Northern Digital orporated VICRA POLARIS VICRA User Manual USERS MANUAL
Northern Digital Incorporated POLARIS VICRA USERS MANUAL
USERS MANUAL
Polaris Vicra User Guide
Revision 2
October 2005
IMPORTANT
Please read this entire document
before attempting to operate
the Polaris Vicra System

Copyright 2005 Northern Digital Inc. All Rights Reserved.
p Printed in Canada.
Revision Status
Revision Number Date (DD/MM/YY) Description
Revision 1 27/09/05 Initial release
Revision 2 19/10/05 minor updates
Part Number: IL-1070100
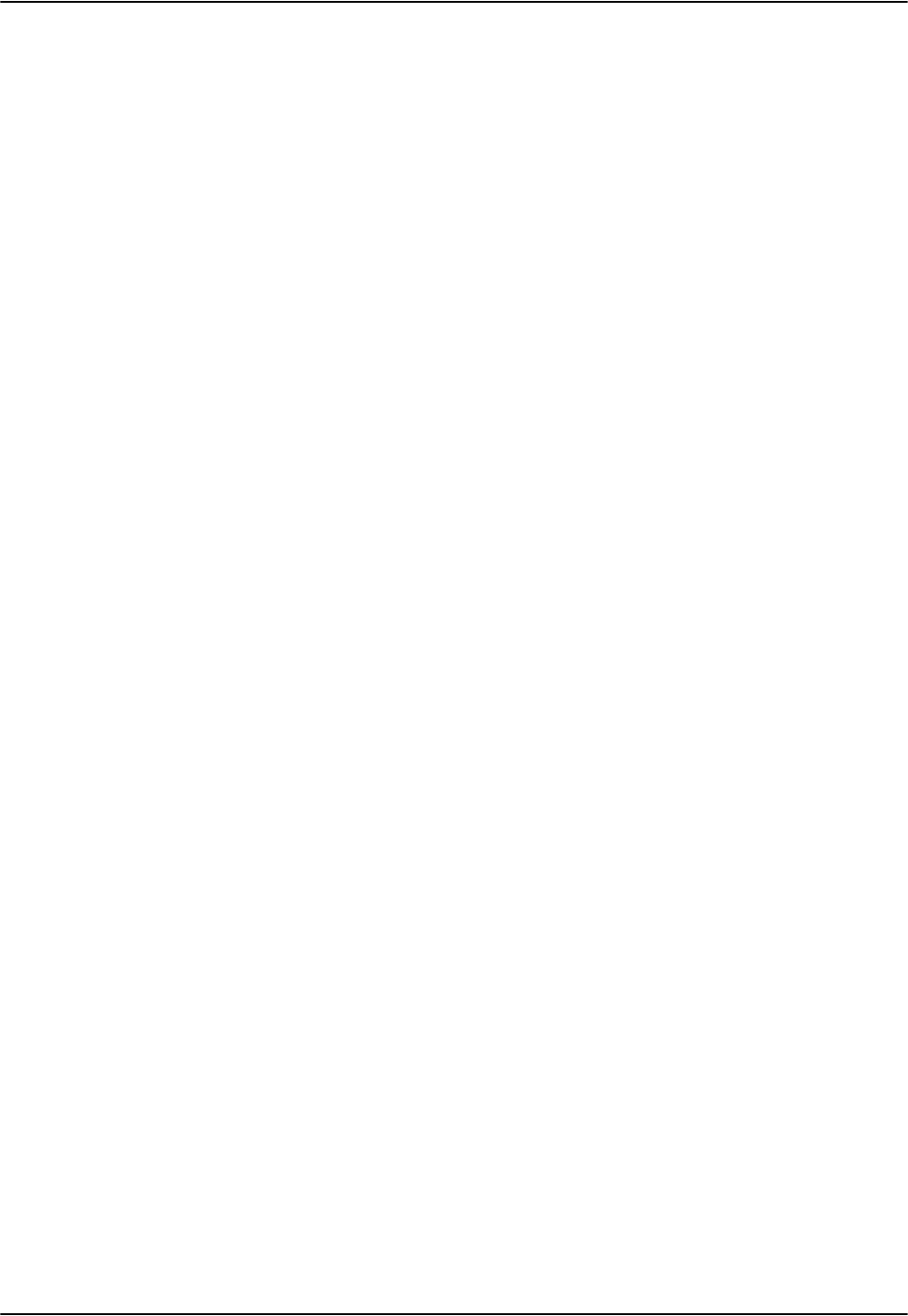
Polaris Vicra User Guide - Revision 2
Published by:
Northern Digital Inc.
103 Randall Dr.
Waterloo, Ontario, Canada N2V 1C5
Telephone: + (519) 884-5142
Toll Free: + (877) 634-6340
Global: + (800) 634 634 00
Facsimile: + (519) 884-5184
Website: www.ndigital.com
Copyright 2005, Northern Digital Inc.
All rights reserved. No part of this document may be reproduced, transcribed, transmitted, distributed, modi-
fied, merged or translated into any language in any form by any means - graphic, electronic, or mechanical,
including but not limited to photocopying, recording, taping or information storage and retrieval systems - with-
out the prior written consent of Northern Digital Inc. Certain copying of the software included herein is unlawful.
Refer to your software license agreement for information respecting permitted copying.
DISCLAIMER OF WARRANTIES AND LIMITATION OF LIABILITIES
Northern Digital Inc. has taken due care in preparing this document and the programs and data on the elec-
tronic media accompanying this document including research, development, and testing.
This document describes the state of Northern Digital Inc.’s knowledge respecting the subject matter herein at
the time of its publication, and may not reflect its state of knowledge at all times in the future. Northern Digital
Inc. has carefully reviewed this document for technical accuracy. If errors are suspected, the user should con-
sult with Northern Digital Inc. prior to proceeding. Northern Digital Inc. makes no expressed or implied warranty
of any kind with regard to this document or the programs and data on the electronic media accompanying this
document.
Northern Digital Inc. makes no representation, condition or warranty to the user or any other party with respect
to the adequacy of this document or accompanying media for any particular purpose or with respect to its ade-
quacy to produce a particular result. The user’s right to recover damages caused by fault or negligence on the
part of Northern Digital Inc. shall be limited to the amount paid by the user to Northern Digital Inc. for the provi-
sion of this document. In no event shall Northern Digital Inc. be liable for special, collateral, incidental, direct,
indirect or consequential damages, losses, costs, charges, claims, demands, or claim for lost profits, data, fees
or expenses of any nature or kind.
Product names listed are trademarks of their respective manufacturers. Company names listed are trademarks
or trade names of their respective companies.
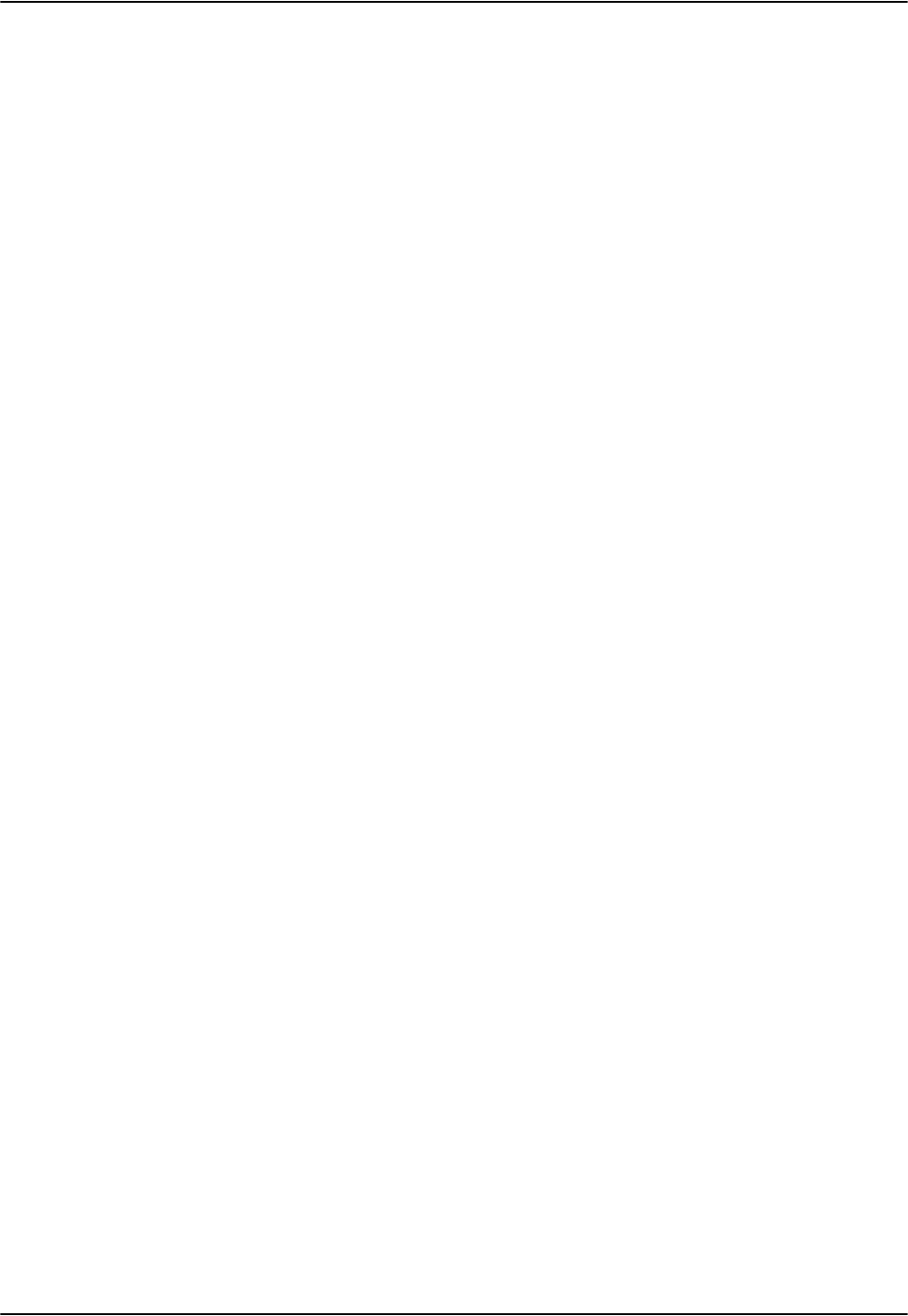
Polaris Vicra User Guide - Revision 2
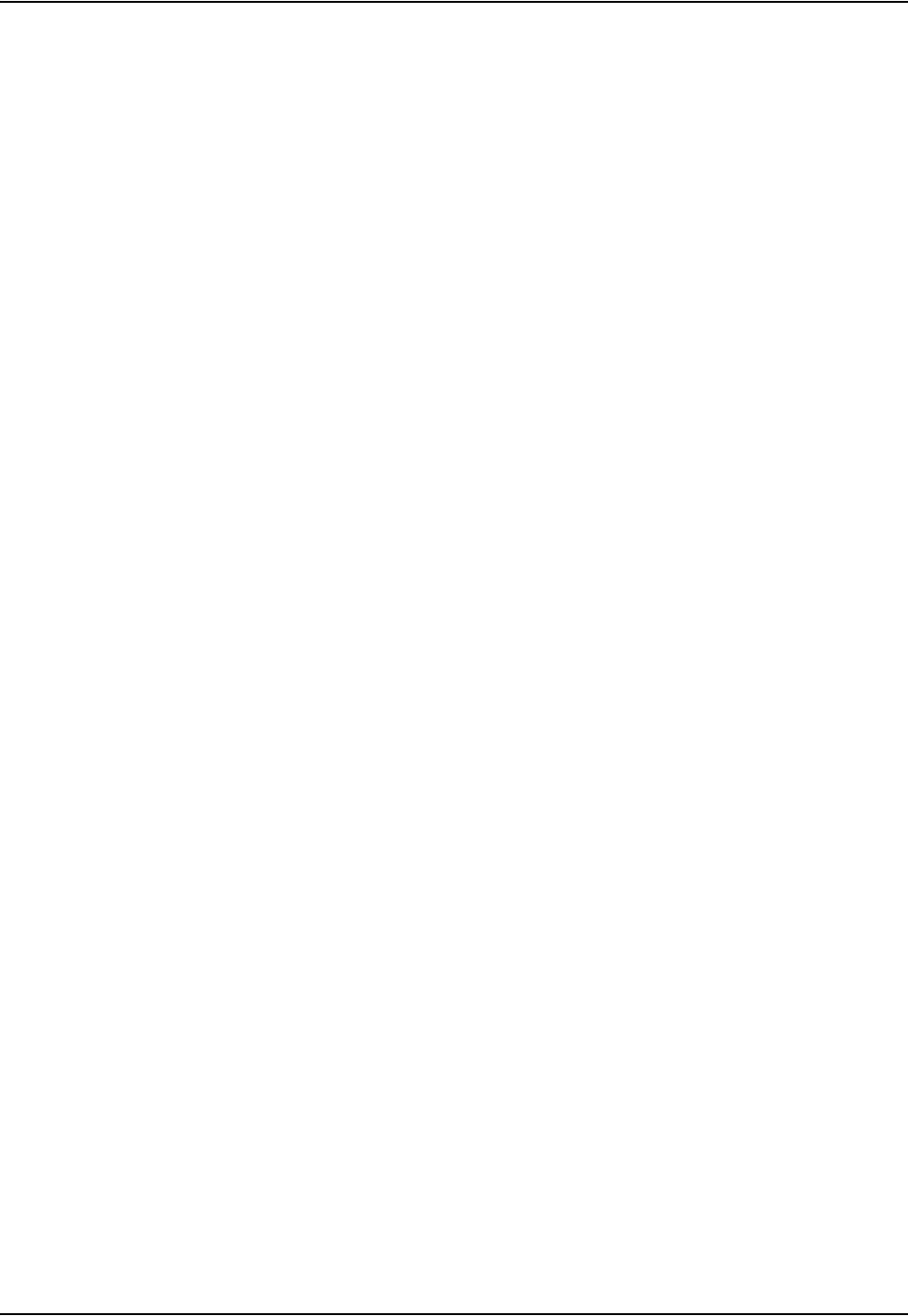
Table of Contents
Polaris Vicra User Guide - Revision 2 i
Table of Contents
Read Me First! . . . . . . . . . . . . . . . . . . . . . . . . . . . . . . . . . . . . . . . . . . . . . . . . . . . . . . . . . . . . . . . . . . . . . . . .1
Warnings . . . . . . . . . . . . . . . . . . . . . . . . . . . . . . . . . . . . . . . . . . . . . . . . . . . . . . . . . . . . . . 1
Cautions . . . . . . . . . . . . . . . . . . . . . . . . . . . . . . . . . . . . . . . . . . . . . . . . . . . . . . . . . . . . . . . 2
Disclaimers . . . . . . . . . . . . . . . . . . . . . . . . . . . . . . . . . . . . . . . . . . . . . . . . . . . . . . . . . . . . 3
Contact Information . . . . . . . . . . . . . . . . . . . . . . . . . . . . . . . . . . . . . . . . . . . . . . . . . . . . . . 4
Updates . . . . . . . . . . . . . . . . . . . . . . . . . . . . . . . . . . . . . . . . . . . . . . . . . . . . . . . . . . . . . . . 4
About This Guide . . . . . . . . . . . . . . . . . . . . . . . . . . . . . . . . . . . . . . . . . . . . . . . . . . . . . . . . . . . . . . . . . . . . .5
Organization of Content . . . . . . . . . . . . . . . . . . . . . . . . . . . . . . . . . . . . . . . . . . . . . . . . . . 5
1 Polaris Vicra System Overview . . . . . . . . . . . . . . . . . . . . . . . . . . . . . . . . . . . . . . . . . . . . . . . . . . . . . . . . 6
1.1 Introduction . . . . . . . . . . . . . . . . . . . . . . . . . . . . . . . . . . . . . . . . . . . . . . . . . . . . . . . . . 6
1.2 Position Sensor . . . . . . . . . . . . . . . . . . . . . . . . . . . . . . . . . . . . . . . . . . . . . . . . . . . . . . 7
1.3 Host USB Converter . . . . . . . . . . . . . . . . . . . . . . . . . . . . . . . . . . . . . . . . . . . . . . . . . 11
1.4 Power Adapter . . . . . . . . . . . . . . . . . . . . . . . . . . . . . . . . . . . . . . . . . . . . . . . . . . . . . . 12
1.5 Cables . . . . . . . . . . . . . . . . . . . . . . . . . . . . . . . . . . . . . . . . . . . . . . . . . . . . . . . . . . . . 12
1.6 Polaris Vicra Tools . . . . . . . . . . . . . . . . . . . . . . . . . . . . . . . . . . . . . . . . . . . . . . . . . . 13
1.7 Polaris Vicra System Software . . . . . . . . . . . . . . . . . . . . . . . . . . . . . . . . . . . . . . . . . 14
1.8 Component Parts List . . . . . . . . . . . . . . . . . . . . . . . . . . . . . . . . . . . . . . . . . . . . . . . . 14
2 Setting Up the Polaris Vicra System . . . . . . . . . . . . . . . . . . . . . . . . . . . . . . . . . . . . . . . . . . . . . . . . . . . 15
2.1 Unpacking the Polaris Vicra System. . . . . . . . . . . . . . . . . . . . . . . . . . . . . . . . . . . . . 15
2.2 Polaris Vicra System Operating Environment . . . . . . . . . . . . . . . . . . . . . . . . . . . . . 15
2.3 Mounting the Position Sensor . . . . . . . . . . . . . . . . . . . . . . . . . . . . . . . . . . . . . . . . . . 18
