Lyngsoe Systems E95 Card Reader Security Device User Manual S95ur
Lyngsoe Systems Ltd. Card Reader Security Device S95ur
users manual
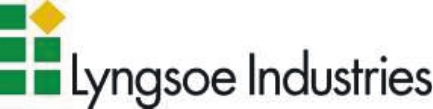
95 Series RFID System
User’s Guide
Lyngsoe 95 Series RFID System User’s Guide
Part Number: 950119
Fourth Edition
April 2002
The information in this manual is for reference purposes only and is subject to change without notice. The contents of this
manual and the associated Lyngsoe 95 Series hardware are the property of Lyngsoe Industries and are copyrighted©. All
rights are reserved by Lyngsoe Industries. In no event is Lyngsoe Industries liable for incidental or consequential damages in
connection with or arising from the use of this manual or any related documentation. This document may not, in whole or in
part, be copied, photocopied, reproduced, translated, or reduced to an electronic medium or machine readable form without
prior written consent from Lyngsoe Industries.
© 1997 - 2002 Lyngsoe Industries. All Rights Reserved.
Lyngsoe is a registered trademark® of Lyngsoe Industries. All other product names and services listed are copyright and
registered trademarks/trade names of their respective owners.
Use, duplication or disclosure by the Government is subject to restrictions as set forth in subdivision (b)(3)(ii) of the Rights in
Technical Data and Computer Software clause at 252.227-7013. Lyngsoe Industries.
Printed in Canada.
Lyngsoe Industries
5570 Kennedy Road, Unit B
Mississauga, Ontario L4Z 2A9
CANADA
Tel: +1 (905) 501-1533
Fax: +1 (905) 501-1538
FCC CLASS A Digital Device or Peripheral - Information to the User
NOTE: This equipment has been tested and found to comply with the limits for a Class A digital device, pursuant to Part 15 of
theFCCRules.Theselimitsaredesignedtoprovidereasonableprotectionagainstharmfulinterferencewhentheequipmentis
operated in a commercial environment. This equipment generates, uses, and can radiate radio energy and, if not installed and
used in accordance with this guide, may cause harmful interference to radio communications. Operation of this equipment in a
residential area is likely to cause harmful interference in which case, the user will be required to correct the interference at his
own expense.
WARNING:
Changes or modifications not expressly approved by Lyngsoe Industries could void the user’s authority to operate the
equipment.
This page intentionally left blank.
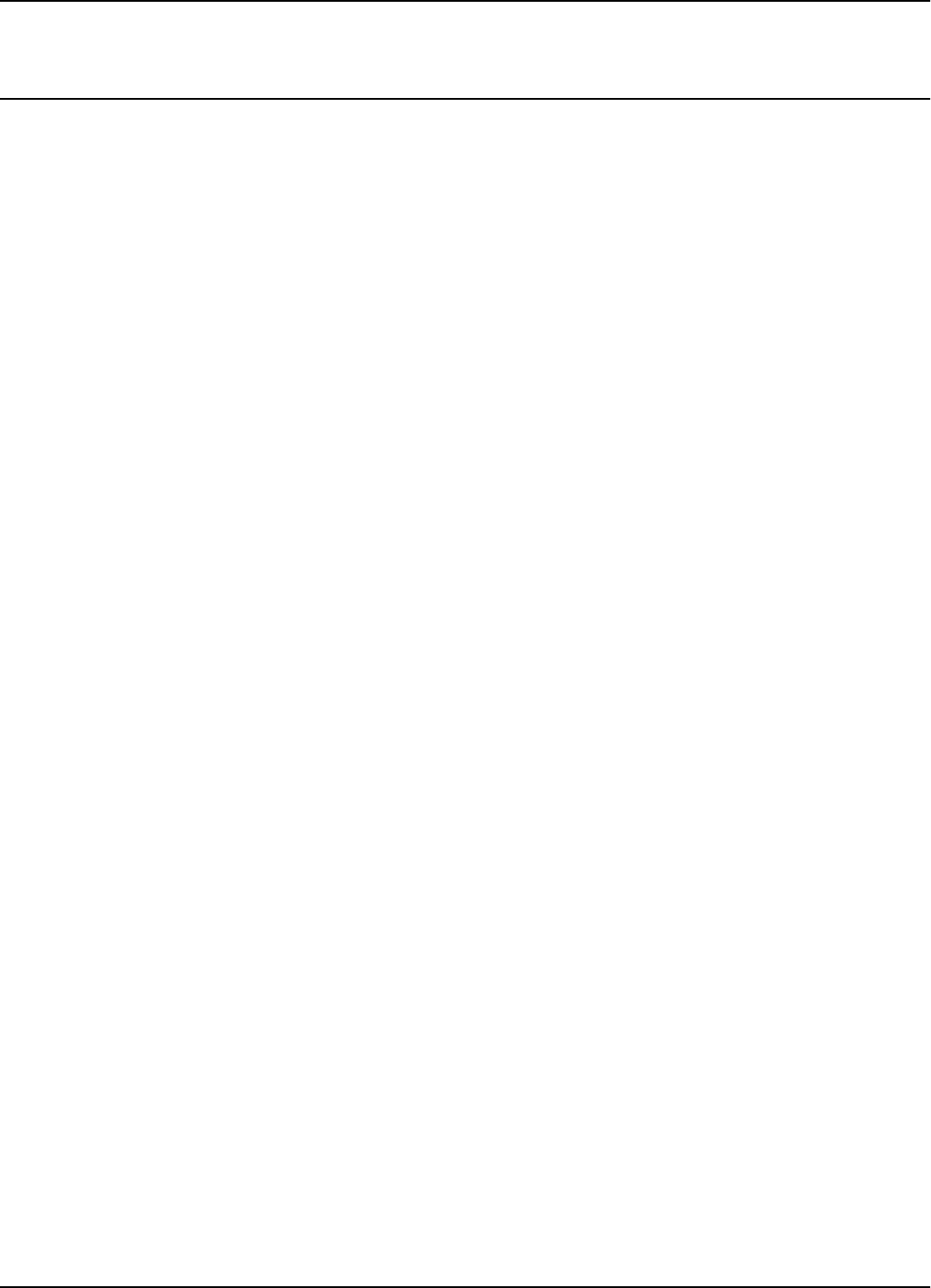
Table of Contents
Table of Contents 1
Table of Contents
Preface
WhatThisManualContains.....................................i
Summary .................................................i
RelatedManuals ..........................................ii
TextConventions..........................................ii
Chapter 1: Introduction
TransponderIdentificationSystem..............................1-1
RFIDSpecificTerms .........................................1-2
Transponder.............................................1-2
ExcitationSignal.........................................1-2
ResponseSignal..........................................1-2
ReadingPoints...........................................1-2
CommunicationLinks.....................................1-2
RFIDSystem ............................................1-2
PostalRFIDSystem..........................................1-2
95SeriesRFIDSystemConfigurationPrinciples ..................1-3
CommunicationLinks.....................................1-3
SystemParameters.......................................1-3
SystemCode.............................................1-4
ReaderAddress ..........................................1-4
RealTimeClock..........................................1-4
ReceivingUHFData......................................1-4
ReaderDataHandling.....................................1-4
ReaderSerialPort........................................1-4
ReaderReset.............................................1-4
ExciterAddress ..........................................1-5
Chapter 2: Reader R95 Installation and Connections
BeforeYouBegin ............................................2-1
MechanicalAssembling.......................................2-1
ConnectingtheRS-232CommunicationLine......................2-2
ConnectingtheRS-485Two-WireCommunicationLine.............2-3
ConnectingtheRS-485Four-WireCommunicationLine.............2-4
ConnectingtheExciterCommunicationLine......................2-6
ConnectingthePowerSupply..................................2-7
ConnectingExternalDevices...................................2-9
Chapter 3: Exciter E95 Installation and Connections
BeforeYouBegin ............................................3-1
Tools...................................................3-1
MechanicalAssembling.......................................3-2
AssemblingtheLFAntennaforE95..........................3-2
LFAntennaConnections......................................3-3
ConnectingtheRS-485CommunicationLines.....................3-3
ConnectingthePowerSupply..................................3-5
PowerSupplyConnections .................................3-5
UHFTransmitter-DirectControl(Optional) .....................3-6
AssemblingOtherModelsofExciters............................3-6
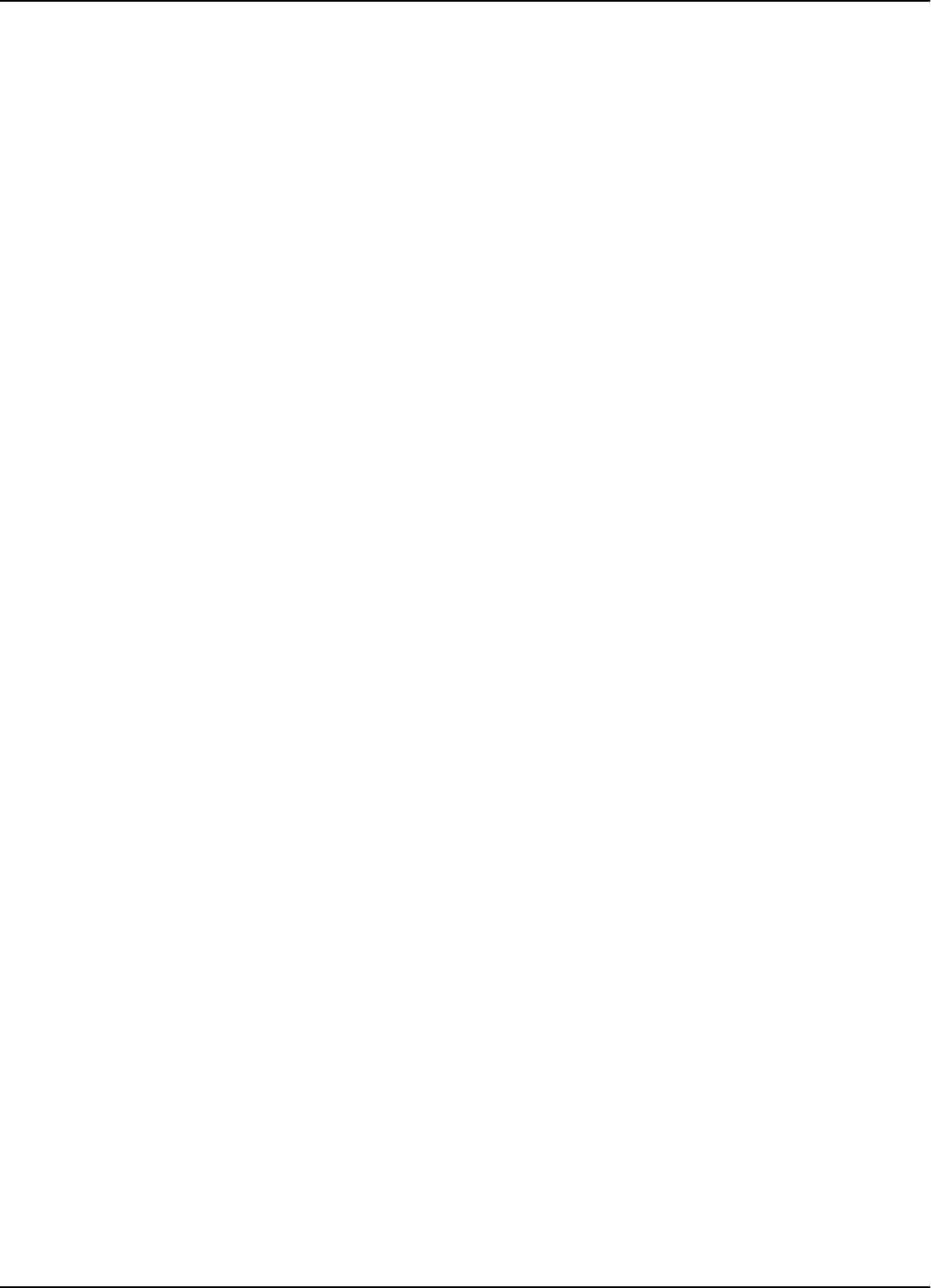
Table of Contents
2 Table of Contents
Chapter 4: Power Supply TRM95 Installation and Connection
BeforeyouBegin.............................................4-1
Tools...................................................4-1
Installing Power Supply TRM95 . . . . . . . . . . . . . . . . . . . . . . . . . . . . . . . .4-1
Placement...............................................4-1
Safety..................................................4-2
WiringConnectionsandSupply ................................4-2
ConnectingEquipmenttothePowerSupplyUnit..................4-3
ConnectingtheACMainsSupply...............................4-3
Chapter 5: Configuration and Operation
BeforeYouBegin ............................................5-1
GeneralProcedureRules......................................5-1
SettingUptheReader/PCConnection...........................5-2
Reader’sPower-upSequence...................................5-3
LearningProcedure(Optional).................................5-3
ResettingtheReader.........................................5-4
CheckingtheReader’sBasicParameters.........................5-4
SettingUptheExciter’sAddress................................5-5
LFTransmitterOutput.......................................5-6
ConfiguringtheReader.......................................5-8
SettingUptheCarrierThreshold...............................5-9
SettingUptheExciter’sTest-Tag..............................5-11
SettingUptheRealTimeClock ...............................5-12
ConfiguringtheReader’sApplicationParameters.................5-12
ConfiguringtheReader’sNetworkParameters...................5-13
StoringtheReader’sConfiguration.............................5-13
Reader-FinalSetup.........................................5-14
95SeriesRFIDSystem-FinalTest............................5-14
Chapter 6: Programming and Testing the Transponder T95
SettingUptheProgrammingSite...............................6-1
ProgrammingProcedures......................................6-2
UsingT95ProgrammingSoftware...........................6-2
UsingaTerminalEmulationProgram........................6-2
ConfidenceTesterTCT95......................................6-2
Chapter 7: Troubleshooting
PreventiveMaintenance ......................................7-1
GeneralGuidelines...........................................7-1
Appendix A: Specifications
TransponderT95C..........................................A-1
ReaderR95................................................A-2
ExciterE95................................................A-4
PowerSupplyTRM95........................................A-5
SystemPerformance.........................................A-5
Appendix B: Transponder T95 Messages
MessageFormat............................................B-1
T95Parameters.........................................B-1
TotalTransmissionTime..................................B-1
Appendix C: Excitation Modes
ExcitationModesandParameterSettings.......................C-1
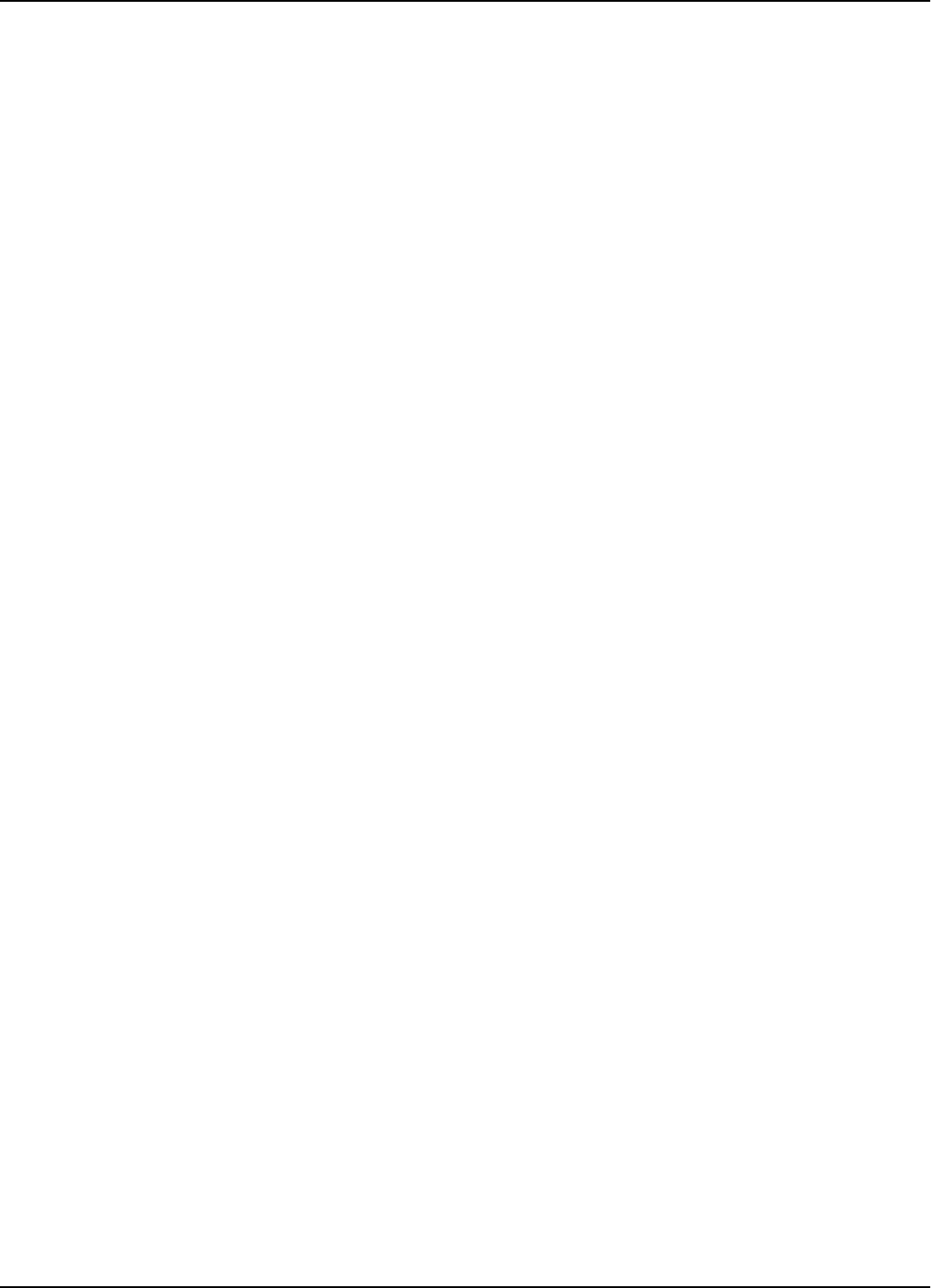
Table of Contents
Table of Contents 3
Appendix D: Reader Software Upgrade Procedure
UpgradingtheFirmware.....................................D-1
SettingtheReader’sAddress ..............................D-1
SavingParameters.......................................D-2
UsingtheRS232Interface.................................D-2
UsingtheRS485Interface.................................D-3
UsingtheRS485Interface.................................D-3
RestoringParameters....................................D-4
SettingtheReader’sNetworkConfiguration..................D-4
FinalInstructions .......................................D-5
Glossary.......................................................G-1
Index ..........................................................I-1
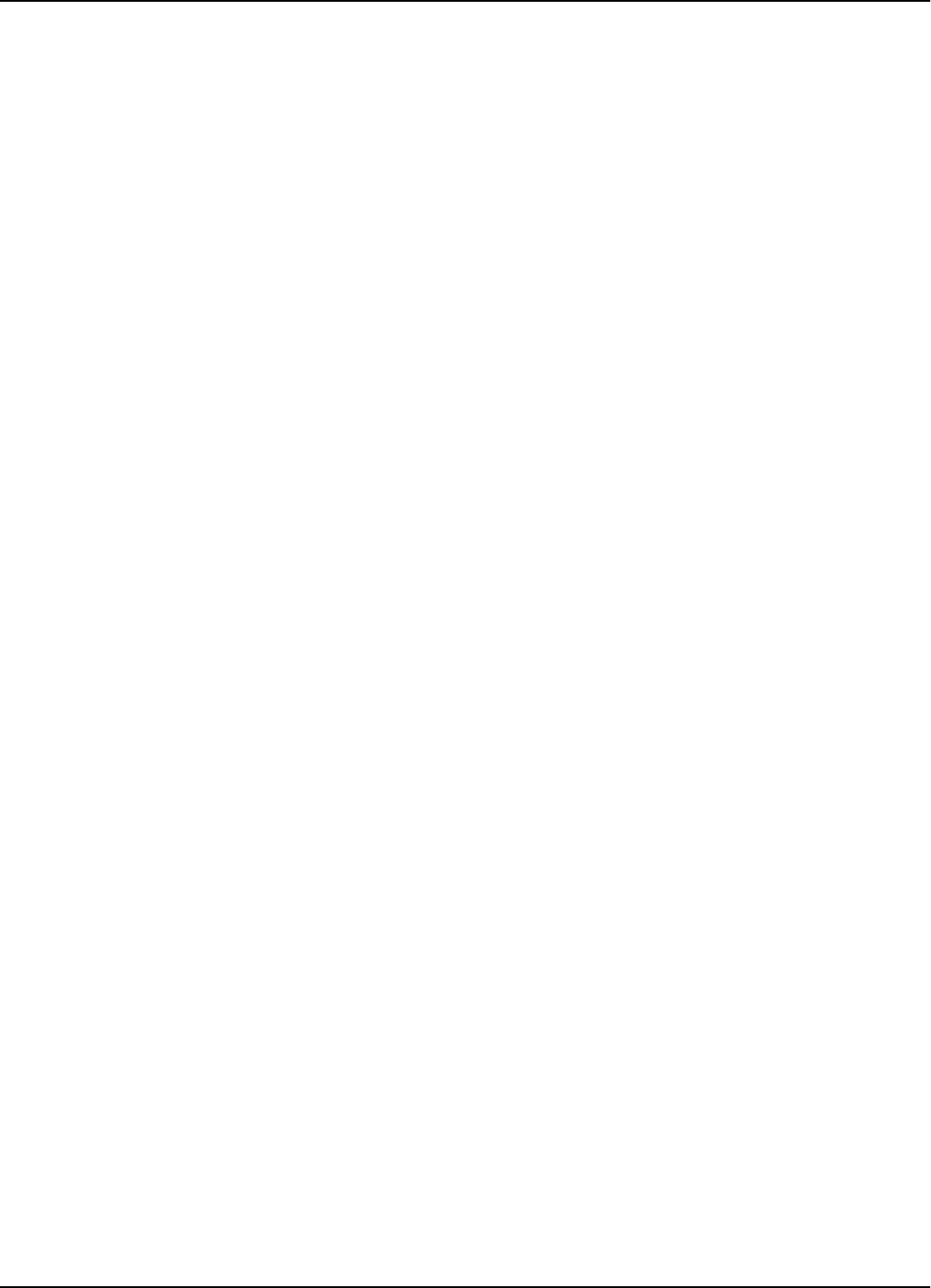
Table of Contents
Table of Contents 4
This page intentionally left blank.
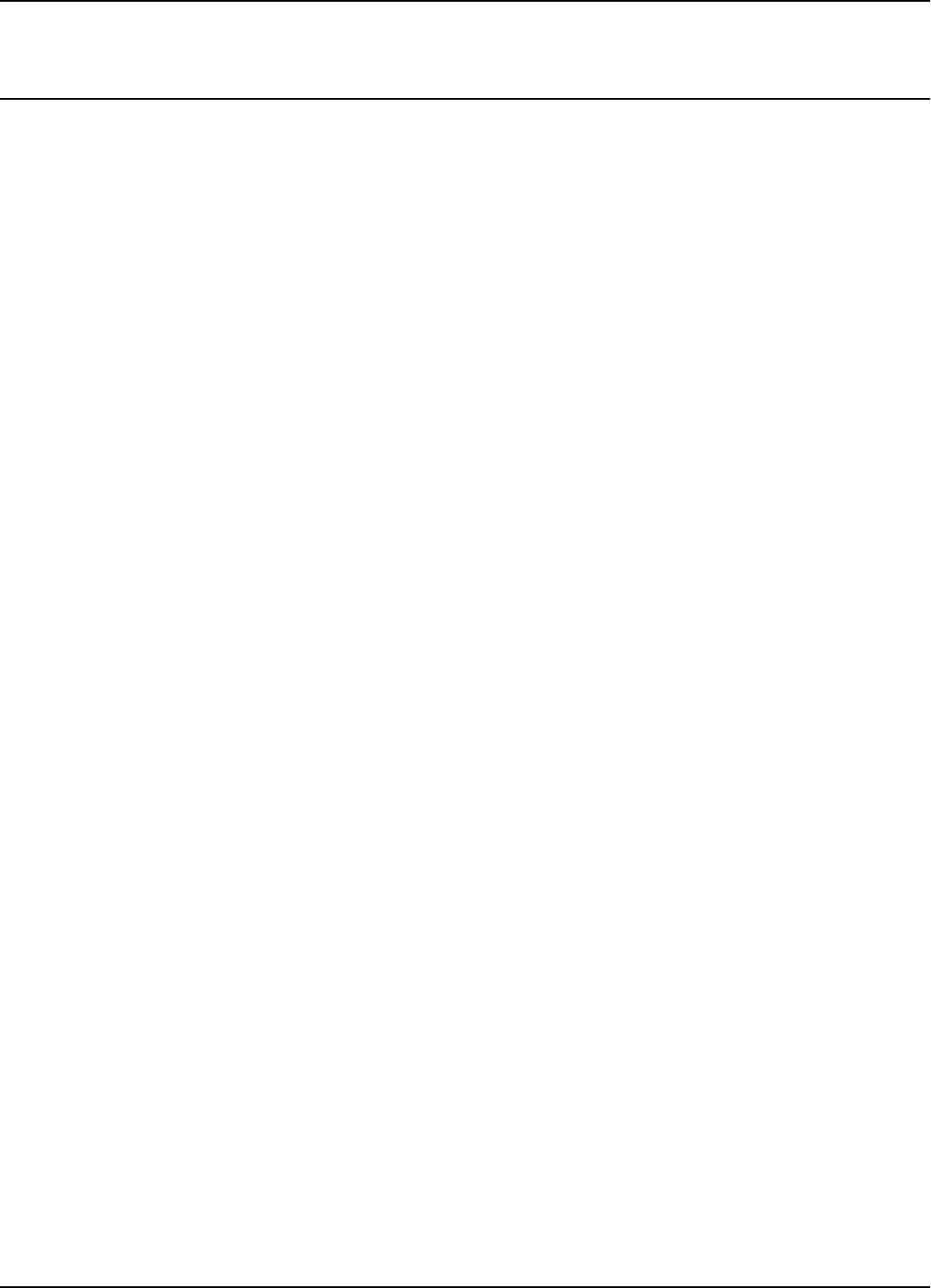
List of Figures
List of Figures 1
List of Figures
Figure1-1:RFIDConcept...........................................................1-1
Figure 2-1: Connections and Jumper Settings for the RS-232 - PC Communication Line . . . . . . . . 2-2
Figure 2-2: Connections and Jumper Settings for the RS-485 Two-Wire Communication Line. . . . 2-3
Figure 2-3: Connections and Jumper Settings for the RS-485 Four-Wire Communication Line . . . 2-5
Figure2-4:ConnectionsandJumperSettingsfortheExciterCommunicationLine.............2-6
Figure2-5:PowerSupplyConnections.................................................2-8
Figure2-6:ExternalDevicesConnections..............................................2-9
Figure3-1:LFAntennaConnections ..................................................3-3
Figure 3-2: Connections and Jumpers Settings for the RS-485 Communication Lines. . . . . . . . . . . 3-4
Figure3-3:ExciterE95PowerSupplyConnections.......................................3-5
Figure5-1:ConnectingtheReadertoaPC/Laptop.......................................5-2
Figure5-2:SettingUptheExciter’sAddress............................................5-5
Figure5-3:LFSignalMeasurement...................................................5-6
Figure6-1:ProgrammingSite........................................................6-1
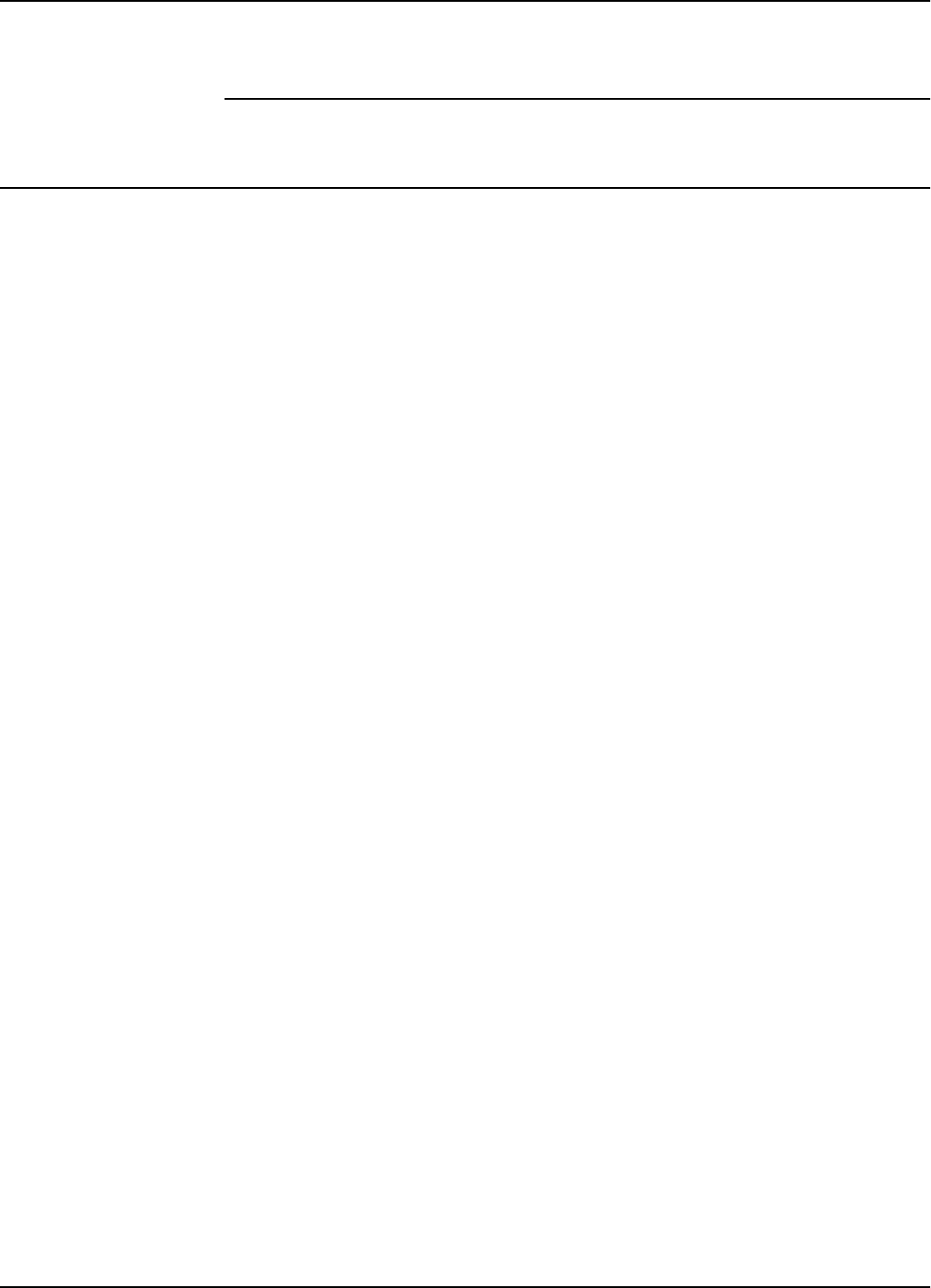
What This Manual Contains
Preface i
Preface
What This Manual Contains
This manual gives procedures for installing and configuring the Reader R95 and the
Exciter E95, and programming the Transponder T59. It also gives you maintenance
and troubleshooting procedures.
Summary A summary of the contents of this manual is given below:
Chapter 1, Introduction, describes the Transponder Identification System and the
Postal RFID System. It also gives information on the 95 Series RFID System
configuration principles.
Chapter 2, Reader R95 Installation and Connections, explains how to install and
connect the Reader, set the jumpers for the interfaces, and connect external devices to
the Reader, if necessary.
Chapter 3, Exciter E95 Installation and Connections, explains how to assemble the
Exciter using the LF antenna kit and the Enclosure E95 kit, make the LF antenna
connection, connect the serial interfaces and power supply, set the jumpers for the
interfaces, and connect remote devices to the Reader.
Chapter 4, Power Supply TRM95 Installation and Connection, explains how to install
the unit and make input and output connections to the unit.
Chapter 5, Configuration and Operation, provides procedures for setting up and
configuring a 95 Series RFID System.
Chapter 6, Programming and Testing the Transponder T95, explains how to set up a
site and gives procedures for programming the Transponder T95.
Chapter 7, Troubleshooting, describes maintenance and troubleshooting procedures
that you must follow when using the 95 Series RFID System.
Appendix A, Specifications, gives electrical, environmental, and physical
specifications for the Transponder T95, the Reader R95, the Exciter E95, and for the
complete 95 RFID System.
Appendix B, Transponder T95 Messages, describes the T95 Message format.
Appendix C, Excitation Modes, describes the various excitation modes (signal
descriptions) and their associated parameter settings.
Appendix D, Reader Software Upgrade Procedure, describes the procedures for
upgrading the Reader R95 (P/N 600405) main software using the serial interface
RS232 or RS485.
The Glossary is an alphabetical listing of terms and acronyms used in this manual.
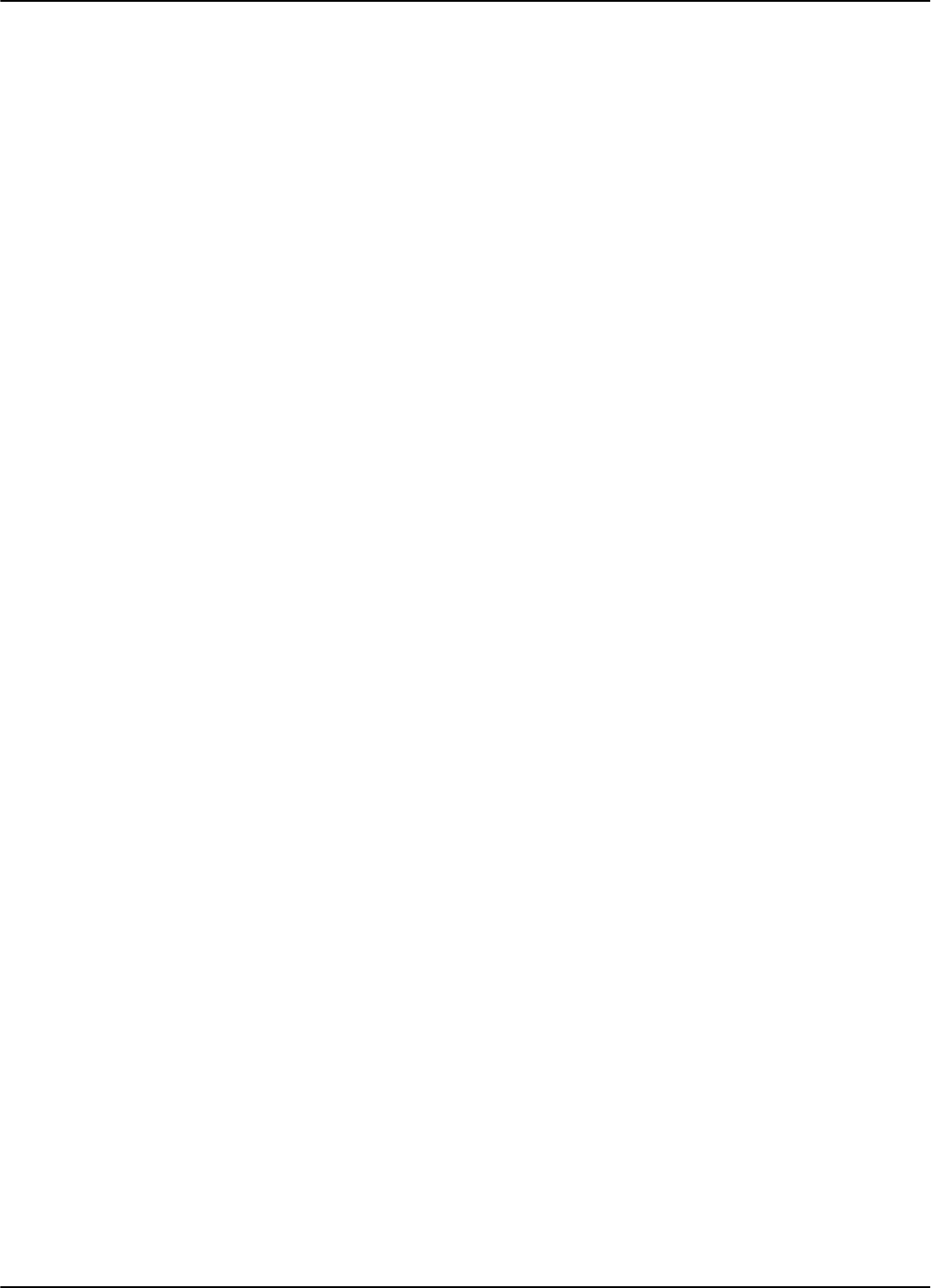
What This Manual Contains
ii Preface
Related Manuals
Technical Guide 95 Series RFID System Technical Guide.ThisGuidedescribesthe95SeriesRFID
System. It includes operation principles, block diagrams and electrical schematics for
all equipment and assembly parts for the 95 Series RFID System.
Reference Guide 95 Series RFID System Reference Guide. This Guide describes all the commands that
control the RFID operating system.
Text Conventions Helvetica is used for commands you must type exactly as it appears.
Italics is used for document titles, file names and new terms being defined.
Courier is used for messages displayed on the screen.
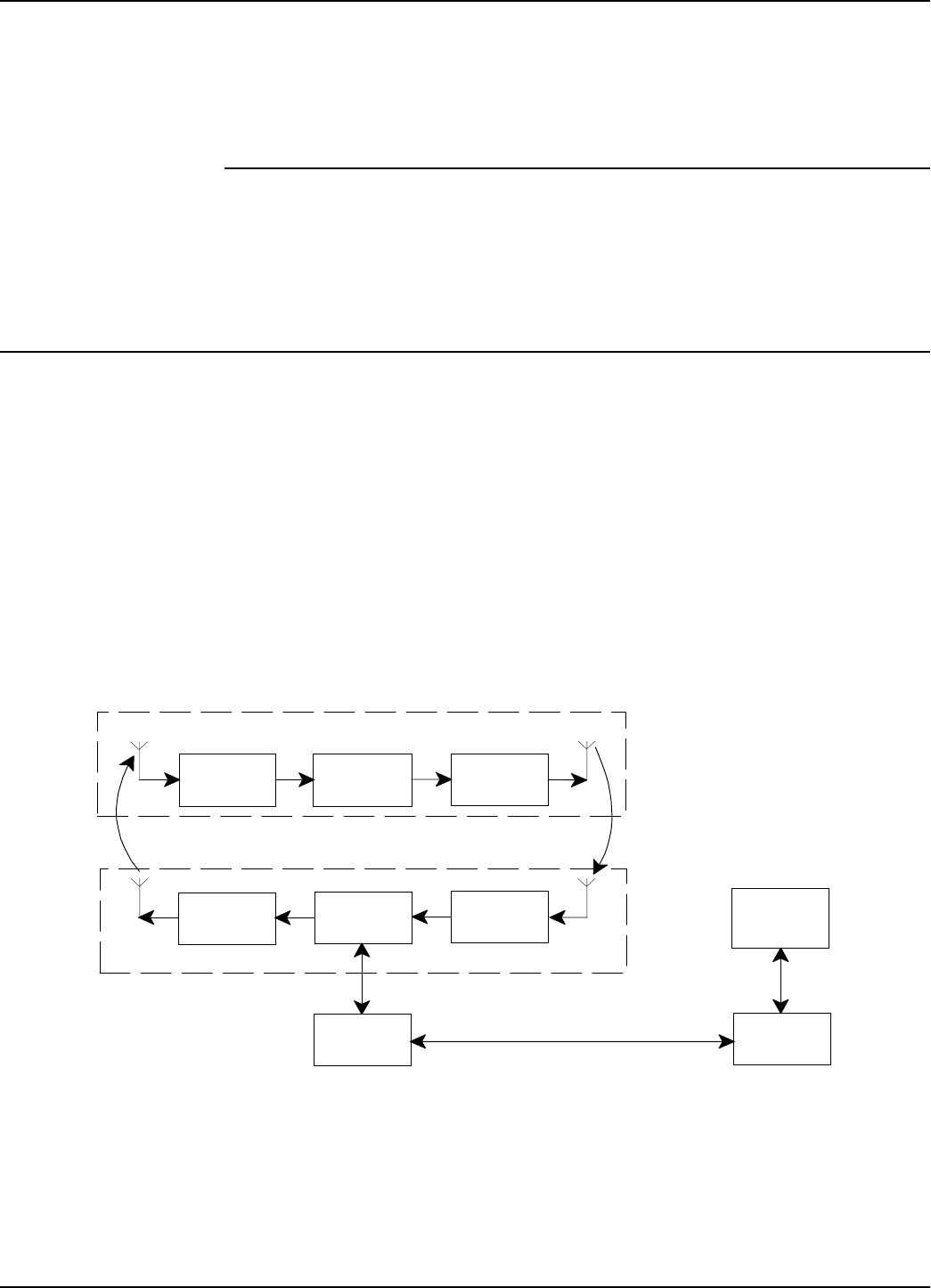
Transponder Identification System
Introduction 1-1
Chapter 1
Introduction
This chapter describes Transponders and their functions, the purpose of the Postal
RFID System and its uses. It also gives information on the 95 Series RFID System
configuration principles.
Transponder Identification System
The purpose of a data capture or identification system that uses a Transponder as an
identification token is:
• To automatically identify animate or inanimate objects having attached a
Transponder with an unique identifier
• To ensure that information is available in a format that can be readily accepted by
acomputer
• To minimize the possibility of errors in the identification process.
The concept of Radio Frequency Identification (RFID) is presented in Figure 1-1.
Figure 1-1: RFID Concept
Reading Point
Transponder
Rx Tx
µC
Tx µCRx
Downlink
Uplink
Interface Interface
Main
PC
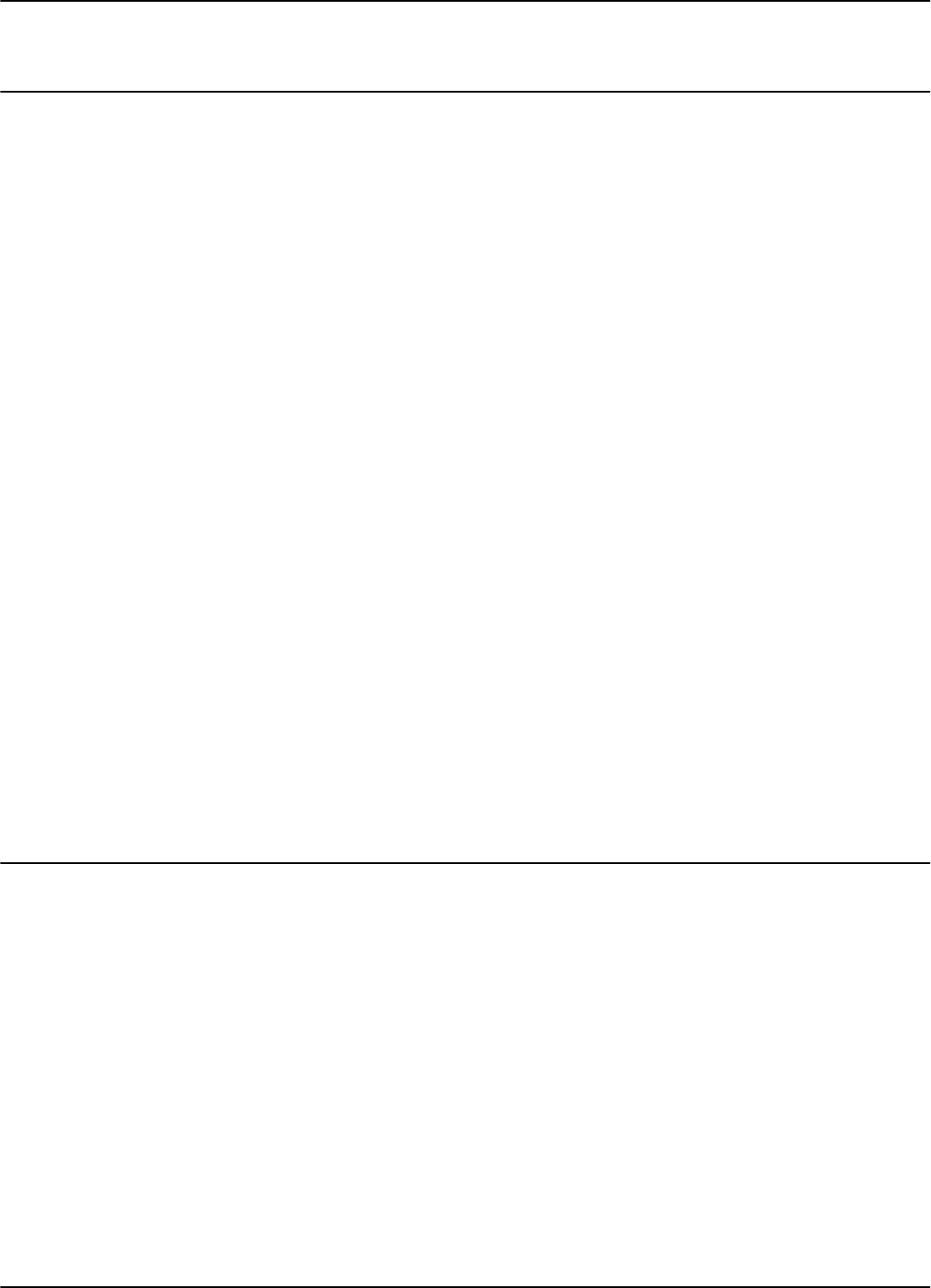
RFID Specific Terms
1-2 Introduction
RFID Specific Terms
Transponder Transponders are devices that receive an excitation signal, and respond by
transmitting back a message. Transponders that are used in identification systems
are sometimes referred to as electronic tags or tags.
Excitation Signal The excitation signal may be in the form of electromagnetic energy and can operate
anywhere in the RF spectrum from a low-radio frequency to infra-red light. It can also
have a special signature (pattern, coding, etc.) to avoid false or unwanted excitations.
When there is no excitation signal, the Transponder is dormant (in sleep mode).
Transponders do not transmit information involuntarily.
Response Signal The Transponder’s response can be a separate RF transmission or a supplementary
modulation of the excitation signal. The response signal contains information that
allows you to identify each Transponder and the object to which it is attached. Some
or all of this information may be stored in memory that can either be pre-coded and
unalterable, or reprogrammable.
Reading Points Reading Points are installed at strategic areas on the site where you want to identify
objects that are passing within a specified range. Reading Points generate the
excitation signal and receive signals transmitted by the Transponders. Data captured
from the Transponders is then transferred to the main computer. In so doing, the
Reading Point functions as a relay or an interface that transfers data from the
Transponders to the main computer and vice-versa.
Communication Links When using Transponders and Reading Points, two wireless communication links
exist. They are: Uplink - from the Reading Point to the Transponder, and Downlink -
from the Transponder to the Reading Point.
RFID System Automatic identification systems vary in their complexity. An example of a simple
system is a car-park barrier that provides automatic vehicular-access control. A more
complex example is a network of on-line Readers and Exciters that communicate with
a host computer that is managing an automated industrial facility.
Postal RFID System
The International Postal Corporation (IPC) required international end-to-end mail
performance monitoring to implement new management and financial control
systems. This monitoring and controlling is supported by an international agreement
known as REIMS (Remunerating Exchanges of International Mails).
The Postal RFID System was developed in response to the IPC’s requirements.
The main objective of the Postal RFID System is:
• To monitor the movement of the probe letters at key points in the system
• To supply evidence of mailing system performance
• To highlight problem areas.
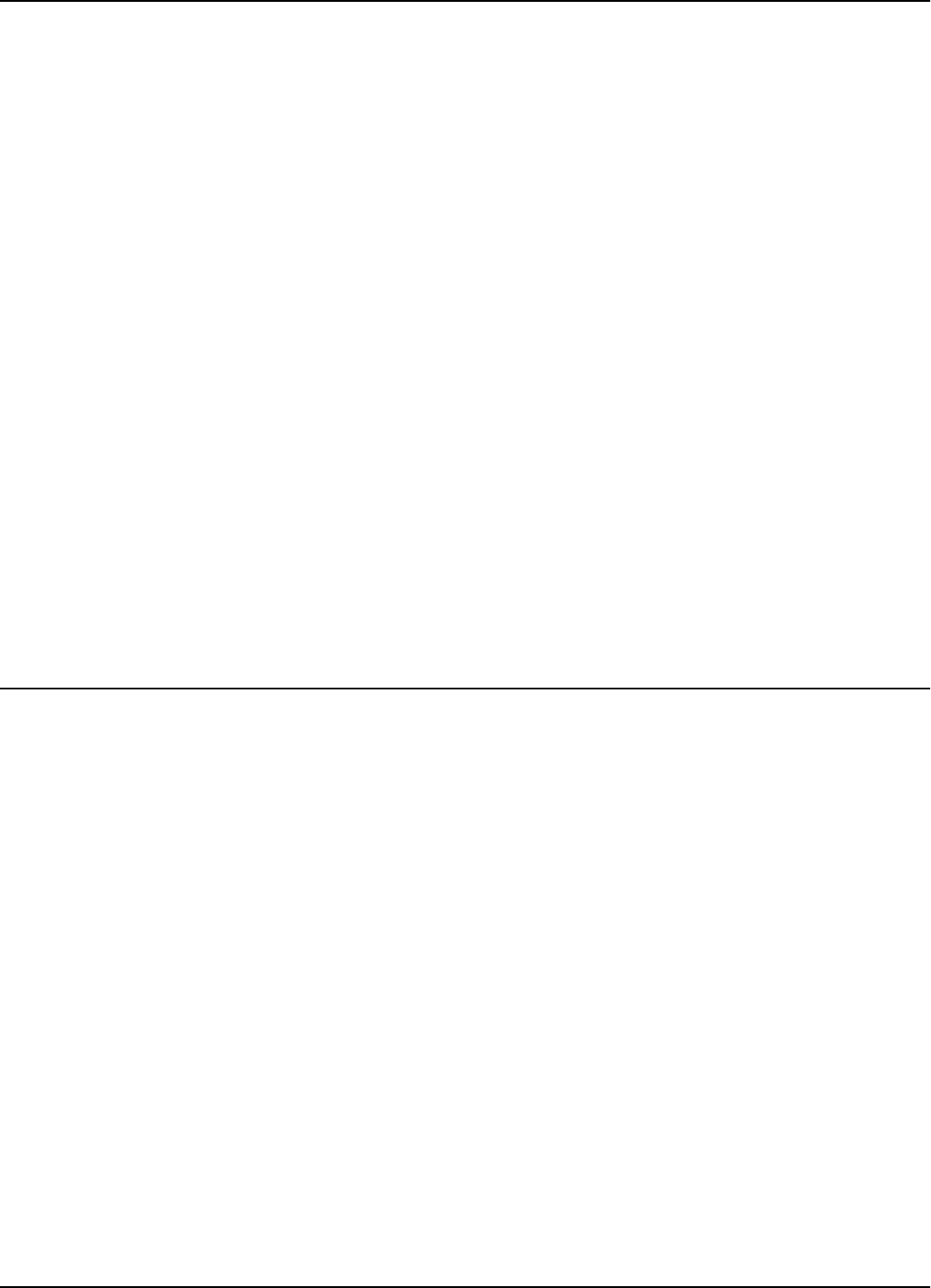
95 Series RFID System Configuration Principles
Introduction 1-3
By using aRFID system comprising of a population of Transponders and strategically
placed Readers and Exciters, you can electronically monitor the path of test letters
through the collection and delivery process, particularly at points between Postal
administrations and their agents.
Each probe letter includes a RFID Transponder bearing a unique identification. The
probe letters are posted, sorted, and delivered in the same way as normal letters. As
they pass pre-determined points en-route (Reading Points/identification zones), the
Transponders are identified. The collected information is then read and stored on
local computers. This information is downloaded on demand to a Central
Management System (CMS).
The Postal RFID System includes the following main specific equipment:
• Transponders T95 carrying the identification data
• Exciters E95 to generate an electromagnetic field that excites the Transponder
T95
• Readers R95 to receive data transmitted by the Transponder T95 and to relay this
information via the RS-485 interface to the main computer
• Power Supply TRM95 to power Readers R95 and Exciters E95 from the local AC
main supply.
IMPORTANT Each piece of equipment can have different commercial models (Transponders T95B,
T95C, TRD95, and TBC95), but they behave similarly. This manual refers to them as
a generic T95 model.
95 Series RFID System Configuration Principles
The RFID System is highly configurable, allowing you to setup operational
parameters for the optimum performance of the System. The sections that follow give
some basic information regarding the 95 Series RFID System configuration. A
detailed description of the configuration, with a focus on an IPC implementation, is
giveninChapter5,Configuration and Operation.
Communication Links There are several communication links between the components of the 95 Series RFID
System. As a general rule, all equipment attached to a particular link must have the
same parameters settings to communicate. Some communication links can be
configured, others, however, have fixed configurations, as follows:
• Reader-to-Transponder: excitation (LF=125.0 kHz) - configurable;
writing (infrared) - fixed configuration.
• Transponder-to-Reader (UHF-433.92 MHz) - configurable.
• Reader-to-Exciter and Exciter-to-Reader (RS485_COM, RS485_SGN) - fixed
configuration.
• Reader- to-Main PC and Main PC-to-Reader (RS-232 or RS-485) - configurable.
