New Holland Tg Series Users Manual NH_Trac_Perf_Tips9
TJ Series to the manual eeb6f2e6-b785-41ce-951b-f94613518e11
2015-02-05
: New-Holland New-Holland-Tg-Series-Users-Manual-494779 new-holland-tg-series-users-manual-494779 new-holland pdf
Open the PDF directly: View PDF .
Page Count: 36
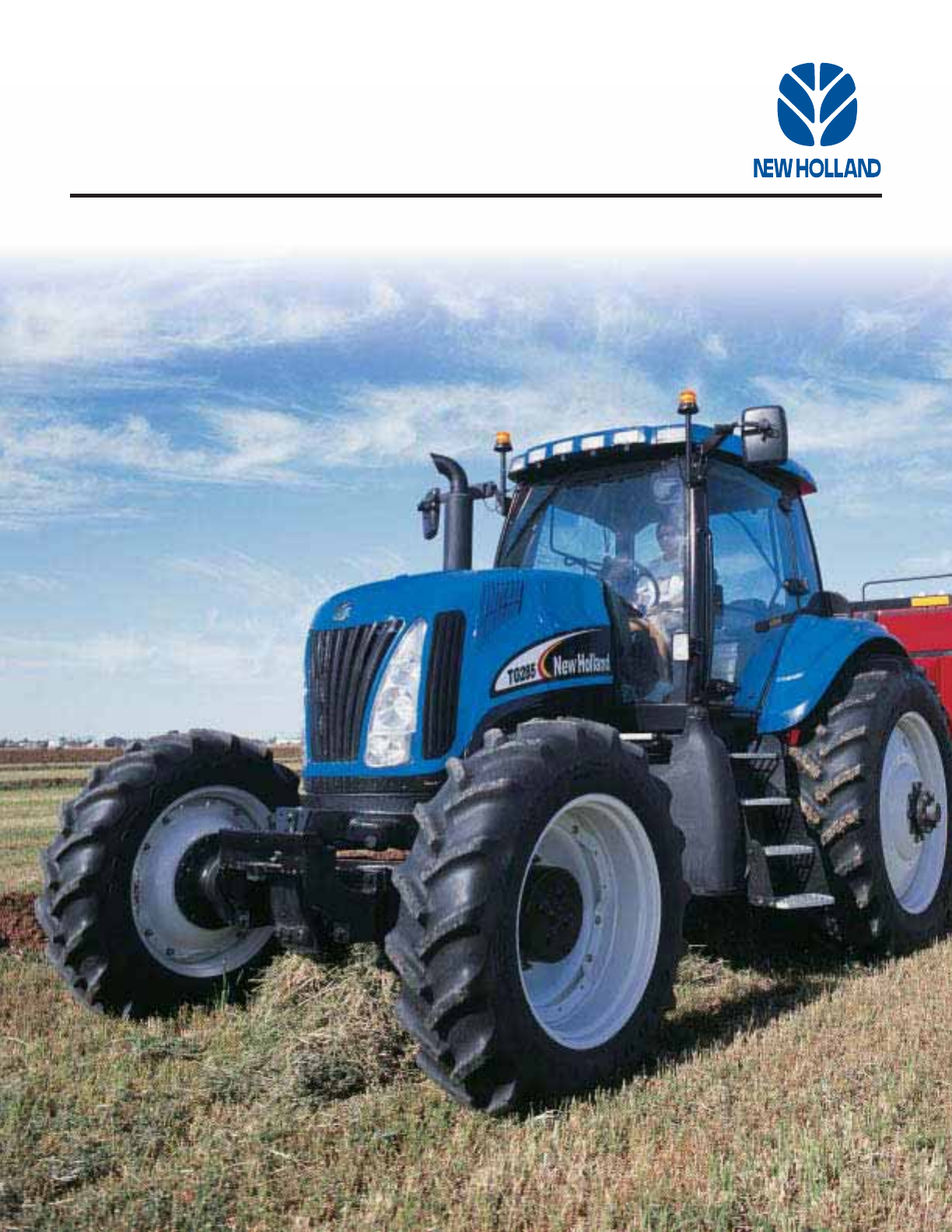
Performance Tips
TG and TJ Series Tractors

TOTAL CONFIDENCE –
THE NEW HOLLAND SERVICE SOLUTION
QUALITY SERVICE
• Factory trained technicians
• Genuine New Holland parts
• Documented maintenance
• Increase productivity
• Reduce downtime
New Holland delivers quality parts
and service every time.
At New Holland, we have what it takes to maximize
your equipment’s power and productivity all season
long. Our extensive dealer network means we’re always
close by. Our resourceful aftersales support team
understands your unique needs to help you operate
more efficiently. And our wide range of precision-
engineered New Holland parts matches your operation’s
systems for greater productivity and uptime.
It’s all the genuine parts and expert support you
expect—under one sign. Visit us today.
NEW HOLLAND
ORIGINAL PARTS
• Designed to meet stringent
New Holland quality, reliability
and performance
• Guaranteed by New Holland
• Designed specifically for New Holland
equipment
• Made by manufacturers with worldwide
reputations
Flexible revolving account financing with the
New Holland Plan is designed to match your unique
cash flow requirements and payment schedules.

,ETTHE3PECIALIST(ELP
9OURLOCAL.EW(OLLANDDEALERUSESTHELATESTTECHNOLOGYANDTRAININGTOKEEPYOUR
INVESTMENTOPERATINGPROFITABLY EFFICIENTLY ANDSAFELY
$OYOUNEEDSERVICEWORKONATRACTOR EMERGENCYFIELDSERVICE ORPARTSINAHURRY
9OURDEALERISREADYANDABLETOHELP
.EW(OLLANDFACTORYTRAINEDSERVICEPROFESSIONALSAREEXPERTSONTHEINNERWORKINGS
OFYOUR.EW(OLLAND TRACTORS4HEPARTSDEPARTMENTISWELLSTOCKEDWITHALLTHEPARTS
BELTS FILTERS LUBRICANTS ANDENGINEPARTSYOULLNEED9OUWOULDNTEXPECTANYTHING
LESSFROMASPECIALISTWHOUNDERSTANDSTHEWAYYOUWORK
3!&%49
-AKE&ARM3AFETYA0RIORITY
4HESECONDMOSTIMPORTANTPARTOFYOURFARMING
OPERATIONISGETTINGTHEJOBDONERIGHT&ARMSAFETYIS
THEMOSTIMPORTANTASPECTINALLFARMINGOPERATIONS
.ONEOFTHETHINGSYOUACCOMPLISHONYOURFARMARE
WORTHMUCH IFYOUDONTENDEACHDAYSAFEANDSOUND
4HE.ATIONAL3AFETY#OUNCILORTHE!MERICAN&ARM
"UREAUCONFIRMSTHATFARMINGISTHEMOSTHAZARDOUS
OCCUPATIONINTHENATIONTODAY4HEYWILLALSOTELLYOU
THATMOSTFARMACCIDENTSARECAUSEDWHENPEOPLEFAILTO
FOLLOWWELLPUBLICIZEDSAFETYPRECAUTIONS
.EW(OLLAND ENGINEERSINCORPORATESAFETYINTOEVERY
MACHINETHEYDESIGN!FTERYOURTRACTORISDELIVERED
READTHE/PERATORS-ANUALANDCAREFULLYNOTEALLOFTHE
SAFETYINSTRUCTIONSCONTAINEDINIT"EALERTTOALLSAFETY
SUGGESTIONS&ARMSAFETYISULTIMATELYYOUROWN
RESPONSIBILITYANDYOUOWEITTOYOURFAMILYTOWORK
SAFELY4HEMOSTIMPORTANTSAFETYDEVICEONATRACTORIS
THEROLLOVERPROTECTIVESTRUCTURE2/03WITHAN
EFFECTIVESEATBELT-OREFARMERSAREKILLEDORSERIOUSLY
INJUREDFROMTRACTORROLLOVERSTHANFROMANYOTHERTYPE
OFFARMACCIDENT2EADALLOFTHESAFETYINSTRUCTIONSIN
YOUR/PERATORS-ANUALANDBESUREYOUCANGIVEA
POSITIVERESPONSETOALLOFTHEFOLLOWING
3HIELDS )STHE04/MASTERSHIELDINPLACE!REALL
OTHERSHIELDSINPLACE
7ARNING$ECALS!REALLWARNINGDECALSINPLACE
ANDREADABLE)STHESLOWMOVINGVEHICLE3-6
EMBLEMINPLACEANDINGOODCONDITION
&UEL3YSTEM)STHEFUELCAPINGOODCONDITION
WITHOUTFUELLEAKS
,IGHTS !RETHEEMERGENCYFLASHINGLIGHTSFORROAD
TRAVEL TURNSIGNALS HEADLIGHTS ANDTAILLIGHTSIN
WORKINGORDER
"RAKES $OTHEBRAKESAPPLYEVENLYWHEN
APPLIEDTOGETHER
3TARTING 3TARTTHEENGINEONLYWHENPROPERLY
SEATEDINTHEOPERATORSSEAT7HENSTARTINGINCOLD
WEATHER THETRACTORCOULDMOVEASTHETRANSMISSION
ISENGAGED EVENWITHTHECLUTCHPEDALDEPRESSED
5SETHEBRAKESTOPREVENTTRACTORMOVEMENT
/THER0EOPLE "ESUREALLOTHERSARECLEAROFTHE
TRACTORANDEQUIPMENT.ORIDERS
2OAD4RAVEL &ORSAFEOPERATIONONTHEROAD
ALWAYSLOCKTHEBRAKEPEDALSTOGETHERWITHTHEPEDAL
INTERLOCK$ONOTEXCEEDMPHKPHWHILE
TRANSPORTINGIMPLEMENTS
4RACTOR3TABILITY !LWAYSREDUCETRAVELSPEEDON
TURNS ROUGHGROUND ANDAVOIDSTEEPSLOPES0ULLONLY
FROMTHEDRAWBARNEVERHIGHER
&UMES "ECAREFULABOUTCARBONMONOXIDEFUMES
2EMEMBERTHATAGRICULTURALHERBICIDESANDOTHER
PESTICIDESCANBEHAZARDOUS9OURTRACTORCABAIR
FILTERCANNOTREMOVEFUMESEXHAUSTORCHEMICAL
&OLLOWINSTRUCTIONSANDPRECAUTIONSFROMTHE
MANUFACTURERSOFTHEEQUIPMENTANDTHECHEMICALS
REGARDINGINHALATIONOFDUST FUMESORSPRAY
)MPLEMENT/PERATION "ESUREIMPLEMENTREFLECTORS
AREUNDAMAGEDANDUNFADED-AKESUREALLGUARDSARE
INPLACEOVERAUGERINTAKEAREAS4ESTREMOTESHUTOFF
DEVICESTOASSURETHEYAREWORKINGPROPERLY

