NORDYNE Air Conditioner/heat Pump(outside Unit) Manual L0611385
User Manual: NORDYNE NORDYNE Air conditioner/heat pump(outside unit) Manual NORDYNE Air conditioner/heat pump(outside unit) Owner's Manual, NORDYNE Air conditioner/heat pump(outside unit) installation guides
Open the PDF directly: View PDF .
Page Count: 32
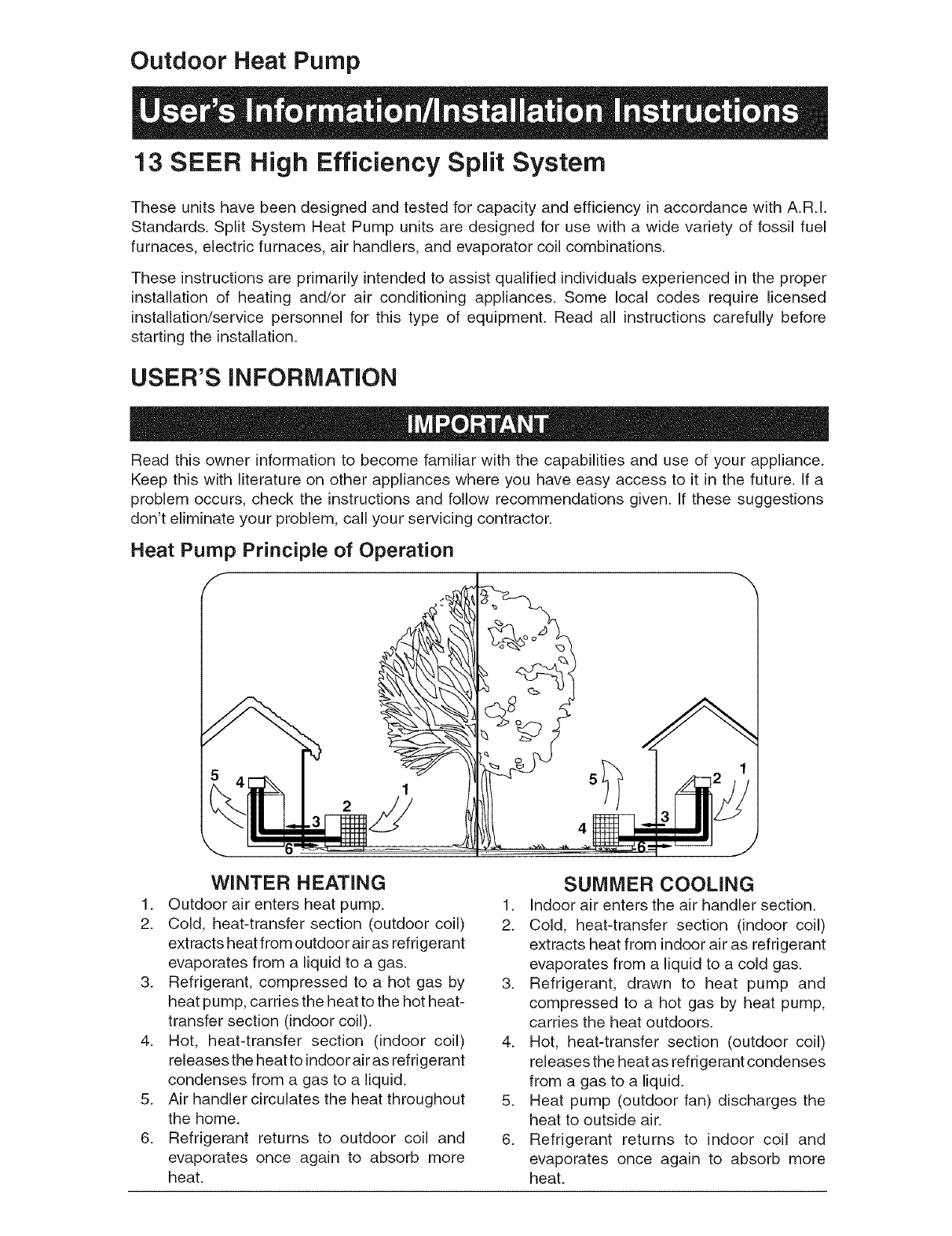
Outdoor Heat Pump
13 SEER High Efficiency Split System
These units have been designed and tested for capacity and efficiency in accordance with A.R.I.
Standards. Split System Heat Pump units are designed for use with a wide variety of fossil fuel
furnaces, electric furnaces, air handlers, and evaporator coil combinations.
These instructions are primarily intended to assist qualified individuals experienced in the proper
installation of heating and/or air conditioning appliances. Some local codes require licensed
installation/service personnel for this type of equipment. Read all instructions carefully before
starting the installation.
USER'S INFORMATION
Read this owner information to become familiar with the capabilities and use of your appliance.
Keep this with literature on other appliances where you have easy access to it in the future. If a
problem occurs, check the instructions and follow recommendations given. If these suggestions
don't eliminate your problem, call your servicing contractor.
Heat Pump Principle of Operation
f
1
WINTER HEATING
1. Outdoor air enters heat pump.
2. Cold, heat-transfer section (outdoor coil)
extracts heat from outdoor air as refrigerant
evaporates from a liquid to a gas.
3. Refrigerant, compressed to a hot gas by
heat pump, carries the heat to the hot heat-
transfer section (indoor coil).
4. Hot, heat-transfer section (indoor coil)
releases the heat to indoor air as refrigerant
condenses from a gas to a liquid.
5. Air handler circulates the heat throughout
the home.
6. Refrigerant returns to outdoor coil and
evaporates once again to absorb more
heat.
SUMMER COOLING
1. Indoor air enters the air handler section.
2. Cold, heat-transfer section (indoor coil)
extracts heat from indoor air as refrigerant
evaporates from a liquid to a cold gas.
3. Refrigerant, drawn to heat pump and
compressed to a hot gas by heat pump,
carries the heat outdoors.
4. Hot, heat-transfer section (outdoor coil)
releases the heat as refrigerant condenses
from a gas to a liquid.
5. Heat pump (outdoor fan) discharges the
heat to outside air.
6. Refrigerant returns to indoor coil and
evaporates once again to absorb more
heat.
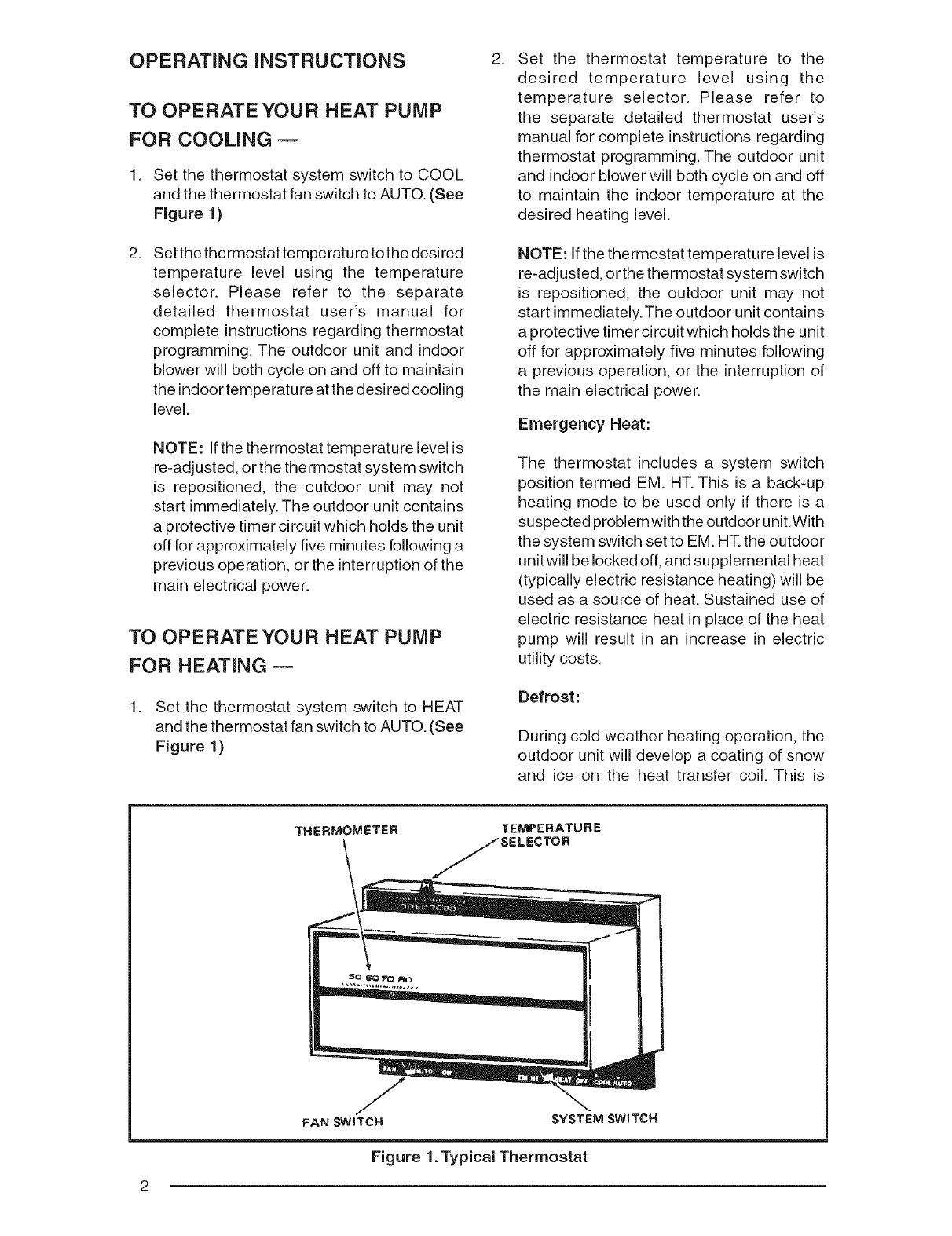
OPERATING iNSTRUCTiONS
TO OPERATE YOUR HEAT PUMP
FOR COOLING
1. Set the thermostat system switch to COOL
and the thermostat fan switch to AUTO. (See
Figure 1)
.Set the thermostat temperatu re to the desired
temperature level using the temperature
selector. Please refer to the separate
detailed thermostat user's manual for
complete instructions regarding thermostat
programming. The outdoor unit and indoor
blower will both cycle on and off to maintain
the indoor temperatu re at the desired cooling
level.
NOTE: If the thermostat temperature level is
re-adjusted, or the thermostat system switch
is repositioned, the outdoor unit may not
start immediately. The outdoor unit contains
a protective timer circuit which holds the unit
off for approximately five minutes following a
previous operation, or the interruption of the
main electrical power.
TO OPERATE YOUR HEAT PUMP
FOR HEATING
1. Set the thermostat system switch to HEAT
and the thermostat fan switch to AUTO. (See
Figure 1)
.Set the thermostat temperature to the
desired temperature level using the
temperature selector. Please refer to
the separate detailed thermostat user's
manual for complete instructions regarding
thermostat programming. The outdoor unit
and indoor blower will both cycle on and off
to maintain the indoor temperature at the
desired heating level.
NOTE: Ifthe thermostat temperature level is
re-adjusted, or the thermostat system switch
is repositioned, the outdoor unit may not
start immediately.The outdoor unit contains
a protective timer circuit which holds the unit
off for approximately five minutes following
a previous operation, or the interruption of
the main electrical power.
Emergency Heat:
The thermostat includes a system switch
position termed EM. HT. This is a back-up
heating mode to be used only if there is a
suspected problem with the outdoor unit.With
the system switch set to EM. HT. the outdoor
unit will be locked off, and supplemental heat
(typically electric resistance heating) will be
used as a source of heat. Sustained use of
electric resistance heat in place of the heat
pump will result in an increase in electric
utility costs.
Defrost:
During cold weather heating operation, the
outdoor unit will develop a coating of snow
and ice on the heat transfer coil. This is
/
FAN SWITCH SYSTEM SWITCH
Figure 1. Typical Thermostat
2

