Inpeco Spa a Socio Unico CANLANQ701 RFID - Radio Frequency Identification Device for Sample Carriers User Manual Sirius Digital Servo Drivers
Inpeco Spa a Socio Unico RFID - Radio Frequency Identification Device for Sample Carriers Sirius Digital Servo Drivers
Users Manual


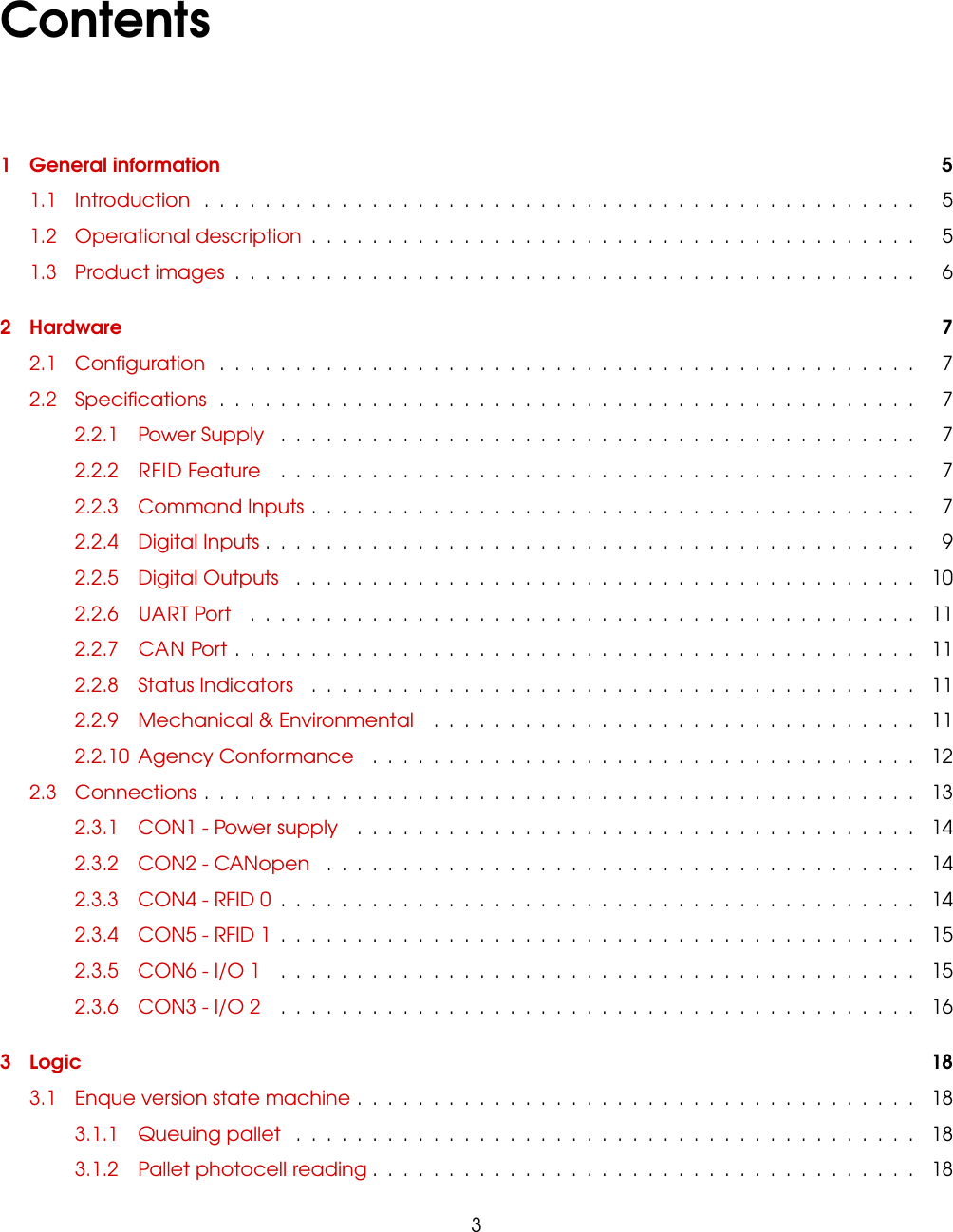


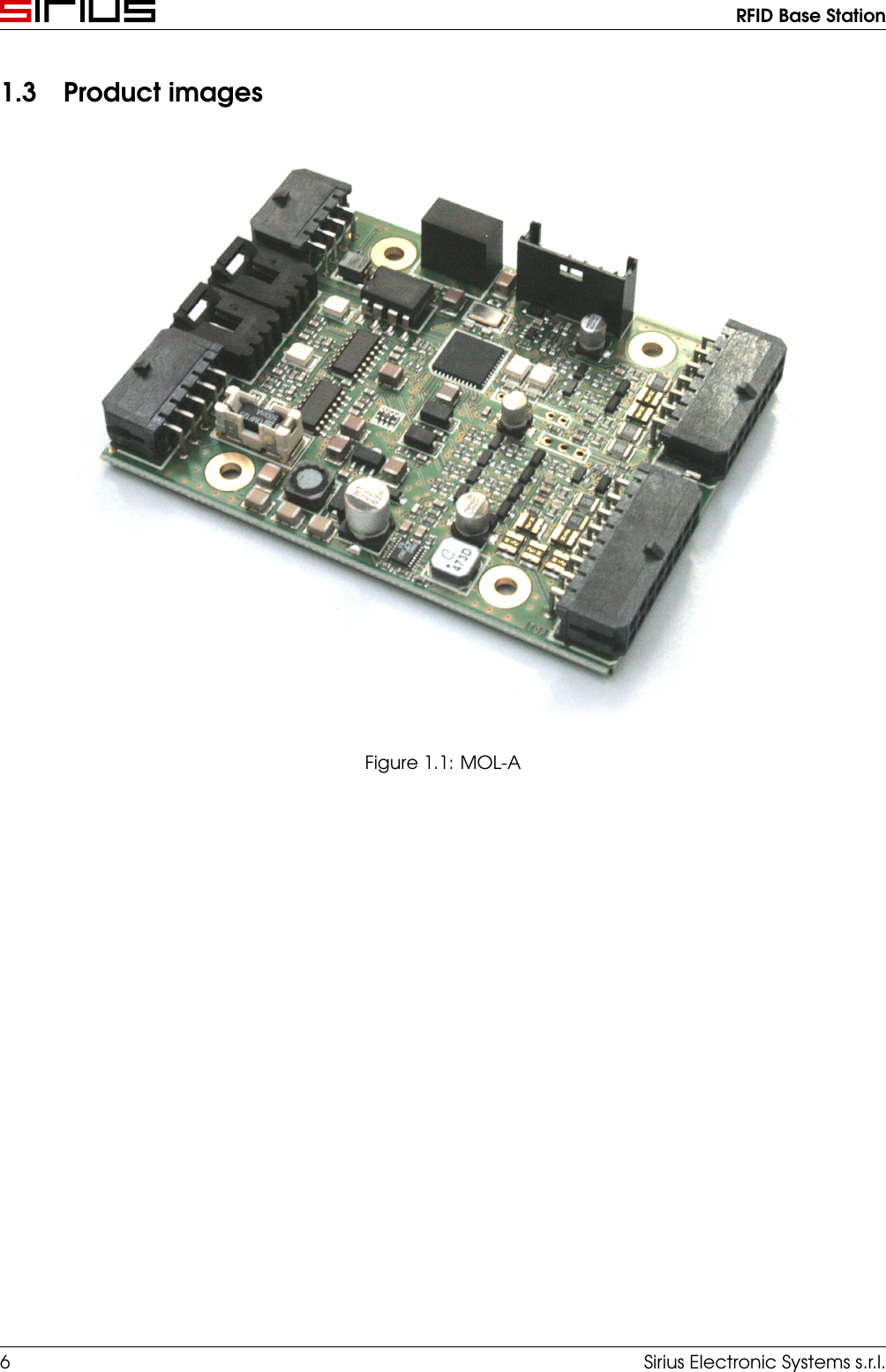
