MARKEM 811RFID FHSS RFID Tag Reader User Manual 10008547aa 800 Series RFID
MARKEM Corporation FHSS RFID Tag Reader 10008547aa 800 Series RFID
MARKEM >
Exhibit D Users Manual per 2 1033 b3
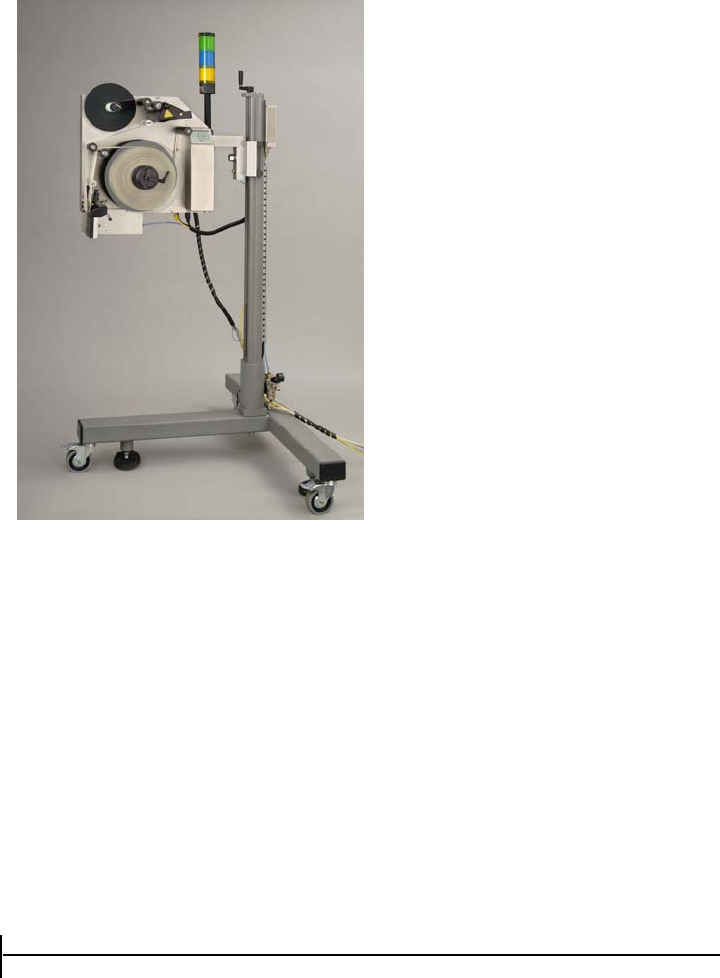
Model 811
Operation/Service Manual
m
®
Operation/Service Manual
Model 811 (English Version)
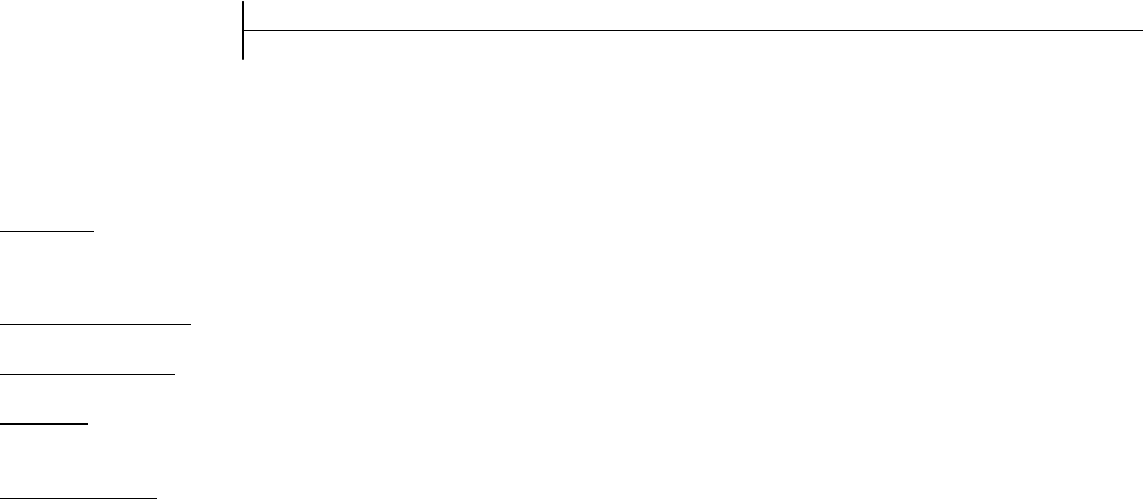
m®
150 Congress Street, PO Box 2100, Keene, New Hampshire 03431-7100
TEL : 603-352-1130 FAX: 603-357-5871 http://WWW.MARKEM.com
WARRANTY
All MARKEM products are warranted to be free of defects in materials and workmanship and to conform to MARKEM
specifications in effect at the date of shipment. Any changes Buyer requests to MARKEM specifications are not effective
without advance, written authorization by MARKEM. The warranty period is as follows:
Machines: One year from date of shipment or 2000 operating hours, whichever expires first, unless any specific
machine is designated as Made to Order ("MTO"), in which event the warranty period is 90 days from date
of shipment.
Ink Jet Orifice Plates (on new machines and as replacement parts): 90 days from date of shipment.
Replacement Parts: 90 days from date of shipment.
Software: 90 days from date of shipment. Warranty does not entitle Buyer to new releases, upgrades or
enhancements introduced during the warranty period.
Supply Products: For the period of shelf life of the supplies as stated in the applicable specification standards or
one year from the date of shipment if not specified.
During the warranty period, MARKEM will, at its option, repair, replace or refund the purchase price of MARKEM
products which prove to be defective in materials or workmanship or which do not conform to the applicable MARKEM
specifications. Within MARKEM service travel areas and for certain products designated by MARKEM, warranty service
for machines and parts will be provided at the installation site. In all other cases, products must be returned to a service
facility designated by MARKEM.
For products returned to MARKEM for warranty repair or replacement, Buyer shall obtain a return authorization number
and shipping instructions from MARKEM and return the product shipping charges prepaid. Shipping charges for the
return of products to Buyer shall be paid by MARKEM within the contiguous forty-eight United States and the District of
Columbia; for all other locations, the warranty excludes all costs of shipping, customs clearance and any other related
charges. All replaced products shall become the property of MARKEM.
The foregoing warranty shall not apply to defects or non-conformance with MARKEM specifications which result from:
(1) improper installation, use, storage, care or maintenance by Buyer; (2) wear resulting from normal use of parts subject
to wear, such as ink rolls, offset pads, foil feeds, thermal transfer print heads, etc.; (3) modification, alteration or retiming
of a MARKEM machine; (4) cycling a MARKEM machine out of specification; or (5) adding a unit timed or driven by a
MARKEM machine; (6) use of products (including supplies) or software not furnished by MARKEM; (7) modification of
products without MARKEM's approval; (8) accident, neglect, misuse or abuse; or (9) exposure conditions outside the
range so the environmental, power and operating specifications provided by MARKEM.
NO OTHER WARRANTY IS EXPRESSED OR IMPLIED. MARKEM SPECIFICALLY DISCLAIMS ANY IMPLIED
WARRANTIES OF MERCHANTABILITY OR FITNESS FOR A PARTICULAR PURPOSE. Determination of the
suitability of the products described on the face hereof is the sole responsibility of the Buyer and MARKEM shall have no
responsibility in connection therewith. BUYER WARRANTS THAT HE IS NOT PURCHASING THE PRODUCTS FOR
PERSONAL, FAMILY OR HOUSEHOLD PURPOSES. THE REMEDIES PROVIDED HEREIN ARE BUYER'S SOLE AND
EXCLUSIVE REMEDIES. MARKEM SHALL NOT BE LIABLE FOR ANY INDIRECT, SPECIAL, INCIDENTAL OR
CONSEQUENTIAL DAMAGES, WHETHER BASED IN CONTRACT, TORT OR ANY OTHER LEGAL THEORY, OR
FOR THE COST OF SUBSTITUTE GOODS. CONSEQUENTIAL DAMAGES for purposes of this Agreement shall
include, without limitation:
1. Loss of use, income or profit, or losses sustained as a result of the injury (including death) to any person or loss or
damage to property, including, without limitation, material manufactured, processed or labeled by the use of the
products.
2. Damages arising out of or in connection with delays in delivery, MARKEM's performance, non-performance or
breach of this contract, defects in the equipment, failure of the products to perform properly or non-conformance of
the products with specifications or the operation, use, installation, repair or replacement of the products.
(Formerly 0874339) REF00037 Rev: 10 12/04
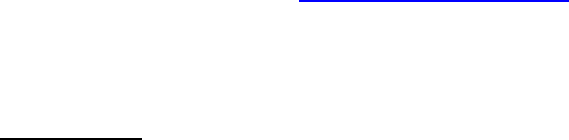
NOTICE
The use of this or any industrial system may involve hazards such as hot
surfaces, sharp objects, or nip points, as well as danger from exposure to
electrical and/or pneumatic power, UV or laser radiation, or hazardous
chemicals. This manual is provided to assist you in the safe and efficient
use of your system. Read and follow the instructions carefully for
maximum safety, and to obtain the best use of your system and supplies.
A Material Safety Data Sheet is provided with each hazardous chemical
product sold by MARKEM. These sheets include information about
composition, properties, usage, and hazards.
All systems and supplies, whether considered hazardous or not, should be
used in accordance with principles of good manufacturing practice.
If you have questions or comments contact
your local MARKEM Business Center
or visit our website at www.MARKEM.com
KNOW HOW TO USE THIS SYSTEM SAFELY
BEFORE YOU START TO USE IT.
0874810 REV. 00 6/96
10008547aa 06/06 m®i
This guide explains the basic operation and care of the Model 811.
Preliminary for Review - June 30, 2006: To the best of our knowledge, the information
contained in this guide was correct at the time of publication. However, continual
enhancement of our products can result in some differences between the instructions
represented in this guide and your machine.
MARKEM is a registered trademark of MARKEM Corporation.
This guide was written by:
MARKEM Corporation
150 Congress Street
Keene, New Hampshire 03431 U.S.A.
Copyright © 2006 by MARKEM Corporation
All rights reserved.
Reference List
The information on your packing slips can be written below for reference. When contacting
MARKEM please give your Model Number, Serial Number, and Customer Account Number.
Model ____________ Serial Number_________________ Date Installed______________
Customer Account Number__________________________________________________
Name of MARKEM Representative_____________________________________________
Options/
Accessories_______________________________________________________________
________________________________________________________________________
________________________________________________________________________
________________________________________________________________________
________________________________________________________________________
________________________________________________________________________
________________________________________________________________________
________________________________________________________________________

TABLE OF CONTENTS
10008547aa 06/06 m®iii
Section 1 General Information
1.0 Welcome to the Model 811. . . . . . . . . . . . . . . . . . . . . . . . . . . . . . . . . . . 1-1
1.1 What is in this Manual?. . . . . . . . . . . . . . . . . . . . . . . . . . . . . . . . . 1-1
1.2 Glossary . . . . . . . . . . . . . . . . . . . . . . . . . . . . . . . . . . . . . . . . . . . . 1-1
2.0 Safety Information . . . . . . . . . . . . . . . . . . . . . . . . . . . . . . . . . . . . . . . . . 1-4
2.1 Machine Safety . . . . . . . . . . . . . . . . . . . . . . . . . . . . . . . . . . . . . . . 1-4
2.2 Modifications to the Model 811 . . . . . . . . . . . . . . . . . . . . . . . . . . . 1-4
2.3 Foreseen Use/misuse. . . . . . . . . . . . . . . . . . . . . . . . . . . . . . . . . . 1-4
2.4 MARKEM Training Programs . . . . . . . . . . . . . . . . . . . . . . . . . . . . 1-4
2.5 Removal from Service. . . . . . . . . . . . . . . . . . . . . . . . . . . . . . . . . . 1-5
3.0 Overview . . . . . . . . . . . . . . . . . . . . . . . . . . . . . . . . . . . . . . . . . . . . . . . . 1-6
3.1 Features . . . . . . . . . . . . . . . . . . . . . . . . . . . . . . . . . . . . . . . . . . . . 1-6
3.2 Tag Dimensions . . . . . . . . . . . . . . . . . . . . . . . . . . . . . . . . . . . . . . 1-6
3.3 Components . . . . . . . . . . . . . . . . . . . . . . . . . . . . . . . . . . . . . . . . . 1-6
3.3.1 Dispenser. . . . . . . . . . . . . . . . . . . . . . . . . . . . . . . . . . . . . . 1-6
3.3.2 Applicator . . . . . . . . . . . . . . . . . . . . . . . . . . . . . . . . . . . . . . 1-6
3.4 Networking . . . . . . . . . . . . . . . . . . . . . . . . . . . . . . . . . . . . . . . . . . 1-7
3.5 Tape Drive System . . . . . . . . . . . . . . . . . . . . . . . . . . . . . . . . . . . . 1-7
3.6 Power Switch . . . . . . . . . . . . . . . . . . . . . . . . . . . . . . . . . . . . . . . . 1-8
3.7 Keypad . . . . . . . . . . . . . . . . . . . . . . . . . . . . . . . . . . . . . . . . . . . . . 1-8
3.8 Beacon Light (Optional) . . . . . . . . . . . . . . . . . . . . . . . . . . . . . . . . 1-9
3.9 Machine Operating Modes . . . . . . . . . . . . . . . . . . . . . . . . . . . . . . 1.9
Section 2 Installation Guide
1.0 Installation . . . . . . . . . . . . . . . . . . . . . . . . . . . . . . . . . . . . . . . . . . . . . . 2-1
1.1 Installation Requirements . . . . . . . . . . . . . . . . . . . . . . . . . . . . . . . 2-1
1.2 Power Configuration . . . . . . . . . . . . . . . . . . . . . . . . . . . . . . . . . . . 2-2
1.3 Air Requirements . . . . . . . . . . . . . . . . . . . . . . . . . . . . . . . . . . . . . 2-3
1.4 I/O Interface . . . . . . . . . . . . . . . . . . . . . . . . . . . . . . . . . . . . . . . . . 2-4
2.0 Positioning the Applicator . . . . . . . . . . . . . . . . . . . . . . . . . . . . . . . . . . . 2-5
3.0 Installation Checklist. . . . . . . . . . . . . . . . . . . . . . . . . . . . . . . . . . . . . . . . 2-5
Section 3 Operating Guide
1.0 Preparing for Operation . . . . . . . . . . . . . . . . . . . . . . . . . . . . . . . . . . . . . 3-1
2.0 The Tape Drive System . . . . . . . . . . . . . . . . . . . . . . . . . . . . . . . . . . . . . 3-1
2.1 Loading Tags . . . . . . . . . . . . . . . . . . . . . . . . . . . . . . . . . . . . . . . . 3-2
2.2 Unwinding a Full Core from the Rewind Hub . . . . . . . . . . . . . . . . 3-6
3.0 Powering Up . . . . . . . . . . . . . . . . . . . . . . . . . . . . . . . . . . . . . . . . . . . . . 3-7
4.0 Operator Interface . . . . . . . . . . . . . . . . . . . . . . . . . . . . . . . . . . . . . . . . . 3-8
4.1 The Keypad. . . . . . . . . . . . . . . . . . . . . . . . . . . . . . . . . . . . . . . . . . 3-8
4.1.1 Keys. . . . . . . . . . . . . . . . . . . . . . . . . . . . . . . . . . . . . . . . . . . 3-8
4.1.2 Keypad LEDs. . . . . . . . . . . . . . . . . . . . . . . . . . . . . . . . . . . 3-10
4.2 Beacon Light (Optional) . . . . . . . . . . . . . . . . . . . . . . . . . . . . . . . 3-10

TABLE OF CONTENTS
iv m®10008547aa 06/06

Model 811
Operation/Service Manual
m
®
SECTION 1
General Information
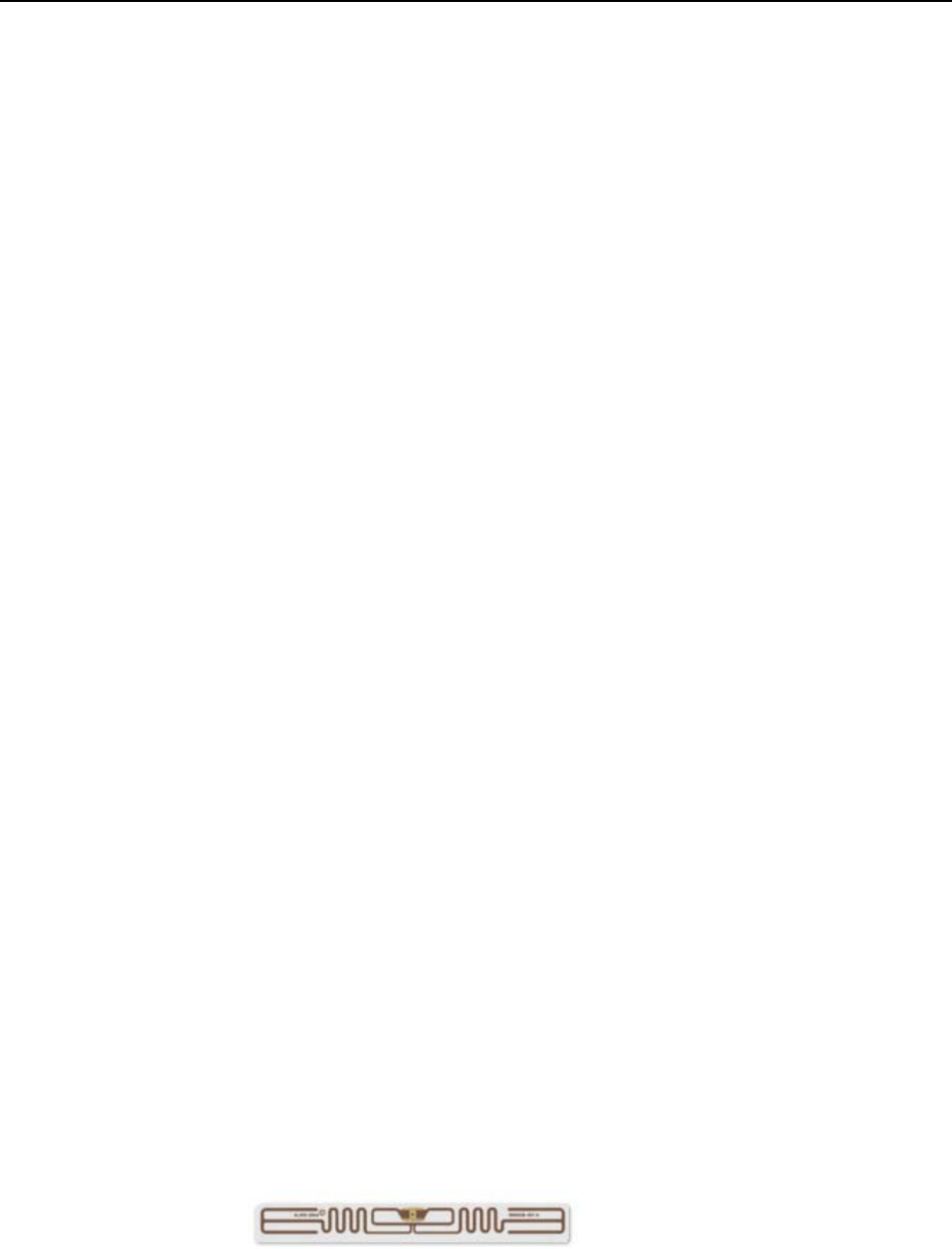
SECTION 1 General Information
10008547aa 06/06 m®1–1
1.0 Welcome to the Model 811
The Model 811 is a high speed, compact RFID tag dispenser and
applicator that is compatible with a full range of MARKEM products.
1.1 What is in this Manual?
The Model 811 manual addresses the basic installation, operation
and care of the RFID tag dispenser, as well as safety, maintenance,
troubleshooting, and service information.
1.2 Glossary
active tags – tags that use batteries as a source of power (can be
either partial or complete power); there are tags with replaceable
batteries and tags that have the batteries inside a sealed unit –
sometimes called unitized active tags
addressability – ability to address bits, fields, files or other portions
of storage in a tag
AK – “Acknowledge” communications response
antenna – conductive elements that radiate and/or receive energy
in the radio frequency spectrum to or from the tag
bi-directional – a tag that can be read or written from either side
capacity – amount of bits or bytes that can be programmed into a
tag; these may be bits accessible to the user, or the total number,
including those reserved for the manufacturer (such as parity or
control bits)
converted RFID – Assembly of an inlay sandwiched between an
adhesive and substrate (usually paper stock) which is then die cut
into a specified size
dispenser – the enclosure that houses the electronics, LUI,
mechanical components, and tape drive system.
electronic tag – a tag that has an electronic RFID tag embedded
within it
EMC – electromagnetic compatibility
frequency – number of times a signal makes a complete pass
through its maximum and minimum values and returns to the same
value (cycles)
gap - the distance between tags (or labels) on the liner (or backing),
measured from the bottom of one tag to the top of the next tag
inlay - an RFID microchip attached to an antenna and mounted on a
substrate; essentially an unfinished RFID label

