LENNOX Package Units(both Units Combined) Manual L0806697
User Manual: LENNOX LENNOX Package Units(both units combined) Manual LENNOX Package Units(both units combined) Owner's Manual, LENNOX Package Units(both units combined) installation guides
Open the PDF directly: View PDF .
Page Count: 20
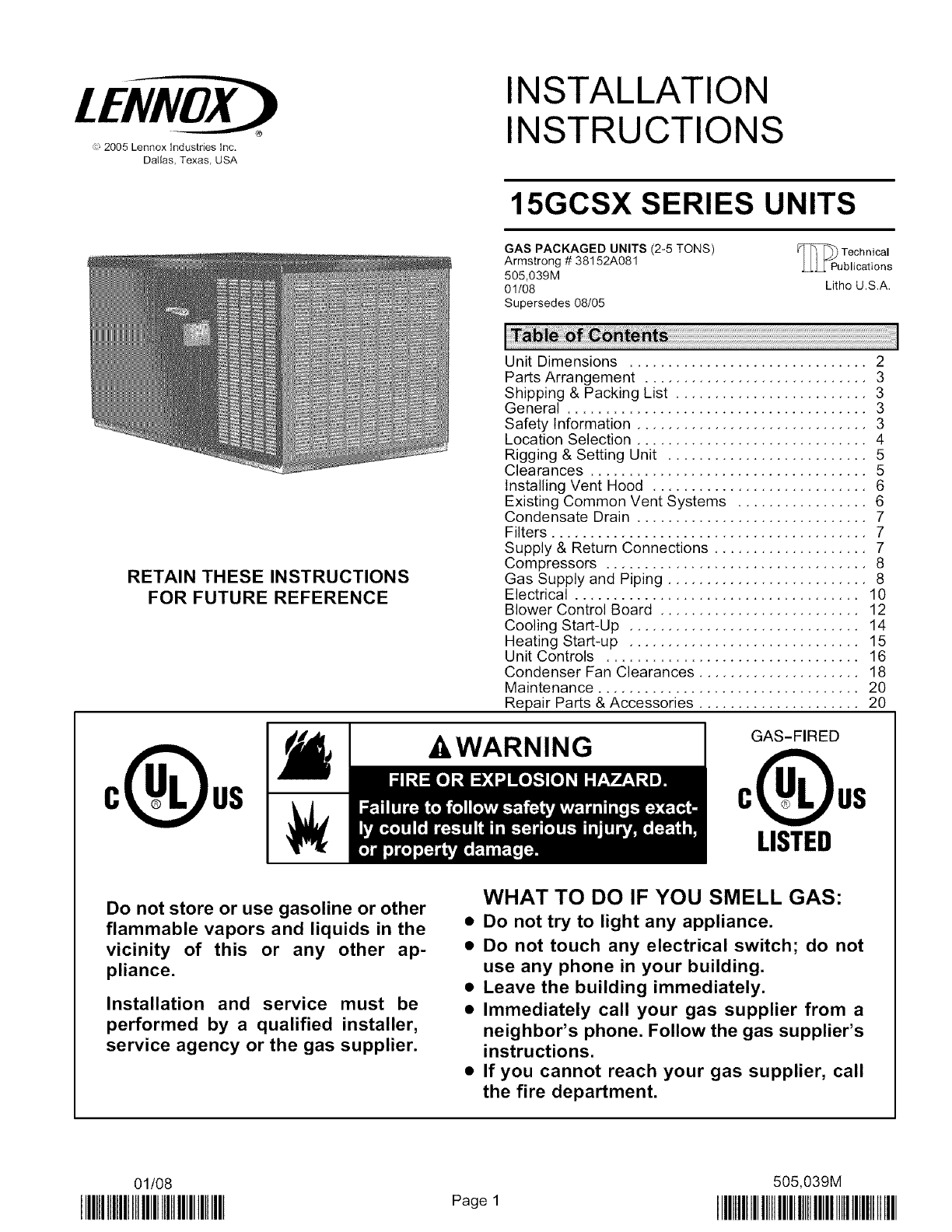
iwvox-)
®
,t_ 2005 Lennox Industries Inc.
Dallas, Texas, USA
INSTALLATION
INSTRUCTIONS
15GCSX SERIES UNITS
GAS PACKAGED UNITS (2-5 TONS)
Armstrong # 38152A081
505,039M
01/08
Supersedes 08/05
_pu Technical
blications
Litho U.S.A.
RETAIN THESE INSTRUCTIONS
FOR FUTURE REFERENCE
Unit Dimensions ............................... 2
Parts Arrangement ............................. 3
Shipping & Packing List ......................... 3
General ....................................... 3
Safety Information .............................. 3
Location Selection .............................. 4
Rigging & Setting Unit .......................... 5
Clearances .................................... 5
Installing Vent Hood ............................ 6
Existing Common Vent Systems ................. 6
Condensate Drain .............................. 7
Filters ......................................... 7
Supply & Return Connections .................... 7
Compressors .................................. 8
Gas Supply and Piping .......................... 8
Electrical ..................................... 10
Blower Control Board .......................... 12
Cooling Start-Up .............................. 14
Heating Start-up .............................. 15
Unit Controls ................................. 16
Condenser Fan Clearances ..................... 18
Maintenance .................................. 20
Repair Parts & Accessories ..................... 20
c( )us -&WARNING GAS-FIRED
o us
LISTED
Do not store or use gasoline or other
flammable vapors and liquids in the
vicinity of this or any other ap-
pliance.
Installation and service must be
performed by a qualified installer,
service agency or the gas supplier.
WHAT TO DO IF YOU SMELL GAS:
• Do not try to light any appliance.
•Do not touch any electrical switch; do not
use any phone in your building.
•Leave the building immediately.
•Immediately call your gas supplier from a
neighbor's phone. Follow the gas supplier's
instructions.
•If you cannot reach your gas supplier, call
the fire department.
01/08
IIIHIIIIIIIIIIIIIIIIIIIIIIIIIIlllllll Page 1
505,039M
IIIlllllllllllllllllllllllllllllllllllllll
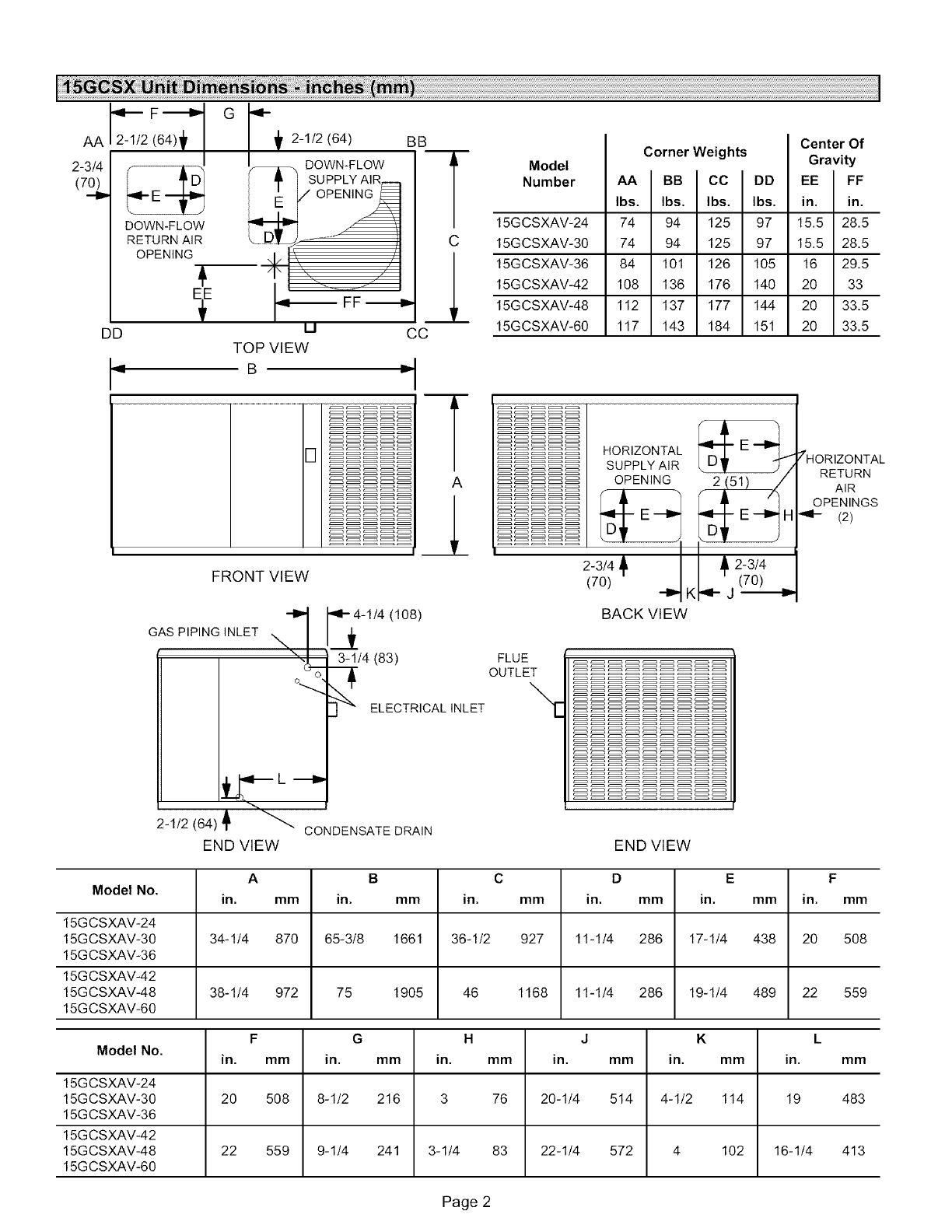
AA (
2-314
(70)
DOWN-FLOW
RETURN AIR
OPENING
Ei
G
2-1/2 (64)
DOWN-FLOW
BB-r
C
_l
DD
,iI
u CC
TOP VIEW
B
A
_2
FRONT VIEW
GAS PIPING INLET _'X'_
_L---P
Model
Number
.91- 4-1/4 (108)
__I
3-1/4 (83) FLUE
OUTLET
\
ELECTRICAL INLET "I-
i
15GCSXAV-24
15GCSXAV-30
15GCSXAV-36
15GCSXAV-42
15GCSXAV-48
15GCSXAV-60
74
74
84
108
112
117
Corner Weights
125 97 15.5
125 97 15.5
126 105 16
176 140 20
177 144 20
184 151 20
94
94
101
136
137
143
Center Of
Gravity
FF
in.
28.5
28.5
29.5
33
33.5
33.5
HORIZONTAL E
SUPPLY AIR
OPENING 22
D : E---_ H
2-3/4 2-314
- (70)
(70) K _I- J -_
BACK VIEW
7HORIZONTAL
RETURN
AIR
OPENINGS
(2)
2-1/2 (64) _i _ CONDENSATE DRAIN
END VIEW END VIEW
A B CD E F
Model No. in. mm in. mm in. mm in. mm in. mm in. mm
15GCSXAV-24
15GCSXAV-30 34-1/4 870 65-3/8 1661 36-1/2 927 11-1/4 286 17-1/4 438 20 508
15GCSXAV-36
15GCSXAV-42
15GCSXAV-48 38-1/4 972 75 1905 46 1168 11-1/4 286 19-1/4 489 22 559
15GCSXAV-60
F G H J K L
Model No. in. mm in. mm in. mm in. mm in. mm in. mm
15GCSXAV-24
15GCSXAV-30 20 508 8-1/2 216 3 76 20-1/4 514 4-1/2 114 19 483
15GCSXAV-36
15GCSXAV-42
15GCSXAV-48 22 559 9-1/4 241 3-1/4 83 22-1/4 572 4 102 16-1/4 413
15GCSXAV-60
Page 2

