Mitsubishi Electronics General Purpose Ac Servo Mr E A Ag Users Manual
MR-E- AAG to the manual 8c5026c0-f7d0-4e9a-ac13-4ba76e2c1ab0
2015-02-09
: Mitsubishi-Electronics Mitsubishi-Electronics-General-Purpose-Ac-Servo-Mr-E-A-Ag-Users-Manual-556547 mitsubishi-electronics-general-purpose-ac-servo-mr-e-a-ag-users-manual-556547 mitsubishi-electronics pdf
Open the PDF directly: View PDF .
Page Count: 310 [warning: Documents this large are best viewed by clicking the View PDF Link!]
- Safety Instructions
- About processing of waste
- COMPLIANCE WITH EC DIRECTIVES
- CONFORMANCE WITH UL/C-UL STANDARD
- CONTENTS
- 1. FUNCTIONS AND CONFIGURATION
- 2. INSTALLATION
- 3. SIGNALS AND WIRING
- 3.1 Standard connection example
- 3.2 Internal connection diagram of servo amplifier
- 3.3 I/O signals
- 3.4 Detailed description of the signals
- 3.5 Alarm occurrence timing chart
- 3.6 Interfaces
- 3.7 Input power supply circuit
- 3.8 Connection of servo amplifier and servo motor
- 3.9 Servo motor with electromagnetic brake
- 3.10 Grounding
- 3.11 Servo amplifier connectors (CNP1, CNP2) wiring method (When MR-ECPN1-B and MR-ECPN2-B of an option are used.)
- 3.12 Instructions for the 3M connector
- 4. OPERATION
- 5. PARAMETERS
- 6. DISPLAY AND OPERATION
- 7. GENERAL GAIN ADJUSTMENT
- 8. SPECIAL ADJUSTMENT FUNCTIONS
- 9. INSPECTION
- 10. TROUBLESHOOTING
- 11. OUTLINE DIMENSION DRAWINGS
- 12. CHARACTERISTICS
- 13. OPTIONS AND AUXILIARY EQUIPMENT
- 14. SERVO MOTOR
- 15. MR-E- AG SERVO AMPLIFIER COMPATIBLE WITH ANALOG INPUT
- REVISIONS

General-Purpose AC Servo
MODEL
MR-E- A/AG
INSTRUCTION MANUAL
B

A - 1
Safety Instructions
(Always read these instructions before using the equipment.)
Do not attempt to install, operate, maintain or inspect the servo amplifier and servo motor until you have read
through this Instruction Manual, Installation guide, Servo motor Instruction Manual and appended documents
carefully and can use the equipment correctly. Do not use the servo amplifier and servo motor until you have a
full knowledge of the equipment, safety information and instructions.
In this Instruction Manual, the safety instruction levels are classified into "WARNING" and "CAUTION".
WARNING Indicates that incorrect handling may cause hazardous conditions,
resulting in death or severe injury.
CAUTION Indicates that incorrect handling may cause hazardous conditions,
resulting in medium or slight injury to personnel or may cause physical
damage.
Note that the CAUTION level may lead to a serious consequence according to conditions. Please follow the
instructions of both levels because they are important to personnel safety.
What must not be done and what must be done are indicated by the following diagrammatic symbols:
: Indicates what must not be done. For example, "No Fire" is indicated by .
: Indicates what must be done. For example, grounding is indicated by .
In this Instruction Manual, instructions at a lower level than the above, instructions for other functions, and so
on are classified into "POINT".
After reading this installation guide, always keep it accessible to the operator.

A - 2
1. To prevent electric shock, note the following:
WARNING
Before wiring or inspection, switch power off and wait for more than 10 minutes. Then, confirm the voltage
is safe with voltage tester. Otherwise, you may get an electric shock.
Connect the servo amplifier and servo motor to ground.
Any person who is involved in wiring and inspection should be fully competent to do the work.
Do not attempt to wire the servo amplifier and servo motor until they have been installed. Otherwise, you
may get an electric shock.
Operate the switches with dry hand to prevent an electric shock.
The cables should not be damaged, stressed, loaded, or pinched. Otherwise, you may get an electric shock.
2. To prevent fire, note the following:
CAUTION
Do not install the servo amplifier, servo motor and regenerative brake resistor on or near combustibles.
Otherwise a fire may cause.
When the servo amplifier has become faulty, switch off the main servo amplifier power side. Continuous
flow of a large current may cause a fire.
When a regenerative brake resistor is used, use an alarm signal to switch main power off. Otherwise, a
regenerative brake transistor fault or the like may overheat the regenerative brake resistor, causing a fire.
3. To prevent injury, note the follow
CAUTION
Only the voltage specified in the Instruction Manual should be applied to each terminal, Otherwise, a
burst, damage, etc. may occur.
Connect the terminals correctly to prevent a burst, damage, etc.
Ensure that polarity ( , ) is correct. Otherwise, a burst, damage, etc. may occur.
During power-on or for some time after power-off, do not touch or close a parts (cable etc.) to the servo
amplifier heat sink, regenerative brake resistor, servo motor, etc. Their temperatures may be high and you
may get burnt or a parts may damaged.
During operation, never touch the rotating parts of the servo motor. Doing so can cause injury.

A - 3
4. Additional instructions
The following instructions should also be fully noted. Incorrect handling may cause a fault, injury, electric
shock, etc.
(1) Transportation and installation
CAUTION
Transport the products correctly according to their weights.
Stacking in excess of the specified number of products is not allowed.
Do not carry the servo motor by the cables, shaft or encoder.
Do not hold the front cover to transport the servo amplifier. The servo amplifier may drop.
Install the servo amplifier in a load-bearing place in accordance with the Instruction Manual.
Do not climb or stand on servo equipment. Do not put heavy objects on equipment.
The servo amplifier and servo motor must be installed in the specified direction.
Leave specified clearances between the servo amplifier and control enclosure walls or other equipment.
Do not install or operate the servo amplifier and servo motor which has been damaged or has any parts
missing.
Provide adequate protection to prevent screws and other conductive matter, oil and other combustible
matter from entering the servo amplifier.
Do not drop or strike servo amplifier or servo motor. Isolate from all impact loads.
Use the servo amplifier and servo motor under the following environmental conditions:
Conditions
Environment Servo amplifier Servo motor
[]0 to 55 (non-freezing) 0 to 40 (non-freezing)
Ambient
temperature [] 32 to 131 (non-freezing) 32 to 104 (non-freezing)
Ambient humidity 90%RH or less (non-condensing) 80%RH or less (non-condensing)
[ ] 20 to 65 (non-freezing) 15 to 70 (non-freezing)
Storage
temperature []4 to 149 (non-freezing) 5 to 158 (non-freezing)
Storage humidity 90%RH or less (non-condensing)
Ambience Indoors (no direct sunlight) Free from corrosive gas, flammable gas, oil mist, dust and dirt
Altitude Max. 1000m (3280 ft) above sea level
HC-KFE Series X Y : 49
HC-SFE52 to 152 X Y : 24.5
[m/s2] 5.9 or less
HC-SFE202 X : 24.5
Y : 49
HC-KFE Series X Y : 161
HC-SFE52 to 152 X Y : 80
(Note)
Vibration
[ft/s2] 19.4 or less
HC-SFE202 X : 80
Y : 161
Note: Except the servo motor with reduction gear.
Securely attach the servo motor to the machine. If attach insecurely, the servo motor may come off during
operation.
The servo motor with reduction gear must be installed in the specified direction to prevent oil leakage.
Take safety measures, e.g. provide covers, to prevent accidental access to the rotating parts of the servo
motor during operation.
Never hit the servo motor or shaft, especially when coupling the servo motor to the machine. The encoder
may become faulty.
Do not subject the servo motor shaft to more than the permissible load. Otherwise, the shaft may break.
When the equipment has been stored for an extended period of time, consult Mitsubishi.

A - 4
(2) Wiring
CAUTION
Wire the equipment correctly and securely. Otherwise, the servo motor may misoperate.
Do not install a power capacitor, surge absorber or radio noise filter (FR-BIF option) between the servo
motor and servo amplifier.
Connect the output terminals (U, V, W) correctly. Otherwise, the servo motor will operate improperly.
Do not connect AC power directly to the servo motor. Otherwise, a fault may occur.
The surge absorbing diode installed on the DC output signal relay must be wired in the specified direction.
Otherwise, the emergency stop and other protective circuits may not operate.
External
24VDC
RA
Servo
Amplifier
Control output
signal
Servo
Amplifier
RA
Control output
signal
External
24VDC
(3) Test run adjustment
CAUTION
Before operation, check the parameter settings. Improper settings may cause some machines to perform
unexpected operation.
The parameter settings must not be changed excessively. Operation will be insatiable.
(4) Usage
CAUTION
Provide an external emergency stop circuit to ensure that operation can be stopped and power switched
off immediately.
Any person who is involved in disassembly and repair should be fully competent to do the work.
Before resetting an alarm, make sure that the run signal is off to prevent an accident. A sudden restart is
made if an alarm is reset with the run signal on.
Do not modify the equipment.
Use a noise filter, etc. to minimize the influence of electromagnetic interference, which may be caused by
electronic equipment used near the servo amplifier.
Use the servo amplifier with the specified servo motor.
The electromagnetic brake on the servo motor is designed to hold the motor shaft and should not be used
for ordinary braking.
For such reasons as service life and mechanical structure (e.g. where a ballscrew and the servo motor
are coupled via a timing belt), the electromagnetic brake may not hold the motor shaft. To ensure safety,
install a stopper on the machine side.

A - 5
(5) Corrective actions
CAUTION
When it is assumed that a hazardous condition may take place at the occur due to a power failure or a
product fault, use a servo motor with electromagnetic brake or an external brake mechanism for the
purpose of prevention.
Configure the electromagnetic brake circuit so that it is activated not only by the servo amplifier signals
but also by an external emergency stop signal (EMG).
EMGRA
24VDC
Contacts must be open when
servo-on signal is off, when an
alarm (trouble) is present and when
an electromagnetic brake signal.
Electromagnetic brake
Servo motor
Circuit must be
opened during
emergency stop signal.
When any alarm has occurred, eliminate its cause, ensure safety, and deactivate the alarm before
restarting operation.
When power is restored after an instantaneous power failure, keep away from the machine because the
machine may be restarted suddenly (design the machine so that it is secured against hazard if restarted).
(6) Storage for servo motor
CAUTION
Note the following points when storing the servo motor for an extended period of time (guideline: three or
more months).
Always store the servo motor indoors in a clean and dry place.
If it is stored in a dusty or damp place, make adequate provision, e.g. cover the whole product.
If the insulation resistance of the winding decreases, reexamine the storage method.
Though the servo motor is rust-proofed before shipment using paint or rust prevention oil, rust may be
produced depending on the storage conditions or storage period.
If the servo motor is to be stored for longer than six months, apply rust prevention oil again especially to
the machined surfaces of the shaft, etc.
Before using the product after storage for an extended period of time, hand-turn the motor output shaft to
confirm that nothing is wrong with the servo motor. (When the servo motor is equipped with a brake,
make the above check after releasing the brake with the brake power supply.)
(7) Maintenance, inspection and parts replacement
CAUTION
With age, the electrolytic capacitor will deteriorate. To prevent a secondary accident due to a fault, it is
recommended to replace the electrolytic capacitor every 10 years when used in general environment.
Please consult our sales representative.
(8) General instruction
To illustrate details, the equipment in the diagrams of this Instruction Manual may have been drawn
without covers and safety guards. When the equipment is operated, the covers and safety guards must be
installed as specified. Operation must be performed in accordance with this Instruction Manual.

A - 6
About processing of waste
When you discard servo amplifier, a battery (primary battery), and other option articles, please follow the law of
each country (area).
FOR MAXIMUM SAFETY
This product is not designed or manufactured to be used in equipment or systems in situations that can
affect or endanger human life.
When considering this product for operation in special applications such as machinery or systems used in
passenger transportation, medical, aerospace, atomic power, electric power, or submarine repeating
applications, please contact your nearest Mitsubishi sales representative.
Although this product was manufactured under conditions of strict quality control, you are strongly advised
to install safety devices to forestall serious accidents when it is used in facilities where a breakdown in the
product is likely to cause a serious accident.
EEP-ROM life
The number of write times to the EEP-ROM, which stores parameter settings, etc., is limited to 100,000. If
the total number of the following operations exceeds 100,000, the servo amplifier and/or converter unit may
fail when the EEP-ROM reaches the end of its useful life.
Write to the EEP-ROM due to parameter setting changes

A - 7
COMPLIANCE WITH EC DIRECTIVES
1. WHAT ARE EC DIRECTIVES?
The EC directives were issued to standardize the regulations of the EU countries and ensure smooth
distribution of safety-guaranteed products. In the EU countries, the machinery directive (effective in
January, 1995), EMC directive (effective in January, 1996) and low voltage directive (effective in January,
1997) of the EC directives require that products to be sold should meet their fundamental safety
requirements and carry the CE marks (CE marking). CE marking applies to machines and equipment
into which servo amplifiers have been installed.
(1) EMC directive
The EMC directive applies not to the servo units alone but to servo-incorporated machines and
equipment. This requires the EMC filters to be used with the servo-incorporated machines and
equipment to comply with the EMC directive. For specific EMC directive conforming methods, refer to
the EMC Installation Guidelines (IB(NA)67310).
(2) Low voltage directive
The low voltage directive applies also to servo units alone. Hence, they are designed to comply with
the low voltage directive.
(3) Machine directive
Not being machines, the servo amplifiers need not comply with this directive.
2. PRECAUTIONS FOR COMPLIANCE
(1) Servo amplifiers and servo motors used (Acquisition schedule)
Use the servo amplifiers and servo motors which comply with the standard model.
Servo amplifier :MR-E-10A to MR-E-200A
Servo motor :HC-KFE
HC-SFE
(2) Configuration
Reinforced
insulating
transformer
NFB MC SM
No-fuse
breaker Magnetic
contactor
Reinforced
insulating type
24VDC
power
supply
Servo
amplifier
Servo
motor
Control box
Use the no-fuse breaker and magnetic contactor which conform to the EN or IEC Standard.
Design notice: Where residual-current-operated protective device (RCD) is used for protection case of
direvt or indirect contact, only RCD of type B is allowed on the supply side of this Electronic
Equipment(EE).
(3) Environment
Operate the servo amplifier at or above the contamination level 2 set forth in IEC664. For this
purpose, install the servo amplifier in a control box which is protected against water, oil, carbon, dust,
dirt, etc. (IP54).
(4) Power supply
(a) Operate the servo amplifier to meet the requirements of the overvoltage category II set forth in
IEC664. For this purpose, a reinforced insulating transformer conforming to the IEC or EN
Standard should be used in the power input section.
(b) As the external power supply for interface, use a 24VDC power supply that has been insulation-
reinforced in I/O.

A - 8
(5) Grounding
(a) To prevent an electric shock, always connect the protective earth (PE) terminals (marked ) of the
servo amplifier to the protective earth (PE) of the control box. Connect PE terminal of the control
box to the NEUTRAL of a power supply. Be sure to ground the NEUTRAL of a power supply.
(b) Do not connect two ground cables to the same protective earth (PE) terminal. Always connect the
cables to the terminals one-to-one.
PE terminals PE terminals
(c) If a leakage current breaker is used to prevent an electric shock, the protective earth (PE) terminals
of the servo amplifier must be connected to the corresponding earth terminals.
(6) Wiring
(a) The cables to be connected to the terminal block of the servo amplifier must have crimping
terminals provided with insulating tubes to prevent contact with adjacent terminals.
Crimping terminal
Insulating tube
Cable
(b) Use the servo motor side power connector which complies with the EN Standard. The EN
Standard-compliant power connector sets are available from us as options. (Refer to Section 13.1.2)
(7) Auxiliary equipment and options
(a) The no-fuse breaker and magnetic contactor used should be the EN or IEC standard-compliant
products of the models described in Section 13.2.2.
(b) The sizes of the cables described in Section 13.2.1 meet the following requirements. To meet the
other requirements, follow Table 5 and Appendix C in EN60204-1.
Ambient temperature: 40 (104) [ ( )]
Sheath: PVC (polyvinyl chloride)
Installed on wall surface or open table tray
(c) Use the EMC filter for noise reduction.
(8) Performing EMC tests
When EMC tests are run on a machine/device into which the servo amplifier has been installed, it
must conform to the electromagnetic compatibility (immunity/emission) standards after it has
satisfied the operating environment/electrical equipment specifications.
For the other EMC directive guidelines on the servo amplifier, refer to the EMC Installation
Guidelines(IB(NA)67310).

A - 9
CONFORMANCE WITH UL/C-UL STANDARD
(1) Servo amplifiers and servo motors used (Acquisition schedule)
Use the servo amplifiers and servo motors which comply with the standard model.
Servo amplifier :MR-E-10A to MR-E-200A
Servo motor :HC-KFE
HC-SFE
(2) Installation
Install a fan of 100CFM (2.8 m3/min) air flow 4 in (10.16 cm) above the servo amplifier or provide
cooling of at least equivalent capability.
(3) Short circuit rating
This servo amplifier conforms to the circuit whose peak current is limited to 5000A or less. Having
been subjected to the short-circuit tests of the UL in the alternating-current circuit, the servo
amplifier conforms to the above circuit.
(4) Capacitor discharge time
The capacitor discharge time is as listed below. To ensure safety, do not touch the charging section for
10 minutes after power-off.
Servo amplifier Discharge time
[min]
MR-E-10A 20A 1
MR-E-40A 2
MR-E-70A to 200A 3
(5) Options and auxiliary equipment
Use UL/C-UL standard-compliant products.
(6) About wiring protection
For installation in United States, branch circuit protection must be provided, in accordance with the
National Electrical Code and any applicable local codes.
For installation in Canada, branch circuit protection must be provided, in accordance with the Canada
Electrical Code and any applicable provincial codes.
<<About the manuals>>
Relevant manuals
Manual name Manual No.
MR-E Series To Use the AC Servo Safely IB(NA)0300057
EMC Installation Guidelines IB(NA)67310

A - 10
MEMO

1
CONTENTS
1. FUNCTIONS AND CONFIGURATION 1- 1 to 1-10
1.1 Introduction..............................................................................................................................................1- 1
1.2 Function block diagram ..........................................................................................................................1- 2
1.3 Servo amplifier standard specifications................................................................................................1- 3
1.4 Function list.............................................................................................................................................1- 4
1.5 Model code definition ..............................................................................................................................1- 6
1.6 Combination with servo motor...............................................................................................................1- 6
1.7 Parts identification..................................................................................................................................1- 7
1.8 Servo system with auxiliary equipment................................................................................................1- 9
2. INSTALLATION 2- 1 to 2- 4
2.1 Environmental conditions.......................................................................................................................2- 1
2.2 Installation direction and clearances ....................................................................................................2- 2
2.3 Keep out foreign materials.....................................................................................................................2- 3
2.4 Cable stress..............................................................................................................................................2- 3
3. SIGNALS AND WIRING 3- 1 to 3- 48
3.1 Standard connection example ................................................................................................................3- 2
3.1.1 Position control mode.......................................................................................................................3- 2
3.1.2 Internal speed control mode............................................................................................................3- 8
3.2 Internal connection diagram of servo amplifier ...................................................................................3- 9
3.3 I/O signals................................................................................................................................................3-10
3.3.1 Connectors and signal arrangements............................................................................................3-10
3.3.2 Signal explanations.........................................................................................................................3-13
3.4 Detailed description of the signals........................................................................................................3-19
3.4.1 Position control mode......................................................................................................................3-19
3.4.2 Internal speed control mode...........................................................................................................3-24
3.4.3 Position/internal speed control change mode................................................................................3-26
3.5 Alarm occurrence timing chart .............................................................................................................3-28
3.6 Interfaces.................................................................................................................................................3-29
3.6.1 Common line ....................................................................................................................................3-29
3.6.2 Detailed description of the interfaces............................................................................................3-30
3.7 Input power supply circuit.....................................................................................................................3-34
3.7.1 Connection example.........................................................................................................................3-34
3.7.2 Terminals..........................................................................................................................................3-35
3.7.3 Power-on sequence...........................................................................................................................3-36
3.8 Connection of servo amplifier and servo motor...................................................................................3-37
3.8.1 Connection instructions ..................................................................................................................3-37
3.8.2 Connection diagram.........................................................................................................................3-37
3.8.3 I/O terminals....................................................................................................................................3-39
3.9 Servo motor with electromagnetic brake .............................................................................................3-41
3.10 Grounding .............................................................................................................................................3-44
3.11 Servo amplifier connectors (CNP1, CNP2) wiring method
(When MR-ECPN1-B and MR-ECPN2-B of an option are used.)...................................................3-45
3.12 Instructions for the 3M connector.......................................................................................................3-48

2
4. OPERATION 4- 1 to 4- 6
4.1 When switching power on for the first time..........................................................................................4- 1
4.2 Startup......................................................................................................................................................4- 2
4.2.1 Selection of control mode..................................................................................................................4- 2
4.2.2 Position control mode.......................................................................................................................4- 2
4.2.3 Internal speed control mode............................................................................................................4- 4
5. PARAMETERS 5- 1 to 5- 30
5.1 Parameter list..........................................................................................................................................5- 1
5.1.1 Parameter write inhibit...................................................................................................................5- 1
5.1.2 Lists....................................................................................................................................................5- 2
5.2 Detailed description ...............................................................................................................................5-25
5.2.1 Electronic gear .................................................................................................................................5-25
5.2.2 Analog monitor.................................................................................................................................5-26
5.2.3 Using forward/reverse rotation stroke end to change the stopping pattern..............................5-29
5.2.4 Alarm history clear..........................................................................................................................5-29
5.2.5 Position smoothing ..........................................................................................................................5-30
6. DISPLAY AND OPERATION 6- 1 to 6-14
6.1 Display flowchart.....................................................................................................................................6- 1
6.2 Status display ..........................................................................................................................................6- 2
6.2.1 Display examples..............................................................................................................................6- 2
6.2.2 Status display list.............................................................................................................................6- 3
6.2.3 Changing the status display screen................................................................................................6- 4
6.3 Diagnostic mode.......................................................................................................................................6- 5
6.4 Alarm mode..............................................................................................................................................6- 6
6.5 Parameter mode ......................................................................................................................................6- 7
6.6 External I/O signal display.....................................................................................................................6- 8
6.7 Output signal (DO) forced output.........................................................................................................6-10
6.8 Test operation mode...............................................................................................................................6-11
6.8.1 Mode change.....................................................................................................................................6-11
6.8.2 Jog operation....................................................................................................................................6-12
6.8.3 Positioning operation.......................................................................................................................6-13
6.8.4 Motor-less operation........................................................................................................................6-14
7. GENERAL GAIN ADJUSTMENT 7- 1 to 7-10
7.1 Different adjustment methods ...............................................................................................................7- 1
7.1.1 Adjustment on a single servo amplifier..........................................................................................7- 1
7.1.2 Adjustment using servo configuration software............................................................................7- 2
7.2 Auto tuning ..............................................................................................................................................7- 3
7.2.1 Auto tuning mode .............................................................................................................................7- 3
7.2.2 Auto tuning mode operation............................................................................................................7- 4
7.2.3 Adjustment procedure by auto tuning............................................................................................7- 5
7.2.4 Response level setting in auto tuning mode...................................................................................7- 6

3
7.3 Manual mode 1 (simple manual adjustment).......................................................................................7- 7
7.3.1 Operation of manual mode 1 ...........................................................................................................7- 7
7.3.2 Adjustment by manual mode 1 .......................................................................................................7- 7
7.4 Interpolation mode.................................................................................................................................7-10
8. SPECIAL ADJUSTMENT FUNCTIONS 8- 1 to 8-10
8.1 Function block diagram ..........................................................................................................................8- 1
8.2 Machine resonance suppression filter...................................................................................................8- 1
8.3 Adaptive vibration suppression control.................................................................................................8- 3
8.4 Low-pass filter .........................................................................................................................................8- 4
8.5 Gain changing function...........................................................................................................................8- 5
8.5.1 Applications.......................................................................................................................................8- 5
8.5.2 Function block diagram....................................................................................................................8- 5
8.5.3 Parameters........................................................................................................................................8- 6
8.5.4 Gain changing operation..................................................................................................................8- 8
9. INSPECTION 9- 1 to 9- 2
10. TROUBLESHOOTING 10- 1 to 10-12
10.1 Trouble at start-up..............................................................................................................................10- 1
10.1.1 Position control mode...................................................................................................................10- 1
10.1.2 Internal speed control mode........................................................................................................10- 4
10.2 When alarm or warning has occurred...............................................................................................10- 5
10.2.1 Alarms and warning list..............................................................................................................10- 5
10.2.2 Remedies for alarms.....................................................................................................................10- 6
10.2.3 Remedies for warnings................................................................................................................10-11
11. OUTLINE DIMENSION DRAWINGS 11- 1 to 11- 8
11.1 Servo amplifiers...................................................................................................................................11- 1
11.2 Connectors............................................................................................................................................11- 5
12. CHARACTERISTICS 12- 1 to 12- 4
12.1 Overload protection characteristics...................................................................................................12- 1
12.2 Power supply equipment capacity and generated loss....................................................................12- 1
12.3 Dynamic brake characteristics...........................................................................................................12- 3
12.4 Encoder cable flexing life....................................................................................................................12- 4
13. OPTIONS AND AUXILIARY EQUIPMENT 13- 1 to 13-32
13.1 Options..................................................................................................................................................13- 1
13.1.1 Regenerative brake options.........................................................................................................13- 1
13.1.2 Cables and connectors..................................................................................................................13- 6
13.1.3 Analog monitor, RS-232C branch cable (MR-E3CBL15-P).....................................................13-19
13.1.4 Servo configurations software....................................................................................................13-20

4
13.2 Auxiliary equipment ..........................................................................................................................13-21
13.2.1 Recommended wires....................................................................................................................13-21
13.2.2 No-fuse breakers, fuses, magnetic contactors...........................................................................13-23
13.2.3 Power factor improving reactors................................................................................................13-23
13.2.4 Relays............................................................................................................................................13-24
13.2.5 Surge absorbers ...........................................................................................................................13-24
13.2.6 Noise reduction techniques.........................................................................................................13-24
13.2.7 Leakage current breaker.............................................................................................................13-30
13.2.8 EMC filter.....................................................................................................................................13-32
14. SERVO MOTOR 14- 1 to 14- 38
14.1 Compliance with the overseas standards..........................................................................................14- 1
14.1.1 Compliance with EC directives...................................................................................................14- 1
14.1.2 Conformance with UL/C-UL standard.......................................................................................14- 1
14.2 Model name make-up..........................................................................................................................14- 2
14.3 Parts identification..............................................................................................................................14- 4
14.4 Installation...........................................................................................................................................14- 5
14.4.1 Environmental conditions............................................................................................................14- 6
14.4.2 Installation orientation................................................................................................................14- 6
14.4.3 Load mounting precautions.........................................................................................................14- 7
14.4.4 Permissible load for the shaft......................................................................................................14- 8
14.4.5 Protection from oil and water.....................................................................................................14-11
14.4.6 Cable .............................................................................................................................................14-12
14.5 Connectors used for servo motor wiring...........................................................................................14-13
14.5.1 HC-KFE series.............................................................................................................................14-13
14.5.2 HC-SFE series..............................................................................................................................14-13
14.6 Specifications......................................................................................................................................14-19
14.6.1 Standard specifications...............................................................................................................14-19
14.6.2 Torque characteristics.................................................................................................................14-21
14.6.3 Servo motors with reduction gears............................................................................................14-22
14.6.4 Servo motors with special shafts................................................................................................14-25
14.6.5 D cut..............................................................................................................................................14-25
14.7 Characteristics....................................................................................................................................14-26
14.7.1 Electromagnetic brake characteristics......................................................................................14-26
14.7.2 Vibration rank..............................................................................................................................14-28
14.7.3 Machine Accuracies.....................................................................................................................14-28
14.8 Outline dimension drawing...............................................................................................................14-29
14.8.1 HC-KFE series.............................................................................................................................14-29
14.8.2 HC-SFE series..............................................................................................................................14-32
14.9 Outline dimension drawing (in inches)............................................................................................14-34
14.9.1 HC-KFE series.............................................................................................................................14-34
14.9.2 HC-SFE series..............................................................................................................................14-37

5
15. MR-E- AG SERVO AMPLIFIER COMPATIBLE WITH ANALOG INPUT 15- 1 to 15- 62
15.1. Functions and configuration..............................................................................................................15- 1
15.1.1 Introduction...................................................................................................................................15- 1
15.1.2 Function block diagram ...............................................................................................................15- 2
15.1.3 Servo amplifier standard specifications.....................................................................................15- 3
15.1.4 Model code definition....................................................................................................................15- 4
15.1.5 Parts identification.......................................................................................................................15- 4
15.1.6 Servo system with auxiliary equipment.....................................................................................15- 6
15.2. Signals and wiring..............................................................................................................................15- 8
15.2.1 Standard connection example .....................................................................................................15- 8
15.2.2 Internal connection diagram of servo amplifier .......................................................................15-11
15.2.3 Connectors and signal arrangements........................................................................................15-12
15.2.4 Signal explanations.....................................................................................................................15-14
15.2.5 Detailed description of the signals.............................................................................................15-18
15.3 Startup.................................................................................................................................................15-25
15.3.1 Speed control mode......................................................................................................................15-25
15.3.2 Torque control mode....................................................................................................................15-27
15.4 Parameters..........................................................................................................................................15-29
15.4.1 Item list.........................................................................................................................................15-29
15.4.2 Details list ....................................................................................................................................15-32
15.5 Display and operation........................................................................................................................15-51
15.5.1 Display flowchart.........................................................................................................................15-51
15.5.2 Status display...............................................................................................................................15-53
15.5.3 Diagnostic mode...........................................................................................................................15-55
15.5.4 External I/O signal display.........................................................................................................15-57
15.6. Troubleshooting.................................................................................................................................15-59
15.6.1 Trouble at start-up ......................................................................................................................15-59
15.6.2 Alarms and warning list.............................................................................................................15-61

6
MEMO

1 - 1
1. FUNCTIONS AND CONFIGURATION
1. FUNCTIONS AND CONFIGURATION
1.1 Introduction
The Mitsubishi MR-E series general-purpose AC servo is based on the MR-J2-Super series, and has the
same high performance and limited functions.
It has position control and internal speed control modes. Further, it can perform operation with the
control modes changed, e.g. position/internal speed control. Hence, it is applicable to a wide range of
fields, precision positioning and smooth speed control of machine tools and general industrial machines.
As this new series has the RS-232C or RS-422 serial communication function, a servo configuration
software-installed personal computer or the like can be used to perform parameter setting, test operation,
status display monitoring, gain adjustment, etc.
With real-time auto tuning, you can automatically adjust the servo gains according to the machine.
The MR-E series servo motor is equipped with an incremental position encoder that has the resolution of
10000 pulses/rev to ensure high precision positioning.
(1) Position control mode
An up to 500kpps high-speed pulse train is used to control the speed and direction of a motor and
execute precision positioning of 10000 pulses/rev resolution.
The position smoothing function provides a choice of two different modes appropriate for a machine, so
a smoother start/stop can be made in response to a sudden position command.
A torque limit is imposed on the servo amplifier by the clamp circuit to protect the power transistor in
the main circuit from overcurrent due to sudden acceleration/deceleration or overload. This torque
limit value can be changed to any value with the parameter.
(2) Internal speed control mode
The parameter-driven internal speed command (max. 7 speeds) is used to control the speed and
direction of a servo motor smoothly.
There are also the acceleration/deceleration time constant setting in response to speed command, the
servo lock function at a stop time.

1 - 2
1. FUNCTIONS AND CONFIGURATION
1.2 Function block diagram
The function block diagram of this servo is shown below.
Regenerative brake option
Servo amplifier
Current
detector
CHARGE
lamp
Servo motor
Regenerative
TR
(Note 1)
Regenerative brake Base amplifier Voltage
detection Overcurrent
protection
Encoder
Dynamic
brake
Control
power
supply
Fan
(MR-E-200A only) Electro-
magnetic
brake
Current
detection
Model position
control
Model speed
control
Pulse
input
Model
position
Actual position
control
Actual speed
control
Current
control
Model torque
Virtual
motor
Virtual
encoder
Model
speed
D I/O control
Servo on
Start
Failure, etc.
Controller
Analog monitor
(2 channels)
RADS
D
C
P
NFB MC L1
L2
L3
CN1 CN3
RS-232C
E2
I/F
CN2
U
V
W
U
V
W
SM
E1
RS-232C D/A
Power
supply
3-phase
200 to
230VAC,
1-phase
230VAC
(Note 2)
(Note 3)
(Note 3)
(Note 3)
(Note 3)
(Note 3)(Note 3)
Note:1. The built-in regenerative brake resistor is not provided for the MR-E-10A/20A.
2. The single-phase 230VAC can be used for MR-E-70A or smaller servo amplifier.
Connect the power supply cables to L1 and L2 while leaving L3 open.
3. The control circuit connectors (CN1, CN2 and CN3) are safely isolated from main circuit terminals
(L1, L2, L3, U, V, W, P, C and D).

1 - 3
1. FUNCTIONS AND CONFIGURATION
1.3 Servo amplifier standard specifications
Servo Amplifier
MR-E-
Item
10A 20A 40A 70A 100A 200A
Voltage/frequency 3-phase 200 to 230VAC, 50/60Hz or 1-phase 230VAC,
50/60Hz 3-phase 200 to 230VAC,
50/60Hz
Permissible voltage fluctuation 3-phase 200 to 230VAC:
170 to 253VAC
1-phase 230VAC: 207 to 253VAC 3-phase 170 to 253VAC
Permissible frequency fluctuation Within 5%
Power supply
Power supply capacity Refer to Section12.2
System Sine-wave PWM control, current control system
Dynamic brake Built-in
Protective functions
Overcurrent shut-off, regenerative overvoltage shut-off, overload shut-off (electronic
thermal relay), encoder error protection, regenerative brake error protection,
undervoltage, instantaneous power failure protection, overspeed protection, excessive
error protection
Max. input pulse frequency 500kpps (for differential receiver), 200kpps (for open collector)
Command pulse multiplying factor Electronic gear A:1 to 65535 B:1 to 65535, 1/50 A/B 50
In-position range setting 0 to 10000 pulse (command pulse unit)
Error excessive 10 revolutions
Position control mode
Torque limit Set by parameter setting
Speed control range Internal speed command 1: 5000
Speed fluctuation ratio 0.01% or less (load fluctuation 0 to 100%)
0% or less (power fluctuation 10%)
Internal speed
control mode
Torque limit Set by parameter setting
Structure Self-cooled, open (IP00) Force-cooling,
open (IP00)
[]0 to 55 (non-freezing)
Operation [] 32 to 131 (non-freezing)
[ ] 20 to 65 (non-freezing)
Ambient
temperature Storage []4 to 149 (non-freezing)
Operation
Ambient
humidity Storage 90%RH or less (non-condensing)
Ambient Indoors (no direct sunlight)
Free from corrosive gas, flammable gas, oil mist, dust and dirt
Altitude Max. 1000m (3280ft) above sea level
5.9 [m/s2] or less
Environment
Vibration 19.4 [ft/s2] or less
[kg] 0.8 0.8 1.2 1.8 1.8 2.0
Weight [lb] 1.8 1.8 2.6 4.0 4.0 4.4

1 - 4
1. FUNCTIONS AND CONFIGURATION
1.4 Function list
The following table lists the functions of this servo. For details of the functions, refer to the corresponding
chapters and sections.
Function Description (Note)
Control mode Refer to
Position control mode This servo is used as position control servo. P Section 3.1.1
Section 3.4.1
Section 4.2.2
Internal speed control mode This servo is used as internal speed control servo. S Section 3.1.2
Section 3.4.2
Section 4.2.3
Position/internal speed
control change mode Using external input signal, control can be switched
between position control and internal speed control. P/S Section 3.4.4
High-resolution encoder High-resolution encoder of 131072 pulses/rev is used as a
servo motor encoder. P, S, T
Gain changing function You can switch between gains during rotation and gains
during stop or use an external input signal to change gains
during operation. P, S Section 8.5
Adaptive vibration
suppression control
Servo amplifier detects mechanical resonance and sets filter
characteristics automatically to suppress mechanical
vibration. P, S Section 8.3
Low-pass filter Suppresses high-frequency resonance which occurs as servo
system response is increased. P, S Section 8.4
Machine analyzer function Analyzes the frequency characteristic of the mechanical
system by simply connecting a servo configuration software-
installed personal computer and servo amplifier. P
Machine simulation Can simulate machine motions on a personal computer
screen on the basis of the machine analyzer results. P
Gain search function Personal computer changes gains automatically and
searches for overshoot-free gains in a short time. P
Slight vibration suppression
control Suppresses vibration of 1 pulse produced at a servo motor
stop. P Parameter No. 20
Electronic gear Input pulses can be multiplied by 1/50 to 50. P Parameters No. 3, 4,
69 to 71
Auto tuning Automatically adjusts the gain to optimum value if load
applied to the servo motor shaft varies. P, S Chapter 7
Position smoothing Speed can be increased smoothly in response to input pulse. P Parameter No. 7
S-pattern acceleration/
deceleration time constant Speed can be increased and decreased smoothly. S Parameter No. 13
Regenerative brake option Used when the built-in regenerative brake resistor of the
servo amplifier does not have sufficient regenerative
capability for the regenerative power generated. P, S Section 13.1.1

1 - 5
1. FUNCTIONS AND CONFIGURATION
Function Description (Note)
Control mode Refer to
Alarm history clear Alarm history is cleared. P, S Parameter No. 16
Restart after instantaneous
power failure
If the input power supply voltage had reduced to cause an
alarm but has returned to normal, the servo motor can be
restarted by merely switching on the start signal. S Parameter No. 20
Command pulse selection Command pulse train form can be selected from among four
different types. P Parameter No. 21
Input signal selection Forward rotation start, reverse rotation start, servo-on and
other input signals can be assigned to any pins. P, S Parameters
No. 43 to 48
Torque limit Servo motor torque can be limited to any value. P, S Section 3.4.1 (5)
Parameter No. 28
Status display Servo status is shown on the 5-digit, 7-segment LED
display P, S Section 6.2
External I/O signal display ON/OFF statuses of external I/O signals are shown on the
display. P, S Section 6.6
Output signal (DO)
forced output
Output signal can be forced on/off independently of the
servo status.
Use this function for output signal wiring check, etc. P, S Section 6.7
Test operation mode Servo motor can be run from the operation section of the
servo amplifier without the start signal entered. P, S Section 6.8
Analog monitor output Servo status is output in terms of voltage in real time. P, S Parameter No. 17
Servo configuration software Using a personal computer, parameter setting, test
operation, status display, etc. can be performed. P, S Section 13.1.8
Alarm code output If an alarm has occurred, the corresponding alarm number
is output in 3-bit code. P, S Section 10.2.1
Note:P: Position control mode, S: Internal speed control mode
P/S: Position/internal speed control change mode

1 - 6
1. FUNCTIONS AND CONFIGURATION
1.5 Model code definition
(1) Rating plate
MR-E-40A
MITSUBISHI AC SERVO
MADE IN JAPAN
MODEL
MITSUBISHI ELECTRIC CORPORATION
AC SERVO
PASSED
POWER
INPUT
OUTPUT
SERIAL
:400W
:2.6A 3PH200-230V 50Hz
:2.6A3PH200-230V 60Hz
:170V 0-360Hz 2.8A
:XXXXYYYYY
:TCXXXAYYYGZZ
:
Model
Capacity
Applicable power supply
Rated output current
Serial number
(2) Model
70 750
40 400
10 100
20 100
200 1000
200 2000
MR-E-200AMR-E-40A or less MR-E-70A, 100A
Rating plate Rating plate Rating plate
Series
Rated output
General-purpose interface
Symbol Rated output [W] Symbol Rated output [W]
- AMR - E
1.6 Combination with servo motor
The following table lists combinations of servo amplifiers and servo motors. The same combinations apply
to the models with electromagnetic brakes and the models with reduction gears.
Servo motors
Servo amplifier HC-KFE HC-SFE
2000r/min
MR-E-10A 13
MR-E-20A 23
MR-E-40A 43
MR-E-70A 73 52
MR-E-100A 102
MR-E-200A 152 202

1 - 7
1. FUNCTIONS AND CONFIGURATION
1.7 Parts identification
(1) MR-E-100A or less
MODE
CN3
SET
CN1
CN2
CNP2
CNP1
L3L2L1 D C P W V U
CHARGE
MITSUBISHI
MR-
Chapter6
Display
The 5-digit, seven-segment LED shows the servo
status and alarm number.
Used to set data.
Used to change the
display or data in each
mode.
Used to change the
mode.
MODE UP DOWN SET
Operation section
Used to perform status display, diagnostic, alarm and
parameter setting operations.
Chapter6
Communication connector (CN3)
Used to connect a command device (RS-232C)
and output analog monitor data.
I/O signal connector (CN1)
Used to connect digital I/O signals. Section3.3
Encoder connector (CN2)
Connector for connection of the servo motor encoder. Section3.3
Section13.1.2
Charge lamp
Lit to indicate that the main circuit is charged. While
this lamp is lit, do not reconnect the cables.
Protective earth (PE) terminal ( )
Ground terminal. Section3.10
Section11.1
Section3.3
Section13.1.2
Chapter14
Section3.7
Section11.1
Section3.7
Section11.1
Section13.1.1
Refer to
Name/Application
Motor power supply connector (CNP2)
Used to connect the servo motor.
Power supply/regenerative connector (CNP1)
Used to connect the input power supply and
regenerative brake option.

1 - 8
1. FUNCTIONS AND CONFIGURATION
(2) MR-E-200A
Refer to
Name/Application
Chapter6
Display
The 5-digit, seven-segment LED shows the servo
status and alarm number.
Used to set data.
Used to change the
display or data in each
mode.
Used to change the
mode.
MODE UP DOWN SET
Operation section
Used to perform status display, diagnostic, alarm and
parameter setting operations.
Chapter6
Communication connector (CN3)
Used to connect a command device (RS232C)
and output analog monitor data.
Section3.3
Section13.1.2
Chapter14
I/O signal connector (CN1)
Used to connect digital I/O signals. Section3.3
Name plate
Charge lamp
Lit to indicate that the main circuit is charged. While
this lamp is lit, do not reconnect the cables.
Encoder connector (CN2)
Connector for connection of the servo motor encoder.
Section1.5
Section3.3
Section13.1.2
Motor power supply connector (CNP2)
Used to connect the servo motor.
Protective earth (PE) terminal ( )
Ground terminal.
Power supply/regenerative connector (CNP1)
Used to connect the input power supply and
regenerative brake option.
Section3.7
Section11.1
Section3.7
Section11.1
Section13.1.1
Section3.10
Section11.1
Cooling fan
Installation notch
(4 places)

1 - 9
1. FUNCTIONS AND CONFIGURATION
1.8 Servo system with auxiliary equipment
WARNING To prevent an electric shock, always connect the protective earth (PE) terminal
(terminal marked ) of the servo amplifier to the protective earth (PE) of the control
box.
(1) MR-E-100A or less
MODE
CN3
SET
CN1
CN2
CNP2
CNP1
L3L2L1 D C P W V U
CHARGE
MITSUBISHI
MR-E-
P
C
L3
L2
L1
(Note 2)
3-phase 200V
to 230VAC power
supply or
1-phase 230VAC
power supply
No-fuse breaker
(NFB) or fuse
Magnetic
contactor
(MC)
To CN2
To CN1
To CN3
Protective earth
(PE) terminal
Servo motor
Personal
computer
Servo amplifier
Regenerative option
Options and auxiliary equipment
No-fuse breaker
Magnetic contactor
Servo configuration software
Regenerative option
Refer to
Section 13.2.2
Section 13.2.2
Section 13.1.4
Section 13.1.1
(Note 1)
Encoder cable
Options and auxiliary equipment Refer to
Cables Section 13.2.1
Command device
(Note 1)
Power supply lead
Power
factor
improving
reactor
(FR-BAL)
Power factor improving reactor Section 13.2.3
Servo configuration
software
MRZJW3-SETUP1
Note: 1. The HC-SFE series have cannon connectors.
2. A 1-phase 230VAC power supply may be used with the servo amplifier of MR-E-70A or less. Connect the power supply to
L1 and L2 terminals and leave L3 open.
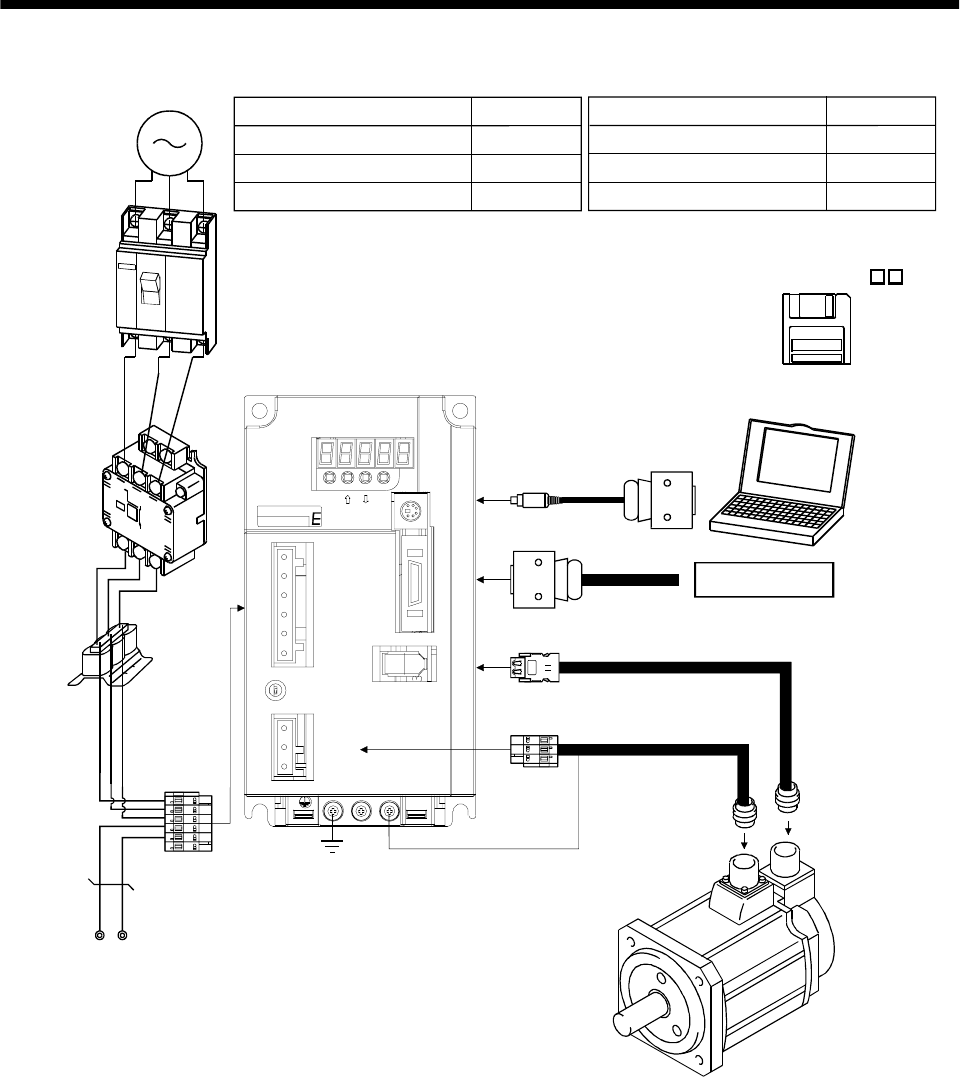
1 - 10
1. FUNCTIONS AND CONFIGURATION
(2) MR-E-200A
L3
L2
L1
DC L3PL1L2
CHARGE
CNP2
CNP1
CN1
CN2
UVW
CN3
MODE SET
MITS U BISHI
EZMotion
PC
Options and auxiliary equipment
No-fuse breaker
Magnetic contactor
Servo configuration software
Regenerative option
Refer to
Section 13.2.2
Section 13.2.2
Section 13.1.4
Section 13.1.1
Options and auxiliary equipment Refer to
Cables Section 13.2.1
Power factor improving reactor Section 13.2.3
Power
f
actor
improving
reactor
(FR-BAL)
3-phase 200V
to 230VAC
power supply
No-fuse
breaker
(NFB) or
fuse
Magnetic
contactor
(MC)
To CN2
To CN1
To CN3
Servo amplifier
Regenerative option
Personal
computer
Command device
Servo configuration
software
MRZJW3-SETUP1
To CNP2

2 - 1
2. INSTALLATION
2. INSTALLATION
CAUTION
Stacking in excess of the limited number of products is not allowed.
Install the equipment to incombustibles. Installing them directly or close to
combustibles will led to a fire.
Install the equipment in a load-bearing place in accordance with this Instruction
Manual.
Do not get on or put heavy load on the equipment to prevent injury.
Use the equipment within the specified environmental condition range.
Provide an adequate protection to prevent screws, metallic detritus and other
conductive matter or oil and other combustible matter from entering the servo
amplifier.
Do not block the intake/exhaust ports of the servo amplifier. Otherwise, a fault may
occur.
Do not subject the servo amplifier to drop impact or shock loads as they are
precision equipment.
Do not install or operate a faulty servo amplifier.
When the product has been stored for an extended period of time, consult
Mitsubishi.
2.1 Environmental conditions
Environment Conditions
[]0 to 55 (non-freezing)
Operation [] 32 to 131 (non-freezing)
[ ] 20 to 65 (non-freezing)
Ambient
temperature Storage []4 to 149 (non-freezing)
Operation
Ambient
humidity Storage 90%RH or less (non-condensing)
Ambience Indoors (no direct sunlight)
Free from corrosive gas, flammable gas, oil mist, dust and dirt
Altitude Max. 1000m (3280 ft) above sea level
[m/s2] 5.9 [m/s2] or less
Vibration [ft/s2] 19.4 [ft/s2] or less

2 - 2
2. INSTALLATION
2.2 Installation direction and clearances
CAUTION
The equipment must be installed in the specified direction. Otherwise, a fault may
occur.
Leave specified clearances between the servo amplifier and control box inside
walls or other equipment.
(1) Installation of one servo amplifier
MODE
CN3
SET
CN1
CN2
CNP2
CNP1
L3L2L1 D C P W V U
CHARGE
MITSUBISHI
MR-
Control box Control box
10mm
(0.4 in.)
or more
10mm
(0.4 in.)
or more
40mm
(1.6 in.)
or more
Servo
amplifier
40mm
(1.6 in.)
or more
Wiring clearance Top
Bottom
(2.8 in.)
70mm
(2) Installation of two or more servo amplifiers
Leave a large clearance between the top of the servo amplifier and the internal surface of the control
box, and install a fan to prevent the internal temperature of the control box from exceeding the
environmental conditions.
MODE
CN3
SET
CN1
CN2
CNP2
CNP1
L3L2L1 D C P W V U
CHARGE
MITSUBISHI
MR-
MODE
CN3
CN1
CN2
CNP2
CNP1
L3L2L1 D C P W V U
CHARGE
MITSUBISHI
MR-
SET
Control box
30mm
(1.2 in.)
or more
30mm
(1.2 in.)
or more
10mm
(0.4 in.)
or more
40mm
(1.6 in.)
or more
100mm
(4.0 in.)
or more

2 - 3
2. INSTALLATION
(3) Others
When using heat generating equipment such as the regenerative brake option, install them with full
consideration of heat generation so that the servo amplifier is not affected.
Install the servo amplifier on a perpendicular wall in the correct vertical direction.
2.3 Keep out foreign materials
(1) When installing the unit in a control box, prevent drill chips and wire fragments from entering the
servo amplifier.
(2) Prevent oil, water, metallic dust, etc. from entering the servo amplifier through openings in the control
box or a fan installed on the ceiling.
(3) When installing the control box in a place where there are much toxic gas, dirt and dust, conduct an
air purge (force clean air into the control box from outside to make the internal pressure higher than
the external pressure) to prevent such materials from entering the control box.
2.4 Cable stress
(1) The way of clamping the cable must be fully examined so that flexing stress and cable's own weight
stress are not applied to the cable connection.
(2) For use in any application where the servo motor moves, fix the cables (encoder, power supply, brake)
supplied with the servo motor, and flex the optional encoder cable or the power supply and brake
wiring cables. Use the optional encoder cable within the flexing life range. Use the power supply and
brake wiring cables within the flexing life of the cables.
(3) Avoid any probability that the cable sheath might be cut by sharp chips, rubbed by a machine corner
or stamped by workers or vehicles.
(4) For installation on a machine where the servo motor will move, the flexing radius should be made as
large as possible. Refer to section 12.4 for the flexing life.

2 - 4
2. INSTALLATION
MEMO

3 - 1
3. SIGNALS AND WIRING
3. SIGNALS AND WIRING
WARNING
Any person who is involved in wiring should be fully competent to do the work.
Before starting wiring, switch power off, then wait for more than 10 minutes, and
after the charge lamp has gone off, make sure that the voltage is safe in the tester
or like. Otherwise, you may get an electric shock.
Ground the servo amplifier and the servo motor securely.
Do not attempt to wire the servo amplifier and servo motor until they have been
installed. Otherwise, you may get an electric shock.
The cables should not be damaged, stressed excessively, loaded heavily, or
pinched. Otherwise, you may get an electric shock.
CAUTION
Wire the equipment correctly and securely. Otherwise, the servo motor may
misoperate, resulting in injury.
Connect cables to correct terminals to prevent a burst, fault, etc.
Ensure that polarity ( , ) is correct. Otherwise, a burst, damage, etc. may occur.
The surge absorbing diode installed to the DC relay designed for control output
should be fitted in the specified direction. Otherwise, the signal is not output due to
a fault, disabling the emergency stop and other protective circuits.
RA RA
Servo
Amplifier
Control output
signal
External
24VDC External
24VDC
Servo
Amplifier
Control output
signal
Use a noise filter, etc. to minimize the influence of electromagnetic interference,
which may be given to electronic equipment used near the servo amplifier.
Do not install a power capacitor, surge suppressor or radio noise filter (FR-BIF
option) with the power line of the servo motor.
When using the regenerative brake resistor, switch power off with the alarm signal.
Otherwise, a transistor fault or the like may overheat the regenerative brake
resistor, causing a fire.
Do not modify the equipment.

3 - 2
3. SIGNALS AND WIRING
3.1 Standard connection example
POINT
Refer to Section 3.7.1 for the connection of the power supply system and to
Section 3.8 for connection with the servo motor.
3.1.1 Position control mode
(1) FX-10GM
9,19
9
12
INP
RD
RA1
RA2
ALM
ZSP
17
16
18
LA
LAR
LB
LBR
SD
15
4
3
SD
6
MO1
LG
MO2
A
A
VIN
VIN
OP
LG
OPC
VIN
PP
SG
NP
CR
SG
SD
10
11
1
1
21
14
2
1
23
13
25
5
13
12
1
2
14
13
7,17
8,18
6
9,19
16
3
4
11
5
15
1
2
4
5
6
8
3
7
START
STOP
FWD
RVS
DOG
LSR
COM1
ZRN
LSF
FX-10GM
CN3
20
19 LZ
LZR
8
4
3
6
7
13
EMG
SON
RES
LSP
LSN
SG
1VIN
CN1
13 SG
SVRDY
COM2
COM2
SVEND
COM4
PGO
VC
FPO
FP
COM5
RP
RPO
CLR
COM3
24
Positioning module
(Note 9) 2m(6.5ft) max.
Servo amplifier
(Note 8) (Note 8)
CN1 CN1
(Note2, 4)
(Note 6)
Trouble
Zero speed
Plate (Note 8)
Plate
(Note 3, 5) Emergency stop
Servo-on
Reset
(Note 5) Forward rotation stroke end
Reverse rotation stroke end
(Note 10)
Servo configuration
software
Personal
computer
10m(32ft) max.
(Note 7)
Communication cable
(Note 7)
Monitor output
Max. 1mA
Reading in both
directions
(Note 8) (Note 1)
CN1
(Note 8) CN3
(Note 8)
10k
10k
2m (6.5ft) max.
Encoder A-phase pulse
(differential line driver)
Encoder B-phase pulse
(differential line driver)
Encoder Z-phase pulse
(differential line driver)
External
power
supply
24VDC
Plate
(Note 11)

3 - 3
3. SIGNALS AND WIRING
Note: 1. To prevent an electric shock, always connect the protective earth (PE) terminal (terminal marked ) of the servo amplifier to
the protective earth (PE) of the control box.
2. Connect the diode in the correct direction. If it is connected reversely, the servo amplifier will be faulty and will not output
signals, disabling the emergency stop and other protective circuits.
3. The emergency stop switch (normally closed contact) must be installed.
4. The sum of currents that flow in the external relays should be 80mA max. If it exceeds 80mA, supply interface power from
external. (Refer to Section 3.6.2)
5. When starting operation, always connect the emergency stop signal (EMG) and forward/ reverse rotation stroke end signal
(LSN/LSP) with SG. (Normally closed contacts)
6. Trouble (ALM) is connected with COM in normal alarm-free condition. When this signal is switched off (at occurrence of an
alarm), the output of the controller should be stopped by the sequence program.
7. When connecting the personal computer together with monitor outputs 1, 2, use the branch cable (MR-E3CBL15-P). (Refer to
Section 13.1.3)
8. The pins with the same signal name are connected in the servo amplifier.
9. This length applies to the command pulse train input in the opencollector system. It is 10m (32ft) or less in the differential line
driver system.
10. Use MRZJW3-SETUP 154E.
11. Connect the external 24VDC power supply if the output signals are not used.

3 - 4
3. SIGNALS AND WIRING
(2) AD75P (A1SD75P )
26
8
24
5
21
4
22
7
23
3
25
6
1
20
12
14
35
16
13
15
11
2
36
19
VIN
INP
LZ
CR
PG
NP
NG
RD
SG
PP
LZR
SD
LG
DOG
COM
RLS
START
CHG
FLS
STOP
COM
READY
COM
INPS
CLEAR
PGO(24V)
PGO(5V)
PGO COM
CLEAR COM
PULSE F-
PULSE F+
PULSE R-
PULSE R+
PULSE F
PULSE COM
PULSE R
PULSE COM
17
16
18
LA
LAR
LB
LBR
SD
15
4
3
SD
6
MO1
LG
MO2
A
A
CN3
21
14 LG
OP
8
4
3
6
7
13
EMG
SON
RES
LSP
LSN
SG
CN1 CN3
CN1
CN1
9
12
RA1
RA2
ALM
ZSP
1VIN
CN1
13 SG
11
1
10
19
20
5
13
22
23
24
25
14
(Note 8)
24VDC
Positioning module
AD75P
(A1SD75P ) (Note 9) 10m(32ft) max. Servo amplifier
(Note 2, 4)
(Note 6)
Trouble
Zero speed
Encoder A-phase pulse
(differential line driver)
Encoder B-phase pulse
(differential line driver)
Control common
Encoder Z-phase pulse
(open collector)
(Note 3, 5) Emergency stop
Servo-on
Reset
(Note 5) Forward rotation stroke end
Reverse rotation stroke end
(Note 10)
Servo configuration
software
Personal
computer
(Note 7)
Communication cable
(Note 1)
(Note 7)
Monitor output
Max. 1mA
Reading in both
directions
2m(6.5ft) max.
(Note 11)
10k
10k
(Note 8) (Note 8)
(Note 8)
(Note 8)
(Note 8)
Plate
Plate
Plate
External
power
supply
24VDC
(Note 12)

3 - 5
3. SIGNALS AND WIRING
Note: 1. To prevent an electric shock, always connect the protective earth (PE) terminal (terminal marked ) of the servo amplifier to
the protective earth (PE) of the control box.
2. Connect the diode in the correct direction. If it is connected reversely, the servo amplifier will be faulty and will not output
signals, disabling the emergency stop and other protective circuits.
3. The emergency stop switch (normally closed contact) must be installed.
4. The sum of currents that flow in the external relays should be 80mA max. If it exceeds 80mA, supply interface power from
external.(Refer to Section 3.6.2)
5. When starting operation, always connect the emergency stop signal (EMG) and forward/ reverse rotation stroke end signal
(LSN/LSP) with SG. (Normally closed contacts)
6. Trouble (ALM) is connected with COM in normal alarm-free condition. When this signal is switched off (at occurrence of an
alarm), the output of the controller should be stopped by the sequence program.
7. When connecting the personal computer together with monitor outputs 1, 2, use the branch cable (MR-E3CBL15-P). (Refer to
Section 13.1.3)
8. The pins with the same signal name are connected in the servo amplifier.
9. This length applies to the command pulse train input in the differential line driver system.
It is 2m (6.5ft) or less in the opencollector system.
10. Use MRZJW3-SETUP 154E.
11. Connect LG and pulse output COM to increase noise immunity.
12. Connect the external 24VDC power supply if the output signals are not used.