System Parameters Parameters controlling the 95 Series RFID System’s configuration are logically
organized in groups. For a detailed explanation on the meaning and usage of the
parameters, refer to the 95 Series RFID System Reference Guide. The parameters
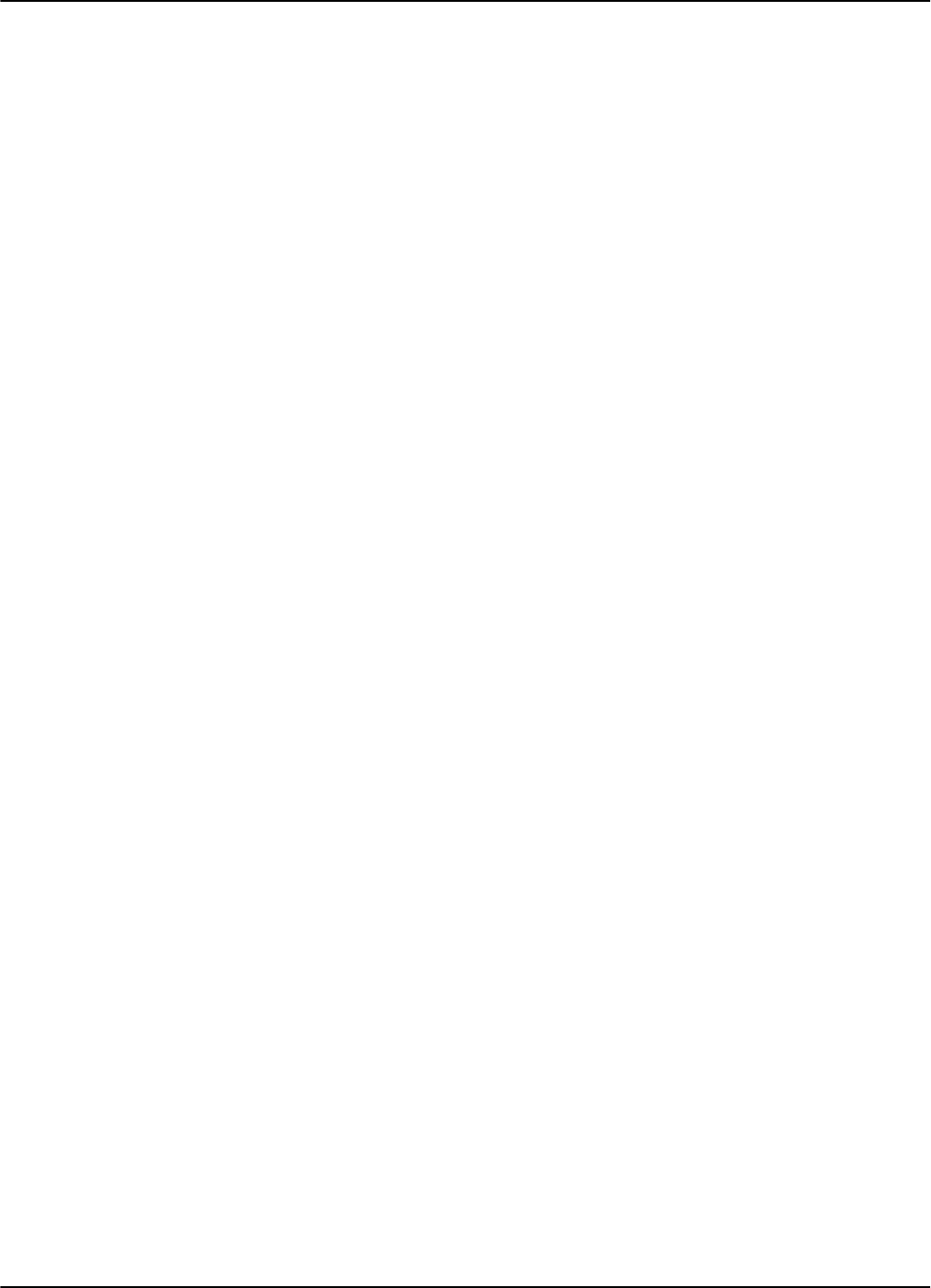
95 Series RFID System Configuration Principles
1-4 Introduction
settings that control the hardware configuration, is described in Chapter 3, Theory of
Operation in the 95 Series RFID System Technical Guide. This chapter gives reasons
for using certain parameters for configuring the hardware.
System Code A Reader R95 needs a System Code to function properly. You use the ISC parameter
to set the System Code the first time. The System Code is a specially encoded number
that distinguishes the RFID System from all other similar systems in use. By
obtaining your System Code from Kasten Chase, you are guaranteed a unique System
Code.
Reader Address When a Reader is part of a network, it must have a unique address. The address is set
by the IAD parameter. Once the Reader has an address assigned, it will only process
commands with the address field matching the Reader’s address. In this way, you can
direct commands over the network to a specific Reader.
Real Time Clock The Reader R95 has an on board Real Time Clock. Make sure that the date and time
is correctly set. The time can be queried and set using the IUT parameter. The time
must be adjusted on Jan. 1st and Feb. 29th.
Receiving UHF Data The Reader needs to know the data format in which the Transponder is transmitting
information to properly receive and interpret the information. The Reader’s setting
can be checked and modified by the Group Rparameters.
A simple method of matching an unknown Transponder with the Reader’s parameters
setting is given below:
1. Use the programming setup described in Chapter 6, Programming and Testing
the Transponder T95.
2. Query the Transponder. (See the Q command).
3. Check the Transponder’s parameters using the Group Tparameters.
4. Set an identical set of parameters for the Reader using the Group Rparameters.
Reader Data Handling Data that is captured from the Transponder is usually stored in an internal buffer. It
is then sent to the monitoring equipment either voluntarily (if DAR=Y), or in response
to a query command. You can customize the format and the fields using the Group D
parameters. By setting appropriate values, you can greatly simplify the
implementation of the monitoring software.
Reader Serial Port When setting the serial port parameters, remember that communication with the
monitoring equipment can result in a bottleneck in the RFID System. We recommend,
therefore, using the highest baud-rate available. Also, the line turn-around delay
(STD parameter) can greatly degrade the RFID System’s performance. This
parameter must be set to 0, unless required otherwise. For more information on the
Group Sparameters, refer to the 95 Series RFID System Reference Guide.
Reader Reset TherearetwomainwaystoresettheReader:
•Hardwarereset
• Software reset.
For the hardware reset, switch off the Reader’s power supply for a least 5 seconds.
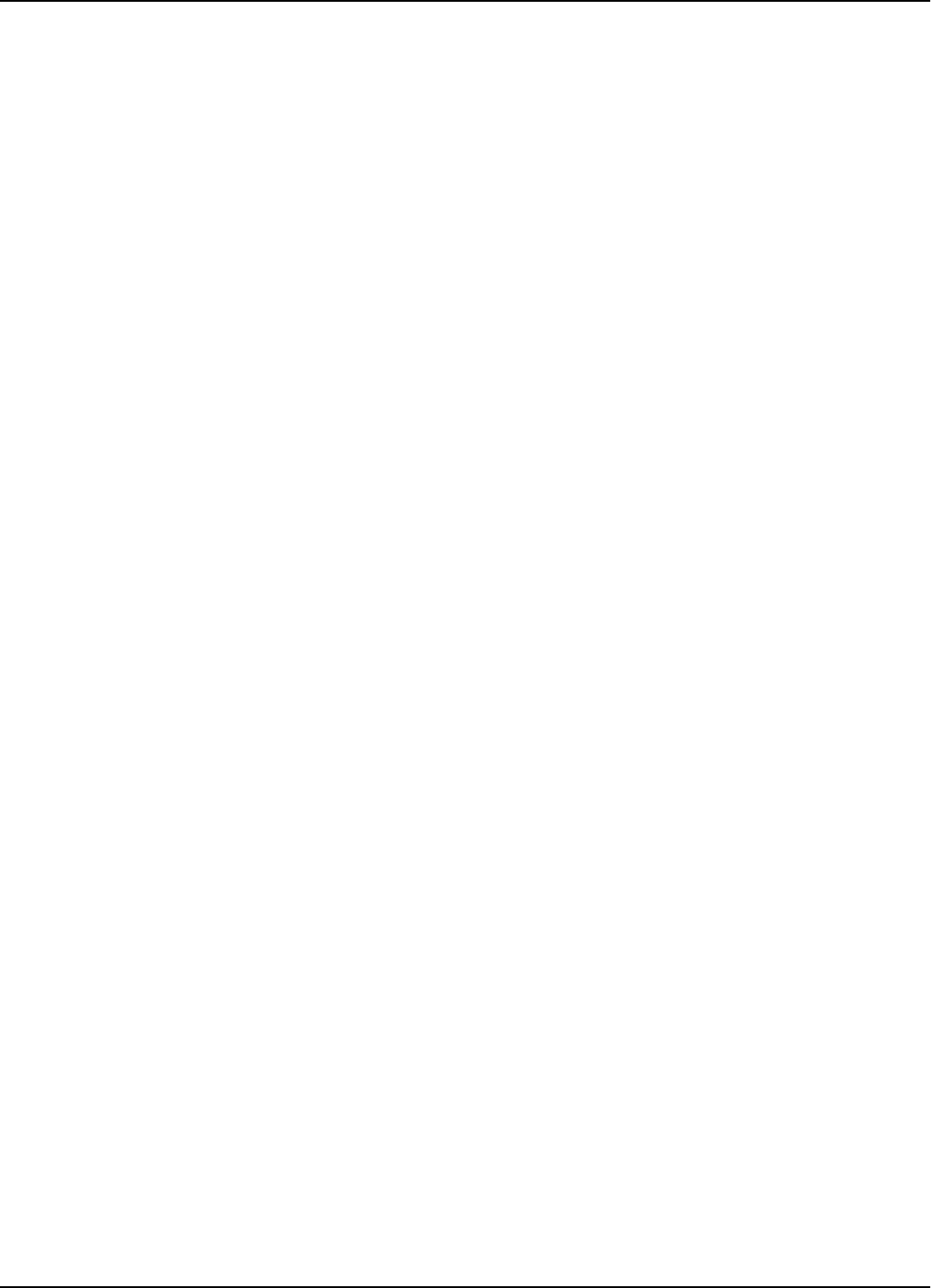
95 Series RFID System Configuration Principles
Introduction 1-5
For the software reset, press the RESET button on the Motherboard MBD95 twice, or
type the command:
:RESET<Enter>
The software reset resets the Microcontroller. The hardware reset resets the
Microcontroller and runs a complete memory test.
Exciter Address When an Exciter E95 is part of a network, it must have an unique address. You can
set the Exciter’s address in a binary format between 0001 and 1110, using the S1
switch on the EXT95SC board.
Once an address is assigned, the Exciter will only process commands with a matching
address field. In this way, you can direct commands in the network to a specific
Exciter E95.
Note Addresses 0000 and 1111 are reserved for special modes of operation.
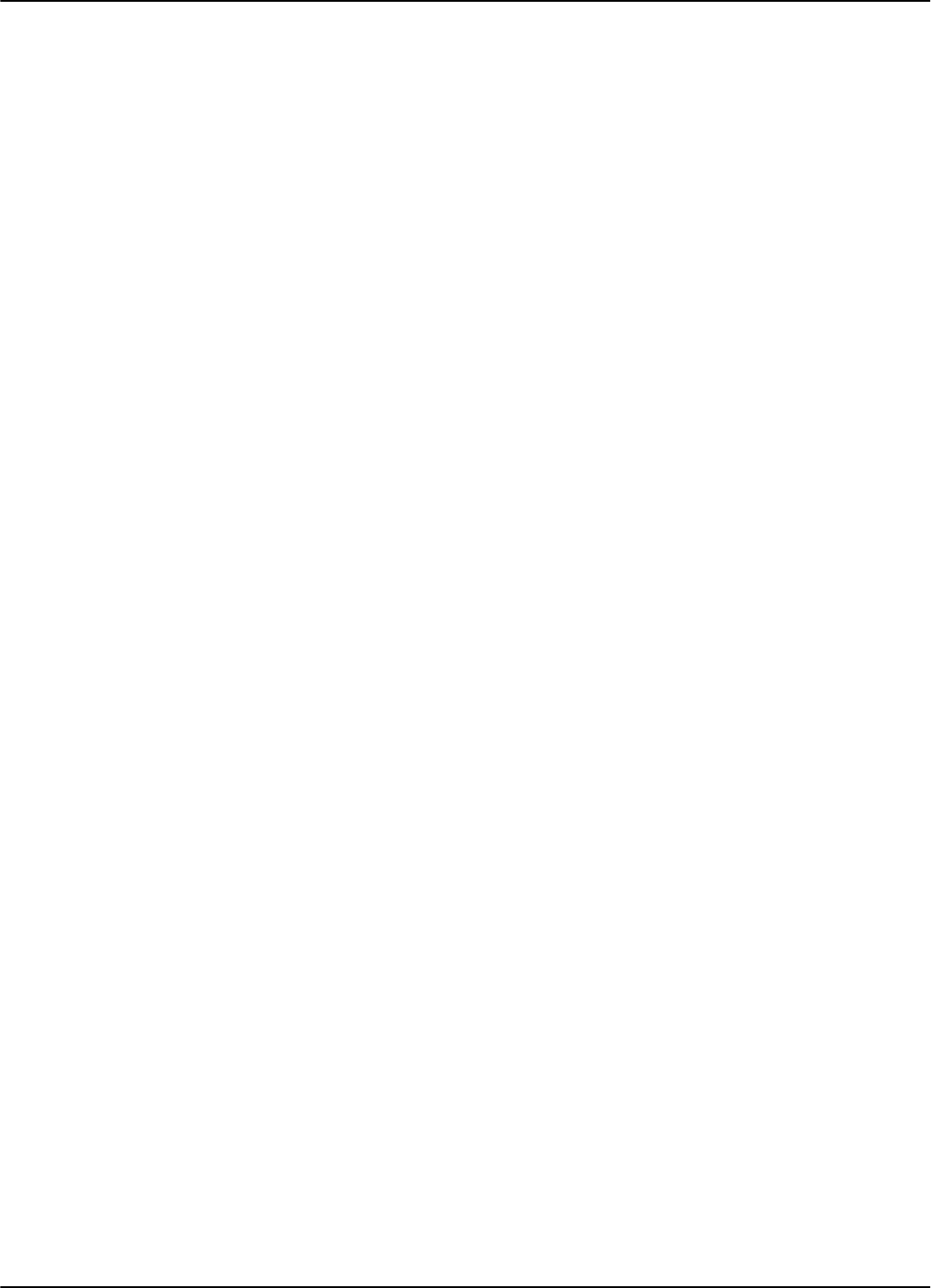
95 Series RFID System Configuration Principles
1-6 Introduction
This page intentionally left blank
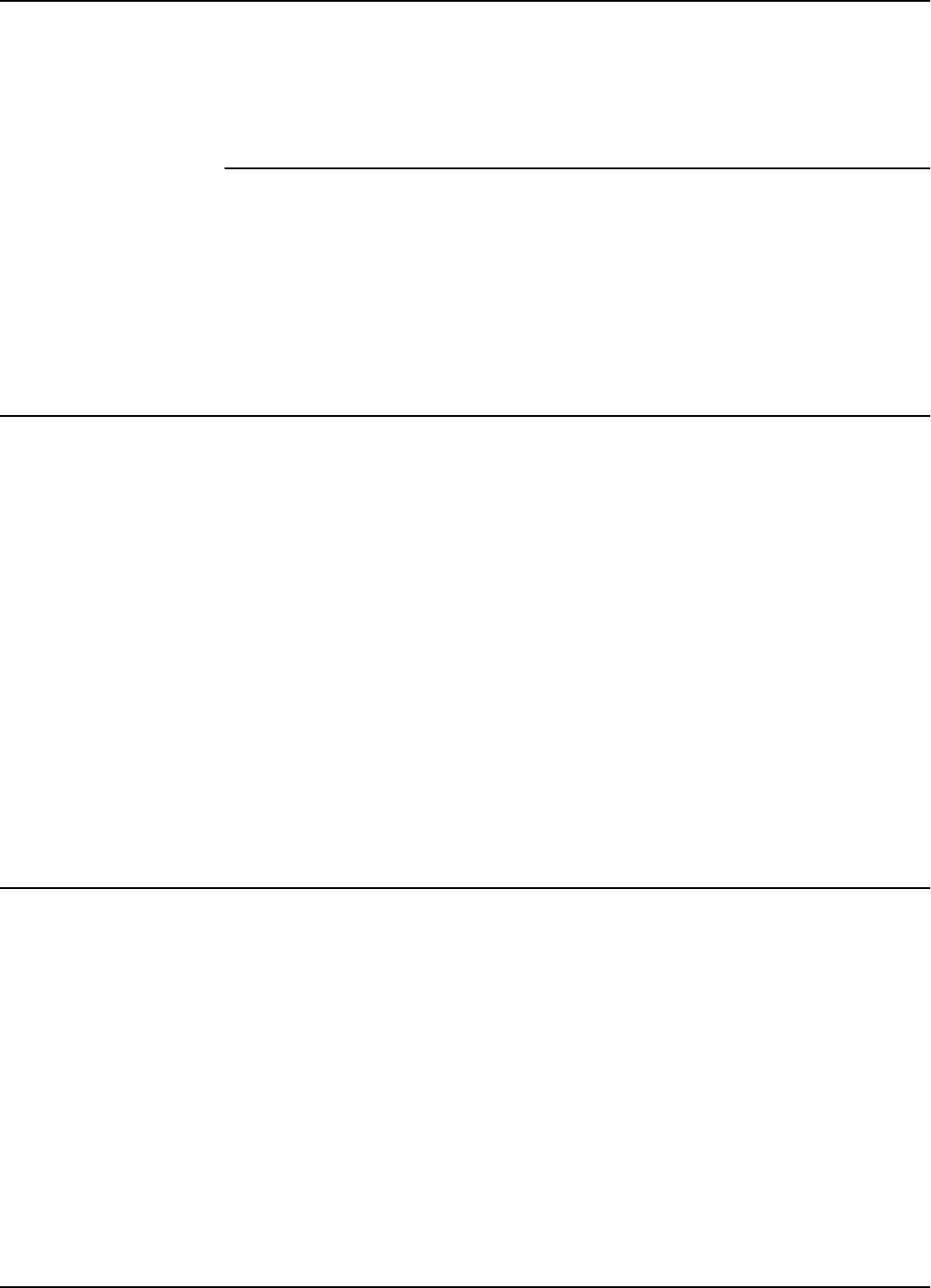
Before You Begin
Reader R95 Installation and Connections 2-1
Chapter 2
Reader R95 Installation and Connections
This chapter explains how to:
• Install the Reader Module Assembly into the Reader’s enclosure
• Connect the serial interfaces and the power supply
• Set the jumpers for interfaces
• Connect the external devices to the Reader R95 (optional)
Before You Begin
Before installing the Reader:
• Read Chapter 4, Setup Guidelines in the 95 Series RFID System Technical Guide.
• Have at your disposal, the complete approved documentation describing the RFID
System configuration, equipment location, and wiring distances between the
equipment (see the Site Survey Documentation).
• Check whether the Reader’s enclosure, power supply and interconnection cable
with the main PC are installed on the site according to the approved
documentation (see the Site Survey Documentation).
• Set a color table for each interface and power supply cables. Pay special attention
to the interface terminals, cable shields, and the ground wires.
• Check whether the Reader’s Kit (P/N 600418) is complete according to the product
shipping list.
Mechanical Assembling
To assembly the Reader R95, refer to assembly drawing M900199 in Chapter 8, Power
Supply Assembly Drawings, and complete the following steps:
1. Install the RF assembly cables (P/N 50053) on the Reader’s enclosure using a
13 mm fix key.
2. Install the Reader R95 Module Assembly (P/N 500048) into the Enclosure Base
and secure it using the four 6-32x1/4 inch screws from the Reader R95 Kit. See
drawing M900120.
3. Connect the two RF cables to the RF connectors on the Receiver Board CRM95
(middleboardoftheReaderModuleAssembly).
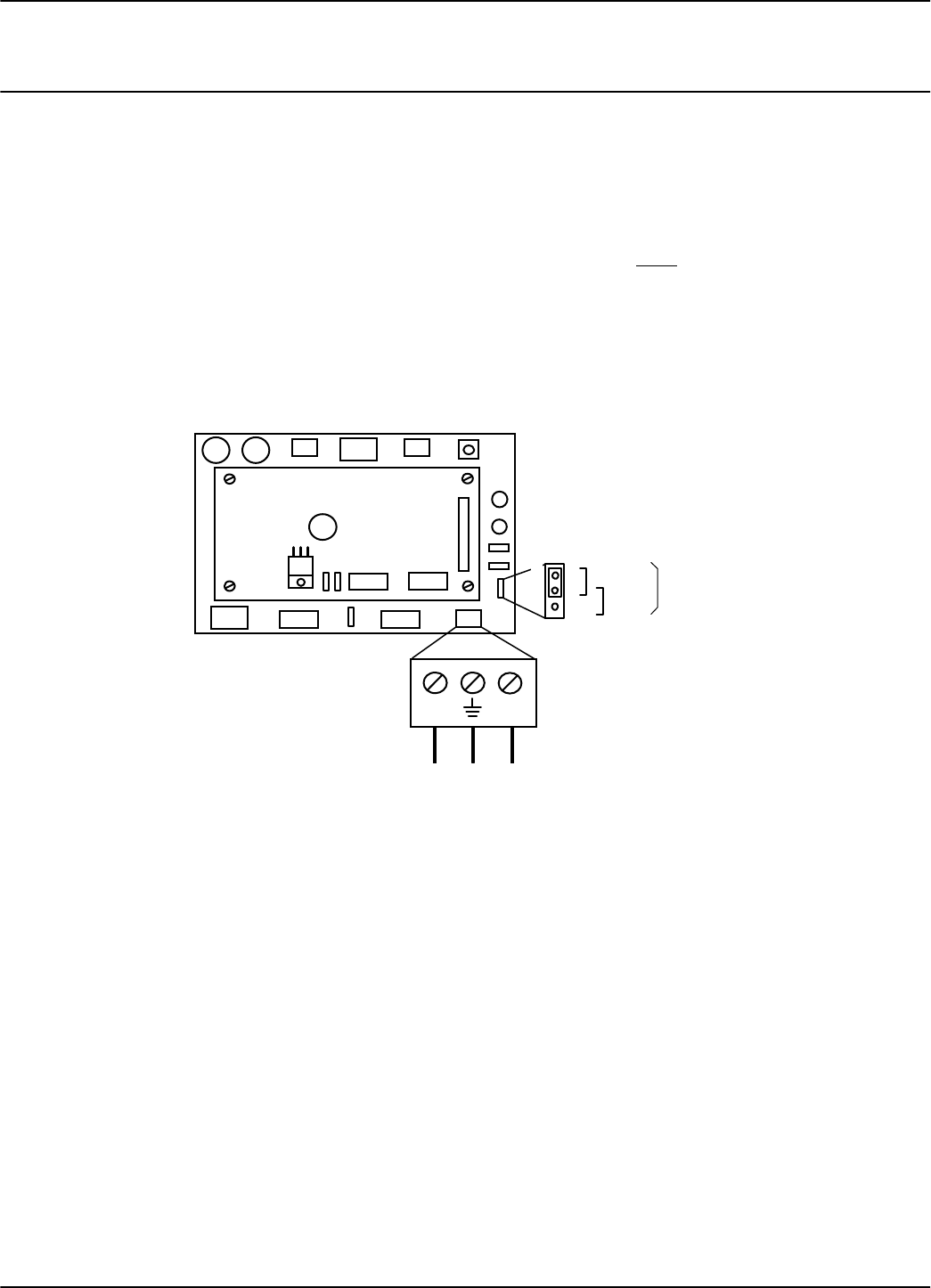
Connecting the RS-232 Communication Line
2-2 Reader R95 Installation and Connections
Connecting the RS-232 Communication Line
The RS-232 data transmission line is used for point-to-point communication with a
local PC. This connection can be used during the 95 Series RFID System configuration
or troubleshooting. The RS-232 connector and jumper are located on the Motherboard
MBD95.TheMBD95isthebottomboardoftheReaderModuleAssembly.
Note For the RS-232 line, use specially designed cables only, such as, BELDEN type 8102,
or a standard PC cable used for RS-232 interconnections. For more information, see
the 95 Series RFID System Technical Guide.
To connect the RS-232 communication line to the Reader, refer to Figure 2-1 below.
Figure 2-1: Connections and Jumper Settings for the RS-232 - PC Communication Line
Complete the following steps:
1. Unplug terminal block TB8 from connector TB7.
2. Connect the communication wires TX, GND and RX to the corresponding TB8
pins.
3. Place the jumper P2 between pins 1-2 of J2 (RS-232 configuration).
4. Plug terminal block TB8 back into connector TB7.
MatherboardMBD95
Controller CTL95
TX RX
1
RS232
TB8
TX GND RX
J2
P2
RS232
RS4852
Interface
Selection
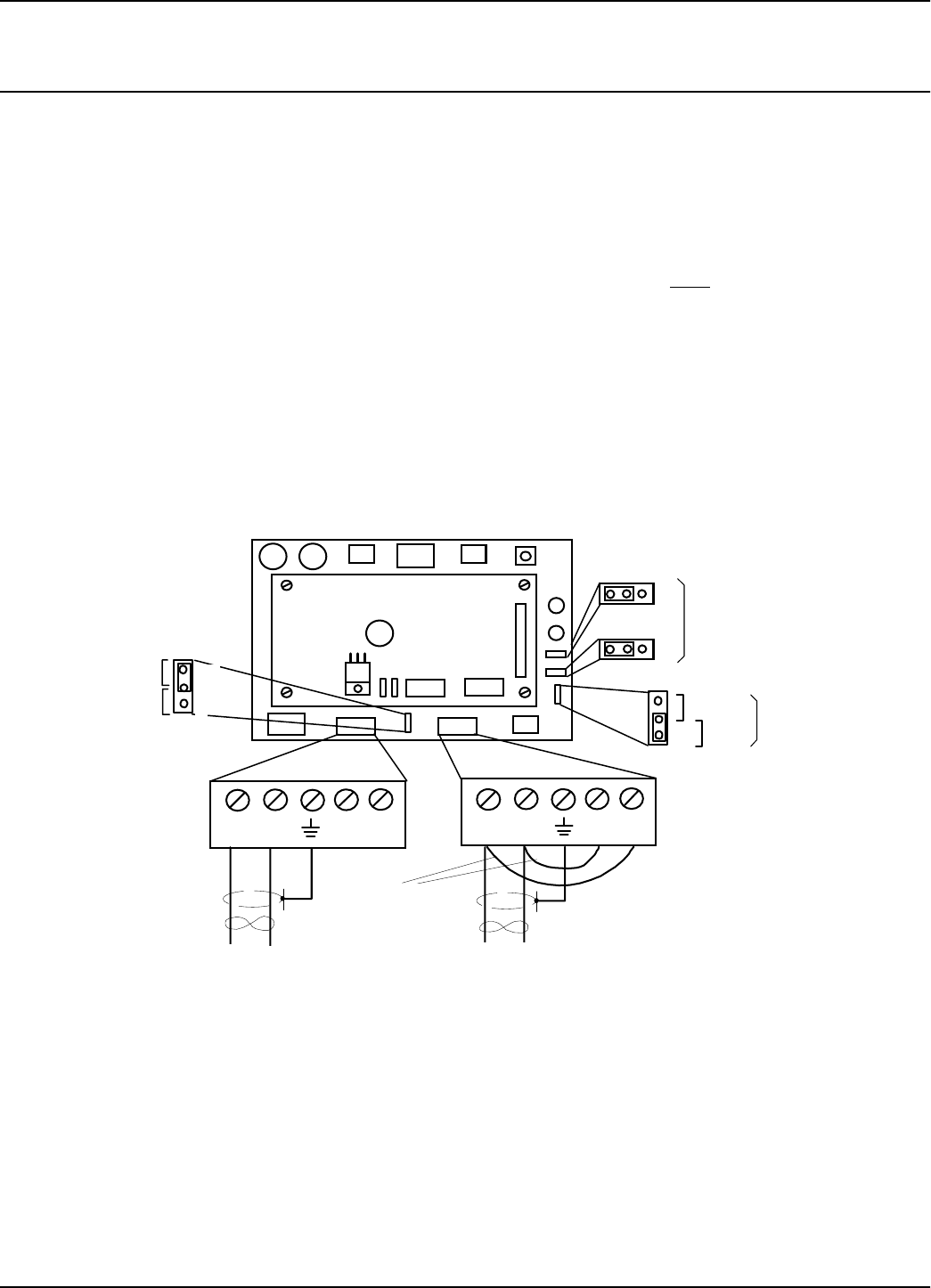
Connecting the RS-485 Two-Wire Communication Line
Reader R95 Installation and Connections 2-3
Connecting the RS-485 Two-Wire Communication Line
The RS-485 is a standard data communication line for an industrial environment. For
detailed information on the two-wire RS-485 interface (half-duplex), see the 95 Series
RFID System Technical Guide. The RS-485 connectors and jumpers are located on the
Motherboard MBD95. The MBD95 is the bottom board of the Reader Module
Assembly.
Notes 1. For the RS-485 line, use specially designed cables only, such as, BELDEN type
9841, or similar. For more information, see the 95 Series RFID System Technical
Guide.
2. To simplify the RS-485 multidrop-type connection, the two RS-485 connectors,
TB4 and TB6 are wired in parallel on the MBD95. Connect the incoming RS-485
cable to one connector and the outcoming RS-485 cable to the other.
To connect RS-485 communication lines to the Reader, refer to Figure 2-2 below.
Figure 2-2: Connections and Jumper Settings for the RS-485 Two-Wire Communication Line
Out-coming cable
Wire Jumpers
In-coming cable
MatherboardMBD95
Controller CTL95
AA
J4
J3
P4
1
1
J2
P3
A Y ABZY
BZRS485
TB6
RS485
TB4
B
B
J1
P1
1
Open
Load
RS-485 Termination
P2
1RS232
RS4852
Interface
Selection
RS485 Interface
Type Selection
2wire
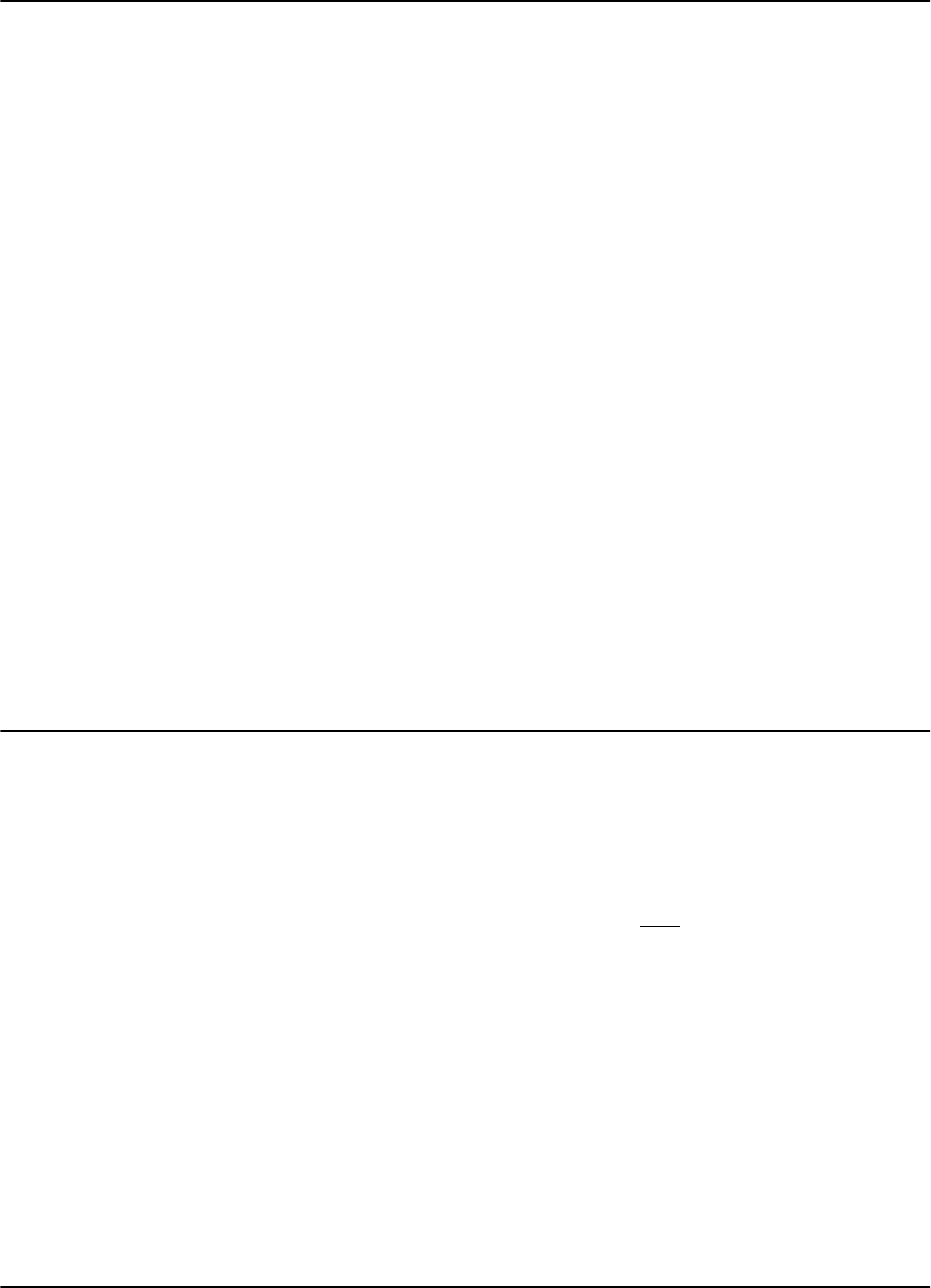
Connecting the RS-485 Four-Wire Communication Line
2-4 Reader R95 Installation and Connections
Complete the following steps:
1. Unplug terminal blocks TB4 and TB6 from connectors TB3 and TB5 respectively.
2. Run the incoming and outcoming RS-485 cables through the cable grips into
Reader’s enclosure.
3. Connect a short piece of wire between pins A and Y of terminal block TB4 (or
TB6). Connect another wire between pins B and Z of terminal block TB4 (or TB6).
4. Connect the two-wire communication line to the corresponding pins A and B of
terminal block TB4 (or TB6). Connect the cable shield to the pin marked with the
ground symbol on terminal block TB4 (or TB6).
Caution Before you install the RFID System, label the 2 wires on the RS-485 line Aand B.
Keep this naming convention for all connections made on this RS-485 communication
line.
5. Place jumpers P3 between pins 2-3 of J3 and P4 between pins 2-3 of J4 to set the
half-duplex mode for the RS-485 interface.
6. Set the RS-485 communication line terminating load. The ends of a multidrop
network line can be easily identified, because only one RS-485 cable is connected
to that equipment. To connect a 120 ohm terminating load, place the jumper P1
between pins 1-2 of J1. For any other equipment connected to this RS-485
communication line, place the jumper P1 between pins 2-3 of J1.
7. To select with the RS-485 interface, set the jumper P2 between pins 2-3 of J2.
8. Plug terminal blocks TB4 and TB6 into connectors TB3 and TB5 respectively.
Connecting the RS-485 Four-Wire Communication Line
The four-wire RS-485 data-communication line is the recommended variant for
connecting the Readers to the main PC. For detailed information regarding the four-
wire RS-485 interface (full-duplex), see the 95 Series RFID System Technical Guide.
The RS-485 connectors and jumper are located on the Motherboard MBD95. The
MBD95 is the bottom board of the Reader Module Assembly.
Notes 1. For RS-485 line, use a specially designed cable only, such as, BELDEN type 9842,
or similar. For more information, see the 95 Series RFID System Technical Guide.
2. To simplify the RS-485 multidrop-type connection, the two RS-485 connectors,
TB4 and TB6 are wired in parallel on the MBD95. Connect the incoming RS-485
cable to one connector and the outcoming RS-485 cable to the other.
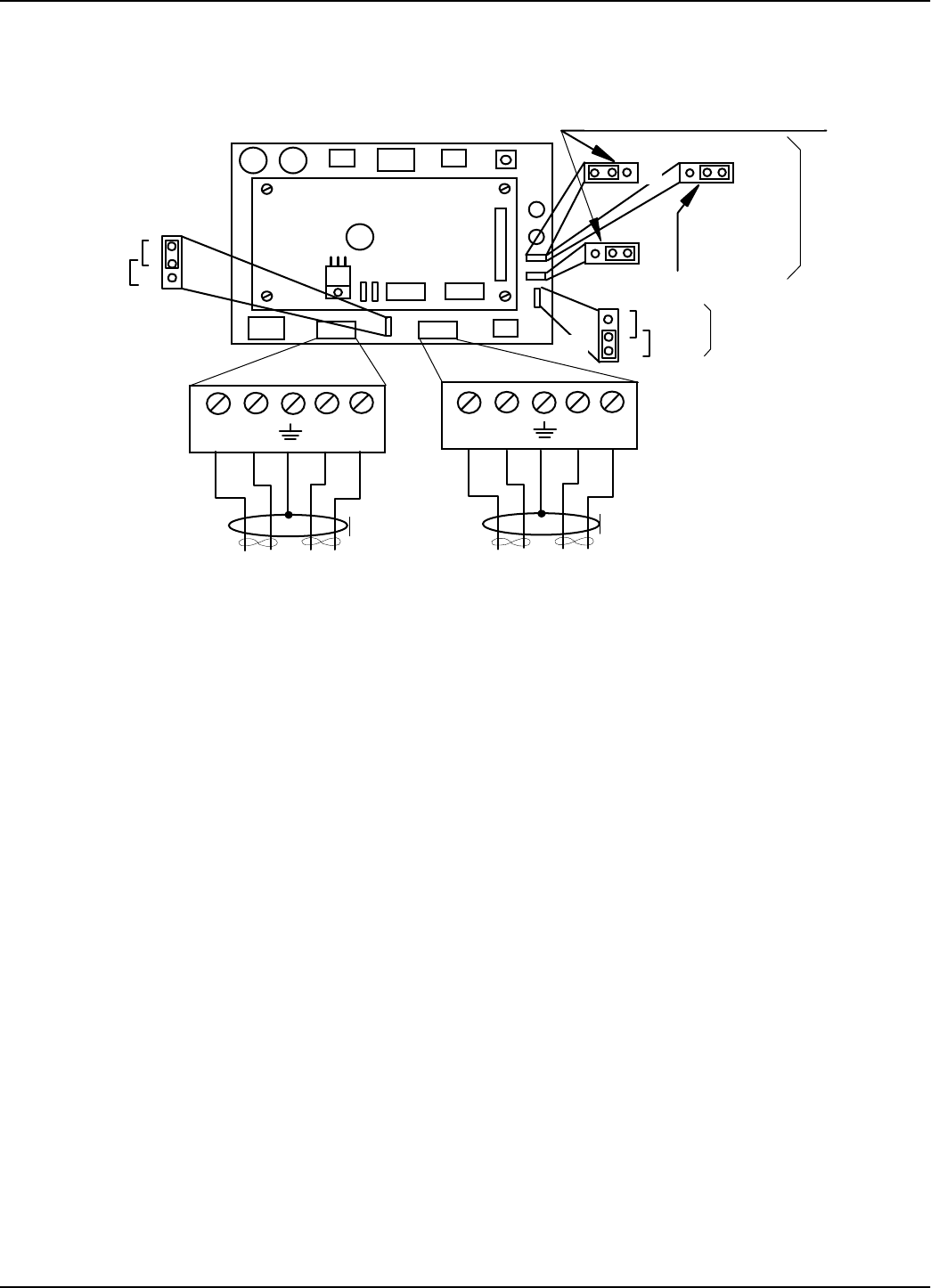
Connecting the RS-485 Four-Wire Communication Line
Reader R95 Installation and Connections 2-5
To connect the RS-485 communication lines to the Reader, refer to Figure 2-3 below.
Figure 2-3: Connections and Jumper Settings for the RS-485 Four-Wire Communication Line
Complete the following steps:
1. Unplug terminal blocks TB4 and TB6 from connectors TB3 and TB5 respectively.
2. Run the RS-485 incoming and outcoming cables through the cable grips into
Reader’s enclosure.
3. Connect the four-wire communication line to the corresponding pins A, B, Z and Y
on terminal block TB4 (or TB6). Connect the cable shield to the pin indicated by
the ground symbol on terminal block TB4 (or TB6).
Caution Before installing the RFID System, label the 4 wires on the RS-485 line A,B,Zand Y.
Keep this naming convention for all connections made on this RS-485 communication
line.
4. Place jumpers P3 between pins 1-2 of J3 and P4 between pins 2-3 of J4 to set a
full-duplex multipoint communication mode on the RS-485 interface.
Note For a full-duplex point-to-point communication mode set, however, you have to place
the jumper P4 between pins 1-2 of J4.
5. Set the RS-485 communication line terminating load. The ends of a multidrop
network line can be easily identified, because only one RS-485 cable is connected
to that equipment. To connect a 120 ohm terminating load, place the jumper P1
between pins 1-2 of J1. For any other equipment connected to this RS-485
communication line, place the jumper P1 between pins 2-3 of J1.
Outcoming cable
Incoming cable
MatherboardMBD95
Controller CTL95
AB ZY
AB ZY
TB6
TB4
RS485 RS485
AB ZY AB ZY
P4
1
J4
J3
P3
1
J4
P4
1
Standard Configuration - 4 wires
1
J2
1
J1
RS485 Termination
Load
Open
P2
RS232
RS4852
Interface
Selection
RS485Interface
TypeSelection
NOTE:
J4 Setting for
point-to-point
application
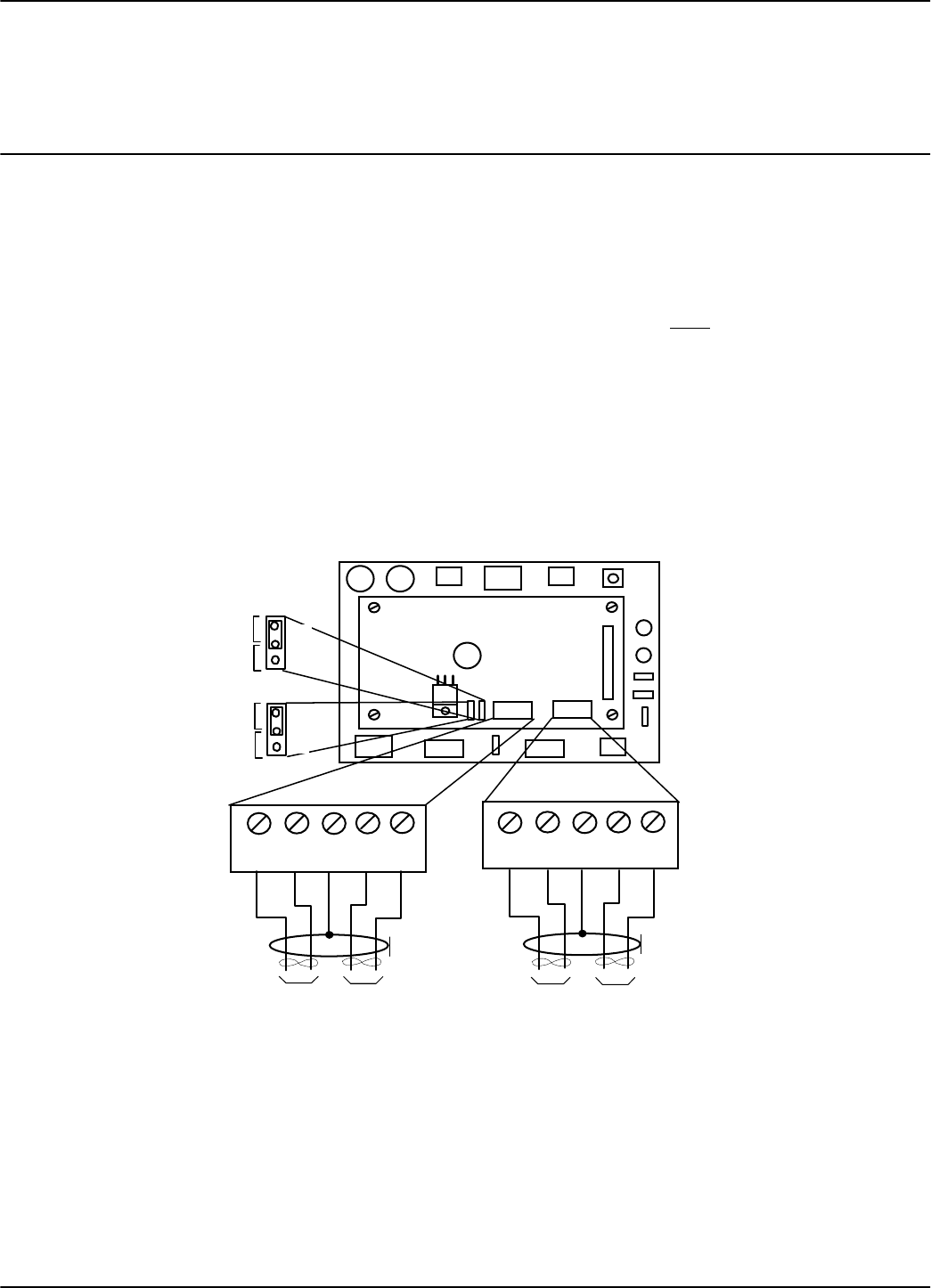
Connecting the Exciter Communication Line
2-6 Reader R95 Installation and Connections
6. To select with the RS-485 interface, place the jumper P2 between pins 2-3 of J2.
7. Plug terminal blocks TB4 and TB6 into connectors TB3 and TB5 respectively.
Connecting the Exciter Communication Line
Two separate RS-485 two-wire interfaces are used to communicate between Readers
and Exciters. For more information, see the 95 Series RFID System Technical Guide.
The RS-485 connectors and jumpers for these lines are located on the Controller
Board CTL95. The CTL95 is the top board of the Reader Module Assembly.
Notes 1. For the RS-485 line, use specially designed cables only, such as, BELDEN type
9842, or similar. For more information, see the 95 Series RFID System Technical
Guide.
2. To simplify the RS-485 multidrop-type connection, the two RS-485 connectors,
TB4 and TB6, are wired in parallel on the MBD95. Connect the incoming RS-485
cable to one connector and the outcoming RS-485 cable to the other.
To connect the RS-485 communication lines to the Reader, refer to Figure 2-4 below.
Figure 2-4: Connections and Jumper Settings for the Exciter Communication Line
A1 B1 G A2 B2
Out-coming cable
In-coming cable
A1 B1 G A2 B2
J2
J1
MatherboardMBD95
Controller CTL95
RS-485 Termination
RS485 RS485
TB6
TB4
Open
Open
Load
Load
P1
1
1
P2
RS485_CMDRS485_SGNRS485_CMD RS485_SGN
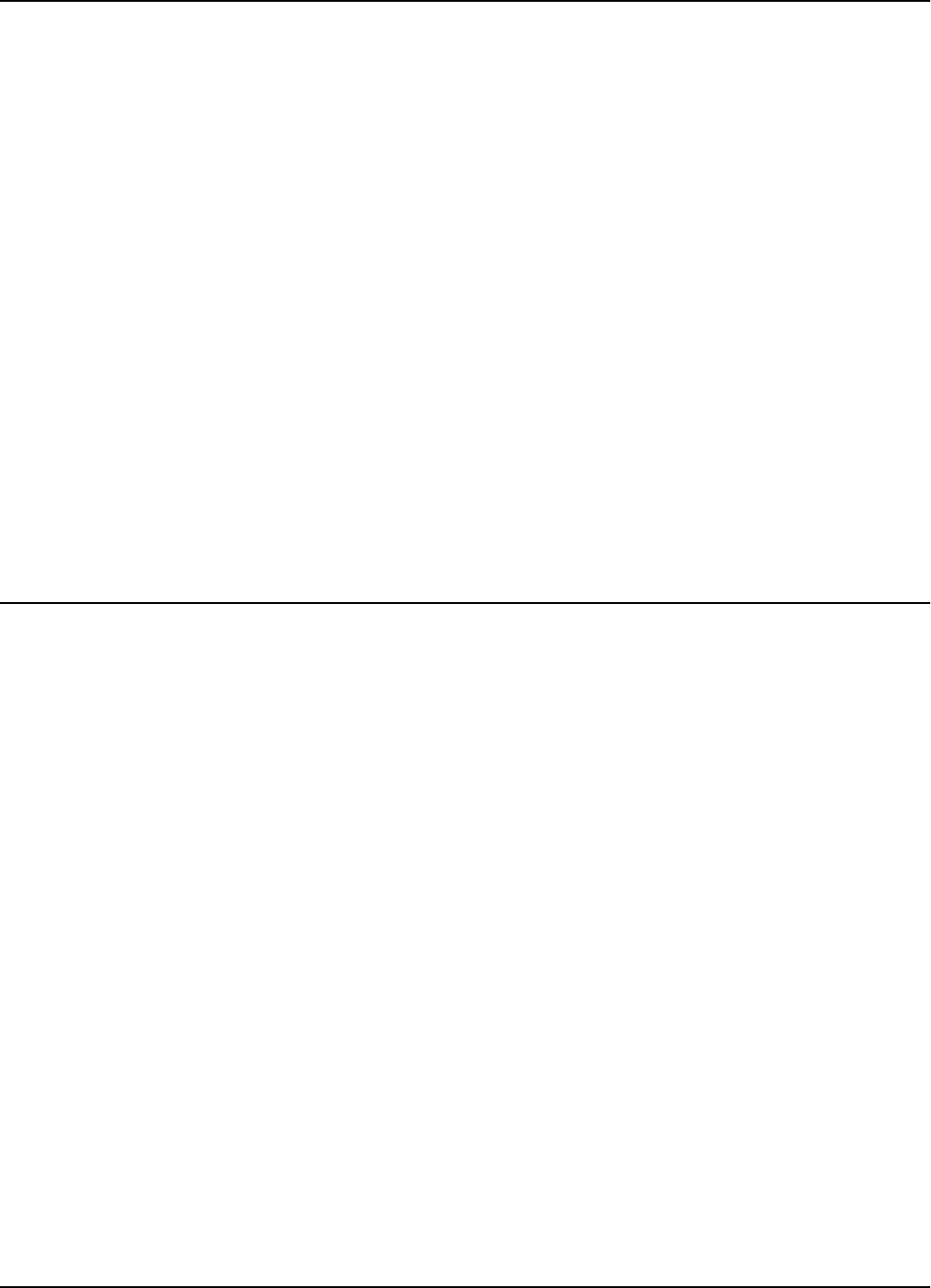
Connecting the Power Supply
Reader R95 Installation and Connections 2-7
Complete the following steps:
1. Unplug terminal blocks TB4 and TB6 from connectors TB3 and TB5 respectively.
2. Run the RS-485 incoming and outcoming cables through the cable grips into the
Reader’s enclosure.
3. Connect the four-wire communication line to the corresponding pins A1, B1, A2,
and B2 on terminal block TB4 (or TB6). Connect the cable shield to the pin
marked Gon terminal block TB4 (or TB6).
Caution Before installing the RFID System, label the two wires of one line of RS-485 as A1 and
B1, and the other two wires of RS-485 as A2 and B2. Keep this naming convention for
all connections made on this RS-485 communication line.
4. Set the RS-485 communication line terminating load for each two-wire line. The
ends of a multidrop network line can be easily identified, because only one RS-485
cable is connected to that equipment. To connect an 100 ohm terminating load on
each separate RS-485 line, place jumper P1 between pins 1-2 of J1, and jumper P2
between pins 1-2 of J2. For any other equipment connected to this RS-485
communication line, place jumpers P1 between pins 2-3 of J1, and P2 between
pins2-3ofJ2respectively.
5. Plug terminal blocks TB4 and TB6 into connectors TB3 and TB5 respectively.
Connecting the Power Supply
The Reader R95 requires a 12Vac or 13 to 16Vdc power source, and a maximum
current of 0.3A. For more information on the Reader, see Appendix A, Specifications.
The power supply connector is located on the Motherboard MBD95. The MBD95 is the
bottom board of the Reader Module Assembly (P/N 500048).
Notes 1. To connect the power supply, use electrical wire gauge 16 AWG (minimum).
2. The main ground connection of the Reader is on the power supply connector. It is
indicated by the ground symbol. Use an electrical wire with at least gauge 16AWG
for the main ground connection.
3. We recommend using Lyngsoe’s Power Supply, model TRM95/120V or TRM95/
230V, as required by the local AC power line voltage.
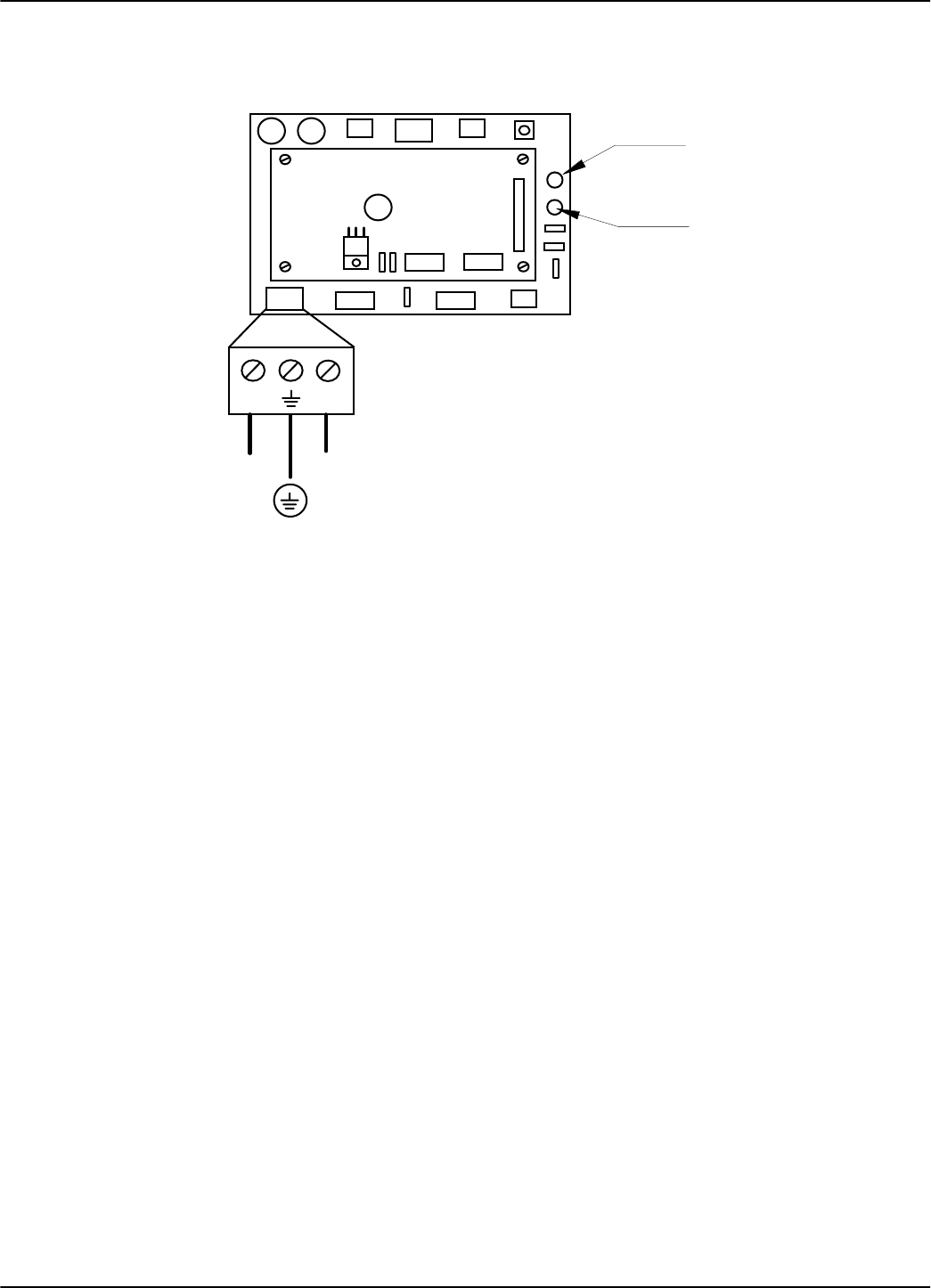
Connecting the Power Supply
2-8 Reader R95 Installation and Connections
To connect the power supply to Reader R95, refer to Figure 2-5 below.
Figure 2-5: Power Supply Connections
Complete the following steps:
1. Unplug terminal block TB2 from its connector TB1.
2. Run the power supply cable through the cable grip into the Reader’s enclosure.
3. Connect the power wires to the TB2 pins marked with the “~”symbol.
4. Connect the main ground connection to the TB2 pin marked with the ground
symbol.
5. Switch on the power supply.
6. Check the voltage on terminal block TB2 (between pins marked with the “~”
symbol).
7. Plug terminal block TB2 into its connector TB1.
8. Re-check the voltage on the terminal block TB2 in Step 6.
9. Check the MBD95 to see whether the green POWER LED goes ON, and the red
DATA LED stays ON continuously for 6-7 seconds and then turns OFF.
