Juniper Networks 8 Users Manual ERX 8.0.x Hardware Guide
8 to the manual 5e4b70f9-f7c0-48ab-b1d0-00212348a2c3
2015-02-09
: Juniper-Networks Juniper-Networks-8-Users-Manual-567129 juniper-networks-8-users-manual-567129 juniper-networks pdf
Open the PDF directly: View PDF .
Page Count: 183 [warning: Documents this large are best viewed by clicking the View PDF Link!]
- ERX Hardware Guide
- About This Guide
- Product Overview
- Initial Installation
- Unpacking and Inspecting ERX Routers
- Installing ERX Routers
- Installing Modules
- Cabling ERX Routers
- Powering Up ERX Routers
- Accessing ERX Routers
- Hardware Maintenance, Replacement, and Troubleshooting Procedures
- Maintaining ERX Routers
- Required Tools and Items
- Storing Modules and Components
- Cleaning the System
- Upgrading from Release 5.1.1 or Lower-Numbered Releases to Release 6.x.x or Higher-Numbered Releases
- Upgrading NVS Cards on SRP Modules
- Replacing an NVS Card
- Upgrading Memory on SRP Modules
- Replacing SFPs on I/O Modules
- Replacing Fan Trays
- Installing a Cable-Management Bracket on ERX-7xx Models
- Troubleshooting
- Maintaining ERX Routers
- Appendixes
- System Specifications
- Installation Guidelines and Requirements
- Cable Pinouts
- Contacting Customer Support and Returning Hardware
- Declaration of Conformity
- Index

E-series™ Routing Platforms
ERX™ Hardware Guide
Release 8.0.x
Juniper Networks, Inc.
1194 North Mathilda Avenue
Sunnyvale, California 94089
USA
408-745-2000
www.juniper.net
Part Number: 162–01539-00, Revision A00
This product includes the Envoy SNMP Engine, developed by Epilogue Technology, an Integrated Systems Company. Copyright
© 1986-1997, Epilogue Technology Corporation. All rights reserved. This program and its documentation were developed
at private expense, and no part of them is in the public domain.
This product includes memory allocation software developed by Mark Moraes, copyright © 1988, 1989, 1993, University of Toronto.
This product includes FreeBSD software developed by the University of California, Berkeley, and its contributors. All of the documentation and
software included in the 4.4BSD and 4.4BSD-Lite Releases is copyrighted by the Regents of the University of California. Copyright © 1979, 1980,
1983, 1986, 1988, 1989, 1991, 1992, 1993, 1994. The Regents of the University of California. All rights reserved.
GateD software copyright © 1995, the Regents of the University. All rights reserved. Gate Daemon was originated and developed through release
3.0 by Cornell University and its collaborators. Gated is based on Kirton’s EGP, UC Berkeley’s routing daemon (routed), and DCN’s HELLO routing
protocol. Development of Gated has been supported in part by the National Science Foundation. Portions of the GateD software copyright © 1988,
Regents of the University of California. All rights reserved. Portions of the GateD software copyright © 1991, D. L. S. Associates.
This product includes software developed by Maker Communications, Inc., copyright © 1996, 1997, Maker Communications, Inc.
Juniper Networks, the Juniper Networks logo, NetScreen, and ScreenOS are registered trademarks of Juniper Networks, Inc. in the
United States and other countries. JUNOS and JUNOSe are trademarks of Juniper Networks, Inc. All other trademarks, service marks,
registered trademarks, or registered service marks are the property of their respective owners.
Juniper Networks assumes no responsibility for any inaccuracies in this document. Juniper Networks reserves the right to
change, modify, transfer, or otherwise revise this publication without notice.
Products made or sold by Juniper Networks or components thereof might be covered by one or more of the following patents that are
owned by or licensed to Juniper Networks: U.S. Patent Nos. 5,473,599, 5,905,725, 5,909,440, 6,192,051, 6,333,650, 6,359,479, 6,406,312,
6,429,706, 6,459,579, 6,493,347, 6,538,518, 6,538,899, 6,552,918, 6,567,902, 6,578,186, and 6,590,785.
Copyright © 2006, Juniper Networks, Inc. All rights reserved.
E-series™ Routing Platforms ERX™ Hardware Guide, Release 8.0.x
Copyright © 2006, Juniper Networks, Inc.
All rights reserved. Printed in USA.
Writing: John Borelli, Helen Shaw
Editing: Ben Mann
Illustration: John Borelli
Cover Design: Edmonds Design
Revision History
15 December 2006—Revision 1
The information in this document is current as of the date listed in the revision history.
SOFTWARE LICENSE
The terms and conditions for using this software are described in the software license contained in the acknowledgment to your purchase order or, to the
extent applicable, to any reseller agreement or end-user purchase agreement executed between you and Juniper Networks. By using this software, you
indicate that you understand and agree to be bound by those terms and conditions.
Generally speaking, the software license restricts the manner in which you are permitted to use the software and may contain prohibitions against certain
uses. The software license may state conditions under which the license is automatically terminated. You should consult the license for further details.
For complete product documentation, please see the Juniper Networks Web site at www.juniper.net/techpubs.
End User License Agreement
READ THIS END USER LICENSE AGREEMENT (“AGREEMENT”) BEFORE DOWNLOADING, INSTALLING, OR USING THE SOFTWARE. BY DOWNLOADING,
INSTALLING, OR USING THE SOFTWARE OR OTHERWISE EXPRESSING YOUR AGREEMENT TO THE TERMS CONTAINED HEREIN, YOU (AS CUSTOMER
OR IF YOU ARE NOT THE CUSTOMER, AS A REPRESENTATIVE/AGENT AUTHORIZED TO BIND THE CUSTOMER) CONSENT TO BE BOUND BY THIS
AGREEMENT. IF YOU DO NOT OR CANNOT AGREE TO THE TERMS CONTAINED HEREIN, THEN (A) DO NOT DOWNLOAD, INSTALL, OR USE THE
SOFTWARE, AND (B) YOU MAY CONTACT JUNIPER NETWORKS REGARDING LICENSE TERMS.
1. The Parties. The parties to this Agreement are Juniper Networks, Inc. and its subsidiaries (collectively “Juniper”), and the person or organization that
originally purchased from Juniper or an authorized Juniper reseller the applicable license(s) for use of the Software (“Customer”) (collectively, the “Parties”).
2. The Software. In this Agreement, “Software” means the program modules and features of the Juniper or Juniper-supplied software, and updates and
releases of such software, for which Customer has paid the applicable license or support fees to Juniper or an authorized Juniper reseller. “Embedded
Software” means Software which Juniper has embedded in the Juniper equipment.
3. License Grant. Subject to payment of the applicable fees and the limitations and restrictions set forth herein, Juniper grants to Customer a
non-exclusive and non-transferable license, without right to sublicense, to use the Software, in executable form only, subject to the following use restrictions:
a. Customer shall use the Embedded Software solely as embedded in, and for execution on, Juniper equipment originally purchased by Customer from
Juniper or an authorized Juniper reseller.
b. Customer shall use the Software on a single hardware chassis having a single processing unit, or as many chassis or processing units for which Customer
has paid the applicable license fees; provided, however, with respect to the Steel-Belted Radius or Odyssey Access Client software only, Customer shall
use such Software on a single computer containing a single physical random access memory space and containing any number of processors. Use of
the Steel-Belted Radius software on multiple computers requires multiple licenses, regardless of whether such computers are physically contained on a
single chassis.
c. Product purchase documents, paper or electronic user documentation, and/or the particular licenses purchased by Customer may specify limits to
Customer’s use of the Software. Such limits may restrict use to a maximum number of seats, registered endpoints, concurrent users, sessions, calls,
connections,subscribers,clusters,nodes,realms,devices,links,portsortransactions,orrequirethepurchaseofseparatelicensestouseparticularfeatures,
functionalities, services, applications, operations, or capabilities, or provide throughput, performance, configuration, bandwidth, interface, processing,
temporal, or geographical limits. In addition, such limits may restrict the use of the Software to managing certain kinds of networks or require the
Software to be used only in conjunction with other specific Software. Customer’s use of the Software shall be subject to all such limitations and purchase
of all applicable licenses.
d. For any trial copy of the Software, Customer’s right to use the Software expires 30 days after download, installation or use of the Software. Customer
may operate the Software after the 30-day trial period only if Customer pays for a license to do so. Customer may not extend or create an additional
trial period by re-installing the Software after the 30-day trial period.
e. The Global Enterprise Edition of the Steel-Belted Radius software may be used by Customer only to manage access to Customer’s enterprise network.
Specifically, service provider customers are expressly prohibited from using the Global Enterprise Edition of the Steel-Belted Radius software to support
any commercial network access services.
The foregoing license is not transferable or assignable by Customer. No license is granted herein to any user who did not originally purchase the applicable
license(s)fortheSoftwarefromJuniperoranauthorizedJuniperreseller.
4. Use Prohibitions. Notwithstanding the foregoing, the license provided herein does not permit the Customer to, and Customer agrees not to and shall
not: (a) modify, unbundle, reverse engineer, or create derivative works based on the Software; (b) make unauthorized copies of the Software (except as
necessary for backup purposes); (c) rent, sell, transfer, or grant any rights in and to any copy of the Software, in any form, to any third party; (d) remove any
proprietary notices, labels, or marks on or in any copy of the Software or any product in which the Software is embedded; (e) distribute any copy of the
Software to any third party, including as may be embedded in Juniper equipment sold in the secondhand market; (f) use any ‘locked’ or key-restricted
feature, function, service, application, operation, or capability without first purchasing the applicable license(s) and obtaining a valid key from Juniper, even
if such feature, function, service, application, operation, or capability is enabled without a key; (g) distribute any key for the Software provided by Juniper
to any third party; (h) use the Software in any manner that extends or is broader than the uses purchased by Customer from Juniper or an authorized
Juniper reseller; (i) use the Embedded Software on non-Juniper equipment; (j) use the Software (or make it available for use) on Juniper equipment thatthe
Customer did not originally purchase from Juniper or an authorized Juniper reseller; (k) disclose the results of testing or benchmarking of the Software to
any third party without the prior written consent of Juniper; or (l) use the Software in any manner other than as expressly provided herein.
5. Audit. Customer shall maintain accurate records as necessary to verify compliance with this Agreement. Upon request by Juniper, Customer shall
furnish such records to Juniper and certify its compliance with this Agreement.
6. Confidentiality. The Parties agree that aspects of the Software and associated documentation are the confidential property of Juniper. As such, Customer
shall exercise all reasonable commercial efforts to maintain the Software and associated documentation in confidence, which at a minimum includes
restricting access to the Software to Customer employees and contractors having a need to use the Software for Customer’s internal business purposes.
7. Ownership. Juniper and Juniper’s licensors, respectively, retain ownership of all right, title, and interest (including copyright) in and to the Software,
associated documentation, and all copies of the Software. Nothing in this Agreement constitutes a transfer or conveyance of any right, title, or interest in
the Software or associated documentation, or a sale of the Software, associated documentation, or copies of the Software.
8. Warranty, Limitation of Liability, Disclaimer of Warranty. The warranty applicable to the Software shall be as set forth in the warranty statement
that accompanies the Software (the “Warranty Statement”). Nothing in this Agreement shall give rise to any obligation to support the Software. Support
services may be purchased separately. Any such support shall be governed by a separate, written support services agreement. TO THE MAXIMUM EXTENT
PERMITTED BY LAW, JUNIPER SHALL NOT BE LIABLE FOR ANY LOST PROFITS, LOSS OF DATA, OR COSTS OR PROCUREMENT OF SUBSTITUTE GOODS
OR SERVICES, OR FOR ANY SPECIAL, INDIRECT, OR CONSEQUENTIAL DAMAGES ARISING OUT OF THIS AGREEMENT, THE SOFTWARE, OR ANY JUNIPER
OR JUNIPER-SUPPLIED SOFTWARE. IN NO EVENT SHALL JUNIPER BE LIABLE FOR DAMAGES ARISING FROM UNAUTHORIZED OR IMPROPER USE OF
ANY JUNIPER OR JUNIPER-SUPPLIED SOFTWARE. EXCEPT AS EXPRESSLY PROVIDED IN THE WARRANTY STATEMENT TO THE EXTENT PERMITTED BY
LAW, JUNIPER DISCLAIMS ANY AND ALL WARRANTIES IN AND TO THE SOFTWARE (WHETHER EXPRESS, IMPLIED, STATUTORY, OR OTHERWISE),
INCLUDING ANY IMPLIED WARRANTY OF MERCHANTABILITY, FITNESS FOR A PARTICULAR PURPOSE, OR NONINFRINGEMENT. IN NO EVENT DOES
JUNIPER WARRANT THAT THE SOFTWARE, OR ANY EQUIPMENT OR NETWORK RUNNING THE SOFTWARE, WILL OPERATE WITHOUT ERROR OR
INTERRUPTION, OR WILL BE FREE OF VULNERABILITY TO INTRUSION OR ATTACK. In no event shall Juniper’s or its suppliers’ or licensors’ liability to
Customer, whether in contract, tort (including negligence), breach of warranty, or otherwise, exceed the price paid by Customer for the Software that gave
rise to the claim, or if the Software is embedded in another Juniper product, the price paid by Customer for such other product. Customer acknowledges
and agrees that Juniper has set its prices and entered into this Agreement in reliance upon the disclaimers of warranty and the limitations of liabilityset
forth herein, that the same reflect an allocation of risk between the Parties (including the risk that a contract remedy may fail of its essential purpose and
cause consequential loss), and that the same form an essential basis of the bargain between the Parties.
9. Termination. Any breach of this Agreement or failure by Customer to pay any applicable fees due shall result in automatic termination of the
license granted herein. Upon such termination, Customer shall destroy or return to Juniper all copies of the Software and related documentation in
Customer’s possession or control.
10. Taxes. All license fees for the Software are exclusive of taxes, withholdings, duties, or levies (collectively “Taxes”). Customer shall be responsible
for paying Taxes arising from the purchase of the license, or importation or use of the Software.
11 . Export. Customer agrees to comply with all applicable export laws and restrictions and regulations of any United States and any applicable foreign
agency or authority, and not to export or re-export the Software or any direct product thereof in violation of any such restrictions, laws or regulations, or
without all necessary approvals. Customer shall be liable for any such violations. The version of the Software supplied to Customer may contain encryption
or other capabilities restricting Customer’s ability to export the Software without an export license.
12. Commercial Computer Software. The Software is “commercial computer software” and is provided with restricted rights. Use, duplication, or
disclosure by the United States government is subject to restrictions set forth in this Agreement and as provided in DFARS 227.7201 through 227.7202-4,
FAR 12.212, FAR 27.405(b)(2), FAR 52.227-19, or FAR 52.227-14(ALT III) as applicable.
13. Interface Information.To the extent required by applicable law, and at Customer’s written request, Juniper shall provide Customer with the
interface information needed to achieve interoperability between the Software and another independently created program, on payment of applicable
fee, if any. Customer shall observe strict obligations of confidentiality with respect to such information and shall use such information in compliance
with any applicable terms and conditions upon which Juniper makes such information available.
14. Third Party Software.Any licensor of Juniper whose software is embedded in the Software and any supplier of Juniper whose products or technology
are embedded in (or services are accessed by) the Software shall be a third party beneficiary with respect to this Agreement, and such licensor or vendor
shall have the right to enforce this Agreement in its own name as if it were Juniper. In addition, certain third party software may be provided with the
Software and is subject to the accompanying license(s), if any, of its respective owner(s). To the extent portions of the Software are distributed under and
subject to open source licenses obligating Juniper to make the source code for such portions publicly available (such as the GNU General Public License
(“GPL”) or the GNU Library General Public License (“LGPL”)), Juniper will make such source code portions (including Juniper modifications, as appropriate)
available upon request for a period of up to three years from the date of distribution. Such request can be made in writing to Juniper Networks, Inc.,
1194 N. Mathilda Ave., Sunnyvale, CA 94089, ATTN: General Counsel. You may obtain a copy of the GPL at http://www.gnu.org/licenses/gpl.html, and a
copy of the LGPL at http://www.gnu.org/licenses/lgpl.html.
15. Miscellaneous. This Agreement shall be governed by the laws of the State of California without reference to its conflicts of laws principles. The
provisions of the U.N. Convention for the International Sale of Goods shall not apply to this Agreement. For any disputes arising under this Agreement,the
Parties hereby consent to the personal and exclusive jurisdiction of, and venue in, the state and federal courts within Santa Clara County, California.
This Agreement constitutes the entire and sole agreement between Juniper and the Customer with respect to the Software, and supersedes all prior and
contemporaneous agreements relating to the Software, whether oral or written (including any inconsistent terms contained in a purchase order), except
that the terms of a separate written agreement executed by an authorized Juniper representative and Customer shall govern to the extent such terms are
inconsistent or conflict with terms contained herein. No modification to this Agreement nor any waiver of any rights hereunder shall be effective unless
expressly assented to in writing by the party to be charged. If any portion of this Agreement is held invalid, the Parties agree that such invalidity shall not
affect the validity of the remainder of this Agreement. This Agreement and associated documentation has been written in the English language, and
the Parties agree that the English version will govern. (For Canada: Les parties aux présentés confirment leur volonté que cette convention de même
que tous les documents y compris tout avis qui s’y rattaché, soient redigés en langue anglaise. (Translation: The parties confirm that this Agreement
and all related documentation is and will be in the English language)).

Table of Contents
About This Guide xi
Objectives ............................................................................xi
Audience..............................................................................xi
E-series Routers..................................................................... xii
Documentation Conventions ...................................................... xii
List of Technical Publications......................................................xiii
Obtaining Documentation ........................................................xvii
Documentation Feedback.........................................................xvii
Requesting Support............................................................... xviii
Part 1 Product Overview
Chapter 1 ERX Overview 3
Overview ..............................................................................3
ERX Routers...........................................................................3
ERX-14xx Models................................................................4
ERX-7xx Models .................................................................6
ERX-310 Router ..................................................................8
ERX Modules..........................................................................9
SRP Module..................................................................... 10
Module Details.............................................................12
SRP Module Redundancy.................................................13
Nonvolatile Storage ....................................................... 13
SRP I/O Module ................................................................ 13
Module Details.............................................................13
Line Modules...................................................................14
Packet Classification ...................................................... 15
I/O Modules .................................................................... 15
Network Management Tools.......................................................16
CLI Management...............................................................16
SNMP MIB Management ......................................................16
NMC-RX Device Management System ....................................... 16
Redundancy Features...............................................................16
SRP Modules ................................................................... 16
NVS Cards.................................................................. 17
Line Modules...................................................................17
Power ...........................................................................19
Fans............................................................................. 20
Table of Contents v

ERX 8.0.x Hardware Guide
Part 2 Initial Installation
Chapter 2 Unpacking and Inspecting ERX Routers 23
Before You Begin....................................................................23
Unpacking ERX-14xx Models......................................................23
Unpacking ERX-7xx Models and ERX-310 Routers ..............................24
Inspecting Router Components and Accessories.................................25
If You Detect or Suspect Damage ................................................. 25
Contacting Juniper Networks ...................................................... 25
The Next Step....................................................................... 25
Chapter 3 Installing ERX Routers 27
Before You Begin....................................................................27
Freestanding Installation...........................................................27
Rack-Mounted Installation .........................................................28
Installation Guidelines.........................................................28
Safety Guidelines............................................................... 30
Preparing the Equipment Racks..............................................32
Installing the Router ...........................................................32
The Next Step....................................................................... 33
Chapter 4 Installing Modules 35
Overview ............................................................................ 35
Slot Groups .....................................................................36
Slot Groups for the ERX-1410 Router....................................36
Slot Groups for the ERX-7xx Models..................................... 37
Combinations of Line Modules In Slot Groups............................... 38
OC48 Line Modules............................................................38
GE-2 Line Modules.............................................................38
Managing Modules Using the Software.......................................38
Hot-Swapping Modules........................................................ 38
Protecting Modules and Slots .................................................38
Order of Installation ...........................................................40
Required Tools and Safety Items .............................................40
Safety Guidelines ...................................................................40
Installing SRP I/O and SRP Modules............................................... 41
Installing an SRP I/O Module..................................................42
Installing an SRP Module......................................................42
Installing Line and I/O Modules....................................................44
Installing a Line Module or an I/O Module................................... 44
Removing a Line Module, SRP Module, or SRP I/O Module .....................46
Installing Components for Line Module Redundancy............................48
Installing the Line Modules....................................................48
Installing the Redundancy Midplane .........................................48
Installing the I/O Modules.....................................................50
Verifying the Installation ...................................................... 51
vi Table of Contents

Table of Contents
Configuring Line Module Redundancy............................................ 51
The Next Step....................................................................... 51
Chapter 5 Cabling ERX Routers 53
Cabling Overview...................................................................53
Required Tools, Wires, and Cables ................................................ 55
Cabling the SRP I/O Module .......................................................56
External Timing Ports .........................................................56
Management Ports ............................................................ 59
Connecting to the Network...............................................60
Connecting to a Console Terminal....................................... 60
Cabling the Router for Power......................................................60
Task 1: Turn Off All Router Power ............................................62
Task 2: Connect the Grounding Cables....................................... 63
Task 3: Connect the Power Cables............................................63
ERX-7xx Models, ERX-14xx Models, ERX-310 Router (DC Model).... 63
ERX-310 Router (AC Model) ..............................................65
Cabling I/O Modules................................................................66
BNC Connectors................................................................66
HSSI Connectors ...............................................................66
RJ-45 Connectors...............................................................67
RJ-48C Connectors.............................................................67
LC Duplex Connectors.........................................................68
SC Duplex Connectors.........................................................68
SMB Connectors................................................................ 70
X.21/V.35 Connectors.......................................................... 71
Redundant Ports ............................................................... 72
The Next Step....................................................................... 72
Chapter 6 Powering Up ERX Routers 73
Before You Power Up the System..................................................73
Powering Up.........................................................................73
Initialization Sequence ........................................................74
Status LEDs.......................................................................... 75
Powering Down..................................................................... 75
The Next Step....................................................................... 75
Chapter 7 Accessing ERX Routers 77
Setting Up Management Access ................................................... 77
Console Port Setup ................................................................. 78
Using HyperTerminal .........................................................78
Connecting Directly to the Router............................................ 78
Assigning an IP Address....................................................... 80
Telnet Setup......................................................................... 80
SNMP ................................................................................82
The Next Step....................................................................... 82
Table of Contents vii

ERX 8.0.x Hardware Guide
Part 3 Hardware Maintenance, Replacement, and Troubleshooting
Procedures
Chapter 8 Maintaining ERX Routers 85
Required Tools and Items.......................................................... 85
Storing Modules and Components ................................................ 86
Cleaning the System................................................................86
Upgrading from Release 5.1.1 or Lower-Numbered Releases to Release 6.x.x or
Higher-Numbered Releases........................................................ 87
Upgrading NVS Cards on SRP Modules ........................................... 87
Upgrading a System That Contains One SRP Module.......................87
Upgrading a System That Contains Two SRP Modules......................88
Replacing an NVS Card.............................................................89
Upgrading Memory on SRP Modules..............................................90
Displaying the Memory Installed ............................................. 91
Removing SODIMMs........................................................... 91
Adding New SODIMMs ........................................................ 92
Verifying the Upgrade ......................................................... 93
Replacing SFPs on I/O Modules....................................................93
Removing SFPs.................................................................94
Installing SFPs..................................................................95
Verifying the Installation ......................................................97
Replacing Fan Trays ................................................................97
Removing the Fan Tray........................................................ 99
Installing the Fan Tray ........................................................99
Installing a Cable-Management Bracket on ERX-7xx Models ..................100
Chapter 9 Troubleshooting 103
Diagnosing Problems..............................................................103
Initialization Sequence .......................................................103
Troubleshooting Power Failures...................................................104
Understanding Status LEDs to Troubleshoot.....................................104
LED Identification.............................................................105
LED Activity ................................................................... 110
Redundancy Status ...........................................................113
Monitoring Temperatures of Modules............................................113
Resetting Line Modules and SRP Modules.......................................114
Double-Bit Errors on SRP Modules ...............................................114
Detecting Double-Bit Errors..................................................114
Fixing Double-Bit Errors......................................................115
viii Table of Contents

Table of Contents
Part 4 Appendixes
Appendix A System Specifications 119
ERX-14xx Models Specifications .................................................119
ERX-7xx Models Specifications...................................................122
ERX-310 Router Specifications ...................................................125
Appendix B Installation Guidelines and Requirements 129
Your Preinstallation Responsibilities .............................................129
Environmental Requirements.....................................................130
Regulatory Compliances ..........................................................130
Safety Guidelines ..................................................................130
ERX-310 Router Warnings (AC Model).......................................132
ERX-310 Power Cord Warnings (AC Model) ............................132
Power Cable Warning (Japanese)........................................132
Equipment Rack Requirements...................................................133
Mechanical Requirements....................................................134
Space Requirements..........................................................135
Proper Rack Installation......................................................135
Cabling Recommendations .......................................................136
Product Reclamation and Recycling Program ...................................137
Hardware Compliance.............................................................138
Federal Communications Commission (FCC) Statement ..................138
FCC Requirements for Consumer Products.................................139
Food and Drug Administration, Center for Devices and Radiological
Health..........................................................................139
Canadian Department Of Communications Radio Interference
Regulations....................................................................139
Réglement sur le brouillage radioélectrique du ministère des
communications ..............................................................139
Industry Canada Notice CS-03...............................................139
Avis CS-03 d’Industrie Canada...............................................140
D.O.C. Explanatory Notes: Equipment Attachment Limitations ..........141
Notes explicatives du ministère des Communications: limites visant les
accessoires ....................................................................141
EC Declaration of Conformity................................................142
Voluntary Control Council for Interference (VCCI) Statement for Japan ..142
Appendix C Cable Pinouts 143
SRP I/O Module....................................................................143
CT1 and CE1 I/O Modules.........................................................146
Appendix D Contacting Customer Support and Returning Hardware 151
Contacting Customer Support ....................................................151
Return Procedure..................................................................151
Locating Component Serial Numbers ...........................................152
Table of Contents ix

ERX 8.0.x Hardware Guide
Information You Might Need to Supply to JTAC .................................153
Tools and Parts Required..........................................................154
Returning Products for Repair or Replacement .................................154
Packing Instructions for Returning a Chassis...............................154
Appendix E Declaration of Conformity 157
Declaration of Conformity ........................................................157
Part 5 Index
Index................................................................................161
xTable of Contents

About This Guide
This preface provides the following guidelines for using the E-series™ Routing
Platforms ERX™ Hardware Guide:
Objectives on page xi
Audience on page xi
E-series Routers on page xii
Documentation Conventions on page xii
List of Technical Publications on page xiii
Obtaining Documentation on page xvii
Documentation Feedback on page xvii
Requesting Support on page xviii
Objectives
This guide provides the information you need to install and start the E-series router.
An E-series router is shipped with the latest system software installed. To install
a future release or reinstall the system software, see JUNOSe System Basics
Configuration Guide, Chapter 3, Installing JUNOSe Software.
NOTE: If the information in the latest JUNOSe Release Notes differs from the
information in this guide, follow the JUNOSe Release Notes.
Audience
This guide is intended for experienced system and network specialists working with
E-series routers in an Internet access environment.
Audience xi