PERFORMANCE TIPS
Take Full Advantage of its Capabilities
Getting the most from your New Holland tractor is the purpose of this booklet.
New Holland wants to help owners achieve peak efficiency from all of their equipment.
Have you, or someone you know, purchased a new tractor in the last few years and continued to use it in much the
same way as the tractor it replaced? Many times we fail to take advantage of the advanced features available on
today’s modern equipment, such as Custom Headland Management. As a result the owner may not be getting all the
value from the money spent.
Many of the items suggested in this booklet can be completed by the owner when preparing for the season or by the
operator when starting a new field. Other adjustments, service procedures, or repairs might be more effectively
completed by your dealer’s trained service technicians.
New Holland Maintenance Inspections —
prepare your tractor for peak performance
Ask your New Holland dealer about New Holland Maintenance Inspections. It is a proactive way to be sure
your tractor will operate at its best possible performance in demanding conditions.
New Holland Maintenance Inspections include a visual and functional inspection of your tractor. They
can be used as a pre-season or as a post-season tune-up. Benefits include:
The combined advantages of New Holland Maintenance Inspections should
result in a lower cost of ownership and higher resale values.
Increased productivity
Less downtime during the season
Lower operating costs
Improved fuel economy
Documented maintenance
Serviced by New Holland-trained service professionals
Serviced with Genuine New Holland lubricants, filters, and parts
Documented Service Promotes High Resale Value
When you schedule your equipment for annual maintenance inspection services, your New Holland dealership
places annual Service Plus Maintenance decals on your equipment after each inspection, distinguishing your
commitment to keep your machines running in top condition. Not only does annual maintenance support your
productivity in the field, each decal symbolizes completed
service—which may increase the resale value of your equipment.
Because New Holland technicians use New Holland Maintenance
Inspection Checklists for each inspection, you can rest assured that
the service is thorough and nothing is overlooked.
PM-11835
2004
2005

SERVICE INSPECTIONS
Checklist
TJ Series Tractors
Ask your dealer about performing a New Holland Maintenance Inspection service to keep you up and running!

Checklist
SERVICE INSPECTIONS
TG Series Tractors

Heating, Ventilation and Air Conditioning Inspections
Checklist
SERVICE INSPECTIONS
How to Make Sure Your
A/C Beats the Heat
Summer’s hot and muggy days can become
down right comfortable with a well-maintained
cab air conditioning system. Here are some
ways to help your A/C system keep you cool.
Check the drive belt. Verify proper tension
and check for signs of wear.
Clean the condenser. It’s often integrated
with the radiator and the oil cooler. All
should be free of any debris that can build
up between units. Use compressed air or
a power washer to remove dust between
condenser fins that can reduce cooling
efficiency.
Inspect the compressor and hoses. Oil seepage
from the compressor, hoses, connectors or
couplings can be a potential problem. Contact
your New Holland dealer for suggested repair
options if you detect leakage.
Keep cab filters clean. Frequently clean both
the fresh air and recirculating air filters.
Check the evaporator drain hose. Don’t let
water collect in the evaporator box. Make
sure the drain hose is unobstructed.
Keep the cab airflow high. Especially in
high humidity, holding the cab’s fan speed
higher will reduce the likelihood of the
evaporator core freezing. For non Automatic
Temperature Control (ATC) systems, you
should change cab temperature by adjusting
the temperature setting before decreasing the
fan speed.
Don’t repair air conditioning systems
yourself. Clean Air Act legislation requires
that air conditioning systems be serviced
only by personnel certified in refrigerant
recovery and recycling.
New Holland dealers offer air conditioning
maintenance inspections and a full line of
compressors, condensers, and other air conditioning
parts to fit your exact need. Use these services and
parts to help keep your air conditioning performing
at its peak.

Superior Media - New Holland filters are designed
to trap more of the small contaminants that are most
damaging to diesel engines. The media is uniformly
resin-impregnated and heat-cured to provide efficient
filtration, while resisting the effects of moisture. The
media used in many of our newer filters combines
microglass and cellulose fibers for doubled
efficiency over standard filters.
Plastisol Adhesive - New Holland filters use
plastisol, a high quality adhesive, to uniformly bond
the filter element to the end caps. Plastisol adhesive
keeps the filter media from bunching and rupturing.
Rubber Seals - Many filter manufacturers use
cardboard seals at the ends of the filters; cardboard
seals can deteriorate or leak. New Holland filters
use a thin piece of rubber which provides a tight,
even seal at the base of the filter. It prevents
unfiltered oil from bypassing the filter media and
re-entering your system.
Metal End Caps - Solid metal end caps provide
additional strength to the filter element. Metal is
superior to the cardboard that many
manufacturers use.
OEM Specified - New Holland
filters meet all specifications
demanded by our design
engineers. When you buy a
New Holland filter, you’re
buying the confidence that
New Holland engineers have
placed in the filter to protect
your engine, and save you
repair costs.
FILTERS
2-stage filtration design
Lube Filtration Systems
To meet the performance demands of today’s tough
off-road environments, your equipment is generating
more usable horsepower than ever before. Tighter
tolerances, higher temperatures, and severe duty cycles
are driving the requirement for high quality filtration
and increased durability without sacrificing filter life.
Today’s low-emission engine designs make engine
filtration extremely critical, especially particles in the
5-10 micron range, which are most damaging to
modern engines.
While the costs for repairing equipment breakdowns
are normally high, they are often miniscule compared
to those associated with delayed harvests or missed
project completion deadlines. Don’t jeopardize
productivity by using “will-fit” filtration. New Holland
lube filters are designed specifically for your
equipment. They’re guaranteed to ensure peak
performance while providing maximum protection for
your investment.
Custom-designed filtration media
Synthetic
Cellulose
Blends
Stacked Disk
Optimized filtration performance in
capacity (life), efficiency
(cleanliness), and restriction to flow
Minimizes progressive wear
Reduces bearing and ring wear
Removes sludge
Filters oil sooner during cold starts
Patented combination full-
flow/bypass filtration products
Guaranteed to meet OEM
specifications