3 - 6
3. SIGNALS AND WIRING
(3) QD75D (differential driver)
VIN
LZ
CR
PG
NP
NG
RD
SG
PP
LZR
SD
LG
17
16
18
LA
LAR
LB
LBR
15
4
3
SD
6
MO1
LG
MO2
A
A
CN3
21
14 LG
OP
8
4
3
6
7
13
EMG
SON
RES
LSP
LSN
SG
CN1 CN3
CN1
9
12
RA1
RA2
ALM
ZSP
1VIN
13 SG
11
1
19
20
5
13
22
23
24
25
14
12
9
13
16
17
18
11
14
15
10
A19
B20
1
4
6
2
5
3
A20
7
B19
READY
RDY COM
CLEAR
DOG
COM
RLS
CHG
FLS
STOP
COM
PGO5
PGO COM
CLEAR COM
PULSE F-
PULSE F+
PULSE R-
PULSE R+
PULSER A+
PULSER A-
PULSER B+
PULSER B-
A
B
0V
5V
5G
SG
(Note 8)
Positioning module
QD75D (Note 9) 10m(32ft) max. Servo amplifier
(Note 8)
CN1
(Note 8)
CN1
(Note 2, 4)
Encoder A-phase pulse
(differential line driver)
Encoder B-phase pulse
(differential line driver)
Control common
Encoder Z-phase pulse
(open collector)
(Note 8)
Plate
(Note 3, 5) Emergency stop
Servo-on
Reset
(Note 5) Forward rotation stroke end
Reverse rotation stroke end
(Note 10)
Servo configuration
software
Personal
computer
(Note 7)
Communication cable
(Note 1)
(Note 7)
Monitor output
Max. 1mA
Reading in both
directions
2m(6.5ft) max.
10k
Plate
10k
(Note 6)
Trouble
Zero speed
(Note 8)
(Note 8)
5V
Plate
External
power
supply
24VDC
External power
supply 24VDC
Manual pulse
generator
MR-HDP01
(Note 11)

3 - 7
3. SIGNALS AND WIRING
Note: 1. To prevent an electric shock, always connect the protective earth (PE) terminal (terminal marked ) of the servo amplifier to
the protective earth (PE) of the control box.
2. Connect the diode in the correct direction. If it is connected reversely, the servo amplifier will be faulty and will not output
signals, disabling the emergency stop and other protective circuits.
3. The emergency stop switch (normally closed contact) must be installed.
4. The sum of currents that flow in the external relays should be 80mA max. If it exceeds 80mA, supply interface power from
external.(Refer to Section 3.6.2)
5. When starting operation, always connect the emergency stop signal (EMG) and forward/ reverse rotation stroke end signal
(LSN/LSP) with SG. (Normally closed contacts)
6. Trouble (ALM) is connected with COM in normal alarm-free condition. When this signal is switched off (at occurrence of an
alarm), the output of the controller should be stopped by the sequence program.
7. When connecting the personal computer together with monitor outputs 1, 2, use the branch cable (MR-E3CBL15-P). (Refer to
Section 13.1.3)
8. The pins with the same signal name are connected in the servo amplifier.
9. This length applies to the command pulse train input in the differential line driver system.
It is 2m (6.5ft) or less in the opencollector system.
10. Use MRZJW3-SETUP 154E.
11. Connect the external 24VDC power supply if the output signals are not used.

3 - 8
3. SIGNALS AND WIRING
3.1.2 Internal speed control mode
1
9
12
RA1
RA2
8
4
3
5
6
7
EMG
SON
ST1
ST2
LSP
LSN
SG 13
ALM
ZSP
CN3
VIN
CN1
4
3
SD
6
MO1
LG
MO2 10k
10k
A
A
CN3
20
19
21
17
16
18
LZ
LZR
LA
LAR
LB
LBR
LG
OP
SD
14
15
11
10 SA
RD
RA5
RA4
13 SG
Plate
(Note 9)
Servo configuration
software
Personal
computer
CN1
(Note 8)
(Note 6)
Trouble
Zero speed
(Note 2, 4)
Control common
Encoder Z-phase pulse
(open collector)
Encoder Z-phase pulse
(differential line driver)
Encoder A-phase pulse
(differential line driver)
Encoder B-phase pulse
(differential line driver)
(Note 7)
Communication cable 2m(6.5ft) max.
(Note 7)
Monitor output
Max. 1mA
Reading in
both directions
(Note 1)
Servo amplifier
(Note 8)
Speed reached
Ready
Plate
(Note 3, 5) Emergency stop
Servo-on
Forward rotation start
Reverse rotation start
(Note 5) Forward rotation stroke end
Reverse rotation stroke end
External
power
supply
24VDC
10m(32ft) max.
(Note 8)
(Note 8)
(Note 10)
Note: 1. To prevent an electric shock, always connect the protective earth (PE) terminal (terminal marked ) of the servo amplifier to
the protective earth (PE) of the control box.
2. Connect the diode in the correct direction. If it is connected reversely, the servo amplifier will be faulty and will not output
signals, disabling the emergency stop and other protective circuits.
3. The emergency stop switch (normally closed contact) must be installed.
4. The sum of currents that flow in the external relays should be 80mA max. If it exceeds 80mA, supply interface power from
external.(Refer to Section 3.6.2)
5. When starting operation, always connect the emergency stop signal (EMG) and forward/ reverse rotation stroke end signal
(LSN/LSP) with SG. (Normally closed contacts)
6. Trouble (ALM) is connected with COM in normal alarm-free condition.
7. When connecting the personal computer together with monitor outputs 1, 2, use the branch cable (MR-E3CBL15-P). (Refer to
Section 13.1.3)
8. The pins with the same signal name are connected in the servo amplifier.
9. Use MRZJW3-SETUP 154E.
10. Connect the external 24VDC power supply if the output signals are not used.

3 - 9
3. SIGNALS AND WIRING
3.2 Internal connection diagram of servo amplifier
The following is the internal connection diagram where the signal assignment has been made in the
initial status in each control mode.
S
RD RD11CR
OPC
PG
RES
EMG
LSP
LSN
SG
EMG
LSP
LSN
SG
ST1
SD
PP
NG
NP
SD
P
13
CN1
CN1
SON SON 4
3
8
6
7
ST2 5
2
22
23
24
25
PS
INP SA10
ALM ALM9
ZSP ZSP12
15
16
18
17
20
21
19
LA
LAR
LBR
LB
LZR
OP
LZ
CN1
4MO1
6
2
MO2
TXD
CN3
1RXD
3LG
LG14
VIN VIN 1
Servo amplifier
(Note) (Note)
Approx. 4.7k
Approx. 4.7k
Approx. 4.7k
Approx. 4.7k
Approx. 4.7k
Approx. 4.7k
Approx. 100k
Approx. 100k
Approx. 1.2k
Approx. 1.2k
Case
PE
External
power
supply
24VDC
Note. P: Position control mode, S: Internal speed control mode
Case SD

3 - 10
3. SIGNALS AND WIRING
3.3 I/O signals
3.3.1 Connectors and signal arrangements
POINT
The pin configurations of the connectors are as viewed from the cable
connector wiring section.
Refer to the next page for CN1 signal assignment.
(1) Signal arrangement
3
MR 57
MD 9
2
LG 4
MRR 68
MDR 10
LG
1
CN1
MODE
CN3
SET
CN1
CN2
CNP2
CNP1
L3L2L1 D C P W V U
CHARGE
MITSUBISHI
MR-E
P5
6
MO2
2
OPC
1
VIN 15
LA
14
LG
16
LAR
17
LB
3
RES
4
SON
6
LSP
5
CR 19
LZ
18
LBR
20
LZR
21
OP
7
LSN
8
EMG
10
INP
9
ALM 23
PP
22
PG
24
NG
25
NP
11
RD
12
ZSP 2613
SG
MO1
42
TXD
2
TXD
5 3
LG
1
RXD
The connector frames are
connected with the PE (earth)
terminal inside the servo amplifier.

3 - 11
3. SIGNALS AND WIRING
(2) CN1 signal assignment
The signal assignment of connector changes with the control mode as indicated below;
For the pins which are given parameter No.s in the related parameter column, their signals can be
changed using those parameters.
(Note2) I/O Signals in control modes
Connector Pin No. (Note1) I/O PP/SS
Related
parameter
1 VIN VIN VIN
2OPCOPC
3 I RES RES/ST1 ST1 No.43 to 48
4I SON SON
SON
No.43 to 48
5I CR LOP
ST2
No.43 to 48
6 I LSP LSP LSP No.43 48
7I LSN LSN LSN No.4348
8 I EMG EMG EMG
9O ALM ALM ALM No.49
10 O INP INP/SA SA No.49
11 O RD RD RD No.49
12 O ZSP ZSP ZSP No.1, 49
13 SG SG SG
14 LG LG LG
15 O LA LA LA
16 O LAR LAR LAR
17 O LB LB LB
18 O LBR LBR LBR
19 O LZ LZ LZ
20 O LZR LZR LZR
21 O OP OP OP
22 I PG PG/
23 I PP PP/
24 I NG NG/
25 I NP NP/
CN1
26
Note: 1. I : Input signal, O: Output signal
2. P : Position control mode, S: Internal speed control mode, P/S: Position/internal speed control change mode.

3 - 12
3. SIGNALS AND WIRING
(3) Symbols and signal names
Symbol Signal name Symbol Signal name
SON Servo-on ZSP Zero speed
LSP Forward rotation stroke end INP In position
LSN Reverse rotation stroke end SA Speed reached
CR Clear ALM Trouble
SP1 Speed selection 1 WNG Warning
SP2 Speed selection 2 OP Encoder Z-phase pulse (open collector)
PC Proportion control MBR Electromagnetic brake interlock
ST1 Forward rotation start LZ
ST2 Reverse rotation start LZR Encoder Z-phase pulse
(differential line driver)
TL Torque limit selection LA
RES Reset LAR Encoder A-phase pulse
(differential line driver)
EMG Emergency stop LB
LOP Control change LBR Encoder B-phase pulse
(differential line driver)
PP VIN Digital I/F power supply input
NP OPC Open collector power input
PG SG Digital I/F common
NG
Forward/reverse rotation pulse train
LG Control common
RD Ready SD Shield

3 - 13
3. SIGNALS AND WIRING
3.3.2 Signal explanations
For the I/O interfaces (symbols in I/O column in the table), refer to Section 3.6.2.
In the control mode field of the table
P : Position control mode, S: Internal speed control mode
: Denotes that the signal may be used in the initial setting status.
: Denotes that the signal may be used by setting the corresponding parameter among parameters 43 to
49.
The pin No.s in the connector pin No. column are those in the initial status.
(1) Input signals
POINT
The acceptance delay time of each input signal is less than 10ms.
Control
mode
Signal Symbol
Connec-
tor pin
No.
Functions/Applications I/O
division PS
Servo-on SON CN1-4 Connect SON-SG to switch on the base circuit and make the servo
amplifier ready to operate (servo-on).
Disconnect SON-SG to shut off the base circuit and coast the
servo motor (servo off) .
Set " 1" in parameter No. 41 to switch this signal on
(keep terminals connected) automatically in the servo
amplifier.
DI-1
Reset RES CN1-3 Disconnect RES-SG for more than 50ms to reset the alarm.
Some alarms cannot be deactivated by the reset signal. (Refer to
Section 10.2.1.)
Shorting RES-SG in an alarm-free status shuts off the base
circuit. The base circuit is not shut off when " 1 " is set in
parameter No. 51.
DI-1
To start operation, short LSP-SG and/or LSN-SG. Open them to
bring the motor to a sudden stop and make it servo-locked.
Set " 1" in parameter No. 22 to make a slow stop.
(Refer to Section 5.2.3.)
(Note) Input signals Operation
LSP LSN CCW
direction
CW
direction
11
Forward rotation
stroke end LSP CN1-6
01
10
00
Note. 0: LSP/LSN-SG off (open)
1: SP/LSN-SG on (short)
Set parameter No. 41 as indicated below to switch on the signals
(keep terminals connected) automatically in the servo amplifier:
Parameter No.41 Automatic ON
1 LSP
1 LSN
Reverse rotation
stroke end LSN CN1-7
DI-1

3 - 14
3. SIGNALS AND WIRING
Control
mode
Signal Symbol
Connec-
tor pin
No.
Functions/Applications I/O
division PS
Internal
torque limit
selection
TL1 When using this signal, make it usable by making the setting of
parameter No. 43 to 48.
(Refer to (5), Section 3.4.1.)
DI-1
Used to start the servo motor in any of the following directions:
(Note) Input signals
ST2 ST1 Servo motor starting direction
Forward rotation
start ST1 CN1-3
0 0 Stop (servo lock)
0 1 CCW
10 CW
1 1 Stop (servo lock)
Reverse rotation
start ST2 CN1-5
Note. 0: ST1/ST2-SG off (open)
1: ST1/ST2-SG on (short)
If both ST1 and ST2 are switched on or off during operation, the
servo motor will be decelerated to a stop according to the parameter
No. 12 setting and servo-locked.
DI-1
Speed selection 1 SP1 <Internal speed control mode>
Used to select the command speed for operation.
When using SP1 to SP3, make it usable by making the setting of
parameter No. 43 to 48.
DI-1
(Note) Input signals
Speed selection 2 SP2
SP3 SP2 SP1
Speed command DI-1
Speed selection 3 SP3 00 0
Internal speed command 1 (parameter No. 8) DI-1
0 0 1 Internal speed command 1 (parameter No. 8)
0 1 0 Internal speed command 2 (parameter No. 9)
0 1 1 Internal speed command 3 (parameter No. 10)
10 0
Internal speed command 4 (parameter No. 72)
1 0 1 Internal speed command 5 (parameter No. 73)
1 1 0 Internal speed command 6 (parameter No. 74)
1 1 1 Internal speed command 7 (parameter No. 75)
Note 0: SP1/SP2/SP3-SG off (open)
1: SP1/SP2/SP3-SG on (short)
Proportion
control PC Connect PC-SG to switch the speed amplifier from the proportional
integral type to the proportional type.
If the servo motor at a stop is rotated even one pulse due to any
external factor, it generates torque to compensate for a position
shift. When the servo motor shaft is to be locked mechanically after
positioning completion (stop), switching on the proportion control
signal (PC) upon positioning completion will suppress the
unnecessary torque generated to compensate for a position shift.
When the shaft is to be locked for a long time, switch on the
proportion control signal and torque control signal (TL) at the same
time to make the torque less than the rated by the analog torque
limit.
DI-1

3 - 15
3. SIGNALS AND WIRING
Control
mode
Signal Symbol
Connec-
tor pin
No.
Functions/Applications I/O
division PS
Emergency stop EMG CN1-8 Disconnect EMG-SG to bring the servo motor to emergency stop
state, in which the servo is switched off and the dynamic brake is
operated.
Connect EMG-SG in the emergency stop state to reset that state.
DI-1
Clear CR CN1-5 Connect CR-SG to clear the position control counter droop pulses on
its leading edge. The pulse width should be 10ms or more.
When the parameter No.42 setting is " 1 ", the pulses are always
cleared while CR-SG are connected.
DI-1
Electronic gear
selection 1 CM1 When using CM1 and CM2, make them usable by the setting of
parameters No. 43 to 48.
The combination of CM1-SG and CM2-SG gives you a choice of four
different electronic gear numerators set in the parameters.
CM1 and CM2 cannot be used in the absolute position detection
system.
DI-1
(Note) Input signals
CM2 CM1 Electronic gear namerator
00 Parameter No. 3
01 Parameter No. 69
10 Parameter No. 70
11 Parameter No. 71
Electronic gear
selection 2 CM2
Note.0: CM1/CM2-SG off (open)
1: CM1/CM2-SG on (short)
DI-1
Gain changing CDP When using this signal, make it usable by the setting of parameter
No. 43 to 48.
Connect CDP-SG to change the load inertia moment ratio into the
parameter No. 61 setting and the gain values into the values
multiplied by the parameter No. 62 to 64 settings.
DI-1
Control change LOP <Position/internal speed control change mode>
Used to select the control mode in the position/internal speed
control change mode.
DI-1
(Note) LOP Control mode
0Position
1 Internal speed
Note.0: LOP-SG off (open)
1: LOP-SG on (short)
Refer to
Functions/
Appli-
cations.
Forward rotation
pulse train
Reverse rotation
pulse train
PP
NP
PG
NG
CN1-23
CN1-25
CN1-22
CN1-24
Used to enter a command pulse train.
In the open collector system (max. input frequency 200kpps):
Forward rotation pulse train across PP-SG
Reverse rotation pulse train across NP-SG
In the differential receiver system (max. input frequency 500kpps):
Forward rotation pulse train across PG-PP
Reverse rotation pulse train across NG-NP
The command pulse train form can be changed using
parameter No. 21.
DI-2

3 - 16
3. SIGNALS AND WIRING
(2) Output signals
Control
mode
Signal Symbol
Connec-
tor pin
No.
Functions/Applications I/O
division PS
Trouble ALM CN1-9 ALM-SG are disconnected when power is switched off or the
protective circuit is activated to shut off the base circuit. Without
alarm, ALM-SG are connected within 1 after power on.
DO-1
Ready RD CN1-11 RD-SG are connected when the servo is switched on and the servo
amplifier is ready to operate. DO-1
In position INP INP-SG are connected when the number of droop pulses is in the
preset in-position range. The in-position range can be changed
using parameter No. 5.
When the in-position range is increased, INP-SG may be kept
connected during low-speed rotation.
DO-1
Speed reached SA
CN1-10
SA-SG are connected when the servo motor speed has nearly
reached the preset speed. When the preset speed is 50r/min or
less, SA-SG are kept connected.
DO-1
Zero speed ZSP CN1-12 ZSP-SG are connected when the servo motor speed is zero speed
(50r/min) or less. Zero speed can be changed using parameter No.
24.
DO-1
Electromagnetic
brake interlock MBR (CN1-12) Set " 1 " in parameter No. 1 to use this parameter. Note that
ZSP will be unusable.
In the servo-off or alarm status, MBR-SG are disconnected.
When an alarm occurs, they are disconnected independently of
the base circuit status.
DO-1
Warning WNG To use this signal, assign the connector pin for output using
parameter No.49. The old signal before assignment will be
unusable.
When warning has occurred, WNG-SG are connected.
When there is no warning, WNG-SG are disconnected within 1
second after power-on.
DO-1

3 - 17
3. SIGNALS AND WIRING
Control
mode
Signal Symbol
Connec-
tor pin
No.
Functions/Applications I/O
division PS
To use this signal, set " 1" in parameter No.49.
This signal is output when an alarm occurs. When there is no
alarm, respective ordinary signals (RD, INP, SA, ZSP) are output.
Alarm codes and alarm names are listed below:
(Note) Alarm code
CN1
12 Pin
CN1
11 Pin
CN1
10 Pin
Alarm
display Name
88888 Watchdog
AL.12 Memory error 1
AL.13 Clock error
AL.15 Memory error 2
AL.17 Board error
AL.19 Memory error 3
AL.37 Parameter error
AL.8A Serial communication
timeout
000
AL.8E Serial communication error
AL.30 Regenerative error
010
AL.33 Overvoltage
001AL.10Undervoltage
AL.45 Main circuit device
AL.46 Servo motor overheat
AL.50 Overload 1
011
AL.51 Overload 2
AL.24 Main circuit error
100
AL.32 Overcurrent
AL.31 Overspeed
AL.35 Command pulse frequency
alarm
110
AL.52 Error excessive
AL.16 Encoder error 1
101
AL.1A Monitor combination error
AL.20 Encoder error 2
Alarm code ACD 0
ACD 1
ACD 2
Note.0: Pin-SG off (open)
1: Pin-SG on (short)
DO-1

3 - 18
3. SIGNALS AND WIRING
Control
mode
Signal Symbol
Connec-
tor pin
No.
Functions/Applications I/O
division PS
Encoder Z-phase
pulse
(Open collector)
OP CN1-21 Outputs the zero-point signal of the encoder. One pulse is output
per servo motor revolution. OP and LG are connected when the
zero-point position is reached. (Negative logic)
The minimum pulse width is about 400 s. For home position
return using this pulse, set the creep speed to 100r/min. or less.
DO-2
Encoder A-phase
pulse
(Differential line
driver)
LA
LAR
CN1-15
CN1-16
Encoder B-phase
pulse
(Differential line
driver)
LB
LBR
CN1-17
CN1-18
Outputs pulses per servo motor revolution set in parameter No.
27 in the differential line driver system. In CCW rotation of the
servo motor, the encoder B-phase pulse lags the encoder A-phase
pulse by a phase angle of /2.
The relationships between rotation direction and phase difference
of the A- and B-phase pulses can be changed using parameter No.
54.
DO-2
Encoder Z-phase
pulse
(Differential line
driver)
LZ
LZR
CN1-19
CN1-20
The same signal as OP is output in the differential line driver
system. DO-2
Analog monitor 1 MO1 CN3-4 Used to output the data set in parameter No.17 to across MO1-LG
in terms of voltage. Resolution 10 bits Analog
output
Analog monitor 2 MO2 CN3-6 Used to output the data set in parameter No.17 to across MO2-LG
in terms of voltage. Resolution 10 bits Analog
output
(3) Communication
Control
mode
Signal Symbol
Connec-
tor pin
No.
Functions/Applications I/O
division PS
RS-232C I/F RXD
TXD
CN3-1
CN3-2
RS-232C communication interface.
(4) Power supply
Control
mode
Signal Symbol
Connec-
tor pin
No.
Functions/Applications I/O
division PS
Digital I/F power
supply input VIN CN1-1 Used to input 24VDC for input interface.
Connect the positive terminal of the 24VDC external power
supply.
24VDC 10%
Open collector
power input OPC CN1-2 When inputting a pulse train in the open collector system, supply
this terminal with the positive ( ) power of 24VDC.
Digital I/F
common SG CN1-13 Common terminal for input signals such as SON and EMG. Pins
are connected internally.
Separated from LG.
Control common LG CN1-14 Common terminal for OP, MO1, and MO2.
Pins are connected internally.
Shield SD Plate Connect the external conductor of the shield cable.

3 - 19
3. SIGNALS AND WIRING
3.4 Detailed description of the signals
3.4.1 Position control mode
(1) Pulse train input
(a) Input pulse waveform selection
Encoder pulses may be input in any of three different forms, for which positive or negative logic
can be chosen. Set the command pulse train form in parameter No. 21.
Arrow or in the table indicates the timing of importing a pulse train.
A- and B-phase pulse trains are imported after they have been multiplied by 4.
Pulse train form Forward rotation
command
Reverse rotation
command
Parameter No. 21
(Command pulse train)
Forward rotation
pulse train
Reverse rotation
pulse train
PP
NP 0010
Pulse train sign
PP
NP LH
0011
Negative logic
A-phase pulse train
B-phase pulse train
PP
NP
0012
Forward rotation
pulse train
Reverse rotation
pulse train
PP
NP
0000
Pulse train sign PP
NP HL0001
Positive logic
A-phase pulse train
B-phase pulse train
PP
NP 0002

3 - 20
3. SIGNALS AND WIRING
(b) Connections and waveforms
1) Open collector system
Connect as shown below:
SG
SD
OPC
PP
NP
Servo amplifier
Approx.
1.2k
Approx.
1.2k
External power
supply 24VDC
The explanation assumes that the input waveform has been set to the negative logic and forward
and reverse rotation pulse trains (parameter No.21 has been set to 0010). The waveforms in the
table in (a), (1) of this section are voltage waveforms of PP and NP based on SG. Their
relationships with transistor ON/OFF are as follows:
(ON)(OFF)
(ON) (OFF) (ON) (OFF) (ON)
(OFF)
Forward rotation
pulse train
(transistor)
Reverse rotation
pulse train
(transistor)
(ON)(OFF)
Forward rotation command Reverse rotation command
(OFF)

3 - 21
3. SIGNALS AND WIRING
2) Differential line driver system
Connect as shown below:
PP
NP
PG
NG
SD
Servo amplifier
The explanation assumes that the input waveform has been set to the negative logic and forward
and reverse rotation pulse trains (parameter No.21 has been set to 0010).
For the differential line driver, the waveforms in the table in (a), (1) of this section are as follows.
The waveforms of PP, PG, NP and NG are based on that of the ground of the differential line
driver.
PP
PG
NP
NG
Forward rotation
pulse train
Reverse rotation
pulse train
Forward rotation command Reverse rotation command

3 - 22
3. SIGNALS AND WIRING
(2) In-position (INP)
PF-SG are connected when the number of droop pulses in the deviation counter falls within the preset
in-position range (parameter No. 5). INP-SG may remain connected when low-speed operation is
performed with a large value set as the in-position range.
Servo-on (SON)
Alarm
Droop pulses
In position (INP)
ON
OFF
Yes
No
In-position range
ON
OFF
(3) Ready (RD)
Servo-on (SON)
Alarm
Ready (RD)
ON
OFF
Yes
No
80ms or less 10ms or less 10ms or less
ON
OFF
(4) Electronic gear switching
The combination of CM1-SG and CM2-SG gives you a choice of four different electronic gear
numerators set in the parameters.
As soon as CM1/CM2 is turned ON or OFF, the namerator of the electronic gear changes. Therefore, if
any shock occurs at this change, use position smoothing (parameter No. 7) to relieve shock.
(Note) External input signal
CM2 CM1 Electronic gear namerator
00 Parameter No. 3
01 Parameter No. 69
10 Parameter No. 70
11 Parameter No. 71
Note.0: CM1/CM2-SG off(open)
1: CM1/CM2-SG on(short)

3 - 23
3. SIGNALS AND WIRING
(5) Torque limit
(a) Torque limit and torque
By setting parameter No. 28 (internal torque limit 1), torque is always limited to the maximum
value during operation. A relationship between the limit value and servo motor torque is shown
below.
00 100
Max. torque
Torque
Torque limit value [%]
(b) Torque limit value selection
When internal torque limit selection (TL1) is made usable by parameter No. 43 to 48, internal
torque limit 2 (parameter No. 76) can be selected. However, if the parameter No. 28 value is less
than the limit value selected by parameter No.76, the parameter No. 28 value is made valid.
(Note) External input signals
TL1 Torque limit value made valid
0 Internal torque limit value 1 (parameter No. 28)
1Parameter No. 76 Parameter No. 28: Parameter No. 28
Parameter No. 76 Parameter No. 28: Parameter No. 76
Note.0: TL/TL1-SG off (open)
1: TL/TL1-SG on (short)

3 - 24
3. SIGNALS AND WIRING
3.4.2 Internal speed control mode
(1) Speed setting
(a) Speed command and speed
The servo motor is run at the speeds set in the parameters.
Forward rotation (CCW)
Reverse rotation (CW)
The following table indicates the rotation direction according to forward rotation start (ST1) and
reverse rotation start (ST2) combination:
(Note) External input signals Rotation direction
ST2 ST1 Internal speed commands
00 Stop (Servo lock)
01 CCW
10 CW
11 Stop (Servo lock)
Note.0: ST1/ST2-SG off (open)
1: ST1/ST2-SG on (short)
The forward rotation start signal (ST1) and reverse rotation start signal (ST2) can be assigned to
any pins of the connector CN1 using parameters No. 43 to 48.
Generally, make connection as shown below:
ST1
ST2
SG
SD
Servo amplifier

3 - 25
3. SIGNALS AND WIRING
(b) Speed selection 1 (SP1), speed selection 2 (SP2), speed selection 3 (SP3) and speed command value
By making speed selection 1 (SP1), speed selection 2 (SP2) and speed selection 3 (SP3) usable by
setting of parameter No. 43 to 47, you can choose the speed command values of internal speed
commands 1 to 7.
(Note) External input signals
SP3 SP2 SP1 Speed command value
0 0 0 Internal speed command 1 (parameter No. 8)
0 0 1 Internal speed command 1 (parameter No. 8)
0 1 0 Internal speed command 2 (parameter No. 9)
0 1 1 Internal speed command 3 (parameter No. 10)
1 0 0 Internal speed command 4 (parameter No. 72)
1 0 1 Internal speed command 5 (parameter No. 73)
1 1 0 Internal speed command 6 (parameter No. 74)
1 1 1 Internal speed command 7 (parameter No. 75)
Note.0 : SP1/SP2/SP3-SG off (open)
1 : SP1/SP2/SP3-SG on (short)
The speed may be changed during rotation. In this case, the values set in parameters No. 11 and
12 are used for acceleration/deceleration.
When the speed has been specified under any internal speed command, it does not vary due to the
ambient temperature.
(2) Speed reached (SA)
SA-SG are connected when the servo motor speed nearly reaches the speed set to the internal speed
command.
ON
OFF
ON
OFF
Set speed selection Internal speed
command 1
Internal speed
command 2
Start (ST1,ST2)
Servo motor speed
Speed reached (SA)
(3) Torque limit
As in Section 3.4.1 (5).

3 - 26
3. SIGNALS AND WIRING
3.4.3 Position/internal speed control change mode
Set "0001" in parameter No. 0 to switch to the position/internal speed control change mode. This function
is not available in the absolute position detection system.
(1) Control change (LOP)
Use control change (LOP) to switch between the position control mode and the internal speed control
mode from an external contact. Relationships between LOP-SG status and control modes are indicated
below:
(Note) LOP Servo control mode
0 Position control mode
1 Speed control mode
Note.0: LOP-SG off (open)
1: LOP-SG on (short)
The control mode may be changed in the zero-speed status. To ensure safety, change control after the
servo motor has stopped. When position control mode is changed to speed control mode, droop pulses are
reset.
If the signal has been switched on-off at the speed higher than the zero speed and the speed is then
reduced to the zero speed or less, the control mode cannot be changed. A change timing chart is shown
below:
ON
OFF
ON
OFF
Position
control mode
Internal speed
control mode
Servo motor speed
Zero speed (ZSP)
Control change (LOP)
Zero speed
level
(Note)
Note: When ZSP is not on, control cannot be changed if LOP is switched on-off.
If ZSP switches on after that, control cannot not be changed.
(Note)
Position
control mode
(2) Torque limit in position control mode
As in Section 3.4.1 (5).

3 - 27
3. SIGNALS AND WIRING
(3) Internal speed setting in speed control mode
(a) Speed command and speed
The servo motor is run at the speed set in parameter No. 8 (internal speed command 1) the forward
rotation start signal (ST1) and reverse rotation start signal (ST2) are as in (a), (1) in section 3.4.2.
Generally, make connection as shown below:
SP2
SG
SD
Servo amplifier
(b) Speed selection 2 (SP2) and speed command value
Use speed selection 2 (SP2) to select between the speed set by the internal speed command 1 and
the speed set by the Internal speed command 2 as indicated in the following table:
(Note) External input signals
SP1 Speed command value
0 Internal speed command 1 (parameter No. 8)
1 Internal speed command 2 (parameter No. 9)
Note.0: SP1-SG off (open)
1: SP1-SG on (short)
The speed may also be changed during rotation. In this case, it is increased or decreased according
to the value set in parameter No. 11 or 12.
When the internal speed command 1 is used to command the speed, the speed does not vary with
the ambient temperature.
(c) Speed reached (SA)
As in Section 3.4.2 (2).

3 - 28
3. SIGNALS AND WIRING
3.5 Alarm occurrence timing chart
CAUTION
When an alarm has occurred, remove its cause, make sure that the operation
signal is not being input, ensure safety, and reset the alarm before restarting
operation.
When an alarm occurs in the servo amplifier, the base circuit is shut off and the servo motor is coated to a
stop. Switch off the power supply in the external sequence. To reset the alarm, switch the power supply
from off to on, press the "SET" button on the current alarm screen, or turn the reset signal (RES) from off
to on. However, the alarm cannot be reset unless its cause is removed.
ON
OFF
ON
OFF
ON
OFF
ON
OFF
ON
OFF
ON
OFF
1s
Brake operation
50ms or more 60ms or more
Alarm occurs.
Remove cause of trouble.
Brake operation
Power off Power on
Valid
Invalid
Power supply
Base circuit
Dynamic brake
Servo-on
(SON)
Reset
(RES)
Ready
(RD)
Trouble
(ALM)
(Note)
Note: Shut off the power as soon as an alarm occurs.
(1) Overcurrent, overload 1 or overload 2
If operation is repeated by switching power off, then on to reset the overcurrent (AL.32),
overload 1 (AL.50) or overload 2 (AL.51) alarm after its occurrence, without removing its cause,
the servo amplifier and servo motor may become faulty due to temperature rise. Securely
remove the cause of the alarm and also allow about 30 minutes for cooling before resuming
operation.
(2) Regenerative alarm
If operation is repeated by switching power off, then on to reset the regenerative (AL.30) alarm
after its occurrence, the external regenerative brake resistor will generate heat, resulting in an
accident.
(3) Instantaneous power failure
Undervoltage (AL.10) occurs if power is restored after a 60ms or longer power failure of the
power supply or after a drop of the bus voltage to or below 200VDC. If the power failure persists
further, the power switches off. When the power failure is reset in this state, the alarm is reset
and the servo motor will start suddenly if the servo-on signal (SON) is on. To prevent hazard,
make up a sequence which will switch off the servo-on signal (SON) if an alarm occurs.
(4) In position control mode (incremental)
When an alarm occurs, the home position is lost. When resuming operation after deactivating
the alarm, make a home position return.

3 - 29
3. SIGNALS AND WIRING
3.6 Interfaces
3.6.1 Common line
The following diagram shows the power supply and its common line.
CN1 CN1
DO-1
SG
OPC
SG
SD
OP
LG
MR
MRR
SD
SM
DI-1
VIN
LG
SD
CN3
RA
CN2
SD
MO1
MO2
LG
SG
TXD
RXD RS-232C
LG
ALM, etc.
(Note)
Servo motor
Servo motor encoder
Isolated
Analog monitor output
Differential line
driver output
35mA max.
SON, etc.
PG NG
PP NP
LA etc.
LAR
etc.
Ground
External
power
supply
24VDC
Note: For the open collection pulse train input. Make the following
connection for the different line driver pulse train input.
SG
PP NP
PG NG
OPC

3 - 30
3. SIGNALS AND WIRING
3.6.2 Detailed description of the interfaces
This section gives the details of the I/O signal interfaces (refer to I/O Division in the table) indicated in
Sections 3.3.2.
Refer to this section and connect the interfaces with the external equipment.
(1) Digital input interface DI-1
Give a signal with a relay or open collector transistor.
VIN
SG
Switch
SON, etc.
External power
supply 24VDC
200mA or more
Servo amplifier
R: Approx. 4.7
(2) Digital output interface DO-1
A lamp, relay or photocoupler can be driven. Provide a diode (D) for an inductive load, or an inrush
current suppressing resister (R) for a lamp load. (Permissible current: 40mA or less, inrush current:
100mA or less)
(a) Inductive load
VIN
SG
Servo amplifier
Load
ALM, etc.
If the diode is not
connected as shown,
the servo amplifier
will be damaged.
External power
supply 24VDC
10%

3 - 31
3. SIGNALS AND WIRING
(b) Lamp load
VIN
SG
R
Servo amplifier
ALM, etc.
External power
supply 24VDC
10%
(3) Pulse train input interface DI-2
Provide a pulse train signal in the open collector or differential line driver system.
(a) Open collector system
1) Interface
VIN
PP, NP
SG
SD
Servo amplifier
Max. input pulse
frequency 200kpps
About 1.2k
External power
supply 24VDC
2) Conditions of the input pulse
0.9
0.1
tc tHL
tc tLH tF
tLH tHL 0.2 s
tc 2 s
tF 3 s
PP
NP

3 - 32
3. SIGNALS AND WIRING
(b) Differential line driver system
1) Interface
SD
PG(NG)
PP(NP)
Max. input pulse
frequency 500kpps
Servo amplifier
Am26LS31 or equivalent
About 100
2) Conditions of the input pulse
0.9
PP PG
tc tHL
tc tLH tF
tLH tHL 0.1 s
tc 1 s
tF 3 s
NP NG
0.1
(4) Encoder pulse output
(a) Open collector system
Interface
Servo amplifier
OP
5 to 24VDC
Photocoupler
SD
Max. output current : 35mA
LG
Servo amplifier
OP
SD
LG

3 - 33
3. SIGNALS AND WIRING
(b) Differential line driver system
1) Interface
Max. output current: 35mA
LA
(LB, LZ)
LAR
(LBR, LZR)
LG
SD
LA
(LB, LZ)
LAR
(LBR, LZR)
SD
Servo amplifier Servo amplifier
Am26LS32 or equivalent High-speed photocoupler
150
100
2) Output pulse
Servo motor CCW rotation
LA
LAR
LB
LBR
LZ
LZR
T
/2
400 s or more
OP
LZ signal varies 3/8T on its leading edge.
(5) Analog output
Output voltage 10V
Max.1mA
Max. output current
Resolution : 10bit
MO1
(MO2)
LG
SD
A
Servo amplifier
Reading in one or
both directions
1mA meter
10k

3 - 34
3. SIGNALS AND WIRING
3.7 Input power supply circuit
CAUTION
When the servo amplifier has become faulty, switch power off on the servo
amplifier power side. Continuous flow of a large current may cause a fire.
Use the trouble signal to switch power off. Otherwise, a regenerative brake
transistor fault or the like may overheat the regenerative brake resistor, causing a
fire.
POINT
The power supply connector (CNP1) is optional. Purchase it without fail.
3.7.1 Connection example
Wire the power supply and main circuit as shown below so that the servo-on signal turns off as soon as
alarm occurrence is detected and power is shut off.
A no-fuse breaker (NFB) must be used with the input cables of the power supply.
(1) For 3-phase 200 to 230VAC power supply
3-phase
200 to 230 VAC
Emergency stop
Servo-on
Trouble
Servo amplifier
External
power
supply
24VDC
(Note)
RA
OFF ON
MC MC
SK
NFB MC
L1
L2
L3
VIN
EMG
SON
SG
ALM
SG
RA
CNP1
P
D
C
Note: To use the built-in regenerative resistor, be sure to connect across P and D of the power supply connector (CNP1).
Emergency
stop

3 - 35
3. SIGNALS AND WIRING
(2) For 1-phase 230VAC power supply
Power supply
1-phase 230VAC
Emergency stop
Servo-on
Servo amplifier
Trouble
Emergency
stop
External
power
supply
24VDC
RA
OFF ON
MC MC
SK
NFB MC
L1
L2
L3
EMG
SON
SG
VIN
ALM
SG
RA
(Note)
CNP1
P
D
C
Note: To use the built-in regenerative resistor, be sure to connect across P and D of the power supply connector (CNP1).
3.7.2 Terminals
Refer to Section 11.1 (4) for the signal arrangement.
Connected terminal
(Application) Symbol Description
Supply L1, L2 and L3 with the following power:
For 1-phase 230VAC, connect the power supply to L1/L2 and leave L3 open.
L1
Servo amplifier
Power supply
MR-E-10A to
70A
MR-E-100A/
200A
L23-phase 200 to 230VAC,
50/60Hz L1L2L3
1-phase 230VAC,
50/60Hz L1L2
Power supply
L3
U
V
Servo motor output WConnect to the servo motor power supply terminals (U, V, W).
P
C
Regenerative brake
option D
To use the built-in regenerative brake resistor of the servo amplifier, connect the
wiring across P-D of the power supply connector (CNP1).
When using the regenerative brake option, always remove the wiring from across
P-D and connect the regenerative brake option across P-C.
Refer to Section 13.1.1 for details.
Protective earth (PE) Connect this terminal to the protective earth (PE) terminals of the servo motor
and control box for grounding.

3 - 36
3. SIGNALS AND WIRING
3.7.3 Power-on sequence
(1) Power-on procedure
1) Always wire the power supply as shown in above Section 3.7.1 using the magnetic contactor with
the power supply (three-phase 200V: L1, L2, L3, single-phase 230V: L1, L2). Configure up an
external sequence to switch off the magnetic contactor as soon as an alarm occurs.
2) The servo amplifier can accept the servo-on signal (SON) 2s or more after the power supply is
switched on. Therefore, when SON is switched on simultaneously with the power supply, the base
circuit will switch on in about 1 to 2s, and the ready signal (RD) will switch on in further about
20ms, making the servo amplifier ready to operate. (Refer to paragraph (2) in this section.)
3) When the reset signal (RES) is switched on, the base circuit is shut off and the servo motor shaft
coasts.
(2) Timing chart
20ms 20ms 20ms10ms 10ms
10ms
10ms
10ms
60ms
60ms
ON
OFF
ON
OFF
ON
OFF
ON
OFF
ON
OFF
power supply
Base circuit
Servo-on
(SON)
Reset
(RES)
Ready
(RD)
SON accepted
(1 to 2s)
2s or longer
(3) Emergency stop
Make up a circuit which shuts off power as soon as EMG-SG are opened at an emergency stop. To
ensure safety, always install an external emergency stop switch across EMG-SG. By disconnecting
EMG-SG, the dynamic brake is operated to bring the servo motor to a sudden stop. At this time, the
display shows the servo emergency stop warning (AL.E6).
During ordinary operation, do not use the external emergency stop signal to alternate stop and run.
The servo amplifier life may be shortened.
Also, if the start signal is on or a pulse train is input during an emergency stop, the servo motor will
rotate as soon as the warning is reset. During an emergency stop, always shut off the run command.
VIN
EMG
SG
Emergency
stop
External power
supply 24VDC

3 - 37
3. SIGNALS AND WIRING
3.8 Connection of servo amplifier and servo motor
3.8.1 Connection instructions
WARNING Insulate the connections of the power supply terminals to prevent an electric
shock.
CAUTION
Connect the wires to the correct phase terminals (U, V, W) of the servo amplifier
and servo motor. Otherwise, the servo motor will operate improperly.
Do not connect AC power supply directly to the servo motor. Otherwise, a fault
may occur.
POINT
Do not apply the test lead bars or like of a tester directly to the pins of the
connectors supplied with the servo motor. Doing so will deform the pins,
causing poor contact.
The connector (CNP2) for supplying the power to the motor is optional. Be
sure to purchase it.
The connection method differs according to the series and capacity of the servo motor and whether or not
the servo motor has the electromagnetic brake. Perform wiring in accordance with this section.
(1) For grounding, connect the earth cable of the servo motor to the protective earth (PE) terminal of the
servo amplifier and connect the ground cable of the servo amplifier to the earth via the protective
earth of the control box. Do not connect them directly to the protective earth of the control panel.
Servo amplifier
Servo moto
r
PE terminal
Control box
(2) Do not share the 24VDC interface power supply between the interface and electromagnetic brake.
Always use the power supply designed exclusively for the electromagnetic brake.
3.8.2 Connection diagram
The following table lists wiring methods according to the servo motor types. Use the connection diagram
which conforms to the servo motor used. For cables required for wiring, refer to Section 13.2.1. For
encoder cable connection, refer to Section 13.1.4. For the signal layouts of the connectors, refer to Section
3.8.3.
For the servo motor connector, refer to Chapter 3 of the Servo Motor Instruction Manual.

3 - 38
3. SIGNALS AND WIRING
Servo motor Connection diagram
HC-KFE13 (B) to 73 (B)
U
V
W
Servo amplifier
B1
B2
24VDC
EMG
CN2
(Note 1)
Encoder
Electro-
magnetic
brake
To be shut off when servo
on signal switches off or by
alarm signal
Encoder cable
U (Red)
V (White)
W (Black)
(Green)
Motor
Servo motor
(Note2)
CNP2
Note:1. To prevent an electric shock, always connect the protective earth (PE) terminal of the
servo amplifier to the protective earth (PE) of the control box.
2. This circuit applies to the servo motor with electromagnetic brake.
HC-SFE52 (B) to 152 (B)
U
V
W
Servo amplifier
B1
B2
24VDC
EMG
CN2
(Note 1)
Encoder
Electro-
magnetic
brake
To be shut off when servo
on signal switches off or by
alarm signal
Encoder cable
Motor
Servo motor
(Note2)
U
V
W
CNP2
Note:1. To prevent an electric shock, always connect the protective earth (PE) terminal of the
servo amplifier to the protective earth (PE) of the control box.
2. This circuit applies to the servo motor with electromagnetic brake.
HC-SFE202 (B)
U
V
W
Servo amplifier
B1
B2
24VDC
EMG
CN2
(Note 1)
Encoder
Electro-
magnetic
brake
To be shut off when servo
on signal switches off or by
alarm signal
Encoder cable
Motor
Servo motor
(Note2)
U
V
W
CNP2
Note:1. To prevent an electric shock, always connect the protective earth (PE) terminal of the
servo amplifier to the protective earth (PE) of the control box.
2. This circuit applies to the servo motor with electromagnetic brake.

3 - 39
3. SIGNALS AND WIRING
3.8.3 I/O terminals
(1) HC-KFE series
24
13
4
Power supply connector (molex)
Without electromagnetic brake
5557-04R-210 (receptacle)
5556PBTL (Female terminal)
With electromagnetic brake
5557-06R-210 (receptacle)
5556PBTL (Female terminal)
Encoder cable 0.3m (0.98ft.)
Power supply lead
4-AWG19 0.3m (0.98ft.)
With connector 1-172169-9
(AMP)
1
2
3
4
1
25
4
36
1
2
3
5
6
Power supply
connector
5557-04R-210 Pin Signal
Earth
U
V
W
Power supply
connector
5557-06R-210 Pin Signal
Earth
U
V
W
MR
123
MRR
CONT
MD
456
MDR
P5
789
LG SHD
Encoder connector signal arrangemen
t
B1
B2
(Note)
(Note)
Note:Supply electromagnetic
brake power (24VDC).
There is no polarity.
a
b
View b
View b
View a

3 - 40
3. SIGNALS AND WIRING
(2) HC-SFE series
Servo motor side connectors
Servo motor For power supply For encoder Electromagnetic
brake connector
HC-SFE52(B) to 152(B) CE05-2A22-
23PD-B
The connector
for power is
shared.
HC-SFE202(B) CE05-2A24-
17PD-B
MS3102A20-
29P MS3102A10SL-
4P
Encoder connector
Brake connector Power supply connector
a
b
c
Pin
A
B
C
D
E
F
G
H
Signal
U
V
W
(Note) B2
(Earth)
Key
A
B
C
D
E
FG
H
(Note) B1
CE05-2A22-23PD-B
Power supply connector signal arrangement
Pin
A
B
C
D
E
F
G
U
V
W
CE05-2A24-10PD-B
Key
A
B
C
D
E
F
G
Signal
(Earth)
(Note) B2
(Note) B1
Note:Supply electromagnetic
brake power (24VDC).
There is no polarity.
Note:Supply electromagnetic
brake power (24VDC).
There is no polarity.
View c View c
H
J
K
M
LN
TP
SR
C
AB
D
E
F
G
Pin
A
B
C
D
E
F
G
H
J
Signal
MR
MRR
Pin
K
L
M
N
P
R
S
T
Signal
SHD
LG
P5
Encoder connector signal arrangement
MS3102A20-29P
Key
MD
MDR
F
View a
CONT
AB
Pin
A
B
Signal
(Note)B1
(Note)B2
Electromagnetic brake connector signal arrangement
MS3102A10SL-4P
Key
Note:Supply electromagneti
c
brake power (24VDC).
There is no polarity.
View b

3 - 41
3. SIGNALS AND WIRING
3.9 Servo motor with electromagnetic brake
CAUTION
Configure the electromagnetic brake operation circuit so that it is activated not only
by the servo amplifier signals but also by an external emergency stop signal.
EMGRA
24VDC
Contacts must be open when
servo-on signal is off or when an
alarm (trouble) is present and when
an electromagnetic brake signal.
Electromagnetic brake
Servo motor
Circuit must be
opened during
emergency stop signal.
The electromagnetic brake is provided for holding purpose and must not be used
for ordinary braking.
POINT
Refer to the Servo Motor Instruction Manual for specifications such as the
power supply capacity and operation delay time of the electromagnetic
brake.
Note the following when the servo motor equipped with electromagnetic brake is used for applications
requiring a brake to hold the motor shaft (vertical lift applications):
1) Set " 1 " in parameter No.1 to make the electromagnetic brake interlock signal (MBR) valid.
Note that this will make the zero speed signal (ZSP) unavailable.
2) Do not share the 24VDC interface power supply between the interface and electromagnetic
brake. Always use the power supply designed exclusively for the electromagnetic brake.
3) The brake will operate when the power (24VDC) switches off.
4) While the reset signal is on, the base circuit is shut off. When using the servo motor with a
vertical shaft, use the electromagnetic brake interlock signal (MBR).
5) Switch off the servo-on signal after the servo motor has stopped.
(1) Connection diagram
SG
MBR
VIN
RA
B2
B1
RA
Servo amplifier Servo motorEmergency
stop
External
power
supply
24VDC
External power
supply 24VDC
(2) Setting
1) Set " 1 " in parameter No.1 to make the electromagnetic brake interlock signal (MBR) valid.
2) Using parameter No. 33 (electromagnetic brake sequence output), set a time delay (Tb) at servo-off
from electromagnetic brake operation to base circuit shut-off as in the timing chart shown in (3) in
this section.

3 - 42
3. SIGNALS AND WIRING
(3) Timing charts
(a) Servo-on signal command (from controller) ON/OFF
Tb [ms] after the servo-on (SON) signal is switched off, the servo lock is released and the servo
motor coasts. If the electromagnetic brake is made valid in the servo lock status, the brake life may
be shorter. Therefore, when using the electromagnetic brake in a vertical lift application or the
like, set Tb to about the same as the electromagnetic brake operation delay time to prevent a drop.
Servo motor speed
Electromagnetic
brake (MBR)
ON
OFF
Base circuit
Invalid(ON)
Valid(OFF)
ON
OFF
Servo-on(SON)
Electromagnetic brake
operation delay time
Tb
Coasting
0 r/min
(60ms)
(80ms)
(b) Emergency stop signal (EMG) ON/OFF
Servo motor speed
Electromagnetic
brake interlock (MBR)
ON
OFF
Base circuit
Invalid (ON)
Valid (OFF)
Emergency stop (EMG)
(10ms) (180ms)
(180ms)
Dynamic brake
Dynamic brake
Electromagnetic brake
Electromagnetic brake
Invalid (ON)
Valid (OFF)
Electromagnetic brake
operation delay time
Electromagnetic brake release

3 - 43
3. SIGNALS AND WIRING
(c) Alarm occurrence
Servo motor speed
ON
OFF
Base circuit
Electromagnetic
brake interlock (MBR)
Invalid(ON)
Valid(OFF)
Trouble (ALM) No(ON)
Yes(OFF)
Dynamic brake
Dynamic brake
Electromagnetic brake
Electromagnetic brake
operation delay time
Electromagnetic brake
(10ms)
(d) Power off
Servo motor speed
ON
OFF
Base circuit
Electromagnetic
brake interlock(MBR)
Invalid(ON)
Valid(OFF)
Trouble (ALM) No(ON)
Yes(OFF)
ON
OFF
Dynamic brake
Dynamic brake
Electromagnetic brake
Electromagnetic brake
power
(Note)
15 to 100ms
(10ms)
(10ms or less)
Electromagnetic brake
operation delay time
Note: Changes with the operating status.
(Note 2)

3 - 44
3. SIGNALS AND WIRING
3.10 Grounding
WARNING
Ground the servo amplifier and servo motor securely.
To prevent an electric shock, always connect the protective earth (PE) terminal of
the servo amplifier with the protective earth (PE) of the control box.
The servo amplifier switches the power transistor on-off to supply power to the servo motor. Depending on
the wiring and ground cablerouting, the servo amplifier may be affected by the switching noise (due to
di/dt and dv/dt) of the transistor. To prevent such a fault, refer to the following diagram and always
ground.
To conform to the EMC Directive, refer to the EMC Installation Guidelines (IB(NA)67310).
Control box
Servo amplifier
L1
L2
L3
CN1
Line filter
NFB MC
Protective earth(PE)
CN2
U
V
W
Outer
box
Servo motor
Ensure to connect it to PE
terminal of the servo amplifier.
Do not connect it directly to
the protective earth of
the control panel.
Encoder
SM
U
V
W
(Note)
Power supply
3-phase
200 to 230VAC,
1-phase
230VAC
Note: For 1-phase 230VAC, connect the power supply to L1 L2 and leave L3 open.
Programmable
controller

3 - 45
3. SIGNALS AND WIRING
3.11 Servo amplifier connectors (CNP1, CNP2) wiring method (When MR-ECPN1-B and MR-ECPN2-B of
an option are used.)
(1) Termination of the cables
Solid wire: After the sheath has been stripped, the cable can be used as it is. (Cable size: 0.2 to
2.5mm2)
8 to 9 mm
Twisted wire: Use the cable after stripping the sheath and twisting the core. At this time, take care to
avoid a short caused by the loose wires of the core and the adjacent pole. Do not solder
the core as it may cause a contact fault. (Cable size: 0.2 to 2.5mm2)Alternatively, a bar
terminal may be used to put the wires together.(Phoenix contact make)
Cable size Bar terminal type
[mm2] AWG For 1 cable For 2 cables Crimping tool Maker
BT1.25-9-1 NH1 NICHIFU
1.25 16 TUB-1.25 YHT-2210 JST
AI-TWIN2 1.5-8BK
1.5 16 AI1.5-8BK AI-TWIN2 1.5-12BK CRIMPFOX-UD6 Phoenix Contact
BT2-9-1 NH1 NICHIFU
214
TUB-2 YHT-2210 JST
2.5 14 AI2.5-8BU
AI2.5-8BK-1000 AI-TWIN2 2.5-10BU
AI-TWIN2 2.5-13BU CRIMPFOX-UD6 Phoenix Contact

3 - 46
3. SIGNALS AND WIRING
(2) Inserting the cable into the connector
(a) Applicable flat-blade screwdriver dimensions
Always use the screwdriver shown here to do the work. [Unit: mm]
3
0.6
(R0.3) (22)
(R0.3)
3 to 3.5
(b) When using the flat-blade screwdriver - part 1
1) Insert the screwdriver into the square hole.
Insert it along the top of the square hole to insert it smoothly.
2) If inserted properly, the screwdriver is held.
3) With the screwdriver held, insert the cable in the direction
of arrow. (Insert the cable as far as it will go.)
4) Releasing the screwdriver connects the cable.

3 - 47
3. SIGNALS AND WIRING
(c) When using the flat-blade screwdriver - part 2
1) Insert the screwdriver into the
square window at top of the
connector.
2) Push the screwdriver in the
direction of arrow. 3) With the screwdriver pushed, insert the cable in the
direction of arrow. (Insert the cable as far as it will go.)
4) Releasing the screwdriver connects the cable.

3 - 48
3. SIGNALS AND WIRING
3.12 Instructions for the 3M connector
When fabricating an encoder cable or the like, securely connect the shielded external conductor of the
cable to the ground plate as shown in this section and fix it to the connector shell.
External conductor Sheath External conductor
Pull back the external conductor to cover the sheath
SheathCore
Strip the sheath.
Screw
Screw
Ground plate
Cable

4 - 1
4. OPERATION
4. OPERATION
4.1 When switching power on for the first time
Before starting operation, check the following:
(1) Wiring
(a) A correct power supply is connected to the power input terminals (L1, L2, L3) of the servo amplifier.
(b) The servo motor power supply terminals (U, V, W) of the servo amplifier match in phase with the
power input terminals (U, V, W) of the servo motor.
(c) The servo motor power supply terminals (U, V, W) of the servo amplifier are not shorted to the
power input terminals (L1, L2, L3) of the servo motor.
(d) The earth terminal of the servo motor is connected to the PE terminal of the servo amplifier.
(e) When using the regenerative brake option, the lead has been removed from across D-P of the servo
amplifier built-in regenerative brake resistor, and twisted cables are used for its wiring.
(f) When stroke end limit switches are used, the signals across LSP-SG and LSN-SG are on during
operation.
(g) 24VDC or higher voltages are not applied to the pins of connectors CN1.
(h) SD and SG of connectors CN1 are not shorted.
(i) The wiring cables are free from excessive force.
(2) Environment
Signal cables and power cables are not shorted by wire offcuts, metallic dust or the like.
(3) Machine
(a) The screws in the servo motor installation part and shaft-to-machine connection are tight.
(b) The servo motor and the machine connected with the servo motor can be operated.

4 - 2
4. OPERATION
4.2 Startup
WARNING Do not operate the switches with wet hands. You may get an electric shock.
CAUTION
Before starting operation, check the parameters. Some machines may perform
unexpected operation.
During power-on for some after power-off, do not touch or close a parts (cable etc.)
to the servo amplifier heat sink, regenerative brake resistor, the servo motor, etc.
Their temperatures may be high and you may get burnt or a parts may damaged.
Connect the servo motor with a machine after confirming that the servo motor operates properly alone.
4.2.1 Selection of control mode
Use parameter No. 0 to choose the control mode used. After setting, this parameter is made valid by
switching power off, then on.
4.2.2 Position control mode
(1) Power on
1) Switch off the servo-on (SON) signal.
2) When power is switched on, the display shows "C (Cumulative feedback pulses)", and in two second
later, shows data.
(2) Test operation 1
Using jog operation in the test operation mode, make sure that the servo motor operates. (Refer to
Section 6.8.2.)
(3) Parameter setting
Set the parameters according to the structure and specifications of the machine. Refer to Chapter 5 for
the parameter definitions and to Sections 6.5 for the setting method.
Parameter No. Name Setting Description
0Control mode, regenerative brake
option selection
3 0 Position control mode
MR-RB12 regenerative brake option is used.
1 Function selection 1
0 0 2 Input filter 3.555ms (initial value)
Electromagnetic brake interlock signal is not used.
Used in incremental positioning system.
2 Auto tuning 1 5 Middle response (initial value) is selected.
Auto tuning mode 1 is selected.
3 Electronic gear numerator (CMX) 1 Electronic gear numerator
4 Electronic gear denominator (CDV) 1 Electronic gear denominator
Turn the power off after setting parameters No. 0 and 1. Then switch power on again to make
the set parameter values valid.

4 - 3
4. OPERATION
(4) Servo-on
Switch the servo-on in the following procedure:
1) Switch on power supply.
2) Switch on the servo-on signal (SON).
When placed in the servo-on status, the servo amplifier is ready to operate and the servo motor is
locked.
(5) Command pulse input
Entry of a pulse train from the positioning device rotates the servo motor. At first, run it at low speed
and check the rotation direction, etc. If it does not run in the intended direction, check the input
signal.
On the status display, check the speed, command pulse frequency, load factor, etc. of the servo motor.
When machine operation check is over, check automatic operation with the program of the positioning
device.
This servo amplifier has a real-time auto tuning function under model adaptive control. Performing
operation automatically adjusts gains. The optimum tuning results are provided by setting the
response level appropriate for the machine in parameter No. 2. (Refer to chapter 7)
(6) Home position return
Make home position return as required.
(7) Stop
In any of the following statuses, the servo amplifier interrupts and stops the operation of the servo
motor:
Refer to Section 3.9, (2) for the servo motor equipped with electromagnetic brake. Note that the stop
pattern of stroke end (LSP/LSN) OFF is as described below.
(a) Servo-on (SON) OFF
The base circuit is shut off and the servo motor coasts.
(b) Alarm occurrence
When an alarm occurs, the base circuit is shut off and the dynamic brake is operated to bring the
servo motor to a sudden stop.
(c) Emergency stop (EMG) OFF
The base circuit is shut off and the dynamic brake is operated to bring the servo motor to a sudden
stop. Alarm AL.E6 occurs.
(d) Forward rotation stroke end (LSP), reverse rotation stroke end (LSN) OFF
The droop pulse value is erased and the servo motor is stopped and servo-locked. It can be run in
the opposite direction.