2.4 Mounting the Host USB Converter . . . . . . . . . . . . . . . . . . . . . . . . . . . . . . . . . . . . . . 19
2.5 Connecting the Hardware . . . . . . . . . . . . . . . . . . . . . . . . . . . . . . . . . . . . . . . . . . . . . 19
2.6 Installing the Software. . . . . . . . . . . . . . . . . . . . . . . . . . . . . . . . . . . . . . . . . . . . . . . . 20
2.7 Installing the USB Drivers (Windows) . . . . . . . . . . . . . . . . . . . . . . . . . . . . . . . . . . . 21
2.8 Linux Support . . . . . . . . . . . . . . . . . . . . . . . . . . . . . . . . . . . . . . . . . . . . . . . . . . . . . . 22
2.9 Keyed Features . . . . . . . . . . . . . . . . . . . . . . . . . . . . . . . . . . . . . . . . . . . . . . . . . . . . . 24
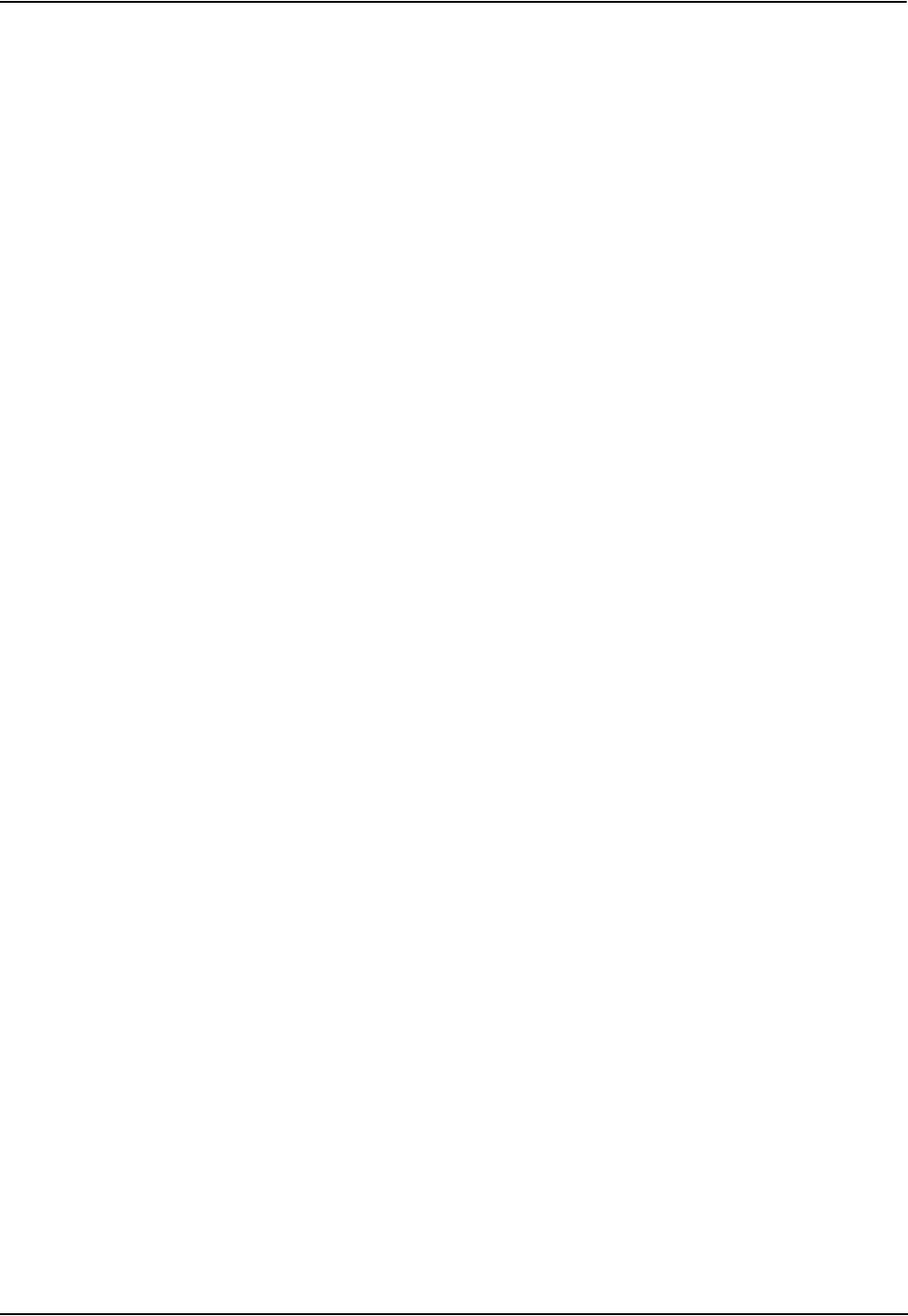
Table of Contents
ii Polaris Vicra User Guide - Revision 2
3 How the Polaris Vicra System Works . . . . . . . . . . . . . . . . . . . . . . . . . . . . . . . . . . . . . . . . . . . . . . . . . . 25
3.1 Introduction . . . . . . . . . . . . . . . . . . . . . . . . . . . . . . . . . . . . . . . . . . . . . . . . . . . . . . . .25
3.2 Information Returned by the Polaris Vicra System . . . . . . . . . . . . . . . . . . . . . . . . . . 25
3.3 Global Coordinate System and Measurement Volume . . . . . . . . . . . . . . . . . . . . . . . 26
3.4 Marker Detection and Tool Tracking. . . . . . . . . . . . . . . . . . . . . . . . . . . . . . . . . . . . . 28
3.5 Polaris Vicra System Tools . . . . . . . . . . . . . . . . . . . . . . . . . . . . . . . . . . . . . . . . . . . . 30
3.6 Tool Definition File . . . . . . . . . . . . . . . . . . . . . . . . . . . . . . . . . . . . . . . . . . . . . . . . . . 31
3.7 Tool Tracking Parameters . . . . . . . . . . . . . . . . . . . . . . . . . . . . . . . . . . . . . . . . . . . . . 31
3.8 Tool Tip Offset. . . . . . . . . . . . . . . . . . . . . . . . . . . . . . . . . . . . . . . . . . . . . . . . . . . . . . 35
3.9 Reference Tool. . . . . . . . . . . . . . . . . . . . . . . . . . . . . . . . . . . . . . . . . . . . . . . . . . . . . . 36
3.10 Stray Marker Reporting . . . . . . . . . . . . . . . . . . . . . . . . . . . . . . . . . . . . . . . . . . . . . . 37
3.11 Phantom Markers . . . . . . . . . . . . . . . . . . . . . . . . . . . . . . . . . . . . . . . . . . . . . . . . . . . 38
3.12 Passive Sphere Markers . . . . . . . . . . . . . . . . . . . . . . . . . . . . . . . . . . . . . . . . . . . . . . 38
3.13 Active Markers. . . . . . . . . . . . . . . . . . . . . . . . . . . . . . . . . . . . . . . . . . . . . . . . . . . . . 39
3.14 Filter Spectral Response. . . . . . . . . . . . . . . . . . . . . . . . . . . . . . . . . . . . . . . . . . . . . . 39
3.15 Data Transmission Rate . . . . . . . . . . . . . . . . . . . . . . . . . . . . . . . . . . . . . . . . . . . . . . 40
3.16 Serial Port Emulation . . . . . . . . . . . . . . . . . . . . . . . . . . . . . . . . . . . . . . . . . . . . . . . . 40
4 Using the Polaris Vicra System . . . . . . . . . . . . . . . . . . . . . . . . . . . . . . . . . . . . . . . . . . . . . . . . . . . . . . . 41
4.1 Getting Started: Tracking Tools. . . . . . . . . . . . . . . . . . . . . . . . . . . . . . . . . . . . . . . . . 41
4.2 Information and Error Flags. . . . . . . . . . . . . . . . . . . . . . . . . . . . . . . . . . . . . . . . . . . . 42
4.3 Setting a Tool as Reference . . . . . . . . . . . . . . . . . . . . . . . . . . . . . . . . . . . . . . . . . . . . 44
4.4 Determining the Tool Tip Offset . . . . . . . . . . . . . . . . . . . . . . . . . . . . . . . . . . . . . . . . 45
5 Error Flags and Codes . . . . . . . . . . . . . . . . . . . . . . . . . . . . . . . . . . . . . . . . . . . . . . . . . . . . . . . . . . . . . . 48
5.1 Missing and Disabled Transformations . . . . . . . . . . . . . . . . . . . . . . . . . . . . . . . . . . . 48
5.2 Tracking Errors and Flags . . . . . . . . . . . . . . . . . . . . . . . . . . . . . . . . . . . . . . . . . . . . . 49
5.3 Polaris Vicra System LEDs and Audio Codes. . . . . . . . . . . . . . . . . . . . . . . . . . . . . . 51
6 Maintenance . . . . . . . . . . . . . . . . . . . . . . . . . . . . . . . . . . . . . . . . . . . . . . . . . . . . . . . . . . . . . . . . . . . . . . 52
6.1 Position Sensor. . . . . . . . . . . . . . . . . . . . . . . . . . . . . . . . . . . . . . . . . . . . . . . . . . . . . . 52
6.2 Cables and Connectors. . . . . . . . . . . . . . . . . . . . . . . . . . . . . . . . . . . . . . . . . . . . . . . . 53
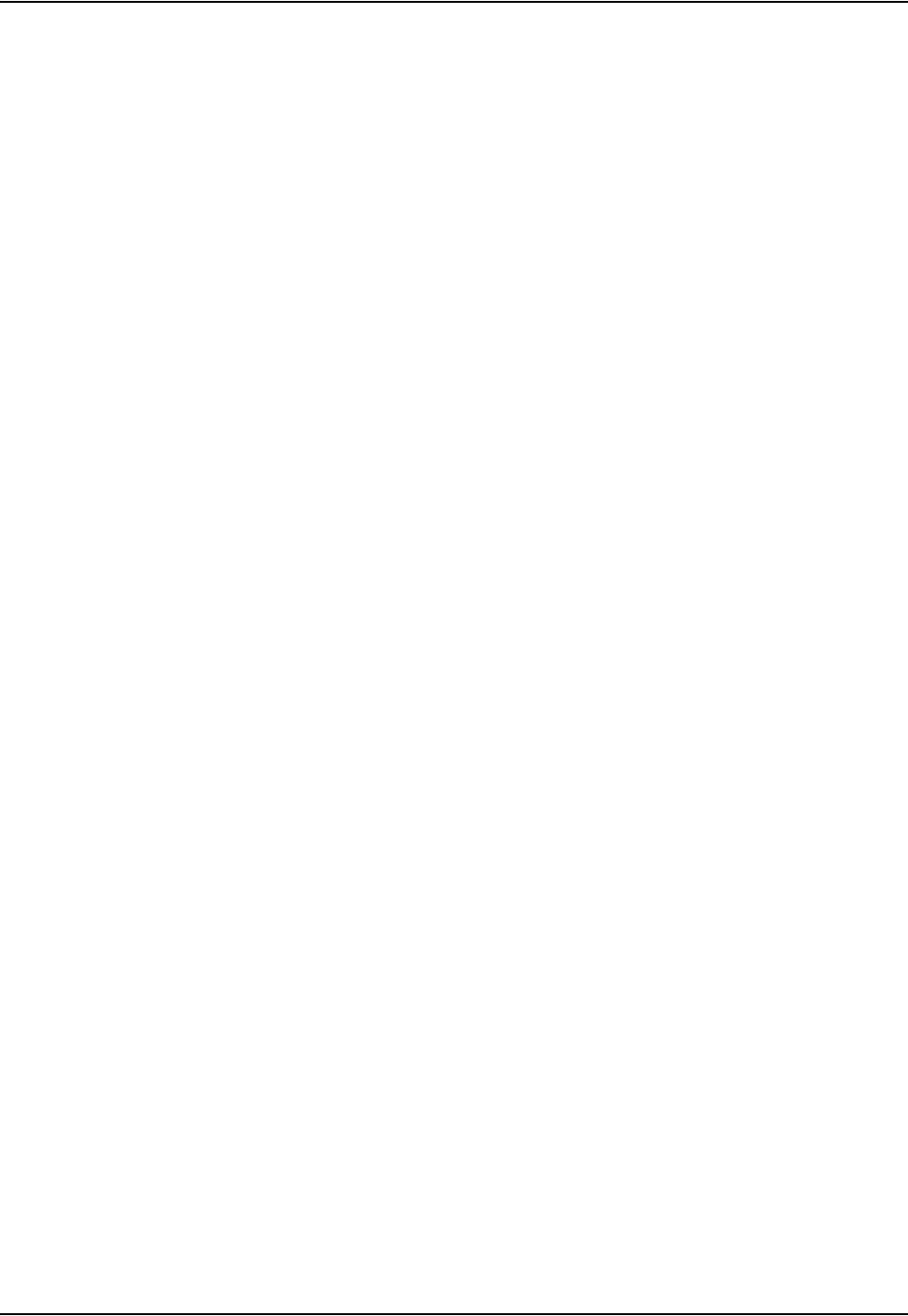
Table of Contents
Polaris Vicra User Guide - Revision 2 iii
7 Setting the Infrared Light Sensitivity. . . . . . . . . . . . . . . . . . . . . . . . . . . . . . . . . . . . . . . . . . . . . . . . . . . 54
7.1 IR Light Sensitivity Levels . . . . . . . . . . . . . . . . . . . . . . . . . . . . . . . . . . . . . . . . . . . . 54
7.2 Changing the Sensitivity Level . . . . . . . . . . . . . . . . . . . . . . . . . . . . . . . . . . . . . . . . . 55
8 Calibration and Firmware . . . . . . . . . . . . . . . . . . . . . . . . . . . . . . . . . . . . . . . . . . . . . . . . . . . . . . . . . . . . 57
8.1 Checking the Calibration of the Polaris Vicra System . . . . . . . . . . . . . . . . . . . . . . . 57
8.2 Updating the Firmware . . . . . . . . . . . . . . . . . . . . . . . . . . . . . . . . . . . . . . . . . . . . . . . 58
9 Approvals . . . . . . . . . . . . . . . . . . . . . . . . . . . . . . . . . . . . . . . . . . . . . . . . . . . . . . . . . . . . . . . . . . . . . . . . .59
9.1 Optical Radiation Safety . . . . . . . . . . . . . . . . . . . . . . . . . . . . . . . . . . . . . . . . . . . . . . 59
10 Classifications . . . . . . . . . . . . . . . . . . . . . . . . . . . . . . . . . . . . . . . . . . . . . . . . . . . . . . . . . . . . . . . . . . . . 60
11 Technical Specifications. . . . . . . . . . . . . . . . . . . . . . . . . . . . . . . . . . . . . . . . . . . . . . . . . . . . . . . . . . . . 61
