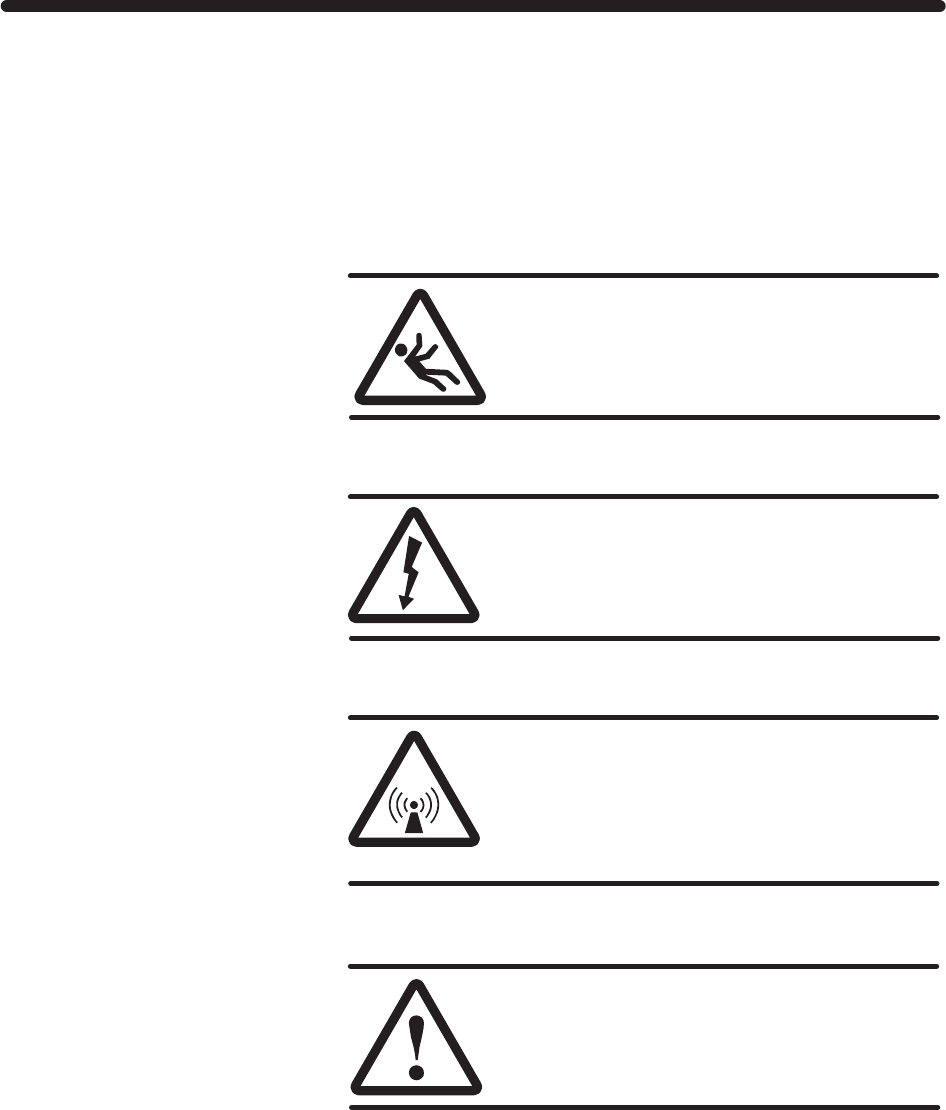
1027144–0001 Draft – Revision D.01 Important safety information ix
RT installation
Important safety information
For your own safety and protection, read this safety section
carefully. Keep this safety information where you can refer to it if
necessary.
This section introduces the types of warnings used in this manual
to alert you to possible safety hazards that could be encountered
while installing AIReach Broadband equipment.
DANGER
Fall hazard: Where you see this symbol
and DANGER heading, strictly follow the
warning instructions to avoid personal
injury or death from falling.
DANGER
Electric shock hazard: Where you see this
symbol and DANGER heading, strictly
follow the warning instructions to avoid
electric shock injury or death.
WARNING
Potential radio frequency (RF) hazard:
Where you see this alert symbol and
WARNING heading, strictly follow the
warning instructions to avoid injury to
eyes or other personal injury.
WARNING
Where you see this symbol and WARNING
heading, strictly follow the warning
instructions to avoid personal injury.
Types of warnings used
in this manual
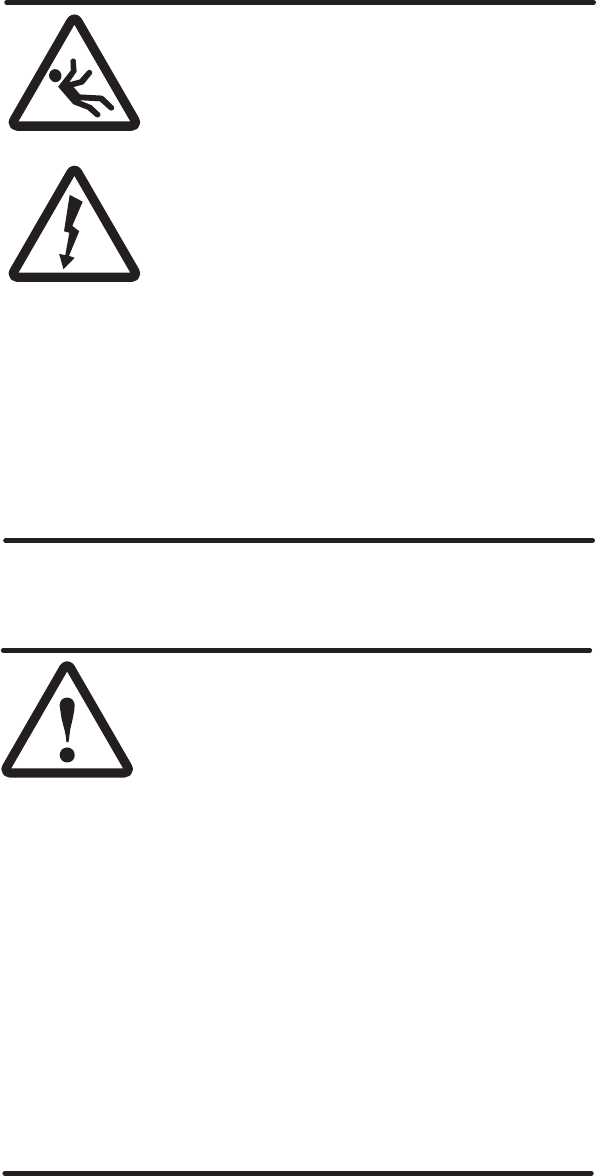
1027144–0001 Draft – Revision D.01 x Important safety information RT installation
This manual includes the following safety warnings:
DANGER
If you have to walk on a roof or use a ladder
to access an installation site or equipment,
follow these precautions to prevent personal
injury or death:
•Do not walk near the edge of the roof.
•Watch out for overhead power lines.
Stay at least 6 meters (20 feet) from
power lines.
•Walk only on sound roof structures.
•Do not work on a roof or ladder in
high wind, rain, lightning, or other
adverse weather conditions.
•Follow all safety precautions from the
ladder or antenna manufacturer.
•Do not walk on a roof if a storm is
visible—even if the storm is distant.
Lightning can travel and strike in
advance of a storm.
WARNING
If you need to hoist materials to the
installation location, observe these
precautions to avoid personal injury:
•Use a rope strong enough to support
all of the materials that need to be
hoisted.
•Never stand under the rope while
materials are being hoisted.
•Hoist one concrete block at a time.
•Pass the rope through the
center
hole
of each concrete block. If you use the
hole on either end, the end can break
off, allowing the concrete block to fall.
•Be advised that the contents of the
mount kit can fall through the end of
the box if the box is tilted—especially
if the box has been damaged.
•Use a back brace.
Warnings appearing in
this manual
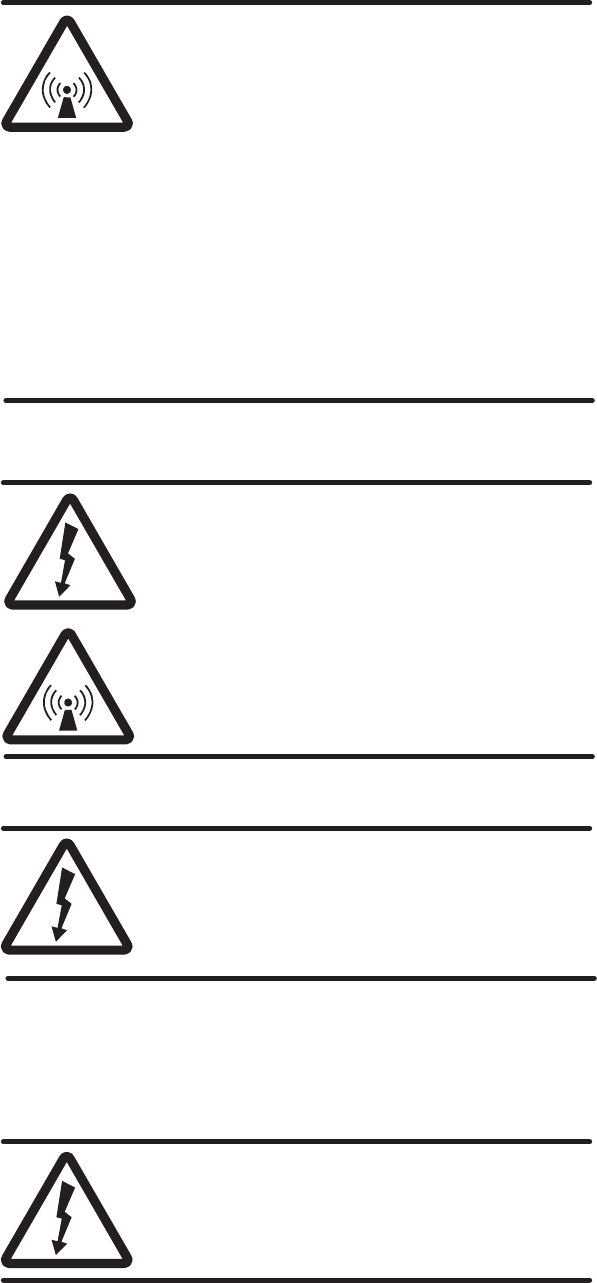
1027144–0001 Draft – Revision D.01 Important safety information xi
RT installation
WARNING
Potential radio frequency (RF) hazard:
•Keep away from the front of the
outdoor unit (ODU) antenna while the
ODU is operating. Note that you cannot
tell from outward appearance whether
the ODU is operating or not.
•Be careful with respect to the ODU you
are installing and ODUs that may
already be operating in the installation
area.
Failure to observe these warnings could
result in injury to eyes or other personal
injury.
WARNING
To avoid the risk of electric shock and
exposure to potentially harmful radio
frequency (RF) waves, make sure the IDU is
turned off, if already installed, before
installing the mechanical attenuator.
Failure to observe these warnings could
result in personal injury.
WARNING
To help avoid death, injury, or damage from a
lightning strike, you
must
install a lightning
arrestor where the IFL enters the building.
The warning immediately below applies only to IDUs with
a dual ac or dc power supply:
WARNING
Multiple power connectors. Disconnect
both ac and dc power before servicing.
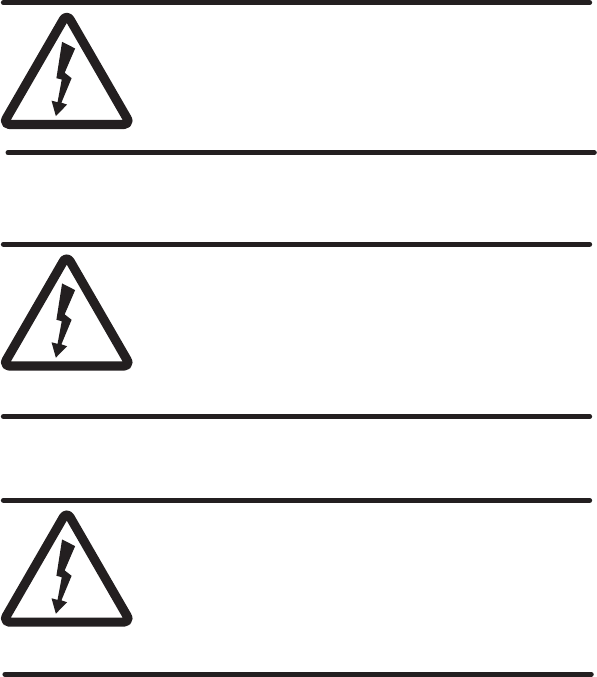
1027144–0001 Draft – Revision D.01 xii Important safety information RT installation
WARNING
To avoid the risk of electric shock,
remove power from the power circuit
before connecting power cables to the
IDU power supply.
WARNING
The IDU chassis must be solidly bonded to a
low–impedance ground (earth) source.
To avoid the risk of electric shock and/or
equipment damage, do not apply power to
the IDU chassis without a ground reference.
WARNING
To avoid the risk of electric shock, make
sure the dc power source breaker is off
before installing a remote power–off
circuit. Use a continuity tester to verify
that power is off.
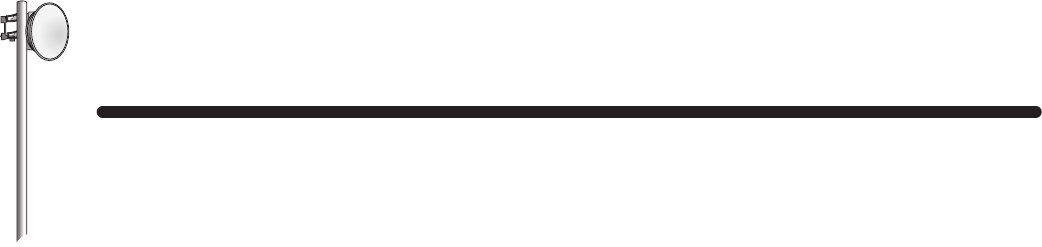
RT INSTALLATION
1027144–0001 Draft – Revision D.01 Installation summary 1–1
RT installation
Chapter 1
Installation summary
This chapter includes:
•Remote terminal (RT) reference drawing – page 1–2
•RT installation summary and checklist – page 1–3
The installation summary previews the entire RT installation
process and serves as a quick reference. For detailed information,
see chapters 2 through 8.
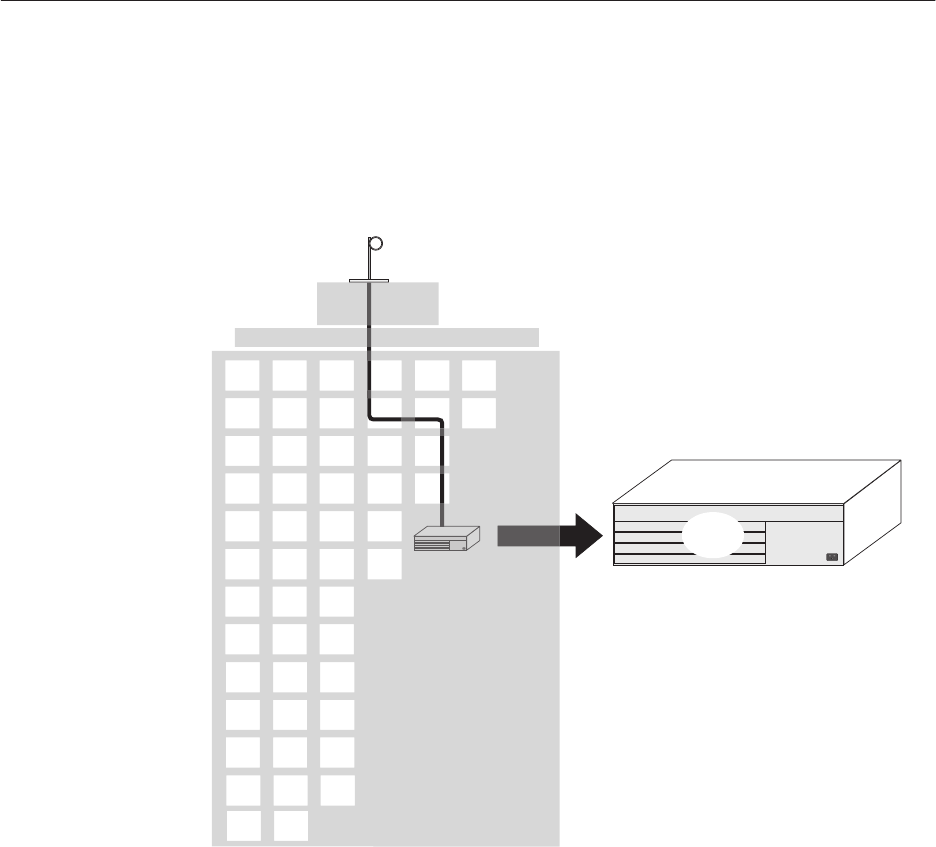
1027144–0001 Draft – Revision D.01 1–2 Installation summary RT installation
Figure 1-1 is provided as a reference. It illustrates the main RT
components:
•Outdoor unit (ODU)
•Intrafacility link (IFL)
•Indoor equipment
Figure 1-1 RT equipment
rt011
RT ODU
IDU
RT indoor
equipment
IFL
1.1
Remote terminal
(RT) reference
drawing
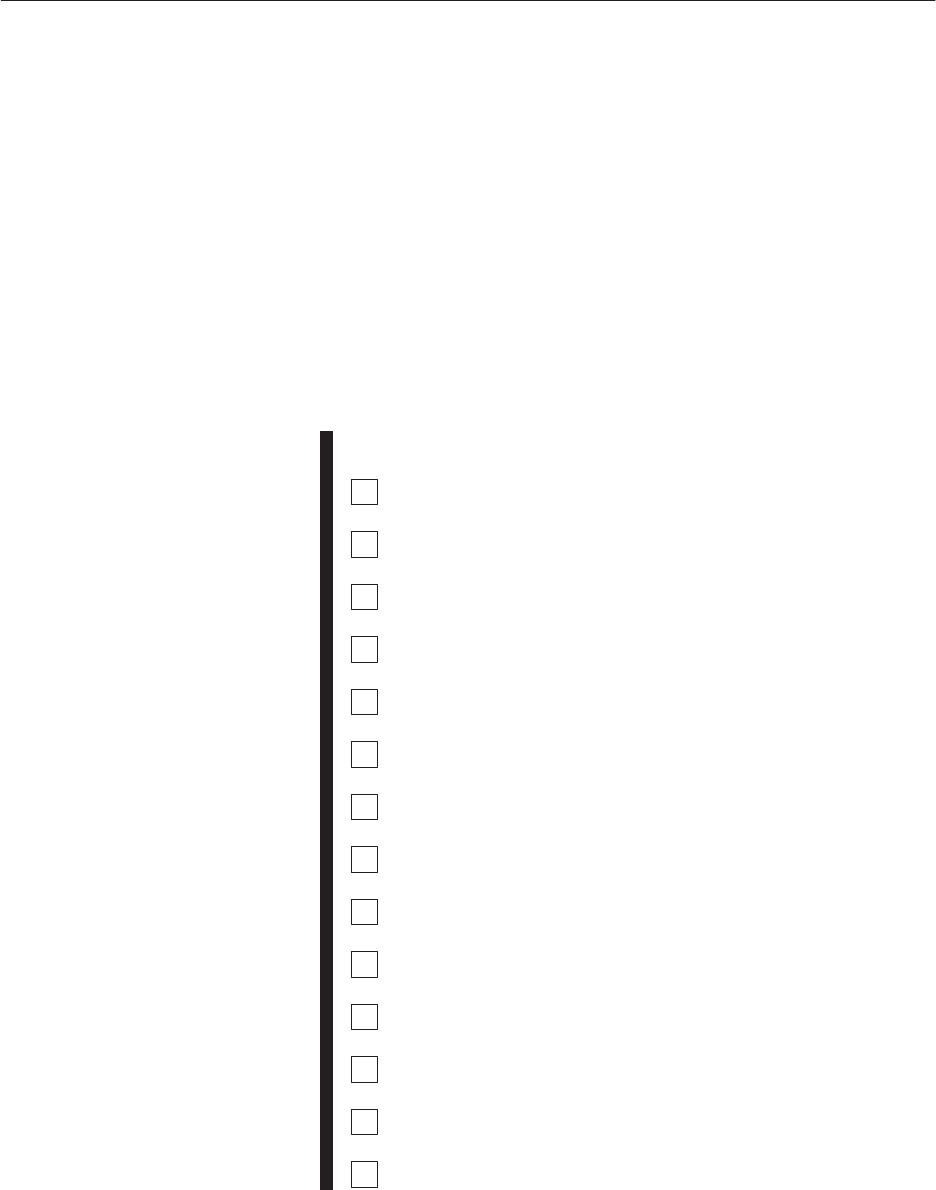
1027144–0001 Draft – Revision D.01 Installation summary 1–3
RT installation
Components to be installed
The following AIReach Broadband components are installed at the
RT site:
•ODU(s) – Integrated antenna and transceiver
•IFL
•Indoor unit(s) (IDU), including:
- IDU channel and control module (CCM)
- IDU service–specific interfaces (SSIs)
Summary of installation steps
RT installation consists of the following main tasks:
Ground the rack (if a rack is used) – page 3–2
Install IDU chassis – page 3–3
Ground the IDU chassis – page 3–12 (ac) or 3–15 (dc)
Connect power to power supply – page 3–13 (ac) or 3–15 (dc)
Install CCM – page 3–24
CCM power–on test – page 3–26
Install SSIs – page 3–28
Install expansion IDUs (EIDUs) (if used) – page 3–34
Determine IFL cable route – page 4–6
Install the IFL cable (inside the building) – page 4–9
Install IFL lightning arrestor – page 4–10
Ground the lightning arrestor– page 4–13
Install the IFL cable (on the roof) – page 4–14
Test the IFL cable – page 4–16
1.2
Installation
summary and
checklist

1027144–0001 Draft – Revision D.01 1–4 Installation summary RT installation
Install the mast mount – page 5–4
Install the antenna mount – page 6–10
Attach the antenna to the mount – page 6–12
Adjust the antenna azimuth – page 6–15
Adjust the antenna elevation – page 6–17
Install the mechanical attenuator (if required) – page 6–19
Attach the transceiver to the antenna – page 6–21
Ground the ODU – page 6–23
Connect the IFL to the ODU – page 6–25
Connect the IFL to the CCM (IDU) – page 7–3
Point the antenna (with voltmeter) – page 7–10
Tighten the mount – page 7–11
Remove the installation tools – page 7–13
Verify HT acquisition – page 7–14
Check component status – page 7–14
Weatherproof connections – page 8–2
Obtain customer signoff – page 8–3
For detailed installation instructions, see chapters 2 through 8.
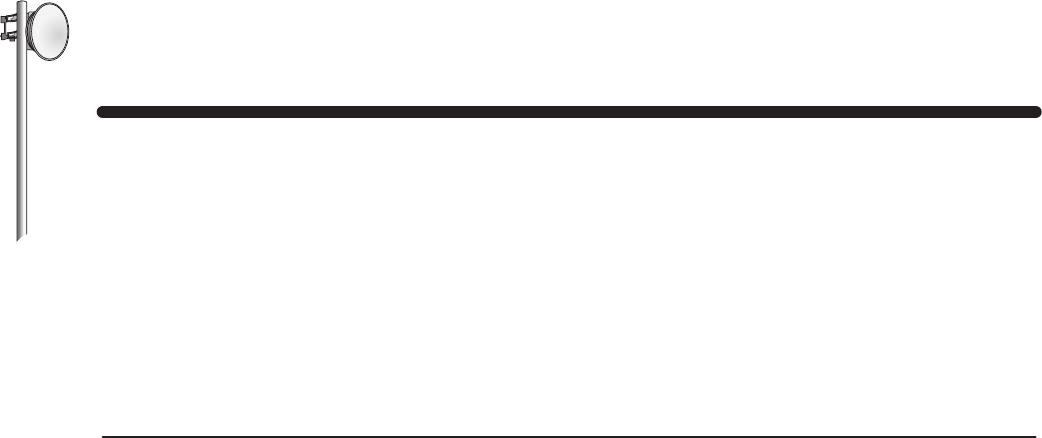
RT INSTALLATION
1027144–0001 Draft – Revision D.01 Prerequisites 2–1
RT installation
Chapter 2
Prerequisites
This chapter discusses steps that are required prior to installation
of AIReach Broadband equipment. It includes:
•Reviewing site data and plans – page 2–1
•Planning ahead for building access – page 2–2
•Tools needed for installation – page 2–3
•Prerequisites for commissioning – page 2–7
Before you begin installing the equipment, review all previously
collected site data and site plans for information you will need to
install the indoor and outdoor equipment, including the IFL
(intrafacility link). For more information on the equipment to be
installed, see section 1.1.
Review:
•The completed Site Data Record from the Hub and Remote
Terminal Site Preparation Guide – The Site Data Record is
completed during and after the pre–installation site survey.
It includes the site address, planned services, information
concerning potential sources of interference, IFL
information, and much other information.
•Site drawings and photographs – These should include
information about the site environment, existing equipment
and building features, equipment to be installed, IFL
routing, customer equipment to be connected to AIReach
Broadband equipment, and other information.
•Planning the ODU location, a section in the Hub and
Remote Terminal Site Preparation Guide – The ODU
location should already be selected; however, this section
contains information that is useful for the installer to know.
2.1
Review site data
and plans

1027144–0001 Draft – Revision D.01 2–2 Prerequisites RT installation
Before you go to the installation site, make sure you have all
necessary information (such as contact names and phone
numbers) for accessing all parts of the building you will need
to visit (roof, equipment rooms—which may be in the basement),
and other locations. This information should be available in the
Site Data Record, which is completed as part of the site survey.
Recommendations:
•Know who to contact for assistance (name, phone number,
working hours).
•Get good directions or a building map or floor plan, if
possible.
•You may need a key or pass code to gain access to the roof.
•Make all necessary arrangements for facility support and
building access before you go to the installation site.
2.2
Plan ahead for
building access
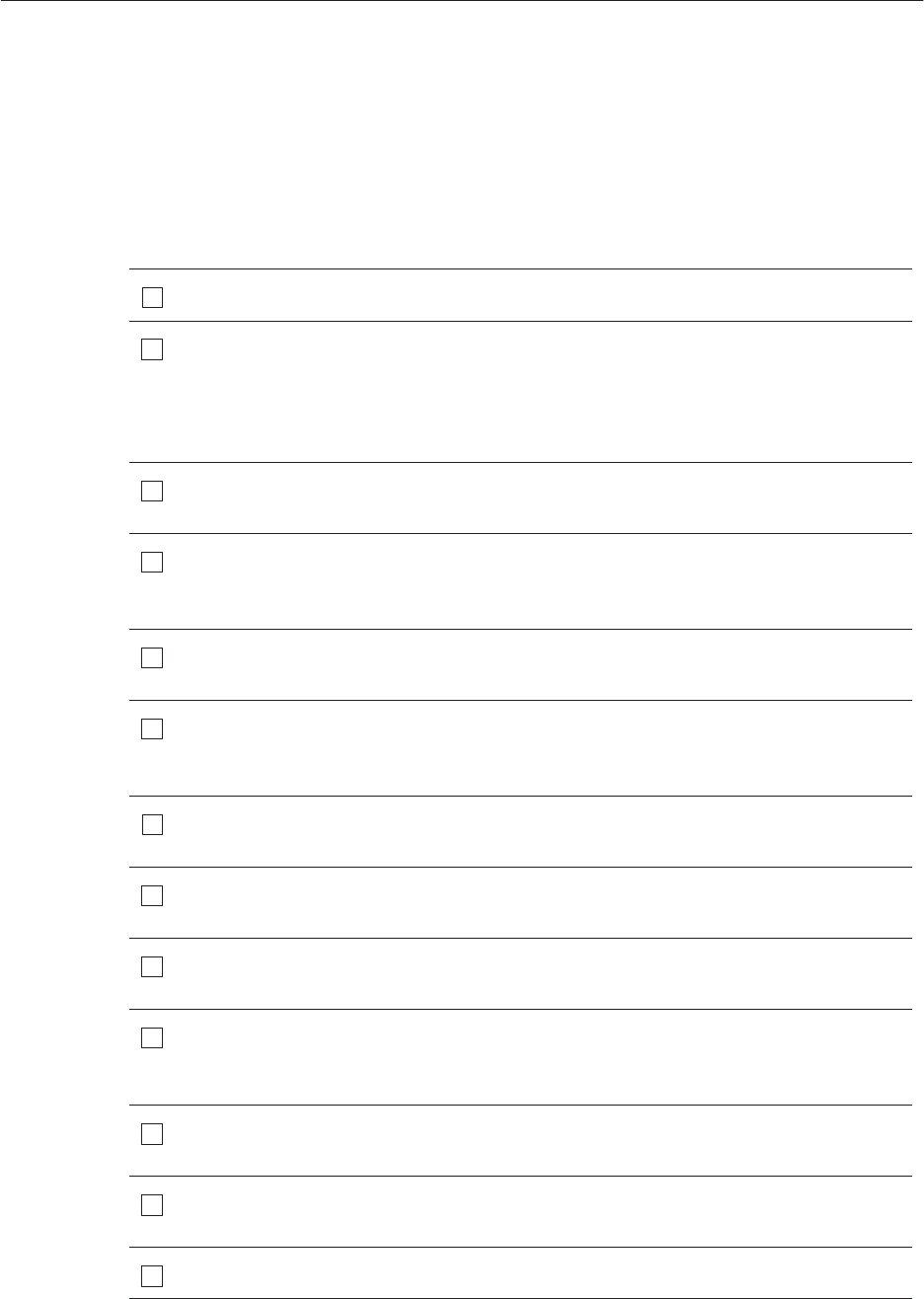
1027144–0001 Draft – Revision D.01 Prerequisites 2–3
RT installation
To install and commission AIReach Broadband remote terminal
equipment, you need the tools listed in table 2-1 . You may need
general–purpose tools in addition to the specific tools listed here.
Table 2-1 Tools required for RT installation
(includes tools for IFL installation, antenna pointing, and initial testing)
√Item Purpose (or other comments)
Ladder May or may not be required; depends on building
Rope To hoist tools and equipment up ladders. Rope
must be long enough for ladders at the site. Must
be able to hold
at least
35 pounds (16 kilograms).
This is the ODU weight. IFL cable is likely to
weigh more.
Snow shovel or
heavy–duty push broom To move roof gravel away from the ODU
installation site
1/2–inch drill Cordless drill preferred for work on roof. Drill with
power cord required for heavy–duty work (such
as mounting a rack to the floor).
Drill with bits for wood and
masonry. May be needed for IFL installation
Combination wrenches:
7/16 inch, 9/16 inch
10 millimeter, 13 millimeter
For installing the mast mount and antenna mount
Ratchet wrench with
9/16–inch socket For installing the mast mount
3/8–inch torque wrench with
13–millimeter deep socket Required for installing the antenna mount
5/32–inch (4–millimeter)
torque hex key wrench Used to tighten the radome band clamp
Custom wrench: Sealcon
part number 1.500.4200.04 Required to tighten IFL cable restraining fitting.
Available from Sealcon, 14853 East Hinsdale
Ave., Suite D, Englewood, CO 80112–4240
No. 6 Phillips screwdriver Needed to attach IDU chassis mounting ears if
IDU chassis is rack mounted
1000° heat gun For applying shrink wrap tubing to protect cable
terminations
Cable cutters
2.3
Tools needed for
installation
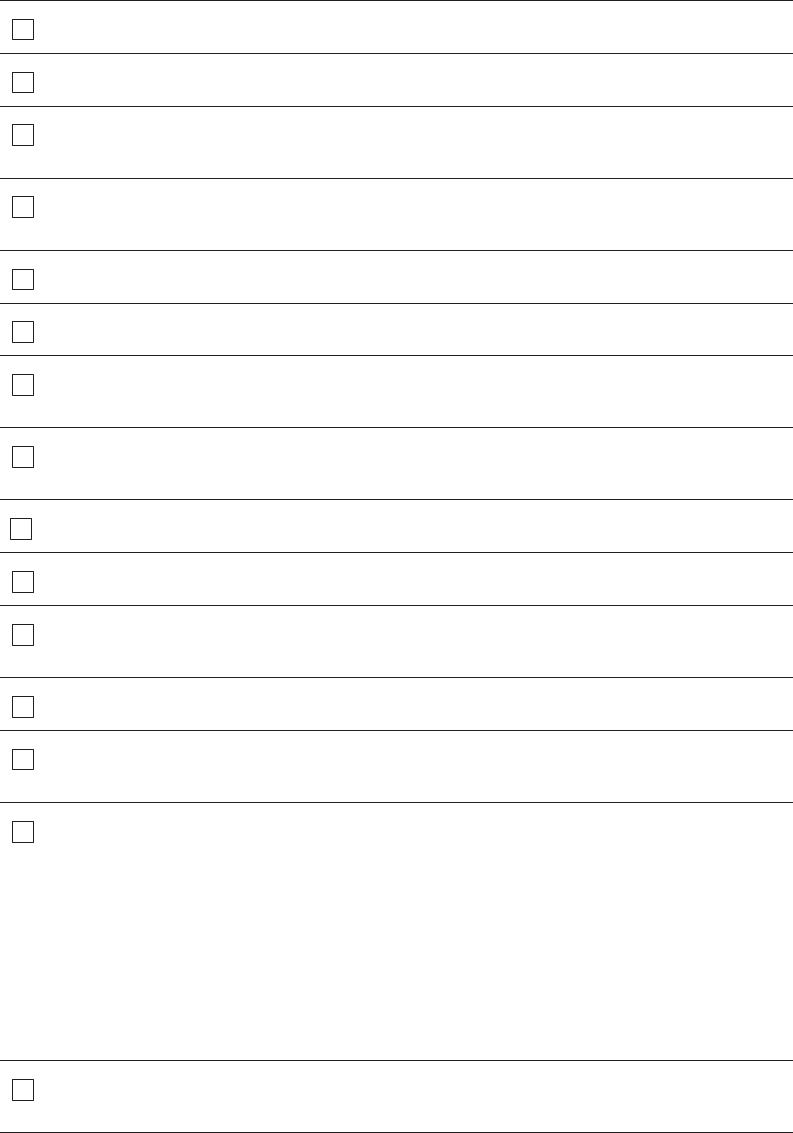
1027144–0001 Draft – Revision D.01 2–4 Prerequisites RT installation
Table 2-1 Tools required for RT installation – Cont’d.
(includes tools for IFL installation, antenna pointing, and initial testing)
√Purpose (or other comments)Item
Diagonal cutters (wire cutters)
Flush mount cutters
Excelta CX–1–78–1 cable
stripping tool Manufacturer: Excelta Corp., Buellton, CA
Crimp tool for #2 and #6
AWG ground lugs Manufacturer: Thomas & Betts, Memphis, TN
HCT–231 crimp tool For terminating N–type connectors
Channel locks
Soft jaw pliers Grip tool with soft surface, for gripping and
turning N–type connectors
Band cutters To remove shipping bands from mast mount
pieces
Carpenter’s knife
Splicer’s knife To terminate cables
Binoculars Suggested, for RT installation, if the HT is too far
to see
Flashlight Primarily for IFL installation
100–foot tape measure
(metric equivalent: 30.5 meters) For measuring cable runs
ODU installer tool kit
(HNS 1024668–0024) This kit consists of several specialized tools as
shown in figure 2-1:
• Temporary installation collar and clamp –
These support the antenna mount and
ODU/antenna during installation and pointing.
• Two azimuth/elevation adjuster assemblies –
Used to adjust the antenna azimuth and
elevation.
The ODU installer tool kit is available from HNS.
Large backpack or
padded bag To haul ODU transceiver and antenna to the roof
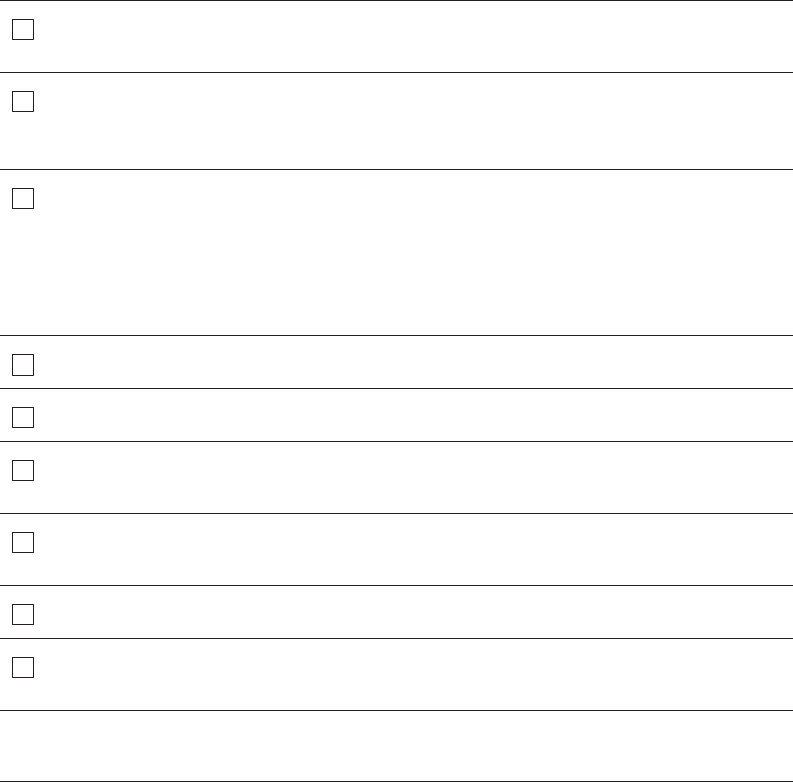
1027144–0001 Draft – Revision D.01 Prerequisites 2–5
RT installation
Table 2-1 Tools required for RT installation – Cont’d.
(includes tools for IFL installation, antenna pointing, and initial testing)
√Purpose (or other comments)Item
Digital voltmeter For pointing and testing
dc voltage measurement accuracy: 0.3%
Test cable terminated with
F–connector and alligator
clips
Used to connect voltmeter to ODU for antenna
pointing
Detailed local map Used to locate the HT. Must show true north,
streets, buildings, and landmarks. Helpful if the
map shows magnetic declination (or magnetic
north versus true north). A U.S. Geological
Survey map is recommended. A travel map will
suffice if it shows sufficient detail.
Ruler or straight edge Used to mark directions on map
Pencil or broad–tip pen Used to add markings to local map
Protractor May be useful as an aid in pointing the antenna.
Must show 0° increments from 0° to 180°.
Compass May be useful as an aid in pointing the antenna.
Must be accurate to within ±1°
Personnel safety lines For safety on roof
Back brace To protect against back injury while hoisting or
lifting equipment and installation materials
Note: Vendor names, model numbers, and part numbers identify equipment known to
be suitable. Other comparable equipment may also be suitable.
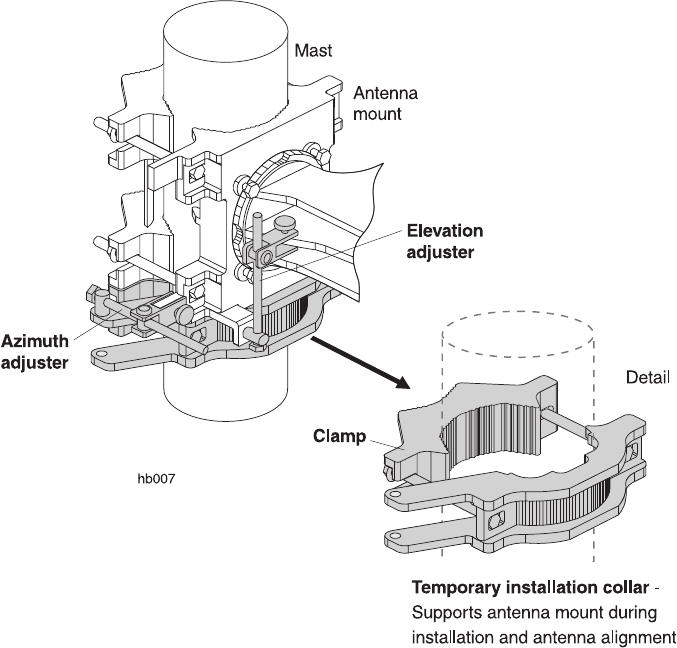
1027144–0001 Draft – Revision D.01 2–6 Prerequisites RT installation
Figure 2-1 shows the specialized tools included in the ODU
installer tool kit (HNS 1024668–0024). These tools can also be
ordered separately: Temporary installation collar with clamp –
HNS 1024668–0022; one azimuth/elevation adjuster
(interchangeable) – HNS 1024668–0023. These tools are removed
after mount installation and pointing so they can be reused for
subsequent installations.
Figure 2-1 Tools included in ODU installer tool kit (shaded)
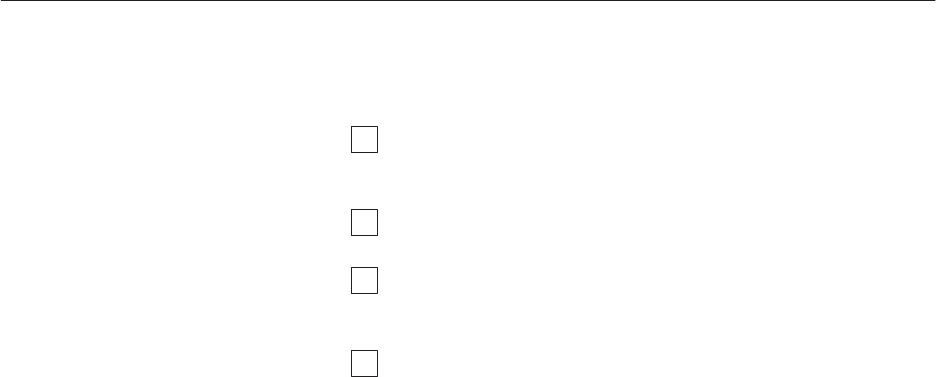
1027144–0001 Draft – Revision D.01 Prerequisites 2–7
RT installation
You will not be able to commission the RT (as detailed in chapter
7) unless the Element Management System (EMS) is operational.
Specific requirements for commissioning are:
The EMS hardware and software must be installed and
operational.
The EMS database must be loaded and operational.
The EMS operator has to enter the hub MAC address
into the EMS database.
The hub and HT are installed and operational. The HT must
be properly aligned.
Additional prerequisites for commissioning are listed in chapter 7.
The additional prerequisites are satisfied when the RT is properly
installed. The prerequisites listed above must be accomplished
prior to RT installation—or commissioning will be delayed
until they are accomplished.
2.4
Prerequisites for
commissioning
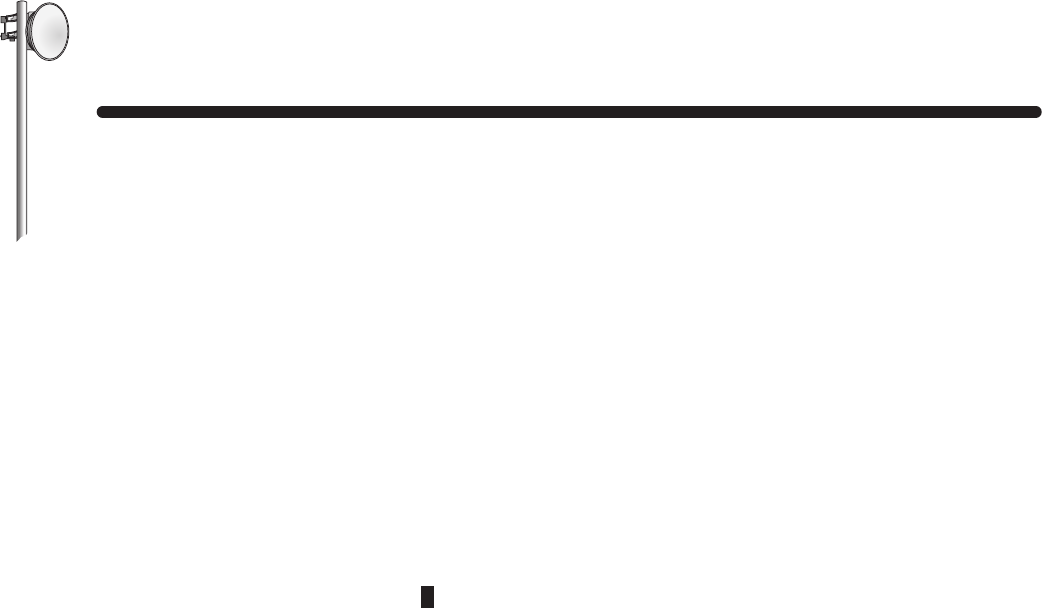
RT INSTALLATION
1027144–0001 Draft – Revision D.01 Installing indoor RT equipment 3–1
RT installation
Chapter 3
Installing indoor RT equipment
This chapter includes:
•Rack grounding
•Installing indoor units (IDUs)
•Power supplies – page 3–8
•Installing the CCM – page 3–24
•CCM power–on test – page 3–26
•SSIs – page 3–28
•Installing expansion IDUs (EIDUs) – page 3–34
For IDU standards compliance information, see appendix B
(page B–3).
All of the tasks in this chapter are done inside.
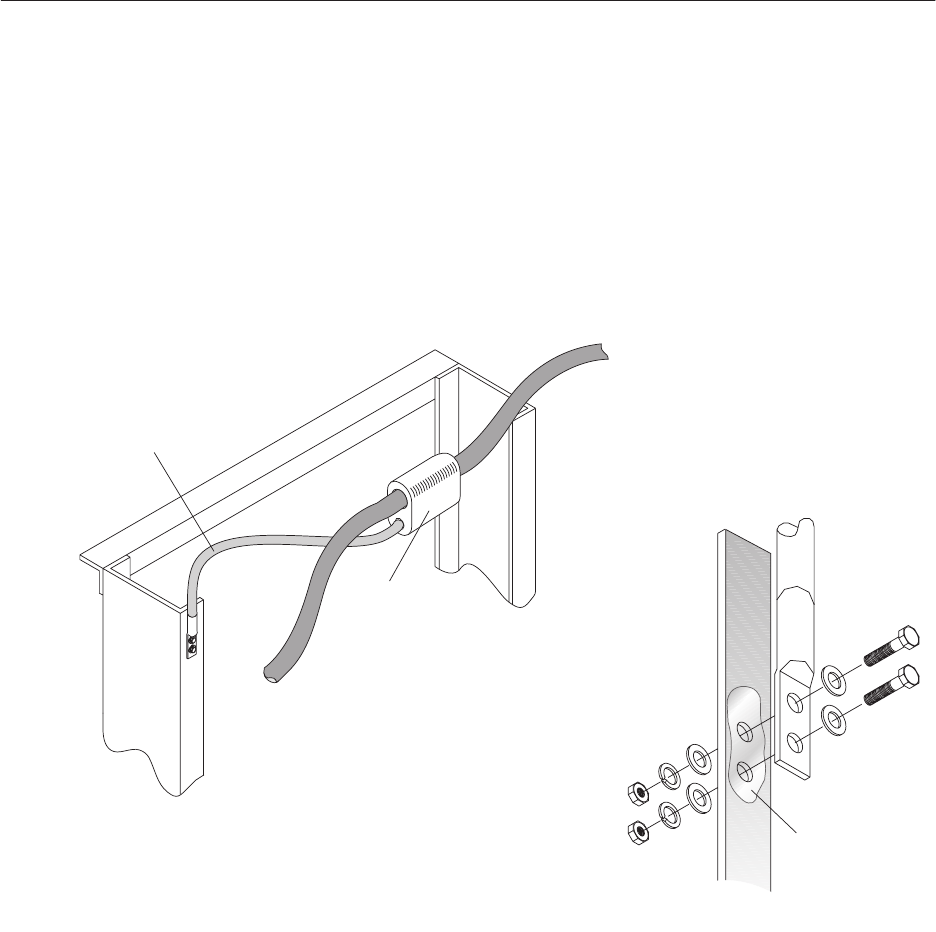
1027144–0001 Draft – Revision D.01 3–2 Installing indoor RT equipment RT installation
If the RT IDU will be mounted in a rack, the rack must be
grounded, as shown in figure 3-1:
1. Run a ground wire from the rack location to the master
ground bar in the equipment room. This wire must be No. 2
AWG, green, stranded, and shielded.
2. Ground the rack by connecting a No. 6 AWG wire from the
rack to the No. 2 AWG ground wire.
Use a 2–hole lug to connect the No. 6 AWG wire to the
rack. Remove paint and apply anti–oxidant as shown in the
illustration.
hb103
Top of rack
from rear
Lug connection
close up view
Frame
lug
Remove paint to
bare metal, and
apply anti-oxidant.
Metal rack
HTAP connector
with cover
No. 2 AWG wire (green)
to master ground bar
No. 6 AWG wire
Frame
lug
To a subsequent
rack (if present)
Figure 3-1 Rack ground connections
3.1
Rack grounding
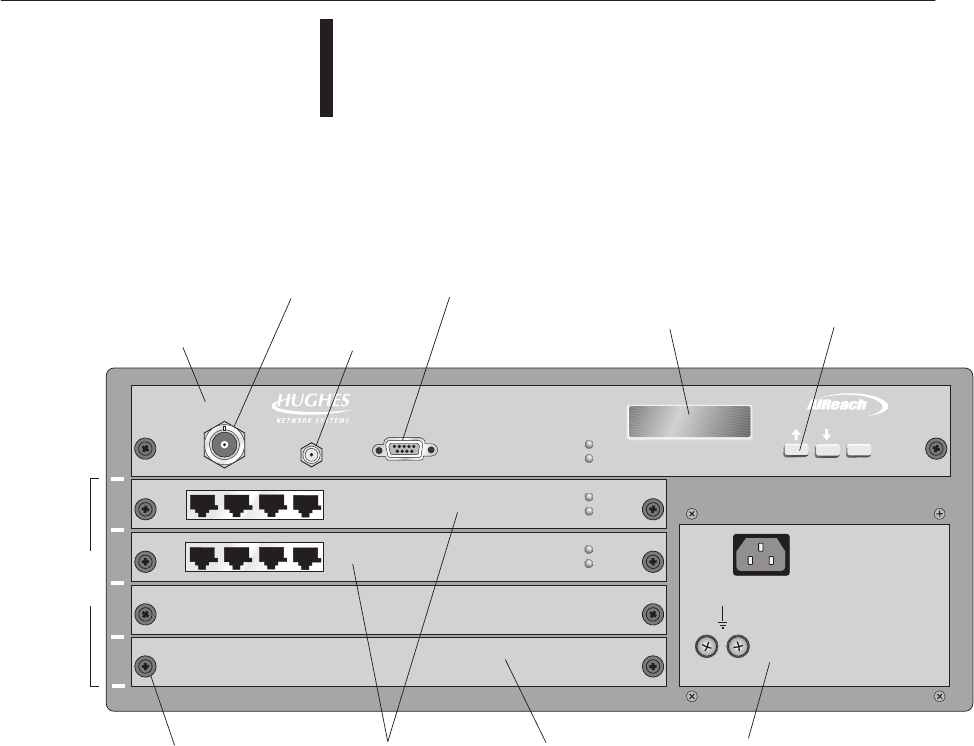
1027144–0001 Draft – Revision D.01 Installing indoor RT equipment 3–3
RT installation
Figures 3-2 and 3-3 show the RT indoor unit (IDU), which houses
the channel and control module (CCM) and service–specific
interfaces (SSIs). The IDU chassis is shipped with the power
supply installed, but the CCM and SSIs are not installed.
For IDU standards compliance information, see appendix B
(page B–3).
Figures 3-2 and 3-3 identify the main IDU components.
Figure 3-2 RT IDU main components (shown: IDU with ac power supply)
1
2
3
4
5
TM
BROADBAND
ENTER
RT CCM
rt018
Channel and
control module
(CCM)
Service-specific
interface (SSI)
Blank panel
Thumbscrew AC power supply
Liquid crystal
display (LCD)
Control pushbuttons
(for LCD)
IFL
interface
Maintenance
port
SSI
slots
Power supply may be ac (as shown
here), dc, or dual mode (ac or dc).
Auxiliary
IF port
3.2
Installing IDUs
IDU components
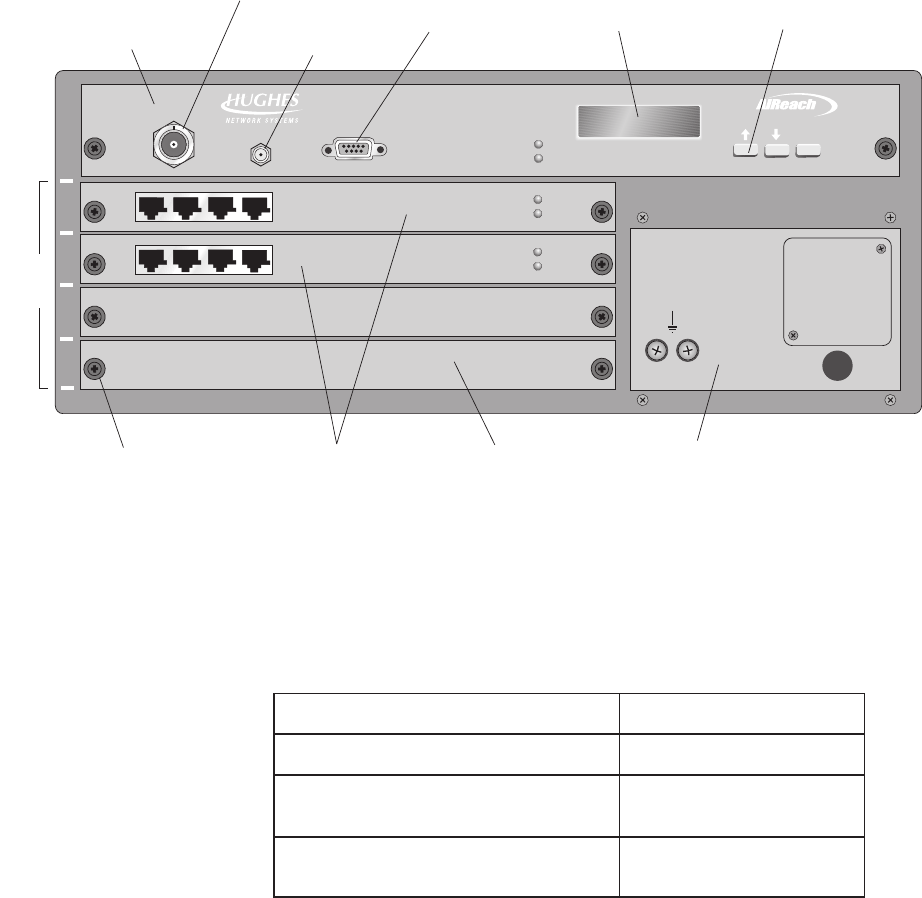
1027144–0001 Draft – Revision D.01 3–4 Installing indoor RT equipment RT installation
1
2
3
4
5
rt050
Channel and
control module
(CCM)
Service-specific
interface (SSI)
Blank panel
Thumbscrew DC power supply
Liquid crystal
display (LCD)
Control pushbuttons
(for LCD)
IFL
interface Maintenance
port
SSI
slots
TM
BROADBAND
ENTER
RT CCM
Auxiliary
IF port
Figure 3-3 RT IDU with dc power supply
Three IDU chassis types are available, each with a different power
supply option:
Table 3-1 IDU types
IDU type HNS part number
IDU chassis with ac power supply 1026356–0001
IDU chassis with dc power supply
(–48 Vdc) 1026356–0002
IDU chassis with dual mode (ac or
dc) power supply 1026356–0003
The power supply is not user replaceable.
Before you install the IDU chassis, make sure a power source is
available. If it is not, you may have to select a different location
for the IDU or install an electrical receptacle.
Note: The IDU is an industrial product. For safety and security
reasons, it must be installed in an area that is accessible only to
authorized servicing personnel.
IDU chassis types
Prerequisites
1027144–0001 Draft – Revision D.01 Installing indoor RT equipment 3–5
RT installation
The IDU can be used on a tabletop or installed in a 19–inch
(48.3–centimeter) rack. With optional adapter brackets, the IDU
can also be installed in a 23–inch (58.4–centimeter) rack.
Safety guidelines
Observe these guidelines from Underwriters Laboratories Inc.
(UL) when you install IDU chassis in a rack (any rack):
•Make sure the power requirements of the IDU chassis plus
the cumulative power draw of other equipment in the rack
do not overload the supply circuit and/or wiring of the rack.
•The IDU weighs about 20 pounds (about 9 kilograms).
Have someone help you when you lift the IDU chassis to
install it in the rack.
•Always load the rack from bottom to top to ensure a stable
and safe rack.
•Installation of the IDU chassis within the rack system
should not reduce air–flow within the rack.
•The maximum recommended ambient temperature for the
IDU chassis is 50 °C (122°F).
•While installing the IDU chassis into the rack, make sure
you maintain a proper earth grounding for the equipment.
Mounting options
Rack mounting
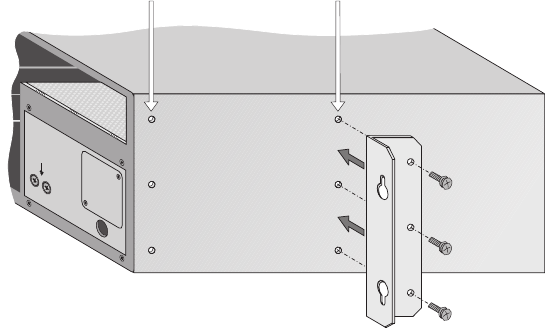
1027144–0001 Draft – Revision D.01 3–6 Installing indoor RT equipment RT installation
Rack mounting instructions
To mount the IDU chassis in a rack, you need the rack mounting
brackets included in HNS kit 1027191–0001. This kit includes two
brackets and six Phillips SEMS screws for attaching the bracket to
the IDU.
To mount the IDU chassis in a rack, follow these steps:
1. Attach the rack mounting brackets as shown in figure 3-4.
Be sure to use the correct sets of holes (front or midpoint)
for each bracket, as indicated in figure 3-4.
Figure 3-4 Attaching rack mounting brackets to the IDU chassis
hb032
Mounting
bracket
Attach bracket here
for .enclosed rack
Attach bracket here
for .open rack
Front
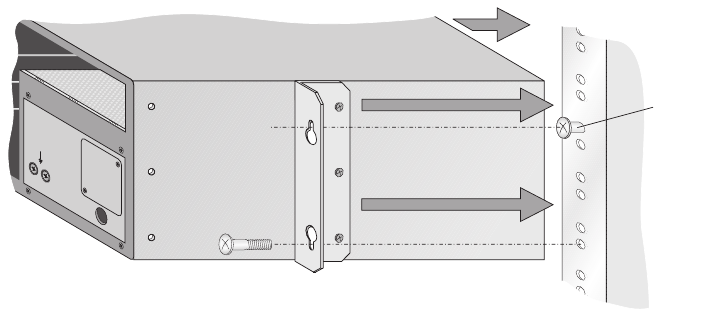
1027144–0001 Draft – Revision D.01 Installing indoor RT equipment 3–7
RT installation
2. Screw the two upper mounting screws into the rack (one on
each side), at the desired installation height. Refer to figure
3-5.
Do not tighten the screws all the way—this allows you to
hang the chassis by the top “teardrop” holes on the brackets
(in step 3).
(The four mounting screws that screw into the rack should
be provided with the rack.)
Figure 3-5 Installing the IDU chassis in a rack
hb033
Rack
Front
Leave part
of the upper
mounting
screws
exposed
so you can
hang the
brackets
on them.
3. Place the chassis into the rack, and slip the top hole of each
bracket over the heads of the upper mounting screws in the
rack.
4. Support the chassis with one hand while you install and
tighten the two lower screws.
5. Tighten the two upper screws.
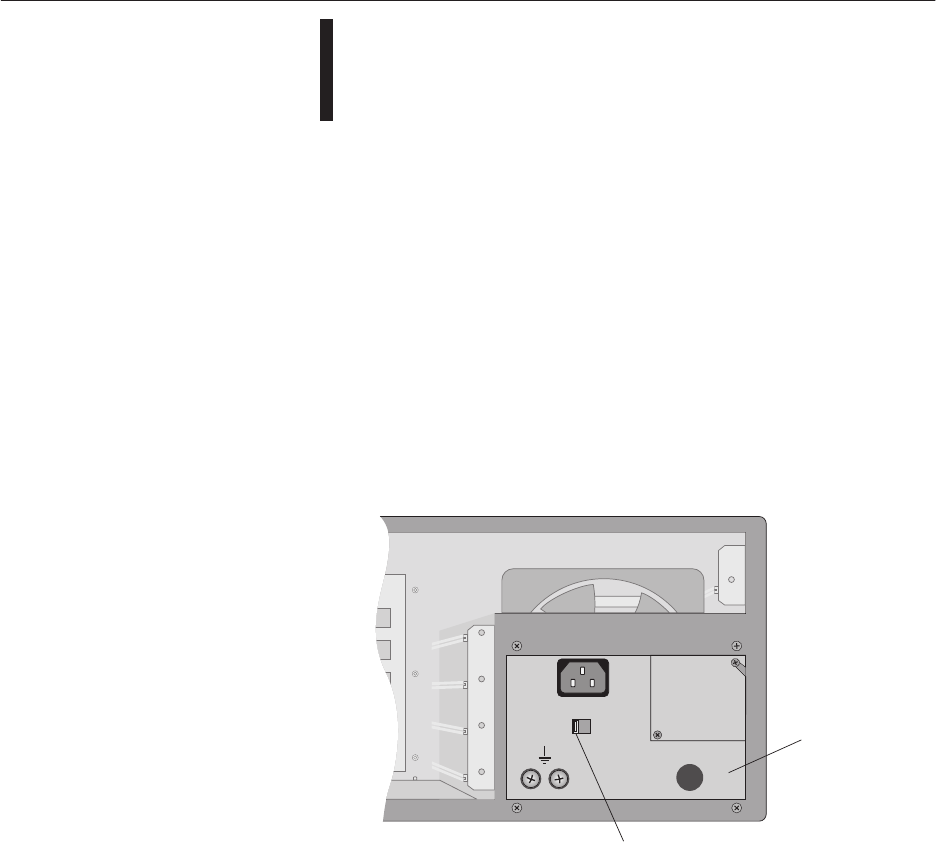
1027144–0001 Draft – Revision D.01 3–8 Installing indoor RT equipment RT installation
The IDU power supply is installed in the chassis at the factory.
However, you need to make sure the power supply is grounded
and connect power to the power supply. Detailed instructions for
these steps follow.
The IDU chassis may be equipped with an ac, dc, or dual (ac or
dc) power supply, depending on the local power environment. In
the following sections, make sure you follow all instructions for
the type of power supply your IDU chassis has.
Do not attempt to replace or substitute power supplies. If there
is a problem with a power supply, return the chassis to HNS for
repair or replacement.
The dual ac or dc power supply (figure 3-6) can be used with an ac
or dc power source. A recessed switch on the front of the power
supply is used to select ac or dc operation.
T0006026
AC DC
Dual ac/dc
power supply
AC/DC switch
Figure 3-6 Dual ac or dc power supply
Selecting ac or dc power
Follow these instructions to set the power supply for ac or dc
operation:
To use the dual power supply with ac power:
Make sure the switch is in the ac position; then follow the
instructions below for ac power supplies.
Note: The ac–dc switch is recessed to prevent accidental
switching. Use a flathead screwdriver to change the switch
position.
To use the dual power supply with dc power:
Make sure the switch is in the dc position; then follow the
instructions below for dc power supplies.
3.3
Power supplies
Power supply options
Dual (ac or dc) power
supply

1027144–0001 Draft – Revision D.01 Installing indoor RT equipment 3–9
RT installation
Selecting ac or dc power
Follow these instructions to set the power supply for ac or dc
operation:
To use the dual power supply with ac power:
Make sure the switch is in the ac position; then follow the
instructions below for ac power supplies.
Note: The ac/dc switch is recessed to prevent accidental
switching. Use a flathead screwdriver to change the switch
position.
To use the dual power supply with dc power:
Make sure the switch is in the dc position; then follow the
instructions below for dc power supplies.