10. Switch off the power supply.
DATA
Red LED
MatherboardMBD95
Controller CTL95
TB2
~
~POWER
POWER
Green LED
12Vac 12Vac
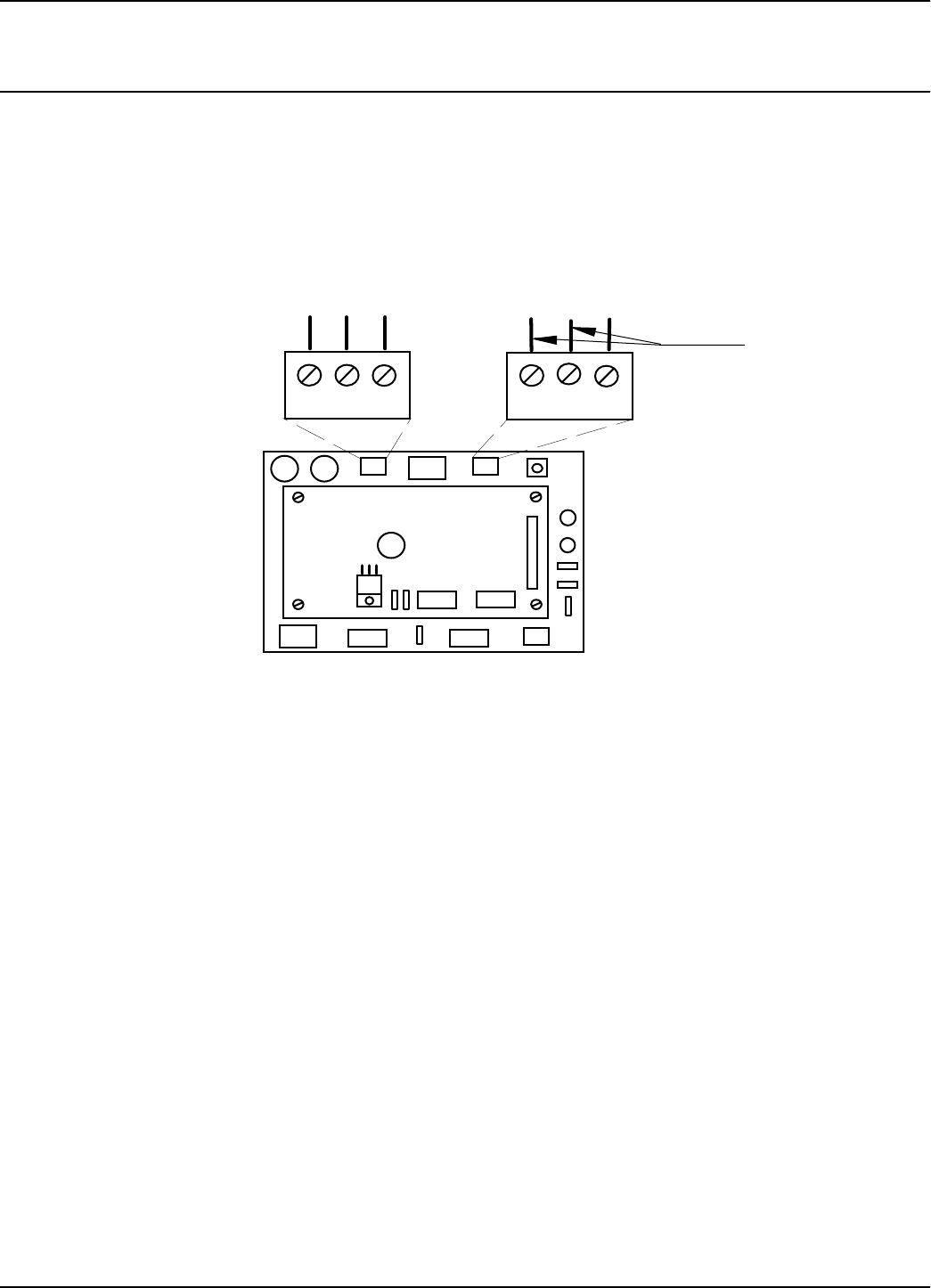
Connecting External Devices
Reader R95 Installation and Connections 2-9
Connecting External Devices
Figure 2-6 shows you how to connect external devices to the Reader.
Caution Do not exceed the maximum ratings for the relay contacts and Object Sensor input as
stated in Appendix A, Specifications.
Figure 2-6: External Devices Connections
MatherboardMBD95
Controller CTL95
TB10
RELAY OS/IO
TB12
CNO COM CNC GNDP OS IO
GND OS I/O
SPDT Contacts NO NC
COM Object Sensor
Contacts
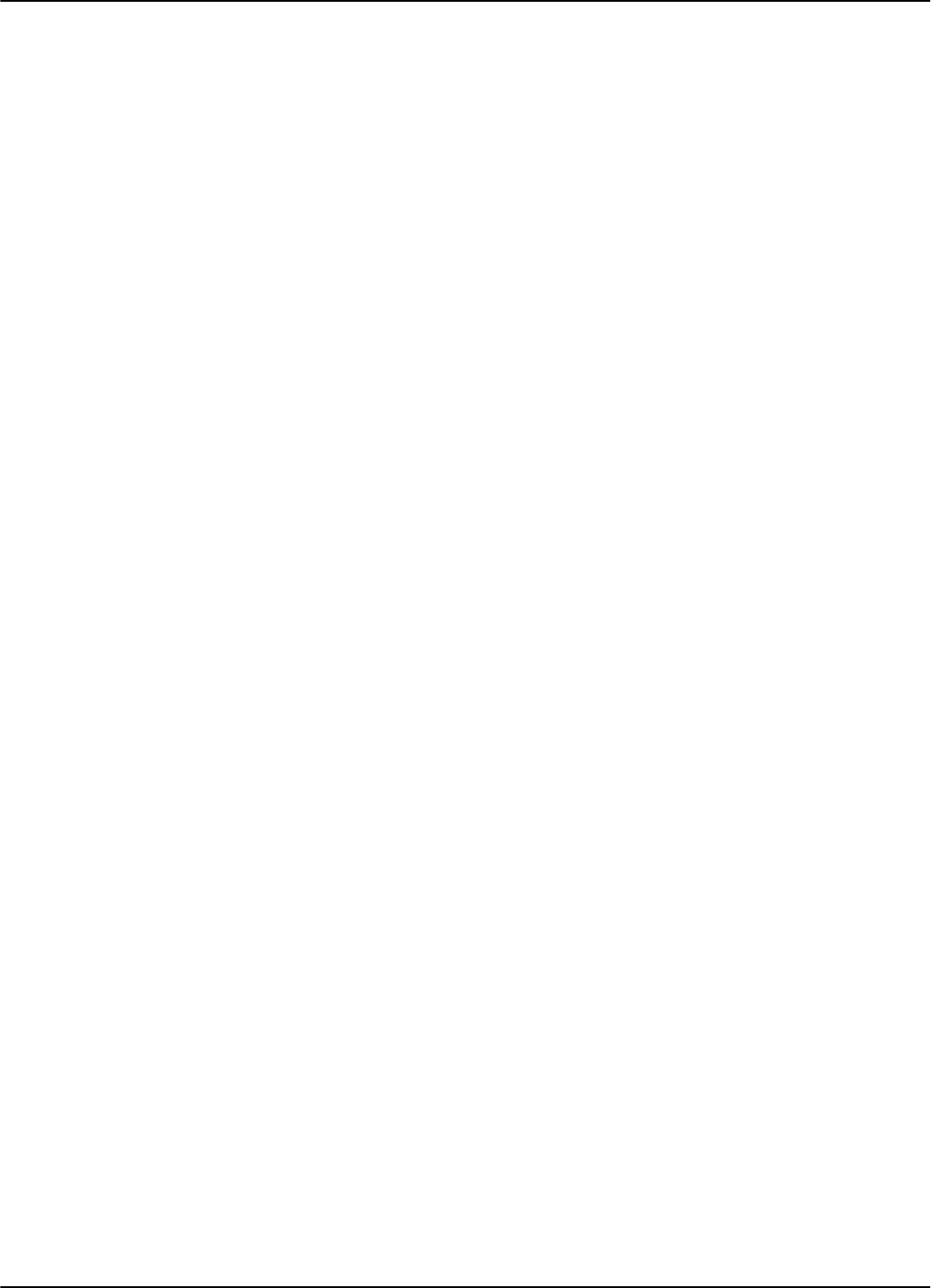
Connecting External Devices
2-10 Reader R95 Installation and Connections
This page intentionally left blank.
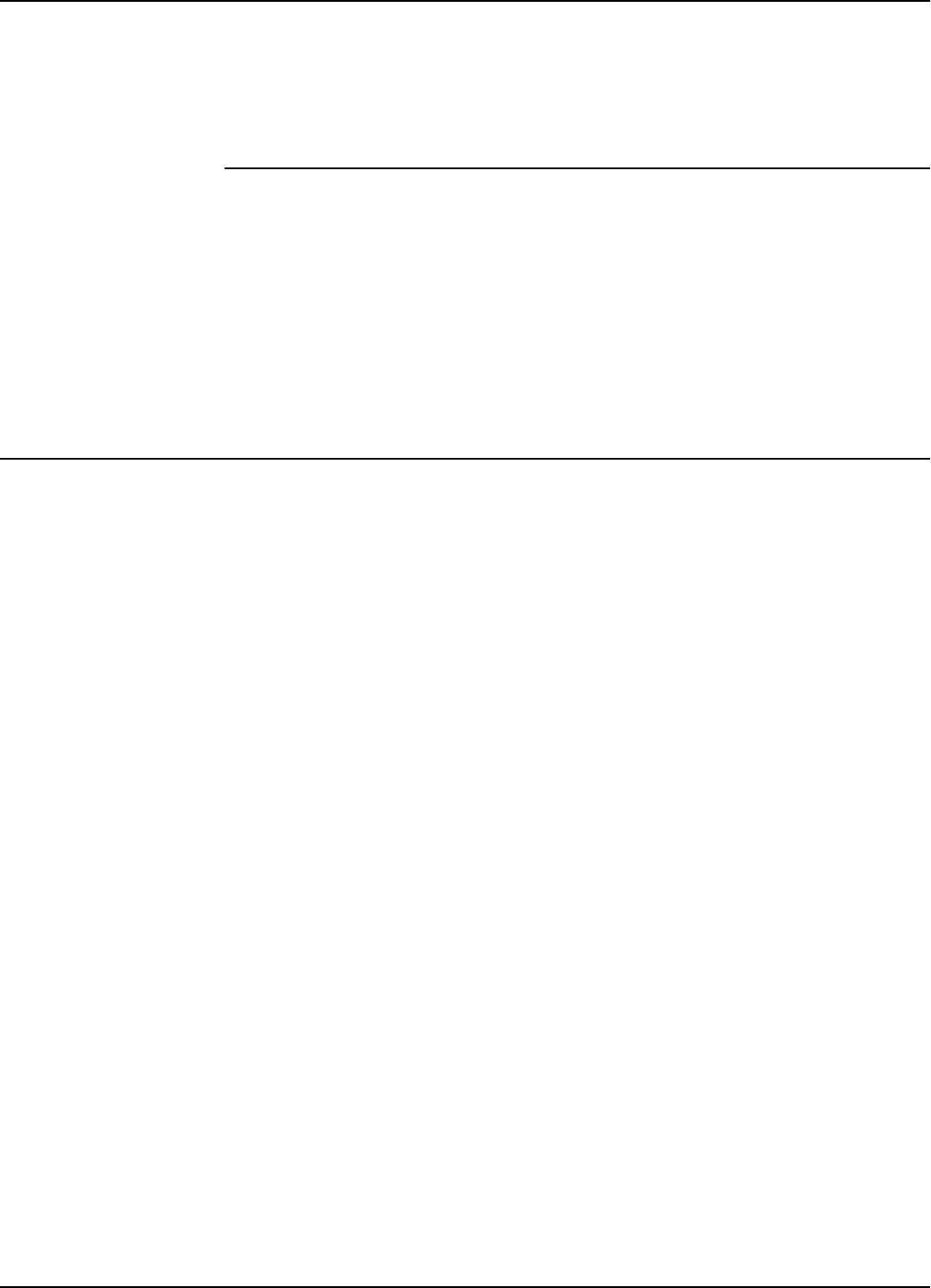
Before You Begin
Exciter E95 Installation and Connections 3-1
Chapter 3
Exciter E95 Installation and Connections
This chapter explains how to:
• Assemble the Exciter E95 using LF Antenna Kit (P/N 600420) and Enclosure E95
Kit (P/N 600421)
• Make the LF antenna connections
• Connect serial interfaces and power supply
• Set the jumpers for interfaces
• Connect remote devices to the Reader R95 (optional)
Before You Begin
Before starting the installation:
• Read Chapter 4, Setup Guidelines in the 95 Series RFID System Technical Guide.
• Have at your disposal, the complete approved documentation describing the RFID
System configuration, equipment location, and wiring distances between
equipment (see the Site Survey Documentation).
• Check whether the mechanical supports for the Exciters are installed on the site
according to the approved documentation (see the Site Survey Documentation).
• Set a color table for the serial interfaces and power supply cables. Pay special
attention to the interface terminals, cable shield, and the ground wires.
• Check whether the LF Antenna Kit (P/N 600420) and Enclosure E95 Kit
(P/N 600421) are complete, according to the product shipping list.
Tools To install the Exciter E95, you will need the following tools:
• Screwdriver SR1 (square recess # 1)
• Rubber mallet
• Hexagonal fix key # 10
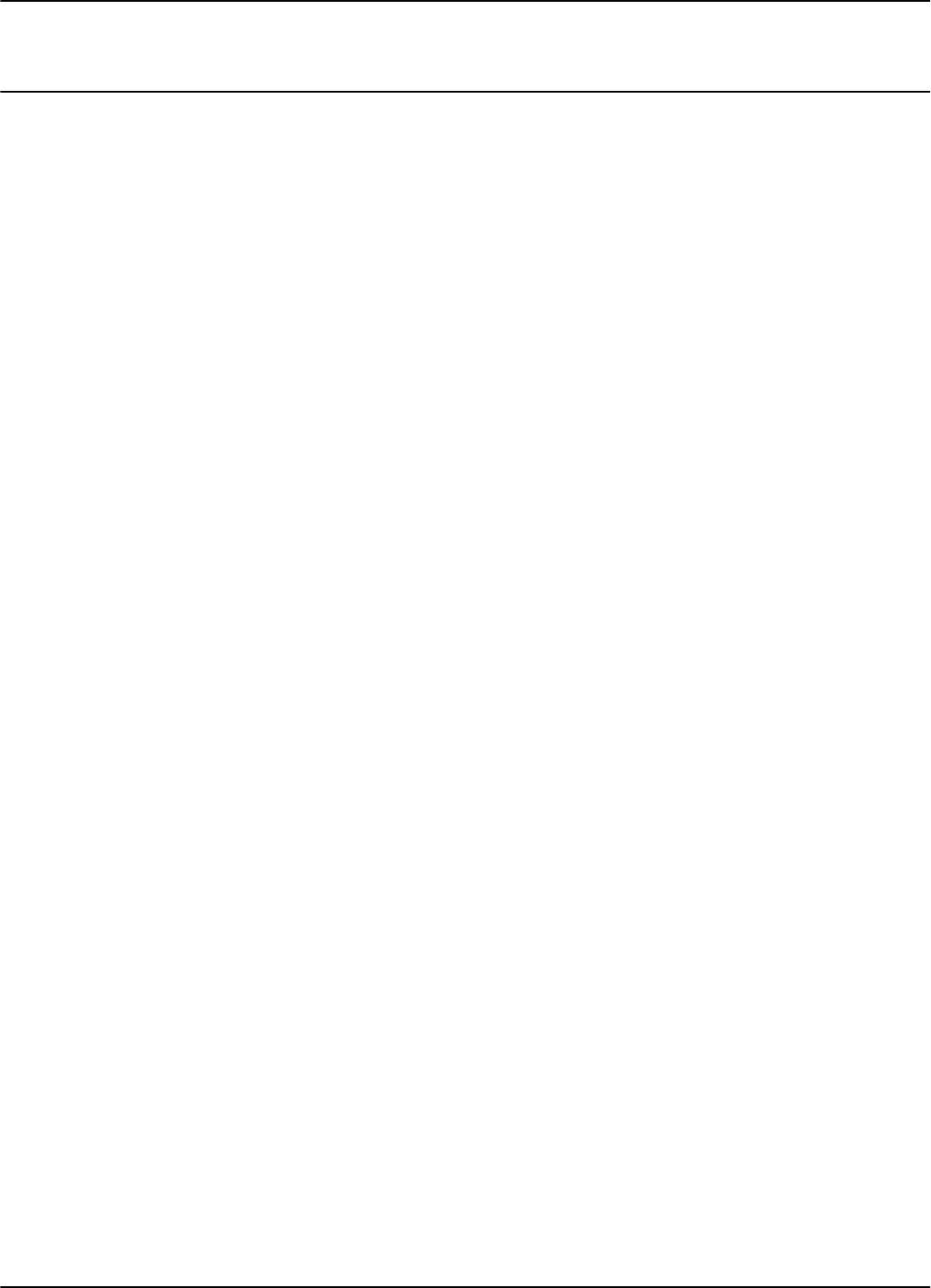
Mechanical Assembling
3-2 Exciter E95 Installation and Connections
Mechanical Assembling
To assemble the Exciter E95, refer to the assembly drawing (M900121), and then
complete the following steps.
Assembling the LF
Antenna for E95
Theantennaframeconsistsoffiveseparatesegments,eachwiththefollowing
dimensions: two pieces - 0.4m long, two pieces - 2.0m long, and one piece - 1.0m long.
Each segment includes an aluminum tube with an internal rubber hose. The
segments are joined together using plastic corners. The antenna cable (7-wire cable)
runs through the rubber hoses inside the aluminum tubes.
To assemble the antenna, do the following:
1. Starting with one side of the antenna frame that is beside the plastic enclosure
(0.4 m segment), place the corresponding rubber hose inside the aluminum tube,
and run the antenna cable through the rubber hose. Run the cable through a
plastic corner, and secure the plastic corner inside the aluminum tube using a
rubber mallet.
2. Repeat Step 1 for each side of the frame, finishing with the last short segment
(0.4m). You should have a 1x2m rectangular aluminum frame with the antenna
cable inside.
3. Terminate the antenna frame with the plastic base connectors.
4. Place the 90° brackets on each ends of the frame, and secure the frame against the
plastic enclosure using M6 screws, washers and nuts.
5. Connect the antenna frame to the ground lead on the board, by securing the
terminal lug of the ground lead on the EXT95SC electronic board with one of the
M6 screws, as shown on the assembly drawing 600406.
Note Always ensure that the ends of the antenna cable inside the plastic enclosure have the
following dimensions: one - 110mm long and the other - 360mm long. For more
information, see the drawing 600406.
6. Use the self-drill screws (M3.5x9.5) to secure the 1 inch square aluminum tube in
each corner of the LF antenna frame, and to secure the 90° brackets against the
aluminum tubes.
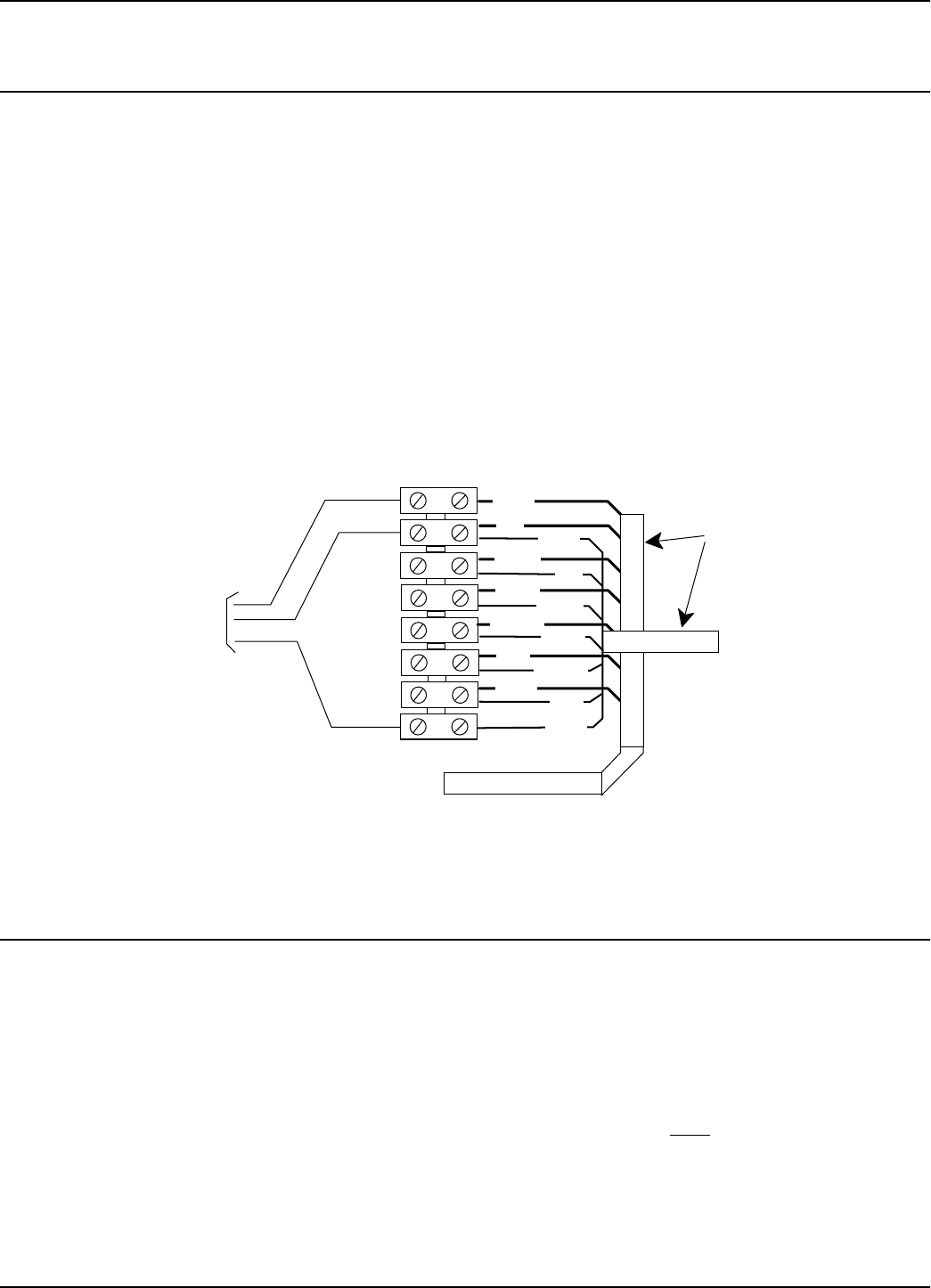
LF Antenna Connections
Exciter E95 Installation and Connections 3-3
LF Antenna Connections
The LF antenna is a 7-turn loop coil with the tap at the first turn. To create this
multiturn loop and the proper tap connection, complete the following steps:
1. Positiontheantennacableinsidetheplasticboxasshownintheassembly
drawing 600406. Cut the end closest to the terminal block - 110mm long, and the
other - 360mm long.
2. Remove 80mm of the outside cable jacket, and strip about 8mm from each
conductor isolation.
3. Using a screwdriver, connect the antenna cable conductors in the terminal block
as shown in Figure 3-1 below.
Figure 3-1: LF Antenna Connections
Connecting the RS-485 Communication Lines
The RS-485 connectors and jumpers are located on the Exciter Slave EXT95SC
assembly placed inside the plastic enclosure (see the assembly drawing M900121).
Two separate RS-485 two-wire lines are used to transmit data from/to the Reader. For
detailed information on the RS-485 two-wires interface (half-duplex), see the 95 Series
RFID System Technical Guide.
Notes 1. For the RS-485 line, use specially designed cables only, such as BELDEN type
9842, or similar. For more information, see the 95 Series RFID System Technical
Guide.
2. To simplify the RS-485 multidrop-type connection, the two RS-485 connectors,
TB4 and TB6 are wired in parallel on the EXT95SC board. Connect the RS-485
1
2
BLACK
WHITE
RED
BROWN
GREEN
BLACK
RED
BROWN
BLUE
ORANGE
ORANGE
GREEN
BLUE
WHITE
Black
Red
White
From Exciter
EXT95SC
Assembly
7 Conductors
Antenna Cable
Ends
7
8
3
4
5
6
Terminal Block
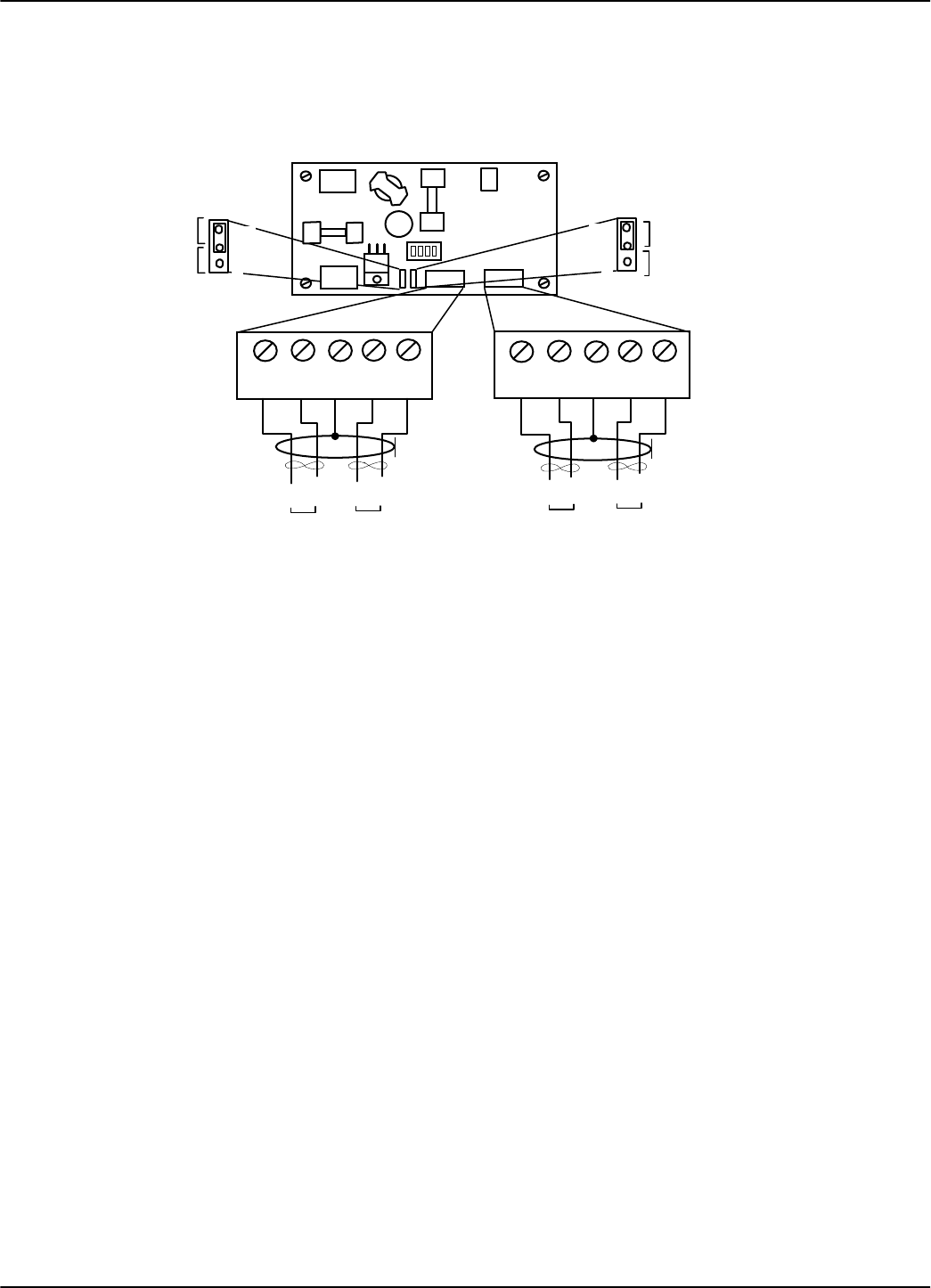
Connecting the RS-485 Communication Lines
3-4 Exciter E95 Installation and Connections
incoming cable to one connector and the RS-485 outcoming cable to the other.
To connect RS-485 communication lines to the EXT95SC, refer to Figure 3-2 below.
Figure 3-2: Connections and Jumpers Settings for the RS-485 Communication Lines
Complete the following steps:
1. Unplug terminal blocks TB4 and TB6 from connectors TB3 and TB5 respectively.
2. Run the RS-485 incoming and outcoming cables through the cable grips into the
plastic enclosure.
3. Connect the RS485_CMD line to pins A1, B1, and RS485_SGN line to the pins A2,
B2 on terminal block TB4 (or TB6). Connect the cable shield to the pin marked G
on terminal block TB4 (or TB6).
Caution Before installing the RFID System, label the 2 wires on the RS485_CMD line A1 and
B1; label the 2 wires on the RS485_SGN line A2 and B2.Keepthisnaming
convention for all connections made on these RS-485 communication lines.
4. Set the terminating load for the each RS-485 communication line. The ends of a
multidrop-network line could be easily identified, because only one RS-485 cable
is connected to the equipment.
5. To connect a 100 ohm terminating load to the RS485_CMD line, place the jumper
P1 between pins 1-2 of J1. When connecting any other equipment to this RS-485
communication line, place the jumper P1 between pins 2-3 of J1.
To connect a 100 ohm terminating load to the RS485_SGN line, place the jumper
P2 between pins 1-2 of J2. When connecting any other equipment to this RS-485
communication line, place the jumper P2 between pins 2-3 of J1.
6. Plug terminal blocks TB4 and TB6 into connectors TB3 and TB5 respectively.
J2
TB6
RS485RS485
TB4
A1 B1 A2 B2 A1 B1 A2 B2
J1
P1
Load
Open
1
G G
Exciter Slave EXT95SC
1
P2
Load
Open
RS485_CMD
Termination
RS485_SGN
Termination
A1 B1 A2 B2
RS485_CMD RS485_SGN
B1
A1
RS485_CMD
B2
A2
RS485_SGN
Outcoming cable
Incoming cable
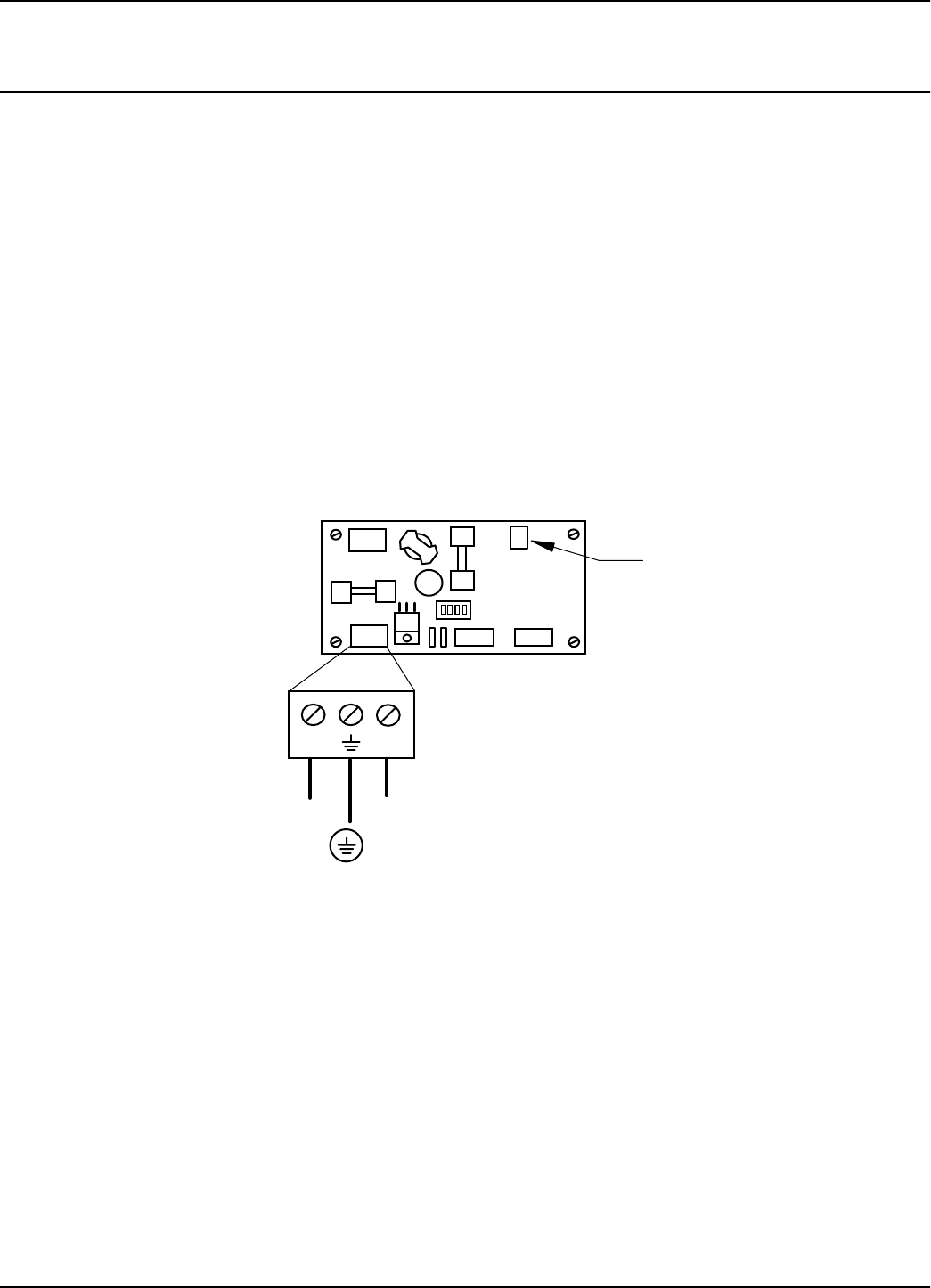
Connecting the Power Supply
Exciter E95 Installation and Connections 3-5
Connecting the Power Supply
Power Supply
Connections
The Exciter requires an 22 Vac or 23 to 28 Vdc power source, and a maximum current
of 0.5 A. For more information, refer to Appendix A, Specifications.
Notes 1. The power connector is located on the EXT95SC assembly.
2. Useanelectricalwirewithatleasta16AWGgaugetoconnectthepowersupply.
3. The Exciter’s main ground connection is on the power supply connector. It is
indicated by the ground symbol. Use an electrical wire with at least a 16 AWG
gauge for the main ground connection.
4. To power the EXT95SC, we recommend using Lyngsoe’s Power Supply, model
TRM95/120V or TRM95/230V, as required by the local AC power line voltage.
To connect the power supply to the Exciter, refer to Figure 3-3 below.
Figure 3-3: Exciter E95 Power Supply Connections
Complete the following steps:
1. Remove terminal block TB8 from connector TB7 on the EXT95SC board.
2. Run the power supply cable through the cable grip into the plastic enclosure.
3. Connect power wires to the TB8 pins marked with the “~”symbol.
4. Connect the main ground connection to the TB8 pin marked with the ground
symbol.
5. Switch on the power supply.
Exciter Slave EXT95SC
~
~
TB8
POWER
TB10
22Vac 22Vac
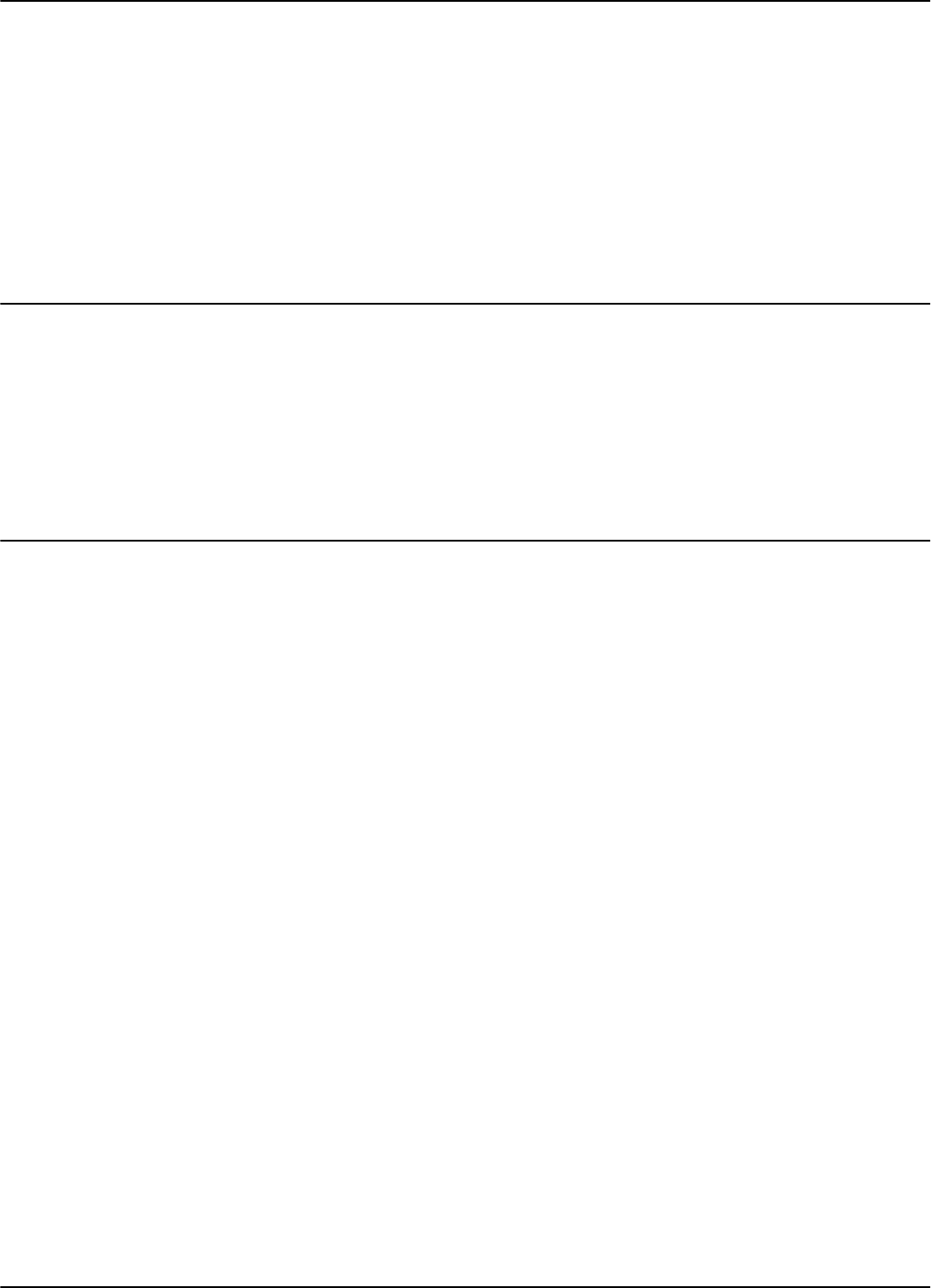
UHF Transmitter - Direct Control (Optional)
3-6 Exciter E95 Installation and Connections
6. Check the voltage on the terminal block TB8 (between pins 1-3).
7. Plug terminal block TB8 into connector TB7.
8. Re-check the voltage in Step 6.
9. Check whether the voltage between pins 1 and 2 on terminal block TB10 is
5.0 ± 0.2 V.
10. Switch off the power supply.
UHF Transmitter - Direct Control (Optional)
The UHF transmitter can be also switched on using a hardware control, by creating a
a short between pins 1-2 on terminal block TB10. After this is done, the UHF
transmitter will start transmitting the pre-programmed messages and then stop. To
startanothertransmission,thecontactmustbeopenedandthenclosedagain.
The location of terminal block TB10 on the EXT95SC board is shown in Figure 3-3.
Assembling Other Models of Exciters
Lyngsoe provides other models of Exciters with different antenna frame sizes for
particular installations. As an example, see Exciter E95S (P/N 600647). For
mechanical assembling and electrical connections, use a similar procedure as
described in the previous paragraphs and drawing M900113.
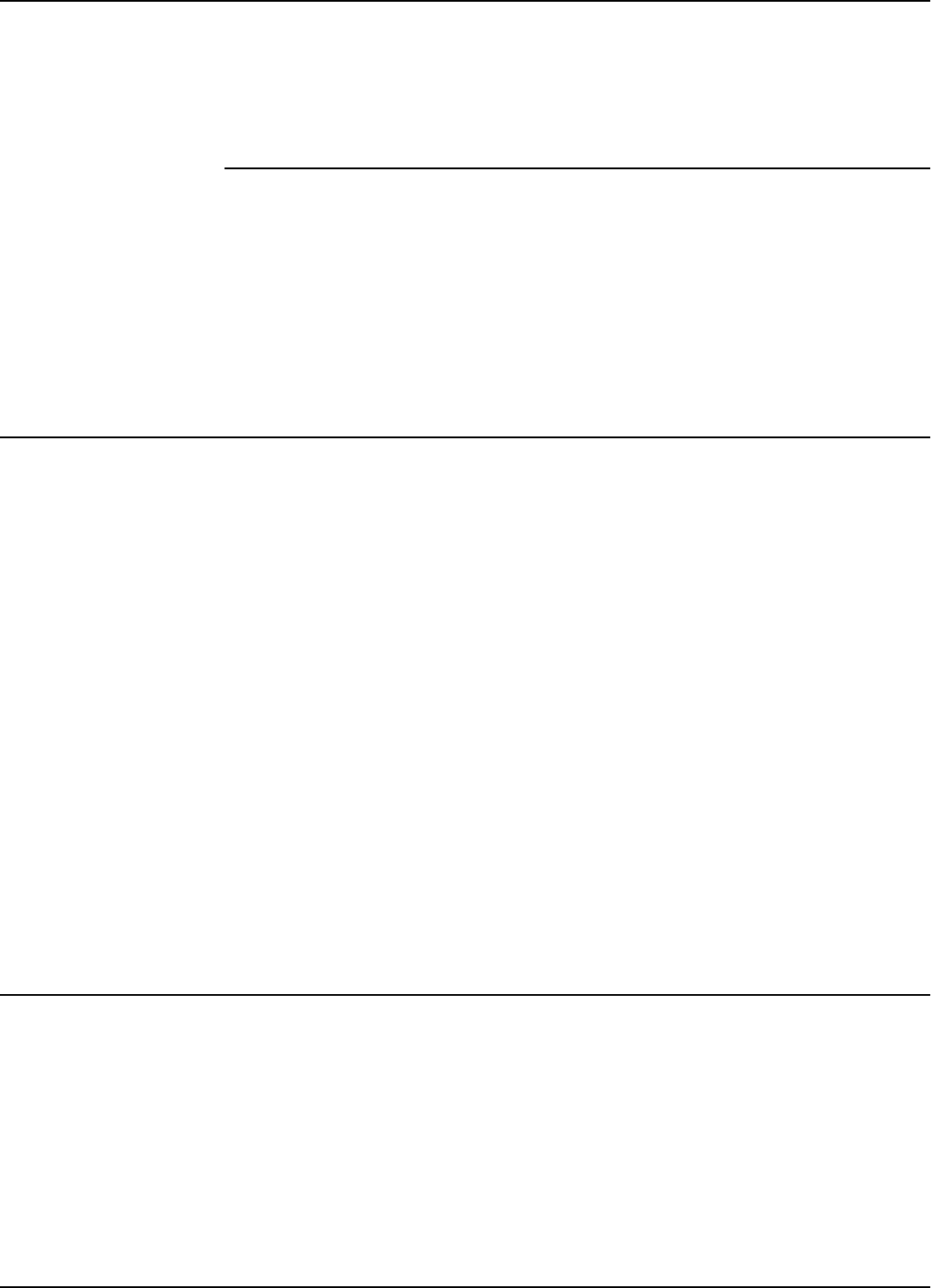
Before you Begin
Power Supply TRM95 Installation and Connection 4-1
Chapter 4
Power Supply TRM95 Installation and Connection
This chapter explains how to:
• Install the Power Supply
• Make the input line and output connections
All data provided in this chapter apply to both Power Supply models TRM95/120V
(P/N 600579) and TRM95/230V (P/N 600626).
Before you Begin
Before installing the Power Supply:
• Read Chapter 4, Setup Guidelines in the 95 Series RFID System Technical Guide.
• Have at your disposal, the complete approved documentation describing the RFID
System configuration, equipment location, and wiring distances between
equipment (see the Site Survey Documentation).
• Check whether the mechanical supports for the Power Supply is installed on the
site according to the documentation.
• Check whether all cables are installed on the site according to the documentation
(type, protection, routing, etc.).
• Check whether the Power Supply unit has the correct rating (120V or 230V) that
is suitable for the local AC power lines voltage.
Tools To install the Power Supply, you will need the following tools:
• Phillips screwdriver size # 1)
• Slotted screwdriver 2mm
Installing Power Supply TRM95
For mechanical details, refer to the Power Supply assembly drawing.
Placement The Power Supply unit can be installed either horizontally or vertically, but must be
secured against its mechanical support with 4 screw (dia. 1/8"). It must be installed in
such a way that the front is easily accessible and visible for inspection. This unit is
designed for indoor use only. You should avoid installing the Power Supply unit in
locations where there is water or excessive humidity. To reduce the risk of
overheating, avoid exposing the Power Supply unit to direct sunlight or near any
heat-emitting devices, such as a room heater or a stove.
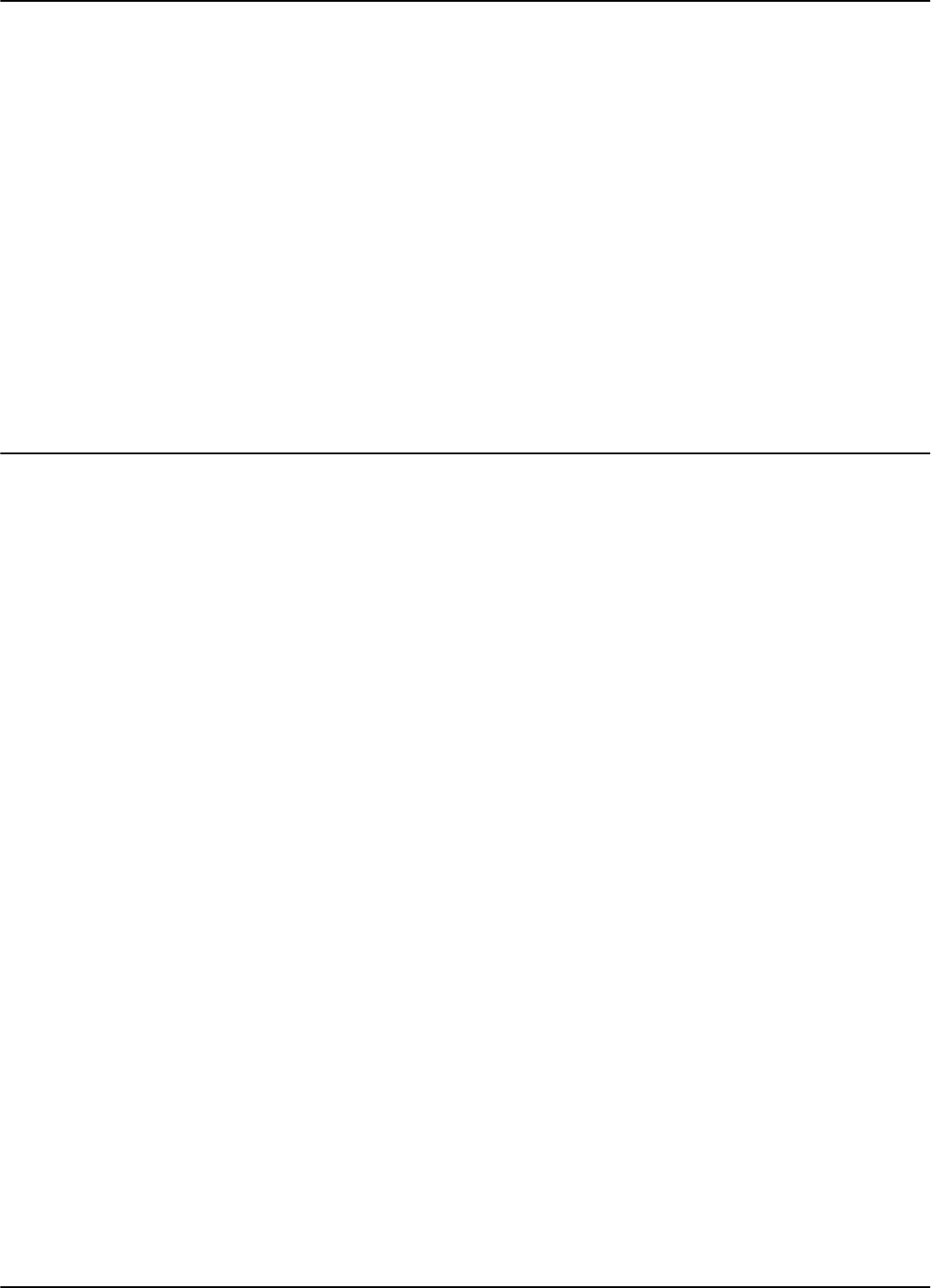
Wiring Connections and Supply
4-2 Power Supply TRM95 Installation and Connection
Safety Please adhere to the following safety precautions:
1. Only authorized personnel are qualified to install and repair the Power Supply
unit.
Caution To reduce the risk of an electrical shock, disconnect the AC main supply before
removing the unit’s cover.
2. Use only approved (CSA,UL, IEC) fuses, size 5x20mm, Type “T” (slow-blow), with
appropriate rating (1A for 120Vac, or 0.5A for 230Vac). The correct fuse rating is
marked on the front panel of the Power Supply unit.
3. Ensure that the Power Supply unit is properly grounded. Always connect the unit
to the 3-wire (with grounding) power systems.
4. Ensure that no water does not get inside the unit. Ensure that no foreign objects
get inside the unit.
Wiring Connections and Supply
To get inside the unit, you must first unscrew the two screws that secure the cover.
Once you remove these screws, you can easily lift the cover.
Note To completely detach the cover, you must also remove the cover’s ground connection.
Remember the ground connections must be in place when the unit is operating
normally.
All unused knockout-punch holes (front and back panels) must be plugged with plugs
or similar stoppers. Lyngsoe recommends using the Hole Plug PG11 (P/N 400617)
with a Polyamid Nut (P/N 400645). You have to order these parts separately.
You must secure all cables passing through the front or back panel with cable grips or
connectors (these are not provided). The connectors must match the conduit type used
to protect the cable outside the Power Supply unit. For more information on these
parts, contact Lyngsoe Industries.
For all interconnections (power line, equipment), Lyngsoe recommends using cable
type SJT, PVC jacketed, 3-conductors with a minimum gauge of 16 AWG (0.75 mm2-
conductor nominal cross-sectional area). Lyngsoe recommends BELDEN cable type
19353.
An external disconnecting device will be provided as part of the building’s installation.
The disconnecting device will have an appropriate rating for the AC power line
voltage (minimum 1A for 120Vac or 0.5A for 230Vac). Installation of the external
wiring will comply with the national wiring rules (code) applicable to the site.
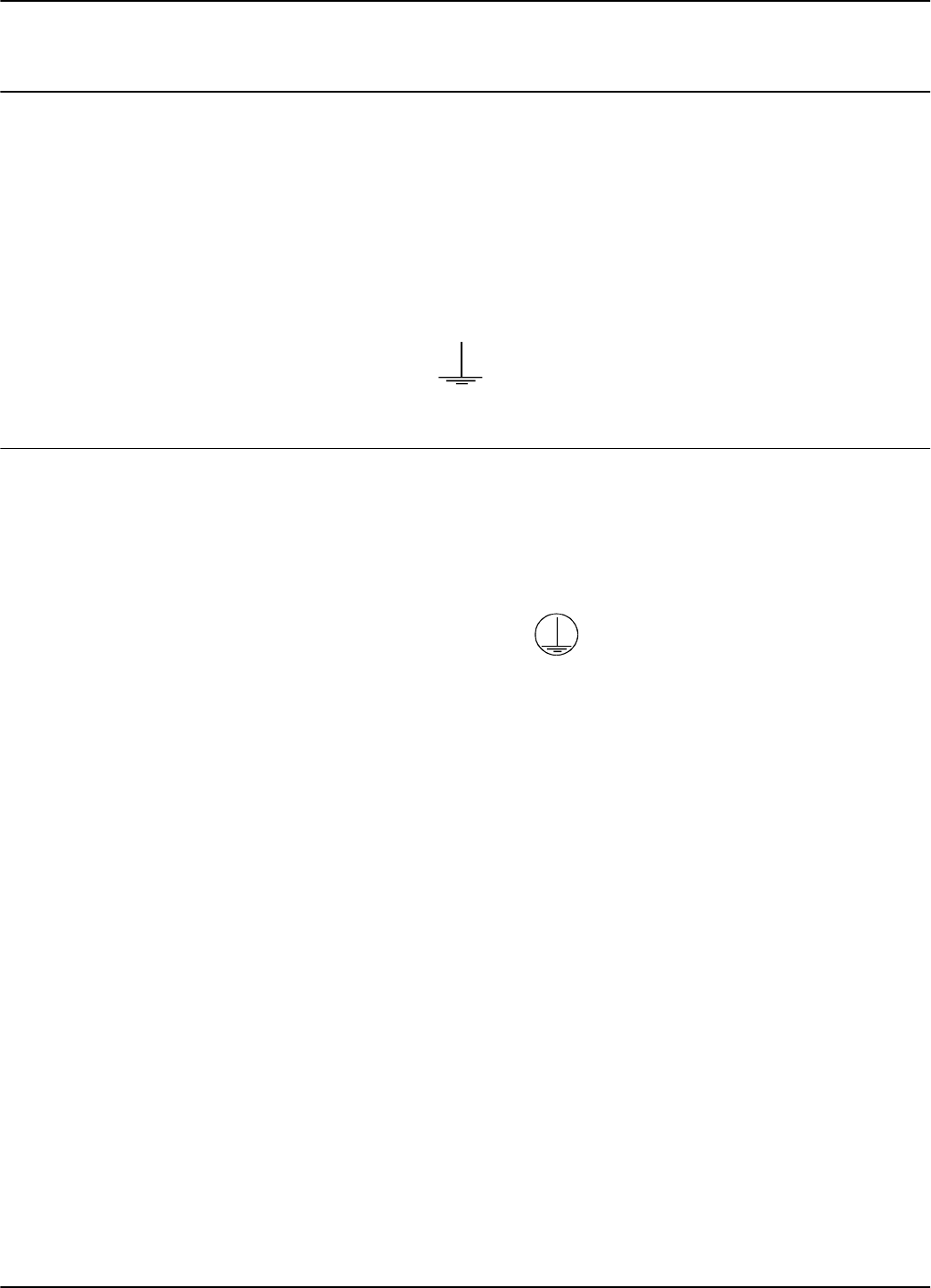
Connecting Equipment to the Power Supply Unit
4-3 Power Supply TRM95 Installation and Connection
Connecting Equipment to the Power Supply Unit
The Power SUpply unit has 2 separate outputs (12Vac/1A and 22Vac/2A) to power up
separate RFID equipment as Readers R95 and Exciters E95. These voltages are
available for connecting an external cable on the Power Supply’s internal terminal
block and is clearly marked.