4 - 4
4. OPERATION
4.2.3 Internal speed control mode
(1) Power on
1) Switch off the servo-on (SON) signal.
2) When circuit power is switched on, the display shows "r (servo motor speed)", and in two second
later, shows data.
(2) Test operation
Using jog operation in the test operation mode, make sure that the servo motor operates. (Refer to
Section 6.8.2.)
(3) Parameter setting
Set the parameters according to the structure and specifications of the machine. Refer to Chapter 5 for
the parameter definitions and to Sections 6.5 for the setting method.
Parameter No. Name Setting Description
0Control mode, regenerative brake
option selection
0 2 Internal speed control mode
Regenerative brake option is not used.
1 Function selection 1 1 2 Input filter 3.555ms (initial value)
Electromagnetic brake interlock signal (MBR) is used.
2 Auto tuning 1 5 Middle response (initial value) is selected.
Auto tuning mode 1 is selected.
8 Internal speed command 1 1000 Set 1000r/min.
9 Internal speed command 2 1500 Set 1500r/min.
10 Internal speed command 3 2000 Set 2000r/min.
11 Acceleration time constant 1000 Set 1000ms.
12 Deceleration time constant 500 Set 500ms.
13 S-pattern acceleration/deceleration
time constant 0 Not used
Turn the power off after setting parameters No. 0 and 1. Then switch power on again to make
the set parameter values valid.
(4) Servo-on
Switch the servo-on in the following procedure:
1) Switch on circuit power supply.
2) Switch on the servo-on signal (SON).
When placed in the servo-on status, the servo amplifier is ready to operate and the servo motor is
locked.
(5) Start
Using speed selection 1 (SP1) and speed selection 2 (SP2), choose the servo motor speed. Turn on
forward rotation start (ST1) to run the motor in the forward rotation (CCW) direction or reverse
rotation start (ST2) to run it in the reverse rotation (CW) direction. At first, set a low speed and check
the rotation direction, etc. If it does not run in the intended direction, check the input signal.
On the status display, check the speed, load factor, etc. of the servo motor.
When machine operation check is over, check automatic operation with the host controller or the like.
This servo amplifier has a real-time auto tuning function under model adaptive control. Performing
operation automatically adjusts gains. The optimum tuning results are provided by setting the
response level appropriate for the machine in parameter No. 2. (Refer to chapter 7)

4 - 5
4. OPERATION
(6) Stop
In any of the following statuses, the servo amplifier interrupts and stops the operation of the servo
motor:
Refer to Section 3.9, (2) for the servo motor equipped with electromagnetic brake. Note that
simultaneous ON or simultaneous OFF of stroke end (LSP, LSN) OFF and forward rotation start
(ST1) or reverse rotation start (ST2) signal has the same stop pattern as described below.
(a) Servo-on (SON) OFF
The base circuit is shut off and the servo motor coasts.
(b) Alarm occurrence
When an alarm occurs, the base circuit is shut off and the dynamic brake is operated to bring the
servo motor to a sudden stop.
(c) Emergency stop (EMG) OFF
The base circuit is shut off and the dynamic brake is operated to bring the servo motor to a sudden
stop. Alarm AL.E6 occurs.
(d) Stroke end (LSP/LSN) OFF
The servo motor is brought to a sudden stop and servo-locked. The motor may be run in the
opposite direction.
(e) Simultaneous ON or simultaneous OFF of forward rotation start (ST1) and reverse rotation start
(ST2) signals
The servo motor is decelerated to a stop.
POINT
A sudden stop indicates deceleration to a stop at the deceleration time
constant of zero.

4 - 6
4. OPERATION
MEMO

5 - 1
5. PARAMETERS
5. PARAMETERS
CAUTION Never adjust or change the parameter values extremely as it will make operation
instable.
5.1 Parameter list
5.1.1 Parameter write inhibit
POINT
After setting the parameter No. 19 value, switch power off, then on to
make that setting valid.
This servo amplifier, its parameters are classified into the basic parameters (No. 0 to 19), expansion
parameters 1 (No. 20 to 49) and expansion parameters 2 (No.50 to 84) according to their safety aspects
and frequencies of use. In the factory setting condition, the customer can change the basic parameter
values but cannot change the expansion parameter values. When fine adjustment, e.g. gain adjustment,
is required, change the parameter No. 19 setting to make the expansion parameters write-enabled.
The following table indicates the parameters which are enabled for reference and write by the setting of
parameter No. 19. Operation can be performed for the parameters marked .
Parameter No. 19 setting Operation Basic parameters
No. 0 to No. 19
Expansion parameters 1
No. 20 to No. 49
Expansion parameters 2
No. 50 to No. 84
Reference
0000
(initial value) Write
Reference No. 19 only
000A Write No. 19 only
Reference
000B Write
Reference
000C Write
Reference
000E Write
Reference
100B Write No. 19 only
Reference
100C Write No. 19 only
Reference
100E Write No. 19 only

5 - 2
5. PARAMETERS
5.1.2 Lists
POINT
For any parameter whose symbol is preceded by *, set the parameter
value and switch power off once, then switch it on again to make that
parameter setting valid.
The symbols in the control mode column of the table indicate the following
modes:
P : Position control mode
S : Internal speed control mode
(1) Item list
No. Symbol Name Control
mode
Initial
value Unit Customer
setting
0 *STY Control mode ,regenerative brake option selection P S(Note 1)
1 *OP1 Function selection 1 P S 0002
2 ATU Auto tuning P S 0105
3 CMX Electronic gear numerator P 1
4 CDV Electronic gear denominator P 1
5 INP In-position range P 100 pulse
6 PG1 Position loop gain 1 P 35 rad/s
7PST
Position command acceleration/deceleration time constant
(Smoothing) P3ms
8 SC1 Internal speed command 1 S 100 r/min
9 SC2 Internal speed command 2 S 500 r/min
10 SC3 Internal speed command 3 S 1000 r/min
11 STA Acceleration time constant S 0 ms
12 STB Deceleration time constant S 0 ms
13 STC S-pattern acceleration/deceleration time constant S 0 ms
14 For manufacturer setting 0
15 *SNO Station number setting P S0station
16 *BPS Serial communication function selection, alarm history clear P S 0000
17 MOD Analog monitor output P S 0100
18 *DMD Status display selection P S 0000
Basic parameters
19 *BLK Parameter block P S 0000

5 - 3
5. PARAMETERS
No. Symbol Name Control
mode
Initial
value Unit Customer
setting
20 *OP2 Function selection 2 P S 0000
21 *OP3 Function selection 3 (Command pulse selection) P 0000
22 *OP4 Function selection 4 P S 0000
23 FFC Feed forward gain P 0 %
24 ZSP Zero speed P S50r/min
25 For manufacturer setting 0
26 For manufacturer setting 100
27 *ENR Encoder output pulses P S 4000 pulse
/rev
28 TL1 Internal torque limit 1 P S 100 %
29 For manufacturer setting 0
30 For manufacturer setting 0
31 MO1 Analog monitor 1 offset P S0mV
32 MO2 Analog monitor 2 offset P S0mV
33 MBR Electromagnetic brake sequence output P S 100 ms
34 GD2 Ratio of load inertia moment to servo motor inertia moment P S700.1
times
35 PG2 Position loop gain 2 P 35 rad/s
36 VG1 Speed loop gain 1 P S 177 rad/s
37 VG2 Speed loop gain 2 P S 817 rad/s
38 VIC Speed integral compensation P S48ms
39 VDC Speed differential compensation P S 980
40 For manufacturer setting 0
41 *DIA Input signal automatic ON selection P S 0000
42 *DI1 Input signal selection 1 P S 0002
43 *DI2 Input signal selection 2 (CN1-4) P S 0111
44 *DI3 Input signal selection 3 (CN1-3) P S 0882
45 *DI4 Input signal selection 4 (CN1-5) P S 0995
46 *DI5 Input signal selection 5 (CN1-6) P S 0000
47 *DI6 Input signal selection 6 (CN1-7) P S 0000
48 *LSPN LSP LSN input terminals selection P S 0403
Expansion parameters 1
49 *DO1 Output signal selection 1 P S 0000

5 - 4
5. PARAMETERS
No. Symbol Name Control
mode
Initial
value Unit Customer
setting
50 For manufacturer setting 0000
51 *OP6 Function selection 6 P S 0000
52 For manufacturer setting 0000
53 *OP8 Function selection 8 P S 0000
54 *OP9 Function selection 9 P S 0000
55 *OPA Function selection A P 0000
56 SIC Serial communication time-out selection P S0 s
57 For manufacturer setting 10
58 NH1 Machine resonance suppression filter 1 P S 0000
59 NH2 Machine resonance suppression filter 2 P S 0000
60 LPF Low-pass filter, adaptive vibration suppression control P S 0000
61 GD2B Ratio of load inertia moment to Servo motor inertia moment 2 P S700.1
times
62 PG2B Position control gain 2 changing ratio P 100 %
63 VG2B Speed control gain 2 changing ratio P S 100 %
64 VICB Speed integral compensation changing ratio P S 100 %
65 *CDP Gain changing selection P S 0000
66 CDS Gain changing condition P S10
(Note 2)
67 CDT Gain changing time constant P S1ms
68 For manufacturer setting 0
69 CMX2 Command pulse multiplying factor numerator 2 P 1
70 CMX3 Command pulse multiplying factor numerator 3 P 1
71 CMX4 Command pulse multiplying factor numerator 4 P 1
72 SC4 Internal speed command 4 S 200 r/min
73 SC5 Internal speed command 5 S 300 r/min
74 SC6 Internal speed command 6 S 500 r/min
75 SC7 Internal speed command 7 S 800 r/min
76 TL2 Internal torque limit 2 P S 100 %
77 100
78 10000
79 10
80 10
81 100
82 100
83 100
Expansion parameters 2
84
For manufacturer setting
0000
Note 1. Depends on the capacity of the servo amplifier.
2. Depends on the parameter No. 65 setting.

5 - 5
5. PARAMETERS
(2) Details list
Class No. Symbol Name and function Initial
value Unit Setting
range
Control
mode
Control mode, regenerative brake option selection
Used to select the control mode and regenerative brake option.
Select the control mode.
0:Position
1:Position and internal speed
2:Internal speed
Selection of regenerative brake option
0:Not used
(The built-in regenerative brake resistor used.)
2:MR-RB032
3:MR-RB12
4:MR-RB32
5:MR-RB30
6:MR-RB50
Motor series selection
0:HC-KFE
1:HC-SFE
Motor capacity selection
0:100W
1:200W
2:400W
3:500W
4:750W
5:1kW
6:1.5kW
7:2kW
POINT
Wrong setting may cause the regenerative brake option to burn.
If the regenerative brake option selected is not for use with the
servo amplifier, parameter error (AL.37) occurs.
0*STY 100W
: 0000
200W
: 1000
400W
: 2000
750W
: 4000
1kW
: 5010
2kW
: 6010
Refer to
Name
and
function
column.
P S
Basic parameters
1 *OP1 Function selection 1
Used to select the input signal filter, the function of pin CN1-12.
Input signal filter
If external input signal causes chattering
due to noise, etc., input filter is used to
suppress it.
0:None
1:1.777[ms]
2:3.555[ms]
3:5.333[ms]
CN1-12 function selection
0:Zero Speed detection signal
1:Electromagnetic brake interlock signal
00
0002 Refer to
Name
and
function
column.
P S

5 - 6
5. PARAMETERS
Class No. Symbol Name and function Initial
value Unit Setting
range
Control
mode
2 ATU Auto tuning
Used to selection the response level, etc. for execution of auto tuning.
Refer to Chapter 7.
Auto tuning response level setting
If the machine hunts or generates
large gear sound, decrease the
set value.
To improve performance, e.g.
shorten the settling time, increase
the set value.
Set
value
Response
level
1Low
response
Middle
response
High
response
Gain adjustment mode selection
(For more information, refer to Section 7.1.1.)
Machine resonance
frequency guideline
15Hz
220Hz
325Hz
430Hz
535Hz
645Hz
755Hz
870Hz
985Hz
A105Hz
B130Hz
C160Hz
D200Hz
E240Hz
F300Hz
Set
value Gain adjustment mode
0
Description
1
3 Simple manual adjustment.
4 Manual adjustment of all gains.
Interpolation mode Fixes position control gain 1
(parameter No. 6).
Auto tuning mode 1 Fixes the load inertia moment
ratio set in parameter No. 34.
Response level setting can be
changed.
Manual mode 1
Manual mode 2
2Auto tuning mode 2 Ordinary auto tuning.
0 0
0105 Refer to
Name
and
function
column.
P S
3 CMX Electronic gear numerator
Used to set the electronic gear numerator value.
For the setting, refer to Section 5.2.1.
Setting "0" automatically sets the resolution of the servo motor
connected.
10
1
to
65535
P
Basic parameters
4 CDV Electronic gear denominator
Used to set the electronic gear denominator value.
For the setting, refer to Section 5.2.1.
11
to
65535
P

5 - 7
5. PARAMETERS
Class No. Symbol Name and function Initial
value Unit Setting
range
Control
mode
5 INP In-position range
Used to set the in-position signal (INP) output range in the command
pulse increments prior to electronic gear calculation.
100 pulse 0
to
10000
P
6 PG1 Position loop gain 1
Used to set the gain of position loop.
Increase the gain to improve trackability in response to the position
command.
When auto turning mode 1,2 is selected, the result of auto turning is
automatically used.
35 red/s 4
to
2000
P
Position command acceleration/deceleration time constant
(position smoothing)
Used to set the time constant of a low pass filter in response to the
position command.
You can use parameter No. 55 to choose the primary delay or linear
acceleration/deceleration control system. When you choose linear
acceleration/deceleration, the setting range is 0 to 10ms. Setting of
longer than 10ms is recognized as 10ms.
POINT
7PST
When you have chosen linear acceleration/deceleration, do not
select control selection (parameter No. 0) and restart after
instantaneous power failure (parameter No. 20). Doing so will
cause the servo motor to make a sudden stop at the time of
position control switching or restart.
3ms0
to
20000
P
Example: When a command is given from a synchronizing detector,
synchronous operation can be started smoothly if started during line
operation.
Synchronizing
detector
Start
Servo amplifier
Servo motor
Without time
constant setting
Servo motor
speed
Start
With time
constant setting
ON
OFF t
Basic parameters
8 SC1 Internal speed command 1
Used to set speed 1 of internal speed commands. 100 r/min 0 to
instan-
taneous
permi-
ssible
speed
S

5 - 8
5. PARAMETERS
Class No. Symbol Name and function Initial
value Unit Setting
range
Control
mode
9 SC2 Internal speed command 2
Used to set speed 2 of internal speed commands. 500 r/min 0 to
instan-
taneous
permi-
ssible
speed
S
10 SC3 Internal speed command 3
Used to set speed 3 of internal speed commands. 1000 r/min 0 to
instan-
taneous
permi-
ssible
speed
S
11 STA Acceleration time constant
Used to set the acceleration time required to reach the rated speed
from 0r/min in response to the internal speed commands 1 to 7.
Tim
e
Parameter
No.12 setting
Parameter
No.11 setting
Zero
speed
Rated
speed
Speed
If the preset speed command is
lower than the rated speed,
acceleration/deceleration time
will be shorter.
For example for the servo motor of 3000r/min rated speed, set 3000
(3s) to increase speed from 0r/min to 1000r/min in 1 second.
0
12 STB Deceleration time constant
Used to set the deceleration time required to reach 0r/min from the
rated speed in response to the internal speed commands 1 to 7.
0
ms 0
to
20000
S
Basic parameters
13 STC S-pattern acceleration/deceleration time constant
Used to smooth start/stop of the servo motor.
Set the time of the arc part for S-pattern acceleration/deceleration.
STA: Acceleration time constant (parameter No.11)
STB: Deceleration time constant (parameter No.12)
STC: S-pattern acceleration/deceleration time con-
stant (parameter No.13)
Speed command
Servo motor
Speed
0r/min
STCSTA STC STC STB STC
Time
Long setting of STA (acceleration time constant) or STB (deceleration time
constant) may produce an error in the time of the arc part for the setting of the
S-pattern acceleration/deceleration time constant.
The upper limit value of the actual arc part time is limited by
At the setting of STA 20000, STB 5000 and STC 200,
the actual arc part times are as follows:
for acceleration or by for deceleration.
(Example)
During acceleration: 100[ms] 2000000
20000 100[ms] 200[ms].
Limited to 100[ms] since
During deceleration: 200[ms] 2000000
5000 400[ms] 200[ms].
200[ms] as set since
2000000
STA 2000000
STB
0ms0
to
1000
S

5 - 9
5. PARAMETERS
Class No. Symbol Name and function Initial
value Unit Setting
range
Control
mode
14 For manufacturer setting
Don’t change this value by any means. 0
15 *SNO Station number setting
Used to specify the station number for serial communication.
Always set one station to one axis of servo amplifier. If one station
number is set to two or more stations, normal communication cannot
be made.
0sta-
tion 0
to
31
PS
16 *BPS Serial communication function selection, alarm history clear
Used to select the serial communication baudrate, select various
communication conditions, and clear the alarm history.
Serial baudrate selection
0: 9600 [bps]
1: 19200[bps]
2: 38400[bps]
3: 57600[bps]
Alarm history clear
0: Invalid
1: Valid
When alarm history clear is made valid,
the alarm history is cleared at next power-on.
After the alarm history is cleared, the setting
is automatically made invalid (reset to 0).
Serial communication response delay time
0: Invalid
1: Valid, reply sent after delay time of 800 s or more
0
0000 Refer to
Name
and
function
column.
P S
Basic parameters
17 MOD Analog monitor output
Used to selection the signal provided to the analog monitor
(MO1) analog monitor (MO2) output. (Refer to Section 5.2.2)
Setting
0
Analog monitor 2 (MO2)
Servo motor speed ( 8V/max. speed)
1 Torque ( 8V/max. torque)
2 Servo motor speed ( 8V/max. speed)
3 Torque ( 8V/max. torque)
4 Current command ( 8V/max. current command)
5 Command pulse frequency ( 10V/500kpulse/s)
6 Droop pulses ( 10V/128 pulses)
7 Droop pulses ( 10V/2048 pulses)
8 Droop pulses ( 10V/8192 pulses)
9 Droop pulses ( 10V/32768 pulses)
A Droop pulses ( 10V/131072 pulses)
00
B Bus voltage ( 8V/400V)
Analog monitor 1 (MO1)
0100 Refer to
Name
and
function
column.
P S

5 - 10
5. PARAMETERS
Class No. Symbol Name and function Initial
value Unit Setting
range
Control
mode
18 *DMD Status display selection
Used to select the status display shown at power-on.
Selection of status display at
power-on
0: Cumulative feedback pulses
1: Servo motor speed
2: Droop pulses
3: Cumulative command pulses
4: Command pulse frequency
7: Regenerative load ratio
8: Effective load ratio
9: Peak load ratio
A: Instantaneous torque
B: Within one-revolution position low
C: Within one-revolution position high
D: Load inertia moment ratio
E: Bus voltage
Status display at power-on in
corresponding control mode
0: Depends on the control mode.
0 0
0000 Refer to
Name
and
function
column.
P S
Control Mode
Position
Position/internal speed
Internal speed
Status display at power-on
Cumulative feedback pulses
Cumulative feedback pulses/servo motor speed
Servo motor speed
1: Depends on the first digit setting of this parameter.
Parameter block
Used to select the reference and write ranges of the parameters.
Operation can be performed for the parameters marked .
Set
value Operation
Basic
parameters
No. 0
to No. 19
Expansion
parameters 1
No. 20
to No. 49
Expansion
parameters 2
No. 50
to No. 84
Reference0000
(Initial
value) Write
Reference No. 19 only
000A Write No. 19 only
Reference
000B Write
Reference
000C Write
Reference
000E Write
Reference
100B Write No. 19 only
Reference
100C Write No. 19 only
Reference
100E Write No. 19 only
Basic parameters
19 *BLK 0000 Refer to
Name
and
function
column.
P S

5 - 11
5. PARAMETERS
Class No. Symbol Name and function Initial
value Unit Setting
range
Control
mode
20 *OP2 0000 Refer to
Name
and
function
column.
S
P S
Function selection 2
Used to select restart after instantaneous power failure,
servo lock at a stop in internal speed control mode, and slight
vibration suppression control.
0: Invalid
1: Valid
If the input power supply voltage
had reduced in the internal speed
control mode to stop the servo motor
due to the undervoltage alarm (AL.10)
but the supply voltage has return-
ed to normal, the servo motor can
be restarted by merely switching
on the start signal without resett-
ing the alarm.
Restart after instantaneous
power failure
Stop-time servo lock selection
The shaft can be servo-locked to
remain still at a stop in the internal
speed control mode.
0: Valid
1: Invalid
Slight vibration suppression control
Made valid when auto tuning selection is
set to "0400" in parameter No. 2.
Used to suppress vibration at a stop.
0: Invalid
1: Valid
Encoder cable communication system selection
Incorrect setting will result in an encoder alarm 1
(AL. 16) or encoder alarm 2 (AL. 20).
0: Two-wire type
1: Four-wire type
In case of the internal speed control mode,
set "1" at the second digit and validate servo
lock at stop to use this setting.
P S
Expansion parameters 1
21 *OP3 Function selection 3 (Command pulse selection)
Used to select the input form of the pulse train input signal.
(Refer to Section 3.4.1.)
Command pulse train input form
0: Forward/reverse rotation pulse train
1: Signed pulse train
2: A/B phase pulse train
Pulse train logic selection
0: Positive logic
1: Negative logic
0 0
0000 Refer to
Name
and
function
column.
P

5 - 12
5. PARAMETERS
Class No. Symbol Name and function Initial
value Unit Setting
range
Control
mode
22 *OP4 Function selection 4
Used to select stop processing at forward rotation stroke end (LSP)
reverse rotation stroke end (LSN) off and choose TLC/VLC output.
00
How to make a stop when forward
rotation stroke end (LSP)
reverse rotation stroke end (LSN)
is valid. (Refer to Section 5.2.3.)
0: Sudden stop
1: Slow stop
0
0000 Refer to
Name
and
function
column.
P S
23 FFC Feed forward gain
Set the feed forward gain. When the setting is 100%, the droop pulses
during operation at constant speed are nearly zero. However, sudden
acceleration/deceleration will increase the overshoot. As a guideline,
when the feed forward gain setting is 100%, set 1s or more as the
acceleration/deceleration time constant up to the rated speed.
0%0
to
100
P
24 ZSP Zero speed
Used to set the output range of the zero speed (ZSP). 50 r/min 0
to
10000
P S
25 For manufacturer setting
Don’t change this value by any means. 0
Expansion parameters 1
26 For manufacturer setting
Don’t change this value by any means. 100

5 - 13
5. PARAMETERS
Class No. Symbol Name and function Initial
value Unit Setting
range
Control
mode
27 *ENR Encoder output pulses
Used to set the encoder pulses (A-phase or B-phase) output by the
servo amplifier.
Set the value 4 times greater than the A-phase or B-phase pulses.
You can use parameter No. 54 to choose the output pulse designation
or output division ratio setting.
The number of A/B-phase pulses actually output is 1/4 times greater
than the preset number of pulses.
The maximum output frequency is 1.3Mpps (after multiplication by
4). Use this parameter within this range.
For output pulse designation
Set " 0 " (initial value) in parameter No. 54.
Set the number of pulses per servo motor revolution.
Output pulse set value [pulses/rev]
At the setting of 5600, for example, the actually output A/B-phase
pulses are as indicated below:
4
5600
A B-phase output pulses 1400[pulse]
For output division ratio setting
Set " 1 " in parameter No. 54.
The number of pulses per servo motor revolution is divided by the
set value.
Output pulse [pulses/rev]
Resolution per servo motor revolution
Set value
At the setting of 8, for example, the actually output A/B-phase
pulses are as indicated below:
A B-phase output pulses 313[pulse]
8
10000 4
1
4000 pulse/
rev 1
to
65535
P S
Internal torque limit 1
Set this parameter to limit servo motor torque on the assumption
that the maximum torque is 100[%].
When 0 is set, torque is not produced.
100 % 0
to
100
P S
(Note)
External
input
signals
TL1
Torque limit value made valid
0 Internal torque limit value 1 (parameter No. 28)
1 Parameter No. 76 Parameter No. 28: Parameter No. 28
Parameter No. 76 Parameter No. 28: Parameter No. 76
28 TL1
Note.0 :off
1 :on
When torque is output in analog monitor output, this set value is the
maximum output voltage ( 8V). (Refer to Section 3.4.1, (5))
29 For manufacturer setting
Don’t change this value by any means. 0
30 For manufacturer setting
Don’t change this value by any means. 0
31 MO1 Analog monitor 1 offset
Used to set the offset voltage of the analog monitor 1 (MO1). 0mV 999
to 999 PS
32 MO2 Analog monitor 2 offset
Used to set the offset voltage of the analog monitor 2 (MO2). 0mV 999
to 999 PS
33 MBR Electromagnetic brake sequence output
Used to set the delay time (Tb) between electronic brake interlock
(MBR) and the base drive circuit is shut-off.
100 ms 0
to
1000
P S
Expansion parameters 1
34 GD2 Ratio of load inertia moment to servo motor inertia moment
Used to set the ratio of the load inertia moment to the servo motor
shaft inertia moment. When auto tuning mode 1 and interpolation
mode is selected, the result of auto tuning is automatically used.
(Refer to section 7.1.1)
In this case, it varies between 0 and 1000.
70 0.1
times 0
to
3000
PS

5 - 14
5. PARAMETERS
Class No. Symbol Name and function Initial
value Unit Setting
range
Control
mode
35 PG2 Position loop gain 2
Used to set the gain of the position loop.
Set this parameter to increase the position response to level load
disturbance. Higher setting increases the response level but is liable
to generate vibration and/or noise.
When auto tuning mode 1,2 and interpolation mode is selected, the
result of auto tuning is automatically used.
35 rad/s 1
to
1000
P
36 VG1 Speed loop gain 1
Normally this parameter setting need not be changed.
Higher setting increases the response level but is liable to generate
vibration and/or noise.
When auto tuning mode 1 2, manual mode and interpolation mode
is selected, the result of auto tuning is automatically used.
177 rad/s 20
to
8000
PS
37 VG2 Speed loop gain 2
Set this parameter when vibration occurs on machines of low rigidity
or large backlash. Higher setting increases the response level but is
liable to generate vibration and/or noise.
When auto tuning mode 1 2 and interpolation mode is selected, the
result of auto tuning is automatically used.
817 rad/s 20
to
20000
P S
38 VIC Speed integral compensation
Used to set the integral time constant of the speed loop.
Higher setting increases the response level but is liable to generate
vibration and/or noise.
When auto tuning mode 1 2 and interpolation mode is selected, the
result of auto tuning is automatically used.
48 ms 1
to
1000
PS
39 VDC Speed differential compensation
Used to set the differential compensation.
Made valid when the proportion control (PC) is switched on.
980 0
to
1000
PS
40 For manufacturer setting
Don’t change this value by any means. 0
Refer to
Name
and
function
column.
P S
Expansion parameters 1
41 *DIA Input signal automatic ON selection
Used to set automatic servo-on (SON) forward rotation stroke end
(LSP) reverse rotation stroke end (LSN).
Servo-on (SON) input selection
0: Switched on/off by external input.
1: Switched on automatically in servo
amplifier.
(No need of external wiring)
0: Switched on/off by external input.
1: Switched on automatically in servo
amplifier.
(No need of external wiring)
0: Switched on/off by external input.
1: Switched on automatically in servo
amplifier.
(No need of external wiring)
Reverse rotation stroke end (LSN)
input selection
Forward rotation stroke end (LSP)
input selection
0
0000
PS

5 - 15
5. PARAMETERS
Class No. Symbol Name and function Initial
value Unit Setting
range
Control
mode
42 *DI1 0002 Refer to
Name
and
function
column. P/S
Expansion parameters 1
Input signal selection 1
Used to assign the control mode changing signal input pins and to set
the clear (CR).
Control change (LOP) input pin
assignment
Used to set the control mode
change signal input connector
pins. Note that this parameter is
made valid when parameter No.
0 is set to select the position/int-
ernal speed change mode.
Set value
0
1
2
Connector pin No.
CN1-4
CN1-3
CN1-5
3CN1-6
Clear (CR) selection
0: Droop pulses are cleared on the
leading edge.
1: While turning on, droop pulses are
always cleared.
4CN1-7
0 0
If forward rotation stroke end (LSP)
or reverse rotation stroke end
(LSN) is assigned to any pin with
parameter No. 48, this setting is
invalid.
PS

5 - 16
5. PARAMETERS
Class No. Symbol Name and function Initial
value Unit Setting
range
Control
mode
Expansion parameters 1
43 *DI2 Input signal selection 2 (CN1-4)
Allows any input signal to be assigned to CN1-pin 4.
Note that the setting digit and assigned signal differ according to the
control mode.
Position
control mode Input signals of
CN1-pin 4
selected.
Internal speed
control mode
0 0
Signals that may be assigned in each control mode are indicated
below by their symbols.
Setting of any other signal will be invalid.
Set value (Note) Control mode
PS
0
1
2
3
4
5
6
7
8
9
SON SON
RES RES
PC PC
SP1
SP2
ST1
ST2
CR CR
ASP3
B
C
DTL1
ECDP
CM1
CM2
TL1
CDP
F
Note: P: Position control mode
S: Internal speed control mode
This parameter is unavailable when parameter No.42 is set to assign
the control change (LOP) to CN1-pin 4.
This parameter is unavailable when parameter No. 48 is set to assign
the Forward rotation stroke end (LSP) and Reverse rotation stroke end
(LSN) to be assigned to CN1-pin 4.
0111 Refer to
Name
and
function
column.
P S

5 - 17
5. PARAMETERS
Class No. Symbol Name and function Initial
value Unit Setting
range
Control
mode
44 *DI3 Input signal selection 3 (CN1-3)
Allows any input signal to be assigned to CN1-pin 3.
The assignable signals and setting method are the same as in input
signal selection 2 (parameter No. 43).
Position
control mode Input signals of
CN1-pin 3
selected.
Internal speed
control mode
00
This parameter is unavailable when parameter No. 42 is set to
assign the control change (LOP) to CN1-pin 3.
This parameter is unavailable when parameter No. 48 is set to
assign the Forward rotation stroke end (LSP) and Reverse rotation
stroke end (LSN) to be assigned to CN1-pin 3.
0882 Refer to
Name
and
function
column.
P S
45 *DI4 Input signal selection 4 (CN1-5)
Allows any input signal to be assigned to CN1-pin 5.
The assignable signals and setting method are the same as in input
signal selection 2 (parameter No. 43).
Position
control mode Input signals of
CN1-pin 5
selected.
Internal speed
control mode
09
This parameter is unavailable when parameter No. 42 is set to
assign the control change (LOP) to CN1-pin 5.
This parameter is unavailable when parameter No. 48 is set to
assign the Forward rotation stroke end (LSP) and Reverse rotation
stroke end (LSN) to be assigned to CN1-pin 5
0995 Refer to
Name
and
function
column.
P S
Expansion parameters 1
46 *DI5 Input signal selection 5 (CN1-6)
Allows any input signal to be assigned to CN1-pin 6.
The assignable signals and setting method are the same as in input
signal selection 2 (parameter No. 43).
Position
control mode Input signals of
CN1-pin 6
selected.
Internal speed
control mode
00
This parameter is unavailable when parameter No. 42 is set to
assign the control change (LOP) to CN1-pin 6.
This parameter is unavailable when parameter No. 48 is set to
assign the Reverse rotation stroke end (LSN) to be assigned to CN1-
pin 6.
0000 Refer to
Name
and
function
column.
P S

5 - 18
5. PARAMETERS
Class No. Symbol Name and function Initial
value Unit Setting
range
Control
mode
47 *DI6 Input signal selection 6 (CN1-7)
Allows any input signal to be assigned to CN1-pin 7.
The assignable signals and setting method are the same as in input
signal selection 2 (parameter No. 43).
Position
control mode Input signals of
CN1-pin 7
selected.
Internal speed
control mode
00
This parameter is unavailable when parameter No. 42 is set to
assign the control change signal (LOP) to CN1-pin 7.
This parameter is unavailable when parameter No. 48 is set to
assign the Forward rotation stroke end (LSP) to be assigned to CN1-
pin 7.
0000 Refer to
Name
and
function
column.
P S
Expansion parameters 1
48 *LSPN LSP/LSN input terminal selection
Select the pins where the forward rotation stroke end (LSP) and
reverse rotation stroke end (LSN) will be assigned. If the signals
have already been assigned using parameter No. 42 to 47, this
parameter setting has preference.
However, if the forward rotation stroke end (LSP) is assigned at pin
6 of CN1 (default setting), the setting of parameter No. 46 takes
priority. Similarly, if the reverse rotation stroke end (LSN) is
assigned at pin 7 of CN1 (default setting), the setting of parameter
No. 47 takes priority. If the forward rotation stroke end (LSP) and
reverse rotation stroke end (LSN) are assigned at the same pin, the
forward rotation stroke end (LSP) takes priority while the reverse
rotation stroke end (LSN) is disabled.
CN1-7
CN1-4
CN1-3
CN1-5
CN1-6
3
4
1
2
0
00
5
Select the pin where the forward rotation stroke
end (LSP) will be assigned.
Set value Connector pin No.
Select the pin where the reverse rotation stroke
end (LSN) will be assigned. The settings are the
same as those of the first digit.
0403 Refer to
Name
and
function
column.
P S

5 - 19
5. PARAMETERS
Class No. Symbol Name and function Initial
value Unit Setting
range
Control
mode
Expansion parameters 1
49 *DO1 Output signal selection 1
Used to select the connector pins to output the alarm code and
warning (WNG).
Setting of alarm code output
Connector pins
Set value CN1-10 CN1-11 CN1-12
0INP or SARD ZSP
1
88888
AL.12
AL.13
AL.15
AL.17
AL.8A
AL.8E
AL.30
AL.45
AL.50
AL.51
AL.24
AL.32
AL.31
AL.35
AL.52
AL.16
AL.20
Name
Watchdog
Memory error 1
Clock error
Memory error 2
Board error 2
Serial communication time-out error
Serial communication error
Regenerative error
Main circuit device overheat
Overload 1
Overload 2
Main circuit
Overcurrent
Overspeed
Command pulse frequency error
Error excessive
Encoder error 1
Encoder error 2
Alarm
display
(Note) Alarm code
CN1
pin 10
0
000
1
CN1
pin 11
00
1
10
1
CN1
pin 12
1
1
0
1
0
10
Set value Connector pin No.
Note: 0:off
1:on
Setting of warning (WNG) output
Select the connector pin to output warning. The old signal
before selection will be unavailable.
AL.19 Memory error 3
AL.37 Parameter error
AL.33 Overvoltage
AL.46 Servo motor overheat
AL.10 Undervoltage
100
AL.1A Motor combination error
0 Not output.
1CN1-11
2CN1-9
3CN1-10
4CN1-12
0
Alarm code is output at alarm occurrence.
0
0000 Refer to
Name
and
function
column.
P S

5 - 20
5. PARAMETERS
Class No. Symbol Name and function Initial
value Unit Setting
range
Control
mode
50 For manufacturer setting
Don’t change this value by any means. 0000
51 *OP6 Function selection 6
Used to select the operation to be performed when the reset (RES)
switches on.
000
Operation to be performed when the
reset (RES) switches on
0: Base circuit not switched off
1: Base circuit switched off
0000 Refer to
Name
and
function
column.
P S
52 For manufacturer setting
Don’t change this value by any means. 0000
53 *OP8 Function selection 8
Used to select the protocol of serial communication.
0 0
Protocol checksum selection
0: Yes (checksum added)
1: No (checksum not added)
Protocol checksum selection
0: With station numbers
1: No station numbers
0000 Refer to
Name
and
function
column.
P S
Expansion parameters 2
54 *OP9 Function selection 9
Use to select the command pulse rotation direction, encoder output
pulse direction and encoder pulse output setting.
0
0
1CCW
CW CW
CCW
Servo motor rotation direction changing
Changes the servo motor rotation
direction for the input pulse train.
Set value
Servo motor rotation direction
At forward rotation
pulse input
At reverse rotation
pulse input
Encoder pulse output phase changing
Changes the phases of A/B-phase encoder pulses output .
Encoder output pulse setting selection (refer to parameter No. 27)
0: Output pulse setting
1: Division ratio setting
Servo motor rotation direction
Set value CCW CW
0
1
A phase
B phase
A phase
B phase
A phase
B phase
A phase
B phase
0000 Refer to
Name
and
function
column.
P S

5 - 21
5. PARAMETERS
Class No. Symbol Name and function Initial
value Unit Setting
range
Control
mode
55 *OPA Function selection A
Used to select the position command acceleration/deceleration time
constant (parameter No. 7) control system.
000
0: Primary delay
1: Linear acceleration/deceleration
Position command acceleration/deceleration
time constant control
0000 Refer to
Name
and
function
column.
P
0
56 SIC Serial communication time-out selection
Used to set the communication protocol time-out period in [s].
When you set "0", time-out check is not made.
0
s1 to 60
PS
57 For manufacturer setting
Don’t change this value by any means. 10
58 NH1 Machine resonance suppression filter 1
Used to selection the machine resonance suppression filter.
(Refer to Section 8.2.)
2
3
0
0
140dB
14dB
8dB
4dB
Notch frequency selection
Set "00" when you have set adaptive vibration
suppression control to be "valid" or "held"
(parameter No. 60: 1 or 2 ).
00
01
02
03
04
05
06
07
Setting
value
Frequency
Invalid
4500
2250
1500
1125
900
750
642.9
08
09
0A
0B
0C
0D
0E
0F
562.5
500
450
409.1
375
346.2
321.4
300
Frequency
10
11
12
13
14
15
16
17
281.3
264.7
250
236.8
225
214.3
204.5
195.7
Frequency
18
19
1A
1B
1C
1D
1E
1F
187.5
180
173.1
166.7
160.1
155.2
150
145.2
Frequency
Notch depth selection
Setting
value
Depth Gain
Deep
Shallow
to
Setting
value
Setting
value
Setting
value
0000 Refer to
Name
and
function
column.
P S
Expansion parameters 2
59 NH2 Machine resonance suppression filter 2
Used to set the machine resonance suppression filter.
0
Notch frequency
Same setting as in parameter No. 58
However, you need not set "00" if you have
set adaptive vibration suppression control to
be "valid" or "held".
Notch depth
Same setting as in parameter No. 58
0000 Refer to
Name
and
function
column.
P S

5 - 22
5. PARAMETERS
Class No. Symbol Name and function Initial
value Unit Setting
range
Control
mode
60 LPF Low-pass filter/adaptive vibration suppression control
Used to selection the low-pass filter and adaptive vibration
suppression control. (Refer to Chapter 8.)
0
Low-pass filter selection
0: Valid (Automatic adjustment)
1: Invalid
When you choose "valid", 2 (1 GD2 setting 0.1)
VG2 setting 10
bandwidth filter is set automatically.
Adaptive vibration suppression control selection
Choosing "valid" or "held" in adaptive vibration
suppression control selection makes the machine
resonance control filter 1 (parameter No. 58) invalid.
0: Invalid
1: Valid
Machine resonance frequency is always detected
and the filter is generated in response to resonance to
suppress machine vibration.
2: Held
The characteristics of the filter generated so far are held,
and detection of machine resonance is stopped.
Adaptive vibration suppression control sensitivity selection
Used to set the sensitivity of machine resonance detection.
0: Normal
1: Large sensitivity
[Hz]
0000 Refer to
Name
and
function
column.
P S
61 GD2B Ratio of load inertia moment to servo motor inertia moment 2
Used to set the ratio of load inertia moment to servo motor inertia
moment when gain changing is valid.
70 0.1
times 0
to
3000
PS
62 PG2B Position control gain 2 changing ratio
Used to set the ratio of changing the position control gain 2 when
gain changing is valid.
Made valid when auto tuning is invalid.
100 % 10
to
200
P
63 VG2B Speed control gain 2 changing ratio
Used to set the ratio of changing the speed control gain 2 when gain
changing is valid.
Made valid when auto tuning is invalid.
100 % 10
to
200
PS
Expansion parameters 2
64 VICB Speed integral compensation changing ratio
Used to set the ratio of changing the speed integral compensation
when gain changing is valid. Made valid when auto tuning is invalid.
100 % 50
to
1000
PS

5 - 23
5. PARAMETERS
Class No. Symbol Name and function Initial
value Unit Setting
range
Control
mode
65 *CDP Gain changing selection
Used to select the gain changing condition. (Refer to Section 8.5.)
000
Gain changing selection
Gains are changed in accordance with the settings
of parameters No. 61 to 64 under any of the following
conditions:
0: Invalid
1: Gain changing (CDP) is ON
2: Command frequency is equal to higher than
parameter No. 66 setting
3: Droop pulse value is equal to higher than
parameter No. 66 setting
4: Servo motor speed is equal to higher than
parameter No. 66 setting
0000 Refer to
Name
and
function
column.
P S
66 CDS Gain changing condition
Used to set the value of gain changing condition (command
frequency, droop pulses, servo motor speed) selected in parameter
No. 65.The set value unit changes with the changing condition item.
(Refer to Section 8.5.)
10 kpps
pulse
r/min
10
to
9999
PS
67 CDT Gain changing time constant
Used to set the time constant at which the gains will change in
response to the conditions set in parameters No. 65 and 66.
(Refer to Section 8.5.)
1ms0
to
100
PS
68 For manufacturer setting
Don’t change this value by any means. 0
69 CMX2 Command pulse multiplying factor numerator 2
Used to set the multiplier for the command pulse.
Setting "0" automatically sets the connected motor resolution.
10
1
to
65535
P
70 CMX3 Command pulse multiplying factor numerator 3
Used to set the multiplier for the command pulse.
Setting "0" automatically sets the connected motor resolution.
10
1
to
65535
P
71 CMX4 Command pulse multiplying factor numerator 4
Used to set the multiplier for the command pulse.
Setting "0" automatically sets the connected motor resolution.
10
1
to
65535
P
Expansion parameters 2
72 SC4 Internal speed command 4
Used to set speed 4 of internal speed commands. 200 r/min 0 to in-
stanta-
neous
permi-
ssible
speed
S

5 - 24
5. PARAMETERS
Class No. Symbol Name and function Initial
value Unit Setting
range
Control
mode
73 SC5 Internal speed command 5
Used to set speed 5 of internal speed commands. 300 r/min 0 to in-
stanta-
neous
permi-
ssible
speed
S
74 SC6 Internal speed command 6
Used to set speed 6 of internal speed commands. 500 r/min 0 to in-
stanta-
neous
permi-
ssible
speed
S
75 SC7 Internal speed command 7
Used to set speed 7 of internal speed commands. 800 r/min 0 to in-
stanta-
neous
permi-
ssible
speed
S
76 TL2 Internal torque limit 2
Set this parameter to limit servo motor torque on the assumption
that the maximum torque is 100[%].
When 0 is set, torque is not produced.
When torque is output in analog monitor output, this set value is the
maximum output voltage ( 8V).
100 % 0
to
100
PS
77 00
78 10000
79 10
80 10
81 100
82 100
83 100
Expansion parameters 2
84
For manufacturer setting
Don’t change this value by any means.
0000

5 - 25
5. PARAMETERS
5.2 Detailed description
5.2.1 Electronic gear
CAUTION Wrong setting can lead to unexpected fast rotation, causing injury.
POINT
The guideline of the electronic gear setting range is 50
1CDV
CMX 50.
If the set value is outside this range, noise may be generated during
acceleration/ deceleration or operation may not be performed at the preset
speed and/or acceleration/deceleration time constants.
The following specification symbols are required to calculate the electronic
gear.
The machine can be moved at any multiplication factor to input pulses.
CDV
CMX Parameter No.4
Parameter No.3
Electronic gear
Feedback pulse
CMX
CDV Deviation
counter
Motor
Encoder
Input pulse train
The following setting examples are used to explain how to calculate the electronic gear:
POINT
The following specification symbols are required to calculate the electronic
gear
Pb : Ballscrew lead [mm]
n : Reduction ratio
Pt : Servo motor resolution [pulses/rev]
0: Travel per command pulse [mm/pulse]
S: Travel per servo motor revolution [mm/rev]
: Angle per pulse [ /pulse]
: Angle per revolution [ /rev]
(1) For motion in increments of 10 m per pulse
Machine specifications
Ballscrew lead Pb 10 [mm]
Reduction ratio: n 1/2
Servo motor resolution: Pt 10000 [pulses/rev] Servo motor
10000 [pulse/rev]
n
NM
NL
Pb 10[mm]
n NL/NM
1/2
CDV
CMX 0Pt
S0Pt
nPb 10 10 31/2 10
10000 20000
1000 20
1
Hence, set 20 to CMX and 1 to CDV.

5 - 26
5. PARAMETERS
(2) Conveyor setting example
For rotation in increments of 0.01 per pulse
Machine specifications
Table : 360 /rev
Reduction ratio: n 1/18
Servo motor resolution: Pt 10000 [pulses/rev]
Table
Timing belt : 4/64
Servo motor
10000 [pulse/rev]
CDV
CMX Pt 10000
0.01 1/18 360 20
100 1
5
Hence, set 5 to CMX and 1 to CDV.
5.2.2 Analog monitor
The servo status can be output to two channels in terms of voltage. Use this function when using an
ammeter to monitor the servo status or synchronizing the torque/speed with the other servo.
(1) Setting
Change the following digits of parameter No.17:
Analog monitor 1 (MO1) output selection
(Signal output to across MO1-LG)
Analog monitor 2 (MO2) output selection
(Signal output to across MO2-LG)
Parameter No. 17
00
Parameters No.31 and 32 can be used to set the offset voltages to the analog output voltages. The setting
range is between 999 and 999mV.
Parameter No. Description Setting range [mV]
31 Used to set the offset voltage for the analog monitor 1 (MO1) output.
32 Used to set the offset voltage for the analog monitor 2 (MO2) output. 999 to 999

5 - 27
5. PARAMETERS
(2) Set content
The servo amplifier is factory-set to output the servo motor speed to Analog monitor 1 (MO1) and the
torque to Analog monitor 2 (MO2). The setting can be changed as listed below by changing the
parameter No.17 value:
Refer to Appendix 2 for the measurement point.
Setting Output item Description Setting Output item Description
0Servo motor speed 8[V]
Max. speed
0Max. speed
8[V]
CCW direction
CW direction
6 Droop pulses
(10V/128pulse) 10[V]
0128[pulse]
10[V]
CCW direction
CW direction
128[pulse]
1Torque 8[V]
Max. torque
0Max. torque
8[V]
Driving in CW direction
Driving in CCW direction 7 Droop pulses
(10V/2048pulse) 10[V]
02048[pulse]
10[V]
CCW direction
CW direction
2048[pulse]
2Servo motor speed
8[V]
Max. speed 0Max. speed
CCW
direction
CW
direction
8 Droop pulses
(10V/8192pulse) 10[V]
08192[pulse]
10[V]
CCW direction
CW direction
8192[pulse]
3Torque
8[V]
Max. torque 0Max. torque
Driving in
CW direction Driving in
CCW direction
9 Droop pulses
(10V/32768pulse) 10[V]
032768[pulse]
10[V]
CCW direction
CW direction
32768[pulse]
4 Current command 8[V]
Max. command
current
0Max. command
current
8[V]
CCW direction
CW direction
A Droop pulses
(10V/131072pulse) 10[V]
0131072[pulse]
10[V]
CCW direction
CW direction
131072[pulse]
5Command pulse
frequency 10[V]
500kpps
0500kpps
10[V]
CCW direction
CW direction
BBus voltage
8[V]
0400[V]

5 - 28
5. PARAMETERS
(3) Analog monitor block diagram
PWM M
Current
control
Speed
control
Current
command
Position
control
Droop pulse
Differ-
ential
Command
pulse frequency Bus voltage
Speed
command
Command
pulse
Current feedback
Position feedback
Servo motor speed
Current
encoder Servo Moto
r
Encoder
Torque

5 - 29
5. PARAMETERS
5.2.3 Using forward/reverse rotation stroke end to change the stopping pattern
The stopping pattern is factory-set to make a sudden stop when the forward/reverse rotation stroke end is
made valid. A slow stop can be made by changing the parameter No. 22 value.
Parameter No.22 Setting Stopping method
0
(initial value)
Sudden stop
Position control mode : Motor stops with droop pulses cleared.
Internal speed control mode : Motor stops at deceleration time constant of zero.
1
Slow stop
Position control mode : The motor is decelerated to a stop in accordance
with the parameter No. 7 value.
Internal speed control mode : The motor is decelerated to a stop in accordance
with the parameter No. 12 value.
5.2.4 Alarm history clear
The servo amplifier stores one current alarm and five past alarms from when its power is switched on
first. To control alarms which will occur during operation, clear the alarm history using parameter No.16
before starting operation.
Clearing the alarm history automatically returns to " 0 ".
After setting, this parameter is made valid by switch power from OFF to ON.
Alarm history clear
0: Invalid (not cleared)
1: Valid (cleared)
Parameter No.16

5 - 30
5. PARAMETERS
5.2.5 Position smoothing
By setting the position command acceleration/deceleration time constant (parameter No.7), you can run
the servo motor smoothly in response to a sudden position command.
The following diagrams show the operation patterns of the servo motor in response to a position command
when you have set the position command acceleration/deceleration time constant.
Choose the primary delay or linear acceleration/deceleration in parameter No. 55 according to the
machine used.
(1) For step input
Command
(3t)
tt
Time
t
: Input position command
: Position command after
filtering for primary delay
: Position command after filtering
for linear acceleration/deceleration
: Position command acceleration/
deceleration time constant (parameter No. 7)
(2) For trapezoidal input
Command
Tim
e
t
(3t)
t
(3t)
t
: Input position command
: Position command after
filtering for primary delay
: Position command after filtering
for linear acceleration/deceleration
: Position command acceleration/
deceleration time constant
(parameter No. 7)

6 - 1
6. DISPLAY AND OPERATION
6. DISPLAY AND OPERATION
6.1 Display flowchart
Use the display (5-digit, 7-segment LED) on the front panel of the servo amplifier for status display,
parameter setting, etc. Set the parameters before operation, diagnose an alarm, confirm external
sequences, and/or confirm the operation status. Press the "MODE" "UP" or "DOWN" button once to move to
the next screen.
To refer to or set the expansion parameters, make them valid with parameter No. 19 (parameter write
disable).
Cumulative feedback
pulses [pulse]
Motor speed
[r/min]
Droop pulses
[pulse]
Cumulative command
pulses [pulse]
Command pulse
frequency [kpps]
Regenerative load
ratio [%]
Effective load ratio
[%]
Peak load ratio
[%]
Within one-revolution
position low [pulse]
Load inertia moment
ratio [times]
Sequence
External I/O
signal display
Output (DO) signal
forced output
Test operation
Jog feed
Test operation mode
Positioning operation
Test operation mode
Motor-less operation
Software version low
Software version high
Manufacturer setting
screen
Current alarm
Last alarm
Second alarm in past
Third alarm in past
Fourth alarm in past
Fifth alarm in past
Sixth alarm in past
Parameter error No.
Parameter No. 0
Parameter No. 1
Parameter No. 18
Parameter No. 19
Parameter No. 20
Parameter No. 21
Parameter No. 48
Parameter No. 49
(Note)
Note: The initial status display at power-on depends on the control mode.
Position control mode: Cumulative feedback pulses(C), Internal speed control mode: Servo motor speed(r)
Also, parameter No. 18 can be used to change the initial indication of the status display at power-on.
MODE
button
DOWN
UP
Status display Diagnosis Basic
parameters Expansion
parameters 1
Alarm Expansion
parameters 2
Parameter No. 50
Parameter No. 51
Parameter No. 83
Parameter No. 84
Instantaneous torque
[%]
Within one-revolution
position, high [100 pulses]
Bus voltage [V]
Test operation mode
Machine analyzer operation
Motor series ID
Motor type ID
Encoder ID

6 - 2
6. DISPLAY AND OPERATION
6.2 Status display
The servo status during operation is shown on the 5-digit, 7-segment LED display. Press the "UP" or
"DOWN" button to change display data as desired. When the required data is selected, the corresponding
symbol appears. Press the "SET" button to display its data. At only power-on, however, data appears after
the symbol of the status display selected in parameter No. 18 has been shown for 2.
The servo amplifier display shows the lower five digits of 16 data items such as the servo motor speed.
6.2.1 Display examples
The following table lists display examples:
Displayed data
Item Status Servo amplifier display
Forward rotation at 3000r/min
Servo motor
speed
Reverse rotation at 3000r/min
Reverse rotation is indicated by " ".
Load inertia
moment 15.5 times
11252pulse
Multi-
revolution
counter 12566pulse Lit
Negative value is indicated by the lit decimal points in the upper four
digits.

6 - 3
6. DISPLAY AND OPERATION
6.2.2 Status display list
The following table lists the servo statuses that may be shown:
Name Symbol Unit Description Display
range
Cumulative feedback
pulses C pulse Feedback pulses from the servo motor encoder are counted and
displayed. The value in excess of 99999 is counted, bus since the
servo amplifier display is five digits, it shows the lower five digits of
the actual value. Press the "SET" button to reset the display value to
zero.
Reverse rotation is indicated by the lit decimal points in the upper
four digits.
99999
to
99999
Servo motor speed r r/min The servo motor speed is displayed.
The value rounded off is displayed in 0.1r/min. 5400
to
5400
Droop pulses E pulse The number of droop pulses in the deviation counter is displayed.
When the servo motor is rotating in the reverse direction, the
decimal points in the upper four digits are lit.
Since the servo amplifier display is five digits, it shows the lower five
digits of the actual value.
The number of pulses displayed is not yet multiplied by the electronic
gear.
99999
to
99999
Cumulative command
pulses P pulse The position command input pulses are counted and displayed.
As the value displayed is not yet multiplied by the electronic gear
(CMX/CDV), it may not match the indication of the cumulative
feedback pulses.
The value in excess of 99999 is counted, but since the servo
amplifier display is five digits, it shows the lower five digits of the
actual value. Press the "SET" button to reset the display value to
zero. When the servo motor is rotating in the reverse direction, the
decimal points in the upper four digits are lit.
99999
to
99999
Command pulse
frequency n kpps The frequency of the position command input pulses is displayed.
The value displayed is not multiplied by the electronic gear
(CMX/CDV).
800
to
800
Regenerative load
ratio L % The ratio of regenerative power to permissible regenerative power is
displayed in %. 0
to
100
Effective load ratio J % The continuous effective load torque is displayed.
The effective value in the past 15 seconds is displayed relative to the
rated torque of 100%.
0
to
300
Peak load ratio b % The maximum torque generated during acceleration/deceleration, etc.
The highest value in the past 15 seconds is displayed relative to the
rated torque of 100%.
0
to
400
Instantaneous torque T % Torque that occurred instantaneously is displayed.
The value of the torque that occurred is displayed in real time
relative to the rate torque of 100%.
0
to
400
Within one-revolution
position low Cy1 pulse Position within one revolution is displayed in encoder pulses.
The value returns to 0 when it exceeds the maximum number of
pulses.
The value is incremented in the CCW direction of rotation.
0
to
99999

6 - 4
6. DISPLAY AND OPERATION
Name Symbol Unit Description Display
range
Within one-revolution
position high Cy2 100
pulse The within one-revolution position is displayed in 100 pulse
increments of the encoder.
The value returns to 0 when it exceeds the maximum number of
pulses.
The value is incremented in the CCW direction of rotation.
0
to
1310
Load inertia moment
ratio dC 0.1
Times The estimated ratio of the load inertia moment to the servo motor
shaft inertia moment is displayed. 0.0
to
300.0
Bus voltage Pn V The voltage (across P-N) of the main circuit converter is displayed. 0
to
450
6.2.3 Changing the status display screen
The status display item of the servo amplifier display shown at power-on can be changed by changing the
parameter No. 18 settings.
The item displayed in the initial status changes with the control mode as follows:
Control mode
Position
Position/
internal speed
Internal speed
Status display at power-on
Cumulative feedback pulses
Cumulative feedback pulses/servo motor speed
Servo motor speed

6 - 5
6. DISPLAY AND OPERATION
6.3 Diagnostic mode
Name Display Description
Not ready.
Indicates that the servo amplifier is being initialized or an alarm
has occurred.
Sequence Ready.
Indicates that the servo was switched on after completion of
initialization and the servo amplifier is ready to operate.
External I/O signal
display
Refer to section 6.6. Indicates the ON-OFF states of the external I/O signals.
The upper segments correspond to the input signals and the
lower segments to the output signals.
Lit: ON
Extinguished: OFF
The I/O signals can be changed using parameters No. 43 to 49.
Output signal (DO)
forced output The digital output signal can be forced on/off. For more
information, refer to section 6.7.
Jog feed Jog operation can be performed when there is no command from
the external command device.
For details, refer to section 6.8.2.
Positioning
operation
The servo configuration software (MRZJW3-SETUP154E) is
required for positioning operation. This operation cannot be
performed from the operation section of the servo amplifier.
Positioning operation can be performed once when there is no
command from the external command device.
Motorless
operation
Without connection of the servo motor, the servo amplifier
provides output signals and displays the status as if the servo
motor is running actually in response to the external input
signal.
For details, refer to section 6.8.4.
Test
operation
mode
Machine
analyzer
operation
Merely connecting the servo amplifier allows the resonance point
of the mechanical system to be measured.
The servo configuration software (MRZJW3-SETUP154E or later)
is required for machine analyzer operation.
Software version low Indicates the version of the software.
Software version high Indicates the system number of the software.
Manufacturer setting
screen
Screen for manufacturer setting. When this screen is being
displayed, do not press any other buttons than "UP" and "DOWN"
button.
Motor series Press the "SET" button to show the motor series ID of the servo
motor currently connected.
Motor type Press the "SET" button to show the motor type ID of the servo
motor currently connected.
Encoder Press the "SET" button to show the encoder ID of the servo motor
currently connected.

6 - 6
6. DISPLAY AND OPERATION
6.4 Alarm mode
The current alarm, past alarm history and parameter error are displayed. The lower 2 digits on the
display indicate the alarm number that has occurred or the parameter number in error. Display examples
are shown below.
Name Display Description
Indicates no occurrence of an alarm.
Current alarm Indicates the occurrence of overvoltage (AL.33).
Flickers at occurrence of the alarm.
Indicates that the last alarm is overload 1 (AL.50).
Indicates that the second alarm in the past is overvoltage (AL.33).
Indicates that the third alarm in the past is undervoltage (AL.10).
Indicates that the fourth alarm in the past is overspeed (AL.31).
Indicates that there is no fifth alarm in the past.
Alarm history
Indicates that there is no sixth alarm in the past.
Indicates no occurrence of parameter error (AL.37).
Parameter error No.
Indicates that the data of parameter No. 1 is faulty.
Functions at occurrence of an alarm
(1) Any mode screen displays the current alarm.
(2) Even during alarm occurrence, the other screen can be viewed by pressing the button in the operation
section. At this time, the decimal point in the fourth digit flickers.
(3) For any alarm, remove its cause and clear it in any of the following methods (for clearable alarms,
refer to Section 10.2.1):
(a) Switch power OFF, then ON.
(b) Press the "SET" button on the current alarm screen.
(c) Turn on the alarm reset (RES).
(4) Use parameter No. 16 to clear the alarm history.
(5) Pressing "SET" button on the alarm history display screen for 2s or longer shows the following detailed
information display screen. Note that this is provided for maintenance by the manufacturer.
(6) Press the "UP" or "DOWN" button to display the next alarm in the history.

6 - 7
6. DISPLAY AND OPERATION
6.5 Parameter mode
The parameters whose abbreviations are marked* are made valid by changing the setting and then
switching power off once and switching it on again. Refer to Section 5.1.2.
(1) Operation example
The following example shows the operation procedure performed after power-on to change the control
mode (parameter No. 0) to the Internal speed control mode.
Using the "MODE" button, show the basic parameter screen.
The set value of the specified parameter number flickers.
UP DOWN
The parameter number is displayed.
Press or to change the number.
Press SET twice.
Press UP once.
During flickering, the set value can be changed.
Use or .
Press SET to enter.
( 2: Internal speed control mode)
UP DOWN
To shift to the next parameter, press the UP DOWN
/ button.
When changing the parameter No. 0 setting, change its set value, then switch power off once and
switch it on again to make the new value valid.
(2) Expansion parameters
To use the expansion parameters, change the setting of parameter No. 19 (parameter write disable).
Refer to section 5.1.1.

6 - 8
6. DISPLAY AND OPERATION
6.6 External I/O signal display
The ON/OFF states of the digital I/O signals connected to the servo amplifier can be confirmed.
(1) Operation
Call the display screen shown after power-on.
Using the "MODE" button, show the diagnostic screen.
Press UP once.
External I/O signal display screen
(2) Display definition
CN1
6
CN1
7
CN1
21
CN1
5
CN1
9
CN1
3CN1
4
CN1
12 CN1
11
CN1
10
Lit: ON
Extinguished: OFF
Input signals
Output signals
CN1
8
Always lit
The 7-segment LED shown above indicates ON/OFF.
Each segment at top indicates the input signal and each segment at bottom indicates the output signal.
The signals corresponding to the pins in the respective control modes are indicated below:
(Note 2) Signal abbreviation
CN1
Pin No.
Input/Output
(Note 1) I/O PS
Related parameter No.
3 I RES ST1 43 to 47
4 I SON SON 43 to 47
5 I CR ST2 43 to 47
6 I LSP LSP 43 to 48
7 I LSN LSN 43 to 48
8IEMGEMG
9OALMALM49
10 O INP SA 49
11 O RD RD 49
12 O ZSP ZSP 49
21 O OP OP
Note: 1. I: Input signal, O: Output signal
2. P: Position control mode, S: Internal speed control mode
3. The signal of CN1A-18 is always output.

