Keston C36 Installation Manual 376\377\000F\000r\000o\000n\000t\000 \000C\000o\000v\000e\000r\000 \000 \000C\0003\0006\000 \000C\000o\000m\000b\000i\000 \
C36 Combi inst serv C36 Combi inst serv
2015-05-15
: Keston Keston-C36-Installation-Manual-719678 keston-c36-installation-manual-719678 keston pdf
Open the PDF directly: View PDF .
Page Count: 57
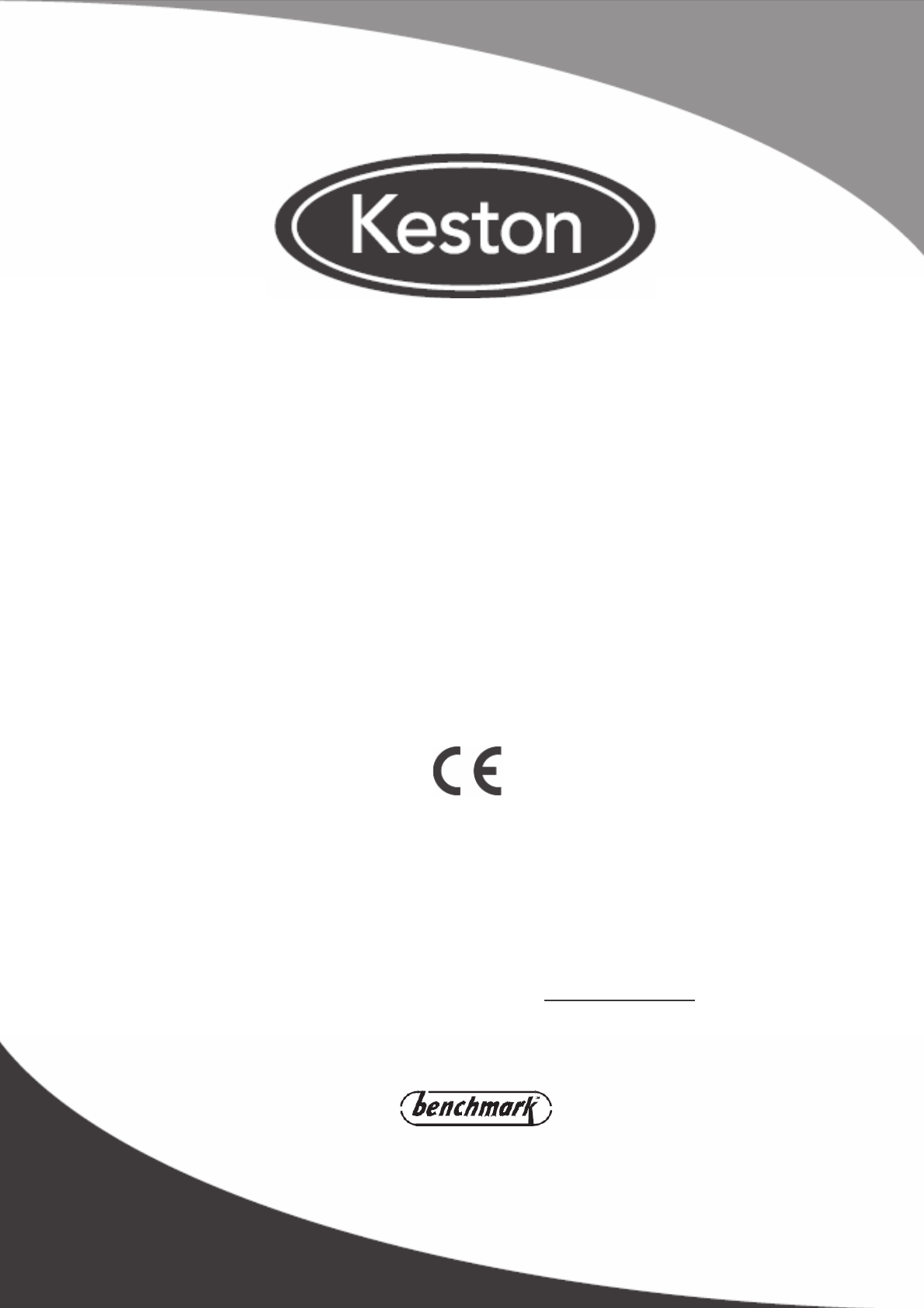
C36 Combi
User, Installation and Servicing
Instructions
FAN POWERED HIGH EFFICIENCY
MODULATING DOMESTIC CONDENSING
GAS COMBINATION BOILER
CE/PI No. 86-CM-44
C36 Combi - GC No. 47-930-01
C36P Combi
–
GC No. 47
-
930
-
02
These instructions must be left either with the
user or next to the site gas meter.
Keston Heating
PO Box 103, National Avenue, Kingston Upon Hull, HU5 4JN
Tel. +44 (0) 1482 443005 Fax. +44 (0) 1482 467133
email : info@keston.co.uk web : www.keston.co.uk
COMPLIANT WITH BUILDING REGULATION PART L1 & L2
SEDBUK A RATED
W D 3 8 8
i s s u e 5 - 2 0 1 1

CONTENTS
NB : These instructions are an integral part of the appliance. This document must be handed over to
the user on completion of the installation to ensure compliance with the Gas Safety (Installation
& Use) Regulations
Section Description
0 HANDLING INSTRUCTIONS
0.1 List of contents
0.2 Recommended handling procedure
1 USER INSTRUCTIONS
1.1 Introduction
1.2 Maintenance
1.3 Boiler Setup and Operation
1.4 Safety Information
2 GENERAL INSTRUCTION
2.1 Description
2.2 Boiler Schematic
2.3 Related Documents
2.4 Physical Data
2.5 Optional Accessories
2.6 Performance Data C36 Combi and C36P Combi
3 BOILER LOCATION
3.1 Dimensions & Minimum Clearances
3.2 Service Connections
3.3 Position
3.4 Electrical
3.5 Boiler Size Selection
3.6 Gas Supply
3.7 CH & DHW Water Systems
3.8 Flue System
3.9 Air Supply
3.10 Compartment Installation
3.11 Condensate Drainage
4 INSTALLATION OF THE BOILER
4.1 Wall Mounting Bracket
4.2 Mounting The Boiler
4.3 Assembly Practice
4.4 Installing Flue And Air Pipes
4.5 Condensate Drainage
4.6 Water System
4.7 Gas Supply
4.8 Electrical Supply
4.9 Exchanging A Boiler
5 COMMISSIONING OF THE BOILER
5.1 Initial Flushing
5.2 Gas Supply
5.3 Electrical Installation
5.4 LP Gas
5.5 Initial Firing
5.6 Hot Flushing
WD388/0/2004 The Keston C36 Combi & C36P Combi Boilers
Page : i

5.7 Combustion Testing
5.8 Checking The Gas Pressure
5.9 Timing The Gas Meter
5.10 Handing Over To The User
6 FAULT FINDING
6.1 Electrical Control Sequence
6.2 Normal Operation
6.3 Fault Modes
6.4 Functional Flow Wiring Diagram
6.5 Electrical Wiring Diagram
6.6 Illustrated Wiring Diagram
6.7 Exploded Assembly Diagrams
7 SERVICING
7.1 Pre Service Checks
7.2 Recommended Routine Service
8 REPLACEMENT OF PARTS
8.0 General
8.1 Precautions
8.2 Access
8.3 Replacement Procedure
8.4 Electrical Components
8.5 Spark Ignition/Flame Detection Electrode
8.6 Burner
8.7 Heat Exchanger
8.8 Condensate Trap
8.9 Pump
8.10 DHW Heat Exchanger
8.11 Expansion Vessel
9 SPARE PARTS LISTINGS
10 GAS BOILER COMMISSIONING CHECKLIST
WD388/0/2004 The Keston C36 Combi & C36P Combi Boilers
Page : ii

0. HANDLING INSTRUCTIONS
0.1 LIST OF CONTENTS
The Keston C36 Combi and C36P Combi are supplied almost totally pre-assembled. The units
use standard 50 mm muPVC (BS5255 and/or BSEN1566-1 and BSEN1329) pipe for the flue
and air intake systems. The boiler is packed in a single box without additional flue kit. All
additional components are packed inside the boiler cabinet itself. The following is a list of
components and their location in the boiler cabinet
Equipment List
Item Quantity Location
Wall Bracket Rawl Plugs 6 Inside accessories bag
Wall Bracket Wall Fixing Screws 6 Inside accessories bag
Wall Mounting Bracket 1 Secured to inside right
hand side of boiler case
Pre-Installation Jig Locator Cross 1 Secured to outside right
hand side of boiler case
Wall Mounting Bracket Nuts 1 Inside accessories bag.
Wall Mounting Bracket Washers 1+1 Inside accessories bag
50 mm muPVC Air/Flue Terminals 2 Inside accessories bag
Air Inlet Spigot (50 mm) 1 Inside accessories bag
Flue Outlet Spigot (50 mm) 1 Inside accessories bag
Air Inlet Spigot Gasket 1 Inside accessories bag
Air Inlet Spigot + Flue Outlet Spigot M6 Screws 4+2 Inside accessories bag
Cabinet Cable Entry Clamps 2 Inside accessories bag
Gas Isolating Cock with PTN 1 Inside accessories bag
Filling Loop Kit 1 Inside accessories bag
Outside Temperature Sensor 1 Inside accessories bag
Document List
Item Quantity Location
Boiler Warranty Registration Form 1 In document bag
Installation Template 1 In document bag
Remove the cabinet shell by removing the two retaining screws in the top of the cabinet and
the two retaining screws in the bottom of the cabinet.
0.2 RECOMMENDED HANDLING PROCEDURE
NB : The following lift operation exceeds the recommended weight for a one-man lift as
specified in the Manual Handling Operations 1992 Regulations.
For the carriage of carton it is recommended at least two people perform any lift. Clear the
carriage route of the carton from point of delivery to point of installation. Take care to avoid trip
hazards, slippery or wet surfaces and when climbing steps and stairs. Always use assistance
if required. If a sack truck is used it is recommended the carton is strapped to the truck.
For the unpacking of the appliance from the carton, it is recommended at least two people
perform any lift. It is recommended to cut the base end of carton and open the carton flaps.
Ensure the protective packing over the boiler tappings at the base of the boiler is kept in place,
then tilt the boiler forwards from its back onto its base and remove carton by sliding up over
the boiler. When lifting this appliance the back should be kept straight at all times. Avoid
twisting at the waist - reposition the feet instead. Avoid upper body bending when holding the
appliance and keep the boiler as close to the body as possible.
Before hanging the appliance on the wall it is best to store the appliance laid on its back with
the casing on. When ready to hang the boiler on the wall remove the casing and place to one
WD388/0/2004 The Keston C36 Combi & C36P Combi Boilers
Page : iii

side. At this stage it is assumed that the wall bracket is correctly positioned and secured on
the wall face.
a) Have the wall bracket nut and washer to hand so that they can be accessed whilst holding
the boiler in position on its mounting bracket. If the optional pre-installation jig is not being
used discard the Pre-Installation Jig Locator Cross.
b) The boiler has a dry weight of 45 kg (99 lbs) and will therefore require at least two people
to lift without the use of lifting aids - ensure co-ordinated movements during lift. Always
use assistance if required.
c) Lift the boiler by gripping at the four corners of the boiler back plate. When lifting this
appliance the back should be kept straight at all times. Avoid twisting at the waist -
reposition the feet instead. Avoid upper body bending when holding the appliance and
keep the boiler as close to the body as possible.
d) Lift the boiler and locate onto the stud and the two pegs of the wall mounting bracket.
e) Place the wall mounting bracket washers over the bracket stud protruding through the
back plate of the boiler.
f) Secure the boiler onto the wall bracket by fixing the wall mounting bracket nut onto the
wall bracket stud. This must be tightened well.
Safety footwear and gloves are recommended PPE when lifting this appliance - to protect
against sharp edges and ensure good grip.
The C36 Combi and C36P Combi boilers can be fitted in compartments with very small
clearances required around the appliance (refer to Section 3.1). Due consideration should
therefore be given to access within the compartment for lifting and positioning.
A pre-installation jig plate (part no C.10C.0.11.00.0) with heating flow, heating return and cold
supply isolation is available as an optional accessory. This jig enables the installation of the
pipework to be carried out and pressure tested before hanging the boiler. Further instructions
for this procedure are included with the jig plate kit.
WD388/0/2004 The Keston C36 Combi & C36P Combi Boilers
Page : iv

1. USER INSTRUCTIONS
1.1 INTRODUCTION
Thank you for choosing this Keston C36 Combi for your household heating and hot water
needs. The boiler is designed to be very straightforward to operate and has no user
serviceable parts inside the cabinet. The following instructions are to provide you with
information on the operation and maintenance of your C36 Combi and what to do in the
unlikely event of a fault.
These user instructions should be read carefully to ensure safe and economical use of your
C36 Combi. The C36 Combi model is for use with natural gas only, the C36P Combi model is
for use with LPG only.
1.2 MAINTENANCE
Servicing
To ensure continual safe and efficient operation and to maintain product warranties it is a
requirement that the appliance is checked and serviced at least once per year. It is the law
that any servicing must be carried out by a competent person. Removal of the appliance
cabinet by anyone other than a competent person will automatically invalidate the
appliance warranty.
Clearances
If fixtures are to be positioned close to the boiler, the following minimum clearances must be
observed: Top 150mm, Left 5mm, Right 5mm, Base 100mm, Front 305mm. Extended
clearance is required to the front for servicing.
Cleaning
Normal case cleaning only requires dusting with a dry cloth. To remove more stubborn marks
wipe with a damp cloth and finish with a dry cloth.
1.3 BOILER SETUP & OPERATION
Check that the gas supply from the gas meter is turned on. Switch on the electrical supply to
the boiler. The display will now run through a self check procedure. Set any controls to call for
heat.
To light the boiler
The C36 Combi features separate adjustment of central heating and domestic hot water
temperature. To set these press the “+” or “-” buttons associated with the heating or hot water
temperature and set the required temperature. After a few seconds the display stop flashing
and will change back to show the actual boiler temperature.
If the actual temperature is less than the desired temperature the boiler will fire and, after a
few seconds, a “.” will appear in the lower right hand corner of the display to show that the
boiler is alight.
In summer you can
switch the boiler to hot
water only by pressing
the “Summer” button to
that the green lamp
above it is illuminated. In
this mode the boiler will
not respond to any
demand for central
heating. Press the
“Summer” button again
to extinguish the green
light above and resume
normal central heating
operation.
WD388/0/2004 Chapter 1 : User Instructions The Keston C36 Combi & C36P Combi Boilers
Boilers
Installation & Servicing Instructions Page : 1

