Husky Def Stainless Steel Nozzle Owner S Manual
2014-07-06
: Husky Husky-Def-Stainless-Steel-Nozzle-Owner-S-Manual husky-def-stainless-steel-nozzle-owner-s-manual husky pdf
Open the PDF directly: View PDF .
Page Count: 4

1. Turn off dispenser and relieve line pressure.
2. Remove old nozzle and drain into approved container.
3. Inspect o-ring for damage. Replace if necessary.
4. Install new nozzle - do not use thread sealant (Teon tape, anti-seize or any other kind
of sealant).
5. Tighten rmly, approximately 15 - 20 lbf•ft / 20.3 - 27.1 N•m, but do not overtighten.
6. Pressurize system and visually inspect for leaks.
7. Test nozzle for proper automatic shut off between 5 - 10 gpm / 18.9 - 37.9 Lpm.
DO NOT OVERTIGHTEN. USE WRENCH ON HOSE NUT ONLY.
Diesel Exhaust Fluid Nozzles
DEF
NOZZLE
Model #731004, 731088 and 731091
Recommended Installation, Maintenance
and Inspection Instructions
Husky Corporation • 2325 Husky Way • Pacic, MO 63069 • Phone: (800) 325-3558 • Fax: (636) 825-7300 • www.husky.com
Page 1 009261-1 9/2010
INSTALLATION INSTRUCTIONS
IF DRIVE OFF OCCURS
TESTING / MAINTENANCE / INSPECTION
WARNING!
Designed for use at diesel exhaust uid dispensing
facilities only.
• Turn off dispenser and relieve line pressure.
• Check for loose or damaged spout.
• Check spout tip - should be in round and sensing port should be clear of debris.
• Perform ow test of nozzle automatic shut off between 5 - 10 gpm / 18.9 - 37.9 Lpm.
• Check for leaks.
Daily
• Check for leaks / stains.
• Check for loose spouts.
• Check for damage.
• Check for bent lever.
• Check for broken clip / trigger
spring.
• Check nozzle for crystallization.
Monthly
• Check nozzle automatic shut off
between 5 - 10 gpm / 18.9 -
37.9 Lpm.
Annually
• Check "remove after" date.
• To remove crystallization, clean / rinse
DEF products by ushing all internal
passages and external parts with
deionized water.
• All drive aways, maintenance and
inspection activities must be logged
using the serial number of the individual
product.
• Apply city, state, or federal testing
regulations as appropriate.
ANY TEST / INSPECTION FAILURE
REQUIRES IMMEDIATE EQUIPMENT
REPLACEMENT OR REMOVAL FROM
SERVICE.
MADE IN THE USA
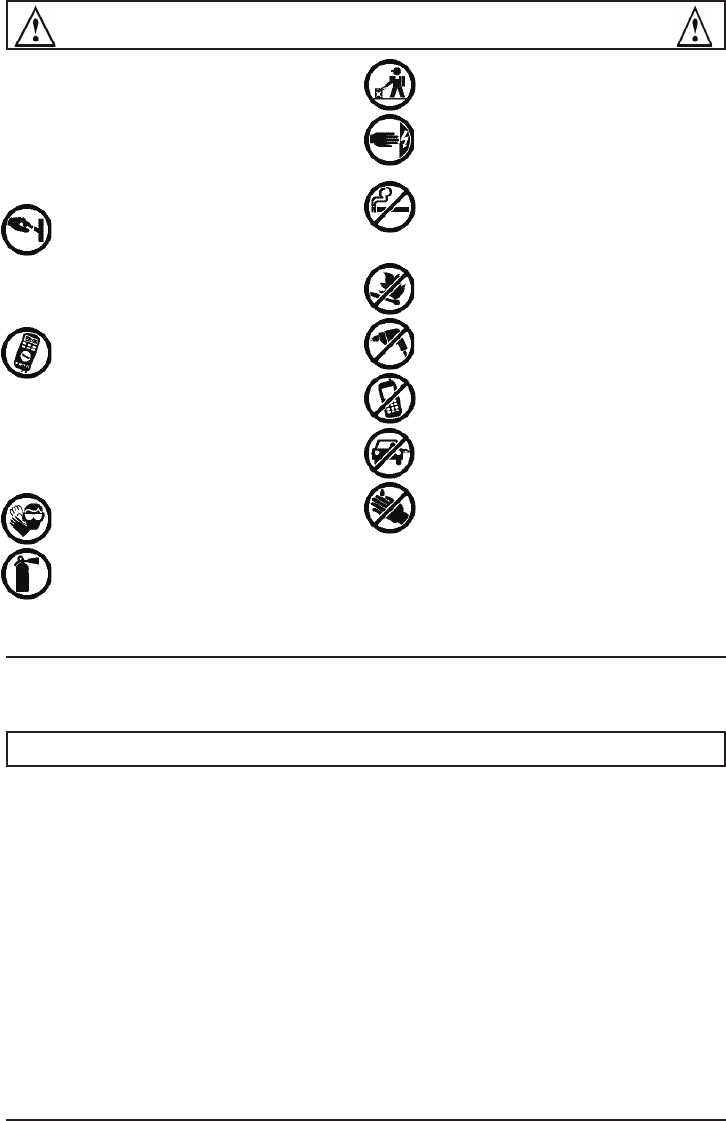
CAUTION: DO NOT TOP OFF!
Topping off can lead to spills and splashes.
ALWAYS ADHERE TO INSTALLATION / USAGE INSTRUCTIONS AND WARNINGS.
Improper use may result in injury, damage, or hazardous spill.
WARRANTY
VAPOR PRODUCTS – Husky Corporation will, at its option, repair, replace, or credit the purchase price of any Husky
manufactured product which proves upon examination by Husky, to be defective in material and/or workmanship for a period of one (1)
year of installation or fteen (15) months from the manufacture date of shipment by Husky, whichever occurs rst. The warranty period on