6 - 9
6. DISPLAY AND OPERATION
(3) Default signal indications
(a) Position control mode
Lit: ON
Extinguished: OFF
Input signals
Output signals
CR (CN 1-5) Clear
RES (CN 1-3) Reset
SON (CN 1-4) Servo-on
LSN (CN 1-7) Reverse rotation stroke end
LSP (CN 1-6) Forward rotation stroke end
RD (CN 1-11) Ready
INP (CN 1-10) In position
ZSP (CN 1-12) Zero speed
ALM (CN 1-9) Trouble
OP (CN 1-21) Encoder Z-phase pulse
EMG (CN 1-8) Emergency stop
(b) Internal speed control mode
Lit: ON
Extinguished: OFF
Input signals
Output signals
SON (CN 1-4) Servo-on
LSN (CN 1-7) Reverse rotation stroke end
LSP (CN 1-6) Forward rotation stroke end
RD (CN 1-11) Ready
ZSP (CN 1-12) Zero speed
ALM (CN 1-9) Trouble
OP (CN 1-21) Encoder Z-phase pulse
EMG (CN 1-8) Emergency stop
SA (CN 1-10) Limiting speed
ST1 (CN 1-3) Forward rotation start
ST2 (CN 1-5) Reverse rotation start

6 - 10
6. DISPLAY AND OPERATION
6.7 Output signal (DO) forced output
POINT
When the servo system is used in a vertical lift application, turning on the
electromagnetic brake interlock (MBR) after assigning it to pin CN1-12 will
release the electromagnetic brake, causing a drop. Take drop preventive
measures on the machine side.
The output signal can be forced on/off independently of the servo status. This function is used for output
signal wiring check, etc. This operation must be performed in the servo off state.
Operation
Call the display screen shown after power-on.
Using the "MODE" button, show the diagnostic screen.
Press UP twice.
Press SET for more than 2 seconds.
Switch on/off the signal below the lit segment.
Indicates the ON/OFF of the output signal. The correspondences
between segments and signals are as in the output signals of the
external I/O signal display.
(Lit: ON, extinguished: OFF)
Press MODE once.
The segment above CN1-pin 10 is lit.
Press UP once.
CN1-pin 10 is switched on.
(CN1-pin 10-SG conduct.)
Press DOWN once.
CN1-pin 10 is switched off.
Press SET for more than seconds.
CN1
12 CN1
9CN1
12 CN1
10 CN1
11
Always lit

6 - 11
6. DISPLAY AND OPERATION
6.8 Test operation mode
CAUTION
The test operation mode is designed to confirm servo operation and not to confirm
machine operation. In this mode, do not use the servo motor with the machine.
Always use the servo motor alone.
If any operational fault has occurred, stop operation using the emergency stop
(EMG) signal.
POINT
The servo configuration software is required to perform positioning
operation.
Test operation cannot be performed if the servo-on (SON) is not turned
OFF.
6.8.1 Mode change
Call the display screen shown after power-on. Choose jog operation/motor-less operation in the following
procedure. Using the "MODE" button, show the diagnostic screen.
When this screen
appears, jog feed can
be performed.
Press UP three times.
Press SET for more
than 2s.
Flickers in the test operation mode.
Press UP five times.
Press SET for more than 2s.
When this screen is displayed,
motor-less operation can be
performed.

6 - 12
6. DISPLAY AND OPERATION
6.8.2 Jog operation
Jog operation can be performed when there is no command from the external command device.
(1) Operation
Connect EMG-SG to start jog operation to use the internal power supply.
Hold down the "UP" or "DOWN" button to run the servo motor. Release it to stop. When using the servo
configuration software, you can change the operation conditions. The initial conditions and setting
ranges for operation are listed below:
Item Initial setting Setting range
Speed [r/min] 200 0 to instantaneous permissible speed
Acceleration/deceleration time constant [ms] 1000 0 to 50000
How to use the buttons is explained below:
Button Description
"UP" Press to start CCW rotation.
Release to stop.
"DOWN" Press to start CW rotation.
Release to stop.
If the communication cable is disconnected during jog operation performed by using the servo
configuration software, the servo motor will be decelerated to a stop.
(2) Status display
You can confirm the servo status during jog operation.
Pressing the "MODE" button in the jog operation-ready status calls the status display screen. With this
screen being shown, perform jog operation with the "UP" or "DOWN" button. Every time you press the
"MODE" button, the next status display screen appears, and on completion of a screen cycle, pressing
that button returns to the jog operation-ready status screen. For full information of the status display,
refer to Section 6.2. In the test operation mode, you cannot use the "UP" and "DOWN" buttons to
change the status display screen from one to another.
(3) Termination of jog operation
To end the jog operation, switch power off once or press the "MODE" button to switch to the next
screen and then hold down the "SET" button for 2 or more seconds.

6 - 13
6. DISPLAY AND OPERATION
6.8.3 Positioning operation
POINT
The servo configuration software is required to perform positioning
operation.
Positioning operation can be performed once when there is no command from the external command
device.
(1) Operation
Connect EMG-SG to start positioning operation to use the internal power supply.
Click the "Forward" or "Reverse" button on the servo configuration software starts the servo motor,
which will then stop after moving the preset travel distance. You can change the operation conditions
on the servo configuration software. The initial conditions and setting ranges for operation are listed
below:
Item Initial setting Setting range
Travel distance [pulse] 10000 0 to 9999999
Speed [r/min] 200 0 to instantaneous permissible speed
Acceleration/deceleration time constant [ms] 1000 0 to 50000
How to use the buttons is explained below:
Button Description
"Forward" Click to start positioning operation CCW.
"Reverse" Click to start positioning operation CW.
"Pause"
Click during operation to make a temporary stop. Pressing the
"Pause" button again erases the remaining distance.
To resume operation, click the button that was clicked to start
the operation.
If the communication cable is disconnected during positioning operation, the servo motor will come
to a sudden stop.
(2) Status display
You can monitor the status display even during positioning operation.

6 - 14
6. DISPLAY AND OPERATION
6.8.4 Motor-less operation
Without connecting the servo motor, you can provide output signals or monitor the status display as if the
servo motor is running in response to external input signals. This operation can be used to check the
sequence of a host programmable controller or the like.
(1) Operation
After turning off the signal across SON-SG, choose motor-less operation. After that, perform external
operation as in ordinary operation.
(2) Status display
You can confirm the servo status during motor-less operation.
Pressing the "MODE" button in the motor-less operation-ready status calls the status display screen.
With this screen being shown, perform motor-less operation. Every time you press the "MODE" button,
the next status display screen appears, and on completion of a screen cycle, pressing that button
returns to the motor-less operation-ready status screen. For full information of the status display,
refer to Section 6.2. In the test operation mode, you cannot use the "UP" and "DOWN" buttons to
change the status display screen from one to another.
(3) Termination of motor-less operation
To terminate the motor-less operation, switch power off.

7 - 1
7. GENERAL GAIN ADJUSTMENT
7. GENERAL GAIN ADJUSTMENT
7.1 Different adjustment methods
7.1.1 Adjustment on a single servo amplifier
The gain adjustment in this section can be made on a single servo amplifier. For gain adjustment, first
execute auto tuning mode 1. If you are not satisfied with the results, execute auto tuning mode 2, manual
mode 1 and manual mode 2 in this order.
(1) Gain adjustment mode explanation
Gain adjustment mode Parameter No. 2
setting
Estimation of load inertia
moment ratio
Automatically set
parameters Manually set parameters
Auto tuning mode 1
(initial value) 010 Always estimated PG1 (parameter No. 6)
GD2 (parameter No. 34)
PG2 (parameter No. 35)
VG1 (parameter No. 36)
VG2 (parameter No. 37)
VIC (parameter No. 38)
Response level setting of
parameter No. 2
Auto tuning mode 2 020 PG1 (parameter No. 6)
PG2 (parameter No. 35)
VG1 (parameter No. 36)
VG2 (parameter No. 37)
VIC (parameter No. 38)
GD2 (parameter No. 34)
Response level setting of
parameter No. 2
Manual mode 1 030 PG2 (parameter No. 35)
VG1 (parameter No. 36) PG1 (parameter No. 6)
GD2 (parameter No. 34)
VG2 (parameter No. 37)
VIC (parameter No. 38)
Manual mode 2 040
Fixed to parameter No.
34 value
PG1 (parameter No. 6)
GD2 (parameter No. 34)
PG2 (parameter No. 35)
VG1 (parameter No. 36)
VG2 (parameter No. 37)
VIC (parameter No. 38)
Interpolation mode 000 Always estimated GD2 (parameter No. 34)
PG2 (parameter No. 35)
VG2 (parameter No. 37)
VIC (parameter No. 38)
PG1 (parameter No. 6)
VG1 (parameter No. 36)

7 - 2
7. GENERAL GAIN ADJUSTMENT
(2) Adjustment sequence and mode usage
Usage
Used when you want to
match the position gain
(PG1) between 2 or more
axes. Normally not used for
other purposes.
Allows adjustment by
merely changing the
response level setting.
First use this mode to make
adjustment.
Used when the conditions of
auto tuning mode 1 are not
met and the load inertia
moment ratio could not be
estimated properly, for
example.
This mode permits
adjustment easily with three
gains if you were not
satisfied with auto tuning
results.
END
Interpolation
made for 2 or more
axes?
START
Operation
Auto tuning mode 2
OK?
Manual mode 1
OK?
Manual mode 2
OK?
OK?
No
No
Yes
No
Yes
No
Yes
No
Yes
Auto tuning mode 1
Operation
Interpolation mode
Operation
Operation
Yes
You can adjust all gains
manually when you want to
do fast settling or the like.
7.1.2 Adjustment using servo configuration software
This section gives the functions and adjustment that may be performed by using the servo amplifier with
the servo configuration software which operates on a personal computer.
Function Description Adjustment
Machine analyzer With the machine and servo motor
coupled, the characteristic of the
mechanical system can be measured by
giving a random vibration command from
the personal computer to the servo and
measuring the machine response.
You can grasp the machine resonance frequency and
determine the notch frequency of the machine
resonance suppression filter.
You can automatically set the optimum gains in
response to the machine characteristic. This simple
adjustment is suitable for a machine which has large
machine resonance and does not require much settling
time.
Gain search Executing gain search under to-and-fro
positioning command measures settling
characteristic while simultaneously
changing gains, and automatically
searches for gains which make settling
time shortest.
You can automatically set gains which make positioning
settling time shortest.
Machine simulation Response at positioning settling of a
machine can be simulated from machine
analyzer results on personal computer.
You can optimize gain adjustment and command
pattern on personal computer.

7 - 3
7. GENERAL GAIN ADJUSTMENT
7.2 Auto tuning
7.2.1 Auto tuning mode
The servo amplifier has a real-time auto tuning function which estimates the machine characteristic (load
inertia moment ratio) in real time and automatically sets the optimum gains according to that value. This
function permits ease of gain adjustment of the servo amplifier.
(1) Auto tuning mode 1
The servo amplifier is factory-set to the auto tuning mode 1.
In this mode, the load inertia moment ratio of a machine is always estimated to set the optimum gains
automatically.
The following parameters are automatically adjusted in the auto tuning mode 1.
Parameter No. Abbreviation Name
6PG1Position control gain 1
34 GD2 Ratio of load inertia moment to servo motor inertia moment
35 PG2 Position control gain 2
36 VG1 Speed control gain 1
37 VG2 Speed control gain 2
38 VIC Speed integral compensation
POINT
The auto tuning mode 1 may not be performed properly if the following
conditions are not satisfied.
Time to reach 2000r/min is the acceleration/deceleration time constant of 5s or
less.
Speed is 150r/min or higher.
The ratio of load inertia moment to servo motor inertia moment is not
more than 100 times.
The acceleration/deceleration torque is 10% or more of the rated torque.
Under operating conditions which will impose sudden disturbance torque
during acceleration/deceleration or on a machine which is extremely loose,
auto tuning may not function properly, either. In such cases, use the auto
tuning mode 2 or manual mode 1,2 to make gain adjustment.
(2) Auto tuning mode 2
Use the auto tuning mode 2 when proper gain adjustment cannot be made by auto tuning mode 1.
Since the load inertia moment ratio is not estimated in this mode, set the value of a correct load
inertia moment ratio (parameter No. 34).
The following parameters are automatically adjusted in the auto tuning mode 2.
Parameter No. Abbreviation Name
6PG1Position control gain 1
35 PG2 Position control gain 2
36 VG1 Speed control gain 1
37 VG2 Speed control gain 2
38 VIC Speed integral compensation

7 - 4
7. GENERAL GAIN ADJUSTMENT
7.2.2 Auto tuning mode operation
The block diagram of real-time auto tuning is shown below.
Servo
motor
Command
Automatic setting
Control gains
PG1,VG1
PG2,VG2,VIC
Current
control
Current feedback
Load inertia
moment
Encoder
Position/speed
feedback
Real-time auto
tuning section
Speed feedback
Load inertia
moment ratio
estimation section
Gain
table
Parameter No. 2
Gain adjustment
mode selection
First digit
Response level
setting
Parameter No. 34
Load inertia moment
ratio estimation value
Set 0 or 1 to turn on.
Switch
When a servo motor is accelerated/decelerated, the load inertia moment ratio estimation section always
estimates the load inertia moment ratio from the current and speed of the servo motor. The results of
estimation are written to parameter No. 34 (the ratio of load inertia moment to servo motor). These
results can be confirmed on the status display screen of the servo configuration software section.
If the value of the load inertia moment ratio is already known or if estimation cannot be made properly,
chose the "auto tuning mode 2" (parameter No.2: 2 ) to stop the estimation of the load inertia
moment ratio (Switch in above diagram turned off), and set the load inertia moment ratio (parameter No.
34) manually.
From the preset load inertia moment ratio (parameter No. 34) value and response level (The first digit of
parameter No. 2), the optimum control gains are automatically set on the basis of the internal gain tale.
The auto tuning results are saved in the EEP-ROM of the servo amplifier every 60 minutes since power-
on. At power-on, auto tuning is performed with the value of each control gain saved in the EEP-ROM
being used as an initial value.
POINT
If sudden disturbance torque is imposed during operation, the estimation
of the inertia moment ratio may malfunction temporarily. In such a case,
choose the "auto tuning mode 2" (parameter No. 2: 2 ) and set the
correct load inertia moment ratio in parameter No. 34.
When any of the auto tuning mode 1, auto tuning mode 2 and manual
mode 1 settings is changed to the manual mode 2 setting, the current
control gains and load inertia moment ratio estimation value are saved in
the EEP-ROM.

7 - 5
7. GENERAL GAIN ADJUSTMENT
7.2.3 Adjustment procedure by auto tuning
Since auto tuning is made valid before shipment from the factory, simply running the servo motor
automatically sets the optimum gains that match the machine. Merely changing the response level
setting value as required completes the adjustment. The adjustment procedure is as follows.
END
Yes
No
Yes
No
No
Yes
Auto tuning adjustment
Acceleration/deceleration repeated
Load inertia moment ratio
estimation value stable?
Auto tuning
conditions not satisfied.
(Estimation of load inertia
moment ratio is difficult)
Adjust response level setting
so that desired response is
achieved on vibration-free level.
Acceleration/deceleration repeated
Requested
performance satisfied?
To manual mode
Choose the auto tuning mode 2
(parameter No.2 : 020 ) and set
the load inertia moment ratio
(parameter No.34) manually.

7 - 6
7. GENERAL GAIN ADJUSTMENT
7.2.4 Response level setting in auto tuning mode
Set the response (The first digit of parameter No.2) of the whole servo system. As the response level
setting is increased, the trackability and settling time for a command decreases, but a too high response
level will generate vibration. Hence, make setting until desired response is obtained within the vibration-
free range.
If the response level setting cannot be increased up to the desired response because of machine resonance
beyond 100Hz, adaptive vibration suppression control (parameter No. 60) or machine resonance
suppression filter (parameter No. 58 59) may be used to suppress machine resonance. Suppressing
machine resonance may allow the response level setting to increase. Refer to Section 8.2, 8.3 for adaptive
vibration suppression control and machine resonance suppression filter.
Parameter No. 2
Response level setting
Gain adjustment mode selection
Machine characteristic
Response level setting Machine rigidity Machine resonance
frequency guideline Guideline of corresponding machine
1 Low 15Hz
2 20Hz
3 25Hz
430Hz
5 35Hz
6 45Hz
7 55Hz
8 Middle 70Hz
9 85Hz
A 105Hz
B 130Hz
C160Hz
D 200Hz
E 240Hz
F High 300Hz
Large conveyor
Arm robot
General machine
tool conveyor
Precision
working
machine
Inserter
Mounter
Bonder

7 - 7
7. GENERAL GAIN ADJUSTMENT
7.3 Manual mode 1 (simple manual adjustment)
If you are not satisfied with the adjustment of auto tuning, you can make simple manual adjustment with
three parameters.
7.3.1 Operation of manual mode 1
In this mode, setting the three gains of position control gain 1 (PG1), speed control gain 2 (VG2) and
speed integral compensation (VIC) automatically sets the other gains to the optimum values according to
these gains.
PG1
VG2
VIC
PG2
VG1
GD2
Automatic setting
User setting
Therefore, you can adjust the model adaptive control system in the same image as the general PI control
system (position gain, speed gain, speed integral time constant). Here, the position gain corresponds to
PG1, the speed gain to VG2 and the speed integral time constant to VIC. When making gain adjustment
in this mode, set the load inertia moment ratio (parameter No. 34) correctly.
7.3.2 Adjustment by manual mode 1
POINT
If machine resonance occurs, adaptive vibration suppression control
(parameter No. 60) or machine resonance suppression filter (parameter No.
58 59) may be used to suppress machine resonance. (Refer to Section 8.2,
8.3.)
(1) For speed control
(a) Parameters
The following parameters are used for gain adjustment:
Parameter No. Abbreviation Name
34 GD2 Ratio of load inertia moment to servo motor inertia moment
37 VG2 Speed control gain 2
38 VIC Speed integral compensation
(b) Adjustment procedure
Step Operation Description
1Set an estimated value to the ratio of load inertia moment to servo
motor inertia moment (parameter No. 34).
2Increase the speed control gain 2 (parameter No. 37) within the
vibration- and unusual noise-free range, and return slightly if vibration
takes place.
Increase the speed control gain.
3Decrease the speed integral compensation (parameter No. 38) within
the vibration-free range, and return slightly if vibration takes place. Decrease the time constant of the speed
integral compensation.
4
If the gains cannot be increased due to mechanical system resonance or
the like and the desired response cannot be achieved, response may be
increased by suppressing resonance with adaptive vibration
suppression control or machine resonance suppression filter and then
executing steps 2 and 3.
Suppression of machine resonance.
Refer to Section 8.2, 8.3.
5While checking the settling characteristic and rotational status, fine-
adjust each gain. Fine adjustment

7 - 8
7. GENERAL GAIN ADJUSTMENT
(c)Adjustment description
1) Speed control gain 2 (parameter No. 37)
This parameter determines the response level of the speed control loop. Increasing this value
enhances response but a too high value will make the mechanical system liable to vibrate. The
actual response frequency of the speed loop is as indicated in the following expression:
Speed loop response
frequency(Hz) Speed control gain 2 setting
(1 ratio of load inertia moment to servo motor inertia moment) 2
2) Speed integral compensation (VIC: parameter No. 38)
To eliminate stationary deviation against a command, the speed control loop is under
proportional integral control. For the speed integral compensation, set the time constant of this
integral control. Increasing the setting lowers the response level. However, if the load inertia
moment ratio is large or the mechanical system has any vibratory element, the mechanical
system is liable to vibrate unless the setting is increased to some degree. The guideline is as
indicated in the following expression:
Speed integral compensation
setting(ms) 2000 to 3000
(1 ratio of load inertia moment to
servo motor inertia moment setting 0.1)
Speed control gain 2 setting/
(2) For position control
(a) Parameters
The following parameters are used for gain adjustment:
Parameter No. Abbreviation Name
6PG1Position control gain 1
34 GD2 Ratio of load inertia moment to servo motor inertia moment
37 VG2 Speed control gain 2
38 VIC Speed integral compensation
(b) Adjustment procedure
Step Operation Description
1Set an estimated value to the ratio of load inertia moment to servo
motor inertia moment (parameter No. 34).
2Set a slightly smaller value to the position control gain 1 (parameter
No. 6).
3Increase the speed control gain 2 (parameter No. 37) within the
vibration- and unusual noise-free range, and return slightly if vibration
takes place.
Increase the speed control gain.
4Decrease the speed integral compensation (parameter No. 38) within
the vibration-free range, and return slightly if vibration takes place. Decrease the time constant of the speed
integral compensation.
5 Increase the position control gain 1 (parameter No. 6). Increase the position control gain.
6
If the gains cannot be increased due to mechanical system resonance or
the like and the desired response cannot be achieved, response may be
increased by suppressing resonance with adaptive vibration
suppression control or machine resonance suppression filter and then
executing steps 3 to 5.
Suppression of machine resonance.
Refer to Section 8.2, 8.3.
7While checking the settling characteristic and rotational status, fine-
adjust each gain. Fine adjustment

7 - 9
7. GENERAL GAIN ADJUSTMENT
(c) Adjustment description
1) Position control gain 1 (parameter No. 6)
This parameter determines the response level of the position control loop. Increasing position
control gain 1 improves trackability to a position command but a too high value will make
overshooting liable to occur at the time of settling.
Position control
gain 1 guideline Speed control gain 2 setting
(1 ratio of load inertia moment to servo motor inertia moment) ( to 1
5
1
3)
2) Speed control gain 2 (VG2: parameter No. 37)
This parameter determines the response level of the speed control loop. Increasing this value
enhances response but a too high value will make the mechanical system liable to vibrate. The
actual response frequency of the speed loop is as indicated in the following expression:
Speed loop response
frequency(Hz) Speed control gain 2 setting
(1 ratio of load inertia moment to servo motor inertia moment) 2
2
3) Speed integral compensation (parameter No. 38)
To eliminate stationary deviation against a command, the speed control loop is under
proportional integral control. For the speed integral compensation, set the time constant of this
integral control. Increasing the setting lowers the response level. However, if the load inertia
moment ratio is large or the mechanical system has any vibratory element, the mechanical
system is liable to vibrate unless the setting is increased to some degree. The guideline is as
indicated in the following expression:
Speed integral
compensation setting(ms) 2000 to 3000
Speed control gain 2 setting/ (1 ratio of load inertia moment to
servo motor inertia moment 2 setting 0.1)

7 - 10
7. GENERAL GAIN ADJUSTMENT
7.4 Interpolation mode
The interpolation mode is used to match the position control gains of the axes when performing the
interpolation operation of servo motors of two or more axes for an X-Y table or the like. In this mode, the
position control gain 2 and speed control gain 2 which determine command trackability are set manually
and the other parameter for gain adjustment are set automatically.
(1) Parameter
(a) Automatically adjusted parameters
The following parameters are automatically adjusted by auto tuning.
Parameter No. Abbreviation Name
34 GD2 Ratio of load inertia moment to servo motor inertia moment
35 PG2 Position control gain 2
37 VG2 Speed control gain 2
38 VIC Speed integral compensation
(b) Manually adjusted parameters
The following parameters are adjustable manually.
Parameter No. Abbreviation Name
6PG1Position control gain 1
36 VG1 Speed control gain 1
(2) Adjustment procedure
Step Operation Description
1Set 15Hz (parameter No. 2: 010 ) as the machine resonance frequency of response
in the auto tuning mode 1. Select the auto tuning mode 1.
2During operation, increase the response level setting (parameter No. 2), and
return the setting if vibration occurs. Adjustment in auto tuning mode
1.
3Check the values of position control gain 1 (parameter No. 6) and speed control
gain 1 (parameter No. 36). Check the upper setting limits.
4 Set the interpolation mode (parameter No. 2: 000 ). Select the interpolation mode.
5Using the position control gain 1 value checked in step 3 as the guideline of the
upper limit, set in PG1 the value identical to the position loop gain of the axis to
be interpolated. Set position control gain 1.
6Using the speed control gain 1 value checked in step 3 as the guideline of the
upper limit, look at the rotation status and set in speed control gain 1 the value
three or more times greater than the position control gain 1 setting. Set speed control gain 1.
7Looking at the interpolation characteristic and rotation status, fine-adjust the
gains and response level setting. Fine adjustment.
(3) Adjustment description
(a) Position control gain 1 (parameter No.6)
This parameter determines the response level of the position control loop. Increasing position
control gain 1 improves trackability to a position command but a too high value will make
overshooting liable to occur at the time of settling. The droop pulse value is determined by the
following expression.
Droop pulse value (pulse) Position control
g
ain 1 settin
g
131,072(pulse)
60
Rotation speed (r/min)
(b) Speed control gain 1 (parameter No. 36)
Set the response level of the speed loop of the model. Make setting using the following expression
as a guideline.
Speed control gain 1 setting Position control gain 1 setting 3

8 - 1
8. SPECIAL ADJUSTMENT FUNCTIONS
8. SPECIAL ADJUSTMENT FUNCTIONS
POINT
The functions given in this chapter need not be used generally. Use them
if you are not satisfied with the machine status after making adjustment
in the methods in Chapter 7.
If a mechanical system has a natural resonance level point, increasing the servo system response may
cause the mechanical system to produce resonance (vibration or unusual noise) at that resonance
frequency.
Using the machine resonance suppression filter and adaptive vibration suppression control functions can
suppress the resonance of the mechanical system.
8.1 Function block diagram
Speed
control
Machine resonance
suppression filter 2
Encoder
Current
command
Low-pass
filter
Parameter
No.58
Parameter
No.60 Parameter
No.59 Parameter
No.60
Machine resonance
suppression filter 1
Adaptive vibration
suppression control
00
or1 2
000 0
1
00
except 00
except
Servo
motor
8.2 Machine resonance suppression filter
(1) Function
The machine resonance suppression filter is a filter function (notch filter) which decreases the gain of
the specific frequency to suppress the resonance of the mechanical system. You can set the gain
decreasing frequency (notch frequency) and gain decreasing depth.
Mechanical
system
response
level
Machine resonance point
Frequency
Notch
depth
Notch frequency Frequency

8 - 2
8. SPECIAL ADJUSTMENT FUNCTIONS
You can use the machine resonance suppression filter 1 (parameter No. 58) and machine resonance
suppression filter 2 (parameter No. 59) to suppress the vibration of two resonance frequencies. Note
that if adaptive vibration suppression control is made valid, the machine resonance suppression filter
1 (parameter No. 58) is made invalid.
Mechanical
system
response
level
Machine resonance point
Frequency
Notch
depth
Parameter No. 58 Parameter No. 59
Frequency
POINT
The machine resonance suppression filter is a delay factor for the servo
system. Hence, vibration may increase if you set a wrong resonance
frequency or a too deep notch.
(2) Parameters
(a) Machine resonance suppression filter 1 (parameter No. 58)
Set the notch frequency and notch depth of the machine resonance suppression filter 1 (parameter
No. 58)
When you have made adaptive vibration suppression control selection (parameter No. 60) "valid" or
"held", make the machine resonance suppression filter 1 invalid (parameter No. 58: 0000).
3
1
2
0 ( 14dB)
( 8dB)
00
01
02
03
04
05
06
07
Invalid
4500
2250
08
09
0A
0B
0C
0D
0E
0F
10
11
12
13
14
15
16
17
18
19
1A
1B
1C
1D
1E
1F
1500
1125
900
750
642.9
500
450
409.1
375
346.2
321.4
300
562.5 281.3
264.7
250
236.8
225
214.3
204.5
195.7
187.5
180
173.1
166.7
160.1
155.2
150
145.2
Frequency
Setting
value Frequency Frequency Frequency
Parameter No. 58
Notch frequency
Notch depth
Setting
value Depth (Gain)
Deep ( 40dB)
Shallow( 4dB)
Setting
value Setting
value Setting
value

8 - 3
8. SPECIAL ADJUSTMENT FUNCTIONS
POINT
If the frequency of machine resonance is unknown, decrease the notch
frequency from higher to lower ones in order. The optimum notch
frequency is set at the point where vibration is minimal.
A deeper notch has a higher effect on machine resonance suppression but
increases a phase delay and may increase vibration.
The machine characteristic can be grasped beforehand by the machine
analyzer on the servo configuration software. This allows the required
notch frequency and depth to be determined.
Resonance may occur if parameter No. 58 59 is used to select a close
notch frequency and set a deep notch.
(b) Machine resonance suppression filter 2 (parameter No. 59)
The setting method of machine resonance suppression filter 2 (parameter No. 59) is the same as
that of machine resonance suppression filter 1 (parameter No. 58). However, the machine
resonance suppression filter 2 can be set independently of whether adaptive vibration suppression
control is valid or invalid.
8.3 Adaptive vibration suppression control
(1) Function
Adaptive vibration suppression control is a function in which the servo amplifier detects machine
resonance and sets the filter characteristics automatically to suppress mechanical system vibration.
Since the filter characteristics (frequency, depth) are set automatically, you need not be conscious of
the resonance frequency of a mechanical system. Also, while adaptive vibration suppression control is
valid, the servo amplifier always detects machine resonance, and if the resonance frequency changes,
it changes the filter characteristics in response to that frequency.
Mechanical
system
response
level
Mechanical
system
response
level
Machine resonance point Machine resonance point
Frequency Frequenc
y
Notch
depth Notch
depth
Notch frequency Notch frequency
Frequency Frequenc
y
When machine resonance is large and frequency is low When machine resonance is small and frequency is high
POINT
The machine resonance frequency which adaptive vibration suppression
control can respond to is about 150 to 500Hz. Adaptive vibration
suppression control has no effect on the resonance frequency outside this
range. Use the machine resonance suppression filter for the machine
resonance of such frequency.
Adaptive vibration suppression control may provide no effect on a
mechanical system which has complex resonance characteristics or which
has too large resonance.
Under operating conditions in which sudden disturbance torque is imposed
during operation, the detection of the resonance frequency may malfunction
temporarily, causing machine vibration. In such a case, set adaptive
vibration suppression control to be "held" (parameter No. 60: 2 ) to fix
the characteristics of the adaptive vibration suppression control filter.

8 - 4
8. SPECIAL ADJUSTMENT FUNCTIONS
(2) Parameters
The operation of adaptive vibration suppression control selection (parameter No.60).
Parameter No. 60
Adaptive vibration suppression control selection
Choosing "valid" or "held" in adaptive vibration suppression
control selection makes the machine resonance suppression
filter 1 (parameter No. 58) invalid.
0: Invalid
1: Valid
Machine resonance frequency is always detected to
generate the filter in response to resonance, suppressing
machine vibration.
2: Held
Adaptive vibration suppression control sensitivity selection
Set the sensitivity of detecting machine resonance.
0: Normal
1: Large sensitivity
Filter characteristics generated so far is held, and detection of
machine resonance is stopped.
POINT
Adaptive vibration suppression control is factory-set to be invalid
(parameter No. 60: 0000).
Setting the adaptive vibration suppression control sensitivity can change
the sensitivity of detecting machine resonance. Setting of "large sensitivity"
detects smaller machine resonance and generates a filter to suppress
machine vibration. However, since a phase delay will also increase, the
response of the servo system may not increase.
8.4 Low-pass filter
(1) Function
When a ballscrew or the like is used, resonance of high frequency may occur as the response level of
the servo system is increased. To prevent this, the low-pass filter is factory-set to be valid for a torque
command. The filter frequency of this low-pass filter is automatically adjusted to the value in the
following expression:
Filter frequency(Hz) (1 Ratio of load inertia moment to servo motor inertia moment setting 0.1)
2Speed control gain 2 setting 10
(2) Parameter
Set the operation of the low-pass filter (parameter No. 60.)
Parameter No. 60
Low-pass filter selection
0: Valid (automatic adjustment) initial value
1: Invalid
POINT
In a mechanical system where rigidity is extremely high and resonance
level is difficult to occur, setting the low-pass filter to be "invalid" may
increase the servo system response level to shorten the settling time.

8 - 5
8. SPECIAL ADJUSTMENT FUNCTIONS
8.5 Gain changing function
This function can change the gains. You can change between gains during rotation and gains during stop
or can use an external input signal to change gains during operation.
8.5.1 Applications
This function is used when:
(1) You want to increase the gains during servo lock but decrease the gains to reduce noise during rotation.
(2) You want to increase the gains during settling to shorten the stop settling time.
(3) You want to change the gains using an external input signal to ensure stability of the servo system
since the load inertia moment ratio varies greatly during a stop (e.g. a large load is mounted on a
carrier).
8.5.2 Function block diagram
The valid control gains PG2, VG2, VIC and GD2 of the actual loop are changed according to the conditions
selected by gain changing selection CDP (parameter No. 65) and gain changing condition CDS (parameter
No. 66).
Valid
GD2 value
Command pulse
frequency
Droop pulses
Model speed
External input
signal CDP
Comparator
Valid
PG2 value
Valid
VG2 value
Valid
VIC value
Changing
PG2 PG2B
100
VIC VICB
100
VG2 VG2B
100
GD2B
Parameter No.61
GD2
Parameter No.34
PG2
Parameter No.35
VG2
Parameter No.37
VIC
Parameter No.38
CDP
Parameter No.65
CDS
Parameter No.66

8 - 6
8. SPECIAL ADJUSTMENT FUNCTIONS
8.5.3 Parameters
When using the gain changing function, always set " 4 " in parameter No.2 (auto tuning) to choose
the manual mode of the gain adjustment modes. The gain changing function cannot be used in the auto
tuning mode.
Parameter
No.
Abbrevi
ation Name Unit Description
6 PG1 Position control gain 1 rad/s
36 VG1 Speed control gain 1 rad/s Position and speed gains of a model used to set the response
level to a command. Always valid.
34 GD2 Ratio of load inertia moment to
servo motor inertia moment 0.1
times
35 PG2 Position control gain 2 rad/s
37 VG2 Speed control gain 2 rad/s
38 VIC Speed integral compensation ms
Control parameters before changing
61 GD2B Ratio of load inertia moment to
servo motor inertia moment 2 0.1
times Used to set the ratio of load inertia moment to servo motor
inertia moment after changing.
62 PG2B Position control gain 2 changing
ratio %Used to set the ratio (%) of the after-changing position
control gain 2 to position control gain 2.
63 VG2B Speed control gain 2 changing
ratio %Used to set the ratio (%) of the after-changing speed control
gain 2 to speed control gain 2.
64 VICB Speed integral compensation
changing ratio %Used to set the ratio (%) of the after-changing speed integral
compensation to speed integral compensation.
65 CDP Gain changing selection Used to select the changing condition.
66 CDS Gain changing condition kpps
pulse
r/min
Used to set the changing condition values.
67 CDT Gain changing time constant ms You can set the filter time constant for a gain change at
changing.

8 - 7
8. SPECIAL ADJUSTMENT FUNCTIONS
(1) Parameters No. 6, 34 to 38
These parameters are the same as in ordinary manual adjustment. Gain changing allows the values of
ratio of load inertia moment to servo motor inertia moment, position control gain 2, speed control gain
2 and speed integral compensation to be changed.
(2) Ratio of load inertia moment to servo motor inertia moment 2 (GD2B: parameter No. 61)
Set the ratio of load inertia moment to servo motor inertia moment after changing. If the load inertia
moment ratio does not change, set it to the same value as ratio of load inertia moment to servo motor
inertia moment (parameter No. 34).
(3) Position control gain 2 changing ratio (parameter No. 62), speed control gain 2 changing ratio (parameter
No. 63), speed integral compensation changing ratio (parameter No. 64)
Set the values of after-changing position control gain 2, speed control gain 2 and speed integral
compensation in ratio (%). 100% setting means no gain change.
For example, at the setting of position control gain 2 100, speed control gain 2 2000, speed integral
compensation 20 and position control gain 2 changing ratio 180%, speed control gain 2 changing
ratio 150% and speed integral compensation changing ratio 80%, the after-changing values are as
follows:
Position control gain 2 Position control gain 2 Position control gain 2 changing ratio /100 180rad/s
Speed control gain 2 Speed control gain 2 Speed control gain 2 changing ratio /100 3000rad/s
Speed integral compensation Speed integral compensation Speed integral compensation changing
ratio /100 16ms
(4) Gain changing selection (parameter No. 65)
Used to set the gain changing condition. Choose the changing condition in the first digit. If you set "1"
here, you can use the gain changing (CDP) external input signal for gain changing. The gain changing
(CDP) can be assigned to the pins using parameters No. 43 to 48.
Parameter No. 65
Gain changing selection
Gains are changed in accordance with the settings of
parameters No. 61 to 64 under any of the following conditions:
0: Invalid
1: Gain changing (CDP) input is ON
2: Command frequency is equal to higher than parameter No. 66 setting
3: Droop pulse value is equal to higher than parameter No. 66 setting
4: Servo motor speed is equal to higher than parameter No. 66 setting
(5) Gain changing condition (parameter No. 66)
When you selected "command frequency", "droop pulses" or "servo motor speed" in gain changing
selection (parameter No.65), set the gain changing level.
The setting unit is as follows:
Gain changing condition Unit
Command frequency kpps
Droop pulses pulse
Servo motor speed r/min
(6) Gain changing time constant (parameter No. 67)
You can set the primary delay filter to each gain at gain changing. This parameter is used to suppress
shock given to the machine if the gain difference is large at gain changing, for example.

8 - 8
8. SPECIAL ADJUSTMENT FUNCTIONS
8.5.4 Gain changing operation
This operation will be described by way of setting examples.
(1) When you choose changing by external input
(a) Setting
Parameter No. Abbreviation Name Setting Unit
6 PG1 Position control gain 1 100 rad/s
36 VG1 Speed control gain 1 1000 rad/s
34 GD2 Ratio of load inertia moment to
servo motor inertia moment 40.1 times
35 PG2 Position control gain 2 120 rad/s
37 VG2 Speed control gain 2 3000 rad/s
38 VIC Speed integral compensation 20 ms
61 GD2B Ratio of load inertia moment to
servo motor inertia moment 2 100 0.1 times
62 PG2B Position control gain 2
changing ratio 70 %
63 VG2B Speed control gain 2 changing
ratio 133 %
64 VICB Speed integral compensation
changing ratio 250 %
65 CDP Gain changing selection 0001
(Changed by ON/OFF of
pin CN1-10)
67 CDT Gain changing time constant 100 ms
(b) Changing operation
OFF ON OFF
Gain changing
(CDP)
Change of
each gain
Before-changing gain
After-changing gain
CDT 100ms
Position control gain 1 100
Speed control gain 1 1000
Ratio of load inertia moment
to servo motor inertia moment 4.0 10.0 4.0
Position control gain 2 120 84 120
Speed control gain 2 3000 4000 3000
Speed integral compensation 20 50 20

8 - 9
8. SPECIAL ADJUSTMENT FUNCTIONS
(2) When you choose changing by droop pulses
(a) Setting
Parameter No. Abbreviation Name Setting Unit
6 PG1 Position control gain 1 100 rad/s
36 VG1 Speed control gain 1 1000 rad/s
34 GD2 Ratio of load inertia moment to
servo motor inertia moment 40 0.1 times
35 PG2 Position control gain 2 120 rad/s
37 VG2 Speed control gain 2 3000 rad/s
38 VIC Speed integral compensation 20 ms
61 GD2B Ratio of load inertia moment to
servo motor inertia moment 2 100 0.1 times
62 PG2B Position control gain 2
changing ratio 70 %
63 VG2B Speed control gain 2 changing
ratio 133 %
64 VICB Speed integral compensation
changing ratio 250 %
65 CDP Gain changing selection 0003
(Changed by droop pulses)
66 CDS Gain changing condition 50 pulse
67 CDT Gain changing time constant 100 ms
(b) Changing operation
CDT 100ms
0
Droop pulses [pulses]
Change of each gain
CDS
CDS
Before-changing gain
After-changing gain
Command pulse Droop pulses
Position control gain 1 100
Speed control gain 1 1000
Ratio of load inertia moment
to servo motor inertia moment 4.0 10.0 4.0 10.0
Position control gain 2 120 84 120 84
Speed control gain 2 3000 4000 3000 4000
Speed integral compensation 20 50 20 50

8 - 10
8. SPECIAL ADJUSTMENT FUNCTIONS
MEMO

9 - 1
9. INSPECTION
9. INSPECTION
WARNING
Before starting maintenance and/or inspection, make sure that the charge lamp is
off more than 10 minutes after power-off. Then, confirm that the voltage is safe in
the tester or the like. Otherwise, you may get an electric shock.
Any person who is involved in inspection should be fully competent to do the work.
Otherwise, you may get an electric shock. For repair and parts replacement,
contact your safes representative.
POINT
Do not test the servo amplifier with a megger (measure insulation
resistance), or it may become faulty.
Do not disassemble and/or repair the equipment on customer side.
(1) Inspection
It is recommended to make the following checks periodically:
(a) Check for loose terminal block screws. Retighten any loose screws.
(b) Check the cables and the like for scratches and cracks. Perform periodic inspection according to
operating conditions.
(c) Check the servo motor bearings, brake section, etc. for unusual noise.
(d) Check the cables and the like for scratches and cracks. Perform periodic inspection according to
operating conditions.
(e) Check the servo motor shaft and coupling for misalignment.
(2) Life
The following parts must be changed periodically as listed below. If any part is found faulty, it must be
changed immediately even when it has not yet reached the end of its life, which depends on the
operating method and environmental conditions. For parts replacement, please contact your sales
representative.
Part name Life guideline
Smoothing capacitor 10 years
Relay Number of power-on and number of
emergency stop times : 100,000 times
Bearings 20,000 to 30,000 hours
Encoder 20,000 to 30,000 hours
Oil seal 5,000 hours
(a) Smoothing capacitor
Affected by ripple currents, etc. and deteriorates in characteristic. The life of the capacitor greatly
depends on ambient temperature and operating conditions. The capacitor will reach the end of its
life in 10 years of continuous operation in normal air-conditioned environment.
(b) Relays
Their contacts will wear due to switching currents and contact faults occur. Relays reach the end of
their life when the cumulative number of power-on and emergency stop times is 100,000, which
depends on the power supply capacity.

9 - 2
9. INSPECTION
(c) Servo amplifier cooling fan
The cooling fan bearings reach the end of their life in 10,000 to 30,000 hours. Normally, therefore,
the fan must be changed in a few years of continuous operation as a guideline.
It must also be changed if unusual noise or vibration is found during inspection.
(d) Bearings
When the servo motor is run at rated speed under rated load, change the bearings in 20,000 to
30,000 hours as a guideline. This differs on the operating conditions. The bearings must also be
changed if unusual noise or vibration is found during inspection.
(e) Oil seal, V ring
Must be changed in 5,000 hours of operation at rated speed as a guideline. This differs on the
operating conditions. These parts must also be changed if oil leakage, etc. is found during
inspection.

10 - 1
10. TROUBLESHOOTING
10. TROUBLESHOOTING
10.1 Trouble at start-up
CAUTION Excessive adjustment or change of parameter setting must not be made as it will
make operation instable.
POINT
Using the optional servo configuration software, you can refer to unrotated
servo motor reasons, etc.
The following faults may occur at start-up. If any of such faults occurs, take the corresponding action.
10.1.1 Position control mode
(1) Troubleshooting
No. Start-up sequence Fault Investigation Possible cause Refer to
Not improved if connectors
CN1, CN2 and CN3 are
disconnected.
1. Power supply voltage fault
2. Servo amplifier is faulty.
Improved when connectors
CN1 is disconnected. Power supply of CNP1 cabling
is shorted.
Improved when connector
CN2 is disconnected. 1. Power supply of encoder
cabling is shorted.
2. Encoder is faulty.
LED is not lit.
LED flickers.
Improved when connector
CN3 is disconnected. Power supply of CN3 cabling is
shorted.
1 Power on (Note)
Alarm occurs. Refer to Section 10.2 and remove cause. Section 10.2
Alarm occurs. Refer to Section 10.2 and remove cause. Section 10.22 Switch on servo-on
signal. Servo motor shaft is
not servo-locked
(is free).
1. Check the display to see if
the servo amplifier is
ready to operate.
2. Check the external I/O
signal indication to see if
the servo-on (SON) signal
is ON.
1. Servo-on signal is not input.
(Wiring mistake)
2. 24VDC power is not
supplied to COM.
Section 6.6
Servo motor does
not rotate. 1. Wiring mistake
(a) For open collector pulse
train input, 24VDC
power is not supplied to
OPC.
(b) LSP/LSN-SG are not
connected.
2. No pulses is input.
Section 6.2
3Enter input
command.
(Test operation)
Servo motor run in
reverse direction.
Check cumulative command
pulses.
1. Mistake in wiring to
controller.
2. Mistake in setting of
parameter No. 54.
Chapter 5

10 - 2
10. TROUBLESHOOTING
No. Start-up sequence Fault Investigation Possible cause Refer to
Rotation ripples
(speed fluctuations)
are large at low
speed.
Make gain adjustment in the
following procedure:
1. Increase the auto tuning
response level.
2. Repeat acceleration and
deceleration several times
to complete auto tuning.
Gain adjustment fault Chapter 7
4 Gain adjustment
Large load inertia
moment causes the
servo motor shaft to
oscillate side to side.
If the servo motor may be
run with safety, repeat
acceleration and
deceleration several times to
complete auto tuning.
Gain adjustment fault Chapter 7
5 Cyclic operation Position shift occurs Confirm the cumulative
command pulses, cumulative
feedback pulses and actual
servo motor position.
Pulse counting error, etc.
due to noise. (2) in this
section
Note: Switch power on again after making sure that the charge lamp has turned off completely.

10 - 3
10. TROUBLESHOOTING
(2) How to find the cause of position shift
Positioning unit
(a) Output pulse
counter
QPCMX
CDV
(C) Servo-on (SON),
stroke end
(LSP/LSN) input
(A) (b) Cumulative command
pulses
Electronic gear (parameters No. 3, 4)
C
Servo motor
SM
Encoder
L
Machine
(d) Machine sto
p
position M
(B)
(c) Cumulative
feedback pulses
Servo amplifier
When a position shift occurs, check (a) output pulse counter, (b) cumulative command pulse display, (c)
cumulative feedback pulse display, and (d) machine stop position in the above diagram.
(A), (B) and (C) indicate position shift causes. For example, (A) indicates that noise entered the wiring
between positioning unit and servo amplifier, causing pulses to be mis-counted.
In a normal status without position shift, there are the following relationships:
1) Q P (positioning unit's output counter servo amplifier's cumulative command pulses)
2) CMX(parameter No.3)
CDV(parameter No.4)
P
C (cumulative command pulses electronic gear cumulative feedback pulses)
3) C M (cumulative feedback pulses travel per pulse machine position)
Check for a position shift in the following sequence:
1) When Q P
Noise entered the pulse train signal wiring between positioning unit and servo amplifier,
causing pulses to be miss-counted. (Cause A)
Make the following check or take the following measures:
Check how the shielding is done.
Change the open collector system to the differential line driver system.
Run wiring away from the power circuit.
Install a data line filter.
2) CMX
CDV
P C
When
During operation, the servo-on signal (SON) or forward/reverse rotation stroke end signal was
switched off or the clear signal (CR) and the reset signal (RES) switched on. (Cause C)
If a malfunction may occur due to much noise, increase the input filter setting (parameter No. 1).
3) When C M
Mechanical slip occurred between the servo motor and machine. (Cause B)

10 - 4
10. TROUBLESHOOTING
10.1.2 Internal speed control mode
No. Start-up sequence Fault Investigation Possible cause Refer to
Not improved if connectors
CN1, CN2 and CN3 are
disconnected.
1. Power supply voltage fault
2. Servo amplifier is faulty.
Improved when connectors
CN1 is disconnected. Power supply of CN1 cabling is
shorted.
Improved when connector
CN2 is disconnected. 1. Power supply of encoder
cabling is shorted.
2. Encoder is faulty.
LED is not lit.
LED flickers.
Improved when connector
CN3 is disconnected. Power supply of CN3 cabling is
shorted.
1 Power on (Note)
Alarm occurs. Refer to Section 10.2 and remove cause. Section 10.2
Alarm occurs. Refer to Section 10.2 and remove cause. Section 10.22 Switch on servo-on
signal. Servo motor shaft is
not servo-locked
(is free).
1. Check the display to see if
the servo amplifier is
ready to operate.
2. Check the external I/O
signal indication to see if
the servo-on (SON) signal
is ON.
1. Servo-on signal is not input.
(Wiring mistake)
2. 24VDC power is not
supplied to COM.
Section 6.6
Call the external I/O signal
display and check the
ON/OFF status of the input
signal.
LSP, LSN, ST1 or ST2 is off. Section 6.6
Check the internal speed
commands 1 to 7
(parameters No. 8 to 10 72
to 75).
Set value is 0.
3Switch on forward
rotation start (ST1)
or reverse rotation
start (ST2).
Servo motor does
not rotate.
Check the internal torque
limit 1 (parameter No. 28). Torque limit level is too low as
compared to the load torque.
(1), Section
5.1.2
Rotation ripples
(speed fluctuations)
are large at low
speed.
Make gain adjustment in the
following procedure:
1. Increase the auto tuning
response level.
2. Repeat acceleration and
deceleration several
times to complete auto
tuning.
Gain adjustment fault Chapter 7
4 Gain adjustment
Large load inertia
moment causes the
servo motor shaft to
oscillate side to side.
If the servo motor may be
run with safety, repeat
acceleration and
deceleration several times to
complete auto tuning.
Gain adjustment fault Chapter 7
Note: Switch power on again after making sure that the charge lamp has turned off completely.

10 - 5
10. TROUBLESHOOTING
10.2 When alarm or warning has occurred
POINT
Configure up a circuit which will detect the trouble (ALM) signal and turn
off the servo-on (SON) signal at occurrence of an alarm.
10.2.1 Alarms and warning list
When a fault occurs during operation, the corresponding alarm or warning is displayed. If any alarm or
warning has occurred, refer to Section 10.2.2 or 10.2.3 and take the appropriate action.
Set " 1" in parameter No. 49 to output the alarm code in ON/OFF status across the corresponding
pin and SG. Warnings (AL.96 to AL.E9) have no alarm codes. Any alarm code is output at occurrence of
the corresponding alarm. In the normal status, the signals available before alarm code setting (CN1-12:
ZSP, CN1-11: RD, CN1-10: INP or SA) are output.
After its cause has been removed, the alarm can be deactivated in any of the methods marked in the
alarm deactivation column.
(Note 2) Alarm code Alarm deactivation
Display CN1-10
pin
CN1-11
pin
CN1-12
pin
Name Power
OFF ON
Press
"SET" on
current
alarm
screen.
Alarm
reset
(RES)
signal
AL.10010Undervoltage
AL.12 0 0 0 Memory error 1
AL.13 0 0 0 Clock error
AL.15 0 0 0 Memory error 2
AL.16 1 0 1 Encoder error 1
AL.17 0 0 0 Board error
AL.19 0 0 0 Memory error 3
AL.1A 1 0 1 Motor combination error
AL.20 1 1 0 Encoder error 2
AL.24 0 0 1 Main circuit error
AL.30 0 1 0 Regenerative error (Note 1) (Note 1) (Note 1)
AL.31011Overspeed
AL.32001Overcurrent
AL.33010Overvoltage
AL.35 0 1 1 Command pulse frequency error
AL.37 0 0 0 Parameter error
AL.45 1 1 0 Main circuit device overheat
AL.46 1 1 0 Servo motor overheat
AL.50110Overload 1 (Note 1) (Note 1) (Note 1)
AL.51110Overload 2 (Note 1) (Note 1) (Note 1)
AL.52 0 1 1 Error excessive
AL.8A 0 0 0 Serial communication time-out error
AL.8E 0 0 0 Serial communication error
Alarms
88888 0 0 0 Watchdog
AL.E0 Excessive regenerative warning
AL.E1 Overload warning
AL.E6 Servo emergency stop warning
Warnings
AL.E9 Under voltage warning
Removing the cause of occurrence
deactivates the alarm
automatically.
Note: 1. Deactivate the alarm about 30 minutes of cooling time after removing the cause of occurrence.
2. 0: off
1: on

10 - 6
10. TROUBLESHOOTING
10.2.2 Remedies for alarms
CAUTION When any alarm has occurred, eliminate its cause, ensure safety, then reset the
alarm, and restart operation. Otherwise, injury may occur.
POINT
When any of the following alarms has occurred, always remove its cause
and allow about 30 minutes for cooling before resuming operation. If
operation is resumed by switching power off, then on to reset the alarm, the
servo amplifier and servo motor may become faulty.
Regenerative error (AL.30)
Overload 1 (AL.50)
Overload 2 (AL.51)
The alarm can be deactivated by switching power off, then on press the
"SET" button on the current alarm screen or by turning on the reset signal
(RES). For details, refer to Section 10.2.1.
When an alarm occurs, the trouble signal (ALM) switches off and the dynamic brake is operated to stop
the servomotor. At this time, the display indicates the alarm No.
The servo motor comes to a stop. Remove the cause of the alarm in accordance with this section. The
optional servo configuration software may be used to refer to the cause.
Display Name Definition Cause Action
1. Power supply voltage is low.
2. There was an instantaneous
control power failure of 60ms or
longer.
3. Shortage of power supply capacity
caused the power supply voltage to
drop at start, etc.
4. Power was restored after the bus
voltage had dropped to 200VDC.
Review the power supply.
AL.10 Undervoltage Power supply
voltage dropped to
160VAC or less.
5. Faulty parts in the servo amplifier Change the servo amplifier.
AL.12 Memory error 1 RAM, memory fault
AL.13 Clock error Printed board fault Faulty parts in the servo amplifier Change the servo amplifier.
1. Faulty parts in the servo amplifier
AL.15 Memory error 2 EEP-ROM fault 2. The number of write times to EEP-
ROM exceeded 100,000.
Change the servo amplifier.
1. Encoder connector (CN2)
disconnected. Connect correctly.
2. Encoder fault Change the servo motor.
AL.16 Encoder error 1 Communication
error occurred
between encoder
and servo amplifier. 3. Encoder cable faulty
(Wire breakage or shorted) Repair or change cable.
AL.17 Board error CPU/parts fault
AL.19 Memory error 3 ROM memory fault Faulty parts in the servo amplifier Change the servo amplifier.

10 - 7
10. TROUBLESHOOTING
Display Name Definition Cause Action
AL.1A Motor
combination
error
Wrong combination
of servo anplifier
and servo motor.
Wrong combination of servo
amplifier and servo motor connected. Use correct combination.
1. Encoder connector (CN2)
disconnected. Connect correctly.
2. Encoder fault Change the servo motor.
AL.20 Encoder error 2 Communication
error occurred
between encoder
and servo amplifier. 3. Encoder cable faulty
(Wire breakage or shorted) Repair or change the cable.
1. Power input wires and servo motor
output wires are in contact at
main circuit terminal block (TE1).
Connect correctly.
2. Sheathes of servo motor power
cables deteriorated, resulting in
ground fault.
Change the cable.
AL.24 Main circuit
error Ground fault
occurred at the
servo motor outputs
(U,V and W phases)
of the servo
amplififer. 3. Main circuit of servo amplifier
failed. Checking method
AL.24 occurs if the servo is
switched on after disconnecting
the U, V, W power cables from
the servo amplifier.
Change the servo amplifier.
1. Wrong setting of parameter No. 0 Set correctly.
2. Built-in regenerative brake
resistor or regenerative brake
option is not connected.
Connect correctly
3. High-duty operation or continuous
regenerative operation caused the
permissible regenerative power of
the regenerative brake option to
be exceeded.
Checking method
Call the status display and check
the regenerative load ratio.
1. Reduce the frequency of positioning.
2. Use the regenerative brake option of
larger capacity.
3. Reduce the load.
4. Power supply voltage is abnormal.
MR-E- A:260V or more Review power supply
Permissible
regenerative power
of the built-in
regenerative brake
resistor or
regenerative brake
option is exceeded.
5. Built-in regenerative brake
resistor or regenerative brake
option faulty.
Change servo amplifier or regenerative
brake option.
AL.30 Regenerative
alarm
Regenerative
transistor fault 6. Regenerative transistor faulty.
Checking method
1) The regenerative brake option
has overheated abnormally.
2) The alarm occurs even after
removal of the built-in
regenerative brake resistor or
regenerative brake option.
Change the servo amplifier.

10 - 8
10. TROUBLESHOOTING
Display Name Definition Cause Action
1. Input command pulse frequency
exceeded the permissible
instantaneous speed frequency.
Set command pulses correctly.
2. Small acceleration/deceleration
time constant caused overshoot to
be large.
Increase acceleration/deceleration time
constant.
3. Servo system is instable to cause
overshoot. 1. Re-set servo gain to proper value.
2. If servo gain cannot be set to proper
value:
1) Reduce load inertia moment ratio; or
2) Reexamine acceleration/
deceleration time constant.
4. Electronic gear ratio is large
(parameters No. 3, 4) Set correctly.
AL.31 Overspeed Speed has exceeded
the instantaneous
permissible speed.
5. Encoder faulty. Change the servo motor.
1. Short occurred in servo amplifier
output phases U, V and W. Correct the wiring.
2. Transistor (IPM) of the servo
amplifier faulty.
Checking method
Alarm (AL.32) occurs if power is
switched on after U,V and W
are disconnected.
Change the servo amplifier.
3. Ground fault occurred in servo
amplifier output phases U, V and
W.
Correct the wiring.
AL.32 Overcurrent Current that flew is
higher than the
permissible current
of the servo
amplifier.
4. External noise caused the
overcurrent detection circuit to
misoperate.
Take noise suppression measures.
1. Lead of built-in regenerative brake
resistor or regenerative brake
option is open or disconnected.
1. Change lead.
2. Connect correctly.
2. Regenerative transistor faulty. Change servo amplifier
3. Wire breakage of built-in
regenerative brake resistor or
regenerative brake option
1. For wire breakage of built-in
regenerative brake resistor, change
servo amplifier.
2. For wire breakage of regenerative brake
option, change regenerative brake
option.
4. Capacity of built-in regenerative
brake resistor or regenerative
brake option is insufficient.
Add regenerative brake option or increase
capacity.
AL.33 Overvoltage Converter bus
voltage exceeded
400VDC.
5. Power supply voltage high. Review the power supply.
1. Pulse frequency of the command
pulse is too high. Change the command pulse frequency to a
proper value.
2. Noise entered command pulses. Take action against noise.
AL.35 Command
pulse frequency
error
Input pulse
frequency of the
command pulse is
too high. 3. Command device failure Change the command device.

10 - 9
10. TROUBLESHOOTING
Display Name Definition Cause Action
1. Servo amplifier fault caused the
parameter setting to be rewritten. Change the servo amplifier.
2. Regenerative brake option or servo
motor not used with servo
amplifier was selected in
parameter No.0.
Set parameter No.0 correctly.
AL.37 Parameter
error Parameter setting is
wrong.
3. The number of write times to EEP-
ROM exceeded 100,000 due to
parameter write, etc.
Change the servo amplifier.
1. Servo amplifier faulty. Change the servo amplifier.
2. The power supply was turned on
and off continuously by overloaded
status.
The drive method is reviewed.
AL.45 Main circuit
device overheat Main circuit device
overheat
3. Air cooling fan of servo amplifier
stops. 1. Exchange the cooling fan or the servo
amplifier.
2. Reduce ambient temperature.
1. Ambient temperature of servo
motor is over 40 (104 ). Review environment so that ambient
temperature is 0 to 40 (104 ).
2. Servo motor is overloaded. 1. Reduce load.
2. Review operation pattern.
3. Use servo motor that provides larger
output.
AL.46 Servo motor
overheat Servo motor
temperature rise
actuated the
thermal protector.
3. Thermal protector in encoder is
faulty. Change servo motor.
1. Servo amplifier is used in excess
of its continuous output current. 1. Reduce load.
2. Review operation pattern.
3. Use servo motor that provides larger
output.
2. Servo system is instable and
hunting. 1. Repeat acceleration/
deceleration to execute auto tuning.
2. Change auto tuning response setting.
3. Set auto tuning to OFF and make gain
adjustment manually.
3. Machine struck something. 1. Review operation pattern.
2. Install limit switches.
4. Wrong connection of servo motor.
Servo amplifier's output terminals
U, V, W do not match servo
motor's input terminals U, V, W.
Connect correctly.
AL.50 Overload 1 Load exceeded
overload protection
characteristic of
servo amplifier.
5. Encoder faulty.
Checking method
When the servo motor shaft is
rotated with the servo off, the
cumulative feedback pulses do
not vary in proportion to the
rotary angle of the shaft but the
indication skips or returns
midway.
Change the servo motor.