SECTION 1 General Information
1–2 m®10008547aa 06/06
LUI – Local User Interface; keypad on the Model 811
misread – a condition that exists when the data presented by the
reader does not match the corresponding data in the tag
NAK – “Negative Acknowledge” communications response
passive tags – An RFID tag without a battery. When radio waves
from the reader or programmer reach the chip's antenna, the energy
is converted by the antenna into electricity that can power up the
microchip in the tag. The tag is able to send back information stored
on the chip.
programming – adding information to or altering a tag
programmability – data and identification information must be
entered into tags in order for them to become identifiers of specific
objects; this capability is called programmability
programmer – tag contents can be changed by a set of electronics
in close proximity or in electrical contact with them; those electronics
and their packaging are called a programmer
RFID – Radio Frequency IDentification. A method of identifying
unique items using radio waves. Typically, a reader communicates
with a tag, which holds digital information in a microchip.
RFID tag: see tag
range – distance at which successful reading and/or writing can be
attained
read – decoding, extraction and presentation of data from
formatting, control and error management bits sent from a tag
readability – ability to extract data under less than optimal
conditions
read rate – maximum rate at which data can be read from a tag,
expressed in bits or bytes per second
read/write – many applications require that new data, or revisions to
data already in the tag, be entered into the tag while it is still
attached to its object; tags with this capability are said to be
reprogrammable and are called read/write tags, memory cards, or
memory modules
reader – device containing the digital electronics that extract and
separate the information from the format definition and error
management bits; digital electronics perform the actual reading
function; these read electronics may also interface to an integral
display and/or provide a parallel or serial communications interface
to a host computer or industrial controller
reader/writer – the set of electronics can change the contents of the
tags while they are still attached to their object; they are called the
transceiver or reader/writer (see reader)

SECTION 1 General Information
10008547aa 06/06 m®1–3
reprogrammable – many applications require that new data, or
revisions to data already in the tag, be entered into the tag while it is
still attached to its object; the ability to read from and write data to
the tag while it is attached to its object is called in-use
programming; tags with this capability are said to be
reprogrammable and are called read/write tags, memory cards, or
memory modules
scanner – the antennae, transmitter (or exciter) and receiver
electronics are integrated in a single package called the scanner;
they may be combined with additional digital electronics, including a
microprocessor in a package called a reader
tag – A microchip attached to an antenna that is packaged in a way
that it can be applied to an object. The tag picks up signals from and
sends signals to a reader. The transceiver plus the information
storage mechanism attached to the object is referred to as the tag,
transponder, electronic tag, code plate, and various other terms.
Although transponder is technically the most accurate term, the
most common term and the one preferred by the Automatic
Identification manufacturers is tag.
transceiver – see reader/writer
transponder – see tag
unitized active tags – see active tags
verify – assure that the desired operation was performed correctly
WebUI – Web User Interface
write – transfer of data to a tag; the tag’s internal operation of
storing the data, sometimes including the data, in order to verify the
operation
write rate – rate at which information is transferred to a tag, written
into the tag’s memory and verified as being correct; it is quantified
as the average number of bits or bytes per second in which the
complete transaction can be performed

SECTION 1 General Information
1–4 m®10008547aa 06/06
2.0 Specifications
Weight: Model 811: Approx: 40,82kg (90 lbs)
Stand: 42,64kg [94 lbs]
Dimensions: Model 811:
Width: 660mm [26.00”] with mounting bar
Width: 508mm [20.00"] to edge of dispenser
Height: 547mm [21.55”] with full rewind roll
Height:495mm [19.50] to top of dispenser
Depth: 395mm [14.76”]
Stand:
Width: 870mm [34.25”]
Height: 17277mm [68.0”]
Depth: 1156mm [45.50”]
See Dimensional Drawing (Paragraph 4.0)
RFID Standards: Frequency 860-925 mHz
Class 1, Class 1 Gen 2
Electrical Standards: CE marked ?
FCC ID: QME811RFID
Voltage: 100/115/200/208/230V, 50–60Hz,
single phase, 450W
Air Supply: 90psi / 6 bar (dry, uncontaminated)
Air Consumption: 0.035 cfm (1 l/min) at 20 labels per minute
Environmental: Operating temperature range
4°–40°C [39°– 104°F]
Relative humidity
10-90%, non-condensing
Noise emission
Does not exceed 80 dB(A)
Sensors: Tag gap / out sensor included
Product detect sensors included
Communications: Connection via Ethernet or network switch
to support Web User Interface (Web UI) to
Windows-based computer

SECTION 1 General Information
10008547aa 06/06 m®1–5
Encode Process: Erases tag, programs tag with EPC code,
reads tag, if good, applies tag, if bad,
rejects tag
Reject Mechanism: bad tags are rejected onto the backing web
for easy disposal
Tag Cycle Rate: Up to 100 per minute depending on tag size,
the applicator used, communication
protocols, and machine settings
Tag Footprints (in inches):
Tall Wide Applicator
Required
On-pitch inlays: 0.5”[12,7mm] x 4.0” [101,6mm] Tamp
0.5”[12,7mm] x 6.0” [152,4] Tamp
Converted tags: 1.5”[38,1mm] x 4.0” [101,6mm] Tamp or blow
2.0”[50,8mm] x 4.0” [101,6mm] Tamp or blow
3.0”[76,2mm] x 3.0” [76,2mm] Tamp or blow
1.5”[38,1mm] x 6.0” [152,4mm] Tamp
2.0”[50,8mm] x 6.0” [152,4mm] Tamp
6.0”[152,4mm] x 4.0” [101,6mm] Tamp
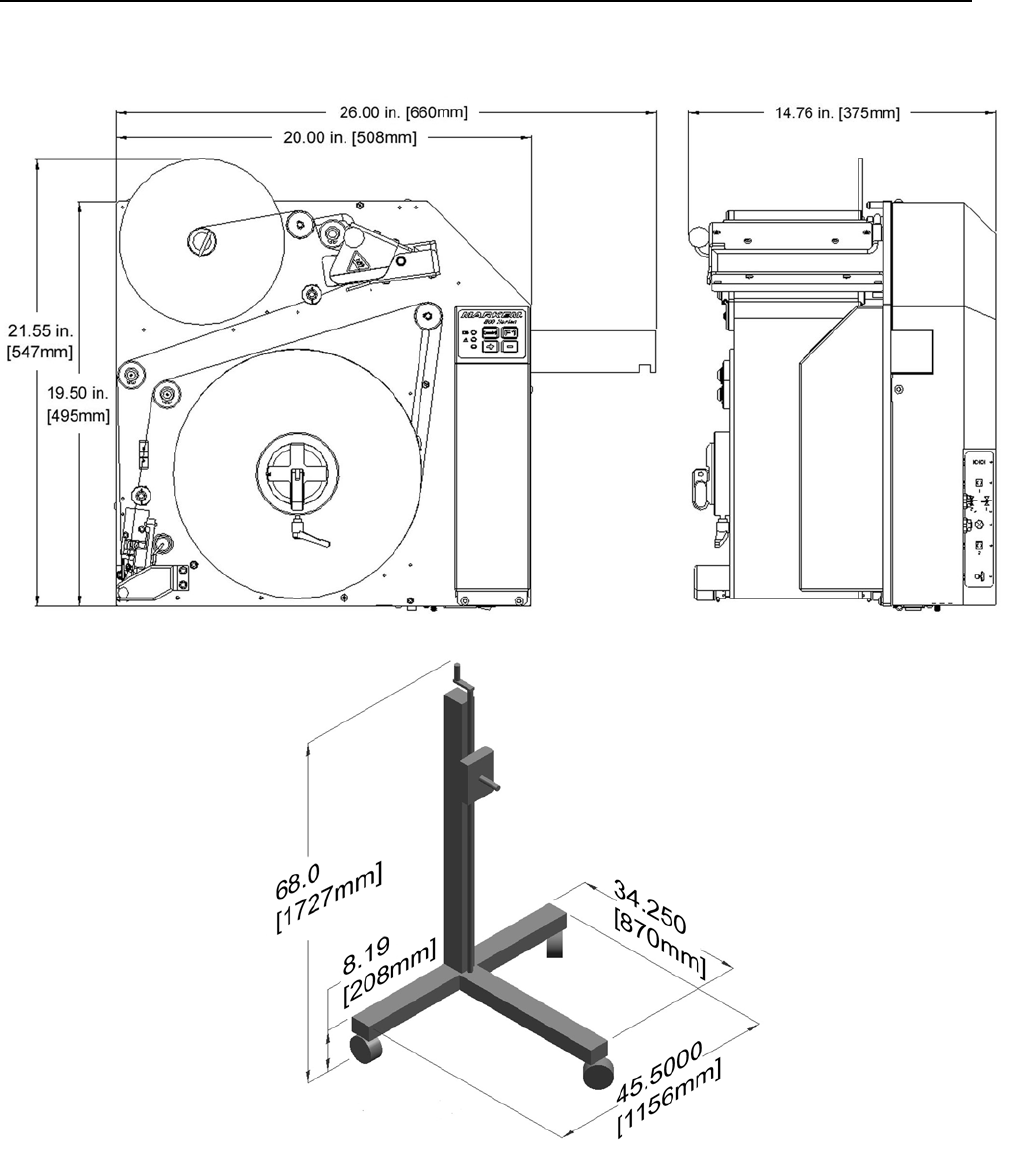
SECTION 1 General Information
1–6 m®10008547aa 06/06
3.0 Dimensional Drawing
Figure 1–1
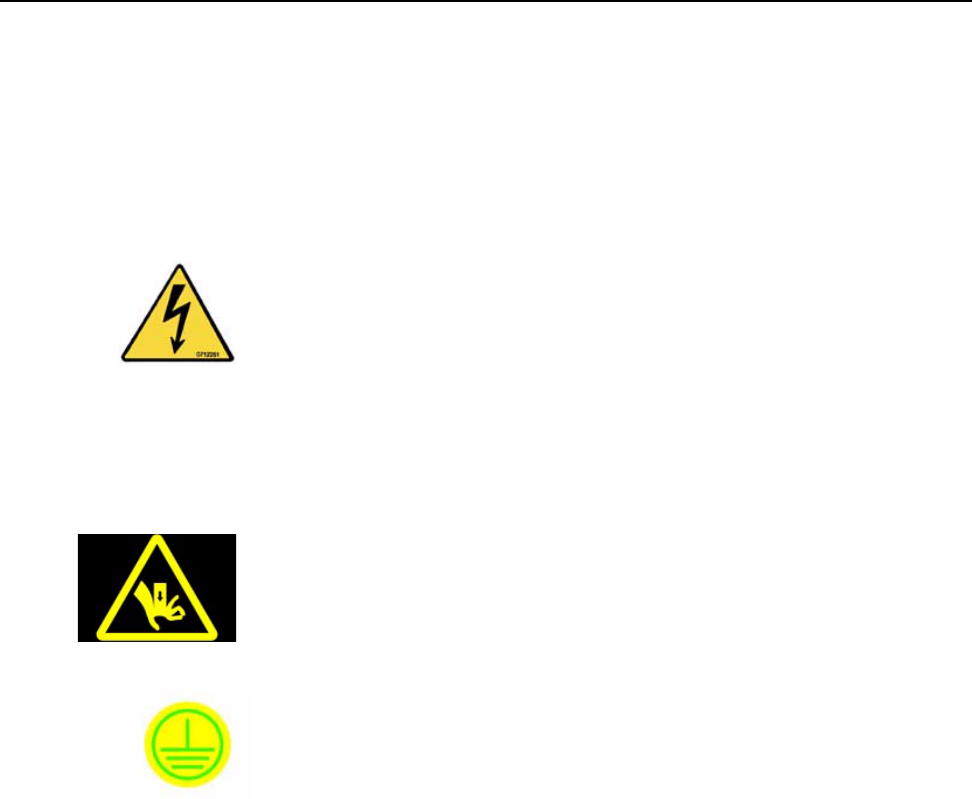
SECTION 1 General Information
10008547aa 06/06 m®1–7
4.0 Safety Information
The Model 811 has been designed to meet various safety
standards. To alert you to potentially hazardous situations, labels
and messages appear on the machine and throughout the manual.
CAUTION refers to a potentially hazardous situation which, if not
avoided, could result in personal injury.
4.1 Machine Safety
High Voltage
This safety label is located on the ourside of the rear cover of the
machine and indicates that line voltages are inside.
To prevent injury from electrical shock, the power cord should be
removed from the electrical outlet before performing troubleshooting
or repair.
Electronic troubleshooting must be performed by personnel trained
to troubleshoot electrical circuits.
Pinching/Crushing
This safety label is located on the drive pressure roller and indicates
that operators should be careful not to pinch or crush their fingers.
Earth
This safety label is located inside the machine and indicates an
earth point.
4.2 Modifications to the Model 811
Any changes or modifications not expressly approved by MARKEM
that could affect FCC Compliance could void the user’s authority to
operate the machine.
CAUTION: Applicator cylinders have been factory-set to 27 PSI for
safety. If the tamp applicator cylinders are operated over 27 PSI, the
machine must be protected by guarding, supplied by the customer.
Do not adjust the tamp applicator regulator pressure above 27 PSI
unless guarding is in place.

SECTION 1 General Information
1–8 m®10008547aa 06/06
4.3 Foreseen Use/Misuse
This manual provides information about Safety, Installation,
Operation, Troubleshooting, Illustrated Parts, Electrical Schematics,
Recommended Spares and Preventive Maintenance Procedures.
Using the Model 811 in any other manner is considered a misuse of
the product. Please consult your local MARKEM Business Center
before using this machine for anything other than the foreseen use.
Misuses include, but are not limited to:
• Operating a system that is incomplete, cannot be serviced, or
has been modified without authorization
• Failing to observe hazard requirements in the manual and/or on
safety labels
• Combining or interfacing non-MARKEM equipment with this
system, other than as intended
• Permitting a person who has not been fully trained to operate
and/or service the system
• Using unspecified supplies or material which may produce
unsatisfactory or unexpected results
4.4 MARKEM Training Programs
Operators, maintenance personnel, and service technicians are
considered “qualified” when they have gained, through training and
experience, an understanding of safe and correct methods of
operation, maintenance, or repair.
MARKEM conducts training programs. In addition to ongoing
courses about current machine models, customers are invited to
inquire about any training need.