repaired or replacement vapor recovery products is only for the remainder of the warranty period of the defective product.
CONVENTIONAL PRODUCTS – Husky Corporation will, at its option, repair, replace, or credit the purchase price of any Husky
manufactured product which proves upon examination by Husky, to be defective in material and/or workmanship for a period of one (1)
year from the manufacture date of shipment by Husky.
Buyer must return the products to Husky, transportation charges prepaid. This Warranty excludes the replaceable bellows,
bellows spring assembly, spout assembly and scuff guard, unless (i) damage is obvious when the product is removed from shipping carton
and (ii) the defective product is returned to Husky prior to use. This warranty does not apply to equipment or parts which have been installed
improperly, damaged by misuse, improper operation or maintenance, or which are altered or repaired in any way.
The warranty provisions contained herein apply only to original purchasers who use the equipment for commercial or
industrial purposes. There are no other warranties of merchantability, tness for a particular purpose, or otherwise, and any other such
warranties are hereby specically disclaimed.
Husky assumes no liability for labor charges or other costs incurred by Buyer incidental to the service, adjustment, repair, return,
removal or replacement of products. Husky assumes no liability for any incidental, consequential, or other damages under any warranty,
express or implied, and all such liability is hereby expressly excluded.
Husky reserves the right to change or improve the design of any Husky fuel dispensing equipment without assuming any
obligations to modify any fuel dispensing equipment previously manufactured.
GENERAL WARNINGS / INSTRUCTIONS
• Use of equipment is at individuals’ own risk.
• Always abide and adhere to city, state,
and federal regulations regarding use and
installation of dispensing equipment.
• Always follow the product manufacturer’s
installation and maintenance instructions.
• Always turn off all power to dispenser during
maintenance and inspection activities.
• Always close the shear valves during
maintenance and inspection activities.
• Always relieve pressure from system prior
to performing maintenance activities.
• Always check continuity after installation
using a megohmeter (Refer to PEI RP 400
for details).
• Always replace or remove from service
damaged or leaking dispensing equipment
immediately.
• Always report leaks / spills / accidents to
appropriate authorities.
• Always wear appropriate safety equipment
during maintenance activities.
• Always have appropriate re extinguishing
equipment within 5 ft / 1.5 m of dispensers.
• Never use thread sealant (Teon tape, anti-
seize or any other kind of sealant).