ERX 8.0.x Hardware Guide
E-series Routers
Five models of E-series routers are available:
ERX-1440 router
ERX-1410 router
ERX-710 router
ERX-705 router
ERX-310 router
All models use the same software.
In the E-series documentation, the term ERX-14xx models refers to both the
ERX-1440 router and the ERX-1410 router. Similarly, the term ERX-7xx models
refers to both the ERX-710 router and the ERX-705 router. Other E-series router
designations refer to specific models.
Documentation Conventions
Table 1 defines the notice icons used in this guide.
Table 1: Notice Icons
Icon Meaning Description
Informational note Indicates important features or
instructions.
Caution Indicates a situation that might result in
loss of data or hardware damage.
Warning Alertsyoutotheriskofpersonalinjury
or death.
Table 2 defines text conventions used in this guide and the command syntax
conventions used primarily in the JUNOSe Command Reference Guide.Formore
information about command syntax, see the JUNOSe System Basics Configuration
Guide, Chapter 2, Command Line Interface.
Table 2: Text and Syntax Conventions
Convention Description Examples
Text Conventions
xii Documentation Conventions

About This Guide
Convention Description Examples
Bold typeface Represents names of commands and
keywords in text.
Issue the clock source
command.
Specify the keyword exp-msg.
Bold sans serif typeface
Represents text that you must type.
host1(config)#traffic class low-loss1
Fixed-width typeface Represents output on the terminal
screen.
host1#show ip community list
Community standard list 1
permit 0:100 0:200 0:300
Italic typeface Emphasizes words.
Identifies variables.
Identifies chapter, appendix,
and book names.
There are two levels of access,
user and privileged .
clusterId ,ipAddress .
Appendix A, System
Specifications.
+ (plus sign) linking key names Indicates that you must press two or
more keys simultaneously.
Press Ctrl+b.
Syntax Conventions in the Command Reference Guide
Plain typeface Represents keywords. terminal length
Italic typeface Represents variables. mask ,accessListName
|(pipesymbol) Indicates a choice between the
keywords or variables on either side of
the symbol. (Specifying a choice can be
either optional or required.)
diagnostic | line
[ ] (square brackets) Enclose an optional choice of a single
keyword or variable. [ internal | external ]
[ ]* (square brackets and the asterisk) Enclose an optional choice of one or
more keywords or variables. [level1|level2|l1]*
{}(braces) Enclosearequiredchoiceofasingle
keyword or variable. { permit | deny } { in | out }
{clusterId |ipAddress }
List of Technical Publications
The E-series and JUNOSe documentation set consists of several hardware and
software guides, which are available in electronic and printed formats.
Table 3 lists and describes the E-series and JUNOSe document set. For a complete
list of abbreviations used in this document set, along with their spelled-out terms,
see JUNOSe System Basics Configuration Guide, Appendix A, Abbreviations and
Acronyms .
List of Technical Publications xiii

ERX 8.0.x Hardware Guide
Table 3: Juniper Networks E-series and JUNOSe Technical Publications
Document Description
E-series Hardware Documentation
E320 Quick Start Guide Shipped in the box with all new E320 routers. Provides the basic
procedures to help you get an E320 router up and running quickly.
E320 Hardware Guide Provides the necessary procedures for getting the E320 router
operational, including information about:
Installing the chassis and modules
Connecting cables
Powering up the router
Configuring the router for management access
Troubleshooting common issues
Describes switch route processor (SRP) modules, line modules, and I/O
adapters (IOAs) available for the E320 router.
E320 Module Guide Provides detailed specifications for line modules and IOAs in E320
routers, and information about the compatibility of these modules
with JUNOSe software releases.
Lists the layer 2 protocols, layer 3 protocols, and applications that line
modules and their corresponding IOAs support.
Provides module LED information.
E-series Installation Quick Start poster or ERX Quick
Start Guide
Shipped in the box with all new ERX routers. Provides the basic
procedures to help you get an ERX router up and running quickly.
ERX Hardware Guide Provides the necessary procedures for getting ERX-14xx models,
ERX-7xx models, and ERX-310 routers operational, including
information about:
Installing the chassis and modules
Connecting cables
Powering up the router
Configuring the router for management access
Troubleshooting common issues
Describes switch router processor (SRP) modules, line modules, and
I/O modules available for the ERX routers.
ERX Module Guide Provides detailed specifications for line modules and I/O modules
in ERX-14xx models, ERX-7xx models, and ERX-310 routers, and
information about the compatibility of these modules with JUNOSe
software releases.
Lists the layer 2 protocols, layer 3 protocols, and applications that line
modules and their corresponding I/O modules support.
Provides module LED information.
xiv List of Technical Publications

About This Guide
Document Description
ERX End-of-Life Module Guide Provides an overview and description of ERX modules that are
end-of-life (EOL) and can no longer be ordered for the following routers:
ERX-7xx models
ERX-14xx models
ER-310 router
JUNOSe Software Guides
JUNOSe System Basics Configuration Guide Provides information about:
Planning and configuring your network
Using the command-line interface (CLI)
Installing JUNOSe software
Configuring the Simple Network Management Protocol (SNMP)
Managing the router and its modules, including the use of high
availability (HA) for SRP redundancy
Configuring passwords and security
Configuring the router clock
Configuring virtual routers
JUNOSe Physical Layer Configuration Guide Explains how to configure, test, and monitor physical layer interfaces.
JUNOSe Link Layer Configuration Guide Explains how to configure and monitor static and dynamic link layer
interfaces.
JUNOSe IP, IPv6, and IGP Configuration Guide Explains how to configure and monitor IP, IPv6 and Neighbor
Discovery, and interior gateway protocols (RIP, OSPF, and IS-IS).
JUNOSe IP Services Configuration Guide Explains how to configure and monitor IP routing services. Topics
include:
Routing policies
Firewalls
Network Address Translation (NAT)
J-Flow statistics
Bidirectional forwarding detection (BFD)
Internet Protocol Security (IPSec)
Digital certificates
IP tunnels
Layer 2 services over GRE and over MPLS
Virtual Router Redundancy Protocol (VRRP)
List of Technical Publications xv

ERX 8.0.x Hardware Guide
Document Description
JUNOSe Multicast Routing Configuration Guide Explains how to configure and monitor IP multicast routing and IPv6
multicast routing. Topics include:
Internet Group Management Protocol (IGMP)
Layer 2 Control (L2C)
Protocol Independent Multicast (PIM)
Distance Vector Multicast Routing Protocol (DVMRP)
Multicast Listener Discovery (MLD)
JUNOSe BGP and MPLS Configuration Guide Explains how to configure and monitor Border Gateway Protocol (BGP)
routing, Multiprotocol Label Switching (MPLS), and related applications,
and configure and monitor the Virtual Private LAN Service (VPLS).
JUNOSe Policy Management Configuration Guide Explains how to configure, manage, and monitor customized policy
rules for packet classification, forwarding, filtering, and flow rates.
Also describes the packet mirroring feature, which uses secure policies.
JUNOSe Quality of Service Configuration Guide Explains how to configure quality of service (QoS) features to queue,
schedule, and monitor traffic flow. These features include:
Traffic classes and traffic-class groups
Drop, queue, QoS, and scheduler profiles
QoS parameters
Statistics
JUNOSe Broadband Access Configuration Guide Explains how to configure and monitor a remote access environment,
which can include the following features:
Authentication, authorization, and accounting (AAA)
Dynamic Host Configuration Protocol (DHCP)
Remote Authentication Dial-In User Service (RADIUS)
Terminal Access Controller Access Control System (TACACS+)
Layer 2 Tunneling Protocol (L2TP)
Subscriber management
JUNOSe System Event Logging Reference Guide Describes the JUNOSe system logging feature and describes how to use
the CLI to monitor your system’s log configuration and system events.
xvi List of Technical Publications

About This Guide
Document Description
JUNOSe Command Reference Guide
AtoM
JUNOSe Command Reference Guide N to Z
Together constitute the JUNOSe Command Reference Guide.Contain
important information about commands implemented in the system
software. Use to look up:
Descriptions of commands and command parameters
Command syntax
A command’s related mode
Starting with JUNOSe Release 7.1.0, a history of when a
command, its keywords, and its variables were introduced
or added
Use with the JUNOSe configuration guides.
JUNOSe Comprehensive Index Provides a complete index of the JUNOSe software documentation set.
Release Notes
JUNOSe Release Notes Provide the latest information about features, changes, known
problems, resolved problems, and system maximum values. If the
information in the Release Notes differs from the information found in
the documentation set, follow the Release Notes .
Release notes are included on the corresponding software CD and
are available on the Web.
Obtaining Documentation
To obtain the most current version of all Juniper Networks technical documentation,
see the products documentation page on the Juniper Networks Web site at
http://www.juniper.net/.
To order printed copies of this guide and other Juniper Networks technical
documents, or to order a documentation CD, which contains this guide, contact
your sales representative.
Copies of the Management Information Bases (MIBs) available in a software release
are included on the documentation CDs and at http://www.juniper.net/.
Documentation Feedback
We encourage you to provide feedback, comments, and suggestions so
that we can improve the documentation. You can send your comments to
techpubs-comments@juniper.net, or fill out the documentation feedback form at
http://www.juniper.net/techpubs/docbug/docbugreport.html. If you are using e-mail, be
sure to include the following information with your comments:
Document name
Document part number
Documentation Feedback xvii

ERX 8.0.x Hardware Guide
Page number
Software release version
Requesting Support
For technical support, open a support case with the Case Manager link at
http://www.juniper.net/support/ or call 1-888-314-JTAC (from the United States,
Canada, or Mexico) or 1-408-745-9500 (from elsewhere).
xviii Requesting Support

2Product Overview

Chapter 1
ERX Overview
This chapter provides introductory information about the ERX routers. It contains
the following sections:
Overview on page 3
ERX Routers on page 3
ERX Modules on page 9
Network Management Tools on page 16
Redundancy Features on page 16
Overview
ERX routers are modular, carrier-class networking devices that deliver performance,
reliability, and service differentiation to both business and consumer Internet
users. The ERX-7xx and ERX–14xx models offer high port density, low power
consumption, and fully redundant Internet access routing and edge aggregation. The
ERX-310 router supports the same services, but with smaller capacity and scaling
capabilities. ERX routers offer the complete edge solution for IP-optimized carriers.
ERX Routers
Five models of ERX routers are available:
ERX-1440 router
ERX-1410 router
ERX-710 router
ERX-705 router
ERX-310 router
All modelsusethesamesoftware.However,the specific model determines the:
Combination of line modules supported
ERX Routers 3

ERX 8.0.x Hardware Guide
Conditions for line rate performance of line modules
Type, capacity, and number of SRP modules used
ERX-14xx Models
NOTE: In the E-series documentation, the term ERX-14xx models refers to both
the ERX-1440 router and the ERX-1410 router. The terms ERX-1440 router and
ERX-1410 router refer to the specific models. See Figure 1 and Figure 2.
The ERX-1440 router manages an extremely high volume of network traffic,
and uses a 40-Gbps switch route processor (SRP) module, either the SRP-40G or
SRP-40G+ module. (The SRP-40G+ module obsoletes the SRP-40G module;
however, the software continues to support both modules.) In this model, all
line modules operate at full wire speed simultaneously.
The ERX-1410 router manages high levels of network traffic, and uses the
10-Gbps SRP module (SRP-10G). You can configure the ERX-1410 router to
enable the line modules either to operateatfulllinerateperformanceorto
allow line modules to operate at a rate dependent on the resources available.
The former option restricts the allowed combinations of line modules. For
information on configuring performanceoflinemodules,seeJUNOSe System
Basics Configuration Guide, Chapter 6, Managing Modules.
NOTE: The 10-Gbps SRP module used in the ERX-310 router is different from the
10-Gbps SRP module used in the ERX-1410 router. See “SRP Module” on page 10
for more information.
Externally, the ERX-1440 chassis is the same as the ERX-1410 chassis. (See Figure 1
and Figure 2.) Both routers contain 14 vertical slots to accommodate modules.
Internally, the ERX-1440 chassis differs from the ERX-1410 chassis, and
includes a special midplane for the 40-Gbps SRP module.
Installation procedures and operating procedures are identical for both
systems. All ERX-7xx and ERX-14xx models use the same SRP I/O module,
but different power input modules are used.
NOTE: The router may look different from the routers shown in the figures in this
chapter, depending on the line modules in the slots.
4ERX Routers

ERX Overview
Figure 1: ERX-14xx Models, Front View
Line module
SRP module
PCMCIA slot
Bezel Cable
management
bracket
Air filter (optional)
behind bezel
Fan tray
behind bezel
g013727
ERX Routers 5

ERX 8.0.x Hardware Guide
Figure 2: ERX-14xx Models, Rear View
I/O
module
Power input
module
Cable
management
bracket
Plenum
Fan tray
SRP I/O
module
g013728
ERX-7xx Models
NOTE: In the E-series documentation, the term ERX-7xx models refers to both the
ERX-705 router and the ERX-710 router. The terms ERX-705 router and ERX-710
router refer to the specific models. See Figure 3 and Figure 4.
The ERX-7xx models are robust, high-density routers with less capacity
than the ERX-14xx models. The ERX-7xx models use either the
SRP-10G module or the SRP-5G module.
YoucanconfiguretheERX-7xxmodelstoenablethelinemodules(LM)tooperate
either at full line rate performance or at a rate dependent on the resources available.
For information about configuring performance of line modules, see JUNOSe
System Basics Configuration Guide, Chapter 6, Managing Modules.
NOTE: The 10-Gbps SRP module used in the ERX-310 router is different from the
10-Gbps SRP module used in the ERX-710 router. See “SRP Module” on page 10
for more information.
6ERX Routers

ERX Overview
The ERX-705 chassis is the same as the ERX-710 chassis. (See Figure 3 and Figure 4.)
The chassis contains seven slots to accommodate modules. Installation procedures
and operating procedures are identical for both systems. All ERX-7xx and ERX-14xx
models use the same SRP I/O module, but different power input modules are used.
NOTE: The router may look different from the routers shown in the figures in this
chapter, depending on the line modules in the slots.
Figure 3: ERX-7xx Models, Front View
PCMCIA slot
SRP module
Fan tray
Line module
g013729
Figure 4: ERX-7xx Models, Rear View
SRP I/O module
I/O
modules
Power switches
Power input
module
g013730
ERX Routers 7

ERX 8.0.x Hardware Guide
ERX-310 Router
The ERX-310 router is a low-end platform that supports all of the same services
as the ERX-7xx and ERX-14xx models, but with smaller capacity and scaling
capabilities. Like the ERX-7xx and ERX-14xx models, the ERX-310 router
uses the same software architecture, providing a single IP entry point into
the network with the same IP-based protocols and services that are available
on other ERX routers. The ERX-310 router is designed to be used as a small
distributed POP router as well as a high-end CPE router.
The ERX-310 router is a three-slot chassis with a midplane architecture. One slot
supports one nonredundant 10-Gbps SRP module, while the other two slots support
line modules. The router supports existing E-series ASIC-based line modules (except
the OC48/STM16 line module), as well as a select number of combination cards.
The combination cards provide a fixed combination of interfaces on the I/O module
so that a single slot can support multiple interfaces (ATM OC3 and GE, for example).
NOTE: The 10-Gbps SRP module used in the ERX-310 router is different from
the 10-Gbps SRP module used in the ERX-7xx and ERX-14xx models. See “SRP
Module” on page 10 for more information.
The ERX-310 router is available in either redundant AC- or DC-powered models.
Figure 5: ERX-310 Router, Front View (AC Model)
Fan tray
Line modules
SRP module
PCMCIA slot
AC power
supply A AC power
supply B
g013731
NOTE: The DC model has blank filler panels in power supply slots.
8ERX Routers

ERX Overview
Figure 6: ERX-310 Router, Rear View (AC Model)
SRP I/O
module
I/O module
Grounding posts
ESD grounding jack
AC power inputs and
switches A and B
g013732
Figure 7: ERX-310 Router, Rear View (DC Model)
DC power inputs
and switches A and B
SRP I/O
module
I/O
module
Grounding posts
ESD grounding jack
g013733
ERX Modules
Each system supports an SRP module and a selection of line modules. You can
use any line module for access or uplink . Access line modules receive traffic
from low-speed circuits, and the system routes the traffic onto higher-speed
uplink line modules and then to the core of the network.
Each moduleconnectstoacorrespondingI/Omoduleviaapassive
midplane. See Figure 8.
The front panel of each module contains a collection of status LEDs
(light-emitting diodes). For information about how to interpret the
LEDs, see “Troubleshooting” on page 103.
ERX Modules 9

ERX 8.0.x Hardware Guide
Figure 8: Modules in ERX-14xx Models
I/O modules
I/O modules
SRP I/O
module
Line modules
Line modules
SRP modules
Connection via
passive midplane
g013734
NOTE: Some line modules require a minimum amount of memory to be used
with JUNOSe Release 5.3.0 or a higher-numbered release. See the ERX Module
Guide for line module specifications.
SRP Module
Switch route processor (SRP) modules perform system management, routing
table calculations and maintenance, forwarding table computations, statistics
processing, configuration storage, and other control plane functions. Each
SRP module is a PowerPC-based system with its own memory, nonvolatile
disk storage, and power supply. (See Figure 9 and Figure 10.)
10 ERX Modules

ERX Overview
Figure 9: SRP Module for ERX-7xx and ERX-14xx Models
Midplane
connectors
Ejector
Status LEDs
Board reset
button
NMI button
PCMCIA
NVS card
System
processor board
Fabric board
g013735
ERX Modules 11

ERX 8.0.x Hardware Guide
Figure 10: SRP Module for ERX-310 router
Ejector
Status
LEDs
Board reset
button
NMI button
PCMCIA
NVS card
Integrated fabric system
processor board
Midplane
connectors
g013736
Module Details
ERX-7xx and ERX-14xx models use up to two redundant SRP modules operating
in an active/standby configuration. ERX-310 routers use only one SRP module.
An SRP module must be present for any system to boot.
SRP modules ranging from 5 Gbps to 40 Gbps can be used in ERX-7xx and
ERX-14xx models. Only a 10-Gbps SRP module (SRP-SE10G) can be used in
ERX-310 routers. See the ERX Module Guide for complete information.
NOTE: Because of different physical dimensions and switch fabric capabilities, SRP
modules are not interchangeable between systems. For example, the 10-Gbps SRP
module used in ERX-7xx and ERX-14xx models cannot be used in the ERX-310
router, and vice versa.
12 ERX Modules

ERX Overview
CAUTION: Do not remove the SRP module while the system is running.
NOTE: Some SRP modules require a minimum amount of memory to be used
with JUNOSe Release 5.3.0 or a higher-numbered release. See the ERX Module
Guide for module specifications.
For details about installing SRP modules, see “Installing Modules” on page 35.
SRP Module Redundancy
SRP module redundancy is available only for ERX-7xx and ERX-14xx models.
See “Redundancy Features” on page 16 for more information.
Nonvolatile Storage
ThePCMCIAslotonthefrontoftheSRPmoduleholdsaTypeIIPCMCIAnonvolatile
storage (NVS) card. (See Figure 9 and Figure 10.) This card is loaded with the
system’s software and configuration files. The PCMCIA card is factory installed.
CAUTION: Although you can remove PCMCIA NVS (Flash) cards from a running
router, we recommend that you do not do so. If you remove the card while data is
being written to or copied from the NVS card, data can be lost or corrupted.
Therefore, we strongly recommend that you shut down the router before removing
a PCMCIA NVS card.
SRP I/O Module
The SRP I/O module is a single corresponding input/output module that interfaces
with the SRP modules through the system’s midplane. The same SRP I/O module
works with all SRP modules, but is router specific. The I/O module used in
ERX-7xx and ERX-14xx models cannot be used in the ERX-310 router, and
vice versa. See Figure 2, Figure 4, and Figure 6 for locations.
Module Details
The SRP I/O module provides standard craft management interfaces, including:
10/100Base-T—The port enables access to the ERX router for Ethernet
management functions via CLI or SNMP, for example.
ERX Modules 13

ERX 8.0.x Hardware Guide
RS-232—The port provides a serial connection for monitoring the system’s
hardware configuration through a PC (running terminal emulation software) or
ASCII terminal. Allows direct CLI access.
Alarm contacts—The contacts provide for remote indication of critical, major,
and minor router alarms (ERX-7xx andERX-14xxmodelsonly;currently
not implemented)
External timing inputs—The inputs provide a method of ensuring that the
clock timing used by the router remains synchronized with the network’s
system clock. BNC connectors and wire wraps are available for ERX-7xx
and ERX-14xx models only.
For details about installing the SRP I/O module, see “Installing Modules” on page 35.
Line Modules
Line modules (LM) process data from different types of network connections.
For information about available line modules and which SRP modules support
specific line modules, see the ERX Module Guide.
Figure 11 shows a representative line module. For details about installing
line modules, see “Installing Modules” on page 35.
14 ERX Modules

ERX Overview
Figure 11: Representative Line Module
Midplane
connectors
Ejector
Status LEDs
Board reset
button
NMI button
g013737
Packet Classification
Most line modules support packet classification on ingress; some non-ASIC line
modules do not. A classification engine on the line module matches specific
fields (such as source and destination IP address, source and destination port,
and protocol), the ingress IP interface, layer 2 fields, or some combination
of these against user-configured filters at wire speed.
I/O Modules
Most line modules have a corresponding input/output (I/O) module that provides
the physical interconnection to the network. Insert each I/O module into the
back of the system, directly behind its corresponding line module.
For information about which line modules pair with which I/O modules, see the
ERX Module Guide. See Figure 2, Figure 4, and Figure 6 for locations. For details
about installing I/O modules, see “Installing Modules” on page 35.
ERX Modules 15

ERX 8.0.x Hardware Guide
Network Management Tools
You can use different management tools to configure the system to
meet the specific networking requirements.
CLI Management
The CLI provides fully developed and automated configuration and status
functionality through a local RS-232 port, Telnet, or SSH via any reachable
network. For a full discussion of the CLI, see JUNOSe System Basics
Configuration Guide, Chapter 2, Command-Line Interface.
SNMP MIB Management
The system offers a complete SNMP interface for configuration, status,
and alarm reporting. The system supports both Standard and Enterprise
MIBs (Management Information Bases). The Juniper Networks E-series
Enterprise MIB is ASN.1 notated for easy importing into third-party SNMP
management applications. For more information, see JUNOSe System Basics
Configuration Guide, Chapter 4, Configuring SNMP.
NMC-RX Device Management System
The NMX-RX application provides a global method of managing all routers,
line modules, and ports through a graphical user interface.
Redundancy Features
This section describes system redundancy features.
SRP Modules
NOTE: This section applies to ERX-7xx and ERX-14xx models only. ERX-310 routers
contain one SRP module and therefore do not offer SRP module redundancy.
ERX-7xx and ERX-14xx models use a 1:1 redundancy scheme for the SRP module.
When two SRP modules of the same type are installed in the chassis, one acts as a
primary (active) and the second as a redundant (standby) module. Both SRP
modules share a single SRP I/O module located in the rear of the chassis.
If the standby SRP module detects that the primary SRP module is not active
(and high-availability mode is not enabled), it reboots the system and takes
control. If high-availability mode has been enabled, automatic switchover
occurs with near hitless failover. If you upgrade software, you must copy
the software to the redundant SRP and reboot it. For information about
configuring and managing SRP module redundancy, see JUNOSe System
Basics Configuration Guide, Chapter 6, Managing Modules.
16 Redundancy Features

ERX Overview
After you install two SRP modules, the modules negotiate for the primary role.
Anumberoffac
tors determine which module becomes the primary; however,
preference is given to the module in the lower-numbered slot. The SRP modules
record their latest roles and retain them the next time you switch on the system.
For information about installing SRP modules, see “Installing Modules” on page 35.
NVS Cards
If you have two SRP modules installed in a system, you can use NVS cards
of different capacities on the SRP modules. The effective capacity of the
higher-capacity NVS card will equal that of the lower-capacity NVS card. For
information about installing NVS cards, see “Installing Modules” on page 35.
When you install new NVS cards or SRP modules, you must issue the synchronize
command to matchthefilesystemoftheNVScardontheredundantSRP
module with the file system of the NVS card on the primary SRP module.
(The NVS card on the redundant SRP module will hereafter be referred to
as the redundant NVS card; the NVS card on the primary SRP module will
hereafter be referred to as the primary NVS card.)
If the capacity of the primary NVS card is equal to or smaller than that of the
redundant NVS card, the system copies all the files from the primary NVS card to the
redundant NVS card. However, if the capacity of the primary NVS card exceeds that
of the redundant NVS card, the system creates an invisible synchronization reserve
file on the primary NVS card, provided that there is enough space for the file.
The purpose of the synchronization file is to prevent the creation of data that
cannot fit on the redundant NVS card. The file contains no useful data, and
is not visible when you view the files in NVS. The size of the file is equal
to the difference in capacities of the two NVS cards. For example, if the
primary NVS card has a capacity of 224 MB and the redundant NVS card has
a capacity of 220 MB, the size of the synchronization file is 4 MB, and only
220 MB of space is available on the primary NVS card.
If the primary NVS card does not have enough space to create the synchronization
reserve file, the synchronize command fails, and a warning message is displayed
on the console. To resolve this issue, either delete unwanted files from the primary
NVS card or replace the redundant NVS card with a higher-capacity NVS card.
Line Modules
NOTE: This section applies to ERX-7xx and ERX-14xx models only. ERX-310 routers
do not offer line module redundancy.
ERX-7xx and ERX-14xx models support line module redundancy for several
line modules. For details about which line modules support redundancy,
see the ERX Module Guide. In this scheme, an extra line module in a group
Redundancy Features 17

ERX 8.0.x Hardware Guide
of identical line modules provides redundancy in case of line module
failure. To use this feature, you need a:
Spare line module
Redundancy midplane
Redundancy I/O module
Aredundancym
idplane can cover 3–6 slots. It provides additional connectivity that
enablesthesparelinemoduletotakecontroloftheI/Omoduleassociatedwith
any failed line module in the redundancy group. The spare I/O module provides
connectivity from the spare line module to the redundancy midplane.
The process by which the system switches to the spare line module is called
switchover . When switchover occurs, the system:
1. BreakstheconnectionbetweentheprimaryI/Omoduleandtheprimary
line module.
2. Connects the primary I/O module to the spare line module via the redundancy
midplane and redundancy I/O module.
Protocol processing then takes place on the spare line module.
Figure 12 shows the data flow when a spare line module becomes active.
18 Redundancy Features

ERX Overview
Figure 12: Data Flow When a Spare Line Module Is Active
Midplane
Redundancy
midplane
Spare line module
Primary line module
Redundancy
I/O module Primary
I/O module
1. A packet arrives at the primary I/O module.
2. The packet passes along the redundancy
midplane from the primary I/O module to
the redundancy I/O module.
3. The packet passes from the redundancy
I/O module to the spare line module.
4. The spare line module processes the packet.
g013738
For information about installing modules for line module redundancy,
see “Installing Modules” on page 35. For information about configuring
and managing SRP module redundancy, see JUNOSe System Basics
Configuration Guide, Chapter 6, Managing Modules.
Power
All E-series routers provide a power architecture that distributes redundant –48 VDC
feeds through the router to each line module, SRP module, and fan module where
DC-to-DC converters provide local conversion to the required secondary voltages.
The ERX-310 router is available with either DC or AC power inputs. The AC-powered
version can be configured with one or two hot-swappable power supplies for optional
redundancy. (See Figure 5 and Figure 6.) The power supplies convert AC power to
internal –48 V redundant DC feeds that are then distributed through the router.
Redundancy Features 19

