Lincoln Electric Power Wave Svm156 A Users Manual
SVM156-A to the manual ab7b28c4-cf35-45da-89fe-87a300e58766
2015-02-09
: Lincoln-Electric Lincoln-Electric-Power-Wave-Svm156-A-Users-Manual-574398 lincoln-electric-power-wave-svm156-a-users-manual-574398 lincoln-electric pdf
Open the PDF directly: View PDF .
Page Count: 150 [warning: Documents this large are best viewed by clicking the View PDF Link!]
- Master Table of Contents
- Safety Section
- Section A - Installation
- Section B - Operation
- Section C - Accessories
- Section D - Maintenance
- Section E - Theory of Operation
- Section F - Troubleshooting & Repair
- Symptoms
- Major physical or electrical damage is evident when the sheet metal covers are removed.
- The input fuses repeatedly fail or the input circuit breakers keep tripping.
- The machine is dead—no lights— no output—the machine appears to be off.
- The Power Wave 455R does not have welding output. The main input contactor CR1 is not activating.
- The thermal light is lit. The machine regularly "overheats."
- The machine often "noodle welds" when running a particular process. The output is limited to approximately 100 amps.
- The Power Wave 455R will not produce full output.
- The Auxiliary Receptacle is "dead." The 120VAC is not present at the receptacle.
- The Power Wave 455R is "triggered" for output but there is no welding output.
- When in the STT mode, the spatter is higher than normal and the arc is inconsistent.
- Section G - Electrical Diagrams
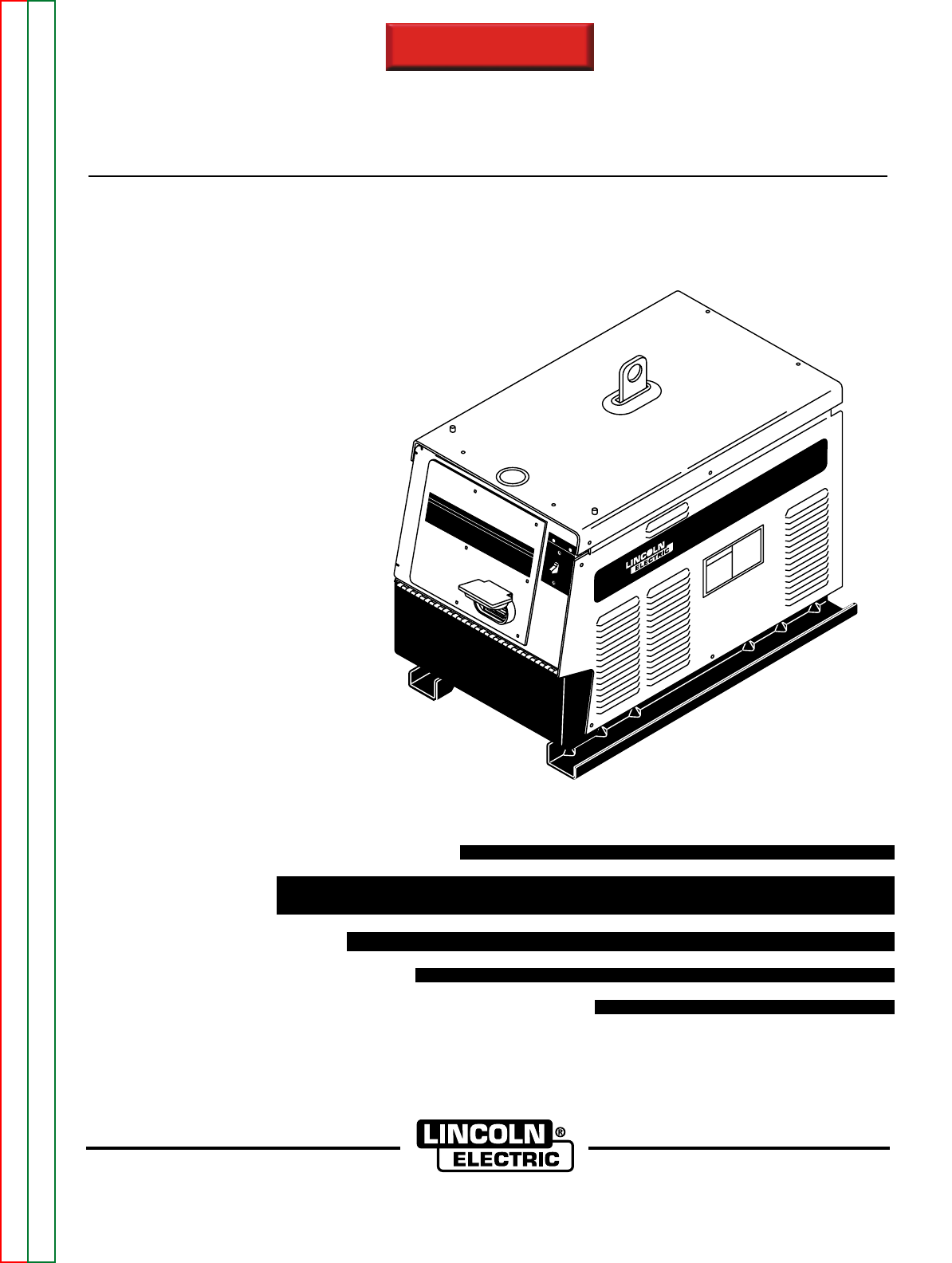
SVM156-A
October, 2001
Safety Depends on You
Lincoln arc welding and cutting
equipment is designed and built
with safety in mind. However,
your overall safety can be in-
creased by proper installation . . .
and thoughtful operation on
your part. DO NOT INSTALL,
OPERATE OR REPAIR THIS
EQUIPMENT WITHOUT
READING THIS MANUAL AND
THE SAFETY PRECAUTIONS
CONTAINED THROUGHOUT.
And, most importantly, think
before you act and be careful.
SERVICE MANUAL
For use with machines having Code Numbers: 10675
10676
POWER WAVE 455/R
TM
Return to Master TOC Return to Master TOC Return to Master TOC Return to Master TOC
View Safety Info View Safety Info View Safety Info View Safety Info
POWERWAVE 455/R
I ON
O OFF
POWERWAVE 455/R
• Sales and Service through Subsidiaries and Distributors Worldwide •
Cleveland, Ohio 44117-1199 U.S.A. TEL: 216.481.8100 FAX: 216.486.1751 WEB SITE: www.lincolnelectric.com
• World's Leader in Welding and Cutting Products •
Copyright © 2001 Lincoln Global Inc.
IEC 60974-1
RETURN TO MAIN MENU

CALIFORNIA PROPOSITION 65 WARNINGS
i i
SAFETY
FOR ENGINE
powered equipment.
1.a. Turn the engine off before troubleshooting and maintenance
work unless the maintenance work requires it to be running.
____________________________________________________
1.b.Operate engines in open, well-ventilated
areas or vent the engine exhaust fumes
outdoors.
____________________________________________________
1.c. Do not add the fuel near an open flame weld-
ing arc or when the engine is running. Stop
the engine and allow it to cool before refuel-
ing to prevent spilled fuel from vaporizing on
contact with hot engine parts and igniting. Do
not spill fuel when filling tank. If fuel is spilled,
wipe it up and do not start engine until fumes
have been eliminated.
____________________________________________________
1.d. Keep all equipment safety guards, covers
and devices in position and in good
repair.Keep hands, hair, clothing and tools
away from V-belts, gears, fans and all other
moving parts when starting, operating or
repairing equipment.
____________________________________________________
1.e. In some cases it may be necessary to remove safety
guards to perform required maintenance. Remove
guards only when necessary and replace them when the
maintenance requiring their removal is complete.
Always use the greatest care when working near moving
parts.
___________________________________________________
1.f. Do not put your hands near the engine fan. Do not attempt to
override the governor or idler by pushing on the throttle con-
trol rods while the engine is running.
___________________________________________________
1.g. To prevent accidentally starting gasoline engines while
turning the engine or welding generator during maintenance
work, disconnect the spark plug wires, distributor cap or
magneto wire as appropriate.
ARC WELDING can be hazardous. PROTECT YOURSELF AND OTHERS FROM POSSIBLE SERIOUS INJURY OR DEATH.
KEEP CHILDREN AWAY. PACEMAKER WEARERS SHOULD CONSULT WITH THEIR DOCTOR BEFORE OPERATING.
Read and understand the following safety highlights. For additional safety information, it is strongly recommended that you
purchase a copy of “Safety in Welding & Cutting - ANSI Standard Z49.1” from the American Welding Society, P.O. Box 351040,
Miami, Florida 33135 or CSA Standard W117.2-1974. A Free copy of “Arc Welding Safety” booklet E205 is available from the
Lincoln Electric Company, 22801 St. Clair Avenue, Cleveland, Ohio 44117-1199.
BE SURE THAT ALL INSTALLATION, OPERATION, MAINTENANCE AND REPAIR PROCEDURES ARE
PERFORMED ONLY BY QUALIFIED INDIVIDUALS.
WARNING
Mar ‘95
ELECTRIC AND
MAGNETIC FIELDS
may be dangerous
2.a. Electric current flowing through any conductor causes
localized Electric and Magnetic Fields (EMF). Welding
current creates EMF fields around welding cables and
welding machines
2.b. EMF fields may interfere with some pacemakers, and
welders having a pacemaker should consult their physician
before welding.
2.c. Exposure to EMF fields in welding may have other health
effects which are now not known.
2.d. All welders should use the following procedures in order to
minimize exposure to EMF fields from the welding circuit:
2.d.1.
Route the electrode and work cables together - Secure
them with tape when possible.
2.d.2. Never coil the electrode lead around your body.
2.d.3. Do not place your body between the electrode and
work cables. If the electrode cable is on your right
side, the work cable should also be on your right side.
2.d.4. Connect the work cable to the workpiece as close as
possible to the area being welded.
2.d.5. Do not work next to welding power source.
1.h. To avoid scalding, do not remove the
radiator pressure cap when the engine is
hot.
Diesel engine exhaust and some of its constituents
are known to the State of California to cause can-
cer, birth defects, and other reproductive harm.
The engine exhaust from this product contains
chemicals known to the State of California to cause
cancer, birth defects, or other reproductive harm.
The Above For Diesel Engines The Above For Gasoline Engines
Return to Master TOC Return to Master TOC Return to Master TOC Return to Master TOC

ii ii
SAFETY
Return to Master TOC Return to Master TOC Return to Master TOC Return to Master TOC
ARC RAYS can burn.
4.a. Use a shield with the proper filter and cover
plates to protect your eyes from sparks and
the rays of the arc when welding or observing
open arc welding. Headshield and filter lens
should conform to ANSI Z87. I standards.
4.b. Use suitable clothing made from durable flame-resistant
material to protect your skin and that of your helpers from
the arc rays.
4.c. Protect other nearby personnel with suitable, non-flammable
screening and/or warn them not to watch the arc nor expose
themselves to the arc rays or to hot spatter or metal.
ELECTRIC SHOCK can kill.
3.a. The electrode and work (or ground) circuits
are electrically “hot” when the welder is on.
Do not touch these “hot” parts with your bare
skin or wet clothing. Wear dry, hole-free
gloves to insulate hands.
3.b. Insulate yourself from work and ground using dry insulation.
Make certain the insulation is large enough to cover your full
area of physical contact with work and ground.
In addition to the normal safety precautions, if welding
must be performed under electrically hazardous
conditions (in damp locations or while wearing wet
clothing; on metal structures such as floors, gratings or
scaffolds; when in cramped positions such as sitting,
kneeling or lying, if there is a high risk of unavoidable or
accidental contact with the workpiece or ground) use
the following equipment:
• Semiautomatic DC Constant Voltage (Wire) Welder.
• DC Manual (Stick) Welder.
• AC Welder with Reduced Voltage Control.
3.c. In semiautomatic or automatic wire welding, the electrode,
electrode reel, welding head, nozzle or semiautomatic
welding gun are also electrically “hot”.
3.d. Always be sure the work cable makes a good electrical
connection with the metal being welded. The connection
should be as close as possible to the area being welded.
3.e. Ground the work or metal to be welded to a good electrical
(earth) ground.
3.f.
Maintain the electrode holder, work clamp, welding cable and
welding machine in good, safe operating condition. Replace
damaged insulation.
3.g. Never dip the electrode in water for cooling.
3.h. Never simultaneously touch electrically “hot” parts of
electrode holders connected to two welders because voltage
between the two can be the total of the open circuit voltage
of both welders.
3.i. When working above floor level, use a safety belt to protect
yourself from a fall should you get a shock.
3.j. Also see Items 6.c. and 8.
FUMES AND GASES
can be dangerous.
5.a. Welding may produce fumes and gases
hazardous to health. Avoid breathing these
fumes and gases.When welding, keep
your head out of the fume. Use enough
ventilation and/or exhaust at the arc to keep
fumes and gases away from the breathing zone. When
welding with electrodes which require special
ventilation such as stainless or hard facing (see
instructions on container or MSDS) or on lead or
cadmium plated steel and other metals or coatings
which produce highly toxic fumes, keep exposure as
low as possible and below Threshold Limit Values (TLV)
using local exhaust or mechanical ventilation. In
confined spaces or in some circumstances, outdoors, a
respirator may be required. Additional precautions are
also required when welding on galvanized steel.
5.b.
Do not weld in locations near chlorinated hydrocarbon
vapors
coming from degreasing, cleaning or spraying operations.
The heat and rays of the arc can react with solvent vapors
to
form phosgene, a highly toxic gas, and other irritating
products.
5.c. Shielding gases used for arc welding can displace air and
cause injury or death. Always use enough ventilation,
especially in confined areas, to insure breathing air is safe.
5.d. Read and understand the manufacturer’s instructions for this
equipment and the consumables to be used, including the
material safety data sheet (MSDS) and follow your
employer’s safety practices. MSDS forms are available from
your welding distributor or from the manufacturer.
5.e. Also see item 1.b. Mar ‘95

iii iii
SAFETY
Return to Master TOC Return to Master TOC Return to Master TOC Return to Master TOC
FOR ELECTRICALLY
powered equipment.
8.a. Turn off input power using the disconnect
switch at the fuse box before working on
the equipment.
8.b. Install equipment in accordance with the U.S. National
Electrical Code, all local codes and the manufacturer’s
recommendations.
8.c. Ground the equipment in accordance with the U.S. National
Electrical Code and the manufacturer’s recommendations.
CYLINDER may explode
if damaged.
7.a. Use only compressed gas cylinders
containing the correct shielding gas for the
process used and properly operating
regulators designed for the gas and
pressure used. All hoses, fittings, etc. should be suitable for
the application and maintained in good condition.
7.b. Always keep cylinders in an upright position securely
chained to an undercarriage or fixed support.
7.c. Cylinders should be located:
•Away from areas where they may be struck or subjected to
physical damage.
•A safe distance from arc welding or cutting operations and
any other source of heat, sparks, or flame.
7.d. Never allow the electrode, electrode holder or any other
electrically “hot” parts to touch a cylinder.
7.e. Keep your head and face away from the cylinder valve outlet
when opening the cylinder valve.
7.f. Valve protection caps should always be in place and hand
tight except when the cylinder is in use or connected for
use.
7.g. Read and follow the instructions on compressed gas
cylinders, associated equipment, and CGA publication P-l,
“Precautions for Safe Handling of Compressed Gases in
Cylinders,” available from the Compressed Gas Association
1235 Jefferson Davis Highway, Arlington, VA 22202.
Mar ‘95
WELDING SPARKS can
cause fire or explosion.
6.a.
Remove fire hazards from the welding area.
If this is not possible, cover them to prevent
the welding sparks from starting a fire.
Remember that welding sparks and hot
materials from welding can easily go through small cracks
and openings to adjacent areas. Avoid welding near
hydraulic lines. Have a fire extinguisher readily available.
6.b. Where compressed gases are to be used at the job site,
special precautions should be used to prevent hazardous
situations. Refer to “Safety in Welding and Cutting” (ANSI
Standard Z49.1) and the operating information for the
equipment being used.
6.c. When not welding, make certain no part of the electrode
circuit is touching the work or ground. Accidental contact can
cause overheating and create a fire hazard.
6.d. Do not heat, cut or weld tanks, drums or containers until the
proper steps have been taken to insure that such procedures
will not cause flammable or toxic vapors from substances
inside. They can cause an explosion even
though
they have
been “cleaned”. For information, purchase “Recommended
Safe Practices for the
Preparation
for Welding and Cutting of
Containers and Piping That Have Held Hazardous
Substances”, AWS F4.1 from the American Welding Society
(see address above).
6.e. Vent hollow castings or containers before heating, cutting or
welding. They may explode.
6.f.
Sparks and spatter are thrown from the welding arc. Wear oil
free protective garments such as leather gloves, heavy shirt,
cuffless trousers, high shoes and a cap over your hair. Wear
ear plugs when welding out of position or in confined places.
Always wear safety glasses with side shields when in a
welding area.
6.g. Connect the work cable to the work as close to the welding
area as practical. Work cables connected to the building
framework or other locations away from the welding area
increase the possibility of the welding current passing
through lifting chains, crane cables or other alternate circuits.
This can create fire hazards or overheat lifting chains or
cables until they fail.
6.h. Also see item 1.c.

iv iv
SAFETY
Return to Master TOC Return to Master TOC Return to Master TOC Return to Master TOC
PRÉCAUTIONS DE SÛRETÉ
Pour votre propre protection lire et observer toutes les instructions
et les précautions de sûreté specifiques qui parraissent dans ce
manuel aussi bien que les précautions de sûreté générales suiv-
antes:
Sûreté Pour Soudage A L’Arc
1. Protegez-vous contre la secousse électrique:
a. Les circuits à l’électrode et à la piéce sont sous tension
quand la machine à souder est en marche. Eviter toujours
tout contact entre les parties sous tension et la peau nue
ou les vétements mouillés. Porter des gants secs et sans
trous pour isoler les mains.
b. Faire trés attention de bien s’isoler de la masse quand on
soude dans des endroits humides, ou sur un plancher
metallique ou des grilles metalliques, principalement dans
les positions assis ou couché pour lesquelles une
grande partie du corps peut être en contact avec la
masse.
c. Maintenir le porte-électrode, la pince de masse, le câble
de soudage et la machine à souder en bon et sûr état
defonctionnement.
d. Ne jamais plonger le porte-électrode dans l’eau pour le
refroidir.
e. Ne jamais toucher simultanément les parties sous tension
des porte-électrodes connectés à deux machines à soud-
er parce que la tension entre les deux pinces peut être le
total de la tension à vide des deux machines.
f. Si on utilise la machine à souder comme une source de
courant pour soudage semi-automatique, ces precautions
pour le porte-électrode s’applicuent aussi au pistolet de
soudage.
2. Dans le cas de travail au dessus du niveau du sol, se pro-
téger contre les chutes dans le cas ou on recoit un choc. Ne
jamais enrouler le câble-électrode autour de n’importe quelle
partie du corps.
3. Un coup d’arc peut être plus sévère qu’un coup de soliel,
donc:
a. Utiliser un bon masque avec un verre filtrant approprié
ainsi qu’un verre blanc afin de se protéger les yeux du
rayonnement de l’arc et des projections quand on soude
ou quand on regarde l’arc.
b. Porter des vêtements convenables afin de protéger la
peau de soudeur et des aides contre le rayonnement de
l‘arc.
c. Protéger l’autre personnel travaillant à proximité au
soudage à l’aide d’écrans appropriés et non-inflamma-
bles.
4. Des gouttes de laitier en fusion sont émises de l’arc de
soudage. Se protéger avec des vêtements de protection
libres de l’huile, tels que les gants en cuir, chemise épaisse,
pantalons sans revers, et chaussures montantes.
5. Toujours porter des lunettes de sécurité dans la zone de
soudage. Utiliser des lunettes avec écrans lateraux dans les
zones où l’on pique le laitier.
6. Eloigner les matériaux inflammables ou les recouvrir afin de
prévenir tout risque d’incendie dû aux étincelles.
7. Quand on ne soude pas, poser la pince à une endroit isolé
de la masse. Un court-circuit accidental peut provoquer un
échauffement et un risque d’incendie.
8. S’assurer que la masse est connectée le plus prés possible
de la zone de travail qu’il est pratique de le faire. Si on place
la masse sur la charpente de la construction ou d’autres
endroits éloignés de la zone de travail, on augmente le risque
de voir passer le courant de soudage par les chaines de lev-
age, câbles de grue, ou autres circuits. Cela peut provoquer
des risques d’incendie ou d’echauffement des chaines et des
câbles jusqu’à ce qu’ils se rompent.
9. Assurer une ventilation suffisante dans la zone de soudage.
Ceci est particuliérement important pour le soudage de tôles
galvanisées plombées, ou cadmiées ou tout autre métal qui
produit des fumeés toxiques.
10. Ne pas souder en présence de vapeurs de chlore provenant
d’opérations de dégraissage, nettoyage ou pistolage. La
chaleur ou les rayons de l’arc peuvent réagir avec les
vapeurs du solvant pour produire du phosgéne (gas forte-
ment toxique) ou autres produits irritants.
11. Pour obtenir de plus amples renseignements sur la sûreté,
voir le code “Code for safety in welding and cutting” CSA
Standard W 117.2-1974.
PRÉCAUTIONS DE SÛRETÉ POUR
LES MACHINES À SOUDER À
TRANSFORMATEUR ET À
REDRESSEUR
1. Relier à la terre le chassis du poste conformement au code
de l’électricité et aux recommendations du fabricant. Le dis-
positif de montage ou la piece à souder doit être branché à
une bonne mise à la terre.
2. Autant que possible, I’installation et l’entretien du poste
seront effectués par un électricien qualifié.
3. Avant de faires des travaux à l’interieur de poste, la
debrancher à l’interrupteur à la boite de fusibles.
4. Garder tous les couvercles et dispositifs de sûreté à leur
place.
Mar. ‘93

v v
- MASTER TABLE OF CONTENTS FOR ALL SECTIONS -
POWER WAVE 455/R
Page
Safety.................................................................................................................................................i-iv
Installation.............................................................................................................................Section A
Operation...............................................................................................................................Section B
Accessories ..........................................................................................................................Section C
Maintenance..........................................................................................................................Section D
Theory of Operation .............................................................................................................Section E
Troubleshooting and Repair ................................................................................................Section F
Electrical Diagrams..............................................................................................................Section G
Parts Manual ................................................................................................................................P-377
RETURN TO MAIN MENU

Installation.............................................................................................................................Section A
Technical Specifications..............................................................................................................A-2
Safety Precautions......................................................................................................................A-4
Select Suitable Location..............................................................................................................A-4
Lifting ....................................................................................................................................A-4
Stacking................................................................................................................................A-4
Machine Grounding.....................................................................................................................A-4
High Frequency Protection..........................................................................................................A-4
Input Connection.........................................................................................................................A-5
Input Fuse and Supply Wire Considerations........................................................................A-5
Input Voltage Change Over (For Multiple Input Voltage Machines Only).............................A-6
Welding with Multiple Power Waves ...........................................................................................A-6
Electrode and Work Cable Connections.....................................................................................A-7
Negative Electrode Polarity.........................................................................................................A-7
Voltage Sensing ..........................................................................................................................A-8
Work Voltage Sensing ..........................................................................................................A-9
Electrode Voltage Sensing ...................................................................................................A-9
Power Wave / Power Feed Wire Feeder Interconnections.........................................................A-9
Control Cable Specifications ................................................................................................A-9
External I/O Connector.........................................................................................................A-9
Dip Switch Settings and Locations.....................................................................................A-10
Control Board Dip Switch ...................................................................................................A-10
Feed Head Board Dip Switch.............................................................................................A-10
Devicenet/Gateway Board Dip Switch, Bank (S2)..............................................................A-11
Section A Section A
TABLE OF CONTENTS
- INSTALLATION SECTION -
POWER WAVE 455/R
Return to Master TOC Return to Master TOC Return to Master TOC Return to Master TOC

A-2 A-2
INSTALLATION
Return to Section TOC Return to Section TOC Return to Section TOC Return to Section TOC
Return to Master TOC Return to Master TOC Return to Master TOC Return to Master TOC
TECHNICAL SPECIFICATIONS - POWER WAVE 455/R (K1761-1), (K1761-2)
OUTPUT
RECOMMENDED INPUT WIRE AND FUSE SIZES
INPUT AT RATED OUTPUT - THREE PHASE ONLY
INPUT
VOLTS
(K1761-1)
208/230/460V - 60HZ
200/220/440V - 50HZ
(K1761-2)
208/230/460/575V-60HZ
200/220/440V - 50HZ
OPEN
CIRCUIT
VOLTAGE
75 VDC
INPUT
VOLTAGE /
FREQUENCY
(K1761-1)
208/230V - 60HZ
460V - 60HZ
200/220V - 50HZ
440V - 50HZ
208/230V - 60HZ
460V - 60HZ
200/220V - 50HZ
440V - 50HZ
(K1761-2)
208/230V - 60HZ
460V - 60HZ
575V - 60HZ
200/220V - 50HZ
440V - 50HZ
208/230V - 60HZ
460V - 60HZ
575V - 60HZ
200/220V - 50HZ
440V - 50HZ
TYPE 75°C
(SUPER LAG)
OR BREAKER
SIZE (AMPS)
90/90
45
90/80
45
110/110
70
100/100
60
70/60
35
30
70/60
30
110/100
50
40
90/80
40
TYPE 75°C
GROUND WIRE
IN CONDUIT
AWG[IEC] SIZES
(mm2)
8 (10)
10 (6)
8 (10)
10 (6)
6 (10)
10 (6)
8 (10)
10 (6)
8 (10)
10 (6)
10 (6)
8 (10)
10 (6)
6 (10)
10 (6)
10 (6)
8 (10)
10 (6)
TYPE 75°C
COPPER WIRE
IN CONDUIT
AWG[IEC] SIZES
(mm2)
4 (25)
8 (10)
4 (25)
8 (10)
4 (25)
8 (10)
4 (25)
8 (10)
4 (25)
10 (6)
10 (6)
6 (10)
10 (6)
4 (25)
8 (10)
10 (6)
8 (10)
10 (6)
INPUT AMPERE
RATING ON
NAMEPLATE
70/65
35
64/58
32
87/82
48
79/74
41
58/53
25
22
49/45
23
82/78
37
31
67/61
31
AMPS/
DUTY
CYCLE
450/100%
450/100%
400/100%
400/100%
570/60%
570/60%
500/60%
500/60%
450/100%
450/100%
450/100%
400/100%
400/100%
570/60%
570/60%
570/60%
500/60%
500/60%
PROCESS CURRENT RANGES (DC)
MIG/MAG
FCAW
SMAW
Pulse
STT
CURRENT
50-570 Average Amps
40-570 Average Amps
30-570 Average Amps
5-750 Peak Amps
40-325 Average Amps
PULSE
VOLTAGE
RANGE
5 - 55 VDC
AUXILIARY POWER
(CIRCUIT BREAKER
PROTECTED)
40 VDC @10 AMPS
115VAC @10 AMPS
PULSE AND
BACKGROUND
TIME RANGE
100 MICRO SEC.
-3.3 SEC.
STT
PARAMETERS
40-325 AMPS
CURRENT
RANGE
5 - 570
PULSE
FREQUENCY
0.15 - 1000 Hz
INPUT
CURRENT
AMPS
70/65/35
87/82/48
64/58/32
79/74/41
58/53/25/22
82/78/37/31
49/45/23
67/61/31
IDLE
POWER
400 Watts
MAX
POWER FACTOR
@ RATED OUTPUT
0.89 MIN
0.95 MIN
EFFICIENCY
@ RATED OUTPUT
88%
OUTPUT
CONDITIONS
450A@38V 100%
570A@43V 60%
400A@36V 100%
500A@40V 60%
450@38V 100%
570@43V 60%
400@36V 100%
500A@40V 60%

A-3 A-3
INSTALLATION
POWER WAVE 455/R
Return to Section TOC Return to Section TOC Return to Section TOC Return to Section TOC
Return to Master TOC Return to Master TOC Return to Master TOC Return to Master TOC
TECHNICAL SPECIFICATIONS - POWER WAVE 455/R (K1761-1), (K1761-2)
(continued)
PHYSICAL DIMENSIONS
TEMPERATURE RANGES
HEIGHT
26.10 in
663 mm
WIDTH
19.86 in
505 mm
DEPTH
32.88 in
835 mm
WEIGHT
(K1761-1) 247 lbs.
112 kg.
(K1761-2) 254 lbs.
115 kg.
OPERATING TEMPERATURE RANGE
-20°C to +40°C STORAGE TEMPERATURE RANGE
-40°C to +40°C

SAFETY PRECAUTIONS
Read this entire installation section before you
start installation.
ELECTRIC SHOCK can kill.
• Only qualified personnel should per-
form this installation.
• Turn the input power OFF at the dis-
connect switch or fuse box before working on this
equipment. Turn off the input power to any other equip-
ment connected to the welding system at the discon-
nect switch or fuse box before working on the equip-
ment.
• Do not touch electrically hot parts.
• Always connect the Power Wave grounding lug
(located inside the reconnect input access door) to a
proper safety (Earth) ground.
SELECT SUITABLE LOCATION
Do not use Power Waves in outdoor environments. The
Power Wave power source should not be subjected to
falling water, nor should any parts of it be submerged
in water. Doing so may cause improper operation as
well as pose a safety hazard. The best practice is to
keep the machine in a dry, sheltered area.
Place the welder where clean cooling air can freely cir-
culate in through the rear louvers and out through the
case sides and bottom. Dirt, dust, or any foreign mate-
rial that can be drawn into the welder should be kept at
a minimum. Do not use air filters on the air intake,
because the air flow will be restricted. Failure to
observe these precautions can result in excessive
operating temperatures and nuisance shutdowns.
Machines above code 10500 are equipped with F.A.N.
(fan as needed) circuitry. The fan runs whenever the
output is enabled, whether under loaded or open circuit
conditions. The fan also runs for a period of time
(approximately 5 minutes) after the output is disabled,
to ensure all components are properly cooled.
If desired, the F.A.N. feature can be disabled (causing
the fan to run whenever the power source is on). To dis-
able F.A.N., connect leads 444 and X3A together at the
output of the solid state fan control relay, located on the
back of the Control PC board enclosure. (See the
Wiring Diagram.)
DO NOT MOUNT OVER COMBUSTIBLE SURFACES.
Where there is a combustible surface directly under
stationary or fixed electrical equipment, that surface
shall be covered with a steel plate at least .06”(1.6mm)
thick, which shall extend not less than 5.90”(150mm)
beyond the equipment on all sides.
LIFTING
Lift the machine by the lift bail only. The lift bail is
designed to lift the power source only. Do not attempt
to lift the Power Wave with accessories attached to it.
STACKING
Power Wave machines can be stacked a maximum of
three high.
The bottom machine must always be placed on a firm,
secure, level surface. There is a danger of machines
toppling over if this precaution is not taken.
MACHINE GROUNDING
The frame of the welder must be grounded. A ground
terminal marked with the symbol is located inside
the reconnect/input access door for this purpose. See
your local and national electrical codes for proper
grounding methods.
HIGH FREQUENCY PROTECTION
Locate the Power Wave away from radio controlled
machinery.
The normal operation of the Power Wave may adverse-
ly affect the operation of RF controlled equipment,
which may result in bodily injury or damage to the
equipment.
A-4 A-4
INSTALLATION
POWER WAVE 455/R
Return to Section TOC Return to Section TOC Return to Section TOC Return to Section TOC
Return to Master TOC Return to Master TOC Return to Master TOC Return to Master TOC
CAUTION
CAUTION
WARNING
CAUTION

INPUT CONNECTION
Only a qualified electrician should connect the input
leads to the Power Wave. Connections should be made
in accordance with all local and national electrical codes
and the connection diagram located on the inside of the
reconnect/input access door of the machine. Failure to
do so may result in bodily injury or death.
Use a three-phase supply line. A 1.75 inch (45 mm)
diameter access hole for the input supply is located on
the upper left case back next to the input access door.
Connect L1, L2, L3 and ground according to the Input
Supply Connection Diagram decal located on the
inside of the input access door, or refer to Figure A.1.
INPUT FUSE AND SUPPLY WIRE
CONSIDERATIONS
Refer to the Technical Specifications at the beginning
of this Installation section for recommended fuse and
wire sizes. Fuse the input circuit with the recommend-
ed super lag fuse or delay type breakers (also called
“inverse time” or “thermal/magnetic” circuit breakers).
Choose an input and grounding wire size according to
local or national electrical codes. Using fuses or circuit
breakers smaller than recommended may result in
“nuisance” shut-offs from welder inrush currents, even
if the machine is not being used at high currents.
A-5 A-5
INSTALLATION
POWER WAVE 455/R
Return to Section TOC Return to Section TOC Return to Section TOC Return to Section TOC
Return to Master TOC Return to Master TOC Return to Master TOC Return to Master TOC
WARNING
NOTE:Turn main input power to the machine OFF before performing connection procedure. Failure to do
so will result in damage to the machine.
FIGURE A.1
(K1761-1) CONNECTION DIAGRAM ON CONNECTION/INPUT ACCESS DOOR
200-208V
220-230V
440-460V
550-575V
200-208V
220-230V
VOLTAGE = 220-230V
220-230V
200-208V
220-230V
440-460V
550-575V
200-208V
U / L1
550-575V
440-460V
inspecting or servicing machine.
Do not operate with covers
removed.
Do not touch electrically live parts.
Only qualified persons should install,
use or service this equipment.
'A'
'A'
VOLTAGE = 440-460V
'A'
S25198
VOLTAGE = 200-208V
THE LINCOLN ELECTRIC CO. CLEVELAND, OHIO U.S.A.
XA
'A'
VOLTAGE = 550-575V
CR1
W / L3
V / L2
440-460V
550-575V
Disconnect input power before
INPUT SUPPLY CONNECTION DIAGRAM
WARNING
CAN KILL
SHOCK
ELECTRIC
(K1761-2) CONNECTION DIAGRAM ON CONNECTION/INPUT ACCESS DOOR
200-208V
220-230V
380-415V
440-460V
200-208V
220-230V
VOLTAGE=220-230V
220-230V
200-208V
220-230V
380-415V
440-460V
200-208V
U / L1
440-460V
380-415V
.
inspecting or servicing machine.
Do not operate with covers
.
removed.
Do not touch electrically live parts.
.
Only qualified persons should install,
use or service this equipment.
.
'A'
'A'
VOLTAGE=380-415V
'A'
S23847
VOLTAGE=200-208V
THE LINCOLN ELECTRIC CO. CLEVELAND, OHIO U.S.A.
A
'A'
VOLTAGE=440-460V
CR1
W / L3
V / L2
380-415V
440-460V
Disconnect input power before
INPUT SUPPLY CONNECTION DIAGRAM
WARNING
ELECTRIC
SHOCK
CAN KILL
ELECTRIC
SHOCK
CAN KILL
WARNING

A-6 A-6
INSTALLATION
POWER WAVE 455/R
Return to Section TOC Return to Section TOC Return to Section TOC Return to Section TOC
Return to Master TOC Return to Master TOC Return to Master TOC Return to Master TOC
INPUT VOLTAGE CHANGE OVER
(FOR MULTIPLE INPUT VOLTAGE
MACHINES ONLY)
Welders are shipped connected for the highest input
voltage listed on the rating plate. To move this con-
nection to a different input voltage, see the diagram
located on the inside of the input access door. (Figure
A.1.) If the main reconnect switch or link position is
placed in the wrong position, the welder will not pro-
duce output power.
If the Auxiliary (A) lead is placed in the wrong position,
there are two possible results. If the lead is placed in
a position higher than the applied line voltage, the
welder may not come on at all. If the auxiliary (A) lead
is placed in a position lower than the applied line volt-
age, the welder will not come on, and the two circuit
breakers in the reconnect area will open. If this occurs,
turn off the input voltage, properly connect the (A) lead,
reset the breakers, and try again.
WELDING WITH MULTIPLE POWER
WAVES
Special care must be taken when more than one Power
Wave is welding simultaneously on a single part. Arc
blow and arc interference may occur or be magnified.
Each power source requires a work lead from the work
terminal to the welding fixture. Do not combine all of the
work leads into one lead. The welding travel directions
should be in the direction moving away from the work
lead as shown in Figure A.2. Connect all of the work
sense leads from each power source to the work piece
at the end of the weld.
For the best results when pulse welding, set the wire
size and wire feed speed the same for all the Power
Waves.
CAUTION
POWERWAVE 455/R
I ON
O OFF POWERWAVE 455/R
I ON
O OFF
FIGURE A.2 – MULTIPLE POWER WAVE CONNECTIONS
TWO POWER WAVES
SENSE LEAD
ELECTRODE
ELECTRODE
SENSE LEAD
CONNECT ALL WORK
SENSE LEADS AT THE
END OF THE JOINT
CONNECT ALL WELDING
WORK LEADS AT THE
BEGINNING OF THE JOINT
TRAVEL
DIRECTION
WORK LEAD WORK LEAD

When these parameters are identical, the pulsing fre-
quency will be the same, helping to stabilize the arcs.
Every welding gun requires a separate shielding gas
regulator for proper flow rate and shielding gas cover-
age.
Do not attempt to supply shielding gas for two or more
guns from only one regulator.
If an anti-spatter system is in use, each gun must have
its own anti-spatter system. See Figure A.2.
ELECTRODE AND WORK CABLE
CONNECTIONS
Connect a work lead of sufficient size and length (per
Table A.1) between the proper output terminal on the
power source and the work. Be sure the connection to
the work makes tight metal-to-metal electrical contact.
To avoid interference problems with other equipment
and to achieve the best possible operation, route all
cables directly to the work or wire feeder. Avoid exces-
sive lengths and do not coil excess cable. Do not tight-
ly bundle the electrode and work cables together.
Use K1796 coaxial welding cables wherever possible.
Minimum work and electrode cables sizes are as
follows:
TABLE A.1
(Current (60% Duty Cycle)
MINIMUM COPPER
WORK CABLE SIZE AWG
Up To 100 Ft. Length (30 m)
400 Amps 2/0 (67 mm2)
500 Amps 3/0 (85 mm2)
600 Amps 3/0 (85 mm2)
When using an inverter type power source like the
Power Wave, use the largest welding (electrode and
ground) cables that are practical. At least 2/0 copper
wire - even if the average output current would not nor-
mally require it.
When pulsing, the pulse current can reach very high
levels. Voltage drops can become excessive, leading
to poor welding characteristics, if undersized welding
cables are used.
Most welding applications run with the electrode being
positive (+). For those applications, connect one end of
the electrode cable to the positive (+) output terminal
on the power source (located beneath the spring
loaded output cover near the bottom of the case front).
Connect the other end of the electrode cable to the
wire drive feed plate using the stud, lockwasher, and
nut provided on the wire drive feed plate. The electrode
cable lug must be against the feed plate. Be sure the
connection to the feed plate makes tight metal-to-metal
electrical contact. The electrode cable should be sized
according to the specifications given in Table A.1.
Connect a work lead from the negative (-) power
source output terminal to the work piece. The work
piece connection must be firm and secure, especially if
pulse welding is planned.
Excessive voltage drops caused by poor work piece
connections often result in unsatisfactory welding per-
formance.
When welding with the STT process, use the positive
output connection labeled (STT) for STT welding. (If
desired, other welding modes can be used on this ter-
minal; however, their average output current will be lim-
ited to 325 amps.) For non-STT processes, use the
positive output connection labeled (Power Wave), so
that the full output range of the machine is available.
Do not connect the STT and Power Wave terminals
together. Paralleling the terminals will bypass STT cir-
cuitry and severely deteriorate STT welding perfor-
mance.
NEGATIVE ELECTRODE POLARITY
When negative electrode polarity is required, such as
in some Innershield applications, reverse the output
connections at the power source (electrode cable to
the negative (-) terminal, and work cable to the positive
(+) terminal).
When operating with electrode polarity negative, the
Dip switch 7 must be set to ON on the Wire Feed Head
PC Board. The default setting of the switch is OFF to
represent positive electrode polarity.
To set the Negative Polarity switch on Wire Feed Head
PC board, refer to the section DIP SWITCH
SETTINGS AND LOCATIONS.
A-7 A-7
INSTALLATION
POWER WAVE 455/R
Return to Section TOC Return to Section TOC Return to Section TOC Return to Section TOC
Return to Master TOC Return to Master TOC Return to Master TOC Return to Master TOC
CAUTION
CAUTION
CAUTION

VOLTAGE SENSING
The best arc performance occurs when the Power
Wave has accurate data about the arc conditions.
Depending upon the process, inductance within the
electrode and work lead cables can influence the volt-
age apparent at the terminals of the welder. Voltage
sense leads improve the accuracy of the arc conditions
and can have a dramatic effect on performance.
If the voltage sensing is enabled but the sense leads
are missing or improperly connected, extremely high
welding outputs may occur.
Do not tightly bundle the work sense lead to the work
lead.
The sense leads connect to the Power Wave at the
four-pin connector located underneath the output ter-
minal cover. Lead 67 senses electrode voltage. Lead
21 senses work voltage.
Enable the voltage sense leads as follows:
TABLE A.2
Process Electrode Voltage Work Voltage
Sensing 67 lead * Sensing 21 lead
GMAW 67 lead required 21 lead optional
GMAW-P 67 lead required 21 lead optional
FCAW 67 lead required 21 lead optional
STT 67 lead required 21 lead required
GTAW Voltage sense at Voltage sense at
terminals terminals
SAW 67 lead required 21 lead optional
* The electrode voltage 67 sense lead is integral to the con-
trol cable to the wire feeder.
A-8 A-8
INSTALLATION
POWER WAVE 455/R
Return to Section TOC Return to Section TOC Return to Section TOC Return to Section TOC
Return to Master TOC Return to Master TOC Return to Master TOC Return to Master TOC
POWERWAVE 455/R
I ON
O OFF
POWERWAVE 455/R
FIGURE A.3 – DIP SWITCH LOCATION
CAUTION
REMOVE
FRONT
COVER
WIRE FEED
HEAD BOARD
ON RIGHT
CONTROL
BOARD
ON LEFT

WORK VOLTAGE SENSING
The Power Wave is shipped from the factory with the
work sense lead enabled.
For processes requiring work voltage sensing, connect
the (21) work voltage sense lead from the Power Wave
to the work. Attach the sense lead to the work as close
to the weld as practical. To enable the work voltage
sensing in the Power Wave, refer to the section DIP
SWITCH SETTINGS AND LOCATIONS.
ELECTRODE VOLTAGE SENSING
Enabling or disabling electrode voltage sensing is auto-
matically configured through software. Electrode sense
lead 67 must be connected at the wire feeder.
POWER WAVE / POWER FEED WIRE
FEEDER INTERCONNECTIONS
Connect the control cable between the power source
and wire feeder. The wire feeder connection on the
robotic Power Wave is located under the spring loaded
output cover, near the bottom of the case front. The
control cable is keyed and polarized to prevent improp-
er connection.
For convenience sake, the electrode and control
cables can be routed behind the left or right strain
reliefs (under the spring loaded output cover), and
along the channels formed into the base of the Power
Wave, out the back of the channels, and then to the
wire feeder.
Output connections on some Power Waves are made
via 1/2-13 threaded output terminals located beneath
the spring-loaded output cover at the bottom of the
case front. On machines which carry the CE mark, out-
put connections are made via Twist-Mate receptacles,
also located beneath the spring-loaded output cover at
the bottom of the case front.
A work lead must be run from the negative (-) power
source output connection to the work piece. The work
piece connection must be firm and secure, especially if
pulse welding is planned.
Excessive voltage drops at the work piece connection
often result in unsatisfactory pulse welding perfor-
mance.
CONTROL CABLE SPECIFICATIONS
It is recommended that genuine Lincoln control cables
be used at all times. Lincoln cables are specifically
designed for the communication and power needs of
the Power Wave / Power Feed system.
The use of non-standard cables, especially in lengths
greater than 25 feet, can lead to communication prob-
lems (system shutdowns), poor motor acceleration
(poor arc starting) and low wire driving force (wire feed-
ing problems).
Lincoln control cables are copper 22 conductor cable in
a SO-type rubber jacket.
EXTERNAL I/O CONNECTOR
The Power Wave is equipped with a port for making sim-
ple input signal connections. The port is divided into
three groups: Trigger group, Cold Inch Group and
Shutdown Group. Because the Power Wave is a “slave”
on the DeviceNet network, the Trigger and Cold Inch
Groups are disabled when the DeviceNet/Gateway is
active.
The Shutdown Group is always enabled. Shutdown 2 is
used for signaling low flow in the water cooler. Unused
shutdowns must be jumpered. Machines from the fac-
tory come with the shutdowns already jumpered. (See
Figure A.4)
A-9 A-9
INSTALLATION
POWER WAVE 455/R
Return to Section TOC Return to Section TOC Return to Section TOC Return to Section TOC
Return to Master TOC Return to Master TOC Return to Master TOC Return to Master TOC
CAUTION
CAUTION
D
E
F
1234567891011 12
G
H
I
A
B
C
+15 VDC for Trigger Group
Trigger Input
Dual Procedure Input
4 Step Input
+15 VDC for Cold Inch Group
Cold Inch Forward
Cold Inch Reverse
Gas Purge Input
+15 for shutdown group
Shutdown1 input
Shutdown2 input
Reserved for future use
FIGURE A.4 – INPUT PORT CONNECTIONS

DIP SWITCH SETTINGS AND LOCATIONS
DIP switches on the PC boards allow for custom con-
figuration of the Power Wave. Access the DIP switch-
es as follows:
ELECTRIC SHOCK CAN KILL.
• Do not touch electrically live parts or
electrodes with your skin or wet cloth-
ing.
• Insulate yourself from the work and
ground.
• Always wear dry insulating gloves.
• Turn off power at the disconnect switch.
• Remove the top four screws securing the front access
panel.
• Loosen, but do not completely remove, the bottom
two screws holding the access panel.
• Open the access panel, allowing the weight of the
panel to be carried by the bottom two screws. Make
sure to prevent the weight of the access panel from
hanging on the harness.
• Adjust the DIP switches as necessary. Using a pen-
cil or other small object, slide the switch left for the
ON position or to the right for the OFF position, as
appropriate.
• Replace the panel and screws and restore power.
CONTROL BOARD DIP SWITCH:
switch 1 = reserved for future use
switch 2 = reserved for future use
switch 3 = reserved for future use
switch 4 = reserved for future use
switch 5 = reserved for future use
switch 6 = reserved for future use
switch 7 = reserved for future use
switch 8 = work sense lead
switch 8 work sense lead
off work sense lead not connected
on work sense lead connected
FEED HEAD BOARD DIP SWITCH:
switch 1 = reserved for future use
switch 2 = reserved for future use
switch 3 = reserved for future use
switch 4 = reserved for future use
switch 5 = reserved for future use
switch 6 = reserved for future use
switch 7 = negative polarity switch
switch 8 = high speed gear
switch 7 electrode polarity
off positive
on negative
switch 8 wire drive gear
off low speed gear
on high speed gear
A-10 A-10
INSTALLATION
POWER WAVE 455/R
Return to Section TOC Return to Section TOC Return to Section TOC Return to Section TOC
Return to Master TOC Return to Master TOC Return to Master TOC Return to Master TOC
CONTROL BOARD
(LOCATED IN
CONTROL BOX
BEHIND CASE
FRONT)
FEED HEAD
BOARD
(LOCATED IN
CONTROL
BOX BEHIND
CASE FRONT)
BANK S1
BANK S2
RIGHT
LEFT
DEVICENET/
GATEWAY
BOARD
(LOCATED
BEHIND
FRONT
COVER)
FRONT
COVER
CASE FRONT
OPENING IN
CASE FRONT
TO ACCESS
CONTROL
BOX
WARNING