• Always clean / rinse DEF products with
deionized water.
• Always place containers on the ground
before lling.
• Always discharge static electricity before
using or servicing equipment by touching a
metal part of the dispenser before and after
fueling vehicle.
• Never smoke within 20 ft / 6.1 m of
dispensers.
• Never keep in service past recommended
life.
• Never leave the nozzle unattended while
dispensing fuel.
• Never use sparking or aming devices within
20 ft / 6.1 m of dispensers.
• Never use power tools near dispensers or to
aid in the installation process.
• Never use cell phone within 20 ft / 6.1 m of
dispensers.
• Never reenter car when fueling vehicle.
• Never allow gasoline to touch eyes or skin.
• Never use at ow rates in excess of
regulatory guidelines.
• Never use at ow rates less than 5 gpm /
18.9 Lpm.
• Never dispense ammable material into
unapproved containers.
• Never dispense fuel without a valid driver’s
license.
Husky Corporation • 2325 Husky Way • Pacic, MO 63069 • Phone: (800) 325-3558 • Fax: (636) 825-7300 • www.husky.com
Page 2 009261-1 9/2010
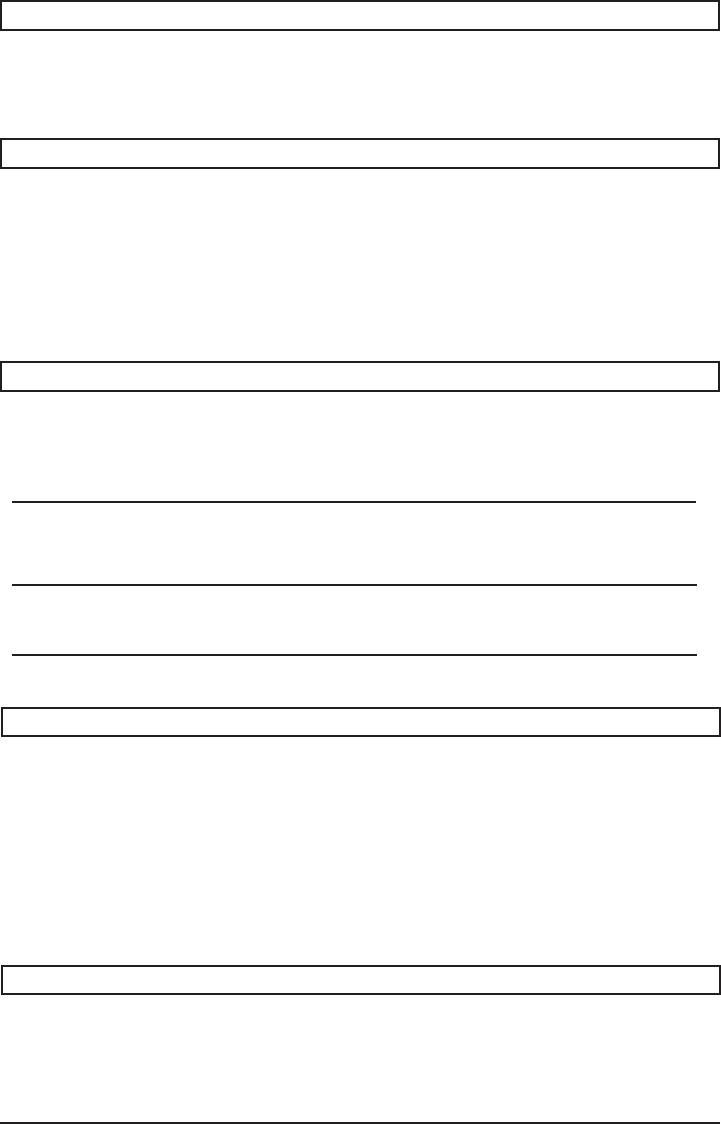
Fuel Type Test and warranty for Diesel Exhaust
Fluid dispensing only
Flow Rate 10 gpm / 37.9 Lpm
Body Stainless steel
Disc Fluorocarbon
Packing Double O-ring seal protected by ber
reinforced Teon
Lever One piece contoured steel
Shipping Weight 4.6 lbs / 2.1 kg
Threads 1" / 25.4 mm BSPP
Spout ¾" / 19 mm O.D.