11.1 Position Sensor . . . . . . . . . . . . . . . . . . . . . . . . . . . . . . . . . . . . . . . . . . . . . . . . . . . . 61
11.2 Host USB Converter . . . . . . . . . . . . . . . . . . . . . . . . . . . . . . . . . . . . . . . . . . . . . . . . 62
11.3 Power Adapter . . . . . . . . . . . . . . . . . . . . . . . . . . . . . . . . . . . . . . . . . . . . . . . . . . . . . 63
12 Electromagnetic Compatibility. . . . . . . . . . . . . . . . . . . . . . . . . . . . . . . . . . . . . . . . . . . . . . . . . . . . . . . 64
12.1 Electrostatic Discharge . . . . . . . . . . . . . . . . . . . . . . . . . . . . . . . . . . . . . . . . . . . . . . 64
12.2 Cables and Accessories . . . . . . . . . . . . . . . . . . . . . . . . . . . . . . . . . . . . . . . . . . . . . . 64
12.3 Guidance and Manufacturer's Declaration - Electromagnetic Emissions . . . . . . . . 65
12.4 Guidance and Manufacturer’s Declaration - Electromagnetic Immunity . . . . . . . . 65
12.5 Recommended Separation Distances . . . . . . . . . . . . . . . . . . . . . . . . . . . . . . . . . . . 68
12.6 RF Emissions. . . . . . . . . . . . . . . . . . . . . . . . . . . . . . . . . . . . . . . . . . . . . . . . . . . . . . 68
13 Troubleshooting. . . . . . . . . . . . . . . . . . . . . . . . . . . . . . . . . . . . . . . . . . . . . . . . . . . . . . . . . . . . . . . . . . . 70
13.1 Introduction . . . . . . . . . . . . . . . . . . . . . . . . . . . . . . . . . . . . . . . . . . . . . . . . . . . . . . . 70
13.2 System Indications. . . . . . . . . . . . . . . . . . . . . . . . . . . . . . . . . . . . . . . . . . . . . . . . . . 70
13.3 NDI ToolBox Error Messages. . . . . . . . . . . . . . . . . . . . . . . . . . . . . . . . . . . . . . . . . 72
13.4 Common Problems . . . . . . . . . . . . . . . . . . . . . . . . . . . . . . . . . . . . . . . . . . . . . . . . . 74

Table of Contents
iv Polaris Vicra User Guide - Revision 2
14 Return Procedure and Warranty . . . . . . . . . . . . . . . . . . . . . . . . . . . . . . . . . . . . . . . . . . . . . . . . . . . . . 77
14.1 Return Procedure . . . . . . . . . . . . . . . . . . . . . . . . . . . . . . . . . . . . . . . . . . . . . . . . . . . 77
14.2 Warranty. . . . . . . . . . . . . . . . . . . . . . . . . . . . . . . . . . . . . . . . . . . . . . . . . . . . . . . . . .77
15 Abbreviations and Acronyms . . . . . . . . . . . . . . . . . . . . . . . . . . . . . . . . . . . . . . . . . . . . . . . . . . . . . . . 79
16 Equipment Symbols . . . . . . . . . . . . . . . . . . . . . . . . . . . . . . . . . . . . . . . . . . . . . . . . . . . . . . . . . . . . . . . 80
17 Glossary. . . . . . . . . . . . . . . . . . . . . . . . . . . . . . . . . . . . . . . . . . . . . . . . . . . . . . . . . . . . . . . . . . . . . . . . . 81
18 Declaration of Conformity . . . . . . . . . . . . . . . . . . . . . . . . . . . . . . . . . . . . . . . . . . . . . . . . . . . . . . . . . . 84
Appendix A Polaris Vicra Calibration Performance and Methodology . . . . . . . . . . . . . . . . . . . . . . . . 85
A.1 Polaris Vicra Performance . . . . . . . . . . . . . . . . . . . . . . . . . . . . . . . . . . . . . . . . . . . 85
A.2 Calibration Method . . . . . . . . . . . . . . . . . . . . . . . . . . . . . . . . . . . . . . . . . . . . . . . . . 85
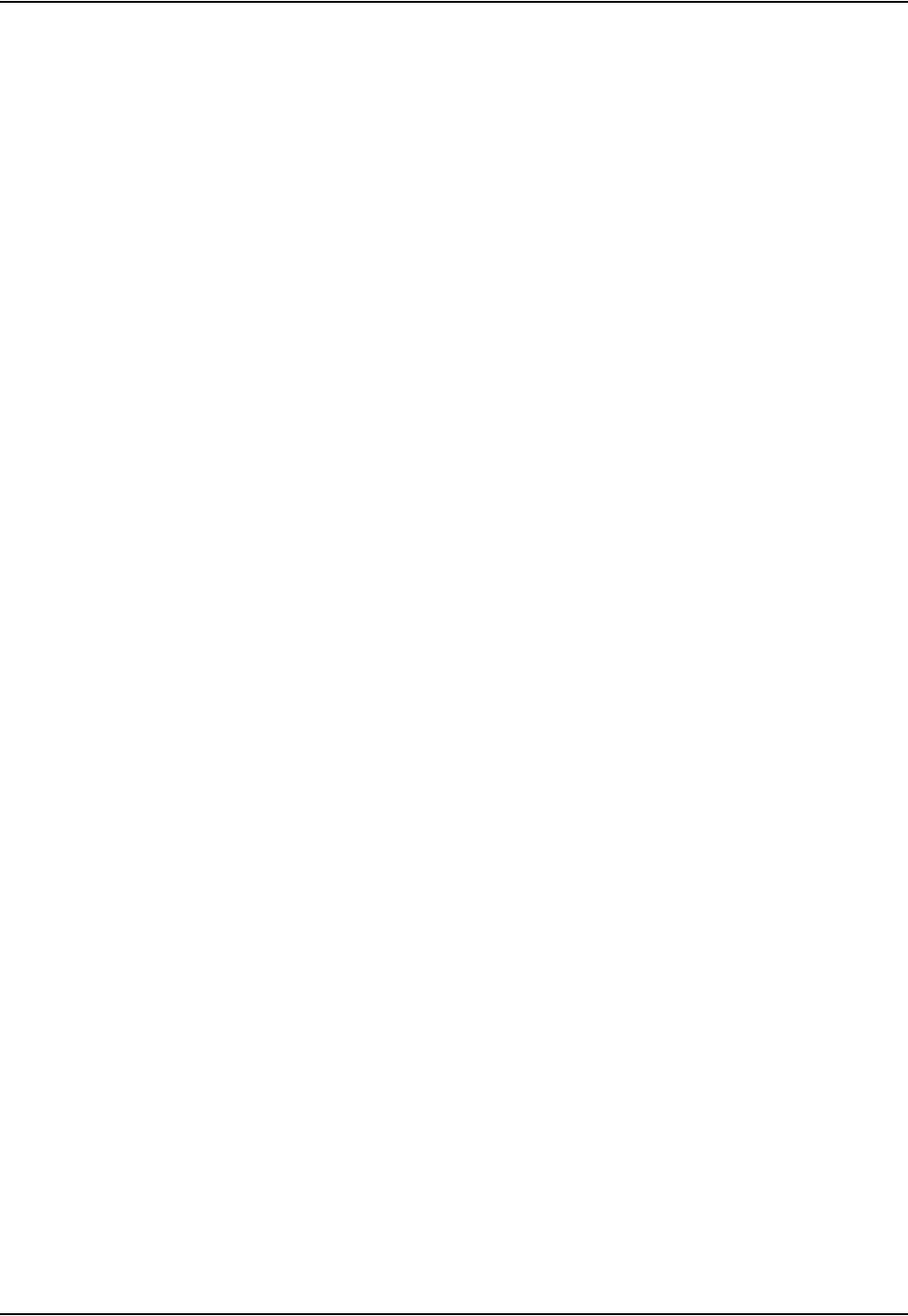
List of Figures
Polaris Vicra User Guide - Revision 2 v
List of Figures
Figure 1-1 Polaris Vicra Measurement Volume . . . . . . . . . . . . . . . . . . . . . . . . . . . . . . . . . . . . . . 6
Figure 1-2 Polaris Vicra System Setup . . . . . . . . . . . . . . . . . . . . . . . . . . . . . . . . . . . . . . . . . . . . .7
Figure 1-3 Position Sensor - Front View . . . . . . . . . . . . . . . . . . . . . . . . . . . . . . . . . . . . . . . . . . . .8
Figure 1-4 Position Sensor - Rear View . . . . . . . . . . . . . . . . . . . . . . . . . . . . . . . . . . . . . . . . . . . .9
Figure 1-5 Position Sensor - Serial Number Label . . . . . . . . . . . . . . . . . . . . . . . . . . . . . . . . . . . . 9
Figure 1-6 Host USB Converter. . . . . . . . . . . . . . . . . . . . . . . . . . . . . . . . . . . . . . . . . . . . . . . . . . 11
Figure 1-7 Host USB Converter Serial Number label . . . . . . . . . . . . . . . . . . . . . . . . . . . . . . . . . 12
Figure 1-8 Sample Passive Tool . . . . . . . . . . . . . . . . . . . . . . . . . . . . . . . . . . . . . . . . . . . . . . . . . 13
Figure 2-1 Position Sensor Mounting Details . . . . . . . . . . . . . . . . . . . . . . . . . . . . . . . . . . . . . . . 18
Figure 2-2 Host USB Converter Mounting Details . . . . . . . . . . . . . . . . . . . . . . . . . . . . . . . . . . . 19
Figure 2-3 Connecting Cables to the Host USB Converter . . . . . . . . . . . . . . . . . . . . . . . . . . . . . 20
Figure 3-1 Position Sensor Global Coordinate System . . . . . . . . . . . . . . . . . . . . . . . . . . . . . . . . 26
Figure 3-2 Characterized Measurement Volume . . . . . . . . . . . . . . . . . . . . . . . . . . . . . . . . . . . . . 27
Figure 3-3 Determining a Marker Position . . . . . . . . . . . . . . . . . . . . . . . . . . . . . . . . . . . . . . . . . 29
Figure 3-4 Marker With Marker Normal . . . . . . . . . . . . . . . . . . . . . . . . . . . . . . . . . . . . . . . . . . . 32
Figure 3-5 Maximum Marker Angle . . . . . . . . . . . . . . . . . . . . . . . . . . . . . . . . . . . . . . . . . . . . . . 32
Figure 3-6 Flowchart of Tool Tracking Parameters Use . . . . . . . . . . . . . . . . . . . . . . . . . . . . . . . 34
Figure 3-7 Sample Calibrator. . . . . . . . . . . . . . . . . . . . . . . . . . . . . . . . . . . . . . . . . . . . . . . . . . . . 36
Figure 3-8 Phantom Markers . . . . . . . . . . . . . . . . . . . . . . . . . . . . . . . . . . . . . . . . . . . . . . . . . . . . 38
Figure 3-9 Filter Spectral Response. . . . . . . . . . . . . . . . . . . . . . . . . . . . . . . . . . . . . . . . . . . . . . . 40
Figure 4-1 Tool Tracking Window . . . . . . . . . . . . . . . . . . . . . . . . . . . . . . . . . . . . . . . . . . . . . . . 42