PureAir_Gas Valve
Air Purification System
(Optional) \
\\ \
Ignition Control
Board Condenser
Coil
/
Evaporator
Coil
Control Box
Variable
Speed
Blower Motor Gas
Manifold Burner Box
Compressor
\\Pressure
Switch
Combustion
Air Inducer
1 - Assembled gas package unit
1 - Vent hood assembly with screen and screws
As soon as the unit is received, it should be inspected for
possible damage during transit. If you find any damage, im-
mediately contact the last carrier.
Ak WARNING
These installation instructions are intended as a general
guide only, for use by an experienced, qualified contractor.
The 15GCSX units are single-package air conditioners
with two-stage gas heat designed for outdoor installation
on a rooftop or a slab.
The unit must be sized based on heat loss and heat gain
calculations made according to the methods of the Air
Conditioning Contractors of America (ACCA).
The units are shipped assembled. All piping, refrigerant
charge, and electrical wiring are factory-installed and
tested. The units require electric power, gas piping,
condensate drain and duct connections at the point of
installation. In addition, the heating vent hood must be
installed before the unit is placed into operation
,CAUTION
&IMPORTANT
Page 3

,&, WARNING
These units must be installed in accordance with all
applicable national and local safety codes,
These instructions are intended as a general guide and do
not supersede local codes in any way, Consult authorities
having jurisdiction before installation.
If components are to be added to a unit to meet local codes,
they are to be installed at the dealer's and/or customer's
expense.
These units are design listed by UL in both the United
States and Canada as follows:
•- For use as a forced air furnace with cooling,
• - For outdoor installation only,
• - For installation on combustible material,
• - For use with natural gas or L.P,/propane gas only. Use
of L.P./propane gas requires installation of an L,P,
conversion kit, which must be ordered separately.
These units are not suitable for use with conventional
venting systems.
The following safety requirements must also be met when
the 15GCSX units are installed:
1 - Use only with the type of fuel approved for use with this
appliance, Refer to the unit rating plate,
2 - Position, locate and install the 15GCSX unit only as
outlined in these instructions.
3 - Provide adequate clearance around the vent hood as
specified in these instructions.
4 - Do not use an open flame to check for gas leaks. Use a
commercially available soap solution, which has been
designed specifically to check for gas leaks, Refer to
the Gas Supply and Piping section,
5 - Check the unit operation after start-up to make sure
that the 15GCSX is operating within the intended tem-
perature rise range. The duct system must be de-
signed to provide an external static pressure within the
allowable range, Refer to the unit rating plate,
Lennox does not recommend the use of 15GCSX units as a
construction heater during any phase of construction, Very
low return air temperatures, harmful vapors and operation
of the unit with clogged or misplaced filters will damage the
unit,
15GCSX units may be used for heating of buildings or
structures under construction, if the following conditions
are met:
•The vent hood must be installed per these installation in-
structions.
• A room thermostat must control the furnace, The use of
fixed jumpers that will provide continuous heating is not
allowed.
• The return air duct must be provided and sealed to the
furnace.
• Return air temperature range between 60°F (16°C) and
80°F (27°C) must be maintained.
• Air filters must be installed in the system and must be
maintained during construction.
• Air filters must be replaced upon construction comple-
tion.
• The input rate and temperature rise must be set per the
unit rating plate.
• One hundred percent (100%) outdoor air must be pro-
vided for combustion air requirements during construc-
tion. Installation of this unit in its intended outdoor loca-
tion will accomplish this.
• The heat exchanger, components, duct system, air fil-
ters and evaporator coil must be thoroughly cleaned fol-
lowing final construction clean-up.
• The unit operating conditions (including ignition, input
rate, temperature rise and venting) must be verified ac-
cording to these installation instructions.
NOTE -The Commonwealth of Massachusetts stipu-
lates these additional requirements:
• Gas furnaces shall be installed by a licensed plumb-
er or gas fitter only.
• The gas cock must be "T handle" type.
• When flexible connectors are used, the maximum
length shall not exceed 36".
Use the following guidelines to select a suitable location for
these units,
1 - Unit is designed for outdoor installation only. Unit must
be installed so all electrical components are protected
from water.
2 - Condenser coils must have an unlimited supply of air.
3 - For ground level installation, use a level pre-fabricated
pad or use a level concrete slab with a minimum thick-
ness of 4 inches. The length and width should be at
least 6 inches greater than the unit base, Do not tie the
slab to the building foundation.
4 - Maintain level within a tolerance of 1/4 inch maximum
across the entire length or width of the unit,
Page 4

5- Donotlocatetheunitwherethecombustionairsupply
willbeexposedtoanycorrosivesubstance,including
thefollowing:
Permanentwavesolutions,
Chlorinatedwaxesorcleaners,
Chlorine-basedswimmingpoolchemicals,
Water-softeningchemicals,
De-icingsaltsorchemicals,
Carbontetrachloride,
Halogen-typerefrigerants,
Cleaningsolvents(e.g.,perchloroethylene),
Printinginks,paintremovers,varnishes,etc.,
Cementsandglues,
Anti-staticfabricsoftenersusedinclothesdryers,
Masonryacid-washingmaterials,
Chlorinatedlaundryproducts,
Hydrochloricacid.
Exercisecarewhenmovingtheunit.Donotremoveany
packaginguntiltheunitisneartheplaceofinstallation.An
optionallifting lug kit (92M51)may be purchased
separatelyfor use in riggingthe unit for lifting.The
spreader lengths must exceed the width across the top
of the unit. Recommended spreader lengths: for use with
2, 2-1/2 and 3-ton units -- 44"; for use with 3-1/2, 4 and 5-ton
units -- 54",
CAUTION
Accessory Lift Kit
Figure 1
Units may also be moved or lifted with a forklift while still in
the factory supplied packaging.
NOTE -Length of forks must be a minimum of 42 inches.
Page
All units require certain clearances for proper operation
and service. Refer to figure 2 for the clearances required
for combustible construction, servicing, and proper unit
operation.
NOTE -Do not permit overhanging structures or shrubs to
obstruct condenser air discharge outlet or vent outleL
Service Clearances
36 (914)
48 (1219)
NOTE - Top Clearance - 36 in. (914 mm)
NOTE - Entire perimeter of unit base requires
support when elevated above mounting surface.
Figure 2
In the U.S. units may be installed on combustible flooring
made from wood or class A, B, or C roof covering material.
In Canada, units may be installed on combustible flooring.
The products of combustion are discharged through a
screened vent outlet in the front mullion.
Install the unit so that the products of combustion will not
damage the outer building structure.
The vent outlet must be at least 4 feet below, 4 feet
horizontally from and 1 foot above any door, window or
gravity air inlet into the building. In addition, install the unit
so that the vent outlet is at least 3 feet above any forced air
inlet located within 10 feet.
Clearances to the vent outlet must also be consistent with
the requirements of the current National Fuel Gas Code
(Z223.1) and/or the standards of the current CSA B149
codes.
Figure 3 shows the minimum clearances to combustibles
required above and below the vent hood. The minimum
clearance in front of the vent hood is 24 inches.
Install the unit so that snow accumulation will not restric the
flow of the flue products. Allow a required minimum
horizontal clearance of 4 feet from electric meters, gas
meters, regulators and relief equipment. In addtion to the
above requirements, ensure that unwanted ice caused by
condensate is not allowed to accumulate around the unit.
Do not locate the unit on the side of the building where the
prevailing winter winds could trap moisture, causing it to
freeze on the walls or on overhangs (under eaves). The

