Microchip Technology A092007 ATRCB256RFR2-XPRO RCB256RF2 extension for XPRO User Manual AT04357 RCB256RFR2 XPRO User Guide USER GUIDE
Atmel Norway AS ATRCB256RFR2-XPRO RCB256RF2 extension for XPRO AT04357 RCB256RFR2 XPRO User Guide USER GUIDE
Manual
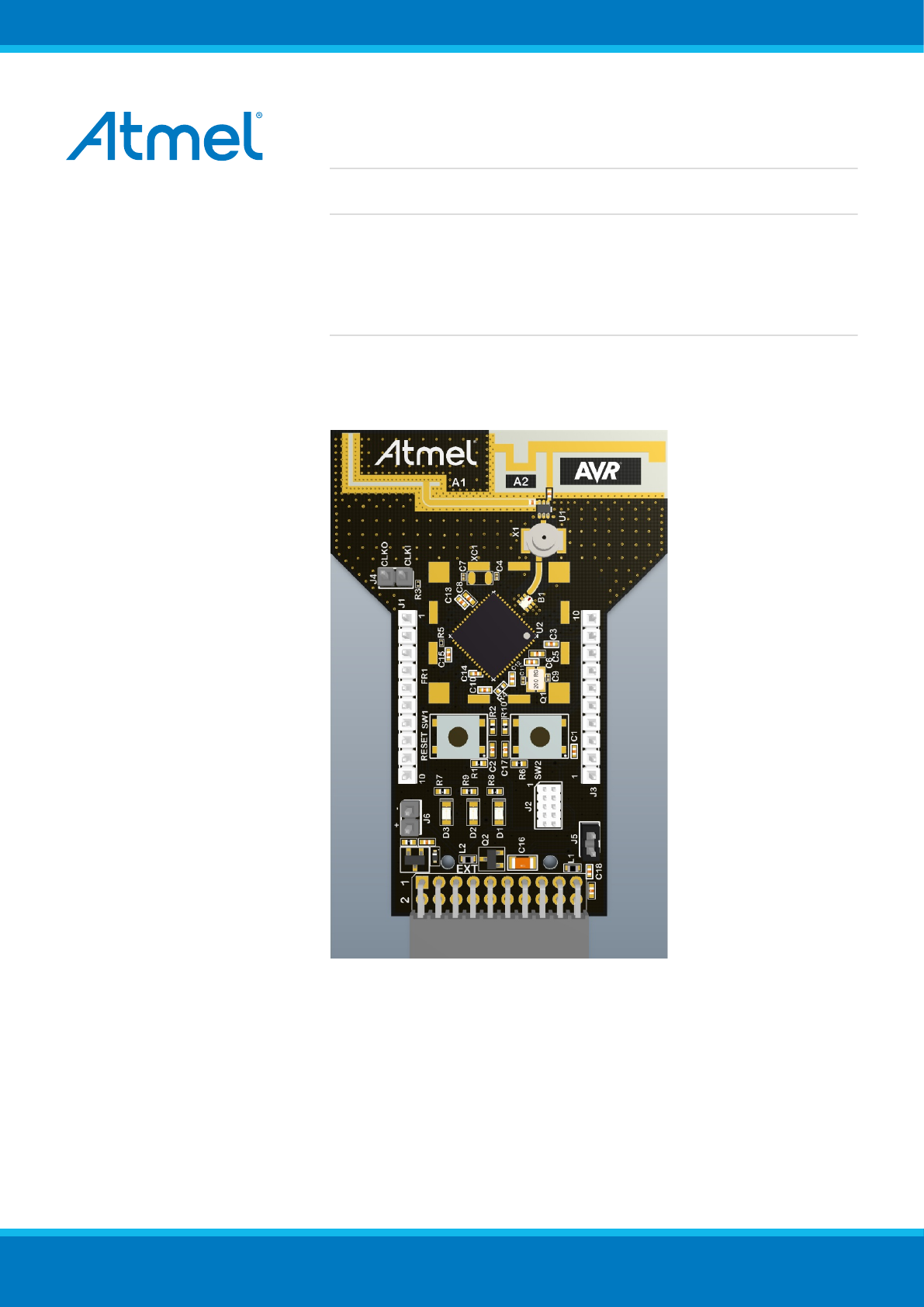
TBDA-MCU-09/2013
USER GUIDE
AT04357 RCB256RFR2-XPRO User Guide
Introduction
This application note describes how to get started with the Atmel®
RCB256RFR2-XPRO Extension board.
The Extension boards is targeted for evaluating the features of the Atmel
ATmega256RFR2 wireless SoC with PCB antenna.
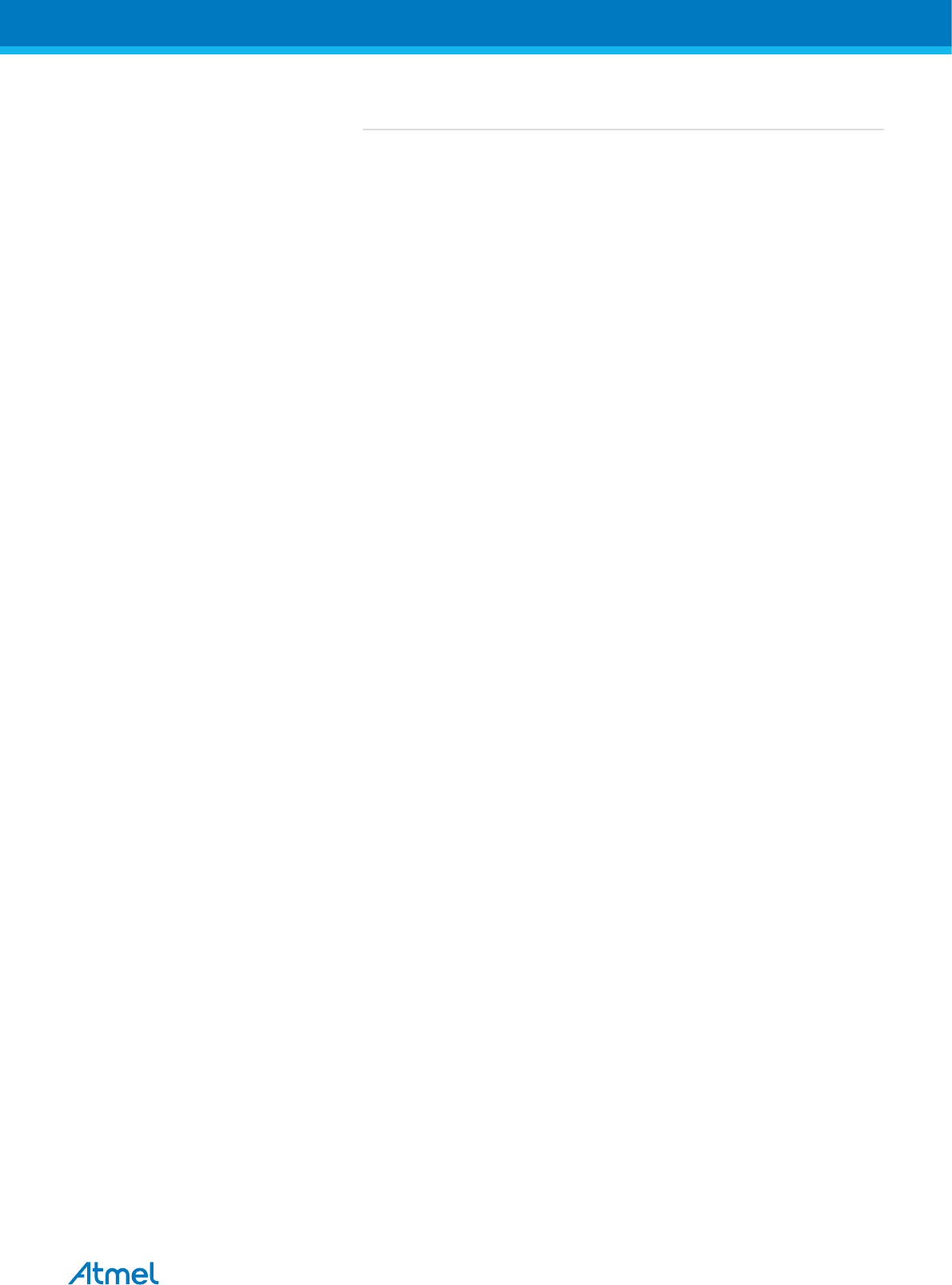
AT04357 RCB256RFR2-XPRO User Guide [USER GUIDE]
TBDA-MCU-09/2013
2
Table of Contents
Introduction .................................................................................... 1
1. Getting Started ........................................................................ 3
1.1. Features .............................................................................. 3
1.2. Design documentation and related links ..................................... 3
1.3. Board Assembly .................................................................... 3
1.3.1. Connect to a Xplained PRO board ............................... 3
1.3.2. Standalone node ....................................................... 3
1.3.3. In customer development assembly .............................. 3
1.4. Connecting the kit ................................................................. 3
1.4.1. Atmel Studio ............................................................ 4
1.4.2. Connect the extension UART to the EBDG COM port ....... 4
1.5. Programming ........................................................................ 4
1.5.1. JTAGICE ................................................................. 4
1.5.2. Boot loader .............................................................. 4
1.6. Available example code .......................................................... 5
2. Performance Analyzer ............................................................. 6
2.1. Introduction .......................................................................... 6
2.2. Program installation ............................................................... 6
2.3. Program use ........................................................................ 9
3. Xplained Pro .......................................................................... 11
3.1. Hardware identification system ............................................... 11
3.2. Standard headers and connectors .......................................... 11
3.2.1. Xplained Pro standard extension header ...................... 11
4. Hardware user guide ............................................................ 13
4.1. Board overview ................................................................... 13
4.2. Headers and connectors ....................................................... 13
4.2.1. J100 Xplained Pro extension connector ....................... 13
4.2.2. J1 & J3 ................................................................. 14
4.2.3. JTAG (J2) .............................................................. 14
4.2.4. CLK (J4) ................................................................ 15
4.2.5. Current monitoring (J5) ............................................. 15
4.2.6. External power (J6) ................................................. 15
4.3. Board GUI .......................................................................... 16
4.3.1. LED's .................................................................... 16
4.3.2. Button ................................................................... 16
4.4. Factory programmed data ..................................................... 16
5. Agency Certifications ............................................................ 17
5.1. United State (FCC) .............................................................. 17
5.2. European Union (ETSI) ........................................................ 17
5.3. Canada (IC) ....................................................................... 18
5.4. Using Limited Modular Certified Products ................................. 18
6. Document revision history ..................................................... 20
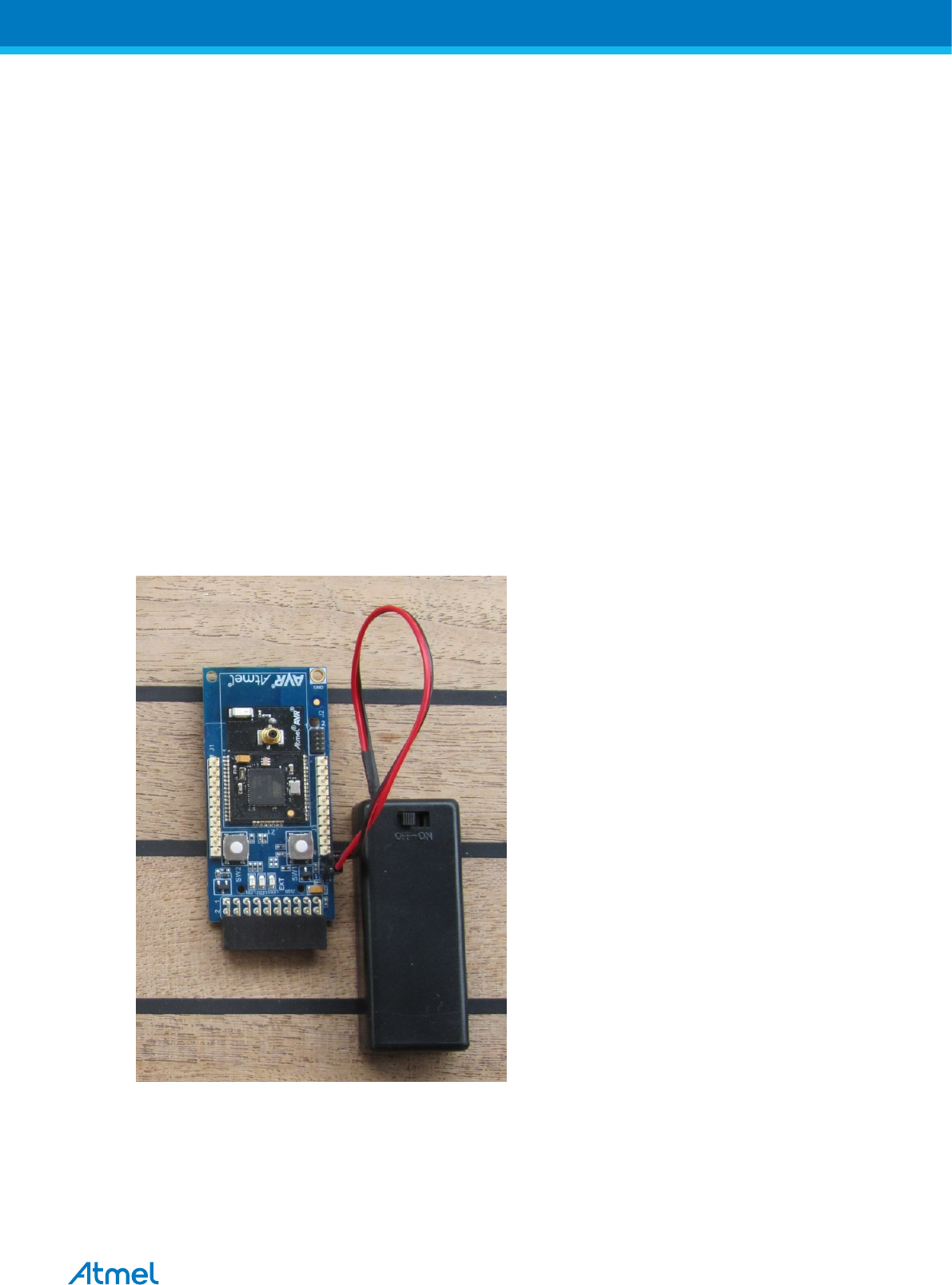
AT04357 RCB256RFR2-XPRO User Guide [USER GUIDE]
TBDA-MCU-09/2013
3
1. Getting Started
1.1 Features
The RCB256RFR2-XPRO extension board provide a development/prototype platform for the Atmel
ATmega256RFR2.