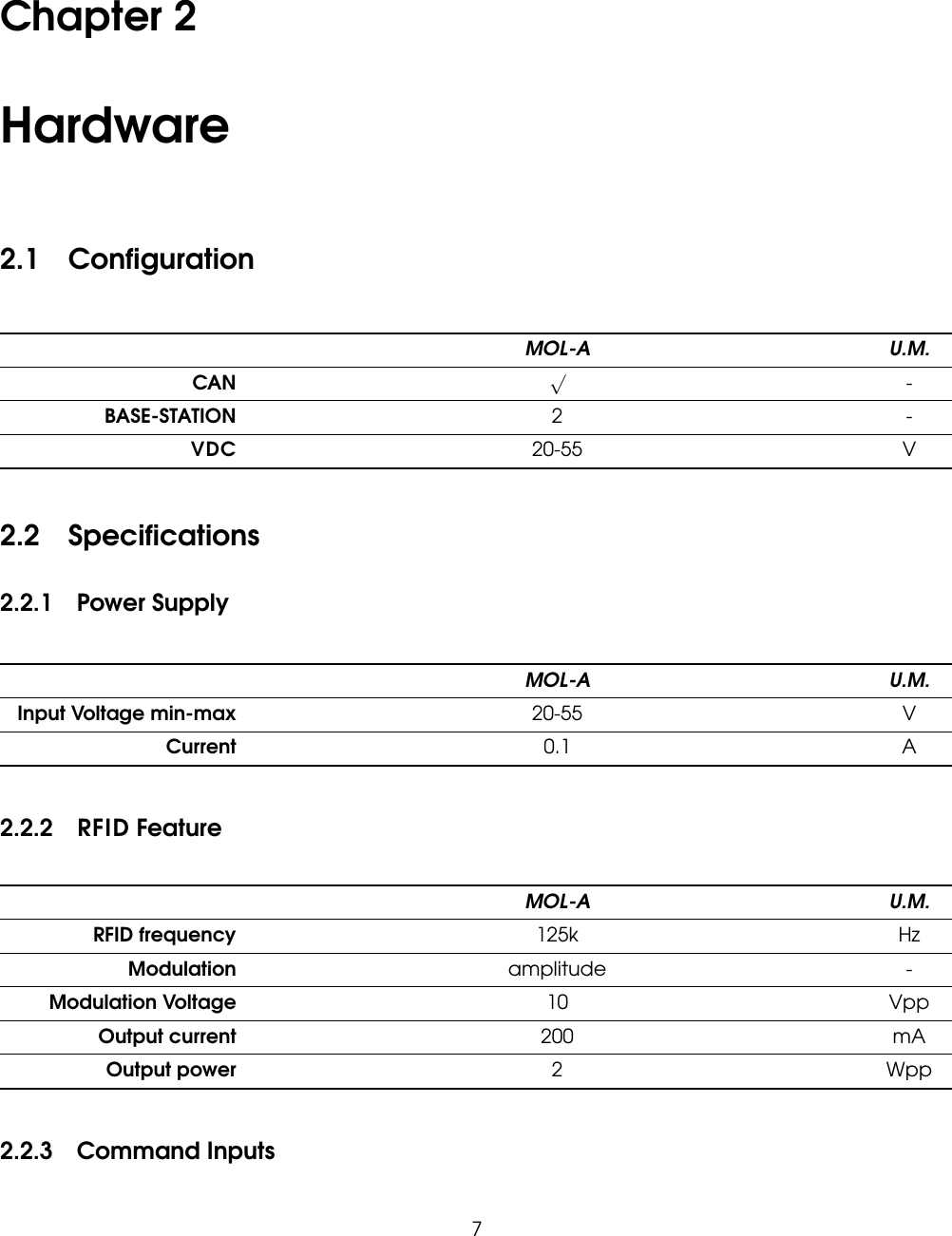
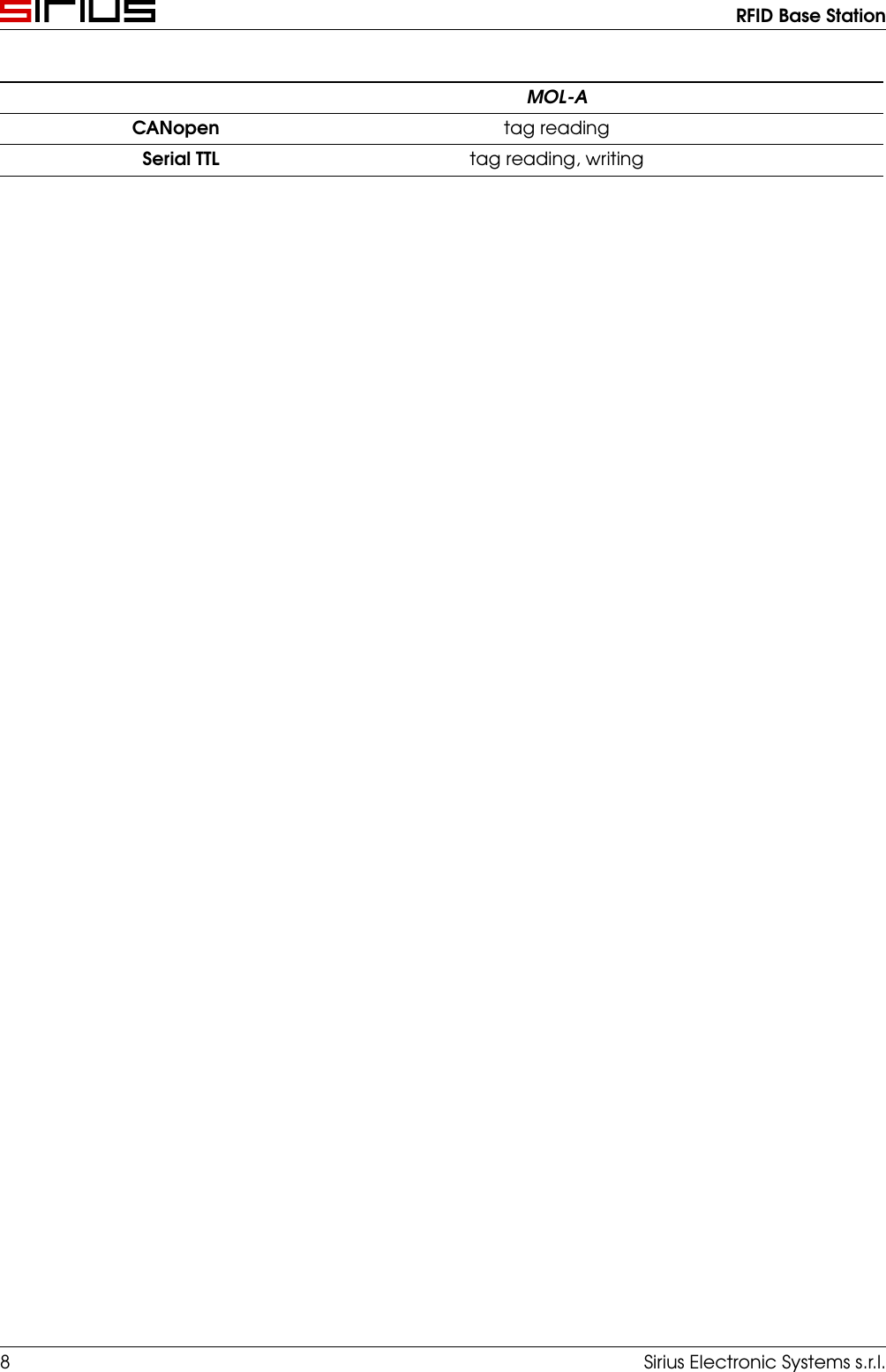
![RFID Base Station2.2.4 Digital InputsMOL-ANumber, type 5, non-insulatedAll