vent outletshouldnot dischargeflue productson a
sidewalk,patioor otherwalkwaywherethe condensate
couldcausethesurfacetobecomeslippery,
Do not install the unit so that the products of
combustionwill be allowedto accumulatewithin a
confinedspaceandrecirculate.
Minimum Clearances to Combustible Materials
Above and Below Vent Hood
Minimum Clearance
Above Vent Hood:
Distance from Top
of Vent Hood
to Top of Unit
Minimum Clearance
Below Vent Hood:
Distance from Bottom
of Vent Hood to Base
of Unit
Figure 3
The vent hood, screen and screws are shipped inside the
unit in the plastic bag which contains the installation
instructions,
1 - Insert the vent screen into the vent tube Once in-
serted, the screen should be flush with the end of the
tube as shown in figure 4.
Vent Hood Installation
Front View Top View
_Vent Tube
NOTE -
Screws
Vent Tube should pass
Screen is pre-formed Vent Hood through
sides of
screen to
hold screen
__ in place.
i Slotted side of
vent hood faces
condenser coil.
Figure 4
2 - Position the vent hood over the vent tube so that the
slotted side of the hood faces the condenser coil. Use
the four sheet metal screws (provided) to secure the
vent hood to the vent tube. The screws should pass
through the sides of the screen in order to hold the
screen in place.
The vent hood must be installed prior to unit start-up.
If the 15GCSX unit is replacing an existing furnace which is
being removed from a venting system commonly run with
separate gas appliances, the venting system is likely to be
too large to properly vent the remaining attached ap-
pliances.
Conduct the following test while each appliance is operat-
ing and the other appliances (which are not operating) re-
main connected to the common venting system. If the vent-
ing system has been installed improperly, you must
correct the system as indicated in the general venting re-
quirements section.
1 - Seal any unused openings in the common venting sys-
tem.
2 - Inspect the venting system for proper size and horizon-
tal pitch. Determine that there is no blockage, restric-
tion, leakage, corrosion, or other deficiencies which
could cause an unsafe condition.
3 - Close all building doors and windows and all doors be-
tween the space in which the appliances remaining
connected to the common venting system are located
and other spaces of the building. Turn on clothes dry-
ers and any appliances not connected to the common
venting system. Turn on any exhaust fans, such as
range hoods and bathroom exhausts, so they will oper-
ate at maximum speed. Do not operate a summer ex-
haust fan. Close fireplace dampers.
4 - Follow the lighting instructions. Turn on the appliance
that is being inspected. Adjust the thermostat so that
the appliance operates continuously.
5 - After the main burner has operated for 5 minutes, test
for leaks of flue gases at the draft hood relief opening.
Use the flame of a match or candle, or smoke from a
cigarette, cigar, or pipe.
6 - After determining that each appliance connected to the
common venting system is venting properly, (step 3)
return all doors, widows, exhaust fans, fireplace damp-
ers, and any other gas-burning appliances to their pre-
vious mode of operation.
7 - If a venting problem is found during any of the preced-
ing tests, the common venting system must be modi-
fied to correct the problem.
Resize the common venting system to the minimum
vent pipe size determined by using the appropriate
tables in Appendix G. (These are in the current stan-
dards of the National Fuel Gas Code
ANSl-Z223.1/NFPA 54 in the USA, and the appropri-
ate Category 1 Natural Gas and Propane appliances
venting sizing tables in the current standards of the
CSA B149 Natural Gas and Propane Installation
Codes in Canada.)
Page 6

The15GCSXunitisequippedwitha 3/4inchFPTcoupling
forcondensatelineconnection.Plumbingmustconformto
local codes.Use a sealingcompoundon malepipe
threads.
Thedrainlinemustbeproperlytrappedandroutedtoa
suitabledrain.Seefigure5forproperdrainarrangement.
Thedrainlinemustpitchto anopendrainor pumpa
minimumof 1inchper10feetto preventcloggingofthe
line.Thedrainlinemustbesupportedso thatweightof
drainlineis not carriedby drainlineconnection.Seal
arounddrainconnectionwithsuitablematerialto prevent
airleakageintoreturnairsystem.
Drainpipingshouldnotbesmallerthandrainconnectionat
coil.Anopenventindrainlinewillsometimesberequired
dueto line length,frictionand staticpressure.Drains
shouldbeconstructedinamannertofacilitatefutureclean-
ing.
NOTE -The condensate drain line MUST be trapped to
provide proper drainage.
CAUTION
vent
Trap must be deep enough to offset maximum
static difference (Generally, 3 inches minimum).
Typical Condensate Drain
Minimum Pitch
1 in. (25 ram) per
10' (3 m) of line unit
open
mounting
frame
Figure 5
Table 1
Unit Filter Size
Unit Model Filter Size Filter Quantity
-24, -30, -36 20 in. X 25 in. 1
-42, -48, -60 16 in. X 25 in. 2
The Healthy Climate ® PureAir ¢ air purification system
(PCO20-28) may be used with 15GCSX units installed in
horizontal air discharge applications only. Installation
hardware kit (Y0629)is required to install the PCO20-28
(X8787) in the packaged unit. The PCO20-28 is designed
for universal voltage, and is ready to operate at 208/230V.
When used, the PCO should be installed before the unit is
set in place and before the duct connections are made.
The duct system should be designed and sized according
to the methods in Manual Q of the Air Conditioning
Contractors of America (ACCA).
A closed return duct system shall be used. This shall not
preclude use of economizers or outdoor fresh air intake. It
is recommended that supply and return duct connections
at the unit be made with flexible joints.
The supply and return air duct systems should be designed
for the CFM and static requirements of the job. They
should NOT be sized by simply matching the
dimensions of the duct connections on the unit.
CAUTION
The 15GCSX unit is shipped ready for horizontal air
discharge (side duct connections). If bottom air discharge
is desired, the covers must be removed from the supply
and return air openings on the bottom of the unit and
re-installed to cover the side openings.
The upper return air opening cover must be removed when
the PureAir ¢ air purification system (PCO20-28) is being
used. In PCO applications, both upper and lower return air
openings must be covered by the return air plenum to
ensure proper PCO operation. The upper return air
opening is not required in horizontal applications when the
PCO is not used.
Filters are not factory-supplied with the unit; however,
optional internally installed filter kits are available. Filter kit
92M54 is used with 2, 2-1/2 and 3-ton units. Filter kit 92M55
is used with 3-1/2, 4 and 5-ton units. The filter kits
accommodate the use of 1", 2" or 4" filters. If the optional
filter kit is not used, a filter must be field-installed.
Filters must always be installed ahead of evaporator coil
and must be kept clean or replaced. Dirty filters will reduce
the airflow of the unit. Filter sizes are shown in table 1.
Removing Supply and Return
Air Opening Covers
1. Remove screw and lift. Base----_ _ I
2. Slide cover to free back pin.
Figure 6
Page 7