Attention Do not exceed the load ratings specified for each output: 1A for the 12Vac, and 2A for
the 22Vac. On the 22Vac source, the 2 terminal blocks are connected in parallel for
each output terminal. Always use a 3-wire cable to connect the equipment to the
Power Supply unit. Always connect the ground wire of each cable to the terminal
block that is indicated by
Connecting the AC Mains Supply
Connect the power lines cable to the internal terminal block of the Power Supply unit
as follows:
• Live(phase)-totheterminalmarkedL
• Neutral - to the terminal N
• Ground - to the terminal marked
For more information, see Chapter 8, Power Supply Assembly Drawings.
IMPORTANT Before you connect power to the Power Supply unit, re-check the following:
• The Power Supply model and rating against the installation plan and line voltage
• The Power Supply fuse rating
• All cable connections to the Power Supply’s internal terminal block
• All cable access into the Power Supply’s enclosure, making sur that they are
properly secured and protected.
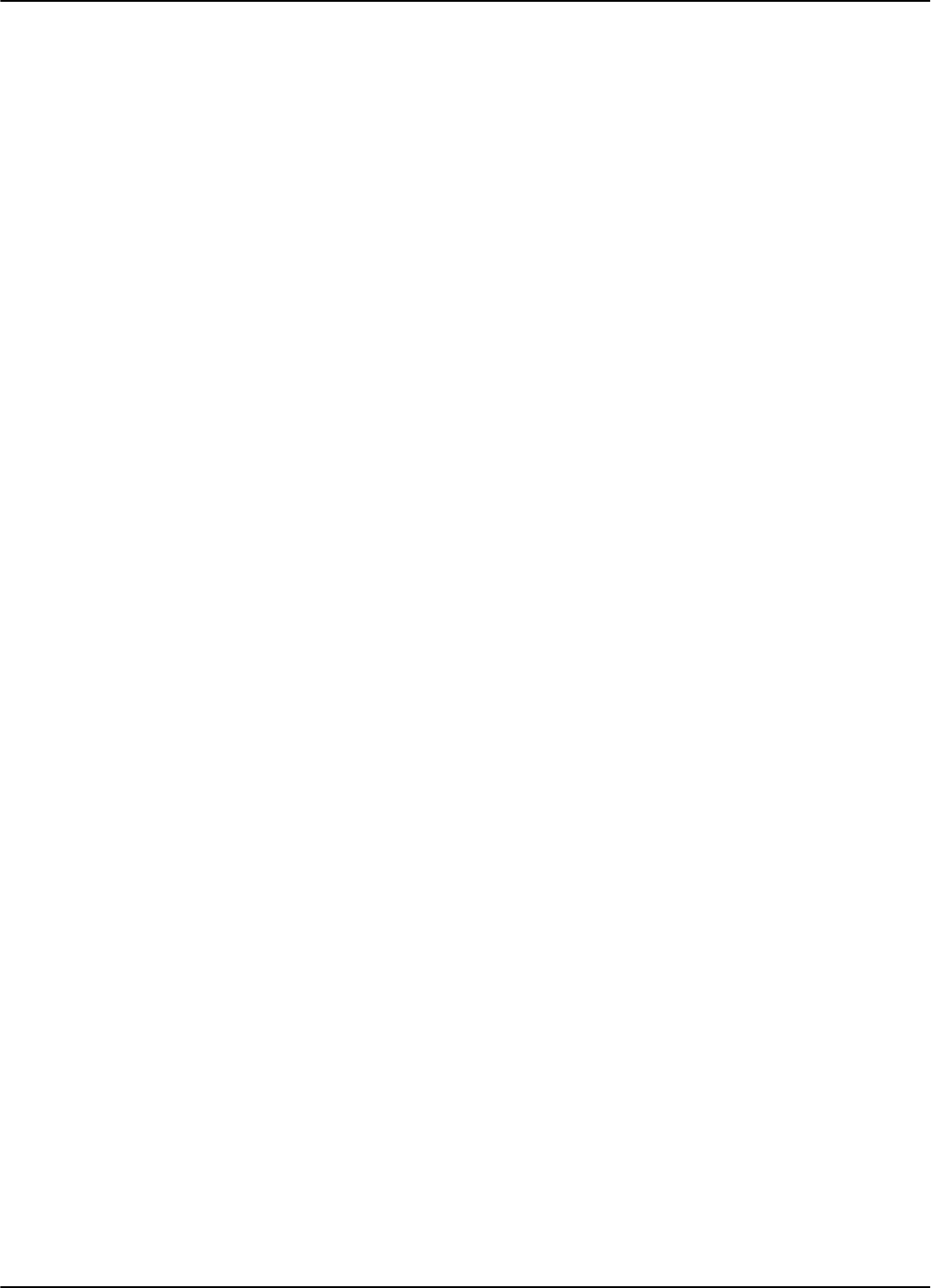
Connecting the AC Mains Supply
4-4 Power Supply TRM95 Installation and Connection
This page intentionally left blank.
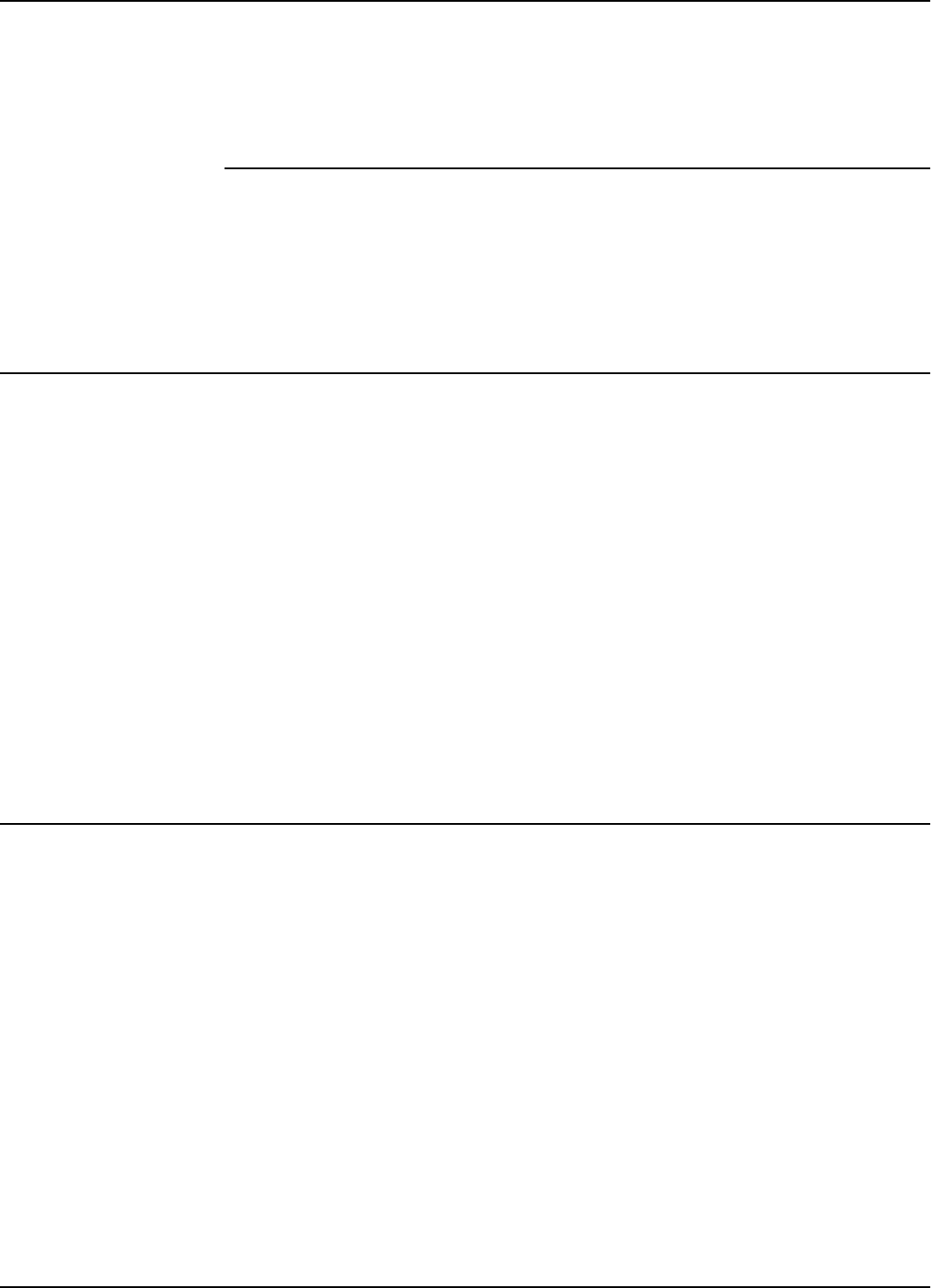
Before You Begin
Configuration and Operation 5-1
Chapter 5
Configuration and Operation
This chapter explains how to set-up and configure a 95 Series RFID System. The IPC
implementation is a practical example of the 95 Series RFID System configuration.
For more information about the 95 Series RFID System configuration, refer to the
95 Series RFID System Technical Guide.
Before You Begin
Before starting the RFID System configuration, do the following:
1. Check whether all equipment is correctly installed and interconnected according
to the requirements stated in Chapter 2, Reader R95 Installation and Connections
and Chapter 3, Exciter E95 Installation and Connections in this guide.
2. Create a unique address for each Reader and Exciter according to the approved
documentation describing the RFID System configuration (see the specific Site
Survey documentation).
3. Familiarize yourself with the instructions format described in the 95 Series RFID
System Reference Guide, and the system’s functionality described in the 95 Series
RFID System Technical Guide.
4. Refer to the section, 95 Series RFID System Configuration Principles on page 1-3,
for some general explanations on configuring the 95 Series RFID System.
General Procedure Rules
You have to configure each Reader and Exciter in the RFID System.
Lyngsoe recommends that you follow the general rules listed below:
1. Configure each identification zone, onebyone,byusingaPC/Laptopthatis
directly connected to a Reader. By doing this, you can control the Reader, and all
Exciters interconnected to it from this PC.
2. Follow the step-by-step instructions described in this chapter.
3. If you do not obtain the expected results, refer to Chapter 7, Troubleshooting.
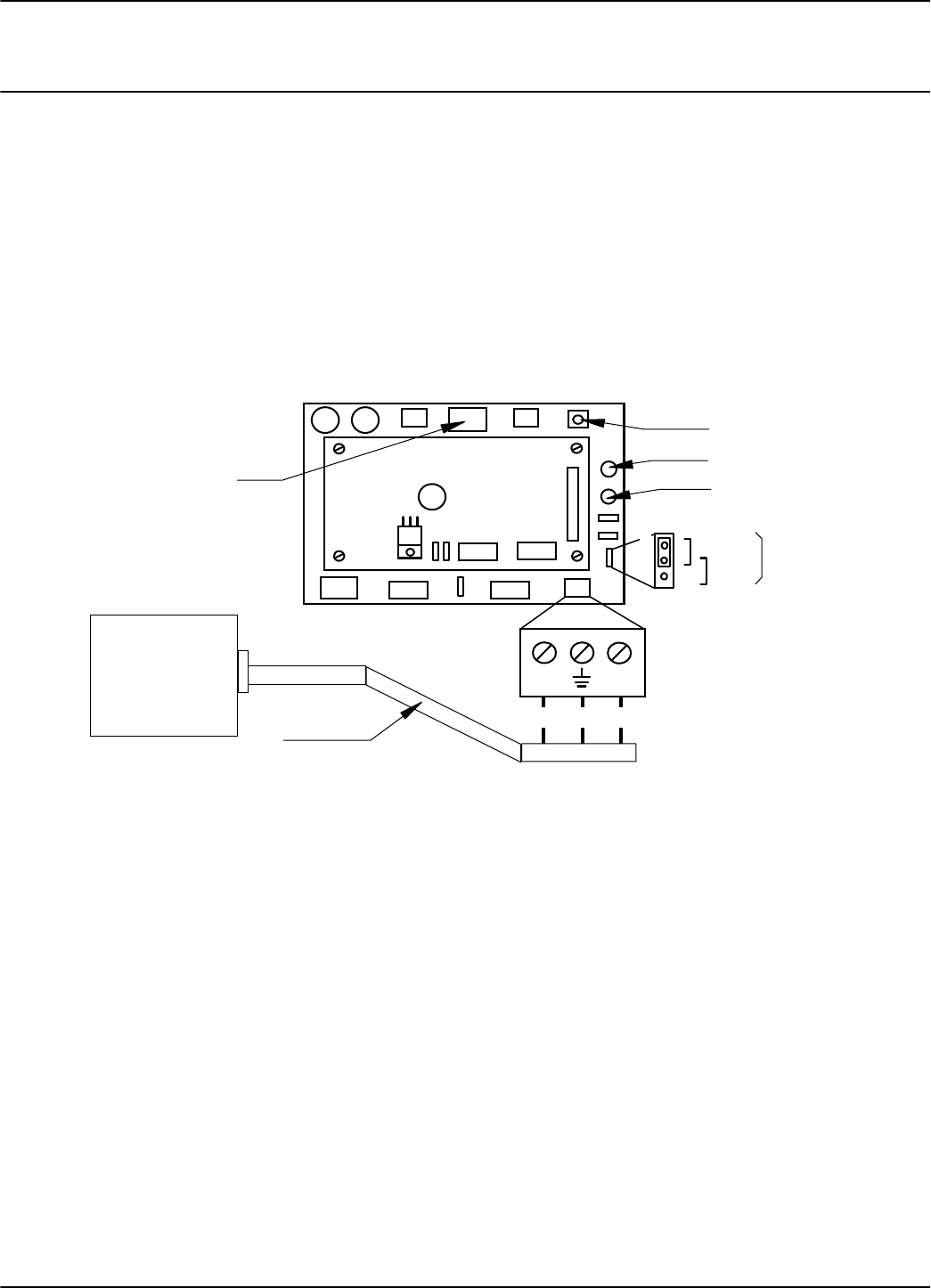
Setting Up the Reader/PC Connection
5-2 Configuration and Operation
Setting Up the Reader/PC Connection
To connect the Reader to a PC, do the following:
1. UsetheRS-232orRS-485communicationlinetoconnecttheReadertothePC.
For more information on these communication lines, see Connecting the RS-232
Communication Line,andConnecting the RS-485 Four-Wire Communication Line
in Chapter 2.
For the initial set-up, Lyngsoe recommends using the RS-232 connection with a local,
mobile PC (Laptop), as shown in Figure 5-1 below.
Figure 5-1: Connecting the Reader to a PC/Laptop
2. Run a terminal emulation program on the PC, such as, HyperTerminal in
Windows 95, Terminal in Windows 3.x, or Procomm in DOS or any version of
Windows. The recommended configuration for the PC’s port is:
• Data rate - 19200 bps
•Databits -8bits
• Parity - none
•Stopbits -1
• Flow control - none
MatherboardMBD95
Controller CTL95
TX RX
1
RS232
TB8
Red LED
DATA
Green LED
POWER
Reset Button
TX GND RX
COM1/DB9
RS232 Cable
RS232
RS4852
Interface
Selection
J2
P2
Relay
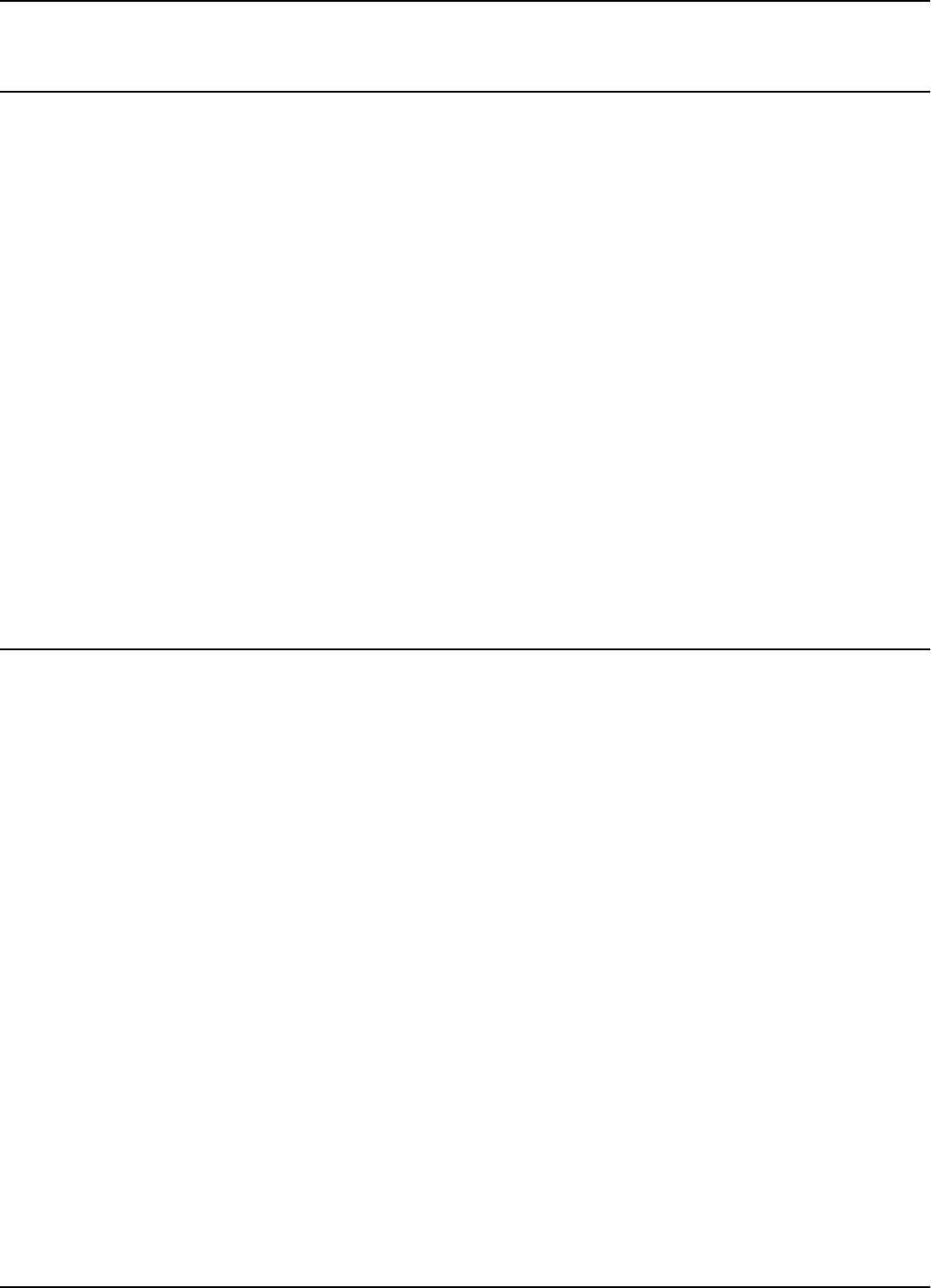
Reader’s Power-up Sequence
Configuration and Operation 5-3
Reader’s Power-up Sequence
To verify the Reader’s power-up sequence, do the following:
1. Turn on the power supply to the Reader.
2. Referring to Figure 5-1, check whether the relay on the MBD95 board
immediately clicks, and the green POWER LED is on.
3. Check whetherthe Reader performs the following power-on test sequence: the red
DATA LED on the MBD95 board remains ON for 6-7 seconds. Afterwards, the
following sign-on message is displayed on the PC’s screen:
DISYS CRM-95 READER (c)Copyright DISYS Corporation 1989-1996.
Notes 1. If you did not assign a System Code identification number (SC) to the Reader, the
DATA LED will flash On and Off at a rate of 1.4 Hz. To set the System Code, type:
ISC=[your SC]<Enter>
2. If a string of unrecognizable characters appears on the PC’s screen, it means that
the communication link between the Reader and the PC is not set properly. Run
the Learning Procedure, as described below, to establish the correct settings.
Learning Procedure (Optional)
This a special mode of operation, specifically designed to allow a Reader to
communicate with the PC to which it is attached, by adapting itself to the serial frame
format that the PC is using.
ToforcetheReaderintothelearning mode,followthestepsbelow.(SeeFigure5-1).
1. Press the RESET button once.
2. Verify whether the DATA LED flashes at a rate of 2 Hz. This means that the
Reader is in the learning mode, and is waiting to determine the frame format sent
by the PC.
3. Send a few characters to the Reader, for example, LYNGSOE.
4. When the learning process is finished, the DATA LED will start flashing at 1.4 Hz
rate and the following message will be displayed on the PC:
Learned: rate,parity,bits
where:
rate: is the serial data rate (baud) expressed as a numeric value, for example,19200.
parity: is a single character that reports the parity bit: Nfor no parity, Yfor parity.
bits: is a single digit (7 or 8) that reports the number of bits per character.
5. Check the values of the Reader’s current serial communication configuration by

Resetting the Reader
5-4 Configuration and Operation
using Group Sparameters. You can change the settings for the PC or Reader so
that the settings match each other. If you modify the Reader’s parameters, you
must save them before leaving the learning mode. For more information on this
procedure, see Storing the Reader’s Configuration on page 5-13.
6. Press the RESET button again to exit from the learning mode.
7. The DATA LED will stop flashing.
Notes 1. The serial communication configuration for an IPC application has the default
values of the Group S parameters. For more information on the Group S
parameters, refer to the 95 Series RFID System Reference Guide.
2. If the noise and interference level on the UHF channel exceeds the carrier
threshold or a Transponder is transmitting information, the DATA LED will start
flashing at a faster rate.
Resetting the Reader
Thereare2waystoresettheReader(seeFigure5-1):
• By resetting the hardware
• By resetting the software
For a hardware reset, switch off the Reader’s power supply for a least 5 seconds.
For a software reset, you can:
1. Press the RESET button twice.
or
2. Type the following command at the prompt:
:RESET <Enter>
Checking the Reader’s Basic Parameters
To check basic parameters on the Reader, do the following:
1. Check the software version number by typing:
IVN <Enter>
Theresponseshouldbe:
IVN=CRM95 V_.__, BUILT: __/__/__ __:__:__.
Note You can upgrade the Reader software, if necessary. For more information on
upgrading the software, refer to Appendix D, Reader Software Upgrade Procedure.
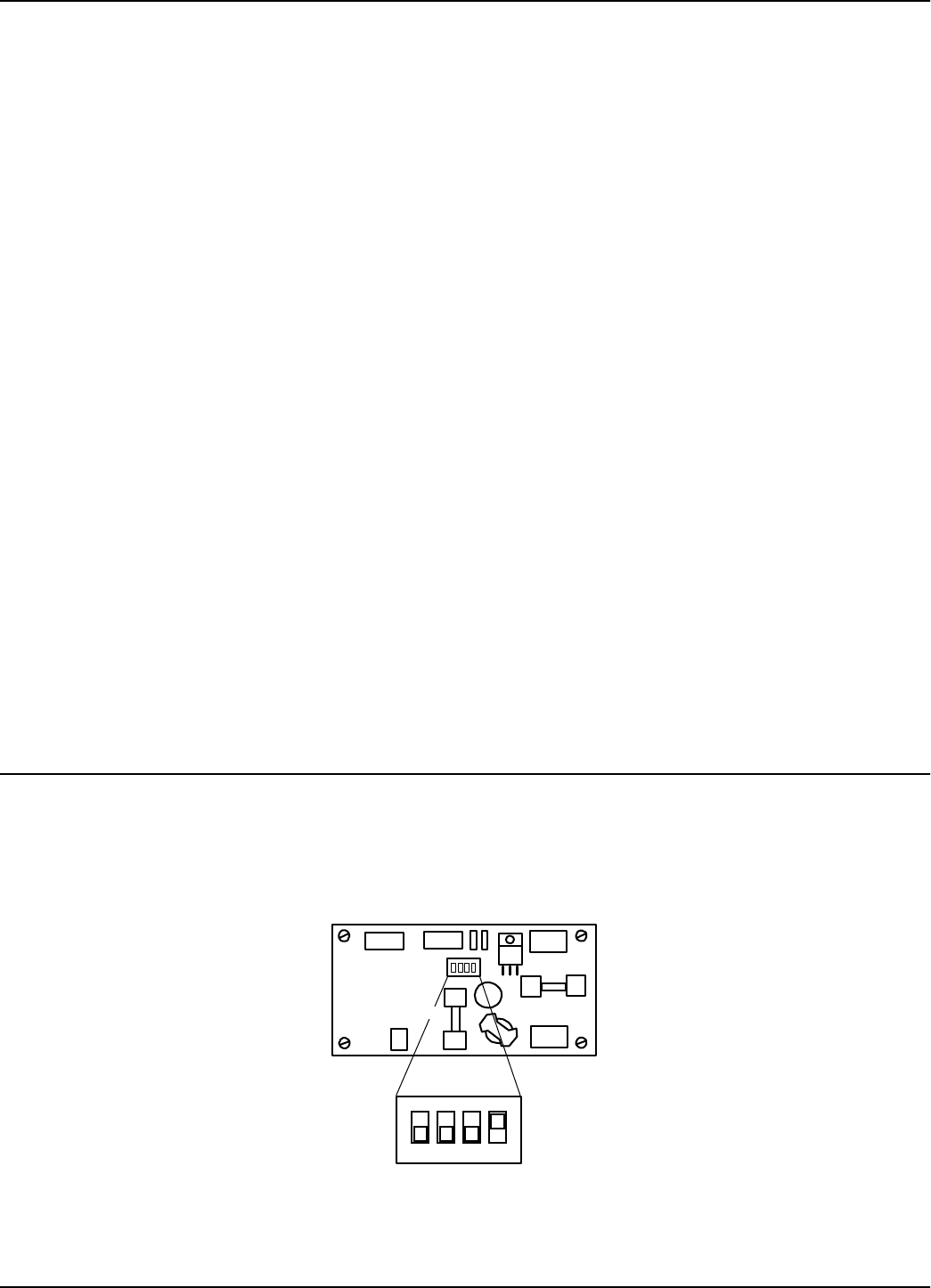
Setting Up the Exciter’s Address
Configuration and Operation 5-5
2. Check the System Code (SC), by typing:
ISC <Enter>
Theresponseshouldbe:
ISC= [your SC]
If the displayed System Code is not identical with the application system code
number, replace the Reader and report the problem to Lyngsoe.
3. Check the Receiver’s Serial Number (SN), by typing:
ISN [your SN]<Enter>
If the displayed serial number is not equal to the serial number on the Receiver’s
CRM95 board, set it to the correct value. For example, if the SN is U123456, then
type:
ISN=U123456<Enter>
4. Store the new SN and/or SC parameter values, by typing:
:CONFIG:STORE <Enter>
:RESET <Enter>
5. Check the correct values of the IVN,ISC,andISN parameters, by repeating
Steps 1 to 3.
6. Switch off the LF field, by typing:
C<Enter>
SettingUptheExciter’sAddress
Your next step is to setup an address for each Exciter by using the S1 slide switch on
the EXT95SC board, as shown in Figure 5-2 below.
Figure 5-2: Setting Up the Exciter’s Address
ExciterSlaveEXT95SC
ON
ADDRESS
"0"
"1"
S1
3210
bit
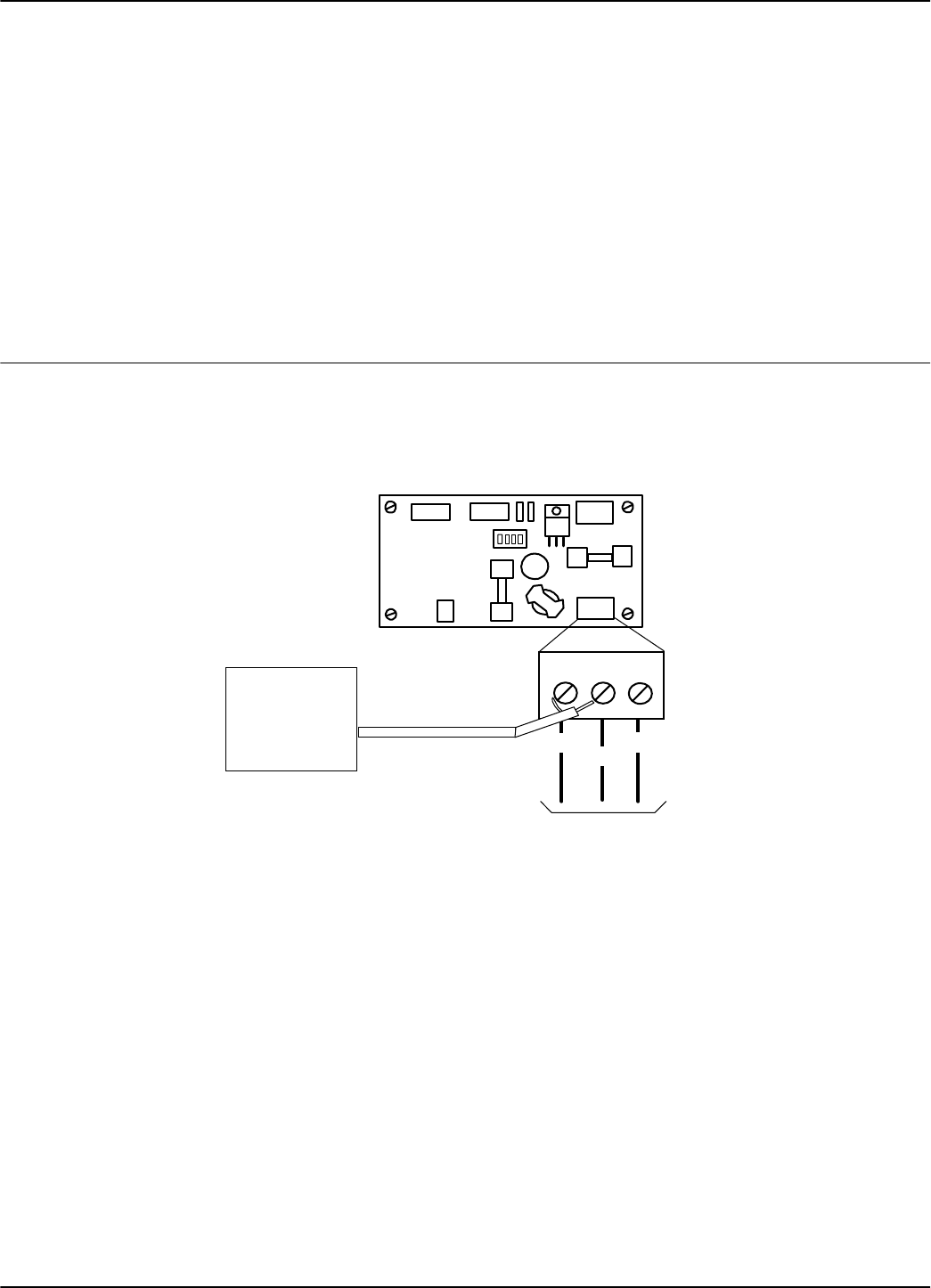
LF Transmitter Output
5-6 Configuration and Operation
The addresses must be sequential between 1 and 14. For example, if there are 4
Exciters, they must be assigned addresses 1, 2, 3, and 4. Use the S1 switch to set the
address to binary format. For example, in binary format:
•address1is0001
2
•address2is0010
2
•address3is0011
2
•address4is0100
2
If the switch is in the ON position, the bit is set to 1. Otherwise, the bit is set to 0.
Note Addresses 00002and 11112are reserved for special modes of operation.
LF Transmitter Output
To check the LF signal, refer to Figure 5-3 below, and do the following:
Figure 5-3: LF Signal Measurement
1. Connect the power to the Exciter.
2. Check the current parameter settings for the excitation mode and write down the
value of the following parameters: RCS,RES,REM,RET,HCC,HCS,HE0,and
HE1.
Note To determine the value of a parameter, for example, HE1,typethecommand:
HE1 <Enter>
ExciterSlaveEXT95SC
TB2
ANT
GND
Black
TAP
Red
White
To LF Antenna
Terminal Block
Oscilloscope
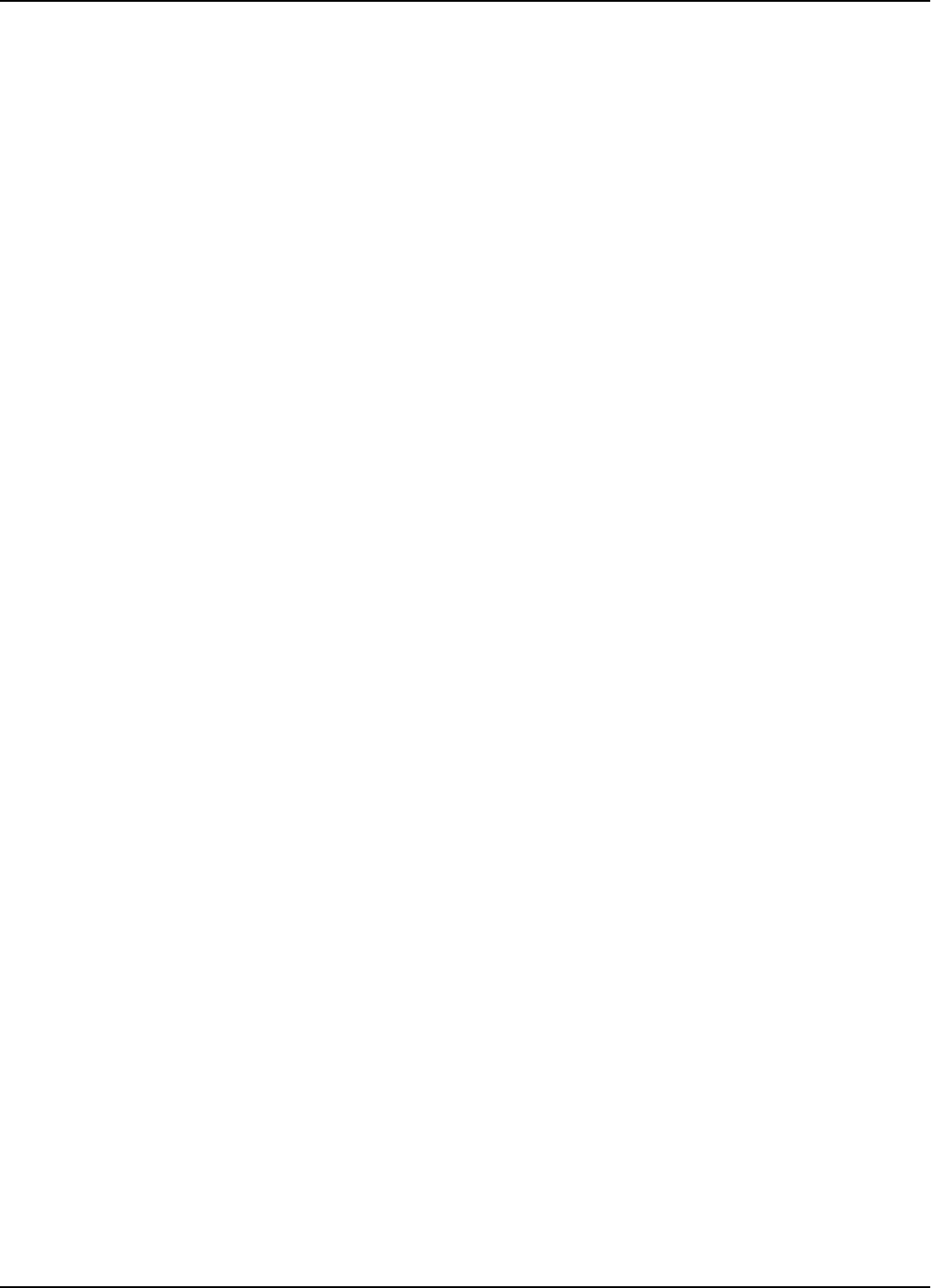
LF Transmitter Output
Configuration and Operation 5-7
The Reader will respond with the parameter value, for example,
HE1=6
where 6is the value for the HE1 parameter.
3. Set the Continuous DC Mode type of execution, by typing:
RCS=N <Enter>
RES=N <Enter>
REM=C <Enter>
RET=D <Enter>
Note If a parameter already has the wanted value (determined in Step 2), you do not have
to reset it.
4. Turn on the excitation field, by typing:
B<Enter>
Check the TAP voltage [VTAP] at the terminal block TB2 on the EXT95SC board
(see Figure 5-3) using an oscilloscope. The signal must be a continuous
unmodulated carrier of 128.25 kHz with a peak-to-peak amplitude of
VTAP =100±20V
pp.
Note When more than one Exciter 95 is used to create a wider excitation zone, a magnetic
coupling can appear. The phenomenon is explained in Chapter 4, Setup Guidelines in
the 95 Series RFID System Technical Guide. The coupling generates an unwanted
amplitude modulation with a frequency of several Hertz, the modulation depth
depending directly on the coupling. The installer has to monitor the TAP signal and
adjust the position of the E95 frames to obtain a minimum unwanted modulation
depth. The installer can increase the distance between frames, level the frames in the
same plane, or place the frames with the shorter sides (1m) in parallel. The minimum
amplitude of VTAP due to unwanted modulation must be larger than 60Vpp.
5. Turn off the excitation field, by typing:
C<Enter>
The TAP voltageamplitudeshouldbezero.
6. Turn on the LF field again, by typing:
B<Enter>
The TAP voltage signal should have the same value as measured in Step 4.
7. Set the wanted excitation mode.
To set a specific excitation mode, refer to Appendix C, Excitation Modes.Ifyou
want to return to the initial excitation mode as determined in Step 2, you have to
restore the values of the parameters modified in Step 3.
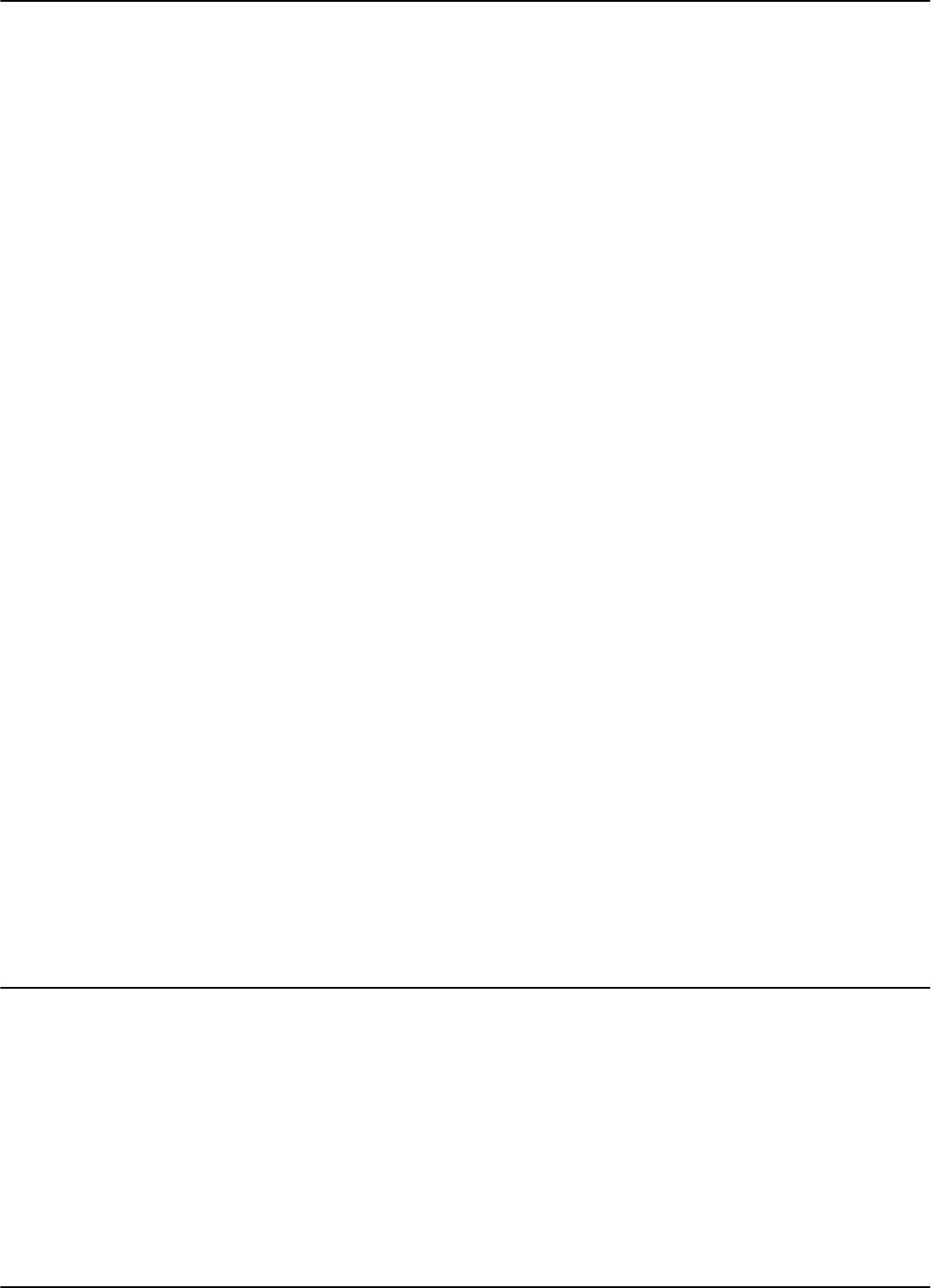
Configuring the Reader
5-8 Configuration and Operation
For example, Lyngsoe recommends the following parameter values for the
Conditional Switching AC mode (CSAC) for the IPC installation:
RCS=Y; RES=Y; REM=C; RET=A; HCC=8; HCS=7; HE0=18; HE1=6
These parameters all have the default values.
8. Check the excitation field pattern as set in Step 7, by monitoring the TAP voltage.
For example, if the IPC’s CSAC mode was set and the Reader did not receive a
valid message, the TAP voltage has the following repetitive pattern: a carrier of
128.25 kHz modulated ON/OFF with 610Hz for 60 ms, followed by no signal for
180 ms.
9. Save the excitation mode set in Step 7, by typing:
:CONFIG:STORE <Enter>
:RESET <Enter>
10. Check the parameter values set in Step 7 again.
11. Check the auto-diagnostic feature, by typing:
:DAR=Y <Enter>
:TEST:EXCITER k<Enter>
where kis the decimal address (1, 2, 3, ...) of the Exciter that you want to test.
The response should be 00, followed by a number (between IP-2 and IP) of
messages from the Test Tag.
12. Turn off the excitation field again, by typing:
C<Enter>
13. Check the auto-diagnostic feature, by typing:
:TEST:EXCITER k<Enter>
The response should be C9.
14. Repeat Steps 1 to 13 (inclusive) for each Exciter that is connected to the Reader.
Configuring the Reader
The Reader’s basic configuration covers the following group of parameters:
• Data buffering/reporting configuration- Group D parameters
• Hardware configuration - Group H parameters
• Instrument generic configuration - Group I parameters
• Tag data reading configuration - Group R parameters
For more information on these parameters, see the 95 Series RFID System Reference
Guide and the 95 Series RFID System Technical Guide.
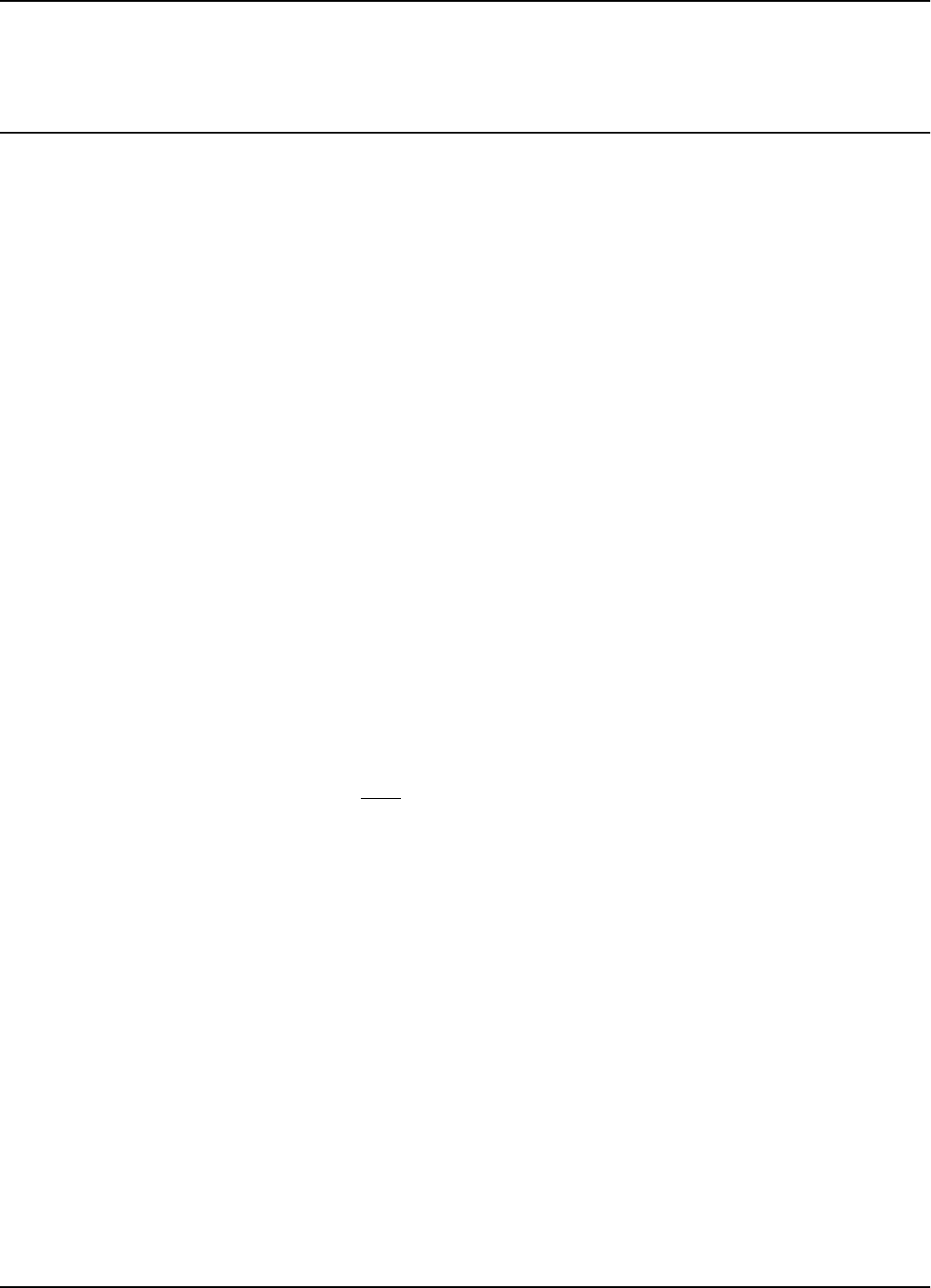
Setting Up the Carrier Threshold
Configuration and Operation 5-9
Note You can set these parameters for each particular application to optimize the
functionality of the Reader and the RFID System.
Setting Up the Carrier Threshold
Warning Before starting this procedure, you have to enable the auto-report and set the data
report in ASCII format, by typing the following:
DAR=Y<Enter>
DHX=N<Enter>
To setup the Reader’s carrier threshold, do the following:
1. Switch off the excitation field, by typing:
C<Enter>
2. Set the Receiver’s signal-to-noise ratio, by typing:
RSS=10<Enter>
Note You can set other values for the RSS parameter. Lyngsoe recommends using a value
between 10 and 20 for the RSS parameter.
3. If you are using Diversity, enable it by typing:
HAD=Y<Enter>
Ensure that both UHF antennas are connected. If you are not using Diversity,
disable it by typing:
HAD=N<Enter>
Ensure that only the right UHF antenna is selected (see the HAS parameter).
4. Check the noise level on the UHF channel, by typing:
HNL<Enter>
The HNL value should be between -107 to -95dBm.
If the HNL value is higher than -95dBm, check if there are unwanted
transmissions on the UHF channel (433.9 MHz). Pay special attention to
Transponders or Exciters in close proximity to the Reader; these can accidentally
transmit data that can be received by the Reader.
If the HNL value is lower than -105dBm, check its value without the UHF
antennas attached. The difference between these two readings must be greater
than 3dB.
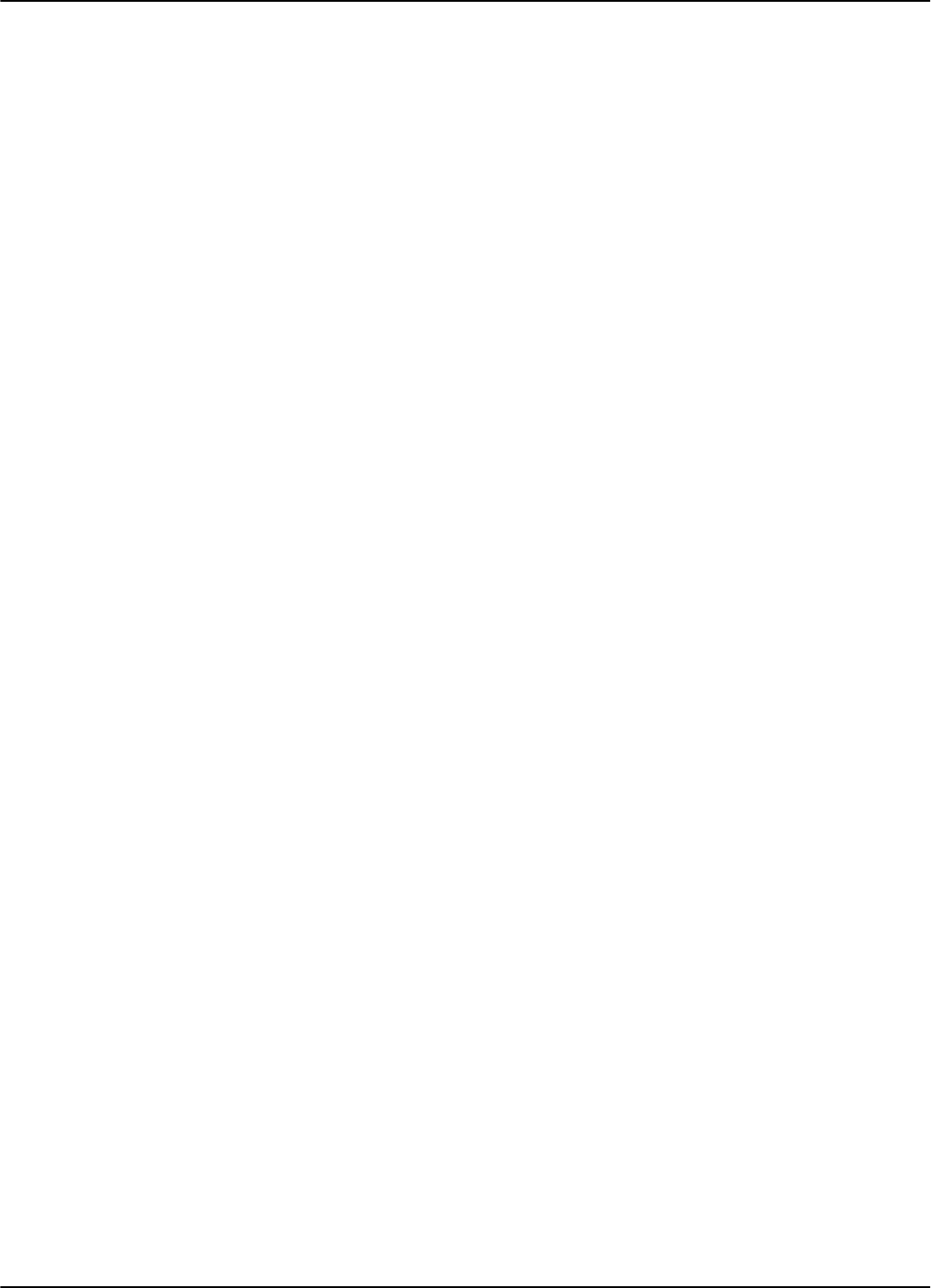
Setting Up the Carrier Threshold
5-10 Configuration and Operation
5. Set the carrier threshold, by typing:
S<Enter>
or
:CONFIG:THRESHOLD<Enter>
Note If the Reader resets itself, repeat the procedure from Step 1.
6. Monitor the DATA LED for at least 10 seconds. The LED must not flicker. If it
does flicker occasionally, increment the RSS parameter value by one. Go to Step 5.
IMPORTANT * For a normal setup, the value of (HNL+RSS) must be less than - 85 dBm.
* If the noise level is higher than -95 dBm, disconnect the UHF antennas from the
Reader, and check whether the HNL value drops below -107 dBm. If this occurs, it
means that there is unwanted transmission on the UHF channel. To correct this
situation, refer to Chapter 4, Setup Guidelines in the 95 Series RFID System
Technical Guide.
7. Place your Test Transponder T95 1-2 m away from an Exciter that is controlled by
the Reader you are configuring. For more information about identification zones
and the Test Transponders, refer to Chapter 4, Setup Guidelines in the 95 Series
RFID System Technical Guide.
8. Start the excitation field, by typing:
B<Enter>
9. Verify that the DATA LED is flickering, and check whether the Test
Transponder’s messages are displayed on the PC’s screen.
If data is not displayed, check the Reader’s parameter configuration, and follows
the troubleshooting instructions in Chapter 7, Troubleshooting.
If the number of displayed messages is below n=IP-2, check the carrier threshold
and try to adjust it again. Go to Step 1.
10. Remove the Test Transponder from the field and make sure that it is no longer
transmitting by ensuring that the DATA LED is not flickering.