DEVICENET/GATEWAY BOARD
DIP SWITCH, BANK (S2):
switch 1,2 = configure the baud rate
for DeviceNET
Prior to S24958-6 software
switch 1 switch 2 baud rate
off off -------
on off 125K
off on 250K
on on 500
S24958-6 and later software
switch 1 switch 2 baud rate
off off 125K
off on 250K
on off 500K
on on 500K
Programmable value. Consult local Lincoln Technical
representative.
switch 5 = reserved for future use
switch 6 = reserved for future use
switch 7 = reserved for future use
switch 8 = reserved for future use
A-11 A-11
INSTALLATION
POWER WAVE 455/R
Return to Section TOC Return to Section TOC Return to Section TOC Return to Section TOC
Return to Master TOC Return to Master TOC Return to Master TOC Return to Master TOC

Operation...............................................................................................................................Section B
Safety Precautions......................................................................................................................B-2
Graphic Symbols.........................................................................................................................B-3
General Description ....................................................................................................................B-4
Design Features and Advantages ........................................................................................B-4
Recommended Processes and Equipment.................................................................................B-5
Recommended Processes....................................................................................................B-5
Recommended Equipment ...................................................................................................B-5
Required Equipment.............................................................................................................B-5
Limitations.............................................................................................................................B-5
Duty Cycle and Time Period.................................................................................................B-5
Case Front Controls....................................................................................................................B-6
Welding Mode Descriptions ........................................................................................................B-7
Constant Voltage Welding ....................................................................................................B-7
Pulse Welding.......................................................................................................................B-8
STT Welding .........................................................................................................................B-9
Section B-1 Section B-1
TABLE OF CONTENTS
- OPERATION SECTION -
POWER WAVE 455/R
Return to Master TOC Return to Master TOC Return to Master TOC Return to Master TOC

SAFETY PRECAUTIONS
Read this entire section of operating instructions
before operating the machine.
ELECTRIC SHOCK can kill.
• Unless using cold feed feature, when
feeding with gun trigger, the electrode and
drive mechanism are always electrically
energized and could remain energized
several seconds after the welding ceases.
• Do not touch electrically live parts or electrodes with
your skin or wet clothing.
• Insulate yourself from the work and ground.
• Always wear dry insulating gloves.
FUMES AND GASES can be
dangerous.
• Keep your head out of fumes.
• Use ventilation or exhaust to remove
fumes from breathing zone.
WELDING SPARKS can cause
fire or explosion.
• Keep flammable material away.
• Do not weld on containers that have held
combustibles.
ARC RAYS can burn.
• Wear eye, ear, and body protection.
Observe additional guidelines detailed in the beginning
of this manual.
B-2 B-2
OPERATION
POWER WAVE 455/R
Return to Section TOC Return to Section TOC Return to Section TOC Return to Section TOC
Return to Master TOC Return to Master TOC Return to Master TOC Return to Master TOC
WARNING

B-3 B-3
OPERATION
POWER WAVE 455/R
Return to Section TOC Return to Section TOC Return to Section TOC Return to Section TOC
Return to Master TOC Return to Master TOC Return to Master TOC Return to Master TOC
INPUT POWER
ON
OFF
HIGH TEMPERATURE
MACHINE STATUS
CIRCUIT BREAKER
WIRE FEEDER
POSITIVE OUTPUT
NEGATIVE OUTPUT
3 PHASE INVERTER
INPUT POWER
THREE PHASE
DIRECT CURRENT
GMAW
FCAW
GTAW
OPEN CIRCUIT VOLT-
AGE
INPUT VOLTAGE
OUTPUT VOLTAGE
INPUT CURRENT
OUTPUT CURRENT
PROTECTIVE
GROUND
WARNING OR
CAUTION
GRAPHIC SYMBOLS THAT APPEAR ON
THIS MACHINE OR IN THIS MANUAL
U0
U1
U2
I1
I2
SMAW

GENERAL DESCRIPTION
The Power Wave power source is designed to be a part
of a modular, multi-process welding system.
Depending on configuration, it can support constant
current, constant voltage, Surface Tension Transfer
and pulse welding modes.
The Power Wave power source is designed to be used
with the family of Power Feed wire feeders, operating
as a system. Each component in the system has spe-
cial circuitry to “talk with” the other system compo-
nents, so each component (power source, wire feeder,
electrical accessories) knows what the other is doing at
all times. The components communicate using ArcLink
protocol.
Robotic systems can communicate with other industri-
al machines via DeviceNET protocol. The result is a
highly intrigated and flexible welding cell.
The Power Wave 455/R is a high performance, digital-
ly controlled inverter welding power source capable of
complex, high-speed waveform control. Properly
equipped, it can support the GMAW, GMAW-P, FCAW,
GTAW and STT processes. It carries an output rating of
either 450 amps, 38 volts; or 400 amps, 36 volts (both
at 100% duty cycle), depending on input voltage and
frequency. The Surface Tension transfer process (STT)
is supported at currents up to 325 amps, at 100% duty
cycle.
If the duty cycle is exceeded, a thermostat will shut off
the output until the machine cools to a reasonable
operating temperature.
DESIGN FEATURES AND ADVANTAGES
• Designed to the IEC 974-1 Standard.
• Power Wave 455 multiple process output ranges:
5 - 570 amps
• Easy access for input connections. Connections are
simple strip and clamp (no lugs required).
• F.A.N. (Fan As Needed). Cooling fan runs only when
necessary (above Code 10500 only, and all STT
machines).
• Modular construction for easy servicing.
• Thermostatically protected.
• Electronic over-current protection.
• Input over-voltage protection.
• Utilizes digital signal processing and microprocessor
control.
• Simple, reliable input voltage change over.
• All system components communicate and transfer
information.
• Auto device recognition simplifies accessory cable
connections.
B-4 B-4
OPERATION
POWER WAVE 455/R
Return to Section TOC Return to Section TOC Return to Section TOC Return to Section TOC
Return to Master TOC Return to Master TOC Return to Master TOC Return to Master TOC

RECOMMENDED PROCESSES
AND EQUIPMENT
RECOMMENDED PROCESSES
The Power Wave 455/R can be set up in a number of
configurations, some requiring optional equipment or
welding programs. Each machine is factory prepro-
grammed with multiple welding procedures, typically
including GMAW, GMAW-P, FCAW, GTAW and STT
for a variety of materials, including mild steel, stainless
steel, cored wires, and aluminum. The STT process
supports mild steel and stainless steel welding.
The Power Wave 455/R is recommended only for
automatic or mechanized applications such as robotic
welding.
RECOMMENDED EQUIPMENT
Automatic Operation
All welding programs and procedures are set through
software for the robotic Power Wave. FANUC robots
equipped with RJ-3 controllers may communicate
directly with the Power Wave. Other pieces of equip-
ment such as PLCs or computers can communicate
with the Power Wave using DeviceNET. All wire weld-
ing processes require a robotic Power Feed wire feeder.
REQUIRED EQUIPMENT
• PF-10/R Wire Feeder, K1780-1
• Control Cables (22 pin to 22 pin), K1795-10,-25,-50,-
100
• Control Cables (for use on FANUC robot arm, 22 pin
to 14 pin, 10 ft), K1804-1
• Control Cables (for use on FANUC robot arm, 22 pin
to 14 pin, 18 in), K1805-1
• Control Cables (for use on FANUC robot arm, 22 pin
to 14 pin, 18 in), K1804-2
LIMITATIONS
• The Power Wave 455/R is not suitable for SMAW,
CAC-A or other processes not listed.
• Power Waves are not to be used in outdoor environ-
ments.
• Only ArcLink Power Feed wire feeders and user
interfaces may be used. Other Lincoln wire feeders
or non-Lincoln wire feeders cannot be used.
DUTY CYCLE AND TIME PERIOD
The Power Feed wire feeders are capable of welding at
a 100% duty cycle (continuous welding). The power
source will be the limiting factor in determining system
duty cycle capability. Note that the duty cycle is based
upon a ten minute period. A 60% duty cycle represents
6 minutes of welding and 4 minutes of idling in a ten
minute period.
B-5 B-5
OPERATION
POWER WAVE 455/R
Return to Section TOC Return to Section TOC Return to Section TOC Return to Section TOC
Return to Master TOC Return to Master TOC Return to Master TOC Return to Master TOC

CASE FRONT CONTROLS
All operator controls and adjustments are located on
the case front of the Power Wave. (See Figure B.1)
1. POWER SWITCH: Controls input power to the
Power Wave.
2. STATUS LIGHT: A two color light that indicates sys-
tem errors. Normal operation is a steady green
light. Error conditions are indicated, per Table B.1.
NOTE: The robotic Power Waves’status light will flash
green, and sometimes red and green, for up to
one minute when the machine is first turned on.
This is a normal situation as the machine goes
through a self test at power up.
TABLE B.1
Light Meaning
Condition
Steady System OK. Power source
Green communicating normally with
wire feeder and its components.
Blinking Normal for first 1-10 seconds
Green after power is turned on.
Alternating Non-recoverable system fault.
Green Must turn power source off, find
and Red source of error, and turn power
back on to reset. See
Troubleshooting Guide.
Steady See Troubleshooting Guide.
Red
3. HIGH TEMPERATURE LIGHT (thermal overload):
A yellow light that comes on when an over tem-
perature situation occurs. Output is disabled until
the machine cools down. When cool, the light
goes out and output is enabled.
4. 10 AMP WIRE FEEDER CIRCUIT BREAKER:
Protects 40 volt DC wire feeder power supply.
5. 10 AMP AUXILIARY POWER CIRCUIT BREAKER:
Protects 115 volt AC case front receptacle auxil-
iary supply.
6. LEAD CONNECTOR S2 (SENSE LEAD)
7. 5-PIN ARC LINK S1
8. 5-PIN DEVICENET CONNECTOR S5
9. I / O CONNECTOR
10. NEGATIVE OUTPUT TERMINAL
11. INTERFACE CONNECTOR S6
12. STT TERMINAL
13. POSITIVE OUTPUT TERMINAL
14. AUXILIARY OUTPUT
B-6 B-6
OPERATION
POWER WAVE 455/R
Return to Section TOC Return to Section TOC Return to Section TOC Return to Section TOC
Return to Master TOC Return to Master TOC Return to Master TOC Return to Master TOC
POWERWAVE 455/R
I ON
O OFF
FIGURE B.1 – POWER WAVE CASE FRONT CONTROLS
1
11
12
13
2 3
4145
6
7
8
9
10

WELDING MODE DESCRIPTIONS
CONSTANT VOLTAGE WELDING
For each wire feed speed, a corresponding voltage is
preprogrammed into the machine through special soft-
ware at the factory. The preprogrammed voltage is the
best average voltage for a given wire feed speed. With
synergic programs, when the wire feed speed changes,
the Power Wave will automatically adjust the corre-
sponding voltage.
Wave control adjusts the inductance of the waveshape.
(This adjustment is often referred to as "pinch". In-
ductance is inversely proportional to pinch.) Increasing
wave control greater than 0 results in a harsher, colder
arc, while decreasing the wave control to less than 0
provides a softer, hotter arc. (See Figure B.2.)
B-7 B-7
OPERATION
POWER WAVE 455/R
Return to Section TOC Return to Section TOC Return to Section TOC Return to Section TOC
Return to Master TOC Return to Master TOC Return to Master TOC Return to Master TOC
Current
Time
Wave Control +10.0
Wave Control -10.0
Wave Control 0.00
FIGURE B.2 – CV WAVE CONTROL CHARACTERISTICS

PULSE WELDING
Pulse welding procedures are set by controlling an
overall “arc length” variable. When pulse welding, the
arc voltage is highly dependent upon the waveform.
The peak current, background current, rise time, fall
time and pulse frequency all affect the voltage. The
exact voltage for a given wire feed speed can only be
predicted when all the pulsing waveform parameters
are known. Using a preset voltage becomes impracti-
cal, and instead the arc length is set by adjusting “trim.”
Trim adjusts the arc length and ranges from 0.50 to
1.50, with a nominal value of 1.00. Trim values greater
than 1.00 increase the arc length, while values less
than 1.00 decrease the arc length.
Most pulse welding programs are synergic. As the wire
feed speed is adjusted, the Power Wave will automati-
cally recalculate the waveform parameters to maintain
similar arc properties.
The Power Wave utilizes “adaptive control” to compen-
sate for changes in electrical stick-out while welding.
(Electrical stick-out is the distance from the contact tip
to the work piece.) The Power Wave waveforms are
optimized for a 0.75" (19mm) stick-out. The adaptive
behavior supports a range of stickouts from 0.50"
(13mm) to 1.25" (32mm). At very low or high wire feed
speeds, the adaptive range may be less due to reach-
ing the physical limitations of the welding process.
Wave control in pulse programs usually adjusts the
focus or shape of the arc. Wave control values greater
than 0 increase the pulse frequency while decreasing
the background current, resulting in a tight, stiff arc
best for high speed sheet metal welding. Wave control
values less than 0 decrease the pulse frequency while
increasing the background current for a soft arc good
for out-of-position welding. (See Figure B.3.)
B-8 B-8
OPERATION
POWER WAVE 455/R
Return to Section TOC Return to Section TOC Return to Section TOC Return to Section TOC
Return to Master TOC Return to Master TOC Return to Master TOC Return to Master TOC
Current
Time
Wave Control +10.0
Wave Control -10.0
Wave Control 0.00
FIGURE B.3 – PULSE WAVE CONTROL CHARACTERISTICS
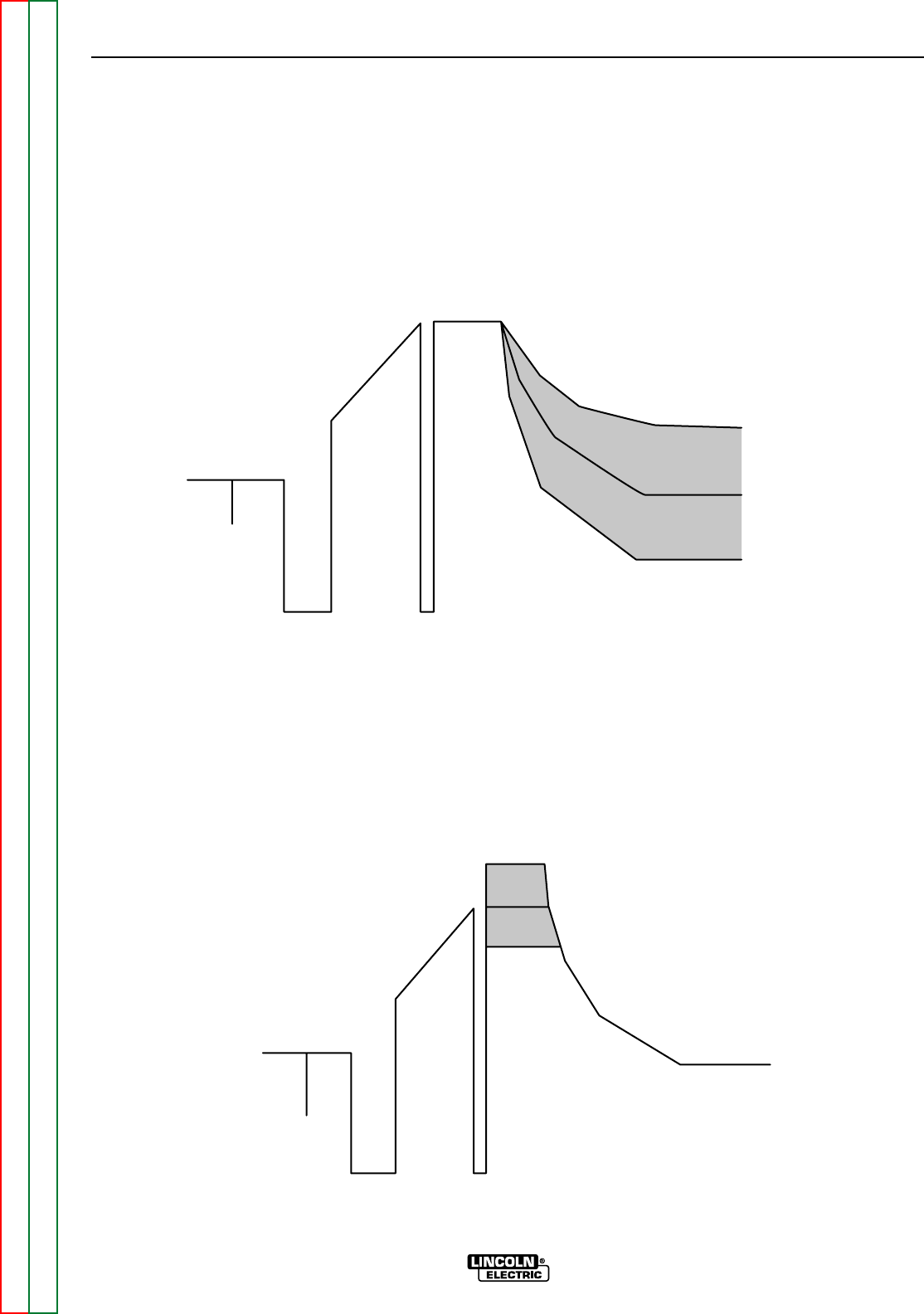
STT WELDING
The pictures illustrate the waveshape of current for the
process. They are not drawn to scale, and are intend-
ed only for the purpose of showing how the variables
affect the waveform.
Trim in the STT mode adjusts the tailout and back-
ground portion of the waveform. Trim values greater
than 1.0 add more energy to the weld and make the
weld puddle hotter; trim values less than 1.0 reduce
energy to weld. A nominal value of 1.0 will work for
most applications. (See Figure B.4.)
B-9 B-9
OPERATION
POWER WAVE 455/R
Return to Section TOC Return to Section TOC Return to Section TOC Return to Section TOC
Return to Master TOC Return to Master TOC Return to Master TOC Return to Master TOC
Current
Time
Trim 1.50
Trim 1.00
Trim 0.50
FIGURE B.4 – STT TRIM CONTROL CHARACTERISTICS
Current
Time
Wave Control +10.0
Wave Control -10.0
Wave Control 0.00
FIGURE B.5 – STT WAVE CONTROL CHARACTERISTICS
For most programs, peak current is adjusted by wave
control values. A value of +10.0 maximizes the peak
current, while a wave control of -10.0 minimizes peak
current. In general, the peak current is proportional to
torch arc length. (See Figure B.5.)
NOTE: The ranges on Wave Control and Trim are
dependent on the weld programs. The values
shown are typical ranges.

Accessories ..........................................................................................................................Section C
Optional Equipment ....................................................................................................................C-2
Factory Installed ...................................................................................................................C-2
Field Installed .......................................................................................................................C-2
Section C-1 Section C-1
TABLE OF CONTENTS
- ACCESSORIES SECTION -
POWER WAVE 455/R
Return to Master TOC Return to Master TOC Return to Master TOC Return to Master TOC

OPTIONAL EQUIPMENT
FACTORY INSTALLED
There are no factory installed options available for the
Power Wave 455R.
FIELD INSTALLED
•Gas Guard Regulator (K659-1)
The Gas Guard regulator is available as an option-
al accessory for the Power Feed Robotic wire drive
unit. Install the 5/8-18 male outlet on the regulator
to the proper 5/8-18 female gas inlet on the back
panel of the wire drive. Secure the fitting with the
flow adjuster key at the top.
•Voltage Sense Leads (K940-10, -25 or -50)
The voltage sense leads connect at the front of the
machine. (See Figure A.2.)
•Power Wave Water Cooler (K1767-1)*
The K1767-1 is the recommended water cooler for
the Power Wave. Incorporated into the cooler is an
automatic flow sensor to detect low coolant flow. In
the event of a low flow condition, a fault signal is
sent to the Power Wave, and welding output auto-
matically stops to protect the torch.
The water cooler is designed to cool only one welding
gun and should be not used to cool multiple guns or
other devices.
Water cooler manufacturers often specify additives
to the coolant such as fungicides or alkalies. Follow
the manufacturers’recommendations to achieve
proper operation and long lifetime without clogging.
•Water Flow Sensor (K1536-1)
Water cooled guns can be damaged very quickly if
they are used even momentarily without water flow-
ing. Recommend practice is to install a water flow
sensor such as on the water return line of the torch.
When fully integrated into the welding system, the
sensor will prevent welding if no water flow is pre-
sent.
•Dual Cylinder Undercarriage, K1570-1*
•Coaxial Welding Cable, K1796
*The Dual Cylinder Undercarriage, K1570-1, is not
compatible in combination with the Power Wave
Water Cooler K1767-1.
C-2 C-2
ACCESSORIES
POWER WAVE 455/R
Return to Section TOC Return to Section TOC Return to Section TOC Return to Section TOC
Return to Master TOC Return to Master TOC Return to Master TOC Return to Master TOC

Maintenance..........................................................................................................................Section D
Safety Precautions......................................................................................................................D-2
Routine and Periodic Maintenance.............................................................................................D-2
Main Assembly (Exploded View) ...............................................................................................D-3
Section D-1 Section D-1
TABLE OF CONTENTS
- MAINTENANCE SECTION -
POWER WAVE 455/R
Return to Master TOC Return to Master TOC Return to Master TOC Return to Master TOC

SAFETY PRECAUTIONS
ELECTRIC SHOCK can kill.
• Only Qualified personnel should
perform this maintenance.
• Turn the input power OFF at the
disconnect switch or fuse box
before working on this equipment.
•Do not touch electrically hot parts.
ROUTINE AND PERIODIC
MAINTENANCE
1. Disconnect input AC power supply lines to the
machine before performing periodic maintenance,
tightening, cleaning, or replacing parts. See
Figure D.1.
PERFORM THE FOLLOWING DAILY:
1. Check that no combustible materials are in the
welding or cutting area or around the machine.
2. Remove any debris, dust, dirt, or materials that
could block the air flow to the machine for cooling.
3. Inspect the electrode cables for any slits or punc-
tures in the cable jacket, or any condition that
would affect the proper operation of the machine.
PERFORM PERIODICALLY:
Clean the inside of the machine with a low pressure air
stream. Clean the following parts. Refer to Figure
D.1.
• Transformer and output rectifier assembly.
• Electrode and work cable connections.
• PC board connections..
• Intake and outlet louvers on the machine case.
• Any obvious accumulations of dirt within the
machine.
• Fan Assembly.
NOTE: The fan motor has sealed bearings which
require no maintenance.
D-2 D-2
MAINTENANCE
POWER WAVE 455/R
Return to Section TOC Return to Section TOC Return to Section TOC Return to Section TOC
Return to Master TOC Return to Master TOC Return to Master TOC Return to Master TOC
WARNING

D-3 D-3
MAINTENANCE
POWER WAVE 455/R
Return to Section TOC Return to Section TOC Return to Section TOC Return to Section TOC
Return to Master TOC Return to Master TOC Return to Master TOC Return to Master TOC
1
7
7
7
3
4
6
5
2
2
2
FIGURE D.1 – MAIN ASSEMBLY (EXPLODED VIEW)
1. CASE FRONT ASSEMBLY
2. TRANSFORMER AND OUTPUT
RECTIFIER ASSEMBLY
3. INPUT ASSEMBLY
4. CONTROL BOX AND VERTICAL
DIVIDER ASSEMBLY
5. BASE, LIFT BAIL AND FAN
ASSEMBLY
6. SWITCH BOARD HEATSINK
ASSEMBLY
7. CASE PARTS

Theory of Operation .............................................................................................................Section E
General Description ....................................................................................................................E-2
Input Voltage and Precharge ......................................................................................................E-3
Switch Boards and Main Transformer.........................................................................................E-4
DC Bus Board, Power Board, Feed Head Board, Gateway Board
and Voltage Sense Board ...........................................................................................................E-5
Control Board..............................................................................................................................E-7
Output Rectifier, Output Choke and STT Chopper Board ..........................................................E-8
Thermal Protection, Protective Circuits, Over Current Protection
and Under/Over Voltage Protection ............................................................................................E-9
General Description of STT (Surface Tension Transfer) Process.............................................E-10
Insulated Gate Bipolar Transistor (IGBT) Operation .................................................................E-11
Pulse Width Modulation ............................................................................................................E-12
Section E-1 Section E-1
TABLE OF CONTENTS
- THEORY OF OPERATION SECTION -
POWER WAVE 455/R
Return to Master TOC Return to Master TOC Return to Master TOC Return to Master TOC
+
+
INPUT
BOARD
RECONNECT
SWITCH
LEFT
SWITCH
BOARD
RIGHT
SWITCH
BOARD
INPUT
RECTIFIER
CR1
GATEWAY
BOARD
DC
BUS
BOARD
FEED
HEAD
BOARD
POWER
BOARD
CONTROL
BOARD
STT CHOPPER
BOARD
OUTPUT
CHOKE
STT
ELECTRODE
TERMINAL
ELECTRODE
TERMINAL
THERMOSTATS
T1
T2
AUX
RECONNECT
RELAY
WATER
COOLER
115 VAC
RECP.
115 VAC
FAN
ARC LINK
WIRE
FEEDER
RECP.
S1
S6 CONNECTION
TO WIRE
DRIVE
S1
S6
VOLT
SENSE
BOARD
MAIN
TRANSFORMER
S5
CONTACTOR AND PRECHARGE
CONTROL SIGNALS FROM
CONTROL BOARD
FROM CONTROL
BOARD
2
4
V
A
C
115 VAC
52 VAC
230 VAC
40 VDC
40 VDC
40 VDC
+20 VDC
TO
CHOPPER
BOARD
40 VDC
ARC LINK CONNECTION
TO
ROBOT
VOLTAGE SENSE
OUTPUT
+20 VDC FROM
POWER BOARD
CT CURRENT
TO CONTROL
BOARD
CAP. V/F
FEEDBACK
CAP. V/F
FEEDBACK
IGBT DRIVE
FROM
CONTROL
BOARD
CT CURRENT
TO CONTROL
BOARD
-15 V
+15 V
+5 V
+5 V ARC LINK
+5V RS232
+15V SPI
STATUS THERMAL
LIGHT LIGHT
S2 WORK
SENSE
LEFT S.B.
CAP. V/F
RIGHT S.B.
CAP. V/F
S3
RS232
LEFT CT
CURRENT
FB
C
U
R
R
E
N
T
F
B
S
T
T
F
B
STT
DRIVE
ARC LINK
IGBT
DRIVES
TO
LEFT
S.B.
TO
RIGHT
S.B.
67A
67B
SW1
BUS BOARD
RECTIFIER
CURRENT
TRANSDUCER
CURRENT
TRANSDUCER
OUTPUT DIODES
D1 -D4
115 VAC
40 VDC
DEVICE NET
VOLTAGE SENSE SELECT
IGBT DRIVE
FROM
CONTROL
BOARD
+5V SPI
RIGHT CT
CURRENT
FB
TO FAN RELAY
CONTACTOR AND
PRECHARGE
CONTROL SIGNALS
65 VDC
WORK
TERMINAL
POWER WAVE 455/R
FIGURE E.1 – BLOCK LOGIC DIAGRAM

GENERAL DESCRIPTION
The Power Wave 455/R power source is designed to
be a part of a modular, multi-process welding system.
It is a high performance, digitally controlled inverter
welding power source capable of complex, high-speed
waveform control. Depending upon configuration, it
can support constant current, constant voltage, surface
tension transfer and pulse welding modes. Each
machine is factory preprogrammed with multiple weld-
ing procedures. Typically these procedures include
GMAW, GMAW-P, FCAW, GTAW and STT (Surface
Tension Transfer) for a variety of materials such as
mild steel, stainless steel, cored wires and aluminum.
The STT process supports mild steel and stainless
steel welding.
The Power Wave 455/R has an output rating of either
450 amps at 38 volts or 400 amps at 36 volts. The two
output ratings are dependent upon input voltage and
frequency. Both have a duty cycle of 100%. The STT
process is rated at currents up to 325 amps at a 100%
duty cycle.
E-2 E-2
THEORY OF OPERATION
POWER WAVE 455/R
Return to Section TOC Return to Section TOC Return to Section TOC Return to Section TOC
Return to Master TOC Return to Master TOC Return to Master TOC Return to Master TOC
+
+
INPUT
BOARD
RECONNECT
SWITCH
LEFT
SWITCH
BOARD
RIGHT
SWITCH
BOARD
INPUT
RECTIFIER
CR1
GATEWAY
BOARD
DC
BUS
BOARD
FEED
HEAD
BOARD
POWER
BOARD
CONTROL
BOARD
STT CHOPPER
BOARD
OUTPUT
CHOKE
STT
ELECTRODE
TERMINAL
ELECTRODE
TERMINAL
THERMOSTATS
T1
T2
AUX
RECONNECT
RELAY
WATER
COOLER
115 VAC
RECP.
115 VAC
FAN
ARC LINK
WIRE
FEEDER
RECP.
S1
S6 CONNECTION
TO WIRE
DRIVE
S1
S6
VOLT
SENSE
BOARD
MAIN
TRANSFORMER
S5
CONTACTOR AND PRECHARGE
CONTROL SIGNALS FROM
CONTROL BOARD
FROM CONTROL
BOARD
2
4
V
A
C
115 VAC
52 VAC
230 VAC
40 VDC
40 VDC
40 VDC
+20 VDC
TO
CHOPPER
BOARD
40 VDC
ARC LINK CONNECTION
TO
ROBOT
VOLTAGE SENSE
OUTPUT
+20 VDC FROM
POWER BOARD
CT CURRENT
TO CONTROL
BOARD
CAP. V/F
FEEDBACK
CAP. V/F
FEEDBACK
IGBT DRIVE
FROM
CONTROL
BOARD
CT CURRENT
TO CONTROL
BOARD
-15 V
+15 V
+5 V
+5 V ARC LINK
+5V RS232
+15V SPI
STATUS THERMAL
LIGHT LIGHT
S2 WORK
SENSE
LEFT S.B.
CAP. V/F
RIGHT S.B.
CAP. V/F
S3
RS232
LEFT CT
CURRENT
FB
C
U
R
R
E
N
T
F
B
S
T
T
F
B
STT
DRIVE
ARC LINK
IGBT
DRIVES
TO
LEFT
S.B.
TO
RIGHT
S.B.
67A
67B
SW1
BUS BOARD
RECTIFIER
CURRENT
TRANSDUCER
CURRENT
TRANSDUCER
OUTPUT DIODES
D1 -D4
115 VAC
40 VDC
DEVICE NET
VOLTAGE SENSE SELECT
IGBT DRIVE
FROM
CONTROL
BOARD
+5V SPI
RIGHT CT
CURRENT
FB
TO FAN RELAY
CONTACTOR AND
PRECHARGE
CONTROL SIGNALS
65 VDC
WORK
TERMINAL
POWER WAVE 455/R
FIGURE E.2 – INPUT VOLTAGE AND PRECHARGE
NOTE: Unshaded areas of Block Logic Diagram are the subject of discussion.

INPUT VOLTAGE AND PRECHARGE
The Power Wave 455/R can be connected for a variety
of three-phase input voltages. Refer to Figure E.2.
The initial input power is applied to the Power Wave
455/R through a line switch located on the front of the
machine. Two phases of the three-phase input power
are applied to the Input Board and both auxiliary trans-
formers. The various secondary voltages developed
by transformer T1 are applied to the Input Board, the
fan motor (via a control relay) and the Bus Board recti-
fier. The 65VDC produced from the Bus Board rectifi-
er is used by the Bus Board to provide various DC volt-
ages for the Power Board, the Feed Head Board and
the wire feeder receptacle. The 115/230VAC devel-
oped on the secondary of auxiliary transformer T2 is
applied to the 115VAC receptacle and to the water
cooler receptacle.
The two phases that are connected to the Input Board,
through the input line switch SW1, are connected to the
input rectifier through the CR1 precharge relay. During
the precharge or "soft start" sequence, these two phas-
es are current limited by the Input Board. The AC input
voltage is rectified, and the resultant DC voltage is
applied through the reconnect switches to the input
capacitors located on the right and left switch boards.
The Control Board monitors the voltage across the
capacitors. When the capacitors have charged to an
acceptable level, the Control Board signals the Input
Board to energize the main input contactor, making all
three phases of input power, without current limiting,
available to the input capacitors. At this point the
Power Wave 455/R is in the "Run Mode" of operation.
If the capacitors become undervoltaged, overvoltaged,
or unbalanced, the Control Board will signal the Input
Board to de-energize the main input contactor, and the
Power Wave 455/R will be disabled. See Figure E.2.
E-3 E-3
THEORY OF OPERATION
POWER WAVE 455/R
Return to Section TOC Return to Section TOC Return to Section TOC Return to Section TOC
Return to Master TOC Return to Master TOC Return to Master TOC Return to Master TOC

SWITCH BOARDS AND MAIN
TRANSFORMER
There are two switch boards in the Power Wave 455/R
machine. Each contains an input capacitor and insu-
lated gate bipolar transistor (IGBT) switching circuitry.
Refer to Figure E.3. When the machine reconnect
switches are configured for a lower input voltage
(below 300VAC), the input capacitors are connected in
parallel. When the machine is configured for higher
input voltages (300VAC and above), the input capaci-
tors are connected in series.
When the input capacitors are fully charged, they act
as power supplies for the IGBT switching circuits. The
insulated gate bipolar transistors switch the DC power
from the input capacitors "on and off," thus supplying
pulsed DC current to the main transformer primary
windings. See IGBT OPERATION DISCUSSION AND
DIAGRAMS in this section.
Each switch board feeds current to a separate, oppo-
sitely wound primary winding in the Main Transformer.
The reverse directions of current flow through the main
transformer primaries, and the offset timing of the IGBT
switch boards induce an AC square wave output signal
at the secondary of the main transformer. Current
transformers located on the switch boards monitor the
primary currents. If the primary currents become
abnormally high, the Control Board will shut off the
IGBTs, thus disabling the machine’s output. The DC
current flow through each primary winding is clamped
back to each respective input capacitor when the
IGBTs are turned off. This is needed due to the induc-
tance of the transformer primary windings. The firing of
the two switch boards occurs during halves of a 50-
microsecond interval, creating a constant 20 KHZ out-
put.
E-4 E-4
THEORY OF OPERATION
POWER WAVE 455/R
Return to Section TOC Return to Section TOC Return to Section TOC Return to Section TOC
Return to Master TOC Return to Master TOC Return to Master TOC Return to Master TOC
NOTE: Unshaded areas of Block Logic Diagram are the subject of discussion.
FIGURE E.3 - SWITCH BOARDS AND MAIN TRANSFORMER
+
+
INPUT
BOARD
RECONNECT
SWITCH
LEFT
SWITCH
BOARD
RIGHT
SWITCH
BOARD
INPUT
RECTIFIER
CR1
GATEWAY
BOARD
DC
BUS
BOARD
FEED
HEAD
BOARD
POWER
BOARD
CONTROL
BOARD
STT CHOPPER
BOARD
OUTPUT
CHOKE
STT
ELECTRODE
TERMINAL
ELECTRODE
TERMINAL
THERMOSTATS
T1
T2
AUX
RECONNECT
RELAY
WATER
COOLER
115 VAC
RECP.
115 VAC
FAN
ARC LINK
WIRE
FEEDER
RECP.
S1
S6 CONNECTION
TO WIRE
DRIVE
S1
S6
VOLT
SENSE
BOARD
MAIN
TRANSFORMER
S5
CONTACTOR AND PRECHARGE
CONTROL SIGNALS FROM
CONTROL BOARD
FROM CONTROL
BOARD
2
4
V
A
C
115 VAC
52 VAC
230 VAC
40 VDC
40 VDC
40 VDC
+20 VDC
TO
CHOPPER
BOARD
40 VDC
ARC LINK CONNECTION
TO
ROBOT
VOLTAGE SENSE
OUTPUT
+20 VDC FROM
POWER BOARD
CT CURRENT
TO CONTROL
BOARD
CAP. V/F
FEEDBACK
CAP. V/F
FEEDBACK
IGBT DRIVE
FROM
CONTROL
BOARD
CT CURRENT
TO CONTROL
BOARD
-15 V
+15 V
+5 V
+5 V ARC LINK
+5V RS232
+15V SPI
STATUS THERMAL
LIGHT LIGHT
S2 WORK
SENSE
LEFT S.B.
CAP. V/F
RIGHT S.B.
CAP. V/F
S3
RS232
LEFT CT
CURRENT
FB
C
U
R
R
E
N
T
F
B
S
T
T
F
B
STT
DRIVE
ARC LINK
IGBT
DRIVES
TO
LEFT
S.B.
TO
RIGHT
S.B.
67A
67B
SW1
BUS BOARD
RECTIFIER
CURRENT
TRANSDUCER
CURRENT
TRANSDUCER
OUTPUT DIODES
D1 -D4
115 VAC
40 VDC
DEVICE NET
VOLTAGE SENSE SELECT
IGBT DRIVE
FROM
CONTROL
BOARD
+5V SPI
RIGHT CT
CURRENT
FB
TO FAN RELAY
CONTACTOR AND
PRECHARGE
CONTROL SIGNALS
65 VDC
WORK
TERMINAL
POWER WAVE 455/R

DC BUS BOARD, POWER BOARD,
FEED HEAD BOARD, GATEWAY
BOARD AND VOLTAGE SENSE
BOARD
The DC Bus Board receives approximately 65VDC
from the Bus Board rectifier. The DC Bus Board regu-
lates that 65VDC to a +40VDC supply. This regulated
40VDC is applied to the Feed Head Board, the Power
Board, and the wire feeder receptacle.
The switching power supplies on the Power Board sup-
ply a variety of regulated DC voltages to the Control
Board and a +20VDC to the STT Chopper Board. The
Control Board uses these regulated voltages to power
the many circuits and communication functions incor-
porated within the Control Board.
When the Feed Head Board activates the Voltage
Sense Board, the actual arc voltage is sensed (lead
67), and this information is delivered through the volt-
age sense board to the Control Board.
The Power Wave 455R uses two digital communication
platforms. Internally the PC boards communicate via
ArcLink. Externally the Power Wave 455R communi-
cates using the industry standard Device Net protocol.
The Gateway Board makes the translation between the
two platforms possible. The Power Wave 455R does
not have a dedicated interface device or board. The
robot (or other input device – PLC, etc.) acts as the
user interface, issuing commands through the Device
Net protocol that are translated by the Gateway Board
to ArcLink compatible messages. The following block
diagram (Figure E.5) depicts the flow of communica-
tion information.
E-5 E-5
THEORY OF OPERATION
POWER WAVE 455/R
Return to Section TOC Return to Section TOC Return to Section TOC Return to Section TOC
Return to Master TOC Return to Master TOC Return to Master TOC Return to Master TOC
NOTE: Unshaded areas of Block Logic Diagram are the subject of discussion.
+
+
INPUT
BOARD
RECONNECT
SWITCH
LEFT
SWITCH
BOARD
RIGHT
SWITCH
BOARD
INPUT
RECTIFIER
CR1
GATEWAY
BOARD
DC
BUS
BOARD
FEED
HEAD
BOARD
POWER
BOARD
CONTROL
BOARD
STT CHOPPER
BOARD
OUTPUT
CHOKE
STT
ELECTRODE
TERMINAL
ELECTRODE
TERMINAL
THERMOSTATS
T1
T2
AUX
RECONNECT
RELAY
WATER
COOLER
115 VAC
RECP.
115 VAC
FAN
ARC LINK
WIRE
FEEDER
RECP.
S1
S6 CONNECTION
TO WIRE
DRIVE
S1
S6
VOLT
SENSE
BOARD
MAIN
TRANSFORMER
S5
CONTACTOR AND PRECHARGE
CONTROL SIGNALS FROM
CONTROL BOARD
FROM CONTROL
BOARD
2
4
V
A
C
115 VAC
52 VAC
230 VAC
40 VDC
40 VDC
40 VDC
+20 VDC
TO
CHOPPER
BOARD
40 VDC
ARC LINK CONNECTION
TO
ROBOT
VOLTAGE SENSE
OUTPUT
+20 VDC FROM
POWER BOARD
CT CURRENT
TO CONTROL
BOARD
CAP. V/F
FEEDBACK
CAP. V/F
FEEDBACK
IGBT DRIVE
FROM
CONTROL
BOARD
CT CURRENT
TO CONTROL
BOARD
-15 V
+15 V
+5 V
+5 V ARC LINK
+5V RS232
+15V SPI
STATUS THERMAL
LIGHT LIGHT
S2 WORK
SENSE
LEFT S.B.
CAP. V/F
RIGHT S.B.
CAP. V/F
S3
RS232
LEFT CT
CURRENT
FB
C
U
R
R
E
N
T
F
B
S
T
T
F
B
STT
DRIVE
ARC LINK
IGBT
DRIVES
TO
LEFT
S.B.
TO
RIGHT
S.B.
67A
67B
SW1
BUS BOARD
RECTIFIER
CURRENT
TRANSDUCER
CURRENT
TRANSDUCER
OUTPUT DIODES
D1 -D4
115 VAC
40 VDC
DEVICE NET
VOLTAGE SENSE SELECT
IGBT DRIVE
FROM
CONTROL
BOARD
+5V SPI
RIGHT CT
CURRENT
FB
TO FAN RELAY
CONTACTOR AND
PRECHARGE
CONTROL SIGNALS
65 VDC
WORK
TERMINAL
POWER WAVE 455/R
FIGURE E-4 – DC BUS BOARD, POWER BOARD, FEED HEAD BOARD,
GATEWAY BOARD AND VOLTAGE SENSE BOARD

E-6 E-6
THEORY OF OPERATION
POWER WAVE 455/R
Return to Section TOC Return to Section TOC Return to Section TOC Return to Section TOC
Return to Master TOC Return to Master TOC Return to Master TOC Return to Master TOC
FIGURE E.5 – POWER WAVE 455/R COMMUNICATIONS
Arc Link
AArrcc LLiinnkk
Device Net
DDeevviiccee NNeett
PW-455R
CCoonnttrrooll
BBooaarrdd
Weld Controller /
Sequencer
GGaatteewwaayy
BBooaarrdd
Translator
FFeeeedd
HHeeaadd
BBooaarrdd
Robot
Controller
PF-10R

CONTROL BOARD
The Control Board performs the primary interfacing
functions to establish and maintain output control of the
Power Wave 455R machine. The function generator
and weld files exist within the Control Board hardware
and software. Digital command signals and feedback
information is received and processed at the Control
Board. Software within the Control Board processes
the command and feedback information and sends the
appropriate pulse width modulation (PWM) signals
(see PULSE WIDTH MODULATION in this section) to
the switch board IGBTs. In this manner, the digitally
controlled high-speed welding waveform is created.
The Control Board also monitors and controls the STT
(Surface Tension Transfer) circuitry incorporated in the
Power Wave 455R. STT output currents and arc volt-
ages are monitored, and the appropriated gate firing
signals are applied (or removed) from the STT
Chopper Board and switch boards to create a low spat-
ter, low fume MIG welding process. See GENERAL
DESCRIPTION OF STT (SURFACE TENSION
TRANSFER PROCESS) in this section.
In addition, the Control Board monitors the ther-
mostats, the main transformer primary currents and
input filter capacitor voltages. Depending on the fault
condition, the Control Board will activate the thermal
and/or the status light and will disable or reduce the
machine output. In some conditions the input contac-
tor will be de-energized.
E-7 E-7
THEORY OF OPERATION
POWER WAVE 455/R
Return to Section TOC Return to Section TOC Return to Section TOC Return to Section TOC
Return to Master TOC Return to Master TOC Return to Master TOC Return to Master TOC
FIGURE E.6 – CONTROL BOARD
+
+
INPUT
BOARD
RECONNECT
SWITCH
LEFT
SWITCH
BOARD
RIGHT
SWITCH
BOARD
INPUT
RECTIFIER
CR1
GATEWAY
BOARD
DC
BUS
BOARD
FEED
HEAD
BOARD
POWER
BOARD
CONTROL
BOARD
STT CHOPPER
BOARD
OUTPUT
CHOKE
STT
ELECTRODE
TERMINAL
ELECTRODE
TERMINAL
THERMOSTATS
T1
T2
AUX
RECONNECT
RELAY
WATER
COOLER
115 VAC
RECP.
115 VAC
FAN
ARC LINK
WIRE
FEEDER
RECP.
S1
S6 CONNECTION
TO WIRE
DRIVE
S1
S6
VOLT
SENSE
BOARD
MAIN
TRANSFORMER
S5
CONTACTOR AND PRECHARGE
CONTROL SIGNALS FROM
CONTROL BOARD
FROM CONTROL
BOARD
2
4
V
A
C
115 VAC
52 VAC
230 VAC
40 VDC
40 VDC
40 VDC
+20 VDC
TO
CHOPPER
BOARD
40 VDC
ARC LINK CONNECTION
TO
ROBOT
VOLTAGE SENSE
OUTPUT
+20 VDC FROM
POWER BOARD
CT CURRENT
TO CONTROL
BOARD
CAP. V/F
FEEDBACK
CAP. V/F
FEEDBACK
IGBT DRIVE
FROM
CONTROL
BOARD
CT CURRENT
TO CONTROL
BOARD
-15 V
+15 V
+5 V
+5 V ARC LINK
+5V RS232
+15V SPI
STATUS THERMAL
LIGHT LIGHT
S2 WORK
SENSE
LEFT S.B.
CAP. V/F
RIGHT S.B.
CAP. V/F
S3
RS232
LEFT CT
CURRENT
FB
C
U
R
R
E
N
T
F
B
S
T
T
F
B
STT
DRIVE
ARC LINK
IGBT
DRIVES
TO
LEFT
S.B.
TO
RIGHT
S.B.
67A
67B
SW1
BUS BOARD
RECTIFIER
CURRENT
TRANSDUCER
CURRENT
TRANSDUCER
OUTPUT DIODES
D1 -D4
115 VAC
40 VDC
DEVICE NET
VOLTAGE SENSE SELECT
IGBT DRIVE
FROM
CONTROL
BOARD
+5V SPI
RIGHT CT
CURRENT
FB
TO FAN RELAY
CONTACTOR AND
PRECHARGE
CONTROL SIGNALS
65 VDC
WORK
TERMINAL
POWER WAVE 455/R