Units are shippedwith the compressormountings
factory-adjustedandreadyforoperation.
CAUTION
Check the unit rating plate to confirm whether unit is
equipped for use with natural gas or LP/propane. If
conversion is required use the approved conversion kit.
NQ TE -Units are shipped equipped for natural gas, but can
be converted to LP/propane with a conversion kit. Conver-
sion must be performed by an approved licensed pipe
fitter or technician.
All LP/propane gas equipment must conform to the safety
standards of the National Fire Protection Association.
Complete information regarding tank sizing for
vaporization, recommended regulator settings, and pipe
sizing is available from most regulator manufacturers and
LP/propane gas suppliers.
Proper sizing of gas piping depends on the cubic feet per
hour of gas flow required, specific gravity of the gas and
length of run. In the United States, the current National Fuel
Gas Code Z223.1 should be followed in all cases unless
superseded by local codes or gas company requirements.
Refer to tables 2 and 3. In Canada, refer to the current CSA
B.149 installation codes.
Table 2
Gas Heat Application Data
Unit Input Rating Output Rating Gas Capacity*
Heating Size (Btu) (Btu) (FT3/HR)
68 67,500 54,000 63
83 82,500 66,000 77
90 90,000 72,000 84
110 110,000 88,000 102
138 137,500 110,000 128
*Based on 1075Btu per cubic foot of natural gas.
Before connecting piping, check with gas company or au-
thorities having jurisdiction for local codes or requirements,
When installing gas supply piping, length of run from gas
meter must be considered in determining pipe size for 0.5
inch w.c, maximum pressure drop, Do not use supply pipe
smaller than unit gas connection, For natural gas unit, sup-
ply pressure at the unit gas connection must be a minimum
of 5 inches w.c. and a maximum of 10.5 w.c. For LP/pro-
pane gas units, supply pressure at the unit gas connection
must be a minimum of 11 inches w.c. and a maximum of
13.0 inches w.c.
Table 3
Gas Pipe Capacity-FT 3/HR
Nominal Iron Pipe Size (inches)
Lengthin Feet 1/2 in.
10 132
20 92
30 73
40 63
50 56
60 50
70 46
80 43
90 40
100 38
3/4in. 1 in.
278 520
190 350
152 285
130 245
115 215
105 195
96 180
90 170
84 160
79 150
1-1/4 in.
1050
730
590
5OO
440
400
370
350
320
305
The gas supply piping should be routed through the grom-
met on the side of the unit. Refer to figure 7.
Gas Piping and Electrical Conduit Access
Gas
Thermostat/_'(_/_(_)
Entry J o
/
Line Voltage
Entry
Figure 7
When making piping connections, a drip leg should be
installed on vertical runs to serve as a trap for sediment or
condensate. A 1/8 inch N.P.T. tap accessible for test gauge
connection must be provided in field piping upstream from
gas supply connection to unit. Install a ground joint union
between gas control manifold and the manual main shut-
off valve. See figure 8.
Compounds used on threaded joints of gas piping shall be
resistant to the action of propane/LP gases.
Page 8
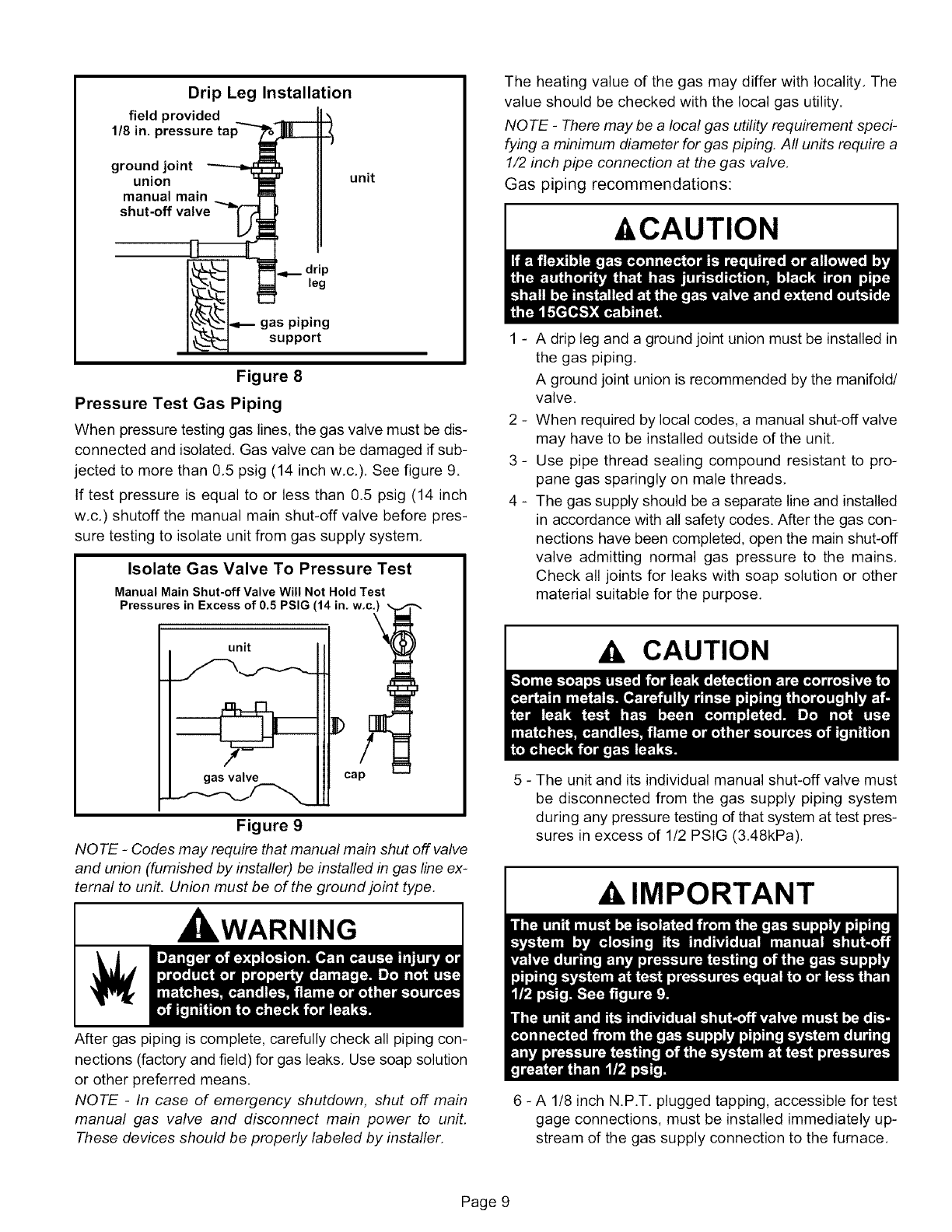
Drip Leg Installation
field provided
1/8 in. !
ground joint
union
manual main
shut-off
unit
I_ leg
gas piping
support
Figure 8
Pressure Test Gas Piping
When pressure testing gas lines, the gas valve must be dis-
connected and isolated. Gas valve can be damaged if sub-
jected to more than 0,5 psig (14 inch w,c,), See figure 9.
If test pressure is equal to or less than 0,5 psig (14 inch
w,c,) shutoff the manual main shut-off valve before pres-
sure testing to isolate unit from gas supply system,
Isolate Gas Valve To Pressure Test
Manual Main Shut-off Valve Will Not Hold Test
Pressures in Excess of 0.5 PSIG (14 in. w.c.)
unit
cap
gas valve
Figure 9
NOTE -Codes may require that manual main shut off valve
and union (furnished by installer) be installed in gas line ex-
ternal to unit. Union must be of the ground joint type.
, WARNING
After gas piping is complete, carefully check all piping con-
nections (factory and field) for gas leaks, Use soap solution
or other preferred means.
NOTE -In case of emergency shutdown, shut off main
manual gas valve and disconnect main power to unit,
These devices should be properly labeled by installer,
The heating value of the gas may differ with locality, The
value should be checked with the local gas utility.
NOTE -There may be a local gas utility requirement speci-
fying a minimum diameter for gas piping. All units require a
1/2 inch pipe connection at the gas valve.
Gas piping recommendations:
-&CAUTION
1 - A drip leg and a ground joint union must be installed in
the gas piping,
A ground joint union is recommended by the manifold/
valve.
2 - When required by local codes, a manual shut-off valve
may have to be installed outside of the unit,
3 - Use pipe thread sealing compound resistant to pro-
pane gas sparingly on male threads,
4 - The gas supply should be a separate line and installed
in accordance with all safety codes. After the gas con-
nections have been completed, open the main shut-off
valve admitting normal gas pressure to the mains,
Check all joints for leaks with soap solution or other
material suitable for the purpose.
Ak CAUTION
5 - The unit and its individual manual shut-off valve must
be disconnected from the gas supply piping system
during any pressure testing dthat system at test pres-
sures in excess of 1/2 PSlG (3.48kPa).
AIMPORTANT
6 - A 1/8 inch N.P.T. plugged tapping, accessible for test
gage connections, must be installed immediately up-
stream of the gas supply connection to the furnace,
Page 9

All wiring should be done in accordance with the
current National Electric Code ANSI/NFPA No. 70 in
the United States. In Canada, wiring must be done in
accordance with the current CSA C22.2 Part 1. Local
codes may take precedence.
Use wiring with a temperature limitation of 75_C min.; run
the 208 or 230 volt, 60 hertz electric power supply through a
fused disconnect switch to control box of unit and connect
as shown in the wiring diagram located on the inside of the
control access panel,
Unit must be electrically grounded in accordance with local
codes or in the absence of local codes with the National
Electric Code, ANSI/NFPA No, 70 (latest edition) or CSA
C22.2 Part 1 (latest edition).
Power supply to the unit must be N.E,C, Class 1, and must
comply with all applicable codes. A fused disconnect
switch should be field provided for the unit, The switch must
be separate from all other circuits, If any of the wire
supplied with the unit must be replaced, replacement wire
must be of the type shown on the wiring diagram.
Electrical wiring must be sized to carry minimum circuit
ampacity marked on the unit. USE COPPER
CONDUCTORS ONLY, Each unit must be wired with a
separate branch circuit and be properly fused.
CAUTION
See figure 10 for field connection of line voltage wiring, See
figure 11 for typical wiring diagram.
208/230 Line Voltage Wiring
contactor
CE_D fused disconnect switch
(furnished by installer)
v
ground L2
lug
NOTE -ff 208 voltage is suppfied, transformer
connections must be made.
Figure 10
Thermostat
The room thermostat should be located on an inside wall
where it will not be subject to drafts, sun exposure or heat
from electrical fixtures or appliances. Follow
manufacturer's instructions enclosed with thermostat for
general installation procedure, Color coded insulated wires
(# 18 AWG) should be used to connect thermostat to unit,
Four wires are required for cooling,
Heat Anticipator Setting
It is important that the anticipator setpoint be correct. Too
high of a setting will result in longer heat cycles and a
greater temperature swing in the conditioned space,
Reducing the value below the correct setpoint will give
shorter "ON" cycles and may result in the lowering of the
temperature within the conditioned space.
Heat Anticipator Setting: 0.70 AMP
Page 10