1.2 Design documentation and related links
The following list contains links to the most relevant documents and software for the extension boards.
http://www.atmel.com/tools/rcb256rfr2-xpro.aspx
1.3 Board Assembly
The extension board can be used in number of combinations. To provide wireless communication to a Xplained
PRO board, to act as a standalone wireless node, to provide wireless communication to your own prototype for
SW development and HW verification.
1.3.1 Connect to a Xplained PRO board
The Extension board can be connected to any Xplained PRO main board using the extension header.
Picture of SAM4L with extension
1.3.2 Standalone node
The Extension board can be used as a standalone node - use the 2AA battery pack available in Atmel store to
provide power as shown in picture below (new picture)
1.3.3 In customer development assembly
The Extension board can be wired into the customer prototype assembly by using the on-board connectors, all
ZigBit signal are available
1.4 Connecting the kit
How to connect the extension board
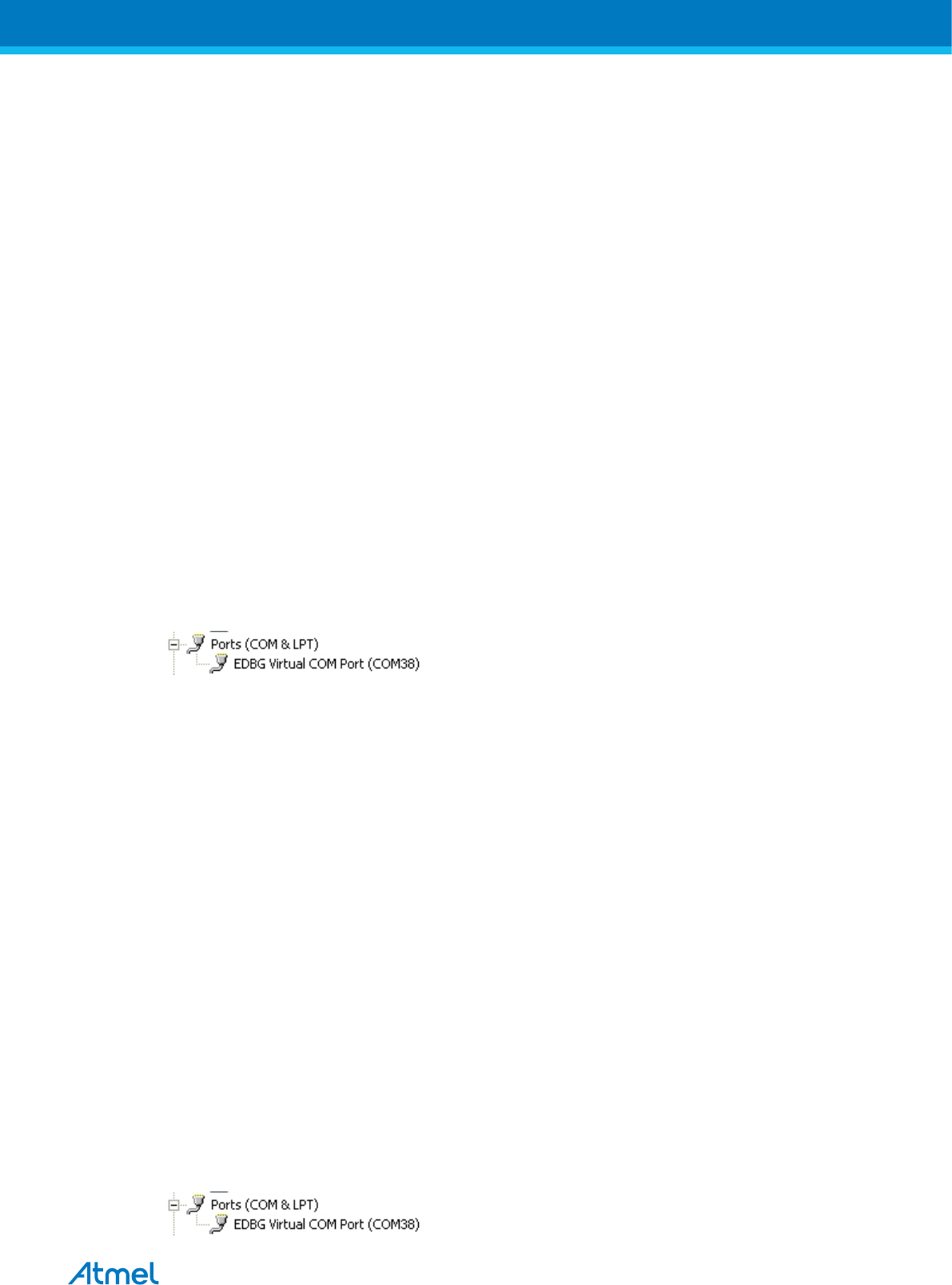
AT04357 RCB256RFR2-XPRO User Guide [USER GUIDE]
TBDA-MCU-09/2013
4
1.4.1 Atmel Studio
How to connect the Extension board + Xplained PRO board assembly to Atmel Studio
1. Download and install Atmel Studio
2. Launch Atmel Studio
3. Connect an USB cable to the DEBUG USB port and the kit will be visible in Atmel Studio
1.4.2 Connect the extension UART to the EBDG COM port
This section describes how to connect to the extension board UART by using the EBDG COM port.
All Xplained PRO boards have an embedded debugger (EBDG) with a number of features, among them a
CDC/COM port which enables the user to connect to the extension board UART and using the boot-loader on
the extension board.
1. Select a Xplained Pro board supported with a "Serial bridge application", currently supported by the
SAM4L XPRO and the ATMEGA256RFR2 XPRO boards.
2. Download the "Wireless Library hex" extension using Atmel Studio Extension Manager
Atmel Studio: Tools/Extension Manager/Wireless, download and unzip in a directory of your choise
3. Connect the EDBG USB to the PC and Program the "Serial bridge application" hex file on the XPRO
board.
Atmel Studio: Tools/Device Programming, select the XPRO-EDBG as Tool and click Apply
Select "Memories" and locate the "Serial bridge application" hex file and click Program
4. The UART on EXT1 should now be connected to the EDBG COM port at 9600baud
1.5 Programming
How to program the extension
1.5.1 JTAGICE
How to program using the JTAGICE mkII and JTAGICE3.
1. Connect the JTAGICE USB to the PC
2. Connect the JTAGICE to the Extension board connector (J2) as shown on picture.
3. Go to Atmel Studio: Tools/Device Programming, and select the JTAGICE connected as Tool and click
Apply.
4. Select Device = ATxmega256A3U
5. Select "Memories" and locate the source hex or elf file and click Program
with pictures of connection to the extension board.
1.5.2 Boot loader
This section describes how to use the bootloader to program the ZigBit on the Extension board
1. Use a Xplained Pro board with a "Serial bridge application" (section 1.4.2) to connect the Extension board
UART to the Embedded debugger COM port or connect the "Extension board UART" using any other level
shifter solution you might have.
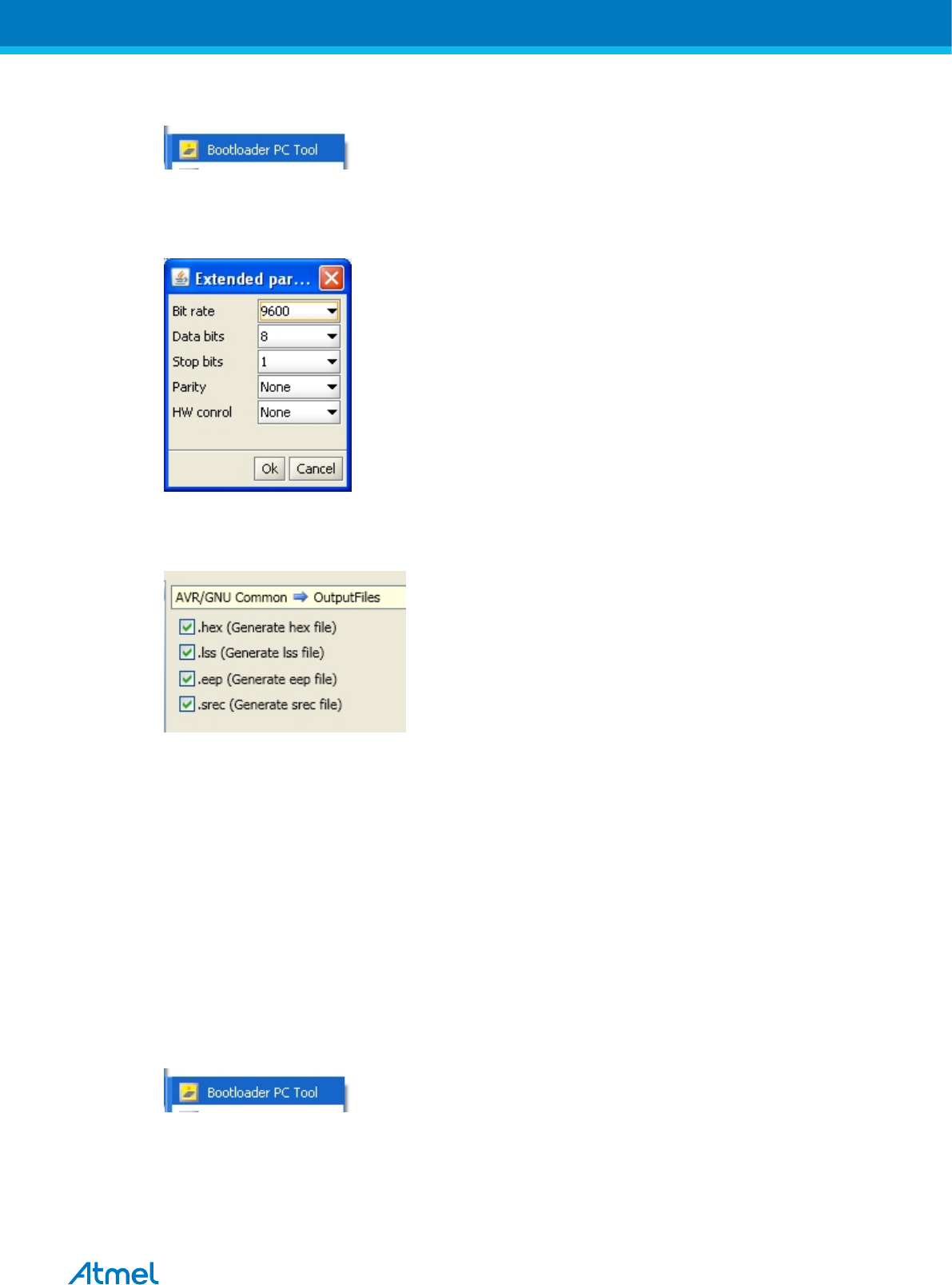
AT04357 RCB256RFR2-XPRO User Guide [USER GUIDE]
TBDA-MCU-09/2013
5
2. Start the "Bootloader PC tool" provided in the "Wireless Library hex" extension
3. Set "Connection" to Serial and "Port" to the COM port number
4. Configure the serial port settings as (click symbol at the right of Port setting)
5. "Select srec file", the file have to be of SREC format.