ERX 8.0.x Hardware Guide
Fans
Forced air-cooling keeps the temperature of the E-series modules and components
within normal operating limits. In ERX-14xx models, six cooling fans are located
in a tray at the top of the router (Figure 1). In ERX-7xx models, four cooling fans
arelocatedinatrayononesideoftherouter(Figure3). IntheERX-310router,
two cooling fans are located in a tray on one side of the router (Figure 5).
The system monitors the temperature of each module. If the temperature of a
module exceeds the maximum limit, the system immediately goes into thermal
protection mode and the modules are powered off. The ERX system controller
enters a low power mode, keeps the modules in a power-off condition, and does
not respond to any management interface commands. For information about
troubleshooting high operating temperatures, see “Troubleshooting” on page 103.
In ERX-7xx and ERX–14xx models, the fan tray has two redundant converters
that power the fans (for the ERX-14xx models, a –24 V, 50 W converter; for the
ERX-7xx models, a –12 V, 15 W converter). If one converter fails, the other
takes over. The ERX-310 router does not have redundant converters.
For all E-series routers, the system software reports an alarm if any
of the fans or converters fail.
20 Redundancy Features

22 Initial Installation

Chapter 2
Unpacking and Inspecting ERX Routers
This chapter reviews shipping contents and unpacking procedures for ERX routers.
It contains the following sections:
Before You Begin on page 23
Unpacking ERX-14xx Models on page 23
Unpacking ERX-7xx Models and ERX-310 Routers on page 24
Inspecting Router Components and Accessories on page 25
If You Detect or Suspect Damage on page 25
Contacting Juniper Networks on page 25
The Next Step on page 25
Before You Begin
Before you begin unpacking the router, be sure you have the following tools:
A No. 2 Phillips screwdriver
A utility knife
Amechanica
l lift, or at least two people to assist in lifting
Unpacking ERX-14xx Models
ERX-14xx models come boxed, bolted, and strapped to a skid. For
your convenience, we recommend that you unpack the router in the
location where you want to install it.
WARNING: Three people are required to install the router in a rack: two to lift the
system into position and one to screw it to the rack.
To unpack ERX-14xx models:
Unpacking ERX-14xx Models 23

ERX 8.0.x Hardware Guide
1. Cut the two straps that secure the carton to the skid, open the carton from the
top, and remove the box of accessories that sits on top of the router.
2. Unlock the four plastic clips that hold the box to the skid by squeezing them in
their center and pulling out, and then lift the carton off the router.
3. Remove the three screws that attach each of the two L-brackets to the router.
4. To avoid scratching the router when removing it from the skid, detach one of
the L-brackets from the skid by removing the three screws. See Figure 13.
Figure 13: Removing an L-Bracket
L-bracket
g013739
Unpacking ERX-7xx Models and ERX-310 Routers
ERX-7xx models and ERX-310 routers are shipped boxed, but not attached
to a skid. For your convenience, we recommend that you unpack the
router in the location where you want to install it.
To unpack an ERX-7xx model or an ERX-310 router:
1. Open the carton from the top.
2. Remove the box of accessories that sits on top of the system.
3. Remove the router from the box.
24 Unpacking ERX-7xx Models and ERX-310 Routers

Unpacking and Inspecting ERX Routers
WARNING: Three people are required to install the router in a rack: two to lift the
system into position and one to screw it to the rack.
Inspecting Router Components and Accessories
After you remove the equipment from the shipping containers:
Confirm the contents of each container.
Inspect all external surfaces and external connectors for visible signs of
damage.
Inspect all accessories shipped with each unit.
Document any damage noted during your inspection.
Confirm that the router has the correct number and type of modules for
your ordered configuration.
If You Detect or Suspect Damage
If you detect or suspect damage to any equipment:
Contact the shipper responsible for delivery, and formally report the damage.
Contact your Juniper Networks sales representative or reseller.
Contacting Juniper Networks
Please contact Juniper Networks at 1-888-314-JTAC (from the United States, Canada,
or Mexico) or 408-745-9500 (from elsewhere), or contact your sales representative
if you have any questions or concerns. See “Contacting Customer Support and
Returning Hardware” on page 151 for complete contact information.
The Next Step
To familiarize yourself with the electrical, environmental, and other guidelines
and requirements for installing ERX routers, turn to “Installation Guidelines
and Requirements” on page 129.
If you are familiar with these guidelines and requirements, turn to “Installing
ERX Routers” on page 27.
The Next Step 25

ERX 8.0.x Hardware Guide
26 The Next Step

Chapter 3
Installing ERX Routers
This chapter describes how to install ERX routers in a rack. It contains the following
sections:
Before You Begin on page 27
Freestanding Installation on page 27
Rack-Mounted Installation on page 28
The Next Step on page 33
Before You Begin
Before installing E-series routers, be sure you:
Haveaplanf
or installing the routers that takes into consideration future
expansion of your system.
Have the tools and accessories needed to complete the installation.
Read and understand the clearance requirements for the front and back of
the chassis for cable routing and other unit access. See “Environmental
Requirements” on page 130 for more information.
Read and understand the clearance requirements for the chassis to ensure
adequate ventilation.
Prepare the equipment racks by measuring and marking space for each
router and plenum you plan to install.
Freestanding Installation
When installing the system on a table top or in any other freestanding mode,
be sure to leave enough space around the system for adequate ventilation.
Position the router with easy access to the connections that it needs for power,
local communications, and remote communications.
See “Installation Guidelines and Requirements” on page 129, and “System
Specifications” on page 119, for more information.
Freestanding Installation 27

ERX 8.0.x Hardware Guide
WARNING: Two people are required to lift an E-series router.
CAUTION: To prevent electrostatic damage to the system and its components, make
sure persons handling the router wear an antistatic device.
Connectors are located on the I/O modules and the power input module. These
modules are installed from the rear of the router. (See Figure 14.) See “Cabling
ERX Routers” on page 53 for cabling installation procedures.
Figure 14: ERX-7xx Models, Rear View
SRP I/O module
I/O
modules
Power switches
Power input
module
g013730
Rack-Mounted Installation
We recommend that you use a standard EIA distribution rack. See “Equipment
Rack Requirements” on page 133 for detailed rack information.
Installation Guidelines
Before installingthesystemsinarack,considerthefollowing
guidelines and refer to Figure 15:
You can install up to 3 ERX-14xx models, 6 ERX-7xx models, or 14 ERX-310
routers in a single 7-ft. (2.1 m) rack.
Installing multiple systems in a single rack enables you to maximize your
availablespace.
28 Rack-Mounted Installation

Installing ERX Routers
You can install an ERX-14xx model, an ERX-7xx model, and an ERX-310
router together in the same rack. (See Figure 15.)
CAUTION: If you install an ERX-7xx model or ERX-310 router directly above an
ERX-14xx model in the same rack, you must install a plenum between the ERX-7xx
model or ERX-310 router and the ERX-14xx model so that the air can circulate
between the systems. (See Figure 51.) This plenum is available from Juniper
Networks.
If you install an ERX-14xx model above an ERX-7xx model or ERX-310 router,
thereisnoneedtoinstallaplenumbetweentheunitsbecausetheERX-7xx
models and ERX-310 routers vent air out the side of the chassis.
Install heavier systems, such as an ERX-14xx model, on the bottom of the
rack. Mount lighter systems, such as the ERX-310 router, higher in the rack.
Rack-Mounted Installation 29

ERX 8.0.x Hardware Guide
Figure 15: ERX Routers Installed in Recommended Order
Safety Guidelines
Observe the following safety guidelines when mounting the router in a rack.
WARNING: Install equipment in the rack from the bottom upward. This helps to
maintain the stability of the rack and reduces the chance of the rack tipping over.
WARNING: Three people are required to install the router in a rack: two to lift the
system into position and one to screw it to the rack.
30 Rack-Mounted Installation

Installing ERX Routers
CAUTION: Evaluate the overall loading of the branch circuit before you install
any equipment into a rack.
WARNING: Connect the router or rack to ground (earth), and ensure that a reliable
grounding path is maintained in the rack.
WARNING: Do not work on the system or connect or disconnect cables during
lightning activity.
WARNING: Be sure circuit breakers for the power source are in the OFF position
before attaching power cables.
WARNING: Before servicing the router, turn off the power.
WARNING: Remove jewelry (including rings, necklaces, and watches) before
working on equipment that is connected to power lines. Metal objects heat up
when connected to power and ground and can cause serious burns or become
welded to the terminals.
WARNING: Do not insert any metal object, such as a screwdriver, into an open slot
or the backplane. Doing so can cause electric shock and serious burns.
WARNING: The ERX-310 router AC model has more than one power-supply cord.
Disconnect two power cords before servicing to avoid electric shock.
Rack-Mounted Installation 31

ERX 8.0.x Hardware Guide
Preparing the Equipment Racks
Following your installation plan, use a tape measure and marking pen to measure
and mark space on each equipment rack for each router component. For horizontal
spacing, follow Network Equipment Building System (NEBS) requirements. If you
choose not to install a plenum, be sure to include 2 U of space between each
chassis for proper exhaust. A plenum, however, is highly recommended.
Installing the Router
To complete the installation of the router in a rack, you need:
A Phillips screwdriver
Depending on the router, up to eight 10-32 x 3/8 Phillips screws (provided with
the router) for each router to be installed
WARNING: Three people are required to install the router in a rack: two to lift the
system into position and one to screw it to the rack.
CAUTION: Make sure all persons handling a router wear an antistatic device.
To install the router in the rack:
1. With one person standing on the left side of the router and another standing
on the right side, lift the router into the rack.
2. Position the router in its designated location in the equipment rack. Make
sure the holes of the mounting brackets align evenly with the holes of the
equipment rack on both sides.
3. Starting at the bottom, have the third person secure the router in the
equipment rack by using the 10-32 x 3/8 Phillips screws.
4. Connect the necessary cables. (See “Cabling ERX Routers” on page 53 for
instructions on installing the cables.)
Figure 15 illustrates a distribution rack with one ERX-310 router, one
ERX-7xx model, and one ERX-14xx model installed.
32 Rack-Mounted Installation

Installing ERX Routers
The Next Step
After you finish installing the router:
If you need to install any modules, see “Installing Modules” on page 35.
If the router was delivered with the modules already installed, see “Cabling
ERX Routers” on page 53 for instructions on connecting cables.
The Next Step 33

ERX 8.0.x Hardware Guide
34 The Next Step

Chapter 4
Installing Modules
This chapter describes how to install and remove E-series modules. For information
about managing installed modules, see JUNOSe System Basics Configuration Guide,
Chapter 6, Managing Modules.
This chapter contains the following sections:
Overview on page 35
Safety Guidelines on page 40
Installing SRP I/O and SRP Modules on page 41
Installing Line and I/O Modules on page 44
Removing a Line Module, SRP Module, or SRP I/O Module on page 46
Installing Components for Line Module Redundancy on page 48
Configuring Line Module Redundancy on page 51
The Next Step on page 51
Overview
Line module slots are located in the front of each ERX chassis, while
I/O module slots are located in the rear. See “ERX Overview” on page 3
for front and rear views of ERX routers.
In ERX-14xx models, modules mount vertically in a chassis with 14 slots.
In ERX-7xx models and ERX-310 routers, modules mount horizontally in a
chassis with 7 slots and 3 slots, respectively. See Figure 16.
Overview 35

ERX 8.0.x Hardware Guide
Figure 16: Orientation of Line Modules in ERX Routers
ERX-310 router
ERX-7xx model
ERX-14xx model
g013742
For details about available line modules and compatibility between line
modules and SRP modules, see the ERX Module Guide.
Slot Groups
The slots in the ERX-1410 router and ERX-7xx models are divided into groups. The
number of groups and number of slots per group depend on the system.
There are no slot groups in the ERX-1440 router or the ERX-310 router.
In the ERX-310 router, slot 0 contains the SRP module and slots 1
and 2 each contain a line module.
Slot Groups for the ERX-1410 Router
Aslotgr
oup in the ERX-1410 router comprises three adjacent chassis slots. The
groups for the ERX-1410 router consist of the following slots (Figure 17):
Slotgroup1—Slots0through2
Slotgroup2—Slots3through5
Slot group 3—Slots 8 through 10
Slot group 4—Slots 11 through 13
Slots 6 and 7 are reserved for the SRP modules.
36 Overview

Installing Modules
Figure 17: ERX-1410 Slot Groups
SRP SRP
CT3 OC3CT1 OC3CT1CT1 CT3 CT3 CT3
Chassis slots
12340 5 6 7 8 9 10 11 12 13
Slot
group 1
Slot
group 2
Slot
group 3
Slot
group 4
g013743
Slot Groups for the ERX-7xx Models
A slot group in an ERX-7xx model comprises one slot or two adjacent slots. The
groups for an ERX-7xx model consist of the following slots (Figure 18):
Slot group1—Slots2and3
Slot group 2—Slot 4
Slot group 3—Slot 5
Slot group4—Slot6
Slots 0 and 1 are reserved for the SRP modules.
Figure 18: ERX-7xx Model Slot Groups
1
2
3
4
0
5
6
Slot group 1
Slot group 2
Slot group 3
Slot group 4
SRP SRP E3 ATM OC3CE1 CE1
Chassis slots
g013744
Overview 37

ERX 8.0.x Hardware Guide
Combinations of Line Modules In Slot Groups
For information about combinations of line modules in slot groups, see JUNOSe
System Basics Configuration Guide, Chapter 6, Managing Modules.
OC48 Line Modules
The ERX-1440 router with the SRP-40G+ SRP module supports OC48 line
modules. Other ERX routers do not support OC48 line modules.
An OC48 line module spans two slots in an ERX-1440 router. You can
install this line module only in slots 2–3 and slots 4–5. Other slots in
the system do not support this line module.
The corresponding OC48 Frame APS I/O module spans only one slot. Install the I/O
module in the lower of the slots (either slot 2 or slot 4) that the line module spans.
GE-2 Line Modules
The ERX-1440 router with the SRP-40G+ SRP module supports GE-2 line
modules in all slots; however, full bandwidth is delivered only when the line
module is in slot 2 or slot 4. The line module can be used with other SRP
modules, but maximum line performance will not be achieved.
The ERX-310 router with the SRP-SE10G SRP module supports GE-2 line modules in
both slots (1 and 2). Maximum line performance is achieved in either slot.
Other ERX routers do not support GE-2 line modules.
Managing Modules Using the Software
For information about software procedures associated with replacing
and managing modules, see JUNOSe System Basics Configuration
Guide, Chapter 6, Managing Modules.
Hot-Swapping Modules
All ERX routers support hot-swapping of modules. Hot-swapping enables you
toaddorremoveamodulewithoutpoweringdownthesystem.
Protecting Modules and Slots
Each ERX chassis has an ESD (electrostatic discharge) grounding jack. See
Table 4 for locations. To prevent damage from electrostatic discharge, connect
an antistatic wrist strap to the jack when handling components.
38 Overview

Installing Modules
Figure 19: Connecting the Wrist Strap to the ERX-310 Router (Rear)
ESD grounding jack
Antistatic
wrist strap
g013745
Table 4: Grounding Jack Locations
E-series Router Location
ERX-14xx models Front: inside front bezel in lower-left corner
Rear: upper-right corner
ERX-7xx models Rear: lower-right corner
ERX-310 router Front: lower-left corner
Rear: lower-right corner
To protect the modules and slots when installing modules, observe
the following guidelines:
CAUTION: When handling modules, use an antistatic wrist strap connected to the
router’s ESD grounding jack. This action helps to protect the module from damage
by electrostatic discharge.
CAUTION: Always handle the module by its edges. Do not touch the components,
pins, leads, or solder connections.
Overview 39

ERX 8.0.x Hardware Guide
CAUTION: If you meet strong resistance when attempting to seat the module using
the ejectors, remove it from the chassis and confirm that the slot is designed to hold
the module. Then verify, if applicable, that the module matches its corresponding
module (I/O module or line module). Also, be sure that you have aligned the top
and bottom edges in the correct matching tracks.
CAUTION: Be sure to cover every empty slot with a blank filler panel to protect the
system from dust or other foreign substances and to ensure proper system cooling.
CAUTION: Do not discard the antistatic bag. When a module is not in use, store it
in an antistatic bag.
Order of Installation
Before you attempt to install or replace a line module (inserted in the front of
the chassis), make sure the corresponding I/O module (inserted in the rear of
the chassis) is already in place. The slot diagnostics run when a line module
is installed in a chassis slot. If the corresponding I/O module is not present, the
diagnostics fail, and you need to remove and reinsert the module.
Required Tools and Safety Items
Youneedthefollowingtoolstoinstallalinemodule:
A Phillips screwdriver
An ESD wrist strap
Safety Guidelines
Before and during the installation process, observe the following precautions:
WARNING: Do not work on the system or connect or disconnect cables during
lightning activity.
40 Safety Guidelines

Installing Modules
WARNING: Be sure circuit breakers for the power source are in the OFF position
before attaching power cables.
WARNING: Remove jewelry (including rings, necklaces, and watches) before
working on equipment that is connected to power lines. Metal objects heat up
when connected to power and ground and can cause serious burns or become
welded to the terminals.
WARNING: Do not insert any metal object, such as a screwdriver, into an open slot
or the backplane. Doing so can cause electric shock and serious burns.
WARNING: Never attempt to repair parts of modules yourself. Only trained
customer service personnel are authorized to service parts. Call Juniper Networks
Customer Service to make arrangements to return defective modules for repair.
Installing SRP I/O and SRP Modules
You must install SRP modules in specific slots in each router. See
Table 5 for SRP module slot assignments.
Table 5: SRP Module Slot Assignments
Router Slot
ERX-14xx models 6 and 7
ERX-7xx models 0and1
ERX-310 router 0
NOTE: Because of different physical dimensions and switch fabric capabilities, SRP
modules are not interchangeable between systems. For example, the 10-Gbps SRP
module used in ERX-7xx and ERX-14xx models cannot be used in an ERX-310
router, and vice versa.
Installing SRP I/O and SRP Modules 41

ERX 8.0.x Hardware Guide
NOTE: Install the SRP I/O module before you install the SRP module; otherwise, the
system diagnostics will fail.
Installing an SRP I/O Module
To install an SRP I/O module:
1. Ground yourself by using an antistatic wrist strap or other device and connect
it to the ESD grounding jack on the chassis.
2. With a Phillips screwdriver, loosen the captive screws that secure the blank filler
panel covering the empty chassis slot, if present, and remove the filler panel.
3. Remove the SRP I/O module from its antistatic bag, being careful not to touch
module components, pins, leads, or solder connections.
4. Slide the module into the chassis by placing it between the guides of the
selected slot and pushing the module until it stops.
NOTE: See the figures in “ERX Overview” on page 3 for module locations.
5. Tighten the module’s captive screws using a Phillips screwdriver. Turn both
screws several times before tightening them completely to allow the module
to sit correctly.
Installing an SRP Module
To install an SRP module:
1. Ground yourself by using an antistatic wrist strap or other device and connect
it to the ESD grounding jack on the chassis.
NOTE: See the figures in “ERX Overview” on page 3 for module locations.
2. Choose the slot in which you want to install the module.
ERX-14xx models—Slot 6 or 7
ERX-7xx models—Slot 0 or 1
ERX-310 router—Slot 0
42 Installing SRP I/O and SRP Modules

Installing Modules
3. With a Phillips screwdriver, loosen the captive screws that secure the blank filler
panel covering the empty chassis slot, if present, and remove the filler panel.
4. Remove the SRP module from its antistatic bag, being careful not to touch
module components, pins, leads, or solder connections.
5. Verify that the ejectors are in the open position, as shown in Figure 20.
Figure 20: Ejectors in the Open Position
Opened
Closed
Opened
Closed
g013746
6. Slide the module into the chassis by placing it between the guides of the
selected slot and pushing the module until it stops.
The module stops sliding when the ejectors make contact with the front
of the chassis.
CAUTION: If you meet strong resistance when attempting to seat the module using
the ejectors, remove it from the chassis and confirm that the slot is designed to hold
the module. Then verify, if applicable, that the module matches its corresponding
Installing SRP I/O and SRP Modules 43

ERX 8.0.x Hardware Guide
module (I/O module or line module). Also, be sure that you have aligned the top
and bottom edges in the correct matching tracks.
7. Insert the module into the backplane by simultaneously depressing both
ejectors (as shown in Figure 20) and exerting forward pressure on the module.
8. Tighten the module’s captive screws using a Phillips screwdriver. Alternately
turn each screw several times before tightening them completely to allow
themoduletositcorrectly.
Installing Line and I/O Modules
This section describes the procedures for installing line and I/O modules.
NOTE: Install the I/O module before you install the corresponding line module;
otherwise, the diagnostics fail and the line module’s status is listed as inactive
when you issue the show version command. If this occurs, remove and reinsert
the line module.
Installing a Line Module or an I/O Module
To install a module:
1. Ground yourself by using an antistatic wrist strap or other device and connect
it to the ESD grounding jack on the chassis.
2. Choose the slotwhereyouwanttoinsertthemodule.
NOTE: Line modules are in the front of the system and I/O modules are in the
back of the system.
44 Installing Line and I/O Modules

Installing Modules
Table 6: Module Slot Assignments
Router Module Slot
ERX-1440 router Install modules other than the OC48
modules in slots 0–5 and slots 8–13
Install the OC48 line module in slots
2–3 and slots 4–5
Install the corresponding I/O module
only in the lower of the two slots
(either slot 2 or slot 4) that the line
module spans
ERX-1410 router Install modules in slots 0–5 and slots 8–13
ERX-7xx models Install modules in slots 2–6
ERX-310 router Install modules in slots 1–2
3. With a Phillips screwdriver, loosen the screws that secure the blank filler panel
covering the empty chassis slot, if present, and remove the filler panel.
4. Remove the module from its antistatic bag, being careful not to touch module
components, pins, leads, or solder connections.
5. Verify that the ejectors are in the open position, as shown in Figure 20.
6. Guide the module into the chassis by placing it between the guides of the
selected slot and pushing the module until it stops.
The module stops sliding when the ejectors make contact with the front
of the chassis.
CAUTION: If you meet strong resistance when attempting to seat the module using
the ejectors, remove it from the chassis and confirm that the slot is designed to hold
the module. Then verify, if applicable, that the module matches its corresponding
module (I/O module or line module). Also, be sure that you have aligned the top
and bottom edges in the correct matching tracks.
7. Insert the module into the midplane by simultaneously depressing both
ejectors (as shown in Figure 20) and exerting forward pressure on the module.
8. Tighten the module’s captive screws using a Phillips screwdriver. Alternately
turn each screw several times before tightening them completely to allow
themoduletositcorrectly.
Installing Line and I/O Modules 45

ERX 8.0.x Hardware Guide
Removing a Line Module, SRP Module, or SRP I/O Module
NOTE: We recommend that you issue the slot disable command from the CLI
beforeremovingalinemoduleorI/Omodule.
CAUTION: If you do not use the halt command before removing or powering down
an SRP, the system’s NVS card can become corrupted.
To remove a line module, SRP module, or SRP I/O module:
1. For SRP modules and SRP I/O modules, issue the appropriate halt command
(halt,halt primary-srp,orhalt standby-srp).
See JUNOSe System Basics Configuration Guide, Chapter 6, Managing Modules for
information about the halt commands.
2. Ground yourself by using an antistatic wrist strap or other device and connect
it to the ESD grounding jack on the chassis.
3. Useascrewdri
ver to loosen the thumb screws located at the top and bottom of
the module panel.
4. Pull the ejector handles located at the top and bottom of the module so that
they are in position 2, as shown in Figure 21.
46 Removing a Line Module, SRP Module, or SRP I/O Module

Installing Modules
Figure 21: Ejectors in the Closed Position
Closed
Opened
Closed
Opened
g013747
5. Carefully slide the module out of the chassis.
6. Place the module in its antistatic bag, being careful not to touch module
components, pins, leads, or solder connections.
7. Cover the empty chassis slot with a blank filler panel, and tighten the filler
panel’s captive screws using a Phillips screwdriver. Turn both screws several
times before tightening them completely.
If you remove an I/O module and not the corresponding line module, the line module
reboots. Its status becomes inactive when you issue the show version command.
If you remove a line module and do not delete the corresponding
configuration, the status of the line module is listed as not present
when you issue the show version command.
Removing a Line Module, SRP Module, or SRP I/O Module 47

ERX 8.0.x Hardware Guide
Installing Components for Line Module Redundancy
A spare line module provides redundancy for a group of identical line
modules for ERX-7xx and ERX-14xx models only.
NOTE: The ERX-310 router does not support line module redundancy.
For line module redundancy to operate, you must install:
The line modules,includingthesparelinemodule
The redundancy midplane
The I/O modules, including the spare I/O module
For more information, see “Redundancy Features” on page 16.
WARNING: Do not insert any metal object, such as a screwdriver, or place your hand
into an open slot or the backplane when the router is on. Remove jewelry (including
rings, necklaces, and watches) before working on equipment that is connected to
power lines. These actions can prevent electric shock and serious burns.
CAUTION: When handling modules, use an antistatic wrist strap connected to the
router’s ESD grounding jack, and hold modules by their edges. Do not touch the
components, pins, leads, or solder connections. These actions help to protect
modules from damage by electrostatic discharge.
Installing theLineModules
To install the line modules in a redundancy group:
1. Install the spare line module in the lowest-numbered slot of the redundancy
group.
2. Install the other line modules in the remaining slots. (See “Installing Line and
I/O Modules” on page 44.)
Installing the Redundancy Midplane
To install the redundancy midplane in a redundancy group:
48 Installing Components for Line Module Redundancy

Installing Modules
CAUTION: Ifyoudonotusethehalt command before removing or powering down
an SRP, the system’s NVS card can become corrupted.
1. Enter the halt command.
See JUNOSe System Basics Configuration Guide, Chapter 6, Managing Modules for
information about the halt command.
WARNING: Turn off the router before you install the redundancy midplane. Working
inside the router when it is on can lead to electric shock and serious burns.
2. Turn off the power switches located on the power input module in the rear
of the system (Figure 22).
3. Remove the I/O modules from the slots that the redundancy midplane will
span.
4. Place the redundancy midplane in the chassis so that it rests against the guides
below the chassis midplane (Figure 22).
5. Align the screw holes in the redundancy midplane with the screw holes in the
guides so that the midplane covers the slots for the redundancy group.
6. Using a Phillips screwdriver and the screws provided, loosely attach, but do not
tighten, the redundancy midplane to the guides.
7. Carefully insert an I/O module in one slot to ensure that the redundancy
midplane is aligned correctly; then tighten the screws.
CAUTION: A misaligned redundancy midplane can result in bent pins on the
backplane and midplane and poor contact between the I/O modules and the
redundancy midplane.
Installing Components for Line Module Redundancy 49

ERX 8.0.x Hardware Guide
Figure 22: Installing a Redundancy Midplane
Redundancy
midplane
g013748
Installing the I/O Modules
To install the I/O modules in a redundancy group:
1. Install the redundancy I/O module in the lowest-numbered slot of the
redundancy group.
CAUTION: When setting up a redundancy group with line modules, be sure to install
the redundancy I/O module in the lowest-numbered slot of the redundancy group.
It is possible to install the redundancy I/O module in other slots; however, doing so
can damage other I/O modules connected to the redundancy midplane.
2. Install the corresponding I/O module for the line module of each slot in the
redundancy group. (See “Installing a Line Module or an I/O Module” on
page 44.)
3. Cable each module to provide a path to the remote interface. (See “Cabling
ERX Routers” on page 53.)
50 Installing Components for Line Module Redundancy