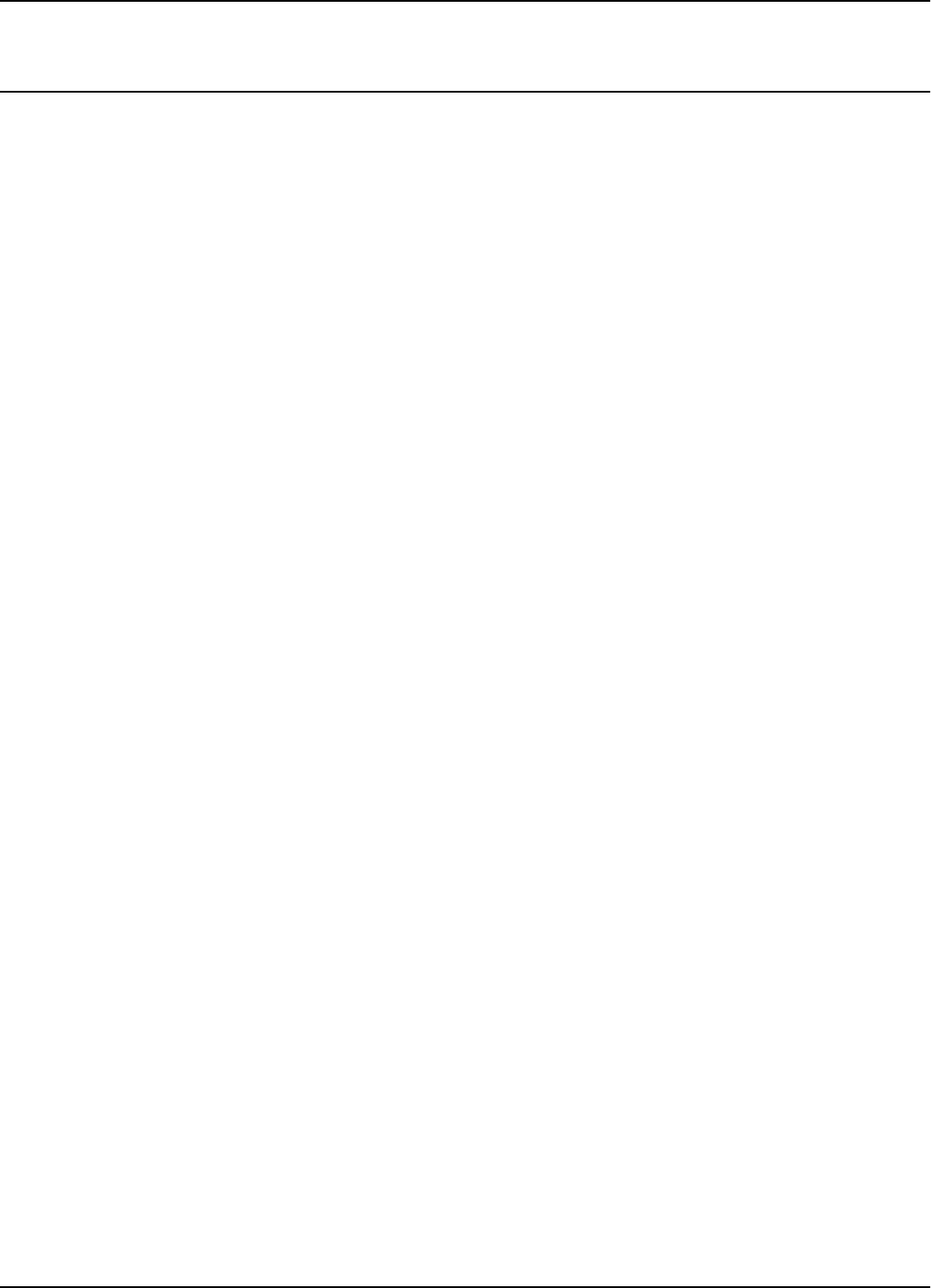
Setting Up the Exciter’s Test-Tag
Configuration and Operation 5-11
Setting Up the Exciter’s Test-Tag
To set up the Exciter’s Test-Tag, do the following:
1. Set the parameters you want for the Test-Tag using the Group W parameters.
Example For an IPC application, you have to program the following parameters, by typing:
WDR=4 <Enter>
WEC=Y <Enter>
WEN=N <Enter>
WHF=N <Enter>
WID=0 <Enter>
WIP=15 <Enter>
WLT=Y <Enter>
WRC=0 <Enter>
WRS=0 <Enter>
WSD=200 <Enter>
WSM=Y <Enter>
WTF=Y <Enter>
WTS=N <Enter>
WWP=Y <Enter>
WUD=$43FEnnrrkk <Enter>
where:
nn isthePC’saddress.IfPC’saddressis1,orthereisonlyonePC/site,nn=01.
rr is the Reader’s address. If Reader’s address is 1, rr =01.
kk is the Exciter’s address. If the Exciter’s address is 1, kk =01.
2. Turn off the LF field, by typing:
C<Enter>
3. Program the Exciter Test-Tag, by typing:
:TAG:MATCH:EXCITER k<Enter>
where kistheaddressoftheExciteryouwanttoprogram.
Iftheresponseisnot00, the Exciter is not programmed. Repeat this command
several times, waiting at least 3 seconds between retries.
Note If you cannot program the Test Tag, see Chapter 7, Troubleshooting.
4. Turn on the LF field, by typing:
B<Enter>
5. Test the Exciter Test-Tag, by typing:
:TEST:EXCITER k<Enter>
where kis the address of the Exciter you want to test. The correct response is 00,
followed by a number of messages between IP-2 and IP. If less messages are
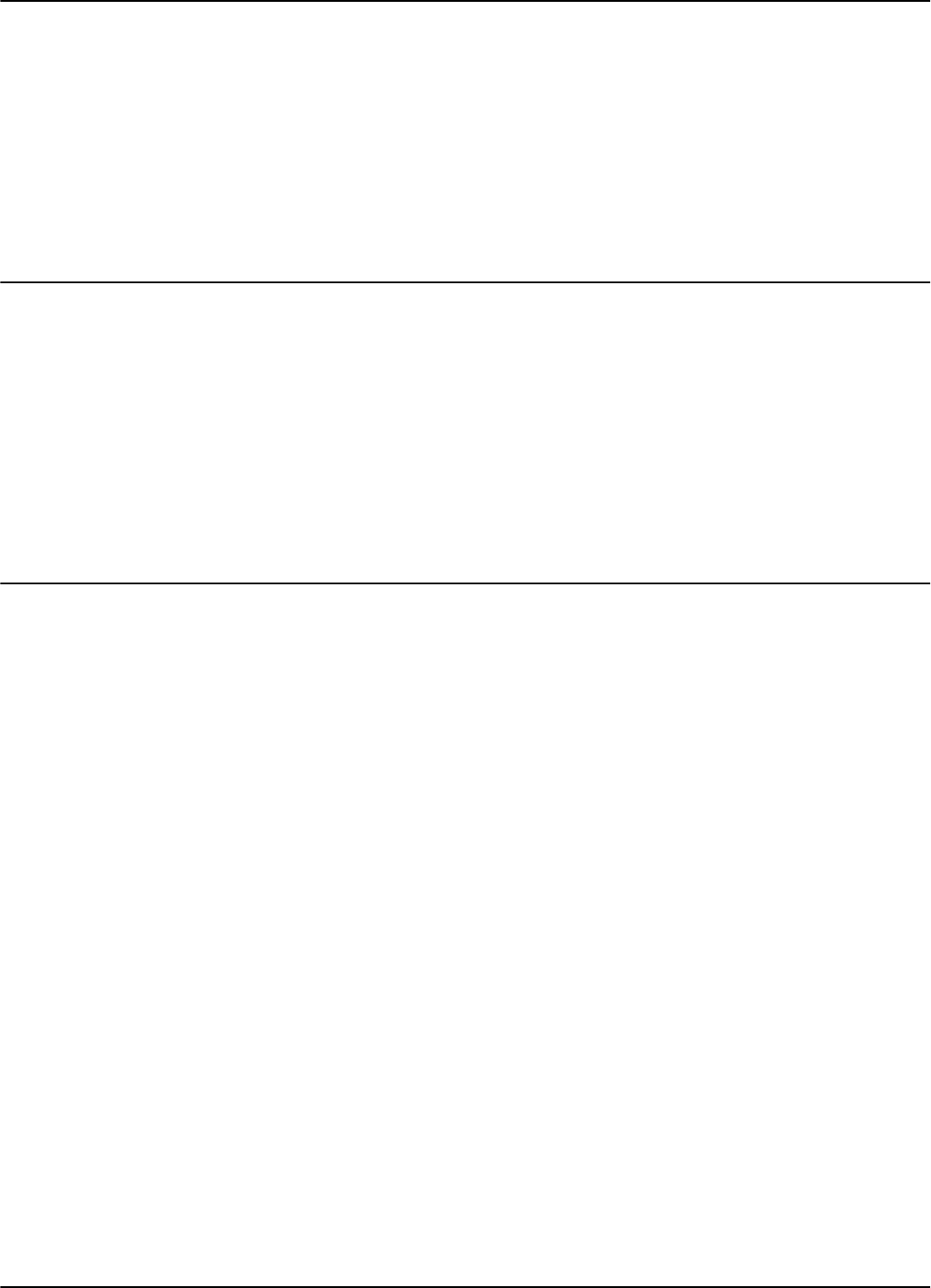
Setting Up the Real Time Clock
5-12 Configuration and Operation
received, verify whether the UHF channel is jammed or replace the EXT95SC
board.
Note If you do not see the expected number of messages on your PC, (13-15 messages for an
IPC site), see Chapter 7, Troubleshooting and check the following parameters:
DAR=Y; DCI=0, DRI=0
6. Repeat Steps 1 to 5 for each Exciter that is connected to the Reader.
SettingUptheRealTimeClock
You can set the Reader’s date and time by using the IUT parameter. For more
information on setting up the Real Time Clock, refer to the 95 Series RFID System
Reference Guide.
Example For an IPC application, you should set the IUT parameter to GMT time. To set it, type:
IUT=YYMMDDhhmmZ<Enter>
where YYMMDDhhmm is the year, month, day, hour, and minute respectively.
Configuring the Reader’s Application Parameters
You can configure the Reader’s application parameters by setting the appropriate
values for the parameters in the following groups:
• Data buffering/reporting configuration (D)
• Hardware configuration (H)
• Instrument generic configuration (I)
• Tag data reading/excitation configuration (R)
• Serial communication configuration (S)
For example, for an IPC application, do the following:
1. Set the data filtration on the Reader, by typing:
DCI=10 <Enter>
DRI=30 <Enter>
2. Set the reported data format as ANS.1 format, by typing:
DHX=Y <Enter>
3. Set the Tag data character count, by typing:
RCC=5 <Enter>
4. Leave the default values for the other parameters.
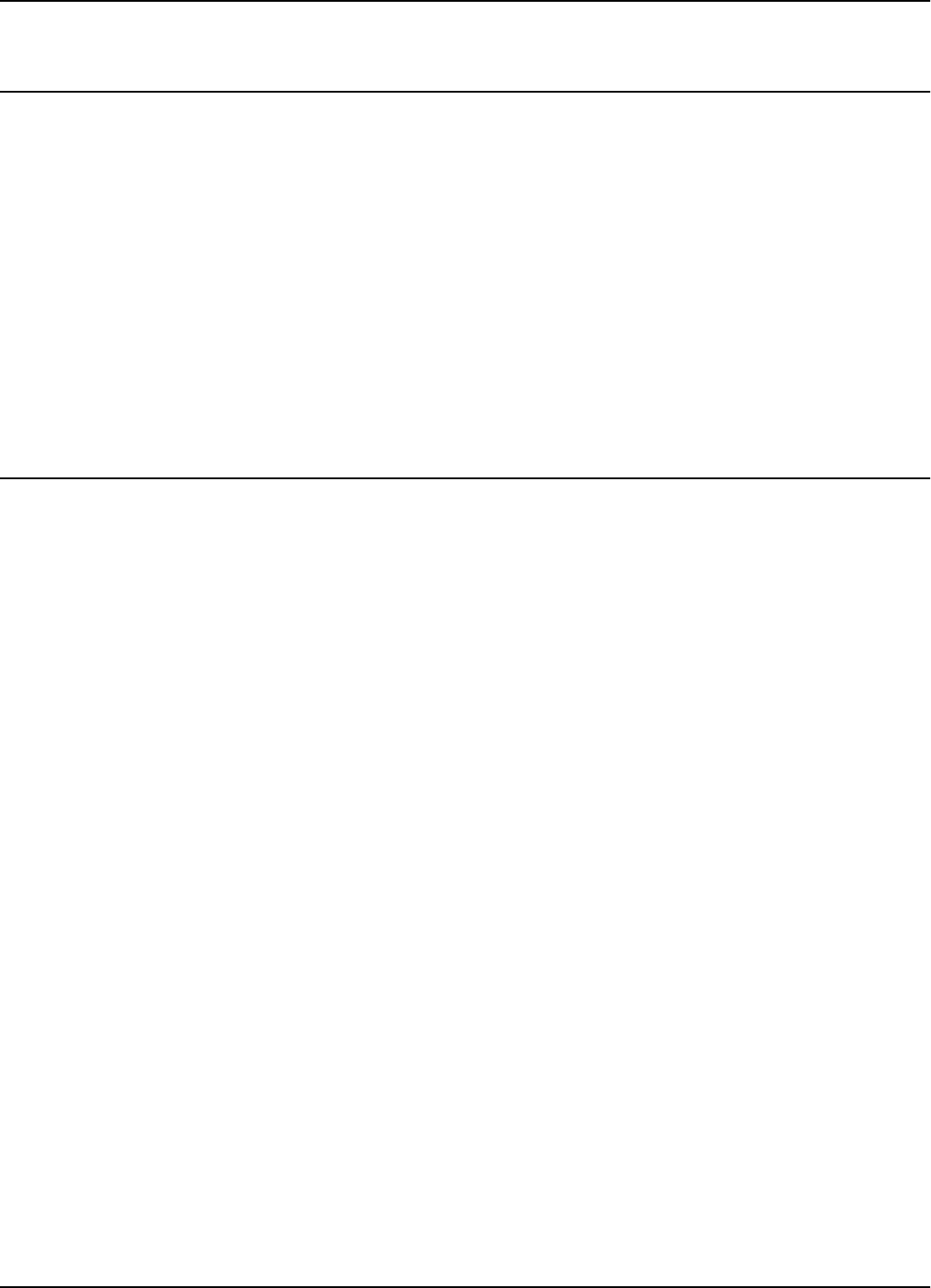
Configuring the Reader’s Network Parameters
Configuration and Operation 5-13
Configuring the Reader’s Network Parameters
To configure the Reader’s network parameters, do the following:
1. Set the reporting mode, by typing:
DAR=N<Enter>.
2. Set the Reader’s address, by typing:
IAD=r<Enter>
where ris the Reader’s address. The lowest value for this address is 1. For
example, if there are 4 Readers in a network, they must be assigned the following
addresses1,2,3and4.
Storing the Reader’s Configuration
To store the Reader’s configuration, do the following:
1. Store the Reader’s parameters, by typing:
:CONFIG:STORE<Enter>
2. Reset the Reader, by typing:
:RESET<Enter>
Note The :CONFIG:STORE command stores the current Reader’s configuration in the non-
volatile memory.
The :RESET command updates the contents of the working memory from the non-
volatile memory.
3. Check whether the Reader is operating properly, by typing:
@rIVN<Enter>
where ris the Reader’s address. The Reader must respond with its software
version number.
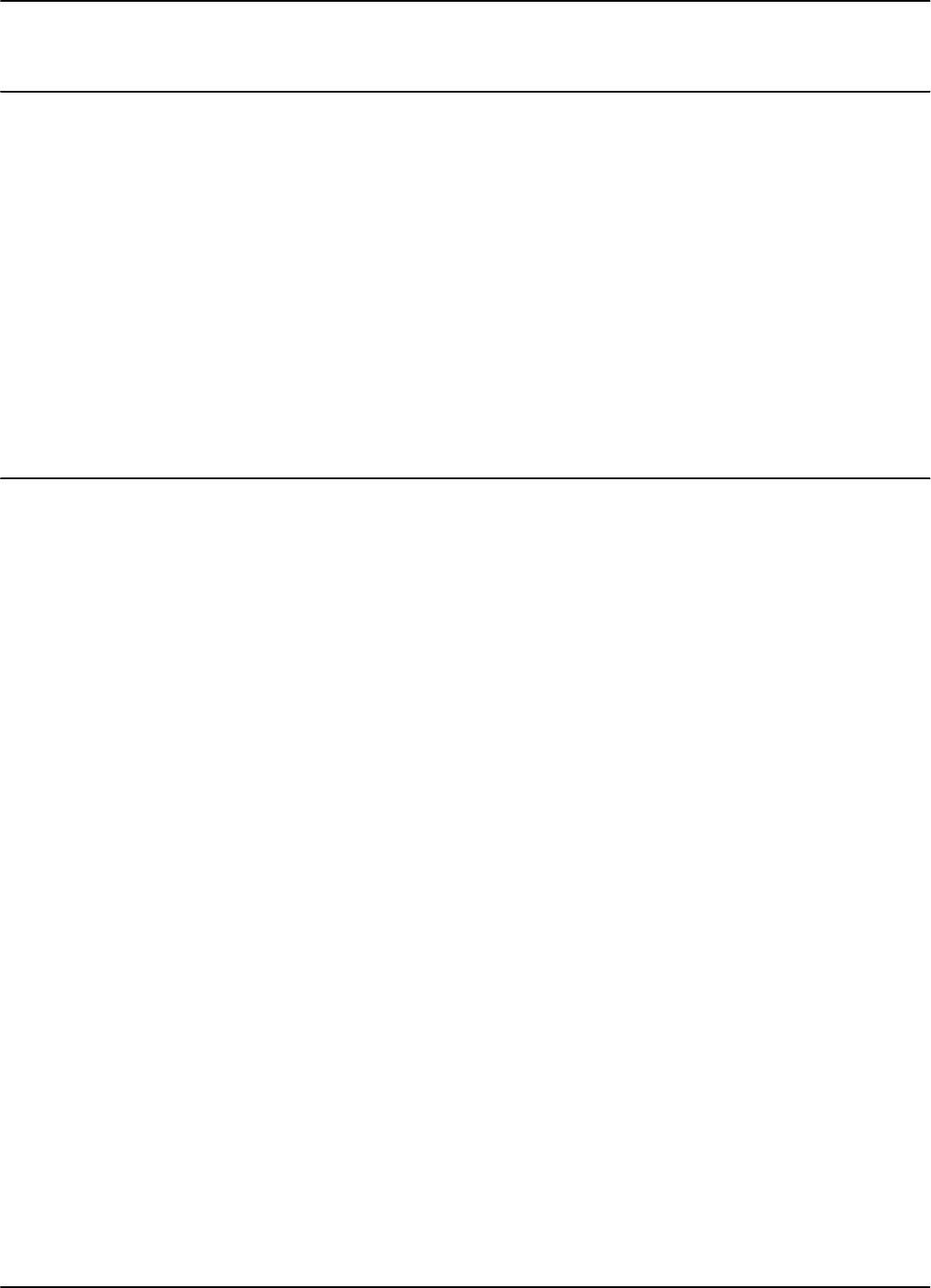
Reader - Final Setup
5-14 Configuration and Operation
Reader - Final Setup
To verify whether the Reader is responding, do the following:
1. Disconnect the PC from the Reader (See Figure 5-1 on page 5-2).
2. Set all jumpers (J1-J4) placed on the Motherboard MBD95 according to the type of
communication line used for the network. For more information on
communication lines used by the Reader R95, refer to Chapter 2, Reader R95
Installation and Connections.
3. Verify the connections between the Reader and the rest of the equipment (shorts,
loose connections, etc.)
4. Close the Reader’s enclosure.
95 Series RFID System - Final Test
IMPORTANT * These tests must be done after all Readers and the Main PC are connected to the
network according to the site documentation.
* To communicate with the Reader, either use a terminal emulation program, such
as HyperTerminal or Procomm in Windows95, or the dedicated service module of
the application software running on the Main PC.
* All commands to the Reader must include the address field @rwhere ris the
Reader’s address (an integer followed by a blank).
You must repeat the following procedure for each Reader that is connected to the
Main PC.
For the final test, do the following:
1. Verify that the Reader is communicating with the Main PC, by typing:
@r IVN <Enter>
where ris the Reader’s address. The Reader must respond with the software’s
version number.
2. Set up the Carrier Threshold for the Reader as follows:
a) Switch on the excitation field, by typing:
@r B <Enter>
b) Check the noise level, by typing:
@rHNL<Enter>
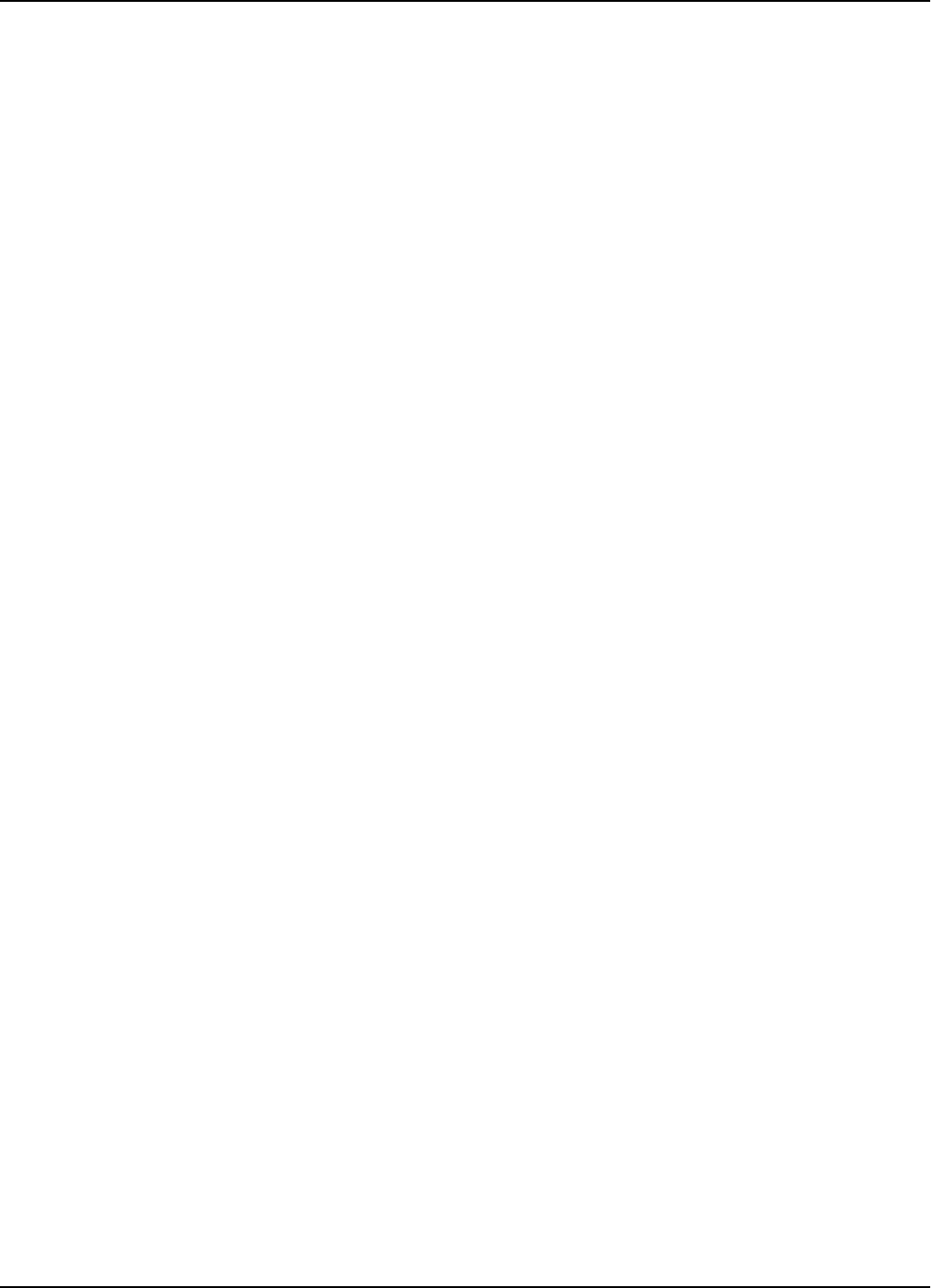
95 Series RFID System - Final Test
Configuration and Operation 5-15
If there is no unwanted transmission on the UHF channel, the Reader must
respond with a value lower than -95dBm for the HNL parameter. If not, refer to
Setting Up the Carrier Threshold on page 5-9.
c) Check and record the value for the existing Reader’s Carrier Threshold level, by
typing:
@rHTL<Enter>
The Reader should respond with the value for this parameter. For example,
HTL=95.
d) If the HNL level measured in Step b is lower than -95dBm, set the Reader’s
Carrier Threshold level again, by typing:
@rS<Enter>
or
@r:CONFIG:THRESHOLD<Enter>
The Carrier Threshold level setting is correct if the new HNL level displayed is
smallerthanorequaltotheleveldisplayedinStepc.Ifnot,checkforunwanted
transmission on the UHF channel. You should also refer to Chapter 4, Setup
Guidelines in the 95 Series RFID System Technical Guide.
3. Verify that an Exciter that is controlled by a Reader communicates with the Main
PC:
a) Delete all Tag records from the Reader’s buffer, by typing:
@r:DATA:PURGE<Enter>
b) Confirm that the Reader’s buffer is empty, by typing:
@rD<Enter>
or
@r:DATA:REPORT<Enter>
The Reader must report a Null value.
Note For an IPC application, the data structure conforms to the ANS.1 standard. If the
Reader’s buffer is empty, the Reader sends a Null value of $0500.InASCIIformat,
the Null value is {}.
c) Switch on the LF field, by typing:
@rB<Enter>
d) Send a Test Exciter command, by typing:
@r:TEST:EXCITER k<Enter>
where ris the Reader’s address and kis the Exciter’s address. The correct
Exciter’s response is 00.
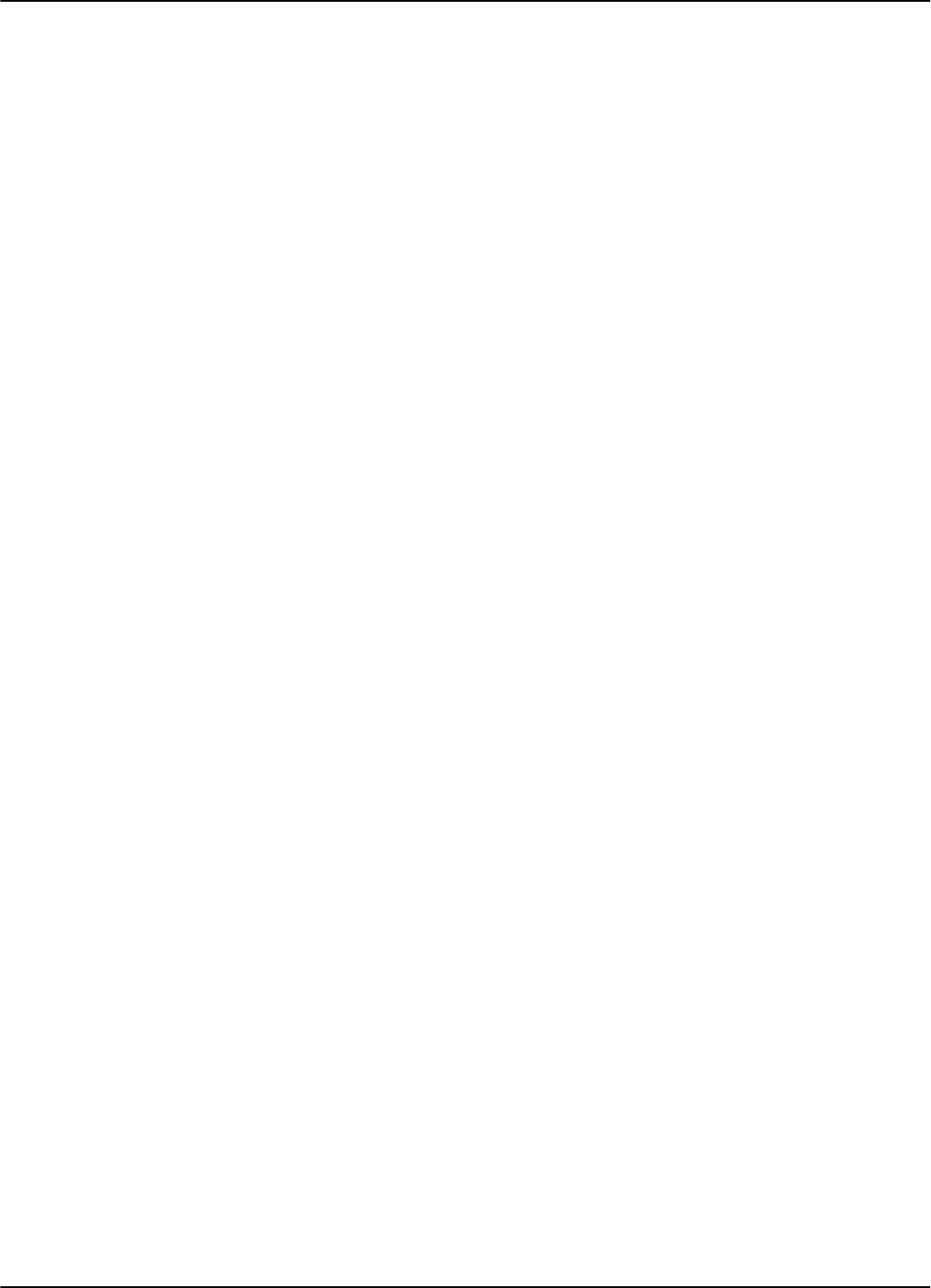
95 Series RFID System - Final Test
5-16 Configuration and Operation
e) Check the received messages, by typing:
@rD<Enter>
or
@r:DATA:REPORT<Enter>
The Reader must respond with the oldest record sent by the Exciter k’s Test-Tag,
in the format set by the DHX parameter. For more information on this parameter,
refer to the 95 Series RFID System Reference Guide.
Note For an IPC application, the Reader’s Tag Record Buffer contains 13-15 identical
messages sent by the Exciter k’s Test Tag in ANS.1 format. To read all messages, you
have to repeat the commands:
@rD<Enter>
@rE<Enter>
until you get the Null value $0500.
f) Empty the Reader’s Tag record buffer, by typing:
@r:DATA:PURGE<Enter>
g) Confirm that the Reader’s buffer is empty, by typing:
@rD<Enter> or @r:DATA:REPORT<Enter>
The Reader must report the Null value ($0500) in ANS.1 format.
4. Repeat Step 3 for all Exciters controlled by the Reader r.
5. Repeat Steps 1 to 4 for all Readers that are connected to the same PC.
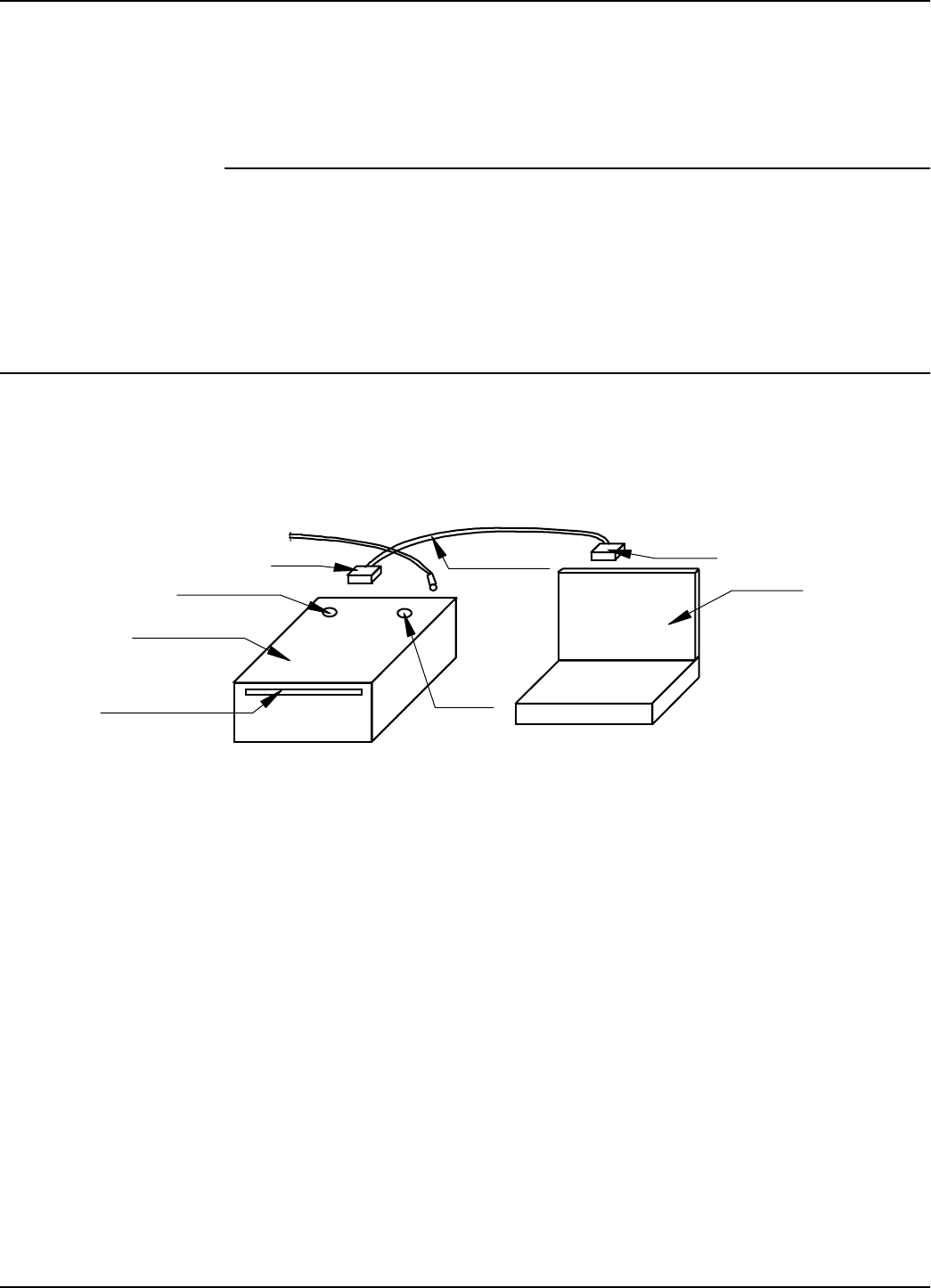
Setting Up the Programming Site
Programming and Testing the Transponder T95 6-1
Chapter 6
Programming and Testing the Transponder T95
This chapter explains how to setup a site and gives the procedure for programming
the Transponders T95. This chapter does not, however, explain how to choose
parameter values. For more information on configuring the Transponder 95, see the
95 Series RFID System Reference Guide.
Setting Up the Programming Site
Setup the programming site, as shown in Figure 6-1:
Figure 6-1: Programming Site
1. Install Lyngsoe’s T95 Programming Software, Version 2.00 or later on your PC.
For more information on the installation, see the Readme.txt on the installation
diskette.
2. The recommended configuration for the PC’s COM port is:
Data rate - 19200 bps
Data bits - 8 bits
Parity - none
Stop bits - 1
Flow control - none.
3. Set all Transponder T95 parameters using the procedure described in the
Readme.txt file.
PC or Laptop
Slot for T95 DATA LED
DB9-F emale
POWER LED
DB9-Male
Power Supply
9Vac/12to14Vdc
RS232 Cable
Programmer PGM95
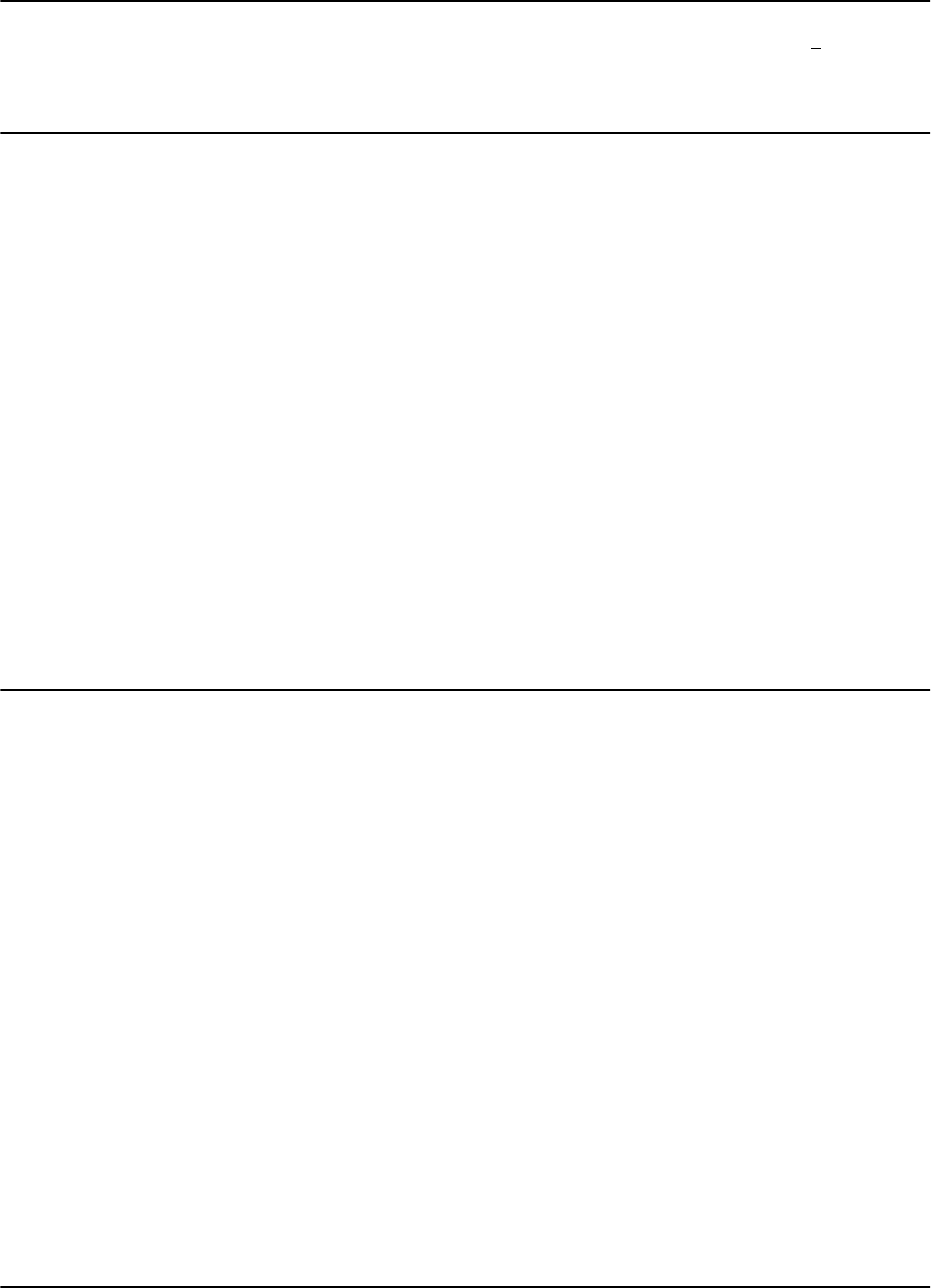
Programming Procedures
6-2 Programming and Testing the Transponder T95
4. Power-up the Programmer PGM95 from an AC power supply 9Vac + 10%, 50/60
Hz, or a DC power supply 11 to 14 Vdc. The maximum power supply is 0.5A.
Programming Procedures
Place the Transponder T95 inside the special slot of the PGM95, with the component
side (battery side) down, and gently push it until it is inside the PGM95.
Using T95
Programming
Software
To program the Transponder T95 using Lyngsoe’s T95 Programming Software, start
the software on your PC and follow the programming instructions in the Readme.txt
file.
Using a Terminal
Emulation Program
To use a terminal emulation program, do the following:
1. Open a terminal emulation program, such as Hyperterminal (Windows 95), on
your PC.
2. Set the PC’s COM configuration as described in the section Setting Up the
Reader/PC Connection in Chapter 5. Use this procedure to set and control the
communication between the PC and the Programmer PGM95 (PGM95
incorporates a Receiver CRM95).
3. Use the commands described in the 95 Series RFID System Reference Guide to set
the desired T95 configuration (Group W).
4. Program the T95 using the command: TAG: MATCH (shortcut M).
Confidence Tester TCT95
The Confidence Tester TCT95 is designed to qualify Transponder T95 programmed
with the IPC format, before they are seeded as probe letters into the mail-monitoring
process.
For more information on the Confidence Tester TCT95, see the Confidence Tester
TCT95 User’s Guide.
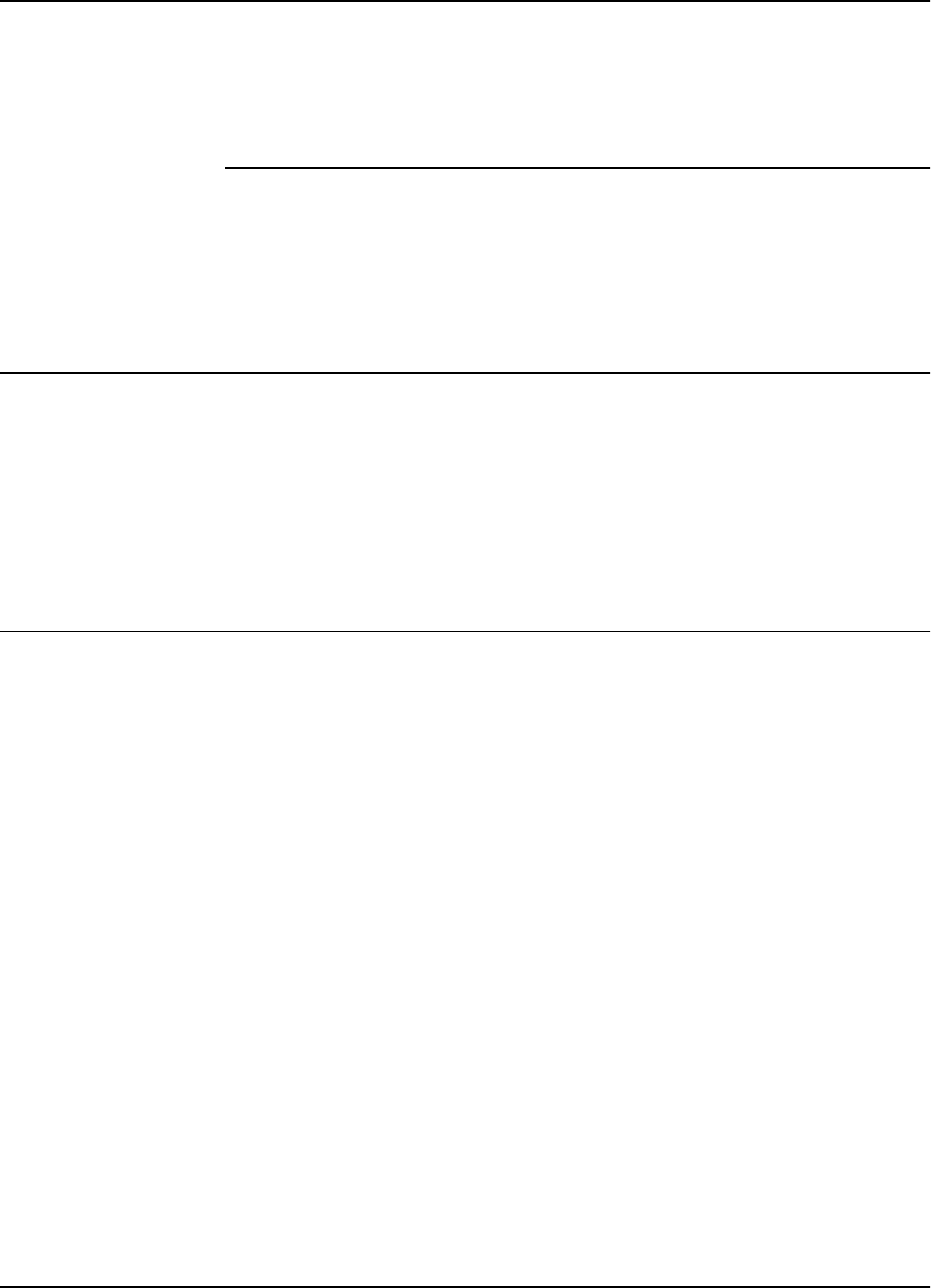
Preventive Maintenance
Troubleshooting 7-1
Chapter 7
Troubleshooting
This chapter describes maintenance and troubleshooting procedures that you must
follow when using the 95 Series RFID System. These procedures complete the
troubleshooting information given in Chapter 5, Configuration and Operation, for the
initial system installation and configuration.
Preventive Maintenance
By using special commands, built-in Self Diagnostic circuits can check any part of the
system and report an error code, if necessary. Depending on the error code received,
the service technician will know the piece of hardware that is malfunctioning, and can
immediately take corrective action to remedy the situation.
All units have a warranty seal placed on their enclosures. Removal of this
seal will void the warranty.
General Guidelines
Below is a list of some assumptions and guidelines:
1. The chapter assumes that repairs for any electronic assemblies are not made on
site. Unless otherwise stated, if a specified condition cannot be met, the electronic
assembly must replaced and returned to the manufacturer for repairs.
2. For a complete technical description of the 95 Series RFID System, refer to the
95 Series RFID System Technical Guide. For a detailed description of the
commands and parameters used to configure or to control the 95 Series RFID
System, refer to the 95 Series RFID System Reference Guide.
3. Information regarding the 95 Series RFID System’s configuration and operation is
described in Chapter 5, Configuration and Operation.
4. The locations of the DATA LED, the POWER LED, and the RESET button are
showninFigure5-1.
5. All the reference to commands are made assuming that the Reader’s address is 0.
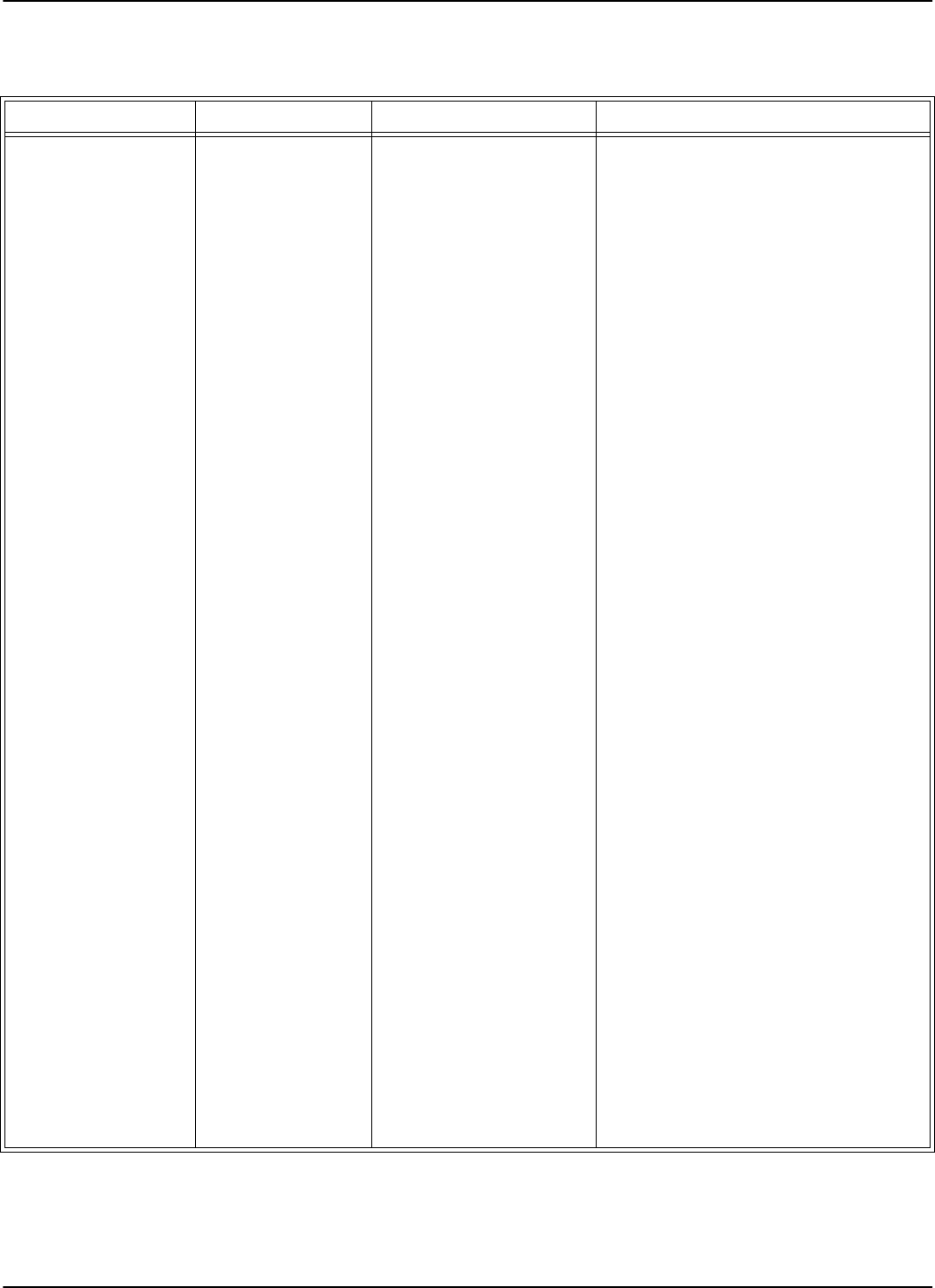
General Guidelines
7-2 Troubleshooting
The following table describes several possible failures for the 95 Series RFID System,
and the troubleshooting steps to correct them.
Problem Symptom Probable Cause Solution
No communication
with a Reader. Reader does not
respond to any
command.
1. Reader has an
incorrect address.
2. Faulty communication
line between the
Reader and PC.
1. Check whether the Reader responds
to commands using different
addresses, by typing the following:
@1 IVN<Enter>, @2 IVN<Enter>,
@3 IVN<Enter>. When a correct
addressissent,theReaderwill
respond with its version number.
2. If, by using a specific address, you
areabletocommunicatewith
Reader, use this address or change
the address to another value.
3. If after checking all possible
addresses (up to 31), you still cannot
communicate with the Reader, check
Probable Cause 2.
1. Open the Reader’s enclosure and
connect the PC directly to the
Reader using the RS-232
communication line. See Connecting
the RS-232 Communication Line on
page 2-2.
2. Switch off the Reader’s power supply
for at least 5 seconds, then perform
the steps in the Reader’s Power-up
Sequence on page 5-3.
3. If the Reader performs the power-on
test successfully, press the RESET
button once. Check whether the
DATA LED starts flashing at the
rate of 2 Hz.
4. Press the RESET button again.
Check whether the DATA LED stops
flashing.
5. Check whether the Reader is
responding to local commands by
typing: @rIVN, and pressing
<Enter>, where ris the Reader’s
address. The Reader must respond
with its version number.

General Guidelines
Troubleshooting 7-3
Problem Symptom Probable Cause Solution
3. Reader lost its System
Code Identification
number and other
configuration
parameters.
6. If you are able to communicate with
the Reader from the local PC, check
the integrity of the communication
line between the Reader and the PC.
7. After fixing the communication
line’s integrity, reconfigure the 95
Series RFID System and check
whether the Reader can
communicate with the PC.
8. If you cannot communicate with the
Reader (Step 5), check Probable
Cause 3.
1. Open the Reader’s enclosure and
connect the PC directly to the
Reader using the RS-232
communication line. See Connecting
the RS-232 Communication Line on
page 2-2.
2. Switch off the Reader’s power supply
for at least 5 seconds, then perform
the steps in the Reader’s Power-up
Sequence on page 5-3.
3. If the power-on test is successful,
the DATA LED should start flashing
continuously at the rate of 1.4 Hz.
4. Check the System Code number by
typing: ISC, and pressing <Enter>.
If the Reader responds with ISC =
0, setup the Reader’s System code
again by typing: ISC = your SC,and
pressing <Enter>.
5. If the Reader restored one of its
parameters to the default value, all
other parameters are also reset to
their default values. Check and
reset all the application- specific
parameters to their original values.
6. Check the HV0 and HV1 parameter
values. If these parameters have
default values 73 and 105
respectively, you must set them
again using the correct values from
Lyngsoe’s database.
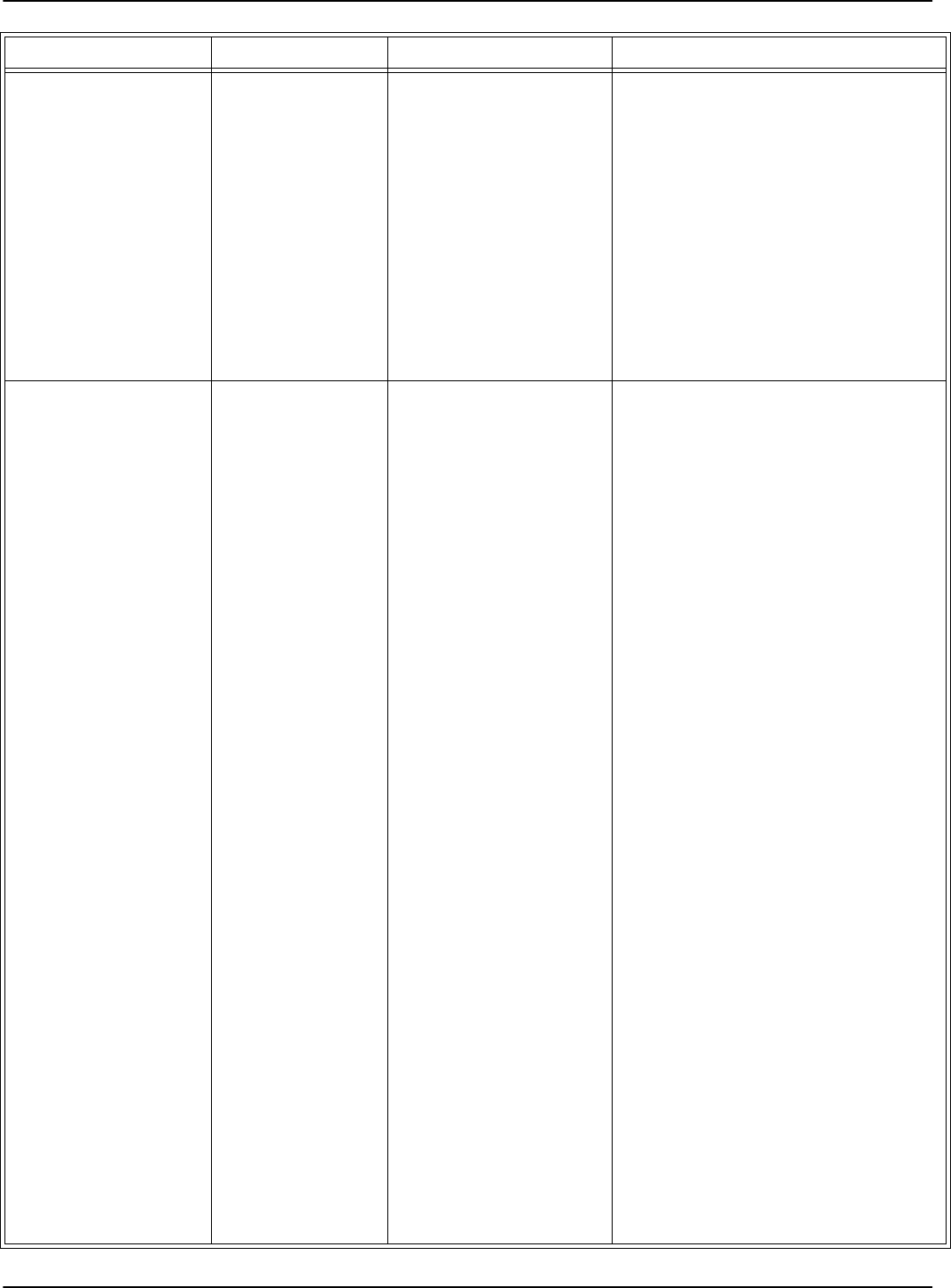
General Guidelines
7-4 Troubleshooting
7. Store the Reader’s configuration by
following the steps in the section,
Storing the Reader’s Configuration
on page 5-13.
Note
The HV0 and HV1 parameters are set
at the factory during the adjusting
procedure and recorded for each
Reader. If you know the Reader’s serial
number, Lyngsoe can supply you with
the values.
Reader does not record
the Transponder’s
messages.
After the power-on
test is finished, the
sign-on message is
displayed on the
PC, but the DATA
LED is flashing
continuously at a
random rate.
An improper carrier
threshold was set, or
there is an unwanted
transmission onthe UHF
channel.
1. Check whether the Reader is
receiving information that has been
accidentally transmitted from other
Transponders in its vicinity. If you
eliminate the unwanted
transmission, the DATA LED will
stop flickering.