1027144–0001 Draft – Revision D.01 3–10 Installing indoor RT equipment RT installation
Labels on dual power supply
A label on the dual ac or dc power supply warns:
WARNING
MULTIPLE POWER
CONNECTORS.
DISCONNECT BOTH
AC & DC POWER
BEFORE SERVICING.
Servicing personnel must heed this warning. Note that the IDU
and power supply should be serviced only by HNS.
A second label on the dual ac or dc power supply advises:
CAUTION
THIS EQUIPMENT HAS A
CONNECTION BETWEEN
THE EARTHED CONDUCTOR
OF THE D.C. SUPPLY CIRCUIT
AND THE EARTHING CONDUCTOR.
SEE EARTHING INSTRUCTIONS
To disconnect dc power, unplug the terminal block (shown on
page 3–17). Do not remove the wires from the terminal block
while it is plugged in. If you do, the IDU chassis will not be
grounded.
Additional instructions
If the power supply is a dual ac or dc unit, follow the instructions
in the following sections for both ac and dc power supplies.
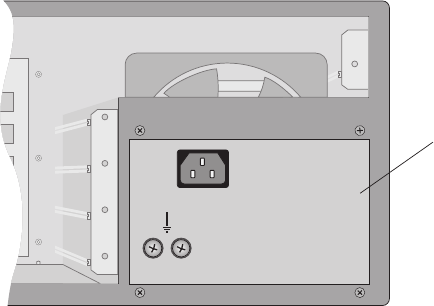
1027144–0001 Draft – Revision D.01 Installing indoor RT equipment 3–11
RT installation
IDU chassis with an ac power supply (figure 3-7) or dual ac or dc
power supply are equipped with a recessed IEC–320–C13
connector and a 7.5–foot (2.3–meter) power cable (HNS
9003024–0013). The power cable includes a NEMA 5–15–P plug
to connect to the power source (receptacle). The cable is rated at
125 Vac, 10 amperes, and is equipped with an internal ground
(earth) conductor.
The primary input requirements for the ac power supply are:
Voltage: 100 – 240 Vac
Current: 6.4 amperes maximum
Frequency: 50 – 60 Hz
Figure 3-7 AC power supply
AC power supply
hb048
AC power supply
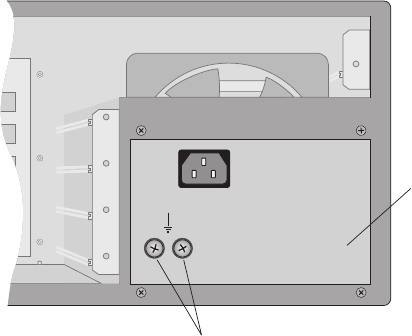
1027144–0001 Draft – Revision D.01 3–12 Installing indoor RT equipment RT installation
Important: In the United States and some international markets,
the required ground bond is provided by the grounding conductor
in the cable and ac service conductors. If grounding is provided
through the grounding conductor and service conductors, no
additional grounding is required.
In environments where ac grounding conductors are not
available, a separate bonding conductor is required.
If a separate bonding conductor is required, ground the ac power
supply as follows:
1. Use a 2–hole lug to connect a No. 16 AWG ground wire to
the ground terminals on the front of the power supply. See
figure 3-8.
Figure 3-8 Ground terminals on ac power supply
AC power supply
hb052
Ground terminals
2. Connect the other end of the ground wire to the rack ground
bar. If the IDU chassis is not rack mounted, connect the
ground wire to a ground point such as a water pipe or
building steel.
Grounding the ac IDU
chassis
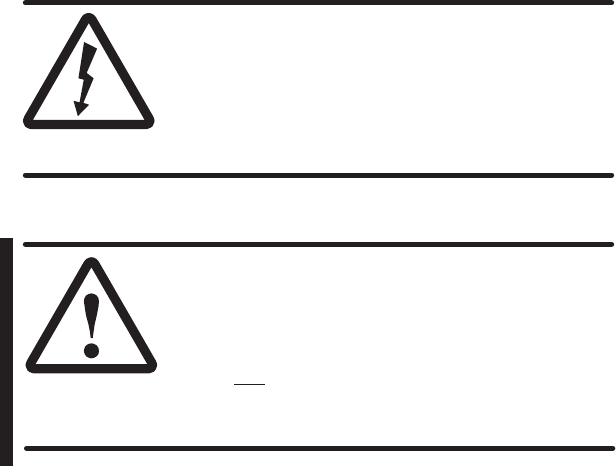
1027144–0001 Draft – Revision D.01 Installing indoor RT equipment 3–13
RT installation
WARNING
The IDU chassis must be solidly bonded to a
low–impedance ground (earth) source.
To avoid the risk of electric shock and/or
equipment damage, do not apply power to
the IDU chassis without a ground reference.
CAUTION
If the ODU and lightening arrestor are not
connected to the IFL, do not power on the
IDU chassis without first making sure the
IFL is not connected to the IDU chassis.
Failure to observe this instruction could
result in damage to the equipment.
To connect ac power:
1. Measure the voltage level of the power source to make
sure it can accommodate the total IDU and ODU power
requirements.
(The IDU supplies power to the ODU through the IFL.)
If the voltage level cannot accommodate the IDU and ODU,
the power source must be upgraded before you can proceed.
2. Connect the power cable to the IEC–320–C13 connector on
the power supply.
3. Route and secure the cable to avoid physical damage.
4. Connect the plug end of the cable to a dedicated ac power
source.
Important: In the United States, ac–power IDU chassis
must be connected to a dedicated power circuit with a
15–ampere single–pole breaker. The circuit must not
include unrelated equipment.
Connecting ac power
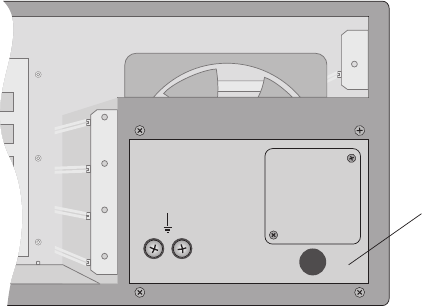
1027144–0001 Draft – Revision D.01 3–14 Installing indoor RT equipment RT installation
Figure 3-9 shows an IDU chassis with a dc power supply.
A power cable is not supplied with the dc IDU chassis because
cable requirements vary, depending on where the chassis will be
used.
The power input requirement for the dc power supply (and dc
portion of the dual ac or dc power supply) is –42 to –56 Vdc.
Figure 3-9 DC power supply
hb050
DC power supply
Label on dc power supply
A label on the dc power supply advises:
CAUTION
THIS EQUIPMENT HAS A
CONNECTION BETWEEN
THE EARTHED CONDUCTOR
OF THE D.C. SUPPLY CIRCUIT
AND THE EARTHING CONDUCTOR.
SEE EARTHING INSTRUCTIONS
To disconnect dc power, unplug the terminal block (shown on
page 3–17). Do not remove the wires from the terminal block
while it is plugged in. If you do, the IDU chassis will not be
grounded.
DC power supply
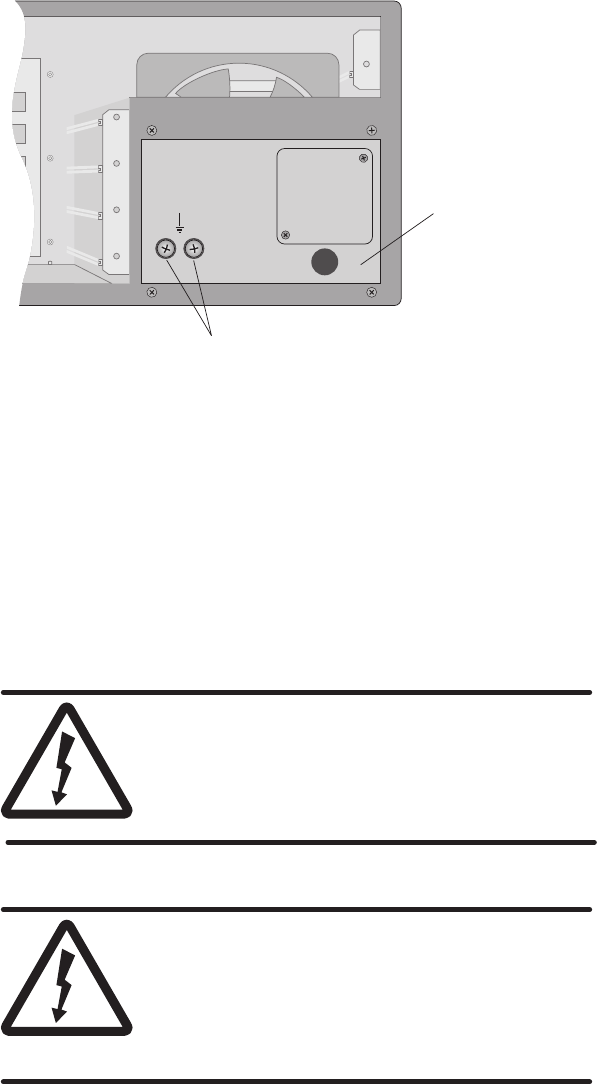
1027144–0001 Draft – Revision D.01 Installing indoor RT equipment 3–15
RT installation
Ground IDU chassis with a dc power supply as follows:
1. Use a 2–hole lug to connect a No. 14 AWG ground wire to
the ground terminals on the front of the power supply
(figure 3-10).
Figure 3-10 Ground terminals on dc power supply
hb049
DC power supply
Ground terminals
2. Connect the other end of the ground wire to the rack ground
bar. If the IDU chassis is not rack mounted, connect the
ground wire to a ground point such as a water pipe or
building steel.
WARNING
To avoid the risk of electric shock,
remove power from the power circuit
before connecting power cables to the
IDU chassis power supply.
WARNING
The IDU chassis must be solidly bonded to a
low–impedance ground (earth) source.
To avoid the risk of electric shock and/or
equipment damage, do not apply power to
the IDU chassis without a ground reference.
Grounding the dc IDU
chassis
Connecting dc power
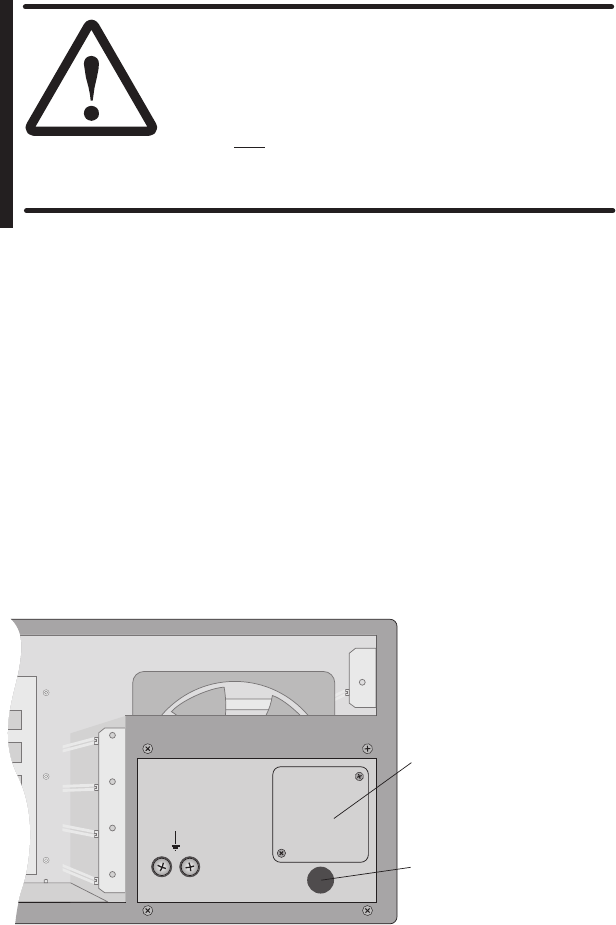
1027144–0001 Draft – Revision D.01 3–16 Installing indoor RT equipment RT installation
CAUTION
If the ODU and lightening arrestor are not
connected to the IFL, do not power on the
IDU chassis without first making sure the
IFL is not connected to the IDU chassis.
Failure to observe this instruction could
result in damage to the equipment.
To connect power cables from the dc power source (usually a
rectifier) to the dc power supply, follow the steps below.
1. Measure the voltage level of the power source to verify it
can accommodate the total IDU and ODU power
requirements.
(The IDU supplies power to the ODU through the IFL.)
If the voltage level cannot accommodate the IDU and ODU,
the power source must be upgraded before you can proceed.
2. Remove power from the power circuit.
3. Loosen the two Phillips screws from the square terminal
block cover plate on the front of the power supply.
Terminal block
cover plate
(Remove)
hb002
Conduit opening
4. Rotate the protective plate to expose the terminal block.
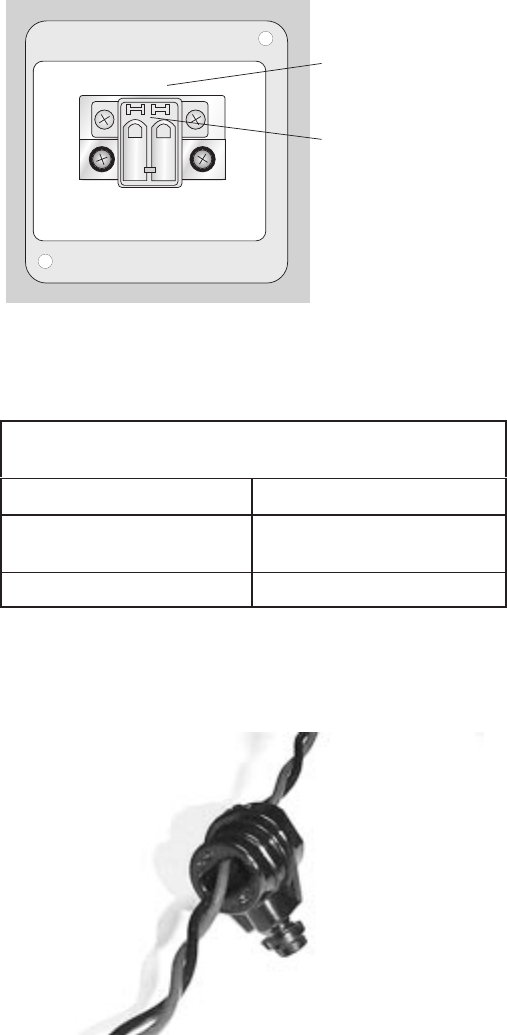
1027144–0001 Draft – Revision D.01 Installing indoor RT equipment 3–17
RT installation
• Follow steps 5 through 14 to insert the power cable wires into
the power supply terminal block:
5. Unplug the terminal block from the power supply socket.
hb108
Plug-in terminal
block
Power supply
(+)RETURN
(-)48VDC
6. Strip both wires from the power source to about ¼ inch (6
centimeters) from the end.
Note: Wires used with the terminal block must meet
these specifications:
Composition Solid or stranded
Wire cross–sectional
area 0.2 to 2.5 square
millimeters
Rated gauge 12 to 24 AWG
7. Twist the wires as shown in the photo below.
8. Insert both wires through the plastic strain relief bushing
(HNS 9005614–0001).
Strain relief
bushing
hbph014
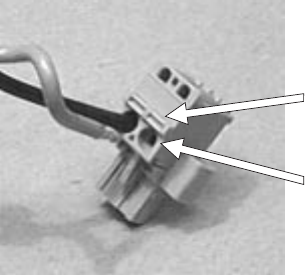
1027144–0001 Draft – Revision D.01 3–18 Installing indoor RT equipment RT installation
9. Lay the terminal block on a flat surface, with the wire entry
holes facing up.
10. Use a small, flat–blade screwdriver (or similar tool) to press
in the tab above the wire entry hole on the terminal block.
Hold the tab in.
Press and hold
tab to insert wire.
Terminal block with
one wire inserted
Wire entry holes
hb004
11. While holding the tab in, insert the stripped wire end.
Important: Insert the return (+) wire from the dc power source
into the terminal block so it will connect to the power supply
terminal marked (+) Return when the terminal block is plugged
in. Likewise, insert the –48 Vdc (–) wire so it will connect to the
–48 VDC (–) power supply terminal.
12. When the wire is fully inserted, release the tab.
13. Gently tug the wire to make sure it is securely inserted.
14. Repeat steps 10 through 13 for the second wire.
• At this point, both wires are inserted into the terminal block.
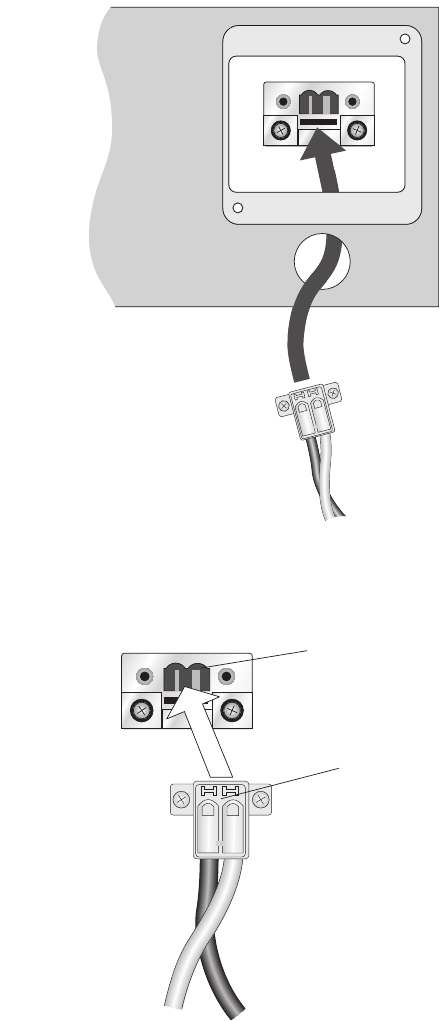
1027144–0001 Draft – Revision D.01 Installing indoor RT equipment 3–19
RT installation
15. Insert the terminal block through the conduit opening and
guide it up to the socket.
Socket
Terminal block
Conduit opening
hb051
(+)RETURN
(-)48VDC
16. Plug the terminal block into the power supply terminal
socket.
hb046
(+)RETURN
(-)48VDC
Socket
Terminal block
1027144–0001 Draft – Revision D.01 3–20 Installing indoor RT equipment RT installation
17. Snap the strain relief bushing into the conduit opening.
18. Tighten the screw on the strain relief bushing just enough to
hold the wires in place. Do not overtighten.
19. Replace the protective plate and tighten the screws.
• This completes the power connections.
The chassis does not have a power off/on switch. In normal
operation, power is always on. If you need to power off the IDU:
•Break the power circuit at the rack fuse panel,
•Break the power circuit at the external fuse or circuit
breaker panel, or
•Use an optional remote power–off circuit.
This section applies only to dc power circuits.
The circuit from the dc power source (usually rectifiers) to the
IDU chassis must include a circuit breaker or other disconnect
device that meets the following Underwriters Laboratories (UL)
requirements:
To install dc power for the IDU chassis, a readily
accessible disconnect device shall be installed
or should be readily available at the site where
the IDU chassis is installed. The disconnect
device must be a UL–listed circuit breaker rated
at 60 Vdc, 6.3 amperes minimum, 15 amperes
maximum.
Powering off the dc IDU
Remote dc
power–off circuit
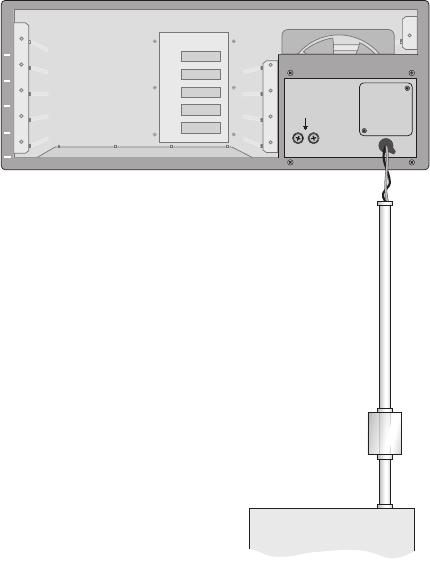
1027144–0001 Draft – Revision D.01 Installing indoor RT equipment 3–21
RT installation
If the rectifier–to–chassis power circuit does not include a suitable
circuit breaker, you can satisfy the disconnect requirement by
including a remote power–off switch as shown in figures 3-11 and
3-12. If the power circuit already includes a suitable circuit
breaker, skip this section.
Figure 3-11 The remote power–off circuit (if needed) is
installed between the IDU chassis and dc power source.
1
2
3
4
5
hb006
DC power cable
Conduit
Remote
power-off
circuit
Rectifier
IDU chassis
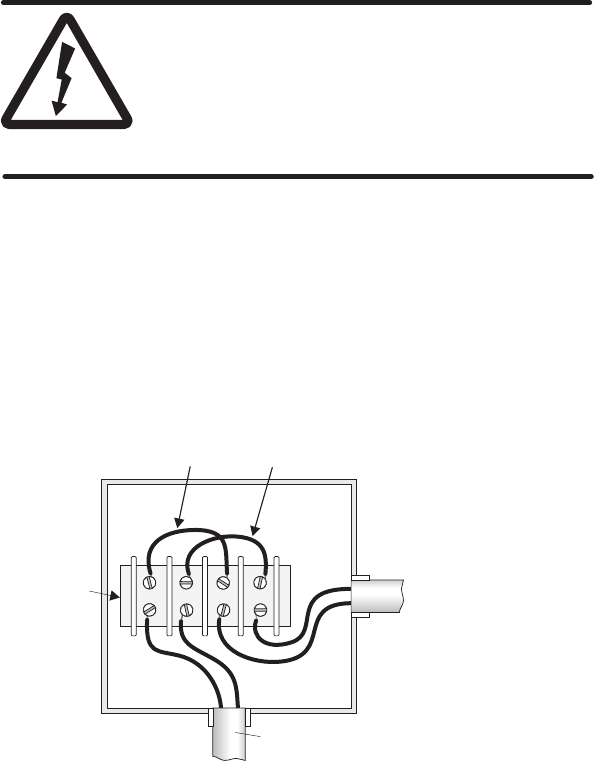
1027144–0001 Draft – Revision D.01 3–22 Installing indoor RT equipment RT installation
WARNING
To avoid the risk of electric shock, make
sure the dc power source breaker is off
before installing a remote power–off
circuit. Use a continuity tester to verify
that power is off.
To install a power–off circuit (if needed), follow these steps:
1. Make sure the rectifier breaker switch is off.
2. Install a UL–approved terminal block inside a UL–approved
electrical junction box as shown in figure 3-12.
Figure 3-12 Remote power–off circuit
hb001
++
––
Use only UL
listed parts.
Junction
box
Terminal
block
Output from
dc power rectifier
Input to IDU
chassis
Conduit with conduit coupler
Jumper 1 Jumper 2
Use insulated jumpers
connect remote power-off
switch in series.
or
3. Choose one of the following three options:
If you plan to add a power–off switch later, install jumpers 1
and 2, and replace the junction box cover. This completes
the circuit installation.
If you are installing a double–pole remote power–off switch,
use a double–pole, single–throw switch rated at 60 Vdc, 15
amperes (minimum):
In place of jumper 1, wire the switch between the (+)
terminal from the rectifier and the (+) terminal from
the IDU.
In place of jumper 2, and wire the switch between the
(–) terminal from the rectifier and the (–) terminal
from the IDU.
1027144–0001 Draft – Revision D.01 Installing indoor RT equipment 3–23
RT installation
If you are installing a single–pole remote power–off switch,
use a single–pole, single–throw switch rated at 60 Vdc, 15
amperes (minimum):
Install jumper 1.
In place of jumper 2, wire the switch between the (–)
terminal from the rectifier and the (–) terminal from
the IDU chassis.
• If you installed a switch, follow steps 4 through 9 to test the
switch:
4. Place the remote power–off switch in the open position.
5. Replace the junction box cover.
6. Turn on the dc breaker.
7. Close the power–off switch. Confirm that the chassis is
receiving power.
8. Open the switch again. Confirm that the chassis is no longer
powered. If the switch does not operate correctly, turn the
rectifier breaker off and make sure the circuit is connected
as shown in figure 3-12.
9. If the switch operates correctly, leave it in the open position
with the breaker off.
Do not install the channel and control module (CCM) or
service–specific interfaces (SSIs) yet.
To test the IDU chassis and power supply, perform these steps
without a CCM or SSIs:
1. If the IDU chassis is dc powered, inspect the power supply
wiring to verify that the polarity is correct.
2. Power on the IDU—with no modules installed; then check
to make sure no breakers have tripped or fuses have blown.
If a breaker trips or fuse blows, be sure to troubleshoot
and correct the problem before proceeding.
Power–on inspection
and test
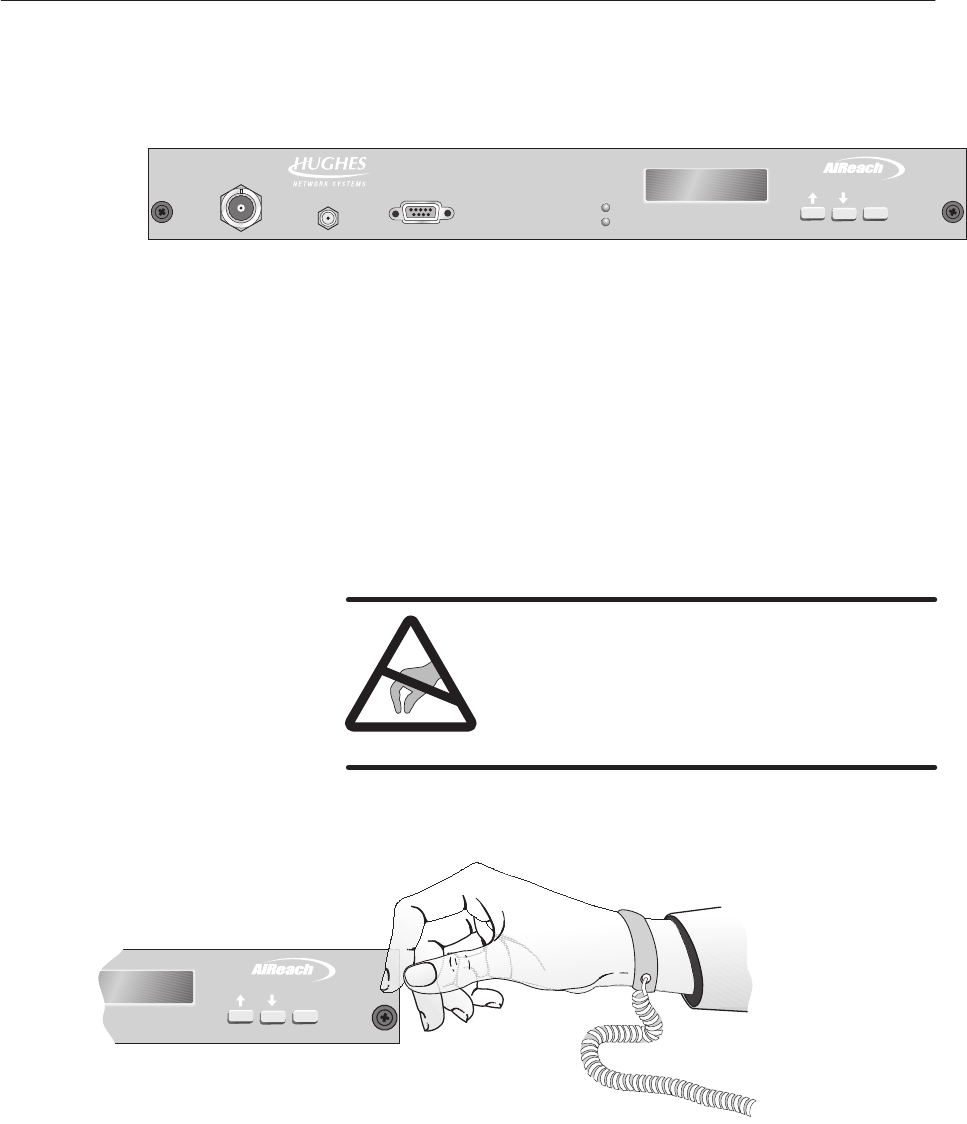
1027144–0001 Draft – Revision D.01 3–24 Installing indoor RT equipment RT installation
A channel and control module (CCM) must be installed in the top
slot (slot 1) of the IDU chassis. For an RT IDU, the CCM must be
a CCM RT (HNS 1027181–0002), as shown in figure 3-13.
Figure 3-13 CCM RT
Liquid crystal
display (LCD)
Control pushbuttons
(for LCD)
IFL
interface
Maintenance
port
rt022
TM
BROADBAND
ENTER
RT CCM
Auxiliary
IF port
The CCM supports the interface modules installed in the IDU
chassis by performing control, bus, upconversion, and
downconversion functions. These modules—SSIs—are described
in section 3.5.
To install the CCM RT, follow the steps below:
CAUTION
Always wear a new or recently tested
electrostatic discharge (ESD) wrist strap
(figure 3-14) when handling circuit
modules. Failure to use a wrist strap may
result in damage to components.
Figure 3-14 ESD wrist strap
TM
BROADBAND
ENTER
hb061
Wrist
strap
Connect to IDU chassis
ground terminal.
3.4
Installing the CCM
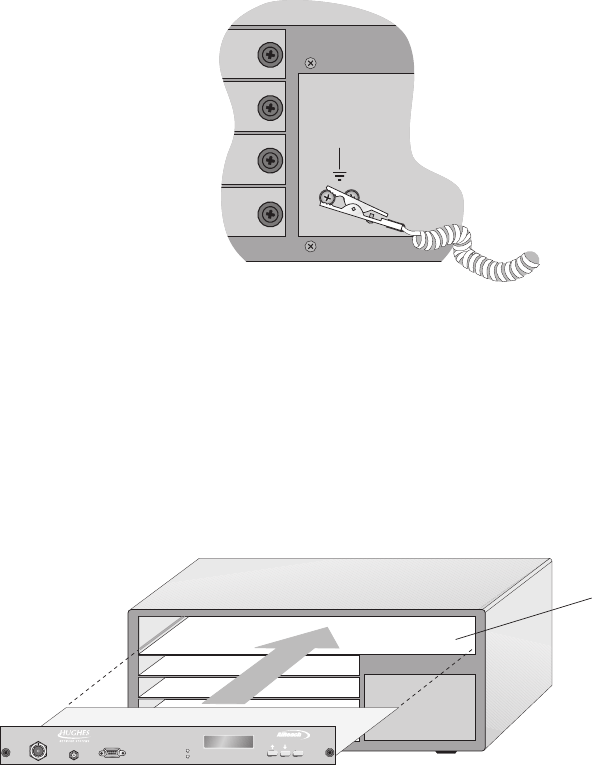
1027144–0001 Draft – Revision D.01 Installing indoor RT equipment 3–25
RT installation
1. Wrap the ESD strap snugly around your wrist and connect
the alligator clip to one of the ground terminals on the IDU
chassis power supply.
hb060
2. Remove the CCM from its ESD protective packaging.
Retain the packaging in case it is necessary to return the
CCM for repair.
3. Slide the module into the guides on each side of the top
chassis module slot (slot 1) and push it firmly into place
until the CCM front panel is flush with the front of the
chassis.
rt024
CCM slot
TM
BROADBAND
ENTER
RT CCM
4. Tighten the thumbscrews at each end of the CCM.
To tighten the thumbscrews, push them toward the IDU
chassis and turn them clockwise. To fully tighten the
thumbscrews, use a Phillips screwdriver.
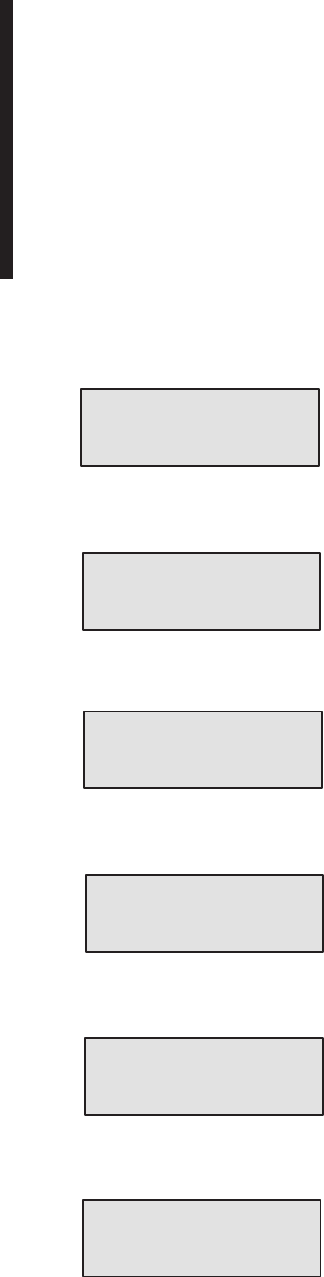
1027144–0001 Draft – Revision D.01 3–26 Installing indoor RT equipment RT installation
Test the CCM for proper operation, as follows:
1. Apply power to the IDU chassis.
2. Observe the LEDs on the CCM front panel:
-Green – CCM startup and normal operation
-Red – Failure
3. Also observe the CCM startup diagnostics (SUDS) on the
CCM’s front panel LCD:
SUDS start on powerup. While they run, the CCM front
panel shows the following messages, in the sequence
shown.
Equipment function is normal when you see the
messages shown below and no failure messages.
Initial powerup
SUDS CPU Reg OK
SUDS DRAM OK
CPU registers and dynamic
RAM are tested.
Timer test
SUDS Timer Test Timers are tested.
Watchdog timer test
SUDS WDT Test The watch dog timer
is tested.
PCI test
SUDS PCI Test The PCI controller is tested.
Static dual port RAM test
SUDS SDPRAM Test Static dual port RAM is tested.
Serial port 1 test
SUDS Ser 1 Test Serial port 1 is tested.
CCM power–on test
(SUDS)
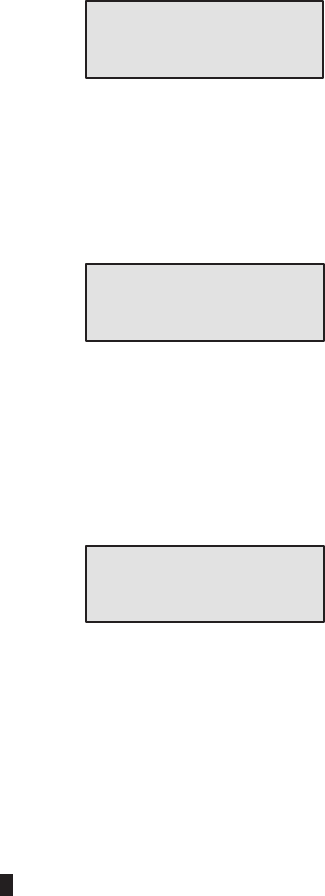
1027144–0001 Draft – Revision D.01 Installing indoor RT equipment 3–27
RT installation
Serial port 2 test
SUDS Ser 2 Test Serial port 2 is tested.
Successful test completion
This message indicates that startup diagnostics have
successfully completed:
SUDS Completed
Failure indication
If a failure occurs during any of the tests listed above,
the LCD message sequence stops. The LCD shows the test
that failed on the first line and FAILED (flashing) on the
second line, as in the example below.
SUDS Ser 2 Test
FAILED
This screen indicates that
serial port 2 failed diagnostics.
The LCD remains inactive unless you power the CCM off,
then on. This restarts SUDS.
If any CCM component fails, replace the CCM.
After SUDS are complete, the LCD displays the CCM boot
up sequence. At this point, you only need to verify that
SUDS have completed.
Leave power on while you install the SSIs (next).
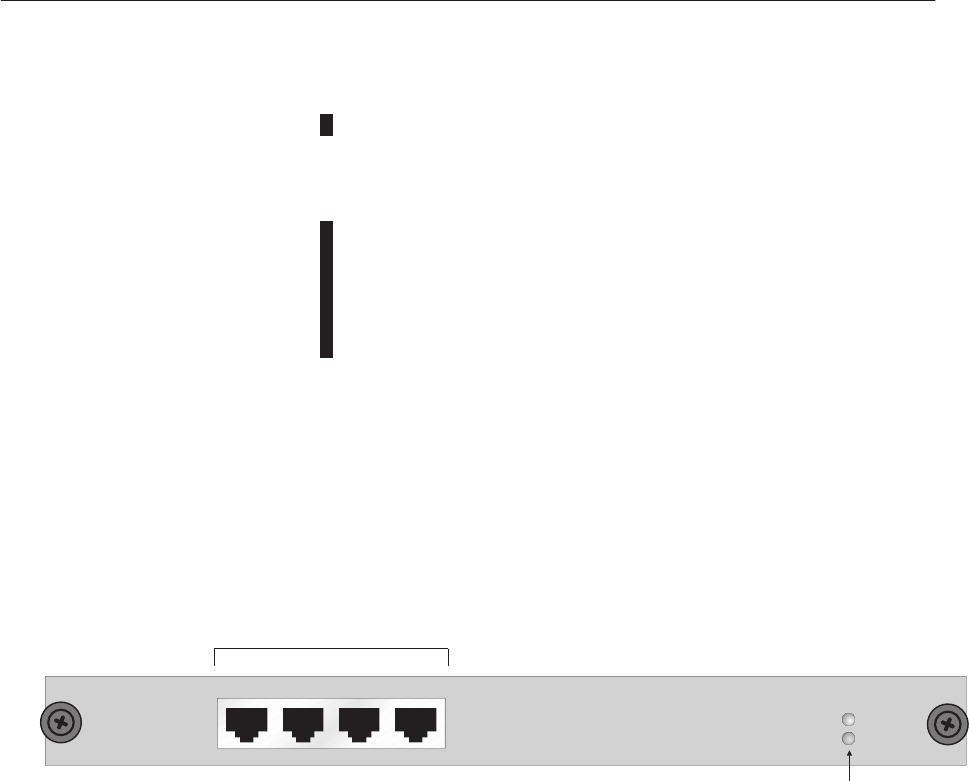
1027144–0001 Draft – Revision D.01 3–28 Installing indoor RT equipment RT installation
Service–specific interface modules (SSIs) provide interfaces to
support specific network services. SSI types used depend on the
needs of the customer network.
The following SSIs can be installed in the RT IDU chassis:
•Quad–DS1 (HNS 1027070–0001)
•DS3–TDM (HNS 1027094–0001)
•Universal–DS1 (HNS 3003132–0001)
•DS3–ATM (HNS 3003136–0002)
•DS3–Transparent (HNS 1027094–0002)
The following RT SSIs are currently in development:
•MPEG
•Ethernet 10BaseT/100BaseT
SSIs are installed in slots 2 through 5 in the RT IDU chassis.
The Quad–DS1 SSI, shown in figure 3-15, provides up to a four
T1 or E1 line link between the HT and RT.
Figure 3-15 Quad–DS1 SSI
QUAD DS1-SSI
OK
PORT 1
STATUS
rt004
LEDs indicate
SSI status
RJ-48X connectors
PORT 2 PORT 3 PORT 4
ALARM
The maximum cable length for a Quad–DS1 SSI is 655 feet
(199.6 meters).
The pinouts for the RJ–48X connectors on the Quad–DS1 SSI are
shown in figure 3-16.
3.5
SSIs
Quad–DS1
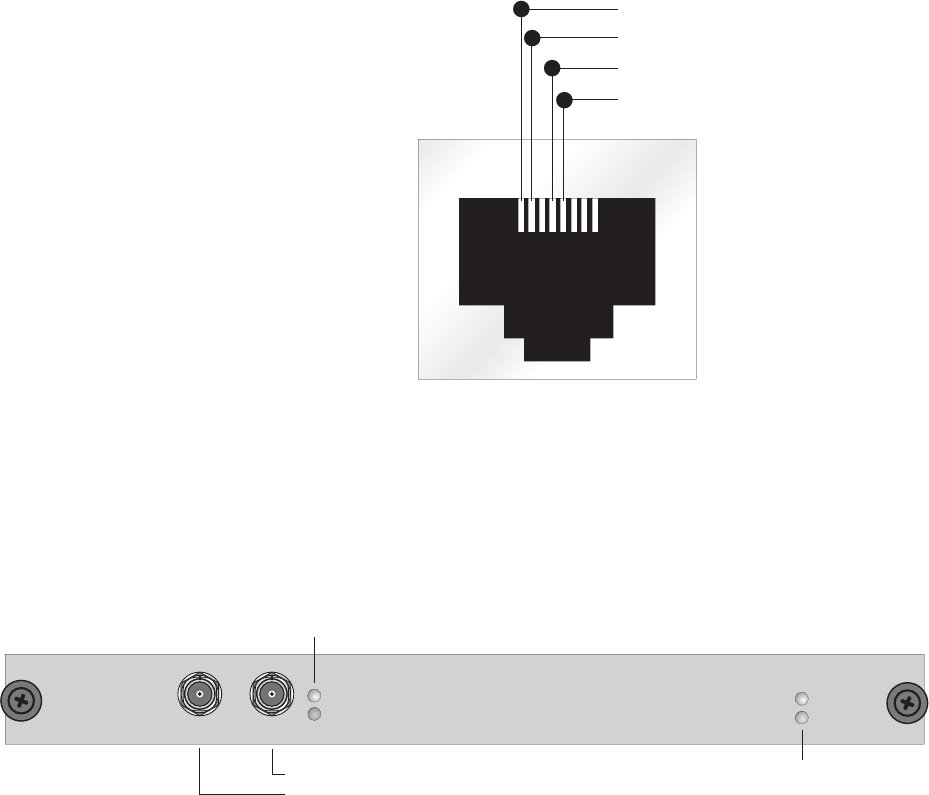
1027144–0001 Draft – Revision D.01 Installing indoor RT equipment 3–29
RT installation
Figure 3-16 RJ–48X connector pinouts
OK
TEST
ALARM
Pin 1 - R1 signal (Ring - RX in)
Pin 2 - T1 signal (Tip - RX in)
Pin 4 - R signal (Ring - TX out)
Pin 5 - T signal (Tip - TX out)
1
2
4
5
Pins not identified
are not used.
rt007
The DS3–TDM SSI, shown in figure 3-17, provides a structured
or transparent D3 service link between the HT and RT.
Tx
ALARM
OK
Rx
TDM SSI
3
DS
T0006022
BNC Rx connector
BNC Tx connector
LEDs indicate status of each link
OK
STATUS
LEDs indicate
SSI status
ALARM
Figure 3-17 DS3–TDM SSI
The maximum cable length for a DS3–TDM SSI is 450 feet
(137.2 meters).
DS3–TDM
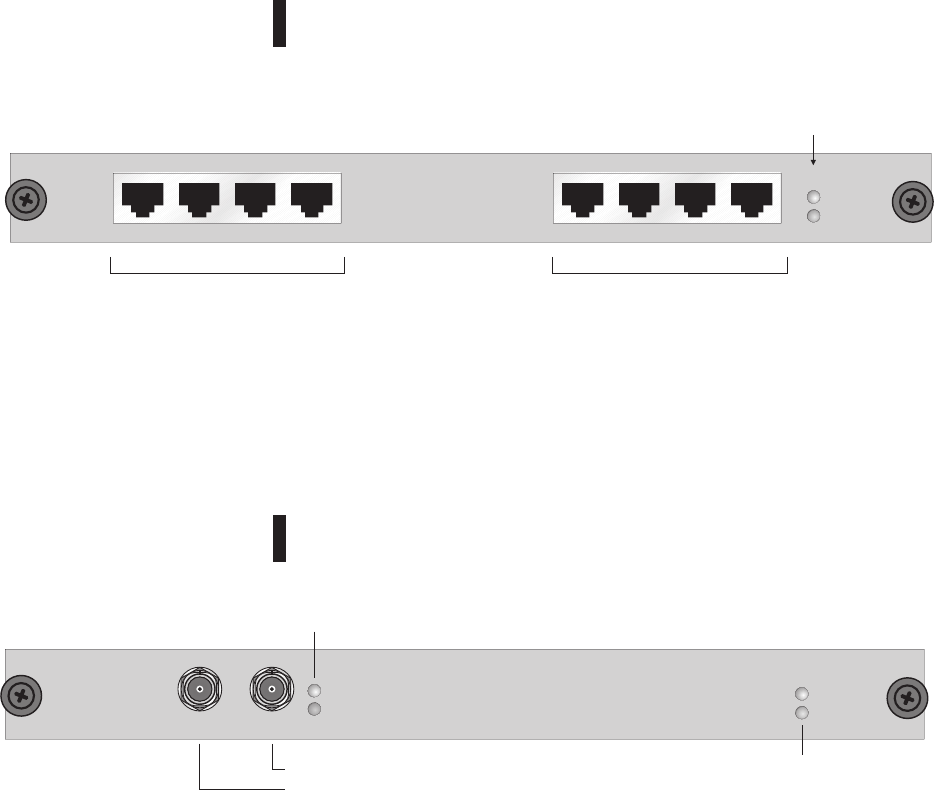
1027144–0001 Draft – Revision D.01 3–30 Installing indoor RT equipment RT installation
The Universal–DS1 SSI, shown in figure 3-18, provides a link to
the HT that can carry up to eight T1 or eight E1 lines.
Figure 3-18 Universal–DS1 SSI
UNIVERSAL SSI
OK
STATUS
rt047
LEDs indicate
SSI status
RJ-48X connectors RJ-48X connectors
PORT 1 PORT 2 PORT 3 PORT 4
ALARM
PORT 1 PORT 2 PORT 3 PORT 4
The maximum cable length for a Universal–DS1 SSI is 655
feet (199.6 meters).
The DS3–ATM SSI, shown in figure 3-19, provides an ATM link
between the RT and the HT.
Tx
ALARM
OK
Rx
ATM SSI3DS
T0009005 BNC Rx connector
BNC Tx connector
LEDs indicate status of each link
OK
STATUS
LEDs indicate
SSI status
ALARM
Figure 3-19 DS3–ATM SSI
The maximum cable length for a DS3–ATM SSI is 450 feet
(137.2 meters).
Universal–DS1
DS3–ATM
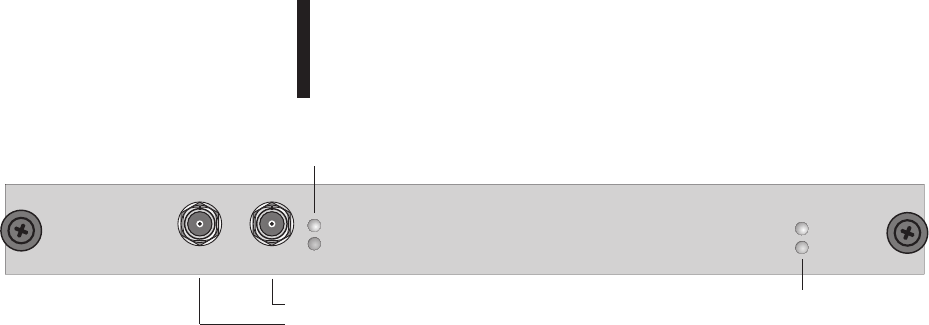
1027144–0001 Draft – Revision D.01 Installing indoor RT equipment 3–31
RT installation
The DS3–transparent SSI, shown in figure 3-20, supports an
unencumbered DS3 point–to–point service. The DS3 framing
structure, clocking, and control bits are transported without
visibility to the AIReach Broadband system.
Tx
ALARM
OK
Rx
TRNSP SSI3DS
T0006023 BNC Rx connector
BNC Tx connector
LEDs indicate status of each link
OK
STATUS
LEDs indicate
SSI status
ALARM
Figure 3-20 DS3–transparent SSI
The maximum cable length for a DS3–transparent SSI is
450 feet (137.2 meters).
Look at the hub network schematic or other configuration
document to determine:
•How many SSIs to install
•What type(s) of SSIs to install
•Which SSI to install in each IDU chassis slot
DS3–transparent
SSI physical
configuration
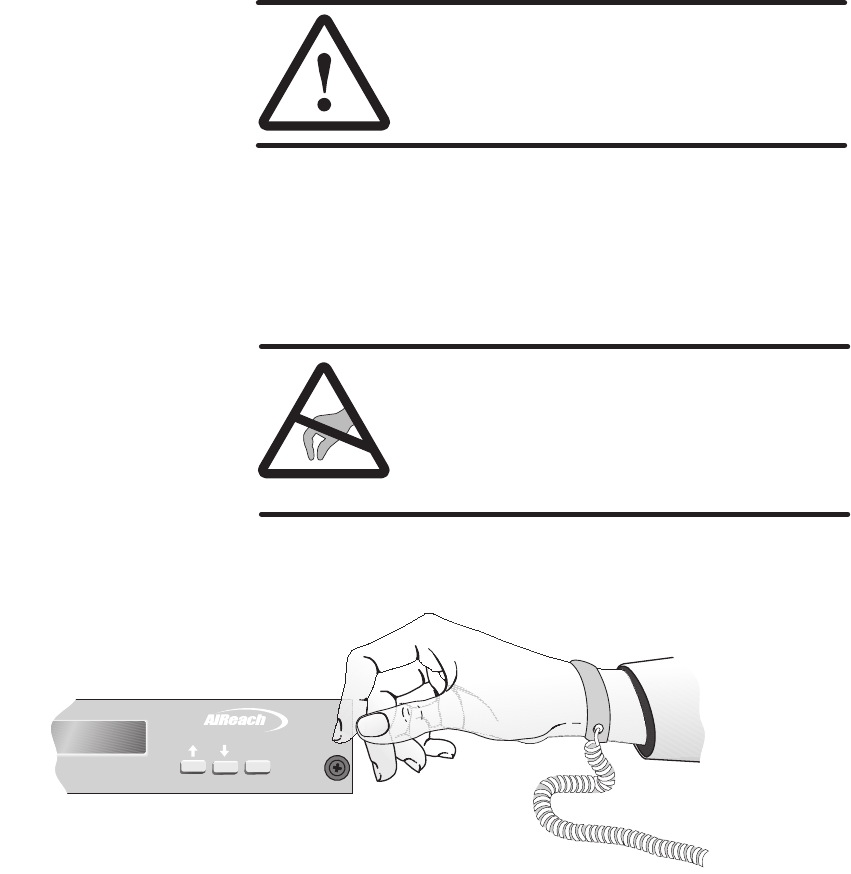
1027144–0001 Draft – Revision D.01 3–32 Installing indoor RT equipment RT installation
Follow these steps to install SSIs:
CAUTION
To maintain proper airflow and protect
against RF interference, keep any empty
chassis slots covered with blank panels.
1. If a blank panel is installed in the slot where you will install
the SSI, loosen the thumbscrews on the blank panel and
remove it.
Keep the blank panel for future use.
CAUTION
Always wear a new or recently tested
electrostatic discharge (ESD) wrist strap
(figure 3-21) when handling circuit
modules. Failure to use a wrist strap may
result in damage to components.
Figure 3-21 ESD wrist strap
TM
BROADBAND
ENTER
hb061
Wrist
strap
Connect to IDU chassis
ground terminal.
2. Wrap the ESD strap snugly around your wrist and connect
the alligator clip to one of the ground terminals on the front
of the IDU chassis power supply.
Installing SSIs
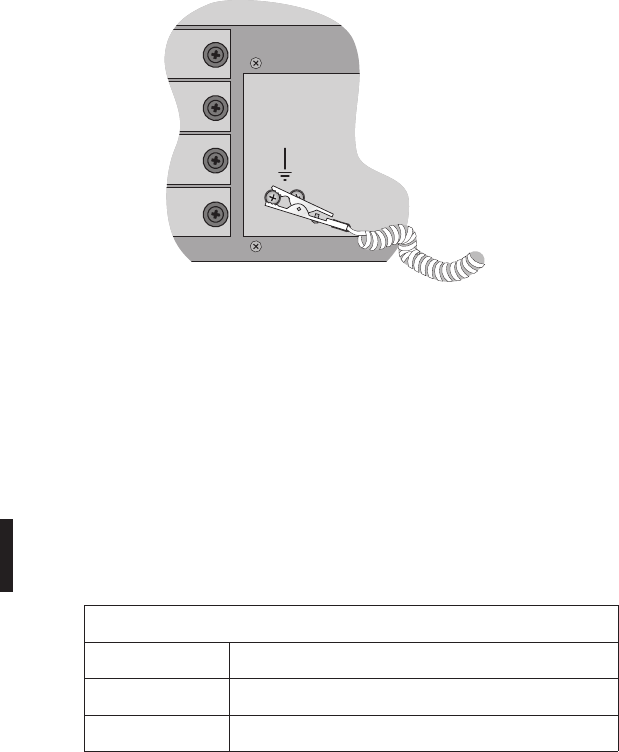
1027144–0001 Draft – Revision D.01 Installing indoor RT equipment 3–33
RT installation
hb060
3. Remove the SSI from its ESD protective packaging.
Retain the packaging in case it is necessary to return the
SSI for repair.
4. Slide the SSI into the guides on each side of the chassis SSI
slot and push it firmly into place until the front of the SSI is
flush with the front of the IDU chassis.
5. When the SSI receives power through contact with the IDU
backplane, it automatically initiates startup diagnostics.
Watch the LEDs to see the diagnostic results:
SSI LED indications:
Green SSI startup and normal operation
Red Failure
Flashing red TDM bus communication failure
6. Tighten the thumbscrews at each end of the SSI.
To tighten the thumbscrews, push them toward the IDU
chassis and turn them clockwise. To fully tighten the
thumbscrews, use a Phillips screwdriver.
7. Repeat steps 1 through 6 for each SSI.
8. If any SSI slots are empty, cover the slot with a blank panel.
(If you need additional blank panels, order HNS part
1026730–0001.)
9. Remove power from the IDU chassis.
This completes the IDU installation.
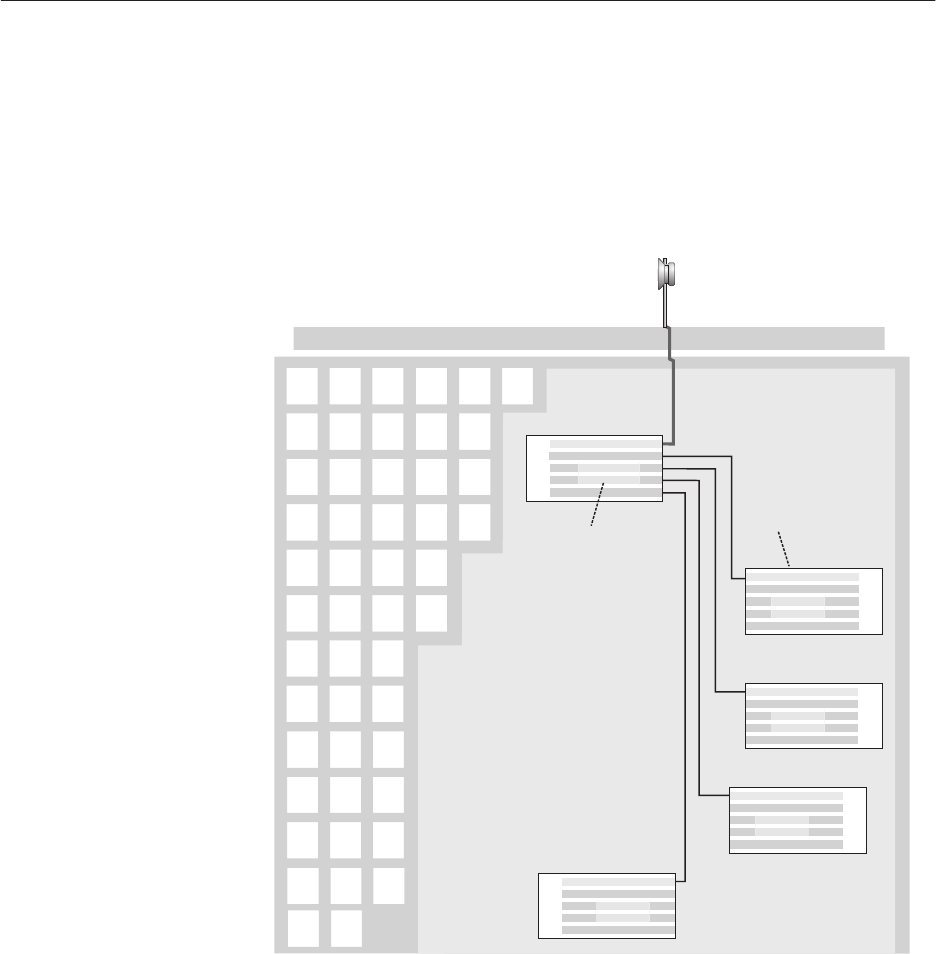
1027144–0001 Draft – Revision D.01 3–34 Installing indoor RT equipment RT installation
If more than 4 SSIs are required at a single site, or SSIs need to be
physically distributed (on different floors, for example), one or
more expansion IDUs (EIDUs) may be installed, at remote sites
only. A single IDU can accommodate up to 4 EIDUs (16 SSI slots)
as shown in figure 3-22.
EIDUs are linked to the IDU with fiber extender modules (FEMs).
These modules use multimode fiber to carry both ATM and TDM
traffic.
ODU
EIDU
FEM
4 SSIs
EIDU
FEM
4 SSIs
EIDU
FEM
4 SSIs
EIDU
FEM
4 SSIs
(In CCM slot)
IFL
Fiber
links
Maximum
link
distance:
2250 feet
(685.8
meters)
CCM
(In SSI slots)
IDU
4 FEMs
rt065
Figure 3-22 EIDUs used to distribute
SSIs throughout a remote site building
3.6
Installing expansion
IDUs (EIDUs)
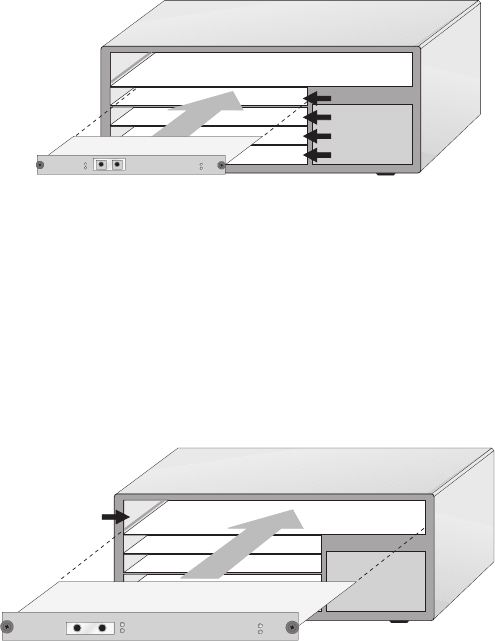
1027144–0001 Draft – Revision D.01 Installing indoor RT equipment 3–35
RT installation
The EIDU can be used on a tabletop or installed in a 19–inch
(48.3–centimeter) rack. With optional adapter brackets, the EIDU
can also be installed in a 23–inch (58.4–centimeter) rack.
Note: HNS does not provide a rack for EIDU installation.
If you are installing the EIDU in a rack, refer to the prerequisites,
safety guidelines, and instructions provided on pages 3–4
through 3–7.
EIDU power supply specifications and requirements are the same
as those for the IDU chassis. To connect power to the EIDU
chassis, refer to section 3.3.
The IDU–EIDU subsystem includes two types of fiber extender
modules (FEMs), which facilitate the fiber links between the IDU
and the EIDU:
•IDU FEMs – IDU FEMs provide the interface on the IDU
for the link to/from the EIDU (as shown in figure 3-22).
IDU FEMs are installed in SSI slots in the IDU chassis, as
shown in figure 3-23. IDU FEMs and SSIs may be installed
in the same chassis.
Figure 3-23 IDU FEM (installed in SSI slot)
rt066
SSI
slots
IDU
IDU FEM
•EIDU FEM – The EIDU FEM provides the interface on the
EIDU for the fiber link to/from the IDU (as shown in figure
3-22).
The EIDU FEM is installed in the CCM slot of the EIDU
chassis, as shown in figure 3-24.
Figure 3-24 EIDU FEM (installed in CCM slot)
rt067
CCM slot
EIDU
EIDU FEM
Mounting options
Rack mounting
Power supplies
Two type of FEMs
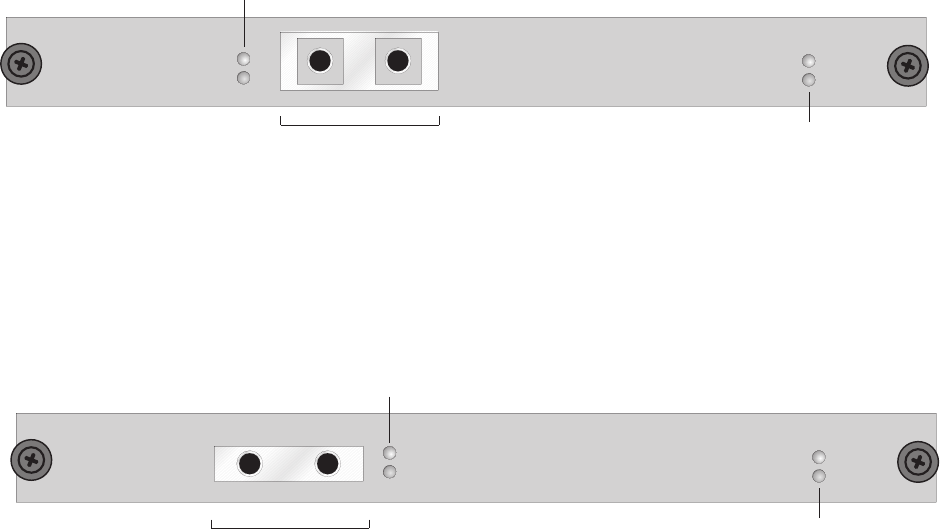
1027144–0001 Draft – Revision D.01 3–36 Installing indoor RT equipment RT installation
IDU FEM
Figure 3-25 shows an IDU FEM.
Figure 3-25 IDU FEM
IDU FEM
OK
STATUS
rt061
LEDs indicate
FEM status
ALARM
Tx Rx
OK
ALARM
SC connectors
LEDs indicate status of each link
EIDU FEM
Figure 3-26 shows the EIDU FEM.
Figure 3-26 EIDU FEM
EIDU FEM
OK
STATUS
rt062
LEDs indicate
FEM status
ALARM
Tx Rx
OK
ALARM
LEDs indicate status of each link
SE connectors
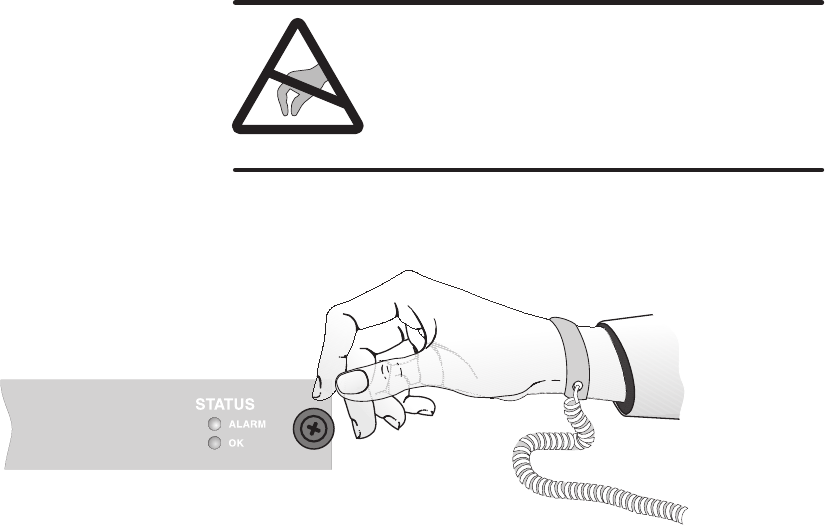
1027144–0001 Draft – Revision D.01 Installing indoor RT equipment 3–37
RT installation
Follow these steps to install an IDU FEM or EIDU FEM:
1. If a blank panel is installed in the slot where you will install
the FEM, loosen the thumbscrews on the blank panel and
remove it.
CAUTION
Always wear a new or recently tested
electrostatic discharge (ESD) wrist strap
(figure 3-27) when handling circuit
modules. Failure to use a wrist strap may
result in damage to components.
Figure 3-27 ESD wrist strap
rt063
Wrist
strap
Connect to IDU or
EIDU chassis
ground terminal.
2. Wrap the ESD strap snugly around your wrist and connect
the alligator clip to one of the ground terminals on the front
of the chassis power supply.
3. Remove the FEM from its ESD protective packaging.
Retain the packaging in case it is necessary to return the
FEM for repair.
Installing FEMs
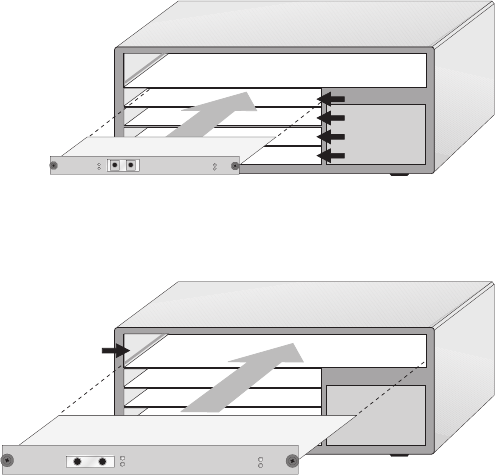
1027144–0001 Draft – Revision D.01 3–38 Installing indoor RT equipment RT installation
4. Slide the FEM into the guides on each side of the chassis
slot and push it firmly into place until the front of the FEM
is flush with the front of the chassis.
rt064
CCM slot
SSI
slots
IDU
EIDU
EIDU FEM
IDU FEM
5. Tighten the thumbscrews at each end of the FEM.
To tighten the thumbscrews, push them toward the IDU
chassis and turn them clockwise. To fully tighten the
thumbscrews, use a Phillips screwdriver.
6. Repeat steps 1 through 5 for each FEM.
7. If any chassis slots are empty, cover the slot with a blank
panel.
(If you need additional blank panels, order HNS part
1026730–0001.)
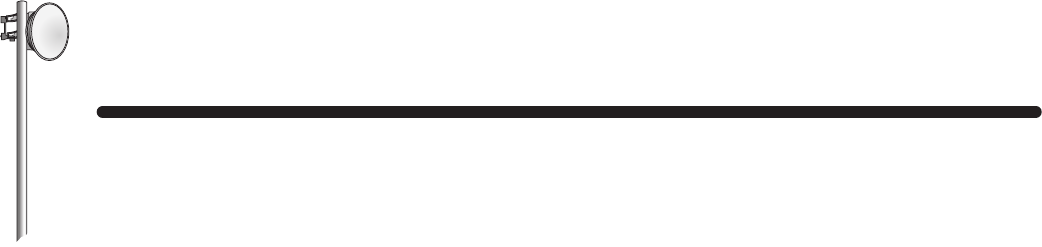
RT INSTALLATION
1027144–0001 Draft – Revision D.01 Installing IFL cables 4–1
RT installation
Chapter 4
Installing IFL cables
This chapter includes:
•Roof and ladder safety – page 4–2
•Handling materials – page 4–3
•IFL cable specifications– page 4–4
•Overview: IFL plan – page 4–5
•Determining the IFL cable route – page 4–6
•Penetrating the roof – page 4–7
•Installing the penetration sleeve – page 4–8
•Installing the IFL cable inside the building – page 4–9
•Installing the remote lightning arrestor – page 4–10
•Installing the IFL cable on the roof – page 4–14
•Testing the IFL cable – page 4–16
•Multiple IFL cables – page 4–17
Appendix C covers IFL cable termination in detail.
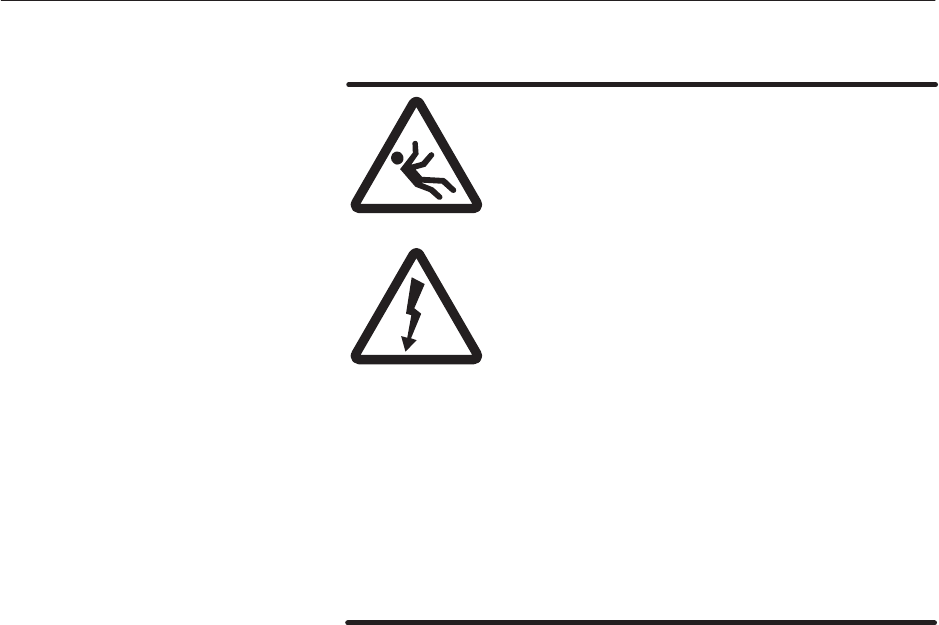
1027144–0001 Draft – Revision D.01 4–2 Installing IFL cables RT installation
DANGER
If you have to walk on a roof or use a ladder
to access an installation site or equipment,
follow these precautions to prevent personal
injury or death:
•Do not walk near the edge of the roof.
•Watch out for overhead power lines.
Stay at least 6 meters (20 feet) from
power lines.
•Walk only on sound roof structures.
•Do not work on a roof or ladder in
high wind, rain, lightning, or other
adverse weather conditions.
•Follow all safety precautions from the
ladder or antenna manufacturer.
•Do not walk on a roof if a storm is
visible—even if the storm is distant.
Lightning can travel and strike in
advance of a storm.
4.1
Roof and ladder
safety
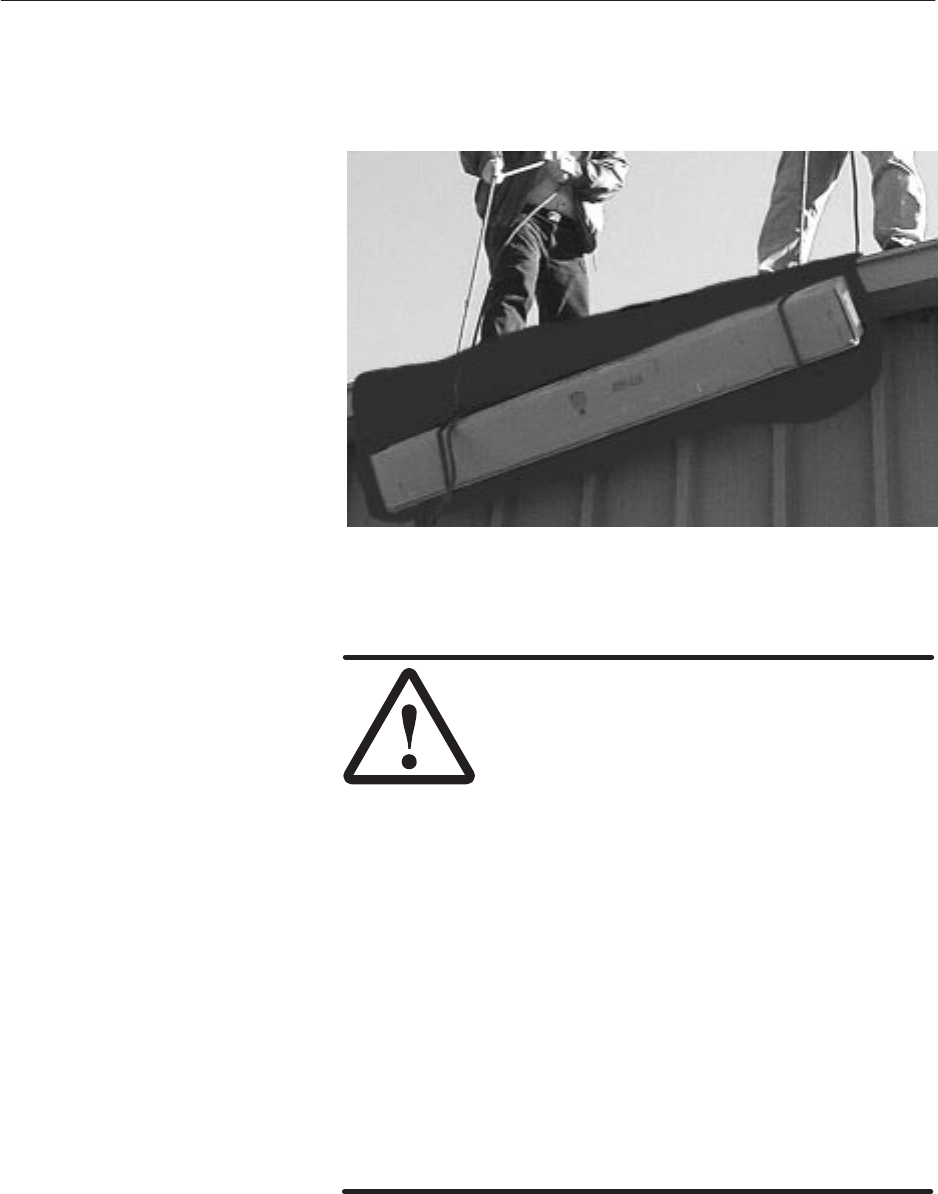
1027144–0001 Draft – Revision D.01 Installing IFL cables 4–3
RT installation
Depending on the installation location, you may have to hoist the
mount kit, ballast (concrete blocks), IFL cable, and tools to the
rooftop as shown in figure 4-1. Using two or more people for this
task will save considerable time.
Figure 4-1 Hoisting materials to the installation location
hbph001
WARNING
If you need to hoist materials to the
installation location, observe these
precautions to avoid personal injury:
•Use a rope strong enough to support
all of the materials that need to be
hoisted.
•Never stand under the rope while
materials are being hoisted.
•Hoist one concrete block at a time.
•Pass the rope through the
center
hole
of each concrete block. If you use the
hole on either end, the end can break
off, allowing the concrete block to fall.
•Be advised that the contents of the
mount kit can fall through the end of
the box if the box is tilted—especially
if the box has been damaged.
•Use a back brace.
If possible, do not hoist the ODU transceiver and antenna on a
rope. If possible, carry these components in a backpack or padded
bag.
4.2
Handling materials
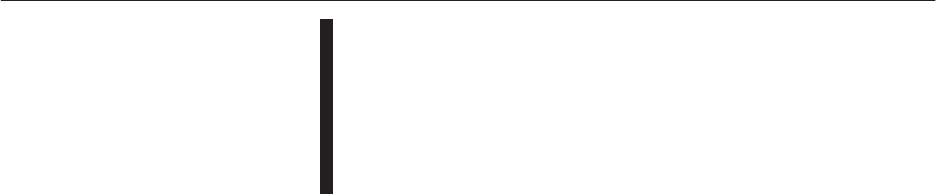
1027144–0001 Draft – Revision D.01 4–4 Installing IFL cables RT installation
The intrafacility (IFL) cable specified for AIReach Broadband
installations is a Type 3 VSAT coaxial cable, HNS 1010812–0001
(1,000–foot / 305–meter spool). This cable is non plenum, CMG
UL/C (UL) approved. An acceptable alternative is LMR–400
plenum cable (available from Times Microwave Systems,
Wallingford, CT). For additional specifications, see the Hub and
Remote Terminal Site Preparation Guide.
The following Underwriters Laboratories (UL) requirement
applies to the IFL cable:
The IFL cable must be installed in a
metal conduit and grounded according
to NEC article 800–40. If the IFL cable will
not
be installed in a metal conduit, the
cable must be a plenum cable, UL/C(UL)
approved, with a CMR rating (or higher).
For specific grounding instructions, see Grounding the lightning
arrestor in section 4.9. Refer also to the grounding guidelines
included in the Hub and Remote Terminal Site Preparation Guide.
4.3
IFL cable
specifications
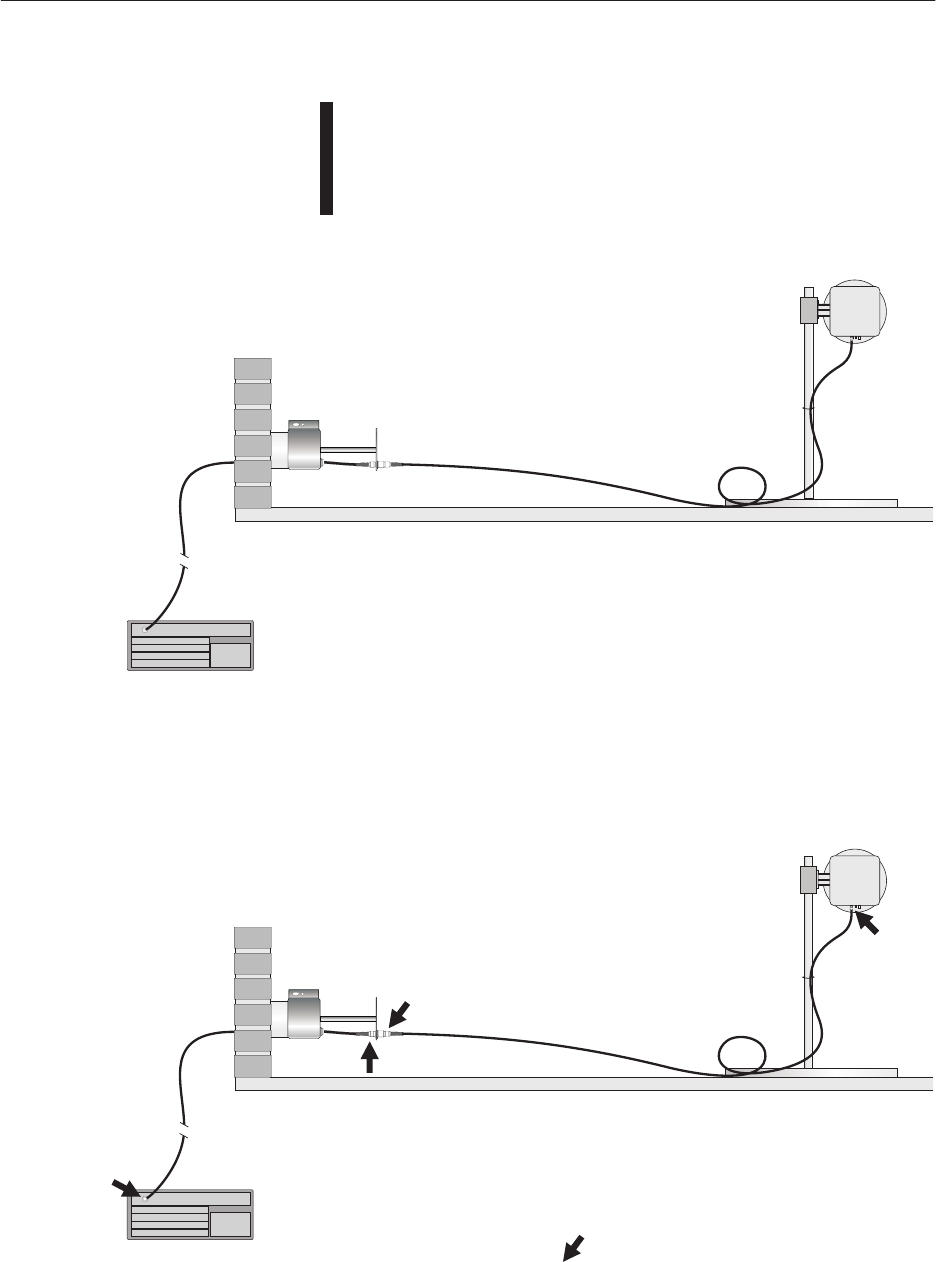
1027144–0001 Draft – Revision D.01 Installing IFL cables 4–5
RT installation
Figure 4-2 shows the IFL and required lightning arrestor. The
lightning arrestor is installed on the roof at the IFL building
penetration point.
Figure 4-2 shows how the IFL cable is installed in two segments
to accommodate the lightning arrestor:
•One segment from the IDU to the rooftop lightning arrestor
•One segment rom the lightning arrestor to the ODU
ODU
(not installed yet)
IFL
(cable
segment 2)
Lightning
arrestor
T0009001
IFL
(cable
segment 1)
Roof
IDU
(Not to scale)
Figure 4-2 IFL plan
Because the IFL cable is installed in two segments, it is cut and
terminated (with an N–type connector) in four locations, as shown
in figure 4-3.
N
ODU
IFL
Lightning
arrestor
T0009002
IFL
Roof
IDU
N
N
N
N= N connector location
Figure 4-3 Four locations where N connectors are installed
4.4
Overview: IFL plan
IFL connections
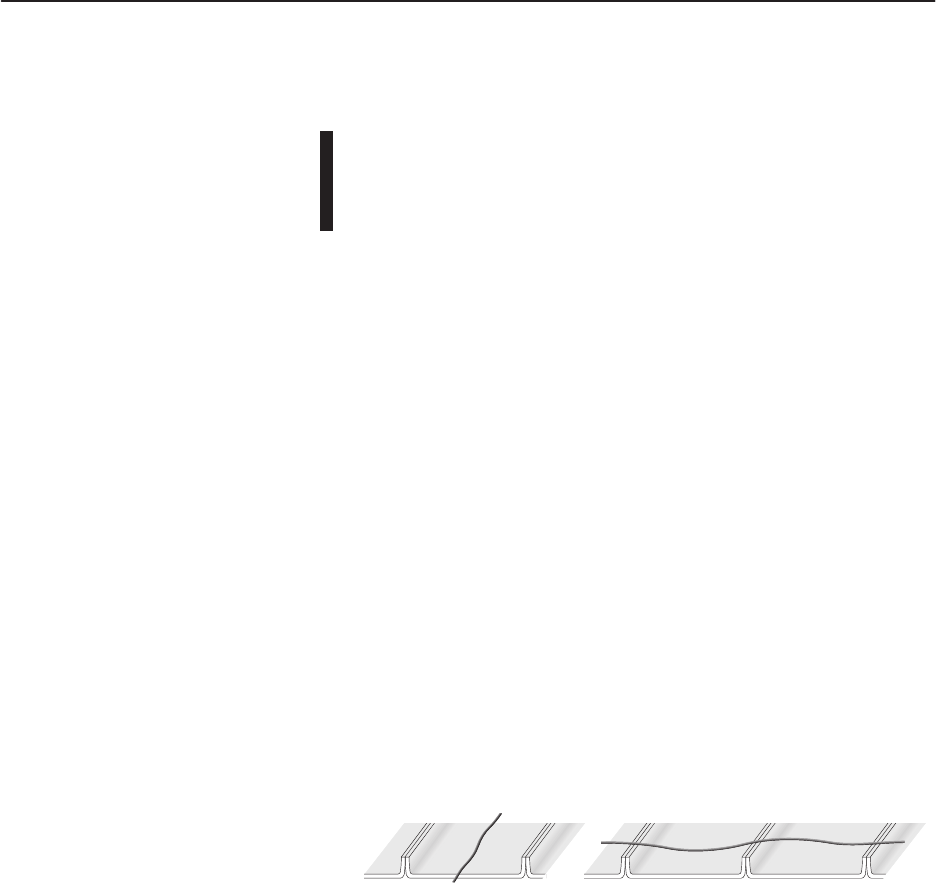
1027144–0001 Draft – Revision D.01 4–6 Installing IFL cables RT installation
Detailed instructions for installing the IFL and lightning arrestor
are included in the following sections.
Determine the IFL cable route, from ODU to IDU. Consider the
guidelines below. Every building and rooftop is unique; for this
reason, some of these guidelines may not apply to your
installation:
•The most important considerations are the ODU and IDU
locations and the building entry point. The entry point
should be as close as possible to the ODU. Refer to the RT
rooftop drawings. (See also page 5–3.)
•The maximum IFL cable length is 1000 feet (305 meters).
•Where possible, use existing conduit.
•You must use a pull box to facilitate pulling cables through
conduits if routing cable through bends totaling more than
360°.
•If existing conduits can not be used and the cable will be
exposed, refer to building codes to determine proper cable
insulation type. For example, plenum rated cable must be
used if cable will be run above suspended ceilings.
•If you are installing the IFL cable(s) inside a conduit
that contains power cables, you must use plenum–rated
cable.
•Look for cable routes that will be easily accessible, such as
stacked telco closets etc.
•Older buildings may not have stacked telco closets. You
may have to route the cable back and forth, from one side of
the building to the other.
•Never run the IFL cable across corrugated roofing. Run the
cable in the corrugation trough:
hb009
Roof
Yes No
Cable
4.5
Determining the IFL
cable route
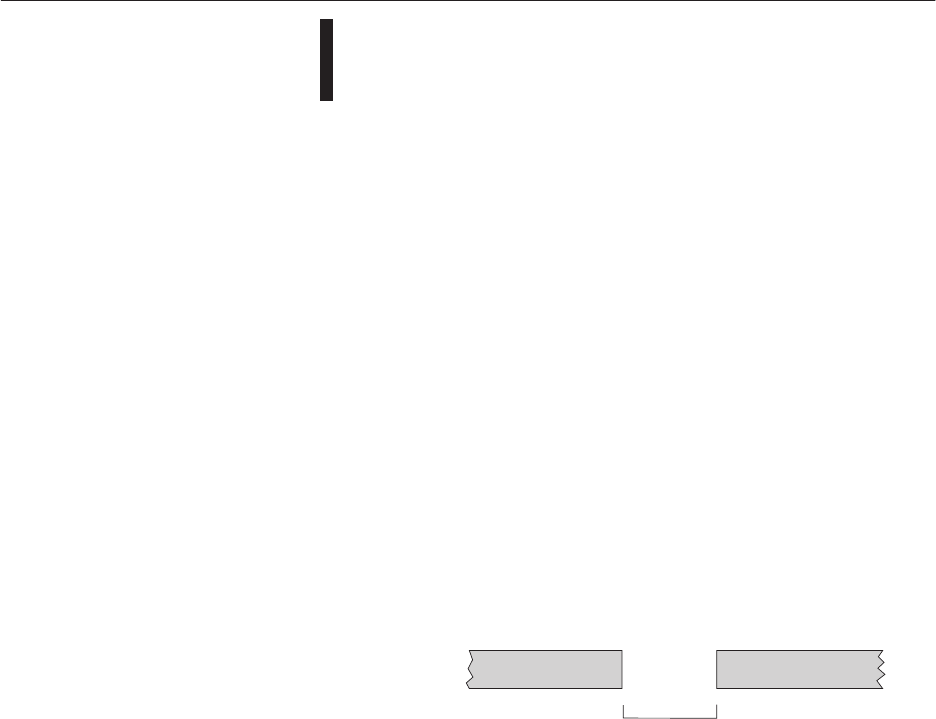
1027144–0001 Draft – Revision D.01 Installing IFL cables 4–7
RT installation
Follow the steps below to drill a hole for the IFL cable only when
there is not an existing entry you can use.
1. Go to the roof.
2. Determine where the IFL cable will penetrate the roof.
Refer to the RT rooftop drawings.
Before you drill, consider these guidelines:
•Important: Do not penetrate any part of the building
structure without first making sure you have the explicit
permission of the customer and building owner.
•Horizontal penetration is preferable to vertical penetration.
(A horizontal hole is less likely to leak.)
•Take care not to destroy cabling or wiring under the roof or
inside the wall.
•Round penetration holes are preferred over square holes.
(They are easier to make and seal.)
3. Drill a 2–inch (51–millimeter) diameter hole at the building
penetration point.
Building
penetration
point
Building surface
2 inches
(51 mm)
rt038
4.6
Penetrating the roof
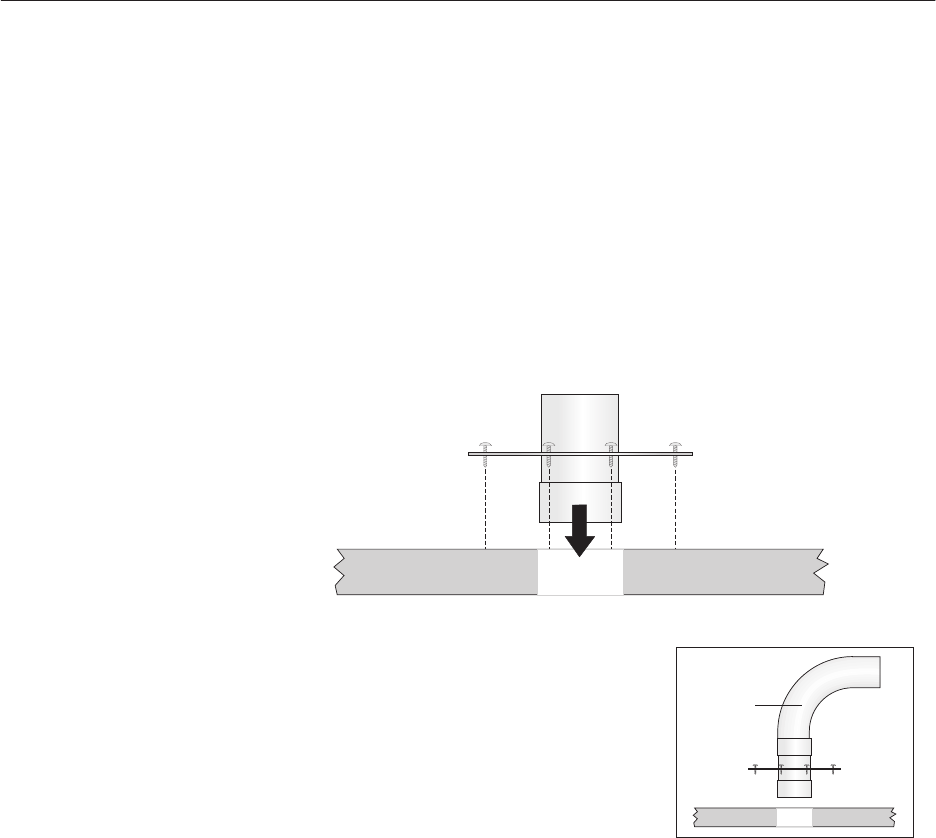
1027144–0001 Draft – Revision D.01 4–8 Installing IFL cables RT installation
The IFL cable must be routed through a penetration sleeve before
it is connected to the lightning arrestor. The lightning arrestor is
attached to the penetration sleeve after cable installation.
1. Use twelve screws to attach the remote penetration sleeve
(sleeve and coupling) to the building surface at the building
penetration point. See figure 4-4.
The type of screw used depends on the roof thickness and
surface composition. The screws must hold the sleeve
assembly securely.
Note: The penetration sleeve location is site–specific and
dependent on the building penetration point. An optional
sweep, shown in figure 4-4, is available for use with the
penetration sleeve for locations where space is limited.
Figure 4-4 Installing the remote penetration sleeve
rt049
Screws
(12 total)
Building
penetration
point
Penetration sleeve with
optional sweep
Sweep
2. Weatherproof the penetration sleeve by applying silicone
caulk to the bolt hole areas and the surface of the sleeve
plate.
Note: Silicone caulk may not be suitable for certain types
of roofs. Choose a type of caulk that is appropriate for your
type of roof.
4.7
Installing the
penetration sleeve
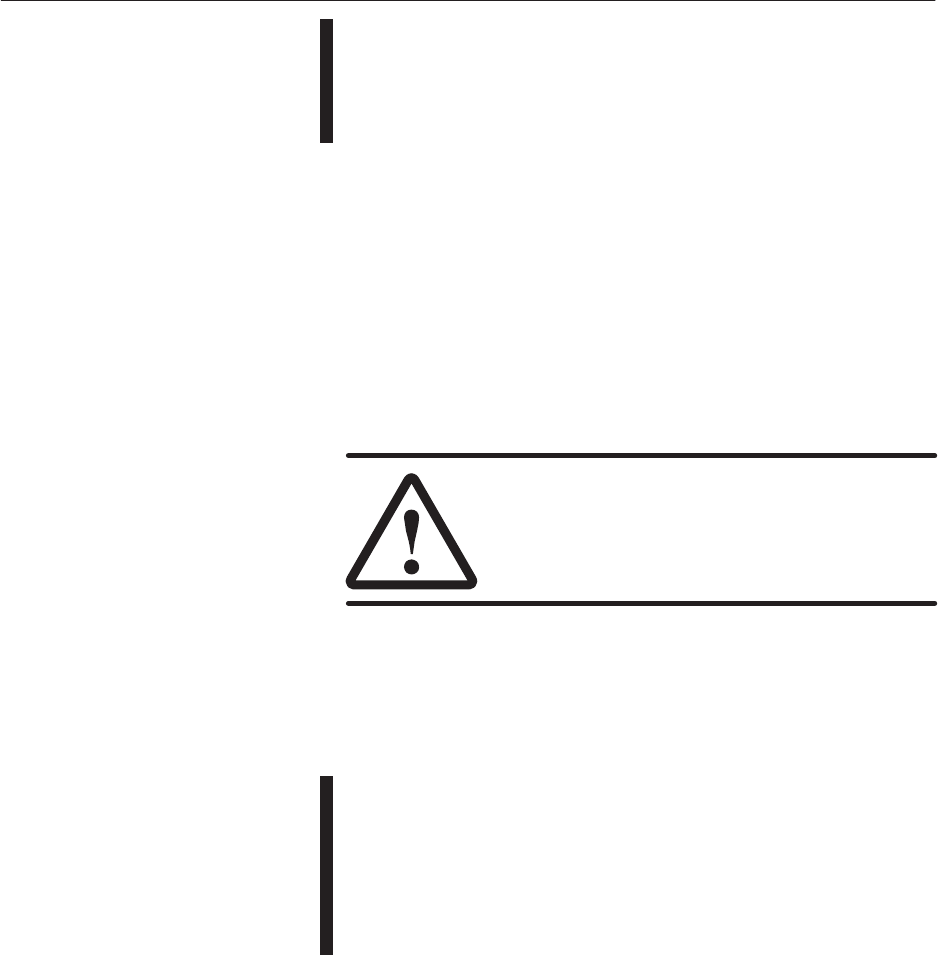
1027144–0001 Draft – Revision D.01 Installing IFL cables 4–9
RT installation
You install the IFL cable in two segments, as shown in figure 4-2
(page 4–5). To install the first cable segment—from the IDU
chassis location to the lightning arrestor—follow the instructions
and guidelines below. Because every building has unique features,
it is not possible to give exact instructions.
1. Measure the cable run length from the IDU chassis location
to the lightning arrestor location (IFL building entry point).
Allow for routing around obstacles and a service loop
(excess cable, in case there is any reason to later cut and
re–terminate the cable).
2. Run the cable from the IDU chassis location, through an
existing conduit if possible, through the remote penetration
sleeve (figure 4-4), to the lightning arrestor location.
Use a stand so the cable spool spins freely as it is pulled.
Leave a service loop.
CAUTION
Avoid making sharp bends in the IFL cable.
The minimum bend radius for IFL cable is 2
inches (51 millimeters). Sharper bends may
cause permanent damage to the cable.
3. Cut the cable at the IDU chassis location and at the
lightning arrestor.
Important: Cut the cable 2 feet (0.6 meters) beyond the
lightning arrestor location (building penetration point).
4. Terminate the cable end at the IDU chassis location with an
N–type connector. For detailed instructions for connecting
an N connector, see appendix C.
Important: Sound IFL cable connections are critical for
proper operation of the AIReach Broadband system.
Therefore, be very careful in terminating the cable. Refer to
the detailed instructions in appendix C if necessary.
Attach N connectors after you route and install the
cable, not before.
Note: The IFL cable installation is completed in section 4.10.
4.8
Installing the IFL
cable inside the
building