(£:I
15GCSX Series Gas Packaged Units
Typical Wiring Diagram

DIAGNOSTIC
LED
BLOWER CONTROL BOARD (A54)
_ HUM
ICMP/N _) CI (RC0m)
AH4103
ADJUST
SELECTOR PINS
(Setting affects both
heating and cooling
modes)
HEATING SPEED
SELECTOR PINS
COOLING SPEED
SELECTOR PINS
WARNING
15GCSX units are equipped with a variable speed motor
that is capable of maintaining a specified CFM throughout
the external static range, A particular CFM can be obtained
by positioning jumpers (COOL, HEAT, and ADJUST) on
the blower control board. The HEAT and COOL jumpers
are labeled A, B, C and D. Each of the numbers corre-
sponds with an air volume (CFM) setting. The ADJUST
jumper is labeled Test, -, +, and Norm. The + and - pin set-
tings are used to add or subtract a percentage of the CFM
selected, The Test jumper is used to operate the motor in
the test mode. See figure 12,
Factory settings for the blower speed jumpers are given in
the wiring diagram in figure 11. Figure 12 shows the blower
control board. Use tables 4, 5 and 6 to determine the cor-
rect air volume for operation in heat and cool mode,
The CFM LED located on the blower control board flashes
one time per 100 cfm to indicate selected blower speed,
For example, if the unit is operating at 1000 CFM, CFM
LED will flash 10 times, If the CFM is 1150, CFM LED will
flash 11 full times plus one fast or half flash.
At times the light may appear to flicker or glow. This takes
place when the control is communicating with the motor be-
tween cycles, This is normal operation,
Read through the jumper settings section before adjusting
the jumper to obtain the appropriate blower speed,
Figure 12
To change jumper positions, gently pull the jumper off the
pins and place it on the desired set of pins, The following
section outlines the different jumper selections available
and conditions associated with each one, Refer to figure
12,
After the CFM for each application has been determined,
the jumper settings must be adjusted to reflect those given
in tables 4, 5 and 6, From the tables, determine which row
most closely matches the desired CFM Once a specific
row has been chosen (% NORMAL, or-), CFM volumes
from other rows cannot be used, Below are descriptions of
the jumper selections,
The variable speed motor slowly ramps up to and down
from the selected air flow during both cooling and heating
demand, This minimizes noise and eliminates the initial
blast of air when the blower is initially energized.
ADJUST
The ADJUST pins allow the motor to run at normal speed,
approximately 15 percent higher, or approximately 15 per-
cent lower than normal speed, Tables 4, 5 and 6 give three
rows (% NORMAL, and -) with their respective CFM vol-
umes. Notice that the normal adjustment setting for heat
speed position C in table 4 is 900 CFM The + adjustment
setting for that position is 1035 CFM and for the - adjust-
ment setting is 765 CFM After the adjustment setting has
been determined, choose the remaining speed settings
from those offered in the table in that row.
The TEST pin is available to bypass the blower control and
run the motor at approximately 70 percent to make sure
that the motor is operational. This is used mainly in trouble-
shooting, The G terminal must be energized for the motor
to run,
Page 12