FLUIDS
Fahrenheit
Celsius
*Use of an engine oil heater, or an engine coolant
heater, is required in gray area.
Selecting Fluids
MASTERGOLD™ ENGINE OIL
Your engine takes a tremendous pounding day in and day out. But you can
protect and preserve it with the best engine oil available — MasterGold.
MasterGold is a premium, high-performance diesel engine oil designed to stand
up to the toughest operating conditions. Less susceptible to thermal and
chemical breakdown, MasterGold provides excellent oil-consumption control
and maximum engine-wear protection.
Compare before you buy. Use the engine oil specifically designed for your
equipment and field conditions. Prolong your hard working engine’s life with
MasterGold heavy-duty engine oil.
TG and TJ Series Tractor Engine Oil Capacity
Tractor Model Engine Oil Capacity
(gallon/liter)
TG210, TG230, TG255, TG285 5.5g/20.8l
TJ275 6.3g/23.8l
TJ325 7.25g/27.5l
TJ375, TJ425, TJ440, TJ450, TJ500 13g/49.2l
MASTERTRAN™ FLUID
Up to 70% of all transmission and hydraulic system failures are fluid
related. So protect and preserve your equipment with MasterTran and
prevent costly downtime.
MasterTran is blended to provide optimum machine performance and
long life in the most severe operating conditions.
It provides superior wear protection for hydraulic components, drive
train gears, and other transmission parts.
Controlled frictional characteristics provide safe, smooth operation of
wet brakes and clutches.
Excellent filterability provides extra protection against system
contamination.
DIESEL FUEL
Use a good grade of fuel which meets SAE/ASTM EN 590 or
equivalent. The use of biodiesel blends is approved for New Holland
engines up to B5 (5% blend ratio).
Oil Viscosity/
Temperature Usage Recommendation
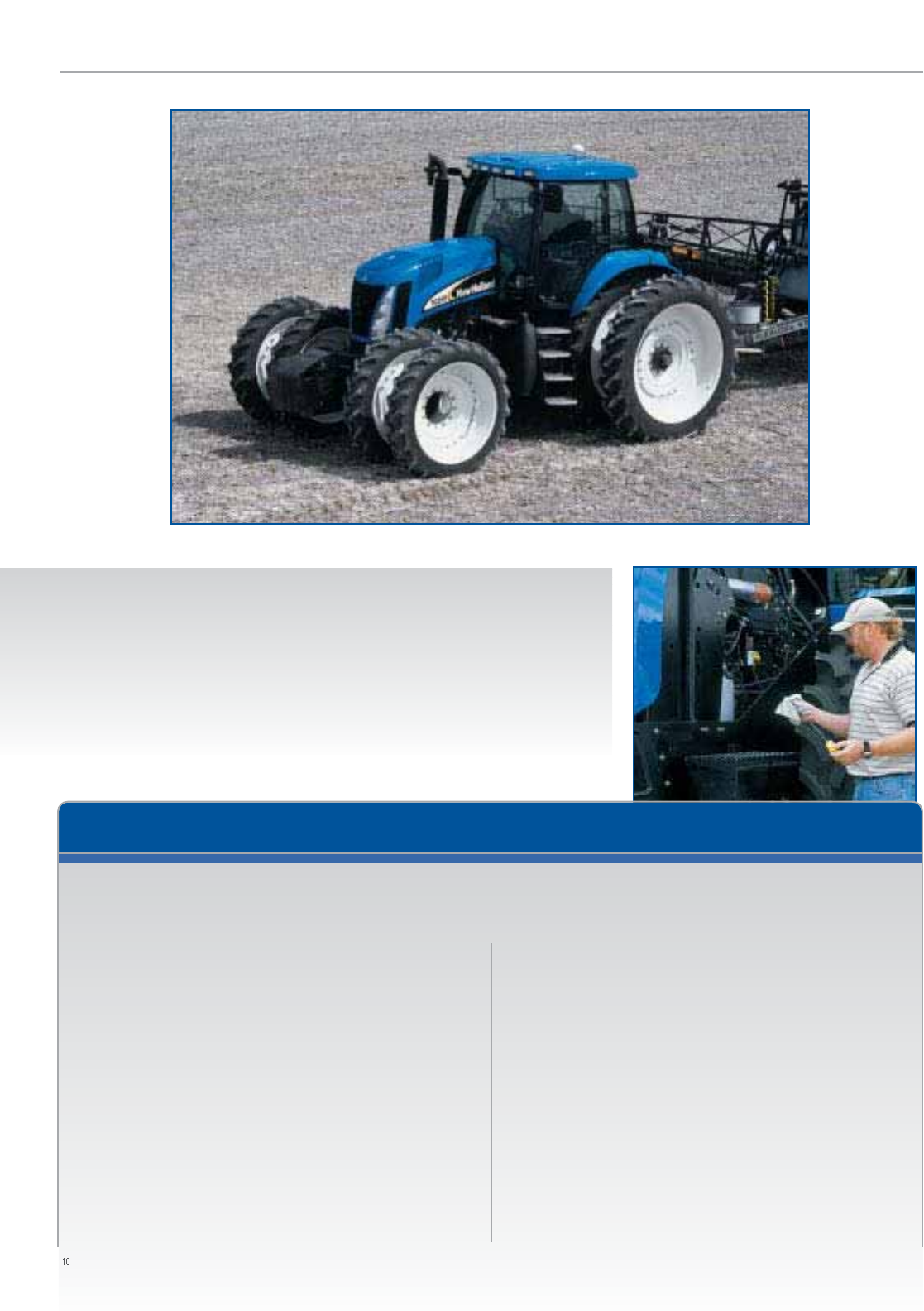
TG Tractor - Daily service functions can be
performed in a single location to get you to the field
faster each day.
Check engine oil level
Check hydraulic/transmission oil level
Check engine coolant reservoir level
Check fuel level
In severe dusty or wet conditions, grease rear
hitch & front axle every 10 hours; otherwise
every 300 hours
50 hours (or Weekly) -
• Drain water from fuel filter drain plug
• Grease SuperSteer Axle linkage pins
Daily Service
Service should be performed every 10 hours or daily (whichever comes first) to keep your New Holland tractor
running at its best.
TJ Tractor - Daily service required:
Check engine oil level
Check hydraulic/axle oil level
Check transmission oil level
Check coolant level (reservoir & deaeration tank)
Check fuel level
50 hours (or Weekly) -
• Drain water from fuel filter drain plug and fuel tank
• Grease articulation/oscillation hinges, articulation
& three point hitch (TPH) cylinders, and center
link fittings
DAILY SERVICE
Note: TG and TJ tractors require daily, weekly, and scheduled
maintenance intervals to keep equipment in top performing condition.
Although service requirements for each New Holland tractor model
may be similar, please refer to the equipment’s Operator’s Manual for
lubrication information, service intervals, and component locations.

SERVICE POINTS
Engine Oil and Coolant Filters
Vertically mounted engine oil filters permit easy, clean,
no-spillage service.
New Holland coolant filters are specially designed to
protect the cooling system from contamination and
condition the coolant to prevent erosion and cavitation.
TG Tractor -
Engine oil and filter – 300 hours
Coolant filter – 600 hours
Coolant and conditioner – 2100 hours
TJ Tractor -
Engine oil and filter – 500 hours
Coolant (check SCA level) – 500 hours
Coolant filter – 1500 hours
Coolant (drain & flush) – 6000 hours
Fuel Filters
Fuel filters protect the fuel system from dirt and
water damage. Use clean fuel, keep the fuel tank full
to prevent water condensation, and drain the water
separator section at regular service intervals.
TG Tractor -
Engine fuel filters – 600 hours
TJ Tractor -
Engine fuel filters – 500 hours (or when service
icon is displayed)
Radiator/Coolers
During regular service, clean the radiator, hydraulic
oil coolers, fuel cooler and air conditioning
equipment as conditions warrant.
Transmission, Hydraulic, and
Axle Filters
TG Tractor -
The combined transmission and hydraulic system are
protected from contamination by two high-performance
spin-on filters on the right hand side of the
transmission.
Transmission oil and filters – 1500 hours
TJ Tractor -
The transmission and hydraulic systems are
independent. The hydraulic system shares its circuit
with the axle lube system.
Hydraulic oil and filter – 1500 hours
Axle lube filter – 1500 hours

SERVICE POINTS
Cab Clean Air & Recirculation
Filters
Proper heating and cooling performance depends on
proper air flow through the cab clean air and
recirculation filters. Recirculation air filters should be
cleaned with mild soap and water as required by
conditions during regular service. Clean cab air
recirculation filters improve air conditioning system
efficiency and make cab comfort easier to maintain.
Note: Be sure cab recirculation filters are not
blocked. A clear flow path must be maintained for
optimum cab comfort.
TG Tractor -
The clean air filter is located below the cab door. The
recirculation filters are located on both sides of the
operator’s seat near the floor mat.
Cab air & recirculation filters – As required
(recommended 1500 hours)
TJ Tractor -
The clean air filter is located underneath the left rear
corner of the cab. The recirculation filter is located
directly behind the operator’s seat.
Cab air & recirculation filters – 1500 hours
Batteries
Current models of New Holland equipment use
maintenance-free batteries. Terminals should be
cleaned as necessary. On
older models without
maintenance-free
batteries, clean terminals
as necessary and check
electrolyte levels before
and after winter storage.
Engine Air Filters
To maintain engine power and performance, clean the
primary filter when notified by tractor instrumentation. Do
not clean the secondary (inner) filter element. The
secondary (inner) filter element should only be replaced.
TG Tractor -
Primary & secondary engine air filters – as required
(recommend 1200 hours or annually)
TJ Tractor -
Primary & secondary
engine air filters –
1500 hours
Fuses & Relays
TG Tractor -
Engine circuit protection fuses are located inside the
engine service door below the engine air filter assembly.
The tractor circuit fuses and relays are located below the
floor mat behind the operator’s seat.
TJ Tractor -
All fuses and relays are located under the removable
panel to the left of the operator’s seat.