SECTION 1 General Information
10008547aa 06/06 m®1–9
4.5 Removal from Service
Follow these instructions to remove the Model 811 from service.
These instructions also pertain to transporting or storing the
machine.
Figure 1–2
1. Turn off the power to the machine.
2. Disconnect the power cable from the system.
3. Disconnect all other cables from the system.
4. Disconnect the air supply.
5. Remove tape supplies from the rewind and supply hubs.
6. Tape the rewind U-pin to the rewind hub.
7. Put the rewind dancer in the forward position.
8. Lock the supply hub and the supply outer disk.
9. Being careful because of the weight of the machine, remove the
machine from the stand.
10.Carefully move the machine to the desired location and
repackage the system in the original shipping containers.
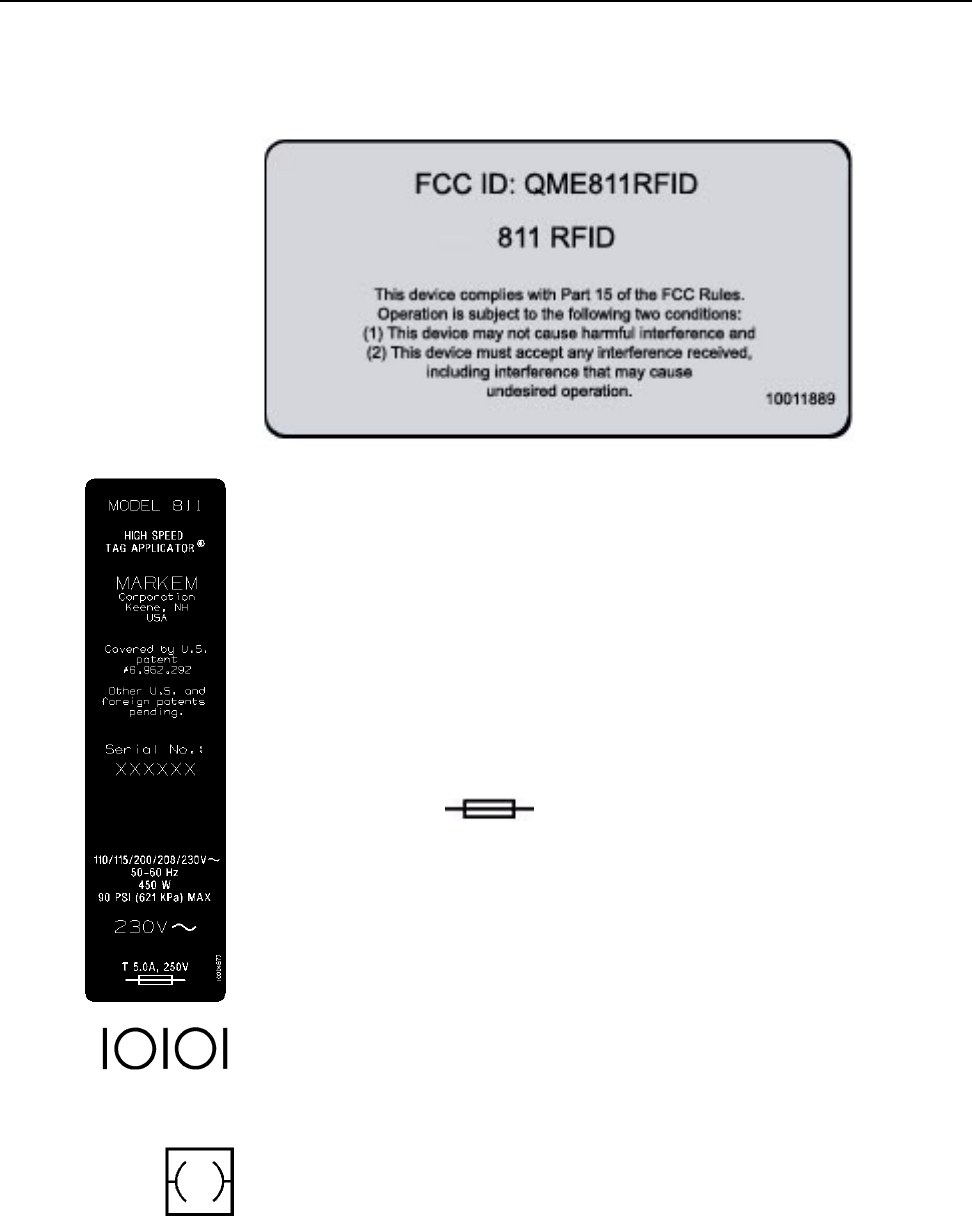
SECTION 1 General Information
1–10 m®10008547aa 06/06
5.0 Label and Symbol Identification
FCC ID Compliance Label
This label is affixed to the rear plate of the Model 811.
Serial/I.D./Rating Label
This label is affixed to the rear of the enclosure and indicates the
following:
Model number
IType of equipment
Information about MARKEM
Patents covered
Serial number (Serial number is also affixed inside the enclosure)
Electrical specifications
AC voltage configuration ~
Fuse information
(X0) Serial Port
This symbol indicates the serial (RS232) ports and connects to the
reader.
(X8) Interface Device Port (1)
This symbol indicates the interface device port that is used for the
scanner port.
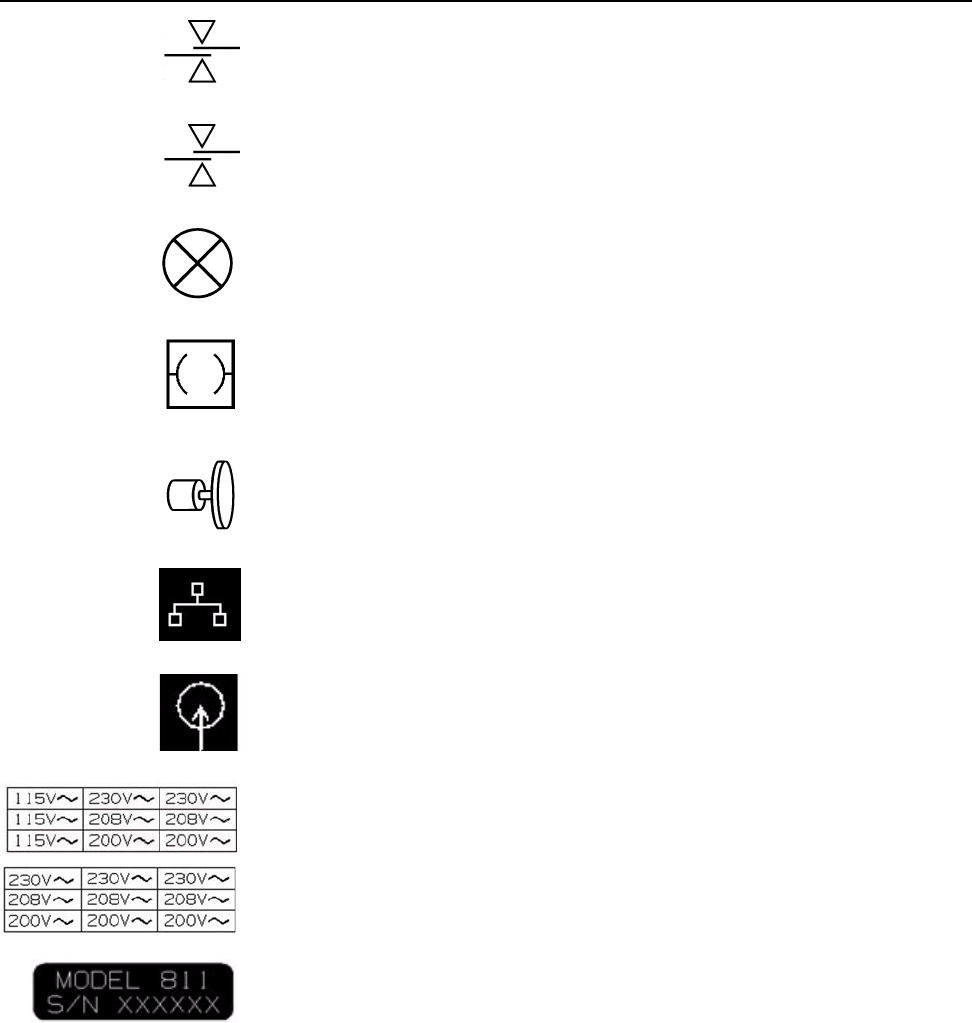
SECTION 1 General Information
10008547aa 06/06 m®1–11
(X1) Sensor (2)
This symbol indicates the feed sensor port.
(X7) Sensor (1)
This symbol indicates the apply sensor port.
(X6) Beacon Light
This symbol indicates the beacon light port.
(X5) Interface Device Port (2)
This symbol indicates the interface device port that is used for a
second scanner port.
(X4) Encoder
This symbol indicates the encoder port.
Ethernet Port
This symbol indicates the port for the Ethernet cable.
(Antenna Port
This symbol indicates the antenna port.
Voltage Configuration Labels
Spare voltage configuration labels are provided. If the AC voltage
configuration of your machine changes, affix the appropriate voltage
configuration label to the Serial/I.D./Rating label on the rear panel of
the enclosure, so it covers the old voltage configuration rating.
Serial Number Label
This label appears inside the enclosure and matched the serial
number on the Serial/I.D./Rating label when the machine was
shipped from the factory. If the serial number on the Serial/I.D./
Rating label and on the label inside the enclosure do not match, the
serial number on the label inside the enclosure is the correct serial
number. (The machine cover may have been switched from another
machine.)
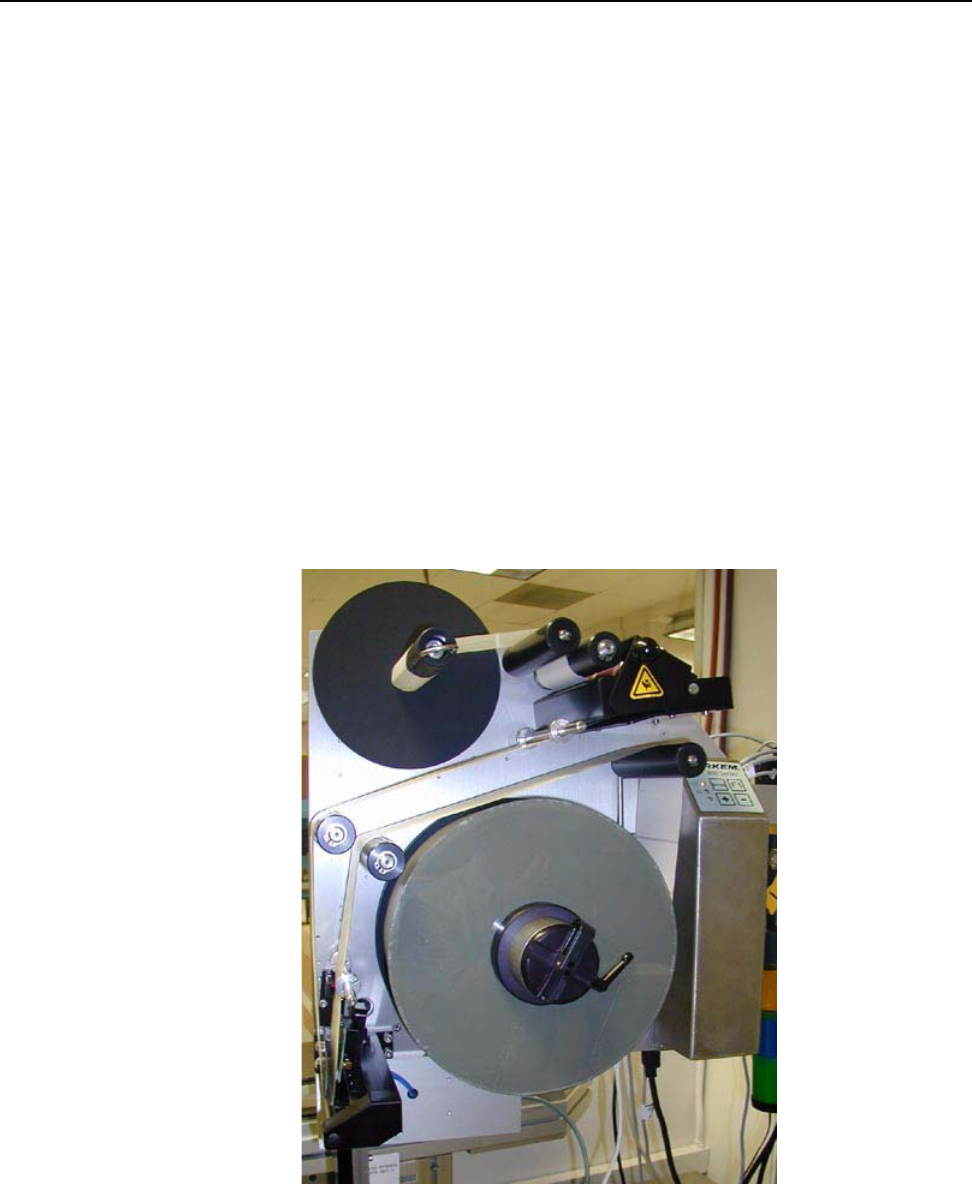
SECTION 1 General Information
1–12 m®10008547aa 06/06
6.0 Components
The Model 811 is a high speed, compact RFID tag dispenser and
applicator and can be supplied with options: an adjustable height
stand; signal tower; signal inputs.
6.1 Dispenser
The dispenser is the main body of the machine and houses the
electronics and mechanical components.
The dispenser supports a variety of different mountable applicator
modules.
The dispenser consists of:
• The tape drive
• Sensors for tag control
• Local user interface (LUI)
6.2 Tape Drive
The tape drive system is shown in Figure 1-3.
Figure 1–3

SECTION 1 General Information
10008547aa 06/06 m®1–13
6.3 Applicator
Applicators are available in blow or tamp to meet your different
requirements.
The different applicators apply tags in different ways. The choice of
applicator also determines the face of the product that is tagged.
6.3.1 Model 824 Blow Applicator
Figure 1–4
6.3.2 Model 854 Tamp Applicator
Figure 1–5

SECTION 1 General Information
1–14 m®10008547aa 06/06
6.4 Reader/Programmer
The device containing the digital electronics that extract and
separate the information from the format definition.
Figure 1–6
6.5 Networking
The Model 811 provides options for communicating with PCs and
other computers. The methods available are:
• A serial link to a single PC
• Ethernet link
The Web user interface (Web UI) connects to the Model 811 via a
Windows-based PC and is needed for such purposes as controlling
settings, querying machine status, and monitoring faults.
6.6 Beacon Light (Optional)
The optional beacon light, which is mounted in a prominent position
on or near the machine has three lamps: green, blue, and amber to
alert the operator of machine status.
Figure 1–7

Model 811
Operation/Service Manual
m
®
SECTION 2
Installation Guide

SECTION 2 Installation Guide
10008547aa 06/06 m®2–1
1.0 Installation Requirements
The Model 811 system includes:
• the dispenser
• applicator
• reader/programmer
• connections for electrical and air supply
• options, such as a stand, beacon light, and product sensor
The Model 811 must be installed by qualified and trained personnel
in accordance with applicable requirements. Installation by the
customer must be sanctioned by MARKEM.
WARNING: Failure to perform installation as stated above will
invalidate the machine warranty.
1.1 Machine Requirements
Ensure that the required services and control signals are available:
• Power: 100/115/200/208/230V single phase power supply rated
at 450W
• Compressed air: a dry, clean air supply at 6 bar (90psi)
• Interfaces and trigger signals appropriate for the application
• Sufficient space for installation and operation
• Machine mounting point
1.2 Installation Overview
Determine a location for the Model 811 that will:
• Provide access to the front and rear of the dispenser
• Provide sturdy, level mounting
• Meet environmental, electrical, air supply, and communications
specifications
Model 811 installation includes:
• Removing the Model 811 and associated components from the
packaging.
• Assembling the stand (optional)
• Securing the Model 811 to the stand or other mounting
• Positioning/Leveling the Model 811
• Verifying or changing the voltage configuration
• Mounting the air supply
• Mounting the reader
• Mounting the beacon light (optional)
• Installing options, such as a product sensor
• Connecting power, devices, and other interfaces

SECTION 2 Installation Guide
2–2 m®10008547aa 06/06
• Connecting to Web UI
• Verifying that the mechanical settings are appropriate for the
RFID tag stock or making necessary changes
• Verifying that the software parameter settings are appropriate for
the RFID tag stock or making necessary changes
1.3 Unpacking the Model 811
Move the cartons containing the Model 811 and associate
components to the installation site.
1. Remove the Model 811 and associated components from the
packaging.
2. If a stand was ordered, unpack the stand.
2.0 Assembling the Stand (Optional)
If the optional stand was purchased, it will need to be assembled.
The stand comes in two boxes: the T-base is in one box and the
upright is in the other.
1. The T-base is in two parts with the feet and casters already
attached. To assemble the T-base, remove the bolt and washer.
Fit the two pieces together and then re-install the bolt.
2. To install the upright, remove the nut and washer from the
upright. Place the upright onto the T-base by guiding the floating
bolt into the proper hole. Re-install the nut and washer.
3. The crank is assembled at the factory. However, using an allen
wrench, the handle needs to be flipped to the opposite side of
the mating piece.
4. A package of M6 button head screws is provided for mounting
the machine to the L-piece. The mounting plate is attached to the
upright with the hardware loosely in place to receive the L-piece.
Remove the 2” bar from the L-piece. The Model 811 has its own
longer 2” bar attached to its main plate and does not use the bar
provided on the stand.
5. The cable channel is already installed onto the upright from the
factory. Remove the cable cover by gently prying and snapping it
off. It will be re-installed after all the cables and tubes have been
connected.

SECTION 2 Installation Guide
10008547aa 06/06 m®2–3
3.0 Mounting the Dispenser
Determine where the Model 811 will be located.
The dispenser is shipped from the factory with an applicator
mounted.
The dispenser is supplied with a mounting bar attached to the main
plate. Although the mounting bar is intended to be fastened to the
optional stand, it can be modified at the installation site for alternate
mounting positions or specialty brackets can be ordered from
MARKEM.
1. If not mounting the dispenser to the optional stand, go to step 6.
2. When mounting the dispenser to the optional stand, it is best to
support the dispenser on a stable work surface and roll the
assembled stand to the dispenser.
3. Using the crank at the top of the stand, adjust the height of the
mounting plate until it is in line with the mounting bar.
4. Slide the dovetail groove of the mounting bar onto the mounting
plate.
5. Fasten the dispenser's mounting bar to the stand's mounting
plate with the supplied screws.
Figure 2–1

SECTION 2 Installation Guide
2–4 m®10008547aa 06/06
3.1 Verifying or Changing the Voltage Configuration / Power Configuration
The power connector (Type STASEI2) is supplied and conforms to
EC regulations.
1. Before installing the Model 811, check that the power supply is
correctly configured for your electrical service.
To do this, check whether the AC voltage on the power input
module on the bottom of the machine cabinet matches your
electrical service. When the white arrows match, the indicated
voltage is selected.
If the AC voltage of the Model 811 matches your electrical
service, continue with step 3.
2. To change the AC voltage configuration, use a slotted
screwdriver and remove the power input module.
With the white arrows matching the correct voltage, install the
power input module.
3. Machines shipped within the United States include a 115V AC
power cord with a molded plug type NEMA 5-15P. If this plug is
not compatible with the mating receptacle and rewiring is
necessary, use the following wire color codes:
Line (L): black
Neutral (N): white
Ground (G): green/yellow
4. A "pigtail" cable is supplied as a 230V AC power cord. wire the
pigtail end of the AC power source to an appropriate plug or
terminal block using the following wire color codes:
Line 1 (L1): brown
Line 2 (L2/Neutral): blue
Ground (G): green/yellow
Note: Do not apply power to the machine until installation is
complete.
Using the p-clip provided, secure the power cord to the machine.
5) Apply label .... open cover, find AC label... put cover back on.
xxxxx
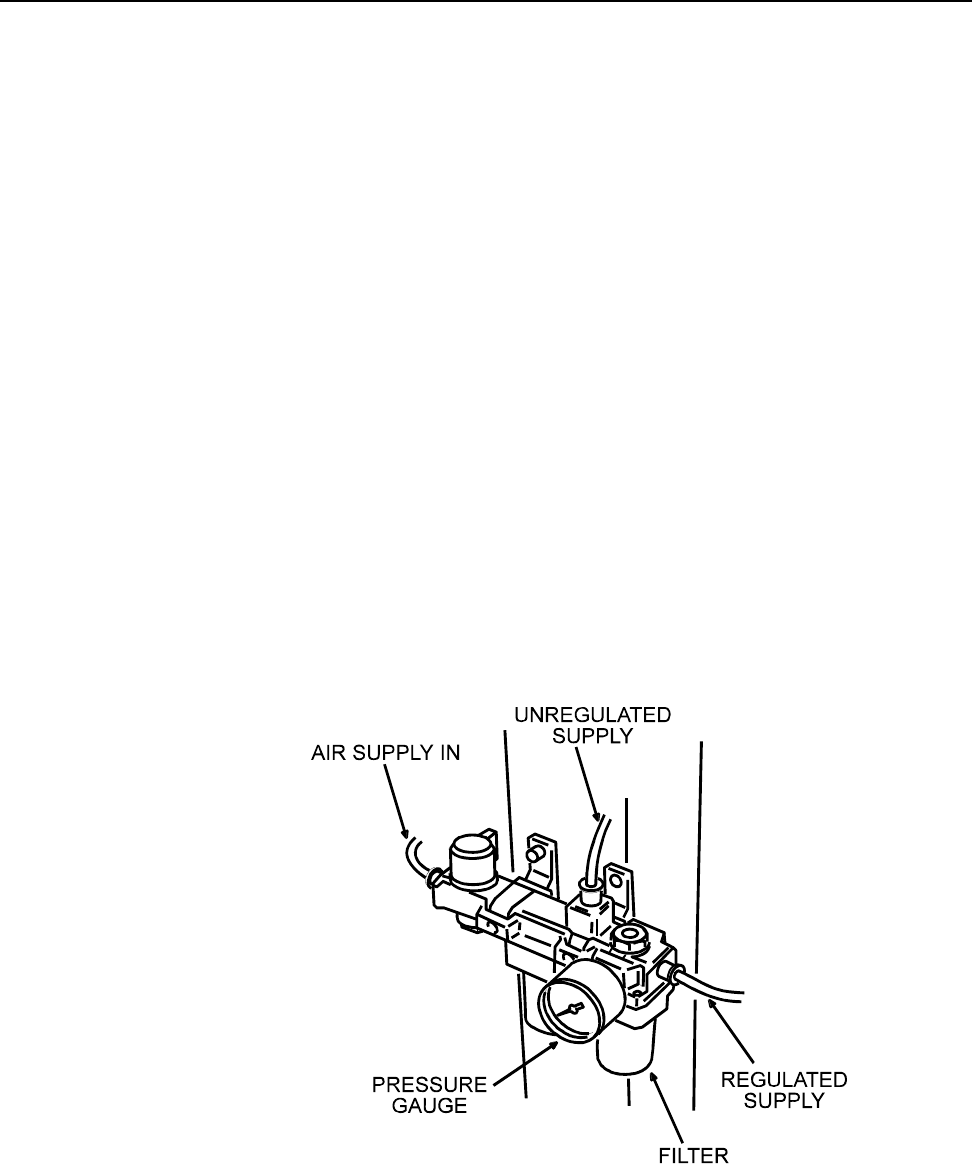
SECTION 2 Installation Guide
10008547aa 06/06 m®2–5
3.2 Mounting and Connecting the Air Supply
A compressed air supply is normally required by the Model 811 to
drive the applicator module. This must be set to 6.2 Bar (90psi) with
a minimum flow rate of 4cfm (cubic feet per minute) (113 liters/
minute) and should be dry, uncontaminated air which should not be
lubricated.
A filter regulator assembly is fitted to the base of the stand; this is
comprised of a manual isolation valve, a water trap and pressure
regulator. The air supply is via a 6mm or 8mm flexible pipe.
A single connection is supplied to the main filter regulator unit; from
here, the regulated supply goes to the applicator (if air operated)
and the unregulated supply goes to the air input on the dispenser.
Figure 2–2
to dispenser
to applicator

SECTION 2 Installation Guide
2–6 m®10008547aa 06/06
WARNING:All applicator cylinders have been factory-set to 27
PSI for safety. If the cylinders are operated over 27
PSI, the machine must be protected by guarding,
supplied by the customer.
SAFETY: Do not adjust the applicator regulator pressure
above 27 PSI under any circumstances. Doing so
could make the machine unsafe.