COOL
TheCOOLjumperis usedto determinetheCFMduring
coolingoperation.Thisjumperselectionis activatedfor
coolingwhenY1isenergized,
Theblowermotorrunsat80percentoftheselectedairflow
forthefirst7-1/2minutesofeachcoolingdemand,Thisfea-
tureallowsforgreaterhumidityremovalandsavesenergy,
In the coolingmode,the blowercontrolboarddelays
bloweroperationfor5secondsafterthecompressorstarts.
Theblowercontinuestooperatefor90secondsafterthe
compressorisde-energized,
HEAT
TheHEATjumperis usedto determineCFMduringgas
heatoperationonly.Thesejumperselectionsareactivated
onlywhenW1isenergized,
In the heatingmode,the blowercontrolboarddelays
bloweroperationfor 30 secondsafter the flame is
established,The blowercontinuesto operatefor 90
secondsafterthegasvalveisde-energized,
CONTINUOUSFAN
Whenthethermostatissetfor"ContinuousFan"operation
andthereisnodemandforheatingorcooling,theblower
controlwillprovide50percentoftheCOOLCFMselected,
NQ TE -With the proper thermostat and subbase, continu-
ous blower operation is possible by closing the R to G cir-
cuit, Cooling blower delay is also functional in this mode.
DEHUMIDIFICATION
The blower control board includes an HUM terminal which
provides for connection of a humidistat. The JV1 resistor
on the blower control board must be cut to activate the
HUM terminal, The humidistat must be wired to open on
humidity rise, When the dehumidification circuit is used,
the variable speed motor will reduce the selected air flow
rate by 25 percent when humidity levels are high. An LED
(D1) lights when the blower is operating in the dehumidifi-
cation mode,
ADJUST
Jumper
Setting
+
NORM
A
cfm L/s
1150 545
1000 470
850 400
"COOL" Speed
B C
cfm L/s cfm L/s
920 435 690 325
800 380 600 285
680 320 510 240
Table 4
15GCSXAV-24, 15GCSXAV-30 Blower Performance
0through 0.80 in. w.g. (0 through 200 Pa) External Static Pressure Range
Jumper Speed Positions
"HEAT" Speed
D
cfm L/s
1035 490
900 425
765 360
A
cfm L/s
1265 595
1100 520
935 440
B
cfm L/s
1150 545
1000 470
850 400
C
cfm L/s
1035 490
900 425
765 360
D
cfm L/s
920 435
800 380
680 320
"CONTINOUS FAN" S
A B
cfm L/s cfm L/s
575 270 460 215
500 235 400 190
425 200 340 160
C
cfm L/s
345 165
300 140
300 140
)eed
D
cfm L/s
520 245
450 210
385 180
ADJUST
Jumper
Setting
+
NORM
A
cfm L/s
1380 650
1200 565
1020 480
Table 5
15GCSXAV-36 Blower Performance
0through 0.80 in. w.g. (0 through 200 Pa) External Static Pressure Range
Jumper Speed Positions
"COOL" Speed "HEAT" Speed "CONTINOUS FAN" Speed
B
cfm L/s
1150 545
1000 470
850 400
C
cfm L/s
920 435
800 380
680 320
D
cfm L/s
1265 575
1100 520
935 440
A
cfm L/s
1555 735
1350 635
1150 540
B
cfm L/s
1265 595
1100 520
935 440
C
cfm L/s
1150 545
1000 470
850 400
D
cfm L/s
1035 490
900 425
765 360
A
cfm L/s
690 325
600 285
510 240
B
ufm L/s
575 270
500 235
425 200
C D
cfm L/s cfm L/s
460 215 635 300
400 190 550 260
350 165 470 220
"AD-
JUST"
Jumper
Setting
+
NORM
A
cfm L/s
2070 975
1800 850
1530 720
Table 6
15GCSXAV-42, 15GCSXAV-48, 15GCSXAV-60, Blower Performance
0 through 0.80 in. w.g. (0 through 200 Pa) External Static Pressure Range
Jumper Speed Positions
"COOL" Speed "HEAT" Speed "CONTINOUS FAN" S 3eed
B
cfm L/s
1840 870
1600 755
1360 640
C
cfm L/s
1610 760
1400 660
1190 560
D
cfm L/s
1380 650
1200 565
1020 480
A
cfm L/s
2015 950
1750 825
1490 700
B
cfm L/s
1900 895
1650 780
1405 660
C
cfm L/s
1555 735
1350 635
1150 540
D
cfm L/s
1325 625
1150 545
980 460
A
cfm L/s
1035 490
900 425
765 360
B
cfm L/s
920 435
800 380
680 320
C D
cfm L/s cfm L/s
805 380 690 325
700 330 600 285
595 280 510 240
Page 13
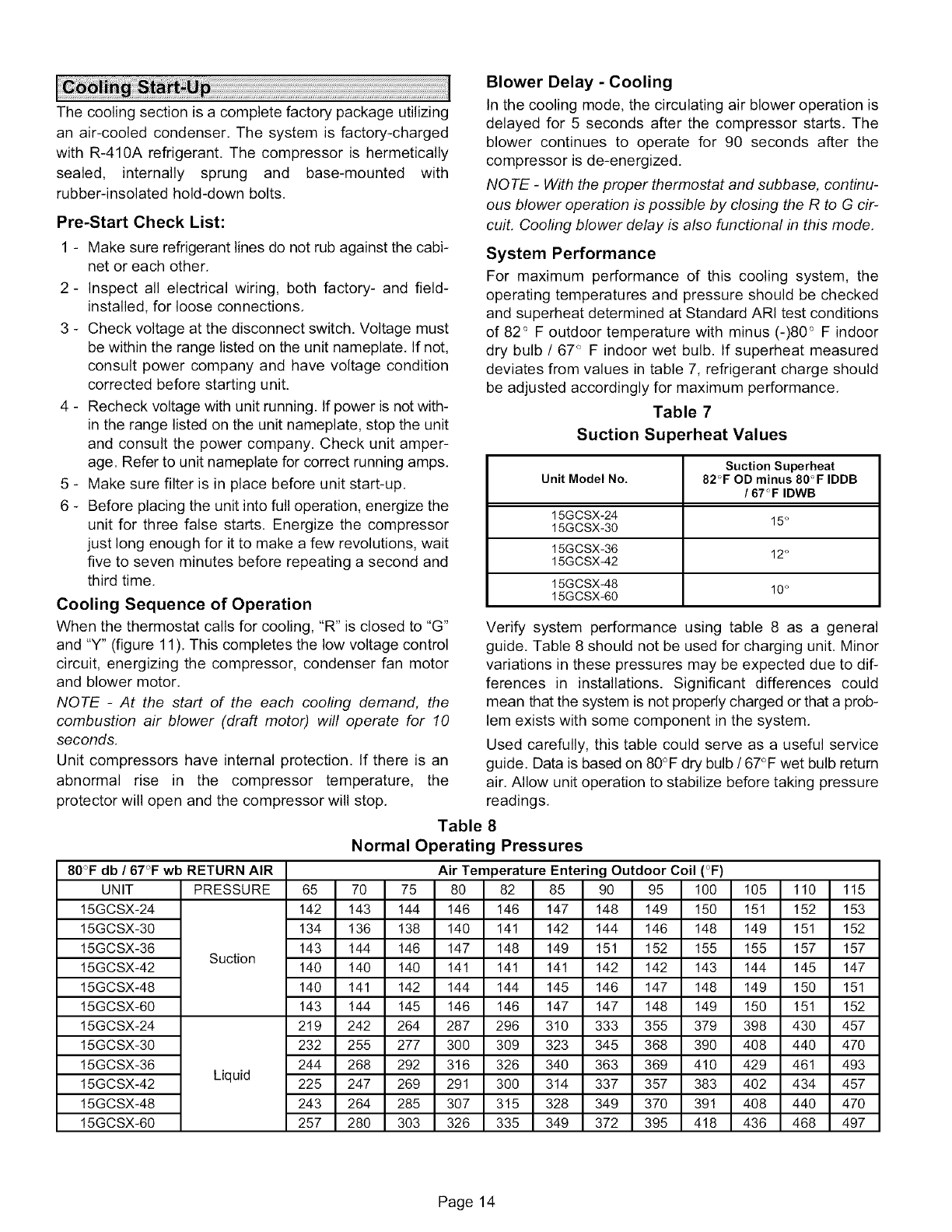
Thecoolingsectionisacompletefactorypackageutilizing
anair-cooledcondenser.Thesystemisfactory-charged
withR-410Arefrigerant.Thecompressoris hermetically
sealed, internally sprung and base-mountedwith
rubber-insolatedhold-downbolts.
Pre-Start Check List:
1 - Make sure refrigerant lines do not rub against the cabi-
net or each other.
2- Inspect all electrical wiring, both factory- and field-
installed, for loose connections.
3 - Check voltage at the disconnect switch. Voltage must
be within the range listed on the unit nameplate. If not,
consult power company and have voltage condition
corrected before starting unit.
4 - Recheck voltage with unit running. If power is not with-
in the range listed on the unit nameplate, stop the unit
and consult the power company. Check unit amper-
age. Refer to unit nameplate for correct running amps.
5 - Make sure filter is in place before unit start-up.
6 - Before placing the unit into full operation, energize the
unit for three false starts. Energize the compressor
just long enough for it to make a few revolutions, wait
five to seven minutes before repeating a second and
third time.
Cooling Sequence of Operation
When the thermostat calls for cooling, "R" is closed to "G"
and "Y" (figure 11). This completes the low voltage control
circuit, energizing the compressor, condenser fan motor
and blower motor.
NOTE -At the start of the each cooling demand, the
combustion air blower (draft motor) will operate for 10
seconds.
Unit compressors have internal protection. If there is an
abnormal rise in the compressor temperature, the
protector will open and the compressor will stop.
Blower Delay - Cooling
In the cooling mode, the circulating air blower operation is
delayed for 5 seconds after the compressor starts. The
blower continues to operate for 90 seconds after the
compressor is de-energized.
NOTE -With the proper thermostat and subbase, continu-
ous blower operation is possible by closing the R to G cir-
cuit. Cooling blower delay is also functional in this mode.
System Performance
For maximum performance of this cooling system, the
operating temperatures and pressure should be checked
and superheat determined at Standard ARI test conditions
of 82 '_F outdoor temperature with minus (-)80 '_ F indoor
dry bulb /67 _ F indoor wet bulb. If superheat measured
deviates from values in table 7, refrigerant charge should
be adjusted accordingly for maximum performance.
Table 7
Suction Superheat Values
Suction Superheat
Unit Model No. 82°F OD minus 80"F IDDB
/67"F IDWB
15GCSX-24 15 o
15GCSX-30
15GCSX-36 12°
15GCSX-42
15GCSX-48 10 °
15GCSX-60
Verify system performance using table 8 as a general
guide. Table 8 should not be used for charging unit. Minor
variations in these pressures may be expected due to dif-
ferences in installations. Significant differences could
mean that the system is not properly charged or that a prob-
lem exists with some component in the system.
Used carefully, this table could serve as a useful service
guide. Data is based on 80°F dry bulb /67°F wet bulb return
air. Allow unit operation to stabilize before taking pressure
readings.
Table 8
Normal Operating Pressures
80°F db /67°F wb RETURN AIR Air Temperature Entering Outdoor Coil (°F)
UNIT PRESSURE 65 70 75 80 82 85 90 95 100 105 110 115
15GCSX-24 142 143 144 146 146 147 148 149 150 151 152 153
15GCSX-30 134 136 138 140 141 142 144 146 148 149 151 152
15GCSX-36 143 144 146 147 148 149 151 152 155 155 157 157
Suction
15GCSX-42 140 140 140 141 141 141 142 142 143 144 145 147
15GCSX-48 140 141 142 144 144 145 146 147 148 149 150 151
15GCSX-60 143 144 145 146 146 147 147 148 149 150 151 152
15GCSX-24 219 242 264 287 296 310 333 355 379 398 430 457
15GCSX-30 232 255 277 300 309 323 345 368 390 408 440 470
15GCSX-36 244 268 292 316 326 340 363 369 410 429 461 493
15GCSX-42 Liquid 225 247 269 291 300 314 337 357 383 402 434 457
15GCSX-48 243 264 285 307 315 328 349 370 391 408 440 470
15GCSX-60 257 280 303 326 335 349 372 395 418 436 468 497
Page 14

Pre-Start Check List:
1 - Check the type of gas being supplied, Be sure it is the
same as listed on the unit nameplate,
2 - Make sure the vent hood has been properly installed,
FOR YOUR SAFETY READ BEFORE LIGHTING
BEFORE LIGHTING smell all around the appliance area
for gas, Be sure to smell around the base of the unit be-
cause some gas is heavier than air and will settle down low,
,WARNING
,WARNING
WARN ING
Use only your hand to turn the gas valve knob, Never use
tools. If the knob will not move by hand, do not try to repair
the gas valve. Call a qualified service technician, Force or
attempted repair may result in a fire or explosion,
This furnace is equipped with a direct ignition control, Do
not attempt to manually light the burners,
1 - Turn off electrical power to unit.
2 - Set thermostat to lowest setting.
3 - Turn the gas valve knob to the ON position, Refer to
figure 13,
4 - Turn on electrical power to unit,
5 - Set room thermostat to desired temperature, (If ther-
mostat setpoint temperature is above room tempera-
ture after the pre-purge time expires, main burners will
light),
Honeywell VR8205 Series Gas Valve
HIGH FIRE
ADJUSTING SCREW
(under cap)
OUTLET
(MANIFOLD)
TAP
LOW FIRE
(under cap)
INLET ._URE
TAP
GAS VALVE SHOWN IN OFF POSITION
Figure 13
To Shut Down:
1 - Turn off electric power to unit.
2 - Turn the gas valve knob to the OFF position.
Post Start-up Check List (Gas)
After the control circuit has been energized and the heating
section is operating, make the following checks:
1 - Use soap solution to check for gas leaks in the unit pip-
ing as well as the supply piping,
2 - Check for correct manifold gas pressures, See "Man-
ifold Gas Pressure Adjustment."
3 - Check the supply gas pressure. It must be within the
limits shown on rating nameplate. Supply pressure
should be checked with all gas appliances in the build-
ing at full fire, At no time should the supply gas pres-
sure exceed 10.5 inches w,c,, nor drop below 5.0 inch-
es w,c. for natural gas units, For propane gas, supply
gas pressure should not drop below 11 inches w.c. If
gas pressure is outside these limits, contact your gas
supplier for corrective action.
4 - Adjust temperature rise to the range specified on the
rating plate,
Checking and Adjusting Gas Input
NQ TE -Units must be converted for use with LP/propane
gas. Conversion kit is ordered separately. Conversion
must be performed by an approved licensed pipe fitter
or technician.
The minimum permissible gas supply pressure is 5,0
inches W.C. for natural gas or 11,0 inches W,C. for
LP/propane gas, The maximum inlet gas supply pressure
is 10.5 inches W,C, for natural gas and 13,0 inches W.C. for
LP/propane gas, Gas input must never exceed the input
capacity shown on the rating plate,
Units fueled by natural gas are rated for manifold pressures
of 2,0 inches W,C, for first stage and 3,5 inches W,C. for
second stage,
Page 15