TG PERFORMANCE ITEMS
TerraGlide™ and SuperSteer™
FWD Axles
ATerraGlide FWD axle is optional on TG model
tractors. The TerraGlide axle helps keep the front
wheels on the ground. This keeps the tractor stable
under the variety of conditions tractors encounter on a
regular basis. The TerraGlide axle provides a smoother
ride over rough terrain. TG models also offer an
optional SuperSteer FWD axle which steers in
conjunction with the wheels to a maximum of 20
degrees. This, added to the 45 degree maximum turn
angle of the wheel ends, gives an effective steer angle
of 65 degrees.
Dual Speed PTO
TG Tractor models offer a dual speed PTO with
interchangeable 540 and 1000 (large and small) speed
shafts. The dual speed PTO capability allows you to
connect to a variety of implements without changing
tractors. The PTO shafts interchange easily, requiring
only small hand tools.
TJ models use a 1000 rpm, 1-3/4˝ shaft.
Drawbar Positioning/PTO
Driveline Adjustment
When switching PTO shaft speeds on TG models, you
must reposition the drawbar to meet SAE dimensions.
Failure to adjust the drawbar length could result in
damage to either the tractor or the implement PTO drive
line. Use the implement PTO driveline height adjustment
to ensure a minimum vertical
angle of the implement PTO
shaft. The horizontal distance
from end of shaft to center of
drawbar pin should be:
True Ground Speed Signal
TG and TJ models have an in-cab, true ground speed
signal socket. Using the socket simplifies connection of
the true ground speed signal to spraying and planting
systems. Order cable part number 324847A2.
Foot Throttle
The optional foot throttle available on TG tractors frees
the operator’s hands for other functions. A foot throttle
can be a valuable enhancement for loader, planting, and
general tillage operations.
TJ models have an optional decelerator pedal available.
Shaft Distance
540 14˝
Small 1000 16˝
Large 1000 20˝

PERFORMANCE ITEMS
High-Capacity Drawbar
A high-capacity drawbar option is available for applications where
heavy drawbar loads are expected. The high-capacity drawbar should
be used for applications like front folding planters, liquid manure
wagons, and large grain carts. Three swing positions, one on each
side of center, are obtainable by moving bolts which extend up
through the drawbar hanger on both sides of the drawbar. Six
drawbar mounting positions are available just like on the standard
drawbar. The high-capacity drawbar allows equal angle hitching
when necessary. The high-capacity drawbar has a vertical tongue
load rating of 4990 kg (11,000 lbs). The “auto pin” clevis is standard.
Heavy Duty Drawbar kit is available for all TG tractors.
Drawbar kit part number - 435788A1 (includes the auto-pin hitch
and mounting hardware).
Drawbar part number - 426511A1.
Motor Return and Power Beyond
An optional motor return kit mounts to the top of
the couplers on the left side. Motor return port
installation reduces back pressure in hydraulic
circuit return lines. This results in more efficient
hydraulic system operation. The motor return
consists of one return coupler (3/4˝) and one
case drain coupler (1/4˝). The motor return
housing is the same housing used for power
beyond applications without the lines,
connections, and couplers required for power
beyond functions.
Note: The motor return kit is required for some
planting and seeding implements.
Power beyond provides a hydraulic supply port, a low
pressure return port, a sensing port, and a case drain
coupler (ported to reservoir). Power beyond provides a
versatile connection point for specialty hydraulic
applications.
IMPORTANT: The case drain coupler should only be
used for low flow, case drain applications. Transmission
lube pressure could be adversely affected if the case
drain coupling is used for other applications.
Note: For maximum performance, use only ISO Tips.

ELECTRONIC SERVICE TOOL
CAN Systems Put the Latest Technology to Work for You
New Holland service professionals use an Electronic Service Tool
(EST) to service New Holland tractors. The latest New Holland
tractors are equipped with a Controller Area Network (CAN),
that allows all the tractor systems to communicate on one
network. No longer is your New Holland service technician tied
to the shop. The EST makes in-field diagnosis easy.
Provide Information to the Operator
Improve Tractor Operation
Enhance Tractor Performance
Prevent System Failures
Provide Quick and Accurate Troubleshooting
Service technicians connect the Electronic Service Tool into the tractors CAN system to communicate using the
CAN network. Fault based diagnostics are used to quickly identify problems. Detailed photographs, diagrams and
component locators on the EST screen provide complete information about related wiring and connectors. Repairs
can be made quickly, assuring maximum productivity. In addition to service diagnostics, the EST can be used to
download new software to upgrade the functions performed by the controller networks. It can also be used to change
the default transmission gears.
Consider several examples of how controllers and other devices within the CAN work together. As the tractor moves
through the field, the controllers in the CAN system continually check a variety of inputs:
Operator Commands
Engine Torque
Gear Selection
Tractor Speed
Wheel Slip
Hitch Position
As conditions vary, this information is used by the system to adjust engine power to the transmission. The
transmission responds to commands from the operator to complete functions that previously required individual
actions by the operator. Therefore, the operator’s time is available to make corrections in the field. As the operator
moves the hand throttle lever or signals other operations, the tractor identifies the change and sends the new
command to the required systems via the CAN system. New Holland tractors are designed as a platform for evolving
technology to provide more usable information.
The Power of Technology

EZ-GUIDE®PLUS LIGHTBAR
New Holland EZ-Guide®Plus Lightbar
The new EZ-Guide Plus is the second generation of lightbar to be offered by New Holland. It is also the first lightbar
in the industry to combine easy-to-read guidance LED’s with a graphical LCD screen, and a high-end GPS receiver
all in one unit. The LED’s display how far to the left or right of center you are, making it easy to follow your swath
guidance, while the added LCD screen displays your vehicle orientation, to help you follow contours easier. By
combining LED guidance with a graphical display, you get the best of both worlds to help you stay on track.
The EZ-Guide Plus is not only easy to learn but it can be installed in any vehicle in minutes. Use it in any field
application that requires parallel swaths including field preparation, chemical or fertilizer applications, and air seeding
applications. Tough working conditions are no problem either—the system works consistently day or night, in wind,
rain, dust or fog with no deterioration in performance. Lightbar guidance technology can help you accomplish more by
extending your hours of operation, making each working day more productive. You can improve your coverage, while
reducing your cost of chemicals, fertilizers, fuel and other input materials, by eliminating costly skips and overlaps. The
EZ-Guide Plus is not just a lightbar, it’s also a fully functioning GPS receiver. The system outputs “NMEA” position
data that enables it to feed position data to other GPS-enabled equipment such as yield monitors, variable rate planters
and field computers. See your New Holland specialist about making this technology work in your operation.
Features
• 35 LEDs for guidance
• 160x120 pixel LCD screen
• Perspective and plan view map
• Integrated 12 channel GPS receiver
• Free WAAS differential correction
• FreeDIFF firmware technology
• High quality antenna resistant to interference
• Optional six button remote control with integrated alarm
• Multiple guidance patterns
• U.S. or Metric units
• Pause/Resume function
• User-definable swath width
• On-board GPS diagnostics
• NMEA output for other applications such as yield monitoring
See your local New Holland dealer for a demonstration.
EZ-Guide and FreeDIFF are trademarks of Trimble Navigation Limited.

Top 10 Ways to Reduce Soil
Compaction With Tires
RIDE, TRACTION & PERFORMANCE
Matching the tractor to the load
Your tractor has been designed for continuous field
operation at the rated horsepower while traveling at a
speed of 5 mph or faster. If the engine lugs continuously
at slow speeds you can be sure that the load is not
correctly matched to the tractor. This could result in
damage to the tractor drive train as well as wasted fuel,
increased tire wear, and soil compaction.
Maximum gross weight - A tractor’s maximum gross
weight is referred to as the combined static weight of the
tractor and any added ballast. This value must not
exceed the rating of the ROPS structure or the maximum
gross vehicle weight as specified in the Operator’s
Manual. When adding ballast to a tractor, the tractor
should be ballasted as light as possible to minimize soil
compaction and still maintain performance.
Many tire manufacturers recommend using cast iron
weights. If liquid ballast must be used, New Holland
requires it be placed in the inside duals only if the
wheels are spacer band type. Flange style duals or hub
style duals may be lightly filled. Spacer band duals
should never have liquid ballast installed in the outside
dual wheel.
Gross Vehicle Weight
Tire Inflation
Radial tires achieve their high level of tractive
performance as a result of the high contact area between
the rubber and the soil.
Proper adjustment of radial tire pressure means using
the correct tire inflation pressure to support the static
load carried by the tire and still maintain the high
contact area between the tire and soil.
A tire can be inflated to safely support a wide range
of loads.
• An 18.4R42 tire used as a dual, supports
approximately 3200 lbs. of static load when inflated
to 8 PSI
• An 18.4R42 tire will support 6950 lbs. when inflated
to 24 PSI
In both instances, the tire deflects approximately the
same amount. This is known as “Rated Deflection” of
the tire. When the Rated Deflection is correct, the tire
achieves its best performance.
The correct tire pressure for a given tractor is found by
weighing the unit and then dividing the weight per axle
by the number of tires. This weight is then compared to
the values on the Tire Inflation vs. Weight Table to find
the correct tire pressure. Tire Inflation vs. Weight Tables
should be used for proper inflation pressures.
1. Use radial tires. They can operate at lower psi than
bias ply tires, have a larger footprint and reduce
soil disturbance.
2. Use the widest and largest diameter tires possible for
the application that allows the minimum air pressure
(example 6 PSI).
3. Use the proper tire pressure for the load, speed,
and application.
4. Check tire pressures regularly.
5. Add duals or triples to help distribute the load and
optimize the air pressure.
6. Add large tires to the implement being used.
(Many times the implement actually causes more
compaction than the tractor!)
7. Run the tractor at the lightest ballasted weight possible.
8. Always ballast with iron, not fluid in the tires.
9. Utilize precision traffic. (For example, drive in the same
tire tracks and keep major traffic on the headlands.)
10. Use the correct tires to improve fuel efficiency.
Less slip over lots of acres can add up to big savings
in fuel usage.