Figure 4-2 Partially Out of Volume Flag . . . . . . . . . . . . . . . . . . . . . . . . . . . . . . . . . . . . . . . . . . . 43
Figure 4-3 Markers Information Pane - Missing Marker. . . . . . . . . . . . . . . . . . . . . . . . . . . . . . . 43
Figure 4-4 Transformation Pane - Too Few Markers . . . . . . . . . . . . . . . . . . . . . . . . . . . . . . . . . 43
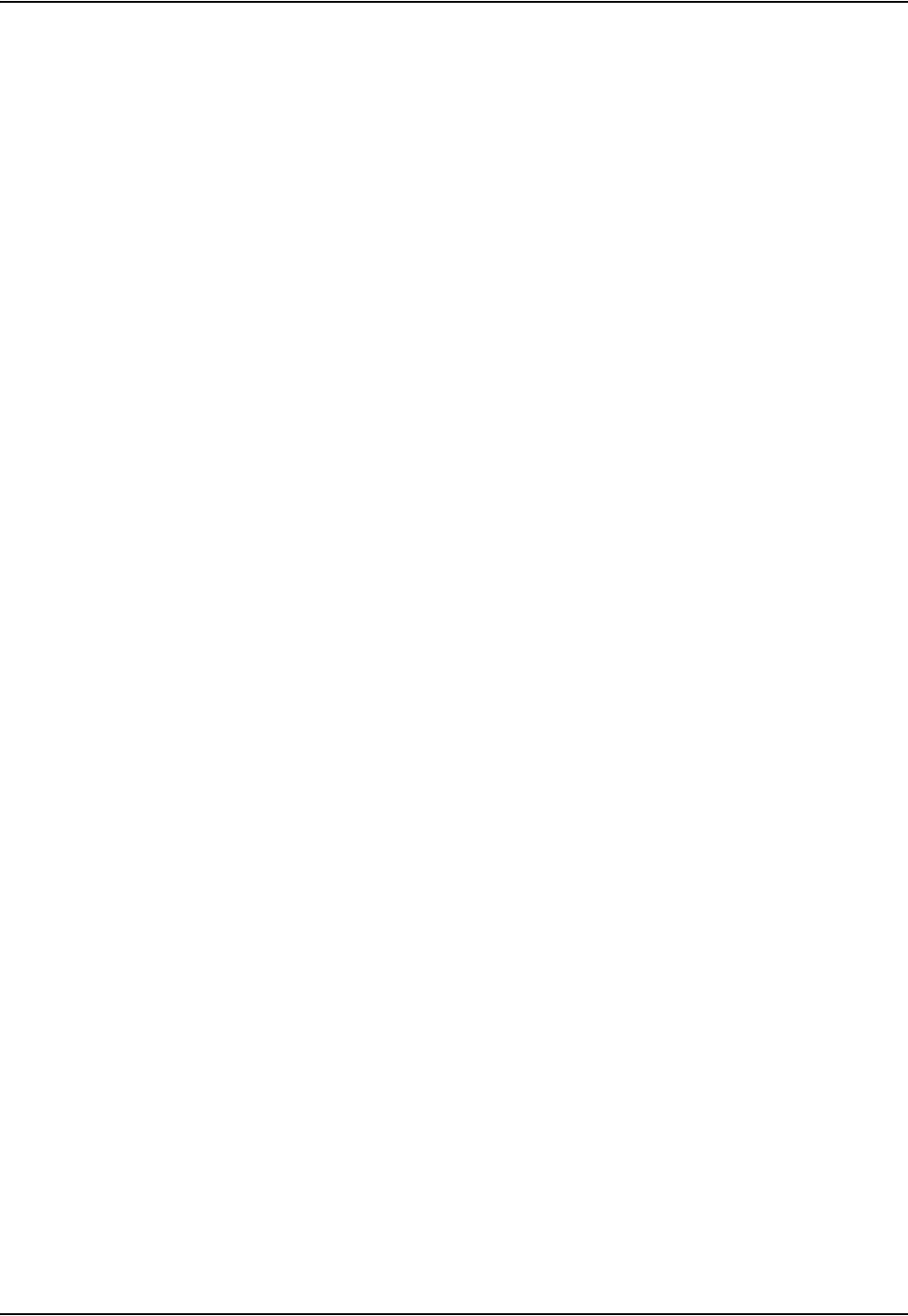
List of Figures
vi Polaris Vicra User Guide - Revision 2
Figure 4-5 Markers Information Pane - Exceeded Max Marker Angle . . . . . . . . . . . . . . . . . . . . 44
Figure 4-6 Selecting a Reference Tool. . . . . . . . . . . . . . . . . . . . . . . . . . . . . . . . . . . . . . . . . . . . .44
Figure 4-7 Selecting a Tool to Pivot . . . . . . . . . . . . . . . . . . . . . . . . . . . . . . . . . . . . . . . . . . . . . . 46
Figure 4-8 Pivoting Technique. . . . . . . . . . . . . . . . . . . . . . . . . . . . . . . . . . . . . . . . . . . . . . . . . . . 47
Figure 4-9 Pivot Result Dialog . . . . . . . . . . . . . . . . . . . . . . . . . . . . . . . . . . . . . . . . . . . . . . . . . . 47
Figure 6-1 How to Avoid Stressed Cables. . . . . . . . . . . . . . . . . . . . . . . . . . . . . . . . . . . . . . . . . . 53
Figure 7-1 Infrared Light Sensitivity Levels . . . . . . . . . . . . . . . . . . . . . . . . . . . . . . . . . . . . . . . . 55
Figure 13-1 Host USB Converter - Error LED Fault Chart . . . . . . . . . . . . . . . . . . . . . . . . . . . . . 72
Figure 18-1 EC Declaration of Conformity . . . . . . . . . . . . . . . . . . . . . . . . . . . . . . . . . . . . . . . . . 84
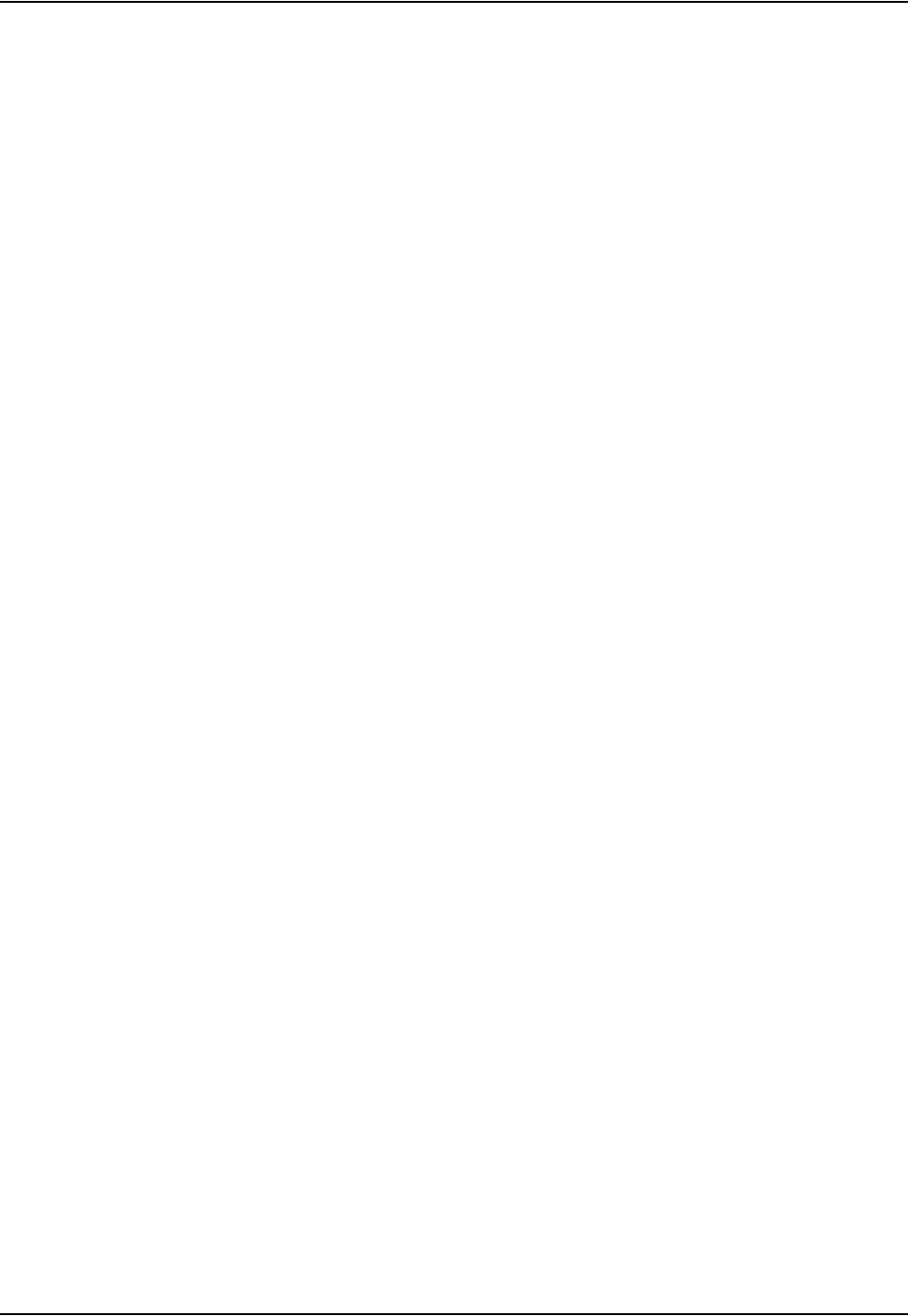
List of Tables
Polaris Vicra User Guide - Revision 2 vii
List of Tables
Table 1-1 Component Parts List . . . . . . . . . . . . . . . . . . . . . . . . . . . . . . . . . . . . . . . . . . . . . . . . . 14
Table 9-1 Electrical Safety . . . . . . . . . . . . . . . . . . . . . . . . . . . . . . . . . . . . . . . . . . . . . . . . . . . . . 59
Table 9-2 Electromagnetic Compatibility . . . . . . . . . . . . . . . . . . . . . . . . . . . . . . . . . . . . . . . . . . 59
Table 10-1 Classifications . . . . . . . . . . . . . . . . . . . . . . . . . . . . . . . . . . . . . . . . . . . . . . . . . . . . . . 60
Table 11-1 Position Sensor - Technical Specifications . . . . . . . . . . . . . . . . . . . . . . . . . . . . . . . . 61
Table 11-2 Position Sensor - Operating Environmental Conditions . . . . . . . . . . . . . . . . . . . . . . 61
Table 11-3 Position Sensor - Transportation and Storage Environmental Conditions . . . . . . . . 62
Table 11-4 Host USB Converter - Technical Specifications. . . . . . . . . . . . . . . . . . . . . . . . . . . . 62
Table 11-5 Host USB Converter - Operating Environmental Conditions. . . . . . . . . . . . . . . . . . 62
Table 11-6 Host USB Converter - Transportation and Storage Environmental Conditions . . . . 62
Table 11-7 Power Adapter - Technical Specifications . . . . . . . . . . . . . . . . . . . . . . . . . . . . . . . . 63
Table 11-8 Power Adapter - Operating Environmental Conditions . . . . . . . . . . . . . . . . . . . . . . 63
Table 11-9 Power Adapter - Transportation and Storage Environmental Conditions . . . . . . . . 63
Table 12-1 Cables and Accessories That Maintain Compliance . . . . . . . . . . . . . . . . . . . . . . . . . 64
Table 12-2 Manufacturer’s Declaration for Electromagnetic Emissions . . . . . . . . . . . . . . . . . . 65
Table 12-3 Electromagnetic Immunity . . . . . . . . . . . . . . . . . . . . . . . . . . . . . . . . . . . . . . . . . . . . 65
Table 12-4 Electromagnetic Immunity - Not Life Supporting . . . . . . . . . . . . . . . . . . . . . . . . . . 67
Table 12-5 Recommended Separation Distances . . . . . . . . . . . . . . . . . . . . . . . . . . . . . . . . . . . . 68
Table 13-1 System Visual and Audio Indications . . . . . . . . . . . . . . . . . . . . . . . . . . . . . . . . . . . . 70
Table 13-2 NDI ToolBox Error Messages . . . . . . . . . . . . . . . . . . . . . . . . . . . . . . . . . . . . . . . . . 73
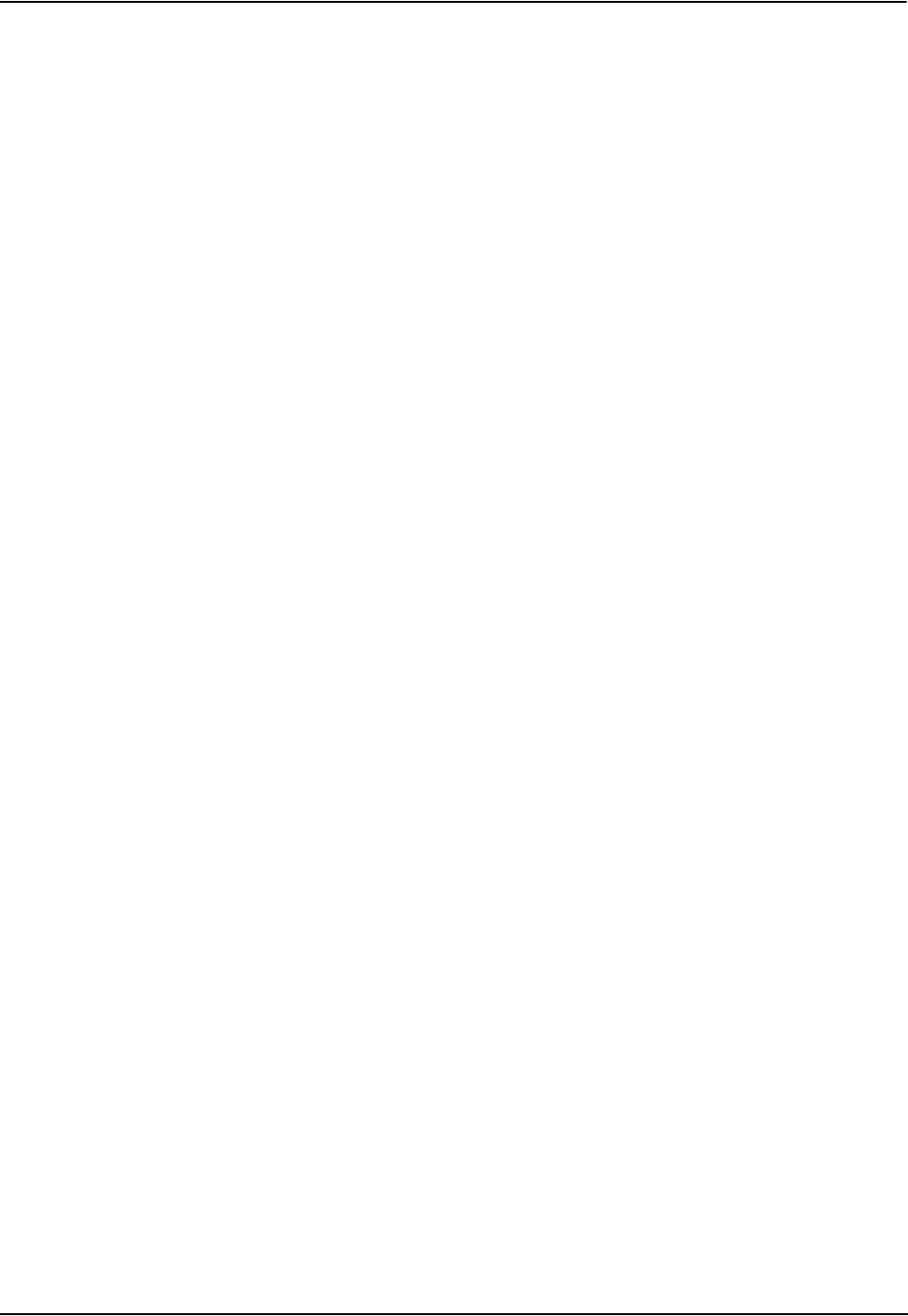
List of Tables
viii Polaris Vicra User Guide - Revision 2
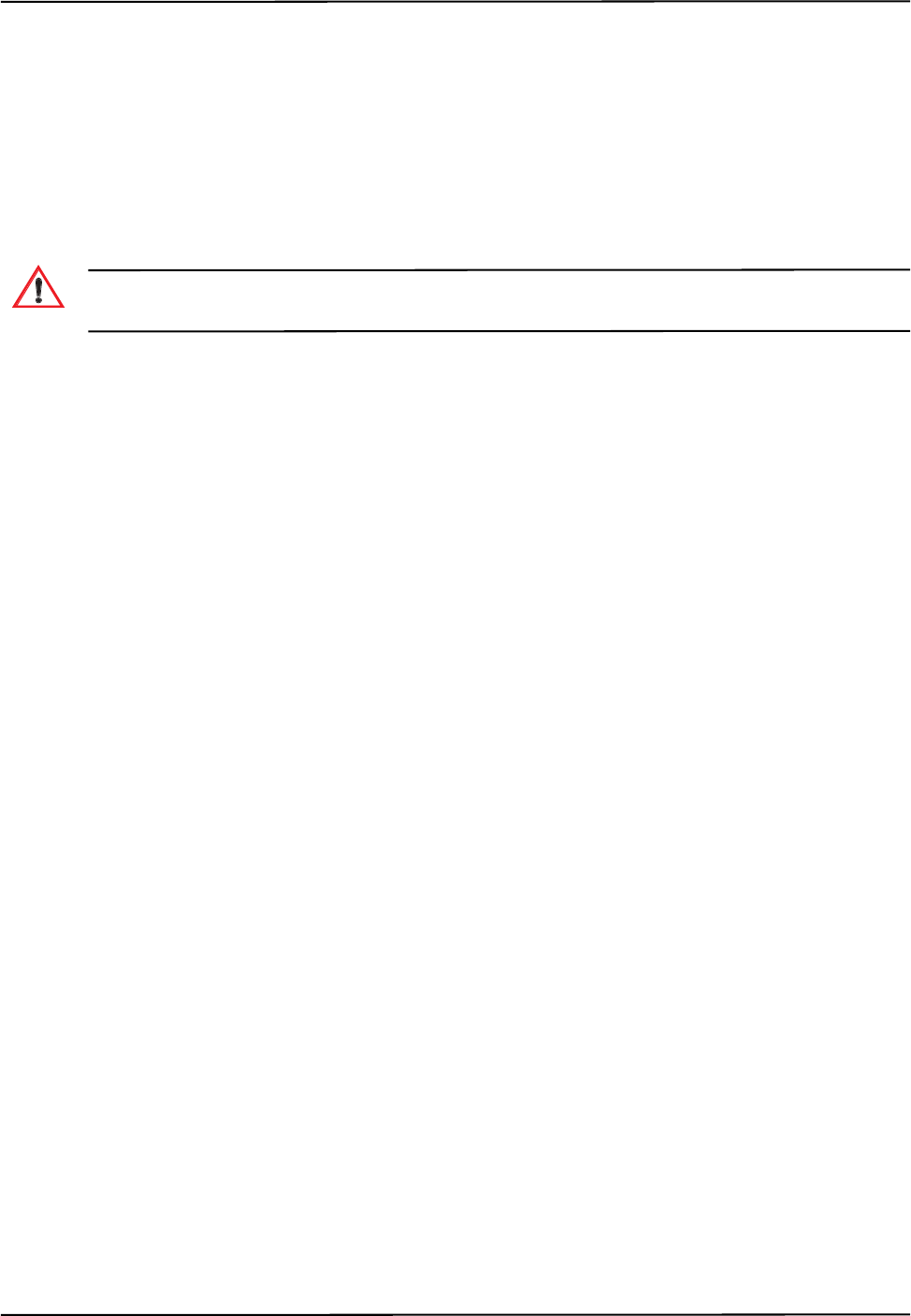
Read Me First!
Polaris Vicra User Guide - Revision 2 1
Read Me First!
This guide provides detailed information about using the Polaris® VicraTM Optical Tracking
System. Read this section before continuing with the rest of the guide.
Warnings
In all NDI documentation, warnings are marked by this symbol. Follow the information in the accompanying
paragraph to avoid personal injury.
1. Do not use the Polaris Vicra System in the presence of flammable materials such as anaesthetics,
solvents, cleaning agents, and endogenous gases. Flammable materials may ignite, causing
personal injury or death.
2. Do not transport or store the Position Sensor outside the recommended storage temperature
range, as this may cause the system to go out of calibration. Reliance on data provided by an out
of calibration Position Sensor may lead to inaccurate conclusions and may cause personal
injury. A calibration procedure must be performed before using the Position Sensor after it has
been transported or stored outside the recommended storage temperature range.
3. Do not protect or shield either the Position Sensor or tools with methods not approved by NDI.
Non-approved methods will interrupt the optical path and degrade the performance of the
system. Reliance on data provided by a Position Sensor without an uninterrupted optical path
may lead to inaccurate conclusions. If your application involves personal safety, inaccurate
conclusions increase the possibility of personal injury.
4. Radio frequency communications equipment, including portable and mobile devices, may affect
the Polaris Vicra System and result in personal injury.
5. Do not use cables or accessories, other than those listed in this guide. The use of other cables or
accessories may result in increased emissions and/or decreased immunity of the Polaris Vicra
System and may result in personal injury.