Unitsfueledby LP/propanegasare ratedfor manifold
pressuresof5.6inchesW.C.forfirststageand10.0inches
W.C.forsecondstage.
Measuremanifoldpressure:Shutoffgassupplyto the
unit. Removeplugfrom pressuretap. Seefigure 13.
Connectmanometerorgaugetotheproperpressuretap,
thenturnonthegassupply.
TheHoneywellVR8205gasvalvehasseparateadjusting
screwsfor firststage(LO)andsecondstage(HI).The
adjustingscrewsare positionedon eitherside of the
barbedfitting.Turnthe adjustingscrewsclockwiseto
increasepressureand input;turn counterclockwiseto
decreasepressureand input. The pressureregulator
adjustmentis sensitive.Oneturnof theadjustingscrew
resultsina largechangeinmanifoldpressure.
Finalfirst-stageand second-stagemanifoldpressures
mustbewithintheallowablerangersfor thegas being
used.
ForNaturalGas:Checkthefurnaceratebyobservinggas
meter,makingsureallothergasappliancesareturnedoff.
Thetesthandonthemetershouldbetimedforatleastone
revolution,Notethenumberofsecondsforonerevolution,
BTU/HR = Cubic Feet Per Revolution X 3600 X Heating Value
INPUT No. Seconds Per Revolution
The heating value of your gas can be obtained from your
local utility.
For LP/Propane Gas: If a gas meter is available, check the
input rate as described in the section above. Heating value
of propane gas is available from propane supplier. Other-
wise, the only check for the output rate is to properly adjust
the manifold pressure using a manometer. Typical man-
ifold setpoint for installations at altitudes from 0 to 4500 feet
above sea level is 10.0 inches W.C.
High Altitude Information
Ratings shown on the rating plate for elevations up to 4,500
feet. For elevations above 4,500 feet, ratings should be
reduced at a rate of four percent for each 1,000 feet above
sea level. See National Fuel Gas Code Z223.1 (latest
edition) or the requirements of the CSA B149 installation
codes.
Heating Sequence of Operation
When the thermostat calls for heating, Wl is energized.
NOTE -The ignition control ignores a carl for second-stage
heat until first-stage heat has been established.
The ignition control checks high temperature limit and
rollout switches to make sure they are closed. The control
then verifies that the pressure switch is open. If the
pressure switch is closed, the control will flash code 3 on
the LED and will wait indefinitely for the pressure switch to
open. If the pressure switch is open, the control proceeds
to the 15-second pre-purge.
The ignition control energizes the combustion air inducer
on high speed, flashes a code 3 on the LED, and waits for
the pressure switch to close.
When the pressure switch has closed, the LED code 3 flash
stops and the control begins the 15-second pre-purge
period. When the pre-purge time has expired, the control
begins the ignition trial.
The ignition control energizes the gas valve and spark. The
control ignores the flame sense signal for the first two
seconds of the ignition trial. If the flame is established
within 10 seconds, the control de-energizes the spark. If
flame is not established within 10 seconds, the gas valve
and spark are de-energized and the ignition control
initiates a 30-second inter-purge sequence.
Approximately 30 seconds after the flame has been
established, the circulating air blower starts and the
combustion air inducer is switched to low speed. The
ignition control inputs are continuously monitored to
ensure that limit switch(es), rollout switch and pressure
switch are all closed, and that the flame remains
established and heating demand is present. First-stage
gas valve, low-speed combustion air inducer and
circulating blower remain energized. If the thermostat
signals a requirement for second-stage heat (W2), the
ignition control initiates high heat operation.
When a signal for second stage heat is received by the
ignition control, the control energizes the second-stage
gas valve and high-speed combustion air inducer until the
demand is satisfied.
If a first-stage heat demand continues after the
second-stage heat demand has been satisfied, the ignition
control immediately de-energizes the second-stage gas
valve. The combustion air inducer is held in high speed
operation for an additional 1 second after the second-stage
gas valve is de-energized. First-stage heat operation
(first-stage gas valve and low-speed combustion air
inducer) continues until heating demand is satisfied.
When the heating demand is satisfied, the control
immediately de-energizes the gas valve. The combustion
air inducer remains energized for a 30-second post-purge
period. The circulating air blower operates for 90 seconds
after the gas valve is de-energized.
Blower Delay - Heating
In the heating mode, the circulating air blower operation is
delayed for 30 seconds after the flame is established. The
blower continues to operate for 90 seconds after the gas
valve is de-energized.
NOTE -With the proper thermostat and subbase, continu-
ous blower operation is possible by closing the R to G cir-
cuit.
Blower Control Board (A54)
15GCSX units are equipped with a variable speed motor
which is controlled by a blower control board. Blower con-
trol board settings and operation are given on page 12.
Ignition Control Board (A3)
The 15GCSX unit includes an ignition control board which
controls the combustion air inducer, gas valve and spark
electrode. It receives signals from the main and auxiliary
limit switches, the rollout switch, the pressure switch and
the flame sensor. LED codes and flash rates are given on
page 17. The ignition control board is shown in figure 14.
Page 16

Ignition Control Board
i( hill -I;,,°°
t
j
CONNECTOR PI
P!N I LIMIT SW}TCB (OUTPUT, COMMON WITH "W" TERMINAL1
P}N 2 GAS VALV _ Z4 VAC COMMON (CHASSIS GROUND}
P}N 5 _OW GAS VALVE OUTPUF
P}N 4 _IMil SW}FCN }NPUF
P}N 5 PRESSURE SWITCH OUIPU]
P}N 6 _OW PRESSURE SWI]CH INPUT
PiN 7 HIGH GAS VALVF OUFPU]
P}N 8 HIGH PRESSURE SW}ICH INPUF (OPFIONAL)
P}N 9 FLAME SENSF INPU]
CONNECTOR P2
'R" 24VAC TO THERMOSTAT
'W" FHERMOS]Aq CALL FOR HEAT
'W2" rHERMOSTAq 2ND SIAGE CALL FOR HEA]
"G" THERMOSTAT CALL FOR CONTINUOUS FAN
'Y" FHEI:_MOSTAI CALL FOR COOLING
QUICK CONNECT TERMINALS
"INDUCER LOW ¸' DRAFT }NDUCER MOTOR OUTPUT
"INDUCER NIGH" 2ND STAGE DRAFT INDUCER MOTOR OUTPUT
"11" (2} 230 VAC LINE }NPUT
"L2" (4) 230 VAC LINE }NPUT
"C" (2} 24 VAC SYSTEM COMMON (GROUND}
"24VAC" CONTINUOUS 24VAC PROM IRANSFORMER
"CIR _' CIRCULATING AIR BLOWER MOTOR
T}M!NGS:
PREPURGE: }5 SECONDS
JGN}T}ON TR}AI I0 SECONDS
INTERPURGE: 30 SECONDS
HEAT SLOWER ON DELAY 30 SECONDS
HEAT SLOWER OFF ¸ DELAY 90 SECONDS
POST PURGE 30 SECONDS
COOL RAN OFF DELAY 90 SECONDS
Figure 14
Ignition Control Board LED Codes
The ignition control board LED flashes codes which indi-
cate normal or abnormal operations:
Slow Flash -- Normal operation, no carl for heat.
One flash per second.
Fast Flash -- Normal operation, call for heat.
Two flashes per second.
Steady Off -- Internal failure or no power.
(Micro-controller failure; self-check.)
Steady On -- Internal control failure.
(Micro-controller failure; self-check).
Code 2 -- System lockout -Failed to detect or sustain
flame.
Two flashes in 1 second with a 1-second pause.
Code 3 -- Pressure switch open with inducer on or
closed with inducer off.
Three flashes in 1-1/2 seconds with a 1-second pause.
Code 4 -- High limit/or rollout switch open.
Four flashes in 2 seconds with a 1-second pause.
Code 5 -- Flame sensed while gas valvede-energized.
Five flashes in 2-1/2 seconds with a 1-second pause.
Code 6 -- Rollout switch is open.
Six flashes in three seconds with a one-second pause.
Limit Control
supply airflow, occurs. The main gas valve is closed. The
circulating air blower will continue to operate until the
blower off delay period has elapsed.
Pressure Switch
If the combustion air inducer motor should fail or if the vent
system is blocked, the pressure switch prevents the gas
valve from being energized.
Spark Electrode and Flame Sensor Rod
The spark electrode and flame sensor rod are part of the
burner assembly. The spark electrode is typically located
on the far-left burner. The flame sensor rod is typically
located on the far-right burner. If the ignition control does
not receive a signal from the flame sensor indicating that
the burners have established flame, the main gas valve will
close after the 10-second ignition trial period built into the
ignition control.
Rollout Switch
The switch is located above the main burners. In the event
of a sustained main burner rollout the main gas valve is
closed. To reset, push the button on top of the switch.
Auxiliary Limit (-42, -48 &-60 units only)
This control is located inside the heating compartment and
is designed to open at abnormally high air temperatures. It
resets automatically. The limit switch operates when a high
temperature condition, caused by inadequate blower
This control is located in the side of the circulating air
blower housing. If the circulating air blower fails to operate,
the temperature rises and opens the auxiliary limit. The
main gas valve closes. This control resets automatically.
Page 17