10 - 10
10. TROUBLESHOOTING
Display Name Definition Cause Action
1. Machine struck something. 1. Review operation pattern.
2. Install limit switches.
2. Wrong connection of servo motor.
Servo amplifier's output terminals
U, V, W do not match servo
motor's input terminals U, V, W.
Connect correctly.
3. Servo system is instable and
hunting. 1. Repeat acceleration/deceleration to
execute auto tuning.
2. Change auto tuning response setting.
3. Set auto tuning to OFF and make gain
adjustment manually.
AL.51 Overload 2 Machine collision or
the like caused max.
output current to
flow successively for
several seconds.
Servo motor locked:
1s or more
During rotation:
2.5s or more
4. Encoder faulty.
Checking method
When the servo motor shaft is
rotated with the servo off, the
cumulative feedback pulses do
not vary in proportion to the
rotary angle of the shaft but the
indication skips or returns
midway.
Change the servo motor.
1. Acceleration/deceleration time
constant is too small. Increase the acceleration/deceleration
time constant.
2. Torque limit value (parameter
No.28) is too small. Increase the torque limit value.
3. Motor cannot be started due to
torque shortage caused by power
supply voltage drop.
1. Review the power supply capacity.
2. Use servo motor which provides larger
output.
4. Position control gain 1 (parameter
No.6) value is small. Increase set value and adjust to ensure
proper operation.
5. Servo motor shaft was rotated by
external force. 1. When torque is limited, increase the
limit value.
2. Reduce load.
3. Use servo motor that provides larger
output.
6. Machine struck something. 1. Review operation pattern.
2. Install limit switches.
7. Encoder faulty Change the servo motor.
AL.52 Error excessive The droop pulse
value of the
deviation counter
exceeded 2.5
rotations.
8. Wrong connection of servo motor.
Servo amplifier's output terminals
U, V, W do not match servo
motor's input terminals U, V, W.
Connect correctly.
1. Communication cable breakage. Repair or change communication cable
2. Communication cycle longer than
parameter No. 56 setting. Set correct value in parameter.
AL.8A Serial
communication
time-out error
RS-232C or RS-422
communication
stopped for longer
than the time set in
parameter No.56. 3. Wrong protocol. Correct protocol.
1. Communication cable fault
(Open cable or short circuit) Repair or change the cable.AL.8E Serial
communication
error
Serial
communication
error occurred
between servo
amplifier and
communication
device (e.g. personal
computer).
2. Communication device (e.g.
personal computer) faulty Change the communication device (e.g.
personal computer).
88888 Watchdog CPU, parts faulty Fault of parts in servo amplifier Change servo amplifier.

10 - 11
10. TROUBLESHOOTING
10.2.3 Remedies for warnings
If AL.E6 occurs, the servo off status is established. If any other warning occurs, operation can be
continued but an alarm may take place or proper operation may not be performed. Use the optional servo
configuration software to refer to the cause of warning.
Display Name Definition Cause Action
AL.E0 Excessive
regenerative
warning
There is a possibility that
regenerative power may
exceed permissible
regenerative power of
built-in regenerative
brake resistor or
regenerative brake
option.
Regenerative power increased to 85% or
more of permissible regenerative power of
built-in regenerative brake resistor or
regenerative brake option.
Checking method
Call the status display and check
regenerative load ratio.
1. Reduce frequency of
positioning.
2. Change regenerative brake
option for the one with larger
capacity.
3. Reduce load.
AL.E1 Overload
warning There is a possibility that
overload alarm 1 or 2
may occur.
Load increased to 85% or more of overload
alarm 1 or 2 occurrence level.
Cause, checking method
Refer to AL.50,51.
Refer to AL.50, AL.51.
AL.E6 Servo emergency
stop warning EMG-SG are open. External emergency stop was made valid.
(EMG-SG opened.) Ensure safety and deactivate
emergency stop.
AL.E9 Under voltage
warning This alarm occurs when
the servo motor speed
decreases to or below
50r/min with the bus
voltage dropping.
Review the power supply.

10 - 12
10. TROUBLESHOOTING
MEMO

11 - 1
11. OUTLINE DIMENSION DRAWINGS
11. OUTLINE DIMENSION DRAWINGS
11.1 Servo amplifiers
(1) MR-E-10A MR-E-20A
6
(0.24)
156 (6.14)
135 (5.32)50 (1.97)
6
(0.24)
70
(2.76)
6 ( 0.24)
Weight: 0.7 [kg] (1.54 [lb])
[Unit: mm]
([Unit: in])
168 (6.61)
PE terminals
Terminal screw: M4
Tightening torque: 1.2 [N m] (169.9 [oz in])

11 - 2
11. OUTLINE DIMENSION DRAWINGS
(2) MR-E-40A
156 (6.14)
22
(0.87)
135 (5.32)
168 (6.61)
6
(0.24)
Weight: 1.1 [kg] (2.43 [lb])
6 ( 0.24)
[Unit: mm]
([Unit: in])
70
(2.76)
70
(2.76)
PE terminals
Terminal screw: M4
Tightening torque: 1.2 [N m] (169.9 [oz in])

11 - 3
11. OUTLINE DIMENSION DRAWINGS
(3) MR-E-70A MR-E-100A
(0.24)
70 (2.76) 190 (7.48)
25
(0.98)
159 (6.26)
42
(1.65) 22
(0.87)
156 (6.14)
6 ( 0.24)
Weight: 1.7 [kg] (3.75 [lb])
70
(2.76)
6
[Unit: mm]
([Unit: in])
168 (6.61)
PE terminals
Terminal screw: M4
Tightening torque: 1.2 [N m] (169.9 [oz in])

11 - 4
11. OUTLINE DIMENSION DRAWINGS
(4) MR-E-200A
90 (3.54)
78
(3.07)
168 (6.61)
156 (6.14)
70 (2.76) 195 (7.68)
6
(0.24)
Weight: 2.0 [kg] (4.41 [lb])
[Unit: mm]
([Unit: in])
156 (6.14)
40
(1.58)
6 ( 0.24)
PE terminal
Terminal screw: M4
Tightening torque: 1.2 [N m]

11 - 5
11. OUTLINE DIMENSION DRAWINGS
11.2 Connectors
(1) Servo amplifier side
<3M >
(a) Soldered type
Model
Connector : 10126-3000VE
Shell kit : 10326-52F0-008
[Unit: mm]
([Unit: in])
10.0(0.39)
Logo, etc. are indicated here.
12.0(0.47)
22.0 (0.87)
39.0 (1.54)
23.8 (0.94)
14.0
(0.55)
12.7(0.50)
33.3 (1.31)
(b) Threaded type
[Unit: mm]
([Unit: in])
10.0
12.0
22.0
39.0
23.8
14.0
12.7
33.3
5.7
27.4
(1.31) (0.50)
(0.22) (0.94)
(1.54)
(
0.39
)
(0.87)
(0.55) (1.08)
(0.47)
Model
Connector : 10126-3000VE
Shell kit : 10326-52A0-008
Note. This is not available as option
and should be user-prepared.

11 - 6
11. OUTLINE DIMENSION DRAWINGS
(2) CN2 Connector
Connector housing : 54593-1011
Cover A : 54594-1015
Cover B : 54595-1005
Shell cover : 58935-1000
Shell body : 58934-1000
Cable clamp : 58934-0000
Screw : 58203-0010
12.5
(0.49)
40 (1.58)
22.7 (0.89) 11 (0.43)
[Unit: mm]
([Unit: in])
(3) CN3 Connector (Marushin electric mfg)
Connector: MP371/6
6
(0.24) 44.5 (1.75)
8.95
(0.35)
56
34
21
14.8
( 0.58)
5
( 0.20)

11 - 7
11. OUTLINE DIMENSION DRAWINGS
(4) CNP1 CNP2 Connector (molex)
(a) Insulation displacement type [Unit: mm]
([Unit: in])
Variable Dimensions
[mm] ([in])
Connector
AB
Number of
Poles Application
51240-0300 17.8
(0.70) 10
(0.39) 3CNP2
(1kW or less)
51240-0600 32.8
(1.29) 25
(0.98) 6CNP1
(1kW or less)
Crimping tool: 57349-5300 (molex)
2.5
(0.10)
5
(0.20)
0.5
(0.02)
25
(0.98)
11.4
(0.45)
8.5
(0.34)
15.3
(0.60)
Pitch
Circuit number indication
(A)
(B)
654321
[Unit: mm]
([Unit: in])
Variable Dimensions
[mm] ([in])
Connector
AB
Number of
Poles Application
51241-0300 22.8
(0.9) 15
(0.59) 3CNP2 (2kW)
51241-0600 45.3
(1.78) 37.5
(1.48) 6CNP1 (2kW)
Crimping tool: 57349-5300 (molex)
3.75
(0.15)
Circuit number indication
(B)
A
321 4 5 6
7.5
(0.3)
Pitch
8.5
(0.34) 25
(0.98)
15.3
(0.60)
0.5
(0.02) 11.4
(0.45)

11 - 8
11. OUTLINE DIMENSION DRAWINGS
(b) Insertion type [Unit: mm]
([Unit: in])
Variable Dimensions
[mm] ([in])
Connector
AB
Number of
Poles Application
55757-0310 16.5
(0.65) 10
(0.39) 3CNP2
(1kW or less)
55755-0610 31.5
(1.24) 25
(0.98) 6CNP1
(1kW or less)
5 (0.20)
1.5
(0.06)
26.5 (1.04)
8.5
(0.34) 18 (0.71)
14.3
(0.56)
Housing Housing cover
Pitch
A
(B)
5 (0.20)
[Unit: mm]
([Unit: in])
Variable Dimensions
[mm] ([in])
Connector
AB
Number of
Poles Application
54927-0310 21.5
(0.85) 22.5
(0.89) 3CNP2
(2kW)
54927-0610 44
(1.73) 37.5
(1.48) 6CNP1
(2kW)
1.5
(0.06)
26.5 (1.04)
8.5
(0.34) 18 (0.71)
14.3
(0.56)
Housing Housing cover
(B)
A
7.5
(0.3)
7.5
(0.3)
Pitch
5
(0.20)

12 - 1
12. CHARACTERISTICS
12. CHARACTERISTICS
12.1 Overload protection characteristics
An electronic thermal relay is built in the servo amplifier to protect the servo motor and servo amplifier
from overloads. Overload 1 alarm (AL.50) occurs if overload operation performed is above the electronic
thermal relay protection curve shown in any of Figs 12.1, Overload 2 alarm (AL.51) occurs if the
maximum current flew continuously for several seconds due to machine collision, etc. Use the equipment
on the left-hand side area of the continuous or broken line in the graph.
In a machine like the one for vertical lift application where unbalanced torque will be produced, it is
recommended to use the machine so that the unbalanced torque is 70% or less of the rated torque.
1000
100
10
1
0.1
050 150 200 250 300
(Note) Load ratio [%]
Operation time[s]
100
During rotation
During servo lock
a. MR-E-10A to MR-E-100A
1000
100
10
1
0.1
050 150 200 250 300
(Note) Load ratio [%]
Operation time[s]
100
During rotation
During servo lock
b. MR-E-200A
Note: If the servo motor is stopped or low-speed (30r/min or less) operation is performed at an abnormally high duty with torque more
than 100% of the rating being generated, the servo amplifier may fail even in a status where the electronic thermal relay
protection is not activated.
Fig 12.1 Electronic thermal relay protection characteristics
12.2 Power supply equipment capacity and generated loss
(1) Amount of heat generated by the servo amplifier
Table 12.1 indicates servo amplifiers' power supply capacities and losses generated under rated load.
For thermal design of an enclosure, use the values in Table 12.1 in consideration for the worst
operating conditions. The actual amount of generated heat will be intermediate between values at
rated torque and zero torque according to the duty used during operation. When the servo motor is run
at less than the maximum speed, the power supply capacity will be smaller than the value in the
table, but the servo amplifier's generated heat will not change.
Table 12.1 Power supply capacity and generated heat per servo amplifier at rated output
(Note 2)
Servo amplifier-generated heat[W] Area required for heat dissipation
Servo amplifier Servo motor
(Note 1)
Power supply
capacity[kVA] At rated torque With servo off [m2] [ft2]
MR-E-10A(1) HC-KFE13 0.3 25 15 0.5 5.4
MR-E-20A(1) HC-KFE23 0.5 25 15 0.5 5.4
MR-E-40A(1) HC-KFE43 0.9 35 15 0.7 7.5
MR-E-60A HC-SFE52 1.0 40 15 0.8 8.6
MR-E-70A HC-KFE73 1.3 50 15 1.0 10.8
MR-E-100A HC-SFE102 1.7 50 15 1.0 10.8
MR-E-200A HC-SFE202 3.5 90 20 1.8 19.4
Note:1. Note that the power supply capacity will vary according to the power supply impedance. This value assumes that the power
factor improving reactor is not used.
2. Heat generated during regeneration is not included in the servo amplifier-generated heat. To calculate heat generated by the
regenerative brake option, use Equation 13.1 in Section 13.1.1.

12 - 2
12. CHARACTERISTICS
(2) Heat dissipation area for enclosed servo amplifier
The enclosed control box (hereafter called the control box) which will contain the servo amplifier
should be designed to ensure that its temperature rise is within 10 at the ambient temperature of
40 (104 ). (With a 5 (41 ) safety margin, the system should operate within a maximum 55
(131 ) limit.) The necessary enclosure heat dissipation area can be calculated by Equation 12.1:
P
AKT
.............................................................................................................................................(12.1)
where, A : Heat dissipation area [m2]
P : Loss generated in the control box [W]
T : Difference between internal and ambient temperatures [ ]
K : Heat dissipation coefficient [5 to 6]
When calculating the heat dissipation area with Equation 12.1, assume that P is the sum of all losses
generated in the enclosure. Refer to Table 12.1 for heat generated by the servo amplifier. "A" indicates
the effective area for heat dissipation, but if the enclosure is directly installed on an insulated wall,
that extra amount must be added to the enclosure's surface area.
The required heat dissipation area will vary wit the conditions in the enclosure. If convection in the
enclosure is poor and heat builds up, effective heat dissipation will not be possible. Therefore,
arrangement of the equipment in the enclosure and the use of a fan should be considered.
Table 12.1 lists the enclosure dissipation area for each servo amplifier when the servo amplifier is
operated at the ambient temperature of 40 (104 ) under rated load.
(Outside) (Inside)
Air flow
Fig. 12.2 Temperature distribution in enclosure
When air flows along the outer wall of the enclosure, effective heat exchange will be possible, because
the temperature slope inside and outside the enclosure will be steeper.

12 - 3
12. CHARACTERISTICS
12.3 Dynamic brake characteristics
Fig. 12.3 shows the pattern in which the servo motor comes to a stop when the dynamic brake is operated.
Use Equation 12.2 to calculate an approximate coasting distance to a stop. The dynamic brake time
constant varies with the servo motor and machine operation speeds. (Refer to Fig. 12.4)
V0Time constant
Emergency stop(EMG) OFF
ON
Machine speed
teTime
Fig. 12.3 Dynamic brake operation diagram
Lmax 60
V0JL
JM
te1.......................................................................................................................(12.2)
Lmax : Maximum coasting distance.................................................................................................[mm][in]
Vo : Machine rapid feedrate......................................................................................... [mm/min][in/min]
JM: Servo motor inertial moment.................................................................................[kg cm2][oz in2]
JL: Load inertia moment converted into equivalent value on servo motor shaft.....[kg cm2][oz in2]
: Brake time constant........................................................................................................................[s]
te: Delay time of control section...........................................................................................................[s]
(There is internal relay delay time of about 30ms.)
0
14
16
2
4
8
10
6
12
0 500 1000 1500 2000 2500 3000
13
73
23
43
Speed [r/min]
Time constant [ms]
0
0.005
0.01
0.015
0.02
0.025
0.03
0.035
0.04
0.045
0 500 1000 1500 2000
202
102 152
52
Speed [r/min]
Time constant [s]
a. HC-KFE series b. HC-SFE series
Fig. 12.4 Dynamic brake time constant
Use the dynamic brake at the load inertia moment indicated in the following table. If the load inertia
moment is higher than this value, the built-in dynamic brake may burn. If there is a possibility that the
load inertia moment may exceed the value, contact Mitsubishi.
Servo amplifier Load inertia moment ratio [times]
MR-E-10A to MR-E-200A 30

12 - 4
12. CHARACTERISTICS
12.4 Encoder cable flexing life
The flexing life of the cables is shown below. This graph calculated values. Since they are not guaranteed
values, provide a little allowance for these values.
1 107
5 107
1 108
5 106
1 106
5 105
1 105
5 104
1 104
5 103
1 103
a
Flexing life [times]
4 7 10 20 40 70 100 200
Flexing radius [mm]
a : Long flexing-life encoder cable
MR-EKCBL M-H
MR-ESCBL M-H
MR-ENCBL M-H

13 - 1
13. OPTIONS AND AUXILIARY EQUIPMENT
13. OPTIONS AND AUXILIARY EQUIPMENT
WARNING
Before connecting any option or auxiliary equipment, make sure that the charge
lamp is off more than 10 minutes after power-off, then confirm the voltage with a
tester or the like. Otherwise, you may get an electric shock.
CAUTION Use the specified auxiliary equipment and options. Unspecified ones may lead to a
fault or fire.
13.1 Options
13.1.1 Regenerative brake options
CAUTION The specified combinations of regenerative brake options and servo amplifiers
may only be used. Otherwise, a fire may occur.
(1) Combination and regenerative power
The power values in the table are resistor-generated regenerative powers and not rated powers.
Regenerative power[W]
Servo amplifier Built-in regenerative
brake resistor
MR-RB032
[40 ]
MR-RB12
[40 ]
MR-RB32
[40 ]
MR-RB30
[13 ]
(Note)
MR-RB50
[13 ]
MR-E-10A 30
MR-E-20A 30 100
MR-E-40A 10 30 100
MR-E-70A 20 30 100 300
MR-E-100A 20 30 100 300
MR-E-200A 100 300 500
Note: Always install a cooling fan.
(2) Selection of the regenerative brake option
(a) Simple selection method
In horizontal motion applications, select the regenerative brake option as described below:
When the servo motor is run without load in the regenerative mode from the running speed to a
stop, the permissible duty is as indicated in Section 5.1 of the separately available Servo Motor
Instruction Manual.
For the servo motor with a load, the permissible duty changes according to the inertia moment of
the load and can be calculated by the following formula:
Permissible
duty Permissible duty for servo motor with no load (value indication Section 5.1 in Servo Motor Instruction Manual)
(m 1)
ratedspeed
running speed [times/min]
2
where m load inertia moment/servo motor inertia moment
From the permissible duty, find whether the regenerative brake option is required or not.
Permissible duty number of positioning times [times/min]
Select the regenerative brake option out of the combinations in (1) in this section.

13 - 2
13. OPTIONS AND AUXILIARY EQUIPMENT
(b) To make selection according to regenerative energy
Use the following method when regeneration occurs continuously in vertical motion applications or
when it is desired to make an in-depth selection of the regenerative brake option:
a. Regenerative energy calculation
Use the following table to calculate the regenerative energy.
M
Friction
torque
Unbalance torque
TF
TU
Servo motor speed
Generated torque
Time
Up
No
tf(1 cycle)
Down
( )
( )
(Driving)
(Regenerative)
Tpsd2
t2 t3 t4t1
Tpsa2
Tpsd1
Tpsa1
1)
2)
3)
4) 5)
6)
7)
8)
Formulas for calculating torque and energy in operation
Regenerative power Torque applied to servo motor [N m] Energy [J]
1) T1(JL JM)
9.55 104
N01
Tpsa1 TUTFE12
0.1047 N0T1Tpsa1
2) T2 TU TFE2 0.1047 N0T2t1
3) T3(JL JM)
9.55 104
N01
Tpsd1 TUTFE32
0.1047 N0T3Tpsd1
4), 8) T4 TUE40 (No regeneration)
5) T5(JL JM)
9.55 104
N01
Tpsa2 TUTFE52
0.1047 N0T5Tpsa2
6) T6 TU TFE6 0.1047 N0T6t3
7) T7(JL JM)
9.55 104
N01
Tpsd2 TUTFE72
0.1047 N0T7Tpsd2
From the calculation results in 1) to 8), find the absolute value (Es) of the sum total of negative
energies.
b. Losses of servo motor and servo amplifier in regenerative mode
The following table lists the efficiencies and other data of the servo motor and servo amplifier in
the regenerative mode.
Servo amplifier Inverse efficiency[%] Capacitor charging[J]
MR-E-10A(1) 55 9
MR-E-20A(1) 70 9
MR-E-40A(1) 85 11
MR-E-70A 80 18
MR-E-100A 80 18
MR-E-200A 85 40
Inverse efficiency ( ) :Efficiency including some efficiencies of the servo motor and servo
amplifier when rated (regenerative) torque is generated at rated speed.
Since the efficiency varies with the speed and torque, allow for about 10%.
Capacitor charging (Ec) :Energy charged into the electrolytic capacitor in the servo amplifier.

13 - 3
13. OPTIONS AND AUXILIARY EQUIPMENT
Subtract the capacitor charging from the result of multiplying the sum total of regenerative energies by
the inverse efficiency to calculate the energy consumed by the regenerative brake option.
ER [J] Es Ec
Calculate the power consumption of the regenerative brake option on the basis of single-cycle operation
period tf [s] to select the necessary regenerative brake option.
PR [W] ER/tf............................................................................................(13.1)
(3) Connection of the regenerative brake option
Set parameter No.2 according to the open to be used.
Parameter No.0
Selection of regenerative
0: Not used.
2: MR-RB032
3: MR-RB12
4: MR-RB32
5: MR-RB30
6: MR-RB50
(4) Connection of the regenerative brake option
The regenerative brake option will generate heat of about 100 . Fully examine heat dissipation,
installation position, used cables, etc. before installing the option. For wiring, use flame-resistant
cables and keep them clear of the regenerative brake option body. Always use twisted cables of max.
5m(16.4ft) length for connection with the servo amplifier.
Always remove the wiring from across P-D and fit the regenerative brake option across P-C.
The G3 and G4 terminals act as a thermal protector. G3-G4 are disconnected when the regenerative
brake option overheats abnormally.
Servo amplifier
Regenerative brake option
Note: 1. When using the MR-RB50, forcibly cool it with a cooling fan (1.0m3/min, 92 or so).
2. Make up a sequence which will switch off the magnetic contactor (MC) when
abnormal heating occurs.
(Note2)
5m (16.4 ft) max.
D
PP
C
G3
G4
C
Always remove the lead from across P-D.
G3-G4 contact specifications
Maximum voltage: 120V AC/DC
Maximum current: 0.5A/4.8VDC
Maximum capacity: 2.4VA
Fan (Note 1)

13 - 4
13. OPTIONS AND AUXILIARY EQUIPMENT
(5) Outline drawing
(a) MR-RB032 MR-RB12
LA
5 (0.20)
LB
TE1
6 (0.23)
6 (0.23) 156 (6.14)
168 (6.61)
144 (5.67)
12 (0.47)
6 (0.23)
12 (0.47)
20
(0.79) LD
1.6 (0.06)
LC
G3
G4
P
C
[Unit: mm (in)]
6 (0.24) mounting hole
MR-RB
TE1
Terminal block
G4
G3
C
P
Terminal screw: M3
Tightening torque:
0.5 to 0.6 [N m](4 to 5 [lb in])
Variable dimensions Weight
Regenerative
brake option
Regenerative
power[W]
Resistance
[]LA LB LC LD [kg] [lb]
MR-RB032 30 40 30
(1.18) 15
(0.59) 119
(4.69) 99
(3.9) 0.5 1.1
MR-RB12 100 40 40
(1.57) 15
(0.59) 169
(6.69) 149
(5.87) 1.1 2.4
(b) MR-RB32 MR-RB30
79
(7.05)
150(5.91)
125(4.92)
Terminal
block 7(0.28)
10
(0.39)
3.2(0.13)
318(12.52) 17
(0.67)
90
(3.54)
100(3.94)
[Unit: mm (in)]
Terminal block
G4
G3
C
P
Terminal screw: M4
Tightening torque: 1.2 [N m](10 [lb in]
)
Weight
Regenerative
brake option
Regenerative
power[W]
Resistance
[][kg] [lb]
MR-RB32 300 40 2.9 6.4
MR-RB30 300 13 2.9 6.4

13 - 5
13. OPTIONS AND AUXILIARY EQUIPMENT
(c) MR-RB50
[Unit: mm (in)]
7 14 slot
7(0.28)
12
(0.47)
116(4.57)
128(5.04)
17(0.67)200(7.87)
2.3(0.09)
350(13.78)
325(12.80)
Terminal
block Terminal block
G4
G3
C
P
Terminal screw: M4
Tightening torque: 1.2 [N m](10 [lb in]
)
Weight
Regenerative
brake option
Regenerative
power [W]
Resistance
[][kg] [lb]
MR-RB50 500 13 5.6 12.3

13 - 6
13. OPTIONS AND AUXILIARY EQUIPMENT
13.1.2 Cables and connectors
(1) Cable make-up
The following cables are used for connection with the servo motor and other models. Those indicated
by broken lines in the figure are not options.
Regenerative
brake option
Servo amplifier
HC-SFE
HC-KFE
Operation
panel
Controller
1) 2)
3) 4) 5)
7) 8)
6)
9)
15) 16) 17)
18) 19)
To U, V, W,
Personal
compute
r
14)
Power
supply
12)
20) 21)
24) 25)
13)
13)
Analog monitor
Analog monitor
10) 11)
22) 23)

13 - 7
13. OPTIONS AND AUXILIARY EQUIPMENT
No. Product Model Description Application
1) Standard encoder
cable MR-EKCBL M-L
Refer to (2) (a) in
this section.
(Note)
(molex or equivalent) Housing: 1-172161-9
Connector pin: 170359-1
(AMP or equivalent)
Standard
flexing life
IP20
2) Long flexing life
encoder cable MR-EKCBL M-H
Refer to (2) (b) in
this section.
Long flexing
life
IP20
3) Standard encoder
cable MR-ESCBL M-L
Refer to (2) (c) in
this section.
(Note)
(molex or equivalent) Plug: MS3106B20-29S
Cable clamp: MS3057-12A
(Japan Aviation Electronics)
Standard
flexing life
IP20
4) Long flexing life
encoder cable MR-ESCBL M-H
Refer to (2) (d) in
this section.
Long flexing
life
IP20
(Note)
(molex or equivalent) Plug: MS3106A20-29S (D190)
Cable clamp
: CE3057-12A-3 (D265)
Back shell: CE02-20BS-S
(DDK)
5) IP65-compliant
encoder cable MR-ENECBL M-H
Refer to (2) (d) in
this section.
Long flexing
life
IP65
IP67
Not oil-
resistant.
(Note)
(molex or equivalent) Housing: 1-172161-9
Pin: 170359-1
Cable clamp: MTI-0002
(AMP or equivalent)
6) Encoder
connector set MR-ECNM IP20
(Note)
(molex or equivalent) Plug: MS3106B20-29S
Cable clamp: MS3057-12A
(JAE)
7) Encoder
connector set MR-ECNS IP20
(Note)
(molex or equivalent) Plug: MS3106A20-29S (D190)
Cable clamp
: CE3057-12A-3 (D265)
Back shell: CE02-20BS-S
(DDK)
8) Encoder
connector set MR-ENECNS IP65
IP67
9) Control signal
connector set MR-ECN1
(In units of 20 pcs.
/box)
Connector: 10126-3000VE
Shell kit: 10326-52F0-008
(3M or equivalent)
10) Amplifier power
supply connector
set
(Insulation
displacement type)
MR-E-10A to 100A
MR-ECNP1-A
(In units of 20 pcs.
/box)
Connector: 51240-0600
(molex or equivalent) Terminal: 56125-0118
(molex or equivalent) Insulation
displacement
type
11) Amplifier power
supply connector
set
(Insertion type)
MR-E-10A to 100A
MR-ECNP1-B
(In units of 20 pcs.
/box)
Connector: 54927-0610
(molex or equivalent) Insertion
type
Note: The models of the soldering type are 54593-1011 (connector housing), 54594-1015 (cover A), 54595-1005 (cover B), 58935-1000
(shell cover), 58934-1000 (shell body), 58937-0000 (cable clamp) and 58203-0010 (screw).
The models of the insulation displacement type are 51209-1001 (connector housing), 54594-1015 (cover A), 54595-1005 (cover
B), 58935-1000 (shell cover), 58934-1000 (shell body), 59351-8187 (terminal), 58937-0000 (cable clamp) and 58203-0010
(screw).

13 - 8
13. OPTIONS AND AUXILIARY EQUIPMENT
No. Product Model Description Application
12)
Analog monitor
RS-232C branch
cable
MR-E3CBL15-P Connector: MP371/6 Connector: MJ372/6
(Marushin Musen Denki or
equivalent)
Analog
monitor RS-
232C branch
cable
13) Analog monitor
RS-232C
connector
MR-ECN3
(In units of 20 pcs.
/box)
Connector: MP371/6
(Marushin Musen Denki or
equivalent)
Analog
monitor for
RS-232C
Connector: MP371/6
(Mini-DIN 6-pin male)
(Marushin Musen Denki or
equivalent)
Connector: DE-9SF-N
Case: DE-C1-J6-S6
(JAE)
14)
Communication
cable Refer to (3) in this
section.
QC30R2
For
connection
with PC-AT
compatible
personal
computer
15)
Motor power supply
connector set MR-PWCNS1
Refer to Servo
Motor Instruction
Manual.
Plug: CE05-6A22-23SD-B-BSS
Cable clamp: CE3057-12A-2 (D265)
(DDK)
16)
Motor power
supply connector
set
MR-PWCNS2
Refer to Servo
Motor Instruction
Manual.
Plug: CE05-6A24-10SD-B-BSS
Cable clamp: CE3057-16A-2 (D265)
(DDK)
Must be
used for
compliance
with the EN
Standard.
IP65
IP67
17)
Brake connector
set MR-BKCN
Refer to Servo
Motor Instruction
Manual.
Plug: MS3106A10SL-4S (D190) (DDK)
Cable connector: YS010-5-8 (Daiwa Dengyo) EN
Standard-
compliant
IP65 IP67
18) Motor power
supply connector
set
MR-PWCNK1 Plug: 5559-04P-210
Terminal: 5558PBT3L (for AWG16) (6 pcs.)
(molex)
IP20
19) Motor power
supply connector
set
MR-PWCNK2 Plug: 5559-06P-210
Terminal: 5558PBT3L (for AWG16) (8 pcs.)
(molex)
For motor
with brake
IP20
20)
Motor power
supply connector
(Insulation
displacement type)
MR-E-10A to 100A
MR-ECNP2-A
(In units of 20 pcs.
/box)
Connector: 51240-0300
(molex or equivalent) Terminal: 56125-0118
(molex or equivalent) Insulation
displacement
type
21)
Motor power
supply connector
(Insertion type)
MR-E-10A to 100A
MR-ECNP2-B
(In units of 20 pcs.
/box)
Connector: 54927-0310
(molex or equivalent) Insertion
type
22)
Amplifier power
supply connector
set
(Insulation
displacement type)
MR-E-200A
MR-ECNP1-A1
(In units of 20 pcs.
/box)
Connector: 54241-0600
(molex or equivalent) Terminal: 56125-0118
(molex or equivalent) Insulation
displacement
type
23)
Amplifier power
supply connector
set
(Insertion type)
MR-E-200A
MR-ECNP1-B1
(In units of 20 pcs.
/box)
Connector: 54928-0610
(molex or equivalent) Insertion
type
24)
Motor power
supply connector
(Insulation
displacement type)
MR-E-10A to 100A
MR-ECNP2-A1
(In units of 20 pcs.
/box)
Connector: 54241-0300
(molex or equivalent) Terminal: 56125-0118
(molex or equivalent) Insulation
displacement
type
25)
Motor power
supply connector
(Insertion type)
MR-E-10A to 100A
MR-ECNP2-B1
(In units of 20 pcs.
/box)
Connector: 54928-0310
(molex or equivalent) Insertion
type

13 - 9
13. OPTIONS AND AUXILIARY EQUIPMENT
(2) Encoder cable
CAUTION If you have fabricated the encoder cable, connect it correctly.
Otherwise, misoperation or explosion may occur.
POINT
The encoder cable is not oil resistant.
Refer to Section 12.4 for the flexing life of the encoder cable.
When the encoder cable is used, the sum of the resistance values of the
cable used for P5 and the cable used for LG should be within 2.4 .
When soldering the wire to the connector pin, insulate and protect the
connection portion using heat-shrinkable tubing.
When using the encoder cable of four-wire type communication system,
set "1 " in parameter No. 20 to select the four-wire type.
Generally use the encoder cable available as our options. If the required length is not found in the
options, fabricate the cable on the customer side.
When fabricating an encoder cable, use the recommended wires given in Section 13.2.1 and the MR-
ECNM connector set for encoder cable fabrication, and fabricate an encoder cable as shown in the
wiring diagram.
Refer to section 14.5 and choose the encode side connector according to the servo motor installation
environment.
(a) MR-EKCBL M-L (standard flex life model)
These encoder cables are used with the HC-KFE series servo motors.
1) Model explanation
Standard flex life
Model: MR-EKCBL M-L
Symbol Cable Length [m(ft)] Communication System
2 (6.56)
5 (16.4)
10 (32.8)
20 (65.6)
30 (98.4)
Two-wire type
(Note) Four-wire type
Note: Set "1 " in parameter No. 20.
2
5
10
20
30
2) Connection diagram
For the pin assignment on the servo amplifier side, refer to Section 3.3.1.
123
456
789
MR MRR
MD MDR
P5E SHD
Encoder connecto
r
172161-9 (AMP)
CN2
30cm
(0.98ft)
Servo amplifier
Encoder connector
Encoder cable
supplied to servo motor
Servo motor
Encoder
Encoder cable
(option or fabricated)
50m(164.0ft) max. CONT
P5G

13 - 10
13. OPTIONS AND AUXILIARY EQUIPMENT
Encoder cable of less than 30m
When fabricating an encoder cable, use the MR-ECNM connector set. Referring to the following
wiring diagram, you can fabricate an encoder cable of up to less than 30m.
MRR
P5
LG
1
2
MR 3
4
3
7
9
SD
1
2
8
9
MR-EKCBL20M-L
P5G
MR
MRR
SHD
P5E
P5
LG
1
2
MR
MRR
3
4
3
7
9
SD
1
2
8
9
MR-EKCBL2M-L
MR-EKCBL5M-L
MR-EKCBL10M-L
P5G
MR
MRR
SHD
P5E
Servo amplifier side Encoder side
Plate Plate
Servo amplifier side Encoder side
(Note) (Note)
Note. When an encoder cable is fabricated, this wire is not required.
AWG23
Encoder cable of 30m or more
POINT
The communication system of the encoder cable in this wiring diagram is
the four-wire type. Set "1 " in parameter No. 20.
When fabricating an encoder cable, use the MR-ECNM connector set. Referring to the following
wiring diagram, you can fabricate an encoder cable of up to 50m.
MRR
P5
LG
1
2
MR 3
4
MDR 8 5
3
7
4
MD 7
9
SD
1
2
8
9
MR-EKCBL30M-L
P5G
MR
MRR
MDR
MD
SHD
P5E
6CONT
Servo amplifier side Encoder side
Plate
(Note)
Note. When an encoder cable is fabricated, this wire is not required.

13 - 11
13. OPTIONS AND AUXILIARY EQUIPMENT
(b) MR-EKCBL M-H (long flex life model)
Use this encoder cable with the HC-KFE series servo motor.
1) Model explanation
Long flex life
Model: MR-EKCBL M-H
Symbol Cable Length [m(ft)] Communication System
2 (6.56)
5 (16.4)
10 (32.8)
20 (65.6)
30 (98.4)
Two-wire type
(Note) Four-wire type
Note: Set "1 " in parameter No. 20.
2
5
10
20
30
40
50
40 (131.2)
50 (164.0)
2) Connection diagram
For the pin assignment on the servo amplifier side, refer to Section 3.3.1.
123
456
789
MR MRR
MD MDR
P5E SHD
Encoder connecto
r
172161-9 (AMP)
CN2
30cm
(0.98ft)
Servo amplifier
Encoder connector
Encoder cable
supplied to servo motor
Servo motor
Encoder
Encoder cable
(option or fabricated)
50m(164.0ft) max. CONT
P5G
Encoder cable of less than 30m
When fabricating an encoder cable, use the MR-ECNM connector set. Referring to the following
wiring diagram, you can fabricate an encoder cable of up to less than 30m.

13 - 12
13. OPTIONS AND AUXILIARY EQUIPMENT
MRR
MRR
P5
LG
1
2
MR 3
4
3
7
9
SD
1
2
8
9
MR-EKCBL20M-H
P5G
MR
MRR
SHD
P5E
P5
LG
1
2
MR 3
4
3
7
9
SD
1
2
8
9
MR-EKCBL2M-H
MR-EKCBL5M-H
MR-EKCBL10M-H
P5G
MR
MRR
SHD
P5E
Servo amplifier side Encoder side
Plate Plate
Servo amplifier side Encoder side
(Note) (Note)
Note. When an encoder cable is fabricated, this wire is not required.
Encoder cable of 30m or more
POINT
The communication system of the encoder cable in this wiring diagram is
the four-wire type. Set "1 " in parameter No. 20.
When fabricating an encoder cable, use the MR-ECNM connector set. Referring to the following
wiring diagram, you can fabricate an encoder cable of up to 50m.
MRR
P5
LG
1
2
MR 3
4
MDR 8 5
3
7
4
MD 7
9
SD
1
2
8
9
MR-EKCBL30M-H
MR-EKCBL40M-H
MR-EKCBL50M-H
P5G
MR
MRR
MDR
MD
SHD
P5E
6CONT
Servo amplifier side Encoder side
Plate
(Note)
Note. When an encoder cable is fabricated, this wire is not required.

13 - 13
13. OPTIONS AND AUXILIARY EQUIPMENT
(c) MR-ESCBL M-L (standard flex life model)
These encoder cables are used with the HC-SFE series servo motors.
1) Model explanation
Standard flex life
Model: MR-ESCBL M-L
Symbol Cable Length [m(ft)] Communication System
2 (6.56)
5 (16.4)
10 (32.8)
20 (65.6)
30 (98.4)
Two-wire type
(Note) Four-wire type
Note: Set "1 " in parameter No. 20.
2
5
10
20
30
2) Connection diagram
For the pin assignment on the servo amplifier side, refer to Section 3.3.1.
CN2
ABC
D
E
F
G
H
J
K
LMA
B
CMR
DMRR
E
F
G
H
J
K
L
M
NSHD
P
RLG
SP5
T
Servo amplifier
50m(164.0ft) max.
Encoder connector
Servo motor
Encoder
Encoder connector Pin Signal
Encoder cable
(Optional or fabricated)
Pin Signal
R
S
TP
N
MD
MDR CONT
Encoder cable of less than 30m
When fabricating an encoder cable, use the MR-ECNS connector set. Referring to the following
wiring diagram, you can fabricate an encoder cable of up to less than 30m.
MRR
MRR
P5
LG
1
2
MR 3
4
F
S
9
SD
C
D
R
N
MR-ESCBL20M-L
P5G
MR
MRR
SHD
P5E
P5
LG
1
2
MR 3
4
F
S
9
SD
C
D
R
N
MR-ESCBL2M-L
MR-ESCBL5M-L
MR-ESCBL10M-L
P5G
MR
MRR
SHD
P5E
AWG23
Servo amplifier side Encoder side
Plate Plate
Servo amplifier side Encoder side
(Note) (Note)
Note. When an encoder cable is fabricated, this wire is not required.

13 - 14
13. OPTIONS AND AUXILIARY EQUIPMENT
Encoder cable of 30m or more
POINT
The communication system of the encoder cable in this wiring diagram is
the four-wire type. Set "1 " in parameter No. 20.
When fabricating an encoder cable, use the MR-ECNS connector set. Referring to the following
wiring diagram, you can fabricate an encoder cable of up to 50m.
MRR
P5
LG
1
2
MR 3
4
MDR 8 B
F
S
A
MD 7
9
SD
C
D
R
N
MR-ESCBL30M-L
P5G
MR
MRR
MDR
MD
SHD
P5E
MCONT
Servo amplifier side Encoder side
Plate
(Note)
Note. When an encoder cable is fabricated, this wire is not required.

13 - 15
13. OPTIONS AND AUXILIARY EQUIPMENT
(d) MR-ESCBL M-H (long flex life model) MR-ENECBL M-H (IP65/IP67-compatible, long flex life
model)
These encoder cables are used with the HC-SFE series servo motors.
1) Model explanation
Long flex life
Model: MR-ESCBL M-H
Symbol Cable Length [m(ft)] Communication System
2 (6.56)
5 (16.4)
10 (32.8)
20 (65.6)
30 (98.4)
Two-wire type
(Note) Four-wire type
Note: Set "1 " in parameter No. 20.
2
5
10
20
30
40
50
40 (131.2)
50 (164.0)
Model: MR-ENECBL M-H
Long flex life
Symbol Cable Length [m(ft)] Communication System
2 (6.56)
5 (16.4)
10 (32.8)
20 (65.6)
30 (98.4)
Two-wire type
(Note) Four-wire type
Note: Set "1 " in parameter No. 20.
2
5
10
20
30
40
50
40 (131.2)
50 (164.0)

13 - 16
13. OPTIONS AND AUXILIARY EQUIPMENT
2) Connection diagram
For the pin assignment on the servo amplifier side, refer to Section 3.3.1.
CN2
ABC
D
E
F
G
H
J
K
LMA
B
CMR
DMRR
E
F
G
H
J
K
L
M
NSHD
P
RLG
SP5
T
Servo amplifier
50m(164.0ft) max.
Encoder connector
Servo motor
Encoder
Encoder connector Pin Signal
Encoder cable
(Optional or fabricated)
Pin Signal
R
S
TP
N
MD
MDR CONT
Encoder cable of less than 30m
When fabricating an encoder cable, use the MR-ECNS (IP20-compatible model) or MR-ENECNS
(IP65/IP67-compatible model) connector set. Referring to the following wiring diagram, you can
fabricate an encoder cable of up to less than 30m.
MRRMRR
P5
LG
1
2
MR 3
4
F
S
9
SD
C
D
R
N
MR-ESCBL20M-H
MR-ENECBL20M-H
P5G
MR
MRR
SHD
P5E
P5
LG
1
2
MR 3
4
F
S
9
SD
C
D
R
N
MR-ESCBL2M-H
MR-ESCBL5M-H
MR-ESCBL10M-H
MR-ENECBL2M-H
MR-ENECBL5M-H
MR-ENECBL10M-H
P5G
MR
MRR
SHD
P5E
Servo amplifier side Encoder side
Plate Plate
Servo amplifier side Encoder side
(Note) (Note)
Note. When an encoder cable is fabricated, this wire is not required.

13 - 17
13. OPTIONS AND AUXILIARY EQUIPMENT
Encoder cable of 30m or more
POINT
The communication system of the encoder cable in this wiring diagram is
the four-wire type. Set "1 " in parameter No. 20.
When fabricating an encoder cable, use the MR-ECNS (IP20-compatible model) or MR-ENECNS
(IP65/IP67-compatible model) connector set. Referring to the following wiring diagram, you can
fabricate an encoder cable of up to 50m.
MRR
P5
LG
1
2
MR 3
4
MDR 8 B
F
S
A
MD 7
9
SD
C
D
R
N
MR-ESCBL30M-H
MR-ESCBL40M-H
MR-ESCBL50M-H
MR-ENECBL30M-H
MR-ENECBL40M-H
MR-ENECBL50M-H
P5G
MR
MRR
MDR
MD
SHD
P5E
MCONT
Servo amplifier side Encoder side
Plate
(Note)
Note. When an encoder cable is fabricated, this wire is not required.

13 - 18
13. OPTIONS AND AUXILIARY EQUIPMENT
(3) Communication cable
POINT
This cable may not be used with some personal computers. After fully
examining the signals of the RS-232C connector, refer to this section and
fabricate the cable.
(a) Model definition
Model: QC30R2 (Cable length 3[m](10[ft]))
(b) Connection diagram for fabrication
3
2
5
7
8
6
4
Plate
1
3
2
TXD
RXD
GND
RTS
CTS
DSR
DTR
SD
RXD
LG
TXD
D-SUB9 pins
MR-CPCATCBL3M
Personal computer side Servo amplifier side
Mini DIN 6 pins
When fabricating the cable, refer to the connection diagram in this section. Though this connection
diagram is not the connection diagram of the QC30R2, it is identical in functions.
The following must be observed in fabrication:
1) Always use a shielded, multi-core cable and connect the shield with SD securely.
2) The optional communication cable is 3m(10ft) long. When the cable is fabricated, its maximum
length is 15m(49ft) in offices of good environment with minimal noise.

13 - 19
13. OPTIONS AND AUXILIARY EQUIPMENT
13.1.3 Analog monitor, RS-232C branch cable (MR-E3CBL15-P)
(1) Usage
The analog monitor, RS-232C branch cable (MR-E3CBL15-P) is designed for use when a personal
computer and analog monitor outputs are used at the same time.
CN3
MO2
MO1
LG
LG
Servo amplifier
Analog monitor, RS-232C branch cable
(MR-E3CBL15-P) Communication cable
(QC30R2)
Analog monitor output 2
Analog monitor output 1
(2) Connection diagram
RXD 1
TXD 2
MO1 4
6
RS-232C
MO2 6
4MO1
MO2
SD
SD
3LG
SD
3
2TXD
LG
1RXD
SD
LG 3
Servo amplifier
Analog monitor
Plate
Plate
Plate
Plate

13 - 20
13. OPTIONS AND AUXILIARY EQUIPMENT
13.1.4 Servo configurations software
The servo configuration software (MRZJW3-SETUP154E) uses the communication function of the servo
amplifier to perform parameter setting changes, graph display, test operation, etc. on a personal
computer.
(1) Specifications
Item Description
Communication signal Conforms to RS-232C.
Baudrate [bps] 57600, 38400, 19200, 9600
Monitor Display, high speed monitor, trend graph
Minimum resolution changes with the processing speed of the personal computer.
Alarm Display, history, amplifier data
Diagnostic Digital I/O, no motor rotation, total power-on time, amplifier version info, motor information,
tuning data, absolute encoder data, automatic voltage control, Axis name setting.
Parameters Parameter list, turning, change list, detailed information
Test operation Jog operation, positioning operation, motor-less operation, Do forced output, program operation.
Advanced function Machine analyzer, gain search, machine simulation.
File operation Data read, save, print
Others Automatic demo, help display
(2) System configuration
(a) Components
To use this software, the following components are required in addition to the servo amplifier and
servo motor:
Model (Note 1) Description
(Note 2)
Personal
computer
IBM PC-AT compatible where the English version of Windows 95, Windows 98, Windows Me, Windows
NT Workstation 4.0 or Windows 2000 Professional operates
Processor: Pentium 133MHz or more (Windows 95, Windows 98, Windows NT Workstation 4.0,
Windows 2000 Professional)
Pentium 150MHz or more (Windows Me)
Memory: 16MB or more (Windows 95), 24MB or more (Windows 98)
32MB or more (Windows Me, Windows NT Workstation 4.0, Windows 2000 Professional)
Free hard disk space: 30MB or more
Serial port used
OS Windows 95, Windows 98, Windows Me, Windows NT Workstation 4.0, Windows 2000 Professional
(English version)
Display One whose resolution is 800 600 or more and that can provide a high color (16 bit) display.
Connectable with the above personal computer.
Keyboard Connectable with the above personal computer.
Mouse Connectable with the above personal computer. Note that a serial mouse is not used.
Printer Connectable with the above personal computer.
Communication
cable QC30R2
When this cannot be used, refer to (3) Section 13.1.2 and fabricate.
Note: 1. Windows and Windows NT are the registered trademarks of Microsoft Corporation in the United State and other countries.
2. On some personal computers, this software may not run properly.
(b) Configuration diagram
CN3 CN2
Personal computer
To RS-232C
connector
Communication cable
Servo amplifier
Servo motor

13 - 21
13. OPTIONS AND AUXILIARY EQUIPMENT
13.2 Auxiliary equipment
Always use the devices indicated in this section or equivalent. To comply with the EN Standard or UL/C-
UL (CSA) Standard, use the products which conform to the corresponding standard.
13.2.1 Recommended wires
(1) Wires for power supply wiring
The following diagram shows the wires used for wiring. Use the wires given in this section or
equivalent.
C
P
U
V
W
B1
B2
U
V
W
L1
L2
L3
D
Power supply
1) Power supply lead
Regenerative brake option
4) Regenerative brake option lead
(Note)
Servo amplifier
3) Motor power supply lead
5) Electromagnetic
brake lead
Encoder cable (refer to Section 13.1.2)
Motor
Electro-
magnetic
brake
Encoder
Servo motor
Note: When using the regenerative brake option, always remove the wiring across D-P.
The following table lists wire sizes. The wires used assume that they are 600V vinyl wires and the
wiring distance is 30m(98.4ft) max. If the wiring distance is over 30m(98.4ft), choose the wire size in
consideration of voltage drop.
Refer to Section 3.11 for connection with the connector (CNP1, CNP2).
The servo motor side connection method depends on the type and capacity of the servo motor. Refer to
Section 3.8.
To enable the built-in regenerative brake, connect the wiring across D-P. (Refer to Section 3.7.2 for the
connection method.)
To comply with the UL/C-UL (CSA) Standard, use UL-recognized copper wires rated at 60 (140 ) or
more for wiring.
Table 13.1 Recommended wires
(Note) Wires [mm2]
Servo amplifier 1) L1L2L33) U V W 4) P C5) B1B2
MR-E-10A
MR-E-20A
MR-E-40A
MR-E-70A
1.25 (AWG16)
MR-E-100A
2 (AWG14)
2 (AWG14)
MR-E-200A (Note) 2.5 (AWG14) (Note) 2.5 (AWG14)
2 (AWG14) 1.25 (AWG16)
Note: Use the heat-resistant PVC coble (more than 105 ), if AWG14 cable is used in ambient temperature more than 40 .

13 - 22
13. OPTIONS AND AUXILIARY EQUIPMENT
(2) Wires for cables
When fabricating a cable, use the wire models given in the following table or equivalent:
Table 13.2 Wires for option cables
Characteristics of one core
Type Model Length
[m(ft)]
Core size
[mm2]
Number
of Cores Structure
[Wires/mm]
Conductor
resistance[ /mm]
Insulation coating
ODd[mm] (Note 1)
(Note 3)
Finishing
OD [mm]
Wire model
0.3 4
(2 pairs) 12/0.18 65.7 1.3
2 to 10
(6.56 to 32.8) 0.08 4
(2 pairs) 7/0.127 234 0.67 7.3
(Note 4)
20276 composite 4-
pair shielded cable
(A-TYPE)
MR-EKCBL M-L
MR-ESCBL M-L 20 30
(65.6 98.4) 0.3 12
(6 pairs) 7/0.18 63.6 1.2 8.2 UL20276AWG#23
6 pair (BLACK)
2 to 10
(6.56 to 32.8) 0.2 12
(6 pairs) 40/0.08 105 0.88 7.2 (Note 2)
A14B2339 4P
20 (65.6) 0.2 12
(6 pairs) 40/0.08 105 0.88 7.2 (Note 2)
A14B2343 6P
Encoder cable
MR-EKCBL M-H
MR-ESCBL M-H
MR-ENECBL M-H 30 to 50
(98.4 to 164) 0.2 14
(7 pairs) 40/0.08 105 0.88 8.0 (Note 3)
J14B0238 (0.2 7P)
Communication
cable QC30R2 3 (9.84) 0.08 6
(3 pairs) 7/0.127 222 0.38 4.6 UL20276 AWG#28
3pair (BLACK)
Note 1: d is as shown below:
d
Conductor Insulation sheath
2: Purchased from Toa Electric Industry
3: Standard OD. Max. OD is about 10% greater.
4: BANDO ELECTRIC WIRE

13 - 23
13. OPTIONS AND AUXILIARY EQUIPMENT
13.2.2 No-fuse breakers, fuses, magnetic contactors
Always use one no-fuse breaker and one magnetic contactor with one servo amplifier. When using a fuse
instead of the no-fuse breaker, use the one having the specifications given in this section.
Fuse
Servo amplifier No-fuse breaker Class Current [A] Voltage [V] Magnetic contactor
MR-E-10A 30A frame 5A K5 10
MR-E-20A 30A frame 5A K5 10
MR-E-40A 30A frame 10A K5 15
MR-E-70A 30A frame 15A K5 15
MR-E-100A 30A frame 15A K5 15
S-N10
MR-E-200A 30A frame 20A K5 15
AC250
S-N18
13.2.3 Power factor improving reactors
The input power factor is improved to be about 90%. For use with a 1-phase power supply, it may be
slightly lower than 90%.
3-phase
200 to 230VAC
NFB
FR-BAL Servo amplifier
R
S
T
X
Y
Z
L1
L2
L3
MC
1-phase
230VAC
NFB
FR-BAL Servo amplifier
R
S
T
X
Y
Z
L1
L2
L3
MC
W
W1C
RXSYTZ
H 5
D1 5
Installation screw
D 5
[Unit : mm]
Dimensions [mm (in) ]
Servo amplifier Model WW1H D D1 C
Mounting
screw size
Terminal
screw size
Weight
[kg (lb)]
MR-E-10A/20A FR-BAL-0.4K 135 (5.31) 120 (4.72) 115 (4.53) 59 (2.32) 45 (1.77) 7.5 (0.29) M4 M3.5 2.0 (4.4)
MR-E-40A FR-BAL-0.75K 135 (5.31) 120 (4.72) 115 (4.53) 69 (2.72) 57 (2.24) 7.5 (0.29) M4 M3.5 2.8 (6.17)
MR-E-70A FR-BAL-1.5K 160 (6.30) 145 (5.71) 140 (5.51) 71 (2.79) 55 (2.17) 7.5 (0.29) M4 M3.5 3.7 (8.16)
MR-E-100A FR-BAL-2.2K 160 (6.30) 145 (5.71) 140 (5.51) 91 (3.58) 75 (2.95) 7.5 (0.29) M4 M3.5 5.6 (12.35)
MR-E-200A FR-BAL-3.7K 220 (8.66) 200 (7.87) 192 (7.56) 90 (3.54) 70 (2.76) 10 (0.39) M5 M4 8.5 (18.74)

13 - 24
13. OPTIONS AND AUXILIARY EQUIPMENT
13.2.4 Relays
The following relays should be used with the interfaces:
Interface Selection example
Input signals (interface DI-1) signals To prevent defective contacts , use a relay for small signal
(twin contacts).
(Ex.) Omron : type G2A , MY
Relay used for digital output signals (interface DO-1) Small relay with 12VDC or 24VDC of 40mA or less
(Ex.) Omron : type MY
13.2.5 Surge absorbers
A surge absorber is required for the electromagnetic brake. Use the following surge absorber or equivalent.
Insulate the wiring as shown in the diagram.
Maximum rating
Permissible circuit
voltage
Surge
immunity
Energy
immunity
Rated
power
Maximum
limit voltage
Static
capacity
(reference
value)
Varistor voltage
rating (range) V1mA
AC[Vma] DC[V] [A] [J] [W] [A] [V] [pF] [V]
140 180 (Note)
500/time 5 0.4 25 360 300 220
(198 to 242)
Note: 1 time 8 20 s
(Example) ERZV10D221 (Matsushita Electric Industry)
TNR-10V221K (Nippon chemi-con)
Outline drawing [mm] ( [in] ) (ERZ-C10DK221)
13.5 (0.53)
16.5
(0.65)
3.0 (0.12)
or less
30.0 (1.18)
or more
Crimping terminal
for M4 screw
Vinyl tube
4.7 1.0 (0.19 0.04)
0.8 (0.03)
13.2.6 Noise reduction techniques
Noises are classified into external noises which enter the servo amplifier to cause it to malfunction and
those radiated by the servo amplifier to cause peripheral devices to malfunction. Since the servo amplifier
is an electronic device which handles small signals, the following general noise reduction techniques are
required.
Also, the servo amplifier can be a source of noise as its outputs are chopped by high carrier frequencies. If
peripheral devices malfunction due to noises produced by the servo amplifier, noise suppression measures
must be taken. The measures will vary slightly with the routes of noise transmission.
(1) Noise reduction techniques
(a) General reduction techniques
Avoid laying power lines (input and output cables) and signal cables side by side or do not bundle
them together. Separate power lines from signal cables.
Use shielded, twisted pair cables for connection with the encoder and for control signal
transmission, and connect the shield to the SD terminal.
Ground the servo amplifier, servo motor, etc. together at one point (refer to Section 3.10).