OUTPUT RECTIFIER, OUTPUT
CHOKE AND STT CHOPPER
BOARD
The output rectifier receives the AC output from the
main transformer secondary and rectifies it to a DC
voltage level. The output choke is in series with the
negative leg of the output rectifier and also in series
with the welding load. Due to the current "smoothing"
capability of the output choke, a filtered DC output cur-
rent is applied through machine output terminals to the
welding arc.
The STT Chopper Board is in series with the STT out-
put terminal and is used to interrupt the welding cur-
rent for very short periods of time during the short-arc
MIG welding process. The IGBT modules incorporat-
ed on this board receive their gate firing commands
from the Control Board.
E-8 E-8
THEORY OF OPERATION
POWER WAVE 455/R
Return to Section TOC Return to Section TOC Return to Section TOC Return to Section TOC
Return to Master TOC Return to Master TOC Return to Master TOC Return to Master TOC
FIGURE E.7 – OUTPUT RECTIFIER, OUTPUT CHOKE AND STT CHOPPER BOARD
+
+
INPUT
BOARD
RECONNECT
SWITCH
LEFT
SWITCH
BOARD
RIGHT
SWITCH
BOARD
INPUT
RECTIFIER
CR1
GATEWAY
BOARD
DC
BUS
BOARD
FEED
HEAD
BOARD
POWER
BOARD
CONTROL
BOARD
STT CHOPPER
BOARD
OUTPUT
CHOKE
STT
ELECTRODE
TERMINAL
ELECTRODE
TERMINAL
THERMOSTATS
T1
T2
AUX
RECONNECT
RELAY
WATER
COOLER
115 VAC
RECP.
115 VAC
FAN
ARC LINK
WIRE
FEEDER
RECP.
S1
S6 CONNECTION
TO WIRE
DRIVE
S1
S6
VOLT
SENSE
BOARD
MAIN
TRANSFORMER
S5
CONTACTOR AND PRECHARGE
CONTROL SIGNALS FROM
CONTROL BOARD
FROM CONTROL
BOARD
2
4
V
A
C
115 VAC
52 VAC
230 VAC
40 VDC
40 VDC
40 VDC
+20 VDC
TO
CHOPPER
BOARD
40 VDC
ARC LINK CONNECTION
TO
ROBOT
VOLTAGE SENSE
OUTPUT
+20 VDC FROM
POWER BOARD
CT CURRENT
TO CONTROL
BOARD
CAP. V/F
FEEDBACK
CAP. V/F
FEEDBACK
IGBT DRIVE
FROM
CONTROL
BOARD
CT CURRENT
TO CONTROL
BOARD
-15 V
+15 V
+5 V
+5 V ARC LINK
+5V RS232
+15V SPI
STATUS THERMAL
LIGHT LIGHT
S2 WORK
SENSE
LEFT S.B.
CAP. V/F
RIGHT S.B.
CAP. V/F
S3
RS232
LEFT CT
CURRENT
FB
C
U
R
R
E
N
T
F
B
S
T
T
F
B
STT
DRIVE
ARC LINK
IGBT
DRIVES
TO
LEFT
S.B.
TO
RIGHT
S.B.
67A
67B
SW1
BUS BOARD
RECTIFIER
CURRENT
TRANSDUCER
CURRENT
TRANSDUCER
OUTPUT DIODES
D1 -D4
115 VAC
40 VDC
DEVICE NET
VOLTAGE SENSE SELECT
IGBT DRIVE
FROM
CONTROL
BOARD
+5V SPI
RIGHT CT
CURRENT
FB
TO FAN RELAY
CONTACTOR AND
PRECHARGE
CONTROL SIGNALS
65 VDC
WORK
TERMINAL
POWER WAVE 455/R

THERMAL PROTECTION
Three normally closed (NC) thermostats protect the
machine from excessive operating temperatures.
These thermostats are wired in series and are con-
nected to the control board. One of the thermostats is
located on the heat sink of the output rectifier, one on
the DC bus, and one on the output choke. Excessive
temperatures may be caused by a lack of cooling air or
by operating the machine beyond its duty cycle or out-
put rating. If excessive operating temperatures should
occur, the thermostats will prevent output from the
machine. The yellow thermal light, located on the front
of the machine, will be illuminated. The thermostats
are self-resetting once the machine cools sufficiently. If
the thermostat shutdown was caused by excessive
output or duty cycle and the fan is operating normally,
the power switch may be left on and the reset should
occur within a 15-minute period. If the fan is not turn-
ing or the intake air louvers are obstructed, the power
must be removed from the machine and the fan condi-
tion or air obstruction corrected. On later production
machines (above code 10500) the cooling fan runs
only when necessary. The F.A.N. (fan as needed) sys-
tem is controlled by the Control Board via a solid state
relay.
PROTECTIVE CIRCUITS
Protective circuits are designed into the Power Wave
455/R to sense trouble and shut down the machine
before damage occurs to the machine’s internal com-
ponents.
OVER CURRENT PROTECTION
If the average current exceeds 570 amps, the peak cur-
rent will be limited to 100 amps until the average cur-
rent decreases to under 50 amps or the system is re-
triggered.
UNDER/OVER VOLTAGE
PROTECTION
A protective circuit is included on the Control Board to
monitor the voltage across the input capacitors. In the
event that a capacitor voltage is too high, too low, or
becomes unbalanced side-to-side, the protection cir-
cuit will de-energize the input contactor. Machine out-
put will be disabled, and the "soft start" mode will be
repeated. The protection circuit will prevent output if
any of the following circumstances occur.
1. Capacitor conditioning is required. (This may be
required if the machine has been off for a long peri-
od of time and is connected for high input voltage
operation.)
2. Voltage across a capacitor exceeds 390 volts. (This
could result from high line surges or improper input
voltage connections.)
3. Voltage across a capacitor is under 70 volts. (This
would be due to improper input voltage connec-
tions.)
4. Internal component damage.
E-9 E-9
THEORY OF OPERATION
POWER WAVE 455/R
Return to Section TOC Return to Section TOC Return to Section TOC Return to Section TOC
Return to Master TOC Return to Master TOC Return to Master TOC Return to Master TOC

GENERAL DESCRIPTION OF
THE STT (SURFACE TENSION
TRANSFER) PROCESS
The STT process cannot be classified as either a con-
stant current (CC) or a constant voltage (CV) applica-
tion. The STT function produces current of a desired
waveform to reduce spatter and fumes. The STT
process is optimized for short-circuit GMAW welding
only.
E-10 E-10
THEORY OF OPERATION
POWER WAVE 455/R
Return to Section TOC Return to Section TOC Return to Section TOC Return to Section TOC
Return to Master TOC Return to Master TOC Return to Master TOC Return to Master TOC
FIGURE E.8 – STT WAVEFORMS
Current
Time
Wave Control +10.0
Wave Control -10.0
Wave Control 0.00
Current
Time
Trim 1.50
Trim 1.00
Trim 0.50
STT Wave control characteristics
STT Trim control characteristics

INSULATED GATE BIPOLAR
TRANSISTOR (IGBT) OPERATION
An IGBT is a type of transistor. IGBTs are semicon-
ductors well suited for high frequency switching and
high current applications.
Drawing A shows an IGBT in a passive mode. There is
no gate signal, zero volts relative to the source, and
therefore, no current flow. The drain terminal of the
IGBT may be connected to a voltage supply; but since
there is no conduction, the circuit will not supply current
to components connected to the source. The circuit is
turned off like a light switch in the OFF position.
Drawing B shows the IGBT in an active mode. When
the gate signal, a positive DC voltage relative to the
source, is applied to the gate terminal of the IGBT, it
is capable of conducting current. A voltage supply
connected to the drain terminal will allow the IGBT to
conduct and supply current to circuit components cou-
pled to the source. Current will flow through the con-
ducting IGBT to downstream components as long as
the positive gate signal is present. This is similar to
turning ON a light switch.
E-11 E-11
THEORY OF OPERATION
POWER WAVE 455/R
Return to Section TOC Return to Section TOC Return to Section TOC Return to Section TOC
Return to Master TOC Return to Master TOC Return to Master TOC Return to Master TOC
FIGURE E.9 – IGBT OPERATION
DRAIN
SOURCE GATE
INJECTING LAYER
BUFFER LAYER
DRAIN DRIFT REGION
BODY REGION
p +
n +
n -
p
n + n +
DRAIN
SOURCE GATE
INJECTING LAYER
BUFFER LAYER
DRAIN DRIFT REGION
BODY REGION
p +
n +
n -
p
n + n +
POSITIVE
VOLTAGE
APPLIED
B. ACTIVE
A. PASSIVE

PULSE WIDTH MODULATION
The term PULSE WIDTH MODULATION (PWM) is
used to describe how much time is devoted to conduc-
tion in the positive and negative portions of the cycle.
Changing the pulse width is known as MODULATION.
Pulse Width Modulation is the varying of the pulse
width over the allowed range of a cycle to affect the
output of the machine.
MINIMUM OUTPUT
By controlling the duration of the gate signal, the IGBT
is turned on and off for different durations during a
cycle. The top drawing below shows the minimum out-
put signal possible over a 50-microsecond time period.
The shaded portion of the signal represents one IGBT
group1, conducting for 1 microsecond. The negative por-
tion is the other IGBT group. The dwell time (off time) is
48 microseconds (both IGBT groups off). Since only 2
microseconds of the 50-microsecond time period are
devoted to conducting, the output power is minimized.
MAXIMUM OUTPUT
By holding the gate signals on for 24 microseconds each
and allowing only 2 microseconds of dwell or off time
(one microsecond during each half cycle) during the 50
microsecond cycle, the output is maximized. The dark-
ened area under the minimum output curve can be com-
pared to the area under the maximum output curve. The
more darkened area, the more power is present.
E-12 E-12
THEORY OF OPERATION
POWER WAVE 455/R
Return to Section TOC Return to Section TOC Return to Section TOC Return to Section TOC
Return to Master TOC Return to Master TOC Return to Master TOC Return to Master TOC
FIGURE E.10 – TYPICAL IGBT OUTPUTS
MINIMUM OUTPUT
50 sec
25 sec
MAXIMUM OUTPUT
sec
sec
sec
24 sec
24 sec
sec
1
50 sec
sec
1
1An IGBT group consists of the sets of IGBT modules grouped onto
one switch board.

Troubleshooting & Repair ...................................................................................................Section F
How to Use Troubleshooting Guide ...........................................................................................F-2
PC Board Troubleshooting Procedures.......................................................................................F-3
Troubleshooting Guide ................................................................................................................F-4
Test Procedures ..........................................................................................................................F-9
Input Filter Capacitor Discharge Procedure .........................................................................F-9
Switch Board Test ...............................................................................................................F-11
Input Rectifier Test .............................................................................................................F-14
Input Contactor Test............................................................................................................F-17
DC Bus Power Supply PC Board Test................................................................................F-20
Power Board Test ..............................................................................................................F-23
Input Board Test .................................................................................................................F-26
STT Chopper Board Test ....................................................................................................F-30
Power Wave Current Transducer Test ...............................................................................F-33
STT Current Transducer Test ............................................................................................F-37
Output Rectifier Test ..........................................................................................................F-41
Auxiliary Transformer No. 1 Test .......................................................................................F-43
Auxiliary Transformer No. 2 Test .......................................................................................F-46
Component Removal and Replacement Procedure..................................................................F-48
Input Rectifier Removal and Replacement ........................................................................F-48
Input Contactor Removal and Replacement ......................................................................F-50
Auxiliary Transformer No. 1 Removal and Replacement Procedure..................................F-52
Auxiliary Transformer No. 2 Removal and Replacement Procedure..................................F-55
Control, Feed Head, or Voltage Sense PC Board Removal and Replacement .................F-58
Gateway PC Board Removal and Replacement ...............................................................F-62
STT Current Transducer Removal and Replacement ...................................................... F-64
Power Wave Current Transducer Removal and Replacement.......................................... F-67
Output Rectifier, STT Chopper Board and Rectifier Module Removal
and Replacement ........................................................................................................F-70
Switch Board and Filter Capacitor Removal and Replacement .........................................F-74
Retest after Repair ...................................................................................................................F-77
Section F-1 Section F-1
TABLE OF CONTENTS
- TROUBLESHOOTING & REPAIR SECTION -
POWER WAVE 455/R
Return to Master TOC Return to Master TOC Return to Master TOC Return to Master TOC

This Troubleshooting Guide is provided to help
you locate and repair possible machine malfunc-
tions. Simply follow the three-step procedure
listed below.
Step 1. LOCATE PROBLEM (SYMPTOM). Look
under the column labeled “PROBLEM” (SYMP-
TOMS). This column describes possible symp-
toms that the machine may exhibit. Find the list-
ing that best describes the symptom that the
machine is exhibiting. Symptoms are grouped
into two main categories: Output Problems and
Function Problems.
Step 2. PERFORM EXTERNAL TESTS. The
second column, labeled “POSSIBLE AREAS OF
MISADJUSTMENT(S)”, lists the obvious external
possibilities that may contribute to the machine
symptom. Perform these tests/checks in the
order listed. In general, these tests can be con-
ducted without removing the case cover.
Step 3. PERFORM COMPONENT TESTS. The
last column, labeled “Recommended Course of
Action” lists the most likely components that may
have failed in your machine. It also specifies the
appropriate test procedure to verify that the sub-
ject component is either good or bad. If there are
a number of possible components, check the
components in the order listed to eliminate one
possibility at a time until you locate the cause of
your problem.
All of the referenced test procedures referred to in
the Troubleshooting Guide are described in detail
at the end of this section. Refer to the
Troubleshooting and Repair Table of Contents to
locate each specific Test Procedure. All of the
referred to test points, components, terminal
strips, etc., can be found on the referenced elec-
trical wiring diagrams and schematics. Refer to
the Electrical Diagrams Section Table of Contents
to locate the appropriate diagram.
F-2 F-2
TROUBLESHOOTING & REPAIR
POWER WAVE 455/R
Return to Section TOC Return to Section TOC Return to Section TOC Return to Section TOC
Return to Master TOC Return to Master TOC Return to Master TOC Return to Master TOC
HOW TO USE TROUBLESHOOTING GUIDE
Service and repair should be performed by only Lincoln Electric Factory Trained Personnel.
Unauthorized repairs performed on this equipment may result in danger to the technician and machine
operator and will invalidate your factory warranty. For your safety and to avoid Electrical Shock, please
observe all safety notes and precautions detailed throughout this manual.
WARNING
CAUTION
If for any reason you do not understand the test procedures or are unable to perform the test/repairs
safely, contact the Lincoln Electric Service Department for electrical troubleshooting assistance before
you proceed. Call 1-800-833-9353.

ELECTRIC SHOCK can kill.
Have an electrician install and service
this equipment. Turn the machine OFF
before working on equipment. Do not
touch electrically hot parts.
Sometimes machine failures appear to be due to PC
board failures. These problems can sometimes be
traced to poor electrical connections. To avoid prob-
lems when troubleshooting and replacing PC boards,
please use the following procedure:
1. Determine to the best of your technical ability that
the PC board is the most likely component causing
the failure symptom.
2. Check for loose connections at the PC board to
assure that the PC board is properly connected.
3. If the problem persists, replace the suspect PC
board using standard practices to avoid static elec-
trical damage and electrical shock. Read the warn-
ing inside the static resistant bag and perform the
following procedures:
PC Board can be damaged by
static electricity.
• Remove your body’s static charge
before opening the static-shielding
bag. Wear an anti-static wrist
strap. For safety, use a 1 Meg
ohm resistive cord connected to a
grounded part of the equipment
frame.
• If you don’t have a wrist strap,
touch an unpainted, grounded,
part of the equipment frame. Keep
touching the frame to prevent sta-
tic build-up. Be sure not to touch
any electrically live parts at the
same time.
• Tools which come in contact with the PC Board must
be either conductive, anti-static or static-dissipative.
• Remove the PC Board from the static-shielding bag
and place it directly into the equipment. Don’t set the
PC Board on or near paper, plastic or cloth which
could have a static charge. If the PC Board can’t be
installed immediately, put it back in the static-
shielding bag.
• If the PC Board uses protective shorting jumpers,
don’t remove them until installation is complete.
• If you return a PC Board to The Lincoln Electric
Company for credit, it must be in the static-shielding
bag. This will prevent further damage and allow prop-
er failure analysis.
4. Test the machine to determine if the failure symp-
tom has been corrected by the replacement PC
board.
NOTE: Allow the machine to heat up so that all electri-
cal components can reach their operating tem-
perature.
5. Remove the replacement PC board and substitute
it with the original PC board to recreate the original
problem.
a. If the original problem does not reappear
by substituting the original board, then the
PC board was not the problem. Continue
to look for bad connections in the control
wiring harness, junction blocks, and termi-
nal strips.
b. If the original problem is recreated by the
substitution of the original board, then the
PC board was the problem. Reinstall the
replacement PC board and test the
machine.
6. Always indicate that this procedure was followed
when warranty reports are to be submitted.
NOTE: Following this procedure and writing on the
warranty report, “INSTALLED AND
SWITCHED PC BOARDS TO VERIFY PROB-
LEM,” will help avoid denial of legitimate PC
board warranty claims.
F-3 F-3
TROUBLESHOOTING & REPAIR
POWER WAVE 455/R
Return to Section TOC Return to Section TOC Return to Section TOC Return to Section TOC
Return to Master TOC Return to Master TOC Return to Master TOC Return to Master TOC
PC BOARD TROUBLESHOOTING PROCEDURES
WARNING
ATTENTION
Static-Sensitive
Devices
Handle only at
Static-Safe
Workstations

Observe Safety Guidelines TROUBLESHOOTING GUIDE
detailed in the beginning of this manual.
CAUTION
If for any reason you do not understand the test procedures or are unable to perform the test/repairs safely,
contact the Lincoln Electric Service Department for electrical troubleshooting assistance before you proceed. Call
1-800-833-9353.
PROBLEMS
(SYMPTOMS) POSSIBLE AREAS OF
MISADJUSTMENT(S) RECOMMENDED
COURSE OF ACTION
OUTPUT PROBLEMS
Major physical or electrical damage
is evident when the sheet metal
covers are removed.
Contact your local authorized
Lincoln Electric Field Service
Facility for technical assistance.
Contact the Lincoln Electric Service
Department at 1-800-833-9353
(WELD).
The input fuses repeatedly fail or
the input circuit breakers keep trip-
ping.
1. Make certain the fuses or break-
ers are properly sized.
2. Make certain the reconnect
panel is configured properly for
the applied voltage.
3. The welding procedure may be
drawing too much input current
or the duty cycle may be too
high. Reduce the welding cur-
rent and /or reduce the duty
cycle.
1. Check the reconnect switches
and associated wiring. See the
Wiring Diagram.
2. Perform the Input Rectifier
Test.
3. Perform the Switch Board Test.
4. Perform the Input Contactor
Test.
F-4 F-4
TROUBLESHOOTING & REPAIR
POWER WAVE 455/R
Return to Section TOC Return to Section TOC Return to Section TOC Return to Section TOC
Return to Master TOC Return to Master TOC Return to Master TOC Return to Master TOC

TROUBLESHOOTING GUIDE Observe Safety Guidelines
detailed in the beginning of this manual.
CAUTION
If for any reason you do not understand the test procedures or are unable to perform the test/repairs safely,
contact the Lincoln Electric Service Department for electrical troubleshooting assistance before you proceed. Call
1-800-833-9353.
PROBLEMS
(SYMPTOMS) POSSIBLE AREAS OF
MISADJUSTMENT(S) RECOMMENDED
COURSE OF ACTION
OUTPUT PROBLEMS
The machine is dead—no lights—
no output—the machine appears to
be off.
1. Make certain the input power
switch SW1 is in the ON posi-
tion.
2. Check the main input fuses (or
breakers). If open, replace or
reset.
3. Check the 6 amp CB4 breaker
located in the reconnect area.
Reset if tripped.
4. Make certain the reconnect
panel is configured correctly for
the applied input voltage.
1. Check the input power switch
SW1 for proper operation. Also
check the associated leads for
loose or faulty connections.
See the Wiring Diagram.
2. Check circuit breaker CB4 for
proper operation.
3. Perform the T1 Auxiliary
Transformer Test.
4. The power board rectifier may
be faulty. Check rectifier and
associated wiring. See the
Wiring Diagram.
5. Perform the DC Bus Board
Test.
6. Perform the Power Board Test.
7. The Control Board may be
faulty.
F-5 F-5
TROUBLESHOOTING & REPAIR
POWER WAVE 455/R
Return to Section TOC Return to Section TOC Return to Section TOC Return to Section TOC
Return to Master TOC Return to Master TOC Return to Master TOC Return to Master TOC
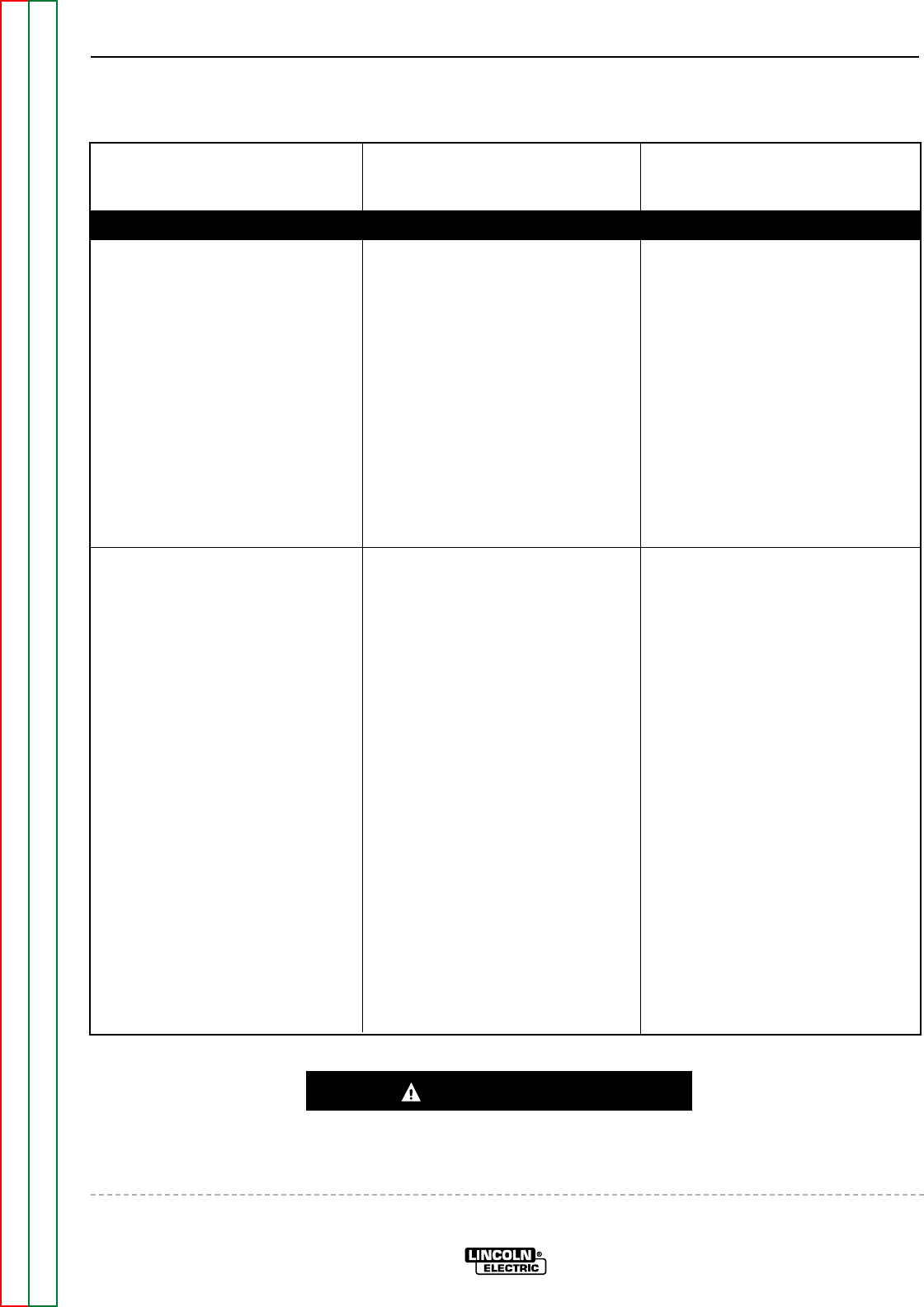
Observe Safety Guidelines TROUBLESHOOTING GUIDE
detailed in the beginning of this manual.
CAUTION
If for any reason you do not understand the test procedures or are unable to perform the test/repairs safely,
contact the Lincoln Electric Service Department for electrical troubleshooting assistance before you proceed. Call
1-800-833-9353.
PROBLEMS
(SYMPTOMS) POSSIBLE AREAS OF
MISADJUSTMENT(S) RECOMMENDED
COURSE OF ACTION
OUTPUT PROBLEMS
The Power Wave 455R does not
have welding output. The main
input contactor CR1 is not activat-
ing.
1. Turn the input power off and
make certain the reconnect
panel is configured correctly for
the applied input voltage.
2. If the Thermal light is lit, the unit
may be overheated. Let the
machine cool and adjust weld-
ing load and /or duty cycle to
coincide with the output limits of
the machine.
1. Perform the Input Contactor
Test.
2. Perform the Input Board Test.
3. Perform the T1 Auxiliary
Transformer Test.
4. Perform the Input Rectifier
Test.
5. Perform the Switch Board Test.
6. Perform the Power Board Test.
7. The Control Board may be faulty.
F-6 F-6
TROUBLESHOOTING & REPAIR
POWER WAVE 455/R
Return to Section TOC Return to Section TOC Return to Section TOC Return to Section TOC
Return to Master TOC Return to Master TOC Return to Master TOC Return to Master TOC
The thermal light is lit. The
machine regularly "overheats." 1. The welding application may be
exceeding the recommended
duty cycle and/or current limits
of the machine.
2. Dirt and dust may have clogged
the cooling channels inside the
machine. Refer to the Maint-
enance Section of this manual.
3. Air intake and exhaust louvers
may be blocked due to inade-
quate clearance around the
machine.
4. Make sure the fan is functioning
correctly. Machines above code
10500 are equipped with F.A.N.
(fan as needed) circuitry. The
fan runs whenever the output is
enabled, whether under load or
open circuit conditions. The fan
also runs for a period of time
(approximately 5 minutes) after
the output is disabled.
1. One of the thermostats may be
faulty. Also check associated
wiring for loose or faulty con-
nections. See the Wiring
Diagram.

TROUBLESHOOTING GUIDE Observe Safety Guidelines
detailed in the beginning of this manual.
CAUTION
If for any reason you do not understand the test procedures or are unable to perform the test/repairs safely,
contact the Lincoln Electric Service Department for electrical troubleshooting assistance before you proceed. Call
1-800-833-9353.
PROBLEMS
(SYMPTOMS) POSSIBLE AREAS OF
MISADJUSTMENT(S) RECOMMENDED
COURSE OF ACTION
FUNCTION PROBLEMS
The machine often "noodle welds"
when running a particular process.
The output is limited to approxi-
mately 100 amps.
1. The machine may be trying to
deliver too much power. When
the average output current
exceeds 570 amps, the
machine will "phase back" to
protect itself. Adjust the proce-
dure or reduce the load to lower
the current draw from the Power
Wave 455R machine.
1. Perform the Current
Transducer Test.
2. The Control Board may be
faulty.
The Power Wave 455R will not pro-
duce full output. 1. The input voltage may be too
low, limiting the output capability
of the machine. Make certain
the input voltage is correct for
the machine and the reconnect
panel configuration.
2. Make sure all three phases of
input power are being applied to
the machine.
3. If using the STT output terminal,
be aware that the STT output is
limited to 325 amps.
1. Perform the Output Rectifier
Test.
2. Perform the Current Trans-
ducer Test.
3. Perform the Power Board Test.
4. The Control Board may be
faulty.
5. If using the STT output terminal,
the STT Chopper Board may be
faulty. See the Wiring Diagram.
F-7 F-7
TROUBLESHOOTING & REPAIR
POWER WAVE 455/R
Return to Section TOC Return to Section TOC Return to Section TOC Return to Section TOC
Return to Master TOC Return to Master TOC Return to Master TOC Return to Master TOC

Observe Safety Guidelines TROUBLESHOOTING GUIDE
detailed in the beginning of this manual.
CAUTION
If for any reason you do not understand the test procedures or are unable to perform the test/repairs safely,
contact the Lincoln Electric Service Department for electrical troubleshooting assistance before you proceed. Call
1-800-833-9353.
PROBLEMS
(SYMPTOMS) POSSIBLE AREAS OF
MISADJUSTMENT(S) RECOMMENDED
COURSE OF ACTION
FUNCTION PROBLEMS
The Auxiliary Receptacle is "dead."
The 120VAC is not present at the
receptacle.
1. Check the 10 amp circuit break-
er (CB2) located on the case
front. Reset if necessary.
2. Check the 6 amp circuit breaker
(CB4) located in the reconnect
area. Reset if necessary.
3. Make sure all three phases of
input power are being applied to
the machine.
1. Check the receptacle and asso-
ciated wiring for loose or faulty
connections. See the Wiring
Diagram.
2. Perform the T2 Auxiliary
Transformer Test.
The Power Wave 455R is "trig-
gered" for output but there is no
welding output.
1. Make sure that the triggering
method and device is correct
and operating properly.
2. Check circuit breaker CB4.
Reset if tripped.
Use troubleshooting software to
find the problem. Contact Lincoln
Electric Service Department to
obtain software.
When in the STT mode,
the spatter is higher than normal
and the arc is inconsistent.
1. Make certain the work sense
lead (21) is connected properly.
2. Make certain the electrode
cable is connected only to the
STT output terminal and NOT
the Power Wave positive output
terminal.
3. Make sure the welding parame-
ters are correct for the process.
1. Perform the STT Chopper
Board Test.
2. Perform the Current
Transducer (STT) Test.
3. The Control Board may be
faulty.
F-8 F-8
TROUBLESHOOTING & REPAIR
POWER WAVE 455/R
Return to Section TOC Return to Section TOC Return to Section TOC Return to Section TOC
Return to Master TOC Return to Master TOC Return to Master TOC Return to Master TOC

TROUBLESHOOTING & REPAIR
F-9 F-9
POWER WAVE 455/R
INPUT FILTER CAPACITOR DISCHARGE PROCEDURE
WARNING
Service and repair should be performed by only Lincoln Electric factory trained personnel.
Unauthorized repairs performed on this equipment may result in danger to the technician
or machine operator and will invalidate your factory warranty. For your safety and to avoid
electrical shock, please observe all safety notes and precautions detailed throughout this
manual.
If for any reason you do not understand the test procedures or are unable to perform the
test/repairs safely, contact the Lincoln Electric Service Department for electrical trou-
bleshooting assistance before you proceed. Call 1-800-833-9353 (WELD).
DESCRIPTION
This “safety” procedure should be performed before any internal maintenance or repair
procedures are attempted on the Power Wave 455/R. Capacitance normally discharges
within 2 minutes of removing input power. This procedure is used to check that the capac-
itors have properly discharged.
MATERIALS NEEDED
3/8” Nut driver
Volt-ohmmeter
25-1000 ohms @ 25 watts (minimum) resistor
Electrically insulated gloves and pliers
This procedure should take approximately 15 minutes to perform.
Return to Section TOC Return to Section TOC Return to Section TOC Return to Section TOC
Return to Master TOC Return to Master TOC Return to Master TOC Return to Master TOC

TROUBLESHOOTING & REPAIR
F-10 F-10
POWER WAVE 455/R
Return to Section TOC Return to Section TOC Return to Section TOC Return to Section TOC
Return to Master TOC Return to Master TOC Return to Master TOC Return to Master TOC
SWITCH
BOARD
CAPACITOR
TERMINALS
FIGURE F.1 – CAPACITOR DISCHARGE PROCEDURE
INPUT FILTER CAPACITOR DISCHARGE PROCEDURE (CONTINUED)
TEST PROCEDURE
1. Remove input power to the Power Wave
455/R.
2. Using the 3/8” nut driver, remove the left and
right case sides.
3. Be careful not to make contact with the
capacitor terminals that are located in the
bottom center of the left and right side switch
boards. See Figure F.1.
4. Carefully check for a DC voltage at the
capacitor terminals on both boards. Note
the polarity is marked on the PC board and
also lead #19 is positive.
5. If any voltage is present, proceed to Step #6.
If no voltage is present, the capacitors are
discharged.
NOTE: Normally the capacitors discharge in
about two minutes after input power is
removed.
6. Using the high wattage resistor (25-1000
ohms @ 25 watts (minimum), electrically
insulated gloves and pliers, connect the
resistor across the two capacitor terminals.
Hold the resistor in place for 10 seconds.
DO NOT TOUCH THE CAPACITOR TERMI-
NALS WITH YOUR BARE HANDS. NEVER
USE A SHORTING STRAP FOR THIS
PROCEDURE.
7. Repeat procedure for the other capacitor.
8. Recheck the voltage across the capacitor
terminals. The voltage should be zero. If
any voltage remains, repeat the discharge
procedure.
NOTE: If the capacitor voltage is present after
the discharge has been performed, this
may indicate a faulty switch board.

TROUBLESHOOTING & REPAIR
F-11 F-11
POWER WAVE 455/R
SWITCH BOARD TEST
WARNING
Service and repair should be performed by only Lincoln Electric factory trained personnel.
Unauthorized repairs performed on this equipment may result in danger to the technician
or machine operator and will invalidate your factory warranty. For your safety and to avoid
electrical shock, please observe all safety notes and precautions detailed throughout this
manual.
If for any reason you do not understand the test procedures or are unable to perform the
test/repairs safely, contact the Lincoln Electric Service Department for electrical trou-
bleshooting assistance before you proceed. Call 1-800-833-9353 (WELD).
DESCRIPTION
This test will help determine if the “power section” of the switch boards are functioning cor-
rectly. This test will NOT indicate if the entire PC board is functional. This resistance test
is preferable to a voltage test with the machine energized because these boards can be
damaged easily. In addition, it is dangerous to work on these boards with the machine
energized.
MATERIALS NEEDED
3/8” Nut driver
3/8” Wrench
Analog volt-ohmmeter
Wiring Diagram
This procedure should take approximately 20 minutes to perform.
Return to Section TOC Return to Section TOC Return to Section TOC Return to Section TOC
Return to Master TOC Return to Master TOC Return to Master TOC Return to Master TOC

TROUBLESHOOTING & REPAIR
F-12 F-12
POWER WAVE 455/R
Return to Section TOC Return to Section TOC Return to Section TOC Return to Section TOC
Return to Master TOC Return to Master TOC Return to Master TOC Return to Master TOC
19C
19D
RECONNECT
SWITCHES
FIGURE F.2 – RECONNECT SWITCHES
SWITCH BOARD TEST (CONTINUED)
TEST PROCEDURE
1. Remove input power to the Power Wave
455/R.
2. Using the 3/8” nut driver, remove the case
top and sides.
3. Perform the Capacitor Discharge
Procedure.
4. Locate label and remove leads 19C and 19D
from the reconnect switches with the 3/8”
wrench. Note lead placement for reassem-
bly. Clear leads. Refer to Figure F.2.
5. Using the Analog ohmmeter, perform the
resistance tests detailed in Table F.1. Refer
to Figure F.3 for the test points.
6. If any test fails replace both switch boards.
See Switch Board Removal and
Replacement.
7. If the switch board resistance tests are OK,
check the molex pin connections and asso-
ciated wiring from the switch boards to the
control board. See the Wiring Diagram.

TROUBLESHOOTING & REPAIR
F-13 F-13
POWER WAVE 455/R
Return to Section TOC Return to Section TOC Return to Section TOC Return to Section TOC
Return to Master TOC Return to Master TOC Return to Master TOC Return to Master TOC
SWITCH
BOARD
11/12
OR
15/16
13/14
OR
17/18
-20 +19
FIGURE F.3 – SWITCH BOARD TEST POINTS
SWITCH BOARD TEST (CONTINUED)
8. Reconnect leads 19C and 19D to the recon-
nect switches. Ensure that the leads are
installed in the same location they were
removed from.
9. Install the right and left case sides and top
using the 3/8” nut driver.
APPLY POSITIVE TEST
PROBE TO TERMINAL APPLY NEGATIVE TEST
NORMAL
PROBE TO TERMINAL
RESISTANCE READING
TABLE F.1 – SWITCH BOARD RESISTANCE TEST
+19
+19
11/12 OR 15/16
13/14 OR 17/18
- 20
- 20
11/12 OR 15/16
13/14 OR 17/18
11/12 OR 15/16
13/14 OR 17/18
- 20
- 20
11/12 OR 15/16
13/14 OR 17/18
+19
+19
Greater than 1000 ohms
Greater than 1000 ohms
Greater than 1000 ohms
Greater than 1000 ohms
Less than 100 ohms
Less than 100 ohms
Less than 100 ohms
Less than 100 ohms

TROUBLESHOOTING & REPAIR
F-14 F-14
POWER WAVE 455/R
INPUT RECTIFIER TEST
WARNING
Service and repair should be performed by only Lincoln Electric factory trained personnel.
Unauthorized repairs performed on this equipment may result in danger to the technician
or machine operator and will invalidate your factory warranty. For your safety and to avoid
electrical shock, please observe all safety notes and precautions detailed throughout this
manual.
If for any reason you do not understand the test procedures or are unable to perform the
test/repairs safely, contact the Lincoln Electric Service Department for electrical trou-
bleshooting assistance before you proceed. Call 1-800-833-9353 (WELD).
TEST DESCRIPTION
This test will help determine if the input rectifier has “shorted” or “open” diodes.
MATERIALS NEEDED
Analog volt-ohmmeter
Phillips head screw driver
Wiring Diagram
3/8” Nut driver
This procedure should take approximately 15 minutes to perform.
Return to Section TOC Return to Section TOC Return to Section TOC Return to Section TOC
Return to Master TOC Return to Master TOC Return to Master TOC Return to Master TOC

TROUBLESHOOTING & REPAIR
F-15 F-15
POWER WAVE 455/R
Return to Section TOC Return to Section TOC Return to Section TOC Return to Section TOC
Return to Master TOC Return to Master TOC Return to Master TOC Return to Master TOC
NEG (-)
POS (+)
A
B
C
INPUT
RECTIFIER
FIGURE F.4 – INPUT RECTIFIER TEST
INPUT RECTIFIER TEST (CONTINUED)
TEST PROCEDURE
1. Remove input power to the Power Wave
455/R.
2. Using the 3/8” nut driver, remove the case
top.
3. Perform the Capacitor Discharge
Procedure.
4. Locate the Input Rectifier and lead locations.
Refer to Figure F.4.
NOTE: Some RTV sealant may have to be
removed from the input rectifier termi-
nals. The RTV should be replaced
when test is complete.
5. With the phillips head screw driver remove
the positive and negative leads from the rec-
tifier.

TROUBLESHOOTING & REPAIR
F-16 F-16
POWER WAVE 455/R
Return to Section TOC Return to Section TOC Return to Section TOC Return to Section TOC
Return to Master TOC Return to Master TOC Return to Master TOC Return to Master TOC
INPUT RECTIFIER TEST (CONTINUED)
6. Use the analog ohmmeter to perform the
tests detailed in Table F.2.
7. If the input rectifier does not meet the
acceptable readings outlined in the table,
the component may be faulty. Replace.
NOTE: Before replacing the input rectifier, per-
form the Switch Board Test and the
Input Contactor Test.
8. When installing a new input rectifier, see
Input Rectifier Removal and
Replacement procedure.
9. If the input rectifier is good, be sure to
reconnect the positive and negative leads
to the correct terminals and torque to 31
in.-lbs. See the Wiring Diagram.
10. Replace any RTV sealant previously
removed.
11. Install the case top.
TEST POINT TERMINALS
A
B
C
A
B
C
NEG
NEG
NEG
POS
POS
POS
NEG
NEG
NEG
POS
POS
POS
A
B
C
A
B
C
Greater than 1000 ohms
Greater than 1000 ohms
Greater than 1000 ohms
Approx. 500 ohms
Approx. 500 ohms
Approx. 500 ohms
Approx. 500 ohms
Approx. 500 ohms
Approx. 500 ohms
Greater than 1000 ohms
Greater than 1000 ohms
Greater than 1000 ohms
TABLE F.2 – INPUT RECTIFIER TEST POINTS AND ACCEPTABLE READINGS
ANALOG METER X100
RANGE
Acceptable Meter Readings
+ Probe - Probe

TROUBLESHOOTING & REPAIR
F-17 F-17
POWER WAVE 455/R
INPUT CONTACTOR TEST
WARNING
Service and repair should be performed by only Lincoln Electric factory trained personnel.
Unauthorized repairs performed on this equipment may result in danger to the technician
or machine operator and will invalidate your factory warranty. For your safety and to avoid
electrical shock, please observe all safety notes and precautions detailed throughout this
manual.
If for any reason you do not understand the test procedures or are unable to perform the
test/repairs safely, contact the Lincoln Electric Service Department for electrical trou-
bleshooting assistance before you proceed. Call 1-800-833-9353 (WELD).
TEST DESCRIPTION
This test will help determine if the input contactor is functional and if the contacts are
functioning correctly.
MATERIALS NEEDED
3/8” Nut driver
Volt-ohmmeter
External 24 VAC supply
This procedure should take approximately 17 minutes to perform.
Return to Section TOC Return to Section TOC Return to Section TOC Return to Section TOC
Return to Master TOC Return to Master TOC Return to Master TOC Return to Master TOC

TROUBLESHOOTING & REPAIR
F-18 F-18
POWER WAVE 455/R
Return to Section TOC Return to Section TOC Return to Section TOC Return to Section TOC
Return to Master TOC Return to Master TOC Return to Master TOC Return to Master TOC
INPUT
CONTACTOR
601
X4
FIGURE F.5 – INPUT CONTACTOR COIL
INPUT CONTACTOR TEST (CONTINUED)
TEST PROCEDURE
1. Remove input power to the Power Wave
455/R.
2. Using the 3/8” nut driver, remove the input
access panel and case top.
3. Locate, mark, and remove the two leads
(601, X4) that are connected to the input
contactor coil. Refer to Figure F.5.
4. Using the external 24 VAC supply, apply 24
VAC to the terminals of the input contactor
coil. If the contactor does NOT activate, the
input contactor is faulty. Replace.

TROUBLESHOOTING & REPAIR
F-19 F-19
POWER WAVE 455/R
Return to Section TOC Return to Section TOC Return to Section TOC Return to Section TOC
Return to Master TOC Return to Master TOC Return to Master TOC Return to Master TOC
L3
L2
L1
T3
T2
T1
FIGURE F.6 – INPUT CONTACTOR TEST POINTS
INPUT CONTACTOR TEST (CONTINUED)
5. With the input contactor activated, check the
continuity across the three sets of contacts.
(Zero ohms or very low resistance is nor-
mal.) Refer to Figure F.6. If the resistance
is high, the input contactor is faulty. Replace
the input contactor.
6. When the contactor is NOT activated, the
resistance should be infinite or very high
across the contacts. If the resistance is low,
the input contactor is faulty.
7. Reconnect the two leads (601, X4) to the
input contactor coil.
8. Install the input access door and case top
using the 3/8” nut driver.