System Operation Monitor (LSOM)
The system operation monitor (A132) detects the most
common fault conditions in the air conditioning system.
When an abnormal condition is detected, the module com-
municates the specific condition through its ALERT and
TRIP lights. The module is capable of detecting both me-
chanical and electrical system problems, See figure 15 for
the system operation monitor,
System Operation Monitor (A132)
POWER LED
DATA OUTPUT
C
R
ALERT LED
TRIP LED
--DATA OUTPUT
CONNECTOR
_'.25"SPADE
CONNECTOR(5)
Figure 15
IMPORTANT
LSOM LED Functions
Power LED (green) -- Voltage within the range of
19-28VAC is present at the system monitor power connec-
tion,
Alert LED (yellow) -- Communicates an abnormal system
condition through a unique flash code. The alert LED
flashes a number of times consecutively; then pauses;
then repeats the process, This consecutive flashing corre-
sponds with a particular abnormal condition.
Trip LED (red) -- Indicates a demand signal from the ther-
mostat; but detects no current to the compressor.
Flash code number -- Corresponds to a number of LED
flashes, followed by a pause, and then repeated,
Trip & Alert LEDs flashing simultaneously -- Indicates that
the control circuit voltage is too low for operation,
Reset ALERT flash code by removing 24VAC power from
monitor. Last ALERT flash code will display for 1 minute af-
ter monitor is powered on.
LSOM codes are given in table 9,
The top of the condenser fan should be 1-1/2 inchs from the
bottom of the top grille, This dimension should be checked
and the fan should be adjusted accordingly any time servic-
ing of the outdoor fan system is required,
Page 18

Table 9
System Operation Monitor LED Troubleshooting Codes
Status LED Description
Module has power
Status LED Condition
Green "Power" LED ON
Green "Power" LED
OFF
Red "Trip" LED ON
Red "Trip" & Yellow
"Alert" LEDs Flashing
Yellow "Alert" Flash
Code 1"
Yellow "Alert" Flash
Code 2*
Yellow "Alert" Flash
Code 3*
Yellow "Alert" Flash
Code 4*
Yellow "Alert" Flash
Code 5*
Module not powering up
System and compressor
check out OK
Thermostat demand signal
Y1 is present, but compres-
sor not running
Status LED Troubleshooting Information
24VAC control power is present at the module terminal.
Determine/verify that both R and C module terminals are connected
and voltage is present at both terminals.
1. Verify Y terminal is connected to 24VAC at contactor coil.
2. Verify voltage at contactor coil falls below 0.5VAC when off.
3. Verify 24VAC is present across Y and C when thermostat
demand signal is present; if not present, R and C wires are reversed.
1. Compressor protector is open.
2. Outdoor unit power disconnect is open.
3. Compressor circuit breaker or fuse(s) is open.
4. Broken wire or connector is not making contact.
5. Low pressure switch open if present in the system.
6. Compressor contactor has failed to close.
Simultaneous flashing. Indicates that the control circuit voltage is too low for operation.
Long Run Time -
Compressor is running
extremely long run cycles
System Pressure Trip -
Discharge or suction
pressure out of limits or
compressor overloaded
Short Cycling - Compres-
sor is running only briefly
Locked Rotor
Open Circuit
1.
2.
3.
4.
5.
6.
7.
1,
2.
aged).
3.
4.
5.
1.
2.
3.
4.
1.
2.
3.
4.
1.
2.
3.
4.
5.
6.
Low refrigerant charge.
Evaporator blower is not running.
Evaporator coil is frozen.
Faulty metering device.
Condenser coil is dirty-
Liquid line restriction (filter drier blocked if present)-
Thermostat is malfunctioning,
High head pressure.
Condenser coil poor air circulation (dirty, blocked, dam-
Condenser fan is not running.
Return air duct has substantial leakage.
If low pressure switch is present, see Flash Code 1 info.
Thermostat demand signal is intermittent.
Time delay relay or control board is defective.
If high pressure switch is present, see Flash Code 2 info.
If low pressure switch is present, see Flash Code 1 info.
Run capacitor has failed.
Low line voltage (contact utility).
Excessive liquid refrigerant in the compressor.
Compressor bearings are seized.
Outdoor unit power disconnect is open.
Unit circuit breaker or fuse(s) is open.
Unit contactor has failed to close.
High pressure switch is open and requires manual reset.
Open circuit in compressor supply wiring or connections.
Unusually long compressor protector reset time due to
extreme ambient temperature.
Compressor windings are damaged.
7.
Yellow "Alert" Flash Open Start Circuit -1. Run capacitor has failed.
Code 6* Current only in run circuit 2. Open circuit in compressor start wiring or connections.
3. Compressor start winding is damaged.
Yellow "Alert" Flash Open Run Circuit - Current 1. Open circuit in compressor start wiring or connections.
Code 7* only in start circuit 2. Compressor start winding is damaged.
Yellow "Alert" Flash Welded Contactor - 1. Compressor contactor failed to open.
Code 8* Compressor always runs 2. Thermostat demand signal not connected to module.
Yellow "Alert" Flash Low Voltage - Control 1. Control circuit transformer is overloaded.
Code 9* circuit <17VAC 2. Low line voltage (contact utility).
*Flash code number corresponds to a number of LED flashes, followed by a pause, and then repeated. Reset ALERT flash code
by removing 24VAC power from monitor; last code will display for 1 minute after monitor is powered on.
Page 19

The GCSX15unitshouldbe inspectedannuallyby a
qualifiedservicetechniciantoensureproperoperation,
Filters
Not supplied. Inspect once a month. Replace disposable,
or clean permanent-type, as necessary. DO NOT replace
permanent type with disposable.
Motors
Indoor, outdoor fan and vent motors are permanently
lubricated and require no further lubrication. Motors should
be cleaned yearly to prevent the accumulation of dust and
dirt on the windings or motor exterior.
Coil
Dirt and debris should not be allowed to accumulate on the
coil surfaces or other parts in the air conditioning circuit.
Cleaning should be performed as often as necessary. Use
a brush, vacuum cleaner attachment, or other suitable
means. If water is used to clean the coil, be sure the power
to unit is shut off prior to cleaning.
NOTE -Care should be used when cleaning the coil so that
the coil fins are not damaged.
Do not permit the hot condenser air discharge to be ob-
structed by overhanging structures or shrubs.
To Clean Burners
Light the burners and allow unit to operate for a few minutes
to establish normal burning conditions. Observe the burner
flames. Compare this observation to figure 16 to determine
if flame is properly adjusted. Flame should be predomi-
nantly blue in color and strong in appearance. Verify that all
burnres are lit and that the flame does not impinge on the
sides of the heat exchanger.
Distorted flame or yellow tipping of the natural gas flame (or
long yellow tips on LP/propane flame) may be caused by
one or more of the following: lint or dirt inside the burner or
burner ports; lint or dirt at the air inlet between the burner
and manifold pipe; or an obstruction over the burner orifice.
Use a soft brush or vacuum to clean the affected areas.
Burner Flame Heat
Burner _L _,/ Exchanger
Gas Burner Flame
Manifold (Blue Only)
Figure 16
Vent Outlet
Visually inspect vent outlet periodically to make sure that
the there is no buildup of soot and dirt. If necessary, clean
to maintain adequate opening to discharge flue products.
The following repair parts are available from your local dealer. When ordering parts, include the complete model number
and serial number which are printed on the unit rating plate.
Controls
Rollout Switch
Transformer
Limit Control
Gas Valve
Ignition Control
Electrode
Flame Sensor
Auxiliary Limit
Pressure Switch
Blower Control
System Operations Monitor
Blower Components
Blower Housing Assembly
Blower Wheel
Blower Motor
Blower Motor Mount
Blower Motor Capacitor (if used)
Combustion Air Inducer
Fan Blade
Fan Motor
Fan Motor Capacitor
Heating Components
Gas Manifold
Main Burner Orifices
Main Burners
Heat Exchanger
Cooling Components
Compressor
Evaporator Coil
Drier
Expansion Valve
Contactor
Capacitor
Condenser Coil
Accessories
Description LENNOX Cat.
Number
LP/Propane Gas Conversion Kit (heat sizes 68 and 90) 92M52
LP/Propane Gas Conversion Kit (heat sizes 83, 110 and 138) 92M56
Filter Kit (2-ton to 3-ton capacity units) 92M54
Filter Kit (3-1/2-ton to 5-ton capacity units) 92M55
PCO20-28 X8787
Installation Hardware Kit for PCO20-28 Y0629
Page 20