Case Quantity 15
Patents Pending
GENERAL TECHNICAL DATA
CLEANING INSTRUCTIONS
Nozzle keeps shutting off or won't dispense... 1. Make sure dispenser is on and activated.
2. Slow down ow rate - use lower notch on clip.
3. Clean spout tip end.
4. Clean or replace lter.
5. Inspect Safe-T-Break®.
6. Replace spout assembly.
7. Clean loss motion diaphragm cartridge assembly.
Nozzle won't shut off... 1. Check ow rate - minimum of 3 gpm / 11.4 Lpm required.
2. Remove nozzle and drain hose.
3. Check vacuum cap screws are tightened securely.
4. Clean loss motion diaphragm cartridge assembly.
5. Clean poppet valve / venturi cartridge assembly.
Nozzle leaks... 1. Check for loose spout.
2. Check hose connection.
3. Check for cracks in nozzle and hose threads.
4. Replace poppet valve / venturi cartridge assembly.
Low ow rate... 1. Verify dispenser is not in slow ow rate mode.
2. Check for system leaks.
TROUBLESHOOTING GUIDE
Husky Corporation • 2325 Husky Way • Pacic, MO 63069 • Phone: (800) 325-3558 • Fax: (636) 825-7300 • www.husky.com
Page 3 009261-1 9/2010
1. Activate dispenser.
2. Insert spout into ll pipe opening.
3. Lower hose end of nozzle so the spout spring catches the inside
of the ll pipe.
4. Raise the lever and begin dispensing.
5. Nozzle will shut off automatically when the tank is full.
6. Wait 15 seconds to allow any uid remaining in the spout to
drain.
7. Remove nozzle from ll pipe by raising hose end of the nozzle.
8. Return nozzle to nozzle boot.
NOTE: Nozzle is equipped with a unique Flo-Stop™ device that shuts off the nozzle if it falls from ll
pipe or raises above horizontal.
OPERATION INSTRUCTIONS
HOLD OPEN CLIP INSTRUCTIONS
Model #3593 Hold Open Clip Kit
INSTALLATION
1. Remove nozzle from hose and drain.
2. Position latch spring under latch clip and hose them in place.
The latch clip should straddle the mating holes in the trigger
lever.
3. Insert latch rivet through latch clip and lever, making sure latch
spring is secured in position by the rivet.
4. Install push nut on rivet - DO NOT hammer in place.
5. Squeeze lever several times to check operation.
6. Verify clip and lever are parallel.
NOTE: Field installation of the hold open clip is NOT UL approved because improper installation
may cause the nozzle to fail.
REMOVAL
1. Remove nozzle from hose and drain.
2. Place nozzle on a at surface in safe location.
3. Hold up on the latch clip to prevent rivet from rotating.
4. Drill off the riveted end using a 1/4 in / 6.4 mm bit.
5. Remove clip, rivet and torsion clip spring.
6. Do not remove latch plate.
NOTE: Nozzles can be ordered without clips.
1. Remove nozzle from hose and drain.
2. Remove nozzle guard and wafe splash guard (if applicable).
3. Remove spout assembly, poppet valve / venturi cartridge,
plunger cartridge, and loss motion diaphragm cartridge
according to the manufacturers instructions included on page 4
of this document.
4. Clean the spout assembly - pour deionized water into
end of the vent tube to ush both the vent tube and
StreamShaper™.
5. Clean the poppet valve / venturi cartridge - flush all internal
passages and external parts with deionized water.
6. Clean the plunger cartridge - flush all internal passages and
external parts with deionized water.
7. Clean the loss motion diaphragm cartridge - flush vacuum
passages and external parts with deionized water.
8. Inspect spout assembly and all cartridges for damage.
9. Replace any damaged or cracked o-rings.
10. Reinstall spout assembly and all cartridges according to the
manufacturers installation instructions included on page 4 of
this document.
11. Reinstall nozzle to hose according to the manufacturers
installation instructions included on page 1 of this document.