normal,andtheunitwillperiodicallydefrost
itself.Duringthedefrostcycle,theoutdoor
fanwillstop,andthecompressorwillcontinue
torunandheattheoutdoorcoil,causingthe
snowandicetomelt.Afterthesnowandice
havemelted,somesteammayrisefromthe
outdoorunitasthewarmcoilcausessome
meltedfrostto evaporate.
TO OPERATEYOUR HEAT PUMP
FOR AUTOMATIC COOLING AND
HEATING--
TO MAINTAIN YOUR HEAT PUMP--
CAUTION:
Be certain the electrical power to
the outdoor unit and the furnace/air
handler is disconnected before
doing the following recommended
maintenance.
1. Regularly:
1. Set the thermostat system switch to AUTO
and the thermostat fan switch to AUTO. (See
Figure 1)
Note: Thermostats will vary. Some models
will not include the AUTO mode, and others
will have the AUTO in place of the HEAT and
COOL, and some will include all three.
2_ Set the thermostat temperature to the
desired heating and cooling temperature
level(s). The outdoor unit and the indoor
blower will then cycle on and off in either
the heating or cooling mode of operation as
required to automatically maintain the indoor
temperature within the desired limits.
TO SHUT OFFYOUR HEAT
PUMP--
Set the thermostat system switch to OFF and the
thermostat fan switch to AUTO. (See Figure 1)
The system will not operate, regardless of the
thermostat temperature selector(s) setting.
TO OPERATE THE INDOOR
BLOWER CONTINUOUSLY--
Set the thermostat fan switch to ON (See Figure
1).The indoor blower will start immediately, and
will run continually until the fan switch is reset
to AUTO.
a_
b_
c_
d_
Clean or replace the indoor air filter at the
start of each heating and cooling season,
and when an accumulation of dust and
dirt is visible on the air filter. Inspect the
filter monthly.
Remove any leaves and grass clippings
from the coil in the outdoor unit, being
careful not to damage the aluminum
fins.
Check for any obstruction such as twigs,
sticks, etc.
Certain models have external panels
fabricated from a premium grade of
stainless steel designed to inhibit cor-
rosion. For such units, if the unit is
located in a coastal region or other area
subjected to high concentrations of salt,
then the unit should be hosed off after
storms and monthly otherwise to maintain
its new appearance.
CAUTION:
Do not over-oil, or oil motors not
factory-equipped with oil tubes. The
compressor is hermetically "sealed"
and does not require lubrication.
2. Before Calling a Service Technician, Be
Certain:
The continuous indoor blower operation can be
obtained with the thermostat system switch set
in any position, including OFR
The continuous indoor blower operation is
typically used to circulate the indoor air to
equalize a temperature unbalance due to a sun
load, cooking, or fireplace operation.
a_
b_
The unit thermostat is properly set--see
"To OperateYour Heat Pump for Cooling"
and "To Operate Your Heat Pump for
Heating."
The unit disconnect fuses are in good
condition, and the electrical power to the
unit is turned on.
3