Atmel Studio output files can be of SREC format
6. Deselect EEPROM erase if not required.
7. Click "Upload"
8. Press the HW reset button (SW1) on the device if requested. The Bootloader PC tool will be waiting for
approximately 30 seconds for the button to be released. If this does not happen, programming will be
aborted.
9. Exit the GUI and reset the board - your new application should be up and running.
How to install the "Bootloader PC tool"
How to install the Bootloader PC GUI tool
1. Run the "Bootloader_PC_Tool_Setup_...exe" provided in the "Atmel AVR2054 Serial Bootloader" extension
from the Extension Gallery and complete the installation.
2. The Bootloader PC Tool is now available in the Atmel program folder
1.6 Available example code
SW examples provided for ATmega256RFR2 in Atmel Studio.
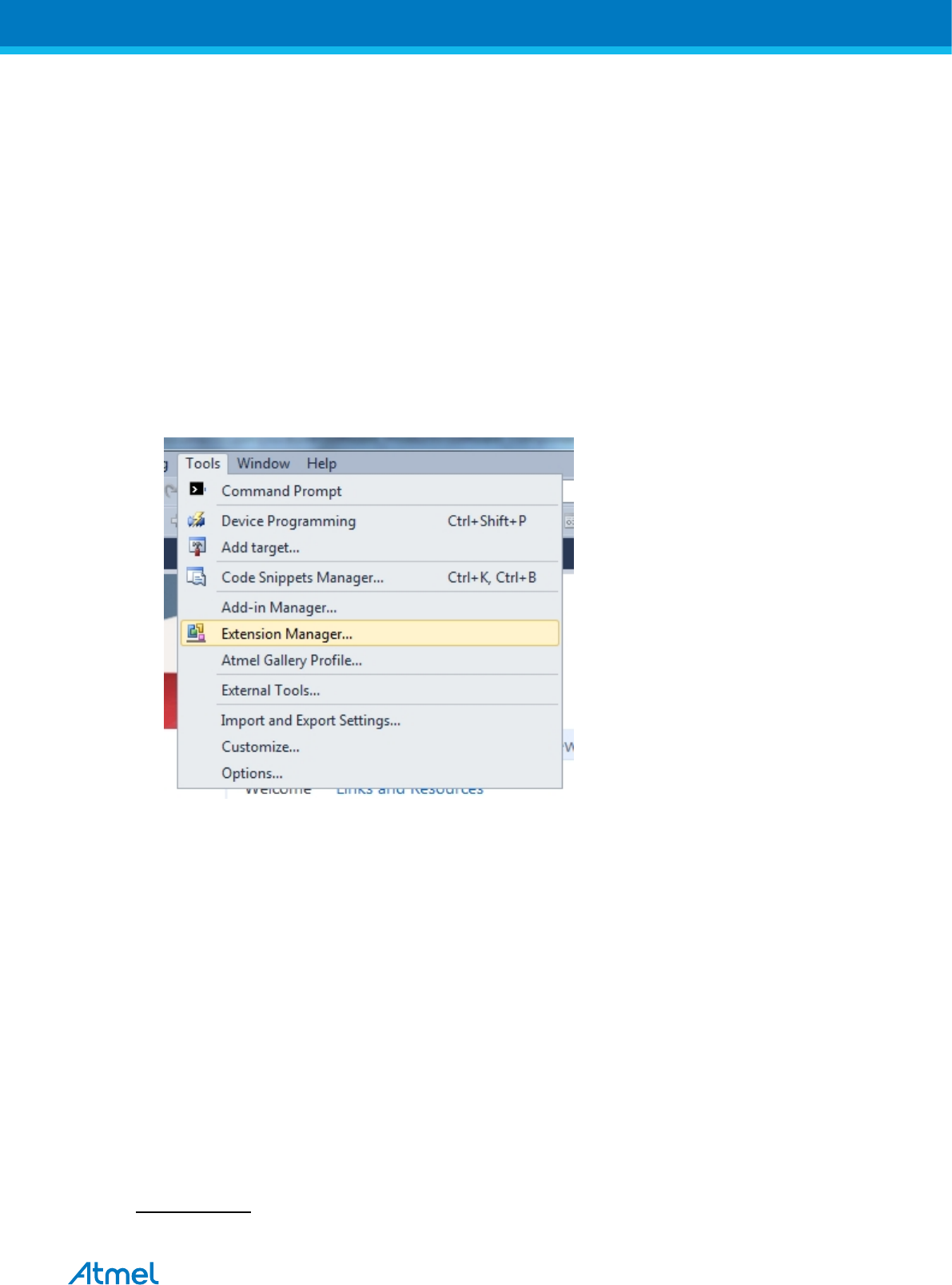
AT04357 RCB256RFR2-XPRO User Guide [USER GUIDE]
TBDA-MCU-09/2013
6
2. Performance Analyzer
2.1 Introduction
The Performance Analyzer FW together with the GUI in Atmel Studio Wireless Composer Extension provides a
number of basic functional RF tests.
A quick start guide and general help is provided in Wireless Composer once started.
2.2 Program installation
How to install necessary SW. (Details provided in "Getting Started Chapter")
1. Install Atmel Studio1
2. Once Studio is installed and started use the Tools - Extension Manager to install the Wireless Composer
Select Wireless and Wireless Composer
1 http://www.atmel.com/tools/atmelstudio.aspx
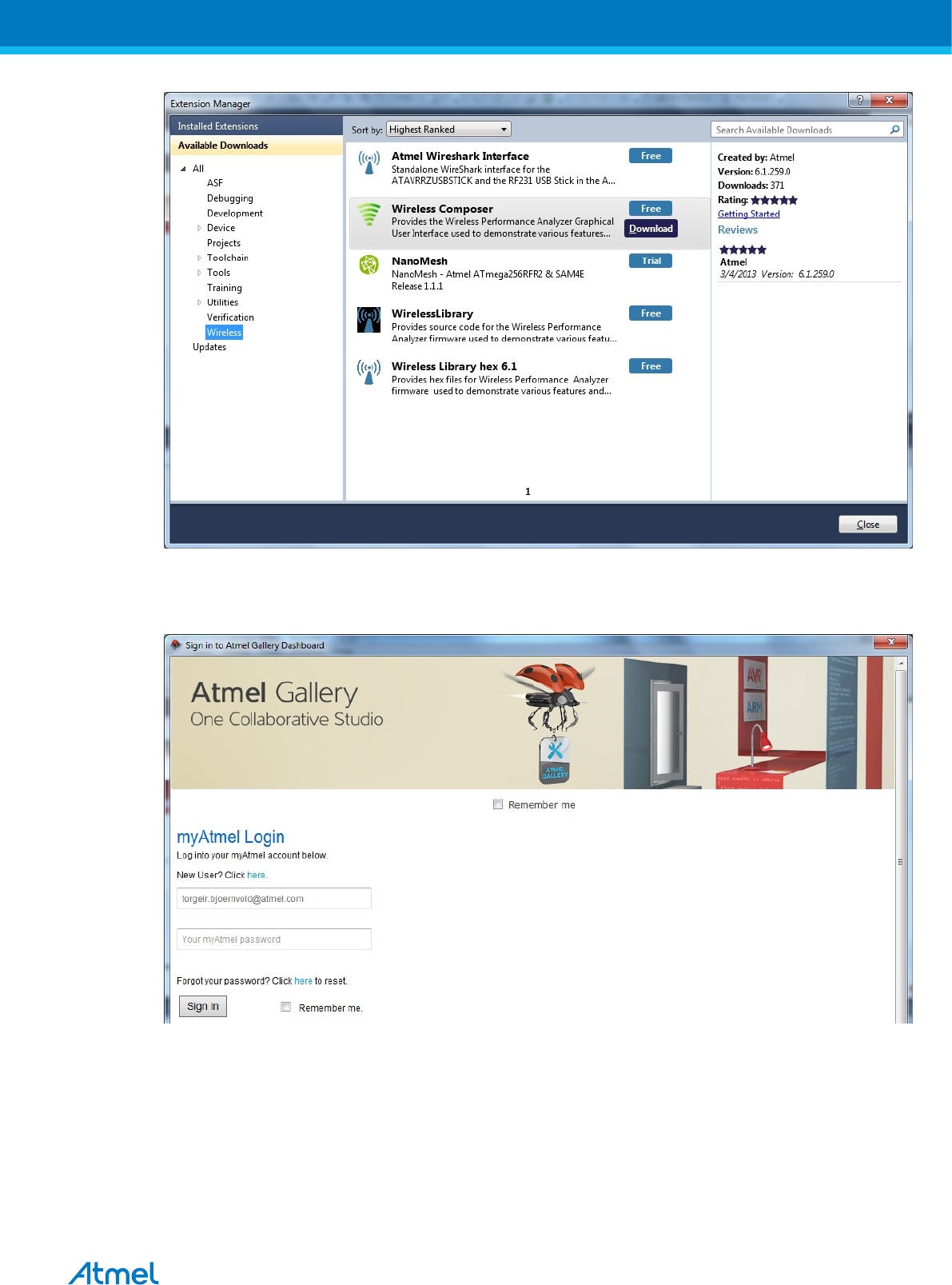
AT04357 RCB256RFR2-XPRO User Guide [USER GUIDE]
TBDA-MCU-09/2013
7
Log in to Atmel Gallery
Click download again and download starts
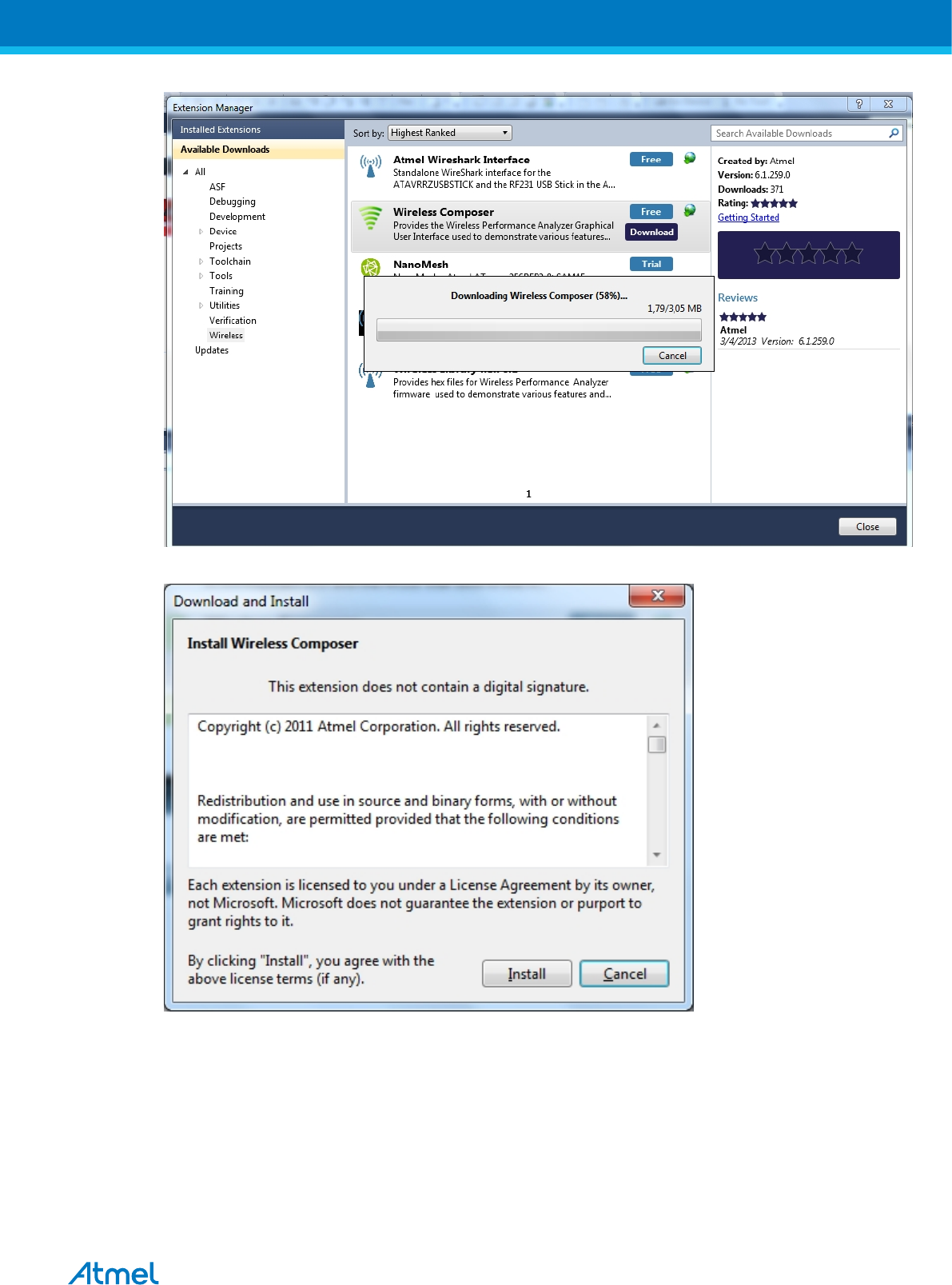
AT04357 RCB256RFR2-XPRO User Guide [USER GUIDE]
TBDA-MCU-09/2013
8
Restart Atmel Studio, allow help to make changes and the Performance Analyzer GUI is available in the