Normal Operation
During normal operation the digital display will dhow the current boiler temperature and will
show a “.” In the lower right corner of the display when the burner is alight. If the green lamp
near the CH or DHW+ - keys is illuminated the boiler is receiving a demand for that function.
If the green lamp is flashing the boiler is either up to temperature or shutting down following
removal of the CH or DHW demand.
Fault Modes
In the event that the boiler detects a situation which it considers to be a fault the display will
change to show a flashing fault code starting with an “E” and then a two digit number. The
table below explains these codes and the action you should take.
Water pressure too high - You have put too much water pressure in your systemE40
Water pressure error - You must top up the water pressure for your systemE37
Mains supply frequency incorrect - There may be a problem with your power supply.E35
Mains supply voltage < 180V - There may be a problem with your power supplyE34
Flame drop out - Check for obstruction of the flue and/or air terminals,
blockage/freezing of the drain pipe or a low gas supply (LPG).
E26
Water pressure losses - You have topped up the water pressure more than 4 times in
24 hours. You may have a leak on the system..
E24
Boiler overheat - Check that any valves to the heating circuit have not been shut down,
that there is no air in the system and that the water pressure is correct..
E03
False flame - There is possibly a problem with the power supply.E02
Ignition failure - the boiler has attempted to light five times and not succeeded - check
the gas supply is on.
E01
Description of faultDisplay
The above is an abbreviate list of possible error codes. If the code is not in the list above
consult a GAS SAFE REGISTER registered engineer. A full list of codes can be found in
Chapter 6 of this manual. If a code appears and you feel the original cause has been rectified,
press the “Reset” button to resume boiler operation. If the code persists consult a GAS SAFE
REGISTER registered engineer.
When topping up the water pressure you can observe the actual pressure by pressing the
“Installer” button repeatedly until the number “5” appears. After a few seconds the display with
then change to show the system water pressure in bar. Set the water pressure to between 1.0
and 2.0 bar.
Precautions
Care must be taken at all times to ensure that no blockage or obstruction is present in the
condensate drainage line. In addition, the air intake and flue exhaust terminals must be free
from obstruction at all times.
Frost Protection
The C36 Combi has an integral frost protection function. However, care should also be taken
that any exposed pipework is adequately insulated to prevent freezing.
1.4 SAFETY INFORMATION
IF YOU SUSPECT A GAS LEAK TURN OFF THE APPLIANCE IMMEDIATELY, TURN OFF
THE GAS TAP TO THE APPLIANCE (LOCATED UNDERNEATH) AND CONTACT YOUR
LOCAL GAS REGION WITHOUT DELAY.
Benchmark Initiative
As part of the industry wide “Benchmark” initiative C36 Combi
boiler manual includes Gas Boiler Commissioning
Checklist (Chapter 10). This form should be completed by
WD388/0/2004 Chapter 1 : User Instructions The Keston C36 Combi & C36P Combi Boilers
Boilers
Installation & Servicing Instructions Page : 2

your installer at the end of the installation and commissioning process. The details of the
Checklist will be required in the event of any warranty work being required. There is also
Service Interval Record (Chapter 10) to be completed after each annual service visit.
These forms (Chapter 10) should be kept in a safe place for the life of the boiler.
The boiler should be installed and serviced only by GAS SAFE REGISTER registered
operatives. All GAS SAFE REGISTER registered Installers carry a GAS SAFE REGISTER ID
card and have a registration number. Both should be recorded in your boiler manual
(Chapter 10: GAS BOILER COMMISSIONING CHECKLIST). You can check your installer by
calling GAS SAFE REGISTER direct on 0800 408 5500.
WD388/0/2004 Chapter 1 : User Instructions The Keston C36 Combi & C36P Combi Boilers
Boilers
Installation & Servicing Instructions Page : 3
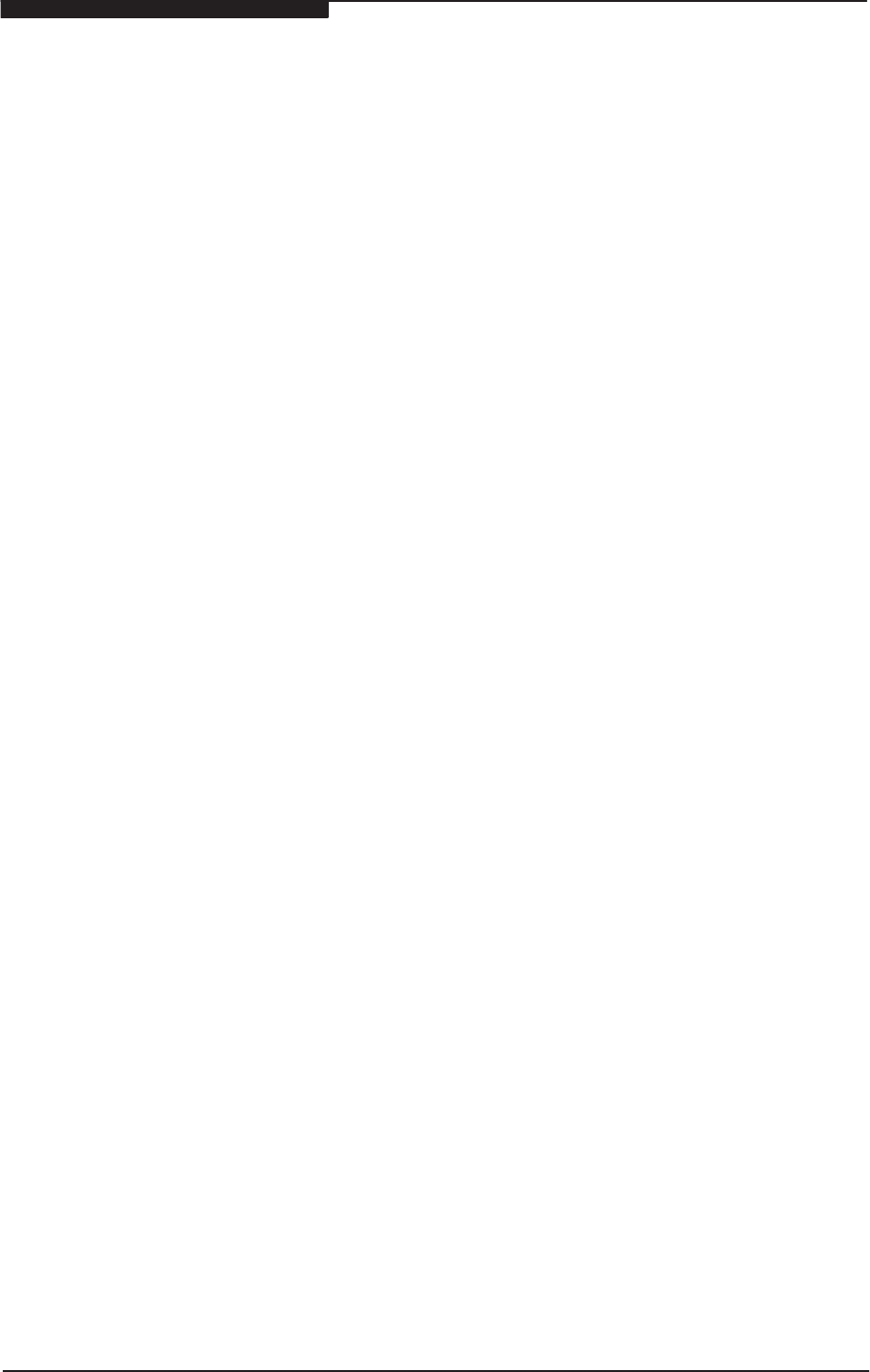
2. GENERAL INSTRUCTION
2.1 DESCRIPTION
The KESTON C36 Combi and C36P Combi combination boilers utilise the latest in
condensing technology to produce a high efficiency boilers that deliver an exceptional hot
water flow rate with SEDBUK A rated efficiency.
The C36 Combi and C36P Combi are unique in concept and design. They comprise a
high efficiency stainless steel heat exchanger coupled with a low emissions burner to
deliver ultra high efficiency condensing mode operation and a plate-to-plate heat
exchanger for domestic hot water production all within a compact wall hung cabinet. The
unit automatically adjusts gas and air rate according to demand to give a heating output in
the range of 7.4kW to 28.0kW [condensing]. The integral pump assembly is automatically
speed controlled to best match water flow rate to heat output & further increase appliance
efficiency. The efficient plate-to-plate heat exchanger provides superior levels of
performance: its has an outstanding hot water performance of 14.5 L/min (at 35C
temperature rise) and 17.0 L/min (at 30C temperature rise - EN625)
In addition, the boilers feature a connection for an optional outside sensor to enable the
boilers inbuilt weather compensation option which delivers enhanced user comfort levels
with peak operating efficiency due to the lower flow temperatures involved. The boiler also
features an “Opentherm” connection point for the Keston Room Control module which
provides further advanced user control for room temperature compensation and optimum
start. The boiler fascia provides separate user controls for central heating and domestic
hot water temperatures. The advanced hot water flow monitoring ensures exceptionally
stable hot water temperatures are provided. The boilers have the added advantage of very
high efficiency, and small diameter muPVC plastic flue which can be extended up to 20
metres horizontally or vertically.
The Keston C36 Combi uses a variable speed combustion blower to deliver a premix of
gas and air to a downward firing burner in a high efficiency, single pass heat exchanger.
The flue system is room sealed and fan powered. The ignition is direct spark and fully
automatic. The boiler housing is not waterproof and should be installed in a position
where it will always be dry. Combustion air is drawn from the cabinet which is connected
to outside atmosphere via a small diameter plastic intake pipe. The cabinet therefore
remains under negative pressure at all times the boiler is operating.
These boilers are designed for use as part of a sealed water central heating system with
fully pumped circulation. The pump, an 8l expansion vessel and associated safety devices
are all fitted within the boiler.
The boiler heat exchanger is made from highly corrosion resistant stainless steel in
corrugated pipe form which provides massive surface area within a compact dimension.
The hot combustion gases from the down firing burner pass around the stainless steel
pipes imparting heat into the system water. The integral variable speed pump within the
appliance cabinet ensures the heat exchanger receives correct water flow when firing.
The C36 Combi is not a high water content boiler and does not contain the metal mass, or
water volume, of a cast iron or steel boiler. This boiler is of low mass and low water
content and therefore responds faster when there is a call for heat. The C36 Combi
features full user diagnostics, integral frost protection function, automatic pump and fan
exercise in periods of inactivity, anti cycle control and dry fire protection.
2.2 BOILER SCHEMATIC
Air is drawn into the boiler through a 50 mm muPVC (BS5255 and/or BSEN1566-1 and
BSEN1329) plastic pipe or, alternatively, via a 75mm Keston composite plastic pipe. Gas
is mixed with combustion air at the inlet to the fan. The gas flow is automatically regulated
by the gas valve according to the air flow generated by the fan. The gas and air are
thoroughly mixed in the blower and fed into the burner located at the top end of the heat
exchanger module. The gas and air mixture is ignited by a direct spark ignition control
WD388/0/2004 Chapter 2 : General Instruction The Keston C36 Combi & C36P Combi Boilers
Installation & Servicing Instructions Page : 4
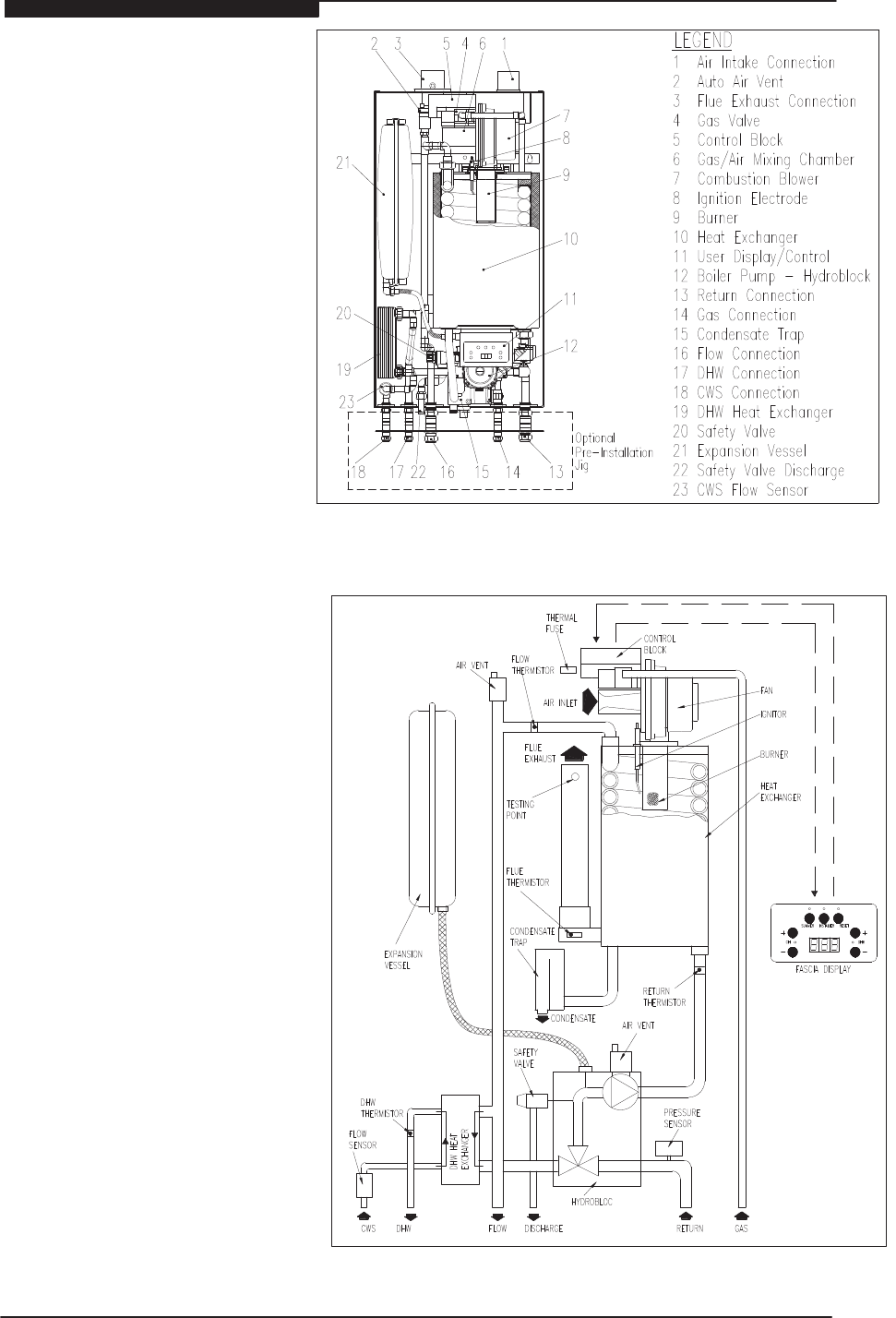
system and burns with
a blue flame just off the
surface of the burner.
As the hot products of
combustion pass
downwards, they are
cooled by exchanging
heat with the circulating
water which enters the
heat exchanger at the
bottom of the heat
exchanger. The
optimum heat input is
detected by monitoring
flow and return
temperatures and is
adjusted by controlling
the speed of the fan.
The optimum pump
speed is also detected
and automatically
selected by the boiler.
When the return water temperature is below 55
o
C, part of the water vapour in the
combustion products will condense inside the heat exchanger, thus increasing the boiler
efficiency further by
releasing the latent heat
of condensation. This
condensate falls to the
bottom of the heat
exchanger where it is
separated from the flue
gases and exits from the
boiler through the
condensate drain. Any
condensate formed in the
flue runs back down the
flueway and is drained at
the base of the flue
connection to the heat
exchanger or drain points
within the flue.
The condensate is very
slightly acidic (about the
same acidity as vinegar)
and should be piped in a
plastic pipe. It is not
harmful to the waste
disposal system and may
be disposed of as normal
waste water.
The flue gases are piped
in a 50 mm muPVC
(BS5255 and/or
BSEN1566-1 and
BSEN1329) plastic or,
alternatively, 75mm
Keston composite plastic pipe to outside. The temperature of the flue gases are usually
WD388/0/2004 Chapter 2 : General Instruction The Keston C36 Combi & C36P Combi Boilers
Installation & Servicing Instructions Page : 5
Boiler
Schematic

around 5
o
C to 10
o
C above the temperature of the return water. The flue pipe should be
terminated outside the building from where they cannot re-enter the building or any other
adjacent building.
The heating level may be controlled by room thermostats, programmer time clocks and
compatible energy management systems. An optional Keston room controller can be
connected which will provide enhanced controls such as room compensation to further
increase efficiency and comfort levels. Once the controls are set the boiler operates
automatically. Further, a Keston outside sensor can be connected to the boiler which will
automatically invoke weather compensated heating which further boosts user comfort and
boiler efficiency.
In the event of the boiler overheating the safety devices will cause a safety shutdown. A
safety discharge valve and discharge pipe is fitted to the boiler.
The C36 Combi features an integral frost protection function which will operate the pump,
regardless of the external controls, should the boiler temperature fall below 10
o
C. In the
event the boiler temperature falls below 5
o
C the boiler will also fire. This is to avoid
damage to the boiler through freezing of boiler water. The boiler will turn off when the flow
temperature exceeds 15
o
C.
The C36 Combi features an integral pump exercise function which will run the pump,
without firing the boiler, for 10 seconds in the event the boiler is on standby for in excess
of 24 hours without firing. This is to help prevent seizing of the pump due to long periods
of inactivity.
2.3 RELATED DOCUMENTS
The Keston C36 Combi and C36P Combi Combination Condensing Boiler must be
installed in accordance with the current issue of the Gas Safety (Installation and Use)
Regulations 1996, current IEE Wiring Regulations, Building Regulations, Building
Standards (Scotland) Consolidation, and the Bye Laws of the local Water Undertaking. It
is the law that ALL gas appliances are installed by a competent person in accordance with
the above regulations.
In addition, due account must be taken to the following Codes Of Practice:
BS 6891 : Low Pressure Installation Pipes
BS 6798 : Installation of Gas Fired Hot Water Boilers of
Rated Input Not Exceeding 70kW
BS 5449 : Installation Pumped Central Heating
BS 5546 : Installation of Gas Hot Water Supplies for
Domestic Purposes (2nd family gases)
BS 5440.1 : Flues (for gas appliances of rated input not
exceeding 70kW)
BS 5440.2 : Air Supply (for gas appliances of rated input not
exceeding 70kW)
BS 5482.1 : Domestic Propane and Butane Burning
Installations
BS 7074.1 : Expansion Vessels
BS 7593 : Treatment of Water in Hot Water Central Heating
Systems
BS 7671 : Requirements for Electrical Installations. IEE
Wiring Regulations 16th Edition.
BSEN 12828:2003 : Heating Systems in Buildings: Design for water
based heating systems
BSEN 12831:2003 : Heating Systems in Buildings: Method for
calculation of design heat load
BSEN 14336:2004 : Heating Systems in Buildings: Installation and
commissioning of water based heating systems
WD388/0/2004 Chapter 2 : General Instruction The Keston C36 Combi & C36P Combi Boilers
Installation & Servicing Instructions Page : 6