inputs operating from 24V with RC filterLogic levels Vin-LO < 5.6V, Vin-HI > 13V[IN0..4] 2 Medium Speed inputs with 22us RCCurrent rating 10mA @ 24VFigure 2.1: MS InputsSirius Electronic Systems s.r.l. 9](https://usermanual.wiki/Inpeco-Spa-a-Socio-Unico/CANLANQ701/User-Guide-3357255-Page-9.png)
![RFID Base Station2.2.5 Digital OutputsMOL-ANumber, type 7, non-insulated[OUT0..6] Current-sourcing MOSFET at 24V (PNP)Current rating 200mA with PTC protectionFigure 2.2: Output10 Sirius Electronic Systems s.r.l.](https://usermanual.wiki/Inpeco-Spa-a-Socio-Unico/CANLANQ701/User-Guide-3357255-Page-10.png)
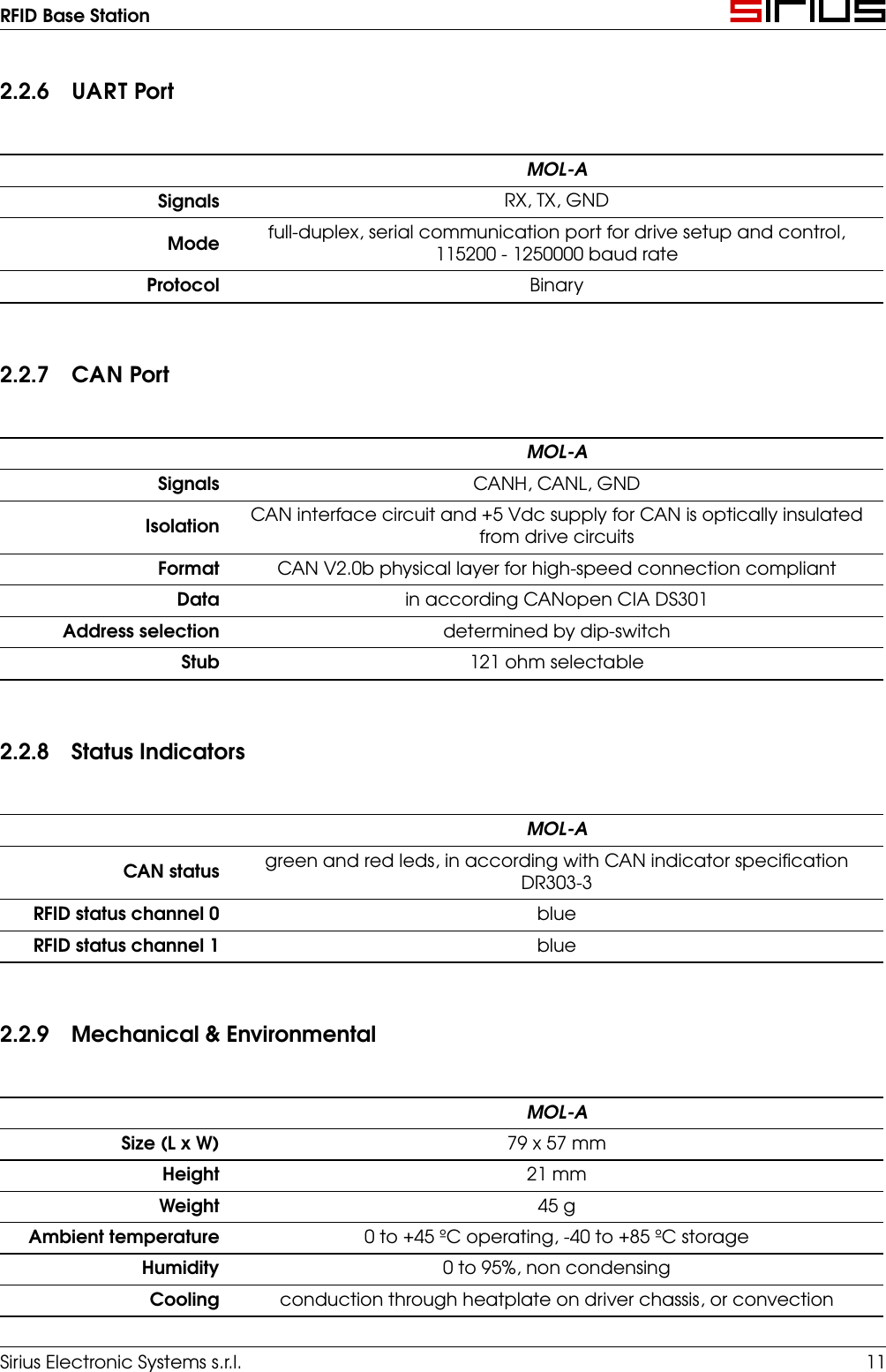
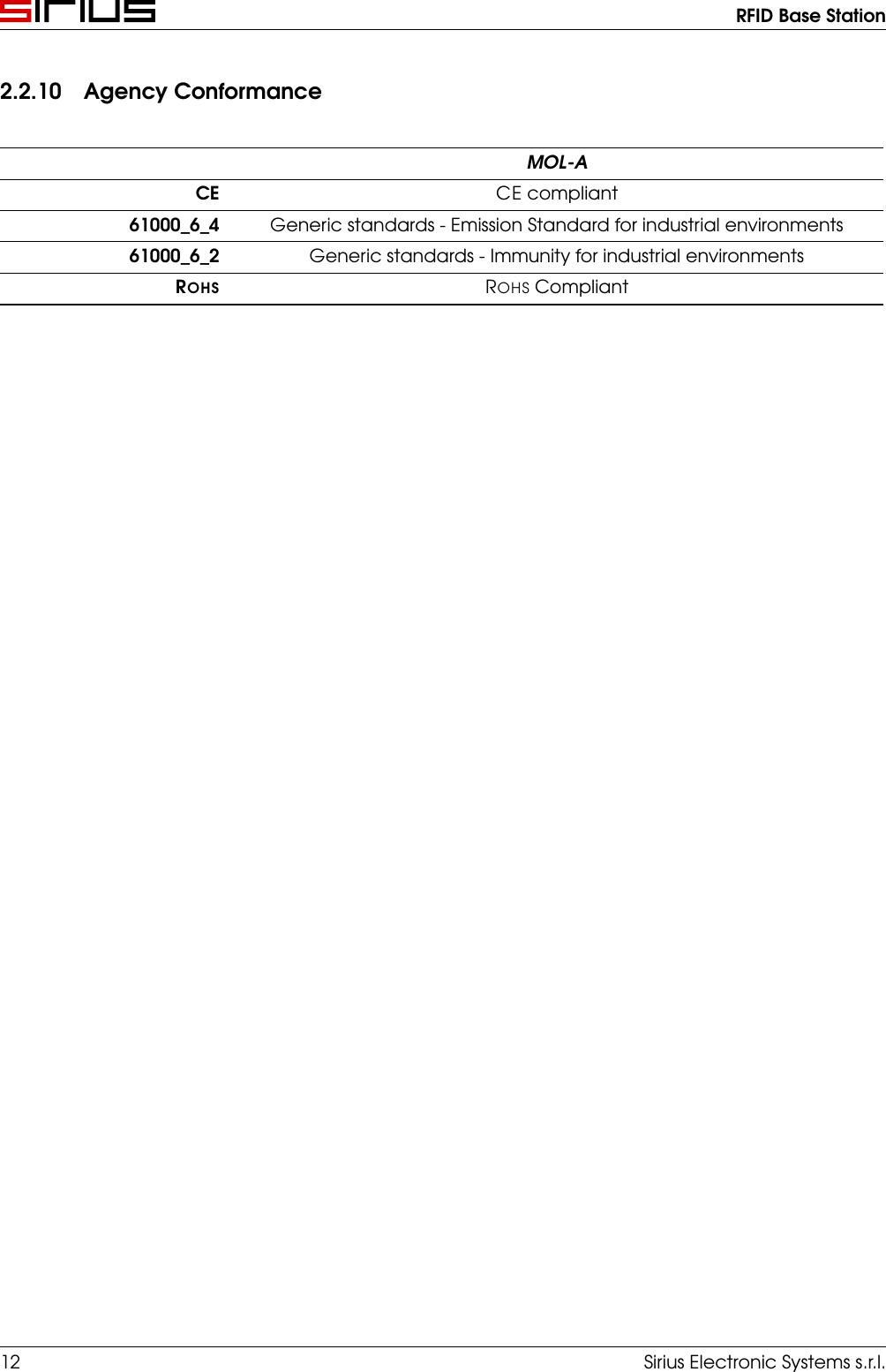