6. Do not incorporate non-NDI components with the Polaris Vicra System. The accuracy of results
produced by applications that incorporate non-NDI components with the Polaris Vicra System is
unknown. If your application involves personal safety, reliance on these results may increase
the possibility of personal injury.
7. All user maintenance must be done by appropriately trained personnel. Individual components
of the Polaris Vicra System contain no user-serviceable parts. Maintenance by untrained
personnel may present an electric shock hazard.
8. Do not attempt to bypass the grounding prong on the power cord by using a three-prong to two-
prong adapter. The system must be properly grounded to ensure safe operation. Failure to do so
presents an electric shock hazard.
9. Do not immerse any part of the Polaris Vicra System or allow fluid to enter the equipment. If
fluids enter any part of the system they may damage it and present a risk of personal injury.
Warning!
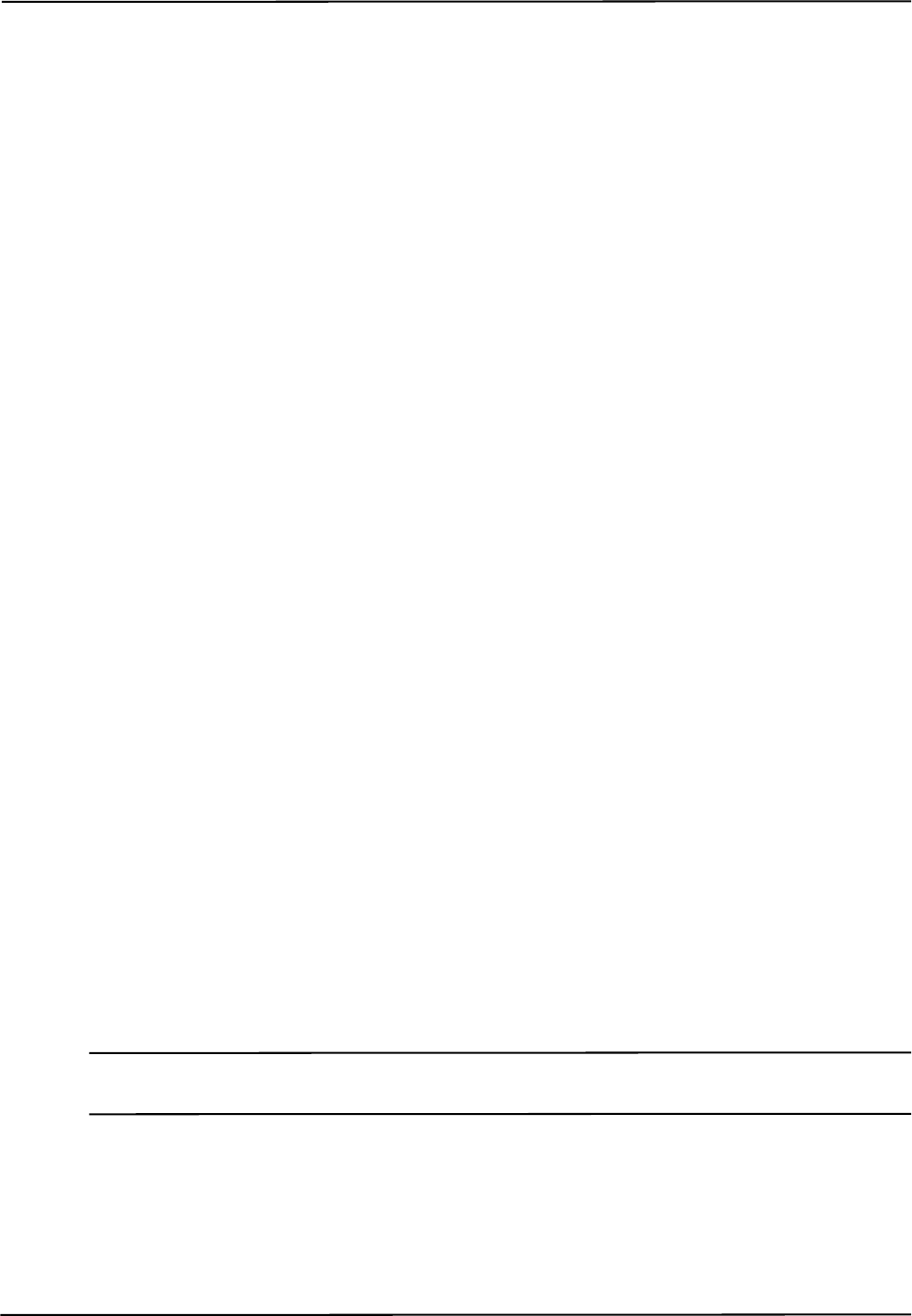
Read Me First!
2Polaris Vicra User Guide - Revision 2
10. Do not sterilize the Polaris Vicra Position Sensor as this may cause irreversible damage to its
components. Reliance on data provided by a damaged Position Sensor may lead to inaccurate
conclusions. If your application involves personal safety, these inaccurate conclusions increase
the possibility of personal injury.
11. Do not use the Position Sensor without inspecting it for cleanliness and damage both before and
during a procedure. Reliance on data provided by an unclean or damaged Position Sensor may
lead to inaccurate conclusions. If your application involves personal safety, inaccurate
conclusions increase the possibility of personal injury.
12. Do not use the Polaris Vicra System for absolute measurements; the system is designed for
relative measurements only. Treating measurements as absolute may result in an incorrect
interpretation of results. If your application involves personal safety, these incorrect
interpretations increase the possibility of personal injury.
13. Do not use a wireless tool whose design does not conform to the Polaris Vicra System's unique
geometry constraints. When a Polaris Vicra System attempts to track more than one wireless
tool in the measurement volume, these unique geometry constraints ensure that they are
distinguishable from each other. Reliance on data produced by two indistinguishable tools can
lead to inaccurate conclusions. If your application involves personal safety, these inaccurate
conclusions increase the possibility of personal injury.
14. Do not use a tool with a tip without first performing a pivot procedure to verify the tip offset.
Reliance on data produced by a tool with an inaccurate tip offset may lead to inaccurate
conclusions. If your application involves personal safety, these inaccurate conclusions increase
the possibility of personal injury.
15. Do not use markers without inspecting them for cleanliness and damage both before and during
a procedure. Reliance on data produced by unclean or damaged markers may lead to inaccurate
conclusions. If your application involves personal safety, inaccurate conclusions increase the
possibility of personal injury.
16. Do not obstruct the normal flow of air around the Position Sensor (for example, draping or
bagging the Position Sensor). Doing so will affect the Position Sensor's operational
environment, possibly beyond its recommended thresholds. Reliance on data provided by a
Position Sensor that is outside of recommended thresholds may lead to inaccurate conclusions.
If your application involves personal safety, inaccurate conclusions increase the possibility of
personal injury.
Cautions
Caution! In all NDI documentation, cautions are marked with the word “Caution!”. Follow the information in the
accompanying paragraph to avoid damage to equipment.
1. To ship the Polaris Vicra System, repack it in the original containers with all protective
packaging. The provided packaging is designed to prevent damage to the equipment.
2. Make sure that the mains power is disconnected before connecting or disconnecting cables.
Failure to do so may cause damage to the equipment.
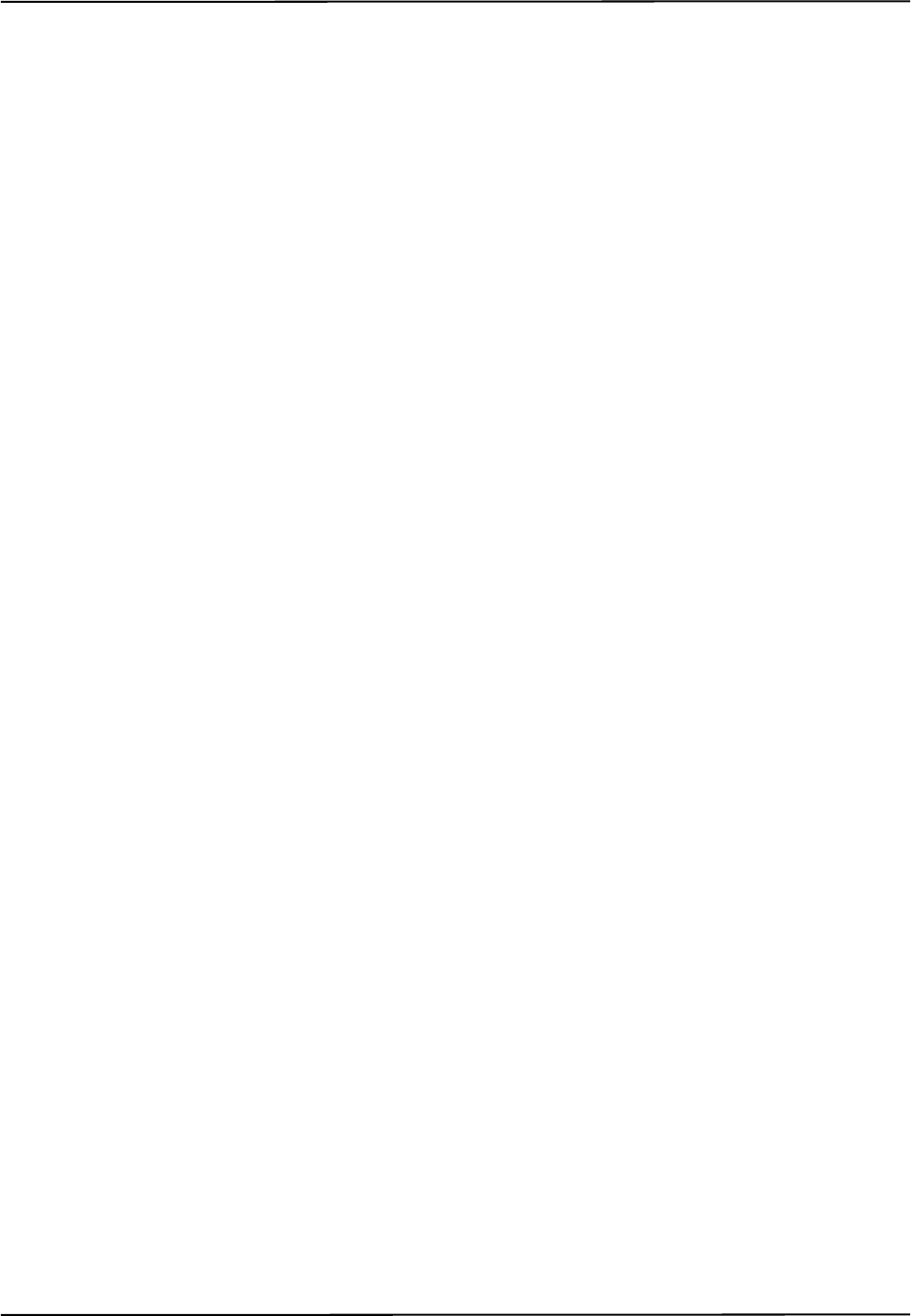
Read Me First!
Polaris Vicra User Guide - Revision 2 3
3. Always place the Position Sensor on a rigid support system. If not supported, the Position
Sensor may fall which will affect the calibration and damage the Position Sensor.
4. Use only 70% isopropanol and a lens cleaning solution formulated for multi-coated lenses (for
example, AR66) to clean the Position Sensor. Other fluids may cause damage to the illuminator
filters. Do not use any paper products for cleaning. Paper products may cause scratches on the
illuminator filters.
Disclaimers
1. Read the entire “Polaris Vicra User Guide” before attempting to operate the Polaris Vicra
System.
2. This device complies with Part 15 of the FCC Rules. Operation is subject to the following two
conditions:
a) this device may not cause harmful interference, and
b) this device must accept any interference received, including interference that may cause
undesired operation.
See Section 12.6 on page 68 for further information.
3. The user must determine the suitability of the Polaris Vicra System for their own application.
4. The Underwriters Laboratories Inc. (UL) recognition of the Polaris Vicra System includes only
the Polaris Vicra Position Sensor, Host USB Converter and the APS APS49ES-24021/Hitron
HES49ES-24021 power adapter. This investigation does not include the use of any other power
adapter or source with the Polaris Vicra System. Any such configuration will require further
investigation. If the Polaris Vicra System is used in a medical application, the final end-use
configuration must be independently investigated to the IEC 60601 family of standards and all
applicable national differences.
5. This equipment has been investigated with regard to safety from electrical shock and fire
hazard. The inspection authority has not investigated other physiological effects.
6. The Polaris Vicra Position Sensor requires a thermal stabilization period in order to provide
reliable measurements. Up to 10 minutes are required for the optical components to reach
operating temperature from a cold-start at normal room temperature. Testing should be
conducted to determine the thermal stabilization time necessary specific to your application
requirements. NDI recommends that a reference tool be used with its systems whenever
possible, to ensure there is no drift in the measurement caused by time, settling and/or
temperature.
7. Northern Digital Inc. has not investigated the implications of incorporating the Polaris Vicra
Position Sensor with an automatic position device, or any other automated closed loop systems.
Using the Polaris Vicra System in such an application is solely the responsibility of the user.
8. Northern Digital Inc. has not fully validated the Polaris Vicra Position Sensor in an MRI
environment. If the Polaris Vicra Position Sensor is used in an MRI environment, the user is
responsible for determining the performance of the system, including accuracy, in an MRI
environment.
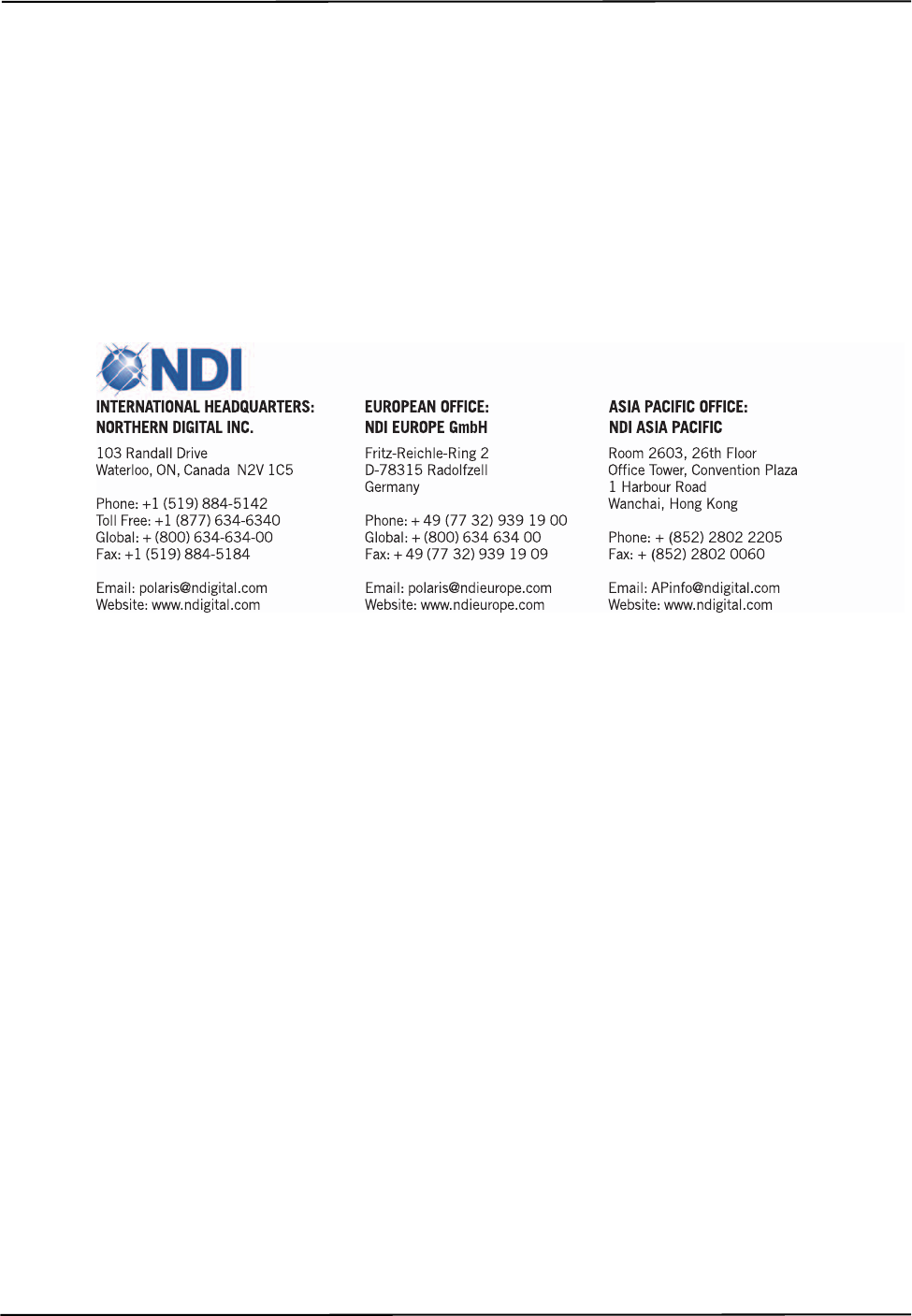
Read Me First!