SECTION 2 Installation Guide
10008547aa 06/06 m®2–7
4.0 Mounting the Reader/Programmer
The Reader/Programmer can be mounted on the optional stand or
any other stable structure. The Reader/Programmer must be
mounted within approximately 3 feet (1m) of the machine due to the
length of the antenna cable. Note that any machine positional
adjustments are limited to the cable length.
It is necessary to slide the Reader into the mounting bracket before
mounting the bracket.
Reference Assembly Drawing 10004788.
1. Slide the Reader into the mounting bracket.
2. To mount to the optional stand, use the hardware provided to
mount the bracket through the center screw to the main post of
the stand.
3. To mount to another surface, use either the two outer mounting
holes or the single center hole and the hardware provided .
4. Attach the I/O connections as follows:
• ANT1 > external antenna cable > Model 811 Antenna Input
• ANT2 > terminated
• SERIAL > RS232 cable > Model 811 X9 Input
• +9VDC > power transformer module > Power Supply
< Insert photo with parts called out>
5.0 Mounting the Beacon Light (Optional)
1. If using the optional beacon light, mount it ...
2. Connect the cable to the

SECTION 2 Installation Guide
2–8 m®10008547aa 06/06
6.0 Installing a Product Sensor

SECTION 2 Installation Guide
10008547aa 06/06 m®2–9
6.1 4.0 After Installation
After installing the stand, dispenser, reader, and options, a few more
tasks need to be completed before powering on the machine.
6.1.1 Positioning the Model 811
The Model 811 is typically supplied with a stand which allows the
positioned tag height on the product to be adjusted within a limited
range. The applicator height will be determined by the conveyor
height and required position of the tag on the product.
Leveling feet are provided and should be down; care should be
taken to align the machine with the product transportation system.
Before final positioning, the machine should be placed so that the
applicator arm is square to the product and the position of the
machine provides the correct tag position on the product.
CAUTION: If the machine is not secured to the floor, it is
possible for the machine to gradually change
position during use. It is, therefore, important to
mark the provisional position of the machine prior
to starting tagging trials.
6.1.2 Final Installation Tasks
1. Verify that all connections are made and are secure.
2. Bundle the cables and tubes in the cable channel and neaten
them. Install the cable cover.
3. Power on the machine and open the air regulator.
7.0 Connecting to Web UI
The Web UI is the manager/technician's interface with the Model
811. It is used to control settings, query machine status, monitor
faults, and is necessary to help with the initial machine set up.
To launch the home page index from a Windows-based PC:
1. Connect the Windows-based PC to the Ethernet port at the
cottom of the Model 811 via a crossover Ethernet cable or
network switch.
2. Launch an Internet Explorer Browser.
3. In the address bar, type in the factory default IP address:
http://010.000.000.015/index.htm
Select the GO button on the browser.
Note: The default address can be altered for communication to
more than one machine. If the IP address is altered, it is
recommended that it be written on the exterior of the
machine for future use.
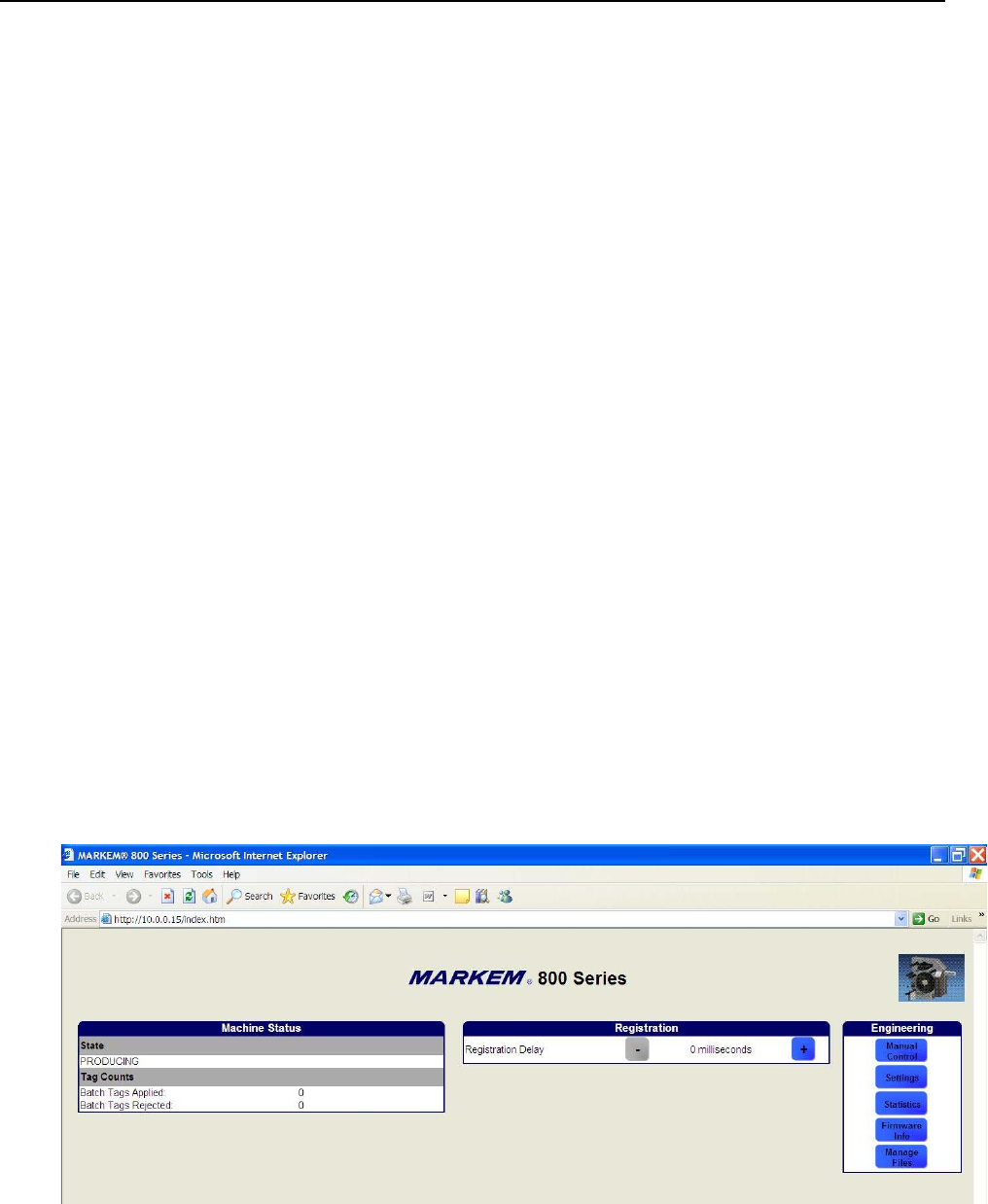
SECTION 2 Installation Guide
2–10 m®10008547aa 06/06
4. Power-cycle the Model 811 and point the PC's browser to the
new IP address. If the altered IP address is lost or forgotten, the
factory default address can be restored via the LUI.
The following browser page should be displayed and represents the
machine's "Home Page":

SECTION 2 Installation Guide
10008547aa 06/06 m®2–11
8.0 Verifying Settings
The dispenser and applicator settings are dependent on the RFID
tag stock being used. When installing the machine or changing tag
type, it is necessary to verify that the mechanical settings are
appropriate for the RFID tag stock.
8.1 Mechanical Settings
If the mechanical settings are inappropriate for the RFID tag stock,
adjustments must be made or the machine may fail to operate
properly.
Some of the mechanical adjustments must be accompanied with
software parameter setting adjustments using the Web UI.
8.1.1 Supply Arbor
The supply arbor position should be checked during installation and
with every new roll added to the machine.
The supply arbor is driven by a motor which is powered by signals
from the supply dancer position. The tag supply roll must be firmly
coupled to the supply arbor for the machine to operate properly.
1. To check the supply arbor position, place the cam handle in the
locked position and try to physically rotate the tag stock on the
supply arbor. If the supply arbor rotates, it is necessary to adjust
the supply arbor compression sleeve pressure.
2. Make sure the machine is the machine in the aborted state.
3. To change compression sleeve pressure, open the cam handle.
Rotate it clockwise to increase pressure or counter clockwise to
decrease pressure.
4. Lock the cam handle against the supply arbor.
5. Verify the adjustment by trying to physically rotate the tag stock
on the supply arbor. .
photo

SECTION 2 Installation Guide
2–12 m®10008547aa 06/06
8.1.2 Tag Guides
The tag guides help guide the tag stock axially in the machine. The
surface of the inner tag guides that are adjacent to the tag are set to
a height of 1.19" (30.2mm) at the factory and should be coplanar
with the supply inner disk and the rewind disk. The outer tag guide
can be adjusted to match the tag width.
The outer tag guide is set at the factory to be appropriate for the tag
stock specified at the time of machine order. The outer tag guide
does not need to be changed during installation unless changing to
a different tag stock than what was ordered.
To change the outer tag guides:
1. Remove power from machine.
2. Loosen the screw holding the clamp collar to the shaft.
3. Slide the outer clamp collar to a position on the shaft that allows
approximately 1/32" (0.75mm) of axial tag stock movement.
4. Refasten the clamp collar screw.
photo

SECTION 2 Installation Guide
10008547aa 06/06 m®2–13
8.1.3 Adjusting Pressure Rolls
The pressure rolls should be checked during installation and with
every new roll added to the machine.
The pressure rolls apply a force which couples the tag stock against
the drive roll. The inner pressure roll is justified against the main
plate while the outer pressure roll can be adjusted to match the tag
width. The gap between the rolls should bridge the RFID chip.
Proper pressure roll adjustment will help with tag tracking and will
prevent the pressure roll and/or the drive roll from prematurely
wearing by the RFID chip.
photo
To change the outer pressure roll position for wider tags:
1. Remove power from machine.
2. Loosen the clamp collars holding the pressure roll.
3. Slide the clamp collars, washers and pressure rolls into their new
position.
4. Refasten the clamp collars. Note that the pressure roll should
have approximately 1/64"-1/32" (0.25mm-0.75mm) axial
movement.
To change the outer pressure roll position for thinner tags:
1. Remove power from machine.
2. Remove the pressure roll guard by removing the four screws.
3. Loosen all the clamp collars.
4. Loosen the two set screws in the lever plate that holds the
pressure roll shaft.
5. Place the pressure roll drive in the open position. Note that the
mechanism is under spring tension. Care should be taken lock
this mechanism in the open position so as to not cause an injury.

SECTION 2 Installation Guide
2–14 m®10008547aa 06/06
6. Slide the roll shaft out of the lever plate while removing the clamp
collars, washers and pressure rolls.
7. Reassemble as shown in Figure X.X.
photo
8. Tighten the two set screws in the lever plate onto the flats of the
pressure roll shaft.
9. Refasten the clamp collars. Note that the pressure roll should
have approximately 1/64"-1/32" (0.25mm-0.75mm) axial
movement.
10.Fasten the pressure roll guard to the lever arm.
8.1.4 Gap Sensor Position
The gap sensor position is set at the factory to be appropriate for the
tag stock specified at the time of machine order. The gap sensor
position does not need to be changed during installation unless
changing to a different tag stock than what was ordered.
When changing to a different tag stock, the gap sensor position
should be adjusted to optimize machine speed capabilities and to
reduce tag queuing and tag waste.
For instructions on changing the gap sensor position, refer to
“Changing the Gap Sensor Position” in section 7, Technical
Information.
8.2 Software Parameter Settings
Detailed instructions on how to adjust parameter settings can be
found in section 4, Web User Interface of this manual.