ReadYour Warranty
Please read the separate warranty document
completely. It contains valuable information
about your system.
GENERAL INFORMATION
Read the following instructionscompletely before
performing the installation.
Outdoor Unit Section -- Each outdoor unit
is shipped with a refrigerant charge adequate
to operate the outdoor section with an indoor
matching coil or air handler. Units with braze
connections include the proper amount of
refrigerant for an additional 15 ft. of refrigerant
lines the same size as the valve fittings.
NOTE: DO NOT USE ANY PORTION OF
THE CHARGE FOR PURGING OR LEAK
TESTING.
Matching coils and air handlers may be shipped
with a small holding charge to pressurize them to
keep out contaminants.To release the pressure,
read the indoor section installation instructions
carefully.
Liquid and Suction Lines -- Fully annealed,
refrigerant grade copper tubing should be used
when installing the system. Refrigerant suction
line tubing should be fully insulated.
Field Connections for Electrical Power
Supply -- All wiring must comply with current
provisions of the "National Electrical Code"
(ANSI/NFPA 70) and with applicable local
codes having jurisdiction. The minimum size of
electrical conductors and circuit protection must
be in compliance with information listed on the
outdoor unit data label.
SAFETY CONSIDERATIONS
Pressures within the System -- Split
system heat pump equipment contains liquid
and gaseous refrigerant under pressure.
Installation and servicing of this equipment
should be accomplished by qualified, trained
personnel thoroughly familiar with this type of
equipment. Under no circumstances should the
Homeowner attempt to install and/or service
the equipment.
Labels, Tags, Precautions -- When working
with this equipment, follow all precautions in the
literature, on tags, and on labels provided with
the equipment. Read and thoroughly understand
the instructions provided with the equipment prior
to performing the installation and operational
checkout of the equipment.
Brazing Operations-- Installation of equipment
may require brazing operations. Safety codes
must be complied with. Safety equipment (e.g.;
safety glasses, work gloves, fire extinguisher,
etc.) must be used when performing brazing
operations.
WARNING".
Ensure all electrical power to the unit
is off prior to installing or servicing the
equipment. Failure to do so may cause
personal injury or death.
SITE PREPARATION
Unpacking Equipment -- Remove the
cardboard carton and User's Manual from the
equipment. Take care to not damage tubing
connections when removing from the carton.
inspect for Damage -- Inspect the equipment
for damage prior to installing the equipment at
the job site. Ensure coil fins are straight and, if
necessary, comb fins to remove flattened and
bent fins.
Preferred Location of the Outdoor Unit at the
Job Site -- Conduct a survey of the job site to
determine the optimum location for mounting
the outdoor unit. Overhead obstructions,
poorly ventilated areas, and areas subject to
accumulation of debris should be avoided. The
outdoor unit should be installed no closer than
18 inches from the outside walls of the facility
and in an area free from overhead obstructions
to ensure unrestricted airflow through the
outdoor unit.
Facility Prerequisites -- Electrical power
supplied must be adequate for proper operation
of the equipment.The system must be wired and
provided with circuit protection in accordance
with local building codes and the National
Electrical Code.

iNSTALLiNG THE OUTDOOR UNiT
Slab Mount--The site selected for a slab mount
installation requires a stable foundation and one
not subject to erosion. The slab should be level
and anchored (if necessary) prior to placing the
equipment on the slab.
Cantilever Mount --The cantilever mount
should be designed with adequate safety factor
to support the weight of the equipment, and for
loads subjected to the mount during operation.
Installed equipment should be adequately
secured to the cantilever mount and levelled
prior to operation of the equipment.
Roof Mount --The method of mounting should
be designed so as not to overload roof structures
nor transmit noise to the interior of the structure.
Refrigerant and electrical line should be routed
through suitably waterproofed openings to
prevent water leaking into the structure.
INSTALLING THE INDOOR UNIT
The indoor section should be installed before
proceeding with routing of refrigerant piping.
Consult the Installation Instructions of the indoor
unit (i.e.: air handler, furnace, etc.) for details
regarding installation.
CONNECTING REFRIGERANT
TUBING BETWEEN THE iNDOOR
AND OUTDOOR UNiT
General -- Once outdoor and indoor unit
placement has been determined, route refrigerant
tubing between the equipment inaccordance with
sound installation practices. Refrigerant tubing
should be routed in a manner that minimizes the
length of tubing and the number of bends in the
tubing. Refrigerant tubing should be supported
in a manner that the tubing will not vibrate or
abrade during system operation. Tubing should
be kept clean of foreign debris during installation
and installation of a liquid line filter drier is
recommended if cleanliness or adequacy of
system evacuation is unknown or compromised.
Every effort should be made by the installer
to ensure that the field installed, refrigerant
containing components of the system have been
installed in accordance with these instructions
and sound installation practices so as to insure
reliable system operation and longevity.
The maximum recommended interconnecting
refrigerant line length is 75 feet, and the
vertical elevation difference between the indoor
and outdoor sections should not exceed 20
feet. Consult long line application guide for
installations in excess of these limits.
Filter Dryer Installation -- A filter dryer is
provided with PS series models only and must
be installed inthe liquid line of the system. If the
installation replaces a system with a filter dryer
already present in the liquid line, the filter dryer
must be replaced with the one supplied with the
unit. The filter dryer must be installed in strict
accordance with the manufacturer's installation
instructions.
For all other series models, installing a filter
dryer is optional. However, it is good installation
practice to install a filter dryer when replacing
the evaporator and/or condenser of a system.
When installing, the filter dryer must be installed
in strict accordance with the manufacturer's
installation instructions.
Optional Equipment- Optional equipment
(e.g.: liquid line solenoid valves, etc.) should
be installed in strict accordance with the
manufacturer's installation instructions.
ELECTRICAL CONNECTIONS
WARNING:
Turn off all electrical power at the main
circuit box before wiring electrical
power to the outdoor unit. Failure to
comply may cause severe personnel
injury or death.
Wiring Diagram/Schematic -- A wiring
diagram/schematic is located on the inside cover
of the electrical box of the outdoor unit. The
installer should become familiar with the wiring
diagram/schematic before making any electrical
connections to the outdoor unit.
Outdoor Unit Connections --The outdoor
unit requires both power and control circuit
electrical connections. Refer to the unit wiring
diagram/schematic for identification and location
of outdoor unit field wiring interfaces.

Control Circuit Wiring --The outdoor unit is
designed to operate from a 24VAC Class IIcontrol
circuit. Control circuit wiring must comply with
the current provisions of the "National Electrical
Code" (ANSI/N FPA 70) and with applicable focal
codes having jurisdiction.
Thermostat connections should be made in
accordance with the instructions supplied with
the thermostat, and with the instructions supplied
with the indoor equipment. A typical residential
installation with a heat pump thermostat and air
handler are shown below.
Electrical Power Wiring -- Electrical power
wiring must comply with the current provisions
of the "National Electrical Code" (ANSI/NFPA
70) and with applicable local codes having
jurisdiction. Use of rain tight conduit is
recommended. Electrical conductors shall have
minimum circuit ampacity in compliance with the
outdoor unit rating label.The facility shall employ
electrical circuit protection at a current rating no
greater than that indicated on the outdoor unit
rating label. Refer to the unit wiring diagram for
connection details.
Minimum Circuit Ampacity-- Electrical wiring
to the equipment must be compatible and in
compliance with the minimum circuit ampacity
listed on the outdoor unit data label.
COPPER WiRE SiZE i AWG
(1% Voltage Drop)
Supply Wire Length-Feet Supply Circuit
200 150 100 50 Ampacity
6 8 10 14 15
4 6 8 12 20
4 6 8 10 25
4 4 6 10 30
3 4 6 8 35
3 4 6 8 40
2 3 4 6 45
2 3 4 6 50
Wire Size based on N.E.C. for 60° type copper
conductors.
Maximum Fuse/Circuit Breaker Size-- Circuit
protection for the outdoor unit must be compatible
with the maximum fuse/circuit breaker size listed
on the outdoor unit data label.
Disconnect Switch--An elect rically compatible
disconnect switch must be within line of sight of
the outdoor unit. This switch shall be capable of
electrically de-energizing the outdoor unit.
Optional Equipment -- Optional equipment
requiring connection to the power or control
circuits must be wired in strict accordance with
current provisions of the "National Electrical
Code" (ANSI/NFPA 70), with applicable local
codes having jurisdiction, and the installation
instructions provided with the equipment.
Optional Equipment (e.g.: liquid line solenoid
valves, hard start kits, low suction pressure
cutout switch kit, high pressure cutout switch kit,
refrigerant compressor crankcase heater, etc.)
should be installed in strict accordance with the
manufacturer's installation instructions.
STARTUP AND CHECKOUT
WARNING:
Ensure electrical power to the unit is
off prior to performing the following
steps. Failure to do so may cause
personal injury or death.
Air FHters -- Ensure air filters are clean and in
place prior to operating the equipment.
Thermostat-- Set the room the rmostat function
switch to OFF, fan switch to AUTO, and adjust the
temperature setpoint to its highest setting.
Prior to applying electrical power to the outdoor
unit, ensure that the unit has been properly and
securely grounded, and that power supply
connections have been made at both the facility
power interface and outdoor unit.
Outdoor Unit -- Ensure the outdoor coil and
top of the unit are free from obstructions and
debris, and all equipment access/control panels
are in place.
Using extreme caution, apply power to the unit
and inspect the wiring for evidence of open,
shorted, and/or improperly wired circuits.