Installing Modules
Verifying the Installation
To verify that the installation is complete:
1. After you have cabled the system for power, as described in “Cabling ERX
Routers” on page 53, turn on the power switches.
The system reboots.
2. Issue the show redundancy command, and verify that the display shows
the redundancy hardware.
Configuring Line Module Redundancy
For information about configuring line module redundancy, see JUNOSe System
Basics Configuration Guide, Chapter 6, Managing Modules.
The Next Step
After you install the modules, you can connect cables to the system.
See “Cabling ERX Routers” on page 53.
The Next Step 51

ERX 8.0.x Hardware Guide
52 The Next Step

Chapter 5
Cabling ERX Routers
This chapter describes how to cable an ERX router. Before you cable the router,
ensure that you have completed all installation instructions identified in previous
chapters.
This chapter contains the following sections:
Cabling Overview on page 53
Required Tools, Wires, and Cables on page 55
Cabling the SRP I/O Module on page 56
Cabling the Router for Power on page 60
Cabling I/O Modules on page 66
The Next Step on page 72
Cabling Overview
Cabling an ERX router requires the following main tasks:
1. Familiarize yourself with the module ports, and ensure that you have the cables
and wires needed to complete each cabling procedure. (See Figure 23.)
2. Read and understand all safety warnings. (See “Installation Guidelines and
Requirements” on page 129.)
3. (Optional) Connect timing ports.
4. Connect the SRP I/O module to the network and to a management console.
5. Connect grounding wires to the router chassis.
6. Connect the power cables from the power source to the power input module.
7. Connect the line I/O modules to their appropriate network interface.
Cabling Overview 53

ERX 8.0.x Hardware Guide
NOTE: We recommend that you use shielded cables where appropriate.
Figure 23: ERX Ports and Connectors (ERX-14xx Model Shown)
A
T
G
R
T1 100 OHM
CLOCK IN
B
T
G
R
E1 75 OHM
CLOCK IN
+
-
+
-
+
-
ALARMSEXTERNAL TIMINGCONSOLE
|
ON
O
OFF
|
ON
O
OFF
THIS PRODUCT IS EQUIPPED WITH
TWO POWER FEEDS. DISCONNECT
BOTH FEEDS PRIOR TO SERVICE. POWER A POWER B
POWER A POWER B
-48VDC -48VDCRTN RTN
-48VDC RTN -48VDC RTN
WARNING!
NO OPERATOR ACCESSIBLE
COMPONENTS. AUTHORIZED
SERVICE PERSONNEL ONLY.
!
CT3
I/O
CT3
I/O
OC3
I/O
OC3-4
I/O
SINGLE
MODE
OC3-4
I/O
SINGLE
MODE
FE-8
I/O
MINOR
MAJOR
CRITICAL
OC3
I/O module
(slot 13)
10/100
BASE T
RS-232
g013749
FE-8 I/O module
(slot 5)
SRP I/O module
(slot positions 6 and 7)
Alarm leads
External timing ports (Europe)
External timing ports (North America)
10/100 BASE T port
RS-232 terminal port
Power input module
Power A and Power B
on/off switches
Power A and Power B
input connectors
Ground terminals
Port 0 RX
TX
Port 1 RX
TX
Blank
faceplate
Ejector
OC3-4
I/O module
(slot 12)
CT3
I/O module
(slot 9)
Port 0
Port 1
Port 2
Port 3
54 Cabling Overview

Cabling ERX Routers
Required Tools, Wires, and Cables
Cabling your system takes only a few minutes. You need the following
items and those listed in Table 7 for proper installation:
1/8–inch flathead screwdriver
3/8–inch wrench or 3/8–inch nut-driver
No. 2 Phillips screwdriver
Ground wires—We recommend a minimum of 10-AWG ground wire.
#10 (ERX-7xx and ERX-14xx models) or #8 (ERX-310 router) kep nut to
connect the ground (earth) wire to the ground terminal.
Power input module wiring—We recommend a minimum of 8-AWG wire for
ERX-14xx models, 12-AWG wire for ERX-7xx models, and 14-AWG wire for
ERX-310 routers (DC model) with a dual stud terminal lug with 5/8–inch
spacing. For the ERX-310 router AC model, use a standard IEC power cord.
Consider the distance from the connection point and the configuration of the
system when determining the size of wire used.
See “System Specifications” on page 119 for more information on router
specifications.
Table 7: Required Cables
Connection Port and Cable Used
Management connection between SRP I/O module and the
LAN
One 10/100Base-T Ethernet management port with an RJ-45
connector
Management connection between SRP I/O module and a
managementconsole
OneRS-232portwithaDB-9connectorforVT100
management access
Direct connections to I/O modules See the ERX Module Guide for specific I/O module connector
information
NOTE: If you plan to use a cable-management bracket (ERX-7xx and ERX-14xx
models only), install it before you begin cabling your router. Cable-management
brackets are helpful to keep network interface cables untangled and orderly
and to prevent cables from hindering access to other slots. See “Installing a
Cable-Management Bracket on ERX-7xx Models” on page 100.
Required Tools, Wires, and Cables 55

ERX 8.0.x Hardware Guide
Cabling the SRP I/O Module
Before powering up the router, you must set up a management console. The
console enables you to communicate with your system during the power-up process
and to manage your system using the command-line interface (CLI).
When connecting a console directly to the SRP I/O module, use a cable appropriate
foryourterminalconnector.ThecablemusthaveafemaleDB-9connectortoattach
to the RS-232 port on the SRP I/O module. See Figure 24 and Figure 25.
The console port is considered a data terminal equipment interface
(DTE). Direct connection to a terminal or PC (which also have DTE
interfaces) requires a crossover cable.
NOTE: The alarm function on the SRP I/O module is currently not implemented.
Only ERX-7xx and ERX-14xx models have external timing ports and alarm leads
located on the SRP I/O module. All ERX routers have console ports located on
the SRP I/O module. See Table 8 for details on each component.
Table 8: SRP I/O Ports
Port Description
Alarm leads (ERX-7xx and ERX-14xx models
only)
Six terminal blocks for external alarm
contacts; use a minimum 26-AWG for each
(currently not implemented)
External timing ports (ERX-7xx and ERX-14xx
models only)
Two 3-pin wire-wrap posts for US
external clock sources; primary (A)
and secondary (B)
Two BNC connectors for E1 clock
sources; primary (A) and secondary (B)
Management console ports One 10/100Base-T Ethernet
management port with an RJ-45
connector
One RS-232 console port with a DB-9
connector for VT100 management
access
External Timing Ports
NOTE: This section applies to ERX-7xx and ERX-14xx models only. The ERX-310
router does not support external timing.
56 Cabling the SRP I/O Module

Cabling ERX Routers
The SRP I/O module has two input ports for external clock sources.
These ports provide a way to ensure that the router system clock remains
synchronized with the network’s system clock. The primary clock is labeled
A; the secondary, redundant clock is labeled B.
Use the connectors appropriate for your locale (European or
North American standard):
European—Two 75-ohm E1 2.048-Mbps inputs with BNC connectors
North American—Two 100-ohm T1 inputs with three pin wire-wrap
connectors. Pins are labeled T (tip), G (ground), and R (ring). We recommend
using 26-AWG wire minimum.
NOTE: Use shielded cables to connect the external clock sources to the clock
source input ports.
Cabling the SRP I/O Module 57

ERX 8.0.x Hardware Guide
Figure 24: SRP I/O Module for ERX-14xx Models
A
T
G
R
T1 100 OHM
CLOCK IN
B
T
G
R
E1 75 OHM
CLOCK IN
+
-
+
-
+
-
ALARMSEXTERNAL TIMING
CONSOLE
MINOR
MAJOR
CRITICAL
10/100
BASE T
RS-232
BNC (Europe)
DB-9
RJ-45
26-AWG wire
Wire-wrap connectors
(North America, Japan)
g013750
To connect the clock source input ports:
1. Depending on the connector type, complete one of the following tasks:
E1: Attach the BNC connector to Clock A’s external timing port.
T1: Wrap the tip wire on pin marked T of Clock A’s external timing port,
the ground wire on G pin, and the ring wire on R pin.
58 Cabling the SRP I/O Module

Cabling ERX Routers
NOTE: You can use a wire-wrap gun to attach wires to pins.
2. Attach the opposite end of the external timing cable or wires to your network’s
clock source A.
3. Repeat Steps 1 and 2 for the Clock B connections.
Management Ports
NOTE: This section applies to all ERX routers.
The Console section of the SRP I/O module has two ports for management
access. (See Figure 24 and Figure 25.)
The 10/100Base-T Ethernet port accepts an RJ-45 (male) connector, providing
an out-of-band connection for LAN access through a Telnet session or SNMP.
The RS-232 port accepts a DB-9 (female) connector for direct CLI access
from a console terminal.
The console port is considered a data terminal equipment interface (DTE).
Direct connection to a terminal or PC (which also have DTE interfaces) requires
a crossover cable.
Figure 25: SRP I/O Module for the ERX-310 Router
RS-232 10/100
BASE T
SRP I/O module
g013751
See “Accessing ERX Routers” on page 77 for more information
about management access.
Cabling the SRP I/O Module 59

ERX 8.0.x Hardware Guide
Connecting to the Network
To connect the router to the network:
1. Insert an Ethernet cable (RJ-45) connector into the 10/100Base-T (RJ-45) port
on the SRP I/O module until it clicks into place.
2. Connect the other end of the cable to the appropriate Ethernet network for
an out-of-bandconnection.
Connecting to a Console Terminal
When you connect a console directly to the router SRP I/O module, use a cable
appropriate for your terminal connector. The cable must have a female DB-9
connector to attach to the RS-232 port on the SRP I/O module.
To connect the console to the SRP I/O module:
1. InsertthefemaleDB-9connectorintotheRS-232port,andtightenthescrews.
2. Connect the other end of the cable to your terminal’s serial port (VT100/ANSI).
Cabling the Router for Power
After you have correctly cabled the modules and I/O modules, you
must attach grounding and electrical wires before you attempt system
power-up. Three main tasks are involved:
1. Switch all router power switches to OFF.
CAUTION: Switches may have inadvertently flipped to ON during shipping and
installation.
2. Connect the grounding wires to the chassis.
WARNING: Always connect the grounding wires first (before connecting the power
cables) and disconnect them last when installing or servicing the router.
3. Connect the power cables (AC or DC) to the power input modules.
See “System Specifications” on page 119 for the power requirements for ERX
routers. Table 9 identifies the power input module cabling requirements, and
Figure 26 shows the main components of a power input module.
60 Cabling the Router for Power

Cabling ERX Routers
Table 9: Power Input Module Cables and Wires Needed
Cable/Wire From To
ERX-14xx models
One 10-AWG ground wire Power input module ground terminal Termination ground
Two 8-AWG wire leads Power input module Power A –48 VDC
and RTN leads
Appropriate leads on power source No.1
Two 8-AWG wire leads Power input module Power B –48 VDC
and RTN leads
Appropriate leads on power source No.2
ERX-7xx models
One 10-AWG ground wire Power input module ground terminal Termination ground
Two 12-AWG wire leads Power input module Power A –48 VDC
and RTN leads
Appropriate leads on power source No.1
Two 12-AWG wire leads Power input module Power B –48 VDC
and RTN leads
Appropriate leads on power source No.2
ERX-310 router
One 10-AWG ground wire Power input module ground terminal Termination ground
Two 14-AWG wire leads (DC model only) Power input module Power A –48 VDC
and RTN leads
Appropriate leads on power source No.1
Two 14-AWG wire leads (DC model only) Power input module Power B –48 VDC
and RTN leads
Appropriate leads on power source No.2
One AC power cord (AC model only) Power input module AC power IEC
receptacle
Appropriate AC power supply
Cabling the Router for Power 61
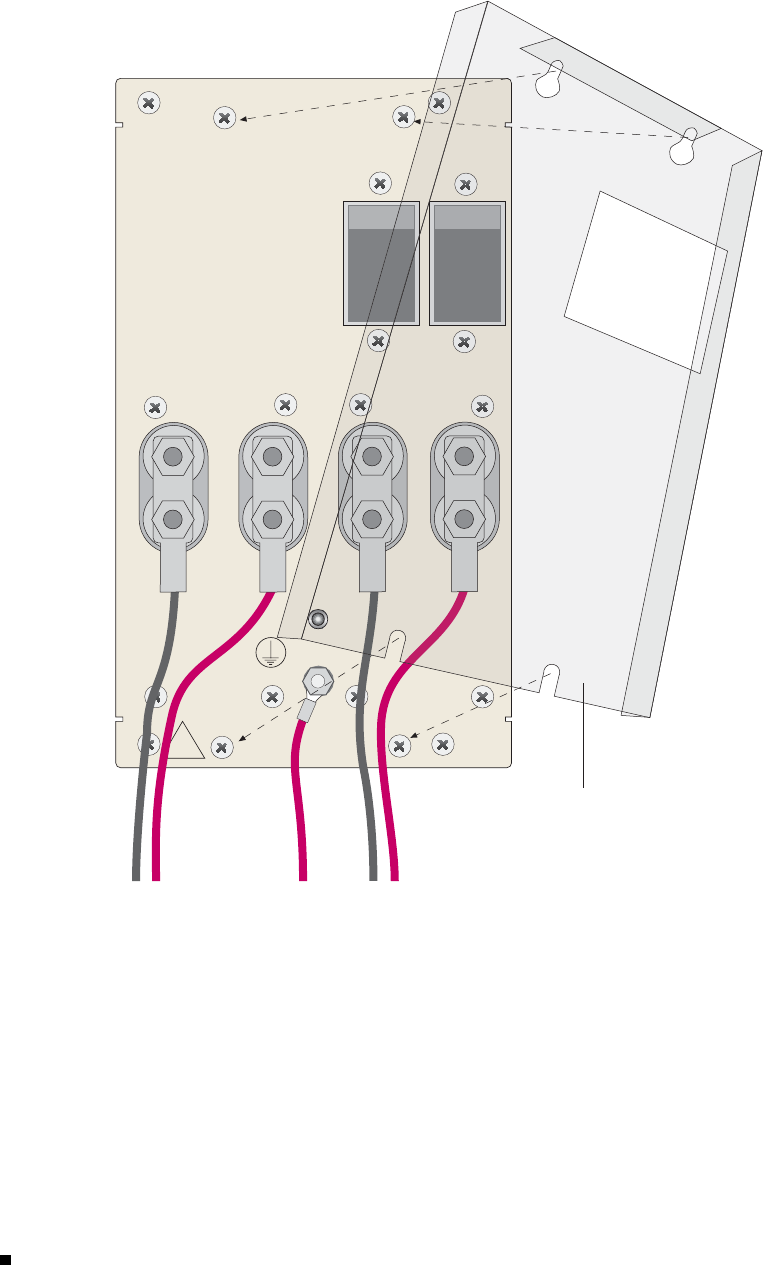
ERX 8.0.x Hardware Guide
Figure 26: Power Input Module for ERX-14xx Models
|
ON
O
OFF
|
ON
O
OFF
Ground
Power A
leads
Power B
leads
THIS PRODUCT IS EQUIPPED WITH
TWO POWER FEEDS. DISCONNECT
BOTH FEEDS PRIOR TO SERVICE. POWER A POWER B
POWER A POWER B
-48VDC -48VDCRTN RTN
-48VDC RTN -48VDC RTN
WARNING!
NO OPERATOR ACCESSIBLE
COMPONENTS. AUTHORIZED
SERVICE PERSONNEL ONLY.
!
Power input
module cover
|
ON
O
OFF
|
ON
O
OFF
WITH
NNECT
VICE. POWER A POWER
POWER B
-48VDCTN RTN
TN -48VDC RTN
|
ON
O
OFF
|
ON
O
OFF
H
CT
POWER A POWER B
POWER B
-48VDC RTN
-48VDC RTN
ARNING!
O
OFF
PO
-48VDC
-48VDC
g013752
Task 1: Turn Off All Router Power
Before starting, you must switch all router power switches to OFF.
To turn off the router, push each power switch to the OFF position.
62 Cabling the Router for Power

Cabling ERX Routers
Task 2: Connect the Grounding Cables
All ERX routers have two grounding studs located in the rear of the chassis, near
the power inputs. Each stud provides grounding for a single power unit.
To ground each power unit:
1. Locate the grounding studs on the router (Figure 26 and Figure 27).
2. Remove the nuts and locking washers from the grounding studs.
NOTE: We recommend a minimum of 10-AWG ground wire with a ring style
terminal.
3. Place the grounding cable lead on one of the grounding studs and tighten
the nuts to secure the connection.
4. Connect the other end of the ground cable to the appropriate ground
termination lead.
5. Repeat Steps 3–4 for the remaining grounding stud.
NOTE: When grounding an ERX router, leave a service loop in the grounding cable
to ensure that the grounding cable is the last cable to disconnect from the shelf if
strain is placed on the electrical cables.
Task 3: Connect the Power Cables
To connect power cables to the router, follow these steps. Refer to
Figure 26, Figure 27, and Figure 28 as needed.
ERX-7xx Models, ERX-14xx Models, ERX-310 Router (DC Model)
WARNING: Before you begin this procedure, ensure that all power switches are
in the OFF position.
1. Be sure you have completed Task 1 and Task 2 in the previous sections.
2. If applicable, loosen the screws from the clear power input module cover
and remove it.
Cabling the Router for Power 63

ERX 8.0.x Hardware Guide
WARNING: Be sure the power source is turned off, the router is turned off, and
proper grounding wires are attached before continuing with this procedure.
WARNING: The wiring color code of the power cables depends on the color
coding of the DC power source installed at your site. Color code standards for DC
wiring do not exist. To ensure that the correct polarity is connected to the router
power units, confirm the connection of the power cables to the + (positive) and
– (negative) leads at the power source.
3. Removethenutsandlockingwashersfromthepostsforthepowerinput(A
or B) using a small insulated adjustable wrench.
4. Place one negative (neutral) cable lead on the post labeled –48 VDC.
5. Replace the locking washers and nuts, and tighten the nuts to secure the
connection.
6. Place the other cable lead on the post labeled RTN.
7. Replace the locking washer and nut, and tighten the nut to secure the
connection.
8. Attach the opposite end of Power A’s wire leads to the appropriate leads on
your power source.
NOTE: To provide redundancy, do not terminate Power A and Power B leads at the
same power source.
9. Place the clear plastic guard over the terminal posts, and secure it in place by
tightening the four screws.
10. Repeat Steps 1–9 for each power input module in your configuration.
64 Cabling the Router for Power

Cabling ERX Routers
Figure 27: ERX-310 Router, Rear View (DC Model)
Ground Power B
switch
DC power
input B
DC power
input A
Power A
leads
POWER B
POWER A
-48VDC RTN
ON
|
O
OFF
-48VDC RTN
ON
|
O
OFF
Power A
switch
g013753
ERX-310 Router (AC Model)
1. Insert the power cord into the AC power IEC receptacle. (See Figure 28.)
2. Insert the other end of the power cord into an appropriate AC power source.
NOTE: To provide redundancy, do not terminate Power A and Power B leads at the
same power source.
3. Repeat Steps 1–2 for the other power input module, if needed.
Figure 28: ERX-310 Router, Rear View (AC model)
Ground
AC power input A
with switch
AC power input B
with switch
POWER A POWER B
100-240V ~ 5A
50/60 Hz
|
O
|
O
g013754
Cabling the Router for Power 65

ERX 8.0.x Hardware Guide
Cabling I/O Modules
This section illustrates the common connector types used with ERX
I/O modules. For information about the connectors on the different
line modules, see the ERX Module Guide.
BNC Connectors
Figure 29: I/O Module with BNCs
CT3
I/O
Port 0
Port 1
TX
RX
RX
TX
g013755
HSSI Connectors
The HSSI I/O module uses a standard 50-pin HSSI connector.
CAUTION: Do not terminate HSSI connections with SCSI connectors. Although
SCSI connectors look very similar to HSSI connectors, using SCSI connectors on
HSSI connections can lead to data loss.
66 Cabling I/O Modules

Cabling ERX Routers
Figure 30: HSSI I/O Module with 50-Pin HSSI Connector
HSSI-3
I/O
Port 0
g013756
RJ-45 Connectors
When inserting an RJ-45 connector, be sure it clicks into the port.
Figure 31: I/O Module with RJ-45 Connector
10/100
FE-2
I/O
Port 0
g013757
RJ-48C Connectors
When inserting an RJ-48C connector, be sure it clicks into the port.
Cabling I/O Modules 67

ERX 8.0.x Hardware Guide
Figure 32: I/O Module with RJ-48C Connectors
CE1
I/O
Port 0
g013758
LC Duplex Connectors
In accordance with EN60825-1, Safety of Laser Products - Part 1: Equipment
Class, Requirements, and User’s Guide (2001), multimode I/O modules
with LC connectors are defined as follows:
CLASS 1 LED PRODUCT.
In accordance with EN60825-1, Safety of Laser Products - Part 1: Equipment
Class, Requirements, and User’s Guide (2001), single-mode I/O modules
with LC connectors are defined as follows:
CLASS 1 LASER PRODUCT.
WARNING: Do not look directly into LC-style fiber connectors. The fiber-optic laser
used in single-mode fiber (SMF) meets the regulatory requirements for casual
exposure to the eye; however, looking directly into a laser can cause eye damage.
WARNING: IEC 825, Class 1 laser fiber connectors are for connection only to
Class 1 laser devices.
SC Duplex Connectors
In accordance with EN60825-1, Safety of Laser Products - Part 1: Equipment
Class, Requirements, and User’s Guide (2001), multimode I/O modules
with SC connectors are defined as follows:
68 Cabling I/O Modules

Cabling ERX Routers
CLASS 1 LED PRODUCT.
In accordance with EN60825-1, Safety of Laser Products - Part 1: Equipment
Class, Requirements, and User’s Guide (2001), single-mode I/O modules
with SC connectors are defined as follows:
CLASS 1 LASER PRODUCT.
WARNING: Do not look directly into SC-style fiber connectors. The fiber-optic laser
used in single-mode fiber (SMF) meets the regulatory requirements for casual
exposure to the eye; however, looking directly into a laser can cause eye damage.
WARNING: IEC 825, Class 1 laser fiber connectors are for connection only to
Class 1 laser devices.
SC duplex connectors have the same basic shape as LC duplex connectors,
but are slightly larger. See Figure 33.
Cabling I/O Modules 69

ERX 8.0.x Hardware Guide
Figure 33: I/O Module with SC Full Duplex Connectors
Port 0
Port 1
TX
RX
TX
RX
OC3
I/O
g013759
SMB Connectors
To cable I/O modules with SMB connectors, pull back the metal sheath on the
connector, insert the connector into the selected port, and release the metal sheath.
70 Cabling I/O Modules

Cabling ERX Routers
Figure 34: I/O Module with SMB Connectors
CT3/T3
12
I/O
Port 0
g013760
X.21/V.35 Connectors
Four cables are available for the X.21/V.35 I/O modules:
X.21DCEcable(terminatedwith8femaleX.21connectors)
X.21DTEcable(terminatedwith8maleX.21connectors)
V.35 DCE cable (terminated with 8 female V.35 connectors)
V.35 DTE cable (terminated with 8 male V.35 connectors)
Each 200-pin proprietary socket on the I/O module provides connections to 8
V.35 or X.21 ports. The remote end of the cable is terminated with either 8 X.21
connectors or 8 V.35 connectors. The cable you attach to the port on the I/O
module determines whether the connection is X.21 or V.35 and DCE or DTE.
Cabling I/O Modules 71

ERX 8.0.x Hardware Guide
Figure 35: X.21/V.35 Module with 50-Pin X.21/V.35 Connector
X.21/V.35
I/O
Port 0
g013761
Redundant Ports
Some modules have redundant ports. See the ERX Module Guide for specifications.
Cabling both ports provides a redundant path to the module.
CAUTION: For port redundancy to operate correctly on a GE I/O module that
supports SFPs, both the primary and redundant ports on an E-series GE I/O module
must use the same type of SFP.
The Next Step
See “Powering Up ERX Routers” on page 73.
72 The Next Step

Chapter 6
Powering Up ERX Routers
This chapter describes how to power up an ERX router and determine whether it
has booted properly. It contains the following sections:
Before You Power Up the System on page 73
Powering Up on page 73
Status LEDs on page 75
Powering Down on page 75
The Next Step on page 75
Before You Power Up the System
Before powering up the system, make sure you complete the following tasks. See
the appropriate chapters in this guide for information about these tasks.
WARNING: Be sure the power source is turned off and the system is turned off
before you perform the installation tasks.
“Installing SRP I/O and SRP Modules” on page 41
“Installing Line and I/O Modules” on page 44
“Cabling the SRP I/O Module” on page 56
“Cabling the Router for Power” on page 60
“Cabling I/O Modules” on page 66
Powering Up
For specifications on the electrical requirements for the system, see “System
Specifications” on page 119. For details on the power consumed by the
different ERX modules, see the ERX Module Guide.
Powering Up 73

ERX 8.0.x Hardware Guide
NOTE: In this procedure, we assume that the system is already connected to a
power source. See “Cabling ERX Routers” on page 53.
CAUTION: Evaluate the overall loading of the branch circuit before you install
any equipment into a rack.
To power up the system:
1. Verify that the power source is operational and turned on.
2. Inspect all grounding and power connections to the router chassis.
3. Confirm that all connections are secure.
4. Switch the powerswitchestoON.
5. Monitor the LEDs on the front of the SRP modules to verify that the system
is booting properly. See Table 12 in “Troubleshooting” on page 103 for LED
status explanations.
When the prompt appears on the system console, the system is in User Exec
mode and is ready to be configured:
host1>
6. Enter the enable command to access Privileged Exec mode:
host1>enable
host1#
In Privileged Exec mode you can begin to configure the system. See JUNOSe
System Basics Configuration Guide, Chapter 2, Command-Line Interface for
more information.
Initialization Sequence
Each line module is initialized independently. As a result, the CLI on the SRP
module can become available before the line modules have completed initialization.
Commands relating to a line module might fail if the module has not completed
initialization. You can use the show version command to display line module
status. Do not enter commands for a line module until its state is listed as online.
74 Powering Up

Powering Up ERX Routers
Status LEDs
Upon initial power-up, the components of the router run boot code, go through
a series of self diagnostic tests, and synchronize with each other.
When the tests are complete, use the LEDs on each module to determine the
status of the router. Observe the line module and SRP module LEDs in the front,
and the I/O line module and SRP I/O module LEDs in the rear.
See “Troubleshooting” on page 103 for information on the system’s LEDs.
Powering Down
If you need to power down or remove the SRP module, first enter the halt
command to temporarily suspend the system’s operation. See JUNOSe System
Basics Configuration Guide, Chapter 5, Managing the System for more information.
CAUTION: Ifyoudonotusethehalt command before removing or powering down
an SRP module, the system’s NVS card might become corrupted.
If you shut down the system improperly, it runs an investigation of the
file allocation table (FAT) the next time it reboots.
The Next Step
If you have problems powering up the system, see “Troubleshooting”
on page 103 for help.
If the system boots properly, see “Accessing ERX Routers” on page 77.
The Next Step 75