1027144–0001 Draft – Revision D.01 4–10 Installing IFL cables RT installation
All AIReach Broadband IFL cables must connect to a
grounded lightning arrestor (provided by HNS) at the building
penetration point, as shown in figure 4-2 (page 4–5) and
explained in this section. A single remote lightning arrestor can
be used for IFL cables for two RTs.
WARNING
To help avoid death, injury, or damage from
a lightning strike, you
must
install a
lightning arrestor where the IFL enters the
building.
Figure 4-5 identifies the remote lightning arrestor components.
Figure 4-5 Remote lightning arrestor components
Restraining
fitting
RF arrestor
rt033
Ground bar
Go to the roof to install the remote lightning arrestor.
4.9
Installing the remote
lightning arrestor
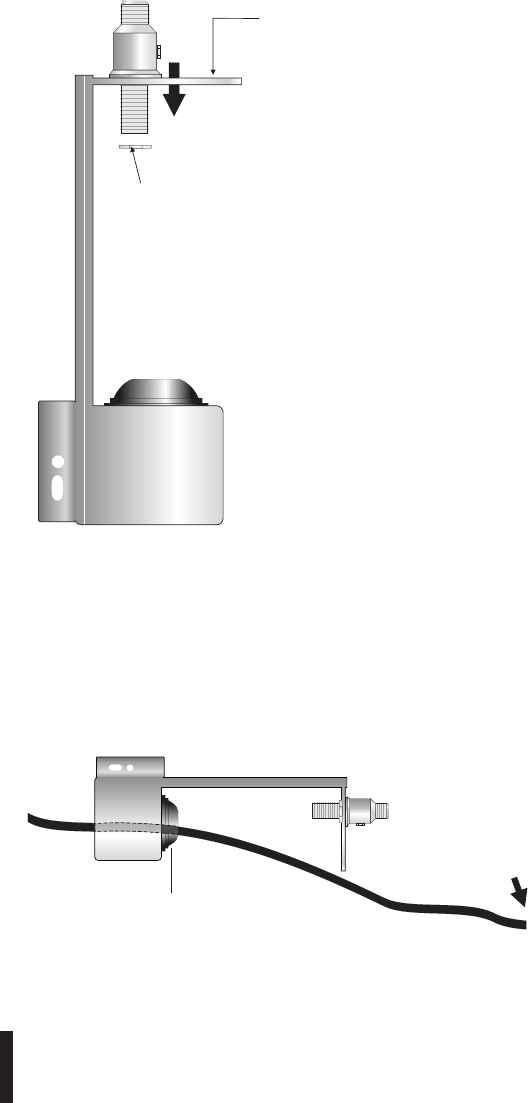
1027144–0001 Draft – Revision D.01 Installing IFL cables 4–11
RT installation
Follow these steps to route the IFL cable through the lightning
arrestor and then connect the cable to the RF arrestor:
1. Attach an RF arrestor to the arrestor body with a 3/4–inch
(19–millimeter) nut. See figure 4-6.
Figure 4-6 Attaching the arrestor to the arrestor body
rt034
3/4-inch
(19-millimeter)
nut
Location of second arrestor, if 2
IFLs are installed.
2. Route the cable from the IDU chassis location through the
base of the lightning arrestor and the restraining fitting, as
shown in figure 4-7.
Figure 4-7 Routing the IFL cable
T0009003
From
IDU
Restraining
fitting
Terminate with
N connector
here.
3. Terminate the end of the IFL cable with an N connector.
For detailed instructions for connecting an N connector, see
appendix C.
4. Connect the cable to the RF arrestor, as shown in figure 4-8.
Connecting the IFL
cable to the RF arrestor
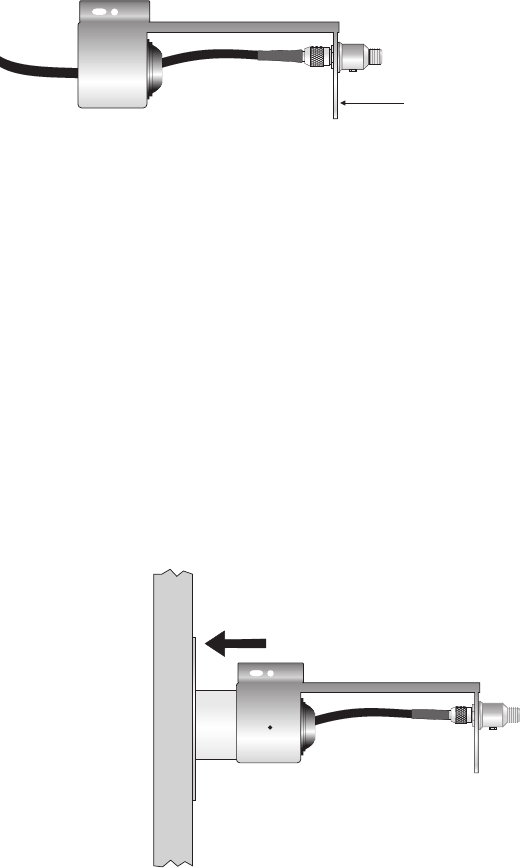
1027144–0001 Draft – Revision D.01 4–12 Installing IFL cables RT installation
Figure 4-8 Connecting the IFL cable to the arrestor
rt036
Location of second arrestor,
if 2 IFLs are installed.
5. Working from inside the arrestor body, use the Sealcon
custom wrench (Sealcon part number 1.500.4200.04) to
tighten the restraining fitting to 44.2 inch–pounds.
6. Repeat steps 1 through 5 if you are installing a second IFL
cable.
Attach the lightning arrestor to the penetration sleeve:
1. Slide the lightning arrestor over the sleeve, as shown in
figure 4-9.
2. Fasten the lightning arrestor to the sleeve with a screw.
Figure 4-9 Attaching the arrestor assembly to the sleeve
rt037
Slide the lightning arrestor
over the sleeve.
Attaching the arrestor
to the penetration
sleeve
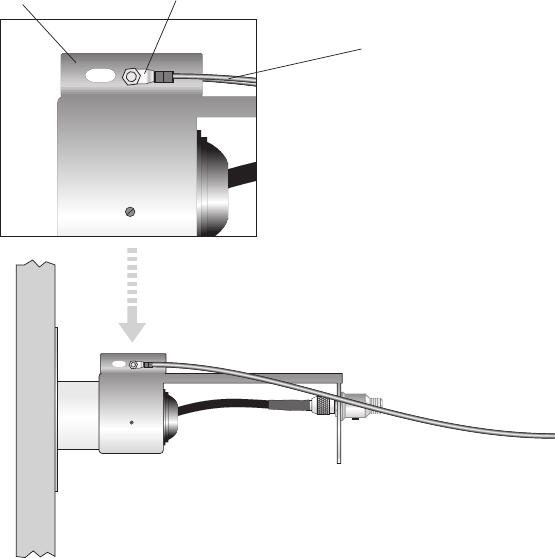
1027144–0001 Draft – Revision D.01 Installing IFL cables 4–13
RT installation
Follow these steps to ground the lightning arrestor:
1. Connect one end of the ground cable (No. 6 AWG or
greater, green) to the lightning arrestor ground bar, as
shown in figure 4-10.
Figure 4-10 Remote lightning arrestor grounding connections
rt051
To ground
point
Ground cable
No. 6 AWG or greater
Single-hole compression lug
Ground bar
2. Route the ground cable to the ground point.
When routing the ground cable, you must:
•Secure the ground cable at 5–foot (1.5–meter)
intervals.
•Keep the ground cable at least 3 feet (0.9 meters)
away from non–grounded metal objects.
•Make sure all bends in the cable have a sweeping
radius of more than 8 inches (20.3 centimeters).
3. Connect the remote lightning arrestor to the same ground
(reference) point as the ODU ground. See section 6.12.
4. Apply anti–oxidant (HNS 9008224–0002) to each ground
lug.
5. Apply 1/2–inch (13–millimeter) heat shrink tubing (HNS
9007488–0005) to each ground lug after the connection is
complete.
Important: You must slip the heat shrink onto the cable
before you make the connections.
Grounding the remote
lightning arrestor
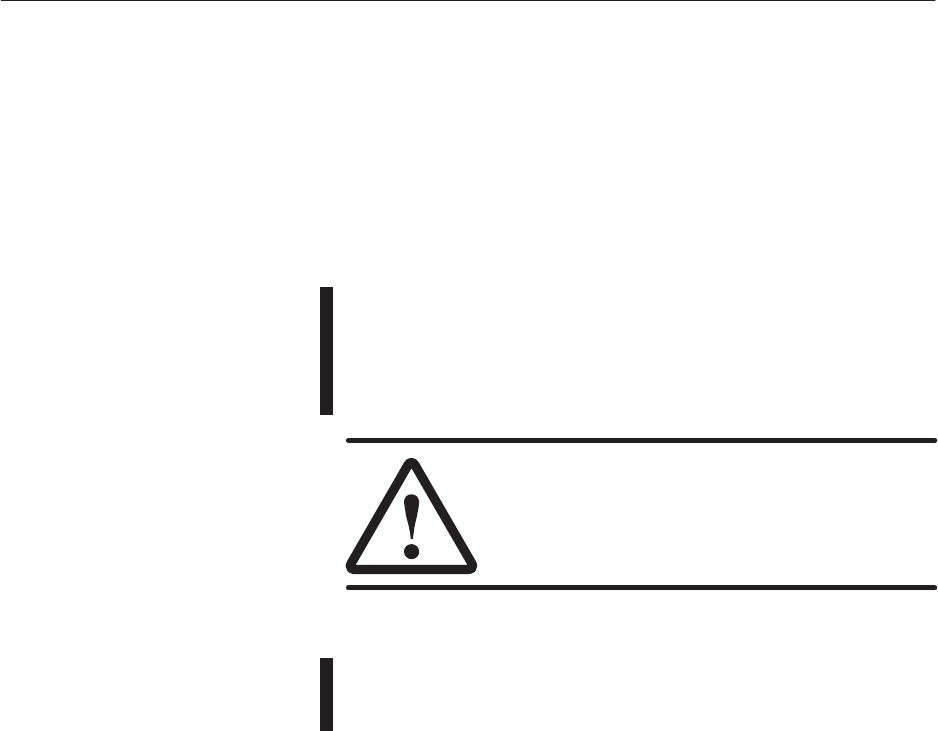
1027144–0001 Draft – Revision D.01 4–14 Installing IFL cables RT installation
To install the second IFL cable segment—from the lightning
arrestor to the ODU—follow the instructions and guidelines
below. Because every rooftop has unique features, it is not
possible to give exact instructions.
Connect the IFL to the lightning arrestor as follows:
1. Measure the cable run length from the lightning arrestor to
the ODU. Allow for routing around obstacles and a service
loop (excess cable, in case there is any reason to later cut
and re–terminate the cable).
2. Run the cable from the lightning arrestor to the ODU
location, and leave enough cable for a service loop.
For now, you must leave the cable unconnected because the
ODU is not installed yet. You will connect the IFL to the
ODU later, after the ODU is installed.
CAUTION
Avoid making sharp bends in the IFL cable.
The minimum bend radius for IFL cable is 2
inches (51 millimeters). Sharper bends may
cause permanent damage to the cable.
3. Cut the cable at the lightning arrestor and at the ODU.
4. Terminate both ends of the cable segment with N
connectors. For detailed instructions for connecting N
connectors, see appendix C.
4.10
Installing the IFL
cable on the roof
Connecting to the
lightning arrestor
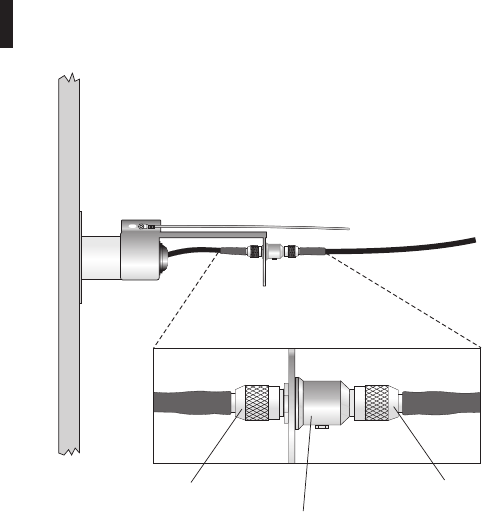
1027144–0001 Draft – Revision D.01 Installing IFL cables 4–15
RT installation
5. Connect the IFL cable to the RF arrestor, as shown in figure
4-11.
You connect the other end of the cable to the ODU later,
after you install the ODU.
Figure 4-11 Connecting the IFL to the RF arrestor
rt040
Ground wire
IFL
To ODU
N connector
RF arrestor
N connector
1027144–0001 Draft – Revision D.01 4–16 Installing IFL cables RT installation
Do not apply weatherproofing compound or tape until the RT
has been tested and commissioned. Weatherproofing is
covered in section 8.1.
Test the IFL cable and connectors as follows:
1. Check each connector: Use a multimeter or continuity tester
to check for continuity (a short circuit) between the center
conductor and the connector body (outer shell).
If the meter or tester does not indicate an open (no
connection), the connector or cable is defective and must be
replaced.
2. Check the connectors and cable:
a. Using a small jumper cable, attach a jumper clip to
the center conductor of the connector on one end of
the cable.
b. Attach the other end of the jumper to the connector
body, so the center conductor and connector body
make electrical contact.
c. At the other end of the cable (at the IDU location),
use a multimeter to measure the resistance between
the center conductor and connector.
Resistance should be less than 10 ohms. If it is
greater than that find and correct the problem.
Testing the IFL cable
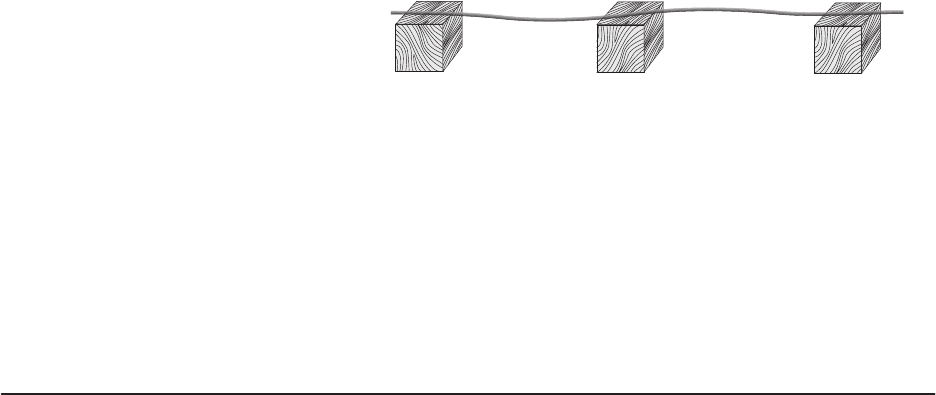
1027144–0001 Draft – Revision D.01 Installing IFL cables 4–17
RT installation
After running the cable, finish the cable installation as follows:
1. Support the cable above the roof surface with a cable trough
or wood blocks approximately 4 inches by 4 inches by 4
inches (10 centimeters by 10 centimeters by 10
centimeters):
hb010
2. Tie down cable runs on the roof and at the IDU location
with tie–wraps.
3. Seal the IFL rooftop entry point with weatherproofing
caulk.
4. Label both ends of the IFL cable to identify the cable in an
appropriate manner. This is especially important if you are
installing multiple IFL cables. (To order IFL labels, request
HNS part number 9005328–0055.)
If you are installing multiple IFL cables for multiple RTs, follow
the instructions in this chapter for each IFL. However, you only
need to install one lightning arrestor for up to two IFL cables,
because the arrestor design accommodates up to two cables.
Finishing the cable
installation
4.11
Multiple IFL cables
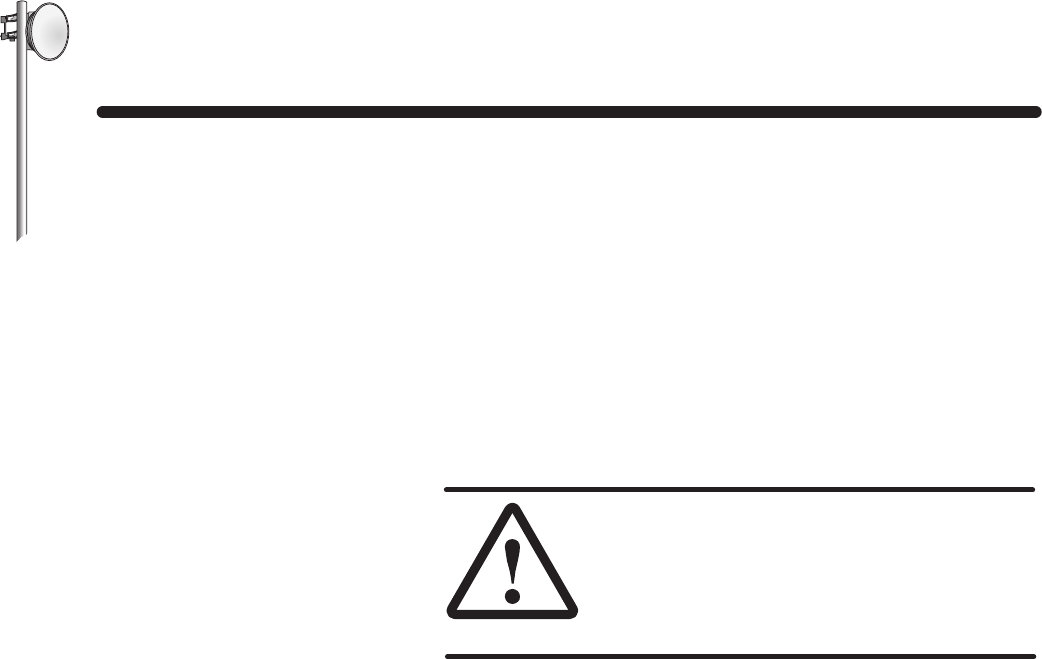
RT INSTALLATION
1027144–0001 Draft – Revision D.01 Installing mast mounts 5–1
RT installation
Chapter 5
Installing mast mounts
This chapter includes:
•Overview – page 5–2
•ODU location – page 5–3
•Roof types – page 5–3
•Mast mount types – page 5–3
•Standard nonpenetrating mount – page 5–4
•Existing structures – page 5–11
DANGER
Do not work on a ladder or roof without
first reading the safety warnings on page x
of this manual. Failure to observe these
warnings could result in personal injury or
death.
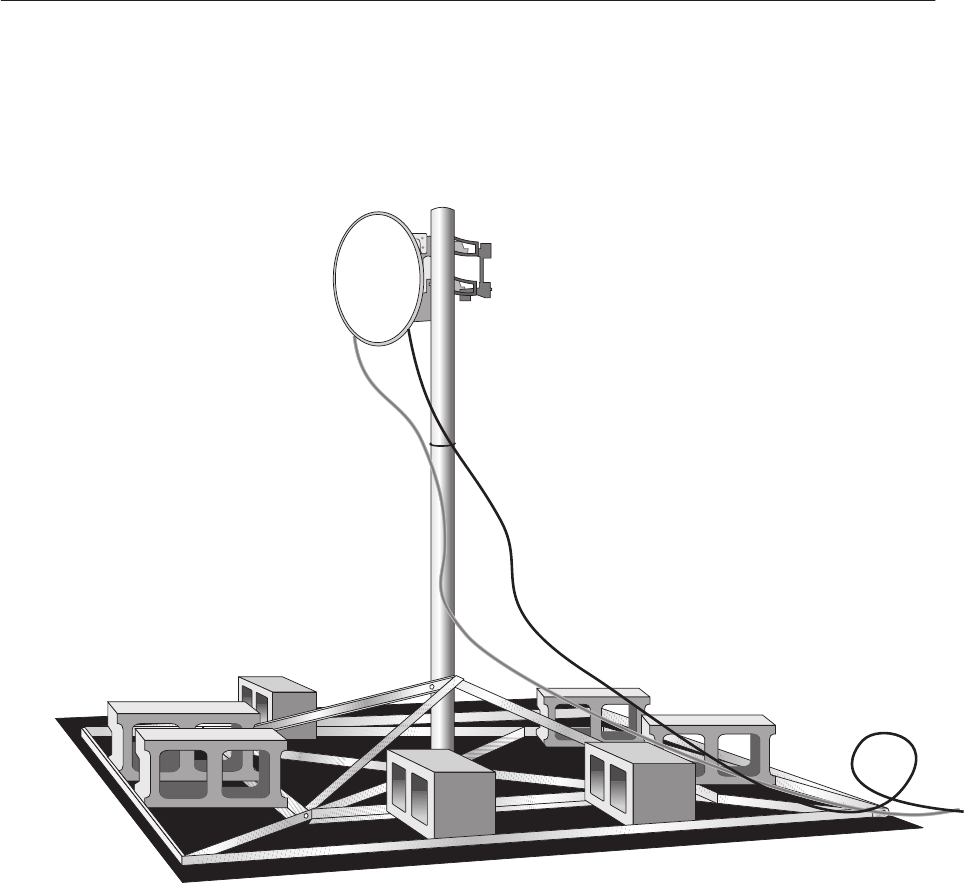
1027144–0001 Draft – Revision D.01 5–2 Installing mast mounts RT installation
Typically, the installers assemble a nonpenetrating roof mount for
each ODU to be installed. In some cases, a different type of mast
mount may be used, or an existing structure may be used.
The mount supports the mast in a vertical or horizontal position,
and the ODU is mounted on the mast, as shown in figure 5-1.
Figure 5-1 Mast mount supporting mast and ODU
rt009
5.1
Overview
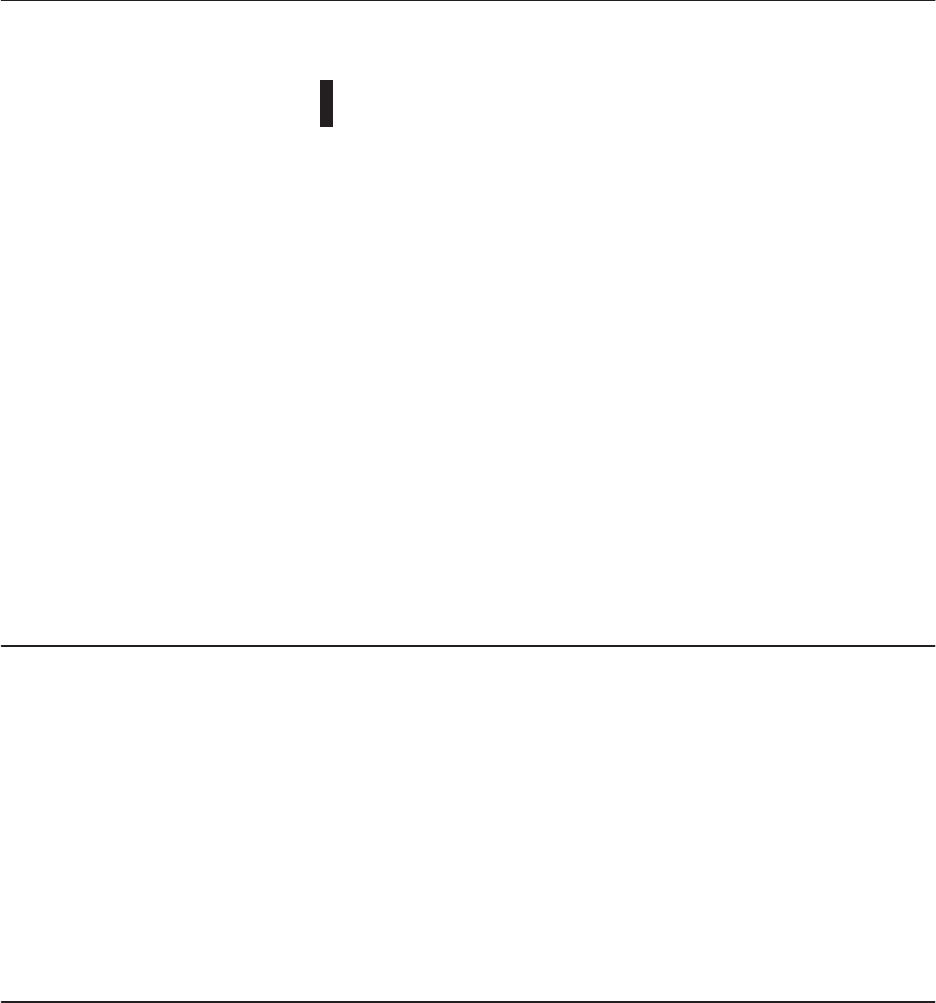
1027144–0001 Draft – Revision D.01 Installing mast mounts 5–3
RT installation
Site preparation personnel specify the ODU location as part of
preparing the RT rooftop drawing.
1. Use the RT rooftop drawing to determine where to install
the mount (at the ODU location) and locate IFL entry point.
2. Make sure the roof penetration or entry point for the IFL is
suitable.
Important: The location(s) used for ODU installation must meet
the requirements listed in the Hub and Remote Terminal Site
Preparation Guide. Key considerations include:
•Line of sight
•Distance from HT
•IFL entry location
•Sources of interference
•Safety
•Ground point location
•Access
•Security
For details, see the Site Preparation Guide.
Many roof types are suitable for AIReach Broadband ODU
installations. Mount installation procedures for the following
common roof types are described later in this chapter:
•Rubber cap sheet/ glued rubber cap sheet
•Loose gravel on rubber cap sheet
•Corrugated metal
The roof type is a factor in the type of mast mount selected. Also,
some mount installation steps may be different, depending on the
roof type.
The following options are available for mounting a mast to
support the ODU:
•Nonpenetrating roof mount – This mount, essentially a
flat platform assembled from a kit, is suitable for most
applications. It can be used on various flat roof types. For
details, see section 5.5.
•Existing structure – An existing structure such as an
antenna tower can be used as a mast, or a mast can be
mounted to the structure, if the structure meets the
requirements given in the Hub and Remote Terminal Site
Preparation Guide.
5.2
ODU location
5.3
Roof types
5.4
Mast mount types
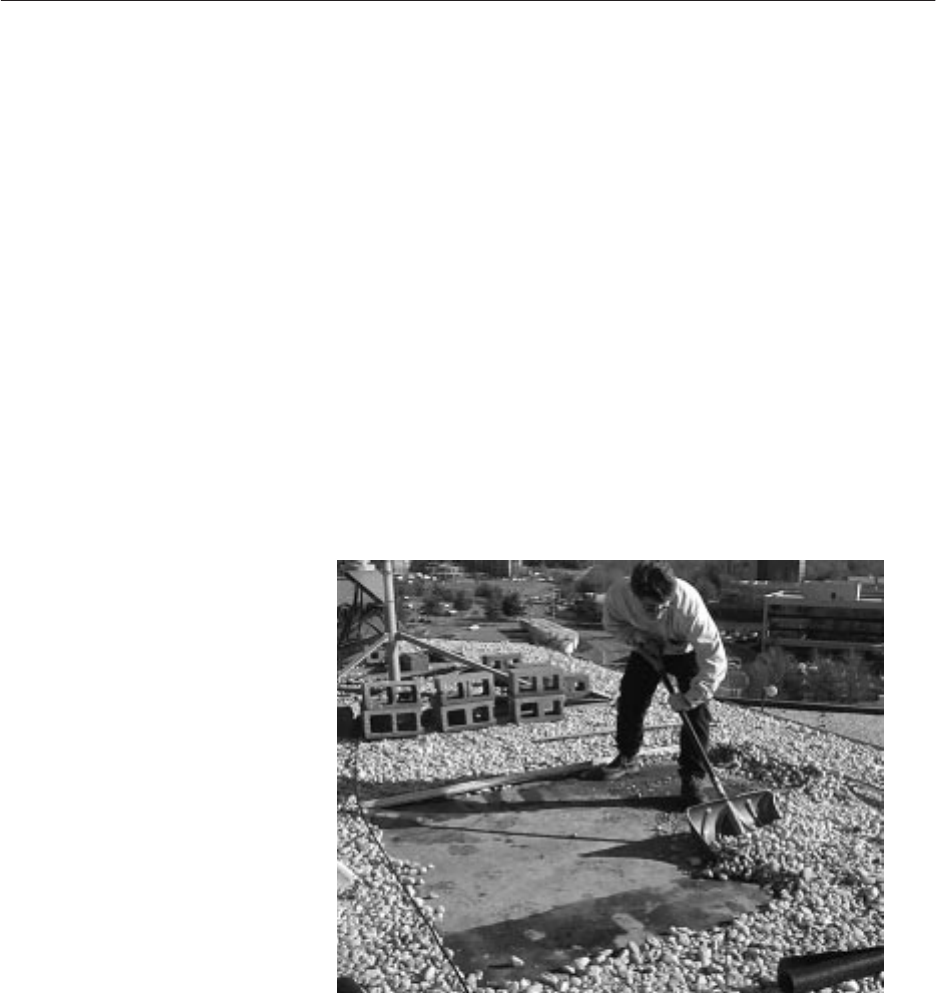
1027144–0001 Draft – Revision D.01 5–4 Installing mast mounts RT installation
The standard nonpenetrating roof mount, HNS 9200375–0001, is a
flat, metal–frame mount assembled from a kit. It requires a
6.5–by–6.5–foot space (1.98 by 1.98 meters) and includes a 7–foot
(2.1–meter) mast. You install the mount on a rubber pad; concrete
blocks are added for ballast.
The standard mount can be used on a variety of flat roof types, as
detailed below.
Instructions are given below for various types of roofs. See also
the manufacturer’s instructions, which are included in the mount
shipping carton.
Most flat roofs are topped with:
•Glued rubber cap sheet or
•Rubber cap sheet with gravel
Follow these instructions for either type of roof:
1. If the cap sheet is covered with gravel, use a push broom or
snow shovel to clear the gravel from the area where the
mount will be installed, as shown in figure 5-2.
hbph005
Figure 5-2 Clearing gravel from the installation location
2. Place the rubber pad on the roof surface where the mount
will be assembled.
5.5
Standard
nonpenetrating
mount
Flat roof – rubber sheet
(with or without gravel)
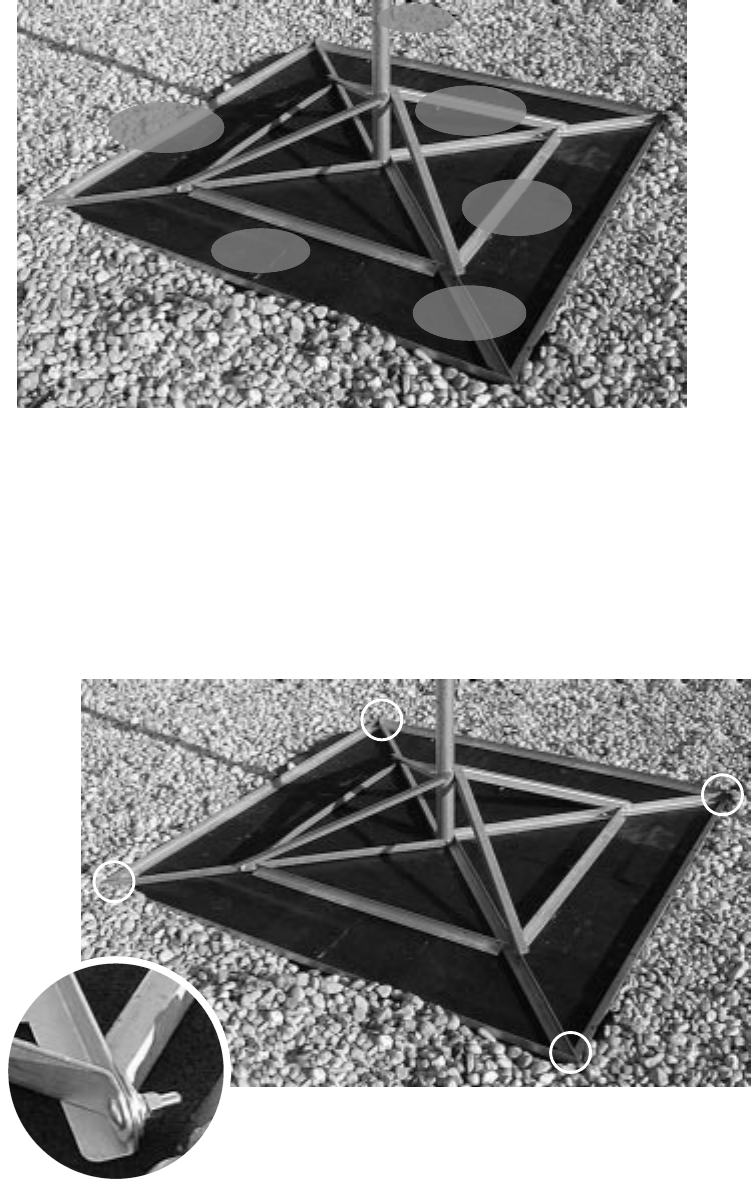
1027144–0001 Draft – Revision D.01 Installing mast mounts 5–5
RT installation
Figure 5-3 identifies the main mount components.
Figure 5-3 Mount components
Outer
base angle
Diagonal
base angle
Inner
brace angle
Mast
Mast
brace angle
rt015
Rubber
pad
•Follow steps 3 through 10 to assemble the mount.
3. Place the mount’s four outer base angles on the rubber pad.
4. Place the mount’s diagonal base angles on the rubber pad
and connect them to the outer base angles at the locations
circled in figure 5-4.
Figure 5-4 Connecting diagonal base angles to outer base angles
Carriage bolt
1
1
1
1
2
2
2
2
Flat washer
Lock washer
Hex nut
rt013
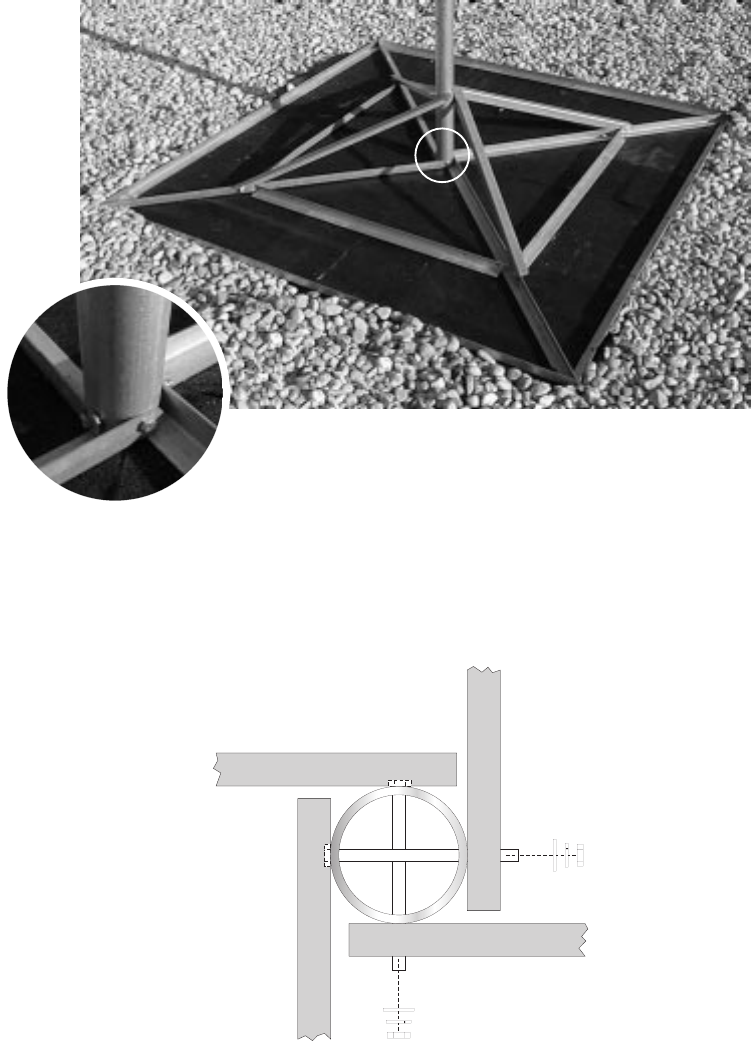
1027144–0001 Draft – Revision D.01 5–6 Installing mast mounts RT installation
5. Place the mast between the diagonal base angles. Secure the
diagonal base angles to the mast as shown in figure 5-5.
1
1
1
1
2
2
2
2
Bolt
Flat washer
Lock washer
Hex nut
rt014
Figure 5-5 Attaching the diagonal base angles to the mast
Diagonal base angles opposite each other are secured to the
mast with one set of hardware as shown below.
rt042
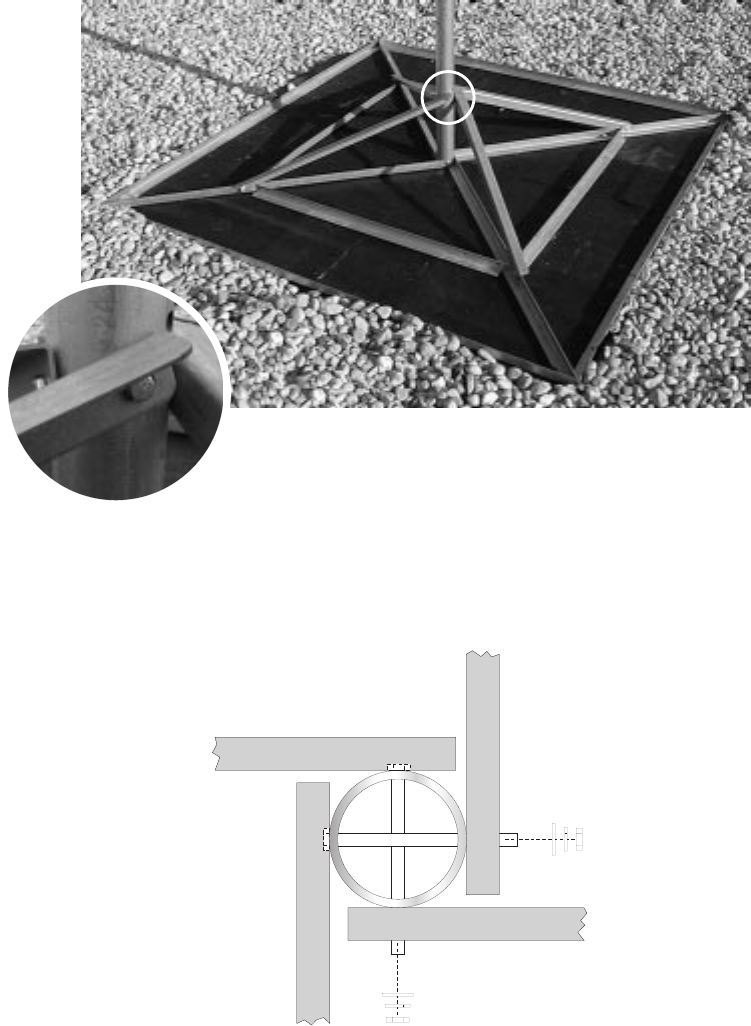
1027144–0001 Draft – Revision D.01 Installing mast mounts 5–7
RT installation
6. Attach the mast brace angles to the mast. See figure 5-6.
Figure 5-6 Attaching the mast brace angles to the mast
Carriage bolt
1
1
1
1
2
2
2
2
Flat washer
Lock washer
Hex nut
rt041
Mast brace angles opposite each other are secured to the
mast with one set of hardware as shown below.
rt042
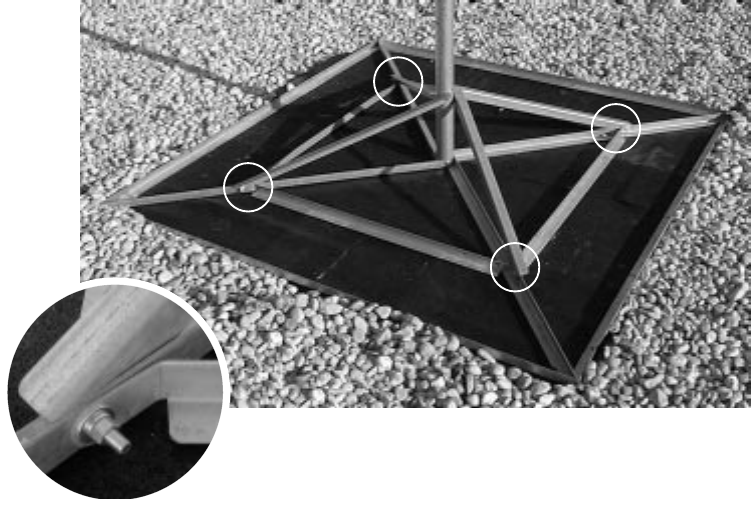
1027144–0001 Draft – Revision D.01 5–8 Installing mast mounts RT installation
7. Place the inner brace angles on the rubber pad and connect
them to the diagonal base angles and mast brace angles as
shown in figure 5-7.
Figure 5-7 Attaching inner brace angles to diagonal base
angles and mast brace angles
Carriage bolt
1
1
1
1
2
2
2
2
Flat washer
Lock washer
Hex nut
rt016
8. Refer to the Site Data Record (from the site survey) to
determine how many concrete blocks are required to anchor
the mount.
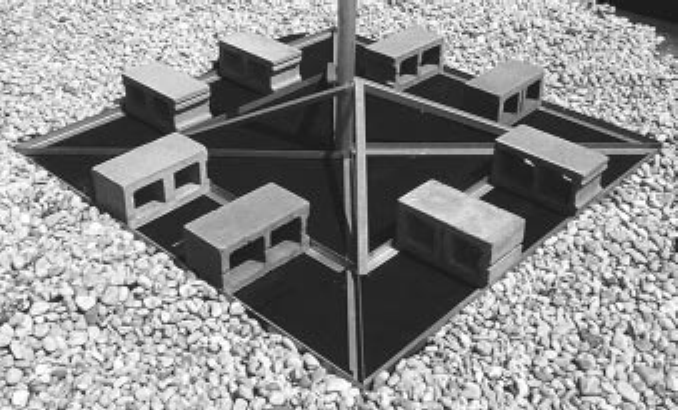
1027144–0001 Draft – Revision D.01 Installing mast mounts 5–9
RT installation
9. Place the concrete blocks on the mount so they are evenly
spaced, with the ends of each block anchoring both the
inner and outer base angles, as shown in figure 5-8.
Figure 5-8 Proper placement of concrete blocks on the mount
rtph010
10. When the mount installation is complete, if the roof is
covered with gravel, replace gravel up to the outside edges
of the mount. See figure 5-8.
Do not replace gravel in the area inside the mount base.
Leave the rubber pad exposed.
This section explains how to install the standard nonpenetrating
roof mount on a corrugated metal roof.
Special requirements:
•Pressure treated lumber, as specified in step 1 below,
and
•Twelve 1–inch–long (2.5–centimeter) lag bolts.
1. Obtain five pieces of pressure treated lumber, each 4 inches
by 4 inches by 8 feet long (10 centimeters by 10 centimeters
by 2.44 meters long).
2. Important: Select an area of the roof that is supported by a
metal I–beam to install the mount.
3. Cut the rubber pad into strips 4 inches wide by 8 feet long
(10 centimeters wide by 2.44 meters long).
4. Use 5–penny shingle nails to nail one strip of rubber pad to
one surface of each piece of lumber. See figure 5-9.
Corrugated metal
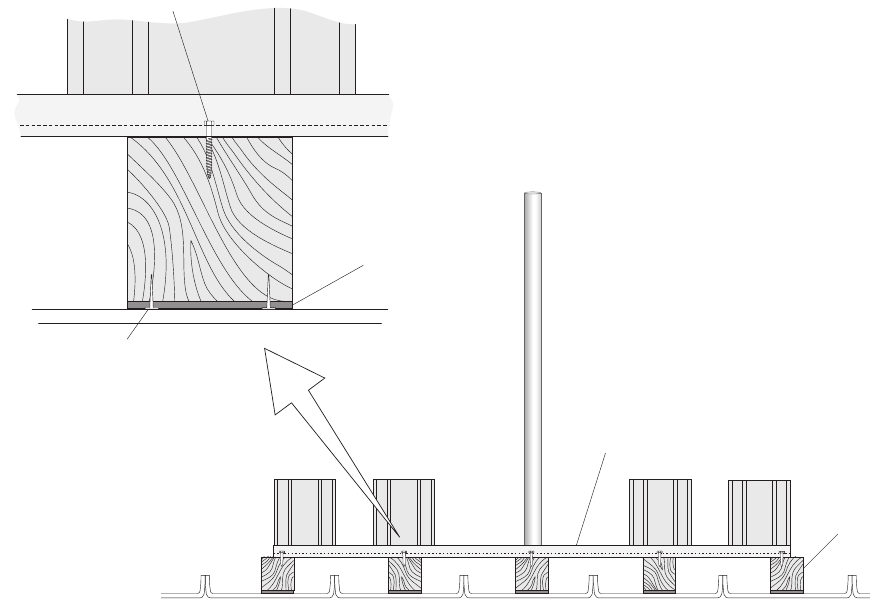
1027144–0001 Draft – Revision D.01 5–10 Installing mast mounts RT installation
5. Lay out the 4 x 4s, as shown in figure 5-9, so that each
piece is:
- In the recessed portion of the roof
- Parallel to the raised seams
- Equally spaced to support the mast, mount braces and
sides, and concrete blocks, as shown in figure 5-9.
Lay the lumber with the pad side down, so that the pad is
between the roof and the lumber.
Figure 5-9 Supporting the mount on a corrugated aluminum roof
Mast
Roof
Cinder block
(ballast)
Cinder
block
Roof
Detail
Rubber pad
(strip)
Wood
(4x4)
Wood
(4x4)
Mast mount
(assembled from kit)
Mast
mount
Lag bolt
hb008
Nail
End view
6. Follow steps 1 through 10 starting on page 5–4 to
assemble the mount.
Assemble the mount on the 4 x 4s so that when completed,
the mount is elevated above the aluminum roof.
7. Make sure the mount is evenly positioned on the 4 x 4s,
then use lag bolts to bolt the mount to the 4 x 4s.
Install the bolts through the holes in the mount’s outer
frame and into the wood. Use one bolt at each end of each
piece of lumber (as shown in figure 5-9). Use one bolt at the
center of each remaining side of the mount.
8. Add the required number of concrete blocks for ballast. See
steps 8 and 9 on page 5–8.