Tools menu
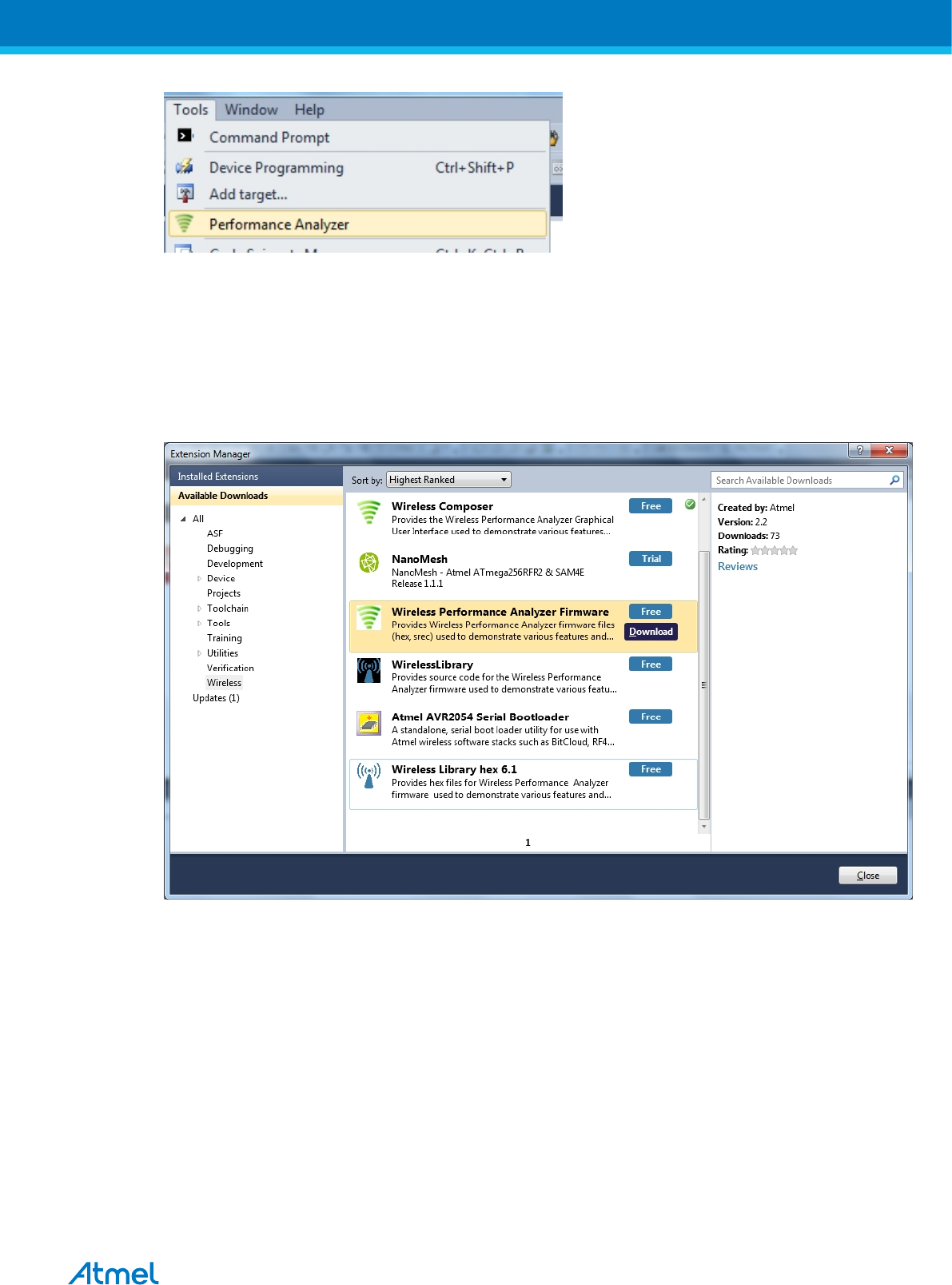
AT04357 RCB256RFR2-XPRO User Guide [USER GUIDE]
TBDA-MCU-09/2013
9
3. If not already preprogrammed - program the node with the Performance Analyzer FW available in the
"Wireless Performance Analyzer Firmware extension" or from source code provided in ASF.
If using an Wireless board with a uC embedded, the Performance Analyzer FW has to be programmed
using the Bootloader or JTAGICE as described in the "Getting started " chapter
If using a extension board which do not have a uC embedded, the Performance Analyzer FW has to be
programmed on the Xplained PRO board using the EBDG as described in the "Getting started " chapter
2.3 Program use
How to get started
1. Connect the Wireless board assembly, with the Performance Analyzer FW programmed, to the PC USB
connector and power on, a COM port should now be available for the kit.
2. Power on any other wireless node assemblies of similar frequency, running the Performance Analyzer FW,
and use it as a reference.
3. Start Performance Analyzer GUI, connect to the kit via the COM port and follow the quick start guide.
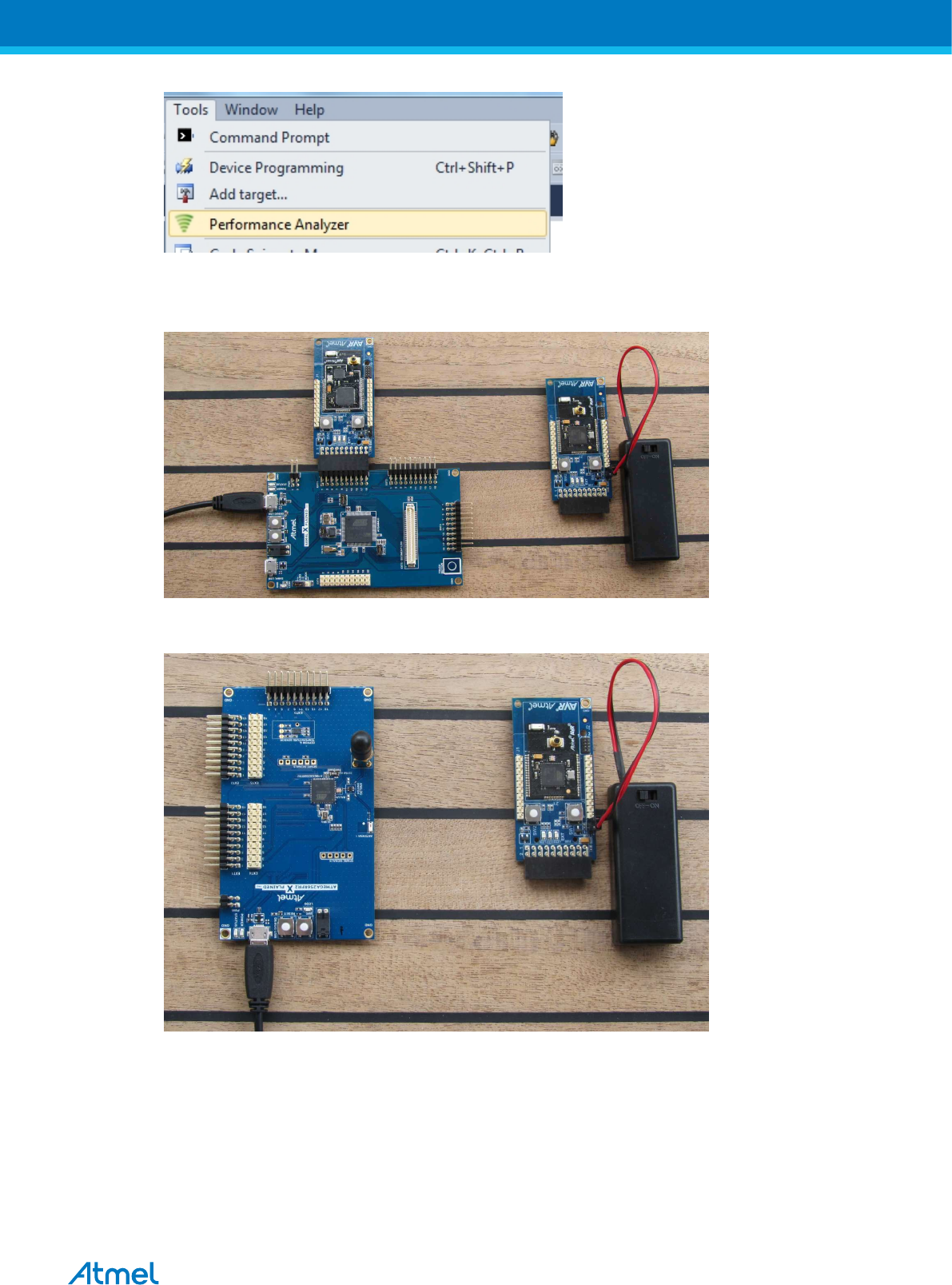
AT04357 RCB256RFR2-XPRO User Guide [USER GUIDE]
TBDA-MCU-09/2013
10
4. Typical use:
SAM4L Xplained PRO with Wireless Extension and remote node
mega256RFR2 Xplained PRO and remote node
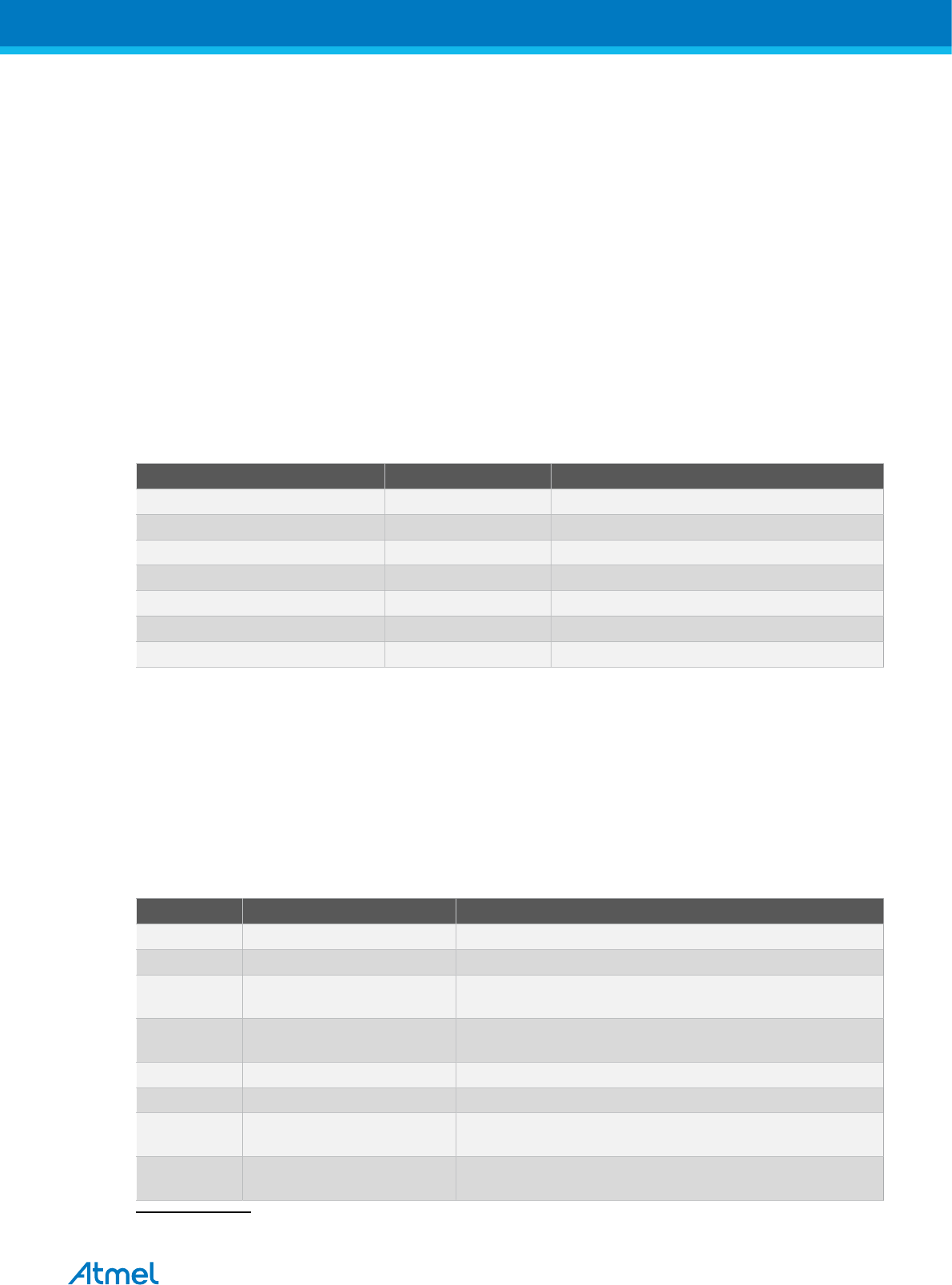
AT04357 RCB256RFR2-XPRO User Guide [USER GUIDE]
TBDA-MCU-09/2013
11
3. Xplained Pro
Xplained Pro is an evaluation platform that provides the full Atmel microcontroller experience. The platform
consists of a series of Microcontroller (MCU) boards and extension boards that are integrated with Atmel
Studio, have Atmel Software Framework (ASF) drivers and demo code, support data streaming and more.