4Polaris Vicra User Guide - Revision 2
9. The Polaris Vicra System emits IR light that may interfere with IR controlled devices, such as
operating room tables. It is recommended that you test the Polaris Vicra System if you intend to
use it in an environment where other IR controlled devices are in use.
10. The Polaris Vicra Position Sensor is designed to ingress protection level IP54, but this
evaluation was not included in the UL investigation.
Contact Information
If you have any questions regarding the content of this guide or the operation of this product, please
contact us:
Updates
NDI is committed to continuous improvements in the quality and versatility of its software and
hardware. To obtain the best results with your NDI system, check the NDI Support Site regularly for
update information:
http://support.ndigital.com
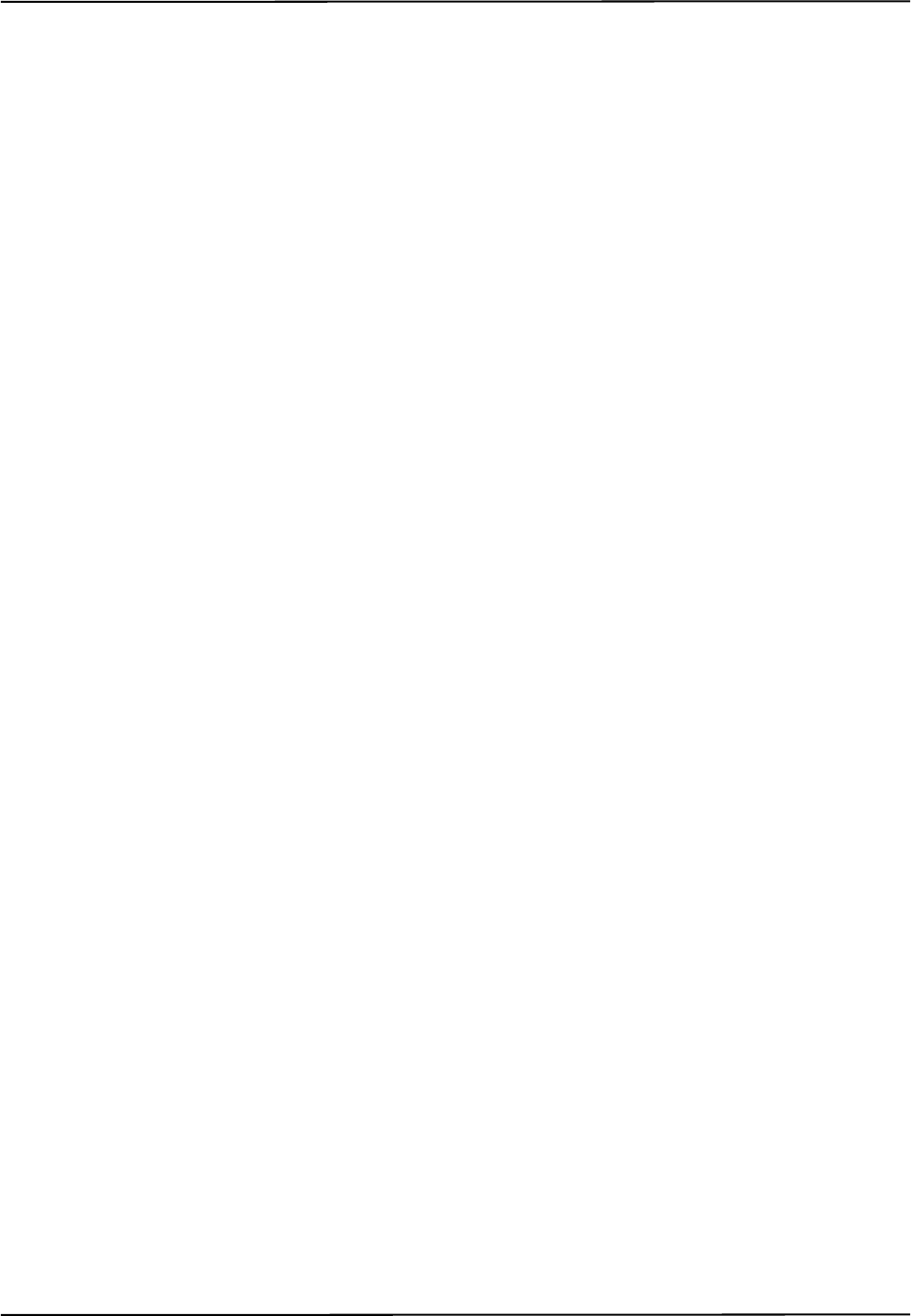
About This Guide
Polaris Vicra User Guide - Revision 2 5
About This Guide
Organization of Content
These sections explain how the system works and how to set it up for use. Read these sections
before using the Polaris Vicra System:
• Polaris Vicra System Overview
• Setting up the Polaris Vicra System
• How the Polaris Vicra System works
• Using the Polaris Vicra System
These sections provide information that may be useful during the operation of the system:
• Error Flags and Codes
• Setting the Infrared Light Sensitivity
• Maintenance
These sections may be needed for occasional reference; typically, you will not need to refer to them
during the day-to-day operation of the Polaris Vicra System:
• Calibration and Firmware
• Approvals and Classifications
• Technical Specifications
• Electromagnetic Compatibility
• Troubleshooting
• Return Procedure and Warranty
• Appendix A: Polaris Vicra Calibration Performance and Methodology

Polaris Vicra System Overview
6Polaris Vicra User Guide - Revision 2
1 Polaris Vicra System Overview
1.1 Introduction
The Polaris Vicra System is an optical measurement system that measures the 3D positions of either
active or passive markers affixed to application-specific tools. Using this information, the Polaris
Vicra System is able to determine the position and orientation of tools within a specific
measurement volume. A 3D representation of the measurement volume is shown below in
Figure 1-1.
Figure 1-1 Polaris Vicra Measurement Volume
The system has applications in a range of industries, including:
• medical
•dental
• research
The system consists of a Position Sensor, a Host USB Converter, a power adapter, and cables, see
Figure 1-2. A host computer is also required to operate the system. The host computer must be
approved to IEC60950 or IEC60601 standard and meet the following minimum specifications:
• Pentium Processor (>1GHz recommended)
• 256Mb Random Access Memory (RAM)
887 mm
557 mm
1336 mm
491 mm 938 mm
392 mm
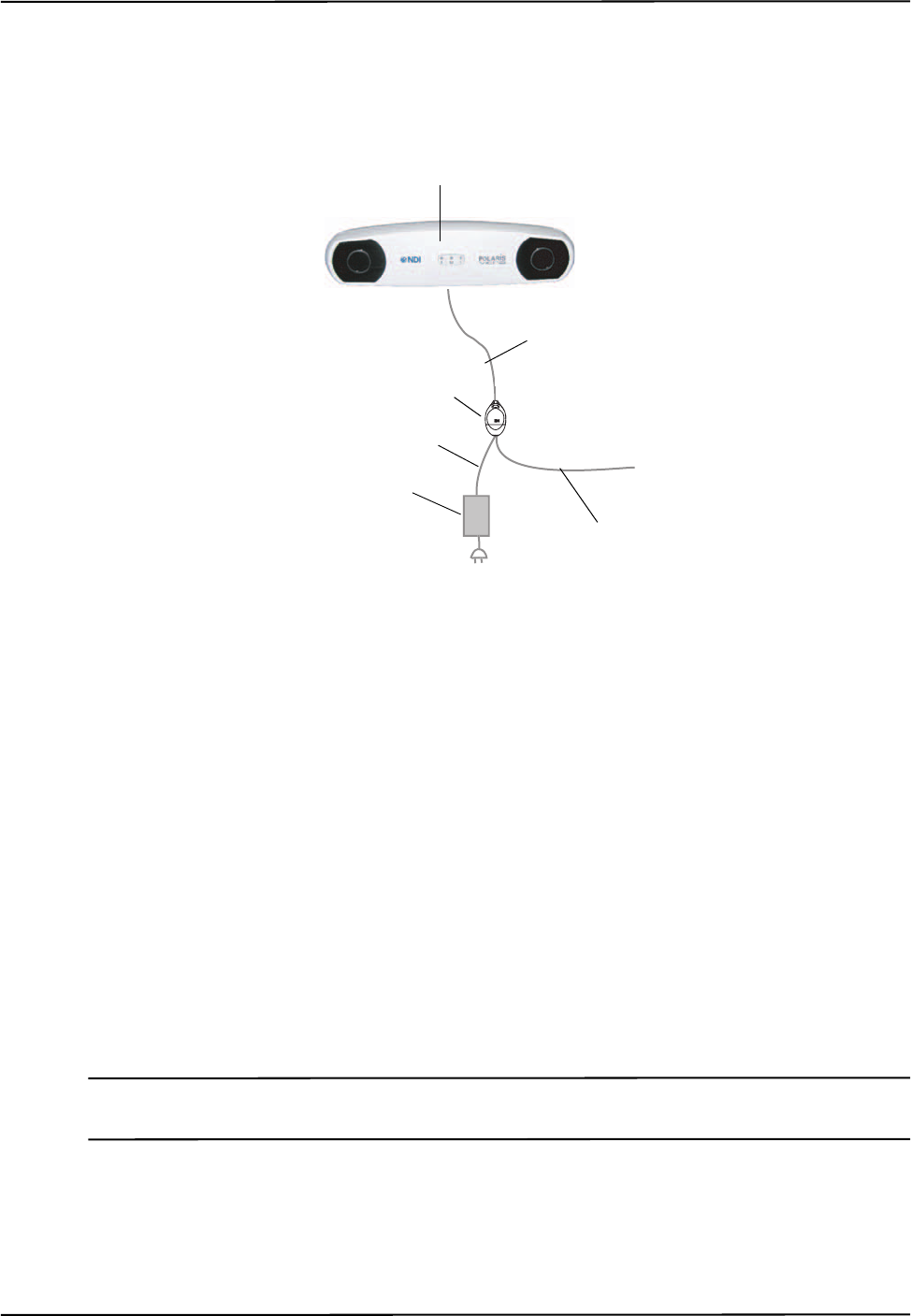
Polaris Vicra System Overview
Polaris Vicra User Guide - Revision 2 7
• 75Mb free disc space
• Windows 200/XP or Linux 2.6.8 or greater
• Screen resolution 1024x768 (1280x1024 recommended)
Figure 1-2 Polaris Vicra System Setup
1.2 Position Sensor
The Position Sensor is the main component of the Polaris Vicra System. An overview of its
operation is as follows:
1. The Position Sensor emits infrared (IR) light from its illuminators, similar to the flash on a
conventional camera.
2. The IR light floods the surrounding area and reflects back to the Position Sensor off passive
sphere markers (passive mode) or triggers markers to activate and emit IR light (active wireless
mode).
3. The Position Sensor then measures the positions of the markers, and calculates the
transformations (the positions and orientations) of the tools to which the markers are attached.
4. The Position Sensor transmits the transformation data, along with status information, to the host
computer for collection, display, or further manipulation.
Note For a more detailed description of how the Position Sensor detects markers, see “Marker Detection and Tool
Tracking” on page 28.
The Position Sensor can operate in two modes; passive mode and active wireless mode. The mode is
automatically selected, controlled by settings in the tool definition file. (A tool definition file stores
information about a tool.)
Host USB Converter
To Computer
USB Cable
Power Adapter
Position Sensor Cable
Position Sensor
Power Adapter Cable
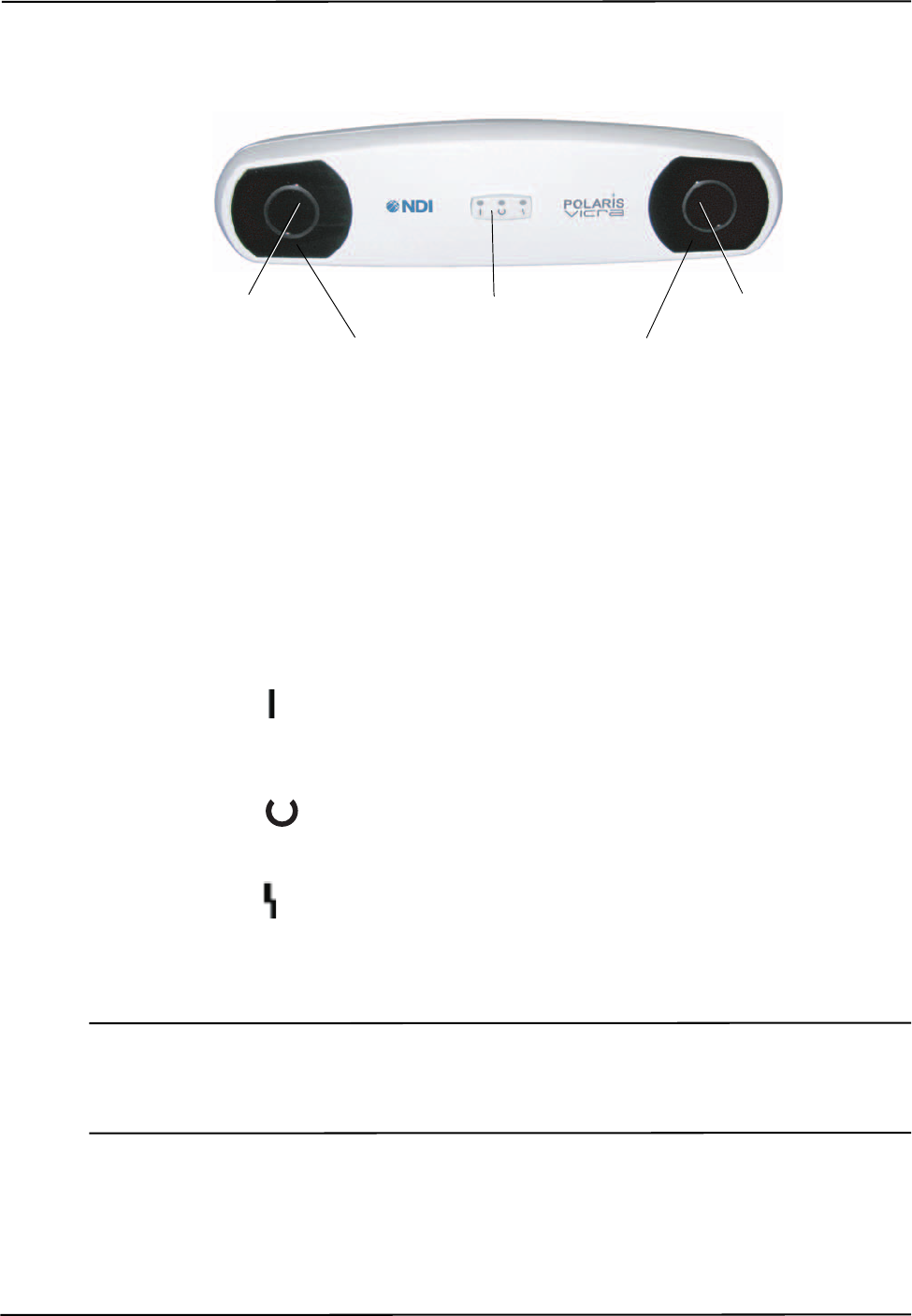
Polaris Vicra System Overview
8Polaris Vicra User Guide - Revision 2
Front View
Figure 1-3 Position Sensor - Front View
The front of the Position Sensor incorporates the following components:
Illuminator Two arrays of infrared Light Emitting Diodes (IREDs) that provide IR light for the
passive sphere markers or a “chirp” activation trigger for active markers.