1027144–0001 Draft – Revision D.01 Installing mast mounts 5–11
RT installation
In some cases, you may be able to mount an ODU to an existing
structure, such as a tower built to support communications
antennas.
The key factors for determining if an existing structure can be
used as mast are that the structure must:
•Be securely attached to the building (and capable of
sustaining specified wind loadings).
•Have an outside diameter of 2.0 to 4.5 inches.
•Meet line of sight (LOS) requirements.
Important: In addition to these criteria, the structure must also
meet other requirements listed in the Hub and Remote Terminal
Site Preparation Guide.
5.6
Using existing
structures as ODU
mounts
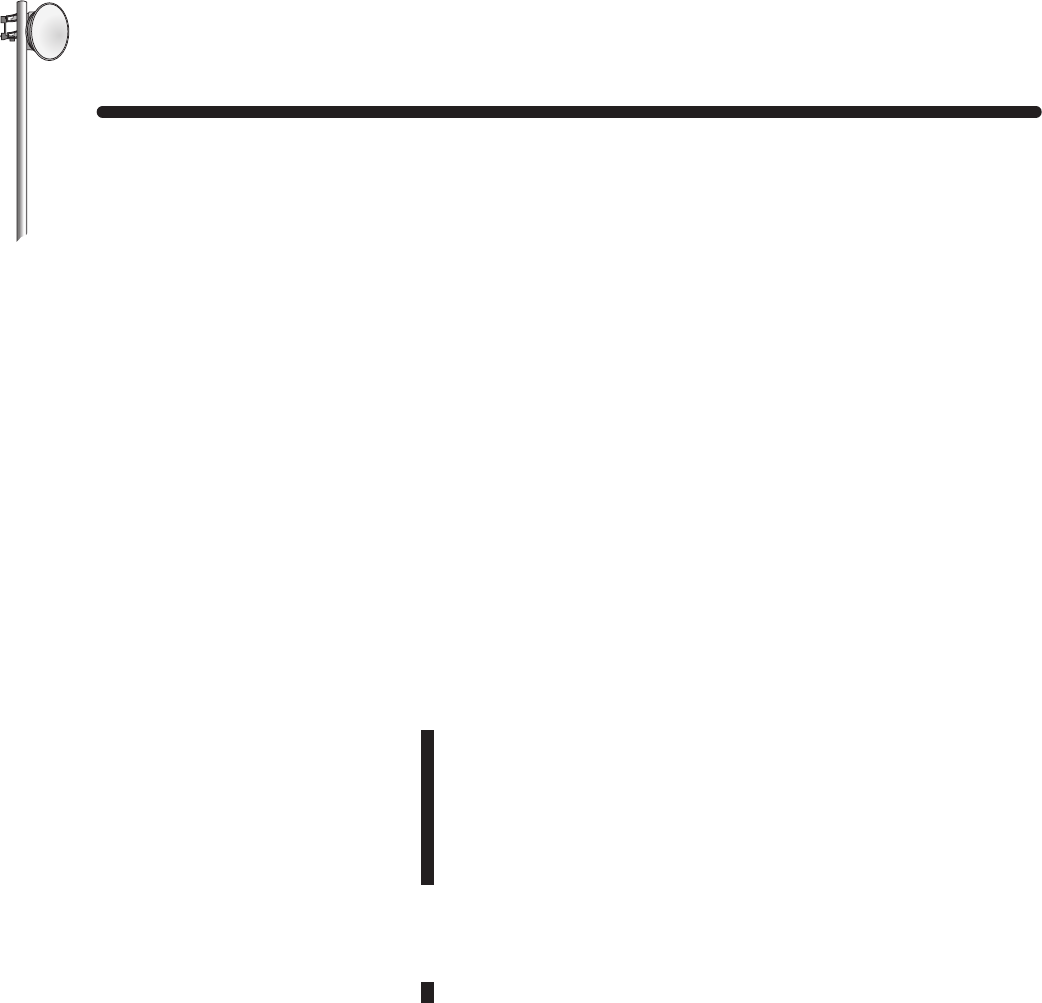
RT INSTALLATION
1027144–0001 Draft – Revision D.01 Installing ODUs 6–1
RT installation
Chapter 6
Installing ODUs
This chapter explains how to install RT ODUs. It includes:
•Introduction – page 6–2
•Transporting the ODU to the roof – page 6–4
•ODU installation and alignment tools – page 6–5
•Installing the temporary collar – page 6–6
•Installing the antenna mount – page 6–10
•Attaching the antenna to the mount – page 6–12
•Adjusting the antenna azimuth (coarse adjustment) –
page 6–15
•Adjusting the antenna elevation (coarse adjustment) –
page 6–17
•Checking the radome drain position – page 6–18
•Installing the mechanical attenuator – page 6–19
•Attaching the transceiver to the antenna – page 6–21
•Grounding the ODU – page 6–23
•Connecting the IFL to the ODU – page 6–25
•Adjusting the antenna azimuth (finer adjustment) –
page 6–26
•Adjusting the antenna elevation (finer adjustment) –
page 6–28
For ODU standards compliance information, see appendix B
(page B–2).
For ODU location requirements, see page 5–3.