RIDE, TRACTION & PERFORMANCE
TG Tractors
Refer to Load/Inflation Chart for inflation and tire size information (starting on
page 26 or in the tire manufacturers’ guide).
Definitions
Rolling Circumference - Rolling circumference is the distance a tire travels in one revolution
Interaxle Ratio - A FWD tractor uses both the front and rear tires to do the work. Since the front tires are smaller
than the rear tires, the front tires must rotate faster to travel the same distance as the rear. The mechanical gear
combination used to allow the front axle to move the tires at a faster speed is referred to as the interaxle ratio. The
tractor manufacturer establishes the interaxle ratio.
Tall, wide, soft radial tires provide:
• The best traction.
• The best ride.
• The least amount of maintenance required to control a powerhop condition.

Easy Ballasting Options
RIDE, TRACTION & PERFORMANCE
The University of Nebraska conducted field tests in the
summer of 1999 to compare the effect of traction on
tractors equipped with and without front dual wheels.
The results showed, when pulling drawbar implements,
generally a 65/35 rear/front weight split performed the
best for tractive efficiency with single or front dual
wheels. Hitch mounted implements generally performed
best with a 60/40 rear/front weight split. The test
emphasizes the importance of proper ballasting.
During tractor ballasting, pay attention to:
• The front to rear weight split on the tractor
• Pounds of weight per PTO hp and drawbar hp
• Tire load/inflation values
Proper ballasting minimizes compaction and enhances
tractor performance. Front duals increase the tire-to-
ground contact area and reduce the ground contact
pressure under the front axle. The tractor used for the
field test was equipped with 520/85R46 rear and
480/70R34 front tires. With these tires, the use of front
duals increases the tire-to-ground contact area by 25%.
Lower air pressure (see Load/Inflation Charts) improves
the tire footprint, while reducing the tire to ground
contact pressure and compaction in the field.
FWD Dual Wheel Field Test Results
Two different front weight frames are available
depending on FWD on SuperSteer options. The
weight frames increase front end vehicle weight and
the weights wrap under the chassis providing greater
ground clearance. The front wheels turn behind the
weights and frame for increased visibility and tighter
turning radius.
Two suitcase weight options are available, weighing
40 kg (88 lb) and 100 kg (220 lb).
• When using the large suitcase weights, a
maximum of 16 weights can be installed
• When using the small suitcase weights, a
maximum of 22 weights can be installed

RIDE, TRACTION & PERFORMANCE
Tires and Tractor Performance
To optimize tractor performance, tires should be selected
to suit the intended application. Key options like tire size
and cast weight packages, combined with proper tire
pressure, determine actual tractor performance.
Front Tire Selection
Choose the largest front tire or front dual option with
the highest weight-carrying capacity that matches the
row spacing. Selection of a larger tire results in reduced
compaction and permits heavier loads on the front axle
without exceeding the tire load-carrying capacity.
Rear Tire Selection
Choose rear tires that are large enough to carry the
total ballasted weight of the tractor with an inflation
pressure in the 6 - 14 psi range. Larger tires require
less inflation pressure to support a given axle load
than narrow tires do. Use only approved tire
combinations. The Lead/Lag should be between 0 -
5%, with a value of 1 - 3% being best. Negative
Lead/Lag is not recommended.
Lead/Lag
The relationship between the front and rear tires is
referred to as Lead/Lag and is stated as a
percentage. New Holland has established a
Lead/Lag range that provides the operator with
acceptable tire wear, front tire steering, and front
tire pulling power. Any tire combination that falls
within this range is acceptable. Lead/Lag
percentages can be calculated using the formula:
Interaxle Ratio - Front/Rear
*Front Axle Reduction Ratio
TG210 & TG230 (Standard).......................................................................................1.3228...........*21.525
TG210 & TG230 (TerraGlide)....................................................................................1.3228...........*21.525
TG210 & TG230 (SuperSteer) ...................................................................................1.3228...........*21.525
TG255 (Standard) .......................................................................................................1.3222...........*21.535
TG255 (TerraGlide) ....................................................................................................1.3222...........*21.535
TG255 (SuperSteer)....................................................................................................1.3222...........*21.535
TG285 (Standard) .......................................................................................................1.3250...........*21.535
TG285 (TerraGlide) ....................................................................................................1.3250...........*21.535
TG285 (SuperSteer)....................................................................................................1.3250...........*21.535
Note: *This ratio number (1) can be found on the axle serial number plate.

RIDE, TRACTION & PERFORMANCE
Tire manufacturers have found practices and procedures developed for bias ply tires may actually reduce the
performance of radial ply tires. Minor adjustments in the tractor weight split (front/rear), ballast, and tire inflation
pressure can dramatically improve performance of the tractor.
TJ Tractors
• Improve Traction
• Reduce Compaction
• Reduce Occurrence of Powerhop
• Increase Powertrain Life
• Reduce Tire Wear
• Improve Ride
Proper weight split, ballast, and tire inflation can:

RIDE, TRACTION & PERFORMANCE
Tractors used in drawbar work only.
Generally these tractors are not equipped with
a 3-point hitch or PTO and are used to pull
standard pull type implements such as disks,
chisel plows, field cultivators, rippers, etc.
Tractors in this type of application should be
ballasted with no more than 55% of the weight
on the front axle.
Tractors used for scrapers or other
implements with high vertical loads.
Tractors in this type of application should be
ballasted with 65% of the weight on the front
axle. This should allow the tractor to achieve a
50/50 weight split while operating under load.
If the tractor is equipped with a 3-point hitch
or PTO it may not be possible to achieve this
level of balance and still stay within the
maximum operating weight limitations. If this
is the case, adjust as close as possible to the
65%-35% specification, and stay within the
maximum operating weight limitation.
Ballasting 4WD Tractors - Drawbar Applications
Ballasting 4WD Tractors - 3-Point Hitch Applications
Tractors used for 3-point hitch work only.
Tractors in this type of application should
be ballasted with 60% of the weight on the
front axle.
Ballasting 4WD Tractors - High Vertical Load Applications

RIDE, TRACTION & PERFORMANCE
Front and Rear Suitcase Weights
Front suitcase weights can be mounted on the front of
the tractor with a weight hanger. A maximum of 18
suitcase weights at 45 kg (100 lb) each can be installed,
depending on the application, tractor static weight ratio
and soil conditions.
Front Frame Weights
Suitcase weights can also be mounted on the rear of the
tractor with a weight frame. However, rear suitcase
weights cannot be used if the tractor is equipped with a
three point hitch.
A maximum of 10 suitcase weights (TJ 275-325) or
14 suitcase weights (TJ375-500) at 45 kg (100 lb) each
can be installed depending on implement application,
front mounted equipment, tractor static weight split and
soil conditions.
Assembly weight:
Weight frame = 468 kg (1032 lb)
Frame + 14 suitcase weights = 1166 kg (2571 lb)
The entire weight assembly can be removed from the
tractor by removing 2 bolts and attaching an overhead
hoist to the rear holes on each side of the lifting bracket.
See your dealer for more information.
IMPORTANT: Total static weight of the tractor with all
equipment and ballast must never be more than the
recommended operating weight. See Maximum
Recommended Operating Weight in Operator’s Manual.
Rear Frame Weights

RIDE, TRACTION & PERFORMANCE
TG Tractor—Tire Load and Inflation
The inflation pressures are based on cold inflation pressure recommended by the Tire and Rim
Association Inc.
How to Use the Load and Inflation Charts:
1. Determine the ballasted tractor front axle weight and tractor rear axle weight.
Note: If using fully mounted or high vertical drawbar implements, add the weight of the implement
to the rear weight (refer to implement manual for weight).
2. Find the appropriate chart (Front Singles or Duals, Rear Singles, Duals or Triples).
3. Find tire size and correct rating.
4. Follow the row across to the first weight that is above your tractor (front or rear) axle weight.
5. Follow the column up to find the minimum recommended tire inflation pressure.
Note: Never exceed the load capacity for a particular tire. To obtain more load capacity, use duals
or change to a different tire.
Note: Never exceed the inflation pressure for a particular tire. The last number in the chart is the
maximum inflation pressure for that particular tire.
Note: Increase tire pressures 2 to 4 PSI over those stated in the chart for any of the following
conditions:
• If tire pressures are not checked daily
• Sharp turning and or braking will be encountered
• In-Furrow operation (Furrow tire only)
• Side hill operation