Xplained Pro MCU boards support a wide range of Xplained Pro extension boards that are connected through
a set of standardized headers and connectors. Each extension board has an identification (ID) chip to uniquely
identify which boards are mounted on a Xplained Pro MCU board. This information is used to present relevant
user guides, application notes, datasheets and example code through Atmel Studio. Available Xplained Pro
MCU and extension boards can be purchased in the Atmel Web Store1.
3.1 Hardware identification system
All Xplained Pro compatible extension boards have an Atmel ATSHA204 crypto authentication chip mounted.
This chip contains information that identifies the extension with its name and some extra data. When an
Xplained Pro extension board is connected to an Xplained Pro MCU board the information is read and sent
to Atmel Studio. The Atmel Kits extension, installed with Atmel Studio, will give relevant information, code
examples and links to relevant documents. Table 3-1, “Xplained Pro ID chip content” on page 11 shows the
data fields stored in the ID chip with example content.
Table 3-1. Xplained Pro ID chip content
Data Field Data Type Example Content
Manufacturer ASCII string Atmel’\0’
Product Name ASCII string Segment LCD1 Xplained Pro’\0’
Product Revision ASCII string 02’\0’
Product Serial Number ASCII string 1774020200000010’\0’
Minimum Voltage [mV] uint16_t 3000
Maximum Voltage [mV] uint16_t 3600
Maximum Current [mA] uint16_t 30
3.2 Standard headers and connectors
3.2.1 Xplained Pro standard extension header
All Xplained Pro kits have one or more dual row, 20 pin, 100mil extension headers. Xplained Pro MCU boards
have male headers while Xplained Pro extensions have their female counterparts. Note that all pins are
not always connected. However, all the connected pins follow the defined pin-out described in Table 3-2,
“Xplained Pro extension header” on page 11. The extension headers can be used to connect a wide variety
of Xplained Pro extensions to Xplained Pro MCU boards and to access the pins of the target MCU on Xplained
Pro MCU board directly.
Table 3-2. Xplained Pro extension header
Pin number Name Description
1 ID Communication line to the ID chip on extension board.
2 GND Ground
3 ADC(+) Analog to digital converter , alternatively positive part of
differential ADC
4 ADC(-) Analog to digital converter , alternatively negative part of
differential ADC
5 GPIO1 General purpose IO
6 GPIO2 General purpose IO
7 PWM(+) Pulse width modulation , alternatively positive part of
differential PWM
8 PWM(-) Pulse width modulation , alternatively positive part of
differential PWM
1 http://store.atmel.com/CBC.aspx?q=c:100113
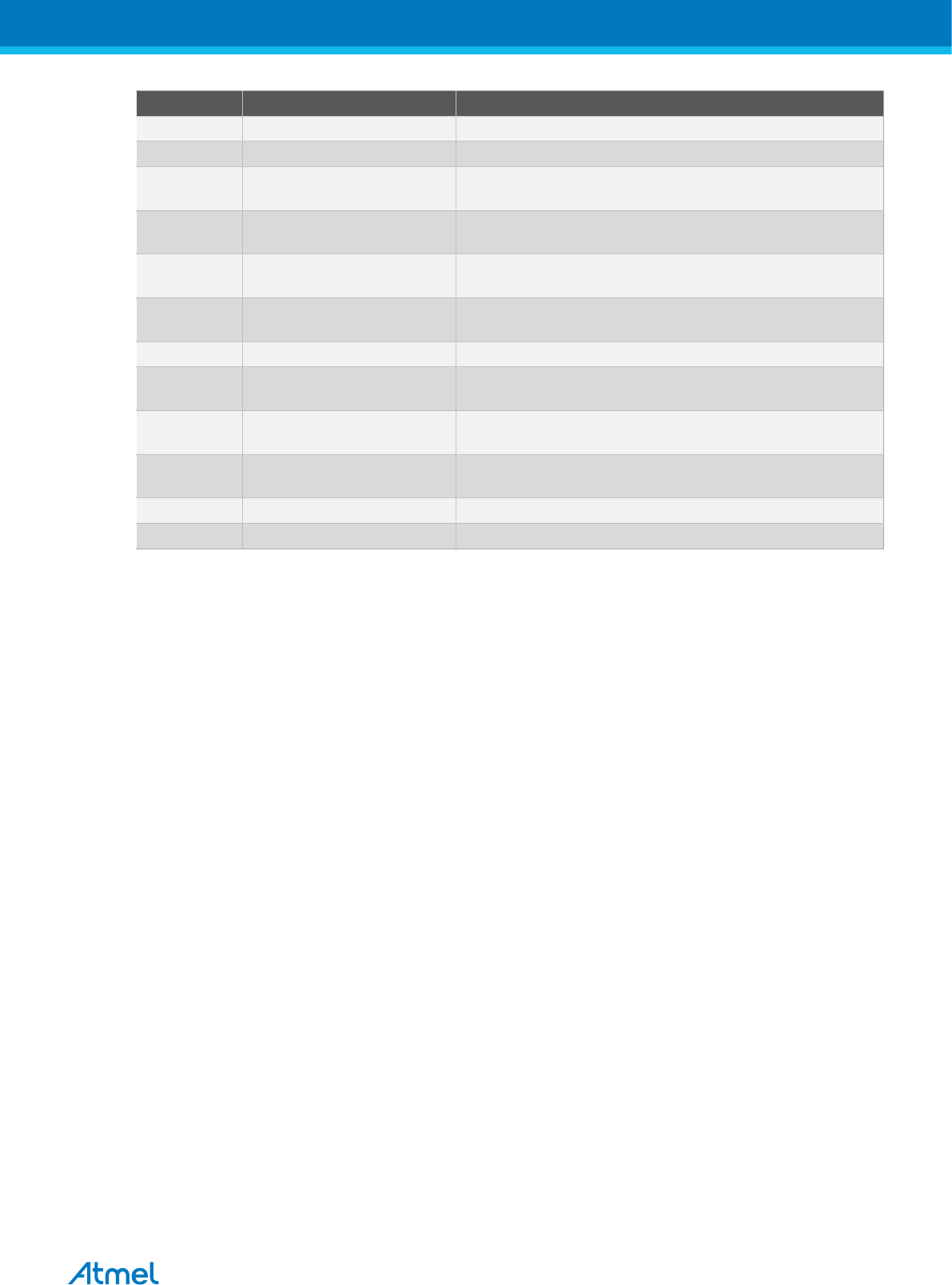
AT04357 RCB256RFR2-XPRO User Guide [USER GUIDE]
TBDA-MCU-09/2013
12
Pin number Name Description
9 IRQ/GPIO Interrupt request line and/or general purpose IO.
10 SPI_SS_B/GPIO Slave select for SPI and/or general purpose IO.
11 TWI_SDA Data line for two wire interface. Always implemented, bus
type.
12 TWI_SCL Clock line for two wire interface. Always implemented, bus
type.
13 USART_RX Receiver line of Universal Synchronous and Asynchronous
serial Receiver and Transmitter
14 USART_TX Transmitter line of Universal Synchronous and
Asynchronous serial Receiver and Transmitter
15 SPI_SS_A Slave select for SPI. Should be unique if possible.
16 SPI_MOSI Master out slave in line of Serial peripheral interface. Always
implemented, bus type
17 SPI_MISO Master in slave out line of Serial peripheral interface. Always
implemented, bus type
18 SPI_SCK Clock for Serial peripheral interface. Always implemented,
bus type
19 GND Ground
20 VCC Power for extension board
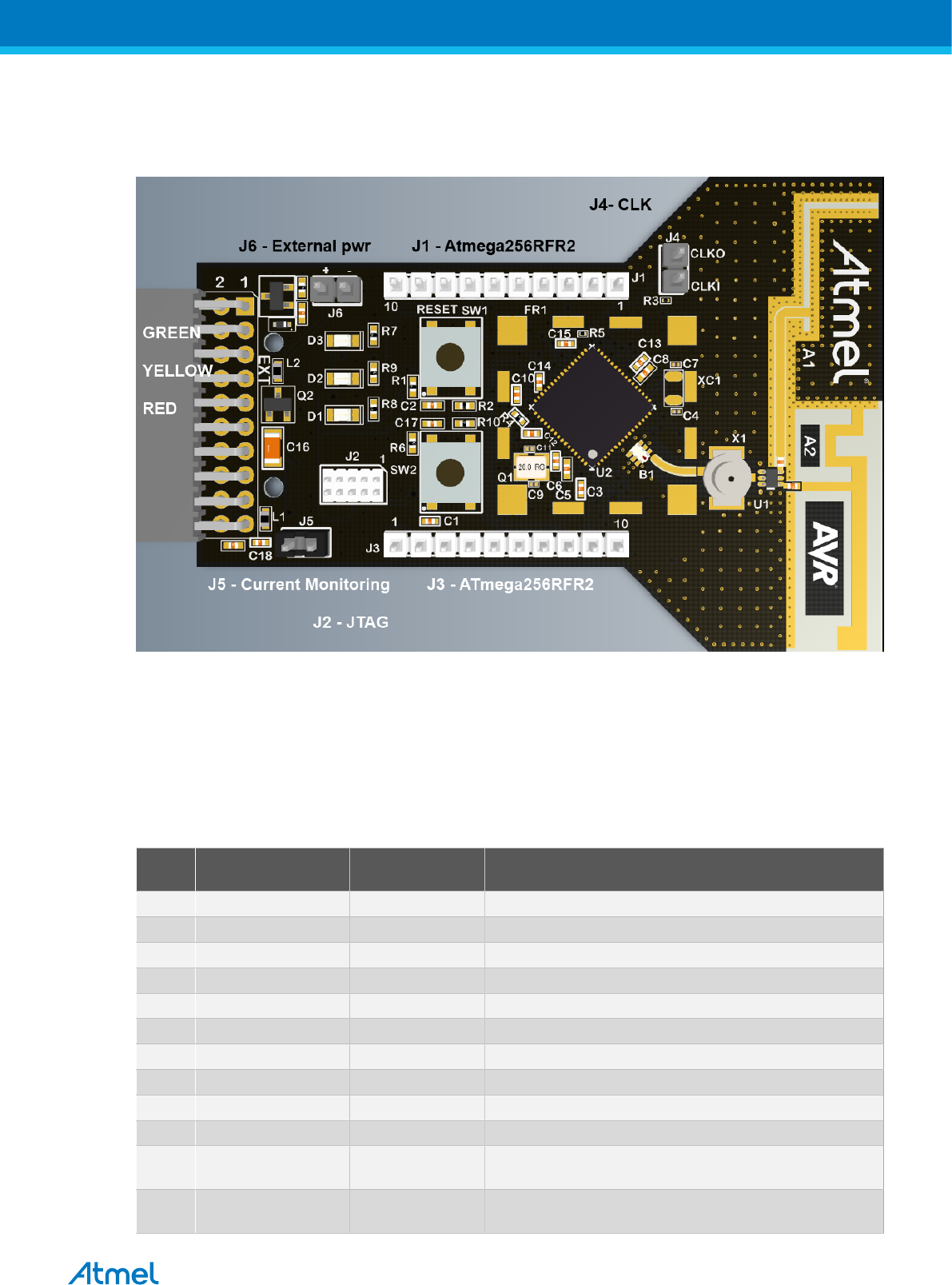
AT04357 RCB256RFR2-XPRO User Guide [USER GUIDE]
TBDA-MCU-09/2013
13
4. Hardware user guide
4.1 Board overview
4.2 Headers and connectors
The extension board connectors.
4.2.1 J100 Xplained Pro extension connector
The Xplained Pro extension connectors, used to connect the extension board to the Xplained Pro board.