1027144–0001 Draft – Revision D.01 6–2 Installing ODUs RT installation
For conceptual reference, figure 6-1 illustrates how hub terminal
(HT) ODUs communicate with remote terminal (RT) ODUs. The
remote terminal (RT) outdoor unit (ODU) and integrated antenna
attach to a mount installed on a vertical or horizontal mast, as
shown in figure 6-2 on page 6–3.
T0006019
Hub terminals
Remote
terminal
Remote terminal
Remote terminal
Figure 6-1 Hub ODUs communicating with RT ODUs
6.1
Introduction
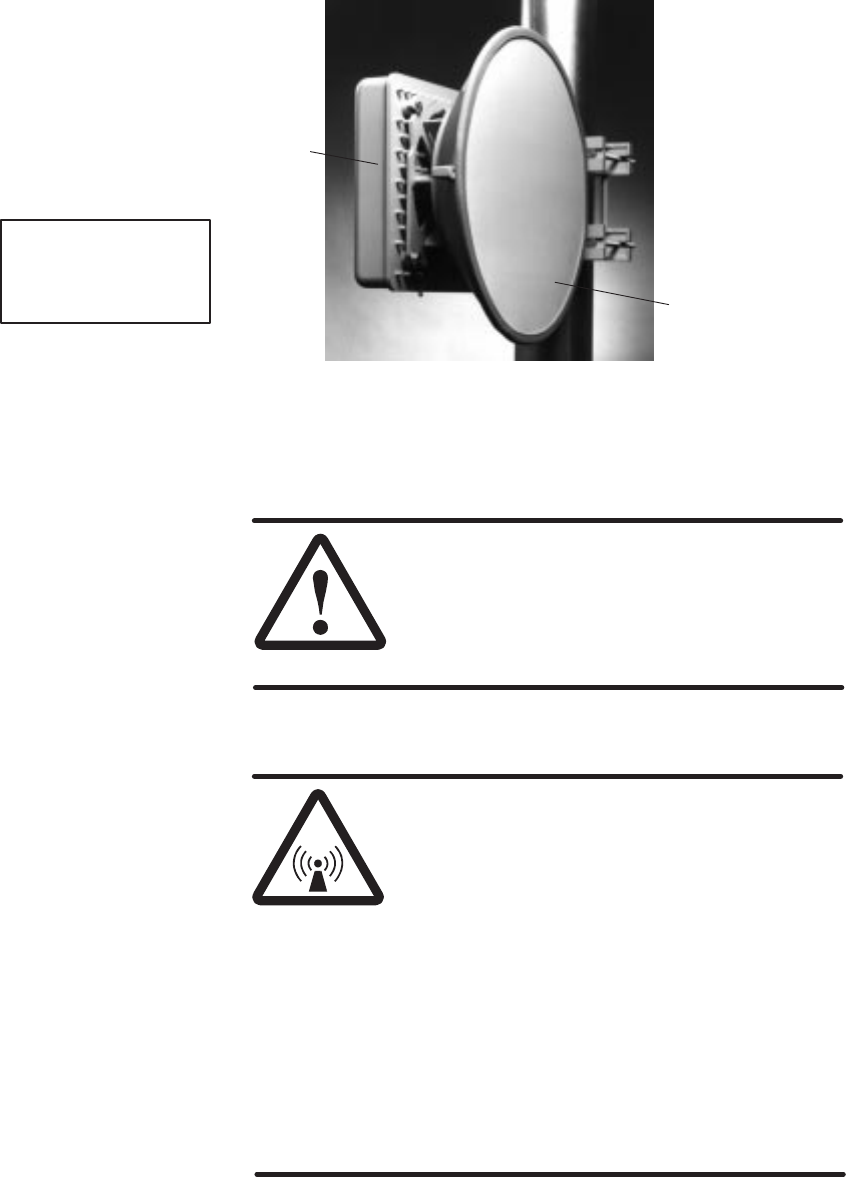
1027144–0001 Draft – Revision D.01 Installing ODUs 6–3
RT installation
Figure 6-2 ODU (installed)
Mount
ODU transceiver
Antenna
Mast
Graphic to be
updated.
When installing ODUs, observe the following safety warnings:
DANGER
Do not work on a ladder or roof without
first reading the safety warnings on page x
of this manual. Failure to observe these
warnings could result in personal injury or
death.
WARNING
Potential radio frequency (RF) hazard:
•Keep away from the front of the
outdoor unit (ODU) antenna while the
ODU is operating. Note that you cannot
tell from outward appearance whether
the ODU is operating or not.
•Be careful with respect to the ODU you
are installing and ODUs that may
already be operating in the installation
area.
Failure to observe these warnings could
result in injury to eyes or other personal
injury.
Safety warnings
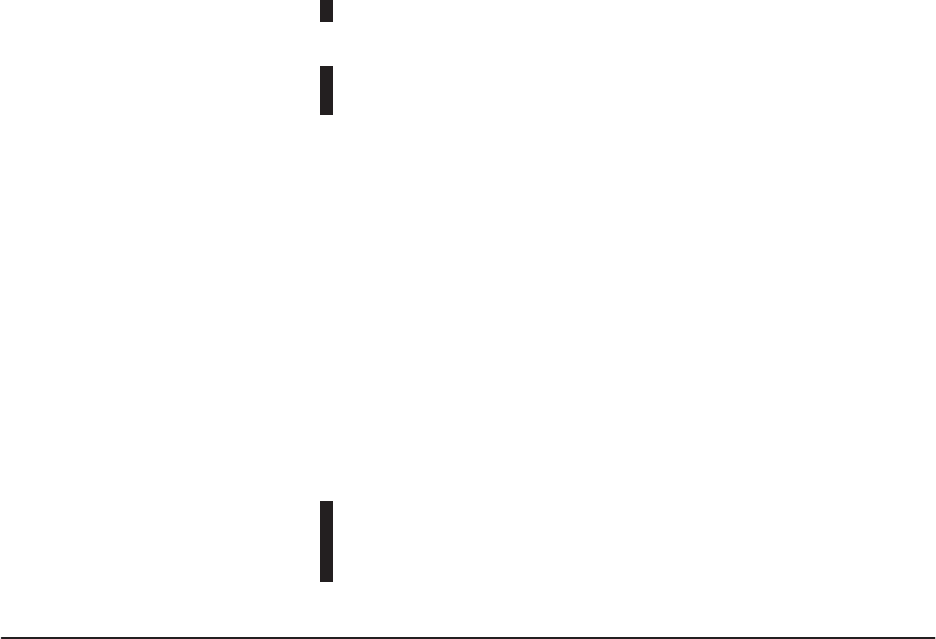
1027144–0001 Draft – Revision D.01 6–4 Installing ODUs RT installation
Before you can install and commission the outdoor RT equipment:
•The hub must be installed and operational.
•The RT ESN (electronic serial number) must be entered in
the EMS database.
•The mast must be installed.
The mast must have an outside diameter of 2.0 to
4.5 inches (5.5 to 11.4 centimeters) and must be securely
mounted in a vertical or horizontal position. If the mast is
not installed, you will need to install it before you
proceed. For additional details concerning the mast, see the
AIReach Broadband Hub and Remote Terminal Site
Preparation Guide.
Before starting, make sure you have:
•Antenna mount
•Antenna
•Transceiver
•3/8–inch torque wrench with 13–millimeter deep socket
•5/32–inch (4–millimeter) torque hex key wrench
Unpack the ODU transceiver and antenna before going up to the
roof. Carry the transceiver and antenna to the roof (in separate
trips) in a backpack or padded bag. Make sure the transceiver or
antenna is secured in the backpack or bag.
Prerequisites
6.2
Transporting the
ODU to the roof
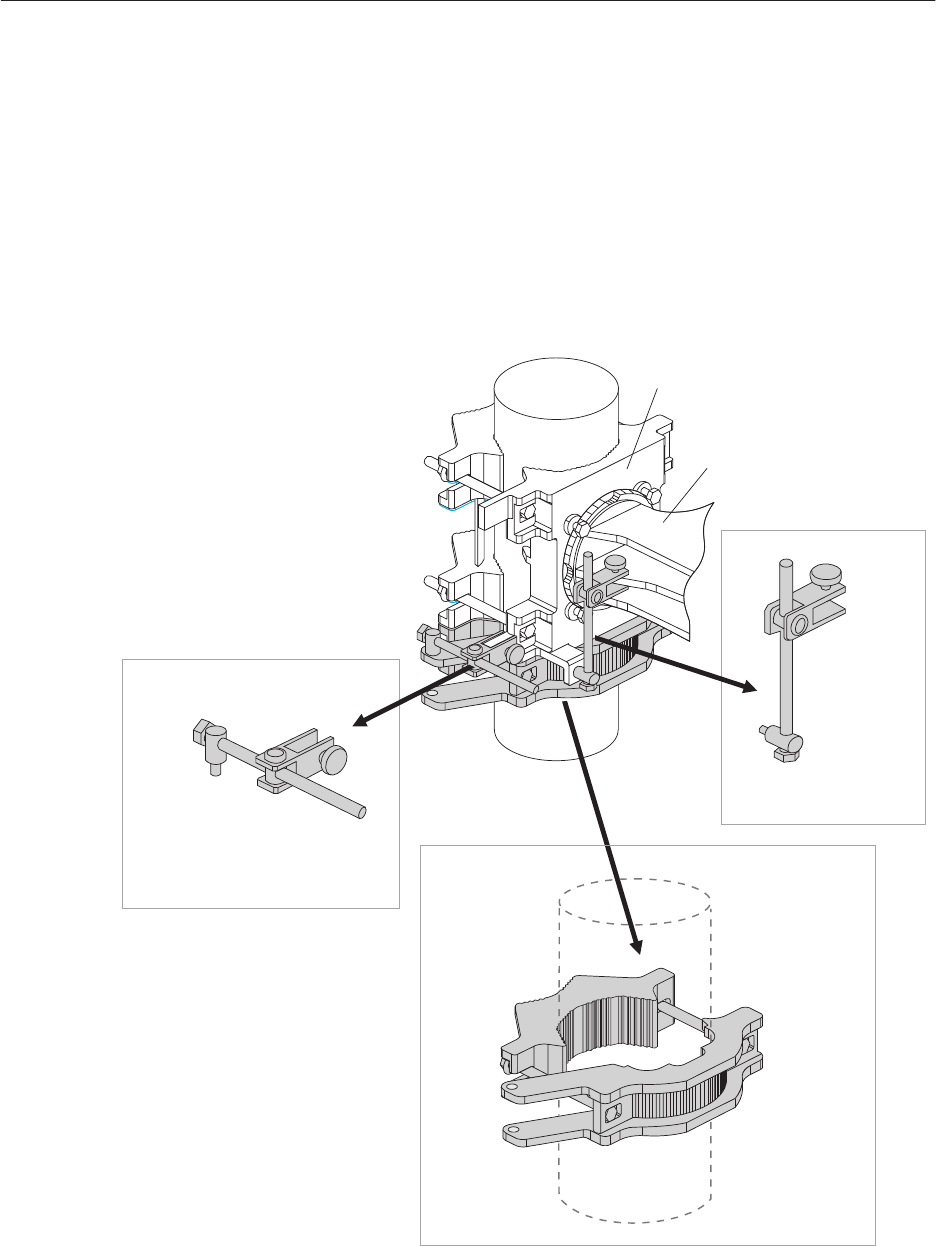
1027144–0001 Draft – Revision D.01 Installing ODUs 6–5
RT installation
Figure 6-3 shows the specialized tools included in the AIReach
Broadband ODU installer tool kit (HNS 1024668–0024).
You use these tools during installation and pointing to:
• Support the antenna mount and ODU and
• Adjust the antenna azimuth and elevation
Instructions for these procedures are included in the following
sections.
When installation and pointing are complete, you remove the
temporary installation collar, clamp, and adjusters so you can
reuse them for subsequent installations.
Figure 6-3 ODU installer tool kit (all shaded parts)
Mast
Adjuster
bolt
Elevation
adjuster
Detail
Adjuster
bolt
Azimuth adjuster
Detail
hb034
Antenna mount
Antenna bracket
The azimuth and elevation
adjusters are identical.
Either adjuster can be
mounted in the horizontal
position to adjust antenna
azimuth or the vertical
position to adjust antenna
elevation, as shown.
Detail
Temporary
installation
collar
Clamp
6.3
ODU installation
and alignment tools
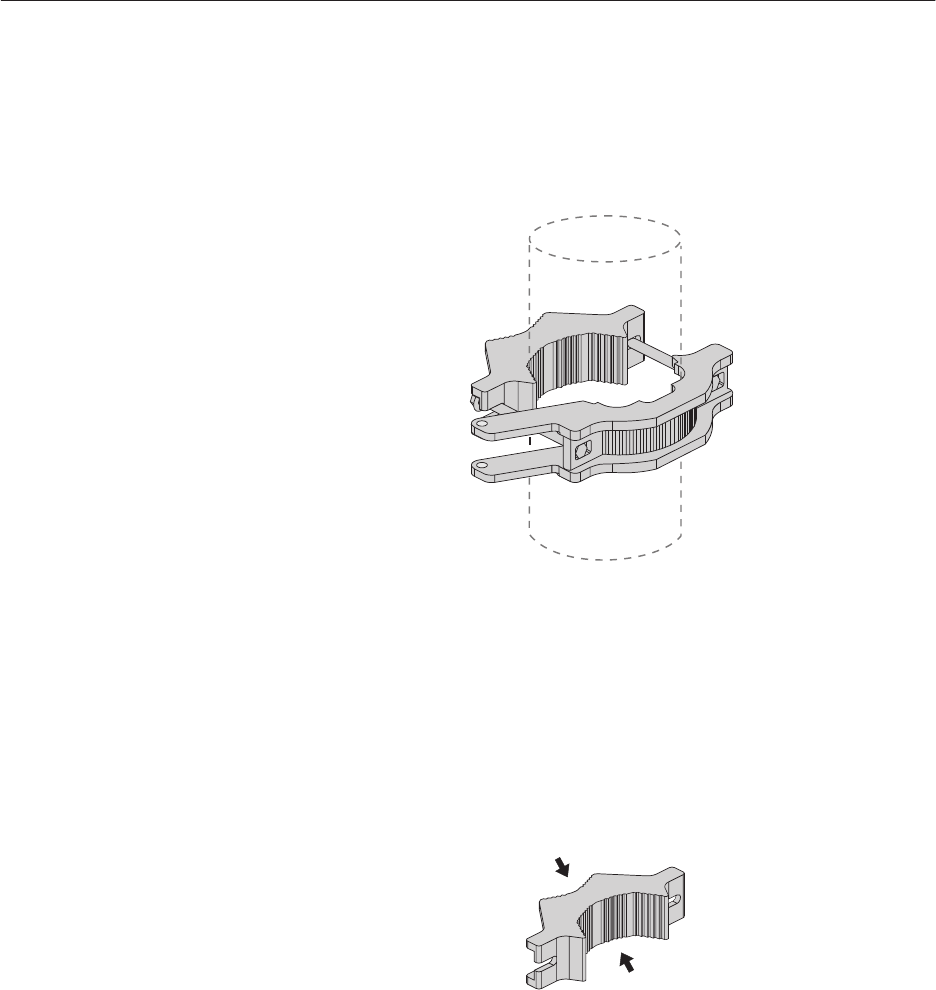
1027144–0001 Draft – Revision D.01 6–6 Installing ODUs RT installation
Important: To correctly install the antenna mount, read and
carefully follow all instructions in sections 6.4 through 6.8.
The temporary installation collar (HNS 1024668–0022; figure 6-4)
supports the antenna mount and ODU during installation (as
shown in figure 6-3).
Figure 6-4 Temporary installation collar
hb036
Temporary
installation collar
Temporary
mast clamp
Mast
Before you install the temporary installation collar:
1. Refer to the illustration below to determine which side of
the temporary mast clamp to use:
hb065
Temporary mast clamp
Use this side against the mast if the
mast outside diameter is
.
less than
3.5 inches (8.9 centimeters)
Use this side against the mast if the
mast outside diameter is 3.5 inches
(8.9 centimeters) or larger.
6.4
Installing the
temporary collar
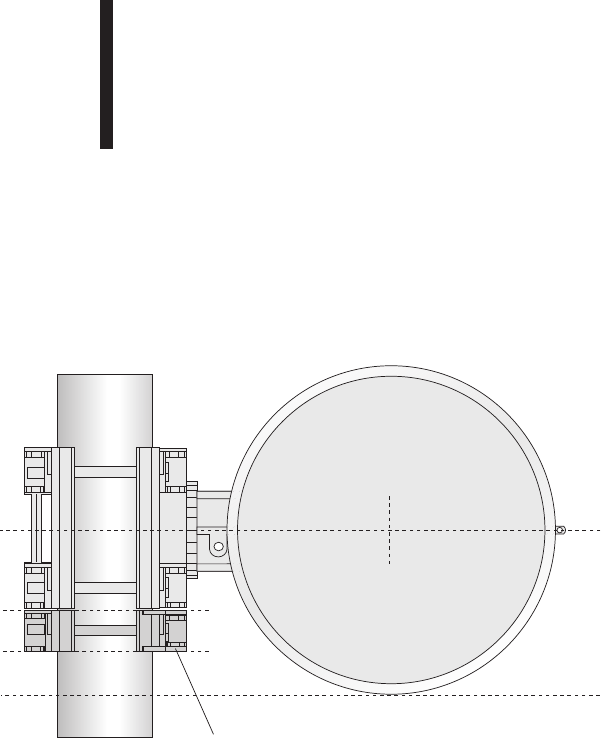
1027144–0001 Draft – Revision D.01 Installing ODUs 6–7
RT installation
2. Determine (approximately) how high on the mast to install
the temporary installation collar:
a. Determine the approximate desired antenna
installation height:
The ODU/antenna must be installed in line of
sight with the hub terminal (HT), with no
obstructions. As a general rule, install the RT ODU
as high as possible on the mast to avoid obstructions,
unless the work order or RF survey specifies the
ODU height.
b. Refer to figure 6-5 for the collar position relative to
the installed antenna position.
As shown in figure 6-5, when the antenna is installed
(later), the top of the collar is below the antenna
center and above the bottom of the antenna.
Figure 6-5 Collar height relative to desired antenna height
rt056
Antenna
Mast
Temporary installation collar
Antenna
center
Antenna
bottom
The antenna and
mount are not
installed yet.
They are shown
here to indicate
where the
temporary
installation collar
should be installed.
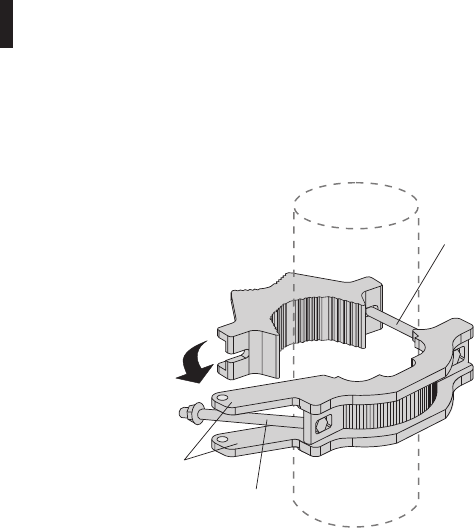
1027144–0001 Draft – Revision D.01 6–8 Installing ODUs RT installation
Attach the temporary installation collar to the mast, as follows:
1. Point the two long arms away from the direction of the HT,
as shown in figures 6-6 and 6-7.
2. Position the collar and clamp on opposite sides of the mast,
and swing the clamp toward the collar until you can
“capture” the clamp by swiveling the free–swinging bolt
into the slot in the clamp.
Figure 6-6 Attaching the temporary
installation collar to the mast
hb067
Collar
Swing clamp
toward collar.
Mast
Bolt
Bolt
Point these arms
from the
assigned HT
sector.
away
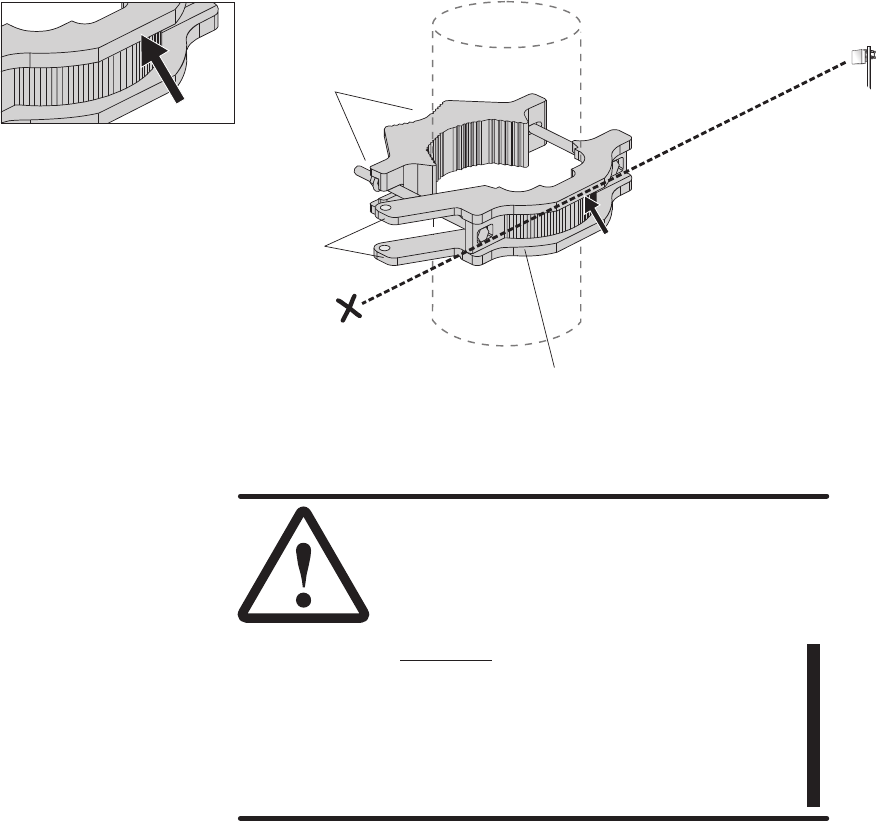
1027144–0001 Draft – Revision D.01 Installing ODUs 6–9
RT installation
3. Align the collar with respect to the target HT as shown in
figure 6-7.
4. Using a torque wrench with a deep socket, tighten the
temporary installation collar locking nuts to 16
foot–pounds torque (21.7 Newton–meters).
Figure 6-7 Aligning the temporary installation collar
Installer position
to align collar.
(Sight from here.)
2 locking nuts:
16 foot-pounds
(21.7 Newton-meters)
rt025
Collar
Mast
Point these arms
from the HT sector.
away
Align this flat surface
with line of sight to HT.
HT
Close-up - Flat surface on collar
CAUTION
Correct torque is
essential
for successful
installation and adjustment. Tighten nuts to
the exact torque stated. Incorrect torque
may result in damage to equipment.
Important: Due to planned enhancements
to the antenna mount design, the specified
torque settings are subject to change.
Verify the torque settings with the HNS
Wireless Networks Division (WND)
Technical Assistance Center (TAC) before
installing the antenna and mount.
Important: The temporary collar, clamp, and adjusters are not
removed until the RT is commissioned and verified as operational.
Commissioning the RT is discussed in chapter 7.
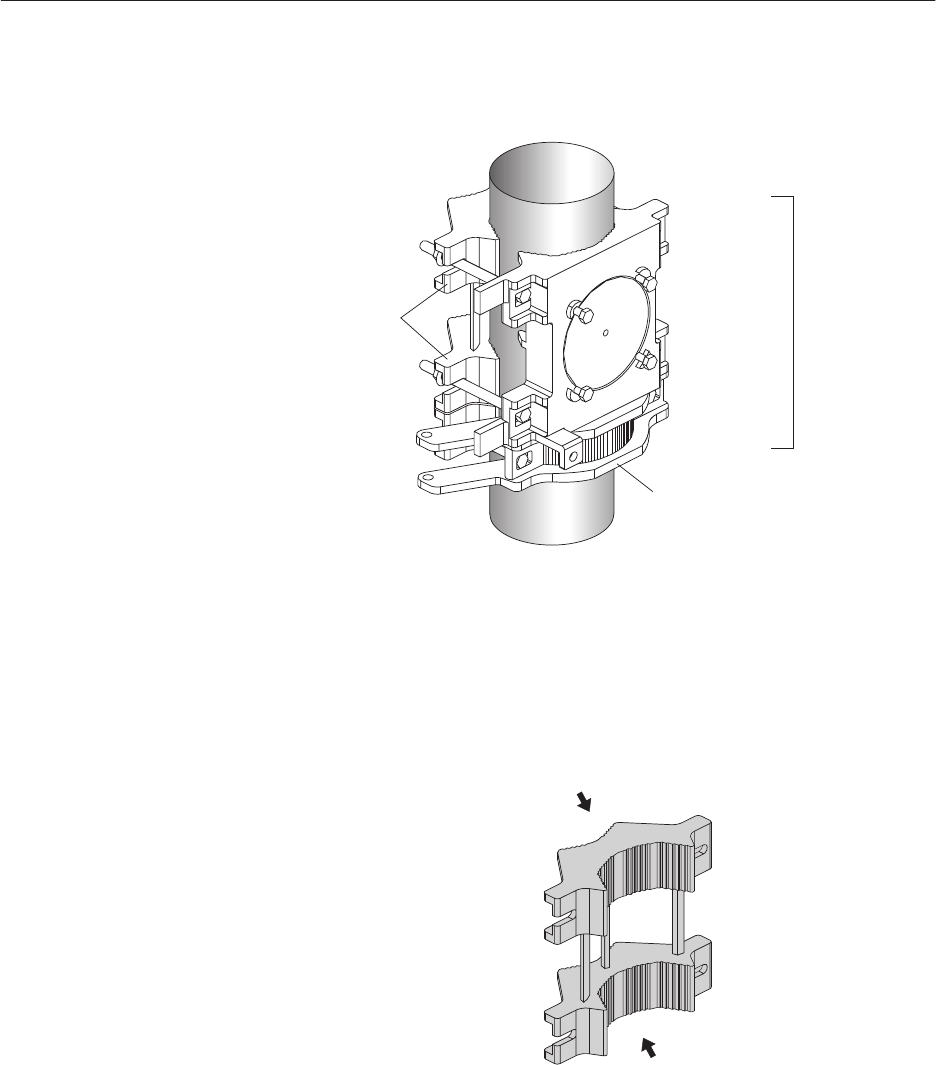
1027144–0001 Draft – Revision D.01 6–10 Installing ODUs RT installation
The antenna mount (HNS 1024668–0025) consists of a mast
interface and permanent mast clamp, as shown in figure 6-8.
Follow the steps below to install the antenna mount.
Figure 6-8 Antenna mount
Antenna
mount
hb037
Temporary
installation collar
Mast
Permanent
mast clamp
Mast
interface
1. Determine which side of the permanent mast clamp to use:
hb069
Permanent mast clamp
Use this side against the mast if the
mast outside diameter is
.
less than
3.5 inches (8.9 centimeters)
Use this side against the mast if the
mast outside diameter is 3.5 inches
(8.9 centimeters) or larger.
6.5
Installing the
antenna mount
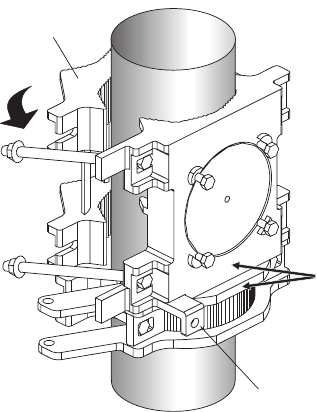
1027144–0001 Draft – Revision D.01 Installing ODUs 6–11
RT installation
2. Position the mast interface and permanent mast clamp on
opposite sides of the mast, with the interface on the same
side as the temporary collar, as shown in figure 6-9.
Allow the bottom surface of the mast interface to rest on the
top surface of the temporary installation collar.
Figure 6-9 Installing the antenna mount
hb068
Mast
Permanent
mast clamp
Mast
interface
Clamp nut
(1 of 4)
Swing clamp
toward interface.
Elevation
adjustment arm
Align the face of the mast
interface so that these two
surfaces are parallel.
3. Swing the clamp toward the interface until you can
“capture” the clamp by swiveling the free–swinging bolts
into the two slots in the clamp, as shown in figure 6-9.
The elevation adjustment arm (shown in figure 6-9) must be
behind the antenna (not installed yet). This means it will be
on the side of the interface that is farthest from the HT.
In some cases, to point the antenna in the right direction, it
is necessary to install the mount upside down, with the
elevation adjustment arm at the top of the mast interface.
This is acceptable, as long as the mount is installed so the
elevation adjustment arm will be behind the antenna.
4. Align the mast interface and temporary installation collar so
the rectangular face of the interface is parallel with the flat
surface of the collar, as shown in figure 6-9.
5. Finger tighten the four mast clamp nuts so the mast
interface and permanent mast clamp are snug and without
excess movement.
You should be able to smoothly pivot the mast interface and
mast clamp around the mast to permit coarse azimuth
adjustment.
(You fully tighten the mast clamp nuts later, after
completing all adjustments.)
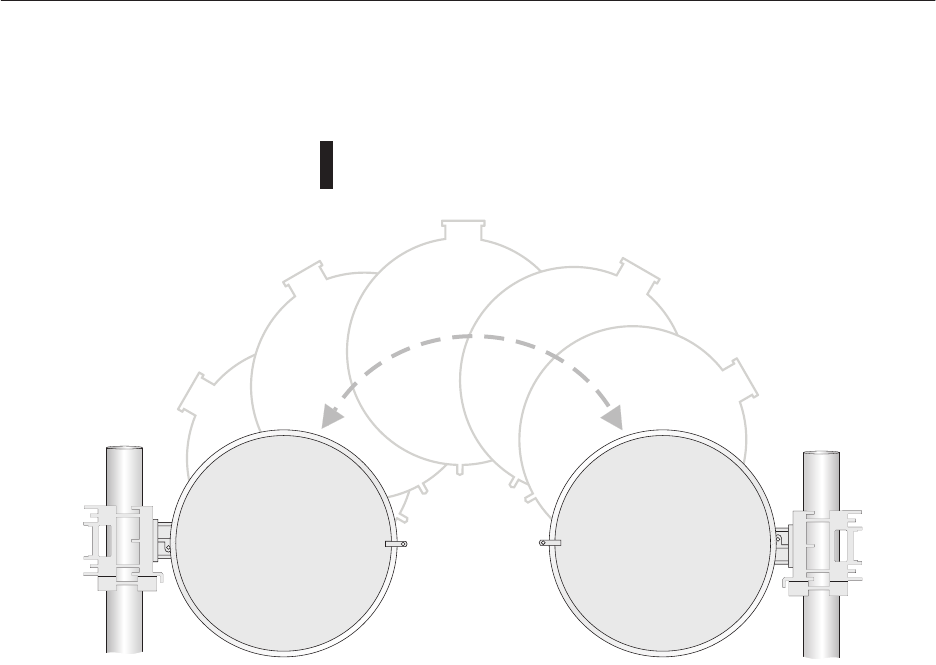
1027144–0001 Draft – Revision D.01 6–12 Installing ODUs RT installation
1. With the radome facing the HT direction, position the
round, flat surface of the antenna bracket approximately
1 inch (2.5 centimeters) from the mast interface.
Note: The RT antenna can be rotated 180°, as shown
below, to attach to a mount to the right or left.
Figure 6-10 The RT antenna can be rotated to attach to the right or left
T0009004
6.6
Attaching the
antenna to the
mount
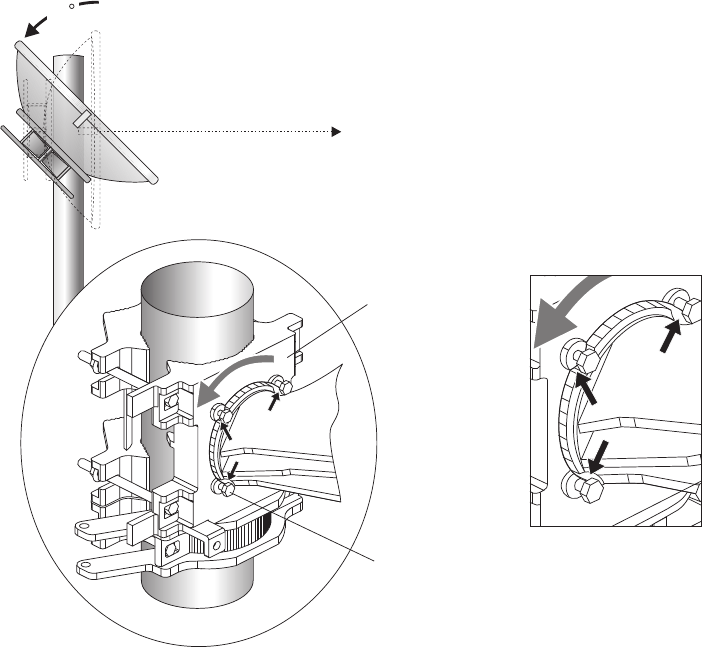
1027144–0001 Draft – Revision D.01 Installing ODUs 6–13
RT installation
2. Rotate the antenna approximately 45° away from the HT
until the antenna bracket reliefs (curved indentations) are
aligned with the four nuts on the mast interface, as shown in
figure 6-11.
Figure 6-11 Rotating the antenna so the antenna
bracket can be placed against the mast interface
Line of sight to HT
45
rt010
Locking nut
(1 of 4)
Mast
interface
Relief (1of 4)
Relief
Close-up view:
Antenna bracket reliefs
3. Press the antenna against the mast interface.
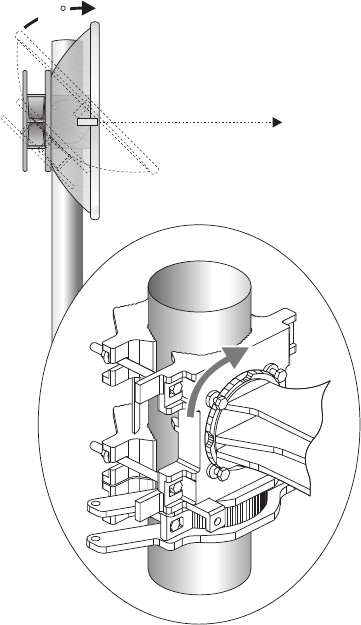
1027144–0001 Draft – Revision D.01 6–14 Installing ODUs RT installation
4. Rotate the antenna approximately 45° toward the HT, to the
upright position, as shown in figure 6-12—then finger
tighten the antenna bracket locking nuts so the antenna is
snug and without excess movement.
The antenna is now “captured” by the antenna mount.
However, because the antenna bracket nuts are not fully
tightened, you can adjust the antenna elevation.
Figure 6-12 Rotating the antenna to the
upright installation position
45
rt027
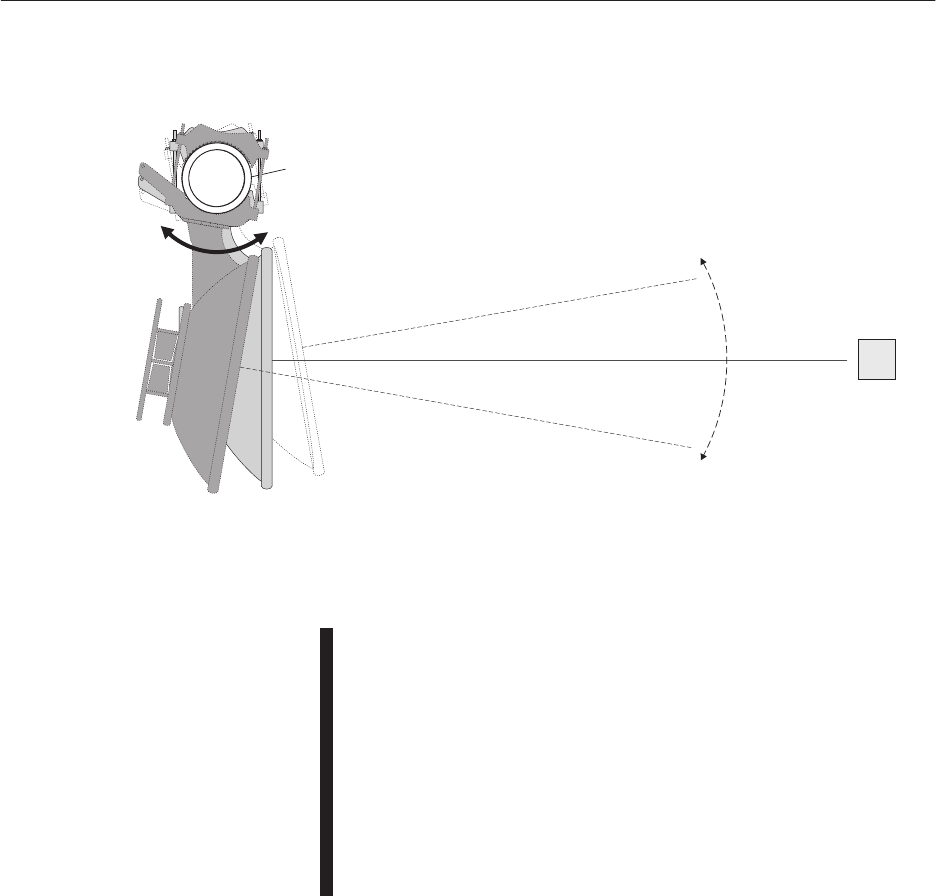
1027144–0001 Draft – Revision D.01 Installing ODUs 6–15
RT installation
To adjust the antenna azimuth (horizontal pointing direction), you
move the antenna to the left or right, as illustrated in figure 6-13.
You adjust the azimuth until the antenna is pointed at the HT.
Figure 6-13 Antenna azimuth adjustment (to right or left)
Mast
HT
RT antenna
Pointing direction
rt052
Top view
Left
Right
adjusted
by 10 .°
+
_
Antenna
azimuth
can be
You adjust the antenna azimuth in three stages:
1. Coarse adjustment, using only the built–in antenna
boresight (steps 1 through 4, on page 6–16)
2. Finer adjustment, using the boresight and azimuth adjuster
tool (section 6.14)—after you attach the transceiver, ground
cable, and IFL cable.
3. Electronic pointing, using a voltmeter and integrated system
software (section 7.4). This procedure, a part of the RT
commissioning process, refines the azimuth adjustment to
point the antenna as accurately as possible.
6.7
Initial (coarse)
antenna azimuth
adjustment

1027144–0001 Draft – Revision D.01 6–16 Installing ODUs RT installation
Obtain a coarse azimuth adjustment as follows:
1. Using the antenna boresight for reference (see figure 6-14),
rotate the antenna mount (and antenna) around the mast
until you can see the HT in the boresight.
rt026
Boresight
Antenna bracket
Figure 6-14 Boresight location
2. Using a torque wrench with a deep socket, tighten the
four mast clamp nuts to 20 foot–pounds torque (27.1
Newton–meters). Tighten each bolt a little at a time,
moving from bolt to bolt in an X pattern.
3. Loosen the temporary installation collar and re–align the
collar with the mast interface, as shown in figure 6-9.
4. Tighten the correctly aligned temporary installation collar to
16 foot–pounds torque (21.7 Newton–meters).
Coarse azimuth
adjustment
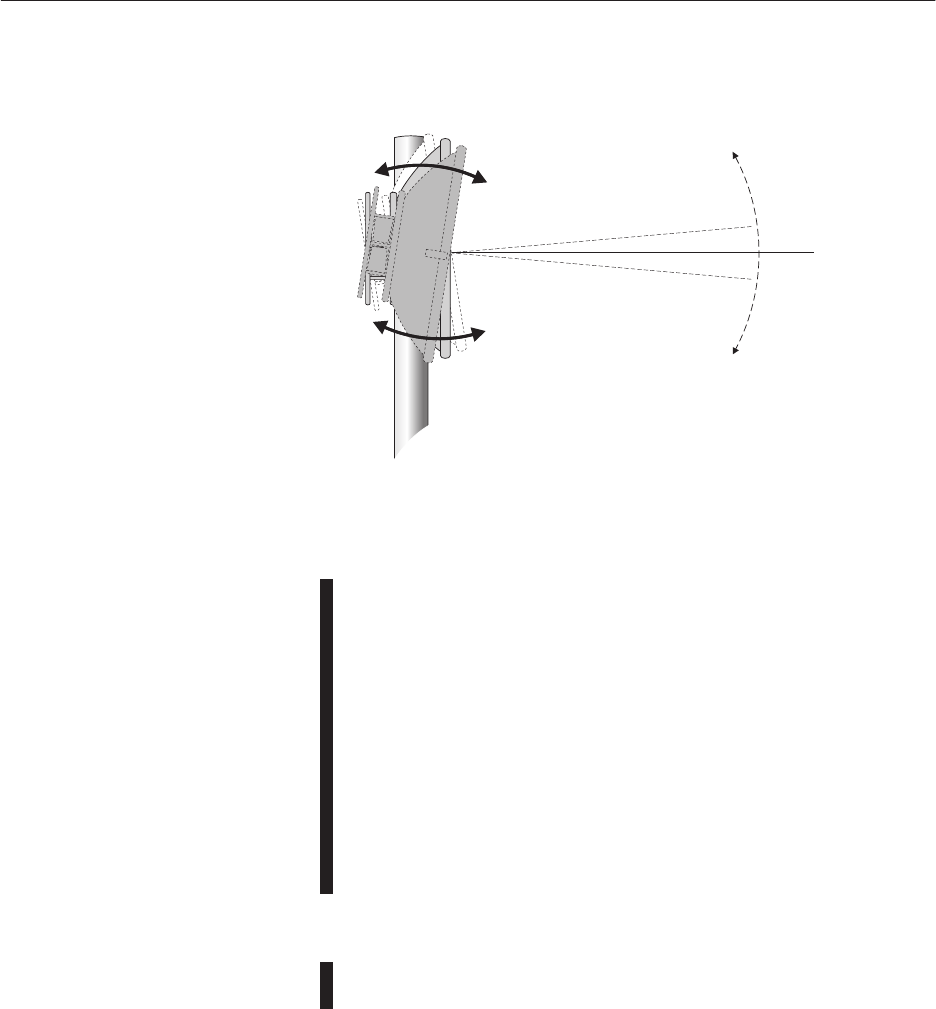
1027144–0001 Draft – Revision D.01 Installing ODUs 6–17
RT installation
To adjust the antenna elevation (upward or downward pointing
direction), you rotate the antenna upward or downward, as
illustrated in figure 6-15, until the elevation is set as desired.
rt053
Antenna
(front)
Side view
0elevation°
Downward
elevation
Upward
elevation
Figure 6-15 Antenna elevation adjustment
(upward or downward adjustment)
You adjust the antenna elevation in three stages:
1. Coarse adjustment, using only the built–in antenna
boresight (steps 1 through 4, on page 6–18)
2. Finer adjustment, using the boresight and elevation adjuster
tool (section 6.15)—after you attach the transceiver, ground
cable, and IFL cable.
3. Electronic pointing, using a voltmeter and integrated system
software (section 7.4). This procedure, a part of the RT
commissioning process, refines the elevation adjustment to
point the antenna as accurately as possible.
Obtain a coarse elevation adjustment as follows:
1. Using the boresight for reference, rotate the antenna until a
coarse alignment is obtained.
When the elevation is properly adjusted, you should be able
to see all of the HT in the boresight.
If the antenna does not rotate freely, loosen each of the
antenna bracket nuts slightly.
2. Finger tighten the reflector bracket locking nuts (again),
so the antenna is snug and without excess movement.
6.8
Initial (coarse)
antenna elevation
adjustment
Coarse elevation
adjustment
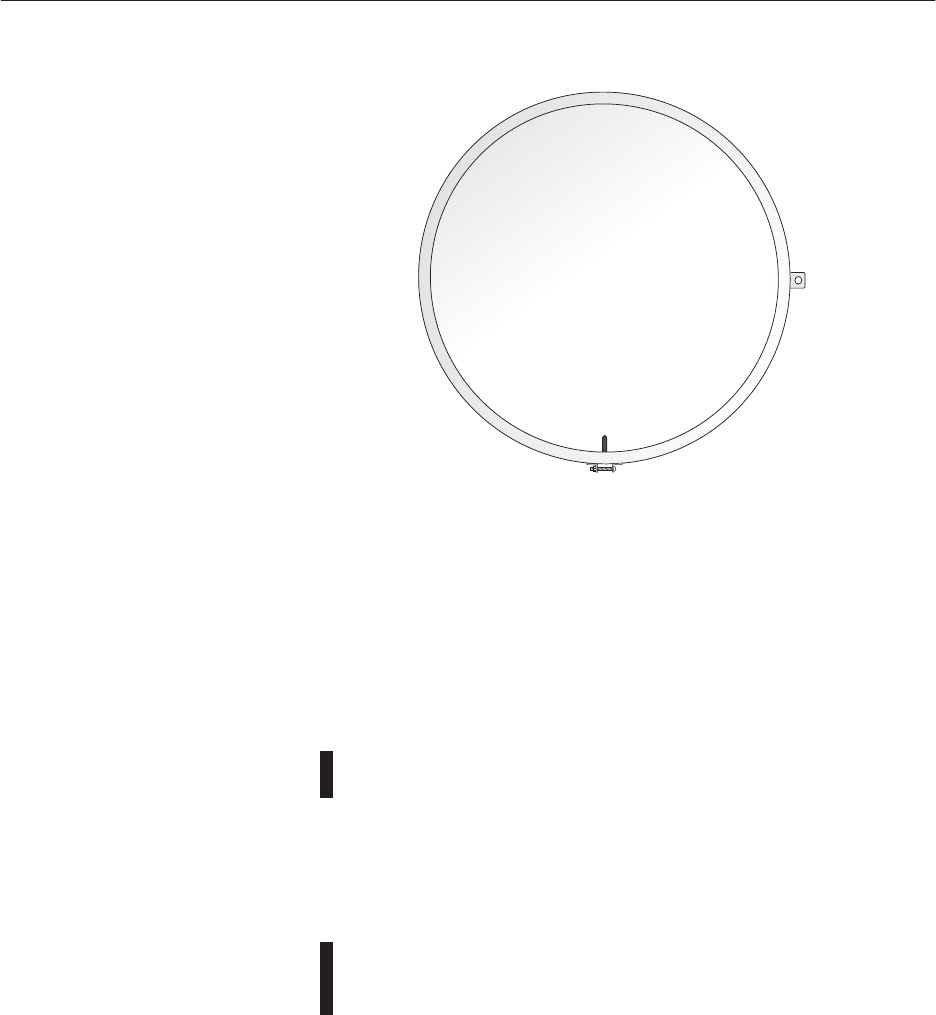
1027144–0001 Draft – Revision D.01 6–18 Installing ODUs RT installation
Check to make sure the radome drain groove is at the bottom of
the antenna.
Figure 6-16 Radome drain groove
Drain
groove
Clamp:
20 inch-pounds
(2.3 Newton-meters)
rt030
If the radome drain groove is at the bottom of the antenna,
proceed to section 6.10.
If the drain groove is not at the bottom of the antenna, rotate the
radome panel as follows:
1. Using a 5/32–inch (4–millimeter) torque hex key wrench,
loosen the radome band clamp locking nut.
2. Rotate the radome panel until the band clamp screw
assembly and drain groove are located at the bottom of the
antenna.
3. Tighten the radome band clamp locking nut to 20
inch–pounds torque (2.3 Newton–meters).
4. Look through the boresight to make sure the antenna is
remains (coarsely) pointed.
Section 6.11 explains how to attach the transceiver to the antenna.
6.9
Checking the
radome drain
position
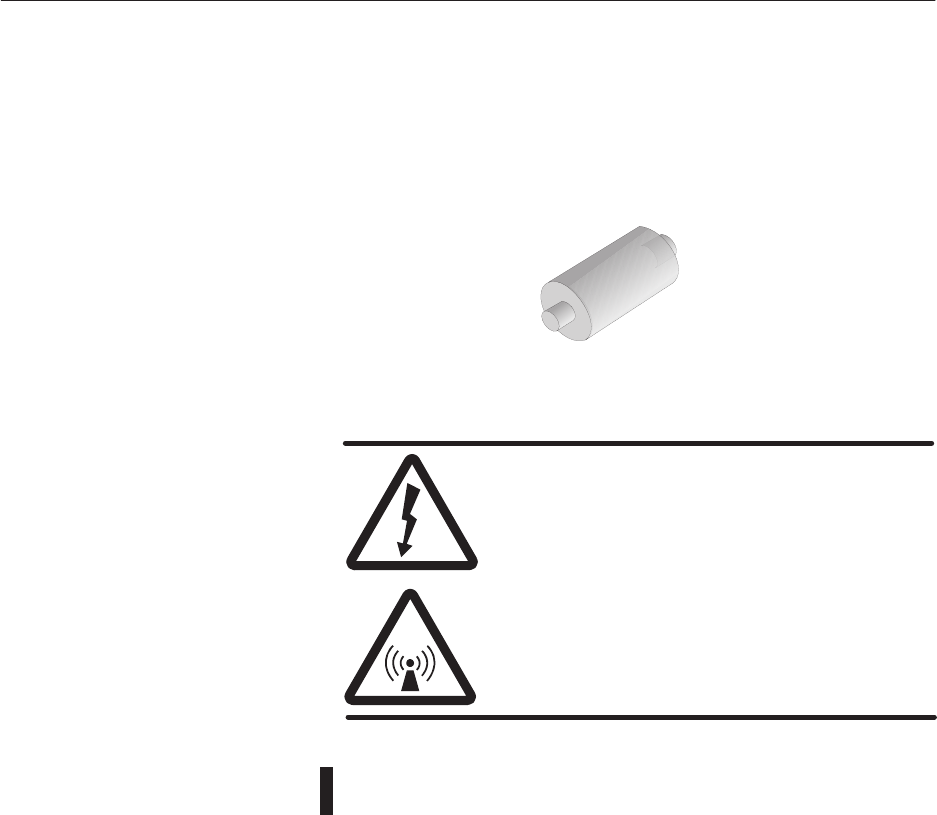
1027144–0001 Draft – Revision D.01 Installing ODUs 6–19
RT installation
You must use a mechanical attenuator, shown in figure 6-17, if:
•The RT is within 328 feet to 1,312 feet (100 to 400 meters)
of the HT.
•The RT pointing voltage, obtained from a voltmeter,
exceeds 4.1 volts.
•The installation work order instructs you to use it.
Figure 6-17 Mechanical attenuator
rt006
WARNING
To avoid the risk of electric shock and
exposure to potentially harmful radio
frequency (RF) waves, make sure the IDU is
turned off, if already installed, before
installing the mechanical attenuator.
Failure to observe these warnings could
result in personal injury.
Use the attenuator size (in decibels) specified in the installation
work order and/or Site Data Record.
Follow these steps to install the mechanical attenuator:
1. Locate the circular waveguide on the rear of the antenna.
See figure 6-18.
2. Insert the mechanical attenuator in the circular waveguide,
as shown in figure 6-18.
6.10
Installing the
mechanical
attenuator
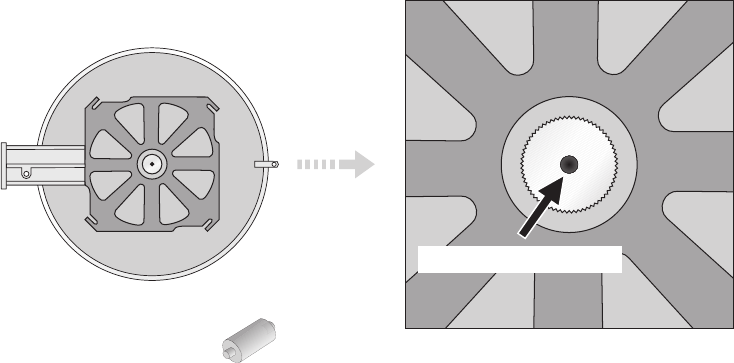
1027144–0001 Draft – Revision D.01 6–20 Installing ODUs RT installation
Important: Do not fully insert the mechanical attenuator.
Ensure that part of the attenuator is exposed so it can be
removed if necessary.
Figure 6-18 Installing the mechanical attenuator
rt023
Close-up: Waveguide
Insert the attenuator here
Attenuator
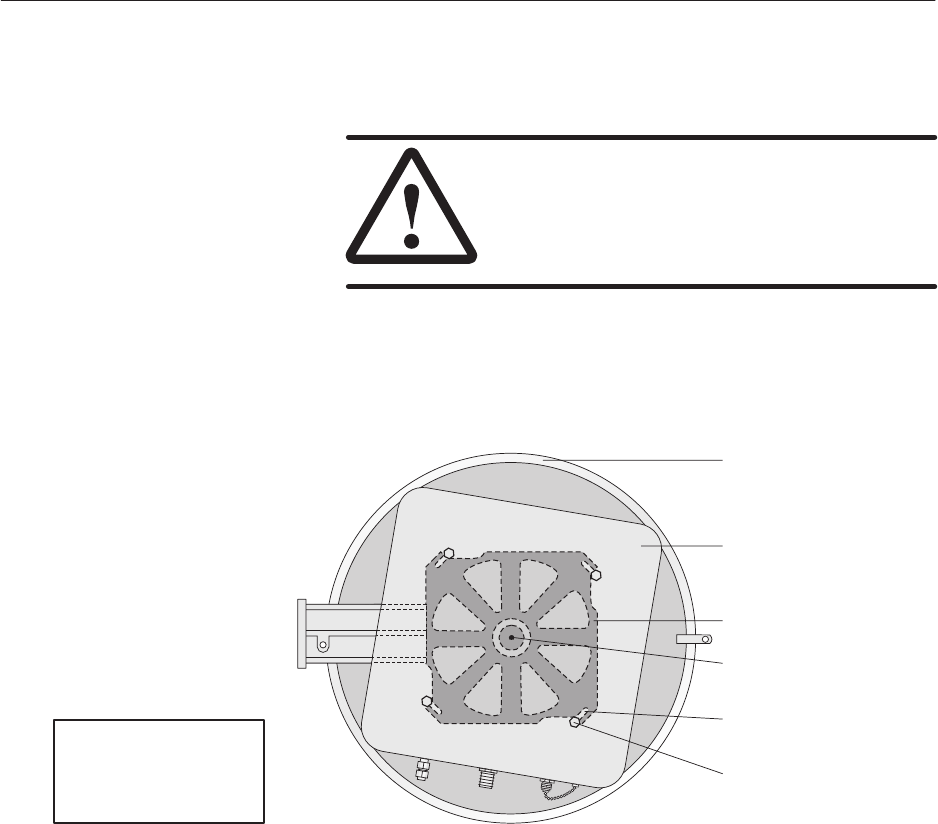
1027144–0001 Draft – Revision D.01 Installing ODUs 6–21
RT installation
Follow these steps to attach the transceiver to the antenna:
1. Remove the plastic plug from the antenna waveguide and
the plastic cap from the transceiver coupling.
CAUTION
Always keep the waveguide and coupling
plugs in place when the transceiver is
detached from the antenna, to keep dust or
other contamination out.
2. Position the transceiver so its four mounting bolts are
aligned with the four grooves on the antenna flange, as
shown in figure 6-19.
Figure 6-19 Aligning the transceiver mounting bolts
rt020
Transceiver
Mounting bolt
(Attached to transceiver)
Antenna flange
Waveguide
Flange groove
Antenna
Graphic to be
updated.
6.11
Attaching the
transceiver to the
antenna
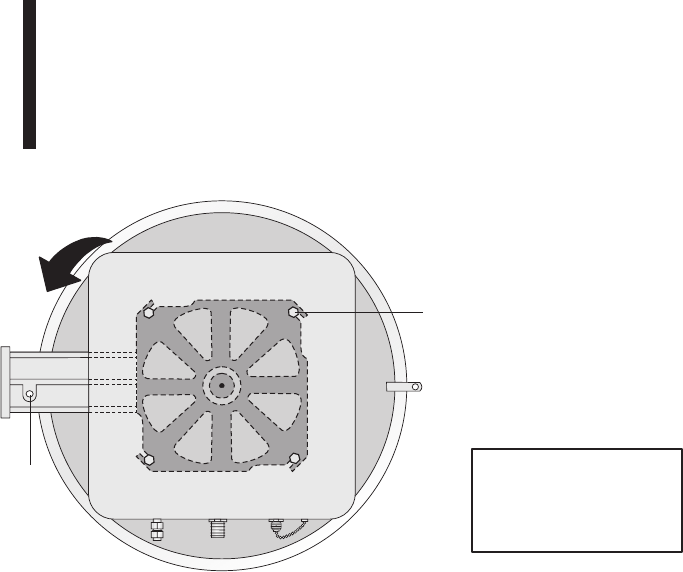
1027144–0001 Draft – Revision D.01 6–22 Installing ODUs RT installation
3. Rotate the transceiver, making sure the transceiver’s
mounting bolts slide into the grooves in the antenna flange.
(The direction of rotation depends on the orientation of the
antenna bracket—to the right or left.) If the mounting bolts
will not slide into the grooves, loosen the bolts. See figure
6-20.
Figure 6-20 Transceiver (installed)
rt021
Rotate transceiver
counter-clockwise
Boresight
Mounting bolts must be
fully inserted in flange
grooves.
Graphic to be
updated.
4. Fully tighten the mounting bolts.
5. After tightening the transceiver, look through the boresight
to make sure the antenna is still accurately pointed at the
HT. See figure 6-20 for boresight location.