Sensor Two sensors that each comprise a lens and CCD. They collect IR light that is reflected from
passive sphere markers (passive mode) or emitted from active markers (active wireless mode).
Indicator LED Three LEDs that provide the following indications (left to right):
•Power LED :
Flashes green during system warm-up.
Steady green when system is ready for use.
•Status LED :
Steady green when the communications connection is available.
•Error LED :
Lights steady amber if a critical error is detected (Position Sensor must be returned to NDI).
Flashes amber if a non-critical error is detected (for example, a firmware update is not
completed).
Note If a non-critical error is detected (error LED is flashing), refer to the NDI ToolBox application to further diagnose
the fault. (The nature of the error is described on the NDI ToolBox initial page.) If you are using your own
applications, use the GET command to read the “Info.StatusAlert” parameter to check the alert status. Refer to
the “Polaris Application Program Interface Guide” for further information.
Sensor
Sensor
Illuminator Illuminator
Indicator LEDs (3)
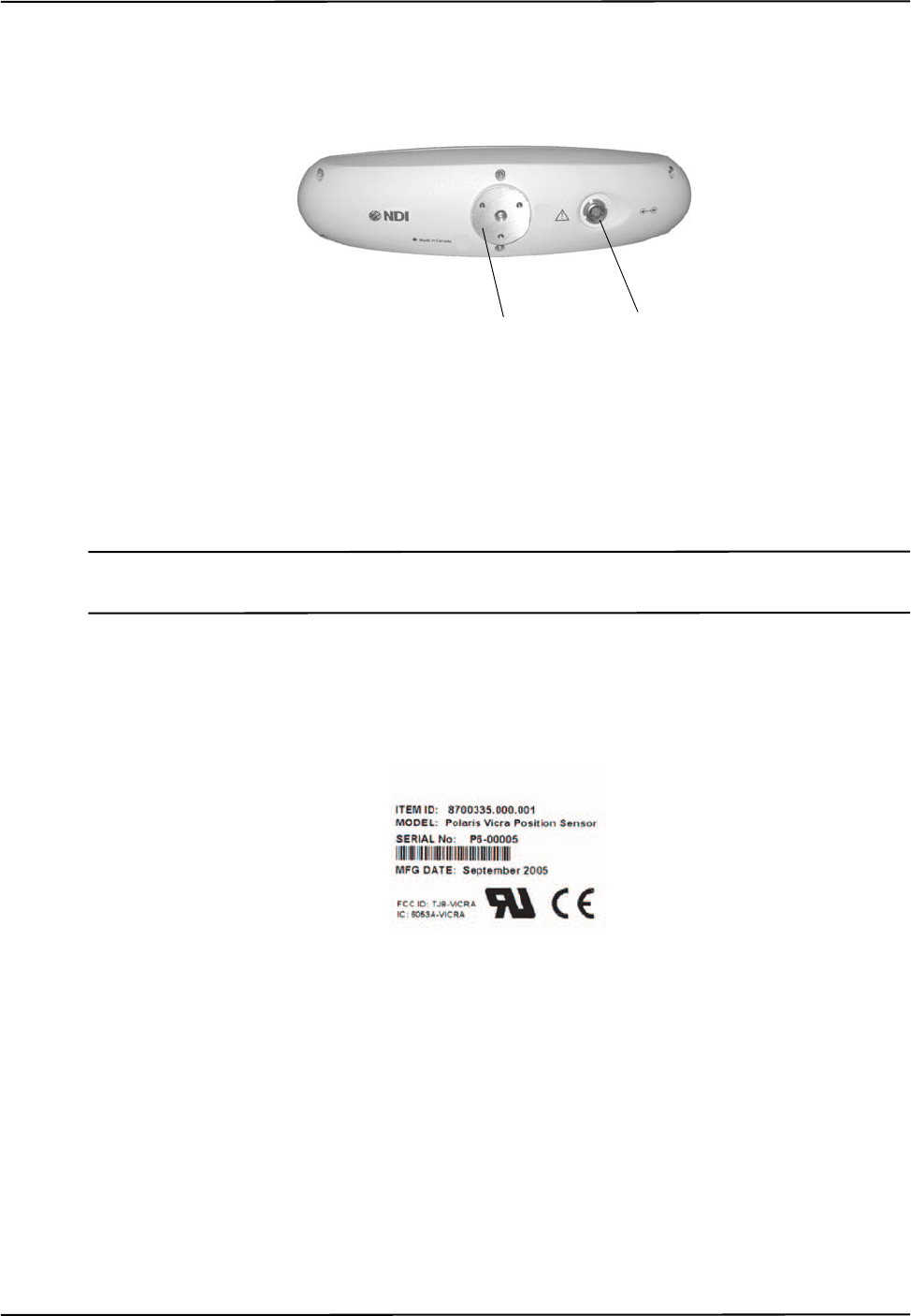
Polaris Vicra System Overview
Polaris Vicra User Guide - Revision 2 9
Rear View
Figure 1-4 Position Sensor - Rear View
The rear of the Position Sensor incorporates the components detailed below:
Mount 1/4” thread tripod mount, that incorporates three M3 x 0.5 mm x 8 mm threads.
Connector (LEMO) A 14 pin connector that provides power to the Position Sensor and allows
communications to/from the Position Sensor.
Note It is good practice to disconnect mains power before connecting or disconnecting cables. Failure to do so may
cause damage to the equipment.
Serial Number Label
The serial number label is located on the bottom of the Position Sensor and shows the Item ID,
model, serial number, and manufacture date of the Position Sensor.
Figure 1-5 Position Sensor - Serial Number Label
Audio Codes
In addition to the indicator LEDs, the Position Sensor emits audio tones to alert the user to events.
The codes are interpreted as follows:
• Two tones are emitted on reset or when power is applied to the Position Sensor. (This
feature can be disabled in NDI Tool Box software.)
• If the host computer does not send a command to the system within a given time, the
Position Sensor will emit two quick tones every three seconds. (This feature is an
application watchdog and is set by the API command HWCDOG.)
Mount Connector
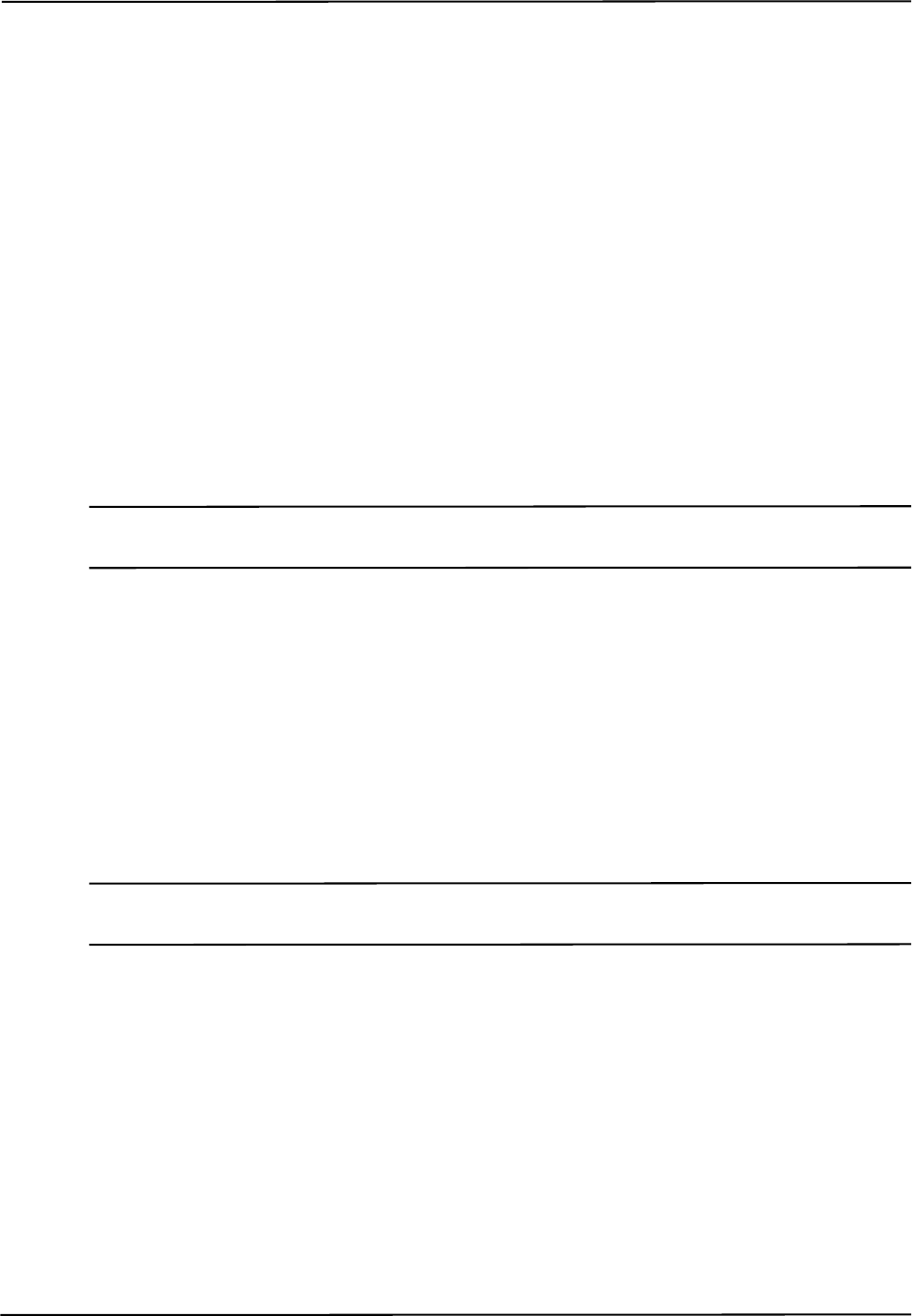
Polaris Vicra System Overview
10 Polaris Vicra User Guide - Revision 2
• The API command BEEP can be used to set up to nine tones as required. Refer to the
“Polaris Application Program Interface Guide” for further details on setting the BEEP
command.
Bump Sensor
The Position Sensor houses a bump sensor that detects when the Position Sensor has been bumped
above a shock limit broadly equivalent to a 200 mm to 254 mm drop onto a vinyl tiled concrete
surface. If a bump is detected above this threshold, the error LED on the Position Sensor will flash,
indicating that a non-critical error has been detected.
You can check the bump sensor status using NDI ToolBox application software. For further
information on NDI ToolBox, refer to the online help.
Because a bump can affect the calibration of the Position Sensor, the system will not report
transformations if the bump sensor has detected a bump, unless:
• the bump sensor has been cleared, or
• reply option 0x0800 is used with the TX or BX command.
Note See the “Polaris Application Program Interface Guide” for details on checking and clearing the bump sensor, and
using the TX, BX and GET commands.
If a bump has been detected, NDI recommends that you perform an accuracy assessment procedure
with the NDI Accuracy Assessment Kit (AAK), to ensure that the Position Sensor is still calibrated.
For information on the accuracy assessment procedure and AAK, contact NDI or visit the support
site at http://support.ndigital.com.
The bump sensor circuit derives its power from an internal battery that has an operational life of
approximately 10 years. As the battery begins to lose power, the battery alert flag (in the
Info.Status.Alerts parameter) will be set intermittently. This will cause the error indicator LED on
the Position Sensor to flash. The intermittent indication is caused by the battery voltage fluctuating
about the fault threshold level. (The Position Sensor must be returned to NDI to have the battery
replaced.)
Note The bump sensor battery is a Lithium battery. If you dispose of the Position Sensor locally, make sure that you
adhere to all applicable legislation and regulations relating to the disposal of Lithium batteries.
Ingress Protection
The Position Sensor is designed to an ingress protection level of IP 54. The “5” denotes that the
Position Sensor is protected against dust. The “4” denotes that the Position Sensor is protected
against liquid sprayed in all directions. To maintain an ingress protection level of IP 54, the Position
Sensor cable (attached to the Host USB Converter) must be plugged in. For details on connecting
the system, see “Connecting the Hardware” on page 19.
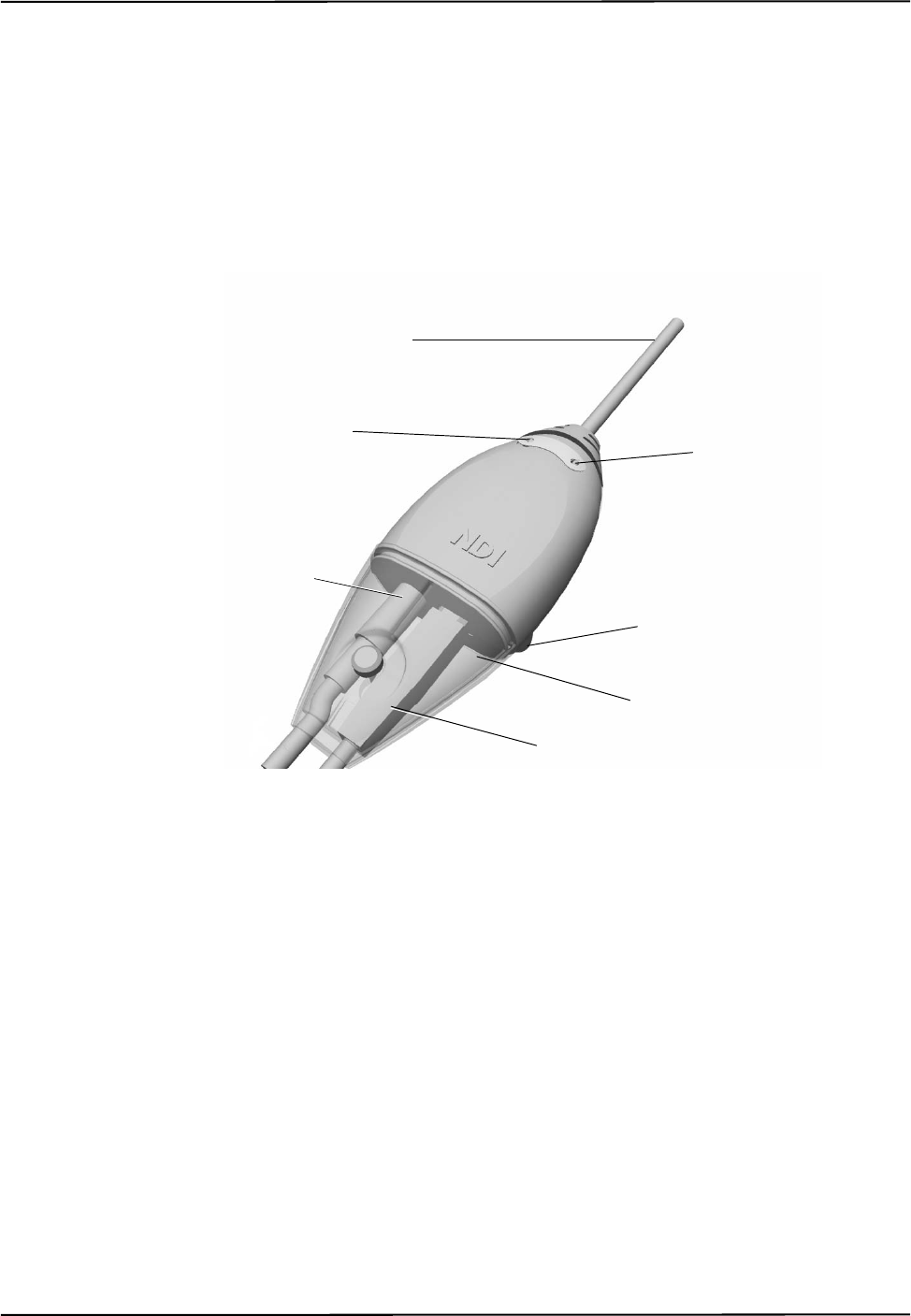
Polaris Vicra System Overview
Polaris Vicra User Guide - Revision 2 11
1.3 Host USB Converter
The Host USB Converter provides the interface between the Position Sensor, the power adapter,
and the host computer:
• The attached Position Sensor cable connects the Host USB Converter to the Position Sensor.
• The power adapter and USB cable plugs into the Host USB Converter.
• Modem status bits are provided see “Serial Port Emulation” on page 40.
Figure 1-6 Host USB Converter
The Host USB Converter incorporates the sub-assemblies detailed below.