ERX 8.0.x Hardware Guide
76 The Next Step

Chapter 7
Accessing ERX Routers
This chapter discusses how to access the system to manage it. Managing your
router includes both configuring and monitoring it. For basic information on
the management of the system, see JUNOSe System Basics Configuration Guide,
Chapter 5, Managing the System.
This chapter contains the following sections:
Setting Up Management Access on page 77
Console Port Setup on page 78
Telnet Setup on page 80
SNMP on page 82
The Next Step on page 82
Setting Up Management Access
Before you power up the system, you must set up a management console.
(See “Connecting to a Console Terminal” on page 60.) You use the console to
communicate with the system during the power-up process, set an IP address,
andmanagethesystemusingthecommand-lineinterface(CLI).
You can manage and monitor the router through either of these methods:
Console terminal—Connect a console (PC, Macintosh, or UNIX workstation)
directly to the system’s RS-232 serial port.
Remote console—Connect the 10/100Base-T port on the SRP I/O module to an
Ethernet network, and run Telnet from a remote console.
For initial access to the system, you need to physically connect your console
directly to the system’s RS-232 port. Through this connection you can use the
CLI to set an IP address on the system. After you configure the IP address,
you can access the system remotely (for example, via Telnet).
Setting Up Management Access 77

ERX 8.0.x Hardware Guide
Console Port Setup
You can connect a console terminal (PC, Macintosh, or UNIX workstation) directly
to the SRP I/O module via the RS-232 terminal port. When you connect a console
directly to the system, you can configure the system without an IP address.
To communicate with the system, you must have a terminal emulation program
running on your PC or Macintosh. You can use any terminal emulation program,
such as HyperTerminal. A UNIX workstation can use the emulator TIP.
Using HyperTerminal
If your console uses a version of Microsoft Windows (such as Windows 95
or Windows NT 4.0) that supports the HyperTerminal application, you
can access the system via HyperTerminal.
1. Click the Start button and select Programs, Accessories, and HyperTerminal.
2. In the HyperTerminal window, select HyperTerminal.
3. In the Connection Description window, enter a name for your router (for
example, erx1400)intheNamefield.
4. Select any icon to represent your terminal emulation, and click OK.
5. In the Connect To dialog box, in the Connect using field, select the appropriate
COM port to use (for example, COM1), and click OK.
6. In the COM1 Properties window, select the following settings:
Bits per second: 9600
Data bits: 8
Parity: None
Stop bits: 1
Flow control: Xon/Xoff
7. Click OK.
Connecting Directly to the Router
When you connectaconsoledirectlytothesystem,useacableappropriate
for your terminal connector. The cable must have a female DB-9 connector
to attach to the RS-232 port on the system.
The console port is considered a data terminal equipment interface
(DTE). Direct connection to a terminal or PC (which also have DTE
interfaces) requires a crossover cable.
78 Console Port Setup

Accessing ERX Routers
To connect a console directly to the system:
1. ConnectthefemaleDB-9connectortotheRS-232portonthesystem’sSRP
I/O module. SeeFigure36.
Figure 36: Management Ports for ERX Routers
2. Connect the crossover adapter connector to your PC’s serial port.
3. Power up the system.
When you power up the system, the CLI appears on your console’s screen.
The system is now in User Exec mode, and you can begin configuration. For
more information on using the CLI and configuring the system, see the JUNOSe
System Basics Configuration Guide.
NOTE: Direct access through the RS-232 serial port enables you to monitor the
system while it boots.
Console Port Setup 79
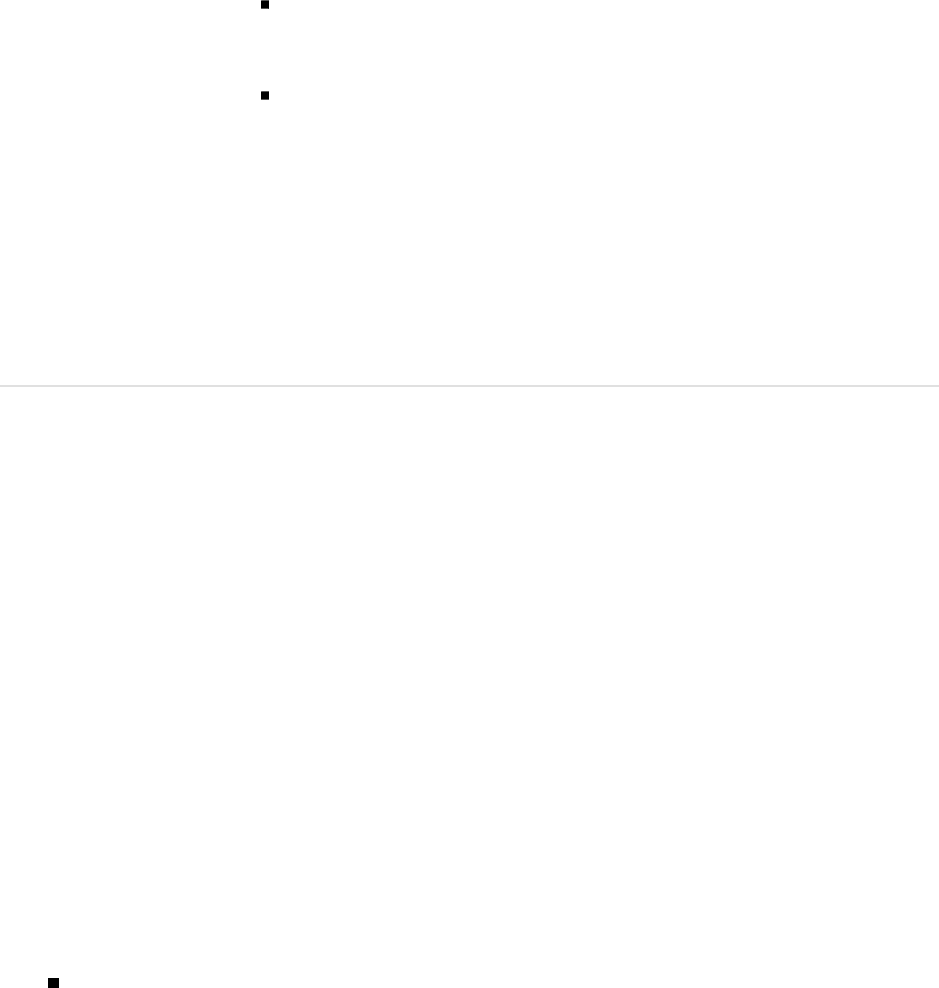
ERX 8.0.x Hardware Guide
Assigning an IP Address
When your console is ready to communicate with the system, power up the system.
(See “Powering Up ERX Routers” on page 73.) Then set an IP address for the
system. The system powers up in User Exec mode. To assign an IP address:
1. Enter the enable command at the User Exec prompt.
host1>enable
host1#
The system is now in Privileged Exec mode.
2. SetanIPaddre
ss on the Ethernet interface:
Substitute the slot number where the SRP module is located for the
slotnumber variable. For redundant SRP modules, specify the lowest slot
number of the two (for example 0/0 or 6/0 ).
UseanIPaddressvalidforthesystem.
host1#configure terminal
Enter configuration commands, one per line. End with CNTL/Z.
host1(config)#interface FastEthernet slotnumber /0
host1(config-if)#ip address 10.10.7.3 255.255.255.0
3. Continue to configure the system’s parameters as needed.
After you have assigned an IP address to the system, you can communicate remotely
by running Telnet over an Ethernet network. See “Telnet Setup” on page 80.
Telnet Setup
After you have configured an IP address for the system, you can run
Telnet from a host to access the system through its Ethernet port. To
connect the Ethernet port to the network:
1. Connect an Ethernet cable (RJ-45) to the system’s 10/100Base-T (RJ-45) port on
the SRP I/O module.
2. Connect the other end of the cable to the appropriate Ethernet network for
an out-of-band connection.
Before you can access the system with Telnet, you must either configure a password
for Telnet access or disable the password requirement from the management
console. In the following example, you disable the password.
1. Enter the enable command.
host1>enable
host1#
The system is now in Privileged Exec mode.
80 Telnet Setup

Accessing ERX Routers
2. Enter the configure command.
host1#configure terminal
Enter configuration commands, one per line. End with CNTL/Z.
host1(config)#
The system is now in Global Configuration mode.
3. Enter the line command.
host1(config)#line vty 0 4
host1(config-line)#
The system is now in Line Configuration mode.
4. Disable the password.
host1(config-line)#no login
NOTE: In this example, you disabled the password requirement, but you can choose
to set a password instead. See JUNOSe System Basics Configuration Guide, Chapter 8,
Passwords and Security for information on setting a password.
5. Run Telnet from a host on the same Ethernet network as the system.
6. Enter the IP address of the system to open the Telnet session.
TheUserExecpromptappearswhentheTelnetsessiontothesystemis
established.
host1>
7. Enter the enable command.
host1>enable
host1#
The system is now in Privileged Exec mode.
8. Enter the configure command.
host1#configure terminal
Enter configuration commands, one per line. End with CNTL/Z.
host1(config)#
The system is now in Global Configuration mode, from which you can
configure the system. See JUNOSe System Basics Configuration Guide, Chapter 2,
Command-Line Interface.
Telnet Setup 81

ERX 8.0.x Hardware Guide
CAUTION: Do not change the IP address for the Ethernet interface that you are
using to communicate with the system. If you change the address, you will lose the
Telnet session.
SNMP
The system supports Simple Network Management Protocol (SNMP),
astandardma
nagement protocol for IP networks. You can configure
the system as an SNMP agent.
As an SNMP agent, the system provides access to management information
that it maintains. See JUNOSe System Basics Configuration Guide, Chapter 4,
Configuring SNMP for information on SNMP. See JUNOSe Command Reference
Guide A to M and JUNOSe Command Reference Guide N to Z for the commands
that are available for configuring the system as an SNMP agent.
The Next Step
See “Maintaining ERX Routers” on page 85.
82 The Next Step

84 Hardware Maintenance, Replacement, and Troubleshooting Procedures

Chapter 8
Maintaining ERX Routers
This chapter lists the tools, items, and steps needed for installing and uninstalling
ERX router components. Other maintenance procedures must be performed by an
authorized Juniper Networks technician.
This chapter contains the following sections:
RequiredToolsandItemsonpage85
Storing Modules and Components on page 86
Cleaning theSystemonpage86
Upgrading from Release 5.1.1 or Lower-Numbered Releases to Release 6.x.x or
Higher-Numbered Releases on page 87
Upgrading NVS Cards on SRP Modules on page 87
Replacing an NVS Card on page 89
Upgrading Memory on SRP Modules on page 90
Replacing SFPs on I/O Modules on page 93
Replacing Fan Trays on page 97
Installing a Cable-Management Bracket on ERX-7xx Models on page 100
Required Tools and Items
You will need the following tools and other items to replace ERX router components:
Flathead and Phillips screwdrivers
Insulated adjustable wrench
Antistatic wrist strap
Antistatic bags (or other protective packaging to hold components)
Plastic boots or other protective cover for fiber-optic SC and LC connectors
Required Tools and Items 85
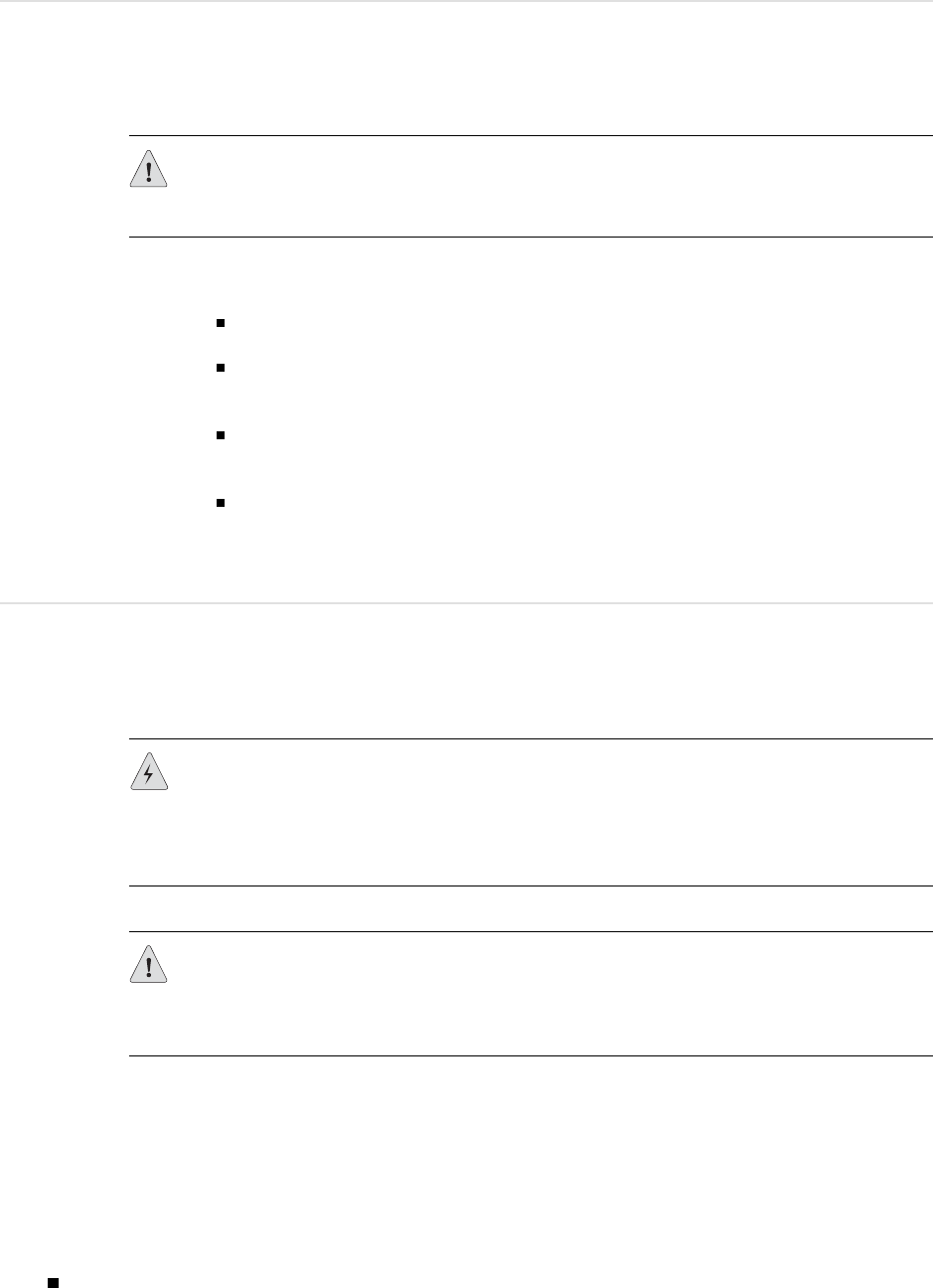
ERX 8.0.x Hardware Guide
Storing Modules and Components
Retain the packaging in which a module or component was shipped, and use this
packaging to store the item. Modules are shipped in antistatic bags and protective
packaging. Components, such as transceivers and nonvolatile storage (NVS) cards,
are shipped in antistatic plastic containers within an antistatic padded box.
CAUTION: Failure to store electronic modules and components correctly can
lead to damage of these items.
Follow these guidelines for storing modules and components:
Store each module in a separate antistatic bag.
Store components in an antistatic plastic container. Some of these containers
can accommodate several components in separate compartments.
Do not store multiple modules or components in an antistatic bag or container
where they can touch other items.
(Optional) Store the item in its antistatic bag or container within the protective
packaging or padded box that the item was shipped in.
Cleaning the System
Dust is attracted to the side of the system on which the air intake vent is located.
Clean this side of the system with a dry cloth every few weeks to prevent
excessive accumulation of dust. This cleaning helps to maintain the efficiency of
the cooling system and prevent damage to electronic components.
WARNING: Do not insert any metal object, such as a screwdriver, or place your
hand into an open slot or the backplane when the router is on. Remove jewelry
(including rings, necklaces, and watches) before working on equipment that is
connected to power lines. These actions prevent electric shock and serious burns.
CAUTION: When cleaning the system, wear an antistatic wrist strap connected
to the system’s ESD grounding jack. This action helps to protect modules from
damage by electrostatic discharge.
86 Cleaning the System

Maintaining ERX Routers
Upgrading from Release 5.1.1 or Lower-Numbered Releases to Release 6.x.x
or Higher-Numbered Releases
Release 5.1.1 or lower-numbered releases support application images only up to
172 MB. To install larger application images for Release 6.0.0 and higher-numbered
releases, you must first install Release 5.1.2 (or a higher-numbered 5.x.x release).
This enables the system to support application images greater than 172 MB. For
example, you cannot go from Release 5.1.1 to Release 7.2.0 without first upgrading
to Release 5.1.2. See the following table for compatibility of releases.
JUNOSe Release Highest Release Able to
Load
Cannot Load Maximum Application Image
5.1.1 or lower-numbered
release
5.3.5p0-2 or the
highest-numbered 5.x.x
release
6.x.x or higher-numbered
release
~172 MB
5.1.2 or higher-numbered
release
No limitation Not applicable ~234 MB
7.2.0 or higher-numbered
release
No limitation Not applicable ~256 MB
Your software upgrades may be available remotely through Telnet or FTP, or may
be delivered on a new NVS card. Depending on how you access the software
updates, there are two different procedures to follow. For more detailed information
on installing software, and about NVS cards and SRP modules, see:
JUNOSe System Basics Configuration Guide, Chapter 6, Managing Modules
“Upgrading NVS Cards on SRP Modules” on page 87
Upgrading NVS Cards on SRP Modules
This section describes how to install higher-capacity NVS cards on SRP modules.
The procedure you use depends on the number of SRP modules in the system.
A new NVS card already contains the software release you ordered.
NOTE: The new NVS card must contain the same software release that you are
running on the system.
Upgrading a System That Contains One SRP Module
If the system contains only one SRP module, you must power down the
system before you upgrade the NVS card.
Upgrading NVS Cards on SRP Modules 87

ERX 8.0.x Hardware Guide
CAUTION: Ifyoudonotusethehalt command before removing or powering down
an SRP module, the system’s NVS card can become corrupted.
To upgrade the NVS card on a system that contains one SRP module:
1. Enter the halt command.
See JUNOSe System Basics Configuration Guide, Chapter 6, Managing Modules for
information about the halt command.
WARNING: Do not insert any metal object, such as a screwdriver, or place your
hand into an open slot or the backplane when the router is on. Remove jewelry
(including rings, necklaces, and watches) before working on equipment that is
connected to power lines. These actions prevent electric shock and serious burns.
CAUTION: When handling modules, use an antistatic wrist strap connected to the
router’s ESD grounding jack. This action helps to protect the module from damage
by electrostatic discharge.
2. Connect the antistatic wrist strap to the ESD grounding jack on the router.
3. Power down the system.
4. Remove the SRP module.
5. Replace the NVS card on the SRP module. (See “Replacing an NVS Card” on
page 89.)
6. Power up the system. (See “Powering Up ERX Routers” on page 73.)
Upgrading a System That Contains Two SRP Modules
In a system that contains two SRP modules, you can upgrade the NVS cards
on the SRP modules without powering down the system.
WARNING: Do not insert any metal object, such as a screwdriver, or place your
hand into an open slot or the backplane when the router is on. Remove jewelry
(including rings, necklaces, and watches) before working on equipment that is
connected to power lines. These actions prevent electric shock and serious burns.
88 Upgrading NVS Cards on SRP Modules

Maintaining ERX Routers
CAUTION: When handling modules, use an antistatic wrist strap connected to the
router’s ESD grounding jack. This action helps to protect the module from damage
by electrostatic discharge.
To upgrade the NVS cards on the SRP modules in a system that
contains two SRP modules:
1. Connect the antistatic wrist strap to the ESD grounding jack on your router.
2. Halt the redundant SRP module.
host1#halt standby-srp
3. Remove the redundant SRP module from the chassis.
4. Replace the NVS card on this SRP module. (See “Replacing an NVS Card” on
page 89.)
5. Reinsert the SRP module into the chassis.
6. When this SRP module is available, synchronize the SRP modules.
host1#synchronize
7. When the SRP modules are synchronized, reboot the SRP module that you
upgraded.
host1#reloadslot7
8. When this SRP module is available, synchronize the SRP modules.
host1#synchronize
9. When the SRP modules are synchronized, force the redundant SRP module to
take over from the primary SRP module.
host1#srp switch
10. Halt the redundant (former primary) SRP module.
host1#halt standby-srp
11 . Immediately remove the former primary SRP module.
12. Repeat Steps 4–8 for the former primary SRP module.
Replacing an NVS Card
To replace an NVS card on an SRP module:
Replacing an NVS Card 89

ERX 8.0.x Hardware Guide
1. Obtain an antistatic container for the NVS card you plan to remove. (See
“Storing Modules and Components” on page 86.)
2. With a small flathead screwdriver, remove the faceplate from the NVS card slot
on the SRP module. (SeeFigure37.)
3. Use the screwdriver to depress the release button next to the NVS card. (See
Figure 37.)
This action releases the NVS card.
Figure 37: NVS Card Slot on SRP Module
Faceplate
Release button
NVS card
g013763
4. Remove the NVS card and place it in the antistatic container.
5. Insert the new NVS card into the slot, and push it until it clicks into place.
6. Replace the faceplate on the NVS card slot.
Upgrading Memory on SRP Modules
This section describes how to upgrade memory on SRP modules. JUNOSe
software releases 3.0.x and higher require at least 512 MB of memory on
each SRP module, while releases 5.3.x and higher require at least 1 GB of
memory. See the ERX Module Guide for more information.
NOTE: The ERX-310 SRP module contains two small outline dual inline memory
module (SODIMM) banks that use 256-MB memory, and currently is not
upgradeable.
90 Upgrading Memory on SRP Modules

Maintaining ERX Routers
Four main steps are involved in upgrading memory on SRP modules:
1. Display how much memory is currently installed on the SRP module.
2. Remove the SRP module and the SODIMMs.
3. Add the new SODIMMs to the SRP module.
4. Reinstall the SRP module and verify the upgrade.
See the following sections for information on each step.
WARNING: Do not insert any metal object, such as a screwdriver, or place your
hand into an open slot or the backplane when the router is on. Remove jewelry
(including rings, necklaces, and watches) before working on equipment that is
connected to power lines. These actions prevent electric shock and serious burns.
CAUTION: When handling modules, use an antistatic wrist strap connected to the
router’s ESD grounding jack, and hold modules by their edges. Do not touch the
components, pins, leads, or solder connections. These actions help to protect
modules from damage by electrostatic discharge.
Displaying the Memory Installed
Before you install the new memory, issue the show hardware command
to see how much memory is installed. Each ERX-7xx and ERX-14xx
model SRP module usually has at least 256 MB of memory. You need one
upgrade kit for each SRP module in the system.
Depending on the upgrade you are performing, the kit contains a
specific number of SODIMMs.
Removing SODIMMs
After removing the SRP module from the router, you might have to remove
lower-memory SODIMMs to upgrade to a higher-capacity SRP module. The
SODIMM sockets are close to the NVS card and have a cream-colored ceramic
connector at one edge. Some or all of the sockets might already contain SODIMMs.
1. PushdownonthebackedgeofaSODIMMtoreleaseitfromthesocket.
(See Figure 38.)
2. Gently pull the SODIMM up and out to disconnect it from the connectors and
remove it from the socket.
Upgrading Memory on SRP Modules 91

ERX 8.0.x Hardware Guide
Adding New SODIMMs
To add new SODIMMs:
1. Locate the four SODIMM sockets on the SRP module. (See Figure 38 and
Figure 39.) See the previous section to learn how to remove SODIMMs.
Figure 38: SODIMM Sockets on the SRP-5 and SRP-10 Module
SODIMM
Cream ceramic connector
Empty SODIMM socket
NVS card
3. Push down on back edge
of SODIMM until it snaps
into socket.
2. Push SODIMM into
connector at an angle of
approximately 45 degrees.
1. Align notches in
SODIMM and connector.
g013451
Figure 39: SODIMM Sockets on the SRP-40 Module
SODIMM
Empty SODIMM socket
g013452
92 Upgrading Memory on SRP Modules

Maintaining ERX Routers
2. Insert a SODIMM from the upgrade kit at an angle of approximately 45 degrees
into an empty ceramic connector, so that the notch in the long gold edge of the
SODIMM aligns with the notch in the connector.
The notch on the long gold edge is no longer visible when the SODIMM
is pressed in far enough.
3. Press the top surface downward into the socket until the socket spring snaps
into place and holds it.
4. Repeat Steps 2–3 with the other SODIMM.
5. Repeat Steps 1–4 for the other SRP module, if present.
Verifying the Upgrade
To verify that the upgrade is complete:
1. Place the SRP modules in the chassis.
The SRP modules reboot.
2. Close the ejector handles and tighten the thumbscrews.
3. Issue the show hardware command, and verify that the display indicates that
the correct amountofmemoryispresent.
Replacing SFPs on I/O Modules
This section describes how to replace small form-factor pluggable transceivers
(SFPs) on modules that support these devices. A range of SFPs that support
different optical modes (multimode and single mode) and cabling distances
is available. You can replace the SFPs without disabling the interfaces
or removing the module from the system.
WARNING: Do not insert any metal object, such as a screwdriver, or place your
hand into an open slot or the backplane when the router is on. Remove jewelry
(including rings, necklaces, and watches) before working on equipment that is
connected to power lines. These actions prevent electric shock and serious burns.
CAUTION: When handling electronic components, use an antistatic wrist strap
connected to the system’s ESD grounding jack, and hold components by their
edges. Do not touch, pins, leads, or solder connections. Store components in
Replacing SFPs on I/O Modules 93

ERX 8.0.x Hardware Guide
antistatic bags. These actions help to protect modules from damage by electrostatic
discharge.
Removing SFPs
To remove the SFPs:
1. Obtain an antistatic container for the SFPs you plan to remove. (See “Storing
Modules and Components” on page 86.)
2. Put the antistatic wrist strap on your wrist, and connect the strap to the
ESD grounding jack on the system.
3. Disconnect the cables from one of the SFPs on the module.
4. Identify the release mechanism for the SFP.
Different SFPs use different release mechanisms. (See Figure 40.) Possible
release mechanisms include:
A button that you press inward
A ring that you press inward
A bar that you pull sideways, then outward
A tab that you pull sideways, then outward
Figure 40: Possible Release Mechanisms on the SFP
Release bar, button,
or tab
Release ring
Transceiver
Release bar, button,
or tab
Module faceplate
g013435
5. Release the SFP and pull it out of the slot.
6. PlacetheSFPinanantistaticbag.
7. If you are using the redundant port on the GE I/O module, repeat Steps 3–6 for
the other SFP.
94 Replacing SFPs on I/O Modules

Maintaining ERX Routers
CAUTION: For port redundancy to operate correctly, both the primary and
redundant portsonaGEI/OmodulemustusethesametypeofSFP.
Installing SFPs
To install SFPs:
1. Put the antistatic wrist strap on your wrist, and connect the strap to the
ESD grounding jack on your system.
2. Identify the followingitemsontheSFP,asshowninFigure41:
The connection circuitry on the base
The cable connectors on the front
The cable connectors are protected by a dust cover.
Figure 41: Example of SFP
Cable connectors
on front
Connection circuitry
on base
g013436
CAUTION: Be sure to position the SFP correctly before you install it.
3. Hold the SFP so that:
The connection circuitry is adjacent to the TX and RX markings on
the module’s faceplate.
The front will be visible when you install the SFP.
For the correct orientation, see Figure 42.
Replacing SFPs on I/O Modules 95