1027144–0001 Draft – Revision D.01 Installing ODUs 6–23
RT installation
Grounding the ODU requires several connections, as shown in
figure 6-21. In making the ground connections, follow these
practices:
•For all ODU ground connections, use compression
connectors (such as compression lugs or compression
clamps).
•For all threaded ground connections, use a flat washer and
lock washer (with the lock washer next to the nut).
Ground the ODU as follows:
1. Connect one end of the ground cable (No. 6 AWG or
greater, green) to the ODU ground connector, which is
shown in figure 6-21.
2. Connect the ground cable to a bolted joint on the mast
mount.
Important: For this connection, strip the cable but do not
cut it. See figure 6-21. The cable continues from the bolted
joint to the ground point.
3. Connect the ground cable to a suitable ground point on the
rooftop.
The best ground point for the ODU is an earth–referenced
roof ring conductor that follows the perimeter of the
building, constructed according to the requirements of
NFPA 780 or a similar regulatory code. However, such a
conductor is not always present. Other alternatives are
acceptable, as long as they comply with the grounding
requirements detailed in the Hub and Remote Terminal Site
Preparation Guide.
Building steel can also be used as a ground point. However,
before using building steel, verify that the steel structure
is electrically continuous throughout the entire building
and that it is properly connected to earth ground. For
detailed grounding requirements, see the Hub and Remote
Terminal Site Preparation Guide.
4. Apply anti–oxidant (HNS 9008224–0002) to each ground
lug (points 1, 2, and 3 in figure 6-21).
5. Apply 1/2–inch (13–millimeter) heat shrink tubing (HNS
9007488–0005) to each ground lug after the connection is
complete.
Important: You must slip the heat shrink onto the cable
before you make the connections.
Note: A resistance of less than 5 ohms is desirable from the
ODU to earth, including the earth field.
6.12
Grounding the ODU
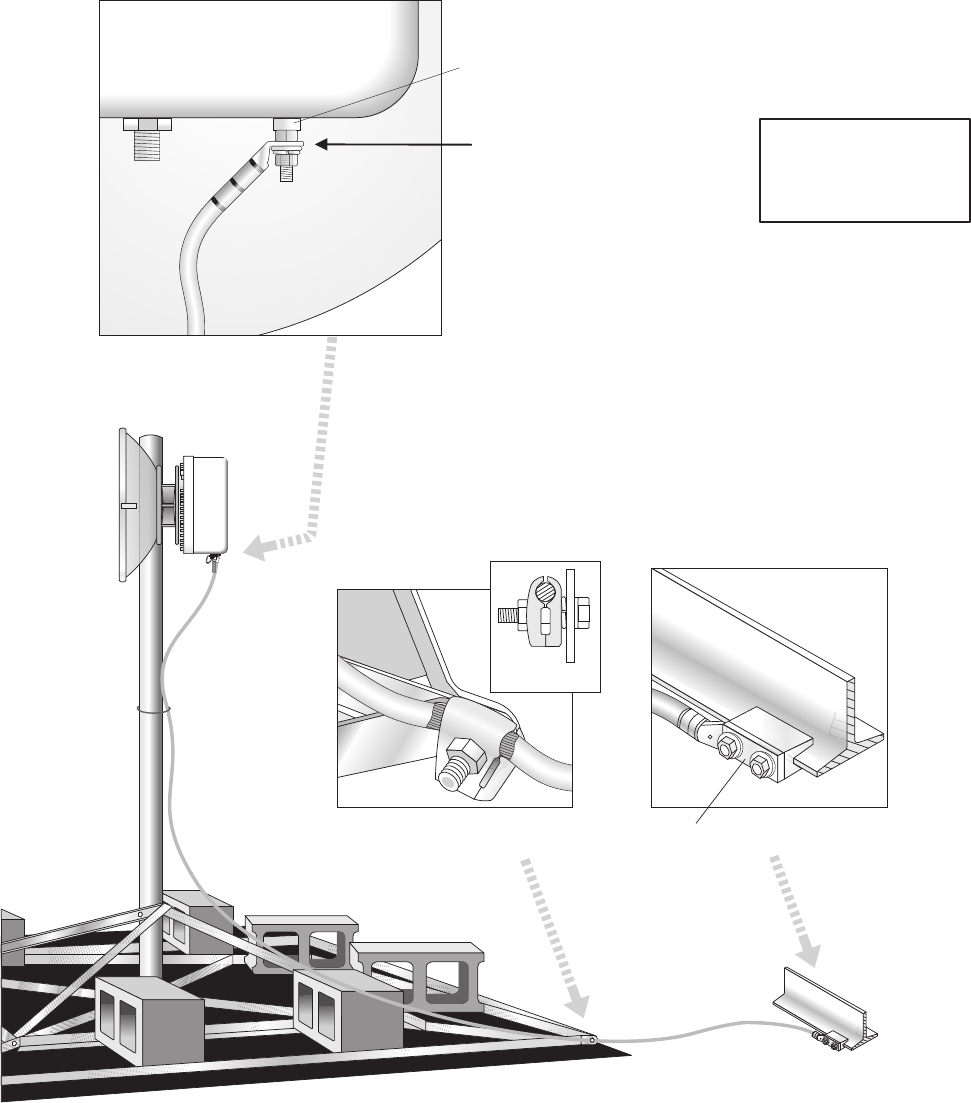
1027144–0001 Draft – Revision D.01 6–24 Installing ODUs RT installation
rt012
Transceiver
Antenna
Ground
point
Ground
cable
2-hole compression lug
(Shown: Bond to structural steel)
Ground point
on roof
3.
ODU
side view
Apply anti-oxidant
and heat shrink to
all ground lugs.
End view
Clamp-type ground connector.
Strip cable at clamp.
Bolted joint on
mast mount
2.
Single-hole
compression lug
ODU ground connector
1.
IFL
connector
Ground cable
No. 6 AWG
or greater
View from rear
Transceiver
Figure 6-21 ODU grounding connections
Graphic to be
updated.
Lightning protection is provided by grounding the ODU as stated
above and installing a lightning arrestor where the IFL cable
enters the roof (as explained in section 4.9). The ODU ground
and IFL lightning arrestor must both be bonded to the same
ground (reference) point.
Lightning protection
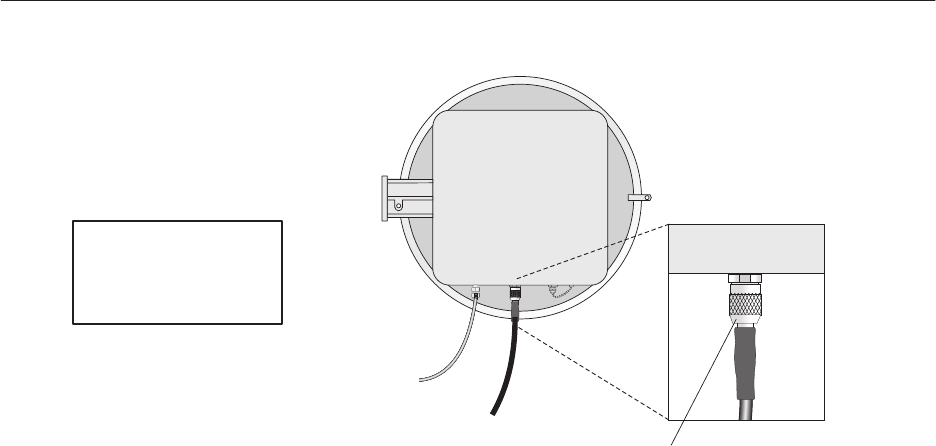
1027144–0001 Draft – Revision D.01 Installing ODUs 6–25
RT installation
Connect the IFL to the ODU as shown in figure 6-22.
Figure 6-22 Connecting the IFL to the ODU
IFL
Ground
wire
N connector
rt058
Graphic to be
updated.
Do not apply weatherproofing compound or tape until the RT
has been tested and commissioned. Weatherproofing is
covered in section 8.1.
6.13
Connecting the IFL
to the ODU
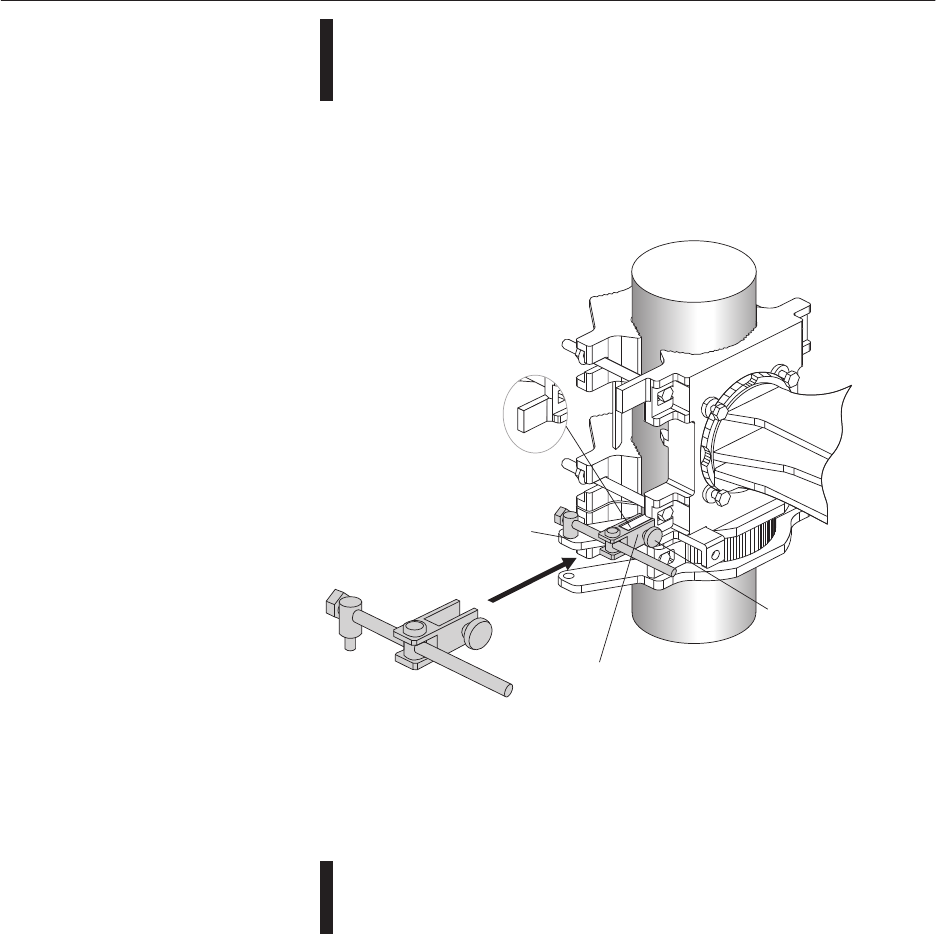
1027144–0001 Draft – Revision D.01 6–26 Installing ODUs RT installation
Now that the transceiver and cables are attached to the ODU,
adjust the antenna azimuth more precisely, as follows:
1. Install the azimuth adjuster as shown in figure 6-23.
The azimuth/elevation adjusters are identical. Use either
one as the azimuth adjuster or elevation adjuster. Two
adjusters are provided for installation convenience. The part
number for one adjuster is HNS 1024668–0023.
Figure 6-23 Installing the first adjuster, for azimuth adjustment
Install adjuster in
horizontal position for
azimuth adjustment.
hb038
Antenna
mount
Insert peg
into hole.
1.
Finger tighten
thumbscrew.
3.
Place clamp on rectangular arm.
(Arm detail is shown above.To move
clamp, turn adjuster bolt.)
Arm must be fully inserted into clamp.
2.
Arm
Adjuster
bolt
Note: Do not remove the adjusters until the antenna is
accurately pointed (after electronic pointing using the
voltmeter).
6.14
Finer antenna
azimuth adjustment
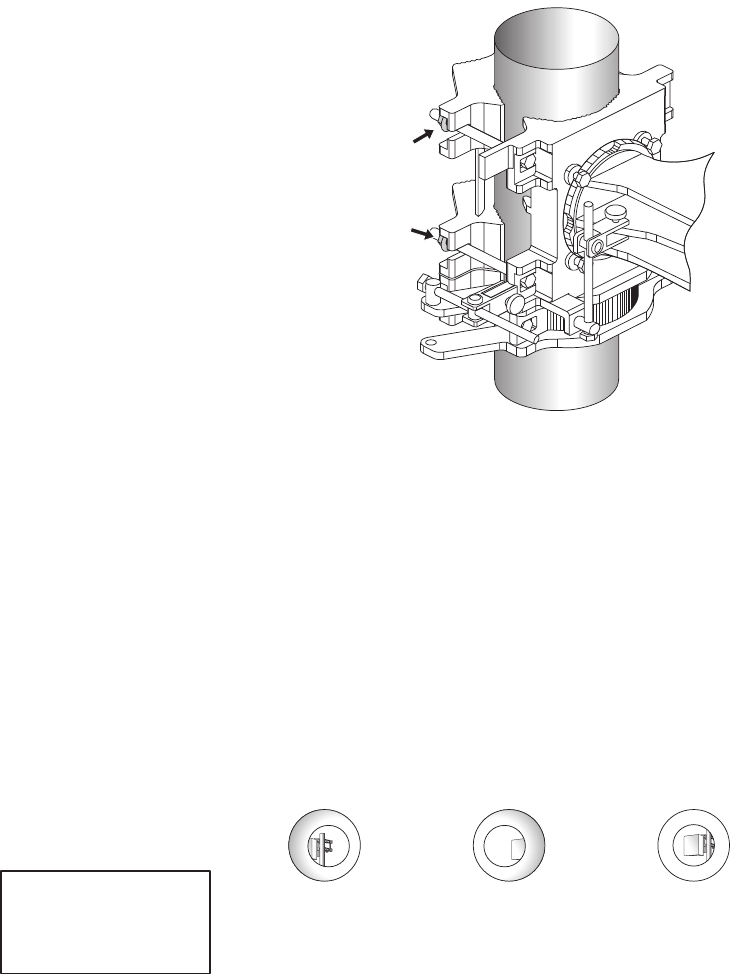
1027144–0001 Draft – Revision D.01 Installing ODUs 6–27
RT installation
2. Using a torque wrench with a deep socket, verify that
the torque of the four mast clamp nuts is 20 foot–pounds
(27.1 Newton–meters).
Figure 6-24 Tightening the mast clamp nuts
hb070
4 mast clamp nuts:
20 foot-pounds
(27.1 Newton-meters)
3. Loosen each nut by one full rotation.
(The mount stays in position, but will move when you turn
the azimuth adjuster with a wrench.)
4. Using a wrench, rotate the adjuster bolt on the azimuth
adjuster until the antenna azimuth is properly aligned.
Azimuth is properly adjusted when you can see the HT in
the boresight with no shadow inside the boresight to the left
or right. See figure 6-25.
Figure 6-25 Using the boresight to adjust azimuth
rt028
Adjust
azimuth
to left.
Adjust
azimuth
to right.
Pointed
Boresight
Graphic to be
updated.
5. When the azimuth is properly adjusted, tighten the mast
clamp nuts to 20 foot–pounds torque (27.1
Newton–meters).
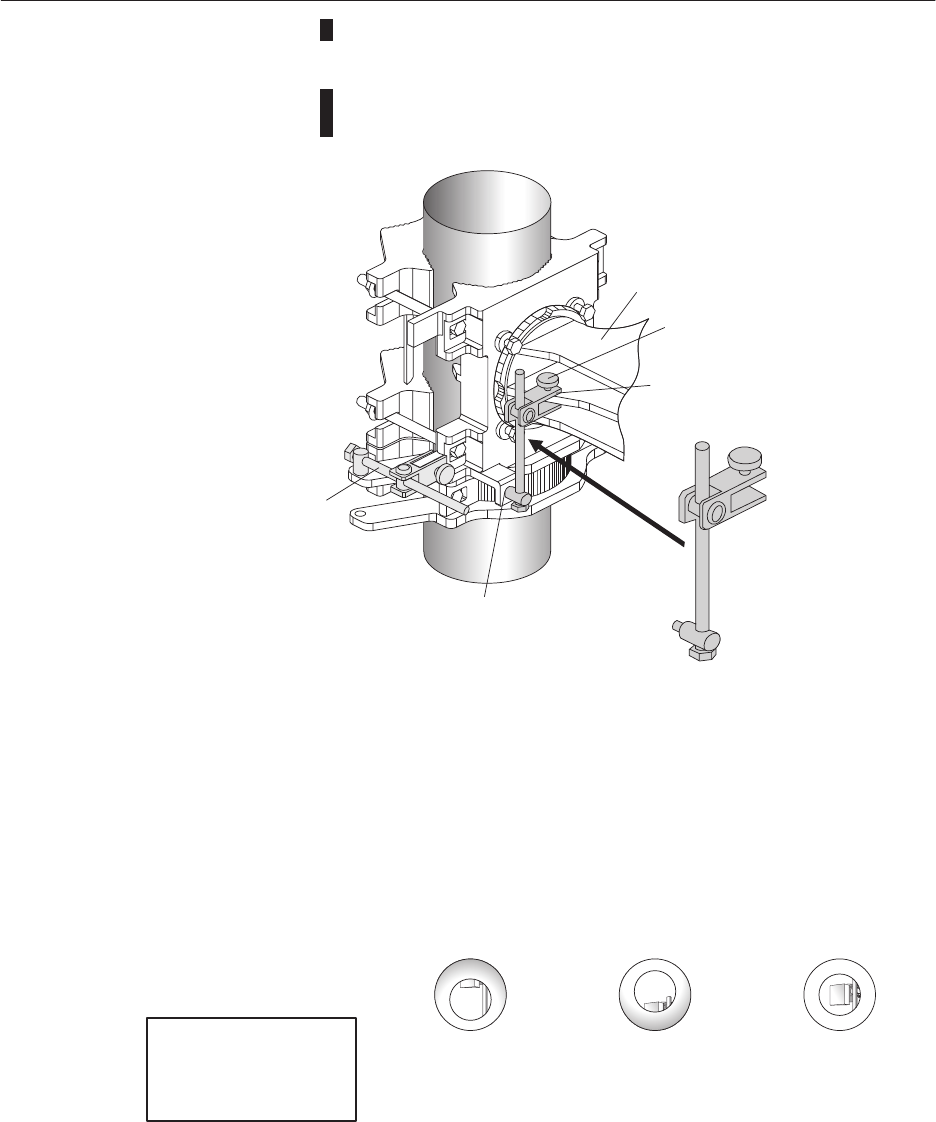
1027144–0001 Draft – Revision D.01 6–28 Installing ODUs RT installation
Adjust the antenna elevation more precisely, as follows:
1. Install the second azimuth/elevation adjuster as shown in
figure 6-26.
Figure 6-26 Installing the second adjuster, for elevation adjustment
hb039
Antenna bracket
Finger tighten
thumbscrew.
3.
Place clamp on antenna bracket.
(To move clamp, turn adjuster bolt.)
2.
Install the second
adjuster in vertical
position for elevation
adjustment.
Insert peg
into hole.
1.
Previously installed
adjusterazimuth
Adjuster
bolt
2. Using a wrench, rotate the adjuster bolt until the proper
elevation alignment is achieved.
Elevation is properly adjusted when you can see the HT in
the boresight with no shadow inside the top or bottom of the
boresight. See figure 6-25.
Figure 6-27 Using the boresight to adjust elevation
rt029
Adjust
elevation
upward.
Adjust
elevation
downward.
Pointed
Boresight
Graphic to be
updated.
3. When the elevation is properly adjusted, tighten the
antenna bracket locking nuts to 16 foot–pounds torque
(21.7 Newton–meters).
6.15
Finer antenna
elevation
adjustment
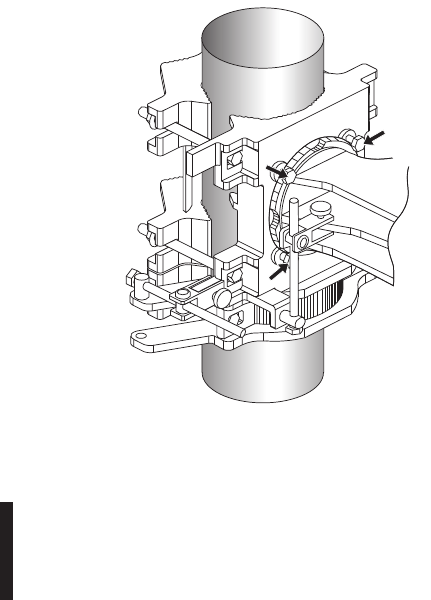
1027144–0001 Draft – Revision D.01 Installing ODUs 6–29
RT installation
Figure 6-28 Tightening the antenna bracket nuts
hb071
4 antenna bracket nuts:
16 foot-pounds
(21.7 Newton-meters)
At this point, antenna installation is complete, and the antenna is
visually pointed. Later, when you commission the RT, you will use
a voltmeter to electronically point the antenna as accurately as
possible.
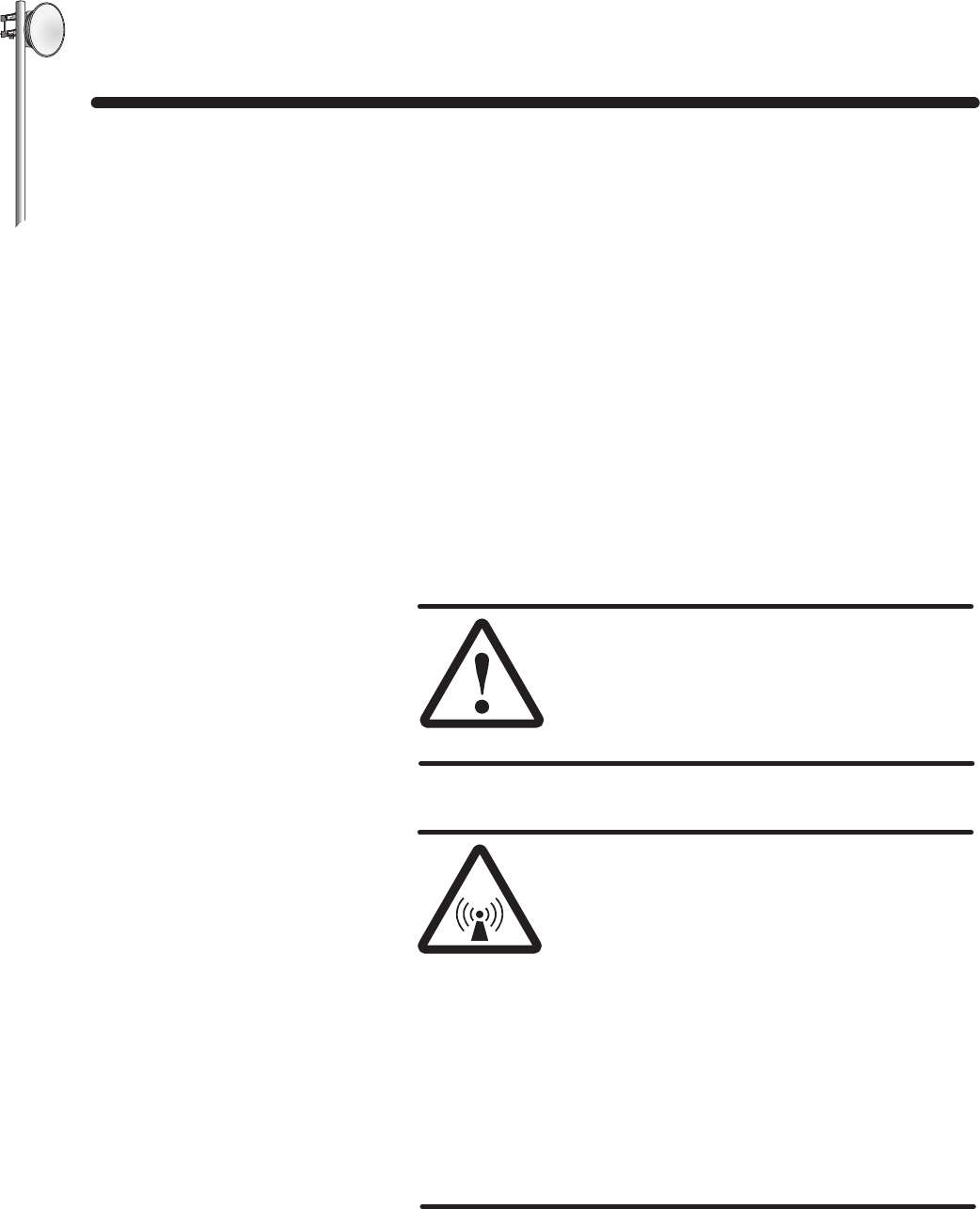
RT INSTALLATION
1027144–0001 Draft – Revision D.01 Commissioning the RT 7–1
RT installation
Chapter 7
Commissioning the RT
This chapter includes:
•Prerequisites for commissioning – page 7–2
•Connecting the IFL to the CCM – page 7–3
•Front panel LCD operation – page 7–4
•Pointing the antenna – page 7–8
•Removing the installation tools – page 7–13
•Verifying HT acquisition – page 7–14
•Checking component status – page 7–14
•RT to HT connection tests – page 7–19
Commissioning refers to verification procedures to ensure that the
newly installed RT is operational.
Note: Each RT must be commissioned separately.
Observe these safety warnings while commissioning RTs:
DANGER
Do not work on a ladder or roof without
first reading the safety warnings on page x
of this manual. Failure to observe these
warnings could result in personal injury or
death.
WARNING
Potential radio frequency (RF) hazard:
•Keep away from the front of the
outdoor unit (ODU) antenna while the
ODU is operating. Note that you cannot
tell from outward appearance whether
the ODU is operating or not.
•Be careful with respect to the ODU you
are installing and ODUs that may
already be operating in the installation
area.
Failure to observe these warnings could
result in injury to eyes or other personal
injury.
Safety warnings
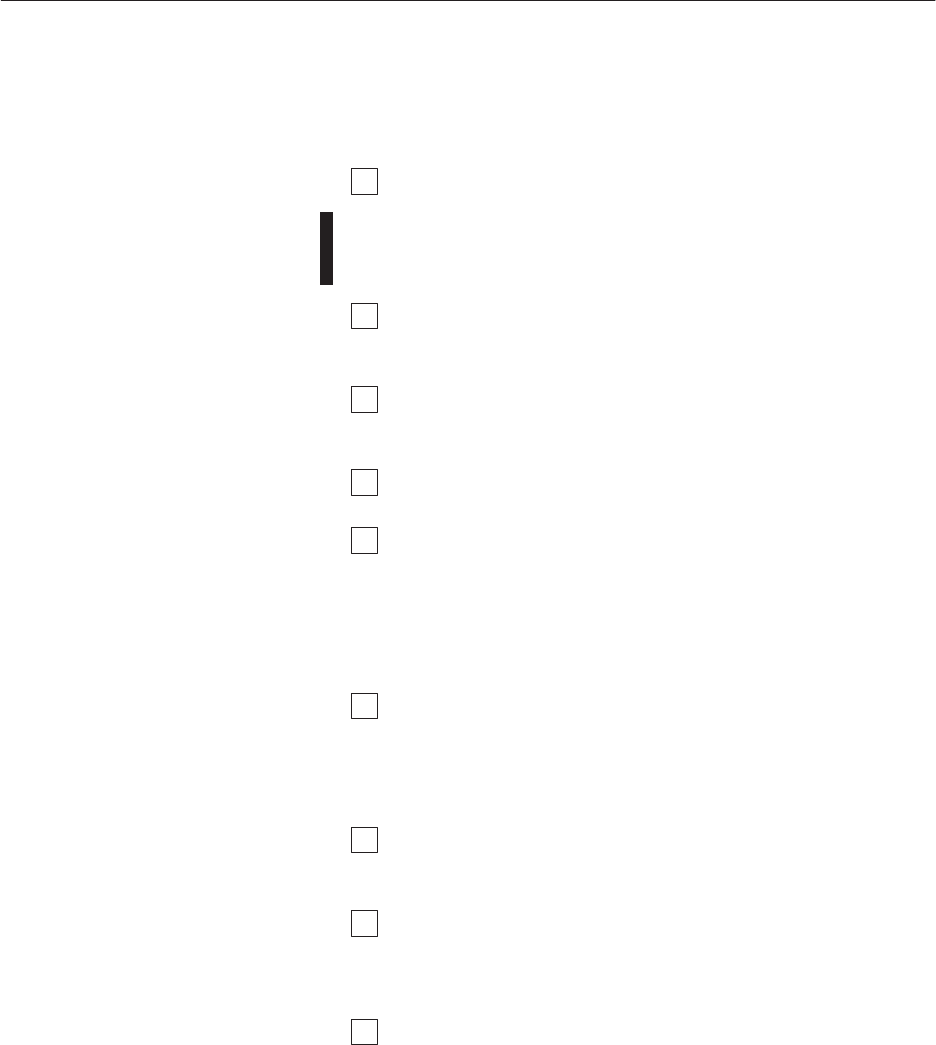
1027144–0001 Draft – Revision D.01 7–2 Commissioning the RT RT installation
To ensure successful commissioning, you must verify that the
prerequisites listed below have been accomplished. These tasks
must all be completed prior to commissioning. If any of them has
not been done, make sure they are completed before you proceed
with commissioning.
The RT ODU, IFL, and IDU must be installed and connected.
If you have followed all previous instructions, this
prerequisite is satisfied when you connect the IFL to the
CCM (IDU), as instructed on page 7–4.
The Element Management System (EMS) hardware and
software must be installed and operational.
All physical LAN connections between the RT and EMS
must be completed.
The EMS database must be loaded and operational.
The EMS operator has entered the RT electronic serial
number (ESN) into the EMS database.
The RT ESN is printed on a tag attached to the CCM and can
also be read from the CCM LCD—from the Main Menu ESN
display.
The installer must know the (RT) ODU frequency to be used
and the identification number of the HT the RT will
communicate with. These are provided by network planning
personnel.
The hub and HT must be installed and operational. The HT
must be properly aligned.
CCM must be installed in the IDU as specified in the
configuration documents. (SSIs are not required for
commissioning.)
The RT cannot be located closer than 109 yards (100 meters)
from the HT.
7.1
Prerequisites for
commissioning
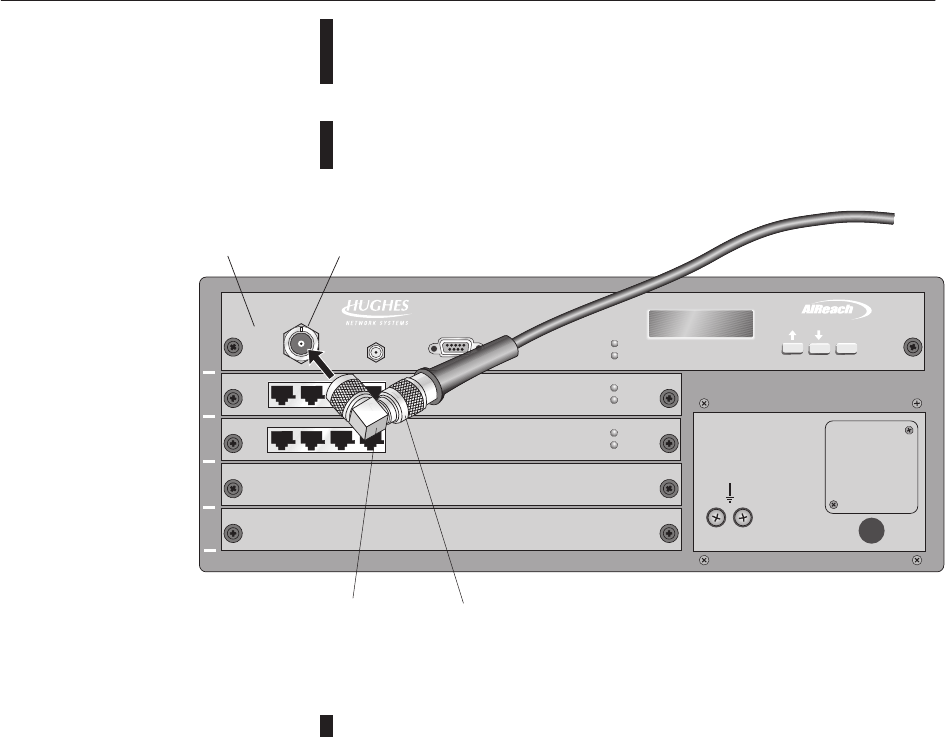
1027144–0001 Draft – Revision D.01 Commissioning the RT 7–3
RT installation
Connect the IFL cable to the CCM (IDU):
1. Go to the IDU location.
2. Make sure power to the IDU is off (or disconnected).
3. Using a 90° adapter, connect the IFL (N connector) to the
CCM IFL interface, as shown in figure 7-1.
Figure 7-1 Connecting the IFL cable
1
2
3
4
5
TM
BROADBAND
ENTER
RT CCM
rt043
CCM
IDU
IFL
interface
IFL
N connector
90 adapter°
4. Power on the IDU.
7.2
Connecting the IFL
to the CCM (IDU)
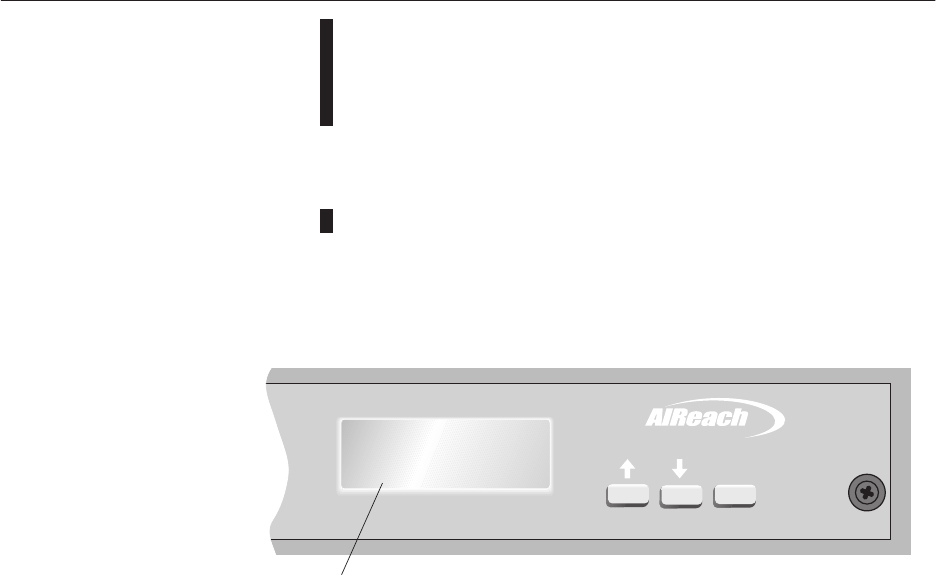
1027144–0001 Draft – Revision D.01 7–4 Commissioning the RT RT installation
This section describes how to use the LCD and buttons on the
CCM front panel (figure 7-2). You need to use the LCD to
commission the RT.
The LCD:
•Shows CCM startup diagnostics (SUDS) tests as they occur
•Shows the system boot up sequence
•Shows the software loading sequence
•Indicates the status and operational state of system
components
•Provides functions necessary for commissioning the RT
Figure 7-2 CCM front panel LCD
rt060
LCD
TM
BROADBAND
ENTER
Main Menu
Install
7.3
Front panel LCD
operation
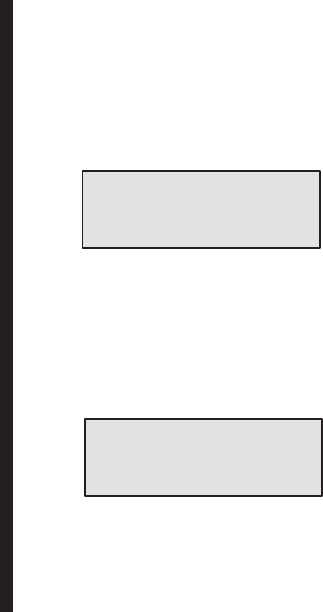
1027144–0001 Draft – Revision D.01 Commissioning the RT 7–5
RT installation
When the CCM/ IDU is powered up or reset:
•SUDS run automatically.
•When SUDS are completed, the CCM LCD displays a
SUDS Completed message.
•The LCD then displays:
Initializing
Press Enter for Menu
To access the CCM LCD Main Menu, press the ENTER button on
the CCM front panel while the Initializing screen is displayed.
This puts the IDU into diagnostic mode. The LCD shows the Main
Menu:
Main Menu
Status
Note: After the CCM downloads its software and is operational
(when it displays RT Enabled), you can access the Main Menu by
pressing Enter.
Accessing the LCD
Main Menu
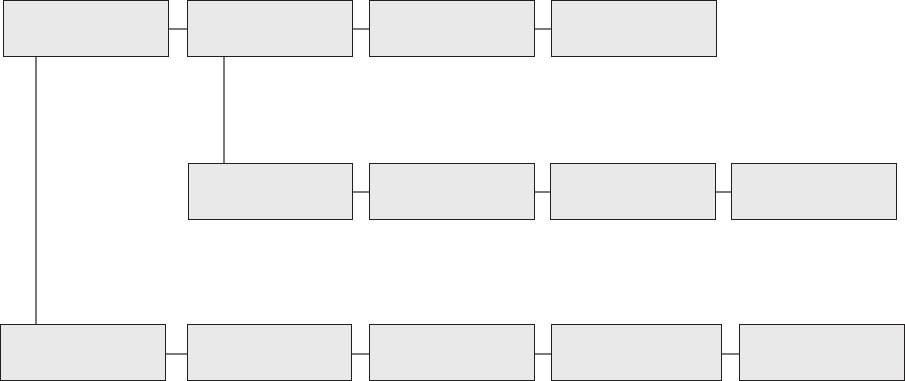
1027144–0001 Draft – Revision D.01 7–6 Commissioning the RT RT installation
The menu map (figure 7-3) shows the available menu options for
RTs.
Note: Menu options are not the same for RTs and HTs.
Figure 7-3 LCD menu map for RT CCM
Main Menu
Install Main Menu
Status Main Menu
ESN Main Menu
Exit
T0009006
Status menu
Install menu
Install
Freq Install
Mech Attn Install
ODU Cable Install
Restart Freq Acq Install
Exit
Exits to
Main Menu
Status
CCM Status
ODU
Status
SSI n
SSI 1 - SSI 4
Status
Exit
Exits to
Main Menu
Note: You will not see ODU status information when the ODU is
not connected (via the IFL) to the IDU. (The status will be
Unknown.)
LCD menu map
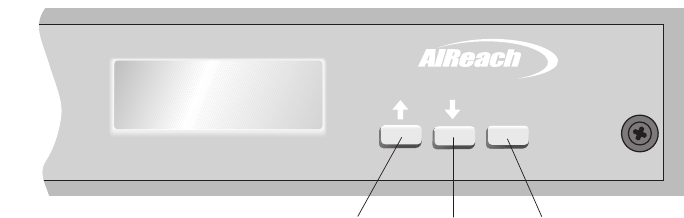
1027144–0001 Draft – Revision D.01 Commissioning the RT 7–7
RT installation
The CCM button functions are explained in figure 7-4:
Figure 7-4 CCM front panel button functions
hb107
Scroll to
next menu
option
Scroll to
previous
menu option
Select
(Selects currently
displayed option
or menu)
TM
BROADBAND
ENTER
Main Menu
Status
Exit options
If you select Exit from the Main Menu . . .
. . . while the system is operating, it remains in
operational mode.
. . . when the system is not in operational mode, the
CCM reboots.
If you select Exit from the Status or Install menu, the display
returns to the Main Menu.
CCM button functions
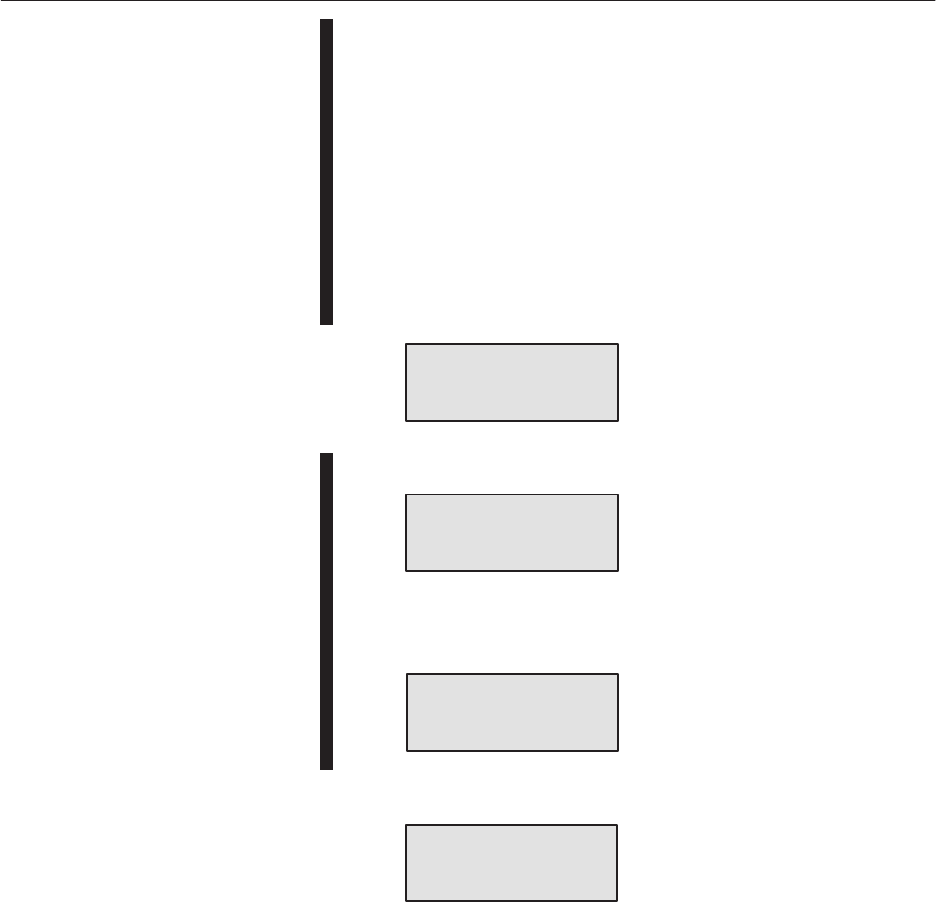
1027144–0001 Draft – Revision D.01 7–8 Commissioning the RT RT installation
Following the RT antenna installation instructions in chapter 6,
you pointed the antenna approximately toward the HT, using the
boresight. This section explains how you more accurately point
the RT antenna, using a digital voltmeter.
To point the antenna, follow steps 1 through 13 below.
Before you can point the antenna using the voltmeter, you must
first put the IDU into Install mode and select the (RT) ODU
frequency, as follows:
1. From the IDU (CCM) LCD main menu, select Install mode,
and press the Enter button.
Main Menu
Install
The LCD displays:
Install
RT at HT
2. Press Enter, select No, and press Enter again.
3. Select Frequency (frequency function) and press Enter.
Install
Frequency
4. The LCD displays Freq and a frequency value:
Freq
8B4
The frequencies displayed on the bottom line are preset,
based on the installed ODU. The correct RT frequency is
the same as the HT frequency, except “B” (indicating
remote), as in 8B4, replaces “A”.
7.4
Pointing the
antenna
Selecting the ODU
frequency
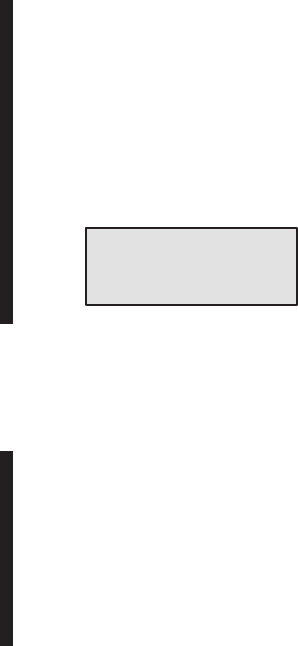
1027144–0001 Draft – Revision D.01 Commissioning the RT 7–9
RT installation
5. Scroll to the correct ODU frequency. Scroll up (up arrow)
for a higher frequency; scroll down (down arrow) for a
lower frequency.
Important: If you do not see the correct frequency on the
LCD, you may have installed the wrong ODU for the site
(high band instead of low band, or vice versa). In this case,
the LCD will not display the correct frequency as one of the
available choices. If the wrong ODU is installed, you will
not be able to proceed until the correct ODU is installed.
6. Press Enter when the LCD shows the correct frequency, for
example:
Freq Set
8B4
The LCD shows Freq Acq in Prog (frequency acquisition
in progress) and then Acq Ack: HT 2 (acquisition
acknowledged—in this example, frequency acquired from
HT 2).
Note: The LCD will display Acq Denied (acquisition
denied) if:
•The RT’s ESN has not been entered in the EMS
database, or
•The RT is pointed toward the wrong HT.
Go to the roof and proceed with steps 7 through 13.
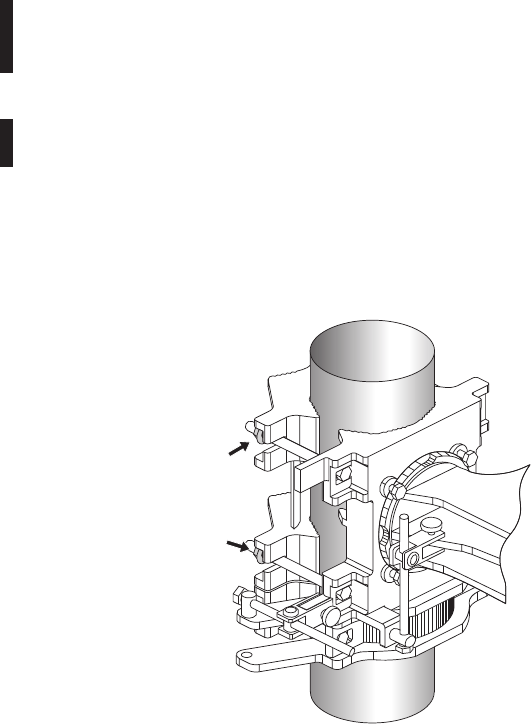
1027144–0001 Draft – Revision D.01 7–10 Commissioning the RT RT installation
Follow these steps to fine–tune the azimuth and elevation
adjustments made when the antenna was installed (sections 6.7
and 6.8).
7. Take the digital voltmeter and torque wrench (with deep
socket) to the ODU.
8. Using a torque wrench with a deep socket, verify that
the torque of the four mast clamp nuts on the antenna
mount is 20 foot–pounds (27.1 Newton–meters). See
figure 7-5.
Figure 7-5 Verifying torque of the mast clamp nuts
hb070
4 mast clamp nuts:
20 foot-pounds
(27.1 Newton-meters)
9. Loosen each nut by one full rotation.
(The mount stays in position, but will move when you turn
the azimuth adjuster with a wrench.)
Voltmeter pointing and
final adjustments
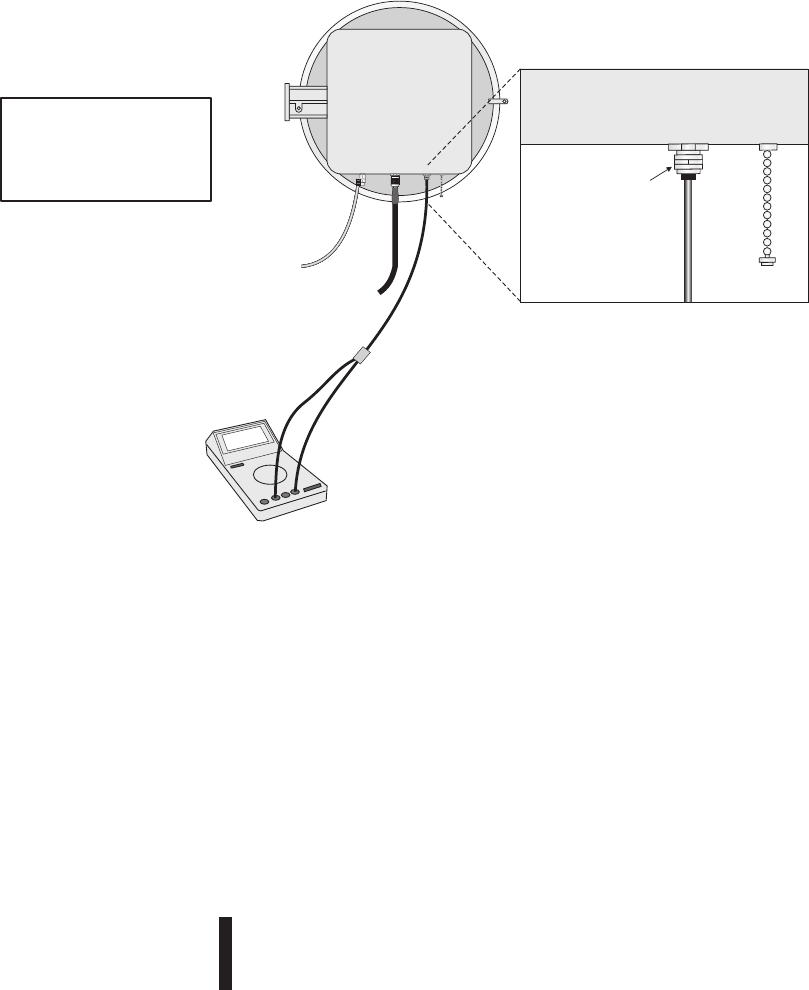
1027144–0001 Draft – Revision D.01 Commissioning the RT 7–11
RT installation
10. Connect a digital voltmeter to the F connector on the ODU,
as shown in figure 7-6, and select the 0 to 10 volt or 0 to 5
volt range.
Figure 7-6 Connecting the digital voltmeter to the ODU
Digital
voltmeter
Voltmeter connections
IFL
Ground wire
Use F connector to
connect cable to
pointing port.
Cap
rt057
BNC connector with
banana plug
Graphic to be
updated.
11. Observe the reading on the voltmeter.
12. Use a wrench to rotate the adjuster bolt on the azimuth
adjuster to slowly adjust the antenna azimuth.
Stop turning the adjuster bolt when you obtain a steady,
peak reading between 0.2 volts and 3.9 volts.
13. When the voltage reading remains steady between 0.2
volts and 3.9 volts, tighten the mast clamp nuts (shown
in figure 7-5) to 20 foot–pounds (27.1 Newton–meters)
torque.
If you cannot obtain a voltmeter reading between 0.2 volts
and 3.9 volts, refer to table 7-1 for the appropriate
corrective action.
Final antenna
tightening
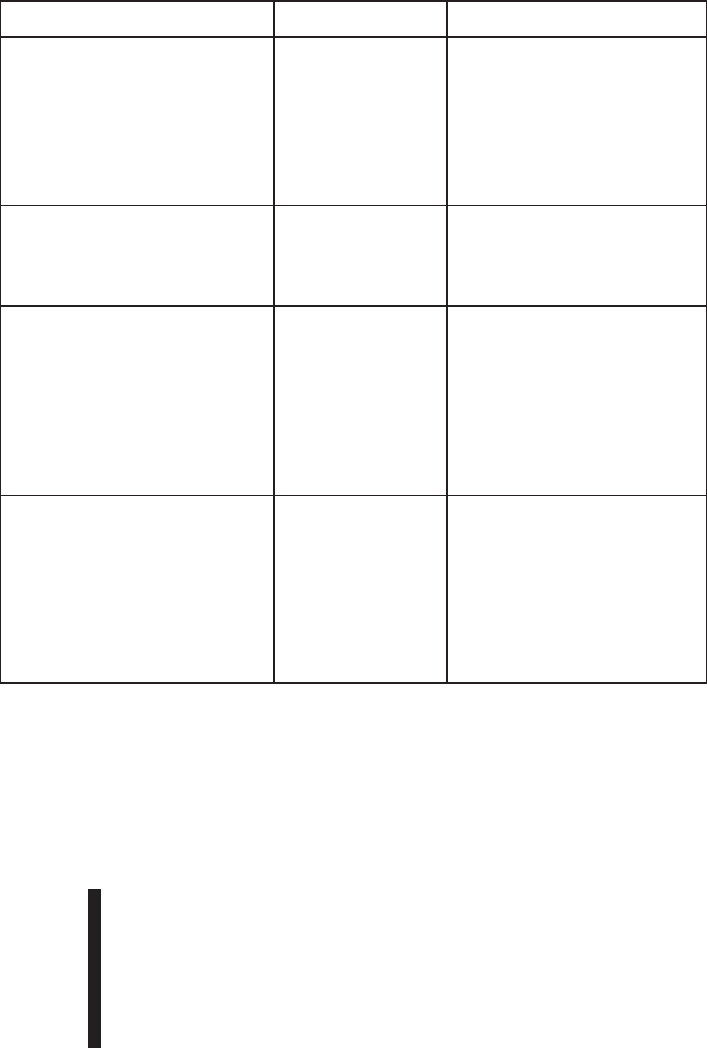
1027144–0001 Draft – Revision D.01 7–12 Commissioning the RT RT installation
Table 7-1 Voltage indications for RT antenna pointing
Voltmeter reading Indication Corrective action
Current voltage level with
oscillation up to 4.1 V
. (The
reading intermittently peaks
at the current voltage level
for 2 seconds and then
rises to 4.1 V for 1 second.)
HT not acquired HT acquisition has not
occurred. Continue
pointing the antenna.
0.2 V to 3.9 V with no
oscillation Correct HT
acquired (Corrective action is not
required.) Continue with
the installation.
3.9 V to 4.1 V with no
oscillation Correct HT
acquired HT acquisition has
occurred but you must
install a mechanical
attenuator before
continuing with the
installation, refer to
section 6.10.
Current voltage level with
oscillation to 0 V.
(The
reading intermittently peaks
at the current voltage level
for 2 seconds and then
drops to 0 V for 1 second.)
Wrong HT
acquired RT has been denied
acquisition by the wrong
HT. You must follow the
procedures listed in
Repointing the RT
antenna
below before
proceeding.
Follow the steps below to repoint the RT antenna only if the ODU
has acquired the wrong HT.
(If you successfully pointed the antenna in step 13—with a steady
voltmeter reading between 0.2 volts and 3.9 volts—you do not
need to follow steps 1 and 2 below; go on to section 7.5.)
1. Repeat steps 7 through 13 (voltmeter pointing and final
adjustments).
2. If you cannot obtain the correct voltmeter readings because
the antenna is grossly mispointed, you may have to repeat
the azimuth and elevation procedures explained in sections
6.7 and 6.8 (respectively).
If you encounter problems in pointing the antenna that are not
addressed above, refer to chapter 9. See the chart titled
Troubleshooting: RT antenna pointing.
Repointing the
RT antenna
Troubleshooting
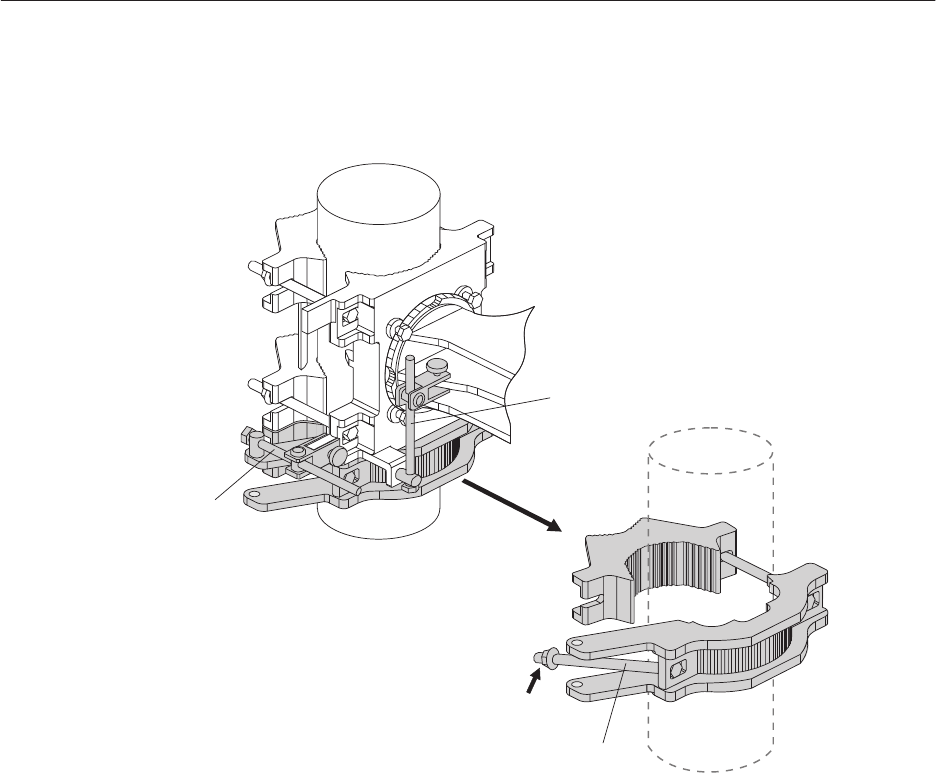
1027144–0001 Draft – Revision D.01 Commissioning the RT 7–13
RT installation
When the antenna is pointed correctly, remove the temporary
collar, clamp, and adjusters (shaded parts in figure 7-7) and retain
these tools for future installations.
Figure 7-7 Removing the temporary collar, clamp, and adjusters
hb057
Azimuth
adjuster
Elevation
adjuster
Remove all shaded parts.
Temporary
installation
collar
Loosen this nut
to remove collar.
Bolt
7.5
Removing the
installation tools
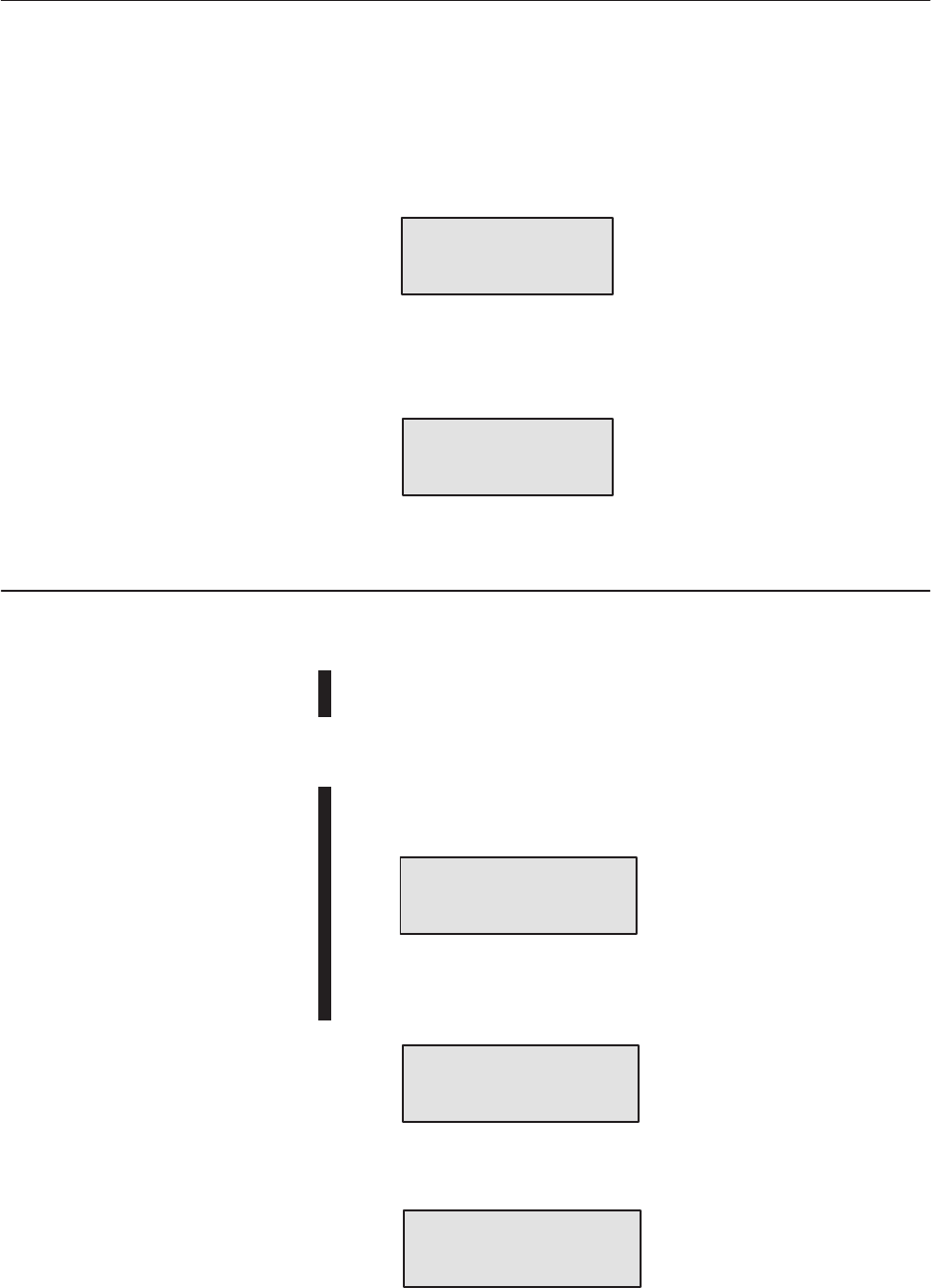
1027144–0001 Draft – Revision D.01 7–14 Commissioning the RT RT installation
Return to the IDU location to verify that the RT has acquired the
RT and then take the IDU out of Install mode:
1. Observe the LCD on the CCM to verify that the HT has
been successfully acquired.
The following display indicates that the RT has successfully
acquired the HT.
Install HT nnn
Acq Ack nnn = HT ID
2. Use the buttons and LCD on the CCM to select Exit and
press the Enter button to take the IDU out of Install mode.
Install
Exit
Use the LCD Status option to check the status of the CCM, SSIs,
and ODU:
(You can only perform these checks after the RT’s ODU frequency
has been selected, as explained in section 7.4.)
Check the CCM status as follows:
1. Press Enter on the CCM front panel while the Initializing
screen shown below is displayed:
Initializing
Press Enter for Menu
(This screen is displayed
only after powerup or
reset, after SUDS.)
This puts the IDU into diagnostic mode. The LCD shows
the Main Menu:
Main Menu
Install
2. Use the up arrow to scroll to Main Menu / Status:
Main Menu
Status
7.6
Verifying HT
acquisition
7.7
Checking
component status
Check CCM status
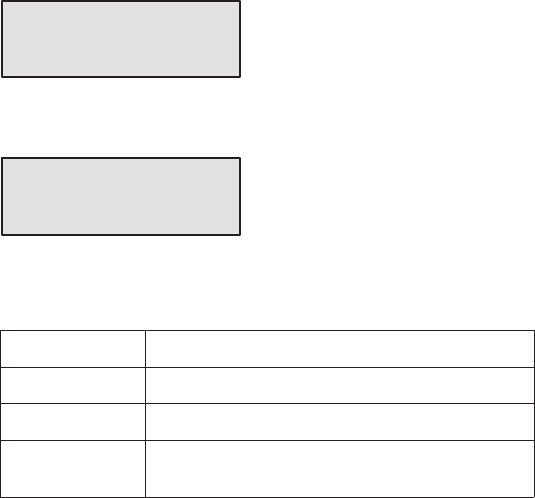
1027144–0001 Draft – Revision D.01 Commissioning the RT 7–15
RT installation
3. Press Enter, to go to (select) the Status menu:
Status
CCM
4. Press Enter to show the CCM status:
CCM
OK
The possible status conditions for CCMs, SSIs, and the
ODU are:
OK The component is operational.
Degraded The component is not fully operational.*
Failed The component has failed.
Unknown The CCM cannot communicate with the
component.
Action for “Failed” or “Degraded”status
If the LCD shows Failed for any component, replace the
component.
If you see Degraded during installation, replace the
component. However, if you see Degraded while the
system is operation, under some circumstances you may not
need to replace the component (for example, if a failed port
is not needed).
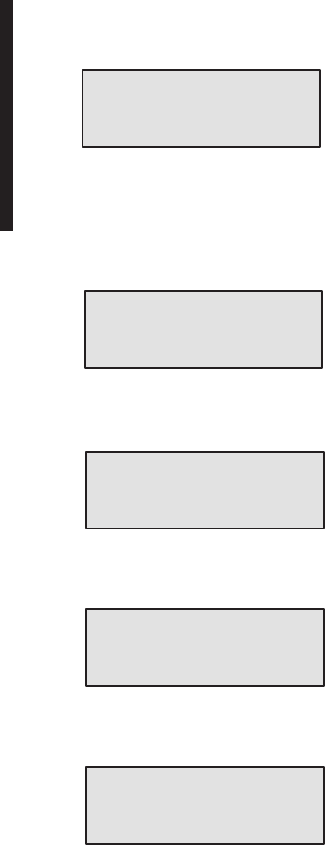
1027144–0001 Draft – Revision D.01 7–16 Commissioning the RT RT installation
Check the status of the installed SSIs as follows:
(Note that SSIs are not required for commissioning. They can be
installed after RT commissioning.)
1. Press Enter on the CCM front panel while the Initializing
screen shown below is displayed:
Initializing
Press Enter for Menu
(This screen is displayed
only after powerup or
reset, after SUDS.)
This puts the IDU into diagnostic mode. The LCD shows
the Main Menu:
The LCD shows:
Main Menu
Install
2. Use the up arrow to scroll to Main Menu / Status:
Main Menu
Status
3. Press Enter, to go to (select) the Status menu:
Status
CCM
4. Press the up arrow button to scroll to the SSI status menu:
Status
SSI 2
Check SSI status
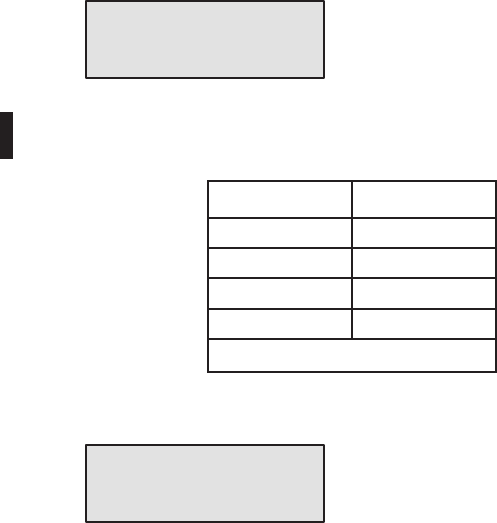
1027144–0001 Draft – Revision D.01 Commissioning the RT 7–17
RT installation
5. Use the arrow button(s) to scroll to the SSI you want to
check:
Status
SSI 3
Note: SSIs are numbered SSI 1 through SSI 4, according to
their positions in the IDU chassis:
Chassis slot SSI number
2 1
3 2
4 3
5 4
Slot 1 is occupied by the CCM.
6. Press Enter to show the status of the selected SSI:
SSI 3
OK
The possible status conditions for CCMs, SSIs, and the
ODU are:
OK
Degraded
Failed
Unknown
(as explained on page 7–15)
Check the status of each installed SSI.