13 - 25
13. OPTIONS AND AUXILIARY EQUIPMENT
(b) Reduction techniques for external noises that cause the servo amplifier to malfunction
If there are noise sources (such as a magnetic contactor, an electromagnetic brake, and many
relays which make a large amount of noise) near the servo amplifier and the servo amplifier may
malfunction, the following countermeasures are required.
Provide surge absorbers on the noise sources to suppress noises.
Attach data line filters to the signal cables.
Ground the shields of the encoder connecting cable and the control signal cables with cable clamp
fittings.
(c) Techniques for noises radiated by the servo amplifier that cause peripheral devices to malfunction
Noises produced by the servo amplifier are classified into those radiated from the cables connected
to the servo amplifier and its main circuits (input and output circuits), those induced
electromagnetically or statically by the signal cables of the peripheral devices located near the
main circuit cables, and those transmitted through the power supply cables.
Noises produced
by servo amplifier Noises transmitted
in the air Noise radiated directly
from servo amplifier
Magnetic induction
noise
Static induction
noise
Noises transmitted
through electric
channels
Noise radiated from the
power supply cable
Noise radiated from
servo motor cable
Noise transmitted through
power supply cable
Noise sneaking from
grounding cable due to
leakage current
Routes 4) and 5)
Route 1)
Route 2)
Route 3)
Route 7)
Route 8)
Route 6)
Instrument Receiver
Servo
amplifier
Servo motor SM
2)
2)
8)
1)
7)
7) 7)
5)
3)
4)
6)
3)
Sensor
power
supply
Sensor

13 - 26
13. OPTIONS AND AUXILIARY EQUIPMENT
Noise transmission route Suppression techniques
1) 2) 3)
When measuring instruments, receivers, sensors, etc. which handle weak signals and may
malfunction due to noise and/or their signal cables are contained in a control box together with the
servo amplifier or run near the servo amplifier, such devices may malfunction due to noises
transmitted through the air. The following techniques are required.
(1) Provide maximum clearance between easily affected devices and the servo amplifier.
(2) Provide maximum clearance between easily affected signal cables and the I/O cables of the servo
amplifier.
(3) Avoid laying the power lines (Input cables of the servo amplifier) and signal cables side by side or
bundling them together.
(4) Insert a line noise filter to the I/O cables or a radio noise filter on the input line.
(5) Use shielded wires for signal and power cables or put cables in separate metal conduits.
4) 5) 6)
When the power lines and the signal cables are laid side by side or bundled together, magnetic
induction noise and static induction noise will be transmitted through the signal cables and
malfunction may occur. The following techniques are required.
(1) Provide maximum clearance between easily affected devices and the servo amplifier.
(2) Provide maximum clearance between easily affected signal cables and the I/O cables of the servo
amplifier.
(3) Avoid laying the power lines (Input cables of the servo amplifier) and signal cables side by side
or bundling them together.
(4) Use shielded wires for signal and power cables or put the cables in separate metal conduits.
7)
When the power supply of peripheral devices is connected to the power supply of the servo
amplifier system, noises produced by the servo amplifier may be transmitted back through the
power supply cable and the devices may malfunction. The following techniques are required.
(1) Insert the radio noise filter (FR-BIF) on the power cables (Input cables) of the servo amplifier.
(2) Insert the line noise filter (FR-BSF01) on the power cables of the servo amplifier.
8) When the cables of peripheral devices are connected to the servo amplifier to make a closed loop
circuit, leakage current may flow to malfunction the peripheral devices. If so, malfunction may be
prevented by disconnecting the grounding cable of the peripheral device.
(2) Noise reduction products
(a) Data line filter
Noise can be prevented by installing a data line filter onto the encoder cable, etc.
For example, the ZCAT3035-1330 of TDK and the ESD-SR-25 of Tokin make are available as data
line filters.
As a reference example, the impedance specifications of the ZCAT3035-1330 (TDK) are indicated
below.
This impedances are reference values and not guaranteed values.
Impedance[ ]
10 to 100MHz 100 to 500MHz
80 150
Outline drawing (ZCAT3035-1330)
[Unit: mm]([Unit: in.])
Loop for fixing the
cable band
Lot number Product name
TDK
39 1(1.54 0.04)
34 1
(1.34 0.04)
13 1
(0.51 0.04)
30 1
(1.18 0.04)

13 - 27
13. OPTIONS AND AUXILIARY EQUIPMENT
(b) Surge suppressor
The recommended surge suppressor for installation to an AC relay, AC valve, AC electromagnetic
brake or the like near the servo amplifier is shown below. Use this product or equivalent.
Relay
This distance should be short
(within 20cm(0.79 in.)).
Surge suppressor
MS
Surge suppressor
Surge suppressor
(Ex.) 972A.2003 50411
(Matsuo Electric Co.,Ltd. 200VAC rating)
Outline drawing [Unit: mm] ([Unit: in.])
Rated
voltage
AC[V]
C [ F] R [Ω] Test voltage AC[V]
200 0.5 50
(1W) Across
T-C 1000(1 to 5s)
Blue vinyl cord Red vinyl cord
Vinyl sheath
200(7.87)
or more 200(7.87)
or more
6(0.24)
31(1.22)
10(0.39)or less 10(0.39)or less
15 1(0.59 0.04)
48 1.5
(1.89 0.06)
10 3
(0.39
0.15)
10 3
(0.39
0.12)
4(0.16)
18 1.5
(0.71 0.06)
Note that a diode should be installed to a DC relay, DC valve or
the like.
Maximum voltage: Not less than 4 times the drive voltage of
the relay or the like
Maximum current: Not less than twice the drive current of
the relay or the like
Diode
RA
(c) Cable clamp fitting (AERSBAN -SET)
Generally, the earth of the shielded cable may only be connected to the connector's SD terminal.
However, the effect can be increased by directly connecting the cable to an earth plate as shown
below.
Install the earth plate near the servo amplifier for the encoder cable. Peel part of the cable sheath
to expose the external conductor, and press that part against the earth plate with the cable clamp.
If the cable is thin, clamp several cables in a bunch.
The clamp comes as a set with the earth plate.
Strip the cable sheath of
the clamped area. cutter
cable
Cable clamp
(A,B)
Cable
Earth plate
External conductor
Clamp section diagram
40(1.57)

13 - 28
13. OPTIONS AND AUXILIARY EQUIPMENT
Outline drawing
Earth plate Clamp section diagram
(Note)M4 screw
11(0.43) 3 (0.12)
6 (0.24)
C
A
622(0.87)
17.5(0.69)
35(1.38)
35 (1.38)
L or less 10(0.39)
30(1.18)
7 (0.28)
24
0
0.2
Note: Screw hole for grounding. Connect it to the earth plate of the control box.
(0.24)
24
0.3
0
(0.940)
(0.940)
[Unit: mm]
([Unit: in.])
B 0.3(0.01)
2- 5(0.20) hole
installation hole
Type A B C Accessory fittings Clamp fitting L
AERSBAN-DSET 100
(3.94) 86
(3.39) 30
(1.18) clamp A: 2pcs. A 70
(2.76)
AERSBAN-ESET 70
(2.76) 56
(2.20) clamp B: 1pc. B 45
(1.77)

13 - 29
13. OPTIONS AND AUXILIARY EQUIPMENT
(d) Line noise filter (FR-BSF01)
This filter is effective in suppressing noises radiated from the power supply side and output side of
the servo amplifier and also in suppressing high-frequency leakage current (zero-phase current)
especially within 0.5MHz to 5MHz band.
Connection diagram Outline drawing [Unit: mm] ([Unit: in.])
Wind the 3-phase wires by the equal number of times in the
same direction, and connect the filter to the power supply side
and output side of the servo amplifier.
The effect of the filter on the power supply side is higher as the
number of winds is larger. The number of turns is generally four.
If the wires are too thick to be wound, use two or more filters
and make the total number of turns as mentioned above.
On the output side, the number of turns must be four or less.
Do not wind the grounding wire together with the 3-phase wires.
The filter effect will decrease. Use a separate wire for grounding.
Example 2
Two filters are used
(Total number of turns: 4)
Power
supply
Servo amplifier
Line noise
filter
NFB
L3
L1
L2
Example 1
(Number of turns: 4)
Power
supply
NFB
L1
L2
L3
Servo amplifier
Line noise
filter
3 (0.12)
FR-BSF01
110 (4.33)
95 (3.74)
22 (0.87)
65 (2.56)
65 (2.56)
33 (1.3)
2- 5 (0.20)
(e) Radio noise filter (FR-BIF)...for the input side only
This filter is effective in suppressing noises radiated from the power supply side of the servo
amplifier especially in 10MHz and lower radio frequency bands. The FR-BIF is designed for the
input side only.
Connection diagram Outline drawing (Unit: mm) ([Unit: in.])
NFB
Radio noise
filter
FR-BIF
L3
L2
L1
Servo amplifier
Power
supply
Make the connection cables as short as possible.
Grounding is always required. Leakage current: 4mA
29 (1.14)
58 (2.28)
42 (1.65)
4 (0.16)
Red BlueWhite Green
44 (1.73)
29 (1.14) 7 (0.28)
hole
About 300(11.81)
5 (0.20)

13 - 30
13. OPTIONS AND AUXILIARY EQUIPMENT
13.2.7 Leakage current breaker
(1) Selection method
High-frequency chopper currents controlled by pulse width modulation flow in the AC servo circuits.
Leakage currents containing harmonic contents are larger than those of the motor which is run with a
commercial power supply.
Select a leakage current breaker according to the following formula, and ground the servo amplifier,
servo motor, etc. securely.
Make the input and output cables as short as possible, and also make the grounding cable as long as
possible (about 30cm (11.8 in)) to minimize leakage currents.
Rated sensitivity current 10 {Ig1 Ign Iga K(Ig2 Igm)} [mA] ..........(13.2)
K: Constant considering the harmonic contents
Leakage current breaker
Type Mitsubishi
products
K
Models provided with
harmonic and surge
reduction techniques
NV-SP
NV-SW
NV-CP
NV-CW
NV-L
1
General models BV-C1
NFB
NV-L 3
SM
Servo
amplifier
Noise
filter
NV
Ig1 Ign Iga Ig2 Igm
Cable
Cable
Ig1: Leakage current on the electric channel from the leakage current breaker to the input terminals
of the servo amplifier (Found from Fig. 13.1.)
Ig2: Leakage current on the electric channel from the output terminals of the servo amplifier to the
servo motor (Found from Fig. 13.1.)
Ign: Leakage current when a filter is connected to the input side (4.4mA per one FR-BIF)
Iga: Leakage current of the servo amplifier (Found from Table 13.4.)
Igm: Leakage current of the servo motor (Found from Table 13.3.)
Table 13.3 Servo motor's
leakage current
example (Igm)
Table 13.4 Servo amplifier's
leakage current
example (Iga)
Servo motor
output [kW]
Leakage
current [mA]
Servo amplifier
capacity [kW]
Leakage
current [mA]
0.1 to 1.0 0.1 0.1 to 0.6 0.1
1.0 to 2.2 0.2 0.7 to 2.0 0.15
Table 13.5 Leakage circuit breaker selection example
Servo amplifier
Rated sensitivity
current of leakage
circuit breaker [mA]
120
100
80
60
40
20
023.5
5.5
81422388015
0
30 60 100
Fig. 13.1 Leakage current example
(Ig1, Ig2) for CV cable run
in metal conduit
Cable size[mm2]
[mA]
Leakage current
MR-E-10A to MR-E-200A 15

13 - 31
13. OPTIONS AND AUXILIARY EQUIPMENT
(2) Selection example
Indicated below is an example of selecting a leakage current breaker under the following conditions:
SM
NV
Ig1 Iga Ig2 Igm
Servo
amplifier
MR-E-40A
2mm2 5m 2mm2 5m
Servo motor
HC-KFE73
Use a leakage current breaker generally available.
Find the terms of Equation (13.2) from the diagram:
Ig1 20 1000
50.1 [mA]
Ig2 20 1000
50.1 [mA]
Ign 0 (not used)
Iga 0.1 [mA]
Igm 0.1 [mA]
Insert these values in Equation (13.2):
Ig 10 {0.1 00.1 1(0.1 0.1)}
4.0 [mA]
According to the result of calculation, use a leakage current breaker having the rated sensitivity
current (Ig) of 4.0[mA] or more. A leakage current breaker having Ig of 15[mA] is used with the NV-
SP/SW/CP/CW/HW series.

13 - 32
13. OPTIONS AND AUXILIARY EQUIPMENT
13.2.8 EMC filter
For compliance with the EMC Directive of the EN Standard, it is recommended to use the following filter:
Some EMC filters are large in leakage current.
(1) Combination with the servo amplifier
Recommended filter
Servo amplifier Model Leakage current [mA] Weight [kg]([lb])
MR-E-10A to MR-E-100A SF1252 38 0.75 (1.65)
MR-E-200A SF1253 57 1.37 (1.65)
(2) Connection example
NFB
L1
L2
L3
L1
L2
L3
LINE LOAD
3-phase
200 to 230V AC,
1-phase
230VAC or
1-phase
100 to120VAC
EMC filter Servo amplifier
(Note 1) Power supply
(Note 2)
Note: 1. For 1-phase 230VAC power supply, connect the power supply to L1,L2 and leave L3 open.
2. Connect when the power supply has earth.
L1
L2
L3
(3) Outline drawing
23.0(0.906)
LABEL
LINELOAD
168.0(6.614)
L1'
L2'
L3'
L1
L2
L3
149.5(5.886)
LINE
(input side)
LOAD
(output side)
140.0(5.512)
156.0(6.142)
16.0(0.63)
42.0
8.5
SF1252
LABEL
LINELOAD
168.0(6.614)
L1'
L2'
L3'
L1
L2
L3
209.5(8.248)
LINE
(input side)
LOAD
(output side)
140.0(5.512)
156.0(6.142)
49.0
8.5
SF1253 [Unit: mm(in)]
(0.335)
(1.654)
(0.335)
(1.929)
6.0(0.236) 6.0(0.236)

14 - 1
14. SERVO MOTOR
14. SERVO MOTOR
14.1 Compliance with the overseas standards
14.1.1 Compliance with EC directives
Use the servo motor compatible with the EN Standard.
Unless otherwise specified, the handling, performance, specifications and others of the EN Standard-
compatible models are the same as those of the standard models.
To comply with the EN Standard, also observe the following items strictly.
(1) Wiring
Use the servo motor side power connector which complies with the EN Standard.
The EN Standard-compliant power connector sets are available from us as options.
Power Connector Set Model Servo Motor Model
MR-PWCNS1 HC-SFE52 (B) to 152 (B)
MR-PWCNS2 HC-SFE202 (B)
(2) Installation
The flange of the machine mounted with the HC-KFE must be connected to the earth.
14.1.2 Conformance with UL/C-UL standard
Mount the servo motor on a flange which has the following size or produces an equivalent or higher heat
dissipation effect: Note that if the servo motor used is the same, the flange size depends on the servo
amplifier combined.
Servo motor
Flange size
[mm] HC-KFE HC-SFE
150 150 613
250 250 623
250 250 12 43 52 to 152
300 300 12 73
300 300 20 202

14 - 2
14. SERVO MOTOR
14.2 Model name make-up
(1) Name plate
AC SERVO MOTOR
HC-SFE152
INPUT 3AC 145V 8.2A
MITSUBISHI ELECTRIC CORPORATION
MADE IN JAPAN
2000r/min IP65CI.F 9.5kg
SER.No. AS958300202X
OUTPUT 1.5kW IEC60034-1 '99
Model
Input power
Rated output
Rated speed, Protection structure,
Insulation class, Weight
Serial number
(2) Model
(a) HC-KFE series (low inertia, small capacity)
3000[r/min]
100
1
Appearance
Shaft type
Symbol Shaft Shape
None
K (Note) With keyway
Note: With key
Symbol Reduction Gear
None Without
G1 For general industrial machine
G2 For precision application
Electromagnetic brake
Symbol Electromagnetic Brake
None Without
BWith
Rated speed
Rated output
Symbol Rated Output [W]
Standard
(Straight shaft)
Reduction gear
3
Series name
HC-KFE
2200
400
4
750
7

14 - 3
14. SERVO MOTOR
(b) HC-SFE series (middle inertia, middle capacity)
Rated Output [W]
Symbol
G1
Symbol
10
500
1000
5
Series name
Reduction gear
None Without
Electromagnetic brake
Electromagnetic Brake
Without
With
Rated speed
2000 [r/min]
Rated output
Appearance
Symbol
B
None
(Note) Reduction Gear
Symbol
Shaft type
None
Shaft Shape
With keyway
Note: Without key
Standard
(Straight shaft)
K
For general
industrial machine
(flange type)
For general
industrial machine
(leg type)
G1H
For precision applicationG2
15
20
1500
2000
2 HC-SFE

14 - 4
14. SERVO MOTOR
14.3 Parts identification
Lead type Name/Application Refer To
Encoder Section 14.7.1
Encoder cable
with encoder connector Section 14.5
Servo motor shaft
Connector type
Encoder connector
Power cable
Power lead (U, V, W)
Earth lead
Brake lead
(for motor with electromagnetic brake)
Section 14.7.4
Name/Application Refer To
Encoder Section 14.7.1
Section 14.5
Servo motor shaft Section 14.7.4
Power connector
Power supply (U, V, W)
Earth
Brake (for motor with electromagnetic brake)
Some motors with electromagnetic brakes
have brake connectors separately.
Section 14.5
Section 14.5

14 - 5
14. SERVO MOTOR
14.4 Installation
CAUTION
Stacking in excess of the limited number of products is not allowed.
Install the equipment to incombustibles. Installing them directly or close to
combustibles will led to a fire.
Install the equipment in a load-bearing place in accordance with this Instruction
Manual.
Do not get on or put heavy load on the equipment to prevent injury.
Use the equipment within the specified environmental condition range.
Do not subject the servo motor to drop impact or shock loads as they are precision
equipment.
Do not install or operate a faulty servo amplifier.
Do not hold the cable, shaft or encoder to carry the servo motor. Otherwise, a fault
or injury may occur.
The lifting eyebolts of the servo motor may only be used to transport the servo
motor. They must not be used to transport the servo motor when it is mounted on a
machine.
The servo motor with reduction gear must be installed in the specified direction.
Otherwise, it can leak oil, leading to a fire or fault.
Securely fix the servo motor to the machine. If fixed insecurely, the servo motor will
come off during operation, leading to injury.
When coupling the shaft end of the servo motor, do not subject the shaft end to
impact, such as hammering. The encoder may become faulty.
Cover the shaft of the servo motor to make its rotary part completely inaccessible
during operation.
Do not subject the servo motor shaft to more than the permissible load. Otherwise,
the shaft may break, leading to injury.
When the product has been stored for an extended period of time, consult
Mitsubishi.

14 - 6
14. SERVO MOTOR
14.4.1 Environmental conditions
Environment Conditions
[]0 to 40 (non-freezing)
Ambient temperature [] 32 to 104 (non-freezing)
Ambient humidity 80%RH or less (non-condensing)
[ ] 15 to 70 (non-freezing)
Storage temperature [] 5 to 158 (non-freezing)
Storage humidity 90%RH or less (non-condensing)
Ambient Indoors (no direct sunlight)
Free from corrosive gas, flammable gas, oil mist, dust and dirt
Altitude Max. 1000m (3280ft) above sea level
HC-KFE series X,Y:49
HC-SFE52 to 152 X,Y:24.5
[m/s2]HC-SFE202 X:24.5
Y:49
HC-KFE series X,Y:161
HC-SFE52 to 152 X,Y:80
(Note)
Vibration
[ft/s2]HC-SFE202 X:80
Y:161
Note: Except the servo motor with reduction gear.
Vibration occurs in the directions shown below.
The values were measured at the portion which
indicates the maximum value (normally the
bracket opposite to load side). When the servo
motor is at a stop, the bearings are likely to fret
and vibration should therefore be suppressed to
about half of the permissible value.
Servo motor
Vibration
XY
Graph of vibration servo amplitude vs. speed
Speed [r/min]
Vibration amplitude (both amplitudes) [ m]
200
100
80
60
50
40
30
20
500 1000 1500 2000 2500 3000 3500
14.4.2 Installation orientation
The following table lists directions of installation:
Servo Motor Series Direction of Installation Remarks
HC-KFE
HC-SFE May be installed in any
direction. For installation in the horizontal direction, it is recommended to set the
connector section downward.
When the servo motor with electromagnetic brake is installed with the shaft end at top, the brake plate
may generate sliding sound but it is not a fault. Refer to Section 14.6.3 for the installation orientation of
the servo motor with reduction gear.

14 - 7
14. SERVO MOTOR
14.4.3 Load mounting precautions
POINT
During assembling, the shaft end must not be hammered.
Doing so can cause the encoder to fail.
(1) When mounting a pulley to the servo motor shaft provided with a keyway, use the screw hole in the
shaft end. To fit the pulley, first insert a double-end stud into the screw hole of the shaft, put a washer
against the end face of the coupling, and insert and tighten a nut to force the pulley in.
Servo motor
Double-end stud
Nut
Washer
Pulley
(2) For the servo motor shaft with a keyway, use the screw hole in the shaft end. For the shaft without a
keyway, use a friction coupling or the like.
(3) When removing the pulley, use a pulley remover to protect the shaft from impact.
(4) To ensure safety, fit a protective cover or the like on the rotary area, such as the pulley, mounted to
the shaft.
(5) When a threaded shaft end part is needed to mount a pulley on the shaft, please contact us.
(6) The orientation of the encoder on the servo motor cannot be changed.
(7) For installation of the servo motor, use spring washers, etc. and fully tighten the bolts so that they do
not become loose due to vibration.

14 - 8
14. SERVO MOTOR
14.4.4 Permissible load for the shaft
POINT
Do not use a rigid coupling as it may apply excessive bending load to the
shaft, leading to shaft breakage.
(a) Use a flexible coupling and make sure that the misalignment of the shaft is less than the
permissible radial load.
(b) When using a pulley, sprocket or timing belt, select a diameter that will fit into the permissible
radial load.
(c) Excess of the permissible load can cause the bearing life to reduce and the shaft to break.
(d) The load indicated in this section is static load in a single direction and does not include eccentric
load. Make eccentric load as small as possible. Not doing so can cause the servo motor to be
damaged.
(1) Without reduction gear
(Note ) L Permissible Radial Load Permissible Thrust Load
Servo Motor [mm] [in] [N] [lb] [N] [lb]
053 / 13 25 0.98 88 20 59 13
23 / 43 30 1.18 245 55 98 22HC-KFE 73 40 1.57 392 88 147 33
52 to 152 55 2.17 980 220 490 110
HC-SFE 202 79 3.11 2058 463 980 220
Note : For the symbols in the table, refer to the following diagram:
Radial load
Thrust load
L
L: Distance from flange mounting surface to load center
(2) With reduction gear
The permissible radial loads in the table are the values at the center of the reduction gear output
shaft. Q/ 2
Q
(a) HC-KFE series
1) General industrial machine-compliant
Item Gear
ratio
HC-KFE13(B)
G1
HC-KFE23(B)
G1
HC-KFE43(B)
G1
HC-KFE73(B)
G1
1/5 150 330 430
1/12 240 710 620
[N] 1/20 370 780 760 970
1/5 34 74 97
1/12 54 160 139
Permissible Radial Load
[lb] 1/20 83 175 171 218
1/5 200 350 430
1/12 320 720 620[N] 1/20 450 780 760 960
1/5 45 79 97
1/12 72 162 139
Permissible Thrust Load
[lb] 1/20 101 175 171 216

14 - 9
14. SERVO MOTOR
2) Precision application-compliant
Item Gear
ratio
HC-KFE13(B)
G2
HC-KFE23(B)
G2
HC-KFE43(B)
G2
HC-KFE73(B)
G2
1/5 160 160 340 390
1/9 200 420 480 600
1/20 540 610 790 1040
[N]
1/29 610 700 900 1190
1/536367688
1/9 45 94 108 135
1/20 121 137 178 234
Permissible Radial Load
[lb]
1/29 137 157 202 268
1/5 220 220 370 390
1/9 270 450 490 600
1/20 660 640 790 1140
[N]
1/29 750 830 1010 1290
1/549498387
1/9 61 101 110 135
1/20 148 144 178 256
Permissible Thrust Load
[lb]
1/29 167 187 227 290
(b) HC-SFE (2000r/min) series
1) General industrial machine-compliant
Item Gear
ratio
HC-SFE52(B)
G1
HC-SFE102(B)
G1
HC-SFE152(B)
G1
HC-SFE202(B)
G1
1/6 2058 2842 2842 2842
1/11 2391 3273 3273 3273
1/17 2832 3646 3646 3646
1/29 3273 4410 5135 7291
1/35 5253 5253 6047 8555
1/43 5253 6047 8555 8555
[N]
1/59 5800 9741 9741 9741
1/6 463 639 639 639
1/11 538 728 728 728
1/17 637 820 820 820
1/29 728 991 1154 1639
1/35 1181 1181 1359 1923
1/43 1181 1359 1923 1923
Permissible
Radial
Load
[lb]
1/59 1304 2190 2190 2190
1/6 1470 2352 2352 2352
1/11 1470 2764 2764 2764
1/17 1470 2940 2940 2940
1/29 1470 2940 3920 6860
1/35 2940 2940 3920 6860
1/43 2940 3920 6860 6860
[N]
1/59 2940 6860 6860 6860
1/6 330 529 529 529
1/11 330 621 621 621
1/17 330 661 661 661
1/29 330 661 881 1542
1/35 661 661 881 1542
1/43 661 881 1542 1542
Permissible
Thrust
Load
[lb]
1/59 661 1542 1542 1542

14 - 10
14. SERVO MOTOR
2) Precision application-compliant
Item Gear
ratio
HC-SFE52(B)
G2
HC-SFE102(B)
G2
HC-SFE152(B)
G2
HC-SFE202(B)
G2
1/5 833 833 833 1666
1/9 980 980 1960 1960
1/20 1274 2646 2646 6076
1/29 2940 2940 6860 6860
[N]
1/45 3430 8036 8036 8036
1/5 187 187 187 375
1/9 220 220 441 441
1/20 286 595 595 1366
1/29 661 661 1542 1542
Permissible
Radial
Load
[lb]
1/45 771 1807 1807 1807
1/5 1176 1176 1176 2156
1/9 1568 1568 2646 2646
1/20 2254 3724 3724 9506
1/29 4704 4704 11760 11760
[N]
1/45 5390 14700 14700 14700
1/5 264 264 264 485
1/9 353 353 595 595
1/20 507 837 837 2137
1/29 1058 1058 2644 2644
Permissible
Thrust
Load
[lb]
1/45 1212 3305 3305 3305

14 - 11
14. SERVO MOTOR
14.4.5 Protection from oil and water
(1) Next, the servo motor is not waterproof (IP44). Do not subject the servo motor to oil and water.
Especially for the HC-KFE series, do not subject the shaft-through portion to oil.
Servo Motor Series Protection
HC-KFE IP55
Oil or water
Servo motor
(2) When the gear box is mounted horizontally, the oil level in the gear box should always be lower than
the oil seal lip on the servo motor shaft. If it is higher than the oil seal lip, oil will enter the servo
motor, leading to a fault. Also, provide a breathing hole in the gear box to hold the internal pressure
low.
The HC-KFE series servo motor is not equipped with a V ring or an oil seal and cannot be used with
the gear box as described above. Oil should be shut off on the gear box side.
Servo motor
V ring
Gear
Lip
Height above oil level h
Height above Oil Level h
Servo Motor [mm] [in]
52 to 152 20 0.79
HC-SFE 202 to 702 25 0.98
(3) When installing the servo motor horizontally, face the power cable and encoder cable downward. When
installing the servo motor vertically or obliquely, provide a trap for the cable.
Cable trap

14 - 12
14. SERVO MOTOR
(4) Do not use the servo motor with its cable soaked in oil or water. (Figure on the right)
Cover
<Incorrect> Capillary phenomenon
Oil/water pool
Servo
motor
(5) When the servo motor is to be installed with the shaft end at top, provide measures so that it is not
exposed to oil and water entering from the machine side, gear box, etc.
Gear
Lubricating oil
Servo motor
(6) If the servo motor is exposed to oil such as coolant, the sealant, packing, cable and others may be
affected depending on the oil type.
(7) In the environment where the servo motor is exposed to oil mist, oil, water and/or like, the servo motor
of the standard specifications may not be usable. Contact us.
(8) In the case of the servo motor with oil seal, the oil seal may sound during operation. It poses no
problems in function.
14.4.6 Cable
The power supply and encoder cables routed from the servo motor should be fixed to the servo motor to
keep them unmovable. Otherwise, cable breaks may occur. In addition, do not modify the connectors,
terminals and others at the ends of the cables.

14 - 13
14. SERVO MOTOR
14.5. Connectors used for servo motor wiring
This section gives connector makeups on an operating environment basis. Use the models of the
manufacturers given or equivalent.
14.5.1 HC-KFE series
Use the connectors indicated in this section or equivalent for connection of the power supply,
electromagnetic brake and encoder. These connectors may be used for the EN Standard and UL/C-UL
Standard but are not waterproof.
1) For connection of power supply and brake
Cable Side Connector
Servo Motor Connector Supplied for
Servo Motor (molex) Plug (molex) Terminal (molex) Manual crimping tool
HC-KFE 5557-04R-210 5559-04P-210 5558PBT3L 57022-5300
Cable Side Connector
Servo Motor Connector Supplied for
Servo Motor (molex) Plug (molex) Terminal (molex) Manual crimping tool
HC-KFE B 5557-06R-210 5559-06P-210 5558PBT3L 57022-5300
2) For connection of encoder
Cable Side Connector
Servo Motor Connector Supplied for
Servo Motor (AMP) Housing (AMP) Connector pin (AMP) Cable clamp
(Toa Electric Industry)
HC-KFE (B) 1-172169-9 1-172161-9 170359-1
170363-1 (loose piece) MTI-0002
14.5.2 HC-SFE series
(1) Non-waterproof, UL/C-UL Standard-compliant
(a) When using cabtyre cables
1) For connection of power supply
1) Plug
2) Cable
clamp Cable 1) Plug
2) Cable
clamp Cable
1) Plug (DDK)
Servo Motor Connector Supplied for Servo Motor Type Model
2) Cable clamp
(DDK)
Straight MS3106B22-23S
HC-SFE52(B) to 152(B) CE05-2A22-23PD-B Angle MS3108B22-23S MS3057-12A
Straight MS3106B24-10S
HC-SFE202(B) CE05-2A24-10PD-B Angle MS3108B24-10S MS3057-16A
2) For connection of encoder
1) Plug
2) Cable
clamp Cable 1) Plug
2) Cable
clamp Cable
1) Plug (DDK)
Servo Motor Connector Supplied for
Servo Motor Type Model
2) Cable clamp
(DDK)
Straight MS3106B20-29S
HC-SFE52(B) to 202(B) MS3102A20-29P Angle MS3108B20-29S MS3057-12A

14 - 14
14. SERVO MOTOR
3) For connection of brake
1) Plug Cable
1) Plug
Cable
2) Connector for cable
2) Connector for cable
2) Connector for Cable
Servo Motor
Connector
Supplied for Servo
Motor
1) Plug
(DDK) Type Maker Cable
OD Model
4 to 8 ACS-08RL-MS10F
Straight Nippon
flex 8 to 12 ACS-12RL-MS10F
Angle Daiwa
Dengyo 5 to 8.3 YSO10-5 to 8
4 to 8 ACA-08RL-MS10F
Straight Nippon
flex 8 to 12 ACA-12RL-MS10F
HC-SFE202B MS3102A10SL-4P MS3106A10SL-4S
Angle Daiwa
Dengyo 5 to 8.3 YLO10-5 to 8
(b) When using flexible conduits
1) For connection of power supply
1) Plug Conduit
1) Plug
2) Connector for
conduit Conduit
2) Connector for conduit
2) Connector for conduit Conduit
Servo Motor
Connector
Supplied for
Servo Motor
1) Plug
(DDK) Type Maker Size Model Model ID
1/2 RCC-104RL-MS22F VF-04 14.0
3/4 RCC-106RL-MS22F VF-06 19.0
Nippon
flex 1 RCC-108RL-MS22F VF-08 24.4
16 MSA-16-22 FCV16 15.8
22 MSA-22-22 FCV22 20.8
Straight Daiwa
Dengyo 28 MSA-28-22 FCV28 26.4
1/2 RCC-304RL-MS22F VF-04 14.0
3/4 RCC-306RL-MS22F VF-06 19.0
Nippon
flex 1 RCC-308RL-MS22F VF-08 24.4
16 MAA-16-22 FCV16 15.8
22 MAA-22-22 FCV22 20.8
HC-SFE52(B) to 152(B) CE05-2A22-
23PD-B MS3106A22-
23S(D190)
Angle Daiwa
Dengyo 28 MAA-28-22 FCV28 26.4
1/2 RCC-104RL-MS24F VF-04 14.0
3/4 RCC-106RL-MS24F VF-06 19.0
Nippon
flex 1 RCC-108RL-MS24F VF-08 24.4
16 MSA-16-24 FCV16 15.8
22 MSA-22-24 FCV22 20.8
Straight Daiwa
Dengyo 28 MSA-28-24 FCV28 26.4
1/2 RCC-304RL-MS24F VF-04 14.0
3/4 RCC-306RL-MS24F VF-06 19.0
Nippon
flex 1 RCC-308RL-MS24F VF-08 24.4
16 MAA-16-24 FCV16 15.8
22 MAA-22-24 FCV22 20.8
HC-SFE202(B) CE05-2A24-
10PD-B MS3106A24-
10S(D190)
Angle Daiwa
Dengyo 28 MAA-28-24 FCV28 26.4

14 - 15
14. SERVO MOTOR
2) For connection of encoder
1) Plug Conduit
1) Plug
2) Connector for
conduit Conduit
2) Connector for conduit
2) Connector for conduit Conduit
Servo Motor
Connector
Supplied for
Servo Motor
1) Plug
(DDK) Type Maker Size Model Model ID
1/2 RCC-104RL-MS20F VF-04 14.0
Nippon
flex 3/4 RCC-106RL-MS20F VF-06 19.0
16 MSA-16-20 FCV16 15.8
Straight Daiwa
Dengyo 22 MSA-22-20 FCV22 20.8
1/2 RCC-304RL-MS20F VF-04 14.0
Nippon
flex 3/4 RCC-306RL-MS20F VF-06 19.0
16 MAA-16-20 FCV16 15.8
HC-SFE52(B) to 202(B) MS3102A20-
29P MS3106A20-
29S(D190)
Angle Daiwa
Dengyo 22 MAA-22-20 FCV22 20.8
3) For connection of brake
1) Plug Conduit
1) Plug
2) Connector for
conduit Conduit
2) Connector for conduit
2) Connector for conduit Conduit
Servo Motor
Connector
Supplied
for Servo
Motor
1) Plug
(DDK) Type Maker Size Model Model ID
Nippon
flex 1/4 RCC-102RL-MS10F VF-02 8.3
Straight Daiwa
Dengyo 10 MSA-10-10 FCV10 10
Nippon
flex 1/4 RCC-302RL-MS10F VF-02 8.3
HC-SFE203B MS3102A
10SL-4P MS3106A10-SL-
4S(D190)
Angle Daiwa
Dengyo 10 MAA-10-10 FCV10 10

14 - 16
14. SERVO MOTOR
(2) Waterproof (IP65), EN Standard, UL/C-UL Standard-compliant
(a) When using cabtyre cables
1) For connection of power supply
1) Plug
2) Cable
clamp Cable 1) Plug
2) Cable
clamp Cable
1) Plug (DDK) 2) Cable clamp
(DDK)
Servo Motor
Connector
Supplied for
Servo Motor Type Model Cable OD Model
Straight CE05-6A22-23SD-B-BSS 9.5 to 13 CE3057-12A-2(D265)
HC-SFE52(B) to 152(B) CE05-2A22-
23PD-B Angle CE05-8A22-23SD-B-BAS 12.5 to 16 CE3057-12A-1(D265)
Straight CE05-6A24-10SD-B-BSS 13 to 15.5 CE3057-16A-2(D265)
HC-SFE202(B) CE05-2A24-
10PD-B Angle CE05-8A24-10SD-B-BAS 15 to 19.1 CE3057-16A-1(D265)
2) For connection of encoder
1) Plug
3) Cable
clamp Cable 2) Back shell
3) Cable clamp
Cable
2) Back shell 1) Plug
2) Back shell 3) Cable clamp
(DDK)
Servo Motor
Connector
Supplied for
Servo Motor
1) Plug
(DDK) Type Model Cable OD Model
Straight CE02-20BS-S
HC-SFE52(B) to 202(B) MS3102A20-
29P MS3106A20-
29S(D190) Angle CE-20BA-S 6.8 to 10 CE3057-12A-3(D265)
3) For connection of brake
1) Plug Cable
1) Plug
Cable
2) Connector for
cable
2) Connector for cable
2) Connector for Cable
Servo Motor Connector Supplied
for Servo Motor
1) Plug
(DDK) Type Maker Cable
OD Model
4 to 8 ACS-08RL-MS10F
Nippon
flex 8 to 12 ACS-12RL-MS10F
Straight Daiwa
Dengyo 5 to 8.3 YSO-10-5 to 8
4 to 8 ACA-08RL-MS10F
Nippon
flex 8 to 12 ACA-12RL-MS10F
HC-SFE202B MS3102A10SL-4P MS3106A10SL-
4S(D190)
Angle Daiwa
Dengyo 5 to 8.3 YLO-10-5 to 8

14 - 17
14. SERVO MOTOR
(b) When using flexible conduits
1) For connection of power supply
1) Plug Conduit
1) Plug
2) Connector for
conduit Conduit
2) Connector for conduit
2) Connector for conduit Conduit
Servo Motor
Connector
Supplied for
Servo Motor
1) Plug
(DDK) Type Maker Size Model Model ID
1/2 RCC-104RL-MS22F VF-04 14.0
3/4 RCC-106RL-MS22F VF-06 19.0
Nippon
flex 1 RCC-108RL-MS22F VF-08 24.4
16 MSA-16-22 FCV16 15.8
22 MSA-22-22 FCV22 20.8
Straight Daiwa
Dengyo 28 MSA-28-22 FCV28 26.4
1/2 RCC-304RL-MS22F VF-04 14.0
3/4 RCC-306RL-MS22F VF-06 19.0
Nippon
flex 1 RCC-308RL-MS22F VF-08 24.4
16 MAA-16-22 FCV16 15.8
22 MAA-22-22 FCV22 20.8
HC-SFE52(B) to 152(B) CE05-2A22-
23PD-B CE05-6A22-
23SD-B
Angle Daiwa
Dengyo 28 MAA-28-22 FCV28 26.4
1/2 RCC-104RL-MS24F VF-04 14.0
3/4 RCC-106RL-MS24F VF-06 19.0
Nippon
flex 1 RCC-108RL-MS24F VF-08 24.4
16 MSA-16-24 FCV16 15.8
22 MSA-22-24 FCV22 20.8
Straight Daiwa
Dengyo 28 MSA-28-24 FCV28 26.4
1/2 RCC-304RL-MS24F VF-04 14.0
3/4 RCC-306RL-MS24F VF-06 19.0
Nippon
flex 1 RCC-308RL-MS24F VF-08 24.4
16 MAA-16-24 FCV16 15.8
22 MAA-22-24 FCV22 20.8
HC-SFE202(B) CE05-
2A24-
10PD-B
CE05-6A24-
10SD-B
Angle Daiwa
Dengyo 28 MAA-28-24 FCV28 26.4

14 - 18
14. SERVO MOTOR
2) For connection of encoder
1) Plug Conduit
1) Plug
2) Connector for
conduit Conduit
2) Connector for conduit
2) Connector for conduit Conduit
Servo Motor
Connector
Supplied for
Servo Motor
1) Plug
(DDK) Type Maker Size Model Model ID
1/2 RCC-104RL-MS20F VF-04 14.0
Nippon
flex 3/4 RCC-106RL-MS20F VF-06 19.0
16 MSA-16-20 FCV16 15.8
Straight Daiwa
Dengyo 22 MSA-22-20 FCV22 20.8
1/2 RCC-304RL-MS20F VF-04 14.0
Nippon
flex 3/4 RCC-306RL-MS20F VF-06 19.0
16 MAA-16-20 FCV16 15.8
HC-SFE52(B) to 202(B) MS3102A20-
29P MS3106A20-
29S(D190)
Angle Daiwa
Dengyo 22 MAA-22-20 FCV22 20.8
3) For connection of brake
1) Plug Conduit
1) Plug
2) Connector for
conduit Conduit
2) Connector for conduit
2) Connector for conduit Conduit
Servo Motor
Connector
Supplied for
Servo Motor
1) Plug
(DDK) Type Maker Size Model Model ID
Nippon
flex 1/4 RCC-102RL-MS10F VF-02 8.3
Straight Daiwa
Dengyo 10 MSA-10-10 FCV10 10
Nippon
flex 1/4 RCC-302RL-MS10F VF-02 8.3
HC-SFE202B MS3102A10S
L-4P MS3106A10SL-
4S(D190)
Angle Daiwa
Dengyo 10 MAA-10-10 FCV10 10

14 - 19
14. SERVO MOTOR
14.6 Specifications
14.6.1 Standard specifications
HA-KFE Series
(Low inertia, small capacity)
Servo Motor
Item 13 23 43 73
Applicable servo
amplifier/drive unit MR-E- A 10204070
Rated output [kW] 0.1 0.2 0.4 0.75
[N m] (Note 14)
0.32 (Note 14)
0.64 (Note 14)
1.3 2.4
(Note 1,11)
Continuous duty Rated
torque [oz in] (Note 14)
45.3 (Note 14)
90.7 (Note 14)
184 340
(Note 1) Rated speed [r/min] 3000
Maximum speed [r/min] 4500
Permissible instantaneous speed [r/min] 5175
[N m] 0.95 1.9 3.8 7.2
Maximum torque [oz in] 135 269 538 1020
Power rate at continuous rated torque
[kW/s] 12.1 9.65 24.2 37.7
J[10 4kg m2] 0.084 0.42 0.67 1.51
(Note 3)
Inertia moment WK2[oz in2] 0.459 2.296 3.663 8.26
(Note 2) Recommended ratio of load inertia
moment to servo motor shaft inertia moment 10 times or less
Servo amplifier' built-
in regenerative brake
resistor (Note 5) (Note 9) 220 190
MR-RB032(30W) (Note 5) (Note 5) 660 280
(Note4,10)
Regenerative brake
duty
[times/min] MR-RB12(100W) (Note 5) (Note 5) 2200 940
Power supply capacity Refer to "Power supply equipment capacity and generated loss of servo amplifiers"
in Servo Amplifier Instruction Manual.
Rated current [A] 0.83 1.1 2.3 5.8
Maximum current [A] 2.5 3.4 6.9 18.6
Speed/position detector Encoder (resolution : 10000 pulse/rev)
Accessories Encoder, V ring
Insulation class Class B
Structure Totally-enclosed, self-cooled
(protection type: IP44 (Note 3,6,8))
(Note 7) Environmental conditions Refer to section 14.4.1
[kg] 0.53 0.99 1.45 3.0
(Note 3) Weight [lb] 1.168 2.18 3.20 6.61

14 - 20
14. SERVO MOTOR
HC-SFE Series
(Middle inertia, middle capacity)
Servo Motor
Item 52 102 152 202
Applicable servo
amplifier/drive unit MR-E- A 70 100 200 200
Rated output [kW] 0.5 1.0 1.5 2.0
[N m] 2.39 4.78 7.16 9.55
(Note 1,11)
Continuous
duty Rated
torque [oz in] 339 677 1015 1353
(Note 1) Rated speed [r/min] 2000
Maximum speed [r/min] 3000 2500
Permissible instantaneous speed [r/min] 345 2850
[N m] 7.16 14.4 21.6 28.5
Maximum torque [oz in] 1015 2041 3061 4039
Power rate at continuous rated torque
[kW/s] 8.7 16.7 25.6 21.5
J[10 4kg m2] 6.6 13.7 20.0 4.5
(Note 3)
Inertia moment WK2[oz in2] 36.1 74.9 109 232
(Note 2) Recommended ratio of load inertia
moment to servo motor shaft inertia moment 15 times or less
Servo amplifier' built-
in regenerative brake
resistor 56 54 136 64
MR-RB032(30W) 165 80
MR-RB12(100W) 560 270
MR-RB32(300W) 810
MR-RB30(300W) 408 192
(Note4)
Regenerati
ve brake
duty
[times/min] MR-E
series
MR-RB50(500W) 680 320
Power supply capacity Refer to "Power supply equipment capacity and generated loss of servo amplifiers"
in Servo Amplifier Instruction Manual.
Rated current [A] 3.2 6 9 11
Maximum current [A] 9.6 18 27 33
Speed/position detector Encoder
(resolution: 10000 pulse/rev)
Accessories Encoder Oil seal
Insulation class Class F
Structure Totally-enclosed, self-cooled
(protection type: IP65(Note 8))
(Note 7) Environmental conditions Refer to section 2.1
[kg] 5.0 7.0 9.0 12.0
(Note 3) Weight [lb] 11.0 15.4 19.8 26.5
Note: 1. When the power supply voltage drops, we cannot guarantee the output and rated speed.
2. If the load inertia moment ratio exceeds the indicated value, please consult us.
3. When the servo motor is equipped with electromagnetic brake, refer to section 14.8.When the servo motor is equipped with
reduction gear, please consult us.
4. The regenerative brake duty indicated is the permissible duty when the servo motor running without load at the rated speed is
decelerated to a stop. When a load is connected, the value in the table is multiplied by 1/(m 1), where m load inertia
moment/motor inertia moment. At the speed higher than the rated, the permissible number of times is in inverse proportion to
the square of (running speed/rated speed). When the running speed varies frequently or when the regenerative mode
continues as in vertical feed, calculate regenerative heat generated during operation. Provisions must be made to keep this
generated heat below the permissible value.
5. If the effective torque is within the rated torque range, there are no restrictions on the regenerative duty. Note that the
recommended load inertia moment ratio is 15 times or less.
6. Except for the shaft-through portion and connector end.
7. When the equipment is to be used in places where it is subjected to oil and/or water, such as on machine field sites, optional
features apply to the equipment. Please contact.
8. When the servo motor is provided with the reduction gear, the protection type of the reduction gear section is IP44.
9. At the load inertia moment ratio of 5 times or less, there are no restrictions on the regenerative duty if the effective torque is
within the rated torque range.
10. The regenerative brake duty of the 400W or less servo amplifier may vary under the influence of the power supply voltage
because of the large ratio of the energy for charging the electrolytic capacitor in the servo amplifier.

14 - 21
14. SERVO MOTOR
14.6.2 Torque characteristics
POINT
For machines which produce unbalance torque, e.g. vertical lift
applications, it is recommended to use the servo motor so that the
unbalance torque will be within 70% of the rated torque.
(1) HC-KFE series
1000 2000 3000 40004500
0
0.25
0.5
1.0
0.75
[HC-KFE13]
Torque [N m]
Speed [r/min]
Continuous operation
region
Short-duration
operation region
Speed [r/min]
Torque [N m]
0
0.5
1.0
2.0
1.5
1000 2000 3000 40004500
Continuous operation
region
Short-duration
operation region
[HC-KFE23]
Speed [r/min]
1000 2000 3000 40004500
Torque [N m]
0
2.0
4.0
8.0
[HC-KFE73]
6.0 Short-duration
operation region
Continuous operation
region
1000 2000 3000 40004500
Speed [r/min]
0
1.0
2.0
4.0
3.0
Torque [N m]
Short-duration
operation region
Continuous operation
region
[HC-KFE43]
(2) HC-SFE series
Torque [N m]
3
6
9
[HC-SFE52]
01000 2000 3000
Speed [r/min]
Continuous operation
region
Short-duration
operation region
5
10
15
[HC-SFE102]
0
Speed [r/min]
1000 2000 3000
Short-duration
operation region
Continuous operation
region
Torque [N m]
8
16
24
[HC-SFE152]
0
Speed [r/min]
1000 2000 3000
Short-duration
operation region
Continuous operation
region
Torque [N m]
10
20
30
[HC-SFE202]
0
Speed [r/min]
1000 2000
Short-duration
operation region
Continuous operation
region
2500
Torque [N m]

14 - 22
14. SERVO MOTOR
14.6.3 Servo motors with reduction gears
CAUTION
The servo motor with reduction gear must be installed in the specified direction.
Otherwise , it can leak oil, leading to a fire or fault.
For the servo motor with reduction gear, transport it in the same status as in the
installation method. Tipping it over can cause oil leakage.
Servo motors are available with reduction gears designed for: general industrial machines and precision
applications.
Servo motors with electromagnetic brakes are also available.
(1) Manufacturing range of servo motor with reduction gear
Servo motors with reduction gears that may be manufactured are indicated by symbols (G1(H), G2) in
the following table. G1 (H) and G2 are symbols appended to the servo motor models.
For General Industrial Machines For Precision Applications
Reduction Gear Series
Reduction ratio
Servo Motor
(Note)
1/5 1/6 1/11
(Note)
1/12 1/17
(Note)
1/20 1/29 1/35 1/43 1/59 1/5 1/9 1/20 1/29 1/45
HC-KFE13 to 73 G1 G1 G1 G2 G2 G2 G2
HC-SFE52 to 202 G1
(H) G1
(H) G1
(H) G1
(H) G1
(H) G1
(H) G1
(H) G2 G2 G2 G2 G2
Note : Reduction ratios for general industrial machines are nominal values. For actual reduction ratios, refer to (2) and (3) in this section.
(2) HC-KFE series
Reduction Gear Series For General Industrial Machines
HC-KFE G1
For Precision Applications
HC-KFE G2
Mounting method Flange mounting
Mounting direction In any directions
Grease lubrication (Already packed) Grease lubrication (Already packed)
200W 400W
100W 1/12 1/20 1/5 750W
Lubrication
method Packed grease Mobilplex 46
Mobil Oil
New Molynoc
No.2 Nisseki
Mitsubishi
Mobil Grease
SP Mobil Oil
LDR101BV American Oil Center Research
Output shaft rotating direction Same as the servo motor output shaft direction.
With electromagnetic brake Available
Backlash 60 minutes or less at reduction gear output shaft 3 minutes or less at reduction gear output shaft
Permissible load inertia moment
ratio (when converting into the
servo motor shaft) 10 times or less
Permissible speed
(at servo motor shaft) 4500 r/min
The actual reduction ratios of the servo motors with reduction gears designed for general industrial
machines are as listed below:
Servo Motor
Nominal
Reduction Ratio
HC-KFE13(B)G1 HC-KFE23(B)G1 HC-KFE43(B)G1 HC-KFE73(B)G1
1/5 9/44 19/96 1/5
1/12 49/576 25/288 525/6048
1/20 25/484 253/5000 625/12544

14 - 23
14. SERVO MOTOR
(3) HC-SFE series
Reduction Gear Series For General Industrial Machines
HC-SFE G1(H)
For Precision Applications
HC-SFE G2
Mounting method As in (a) in this section Flange mounting
Mounting direction As in (a) in this section In any directions
As in (a)(b) in this section Grease lubrication (Already packed)
Lubrication
method (Note2)
Recommended
products As in (b) in this section LDR101BJ of American Oil Center
Research make
Output shaft rotating direction Opposite direction to the servo motor shaft Same direction as the servo motor shaft
With electromagnetic brake Available
Backlash 40 minutes to 2*at reduction gear output
shaft (Note1)
3 minutes or less at reduction gear output
shaft
Permissible load inertia moment
ratio (when converting into the
servo motor shaft) 4 times or less 5 times or less
Permissible speed
(at servo motor shaft) 2000[r/min] 0.5 to 1.5kW:3000[r/min]
2kW:2500[r/min]
Note1. The above values are typical values and not guaranteed values.
2. For grease lubrication, the reduction gear is already grease-packed.
(a) Lubrication of reduction gears for general industrial machines
Oil lubrication cannot be used in applications where the servo motor will move. Specify grease
lubrication.
For grease lubrication, the reduction gear is already grease-packed.
For oil lubrication, pack the reduction gear with oil on the customer side.
Mounting
Direction Shaft in Any Direction Shaft Horizontal Shaft Downward Shaft Upward
Reduction gear
model
Reduction gear
frame No.
CNHM
(leg type)
CNVM
(flange type)
CHHM
(leg type)
CHVM
(flange type
)
CVHM
(leg type)
CVVM
(flange type
)
CWHM
(leg type)
CWVM
(flange type
)
4105 Grease Grease
4115 Grease Grease
4135 (Note) Oil (Note) Oil (Note) Oil (Note) Oil Grease Grease
4165 (Note) Oil (Note) Oil (Note) Oil (Note) Oil Grease Grease
Note: Grease-lubricated type is also available.
The reduction gear frame numbers are as follows:
Reduction Ratio
Servo Motor 1/6 1/11 1/17 1/29 1/35 1/43 1/59
HC-SFE52(B)G1 (H) 4105 4115
HC-SFE102(B)G1 (H) 4115 4135 4165
HC-SFE152(B)G1 (H) 4115 4135 4165
HC-SFE202(B)G1 (H) 4115 4165

14 - 24
14. SERVO MOTOR
(b) Recommended lubricants
1) Grease
Albania Grease/Shell OIL
2) Lubricating oil
Ambient
Temperature COSMO OIL
NISSEKI
MITSUBISHI
OIL
IDEMITSU
KOSAN
CO., LTD
GENERAL
OIL
Shell
OIL ESSO OIL Mobil OIL Japan
Energy
10 to 5 COSMO
GEAR
SE
68
BONNOC
SP
68
DIAMOND
GEAR LUBE
SP
68
DAPHNE CE
68S
DAPHNE SUPER
GEAR OIL
68
Omala
Oils
68
SPARTANEP
68 Mobilgear
626
(ISO VG68)
JOMO.
Reductus
68
0 to 35 COSMO
GEAR
SE
100, 150
BONNOC
SP
100, 150
DIAMOND
GEAR LUBE
SP
100, 150
DAPHNE CE
100S,150S
DAPHNE SUPER
GEAR OIL
100, 150
GENERAL
SP
GEAROL
100, 150
Omala
Oils
100, 150
SPARTANEP
150 Mobilgear
629
(ISO VG150)
JOMO.
Reductus
100, 150
30 to 50 COSMO
GEAR
SE
200,320,460
BONNOC
SP
200 to 460
DIAMOND
GEAR LUBE
SP
220 to 460
DAPHNE CE
220S to 460S GENERAL
SP
GEAROL
200 to 260
Omala
Oils
200 to
460
SPARTANEP
220 to 460 Mobilgear
630 to 634
(ISO VG
220 to 460)
JOMO.
Reductus
200 to 460
Lubricating oil fill amount ( )
Fill amount [ ]
Reduction gear frame No. Horizontal type Vertical type
4135 0.7 1.1
4165 1.4 1.0
(c) Lubricating product changing intervals
1) Grease:
20000 hours or 4 to 5 years
2) Lubricant
Operation hours per day
Changing intervals Less than 10 hours 10 to 24 hours
First time 500 hours
Second time and later Half year 2500 hours

14 - 25
14. SERVO MOTOR
14.6.4 Servo motors with special shafts
The standard shaft of the servo motor is straight without a keyway. Shafts with keyway and D cut are
also available. Except for the servo motor with reduction gear.
These shafts are not appropriate for applications where the servo motor is started and stopped frequently.
Use a friction coupling or the like with such keys since we cannot guarantee such trouble as broken shafts
due to loose keys.
Shaft Shape
Servo Motor Keyway D cut Straight
HC-SFE52 to 202 (Note 2) (Note 3)
HC-KFE13 (Note 3)
HC-KFE23 to 73 (Note 1) (Note 3)
Note: 1. With a key.
2. Without a key.
3. This is a standard. For shape, refer to Section 14.9.
(1) Keyway
(a) With key
R
Q
QL
QK
A
A
HC-MF23K to 73K
R
HC-UF23K to 73K
QL
QK
A
A
Q
H
W
U
SY
Section A-A [Unit: mm]
([Unit: in])
Variable Dimensions
Servo Motor Model S R Q W QK QL U H Y
HC-KFE23K 43K 14h6
(14) 30
(1.18) 27
(1.06) 5
(0.20) 20
(0.79) 3
(0.12) 3
(0.12) 5
(0.20) M4 Depth 15
(0.59)
HC-KFE73K 19h6
(19) 40
(1.57) 37
(1.46) 6
(0.24) 25
(0.98) 5
(0.20) 3.5
(0.14) 6
(0.24) M5 Depth 20
(0.79)
(b) Without key [Unit: mm]
([Unit: in])
Variable Dimensions
Servo motor S R Q W QK QL U r
HC-SFE52K to 152K 24h6
(0.94) 55
(2.17) 50
(1.97) 800.036
(0.31) 36
(1.42) 5
(0.20) 40.2
0
(0.16) 4
(0.16)
HC-SFE202K 35
(1.38) 79
(3.11) -1000.036
(0.39) 55
(2.17) 5
(0.20) 50.2
0
(0.20) 5
(0.20)
R
Q
QLQK
S
U
A
A
r
W
Section A-A
M8 threads
Depth 20(0.79
)
14.6.5 D cut
[Unit: mm]
([Unit: in])
Variable Dimensions
Servo Motor Model RQKS
HC-KFE053D 13D 25(0.98) 20.5(0.81) 8h(0.32)
R
S
QK
1(0.039)

14 - 26
14. SERVO MOTOR
14.7 Characteristics
14.7.1 Electromagnetic brake characteristics
CAUTION
Configure the electromagnetic brake operation circuit so that it is activated not
only by the servo amplifier signals but also by an external emergency stop signal.
Refer to Section 3.9 for details.
The electromagnetic brake is designed to hold a load. Do not use it for braking.
(1) Characteristics
Though the brake lining may rattle during operation, it poses no functional problem.
A leakage magnetic flux will occur at the shaft end of the servo motor equipped with electromagnetic
brake.
HC-SFE Series HC-KFE Series(Note 5) Servo Motor
Item
52B to 152B 202B 13B 23B 43B 73B
(Note 1) Type Spring-loaded safety brake
(Note 4) Rated voltage 24V 0
10% DC
Rated current at 20 (68 ) [A] 0.8 1.4 0.26 0.33 0.42
Excitation coil resistance at
20 (68 )[]29 16.8 9.1 73 57
Capacity [W] 19 34 6.3 7.9 9
[N m] 8.3 43.1 0.32 43.1 2.4
Static friction torque [oz in] 1176 6103 45 6108 340
(Note 2) Release delay time [S] 0.04 0.1 0.03 0.1 0.03
AC off (Fig. a) 0.12 0.12 0.08 0.12 0.12
Braking delay time
(Note 2) [s] DC off(Fig.s b, c) 0.03 0.03 0.01 0.03 0.03
[J] 400 4500 5.6 22.0 64.0
Per
braking [oz in] 56683.3 637687.1 793.6 3117.6 9069.3
[J] 4000 45000 56 220 640
Permissible braking
work Per
hour [oz in] 566833 6376871 7936 31176 90693
Brake looseness at servo motor shaft
(Note 5) [degrees] 0.2 to 0.6 0.2 to 0.6 0.19 to 2.5 0.12 to 1.2 0.1 to 0.9
Number of braking
cycles [times] 20000 20000 20000 20000 20000
[J] 200 1000 4 15 32
Brake life (Note 3) Work per
braking [oz in] 28342 141708 567 2124.18 4535
Note:1. There is no manual release mechanism. When it is necessary to hand-turn the servo motor shaft for machine centering,
etc., use a separate 24VDC power supply to release the brake electrically.
2. The value for initial ON gap at 20 (68 ).
3. The brake gap will increase as the brake lining wears, but the gap is not adjustable. The brake life indicated is the
number of braking cycles after which adjustment will be required.
4. 24VDC of the power output for interface (VDD) cannot be used. Always use a separate power supply.
5. The above values are typical initial values and not guaranteed values.

14 - 27
14. SERVO MOTOR
(2) Electromagnetic brake power supply
Prepare the following power supply for use with the electromagnetic brake only.
Switch
Electromagnetic
brake
VAR24VDC
B1
B2
VAR : Surge absorber
The surge absorber must be installed across B1-B2. For the selection of the surge absorber, refer to
section 13.2.5.
The electromagnetic brake terminals (B1, B2) have no polarity.
(3) Coasting distance
At an emergency stop, the servo motor will decelerate to a stop in the pattern shown in the following
diagram. Here, the maximum coasting distance (during fast feed), Lmax, will be the area shown with
the diagonal line in the figure and can be calculated approximately with Equation 6.1. The effect of the
load torque is greater near the stopping area. When the load torque is large, the servo motor will stop
faster than the value obtained in the equation.
Emergency stop
Brake current
Machine speed
V0
t1t2t3
L max =60
Vo t1 t2 2
t3 ...................................................................................................(6.1)
Where,
L max :Maximum coasting distance [mm]
Vo: Machine's fast feed speed [mm/min]
t1: Delay time of control section [s]
t2: Braking delay time of brake (Note) [s]
t3:Braking time [s]
9.55 104(TL 0.8TB)
(JL JL)No
t3
JL: Load inertia moment converted into equivalent [kg cm2]
value on servo motor shaft (Note)
JM : Servo motor inertia moment [kg cm2]
No : Servomotor speed during fast feed [r/min]
TL: Load torque converted into equivalent [N m]
value on servo motor shaft
TB: Brake static friction torque (Note) [N m]
Note: t2 and TB are the values noted in this section Characteristics. JL is the machine's inertia moment at the servo motor shaft.