TROUBLESHOOTING & REPAIR
F-20 F-20
POWER WAVE 455/R
DC BUS POWER SUPPLY PC BOARD TEST
WARNING
Service and repair should be performed by only Lincoln Electric factory trained personnel.
Unauthorized repairs performed on this equipment may result in danger to the technician
or machine operator and will invalidate your factory warranty. For your safety and to avoid
electrical shock, please observe all safety notes and precautions detailed throughout this
manual.
If for any reason you do not understand the test procedures or are unable to perform the
test/repairs safely, contact the Lincoln Electric Service Department for electrical trou-
bleshooting assistance before you proceed. Call 1-800-833-9353 (WELD).
TEST DESCRIPTION
This test will determine if the DC Bus Power Supply PC Board is receiving and process-
ing the proper voltages.
MATERIALS NEEDED
3/8” Nut driver
Volt/ohmmeter
Wiring Diagram
This procedure should take approximately 30 minutes to perform.
Return to Section TOC Return to Section TOC Return to Section TOC Return to Section TOC
Return to Master TOC Return to Master TOC Return to Master TOC Return to Master TOC

TROUBLESHOOTING & REPAIR
F-21 F-21
POWER WAVE 455/R
Return to Section TOC Return to Section TOC Return to Section TOC Return to Section TOC
Return to Master TOC Return to Master TOC Return to Master TOC Return to Master TOC
DC BUS
POWER
SUPPLY
PC BOARD
CAPACITOR
C3
CAUTION!
J47
J46
J46 J47
3 4 5 6 7 8
LED
1 2 3 4
1 2
FIGURE F.7 – DC BUS POWER SUPPLY POWER SUPPLY PC BOARD
DC BUS POWER SUPPLY PC BOARD TEST (CONTINUED)
TEST PROCEDURE
1. Remove input power to the machine.
2. Using the 3/8” nut driver, remove the case
top.
3. Locate the DC Bus Power Supply PC Board
and plugs P46 and P47. See Figure F.7.
4. Carefully apply input power to the Power
Wave 455/R.
ELECTRIC SHOCK can kill.
High voltage is present when
input power is applied to the
machine.
5. Turn on the Power Wave 455/R. The LED
on the DC Bus Power Supply PC Board
should light.
WARNING

TROUBLESHOOTING & REPAIR
F-22 F-22
POWER WAVE 455/R
Return to Section TOC Return to Section TOC Return to Section TOC Return to Section TOC
Return to Master TOC Return to Master TOC Return to Master TOC Return to Master TOC
DC BUS POWER SUPPLY PC BOARD TEST(CONTINUED)
6. Check the DC Bus Power Supply PC Board
input and output voltages according to Table
F.3. See Figure F.7 and the Wiring
Diagram.
ELECTRIC SHOCK can kill.
High voltage is present at the
terminals of Capacitor C3 near
where testing is to be done.
7. If all the voltages are correct, the DC Bus
Power Supply PC Board is operating prop-
erly.
8. If any of the output voltages are not cor-
rect and the input voltage is correct, the
DC Bus Power Supply PC Board may be
faulty.
9. If the input voltage is not correct, check
the leads between the DC Bus Power
Supply PC Board and the Power PC
Board Rectifier. See the Wiring Diagram.
10. When finished testing, replace the case
top.
WARNING
Plug P46 – Pin 1
Plug P47 – Pin 7
Plug P47 – Pin 8
Plug P47 – Pin 4
Plug P47 – Pin 3
Plug P46 – Pin 3
Plug P47 – Pin 6
Plug P47 – Pin 6
Plug P47 – Pin 2
Plug P47 – Pin 1
65 – 75 VDC
38.0 – 42.0 VDC
38.0 – 42.0 VDC
38.0 – 42.0 VDC
38.0 – 42.0 VDC
Should be same as the
Power PC Board
Rectifier
Supply to Power PC
Board
Supply to Power PC
Board
Supply to Feed Head PC
Board
Supply to S1 Wire
Feeder Receptacle
Positive Meter Probe
Test Point Negative Meter Probe
Test Point Approximate Voltage
Reading Conditions/Comments
TABLE F.3 – DC BUS POWER SUPPLY PC BOARD VOLTAGE TABLE

TROUBLESHOOTING & REPAIR
F-23 F-23
POWER WAVE 455/R
POWER BOARD TEST
WARNING
Service and repair should be performed by only Lincoln Electric factory trained personnel.
Unauthorized repairs performed on this equipment may result in danger to the technician
or machine operator and will invalidate your factory warranty. For your safety and to avoid
electrical shock, please observe all safety notes and precautions detailed throughout this
manual.
If for any reason you do not understand the test procedures or are unable to perform the
test/repairs safely, contact the Lincoln Electric Service Department for electrical trou-
bleshooting assistance before you proceed. Call 1-800-833-9353 (WELD).
TEST DESCRIPTION
This test will help determine if the Power Board is receiving the correct voltages and also
if the Power Board is regulating and producing the correct DC voltages.
MATERIALS NEEDED
3/8” Nut driver
Volt-ohmmeter
Wiring Diagram
This procedure should take approximately 30 minutes to perform.
Return to Section TOC Return to Section TOC Return to Section TOC Return to Section TOC
Return to Master TOC Return to Master TOC Return to Master TOC Return to Master TOC

TROUBLESHOOTING & REPAIR
F-24 F-24
POWER WAVE 455/R
Return to Section TOC Return to Section TOC Return to Section TOC Return to Section TOC
Return to Master TOC Return to Master TOC Return to Master TOC Return to Master TOC
J42 J41 J43
4 5 6 3 4 7 8 9 10 11 12
J42 J41 J43
1 2 3 1 2 1 2 3 4 5 6
FIGURE F.8 – POWER BOARD TEST
POWER BOARD TEST (CONTINUED)
TEST PROCEDURE
1. Remove input power to the Power Wave
455/R.
2. Using the 3/8” nut driver, remove the case
top.
3. Perform the Capacitor Discharge
Procedure.
4. Locate the Power Board and plugs J42 and
J43. Do not remove plugs or leads from
the Power Board. Refer to Figure F.8.
5. Carefully apply input power to the Power
Wave 455/R.
ELECTRIC SHOCK can kill.
High voltage is present when
input power is applied to the
machine.
6. Turn on the Power Wave 455/R. Carefully
test for the correct voltages at the Power
Board according to Table F.4.
7. If either of the 40 VDC voltages is low or not
present at plug J41, perform the DC Bus PC
Board Test. See the Wiring Diagram. Also
perform the T1 Auxiliary Transformer Test.
8. If any of the DC voltages are low or not pre-
sent at plugs J42 and/or 43, the Power
Board may be faulty.
9. Install the case top using the 3/8” nut driver.
WARNING

POWER BOARD
CONNECTOR
PLUG J41
POWER BOARD
CONNECTOR
PLUG J42
POWER BOARD
CONNECTOR
PLUG J42
POWER BOARD
CONNECTOR
PLUG J42
POWER BOARD
CONNECTOR
PLUG J43
POWER BOARD
CONNECTOR
PLUG J43
POWER BOARD
CONNECTOR
PLUG J43
POWER BOARD
CONNECTOR
PLUG J41
POWER BOARD
CONNECTOR
PLUG J43
POWER BOARD
CONNECTOR
PLUG J43
CHECK 40 VDC
INPUT FROM
DC BUS BOARD
CHECK +15
VDC SUPPLY FROM
POWER BOARD
CHECK +5 VDC
SUPPLY FROM
POWER BOARD
CHECK -15 VDC
SUPPLY FROM
POWER BOARD
CHECK +5 VDC
ARCLINK SUPPLY
FROM POWER BOARD
CHECK +5 VDC
“RS-232” SUPPLY
FROM POWER BOARD
CHECK +15 VDC
SPI SUPPLY FROM
POWER BOARD
CHECK +40 VDC
INPUT FROM
DC BUS BOARD
CHECK +5 VDC
SPI SUPPLY FROM
POWER BOARD
CHECK +20 VDC STT
SUPPLY FROM
POWER BOARD
2 (+)
1 (-)
1 (+)
5 (-)
3 (+)
5 (-)
2 (+)
5 (-)
5 (+)
10 (-)
4 (+)
9 (-)
6 (+)
11 (-)
4 (+)
3 (-)
3 (+)
12 (-)
7 (+)
1 (-)
477 (+)
475 (-)
225 (+)
222 (-)
221 (+)
222 (-)
222 (+)
223 (-)
274 (+)
273 (-)
226 (+)
228 (-)
266 (+)
267 (-)
478 (+)
476 (-)
268A (+)
262 (-)
345 (+)
346 (-)
38 – 42 VDC
+15 VDC
+5 VDC
-15 VDC
+5 VDC
+5 VDC
+15 VDC
38 – 42 VDC
+5 VDC
+20 VDC
TROUBLESHOOTING & REPAIR
F-25 F-25
POWER WAVE 455/R
Return to Section TOC Return to Section TOC Return to Section TOC Return to Section TOC
Return to Master TOC Return to Master TOC Return to Master TOC Return to Master TOC
TABLE F.4 – POWER BOARD VOLTAGE CHECKS
POWER BOARD TEST (CONTINUED)
CHECK POINT
LOCATION TEST
DESCRIPTION CONNECTOR
PLUG PIN NO. LEAD NO. OR
IDENTITY NORMAL
ACCEPTABLE
VOLTAGE
READING
475 477
225
222
221
222
223
222
273
274
228
226
267
266
476 478
262
268A
345
346

TROUBLESHOOTING & REPAIR
F-26 F-26
POWER WAVE 455/R
INPUT BOARD TEST
WARNING
Service and repair should be performed by only Lincoln Electric factory trained personnel.
Unauthorized repairs performed on this equipment may result in danger to the technician
or machine operator and will invalidate your factory warranty. For your safety and to avoid
electrical shock, please observe all safety notes and precautions detailed throughout this
manual.
If for any reason you do not understand the test procedures or are unable to perform the
test/repairs safely, contact the Lincoln Electric Service Department for electrical trou-
bleshooting assistance before you proceed. Call 1-800-833-9353 (WELD).
TEST DESCRIPTION
This test will help determine if the Input Board is sending the correct voltages and also if
the Input Board is regulating and producing the correct DC voltages.
MATERIALS NEEDED
3/8” Nut driver
Volt-ohmmeter
Wiring Diagram
This procedure should take approximately 30 minutes to perform.
Return to Section TOC Return to Section TOC Return to Section TOC Return to Section TOC
Return to Master TOC Return to Master TOC Return to Master TOC Return to Master TOC

TROUBLESHOOTING & REPAIR
F-27 F-27
POWER WAVE 455/R
Return to Section TOC Return to Section TOC Return to Section TOC Return to Section TOC
Return to Master TOC Return to Master TOC Return to Master TOC Return to Master TOC
INPUT
CONTACTOR
601
X4
J60 J61
6 7 8 9 10
J61
1 2 3 4
5 6 7 8
1 2 3 4 5
J60
FIGURE F.9 – INPUT CONTACTOR CR1
INPUT BOARD TEST (CONTINUED)
TEST PROCEDURE
1. Remove input power to the Power Wave
455/R.
2. Using the 3/8” nut driver, remove the case
top.
3. Remove lead X4 from the coil terminal of
main input contactor CR1. Insulate lead X4.
Refer to Figure F.9.
4. Carefully apply input power to the Power
Wave 455/R.
ELECTRIC SHOCK can kill.
High voltage is present when
input power is applied to the
machine.
5. Turn on the Power Wave 455/R. Carefully
test for the correct voltages according to
Table F.5.
WARNING

TROUBLESHOOTING & REPAIR
F-28 F-28
POWER WAVE 455/R
Return to Section TOC Return to Section TOC Return to Section TOC Return to Section TOC
Return to Master TOC Return to Master TOC Return to Master TOC Return to Master TOC
INPUT BOARD TEST(CONTINUED)
6. Remove input power to the Power Wave
455/R. If any of the voltages are low or not
present, perform the Input Contactor Test.
If that checks out, the Input Board may by
faulty.
7. Reconnect lead X4 to the main input contac-
tor CR1 coil terminal.
8. Carefully apply the correct input voltage to
the Power Wave 455/R.
ELECTRIC SHOCK can kill.
High voltage is present when
input power is applied to the
machine.
9. Turn on the Power Wave 455/R. Check for
the presence of 24 VAC from lead X4 to
lead 601. See Figure F. 9. If the voltage
is not present, perform the Auxiliary
Transformer #1 Test.
9. This 24 VAC is the coil voltage for main
input contactor CR1. It will normally be
present approximately 12 seconds after
input line switch (SW1) is activated.
10. When the test is completed, remove input
power from the Power Wave 455/R.
11. Install the case top using the 3/8” nut driver.
WARNING

TROUBLESHOOTING & REPAIR
F-29 F-29
POWER WAVE 455/R
Return to Section TOC Return to Section TOC Return to Section TOC Return to Section TOC
Return to Master TOC Return to Master TOC Return to Master TOC Return to Master TOC
TABLE F.5 – INPUT BOARD VOLTAGE CHECKS
INPUT BOARD TEST(CONTINUED)
TEST POINTS
PLUG J61 PIN 8 (H1D)
TO
PLUG J61 PIN 2 (612)
PLUG J61 PIN 10 (T3)
TO
PLUG J61 PIN 2 (T1)
PLUG J60 PIN 3 (238)
TO
PLUG J60 PIN 4 (604)
PLUG J60 PIN 3 (238)
TO
PLUG J60 PIN 5 (232)
LEAD
NUMBERS
J61
J61
J60
J60
EXPECTED
VOLTAGE
READINGS
SAME AS
INPUT
VOLTAGE
A LITTLE LESS
THAN INPUT
VOLTAGE
13 – 15 VDC
13 – 15 VDC
COMMENTS
Present when Input
Switch SW1 is closed.
This is Pre-Charge Voltage and
will normally be present 6 sec-
onds after activating Input Switch
SW1. The Pre-Charge Voltage
should remain for approximately 6
seconds and then be removed.
This is the Coil Voltage for the
Pre-Charge Relay. Normally this
DC Voltage will be present 6 sec-
onds after Input Switch SW1 is
activated. This 13 - 15 VDC will
remain for approximately 6 sec-
onds and then be removed. The
Relay is controlled by the Control
Board. See the Wiring Diagram.
This is the DC Coil Voltage for the
Control Relay. Normally this DC
Voltage will be present approxi-
mately 12 seconds after Input
Switch SW1 is activated. The
Relay is controlled by the Control
PC Board. See the Wiring
Diagram.
#612
H1D
T1
T3
#238 #604
#238
#232

TROUBLESHOOTING & REPAIR
F-30 F-30
POWER WAVE 455/R
STT CHOPPER BOARD TEST
WARNING
Service and repair should be performed by only Lincoln Electric factory trained personnel.
Unauthorized repairs performed on this equipment may result in danger to the technician
or machine operator and will invalidate your factory warranty. For your safety and to avoid
electrical shock, please observe all safety notes and precautions detailed throughout this
manual.
If for any reason you do not understand the test procedures or are unable to perform the
test/repairs safely, contact the Lincoln Electric Service Department for electrical trou-
bleshooting assistance before you proceed. Call 1-800-833-9353 (WELD).
TEST DESCRIPTION
This test will help determine if the STT Chopper Board is receiving the necessary voltages
to function and if the related circuitry is correct.
MATERIALS NEEDED
3/8” Nut driver
Volt-ohmmeter
Wiring Diagram
This procedure should take approximately 30 minutes to perform.
Return to Section TOC Return to Section TOC Return to Section TOC Return to Section TOC
Return to Master TOC Return to Master TOC Return to Master TOC Return to Master TOC

TROUBLESHOOTING & REPAIR
F-31 F-31
POWER WAVE 455/R
Return to Section TOC Return to Section TOC Return to Section TOC Return to Section TOC
Return to Master TOC Return to Master TOC Return to Master TOC Return to Master TOC
J7
9 10 11 12 13 14 15 16
1 2 3 4 5 6 7 8
J7
4W 4R
J43
7 8 9 10 11 12
J43
1 2 3 4 5 6
346
345
STT OUTPUT
TERMINAL
POWER WAVE
+ OUTPUT
TERMINAL
CONTROL PC BOARD POWER PC BOARD
FIGURE F.10 – STT CHOPPER BOARD TEST DETAILS
STT CHOPPER BOARD TEST (CONTINUED)
TEST PROCEDURE
1. Remove input power to the Power Wave
455/R.
2. Using the 3/8” nut driver, remove the case
top and the control box cover. See Figure
F.10.
3. Perform the following resistance tests:
+ probe on the STT output terminal
- probe on the Power Wave + output ter-
minal
The reading should be approximately
300,000 ohms
+ probe on the Power Wave + output ter-
minal
- probe on the STT output terminal
The reading should be less than 500 ohms
If both the polarity resistance tests are low,
either the STT Chopper Module is faulty or
diode D6 is shorted. See the Wiring
Diagram.

TROUBLESHOOTING & REPAIR
F-32 F-32
POWER WAVE 455/R
Return to Section TOC Return to Section TOC Return to Section TOC Return to Section TOC
Return to Master TOC Return to Master TOC Return to Master TOC Return to Master TOC
STT CHOPPER BOARD TEST (CONTINUED)
4. Carefully apply input power to the Power
Wave 455/R.
ELECTRIC SHOCK can kill.
High voltage is present when
input power is applied to the
machine.
For steps 5 and 6, see Figure F.10.
5. Turn on the Power Wave 455/R. Measure
the voltage from Power Board plug J43 lead
345 pin 7 (+) to lead 346 pin 1 (-). The volt-
age should be approximately 20 VDC. If not
correct, the Power Board may be faulty.
6. Measure the voltage from Control Board
plug J7 lead 4W pin 13 (-) to lead 4R pin 14
(+). The voltage should be 4 – 5 VDC. This
is the pulse width modulation signal to the
STT Chopper Board. If not correct, the
Control Board may be faulty.
7. When the test is completed, remove input
power from the Power Wave 455/R.
8. Install the case top using the 3/8” nut driver.
WARNING

TROUBLESHOOTING & REPAIR
F-33 F-33
POWER WAVE 455/R
POWER WAVE CURRENT TRANSDUCER TEST
WARNING
Service and repair should be performed by only Lincoln Electric factory trained personnel.
Unauthorized repairs performed on this equipment may result in danger to the technician
or machine operator and will invalidate your factory warranty. For your safety and to avoid
electrical shock, please observe all safety notes and precautions detailed throughout this
manual.
If for any reason you do not understand the test procedures or are unable to perform the
test/repairs safely, contact the Lincoln Electric Service Department for electrical trou-
bleshooting assistance before you proceed. Call 1-800-833-9353 (WELD).
TEST DESCRIPTION
This test will help determine if the Power Wave current transducer and associated wiring
is functioning correctly.
MATERIALS NEEDED
3/8” nut driver
Volt-Ohmmeter
This procedure should take approximately 25 minutes to perform.
Return to Section TOC Return to Section TOC Return to Section TOC Return to Section TOC
Return to Master TOC Return to Master TOC Return to Master TOC Return to Master TOC

TROUBLESHOOTING & REPAIR
F-34 F-34
POWER WAVE 455/R
Return to Section TOC Return to Section TOC Return to Section TOC Return to Section TOC
Return to Master TOC Return to Master TOC Return to Master TOC Return to Master TOC
J8
216
211 212 213
P91
CURRENT
TRANSDUCER
1234
CONTROL BOARD
J8
5 6 7 8
1 2 3 4
FIGURE F.11 – POWER WAVE CURRENT TRANSDUCER TEST
POWER WAVE CURRENT TRANSDUCER TEST (CONTINUED)
TEST PROCEDURE
1. Remove input power to the Power Wave
455/R.
2. Using the 3/8” nut driver, remove the case
top and the control box cover.
3. Locate the Power Wave current transducer
leads at Control Board plug J8. See Figure
F.11.
4. Carefully apply input power to the Power
Wave 455/R.
ELECTRIC SHOCK can kill.
High voltage is present when
input power is applied to the
machine.
WARNING

TROUBLESHOOTING & REPAIR
F-35 F-35
POWER WAVE 455/R
Return to Section TOC Return to Section TOC Return to Section TOC Return to Section TOC
Return to Master TOC Return to Master TOC Return to Master TOC Return to Master TOC
FIGURE F.12 – RECEPTACLE S7 TRIGGERED
POWER WAVE CURRENT TRANSDUCER TEST (CONTINUED)
RECEPTACLE
S7
STT POWER
WAVE
5. Turn on the Power Wave 455/R. Check for
the correct DC supply voltage to the current
transducer at plug J8. See Figure F.11.
A. Pin 2 (lead 212+) to pin 6 (lead 216-)
should read +15 VDC.
B. Pin 3 (lead 213-) to pin 6 (lead 216+)
should read -15 VDC.
If the DC supply voltages are not present,
the control board may be faulty.
6. If both of the supply voltages are low or
missing, check the associated leads
between plug J8 and current transducer plug
P91 and the Control Board.
NOTE: The machine can be triggered by
jumpering pin 1 to pin 2 at receptacle
S7. See Figure F.12.
7. With the Power Wave 455/R triggered,
check the feedback voltage from the current
transducer. The current feedback voltage
can be read at plug J8 on the Control Board.
A. Pin 1 (lead 211) to pin 6 (lead 216)
should read 2.0 VDC (machine loaded
to 250 amps).

TROUBLESHOOTING & REPAIR
F-36 F-36
POWER WAVE 455/R
Return to Section TOC Return to Section TOC Return to Section TOC Return to Section TOC
Return to Master TOC Return to Master TOC Return to Master TOC Return to Master TOC
TABLE F.6 - CURRENT FEEDBACK AT VARIOUS OUTPUT LOADS
POWER WAVE CURRENT TRANSDUCER TEST (CONTINUED)
8. If for any reason the machine cannot be
loaded to 250 amps, Table F.6 shows what
feedback voltage is produced at various cur-
rent loads.
9. If the correct supply voltages are applied to
the current transducer, and with the machine
loaded, the feedback voltage is missing or
not correct, the current transducer may be
faulty. Also make certain that lead 211
(plug J8 pin 1) has continuity (zero ohms)
between the current transducer and the
control board. See the Wiring Diagram.
10. Install the right side case cover using the
3/8” nut driver.
OUTPUT LOAD CURRENT
500
450
400
350
300
250
200
150
100
50
EXPECTED TRANSDUCER FEEDBACK
VOLTAGE
4.0
3.6
3.2
2.8
2.4
2.0
1.6
1.2
0.8
0.4

TROUBLESHOOTING & REPAIR
F-37 F-37
POWER WAVE 455/R
STT CURRENT TRANSDUCER TEST
WARNING
Service and repair should be performed by only Lincoln Electric factory trained personnel.
Unauthorized repairs performed on this equipment may result in danger to the technician
or machine operator and will invalidate your factory warranty. For your safety and to avoid
electrical shock, please observe all safety notes and precautions detailed throughout this
manual.
If for any reason you do not understand the test procedures or are unable to perform the
test/repairs safely, contact the Lincoln Electric Service Department for electrical trou-
bleshooting assistance before you proceed. Call 1-800-833-9353 (WELD).
TEST DESCRIPTION
This test will help determine if the STT current transducer and associated wiring is func-
tioning correctly.
MATERIALS NEEDED
3/8” nut driver
Volt-Ohmmeter
This procedure should take approximately 25 minutes to perform.
Return to Section TOC Return to Section TOC Return to Section TOC Return to Section TOC
Return to Master TOC Return to Master TOC Return to Master TOC Return to Master TOC

TROUBLESHOOTING & REPAIR
F-38 F-38
POWER WAVE 455/R
Return to Section TOC Return to Section TOC Return to Section TOC Return to Section TOC
Return to Master TOC Return to Master TOC Return to Master TOC Return to Master TOC
J8
811
813
CURRENT
TRANSDUCER
CONTROL BOARD
816 812
P90
1234
J8
5 6 7 8
1 2 3 4
FIGURE F.13 – STT CURRENT TRANSDUCER TEST
STT CURRENT TRANSDUCER TEST (CONTINUED)
TEST PROCEDURE
1. Remove input power to the Power Wave
455/R.
2. Using the 3/8” nut driver, remove the case
top and the control box cover.
3. Locate the STT current transducer leads at
Control Board plug J8. See Figure F.13.
4. Carefully apply input power to the Power
Wave 455/R.
ELECTRIC SHOCK can kill.
High voltage is present when
input power is applied to the
machine.
WARNING
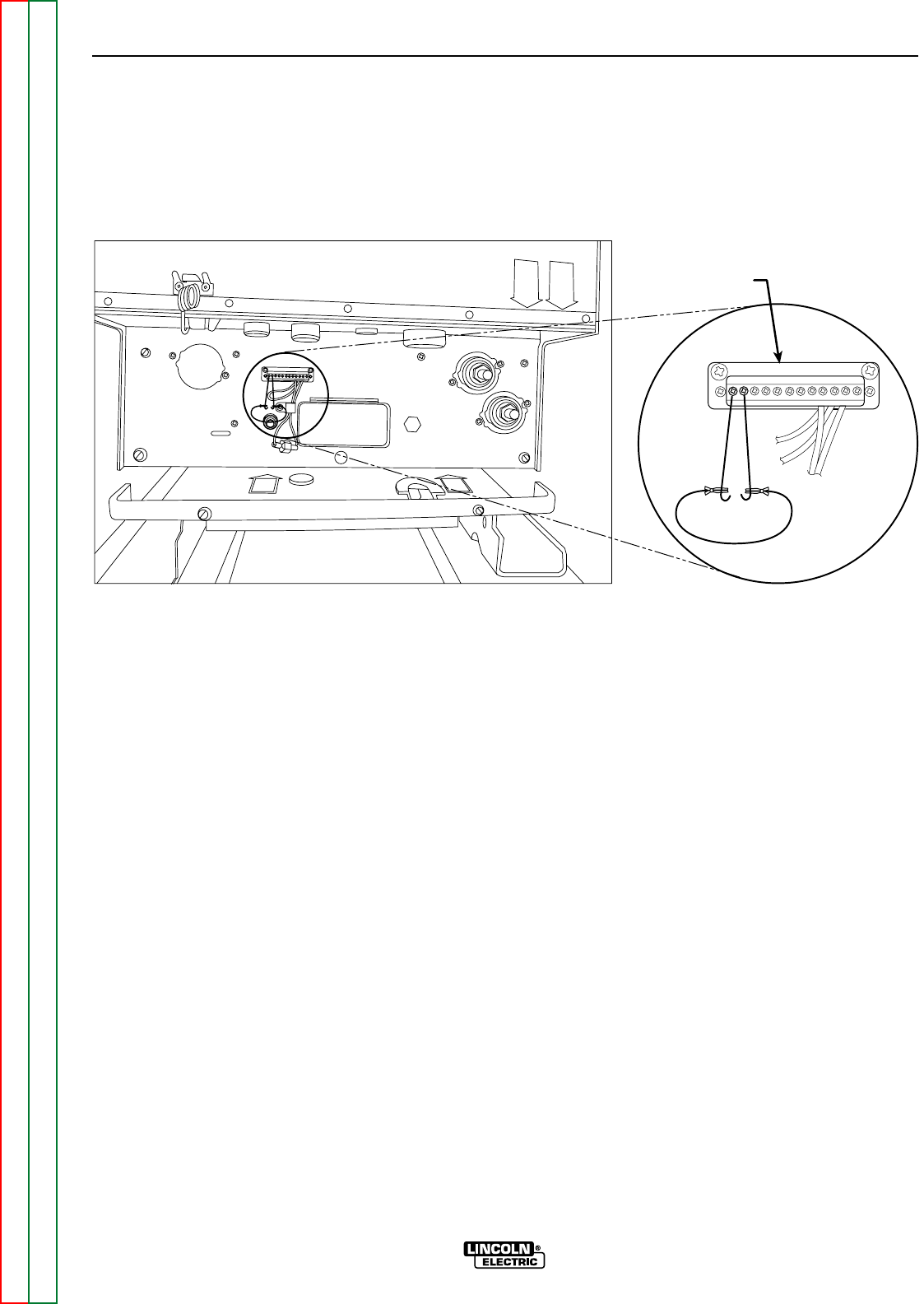
TROUBLESHOOTING & REPAIR
F-39 F-39
POWER WAVE 455/R
Return to Section TOC Return to Section TOC Return to Section TOC Return to Section TOC
Return to Master TOC Return to Master TOC Return to Master TOC Return to Master TOC
RECEPTACLE
S7
STT POWER
WAVE
FIGURE F.14 – RECEPTACLE S7 TRIGGERED
STT CURRENT TRANSDUCER TEST (CONTINUED)
5. Turn on the Power Wave 455/R. Check for
the correct DC supply voltage to the current
transducer at plug J8.
A. Pin 8 (lead 812+) to pin 7 (lead 816-)
should read +15 VDC.
B. Pin 4 (lead 813-) to pin 7 (lead 816+)
should read -15 VDC.
If the DC supply voltages are not present,
the control board may be faulty.
6. If both of the supply voltages are low or
missing, check the associated leads
between plug J8 and current transducer plug
P90 and the Control Board.
NOTE: The machine can be triggered by
jumpering pin 1 to pin 2 at receptacle
S7. See Figure F. 14.
7. With the Power Wave 455/R triggered,
check the feedback voltage from the current
transducer. The current feedback voltage
can be read at plug J8 on the Control Board.
A. Pin 5 (lead 811) to pin 7 (lead 816)
should read 2.0 VDC (machine loaded
to 50 amps).

TROUBLESHOOTING & REPAIR
F-40 F-40
POWER WAVE 455/R
Return to Section TOC Return to Section TOC Return to Section TOC Return to Section TOC
Return to Master TOC Return to Master TOC Return to Master TOC Return to Master TOC
STT CURRENT TRANSDUCER TEST (CONTINUED)
8. If for any reason the machine cannot be
loaded to 50 amps, Table F.6 shows what
feedback voltage is produced at various cur-
rent loads.
9. If the correct supply voltages are applied to
the current transducer, and with the machine
loaded, the feedback voltage is missing or
not correct, the current transducer may be
faulty. Also make certain that lead 811 (plug
J8 pin 5) has continuity (zero ohms)
between the current transducer and the
control board. See the Wiring Diagram.
10. Install the right side case cover using the
3/8” nut driver.

TROUBLESHOOTING & REPAIR
F-41 F-41
POWER WAVE 455/R
OUTPUT RECTIFIER TEST
WARNING
Service and repair should be performed by only Lincoln Electric factory trained personnel.
Unauthorized repairs performed on this equipment may result in danger to the technician
or machine operator and will invalidate your factory warranty. For your safety and to avoid
electrical shock, please observe all safety notes and precautions detailed throughout this
manual.
If for any reason you do not understand the test procedures or are unable to perform the
test/repairs safely, contact the Lincoln Electric Service Department for electrical trou-
bleshooting assistance before you proceed. Call 1-800-833-9353 (WELD).
TEST DESCRIPTION
The test will help determine if any of the output rectifiers are shorted.
MATERIALS NEEDED
Analog Volt-Ohmmeter
3/8” Nut driver
5/16” Wrench
This procedure should take approximately 20 minutes to perform.
Return to Section TOC Return to Section TOC Return to Section TOC Return to Section TOC
Return to Master TOC Return to Master TOC Return to Master TOC Return to Master TOC

TROUBLESHOOTING & REPAIR
F-42 F-42
POWER WAVE 455/R
Return to Section TOC Return to Section TOC Return to Section TOC Return to Section TOC
Return to Master TOC Return to Master TOC Return to Master TOC Return to Master TOC
STT OUTPUT
TERMINAL
POSITIVE (+)
OUTPUT
TERMINAL
NEGATIVE (-)
OUTPUT
TERMINAL
POWERWAVE 455/R
I ON
O OFF
FIGURE F.15 – OUTPUT RECTIFIER TEST
OUTPUT RECTIFIER TEST (CONTINUED)
TEST PROCEDURE
1. Remove main input supply power to the
Power Wave 455/R.
2. Remove the case top and sides and perform
the Input Filter Capacitor Discharge pro-
cedure.
3. Using the 5/16” wrench, remove and insu-
late lead 202A from the negative output ter-
minal.
4. Remove any output load that may be con-
nected to the Power Wave 455/R.
5. With the analog ohmmeter, measure the
resistance between the positive and nega-
tive output terminals (NOT the STT termi-
nal). Refer to Figure F.15.
IMPORTANT: The positive (+) meter probe
must be attached to the positive (+) output ter-
minal and the negative (-) meter probe must be
attached to the negative (-) output terminal.
6. If the reading is more than 200 ohms, the
output rectifier modules are not shorted. If
the reading is less than 200 ohms, one or
more of the rectifier modules are shorted.
Refer to the Output Rectifier Module
Replacement procedure.
7. Reconnect lead 202A to the negative output
terminal.
8. Replace the case top and sides.

TROUBLESHOOTING & REPAIR
F-43 F-43
POWER WAVE 455/R
AUXILIARY TRANSFORMER NO. 1 TEST
WARNING
Service and repair should be performed by only Lincoln Electric factory trained personnel.
Unauthorized repairs performed on this equipment may result in danger to the technician
or machine operator and will invalidate your factory warranty. For your safety and to avoid
electrical shock, please observe all safety notes and precautions detailed throughout this
manual.
If for any reason you do not understand the test procedures or are unable to perform the
test/repairs safely, contact the Lincoln Electric Service Department for electrical trou-
bleshooting assistance before you proceed. Call 1-800-833-9353 (WELD).
TEST DESCRIPTION
This test will determine if the correct voltage is being applied to the primary of Auxiliary
Transformer No. 1 and also if the correct voltages are being induced on the secondary
windings of the transformer.
MATERIALS NEEDED
Volt-ohmmeter (Multimeter)
3/8” Nut driver
Wiring Diagram
This procedure should take approximately 30 minutes to perform.
Return to Section TOC Return to Section TOC Return to Section TOC Return to Section TOC
Return to Master TOC Return to Master TOC Return to Master TOC Return to Master TOC

TROUBLESHOOTING & REPAIR
F-44 F-44
POWER WAVE 455/R
Return to Section TOC Return to Section TOC Return to Section TOC Return to Section TOC
Return to Master TOC Return to Master TOC Return to Master TOC Return to Master TOC
INPUT
CONTACTOR
601
X4
FAN MOTOR
LEADS
X3 X5
POWER BOARD
RECTIFIER BRIDGE
X1
X2
+
-
FIGURE F.16 – AUXILIARY TRANSFORMER NO. 1 TEST
AUXILIARY TRANSFORMER NO. 1 TEST (CONTINUED)
TEST PROCEDURE
1. Remove the main input power to the Power
Wave 455/R machine.
2. Using the 3/8” nut driver, remove the case
top and sides.
3. Perform the Capacitor Discharge proce-
dure.
4. Locate secondary leads X1 and X2 (at
power board rectifier bridge). Refer to
Figure F.16.
5. Locate secondary leads X3 and X5 (fan
motor leads).
6. Locate secondary lead X4 (at main contac-
tor).

TROUBLESHOOTING & REPAIR
F-45 F-45
POWER WAVE 455/R
Return to Section TOC Return to Section TOC Return to Section TOC Return to Section TOC
Return to Master TOC Return to Master TOC Return to Master TOC Return to Master TOC
TABLE F.7 – SECONDARY VOLTAGES
AUXILIARY TRANSFORMER NO. 1 TEST (CONTINUED)
7. Carefully apply the correct input voltage to
the Power Wave 455/R.
ELECTRIC SHOCK can kill.
High voltage is present at prima-
ry of the Auxiliary Transformer.
8. Check for the correct secondary voltages
according to Table F.7.
NOTE: The secondary voltages will vary if the
input line voltage varies.
9. If the correct secondary voltages are pre-
sent, the T1 auxiliary transformer is func-
tioning properly. If any of the secondary
voltages are missing or low, check to make
certain the primary is configured correctly
for the input voltage applied. See the
Wiring Diagram.
10. If the correct input voltage is applied to the
primary, and the secondary voltage(s) are
not correct, the T1 transformer may be
faulty.
11. Replace any cables ties and insulation
removed earlier.
12. Install the case sides and top using the 3/8”
nut driver.
LEAD IDENTIFICATION
X1 to X2
X3 to X5
X3 to X4
NORMAL EXPECTED VOLTAGE
52 VAC
115 VAC
24 VAC
WARNING

TROUBLESHOOTING & REPAIR
F-46 F-46
POWER WAVE 455/R
AUXILIARY TRANSFORMER NO. 2 TEST
WARNING
Service and repair should be performed by only Lincoln Electric factory trained personnel.
Unauthorized repairs performed on this equipment may result in danger to the technician
or machine operator and will invalidate your factory warranty. For your safety and to avoid
electrical shock, please observe all safety notes and precautions detailed throughout this
manual.
If for any reason you do not understand the test procedures or are unable to perform the
test/repairs safely, contact the Lincoln Electric Service Department for electrical trou-
bleshooting assistance before you proceed. Call 1-800-833-9353 (WELD).
TEST DESCRIPTION
This test will determine if the correct voltage is being applied to the primary of Auxiliary
Transformer No. 2 and also if the correct voltages are being induced on the secondary
windings of the transformer.
MATERIALS NEEDED
Volt-ohmmeter (Multimeter)
3/8” Nut driver
Wiring Diagram
This procedure should take approximately 25 minutes to perform.
Return to Section TOC Return to Section TOC Return to Section TOC Return to Section TOC
Return to Master TOC Return to Master TOC Return to Master TOC Return to Master TOC

TROUBLESHOOTING & REPAIR
F-47 F-47
POWER WAVE 455/R
Return to Section TOC Return to Section TOC Return to Section TOC Return to Section TOC
Return to Master TOC Return to Master TOC Return to Master TOC Return to Master TOC
P50
P52
4 5 6
3 4
1 2 3
1 2
H4 H3 H1
H5 H6 H2
33A
350 352
VIEWED FROM
TRANSFORMER
LEAD END
VIEWED FROM
TRANSFORMER
LEAD SIDE
FIGURE F.17 – AUXILIARY TRANSFORMER NO. 2 TEST
AUXILIARY TRANSFORMER NO. 2 TEST (CONTINUED)
TEST PROCEDURE
1. Remove the main input power to the Power
Wave 455/R machine.
2. Remove any load that may be connected to
the 115 VAC receptacle.
3. Using the 3/8” nut driver, remove the case
top.
4. Locate plugs P52 and P50 at the Auxiliary
Transformer No. 2. Refer to Figure F.17.
5. Carefully apply the correct input power.
ELECTRIC SHOCK can kill.
High voltage is present at both
plugs.
6. Check for 115 VAC at plug P52 pins 1 and
4 (leads 350 to 33A). Check for 230 VAC
at plug P52 pins 1 and 2 (leads 350 to
352).
7. If 115 VAC and 230 VAC are present,
Auxiliary Transformer No. 2 is good.
8. If 115 is not present between pins 1 and 4,
and 230 VAC is not present between pins 1
and 2, check the associated leads and
plugs for loose or faulty connections.
9. Carefully test for the correct AC input volt-
age applied to the primary windings at plug
P50. See the Wiring Diagram.
10. If the correct AC input voltage is applied to
the primary of the Auxiliary Transformer
No. 2 and the secondary voltage is NOT
correct, the transformer may be faulty.
Replace.
11. Replace any cables ties and insulation
removed earlier.
12. Install the case top using the 3/8” nut dri-
WARNING

TROUBLESHOOTING & REPAIR
F-48 F-48
POWER WAVE 455/R
INPUT RECTIFIER REMOVAL AND REPLACEMENT
WARNING
Service and repair should be performed by only Lincoln Electric factory trained personnel.
Unauthorized repairs performed on this equipment may result in danger to the technician
or machine operator and will invalidate your factory warranty. For your safety and to avoid
electrical shock, please observe all safety notes and precautions detailed throughout this
manual.
If for any reason you do not understand the test procedures or are unable to perform the
test/repairs safely, contact the Lincoln Electric Service Department for electrical trou-
bleshooting assistance before you proceed. Call 1-800-833-9353 (WELD).
DESCRIPTION
This procedure will aid the technician in the removal and replacement of the input rectifi-
er module.
MATERIALS NEEDED
3/8” nut driver
3/16” Allen wrench
Phillips head screwdriver
This procedure should take approximately 15 minutes to perform.
Return to Section TOC Return to Section TOC Return to Section TOC Return to Section TOC
Return to Master TOC Return to Master TOC Return to Master TOC Return to Master TOC

TROUBLESHOOTING & REPAIR
F-49 F-49
POWER WAVE 455/R
Return to Section TOC Return to Section TOC Return to Section TOC Return to Section TOC
Return to Master TOC Return to Master TOC Return to Master TOC Return to Master TOC
NEG (-)
POS (+)
A
B
C
INPUT
RECTIFIER
FIGURE F.18 – INPUT RECTIFIER REMOVAL AND REPLACEMENT
INPUT RECTIFIER REMOVAL AND REPLACEMENT (CONTINUED)
REMOVAL PROCEDURE
1. Remove input power to the Power Wave
455/R.
2. Using the 3/8” nut driver, remove the case
top, sides, and input access panel.
3. Perform the Capacitor Discharge proce-
dure.
4. Locate and remove the RTV sealant from
the input rectifier connection terminals. See
Figure F. 18.
5. Label and, using the phillips head screwdriv-
er, carefully remove the five leads from the
input rectifier terminals. Note placement for
reassembly. See Figure F.18.
6. Using the 3/16” allen wrench, remove the
two mounting screws and washers from the
rectifier module.
7. Carefully remove the input rectifier module.
REPLACEMENT PROCEDURE
1. Clean heat sink surfaces.
2. Apply an even coating of joint compound
(Penetrox A-13) to both the heat sink and
module mounting surfaces. The joint com-
pound should be 0.002 - 0.005 in. thick per
surface.
3. Mount the module to the heat sink and even-
ly torque the mounting screws (with wash-
ers) to 44 in/lbs.
4. Assemble the leads to the correct module
terminals and torque to 26 in/lbs. See
Figure F.18.
5. Apply RTV sealant to the rectifier connection
terminals.
6. Install the case top, sides, and input access
panel using the 3/8” nut driver.

TROUBLESHOOTING & REPAIR
F-50 F-50
POWER WAVE 455/R
INPUT CONTACTOR REMOVAL AND REPLACEMENT
WARNING
Service and repair should be performed by only Lincoln Electric factory trained personnel.
Unauthorized repairs performed on this equipment may result in danger to the technician
or machine operator and will invalidate your factory warranty. For your safety and to avoid
electrical shock, please observe all safety notes and precautions detailed throughout this
manual.
If for any reason you do not understand the test procedures or are unable to perform the
test/repairs safely, contact the Lincoln Electric Service Department for electrical trou-
bleshooting assistance before you proceed. Call 1-800-833-9353 (WELD).
TEST DESCRIPTION
This procedure will aid the technician in the removal and replacement of the input con-
tactor.
MATERIALS NEEDED
3/8” nut driver
5/16” nut driver
Phillips head screwdriver
This procedure should take approximately 15 minutes to perform.
Return to Section TOC Return to Section TOC Return to Section TOC Return to Section TOC
Return to Master TOC Return to Master TOC Return to Master TOC Return to Master TOC

TROUBLESHOOTING & REPAIR
F-51 F-51
POWER WAVE 455/R
Return to Section TOC Return to Section TOC Return to Section TOC Return to Section TOC
Return to Master TOC Return to Master TOC Return to Master TOC Return to Master TOC
INPUT
CONTACTOR
601
X4
FIGURE F.19 – INPUT CONTACTOR REMOVAL AND REPLACEMENT
INPUT CONTACTOR REMOVAL AND REPLACEMENT (CONTINUED)
REMOVAL PROCEDURE
1. Remove input power to the Power Wave
455/R.
2. Using the 3/8” nut driver, remove the case
top, sides, and input access panel.
3. Perform the Capacitor Discharge proce-
dure
4. Locate the input contactor. Label and,
using the phillips head screwdriver, careful-
ly remove the leads from the input contac-
tor terminals. Note placement for reassem-
bly. See Figure F.19.
5. With the 5/16” nut driver, remove the three
mounting screws. See Figure F.19.
6. Carefully remove the input contactor.
REPLACEMENT PROCEDURE
1. Mount the contactor and tighten the mount-
ing screws.
2. Assemble the leads to the correct terminals.
See Figure F.18.
3. Install the case top, sides, and input access
panel using the 3/8” nut driver.

TROUBLESHOOTING & REPAIR
F-52 F-52
POWER WAVE 455/R
AUXILIARY TRANSFORMER NO. 1 REMOVAL AND
REPLACEMENT PROCEDURE
WARNING
Service and repair should be performed by only Lincoln Electric factory trained personnel.
Unauthorized repairs performed on this equipment may result in danger to the technician
or machine operator and will invalidate your factory warranty. For your safety and to avoid
electrical shock, please observe all safety notes and precautions detailed throughout this
manual.
If for any reason you do not understand the test procedures or are unable to perform the
test/repairs safely, contact the Lincoln Electric Service Department for electrical trou-
bleshooting assistance before you proceed. Call 1-800-833-9353 (WELD).
DESCRIPTION
This procedure will aid the technician in the removal and replacement of auxiliary trans-
former No. 1.
MATERIALS NEEDED
3/8” Nut driver
Wire cutters
Wire splicer or soldering equipment
This procedure should take approximately 25 minutes to perform.
Return to Section TOC Return to Section TOC Return to Section TOC Return to Section TOC
Return to Master TOC Return to Master TOC Return to Master TOC Return to Master TOC

TROUBLESHOOTING & REPAIR
F-53 F-53
POWER WAVE 455/R
Return to Section TOC Return to Section TOC Return to Section TOC Return to Section TOC
Return to Master TOC Return to Master TOC Return to Master TOC Return to Master TOC
INPUT
CONTACTOR
601
X4
FAN MOTOR
LEADS
X3 X5
POWER BOARD
RECTIFIER BRIDGE
X1
X2
+
-
RECONNECT
TERMINALS
CB4
H1
H2
H3
H4
H5
FIGURE F.20 – AUXILIARY TRANSFORMER NO. 1 REMOVAL AND REPLACEMENT
AUXILIARY TRANSFORMER NO. 1 REMOVAL AND
REPLACEMENT PROCEDURE (CONTINUED)
REMOVAL PROCEDURE
1. Remove input power to the Power Wave
455/R.
2. Using the 3/8” nut driver, remove the case
top, sides and input access panel.
3. Perform the Capacitor Discharge proce-
dure.
4. Using the 3/8” nut driver, remove the case
back.
5. Remove lead X4 from the input contactor
coil terminal.

TROUBLESHOOTING & REPAIR
F-54 F-54
POWER WAVE 455/R
Return to Section TOC Return to Section TOC Return to Section TOC Return to Section TOC
Return to Master TOC Return to Master TOC Return to Master TOC Return to Master TOC
AUXILIARY TRANSFORMER NO. 1 REMOVAL AND
REPLACEMENT PROCEDURE (CONTINUED)
6. Remove leads X1 and X2 from the power
board rectifier bridge. Refer to Figure
F.20.
7. Cut X3 and X5 from the fan motor leads.
Leave enough lead length to splice in the
new transformer leads.
8. Cut the X3 lead that is connected to the
input board. Leave enough lead length to
splice in the new transformer lead.
9. Locate, label, and remove primary lead H1
from circuit breaker CB4.
10. Label and remove primary leads H2, H3,
H4, and H5 from the reconnect terminals
on the reconnect panel. Note lead place-
ment for reassembly.
11. Cut any necessary cable ties and clear the
leads.
12. Using the 3/8” nut driver, remove the two
mounting screws that hold the transformer
to the fan baffle and the machine base.
13. Carefully remove the transformer from the
Power Wave 455/R.
REPLACEMENT PROCEDURE
1. Carefully place the transformer into the
Power Wave 455/R.
2. Install the two mounting screws that hold
the transformer to the fan baffle and the
machine base using the 3/8” nut driver.
3. Install the primary leads H2, H3, H4, and
H5 to the reconnect terminals on the
reconnect panel.
4. Connect primary lead H1 to circuit breaker
CB4.
5. Splice the new transformer lead with the
X3 lead connected to the input board.
6. Splice the new transformer fan leads to
the fan motor leads X3 and X5.
7. Connect lead X4 to the main contactor
coil terminal.
8. Connect leads X1 and X2 to the power
board rectifier bridge.
9. Reposition any wire leads and install
cable ties as necessary.
10. Install the case back using the 3/8” nut
driver.
11. Install the case top, sides, and input
access panel using the 3/8” nut driver.

TROUBLESHOOTING & REPAIR
F-55 F-55
POWER WAVE 455/R
AUXILIARY TRANSFORMER NO. 2 REMOVAL AND
REPLACEMENT PROCEDURE
WARNING
Service and repair should be performed by only Lincoln Electric factory trained personnel.
Unauthorized repairs performed on this equipment may result in danger to the technician
or machine operator and will invalidate your factory warranty. For your safety and to avoid
electrical shock, please observe all safety notes and precautions detailed throughout this
manual.
If for any reason you do not understand the test procedures or are unable to perform the
test/repairs safely, contact the Lincoln Electric Service Department for electrical trou-
bleshooting assistance before you proceed. Call 1-800-833-9353 (WELD).
TEST DESCRIPTION
This procedure will aid the technician in the removal and replacement of auxiliary trans-
former No. 2.
MATERIALS NEEDED
3/8” Nut driver
Wire cutters
This procedure should take approximately 25 minutes to perform.
Return to Section TOC Return to Section TOC Return to Section TOC Return to Section TOC
Return to Master TOC Return to Master TOC Return to Master TOC Return to Master TOC

TROUBLESHOOTING & REPAIR
F-56 F-56
POWER WAVE 455/R
Return to Section TOC Return to Section TOC Return to Section TOC Return to Section TOC
Return to Master TOC Return to Master TOC Return to Master TOC Return to Master TOC
INPUT
CONTACTOR
601
X4
CB4 CIRCUIT
BREAKER &
115V RECEPTACLE
LEADS 33/32
P50
P52
FIGURE F.21 – AUXILIARY TRANSFORMER NO. 2 REMOVAL AND REPLACEMENT
AUXILIARY TRANSFORMER NO. 2 REMOVAL AND
REPLACEMENT PROCEDURE (CONTINUED)
REMOVAL PROCEDURE
1. Remove input power to the Power Wave
455/R.
2. Using the 3/8” nut driver, remove the case
top, sides and input access panel.
3. Perform the Capacitor Discharge proce-
dure.
4. Using the 3/8” nut driver, remove the case
back.
5. Disconnect plugs P50 and P52.
6. Disconnect leads 33 and 32 to circuit breaker
CB2 and the 115 V receptacle.
7. Using the 3/8” nut driver, remove the two
transformer mounting screws.