1027144–0001 Draft – Revision D.01 7–18 Commissioning the RT RT installation
Check the status of the ODU as follows:
1. Press Enter on the CCM front panel. (The CCM must be in
operational mode, as indicated by RT Enabled on the
LCD.)
The LCD shows:
Main Menu
Install
2. Use the up arrow to scroll to Main Menu / Status:
Main Menu
Status
3. Press Enter, to go to (select) the Status menu:
Status
CCM
4. Press the up arrow button twice to scroll to the ODU status
option:
Status
ODU
5. Press Enter to show the ODU status:
ODU
OK
The possible status conditions for CCMs, SSIs, and the
ODU are:
OK
Degraded
Failed
Unknown
(as explained on page 7–15)
To exit the Status menu, scroll to Exit, and then press Enter.
If a failure is indicated for any component, replace that
component. Run SUDS again, and check the status of the new
component.
Check ODU status
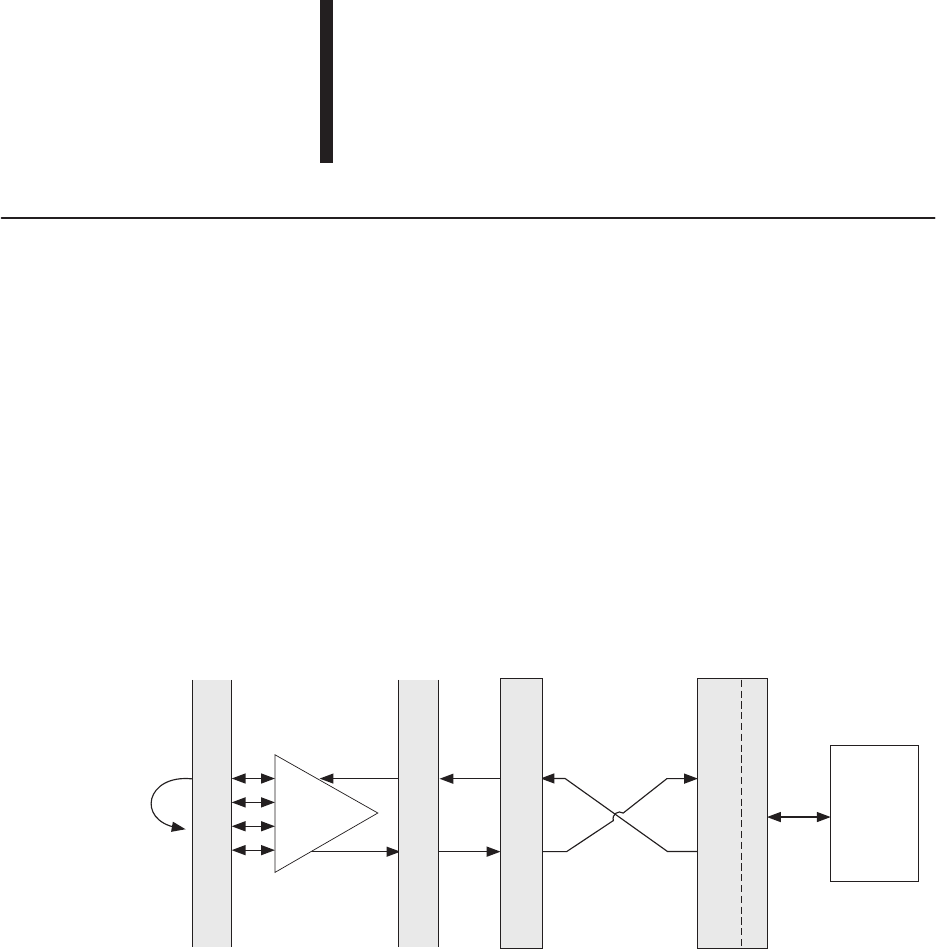
1027144–0001 Draft – Revision D.01 Commissioning the RT 7–19
RT installation
At this point, RT commissioning is complete, except for the RT to
HT tests described in section 7.8. You may or may not be able to
complete these tests, depending on whether or not other network
components are installed and operational. (See the test
requirements listed in section 7.8.)
Leave the RT powered on for testing and operation.
Perform the applicable tests described below if the newly installed
RT meets the listed requirements. If the RT/network does not yet
meet these requirements, perform the tests at a later time.
This test verifies the DS1 connection from the RT to the HT.
Requirements
The DS1 test described below requires the following:
•The RT must be fully installed, commissioned, and in
contact with the EMS through the hub.
•The HT must be operational and in contact with the EMS.
•DS1 services must be configured and provisioned.
•There must be no alarms present at the RT location.
•A loopback connector must be connected to the input/out
port of the patch panel, as illustrated in figure 7-8.
Figure 7-8 RT to HT connection test setup
DS3
mux
Bit error
rate test
set
P
a
t
c
h
p
a
n
e
l
HT RT
P
a
t
c
h
p
a
n
e
l
Hub site
Customer premises
Loopback
connector
QRSS (2E20-1
pseudo-random)
test pattern
DS1
DS3 DS3
DS1
Over the air
interface
T0009007
Test procedure
1. Connect a DS1 test set to the out/input points at DS1 RJ–48
port on the SSI board.
2. Select:
- QRSS (quasi random signal source) test pattern
- Recovered clock
- DS1 interface
3. Run the test for 1 hour.
7.8
RT to HT connection
tests
DS1 test
1027144–0001 Draft – Revision D.01 7–20 Commissioning the RT RT installation
Results
The RT passes if there are no errors and no clock or frame slips
during the test.
Record the results on the form on the following page (or make a
photocopy).
RT to HT DS1 test results
RT location: ____________________________________________
Test successful? ___ Yes ___ No RSSI __________
If not successful, complete:
Bit error rate _______________ Frame slips _______________
Frame errors _______________ Clock slips ________________
Trouble report generated? ___ Yes ___ No
If yes, report number: ____________________
If applicable: Faulty module part number ______________________
Serial number _____________________
If applicable: Replacement board part number __________________
Serial number______________________
BER test printout attached? ___ Yes ___ No
Comments:
_________________________________________________________________________________
_________________________________________________________________________________
Tested by (print name and sign): _______________________________________________________
Customer (print name and sign): ________________________________________________________
Date __________________________
1027144–0001 Draft – Revision D.01 Commissioning the RT 7–21
RT installation
This test verifies the DS3 connection from the RT to the HT.
Requirements
The DS3 test described below requires the following:
•The RT must be fully installed, commissioned, and in
contact with the EMS through the hub.
•The HT must be operational and in contact with the EMS.
•DS3 services must be configured and provisioned.
•There must be no alarms present at the RT location.
•A loopback connector must be connected to the input/out
port at the patch panel nearest to the HT. (Figure 7-8
indicates a loopback connector but also shows the patch
panel nearest to the HT.)
Test procedure
1. Connect a DS1 test set to the out/input connector on the
Universal SSI board.
2. Select:
- Correct coding
- Correct framing
- Recovered clock
- DS1 interface
The configured DS0 may be dropped from the DS1 data
stream and tested using QRSS test patten.
3. Run the test for 1 hour.
Results
The RT passes if there are no errors and no clock or frame slips
during the test.
Record the results on the form on the following page (or make a
photocopy).
DS3 test
1027144–0001 Draft – Revision D.01 7–22 Commissioning the RT RT installation
RT to HT DS3 test results
RT location: ____________________________________________
Number of configured DS0: ________________________________
Test successful? ___ Yes ___ No RSSI __________
If not successful, complete:
Bit error rate _______________ Frame slips _______________
Frame errors _______________ Clock slips ________________
Trouble report generated? ___ Yes ___ No
If yes, report number: ____________________
If applicable: Faulty module part number ______________________
Serial number _____________________
If applicable: Replacement board part number __________________
Serial number______________________
BER test printout attached? ___ Yes ___ No
Comments:
_________________________________________________________________________________
_________________________________________________________________________________
Tested by (print name and sign): _______________________________________________________
Customer (print name and sign): ________________________________________________________
Date __________________________
1027144–0001 Draft – Revision D.01 Commissioning the RT 7–23
RT installation
This test verifies the fractional DS3 connection from the HT to the
RT.
Requirements
The fractional DS3 test described below requires the following:
•The RT must be fully installed, commissioned, and in
contact with the EMS through the hub.
•The HT must be operational and in contact with the EMS.
•Fractional DS3/DS1 services must be configured and
provisioned.
•There must be no alarms present at the RT location.
•A loopback connector must be connected at the HT, either
at the input/out port connector of the HT DS3 SSI or at the
DS3 patch panel. (Refer to figure 7-8.)
Test procedure
1. Connect a DS3 test set to the out/input connector on the RT
DS3 SSI.
2. Select:
- C bit framing
- Recovered clock
- DS3 interface
Fractional DS1 services may be dropped from the DS3 data
stream and tested using QRSS test pattern.
3. Run the test for 1 hour.
Results
The RT passes if there are no errors and no clock or frame slips
during the test.
Record the results on the form on the following page (or make a
photocopy).
Fractional DS3 test
1027144–0001 Draft – Revision D.01 7–24 Commissioning the RT RT installation
RT to HT fractional DS3 test results
RT location: ____________________________________________
Number of DS1s tested ______
Test successful? ___ Yes ___ No RSSI __________
If not successful, complete:
Bit error rate _______________ Frame slips _______________
Frame errors _______________ Clock slips ________________
Trouble report generated? ___ Yes ___ No
If yes, report number: ____________________
If applicable: Faulty module part number ______________________
Serial number _____________________
If applicable: Replacement board part number __________________
Serial number______________________
BER test printout attached? ___ Yes ___ No
Comments:
_________________________________________________________________________________
_________________________________________________________________________________
Tested by (print name and sign): _______________________________________________________
Customer (print name and sign): ________________________________________________________
Date __________________________
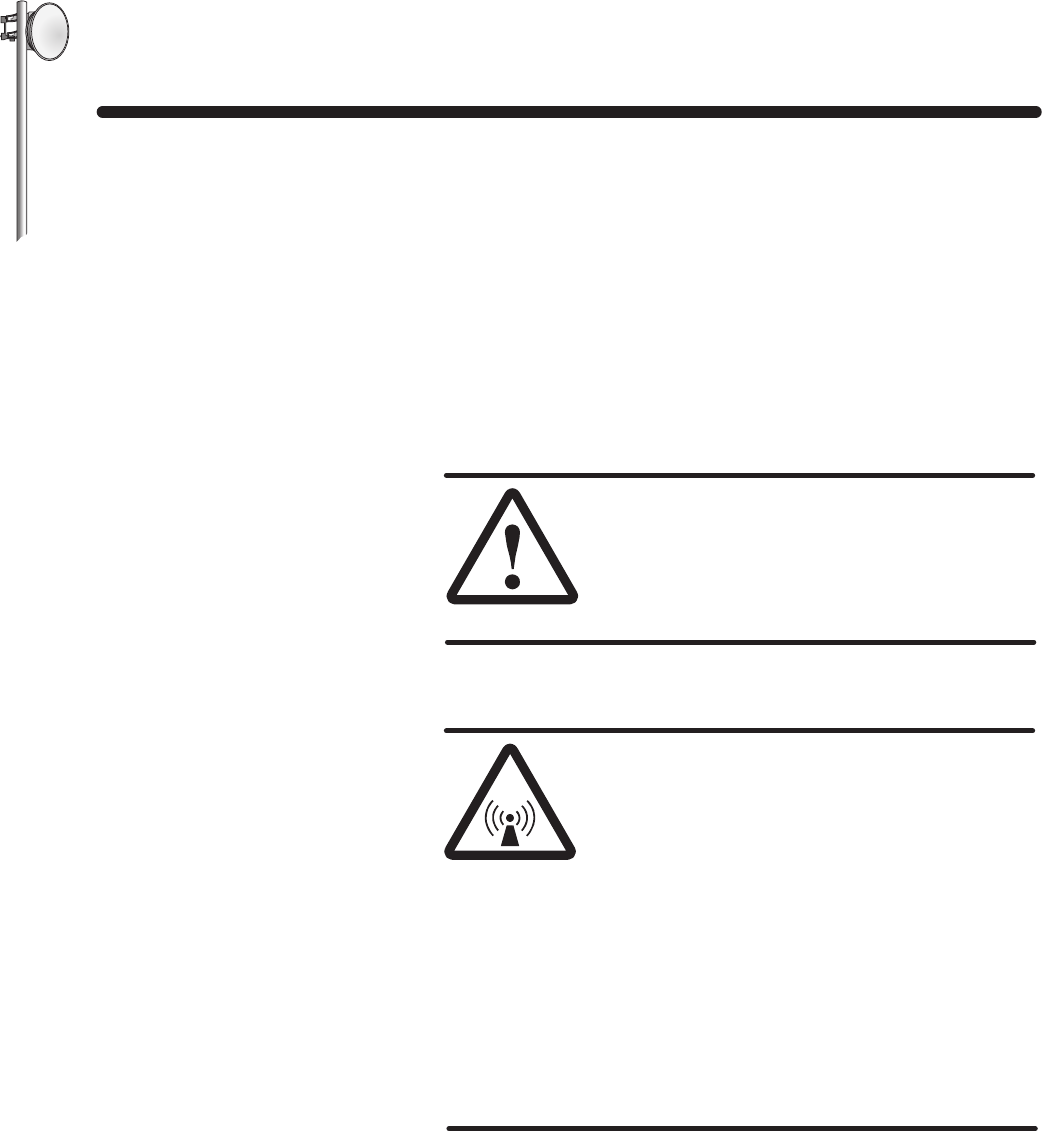
RT INSTALLATION
1027144–0001 Draft – Revision D.01 Final steps 8–1
RT installation
Chapter 8
Final steps
This chapter describes the final steps to take before you leave the
customer site after completing the installation:
•Weatherproofing – page 8–2
•Inspection, cleanup, and customer sign–off – page 8–3
•Connecting customer equipment – page 8–3
Observe these safety warnings while performing final inspections
and related tasks:
DANGER
Do not work on a ladder or roof without
first reading the safety warnings on page x
of this manual. Failure to observe these
warnings could result in personal injury or
death.
WARNING
Potential radio frequency (RF) hazard:
•Keep away from the front of the
outdoor unit (ODU) antenna while the
ODU is operating. Note that you cannot
tell from outward appearance whether
the ODU is operating or not.
•Be careful with respect to the ODU you
are installing and ODUs that may
already be operating in the installation
area.
Failure to observe these warnings could
result in injury to eyes or other personal
injury.
Safety warnings
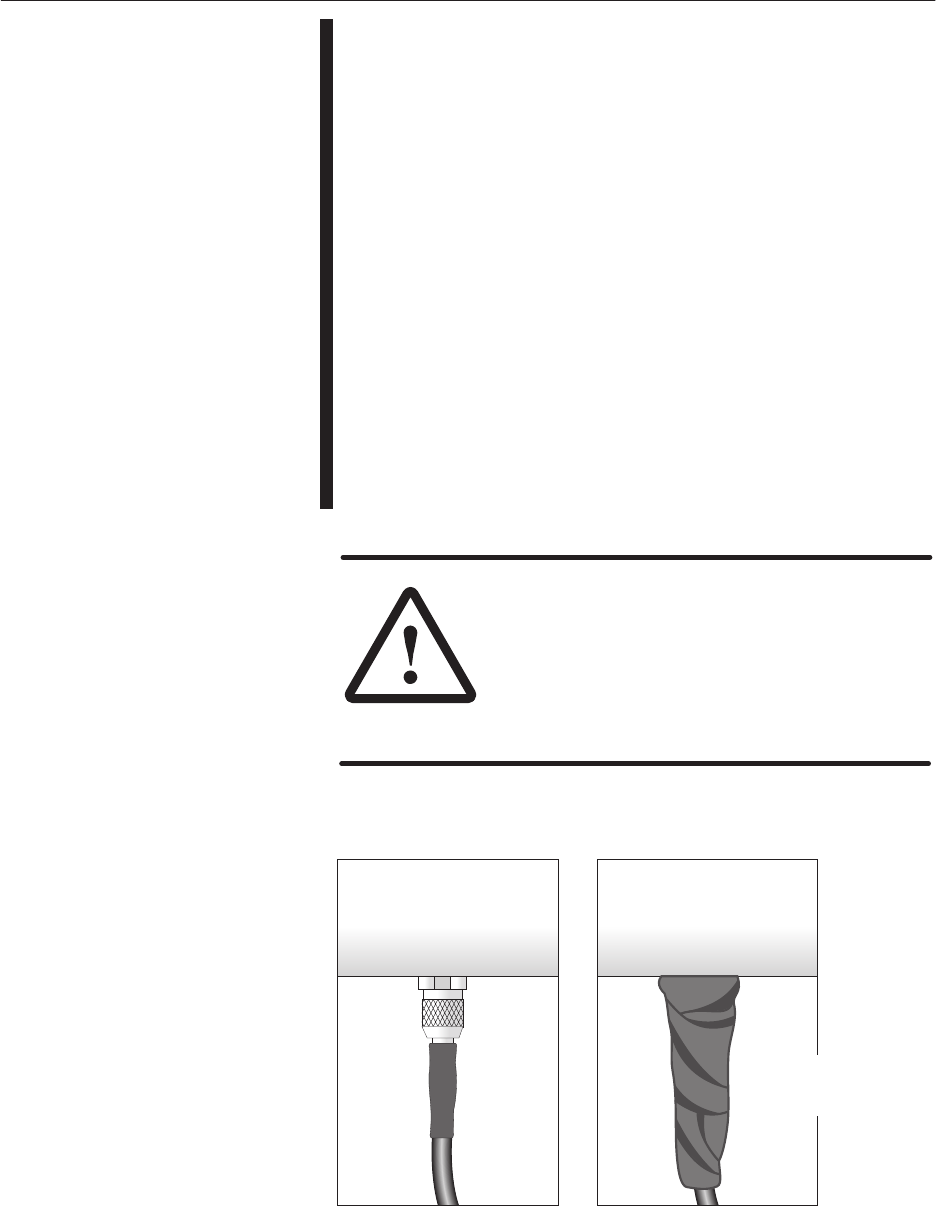
1027144–0001 Draft – Revision D.01 8–2 Final steps RT installation
After the RT has been successfully commissioned, go to the ODU
and seal all outdoor IFL connections (including connections to the
lightning arrestor assembly). Use weatherproofing compound and
tape to protect against moisture penetration:
See figure 8-1.
1. Starting at the connector end, wrap electrical tape around
the connector and part of the cable.
2. Cover the electrical tape with weatherproofing compound,
and work the compound into all joints and cracks where
water could enter.
3. Smooth the weatherproofing compound, giving the
connection a tapered appearance, as shown in figure 8-1.
4. Again starting at the connector end, wrap a second layer of
electrical tape around (on top of) the weatherproofing
compound.
5. Press the tape into the weatherproofing compound.
The resulting seal should be tight and compact, with no
loose tape ends.
CAUTION
Outdoor connectors are subject to
moisture contamination. Even minute
amounts of water vapor can condense
and cause a short circuit. Thoroughly
seal all outdoor IFL connections with
weatherproofing compound and tape.
Figure 8-1 Applying weatherproofing compound and tape
Before weatherproofing After weatherproofing
Heat
shrink Weatherproofing
compound and tape
T0006027
8.1
Weatherproofing
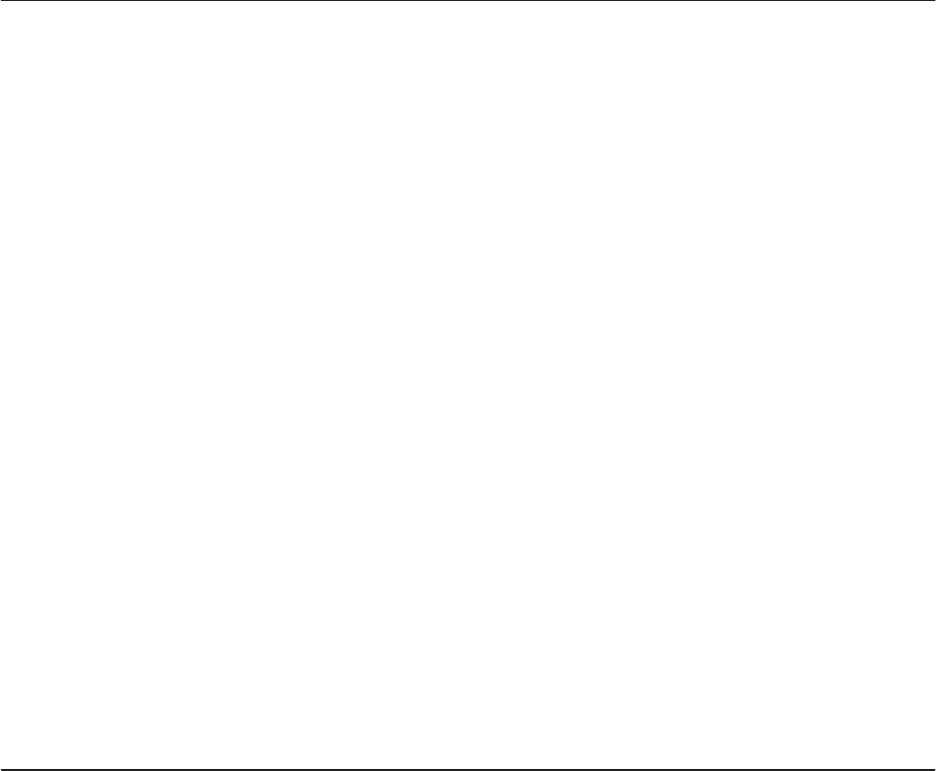
1027144–0001 Draft – Revision D.01 Final steps 8–3
RT installation
After all equipment is installed and commissioned, visit each
installation area to inspect the equipment and make sure the area is
left clean and orderly.
Inspect all equipment to make sure:
•All cables are dressed (as necessary) and not bent
excessively.
•All connections are secure.
•IFL connections are properly waterproofed.
•IDUs, racks, and ODUs are properly grounded.
•Antenna mount bolts are tightened.
•ODU adjusters and the temporary installation collar have
been removed for future use.
Clean up all installation areas:
•Make sure no tools or other objects are left on or near the
equipment.
•Remove or neatly store any excess materials.
•Remove all debris.
Before leaving the site, notify the appropriate customer
representative that the work has been completed. Ask the
representative to sign the work order, indicating that the
equipment has been installed and has passed the initial loopback
verification test(s).
The customer is responsible for connecting customer equipment to
the AIReach Broadband equipment through connections to
service–specific interface modules (SSI) modules. Refer to section
3.5 for information on the services and specific interfaces
provided by each SSI type.
8.2
Inspection, cleanup,
and sign–off
Inspection
Cleanup
Customer sign–off
8.3
Connecting
customer
equipment
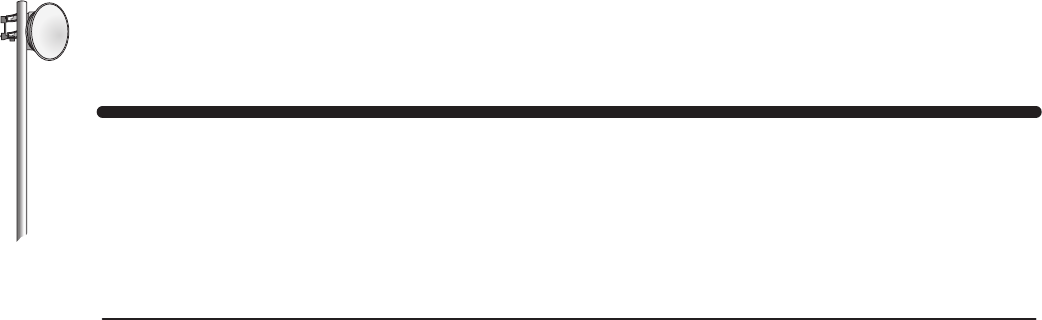
RT INSTALLATION
1027144–0001 Draft – Revision D.01 Troubleshooting 9–1RT installation
Chapter 9
Troubleshooting
This chapter includes:
•Troubleshooting flow charts – page 9–1
•Service information – page 9–6
The troubleshooting flow charts in this chapter will help isolate
most problems you might encounter during installation and
operation of the AIReach Broadband system.
Each flow chart begins with a specific problem, then leads you to
specific corrective actions you should take. Where actions are
numbered in these charts, you many not need to perform all of
the actions. Perform the actions in order, and check after each
action to see if the problem has been resolved. Proceed to the
next action only if the previous action did not correct the
problem.
The information in this chapter is intended for use by technicians
experienced in electronics troubleshooting. Therefore, it suggests
corrective actions but does not include detailed instructions for
each action.
9.1
Troubleshooting
flow charts
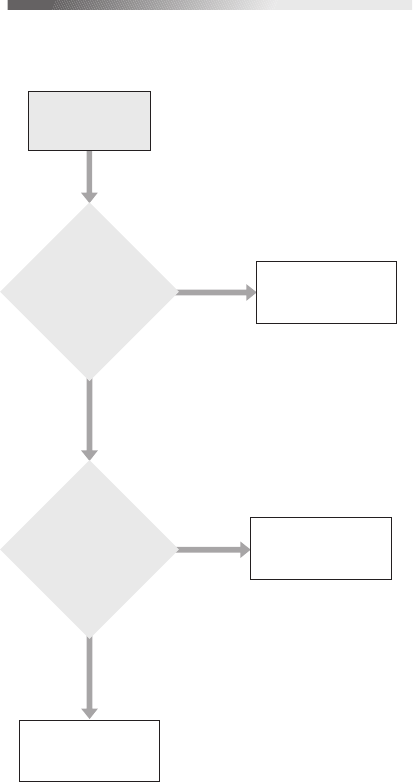
1027144–0001 Draft – Revision D.01 9–2 Troubleshooting RT installation
Troubleshooting the CCM
CCM will not
power up.
Is the correct
voltage present at
the IDU chassis
input?
Does chassis
cooling fan operate
when power is
applied?
Check power
source.
Replace CCM.
Replace
IDU chassis.
Yes
Yes
No
No
hb109
Problem:
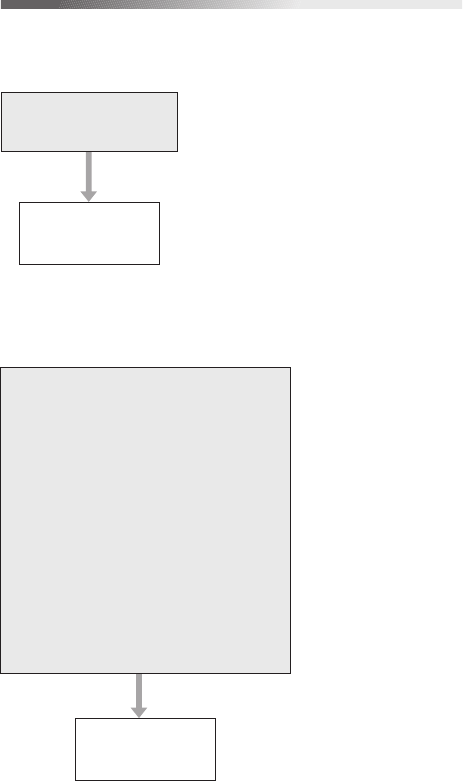
1027144–0001 Draft – Revision D.01 Troubleshooting 9–3RT installation
CCM failed startup
diagnostics (SUDS).
Replace CCM.
Problem:
During CCM bootup / hardware
initialization, LCD displays any of
the following messages, indicating
a device failure:
Host Cfg Failed
PLX Failed
PLX IO Failed
LAN Failed
RCC FPGA Failed
BSB FPGA Failed
QPIG FPGA Failed
Tim syn Failed
Replace CCM.
hb110
Problem:
Troubleshooting the CCM -
Continued
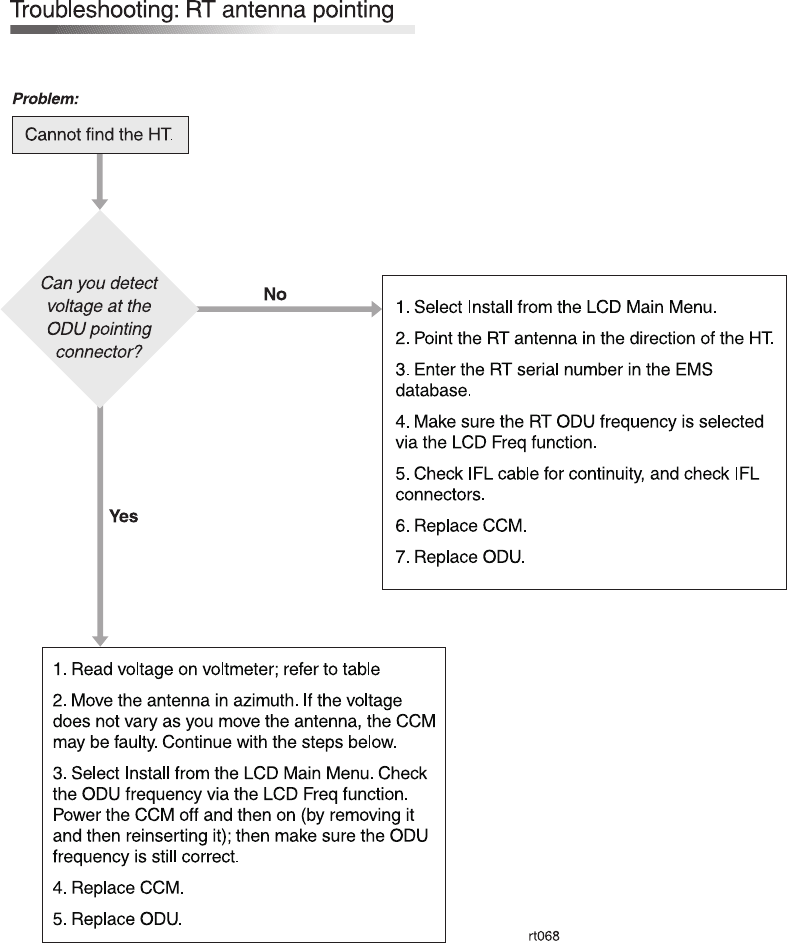
1027144–0001 Draft – Revision D.01 9–4 Troubleshooting RT installation
7-1 .
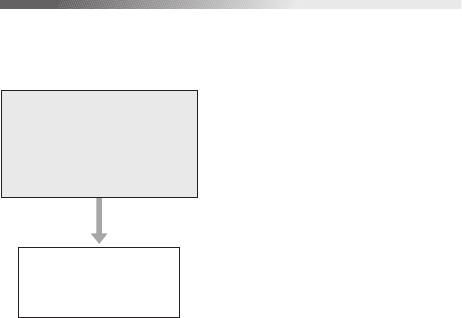
1027144–0001 Draft – Revision D.01 Troubleshooting 9–5RT installation
rt070
CCM will not download
its software over the air
(No "Loading Software"
message on LCD.)
Problem:
Troubleshooting: CCM won't download
1. Replace ODU.
2. Replace CCM.
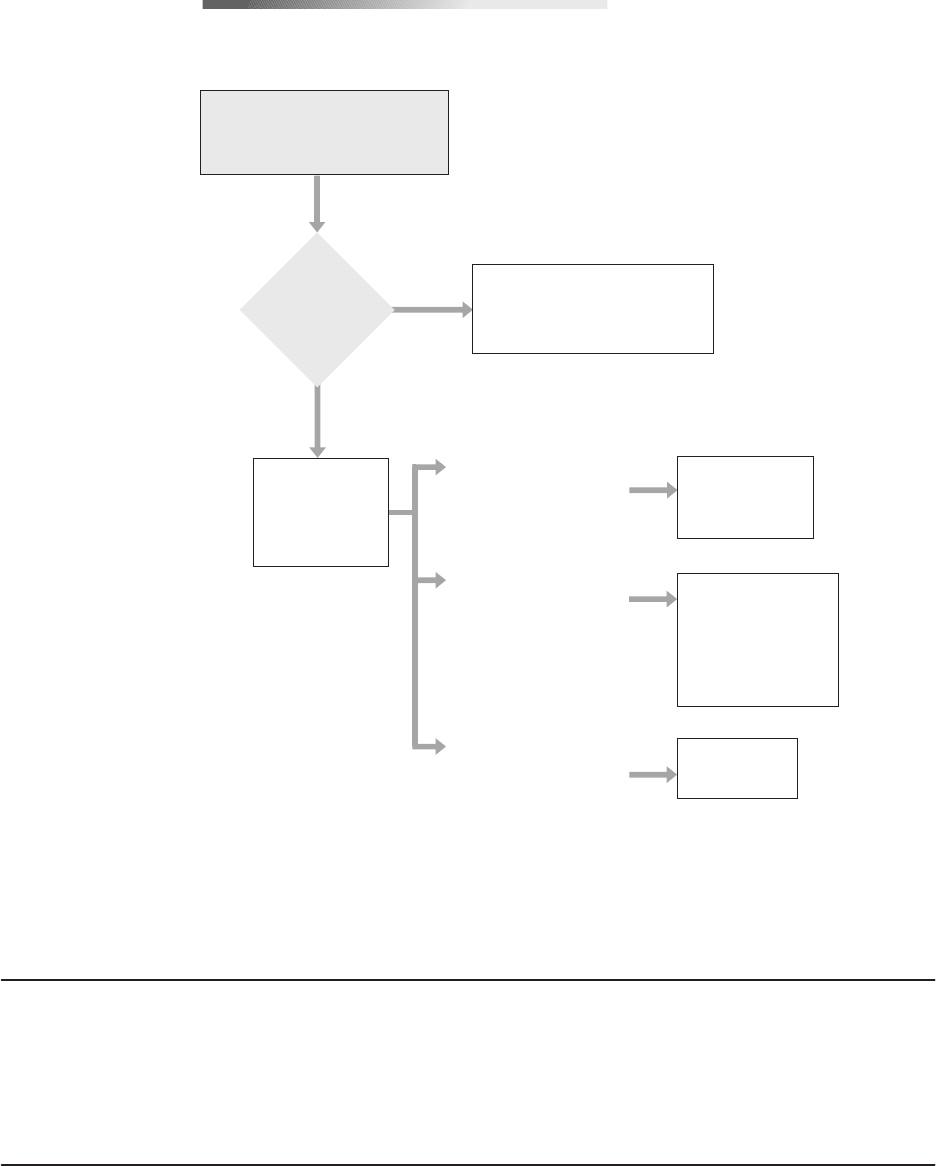
1027144–0001 Draft – Revision D.01 9–6 Troubleshooting RT installation
rt069
After CCM has downloaded
its software, CCM LCD shows
"RT Disabled" message.
Problem:
Troubleshooting: "RT Disabled"
If Status screen shows
"Degraded" or
"Unknown" for any
component . . .
Check CCM,
SSIs, and ODU
via CCM LCD
Status menu.
If Status screen shows
"CCM Failed" or
"SSI Failed" . . .
(number)
Refer to
section
If Status screen shows
"ODU Failed" . . .
Replace the
CCM or
indicated SSI.
1. Check IFL cable
for continuity.
2. Check IFL cable
connectors.
3. Replace ODU.
Are SSIs
installed and
configured?
"RT Disabled" message is
normal if SSIs have not been
installed and configured.
Yes
No
7.7.
IDU chassis fan doesn’t work. If the chassis is a dc powered unit,
make sure the polarity of the wires to the power supply is not
reversed..
If you find a faulty component, contact your contract administer to
arrange for repair or replacement.
9.2
Additional
troubleshooting
information
9.3
Repair or
replacement service
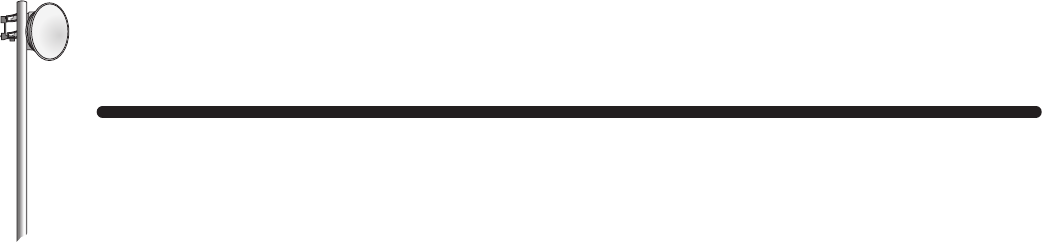
RT INSTALLATION
1027144–0001 Draft – Revision D.01 Maintenance 10–1RT installation
Chapter 10
Maintenance
The AIReach Broadband physical system requires no routine
maintenance. However, to facilitate expansion, reconfiguration, or
repairs, you may need to add, move, or replace components. This
chapter includes instructions for:
•Adding or moving SSIs – page 10–2
•Replacing components – page 10–3
•Replacing the ODU – page 10–3
•Replacing the IDU chassis – page 10–10
•Replacing the CCM – page 10–12
•Replacing SSIs – page 10–13
•Replacing the IFL – page 10–14
•Dismantling an RT – page 10–16
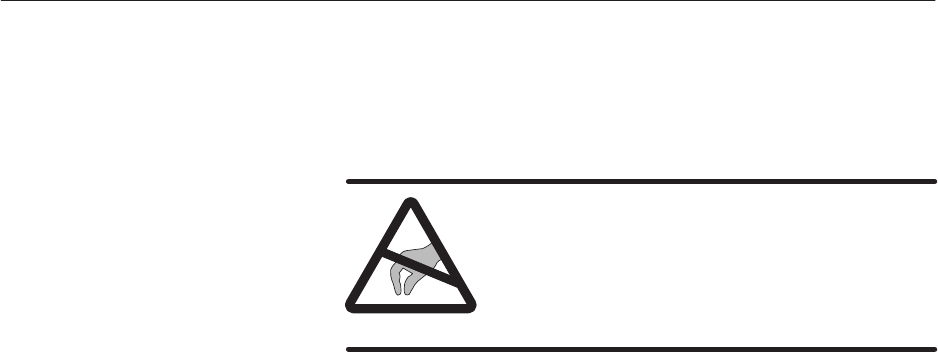
1027144–0001 Draft – Revision D.01 10–2 Maintenance RT installation
Notify the EMS operator before you add or move SSIs. Make
sure the EMS operator has performed any prerequisite steps that
may be necessary before you add or move an SSI.
For instructions on replacing SSIs, see section 10.6.
CAUTION
Always wear a new or recently tested
electrostatic discharge (ESD) wrist strap
(figure 3-14) when handling circuit
modules. Failure to use a wrist strap may
result in damage to components.
You can install additional SSIs while the system is powered on. To
add an SSI, follow the instructions in section 3.5 (page 3–28).
After installing an SSI, use the CCM LCD Status function to
check its operational status. The LCD should display OK. (For an
explanation of the CCM LCD Status function, see section 7.7.)
SSIs are hot–swappable, meaning you can move them from one
slot to another or to another chassis while the chassis are powered
on.
To move an SSI:
1. Loosen the thumbscrews at each end of the SSI.
2. Using an ESD wrist strap connected to a chassis ground
terminal, slide the SSI out of its slot.
3. Move the SSI to its new location and insert it into the slot.
4. Tighten the thumbscrews at each end of the SSI.
5. Use the CCM LCD to check the SSI status. (For details, see
section 7.7).
10.1
Adding or moving
SSIs
Adding SSIs
Moving SSIs
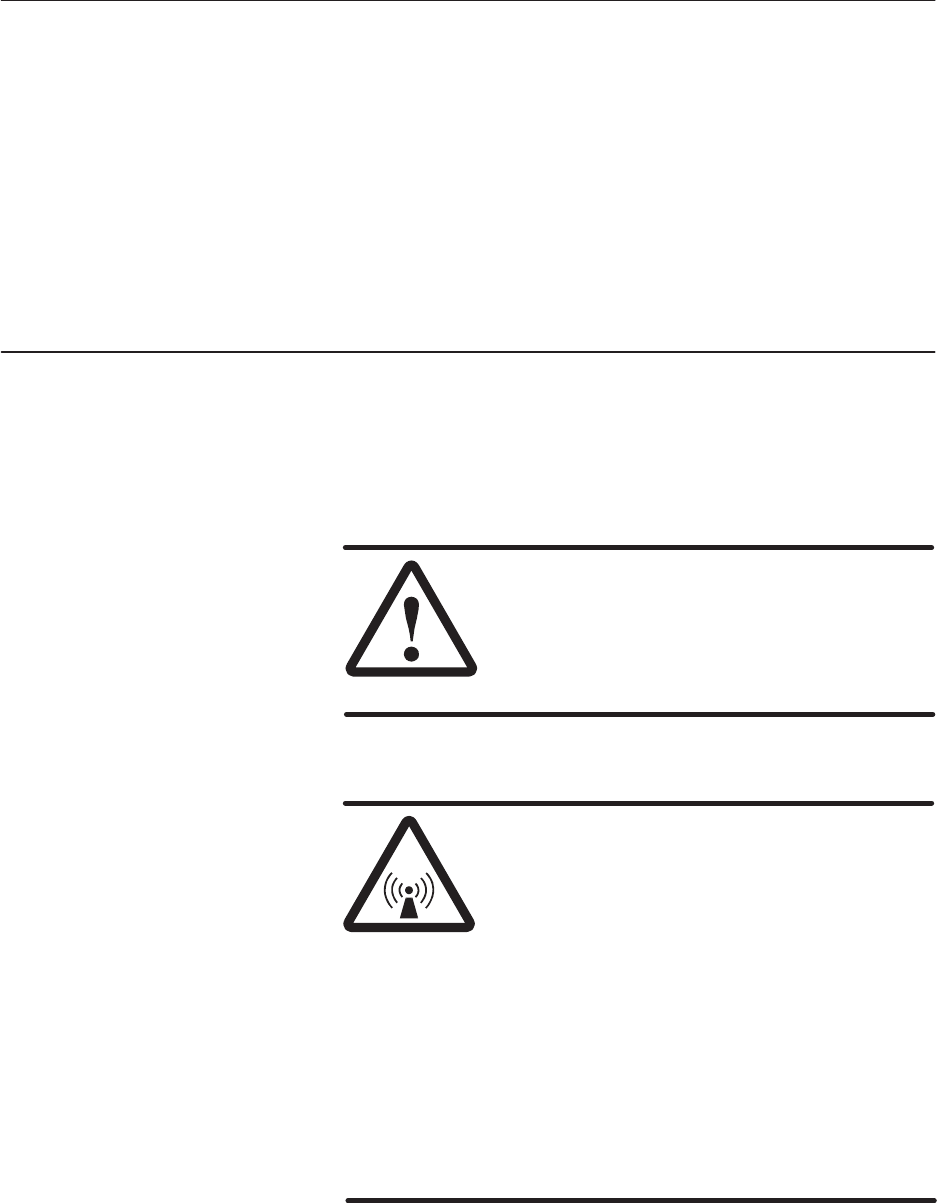
1027144–0001 Draft – Revision D.01 Maintenance 10–3RT installation
The following RT components can be replaced at the installation
site if a problem is attributed to the component:
•ODU
•IDU chassis
•CCM
•SSIs
•IFL
Specific instructions for replacing each component follow, in
sections 10.3 through 10.7.
If the ODU is faulty, you normally replace the transceiver only
(which contains the ODU electronics). Replace the antenna only if
it is physically damaged (for example, wind or water damage) or
has some other known problem.
DANGER
Do not work on a ladder or roof without
first reading the safety warnings on page x
of this manual. Failure to observe these
warnings could result in personal injury or
death.
WARNING
Potential radio frequency (RF) hazard:
•Keep away from the front of the
outdoor unit (ODU) antenna while the
ODU is operating. Note that you cannot
tell from outward appearance whether
the ODU is operating or not.
•Be careful with respect to the ODU you
are installing and ODUs that may
already be operating in the installation
area.
Failure to observe these warnings could
result in injury to eyes or other personal
injury.
10.2
Replacing
components
10.3
Replacing the ODU
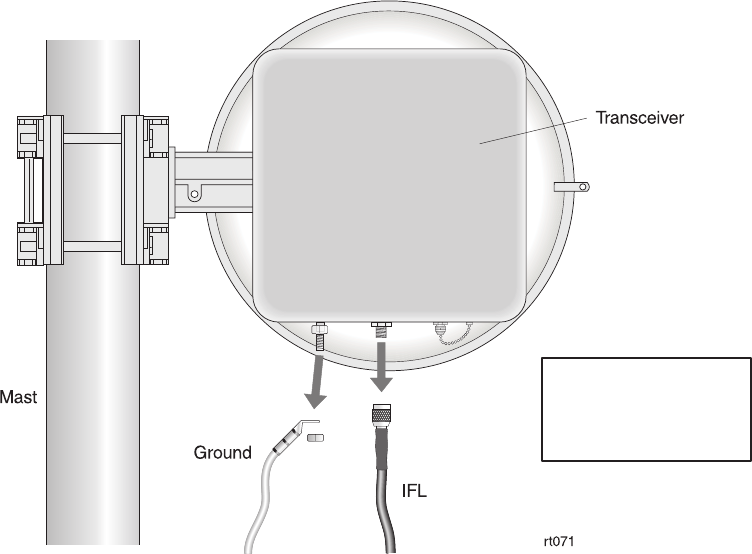
1027144–0001 Draft – Revision D.01 10–4 Maintenance RT installation
To replace the transceiver, follow these steps:
Removing the existing transceiver
1. Make sure the EMS operator has taken the RT out of
service.
2. At the IDU location: Remove power from the IDU chassis
power supply.
3. On the roof: Disconnect the ground cable and IFL from the
ODU transceiver, as shown in figure 10-1.
Figure 10-1 Disconnecting the ODU
ground and IFL cables
Graphic to be
updated.
Replacing the
transceiver
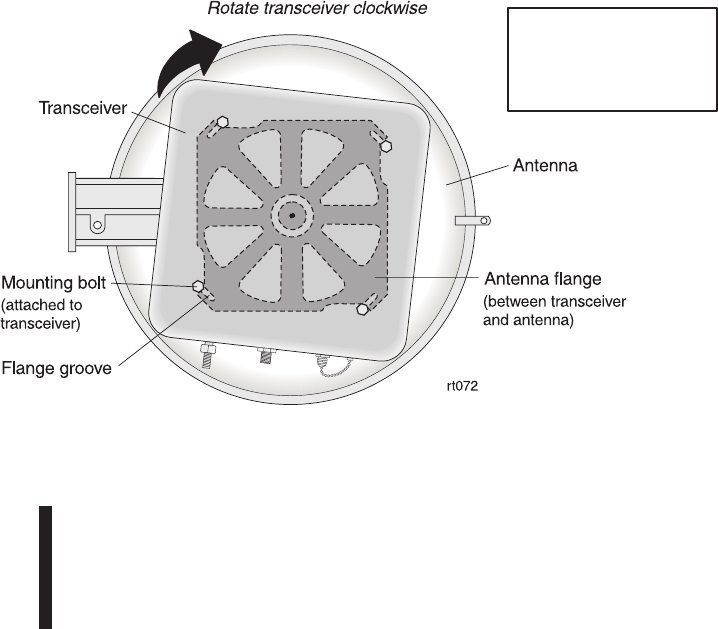
1027144–0001 Draft – Revision D.01 Maintenance 10–5RT installation
4. Loosen the four transceiver mounting bolts (shown in figure
10-2).
Figure 10-2 Removing the transceiver
Graphic to be
updated.
5. Rotate the transceiver until the bolts slide out of the four
grooves in the antenna bracket. (The direction of rotation
depends on the orientation of the antenna bracket—to the
right or left.) If the mounting bolts will not slide into the
grooves, loosen the bolts. See figure 10-2.
Important: A mechanical attenuator may be installed
(previously) in the antenna waveguide. If an attenuator is
installed, make sure it does not get lost or misplaced. Leave
the attenuator in the waveguide.
6. Cover the transceiver coupling (center hole) with a plastic
coupling plug (if available) or tape to prevent
contamination.
1027144–0001 Draft – Revision D.01 10–6 Maintenance RT installation
Installing the replacement transceiver
7. To install the replacement transceiver, follow the steps in
section 6.11 (page 6–21).
Important: If a mechanical attenuator was previously
installed in the antenna waveguide, make sure it is still in
place in the waveguide before you attach the transceiver to
the antenna.
8. Connect the IFL cable to the IFL connector on the
transceiver.
9. Ground the ODU, as explained in section 6.12 (page 6–23).
10. After you replace the transceiver:
- Go to the next subsection (Replacing the antenna) only
if you need to replace the antenna.
- Apply power to the IDU chassis power supply.
- Use the CCM LCD to check the ODU status. (For
details, see section 7.7).
- Notify the EMS operator that the RT is ready to resume
service.
If you are replacing the transceiver only, you should not need to
repoint the antenna.
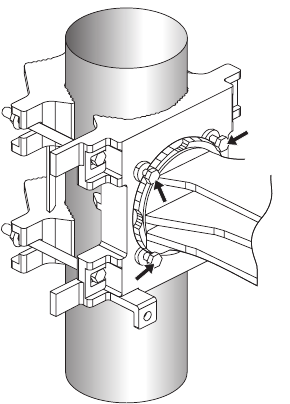
1027144–0001 Draft – Revision D.01 Maintenance 10–7RT installation
If you need to replace the antenna, follow these steps:
Removing the existing antenna
1. Remove the transceiver (steps 1 through 6 above, beginning
on page 10–4). Be sure to remove power from the IDU
chassis power supply.
Important: A mechanical attenuator may be installed
(previously) in the antenna waveguide. If an attenuator is
installed, make sure it does not get lost or misplaced. Leave
the attenuator in the waveguide.
2. Loosen the four antenna bracket locking nuts.
Figure 10-3 Antenna bracket locking nuts
hb116
Antenna bracket
locking nuts
Antenna
mount
Antenna
bracket
Replacing the antenna
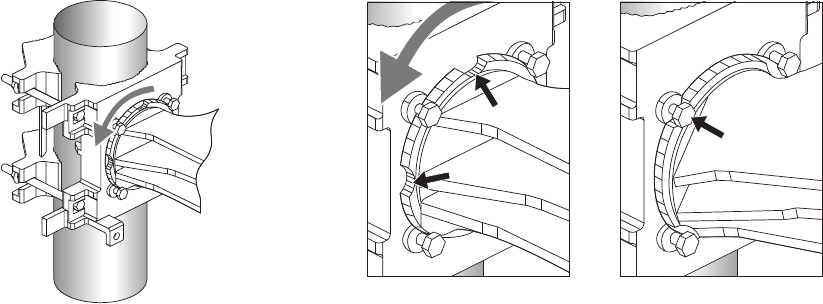
1027144–0001 Draft – Revision D.01 10–8 Maintenance RT installation
3. Rotate the antenna (clockwise or counterclockwise) until
the antenna bracket reliefs (curved indentations) are aligned
with the four nuts on the mast interface, as shown in figure
10-4.
Figure 10-4 Removing the antenna
hb117
Relief
Relief
Reliefs not aligned
with nuts
Nut
Reliefs aligned with nuts
(Antenna in position
to be removed)
Rotate antenna and antenna bracket until
reliefs are aligned with the 4 antenna
bracket locking nuts, as show at right.
Antenna
mount
Antenna
bracket
4. Move the antenna away from the mast interface.
5. Cover the antenna waveguide (center hole) with a plastic
plug or tape to protect against contamination.