For Timber Framed Buildings, British Gas Publications DM2. Also British Gas
Publications 'Guidance Notes For The Installation Of Domestic Gas Condensing
Boilers' and 'Specification For Domestic Wet Central Heating Systems'.
In IE, the installation must be carried out by a competent person and installed in
accordance with the current edition of IS813 “Domestic Gas Installations”, the current
Building Regulation and reference should be made to the current ETC1 rules for electrical
installations.
No alterations should be made to the boiler without written permission from KESTON
Heating. Any unauthorised modification will invalidate the warranty and may affect the
safe and efficient operation of the boiler.
2.4 PHYSICAL DATA - C36 COMBI & C36P COMBI
Cabinet Height mm 840
Cabinet Width mm 450
Cabinet Depth mm 300
Top Clearance mm 150
Side Clearance mm 5
Base Clearance mm 100
Front Clearance (for servicing) mm 300
Weight - Full kg / (lbs) 50/(110)
Weight - Empty kg / (lbs) 45/(99)
Flow and Return Connection (using pre-installation jig) 22mm Compression
DHW and CWS Connection (using pre-installation jig) 15mm Compression
Gas Connection 15mm Compression
Condensate Connection overflow 22mm plastic
Safety Valve Connection discharge 15mm copper
IP Rating IP20 (IPX0)
Flue and Air Intake Material 50mm muPVC (BS5255 and/or BSEN1566-1 and BSEN1329)
Flue Pipe Size (nominal bore) mm / (in) 50 / (2)
Air Intake Pipe Size (nominal bore) mm / (in) 50 / (2)
Max. Air Intake Length m 39
Max. Flue Outlet Length m 20*
Max. Total Flue Outlet and Air Intake Length m 40
* Flue lengths between 16 and 20m will create a 1% reduction in DHW output.
Flue and Air Intake Material 75mm Keston Composite
Flue Pipe Size (nominal bore) mm / (in) 75 / (3)
Air Intake Pipe Size (nominal bore) mm / (in) 75 / (3)
Max. Air Intake Length m 117
Max. Flue Outlet Length m 60**
Max. Total Flue Outlet and Air Intake Length m 120
** Flue lengths between 48 and 60m will create a 1% reduction in DHW output
2.5 OPTIONAL ACCESSORIES
A range of accessories are available from KESTON Heating to compliment an
installation. Terminal wall sealing collars are available to make good the external all face
whilst working from the inside of the building using 50mm muPVC (BS5255 and/or
BSEN1566-1 and BSEN1329) pipe. Stand-off frames are available to leave a 50mm gap
behind the boiler to allow routing of pipes behind the boiler.
WD388/0/2004 Chapter 2 : General Instruction The Keston C36 Combi & C36P Combi Boilers
Installation & Servicing Instructions Page : 7

Description Part Number
Pre-Installation Jig Plate C.10C.0.11.00.0
Flue Terminal Wall Sealing Collar (50mm) C.08.0.00.07.0
Air Terminal Wall Sealing Collar (50mm) C.08.0.00.07.0
50/75mm Flue Adapter C.17.2.00.60.0
Flue Outlet Terminal (75mm) C.17.2.26.00.0
Air Inlet Terminal (75mm) C.17.2.26.00.0
Stand Off Back Plate C.10C.0.01.00.0
Keston Chronotherm Room Controller C.17.4.21.00.0
2.6 PERFORMANCE DATA - C36 COMBI & C36P COMBI
WD388/0/2004 Chapter 2 : General Instruction The Keston C36 Combi & C36P Combi Boilers
Installation & Servicing Instructions Page : 8
C36 COMBI C36P COMBI
Nat. Gas (G20) LPG (G31)
Min. Input (Gross CV) kW/(Btu/h) 8.3/(28,300) 8.1/(27,600)
Max. CH Input (Gross CV) kW/(Btu/h) 28.3/(96,500) 27.7/(94,500)
Max. DHW Input (Gross CV) kW (Btu/h) 40.0/(136,500) 39.0/(133,000)
Max. DHW Output to Water kW/(Btu/h) 36.0/((122,800) 36.0/(122,800)
Max. CH Output To Water
(80/60
o
C Flow/Return) kW/(Btu/h) 25.2/(86,000) 25.2/(86,000)
(50/30
o
C Flow/Return) kW/(Btu/h) 28.0/(95,500) 27.7/(94,500)
Min. CH Output To Water
(80/60
o
C Flow/Return) kW/(Btu/h) 7.4/(25,250) 7.4(25,250)
(50/30
o
C Flow/Return) kW/(Btu/h) 8.2/(28,000) 8.1/(27,600)
Max. Domestic Hot Water Flow Rate litre/min 14.5 14.5
(at 35
O
C Rise)
Specific DHW Rate (30
O
C Rise) litre/min 17.0 17.0
Min. Domestic Hot Water Flow Rate litre/min 0.35 0.35
Max. Domestic Hot Water Flow Temp.
O
C 65 65
Max. Burner Press.-Hot
(Factory Preset)
mbar/(in w.g) 0/(0) 0/(0)
Max. Gas Cons. After 10 mins (DHW) l/s / (Ft
3
/hr) 1.03/(131) 0.48/(61)
Max. Operating Flow Temp.
o
C 82 82
Max. Press. (Sealed System) bar 2 2
Inlet Gas Pressure mbar/(in w.g) 20.0 / (8.0) 37.0/(14.8)
Recommended Temp Diff.
o
C 8 to 20 8 to 20
Electrical Supply 230V 50Hz 230V 50Hz
Power Consumption (Max) W 180 180
Power Consumption (Standby) W 6 6
Type of Gas G20 Natural Gas G31 LPG
Optimum Flue Gas CO
2
Level (at max CH rate, case on) 9.3±0.2 10.6±0.2
Expected CO/CO2 Ratio (at max CH rate, case on) 0.0006 0.001
Destination Countries GB/IE GB/IE
SEDBUK Efficiency 90.7 92.8
NOx Class 5 5
Safety Valve bar / (lbf/sq in) 3 / (43.5) 3 / (43.5)
Expansion Vessel Capacity litre 8 8
[NB: For larger systems an additional expansion vessel may be required]
Expansion Vessel Charge Pressure bar / (lbf/sq in) 1.0 / (14.5)
Heating System Minimum Pressure bar / (lbf/sq in) 0.6 / ( 8.7)
DHW Max. Working Pressure bar / (lbf/sq in) 8/ (116)
Min. Working Pressure for Max. Domestic Flow Rate bar / (lbf/sq in) 2
Maximum CWS Inlet Temperature
o
C 50 50

Seasonal Efficiency (SEDBUK) =90.7 (C36 Combi) & 92.8 (C36P Combi)
This value is used in the UK Government's Standard Assessment Procedure (SAP) for
energy rating of dwellings. The test data from which it has been calculated have been
certified by Advantica Technologies Ltd
KESTON Heating declare that there are no substances harmful to health within the
appliance or used during the production of the appliance.
The C36 Combi is intended for domestic and commercial EMC environments and on a
governed G20 meter supply.
The C36P Combi is intended for domestic and commercial EMC environments and on a
governed G31 supply.
This boiler meets the requirements of SI 3083 The Boiler (Efficiency) Regulations and is therefore
deemed to meet the requirements of Directive 92/42/EEC. The CE mark on the appliance shows
compliance with Directives 90/396/EEC, 73/23/EEC and 89/336/EEC.
IMPORTANT
This product contains ceramic fibre boards, which although not regarded as a risk, contain
ceramic fibre which may cause temporary irritation to eyes, skin and respiratory tract. The
fibres are held in place by inorganic binders. Therefore as long as the boards are not
disturbed they will not be released. Since the boards are non-serviceable parts there
should be no risk. Under no circumstances should the user interfere with any sealed parts.
To ensure that the release of fibres from these RCF articles is kept to a minimum, during
installation and servicing we recommend that you use a HEPA filtered vacuum to remove
any dust accumulated in and around the appliance before and after working on the appli-
ance. When replacing these articles we recommend that the replaced items are not broken
up, but are sealed within heavy duty polythene bags, and clearly labelled as RCF waste.
RCF waste is classed as a stable, non-reactive hazardous waste and may be disposed at a
landfill licensed to accept such waste. Protective clothing is not required when handling
these articles, but we recommend you follow the normal hygiene rules of not smoking,
eating or drinking in the work area and always wash your hands before eating or drinking.
This appliance is not intended for use by persons (including children) with reduced
physical, sensory or mental capabilities, or lack of experience and knowledge, unless they
have been given supervision or instruction concerning use of the appliance by a person
responsible for their safety.
Children should be supervised to ensure that they do not play with the appliance.
Benchmark Initiative
As part of the industry wide “Benchmark” initiative C36 Combi
boiler manual includes Gas Boiler Commissioning Checklist
(Chapter 10). This form should be completed by your installer at
the end of the installation and commissioning process. The details
of the Checklist will be required in the event of any warranty work being required. There is also
Service Interval Record (Chapter 10) to be completed after each annual service visit.
These forms (Chapter 10) should be kept in a safe place for the life of the boiler.
The boiler should be installed and serviced only by GAS SAFE REGISTER registered operatives.
All GAS SAFE REGISTER registered Installers carry a GAS SAFE REGISTER ID card and have a
registration number. Both should be recorded in your boiler manual (Chapter 10: GAS
BOILER COMMISSIONING CHECKLIST). You can check your installer by calling GAS SAFE
REGISTER direct on 0800 408 5500.
WD388/0/2004 Chapter 2 : General Instruction The Keston C36 Combi & C36P Combi Boilers
Installation & Servicing Instructions Page : 9
IN THE EVENT OF A GAS LEAK
Turn off the gas isolation valve to the property immediately. Extinguish
all naked flames or other sources of ignition. Do not operate electrical
switches on or off. Open all doors and windows to ventilate the area.

3. BOILER LOCATION
3.1 DIMENSIONS AND MINIMUM
CLEARANCES
The boiler must be installed in minimum
clearances shown to allow subsequent
servicing, and safe operation. However, larger
clearances may be required during installation.
3.2 SERVICE CONNECTIONS
Without Optional Pre-Installation Jig:
Gas, water, air and flue pipe, condensation,
and electrical connections are as shown. Gas :
15mm compression. Flow/Return 0.75BSPM
compression. DHW/CWS 0.5BSPM
compression.
With Optional Pre-Installation Jig:
Gas, water, air and flue pipe, condensation,
and electrical connections are as shown. Gas :
15mm compression. Flow/Return 22mm
compression. DHW/CWS 15mm
compression.
An optional stand-off frame is also available
which mounts behind the boiler to leave a
50mm deep space behind the boiler. This is
to permit pipe routing behind the boiler if
required. See Section 2.5 - Optional
Accessories.
3.3 POSITION
The C36 Combi and C36P Combi are not
suitable for external installation. The boiler
may be installed in any room or internal
space, although particular attention is drawn
to the requirements of the current IEE Wiring
Regulations and, in Scotland, the electrical
provisions of the Building Regulations
WD388/0/2004 Chapter 3 - Boiler Location The Keston C36 Combi & C36P Combi Boilers
Installation & Servicing Instructions Page : 10
$OOGLPHQVLRQVLQPP
:KHQVHUYLFLQJDSSOLDQFH
)LJXUH
0LQLPXP&OHDUDQFHV
:KHQDSSOLDQFHLVRSHUDWLQJ
$OOGLPHQVLRQVLQPP
300
Figure 3.1.2
Dimensions
)OXH
$LU,QWDNH

applicable in Scotland, with respect to the installation of the boiler in a room or internal
space containing a bath or shower.
Where a room-sealed appliance is installed in a room containing a bath or shower, any
electrical switch or appliance control, utilising mains electricity, should be so situated that
it cannot be touched by a person using the bath or shower. The C36 Combi and C36P
Combi are classified as IP20 (IPX0) and are therefore suitable for installation in Zone 3
areas, unless subject to hose down.
Compartment installation is permitted - such compartments must be constructed in
accordance with BS 6798.
The wall on which the boiler is mounted must be of suitable load bearing capacity and
must be non-combustible.
The Keston C36 Combi can be located virtually anywhere desired provided that all
regulations are complied with. Because of the boiler's compact size and venting flexibility,
the installation is not limited to a boiler room setting. Before locating the boiler near a living
space consider whether the sounds generated by the boiler will be objectionable. The
boiler may be located within a cupboard enclosure to reduce noise levels if located within
a living space. LPG boilers must not be installed in a cellar.
3.4 ELECTRICAL
3.4.1 Electrical Connections
The boiler must be connected to a permanent 230V ~ 50Hz supply, fused at 3A.
The boiler has provision to receive a 230VAC switched live signal from a
room thermostat/time clock. Alternatively, a Keston Room Controller can be
connected directly, via two core low voltage cable, to the terminals marked
“OT”. The Keston Room Controller will then provide fully room
compensated control to ensure the boiler output is matched to the rooms
requirements at optimum boiler efficiency. DHW demand will always take
priority over heating demand. Wiring external to the boiler must be in
accordance with current I.E.E wiring regulations and local regulations.
WD388/0/2004 Chapter 3 - Boiler Location The Keston C36 & C36P Combi Boilers
Installation & Servicing Instructions Page : 11
&KLPQH\VQRWXVHGIRU
YHQWLQJDQ\RWKHU
DSSOLDQFHPD\EHXVHG
)LJXUH
6HFXUHDLUIOXHSLSHVDW
FKLPQH\RXWOHW
[NB: Refer to
Section 3.8.3]