TROUBLESHOOTING & REPAIR
F-57 F-57
POWER WAVE 455/R
Return to Section TOC Return to Section TOC Return to Section TOC Return to Section TOC
Return to Master TOC Return to Master TOC Return to Master TOC Return to Master TOC
AUXILIARY TRANSFORMER NO. 2 REMOVAL AND
REPLACEMENT PROCEDURE (CONTINUED)
REPLACEMENT PROCEDURE
1. Carefully place the transformer into the
Power Wave 455/R.
2. Install the two mounting screws that hold the
transformer to the machine base using the
3/8” nut driver.
3. Connect leads 33 and 32 to circuit breaker
CB4 and the 115 V receptacle.
4. Connect plugs P50 and P52.
5. Reposition any wire leads and install cable
ties as necessary.
6. Install the case back using the 3/8” nut driver.
7. Install the case top, sides, and input access
panel using the 3/8” nut driver.

TROUBLESHOOTING & REPAIR
F-58 F-58
POWER WAVE 455/R
CONTROL, FEED HEAD, OR VOLTAGE SENSE PC BOARD
REMOVAL AND REPLACEMENT
WARNING
Service and repair should be performed by only Lincoln Electric factory trained personnel.
Unauthorized repairs performed on this equipment may result in danger to the technician
or machine operator and will invalidate your factory warranty. For your safety and to avoid
electrical shock, please observe all safety notes and precautions detailed throughout this
manual.
If for any reason you do not understand the test procedures or are unable to perform the
test/repairs safely, contact the Lincoln Electric Service Department for electrical trou-
bleshooting assistance before you proceed. Call 1-800-833-9353 (WELD).
DESCRIPTION
This procedure will aid the technician in the removal and replacement of either the
Control Board the Feed Head Board, or the Voltage Sense Board.
MATERIALS NEEDED
3/8” Nut driver
Anti-static wrist strap
This procedure should take approximately 15 minutes to perform.
Return to Section TOC Return to Section TOC Return to Section TOC Return to Section TOC
Return to Master TOC Return to Master TOC Return to Master TOC Return to Master TOC

TROUBLESHOOTING & REPAIR
F-59 F-59
POWER WAVE 455/R
Return to Section TOC Return to Section TOC Return to Section TOC Return to Section TOC
Return to Master TOC Return to Master TOC Return to Master TOC Return to Master TOC
COMPARTMENT
COVER
CONTROL
BOARD
POWER
BOARD
FIGURE F.22 – CONTROL OR FEED HEAD BOARD REMOVAL AND REPLACEMENT
CONTROL, FEED HEAD, OR VOLTAGE SENSE PC BOARD
REMOVAL AND REPLACEMENT (CONTINUED)
REMOVAL PROCEDURE
1. Remove input power to the Power Wave
455/R.
2. Using the 3/8” nut driver, remove the case
top and sides.
3. Perform the Capacitor Discharge proce-
dure.
4. Observe all static electricity precautions.
5. Using the 3/8” nut driver, remove the PC
board compartment cover. Refer to Figure
F.22.
6. Using the 3/8” nut driver, remove the two
screws holding the rear of the Control Box in
place.
7. Clear the leads in the sleeving and the grom-
mets on the sides of the control box.
8. Label and remove the molex plugs from the
Control Board and the Feed Head Board.

TROUBLESHOOTING & REPAIR
F-60 F-60
POWER WAVE 455/R
Return to Section TOC Return to Section TOC Return to Section TOC Return to Section TOC
Return to Master TOC Return to Master TOC Return to Master TOC Return to Master TOC
CONTROL, FEED HEAD, OR VOLTAGE SENSE PC BOARD
REMOVAL AND REPLACEMENT (CONTINUED)
9. Tilt back the rear of the control box to
access the PC board mounting nuts. Using
the 3/8” nut driver, remove the self-locking
mounting nuts from the Control and Feed
Head Boards. Carefully remove the
boards.
10. Remove plugs J1 and J2 from the Voltage
Sense Board. See Figure F.23.
11. Using the needle-nose pliers, carefully
pinch the three plastic standoffs. Remove
the Voltage Sense Board.
REPLACEMENT PROCEDURE
1. Install either the Control or the Feed Head
Board to the back of the control box with the
self-locking nuts. Use the 3/8” nut driver.
2. Connect the molex plugs to the Control
Board and the Feed Head Board. Be sure
the lead harnesses are securely and proper-
ly positioned.
3. Secure the rear of the control box in place
using two screws and the 3/8” nut driver.
COMPARTMENT
COVER
CONTROL
BOARD
POWER
BOARD
VOLTAGE
SENSE
BOARD
FIGURE F.23 – VOLTAGE SENSE BOARD REMOVAL AND REPLACEMENT

TROUBLESHOOTING & REPAIR
F-61 F-61
POWER WAVE 455/R
Return to Section TOC Return to Section TOC Return to Section TOC Return to Section TOC
Return to Master TOC Return to Master TOC Return to Master TOC Return to Master TOC
3. Secure the rear of the control box in place
using two screws and the 3/8” nut driver.
4. Press the Voltage Sense Board onto its
standoffs. Make sure the board snaps into
place on all three standoffs.
5. Connect the two molex plugs to the Voltage
Sense Board.
6. Install the PC board compartment cover
using the 3/8” nut driver.
7. Install the case top and sides using the 3/8”
nut driver.
CONTROL, FEED HEAD, OR VOLTAGE SENSE PC BOARD
REMOVAL AND REPLACEMENT (CONTINUED)

TROUBLESHOOTING & REPAIR
F-62 F-62
POWER WAVE 455/R
GATEWAY PC BOARD REMOVAL AND REPLACEMENT
WARNING
Service and repair should be performed by only Lincoln Electric factory trained personnel.
Unauthorized repairs performed on this equipment may result in danger to the technician
or machine operator and will invalidate your factory warranty. For your safety and to avoid
electrical shock, please observe all safety notes and precautions detailed throughout this
manual.
If for any reason you do not understand the test procedures or are unable to perform the
test/repairs safely, contact the Lincoln Electric Service Department for electrical trou-
bleshooting assistance before you proceed. Call 1-800-833-9353 (WELD).
DESCRIPTION
This procedure will aid the technician in the removal and replacement of the Gateway PC
Board.
MATERIALS NEEDED
Phillips head screw driver
3/8” Nut driver
Anti-static wrist strap
This procedure should take approximately 15 minutes to perform.
Return to Section TOC Return to Section TOC Return to Section TOC Return to Section TOC
Return to Master TOC Return to Master TOC Return to Master TOC Return to Master TOC

TROUBLESHOOTING & REPAIR
F-63 F-63
POWER WAVE 455/R
Return to Section TOC Return to Section TOC Return to Section TOC Return to Section TOC
Return to Master TOC Return to Master TOC Return to Master TOC Return to Master TOC
PHILLIPS
SCREW
DEVICENET/
GATEWAY BOARD
(LOCATED BEHIND
FRONT COVER)
FIGURE F.24 – GATEWAY BOARD REMOVAL AND REPLACEMENT
GATEWAY PC BOARD REMOVAL AND REPLACEMENT (CONTINUED)
REMOVAL PROCEDURE
1. Remove input power to the Power Wave
455/R.
2. Using the phillips head screw driver, remove
the six screws from the case front cover. Tilt
open the cover and support it. See Figure
F.24.
3. Observe all static electricity precautions.
4. Label and remove the four molex plugs from
the Gateway Board.
5. Using the 3/8” nut driver, remove the self-
locking mounting nuts from the Gateway
Board. Carefully remove the board. Refer
to Figure F.24.
REPLACEMENT PROCEDURE
1. Install the Gateway Board to the case front
cover with the self-locking nuts. Use the 3/8”
nut driver.
2. Connect the four molex plugs to the
Gateway Board.
3. Using the phillips head screw driver, attach
the cover to the case front.

TROUBLESHOOTING & REPAIR
F-64 F-64
POWER WAVE 455/R
STT CURRENT TRANSDUCER
REMOVAL AND REPLACEMENT
WARNING
Service and repair should be performed by only Lincoln Electric factory trained personnel.
Unauthorized repairs performed on this equipment may result in danger to the technician
or machine operator and will invalidate your factory warranty. For your safety and to avoid
electrical shock, please observe all safety notes and precautions detailed throughout this
manual.
If for any reason you do not understand the test procedures or are unable to perform the
test/repairs safely, contact the Lincoln Electric Service Department for electrical trou-
bleshooting assistance before you proceed. Call 1-800-833-9353 (WELD).
DESCRIPTION
This procedure will aid the technician in the removal and replacement of the STT Current
Transducer.
MATERIALS NEEDED
3/8” Nut driver
5/16” Open end wrench
5/16” Socket wrench with extension
Universal adapter
3/4” Wrench
Phillips head screw driver
Wire cutters
Wiring Diagram
This procedure should take approximately 25 minutes to perform.
Return to Section TOC Return to Section TOC Return to Section TOC Return to Section TOC
Return to Master TOC Return to Master TOC Return to Master TOC Return to Master TOC

TROUBLESHOOTING & REPAIR
F-65 F-65
POWER WAVE 455/R
Return to Section TOC Return to Section TOC Return to Section TOC Return to Section TOC
Return to Master TOC Return to Master TOC Return to Master TOC Return to Master TOC
CURRENT
TRANSDUCER
P90
1234
RESISTOR
ASSEMBLY
STT OUTPUT
TERMINAL
(TOP RIGHT)
FIGURE F.25 – STT CURRENT TRANSDUCER REMOVAL AND REPLACEMENT PROCEDURE
STT CURRENT TRANSDUCER
REMOVAL AND PLACEMENT (CONTINUED)
REMOVAL PROCEDURE
1. Remove input power to the Power Wave
455/R.
2. Using the 3/8” nut driver, remove the case
top and right side.
3. Perform the Capacitor Discharge proce-
dure.
4. Using the wire cutters, cut all cable ties to
the transducer lead harness. Unplug the
harness and swing it aside.
5. Label and remove the leads to the resistor
assembly. See Figure F.25. Using the
5/16” socket wrench, extension and univer-
sal adapter, remove the resistor assembly.
It may be necessary to remove the glastic
high voltage protection shield. (Use the
3/8” nut driver.) It may also be necessary to
use a 5/16” open end wrench to remove the
inside screws. Carefully swing the resistor
assembly aside.

TROUBLESHOOTING & REPAIR
F-66 F-66
POWER WAVE 455/R
Return to Section TOC Return to Section TOC Return to Section TOC Return to Section TOC
Return to Master TOC Return to Master TOC Return to Master TOC Return to Master TOC
STT CURRENT TRANSDUCER
REMOVAL AND REPLACEMENT (CONTINUED)
6. With the 5/16” open end wrench, remove
the small screw from the STT output termi-
nal. Label and remove the small leads.
See the Wiring Diagram.
7. Using the 3/4” wrench, remove the bolt,
lock washer and flat washer from the STT
output terminal. Remove the double heavy
output leads. Cut any necessary cable
ties.
8. Using the phillips head screw driver,
remove the screws and lock washers that
hold the transducer to the front panel.
9. Remove the STT current transducer, care-
fully feeding the output leads through it.
10. Remove the standoffs from the transducer
and save them for reassembly with the new
transducer.
REPLACEMENT PROCEDURE
1. Attach the standoffs to the transducer.
2. Position the transducer on the back of the
front panel and attach it with the two
phillips screws and lock washers. Feed the
output leads through the transducer.
3. Attach the double heavy leads to the STT
output terminal with the 3/4” bolt, lock wash-
er and flat washer.
4. Attach the small leads to the STT output ter-
minal with the 5/16” screw.
5. Install the resistor assembly using the 5/16”
socket wrench, extension and universal
adapter. Install the glastic high voltage pro-
tection shield with the 3/8” nut driver.
6. Replace all cable ties cut during removal.
7. Install the case top and right side using the
3/8” nut driver.

TROUBLESHOOTING & REPAIR
F-67 F-67
POWER WAVE 455/R
POWER WAVE CURRENT TRANSDUCER
REMOVAL AND REPLACEMENT
WARNING
Service and repair should be performed by only Lincoln Electric factory trained personnel.
Unauthorized repairs performed on this equipment may result in danger to the technician
or machine operator and will invalidate your factory warranty. For your safety and to avoid
electrical shock, please observe all safety notes and precautions detailed throughout this
manual.
If for any reason you do not understand the test procedures or are unable to perform the
test/repairs safely, contact the Lincoln Electric Service Department for electrical trou-
bleshooting assistance before you proceed. Call 1-800-833-9353 (WELD).
TEST DESCRIPTION
This procedure will aid the technician in the removal and replacement of the Power Wave
Current Transducer.
MATERIALS NEEDED
3/8” Nut driver
5/16” Open end wrench
9/16” Wrench
3/4” Wrench
Phillips head screw driver
Wire cutters
Wiring Diagram
This procedure should take approximately 25 minutes to perform.
Return to Section TOC Return to Section TOC Return to Section TOC Return to Section TOC
Return to Master TOC Return to Master TOC Return to Master TOC Return to Master TOC

TROUBLESHOOTING & REPAIR
F-68 F-68
POWER WAVE 455/R
Return to Section TOC Return to Section TOC Return to Section TOC Return to Section TOC
Return to Master TOC Return to Master TOC Return to Master TOC Return to Master TOC
CURRENT
TRANSDUCER
HEAVY LEAD
BOLTED CONNECTION
(BEHIND CASE FRONT)
FIGURE F.26 – POWER WAVE CURRENT TRANSDUCER REMOVAL AND REPLACEMENT PROCEDURE
POWER WAVE CURRENT TRANSDUCER
REMOVAL AND REPLACEMENT (CONTINUED)
REMOVAL PROCEDURE
1. Remove input power to the Power Wave
455/R.
2. Using the 3/8” nut driver, remove the case
top and sides and the control box cover.
3. Perform the Capacitor Discharge proce-
dure.
4. Using the 3/8” socket wrench or nut driver,
remove the three screws along the bottom
case front. See Figure F.26.
5. Using the 3/8” socket wrench, remove the
four screws that hold the case front to the
machine.
6. Label all leads to all output terminals. Using
the 5/16” wrench and the 3/4” wrench,
remove all leads from the three output termi-
nals. See the Wiring Diagram.
7. Cut any necessary cable ties. Then careful-
ly swing the front panel aside.
8. Remove the insulating tape from the heavy
lead bolted connection. See Figure F.26.
Using the 9/16” wrenches, remove the bolt,
lock washer and nut.

TROUBLESHOOTING & REPAIR
F-69 F-69
POWER WAVE 455/R
Return to Section TOC Return to Section TOC Return to Section TOC Return to Section TOC
Return to Master TOC Return to Master TOC Return to Master TOC Return to Master TOC
POWER WAVE CURRENT TRANSDUCER
REMOVAL AND REPLACEMENT (CONTINUED)
9. Using the phillips head screw driver,
remove the screws and lock washers that
hold the transducer to the front panel.
10. Remove the Power Wave current trans-
ducer.
11. Remove the standoffs from the transducer
and save them for reassembly with the
new transducer.
REPLACEMENT PROCEDURE
1. Attach the standoffs to the transducer.
2. Position the transducer on the back of the
front panel and attach it with the two
phillips screws and lock washers. Feed the
output leads through the transducer.
3. Run the heavy lead through transducer
and secure the bolted connection with the
9/16” bolt, lock washer and nut. Replace
the insulating tape around the connection.
4. Using the 5/16” wrench and the 3/4” wrench,
attach all leads to the three output terminals.
See the Wiring Diagram.
5. Replace all cable ties cut during removal.
6. Install the case top and sides using the 3/8”
nut driver.

TROUBLESHOOTING & REPAIR
F-70 F-70
POWER WAVE 455/R
OUTPUT RECTIFIER, STT CHOPPER BOARD AND RECTIFIER MODULE
REMOVAL AND REPLACEMENT
WARNING
Service and repair should be performed by only Lincoln Electric factory trained personnel.
Unauthorized repairs performed on this equipment may result in danger to the technician
or machine operator and will invalidate your factory warranty. For your safety and to avoid
electrical shock, please observe all safety notes and precautions detailed throughout this
manual.
If for any reason you do not understand the test procedures or are unable to perform the
test/repairs safely, contact the Lincoln Electric Service Department for electrical trou-
bleshooting assistance before you proceed. Call 1-800-833-9353 (WELD).
TEST DESCRIPTION
This procedure will aid the technician in the removal and replacement of the output recti-
fier assembly and individual rectifier module replacement.
This procedure takes approximately 35 minutes to remove and replace the output rectifi-
er, 5 minutes to remove the STT Chopper Board and 5 minutes to remove and replace the
rectifier module.
MATERIALS NEEDED
3/8” Nut driver
7/16” Wrench
9/16” Wrench
9/64” Allen wrench
3/16” Allen wrench
Needle-nose pliers
Slot head screwdriver
Penetrox A13 Thermal Joint Compound
Wiring Diagram
This procedure should take approximately 45 minutes to perform.
Return to Section TOC Return to Section TOC Return to Section TOC Return to Section TOC
Return to Master TOC Return to Master TOC Return to Master TOC Return to Master TOC

TROUBLESHOOTING & REPAIR
F-71 F-71
POWER WAVE 455/R
Return to Section TOC Return to Section TOC Return to Section TOC Return to Section TOC
Return to Master TOC Return to Master TOC Return to Master TOC Return to Master TOC
TRANSFORMER
LEADS
RECTIFIER
MODULE
POSITIVE
OUTPUT
LEAD
HEATSINK
MOUNT
BOLTS (4X)
RECTIFIER
THERMOSTAT
(LEADS 291 & 292)
HEATSINK
STT LEAD
LEAD 287
(SNUBBER
DIODE)
PLUG J10
LEAD 289B
(STT SNUBBER
CAPACITOR)
FIGURE F.27 – OUTPUT RECTIFIER, STT CHOPPER BOARD AND RECTIFIER MODULE
REMOVAL AND REPLACEMENT
OUTPUT RECTIFIER, STT CHOPPER BOARD AND RECTIFIER MODULE
REMOVAL AND REPLACEMENT (CONTINUED)
RECTIFIER ASSEMBLY
REMOVAL PROCEDURE
1. Remove input power to the Power Wave
455/R.
2. Using the 3/8” nut driver, remove the case
top and sides.
3. Perform the Capacitor Discharge proce-
dure.
4. Using the 9/16” wrench, remove the Power
Wave positive output lead from the rectifier
heat sink. Note fastener hardware for
reassembly. Refer to Figure F.27.
5. Using the 7/16” wrench, remove the STT
output lead from the rectifier heat sink. Note
fastener hardware for reassembly. Refer to
Figure F.27.
6. Using the 7/16” wrench, remove the eight
transformer leads from the rectifier modules.
Label the leads and take note of lead place-
ment for reassembly. Note that each screw
has two flat washers and one lock washer.

TROUBLESHOOTING & REPAIR
F-72 F-72
POWER WAVE 455/R
Return to Section TOC Return to Section TOC Return to Section TOC Return to Section TOC
Return to Master TOC Return to Master TOC Return to Master TOC Return to Master TOC
OUTPUT RECTIFIER, STT CHOPPER BOARD AND RECTIFIER MODULE
REMOVAL AND REPLACEMENT (CONTINUED)
7. Using the needle-nose pliers, remove
leads #292 and #291 from the rectifier ther-
mostat.
8. Disconnect plug J10 from the STT
Chopper Board.
9. With the 7/16” wrench, remove lead #287
from the STT Snubber Diode D5.
10. With the 7/16” wrench, remove lead #289B
from the STT Snubber Capacitor C10.
11. Using the 7/16” wrench, remove the four
nuts and associated washers from the heat
sink mounting bolts. The heat-sink assem-
bly can be removed by carefully sliding the
assembly forward and removing the mount-
ing bolts.
STT CHOPPER BOARD REMOVAL
AND REPLACEMENT PROCEDURE
1. Place the output rectifier assembly on a
clean bench surface.
2. Using a slot head screw driver, remove the
two nylon screws holding the board to the
heat sink. Save the standoffs for reassem-
bly.
3. Using the 7/16” wrench, remove the two
bolts, lock washers and flat washers. Save
the standoffs for reassembly.
4. Using the 3/16” allen wrench, remove the
four screws and lock washers holding the
board to the heat sink.
5. Carefully remove the STT Chopper Board.
REPLACEMENT PROCEDURE
1. Position the new board on the heat sink,
using the standoffs for the slot head nylon
screws and the allen head screws.
2. Install the four 3/16” allen head screws and
lock washers.
3. Install the two nylon slot head screws.
4. Install the two 7/16” bolts, lock washers and
flat washers.

TROUBLESHOOTING & REPAIR
F-73 F-73
POWER WAVE 455/R
Return to Section TOC Return to Section TOC Return to Section TOC Return to Section TOC
Return to Master TOC Return to Master TOC Return to Master TOC Return to Master TOC
OUTPUT RECTIFIER, STT CHOPPER BOARD AND RECTIFIER MODULE
REMOVAL AND REPLACEMENT (CONTINUED)
RECTIFIER MODULE REMOVAL AND
REPLACEMENT PROCEDURE
1. Using the 9/64” allen wrench, remove the
cap screw from the center of the rectifier
module that is to be replaced.
2. Using the 7/16” wrench, remove the two
mounting bolts and associated washers
from the rectifier module to be replaced.
3. Remove the faulty module.
4. This module requires special mounting con-
siderations to prevent warping of the base
plate. The heat sink surfaces must be clean
and flat. Apply a thin, even coating of ther-
mal compound, (Penetrox A13) 0.004 to
0.010 inches thick. Keep the compound
away from the area of the mounting holes.
5. Press the new module firmly against the
heat sink while aligning the mounting holes.
Start all three screws two to three turns by
hand.
6. Tighten each of the outer screws to between
5 and 10 in-lbs.
7. Tighten the center screw to between 12 and
18 in-lbs.
8. Tighten each of the outer screws again, this
time to between 30 and 40 in/lbs.
RECTIFIER ASSEMBLY REPLACE-
MENT PROCEDURE
1. Position the assembly in place with the
mounting bolts.
2. Assemble the nuts and associated wash-
ers to the mounting bolts.
3. Using the 7/16” wrench, tighten the four
nuts on the mounting bolts.
4. Replace leads #292 and #291 to the ther-
mostat.
5. Connect plug J10 to the STT Chopper
Board.
6. With the 7/16” wrench, attach lead #287
from the STT Snubber Diode D5.
7. With the 7/16” wrench, attach lead #289B
from the STT Snubber Capacitor C10.
8. Connect the eight transformer leads to the
correct rectifier modules. Tighten the
screws (with two flat washers and one lock
washer) to between 30 and 40 in/lbs. Do
not stress the terminals when making
these connections.
9. Apply a thin coat of Penetrox A13 to the
heat sink where the Power Wave positive
output lead and the STT output lead attach.
10. Attach the Power Wave positive output
lead to the heat sink using the 9/16”
wrench.
11. Attach the STT output lead to the heat sink
using the 7/16” wrench.
12. Install the case top and sides using the 3/8”
nut driver.

TROUBLESHOOTING & REPAIR
F-74 F-74
POWER WAVE 455/R
SWITCH BOARD AND FILTER CAPACITOR
REMOVAL AND REPLACEMENT
WARNING
Service and repair should be performed by only Lincoln Electric factory trained personnel.
Unauthorized repairs performed on this equipment may result in danger to the technician
or machine operator and will invalidate your factory warranty. For your safety and to avoid
electrical shock, please observe all safety notes and precautions detailed throughout this
manual.
If for any reason you do not understand the test procedures or are unable to perform the
test/repairs safely, contact the Lincoln Electric Service Department for electrical trou-
bleshooting assistance before you proceed. Call 1-800-833-9353 (WELD).
TEST DESCRIPTION
This procedure will aid the technician in the removal and replacement of the switch
board(s) and/or filter capacitor(s).
MATERIALS NEEDED
3/8” Nut driver
7/16” Wrench
3/16” Allen wrench
Slot head screwdriver
Penetrox A13 thermal joint compound
This procedure should take approximately 25 minutes to perform.
Return to Section TOC Return to Section TOC Return to Section TOC Return to Section TOC
Return to Master TOC Return to Master TOC Return to Master TOC Return to Master TOC

TROUBLESHOOTING & REPAIR
F-75 F-75
POWER WAVE 455/R
Return to Section TOC Return to Section TOC Return to Section TOC Return to Section TOC
Return to Master TOC Return to Master TOC Return to Master TOC Return to Master TOC
13/14
OR
17/18
NYLON
SCREW
(2X)
19+
20-
11/12
OR
15/16
SWITCH
BOARD
MOLEX PLUG
MOUNTING
SCREW (4X)
FIGURE F.28 – SWITCH BOARD AND FILTER CAPACITOR REMOVAL AND REPLACEMENT
SWITCH BOARD AND FILTER CAPACITOR
REMOVAL AND REPLACEMENT (CONTINUED)
REMOVAL PROCEDURE
NOTE: Observe all static electricity precautions.
Lead and plug references below use a slash (/)
to indicate machine right side/left side wire
number differences.
1. Remove input power to the Power Wave
455/R.
2. Using the 3/8” nut driver, remove the case
top and sides.
3. Perform the Capacitor Discharge proce-
dure.
4. Using the 5/16” nut driver, remove the three
screws mounting the glastic high voltage
protective shield. Remove the shield.
5. Remove molex plug J40/J50 from the top of
the switch board. Refer to Figure F.28.
6. Remove the mylar insulating shield covering
leads 13/14 or 17/18. Cut the cable tie.

TROUBLESHOOTING & REPAIR
F-76 F-76
POWER WAVE 455/R
Return to Section TOC Return to Section TOC Return to Section TOC Return to Section TOC
Return to Master TOC Return to Master TOC Return to Master TOC Return to Master TOC
SWITCH BOARD AND FILTER CAPACITOR
REMOVAL AND REPLACEMENT (CONTINUED)
7. Using the 7/16” wrench, remove leads
13/14 or 17/18 from the switch board.
8. Using the 7/16” wrench, remove leads
11/12 or 15/16 from the switch board.
9. Using the 7/16” wrench, remove leads
19C/D+ and 20C/D- from the switch board
capacitor connection bolts.
10. With the slot head screwdriver, remove the
two nylon mounting screws at the bottom of
the switch board. Note placement of the
shake-proof washers and fiber spacers.
11. Using the 3/16” allen wrench, carefully
remove the four cap screws that mount the
switch board to the heat sink.
12. Carefully remove the switch board from the
heat sink.
13. If the filter capacitor is to be removed, care-
fully slide it out of the mounting bracket.
REPLACEMENT PROCEDURE
1. If the filter capacitor is to be replaced, care-
fully slide the new capacitor into the mount-
ing bracket. Position the capacitor so the
correct polarity terminal is lined up with the
correct hole on the switch board.
2. All heat sink and IGBT mounting surfaces
must be clean.
3. Apply a thin coat of thermal compound
(Penetrox A13) 0.005 to 0.010 inches thick
to the mating surfaces. Do not apply
around mounting holes.
4. Apply a thin coat of Penetrox A13 to the
capacitor terminals. Be careful not to apply
compound to screw threads or threaded
area of terminals.
5. Mount the new switch board and tighten
the four cap head screws in the following
manner.
Tighten all until snug.
Tighten all from 24 to 28 in-lbs.
Tighten all from 40 to 48 in-lbs.
6. Make sure the capacitor is positioned cor-
rectly. Connect leads 19C/D+ and 20C/D-
to the correct terminals. Tighten to 55
in/lbs.
7. Position and mount the two nylon screws,
fiber spacers, and washers. Torque from 4
to 8 in-lbs.
8. Connect leads 11/12 or 15/16 to the correct
terminal.
9. Connect leads 13/14 or 17/18 to the correct
terminal.
10. Install the mylar insulating shield covering
leads 11/12 or 15/16. Replace the cable
tie.
11. Connect molex plug J40/J50 to the top of
the switch board.
12. Using the 5/16” nut driver, install the glastic
high voltage protective shield.
13. Install the case top and sides using the 3/8”
nut driver.

Retest a machine:
If it is rejected under test for any reason that requires you to remove any part which could affect the machine’s
electrical characteristics.
OR
If you repair or replace any electrical components.
INPUT IDLE AMPS AND WATTS
MAXIMUM OUTPUT VOLTAGES
TROUBLESHOOTING & REPAIR
F-77 F-77
POWER WAVE 455/R
Return to Section TOC Return to Section TOC Return to Section TOC Return to Section TOC
Return to Master TOC Return to Master TOC Return to Master TOC Return to Master TOC
RETEST AFTER REPAIR
Input Volts/Hertz
208/60
230/60
400/60
460/60
575/60
Maximum Idle Amps
4.0
3.3
2.1
2.0
1.8
Maximum Idle KW
0.45
0.45
0.45
0.45
0.45
Input Volts/Hertz
208/60
230/60
400/60
460/60
575/60
50-70 VDC 48.5 - 55 VDC OCV
115 - 123 VAC
10 Amp Load
111 - 119 VAC
Output Terminals
- No load X1 - X2 115 Volt Receptacles

Section G-1 Section G-1
TABLE OF CONTENTS
- ELECTRICAL DIAGRAMS SECTION -
POWER WAVE 455/R
Return to Master TOC Return to Master TOC Return to Master TOC Return to Master TOC
Electrical Diagrams..............................................................................................................Section G
Wiring Diagram (Code 10675)....................................................................................................G-2
Wiring Diagram (Code 10676)....................................................................................................G-3
Schematic - Complete Machine (Code 10675) ..........................................................................G-4
Schematic - Complete Machine (Code 10676) ..........................................................................G-5
Schematic - Chopper PC Board .................................................................................................G-6
PC Board Assembly - Chopper PC Board..................................................................................G-7
Schematic - DeviceNet/Gateway PC Board ...............................................................................G-8
PC Board Assembly - DeviceNet/Gateway PC Board................................................................G-9
Schematic - Control PC Board .................................................................................................G-10
PC Board Assembly - Control PC Board ..................................................................................G-11
Schematic - Digital Power Supply PC Board............................................................................G-12
PC Board Assembly - Digital Power Supply PC Board ............................................................G-13
Schematic - FeedHead PC Board #1 .......................................................................................G-14
Schematic - FeedHead PC Board #2 .......................................................................................G-15
Schematic - FeedHead PC Board #3 .......................................................................................G-16
PC Board Assembly - FeedHead PC Board.............................................................................G-17
Schematic - Input PC Board .....................................................................................................G-18
PC Board Assembly - Input PC Board......................................................................................G-19
Schematic - Switch PC Board ..................................................................................................G-20
PC Board Assembly - Switch PC Board...................................................................................G-21
Schematic - Voltage Sense PC Board......................................................................................G-22
PC Board Assembly - Voltage Sense PC Board ......................................................................G-23
Schematic - 40 VDC Bus PC Board .........................................................................................G-24
PC Board Assembly - 40 VDC Bus PC Board..........................................................................G-25

ELECTRICAL DIAGRAMS G-2
POWER WAVE 455/R
WIRING DIAGRAM - POWER WAVE 455/R CODE 10675
-
TO J9
202
WORK
202A
TO R1
TO TP6
TO TP3 TO
CB1
S1
WIRE
FEEDER
RECEPTACLE
J47
+
ELECTRODE
223
221
206A
R3
C8
TO D5
289D
R2
2Ω
288C
288D
289E288E
TM
J1 4
5
TO
3R3R
3W
238
15
5
J10
TO
SSR
RECT
THERM
223
222
CHOPPER BD
SEC
(BOTTOM
LEFT)
POWER BD
RECTIFIER
AC
EMITTER
212
213
813
811
216
4
CONTROL BOARD
+
TO J61
CR1
X4
6
TO AUX #1
503
504
505
506
INPUT
20D
1718
STT SNUBBER
15 16
F1
F1
TO
CB1
J41
1
4R
J4
251
20
C
J47
TO
P90
P91
RECT
292
1
2
3
4
SEC
(TOP
LEFT)
6
U
TO SW1
L1A
V
L3
AC
3
TO
CR1
SW1
CB4
L3A
T2
L2
AC
2
H1D
T3
T1
T2
612
T3
NEG
1
2
3
4
+
4W
346
C3
AUX. #1
TO
4
3
D3
TO
CHOKE
THERM
D
CURRENT
TRANSDUCER
TO C8
19D
SWITCH BOARD
#2
289A
-
+
288B
TO C10
SW1
POWER
C10
289F
A
202
225
J7
2
5
J2
206
S1
TO
52
J5
ELECTRODE
CB2
AUX 2
TO
32
STT
WORK
TO
TP6
1
2
3
4
5
6
7
J3
4
5
6
3
2
4
1
8
7
6
5
4
3
2
1
289E
289D
289C
289B
288E
288D
288C
288B
289C
R4
289A
2Ω
TO C10
289B
NEG
STT
X1
+
8
G
601
TO J60
L1
NEG
20C
19C
T1
TO
INPUT RECT
REAR OF MACHINE
TO J6,J10B
6
TO SOLID STATE RELAY
3
2
TO SOLID STATE RELAY
444
FAN
THIS AREA VIEWED FROM
288F
RECONNECT
PANEL
TO
CR1
J6
231
AUX #1
J61 5
6
7
8
9
POS
D1
TO
MAIN
TRANSFORMER
H5
H4
H3
H1
50
TO
L2
CB1
10A CIRCUIT
BREAKER
R
1
TO
WORK
BUSS BD
TP3
TO R1
CB2
10A CIRCUIT
BREAKER
1B
TP2
206
TO J9
202A
TO
S4
31
AUX 2
TP5
33
WORK
206A
NEG
7
PRI
(BOTTOM
RIGHT)
TO
SWITCH
BD #2
15
14
12
18
TO
SWITCH
BD #1
TO
SWITCH
BD #2
MAIN
TRANSFORMER
LEFT SIDE
X2
NEG
1
POS
2
3
C3
J2
TO
J9
.05/600V
2W
403
288A
2
1
6
2B
511
604
14
7
9
8
1
12 16
7
10
8
CONNECTOR CAVITY NUMBERING SEQUENCE (VIEWED FROM COMPONENT SIDE OF BOARD)
11
6
561
H1A
TO AUX #2
612A
3
CB3
10A
BREAKER
TO SW1
200-208V
220-230V
380-415V
440-460V
POS
POS
AC
1
TO SUPPLY LINES
S2
VOLTAGE
SENSE
RECEPTACLE
TO A SYSTEM GROUND PER
NATIONAL ELECTRICAL CODE.
S3
RS232
CONNECTOR
FRONT OF MACHINE
115V
RECEPTACLE
TO RECONNECT PANEL
TO CB4
1
2
J74
12
J76
PRI
(BOTTOM
LEFT) 11 12
20C
++
TO AUX#1
404
405
406
21A
2
51
3
4
54
E
53
J9
15
14
J71
11
12
TO
J70
8
3
1
16
67A
TO C3
4
J46 3
2
1
POS
POS
DC BUS
BOARD
12
J41
ELECTRODE
C6
TO TP6
50Ω
C2
N.A.
.05/600V
STATUS LED (R/G)
TO J7
N.A.
THERMAL LED (Y)
TO J7
1W
TO
J4
J11
C4
13
14
+
SWITCH BOARD
#1
1
4
5
X3A
TO
INPUT RECT
POS
TO FAN
POWER WAVE 455 / R WIRING DIAGRAM
TO SW1
X1
224A
291
CB4
TO J61
CB3
612A
612
H1
TO AUX #1
AUXILIARY TRANSFORMER #1
SEC
(BOTTOM
RIGHT)
TO
SWITCH BD #2
19D
TO
SWITCH BD #1
11 12
20D
TO
SWITCH BD #2
TO RECONNECT SWITCH
H4
H5
CAPACITORS=MFD/VOLTS
RESISTORS=OHMS/WATTS
H1
(200-208)
H2
(220-230)
PRI
(TOP
LEFT)
R
(115V)
N
(24V)
X4
COLLECTOR
2
6
TO J61
H1D
(TOP)
LOAD LINE
TO CB3
612B
TO CONTACTOR
L3A
L1A
TO CONTACTOR
S4
TO
TO TP3
31
1
2
3
4
5
6
7
8
9
1
2
3
4
5
6
8
7
9
232
X3
604
238
601
INPUT BOARD
NEG
H3
H2
TO AUX #1
H2A
H3A
H1
H2
H3
812
813
287
811
816
F3
F3
++
F2
F2
19C
17
11
TO
SWITCH
BD #1
514
1
6
(440-460) H5A
3
(380-415)
AUXILIARY TRANSFORMER #2
NOTES:
N.A. PIN NEAREST THE FLAT EDGE OF LED LENS (CATHODE)
ALIGNS WITH BLACK LEAD OF LED SOCKET.
N.B. PLACE SWITCH IN APPROPRIATE POSITION FOR INPUT
OPERATION.
N.C. PLACE "A" LEAD ON APPROPRIATE CONNECTION FOR
OPERATION.
RIGHT SIDE OF MACHINE
1
J8
J9
228
226
1
224
220
504
503
406
505
4
506
2
3
211
2
3
816
7
8
21A
418
514
1
273
274
5
6
2
1
TO J6, J10B
RIGHT SIDE
13
512
4R
4
3
4W
2
1
VOLTAGE SENSE
SELECT
BOARD
TO
SWITCH BD #1
D4
J40
F4
403
F4
THERM
9
1
2
3
4
1
2
3
4
J72
J75
FEED HEAD
BOARD
11
J42
TO J5
6
5
4
3
2
+
225
1
SEC
(TOP
RIGHT)
15 16
2
3
5
J50
C5
J60
10
10
9
8
7
6
5
4
273
3
228
274
226
TO J8
4
TO
S3
1
2
J43
251
253
254
J1 9
13
7
DEVICE NET
GATEWAY
BOARD
14
8
6
5
4
1
3
2
NEG
DIGITAL POWER
SUPPLY BOARD
3R TO 3W
J7
MAIN CHOKE
L1
221
4
3
231
232
291
X3A
1
3
2
16
10
5
1
2
.05/600V
C1
TP1
TO C8
288A
345 287
TP7 RECTIFIER
SWITCH
RECONNECT
TO
16
414
H4
'A
'
LEFT SIDE OF MACHINE
RECONNECT SWITCH
H4A
6
5
1
9
8
7
6
5
4
1
9
8
7
6
TP4
444
TO FAN
TO
J47
475
477
1
2
476
216
478
211
3
213
212
4
5
6
4
4
W
11
W=WHITE
U=BLUE
R=RED
COMPONENT VALUES:
N=BROWN
REAR OF MACHINE
G=GREEN
B=BLACK
LEAD COLOR CODING
4
H3A
2
(200-208)
H4A
H2
(220-230) TO
H2A CB3
ELECTRICAL SYMBOLS PER E1537
H1A AUX #1
J10,J2VS
J74
21
3 4
TO SW1
X5
TO AUX#1
2
1
OUTPUT
RECT
D2
J6
5
6
253
7
2
254
8
39
4
13
B
11
A
10
L2
4
3
TO J46
1
2
3
4
POWER BD RECT
1
2
3
4
TO J1 VOLTAGE SENSE
WORK
ELECTRODE
J10A
J11
STT CURRENT
TRANSDUCER
812
TO
886
880
TO J8
X2 U
TO
J42
J43
TO POWER BD.
RECTIFIER
(51V)
(380-415)
X3 WH3
TO
X3
AUX #2
X5
RECONNECT PANEL
TO
MAIN TRANSFORMER
TO D5
34-
TO
J4 SOLID
STATE
RELAY
21
W
H5
(440-460) H5A
H4 H5
2Ω
10
10
15
14
11
12
13
16
10
11
12
10
14
15
11
12
13
16
10
2.7 10W
.022
800V
PRI
(TOP
RIGHT)
POS
POS
NEG
NEG
AC
J10CH
DIODE
.022
800V
2.7 10W
2.7 10W
.022
800V
N.C.
INPUT VOLTAGE. CONNECTION SHOWN IS FOR 440-460V
500
2
51
1
50
3
540
4
4755
4766
4777
4788
52
CONNECTOR
DEVICENET
5
1
4
2
3
CONNECTOR
12 PIN
3
4
2
1
5
6
ROBOTIC/
WIREDRIVE
INTERFACE
RECEPTACLE
CIRCUIT
CB4
6A
BREAKER
CIRCUIT
J83
D6
S2
J2
P90
P91
J82
N.B.
67
67A
1W
1B
892
892
1
2
851
852
853
854
855
856
154
153
222
891
TO
J75
7
8
9
10
857
858
859
860
3 CONDUCTOR
TWISTED/SHI ELDED
SHIELD GROUND TO CASE
L4
2B 2W
+40VDC
J85
TO
267
266
268
THERM
TO
J20
J40
J50
67
TO
J43
J88
S5
S6
S7
GND-A
GND-B
267
266
268A
893
894
67B S1
S6
227
227
J73
TO
S1
D6
TO
J11
J47
IFACE
ROBOT
TO
J2,J5,J11,
J41,J46,J72
J73,J76,J81
J82
J1VS,J9,J10CH,
J14,J40J42,
J50,J75,J83
J8,
J47,J60
J84
J3,
J61,J86
J4,J13,
J43,J71
J1,J6,J7
J10,J70,J85
J87
WATER
COOLER
RECEPTACLE
2
1
350
352
N
P
R
S
T
U
V
W
X
A
B
C
D
E
F
G
H
I
J
K
L
M
841
844
842
843
845
846
847
67B
539
541
521
522
GND-A
11
12
861
862
TO
P73
J2VS
CB1
J47
TO
S5
J81 741
743
4
3
2
1
J82 154
153
4
3
2
1
500
540
TO
J11
J47
TO
S6
846
845
844
843
842
841
J84
6
5
1
2
3
4
847
8
7
TO
S6
D6
880
886
522
521
541
539
J83
6
5
1
2
3
4
TO
S7
856
855
854
853
852
851
J85
6
5
1
2
3
4
857
8
7
511
512
862
861
860
859
9
15
12
16
14
13
11
10
858
6
5
1
2
3
4
8
7
9
10
J86
6
5
1
2
3
4
8
7
9
10
J87
11
12
13
14
15
16
H6
(550-575) H6A
H6
TO
CR1
J60
CHOKE
THERMTO RECT
THERM
TO
RECONNECT
SWITCH
H6 5
(550-575) H6A
P50
11-3-2000A
G3792
TO
J85
VOLTAGE. CONNECTION SHOWN IS FOR 380-460V
S8
STT SNUBBER
CAPACITOR BANK
STT SNUBBER
20uF
400V
20uF
400V
+24V
+24V GND
CAN_H
CAN_L
418
518
TO
J1VS
800
840
1
518
2
414
J10B
TO
SSR, J10 CHOPPER BD.
405
404
893
891
894
1
2
3
4
J73
53
54
TO
S1
TO
J81
743
741
800
840
RESISTOR BANK
DIODE D5
TO
J40,J50
612B
AC AC
TO
J72
346
345
830
R5
TO
262
268
268A
R5
220A
292
262
R5
W
R
4
1
(115V)
TO
S4
CB2
350
352
P52
4
32
33
1
2
33A
2(230V)
3
4
33A
224A
224
220
220A
TO
J4
J43
TO RECT
THERM
DC BUS
THERM
L5
TO
AUX #2
S1
TO
J83
J84
J2VS
100V
2400µF
500V
3500µF
500V
3500µF
G-2
NOTE: This diagram is for reference only. It may not be accurate for all machines covered by this manual. The wiring diagram specific to your code is pasted inside one of the enclosure panels of your machine.
Return to Section TOC Return to Section TOC Return to Section TOC Return to Section TOC
Return to Master TOC Return to Master TOC Return to Master TOC Return to Master TOC