Thermostat
G R W2C E 0 Y
0 C {
I
Brown i/li! W|
ora_ q2-J
_or_-__ -_
Heater
Kits
Grey _ C
j4 _ NOTE: Jumper
betweenW2 and E is
required when no OD
T-Star is used.
)
Air Handier
R
i!_ w2
COY
Heat Pump OD
Section
Typical Heat Pump with Standard Air Handier
A typical installation with a heat pump thermostat, air handler, and heat pump with an outdoor
thermostat.
Thermostat ]
GRW2C EOY
Gteen _/G_=-----J L}_
R
Red j
White j W
Grey :tRY'c
,Iii
Air Handier
E
--R
J_,--w2
COY
Heat Pump OD
Section
Typical Heat Pump with
OutdoorThermostat and Air Handier

Functional Checkout:
CAUTION:
if equipped with a compressor
crankcase heater, wait 24 hours prior
to performing a function checkout to
allow for heating of the compressor
crankcase. Failure to comply may
result in damage and could cause
premature failure of the system.
Indoor Blower -- Set the thermostat function
switch to COOLING and the fan switch to ON.
Verify that the indoor blower is operating and
that airflow is not restricted. Set the fan switch
back to AUTO.
NOTE: This module does not provide safety
protection! The Comfort Alert TM module is a
monitoring device and cannot shut down the
compressor directly.
LED Description (See Figure 2)
POWER LED (Green): indicates voltage
is present at the power connection of the
module.
ALERT LED (Yellow): communicates an
abnormal system condition through a unique
flash code.The ALERT LED will flash a number
of times consecutively, pause and then repeat
the process. The number of consecutive
flashes, defined as the Flash Code, correlates
to a particular abnormal condition. Detailed
descriptions of specific ALERT Flash Codes are
shown in Table 1 of this manual.
Positive Temperature Coefficient Resistor
(PTCR) -- (select models) A PTCR is factory
installed and located on the control panel of the
outdoor unit. The PTCR is a soft start device for
use with reciprocating compressors. If a hard
start kit is needed on this model the soft start
(PTCR) must be removed first.
Low=Pressure Switch -- A low-pressure
switch is factory-installed in select models only.
If provided, this switch is located in the suction
line internal to the outdoor unit. The switch is
designed to protect the compressor from a loss
of charge. Under normal conditions, the switch
is closed. If the suction pressure falls below 5
psig, then the switch will open and de-energize
the outdoor unit. The switch will close again
once the suction pressure increases above 20
psig. Please note that the switch interrupts the
thermostat inputs to the unit. Thus, when the
switch opens and then closes, there will be a 5
minute short cycling delay before the outdoor
unit will energize.
Comfort Alert TM Diagnostics (Select Models)
-- The Comfort Alert TM diagnostics module is
a breakthrough innovation for troubleshooting
heat pump and air conditioning system failures.
The module installs easily in the electric box of
the outdoor unit near the compressor contac-
tot. By monitoring and analyzing data from the
Copeland Scroll compressor® and the thermo-
stat demand, the module can accurately detect
the cause of electrical and system related failures
without any sensors. A flashing LED indicator
communicates the ALERT code and guides the
service technician more quickly and accurately
to the root cause of a problem.
TRIP LED (Red): indicates there is a demand
signal from the thermostat but no current to the
compressoris detected bythe module.TheTRIP
LED typically indicatesthe compressor protector
is open or may indicate missing supply power
to the compressor.
The scroll compressor's run (R), common (C) and
start (S) wires are routed through the holes inthe
Comfort Alert TM module marked "R,'"C" and "S."
The common (C) wire need not be routed through
the module for it to operate properly.
24 VAC Power Wiring -- The Comfort Alert TM
module requires a constant nominal 24 VAC
power supply.The wiring to the module's R and
C terminals must be directly from the indoor unit
or thermostat.
iiL ....iJ
. i .......
XI
=/i
i
_J
Figure 2. Comfort Alert TM Diagnostics
Module

cc_fortIc
Alert i
LOW Voltage
Terminals
L
,L
:1
DFT IDFT DF2
I¥ v
,c
Fa IT2 I _Ap
_CD_ _L=J |
\/ I.L
LPS HPS Defrost Control Board
Figure 3.24VAC Comfort Alert TM
Wiring Diagram
The module cannot be powered by the C terminal
on a defrost board or other control board without
experiencing nuisance alerts.
NOTE: After the thermostat demand signal is
connected, verify that 24 VAC across Y and
C when demand is present.
NOTE: Factory installed modules may have
different thermostat demand signal wiring.
Follow manufacturer's wiring instructions
when replacing module.
TROUBLESHOOTING
interpreting The Diagnostic LEDs - When
an abnormal system condition occurs, the
Comfort Alert TM module displays the appropriate
ALERT and/orTRIP LED will flash a number of
times consecutively, pause and then repeat the
process.To identify a Flash Code number, count
the number of consecutive flashes.
Every time the module powers up, the last ALERT
Flash Code that occurred prior to shut down is
displayed for one minute.
Cooling -- Gradually lower the thermostat
temperature setpoint below the actual room
temperature and observe that the outdoor unit
and indoor blower energize. Feel the air being
circulated by the indoor blower and verify that
it is cooler than ambient temperature. Listen
for any unusual noises. If present, locate and
determine the source of the noise and correct
as necessary.
Short Cycle Protection -- With the system
operating in COOLING mode, note the setpoint
temperature setting of the thermostat, and
gradually raise the setpoint temperature until
the outdoor unit and indoor blower de-energize.
Immediately lower the setpoint temperature of
the thermostat to its original setting and verify
that the indoor blower is energized and that the
outdoor unit remains de-energized. Verify that,
after approximately 5 minutes, the outdoor unit
energizes and that the temperature of the air
supplied to the facility is cooler than ambient
temperature.
Heating -- Lower the thermostat setpoint
temperature to the lowest obtainable setting and
set the thermostat function switch to HEATING.
The indoor blower and outdoor unit should stop
running.After a minimum of five minutes, increase
the setpoint temperature of the thermostat to the
maximum setting.Verify that the outdoor unit and
indoor blower have energized. Feel the air being
circulated by the indoor blower and verify that
it is warmer than ambient temperature. Listen
for any unusual noises. If present, locate and
determine the source of the noise and correct
as necessary.
NOTE: Other sources for heating (i.e.: electric
furnace, fossil fuel furnace, air handler with
electric heat options, etc.) that interface with
the unit should be functionally checked to verify
system operation and compatibility. Refer to the
installation instructions for this equipment and
perform a functional checkout in accordance
with the manufacturer's instructions.
OUTDOOR THERMOSTAT (if supplied)
The outdoor thermostat prevents the electrical
auxiliary heat (if used) from operating above a
desired set point. Selection of the set point is
determined from the building design heat load.
The thermostat is adjustable from 45°F to 0°R
The factory temperature setting is at 40°R
Defrost CycleTimer --The defrost cycle timer
controls the time interval of the hot gas defrost
after the defrost sensor closes. It is located
in the lower left corner of the defrost control
board. Three interval settings are available: 30
minutes, 60 minutes, and 90 minutes.Time setting
selection is dependent on the climate where the
unit is being installed.
Example 1. Dry climate of Southern
Arizona. A 90 minute setting is
recommended.
Example 2. Moist climate of Seattle,
Washington. A 30 minute setting is
recommended.