The method of connection to the mains electricity supply must facilitate complete
electrical isolation of the boiler, preferably by the use of a fused, unswitched three
pin plug and a shuttered socket-outlet, both complying with the requirements of
BS 1363. There must be only one common method of isolation for the boiler and
its control system.
The appliance must be connected to the 3A supply via a fused double-pole switch
having at least 3 mm (1/8 inch) contact separation in both poles, serving only the
boiler and the system controls.
The connection point to the mains supply should be readily accessible and
adjacent to the boiler, except for rooms containing a bath or a shower. Refer to
section 3.3 Position.
3.4.2 External Wiring & Controls
1. The boiler is designed so that all control wiring is external to the boiler.
2. Heating control signal inputs must the 230VAC "switched live" type unless
using a Keston Room Controller (see below)
3.4.2.1 Enhanced Control Options
Room Compensation (Opentherm)
A Keston Room Controller may be used to provide room compensated
control to ensure the boiler output is matched to the rooms requirements
at optimum boiler efficiency
Weather Compensation
A Keston outside temperature sensor may be connected as an option.
The boiler will automatically detect this connection and will operate on a
"weather compensation" basis when receiving a heating demand signal
from the SL terminal or from a Keston Room Controller. Screened cable
(80% density) must be used to connect the outside temperature sensor.
3.5 BOILER SIZE SELECTION
The C36 Combi will automatically adjust heat output and pump speed to match the
system requirements at any given time. Efficiency and combustion levels are maintained
at optimum levels throughout the possible output range. The C36 Combi is therefore
suitable for all systems with a total heat load within the maximum range of the boiler.
3.6 GAS SUPPLY
A gas meter should be connected to the service pipe by the local gas region or their
contractor. An existing meter should be checked preferably by the gas region to ensure
that the meter is adequate to deal with the rate of gas supply required. Installation pipes
should be fitted in accordance with BS 6891.
Minimum/Maximum Gas Pressure:
Natural gas pressure before the gas valve must be maintained at between 18 mbar (7.2 in
WG) and 22 mbar (8.8 in) while the boiler is running.
LPG pressure must be maintained between 31.5 mbar (12.4 in w.g) and 37.6 mbar (14.8
in w.g) while the boiler is running.
WD388/0/2004 Chapter 3 - Boiler Location The Keston C36 Combi & C36P Combi Boilers
Installation & Servicing Instructions Page : 12
Live
Neutral
Earth
Mains Supply
230V
Fused @ 3A
Room Thermostat
T6360B1028
1
2
3
KESTON
C36 Combi
L
N
E
SL
3.4.2 Wiring Example
OTC
OTC
To Keston
Ext. Sensor
[Optional]
OT
OT
To Keston
Room Controller
[Optional - instead of room thermostat]

Gas pressures above or below these levels will lead to problems associated with the gas
valve's internal pressure regulator.
Supply pipes to the boiler must not be sized less than the boiler inlet connection
(15 mm). Due consideration must be given to the supply pressure to other gas
appliances in the premises. Reduction in dynamic gas supply pressure will result in
intermittent ignition failures. Ensure gas supply pipe work is adequately sized for
the length of run from the meter to the boiler at a supply rate of 40kW (i.e. a natural
gas supply should be considered to be a minimum of 22mm diameter, reducing to 15mm
at the boiler. If gas runs greater than 12m, including the allowance for bends, are involved
the pipe size should be increased further).
3.7 CH & DHW WATER SYSTEMS
All piping must be installed in accordance with all applicable local and Water Supply
Bylaws for forced hot water heating systems.
Consideration must be given to pipe capabilities and pressure drop through the piping
when selecting pipe sizes. The primary pipe connections to the boiler must be sized
according to the system load, not dictated by the boiler connection sizes.
Water treatment must be carried out to BS 7593 : Treatment of Water in Hot Water
Central Heating Systems.
In IE the requirements given in the current edition of IS813 and the current Building
Regulations must be followed.
a The Keston C36 Combi is designed for installation on sealed water systems only.
With fully pumped water circulation. The pump, an 8l expansion vessel and
associated safety devices are fitted within the boiler.
b Any system must be thoroughly flushed clean of grease, dirt and debris, prior to
connection with the boiler. A trap may be installed in the flow line to collect any
solder, or other debris, from the installation.
c All water systems must be constructed to comply with requirements of the Local
Water Authority.
d Always use a system complying with the requirements of BS 5449 and BS 6798.
e System design must ensure an open circuit is always available to ensure
circulation when the pump overrun function is operating after boiler shutdown.
f Isolation valves must be fitted on the cold mains supply, the heating flow and the
heating return to enable isolation when maintaining the boiler. Such isolation
valves are included in the optional pre-installation jig (C.10C.0.11.00.0)
g Copper tubing to BS 2871 Part 1 or barrier plastic pipe suitable to 110
o
C, such as
Unipipe, is recommended.
h Jointing should be either with capillary, threaded or compression fittings. Pipes
should have a gradient to ensure air is passed easily to vent points and water
flows readily to drain points.
i Draining taps must be located in accessible positions which permit the draining of
the boiler. Draining taps should be at least 22 mm in nominal size and be in
accordance with BS 2879. A drain tap is incorporated into the optional
pre-installation jig (C.10C.0.11.00.0)
AIR VENT POINTS
j These must be fitted at all high points where air will naturally collect and must be
sited to allow complete draining of the system.
Table 3.7 Additional Expansion Vessel Selection
13.6
125 litres
10.9
100 litres
8.2
75 litres
5.4
50 litres
2.7
25 litres
Vessel
Volume
Total Water Content of system in
excess of 125 litres
1.0 bar
Vessel charge & initial system
pressure.
3.0 bar
Safety Valve Setting
WD388/0/2004 Chapter 3 - Boiler Location The Keston C36 & C36P Combi Boilers
Installation & Servicing Instructions Page : 13

k. The boiler is supplied with an integral expansion vessel of 8l capacity. This is
suitable for systems of up to 125 Litres system volume. Table 3.7 Expansion
Vessel Selection provides guidance for the correct additional expansion vessel
size to use for systems with a water content larger than 125 Litres. Any additional
vessel must be fitted on the boiler primary return.
l A filling point must be fitted, in accordance with local water authority
requirements. An approved filling loop is supplied loose with the boiler installation
jig. There must be no permanent connection to the mains water supply. The filling
loop must therefore be left isolated at both ends and disconnected after the
system is filled.
m The installation must be designed to work with flow temperatures of up to 110
o
C.
All components of the system must be suitable for a working pressure of 3 bar
and a temperature of 110
o
C. Care should be taken in making all connections that
the risk of leakage is minimised.
n The pipe from the safety discharge valve must not discharge above an entrance,
window or any type of public access area. The boiler safety discharge valve pipe
must be extended using not less than 15mm pipe to discharge, in a visible
position, outside the building, facing downwards, preferably over a drain. The
pipe must have a continuous fall and be routed to a position so that any discharge
of water, possibly boiling, or steam cannot create any danger to persons, damage
to property or external electrical components or wiring. To ease future servicing it
is advisable to use a compression type fitting to extend the safety discharge valve
pipe.
3.7.1 Boiler By-pass Piping
Boiler water flows are critical to the operation of the boiler. If flow cannot be maintained
through the system piping to meet the minimums required by the boiler, insufficient water
flows through the boiler will cause the boiler to "kettle" or even produce steam which can
damage the heat exchanger and will invalidate the heat exchanger warranty. In addition,
an open circuit is required after boiler shutdown to permit circulation during the boilers 2
minute pump overrun sequence.
It is advisable to incorporate a boiler by-pass in the system, especially if thermostatic
radiator valves are used. The flow/return differential should be 10
o
C to 20
o
C. To comply
with the Building Regulations Part L1 the bypass must of the automatic type.
3.7.2 Air Elimination
In the initial charge of water to the boiler system and in all subsequent additions of water
to the system some air will be dissolved in the water. As the water is heated the air is
WD388/0/2004 Chapter 3 - Boiler Location The Keston C36 Combi & C36P Combi Boilers
Installation & Servicing Instructions Page : 14
COMBI
KESTON
Expansion
Isolating Valve
HEATING CIRCUIT
FLOW
RETURN
(disconnected
after filling)
Flex Hose
Isolating & Dbl Chekc Valve
By-pass
(if required)
Drain
Cock
(if required)
DOMESTIC WATER
DOMESTIC HOT WATER
COLD WATER SUPPLY
Vessel
Figure 3.7 : CH & DHW Sealed Systems Diagram

driven out of the solution and will
collect in high spots in the
system. These air bubbles can
interfere with pumping and
heat transfer and must be
eliminated.
Installation of air bleed valves at
the high spot(s) in the system
will allow for air elimination when
filling the system and will allow
re-venting in a day or so after all
air has been driven out of
solution.
3.7.3 System Pump Selection (if
required)
The C36 Combi features an
integral circulating pump which
has sufficient excess head to
drive most domestic systems.
The available head is shown in
the graph below. If the system
index circuit resistance is in
excess of the available head
from the integral pump an
additional system pump will be
required.
The schematic below
illustrates a
recommended approach
to using an additional
system pump. The
additional system pump
should be sized to
overcome the index
circuit resistance only as
the boilers integral pump
will overcome boiler
resistance.
If an additional pump is
required the selected
pump must comply with
BS 1394. Provision must
be made in the system
design for control of the additional pump.
3.7.4 Filling The System
The boiler is supplied with an approved filling loop device. This filling device is designed to
enable initial fill and topping up of system pressure. The system should be set to a
pressure of between 1.0 and 1.5 bar. To display the system water pressure press the
“Installer” button, on the boiler fascia, repeatedly until the number 5 appears on the
display. After a few seconds the display will change to show the water pressure, in bars.
Using the filling loop set the pressure to 1.0 to 1.5 bar,
WD388/0/2004 Chapter 3 - Boiler Location The Keston C36 & C36P Combi Boilers
Installation & Servicing Instructions Page : 15
Additional System
Pump
(if required)
COLD WATER SUPPLY
DOMESTIC HOT WATER
DOMESTIC WATER
(if required)
COMBI
HEATING CIRCUIT
KESTON
Expansion
Vessel
Drain
Cock
RETURN
FLOW
Permanently
Open 28mm
By-pass
C36 Combi Available pum p head
0
1
2
3
4
5
6
7
0 5 1 0 1 5 20 25 30 35 40
F l o w R a t e ( l p m )

3.8 FLUE SYSTEM
NB: When installing a replacement boiler a new flue system must be used. Do
not re-use the existing boiler flue installation.
3.8.1 Design
Individual air supply and flue outlet pipes are used. The material used for flue outlet &/or
air inlet must be muPVC to BS 5255 and/or BSEN1566-1 and BSEN1329 of an internal
diameter of 51 mm. (i.e. nominal 50 mm diameter muPVC solvent weld waste pipe).
Marley muPVC Solvent Weld Waste System (50mm) and Polypipe System 2000 muPVC
Solvent Weld Waste (50mm) are recommended systems. DO NOT USE ABS PIPE OR
FITTINGS.
Alternatively, where flue or air intake lengths of up to 60m are require, Keston Composite
75mm flue and air pipe can be used (contact your KESTON Heating stockist for details).
Keston Composite 75mm pipe MUST be painted where exposed to UV light.
Both 50mm flue outlet terminal and 50mm air inlet terminal are supplied and are illustrated
in Figure 3.8.1. Both terminals are identical. If 75mm terminals are required these can be
obtained from your KESTON Heating stockist. Request part numbers C.17.2.26.00.0
(terminals) and C.17.2.00.60.0 (50 to 75 adapters).
3.8.2 Maximum Lengths
The maximum lengths of both air inlet pipe and flue outlet pipe, when no bends are used,
are as detailed below.
However, each bend used has an equivalent length that must be deducted from the
maximum straight length stated above. Knuckle bends must not be used.
A 92.5
o
sweep elbow is equivalent to 1.0m straight length. A 45
o
bend is equivalent to
0.5m straight length
50mm 75mm
Maximum Air Inlet Length : 39.0m 117.0m
Maximum Flue Outlet Length: 20.0m* 60m**
Maximum Total Flue and Air Intake Length : 40.0m 120.0m
* A flue length of between 16 and 20m in 50mm pipe will reduce the DHW output by 1%
** A flue length of between 48 and 60m in 75mm pipe will reduce the DHW output by 1%
Example (assuming 50mm muPVC flue
and air pipework)
Air inlet uses two 92.5
o
sweep elbows.
Hence, maximum length permissible
(i.e. a+b in figure 3.8.2) = 39.0m - 1.0m -
1.0m = 37.0m
Flue outlet uses one 92.5
o
sweep elbow.
Hence, maximum length permissible (i.e.
c+d in figure 3.8.2 = 20.0m - 1.0 m =
19.0m
3.8.3 Slope
‘Horizontal' flue outlet pipework MUST
slope at least 2 degrees (35 mm per
metre run) downwards towards the boiler.
Pipework can be vertical. Only swept
elbows can be used.
Air inlet pipework can be truly horizontal or vertical, or sloping in a downward direction
towards the boiler but in this case rain, etc., must be prevented from entering the pipe.
WD388/0/2004 Chapter 3 - Boiler Location The Keston C36 Combi & C36P Combi Boilers
Installation & Servicing Instructions Page : 16
$,5
)/8(
D
EG
F
Figure 3.8.2 : Flue Air Maximum Length Example
KESTON COMBI
(COMBI P)

There must be no troughs in any of the
pipework, whether it be air inlet or flue outlet.
Due the low temperature of the flue gases further
condensate will form within the flue system. Drain
points, with suitable traps, must therefore be
incorporated within the flue system at the base of
vertical flue sections in excess of 6m, for 50mm
muPVC pipe flue systems. These additional
condensate drains must be run to discharge as
detailed in section 3.11. Such drain points can be
formed using standard muPVC fittings. Refer to the
example in Figure 3.8.3.
3.8.4 Terminations
Air inlet terminals must be facing horizontally or
downwards to prevent entry of rain into the terminal
and positioned to ensure only fresh air is drawn
into the boiler. The air terminal must be located
outside of the building.
Drawing of combustion air directly from a ventilated
boiler room invalidates the heat exchanger warranty.
The flue outlet terminal is designed to face outwards
but can, if desired, be adapted to face in any direction
BUT must not be directed in the region of the air inlet.
The flue terminal and air inlet terminal can be located
on different, but not opposing wall faces.
The two terminals are subject to the requirements of
BS 5440 Pt 1 for clearances from features of the
building although some can be decreased to the
values indicated.
The Keston C36 Combi and C36P Combi, as with any condensing boiler, will
generate a condensate “plume” from the flue terminal in all weather conditions.
Consideration must therefore be given to the effect of this “plume” when selecting
a location for the flue terminal. It is the responsibility of the installer to ensure the
selected terminal location does not cause nuisance.
300300L Horizontally from terminal on same wall.
1,5001,500K Vertically from terminal on same wall.
1001,200J From opening in a car port.(not recommended)
1,2001,200I From terminal facing a terminal.
100600H From surface facing a terminal *
100200G Above ground or balcony or roof.
50200F From internal or external corner.
5075E From vertical drain or soil pipes.
50200D Below balconies or car port roof.
50200C Below eaves.
7575B Below gutters, soil pipes, drain pipes.
50300A Below or beside openable window, air brick,
etc.
Air
Inlet
Flue
Terminal
Dimensions (mm)
*The dimensions given in the table above may need to be increased to avoid wall
staining and nuisance depending on site conditions.
WD388/0/2004 Chapter 3 - Boiler Location The Keston C36 & C36P Combi Boilers
Installation & Servicing Instructions Page : 17
*
+,
!-
.)/
0
01
00
Flue Outlet/Air Inlet Terminals
Figure 3.8.1 : Terminals