14 - 28
14. SERVO MOTOR
14.7.2 Vibration rank
The vibration rank of the servo motor is V-10 at the rated speed. Measure vibration in the following
position with the servo motor installed as shown below.
Top
Bottom
Servo motor
Measuring position
Servo Motor Vibration
Measuring Conditions
14.7.3 Machine Accuracies
The following table indicates the machine accuracies of the servo motor around the output shaft and
mounting. (except the optional products)
Flange Size
Accuracy
[mm]
Measuring
Position Less than 100 100 130 176
Runout of flange surface to output shaft a) 0.05 0.06 0.08
Runout of fitting OD of flange surface b) 0.04 0.04 0.06
Runout of output shaft end c) 0.02 0.02 0.03
Reference diagram
a)
b) c)

14 - 29
14. SERVO MOTOR
14.8 Outline dimension drawing
14.8.1 HC-KFE series
(1) Standard (without electromagnetic brake, without reduction gear)
Model Output
[W]
Inertia Moment
J[ 10 4kg m2]
Weight
[kg]
HC-KFE13 100 0.084 0.53
Power supply
connector pin
connection list
1
2
3
4
Pin No. Application
Phase U
Phase V
Phase W
Earth
BC24190*
20
5557-04R-210 (Receptacle)
5556PBTL (Female terminal)
With connector 1-172169-9
(AMP) Arrow A
35.7
Bottom
Top
Protective tube
Motor plate
(Opposite side)
30h7
46
40
8h6
Power supply connector (Molex)
Encoder cable 0.3m
Motor plate
Caution plate
Bottom
Top
Top
25
2.5
5
40.5
6.8
9.9
25.2
42
28.7
2- 4.5
Power supply lead 4-AWG19 0.3m
TUV plate
Arrow A
Bottom
Top
Bottom
Note: The dimensions without tolerances are reference dimensions.
96.5
21.5
44.5
45
(Note)[Unit: mm]
Top
Bottom
Variable Dimensions
Model Output
[W] LKL
Inertia Moment
J[ 10 4kg m2]
Weight
[kg]
HC-KFE23 200 99.5 49.1 0.42 0.99
HC- KFE 43 400 124.5 72.1 0.67 1.45
(Note)[Unit: mm]
20
5557-04R-210 (Receptacle)
5556PBTL (Female terminal)
With connector 1-172169-9
(AMP) Arrow A
42.8
Bottom
Top
Protective tube
Motor plate
(Opposite side)
50h7
70
60
14h6
Power supply connector (Molex)
Encoder cable 0.3m
Motor plate
Caution plate
Bottom
Top
KL
30
3
7
L
41
10.6 9.9
25.2
62
38.4
4- 5.8
Power supply lead 4-AWG19 0.3m
TUV plate
Arrow A
Top
Bottom
2.7
Note: The dimensions without tolerances are reference dimensions.
45
Power supply
connector pin
connection list
1
2
3
4
Pin No. Application
Phase U
Phase V
Phase W
Earth
BC24191*
Top
Bottom

14 - 30
14. SERVO MOTOR
Model Output
[W]
Inertia Moment
J[ 10 4kg m2]
Weight
[kg]
HC-KFE73 750 1.51 3
(Note)[Unit: mm]
Note: The dimensions without tolerances are reference dimensions.
Power supply
connector pin
connection list
1
2
3
4
Pin No. Application
Phase U
Phase V
Phase W
Earth
BC24192*
20
5557-04R-210 (Receptacle)
5556PBTL (Female terminal)
With connector 1-172169-9
(AMP) Arrow A
58.1
Bottom
Top
Protective tube
Motor plate
(Opposite side)
70h7
90
80
19h6
Power supply connector (Molex)
Encoder cable 0.3m
Motor plate
Caution plate
Bottom
Top
86.7
40
3
8
142
39
11 9.9
25.2
82
48.7
4- 6.6
Power supply lead 4-AWG19 0.3m
TUV plate
Arrow A
Top
Bottom
2.7
Top
Bottom
45
(2) With electromagnetic brake
Model Output
[W]
Braking Force
[N m]
Inertia Moment
J[ 10 4kg m2]
Weight
[kg]
HC-KFE13B 100 0.32 0.087 0.89
BC24193*
Note: The dimensions without tolerances are reference dimensions.
(Note)[Unit: mm]
20
5557-06R-210 (Receptacle)
5556PBTL (Female terminal)
With connector 1-172169-9
(AMP) Arrow A
35.7
Bottom
Top
Protective tube
Motor plate
(Opposite side)
30h7
46
40
8h6
Power supply connector (Molex)
Encoder cable 0.3m
Motor plate
Caution plate
Bottom
Top
Top
25
2.5
5
40.5
6.8
9.9
25.2
42
2- 4.5
Power supply lead 4-AWG19 0.3m
TUV plate
Arrow A
Bottom
Top
Bottom
124.5
21.5
44.5
Top
Bottom
Insulock
Brake lead
65.5
2 - 0.3 0.3m
2
45
28.7
Power supply
connector pin
connection list
1
2
3
4
Pin No. Application
Phase U
Phase V
Phase W
Earth
5
6
B1
B2

14 - 31
14. SERVO MOTOR
Variable Dimensions
Model Output
[W] LKL
Braking Force
[N m]
Inertia Moment
J[ 10 4kg m2]
Weight
[kg]
HC-KFE23B 200 131.5 49.1 1.3 0.47 1.6
HC- KFE43B 400 156.5 72.1 1.3 0.72 2.1
(Note)[Unit: mm]
Note: The dimensions without tolerances are reference dimensions.
BC24194*
20
5557-06R-210 (Receptacle)
5556PBTL (Female terminal)
With connector 1-172169-9
(AMP) Arrow A
42.8
Bottom
Top
Protective tube
Motor plate
(Opposite side)
50h7
70
60
14h6
Power supply connector (Molex)
Encoder cable 0.3m
Motor plate
Caution plate
Bottom
Top
KL
30
3
7
L
41
10.6
68
25.2
62
38.4
4- 5.8
Power supply lead 4-AWG19 0.3m
TUV plate
Arrow A
Top
Bottom
2.7
Top
Bottom
9.9
Insulock
Brake lead
2 - 0.3 0.3m
2
45
Power supply
connector pin
connection list
1
2
3
4
Pin No. Application
Phase U
Phase V
Phase W
Earth
5
6
B1
B2
Model Output
[W]
Braking Force
[N m]
Inertia Moment
J[ 10 4kg m2]
Weight
[kg]
HC-KFE73B 750 2.4 1.635 4.0
(Note)[Unit: mm]
20
5557-06R-210 (Receptacle)
5556PBTL (Female terminal)
With connector 1-172169-9
(AMP) Arrow A
58.1
Bottom
Top
Protective tube
Motor plate
(Opposite side)
70h7
90
60
19h6
Power supply connector (Molex)
Encoder cable 0.3m
Motor plate
Caution plate
Bottom
Top
3
8
40
39
11
72
25.2
82
48.7
4- 5.6
Power supply lead 4-AWG19 0.3m
TUV plate
Arrow A
Top
Bottom
2.7
Note: The dimensions without tolerances are reference dimensions.
BC24195*
Top
Bottom
177.5
19.5
Insulock
Brake lead
2 - 0.3 0.3m
2
45
Power supply
connector pin
connection list
1
2
3
4
Pin No. Application
Phase U
Phase V
Phase W
Earth
5
6
B1
B2
86.7

14 - 32
14. SERVO MOTOR
14.8.2 HC-SFE series
(1) Standard (without electromagnetic brake, without reduction gear)
Variable dimensions
Model Output
[kW] LKL
Inertia Moment
J[ 10 4kg m2]
Weight
[kg]
HC-SFE52 0.5 150.5 51.5 6.7 5.5
HC-SFE102 1.0 175.5 76.5 13.8 7.5
HC-SFE152 1.5 200.5 101.5 20.1 9.5
BC25010*
21
W
U
S30457B
MS3102A20-29P
CE05-2A22-23P
93
70
L55
12 3
50
41
111
45°
Encoder connector
Power supply connector
Oil seal
Motor flange direction
Earth
Power supply connector layout
CE05-2A22-23P
(Note)[Unit: mm]
Motor plate
(Opposite side)
Bottom
Top
130
145
Note: The dimensions without tolerances are reference dimensions.
Caution plate
TUV plate
Bottom
Top Bottom
Top
Bottom
Top
110h7
24h6
KL
165
4- 9 mounting hole
Use hexagon socket
head cap screw.
V
Model Output
[kW]
Inertia Moment
J[ 10 4kg m2]
Weight
[kg]
HC-SFE202 2.0 42.6 12.5
BC25012*
V
U
68.5
21
93
70
175.5 79
18 3
75
46
142
S40608B
MS3102A20-29P
CE05-2A24-10P
Encoder connector
Power supply connector
Oil seal
Motor flange direction
Power supply connector layout
CE05-2A24-10P
Motor plate
(Opposite side)
Bottom
Top
Earth
Bottom
Top
(Note)[Unit: mm]
176
230
200
4- 13.5 mounting hole
Use hexagon socket
head cap screw.
0.025
0
114.3
Note: The dimensions without tolerances are reference dimensions.
W
45
Caution plate
TUV plate
Bottom
Top Bottom
Top
0
0.010
35

14 - 33
14. SERVO MOTOR
(2) With electromagnetic brake
Variable dimensions
Model Output
[kW] LKL
Braking Force
[N m]
Inertia Moment
J[ 10 4kg m2]
Weight
[kg]
HC-SFE52B 0.5 183.5 51.5 8.3 8.7 7.5
HC-SFE102B 1.0 208.5 76.5 8.3 15.8 9.5
HC-SFE152B 1.5 233.5 101.5 8.3 22.1 11.5
BC25011*
V
U
KL
21
93
70
L55
12 3
50
41
111
S30457B
MS3102A20-29P
CE05-2A22-23P
Encoder connector
Power supply connector
Oil seal
Motor flange direction
Power supply connector layout
CE05-2A22-23P
Motor plate
(Opposite side)
Bottom
Top
Earth
Bottom
Top
(Note)[Unit: mm]
130
145
165
Note: The dimensions without tolerances are reference dimensions.
W
Caution plate
TUV plate
Bottom
Top
Bottom
Top
Brake
4- 9 mounting hole
Use hexagon socket
head cap screw.
110h7
24h6
45°
Model Output
[kW]
Braking Force
[N m]
Inertia Moment
J[ 10 4kg m2]
Weight
[kg]
HC-SFE202B 2.0 43.1 52.6 18.5
BC25013*
68.5
21
93
70
223.5 79
18 3
142
99.5
Bottom
Top
Power supply connector
CE05-2A24-10P
(Note)[Unit: mm]
Motor plate
(Opposite side)
MS3102A20-29P
Encoder connector Brake connector
MS3102A10SL-4P
S40608B
Oil seal
Bottom
Top
V
U
Motor flange direction
Earth
Power supply connector layout
CE05-2A24-10P
Brake connector layout
MS3102A10SL-4P
Motor flange direction
Brake
176
Note: The dimensions without tolerances are reference dimensions.
4- 13.5 mounting hole
Use hexagon socket
head cap screw.
114.3 0.025
0
0.010
0
35
75
W
230
200
46
45
Caution plate
TUV plate
Bottom
Top Bottom
Top
117

14 - 34
14. SERVO MOTOR
14.9 Outline dimension drawing (in inches)
POINT
The values in yards/pounds are reference values.
14.9.1 HC-KFE series
(1) Standard (without electromagnetic brake, without reduction gear)
Model Output
[W]
Inertia Moment
WK2[oz in2]
Weight
[lb]
HC-KFE13 100 0.459 1.17
Power supply
connector pin
connection list
1
2
3
4
Pin No. Application
Phase U
Phase V
Phase W
Earth
BC24190*
0.737
5557-04R-210 (Receptacle)
5556PBTL (Female terminal)
With connector 1-172169-9
(AMP) Arrow A
1.406
Bottom
Top
Protective tube
Motor plate
(Opposite side)
1.181
1.81
1.575
0.315
Power supply connector (Molex)
Encoder cable 11.8 in
Motor plate
Caution plate
Bottom
Top
Top
0.984
0.098
0.197
1.59
0.268
0.39
0.992
1.65
1.13
2- 0.177
Power supply lead 4-AWG19 11.8 in
TUV plate
Arrow A
Bottom
Top
Bottom
3.70
0.846
1.75
45
[Unit: in]
Top
Bottom
Variable Dimensions [in]
Model Output
[W] LKL
Inertia Moment
WK2[oz in2]
Weight
[lb]
HC-KFE23 200 3.92 1.93 2.296 2.183
HC-KFE43 400 4.90 2.84 3.663 3.197
[Unit: in]
0.737
5557-04R-210 (Receptacle)
5556PBTL (Female terminal)
With connector 1-172169-9
(AMP) Arrow A
1.685
Bottom
Top
Protective tube
Motor plate
(Opposite side)
1.969
2.758
2.362
0.551
Power supply connector (Molex)
Encoder cable 11.8 in
Motor plate
Caution plate
Bottom
Top
KL
1.181
0.118
0.276
L
1.614
0.417 0.390
0.992
3.23
1.512
4- 0.228
Power supply lead 4-AWG19 11.8 in
TUV plate
Arrow A
Top
Bottom
0.106
45
Power supply
connector pin
connection list
1
2
3
4
Pin No. Application
Phase U
Phase V
Phase W
Earth
BC24191*
Top
Bottom

14 - 35
14. SERVO MOTOR
Model Output
[W]
Inertia Moment
WK2[oz in2]
Weight
[lb]
HC-KFE73 750 8.256 6.614
[Unit: in]
Power supply
connector pin
connection list
1
2
3
4
Pin No. Application
Phase U
Phase V
Phase W
Earth
BC24192*
0.787
5557-04R-210 (Receptacle)
5556PBTL (Female terminal)
With connector 1-172169-9
(AMP) Arrow A
Bottom
Top
Protective tube
Motor plate
(Opposite side)
2.756
3.543
3.150
0.784
Power supply connector (Molex)
Encoder cable 11.8 in
Motor plate
Caution plate
Bottom
Top
3.413
1.575
0.118
0.315
5.591
1.535
0.433 0.390
0.992
3.228
1.917
4- 0.260
Power supply lead 4-AWG19 11.8 in
TUV plate
Arrow A
Top
Bottom
0.106
Top
Bottom
45
2.287
(2) With electromagnetic brake
Model Output
[W]
Braking Force
[oz in]
Inertia Moment
WK2[oz in2]
Weight
[lb]
HC-KFE13B 100 45.316 0.476 1.962
BC24193*
[Unit: in]
0.787
5557-06R-210 (Receptacle)
5556PBTL (Female terminal)
With connector 1-172169-9
(AMP) Arrow A
1.406
Bottom
Top
Protective tube
Motor plate
(Opposite side)
1.181
1.811
1.575
0.315
Power supply connector (Molex)
Encoder cable 11.8 in
Motor plate
Caution plate
Bottom
Top
Top
0.984
0.098
0.197
1.594
0.268
0.390
0.992
1.654
2- 0.177
Power supply lead 4-AWG19 11.8 in
TUV plate
Arrow A
Bottom
Top
Bottom
4.902
0.846
1.752
Top
Bottom
Insulock
Brake lead
2.579
2 - 0.3 11.8 in
2
45
1.130
Power supply
connector pin
connection list
1
2
3
4
Pin No. Application
Phase U
Phase V
Phase W
Earth
5
6
B1
B2

14 - 36
14. SERVO MOTOR
Variable Dimensions [in]
Model Output
[W] LKL
Braking Force
[oz in]
Inertia Moment
WK2 [oz in2]
Weight
[lb]
HC-KFE23B 200 5.177 1.933 184.096 2.57 3.527
HC-KFE43B 400 6.161 2.839 184.096 3.937 4.63
[Unit: in]
BC24194*
0.787
5557-06R-210 (Receptacle)
5556PBTL (Female terminal)
With connector 1-172169-9
(AMP) Arrow A
1.685
Bottom
Top
Protective tube
Motor plate
(Opposite side)
1.969
2.756
2.362
0.551
Power supply connector (Molex)
Encoder cable 11.8 in
Motor plate
Caution plate
Bottom
Top
KL
1.181
0.118
0.276
L
1.614
0.417
2.677
0.992
2.441
1.512
4- 0.228
Power supply lead 4-AWG19 11.8 in
TUV plate
Arrow A
Top
Bottom
0.106
Top
Bottom
0.390
Insulock
Brake lead
2 - 0.3 11.8 in
2
45
Power supply
connector pin
connection list
1
2
3
4
Pin No. Application
Phase U
Phase V
Phase W
Earth
5
6
B1
B2
Model Output
[W]
Braking Force
[oz in]
Inertia Moment
WK2 [oz in2]
Weight
[lb]
HC-KFE73B 750 339.869 8.939 8.818
4- 0.260
[Unit: in]
0.787
5557-06R-210 (Receptacle)
5556PBTL (Female terminal)
With connector 1-172169-9
(AMP) Arrow A
2.287
Bottom
Top
Protective tube
Motor plate
(Opposite side)
2.756
3.543
3.150
0.748
Power supply connector (Molex)
Encoder cable 11.8 in
Motor plate
Caution plate
Bottom
Top
0.315
1.575
1.535
0.433 2.835
0.992
3.228
1.917
Power supply lead 4-AWG19 11.8 in
TUV plate
Arrow A
Top
Bottom
0.106
BC24195*
Top
Bottom
6.988
0.768
Insulock
Brake lead
2 - 0.3 11.8 in
2
45
3.413
0.390
0.118
Power supply
connector pin
connection list
1
2
3
4
Pin No. Application
Phase U
Phase V
Phase W
Earth
5
6
B1
B2

14 - 37
14. SERVO MOTOR
14.9.2 HC-SFE series
(1) Standard (without electromagnetic brake, without reduction gear)
Variable Dimensions [in]
Model Output
[kW] LKL
Inertia Moment
WK2[oz in2]
Weight
[lb]
HC-SFE52 0.5 5.925 2.028 36.632 12.125
HC-SFE102 1.0 6.909 3.012 75.451 16.535
HC-SFE152 1.5 7.894 3.996 109.896 20.944
BC25010*
0.77
W
U
S30457B
MS3102A20-29P
CE05-2A22-23P
3.21
2.756
L 2.165
0.47 0.12
1.97
1.61
4.37
45°
Encoder connector
Power supply connector
Oil seal
Motor flange direction
Earth
Power supply connector layout
CE05-2A22-23P
[Unit: in]
Motor plate
(Opposite side)
Bottom
Top
5.118
5.709
Caution plate
TUV plate
Bottom
Top Bottom
Top
Bottom
Top
4.331
0.945
KL
6.496
4- 0.354 mounting hole
Use hexagon socket
head cap screw.
V
Model Output
[kW]
Inertia Moment
WK2[oz in2]
Weight
[lb]
HC-SFE202 2.0 232.913 27.558
BC25012*
V
U
2.736
0.77
3.21
2.756
6.909 3.11
0.71 0.12
2.95
1.81
5.59
S40608B
MS3102A20-29P
CE05-2A24-10P
Encoder connector
Power supply connector
Oil seal
Motor flange direction
Power supply connector layout
CE05-2A24-10P
Motor plate
(Opposite side)
Bottom
Top
Earth
Bottom
Top
[Unit: in]
6.93
7.87
9.06
4- 0.531 mounting hol
e
Use hexagon socket
head cap screw.
4.5
W
45
Caution plate
TUV plate
Bottom
Top Bottom
Top
1.378

14 - 38
14. SERVO MOTOR
(2) With electromagnetic brake
Variable dimensions [in]
Model Output
[kW] LKL
Braking Force
[oz in]
Inertia Moment
WK2[oz in2]
Weight
[lb]
HC-SFE52B 0.5 7.224 2.028 1175.382 47.567 16.535
HC-SFE102B 1.0 8.209 3.012 1175.382 86.386 20.944
HC-SFE152B 1.5 9.193 3.996 1175.382 120.831 25.353
BC25011*
V
U
KL
0.77
93
2.756
L2.165
0.47 0.12
50
1.61
4.30
S30457B
MS3102A20-29P
CE05-2A22-23P
Encoder connector
Power supply connector
Oil seal
Motor flange direction
Power supply connector layout
CE05-2A22-23P
Motor plate
(Opposite side)
Bottom
Top
Earth
Bottom
Top
[Unit: in]
5.118
5.709
6.496
W
Caution plate
TUV plate
Bottom
Top
Bottom
Top
Brake
4- 0.354 mounting hole
Use hexagon socket
head cap screw.
4.331
0.945
3.21
45°
Model Output
[kW]
Braking Force
[oz in]
Inertia Moment
WK2[oz in2]
Weight
[lb]
HC-SFE202B 2.0 6103.49 287.588 40.785
BC25013*
2.697
0.77
3.21
2.756
8.799 174.165
0.71 0.12
5.59
3.917
Bottom
Top
Power supply connector
CE05-2A24-10P
[Unit: in]
Motor plate
(Opposite side)
MS3102A20-29P
Encoder connector Brake connector
MS3102A10SL-4P
S40608B
Oil seal
Bottom
Top
V
U
Motor flange direction
Earth
Power supply connector layout
CE05-2A24-10P
Brake connector layout
MS3102A10SL-4P
Motor flange direction
Brake
6.93
4- 0.531 mounting hole
Use hexagon socket
head cap screw.
2.95
W
7.87
9.06
1.81
45
Caution plate
TUV plate
4.5
1.378
Bottom
Top
Bottom
Top
4.606

15 - 1
15. MR-E- AG SERVO AMPLIFIER COMPATIBLE WITH ANALOG INPUT
15. MR-E- AG SERVO AMPLIFIER COMPATIBLE WITH ANALOG INPUT
POINT
In this chapter, difference of the operation of MR-E- AG from that of
MR-E- A is described. For description not given in this Chapter, refer to
Chapters 1 through 14.
15.1. Functions and configuration
15.1.1 Introduction
The analog input MR-E- AG Servo Amplifier is based on the MR-E- A Servo Amplifier with capability
of speed control and torque control.
(1) Speed control mode
An external analog speed command (0 to 10VDC) or parameter-driven internal speed command
(max. 7 speeds) is used to control the speed and direction of a servo motor smoothly.
There are also the acceleration/deceleration time constant setting in response to speed command, the
servo lock function at a stop time, and automatic offset adjustment function in response to external
analog speed command.
(2) Torque control mode
An external analog torque command (0 to 8VDC) or parameter-driven internal torque command is
used to control the torque output by the servo motor.
To protect misoperation under no load, the speed limit function (external or internal setting) is also
available for application to tension control, etc.

15 - 2
15. MR-E- AG SERVO AMPLIFIER COMPATIBLE WITH ANALOG INPUT
15.1.2 Function block diagram
The function block diagram of this servo is shown below.
(Note 3)
(Note 3)
Regenerative
brake Base amplifier Voltage
detection
Over-
current
protection
Detector
Dynamic brake
Current
detector
Regenerative
TR
CHARGE
lamp
RADS
Control
power
supply
Electro-
magnetic
brake
Servo motor
D
C
P
Regenerative brake option
NFB
(Note 2)
Power
s
upply
3
-phase
2
00 to
2
30VAC
S
ingle-phase
2
30VAC
MC L1
L2
L3
CN1 CN3
RS-232C
Controller
E2
I/F
Servo amplifier
Analog monitor
(2 channels)
Current
detection
Model
speed control
Actual speed
control
Current
control
Model
speed
Model torque
Virtual
motor
Virtual
encoder
CN2
U
V
W
U
V
W
SM
E1
(Note 1)
Fan
(MR-E-200AG only)
RS-232C D/A
(Note 3)
(Note 3)(Note 3)
A/D
Analog
(2 channels)
(Note3)
D I/O control
Servo On
Start
Failure, etc.
Note: 1. The built-in regenerative brake resistor is not provided for the MR-E-10AG/20AG.
2. Single-phase 230VAC power supply can be used for MR-E-70AG or servo amplifiers with smaller
capacities. Connect the power cables to L1 and L2 while leaving L3 open.
3. The control circuit connectors (CN1, CN2 and CN3) are safely isolated from main circuit terminals
(
L1
,
L2
,
L3
,
U
,
V
,
W
,
P
,
C and D
)
.

15 - 3
15. MR-E- AG SERVO AMPLIFIER COMPATIBLE WITH ANALOG INPUT
15.1.3 Servo amplifier standard specifications
Servo Amplifier
MR-E-
Item
10AG 20AG 40AG 70AG 100AG 200AG
Voltage/frequency 3-phase 200 to 230VAC, 50/60Hz or 1-phase 230VAC,
50/60Hz 3-phase 200 to 230VAC,
50/60Hz
Permissible voltage fluctuation 3-phase 200 to 230VAC:
170 to 253VAC
1-phase 230VAC: 207 to 253VAC 3-phase 170 to 253VAC
Permissible frequency fluctuation Within 5%
Power supply
Power supply capacity Refer to Section12.2
System Sine-wave PWM control, current control system
Dynamic brake Built-in
Protective functions Overcurrent shut-off, regenerative overvoltage shut-off, overload shut-off (electronic
thermal relay), encoder error protection, regenerative brake error protection,
undervoltage, instantaneous power failure protection, overspeed protection
Speed control range Analog speed command 1: 2000, internal speed command 1: 5000
Analog speed command input 0 to 10VDC / Rated speed
Speed fluctuation ratio 0.01% or less (load fluctuation 0 to 100%)
0% or less (power fluctuation 10%)
0.2% max.(ambient temperature 25 10 ) for external speed setting only
Speed control mode
Torque limit Set by parameter setting or external analog input (0 to 10VDC/maximum torque)
Analog torque command input 0 to 8VDC / Maximum torque (input impedance 10 to 12k )
Torque
control
mode Speed limit Set by parameter setting or external analog input (0 to 10VDC/Rated speed)
Structure Self-cooled, open (IP00) Force-cooling,
open (IP00)
[]0 to 55 (non-freezing)
Operation [] 32 to 131 (non-freezing)
[ ] 20 to 65 (non-freezing)
Ambient
temperature Storage []4 to 149 (non-freezing)
Operation
Ambient
humidity Storage 90%RH or less (non-condensing)
Ambient Indoors (no direct sunlight)
Free from corrosive gas, flammable gas, oil mist, dust and dirt
Altitude Max. 1000m (3280ft) above sea level
5.9 [m/s2] or less
Environment
Vibration 19.4 [ft/s2] or less
[kg] 0.8 0.8 1.2 1.8 1.8 2.0
Weight [lb] 1.8 1.8 2.6 4.0 4.0 4.4
Note. The MR-E-200A is scheduled for release.

15 - 4
15. MR-E- AG SERVO AMPLIFIER COMPATIBLE WITH ANALOG INPUT
15.1.4 Model code definition
AG
70 750
40 400
10 100
20 100
200 1000
200 2000
MR-E-200AGMR-E-40AG or less MR-E-70AG, 100AG
Rating plate Rating plate
Rating plate
Series
Rated output
Analog input
Symbol Rated output [W] Symbol Rated output [W]
- MR - E
15.1.5 Parts identification
(1) MR-E-100AG or less
MODE
CN3
SET
CN1
CN2
CNP2
CNP1
L3L2L1 D C P W V U
CHARGE
MITSUBISHI
MR-
Chapter6
Display
The 5-digit, seven-segment LED shows the servo
status and alarm number.
Used to set data.
Used to change the
display or data in each
mode.
Used to change the
mode.
MODE UP DOWN SET
Operation section
Used to perform status display, diagnostic, alarm and
parameter setting operations.
Chapter6
Communication connector (CN3)
Used to connect a command device (RS-232C)
and output analog monitor data.
I/O signal connector (CN1)
Used to connect digital I/O signals. Section3.3
Encoder connector (CN2)
Connector for connection of the servo motor encoder. Section3.3
Section13.1.2
Charge lamp
Lit to indicate that the main circuit is charged. While
this lamp is lit, do not reconnect the cables.
Protective earth (PE) terminal ( )
Ground terminal. Section3.10
Section11.1
Section3.3
Section13.1.2
Chapter14
Section3.7
Section11.1
Section3.7
Section11.1
Section13.1.1
Refer to
Name/Application
Motor power supply connector (CNP2)
Used to connect the servo motor.
Power supply/regenerative connector (CNP1)
Used to connect the input power supply and
regenerative brake option.

15 - 5
15. MR-E- AG SERVO AMPLIFIER COMPATIBLE WITH ANALOG INPUT
(2) MR-E-200AG
Refer to
Name/Application
Section15.5
Display
The 5-digit, seven-segment LED shows the servo
status and alarm number.
Used to set data.
Used to change the
display or data in each
mode.
Used to change the
mode.
MODE UP DOWN SET
Operation section
Used to perform status display, diagnostic, alarm and
parameter setting operations.
Section15.5
Communication connector (CN3)
Used to connect a command device (RS232C)
and output analog monitor data.
Section3.3
Section13.1.2
Chapter14
I/O signal connector (CN1)
Used to connect digital I/O signals. Section15.2
Name plate
Charge lamp
Lit to indicate that the main circuit is charged. While
this lamp is lit, do not reconnect the cables.
Encoder connector (CN2)
Connector for connection of the servo motor encoder.
Section1.5
Section3.3
Section13.1.2
Motor power supply connector (CNP2)
Used to connect the servo motor.
Protective earth (PE) terminal ( )
Ground terminal.
Power supply/regenerative connector (CNP1)
Used to connect the input power supply and
regenerative brake option.
Section3.7
Section11.1
Section3.7
Section11.1
Section13.1.1
Section3.10
Section11.1
Cooling fan
Installation notch
(4 places)

15 - 6
15. MR-E- AG SERVO AMPLIFIER COMPATIBLE WITH ANALOG INPUT
15.1.6 Servo system with auxiliary equipment
WARNING To prevent an electric shock, always connect the protective earth (PE) terminal
(terminal marked ) of the servo amplifier to the protective earth (PE) of the control
box.
(1) MR-E-100AG or less
MODE
CN3
SET
CN1
CN2
CNP2
CNP1
L3L2L1 D C P W V U
CHARGE
P
C
L3
L2
L1
(Note 2)
3-phase 200V
to 230VAC power
supply or
1-phase 230VAC
power supply
No-fuse breaker
(NFB) or fuse
Magnetic
contactor
(MC)
To CN2
To CN1
To CN3
Protective earth
(PE) terminal
Servo motor
Personal
computer
Servo amplifier
Regenerative option
Options and auxiliary equipment
No-fuse breaker
Magnetic contactor
Servo configuration software
Regenerative option
Refer to
Section 13.2.2
Section 13.2.2
Section 13.1.4
Section 13.1.1
(Note 1)
Encoder cable
Options and auxiliary equipment Refer to
Cables Section 13.2.1
Command device
(Note 1)
Power supply lead
Power
factor
improving
reactor
(FR-BAL)
Power factor improving reactor Section 13.2.3
Note: 1. The HC-SFE series have cannon connectors.
2. A 1-phase 230VAC power supply may be used with the servo amplifier of MR-E-70AG or less. Connect the power supply to
L1 and L2 terminals and leave L3 open.
Servo configuration
software
MRZJW3-SETUP1
MITSUBISHI
MR-E-

15 - 7
15. MR-E- AG SERVO AMPLIFIER COMPATIBLE WITH ANALOG INPUT
(2) MR-E-200AG
L3
L2
L1
DC L3PL1L2
CHARGE
CNP2
CNP1
CN1
CN2
UVW
CN3
MODE SET
MITS U BISHI
EZMotion
PC
Options and auxiliary equipment
No-fuse breaker
Magnetic contactor
Servo configuration software
Regenerative option
Refer to
Section 13.2.2
Section 13.2.2
Section 13.1.4
Section 13.1.1
Options and auxiliary equipment Refer to
Cables Section 13.2.1
Power factor improving reactor Section 13.2.3
Power
f
actor
improving
reactor
(FR-BAL)
3-phase 200V
to 230VAC
power supply
No-fuse
breaker
(NFB) or
fuse
Magnetic
contactor
(MC)
To CN2
To CN1
To CN3
Servo amplifier
Regenerative option
Personal
computer
Command device
Servo configuration
software
MRZJW3-SETUP1
To CNP2

15 - 8
15. MR-E- AG SERVO AMPLIFIER COMPATIBLE WITH ANALOG INPUT
15.2. Signals and wiring
15.2.1 Standard connection example
(1) Speed control mode
1
9
12
10m (32ft) or less
RA1
RA2
8
4
3
5
6
7
EMG
SON
ST1
ST2
LSP
LSN
SG 13
ALM
ZSP
Servo amplifier
(Note 1)
CN3
(Note 8)
CN1
Trouble
(Note 6)
Zero speed
VIN (Note 2, 4)
CN1
(Note 8)
4
3
SD
6
MO1
LG
A
A
2m (6.5ft) or less
Plate
CN3
(Note 8)
20
19
21
17
16
18
LZ
LZR
LA
LAR
LB
LBR
LG
OP
SD
14
15
Encoder Z-phase pulse
(differential line driver)
11
10 SA
RD
RA5
RA4
Speed reached
Ready
13 SG
Plate
External
power
supply
24VDC
(Note 10)
2m (6.5ft) or less
Plate
14
SD
LG
26
VC
2TLA
Upper limit setting
Upper limit setting CN1
(Note 8)
Encoder A-phase pulse
(differential line driver)
Encoder B-phase pulse
(differential line driver)
Control common
Encoder Z-phase pulse
(open collector)
(Note 8)
MO2
(Note 3, 5) Emergency stop
Servo-on
Forward rotation start
Reverse rotation start
(Note 5) Forward rotation stroke end
Reverse rotation stroke end
(Note 9)
Servo configuration
software
Personal
computer (Note 7)
Communication cable
Analog speed command
10V/rated speed
Analog torque limit
10V/max. torque
(Note 7)
Monitor output
Max. 1mA
Reading in
both directions
10k
10k
Use external power
supply ( 15VDC).

15 - 9
15. MR-E- AG SERVO AMPLIFIER COMPATIBLE WITH ANALOG INPUT
Note: 1. To prevent an electric shock, always connect the protective earth (PE) terminal (terminal marked ) of the servo amplifier to
the protective earth (PE) of the control box.
2. Connect the diode in the correct direction. If it is connected reversely, the servo amplifier will be faulty and will not output
signals, disabling the emergency stop and other protective circuits.
3. The emergency stop switch (normally closed contact) must be installed.
4. The sum of currents that flow in the external relays should be 80mA max. If it exceeds 80mA, supply interface power from
external.(Refer to Section 3.6.2)
5. When starting operation, always connect the emergency stop signal (EMG) and forward/ reverse rotation stroke end signal
(LSN/LSP) with SG. (Normally closed contacts)
6. Trouble (ALM) is connected with COM in normal alarm-free condition.
7. When connecting the personal computer together with monitor outputs 1, 2, use the branch cable (MR-E3CBL15-P). (Refer to
Section 13.1.3)
8. The pins with the same signal name are connected in the servo amplifier.
9. Use MRZJW3-SETUP 154E.
10. Connect the external 24VDC power supply if the output signals are not used.

15 - 10
15. MR-E- AG SERVO AMPLIFIER COMPATIBLE WITH ANALOG INPUT
(2) Torque control mode
1
9
12
10m (32ft) or less
RA1
RA2
Personal
computer
8
4
5
3
EMG
SON
RS1
RS2
SG 13
ALM
ZSP
Servo amplifier
(Note 1)
CN3
(Note 8)
CN1
Trouble
(Note 6)
Zero speed
VIN
(Note 9)
Servo configuration
software (Note 7)
Communication cable
(Note 2, 4)
(Note 8)
CN1
(Note 8)
4
3
SD
6
MO1
LG
MO2 10k
10k
A
A
2m (6.5ft) or less
Plate
CN3
(Note 8)
20
19
21
17
16
18
LZ
LZR
LA
LAR
LB
LBR
LG
OP
SD
14
15
11 RD RA3 Ready
13 SG
Plate
Encoder Z-phase pulse
(differential line driver)
External
power
supply
24VDC
(Note 10)
2m (6.5ft) or less
Plate
14
SD
LG
2
TC
26VLA
Upper limit setting CN1
(Note 8)
Encoder A-phase pulse
(differential line driver)
Encoder B-phase pulse
(differential line driver)
Control common
Encoder Z-phase pulse
(open collector)
Analog torque command
8V/max. torque
Upper limit setting
Analog speed limit
0 to 10V/rated speed
(Note 3, 5) Emergency stop
Servo-on
Forward rotation
selection
Reverse rotation
selection
(Note 7)
Monitor output
Max. 1mA
Reading in
both directions
Use external power
supply ( 15VDC).
Note: 1. To prevent an electric shock, always connect the protective earth (PE) terminal (terminal marked ) of the servo amplifier to
the protective earth (PE) of the control box.
2. Connect the diode in the correct direction. If it is connected reversely, the servo amplifier will be faulty and will not output
signals, disabling the emergency stop and other protective circuits.
3. The emergency stop switch (normally closed contact) must be installed.
4. The sum of currents that flow in the external relays should be 80mA max. If it exceeds 80mA, supply interface power from
external.(Refer to Section 3.6.2)
5. When starting operation, always connect the emergency stop signal (EMG) with SG. (Normally closed contacts)
6. Trouble (ALM) is connected with COM in normal alarm-free condition.
7. When connecting the personal computer together with monitor outputs 1, 2, use the branch cable (MR-E3CBL15-P). (Refer to
Section 13.1.3)
8. The pins with the same signal name are connected in the servo amplifier.
9. Use MRZJW3-SETUP 154E.
10. Connect the external 24VDC power supply if the output signals are not used.

15 - 11
15. MR-E- AG SERVO AMPLIFIER COMPATIBLE WITH ANALOG INPUT
15.2.2 Internal connection diagram of servo amplifier
The following is the internal connection diagram where the signal assignment has been made in the
initial status in each control mode.
T
RD RD11ST2
ST1
EMG
LSP
LSN
SG
EMG
SG
RS2
SDSD
S
13
Servo amplifier
CN1
CN1
(Note)
SON SON 4
3
8
6
7
RS1 5
Case
ST
SA10
ALM ALM9
ZSP ZSP12
15
16
18
17
20
21
19
LA
LAR
LBR
LB
LZR
OP
LZ
(Note)
CN1
4MO1
6
2
MO2
TXD
CN3
1RXD
3LG
PE
LG14
External
power
supply
24VDC
VIN VIN 1
Case SD
ST
VC VLA
TLA TC
LG LG
26
2
14
(Note)
Note: S: Speed control mode, T: Torque control mode
Approx. 4.7k
Approx. 4.7k
Approx. 4.7k
Approx. 4.7k
Approx. 4.7k
Approx. 4.7k

15 - 12
15. MR-E- AG SERVO AMPLIFIER COMPATIBLE WITH ANALOG INPUT
15.2.3 Connectors and signal arrangements
POINT
The pin configurations of the connectors are as viewed from the cable
connector wiring section.
Refer to the next page for CN1 signal assignment.
(1) Signal arrangement
3
MR 57
MD 9
2
LG 4
MRR 68
MDR 10
LG
1
MODE
CN3
SET
CN1
CN2
CNP2
CNP1
L3L2L1 D C P W V U
MITSUBISHI
MR-E
The connector frames are
connected with the PE (earth)
terminal inside the servo amplifier.
P5
53
LG
1
RXD
6
MO2
4
MO1
2
TXD
2
TLA
1
VIN 15
LA
14
LG
16
LAR
17
LB
3
ST1
4
SON
6
LSP
5
ST2 19
LZ
18
LBR
20
LZR
21
OP
7
LSN
8
EMG
10
SA
9
ALM 23
22
24
25
11
RD
12
ZSP 2613
SG
2
TC
1
VIN 15
LA
14
LG
16
LAR
17
LB
3
RS2
4
SON
6
5
RS1 19
LZ
18
LBR
20
LZR
21
OP
7
8
EMG
10
9
ALM 23
22
24
25
11
RD
12
ZSP 2613
SG
CN1(Speed control mode) CN1(Torque control mode)
Refer to Section 3.3.2
VC VLA
CHARGE

15 - 13
15. MR-E- AG SERVO AMPLIFIER COMPATIBLE WITH ANALOG INPUT
(2) CN1 signal assignment
The signal assignment of connector changes with the control mode as indicated below;
For the pins which are given parameter No.s in the related parameter column, their signals can be
changed using those parameters.
(Note2)I/O Signals in control modes
Connector Pin No. (Note1)I/O SS/TT
Related
parameter
1 VIN VIN VIN
2 I TLA TLA/TC TC
3 I ST1 ST1/RS2 RS2 No.43 to 48
4 I SON SON SON No.43 to 48
5 I ST2 LOP RS1 No.43 to 48
6I LSP LSP/ No.43 48
7I LSN LSN/ No.43 48
8 I EMG EMG EMG
9O ALM ALM ALM No.49
10 O SA SA/ No.49
11 O RD RD RD No.49
12 O ZSP ZSP ZSP No.1, 49
13 SG SG SG
14 LG LG LG
15 O LA LA LA
16 O LAR LAR LAR
17 O LB LB LB
18 O LBR LBR LBR
19 O LZ LZ LZ
20 O LZR LZR LZR
21 O OP OP OP
22
23
24
25
CN1
26 I VC VC/VLA VLA
Note: 1. I : Input signal, O: Output signal
2. S : Speed control mode, T: Torque control mode, S/T: Speed/torque control switching mode

15 - 14
15. MR-E- AG SERVO AMPLIFIER COMPATIBLE WITH ANALOG INPUT
15.2.4 Signal explanations
For the I/O interfaces (symbols in I/O column in the table), refer to Section 3.6.2.
In the control mode field of the table
S: speed control mode, T: Torque control mode
: Denotes that the signal may be used in the initial setting status.
: Denotes that the signal may be used by setting the corresponding parameter among parameters 43 to
49.
The pin No.s in the connector pin No. column are those in the initial status.
(1) Input signals
POINT
The acceptance delay time of each input signal is less than 10ms.
Control
mode
Signal Symbol
Connec-
tor pin
No.
Functions/Applications I/O
division ST
To start operation, short LSP-SG and/or LSN-SG. Open them to
bring the motor to a sudden stop and make it servo-locked.
Set " 1" in parameter No. 22 to make a slow stop.
(Refer to Section 5.2.3.)
(Note) Input signals Operation
LSP LSN CCW
direction
CW
direction
11
Forward rotation
stroke end LSP CN1
6
01
10
00
Note. 0: LSP/LSN-SG off (open)
1: SP/LSN-SG on (short)
Set parameter No. 41 as indicated below to switch on the signals
(keep terminals connected) automatically in the servo amplifier:
Parameter No.41 Automatic ON
1 LSP
1 LSN
Reverse rotation
stroke end LSN CN1
7
DI-1
Outside torque
limit selection TL Turn TL off to make Internal torque limit 1 (parameter No. 28)
valid, or turn it on to make Analog torque limit (TLA) valid.
For details, refer to (1)(C), Section 15.2.5.
DI-1
Internal
torque limit
selection
TL1 When using this signal, make it usable by making the setting of
parameter No. 43 to 48.
(Refer to (5), Section 3.4.1.)
DI-1

15 - 15
15. MR-E- AG SERVO AMPLIFIER COMPATIBLE WITH ANALOG INPUT
Control
mode
Signal Symbol
Connec-
tor pin
No.
Functions/Applications I/O
division ST
Used to start the servo motor in any of the following directions:
(Note) Input signals
ST2 ST1 Servo motor starting direction
Forward rotation
start ST1 CN1
-3
0 0 Stop (servo lock)
0 1 CCW
10 CW
1 1 Stop (servo lock)
Reverse rotation
start ST2 CN1
-5
Note. 0: ST1/ST2-SG off (open)
1: ST1/ST2-SG on (short)
If both ST1 and ST2 are switched on or off during operation, the
servo motor will be decelerated to a stop according to the parameter
No. 12 setting and servo-locked.
DI-1
Used to select any of the following servo motor torque generation
directions:
(Note) Input signals
RS2 RS1 Torque generation direction
Forward rotation
selection RS1 CN1
-5
0 0 Torque is not generated.
01
Forward rotation in driving mode /
reverse rotation in regenerative mode
10
Reverse rotation in driving mode /
forward rotation in regenerative mode
1 1 Torque is not generated.
Reverse rotation
selection RS2 CN1
-3
Note. 0: off
1: on
DI-1
Speed selection 1 SP1 <Speed control mode>
Used to select the command speed for operation.
When using SP1 to SP3, make it usable by making the setting of
parameter No. 43 to 48.
DI-1
(Note) Input signals
Speed selection 2 SP2
SP3 SP2 SP1
Speed command
DI-1
Speed selection 3 SP3 0 0 0 Analog speed command (VC) DI-1
0 0 1 Internal speed command 1 (parameter No. 8)
0 1 0 Internal speed command 2 (parameter No. 9)
0 1 1 Internal speed command 3 (parameter No. 10)
1 0 0 Internal speed command 4 (parameter No. 72)
1 0 1 Internal speed command 5 (parameter No. 73)
1 1 0 Internal speed command 6 (parameter No. 74)
1 1 1 Internal speed command 7 (parameter No. 75)
Note 0: SP1/SP2/SP3-SG off (open)
1: SP1/SP2/SP3-SG on (short)
<Torque control mode>
Used to select the limit speed for operation.
When using SP1 to SP3, make it usable by making the setting of
parameter No. 43 to 48.
(Note) Input signals
SP3 SP2 SP1
Speed liimit
0 0 0 Analog speed limit (VLA)
0 0 1 Internal speed limit 1 (parameter No. 8)
0 1 0 Internal speed limit 2 (parameter No. 9)
0 1 1 Internal speed limit 3 (parameter No. 10)
1 0 0 Internal speed limit 4 (parameter No. 72)
1 0 1 Internal speed limit 5 (parameter No. 73)
1 1 0 Internal speed limit 6 (parameter No. 74)
1 1 1 Internal speed limit 7 (parameter No. 75)
Note 0: SP1/SP2/SP3-SG off (open)
1: SP1/SP2/SP3-SG on (short)

15 - 16
15. MR-E- AG SERVO AMPLIFIER COMPATIBLE WITH ANALOG INPUT
Control
mode
Signal Symbol
Connec-
tor pin
No.
Functions/Applications I/O
division ST
Servo-on SON CN1-4 Same as MR-E- A. (Refer to (1) in Section 3.3.2) DI-1
Reset RES DI-1
Proportion
control PC DI-1
Emergency stop EMG CN1-8 DI-1
Gain changing CDP DI-1
Analog torque
limit TLA To use this signal in the speed control mode, set any of parameters
No. 43 to 48 to make TL available.
When the analog torque limit (TLA) is valid, torque is limited in the
full servo motor output torque range. Apply 0 to 10VDC across
TLA-LG. Connect the positive terminal of the power supply to TLA.
Maximum torque is generated at 10V. (Refer to (1)(a) in Section
15.2.5.) Resolution:10bit
Analog
input
Analog torque
command TC
CN1-2
Used to control torque in the full servo motor output torque range.
Apply 0 to 8VDC across TC-LG. Maximum torque is generated at
8V. (Refer to (2)(a) in Section 15.2.5.)
The torque at 8V input can be changed using parameter No. 26.
Analog
input
Analog speed
command VC Apply 0 to 10VDC across VC-LG. Speed set in parameter No. 25 is
provided at 10V. (Refer to (1)(a) in Section 15.2.5.)
Resolution:14bit or equivalent
Analog
input
Analog speed
limit VLA
CN1-26
Apply 0 to 10VDC across VLA-LG. Speed set in parameter No. 25
is provided at 10V (Refer to (2)(c) in Section 15.2.5.). Analog
input

15 - 17
15. MR-E- AG SERVO AMPLIFIER COMPATIBLE WITH ANALOG INPUT
(2) Output signals
Control
mode
Signal Symbol
Connec-
tor pin
No.
Functions/Applications I/O
division ST
Speed reached SA SA-SG are connected when the servo motor speed has nearly
reached the preset speed. When the preset speed is 50r/min or
less, SA-SG are kept connected.
DO-1
Limiting speed VLC VLC turns on when speed reaches the value limited using any of
the internal speed limits 1 to 7 (parameter No. 8 to 10, 72 to 75)
or the analog speed limit (VLA) in the torque control mode.
VLC turns off when servo on (SON) turns off.
DO-1
Limiting torque TLC TLC turns on when the torque generated reaches the value set to
the internal torque limit 1 (parameter No. 28) or analog torque
limit (TLA). TLC turns off when servo on (SON) turns off.
DO-1
Trouble ALM CN1-9 Same as MR-E- A. (Refer to (2) in Section 3.3.2) DO-1
Ready RD CN1-11 DO-1
Zero speed ZSP CN1-12 DO-1
Electromagnetic
brake interlock MBR
[CN1-12]
DO-1
Warning WNG DO-1
Alarm code ACD0
ACD1
ACD2
DO-1
Encoder Z-phase
pulse
(Open collector)
OP CN1-21 DO-2
Encoder A-phase
pulse
(Differential line
driver)
LA
LAR CN1-15
CN1-16
Encoder B-phase
pulse
(Differential line
driver)
LB
LBR CN1-17
CN1-18
Encoder Z-phase
pulse
(Differential line
driver)
LZ
LZR CN1-19
CN1-20
Analog monitor 1 MO1 CN3-4 Analog
output
Analog monitor 2 MO2 CN3-6 Analog
output
(3) Power
Control
mode
Signal Symbol
Connec-
tor pin
No.
Functions/Applications I/O
division ST
Digital I/F power
supply input VIN CN1-1 Same as MR-E- A. (Refer to (4) in Section 3.3.2)
Open collector
power input OPC CN1-2
Digital I/F
common SG CN1-13
Control common LG CN1-14
Shield SD Plate

15 - 18
15. MR-E- AG SERVO AMPLIFIER COMPATIBLE WITH ANALOG INPUT
15.2.5 Detailed description of the signals
(1) Speed control mode
(a) Speed setting
1) Speed command and speed
The servo motor is run at the speeds set in the parameters or at the speed set in the applied
voltage of the analog speed command (VC). A relationship between the analog speed command
(VC) applied voltage and the servo motor speed is shown below:
The maximum speed is achieved at 10V. The speed at 10V can be changed using parameter
No. 25.
10
010
Rated speed [r/min]
Speed [r/min]
CW direction VC applied voltage [V]
CCW direction
Rated speed
Forward rotation (CCW)
Reverse rotation (CW)
The following table indicates the rotation direction according to forward rotation start (ST1)
and reverse rotation start (ST2) combination:
(Note) External input signals Rotation direction
Analog speed command (VC)
ST2 ST1 Polarity 0V Polarity
Internal speed
commands
00 Stop
(Servo lock) Stop
(Servo lock) Stop
(Servo lock) Stop
(Servo lock)
0 1 CCW CW CCW
10 CW Stop
(No servo lock) CCW CW
11 Stop
(Servo lock) Stop
(Servo lock) Stop
(Servo lock) Stop
(Servo lock)
Note.0: off
1: on
The forward rotation start signal (ST1) and reverse rotation start signal (ST2) can be
assigned to any pins of the connector CN1 using parameters No.43 to 48.
Generally, make connection as shown below:
ST1
ST2
SG
P15R
VC
LG
SD
2k
2k
Servo amplifier
Japan resistor
RRS10 or equivalent

15 - 19
15. MR-E- AG SERVO AMPLIFIER COMPATIBLE WITH ANALOG INPUT
2) Speed selection 1 (SP1), speed selection 2 (SP2), speed selection 3 (SP3) and speed command
value By making speed selection 1 (SP1), speed selection 2 (SP2) and speed selection 3 (SP3)
usable by setting of parameter No. 43 to 47, you can choose the speed command values of
internal speed commands 1 to 7.
(Note) External input signals
SP3 SP2 SP1 Speed command value
0 0 0 Analog speed command (VC)
0 0 1 Internal speed command 1 (parameter No. 8)
0 1 0 Internal speed command 2 (parameter No. 9)
0 1 1 Internal speed command 3 (parameter No. 10)
1 0 0 Internal speed command 4 (parameter No. 72)
1 0 1 Internal speed command 5 (parameter No. 73)
1 1 0 Internal speed command 6 (parameter No. 74)
1 1 1 Internal speed command 7 (parameter No. 75)
Note.0 : SP1/SP2/SP3-SG off (open)
1 : SP1/SP2/SP3-SG on (short)
The speed may be changed during rotation. In this case, the values set in parameters No. 11
and 12 are used for acceleration/deceleration.
When the speed has been specified under any internal speed command, it does not vary due to
the ambient temperature.
(b) Speed reached (SA)
SA-SG are connected when the servo motor speed nearly reaches the speed set to the internal
speed command.
ON
OFF
ON
OFF
Set speed selection Internal speed
command 1
Internal speed
command 2
Start (ST1,ST2)
Servo motor speed
Speed reached (SA)

15 - 20
15. MR-E- AG SERVO AMPLIFIER COMPATIBLE WITH ANALOG INPUT
(c) Torque limit
1) Torque limit and torque
By setting parameter No. 28 (internal torque limit 1), torque is always limited to the maximum
value during operation. A relationship between the limit value and servo motor torque is shown
below.
00 100
Max. torque
torque
Torque limit value [%]
A relationship between the applied voltage of the analog torque limit (TLA) and the torque limit
value of the servo motor is shown below. Torque limit values will vary about 5% relative to the
voltage depending on products.
At the voltage of less than 0.05V, torque may vary as it may not be limited sufficiently.
Therefore, use this function at the voltage of 0.05V or more.
2k 2k
Servo amplifier
Japan resistor
RRS10 or equivalent
TL
SG
P15R
TLA
LG
SD
100
0
010
5%
0.05
Torque limit value [%]
TLA application voltage vs.
torque limit value
TLA application voltage [V]
2) Torque limit value selection
Use parameters No. 43 through 48 to enable external torque limit (TL) and internal torque
limit. Torque limit values can be selected as shown in the following table. However, if the
parameter No. 28 value is less than the limit value selected by TL/TL1, the parameter No. 28
value is made valid.
(Note) External input signals
TL1 TL Torque limit value made valid
0 0 Internal torque limit value 1 (parameter No. 28)
01 TLA Parameter No. 28: Parameter No. 28
TLA Parameter No. 28: TLA
10 Parameter No. 76 Parameter No. 28: Parameter No. 28
Parameter No. 76 Parameter No. 28: Parameter No. 76
11 TLA Parameter No. 76: Parameter No. 76
TLA Parameter No. 76: TLA
Note.0: off
1: on

15 - 21
15. MR-E- AG SERVO AMPLIFIER COMPATIBLE WITH ANALOG INPUT
(2) Torque control mode
(a) Torque control
1) Torque command and torque
A relationship between the applied voltage of the analog torque command (TC) and the torque
by the servo motor is shown below.
The maximum torque is generated at 8V. Note that the torque at 8V input can be changed
with parameter No. 26.
8
0.05 8
0.05
Max. torque
Generated torque
CCW direction
CW direction Max. torque (Note)
TC applied voltage [V]
Forward rotation (CCW)
Reverse rotation (CW)
Generated torque limit values will vary about 5% relative to the voltage depending on
products.
Also the torque may vary if the voltage is low ( 0.05 to 0.05V) and the actual speed is close
to the limit value. In such a case, increase the speed limit value.
The following table indicates the torque generation directions determined by the forward
rotation selection (RS1) and reverse rotation selection (RS2) when the analog torque command
(TC) is used.
(Note) External input signals Rotation direction
Torque control command (TC)
RS2 RS1 Polarity 0V Polarity
0 0 Torque is not generated. Torque is not generated.
01
CCW (reverse rotation in
driving mode/forward
rotation in regenerative
mode)
CW (forward rotation in
driving mode/reverse
rotation in regenerative
mode)
10
CW (forward rotation in
driving mode/reverse
rotation in regenerative
mode)
CCW (reverse rotation in
driving mode/forward
rotation in regenerative
mode)
1 1 Torque is not generated.
Torque is not
generated.
Torque is not generated.
Note. 0: off
1: on
Generally, make connection as shown below:
RS1
RS2
SG
TC
LG
SD
8 to 8V
Servo amplifie
r

15 - 22
15. MR-E- AG SERVO AMPLIFIER COMPATIBLE WITH ANALOG INPUT
2) Analog torque command offset
Using parameter No. 30, the offset voltage of 999 to 999mV can be added to the TC applied
voltage as shown below.
08( 8)
Max. torque
Generated torque
TC applied voltage [V]
Parameter No.30 offset range
999 to 999mV
(b) Torque limit
By setting parameter No. 28 (internal torque limit 1), torque is always limited to the maximum
value during operation. A relationship between limit value and servo motor torque is as in (1)(c)
in this section. Note that the analog torque limit (TLA) is unavailable.
(c) Speed limit
1) Speed limit value and speed
The speed is limited to the values set in parameters No. 8 to 10, 72 to 75 (internal speed limits 1
to 7) or the value set in the applied voltage of the analog speed limit (VLA).
A relationship between the analog speed limit (VLA) applied voltage and the servo motor speed
is shown below.
When the servo motor speed reaches the speed limit value, torque control may become unstable.
Make the set value more than 100r/m greater than the desired speed limit value.
10
010
Rated speed
Speed [r/min] CCW direction
CW direction VLA applied voltage [V]
Forward rotation (CCW)
Reverse rotation (CW)
Rated speed
The following table indicates the limit direction according to forward rotation selection (RS1)
and reverse rotation selection (RS2) combination:
(Note) External input signals Speed limit direction
Analog speed limit (VLA)
RS1 RS2 Polarity Polarity
Internal speed
commands
1 0 CCW CW CCW
0 1 CW CCW CW
Note.0: off
1: on
Generally, make connection as shown below:
SP1
SP2
SG
P15R
VC
LG
SD
2k
2k
Servo amplifier
Japan resistor
RRS10 or equivalent

15 - 23
15. MR-E- AG SERVO AMPLIFIER COMPATIBLE WITH ANALOG INPUT
2) Speed selection 1(SP1)/speed selection 2(SP2)/speed selection 3(SP3) and speed limit values
Choose any of the speed settings made by the internal speed limits 1 to 7 using speed selection
1(SP1), speed selection 2(SP2) and speed selection 3(SP3) or the speed setting made by the
analog speed limit command (VLA), as indicated below.
(Note) External input signals
SP3 SP2 SP1 Speed limit value
0 0 0 Analog speed limit (VLA)
0 0 1 Internal speed limit 1 (parameter No. 8)
0 1 0 Internal speed limit 2 (parameter No. 9)
0 1 1 Internal speed limit 3 (parameter No. 10)
1 0 0 Internal speed limit 4 (parameter No. 72)
1 0 1 Internal speed limit 5 (parameter No. 73)
1 1 0 Internal speed limit 6 (parameter No. 74)
1 1 1 Internal speed limit 7 (parameter No. 75)
Note.0: off
1: on
When the internal speed limits 1 to 7 are used to command the speed, the speed does not vary
with the ambient temperature.
3) Limiting speed (VLC)
VLC turns on when the servo motor speed reaches the speed limited using any of the internal
speed limits 1 to 7 or the analog speed limit (VLA).

15 - 24
15. MR-E- AG SERVO AMPLIFIER COMPATIBLE WITH ANALOG INPUT
(3) Speed/torque control change mode
Set "0003" in parameter No. 0 to switch to the speed/torque control change mode.
(a) Control change (LOP)
Use control change (LOP) to switch between the speed control mode and the torque control mode
from an external contact. Relationships between LOP and control modes are indicated below:
(Note) LOP Servo control mode
0 Speed control mode
1 Torque control mode
Note.0: off
1: on
The control mode may be changed at any time. A change timing chart is shown below:
Note: When the start (ST1 ST2) is switched off as soon as the mode is changed to speed control,
the servo motor comes to a stop according to the deceleration time constant.
10V
0
ON
OFF
Torque
control mode
Servo motor speed
Control change (LOP)
(Note)
Speed
control mode
Speed
control mode
Analog torque
command (TC)
Load torque
Forward rotation in driving mode
(b) Speed setting in speed control mode
Same as (1)(a).
(c) Torque limit in speed control mode
Same as (1)(c).
(d) Speed limit in torque control mode
Same as (2)(c).
(e) Torque control in torque control mode
Same as (2)(a).
(f) Torque limit in torque control mode
Same as (2)(b).

15 - 25
15. MR-E- AG SERVO AMPLIFIER COMPATIBLE WITH ANALOG INPUT
15.3 Startup
WARNING Do not operate the switches with wet hands. You may get an electric shock.
CAUTION
Before starting operation, check the parameters. Some machines may perform
unexpected operation.
During power-on for some after power-off, do not touch or close a parts (cable etc.)
to the servo amplifier heat sink, regenerative brake resistor, the servo motor, etc.
Their temperatures may be high and you may get burnt or a parts may damaged.
Perform pre-operation checks while referring to Section 4.1. Connect the servo motor with a machine after
confirming that the servo motor operates properly alone.
Use parameter No. 0 to choose the control mode used. After setting, this parameter is made valid by
switching power off, then on.
15.3.1 Speed control mode
(1) Power on
1) Switch off the servo-on (SON).
2) When power is switched on, the display shows "r (servo motor speed)", and in two second later,
shows data.
(2) Test operation
Using jog operation in the test operation mode, make sure that the servo motor operates. (Refer to
Section 6.8.2.)
(3) Parameter setting
Set the parameters according to the structure and specifications of the machine. Refer to Chapter 5 for
the parameter definitions and to Sections 6.5 for the setting method.
Parameter No. Name Setting Description
0Control mode, regenerative brake
option selection
0 2 Speed control mode
Regenerative brake option is not used.
1 Function selection 1 1 2 Input filter 3.555ms (initial value)
Electromagnetic brake interlock (MBR) is used.
2 Auto tuning 1 5 Middle response (initial value) is selected.
Auto tuning mode 1 is selected.
8 Internal speed command 1 1000 Set 1000r/min.
9 Internal speed command 2 1500 Set 1500r/min.
10 Internal speed command 3 2000 Set 2000r/min.
11 Acceleration time constant 1000 Set 1000ms.
12 Deceleration time constant 500 Set 500ms.
13 S-pattern acceleration/deceleration
time constant 0 Not used
Turn the power off to validate changes in parameters No. 0 and 1. Then switch power on again to
make the set parameter values valid.

15 - 26
15. MR-E- AG SERVO AMPLIFIER COMPATIBLE WITH ANALOG INPUT
(4) Servo-on
Switch the servo-on in the following procedure:
1) Switch on power supply.
2) Switch on the servo-on (SON).
When placed in the servo-on status, the servo amplifier is ready to operate and the servo motor is
locked.
(5) Start
Using speed selection 1 (SP1) and speed selection 2 (SP2), choose the servo motor speed. Turn on
forward rotation start (ST1) to run the motor in the forward rotation (CCW) direction or reverse
rotation start (ST2) to run it in the reverse rotation (CW) direction. At first, set a low speed and check
the rotation direction, etc. If it does not run in the intended direction, check the input signal.
On the status display, check the speed, load factor, etc. of the servo motor.
When machine operation check is over, check automatic operation with the host controller or the like.
This servo amplifier has a real-time auto tuning function under model adaptive control. Performing
operation automatically adjusts gains. The optimum tuning results are provided by setting the
response level appropriate for the machine in parameter No. 2. (Refer to chapter 7)
(6) Stop
In any of the following statuses, the servo amplifier interrupts and stops the operation of the servo
motor:
Refer to Section 3.9, (2) for the servo motor equipped with electromagnetic brake. Note that
simultaneous ON or simultaneous OFF of stroke end (LSP, LSN) OFF and forward rotation start
(ST1) or reverse rotation start (ST2) has the same stop pattern as described below.
(a) Servo-on (SON) OFF
The base circuit is shut off and the servo motor coasts.
(b) Alarm occurrence
When an alarm occurs, the base circuit is shut off and the dynamic brake is operated to bring the
servo motor to a sudden stop.
(c) Emergency stop (EMG) OFF
The base circuit is shut off and the dynamic brake is operated to bring the servo motor to a sudden
stop. Alarm AL.E6 occurs.
(d) Stroke end (LSP/LSN) OFF
The servo motor is brought to a sudden stop and servo-locked. The motor may be run in the
opposite direction.
(e) Simultaneous ON or simultaneous OFF of forward rotation start (ST1) and reverse rotation start
(ST2)
The servo motor is decelerated to a stop.
POINT
A sudden stop indicates deceleration to a stop at the deceleration time
constant of zero.

15 - 27
15. MR-E- AG SERVO AMPLIFIER COMPATIBLE WITH ANALOG INPUT
15.3.2 Torque control mode
(1) Power on
1) Switch off the servo-on (SON).
2) When power is switched on, the display shows "U (torque command voltage)", and in two second
later, shows data.
(2) Test operation
Using jog operation in the test operation mode, make sure that the servo motor operates. (Refer to
Section 6.8.2.)
(3) Parameter setting
Set the parameters according to the structure and specifications of the machine. Refer to Chapter 5 for
the parameter definitions and to Sections 6.5 for the setting method.
Parameter No. Name Setting Description
0Control mode, regenerative brake
option selection 0 4 Torque control mode
Regenerative brake option is not used.
1 Function selection 1 0 2 Input filter 3.555ms (initial value)
Electromagnetic brake interlock (MBR) is not used.
8 Internal speed limit 1 1000 Set 1000r/min.
9 Internal speed limit 2 1500 Set 1500r/min.
10 Internal speed limit 3 2000 Set 2000r/min.
11 Acceleration time constant 1000 Set 1000ms.
12 Deceleration time constant 500 Set 500ms.
13 S-pattern acceleration/deceleration time
constant 0 Not used
14 Torque command time constant 2000 Set 2000ms
28 Internal torque limit 1 50 Controlled to 50% output
Turn the power off after setting parameters No. 0 and 1. Then switch power on again to make the set
parameter values valid.
(4) Servo-on
Switch the servo-on in the following procedure:
1) Switch on power supply.
2) Switch on the servo-on (SON).
When placed in the servo-on status, the servo amplifier is ready to operate and the servo motor is
locked.
(5) Start
Using speed selection 1 (SP1) and speed selection 2 (SP2), choose the servo motor speed. Turn on
forward rotation select (DI4) to run the motor in the forward rotation (CCW) direction or reverse
rotation select (DI3) to run it in the reverse rotation (CW) direction, generating torque. At first, set a
low speed and check the rotation direction, etc. If it does not run in the intended direction, check the
input signal.
On the status display, check the speed, load factor, etc. of the servo motor.
When machine operation check is over, check automatic operation with the host controller or the like.