10
Green"POWER"
Red"TRIP"
Yellow"ALERT"
FlashCode1
Yellow"ALERT"
FlashCode2
Yellow"ALERT"
FlashCode3
Yellow"ALERT"
FlashCode5
Yellow"ALERT"
FlashCode6
Yellow"ALERT"
FlashCode7
YeIIow"ALERT" WeldedContoctor
FlashCede8 Compressoralwaysruns
Yellow"ALERT" LewVoltage
FlashCede9 Controlcircuit<17VAC
i_i!!iiiiii_i!_i_i_i_i_ili_i_i_i_i_i_i_i!_ii_!i_i_i_i_!i!I¸!I!I¸!I!I¸!I!I¸!I!I¸!I!I¸!I!I¸!I!I¸!I!I¸!I!I¸!I!I!_
Modulehaspower
Thermostatdemandsignal
Yis present,butthe 2.
compressorisnot 3.
running 4.
5.
6.
LongRnnTime 1.
Compressoris 2.
runningextremely 3.
longruncycles 4.
5.
6.
7.
8.
9.
SystemPressureTrip 1.
Dischargeorsuction 2.
pressureoutoflimitsor 3.
compressoroverloaded 4.
5.
ShortCycling
Compressorisrunning
onlybriefly
LockedRotor
OpenCircuit
4.
5.
6.
7.
OpenStartCircuit 1.
Currentonlyinruncircuit 2.
3.
OpenRanCircuit 1.
Currentonlyinstartcircuit
iiii_i_i_i_!i_i_i_i_i_!_!_i_!_!i!!i!i_!i_i!i_!i!;!;!;!;!;!;!;!;!;!;!;!;!;i_i_!!!_!!_!_i_ii_ii_i_i!iiii_iiiiiiiiii_iiiiiiiii_i_i_i_i;i;_!_!_ifi_ii__!!_i_!_i_i_i_i_i_i_i_i_i_i_i_i_i_i_i_i_i_i_i_i_i_i_i_i_i_i_i_i_i_i_i_i_i_i_i_i_i_i_i_i_i_i_i_i_i_i_i_i_i_i_i_i_i_i_i_i_
Supplyvoltageispresentatmoduleterminals
1. Compressorprotectorisopen
Outdoorunitpowerdisconnectisopen
Compressorcircuitbreakerorfuse(s)isopen
Brokenwireorconnectorisnotmakingcontact
Lowpressureswitchopenifpresentinsystem
Compressorcontactorhasfailedopen
Lowrefrigerantcharge
Evaporatorblowerisnotrunning
Evaporatorcoilisfrozen
Faultymeteringdevice
Condensercoilisdirty
Liquidlinerestriction(filterdrierblockedifpresentinsystem)
Thermostatismalfunctioning
ComfortAlertFailure
ComfortAlertFailure
Highheadpressure
Condensercoil poorair circulation(dirty, blocked,damaged)
Condenserfanisnotrunning
Returnairducthassubstantialleakage
Iflowpressureswitchpresentinsystem,checkFlash
Code1information
1.Thermostatdemandsignalisintermittent
2.Timedelayrelayorcontrolboarddefective
3. IfhighpressureswitchpresentgotoFlashCode2information
4. IflowpressureswitchpresentgotoFlashCode1information
1. Runcapacitorhasfailed
2. Lowlinevoltage(contactutilityifvoltageatdisconnectislow)
,, Checkwiringconnections
3. Excessiveliquidrefrigerantincompressor
4. Compressorbearingsareseized
,, Measurecompressoroillevel
1. Outdoorunitpowerdisconnectisopen
2. Compressorcircuitbreakerorfuse(s)is open
3.Compressorcontactorhasfailedopen
* Checkcompressorcontactorwiringandconnectors
o Checkforcompressorcontactorfailure(burned,pittedor
open)
,, Checkwiringandconnectorsbetweensupplyand
compressor
,, Checkforlowpilotvoltageatcompressorcontactorcoil
Highpressureswitchisopenandrequiresmanualreset
Opencircuitincompressorsupplywiringorconnections
Unusuallylongcompressorprotectorresettimedueto
extremeambienttemperature
Compressorwindingsaredamaged
,, Checkcompressormotorwindingresistance
Runcapacitorhasfailed
Opencircuitincompressorstartwiringorconnections
o Checkwiringandconnectorsbetweensupplyandthe
compressor"S"terminal
Compressorstartwindingisdamaged
* Checkcompressormotorwindingresistance
Opencircuitincompressorrunwiringorconnections
,, Checkwiringandconnectorsbetweensupplyandthe
compressor"R'terminal
2. Compressorrunwindingisdamaged
,, Checkcompressormotorwindingresistance
1. Compressorcontactorhasfailedclosed
2. Thermostatdemandsignalnotconnectedto module
1. Controlcircuittransformerisoverloaded
2. Lowlinevoltage(contactutilityifvoltageatdisconnectis low)
,, Checkwiringconnections
Flash Code number corresponds to a number of LED flashes followed by a pause and then repeated
TRIP and ALERTLFDe flashing at same time means control circuit vollage is too low for operation
Table 1. interpreting the Diagnostic LEDS
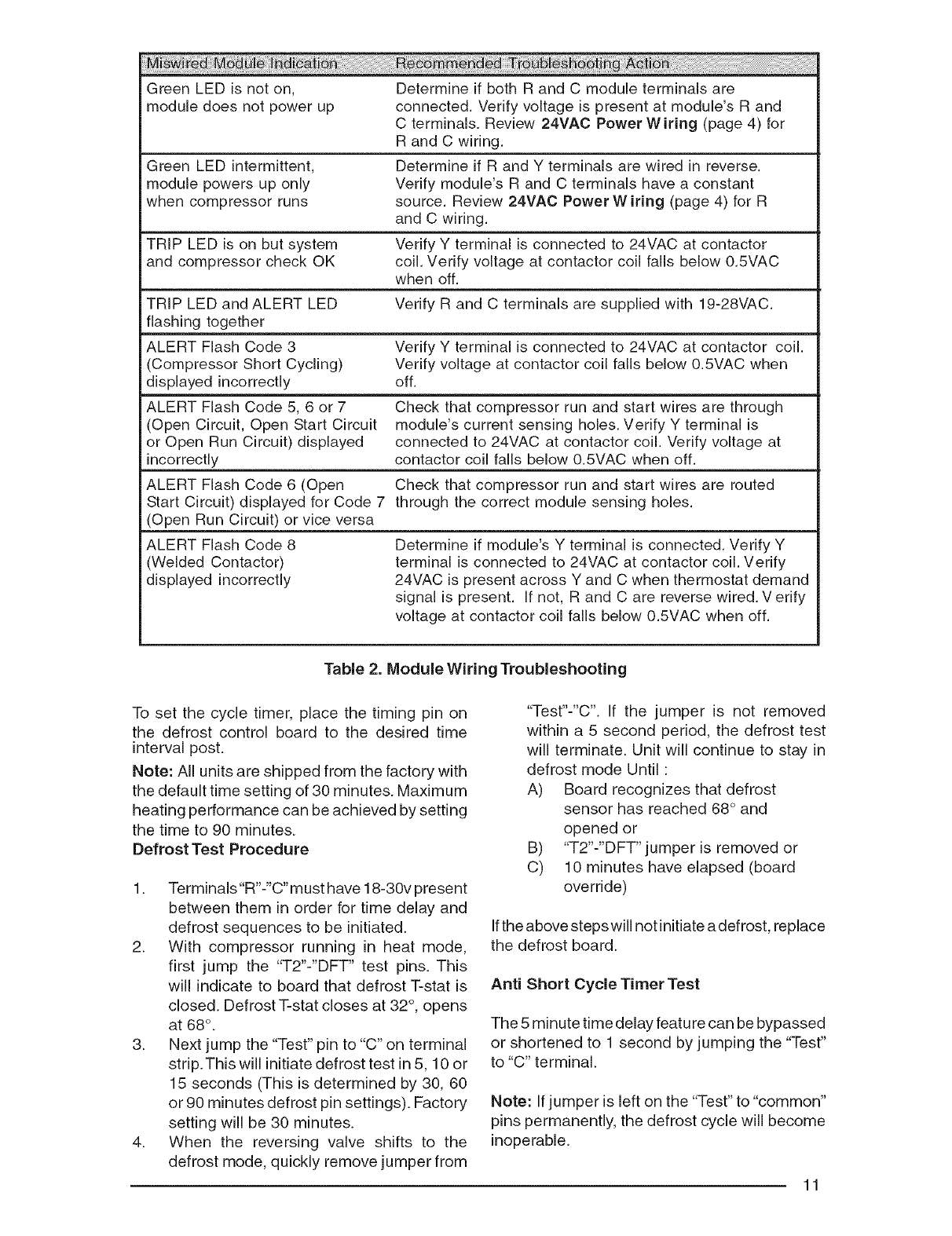
ii!i!;! il
Green LED is not on, Determine if both R and C module terminals are
module does not power up connected. Verify voltage is present at module's R and
C terminals. Review 24VAC Power Wiring (page 4) for
R and C wiring.
Green LED intermittent, Determine if R and Y terminals are wired in reverse.
module powers up only Verify module's R and C terminals have a constant
when compressor runs source. Review 24VAC Power W iring (page 4) for R
and C wiring.
TRIP LED is on but system Verify Y terminal is connected to 24VAC at contactor
and compressor check OK coil. Verify voltage at contactor coil falls below 0.5VAC
when off.
TRIP LED and ALERT LED Verify R and C terminals are supplied with 19-28VAC.
flashing together
ALERT Flash Code 3 Verify Y terminal is connected to 24VAC at contactor coil.
(Compressor Short Cycling) Verify voltage at contactor coil falls below 0.5VAC when
displayed incorrectly off.
ALERT Flash Code 5, 6 or 7 Check that compressor run and start wires are through
(Open Circuit, Open Start Circuit module's current sensing holes. Verify Y terminal is
or Open Run Circuit) displayed connected to 24VAC at contactor coil. Verify voltage at
incorrectly contactor coil falls below 0.5VAC when off.
ALERT Flash Code 6 (Open Check that compressor run and start wires are routed
Start Circuit) displayed for Code 7 through the correct module sensing holes.
(Open Run Circuit) or vice versa
ALERT Flash Code 8
(Welded Contactor)
displayed incorrectly
Determine if module's Y terminal is connected. Verify Y
terminal is connected to 24VAC at contactor coil. Verify
24VAC is present across Y and C when thermostat demand
signal is present. If not, R and C are reverse wired. V erify
voltage at contactor coil falls below 0.5VAC when off.
Table 2. Module Wiring Troubleshooting
To set the cycle timer, place the timing pin on
the defrost control board to the desired time
interval post.
Note: All units are shipped from the factory with
the default time setting of 30 minutes. Maximum
heating performance can be achieved by setting
the time to 90 minutes.
Defrost Test Procedure
1. Terminals"R'-'C" must have 18-30v present
between them in order for time delay and
defrost sequences to be initiated.
2. With compressor running in heat mode,
first jump the "T2"-'DFT" test pins. This
will indicate to board that defrost T-stat is
closed. Defrost T-stat closes at 32 °, opens
at 68° .
3. Next jump the "Test" pin to "C" on terminal
strip.This will initiate defrost test in 5, 10 or
15 seconds (This is determined by 30, 60
or 90 minutes defrost pin settings). Factory
setting will be 30 minutes.
4. When the reversing valve shifts to the
defrost mode, quickly remove jumper from
"Test'-'C'. If the jumper is not removed
within a 5 second period, the defrost test
will terminate. Unit will continue to stay in
defrost mode Until :
A) Board recognizes that defrost
sensor has reached 68° and
opened or
B) "T2"-'DFT'jumper is removed or
C) 10 minutes have elapsed (board
override)
Ifthe above steps will not initiate a defrost, replace
the defrost board.
Anti Short Cycle Timer Test
The 5 minute time delay featu re can be bypassed
or shortened to 1 second by jumping the "Test"
to "C" terminal.
Note: If jumper is left on the "Test" to "common"
pins permanently, the defrost cycle will become
inoperable.
11