2. Check whether an Exciter’s Test Tag
is transmitting accidentally. Switch
off the power supply of all Exciters
surrounding the Reader and monitor
the DATA LED. If the DATA LED
stops flickering, the unwanted
transmission originated in one of the
Exciters.
3. Run the procedure, 95 Series RFID
System - Final Test on page 5-14.
Step 2 - Set up the Carrier Threshold
for the Reader.
4. If the Reader reports a channel noise
level below -95dBm, but you are still
not receiving the Transponders’
messages, check the noise level
reported by the Reader with and
without UHF antennas connected. If
the noise level is identical or varies
slightly (±1 dBm), replace the
Reader.
5. If the Reader reports a noise level
(HNL) above -95 dBm, the unwanted
transmission is on theUHF channel.
For procedures on eliminating the
unwanted transmission, refer to
Chapter 4, Setup Guidelines in the
95 Series RFID System Technical
Guide.
Problem Symptom Probable Cause Solution
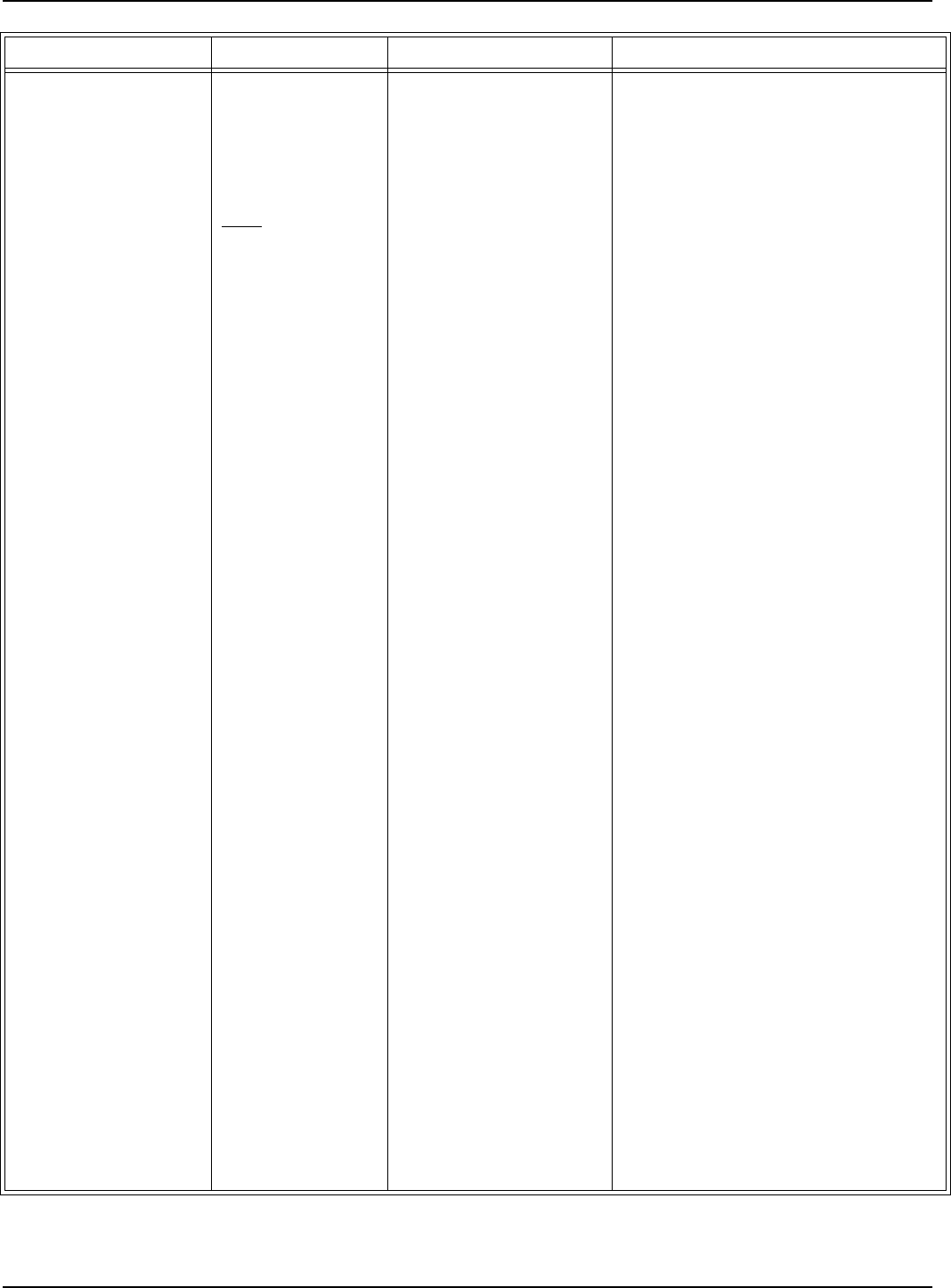
General Guidelines
Troubleshooting 7-5
After the power-on
test is finished, the
sign-on message is
displayed on the
PC, and the DATA
LED is flashing
only when a
Transponder is
activated.
After the power-on
test is finished, the
sign-on message is
displayed on the
PC, but the DATA
LED is not flashing
when a
Transponder is
activated.
The configurations of the
Transponder and the
Reader do not match.
The carrier threshold
value is too high.
1. Using a Test Transponder TST95
that has been programmed for your
application, test the Reader’s
receiving capability.
2. If you can receive transmitted
messages from the TST95, the
Transponders are either not
correctly configured for your
application, or they are out of
specifications. Reprogram the
Transponders and check whether
the Reader can receive messages.
3. If you cannot receive transmitted
messages from the TST95, the
Reader has an incorrect
configuration. Go to Steps 4and 5.
4. Check whether the DAR parameter
and the Group R parameters are set
according to the application’s
specifications.
5. With this new set of parameters,
check whether the Reader can
receive transmitted messages from
the TST95. If the Reader can receive
the messages, save its configuration,
by typing the following commands
and pressing <Enter> after each
command: :CONFIG:STORE,
:RESET.
1. Run the procedure, 95 Series RFID
System - Final Test on page 5-14.
Step 2 - Set up the Carrier Threshold
for the Reader.
2. If the Reader reports a channel noise
level below -95dBm, but you are still
not receiving the Transponders’
messages, check the noise level
reported by the Reader with and
without connected UHF antennas. If
the noise level is identical or varies
slightly (±1 dBm), replace the
Reader.
3. Check the HNL and RSS parameter
values.
Problem Symptom Probable Cause Solution
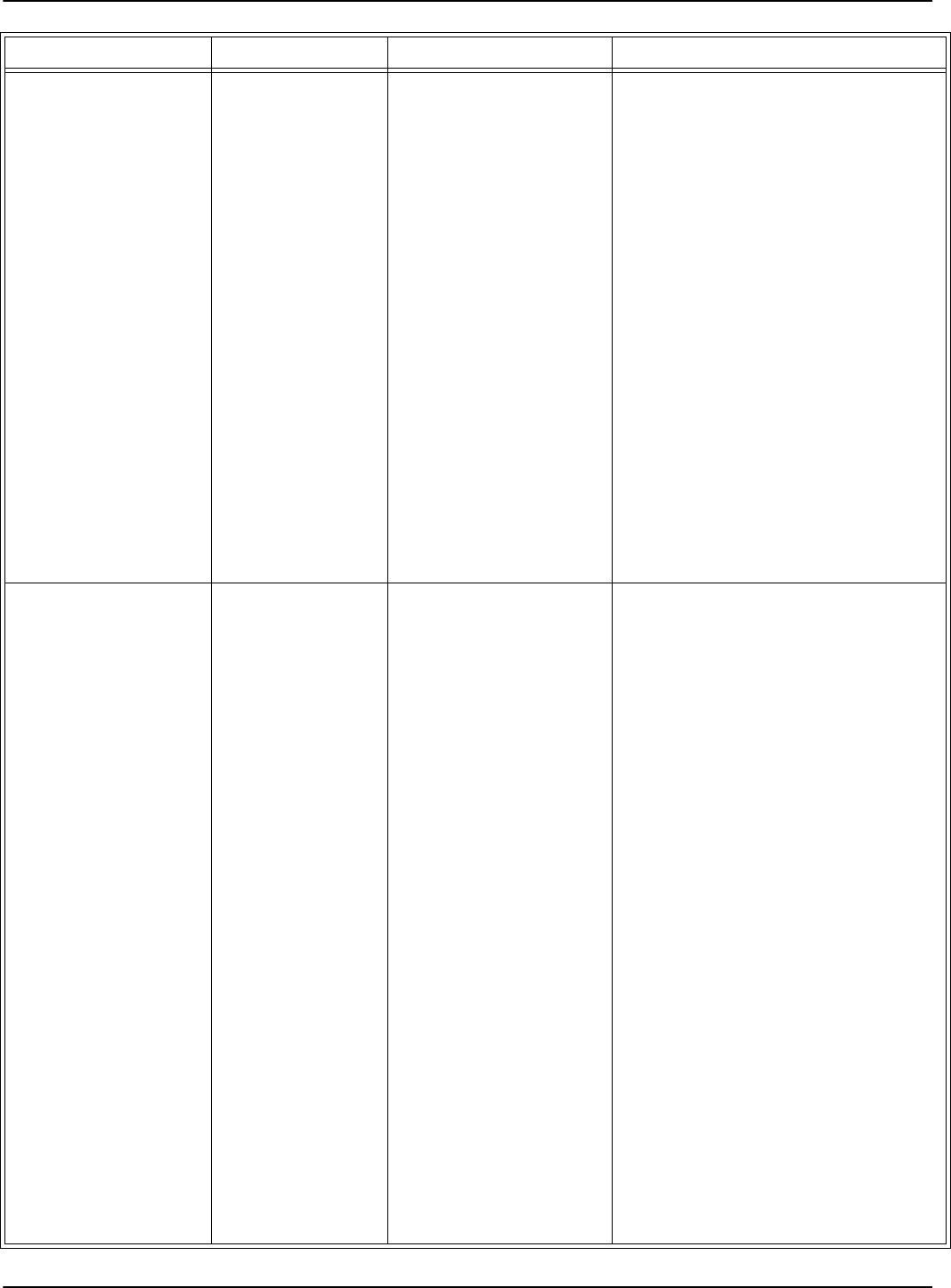
General Guidelines
7-6 Troubleshooting
4. If the value of (HNL +RSS) is higher
than -85dBm, there is either an
unwanted transmission on the UHF
channel, or the value of the RSS
parameter is too high. The value
for the RSS parameter must be
between 10 and 20.
5. Check whether there are
Transponders or an Exciter’s Test
Tag in the immediate vicinity that
transmit messages accidentally.
6. Run the procedure, Setting Up the
Carrier Threshold again, and
monitor the value for the HNL
parameter after each setup.
7. For procedures on eliminating the
unwanted transmission, refer to
Chapter 4, Setup Guidelines in the
95 Series RFID System Technical
Guide.
Reader does not record
all transmitted
messages.
Reader does not
record all
transmitted
messages by the
Transponder.
The receiving zone is too
small because of either a
high carrier threshold, or
there is random
interference on the UHF
channel.
1. Run the procedure, 95 Series RFID
System - Final Test on page 5-14.
Step 2 - Set up the Carrier Threshold
for the Reader.
2. If you observe a random variation of
noise and interference on the UHF
channel, either increase the value of
the RSS parameter, or set the HTL
parameter to a higher value than the
one that was automatically set by
the Reader.
3. If the receiving zone is too small
after you set a higher carrier
threshold, follow the setup
guidelines recommended in Chapter
4, Setup Guidelines in the 95 Series
RFID System Technical Guide.
Note
A UHF channel is subject to random
noise and interference. The Reader
disregards the messages with data
errors. For an optimal channel, free of
interference and industrial noise, the
Reader must be able to receive all
messages transmitted by a single
Transponder placed in its reading
Problem Symptom Probable Cause Solution
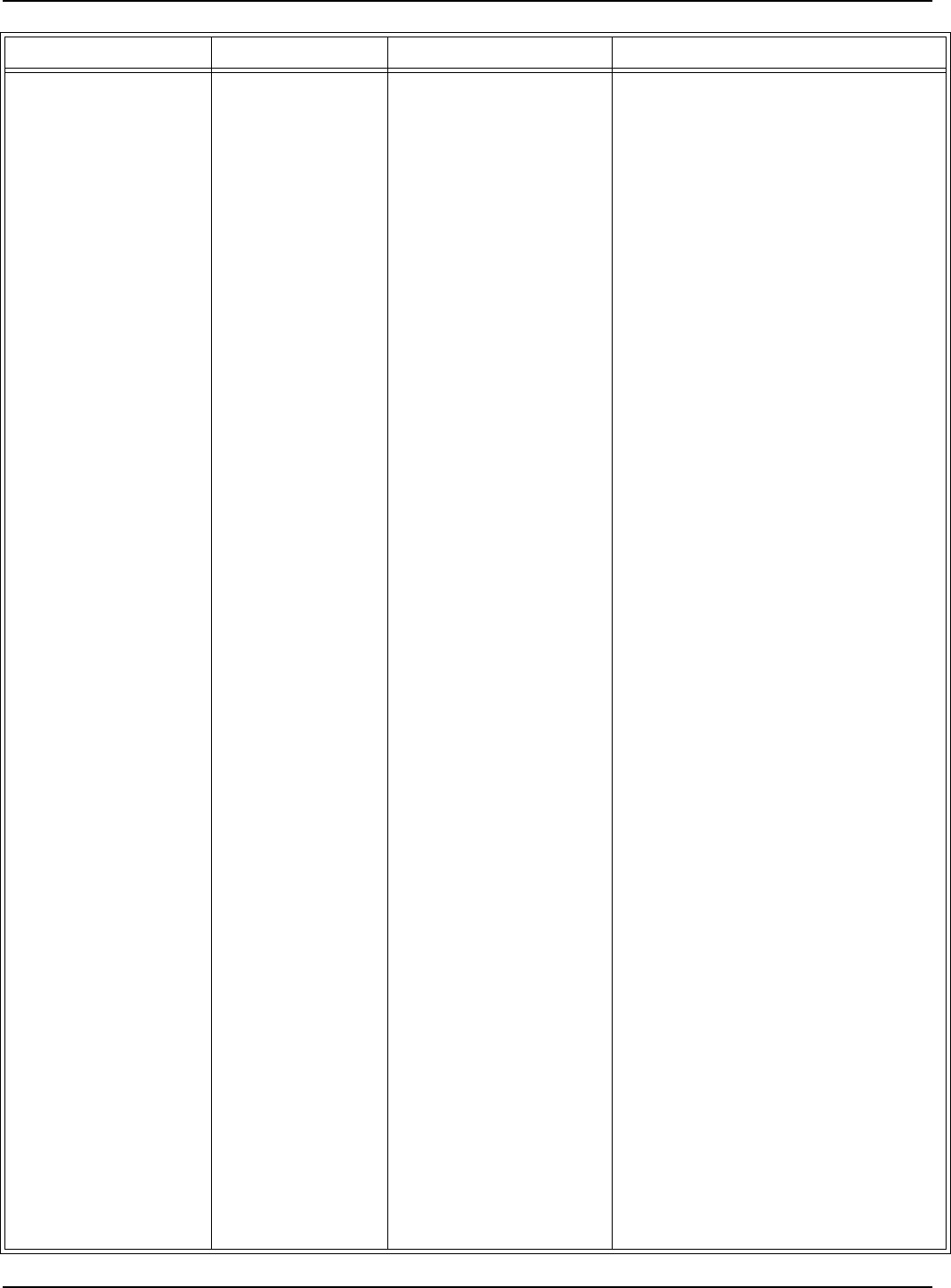
General Guidelines
Troubleshooting 7-7
Time-out error.
(At the command
:TEST:EXCITER k,the
response is 00,butthe
Main PC does not
receive a message, or a
correct message from
the Test Tag of the
Exciter kafter a
predetermined period
of time).
DATA LED is
flickering, the
Reader’s Tag
Record Buffer
contains messages
from the Test Tag.
DATA LED is
flickering, but the
Reader’s Tag
Record Buffer is
empty.
DATA LED is not
flickering
Test tag was incorrectly
programmed.
Test tag was incorrectly
programmed.
Exciter’s Test Tag is
placed beyond the limits
of the receiving zone, or
there is a random
interference on the UHF
channel, or the Test Tag
is out of specifications.
range. When using multiple
Transponders, some messages are lost
due to the inherent collision between
them.
1. Query the Test Tag programming
parameters using
:TAG:QUERY:EXCITER k.
2. Check the value of all group T
parameters.
3. Correct the values using the group
Wparameters.
4. Reprogram the Test TAg using the
command :TAG:MATCH:EXCITER k.
1. Query the Test Tag programming
parameters using
:TAG:QUERY:EXCITER k.
2. Check the value of all group T
parameters.
3. Correct the values using the group
Wparameters.
4. Reprogram the Test Tag using the
command :TAG:MATCH:EXCITER k.
1. Run the procedure, 95 Series RFID
System - Final Test on page 5-14.
Step 2 - Set up the Carrier
Threshold for the Reader.
2. Check the RF level of the messages
received from the Test Tag; it must
be higher than (RSS+HNL+3)dBm,
that means 3dB above the carrier
threshold value.
Note
The Reader reports the RF level of the
received message only if the parameter
DLI=Y.
3. If the RF level of the Test Tag’s
received messages is lower than
-85dBm, either reposition the
Reader or Exciter, or use a higher
gain UHF antenna for the Reader.
Problem Symptom Probable Cause Solution
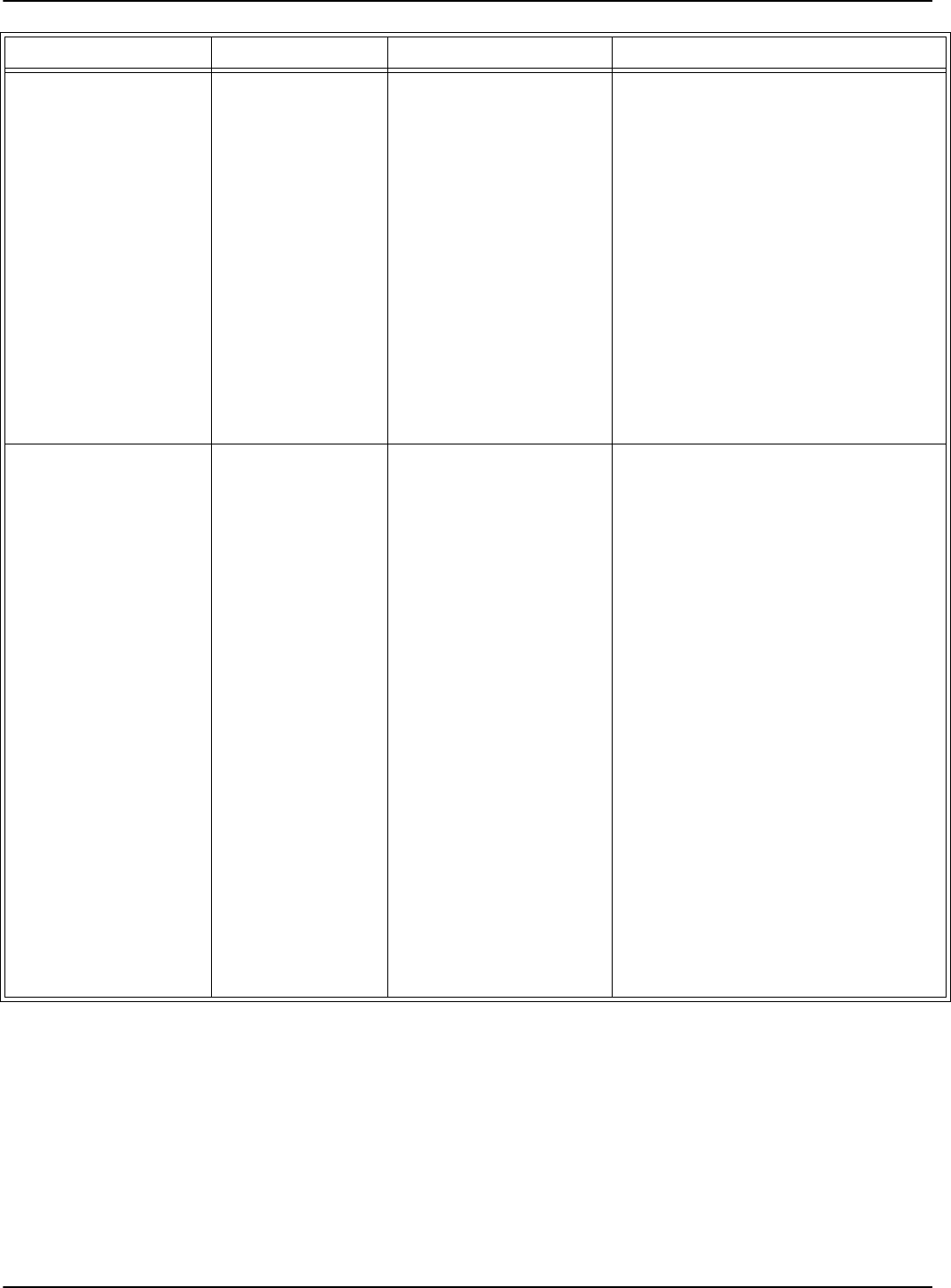
General Guidelines
7-8 Troubleshooting
Excitation field
generated by the
Exciter is below
Specifications.
LF Transmitter
Output is low
(VTAP<80V
pp).
The LF antenna loop has
a loose connection, or the
LF antenna is detuned
by a metallic object.
1. Check whether the LF antenna
wires are connected to the terminal
block (See LF Antenna Connections
on page 3-3).
2. Check the 3-wire connection
between the LF antenna terminal
block and the EXT95SC assembly
(terminal block TB2).
3. Check whether the recommended
setup guidelines for the Exciter’s
location are met. Pay special
attention to metallic surfaces
surrounding the Exciter, short-
circuit loops, and the spacing
between adjacent Exciters.
The Exciter responds
with C9 at the Self-
Diagnostic Procedure.
Exciter k responds
with C9 at the
command:
:TEST:EXCITER k
sent by the Main
PC (kis the
Exciter’s address).
A faulty Exciter or a
loose connection in the
power cable or
communication cable
between the Reader and
the Exciter.
A large magnetic
coupling between 2
adjacent Exciter E95
frames
The LF antenna is
detuned by metallic
objects that are in close
proximity.
1. Check the power cable and the
communication cable between the
Reader and the Exciter.
2. Check the Exciter’s address setting.
3. Check the LF Transmitter’s output.
(See LF Antenna Connections on
page 3-3).
1. Check the Exciter’s TAP voltage.
(See LF Transmitter Output on page
5-6).
2. Reposition the E95 frames to
minimize the unwanted modulation;
theamplitudeofV
TAPmin>60V
pp.
1. Check the Exciter’s VTAP.
2. Reposition the E95 frames to
minimize the detuning;
theamplitudeofV
TAP>80V
pp.
Problem Symptom Probable Cause Solution
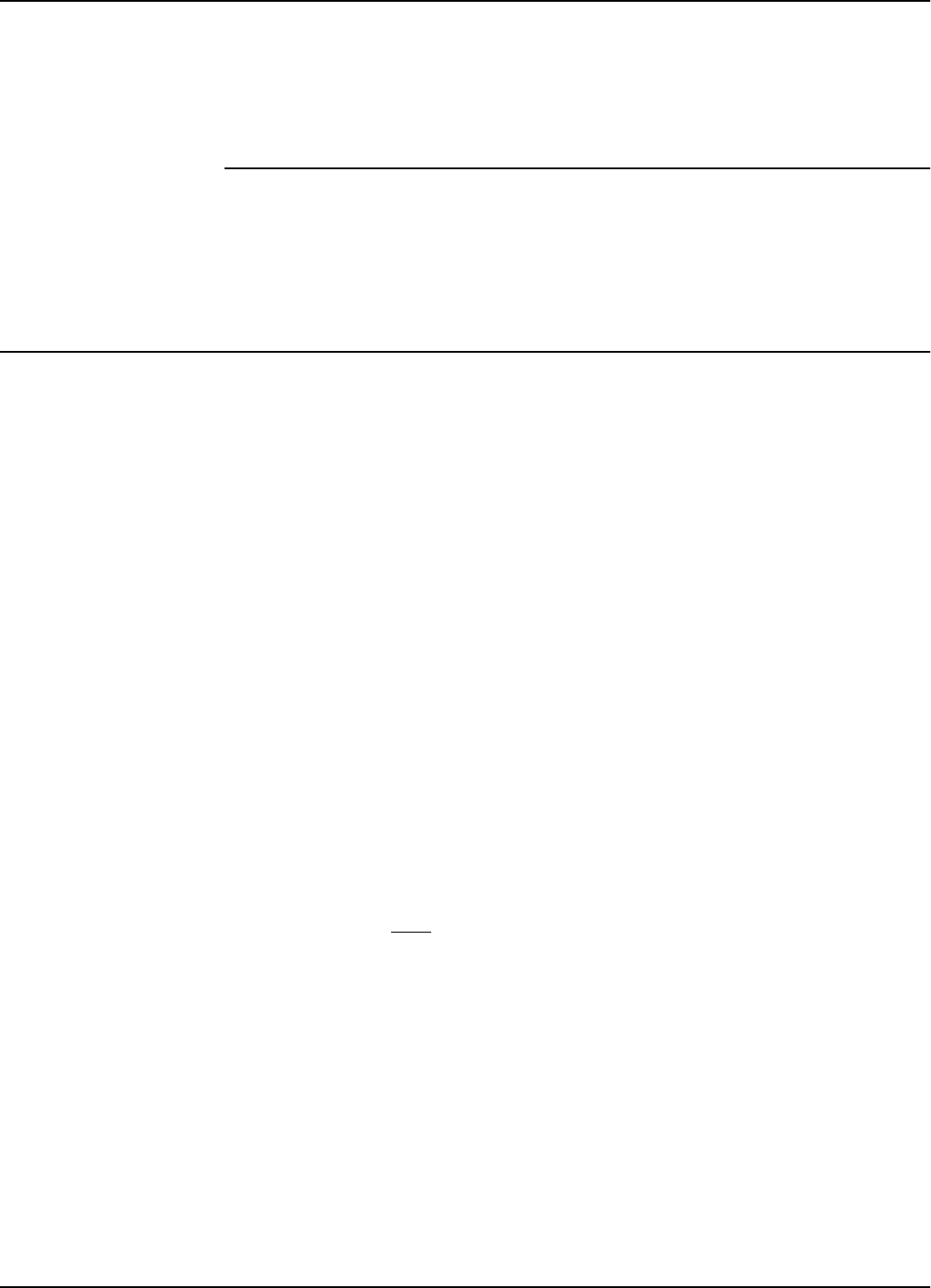
Transponder T95C
Specifications A-1
Appendix A
Specifications
This appendix gives technical specifications for the Transponder T95, the Reader R95,
the Exciter E95, and the AC Source TRM95. It also gives information on system
performances and special features.
Transponder T95C
LF Receiver • Configuration: Direct detection for 125.0 kHz signals modulated On/Off (OOK)
with 610 Hz.
• Carrier Frequency (125.0 kHz) Bandwidth @3dB:12 to 18 kHz.
• Modulation Frequency (600 kHz) Bandwidth @ 3dBm: 80 to 200 Hz.
• Sensitivity: better than H = 10mA/m[80 dBµA/m] or B=12.6nT in specific test
conditions.
UHF Transmitter • Carrier Frequency, nominal: 433.92 MHz ±50 kHz, stabilized by a SAW resonator.
• Carrier Frequency, max. variation: ±100 kHz, temperature and aging
• Modulation Type: Frequency-Shift Keying (FSK).
• Total Frequency Deviation, nominal: 15 ±3 kHz.
• Total Frequency Deviation, max. variation: 8 to 40 kHz.
• Radiated Power (ERP): less than 10 µW.
• Data Rate: 19.2 or 38.4 kbps.
Excitation Signal The Transponder is only awaken by signals accepted by the LF Receiver that have a
duration of at least 50ms.
Programming • Mode: optical.
• Data Rate: 1.2 kbps.
• Parameters: see the 95 Series RFID System Reference Guide.
Writing and
Transmitting Data
Asynchronous, NRZ, using a specially developed protocol.
Message Format For more information, see Appendix B, Transponder T95 Messages.
Power Supply 3 V/150 mAh, lithium cell battery.
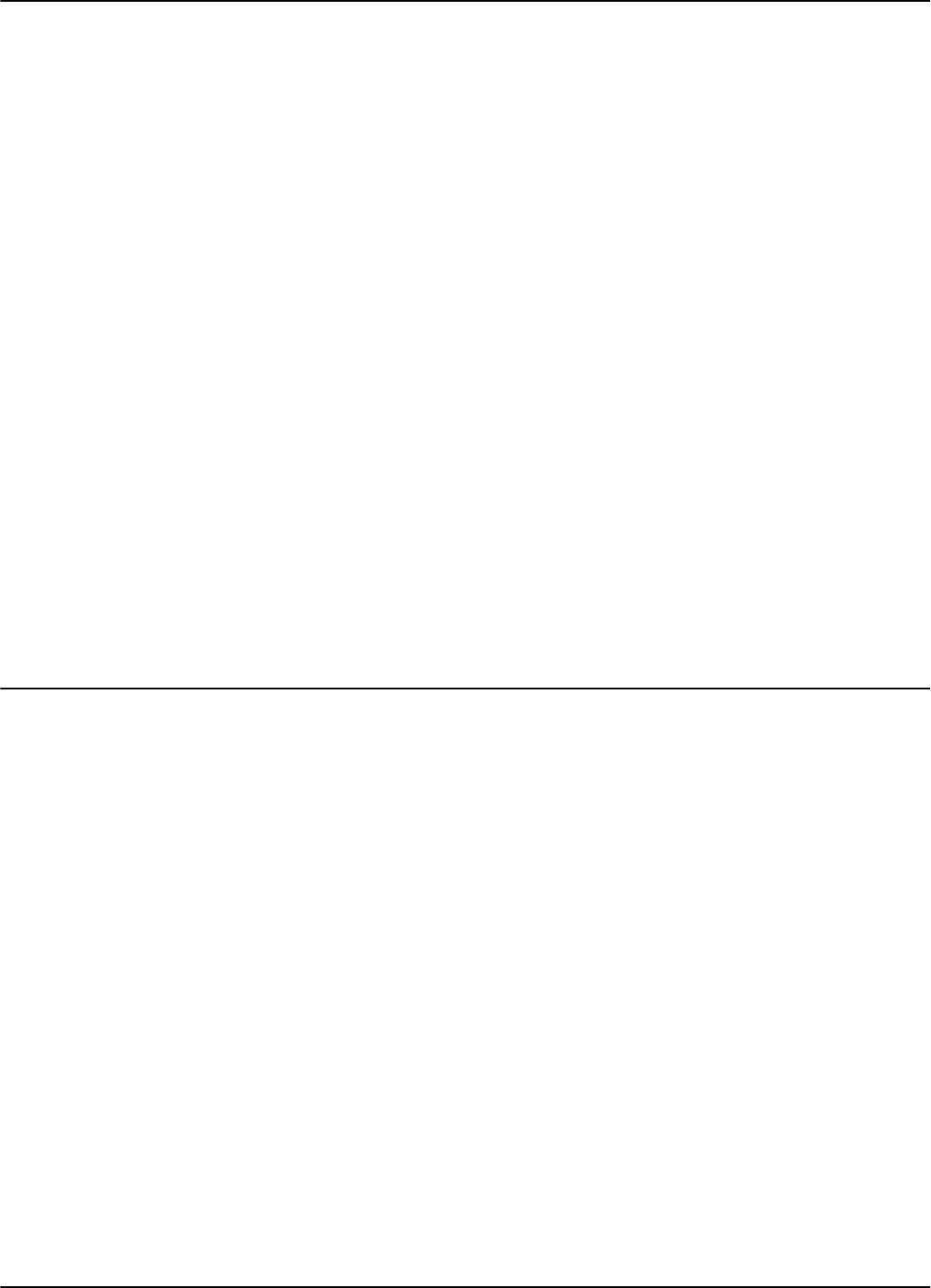
Reader R95
A-2 Specifications
Power
Consumption
Maximum 3 µA in sleep mode; 2.5mA in transmission mode.
Transponder
Lifetime
More than 5 years under normal use (1000 transmission/year).
Environmental
Operation
Temperature
- 20°C to +55°C.
Storage
Temperature
- 40°C to +70°C.
Relative
Humidity
Maximum 95%, non-condensing at +40°C
Mechanical • Dimensions, max
Length: 143.0 mm
Width: 107 mm
Height:max.2.8mm
• Weight: max 12 g
• Survives at least 1000 times through the automatic mail sorting machine.
Approvals Approved under I-ETS 300 220, I-ETS 300 330, RS-210 and FCC Part 15.
Reader R95
Configuration Superheterodyne receiver for 433.92 MHz signals modulated FSK.
Sensitivity Better than -105 dBm at 12 dB SINAD for 1 kHz modulation and 15 kHz total
deviation.
Successful
Message Ratio
(Throughput)
Better than 98% for any of the following conditions:
• RF Input Signal: -90 dBm to -10 dBm
• Frequency Range: 433.92 MHz ± 75 kHz.
• Total Frequency Deviation: 7 to 45 kHz.
• Data Rate: 19.2, or 38.4 kbps.
Object Sensor
Input
• Voltage limits: -0.5 to 5.5V
• Current: max 50µA
Relay Driving
Capabilities
• Max. Switching Current: 1A
• Max. Switched Voltage: 150Vdc or 300Vac
• Max. Switched Power: 30 W or 60 VA
• UL Rating: 1A @ 30Vdc
0.5A @ 120Vdc
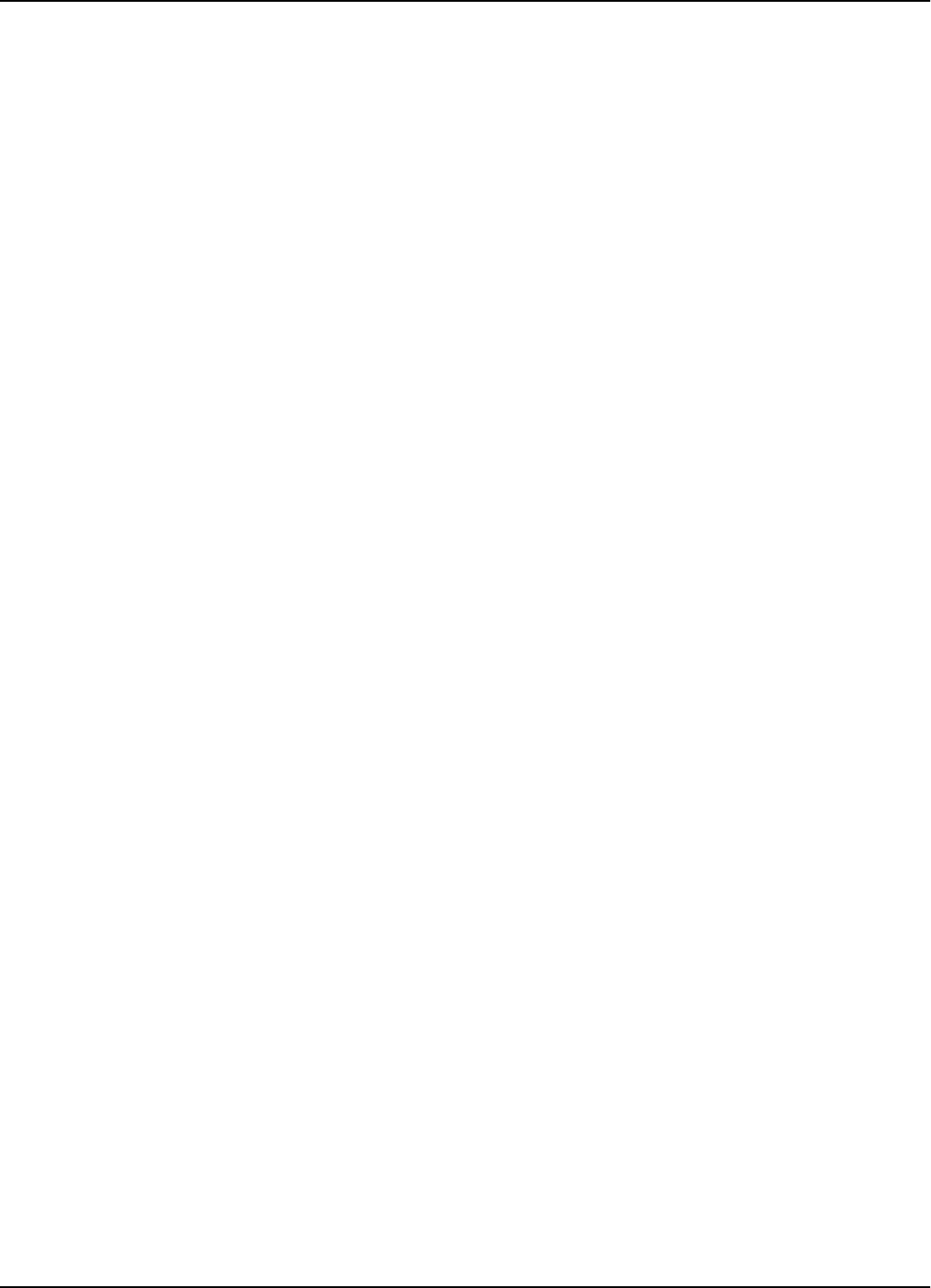
Reader R95
Specifications A-3
Additional
Features
• RF antenna diversity.
• RF input signal level measurement. This information is attached to every received
message.
• Programmable carrier threshold. Only input RF signals above this threshold are
processed.
• Real time clock: a time stamp (Month/Day/Hour/Minute) can be added to every
received message.
• Reads data with or without error checking and encryption in hexadecimal or
ASCII format.
• Received messages can be filtrated by time, RF signal level, system code, and data
content.
• Stores over 50 kbytes of received messages in an internal buffer.
• Interfaces with a PC through the RS-232 or RS-485 interface. The RS-485 can be
configured for half-duplex (2 wires) or full-duplex (4 wires).
• Controls up to 15 Exciters E95 through a dedicated RS-485 interface.
• Reader’s firmware can be upgraded using the serial interface.
Power Supply 12Vac ±10%, 50/60 Hz, or 13 to 16 Vdc.
Power
Consumption
Maximum 0.3 A.
Environmental
Operation
Temperature
-20°Cto+55°C.
Storage
Temperature
-40°Cto+70°C.
Relative
Humidity
Maximum95%,non-condensingat+40°C.
Mechanical • Dimensions (without UHF antennas)
Length: 250 ± 5 mm
Width: 210 ± 5 mm
Height: 100 ± 5 mm
•Weight:max4kg
Approvals Approved under I-ETS 300-220, I-ETS 300-330, RS-210 and FCC Part 15.
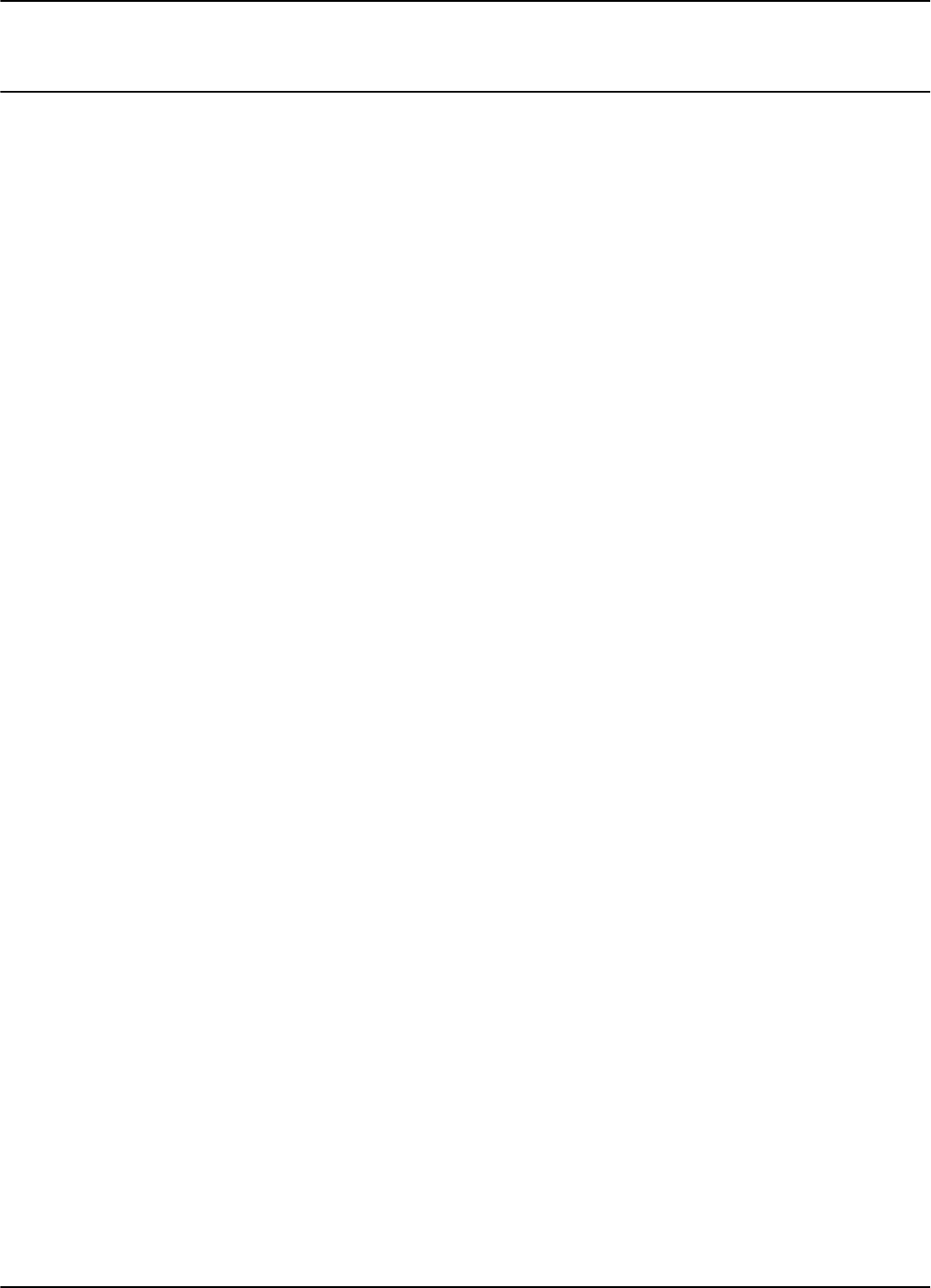
Exciter E95
A-4 Specifications
Exciter E95
LF Transmitter • Carrier Frequency: 125.0 kHz, quartz crystal generated.
• Modulation type: On/Off Keying (OOK).
• Modulation Frequency: 600 ±10 Hz.
• Carrier and modulation frequency tolerance: ± 50 ppm (± 6.6 kHz).
• Carrier and modulation frequency stability: better than 100 ppm (±13.2 kHz) over
the temperature range.
• Carrier and modulation frequency aging: maximum 3 ppm/year (0.4 Hz/year).
• Maximum radiated E-field at 10 m: 105 ±6 dB µV/m.
Additional
Features
• Exciter E95 incorporates a UHF transmitter that simulates the Transponder T95
to check the Reader’s capability.
• Test Transponder can be programmed and activated from the main PC.
• Self diagnostic for LF-Transmitter output level.
• Self diagnostic for power supply voltage level.
• Output relay driving
• Input Object Sensor
Power Supply 22 Vac ±10%, 50/60 Hz; or 23 - 28 Vdc.
Power
Consumption
Maximum 0.5 A.
Environmental
Operation
Temperature
- 20°C to +55°C.
Storage
Temperature
- 40°C to +70°C.
Relative
Humidity
Maximum 95%, non-condensing at +40°C.
Mechanical • Dimensions
Length: 2060 ± 10 mm
Width: 1000 ± 10 mm
Height: 75 ± 5 mm
• Weight: max 5.5 kg
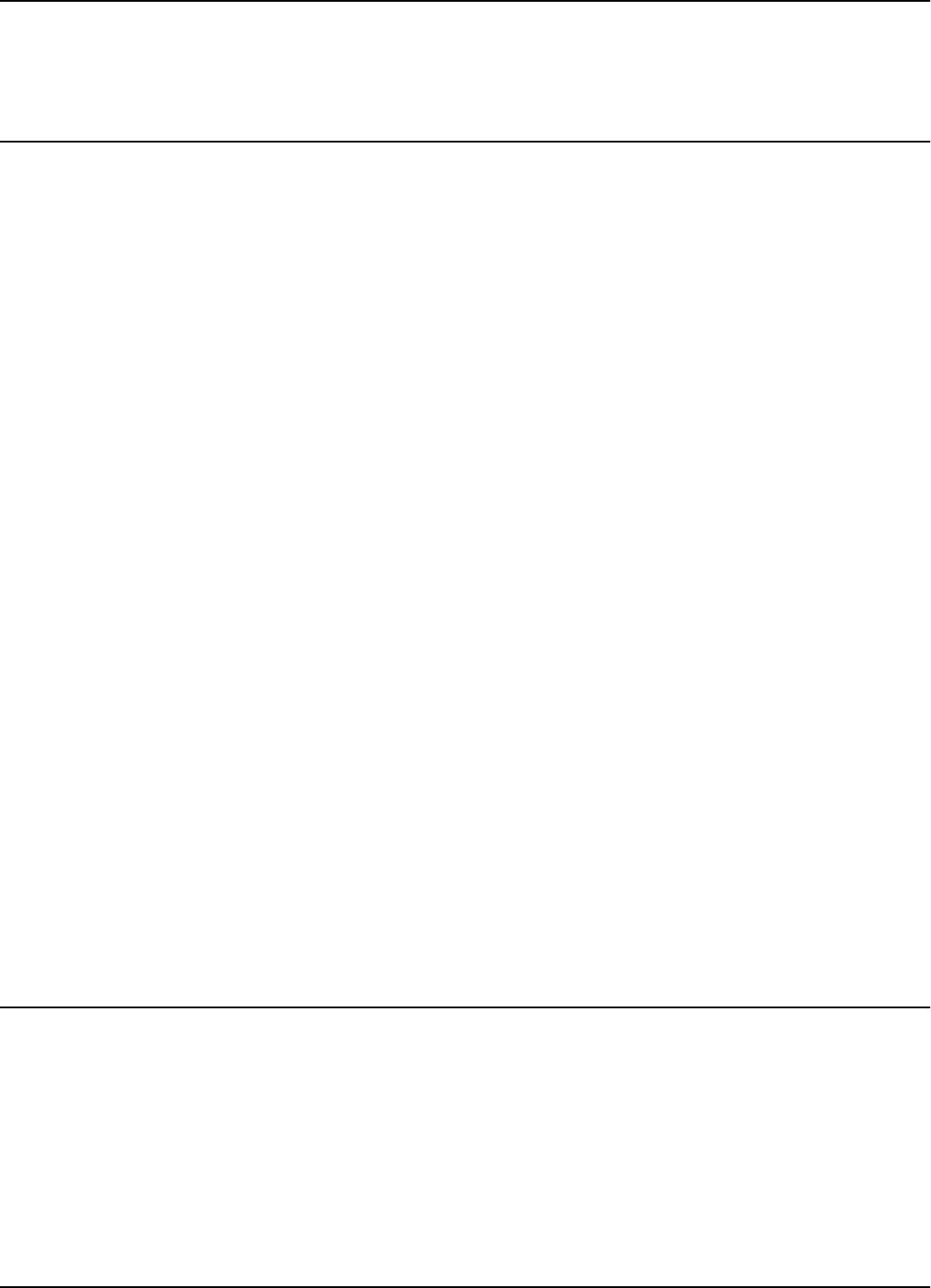
Power Supply TRM95
Specifications A-5
Approvals Approved under I-ETS 300 330, I-ETS 300 220, RSS-210 and FCC Part 15.
Power Supply TRM95
Input • AC line voltage:120Vac - model TRM95/120V
230Vac - model TRM95/230V
• Ratings: Model TRM95/120V - 0.7A, 60 Hz
Model TRM95/230V - 0.35A, 50 Hz
• Voltage tolerance: ±10%
• Fusing: Type T (“Slo-Blo”), 5x20mm; 1A for TRM95/120V; 0.5A for TRM95/230V
Output • Dual: 12 Vac/1A, 22Vac/2A
• Frequency: 50/60Hz
• Voltage tolerance: ±10%
Environmental
Operation
Temperature
-30°Cto+50°C.
Storage
Temperature
-40°Cto+70°C.
Relative
Humidity
Maximum95%,non-condensingat+40°C.
Mechanical • Dimensions
Length: 300 ± 5 mm
Width: 168 ± 5 mm
Height: 132 ± 5 mm
Approvals Approved under CSA, UL, and CE.
System Performance
Excitation Range Larger than 4.0 m in open space conditions.
Reading Range Larger than 20.0 m in open space conditions.
Identification
Capability
Transponders can be identified (excited and recorded) when they are placed inside
standard mail trays and bags, or collated on rollercages when they are moving
through the RFID system at the normal operational speed (less than 5 m/s).
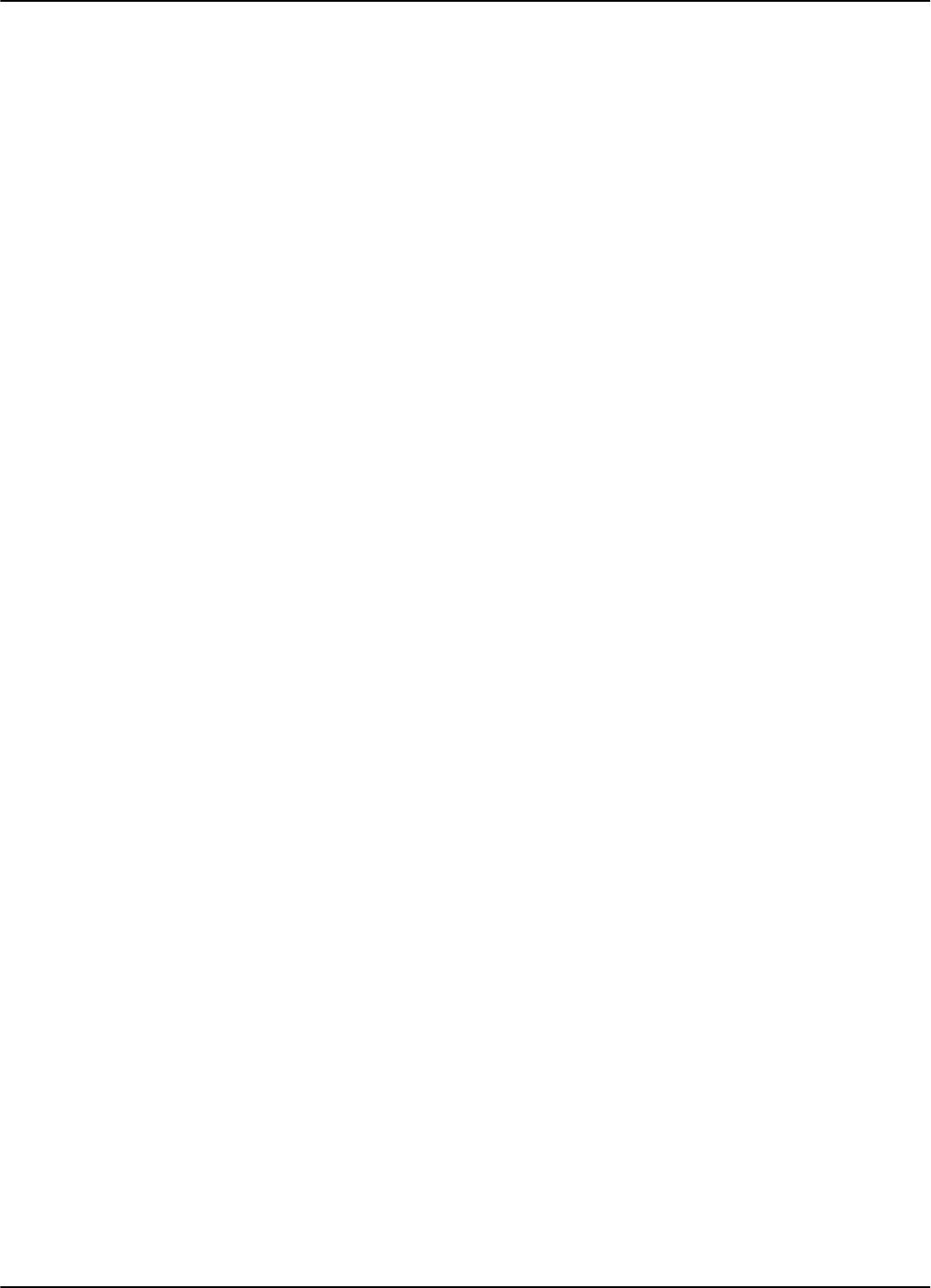
System Performance
A-6 Specifications
Readers can simultaneously identify up to 15 Transponders present in the excitation
field. The level of accuracy is greater than 95%.
System Capacity Up to 31 Readers R95 can be connected through the RS-485 interface to the main PC.
Up to 15 Exciters E95 can be controlled by any Reader R95. More Exciters E95 can be
used to generate a specific shape for the excitation gate.
Self Testing
Capabilities
At the request of the main computer, the RFID System automatically reports the
status of the LF excitation field generated by each Exciter E95, and the receiving
capability of each Reader R95.
Object Sensor
Monitoring
An external object sensor device can switch the excitation field On and Off.
Driving Output A Single Pole Double Throw (SPDT) relay contact is available to drive external
devices. The relay is activated each time the Reader receives a correct message.