Model 811
Operation/Service Manual
m
®
SECTION 3
Operation Guide
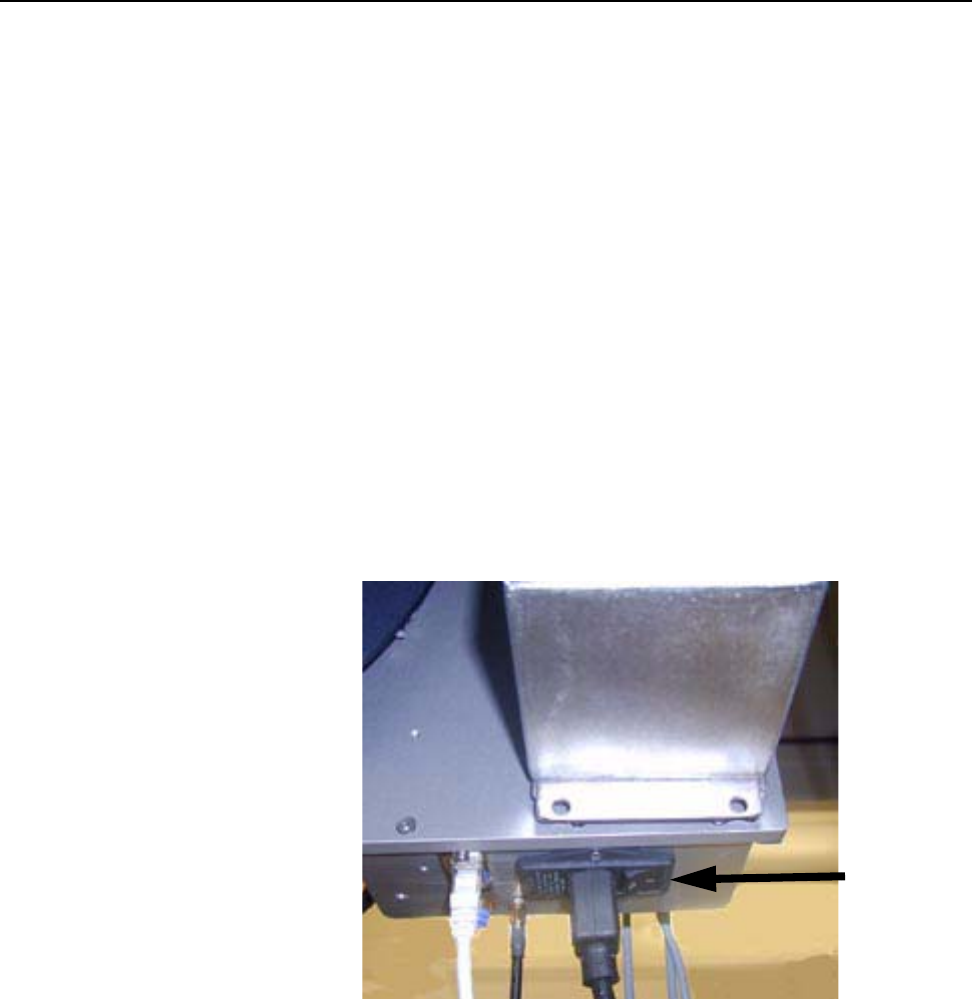
SECTION 3 Operation Guide
10008547aa 06/06 m®3–1
1.0 Preparing for Operation
Installation of the Model 811 is normally carried out by a qualified
MARKEM service technician and usually involves connecting an
apply sensor to the product conveyor transport system and setting
parameters.
Once the machine has been installed and checked for safety, the
machine can be loaded with tags ready for use.
The machine uses inside-wound tags.
Note: The tag manufacturer should be qualified by MARKEM to
assure reliability of tag stock.
2.0 Operating the Model 811
The operator loads tags onto the tape drive system and uses the
LUI or the Web UI to apply RFID tags to the product.
2.1 Power Switch
The power switch is located at the bottom of the machine cabinet
(Figure 3-1).
Figure 3–1
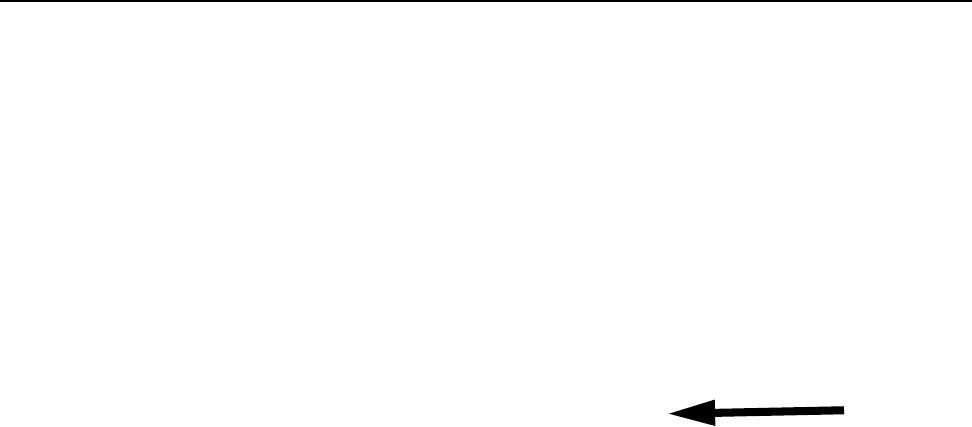
SECTION 3 Operation Guide
3–2 m®10008547aa 06/06
2.2 Air Supply
The air supply is used by the applicator to apply tags to the product.
Figure 3–2
2.3 Powering Up
1. To turn the air supply on, rotate the air supply control valve
handle.
2. Check that tags are correctly loaded and that the drive pressure
roller is latched in position. See “Loading Tags” in this section if
needed.
WARNING:Be aware that items such as loose clothing or long
hair, could become entangled or trapped in the tag
drive pressure roller or tape path while operating
the machine. A warning sticker highlights the
hazard.
3. Make sure that the AC power cord is connected. Locate the
power switch at the bottom of the machine cabinet and turn it on
(I position). (Figure 3-1)
4. During power up, the machine calibrates and goes into
Automatic mode unless a fault is detected.
5. If the Fault LED on the keypad is blinking, clear the fault.
6. The machine is now ready to operate.
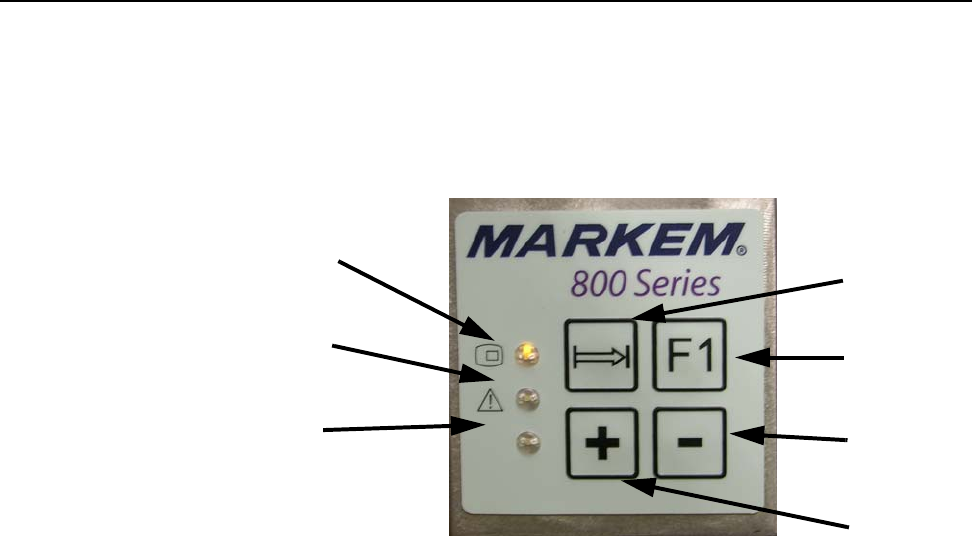
SECTION 3 Operation Guide
10008547aa 06/06 m®3–3
2.4 LUI
The keypad (Figure 3-2) on the front of the machine has four keys
and three LEDs to facilitate setup and to inform the operator of
critical status conditions. The keypad is also referred to as the local
user interface (LUI).
Figure 3–3
2.4.1 Keys
The keypad has the following keys:
• Mode key
• F1 key
• “+” (Plus or increment) key
• “-” (Minus or decrement) key
The function of these keys is detailed in Table 3-1.
2.4.2 Web UI
Mode Key
F1 Key
“-” Key
+” Key
Status
LED
Fault
LED
Test
LED
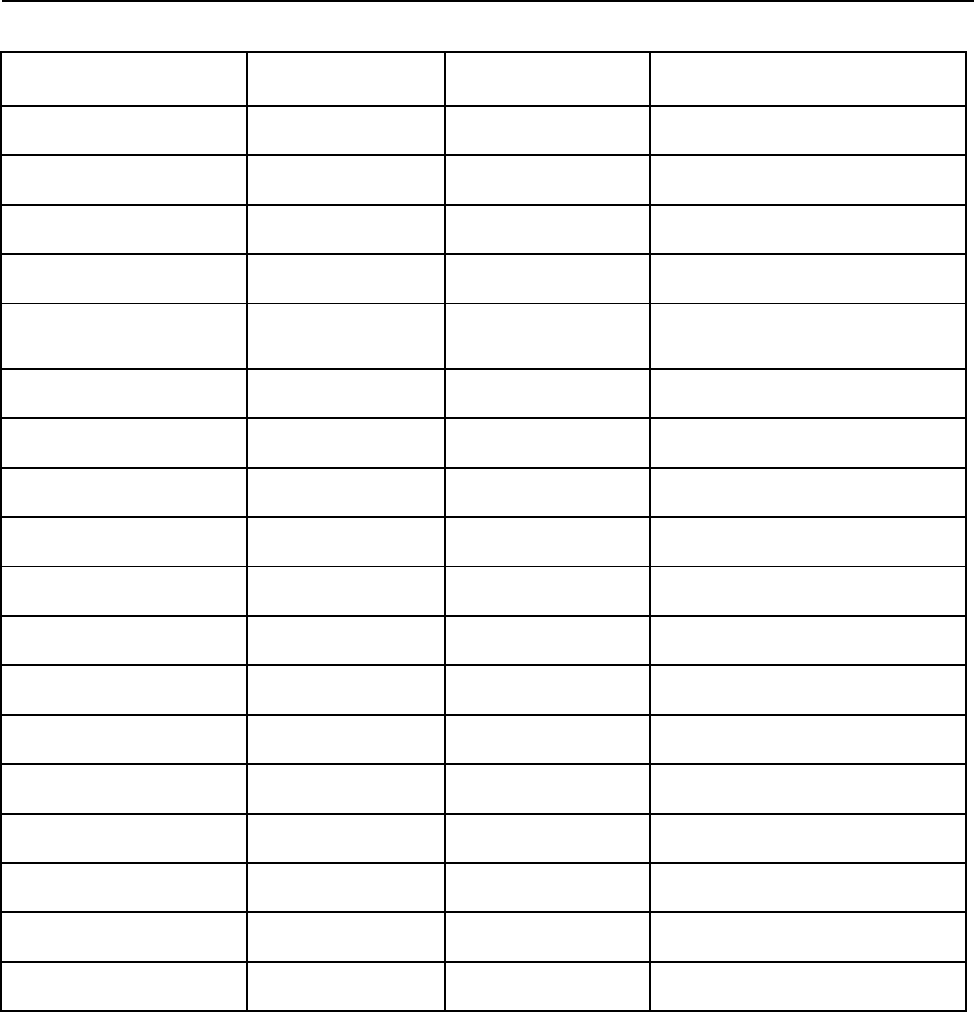
SECTION 3 Operation Guide
3–4 m®10008547aa 06/06
Table 3–1
Key / Command Automatic Mode
Producing State Automatic Mode
Aborted State Manual Mode
Press Mode Key Go to Manual Mode NA Go To Producing State
Press F1 Key NA Clear Fault NA
Hold F1, Press '-' Key
Decrement
Registration Delay NA Reject Tag
Hold F1, Press '+' Key
Increment
Registration Delay NA Feed & Apply
Hold F1, Press Mode Key NA NA
Starts / Stops Continuous Test Write
Without Reject - Blue Lamp: Success,
Fault Lamp: Fail
Press '+' Key NA NA Increment Feed Forward
Press '-' Key NA NA Decrement Feed Forward
Press '+' and '-' Keys NA NA Reset Feed Forward To Default
Hold '+', Press '-', 'F1',
Mode Keys in Sequence NA
Restore To Factory
Defaults NA
Hold F1, Press Mode, '-'
Keys in Sequence NA NA Burst 5 Feed & Apply
Web UI Manual Control
Buttons No No Yes
Line Manager GetStatus Yes Yes Yes
Line Manager ReadTag Yes No Yes
Line Manager WriteTag Yes No No
Line Manager Enable Run
Mode No No Yes
Line Manager Abort Yes No No
Line Manager RejectTag Yes No No
Line Manager Good Tag
Cycle Yes No No
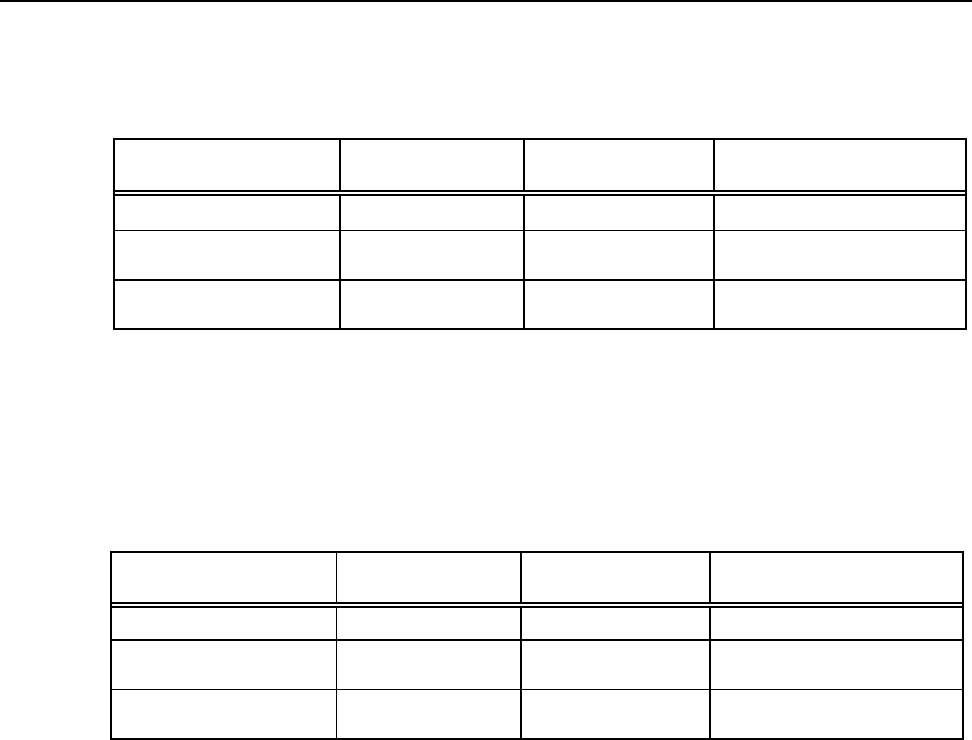
SECTION 3 Operation Guide
10008547aa 06/06 m®3–5
2.4.3 Keypad LEDs
The LEDs are designed to help the operator determine the status of
the machine. The function of the LEDs are detailed in Table 3-2.
Table 3–2
2.5 Beacon Light (Optional)
The optional beacon has three lamps: green, blue, and amber which
correspond with the LED indicators on the keypad. The function of
the lamp depends on the operational state of the machine.
Table 3–3
Indicator
A
utomatic Mode
Producing State
A
utomatic Mode
Aborted State Manual Mode
Green / Amber LED On - Green Off On - Amber
Fault LED Off Blinking
Blinks when Failed Tag
Program Test
Blue LED Off Off
Blinks when Successful
Tag Program Test
Indicator
A
utomatic Mode
Producing State
A
utomatic Mode
Aborted State Manual Mode
Green Beacon Lamp On Off Off
Blue Beacon Lamp Off Off
Blinks when Successful
Tag Program Test
Amber Fault Beacon
Lamp Off Blinking
Blinks when Failed Tag
Program Test
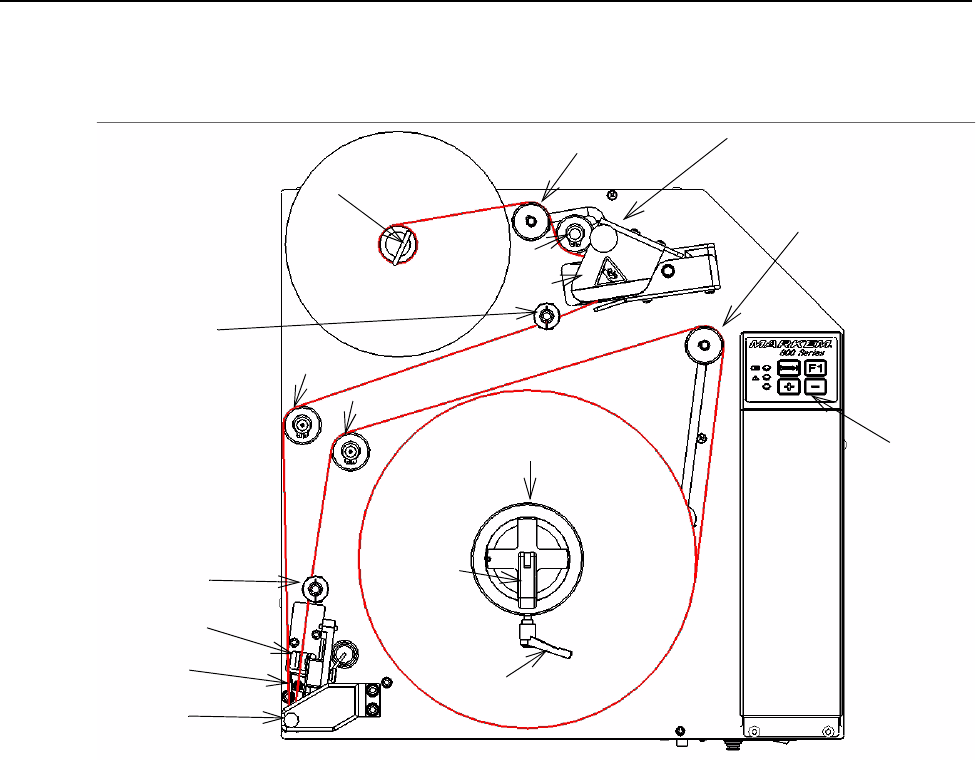
SECTION 3 Operation Guide
3–6 m®10008547aa 06/06
2.6 The Tape Drive System
Figure 3-3 shows the tape drive system with parts identified.
Figure 3–4
U-pin
Rewind Hub
Dead Post 2
Dead Post 1
Antenna
Peel Bar
Gap Sensor
Rewind Dancer Pressure Rollers
Supply Dancer
Drive
Idler 3
Drive
Roller
Supply Hub
Supply Roll
Outer Disk Handle
Supply Hub
Cam Handle
Idler 2
Idler 1
Keypad (LUI)
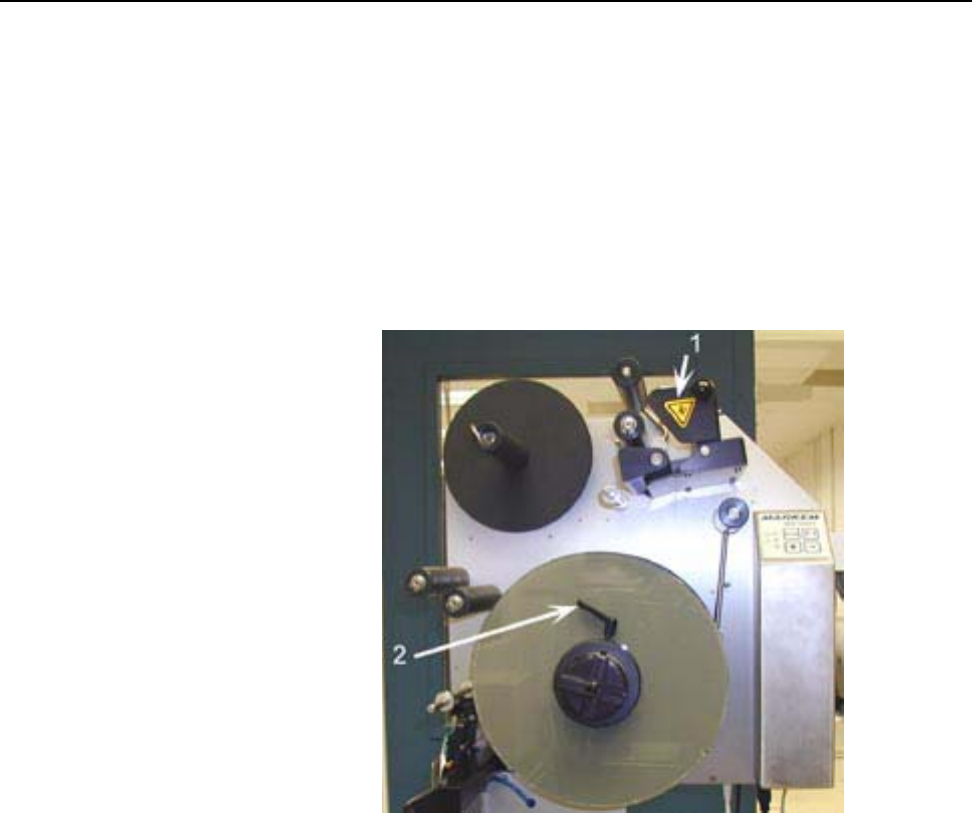
SECTION 3 Operation Guide
10008547aa 06/06 m®3–7
3.0 Loading Tags
The tape drive can be loaded either with the power on or off.
1. If the machine is powered on, leave it in Manual Mode or the
Fault State.
2. Open the drive pressure roller (1, Figure, 3-2), being careful not
to pinch your fingers.
3. Remove the disk from the outer supply roller by rotating the outer
disk handle (2, Figure, 3-2) counterclockwise.
Figure 3–5
4. Open the supply hub cam handle so it points straight out toward
you.
5. Remove the supply roller disk. It is suggested that you
temporarily place it on the crank handle of the stand for safe
keeping.
6. Position a new roll of tags on the supply hub disk with the slack
unrolling on your left as shown in Figure 3-3.
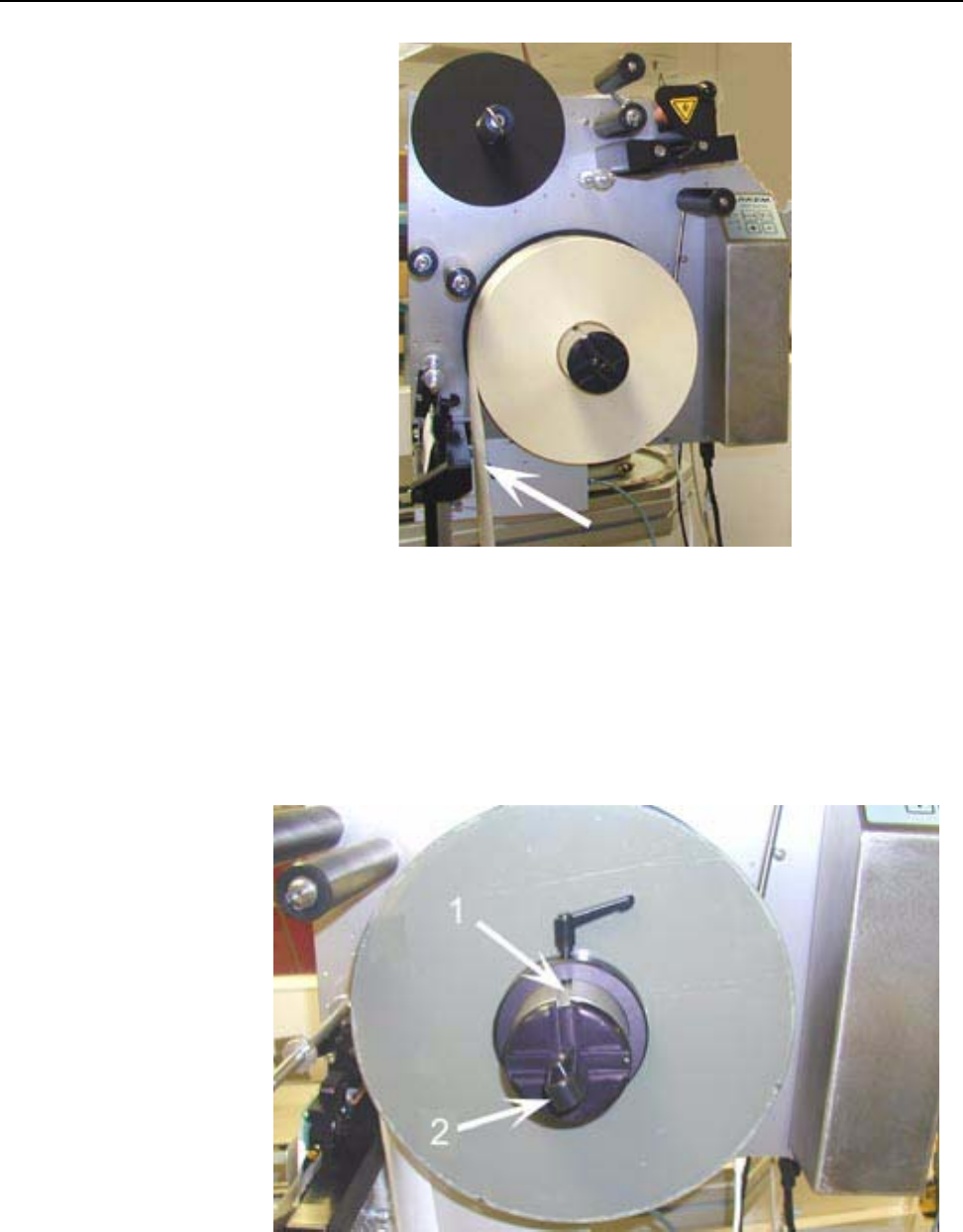
SECTION 3 Operation Guide
3–8 m®10008547aa 06/06
Figure 3–6
7. Slide on the supply roller disk, ensuring that the pin in the outer
disk handle aligns with the groove in the supply hub (1, Figure 3-
4). Ensure that the roll is seated.
8. Lock the cam handle (2, Figure 3-4), making sure it is aligned in
one of the four grooves. To increase pressure on the roll, rotate
the cam handle clockwise before locking.
Figure 3–7
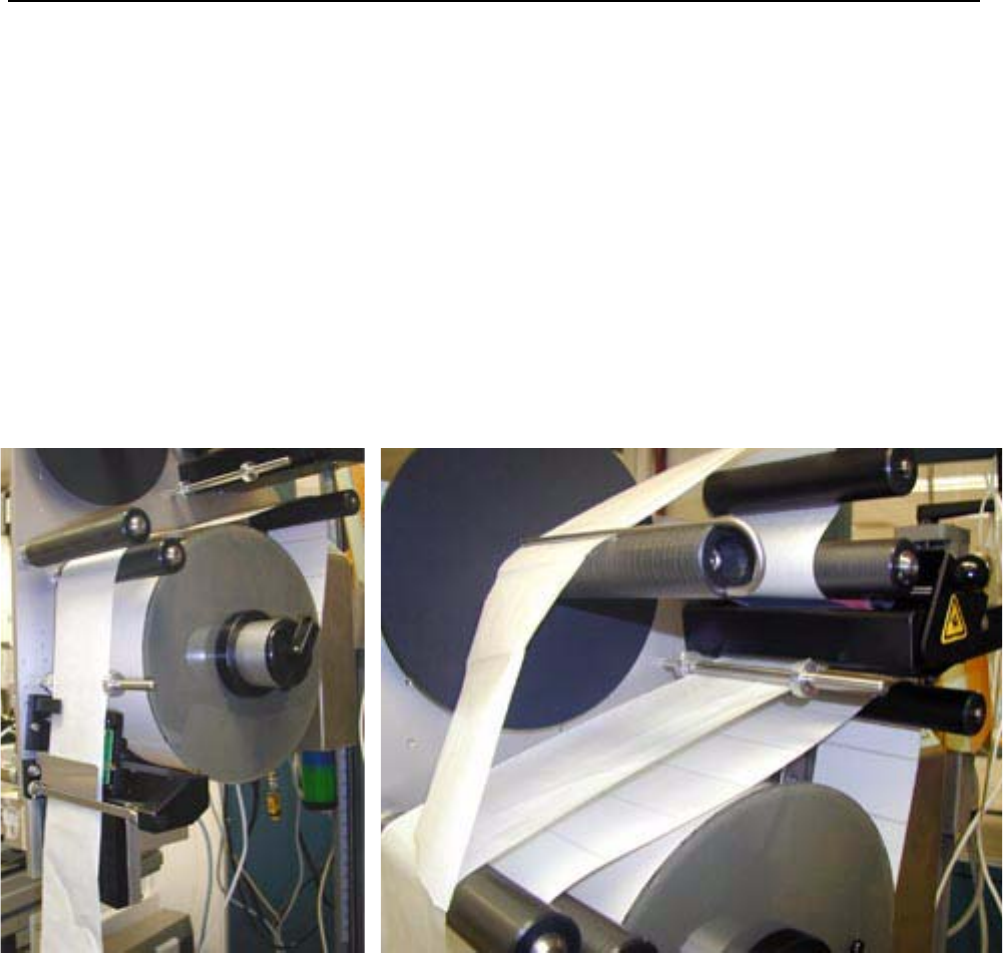
SECTION 3 Operation Guide
10008547aa 06/06 m®3–9
9. Lock the outer disk by rotating the outer disk handle clockwise.
10.To thread the tape, roll out approximately one meter of leader.
Thread the tape:
over the supply dancer
over idler 1
over dead post 1
through the gap sensor
between the antenna and shield
around the peel bar
over idler 2
under dead post 2
over the drive roll
and under idler 3
(Figure 3-5)
Figure 3–8
11. Close the drive pressure roller, being careful not to pinch your
fingers.
12.Wrap the tape over the rewind dancer to the rewind post.
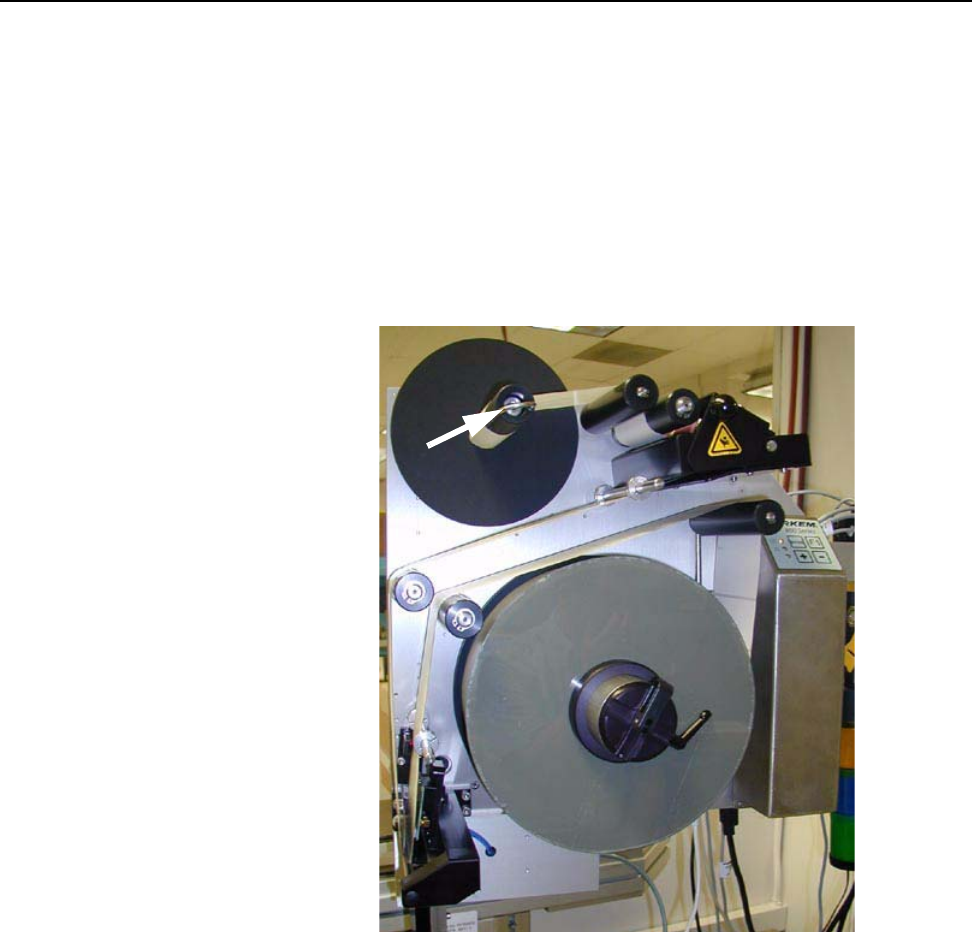
SECTION 3 Operation Guide
3–10 m®10008547aa 06/06
13.Secure the tape to the rewind post using the U-pin: put the long
leg of the U-pin over the tape and the short leg of the pin in the
hole in the end of the rewind post (1, Figure 3-6).
14.Manually rotate the rewind post counterclockwise until the
rewind dancer is against its lower stop.
15.Check the tags above the peel bar, ensuring that they are either
removed or securely adhered. Any partially peeling labels may
jam when feeding through the drive roller.
Figure 3-6 shows the tape properly threaded.
Figure 3–9
1
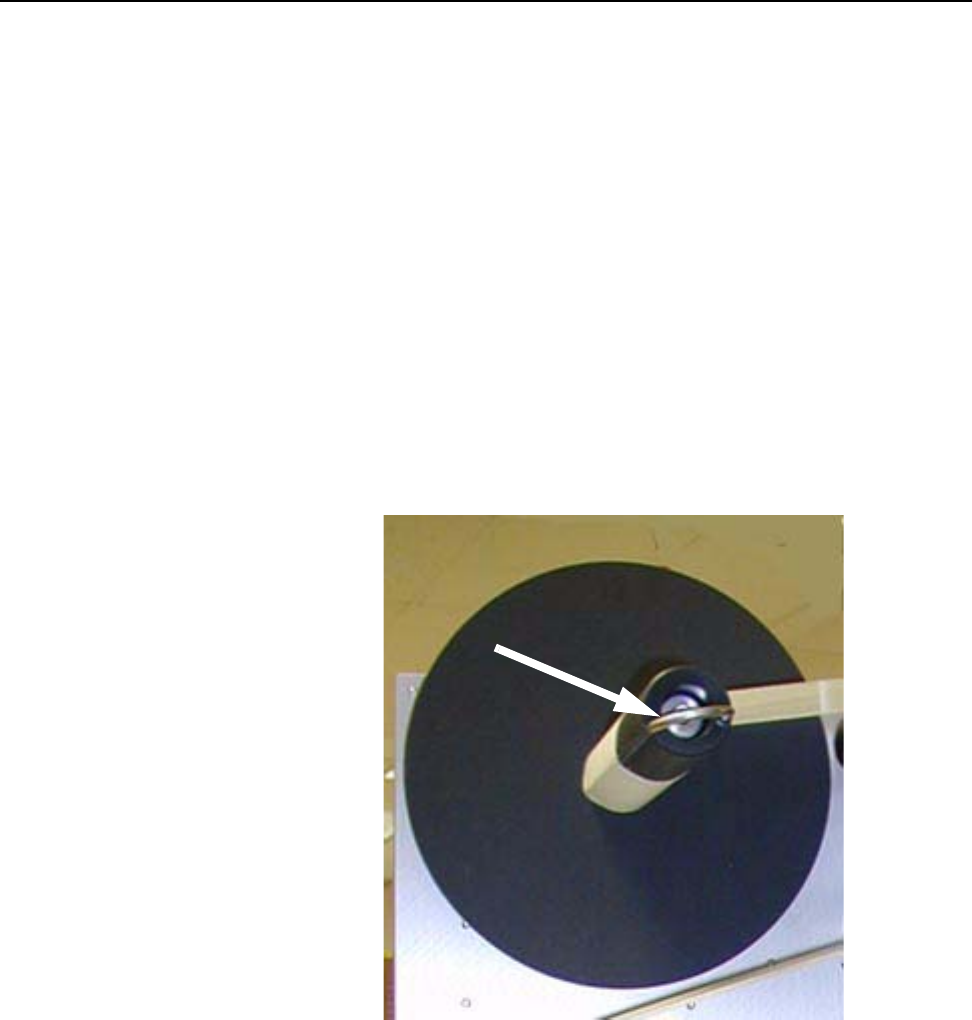
SECTION 3 Operation Guide
10008547aa 06/06 m®3–11
4.0 Unloading a Full Rewind Core
1. Remove the disk from the outer supply roller by rotating the outer
disk handle counterclockwise.
2. Open the supply hub cam handle so it points straight out toward
you.
3. Remove the supply roller disk. It is suggested that you
temporarily place it on the crank handle of the stand for safe
keeping.
4. Remove the empty core from the supply hub disk and discard.
5. Remove the U-pin from the rewind post (Figure 3-7). It is
suggested that you temporarily hang it on the crank handle of the
stand for safe keeping.
6. To remove the roll, pull the waste tape toward you. Or pull the
rewind disk to push the waste tape off. Discard the waste tape.
Figure 3–10