ELECTRICAL DIAGRAMS G-3
POWER WAVE 455/R
WIRING DIAGRAM- POWER WAVE 455/R CODE 10676
-
TO J9
202
WORK
202A
TO R1
TO TP6
TO TP3 TO
CB1
S1
WIRE
FEEDER
RECEPTACLE
J47
+
ELECTRODE
223
221
206A
R3
C8
TO D5
289D
R2
2Ω
288C
288D
289E288E
TM
J1 4
5
TO
3R3R
3W
238
15
5
J10
TO
SSR
RECT
THERM
223
222
CHOPPER BD
SEC
(BOTTOM
LEFT)
POWER BD
RECTIFIER
AC
EMITTER
212
213
813
811
216
4
CONTROL BOARD
+
TO J61
CR1
X4
6
TO AUX #1
503
504
505
506
INPUT
20D
1718
STT SNUBBER
15 16
F1
F1
TO
CB1
J41
1
4R
J4
251
20
C
J47
TO
P90
P91
RECT
292
1
2
3
4
SEC
(TOP
LEFT)
6
U
TO SW1
L1A
V
L3
AC
3
TO
CR1
SW1
CB4
L3A
T2
L2
AC
2
H1D T3
T1
T2
612
T3
NEG
1
2
3
4
+
4W
346
C3
AUX. #1
TO
4
3
D3
TO
CHOKE
THERM
D
CURRENT
TRANSDUCER
TO C8
19D
SWITCH BOARD
#2
289A
-
+
288B
TO C10
SW1
POWER
C10
289F
A
202
225
J7
2
5
J2
206
S1
TO
52
J5
ELECTRODE
CB2
AUX 2
TO
32
STT
WORK
TO
TP6
1
2
3
4
5
6
7
J3
4
5
6
3
2
4
1
8
7
6
5
4
3
2
1
289E
289D
289C
289B
288E
288D
288C
288B
289C
R4
289A
2Ω
TO C10
289B
NEG
STT
X1
+
8
G
601
TO J60
L1
20
NEG
19C
T1
TO
HARMONIC
REAR OF MACHINE
TO J6,J10B
6
TO SOLID STATE RELAY
3
2
TO SOLID STATE RELAY
444
FAN
THIS AREA VIEWED FROM
288F
RECONNECT
PANEL
TO
CR1
J6
231
AUX #1
J61 5
6
7
8
9
POS
D1
TO
MAIN
TRANSFORMER
H5
H4
H3
H1
50
TO
L2
CB1
10A CIRCUIT
BREAKER
R
1
TO
WORK
BUSS BD
TP3
TO R1
CB2
10A CIRCUIT
BREAKER
1B
TP2
206
TO J9
202A
TO
S4
31
AUX 2
TP5
33
WORK
206A
NEG
7
PRI
(BOTTOM
RIGHT)
TO
SWITCH
BD #2
15
14
12
18
TO
SWITCH
BD #1
TO
SWITCH
BD #2
MAIN
TRANSFORMER
LEFT SIDE
X2
NEG
1
POS
2
3
C3
J2
TO
J9
.05/600V
2W
403
288A
2
1
6
2B
511
604
14
7
9
8
1
12 16
7
10
8
CONNECTOR CAVIT Y NUMBERING SEQUENCE (VIEWED FROM COMPONENT SIDE OF BOARD)
11
6
561
H1A
TO AUX #2
612A
3
CB3
10A
BREAKER
TO SW1
200-208V
220-230V
440-460V
550-575V
POS
POS
AC
1
TO SUPPLY LINES
S2
VOLTAGE
SENSE
RECEPTACLE
TO A SYSTEM GROUND PER
NATIONAL ELECTRICAL CODE.
S3
RS232
CONNECTOR
FRONT OF MACHINE
115V
RECEPTACLE
TO RECONNECT PANEL
TO CB4
1
2
J74
12
J76
PRI
(BOTTOM
LEFT) 11 12
20C
++
TO AUX#1
404
405
406
21A
2
51
3
4
54
E
53
J9
15
14
J71
11
12
TO
J70
8
3
1
16
67A
TO C3
4
J46 3
2
1
POS
POS
DC BUS
BOARD
12
J41
ELECTRODE
C6
TO TP6
50Ω
C2
N.A.
.05/600V
STATUS LED (R/G)
TO J7
N.A.
THERMAL LED (Y)
TO J7
1W
TO
J4
J11
C4
13
14
+
SWITCH BOARD
#1
1
4
5
X3A
TO
HARMONIC
19
TO FAN
POWER WAVE 455 / R WIRING DIAGRAM
TO SW1
X1
224A
291
CB4
TO J61
CB3
612A
612
H1
TO AUX #1
AUXILIARY TRANSFORMER #1
SEC
(BOTTOM
RIGHT)
TO
SWITCH BD #2
POS
TO
SWITCH BD #1
11 12
20D
TO
SWITCH BD #2
TO RECONNECT SWITCH
H5
H6
CAPACITORS=MFD/VOLTS
RESISTORS=OHMS/WATTS
H1
(200-208)
H2
(220-230)
PRI
(TOP
LEFT)
R
(115V)
N
(24V)
X4
COLLECTOR
2
6
TO J61
H1D
(TOP)
LOAD LINE
TO CB3
612B
TO CONTACTOR
L3A
L1A
TO CONTACTOR
S4
TO
TO TP3
31
1
2
3
4
5
6
7
8
9
1
2
3
4
5
6
8
7
9
232
X3
604
238
601
INPUT BOARD
NEG
H3
H2
TO AUX #1
H2A
H3A
H1
H2
H3
812
813
287
811
816
F3
F3
++
F2
F2
19C
17
11
TO
SWITCH
BD #1
514
1
6
(440-460) H5A
3
(380-415)
AUXILIARY TRANSFORMER #2
NOTES:
N.A. PIN NEAREST THE FLAT EDGE OF LED LENS (CATHODE)
ALIGNS WITH BLACK LEAD OF LED SOCKET.
N.B. PLACE SWITCH IN APPROPRIATE POSITION FOR INPUT
OPERATION.
N.C. PLACE "A" LEAD ON APPROPRIATE CONNECTION FOR
OPERATION.
RIGHT SIDE OF MACHINE
1
J8
J9
228
226
1
224
220
504
503
406
505
4
506
2
3
211
2
3
816
7
8
21A
418
514
1
273
274
5
6
2
1
TO J6, J10B
RIGHT SIDE
13
512
4R
4
3
4W
2
1
VOLTAGE SENSE
SELECT
BOARD
TO
SWITCH BD #1
D4
J40
F4
403
F4
THERM
9
1
2
3
4
1
2
3
4
J72
J75
FEED HEAD
BOARD
11
J42
TO J5
6
5
4
3
2
+
225
1
SEC
(TOP
RIGHT)
15 16
2
3
5
J50
C5
J60
10
10
9
8
7
6
5
4
273
3
228
274
226
TO J8
4
TO
S3
1
2
J43
251
253
254
J1 9
13
7
DEVICE NET
GATEWAY
BOARD
14
8
6
5
4
1
3
2
NEG
DIGITAL POWER
SUPPLY BOARD
3R TO 3W
J7
MAIN CHOKE
L1
221
4
3
231
232
291
X3A
1
3
2
16
10
5
1
2
.05/600V
C1
TP1
TO C8
288A
345 287
TP7 RECTIFIER
SWITCH
RECONNECT
TO
16
414
H4
'A
'
LEFT SIDE OF MACHINE
RECONNECT SWITCH
H4A
6
5
1
9
8
7
6
5
4
1
9
8
7
6
TP4
444
TO FAN
TO
J47
475
477
1
2
476
216
478
211
3
213
212
4
5
6
4
4
W
11
W=WHITE
U=BLUE
R=RED
COMPONENT VALUES:
N=BROWN
REAR OF MACHINE
G=GREEN
B=BLACK
LEAD COLOR CODING
4
H3A
2
(200-208)
H4A
H2
(220-230) TO
H2A CB3
ELECTRICAL SYMBOLS PER E1537
H1A AUX #1
J10,J2VS
J74
21
3 4
TO SW1
X5
TO AUX#1
2
1
OUTPUT
RECT
D2
J6
5
6
253
7
2
254
8
39
4
13
B
11
A
10
L2
4
3
TO J46
1
2
3
4
POWER BD RECT
1
2
3
4
TO J1 VOLTAGE SENSE
WORK
ELECTRODE
J10A
J11
STT CURRENT
TRANSDUCER
812
TO
886
880
TO J8
X2 U
TO
J42
J43
TO POWER BD.
RECTIFIER
(51V)
(380-415)
X3 WH3
TO
X3
AUX #2
X5
RECONNECT PANEL
TO
MAIN TRANSFORMER
TO D5
34-
TO
J4 SOLID
STATE
RELAY
21
W
H5
(440-460) H5A
H4 H5
2Ω
10
10
15
14
11
12
13
16
10
11
12
10
14
15
11
12
13
16
10
2.7 10W
.022
800V
PRI
(TOP
RIGHT)
POS
POS
NEG
NEG
AC
J10CH
DIODE
.022
800V
2.7 10W
2.7 10W
.022
800V
N.C.
INPUT VOLTAGE. CONNECTION SHOWN IS FOR 550-575V
500
2
51
1
50
3
540
4
4755
4766
4777
4788
52
CONNECTOR
DEVICENET
5
1
4
2
3
CONNECTOR
12 PIN
3
4
2
1
5
6
ROBOTIC/
WIREDRIVE
INTERFACE
RECEPTACLE
CIRCUIT
CB4
6A
BREAKER
CIRCUIT
J83
D6
S2
J2
P90
P91
J82
N.B.
67
67A
1W
1B
892
892
1
2
851
852
853
854
855
856
154
153
222
891
TO
J75
7
8
9
10
857
858
859
860
3 CONDUCTOR
TWISTED/SHIELDED
SHIELD GROUND TO CASE
L4
2B 2W
+40VDC
J85
TO
267
266
268
THERM
TO
J20
J40
J50
67
TO
J43
J88
S5
S6
S7
GND-A
GND-B
267
266
268A
893
894
67B S1
S6
227
227
J73
TO
S1
D6
TO
J11
J47
IFACE
ROBOT
TO
J2,J5,J11,
J41,J46,J72
J73,J76,J81
J82
J1VS,J9,J10CH,
J14,J40J42,
J50,J75,J83
J8,
J47,J60
J84
J3,
J61,J86
J4,J13,
J43,J71
J1,J6,J7
J10,J70,J85
J87
WATER
COOLER
RECEPTACLE
2
1
350
352
N
P
R
S
T
U
V
W
X
A
B
C
D
E
F
G
H
I
J
K
L
M
841
844
842
843
845
846
847
67B
539
541
521
522
GND-A
11
12
861
862
TO
P73
J2VS
CB1
J47
TO
S5
J81 741
743
4
3
2
1
J82 154
153
4
3
2
1
500
540
TO
J11
J47
TO
S6
846
845
844
843
842
841
J84
6
5
1
2
3
4
847
8
7
TO
S6
D6
880
886
522
521
541
539
J83
6
5
1
2
3
4
TO
S7
856
855
854
853
852
851
J85
6
5
1
2
3
4
857
8
7
511
512
862
861
860
859
9
15
12
16
14
13
11
10
858
6
5
1
2
3
4
8
7
9
10
J86
6
5
1
2
3
4
8
7
9
10
J87
11
12
13
14
15
16
H6
(550-575) H6A
H6
TO
CR1
J60
CHOKE
THERMTO RECT
THERM
TO
RECONNECT
SWITCH
H6 5
(550-575) H6A
P50
5-11-2001F
G4010
TO
J85
VOLTAGE. CONNECTION SHOWN IS FOR 440-575V
S8
STT SNUBBER
CAPACITOR BANK
STT SNUBBER
20uF
400V
20uF
400V
+24V
+24V GND
CAN_H
CAN_L
418
518
TO
J1VS
800
840
1
518
2
414
J10B
TO
SSR, J10 CHOPPER BD.
405
404
893
891
894
1
2
3
4
J73
53
54
TO
S1
TO
J81
743
741
800
840
RESISTOR BANK
DIODE D5
TO
J40,J50
612B
AC AC
TO
J72
346
345
830
R5
TO
262
268
268A
R5
220A
292
262
R5
W
R
4
1
(115V)
TO
S4
CB2
350
352
P52
4
32
33
1
2
33A
2(230V)
3
4
33A
224A
224
220
220A
TO
J4
J43
TO RECT
THERM
DC BUS
THERM
L5
TO
AUX #2
S1
TO
J83
J84
J2VS
100V
2400µF
500V
3500µF
500V
3500µF
19
20 HARMONIC
FILTER
FILTER
FILTER
20C 19D
G-3
NOTE: This diagram is for reference only. It may not be accurate for all machines covered by this manual. The wiring diagram specific to your code is pasted inside one of the enclosure panels of your machine.
Return to Section TOC Return to Section TOC Return to Section TOC Return to Section TOC
Return to Master TOC Return to Master TOC Return to Master TOC Return to Master TOC

Return to Section TOC Return to Section TOC Return to Section TOC Return to Section TOC
Return to Master TOC Return to Master TOC Return to Master TOC Return to Master TOC
ELECTRICAL DIAGRAMS G-4
POWER WAVE 455/R
SCHEMATIC - COMPLETE MACHINE 10675
MANUFACTURING TOLERANCE PER E2056
UNLESS OTHERWISE SPECIFIED TOLERANCE
SCALE:
DO NOT SCALE THIS DRAWING
ON 3 PLACE DECIMALS IS ± .002
THIS SHEET CONTAINS PROPRIETARY INFORMATION OWNED BY THE LINCOLN ELECTRIC COMPANY AND IS NOT TO BE REPRODUCED, DISCLOSED OR USED WITHOUT THE EXPRESS WRITTEN PERMISSION OF THE LINCOLN ELECTRIC COMPANY, CLEVELAND, OHIO U.S.A.
DESIGN INFORMATION
t
DRAWN BY:
WITH PUBLISHED STANDARDS.
DATE:
ON 2 PLACE DECIMALS IS ±.02
MATERIAL TOLERANCE (" ") TO AGREE
ON ALL ANGLES IS ± .5 OF A DEGREE
SUBJECT:
ENGINEER:
EQUIPMENT TYPE:
DRAWING No.:
KJ
KJ
INVERTER WELDERS
PW455/R MACHINE SCHEMATIC
G
NONE 7/11/00
REFERENCE:
SUPERSEDING:
G3450
APPROVED: 3791
Chg. Sheet No."X" INFO.
XB
11-3-2000A
A
B
FAN CONTROL (-)
IGBT DRIVE (-)
-15V
RS232 +5V
TP4
RS232 COMMON
3J40
403
MAIN TRANSFORMER T1
+
404 4J40
405 5J40
6J40
406
+
418
H3
H4
H3A
H2
H5
H2A
H6
NEG
C3
TRANSFORMER T2
X2
POS
X5
H2A
H3A
H4A
H5A
24000uF/100V
213
212
812
4R
813
ARCLINK -
811
A
ARCLINK +
1W
1B
RED/GREEN
STATUS
LED
53
54
67A
B
+13V
WORK VOLTAGE SENSE
THERMAL LED
S2 VOLTAGE SENSE
RECEPTACLE
THERMAL LED 2B
2W
ARCLINK +
216
292
816
4W
1J90
2J90
3J90
4J90
+15V
-15V
I OUT
202
506
GND
CURRENT FEEDBACK
IGBT DRIVE (+)
-
TRANSDUCER
816
811
813
812
CURRENT
C5
(CAP "B")
3500uF
500V
H3
(550-575)
H1
5
H2
612A
H4
(200-208)
H1
232
CR1
X4
612
L1
U
L3A
OFF
H1D
A
SW1
612B
L1A
ON
V
POWER
G
(220-230)
612
4
1
F
S
F
14
15
16
13
CB4
6A
7J7
3J7
4J7
DCBUS
THERMOSTAT
CHOKE
THERMOSTAT
2J60
D5
5J60
10J61
8J61
2J61
4J60
3J60
8J60
1J46
2J46
3J46
4J46
FAN
10J6
1J9
3J9
6J8
1J8
3J8
2J8
1J10B
13J7
5J6
14J6
14J7
P90
8J8
7J8
5J8
4J8
R1
CONTROL BOARD
0V
24V
H5
(440-460)
(380-415)
POS
ELECTRICAL SYMBOLS PER E1537
15J6
2J5
3J5
15J7
16J7
9J6
12J6
1J6
2J6
12J4
8J4
10J4
11J4
4J11
5J4
10J43
5J47
7J47
6J47
8J47
5J43
9J43
6J4
4J43
1J47
3J11
3J47
65VDC
X4
}
10A
CONTROL BOARD COMMON
+5V ARCLINK +5V
ARCLINK COMMON
6J10
ELECTRODE
SWITCH BOARD #1 (LEFT)
INPUT
RECTIFIER
RECONNECT
SWITCH
3R
475
+
477
3W
476
478
274
273
DC BUS BD
NEG
NEG
226
POS
POS
SOLID STATE RELAY
3J10
+
STT
PRECHARGE RELAY
T2
+13V
T1
T3
+13V
SINGLE PHASE DETECT
(LOW=1 PHASE)
MAIN CONTACTOR CONTROL
+13V
INPUT BOARD
6J61
X3
612B
4
4J61
1J60
33
S4
110V
RECEPTACLE
32
.05uF
-
320V
80J
TRANSDUCER
CURRENT
202A
TP3
206A
+15V
I OUT
MAIN
CHOKE
L1
+
ELECTRODE
-15V
GND
150V
P91
OUTPUT DIODES
D1-D4
212
601
CR1
T3
T2
T1
L3
POS
L2
W
AC1 NEG
AC2 NEG
AC3
604
238
231
STT CHOPPER DRIVE (-)
STT CHOPPER DRIVE (+)
-15V
+
10W
+
150V
R3
R2
C8
4J91
213
216
3J91
211
2J91
1J91
80J
YELLOW
THERMAL
LED
253
254
S3 RS232
CONNECTOR
251
RS232 TRANSMIT
E
D
RS232 COMMON
0VDC
21A
+40VDC
THERMOSTAT
H4A
H5A
H6A
P80
X1
50
10A
+40VDC POWER
444
X3A
NEG
SWITCH BOARD #2 (RIGHT)
NOTES :
N.A. PC BOARD COMPONENTS SHOWN FOR
REFERENCE ONLY. ALL COMPONENTS
ARE NOT SHOWN.
N.C. R2, R3 AND R4 ARE 2 /300.
C8 AND C10 ARE 20 mfd/400V.
51
228
31
+15
50
CONTROL BOARD COMMON
- ELECTRODE VOLTAGE SENSE
+ELECTRODE VOLTAGE SENSE
2J40
C4
(CAP "A")
3500uF
500V
2
3
4
5
6
7
1
4
2
3
20
3J2
4J2
1J2
6J9
8J7
L5
ELECTRODE SENSE
S1 WIRE FEEDER
RECEPTACLE
ARCLINK -
STATUS LED (HI FOR RED)
52
C
51
L2
L4
+5V
+15V
232
STATUS LED (HI FOR GREEN)
231
604
238
3W
3R
MAIN CONTACTOR CONTROL
220
224
PRECHARGE CONTROL
403
505
514
504
RS232 RECEIVE
FAN CONTROL (+)
(NORMALLY CLOSED)
THERMOSTAT
211
4R
206
COMMON
4W
17
12
F
F
SCHOPPER BOARD
11
D
S
15
16 S
18
C
(380-415)
3
(440-460)
2
(220-230)
52V
6
115V
X3
H2
H4
H3
H5
A200-208V
220-230V
380-415V
440-460V
AUX. RECONNECT
19C
19D
20C
20D
380-460V 208-230V
.022u
800V
.022u
800V
.022u
800V
.022u
800V
2.7
2.7
2.7
2.7
10W
10W
10W
CONTROL BOARD COMMON
STT FEEDBACK
-15V
+15V
414 1J40
AUXILIARY
TRANSFORMER T1
H6A (550-575)
H6
H1
H1A 1
10A
CB3 (200-208)
2
X3
1J42
3J42
5J42
2J42
225
221
222
223
1J41
2J41
3J41
4J41
POWER BOARD
52
352A
32
33A
352
350
2
3
4
1
S8 WATER COOLER
RECEPTACLE
TP6
R4
C10
TP2C2
600V 160J
320V
TP1
160J
.05uF
C1
600V
320V
TP5
160J
.05uF
C6
600V
2J10B
518
220A
OUTPUT RECTIFIER
THERMOSTAT
291
224A
FEED HD BD
GATEWAY BD
4J81
3J81
4J82
3J82
2J81
1J81
1J85
851
2J85
852
3J85
853
4J85
854
5J85
855
6J85
856
7J85
857
8J85
858
9J85
859
10J85
860
11J85
861
12J85
862
7J4
4J42 227
1J84
841
2J84
842
3J84
843
4J84
844
5J84
845
6J84
846
7J84
847
RECEPTACLE
841
A
B
C
D
E
F
G
I
J
K
N
P
T
S7 I/O
RECEPTACLE
851
1
2
3
4
5
6
7
8
9
10
11
12
INTERFACE
S6 ROBOTIC
844
842
843
845
846
847
67B
539
541
521
522
GND-A
852
853
854
855
856
857
858
859
860
861
862
TACH 1A DIFF SIGNAL
TACH 1B DIFF SIGNAL
TACH 2A DIFF SIGNAL
TACH 2B DIFF SIGNAL
SINGLE TACH INPUT
VOLTAGE SENSE
MOTOR "+"
MOTOR "-"
SOLENOID +40VDC
SOLENOID INPUT
TACH COMMON
TACH +15VDC
TRIGGER +15VDC
TRIGGER INPUT
DUAL PROC. INPUT
4 STEP INPUT
COLD INCH +15VDC
COLD IN. FORWARD
COLD IN. REVERSE
GAS PURGE INPUT
SHUTDOWN +15VDC
SHUTDOWN 1 INPUT
SHUTDOWN 2 INPUT
INPUT B
TRIGGER +15VDC
TRIGGER INPUT
DUAL PROC. INPUT
4 STEP INPUT
COLD INCH +15VDC
COLD IN. FORWARD
COLD IN. REVERSE
GAS PURGE INPUT
SHUTDOWN +15VDC
SHUTDOWN 1 INPUT
SHUTDOWN 2 INPUT
INPUT B
POWER BD. RECT.
COMMON
+40VDC FEEDER
COMMON
+40VDC POWER
COMMON
COMMON
+15VDC TACH
TACH 1A DIFF. INPUT
TACH 1B DIFF. INPUT
TACH COMMON
TACH 2A DIFF. INPUT
TACH 2B DIFF. INPUT
SINGLE TACH INPUT
CB2
33
2J83
1J83
4J83
3J83
541
539
522
521 SOLENOID +40VDC
SOLENOID INPUT
MOTOR "+"
MOTOR "-"
POWER DOWN INTERUPT
+15V
+5V
CONTROL BOARD COMMON
-15V
ARCLINK +5V
ARCLINK COMMON
RS232 +5V
RS232 COMMON
1J43 STT COMMON
346
7J43
345 STT +20V
POWER DOWN INTERUPT
+24VDC
2
+24V GND
894
3
5CAN_L
CAN_H
S5 DEVICENET
CONNECTOR
4
893
892
891
3J50
503
504 4J50
505 5J50
6J50
506
518 2J50
514 1J50
511
512
741
743
800
840
500
540
ARCLINK H
ARCLINK L
COMMON
+40VDC
2J72
1J72
3J72
4J72
ARCLINK H
ARCLINK L
5J75
2J75
1J75
4J75
IGBT DRIVE (+)503 6J6
16J6
404
8J6
405
7J6
406
1J10A
414
418
IGBT DRIVE (-)
2J10A
N.A.
N.A.
N.A.
CB1
1J73
2J73
53
894
893
892
891
+24VDC
+24V GND
CAN_L
CAN_H
N.A.
N.A.
N.A.
N.C.
115V
230V
0V
1J76
3J76
830
54
346
345 1J10
4J10
D6
880
886
6J83
5J83
+40VDC 880
886
+40VDC
VOLT SENSE BD
N.A.
14J85
13J85
1J1
3J1
1J2
4J1 511
N.A.
2J47
4J47
500
540 +40VDC POWER
512
67
67A
4J9
67
2J2
67B
R5
10
3J4
268
12J43
262
3J43
268A
268A
262
N.C.
ROBOTIC VOLTAGE SENSE
VOLTAGE SENSE SELECT (-)
VOLTAGE SENSE OUTPUT
WIRE FEEDER VOLTAGE SENSE
VOLTAGE SENSE SELECT (+)
COMMON
+40VDC
VOLTAGE SENSE SELECT (-)
VOLTAGE SENSE SELECT (+)
CT CURRENT (-)
CT CURRENT (+)
IGBT DRIVE (+)
V/F (+)
V/F (-)
IGBT DRIVE (-)
CT CURRENT (-)
CT CURRENT (+)
IGBT DRIVE (+)
V/F (+)
V/F (-)
IGBT DRIVE (-)
+20V STT
COMMON
+40VDC
CT CURRENT (-)
CT CURRENT (+)
V/F (+)
V/F (-)
V/F (+)
V/F (-)
CT CURRENT (-)
CT CURRENT (+)
SPI COMMON
SPI +5V
+40V
+40V
+40V COMMON
+40V COMMON
SINGLE PHASE DETECT
(LOW=1 PHASE)
+5V SPI
VOLTAGE SENSE
1J4
11J43 267 SPI COMMON
2J4
6J43 266 +15V SPI
+15V SPI
SPI COMMON
N.A.
154
ARC LINK L
1J11
2J11
ARC LINK H
153
2J82
1J82
ARCLINK H 154
153
ARCLINK L
G-4
NOTE: This diagram is for reference only. It may not be accurate for all machines covered by this manual.

ELECTRICAL DIAGRAMS G-5
POWER WAVE 455/R
SCHEMATIC-COMPLETE MACHINE CODE 10676
MANUFACTURING TOLERANCE PER E2056
UNLESS OTHERWISE SPECIFIED TOLERANCE
SCALE:
DO NOT SCALE THIS DRAWING
ON 3 PLACE DECIMALS IS ± .002
THIS SHEET CONTAINS PROPRIETARY INFORMATION OWNED BY THE LINCOLN ELECTRIC COMPANY AND IS NOT TO BE REPRODUCED, DISCLOSED OR USED WITHOUT THE EXPRESS WRITTEN PERMISSION OF THE LINCOLN ELECTRIC COMPANY, CLEVELAND, OHIO U.S.A.
DESIGN INFORMATION
t
DRAWN BY:
WITH PUBLISHED STANDARDS.
DATE:
ON 2 PLACE DECIMALS IS ±.02
MATERIAL TOLERANCE (" ") TO AGREE
ON ALL ANGLES IS ± .5 OF A DEGREE
SUBJECT:
ENGINEER:
EQUIPMENT TYPE:
DRAWING No.:
TR
LW
INVERTER WELDERS
PW455/R MACHINE SCHEMATIC
G
NONE 9/11/00
REFERENCE:
SUPERSEDING:
G3791
APPROVED: 4009
Chg. Sheet No."X" INFO.
XB-S 5-11-2001F
A
B
FAN CONTROL (-)
IGBT DRIVE (-)
-15V
RS232 +5V
TP4
RS232 COMMON
3J40
403
MAIN TRANSFORMER T1
+
404 4J40
405 5J40
6J40
406
+
418
H3
H4
H3A
H2
H5
H2A
H6
NEG
C3
TRANSFORMER T2
X2
POS
X5
H2A
H3A
H4A
H5A
24000uF/100V
213
212
812
4R
813
ARCLINK -
811
A
ARCLINK +
1W
1B
RED/GREEN
STATUS
LED
53
54
67A
B
+13V
WORK VOLTAGE SENSE
THERMAL LED
S2 VOLTAGE SENSE
RECEPTACLE
THERMAL LED 2B
2W
ARCLINK +
216
292
816
4W
1J90
2J90
3J90
4J90
+15V
-15V
I OUT
202
506
GND
CURRENT FEEDBACK
IGBT DRIVE (+)
-
TRANSDUCER
816
811
813
812
CURRENT
C5
(CAP "B")
3500uF
500V
H3
(550-575)
H1
5
H2
612A
H4
(200-208)
H1
232
CR1
X4
612
L1
U
L3A
OFF
H1D
A
SW1
612B
L1A
ON
V
POWER
G
(220-230)
612
4
1
F
S
F
14
15
16
13
CB4
6A
7J7
3J7
4J7
DCBUS
THERMOSTAT
CHOKE
THERMOSTAT
2J60
D5
5J60
10J61
8J61
2J61
4J60
3J60
8J60
1J46
2J46
3J46
4J46
FAN
10J6
1J9
3J9
6J8
1J8
3J8
2J8
1J10B
13J7
5J6
14J6
14J7
P90
8J8
7J8
5J8
4J8
R1
CONTROL BOARD
0V
24V
H5
(440-460)
(380-415)
ELECTRICAL SYMBOLS PER E1537
15J6
2J5
3J5
15J7
16J7
9J6
12J6
1J6
2J6
12J4
8J4
10J4
11J4
4J11
5J4
10J43
5J47
7J47
6J47
8J47
5J43
9J43
6J4
4J43
1J47
3J11
3J47
65VDC
X4
}
10A
CONTROL BOARD COMMON
+5V ARCLINK +5V
ARCLINK COMMON
6J10
ELECTRODE
SWITCH BOARD #1 (LEFT)
INPUT
RECTIFIER
RECONNECT
SWITCH
3R
475
+
477
3W
476
478
274
273
DC BUS BD
NEG
NEG
226
POS
POS
SOLID STATE RELAY
3J10
+
STT
PRECHARGE RELAY
T2
+13V
T1
T3
+13V
SINGLE PHASE DETECT
(LOW=1 PHASE)
MAIN CONTACTOR CONTROL
+13V
INPUT BOARD
6J61
X3
612B
4
4J61
1J60
33
S4
110V
RECEPTACLE
32
.05uF
-
320V
80J
TRANSDUCER
CURRENT
202A
TP3
206A
+15V
I OUT
MAIN
CHOKE
L1
+
ELECTRODE
-15V
GND
150V
P91
OUTPUT DIODES
D1-D4
212
601
CR1
T3
T2
T1
L3
POS
L2
W
AC1 NEG
AC2 NEG
AC3
604
238
231
STT CHOPPER DRIVE (-)
STT CHOPPER DRIVE (+)
-15V
+
10W
+
150V
R3
R2
C8
4J91
213
216
3J91
211
2J91
1J91
80J
YELLOW
THERMAL
LED
253
254
S3 RS232
CONNECTOR
251
RS232 TRANSMIT
E
D
RS232 COMMON
0VDC
21A
+40VDC
THERMOSTAT
H4A
H5A
H6A
P80
X1
50
10A
+40VDC POWER
444
X3A
SWITCH BOARD #2 (RIGHT)
NOTES :
N.A. PC BOARD COMPONENTS SHOWN FOR
REFERENCE ONLY. ALL COMPONENTS
ARE NOT SHOWN.
N.C. R2, R3 AND R4 ARE 2 /300.
C8 AND C10 ARE 20 mfd/400V.
51
228
31
+15
50
CONTROL BOARD COMMON
- ELECTRODE VOLTAGE SENSE
+ELECTRODE VOLTAGE SENSE
2J40
C4
(CAP "A")
3500uF
500V
2
3
4
5
6
7
1
4
2
3
20
3J2
4J2
1J2
6J9
8J7
L5
ELECTRODE SENSE
S1 WIRE FEEDER
RECEPTACLE
ARCLINK -
STATUS LED (HI FOR RED)
52
C
51
L2
L4
+5V
+15V
232
STATUS LED (HI FOR GREEN)
231
604
238
3W
3R
MAIN CONTACTOR CONTROL
220
224
PRECHARGE CONTROL
403
505
514
504
RS232 RECEIVE
FAN CONTROL (+)
(NORMALLY CLOSED)
THERMOSTAT
211
4R
206
COMMON
4W
17
12
F
F
SCHOPPER BOARD
11
D
S
15
16 S
18
C
(380-415)
3
(440-460)
2
(220-230)
52V
6
115V
X3
H2
H5
H3
H6
A200-208V
220-230V
440-460V
550-575V
AUX. RECONNECT
19C
19D
20C
20D
380-460V 208-230V
.022u
800V
.022u
800V
.022u
800V
.022u
800V
2.7
2.7
2.7
2.7
10W
10W
10W
CONTROL BOARD COMMON
STT FEEDBACK
-15V
+15V
414 1J40
AUXILIARY
TRANSFORMER T1
H6A (550-575)
H6
H1
H1A 1
10A
CB3 (200-208)
2
X3
1J42
3J42
5J42
2J42
225
221
222
223
1J41
2J41
3J41
4J41
POWER BOARD
52
352A
32
33A
352
350
2
3
4
1
S8 WATER COOLER
RECEPTACLE
TP6
R4
C10
TP2C2
600V 160J
320V
TP1
160J
.05uF
C1
600V
320V
TP5
160J
.05uF
C6
600V
2J10B
518
220A
OUTPUT RECTIFIER
THERMOSTAT
291
224A
FEED HD BD
GATEWAY BD
4J81
3J81
4J82
3J82
2J81
1J81
1J85
851
2J85
852
3J85
853
4J85
854
5J85
855
6J85
856
7J85
857
8J85
858
9J85
859
10J85
860
11J85
861
12J85
862
7J4
4J42 227
1J84
841
2J84
842
3J84
843
4J84
844
5J84
845
6J84
846
7J84
847
RECEPTACLE
841
A
B
C
D
E
F
G
I
J
K
N
P
T
S7 I/O
RECEPTACLE
851
1
2
3
4
5
6
7
8
9
10
11
12
INTERFACE
S6 ROBOTIC
844
842
843
845
846
847
67B
539
541
521
522
GND-A
852
853
854
855
856
857
858
859
860
861
862
TACH 1A DIFF SIGNAL
TACH 1B DIFF SIGNAL
TACH 2A DIFF SIGNAL
TACH 2B DIFF SIGNAL
SINGLE TACH INPUT
VOLTAGE SENSE
MOTOR "+"
MOTOR "-"
SOLENOID +40VDC
SOLENOID INPUT
TACH COMMON
TACH +15VDC
TRIGGER +15VDC
TRIGGER INPUT
DUAL PROC. INPUT
4 STEP INPUT
COLD INCH +15VDC
COLD IN. FORWARD
COLD IN. REVERSE
GAS PURGE INPUT
SHUTDOWN +15VDC
SHUTDOWN 1 INPUT
SHUTDOWN 2 INPUT
INPUT B
TRIGGER +15VDC
TRIGGER INPUT
DUAL PROC. INPUT
4 STEP INPUT
COLD INCH +15VDC
COLD IN. FORWARD
COLD IN. REVERSE
GAS PURGE INPUT
SHUTDOWN +15VDC
SHUTDOWN 1 INPUT
SHUTDOWN 2 INPUT
INPUT B
POWER BD. RECT.
COMMON
+40VDC FEEDER
COMMON
+40VDC POWER
COMMON
COMMON
+15VDC TACH
TACH 1A DIFF. INPUT
TACH 1B DIFF. INPUT
TACH COMMON
TACH 2A DIFF. INPUT
TACH 2B DIFF. INPUT
SINGLE TACH INPUT
CB2
33
2J83
1J83
4J83
3J83
541
539
522
521 SOLENOID +40VDC
SOLENOID INPUT
MOTOR "+"
MOTOR "-"
POWER DOWN INTERUPT
+15V
+5V
CONTROL BOARD COMMON
-15V
ARCLINK +5V
ARCLINK COMMON
RS232 +5V
RS232 COMMON
1J43 STT COMMON
346
7J43
345 STT +20V
POWER DOWN INTERUPT
+24VDC
2
+24V GND
894
3
5CAN_L
CAN_H
S5 DEVICENET
CONNECTOR
4
893
892
891
3J50
503
504 4J50
505 5J50
6J50
506
518 2J50
514 1J50
511
512
741
743
800
840
500
540
ARCLINK H
ARCLINK L
COMMON
+40VDC
2J72
1J72
3J72
4J72
ARCLINK H
ARCLINK L
5J75
2J75
1J75
4J75
IGBT DRIVE (+)503 6J6
16J6
404
8J6
405
7J6
406
1J10A
414
418
IGBT DRIVE (-)
2J10A
N.A.
N.A.
N.A.
CB1
1J73
2J73
53
894
893
892
891
+24VDC
+24V GND
CAN_L
CAN_H
N.A.
N.A.
N.A.
N.C.
115V
230V
0V
1J76
3J76
830
54
346
345 1J10
4J10
D6
880
886
6J83
5J83
+40VDC 880
886
+40VDC
VOLT SENSE BD
N.A.
14J85
13J85
1J1
3J1
1J2
4J1 511
N.A.
2J47
4J47
500
540 +40VDC POWER
512
67
67A
4J9
67
2J2
67B
R5
10
3J4
268
12J43
262
3J43
268A
268A
262
N.C.
ROBOTIC VOLTAGE SENSE
VOLTAGE SENSE SELECT (-)
VOLTAGE SENSE OUTPUT
WIRE FEEDER VOLTAGE SENSE
VOLTAGE SENSE SELECT (+)
COMMON
+40VDC
VOLTAGE SENSE SELECT (-)
VOLTAGE SENSE SELECT (+)
CT CURRENT (-)
CT CURRENT (+)
IGBT DRIVE (+)
V/F (+)
V/F (-)
IGBT DRIVE (-)
CT CURRENT (-)
CT CURRENT (+)
IGBT DRIVE (+)
V/F (+)
V/F (-)
IGBT DRIVE (-)
+20V STT
COMMON
+40VDC
CT CURRENT (-)
CT CURRENT (+)
V/F (+)
V/F (-)
V/F (+)
V/F (-)
CT CURRENT (-)
CT CURRENT (+)
SPI COMMON
SPI +5V
+40V
+40V
+40V COMMON
+40V COMMON
SINGLE PHASE DETECT
(LOW=1 PHASE)
+5V SPI
VOLTAGE SENSE
1J4
11J43 267 SPI COMMON
2J4
6J43 266 +15V SPI
+15V SPI
SPI COMMON
N.A.
154
ARC LINK L
1J11
2J11
ARC LINK H
153
2J82
1J82
ARCLINK H 154
153
ARCLINK L
POS
NEG
HARMONIC
FILTER
19
20
G-5
NOTE: This diagram is for reference only. It may not be accurate for all machines covered by this manual.
Return to Section TOC Return to Section TOC Return to Section TOC Return to Section TOC
Return to Master TOC Return to Master TOC Return to Master TOC Return to Master TOC

Return to Section TOC Return to Section TOC Return to Section TOC Return to Section TOC
Return to Master TOC Return to Master TOC Return to Master TOC Return to Master TOC
ELECTRICAL DIAGRAMS G-6
POWER WAVE 455/R
SCHEMATIC - CHOPPER PC BOARD
100V
100p
C15
X3
9
8
10
100V
100p
C16
475
R6
D7
50V
820p
C17
301
R19
301
R17
4.75K
R23
301
R21
301
R18
301
R22
301
R20
54
8
1
OUT
OUT
GNDGND
IN
VS
VS
NC
X2
MIC4451BN
6
27
3
1.0A
30V
D5
1.0A
30V
D6
4.75K
R8
301
R14
1W
15V
DZ1
301
R11
301
R10
301
R15
301
R13
301
R16
G4
com
3.32K
R27
301
R12
50V
820p
C12
3.32K
R4
X3
1
2
3
14 to 22 Vac
J10
3
50V
0.1
C3
50
25V
C2
332
R2
50V
.0047
C11
J10
6
D4
D2
3.32K
R3
CNY17-3
OCI1
42
1
6
5
221K
R25
11340
PWM
50V
150p
C22
L
INPUT
J10
5
D3
D1
J10
4
J10
1
+
t
.24
R1
J10
2
500
50V
C1
GND
IN
OUT
X4
+15
com
+15
50V
.0047
C14
com
RST
/Q
T2
QA
B
T1
X1
1
3
4
2
6
57
630Vdc
.47
C18
com
630Vdc
.47
C19
RST
/Q
T2
QA
B
T1
X1
15
13
12
14
10
11
9
+15
THE LINCOLN ELECTRIC CO.
Ch'ge.Sht.No.
ON ALL ANGLES IS + .5 OF A DEGREE
N.A. SINCE COMPONENTS OR CIRCUITRY ON A PRINTED CIRCUIT BOARD MAY CHANGE
ON 3 PLACE DECIMALS IS + .OO2
THIS SHEET CONTAINS PROPRIETARY INFORMATION OWNED BY
To STT Output
From Bridge
AND IS NOT TO BE REPRODUCED, DISCLOSED OR USED WITHOUT THE EXPRESS PERMISSION OF
WITH PUBLISHED STANDARDS
To STT Output
ON 2 PLACE DECIMALS IS + .O2
ON HOLES SIZES PER E-2056
NUMBER.
NOTES :
MATERIAL TOLERANCE ("t") TO AGREE
UNLESS OTHERWISE SPECIFIED TOLERANCE
com
47.5K
R5
com
+15
+15
com
MC14538B
X1
16
8
+15
com
63V
1.0
C8
63V
1.0
C6
50V
0.1
C7
GNDGND
VS VS
X2
MIC4451BN
54
1
8
50V
0.1
C9
50V
0.1
C10
63V
1.0
C20
C6
G3
G5
G1
C4
C3
C2 C5
E6
C1
G4
G2
E4
E2
E1
E3
E5
C7
E7
G6
G7
A2
40N60B3
9
8
20
1417
13
10
16
19
3
1
11
25
18 1521 12
7
6
4
C6
G3
G5
G1
C4
C3
C2 C5
E6
C1
G4
G2
E4
E2
E1
E3
E5
C7
E7
G6
G7
A1
40N60B3
9
8
20
1417
13
10
16
19
3
1
11
25
18 1521 12
7
6
4
332K
R26
X3
13
12
11
100V
100p
C13
X3
6
5
4
+15
4.7
35V
C23
301
R9
50V
0.1
C21
4093B
X3
14
7
FILENAME: L11340-1CA
(UNLESS OTHERWISE SPECIFIED)
1/4W
.022/50V
CHK.
LAST NO. USED
D-
FRAME CONNECTION
R-
SUPPLY
23
TYPE
POWER SUPPLY SOURCE POINT
UNLESS OTHERWISE SPECIFIED)
NONE
SUP'S'D'G.
EQUIP.
COMMON CONNECTION
VOLTAGE NET
NO.
C-
27
L
LABELS
7
GENERAL INFORMATION
CLEVELAND, OHIO U.S.A.
(
DATE
ELECTRICAL SYMBOLS PER E1537
NOT SHOW THE EXACT COMPONENTS OR CIRCUITRY OF CONTROLS HAVING A COMMON CODE
THE LINCOLN ELECTRIC CO.
SCALE
WITHOUT AFFECTING THE INTERCHANGEABILITY OF A COMPLETE BOARD, THIS DIAGRAM MAY
JLJ
ll340
1A, 400V
MFD
DIODES =
RESISTORS = Ohms (
CAPACITORS =
THE LINCOLN ELECTRIC CO.
From Bridge
EARTH GROUND CONNECTION
DZ1
UNLESS OTHERWISE SPECIFIED)
SUBJECT
SHT.
DR.
INVERTER WELDERS
SCHEMATIC, CHOPPER PCB
3-3-99 K.J.
XA
2-11-2000
G-6
NOTE: This diagram is for reference only. It may not be accurate for all machines covered by this manual.

Return to Section TOC Return to Section TOC Return to Section TOC Return to Section TOC
Return to Master TOC Return to Master TOC Return to Master TOC Return to Master TOC
ELECTRICAL DIAGRAMS G-7
POWER WAVE 455/R
PC BOARD ASSEMBLY -CHOPPER
SOLID EDGE
EN-170
MANUFACTURING TOLERANCE PER E2056
UNLESS OTHERWISE SPECIFIED TOLERANCE
SCALE:
DO NOT SCALE THIS DRAWING
ON 3 PLACE DECIMALS IS ± .002
THIS SHEET CONTAINS PROPRIETARY INFORMATION OWNED BY THE LINCOLN ELECTRIC COMPANY AND IS NOT TO BE REPRODUCED, DISCLOSED OR USED WITHOUT THE EXPRESS WRITTEN PERMISSION OF THE LINCOLN ELECTRIC COMPANY, CLEVELAND, OHIO U.S.A.
DESIGN INFORMATION
t
DRAWN BY:
WITH PUBLISHED STANDARDS.
DATE:
ON 2 PLACE DECIMALS IS ±.02
MATERIAL TOLERANCE (" ") TO AGREE
ON ALL ANGLES IS ± .5 OF A DEGREE
SUBJECT:
ENGINEER:
EQUIPMENT TYPE:
DRAWING No.:
DRS
KJ
JLV/RAS
INVERTER WELDERS
CHOPPER P.C. BOARD ASSEMBLY
G
1:1 2-23-98
REFERENCE:
SUPERSEDING:
G3135-1
APPROVED: 3339-1
Chg. Sheet No."X" INFO.
2-11-2000
8-4-2000J
9-22-2000A
G3339-1
R2
C3
C2
D4
D3
D2
D1
R1
CHOPPER
R11
R15
R14
R13
R12R10R9
R16
R17R18R19R20R21R22
J10
C11
X4
B48 B49
B53 B55
C1
C6
C7
C8
C9
C10
C12
C13
C14
C15
C16
C17
C18
C19
C20
C21
C22
DZ1 D5
D6
OCI1
R3
R4
R5
R6
R8
R23
R25
X1
X2
X3
D7
R27
R26
C23
STT
A2
A1
1.304.00
1.30
.45
±.04
5.50
±.04
7.50
ITEM REQ'D PART NO. I DENTIFICATION
C1 1 T11577-49 500/50
C2 1 S13490-8 50/25
C3,C7,C9,10,C21 5 S16668-11 .1/50
C6,C8,C20 3 S13490-173 CAP.,MPF,1.0 uF,63VDC
C11,C14 2 S16668-10 4700pF/50
C12,C17 2 S16668-7 820pF/50
C13,C15,C16 3 S16668-3 100pF/100
C18,C19 2 S20500-2 .47/630
C22 1 S16668-9 150pF/100
C23 1 S13490-25 4.7/35
D1,D2,D3,D4,D7 5 T12199-1 1N4004
D5,D6 2 T12705-23 1N5818
DZ1 1 T12702-29 1N4744A
J10 1 S20351-6 HEADER
OCI1 1 S15000-10 OPTO ISOLATOR
R1 1 S18380-5 THERM.,PTC,.5-1.17 OHM, .5A
R2 1 S19400-3320 332 1/4W
R3,R4,R27 3 S19400-3321 3.32K 1/4W
R5 1 S19400-4752 47.5K 1/4W
R6 1 S19400-4750 475 1/4W
R8,R23 2 S19400-4751 4.75K 1/4W
R9,R10,R11,R12,R13,R14,
R15,R16,R17,R18,R19,R20, 14 S19400-3010 301 1/4W
R21,R22
R25 1 S19400-2213 221K 1/4W
R26 1 S19400-3323 332K 1/4W
X1 1 S15018-9 CMOS MC14538B
X2 1 S15018-21 IC,DRIVER,12A MOSFET(SS)
X3 1 S15018-15 14 PIN IC
X4 1 S15128-6 VOLTAGE REGULATOR
CAPACITORS = MFD/VOLTS
RESISTORS = OHMS
0
0
x
x
x
x
x
x
x
x
x
x
x
x
x
x
x
xx
xxx
x
x
x
x
xx
xxx
x
x
x
x
x
x
x
x
x
x
x
x
x
x
x
x
x
x
x
x
x
x
x
x
x
x
x
x
x
x
x
x
x
x
x
x
x
x
x
x
xx
xxx
x
x
x
x
xx
xxx
x
:
G-7
NOTE: Lincoln Electric assumes no responsibility for liablilities resulting from board level troubleshooting. PC Board repairs will invalidate your factory warranty. Individual Printed Circuit Board Components are not available from Lincoln Electric. This information is pro-
vided for reference only. Lincoln Electric discourages board level troubleshooting and repair since it may compromise the quality of the design and may result in danger to the Machine Operator or Technician. Improper PC board repairs could result in damage to the
machine.