RIDE, TRACTION & PERFORMANCE
TJ Tractor
Tire Pressure for Maximum Tire Load at Rated Inflation
To achieve the best tire pressure and load capacity, scale weigh the front and rear axle of the tractor.
1) Determine proper ballast weight split.
60% Front/40% Rear - Tractor used with hitch mounted implements.
55% Front/45% Rear - Tractor used with drawbar towed high draft implement.
65% Front/35% Rear - Tractor used with high vertical drawbar loads.
See Tractor Ballast information for additional information.
2) Determine correct static load distribution and tire pressure from chart.
Example: Tractor used with standard drawbar implements, 18.4R-42 dual tires and a full tank of fuel. Desired
weight split = 55% Front/45% Rear.
Front Weight of Tractor = 14,000 lb (6350 kg)
Rear Weight of Tractor = 9392 lb (4260 kg)
Total Weight of Tractor = 23,392 lb (10610 kg)
3) Determine weight distribution by dividing front and rear weight by total weight.
Tractor Weight Distribution = 59.8% Front Axle
40.2% Rear Axle
4) Adjust the weight distribution by adding 2000 lb (907 kg) weight to the rear wheels.
Adjusted Weight:
Front weight = 14,000 lb (6350 kg)
Rear weight = 11,392 lb (5167 kg)
Total weight = 25,392 lb (11 517 kg)
Total weight distribution = 55.1% Front Axle
44.9% Rear Axle
5) Front Static Load - weight divided by number of tires.
14,000 lb/4 = 3500 lb
(6350 kg/4 = 1588 kg)
Front Chart: 18.4R-42 Dual Tires - 3500 lb = 9 PSI
(1588 kg = 62 kPa)
Rear Static Load - weight divided by number of tires.
11,392 lb/4 = 2848 lb
(5167 kg/4 = 1292 kg)
From Chart = 18.4R-42 Dual Tires - 2848 lb = 7 PSI
(1292 kg = 48 kPa)
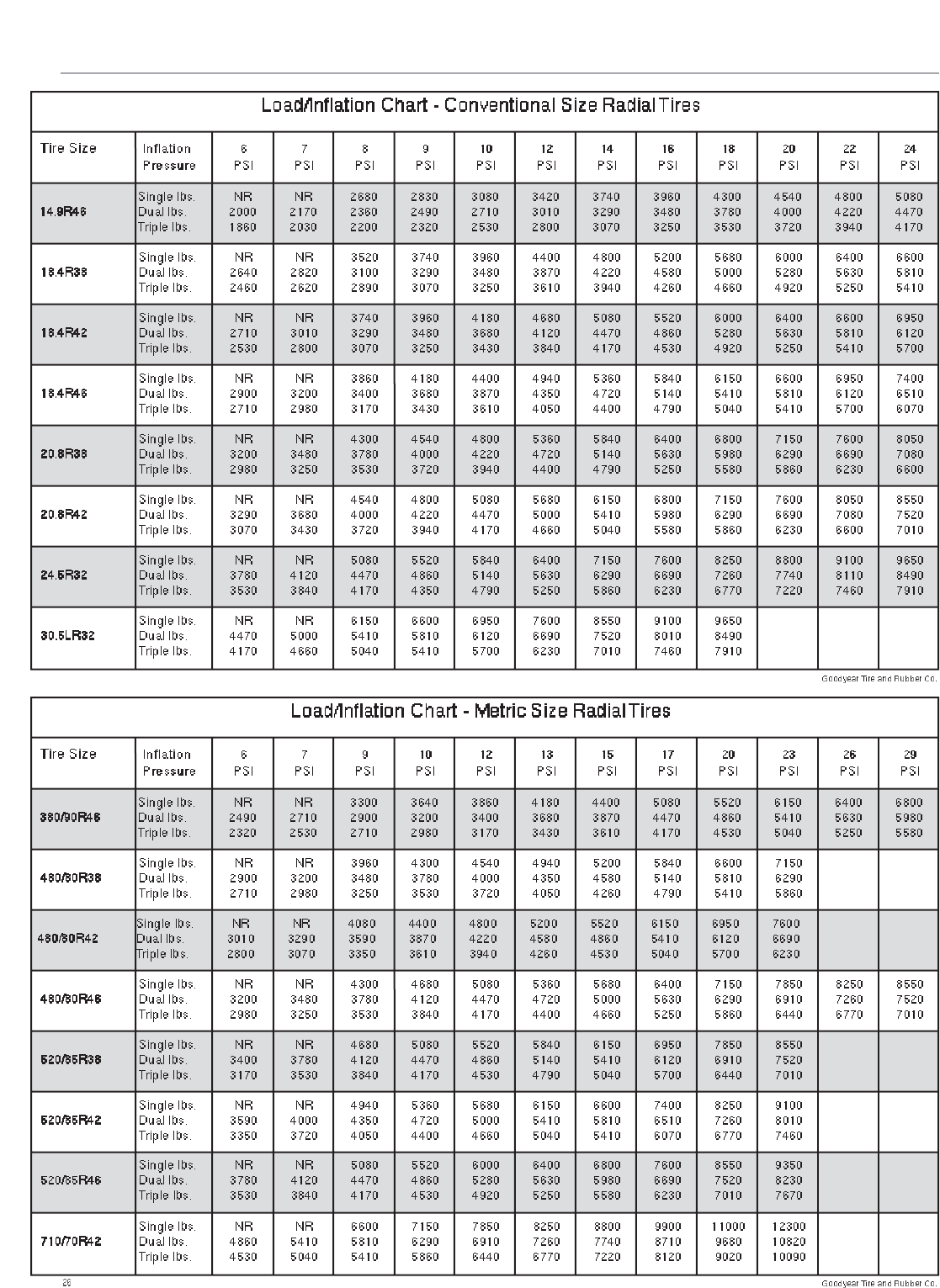
RIDE, TRACTION & PERFORMANCE
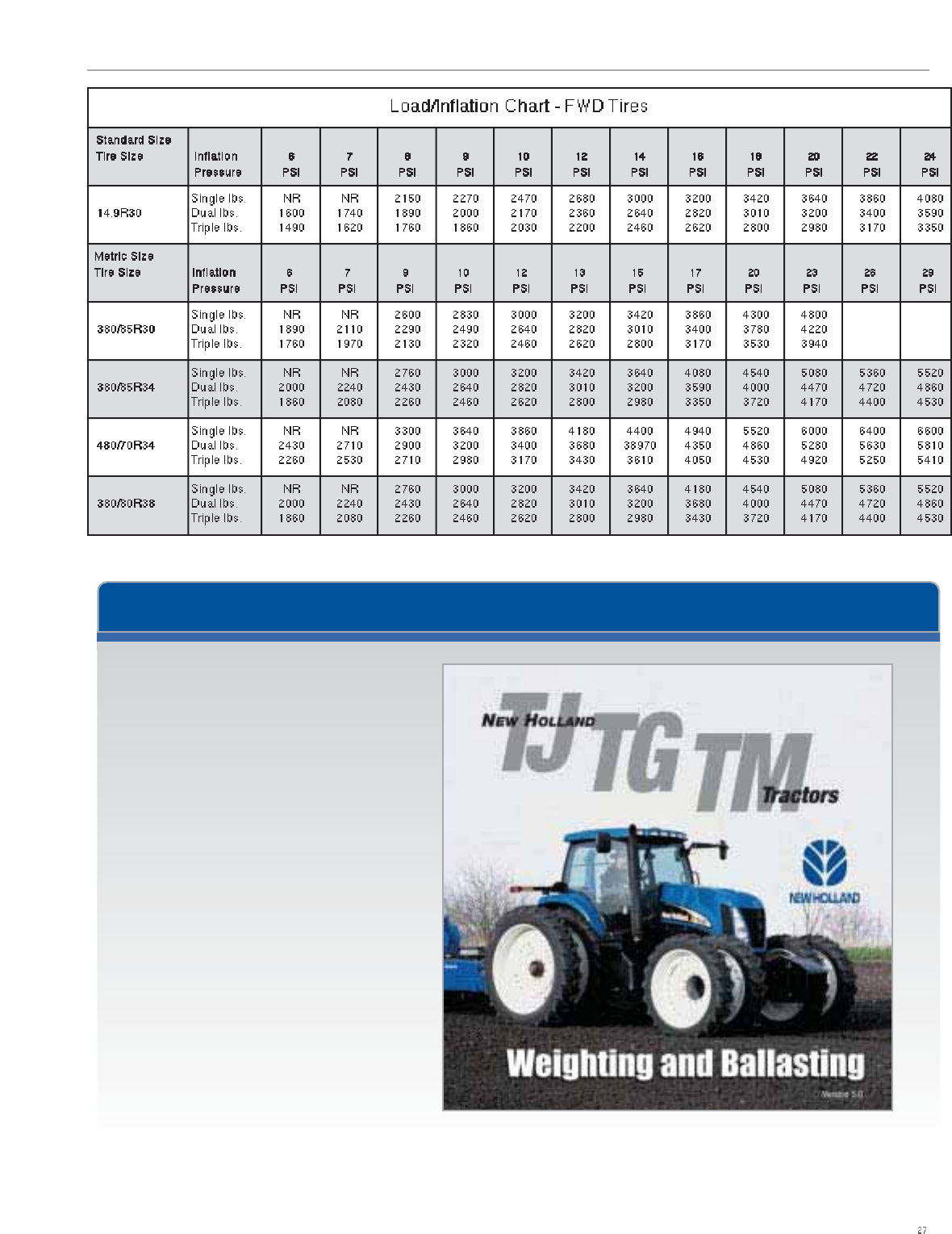
Ballasting CD
RIDE, TRACTION & PERFORMANCE
New Holland offers a variety of
CD based tools to assist in
preparing your tractor for the
field. Contact your dealer for
more information.
CD Rom Order # NH202013