It is advisable for horizontal flue terminals to place a 45
o
elbow at the end of the
flue to direct the condensate plume up and away from the property. If the air
intake is within 500mm of the flue outlet the air must not terminal at a level above
that of the flue
If either the air inlet or flue outlet terminate at a height of less than 2.1m above
ground level, the terminal must be protected by a suitable guard. The K4 terminal
guard (with plastic coating), manufactured by Tower Flue Components Ltd is
suitable for this purpose.
3.8.5 Clearances From Wall
Flue outlet and air inlet terminations must be at least 40 mm from the wall face.
3.8.6 Distance Between Flue Outlet & Air Inlet
There is no maximum - the terminations must not be on opposite sides of the
dwelling but can be in areas of unequal pressure..
A minimum clearance of at least 200 mm must be left between the terminations.
3.8.7 General Installations
All parts of the system must be constructed in accordance with BS 5440 Part 1,
except where specifically mentioned in these instructions.
All pipe work must be adequately supported.
All joints other than push-on or plastic compression connectors must be made
and sealed with solvent cement suitable for muPVC pipes and conforming to BS
6209: 1982.
Consideration must be given to Corgi/Gas Safe bulletin TB200/TB008 regarding
flues in voids.
The boiler casing must always be correctly fitted to the boiler when leaving the
appliance operational.
External wall faces and any internal faces of cavity walls must be made good.
Rubber collars are available for flue and air terminals to finish the external wall
face around the terminals (Part No C.08.0.00.07.0)
3.9 AIR SUPPLY
The KESTON C36 Combi and C36P Combi are room sealed appliances and therefore do
not require purpose provided ventilation to the boiler room for combustion air.
3.10 COMPARTMENT INSTALLATION
Due to the low casing temperatures generated by the boiler, no compartment ventilation is
required. However, the cupboard or compartment must not be used for storage.
3.11 CONDENSATE DRAINAGE
Being a condensing boiler, the C36 Combi and C36P Combi are fitted with a condensate
trap at the base of the heat exchanger and flue assembly, with facility to connect to a
drain point underneath the appliance.
Use only plastic piping and do not reduce below 15 mm internal diameter within the
dwelling. Condensate should preferably be drained into the sanitary waste system or,
alternatively, the rainwater system of the property in most cases. Ensure in all cases that
the disposal of the condensate is in accordance with any local regulations in force.
Termination of the pipe must be either at a branch or stack internal to the house, or
externally at an open gully. Alternatively, discharge into a purpose made condensate
soakaway can be considered. Existing or purpose built drains must use suitable corrosion
resistant material as condensate is mildly acidic.
The connection to the condensate drain of the boiler, and the condensate drain pipework
itself, should be properly sealed to ensure there is no possibility of leakage into the
dwelling.
WD388/0/2004 Chapter 3 - Boiler Location The Keston C36 Combi & C36P Combi Boilers
Installation & Servicing Instructions Page : 18

A minimum slope downwards towards the drain of 1 in 20 is essential. Freezing of the
termination and pipework must be prevented. Any drainage pipes outside the property
must be at least 32 mm inside diameter.
WD388/0/2004 Chapter 3 - Boiler Location The Keston C36 & C36P Combi Boilers
Installation & Servicing Instructions Page : 19

4. INSTALLATION OF THE BOILER
Read Chapter 3 - Boiler Location and decide upon the position of the boiler.
Installation of the boiler is straightforward but consideration must be given to access to allow flue
and air pipes to be pushed through walls and ceilings. The order in which the components are
installed will depend upon particular site conditions, but in general it will be easiest and most
accurate to install the boiler and then build up the flue outlet and air inlet pipes to the terminal - this
is the sequence described.
4.1 WALL MOUNTING BRACKET
a Place the bracket on the wall
horizontally with the
pre-drilled holes at the
bottom and position as
dictated by the template
supplied within the boiler
packaging.
b Drill through the centre hole
of the bracket, plug the hole
and fix in position.
c Using a spirit level make
sure the bracket is
completely level and mark
the position of the other
screw holes.
d Remove the bracket and drill
the holes in the positions
marked. Plug these holes.
e Screw the bracket to the wall
using screws of an
appropriate size for the wall
type (No. 12 x 2 inch wood
screws normally suffice).
f Fix the cross spacer to the
wall bracket locating pegs
and mark the resulting
location for the pre-installation jig dictated by the lower ends of the cross spacer.
g Drill and plug the holes for the pre-installation jig.
h Screw the pre-installation jig to the wall using screws of an appropriate size for the wall
type.
If you have purchase the optional pre-installation jig you are now able to connect system
pipework to the pre-installation jig, isolate using the valves supplied as part of the jig and
pressure test the system pipework prior to mounting of the boiler. System flushing and
cleaning should also be carried out at this stage prior to boiler mounting.
4.2 MOUNTING THE BOILER (after system cleaning and testing)
a Lift and locate the boiler onto the stud and the two locating pegs protruding from
the wall bracket. (lift the boiler via the back frame only)
b Lower the boiler for hanging on the two pegs.
c Fix the boiler on the bracket stud using the nut and the washers supplied.
d Make the gas, DHW, CWS, flow and return connections to the system or, if a
pre-installation jig is being used, the pre-installation jig valves using the swivel nut
connections supplied. Ensure the compound gasket inserts are in place inside the
swivel nut face before tightening. Check all joints for soundness.
WD388/0/2004 Chapter 4 : Installation The Keston C36 Combi & C36P Combi Boilers
Installation & Servicing Instructions Page : 20
All dimensions in mm.
Figure 4.1 Wall Mounting Fixing Locations
173
915
Fixing Jig

4.3 ASSEMBLY PRACTICE
Remove all plastic debris and burrs when installing air intake piping. Plastic filings caused
by cutting muPVC pipe must not be allowed to be drawn into the combustion air blower.
Prevent dust entering the air intake when cutting on building sites. Blower failure which is
determined to be caused by plastic filings or other debris will not be covered by guarantee.
4.4 INSTALLING FLUE AND AIR PIPES
IMPORTANT - When installing the boiler on an existing system a new flue and air
intake system MUST also be installed. You must NOT re-use existing flue or air
pipework components.
NB: When installing the boiler, consider:
Flue Spigot Assembly
The flue spigot (50mm muPVC) is inside the accessory bag.
Put the flue spigot assembled with the test plug on the cabinet frame and secure
it by fastening the two M6 screws. Couple the spigot to the internal flue pipe using
the flexible couple and fastening clips. Ensure the clips are properly secured and
no leakage can occur.
Remember the flue pipe must slope downwards back towards the boiler and this
is best achieved using 92.5
o
bends.
a Using the template supplied within the boiler packaging mark the
positions of the two holes for the flue and air pipes on the wall(s) or
ceiling.
b Drill the two holes in the wall/ceiling, preferably using a core drill.
c Measure, cut and check the air and flue pipes to pass to the exit from the
wall(s) or ceiling.
Always thoroughly deburr all pipes and, most important, remove shavings from
within the pipe.
d Mount the boiler on the wall bracket and fix the air spigot (packed loose
with the boiler and with appropriate gasket) to the boiler air inlet
connection tightly to ensure there is no leakage. Assemble, using
adhesive, the pipework from the boiler connections to the exit from the
first wall/ceiling (remount the boiler if removed). When pushing pipe
through walls, ensure grit and dust is not allowed to enter the pipe.
Ensure pipes are fully engaged into sockets and solvent welded with no
leaks.
e Using the same methods drill any further holes (always covering existing
pipework), cut and assemble the pipework.
f From outside, complete the two terminations - See Section 3.8 Flue
System and make good all holes. (wall sealing collars are available to
make good hole areas on the wall face (part number C.08.0.00.07.0)
g Support any pipes whose route could be displaced either of its own
accord or by accident. Any horizontal run over 1m or vertical runs of any
length must always be supported. Brackets should be placed at intervals
of approximately 1m.
h Check all connections for security and re-seal any joints using solvent
cement where soundness may be in doubt.
Note: It is equally important to seal the air inlet with solvent cement as the flue outlet
pipe joints.
4.5 CONDENSATE DRAINAGE
NB: When installing the boiler, consider:
Condensate Trap Assembly
The condensate trap is fitted loose inside the cabinet.
i) remove the nut from the condensate trap spigot;
ii) fit the condensate trap through the two holes in the bottom of the
frame;
WD388/0/2004 Chapter 4 : Installation The Keston C36 Combi & C36P Combi Boilers
Installation & Servicing Instructions Page : 21

iii) replace the nut from the frame bottom
Connect the condensate drainage system to the boiler. It is advisable to use a detachable
fitting at connection to the boiler to enable easy removal for servicing.
Fill the condensate trap by pouring water into the boiler flue until water is seen to flow
freely from the condensate drainage system. Make the final connection of flue pipe to the
boiler.
Details are provided in Chapter 3 - Section 3.11 Condensate Drainage
Connection : 22 mm plastic pipe.
4.6 WATER SYSTEM
Installation Without Optional Pre-Installation Jig:
Connect the flow and return HEATING CIRCUIT system pipework to the boiler. Details of
system requirements are given in Chapter 3 - Section 3.7 Water Systems.
Connections : 0.75 BSPM
Connect the flow and return DOMESTIC WATER pipework to the boiler. Details of system
requirements are given in Chapter 3 - Section 3.7 Water Systems.
Connections : 0.5 BSPM
Installation With Optional Pre-Installation Jig:
Connect the flow and return HEATING CIRCUIT system pipework to the boiler jig valves.
Details of system requirements are given in Chapter 3 - Section 3.7 Water Systems.
Connections : 22mm compression
Connect the flow and return DOMESTIC WATER pipework to the boiler jig valves. Details
of system requirements are given in Chapter 3 - Section 3.7 Water Systems.
Connections : 15mm compression
For optimum performance after installation, this boiler and its associated central heating
system must be flushed in accordance with the guidelines given in BS7592:1992,
"Treatment of water in domestic hot water central heating systems".
This must involve the use of a proprietary cleaner, such as Fernox Superfloc, or
BetzDearborn's Sentinel X300 or X400. Full instructions are supplied with the products,
but for immediate information, please contact Fernox on 01799 550811 or BetzDearborn
on 0151 420 9563.
For long term protection against corrosion and scale, after flushing, it is recommended
that an inhibitor such a Fernox MB1 or BetzDearborn's Sentinel X100 is dosed in
accordance with the guidelines given in BS7593:1992.
4.7 GAS SUPPLY
Connect the gas supply to the appliance. Details of gas supply requirements are given in
Chapter 3 - Section 3.6 Gas Supply. Supply of adequate gas pressure (with the boiler
running) is critical to ensure reliable operation of the boiler.
Connections : 15mm compression
4.8 ELECTRICAL SUPPLY
The entry point(s) for the electrical supply cable(s) is in the base of the appliance (see
Section 3.2 Service Connections fig. 3.1.2) via a cordgrip bush. Feed the cable through
the bush and route inside the cabinet to the connection strip located to the front bottom
right area of the cabinet.
1. The electrical supply must be as specified in Chapter 3 - Section 3.4 Electrical
Supply.
WARNING : THIS APPLIANCE MUST BE EARTHED.
2. All external controls and wiring must be suitable for mains voltage. Supply wiring
should be in PVC insulated cable not less than 0.75mm
2
(8.0mm dia) to BS 6500
Table 16 (material code H05VV-F).
3. The permanent live supply connection may be via a 3 amp fused double pole
switch, serving only the boiler. (Refer to Chapter 3 - Section 3.4 Electrical Supply).
The system controls for the boiler must also be supplied via this isolator.
WD388/0/2004 Chapter 4 : Installation The Keston C36 Combi & C36P Combi Boilers
Installation & Servicing Instructions Page : 22

4. Securely tighten the terminal screws and route the cable(s) through the
re-openable cable clips. Ensure all cables are secured and that the cord grip bush
is tightened to securely grip the main cable at entry to the cabinet. Remove the
factory fitted link wire between the room thermostat terminals on the boiler.
The supply cable(s) must be connected to the main terminals as follows:-
L- Brown wire (Live) 3A permanent supply
N- Blue wire (Neutral) for 3A permanent
E- Yellow/Green Wire (Earth)
SL - 230V Switched Live - i.e. Room Thermostat
Opentherm -Optional Keston Chronotherm room compensating
programmable room thermostat. (Part no C.17.4.21.00.0)
Ext. sens. -Optional outside temperature sensor for weather
compensation. (Sensor part no C.10C.0.09.00.0)
Ensure connection is made such that if the cable slips in its anchorage the current
carrying conductors become taut before the earthing conductor.
4.9 EXCHANGING A BOILER
Before removing an existing boiler add Fernox Supafloc , or equivalent cleaning agent, in
accordance with the manufacturers instructions. Open all radiator valves and fire the
boiler. When the system is fully heated, shut off the gas supply and drain down the central
heating system.
Important
The C36 Combi and C36P Combi combination condensing boilers contain components
which could be damaged or blocked by grease, dirt or solder etc. It is essential that sludge
or scale is removed from an existing system before fitting the boiler.
The guarantee provided with the Keston C36 Combi and C36P Combi does not cover
damage caused by system debris or sludge.
Connect the new boiler as instructed in this manual and fit in accordance with Sections
4.1 to 4.8
Fill to a pressure of about 2.5 bar. Check the complete system for water soundness. If
leaks need to be rectified using flux or solder the system must be flushed cold again
before proceeding.
Reduce the pressure to the Initial System Design Pressure. Vent the system.
Gas Supply
The complete gas installation up to the boiler gas control valve must be checked for
soundness. BS 6891.
Electrical Installation
Carry out preliminary electrical safety checks, i.e. Earth continuity, Polarity, Resistance to
Earth, Short Circuit and earth loop impedance using a suitable test meter.
Initial Firing
The gas pressure setting is factory adjusted to within the required range and does
not need readjustment. If the reading is incorrect then check such factors as soundness
of the air and flue pipe joints, pressure sensible joints and the gas inlet pressure
(minimum 18 mbar required for Natural Gas and 31 mbar required for LP gas). If all joints
are sound and the gas inlet pressure is satisfactory set the gas pressure check the gas
input. Full details of this procedure are given in Section 5.9 Timing The Gas Meter.
Combustion Testing
It is advisable on all installations that the combustion quality is checked by measuring the
carbon dioxide (CO
2
), or oxygen (O
2
), level. This procedure is detailed in Section 5.7
Combustion Testing. Badly tuned combustion will lead to reduce the life of the boiler and
invalidate the warranty.
WD388/0/2004 Chapter 4 : Installation The Keston C36 Combi & C36P Combi Boilers
Installation & Servicing Instructions Page : 23