Table 4-1. J100 Xplained Pro extension header
Pin
number
Name mega256RFR2
pin
Description
1 ID Communication line to the ID chip on extension board.
2 GND Ground
3 ADC(+) NC
4 ADC(-) NC (R7 NM) DIG2
5 GPIO1 49-PE3 General purpose IO
6 GPIO2 NC (R6 NM) CLK_OUT - can be disconnected by not mounting R6
7 PWM(+) 12-RSTN RESET to Extension board
8 PWM(-) 33-CLKI FEM_SEL, disable AMP to save power
9 IRQ/GPIO 32-PD7 Interrupt request line to uC on Xplained Pro board
10 SPI_SS_B/GPIO 50-PE4 (INT4) Wake up interrupt to RF
11 TWI_SDA 26-PD1 Data line for two wire interface. Always implemented,
bus type.
12 TWI_SCL 25-PD0 Clock line for two wire interface. Always implemented,
bus type.
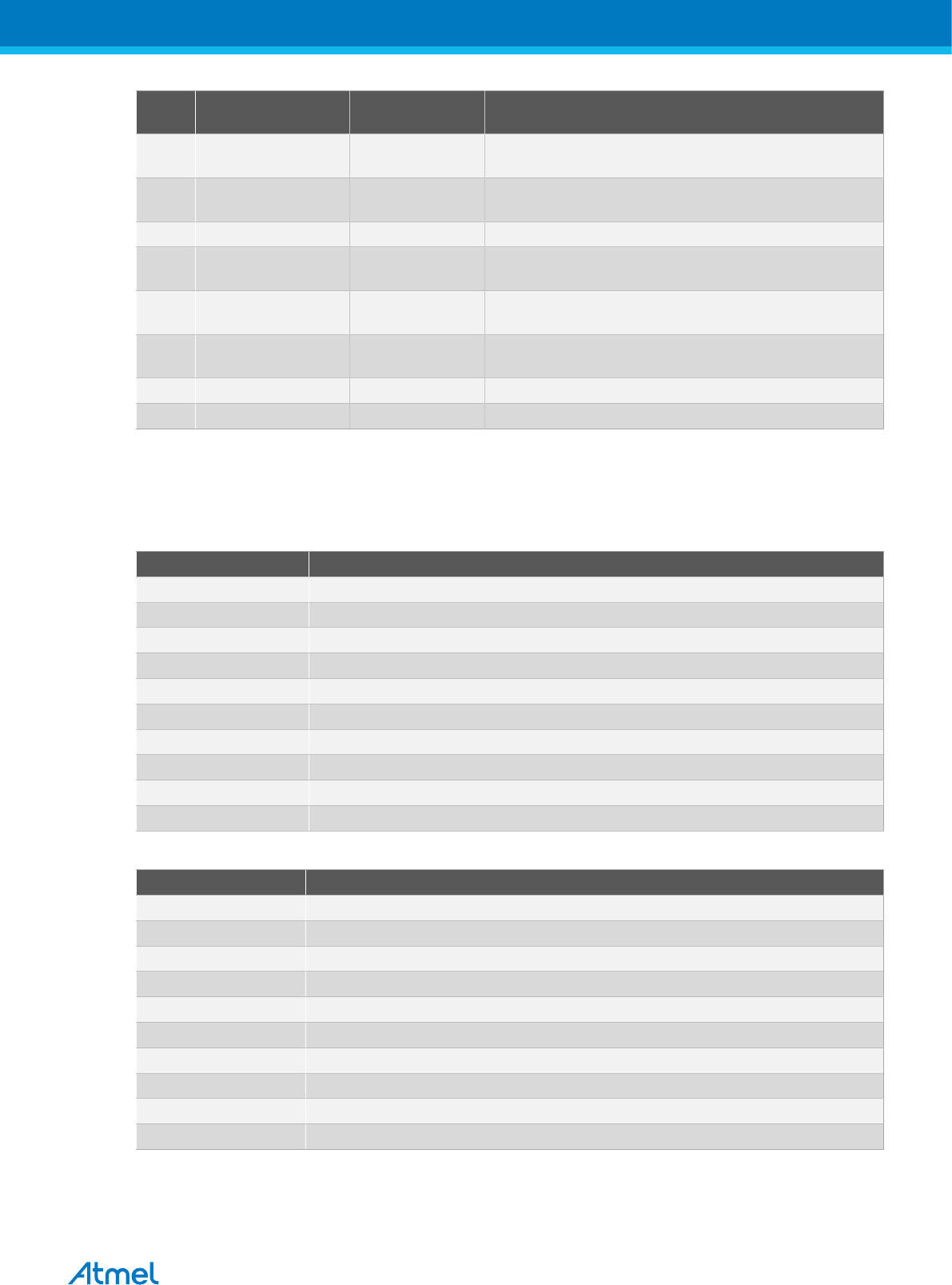
AT04357 RCB256RFR2-XPRO User Guide [USER GUIDE]
TBDA-MCU-09/2013
14
Pin
number
Name mega256RFR2
pin
Description
13 USART_RX 28-PD3-TXD1 Receiver line of Universal Synchronous and
Asynchronous serial Receiver and Transmitter
14 USART_TX 27-PD2-RXD1 Transmitter line of Universal Synchronous and
Asynchronous serial Receiver and Transmitter
15 SPI_SS_A 36-PB0 Slave select for SPI. Should be unique if possible.
16 SPI_MOSI 38-PB2 Master out slave in line of Serial peripheral interface.
Always implemented, bus type
17 SPI_MISO 39-PB3 Master in slave out line of Serial peripheral interface.
Always implemented, bus type
18 SPI_SCK 37-PB1 Clock for Serial peripheral interface. Always
implemented, bus type
19 GND Ground
20 VCC Power for extension board
4.2.2 J1 & J3
J1 and J3 provide access to all ZigBit pin's not routed to the J100 Xplained PRO interface
Table 4-2. J1
Pin 256RFR2 pin
J1-1 PE2/XCK0/AIN0
J1-2 PE3/OC3A/AIN1
J1-3 PD2/RXD1/INT2
J1-4 PD3/TXD1/INT3
J1-5 PD5/XCK1
J1-6 PD4/ICP1
J1-7 PD6/T1
J1-8 PG2/AMR
J1-9 PB4/OC2A/PCINT4
J1-10 PB6/OC1B/PCINT6
Table 4-3. J3
pin 256RFR2 pin
J3-1 PF0/ADC0
J3-2 PF1/ADC1
J3-3 PF2/ADC2/DIG2
J3-4 PF3/ADC3/DIG4
J3-5 AREF
J3-6 PE1/TXD0
J3-7 PE0/RXD0/PCINT8
J3-8 PB7/OC0A/OC1C/PCINT7
J3-9 PG5/OC0B
J3-10 PE7/ICP3/INT7/CLKO
4.2.3 JTAG (J2)
J2 is the JTAG programming header typically used by the JTAGICE.
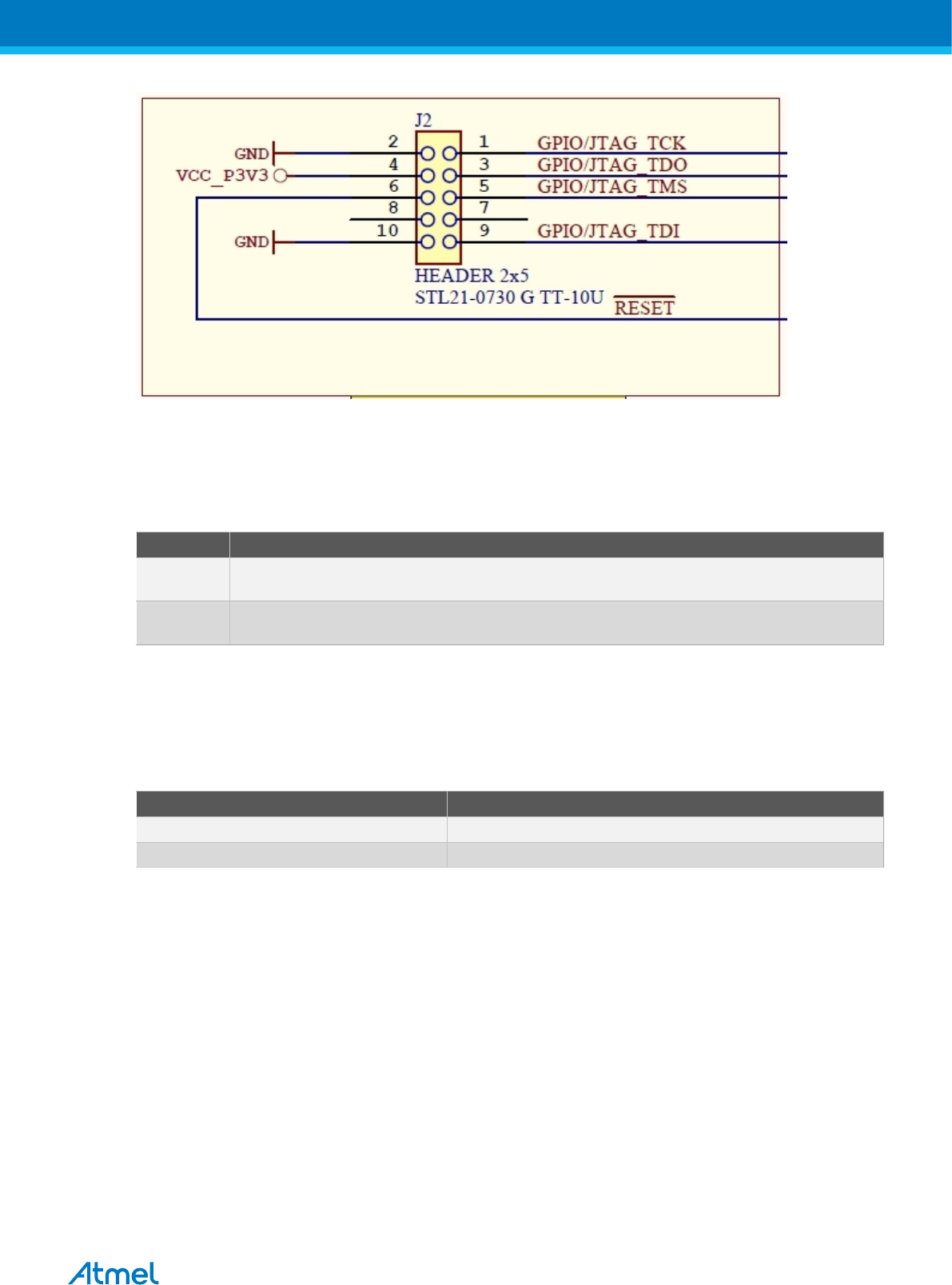
AT04357 RCB256RFR2-XPRO User Guide [USER GUIDE]
TBDA-MCU-09/2013
15
4.2.4 CLK (J4)
J4 enable easy connection to the CLK signals.
Table 4-4. J4 CLK
J4-pin function
J4-1 CLKI ATmega256RFR2 pin 33, Input to the clock system. If selected, it provides the operating clock
of the microcontroller.
J4-2
CLKO
ATmega256RFR2 pin 53, The device can output the system clock on the CLKO pin. To enable
the output, the CKOUT Fuse has to be programmed.
4.2.5 Current monitoring (J5)
J5 enables current monitoring using an external multimeter.
Connect multimeter between J5-1 and J5-2 and measure current used by the ZigBit
Table 4-5. J5 Current measurement
J5 Pin function
1 - VCC_MCU_P3V3 3.3V pin on the ATmega256RFR2
2 - VCC_P3V3 3.3V on extension board
4.2.6 External power (J6)
J6 enable connection of external power supply when not inserted into an Xplaine PRO mother board.
The connector has reverse voltage protection.