ERX 8.0.x Hardware Guide
Figure 42: Installing an SFP on a GE I/O Module
g013437
TX and RX markings on I/O module
Connection circuitry on base of SFP
4. Insert theSFPintotheI/Omoduleuntilitclicksintoplace.
IftheSFPdoesnotslidesmoothlyintotheI/Omodule,makesurethatthe
orientation of the SFP is correct.
5. Gently pull the SFP to confirm that it is inserted correctly.
If the SFP comes out of the slot when you pull it, repeat Step 4.
6. Remove the dust cover that protects the ports.
7. Connect the new cables to the SFP.
If you are using the redundant port on the GE I/O module, repeat
Steps 2–7 for the other port.
96 Replacing SFPs on I/O Modules

Maintaining ERX Routers
Verifying the Installation
After you have replaced the SFPs and connected the cables, issue the
show interface gigabitEthernet command for each interface to make
sure that the interface is operational (up).
Field descriptions
gigabitEthernet interfaceSpecifier —Status of the hardware on this
interface
Up—Hardware is operational
Down—Hardware is not operational
Administrative status—Operational state that you configured for this
interface
Up—Interfaceisenabled
Down—Interface is disabled
Example
host1:vr2#show interfaces gigabitEthernet2/0
gigabitEthernet2/0 is Up, Administrative status is Up
Replacing FanTrays
Atrayofcool
ing fans provides forced air cooling for components in the ERX routers.
The fan trays are hot-swappable; you can replace them without powering down
the system. However, if you do not replace the fan tray within approximately 2
minutes, the system enters thermal protection mode. For information about
thermal protection mode, see “Monitoring Temperatures of Modules” on page 113.
You can monitor fan status by observing the LEDs on the SRP module or
on the fan tray behind the faceplate. For complete LED information, see
“UnderstandingStatusLEDstoTroubleshoot”onpage104.
NOTE: On the SRP module, when the LED alternates between OK and FAIL in
10–second intervals, a non-critical fan failure exists. Noncritical warnings are not
indicated on the fan tray LEDs; if the red FAN FAIL LED is illuminated, either a
critical or non-critical failure exists.
CAUTION: If the red FAN FAIL LED on the SRP module is illuminated and none
of the fans are spinning when you remove the fan tray, power down the system
Replacing Fan Trays 97

ERX 8.0.x Hardware Guide
until a new fan tray is available. Operating an ERX router with inadequate air
circulation can damage the modules.
CAUTION: Do not use the fan tray handle to carry the fan tray assembly. Use the
handle only to pull the tray out of the chassis.
Figure 43: Fan Tray in ERX-14xx Models
Fan tray
g013764
Figure 44: Fan Tray in ERX-7xx Models
g013766
98 Replacing Fan Trays

Maintaining ERX Routers
Figure 45: Fan Tray in ERX-310 Router
g013765
Removing the Fan Tray
To remove the fan tray:
1. (ERX-14xx models only) Place a flathead screwdriver in the groove where
the top bezel meets the chassis on the top of the system, and lever the top
bezel off thefrontofthesystem.
2. With an appropriate screwdriver, loosen the captive screws located at the
corners ofthefantray.
WARNING: Do not place your fingers near the fans when removing the fan tray.
The blades might still be moving.
3. Pull the fantrayhalfwayoutoftheshelf.
WARNING: Slowly slide the fan tray out of the chassis. The tray does not have stops
topreventitfromslidingallthewayout.
4. Pull the trayoutofthechassis.
Installing the Fan Tray
To installthefantray:
Replacing Fan Trays 99

ERX 8.0.x Hardware Guide
CAUTION: Do not use the fan tray handle to carry the fan tray assembly. Use the
handle only to push the tray into the chassis.
1. Hold the tray horizontally (ERX-14xx models) or vertically (ERX-7xx models
and ERX-310 routers) or so that the captive screws point toward you and you
can read text on the labels.
2. Place the bottom corners of the tray housing in the plastic shelf guides of the
fan tray compartment; push toward the back of the chassis halfway, and stop.
3. Push the fan tray toward the back of the shelf until it stops.
An electrical connector on the back of the fan tray pairs with an electrical
connector at the back of the shelf.
4. With an appropriate screwdriver, tighten the captive screws.
Alternate between screws when tightening them to ensure that the electrical
connectors at the back of the tray fit tightly.
5. (ERX-14xx model only) Push the top bezel back on the front of the system.
Installing a Cable-Management Bracket on ERX-7xx Models
You can install a cable-management bracket to accommodate cables of
different sizes on ERX-7xx models. See Figure 46.
For wider X.21/V.35 cables, mount the bracket in the last row of perforation
holes in the chassis so that the bracket allows for maximum spacing (A).
For smaller cables, mount the bracket closer to the front of the chassis (B).
Use two (2) #10 self-tapping screws to secure the bracket.
100 Installing a Cable-Management Bracket on ERX-7xx Models

Maintaining ERX Routers
Figure 46: Attaching a Cable Management Bracket
Perforated area
Front of
ERX-7xx model
Mount here for wider X.21/V.35 cables
Mount in this area for smaller cables
g013767
Installing a Cable-Management Bracket on ERX-7xx Models 101

ERX 8.0.x Hardware Guide
102 Installing a Cable-Management Bracket on ERX-7xx Models

Chapter 9
Troubleshooting
This chapter explains how you can troubleshoot a specific problem, such as
abnormal LED activity or no system power, when you power up the router. It
contains thefollowingsections:
Diagnosing Problems on page 103
Troubleshooting Power Failures on page 104
Understanding Status LEDs to Troubleshoot on page 104
Monitoring Temperatures of Modules on page 113
Resetting Line Modules and SRP Modules on page 114
Double-Bit Errors on SRP Modules on page 114
Diagnosing Problems
When you first encounter a system problem:
1. Make sure power connections are securely attached.
2. Observe the system’s LEDs carefully.
3. Make sure cable connections on the system modules are securely attached.
If a problem is beyond the scope of this chapter, see “Contacting Customer
Support and Returning Hardware” on page 151 for further instructions.
NOTE: Running the show version and show hardware commands is often a good
first step when trying to troubleshoot a problem.
Initialization Sequence
Each line module is initialized independently. As a result, the command-line
interface (CLI) on the SRP module can become available before the line
modules have completed initialization. Commands relating to a line module
Diagnosing Problems 103

ERX 8.0.x Hardware Guide
might fail if the module has not completed initialization. Use the show
version command to display line module status. Do not enter commands
for a line module until its state is listed as online.
Troubleshooting Power Failures
The system’s distributed power system is designed to consume low levels
of power and dissipate low levels of heat. See “System Specifications” on
page 119 for specifications of power consumption and heat dissipation. If
you suspect a power problem, see Table 10.
Table 10: Causes of Power Failures
Symptom Possible Problems Actions
System does not power up. System is not receiving power.
Module’s power supply has
malfunctioned.
Power source cannot handle
system load.
The following actions apply to all of the
possible problems:
1. Verify that all power connections
are correct.
2. Verify that the power supply is
delivering the correct voltage,
current, and wattage to the system.
See “System Specifications” on
page 119.
3. If the system still does not
operate, contact Juniper Networks
Customer Service.
System shuts down. Temperature is too high.
Power is lost.
The following actions apply to all of the
possible problems:
1. Verify that power connections are
properly attached.
2. Verify that system is receiving
power.
3. Look to see whether or not the
LEDs are lit.
4. Run diagnostics on SRP and line
modules.
5. If system does not not reset,
contact Juniper Networks
Customer Service.
Understanding Status LEDs to Troubleshoot
Module LEDscanshowyouthecurrentstatusofamoduleandalertyou
toaproblemwiththemoduleoroneofitsports. Werecommendyou
104 Understanding Status LEDs to Troubleshoot

Troubleshooting
familiarize yourself with LED activity so that you can easily detect and correct
a module-related problem with minimal or no system downtime.
LED Identification
The system’s modules have two sets of status LEDs. The top set indicates
overall router and module status. The bottom set indicates module-specific
status, such as port status (line modules) or fan status (SRP module).
The number next to the port status LED on a line module corresponds to the
number of the port on the I/O module. Some line modules have more port
status LEDs than the number of ports on the I/O module. In these cases, only
the LEDs for the corresponding ports on the I/O modules are active.
For example, an OCx/STMx line module can pair with either an OC3-4 or
an OC12/STM4 I/O module. Consequently, the line module has four port
status LEDs for OC3/STM1 operation. However, only the top set of port
status LEDs is active during OC12/STM4 operation.
Table 11 presents the functions of the module LEDs and port status LEDs.
Table 11: LED Identification and Activity Descriptions
LED Location LED Label LED Indicator LED Color OFF to ON ON to OFF
OK Module status Green Self-test passed Failure detected
FAIL Module status Red Failure detected Diagnostic test
running
All modules
ONLINE Module status Green Module online Module offline
All modules REDUNDANT Redundancy Green See “Redundancy Status” on page 113.
NOTE: The REDUNDANT LED on the cOCx/STMx, FE-8, GE/FE, HSSI, OCx/STMx,
and X.21/V.35 line modules is nonfunctional.
SRP module POWER A OK Power Green Power online on
source A
Power off
POWER B OK Power Green Power online on
source B
Power off
FAN OK Fan Green Fan online Critical fan failure
FAN FAIL Fan Red Critical fan failure Fan online
NOTE: When the LED alternates between OK and FAIL at 10-second intervals, a
noncritical fan failure exists.
LINK Ethernet Green Ethernet link up Ethernet link
down
ACTIVITY Ethernet Green Blinks when
Ethernet traffic
on link
No Ethernet traffic
on link
Understanding Status LEDs to Troubleshoot 105

ERX 8.0.x Hardware Guide
Table 11: LED Identification and Activity Descriptions (continued)
LED Location LED Label LED Indicator LED Color OFF to ON ON to OFF
LINK Ethernet Green Ethernet link up Ethernet link
down
Ethernet line
modules
ACTIVITY Ethernet Green Blinks when
Ethernet traffic
on link
No Ethernet traffic
on link
SYNC Port status Green If the port is
configured as
DTE, the LED
lights when both
the DCE and the
clock source are
available.
If the port is
configured as
DCE, the LED
lights when the
DTE is available.
If the port is
configured as DTE,
the LED goes out
when either the
DCE or the clock
source becomes
unavailable.
If the port is
configured as
DCE, the LED
goes out when
the DTE becomes
unavailable.
YEL ALM NOTE: This LED is not functional on the HSSI line module.
HSSI line module
RED ALM Port status Red If the port is
configured as DTE,
the LED lights
when either the
DCE or the clock
source becomes
unavailable.
If the port is
configured as
DCE, the LED
lights when the
DTE becomes
unavailable.
If the port is
configured as
DTE, the LED goes
out when both
the DCE and the
clock source are
available.
If the port is
configured as
DCE, the LED goes
out when the DTE
is available.
106 Understanding Status LEDs to Troubleshoot

Troubleshooting
Table 11: LED Identification and Activity Descriptions (continued)
LED Location LED Label LED Indicator LED Color OFF to ON ON to OFF
ACTIVE Port status Green Port configured Port not
configured
LOOPBK Port status Yellow Port in local
loopback or
remote loopback,
depending on
thetypeof
connection.
Port not in
loopback
ERROR Port status Red Port is enabled or
comes online
Port is disabled or
goes offline
V.35 Port status Green V.35 cable
connected
V.35 cable
disconnected
X.21 Port status Green X.21 cable
connected
X.21 cable
disconnected
DCE Port status Green DCE cable
connected
DCE cable
disconnected
X.21/V.35 line
module
DTE Port status Green DTE cable
connected
DTE cable
disconnected
SYNC Port status Green In frame Not in frame
YEL ALM Port status Yellow Far-end receive
failure (FERF)
exists
No FERF present
Other line
modules
RED ALM Port status Red Loss of sync/frame In frame
The following figures show a representative module for each of the three variations:
SRP module (Figure 47)
Ethernet line module (Figure 48)
Other line modules (Figure 49)
Understanding Status LEDs to Troubleshoot 107

ERX 8.0.x Hardware Guide
Figure 47: SRP Module LEDs
Status LEDs
Status LEDs
OK
FAIL
ONLINE
REDUNDANT
POWER A OK
POWER B OK
FAN OK
FAN FAIL
LINK
ACTIVITY
g013768
NOTE: The primary SRP module illuminates the REDUNDANT LED only when the
SRP module detects a secondary or standby SRP module online. The standby SRP
module monitors an activity signal from the primary SRP module to determine its
state; it does not shadow the operations of the primary SRP module.
IfthestandbySRPmoduledetectsthattheprimarySRPmoduleisnotactive(and
high-availability mode is not enabled), it reboots the system and takes control. If
high-availability mode has been enabled, automatic switchover occurs with near
hitless failover. (ERX-7xx and ERX-14xx models only)
108 Understanding Status LEDs to Troubleshoot

Troubleshooting
Figure 48: FE2 Module LEDs
Functional status LEDs
Interface status LEDs
01
OK
FAIL
ONLINE
REDUNDANT
01
ACTIVITY
LINK
g013769
Understanding Status LEDs to Troubleshoot 109

ERX 8.0.x Hardware Guide
Figure 49: E3 and T3 Module LEDs
Functional status LEDs
Interface status LEDs
OK
FAIL
ONLINE
REDUNDANT
012
RED ALM
YEL ALM
SYNC
g013770
LED Activity
When the system boots, it runs a series of tests for each module installed in
the system, and the LEDs display various configurations. See Table 12 and
Table 13 to understand normal and abnormal LED activity.
NOTE: When you reboot the system after installing a new version of the software,
the line modules appear to boot twice.
Table 12: Normal Activity of Functional Status LEDS During Booting
OK FAIL ONLINE Status Process
off on
(off for GE-2 LM and
GE-HDE LM)
off 1. Module is in the
power-up restart
state; the FAIL LED
stays on briefly.
off on off 2. Module is
initializing, and
diagnostic tests are
running;theFAILLED
stays on briefly.
110 Understanding Status LEDs to Troubleshoot

Troubleshooting
Table 12: Normal Activity of Functional Status LEDS During Booting (continued)
OK FAIL ONLINE Status Process
on off off 3. Module passed
the diagnostics; the
system boots.
on off on 4. Module is now up
and running.
If the system detects an error during booting, the FAIL LED lights. Some
failure conditions can cause the module not to boot. In this case, the LEDs
might all be off. The system then resets the module.
If the operational software detects an error, the FAIL LED lights. Some
errors can cause a module reset. Crash information is displayed
at the console at the next reboot.
Table 13: Troubleshooting Abnormal LED Activity on Modules
Diagnostic Signs Possible Problems Actions
POWER A OK LED is not lit
POWER B OK LED is not lit
System is not receiving power
from Power A.
System is not receiving power
from Power B.
1. Make sure Power A and Power B
terminal connections are securely
attached.
2. Verify that power switches are on.
3. Make sure connections to power
sources are securely attached.
4. If system still does not operate,
contact Juniper Networks Customer
Service.
FAIL LED lights Thelinemo
dule and I/O module
are incompatible.
A hardware failure, such as a
failed module.
1. Make sure that the line modules
and I/O modules are compatible;
replace if necessary.
2. If you replaced the I/O module only,
issue the reload slot slot_number
command.
3. If you replaced the line module
or if there was a hardware
failure, the system is supposed to
automatically reset the module.
4. If the condition persists, contact
Juniper Networks Customer
Service.
FAN OK LED does not light
FAN FAIL LED lights
Fan is not working properly or
has slowed down.
Fan needs replacement.
Contact Juniper Networks Customer
Service; the system must be serviced.
Understanding Status LEDs to Troubleshoot 111

ERX 8.0.x Hardware Guide
Table 13: Troubleshooting Abnormal LED Activity on Modules (continued)
Diagnostic Signs Possible Problems Actions
LINK LED is not lit Ethernet connection is down. 1. Make sure that Ethernet cables are
properly connected to both the
Ethernet port and the appropriate
network device.
2. Contact Juniper Networks Customer
Service.
RED ALM is lit System does not recognize a
port connection.
Cabling is not connected
properly.
Cable is faulty.
Clocking problem exists.
1. Make sure that all cables are firmly
plugged into the ports and the
attached network device.
2. Verify thatcablesareclean.
3. Test for faulty cables.
4. Verify clock source and
configuration.
5. Reset system.
NOTE: Problem is corrected when
normal LED activity occurs.
YEL ALM is lit
NOTE: This LED is not functional on the
HSSI line module.
Far end receive failure (FERF)
exists.
1. Correct FERF problem.
2. Reset system.
NOTE: Problem is corrected when
normal LED activity occurs.
System does not boot.
Modules held offline.
FAIL LED lights.
A slot group is overloaded. 1. Issue the show version command
to display module status.
2. Reviewsectiononproperslot
group configuration in “Installing
Modules” on page 35.
3. Reconfigure system with correct
slot group configuration.
4. Reset system.
No LED indications or obvious signs. System temperature is too high.
Vents are blocked.
Fans are not operating.
1. Look at your console for a message
indicating the problem. If you have
the system log set to a severity of
WARNING or higher, a Warning
message indicates the failure.
2. Issue the show environment
command to display the
temperatures. If the temperature is
too high, power down the system.
3. Regulate temperature.
4. Reset system.
112 Understanding Status LEDs to Troubleshoot

Troubleshooting
Redundancy Status
You can determine the redundancy state of line modules by examining the ONLINE
and REDUNDANT status LEDs (ERX-7xx and ERX-14xx models only). See Table 14.
NOTE: The REDUNDANT LED on the cOCx/STMx, FE-8, GE/FE, HSSI, and
OCx/STMx modules is nonfunctional.
Table 14: Redundancy Status of a Line Module
ONLINE LED REDUNDANT LED State of the Line Module
Off Off Module is booting or is an
inactive primary line module.
On Off Module is active, but no
standby module is available.
Off On Module is in standby state.
On On Module is active, and a
standby module is available.
Monitoring Temperatures of Modules
You can view the temperature of each module by issuing the show environment all
and show environment table commands. In addition, the system generates detailed
log messages if the temperature of a module is outside normal operating limits.
For example, if the temperature of any forwarding controller exceeds 212° F
(100° C), a message appears on the console and the event is added to the system
log. If you receive this message, report it to your customer service representative.
If the temperature of any module exceeds the upper temperature limit,
the system immediately goes into thermal protection mode. After the
system has entered thermal protection mode, you must resolve the
cause of the high temperature quickly.
Table 15: Troubleshooting High-Temperature Conditions
Cause of High Operating
Temperature Symptoms Resolution
Air vents to system are blocked Space around system does not
meet specifications. (See “System
Specifications” on page 119.)
Increase space around system.
Ambient temperature exceeds
specifications
Ambient temperature exceeds
specifications. (See “System
Specifications” on page 119.)
Provideextracoolingorheatinginthe
room where the system is located.
Monitoring Temperatures of Modules 113

ERX 8.0.x Hardware Guide
Table 15: Troubleshooting High-Temperature Conditions (continued)
Cause of High Operating
Temperature Symptoms Resolution
Cooling fan failure FAN OK LED on SRP module is
not illuminated.
FAN FAIL LED on SRP module
is illuminated.
Replace fan tray. (See “Maintaining ERX
Routers” on page 85.)
Module failure FAIL LED on module is illuminated. Replace module. (See “Installing
Modules” on page 35.)
When you have resolved the cause of the high temperature, you must
power cycle the system to reset the modules.
Resetting Line Modules and SRP Modules
Two recessed buttons on line modules and SRP modules provide the mechanisms
for resetting. You can use the NMI button to reset the software on the module
and the module reset button to reset the module. See Figure 9.
If a line module fails to respond for an extended time, that module might
haveasoftw
are problem. You can depress the software reset button with a
paper clip to suspend the current software task. Depending on the situation,
this action might also reset the software on the module.
If depressing the software reset button fails to correct the issue with the line
module, depress the module reset button to reboot the line module.
The buttons work in the same way for the SRP module. Depressing the
module reset button on an SRP module is equivalent to rebooting the
router and causes all the line modules to reboot.
Double-Bit Errors on SRP Modules
SRP modules include error checking and correction (ECC) to protect their
SDRAM. ECC provides error detection of single-bit and double-bit errors and
correction of single-bit errors for the SDRAM as follows:
If ECC detects a single-bit error, it automatically corrects the error, and
operation continues.
If ECC detects a double-bit error, it logs the error, stops the main processor on
the controller, and takes the SRP module offline.
Detecting Double-Bit Errors
The following message appears on the console if ECC detects a double-bit error:
114 Double-Bit Errors on SRP Modules

Troubleshooting
ALERT 05/10/2000 13:10:33 os: failed: ECC DOUBLE BIT ERROR OCCURRED
Address = 0xe95db10
Data (Upper 32Bits) = 0xe95db20
Data (Lower 32Bits) = 0x55d06c
ECC Data Bits = 0x2b
ECC 1Bit Error Counter = 0x0
*** YOU MUST PERFORM A HARD RESET TO CONTINUE ***
ALERT 05/10/2000 13:10:34 os: PROCESSOR EXCEPTION: 0x200n
If ECC detects a double-bit error in a system that contains a redundant SRP
module, the redundant module becomes active and the system continues
to operate. However, you must still troubleshoot the SRP module with the
double-bit error. When ECC detects a double-bit error in a system that does
not contain a redundant SRP module, you must troubleshoot the SRP module
immediately. See “Fixing Double-Bit Errors” on page 115.
Fixing Double-Bit Errors
To fix a double-bit error:
1. Remove the second SRP module, if there is one.
2. Reboot the system with the module reset button on the primary SRP module.
(See Figure 9.)
These actions attempt to correct a transient double-bit error. However, if the
console displays a memory test failure for the SRP module after you reboot,
oriftheFAILL
ED on the SRP module stays on during rebooting, the SDRAM
is permanently damaged and needs replacing. In this event, call Juniper
Networks Customer Service to arrange for repair.
Double-Bit Errors on SRP Modules 115

ERX 8.0.x Hardware Guide
116 Double-Bit Errors on SRP Modules

118 Appendixes

Appendix A
System Specifications
This appendix lists the system specifications, requirements, and certifications
for ERX routers.
ERX-14xx Models Specifications on page 119
ERX-7xx Models Specifications on page 122
ERX-310 Router Specifications on page 125
ERX-14xx Models Specifications
Table 16: ERX-14xx Models Specifications
Category Specification
Weight Weights are approximate.
Chassisonly 42lb(18.9kg)
Chassis fully configured 88 lb (39.6 kg)
Dimensions 22.75 (H) x 19 (W) x 16 (D) inches; 57.78 x 48.26 x 40.64 cm
Environmental Requirements NEBS GR-63-CORE compliant
Ambient operating temperature Long term: 41° to 104° F (5° to 40° C)
Short term: 23° to 122° F (–5° to 50° C)
Ambient operating humidity Long term: 5% to 85% (noncondensing)
Short term: 5% to 95% (noncondensing)
Ambient storage temperature –40° to 158° F (–40° to +70° C), 95% relative humidity
Ambient storage humidity 5% to 95% (noncondensing)
Heat Dissipation 2400 W, 8190 BTU/hour maximum
DC Input
Voltage –40 to –72 VDC
NOTE: If the voltage rises above –40 VDC, the system powers
off. The system does not power on again until the input
voltage reaches –43 +/– 0.5 VDC.
Current 50 A @ –48 VDC
ERX-14xx Models Specifications 119

ERX 8.0.x Hardware Guide
Category Specification
Power 2400 W maximum
Redundancy (input power) 2 independent line feeds
Space Requirements 3 feet (90 cm) behind router or rack
No space requirements for sides of units or rack
Do not block air vents on top, front, or back of the
router
Airflow An integral air plenum directs router’s exhaust air
below the router and out the back. See Figure 51.
NEBS Certification SR-3580 (FD-15): Network Equipment Building
System (NEBS) Criteria Levels, Issue 1, November
1995
GR-63–CORE: Network Equipment Building System
(NEBS) Requirements: Physical Protection, Issue 2,
April 2002
GR-1089 (LSSGR, FD-15): Electromagnetic
Compatibility and Electrical Safety - Generic Criteria
for Network Telecommunications Equipment, Issue
2, Revision 1, February 1999
Safety Agency Certification AS/NZS 60950:2000 Safety of Information
Technology Equipment
CAN/CSA-C22.2, No. 60950-1–03, First Edition,
Information Technology Equipment - Safety - Part
1: General Requirements
EN60825-1, Safety of Laser Products - Part 1:
Equipment Class, Requirements, and User’s Guide
(2001)
EN60950-1:2001, First Edition, Information
Technology Equipment - Safety - Part 1: General
Requirements
IEC 60950-1(2001-10) Ed. 1.0 Information
Technology Equipment - Safety - Part 1: General
Requirements
Low Voltage Directive (73/23/EEC)
UL 60950-1, First Edition, Information Technology
Equipment - Safety - Part 1: General Requirements
120 ERX-14xx Models Specifications

System Specifications
Category Specification
Electromagnetic Emissions Agency Certification AS/NZS 3548:1995 (CISPR 22 Class A)
EMC Directive (89/336/EEC)
EN55022 Class A (CISPR-22 Class A)
EN55024, Annex C for WAN Equipment Performance
Criteria A, B, and C
ETSI 300-386, Telecommunication Network
Equipment; ElectroMagnetic Compatibility (EMC)
requirements
FCC Part 15 Class A
IECS-003 Issue 3 Class A
VCCI (Voluntary Control Council for Interference by
Information Technology Equipment)
Telecommunications Certification ACA TS 016-1997
CTR13 – Commission Decision of 9 July 1997 on
a common technical regulation for attachment
requirements for terminal equipment interface for
connection to 2048 kbit/s digital structured ONP
leased lines: 97/521/EC – OJ No. L215 Vol. 40,
August 1997
CTR24 – Commission Decision of 9 September 1997
on a common technical regulation for attachment
requirements for terminal equipment interface for
connection to 34 Mbit/s digital unstructured and
structured leased lines: 97/639/EC – OJ No. L271
Vol. 40, 3 October 1997
FCC PART 68
IECS-003 Issue 3 Class A
PD7024 – Essential requirements for terminal
equipment intended for connection to
unstructured digital leased circuits of the public
telecommunications network using a CCITT
recommendation G,703 interface at a rate of 2048
kbit/s with a 75 ohm unbalanced presentation, 1994
RTTE Directive (1999/5/EEC)
ERX-14xx Models Specifications 121

ERX 8.0.x Hardware Guide
ERX-7xx Models Specifications
Table 17: ERX-7xx Models Specifications
Category Specification
Weight Weights are approximate.
Chassisonly 22lb(9.9kg)
Chassis fully configured 46 lb (20.7 kg)
Dimensions 10.5 (H) x 19 (W) x 16 (D) inches; 26.67 x 48.26 x 40.64 cm
Environmental Requirements NEBS GR-63-CORE compliant
Ambient operating temperature Long term: 41° to 104° F (5° to 40° C)
Short term: 23° to 122° F (–5° to 50° C)
Ambient operating humidity Long term: 5% to 85% (noncondensing)
Short term: 5% to 95% (noncondensing)
Ambient storage temperature –40° to 158° F (–40° to +70° C), 95% relative humidity
Ambient storage humidity 5% to 95% (noncondensing)
Heat Dissipation 1400 W, 4780 BTU/hour maximum
DC Input
Voltage –40 to –72 VDC
NOTE: If the voltage rises above –40 VDC, the system powers
off. The system does not power on again until the input
voltage reaches –43 +/– 0.5 VDC.
Current 30 A @ –48 VDC
Power 1400 W maximum
Redundancy (input power) 2 independent line feeds
Space Requirements 3 feet (90 cm) behind router or rack
Do not block air vents on sides of the router.
Donotplaceequipmentthatexhaustshotairtoleft
on the right of the router.
Be aware that router exhausts hot air from its left side.
Airflow Airflow direction is in through the right side and out
through the left side. See Figure 51.
122 ERX-7xx Models Specifications