5. COMMISSIONING OF THE BOILER
Important: This condensing combination boiler contains components which could be damaged or
blocked by grease, dirt, solder etc., from the water system. The following
commissioning procedures must be followed precisely.
It is essential that combustion is checked at high and low rate , as per Section 5.7,
using a calibrated flue gas analyser set for the relevant gas type.
5.1 INITIAL FLUSHING
All waterways within the Keston C36 Combi and C36P Combi are either copper or high
alloy stainless steel. As a result water treatment chemicals for central heating boilers such
as Fernox MB1, Sentinel X100 or equivalent, are suitable. In any event reference must be
made to BS 7593 : Treatment Of Water In Hot Water Central Heating Systems.
a. Disconnect the boiler from the system at the flow and return connections and
temporarily link the flow and return pipes on the system.
b. Flush the entire system until clean water is discharged, free from dirt, flux, solder
etc. The use of a flushing chemical is recommended, e.g. Fernox Supafloc, or
equivalent.
Sludge and scale must be removed from an existing system. Boiler failure due to
system debris or sludge shall invalidate the guarantee.
c. Connect the system to the boiler and fill in accordance with Section 3.7 - CH &
DHW Water Systems. At this stage fill to a pressure of about 2.5 bar.
d. Check the complete system for water soundness. If leaks need to be rectified
using flux and solder, the system must be flushed cold again before proceeding.
e. Reduce the pressure to the Initial System Design Pressure. Vent the system
5.2 GAS SUPPLY
The complete gas installation up to the boiler service cock must be checked for
soundness. BS 6891.
5.3 ELECTRICAL INSTALLATION
Carry out preliminary electrical safety checks, i.e. Earth continuity, Polarity, Resistance to
Earth, Short Circuit using a suitable test meter.
5.4 LP GAS
The Keston C36 Combi and C36P Combi are supplied preset for the gas designated on
the boiler packing. No field conversion is possible. LPG installations must use C36P
Combi models only.
5.5 INITIAL FIRING
Important
Checking the gas pressure to the pre-mix burner requires a special procedure, outlined
below, which must be carried out.
a. Purge the gas supply in accordance with BS 6891.
b. Vent the water system.
Important:
The heat exchanger consists of corrugated tubes which can trap an air pocket.
Great care must be taken to ensure that water flow has been established through
the heat exchanger and thus ensuring no air pockets remain in the heat
exchanger and pipe work. Firing the boiler while an air pocket exists in the heat
exchanger could damage it.
c. Turn the gas service cock to ON.
d. Turn on the electrical supply, setting any external controls to call for heat.
e. Using the “+” button on the left hand side of the control panel, set the CH
temperature to 80C. After a few seconds the display will revert to show the actual
WD388/0/2004 Chapter 5 : Commissioning The Keston C36 Combi & C36P Combi Boilers
Installation & Servicing Instructions Page : 24

flow temperature of the boiler. Also press the “Summer” button until the green
light above this button is extinguished. Once a heating demand is received the fan
will start and the boiler will enter the pre-purge phase. During this phase the boiler
pump will also start to run. After 5 Seconds the boiler will start to spark and will
energise the gas valve. When ignition is achieved a dot will appear in the lower
right corner of the digital display to show the boiler is alight.
If an air lock or other blockage is present the unit may go to overheat or water
pressure lockout. This will be indicated by the display flashing error code “E03” or
“E37”. If this occurs clear the blockage and/or purge the air from the system, and
press the “Reset” button to restart the ignition sequence.
If ignition does not occur, the boiler, at approximately 20 second intervals, will
make four further attempts to light the burner.
If after five automatic attempts the boiler still fails to ignite, the display will show
the code “E 01” indicating no ignition.
If, after five manual attempts (to allow for purging of any air in the gas line), the
boiler still fails to ignite (indicated by the red (lockout) lamp) refer to Section 6.3 -
Fault Modes.
f. Check for gas soundness between the gas service cock and connection to
the burner manifold.
5.6 HOT FLUSHING
a. Allow the system to heat up, checking for water soundness.
b. Follow instructions provided with the cleaning agent, i.e. Fernox Supafloc, or
equivalent. Turn off the boiler and flush the water system while still hot.
Thoroughly flush the system with clear water.
c. Refill the system using a quality water treatment such as Fernox MB1 or Sentinel
X100. For sealed systems, fill to the required Initial Design Pressure.
5.7 COMBUSTION TESTING - MANDATORY CHECK
Competence to carry out the check of combustion performance
PLEASE NOTE: BS 6798:2009 Specification for installation and maintenance of gas fired
boilers of rated input not exceeding 70kW net advises that:
y
The person carrying out a combustion measurement should have been assessed as
competent in the use of a flue gas analyser and the interpretation of the results;
y
The flue gas analyser used should be one meeting the requirements of BS7927 or
BS-EN50379-3 and be calibrated in accordance with the analyser manufacturers’
requirements, and
y
Competence can be demonstrated by satisfactory completion of the CPA1 ACS
assessment which covers the use of electronic portable combustion gas analysers in
accordance with BS 7967, Parts 1 to 4.
Although the gas pressure is preset at the factory it is required to assure proper
combustion by measuring gas input and the level of carbon dioxide, or oxygen and carbon
monoxide, in the flue outlet from the boiler. Over firing or under firing the burner will
reduce the longevity of the appliance and may result in excessive carbon monoxide levels
Carbon dioxide and carbon monoxide are colourless, odourless gases produced by all
combustion processes. When the Keston condensing boiler is operating properly, carbon
dioxide (CO
2
) levels will be between 8.6 & 9% (low rate) and 9.1 & 9.5% (high rate) and
carbon oxide (CO) levels will be between 5 to 20 ppm (low rate) and 50 to 150 ppm (high
rate) for natural gas. For LP gas, carbon dioxide (CO
2
) levels will be between 9.6 & 10%
(low rate) and 10.4 & 10.8% (high rate) and the carbon monoxide will be between 5 & 20
ppm (low rate) and 50 & 150 ppm.
In any event, the CO
2
level at low rate must ALWAYS be less than CO
2
levels at high rate.
To measure CO
2
levels in the Keston boiler remove the 1/8" plug from the flue outlet pipe
spigot (Figure 6.7.4 item 7). Insert the probe of a calibrated combustion analysis meter
and sample the gases as instructed in the test equipment's instructions.
When firing the boiler for the first time since installation, the CO level at high rate may be
between 100-220 ppm and between 50-80 ppm at low rate. This is due to compounds
WD388/0/2004 Chapter 5 : Commissioning The Keston C36 Combi & C36P Combi Boilers
Installation & Servicing Instructions Page : 25

used during manufacture curing within
the combustion chamber. On boilers
which have been fired for more than one
hour since installation, the CO levels
should not exceed 150 ppm at high rate
and 50 ppm at low rate. If CO levels
above these values are experienced, the
combustion chamber and flue system
should be investigated.
The C36 Combi is factory set for
combustion and should need no
adjustment. However, in the event
adjustment is required.
Check combustion errors are not a result
of incorrectly installed flue and/or air
system, terminal location or damage or
debris on the burner. If all these factors
are found to be in order precede as follows:
1) Set any controls to call for heat.
2) Press and hold the “Summer” button until the display changes to blinking “t99”
then release the “Summer” button.
3) Measure the CO
2
reading in the flue gases and adjust, if necessary, the
adjustment screw (pos 4) to produce a CO
2
reading of 9.1% to 9.5% with a
corresponding CO level of 50 to 150 ppm for natural gas and 10.4 to 10.8% with a
corresponding CO level of 50 to 150 ppm for LPG. NORMAL ADJUSTMENT, IF
REQUIRED, SHOULD NEED NO MORE THAN HALF OF ONE ROTATION OF
THE ADJUSTMENT SCREW (pos. 4). ADJUSTMENTS, IF MADE, SHOULD BE
IN STEPS OF NO MORE THAN 1/8 OF A TURN. YOU MUST WAIT 1 MINUTE
AFTER EACH ADJUSTMENT TO ALLOW THE SETTING TO STABILISE
BEFORE TAKING A READING
4) Using the “-” button for CH temperature control, adjust the display to “t00”
5) Measure the CO
2
reading in the flue gases. The CO
2
reading must be 8.6% to 9%
with a corresponding CO level of 5 to 20 ppm for natural gas and 9.6% to 10%
with a corresponding CO level of 5 to 20 ppm for LPG. THE CO2 LEVEL AT LOW
RATE MUST ALWAYS BE LESS THAN THE CO2 LEVEL AT HIGH RATE.
ADJUSTMENTS, IF MADE, SHOULD BE IN STEPS OF NO MORE THAN 1/8 OF
A TURN. YOU MUST WAIT 1 MINUTE AFTER EACH ADJUSTMENT TO
ALLOW THE SETTING TO STABILISE BEFORE TAKING A READING
6) Using the “+” button for CH temperature control, adjust the display back to “t99”
and check the CO
2
level is in the range indicated at point 3)
IN THE EVENT THAT AN ACCEPTABLE COMBUSTION LEVEL CANNOT BE
OBTAINED AT EITHER HIGH OR LOW RATE, CONTACT KESTON HEATING
TECHNICAL SUPPORT ON 0208 462 0262. DO NOT LEAVE THE APPLIANCE
RUNNING UNLESS ACCEPTABLE COMBUSTION LEVELS ARE ACHIEVED.
5.8 CHECKING THE GAS PRESSURE
NB: It is advisable to carry out this test with the user control knob turned to maximum
and the system water cold to ensure the boiler is running at maximum rate.
The gas setting is factory adjusted to within the required range and should not need
adjustment. If the reading is incorrect then check such factors as soundness of the air and
flue pipe joints and the gas inlet pressure (pos. 3) (minimum 18 mbar required for natural
gas, minimum 31 mbar required for LP gas).
If all joints are sound and the gas inlet pressure is satisfactory check the gas input
by timing the gas meter as detail in Section 5.9 Timing The Gas Meter. If the gas
input cannot be measured then it’s compulsory to measure the combustion quality
as detail in Section 5.7 Combustion Testing.
WD388/0/2004 Chapter 5 : Commissioning The Keston C36 Combi & C36P Combi Boilers
Installation & Servicing Instructions Page : 26

5.9 TIMING THE GAS METER
Set the boiler DHW temperature to 65C and open two hot taps in the property fully. With
no other appliances using gas, time the gas meter to be certain that the unit is running at
the proper gas input. Determine the cubic feet of gas passing through the meter and
determine the input in Btu per hour. Input must be within plus or minus 5% of the rated
input.
Time, in seconds, the time taken to pass 2 cubic feet of gas through the meter (i.e. one
revolution of a 2 cu ft dial) or 0.1 cubic metres if the meter is of the new metric digital type.
Model Time for 2 cu ft Time for 0.1 cu m
C36 Combi (natural gas) 54 95
C36P Combi (LPG) 141 249
If the meter timing is found to be incorrect when the boiler is firing at maximum rate
contact KESTON Heating for further guidance.
5.10 HANDING OVER TO THE USER
It is important to fully explain the following:
a. Procedure to light and turn off the boiler, including isolation of the electrical supply
if necessary.
b. The function of the lockout feature must be explained :
If the display shows “E 01” this means that the boiler has failed to light. Press the
“Reset” button and wait.
i) If lockout recurs immediately then the gas supply should be checked as
ON, otherwise consult a Service Engineer.
ii) If it is not possible to relight, the boiler must be isolated and a Service
Engineer called in to rectify the fault.
c. Advise that a reduction in the water pressure reading on the system pressure
gauge, for sealed systems, indicates a leak which should be rectified before
further use.
d. Advise that the appliance should be serviced by a competent person at least once
a year.
Complete all sections of the Chapter 10 Gas Boiler Commissioning Checklist that are
relevant to the appliance installation. The details will be required in the event of any
warranty work.
e. Advise on the frost protection and pump/fan exercise feature.
f. Advise the user that a plume of water vapour (steam) from the flue terminal is
normal and that there is no need for concern.
WD388/0/2004 Chapter 5 : Commissioning The Keston C36 Combi & C36P Combi Boilers
Installation & Servicing Instructions Page : 27

6. FAULT FINDING
6.1 ELECTRICAL CONTROL SEQUENCE
6.1.1 HEATING DEMAND
When the external control(s) are calling for heat, power will be fed to the boiler connection
strip at terminal SL (Switched Live) and N (Neutral) and the CH green light will illuminate.
If the user control setting of the CH temperature is to a temperature above the actual
boiler flow temperature and provided all safety sensors are confirmed as OK the control
PCB will initiate the following sequence.
(1) The fan will start.
(2) When the fan reaches running speed, the control PCB will start the ignition
sequence.
(3) After a pre-purge period of about 5 seconds, the gas valve will open to allow gas
to mix with the air at the suction side of the fan and the ignition spark will occur at
the main burner.
(4) When the burner ignites, the flame is detected by the control PCB through the
combined flame sensor/ignitor and the ignition spark is stopped. A dot is
illuminate in the lower right corner of the temperature display. The boiler is now in
its normal run condition.
(5) The boiler will automatically and continuously adjust its power output and pump
speed to best match the demands of the system at any time.
(6) The burner will continue to operate until the gas valve interrupts the gas supply.
The gas valve will be closed by the control PCB if power is interrupted to the
boiler by any external control or the boiler exceeds the requested temperature. If
an interruption to the gas supply causes loss of the flame, the control box will
pause for approximately 10 seconds and then attempt to re-ignite the unit. If this
attempt fails, i.e. due to continued lack of gas supply, the boiler will make four
further attempts to ignite at intervals of approximately 10 seconds and will then go
to a lockout state (the display shows “E01”). Once the gas supply has been
resumed the boiler can be reset by pressing the “Reset” button.
(7) The boiler can also be shut down by the cabinet temperature sensor, water
pressure sensor or flue overheat sensor.
6.1.2 HOT WATER DEMAND
When a hot tap is opened to allow flow of more than 2.5 litres per minute the DHW green
light will illuminate. If the user control setting of the DHW temperature is to a temperature
above the actual DHW temperature, and provided all safety sensors are confirmed as OK
the control PCB will make the following sequence.
(1) The fan will start (if not already running for a CH demand)
(2) The diverter valve, integral to the boiler pump, will move to the DHW plate heat
exchanger position.
(3) As steps (2) to (7) above.
Any failure of the boiler to sequence in the above manner should be investigated using the
following trouble shooting flow diagram.
Before attempting any electrical fault finding, always carry out preliminary electrical system
checks. On completion of any service/fault finding task which has required the breaking
and remaking of electrical connections, the checks, earth continuity, polarity, short circuit,
resistance to earth must be repeated.
WD388/0/2004 Chapter 6 : Fault Finding The Keston C36 & C36P Combi Boilers
Installation & Servicing Instructions Page : 28

QUICK REFERENCE
6.2 NORMAL OPERATION
The C36 Combi and C36P Combi
boilers feature a user display
which shows actual flow
temperature at all times when not
serving a DHW demand. If a
DHW demand is detected the
boiler display changes to show the
actual DHW temperature.
However, the display can also be
used to show other information
about the operation of the boiler.
By pressing the “Installer” button
once the display changes to show
the number 1. Each time the
“Installer” button is pressed the number increases up to a maximum of 7. Having select the
required number in this way the display, if not touched for a further 5 seconds the display changes
again to show the value relative to that number. The table below shows the values associated with
each number
INSTALLER INFORMATION NUMBERS
DHW Flow rate. Divide this number by 6 to read the actual DHW flow rate through
the boiler in litres per minute.
8
Actual flue temperature (of the flue temperature reaches 80C the boiler will drop to
minimum rate until the flue temperature drops to 70C. If the flue temperature
reaches 90C the boiler will shutdown.)
7
Software version of boiler (not relevant to normal fault diagnosis)6
System water pressure, in bar. (Maximum 2.5 bar, minimum 0.6 bar. The boiler will
shut down if the water pressure drops below 0.5 bar)
5
Actual DHW temperature (maximum 69C)4
Actual CH return temperature (maximum 72C) (NB Flow temperatures more than
20C above return temperature may lead to overheat and noise problems. Check
the pump performance and the system for blockages)
3
Actual CH flow temperature (maximum 84C)2
The flame current (in micro amps) detected from the burner (should be <2 when off
and >5 when burner on. Low flame current readings suggest poor combustion and
may lead to flame lockouts. Check gas supply, air supply and combustion setting.)
1
MeaningDisplay
You can return to the normal display mode at any time by pressing the “Reset” button once.
During normal operation the green lamps beside the CH +/- buttons and DHW +/- buttons indicate
the mode of operation. If the lamp is not lit then no demand for that function (ie CH or DHW) is
present. In CH mode a demand is received by a 230V signal to SL or via the Keston Room Control
unit. In DHW mode a demand is received by drawing >2.5 litres per second from a hot tap.
If the lamp is lit the boiler is on, or is starting up, to serve the demand for that function. If the lamp
is flashing the demand is still present but the burner is off because the unit exceeded the desired
temperature and the forced anti-cycle (in CH mode) delay has not elapsed.
6.3 FAULT MODES
If a situation is detected which the boiler considers may cause damage to the appliance the boiler
will enter a lockout mode and stop functioning. After clearing the problem the user must also press
the “Reset” button once to resume boiler operation. TURNING THE POWER ON THEN OFF
WILL NOT CLEAR A LOCKOUT SITUATION
WD388/0/2004 Chapter 6 : Fault Finding The Keston C36 & C36P Combi Boilers
Installation & Servicing Instructions Page : 29