ELECTRICAL DIAGRAMS G-8
POWER WAVE 455/R
SCHEMATIC-DEVICENET/GATEWAY PC BOARD
G-8
NOTE: This diagram is for reference only. It may not be accurate for all machines covered by this manual.
Return to Section TOC Return to Section TOC Return to Section TOC Return to Section TOC
Return to Master TOC Return to Master TOC Return to Master TOC Return to Master TOC

Return to Section TOC Return to Section TOC Return to Section TOC Return to Section TOC
Return to Master TOC Return to Master TOC Return to Master TOC Return to Master TOC
ELECTRICAL DIAGRAMS G-9
POWER WAVE 455/R
PC BOARD ASSEMBLY-DEVICENET/GATEWAY
.
L11046-1
11-3-2000A
UNLESS OTHERWISE SPECIFIED:
RESISTANCE = OHMS
.
(5.84)
(6.34)
ITEM PART NO. QTY PC BOARD REFERENCE
DESIGNATORS
DESCRIPTION
1G3820-D 1 GATEW AY PC BOARD BLANK
2S24671 1 PLUG, KEYING PLUG
3M19436-5 1 POTTING TRAY
4S8025-80 2 SELF TAPPING SCREW
5E2527 195g.
(
6.87OZ
)
EPOXY ENCAPSULATING RESIN
6E3539
A
S REQ. ELECTRICAL INSULATING COMPOUND
7S24824-3 1 X11 SOFTW ARE CPLD
8S24825-1 1 X13 SOFTW ARE, FLASH
FOR ITEMS LISTED BELOW REFER TO ELECTRONIC COMPONENT DATABASE FOR COMPONENT SPECIFICATIONS
9S25020-13SMT 2 C2,C7 CAPACITOR,SMD,CERAMIC,150pF,100V,5%,C
10 S25024-8SMT 5 C3,C4,C5,C6,C8 CAPACITOR,SMD,TANTALUM,10MF,16V,10%,S
11 S13490-179 1 C9 CAPACITOR,ALEL,1000,35V,20%
12 S25024-5SMT 4 C10,C13,C27,C30 CAPACITOR,SMD,TANTALUM,4.7MF,35V,10%,
13 S25024-6SMT 4 C11,C12,C43,C60 CAPACITOR,SMD,TANTALUM,22MF,16V,10%,S
14 S25024-2SMT 4 C14,C16,C20,C25 CAPACITOR,SMD,TANTALUM,1.0MF,35V,10%,
15 S25020-3SMT 30 C15,C17,C18,C19,C21,C22
C23,C24,C26,C28,C31,C32
C33,C35,C36,C37,C38,C41
C42,C44,C45,C46,C47,C48
C49,C50,C51,C53,C54,C58
CAPACITOR,SMD,CERAMIC,0.1MF,50V,10%,X
16 S25020-15SMT 3 C29,C39,C40 CAPACITOR,SMD,CERAMIC,22PF,50V,5%,COG
17 S13490-182 1 C56 CAP,ALEL,3300,63V,20%
18 S13490-181 1 C59 CAP,ALEL,22,63V,20%
19 S25040-10SMT 2 D1,D5 DIODE,SMD,3A,400V,D0-214AB
20 S25040-9SMT 1 D2 DIODE,SMD,3A,200V,D0-214AB,ULTRA-FAST
21 S25040-2SMT 3 D3,D6,D21 DIODE,SMD,1A,400V,DO-214BA/AC
22 S25040-11SMT 3 D4,D16,D20 DIODE,SMD,1A,600V,S403A,ULTRA-FAST RE
23 S25040-4SMT 8 D7,D8,D9,D10,D12,D13,D14
D15
DIODE,SMD,DUAL,0.200A,70V,UFR
24 S25049-3SMT 1 D17 DIODE,SMD,3A,40V,SCHOTTKY,CASE 403-3
25 S25049-4SMT 1 D19 DIODE,SMD,DUAL,200MA,30V,SCHOTTKY,SOT
26 S25040-5SMT 6 D22,D23,D24,D25,D26,D27 DIODE,SMD,DUAL,0.200A,70V,UFR
27 S25046-1SMT 1 DZ1 ZENER DIODE,SMD,0.5W,5.1V, 5%,SOD123
28 S25046-3SMT 4 DZ2,DZ3,DZ4,DZ5 ZENER DIODE,SMD,0.5W ,18V, 5%,SOD123
29 S25044-9SMT 7 DZ6,DZ7,DZ8,DZ10,DZ11,DZ12
DZ13
ZENER DIODE,SMD,3W,6.2V,5%, SMB
30 S18248-16 1 J70 CONNECTOR,MOLEX,MINI,PCB,16-PIN
31 S18248-10 1 J71 CONNECTOR,MOLEX,MINI,PCB,10-PIN
32 S24020-4 3 J72,J73,J76 CONNECTOR,MOLEX,MINI,PCB,4-PIN,TIN
33 S24020-2 1 J74 CONNECTOR,MOLEX,MINI,PCB,2-PIN,TIN
34 S24020-6 1 J75 CONNECTOR,MOLEX,MINI,PCB,6-PIN,TIN
35 S25080-2SMT 6 LED1,LED2,LED3,LED5,LED7
LED9
LED,SMD,GREEN,CLEAR,S1206
36 S25080-1SMT 3 LED4,LED6,LED8 LED,SMD,RED,CLEAR,S1206
37 S15000-28SMT 4 OCI1,OCI2,OCI3,OCI4 OPTOCOUPLER,SMD,TTL-OUT,HI-SPD,HI-CMR
38 S15000-32SMT 2 OCI5,OCI6OPTOCOUPLER,SMD,CMOS,HIGH SPEED,HIGH
39 S25050-2SMT 5 Q2,Q4,Q5,Q12,Q13 TRANSISTOR,SMS,PNP,SOT23,0.5A, 40V,MM
40 S25051-4SMT 6 Q6,Q7,Q8,Q9,Q10,Q11 TRANSISTOR,SMD,NMF,SOT-23,0.115A,60V,
41 S25000-4750SMT 6 R1,R2,R39,R40,R66,R67 RESISTOR,SMD,METAL FILM,1/10W ,475OHMS
42 S25003-2000SMT 2 R3,R4 RESISTOR,S MD,1W ,200OHMS,1%
43 S25000-1002SMT 25 R5,R8,R9,R10,R11,R12,R13
R14,R15,R16,R17,R19,R20
R21,R22,R23,R24,R25,R29
R34,R35,R42,R60,R61,R69
RESISTOR,SMD,METAL FILM,1/10W ,10.0K,1
44 S25000-4751SMT 5 R6,R38,R43,R45,R101 RESISTOR,SMD,METAL FILM,1/10W ,4.75K,1
45 S25000-1001SMT 6 R18,R37,R41,R65,R68,R100 RESISTOR,SMD,METAL FILM,1/10W ,1.00K,1
46 S25001-1002SMT 2 R27,R28 RESISTOR,SMD,10K,1/4W ,1206,1%,TR
47 S25000-1501SMT 1 R30 RESISTOR,SMD,METAL FILM,1/10W ,1.50K,1
48 S25001-3320SMT 6 R31,R32,R33,R46,R47,R72 RESISTOR,SMD,332OHMS,1/4W ,1206,1% ,TR
49 S25000-7500SMT 3 R36,R44,R76 RESISTOR,SMD,METAL FILM,1/10W ,750OHMS
50 S25001-1211SMT 2 R48,R49 RESISTOR,SMD,1.21K,1/4W ,1206,1%,TR
51 S25001-2670SMT 7 R50,R51,R52,R53,R57,R58
R59
RESISTOR,SMD,267OHMS,1/4W ,1206,1% ,TR
52 S25000-1000SMT 6 R54,R55,R56,R80,R81,R82 RESISTOR,SMD,METAL FILM,1/10W ,100OHMS
53 S25001-24R9SMT 3 R73,R74,R75 RESISTOR,SMD,24.9OHMS,1/4W ,1206,1%,TR
54 S25001-2000SMT 3 R77,R78,R79 RESISTOR,SMD,200OHMS,1/4W ,1206,1% ,TR
55 S18380-5 1 R83 THERMISTOR,PTC,0.5-1.17 OHMS,0.5A
56 S19869-8 2 S1,S2 SW ITCH,DIP,SPST,8-CIRCUITS
57 S20375-8 1 T1 TRANSFORMER,PCB,PWM ,FLYBACK
58 S20353-1SMT 1 X2 IC,SMD,CMOS,DRIVER,RECEIVER,EIA232,14
59 S15128-25SMT 1 X3 IC,SMD,VOLTAGE REGULATOR,FIXED,POSITI
60 S25068-6SMT 2 X4,X24 IC,SMD,VOLT REG,FIXED,3-T,(+),0.1A,5V
61 S15128-5SMT 1 X5 IC,VOLT REG,SMD,FIXED,3-T,(+),1A,5V
62 S24841-1 1 X6 IC,MODULE,CONVERTER,DC-DC,+5V/3A OUT
63 S25068-7SMT 2 X7,X9 IC,SMD,CMOS,UNDERVOLT-SENSING,RESET,M
64 S25069-2SMT 1 X8 IC,SMD,CMOS,EEPROM,SERIAL,SPI,64Kx8,S
65 M15101-14SMT 1 X10 IC,SMD,CMOS,MCU,32-BIT,2K-RAM,TPU,25M
66 S25070-3SMT 1 X11 CPLD,PROGRAMMABLE,XC9536,44-PIN,VQFP(
67 S25069-3SMT 1 X13 IC,SMD,CMOS,EEPROM,FLASH,16-BIT,512K
68 S17900-11SMT 1 X14 IC,SMD,CMOS,TRANCEIVER,BUS,3-STATE,OC
69 S25069-4SMT 1 X15 RAM,STATIC,16-BIT,128K,44-PIN,TSOP
70 S20353-5SMT 2 X16,X18 IC,CMOS,CONTROLLER,COMMUNICATION,SERI
71 S20353-4SMT 2 X17,X22 IC,CMOS,SMD,XCVR,EIA485(SS)
72 S25068-4SMT 1 X20 IC,SMD,TRANSCEIVER,CAN,UC5350,S0IC-8
73 S17900-24SMT 1 X23 IC,SMD,CMOS,GATE,NAND,2-INPUT,QUAD,SC
74 S25065-2SMT 1 X31 IC,SMD,ACT,LATCH,OCTAL,3-STATE,TSSOP-
75 S25082-1SMT 1 Y1 CRYSTAL,SMD,QUARTZ,16MHZ
G-9
NOTE: Lincoln Electric assumes no responsibility for liablilities resulting from board level troubleshooting. PC Board repairs will invalidate your factory warranty. Individual Printed Circuit Board Components are not available from Lincoln Electric. This information is pro-
vided for reference only. Lincoln Electric discourages board level troubleshooting and repair since it may compromise the quality of the design and may result in danger to the Machine Operator or Technician. Improper PC board repairs could result in damage to the
machine.

ELECTRICAL DIAGRAMS G-10
POWER WAVE 455/R
SCHEMATIC - CONTROL PC BOARD
SOLID EDGE
MANUFACTURING TOLERANCE PER E2056
UNLESS OTHERWISE SPECIFIED TOLERANCE
SCALE:
DO NOT SCALE THIS DRAWING
ON 3 PLACE DECIMALS IS ± .002
THIS SHEE T CONTAI NS PRO PRIETARY INFORMATIO N OWNED BY THE LINCOLN ELECTRIC COMPANY AND IS NOT TO BE REPRODUCED, DISCLOSED OR USED WITHOUT THE EXPRESS WRITTEN PERMISSIO N OF THE LINCOLN ELECTRIC COMPANY, CLEVELAND, OHIO U.S.A.
DESIGN INFORMATION
t
DRAWN BY:
WITH PUBLISHED STANDARDS.
DATE:
ON 2 PLACE DECIMALS IS ± .02
MATERIAL TOLERANCE (" ") TO AGREE
ON ALL ANGLES IS ± .5 OF A DEGREE
SUBJECT:
ENGINEER:
EQUIPMENT TYPE:
DRAWING No.:
T. KOOKEN
F.V.
INVERTER WELDERS
DIGITAL CONTROL SCHEMATIC
G
NONE 12-15-99
REFERENCE:
SUPERSEDING:
APPROVED:
Chg. Sheet No."X" INFO.
XM5626
XA
6-2-2000A
ADDR17
ADDR17
ADDR17
CAPB_OV
CAPB_OV
FAULT_INT
FAULT_INT
MN_CNT
MN_CNT
VPP_CTRL
PWRDN_INT
PWRDN_INT
PWRDN_INT
SOFTST
SOFTST
CAPB_UV
CAPB_UV
CRYSTAL
CRYSTAL
CAPBOV
CAPBUV
CAPA_UV
CAPA_UV
CAPAOV
CAPAUV
CAPA_OV
CAPA_OV
/IPIPE
THERMOSTAT
/IFETCH
MN_OUT
SSOUT
FREEZE
FREEZE
/CS2
/CS2
/CS2
ADDR19
ADDR19
ADDR18
ADDR18
ADDR16
ADDR16
ADDR16
/BKPT
/BKPT
TSC
ADDR13
ADDR13
ADDR13
LEVEL_IN
LEVEL_IN
/BERR
/BERR
/CSB
/CSB
ADDR14
ADDR14
ADDR14
ADDR15
ADDR15
ADDR15
+15V
SRAM
128KX16
VCC1
VCC2
GND1
GND2
CE'
WE'
OE'
LB'
UB'
D0
D1
D2
D3
D4
D5
D6
D7
D8
D9
D10
D11
D12
D13
D14
D15
A0
A1
A2
A3
A4
A5
A6
A7
A8
A9
A10
A11
A12
A13
A14
A15
A16
22
33
11
40
39
41
17
6
34
12
38
37
36
35
32
31
30
29
16
15
14
13
10
9
8
7
1
2
3
4
5
18
19
20
21
24
25
26
27
42
43
44 X27
IS61C12816
INPUT
NC
GND2
GND1
OUTPUT2
OUTPUT1
VS2
VS1
2
3
5
4
7
6
8
1
X2
MIC4451BM
INPUT
NC
GND2
GND1
OUTPUT2
OUTPUT1
VS2
VS1
2
3
5
4
7
6
8
1
X3
MIC4451BM
1
3
2
D83
BAT54S
1
3
2
D82
BAT54S
1
3
2
D80
BAT54S
1
3
2
D81
BAT54S
DQ
12
111
9X21
DQ
13
111
8X21
DQ
14
111
7X21
DQ
15
111
6X21
DQ
16
111
5X21
DQ
17
111
4X21
DQ
18
111
3X21
PTC
MF-R050
+5V
+5V
+15V
+5V
+5V
+5V
+15V
+15V
+15V
+15V
+5V
+15V
+15V
+5V
+5V
+5V
+5V
+5V
+5V
+5V
+5V
+5V
+5V
+5V
+5V
+5V
1
3
2
D19
BAV99
1
3
2D78
BAV99
1
3
2D79
BAV99
C110
20V
22uF
C13
50V
120uF
C46
35V
1uF
C2
35V
1uF
C107
35V
1uF
C119
20V
22uF
C104
1uF
35V
C94
35V
1uF
C12
35V
4.7uF
56
X10
74AC14
13 12
X30
74AC14
12
X30
74AC14
34
X30
74AC14
11 10
X30
74AC14
11 10
X10
74AC14
98
X10
74AC14
1
2
3
Q20
MMBT4401
1
2
3
Q1
MMBT4401
1
2
3
Q6
MMBT4401
1
2
3
Q5
MMBT4401
1
2
3
Q7
MMBT4401
1
2
3
Q4
MMBT4401
1
2
3
Q19
MMBT4401
7
J4
MICRO_CONTROLLER
D8
D7
D6
D5
D4
D3
D2
D1
D0
A18
FC1
A1
A2
A3
A4
A5
A6
A7
A8
A9
A10
A11
A12
A13
A14
A15
A16
A17
D15
D14
D13
D12
D11
D10
D9
CS0'
CS1'
CS2'
RESET'
BERR'
HALT'
FC2
FC0
/
/
/
/
/
/
/
/
A0
A23
A22
A21
A20
A19/
/
/
/
/
CS6'
CS7'
CS8'
CS9'
CS10'
/
/
/
CS3'
CS4'
CS5'
PC0/
PC1/
PC2/
PC3/
PC4/
PC5/
PC6/
CSBOOT'
/
/
/
BR'
BG'
BGACK'
DSI
DSO
R/W
/
/
IPIPE'
IFETCH'
CLKOUT
XFC
TSC
FREEZE
BKPT'/DSCLK
PF7
PF6
PF5
PF4
PF3
PF2
PF1
PF0 MODCLK
IRQ1'
IRQ2'
IRQ3'
IRQ4'
IRQ5'
IRQ6'
IRQ7'
TPUCH15
TPUCH14
TPUCH13
TPUCH12
TPUCH11
TPUCH10
TPUCH9
TPUCH8
TPUCH7
TPUCH6
TPUCH5
TPUCH4
TPUCH3
TPUCH2
TPUCH1
TPUCH0
T2CLK
RXD
PQS7
PQS6
PQS5
PQS4
PQS3
PQS2
PQS1
PQS0/MISO
/MOSI
/SCK
/PCS0/ SS'
/PCS1
/PCS2
/PCS3
/TXD
SIZ1
SIZ0
DS'
AS'
RMC'
AVEC'
DSACK1'
DSACK0'/PE0
/PE1
/PE2
/PE3
/PE4
/PE5
/PE6
/PE7
XTAL
EXTAL
83
85
104
105
110
106
111
112
113
114
76
75
71
70
69
68
67
66
65
14
15
16
17
21
22
23
24
27
28
29
30
31
32
33
34
13
95
96
97
98
99
100
101
102
79
81
80
87
90
78
77
103
140
10
9
8
7
6
115
116
117
118
119
122
124
125
127
130
131
132
133
136
137
138
139
64
63
60
58
57
56
52
51
50
49
46
45
44
43
42
41
40
39
143
142
141
5
4
3
94
93
92
X24
MC68332PV
+5V
RES'
VSS
VDD 1
3
2X23
S80746AN
4.6V/2%
9
J7
2J7
5J7
8J7
13 J7
16 J7
10
J7
6J7
7J7
1J7
15 J7
14 J7
13
J6
14 J6
15 J6
16
J6
9J6
10
J6
11
J6
12 J6
15
J1
12 J1
5
J1
6
J1
8J1
7
J1
4J1
9J1
14
J1
13
J1
5
J6
6J6
7J6
8
J6
4
J6
3
J6
2J6
1
J6
3J1
11 J1
10 J1
VDDE
VDDSYN
VSSE
G1
G2
G3
G4
G5
G6
G7
G8
G9
G10
G11
G12
G13
G14
VSTDBY
V10
V9
V8
V7
V6
V5
V4
V3
V2
V1
V11
V12 144
135
121
109
89
86
72
61
47
37
19
11
38
2
12
20
35
48
54
62
74
82
91
107
120
128
134
26
25
84
X24
MC68332
512Kx16
FLASH
A15
A14
A13
A12
A11
A10
A9
A8
A7
A6
A5
A4
A3
A2
A1
A0
D15
D14
D13
D12
D11
D10
D9
D8
D7
D6
D5
D4
D3
D2
D1
D0
OE'
WE'
CE'
GND2
GND1
BYTE'
RP'
WP'
A18
A17
A16
VCC
VPP 37
13
16
17
48
47
12
14
28
11
26
27
46
45
43
41
39
36
34
32
30
44
42
40
38
35
33
31
29
1
2
3
4
5
6
7
8
18
19
20
21
22
23
24
25
X25
TE28F800B5-B90
3
21
D90
BAV70LT1
3
21
D91
BAV70LT1
3
21
D89
BAV70LT1
3
21
D86
BAV70LT1
3
21
D85
BAV70LT1
3
21
D84
BAV70LT1
CPLD
IO9B
IO10B
IO11B
IO12B
IO13B
IO14B
IO15B
IO16B
IO17B
GND1
GND2
GND3
IO1A
IO2A
IO4A
IO6A
IO8A
IO9A
IO10A
IO11A
IO12A
IO13A
IO14A
IO15A
IO16A
IO17A
IO1B
IO2B
IO4B
IO7B
IO8B
GCK1
GCK2
GCK3
GTS1
GTS2
GSR
TCK
TMS
TDI
TDO
VCC2
VCC1
VCCIO
25
17
4
19
20
21
22
23
27
28
29
30
31
32
37
38
39
18
16
14
13
12
8
7
6
5
3
2
42
41
40
33
34
36
1
44
43
26
15
35
24
9
10
11
X17
XC9536-15-VQ44I
LED7
RED
3
1
2
Q10
IRLR120N
10A,100V
3
1
2
Q9
IRLR120N
10A,100V
(4)
(4)
(4)
(4)
(4)
(4)
(2)
(2)
(4)
(4)
(4)
(4)
(4)
(4)
(4)
(3)
(3)
(4)
(2)
(1)
(4)
(4)
(4)
(4)
(4)
(4)
(4)
(3)
(3)
(3)
(4)
(4)
(4)
(4)
(4)
(4)
(4)
(1,4)
(2)
(2,3,4)
(4)
(3)
(2)
(3)
(4)
(3)
(3)
(4)
(4)
(2,4)
(3,4)
(3,4)
(4)
(2)
2
J5
3
J5
4
J5
1
J5
D114
MMBR130LT3
D115
MMBR130LT3
D76
MMBR130LT3
D77
MMBR130LT3
D8
1/2W
5.1V
MMSZ5231
D7
1/2W
5.1V
MMSZ5231
D5
1/2W
5.1V
MMSZ5231
D2
1/2W
5.1V
MMSZ5231
D24
1.5W
18V
1SMB5931
D29
1.5W
18V
1SMB5931
D6
1/2W
5.1V
MMSZ5231
D31
1.5W
18V
1SMB5931
D9
1/2W
5.1V
MMSZ5231
D30
1.5W
18V
1SMB5931
D17
1/2W
5.1V
MMSZ5231
D32
1.5W
18V
1SMB5931
D15
1.5W
16V
1SMB5930
D44
1/2W
5.1V
MMSZ5231
D18
1.5W
16V
1SMB5930
D25
1/2W
5.1V
MMSZ5231
C135
1uF
C141
0.1uF
C122
0.1uF
C123
0.1uF
C6
820pF
C72
820pF
C69
4700pF
C5
820pF
C70
820pF
C71
820pF
C3
820pF
C74
820pF
C15
100pF
C18
100pF
C4
820pF
C43
820pF
C67
0.1uF
C25
100pF
C44
4700pF
C22
100pF
C99
0.1uF
C108
0.1uF
C27
100pF
C68
0.1uF
C73
0.1uF
C105
0.1uF C95
0.1uF
C106
0.1uF
C120
0.1uF
C109
0.1uF
C93
0.1uF
C90
0.1uF
C113
0.1uF
C111
0.1uF
C11
0.1uF
C14
0.1uF
C136
1uF
C142
0.1uF
QD
OE'
LE
192
1
11
X21
74AC573
C143
330pF
D3
S1G
D4
S1G
1
2
3
Q15
MMBT4403
R261
10.0K
R260
10.0K
R259
10.0K
R256
1K
R255
1K
R254
10.0K
R258
10.0K
R257
10.0K
R203
22.1K
R242
10.0K
R36
475
R40 475
R84
475
R85
475
R199
10.0K
R200
10.0K
R168
1.00k
R169
1.00K
R1361.00k
R135
1.00K
R35
22.1K
R38
22.1K
R100
475K
R99
10.0K
R33
10.0K
R2
47.5
R3
47.5
R34
1.00K
R16
475
R18
475
R10
475
R19
475
R17
475
R9
475
R42
4.75K
R14
475
R43
4.75K
R37
22.1K
R39
22.1K
R81
475
R88
475
R87
10.0K
R183
750
R20
475
R90
1.00K
R8
22.1K
R32
2.21K
R47
4.75K
R15
475
R46
4.75K
R185
10.0K
R21
475
R51
4.75K
R174
10.0K
R11
475
R41
475
R187
26.7K
R179
3.32K
R180
10.0K
R186 10.0K
R18910.0k
R172
10.0K
R170
10.0K
R16410.0K
R18110.0K
R171
1.00K
NOISE_GND
NOISE_GND
D
D
D
D
D
D
DD
NOISE_GND D
NOISE_GND
D
NOISE_GND
D
NOISE_GND
NOISE_GND
NOISE_GND
D
D
DNOISE_GND
D
NOISE_GND
NOISE_GND
D
NOISE_GND
NOISE_GND
NOISE_GND
DDD
D
NOISE_GND D
D
NOISE_GND
D
D
D
D
D
D
D
DATA[0:15]
DATA[0:15]
ADDR[1:19]
ADDR[1:19]
BANK1
FAULT
SIGNAL
0V = NORMAR
0V = NORMAR
5V = FAULT
5V = FAULT
SINGLE/THREE PHASE DETECT THERMOSTAT
FILTER CAPACITOR VOLTAGE MONITORING
ADDR8
ADDR8
ADDR8
DATA5 DATA5
DATA5
RMCRMC
DATA15 DATA15
DATA15
DATA9 DATA9
DATA9
DATA4 DATA4
DATA4
DATA12 DATA12
DATA12
DATA8 DATA8
DATA8
DATA8
DATA7 DATA7
DATA7
DATA7
DATA11 DATA11
DATA11
DATA11
DATA10 DATA10
DATA10
ADDR9
ADDR9
ADDR9
ADDR10
ADDR10
ADDR10
ADDR11
ADDR11
ADDR11
ADDR12
ADDR12
ADDR12
DATA1 DATA1
DATA1
DATA1
DATA3 DATA3
DATA3
DATA3
DATA2 DATA2
DATA2
DATA2
DATA14 DATA14
DATA14
ADDR6
ADDR6
ADDR6
ADDR7
ADDR7
ADDR7
DATA13 DATA13
DATA13
DATA6 DATA6
DATA6
DATA6
ADDR3
ADDR3
ADDR3
ADDR4
ADDR4
ADDR4
FPGA_BADFPGA_BAD
IACK
INT_1_3PH
/AS /AS
ADDR5
ADDR5
ADDR5
TPU2
MOSI
TPU3
SCK
SPI_CS2
/CS0
/CS0
/CS0
FPGA_CS
SPI_CS0
CLK
CLK
STT_ON
SPI_CS3
R/W R/W
R/W
R/W
R/W
TPU5
TPU6
ADDR2
ADDR2
ADDR2
/DS
/DS /DS
DATA0 DATA0
DATA0
DATA0
MISO
ADDR1
ADDR1
ADDR1
OUTPUT_ON
OUTPUT_ON
OUTPUT_ON
TPU0
SPI_CS1
CLK_8
TPU1
SCK7
MISO7
SPI_LATCH7
FAN_CONTROL
FPGA_INT FPGA_INT
THERMAL_LED
MISC1
MISC0
TPU4
INT_100
/CS1
/CS1
/CS1
FPGA_DONEFPGA_DONE
FET_B
DSP_RESET
CAP1
FPGA_RESET FPGA_RESET
CAP0
FET_A
FUNCEN
CMP0
CMP2
CMP4
DISABLE_455
VPP
PRI_OC
OVR_CUR RESET_RAMP
CLR_CAP
SYS_RESETSYS_RESET
STROBE_AD
/RES
/RES
/RES
/RES
/RES
/RES
/RES
/RES
/RES
/RES
/RES
CAN_CS
INT_CAN INT_CAN
RS232_RXD
RS232_TXD
3789-1D0/1
G-10
Return to Section TOC Return to Section TOC Return to Section TOC Return to Section TOC
Return to Master TOC Return to Master TOC Return to Master TOC Return to Master TOC
NOTE: This diagram is for reference only. It may not be accurate for all machines covered by this manual.

NOTE: Lincoln Electric assumes no responsibility for liablilities resulting from board level troubleshooting. PC Board repairs will invalidate your factory warranty. Individual Printed Circuit Board Components are not available from Lincoln Electric. This information is pro-
vided for reference only. Lincoln Electric discourages board level troubleshooting and repair since it may compromise the quality of the design and may result in danger to the Machine Operator or Technician. Improper PC board repairs could result in damage to the
machine.
ELECTRICAL DIAGRAMS G-11
POWER WAVE 455/R
MANUFACTURING TOLERANCE PER E2056
UNLESS OTHERWISE SPECIFIED TOLERANCE
SCALE:
DO NOT SCALE THIS DRAWING
ON 3 PLACE DECIMALS IS ± .002
THIS SHEET CONTAINS PROPRIETARY INFORMATION OWNED BY THE LINCOLN ELECTRIC COMPANY AND IS NOT TO BE REPRODUCED, DISCLOSED OR USED WITHOUT THE EXPRESS WRITTEN PERMISSION OF THE LINCOLN ELECTRIC COMPANY, CLEVELAND, OHIO U.S.A.
DESIGN INFORMATION
t
DRAWN BY:
WITH PUBLISHED STANDARDS.
DATE:
ON 2 PLACE DECIMALS IS ±.02
MATERIAL TOLERANCE (" ") TO AGREE
ON ALL ANGLES IS ± .5 OF A DEGREE
SUBJECT:
Chg. Sheet No.
ENGINEER:
EQUIPMENT TYPE:
DRAWING No.:
T. O'DONNEL
F.V.
INVERTER WELDERS
CONTROL P.C. B OARD AS'BLY
L
NONE 4-6-99
REFERENCE:
SUPERSEDING:
APPROVED:
"X" INFO.
11088-1D2
5-25-2001F
CAPACITORS = MFD/VOLTS
INDUCTANCE = HENRIES
RESISTANCE = OHMS
COMPONENT SIDE
OTHER COMPONENT SIDE (BACKSIDE)
(6.34)
(8.09)
11 S25020-3SMT 68 SCAP, 0.1uF,0805, 50V,X7R,10%,TR
C138 C134 C133 C125 C55 C96 C98 C100 C28
C82 C14 C11 C83 C103 C121 C101 C117 C115
C111 C113 C85 C90 C48 C93 C109 C120 C127
C106 C95 C105 C73 C68 C8 C114 C108 C99
C77 C76 C75 C84 C79 C67 C88 C80 C50 C78
C23 C21 C91 C51 C92 C58 C57 C52 C60 C59
C131 C123 C122 C124 C30 C129 C139 C140
C42 C137 C141 C142
12 S14390-173 2 CAP,1uF,RA,63V ,10%,NP C136 C135
13 S25020-2SMT 2 SCAP,0.022uF,0805,50V ,X7R,10%, C86 C7
14 S25020-10SMT 2 SCAP,4700pF, 0805, 50V,X7R,10% C44 C69
15 S25020-5SMT 4 SCAP,22pF, 0805, 50V,COG,5% , TR,N C118 C116 C128 C130
16 S25020-18SMT 1 SCAP,10pF, CER,0805,100V,5% C32
17 S25020-13SMT 7 SCAP,150pF,0805,100V,COG,5% ,TR, C64 C89 C26 C35 C36 C38 C37
18 S25020-4SMT 11 SCAP,820pF,0805,50V,COG,5% ,TR, C43 C4 C74 C3 C71 C19 C70 C5 C72 C6 C17
19 S24833-1 2 CAP, 0. 27uF, MF,50V,5mm,5%,TR,NP C56 C34
20 S25020-14SMT 2 SCAP, 330pF,100V C126 C143
21 S25025-5SMT 9 SCAP,4. 7uF,7343,35V,10%,TR,NP C12 C102 C1 C9 C10 C39 C40 C16 C61
22 S25024-2SMT 8 SCAP, 1uF,TAN,3528,35V,TR,NP C94 C97 C104 C107 C47 C81 C2 C46
23 S25024-8SMT 4 SCAP,10uF,TAN,6032,TR,NP C66 C62 C65 C63
24 S25024-10SMT 4 SCAP, 22uF,TAN,7343, 25V,10% C119 C110 C49 C54
25 S13490-179 1 CAP,1000uF,ALU,35V, 20%,NP C45
26 S13490-183 1 SCAP,120MF,50V ,20%,RADIAL,AE C13
27 S25040-2SMT 13 SDIO,1A,400V,DO-214BA,GLS D68 D67 D4 D3 D75 D63 D64 D65 D70 D72 D71
D73 D74
28 S25046-1SMT 19 SDIO,MMSZ5231BT1,5.1V,NP D25 D45 D44 D17 D9 D6 D2 D5 D7 D8 D35 D36
D38 D37 D42 D41 D40 D39 D69
29 S25044-9SMT 7 SDIO,1SMB 5920BT3,6. 2V,NP D62 D61 D60 D13 D12 D1 D46
30 S25046-3SMT 4 SDIO,MMSZ5248B,18V,ZENER,TR,NP D53 D52 D58 D59
31 S25044-10SMT 3 SDIO,B5930, 16V,1.5W , ZENER,TR,N D18 D15 D43
32 S25044-5SMT 9 SDIO,1SMB5931BT3,3W ,18V,5% D27 D32 D26 D30 D31 D29 D24 D14 D16
33 S25044-4SMT 2 SDIO,B5929,15V,1.5W,ZENER,TR,N D10 D11
34 S25040-5SMT 13 SDIO,B AV99LT1,SOT23,DUAL SW ITC D66 D50 D33 D49 D19 D78 D79 D102 D103
D104 D105 D106 D107
35 S25049-4SMT 8 SDIO,BAT54S,DUAL,30V,200mA D34 D54 D28 D47 D80 D81 D82 D83
36 S25080-2SMT 8 S LED,GRN,1206, TR,NP LED8 LED1 LED5 LED3 LED2 LED4 LED6
LED9
37 S25080-1SMT 2 SLE D,RED,1206,TR,NP LED7 LED10
38 S25083-1SMT 1 SIND,FERRITEBEAD,TR,NP E1
39 S25001-4752SMT 8 SRES,47.5K, 1206, 1%,1/8W , TR,NP R230 R27 R28 R26 R53 R29 R110 R57
40 S25001-2211SMT 8 SRES,2.21K , 1206, 1%,1/8W ,NP R25 R13 R12 R32 R1 R31 R134 R66
41 S25001-1001SMT 33 SRES,1K,1206,1%, 1/8W,TR(9X0056
R171 R178 R177 R193 R231 R167 R61 R34
R89 R82 R163 R135 R136 R169 R131 R112
R60 R56 R126 R71 R54 R69 R68 R143 R144
R58 R206 R213 R214 R90 R168 R255 R256
42 S25001-1002SMT 57 SRES,10K,MF,1206,1%,1/8W
R173 R191 R181 R164 R170 R172 R189 R186
R180 R91 R92 R93 R94 R95 R96 R97 R98 R22
R174 R201 R185 R104 R87 R33 R99 R260
R261 R139 R140 R121 R200 R107 R199 R103
R221 R229 R204 R242 R241 R216 R217 R218
R243 R246 R244 R245 R247 R248 R249 R250
R251 R252 R253 R254 R257 R258 R259
43 S25001-4750SMT 28 SRES ,475,1206,1%,1/8W,TR,NP
R195 R194 R41 R11 R83 R86 R166 R165 R21
R15 R20 R88 R81 R14 R9 R17 R19 R10 R18
R16 R141 R138 R119 R116 R85 R84 R40 R36
44 S25001-4751SMT 15 SRES ,4.75K ,1206,1%, 1/8W,SM100- R190 R192 R182 R184 R137 R146 R209 R210
R222 R42 R43 R46 R47 R51 R67
45 S25003-2000SMT 2 SRES,200,2512,1%,1W,TR,NP R132 R133
46 S25001-1501SMT 7 SRES,1.5K,1206,1% ,1/8W,NP R113 R118 R122 R74 R76 R80 R78
47 S25001-7500SMT 1 SRES,750,1206,1%,1/8W , NP R183
48 S25001-5110SMT 2 SRES,511,MF,1206,1%,1/ 8W,TR R24 R23
49 S25001-1004SMT 2 SRES,1M,1206,1%,1/8W , TR(9X0098 R212 R211
50 S25001-2672SMT 4 S RES,26.7K, THK,1206,1%, 1/8W,10 R187 R114 R120 R72
51 S25001-3321SMT 4 SRES,3.32K,1206,1%,1/8W ,NP
(
AM2 R123 R128 R129 R179
52 S25001-2212SMT 6 SRES,22.1K,1206,1%,1/8W,TR,NP R37 R38 R35 R203 R8 R39
53 S25001-47R5SMT 2 SRES,47.5,1206,1%,1/8W,TR,NP R3 R2
54 S25001-4753SMT 1 SRES,475K,1206,1%,1/8W,TR,NP R100
55 S25001-1003SMT 10 SRES,100K,1206,1%,1/8W,200PPM, R55 R111 R49 R108 R115 R124 R142 R208
R20 7 R1 06
56 S25001-1213SMT 1 SRES,121K,1206,MF,1%,1/4W R70
57 S25001-3322SMT 3 SRES,33.2K,1206, 1%,1/8W ,TR,NP R63 R65 R233
58 S25001-1000SMT 4 SRES,100,1206,1%,1/8W ,TR,NP R62 R44 R52 R30
59 S25001-2210SMT 5 SRES,221,1206,1%,1/8W,NP R59 R48 R102 R197 R45
60 S25001-2671SMT 1 SRES,2.67K,1206,1%,1/8W,TR,NP R109
61 S25001-1502SMT 2 SRES,150K,1206,1%,1/8W ,NP R117 R125
62 S25001-6811SMT 2 SRES,6.81K,1206,1%,1/8W ,NP R127 R130
63 S25001-1500SMT 2 SRES,150,1206,1%,1/8W ,TR,NP R196 R198
64 S25006-10R0 10 SRES,10, R151 R154 R157 R16 0 R148 R161 R15 8 R155
R15 2 R1 49
65 S25050-2SMT 5 STRA,2N4403,SO23,TR,
(
500475
)
,N Q17 Q16 Q15 Q13 Q14
66 S25051-6SMT 2 STRA,IRLR120N,10A,100V,MOSFET, Q9 Q10
67 S25050-1SMT 9 STRA,MMBT4401LT,NPN,SOT-23 Q12 Q4 Q7 Q5 Q6 Q1 Q18 Q19 Q20
68 S25051-4SMT 2 STRA,2N7002,TR,NP Q3 Q2
69 S25051-7SMT 1 SICS,IRF7103,NP Q11
70 S24020-4 3 CON,4P,TIN,MI NI,NP J5 J11 J2
71 S24020-6 1 CON,6P,TIN,MINI,NP J9
72 S24020-2 2 CON,2P,TIN,MINI,NP J10A J10B
73 S18248-10 1 CON,10P,MINI,NP J3
74 S18248-16 1 CON,16P,MINI,NP J1
75 S24020-16 2 CON,16P,TIN,MINI,NP J6 J7
76 S24020-12 1 CON,12P,TIN,MINI,NP J4
77 S24020-8 1 CON,8P,TIN,MINI,NP (or TH600-265) J8
78 S20353-4SMT 1 SICS,MAX485ESA,NP X29
79 S25065-2SMT 1 SICS,74ACT573,OCTAL,TRANS.,LAT X21
80 S25070-7SMT 1 SICS,TMS320F240PQA,NP X22
81 S15000-28SMT 4 S ICS, HCPL-0601, OP TOCOUPLER OCI1 OCI2 OCI3 OCI4
82 S20353-5 1 SICS,AN82527 X28
83 S25082-1SMT 1 SXTL,16MHZ,HC40,20PF,NP Y1
84 S20353-1SMT 1 SICS,MC145407,RECEIVER/DRVR,RS X16
85 S25067-3SMT 2 SICS,ADG417,SPST,CMOS,SWT,SO8 X13 X31
86 S17900-1SMT 1 74HC245, NEW PACKAGE X33
87 S15128-13SMT 1 SICS,OP-27G, OPAMP,SO8,TR,NP X1
88 S15128-18SMT 3 S ICS,MC33074, QUAD, OP AMP,S O14,T X8 X14 X20
89 S25069-3SMT 1 SICS,28F800B5-90,FLASH RO,90n X25
90 S25069-4SMT 1 SICS,128Kx16,20nS,TSOP X27
91 M15101-14SMT 1 SICS,MC68332 X24
92 S25068-8SM 1 SICS,MC79L05ABD X4
93 S25065-3SMT 2 SICS,74VHC14,NP X10 X30
94 S25057-3SMT 2 SICS,AD8403ARU10 X6 X32
95 M15105-9SMT 1 SICS,7945 X 12
96 S15018-21SMT 2 ICS,MIC4451BM X2 X3
97 S25067-2SMT 1 SICS,ADG409BR X15
98 S25070-3SMT 1 ICS,XC9536-15 VQ44 X17
99 S25069-2SMT 1 SICS,25128,SERIAL EEPR,NP X11
100 S15128-21SMT 2 SICS,LT1016,COMPARATOR X5 X7
101 S19869-8 1 SWT,78B08S,DIP,SPST,8P,NP S1
102 S25066-2SMT 1 SICS,AD7862,DUAL,12BIT,250kSPS X19
103 S25068-7SMT 1 SICS, 4.6V,2%,VOLT. DETECTOR,SO X23
104 S25070-4SMT 1 SICS,XCS20,FPGA X18
105 S20620-1003 4 RES,100K,AX,5%, 1/ 2W ,HI VOLT,TR R73 R79 R75 R77
106 S25040-12SMT 8 SDIO,MURS320T3,3A,200V,ULTRAFA D51 D55 D56 D57 D98 D99 D100 D101
107 S25020-SMT 5 SCAP,100pF,0805,COG,100V,5% C15, C18, C22, C25, C27
108 S25000-1000SMT 6 SRES,100,0805,1%,1/10W R223, R224, R240, R226, R227, R228
109 T12702-60 2 DIO,1N5358B DZ3 DZ4
110 T12702-59 2 DIO,1N5333B DZ1 DZ2
111 S25049-2SMT 4 SDIO,MB RA130LT3,1A,30V,SCHOTKY D76 D77 D114 D115
112 S25001-3320SMT 6 SRES,332,1206,1%,1/4W R262 R263 R264 R265 R266 R267
113 S25040-6SMT 6 SDIO,BAV70 D84 D85 D86 D89 D90 D91
FOR ITEMS LISTED BELOW REFER TO ELECTRICAL DATABASE FOR COMPONEN
T
SPECIFICATIONS
G-11
Return to Section TOC Return to Section TOC Return to Section TOC Return to Section TOC
Return to Master TOC Return to Master TOC Return to Master TOC Return to Master TOC

Return to Section TOC Return to Section TOC Return to Section TOC Return to Section TOC
Return to Master TOC Return to Master TOC Return to Master TOC Return to Master TOC
ELECTRICAL DIAGRAMS G-12
POWER WAVE 455/R
SCHEMATIC - DIGITIAL POWER SUPPLY PC BOARD
.1
C53
Vfb2
Vref 1
100K
R29
CNY17-3
OCI2
42
1
6
5
.5W
27V
DZ2
VFB
CS
COMPRT/CT
VCC
OUT
VREF
GND
X4
2
3
5
1
6
4
8
7
.5W
27V
DZ3
Vref 2
15.0K
R1
4.7
35V
C3
.022
C49
221K
R34
10.0K
R56
100V
150p
C27
200V
1
C26
56.2K
R38
gnd_mcps
1.0A
30V
D23
T2
12
3
+5V
2000V
.0015
C31
50V
0.1
C2
J42
4
50V
0.1
C25
1.0
35V
C23
D10
1.00K
R26
J43
9
D9
4.7
35V
C24
D25
G
D
S
21A
200V
Q2
150p
C52
1.0A
30V
D20
3W
0.05
R30
1.2 1K
R37
75K
R31
15.0
R32
3W
18V
DZ7
OV2
Detect
600V
1A
30-55 VDC
<30VDC
Undervoltage
1A
600V
ADJ
IN
OUT
X3
1.82K
R20
15
R43
J43
1
5.62K
R28
D2
T2
14
1
OV1
4.7
35V
C1
D15
3W
3.3V
DZ4
D14 D17
4.7
35V
C33
4.7
35V
C10
D1
D12
T2
10
5
50V
0.1
C5
5.62K
R45
GND
IN
OUT
X6
OV2
GND
IN
OUT
X7
1.0
35V
C29
D13
100V
10p
C28
T2
11
4
Shutdown
249
R33
1.0
35V
C30
50V
0.1
C9
J43
5
150
R44
J43
4
150
R25
J43
10
> 55 VDC
Overvoltage
600V
1A
600V
1A
.33W
CAN
+5Volts, .100 Amp
RS232
+5Volts, .100 Amp
.33W
50V
820p
C4
Shut Down
Capacitor
DC Input (+)
1A
OV1
600V
56.2K
R39
J41
1
J41
4
4.7
35V
C6
3W
24V
DZ1
+
t
R55
T1
7
6
100V
10p
C32
50V
820p
C8
J41
3
6.19K
R3
J41
2
D3
VFB
CS
COMPRT/CT
VCC
OUT
VREF
GND
X5
2
3
5
1
6
4
8
7
DC Input (-)
50V
0.1
C7
Machine Control
100K
R10
5.62K
R12
1.0A
30V
D21
GND
N.A. SINCE COMPONENTS OR CIRCUITRY ON A PRINTED CIRCUIT BOARD MAY CHANGE
NUMBER.
NOT SHOW THE EXACT COMPONEN TS OR CIRC UITR Y OF CONTROLS HAVING A COMMON CODE
WITHOUT AFFECTING THE INTERCHANGEABILITY OF A COMPLETE BOARD, THIS DIAGRAM MAY
NOTES :
15Volts, .250Amps
SPI
.33W
Operation
J43
6
10.0K
R22
J43
3
100V
150p
C46
43.2K
R18
+
t
60V
.13
R40
J43
11
X2
TL431 REF
8
1
6
44.2K
R42
J43
12
CNY17-3
OCI3
42
1
6
5
50V
2700p
C16
Vfb2
Vref 2
+5Volts, 3 Amps
SPI
475K
R21
200V
1
C13
10.0K
R4
6A
200V
D4
10.0K
R27
10.0K
R2
Operation
10-55 VDC
33.2
R15
100
16V
C43
47.5
R58
T1
1
2
11
12
10.0
R60
+
t
60V
.13
R50
10.0
R9
47.5
R6
47.5
R7
10.0
R61
+5Volts, .750 Amp
100
16V
C41
332
R53
50V
0.1
C39
6A
200V
D18
33.2
R16
LED2
+5V
Vref 1
Machine Control Power Supply
47.5
R57
T1
10
3
1.0A
30V
D22
2000V
.0015
C12
J42
3
43.2K
R49
100K
R5
221K
R52
44.2K
R51
50V
2700p
C42
10.0K
R13
CNY17-3
OCI1
42
1
6
5
1.82K
R14
D24
J42
5
J42
2
J42
6
3A
600V
D19
G
D
S
21A
200V
Q1
30.1
R35
475
R8
30.1
R36
3W
18V
DZ8
3W
0.05
R11
T1
5
8
22
35V
C11
50V
0.1
C14
.33W
1.0
35V
C47
1.21 K
R46
ADJ
IN
OUT
X8
ADJ
IN
OUT
X9
T1
9
4
1.0
35V
C40
J42
1
X1
TL431 REF
8
1
6
1.21 K
R48
50V
0.1
C44
4.7
35V
C38
gnd_mcps
Vfb1
Vfb1
.750 Amp
+15Volts
-15Volts, .100Amp
1A
600V
.33W
D8
100V
150p
C45
2.49K
R23
50V
0.1
C21
J43
2
J43
7
150
R64
J43
8
+
t
.24
R17
150
R62
LED1
2.49K
R19
100
16V
C35
150
R63
332
R41
50V
0.1
C34
100
16V
C37
16A
200V
D16
100
16V
C36
D7
D6
4.7
35V
C19
4.7
35V
C20
T2
8
7
4.7
35V
C18
4.7
35V
C17
T2
13
2
50V
0.1
C22
+
t
.24
R24
.33W
.33W
1A
1A
600V
600V
.33W.33W.33W
.200 Amps
Gate Drive
+20Volts
Gate Drive
+20Volts
.200 Amps
T2
9
6
SOLID EDGE
EN-170
MANUFACTURING TOLERANCE PER E2056
UNLESS OTHERWISE SPECIFIED TOLERANCE
SCALE:
DO NOT SCALE THIS DRAWING
ON 3 PLACE DECIMALS IS ± .002
THIS SHEE T CONTAI NS PROPRIETARY INFORMATION OWNED BY THE LINCOLN ELECTRIC COMPANY AND IS NOT TO BE REPRODUCED, DISCLOSED OR USED WITHOUT THE EXPRESS WRITTEN PERMISSIO N OF THE LINCOLN ELECTRIC COMPANY, CLEVELAND, OHIO U.S.A.
DESIGN INFORMATION
t
DRAWN BY:
WITH PUBLISHED STANDARDS.
DATE:
ON 2 PLACE DECIMALS IS ± .02
MATERIAL TOLERANCE (" ") TO AGREE
ON ALL ANGLES IS ± .5 OF A DEGREE
SUBJECT:
ENGINEER:
EQUIPMENT TYPE:
DRAWING No.:
JP\TK Digital Systems
Schematic, Digital Power Supply
G
NONE 11-30-98
REFERENCE:
SUPERSEDING:
APPROVED: 3631
Chg. Sheet No."X" INFO.
6-2-2000A
10-27-2000E
EARTH GROUND CONNECTION
POWER SUPPLY SOURCE POINT
VOLTAGE NETSUPPLY
R-
FRAME CONNECTION
LAST NO. USED
COMMON CONNECTION
D-
C-
LABELS
CAPACITORS =
UNLESS OTHERWISE SPECIFIED)
DIODES =
FILENAME: G3631-2D2
MFD
(
GENERAL INFORMATION
UNLESS OTHERWISE SPECIFIED)
RESISTORS = Ohms (
(UNLESS OTHERWISE SPECIFIED)1A, 400V
ELECTRICAL SYMBOLS PER E1537
1/4W
.022/50V
G-12
NOTE: This diagram is for reference only. It may not be accurate for all machines covered by this manual.