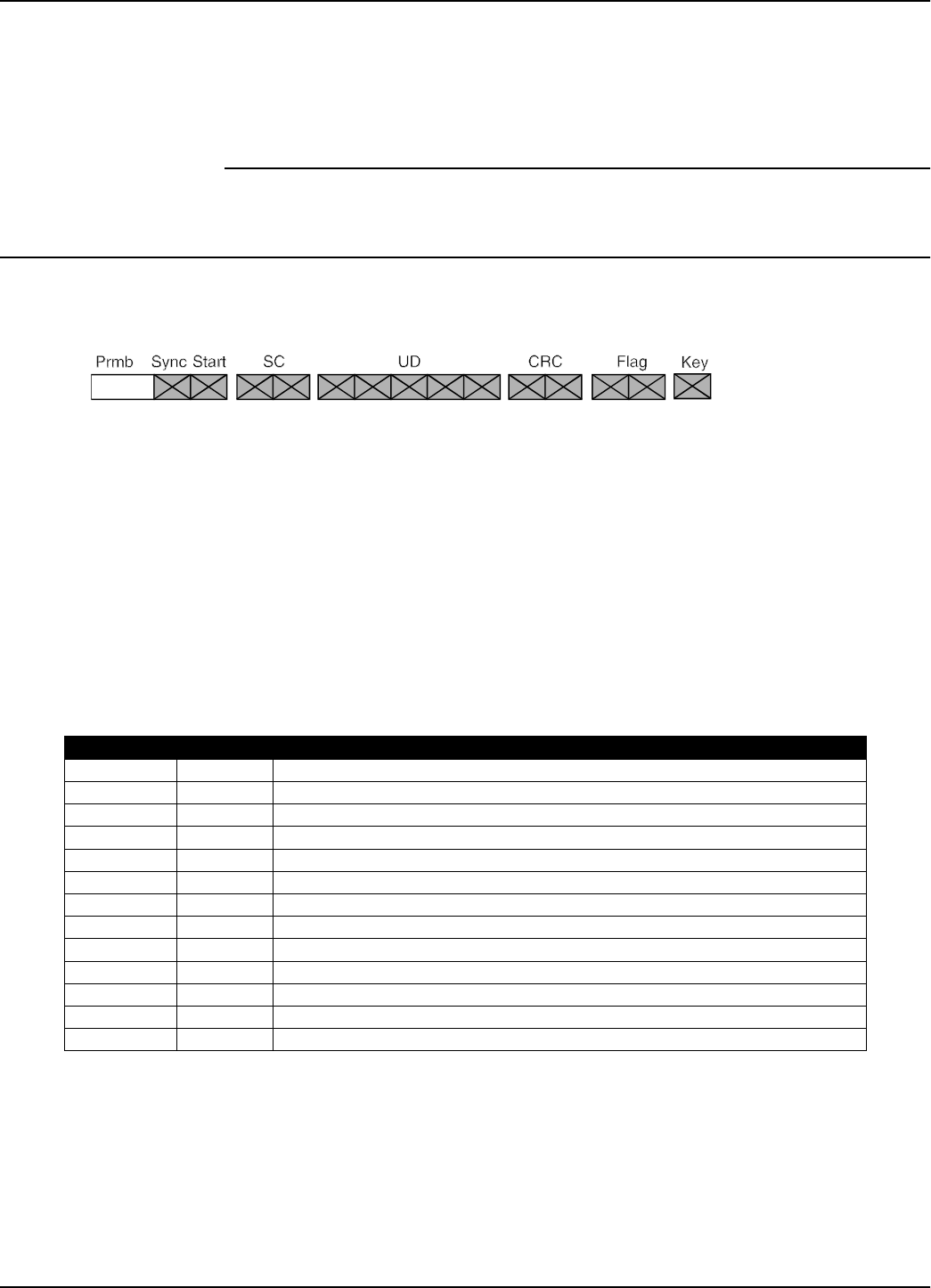
Message Format
Transponder T95 Messages B-1
Appendix B
Transponder T95 Messages
Message Format
Each message has the following format
where:
Prmbl = 0.7 ms continue 1.
Sync = a string of 10 bits of “0101010101”; transmitted only if SM=Y.
Start = a string of 13 bits “0101010000111”; transmitted only if SM=Y.
SC = 2 bytes system code; transmitted only if TS=Y.
UD = user definable data; number of bytes is set by CC (1 to 32).
CRC = 2 bytes CRC; transmitted only if EC=Y.
Flag = 2 bytes message flags; transmitted only if TF=Y. It has 1 byte if HF=N and
2 bytes if HF=Y.
Key = 1 byte message key; transmitted only if EN=Y.
T95 Parameters The parameters that control the message transmission for T95 are shown in the table
below:
Total Transmission
Time
After a valid excitation, the T95 transmits the initial number of messages defined by
the IP parameter, followed by an extra number of messages (up to the RC) for as long
as the excitation exists. Then it goes to sleep.
There is a random delay called InterMsgDelay that occurs between two consecutive
messages. This is implemented to ensure that the delay time does not repeat itself
before 32 messages have occurred.
Parameter Range Description
DR 3,4 Data rate; DR3 = 19.2 kbps, DR4= 38.4 kbps
EC Y/N Standard error check transmitted
EN Y/N Data encryption available
HF Y/N Flags in hexadecimal
ID 0...200 Initial delay
IP 1...200 Initial number of messages transmitted after a valid execution
LT Y/N Limit repeated transmissions
RC 0...255 Number of extra messages transmitted after IP during a continuous excitation
RS 0...255 Random seed
SD 1...220 Subsequent delay
SM Y/N Synchronous preamble transmitted
TF Y/N Transmit Flags
TS Y/N Transmit System Code
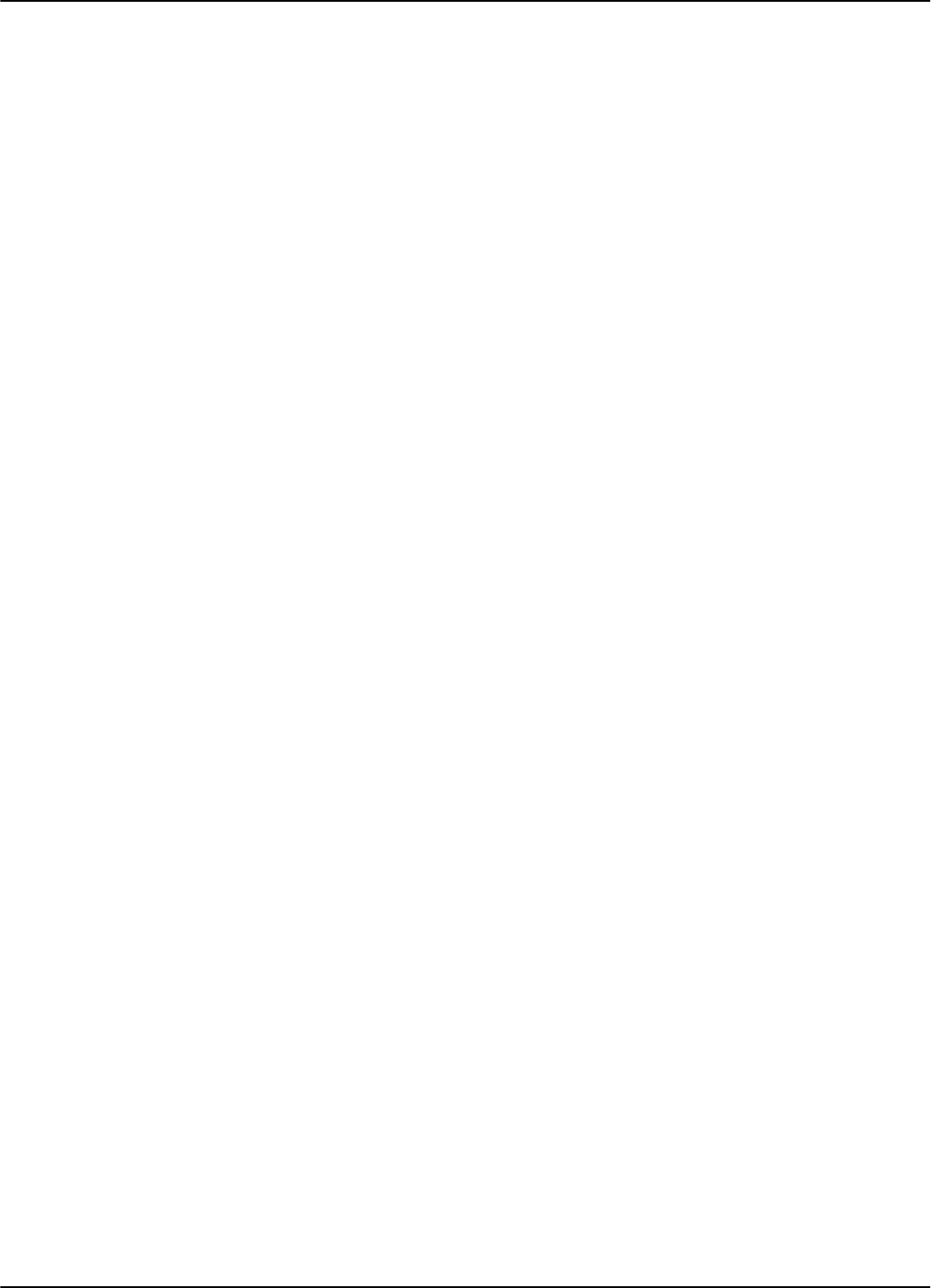
Message Format
B-2 Transponder T95 Messages
The following is the method of evaluating the maximum transmission time for the
T95:
Number of bytes per message: TXBytes = SC + UD + CRC + Flag + Key
Number of bits per byte: BitsPerByte = 12 for DR4, and = 11 for DR3
Number of bits per message: TXBits = Sync + BitsPerByte*TXBytes
Bit duration: BitLen = 1/DR
Message length: MsLen = 0.0007 +TXBit*BitLen
Intermessage constant: InterMsgUnit = (UD + Flag)*0.0003066, for DR4;
= (UD + Flag)*0.0005657), for DR3
Intermessage delay: InterMsgDelay = [SD +RND(0…31)]*InterMsgUnit;
(RND - random value)
Maximum number of transmitted messages: NM = IP +RC; if LT = N
Total transmission time: TXTime = NM (MsLen +(NM-1) (InterMsgDelay)
Thefollowingtablespresentthemaximumnumberofmessages(NM)thatcanbe
transmitted in five seconds, using different sets of parameters for the T95.
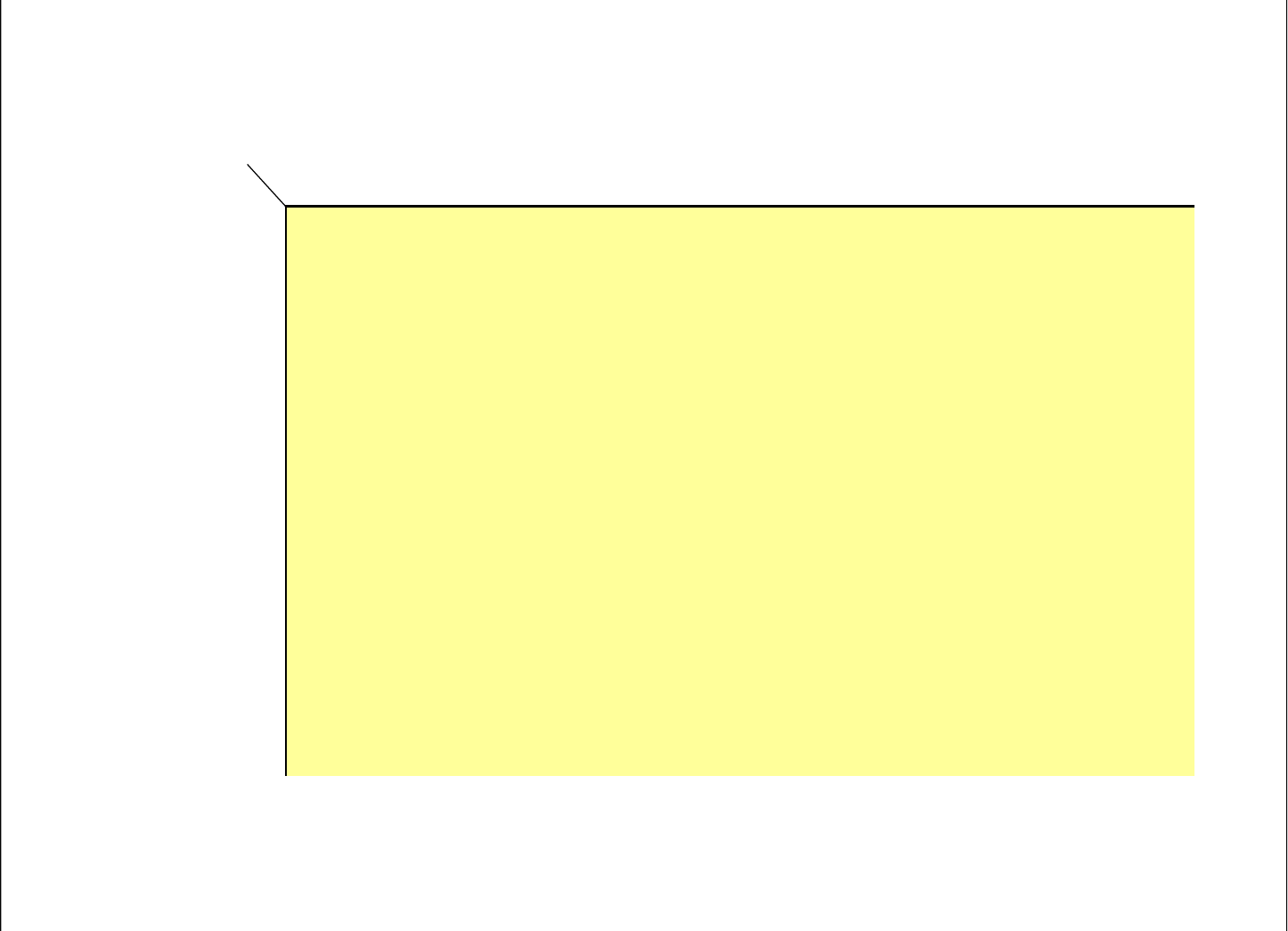
Message Format
Transponder T95 Messages B-3
DR= 4
SM=Y,TF=Y,HF=Y,TS=Y,EC=Y,EN=Y
SD
CC
1 3 5 7 9 11 13 15 17 19 21 23 25 27 29 31 33 35 37 39 41 43 45 47 49 51 53 55 57 59 61 63 65 67 69 71 73 75 77 79 81 83 85 87 89 91
1
261 236 220 202 192 175 167 158 147 140 134 130 122 116 111 107 104 101 98 94 90 87 84 82 79 77 75 73 72 70 69 67 66 65 62 61 59 58 57 55 54 53 52 51 50 49
2
201 183 168 157 143 136 130 119 112 107 102 99 94 88 84 81 78 75 73 71 69 67 65 64 60 58 57 55 53 52 51 49 48 47 46 45 44 43 43 42 41 40 40 39 38 38
3
165 148 137 129 116 108 103 99 92 86 81 77 74 72 69 67 65 61 59 56 54 52 51 49 48 46 45 44 43 42 41 40 39 39 38 37 36 36 35 34 34 33 33 31 31 30
4
138 129 113 106 100 93 85 80 76 72 69 67 65 60 57 54 52 50 48 47 45 44 43 41 40 39 38 37 37 36 35 34 34 33 32 31 30 29 28 28 27 27 26 26 25 25
5
118 107 101 92 83 78 73 70 67 65 59 55 53 50 48 46 45 43 42 40 39 38 37 36 35 35 34 33 31 30 29 29 28 27 26 26 25 25 24 23 23 22 22 22 21 21
6
104 98 86 78 74 70 67 62 57 53 50 48 46 44 42 41 40 38 37 36 35 34 33 33 31 30 29 28 27 26 25 25 24 23 23 22 22 21 21 20 20 19 19 19 18 18
7
97 83 76 71 68 65 57 53 50 47 45 43 41 40 38 37 36 35 34 33 31 30 29 27 27 26 25 24 23 23 22 22 21 20 20 20 19 19 18 18 18 17 17 17 16 16
8
82 75 70 66 60 54 50 47 45 43 41 39 38 36 35 34 33 31 30 28 27 26 25 24 23 23 22 21 21 20 20 19 19 18 18 17 17 17 16 16 16 15 15 15 15 14
9
75 70 66 58 52 49 46 43 41 39 38 36 35 34 33 30 29 27 26 25 24 23 22 22 21 20 20 19 19 18 18 17 17 17 16 16 15 15 15 15 14 14 14 14 13 13
10
71 66 58 52 48 45 42 40 38 37 35 34 33 30 29 27 26 25 24 23 22 21 20 20 19 19 18 18 17 17 16 16 15 15 15 14 14 14 14 13 13 13 13 12 12 12
11
67 59 52 47 44 42 39 38 36 35 33 31 29 27 26 24 23 22 21 21 20 19 19 18 17 17 17 16 16 15 15 15 14 14 14 13 13 13 13 12 12 12 12 11 11 11
12
65 52 47 44 41 39 37 36 34 33 30 28 26 25 23 22 21 20 20 19 18 18 17 17 16 16 15 15 14 14 14 13 13 13 13 12 12 12 12 11 11 11 11 11 10 10
13
54 48 44 41 39 37 36 34 33 29 27 25 24 23 22 21 20 19 18 18 17 16 16 15 15 15 14 14 13 13 13 13 12 12 12 12 11 11 11 11 10 10 10 10 10 10
14
50 45 42 39 37 36 34 33 29 27 25 23 22 21 20 19 18 18 17 16 16 15 15 14 14 14 13 13 13 12 12 12 11 11 11 11 11 10 10 10 10 10 9 9 9 9
15
47 43 40 38 36 34 33 29 26 24 23 22 20 19 19 18 17 16 16 15 15 14 14 14 13 13 12 12 12 12 11 11 11 11 10 10 10 10 10 9 9 9 9 9 9 8
16
44 41 38 36 34 33 29 26 24 23 21 20 19 18 17 17 16 15 15 14 14 14 13 13 12 12 12 11 11 11 11 10 10 10 10 10 9 9 9 9 9 9 8 8 8 8
17
42 39 37 35 33 30 26 24 22 21 20 19 18 17 16 16 15 15 14 14 13 13 12 12 12 11 11 11 11 10 10 10 10 9 9 9 9 9 9 8 8 8 8 8 8 8
18
40 38 36 34 31 27 24 23 21 20 19 18 17 16 15 15 14 14 13 13 12 12 12 11 11 11 11 10 10 10 10 9 9 9 9 9 8 8 8 8 8 8 8 7 7 7
19
39 37 35 33 28 25 23 21 20 19 18 17 16 15 15 14 14 13 13 12 12 12 11 11 11 10 10 10 10 9 9 9 9 9 8 8 8 8 8 8 8 7 7 7 7 7
20
38 36 34 30 26 23 21 20 19 18 17 16 15 14 14 13 13 12 12 12 11 11 11 10 10 10 10 9 9 9 9 9 8 8 8 8 8 8 7 7 7 7 7 7 7 7
21
37 35 33 27 24 22 20 19 18 17 16 15 14 14 13 13 12 12 11 11 11 10 10 10 10 9 9 9 9 9 8 8 8 8 8 8 7 7 7 7 7 7 7 7 6 6
22
36 34 29 25 22 20 19 18 17 16 15 14 14 13 13 12 12 11 11 11 10 10 10 9 9 9 9 9 8 8 8 8 8 8 7 7 7 7 7 7 7 7 6 6 6 6
23
35 33 27 23 21 19 18 17 16 15 14 14 13 13 12 12 11 11 11 10 10 10 9 9 9 9 8 8 8 8 8 8 7 7 7 7 7 7 7 6 6 6 6 6 6 6
24
34 30 25 22 20 18 17 16 15 14 14 13 13 12 12 11 11 10 10 10 10 9 9 9 9 8 8 8 8 8 7 7 7 7 7 7 7 6 6 6 6 6 6 6 6 6
25
33 27 23 21 19 18 16 15 15 14 13 13 12 12 11 11 10 10 10 9 9 9 9 8 8 8 8 8 7 7 7 7 7 7 7 6 6 6 6 6 6 6 6 6 6 5
26
332522201817161514 13131212 11 11 1010109999888887777776666666666555
27
302421191716151413 13121211 11 10 1010 99998888777777766666666655555
28
272220181715141413 121211 11 10 1010 9 99888887777776666666665555555
29
252119171615141312 1211 11 101010 9 9 98888877777766666666555555555
30
232018161514131312 11 11 11 1010 9 9 9 88888777776666666665555555555
31
221917161514131212 11 11 1010 9 9 9 8 88887777766666666555555555555
32
211817151413131211 11 1010 9 9 9 9 8 88877777666666665555555555544
Maximum allowable number of messages ( IP + RC ) that can be transmitted in 5 seconds
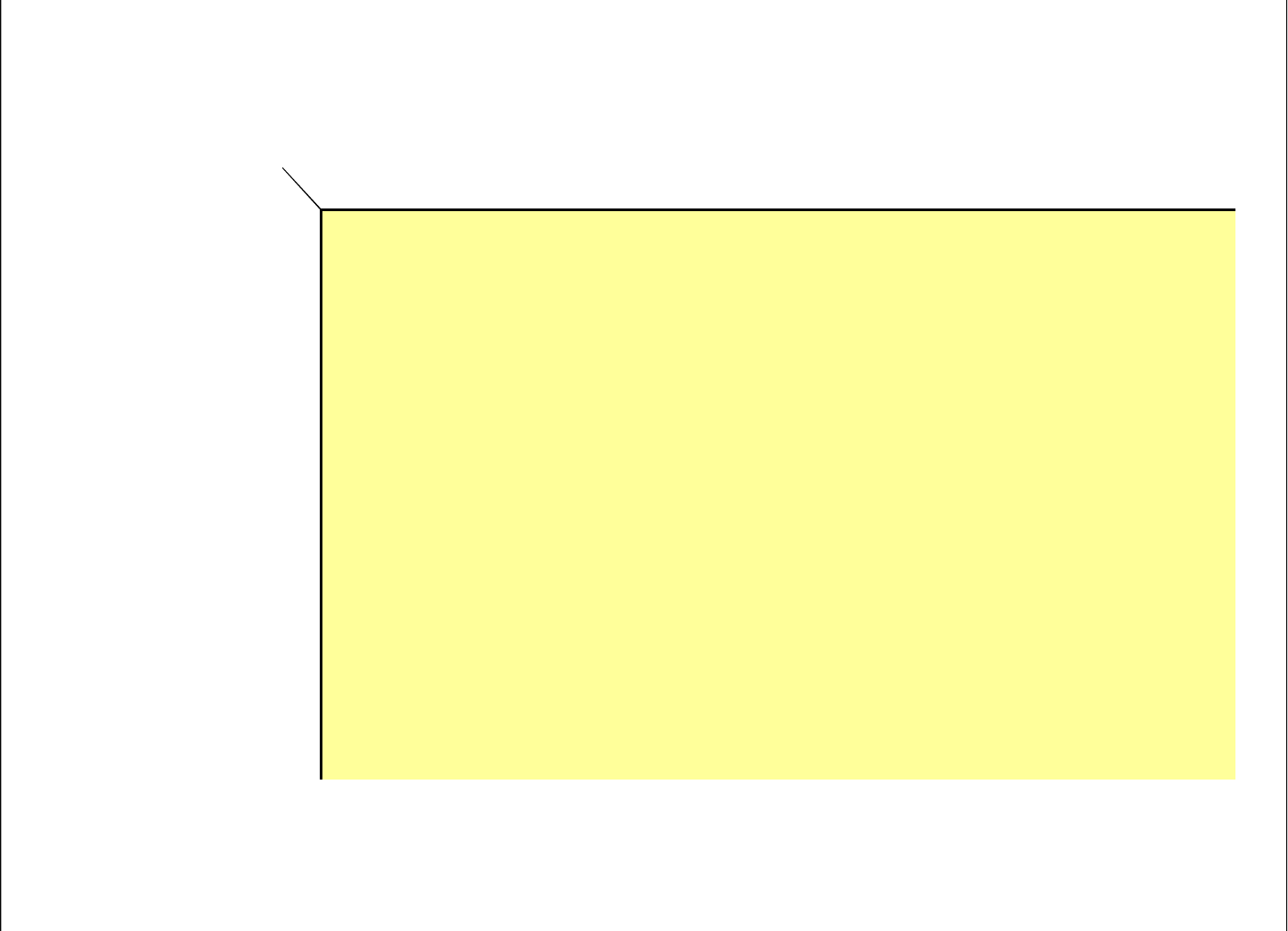
Message Format
B-4 Transponder T95 Messages
DR= 3
SM=Y, TF=Y, HF=Y, TS=Y, EC=Y, EN=Y
SD
CC
135791113151719212325272931333537394143454749515355575961636567697173757779818385878991
1
140131 117 109103 98 90 84 79 75 72 70 67 65 61 58 55 5351494846454443424140393837363635343433323130292928282726
2
107 100 91 82 77 73 69 66 62 57 54 51 49 47 45 43 42 41 39 38 37 36 35 34 34 33 31 30 29 28 27 27 26 25 25 24 23 23 22 22 21 21 21 20 20 20
3
87 78 73 69 65 59 54 50 48 45 43 41 40 38 37 36 35 34 33 31 30 28 27 26 25 25 24 23 23 22 21 21 20 20 19 19 18 18 18 17 17 17 16 16 16 15
4
73 68 65 56 51 47 45 42 40 39 37 36 35 33 32 30 28 27 26 25 24 23 22 21 21 20 19 19 18 18 18 17 17 16 16 16 15 15 15 14 14 14 14 13 13 13
5
66 57 51 47 44 41 39 37 36 35 33 31 29 27 26 24 23 22 21 21 20 19 19 18 17 17 17 16 16 15 15 15 14 14 14 13 13 13 13 12 12 12 12 11 11 11
6
54 48 44 41 39 37 36 34 33 29 27 26 24 23 22 21 20 19 18 18 17 17 16 16 15 15 14 14 14 13 13 13 12 12 12 12 11 11 11 11 11 10 10 10 10 10
7
47 43 40 38 36 34 33 29 27 25 23 22 21 20 19 18 17 17 16 16 15 15 14 14 13 13 13 12 12 12 12 11 11 11 11 10 10 10 10 10 9 9 9 9 9 9
8
4340373534 31272523222019181817161515141413131312121211111111101010101099999888888
9
4037353329 262422201918171616151414131313121212111111101010109999988888887777
10
3735332925 23211918171616151414131312121211111110101099999888888877777777
11
3634292522 20191817161514141313121211111110101099999888888777777766666
12
343025 22201817161514 141313121211 11 101010109999888887777777666666666
13
332522 20181716151413 13121211 11 1010109999888887777777666666666555
14
272320 18171615141312 1211 11 11 1010 9 99988888777777666666666555555
15
2420181716151413121211111010109998888777777666666666555555555
16
21191716141413121211101010999888877777766666666555555555555
17
1917161514131211111010109998887777776666666555555555554444
18
18161514131211111010999888877777666666655555555555444444
19
1715141312111110109998887777766666665555555555444444444
20
161413121211101099988877776666666555555555544444444444
21
15141312111010998888777766666655555555544444444444444
22
1413121110109998887777666666555555554444444444444443
23
131211111099988777766666655555555544444444444444333
24
131211101099888777666666555555554444444444444433333
25
12111010998887776666655555555444444444444443333333
26
1211109988877766666555555554444444444444333333333
27
1110109988777666665555555544444444444433333333333
28
111099887777666655555554444444444443333333333333
29
101098887776666555555544444444444433333333333333
30
10998877766665555555444444444443333333333333333
31
10988777666665555554444444444433333333333333333
32
9988777666655555544444444443333333333333333333
Maximum allowable number of messages ( IP + RC ) that can be transmitted in 5 seconds
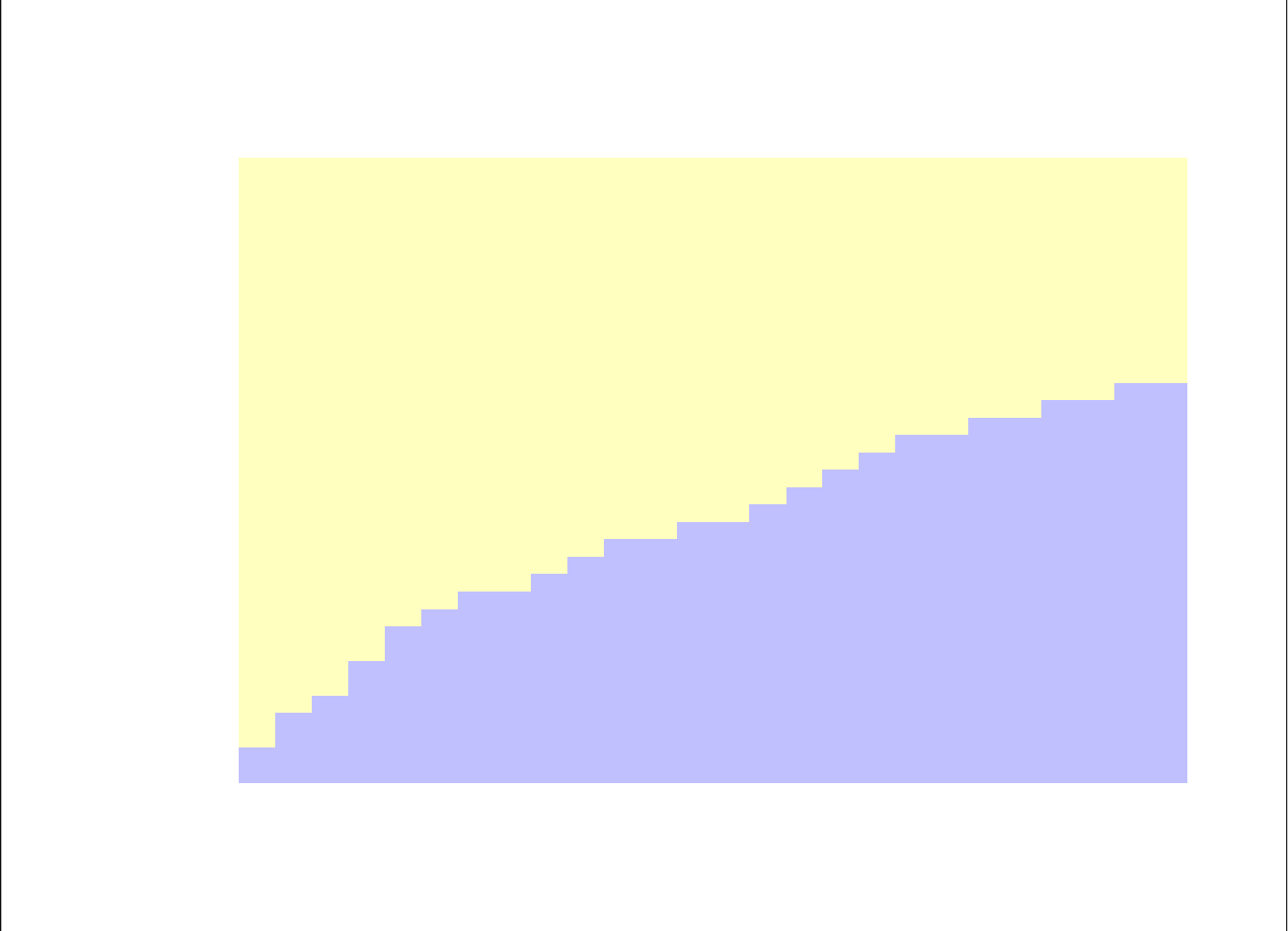
Message Format
Transponder T95 Messages B-5
DR =4 SM=Y TF=Y HF=Y TS=Y EC=Y CC=5 EN=Y
SD
RC+IP 1 3 5 7 9 11 13 15 17 19 21 23 25 27 29 31 33 35 37 39 41 43 45 47 49 51
10
0.591 0.629 0.668 0.706 0.745 0.784 0.822 0.861 0.9 0.938 0.977 1.015 1.054 1.093 1.131 1.17 1.209 1.247 1.286 1.325 1.363 1.402 1.44 1.479 1.518 1.556
12
0.697 0.744 0.792 0.839 0.886 0.933 0.98 1.028 1.075 1.122 1.169 1.216 1.264 1.311 1.358 1.405 1.453 1.5 1.547 1.594 1.641 1.689 1.736 1.783 1.83 1.877
14
0.795 0.851 0.907 0.962 1.018 1.074 1.13 1.186 1.241 1.297 1.353 1.409 1.465 1.52 1.576 1.632 1.688 1.744 1.799 1.855 1.911 1.967 2.023 2.078 2.134 2.19
16
0.884 0.949 1.013 1.078 1.142 1.206 1.271 1.335 1.399 1.464 1.528 1.593 1.657 1.721 1.786 1.85 1.915 1.979 2.043 2.108 2.172 2.236 2.301 2.365 2.43 2.494
18
0.965 1.038 1.111 1.184 1.257 1.33 1.403 1.476 1.549 1.622 1.695 1.768 1.841 1.914 1.987 2.06 2.133 2.206 2.279 2.352 2.425 2.498 2.57 2.643 2.716 2.789
20
1.037 1.119 1.2 1.282 1.364 1.445 1.527 1.608 1.69 1.771 1.853 1.934 2.016 2.098 2.179 2.261 2.342 2.424 2.505 2.587 2.668 2.75 2.832 2.913 2.995 3.076
22
1.101 1.191 1.281 1.371 1.461 1.552 1.642 1.732 1.822 1.912 2.002 2.092 2.183 2.273 2.363 2.453 2.543 2.633 2.723 2.814 2.904 2.994 3.084 3.174 3.264 3.354
24
1.156 1.255 1.353 1.452 1.551 1.65 1.748 1.847 1.946 2.044 2.143 2.242 2.341 2.439 2.538 2.637 2.736 2.834 2.933 3.032 3.13 3.229 3.328 3.427 3.525 3.624
26
1.202 1.31 1.417 1.524 1.632 1.739 1.846 1.954 2.061 2.168 2.275 2.383 2.49 2.597 2.705 2.812 2.919 3.027 3.134 3.241 3.349 3.456 3.563 3.67 3.778 3.885
28
1.24 1.356 1.472 1.588 1.704 1.82 1.936 2.051 2.167 2.283 2.399 2.515 2.631 2.747 2.863 2.979 3.095 3.21 3.326 3.442 3.558 3.674 3.79 3.906 4.022 4.138
30
1.269 1.394 1.518 1.643 1.767 1.892 2.016 2.141 2.265 2.39 2.514 2.639 2.763 2.888 3.012 3.137 3.261 3.386 3.51 3.635 3.759 3.884 4.008 4.132 4.257 4.381
32
1.219 1.348 1.477 1.606 1.734 1.863 1.992 2.121 2.249 2.378 2.507 2.636 2.765 2.893 3.022 3.151 3.28 3.408 3.537 3.666 3.795 3.924 4.052 4.181 4.31 4.439
34
1.369 1.506 1.643 1.781 1.918 2.056 2.193 2.33 2.468 2.605 2.742 2.88 3.017 3.154 3.292 3.429 3.566 3.704 3.841 3.979 4.116 4.253 4.391 4.528 4.665 4.803
36
1.51 1.656 1.801 1.947 2.093 2.239 2.385 2.531 2.677 2.823 2.969 3.115 3.261 3.407 3.553 3.699 3.845 3.991 4.137 4.282 4.428 4.574 4.72 4.866 5.012 5.158
38
1.642 1.796 1.951 2.105 2.26 2.415 2.569 2.724 2.878 3.033 3.187 3.342 3.496 3.651 3.805 3.96 4.114 4.269 4.423 4.578 4.732 4.887 5.041 5.196 5.351 5.505
40
1.766 1.929 2.092 2.255 2.418 2.581 2.744 2.907 3.07 3.234 3.397 3.56 3.723 3.886 4.049 4.212 4.375 4.538 4.702 4.865 5.028 5.191 5.354 5.517 5.68 5.843
42
1.881 2.052 2.224 2.396 2.567 2.739 2.911 3.083 3.254 3.426 3.598 3.769 3.941 4.113 4.284 4.456 4.628 4.799 4.971 5.143 5.315 5.486 5.658 5.83 6.001 6.173
44
1.987 2.167 2.348 2.528 2.708 2.889 3.069 3.249 3.429 3.61 3.79 3.97 4.151 4.331 4.511 4.691 4.872 5.052 5.232 5.413 5.593 5.773 5.953 6.134 6.314 6.494
46
2.085 2.274 2.463 2.652 2.841 3.029 3.218 3.407 3.596 3.785 3.974 4.163 4.352 4.54 4.729 4.918 5.107 5.296 5.485 5.674 5.862 6.051 6.24 6.429 6.618 6.807
48
2.174 2.372 2.569 2.767 2.964 3.162 3.359 3.557 3.754 3.952 4.149 4.346 4.544 4.741 4.939 5.136 5.334 5.531 5.729 5.926 6.123 6.321 6.518 6.716 6.913 7.111
50
2.255 2.461 2.667 2.873 3.079 3.285 3.491 3.697 3.904 4.11 4.316 4.522 4.728 4.934 5.14 5.346 5.552 5.758 5.964 6.17 6.376 6.582 6.788 6.994 7.2 7.406
55
2.42 2.647 2.875 3.102 3.33 3.557 3.785 4.012 4.24 4.467 4.695 4.922 5.15 5.377 5.605 5.832 6.06 6.287 6.515 6.742 6.97 7.197 7.425 7.652 7.88 8.107
60
2.53 2.779 3.028 3.277 3.526 3.775 4.024 4.273 4.522 4.771 5.02 5.269 5.518 5.767 6.016 6.265 6.514 6.763 7.012 7.261 7.509 7.758 8.007 8.256 8.505 8.754
65
2.585 2.851 3.117 3.384 3.65 3.916 4.182 4.448 4.714 4.98 5.246 5.513 5.779 6.045 6.311 6.577 6.843 7.109 7.376 7.642 7.908 8.174 8.44 8.706 8.972 9.238
70
2.932 3.22 3.507 3.795 4.082 4.37 4.658 4.945 5.233 5.52 5.808 6.095 6.383 6.671 6.958 7.246 7.533 7.821 8.109 8.396 8.684 8.971 9.259 9.547 9.834 10.12
75
3.225 3.534 3.843 4.152 4.461 4.77 5.079 5.388 5.698 6.007 6.316 6.625 6.934 7.243 7.552 7.861 8.17 8.479 8.788 9.097 9.406 9.715 10.02 10.33 10.64 10.95
80
3.465 3.795 4.126 4.456 4.787 5.117 5.448 5.778 6.109 6.439 6.77 7.1 7.431 7.761 8.092 8.422 8.753 9.083 9.414 9.744 10.07 10.41 10.74 11.07 11.4 11.73
85
3.65 4.002 4.354 4.706 5.058 5.41 5.762 6.114 6.466 6.818 7.17 7.522 7.874 8.226 8.578 8.93 9.282 9.634 9.986 10.34 10.69 11.04 11.39 11.75 12.1 12.45
90
3.783 4.156 4.529 4.903 5.276 5.65 6.023 6.397 6.77 7.144 7.517 7.89 8.264 8.637 9.011 9.384 9.758 10.13 10.5 10.88 11.25 11.62 12 12.37 12.75 13.12
95
3.861 4.256 4.651 5.046 5.441 5.836 6.23 6.625 7.02 7.415 7.81 8.205 8.6 8.995 9.39 9.785 10.18 10.57 10.97 11.36 11.76 12.15 12.55 12.94 13.34 13.73
100
4.09 4.502 4.914 5.326 5.738 6.15 6.562 6.974 7.386 7.798 8.211 8.623 9.035 9.447 9.859 10.27 10.68 11.1 11.51 11.92 12.33 12.74 13.16 13.57 13.98 14.39
105
4.404 4.838 5.271 5.705 6.139 6.572 7.006 7.439 7.873 8.306 8.74 9.173 9.607 10.04 10.47 10.91 11.34 11.77 12.21 12.64 13.08 13.51 13.94 14.38 14.81 15.24
110
4.665 5.12 5.575 6.03 6.485 6.94 7.395 7.85 8.305 8.76 9.215 9.67 10.13 10.58 11.04 11.49 11.95 12.4 12.86 13.31 13.77 14.22 14.68 15.13 15.59 16.04
115
4.873 5.349 5.826 6.302 6.778 7.255 7.731 8.208 8.684 9.161 9.637 10.11 10.59 11.07 11.54 12.02 12.5 12.97 13.45 13.93 14.4 14.88 15.35 15.83 16.31 16.78
120
5.026 5.524 6.022 6.52 7.018 7.516 8.014 8.512 9.01 9.508 10.01 10.5 11 11.5 12 12.5 12.99 13.49 13.99 14.49 14.98 15.48 15.98 16.48 16.98 17.47
125
5.126 5.646 6.165 6.684 7.204 7.723 8.243 8.762 9.281 9.801 10.32 10.84 11.36 11.88 12.4 12.92 13.44 13.96 14.48 14.99 15.51 16.03 16.55 17.07 17.59 18.11
Transmission Time, sec
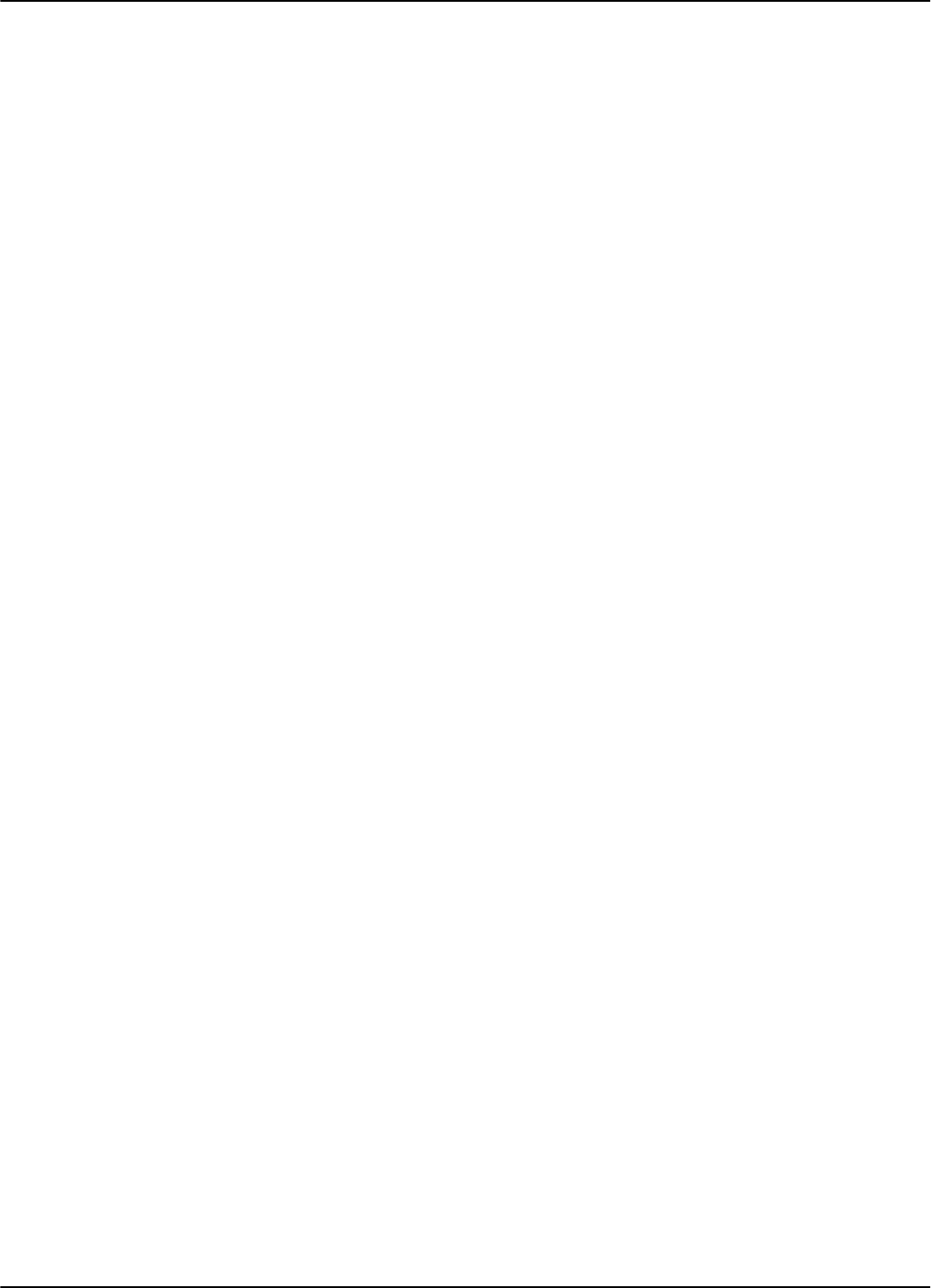
Message Format
B-6 Transponder T95 Messages
This page intentionally left blank.
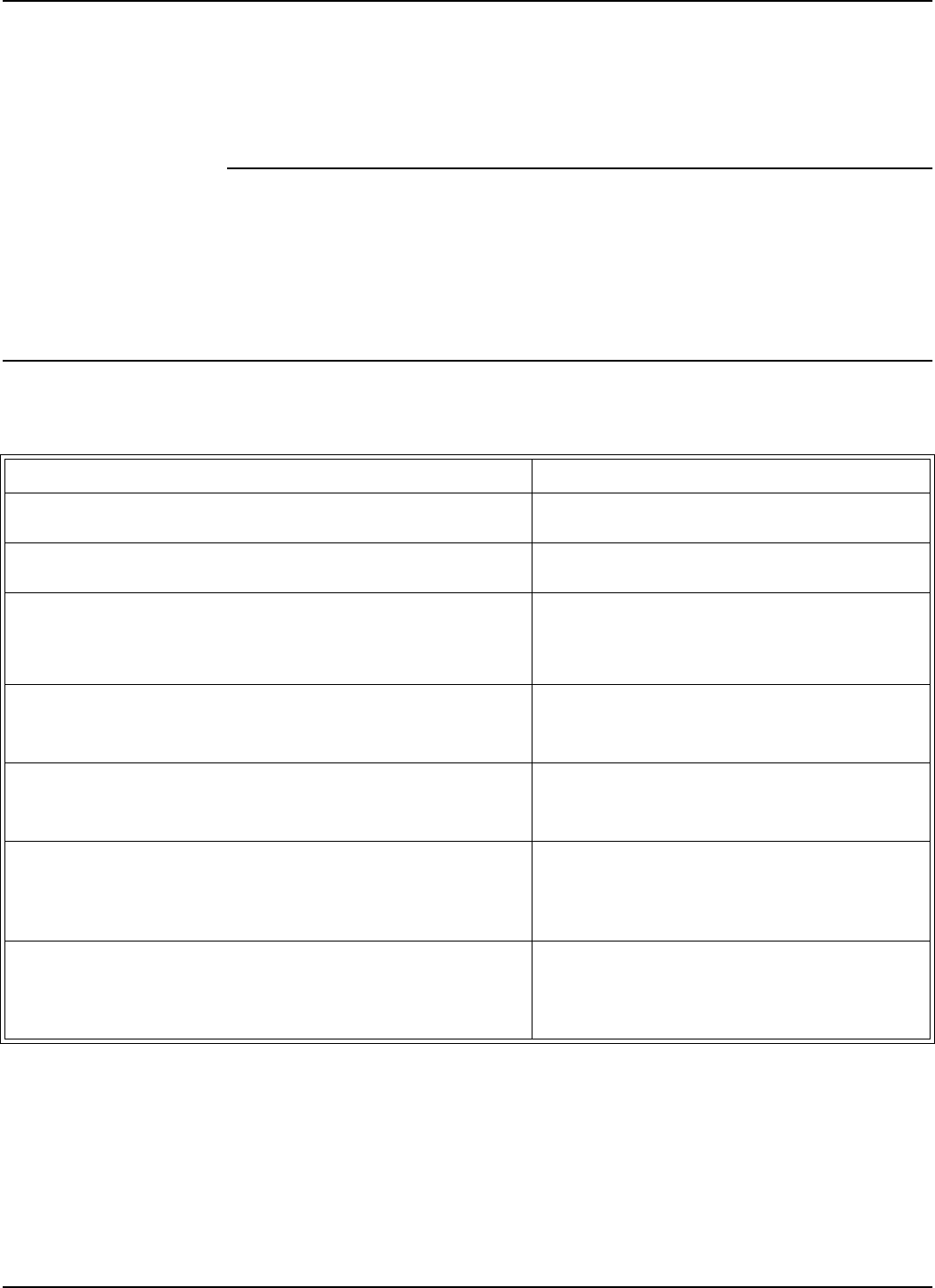
Excitation Modes and Parameter Settings
Excitation Modes C-1
Appendix C
Excitation Modes
This appendix describes the various excitation modes (signal descriptions) and their
associated parameter settings.
Excitation Modes and Parameter Settings
The table below lists the excitation modes and the associated parameter settings.
Note (x)-canbeanything.
Excitation Mode [Signal Description] Parameter Settings
Continuous DC Mode (DC)
[Continuous Unmodulated Carrier (131.5kHz))]
RCS =N; RES=N; REM=C; RET=D; HCC=x;
HCS=x; HE1=x; HE0=x
Continuous AC Mode (AC)
[Continuous Carrier (131.5kHz), modulated ON/OFF by 610 Hz.]
RCS =N; RES=N; REM=C; RET=A; HCC=x;
HCS=x; HE1=x; HE0=x
Alternating Mode (ACDC)
[AC mode for 0.2s, followed by DC mode for 0.2s, and NO signal
for 0.1s. When a message is received, the existing excitation
type is extended for 0.5 s, and the cycle starts again.]
RCS =N; RES=N; REM=A; RET=x HCC=x;
HCS=x; HE1=x; HE0=x
Switching DC Mode (SMDC).
[Switching between DC mode for *10ms, and NO signal for
*10ms.]
RCS =N; RES=Y; REM=C; RET=D; HCC=x;
HCS=x; HE1= ; HE0=
Switching AC Mode (SMAC).
[Switching between AC mode for *10ms, and NO signal for
*10ms.]
RCS =N; RES=Y; REM=C; RET=A; HCC=x;
HCS=x; HE1= ; HE0=
Conditional Switching DC Mode (CSDC).
[When a valid message is received, the SMDC mode is modified
as follows: SMDC mode continues for *s, followed by DC mode
for *s, then back to the SMDC mode.]
RCS =Y; RES=Y; REM=C; RET=D; HCC= ;
HCS= ; HE1= ; HE0=
Conditional Switching AC Mode (CSAC).
[When a valid message is received, the SMAC mode is modified
as follows: SMAC mode continues for *s, followed by AC mode
for *s, then back to the SMAC mode.]
RCS =Y; RES=Y; REM=C; RET=A; HCC= ;
HCS= ; HE1= ; HE0=
Table C-1: Excitation Modes - Parameter Settings
α
β
αβ
α
β
αβ
γ
δ
δ
γαβ
γ
δ
δ
γαβ
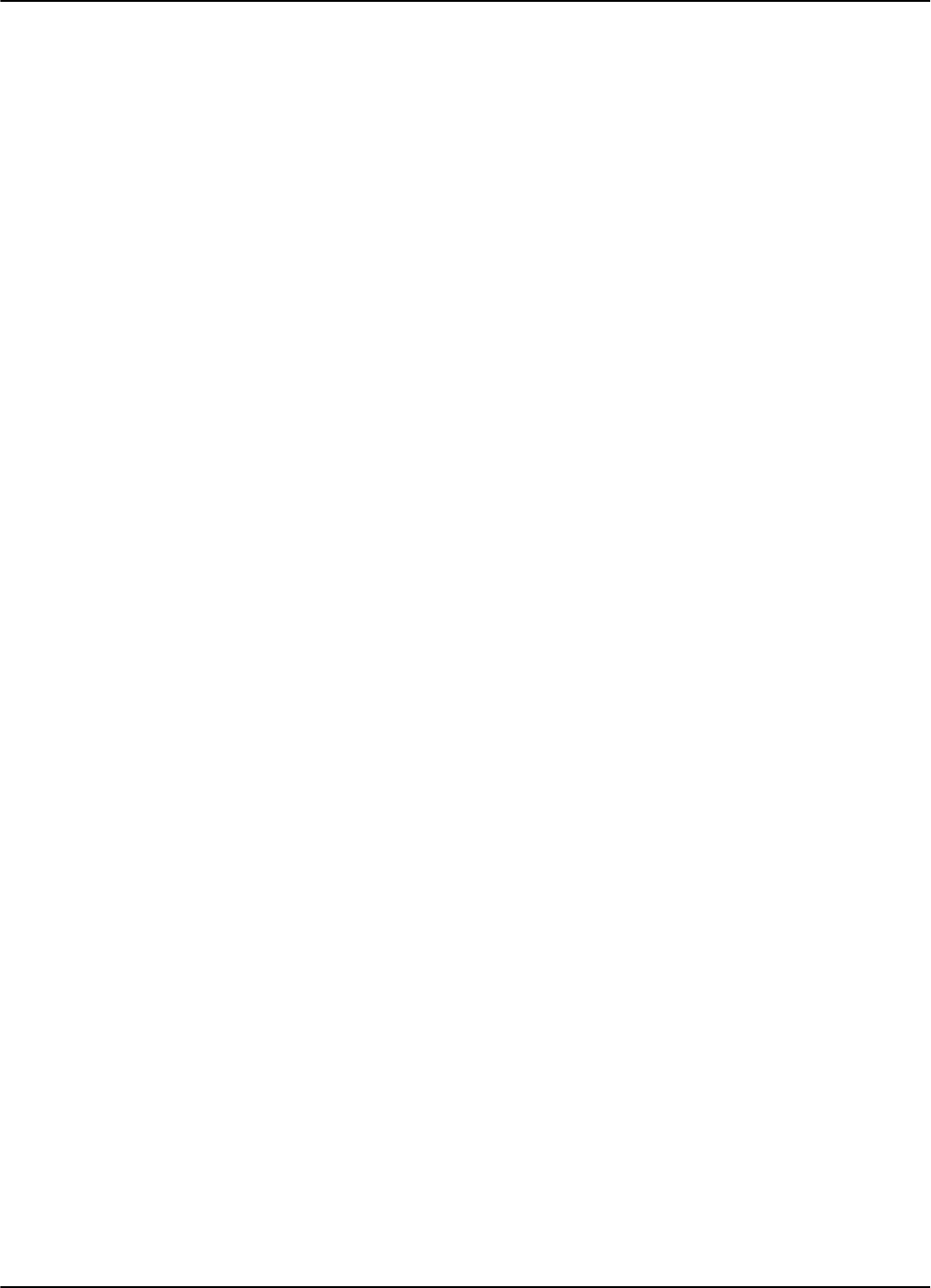
Excitation Modes and Parameter Settings
C-2 Excitation Modes
This page intentionally left blank.