System Specifications
Category Specification
NEBS Certification SR-3580 (FD-15): Network Equipment Building
System (NEBS) Criteria Levels, Issue 1, November
1995
GR-63–CORE: Network Equipment Building System
(NEBS) Requirements: Physical Protection, Issue 2,
April 2002
GR-1089 (LSSGR, FD-15): Electromagnetic
Compatibility and Electrical Safety - Generic Criteria
for Network Telecommunications Equipment, Issue
2, Revision 1, February 1999
Safety Agency Certification AS/NZS 60950:2000 Safety of Information
Technology Equipment
CAN/CSA-C22.2, No. 60950-1–03, First Edition,
Information Technology Equipment - Safety - Part
1: General Requirements
EN60825-1, Safety of Laser Products - Part 1:
Equipment Class, Requirements, and User’s Guide
(2001)
EN60950-1:2001, First Edition, Information
Technology Equipment - Safety - Part 1: General
Requirements
IEC 60950-1(2001-10) Ed. 1.0 Information
Technology Equipment - Safety - Part 1: General
Requirements
Low Voltage Directive (73/23/EEC)
UL 60950-1, First Edition, Information Technology
Equipment - Safety - Part 1: General Requirements
ERX-7xx Models Specifications 123

ERX 8.0.x Hardware Guide
Category Specification
Electromagnetic Emissions Agency Certification AS/NZS 3548:1995 (CISPR 22 Class A)
EMC Directive (89/336/EEC)
EN55022 Class A (CISPR-22 Class A)
EN55024, Annex C for WAN Equipment Performance
Criteria A, B, and C
ETSI 300-386, Telecommunication Network
Equipment; ElectroMagnetic Compatibility (EMC)
requirements
FCC Part 15 Class A
IECS-003 Issue 3 Class A
VCCI (Voluntary Control Council for Interference by
Information Technology Equipment)
Telecommunications Certification ACA TS 016-1997
CTR13 – Commission Decision of 9 July 1997 on
a common technical regulation for attachment
requirements for terminal equipment interface for
connection to 2048 kbit/s digital structured ONP
leased lines: 97/521/EC – OJ No. L215 Vol. 40,
August 1997
CTR24 – Commission Decision of 9 September 1997
on a common technical regulation for attachment
requirements for terminal equipment interface for
connection to 34 Mbit/s digital unstructured and
structured leased lines: 97/639/EC – OJ No. L271
Vol. 40, 3 October 1997
FCC PART 68
IECS-003 Issue 3 Class A
PD7024 – Essential requirements for terminal
equipment intended for connection to
unstructured digital leased circuits of the public
telecommunications network using a CCITT
recommendation G,703 interface at a rate of 2048
kbit/s with a 75 ohm unbalanced presentation, 1994
RTTE Directive (1999/5/EEC)
124 ERX-7xx Models Specifications

System Specifications
ERX-310 Router Specifications
Table 18: ERX-310 Router Specifications
Category Specification
Weight: DC model Weights are approximate.
Chassis only 25.5 lb (11.57 kg)
Chassis, fully configured 36 lb (16.33 kg)
Weight: AC model Weights are approximate.
Chassis with single power supply 27.5 lb (12.47 kg)
Chassis with dual power supply 31.5 lb (14.29 kg)
Chassis with single power supply, fully configured 38 lb (17.24 kg)
Chassis with dual power supply, fully configured 42 lb (19.05 kg)
Dimensions 5.2(H)x19(W)x16(D)inches;13.21x48.26x40.64cm
Environmental Requirements NEBS GR-63-CORE compliant
Ambient operating temperature Long term: 41° to 104° F (5° to 40° C)
Short term: 23° to 122° F (–5° to 50° C)
Ambient operating humidity Long term: 5% to 85% (noncondensing)
Short term: 5% to 95% (noncondensing)
Ambient storage temperature –40° to 158° F (–40° to +70° C), 95% relative humidity
Ambient storage humidity 5% to 95% (noncondensing)
Heat Dissipation 500 W, 1706 BTU/hour maximum
DC Input
Voltage –40 to –72 VDC
NOTE: If the voltage rises above –40 VDC, the system powers
off. The system does not power on again until the input
voltage reaches –43 +/– 0.5 VDC.
Current 9 A @ –48 VDC
Power 500 W maximum
Redundancy (input power) 2 independent line feeds
AC Input
Power required 90-265 VAC @ ~5 A
AC line frequency 50-60 Hz
Power 500 W
ERX-310 Router Specifications 125

ERX 8.0.x Hardware Guide
Category Specification
Space Requirements 3 feet (90 cm) behind router or rack
Do not block air vents on sides of the router.
Donotplaceequipmentthatexhaustshotairtoleft
on the right of the router.
Be aware that router exhausts hot air from its left side.
Airflow Airflow direction is in through the right side and out
through the left side. See Figure 51.
NEBS Certification SR-3580 (FD-15): Network Equipment Building
System (NEBS) Criteria Levels, Issue 1, November
1995
GR-63–CORE: Network Equipment Building System
(NEBS) Requirements: Physical Protection, Issue 2,
April 2002
GR-1089 (LSSGR, FD-15): Electromagnetic
Compatibility and Electrical Safety - Generic Criteria
for Network Telecommunications Equipment, Issue
2, Revision 1, February 1999
Safety Agency Certification AS/NZS 60950:2000 Safety of Information
Technology Equipment
CAN/CSA-C22.2, No. 60950-1–03, First Edition,
Information Technology Equipment - Safety - Part
1: General Requirements
EN60825-1, Safety of Laser Products - Part 1:
Equipment Class, Requirements, and User’s Guide
(2001)
EN60950-1:2001, First Edition, Information
Technology Equipment - Safety - Part 1: General
Requirements
IEC 60950-1(2001-10) Ed. 1.0 Information
Technology Equipment - Safety - Part 1: General
Requirements
Low Voltage Directive (73/23/EEC)
UL 60950-1, First Edition, Information Technology
Equipment - Safety - Part 1: General Requirements
126 ERX-310 Router Specifications

System Specifications
Category Specification
Electromagnetic Emissions Agency Certification AS/NZS 3548:1995 (CISPR 22 Class A)
EMC Directive (89/336/EEC)
EN55022 Class A (CISPR-22 Class A)
EN55024, Annex C for WAN Equipment Performance
Criteria A, B, and C
ETSI 300-386, Telecommunication Network
Equipment; ElectroMagnetic Compatibility (EMC)
requirements
FCC Part 15 Class A
IECS-003 Issue 3 Class A
VCCI (Voluntary Control Council for Interference by
Information Technology Equipment)
Telecommunications Certification ACA TS 016-1997
CTR13 – Commission Decision of 9 July 1997 on
a common technical regulation for attachment
requirements for terminal equipment interface for
connection to 2048 kbit/s digital structured ONP
leased lines: 97/521/EC – OJ No. L215 Vol. 40,
August 1997
CTR24 – Commission Decision of 9 September 1997
on a common technical regulation for attachment
requirements for terminal equipment interface for
connection to 34 Mbit/s digital unstructured and
structured leased lines: 97/639/EC – OJ No. L271
Vol. 40, 3 October 1997
FCC PART 68
IECS-003 Issue 3 Class A
PD7024 – Essential requirements for terminal
equipment intended for connection to
unstructured digital leased circuits of the public
telecommunications network using a CCITT
recommendation G,703 interface at a rate of 2048
kbit/s with a 75 ohm unbalanced presentation, 1994
RTTE Directive (1999/5/EEC)
ERX-310 Router Specifications 127

ERX 8.0.x Hardware Guide
128 ERX-310 Router Specifications

Appendix B
Installation Guidelines and
Requirements
This chapter reviews preinstallation considerations such as electrical,
environmental, and safety compliances for ERX routers. For complete system
specifications, see “System Specifications” on page 119.
This chapter contains the following sections:
Your Preinstallation Responsibilities on page 129
Environmental Requirements on page 130
Regulatory Compliances on page 130
Safety Guidelines on page 130
Equipment Rack Requirements on page 133
Cabling Recommendations on page 136
Product Reclamation and Recycling Program on page 137
Hardware Complianceonpage138
Your Preinstallation Responsibilities
Complete the following tasks before installing the system:
Verify that the electrical supply meets all AC and DC power requirements. See
“System Specifications” on page 119.
Verify that the site meets all environment specifications. See “Environmental
Requirements” on page 130 and “System Specifications” on page 119.
Verify that the cables you plan to use meet the specifications, and review the
cabling recommendations. See “Cabling Recommendations” on page 136.
Your Preinstallation Responsibilities 129

ERX 8.0.x Hardware Guide
Verify the operation of all telephone circuits, digital services, and T1 facilities
required for installation.
Ensure that all IP environment requirements are met, such as IP addresses,
subnet masks, and any specific routing protocol information.
Environmental Requirements
See “System Specifications” on page 119 for complete environmental specifications.
Choose a location for the router that is dry, relatively dust free, well ventilated, and
air conditioned. If you install equipment in a rack, be sure that the floor is capable
of supporting the combined weight of the rack and the installed equipment. Place
the router in a location with sufficient access to power and network cables.
Like other network devices, the router generates a significant amount
of heat. You must provide a balanced environment so that the router
performs properly and safely. See “System Specifications” on page 119 for
acceptable ranges of temperature and humidity.
Be sure to allow enough space around the router for adequate ventilation.
Inadequate ventilation can cause the system to overheat.
CAUTION: Do not block the air vents on the routers. Otherwise, the router might
overheat.
Regulatory Compliances
See “System Specifications” on page 119, for a complete list of regulatory
compliance requirements, including safety, EMC, and telecommunications.
Safety Guidelines
For your safety, before installing the system, review all safety warnings in this section.
WARNING: The recommended maximum ambient temperature is 50° C (122° F).
For safe operation, take into consideration the internal temperature of the rack.
WARNING: Install equipment in the rack from the bottom upward. Doing this helps
maintain the stability of the rack and reduces the chance of the rack tipping over.
130 Safety Guidelines

Installation Guidelines and Requirements
WARNING: Do not insert any metal object, such as a screwdriver, into an open slot
or the backplane. Doing so might cause electric shock and serious burns.
WARNING: Three people are required to install the router in a rack: two to lift the
system into position and one to screw it to the rack.
WARNING: Connect the router or rack to ground (earth), and ensure that a reliable
grounding path is maintained in the rack.
WARNING: Do not work on the system or connect or disconnect cables during
lightning activity.
WARNING: Be sure circuit breakers for the power source are in the OFF position
before attaching power cables.
WARNING: Before servicing the router, turn off the power.
WARNING: Remove jewelry (including rings, necklaces, and watches) before
working on equipment that is connected to power lines. Metal objects heat up
when connected to power and ground and can cause serious burns or become
welded to the terminals.
CAUTION: Evaluate the overall loading of the branch circuit before you install
any equipment into a rack.
Safety Guidelines 131

ERX 8.0.x Hardware Guide
ERX-310 Router Warnings (AC Model)
The following warnings apply only to the ERX-310 router.
ERX-310 Power Cord Warnings (AC Model)
WARNING: This unit has more than one power-supply cord. Disconnect 2 power
cords BEFORE servicing to avoid electric shock.
Denne enhed har mere end een strømfordelingsledning. Fjern ledning(er) nummer 2 FØR eftersyn for at
undgå elektrisk stød.
Waarschuwing! Dit apparaat heeft meerdere netsnoeren. Vermijd elektrische schok! Verwijder 2
netsnoeren ALVORENS onderhoud te verrichten.
Tässä laitteessa on useampi kuin yksi verkkojohto. Irrottakaa 2 verkkojohtoa ENNEN huoltoa sähköiskujen
välttämiseksi.
Attention: Cet appareil comporte plus d’un cordon d’alimentation. Afin de prévenir les chocs électriques,
débrancher les 2 (donner le nombre de cordons) cordons d’alimentation AVANT le dépannage.
Dieses Gerät hat mehrere Stromversorgungskabel. Klemmen Sie 2 Stromkabel VOR der Wartung ab, um
einen elektrischen Schlag zu vermeiden.
L’unità ha più di un cavo di alimentazione. Scollegare 2 cavi di alimentazione PRIMA di usarla, onde
evitarescosseelettriche.
Denne enheten har mer enn en nett-tilkobling. 2 nettkabler må frakobles FØR service for å unngå
elektrisk støt.
Este equipamento tem mais do que um cabo de alimentação. Para que se evitem choques, desligar 2
cabos, ANTES de servir o equipamento.
Estaunidadtienemásdeuncabledetomadecorriente. Desconecte2cablesANTESdedarle
mantenimiento a la unidad, para evitar descargas eléctricas.
Denna enhet har fler än en nätanslutningskabel. Koppla bort 2 nätanslutingskablar INNAN du påbörjar
service.
Power Cable Warning (Japanese)
WARNING: The attached power cable is only for this product. Do not use the cable
for another product.
132 Safety Guidelines

Installation Guidelines and Requirements
g017253
Equipment Rack Requirements
When allocating equipment rack space, consider the following:
Type of equipment racks recommended for ERX routers
Number of equipment racks required to hold your current router configuration
Future expansion
Make sure your distribution rack meet basic mechanical and space requirements
and complies with conventional standards. In the United States, use EIA-310-D
Cabinets, Racks, Panels, and Associated Equipment, September 1992.
Equipment Rack Requirements 133

ERX 8.0.x Hardware Guide
Figure 50: ERX Routers Installed in a Rack
Mechanical Requirements
Follow these mechanical requirements for your rack:
Select from the following rack options:
Two-post rack—A freestanding enclosed cabinet with two mounting
posts in the front
Telco-type rack—Two adjacent mounting posts that you must secure to
the floor or an overhead structure
Four-post rack—A freestanding open rack, either open or closed
Therackmusthaveatleasttwomountingposts.
134 Equipment Rack Requirements

Installation Guidelines and Requirements
The distance between the mounting holes in the two posts must be 18.31
inches ±.063 inch, as specified in the EIA-310-D.
Do not use an enclosed rack for ERX-7xx models or the ERX-310 router. It
does not provide adequate ventilation.
A fully loaded rack with three ERX-14xx models must structurally support
300 pounds (136 kilograms).
Optional mounting kits are available for 19-inch and 23-inch rack mounting
(mid-chassis and front-chassis mounting). Contact your Juniper Networks sales
representative for more information.
Space Requirements
If you use an enclosed rack for an ERX-14xx model, ensure that there is
a minimum of 3 inches of clearance between the inner side wall and the
router. This clearance space ensures adequate air flow.
Proper Rack Installation
To confirm proper equipment rack installation, verify the following:
Racks are installed and electrically grounded according to manufacturer
instructions.
Equipment racks are anchored to the floor and, when possible, anchored to
the ceiling as well.
Equipment rack installations comply with applicable local, state, and national
codes.
CAUTION: To maintain airflow requirements, a plenum must be installed above
ERX-14xx models before any other piece of equipment is installed above the router.
Equipment Rack Requirements 135

ERX 8.0.x Hardware Guide
Figure 51: Airflow for ERX Routers
Cabling Recommendations
Comply with the following recommendations:
Use only shielded cables.
136 Cabling Recommendations

Installation Guidelines and Requirements
Ensure that cable distance and rate limits meet IEEE-recommended maximum
speeds and distances for signaling purposes. For information about
attenuation and power loss in optical fiber cables see:
ANSI T1.646a-1997 Telecommunications – Broadband ISDN - Physical
Layer Specification for User-Network Interfaces Including DS1/ATM (1997)
ANSI T1.646-1995 Telecommunications – Broadband ISDN - Physical
Layer Specification for User-Network Interfaces Including DS1/ATM (1995)
Ensure that power cables deliver sufficient power to the system.
Attach laser fiber connectors only to Class 1 laser devices in accordance with
IEC 825-1, Safety of Laser Products - Part 1.
Route cables so that they do not restrict ventilation or airflow.
Route cables so that modules and field-replaceable units are easily accessible.
Route cables in a logical direction to prevent loss of connectivity to other
equipment in the rack, associated equipment in adjacent racks, or to the
backbone network.
Consider using cable-management brackets to keep network cables untangled
and orderly and to prevent cables from hindering access to other slots.
For specifications on cables for line modules, see the ERX Module Guide.
You may want to consult the document GR-63 (LSSGR, FD-15): Network
Equipment Building System (NEBS) Requirements: Physical Protection, Issue
1, October 1995 for additional cable recommendations.
Product Reclamation and Recycling Program
Juniper Networks is committed to environmentally responsible behavior. As part of
this commitment, we continually work to comply with environmental standards
such as the European Union’s Waste Electrical and Electronic Equipment (WEEE)
Directive and Restriction of Hazardous Substances (RoHS) Directive.
These directives and other similar regulations from countries outside the European
Union regulate electronic waste management and the reduction or elimination of
specific hazardous materials in electronic products. The WEEE Directive requires
electrical and electronics manufacturers to provide mechanisms for the recycling and
reuse of their products. The RoHS Directive restricts the use of certain substances
that are commonly found in electronic products today. Restricted substances
include heavy metals, including lead, and polybrominated materials. The RoHS
Directive, with some exemptions, applies to all electrical and electronic equipment.
In accordance with Article 11(2) of Directive 2002/96/EC (WEEE), products put on
the market after 13 August 2005 are marked with the following symbol or include it
in their documentation: a crossed-out wheeled waste bin with a bar beneath.
Product Reclamation and Recycling Program 137

ERX 8.0.x Hardware Guide
Juniper Networks provides recycling support for our equipment worldwide
to comply with the WEEE Directive. For recycling information, go to
http://www.juniper.net/environmental, and indicate the type of Juniper Networks
equipment that you wish to dispose of and the country where it is currently
located, or contact your Juniper Networks account representative.
Products returned through our reclamation process are recycled, recovered, or
disposed of in a responsible manner. Our packaging is designed to be recycled and
should be handled in accordance with your local recycling policies.
Hardware Compliance
The router meets the following hardware compliance requirements.
Federal Communications Commission (FCC) Statement
This equipment has been tested and found to comply with the limits for a
Class A digital device, pursuant to Part 15 of the FCC Rules. These limits are
designed to provide reasonable protection against harmful interference when
the equipment is operated in a commercial environment. This equipment
generates, uses, and can radiate radio frequency energy and, if not installed
and used in accordance with the instruction manual, may cause harmful
interference to radio communications. Operation of this equipment in a
residential area is likely to cause harmful interference in which case the user
will be required to correct the interference at his own expense.
This equipment is designed for use with properly shielded and terminated cables.
Refer to the installation sections of this manual before operation.
Reference: CFR 47, Part 15J, Sect 15.105 April 18, 1989
Caution: Changes or Modifications to this equipment not expressly
approved by the party responsible for compliance could void the user’s
authority to operate the equipment.
138 Hardware Compliance

Installation Guidelines and Requirements
FCC Requirements for Consumer Products
This equipment complies with FCC rules, Part 68. On the back side of this
equipment is a label that contains, among other information, the FCC Registration
Number and Ringer Equivalence Number (REN) for this equipment. If requested,
provide this information to your telephone company.
If this equipment causes harm to the telephone network, the Telephone Company
may discontinue your service temporarily. If possible, they will notify you in
advance. But if advance notice isn’t practical, you will be notified as soon as
possible. You will be advised of your right to file a complaint with the FCC.
Your telephone company may make changes in its facilities, equipment,
operations, or procedures that could affect the proper operation of your
equipment. If they do, you will be given advance notice so as to give you
an opportunity to maintain uninterrupted service.
If you experience trouble with this equipment, please contact the manufacturer
for warranty/repair information. The telephone company may ask that you
disconnect this equipment from the network until the problem has been corrected
or until you are sure that the equipment is not malfunctioning.
Food and Drug Administration, Center for Devices and Radiological Health
This equipment complies with 21 CFR 1040.10 and 1040.11 for the safe use of lasers.
Canadian Department Of Communications Radio Interference Regulations
This Class B (or Class A, if so indicated on the registration label) digital
apparatus meets the requirements of the Canadian Interference-Causing
Equipment Regulations.
Réglement sur le brouillage radioélectrique du ministère des communications
CetappareilnumériquedelaClasseB(ou Classe A, si ainsi indiqué sur
l’étiquette d’enregistration) respecte toutes les exigences du Reglement
sur le Materiel Brouilleur du Canada.
Industry Canada Notice CS-03
The Industry Canada label identifies certified equipment. This certification means
that the equipment meets certain telecommunications network protective,
operation and safety requirements as prescribed in the appropriate Terminal
Equipment Technical Requirements document(s). The Department does not
guarantee the equipment will operate to the user’s satisfaction. Before installing
this equipment, users should ensure that it is permissible to be connected
to the facilities of the local telecommunications company. The equipment
must also be installed using and acceptable method of connection. The
customer should be aware that compliance with the above conditions may
not prevent degradation of service in some situations.
Hardware Compliance 139

ERX 8.0.x Hardware Guide
Repairs to certified equipment should be coordinated by a representative
designated by the supplier. Any repairs or alterations made by the user to
this equipment, or equipment malfunctions, may give the telecommunications
company cause to request the user to disconnect the equipment.
Users should ensure for their own protection that the electrical ground
connections of the power utility, telephone lines and internal metallic
water pipe system, if present, are connected together. This precaution
may be particularly important in rural areas.
Caution: Users should not attempt to make such connections themselves, but should
contact the appropriate electric inspection authority, or electrician, as appropriate.
Notice: The Ringer Equivalence Number (REN) assigned to each terminal device
provides an indication of the maximum number of terminals allowed to be
connected to a telephone interface. The termination on an interface may consist
of any combination of devices subject only to the requirement that the sum of
the Ringer Equivalence Numbers of all the devices does not exceed 5.
Avis CS-03 d’Industrie Canada
L’ é t i q u e t t e du ministère des Communications du Canada indique que l’appareillage
est certifié, c’est-à-dire qu’il respecte certaines exigences de sécurité et de
fonctionnement visant les réseaux de télécommunications. Le ministère ne
garantit pas que l’appareillage fonctionnera à la satisfaction de l’utilisateur. Avant
d’installer l’appareillage, s’assurer qu’il peut être branché aux installations du
service de télécommunications local. L’appareillage doit aussi être raccordé
selon des méthodes acceptées. Le client doit toutefois prendre note qu’une
telle installation n’assure pas un service parfait en tout temps.
Les réparations de l’appareillage certifié devraient être confiées à un
service d’entretien canadien désigné par lefournisseur. En cas de
réparation ou de modification effectuées par l’utilisateur ou de mauvais
fonctionnement del’appareillage, le service de télécommunications peut
demander le débranchment de l’appareillage.
Pour leur propre sécurité, les utilisateurs devraient s’assurer que les mises
àlaterr
e des lignes de distribution d’électricité, des lignes téléphoniques et
de la tuyauterie métallique interne sont raccordées ensemble. Cette mesure
de sécurité est particulièrement importante en milieu rural.
Attention:Lesutilisateursnedoiventpasprocéderàcesraccordements
eux-mêmes mais doivent plutôt faire appel aux pouvoirs de réglementation
en cause ou à un électricien, selon le cas.
Avis:Veuillez prendre note que pour tout appareillage supportant des lignes de
type“loopstart,”l’indiced’équivalencedelasonnerie(IES)assignéàchaque
dispositif terminal indique le nombre maximal de terminaux qui peuvent être
raccordés à une interface. La terminaison d’une interface téléphonique peut
consister en une combinaison de quelques dispositifs, à la seule condition
que la somme d’indices d’équivalence de la sonnerie de tous les dispositifs
140 Hardware Compliance

Installation Guidelines and Requirements
n’excède pas 5. Le REN figure sur l’étiquette “FCC Rules Part 68” située
sur le support du module ou à l’arrière de l’unité.
D.O.C. Explanatory Notes: Equipment Attachment Limitations
The Canadian Department of Communications label identifies certified
equipment. This certification meets certain telecommunication network
protective, operational and safety requirements. The department does not
guarantee the equipment will operate to the users satisfaction.
Before installing the equipment, users should ensure that it is permissible to
be connected to the facilities of the local telecommunications company. The
equipment must also be installed using an acceptable method of connection. In
some cases, the company’s inside wiring associated with a single line individual
service may be extended by means of a certified connector assembly (telephone
extension cord). The customer should be aware that compliance with the above
condition may not prevent degradation of service in some situations.
Repairs to certified equipment should be made by an authorized
Canadian maintenance facility designated by the supplier. Any repairs
or alterations made by the user to this equipment, or equipment
malfunctions, may give the telecommunications company cause to
request the user to disconnect the equipment.
Users should ensure for their own protection that the electrical ground
connections of the power utility, telephone lines and internal metallic
water pipe system, if present, are connected together. This precaution
may be particularly important in rural areas.
Caution: Users should not attempt to make such connections themselves, but should
contact the appropriate electrical inspection authority, or electrician, as appropriate.
Notes explicatives du ministère des Communications: limites visant les accessoires
L’ é t i q u e tte du ministère des Communications du Canada indique que l’appareillage
est certifié, c’est-à-dire qu’il respecte certaines exigences de sécurité et de
fonctionnement visant les réseaux de télécommunications. Le ministère ne garantit
pas que l’appareillage fonctionnera à la satisfaction de l’utilisateur.
Avant d’installer l’appareillage, s’assurer qu’il peut être branché aux installations
du service de télécommunications local. L’appareillage doit aussi être raccordé
selon des méthodes acceptées. Dans certains cas, le câblage interne du service
de télécommunications utilisé pour une ligne individuelle peut être allongé au
moyen d’un connecteur certifié (prolongateur téléphonique). Le client doit toutefois
prendre note qu’une telle installation n’assure pas un service parfait en tout temps.
Les réparations de l’appareillage certifié devraient être confiées à un
service d’entretien canadien désigné par le fournisseur. En cas de
réparation ou de modification effectuées par l’utilisateur ou de mauvais
fonctionnement de l’appareillage, le service de télécommunications peut
demander le débranchment de l’appareillage.
Hardware Compliance 141

ERX 8.0.x Hardware Guide
Pour leur propre sécurité, les utilisateurs devraient s’assurer que les mises
àlaterredesl
ignes de distribution d’électricité, des lignes téléphoniques et
de la tuyauterie métallique interne sont raccordées ensemble. Cette mesure
de sécurité est particulièrement importante en milieu rural.
Attention:Lesutilisateursnedoiventpasprocéderàcesraccordements
eux-mêmes mais doivent plutôt faire appel aux pouvoirs de réglementation
en cause ou à un électricien, selon le cas.
EC Declaration of Conformity
The EC Declaration of Conformity is available in “Declaration of
Conformity” on page 157.
Voluntary Control Council for Interference (VCCI) Statement for Japan
The preceding translates as:
This is a Class A product. In a domestic environment this product
may cause radio interference in which case the user may be required
to take adequate measures. VCCI-A
142 Hardware Compliance

Appendix C
Cable Pinouts
This appendix lists the cables and connector pinout assignments for the cables used
with the ERX-7xx models and ERX-14xx models. It contains the following sections:
SRP I/O Module on page 143
CT1andCE1I
/O Modules on page 146
SRP I/O Module
The SRP I/O module provides two management ports. You can connect a
console directly to the RS-232 serial port using a shielded straight-through
cable with a female DB-9 connector on one end and a male DB-25 with a
crossover adapter on the DB-25 end. This port is called the serial port, the
RS-232 port, or the console serial port. Figure 52 shows the location of the
serial port and the sequence of the pins in the RS-232 connector.
The console port is considered a data terminal equipment interface
(DTE). Direct connection to a terminal or PC (which also have DTE
interfaces) requires a crossover cable.
SRP I/O Module 143