1027144–0001 Draft – Revision D.01 Maintenance 10–9RT installation
Installing the replacement antenna
6. Install a temporary installation collar below the antenna
mount, as explained in section 6.4 (page 6–6).
You need the temporary installation collar so you can point
the replacement antenna.
7. Attach the replacement antenna to the mount, as explained
in section 6.6 (page 6–12).
8. Point the replacement antenna by adjusting the azimuth and
elevation as detailed in chapter 6.
9. Attach the transceiver to the antenna, as explained in
section 6.11 (page 6–21).
Important: If a mechanical attenuator was previously
installed in the antenna waveguide, make sure it is still in
place in the waveguide before you attach the transceiver to
the antenna.
10. Connect the IFL cable to the IFL connector on the
transceiver.
11. Ground the ODU, as explained in section 6.12 (page 6–23).
12. Apply power to the IDU chassis power supply (section 3.3,
page 3–8).
13. Use the CCM LCD to check the ODU status. (For details,
see section 7.7).
14. Re–commission the RT as detailed in chapter 7.
15. Notify the EMS operator that the RT is ready to resume
service.
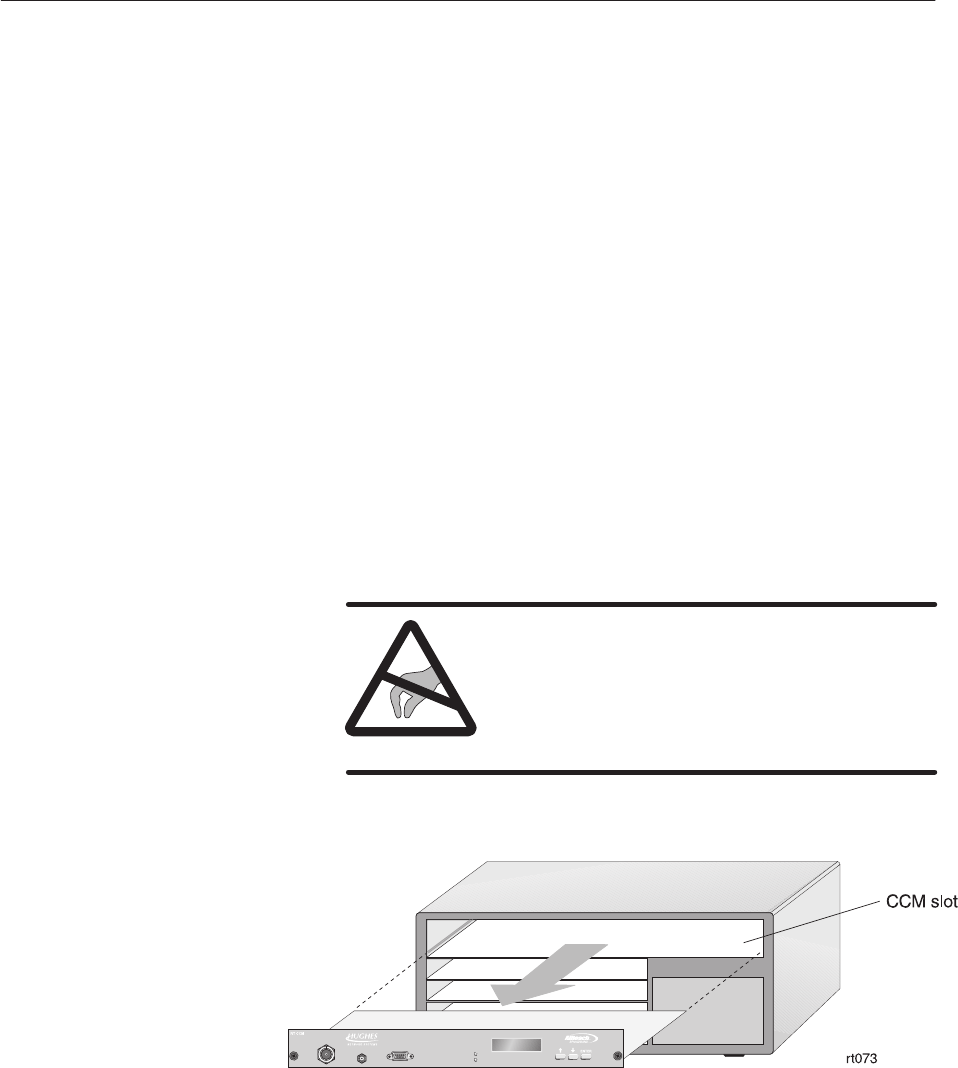
1027144–0001 Draft – Revision D.01 10–10 Maintenance RT installation
Do not attempt to service or replace the IDU chassis power supply.
If there is a problem with the power supply, replace the entire
IDU chassis.
To replace the IDU chassis, follow these steps:
If you need additional details concerning the instructions below,
see chapter 3.
Removing the existing IDU chassis
1. Make sure the EMS operator has taken the RT out of
service.
2. Remove power from the IDU chassis power supply.
3. Mark each cable or otherwise note where each cable is
connected.
4. Remove all cables from all modules.
5. Remove the CCM:
a. Loosen the thumbscrews at each end.
b. Using an ESD wrist strap connected to a chassis
ground terminal, slide the CCM out of its slot, as
shown in figure 10-5.
CAUTION
Always wear a new or recently tested
electrostatic discharge (ESD) wrist strap
(figure 3-14) when handling circuit
modules. Failure to use a wrist strap may
result in damage to components.
Figure 10-5 Removing the CCM
10.4
Replacing the IDU
chassis
1027144–0001 Draft – Revision D.01 Maintenance 10–11RT installation
6. Place the CCM in its ESD protective packaging.
7. Remove all SSIs:
a. Using a piece of tape on the SSI front panel, mark the
slot number where each SSI was installed.
b. Loosen the thumbscrews at each end.
c. Using an ESD wrist strap connected to a chassis
ground terminal, slide the SSI out of its slot.
8. Place each SSI in ESD protective packaging.
9. If the IDU chassis is rack mounted, remove the four
mounting screws and remove the chassis from the rack.
10. Remove the rack mounting brackets from the chassis.
Installing the replacement IDU chassis
Refer to the instructions in chapter 3 to:
11. Install the replacement chassis in a rack, if the original
chassis was installed in a rack (section 3.2).
12. Re–connect power to the IDU chassis power supply
(section 3.3).
13. Conduct a power–on test (section 3.3).
14. Re–install the CCM (section 3.4).
15. Re–install the SSIs (section 3.5).
Install each SSI in the slot it was in before. Refer to the slot
numbers you marked on the tape on each SSI.
16. Re–connect the IFL cable and all other cables to the CCM
and SSIs.
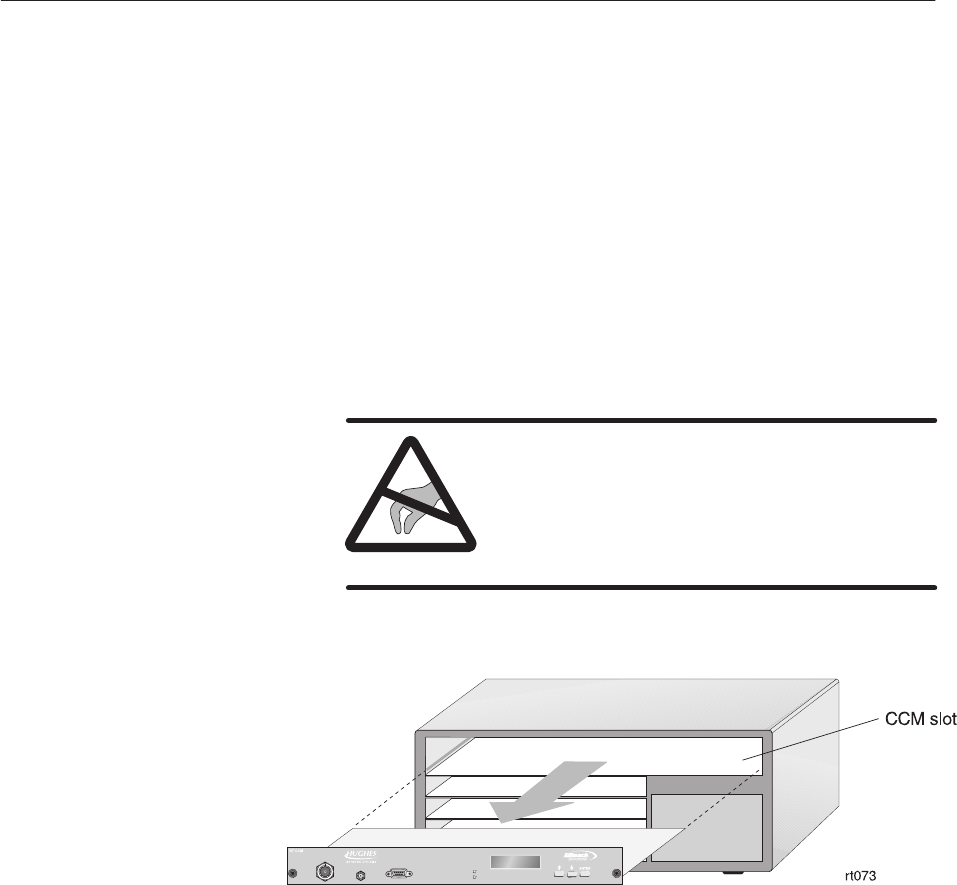
1027144–0001 Draft – Revision D.01 10–12 Maintenance RT installation
If you need to replace the CCM, follow these steps:
If you need additional details concerning the instructions below,
see section 3.4 (page 3–24).
Removing the existing CCM
1. Make sure the EMS operator has taken the RT out of
service.
2. Remove power from the IDU chassis power supply.
3. Loosen the thumbscrews at each end of the (existing) CCM.
4. Using an ESD wrist strap connected to a chassis ground
terminal, slide the CCM out of its slot, as shown in
figure 10-6.
CAUTION
Always wear a new or recently tested
electrostatic discharge (ESD) wrist strap
(figure 3-14) when handling circuit
modules. Failure to use a wrist strap may
result in damage to components.
Figure 10-6 Removing the CCM
5. Place the CCM in ESD protective packaging.
Installing the replacement CCM
6. Slide the replacement CCM into the CCM slot (slot 1).
7. Tighten the thumbscrews at each end of the CCM.
8. Apply power to the IDU chassis power supply.
9. Use the CCM LCD to check the CCM status. (For details,
see section 7.7).
10. Notify the EMS operator that the RT is ready to resume
service.
10.5
Replacing the CCM
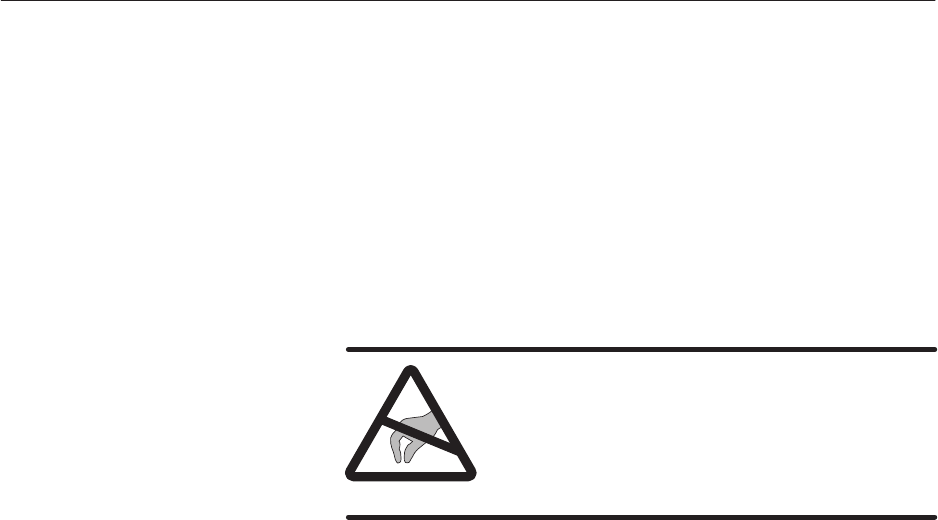
1027144–0001 Draft – Revision D.01 Maintenance 10–13RT installation
To replace an SSI, follow the steps below.
SSIs are hot swappable, so you do not need to power off the IDU
to replace an SSI. If you need additional details concerning the
instructions below, see section 3.5 (page 3–28).
Removing the SSI
1. Note which slot the SSI to be replaced is in.
2. Loosen the thumbscrews at each end of the SSI.
3. Using an ESD wrist strap connected to a chassis ground
terminal, slide the SSI out of its slot.
CAUTION
Always wear a new or recently tested
electrostatic discharge (ESD) wrist strap
(figure 3-14) when handling circuit
modules. Failure to use a wrist strap may
result in damage to components.
4. Place the SSI in ESD protective packaging.
Installing the replacement SSI
5. Slide the replacement SSI into the slot from which you
removed the previously installed SSI.
6. Tighten the thumbscrews at each end of the SSI.
7. Use the CCM LCD to check the SSI status. (For details, see
section 7.7).
8. Notify the EMS operator that the replacement SSI is ready
for service.
10.6
Replacing SSIs
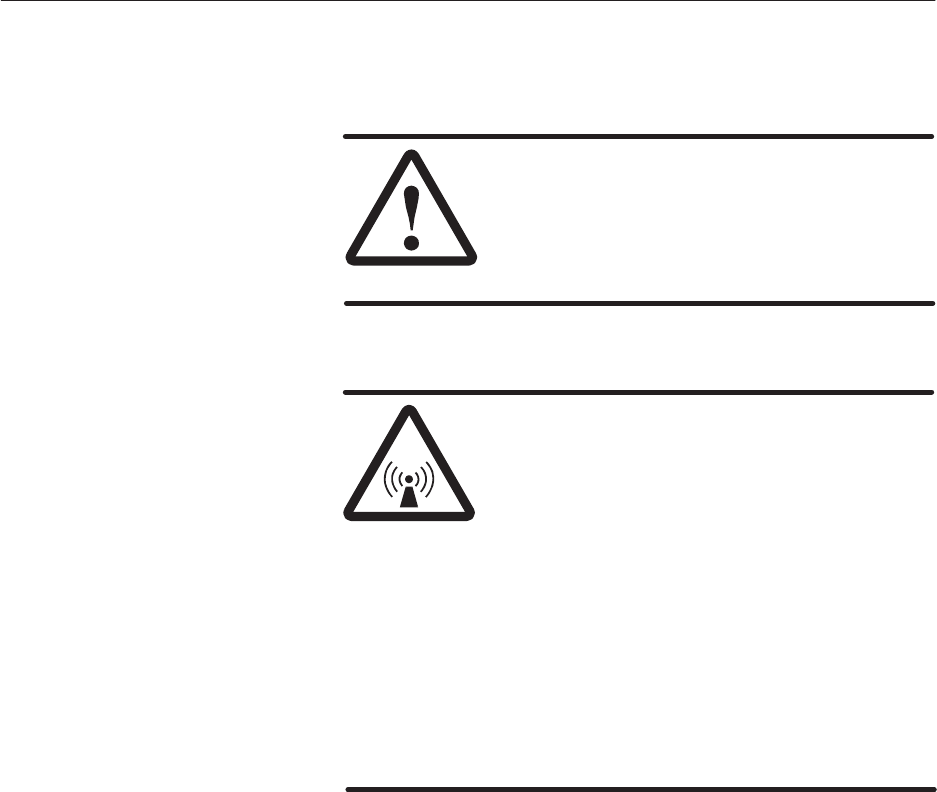
1027144–0001 Draft – Revision D.01 10–14 Maintenance RT installation
If you suspect problems with the IFL, check all IFL connections
and then test the IFL. Replace the IFL only if there is a known
problem that cannot be corrected any other way.
DANGER
Do not work on a ladder or roof without
first reading the safety warnings on page x
of this manual. Failure to observe these
warnings could result in personal injury or
death.
WARNING
Potential radio frequency (RF) hazard:
•Keep away from the front of the
outdoor unit (ODU) antenna while the
ODU is operating. Note that you cannot
tell from outward appearance whether
the ODU is operating or not.
•Be careful with respect to the ODU you
are installing and ODUs that may
already be operating in the installation
area.
Failure to observe these warnings could
result in injury to eyes or other personal
injury.
10.7
Replacing the IFL
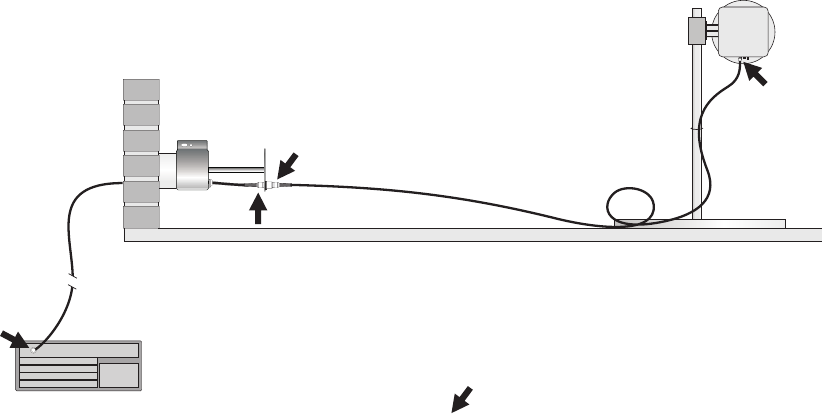
1027144–0001 Draft – Revision D.01 Maintenance 10–15RT installation
Environments where IFLs are installed vary widely. Therefore, use
the general instructions below as guidelines.
If you need to replace the IFL:
1. Make sure the EMS operator has taken the RT out of
service.
2. Remove power from the IDU chassis power supply.
3. Disconnect all four IFL N connectors, as shown in
figure 10-7:
- 1 connector at the IDU
- 1 connector at the ODU
- 2 connectors at the lightning arrestor
N
ODU
IFL
Lightning
arrestor
T0009002
IFL
Roof
IDU
N
N
N
N= N connector location
Figure 10-7 Disconnect N connectors at the
four locations shown here
4. Remove the two IFL cable segments:
- From IDU to the lightning arrestor
- From the lightning arrestor to the ODU
5. Install the replacement IFL cable according to the
instructions in chapter 4.
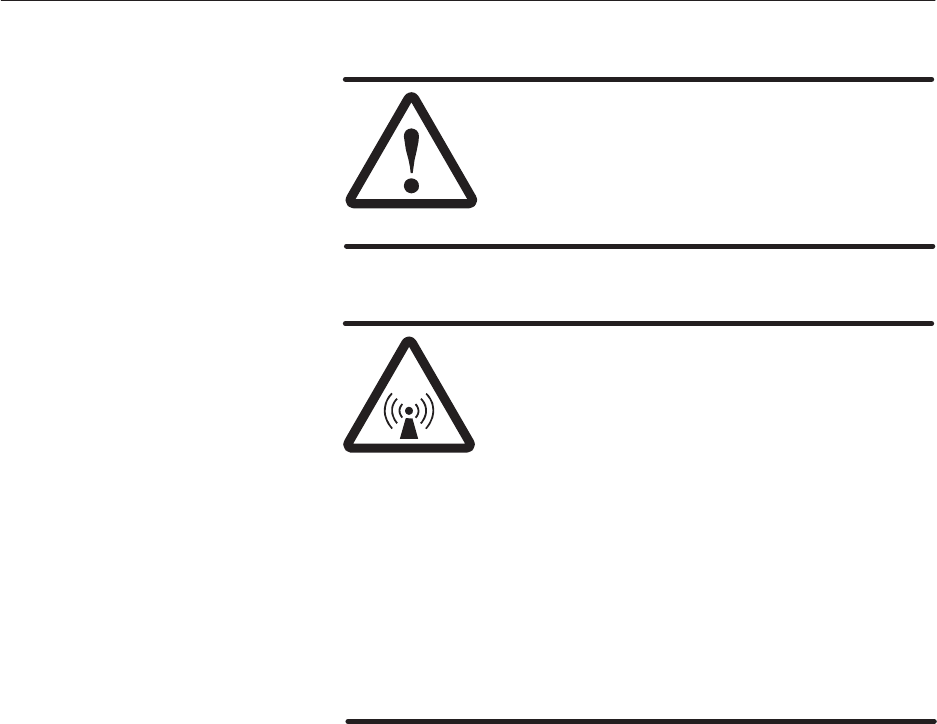
1027144–0001 Draft – Revision D.01 10–16 Maintenance RT installation
If you need to dismantle an entire RT, follow the steps below.
DANGER
Do not work on a ladder or roof without
first reading the safety warnings on page x
of this manual. Failure to observe these
warnings could result in personal injury or
death.
WARNING
Potential radio frequency (RF) hazard:
•Keep away from the front of the
outdoor unit (ODU) antenna while the
ODU is operating. Note that you cannot
tell from outward appearance whether
the ODU is operating or not.
•Be careful with respect to the ODU you
are installing and ODUs that may
already be operating in the installation
area.
Failure to observe these warnings could
result in injury to eyes or other personal
injury.
Follow these steps:
1. Make sure the EMS operator has taken the RT out of
service.
2. Remove power from the IDU chassis power supply.
3. On the roof: Disconnect the IFL and ground cable from the
ODU. See section 10.3.
4. Remove the transceiver. See section 10.3.
5. Remove the antenna. See section 10.3.
6. Disassemble the mast and mast mount.
7. At the IDU location: Remove all cables from all modules.
If the cables will be reused, mark them to identify them.
8. Optional: Remove the CCM and SSIs from the chassis.
(Depending on what you will do with the equipment, you
might want to leave the CCM and SSIs installed.) See
sections 10.5 and 10.6.
9. Remove the IDU chassis.
10. Remove the IFL cable and lightning arrestor (unless the
lightning arrestor is being used for another RT or will be
reused).
10.8
Dismantling an RT

1027144–0001 Draft – Revision D.01 A- 1
Appendix A
Acronyms and abbreviations
ac – alternating current
ATM – asynchronous transfer mode
AWG – American wire gauge
BER – bit error rate
BSP – baseband signal processor
C – Celsius
CCM – channel and control module
cm – centimeter
CMR – communication riser
CPU – central processing unit
dc – direct current
DRAM – dynamic RAM
EIDU – expansion indoor unit
EMS – Element Management System
ESD – electrostatic discharge
ESN – electronic serial number
F – Fahrenheit
FCC – Federal Communications Commission
FEM – fiber extender module
FRAD – frame relay access device
ft – foot
HNS – Hughes Network Systems
HT – hub terminal
Hz – hertz
ID – identification
IDU – indoor unit
IEC – International Electrotechnical Commission
IF – intermediate frequency
IFL – intrafacility link
in. – inch
LAN – local area network
lb – pound(s)
LCD – liquid crystal display
LED – light emitting diode
LOS – line of sight
m – meter
MAC – media access control
mm – millimeter
NEBS – Network Equipment Building Standards
NEC – National Electric Code
NEMA – National Electrical Manufacturing
Association
NFPA – National Fire Protection Association
ODU – outdoor unit
PC – personal computer
PCI – PC interface
PMP – point–to–multipoint
RAM – random–access memory
RF – radio frequency
ROM – read–only memory
RT – remote terminal
SC – signaling controller
SDRAM – static dual port RAM
SSI – service–specific interface
SUDS – startup diagnostics
TAC – Technical Assistance Center
TDM – time division multiplexing
UL – Underwriters Laboratories
1027144–0001 Draft – Revision D.01A- 2
V – volt
Vac – volt, alternating current
Vdc – volt, direct current
VSAT – very small aperture terminal
WND – Wireless Networks Division
WDT – watch dog timer

1027144–0001 Draft – Revision D.01 Standards compliance B–1RT installation
Appendix B
Standards compliance
This appendix includes standards compliance information for the
AIReach Broadband outdoor unit (ODU) and ac power indoor unit
(IDU). Information is included for:
•Interference standards compliance
•Underwriters Laboratories, Inc., safety compliance
•RF, electrical fast transient, and ESD immunity

B.1
1027144–0001 Draft – Revision D.01 B–2 Standards compliance RT installation
This section provides information on the AIReach Broadband
outdoor unit (ODU).
This equipment complies with Part 15 of United States Federal
Communication Commission (FCC) Rules. Operation is subject to
the following two conditions: (1) This device may not cause
harmful interference, and (2) this device must accept any
interference received, including interference that may cause
undesired operation.
This equipment has been tested and found to comply with the
limits for a Class A digital device, pursuant to Part 15 of FCC
Rules. These limits are designed to provide reasonable protection
against harmful interference when the equipment is operated in a
commercial environment.
This equipment generates, uses, and can radiate radio frequency
energy and, if not installed and used in accordance with this
instruction manual, may cause harmful interference to radio
communications. Operation of this equipment in a residential area
is likely to cause interference, in which case the user will be
required to correct the interference at the user’s own expense.
Type acceptance: FCC Part 101
This class A digital apparatus meets all requirements of the
Canadian Interference–Causing Equipment Regulations.
Cet appareil numérique de la Classe A respecte toutes les
exigences du Règlement sur le matériel brouilleur du Canada.
This equipment has been evaluated by Underwriters Laboratories
Inc. (UL) and determined to be in compliance with the Standard
for Safety of Information Technology Equipment Including
Electrical Business Equipment, UL 1950, third edition; and
Canadian Standards Association CAN/CSA C22.2 No. 950–95,
third edition. This equipment is UL listed and UL certified for
Canada as Information Technology Equipment.
The ODU complies with the following immunity standards of the
International Electrotechnical Commission (IEC):
•Radio frequency immunity – IEC 801–3 (3 V/m)
•Electrical fast transient immunity – IEC 801–4
•Electrostatic discharge immunity – 25 KV level tested using
method in IEC 801–2
The ODU complies with requirements of the National Electric
Code (NEC), article 800.
The ODU complies with EN 55022.
Outdoor unit
FCC compliance
Canadian interference
compliance
Underwriters
Laboratories (UL)
Immunity
National Electric Code
(NEC)
Emissions

B.2
1027144–0001 Draft – Revision D.01 Standards compliance B–3RT installation
This section provides information on the AIReach Broadband
ac power indoor unit (IDU).
This equipment complies with Part 15 of United States Federal
Communication Commission (FCC) Rules. Operation is subject to
the following two conditions: (1) This device may not cause
harmful interference, and (2) this device must accept any
interference received, including interference that may cause
undesired operation.
This equipment has been tested and found to comply with the
limits for a Class A digital device, pursuant to Part 15 of FCC
Rules. These limits are designed to provide reasonable protection
against harmful interference when the equipment is operated in a
commercial environment.
This equipment generates, uses, and can radiate radio frequency
energy and, if not installed and used in accordance with this
instruction manual, may cause harmful interference to radio
communications. Operation of this equipment in a residential area
is likely to cause interference, in which case the user will be
required to correct the interference at the user’s own expense.
This class A digital apparatus meets all requirements of the
Canadian Interference–Causing Equipment Regulations.
Cet appareil numérique de la Classe A respecte toutes les
exigences du Règlement sur le matériel brouilleur du Canada.
This equipment has been evaluated by Underwriters Laboratories
Inc. (UL) and determined to be in compliance with the Standard
for Safety of Information Technology Equipment Including
Electrical Business Equipment, UL 1950, third edition; and
Canadian Standards Association CAN/CSA C22.2 No. 950–95,
third edition. This equipment is UL listed and UL certified for
Canada as Information Technology Equipment.
The ODU complies with the following immunity standards of the
International Electrotechnical Commission (IEC):
•Radio frequency immunity – IEC 801–3 (3 V/m)
•Electrical fast transient immunity – IEC 801–4
•Electrostatic discharge immunity – 25 KV level tested using
method in IEC 801–2
The ODU complies with EN 55022.
Indoor unit (ac)
FCC compliance
Canadian interference
compliance
Underwriters
Laboratories (UL)
Immunity
Emissions

1027144–0001 Draft – Revision D.01 Terminating the IFL cable C–1RT installation
Appendix C
Terminating the IFL cable
This appendix explains in detail how to terminate the IFL cable
ends by attaching an N–type connector. It includes:
•Cable parts and terminology – page C–2
•Preparing the cable end – page C–3
•Attaching the connector – page C–6
•Applying heat–shrink tubing – page C–11
As part of the RT installation, you attach N connectors in four
locations, as shown in figure 4-3 (on page 4–5):
•One N connector at the IDU location
•Two N connectors to connect to the lightning arrestor
assembly
•One N connector at the ODU location
Important: Sound IFL cable connections are critical for
proper operation of the AIReach Broadband system.
Therefore, be very careful in terminating the cable. If you are
unsure about the success of any of the following steps, repeat
them.
Attach N connectors after you route and install the cable, not
before.
Note: The instructions below are for the connectors in HNS kit
9006284–0002. If you use a different N–type connector, follow the
manufacturer’s instructions.

C.1
1027144–0001 Draft – Revision D.01 C–2 Terminating the IFL cable RT installation
Figure C-1 shows the main cable components.
Figure C-1 IFL cable components
hb013
Outer jacket
Braid
Center conductor
(solid or stranded copper)
7/32 inch
(6 millimeters)
Dielectric
(foam or flexible plastic)
N connector N connector
IFL cable, terminated - shown without heat-shrink tubing
HNS kit 9006284–0002 contains two N connectors.
Cable parts and
terminolo
gy
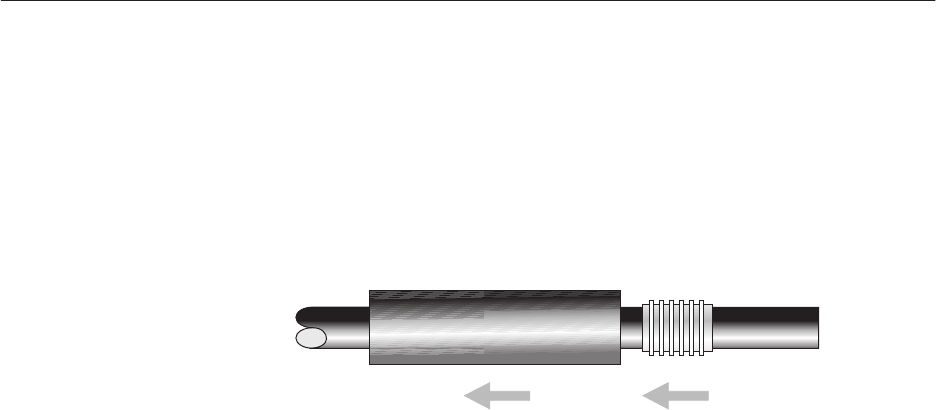
C.2
1027144–0001 Draft – Revision D.01 Terminating the IFL cable C–3RT installation
Prepare the cable end as follows:
1. Inspect the cable end for damage from handling and trim off
any damaged portions.
2. Cut the cable as cleanly and squarely as possible.
3. Slip the crimp ring and a piece of heat–shrink tubing
(HNS9007488–0005) onto the cable, as shown in figure
C-2.
Figure C-2 Slipping the crimp ring and
heat–shrink tubing onto the cable
Heat-shrink tubing Crimp
ring
hb014
Butt-cut
cable end
4. Use the spin–stripping tool (Excelta CX 1–78–1, gold
color–coded) to remove the cable jacket and dielectric,
leaving about 7/32 inch (6 millimeters) of the center
conductor exposed, as shown in figure C-3.
a. Open the stripping jaws of the spin–stripping tool
enough to allow the cable end to enter the cable
barrel fully. (See figure C-3.)
b. While holding the cable firmly in the tool and tightly
against the cable stop, squeeze the stripper jaws.
c. Rotate the tool around the cable two or three times
until the outer cable jacket and dielectric are
completely cut through, but do not score the center
conductor. Rotate the tool in the direction indicated in
figure C-3.
d. Remove the cut–off end of the cable jacket and
dielectric.
Preparing the cable
end
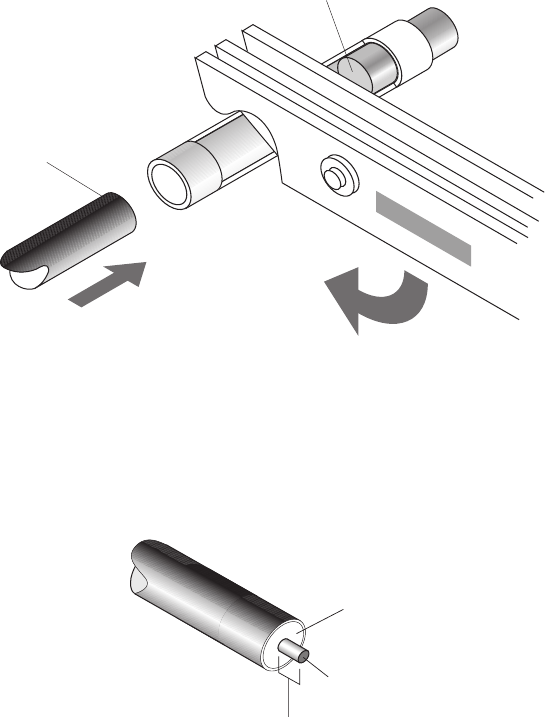
1027144–0001 Draft – Revision D.01 C–4 Terminating the IFL cable RT installation
Figure C-3 Using the spin–stripping tool to
expose the center conductor
hb012
Stripper
jaws
Gold-colored
cable stop
Barrel
Butt-cut
cable end
Squeeze and rotate
tool to strip cable.
2.
1. Insert cable
into barrel.
3. Remove jacket and dielectric
to expose center conductor.
Jacket
Dielectric
Center conductor
7/32 inch
(6 millimeters)
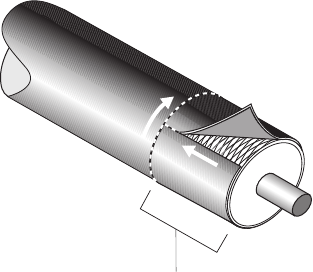
1027144–0001 Draft – Revision D.01 Terminating the IFL cable C–5RT installation
5. Using a razor knife, carefully slit the outer jacket as shown
in figure C-4.
Cut around the cable; then cut from the cable end to the first
cut. Cut completely through the jacket, but do not cut into
the braid.
6. Using the razor knife or a pair of diagonal cutters, lift the
jacket and peel it away as shown in figure C-4.
Remove jacket.
hb016
1
2
5/8 inch
(16 millimeters)
Figure C-4 Cutting and removing the jacket
7. Check:
- Braid for nicked or broken strands
- Dielectric end for a straight cut
- Center conductor for nicks and a straight cut
If you see significant damage to the braid, dielectric, or
conductor, you must cut the cable and start over. (Start
with step 1.)
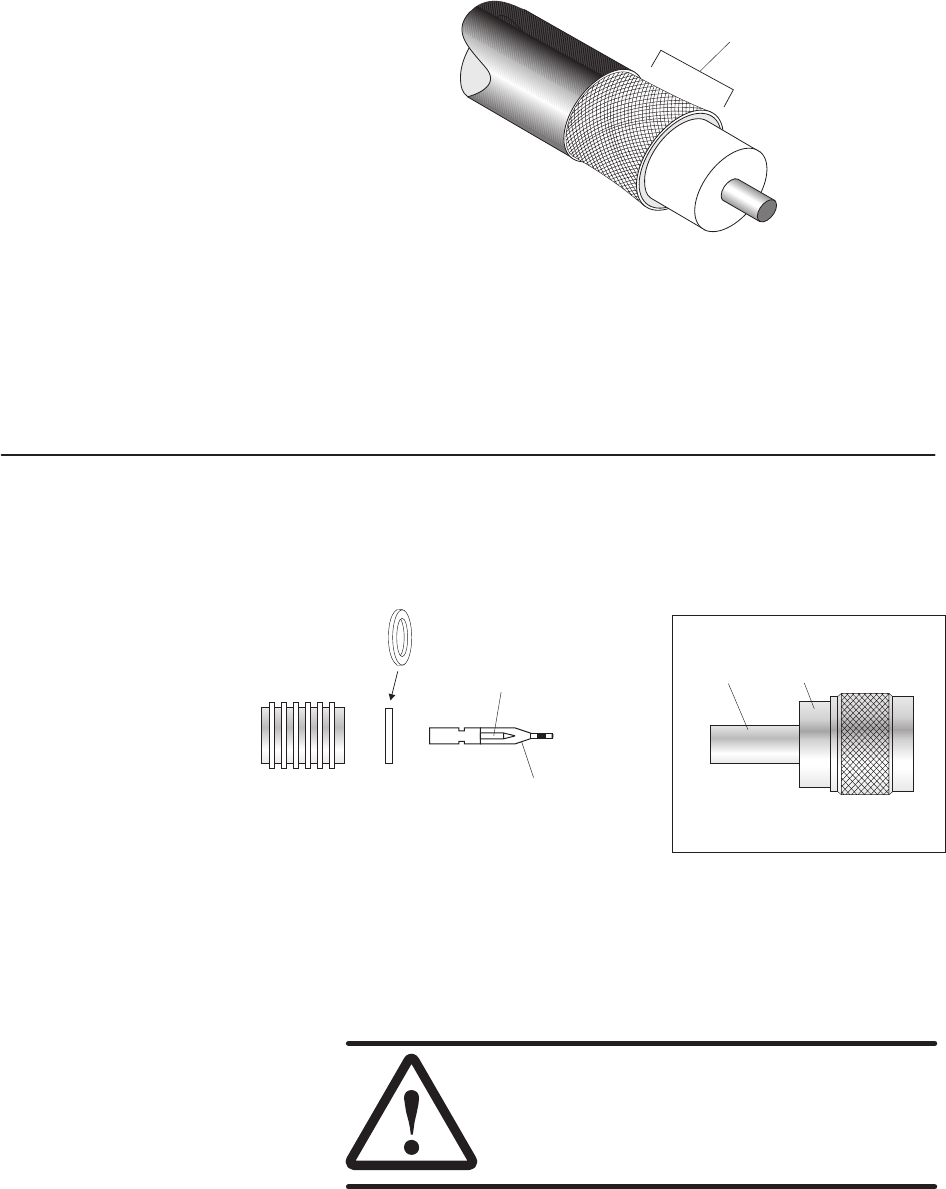
C.3
1027144–0001 Draft – Revision D.01 C–6 Terminating the IFL cable RT installation
8. Flare the braid slightly and trim to 7/16 inch (11
millimeters), as shown in figure C-5.
Jacket
Braid
hb093
7/16 inch
(11 millimeters)
Figure C-5 Braid, flared and trimmed
9. Cut approximately 1/4 inch (6 millimeters) of the excess
braid so that all braids will be under the crimp ring when
the connector is completed.
The following steps explain how to attach the IFL (N) connector.
The same type of connector is used at both ends. The connector
includes a plastic guide pin to protect the dielectric during
installation, as shown in figure C-6.
Crimp
ring
Insulating
washer
Center
pin
Plastic
guide
pin
T0006020
Support
shoulder Jam
nut
Connector body
Collar
Figure C-6 IFL (N) connector (HNS 9006284–0002)
Do not remove the plastic guide pin until instructed to do so
(step 4 on page C–8).
CAUTION
Do not install the center pin without the
plastic guide pin—doing so will damage
the dielectric material inside the connector
body.
Attaching the
connector
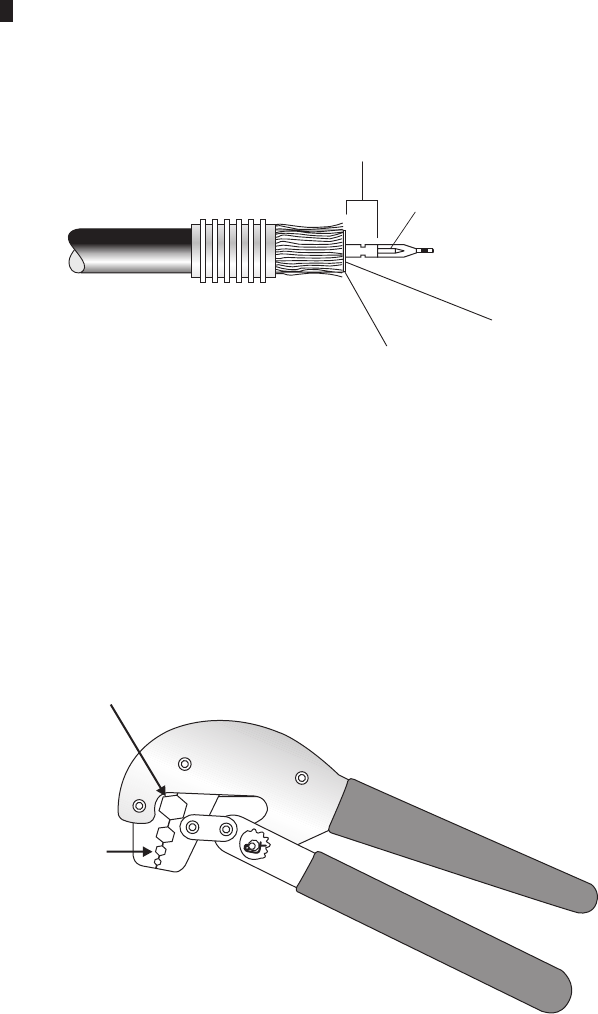
1027144–0001 Draft – Revision D.01 Terminating the IFL cable C–7RT installation
To install the cable connector, follow these steps.
1. Place the insulating washer against the dielectric.
2. Push the center pin (with guide pin attached) over the cable
center conductor, as shown in figure C-7.
T0006021
Crimp
area
Center
pin
Guide pin
Crimp flush
with washer.
Insulating
washer
Figure C-7 Installing the insulator and center pin
3. Use the HCT–231 crimp tool (figure C-8) to crimp the
center pin flush with the washer, as shown in figure C-7.
If the center pin is bent after crimping, cut the cable,
re–strip it, and attach a new center pin.
HCT - 231
Use
setting to crimp
center pin.
0.108
Use setting to crimp
the crimp ring
0.475
—but not yet.
This is a later step.
hb021
Figure C-8 Crimping tool
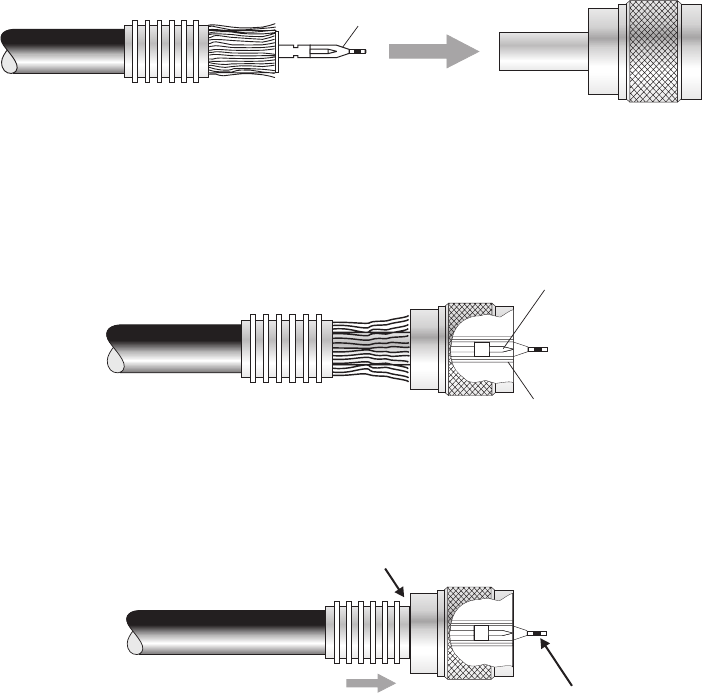
1027144–0001 Draft – Revision D.01 C–8 Terminating the IFL cable RT installation
4. Follow the instructions in figure C-9 to install the connector
body and crimp ring, and remove the guide pin.
hb022
Connector
body
Guide pin and
center pin
1. Insert guide pin through back of
connector body until the cable stops.
Crimp
ring Center pin
Guide pin
Ground socket
Center pin inside connector body
Slide crimp ring over
braid and into recess.
2. Remove and
discard guide pin.
3.
Recess
Figure C-9 Installing the connector body and crimp ring
5. Important: Verify that the center pin aligns flush or
within 1/64–inch from the ground socket edge.
If the pin is not flush or within this range, the connection
will probably be faulty.
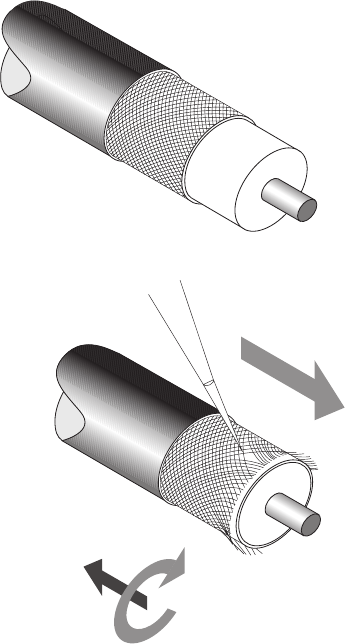
1027144–0001 Draft – Revision D.01 Terminating the IFL cable C–9RT installation
6. Comb the braid only if the crimp ring will not fit over the
shoulder and braid. If the crimp ring fits over the
shoulder and braid, skip to step 7).
a. Insert a pick or scribe into the braid and carefully
comb the strands as shown in figure C-10.
Start combing at the cut end. Comb the strands
around the entire perimeter. Work backward, from the
cut end toward the jacket—but always combing away
from the jacket, as shown in figure C-10.
Figure C-10 Combing the braid
Jacket
Braid
Comb action
Direction of travel
hb017
Note: Comb the braid all the way back to the jacket.
If part of the braid is uncombed at the jacket end,
stretching will cause the jacket and center pin to
become loose, resulting in poor conductivity.
b. Re–trim the braid to 7/16 inches (6 millimeters), as
shown in figure C-5.
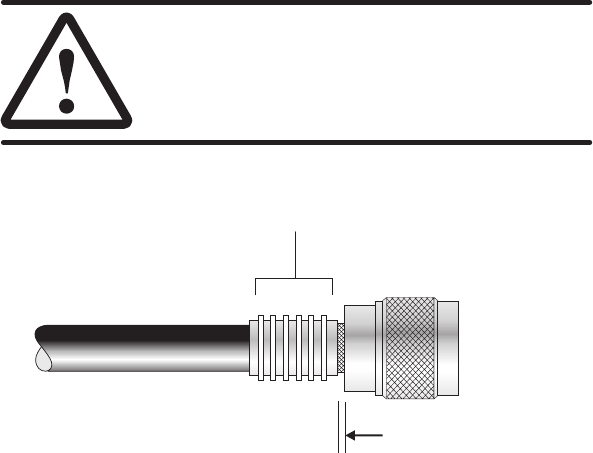
1027144–0001 Draft – Revision D.01 C–10 Terminating the IFL cable RT installation
7. While holding the connector assembly together snugly,
position the HCT–231 crimping tool, at setting 0.475, onto
the area shown in figure C-11 and securely crimp the crimp
ring into place.
CAUTION
To avoid damaging the connector body,
make sure the crimping tool does not
touch the connector jam nut.
Crimp
hb024
Maximum gap
(exposed braid):
0.03 inch (0.8 millimeter)
Best if no gap.
Figure C-11 Crimp location
Note: If the crimp ring slips and results in a gap greater
than 0.03 inch (0.8 millimeter) between the crimp ring and
the connector collar, reject the connection. Cut off the
connector and start over.
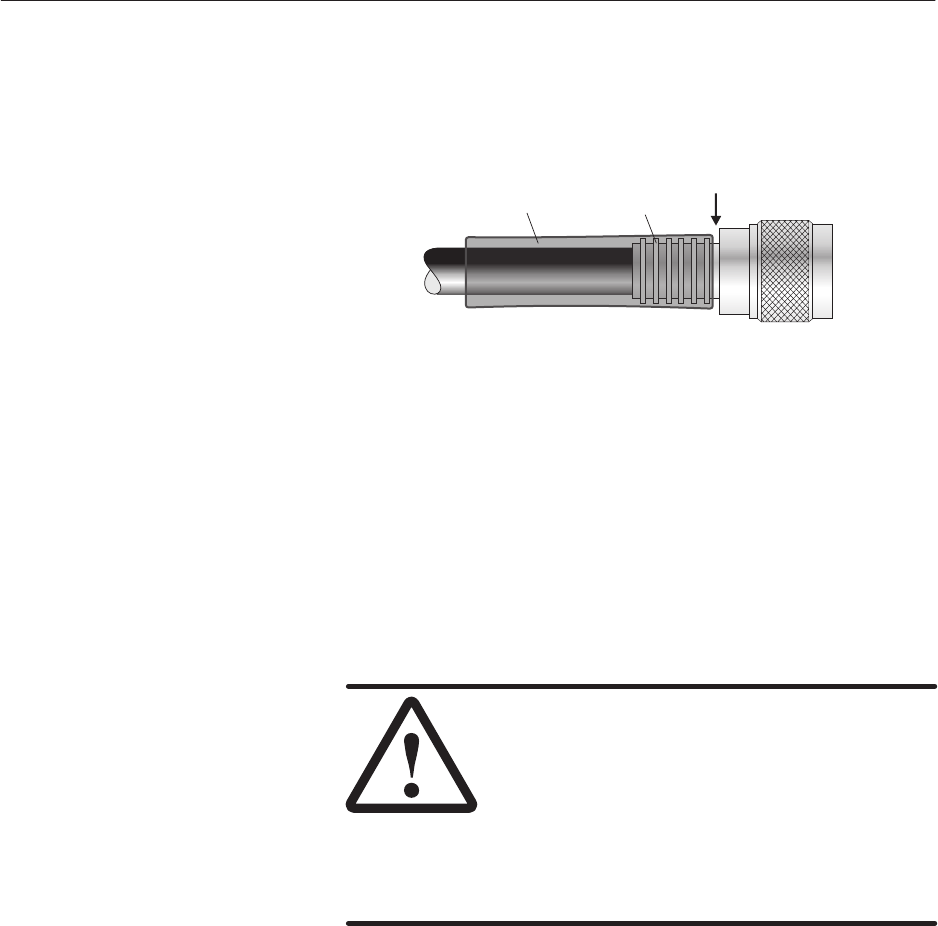
C.4
1027144–0001 Draft – Revision D.01 Terminating the IFL cable C–11RT installation
Apply the heat–shrink tubing as follows:
1. Position the heat–shrink tubing near (but not touching) the
jam nut, so it covers the crimp ring and a portion of the
connector collar, as shown in figure C-12.
Figure C-12 Heat–shrink tubing,
properly placed for shrinking
Heat-shrink
tubing
hb026
Collar Jam
nut
Crimp
ring
2. Using a heat gun, heat-shrink the tubing until it snugly fits
around the cable, crimp ring, and part of the connector
collar.
Point the connector upward. Begin heating at the connector
end, and work toward the cable. The adhesive should flow
away from the jam nut.
CAUTION
Do not allow the cable jacket and dielectric
to overheat. This can damage the cable and
cause cable failure.
During heating, the tubing may shift and
the adhesive lining may bleed. Make sure
the adhesive does not bleed onto the jam
nut and damage the connector.
To install another N connector, repeat all steps above, beginning
with the section Preparing the cable ends (page C–3).
Applying
heat–shrink tubin
g

1027144–0001 Draft – Revision D.01 Index-1
Index has not been updated
Index
A
Abbreviations (identified), A- 1
Access, buildings and equipment locations, 2–2
Acronyms (identified), A- 1
Adding SSIs, 10–2
Adjuster (for azimuth and elevation), 2–5
Adjusters (to adjust azimuth or elevation), 4–6
installing azimuth adjuster, 4–16
installing elevation adjuster, 4–19
Antenna
adjusting azimuth, 4–15
adjusting elevation, 4–18
attaching to the antenna mount, 4–13
pointing
final commissioning adjustments, 7–5
initial azimuth adjustment, 4–15
initial elevation adjustment, 4–18
troubleshooting, 9–4
voltage indications, 7–7
replacing, 10–7
repointing, 7–8
Antenna mount
collar, 4–6
installing, 4–7
installing, 4–11
torque wrench, 4–5
ATM. See OC3c–ATM SSI
Attenuator
installing, 4–22
replacing the antenna, 10–7
replacing transceiver, 10–5
types, 4–22
Azimuth
adjusting, 4–15
explained and illustrated, 4–15
Azimuth/elevation adjuster, 2–5
Azimuth/elevation adjusters. See Adjusters (to
adjust azimuth or elevation)
B
Ballast. See Concrete blocks
Bend radius (IFL cable), 5–8, 5–23
Blocks. See Concrete blocks (ballast)
Buttons on CCM, 6–37
functions, 6–38
C
Cable length
DS3–ATM, 6–26
DS3–TDM SSI, 6–25
DS3–Transparent SSI, 6–27
IFL, 5–5
Quad–DS1 SSI, 6–24
Universal–DS1 SSI, 6–26
Canadian Interference–Causing Equipment
Regulations, B–2, B–3
Canadian Standards Association, B–2, B–3
CCM
button functions, 6–38
buttons on front panel, 6–37
functions, 6–22
installing, 6–22
LEDs, indications, explained, 6–23
power–on test, 6–39
replacing, 10–12
status, 6–41
SUDS, 6–39
troubleshooting, 9–2
Channel and control module. See CCM
Chassis. See IDU chassis
Checklist. See Task checklist
Commissioning
pointing the antenna, 7–5
prerequisites, 2–6, 7–3
procedure, 7–4
RT ESN, 7–3
task checklist, 7–2
Components to be installed, 1–3
Concrete blocks (ballast), 3–11
arrangement on mount, 3–12
Connections
checking, 6–39
weatherproofing, 8–2
Corrugated metal roof, 3–12
1027144–0001 Draft – Revision D.01Index-2
Crimp tool, 5–14
Customer equipment, connecting, 8–3
Customer sign–off, 8–3
D
Diagnostic mode, 6–37
Diameter of ODU mast, 4–5
Digital voltmeter, connecting to ODU, 7–6
Dismantling an RT, 10–16
Distance – RT to HT, 7–3
Documents, related, v
Drawings
hub network schematic, 2–1
hub rooftop drawing, 2–1
RT reference drawing, 1–2
DS3–ATM SSI, 6–26
DS3–TDM SSI, 6–25
DS3–Transparent SSI, 6–27
E
EIDU
installing, 6–31
mounting, 6–32
power supplies, 6–32
uses, 6–31
EIDU FEM, 6–32
Electronic serial number. See ESN
Element Management System. See EMS
Elevation
adjusting, 4–18
explained and illustrated, 4–18
Emissions, B–2, B–3
EMS, 2–6
database, 7–3
Equipment from other vendors, v
ESN, 7–3
location, 7–3
Existing structures as ODU mounts, 3–14
Exit (LCD), 6–38
Expansion IDU. See EIDU
F
F connector location for connecting voltmeter,
7–6
Failure indication on CCM LCD, 6–40
FCC, B–2, B–3
FEMs, 6–31
EIDU FEMs, 6–32
IDU FEMs, 6–32
installing, 6–34
types, 6–32
where installed, 6–32
Fiber extender modules. See FEMs
Front panel display. See LCD
G
Grounding
lightning arrestor, 5–22
ODU, 4–26
power supply
ac, 6–12
dc, 6–13, 6–18
dual ac or dc, 6–10
H
Handling materials, 3–5
Heat–shrink tubing (for IFL cable) , 5–10, 5–18
HT
acquisition, 7–10
ID, 7–10
Hub installation, v
I
IDU, 6–4
See also IDU chassis
components, 6–4
illustrated, 6–4
standards compliance, B–3
IDU chassis
See also IDU
connecting the IFL, 6–30
dccircuit breaker, 6–19
disconnect device, 6–19
power–off circuit, 6–19
power–on test, 6–21
powering off, 6–18
Install mode, 7–4
1027144–0001 Draft – Revision D.01 Index-3
LCD. See LCD
power supply, 6–5, 6–9
ac, 6–11
dc, 6–13
dual ac or dc, 6–9
rack mounting, 6–6
options, 6–6
replacing, 10–10
slots, numbering of, 6–4
specifications. See Hub and Remote Terminal
Site Preparation Guide
temperature, 6–6
types, 6–5
IDU FEM, 6–32
IEC, B–2, B–3
IFL, replacing, 10–14
IFL cable
bend radius, 5–8, 5–23
connecting to CCM (IDU), 6–30
connecting to ODU, 5–24
connections, 5–4
finishing the installation, 5–25
installed in two segments, 5–4
installing inside the building, 5–8
installing on the roof, 5–23
length, 5–8, 5–23
maximum, 5–5
moisture contamination, 8–2
penetration sleeve, 5–7
plan, 5–4
plenum (in conduit with power cables), 5–5
routing guidelines, 5–5
specifications, 5–3
terminating, 5–9
testing, 5–24
UL requirements, 5–3
weatherproofing connections, 8–2
Immunity, B–2, B–3
Indoor unit. See IDU and IDU chassis
Inspecting the installed equipment, 8–3
Install mode, 7–4
Installation summary, 1–3
Installers
number needed, v, 3–5
qualifications, v
Intrafacility link. See IFL cable
L
LCD, 6–36, 6–39
button functions, 6–38
buttons (for scrolling, selecting), 6–37
diagnostic mode, 6–37
Exit, 6–38
menu map, 6–37
status conditions (explained), 6–41
status of CCM, SSIs, or ODU, 6–41
SUDS (diagnostics) sequence, 6–36, 6–39
LEDs, indications, explained
CCM, 6–23
SSIs, 6–29
Lightning arrestor (for IFL), 5–4, 5–19
grounding, 5–22
Lightning protection, 4–27
Liquid crystal display. See LCD
Location
IDU, 6–5
ODU, 3–4
M
Main Menu (CCM LCD), 6–37
Maintenance, 10–1
Mast, diameter, 4–5
Mast mount, 3–3
location, 3–4
standard type, 3–7
assembly instructions, 3–7
types, 3–6
using existing structures, 3–14
Materials, handling, 3–5
Mechanical attenuator
installing, 4–22
replacing the antenna, 10–7
replacing tranceiver, 10–5
types, 4–22
Menu map for CCM LCD, 6–37
Moisture contamination, 8–2
Mounts. See Mast mount and Antenna mount
Moving SSIs, 10–2
Multiple IFL cables, 5–25
1027144–0001 Draft – Revision D.01Index-4
N
N connectors
attaching to IFL cable, 5–13
location (IFL cable), 5–4
National Electric Code (NEC), B–2
O
ODU, 4–1
connecting digital voltmeter, 7–6
connecting the IFL cable, 5–24
frequency, 7–4
grounding, 4–26
illustration, 4–4
location, 2–1
replacing, 10–3
standards compliance, B–2
status, 6–43
transporting to the roof, 4–5
ODU installer tool kit, 2–4
illustration, 2–5
removing tools, 7–9
tools included, 4–6
uses, 4–6
ODU location, 3–4
Outdoor unit. See ODU
P
Penetrating the roof, 5–6
Penetration sleeve, 5–7
Personnel
number of installers, v
qualifications, installers, v
Pointing the antenna
final commissioning adjustments, 7–5
initial azimuth adjustment, 4–15
initial elevation adjustment, 4–18
troubleshooting, 9–4
Power input requirement
ac power supply, 6–11
dc power supply, 6–13
Power supply (IDU), 6–5, 6–9
ac, 6–11
connecting power, 6–11
grounding, 6–12
power input requirement, 6–11
dc, 6–13
connecting power, 6–14
grounding, 6–13, 6–18
power input requirement, 6–13
powering off, 6–18
dual ac or dc, 6–9
See also Power supply (IDU), dc
grounding, 6–10
Power–on test, CCM, 6–39
Prerequisites
commissioning, 2–6, 7–3
installation, 2–1
Publications, related, v
Q
Quad–DS1 SSI, 6–24
RJ–48X connector pinouts, 6–24
Qualifications for installers, v
R
Rack
grounding, 6–3
mounting, 6–6
options, 6–6
safety guidelines, 6–6
Related publications, v
Remote terminal. See RT
Removing the installation tools, 7–9
Repairs, 9–5
Replacing
antenna, 10–7
CCM, 10–12
faulty components, 9–5
IDU chassis, 10–10
IFL, 10–14
ODU, 10–3
SSIs, 10–13
transceiver, 10–4
Repointing the antenna, 7–8
RF arrestor, 5–20, 5–23
RJ–48X connector pinouts, 6–24
Roof types, 3–6
corrugated metal, 3–12
RT
defined, 1–2
dismantling, 10–16
1027144–0001 Draft – Revision D.01 Index-5
S
Safety information, vii
rack mounting, 6–6
Service loops, 5–8
Service–specific interface. See SSI
Site Data Record, 2–1
Site preparation, v
Slots, IDU chassis
numbering of, 6–4
where CCM and SSIs are installed, 6–22,
6–24, 6–42
Spin–stripping tool (for IFL cable), 5–10
SSIs
adding, 10–2
DS3–ATM, 6–26
DS3–TDM, 6–25
DS3–Transparent, 6–27
function, 6–24
hot swapping, 10–2
installing, 6–28
chassis slots, 6–24
LEDs, indications, explained, 6–29
moving, 10–2
numbering, 6–42
Quad–DS1, 6–24
replacing, 10–13
status, 6–42
types, 6–24
Universal–DS1, 6–26
Standards compliance, B–1
Startup diagnostics. See SUDS
Status of CCM, SSIs, or ODU, 6–41
SUDS, 6–36, 6–39
failure indication, 6–40
test and display sequence, 6–36, 6–39
Summary of installation, 1–3
T
Task checklist
IFL cable and lightning arrestor installation,
5–2
indoor equipment installation, 6–2
mast mount assembly and installation, 3–2
ODU installation, 4–2
RT commissioning, 7–2
Temperature, IDU chassis, 6–6
Terminating the IFL cable, 5–9
Testing, IFL cable and connectors, 5–24
Tools required for installation, 2–3
removing, 7–9
Torque
antenna bracket, 4–20
antenna mast clamp, 4–16, 7–5
temporary installation collar, 4–16
Torque wrench for antenna mount, 4–5
Transceiver
attaching to the antenna, 4–24
replacing, 10–4
Troubleshooting, 9–1
antenna pointing, 9–4
CCM, 9–2
CCM won’t download, 9–5
RT Disabled message, 9–6
U
Underwriters Laboratories (UL), B–2, B–3
Universal–DS1 SSI, 6–26
V
Voltage indications for antenna pointing, 7–7
W
Warnings (safety), explained, vii
Weatherproofing, 8–2
Wrist strap (ESD), 6–22, 6–28, 6–34, 10–2,
10–10, 10–12, 10–13