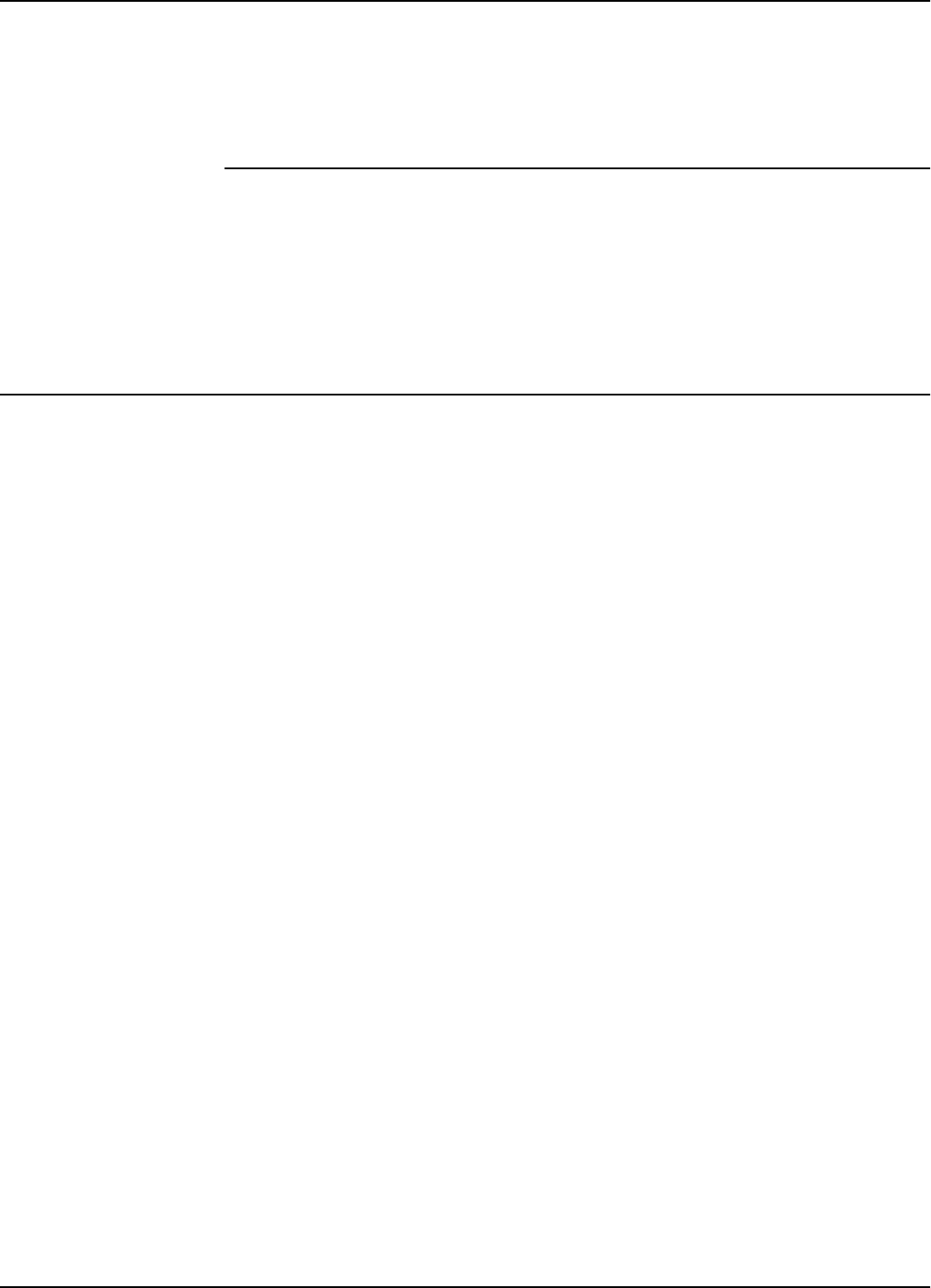
Upgrading the Firmware
Reader Software Upgrade Procedure D-1
Appendix D
Reader Software Upgrade Procedure
This appendix describes the procedures for upgrading the Reader R95 (P/N 600405)
main software using the serial interface RS232 or RS485. This software controls the
functionality of the Microcontroller placed on the Receiver assembly CRM95
(P/N 500056). This procedure refers particularly to the upgrading process for software
version 1.68.02.
Upgrading the Firmware
Upgrading the firmware involve the following steps:
1. Setting the Reader’s Address to 0
2. Saving parameters: HV0, HV1, ISC, ISN
3. Upgrading the firmware itself by using:
a) The RS232 interface
or b) The RS485 interface: 4-wire communication line or 2-wire communication line
3. Restoring parameters: HV0, HV1, ISC, ISN
4. Setting the Reader’s Network Configuration
5. Final instructions
Setting the Reader’s
Address
To set the Reader’s address, do the following:
1. If the Reader already has an address, for example r, then set this address to 0 by
typing the following commands:
@r IAD=0<Enter>
@r :CONFIG:STORE<Enter>
@r :RESET<Enter>
For more information, refer to Storing the Reader’s Configuration on page 5-13.
2. Check whether the Reader’s address is 0, by typing the following command:
IVN<Enter>
The Reader must respond with its software version number. If not, repeat Step 1.
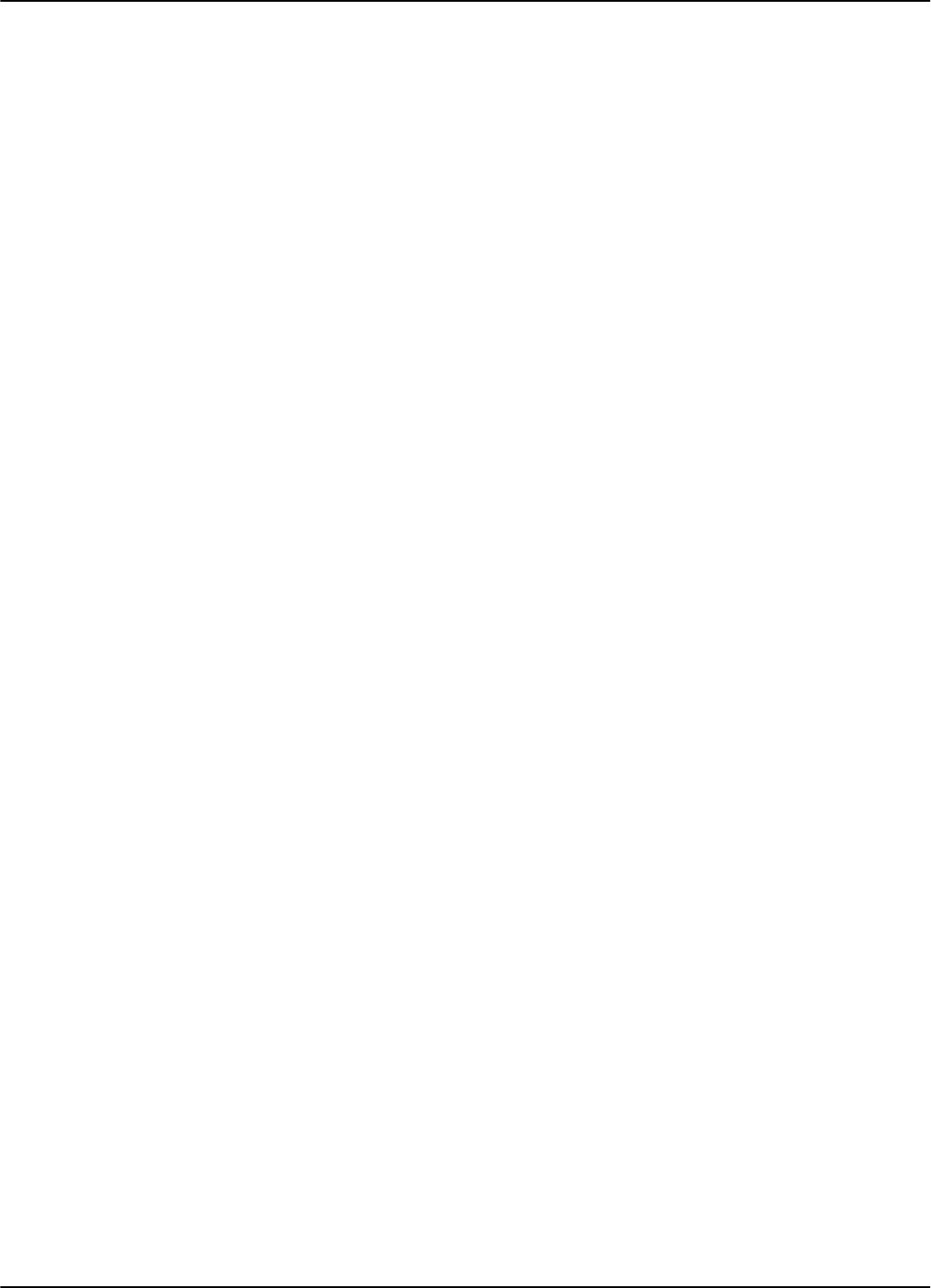
Upgrading the Firmware
D-2 Reader Software Upgrade Procedure
Saving Parameters Follow these steps:
1. Write down the values of the following parameters: HV0, HV1, ISC, ISN.
Note To determine a parameter’s value, for example, HV1, type the following command:
HV1<Enter>
For example, the Reader responds:
HV1=125
where 125 is the parameter value.
2. If the Reader was already configured, write down all parameters whose values
differ from the set default values. For more information, refer to Chapter 1, Quick
Reference in the 95 Series RFID System Reference Guide.
For example, for an IPC installation, write down the values for the following
parameters: DCI, DRI, HTL, RCC, RSS.
Using the RS232
Interface
Follow these steps:
1. Connect your PC (COM port) to the Reader R95 (RS232 interface) using a
standard RS232 cable. For more information, refer to Setting Up the Reader/PC
Connection on page 5-2.
2. Start the upgrading procedure by typing the following command:
:CONFIG:FIRMWARE:LOAD<Enter>
or type the following shortcut:
F<Enter>
3. Start XMODEM, send protocol on the PC, and then send the new firmware file.
Lyngsoe recommends having the new file on your hard drive and not on a floppy
disk.
4. Wait until the transfer process is complete. If the 95 Series RFID System aborted
the transfer process, repeat Step 2.
5. If the downloading process was successful, wait for the Reader to reset - it takes
about 5-7 seconds. For more information on the Reader’s power-up sequence, refer
to Reader’s Power-up Sequence on page 5-3. If the Reader did not reset properly
anddidnotsendasign-onmessage,thenswitchtheReader’spowersupplyOff
and then On.
6. To verify whether the upgrade process was successful, type the following
command:
IVN<Enter>
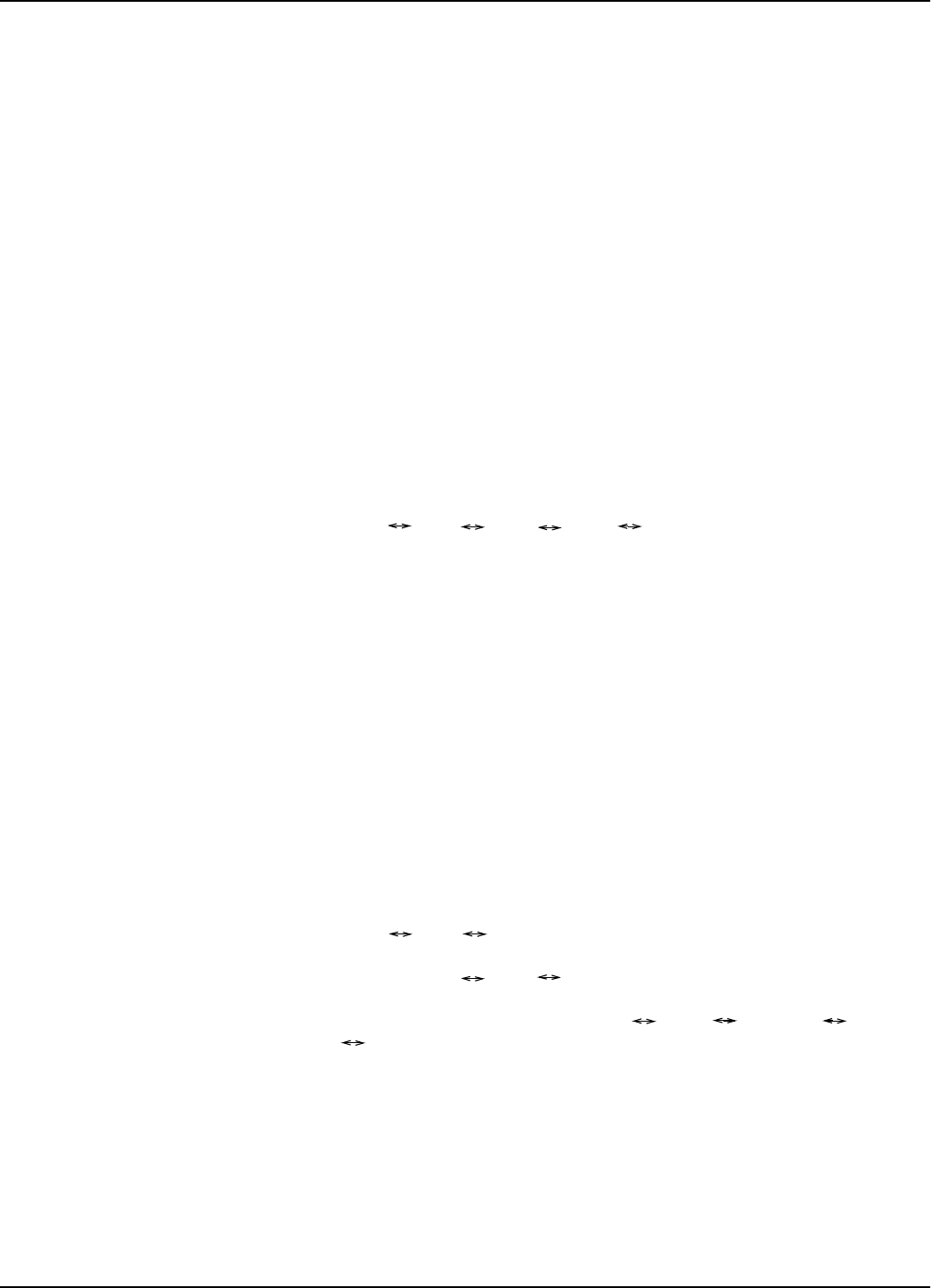
Upgrading the Firmware
Reader Software Upgrade Procedure D-3
The Reader must respond with the new firmware version number:
CRM95 V1.68.02, BUILT: 02/03/98 13:01:12
If not, repeat the procedure from Step 2.
7. If after completing Step 5, you still cannot communicate with the Reader, replace
the Reader with another unit and return the faulty one to Lyngsoe.
Using the RS485
Interface
4-wire
Communication
Line
Follow these steps:
1. Connect your PC (COM port) to a Converter RS232/RS485. Connect the 4-wire
communication line to the Converter (RS485 side). For more information on the
communication line connection to the Reader, refer to Connecting the RS-485
Four-Wire Communication Line on page 2-4 and Setting Up the Reader/PC
Connection on page 5-2.
You can have a different assignment for the RS485 interface on the Converter
side. Use the following conventions for the connections between the Reader R95
and the PC:
2. To upgrade the Reader’s software, follow steps Steps 2 - 5 in Using the RS232
Interface above.
Using the RS485
Interface
2-wire
Communication
Line
Follow these steps:
1. Connect your PC (COM port) to a Converter RS232/RS485. Connect the 2-wire
communication line to the Converter (RS485 side). For more information on the
communication line connection to the Reader, refer to Connecting the RS-485
Two-Wire Communication Line on page 2-3 and Setting Up the Reader/PC
Connection on page 5-2.
You can have a different assignment for the RS485 interface on the Converter
side. Use the following conventions for the connections between the Reader R95
and the PC:
Or as an alternative:
Place the wire jumpers between terminal
and
2. To control the RS485 interface on a 2-wire communication line, you must use the
special software on the PC to allow hardware flow control. For example, Lingso’s
RS485 software to communicate with the Reader and Readerfw to upgrade the
Reader’s software. For more information on the software, refer to the Lingso
documentation.
3. To upgrade the Reader’s software, follow steps Steps 2 - 5 in Using the RS232
Interface above.
ATX+;BTX+;
YRX+;ZRX-.
AY,andBZ;andTX+ RX+
TX- RX- respectively.
A TX+; B TX+;Y RX+; Z RX-.
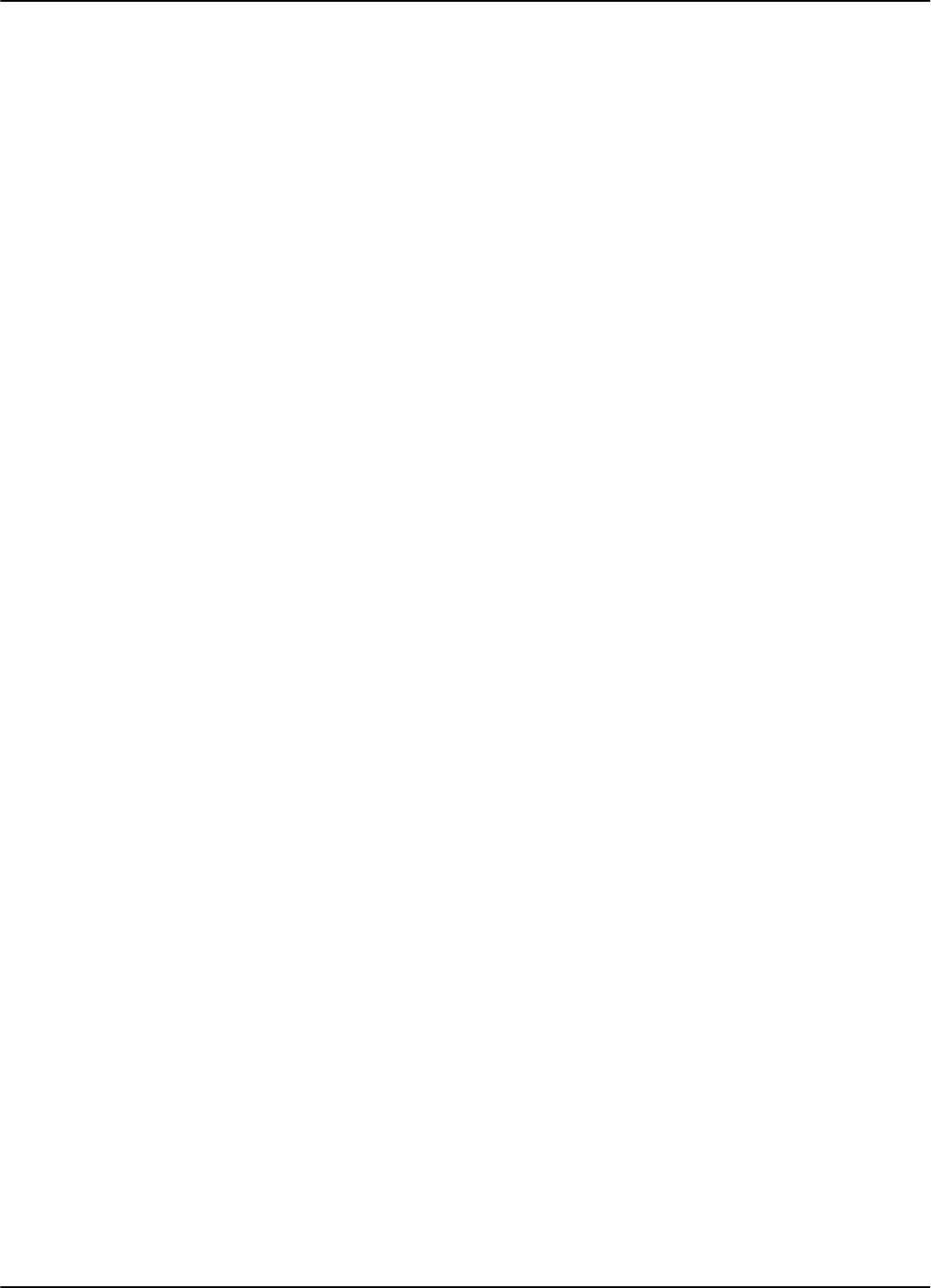
Upgrading the Firmware
D-4 Reader Software Upgrade Procedure
Restoring Parameters Follow these steps:
1. Verify whether parameters were erased during the upgrade procedure, by typing:
ISC<Enter>
2. If the Reader responds with
ISC=0
then the original parameter values were erased and they were set to their default
values.
3. Reset the parameters HV0, HV1, ISC, ISN to their original values prior to the
upgrade process. You recorded them during the Saving Parametersstep.
Note a) Firmware V1.68.02 ignores leading zeros for integers.
b) If the Reader was already configured on the site, you have to restore all
application parameters queried during the Saving Parametersstep, or restart the
configuration process as described in Chapter 5, Configuration and Operation.
3. Check the values of the new parameters that were introduced by this software
version. For example, For an IPC installation, the following parameters must
have the default values as follows:
HCC=8, HCS=7, HE0=18, HE1=6, RCS=Y, RES=Y, SFC=N
Setting the Reader’s
Network Configuration
To set the Reader’s network configuration, do the following:
1. Set the Reader’s address to it initial value (see step 1 in Setting the Reader’s
Address): by typing:
IAD=r<Enter>
2. Store the Reader’s parameters, by typing:
:CONFIG:STORE<Enter>
3. Reset the Reader, by typing:
:RESET<Enter>
4. Verify that the Reader is functioning properly, by typing:
@r IVN<Enter>
where ris the Reader’s address. The Reader must respond with its software
version number.
5. Verify that the parameters set in the following sections are correct:
•Steps2and3fromthesection,Restoring Parameters above.
• Step 1 in this section.
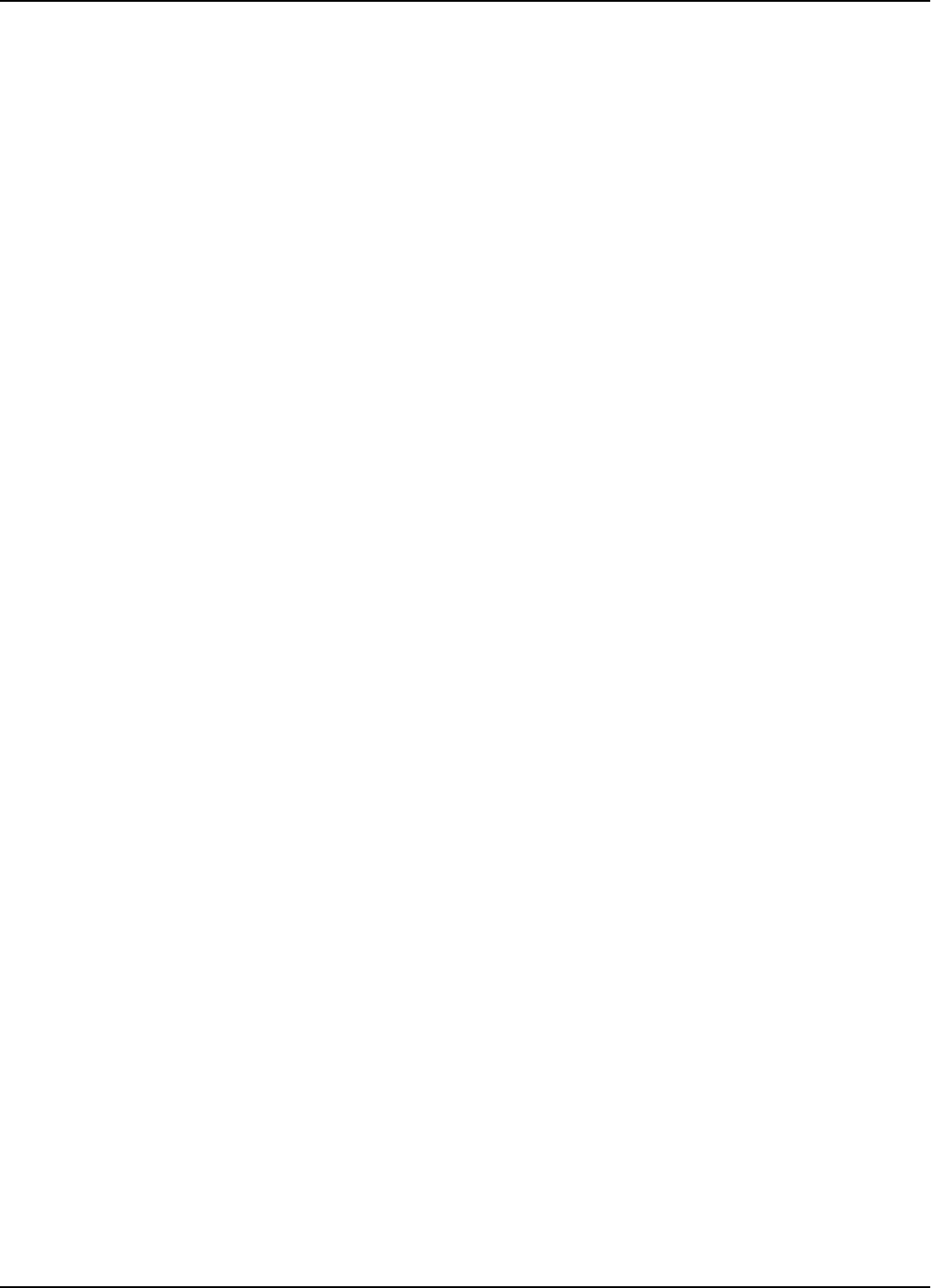
Upgrading the Firmware
Reader Software Upgrade Procedure D-5
Final Instructions 1. You must repeat this procedure for each Reader R95 that is installed on the site.
2. Lyngsoe recommends using the RS232 or RS485 4-wire communication line to
upgradetheReader’ssoftware(thesearemorereliablecommunicationlinks).
3. For more information on the Reader’s R95 configuration, see Chapter 5,
Configuration and Operation.
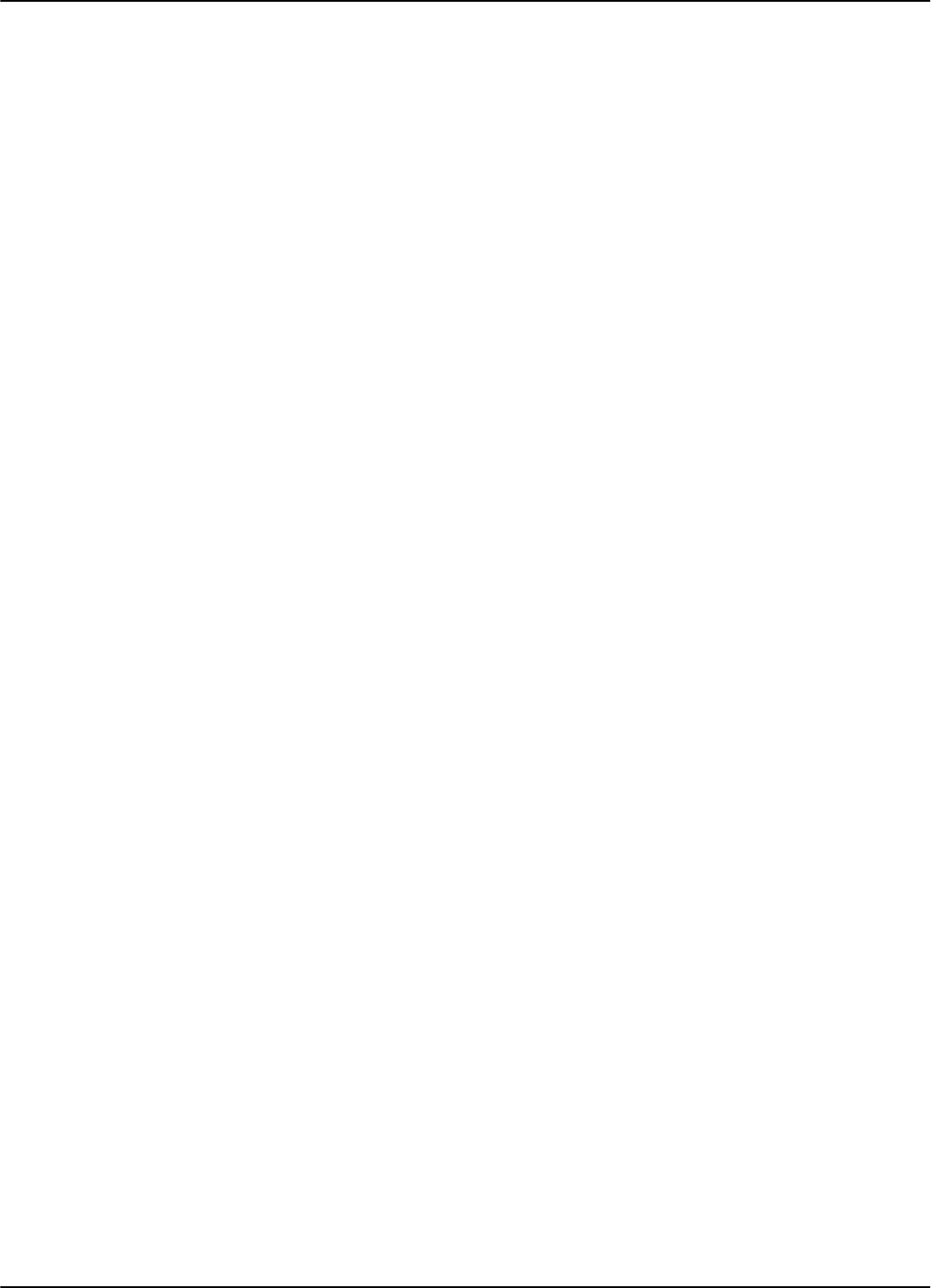
Upgrading the Firmware
D-6 Reader Software Upgrade Procedure
This page intentionally left blank.
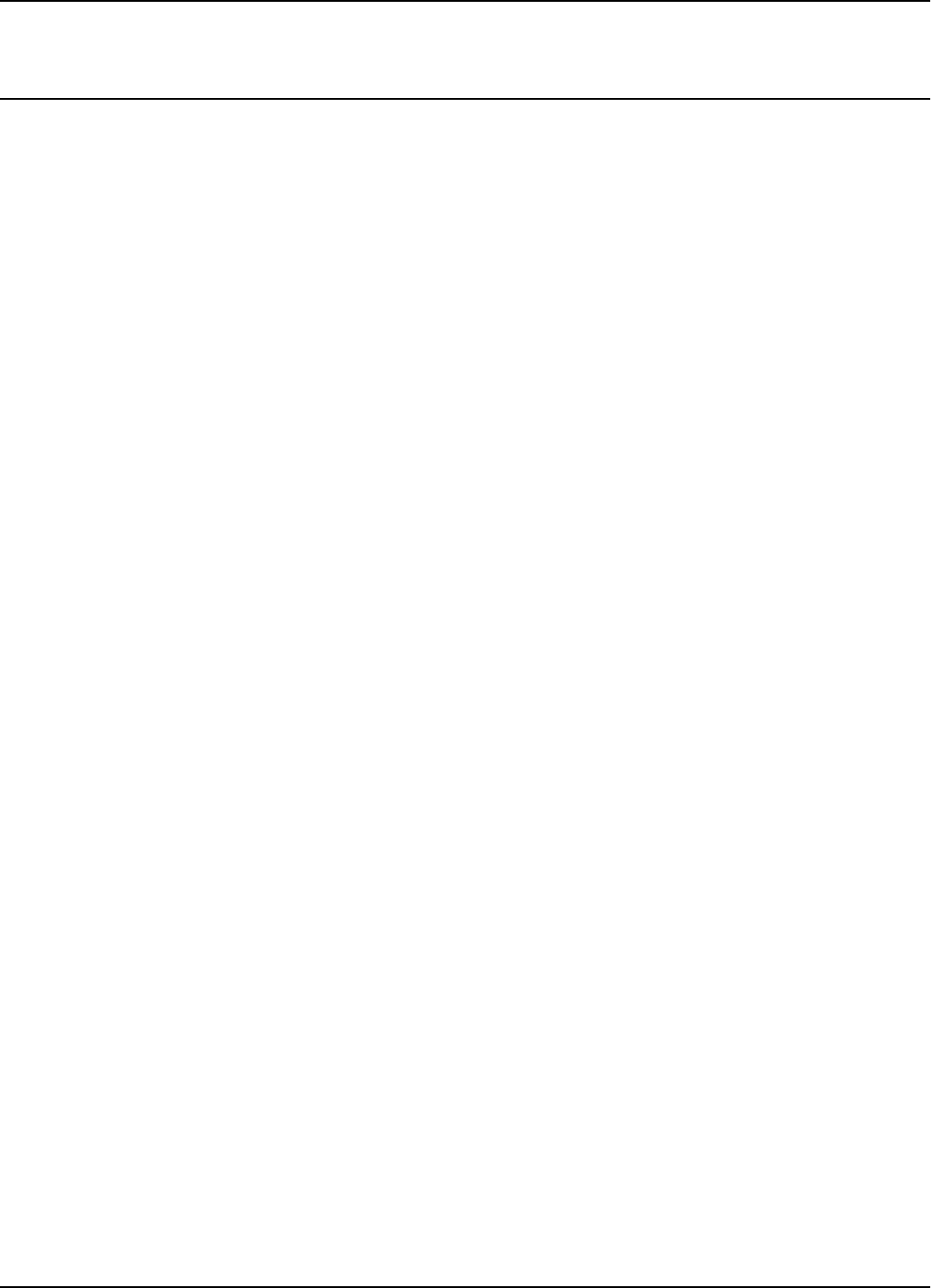
Glossary
Glossary G-1
Glossary
a.c. (ac)
Alternating current.
ASCII (American Standard Code for Information Interchange)
A system used to represent alphanumeric data; a 7-bit-plus-parity character set established by ANSI and
used for data communications and data processing.
Bit A binary digit; the smallest unit of data in the binary counting system, A bit has a value of either 0 or 1.
Byte
A group of eight bits that represent one data character.
Carrier
A signal that is modulated by a message signal to allow communication.
Channel
A communication path between a transmission source and receiver.
CMOS
See Complementary metal-oxide semiconductor.
Complementary metal-oxide semiconductor (CMOS)
A technology that combines the electrical properties of n-type semiconductors and p-type semiconductors.
Cut-off frequency
Frequency at which a circuit output falls to a specified fraction (usually half) of the maximum.
dB Decibel. Dimensionless unit expressing the ratio of two powers, voltages or currents.
d.c. (dc)
Direct current.
Duplex
Simultaneous operation of both channels of a communication link.
EEPROM
Electrically erasable programmable read only memory.
FM See Frequency modulation.
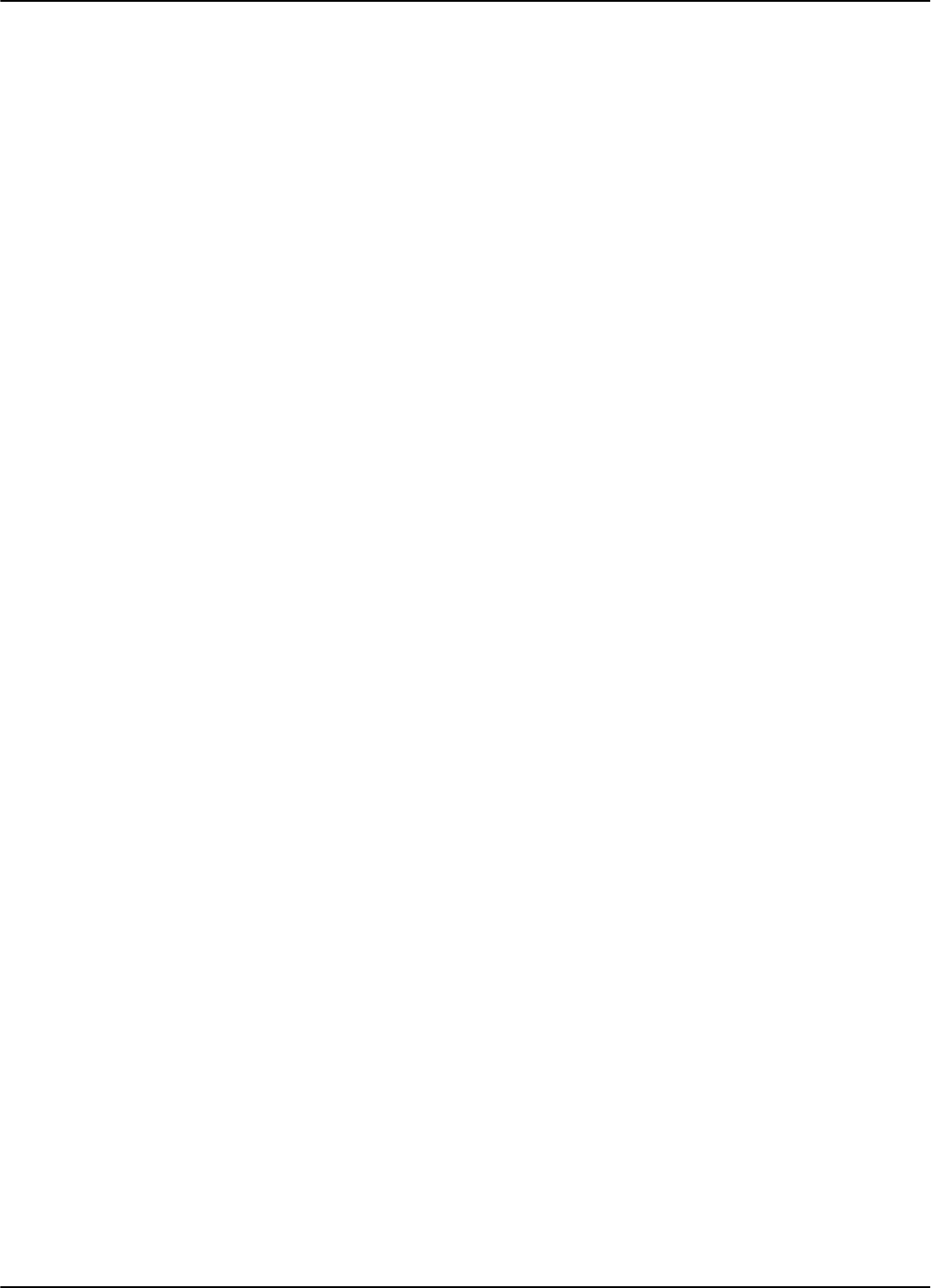
Glossary
G-2 Glossary
Frequency Modulation (FM)
Modulation by varying the frequency of a fixed-amplitude carrier signal in accordance with an
information signal. Contrast with amplitude modulation (AM).
Frequency-Shift Keying (FSK)
Frequency modulation of a carrier by a digital modulating signal.
FSKSee Frequency-shift keying.
LEDSee light emitting diode.
LF Abbreviation for low frequency band-30 to 300 kHz.
Light-emitting diode (LED)
A unit that accepts electrical impulses and converts them into a light signal.
OOK
On/Off Keying.
PCBPrinted circuit board.
PEROM
Programmable and erasable read only memory.
RAM
See Random Access Memory.
Random Access Memory (RAM)
Semiconductor-based memory that can be read and written by the microprocessor or other hardware
devices. (Generally referred to as volatile memory that can be written or read.)
Read Only Memory (ROM)
Semiconductor-based memory that contains instruction or data that can be read but not modifies.
(Generally, the term ROM often means any read-only device.)
RFID
Radio Frequency Identification.
ROM
See Read Only Memory.
Rx Receiver.
SRAM
Static Read Only Memory.
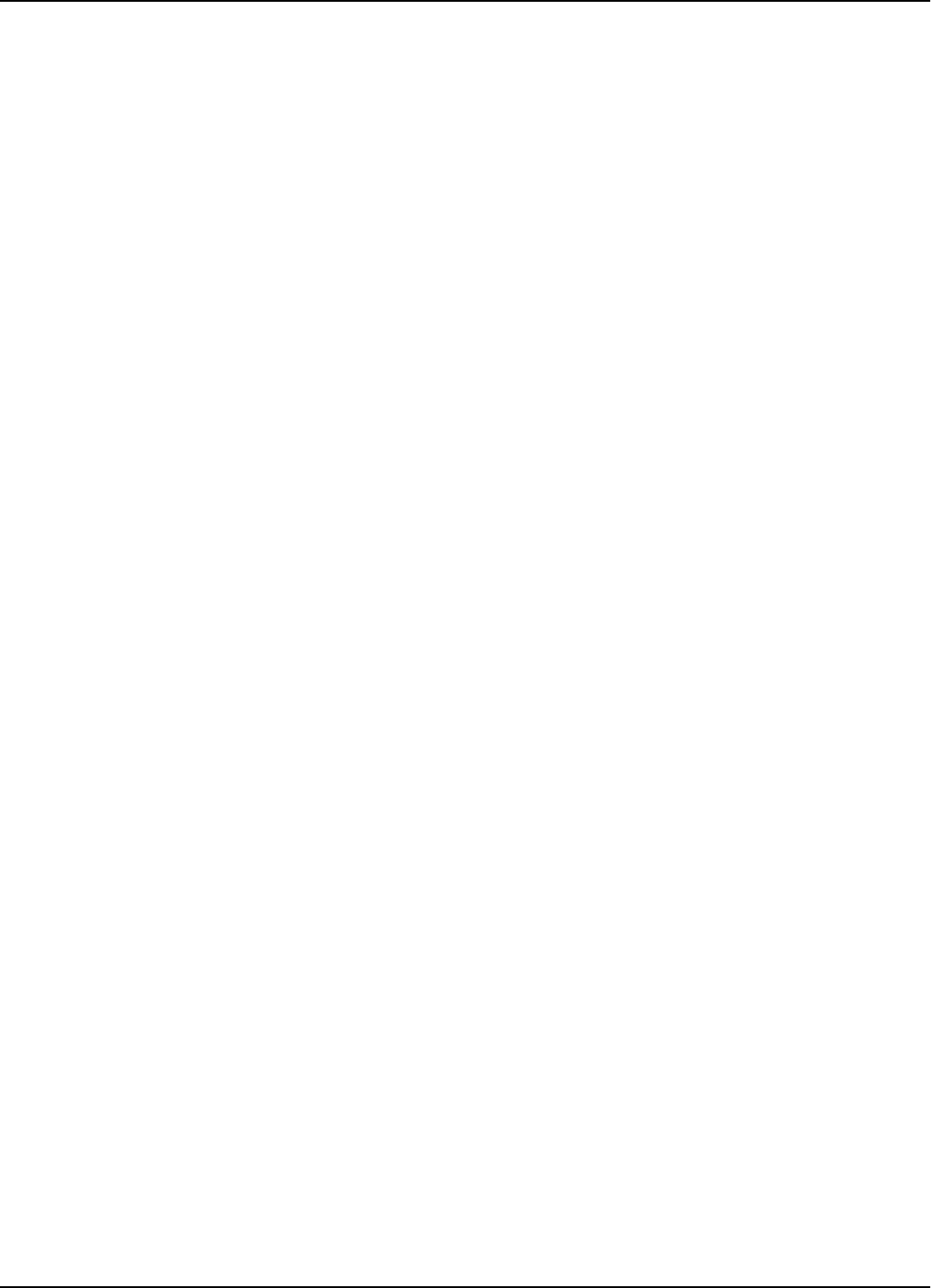
Glossary
Glossary G-3
Tx Transmitter.
UHF
Ultra High Frequency band - 30 to 300 MHz.
µC Microcontroller.
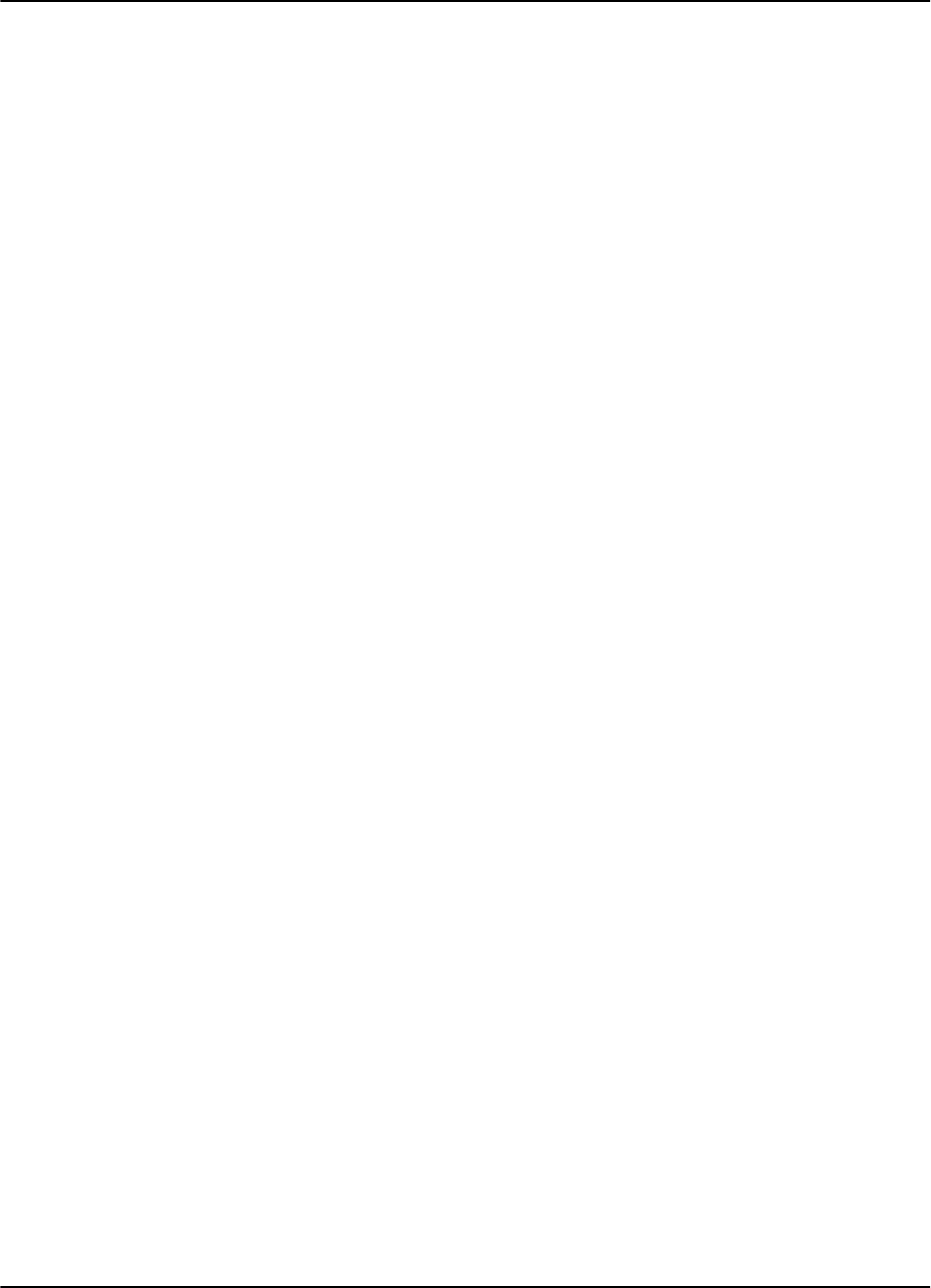
Glossary
G-4 Glossary
This page intentionally left blank.
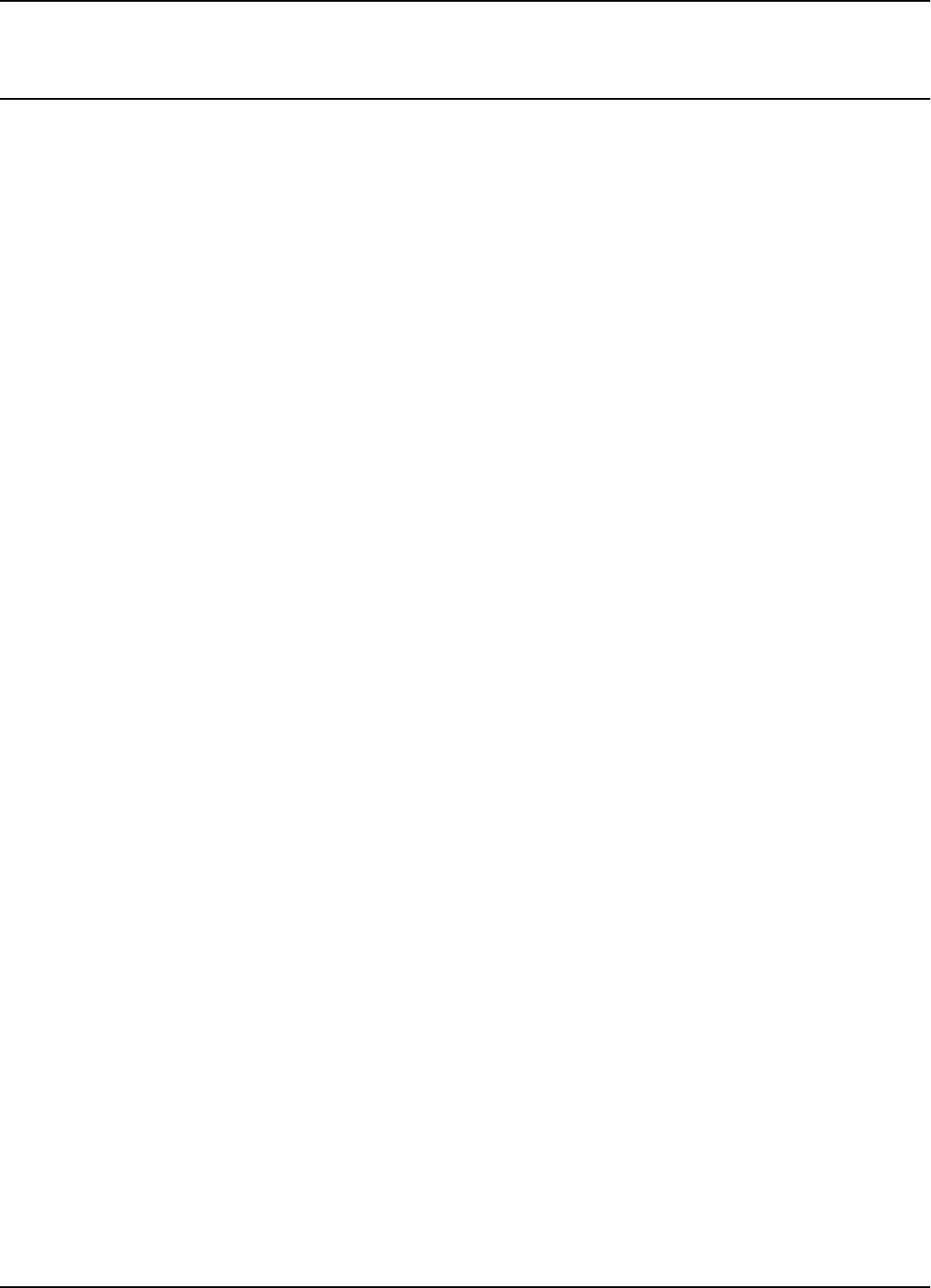
Index
Index I-1
Index
A
AC Source TRM95 A-5
C
configuration principles 1-3–1-5
Configuring
Reader’s application
parameters 5-12
D
description
reading points 1-2
response signal 1-2
Transponders 1-2
E
excitation modes C-1
Exciter
assembling the LF antenna 3-2
connecting the power supply 3-5
connecting the RS-485
communication lines 3-3
installing 3-1
LF antenna connections 3-3
setting up addresses 5-5
setting up the test-tag 5-11
tools required 3-1
UHF tranmsitter 3-6
Exciter address 1-5
Exciters
hardware specifications A-4
G
general rules 1-3
H
hardware specifications A-1
L
learning procedure 5-3
LF transmitter output 5-6
M
manual
definitions i
summary i
text conventions i
message format
Transponder B-1
P
parameter settings C-1
parameters
Transponder B-1
Postal RFID System
components 1-3
descripiton 1-3
using 1-2
Power Supply
tools required 4-1
programming site
setting up 6-1
R
Reader 2-1
assembling 2-1
checking parameters 5-4
configuring 5-8
configuring application
parameters 5-12
configuring the network
parameters 5-13
connecting external devices 2-9
connecting the Exciter
communication line 2-6
connecting the power supply 2-7
connecting the RS-232
communication line 2-2
connecting the RS-485 2-wire
communication line 2-3
connecting the RS-485 4-wire
communication line 2-4
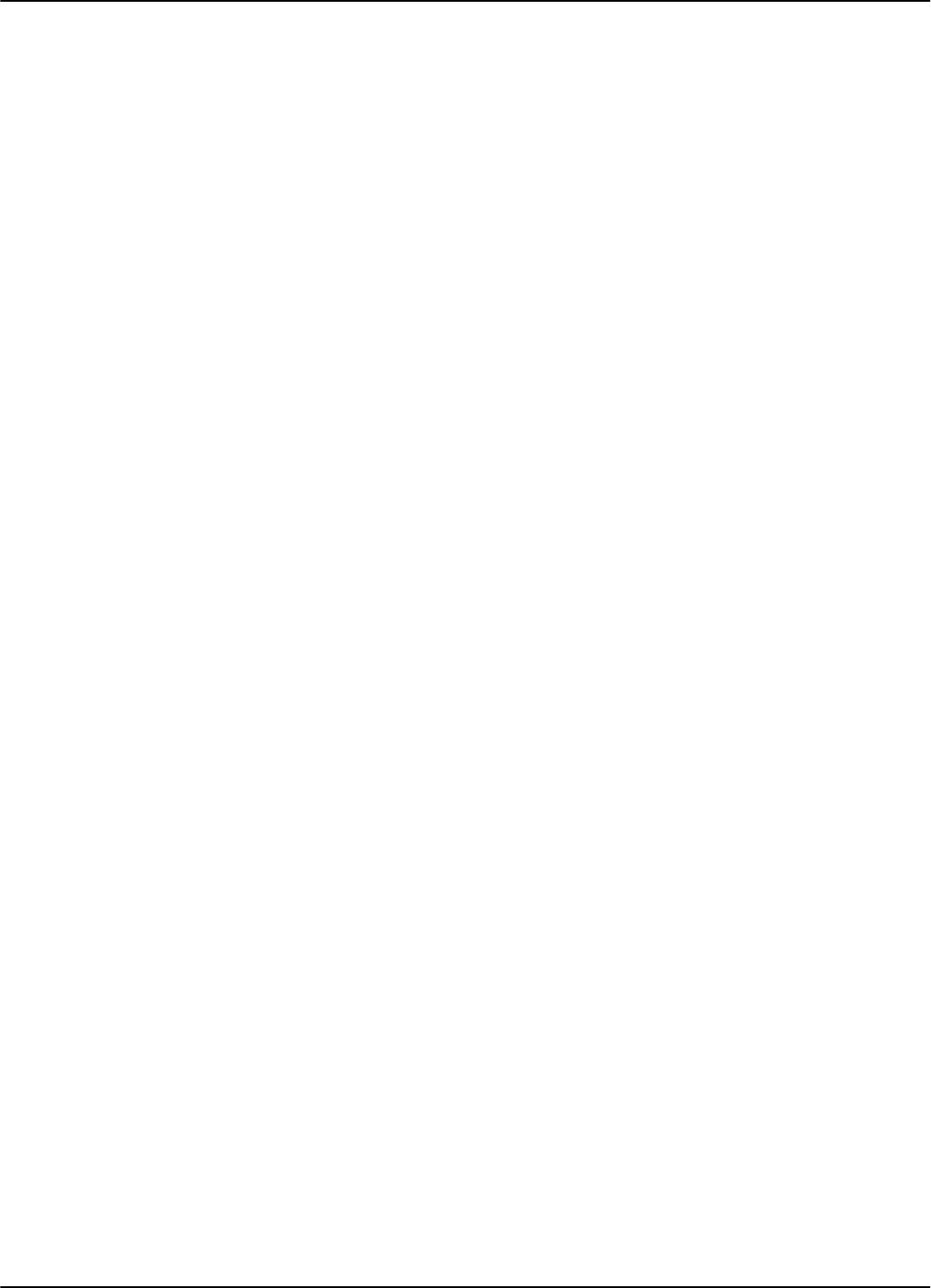
Index
I-2 Index
power-up sequence 5-3
resetting 5-4
storing the configuration 5-13
reader address 1-4
Reader data handling 1-4
Reader serial port 1-4
Readers
communicating with
Transponders 1-2
hardware specifications A-2
system performance A-5
reading points
description 1-2
real time clock 1-4
related manuals ii
response signal
description 1-2
RFID System
configuring 5-1–5-16
self testing capabilities A-6
S
setting up carrier threshold 5-9
setting up the Reader/PC
connection 5-2
setting up the Real Time Clock 5-12
system code 1-4
system performance
Readers A-5
Transponders A-5
T
testing
System 95 5-14
text conventions ii
Transponder
message format B-1
parameters B-1
programming 6-1–6-2
programming procedure 6-2
Transponder Identification System
purpose 1-1
Transponders
communicating with Readers 1-2
decription 1-2
examples 1-2
hardware specifications A-1
system performance A-5
Troubleshooting 7-1–7-8
U
UHF data receiving 1-4
upgrade procedures
upgrading the firmware D-1
upgrading procedures
final instructions D-5
restoring parameters D-4
saving parameters D-2
setting the Reader’s address D-1
setting the Reader’s network
configuration D-4
using the RS232 Interface D-2
using the RS485 Interface D-3