ERROR CODES
As E41E99
Flue sensor open circuit - check connections to flue sensor are in placeE46
Flue sensor short circuit - check connections to flue sensorE45
Return sensor open circuit - check connections to return sensor are in placeE44
Return sensor short circuit - check connections to return sensorE43
Communication error between fascia and control box - check cablesE41
Water pressure too high - check expansion vessel charge and operationE40
Reset key fault - replace fascia PCBE38
Water pressure error - check system pressure and pressure sensorE37
Mains supply frequency incorrect - Check mains voltage system in dwellingE35
Mains supply voltage < 180V - Check mains voltage system in dwellingE34
DHW sensor open circuit - check connections to DHW sensor are in placeE33
DHW sensor short circuit - check connections to DHW sensorE32
Flow sensor open circuit - check connections to flow sensor are in placeE31
Flow sensor short circuit - check connections to flow sensorE30
Flame signal lost 5 times in 4 minutes - The flame is unstable, check
combustion, gas supply, air supply and flue.
E26
Control box errors - possible faulty control box.E25
Water pressure lost 4 times in 24 hours - possible leak, check system and boiler.E24
Water filling error - check water pressure sensor.E23
Control box errors - possible faulty control box.E12 to E22
The automatic test for calibration of flow and return sensors has failed. Check
both flow and return sensors are located on the correct pipes and are producing
the correct readings.
E11
Control box errors - possible faulty control box.E10
Valve drive error - possible gas valve or control box fault.E09
Flame circuit error - possible control box fault..E08
Flue overheat - check combustion and flue temperature vs. return temperature
(Installer numbers 7 and 3 above). The flue temperature should be no more
than 10C above return temperature. Possible heat exchanger fault
E07
Fan failure - boiler cannot detect fan rotation. Check fan operation and BOTH
connectors onto fan.
E05
Boiler overheat - check system for blockage, by-pass provision and pump
operation
E03
False flame - the unit is detecting a flame BEFORE ignition. Check gas valve
closure, power supply polarity and voltage and earth connection.
E02
Ignition failure - the boiler has attempted to light five times and not succeeded -
check gas supply, air supply, flue, ignitor condition and spark gap.
E01
Description of faultDisplay
WD388/0/2004 Chapter 6 : Fault Finding The Keston C36 & C36P Combi Boilers
Installation & Servicing Instructions Page : 30

6.4 FUNCTIONAL FLOW WIRING DIAGRAM
WD388/0/2004 Chapter 6 : Fault Finding The Keston C36 & C36P Combi Boilers
Installation & Servicing Instructions Page : 31

6.5 ELECTRICAL WIRING DIAGRAM
WD388/0/2004 Chapter 6 : Fault Finding The Keston C36 & C36P Combi Boilers
Installation & Servicing Instructions Page : 32

6.6 ILLUSTRATED WIRING DIAGRAM
WD388/0/2004 Chapter 6 : Fault Finding The Keston C36 & C36P Combi Boilers
Installation & Servicing Instructions Page : 33

6.7 Exploded Assembly Diagrams
6.7.1 Boiler Controls Assembly
WD388/0/2004 Chapter 6 : Fault Finding The Keston C36 & C36P Combi Boilers
Installation & Servicing Instructions Page : 34

6.7.2 Waterway, Condensate & Flue Assembly
WD388/0/2004 Chapter 6 : Fault Finding The Keston C36 & C36P Combi Boilers
Installation & Servicing Instructions Page : 35
57-4
57-1
58
58
56
57-3
57
57-2
56
39

WD388/0/2004 Chapter 6 : Fault Finding The Keston C36 & C36P Combi Boilers
Installation & Servicing Instructions Page : 36
57-2
56
56
39
56
57-4
57-3
56
57-1
39

6.7.3 Air - Gas Assembly
WD388/0/2004 Chapter 6 : Fault Finding The Keston C36 & C36P Combi Boilers
Installation & Servicing Instructions Page : 37

6.7.4 Casing Assembly
WD388/0/2004 Chapter 6 : Fault Finding The Keston C36 & C36P Combi Boilers
Installation & Servicing Instructions Page : 38

6.7.5 Exploded Diagrams Parts Reference List
Boiler Controls Assembly (Fig. 6.7.1)
GC Number Code Description
135 Main Control Box (C.10C.4.01.00.0 B)
138 Control Panel (C.10C.4.04.00.0 A)
146 Terminal Block (C.12.4.00.03.0)
206 Terminal Block (C.10C.4.28.00.0)
E72-401 153 Thermal Fuse (C.08.4.21.00.0)
136 Ignitor Cable (C.10C.4.02.00.0)
Waterway, Condensate & Flue Assembly (Fig. 6.7.2)
GC Number Code Description
39 Heat Exchanger (C.10C.2.01.00.1)
57 DHW Heat Exchanger (C.10C.2.09.00.0)
58 Expansion Vessel (C.08.0.08.00.0 A)
46 Burner (C.10C.2.04.00.0)
161 Burner Head Gasket
(C.10C.2.00.45.0 A)
49 Ignitor Gasket (C.10C.2.00.52.0 A)
48 Spark Electrode (C.10C.2.06.00.1)
51 Condensate Trap (C.10C.2.07.00.0)
67 Flow/Return Sensor (C.10C.2.23.00.0)
68 Flue Sensor (C.10C.2.11.00.0)
108 DHW Sensor (C.10C.2.16.00.0)
112 Pressure Sensor (C.10C.2.17.00.1)
94 Flow Sensor (C.10C.2.33.00.0)
56 Hydroblock (C.10C.2.08.00.0)
Air - Gas Assembly (Fig. 6.7.3)
GC Number Code Description
119 Combustion Blower (C.12.3.01.00.1)
215 C36 Combi Gas Valve - Mixer Air Gas
Assembly (C.10C.3.06.00.0)
215 C36P Combi Gas Valve - Mixer Air Gas
Assembly (C.10C.3.07.00.0)
Casing Assembly (Fig. 6.7.4)
GC Number Code Description
2 Cabinet Cover (C.10C.1.02.00.0 A)
19 Databadge - NG (C.10C.1.00.06.0)
19 Databadge - LPG (C.10C.1.00.06.1)
E73-355 10 Combustion Test Plug (B.04.2.00.49.1)
WD388/0/2004 Chapter 6 : Fault Finding The Keston C36 & C36P Combi Boilers
Installation & Servicing Instructions Page : 39

7. ROUTINE (ANNUAL) SERVICING
To ensure the continued safe and efficient operation of the boiler it is necessary to carry out
routine servicing at regular intervals. Servicing must be carried out at least once per year. The
frequency of the servicing will depend upon the particular operating conditions.
It is the law that any service work must be carried out by competent qualified persons.
NB: When servicing ensure that the gas and electrical supplies to the boiler are isolated before
any work starts.
Hazardous materials are not used in the construction of the C36 and C36P Combi. However, due
care should be taken when handling boiler components.
All joints should be checked for soundness after servicing and before firing the appliance.
After servicing complete the Gas Boiler Commissioning Checklist - Service Interval Record
(Chapter 10). These forms (Chapter 10) should be kept in a safe place for the life of the
boiler.
PLEASE NOTE: During routine servicing, and after any maintenance or change of part of
the combustion circuit, the following must be checked:
y
The integrity of the flue systems and flue joints, as described in Section 4.4
y
The integrity of the boiler combustion circuit and the relevant seals
y
The operational (working) gas inlet pressure at maximum rate, as described in
Section 5.8
y
The gas rate, as described in Section 5.9
y
The combustion performance, as described in Section 5.7
7.1 Pre-Service Checks
It is recommended that an inspection should be carried out prior to shutting down the unit
for servicing. Remove the front cover by removing the screws retaining the top and
bottom. The following items should be observed:
a. Smooth starting and running of the blower.
b. Smooth lighting of the burner.
c. Check for leakage of gas, gas/air or combustion products.
d. Check for condensate leaks.
e. Check for water soundness.
f. Inspect the flue vent and air intake pipework. Joints must be sound and all
pipework well bracketed.
g. Check that there is a steady fall back to the boiler from the flue pipe to allow
condensate to run back into the boiler.
h. With the boiler operating at a low return temperature (i.e. less than 50
o
C) check
that the condensate flows freely from the condensate line.
7.2 Recommended Routine Service
a. Remove the outer case by first removing the securing screws at the top and
bottom of the appliance.
b. Remove the burner head (Section 8.6) and inspect the burner appearance. Black
markings or other discoloration's on the gauze indicate too much gas or a lack of
air possibly due to a blocked air inlet. Any breakage's or damage to the burner
mesh indicate the burner must be replaced.
c. If necessary clean the burner with a mild household detergent and rinse under a
hot running tap.
WD388/0/2004 Chapter 7 : Servicing The Keston C36 Combi & C36P Combi Boilers
Installation & Servicing Instructions Page : 40

d. If necessary, from visual inspection, clean the heat exchanger using a suitable
stiff plastic bristle brush, vacuum out any large particles and flush the heat
exchanger with fresh water until the water flowing from the condensate drain is
clear.
e. Remove the condensate trap (Section 8.8) and clean by flushing through with
clean running water.
f. Check the electrode assembly mounted on the heat exchanger. If the point is
damaged or burnt replace it.
Check that the spark gap measures 4 mm.
g. Replace the burner head, renewing the gasket, and reconnect the gas/air supply.
Ensure the flanged gas/air supply joint is air tight.
h. Turn on the electrical supply to the boiler and allow the boiler to reach operating
temperature levels.
i. Remove the combustion test point plug from the flue pipe. This is situated on the
flue spigot out of the cabinet.
j. Carry the full procedure detailed in section 5.7 COMBUSTION TESTING -
MANDATORY
k. Replace the combustion test point plug.
l. Recheck the burner pressure by following the procedure detailed in Section 4.7.
m. Check all joints for soundness up to the gas burner.
n. Complete the Gas Boiler Commissioning Checklist - Service Interval Record
(Chapter 10).
WD388/0/2004 Chapter 7 : Servicing The Keston C36 Combi & C36P Combi Boilers
Installation & Servicing Instructions Page : 41

8. REPLACEMENT OF PARTS
CONTENTS
8.0 GENERAL
8.1 PRECAUTIONS
8.2 ACCESS
8.3 REPLACEMENT PROCEDURE
8.4 ELECTRICAL COMPONENTS
8.4.1 CONTROL PANEL
8.4.2 BOILER FLOW & RETURN THERMISTORS
8.4.3 CABINET TEMPERATURE SENSOR
8.4.4 FLUE THERMISTOR
8.4.5 PRESSURE SENSOR
8.4.6 MAIN CONTROL BOX
8.4.7 COMBUSTION BLOWER
8.4.8 GAS CONTROL VALVE / VENTURI ASSEMBLY
8.4.9 DHW THERMISTOR
8.4.10 FLOW SENSOR
8.5 SPARK IGNITION/FLAME DETECTION ELECTRODE
8.6 BURNER
8.7 HEAT EXCHANGER
8.8 CONDENSATE TRAP
8.9 HYDROBLOCK
8.10 DHW HEAT EXCHANGER
8.11 EXPANSION VESSEL
8.0 GENERAL
The following must always be carried out by a competent/qualified person.
8.1 PRECAUTIONS
i) Always switch off the mains electricity supply and disconnect the plug at the isolating
switch and socket. (If a switch only is used then remove the fuse.)
ii) Gain access to the appliance (Section 8.2) and turn off the gas supply at the
appliance service cock.
WARNING : Parts of the boiler internal wiring will remain live even after setting the
User Controls to Standby. Shut off the power supply at the isolating
switch before working on the appliance.
8.2 ACCESS
i) Remove the cabinet by removing the screws to the top and bottom of the cabinet.
8.3 REPLACEMENT PROCEDURE
i) Always replace in the reverse order unless otherwise stated.
ii) Electrical connections must be remade in accordance with the Electrical Wiring
Diagram (Section 6.5).
iii) Test the soundness of any gas carrying or water carrying joint broken during the
service procedures.
8.4 ELECTRICAL COMPONENTS
8.4.1 Control Panel (Fig. 6.7.1 item 138)
i) Isolate the appliance (Section 8.1)
ii) Gain access (Section 8.2)
iii) Remove the user control cover by removing the four retaining screws (Fig
6.7.1, item 99 and item 145).
iv) Disconnect the Control Panel by unplugging the cable connectors.
v) Reassemble (Section 8.3)
vi) Check for correct operation of the Control Panel.
WD388/0/2004 Chapter 8 : Replacement Of Parts The Keston C36 Combi & C36P Combi Boilers
Boilers
Installation & Servicing Instructions Page : 42

8.4.2 Boiler Flow and Return Thermistors (Fig. 6.7.2 - 2/3 item 67)
i) Isolate the appliance (Section 8.1)
ii) Gain access (Section 8.2)
iii) Remove the push on connectors from the thermistor taking note of the correct
positions.
iv) Unclip the thermistor from the pipe.
v) Reassemble (Section 8.3)
NB: When fitting the new thermistor it is an advantage to smear a thin film
of heat sink compound between the thermistor and pipe. This,
combined with fitting the new thermistor tightly to the pipe, ensures a
good contact.
8.4.3 Cabinet Temperature Sensor (Fig 6.7.1 item 153)
i) Isolate the appliance (Section 8.1)
ii) Gain access (Section 8.2)
iii) Remove the cabinet temperature sensor from the connector block by
slackening the retaining screws.
iv) Reassemble (Section 8.3)
8.4.4 Flue Thermistor (Fig. 6.7.2 - 1/3 item 68)
i) Isolate the appliance (Section 8.1)
ii) Gain access (Section 8.2)
iii) Remove the push on connectors from the thermistor taking note of the correct
positions.
iv) Unscrew the retaining nut, and remove the thermistor.
v) Reassemble (Section 8.3)
NB: When fitting the new thermistor it is an advantage to smear a thin film
of heat sink compound between the thermistor and plate. This,
combined with fitting the new thermistor tightly to the plate, ensures a
good contact.
8.4.5 Pressure Sensor (Fig. 6.7.2 - 2/3 item 112)
i) Isolate the appliance (Section 8.1)
ii) Shut off the water supply to the appliance.
iii) Gain access (Section 8.2)
iv) Drain the system to below the level of the appliance using the drain off tap
(fig. 6.7.4 - 2/2 item 180) at the base of the return pipe from the heat
exchanger.
v) Remove the push on connectors from the pressure sensor taking note of the
correct positions.
vi) Unscrew the pressure sensor.
vii) Reassemble (Section 8.3).
NB: Use a little jointing compound or PTFE tape on the thread.
viii) Refill the system (See Section 5 - Commissioning).
8.4.6 Main Control Box (Fig. 6.7.1 item 135)
i) Isolate the appliance (Section 8.1)
ii) Gain access (Section 8.2)
iii) Pull off the multi-pin connectors and HT lead away from the board.
iv) Remove the retaining screw (fig. 6.7.1 item 152) securing the control block to
the gas valve (fig. 6.7.3 item 126).
v) Remove the control box.
vi) Reassemble (Section 8.3)
8.4.7 Combustion Blower (Fig. 6.7.3 item 119)
i) Isolate the appliance (Section 8.1)
ii) Gain access (Section 8.2)
iii) Disconnect the two connector blocks from the combustion blower.
iv) Unscrew the bolts securing the venturi (fig 6.7.3 item 125) to the inlet port of
the combustion blower.
v) Remove the four nuts securing the combustion blower (fig. 6.7.3 item 121)
outlet flange to the burner and remove the combustion blower.
vi) Reassemble (Section 8.3)
WD388/0/2004 Chapter 8 : Replacement Of Parts The Keston C36 Combi & C36P Combi Boilers
Boilers
Installation & Servicing Instructions Page : 43