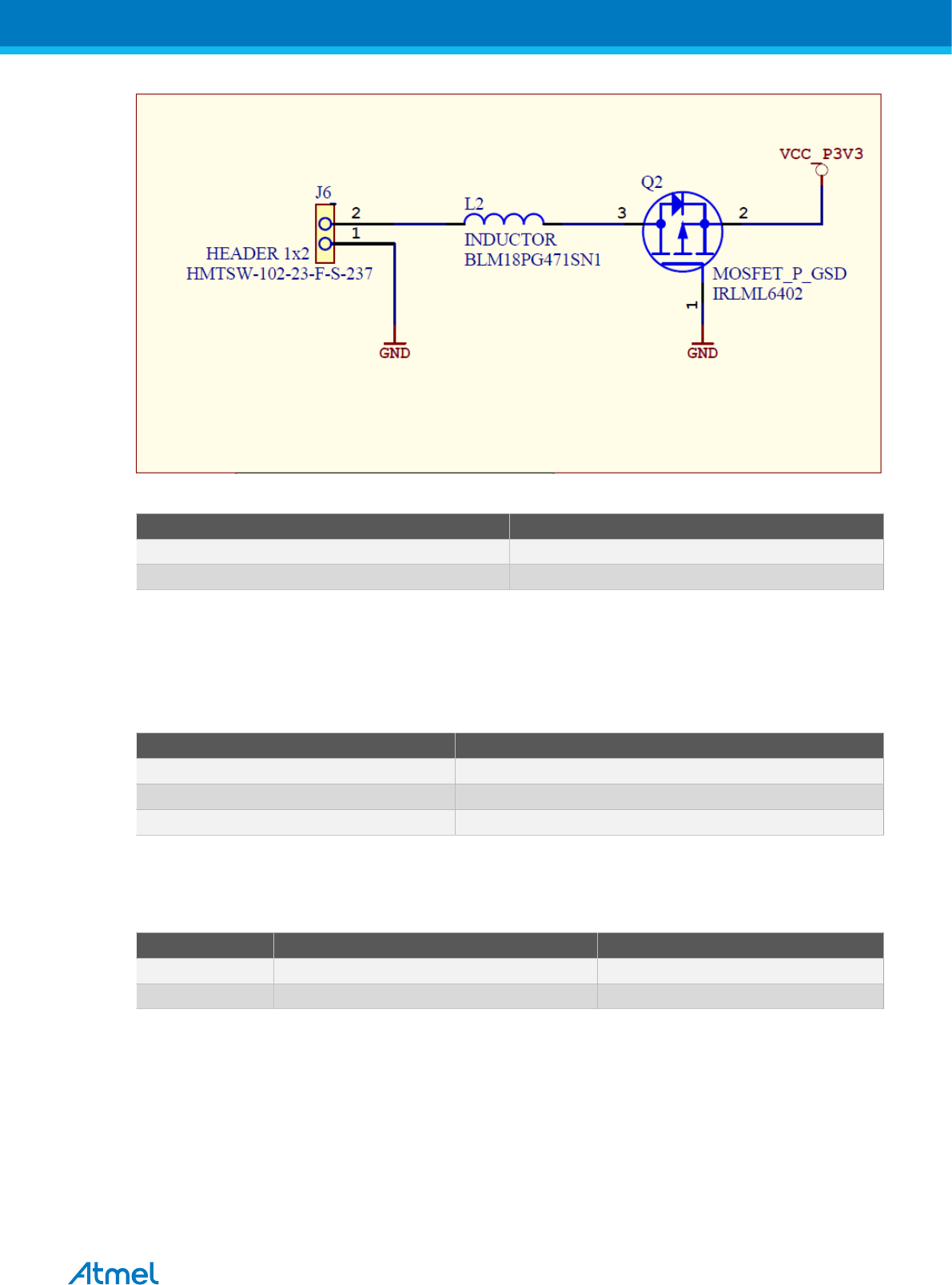
AT04357 RCB256RFR2-XPRO User Guide [USER GUIDE]
TBDA-MCU-09/2013
16
Table 4-6. J6 power
J6 pin function
1 - External power External 3.3V source - typical 2 AAA battery pack
2 - GND Extension board GND
4.3 Board GUI
4.3.1 LED's
There are 3 LED available for use by application SW
Table 4-7. LED's
LED mega256RFR2 pin
LED1 - Red 31 - PD6
LED2 - Green 16 - PG2
LED3 - Yellow 48 - PE2
4.3.2 Button
There are two buttons - one RESET and one for general use by application SW
Table 4-8. Buttons
Button Function mega256RFR2 pin
SW1 ZigBit Reset, press to reset 12 - RSTN
SW2 User defined high signal, press to negate 46 - PE0
4.4 Factory programmed data
MAC etc. in ZigBit data sheet
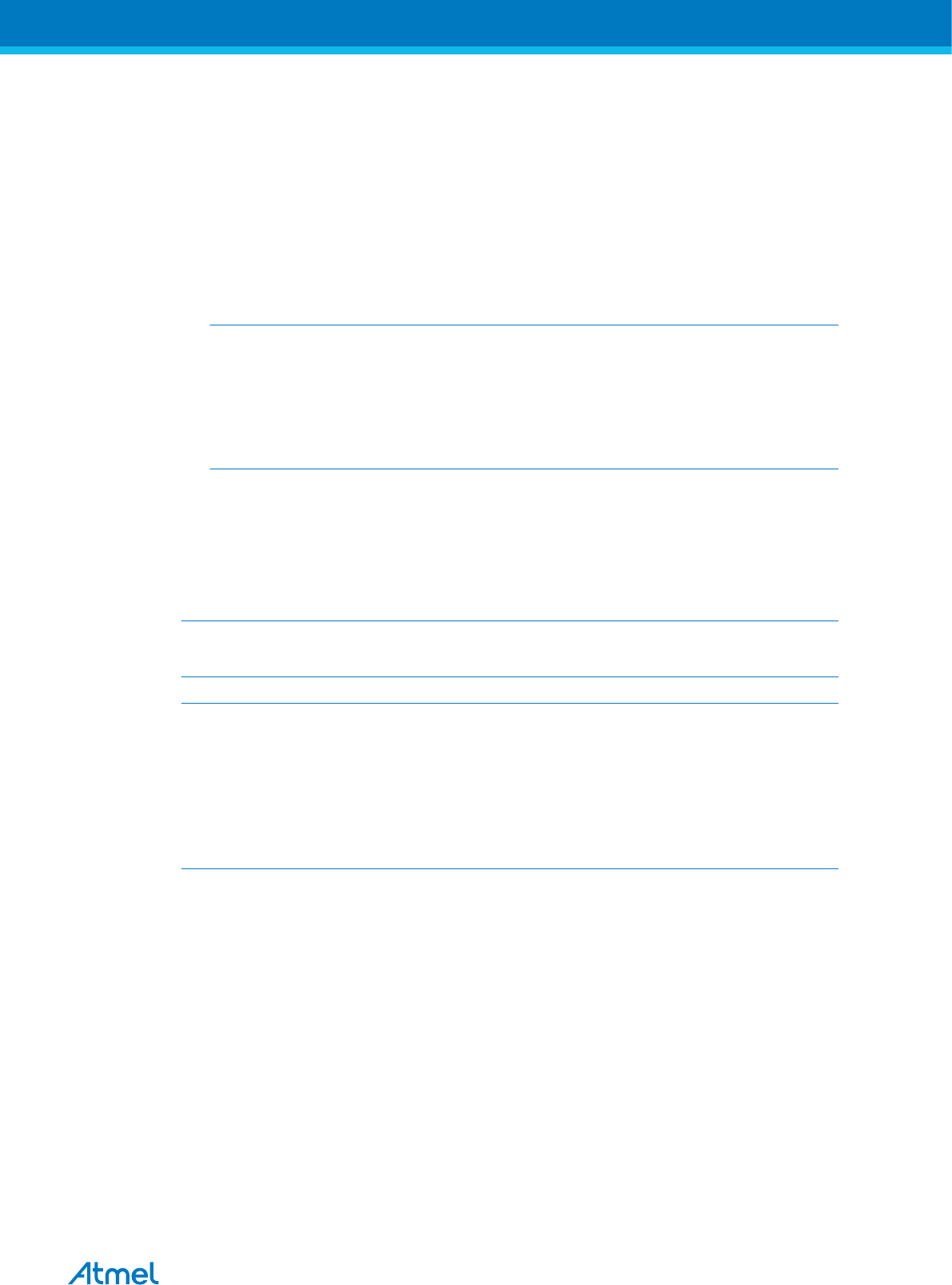
AT04357 RCB256RFR2-XPRO User Guide [USER GUIDE]
TBDA-MCU-09/2013
17
5. Agency Certifications
5.1 United State (FCC)
This equipment complies with Part 15 of the FCC rules and regulations. To fulfill FCC Certification
requirements, an OEM manufacturer must comply with the following regulations:
1. The ATRCB256RFR2-XPRO modular transmitter must be labelled with its own FCC ID number, and, if the
FCC ID is not visible when the module is installed inside another device, then the outside of the device into
which the module is installed must also display a label referring to the enclosed module. This exterior label
can use wording such as the following:
Important Contains FCC ID : VW4A092007. This equipment complies with Part 15 of the FCC Rules.
Operation is subject to the following two conditions:
a. this device may not cause harmful interference, and
b. this device must accept any interference received, including interference that may cause
undesired operation (FCC 15.19)
The internal antenna used for this mobile transmitter must provide a separation distance of at least 20 cm
from all persons and must not be co-located or operating in conjunction with any other antenna or transmitter.
Installers must be provided with antenna installation instructions and transmitter operating conditions for
satisfying RF exposure compliance. This device is approved as a mobile device with respect to RF exposure
compliance, and may only be marketed to OEM installers. Use in portable exposure conditions (FCC 2.1093)
requires separate equipment authorization.
Important Modifications not expressly approved by this company could void the user's authority to operate
this equipment (FCC section 15.21).
Important This equipment has been tested and found to comply with the limits for a Class A digital device,
pursuant to Part 15 of the FCC Rules. These limits are designed to provide reasonable protection
against harmful interference when the equipment is operated in a commercial environment.
This equipment generates, uses, and can radiate radio frequency energy and, if not installed
and used in accordance with the instruction manual, may cause harmful interference to radio
communications. Operation of this equipment in a residential area is likely to cause harmful
interference in which case the user will be required to correct the interference at his own expense
(FCC section 15.105).
ATRCB256RFR2-XPRO is limited modular approved and required separate approval for this module when
used on an application board.
Cet appareil est conforme à la section 15 des réglementations de la FCC. Le fonctionnement de l’appareil est
sujetaux deux conditions suivantes:
1. cet appareil ne doit pas provoquer d’interférences néfastes, et
2. cet appareil doit tolérer les interférences reçues, y compris celles qui risquent de provoquer un
fonctionnement indésirable.
5.2 European Union (ETSI)
The ATRCB256RFR2-XPRO Module has been certified for use in European Union countries. If these modules
are incorporated into a product, the manufacturer must ensure compliance of the final product to the European
harmonized EMC and low voltage/safety standards. A Declaration of Conformity must be issued for each of
these standards and kept on file as described in Annex II of the R&TTE Directive.
Furthermore, the manufacturer must maintain a copy of the modules' documentation and ensure the final
product does not exceed the specified power ratings, antenna specifications, and/or installation requirements
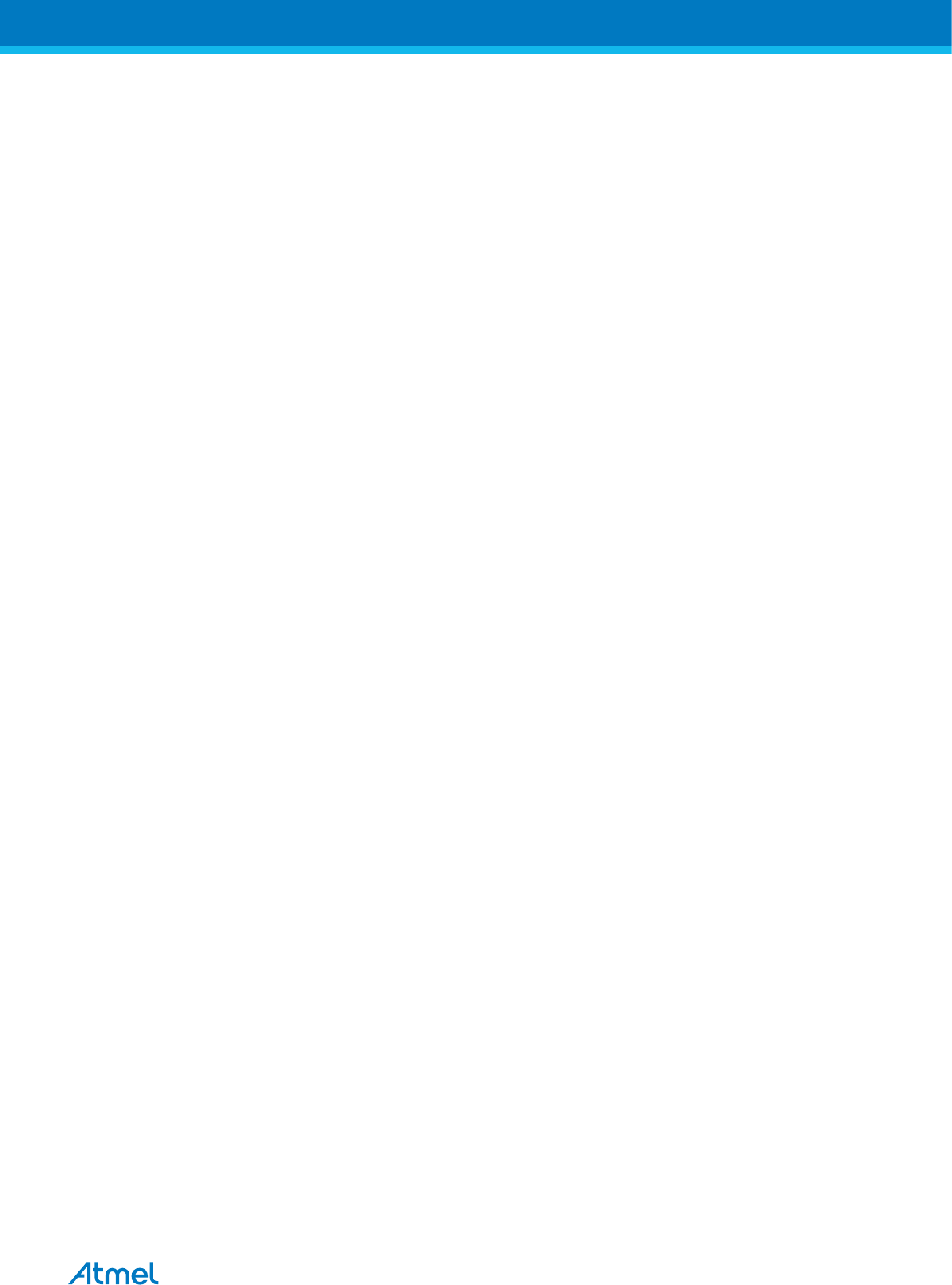
AT04357 RCB256RFR2-XPRO User Guide [USER GUIDE]
TBDA-MCU-09/2013
18
as specified in the user manual. If any of these specifications are exceeded in the final product, a submission
must be made to a notified body for compliance testing to all required standards.