SECTION 3 Operation Guide
3–12 m®10008547aa 06/06

Model 811
Operation/Service Manual
m
®
SECTION 4
Web User Interface
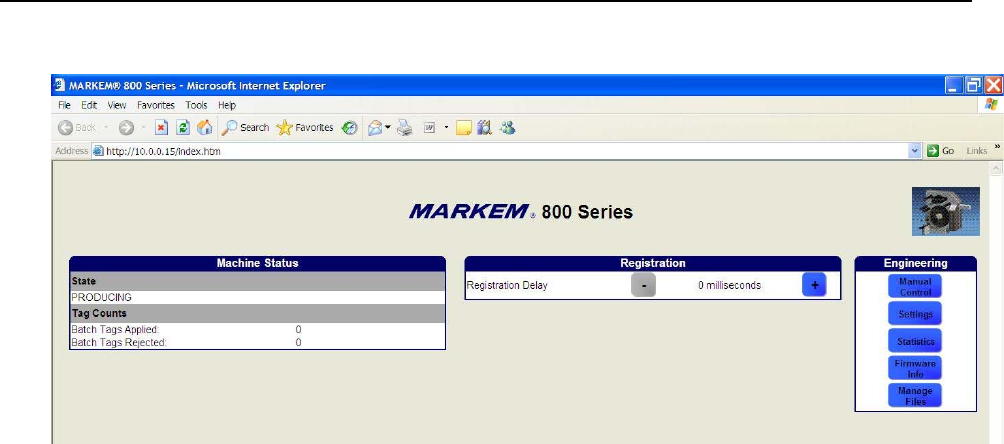
SECTION 4 Restricted Access Mode User Guide
10008547aa 06/06 m®4–1
1.0 Web UI
To access the Machine Settings menu, select the "Settings" button.

SECTION 4 Restricted Access Mode User Guide
4–2 m®10008547aa 06/06

Model 811
Operation/Service Manual
m
®
SECTION 5
Operating Modes

SECTION 5 Operating Modes
10008547aa 03/06 m®5–1
1.0 Operating Modes
Three LEDs on the LUI and three lamps on the optional beacon
inform the operator of the mode or state of the machine.
Automatic Mode
This is the "run" mode or normal operating mode. In this mode, LUI,
WebUI, and Line Manager Manual Control commands are disabled.
Starting State
State within Automatic Mode where the machine checks all systems
and peripheral devices. If everything is okay, the machine moves to
the Producing State. If a problem is encountered, the machine
moves to the Aborted State.
Producing State
State within Automatic Mode where the machine is online and ready
to encode and apply tags. In this state, the green LED and beacon
lamp are on and the only LUI functions that are available are the
Mode key and Registration Delay increment and decrement. WebUI
functionality is enabled with the exception of Manual Control
commands. To exit the Producing State and enter the Manual Mode,
the Mode key can be pressed.
Aborted State
State within Automatic Mode where the machine is 'idle' and the
motors are off. In this state, all LUI and WebUI Manual Control
commands and all Line Manager commands are disabled. This
state is entered when a machine fault such as opening the nip
occurs. The machine will respond to all communications with a NAK
except for "Get Status."
Note: In addition to being the state resulting from a fault, this is the
state used to replenish tag stock as the motors are disabled
via opening the nip. When in the Aborted State, the Fault
LED is blinking and the fault relay signal is activated.
In order to exit the Fault State, the fault condition must be corrected
and the F1 key must be pressed. The machine will then transition to
Manual Mode so that any necessary setup operations can be
performed.
The machine will "boot-up" in the Aborted State.

SECTION 5 Operating Modes
5–2 m®10008547aa 03/06
Manual Mode
This is the "setup" mode for the machine during which the motors
are online and all manual control keys on the LUI and WebUI are
active. All Line Manager commands are disabled except the “Get
Status” Command and the “Enable Run Mode” Command. The top
LED will be amber

Model 811
Operation/Service Manual
m
®
SECTION 6
Preventive Maintenance Guide

SECTION 6 Preventive Maintenance Guide
10008547aa 06/06 m®6–1
1.0 General Maintenance and Cleaning
For the best performance of your machine, general cleaning must
be carried out as a normal part of machine use.
This section describes cleaning and maintenance procedures which
will help to keep the machine in good working condition.
1.1 General Information
Carry out a daily general machine inspection, which should include:
• Check all guards to ensure they are correctly fitted using all
required fasteners
• Check that movement is smooth and that slides and cylinders
are not damaged
• Check for wear
• Check for trapped cabling and pipes
• Check for inaccurate tag placement
1.2 Positioning of Safety Labels
Labels are placed on the Model 811 in various positions by
MARKEM to warn of potential safety hazards. As part of regular
maintenance, safety labels must be checked and replaced
whenever any are missing or damaged.
Refer to Section 1 – General Information for further information.
2.0 Maintaining the Compressed Air
The compressed air supply to the machine may contain moisture. A
water trap is provided in the main pressure regulator, and this will
require draining at regular intervals before machine use.
Carry out the following procedures:
• Check the water level in the water trap
• Place a suitable container under the water trap and drain by
pressing the valve pin in the base of the filter
• Check all of the air lines for leaks, security and condition
• Replace any defective air lines or connectors

SECTION 6 Preventive Maintenance Guide
6–2 m®10008547aa 06/06
3.0 Cleaning Adhesive from Machine Components
During operation, adhesive from the tags and liner material will build
up on various posts and rolls within the machine. Excessive
adhesive build up will increase tension in the system and/or cause
tracking errors.
Isopropyl alcohol (IPA) is the recommended solvent to clean
adhesive from machine components.
CAUTION: When using IPA to clean the machine, use
approved personal protection recommended by
the manufacturer.
1. Pour IPA on a clean cloth or paper towel.
2. Wipe adhesive buildup off affected components as needed.
4.0 Cleaning of All Rollers
When tags are fed, the tag adhesive may bleed onto the backing
web. This adhesive can build up on the feed roller, tag nip, and idler
rollers which may eventually cause feed problems.
To prevent these problems, the machine must be cleaned regularly
using a suitable cleaning agent such as Isopropanol. Care must be
taken when cleaning to prevent damage to the machine and its
delicate components. Cleaning agents which will damage rubber or
plastic MUST NOT be used. If in doubt, consult MARKEM.
It is recommended that the rollers be cleaned regularly every time
the tags are replaced and before using the machine if it has not
been operated for several days.
• Turn off power to the machine and remove tags
• Use a cotton swab or soft cloth, moistened in Isopropanol, to
remove any residue from the feed roller and the idler rollers
Note: NEVER use abrasive materials or sharp instruments such as
screwdrivers to remove residue.

Model 811
Operation/Service Manual
m
®
SECTION 7
Technical Information
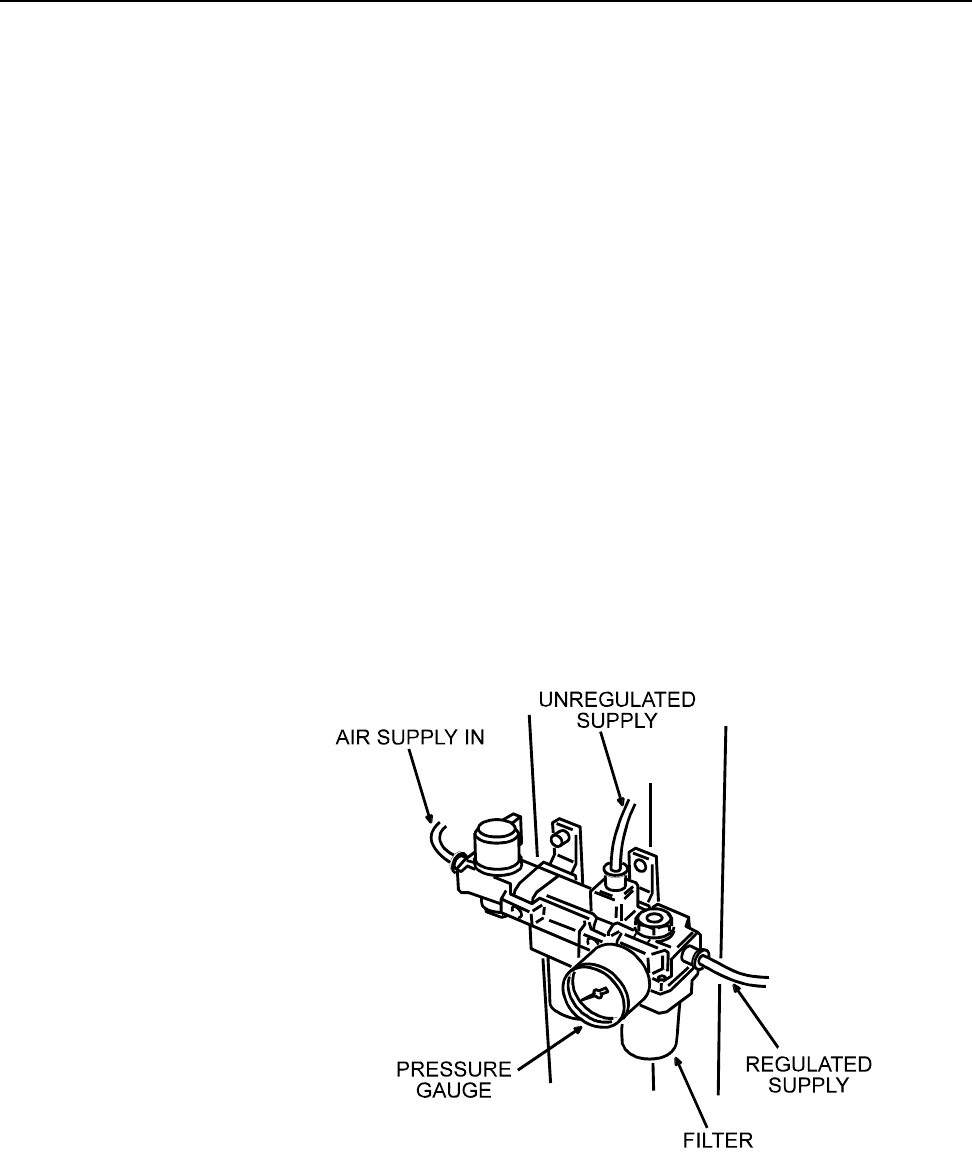
SECTION 7 Technical Information
10008547aa 06/06 m®7–1
1.0 Air Requirements
A compressed air supply is required by the Model 811 to drive the
applicator. This must be air at 90psi (6 bar) and should be: dry,
uncontaminated air, and not lubricated.
A filter regulator assembly is fitted to the base of the stand; this is
comprised of a manual isolation valve, a water trap, pressure
regulator, and dump valve. The air supply is via a 6mm or 8mm
flexible pipe.
1.1 System Air Supply
WARNING: Do not adjust the regulator pressure under any
circumstances. Doing so could make the Model
811 unsafe.
A filter regulator is provided as standard and includes:
• Isolation value (non-lockable)
• Pressure regulator
• Pressure indication dial (0-10 bar)
• Filter (micro mesh)
• Water trap
The unregulated supply goes to the dispenser.
The regulated supply goes to the applicator.
Figure 7–1 Air Filter/Regulator Unit
A 6mm (.236”) push fitting is provided to accept flexible pipe.
The supply should be at 90psi (6 bar) and should be dry, clean, and
not lubricated.
to dispenser
to applicator
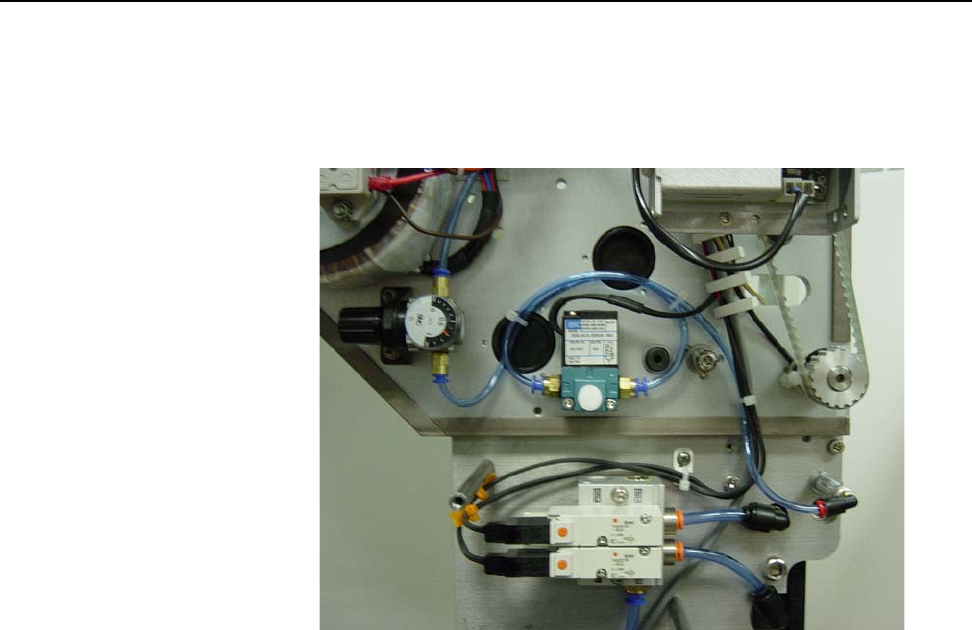
SECTION 7 Technical Information
7–2 m®10008547aa 06/06
1.2 Applicator Air Supply
The applicator has a separate air regulator which is mounted
inside the dispenser cover next to the solenoid valve that operates
it.
Figure 7–2
The air pressure for the Tag Reject Mechanism does not normally
have to be adjusted and should be set to 3.5 to 4.0 Bar.