RIDE, TRACTION & PERFORMANCE
Regardless of model or manufacturer, under certain
conditions tractors may hop fore and aft or the tires
may bounce up and down. You may experience this
type of out-of-phase movement that results in a
twisting motion of the tractor. Engineers call this type
of movement “powerhopping” but some customers
have termed it “grasshoppering.”
This results most commonly in heavy tillage
operations with pull-type equipment.
What Causes Powerhopping?
The tractor is not properly matched to
the implement.
Tire pressures are not properly balanced
from front to rear.
Improper tire size combinations are installed
on the tractor (creating improper lead/lag
ratio on the FWD equipped tractor).
The operator is attempting to go too fast
for the implement, the operation, or the
operating conditions.
Improper front to rear weight ratio on tractor.
Possible Solutions for
Powerhopping Problems.
If powerhop occurs after following all of the
guidelines on leveling implement tire size, weight
split, ballast type, and inflation pressures, make the
following adjustments to inflation pressures:
FWD
Raise front inflation pressure by 2 PSI. If powerhop
is not eliminated, further front tire inflation pressure
increases in 2 PSI increments is advised until hop is
eliminated. Rear tire inflation pressures should
remain at the correct pressures for the load. The
maximum front pressure should not exceed 6 PSI
above the maximum rated pressure for the tire
(radial or bias.) If the tractor continues to powerhop,
take weight off of the front axle.
4WD
Raise the rear inflation pressure from the correct
inflation by 2 PSI. If powerhop is not eliminated,
increasing rear tire inflation pressure in 2 PSI
increments is advised until hop is eliminated. The
maximum pressure should not exceed 6 PSI above
the maximum rated pressure for the tire (radial or
bias.) If raising the rear pressure fails to control hop,
take weight off of the rear of the tractor. On
extremely steep hillside operations, keep the fronts at
the correct pressure for the load and raise the rear
pressures.
Preventing Powerhop
On MFD tractors, powerhop occurs when the front axle attempts to out-pull the
rear axle. On 4WD tractors, powerhop occurs when the rear axle attempts to out-
pull the front axle.

Hydraulic Orbital Motors
Orbital motors (sprayers, planters, etc.) should be
connected with the motor supply connected to the
lower side of the circuit.
Orbital motor supply/return lines should not contain
load checks or other in-line restrictions.
The return side of the circuit should be connected
to a motor return port. A motor return connection
minimizes restrictions and improves operating
efficiency in the hydraulic circuit.
Hydraulic Productivity
The more demanding your application, the greater the
need to properly manage the tractor hydraulic system.
Proper circuit connection, use of the flow control, and
removal of unintended circuit restrictions can improve
hydraulic system performance.
A basic hydraulic circuit consists of:
A pump
Control valve(s)
Hydraulic function
(steering, implement, 3-point hitch, or other).
Larger implements equipped with several lift cylinders
will require more flow to properly lift and lower the
implement. If the flow control is set to deliver the
necessary flow requirement the operator can activate the
circuit and tend to other necessary activities while the
hydraulic circuit completes its cycle.
After connection, operate the circuit and
adjust the flow control dial until the
desired raise/lift time is obtained.
Hydraulic Connection Basics
Hydraulic circuits must be properly connected to
the tractor to operate correctly.
Implement Raise/Lower Cylinders
Implement raise/lower cylinders should be connected
with the remote valve load check in the raise side of the
circuit. If the cylinder is not connected in this way, the
implement will settle while the control valve is in the
neutral position.
Megaflow Option
The optional megaflow pump adds an additional
hydraulic pump to the system, an additional 29.4 gpm
for a total hydraulic system output of 68 gpm overall.
This is very beneficial when low flow high pressure is
needed at the same time as high flow low pressure.
With the Megaflow option:
The Megaflow pump supplies oil to remotes 3, 4, and 5.
The standard pump supplies oil to steering, remotes
1 & 2, three-point hitch, and power beyond.
HYDRAULIC SYSTEM

With the optional performance
monitor, performance items
such as individual remote flow
adjustments, fuel consumption,
and more can be monitored on
the screen.
Tractor Controls - TG and TJ Tractors
The remote control levers on TG and TJ tractors
electronically activate the remote hydraulic circuits.
The control levers have four positions:
• Raise
• Neutral
•Lower
• Float
Contact your New Holland dealer for a detailed
demonstration on the proper use of the hydraulic controls.
INSTRUMENTATION
A key to efficient tractor operation is knowing what your tractor is doing and understanding what’s going on
internally. The most effective tool for accomplishing this is the tractor’s own instrumentation.
1. Tractor Monitor (Standard)
The Tractor Monitor displays basic tractor operations and
provides an interface for configuration and calibration.
• Engine Oil Pressure
• Engine Coolant Temperature
• Fuel Level
• Operation Indicators (gear, direction, etc.)
• Warning Indicators
2. Performance Monitor (Optional)
The Performance Monitor displays performance related
functions including:
• Engine Power (electronic engines only)
• Area Count
• Timer Function
• Slip Percentage
• Remote Hydraulic Flows
• Remote Hydraulic Timers
• Service Reminders
• Automatic Engine Shut-down Protection
• Custom Headland Management
Behind each control lever is a Remote Function
control.The remote function control has five positions:
• Lock
• No Float
• Full Function
• Loader
• Hydraulic Motor
TG console shown.

MAINTENANCE PARTS
MasterGold™ Engine Oil
Your engine takes a tremendous
pounding day in and day out. But
you can protect and preserve it with
the best engine oil available —
MasterGold.
MasterGold is a premium, high-
performance diesel engine oil
designed to stand up to the toughest operating
conditions. Less susceptible to thermal and chemical
breakdown, MasterGold provides excellent oil-
consumption control and maximum engine-wear
protection.
Compare before you buy. Use the engine oil
specifically designed for your equipment and field
conditions. Prolong your hard working engine’s life
with MasterGold heavy-duty engine oil.
MasterTran™ Fluid
Up to 70% of all transmission and
hydraulic system failures are fluid
related. So protect and preserve
your equipment with MasterTran
and prevent costly downtime.
MasterTran is blended to provide
optimum machine performance and
long life in the most severe operating conditions.
It provides superior wear protection for hydraulic
components, drive train gears, and other
transmission parts.
Controlled frictional characteristics provide safe,
smooth operation of wet brakes and clutches.
Excellent filterability provides extra protection against
system contamination.
Hypoide 140 Gear Lube
Recommended for differential
and planetaries in TG tractors
with FWD axles. This
transmission and gear oil, with
extreme pressure (E.P.)
characteristics, is designed for
hypoid gears and final drives of
agricultural and construction
equipment.
GR-9 Multipurpose Grease
GR-9 is a general
purpose NLGI 2, lithium-
soap, extreme-pressure
grease for use in agricultural, construction and
industrial equipment. GR-9 is for anti-friction and
plain bearings (including non-disc brake wheel
bearings), universal joints, spline shafts, water pumps
and general chassis lubrication.
Systemgard®Oil Analysis
Let Systemgard oil
analysis tell you what’s
really going on inside
your engine, transmission,
and hydraulic system.
Detect potential problems
early, spot trends, and keep small, easily fixed
problems from becoming serious ones. See your New
Holland dealer for more information.
New Holland
Maintenance Inspections
Everyone agrees that routine inspections by trained
technicians are essential to good maintenance.
Inspections not only need to be routine, they need
to be consistent with the needs of the equipment
and its owner.
Our New Holland Maintenance Inspection programs
are based upon prearranged inspections at intervals
consistent with your needs. A professional and
systematic approach to equipment service can:
• Reduce costly downtime.
• Extend the service life of your equipment.
• Increase machine productivity.
Ask about New Holland Maintenance Inspections today!

MAINTENANCE PARTS
TG Tractors/TJ Tractors
Qty. Filter Number Description
1 86990980 Engine Oil
1 in-line 87400496 AND Fuel
1 (primary) 86991002 &
1 (final) 86991003
1 87413809 AND 87413810 Hydraulic
1 451525A1 Air (outer)
1 451526A1 Air (inner)
1 86994156 AND Cab
2 293615A1 (recirculating) Cab
1 86990977 Coolant
Qty. Filter Number Description
1 86990980 Engine Oil
1 86991015 AND Fuel
1 in-line 87400496
1 87413809 AND 87413810 Hydraulic
1 451525A1 Air (outer)
1 451526A1 Air (inner)
1 86994156 AND Cab
2 293615A1 (recirculating) Cab
1 86990977 Coolant
Models TG210/TG230 Models TG255/TG285
Protect your equipment with genuine
New Holland filters and lubricants.
Models TJ275/TJ325
Qty. Filter Number Description
1 441703A1 Engine Oil
1 448545A1 AND (in-line) 87400496 Fuel
1 (near batt. compartment) 86018758 Hydraulic
AND EITHER
2 435140A1 (std hyd.) OR
3 435140A1 (mega-flow)
1 87408704 Air (outer)
1 87408705 Air (inner)
1 259288A1 AND 386751A1 Cab
1 9672301 Coolant
Models TJ375/TJ425/TJ450
Qty. Filter Number Description
1 441700A1 Engine Oil
1 441701A1 Fuel
1 (near batt. compartment) 86018758 Hydraulic
AND EITHER
2 435140A1 (std hyd.) OR
3 435140A1 (mega-flow)
1 87408712 Air (outer)
1 87408713 Air (inner)
1 259288A1 AND 386751A1 Cab
1 441702A1 Coolant
Models TJ500
Qty. Filter Number Description
1 441700A1 Engine Oil
1 441701A1 Fuel
1 (near batt. compartment) 86018758 Hydraulic
AND EITHER
2 435140A1 (std hyd.) OR
3 435140A1 (mega-flow)
1 87417042 Air (outer)
1 87417043 Air (inner)
1 259288A1 AND 386751A1 Cab
1 441702A1 Coolant