OptionalEquipment-- A functionalcheckout
should be performed in accordance with
the checkout procedures supplied with the
equipment.
Adjustment of Refrigerant Charge:
CAUTION'.
Split system heat pump equipment
contains liquid and gaseous refrigerant
under pressure. Adjustment of
refrigerant charge should only be
attempted by qualified, trained
personnel thoroughly familiar with the
equipment. Under no circumstances
should the homeowner attempt to
install and/or service this equipment.
Failure to comply with this warning
could result in equipment damage,
personal injury, or death.
NOTE: The following Refrigerant Charging
Charts are applicable to listed assemblies of
equipment and at listed airflows for the indoor
coil. Assemblies of indoor coils and outdoor units
not listed are not recommended and deviations
from rated airflows or non-listed equipment
combinations may require modifications to the
expansion device(s) and refrigerant charging
procedures for proper and efficient system
operation.
Refrigerant Charging Chart -- Refer to
Refrigerant Charging Charts for correct system
charging, and to Orifice Usage Chart for correct
restrictor sizes.
NOTE: Linesets over 15 feet in length may
require additional refrigerant charge. NORDYNE
recommends 0.6 oz. of refrigerant per foot for
any lineset over 15 feet.
13 SEER Split System Heat Pump Orifice
Usage with ZRK3 Compressor
Model Restrictor Bore Size (inches)
Number indoor Outdoor
1.5 ton 0.053 0.040
2.0 ton 0.061 0.047
2.5 ton 0.069 0.049
3.0 ton 0.078 0.057
3.5 ton 0.083 0.059
4.0 ton 0.090 0.065
5.0 ton 0.101 0.067
System Charge
R-22 (oz.)
101
96
139
155
248
246
268
13 SEER Split System Heat Pump Orifice
Usage with CRK7 Compressor
Model
Number System Charge
R-22 (oz.)
Restrictor Bore
Size (inches)
Indoor Outdoor
0.061 0.049
0.068 0.049
2.0 ton 120
2.5 ton 144
12

Refrigerant Charging Charts for Cooling Mode of Operation
13 SEER Split System Restrictor Cooling Charging Charts with ZRK3 Compressors
REFRIGERANT CHARGING CHARTS LEGEND FOR COOLING/HEATING MODES OF OPERATION
*Note: All pressures are listed in psig. and all temperatures in deg. F.
Shaded boxes indicate flooded conditions
- Rated design values. Suction Pressure will be lower than design value if indoor air flow, entering dry bulb,
or entering wet bulb temperatures are lower than design.
Discharge temperatures greater than charted values indicates a refrigerant undercharge.
1-1/2
TON
Suction
Press.
73
75
77
79
81
83
85
87
89
91
93
95
97
99
OUTDOOR TEMPERATURE (°F)
70 75 80 85 90 95 100 105
Dis. Dis. Dis. Dis. Dis. Dis. Dis. Dis. Dis. Dis. Dis. Dis. Dis. Dis. Dis. Dis.
Press. Temp. Press. Temp. Press. Temp. Press. Temp. Press. Temp. Press. Temp. Press. Temp. Press. Temp.
140 135
143 140 155 137
145 146 157 143 170 140
147 150 160 148 172 145 185 142
151 153 162 152 175 150 187 147 200 144
166 155 177 154 189 151 202 149
181 157 192 155 204 153 217 151 I
196 159 207 157 219 155
199 163 211 161 222 159
214 165 226 163 237 161
229 167 241 165 252 I163
244 169 256 I167
259 172

Refrigerant Charging Charts for Cooling Mode of Operation
13 SEER Split System Restrictor Cooling Charging Charts with ZRK3 Compressors
2
TON
Suction
Press.
71 149
73 151
75 154
77 156
79 160
81
83
85
87
89
91
93
95
97
70 75
Dis. Dis. Dis. Dis.
Press. Temp. Press. Temp.
137
143 164 141
148 166 146
153 169 151
155 171 156
175 159
OUTDOOR TEMPERATURE (°F)
80 85 90 95
Dis. Dis. Dis. Dis. Dis. Dis. Dis. Dis.
Press. Temp. Press. Temp. Press. Temp. Press. Temp.
100 105
Dis. Dis. Dis. Dis.
Press. Temp. Press. Temp.
179 145
181 150 194 149
184 155 196 153 209 152
186 159 198 158 211 157
190 162 202 162 213 161 226 160
205 166 217 165 228 164
208 169 220 169 232 168
224 173 235 173
239 177
247 172
250 176
254 180
262 175
265 180
269 184

Refrigerant Charging Charts for Cooling Mode of Operation
13 SEER Split System Restrictor Cooling Charging Charts with ZRK3 Compressors
2-1/2
TON
Suction
Press.
70
72
74
76
78
80
82
84
86
88
90
92
94
96
OUTDOOR TEMPERATURE (°F)
85 9070 75 80 95
Dis. Dis. Dis. Dis. Dis. Dis. Dis. Dis. Dis. Dis. Dis. Dis.
Press. Temp. Press. Temp. Press. Temp. Press. Temp. Press. Temp. Press. Temp.
100 105
Dis. Dis. Dis. Dis.
Press. Temp. Press. Temp.
240 164
243 169 255
247 173 258
261
143 136
145 141 158 139
147 147 160 144 173 142
150 152 162 149 175 147 188 145
153 155 165 154 177 152 190 149 202 147
168 157 180 156 192 154 204 152
183 159 195 158 207 156 219 154
198 161 210 160 221 158
202 165 213 164 225 162
217 168 228 166
232 170 167
171
176