Only clean DEF products with deionized water.
Do not reinstall damaged spout assemblies or cartridges.
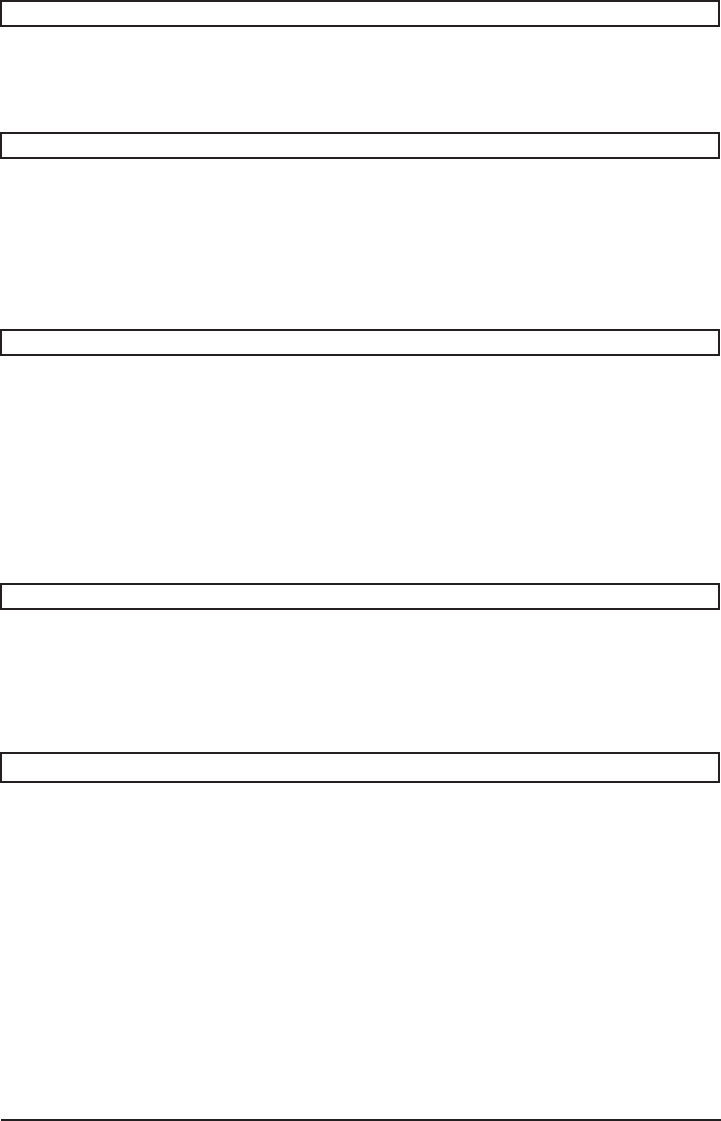
GUARD REPLACEMENT INSTRUCTIONS
EASY-ON MATE GUARD
Model #0226
1. Turn off dispenser and relieve line pressure.
2. Remove wafe splash guard (if applicable).
3. Remove old nozzle guard.
4. Install new easy-on mate guard over spout and pull back.
5. Re-install wafe splash guard (if applicable) over spout
lock nut.
HANDLE COVER
Model #7376
1. Remove old handle cover.
2. Snap new handle cover in place.
LEVER COVER
Model #5494
1. Remove old lever cover.
2. Snap new lever cover into place.
WAFFLE SPLASH GUARD
Model #1808
1. Remove old wafe splash guard.
2. Install new wafe splash guard over spout lock nut.
POPD™ MATE GUARD
Model #8169, #8170
1. Turn off dispenser and relieve line pressure.
2. Remove wafe splash guard (if applicable).
3. Remove old nozzle guard.
4. Install new POPD™ mate guard over spout and pull back.
5. Re-install wafe splash guard (if applicable) over spout
lock nut.
6. Install desired advertisement and clear cover.
POPD™ CLEAR COVER
Model #6628, #8181
1. Trim advertisement to appropriate size.
2. Turn clear cover "inside out".
3. Center advertisement on POPD™ guard.
4. Lay clear cover over advertisement, making sure the
advertisement stays centered, and turn it "right side out".