Important The 'CE' marking must be affixed to a visible location on the OEM product. The CE mark shall
consist of the initials "CE" taking the following form:
The CE marking must have a height of at least 5mm except where this is not possible on account
of the nature of the apparatus. The CE marking must be affixed visibly, legibly, and indelibly. More
detailed information about CE marking requirements you can find at "DIRECTIVE 1999/5/EC OF
THE EUROPEAN PARLIAMENT AND OF THE COUNCIL" on 9 March 1999 at section 12.
5.3 Canada (IC)
The ATRCB256RFR2-XPRO Module complies with Industry Canada specifications RSS-210 and RSS – GenIC
ID for ATRCB256RFR2-XPRO is 11019A-092007
ATRCB256RFR2-XPRO is limited modular approved and required separate approval for this module when
used on an application board.
User manuals for licence-exempt radio apparatus shall contain the following or equivalent notice in a
conspicuous location in the user manual or alternatively on the device or both.
This device complies with Industry Canada licence-exempt RSS standard(s). Operation is subject to the
following two conditions:
(1) this device may not cause interference, and
(2) this device must accept any interference, including interference that may cause undesired operation of the
device.
Le présent appareil est conforme aux CNR d'Industrie Canada applicables aux appareils radio exempts de
licence. L'exploitation est autorisée aux deux conditions suivantes:
(1) l'appareil ne doit pas produire de brouillage, et
(2) l'utilisateur de l'appareil doit accepter tout brouillage radioélectrique subi, même si le brouillage est
susceptible d'en compromettre le fonctionnement.
This equipment complies with radio frequency exposure limits set forth by Industry Canada for an uncontrolled
environment. This equipment should be installed and operated with minimum distance 20 cm between the
device and the user or bystanders.
Cet équipement est conforme aux limites d'exposition aux radiofréquences définies par Industrie Canada pour
un environnement non contrôlé. Cet équipement doit être installé et utilisé avec un minimum de 20 cm de
distance entre le dispositif et l'utilisateur ou des tiers
CAUTION: Any changes or modifications not expressly approved by the party responsible for compliance could
void the user’s authority to operate the equipment. The OEM integrator is still responsible for testing their end-
product for any additional compliance requirements required with this module installed (for example, digital
device emissions, PC peripheral requirements, etc.).
This Module is labelled with its own IC ID. If the IC ID Certification Number is not visible while installed inside
another device, then the device should display the label on it referring the enclosed module. In that case,
the final end product must be labelled in a visible area with the following: “Contains Transmitter Module
IC:11019A-092007 ” (Mention IC ID) OR “Contains IC: 11019A-092007 ”
Ce module est étiqueté avec son propre ID IC. Si le numéro de certification IC ID n'est pas visible lorsqu'il est
installé à l'intérieur d'un autre appareil, l'appareil doit afficher l'étiquette sur le module de référence ci-joint.
Dans ce cas, le produit final doit être étiqueté dans un endroit visible par le texte suivant: “Contains Transmitter
Module IC: 11019A-092007 ” OR “Contains IC: 11019A-092007 ”
5.4 Using Limited Modular Certified Products
The ATRCB256RFR2-XPRO Module is certified under part 15 of FCC rules. The Modular certification category
of this module is “Limited Modular”. The End product using these modules hence has to undergo compliance
testing and receive a new FCC ID for the final product carrying these modules. Certification of the final product
lies solely with the type of design of the final product, excluding the ZigBit.
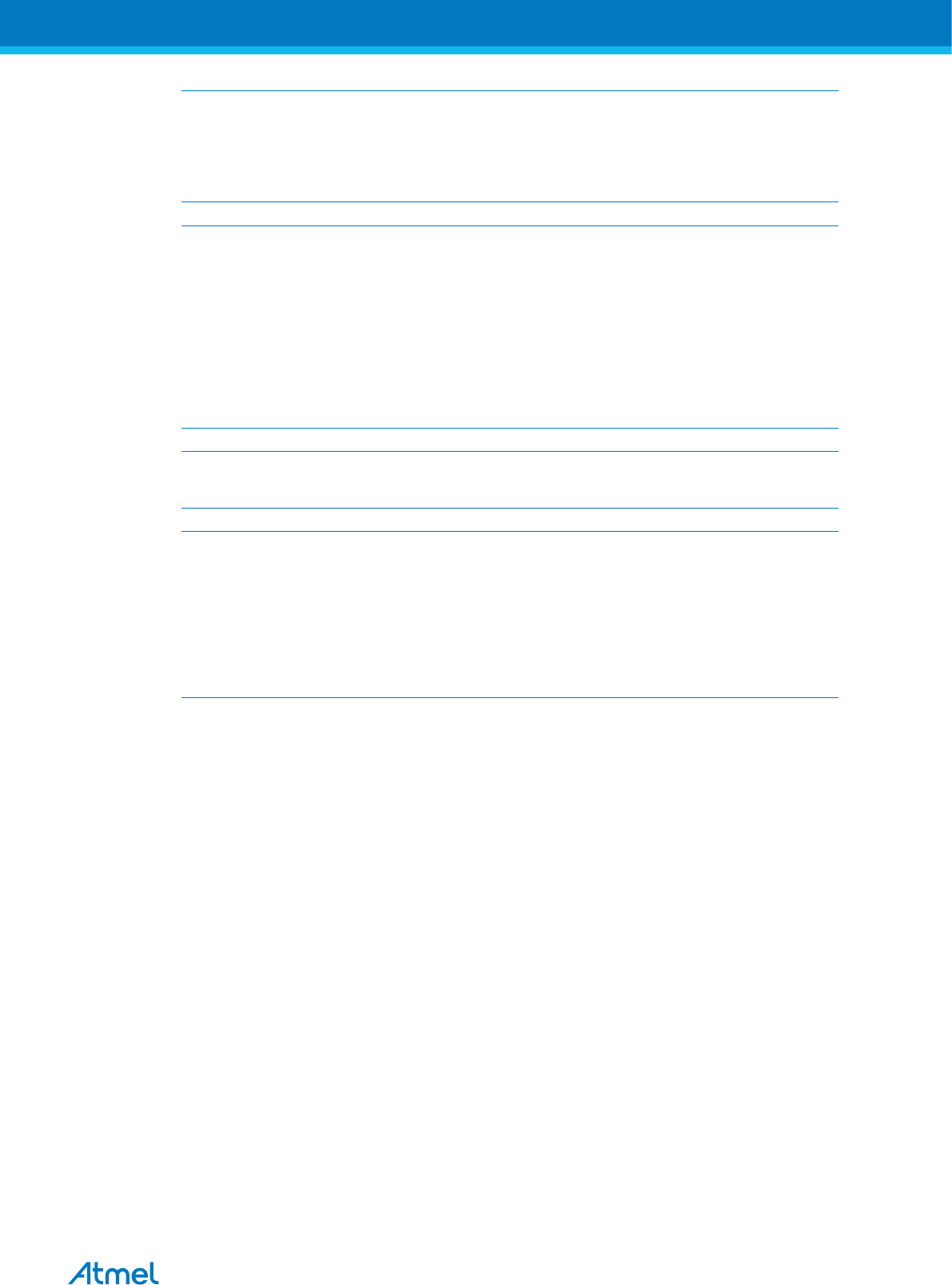
AT04357 RCB256RFR2-XPRO User Guide [USER GUIDE]
TBDA-MCU-09/2013
19
Warning The Original Equipment Manufacturer (OEM) must ensure that the OEM modular transmitter must
be labeled with its own FCC ID number. This includes a clearly visible label on the outside of the
final product enclosure that displays the contents shown below. If the FCC ID is not visible when
the equipment is installed inside another device, then the outside of the device into which the
equipment is installed must also display a label referring to the enclosed equipment.
Important This equipment complies with Part 15 of the FCC Rules. Operation is subject to the following
two conditions: (1) this device may not cause harmful interference, and (2) this device must
accept any interference received, including interference that may cause undesired operation
(FCC 15.19). The internal / external antenna(s) used for this mobile transmitter must provide
a separation distance of at least 20cm from all persons and must not be co-located or
operating in conjunction with any other antenna or transmitter. Installers must be provided
with antenna installation instructions and transmitter operating conditions for satisfying RF
exposure compliance. This device is approved as a mobile device with respect to RF expo- sure
compliance, and may only be marketed to OEM installers. Use in portable exposure conditions
(FCC 2.1093) requires separate equipment authorization.
Important Modifications not expressly approved by this company could void the user's authority to operate
this equipment (FCC section 15.21).
Important This equipment has been tested and found to comply with the limits for a Class A digital device,
pursuant to Part 15 of the FCC Rules. These limits are designed to provide reasonable protection
against harmful interference when the equipment is operated in a commercial environment.
This equipment generates, uses, and can radiate radio frequency energy and, if not installed
and used in accordance with the instruction manual, may cause harmful interference to radio
communications. Operation of this equipment in a residential area is likely to cause harmful
interference in which case the user will be required to correct the interference at his own expense
(FCC section 15.105).

AT04357 RCB256RFR2-XPRO User Guide [USER GUIDE]
TBDA-MCU-09/2013
20
6. Document revision history
Document
revision
Date Comment
A 15/05/2013 Draft

Atmel Corporation 1600 Technology Drive, San Jose, CA 95110 USA T: (+1)(408) 441.0311 F: (+1)(408) 436.4200 | www.atmel.com
© 2013 Atmel Corporation. All rights reserved. / Rev.: TBDA-MCU-09/2013
Atmel®, Atmel logo and combinations thereof, Enabling Unlimited Possibilities®, and others are registered trademarks or trademarks of Atmel
Corporation or its subsidiaries. Other terms and product names may be trademarks of others.
Disclaimer: The information in this document is provided in connection with Atmel products. No license, express or implied, by estoppel or otherwise, to any intellectual property right is granted
by this document or in connection with the sale of Atmel products. EXCEPT AS SET FORTH IN THE ATMEL TERMS AND CONDITIONS OF SALES LOCATED ON THE ATMEL WEBSITE,
ATMEL ASSUMES NO LIABILITY WHATSOEVER AND DISCLAIMS ANY EXPRESS, IMPLIED OR STATUTORY WARRANTY RELATING TO ITS PRODUCTS INCLUDING, BUT NOT
LIMITED TO, THE IMPLIED WARRANTY OF MERCHANTABILITY, FITNESS FOR A PARTICULAR PURPOSE, OR NON-INFRINGEMENT. IN NO EVENT SHALL ATMEL BE LIABLE FOR
ANY DIRECT, INDIRECT, CONSEQUENTIAL, PUNITIVE, SPECIAL OR INCIDENTAL DAMAGES (INCLUDING, WITHOUT LIMITATION, DAMAGES FOR LOSS AND PROFITS, BUSINESS
INTERRUPTION, OR LOSS OF INFORMATION) ARISING OUT OF THE USE OR INABILITY TO USE THIS DOCUMENT, EVEN IF ATMEL HAS BEEN ADVISED OF THE POSSIBILITY OF
SUCH DAMAGES. Atmel makes no representations or warranties with respect to the accuracy or completeness of the contents of this document and reserves the right to make changes to
specifications and products descriptions at any time without notice. Atmel does not make any commitment to update the information contained herein. Unless specifically provided otherwise,
Atmel products are not suitable for, and shall not be used in, automotive applications. Atmel products are not intended, authorized, or warranted for use as components in applications intended
to support or sustain life.