Refrigerant Charging Charts for Cooling Mode of Operation
13 SEER Split System Restrictor Cooling Charging Charts with ZRK3 Compressors
3
TON
Suction
Press.
71
73
75
77
79
81
83
85
87
89
91
93
95
97
OUTDOOR TEMPERATURE (°F)
70 75 80 85 90 95 100 105
Dis. Dis. Dis. Dis. Dis. Dis. Dis. Dis. Dis. Dis. Dis. Dis. Dis. Dis. Dis. Dis.
Press. Temp. Press. Temp. Press. Temp. Press. Temp. Press. Temp. Press. Temp. Press. Temp. Press. Temp.
148 144
150 149 164 147
152 155 166 152 179 149
155 158 168 157 181 154 195 152
159 161 171 161 183 159 197 156 210 154
174 164 187 163 199 161 212 158
190 166 202 165 214 163 228 161 I
206 168 218 167 230 165
209 172 221 171 233 169
225 174 237 173 249 171
240 177 252 175 264 173
256 180 268 178
271 182

Refrigerant Charging Charts for Cooling Mode of Operation
13 SEER Split System Restrictor Cooling Charging Charts with ZRK3 Compressors
3-1/2
TON
Suction
Press.
71
73
75
77
79
81
83
85
87
89
91
93
95
97
OUTDOOR TEMPERATURE (°F)
70 75 80 85 90 95 100 105
Dis. Dis. Dis. Dis. Dis. Dis. Dis. Dis. Dis. Dis. Dis. Dis. Dis. Dis. Dis. Dis.
Press. Temp. Press. Temp. Press. Temp. Press. Temp. Press. Temp. Press. Temp. Press. Temp. Press. Temp.
144 150
146 155 159 152
148 161 161 157 175 153
152 163 164 162 177 158 191 154
155 165 167 164 179 163 193 159 206 156
171 167 183 166 195 164 208 160
186 169 198 167 210 165 224 162 I
202 171 214 169 226 166
205 174 217 172 229 170
221 176 233 174 245 171
236 178 248 175 260 172
252 180 264 177
267 181

_o Refrigerant Charging Charts for Cooling Mode of Operation
13 SEER Split System Restrictor Cooling Charging Charts with ZRK3 Compressors
4
TON
Suct.
Press.
69
71
73
75
77
79
81
83
85
87
89
91
93
95
OUTDOOR TEMPERATURE (°F)
70 75 80 85 90 95 100 105
Dis. Dis. Dis. Dis. Dis. Dis. Dis. Dis. Dis. Dis. Dis. Dis. Dis. Dis. Dis. Dis.
Press. Temp. Press. Temp. Press. Temp. Press. Temp. Press. Temp. Press. Temp. Press. Temp. Press. Temp.
132 130
134 136 149 135
136 141 151 140 166 140
137 149 153 145 168 145 183 145
140 152 154 152 170 150 185 149 200 149
158 155 172 155 188 154 203 153
176 158 190 158 205 158 220 157
193 162 207 162 222 162
197 166 211 166 225 166
214 170 229 170
232 174
243 170
246 174 260 174
250 178 264 178
267 183

Refrigerant Charging Charts for Cooling Mode of Operation
13 SEER Split System Restrictor Cooling Charging Charts with ZRK3 Compressors
5
TON
Suct.
Press.
66
68
70
72
74
76
78
80
82
84
86
88
90
92
70 75
Dis. Dis. Dis. Dis.
Press. Temp. Press. Temp.
143 146
145 152 159 149
147 157 161 154
148 164 163 159
152 167 165 165
169 168
OUTDOOR TEMPERATURE (°F)
80 85 90 95
Dis. Dis. Dis. Dis. Dis. Dis. Dis. Dis.
Press. Temp. Press. Temp. Press. Temp. Press. Temp.
100 105
Dis. Dis. Dis. Dis.
Press. Temp. Press. Temp.
175 152
178 157 192 155
180 162 194 159 208 157
182 167 196 164 210 161
185 170 198 168 212 166 226 164
202 172 215 170 228 168
205 175 218 174 232 172
222 178 235 176
238 180
248 174
252 178 265 176
255 182 268 180
271 185
_o

I'o
oRefrigerant Charging Charts for Cooling Mode of Operation
13 SEER Split System Restrictor Cooling Charging Charts with CRK7 Compressors
2
TON
Suct.
Press.
73
75
77
79
81
83
85
87
89
91
93
95
97
99
OUTDOOR TEMPERATURE (°F)
70 75 80 85 90 95 100 105
Dis. Dis. Dis. Dis. Dis. Dis. Dis. Dis. Dis. Dis. Dis. Dis. Dis. Dis. Dis. Dis.
Press. Temp. Press. Temp. Press. Temp. Press. Temp. Press. Temp. Press. Temp. Press. Temp. Press. Temp.
159 152
162 157 173 152
164 162 175 157 187 152
167 166 178 162 189 157 201 152
171 168 181 165 191 162 203 157 215 152
184 168 195 165 205 161 217 157
198 169 208 165 219 161 230 156
212 169 222 165 233 161
215 172 226 169 236 165 I2461160
229 173 239 169 250 164
243 173 253 169 263 164
257 173 267 169
270 173

Refrigerant Charging Charts for Cooling Mode of Operation
13 SEER Split System Restrictor Cooling Charging Charts with CRK7 Compressors
2-1/2
TON
Suction
Press.
7O
72
74
76
78
8O
82
84
86
88
90
92
94
96
OUTDOOR TEMPERATURE (°F)
70 75 80 85 90 95 100 105
Dis. Dis. Dis. Dis. Dis. Dis. Dis. Dis. Dis. Dis. Dis. Dis. Dis. Dis. Dis. Dis.
Press. Temp. Press. Temp. Press. Temp. Press. Temp. Press. Temp. Press. Temp. Press. Temp. Press. Temp.
149 153
151 158 164 153
154 164 166 158 179 153
156 167 168 163 181 158 194 153
160 170 171 167 183 163 196 158 208 153
175 170 186 167 198 162 210 158
190 170 201 166 213 162 225 157
204 170 216 166 227 162
208 174 219 170 231 166
223 174 234 170
238 174
246 165
249 170 260 165
252 174 264 169
267 174
I'o

TXV Refrigerant Charging Chart with ZRK3 Compressors
1.5 Ton HP ZRK3 TXV Charging Chart
_s
1/)
v,=
1/)
1/)
,=
O.
"O
'5
.E
--I
375
350
325
300
275
25O
225
200
175
150
125
75
Remove refrigerantwhen above curve f
/
/
/
/
/
/
/
/
/
f
80 85 90 95
Add refrigerantwhen below cuwe_
100 105 110 115 120 125 130
Liquid Temperature (F)
2.0 Ton HP ZRK3 TXV Charging Chart
350
325
300
#,,,
"_ 275
3
250
"0 225
"5
rJ"
.m
--I 200
175
/
Remove refrigerantwhen above curve
/
/
/
/
/
f
/
/
150 '' '' ' ''' '''' ''' ' '' '' ' ''' '''' ''' ' '' '' ''' ' '' ''
75 80 85 90 95 100 105 110 115 120 125 130
Liquid Temperature (F)
22
Add refrigerantwhenbelow cuwe_
/
/
/

TXV Refrigerant Charging Chart with ZRK3 Compressors Continued
2.5 Ton HP ZRK3 TXV Charging Chart
350
325
_"_ 300
O't
D..
_" 275
250
a.
"_ 225
.._
--I 2OO
175
150
75
:S.
J
f
J
Remove refrigerant when above curve
.4
J
J
f
J
J
f
J
J" Add refrigerantwhen below cuwe_
/
/
/
80 85 90 95 100 105 110 115 120 125 130
Liquid Temperature (F)
3.0 Ton HP ZRK3 TXV Charging Chart
350
325
300
,_ 275
250
225
0"
•-, 2oo
175
Remove refrigerant when above cu_e_ f
7
J
f
J
J
J
f
JJ
J Add refrigerant when below curve
J
J
150 '''' '''' '''' '''' '''' '''' '''' '''' '''' '''' '''' ''''
75 80 85 90 95 100 105 110 115 120 125 130 135
Liquid Temperature (F)
23