SECTION 7 Technical Information
10008547aa 06/06 m®7–3
2.0 Gap Sensor
The gap sensor is located inside the machine enclosure and should
be adjusted when changing to a different tag stock.
CAUTION: The technician will be working inside the machine with
the rear cover removed and the power connected. To
prevent injury from electrical shock and moving parts,
avoid contact with electrical components, motors, pul-
leys, and belts.
Figure 8 Figure 9
Below are some definitions and illustrations of RFID tags that should
be helpful when adjusting and teaching the gap sensor.
RFID: Radio Frequency IDentification. A method of identifying
unique items using radio waves. Typically, a reader communicates
with a tag, which holds digital information in a microchip.
RFID tag: A microchip attached to an antenna that is packaged in a
way that it can be applied to an object. The tag picks up signals from
and sends signals to a reader.
Passive tag: An RFID tag without a battery. When radio waves from
the reader or programmer reach the chip's antenna, the energy is
converted by the antenna into electricity that can power up the
microchip in the tag. The tag is able to send back information stored
on the chip.
Inlay: An RFID microchip attached to an antenna and mounted on a
substrate. Inlays are essentially unfinished RFID labels.
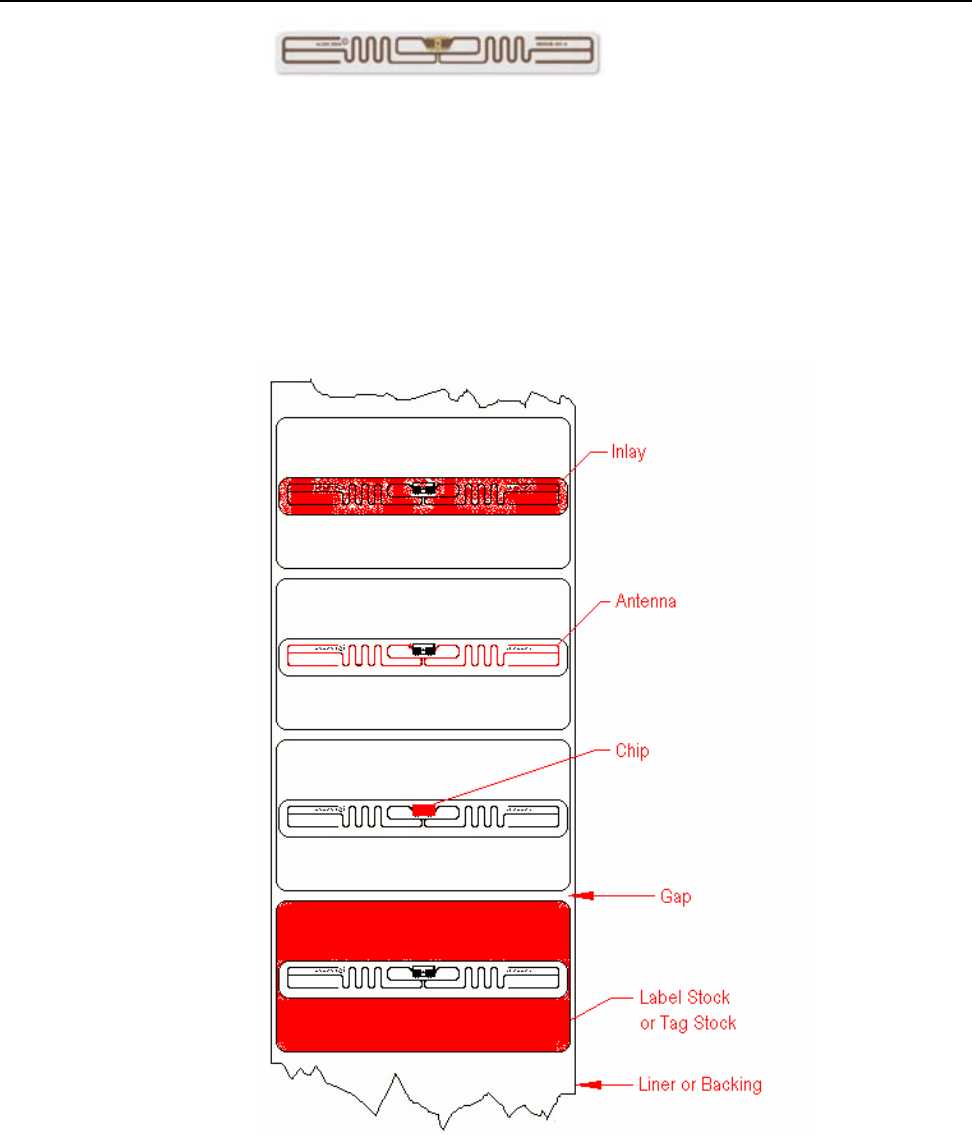
SECTION 7 Technical Information
7–4 m®10008547aa 06/06
Converted RFID Tag: Assembly of an inlay sandwiched between
an adhesive and substrate (usually paper stock) which is then die
cut into a specified size.
Gap: The distance between tags (or labels) on the liner (or backing),
measured from the bottom of one tag to the top of the next tag.
Components of a converted RFID tag on a backing are shown
below.

SECTION 7 Technical Information
10008547aa 06/06 m®7–5
2.1 Changing the Gap Sensor Position
When changing to a different tag stock, the gap sensor position
should be adjusted to optimize machine speed capabilities and to
reduce tag queuing and tag waste.
To determine current gap sense position, look at the gap sense
bracket from the front of the machine; a letter "A" or "B" should be
visible.
• Position "A" required for all tags less than 2.00" (50.8mm) high.
• Position "B" required for all tags 2.00" (50.8mm) high and
higher.
picture
Figure 7–1
1. Remove power from machine.
2. Remove the rear cover.
3. Release gap sensor amplifier fiber lock by sliding the tab up as
shown.
Figure 7–2
4. Slide both fibers out of their ports.
5. Remove the two screws attaching sensor bracket to main plate.
6. Pull the gap sensor and bracket away from main plate.

SECTION 7 Technical Information
7–6 m®10008547aa 06/06
7. Rotate the sensor and bracket for new position. Thread the fibers
through the corresponding holes and fasten the bracket to the
main plate. Note that position "A" positions the sensor closer to
the peel bar than position "B".
8. Fully seat the fibers back into their ports and slide down the fiber
lock.
9. Reinstall the rear cover.
10.Power on the machine and the Windows-based computer.
11. From the Web UI, set the gap sense position:
Homepage > Settings > General System Configuration >
Gap Sensor Position - Edit >"Select A or B" > Apply.
2.2 Teaching the Gap Sensor
The gap sensor amplifier and fiber optic gap sense head
combination optically scan the tag stock as it moves through the
system. A properly programmed amplifier will determine where the
gaps are between the tags and provide feed data to the tag drive
motor which in turn will index the tag to the proper position on the
peel bar.
Gap sensor teach modes should only be performed by trained
personnel as this procedure requires working inside the dispenser
enclosure with power energized to the machine.
2.2.1 Teach
Once the sensor is properly set up, it needs to be “taught” in the
areas it needs to signal on. The Model 811 requires that the sensor
trigger on the leading edge of the tag for proper feeding. For the
most accurate setting, present the sensor head only, the leading
edge gap, and the trailing edge of the tag during the teach session.
1. Ensure the machine is in the aborted state.
2. Advance the tag stock by manually rotating the rewind roll
counter clockwise until the sensor head (red light) is positioned
on the trailing edge of the tag.
3. After entering the dynamic teach mode, rotate the rewind roll
counter clockwise again, making sure that a gap and the leading
edge of the next tag has been presented to the sensor head.
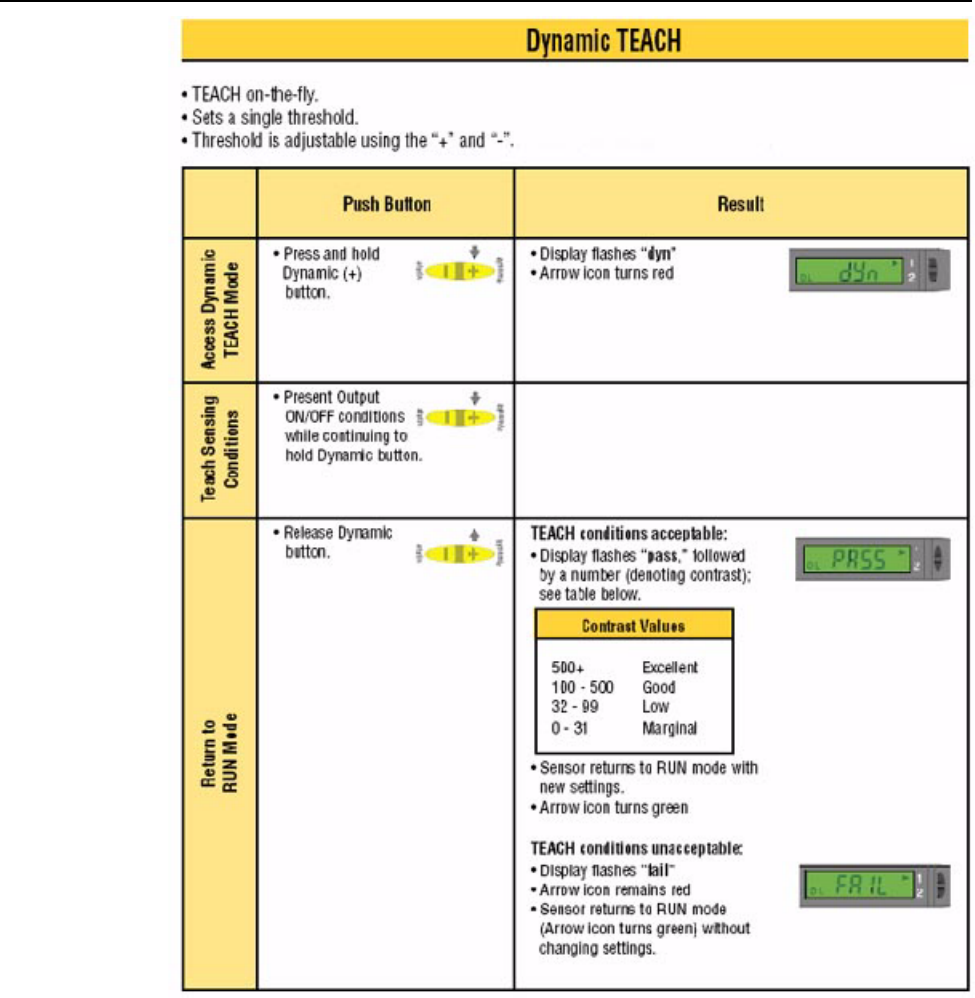
SECTION 7 Technical Information
10008547aa 06/06 m®7–7
Figure 7–3
4. Click the static (-) button once quickly after the teach mode is
exited.
5. While watching the sensor and tag stock, manually rotate the tag
stock through the machine to verify the sensor was taught
correctly. The amber output indicator #1 should light at a gap
and the amber indicator #2 should trigger at a tag. This should
give adequate results with a threshold value that was selected by
the amplifier.
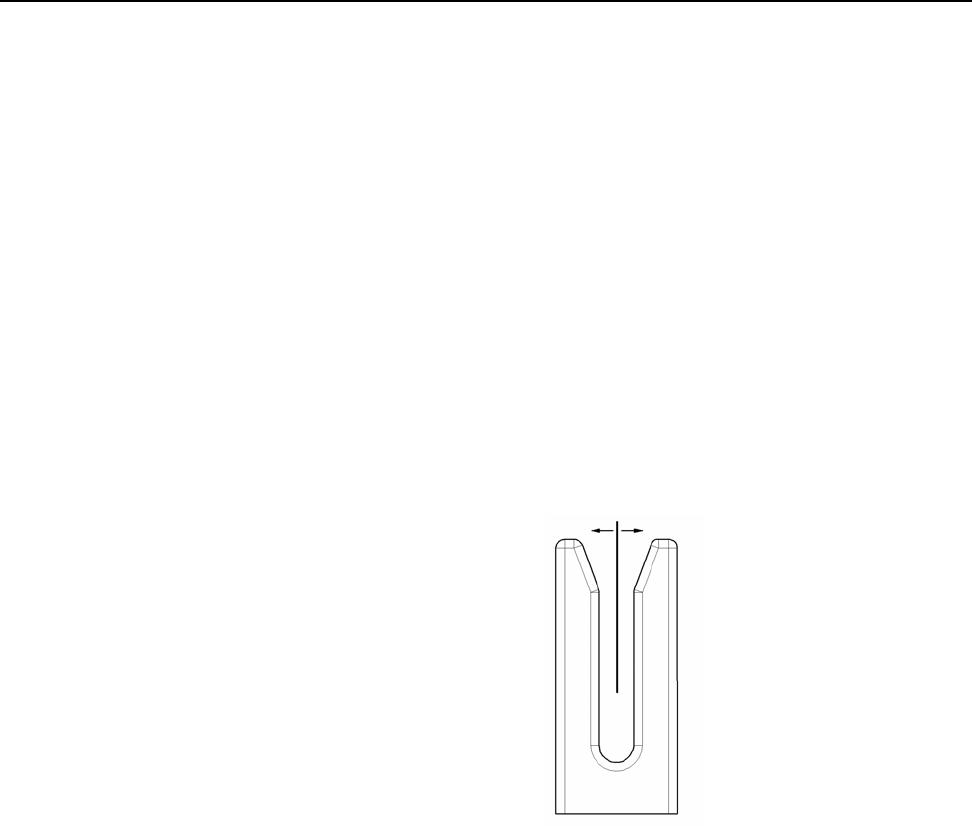
SECTION 7 Technical Information
7–8 m®10008547aa 06/06
2.2.2 Manual Override Teach
With some tag stocks it may be necessary to manually force a
threshold value. This is done by first determining the amplifier output
value variations for the tag and for the gap. The threshold value
between the gap and the tag material can then be manually set.
1. Present the tag portion of the tag stock to the sensor head and
move it back and forth between the forks (as shown below) while
noting the signal values of the amplifier. Make sure to not include
the inlay or copper portion of the tag. Record these values.
2. Present the gap portion of the tag stock to the sensor head and
move it back and forth between the forks (as shown in Figure 7-
6) while noting the signal values of the amplifier.
Hint: To increase the sense area of a gap, remove a tag from the
backing liner.
3. Record the signal values of the amplifier.
Figure 7–4
4. Set the threshold at the midpoint value between the lowest gap
number and highest tag number. Check the current threshold by
single clicking either the "+" or "-" button on the amplifier. The
display threshold value will briefly display. To change the value
to newly calculated midpoint threshold value single click "+"
button to increment the value (do not hold the button down) or
single click the "-" button to decrement the value.
5. While watching the sensor and tag stock, manually rotate the tag
stock through the machine to verify the sensor was taught
correctly. The amber output indicator #1 should light at a gap
and the amber indicator #2 should trigger at a tag. This should
give adequate results with a threshold value that was selected by
the amplifier.
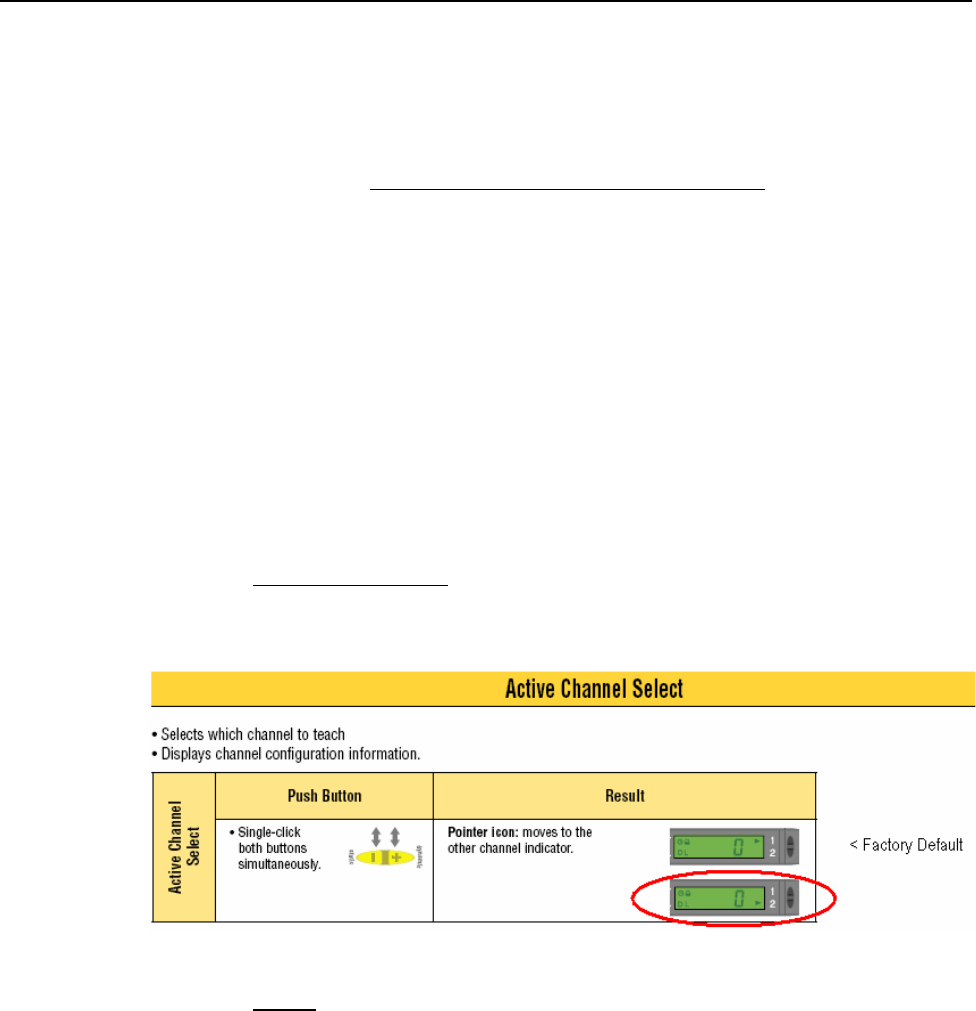
SECTION 7 Technical Information
10008547aa 06/06 m®7–9
Examples:
• Recorded amplifier reading for tag stock varies between 2800-
3800
• Recorded amplifier reading for gap varies between 4100-4150
• New Midpoint Threshold value:
3900 = (lowest gap 4100 + highest tag 3800)
2
Note that the amplifier value will decrease as the material opacity
increases. A typical empty sense amplifier value will read
approximately 4350 while a totally blocked sense head will typically
return a value between 10-20.
Typical readings for the Alien Gen 1 2x4 tag:
• Gap: 4100-4150
• Tag material: 2800-3800
• Inlay: 2130-3100
• Copper: 275-750
2.2.3 Verifying or Changing Amplifier Settings
Channel Selection
The Model 811 only uses the output signal from channel 2. Follow
the steps shown to verify/setup the sensor:
Figure 7–5
Setup
The sensor comes stored with factory defaults. Some of these must
be altered to work with the Model 811. Follow the steps shown in
Figure 7-8 to verify/setup the sensor
The amplifier comes stored with factory defaults. Some of these
settings have been altered by MARKEM to work with the Model 811.
To verify or change these settings, follow the steps shown in Figure
7-8.
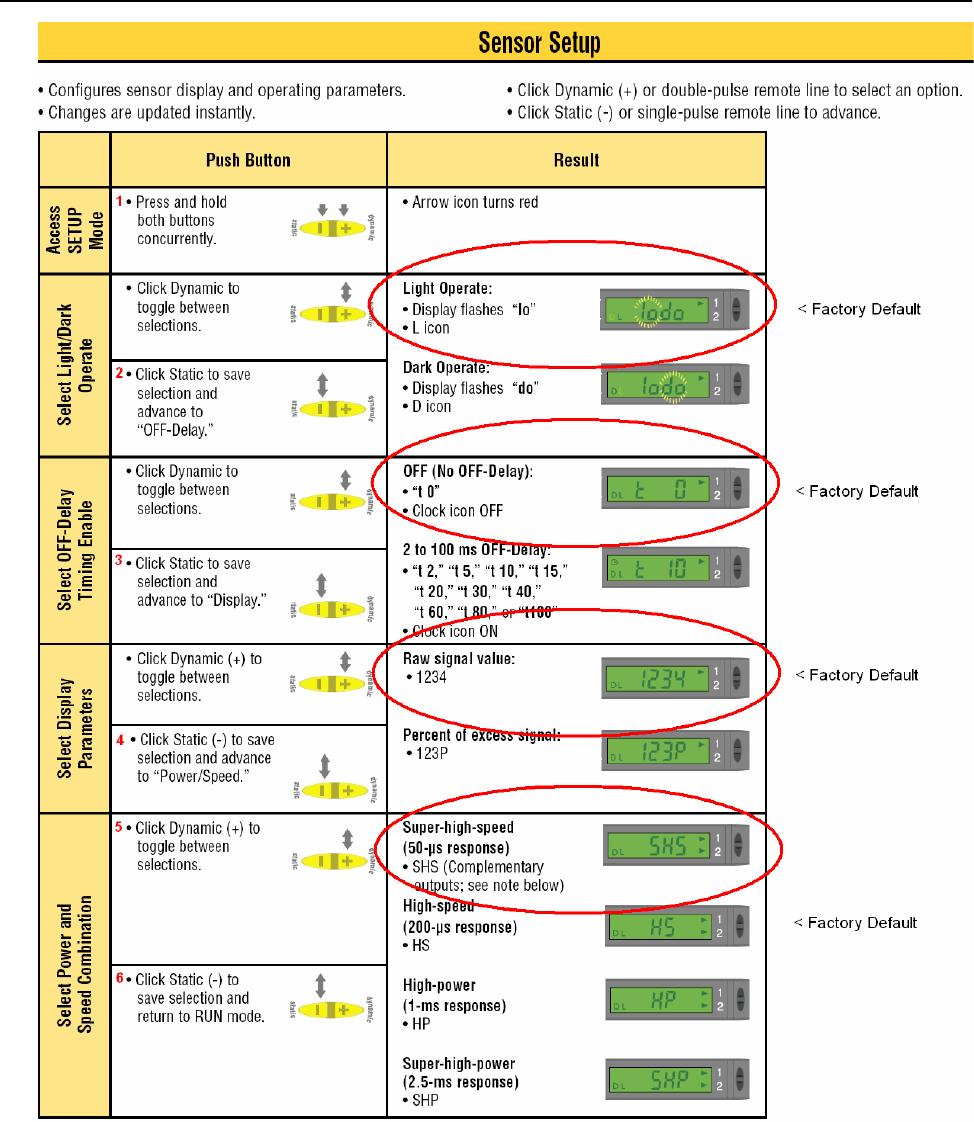
SECTION 7 Technical Information
7–10 m®10008547aa 06/06
Figure 7–6

SECTION 7 Technical Information
10008547aa 06/06 m®7–11
3.0 Antenna
The antenna shield and program antenna can be adjusted by the
user.
3.1 Repositioning the Antenna Shield
The antenna shield limits the range of the RFID program antenna by
providing a ground plane for the RF energy. This shield, along with
the program antenna, ensures that only the target tag gets
programmed. This will eliminate a false read/write of an upstream or
downstream (rejected) tag. The factory-set position should work in
most instances.
1. Loosen the mounting screw to swivel the shield around the
mounting point (Figure 7-9).
2. Ensure that a good tag can be programmed in the target
position. Remove the first upstream and all downstream tags
from the liner to verify that only the target tag is being
programmed.
3. Ensure that upstream and all downstream tags cannot be
programmed with the target tag removed from the liner.
4. Refasten the antenna shield.
picture
Figure 7–7

SECTION 7 Technical Information
7–12 m®10008547aa 06/06
3.2 Program Antenna
The program antenna can be adjusted in two axes in relation to the
tag stock as it is threaded in the machine. Aligning the program
antenna to the tag antenna will increase the tag writing capability of
the machine and eliminate rejects due to poor antenna positioning
and eliminate the possibility of writing to the incorrect tag.
3.3 Adjusting the Antenna Cross-track Position
The best position of the program antenna in the axis perpendicular
to the tag travel is to have the tag chip aligned as close as possible
between the program antenna witness line between the first and
second mounting holes. (See Figure 7-10)
picture
Figure 7–8
1. Verify the tag stock is threaded correctly in the machine.
2. Remove the two screws holding program antenna to antenna
slide.
3. Reposition the program antenna and re-fasten to the antenna
slide, using the two screws.
4. Check the tag chip alignment.
5. If a larger move is required:
Remove the (two) screws attaching the antenna bracket to the
peel bar bracket.
Reposition the antenna bracket to the alternate mounting holes
provided in the peel bar and re-fasten, using the two screws.
Repeat steps 1-4.