MAINTENANCE PARTS
Oil/Filter Change Intervals & Capacities Hours/Yrs. Capacity w/ Filter
Engine Oil/Filter 300 5.5G (21L)
Fuel Filters 600 —
Engine Coolant Filter 600 —
FWD Differential Oil* - Standard/TerraGlide - 10-Bolt Axle 1200 / 1 Yr 13Qts (12.3L)
- Standard/TerraGlide - 12-Bolt Axle 12.5Qts (11.8L)
- SuperSteer 14Qts (13.2L)
FWD Planetary Oil (Each) - 10-Bolt Axle 1200 / 1 Yr 3 Pints (1.4L)
- 12-Bolt Axle 7 Pints (3.3L)
Transmission Oil, Filter(s) & Breather 1500 45.5G (172L)
Engine Coolant & Coolant Conditioner - TG210/230 2100 6G (22.7L)
- TG255/285 6.5G (24.6L)
Engine Primary & Secondary Air Filters as required —
Cab Air & Recirculation Filters as required —
* When changing FWD differential oil, also add 1 pint New Holland Limited Slip Additive (B96606).
NOTE: See your operator manual for complete information.
Oil/Filter Change Intervals & Capacities Hours/Yrs. Capacity w/ Filter
Engine Oil/Filter - TJ275 500 / 6 mos. 6.3G (24L)
- TJ325 7.3G (28L)
- TJ375/425/450 13G (49L)
Fuel Filter 500 / 6 mos. —
Engine Coolant Filter 1500 / 1 Yr. —
Engine Air Filters - Primary & Secondary 1500 / 1 Yr. —
Axle/Hydraulic Oil - TJ275/325 1500 / 1 Yr. 63G (238L)*
- TJ375/425/450 69G (261L)*
Axle Lube Filter 1500 / 1 Yr. —
Hydraulic Oil Filter 1500 / 1 Yr. —
Megaflow Oil Filter (Option) 1500 / 1 Yr. —
Transmission Oil - with PTO 1500 / 1 Yr. 13.5G (51.1L)
- without PTO 13G (49.2L)
Transmission Oil Filter 1500 / 1 Yr. —
Cab Air Filter 1500 / 1 Yr. —
Engine Coolant & Coolant Conditioner - TJ275 6000 / 2 Yr. 11.4G (43L)
- TJ325 12.4G (47L)
- TJ375/425/450 21.2G (80L)
* Total Axle System Capacity includes filters, front and rear axle and reservoir. If TPH equipped add 5G (19L).
NOTE: More frequent changes may be signaled by service monitor. Operator manual has complete information.
TG Tractors/TJ Tractors

NOTES

NOTES

->viÌÞÊ Li}ÃÊ ÜÌÊ >Ê ÌÀÕ}Ê Õ`iÀÃÌ>`}
vÊÌiÊiµÕ«ḭÊÊÜ>ÞÃÊ>iÊÃÕÀiÊÞÕÊ>`
ÞÕÀÊ«iÀ>ÌÀÃÊ Ài>`ÊÌiÊ "«iÀ>ÌÀ½ÃÊ>Õ>
LivÀiÊ ÕÃ}Ê ÌiÊ iµÕ«iÌ°Ê *>ÞÊ VÃi
>ÌÌiÌÊ ÌÊ >Ê Ã>viÌÞÊ >`Ê «iÀ>Ì}
`iV>ÃÊ >`Ê iÛiÀÊ «iÀ>ÌiÊ >ViÀÞ
ÜÌÕÌÊ>ÊÃi`Ã]Ê«ÀÌiVÌÛiÊ`iÛViÃ
>`ÊÃÌÀÕVÌÕÀiÃÊÊ«>Vi°
iÃ}]Ê >ÌiÀ>ÃÊ >`ÉÀÊ Ã«iVvV>ÌÃÊ >ÀiÊ ÃÕLiVÌÊ Ì
V>}iÊ ÜÌÕÌÊ ÌViÊ >`Ê ÜÌÕÌÊ >LÌÞÊ ÌiÀivÀ°
-«iVvV>ÌÃÊ>ÀiÊ>««V>LiÊÌÊÕÌÃÊÃ`ÊÊ>>`>]ÊÌi
1Ìi`Ê -Ì>ÌiÃ]Ê ÌÃÊ ÌiÀÀÌÀiÃÊ >`Ê «ÃÃiÃÃÃ]Ê >`Ê >Þ
Û>ÀÞÊÕÌÃ`iÊÌiÃiÊ>Ài>ð
ÞÊ ÌÀ>`i>ÀÃÊ ÀiviÀÀi`Ê ÌÊ iÀiÊ Ê >ÃÃV>ÌÊ ÜÌÊ Ìi
}`ÃÊ>`ÉÀÊÃiÀÛViÃÊvÊV«>iÃÊÌiÀÊÌ>Ê iÜÊ>`
ÀÌÊ iÀV>]Ê V°Ê >ÀiÊ ÌiÊ «À«iÀÌÞÊ vÊ ÌiÃiÊ ÀiëiVÌÛi
V«>ið
*£Ó£££ÊÊÊÊ^Ê Óää{Ê ÊiÀV>ʰ
6ÃÌÊÕÀÊ7iLÊÃÌiÊ>ÌÊÊ "À]ÊV>ÊÌvÀii\Ê£nnnÓäÇÎÇÇ
3XWWKHVSHFLDOLVWVDW
1HZ+ROODQGWRZRUNIRU\RX
1HZ+ROODQGDQG\RXUORFDO
1HZ+ROODQGGHDOHUDUHVSHFLDOLVWVLQ
KHOSLQJ\RXPDNHWKHEHVWFKRLFHVIRU
SURGXFWLYLW\DQGSURILWDELOLW\,WVWDUWV
ZLWKLQQRYDWLYH1HZ+ROODQGHTXLS
PHQWDQGFRQWLQXHVZLWK
H[SHUWVHUYLFHDQGVXSSRUW
SURJUDPVWKDWDUHEXLOW
DURXQG\RXUQHHGV
)URPWUDFWRUVWR
KD\WRROVWRFRPELQHV
DQGPRUH\RXZRQ·WILQGDPRUHFRP
SUHKHQVLYHUDQJHRIHTXLSPHQWWKDQ
WKH1HZ+ROODQGEUDQG RUDEXVL
QHVVSDUWQHU ZLWKDEURDGHUUDQJHRI
H[SHUWLVHWKDQ\RXU1HZ+ROODQG
GHDOHU&RPPLWWHGWR\RXUVXFFHVV
\RXUGHDOHUZLOOZRUNKDQGLQKDQGZLWK
\RX WRGHWHUPLQHZKLFK1HZ+ROODQG
HTXLSPHQWLVULJKWIRU\RXURSHUDWLRQ
7RNHHS\RXPRYLQJIRUZDUG\RXU
1HZ+ROODQGGHDOHUZLOODVVLVW\RX
ZLWKFRPSHWLWLYHUDWHILQDQFHOHDVH
DQGLQVXUDQFHSODQVDYDLODEOHWKURXJK
1HZ+ROODQG&UHGLW³FXVWRPHUWDLORUHG
SODQV
GHVLJQHG WR
PD[LPL]H
FDVKIORZDQG SUHVHUYHZRUNLQJFDSLWDO
7DONWR\RXUGHDOHUWRRDERXWWKH
SXUFKDVLQJFRQ
YHQLHQFHDIIRUGHG
E\WKH1HZ
+ROODQG3ODQ
$QGDIWHUWKH
VDOHWXUQWR\RXUGHDOHUIRUIDFWRU\
WUDLQHGVHUYLFHDQGWRWDOSDUWVVXSSRUW
<RXU1HZ+ROODQGGHDOHULVUHDG\WR
DQVZHUDOO\RXUTXHVWLRQVKHOSLQDQ\
GHFLVLRQVDQGUHVROYHSUREOHPV³LQ
WKHILHOGRUDWWKHGHDOHUVKLS<RX
ZRXOGQ·WH[SHFWDQ\WKLQJOHVVIURPD
VSHFLDOLVWZKRXQGHUVWDQGVWKHZD\
\RXZRUN
6HH\RXU1HZ+ROODQGGHDOHUWRGD\
DQGWDONWRWKHVSHFLDOLVWV
#.(/2)').!,0!243%.').%%2%$&/2.%7(/,,!.$%15)0-%.4350%2)/215!,)49',/"!,3500/24