TXV Refrigerant Charging Chart with ZRK3 Compressors Continued
3.5 Ton HP ZRK3 TXV Charging Chart
O.
,=
(/}
,=
rt
"o
.m
O"
.-I
350
325
3OO
275
25O
225
2OO
175
J
J
J
.J
Remove refrigerant when above curve_
J
J
J
JAdd refrigerant when below curve I
J
f
J
f
J
150 ' ' ' ' ' ' ' ' ' ' ' ' ' ' ' ' ' ' ' ' ' ' ' ' ' ' ' ' ' ' ' ' ' ' ' ' ' ' ' ' ' ' ' ' ' ' ' '
75 80 85 90 95 100 105 110 115 120 125 130 135
LiquidTemperature (F)
4.0 Ton HP ZRK3 TXV Charging Chart
,=
o_
o_
,=
a.
"o
o"
_1
350
325
300
275
250
225
200
175
150
Remove refrigerant when above curve_ J
f
J
J
J
J
f
f
J
J
J Add refrigerant when below curve I
j"
75 80 85 90 95 100 105 110 115 120 125 130 135
LiquidTemperature (F)
24

TXV Refrigerant Charging Chart with ZRK3 Compressors Continued
5.0 Ton HP ZRK3 TXV Charging Chart
350 /-
/
330 /
310
_,. 290
_270
@ 250
E
¢ 230
I-
"_ 210
0"
,,-I 190
170
150
Removerefrigerantwhen above curve_
/
/
/
/
/
f
/
f
/
/
J Add refrigerant when below curve I
/
/
75 80 85 90 95 100 105 110 115 120 125 130 135
Liquid Temperature (F)
25

TXV Refrigerant Charging Chart with CRK7 Compressors
2.0Ton HP CRK7TXV Charging Chart
350
Q,,
o_
o_
a=
_=
.=J
325
3O0
275
250
225
200
175
150
75
_
jJ
Removerefrigerantwhen above 3urve j
J
f
J
1/
J EAdd refrigerant When below curve]
J
J
80 85 90 95 100 105 110 115 120 125 130
Liquid Temperature (F)
2.5 Ton HP CRK7 TXV Charging Chart
350
325
.m 300
_ 275
250
225
._" 200
!
Remove refrigerant when above curve
.J
175 _j_.._
150
j/
J
J
J
f
J
j_
J
J
125 _± _ _±_ 1_ • _ L_
75 80 85 90 95 100
Add refrigerantwhen below curve_
105 110 115 120 125 130
Liquid Temperature (F)
26

Refrigerant Charging Charts for Heating Mode of Operation
13 SEER Split System Heating Charts with ZRK3 Compressors
i 1.5 Ton
o10
OUTDOOR TEMPERATURE (DEG. F)
20 30 40 50 6O
2.0Ton
010
OUTDOOR TEMPERATURE
20 30 40 50 6O
r',o
,.,.,j

I'o
(3o Refrigerant Charging Charts for Heating Mode of Operation
13 SEER Split System Heating Charts with ZRK3 Compressors
2.5 Ton OUTDOOR TEMPERATURE (DEG. F)
0 10
Suc. I Liquid Disch. Suc.
Press.! Press. Temp. Press.
22 _ 137 119
14 23
30 138
31 1164 1127 140 1185 1136
32 41
33 42
34 43 52
20 30 40
I O,soh
Press. Temp. Press.! Press. Temp. Press. Press. Temp.
i 159 129 39 I 181 48 191 I 153
49 198 I 150
50 205 I 147
51
18 27 35 44 53
19 28 36 45 54
50 60
Suc. Liquid Disch. Suc. Liquid Disch.
Press Press. Temp. Press. Press. Temp.
56 211 174 65 230 196
57 218 170 66 237 190
58 225 165 67 244 183
59 232 161 68 251 177
60 239 157 69 258 171
61 70 265 165
62 71 272 159
3.0 Ton OUTDOOR TEMPERATURE (DEG. F)
10 20 30
Press!Press. I Temp. Press. ! Press. I Temp. Pres& ! Press. ! Temp.
22 I 136 I 125 31 _ 156 I 130 40 _ 176 I 136
40
Suc. Liquid
Press. Press.
m
Disch.
Temp.
151
Suc.
Press
49 183 59 175 68 218
14 23 32I 1511128I 41I 18oI1_ I 5o 19o11_8I 8o 208117o 89 225
42 32 I 51 61 215 I 166 70 232 187
m
43 _ 52 62 222 I 161 71 239 181
44 53 63 229 157 72 246 174
18 27 36 45 54 64 73 253 168
19 28 37 46 55 65 74 260 162
50 60
Liquid [ Disch. Suc. Liquid Disch.
/
Press.| Temp. Press. Press. Temp.
/
201 | 199
193

Refrigerant Charging Charts for Heating Mode of Operation
13 SEER Split System Heating Charts with ZRK3 Compressors
57 233
58 240
3.5Ton OUTDOORTEMPERATURE (DEG. F)
Diseh_. Suc'--m_ Disch-'--m'Suc_=_" Suc_-_" Suc. Liquid
Press. Temp. Press. Press. Temp. Press. Press. I Temp. Press. Press. ! Temp. Press Press. /
132 _0 2_ 1s4 113 37 1781138 48 187I 1s8j54 212! 178 82 237 1_8
,_ _ _oI ,5_I,,, I _ I 179 I,_ I 47 I 194 1155I 55 219 1173 63 244 192
58 228_ 8.....5_4251 185
65 258 179
I 160 66 265 173
67 272 167
60
Disch. Suc. Liquid Disch.
Temp. Press. Press. Temp.
19 27 35 43 52 60 68 279 161
IX)
t.o
4.0Ton
o
OUTDOOR TEMPERATURE (DEG. F)
10 20 30
P_ss! P_.!_mp.P_ss!P_.!_mp.Press.!Press.Temp.
21 I 132 I 121 30 I 15o I 127 38 I 168 I 133
131
40 50 60
.l-!
Suc. Liquid Disch. Suc. Liquid Disch. Suc. Liquid Disch.
Press.! Press. Temp. Press Press. Temp. Press. Press. Temp.
47 | 175 150 57 194 178 66 213 205
199173 67 220
169 68 227 193
164 69 234 187
160 70 241 180
71 248 174
72 255 168
48 I _ I 147 58 201
_ ! 18_I1_ 5_ 208
50 2 60 215
51 _ 61 222
52 62
53 63

Co
oRefrigerant Charging Charts for Heating Mode of Operation
13 SEER Split System Heating Charts with ZRK3 Compressors
5.0Ton OUTDOOR TEMPERATURE (DEG. F)
10 20 30
Sue.
Press.
45
46
47
1481
49
50
51
4O
n
ICJ II JI 8UC.
Press.
55
56
57
58
59
60
61
5O
Liquid
Press
236
243
250
257
264
Suc. I
Press.I
65 I
66 I
67 I
68 I
69 I
7O I
71 I
6O
Liquid
Press.
262
269
276
283
290
297
304
m
Disch.
Temp.
212
206
200
193
187
181
175

Refrigerant Charging Charts for Heating Mode of Operation
13 SEER Split System Heating Charts with CRK7 Compressors
2.0 Ton
0 10
OUTDOOR TEMPERATURE
20 30 40 50 60
2.5 Ton
0 10
OUTDOOR TEMPERATURE
20 30 40 50 60
Co

iNSTALLER: PLEASE LEAVE
THESE iNSTALLATiON iNSTRUCTiONS
WiTH THE HOMEOWNER.
II 708452A
@We £n_urage
profess{onalfsm
ThroughTechnician
CedJf_cat_onby Nt_TE
708452A (Replaces 7084520)
Specifications and illustrations subject to change
without notice and without incurring obligations.
Printed in U.S.A. (02/06)