ERX 8.0.x Hardware Guide
Figure 52: SRP I/O Module Serial Port
CONSOLE
10/100
BASE T
RS-232
DB-9
PIN 1
PIN 9
g013771
Table19liststhepinoutfortheserialcable’sRS-232connector.
Table 19: SRP I/O Module—RS-232 Serial Connector Pinout
Pin Signal
1DCD
2RXD
3TXD
4DTR
5GND
6DSR
7RTS
8CTS
9RNG
After you have configured an IP address on the system, you can connect using
a host running Telnet over the 10/100Base-T Ethernet port on the SRP I/O
module. The router ships with a straight-through cable having a male RJ-45
Ethernet connector on each end. Figure 53 shows the location of the Ethernet
port and the sequence of the pins in the RJ-45 connector.
144 SRP I/O Module

Cable Pinouts
Figure 53: SRP I/O Module Ethernet Port
CONSOLE
10/100
BASE T
RS-232
PIN 1
PIN 8
PIN 1
PIN 8
RJ-45
g013772
Table 20 lists the pinouts for the Ethernet cable’s RJ-45 connector.
Table 20: SRP I/O Module—RJ-45 Connector Pinout
Pin Signal
1TX+
2TX–
3RX +
4no connect
5no connect
6RX –
7no connect
8no connect
To facilitate connecting the system to a terminal, the system is shipped
with one of each of the following cable adapters:
DB-9 female to RJ-45 female crossover null modem adapter
DB-9 female to RJ-45 female straight-through adapter
Table 21 lists the pinouts for the crossover adapter.
SRP I/O Module 145

ERX 8.0.x Hardware Guide
Table 21: DB-9—RJ-45 Crossover Adapter Pinout
DB-9 Pin Signal RJ-45 Pin
1DCD1
2RXD 3
3TXD2
4DTR 6
5GND5
6DSR
4
7RTS8
8CTS7
9RNG
no connect
Table 22 lists the pinout for the straight-through adapter.
Table 22: DB-9—RJ-45 Straight-Through Adapter Pinout
DB-9 Pin
RS-232 Signal
Name RJ-45 Pin
Ethernet Signal
Name
1DCD1TX+
2RXD 2TX–
3TXD3RX +
4DTR 4no connect
5GND (signal) 5no connect
6DSR6RX –
7RTS7no connect
8CTS8no connect
9RNG
no connect none
CT1 and CE1 I/O Modules
CT1 I/O modules have 24 RJ-48C female connectors. CE1 I/O modules have either
20 RJ-48C female connectors or two 25-pair female Telco connectors. Figure 54
shows the location of the ports on a CT1 I/O module and the sequence of the pins
in the RJ-48C connector. CE1 I/O modules equipped with RJ-48C connectors have
the same configuration as CT1 I/O modules equipped with RJ-48C connectors.
146 CT1 and CE1 I/O Modules

Cable Pinouts
Figure 54: CT1 I/O Module Ports
PIN 1
PIN 8
Port 0
Port 1
Port 2
Port 3
CT-1
I/O
g013773
Ta b l e 2 3 l ists the pinout for the CT1/CE1 connector.
Table 23: CT1/CE1 I/O Module—RJ-48C Connector Pinout
Pin Signal
1RXRing
2RXTip
3no connect
4TX Ring
5TXTip
6no connect
7no connect
8no connect
For CE1 I/O modules with Telco connectors, the other ends of the cables are
attached to a balun panel that splits the signals from two Telco connectors to
20 pairs of BNC connectors. We supply the Telco cables if you purchase a
balun panel. Figure 55 shows the location of the Telco connectors on a CE1
I/O module and the sequence of the pins in the connectors.
CT1 and CE1 I/O Modules 147

ERX 8.0.x Hardware Guide
Figure 55: CE1 I/O Module with Telco Connectors
PIN 25
PIN 1
CE1
I/O
PIN 50
PIN 26
0-9
g013774
Figure 56 shows the location of the 20 pairs of BNC connectors on a balun
panel. The cables from the CE1 I/O module are plugged into the two 50-pin
Telco connectors on the other side of the panel.
Figure 56: Twenty-Port Balun Panel
TX
RX
PORT 1021 3456789 111213141516171819
g013775
Table24andTable25listthepinoutsfortheTelcoconnectorsoneachcable.
Table 24: Pinout of 50-Pin Telco Connector to Ports 0–9
Pin Signal Pin Signal
1 Port 0 RX TIP 26 Port 0 RX RING
2 Port 0 TX TIP 27 Port 0 TX RING
3 Port 1 RX TIP 28 Port 1 RX RING
4Port 1 TX TIP 29 Port 1 TX RING
5 Port 2 RX TIP 30 Port 2 RX RING
148 CT1 and CE1 I/O Modules

Cable Pinouts
Pin Signal Pin Signal
6 Port 2 TX TIP 31 Port 2 TX RING
7 Port 3 RX TIP 32 Port 3 RX RING
8 Port 3 TX TIP 33 Port 3 TX RING
9 Port 4 RX TIP 34 Port 4 RX RING
10 Port 4 TX TIP 35 Port 4 TX RING
11 Port 5 RX TIP 36 Port 5 RX RING
12 Port 5 TX TIP 37 Port 5 TX RING
13 Port 6 RX TIP 38 Port 6 RX RING
14 Port 6 TX TIP 39 Port 6 TX RING
15 Port 7 RX TIP 40 Port 7 RX RING
16 Port 7 TX TIP 41 Port 7 TX RING
17 Port 8 RX TIP 42 Port 8 RX RING
18 Port 8 TX TIP 43 Port 8 TX RING
19 Port 9 RX TIP 44 Port 9 RX RING
20 Port 9 TX TIP 45 Port 9 TX RING
21 no connect 46 no connect
22 no connect 47 no connect
23 no connect 48 no connect
24 no connect 49 no connect
25 no connect 50 no connect
Table 25: Pinout of 50-Pin Telco Connector to Ports 10–19
Pin Signal Pin Signal
1Port10RXTIP26Port10RXRING
2 Port 10 TX TIP 27 Port 10 TX RING
3 Port 11 RX TIP 28 Port 11 RX RING
4Port 11 TX TIP 29 Port 11 TX RING
5 Port 12 RX TIP 30 Port 12 RX RING
6 Port 12 TX TIP 31 Port 12 TX RING
7 Port 13 RX TIP 32 Port 13 RX RING
8 Port 13 TX TIP 33 Port 13 TX RING
9 Port 14 RX TIP 34 Port 14 RX RING
10 Port 14 TX TIP 35 Port 14 TX RING
11 Port 15 RX TIP 36 Port 15 RX RING
12Port 15 TX TIP 37Port 15 TX RING
13 Port 16 RX TIP 38 Port 16 RX RING
CT1 and CE1 I/O Modules 149

ERX 8.0.x Hardware Guide
Pin Signal Pin Signal
14 Port 16 TX TIP 39 Port 16 TX RING
15 Port 17 RX TIP 40 Port 17 RX RING
16 Port 17 TX TIP 41 Port 17 TX RING
17 Port 18 RX TIP 42 Port 18 RX RING
18 Port 18 TX TIP 43 Port 18 TX RING
19 Port 19 RX TIP 44 Port 19 RX RING
20 Port 19 TX TIP 45 Port 19 TX RING
21 no connect 46 no connect
22 no connect 47 no connect
23 no connect 48 no connect
24 no connect 49 no connect
25 no connect 50 no connect
150 CT1 and CE1 I/O Modules

Appendix D
Contacting Customer Support and
Returning Hardware
See the Juniper Networks Web site for complete customer service information:
http://www.juniper.net/support/guidelines.html
This appendix contains the following sections:
Contacting Customer Support on page 151
Return Procedure on page 151
Locating Component Serial Numbers on page 152
InformationYouMightNeedtoSupplytoJTAConpage153
Tools and Parts Required on page 154
Returning Products for Repair or Replacement on page 154
Contacting Customer Support
Foryourco
nvenience, we provide multiple options for requesting and receiving
technical support from the Juniper Networks Technical Assistance Center (JTAC):
By the Web using Juniper Networks, Inc. Case Manager:
https://www.juniper.net/cm/index.jsp
By telephone:
From the US, Canada, and Mexico at 1–888–314–JTAC
From all other locations at 408–745–9500
Return Procedure
When you need to return a component, follow this procedure:
Return Procedure 151

ERX 8.0.x Hardware Guide
1. Determine the part number and serial number of the component. For
instructions, see “Locating Component Serial Numbers ” on page 152.
2. Obtain a Return Materials Authorization (RMA) number from the Juniper
Networks Technical Assistance Center (JTAC). See “Information You Might
Need to Supply to JTAC” on page 153.
Provide the following information in your e-mail message or during the
telephone call:
Part number and serial number of component
Your name, organization name, telephone number, and fax number
The shipping address for the replacement component, including contact
name and phone number
Description of the failure
The support representative validates your request and issues an RMA number
for return of the component.
3. Pack the routing node or component for shipment, performing the procedure
described in “Returning Products for Repair or Replacement” on page 154.
Locating Component Serial Numbers
Before contacting Juniper Networks to request a Return Materials Authorization
(RMA), you must find the serial number on the chassis or component. To list all the
chassis modules and their serial numbers, enter the following command:
host1#show hardware
You can also find the serial numbers on the modules. ID stickers are
usually applied near the ejector. See Figure 57.
Fan trays are not listed in the show hardware command output. ERX-7xx model
and ERX-14xx model fan trays have stickers on the faceplate. For the ERX-310
router, you must remove the fan tray to view the serial number ID sticker.
152 Locating Component Serial Numbers

Contacting Customer Support and Returning Hardware
Figure 57: Representative Module Serial Number ID Label
Ejector
P/C: SRP_I/O
ASY: xxx-xxxxx-xx
S/N: xxxxxxxxxx
SRP I/O
Serial number
ID label
g013777
Information You Might Need to Supply to JTAC
When requesting technical support from the JTAC by phone, be prepared
to provide the following information:
Priority level
Indication of what activity was being performed on the router when the
problem occurred
Problem detail and configuration data, obtained by these commands:
show version
show hardware
show environment
show configuration
When a new request for technical support is submitted, the JTAC engineer:
1. Opens a case and assigns a number
Information You Might Need to Supply to JTAC 153

ERX 8.0.x Hardware Guide
2. Begins troubleshooting, diagnostics, and problem replication (if appropriate)
3. Provides you with periodic updates on problem status and escalates the
problem as appropriate according to escalation management guidelines
4. Closesthecasewhenyouagreethattheproblemhasbeenresolved
Tools and Parts Required
To remove components from the chassis or the chassis from a rack
prior to returning the chassis or components for repair or replacement,
you need the following tools and parts:
Mechanical lift, if available
3/8–inch nut driver or 3/8–inch wrench
Blank filler panels
Electrostatic bag or antistatic mat
Electrostatic discharge (ESD) grounding wrist strap
Flat-blade (—) screwdriver
Phillips (+) screwdrivers, numbers 1 and 2
Plastic boots or other protective cover for fiber-optic SC and LC connectors
Wire cutters
Returning Products for Repair or Replacement
In the event of a hardware failure, please contact Juniper Networks to obtain
a Return Material Authorization (RMA) number. This number is necessary to
ensure proper tracking and handling of returned material at the factory. Do
not return any hardware until you have received an RMA. Juniper Networks
reserves the right to refuse shipments that do not have an RMA. Refused
shipments will be returned to the shipper via collect freight.
See the customer support Web page for complete repair and return
policies and procedures.
Packing Instructions for Returning a Chassis
If possible, use the original shipping crate, pallet, and packing materials in
which the chassis was originally shipped. If these materials are unavailable, use
comparable shipping material, or contact your Juniper Networks representative
for information on approved packaging material.
154 Returning Products for Repair or Replacement

Contacting Customer Support and Returning Hardware
To pack the chassis for shipment, follow these steps:
1. Ground yourself by using an antistatic wrist strap or other device and connect
it to the ESD grounding jack on the chassis.
2. Issue the proper shutdown commands to halt your system.
3. Switch all power switches to the OFF position.
4. Remove all cables from the chassis.
5. Remove all major components from the chassis, including line modules, I/O
modules, fan trays, and cable management systems.
6. Remove the chassis from the rack and bolt it to the shipping pallet.
7. Cover the chassis with an ESD bag and place packing foam on top of and
around the chassis.
8. Place the crate cover over the chassis and fasten the cover to the pallet.
Returning Products for Repair or Replacement 155

ERX 8.0.x Hardware Guide
156 Returning Products for Repair or Replacement

Appendix E
Declaration of Conformity
Declaration of Conformity on page 157
Declaration of Conformity
Declaration of Conformity according to ISO/IEC Guide 22 and EN4514
Manufacturer’s Name: Juniper Networks, Inc.
Manufacturer’s Address: Juniper Networks, Inc.
10 Technology Park Drive
Westford, Massachusetts 01886 USA
Declares, that the product(s)
Product Name: Edge Switching Router
Model Number(s): ERX-310, ERX-700, ERX-705, ERX-1400, ERX-1440
Product Options: All Modules
Conforms to the following Product Specifications:
Safety: IEC 60950-1(2001-10) Ed. 1.0 Information technology equipment - Safety - Part 1:
General requirements
EN60950:2000, 3rd Edition, Safety of Information Technology Equipment
EN60825-1, Safety of Laser Products - Part 1: Equipment Class, Requirements,
and User’s Guide (2001)
EMC: EN55022 Class A (CISPR-22 Class A)
EN55024, Annex C for WAN Equipment Performance Criteria A, B, and C
ETSI 300-386, Telecommunication Network Equipment; ElectroMagnetic
Compatibility (EMC) requirements
Supplementary Information: The products herewith comply with the requirements of the Low Voltage
Directive (73/23/EEC), the EMC Directive (89/336/EEC), and the RTTE Directive
(1999/5/EEC), and carry the CE markings accordingly.
Products were tested in a typical configuration.
Westford, MA, May 01, 2003
David H. Schilling
Regulatory Affairs
Declaration of Conformity 157

ERX 8.0.x Hardware Guide
158 Declaration of Conformity

Part 5
Index
Index 159

160 Index

Index
Symbols
10/100Base-T port ...............................56, 59, 78
10-Gbps SRP module .....................................12
–48 VDC...................................................19
A
access line modules .......................................9
access, management ............. ...... ............. 16, 77
setting up console .............................. 78, 80
SNMP............................................ 16, 82
Telnet setup..........................................80
accessing
fan tray...............................................97
agency certification.... ...... ................ 119, 122, 125
airflow................................................... 130
rack-mounted installation and ......................28
specifications ........................... 119, 122, 125
alarm ports................................................56
amperage .................................... 119, 122, 125
antistatic bags and containers............................86
assembly numbers, locating ........................... 152
assigning an IP address...................................80
audience for documentation ............................. xi
B
BNC connector....................................... 58, 66
booting
LED activity.........................................110
C
cable-management bracket ......... ...... .......... .....55
installing ........................................... 100
cables
failure ...............................................111
I/O modules..........................................66
pinouts ............................................. 143
power input module.................................60
recommendations ................................. 136
redundant port.......................................72
required..............................................55
SRP I/O modules................................ 56, 59
cabling
ERX routers ..........................................53
HSSI connectors .....................................66
RJ-45 connectors.....................................67
SC duplex connectors .......................... 68, 70
SRP I/O modules................................ 56, 59
X.21/V.35 connectors................................71
Case Manager ... ... ... ... ... ..... .. ... ... ... ... .. ... ... . 151
certifications ................120–121, 123–124, 126–127
circulation, air.............................................28
classification, packet......................................15
cleaning ...................................................86
CLI (command-line interface) ............................16
clock source input ports..................................58
clocking problems .......................................111
color code, power cable ..................................64
combinations of line modules............................38
command-line interface..................................16
compliance
product reclamation and recycling ............... 137
compliance requirements ........................ 138–142
components
returning .............................................86
storing................................................86
configuring
cables ..........................................53, 136
management access.................. ...... .........77
Telnet.................................................80
connecting console to router.............................78
connectors, pinouts..................................... 143
console
for management access ......... ..... ...... .... 78, 80
ports
RS-232 ..................................... 56, 59
consumption, power......................... 119, 122, 125
conventions
notice icons..........................................xii
conventions defined
icons..................................................xii
syntax................................................xii
text...................................................xii
current (electrical) requirements .. .. .. .. ... . 119, 122, 125
customer support ..................... ............ xviii, 151
contacting JTAC ....................................xviii
Index 161

ERX 8.0.x Hardware Guide
D
DB-9 connector ...........................55–56, 143, 146
DC power............................................64, 125
detecting double-bit error ...............................114
Device Management System, NMC-RX ..... ...... .......16
diagnosing problems ................................... 103
diagnostic LEDs......................................... 104
dimensions of ERX routers..................119, 122, 125
dissipation, heat .............................119, 122, 125
distribution rack ........................................ 133
documentation set
comments on...................................... xvii
double-bit errors
detecting ............................................114
troubleshooting.....................................115
E
E-series routers
assigning IP address to..............................80
cabling ...............................................53
cabling recommendations ........................ 136
dimensions.............................. 119, 122, 125
electrical requirements................. 119, 122, 125
hardware.............................................16
installing ........................................ 23, 27
installing components...............................85
installing modules ...................................35
lifting............................................ 23–24
maintenance.........................................85
management access......... ......... .......... 16, 77
models ................................................3
modules...............................................9
power requirements.................... 119,1
22,125
powering down ......................................75
powering up..........................................73
safety guidelines......................... 30, 130, 132
site planning....................................... 129
slot groups and identification.......................36
space requirements..................................28
troubleshooting...............................103–104
EIA distribution rack......................................28
ejectors, module ..........................................43
electrical requirements......................119, 122, 125
electronic equipment, recycling........................ 137
environmental requirements........................... 130
ERX-1440 router...........................................4
ERX-14xx models..........................................4
fan tray...............................................20
front view.............................................5
rear view..............................................6
ERX-310 router
fan tray...............................................20
front view.............................................8
power cord warnings.............................. 132
rear view (AC model) .................................9
rear view (DC model).................................9
ERX-705 router ............................................7
ERX-7xx models...........................................6
fan tray...............................................20
front view .............................................7
rear view..............................................7
slot identification and grouping.....................37
ESD (electrostatic discharge).............................28
ESD grounding jack, chassis .............................38
Ethernet link .............................................111
external timing ports .....................................56
F
failure, fan................................................113
failures....................................................111
FAN FAIL LED .............................................97
FAN OK LED ..............................................97
fan tray....................................................20
hot-swapping ........................................97
fans
failure .......................................... 97, 113
installing .............................................99
location...............................................20
redundancy ..........................................20
removing.............................................99
status.................................................97
far-end receive failure ...................................111
FERF (far end receive failure) ...........................111
filler panel.................................................40
Flash cards................................................13
flow, air....................................................28
G
grounding jack, ESD......................................38
H
halt command ....................................... 46, 87
hardware
cable configuration ............................53, 136
reclamation and recycling......................... 137
redundancy features.................................16
repairing and replacing..............................41
hazardous materials, reclamation and recycling ...... 137
heat dissipation........................ 119, 122, 125, 130
high-availability mode.................................. 108
hot-swapping
fan trays..............................................97
modules..............................................38
HSSI connectors, cabling .................................66
humidity requirements......................119, 122, 125
HyperTerminal............................................78
162 Index

Index
I
I/O modules...............................................15
cables ................................................66
installing .............................................44
installing redundancy................................50
OC48 Frame APS....................................38
removing.............................................46
SFPs..................................................93
SRP...................................................56
icons defined, notice .....................................xii
installing
ERX routers ..................................... 23, 27
site planning.................................. 129
modules
I/O modules.....................................44
line modules....................................44
order of installation.............................40
slot groups and module arrangements ........36
SRP I/O modules................................42
SRP modules....................................42
NVS cards ....................................... 87, 89
redundancy I/O modules............................50
redundancy midplane...............................48
SFPs..................................................95
spare line modules ..................................48
IP address, assigning .....................................80
J
JTAC, contacting......................................... 151
L
lead in equipment, reclamation and recycling ........ 137
LEDs..................................................... 104
abnormal activity...................................111
fans...................................................97
line modules..........................................9
normal activity......................................110
redundancy status ..................................113
SRP modules.................................... 9, 108
lifting router...............................................24
line modules ..............................................14
access .................................................9
combinations .........................................4
installing .............................................44
installing spare.......................................48
LEDs............................................. 9, 104
OC48.................................................38
performance rate.....................................4
redundancy .................................... 48, 113
removing.............................................46
slot groups ...........................................36
uplink .................................................9
location, for ERX routers ............................... 130
M
maintenance, system.....................................85
management access .. .. ... .. ... .. ... .. .. ... .. ... ... . 16, 77
setting up console .............................. 78, 80
SNMP............................................ 16, 82
Telnet setup..........................................80
Management Information Bases ................ .........16
management port
10/100Base-T ................................... 56, 59
managing modules .......................................38
manuals
comments on...................................... xvii
mechanical requirements for distribution rack........ 134
memory, upgrading.......................................90
MIBs (Management Information Bases) ........... ......16
midplane...................................................9
redundancy ..........................................48
models
ERX router ............................................3
module reset button .....................................114
modules
failure ...............................................111
hot-swapping ........................................38
installing ........................................ 35, 42
order of installation.............................40
managing ............................................38
removing.............................................46
repairing and replacing..............................41
replacing .............................................38
self-testing ......................................... 105
storing................................................86
types of................................................9
monitoring LEDs........................................ 104
monitoring temperature.................................113
mounting kits ........................................... 134
mounting posts for rack................................ 134
N
network management ... .. .. .. .. .. ... .. .. .. .. ... .. .. 16, 77
setting up console .............................. 78, 80
SNMP............................................ 16, 82
Telnet setup..........................................80
NMC-RX Device Management System...................16
notice icons ...............................................xii
notice icons defined......................................xii
NVS cards .................................................13
installing ........................................ 87, 89
storing................................................86
O
OC48 modules............................................38
ONLINE LED .............................................113
order of module installation..............................40
Index 163

ERX 8.0.x Hardware Guide
P
packaging, recycling.................................... 138
packet classification ......................................15
packing instructions .................................... 154
PCMCIA slot, SRP modules...............................13
performance rate, line modules...........................4
pinouts, router cables and connectors................. 143
planning site for installation............................ 129
plenum....................................................28
ports
alarm.................................................56
external timing ......................................56
management.... ................ ...... .......... .....56
redundancy ..................................... 38, 51
status LEDs......................................... 105
power
cabling power input module ........................60
consumption
system ............................. 119, 122, 125
dissipation .............................. 119, 122, 125
failures ........................................ 104, 111
redundancy ..........................................64
source A.............................................111
source B.............................................111
specifications ........................... 119, 122, 125
power cord warnings ................................... 132
power input module, cabling.............................60
power requirements......................... 119, 122, 125
power switches ...................................... 60, 73
powering down router....................................75
powering up router .......................................73
preinstallation responsibilities ......................... 129
preparing site for installation........................... 129
primary SRP module .....................................16
problems.................................................111
product numbers, locating ............................. 152
Q
QoS, packet classification for ............................15
R
rack, distribution..........................................28
reclamation and recycling.............................. 137
recycling Juniper Networks equipment................ 137
redundancy
line module status..................................113
midplane.............................................16
SRP modules.........................................13
status................................................113
redundancy features (hardware) .........................16
fans...................................................20
line modules.........................................48
ports............................................. 38, 51
SRP modules.........................................16
redundancy midplane ....................................17
installing .............................................48
REDUNDANT LED .......................................113
release mechanisms for SFPs ............................94
removing
components..........................................85
modules..............................................46
SFPs..................................................94
repacking components ................................. 154
repairing hardware components.........................41
replacing
components..........................................85
modules..............................................38
NVS cards ....................................... 87, 89
SFPs............................................. 93, 95
reset button, module ....................................114
Restriction of Hazardous Substances (RoHS) Directive,
recycling equipment ................................. 137
Return Materials Authorization......................... 151
returning product....................................... 151
RJ-45 connectors, cabling ................................67
RMA ..................................................... 151
RoHS (Restriction of Hazardous Substances) Directive,
recycling equipment ................................. 137
RS-232 port ......................................56, 59, 78
S
safety
agency certification..................... 119, 122, 125
guidelines ................................ 30, 130, 132
SC duplex connectors, cabling ...................... 68, 70
self-testing, modules.................................... 105
serial numbers, locating................................ 152
SFPs (small form-factor pluggable transceivers)........ .93
installing .............................................95
removing.............................................94
storing................................................86
show configuration command ......................... 153
show environment command.....................113, 153
show hardware command.............................. 153
show interface gigabitEthernet command...............97
show version command............................44, 153
site planning ............................................ 129
size
of ERX routers ..........................119, 122, 125
of rack.............................................. 135
slot disable command....................................46
slot groups ................................................36
ERX-1410 router.....................................36
ERX-7xx models.....................................37
overloading .........................................111
small form-factor pluggable transceivers ................93
SMB connectors...........................................70
SNMP for management access...................... 16, 82
SODIMMs .................................................91
164 Index

Index
software
configuration.........................................13
software, upgrading.......................................87
space requirements................ 28, 119, 122, 125, 130
spare line modules, installing ............................48
specifications
airflow................................... 119, 122, 125
dimensions.............................. 119, 122, 125
distribution rack ................................... 133
electrical ................................ 119, 122, 125
heat dissipation......................... 119, 122, 125
space....................................119, 122, 125
weight...................................119, 122, 125
SRP I/O modules..........................................13
cabling .......................................... 56, 59
installing .............................................42
removing.............................................46
SRP modules...............................................9
errors on ............................................114
installing .............................................42
LEDs on ......................................... 9, 108
models ................................................7
PCMCIA slot..........................................13
powering down ......................................75
redundancy ..................................... 13, 16
removing........................................ 46, 75
standby SRP module......................................16
starting ERX routers ......................................73
status, redundancy.......................................113
storing, modules and components.......................86
support, technical See technical support
switches, power...................................... 60, 73
switching on router.......................................73
switchover to spare line module .........................18
synchronize command...................................17
syntax conventions defined..............................xii
system maintenance .....................................85
T
technical support ....................................... 151
contacting JTAC ....................................xviii
Telnet connection to router ..............................80
temperature
excessive.......................................111, 113
monitoring..........................................113
requirements.................................. 111, 130
text conventions defined.................................xii
thermal protection mode.......................20, 97, 113
timing inputs, external .............................. 14, 56
tools needed ...........................23, 40, 55, 85, 154
troubleshooting ....................................103–104
booting..............................................111
cables ...............................................111
clocking .............................................111
double-bit errors....................................115
Ethernet link........................................111
fans............................................105, 113
FERF.................................................111
LED activity for .................................... 104
modules....................................... 105, 111
power failure.................................. 104, 111
safety guidelines............................. 130, 132
U
uninstalling modules......................................46
upgrading software .......................................87
uplink line modules........................................9
V
ventilation.................................................28
voltage requirements........................ 119, 122, 125
W
warnings, safety ..........................................40
Waste Electrical and Electronic Equipment (WEEE)
Directive, recycling equipment ...................... 137
WEEE (Waste Electrical and Electronic Equipment)
Directive, recycling equipment ...................... 137
weight
of ERX routers ..........................119, 122, 125
of rack........................................ 130, 134
wrist strap, antistatic .....................................38
X
X.21/V.35 connectors, cabling............................71
Index 165