15 - 28
15. MR-E- AG SERVO AMPLIFIER COMPATIBLE WITH ANALOG INPUT
(6) Stop
In any of the following statuses, the servo amplifier interrupts and stops the operation of the servo
motor:
Refer to Section 3.9, (2) for the servo motor equipped with electromagnetic brake.
(a) Servo-on (SON) OFF
The base circuit is shut off and the servo motor coasts.
(b) Alarm occurrence
When an alarm occurs, the base circuit is shut off and the dynamic brake is operated to bring the
servo motor to a sudden stop.
(c) Emergency stop (EMG) OFF
The base circuit is shut off and the dynamic brake is operated to bring the servo motor to a sudden
stop. Alarm AL.E6 occurs.
(d) Simultaneous ON or simultaneous OFF of forward rotation selection (RS1) and reverse rotation
selection (RS2)
The servo motor coasts.
POINT
A sudden stop indicates deceleration to a stop at the deceleration time
constant of zero.

15 - 29
15. MR-E- AG SERVO AMPLIFIER COMPATIBLE WITH ANALOG INPUT
15.4 Parameters
POINT
Before changing the settings of parameters No. 20 through 84, cancel
write protection while referring to Section 5.1.1.
For any parameter whose symbol is preceded by *, set the parameter
value and switch power off once, then switch it on again to make that
parameter setting valid.
The symbols in the control mode column of the table indicate the following
modes:
S : Speed control mode
T : Torque control mode
15.4.1 Item list
No. Symbol Name Control
mode
Initial
value Unit Customer
setting
0 *STY Control mode ,regenerative brake option selection S T(Note 1)
1 *OP1 Function selection 1 S T 0002
2 ATU Auto tuning S 0105
3 For manufacturer setting 1
4 1
5100
6 PG1 Position loop gain 1 S 35 rad/s
7 For manufacture setting 3
Internal speed command 1 S 100 r/min
8SC1
Internal speed limit 1 T 100 r/min
Internal speed command 2 S 500 r/min
9SC2
Internal speed limit 2 T 500 r/min
Internal speed command 3 S 1000 r/min
10 SC3 Internal speed limit 3 T 1000 r/min
11 STA Acceleration time constant S T0ms
12 STB Deceleration time constant S T0ms
13 STC S-pattern acceleration/deceleration time constant S T0ms
14 TQC Torque command time constant T 0 ms
15 *SNO Station number setting S T0station
16 *BPS Serial communication function selection, alarm history clear S T 0000
17 MOD Analog monitor output S T 0100
18 *DMD Status display selection S T 0000
Basic parameters
19 *BLK Parameter block S T 0000

15 - 30
15. MR-E- AG SERVO AMPLIFIER COMPATIBLE WITH ANALOG INPUT
No. Symbol Name Control
mode
Initial
value Unit Customer
setting
20 *OP2 Function selection 2 S T 0000
21 For manufacturer setting 0000
22 *OP4 Function selection 4 S T 0000
23 For manufacturer setting 0
24 ZSP Zero speed S T50r/min
Analog speed command maximum speed S (Note3)0(r/min)
25 VCM Analog speed limit maximum speed T (Note3)0(r/min)
26 TLC Analog torque command maximum output T 100 %
27 *ENR Encoder output pulses S T 4000 pulse
/rev
28 TL1 Internal torque limit 1 S T 100 %
Analog speed command offset S (Note2) mV
29 VCO Analog speed limit offset T (Note2) mV
Analog torque command offset T 0 mV
30 TLO Analog torque limit offset S 0 mV
31 MO1 Analog monitor 1 offset S T0mV
32 MO2 Analog monitor 2 offset S T0mV
33 MBR Electromagnetic brake sequence output S T 100 ms
34 GD2 Ratio of load inertia moment to servo motor inertia moment S T700.1
times
35 PG2 Position loop gain 2 S 35 rad/s
36 VG1 Speed loop gain 1 S 177 rad/s
37 VG2 Speed loop gain 2 S 817 rad/s
38 VIC Speed integral compensation S 48 ms
39 VDC Speed differential compensation P S 980
40 For manufacturer setting 0
41 *DIA Input signal automatic ON selection S T 0000
42 *DI1 Input signal selection 1 S T 0002
43 *DI2 Input signal selection 2 (CN1-4) S T 0111
44 *DI3 Input signal selection 3 (CN1-3) S T 0882
45 *DI4 Input signal selection 4 (CN1-5) S T 0995
46 *DI5 Input signal selection 5 (CN1-6) S T 0000
47 *DI6 Input signal selection 6 (CN1-7) S T 0000
48 *LSPN LSP LSN input terminals selection S 0403
Expansion parameters 1
49 *DO1 Output signal selection 1 S T 0000
50 For manufacturer setting 0000
51 *OP6 Function selection 6 S T 0000
52 For manufacturer setting 0000
53 *OP8 Function selection 8 S T 0000
54 *OP9 Function selection 9 S T 0000
55 For manufacturer setting 0000
56 SIC Serial communication time-out selection S T0 s
57 For manufacturer setting 10
58 NH1 Machine resonance suppression filter 1 S T 0000
59 NH2 Machine resonance suppression filter 2 S T 0000
60 LPF Low-pass filter, adaptive vibration suppression control S T 0000
61 GD2B Ratio of load inertia moment to Servo motor inertia moment 2 S 70 0.1
times
62 For manufacturer setting 100 %
63 VG2B Speed control gain 2 changing ratio S 100 %
Expansion parameters 2
64 VICB Speed integral compensation changing ratio S 100 %

15 - 31
15. MR-E- AG SERVO AMPLIFIER COMPATIBLE WITH ANALOG INPUT
No. Symbol Name Control
mode
Initial
value Unit Customer
setting
65 *CDP Gain changing selection S 0000
66 CDS Gain changing condition S 10 (Note 2)
67 CDT Gain changing time constant S 1 ms
68 For manufacturer setting 0
69 1
70 1
71 1
Internal speed command 4 S
72 SC4 Internal speed limit 4 T 200 r/min
Internal speed command 5 S
73 SC5 Internal speed limit 5 T 300 r/min
Internal speed command 6 S
74 SC6 Internal speed limit 6 T 500 r/min
Internal speed command 7 S
75 SC7 Internal speed limit 7 T 800 r/min
76 TL2 Internal torque limit 2 S T 100 %
77 100
78 10000
79 10
80 10
81 100
82 100
83 100
Expansion parameters 2
84
For manufacturer setting
0000
Note 1. Depends on the capacity of the servo amplifier.
2. Depends on the parameter No. 65 setting.
3. The setting of "0" provides the rated servo motor speed.

15 - 32
15. MR-E- AG SERVO AMPLIFIER COMPATIBLE WITH ANALOG INPUT
15.4.2 Details list
Class No. Symbol Name and function Initial
value Unit Setting
range
Control
mode
Control mode, regenerative brake option selection
Used to select the control mode and regenerative brake option.
Select the control mode.
0:Speed
1:Speed and torque
2:Torque
Selection of regenerative brake option
0:Not used
(The built-in regenerative brake resistor used.)
2:MR-RB032
3:MR-RB12
4:MR-RB32
5:MR-RB30
6:MR-RB50
Motor series selection
0:HC-KFE
1:HC-SFE
Motor capacity selection
0:100W
1:200W
2:400W
3:500W
4:750W
5:1kW
6:1.5kW
7:2kW
POINT
Wrong setting may cause the regenerative brake option to burn.
If the regenerative brake option selected is not for use with the
servo amplifier, parameter error (AL.37) occurs.
0*STY 100W
: 0000
200W
: 1000
400W
: 2000
700W
: 4000
1kW
: 5010
2kW
: 6010
Refer to
Name
and
function
column.
S T
Basic parameters
1 *OP1 Function selection 1
Used to select the input signal filter, the function of pin CN1-12.
Input signal filter
If external input signal causes chattering
due to noise, etc., input filter is used to
suppress it.
0:None
1:1.777[ms]
2:3.555[ms]
3:5.333[ms]
CN1-12 function selection
0:Zero Speed detection signal
1:Electromagnetic brake interlock signal
00
0002 Refer to
Name
and
function
column.
S T

15 - 33
15. MR-E- AG SERVO AMPLIFIER COMPATIBLE WITH ANALOG INPUT
Class No. Symbol Name and function Initial
value Unit Setting
range
Control
mode
2 ATU Auto tuning
Used to selection the response level, etc. for execution of auto tuning.
Refer to Chapter 7.
Auto tuning response level setting
If the machine hunts or generates
large gear sound, decrease the
set value.
To improve performance, e.g.
shorten the settling time, increase
the set value.
Set
value
Response
level
1Low
response
Middle
response
High
response
Gain adjustment mode selection
(For more information, refer to Section 7.1.1.)
Machine resonance
frequency guideline
15Hz
220Hz
325Hz
430Hz
535Hz
645Hz
755Hz
870Hz
985Hz
A105Hz
B130Hz
C160Hz
D200Hz
E240Hz
F300Hz
Set
value Gain adjustment mode
0
Description
1
3 Simple manual adjustment.
4 Manual adjustment of all gains.
Interpolation mode Fixes position control gain 1
(parameter No. 6).
Auto tuning mode 1 Fixes the load inertia moment
ratio set in parameter No. 34.
Response level setting can be
changed.
Manual mode 1
Manual mode 2
2Auto tuning mode 2 Ordinary auto tuning.
0 0
0105 Refer to
Name
and
function
column.
S
3 1
4 1
5
For manufacturer setting
Don’t change this value by anymeans.
100
6 PG1 Position loop gain 1
Used to set the gain of position loop.
Increase the gain to improve trackability in response to the position
command.
When auto turning mode 1,2 is selected, the result of auto turning is
automatically used.
To use this parameter, set " 1 " to parameter No. 20 to validate
servo lock at stop.
35 S
Basic parameters
7 For manufacturer setting
Don’t change this value by anymeans. 3

15 - 34
15. MR-E- AG SERVO AMPLIFIER COMPATIBLE WITH ANALOG INPUT
Class No. Symbol Name and function Initial
value Unit Setting
range
Control
mode
Internal speed command 1
Used to set speed 1 of internal speed commands. S8SC1
Internal speed limit 1
Used to set speed 1 of internal speed limits.
100 r/min 0 to
instan-
taneous
permi-
ssible
speed
T
Internal speed command 2
Used to set speed 2 of internal speed commands. S9SC2
Internal speed limit 2
Used to set speed 2 of internal speed limits.
500 r/min 0 to
instan-
taneous
permi-
ssible
speed
T
Internal speed command 3
Used to set speed 3 of internal speed commands. S10 SC3
Internal speed limit 3
Used to set speed 3 of internal speed limits.
1000 r/min 0 to
instan-
taneous
permi-
ssible
speed
T
11 STA Acceleration time constant
Used to set the acceleration time required to reach the rated speed
from 0r/min in response to the analo
g
speed command and internal
speed commands 1 to 7.
Tim
e
Parameter
No.12 setting
Parameter
No.11 setting
Zero
speed
Rated
speed
Speed
If the preset speed command is
lower than the rated speed,
acceleration/deceleration time
will be shorter.
For example for the servo motor of 3000r/min rated speed, set 3000
(3s) to increase speed from 0r/min to 1000r/min in 1 second.
0
12 STB Deceleration time constant
Used to set the deceleration time required to reach 0r/min from the
rated speed in response to the analo
g
speed command and internal
speed commands 1 to 7.
0
ms 0
to
20000
ST
Basic parameters
13 STC S-pattern acceleration/deceleration time constant
Used to smooth start/stop of the servo motor.
Set the time of the arc part for S-pattern acceleration/deceleration.
STA: Acceleration time constant (parameter No.11)
STB: Deceleration time constant (parameter No.12)
STC: S-pattern acceleration/deceleration time con-
stant (parameter No.13)
Speed command
Servo motor
Speed
0r/min
STCSTA STC STC STB STC
Time
Long setting of STA (acceleration time constant) or STB (deceleration time
constant) may produce an error in the time of the arc part for the setting of the
S-pattern acceleration/deceleration time constant.
The upper limit value of the actual arc part time is limited by
At the setting of STA 20000, STB 5000 and STC 200,
the actual arc part times are as follows:
for acceleration or by for deceleration.
(Example)
During acceleration: 100[ms] 2000000
20000 100[ms] 200[ms].
Limited to 100[ms] since
During deceleration: 200[ms] 2000000
5000 400[ms] 200[ms].
200[ms] as set since
2000000
STA 2000000
STB
0ms0
to
1000
S T

15 - 35
15. MR-E- AG SERVO AMPLIFIER COMPATIBLE WITH ANALOG INPUT
Class No. Symbol Name and function Initial
value Unit Setting
range
Control
mode
14 TQC Torque command time constant
Used to set the constant of a low pass filter in response to the torque
command. Torque command
TQC TQC Time
After
filtered
TQC: Torque command time constant
Torque
0ms0
to
20000
T
15 *SNO Station number setting
Used to specify the station number for serial communication.
Always set one station to one axis of servo amplifier. If one station
number is set to two or more stations, normal communication cannot
be made.
0sta-
tion 0
to
31
ST
Basic parameters
16 *BPS Serial communication function selection, alarm history clear
Used to select the serial communication baudrate, select various
communication conditions, and clear the alarm history.
Serial baudrate selection
0: 9600 [bps]
1: 19200[bps]
2: 38400[bps]
3: 57600[bps]
Alarm history clear
0: Invalid
1: Valid
When alarm history clear is made valid,
the alarm history is cleared at next power-on.
After the alarm history is cleared, the setting
is automatically made invalid (reset to 0).
Serial communication response delay time
0: Invalid
1: Valid, reply sent after delay time of 800 s or more
0
0000 Refer to
Name
and
function
column.
S T

15 - 36
15. MR-E- AG SERVO AMPLIFIER COMPATIBLE WITH ANALOG INPUT
Class No. Symbol Name and function Initial
value Unit Setting
range
Control
mode
17 MOD Analog monitor output
Used to selection the signal provided to the analog monitor
(MO1) analog monitor (MO2) output. (Refer to Section 5.2.2)
Setting
0
Analog monitor 2 (MO2)
Servo motor speed ( 8V/max. speed)
1 Torque ( 8V/max. torque)
2 Servo motor speed ( 8V/max. speed)
3 Torque ( 8V/max. torque)
4 Current command ( 8V/max. current command)
5
6
7
8
9
A
00
B
Analog monitor 1 (MO1)
Cannot be used.
0100 Refer to
Name
and
function
column.
S T
18 *DMD Status display selection
Used to select the status display shown at power-on.
Selection of status display at
power-on
0: Cumulative feedback pulses
1: Servo motor speed
2: Cannot be used
3: Cannot be used
4: Cannot be used
7: Regenerative load ratio
8: Effective load ratio
9: Peak load ratio
A: Instantaneous torque
B: Within one-revolution position low
C: Within one-revolution position high
D: Load inertia moment ratio
E: Bus voltage
Status display at power-on in
corresponding control mode
0: Depends on the control mode.
0 0
0000 Refer to
Name
and
function
column.
S T
Control Mode
Speed
Speed/torque
Torque
Status display at power-on
Servo motor speed
Servo motor speed/analog torque command voltage
A
nalog torque command voltage
1: Depends on the first digit setting of this parameter.
Basic parameters

15 - 37
15. MR-E- AG SERVO AMPLIFIER COMPATIBLE WITH ANALOG INPUT
Class No. Symbol Name and function Initial
value Unit Setting
range
Control
mode
Parameter block
Used to select the reference and write ranges of the parameters.
Operation can be performed for the parameters marked .
Set
value Operation
Basic
parameters
No. 0
to No. 19
Expansion
parameters 1
No. 20
to No. 49
Expansion
parameters 2
No. 50
to No. 84
Reference0000
(Initial
value) Write
Reference No. 19 only
000A Write No. 19 only
Reference
000B Write
Reference
000C Write
Reference
000E Write
Reference
100B Write No. 19 only
Reference
100C Write No. 19 only
Reference
100E Write No. 19 only
Basic parameters
19 *BLK 0000 Refer to
Name
and
function
column.
S T

15 - 38
15. MR-E- AG SERVO AMPLIFIER COMPATIBLE WITH ANALOG INPUT
Class No. Symbol Name and function Initial
value Unit Setting
range
Control
mode
0000 Refer to
Name
and
function
column.
S
S
20 *OP2 Function selection 2
Used to select restart after instantaneous power failure,
servo lock at a stop in speed control mode, and slight vibration
suppression control.
0: Invalid
1: Valid
If the input power supply voltage
had reduced in the speed control
mode to stop the servo motor
due to the undervoltage alarm (AL.10
)
but the supply voltage has return-
ed to normal, the servo motor can
be restarted by merely switching
on the start signal without resett-
ing the alarm.
Restart after instantaneous
power failure
Stop-time servo lock selection
The shaft can be servo-locked to
remain still at a stop in the internal
speed control mode.
0: Valid
1: Invalid
Slight vibration suppression control
Made valid when auto tuning selection is
set to "0400" in parameter No. 2.
Used to suppress vibration at a stop.
0: Invalid
1: Valid
Encoder cable communication system selection
Incorrect setting will result in an encoder alarm 1
(AL. 16) or encoder alarm 2 (AL. 20).
0: Two-wire type
1: Four-wire type
ST
Expansion parameters 1
21 For manufacturer setting
Don’t change this value by anymeans. 0000

15 - 39
15. MR-E- AG SERVO AMPLIFIER COMPATIBLE WITH ANALOG INPUT
Class No. Symbol Name and function Initial
value Unit Setting
range
Control
mode
S
22 *OP4 Function selection 4
Used to select stop processing at forward rotation stroke end (LSP)
reverse rotation stroke end (LSN) off, choose TLC/VLC output and
choose VC/VLA voltage averaging.
How to make a stop when forward
rotation stroke end (LSP)
reverse rotation stroke end (LSN)
is valid. (Refer to Section 5.2.3.)
0: Sudden stop
1: Slow stop
Set value
0
1
2
Filtering time [ms]
0
0.444
0.888
31.777
VC/VLA voltage averaging
Used to set the filtering time when the
analog speed command (VC) voltage
or analog speed limit (VLA) is imported.
Set 0 to vary the speed to voltage fluctua-
tion in real time. Increase the set value
to vary the speed slower to voltage flu-
ctuation.
43.555
0
Set value
0
1
2
Connector pin No.
Not output
CN1-11
CN1-9
3CN1-10
TLC/VLC output selection
Select the connector pin at which
Torque Limit (TLC) or Speed Limit
(VLC) is output.
4CN1-12
0000 Refer to
Name
and
function
column.
S T
23 For manufacturer setting
Don’t change this value by anymeans. 0
24 ZSP Zero speed
Used to set the output range of the zero speed (ZSP). 50 r/min 0
to
10000
S T
0
Analog speed command maximum speed
Used to set the speed at the maximum input voltage (10V) of the
analog speed command (VC).
Set "0" to select the rated speed of the servo motor connected.
0r/min 1
to
50000
S
0
25 VCM
Analog speed limit maximum speed
Used to set the speed at the maximum input voltage (10V) of the
analog speed limit (VLA).
Set "0" to select the rated speed of the servo motor connected.
0r/min 1
to
50000
T
Expansion parameters 1
26 TLC Analog torque command maximum output
Used to set the output torque at the analog torque command voltage
(TC 8V) of 8V on the assumption that the maximum torque is
100[%]. For example, set 50 to output (maximum torque 50/100) at
the TC of 8V.
100 %0
to
1000
T

15 - 40
15. MR-E- AG SERVO AMPLIFIER COMPATIBLE WITH ANALOG INPUT
Class No. Symbol Name and function Initial
value Unit Setting
range
Control
mode
27 *ENR Encoder output pulses
Used to set the encoder pulses (A-phase or B-phase) output by the
servo amplifier.
Set the value 4 times greater than the A-phase or B-phase pulses.
You can use parameter No. 54 to choose the output pulse designation
or output division ratio setting.
The number of A/B-phase pulses actually output is 1/4 times greater
than the preset number of pulses.
The maximum output frequency is 1.3Mpps (after multiplication by
4). Use this parameter within this range.
For output pulse designation
Set " 0 " (initial value) in parameter No. 54.
Set the number of pulses per servo motor revolution.
Output pulse set value [pulses/rev]
At the setting of 5600, for example, the actually output A/B-phase
pulses are as indicated below:
4
5600
A B-phase output pulses 1400[pulse]
For output division ratio setting
Set " 1 " in parameter No. 54.
The number of pulses per servo motor revolution is divided by the
set value.
Output pulse [pulses/rev]
Resolution per servo motor revolution
Set value
At the setting of 8, for example, the actually output A/B-phase
pulses are as indicated below:
A B-phase output pulses 313[pulse]
8
10000 4
1
4000 pulse/
rev 1
to
65535
S T
Internal torque limit 1
Set this parameter to limit servo motor torque on the assumption
that the maximum torque is 100[%].
When 0 is set, torque is not produced.
(Note)
TL Torque limit
0 Internal torque limit 1 (Parameter No. 28)
1 Analog torque limit internal torque limit 1
: Analog torque limit
Analog torque limit internal torque limit 1
: Internal torque limit 1
28 TL1
Note.0 :off
1 :on
When torque is output in analog monitor output, this set value is the
maximum output voltage ( 8V). (Refer to Section 15.2.5, (1)(c))
100 % 0
to
100
ST
Analog speed command offset
Used to set the offset voltage of the analog speed command (VC).
For example, if CCW rotation is provided by switching on forward
rotation start (ST1) with 0V applied to VC, set a negative value.
When automatic VC offset is used, the automatically offset value is
set to this parameter. (Refer to Section 15.5.3.)
The initial value is the value provided by the automatic VC offset
function before shipment at the VC-LG voltage of 0V.
S
Expansion parameters 1
29 VCO
Analog speed limit offset
Used to set the offset voltage of the analog speed limit (VLA).
For example, if CCW rotation is provided by switching on forward
rotation selection (RS1) with 0V applied to VLA, set a negative value.
When automatic VC offset is used, the automatically offset value is
set to this parameter. (Refer to Section 15.5.3.)
The initial value is the value provided by the automatic VC offset
function before shipment at the VLA-LG voltage of 0V.
Depends
on servo
amplifier
mV 999
to
999
T

15 - 41
15. MR-E- AG SERVO AMPLIFIER COMPATIBLE WITH ANALOG INPUT
Class No. Symbol Name and function Initial
value Unit Setting
range
Control
mode
Analog torque command offset
Used to set the offset voltage of the analog torque command (TC). T30 TLO
Analog torque limit offset
Used to set the offset voltage of the analog torque limit (TLA).
0mV999
to
999 S
31 MO1 Analog monitor 1 offset
Used to set the offset voltage of the analog monitor 1 (MO1). 0mV 999
to 999 ST
32 MO2 Analog monitor 2 offset
Used to set the offset voltage of the analog monitor 2 (MO2). 0mV 999
to 999 ST
33 MBR Electromagnetic brake sequence output
Used to set the delay time (Tb) between electronic brake interlock
(MBR) and the base drive circuit is shut-off.
100 ms 0
to
1000
ST
34 GD2 Ratio of load inertia moment to servo motor inertia moment
Used to set the ratio of the load inertia moment to the servo motor
shaft inertia moment. When auto tuning mode 1 and interpolation
mode is selected, the result of auto tuning is automatically used.
(Refer to section 7.1.1)
In this case, it varies between 0 and 1000.
70 0.1
times 0
to
3000
ST
35 PG2 Position loop gain 2
Used to set the gain of the position loop.
Set this parameter to increase the position response to level load
disturbance. Higher setting increases the response level but is liable
to generate vibration and/or noise.
When auto tuning mode 1,2 and interpolation mode is selected, the
result of auto tuning is automatically used.
To use this parameter, set " 1 " to parameter No. 20 to validate
servo lock at stop.
35 rad/s 1
to
1000
S
36 VG1 Speed loop gain 1
Normally this parameter setting need not be changed.
Higher setting increases the response level but is liable to generate
vibration and/or noise.
When auto tuning mode 1 2, manual mode and interpolation mode
is selected, the result of auto tuning is automatically used.
177 rad/s 20
to
8000
S
37 VG2 Speed loop gain 2
Set this parameter when vibration occurs on machines of low rigidity
or large backlash. Higher setting increases the response level but is
liable to generate vibration and/or noise.
When auto tuning mode 1 2 and interpolation mode is selected, the
result of auto tuning is automatically used.
817 rad/s 20
to
20000
S
38 VIC Speed integral compensation
Used to set the integral time constant of the speed loop.
Higher setting increases the response level but is liable to generate
vibration and/or noise.
When auto tuning mode 1 2 and interpolation mode is selected, the
result of auto tuning is automatically used.
48 ms 1
to
1000
S
39 VDC Speed differential compensation
Used to set the differential compensation.
Made valid when the proportion control (PC) is switched on.
980 0
to
1000
S
Expansion parameters 1
40 For manufacturer setting
Don’t change this value by any means. 0

15 - 42
15. MR-E- AG SERVO AMPLIFIER COMPATIBLE WITH ANALOG INPUT
Class No. Symbol Name and function Initial
value Unit Setting
range
Control
mode
S T41 *DIA Input signal automatic ON selection
Used to set automatic servo-on (SON) forward rotation stroke end
(LSP) reverse rotation stroke end (LSN).
Servo-on (SON) input selection
0: Switched on/off by external input.
1: Switched on automatically in servo
amplifier.
(No need of external wiring)
0: Switched on/off by external input.
1: Switched on automatically in servo
amplifier.
(No need of external wiring)
0: Switched on/off by external input.
1: Switched on automatically in servo
amplifier.
(No need of external wiring)
Reverse rotation stroke end (LSN)
input selection
Forward rotation stroke end (LSP)
input selection
0
0000 Refer to
Name
and
function
column.
S
S/T
Expansion parameters 1
42 *DI1 Input signal selection 1
Used to assign the control mode changing signal input pins and to set
the clear (CR).
Control change (LOP) input pin
assignment
Used to set the control mode
change signal input connector
pins. Note that this parameter is
made valid when parameter No.
0 is set to select the position/int-
ernal speed change mode.
Set value
0
1
2
Connector pin No.
CN1-4
CN1-3
CN1-5
3CN1-6
4CN1-7
000
If forward rotation stroke end (LSP) or reverse rotation stroke
end (LSN) is assigned to any pin with parameter No. 48, this
parameter cannot be used.
0002 Refer to
Name
and
function
column.

15 - 43
15. MR-E- AG SERVO AMPLIFIER COMPATIBLE WITH ANALOG INPUT
Class No. Symbol Name and function Initial
value Unit Setting
range
Control
mode
Expansion parameters 1
43 *DI2 Input signal selection 2 (CN1-4)
Allows any input signal to be assigned to CN1-pin 4.
Note that the setting digit and assigned signal differ according to the
control mode.
Speed
control mode Input signals of
CN1-pin 4
selected.
Torque
control mode
0 1
Signals that may be assigned in each control mode are indicated
below by their symbols.
Setting of any other signal will be invalid.
Set value (Note) Control mode
ST
0
1
2
3
4
5
6
7
8
9
SON SON
RES RES
PC PC
SP1
SP2
RS2
RS1
CR CR
ASP3
B
C
DTL1
ECDP
TL1
CDP
F
TL TL
SP1
SP2
ST1
ST2
SP3
Note: P: Position control mode
S: Internal speed control mode
This parameter is unavailable when parameter No.42 is set to assign
the control change (LOP) to CN1-pin 4.
If rotation stroke end (LSP) or reverse rotation stroke end (LSN) is
assigned to pin 4 of CN1 with parameter No. 48, this parameter
cannot be used.
0111 Refer to
Name
and
function
column.
S T

15 - 44
15. MR-E- AG SERVO AMPLIFIER COMPATIBLE WITH ANALOG INPUT
Class No. Symbol Name and function Initial
value Unit Setting
range
Control
mode
44 *DI3 Input signal selection 3 (CN1-3)
Allows any input signal to be assigned to CN1-pin 3.
The assignable signals and setting method are the same as in input
signal selection 2 (parameter No. 43).
Speed
control mode Input signals of
CN1-pin 3
selected.
Torque
control mode
02
This parameter is unavailable when parameter No. 42 is set to
assign the control change (LOP) to CN1-pin 3.
If forward rotation stroke end (LSP) or reverse rotation stroke end
(LSN) is assigned to pin 3 of CN1 with parameter No. 48, this
parameter cannot be used.
0882 Refer to
Name
and
function
column.
S T
45 *DI4 Input signal selection 4 (CN1-5)
Allows any input signal to be assigned to CN1-pin 5.
The assignable signals and setting method are the same as in input
signal selection 2 (parameter No. 43).
Speed
control mode Input signals of
CN1-pin 5
selected.
Torque
control mode
05
This parameter is unavailable when parameter No. 42 is set to
assign the control change (LOP) to CN1-pin 5.
If forward stroke end (LSP) or reverse rotation stroke end (LSN) is
assigned to pin 5 of CN1 with parameter No. 48, this parameter
cannot be used.
0995 Refer to
Name
and
function
column.
S T
Expansion parameters 1
46 *DI5 Input signal selection 5 (CN1-6)
Allows any input signal to be assigned to CN1-pin 6.
The assignable signals and setting method are the same as in input
signal selection 2 (parameter No. 43).
Speed
control mode Input signals of
CN1-pin 6
selected.
Torque
control mode
00
This parameter is unavailable when parameter No. 42 is set to
assign the control change (LOP) to CN1-pin 6.
If reverse rotation stroke end (LSN) is assigned to pin 6 of CN1 with
parameter No. 48, this parameter cannot be used.
0000 Refer to
Name
and
function
column.
S T

15 - 45
15. MR-E- AG SERVO AMPLIFIER COMPATIBLE WITH ANALOG INPUT
Class No. Symbol Name and function Initial
value Unit Setting
range
Control
mode
47 *DI6 Input signal selection 6 (CN1-7)
Allows any input signal to be assigned to CN1-pin 7.
The assignable signals and setting method are the same as in input
signal selection 2 (parameter No. 43).
Speed
control mode Input signals of
CN1-pin 7
selected.
Torque
control mode
00
This parameter is unavailable when parameter No. 42 is set to
assign the control change signal (LOP) to CN1-pin 7.
If forward rotation stroke end (LSP) is assigned to pin 7 of Cn1 with
parameter No. 48, this parameter cannot be used.
0000 Refer to
Name
and
function
column.
S T
Expansion parameters 1
48 *LSPN LSP/LSN input terminal selection
Select the pins where the forward rotation stroke end (LSP) and
reverse rotation stroke end (LSN) will be assigned. If the signals
have already been assigned using parameter No. 42 to 47, this
parameter setting has preference.
However, if forward rotation stroke end (LSP) is assigned to pin 6 of
CN1 (default setting), the setting of parameter No. 46 takes priority.
Similarly, if reverse rotation stroke end (LSN) is assigned to pin 7 of
CN1 (default setting), the setting of parameter No .47 takes priority.
CN1-7
CN1-4
CN1-3
CN1-5
CN1-6
3
4
1
2
0
00
5
Select the pin where the forward rotation stroke
end (LSP) will be assigned.
Set value Connector pin No.
Select the pin where the reverse rotation stroke
end (LSN) will be assigned. The settings are the
same as those of the first digit.
0403 Refer to
Name
and
function
column.
S T

15 - 46
15. MR-E- AG SERVO AMPLIFIER COMPATIBLE WITH ANALOG INPUT
Class No. Symbol Name and function Initial
value Unit Setting
range
Control
mode
Expansion parameters 1
49 *DO1 Output signal selection 1
Used to select the connector pins to output the alarm code and
warning (WNG).
Setting of alarm code output
Connector pins
Set value CN1-10 CN1-11 CN1-12
0SARD ZP
1
88888
AL.12
AL.13
AL.15
AL.17
AL.8A
AL.8E
AL.30
AL.45
AL.50
AL.51
AL.24
AL.32
AL.31
AL.16
AL.20
Name
Watchdog
Memory error 1
Clock error
Memory error 2
Board error 2
Serial communication time-out error
Serial communication error
Regenerative error
Main circuit device overheat
Overload 1
Overload 2
Main circuit
Overcurrent
Overspeed
Encoder error 1
Encoder error 2
Alarm
display
(Note) Alarm code
CN1
pin 10
0
000
1
CN1
pin 11
00
1
101
CN1
pin 12
1
1
0
1
0
1
0
Set value Connector pin No.
Note: 0:off
1:on
Setting of warning (WNG) output
Select the connector pin to output warning. The old signal
before selection will be unavailable.
AL.19 Memory error 3
AL.37 Parameter error
AL.33 Overvoltage
AL.46 Servo motor overheat
AL.10 Undervoltage
100
AL.1A Motor combination error
0 Not output.
1CN1-11
2CN1-9
3CN1-10
4CN1-12
0
Alarm code is output at alarm occurrence.
0
0000 Refer to
Name
and
function
column.
S T

15 - 47
15. MR-E- AG SERVO AMPLIFIER COMPATIBLE WITH ANALOG INPUT
Class No. Symbol Name and function Initial
value Unit Setting
range
Control
mode
50 For manufacturer setting
Don’t change this value by any means. 0000
51 *OP6 Function selection 6
Used to select the operation to be performed when the reset (RES)
switches on.
000
Operation to be performed when the
reset (RES) switches on
0: Base circuit not switched off
1: Base circuit switched off
0000 Refer to
Name
and
function
column.
S T
52 For manufacturer setting
Don’t change this value by any means. 0000
53 *OP8 Function selection 8
Used to select the protocol of serial communication.
0 0
Protocol checksum selection
0: Yes (checksum added)
1: No (checksum not added)
Protocol checksum selection
0: With station numbers
1: No station numbers
0000 Refer to
Name
and
function
column.
S T
54 *OP9 Function selection 9
Use to select the command pulse rotation direction, encoder output
pulse direction and encoder pulse output setting.
0
Encoder pulse output phase changing
Changes the phases of A/B-phase encoder pulses output .
Encoder output pulse setting selection (refer to parameter No. 27)
0: Output pulse designation
1: Division ratio setting
Servo motor rotation direction
Set value CCW CW
0
1
A phase
B phase
A phase
B phase
A phase
B phase
A phase
B phase
0
0000 Refer to
Name
and
function
column.
S T
55 For manufacturer setting
Don’t change this value by any means. 0000
0
56 SIC Serial communication time-out selection
Used to set the communication protocol time-out period in [s].
When you set "0", time-out check is not made.
0
s1 to 60
ST
Expansion parameters 2
57 For manufacturer setting
Don’t change this value by any means. 10

15 - 48
15. MR-E- AG SERVO AMPLIFIER COMPATIBLE WITH ANALOG INPUT
Class No. Symbol Name and function Initial
value Unit Setting
range
Control
mode
58 NH1 Machine resonance suppression filter 1
Used to selection the machine resonance suppression filter.
(Refer to Section 8.2.)
2
3
0
0
140dB
14dB
8dB
4dB
Notch frequency selection
Set "00" when you have set adaptive vibration
suppression control to be "valid" or "held"
(parameter No. 60: 1 or 2 ).
00
01
02
03
04
05
06
07
Setting
value
Frequency
Invalid
4500
2250
1500
1125
900
750
642.9
08
09
0A
0B
0C
0D
0E
0F
562.5
500
450
409.1
375
346.2
321.4
300
Frequency
10
11
12
13
14
15
16
17
281.3
264.7
250
236.8
225
214.3
204.5
195.7
Frequency
18
19
1A
1B
1C
1D
1E
1F
187.5
180
173.1
166.7
160.1
155.2
150
145.2
Frequency
Notch depth selection
Setting
value
Depth Gain
Deep
Shallow
to
Setting
value
Setting
value
Setting
value
0000 Refer to
Name
and
function
column.
S T
Expansion parameters 2
59 NH2 Machine resonance suppression filter 2
Used to set the machine resonance suppression filter.
0
Notch frequency
Same setting as in parameter No. 58
However, you need not set "00" if you have
set adaptive vibration suppression control to
be "valid" or "held".
Notch depth
Same setting as in parameter No. 58
0000 Refer to
Name
and
function
column.
S T

15 - 49
15. MR-E- AG SERVO AMPLIFIER COMPATIBLE WITH ANALOG INPUT
Class No. Symbol Name and function Initial
value Unit Setting
range
Control
mode
60 LPF Low-pass filter/adaptive vibration suppression control
Used to selection the low-pass filter and adaptive vibration
suppression control. (Refer to Chapter 8.)
0
Low-pass filter selection
0: Valid (Automatic adjustment)
1: Invalid
When you choose "valid", 2 (1 GD2 setting 0.1)
VG2 setting 10
bandwidth filter is set automatically.
Adaptive vibration suppression control selection
Choosing "valid" or "held" in adaptive vibration
suppression control selection makes the machine
resonance control filter 1 (parameter No. 58) invalid.
0: Invalid
1: Valid
Machine resonance frequency is always detected
and the filter is generated in response to resonance to
suppress machine vibration.
2: Held
The characteristics of the filter generated so far are held,
and detection of machine resonance is stopped.
Adaptive vibration suppression control sensitivity selection
Used to set the sensitivity of machine resonance detection.
0: Normal
1: Large sensitivity
[Hz]
0000 Refer to
Name
and
function
column.
S T
61 GD2B Ratio of load inertia moment to servo motor inertia moment 2
Used to set the ratio of load inertia moment to servo motor inertia
moment when gain changing is valid.
70 0.1
times 0
to
3000
S
62 For manufacturer setting
Don’t change this value by any means. 100
63 VG2B Speed control gain 2 changing ratio
Used to set the ratio of changing the speed control gain 2 when gain
changing is valid.
Made valid when auto tuning is invalid.
100 % 10
to
200
PS
Expansion parameters 2
64 VICB Speed integral compensation changing ratio
Used to set the ratio of changing the speed integral compensation
when gain changing is valid. Made valid when auto tuning is invalid.
100 % 50
to
1000
PS

15 - 50
15. MR-E- AG SERVO AMPLIFIER COMPATIBLE WITH ANALOG INPUT
Class No. Symbol Name and function Initial
value Unit Setting
range
Control
mode
65 *CDP Gain changing selection
Used to select the gain changing condition. (Refer to Section 8.5.)
000
Gain changing selection
Gains are changed in accordance with the settings
of parameters No. 61 to 64 under any of the following
conditions:
0: Invalid
1: Gain changing (CDP) is ON
2: For manufacturer setting
3: For manufacturer setting
4: Servo motor speed is equal to higher than
parameter No. 66 setting
0000 Refer to
Name
and
function
column.
S
66 CDS Gain changing condition
Used to set the value of gain changing condition (command
frequency, droop pulses, servo motor speed) selected in parameter
No. 65.The set value unit changes with the changing condition item.
(Refer to Section 8.5.)
10 kpps
pulse
r/min
10
to
9999
S
67 CDT Gain changing time constant
Used to set the time constant at which the gains will change in
response to the conditions set in parameters No. 65 and 66.
(Refer to Section 8.5.)
1ms0
to
100
S
68 For manufacturer setting
Don’t change this value by any means. 0
69 1
70 1
71 1
Internal speed command 4
Used to set speed 4 of internal speed commands. S72 SC4
Internal speed limit 4
Used to set speed 4 of internal speed limits.
200 r/min 0 to in-
stanta-
neous
permi-
ssible
speed
T
Internal speed command 5
Used to set speed 5 of internal speed commands. S73 SC5
Internal speed limit 5
Used to set speed 5 of internal speed limits.
300 r/min 0 to in-
stanta-
neous
permi-
ssible
speed
Internal speed command 6
Used to set speed 6 of internal speed commands. S74 SC6
Internal speed limit 6
Used to set speed 6 of internal speed limits.
500 r/min 0 to in-
stanta-
neous
permi-
ssible
speed
T
Internal speed command 7
Used to set speed 7 of internal speed commands. S
Expansion parameters 2
75 SC7
Internal speed limit 7
Used to set speed 7 of internal speed limits.
800 r/min 0 to in-
stanta-
neous
permi-
ssible
speed
T

15 - 51
15. MR-E- AG SERVO AMPLIFIER COMPATIBLE WITH ANALOG INPUT
Class No. Symbol Name and function Initial
value Unit Setting
range
Control
mode
76 TL2 Internal torque limit 2
Set this parameter to limit servo motor torque on the assumption
that the maximum torque is 100[%].
When 0 is set, torque is not produced.
When torque is output in analog monitor output, this set value is the
maximum output voltage ( 8V).
100 % 0
to
100
ST
77 00
78 10000
79 10
80 10
81 100
82 100
83 100
Expansion parameters 2
84
For manufacturer setting
Don’t change this value by any means.
0000
15.5 Display and operation
POINT
For the alarm mode, parameter mode output signal (DO) forcible output
and test operation mode, refer to Chapter 6.
15.5.1 Display flowchart
Use the display (5-digit, 7-segment LED) on the front panel of the servo amplifier for status display,
parameter setting, etc. Set the parameters before operation, diagnose an alarm, confirm external
sequences, and/or confirm the operation status. Press the "MODE" "UP" or "DOWN" button once to move
to the next screen.
To refer to or set the expansion parameters, make them valid with parameter No. 19 (parameter write
disable).

15 - 52
15. MR-E- AG SERVO AMPLIFIER COMPATIBLE WITH ANALOG INPUT
Cumulative feedback
pulses [pulse]
Motor speed
[r/min]
Command pulse
frequency [kpps]
Speed command voltage
Speed limit voltage[mV]
Torque limit voltage
Torque command voltage
Regenerative load
ratio [%]
Effective load ratio
[%]
Peak load ratio
[%]
Within one-revolution
position low [pulse]
Load inertia moment
ratio [times]
Sequence
External I/O
signal display
Output signal
forced output
Test operation
Jog feed
Test operation
Motor-less operation
Software version L
Software version H
Automatic VC offset
Current alarm
Last alarm
Second alarm in past
Third alarm in past
Fourth alarm in past
Fifth alarm in past
Sixth alarm in past
Parameter error No.
Parameter No. 0
Parameter No. 1
Parameter No. 18
Parameter No. 19
Parameter No. 20
Parameter No. 21
Parameter No. 48
Parameter No. 49
(Note)
Note: The initial status display at power-on depends on the control mode.
Speed control mode: Servo Motor speed(r),
Torque control mode: Torque command voltage(U)
Also, parameter No. 18 can be used to change the initial indication of the status display at power-on.
MODE
button
DOWN
UP
Status display Diagnosis Basic
parameters Expansion
parameters 1
Alarm Expansion
parameters 2
Parameter No. 50
Parameter No. 51
Parameter No. 83
Parameter No. 84
Instantaneous torque
[%]
Within one-revolution
position, high [100 pulses]
Bus voltage [V]
Motor series ID
Motor type ID
Encoder ID
[mV]
Test operation mode
Machine analyzer operation

15 - 53
15. MR-E- AG SERVO AMPLIFIER COMPATIBLE WITH ANALOG INPUT
15.5.2 Status display
(1) Status display list
The following table lists the servo statuses that may be shown:
Name Symbol Unit Description Display
range
Cumulative feedback
pulses C pulse Feedback pulses from the servo motor encoder are counted and
displayed. The value in excess of 99999 is counted, bus since the
servo amplifier display is five digits, it shows the lower five digits of
the actual value. Press the "SET" button to reset the display value to
zero.
Reverse rotation is indicated by the lit decimal points in the upper
four digits.
99999
to
99999
Servo motor speed r r/min The servo motor speed is displayed.
The value rounded off is displayed in 0.1r/min. 5400
to
5400
(1) Torque control mode
Analog speed limit (VLA) voltage is displayed.
Analog speed
command voltage
Analog speed limit
voltage
FV
(2) Speed control mode
Analog speed command (VC) voltage is displayed.
10.00
to
10.00
U V (1) Position control mode, speed control mode
Analog torque limit (TLA) voltage is displayed. 0
to
10V
Analog torque
command voltage
Analog torque limit
voltage (2) Torque control mode
Analog torque command (TLA) voltage is displayed. 10
to
10V
Regenerative load
ratio L % The ratio of regenerative power to permissible regenerative power is
displayed in %. 0
to
100
Effective load ratio J % The continuous effective load torque is displayed.
The effective value in the past is seconds is displayed relative to the
rated torque of 100%.
0
to
300
Peak load ratio b % The maximum torque generated during acceleration/deceleration, etc.
The highest value in the past 15 seconds is displayed relative to the
rated torque of 100%.
0
to
400
Instantaneous torque T % Torque that occurred instantaneously is displayed.
The value of the torque that occurred is displayed in real time
relative to the rate torque of 100%.
0
to
400
Within one-revolution
position low Cy1 pulse Position within one revolution is displayed in encoder pulses.
The value returns to 0 when it exceeds the maximum number of
pulses.
The value is incremented in the CCW direction of rotation.
0
to
99999
Within one-revolution
position high Cy2 100
pulse The within one-revolution position is displayed in 100 pulse
increments of the encoder.
The value returns to 0 when it exceeds the maximum number of
pulses.
The value is incremented in the CCW direction of rotation.
0
to
1310
Load inertia moment
ratio dC 0.1
Times The estimated ratio of the load inertia moment to the servo motor
shaft inertia moment is displayed. 0.0
to
300.0
Bus voltage Pn V The voltage (across P-N) of the main circuit converter is displayed. 0
to
450

15 - 54
15. MR-E- AG SERVO AMPLIFIER COMPATIBLE WITH ANALOG INPUT
(2) Changing the status display screen
The status display item of the servo amplifier display shown at power-on can be changed by changing
the parameter No. 18 settings.
The item displayed in the initial status changes with the control mode as follows:
Control mode
Speed
Speed/torque
Torque
Status display at power-on
Servo motor speed
Servo motor speed/analog torque command voltage
Analog torque command voltage

15 - 55
15. MR-E- AG SERVO AMPLIFIER COMPATIBLE WITH ANALOG INPUT
15.5.3 Diagnostic mode
Name Display Description
Not ready.
Indicates that the servo amplifier is being initialized or an alarm
has occurred.
Sequence Ready.
Indicates that the servo was switched on after completion of
initialization and the servo amplifier is ready to operate.
External I/O signal
display
Refer to section 15.5.4. Indicates the ON-OFF states of the external I/O signals.
The upper segments correspond to the input signals and the
lower segments to the output signals.
Lit: ON
Extinguished: OFF
The I/O signals can be changed using parameters No. 43 to 49.
Output signal (DO)
forced output The digital output signal can be forced on/off. For more
information, refer to section 6.7.
Jog feed Jog operation can be performed when there is no command from
the external command device.
For details, refer to section 6.8.2.
Screen for manufacturer setting. When this screen is being
displayed, do not press any other buttons than "UP" and
"DOWN".
Motorless
operation
Without connection of the servo motor, the servo amplifier
provides output signals and displays the status as if the servo
motor is running actually in response to the external input
signal.
For details, refer to section 6.8.4.
Test
operation
mode
Machine
analyzer
operation
Merely connecting the servo amplifier allows the resonance point
of the mechanical system to be measured.
The servo configuration software (MRZJW3-SETUP154E or later)
is required for machine analyzer operation.
Gain search cannot be used.
Software version low Indicates the version of the software.
Software version high Indicates the system number of the software.
Automatic VC offset
If offset voltages in the analog circuits inside and outside the
servo amplifier cause the servo motor to rotate slowly at the
analog speed command (VC) or analog speed limit (VLA) of 0V,
this function automatically makes zero-adjustment of offset
voltages.
When using this function, make it valid in the following
procedure. Making it valid causes the parameter No. 29 value to
be the automatically adjusted offset voltage.
1) Press "SET" once.
2) Set the number in the first digit to 1 with "UP"/"DOWN".
3) Press "SET".
You cannot use this function if the input voltage of VC or VLA
is 0.4V or more.

15 - 56
15. MR-E- AG SERVO AMPLIFIER COMPATIBLE WITH ANALOG INPUT
Name Display Description
Motor series Press the "SET" button to show the motor series ID of the servo
motor currently connected.
Motor type Press the "SET" button to show the motor type ID of the servo
motor currently connected.
Encoder Press the "SET" button to show the encoder ID of the servo motor
currently connected.

15 - 57
15. MR-E- AG SERVO AMPLIFIER COMPATIBLE WITH ANALOG INPUT
15.5.4 External I/O signal display
The ON/OFF states of the digital I/O signals connected to the servo amplifier can be confirmed.
(1) Operation
Call the display screen shown after power-on.
Using the "MODE" button, show the diagnostic screen.
Press UP once.
External I/O signal display screen
(2) Display definition
CN1
6
CN1
7
CN1
21
CN1
5
CN1
9
CN1
3CN1
4
CN1
12 CN1
11
CN1
10
Lit: ON
Extinguished: OFF
Input signals
Output signals
CN1
8
Always lit
The 7-segment LED shown above indicates ON/OFF.
Each segment at top indicates the input signal and each segment at bottom indicates the output
signal. The signals corresponding to the pins in the respective control modes are indicated below:
(Note 2) Signal abbreviation
CN1
Pin No.
Input/Output
(Note 1) I/O ST
Related parameter No.
3 I ST1 RS2 43 to 47
4 I SON SON 43 to 47
5 I ST2 RS1 43 to 47
6 I LSP 43 to 48
7 I LSN 43 to 48
8IEMGEMG
9OALMALM49
10 O SA 49
11 O RD RD 49
12 O ZSP ZSP 49
21 O OP OP
Note: 1. I: Input signal, O: Output signal
2. S: Speed control mode, T: Torque control mode.
3. The signal of CN1A-18 is always output.

15 - 58
15. MR-E- AG SERVO AMPLIFIER COMPATIBLE WITH ANALOG INPUT
(3) Default signal indications
(a) Speed control mode
Lit: ON
Extinguished: OFF
Input signals
Output signals
SON (CN 1-4) Servo-on
LSN (CN 1-7) Reverse rotation stroke end
LSP (CN 1-6) Forward rotation stroke end
RD (CN 1-11) Ready
ZSP (CN 1-12) Zero speed
ALM (CN 1-9) Trouble
OP (CN 1-21) Encoder Z-phase pulse
EMG (CN 1-8) Emergency stop
SA (CN 1-10) Limiting speed
ST1 (CN 1-3) Forward rotation start
ST2 (CN 1-5) Reverse rotation start
(b) Torque control mode
Lit: ON
Extinguished: OFF
Input signals
Output signals
RS1 (CN 1-5) Forward rotation selection
RS2 (CN 1-3) Reverse rotation selection
SON (CN 1-4) Servo-on
(CN 1-7)
(CN 1-6)
RD (CN 1-11) Ready
(CN 1-10)
ZSP (CN 1-12) Zero speed
ALM (CN 1-9) Trouble
OP (CN 1-21) Encoder Z-phase pulse
EMG (CN 1-8) Emergency stop

15 - 59
15. MR-E- AG SERVO AMPLIFIER COMPATIBLE WITH ANALOG INPUT
15.6. Troubleshooting
15.6.1 Trouble at start-up
The following faults may occur at start-up. If any of such faults occurs, take the corresponding action.
(1) Speed control mode
No. Start-up sequence Fault Investigation Possible cause Reference
Not improved if connectors
CN1, CN2 and CN3 are
disconnected.
1. Power supply voltage fault
2. Servo amplifier is faulty.
Improved when connectors
CN1 is disconnected. Power supply of CN1 cabling is
shorted.
Improved when connector
CN2 is disconnected. 1. Power supply of encoder
cabling is shorted.
2. Encoder is faulty.
LED is not lit.
LED flickers.
Improved when connector
CN3 is disconnected. Power supply of CN3 cabling is
shorted.
1 Power on (Note)
Alarm occurs. Refer to Section 10.2 and remove cause. Section 10.2
Alarm occurs. Refer to Section 10.2 and remove cause. Section 10.22 Switch on servo-on
(SON). Servo motor shaft is
not servo-locked
(is free).
1. Check the display to see if
the servo amplifier is
ready to operate.
2. Check the external I/O
signal indication to see if
the servo-on (SON) is ON.
1. Servo-on (SON) is not input.
(Wiring mistake)
2. 24VDC power is not
supplied to COM.
Section 6.6
Call the status display and
check the input voltage of
the analog speed command
(VC).
Analog speed command is 0V. Section 6.2
Call the external I/O signal
display and check the
ON/OFF status of the input
signal.
LSP, LSN, ST1 or ST2 is off. Section 6.6
Check the internal speed
commands 1 to 7
(parameters No. 8 to 10 72
to 75).
Set value is 0.
Check the internal torque
limit 1 (parameter No. 28). Torque limit level is too low as
compared to the load torque.
3Switch on forward
rotation start (ST1)
or reverse rotation
start (ST2).
Servo motor does
not rotate.
When the analog torque
limit (TLA) is usable, check
the input voltage on the
status display.
Torque limit level is too low as
compared to the load torque.
(1), Section
5.1.2
Rotation ripples
(speed fluctuations)
are large at low
speed.
Make gain adjustment in the
following procedure:
1. Increase the auto tuning
response level.
2. Repeat acceleration and
deceleration several
times to complete auto
tuning.
Gain adjustment fault Chapter 7
4 Gain adjustment
Large load inertia
moment causes the
servo motor shaft to
oscillate side to side.
If the servo motor may be
run with safety, repeat
acceleration and
deceleration several times to
complete auto tuning.
Gain adjustment fault Chapter 7
Note: Switch power on again after making sure that the change lamp has turned off completely.

15 - 60
15. MR-E- AG SERVO AMPLIFIER COMPATIBLE WITH ANALOG INPUT
(2) Torque control mode
No. Start-up sequence Fault Investigation Possible cause Reference
Not improved if connectors
CN1, CN2 and CN3 are
disconnected.
1. Power supply voltage fault
2. Servo amplifier is faulty.
Improved when connectors
CN1 is disconnected. Power supply of CN1 cabling is
shorted.
Improved when connector
CN2 is disconnected. 1. Power supply of encoder
cabling is shorted.
2. Encoder is faulty.
LED is not lit.
LED flickers.
Improved when connector
CN3 is disconnected. Power supply of CN3 cabling is
shorted.
1 Power on (Note)
Alarm occurs. Refer to Section 10.2 and remove cause. Section 10.2
Alarm occurs. Refer to Section 10.2 and remove cause. Section 10.22 Switch on servo-on
(SON). Servo motor shaft is
free. Call the external I/O signal
display and check the
ON/OFF status of the input
signal.
1. Servo-on (SON) is not input.
(Wiring mistake)
2. 24VDC power is not
supplied to COM.
Section 6.6
Call the status display and
check the analog torque
command (TC).
Analog torque command is 0V. Section 6.2
Call the external I/O signal
display and check the
ON/OFF status of the input
signal.
RS1 or RS2 is off. Section 6.6
Check the internal speed
limits 1 to 7
(parameters No. 8 to 10 72
to 75).
Set value is 0.
Check the analog torque
command maximum output
(parameter No. 26) value.
Torque command level is too
low as compared to the load
torque.
3Switch on forward
rotation start (RS1)
or reverse rotation
start (RS2).
Servo motor does
not rotate.
Check the internal torque
limit 1 (parameter No. 28). Set value is 0.
(1),
Section 5.1.2
Note: Switch power on again after making sure that the change lamp has turned off completely.

15 - 61
15. MR-E- AG SERVO AMPLIFIER COMPATIBLE WITH ANALOG INPUT
15.6.2 Alarms and warning list
POINT
Configure up a circuit which will detect the trouble (ALM) signal and turn
off the servo-on (SON) signal at occurrence of an alarm.
When a fault occurs during operation, the corresponding alarm or warning is displayed. If any alarm or
warning has occurred, refer to Section 10.2.2 or 10.2.3 and take the appropriate action.
Set " 1" in parameter No. 49 to output the alarm code in ON/OFF status across the corresponding
pin and SG. Warnings (AL.E0 to AL.E9) have no alarm codes. Any alarm code is output at occurrence of
the corresponding alarm. In the normal status, the signals available before alarm code setting (CN1-12:
ZSP, CN1-11: RD, CN1-10: SA) are output.
The alarms marked in the alarm deactivation column can be deactivated by the corresponding
operations.
(Note 2) Alarm code Alarm deactivation
Display CN1-10
pin
CN1-11
pin
CN1-12
pin
Name Power
OFF ON
Press
"SET" on
current
alarm
screen.
Alarm
reset
(RES)
signal
AL.10010Undervoltage
AL.12 0 0 0 Memory error 1
AL.13 0 0 0 Clock error
AL.15 0 0 0 Memory error 2
AL.16 1 0 1 Encoder error 1
AL.17 0 0 0 Board error
AL.19 0 0 0 Memory error 3
AL.1A 1 0 1 Motor combination error
AL.20 1 1 0 Encoder error 2
AL.24 0 0 1 Main circuit error
AL.30 0 1 0 Regenerative error (Note 1) (Note 1) (Note 1)
AL.31011Overspeed
AL.32001Overcurrent
AL.33010Overvoltage
AL.37 0 0 0 Parameter error
AL.45 1 1 0 Main circuit device overheat
AL.46 1 1 0 Servo motor overheat
AL.50110Overload 1 (Note 1) (Note 1) (Note 1)
AL.51110Overload 2 (Note 1) (Note 1) (Note 1)
AL.8A 0 0 0 Serial communication time-out error
AL.8E 0 0 0 Serial communication error
Alarms
88888 0 0 0 Watchdog
AL.E0 Excessive regenerative warning
AL.E1 Overload warning
AL.E6 Servo emergency stop warning
Warnings
AL.E9 Undervoltage warning
Removing the cause of occurrence
deactivates the alarm
automatically.
Note: 1. Deactivate the alarm about 30 minutes of cooling time after removing the cause of occurrence.
2. 0: off
1: on

15 - 62
15. MR-E- AG SERVO AMPLIFIER COMPATIBLE WITH ANALOG INPUT
MEMO

REVISIONS
*The manual number is given on the bottom left of the back cover.
Print data *Manual number Revision
Sep.,2002 SH(NA)030031-A First edition
Mar.,2003 SH(NA)030031-B "Note 2" in (1) Environmental Condition is deleted from Safety Precautions 4.
The "concerning sale" item is deleted.
The "Compliance with EU Directives (2)" paragraph is added.
The "Compliance with UL and C-UL Standards (4)" note is deleted.
Section 1.2: Parts of figures are changed. "Note 3" is changed.
Section 1.3: Mass of 2kW is added.
Section 1.5 (2): Note is deleted.
Section 1.6: Note 2 is deleted.
Section 1.7 (2): Figure is changed.
Section 1.8 (2): Figure is changed.
Section 3.1.2: Part of figure is changed.
Section 3.7.1: Figure is changed.
Section 3.7.2: Paragraph and table are changed.
Section 3.8.1: Point is added.
Section 3.8.2: Note is deleted. Part of figure is changed.
Section 3.8.3 (2): Note is deleted.
Section 4.1 (1) (e): Paragraph is changed.
Section 5.1.2 (2): Initial setting of parameter No. 0 is examined and note is
deleted.
Paragraph for third digit of parameter No. 20 is added.
TLC/VLC output selection of parameter No. 22 is added.
Paragraph is added to parameter No. 42.
Body of description is added to parameters No. 43 to 48.
Description of setting of first digit of parameter No. 49 is
changed.
Section 10.2.1: Name of AL.E9 is changed.
Section 10.2.2: AL. 12, 13 and 14 are changed.
AL. 37 3. is added.
Section 11.1: Dimensional drawing is changed.
Section 11.2 (4): Dimensional drawing is added.
Section 12.1: "Note 2" is deleted.
Section 12.2: "Note 3" is deleted.
Section 12.3: Note is deleted.
Section 13.1.1: "Note 2" is deleted.
Section 13.1.1 (2) (b): Note is deleted.
Section 13.1.2: Paragraphs 20, 21, 22 and 23 are added.
Section 13.2.1: Cable size of 2kW is changed. Note is changed. Part of
description is deleted.
Table of recommended crimp terminal is deleted.
Section 13.2.2: Note is deleted. Amperage of 70A to 200A fuses of MR-E is
changed.
Section 13.2.3: Note is deleted.
Section 13.2.7: Note is deleted.
Section 13.2.8: Note is deleted.

Print data *Manual number Revision
Mar.,2003 SH(NA)030031-B Chapter 14: Point is deleted.
Section 14.2: Rating plate is changed.
Section 14.7.3: Added.
Chapter 15: Added.

HEAD OFFICE:MITSUBISHI DENKI BLDG MARUNOUCHI TOKYO 100-8310
SH (NA) 030031-B (0303) MEE Printed in Japan Specifications subject to change without notice.
This Instruction Manual uses recycled paper.
MODEL
MODEL
CODE