5. Conrm the cover is securely in place.
Husky Corporation • 2325 Husky Way • Pacic, MO 63069 • Phone: (800) 325-3558 • Fax: (636) 825-7300 • www.husky.com
Page 4 009261-1 9/2010
POPPET VALVE / VENTURI CARTRIDGE INSTRUCTIONS
PLUNGER CARTRIDGE INSTRUCTIONS
LOSS MOTION DIAPHRAGM CARTRIDGE INSTRUCTIONS
Model #7150 Poppet Valve / Venturi Cartridge Assembly
1. Remove nozzle from hose and drain.
2. Place nozzle on at surface.
3. Remove body cap - CAUTION: Body cap will be under spring
pressure.
4. Remove poppet spring.
5. Remove Poppet Valve / Venturi Cartridge Assembly by pulling
on the tab.
6. Insert new Poppet Valve / Venturi Cartridge Assembly.
7. Verify top of the cartridge is ush with the bottom of the body
cap threads in nozzle casting.
8. Reinstall poppet spring.
9. Reinstall body cap - tighten rmly, approximately 15 - 20 lbf•ft
/ 20.3 - 27.1 N•m. Do not overtighten.
10. Reinstall nozzle to hose.
11. Perform ow test of nozzle automatic shut off between 5 -
10 gpm / 18.9 - 37.9 Lpm.
12. Check for leaks.
Model #7160 Plunger Cartridge Assembly
1. Remove nozzle from hose and drain.
2. Place nozzle upside down on at surface.
3. Remove nozzle hand guard and screws.
4. Remove lever pin from Plunger Cartridge Assembly.
5. Remove lever assembly and latch plate.
6. Turn nozzle right-side up.
7. Remove vacuum cap, screws and washers - CAUTION:
Vacuum cap will be under spring pressure.
8. Remove Loss Motion Diaphragm Cartridge Assembly.
9. Remove Plunger Cartridge Assembly.
10. Insert new Plunger Cartridge Assembly.
11. Reinstall Loss Motion Diaphragm Cartridge Assembly.
12. Verify holes in cartridge align with the holes in the nozzle
casting.
13. Reinstall vacuum cap.
14. Tighten screws rmly - approximately 10 lbf•in / 13 N•m. Do
not overtighten.
15. Align lever assembly and latch plate to Plunger Cartridge
lever pin hole.
16. Reinstall lever pin.
17. Reinstall nozzle hand guard.
18. Tighten screws one half (½) turn past hand tight - do not
overtighten.
19. Reinstall nozzle to hose.
20. Perform ow test of nozzle automatic shut off between 5 -
10 gpm / 18.9 - 37.9 Lpm.
21. Check for leaks.
Model #7163 Loss Motion Diaphragm Cartridge Assembly
1. Remove nozzle from hose and drain.
2. Place nozzle on at surface.
3. Remove vacuum cap, screws and washers - CAUTION:
Vacuum cap will be under spring pressure.
4. Remove Loss Motion Diaphragm Cartridge Assembly.
5. Insert new Loss Motion Diaphragm Cartridge Assembly.
6. Verify holes in cartridge align with the holes in the nozzle
casting.
7. Reinstall vacuum cap.
8. Tighten screws rmly - approximately 10 lbf•in / 13 N•m. Do
not overtighten.
9. Reinstall nozzle to hose.
10. Perform ow test of nozzle automatic shut off between 5 -
10 gpm / 18.9 - 37.9 Lpm.
11. Check for leaks.
SPOUT REPLACEMENT INSTRUCTIONS
Model #7360 Spout with Spout Ring, without Magnetic Steel Ball;
#7364 Spout with Spout Ring and Magnetic Steel Ball;
#7362 Spout without Spout Ring and Magnetic Steel Ball
1. Remove spout lock nut and spout.
2. Remove and discard spout seal.
3. Place new spout seal in groove.
4. Insert new spout into body making sure the vent tube is in the
port.
5. While holding the spout in proper alignment, tighten the spout
lock nut rmly, approximately 35 - 60 lbf•ft / 47 - 81 N•m. Do
not overtighten.