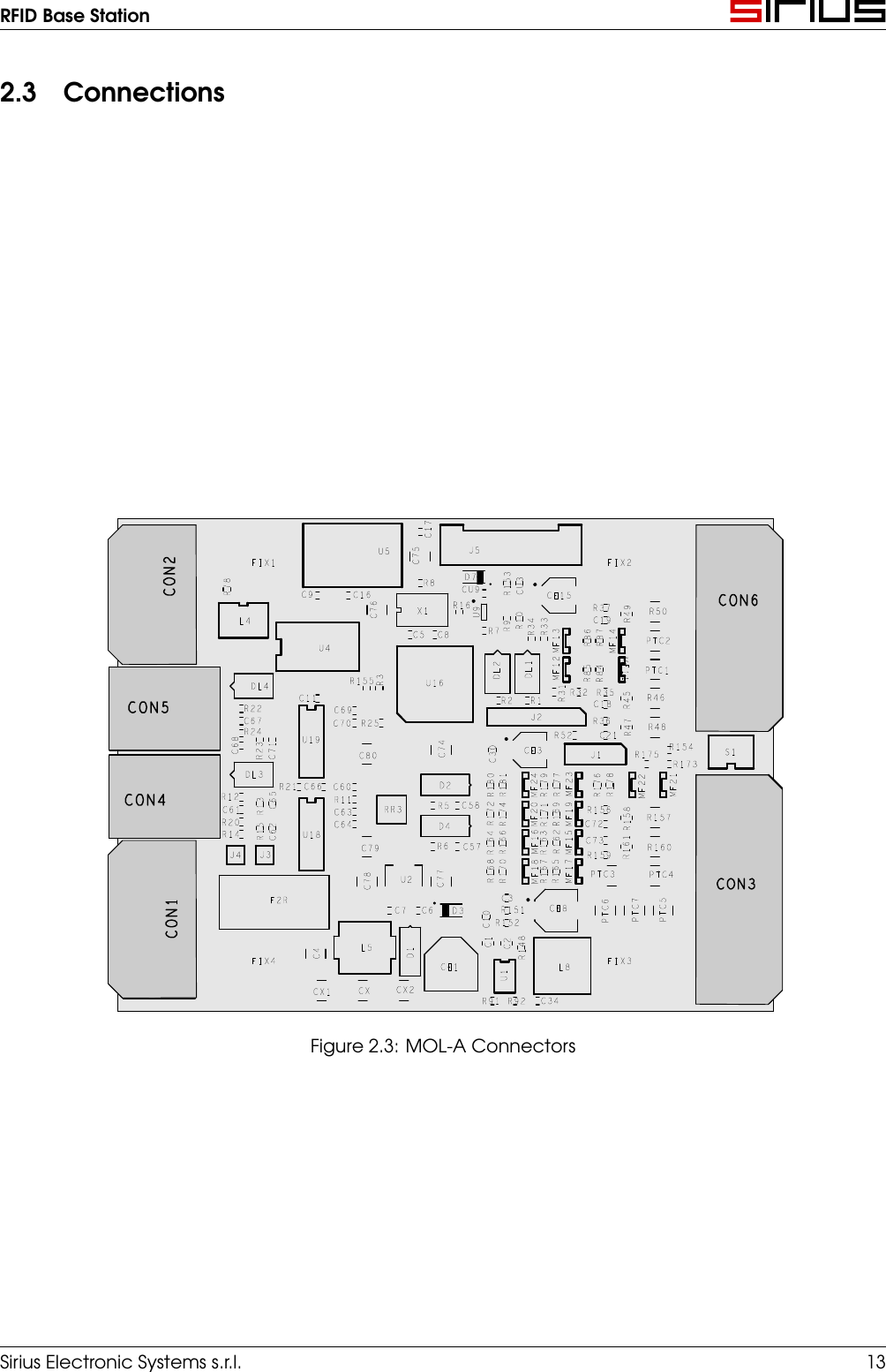




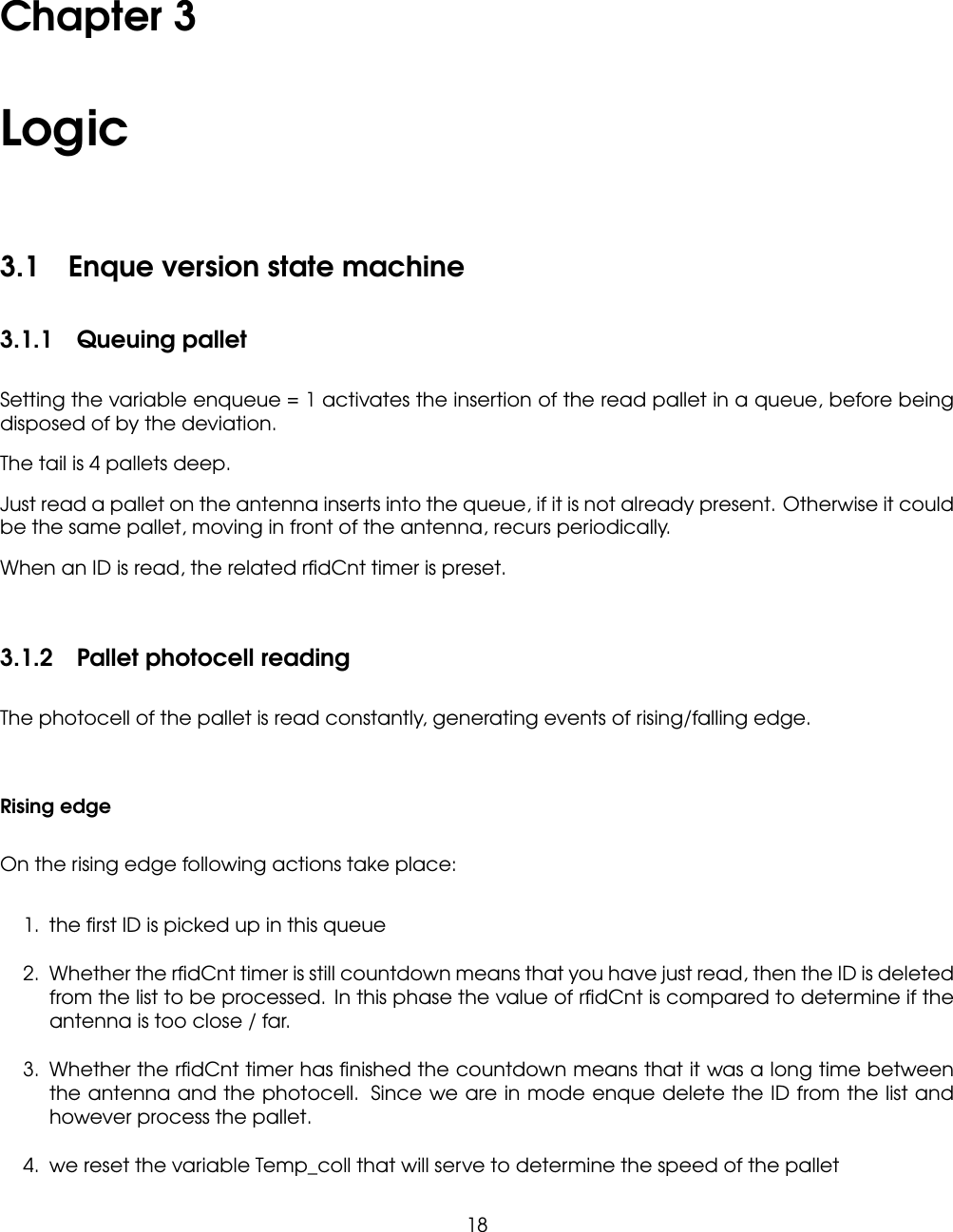
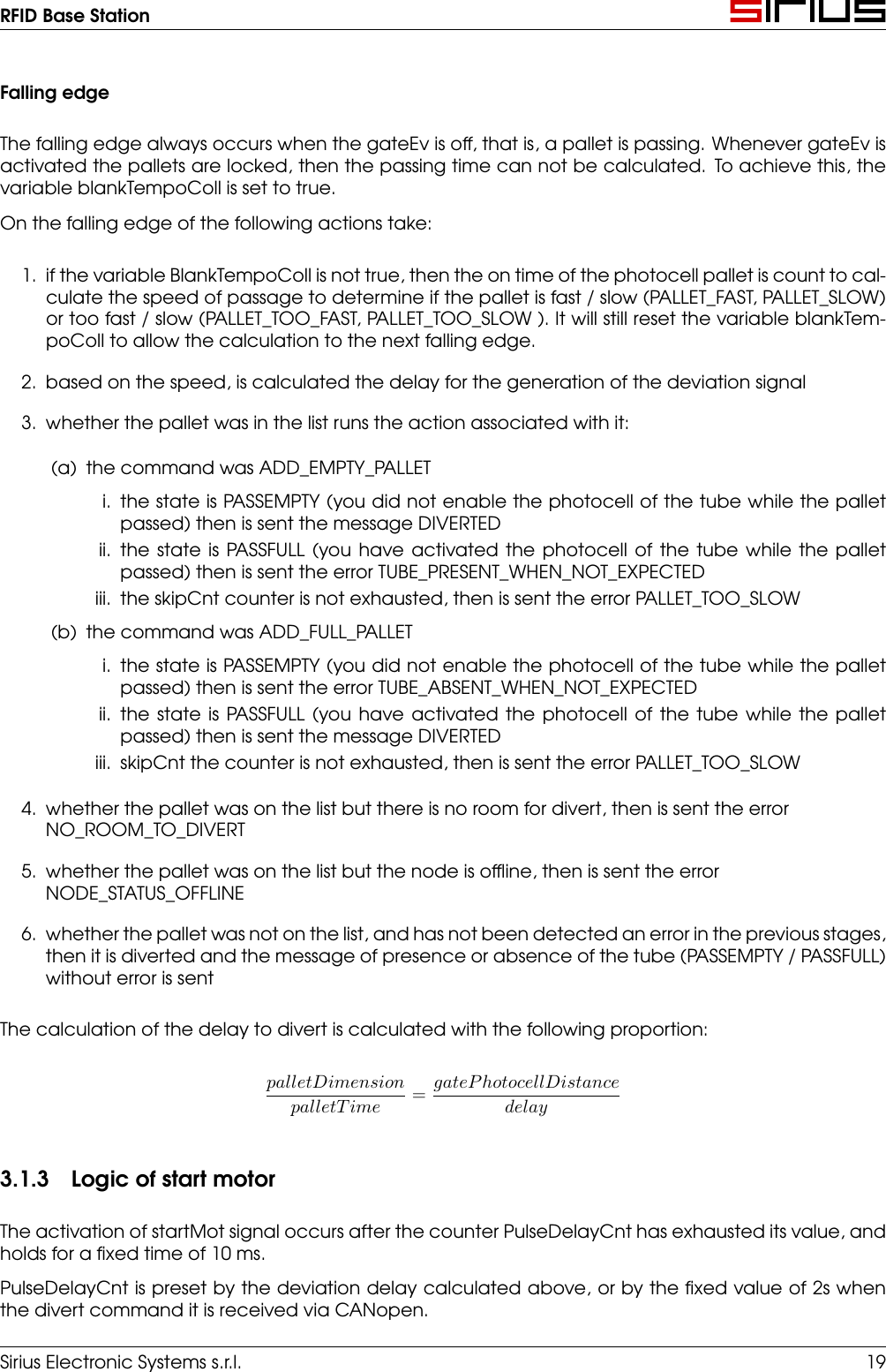
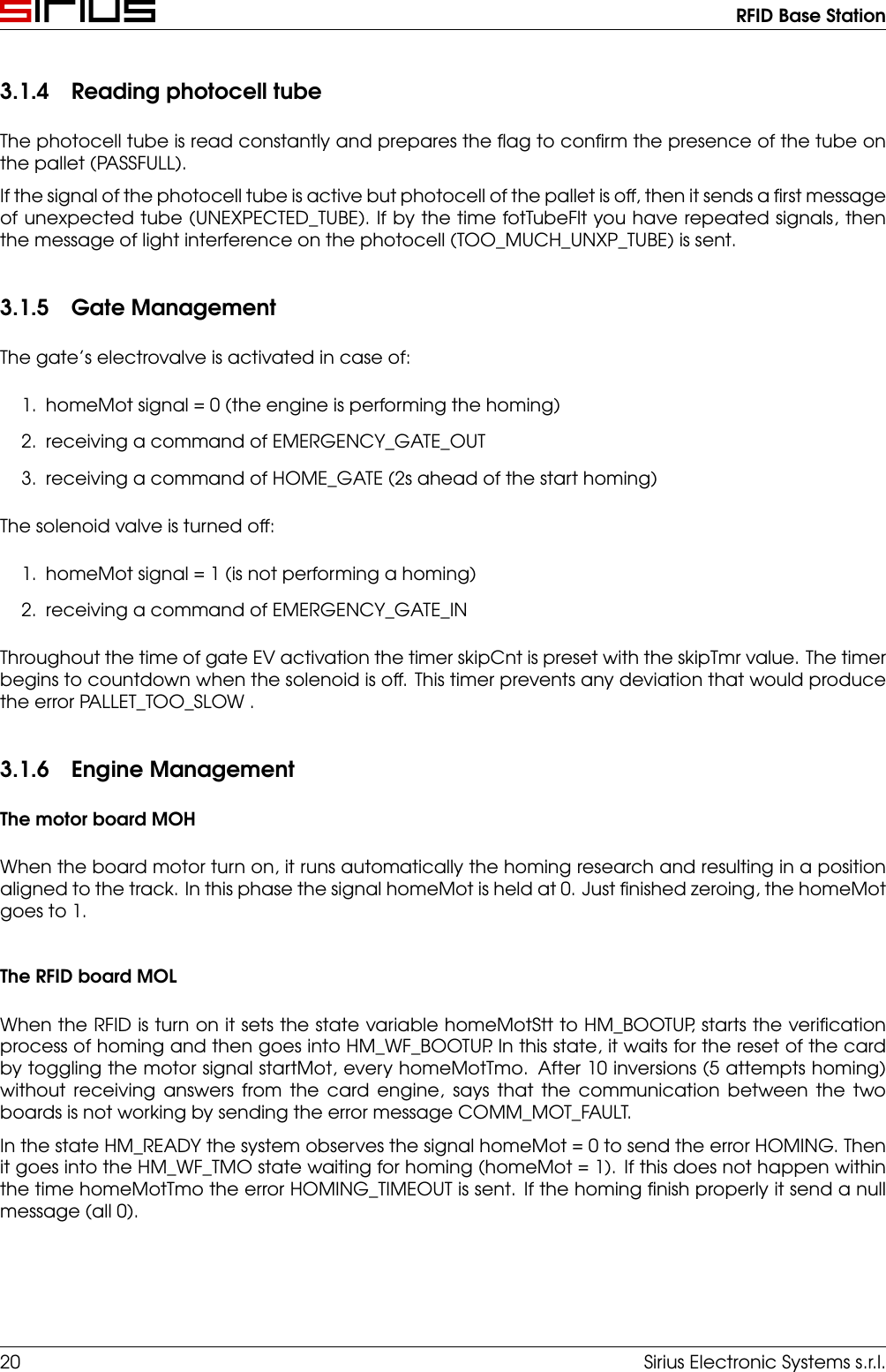