SECTION 7 Technical Information
10008547aa 06/06 m®7–13
3.4 Adjusting the Antenna In-track Position
The best position of the program antenna in the axis parallel to the
tag travel is to have the bottom edge of the antenna in-line with the
tag chip. This position may be different for various tag types
dependent on the tag antenna design.
If the program antenna does not have enough in-track travel to be
properly adjusted to the tag stock, contact MARKEM to obtain a
custom bracket.
picture
Figure 7–9
1. Verify the tag stock is threaded correctly in the machine and the
machine is in the non producing state.
2. Index the tag stock so it is in its correct peel position.
3. Loosen the two thumb screws that fasten the antenna slide to
the antenna bracket.
4. Align the bottom edge of the program antenna to the tag chip by
rotating the adjustment screw CW to raise the antenna or CCW
to lower it.
5. From the LUI, put the machine into Manual Mode.
Hold the F1 key and press the Mode key.
This will put the machine in a continuous program mode.
A blinking blue LED signifies a successful write while the blinking
amber fault lamp signifies a failed write attempt.
6. Continue trying to program a tag while raising and lowering the
antenna and watching the program status. Note extremes of
antenna travel where the tag stops programming.

SECTION 7 Technical Information
7–14 m®10008547aa 06/06
7. Position the antenna at the midpoint of the successful write
program band.
8. Tighten the two thumb screws that fasten the antenna slide to
the antenna bracket.
9. Verify position by feeding tags from the LUI by holding the F1
key and pressing the Minus key to reject tags. Note that even
with the program antenna correctly positioned, a small
percentage of tags as provided from the manufacturer may not
write successfully due to the manufacturing process.
10.From the LUI, hold the F1 key and press the Mode key to
remove the machine from continuous program mode.

SECTION 7 Technical Information
10008547aa 06/06 m®7–15
4.0 Tag Peel Position
The tag peel position is the relative position of peeled tag with
respect to the peel bar. This position is critical to the proper
transition of the programmed tag from the liner to the applicator
faceplate. The position can be adjusted forward or backward from
either the Setup screen of the Web UI or the LUI.
Note that the feed forward steps are active and movement can
visibly be seen. Backup steps will not be active until the next tag is
cycled into position.
4.1 Adjusting the Tag Peel Position Using the Web UI
1. Open the Web UI.
2. Go to: Home Page > Settings > General System Configuration >
Feed Forward Steps > Edit >
+ (to advance tag forward) or - (to back up tag) >
Apply
4.2 Adjusting the Tag Peel Position Using the LUI
1. Set the machine into Manual Mode.
2. Press the "+" key to advance the tag forward or press the "-" key
to backup the tag with relation to the peel bar.
5.0 Applicator Selection
In order for the dispenser to communicate with the applicator, the
machine firmware must match the applicator type that is mounted to
the dispenser. If the improper applicator is selected, the machine will
fail to apply tags.
To verify or change the applicator selection:
1. Open the Web UI.
2. Go to: Home Page > Settings > General System Configuration >
Applicator Type - Edit > "select the appropriate applicator" >
Apply

SECTION 7 Technical Information
7–16 m®10008547aa 06/06
6.0 Tag Type and SIze
6.1 Verifying and Editing Tag Length
To optimize machine speeds, the tag length needs to be input into
Web UI. If a tag length shorter than actual is input into the Web UI,
the machine will run at reduced throughput speeds. If a tag length
longer than actual is input into the Web UI, the machine will not run.
1)From the host's web based user interface: Homepage > Settings >
General System Configuration > Tag Length - Edit > "select the
appropriate length" > Apply.
6.2 Verifying and Edting Tag Generation
In order to program an RFID tag, the machine firmware must match
the tag type that is being loaded into the machine. If the improper
tag generation is selected, the machine will fail to program tags.
Check with the manufacturer of the tag to verify type. This
information may be found on the manufacturer's label on the inside
of the tag stock core.
To Verify/Edit Tag Generation Type:
1)From the host's web based user interface: Homepage > Settings >
RFID Configuration > Tag Generation - Edit > "select the
appropriate Gen" > Apply.
6.3 Verifying and Editing Tag Data Size
In order to program an RFID tag, the machine firmware must match
the tag type that is being loaded into the machine. If the improper
tag data size is selected, the machine will fail to program tags.
Check with the manufacturer of the tag to verify type. This
information may be found on the manufacturer's label on the inside
of the tag stock core.
To Verify/Edit Tag Data Size:
1)From the host's web based user interface: Homepage > Settings >
RFID Configuration > Tag Data Size - Edit > "select the appropriate
bit size" > Apply.
Tag Data Size Selection
In order to program an RFID tag, the machine firmware must match
the tag type that is being loaded into the machine. If the improper
tag data size is selected, the machine will fail to program tags.
Check with the manufacturer of the tag to verify type. This
information may be found on the manufacturer's label on the inside
of the tag stock core.

SECTION 7 Technical Information
10008547aa 06/06 m®7–17
To Verify/Edit Tag Data Size:
1)From the host's web based user interface: Homepage > Settings >
RFID Configuration > Tag Data Size - Edit > "select the appropriate
bit size" > Apply.
Write Power/ Read Power
The amount of RF read and program energy can be adjusted
dependant on specific tag requirements. The default setting will
work in most conditions for most tag types. If a known good tag
cannot be written to after attempts with altering the antenna position,
the write/read power can be adjusted. The value of the Read Power
should mimic the value of the write power. Note that adjusting the
power too high can flood the program area with too much energy
and give inadequate results and/or program upstream or
downstream tags. Adjusting the power too low may result in a high
reject rate.
To Verify/Edit the Write Power:
1)From the host's web based user interface: Homepage > Settings >
RFID Configuration > Write Power - Edit > "increment or decrement
the write power setting" > Apply.
To Verify/Edit the Read Power:
1)From the host's web based user interface: Homepage > Settings >
RFID Configuration > Read Power - Edit > "increment or decrement
the read power setting" > Apply.

SECTION 7 Technical Information
7–18 m®10008547aa 06/06

Model 811
Operation/Service Manual
m
®
SECTION 8
Troubleshooting Guide
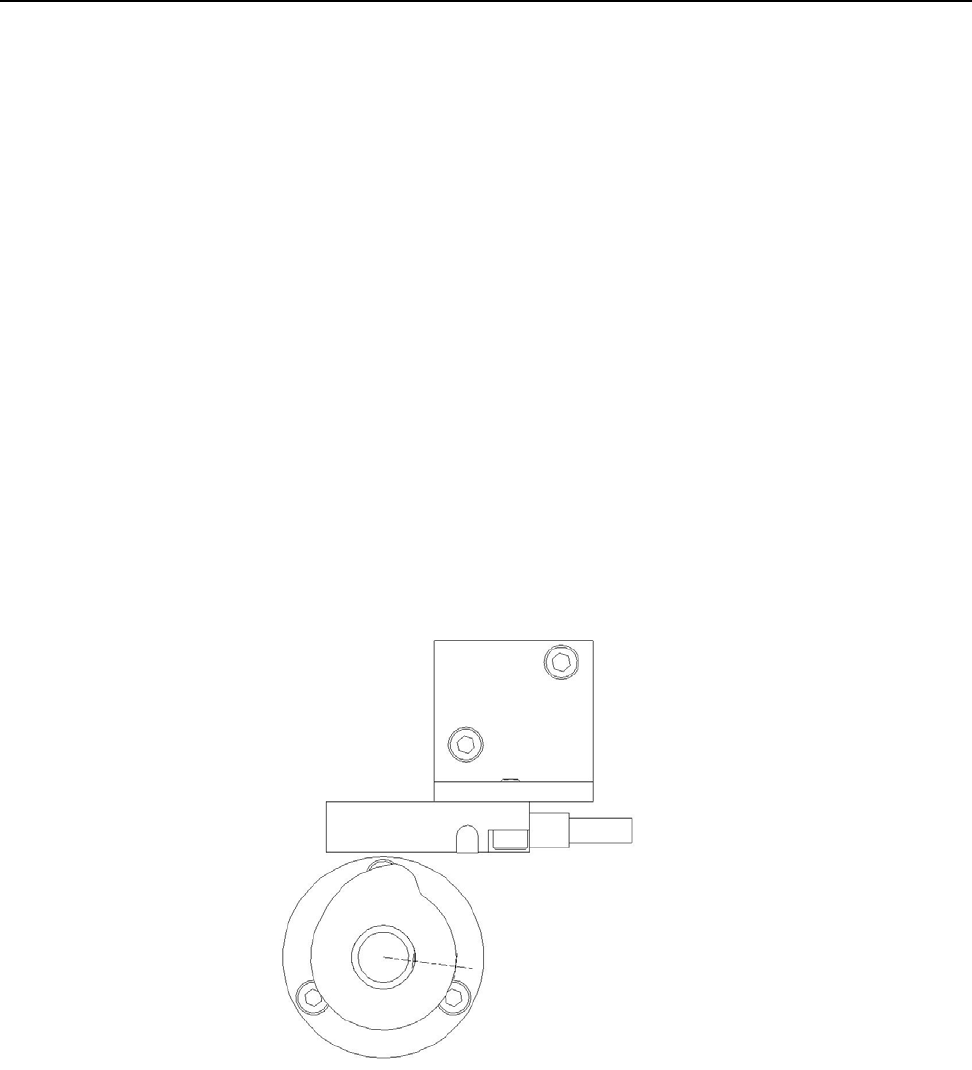
SECTION 8 Troubleshooting Guide
10008547aa 06/06 m®8–1
1.0 Supply Dancer Cam Position
If the supply dancer cam is not positioned correctly, the supply arbor
could either unwind the supply or create excessive tensions on the
web that could damage the dancer arm.
The dancer cam position should only be adjusted by trained
personnel as this procedure requires working inside the dispenser
enclosure with power energized to the machine.
The supply dancer cam position is locked to the supply dancer arm
with a set screw. The cam profile is read from an inductive proximity
sensor which outputs an analog signal to the digital board which
controls the supply motor output speed and direction of rotation. The
position and distance of the cam to inductive proximity sensor is set
at the factory to maintain a constant tension on the web during
normal operation of the machine.
1. Remove power and the rear cover from the machine.
2. Disconnect the supply motor connector from the analog board
connector X16.
3. If required adjust the cam so the high point is facing the sensor
when the dancer is in the home position as shown.
Figure 8–1
4. Connect power to the machine.
5. Attach a multi-meter positive lead to pin 2 on the X10 connector
and negative lead to pin 4 on the X10 connector. The multi-meter
should read 0.75+/- 0.02 VDC with the dancer arm in the home
(back) position.
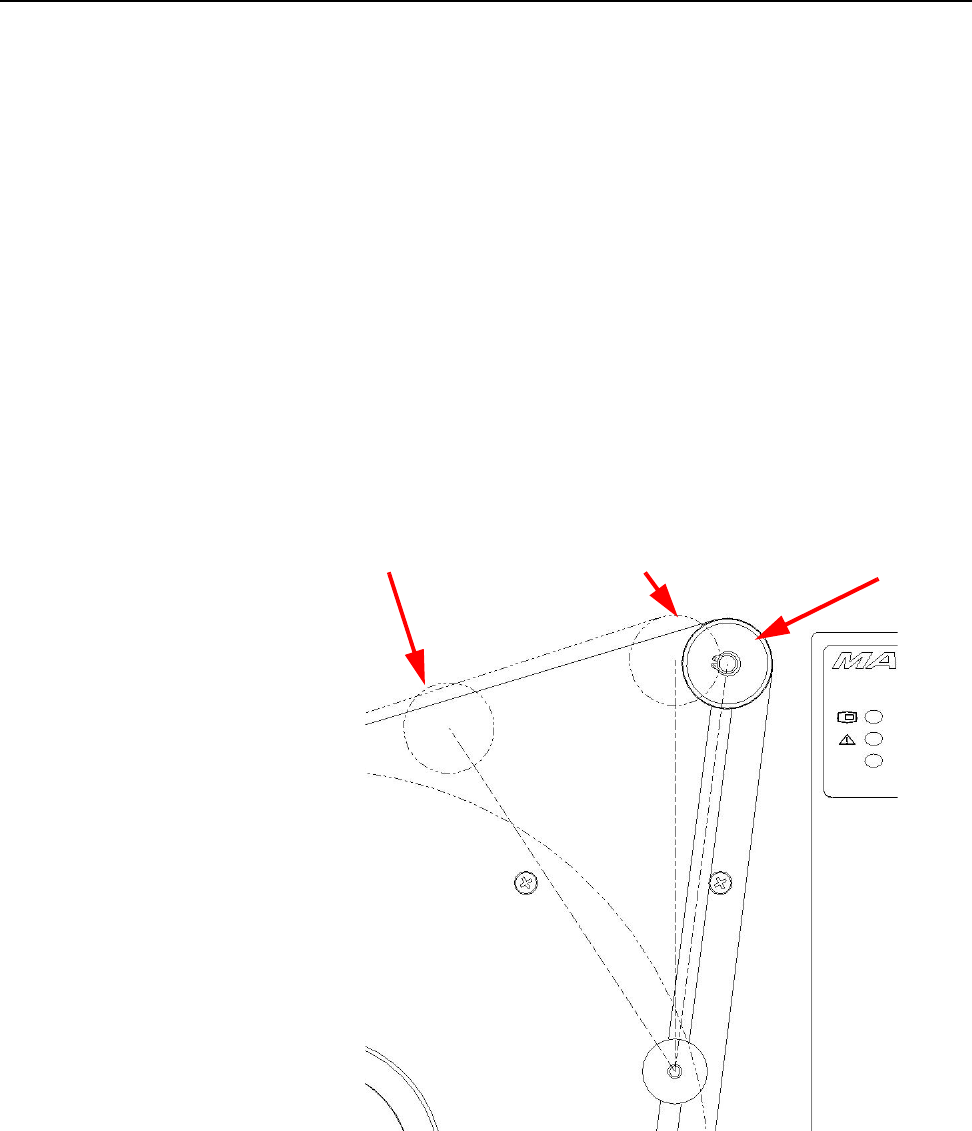
SECTION 8 Troubleshooting Guide
8–2 m®10008547aa 06/06
6. Loosen the screws on the sensor bracket to adjust the sensor
distance to the cam which will vary the readings.
7. When the home position is set within the specified limits, tighten
the bracket screws.
8. Verify the output is 2.55+/- 0.04 VDC with the dancer arm in the
full forward position against the stop. It may be helpful to tie-wrap
the arm to the forward stop post. If it is not within the specified
limits, the cam is not positioned correctly. Repeat steps 3-7.
9. Disconnect power from the machine. Plug in the supply motor.
Connect power to the machine. While moving the dancer arm
through its limits, the supply motor should drive the supply arbor
as follows:
• Home position: Rewind
• Neutral Position: Static
• Forward position: Unwind
10.When the supply dancer position is correct, install the rear cover
on the machine.
FORWARD POSITION
UNWINDING NEUTRAL POSITION
STATIC HOME POSITION
REWINDING

SECTION 8 Troubleshooting Guide
10008547aa 06/06 m®8–3
2.0 Tag Feed Problems
Tag feed problems can be caused by several things such as:
• Machine being incorrectly webbed
• Drive belts slipping
• Stepper motor stalling
• Faulty gap sensor
• Incorrect parameter settings
2.1 Incorrect Tag Stopping Position
2.2 Erratic Tag Feeding
2.3 Inconsistent Tag Stopping Position
3.0 No Driving of Tags

SECTION 8 Troubleshooting Guide
8–4 m®10008547aa 06/06

Model 811
Operation/Service Manual
m
®
SECTION 9
Recommended Spare Parts
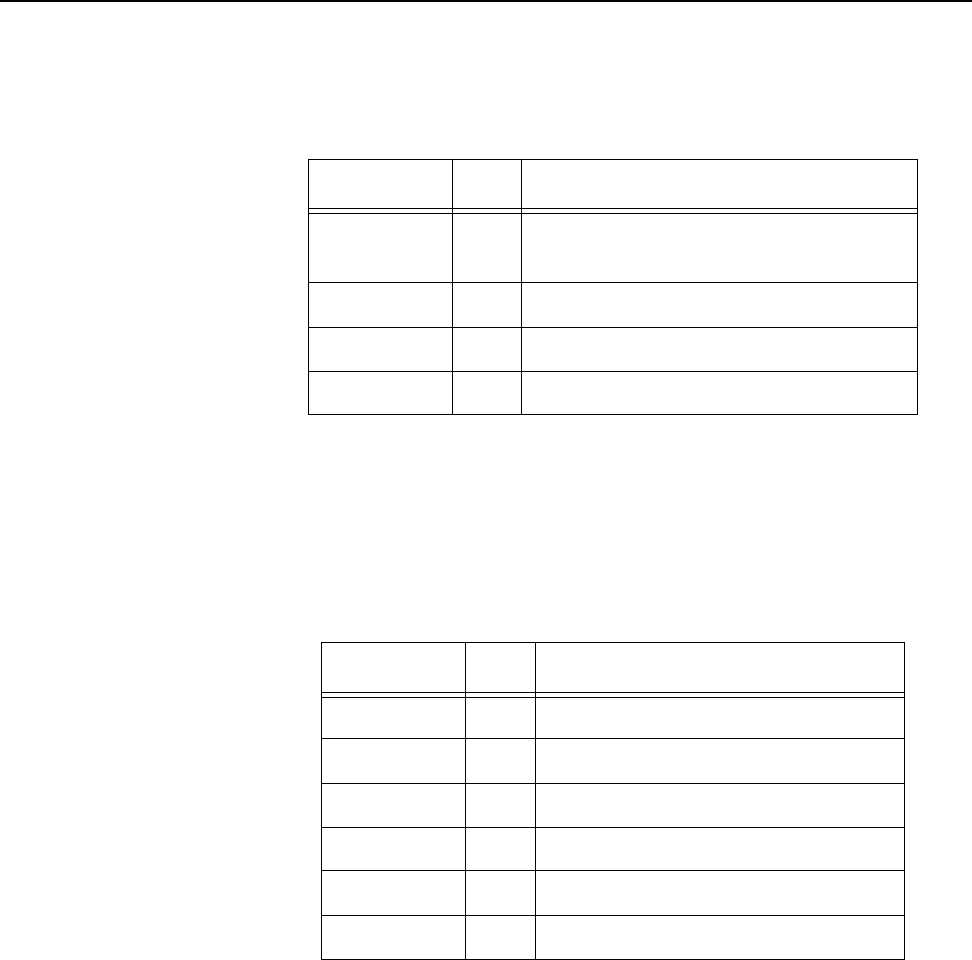
SECTION 9 Recommended Spare Parts
10008547aa 06/06 m®9–1
1.0 Preventive Maintenance Spare Parts
Preventive maintenance spare parts are listed below.
2.0 General Spare Parts
General spare parts are listed below.
Table 9–1 Preventive Maintenance Spare Parts
Part No. Qty Description
0947820 1 Drive Roll (requires bearing Part
No. 0210108)
0651328 1 Pinch Roll
1002161 1 Clutch Facing
0686057 1 Fuse
Table 9–2 General Spare Parts
Part No. Qty Description
0672701 1 Keypad (Local User Interface)
10002277 1 U-Pin
10009448 1 Motor
0630920 1 Belt
0630922 1 Belt
10003908 1 Solenoid

SECTION 9 Recommended Spare Parts
9–2 m®10008547aa 06/06

Model 811
Operation/Service Manual
m
®
Section 10
Parts Illustrations and
Electrical Schematics