NOTE: Lincoln Electric assumes no responsibility for liablilities resulting from board level troubleshooting. PC Board repairs will invalidate your factory warranty. Individual Printed Circuit Board Components are not available from Lincoln Electric. This information is pro-
vided for reference only. Lincoln Electric discourages board level troubleshooting and repair since it may compromise the quality of the design and may result in danger to the Machine Operator or Technician. Improper PC board repairs could result in damage to the
machine.
ELECTRICAL DIAGRAMS G-13
POWER WAVE 455/R
PC BOARD ASSEMBLY-DIGITAL POWER SUPPLY
INVERTER WELDERS
DIGITAL POWER P.C. BOARD AS'BLY
G3632-1
6-2-2000A
CAPACITORS = MFD/VOL TS
INDUCTANCE = HENRIES
RESISTANCE = OHMS
(3.64)
(6.14)
ITEM PART NUMBER REQ'D. DESCRIPTION REFERENCE
DESIGNATOR
1G3632-C 1 POWER PC BOARD BLANK
2M19436-3 1 POTTING TRAY
3S8025-80 2 SELF TAPPING SCREW
4E2527 115g EPOXY ENCAPSULATIOG RESIN
5E2861 AS REQ'D ELECTRICAL INSULATING COMPOUND
SPECIFICATIONS
FOR ITEMS LISTED BELOW REFER TO ELECTRONIC COMPONENT DATABASE FOR COMPONENT
ITEM PART NUMBER QTY. DESCRIPTION REFERENCE
6PCLIN-503-3 1 PCB,MTP,DC POWER ASSY,NP N/A
7707W04095 2 SDIO,MURS120T3,NO PRINT D1 D15
8A262564400 2 SRES,1.82K,1206,1%,1/8W,NP R14 R20
9A262566900 3 SRES,5.62K,1206,1%,1/8W,TR,NP R12 R28 R45
10 A262569000 6 SRES,10K,1206,1%,1/4W,(09X-007 R4 R13 R22 R2 R27 R56
11 A262576200 2 SRES,56.2K,1206,1%,1/8W,NP(500 R38 R39
12 A262577900 4 SRES,100K,TKF,1206,1%,1/8W,TR, R5 R10 R21 R29
13 SM100-035 2 SRES,330,1206,5%,1/4W R41 R53
14 SM100-444 1 SRES,249,1206,1%,1/4W,TR,NP R33
15 SM100-411 2 SRES,221K,1206,1%,1/8W,TR,NP R34 R52
16 SM100-420 1 SRES,20,1206,1%,1/8W,TR,NP R32
17 SM100-440 2 SRES,0.05,1%,2W,TR,NP R11 R30
18 SM100-441 1 SRES,1K,5%,2W,TR,NP R26
19 SM100-443 3 SRES,33.2,1206,1%,1/4W,TR,NP R15 R16 R43
20 SM100-445 2 SRES,43.2K,1206,1%,1/4W,TR,NP R18 R49
21 SM100-446 2 SRES,44.2K,1206,1%,1/4W,TR,NP R42 R51
22 SM100-447 1 SRES,THERMISTOR,POS TEMP,TR,NP R50
23 SM100-448 2 SRES,THERMISTOR,POS TEMP,TR,NP R17 R24
24 SM200-145 11 SCAP,4.7uF,TAN,35V,20%,TR,NP
C1 C10 C17 C18 C19 C20 C24
C33 C38 C3 C6
25 SM200-183 3 SCAP,150pF,0805,50V,COG,5%,TR, C27 C45 C46
26 SM200-188 5 SCAP,1uF,TAN,3528,35V,TR,NP C23 C29 C30 C40 C47
27 SM200-192 2 SCAP,820pF,0805,50V,COG,5%,TR, C4 C8
28 SM200-193 2 SCAP,2700pF,0805,5OV,X7R,5%,TR C16 C42
29 SM200-194 11 SCAP,0.1uF,0805,50V,X7R,10%,TR
C2 C5 C7 C9 C14 C21 C22 C25
C34 C39 C44
30 SM200-200 2 SCAP,10pF,CER,0805,100V,5%,TR, C28 C32
31 SM200-201 1 SCAP,33uF,TAN,7343,25V,10%,TR,LOW ESR C11
32 SM200-202 5 SCAP,100uF,TAN,7343,10V,20%,TR C35 C36 C37 C41 C43
33 SM550-079 7 SDIO,1A,400V,DO-214BA,GLS,NP D10 D12 D13 D14 D17 D24 D25
34 SM550-109 2 SLED,RED,1206,TR,NP LED1 LED2
35 SM550-122 2 SDIO,MURD620CT,6A,200V,ULTRA-F D4 D18 D16
36 SM550-123 4 SDIO,MBRA130LT3,1A,30V,SCHOTTK D20 D21 D22 D23
37 SM550-148 1 SDIO,MURB1620CT,16A,200V D16
38 SM550-149 1 SDIO,1SMB5934BT3,24V,3W DZ1
39 SM550-125 2 SDIO,MMSZ5254BT1,0.5W,27V,5%,T DZ2 DZ3
40 SM550-126 1 SDIO,1SMB5913BT3,3W,3.3V,5%,TR DZ4
CR
41 SM550-128 2 SDIO,1SMB5931BT3,3W,18V,5%,TR, DZ7 DZ8
42 703W31526 1 SRES,15K,FXD,1206,1%,1/8W,TR R1
43 A262567400 1 SRES,6.19K,1206,1%,1/8W,TR,NP R3
44 SM550-104 6 SDIO,MURS160,1A,600V,FAST RECO D2 D3 D6 D7 D8 D9
45 A287245100 2 SICS,TL4311D,LIN,V-REF,36V,-40 X1 X2
46 SM800-299 2 SICS,PWM CONTROLLER,I-MODE,NP X4 X5
47 SM800-297 2 SICS,MC78M05,V-REG,100mA,5V,NP X6 X7
48 707W03410 3 TRA,CNY17-3,NP OCI1 OCI2 OCI3
49 HW900-379 2 HSS,MTP,VERT MOUNT,TO220,NP Q1,Q2 HEATSINKS
50 TH100-160 1 RES,THERMISTOR,PTC,POS TEMP,TR R40
51 TH100-161 1 RES,THERMISTOR,NTC,NEG TEMP,NP R55
52 TH200-132 2 CAP,1uF,PEMF,200V,10%,NP C13 C26
53 TH300-023-A 1 TFM,L-5763-3,FLYBACK,NP T1
54 TH300-024-A 1 TFM,L-5764-3,FLYBACK,NP T2
55 TH400-053 2 TRA,BUZ30A,NMF,21A,200V,T0220, Q1 Q2
56 TH600-263 1 CON,4P,TIN,MINI,NP J41
57 TH600-264 1 CON,6P,TIN,MINI,NP J42
58 TH600-266 1 CON,12P,TIN,MINI,NP J43
59 PPW-11110-1 2 SCREW N/A
60 PPW-11160-1 2 WASHER N/A
61 707W04224 1 SDIO,MURS360T3,NP D19
62 TH200-219 2 CAP, 1500pF,200V,MET POLYPROP C12,31
63 SM200-220 1 SCAP,0.022uF,50v, X7R C49
64 SM200-221 1 SCAP,330pF,0805,50V,5%, COG C52
65 SM200-522 4 SRES,47.5,1210,5%,1/2W,TR,NP R6 R7 R57 R58
66 703W01044 3 SRES,10,TKF,0805,1%,1/10W R9 R60 R61
67 SM100-523 2 SRES,30.1,FXD,1210,5%,1/2W,TR R35 R36
68 SM400-057 1 STRA,78M15C,DPACK X3
69 SM400-058 1 STRA,7815C,DPACK X8
70 SM400-059 1 STRA,79M15C,DPACK X9
71 SM100-524 2 SRES,2.49K,1210,5%,1/2W,T/R R19 R23
72 SM100-525 3 SRES,1.21K,1210,5%,1/2W,TR,NP R46 R48 R37
73 SM100-526 2 SRES,150,1210,5%,1/2W,TR,NP R25 R44
74 SM100-409 1 SRES,475,1206 R8
75 SM900-001 2 SHSS,MTP,D2PACK,TO263 X8,D16 HEATSINKS
76 9P7951 AS REQ'D THERMAL JOINT COMPOUND N/A
77 SM200-194 1 SCAP,0.1uF,0805,50V,X7R,10%,TR C53
78 A262577600 1 SRES,75K,TKF,1206,1%,1/8W,TR, R31
79 SM100-526 1 SRES,150,1210,5%,1/2W,TR,NP R62, R63, R64
G-13
Return to Section TOC Return to Section TOC Return to Section TOC Return to Section TOC
Return to Master TOC Return to Master TOC Return to Master TOC Return to Master TOC

ELECTRICAL DIAGRAMS G-14
POWER WAVE 455/R
SCHEMATIC - FEEDHEAD PC BOARD #1
3823-1C1/1
07/17/2000
LRW
COMMON DIGITAL CONTROLS
FEEDHEAD PC BOARD SCHEMATIC
11-3-2000A
XA
1 OF 3
G-14
NOTE: This diagram is for reference only. It may not be accurate for all machines covered by this manual.
Return to Section TOC Return to Section TOC Return to Section TOC Return to Section TOC
Return to Master TOC Return to Master TOC Return to Master TOC Return to Master TOC

ELECTRICAL DIAGRAMS G-15
POWER WAVE 455/R
SCHEMATIC- FEEDHEAD PC BOARD #2
3823-1C1/2
07/17/2000
LRW
COMMON DIGITAL CONTROLS
FEEDHEAD PC BOARD SCHEMATIC
11-3-2000A
XA
TPD
TPE
2 OF 3
G-15
NOTE: This diagram is for reference only. It may not be accurate for all machines covered by this manual.
Return to Section TOC Return to Section TOC Return to Section TOC Return to Section TOC
Return to Master TOC Return to Master TOC Return to Master TOC Return to Master TOC

ELECTRICAL DIAGRAMS G-16
POWER WAVE 455/R
SCHEMATIC- FEEDHEAD PC BOARD #3
3823-1C1/3
07/17/2000
LRW
COMMON DIGITAL CONTROLS
FEEDHEAD PC BOARD SCHEMATIC
11-3-2000A
XA
3 OF 3
G-16
NOTE: This diagram is for reference only. It may not be accurate for all machines covered by this manual.
Return to Section TOC Return to Section TOC Return to Section TOC Return to Section TOC
Return to Master TOC Return to Master TOC Return to Master TOC Return to Master TOC

NOTE: Lincoln Electric assumes no responsibility for liablilities resulting from board level troubleshooting. PC Board repairs will invalidate your factory warranty. Individual Printed Circuit Board Components are not available from Lincoln Electric. This information is pro-
vided for reference only. Lincoln Electric discourages board level troubleshooting and repair since it may compromise the quality of the design and may result in danger to the Machine Operator or Technician. Improper PC board repairs could result in damage to the
machine.
ELECTRICAL DIAGRAMS G-17
POWER WAVE 455/R
PC BOARD ASSEMBLY-FEEDHEAD
COMMON DIGITAL CONTROLS
FEED HEAD PC BOARD ASSEMBLY
L11087-2
4-20-2001C
UNLESS OTHERWISE SPECIFIED:
RESISTANCE = OHMS
(6.34)
N.D.
ITEM PART NO. QTY PC BOARD REFERENCE
DESIGNATORS DESCRIPTION
1G3822-D 1 FEED HEAD PC BOARD BLANK
2M19436-5 1 POTTING TRAY
3S8025-80 2 SELF TAPPING SCREW
4E2527 195
g
6.88 OZ. EPOXY ENCAPSULATING RESIN
5E3539 AS REQ. ELECTRICAL INSULATING COMPOUND
6S24822-21X5 SOFTWARE,CPLD
7S24823-21X9 SOFTWARE,FLASH
8S25024-2SMT 4 C1,C2,C7,C50 SCAP,1uF,TAN,3528,35V,TR,NP
9S25020-3SMT 47
C3,C4,C5,C6,C8,C9,C12,C14,
C15,C19,C20,C22,C25,
C26,C27,C28,C29,C30,C31,
C32,C34,C35,C38,C39,C41,
C43,C45,C46,C47,C48,C49,
C51,C54,C56,C57,C59,C60,
C64,C65,C69,C72,C75,C76,
C77,C78,C81,C82
SCAP,0.1uF,0805,50V,X7R,10%,TR
10 S25024-8SMT 5 C10,C11,C17,C18,C80 SCAP,10uF,TAN,6032,16V,10%,TR,NP
11 S25020-13SMT 2 C13,C16 SCAP,150pF,CER,0805,100V,COG,5%,TR,NP
12 S25024-5SMT 6 C23,C63,C66,C67,C68,C71 SCAP,4.7uF,TAN,7343,35V,10%,TR,NP
13 S25024-10SMT 3 C24,C36,C73 SCAP,22uF,TAN,7343,25V,10%,POLAR,TR
14 S25020-2SMT 1 C37 SCAP,0.022uF,0805,50V,X7R,10%,
15 S25020-10SMT 3 C40,C42,C44 SCAP,4700pF,0805,50V,X7R,10%,T
16 S25020-9SMT 2 C52,C79 SCAP,47pF,0805,50V,COG,5%,TR,N
17 S25020-15SMT 3 C55,C58,C83 SCAP,22pF,0805,50V,COG,5%,TR,N
18 S24833-1 2 C61,C62 CAP,0.27uF,PCF,63V,5%,TR,NP
19 S13490-179 1 C70 CAP,1000uF,ALU,35V,20%,NP
20 S13490-182 1 C74 CAP,3300uF,ALU,63V,20%,NP
21 S13490-184 1 C84 CAP,330uF,100V
22 S25020-4SMT 2 C85,C86 CAPACITOR ,SMD CERAMIC,820PF,50V,5%COG,S0805
23 S25040-12SMT 2 D1,D12 SDIO,MURS320T3,3A,200V,ULTRAFA
24 S25040-2SMT 4 D2,D17,D20,D27 SDIO,400V,0.8A,NP
25 S25040-5SMT 10 D3,D4,D5,D6,D9,D18,D21,D28,D29,
D31 SDIO,BAV99LT1,SOT23,DUAL SWITC
26 S25049-4SMT 4 D7,D8,D10,D19 SDIO,BAT54S,DUAL/SERIES,30V,20
27 S25040-4SMT 5 D11,D13,D14,D15,D16 SDIO,BAW56LT1,SOT23,DUAL SWT,T
28 S25040-11SMT 4 D22,D23,D24,D25 SDIO,MURS160,1A,600V,FAST RECO
29 S25040-9SMT 1 D26 SDIO,3A,200V,D0-214AB,UFR
30 S25040-10SMT 1 D30 DIODE,SMD,3A,400V
31 S25046-3SMT 4 DZ1,DZ2,DZ3,DZ4 SDIO,MMSZ5248B,18V,ZENER,TR,NP
32 S25046-1SMT 3 DZ5,DZ28,DZ29 SDIO,MMSZ5231BT1,5.1V,NP
33 S25044-9SMT 6 DZ6,DZ7,DZ8,DZ9,DZ26,DZ27 SDIO,1SMB5920BT3,6.2V,NP
34 S25044-1SMT 9 DZ10,DZ11,DZ12,DZ13,DZ14,
DZ15,DZ16,DZ17,DZ18 SDIO,1SMB5918BT3,3W,5.1V,5%,TR,NP
35 S25046-2SMT 4 DZ20,DZ21,DZ22,DZ23 SDIO,MMSZ5240BT1,10V,500mW,ZEN
36 S18380-5 2 F1,F2 RES,50,VAR,PTC,NP
37 S18380-14 12 F3,F4,F5,F6,F7,F8,F9,F10,
F11,F12,F13,F14 RES,500,PTC,265V
38 S24020-4 2 J81,J82 CON,MOLEX,15-97-7042,MINI,PCB,4 PIN,TIN
39 S24020-6 1 J83 CON,MOLEX,15-97-7062,MINI,PCB,6 PIN,TIN
40 S24020-8 1 J84 CON,MOLEX,15-97-7082,MINI,PCB,8 PIN,TIN
41 S24020-16 1 J85 CON,MOLEX,15-97-7162,MINI,PCB,16 PIN,TIN
42 S18248-10 1 J86 CON,10P,MINI,NP
43 S18248-16 1 J87 CON,MOLEX,39-28-1163,PCB,16 PIN,TIN
44 S15000-28SMT 4 OCI1,OCI2,OCI3,OCI4 SICS,Optocoupler, HCPL-0601 (SO-8)
45 S15000-26SMT 1 OCI5 SICS,HCPL-0201,OPTOCOUPLE
46 S25051-4SMT 5 Q1,Q12,Q13,Q15,Q16 STRA,2N7002,TR,NP, (SM400-020)
47 S25050-2SMT 5 Q2,Q3,Q7,Q14,Q17 STRA,2N4403,SO23,TR,(500475),N
FOR ITEMS LISTED BELOW REFER TO ELECTRONIC COMPONENT DATABASE FOR COMPONENT SPECIFICATIONS
(5.84)
74 S25001-3320SMT 6 R139,R140,R141,R142,R143,R144 RESISTOR,SMD,332ohms,1/4W,1206,1%
75 S25005-1SMT 2 R97,R98 SRES,0.05,3W,1%,TR,NP
76 S25001-4751SMT 4 R99,R114,R132,R137 SRES,4.75K,1206,1%,1/8W,NP,(SM
77 S25000-4751SMT 14
R101,R104,R125,R126,R127,
R128,R129,R130,R131,R133,
R134,R145,R90,R109
SRES,4.75K,0805,1%,TR,NP
78 S25001-1503SMT 1 R115 SRES,150K,1206,1%,1/8W,NP
79 S25000-1211SMT 1 R135 SRES,1.21K,0805,1%,1/10W,TR,NP
80 S25000-2002SMT 3 R146,R147,R76 SRES,20K,TKF,0805,1%,01/10W,TR
81 S25000-1002SMT 24
R2,R3,R4,R5,R6,R7,R9,R16,R17,
R18,R19,R20,R21,R22,R23,R53,
R54,R77,R80,R106,R116,R138,
R148
,
R149
RESISTOR,SMD,METAL FILM,1/10W,10.0K,1%
82 S19869-8 1 S1 SWT,78B08S,DIP,SPST,8P,NP
83 S20375-8 1 T1 TFM,L5936,Noreast,Switching Pwr
84 S25068-7SMT 1 X1 SICS,4.6V,2%,VOLT. DETECTOR
85 M15101-14SMT 1 X2 SICS,MC68332,MICRCONTROLLER,TQ
86 S25069-2SMT 1 X3 SICS,25128,SERIAL EEPR,NP
87 S20353-1SMT 1 X4 SICS,MC145407,RECEIVER/DRVR,RS
88 S25070-6SMT 1 X5 SICS,XC9572-15,CPLD,TQ100,NP
89 S17900-24SMT 1 X7,X29 SICS,74HC132,NP
90 S25069-3SMT 1 X9 SICS,28F800B5B90,FLASH ROM,90n
91 S25066-2SMT 1 X10 SICS,AD7862,DUAL,12BIT,250kSPS
92 S25057-3SMT 1 X11 SICS,AD8403ARU10,DIGITAL POT,NP
93 M15105-9SMT 1 X12 SICS,AD7945,12BIT,PARALLEL,DAC
94 S15128-21SMT 1 X13 SICS,LT1016,COMPARATOR,NP
95 S15128-18SMT 2 X14,X20 SICS,MC33074,QUAD,OPAMP,S014,T
96 S15128-16SMT 1 X15 ICS,SMD,OP-AMP,QUAD,HIGH PERFORMANCE 1014
97 S15018-20SMT 1 X16 SICS,HIP4082,H-BRIDGE,FET DRIVE
98 S25069-4SMT 1 X17 SICS,128Kx16,20nS,TSOP(II)
99 S20353-5 1 X18 SICS,AN82527,CAN CONTROLLER,PL
100 S25065-2SMT 1 X19 SICS,74ACT573,OCTAL,TRANS. LAT
101 S20353-4SMT 3 X21,X26,X27 SICS,MAX485,TRANSCEIVER,NP
102 S25068-8SMT 1 X22 SICS,79L05,V-REG,-5V,SO8
103 S25068-6SMT 2 X23,X24 SICS,78L05,V-REG,+5V,SO8
104 S15128-25SMT 1 X25 SICS,LM2576HVS-5.0,VREG,60V,SWI
105 S17900-11SMT 1 X28 SICS,74HC245,SOL20,HCMOS,NP
106 S24841-1 1 X30 ICS,DC/DC,5V 3A OUT,36-75V IN
107 S25082-1SMT 1 Y1 SXTL,16MHz,HC40,20pF,NP
48 S25050-1SMT 9 Q4,Q5,Q6,Q19,Q20,Q21,Q22,Q23,Q2
4STRA,2N4401,SOT-23,NPN,TR,
49 S25051-5SMT 4 Q8,Q9,Q10,Q11 STRA,75A,55V,0.007 OHM FET,N-CHAN
50 S23060-1SMT 1 Q18 IC,SMD,SWITCH,LO-SIDE,2.2A60V,
51 S25000-1002SMT 24
R2,R3,R4,R5,R6,R7,R9,R16,
R17,R18,R19,R20,R21,R22,
R23,R53,R54,R77,R80,R106,
R116
,
R138
,
R148
,
R149
SRES,10K,0805,1%,1/10W,TR,NP
52 S25001-1002SMT 6 R8,R10,R13,R83,R100,R118 SRES,10K,MF,1206,1%,1/8W,TR
53 S25001-4752 4 R84,R85,R86,R152 RESISTOR,SMD,47.5K,1/4W,1206,1%
54 S25003-2000SMT 2 R11,R12 SRES,200,2512,5%,1W,TR,NP
55 S25001-4750SMT 9 R14,R15,R62,R68,R78,R102,
R103,R107,R112 SRES,475,1206,1%,1/8W,TR,NP
56 S25000-1001SMT 8 R24,R25,R55,R105,R113,
R136,R153,R154 SRES,1K,0805,1%,1/10W,TR,NP
57 S25000-4750SMT 2 R26,R27 SRES,475,0805,1%,TR,NP
58 S25004-2430SMT 12 R28,R29,R30,R31,R32,R33,
R34,R35,R36,R37,R38,R39 SRES,243,WSC-1,1%,1W,TR,NP
59 S25000-3320SMT 9 R41,R42,R48,R49,R50,R51,
R52,R121,R123 SRES,332,0805,1%,1/10W,TR,NP
60 S25000-2210SMT 9 R43,R44,R45,R46,R47,R65,
R108,R122,R124 SRES,221,TKF,0805,1%,1/10W,TR
61 S25001-2000SMT 8 R56,R57,R58,R61,R64,R66,
R110,R111 SRES,200,1206,1%,1/8W,TR,NP
62 S25001-7500SMT 1 R1 RESISTOR,SMD,750ohms,1/4W,1206,1%
63 S25000-2213SMT 1 R63 SRES,221K,TKF,0805,1%,01/10W,TR
64 S25000-4752SMT 2 R67,R72 SRES,47.5K,TKF,0805,1%,01/10W,TR
65 S25000-1003SMT 6 R69,R71,R73,R75,R82,R117 SRES,100K,TKF,0805,1%,01/10W,TR
66 S25001-1001SMT 1 R70 SRES,1K,1206,1%,1/8W,TR,NP,
(
09
67 S25000-9092SMT 2 R74,R81 SRES,90.9K,TKF,0805,1%,1/10W
68 S25000-3921SMT 1 R79 SRES,3.92K,TKF,0805,1%,1/10W,TR
69 S25001-4753SMT 2 R87,R120 SRES,475K,1206,1%,1/8W,TR,NP
70 S25001-4752SMT 2 R88,R119 SRES,47.5K,1206,1%,1/8W,TR,NP
71 S25001-1000SMT 9 R89,R93,R96,R155,R156,R157, SRES,100,1206,1%,1/8W,TR,NP
72 S25001-15R0SMT 2 R91,R92 SRES,15,1206,1%,1/8W,TR,NP
73 S25001-1500SMT 4 R94,R95,R150,R151 SRES,150,1206,1%,1/8W,TR,NP
N.E.
G-17
Return to Section TOC Return to Section TOC Return to Section TOC Return to Section TOC
Return to Master TOC Return to Master TOC Return to Master TOC Return to Master TOC

Return to Section TOC Return to Section TOC Return to Section TOC Return to Section TOC
Return to Master TOC Return to Master TOC Return to Master TOC Return to Master TOC
ELECTRICAL DIAGRAMS G-18
POWER WAVE 455/R
SCHEMATIC - INPUT PC BOARD
FILENAME: M19528-1AA
J60
2
J60
4
J61
8
10W
100
R7
10W
100
R10
10W
100
R2
J61
6
10W
100
R8
10W
100
R1
250J
660V
TP2
10W
100
R9
10W
100
R3
CR2
4
3
10W
100
R6
J60
3
J61
10
1A
1500V
D2
267K
R4
D3
3.01K
R19
3.01K
R23
3.01K
R20
3.01K
R21
3.01K
R13
3.01K
R17
3.01K
R16
3.01K
R15
3.01K
R14
3.01K
R12
3.01K
R18
3.01K
R11
D1
475
R5
50V
.022
C1
CNY17-3V
OCI1
42
1
6
5
J60
5
3.01K
R24
CR2
3.01K
R25
CR1
J60
1
3.01K
R22
CR2
6
5
J61
4
J60
8
CR1
4
3
250J
660V
TP4
250J
660V
TP3
J61
1
J61
5
J61
7
J61
3
J60
6
J60
7
25
250J
660V
TP1
+13V
+13V
VOLTAGE NET
CONTACTOR CONTROL
PRE-CHARGE CONTROL
+13V FROM CONTROL BOARD
DIODES =
.022/50V
MFD
RESISTORS = Ohms (
LAST NO. USED
LABELS
D-
UNUSED PINS
NOTES :
1
C-
R-
SUPPLY
EQUIP.
1/4W
(
UNLESS OTHERWISE SPECIFIED)
UNLESS OTHERWISE SPECIFIED)
(UNLESS OTHERWISE SPECIFIED)
UNLESS OTHERWISE SPECIFIED TOLERANCE
GENERAL INFORMATION
THE LINCOLN ELECTRIC CO.
NOT SHOW THE EXACT COMPONENTS OR CIRCUITRY OF CONTROLS HAVING A COMMON CODE
AND IS NOT TO BE REPRODUCED, DISCLOSED OR USED WITHOUT THE EXPRESS PERMISSION OF
WITHOUT AFFECTING THE INTERCHANGEABILITY OF A COMPLETE BOARD, THIS DIAGRAM MAY
THE LINCOLN ELECTRIC CO.
THIS SHEET CONTAINS PROPRIETARY INFORMATION OWNED BY
N.A. SINCE COMPONENTS OR CIRCUITRY ON A PRINTED CIRCUIT BOARD MAY CHANGE
Ch’ge.Sht.No.
NUMBER.
J61
2
POWER SUPPLY SOURCE POINT
COMMON CONNECTION
EARTH GROUND CONNECTION
INPUT P.C. BOARD SCHEMATIC
INVERTEC 450 - 650
OCI- 1
CR- 2
TP- 4
FRAME CONNECTION
3
ON HOLES SIZES PER E-2056
DR.
DATE
SUP’S’D’G.
ELECTRICAL SYMBOLS PER E1537
CLEVELAND, OHIO U.S.A.
THE LINCOLN ELECTRIC CO.
MAB
SINGLE PHASE DETECT
CHK.
5-25-99
1A, 400V
CAPACITORS =
M
CONTACTOR
COIL CONNECT
Input
CONTACTOR OUTPUT
VAC
PRE-CHARGE CONNECTIONS
CENTER LEG TO OUTSIDE LEG OF INPUT
19528
19528
WITH PUBLISHED STANDARDS
MM
NO.
SHT.
ON ALL ANGLES IS + .5 OF A DEGREE
SUBJECT
TYPE
NONE
ON 3 PLACE DECIMALS IS + .OO2
ON 2 PLACE DECIMALS IS + .O2
MATERIAL TOLERANCE ("t") TO AGREE
SCALE
J61
9
XA
11-3-2000A
G-18
NOTE: This diagram is for reference only. It may not be accurate for all machines covered by this manual.

NOTE: Lincoln Electric assumes no responsibility for liablilities resulting from board level troubleshooting. PC Board repairs will invalidate your factory warranty. Individual Printed Circuit Board Components are not available from Lincoln Electric. This information is pro-
vided for reference only. Lincoln Electric discourages board level troubleshooting and repair since it may compromise the quality of the design and may result in danger to the Machine Operator or Technician. Improper PC board repairs could result in damage to the
machine.
ELECTRICAL DIAGRAMS G-19
POWER WAVE 455/R
PC BOARD ASSEMBLY-INPUT
11-3-2000A
INVERTER WELDERS
L11396-1
CAPACITORS = MFD/VOLTS
ITEM REQ’D PART NO. IDENTIFICATION
0
0
3.00
.25
.25
4.50
~.04
6.00
~.04
RESISTORS = OHMS/WATTS
INPUT P.C. BOARD ASSEMBLY
4.25
5.75
xxxxx
xxxxx
xxx
2.80
x
x
x
x
x
x
x
x
x
x
x
x
x
x
x
x
x
x
x
x
x
x
x
x
x
x
x
x
x
x
x
x
x
x
x
x
TP1
TP2
TP3 OCI1
TP4
CR2
CR1
C1
R4
R5
D3
R2
R3
R10
R9
R6
R7
R8
INVERTEC 455-655 INPUT
R22
R24
R25
R23 R13
R14
R15
R16
R17
R18
R19
R20
R21
R12
R11
J60 J61
R1
D2
D1
L11396-1
xxx
G-19
Return to Section TOC Return to Section TOC Return to Section TOC Return to Section TOC
Return to Master TOC Return to Master TOC Return to Master TOC Return to Master TOC

Return to Section TOC Return to Section TOC Return to Section TOC Return to Section TOC
Return to Master TOC Return to Master TOC Return to Master TOC Return to Master TOC
ELECTRICAL DIAGRAMS G-20
SCHEMATIC -SWITCH PC BOARD
G-20
NOTE: This diagram is for reference only. It may not be accurate for all machines covered by this manual.

NOTE: Lincoln Electric assumes no responsibility for liablilities resulting from board level troubleshooting. PC Board repairs will invalidate your factory warranty. Individual Printed Circuit Board Components are not available from Lincoln Electric. This information is pro-
vided for reference only. Lincoln Electric discourages board level troubleshooting and repair since it may compromise the quality of the design and may result in danger to the Machine Operator or Technician. Improper PC board repairs could result in damage to the
machine.
ELECTRICAL DIAGRAMS G-21
POWER WAVE 455/R
PC BOARD ASSEMBLY-SWITCH
SOLID EDGE
EN-170
MANUFACTURING TOLERANCE PER E20 56
UNLESS OTHERWISE SPECIFIED TOLERANCE
SCALE:
DO NOT SCALE THIS DRAWING
ON 3 PLACE DECIMALS IS ± .002
THIS SHEET CONTAINS PROPRIETARY INFORMATION OWNED BY THE LINCOLN ELECTRIC COMPANY AND IS NOT TO BE REPRODUCED, DISCLOSED OR USED WITHOUT THE EXPRESS WRITTEN PERMISSION OF THE LINCOLN ELECTRIC COMPANY, CLEVELAND, OHIO U.S.A.
DESIGN INFORMATION
t
DRAWN BY:
WITH PUBLISHED STANDARDS.
DATE:
ON 2 PLACE DECIMALS IS ±.02
MATERIAL TOLERANCE (" ") TO AGREE
ON ALL ANGLES IS ± .5 OF A DEGREE
SUBJECT:
ENGINEER:
EQUIPMENT TYPE:
DRAWING No.:
L. C.
F.V.
INVERTER WELDERS
SWITCH P.C. BOARD AS'BLY
G
1:1 10-3-2000
REFERENCE:
SUPERSEDING:
G3734-1
APPROVED: 3734-2
Chg. Sheet No."X" INFO.
5-11-2001FXD-RW
D1
C16
T1
J40
D2
R9
X2
R8
X1
C6
C7
C3
C2
C5
OCI1
R15
R12
R10
R11
R3
R16
R21 R20 R19 R18 R17
R4
R13
R28 R29 R30
R31
R14
R22
R23 R24 R25 R26 R27
R32
R5
R7
R6
R2
T2
12
B13
B19 B20
C4
C17
C8
C9
C10
C11
C12
D8
D9
D10
D11
D12
D3
D4
D5
D6
D7
L10 L9 L8 L7 L6
L1 L2 L3 L4 L5
C15
C14
C13
A1
A2
DZ4
DZ7
DZ3 DZ2
DZ6
DZ5
DZ1
SH1
B14
C1
R1
B11
C1 1 S2 0500-14 CAPACITOR,PPMF,.022,100V,BOX,5%
C2 1S16668-11 CAPACITOR,CEMO,0.1, 50V,10%
C3 1S16668-5 CAPACITOR,CEMO,.022, 50V,20%
C4,C6,C7 3S16668-6 CAPACITOR,CEMO,4700p,50V,10%
C5 1S13490-93 CAPACITOR,TAEL,27,35V,10%
C8,C9,C10,C11,C12,C13,C14 10 S20500-1 CAPACITOR,PPMF,0.1,1000V,10%,BOX
C15,C16,C17
D1,D2 2T12705-44 DIODE,AXLDS,1A,1000V,FR, 818
D3,D4,D5,D6,D7,D8,D9,D10 10 T12705-32 DIODE,T220,15A,600V,FR,MUR1560
D11,D12
DZ1 1T12702-4 ZENER DIODE, 1W,20V,5% 1N4747A
DZ2,DZ3,DZ5,DZ6 4T12702-29 ZENER DIODE, 1W,15V,5% 1N4744A
DZ4,DZ7 2T12702-40
ZENER DIODE, 1W,6.2V,5% 1N4735A
J40 1S24020-6 CONNECTOR,MOLEX,MINI,PCB,6-PIN,TIN
L1,L2,L3,L4,L5,L6,L7,L8,L9 10 T 12218-15 CHOKE,RF,FERRITE BEAD,180 OHM
L10
OCI1 1S15000-22 OPTOCOUPLER,PHOTO-Q,70V,CNY17-3/VDE
R1 1S16296-5 TRIMMER,MT,1/2W,10K, 10%,LINEAR
R2 1 S19400-6811 RESISTOR,MF,1/4W,6.81K,1%
R3,R8 2 S19400-1002 RESISTOR,MF,1/4W,10.0K,1%
R4,R13,R14,R17,R18,R19,R2
0
13 S19400-10R0 RESISTOR,MF,1/4W,10.0,1%
R21,R23,R24,R25,R26,R27
R5,R9 2S19400-2001 RESISTOR,MF,1/4W,2.00K,1%
R6 1S19400-2213 RESISTOR,MF,1/4W,221K,1%
R7 1S19400-1000 RESISTOR,MF,1/4W,100,1%
R10,R12,R15 3S19400-1003 RESISTOR,MF,1/4W,100K,1%
R11 1S19400-6191 RESISTOR,MF,1/4W,6.19K,1%
R16,R22 2S19400-1001 RESISTOR,MF,1/4W,1.00K,1%
R28,R29,R30,R31,R32 5T14648-9 RESISTOR,WW,5W,2.5K,5%,SQ
T1 1T12737-7 TRANSFORMER,PULSE,3-WINDING
T2 1M19612 CURRENT-TRANSDUCER,125-TURN
X1 1M13552-3 IC,CONVERTER,V/F,654
X2 1S15128-10 VOLTAGE REF,ADJ, PECISION,431I
ITEM REQ'D PART NO IDENTIFICATION
R1.62
.00 1.20
2.00 ±.12 11.15 ±.04
.30 +.12
-.00
1.38 +.12
-.00
N.T.,N.U.,N.V.
.30 +.12
-.00
0
6.00 ±.04
3.00
G-21
Return to Section TOC Return to Section TOC Return to Section TOC Return to Section TOC
Return to Master TOC Return to Master TOC Return to Master TOC Return to Master TOC

Return to Section TOC Return to Section TOC Return to Section TOC Return to Section TOC
Return to Master TOC Return to Master TOC Return to Master TOC Return to Master TOC
ELECTRICAL DIAGRAMS G-22
POWER WAVE 455/R
SCHEMATIC - VOLTAGE SENSE PC BOARD
G-22
NOTE: This diagram is for reference only. It may not be accurate for all machines covered by this manual.

NOTE: Lincoln Electric assumes no responsibility for liablilities resulting from board level troubleshooting. PC Board repairs will invalidate your factory warranty. Individual Printed Circuit Board Components are not available from Lincoln Electric. This information is pro-
vided for reference only. Lincoln Electric discourages board level troubleshooting and repair since it may compromise the quality of the design and may result in danger to the Machine Operator or Technician. Improper PC board repairs could result in damage to the
machine.
ELECTRICAL DIAGRAMS G-23
POWER WAVE 455/R
PC BOARD ASSEMBLY-VOLTAGE SENSE
0
1.55
1.75
0
±.04
2.00
.20
1.00
1.80
.20
±.04
COMMON DIGITAL CONTROLS
VOLTAGE SENSE SELECT P.C. BD AS'BLY
M19540-1
1-3-2000A
ITEM REQD PART NO.
IDENTIFICATION
INDUCTANCE = HENRYS
RESISTORS = OHMS
CAPACITORS = MFD/VOLTS
.
.
D1 1 T12199-1 1N4004
J1 1 S24020-6 HEADER
J2 1 S24020-2G HEADER
L1 1 T12218-7 330uH
OCI1,OCI2 2 S15000-20 PHOTO FET
R1,R2 2 S19400-4750 475 1/4W
R3 1 S18380-1 THERMISTOR,PTC
TP1,TP2 2 T13640-18 160J
D1
L1
OCI1 OCI2
R1
R2
R3
TP1
TP2
J1 J2
ARA
M19540-1M19540-1
A
M19540-1
VOLTAGE SENSE SELECT
G-23
Return to Section TOC Return to Section TOC Return to Section TOC Return to Section TOC
Return to Master TOC Return to Master TOC Return to Master TOC Return to Master TOC

Return to Section TOC Return to Section TOC Return to Section TOC Return to Section TOC
Return to Master TOC Return to Master TOC Return to Master TOC Return to Master TOC
ELECTRICAL DIAGRAMS G-24
POWER WAVE 455/R
SCHEMATIC - 40 VDC BUS PC BOARD
G-24
NOTE: This diagram is for reference only. It may not be accurate for all machines covered by this manual.

NOTE: Lincoln Electric assumes no responsibility for liablilities resulting from board level troubleshooting. PC Board repairs will invalidate your factory warranty. Individual Printed Circuit Board Components are not available from Lincoln Electric. This information is pro-
vided for reference only. Lincoln Electric discourages board level troubleshooting and repair since it may compromise the quality of the design and may result in danger to the Machine Operator or Technician. Improper PC board repairs could result in damage to the
machine.
ELECTRICAL DIAGRAMS G-25
POWER WAVE 455/R
PC BOARD ASSEMBLY-40 VDC BUS
9-22-2000
L11078-1
CAPACITORS = MFD/VOLTS
RESISTORS = OHMS, 1/4 WATT (UNLESS OTHERWISE SPECIFIED)
ITEM REQ’D PART NO IDENTIFICATION
0
3.85~.04
40V DC BUS P.C. BOARD ASSEMBLY
MULTI-WELD 350
04.50~.04
A1
C13
L1
C15
R12
R9
R10
R11
R25
D1
D2
DZ4
C6
R4
R5
R7
R8
R19
X1 X2
C2
C3
C5
C7
C8
C9
C10
C11
MOV1
LED1
R3
R13
R14
R20
R21
R22
R23
DZ5 DZ6
R15 R16
D3
J47 J46
C14
C16
C17
D4
D5
MOV2
R26
R27
R28
R29
C1
.20
.20
3.65
4.30
X1 1 M15458-4 IC,PWM-CONTROLLER,IMODE,2842A
C2,C3,C5 3 S13490-25 CAPACITOR,TAEL,4.7,35V 10%
C16 1 S13490-42 CAPACITOR,TAEL,1.0,35V,10%
C6 1 S13490-66 CAPACITOR,TAEL,47,35V 10%
C1 1 S13490-93 CAPACITOR,TAEL,27,35V,10%
X2 1 S15018-16 IC,CMOS,DRIVER,MOSFET,2110(SS)
C14 1 S16668-3 CAPACITOR,CEMO,100P, 100V,5%
C11,C17 2 S16668-10 CAPACITOR,CEMO,4700P, 50V,2%
C7,C8,C9,C10 4 S16668-11 CAPACITOR,CEMO,0.1, 50V,10%
R15,R16 2 S19400-47R5 RESISTOR,MF,1/4W,47.5,1%
R12,R13 2 S19400-1000 RESISTOR,MF,1/4W,100,1%
R3,R4,R5,R7,R8 5 S19400-1002 RESISTOR,MF,1/4W,10.0K,1%
R14,R22 2 S19400-1821 RESISTOR,MF,1/4W,1.82K,1%
R23 1 S19400-2213 RESISTOR,MF,1/4W,221K,1%
R20,R21 2 S19400-2672 RESISTOR,MF,1/4W,26.7K,1%
R29 1 S19400-3323 RESISTOR,MF,1/4W,332K,1%
R28 1 S19400-4752 RESISTOR,MF,1/4W,47.5K ,1%
R19 1 S19400-5622 RESISTOR,MF,1/4W,56.2K,1%
R9,R10,R11 3 S19400-8251 RESISTOR,MF,1/4W,8.25K,1%
C13 1 S20500-2 CAPACITOR,PPMF,0.47,630V,10%,BOX
J46 1 S24020-4 CONNECTOR,MOLEX,MINI,PCB,4-PIN,TIN
J47 1 S24020-8 CONNECTOR,MOLEX,MINI,PCB,8-PIN,TIN
D2 1 T12199-1 DIODE,AXLDS,1A,400V
D1 1 T12199-2 DIODE,AXLDS,1A,1000V
L1 1 T12218-16 CHOKE,HIGH-CURRENT,100UH,10A,10%, LOW
R26,R27 2 T12300-86 RESISTOR,WW,3W,0.05,1%
DZ4 1 T12702-25 ZENER DIODE,5W,20V,5% 1N5357B
DZ5,DZ6 2 T12702-45 ZENER DIODE, 1W,18V,5% 1N4746A
D4 1 T12705-23 DIODE,AXLDS,1A,30V,SCHOTTKY,1N5818
D5 1 T12705-34 DIODE,AXLDS,1A,400V,FR,1N4936
D3 1 T12705-59 DIODE,AXLDS,3A,600V,UFR
MOV1 1 T13640-15 MOV,50VRMS,15J,14MM
MOV2 1 T13640-24 MOV,175VRMS,120J,20MM
LED1 1 T13657-2 LED,T-1,3/4,RED,HLMP-3003
R25 1 T14648-17 RESISTOR,WW,5W,270,5%,SQ
C15 1 S13490-174 CAPACITOR,ALEL,470,100V,+50/-10%
G-25
Return to Section TOC Return to Section TOC Return to Section TOC Return to Section TOC
Return to Master TOC Return to Master TOC Return to Master TOC Return to Master TOC

SVM ERROR REPORTING FORM
We need to know if there are errors in our manuals. We also value any suggestions as to
additional tests or procedures that would make this SVM a better tool for you.
If you discover new or different “Problems or Symptoms” that are not covered in the three col-
umn troubleshooting chart, please share this information with us. Please include the
machine’s code number and how the problem was resolved.
Thank You,
Technical Services Group
Lincoln Electric Co.
22801 St. Clair Ave.
Cleveland, Ohio 44117-1199
FAX 216-481-2309
SVM Number ___________________________
Page Number if necessary__________________
Your Company__________________________
Your Name_____________________________
Please give detailed description below:
___________________________________________________________________________
___________________________________________________________________________
___________________________________________________________________________
___________________________________________________________________________
___________________________________________________________________________
___________________________________________________________________________
___________________________________________________________________________
___________________________________________________________________________
___________________________________________________________________________
___________________________________________________________________________
___________________________________________________________________________
___________________________________________________________________________
___________________________________________________________________________
SD287 01/99
Return to Section TOC Return to Section TOC Return to Section TOC Return to Section TOC
Return to Master TOC Return to Master TOC Return to Master TOC Return to Master TOC