NB: When reassembling inspect any gaskets for damage and replace if
necessary.
8.4.8 Gas Control Valve /Venturi Assembly (Fig. 6.7.3 item 215)
i) Isolate the appliance (Section 8.1)
ii) Gain access (Section 8.2)
iii) Remove the Main Control Box (Section 8.4.6)
iv) Remove the push on connector block to the gas valve.
v) Unscrew the bolts (Fig 6.7.3 item 129) securing the gas inlet pipe to the gas
control valve.
vi) Unscrew the bolts securing the gas valve (Fig 6.7.3 item 125) to the inlet port
of the combustion blower.
vii) Remove the gas valve/venturi assembly as a complete unit.
viii) Reassemble (Section 8.3)
ix) Check the gas rate and combustion(See Section 5 - Commissioning)
NB: Always change the gas valve/venturi assembly together. This
assembly is factory preset but must be checked using the procedure
set out in Section 5.7 (Combustion testing).
8.4.9 DHW Thermistor (Fig. 6.7.2 - 2/3 item 108)
i) Isolate the appliance (Section 8.1)
ii) Gain access (Section 8.2)
iii) Remove the push on connectors from the thermistor taking note of the correct
positions.
iv) Unclip the thermistor from the pipe.
v) Reassemble (Section 8.3)
NB: When fitting the new thermistor it is an advantage to smear a thin film
of heat sink compound between the thermistor and pipe. This,
combined with fitting the new thermistor tightly to the pipe, ensures a
good contact.
8.4.10 Flow Sensor (Fig. 6.7.2 - 3/3 item 94)
i) Isolate the appliance (Section 8.1)
ii) Gain access (Section 8.2)
iii) Shut off the water supply (CWS) to the DHW heat exchanger (Fig. 6.7.2 -
1/3 item 57).
iv) Remove the push on connector from the sensor taking note of the correct
position.
v) Disconnect the union nuts (Fig. 6.7.2 - 3/3 item 100 and Fig. 6.7.4 - 2/2 item
177) and the fixing nut (Fig. 6.7.2 - 3/3 item 203) from the sensor.
vi) Reassemble (Section 8.3)
NB: When reassembling inspect the gaskets for damage and replace
if necessary.
8.5 SPARK IGNITION/FLAME DETECTION ELECTRODE (Fig. 6.7.2 - 1/3 item 48)
i) Isolate the appliance (Section 8.1)
ii) Gain access (Section 8.2)
iii) Remove the pull off HT lead to the spark ignition electrode.
iv) Undo the screws to the spark ignition electrode flange located on the heat exchanger
top panel and withdraw the spark ignition electrode.
v) Reassemble (Section 8.3)
NB: When reassembling inspect the gasket for damage and replace if necessary.
With the new spark ignition electrode in place it is essential to ensure the gap
between the tip of the electrode and the burner surface is 4 mm. Distances
above or below 4 mm will affect ignition performance. If necessary gently
bend the electrode taking care not to damage the ceramic insulator.
8.6 BURNER (Fig. 6.7.2 - 1/3 items 46)
i) Isolate the appliance (Section 8.1)
ii) Gain access (Section 8.2)
WD388/0/2004 Chapter 8 : Replacement Of Parts The Keston C36 Combi & C36P Combi Boilers
Boilers
Installation & Servicing Instructions Page : 44

iii) Remove the combustion blower (Section 8.4.7)
iv) Remove the 4 nuts fixing the burner to the top of the heat exchanger.
v) Withdraw the burner from the top of the heat exchanger.
vi) Reassemble (Section 8.3)
NB: When reassembling inspect any gaskets for damage and replace if
necessary.
8.7 HEAT EXCHANGER (Fig. 6.7.2 - 1/3 item 39)
i) Isolate the appliance (Section 8.1)
ii) Gain access (Section 8.2)
iii) Shut off the water supply to the appliance.
iv) Remove the burner (Section 8.6)
v) Drain the system to below the level of the appliance using the drain off tap (Fig.
6.7.4 - 2/2 item 180) at the base of the boiler return pipe.
vi) Remove the flue thermistor (Section 8.4.4)
vii) Remove the spark ignition/flame detection electrode (Section 8.5)
viii) Remove the flue connection by slackening the retaining strap and pulling the flue off
the heat exchanger spigot.
ix) Remove the condensate trap hose (Fig 6.7.2 - 1/3 item 54) by releasing the retaining
clamp and pulling the hose away from the spigot at the base of the heat exchanger.
x) Disconnect the flow and return pipe union nuts (Fig 6.7.2 - 2/3 & Fig. 6.7.2 - 3/3 item
60) from the heat exchanger.
xi) Remove the two screws (Fig. 6.7.2 - 1/3 item 41) fixing the heat exchanger to the top
and the screw (Fig. 6.7.2 - 1/3 item 42) fixing the heat exchanger to the bottom.
xii) Remove the heat exchanger
xiii) Reassemble (Section 8.3)
xiv) Recommission (Section 5 - Commissioning)
8.8 CONDENSATE TRAP (Fig. 6.7.2 - 1/3 item 51)
i) Isolate the appliance (Section 8.1)
ii) Gain access (Section 8.2)
iii) Disconnect the condensate line from the base of the heat exchanger.
iv) Disconnect the condense line from the projection of the condensate trap from the
base of the cabinet.
v) Withdraw the condensate trap.
vi) Mop up any spilled condensate.
vii) Reassemble (Section 8.3)
NB: When re-fitting the condensate trap pour water onto the condensate hose
from the base of the heat exchanger until nearly full. Then reconnect the
condensate hose to the base of the heat exchanger.
8.9 HYDROBLOCK PUMP (Fig. 6.7.2 - 1/3 item 56)
i) Isolate the appliance (Section 8.1)
ii) Gain Access (section 8.2)
iii) Isolate the waterways to the boiler using the system isolation valves.
iv) Drain the system to below the level of the appliance using the drain off tap (Fig.
6.7.4 - 2/2 item 180) at the base of the boiler return pipe.
v) Undo the screw (Fig. 6.7.1 item 145) to the panel support (Fig. 6.7.4 - 1/2 item 35)
and rotate it on the right.
vi) Disconnect the pump electrical cable from the connections box of the pump head
taking note of the correct position.
vii) Remove the four allen bolts securing the pump head to the hydroblock back body.
viii) Remove the pump head.
ix) Reassemble (Section 8.3)
8.10 DHW HEAT EXCHANGER (Fig. 6.7.2 - 1/3 item 57)
i) Isolate the appliance (Section 8.1)
WD388/0/2004 Chapter 8 : Replacement Of Parts The Keston C36 Combi & C36P Combi Boilers
Boilers
Installation & Servicing Instructions Page : 45

ii) Gain Access (section 8.2)
iii) Shut off the water supply (CWS) to the DHW heat exchanger.
iv) Isolate the waterways to the pump using the system isolation valves.
v) Drain the system to below the level of the appliance using the drain off tap (Fig.
6.7.4 - 2/2 item 180) at the base of the boiler return pipe.
vi) Disconnect the two union nuts from the DHW heat exchanger (Fig. 6.7.2 - 3/3
item 86 & 100 and Fig. 6.7.2 - 2/3 item 86).
vii) Remove the DHW heat exchanger.
viii) Reassemble (Section 8.3)
NB: When reassembling inspect the gaskets for damage and replace if
necessary.
8.11 EXPANSION VESSEL (Fig. 6.7.2 - 1/3 item 58)
i) Isolate the appliance (Section 8.1)
ii) Gain Access (section 8.2)
iii) Isolate the waterways to the pump using the system isolation valves.
iv) Drain the system to below the level of the appliance using the drain off tap (Fig.
6.7.4 - 2/2 item 180) at the base of the boiler return pipe.
v) Disconnect the flexible hose (Fig. 6.7.2 - 1/3 item 116) from the expansion vessel.
vi) Undo the pin (Fig. 6.7.4 - 1/2 item 4) and the EV bracket (Fig. 6.7.4 - 1/2 item 211)
from the cabinet frame.
vii) Remove the expansion vessel.
viii) Reassemble (Section 8.3)
NB: When reassembling inspect the gasket for damage and replace if necessary.
WD388/0/2004 Chapter 8 : Replacement Of Parts The Keston C36 Combi & C36P Combi Boilers
Boilers
Installation & Servicing Instructions Page : 46

9. SHORT SPARE PARTS LIST
Item GC No Part Denomination Item GC No PartDenomination
46 Burner 161 Burner Gasket
49 Ignitor Gasket 48 Ignitor/Sensor Probe
67 Flow/Return 68 Flue Thermistor
Thermistors
108 DHW Thermistor
94 Flow Sensor 112 Pressure Sensor
WD388/0/2004 Chapter 9 : Spare Parts Listings The Keston C36 & C36P Combi Boilers
Installation & Servicing Instructions Page : 47

215 C36 Combi Gas Valve - Mixer Assem. 119 Fan
C36P Combi Gas Valve - Mixer Assem.
135 Control Box 138 Fascia Panel
56 Pump Block 57 DHW Heat
Exchanger
58 Expansion Vessel
WD388/0/2004 Chapter 9 : Spare Parts Listings The Keston C36 & C36P Combi Boilers
Installation & Servicing Instructions Page : 48

SHORT SPARE PARTS LIST FOR THE KESTON
CONDENSING BOILER RANGE
Item GC No Part Denomination
46 Burner
161 Burner Gasket
48 Ignitor
49 Ignitor Gasket
108 DHW Thermistor
67 Flow/Return Thermistor
68 Flue Thermistor
94 Flow Sensor
112 Pressure Sensor
119 Fan
215 Gas Valve - Mixer Air-Gas Assembly
(NG-C36 Combi)
215 Gas Valve - Mixer Air-Gas Assembly
(LPG-C36P Combi)
138 Control Panel
135 Control Block
57 DHW Heat Exchanger
56 Hydroblock
58 Expansion Vessel
WD388/0/2004 Chapter 9 : Spare Parts Listings The Keston C36 & C36P Combi Boilers
Installation & Servicing Instructions Page : 49

WD388/0/2004 Chapter 10 : Benchmark Checklist Final The Keston C36 Combi & C36P COMBI Boilers
Installation & Servicing Instructions Page : 50
10. GAS BOILER COMMISSIONING CHECKLIST
BENCHMARK No.
GAS BOILER COMMISSIONING CHECKLIST
BOILER SERIAL No. ___________________ NOTIFICATION No. ____________________
CONTROLS
To comply with the Building Regulation, each section must have a tick in one or other of the boxes
7,0(7(03(5$785(&21752/72
+($7,1*
5220767$7
352*5$00(57,0(5
352*5$00$%/(522067$7
7,0(7(03(5$785(&21752/72+27
:$7(5
&</,1'(5767$7
352*5$00(57,0(5
&20%,%2,/(5
+($7,1*=21(9$/9(6 ),77('
1275(48,5('
+27:$7(5=21(9$/9(6 ),77('
1275(48,5('
7+(50267$7,&5$',$7259$/9(6 ),77('
$8720$7,&%<3$66726<67(0 ),77('
1275(48,5('
FOR ALL BOILERS CONFIRM THE FOLLOWING
7+(6<67(0+$6%((1)/86+(',1$&&25'$1&(:,7+7+(%2,/(50$18)$&785(5·6,16758&7,216"
7+(6<67(0&/($1(586('
7+(,1+,%,72586('
FOR THE CENTRAL HEATING MODE, MEASURE & RECORD
*$65$7( P
KU IW
KU
%851(523(5$7,1*35(6685(,)$33/,&$%/( 1$ PEDU
&(175$/+($7,1*)/2:7(03(5$785(
2
&
&(175$/+($7,1*5(78517(03(5$785(
2
&
FOR COMBINATION BOILERS ONLY
+$6$:$7(56&$/(5('8&(5%((1),77('" <(6
12
:+$77<3(2)6&$/(5('8&(5+$6%((1),77('"
FOR THE DOMESTIC HOT WATER MODE, MEASURE & RECORD
*$65$7( P
KU IW
KU
0$;,080%851(523(5$7,1*35(6685(,)$33/,&$%/( 1$ PEDU
&2/':$7(5,1/(77(03(5$785(
2
&
+27:$7(5287/(77(03(5$785(
2
&
:$7(5)/2:5$7( OWVPL
Q
FOR CONDENSING BOILERS ONLY CONFIRM THE FOLLOWING
7+(&21'(16$7('5$,1+$6%((1,167$//(',1$&&25'$1&(:,7+
7+(0$18)$&785(5·6,16758&7,216" <(6
FOR ALL INSTALLATIONS CONFIRM THE FOLLOWING
7+(+($7,1*$1'+27:$7(56<67(0&203/,(6
:,7+&855(17%8,',1*5(*8/$7,216
7+($33/,$1&($1'$662&,$7('(48,30(17+$6%((1,167$//('$1'&20,66,21('
,1$&&25'$1&(:,7+7+(0$18)$&785(5·6,16758&7,216
,)5(48,5('%<7+(0$18)$&785(5+$9(<285(&25'($&2&2
5$7,25($',1*" 1$
<(6
&2&2
5$7,2
7+(23(5$7,212)7+($33/,$1&($1'6<67(0
&21752/6+$9(%((1'(021675$7('727+(&86720(5

WD388/0/2004 Chapter 10 : Benchmark Checklist Final The Keston C36 Combi & C36P COMBI Boilers
Installation & Servicing Instructions Page : 51
SERVICE INTERVAL RECORD
It is recommended that your heating system is serviced regularly
and that you complete the appropriate Service Interval Record Below
Service Provider. Before completing the appropriate Service Interval Record below, please ensure you have carried out the service
as described in the boiler manufacturer’s instructions. Always use the manufacturer’s specified spare part when replacing all controls
SERVICE 2
DATE
ENGINEER NAME
COMPANY NAME
TEL No.
GAS SAFE REGISTER ID CARD SERIAL No.
COMMENTS
SIGNATURE
SERVICE 1
DATE
ENGINEER NAME
COMPANY NAME
TEL No.
GAS SAFE REGISTER ID CARD SERIAL No.
COMMENTS
SIGNATURE
SERVICE 3
DATE
ENGINEER NAME
COMPANY NAME
TEL No.
GAS SAFE REGISTER ID CARD SERIAL No.
COMMENTS
SIGNATURE
SERVICE 4
DATE
ENGINEER NAME
COMPANY NAME
TEL No.
GAS SAFE REGISTER ID CARD SERIAL No.
COMMENTS
SIGNATURE
SERVICE 6
DATE
ENGINEER NAME
COMPANY NAME
TEL No.
GAS SAFE REGISTER ID CARD SERIAL No.
COMMENTS
SIGNATURE
SERVICE 5
DATE
ENGINEER NAME
COMPANY NAME
TEL No.
GAS SAFE REGISTER ID CARD SERIAL No.
COMMENTS
SIGNATURE
SERVICE 7
DATE
ENGINEER NAME
COMPANY NAME
TEL No.
GAS SAFE REGISTER ID CARD SERIAL No.
COMMENTS
SIGNATURE
SERVICE 8
DATE
ENGINEER NAME
COMPANY NAME
TEL No.
GAS SAFE REGISTER ID CARD SERIAL No.
COMMENTS
SIGNATURE
SERVICE 9
DATE
ENGINEER NAME
COMPANY NAME
TEL No.
GAS SAFE REGISTER ID CARD SERIAL No.
COMMENTS
SIGNATURE
SERVICE 10
DATE
ENGINEER NAME
COMPANY NAME
TEL No.
GAS SAFE REGISTER ID CARD SERIAL No.
COMMENTS
SIGNATURE

b
Read Installation Manual Carefully
b
Ensure that ALL dust particles, filings , plastic chips etc. are
removed from the inlet pipe.
b
If the installation is a replacement the system must be flushed
clean. System should be drained hot, then refilled, then drained
again until the water is clean.
b
Ensure that there is a proper electrical supply i.e. 230V fused at
3A for the permanent live.
b
Take great care with pipe connections to ensure that no
damage is done to the internal pipework.
b
Ensure that the 22mm condensate pipe is not exposed to
freezing conditions.
b
Make sure that the exhaust pipe terminates away from windows
or vents and is out of reach.
b
Make sure that the air inlet and exhaust pipe outlets are at least
200mm apart.
b
Check tightness of all connections in the boiler before firing.
b
Ensure that the terminals supplied are fitted to both the exhaust
and air inlet pipes.
b
The system must be free from air before firing.
b
If TRV's are installed on radiators ensure that a bypass is
installed to maintain required flow.
b
Complete the Gas Boiler Commissioning Checklist - Service
Interval Record (Chapter 10).
b
Complete the combustion testing (Section 5.7) using a
calibrated flue gas analyser.
WD388/0/2004 The Keston C36 Combi & C36P Combi Boilers
KESTON CONDENSING BOILERS
IMPORTANT
C36 and C36P Combi
INSTALLATION KEY POINTS