Cable Covers: Two covers (top and bottom) that are secured together by means of a thumbscrew.
The covers retain the USB and power adapter cables in place.
Position Sensor Cable: Provides connection for data and power between the Position Sensor and
Host USB Converter. This cable is permanently connected to the Host USB Converter and is either
4.5 m or 8 m, depending on the configuration of your system.
Power Indicator: Lights green when power is applied to the Host USB Converter.
Error Indicator: Lights amber when the Host USB Converter has detected a fault.
Mounting Feet: Three feet that incorporate an internal thread (M6 x 1 mm pitch x 4 mm depth) to
allow the Host USB Converter to be attached to an external structure (for example, a cart). For free-
standing use, rubber inserts are located in the mounting feet.
Indicator LED
(Error) Indicator LED
(Power)
Position Sensor Cable
Power Connector
Mounting Feet x 3
USB Connector
Cable Covers
(top and bottom)
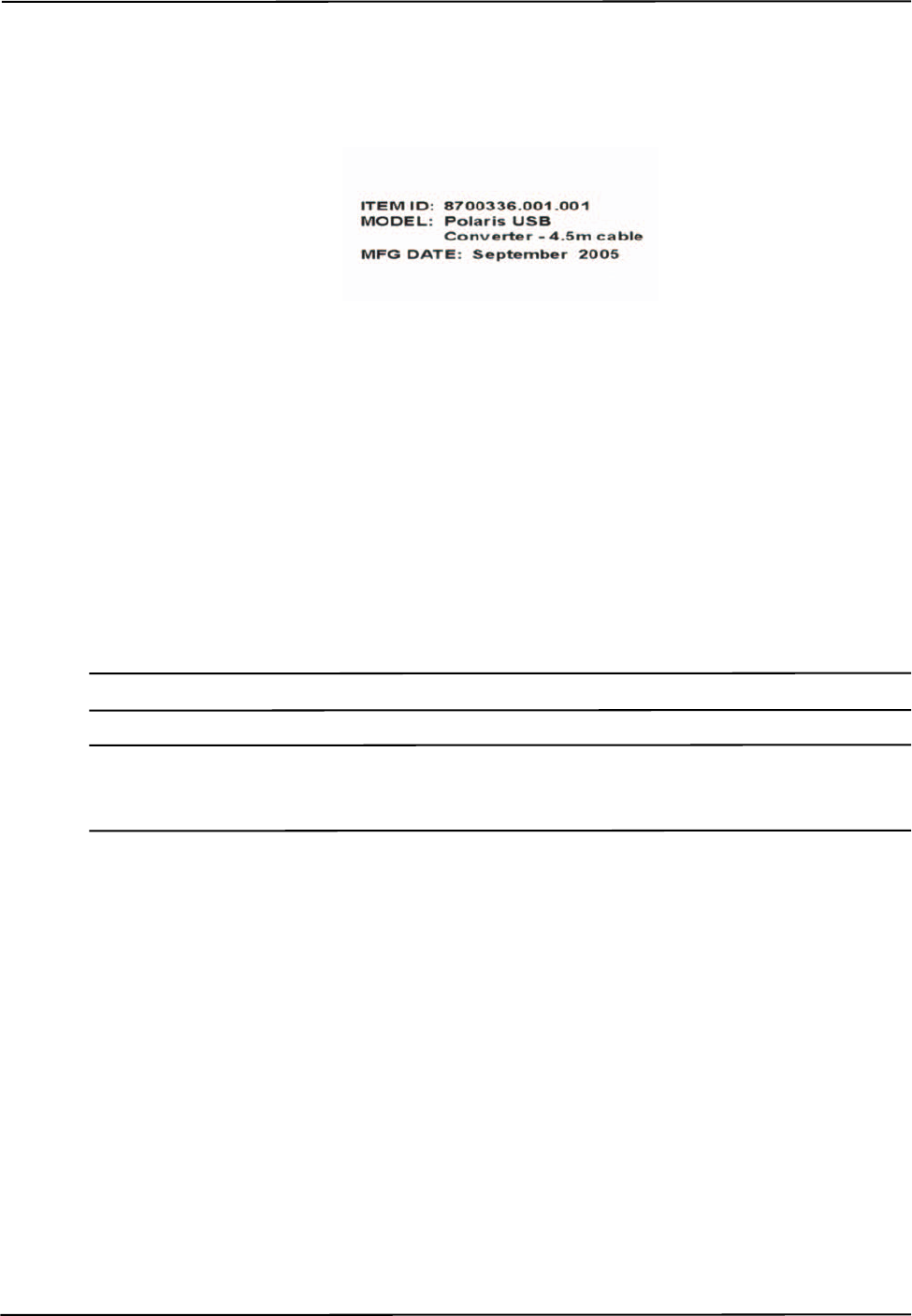
Polaris Vicra System Overview
12 Polaris Vicra User Guide - Revision 2
Serial Number Label
The serial number label is located on the bottom of the Host USB Converter and shows the Item ID,
model, serial number, and manufacture date of the Host USB Converter.
Figure 1-7 Host USB Converter Serial Number label
1.4 Power Adapter
The system is powered by an NDI supplied power adapter (Advanced Power Systems, part number
APS49ES-24021/Hitron HES49ES-24021). The power adapter connects to the mains supply and
provides DC power to the Position Sensor via the Host USB Converter. Alternatively, power may be
supplied by a customer provided power adapter that meets the following criteria:
• medical grade, double insulated (required if end use will be in a medical environment)
• 12/24 V DC, 1.2 A output (40 W typical)
• Switchcraft part number 760 plug (or equivalent)
Note Please see disclaimer #4 on page 3 for information regarding the UL recognition and alternate power supplies.
Note If a non-NDI supplied power adapter is used, it should be chosen to suit the particular use and the resulting
system configuration must be verified for electrical safety by an approved test laboratory.For further information
contact NDI.
1.5 Cables
NDI supplies additional cables for use with the system:
Position Sensor Cable: Provides connection for data and power between the Position Sensor and
Host USB Converter. This cable is permanently connected to the Host USB Converter and is either
4.5 m or 8 m, depending on the configuration of your system.
USB Cable: Provides connection for data between the host computer and Host USB Converter. This
cable is a USB, A-B male, double shielded, 5 m cable.
Power Adapter Output Cable: Provides connection for power to the Host USB Converter. This cable
is permanently connected to the power adapter and has a plug-in jack connector to connect to the
Host USB Converter.
Power Adapter Power Cable: Connects the power adapter to the mains supply. This cable is a
medical grade AC line cord.
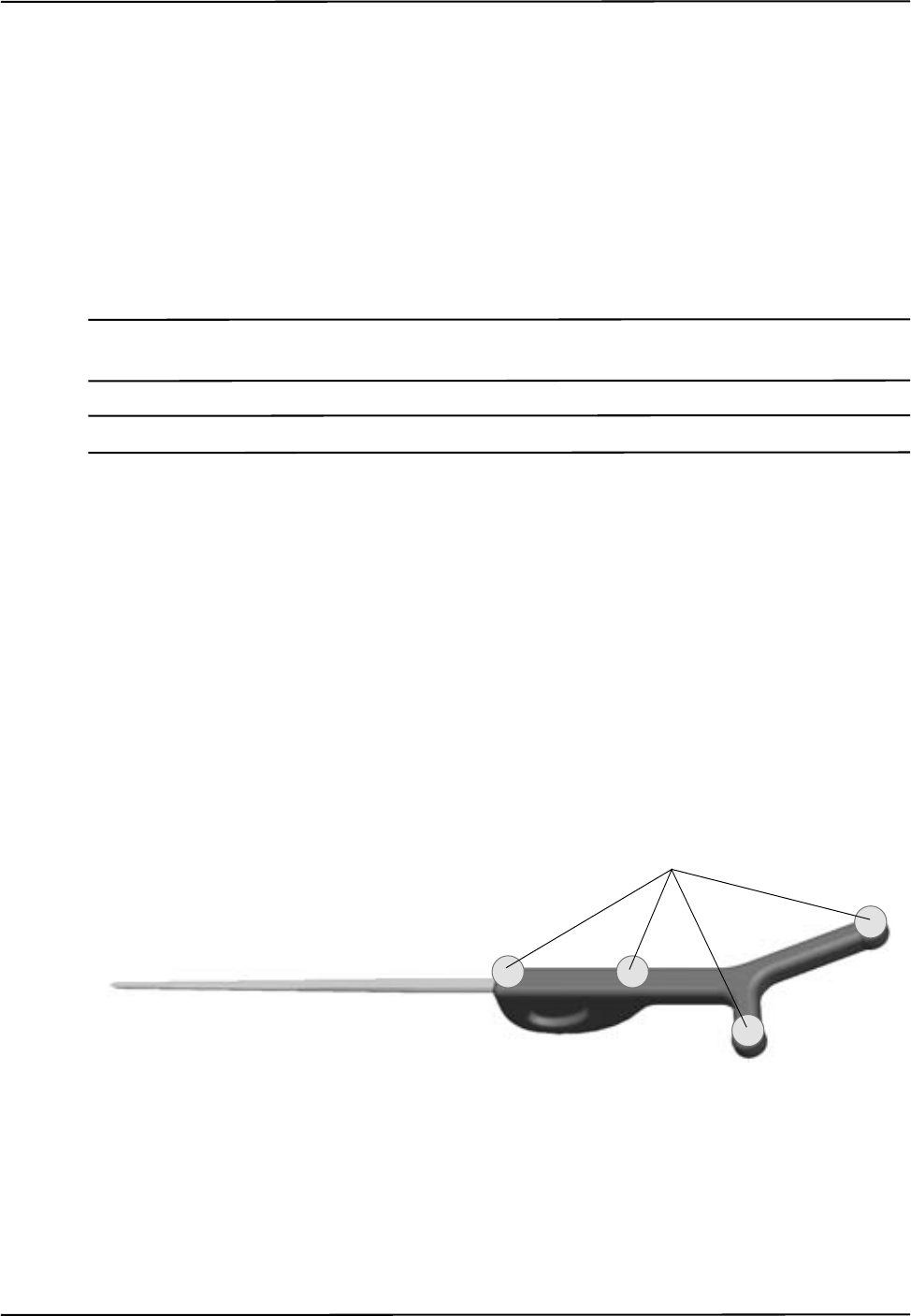
Polaris Vicra System Overview
Polaris Vicra User Guide - Revision 2 13
1.6 Polaris Vicra Tools
The Polaris Vicra System utilizes wireless tools, which may be active or passive. Passive tools
incorporate retro-reflective passive markers and active wireless tools incorporate IRED markers.
The Position Sensor tracks tools based on the geometry of the markers on each tool. The system can
track up to six compatible tools simultaneously and these may include both active wireless and
passive tools.
The Position Sensor requires a tool definition file for each tool. A tool definition file describes a tool
to the Position Sensor (including the tool’s marker geometry). The tool definition file for a particular
tool must be loaded from the host computer before the Polaris Vicra System can track that tool.
Note For more information on tool definition files, see “Tool Definition File” on page 31. Polaris Vicra System tools are
described in more detail in “Polaris Vicra System Tools” on page 30.
Note For information on tool design and construction, refer to the “Polaris Tool Design Guide”.
Passive Tools
Passive tools incorporate NDI passive sphere markers. The passive sphere markers have a retro-
reflective coating that reflects IR light back to its source, instead of scattering it. As such, the IR
light from the Position Sensor illuminators reflects off the markers directly back to the sensors.
Markers can be attached to an object such that the markers are fixed with respect to one another, to
form a tool. The markers must be attached to the object using NDI mounting posts, which are
manufactured to firmly hold NDI spheres. The Polaris Vicra System can track the positions and
orientations of tools, and can also report the positions of individual passive spheres.
An example of a passive tool is shown in Figure 1-8. The example shows a probe that incorporates
four passive sphere markers.
For more information on passive sphere markers, see “Passive Sphere Markers” on page 38.
Figure 1-8 Sample Passive Tool
Active Wireless Tools
Active wireless tools incorporate IRED markers that emit IR light. The markers are incorporated in
tools that also house an IR receiver and a (battery) power source. The (previously loaded) tool
definition file identifies it to the system as an active wireless tool.
Passive Sphere Markers
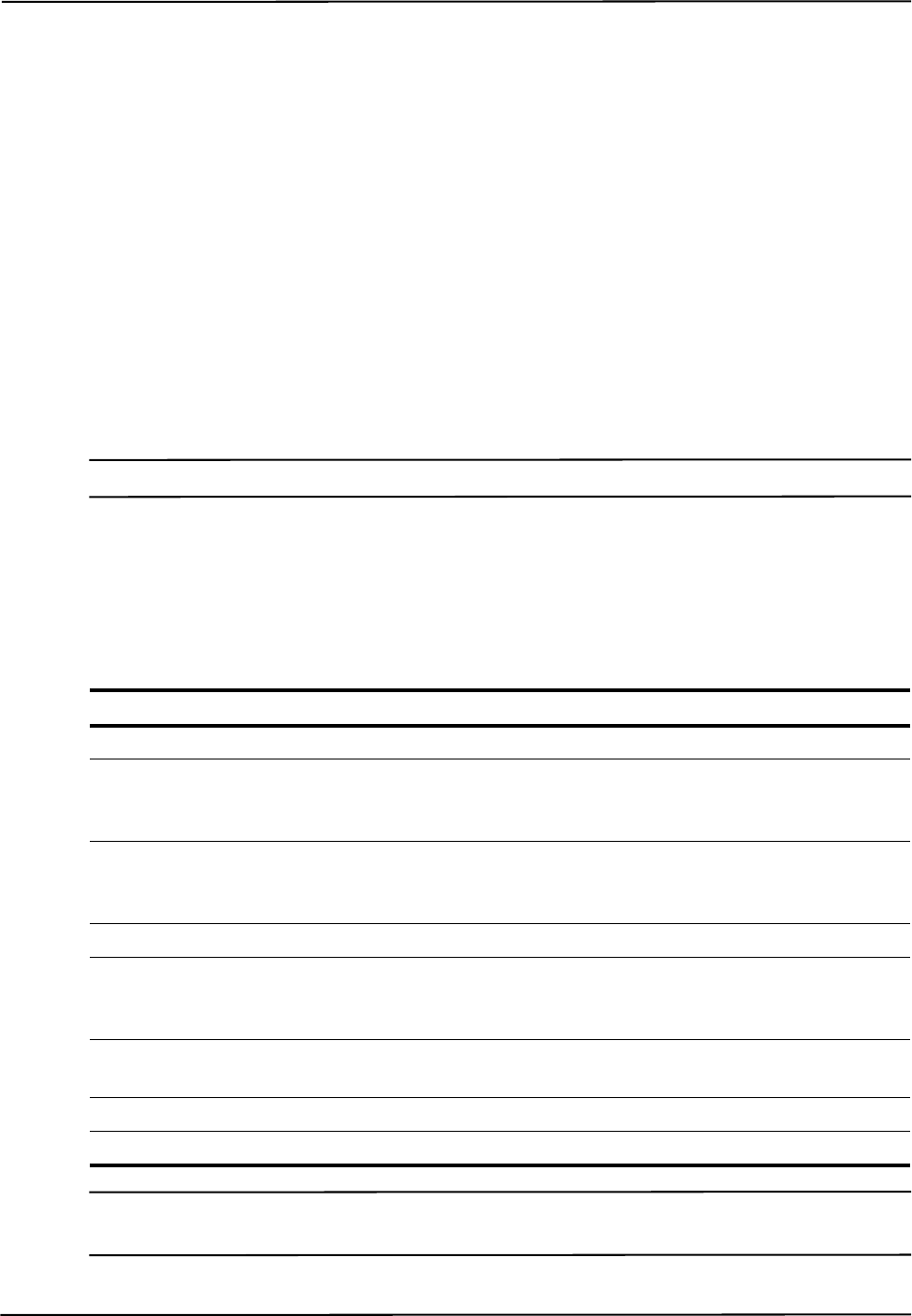
Polaris Vicra System Overview
14 Polaris Vicra User Guide - Revision 2
The Position Sensor codes (“chirps”) the IR pulses emitted from its illuminators. These coded IR
pulses are received by the IR receiver on the tool which then activates the IREDs. The Position
Sensor receives the IR emitted by the IREDs and processes it in the same manner as passive tool
reflections.
For more information on IRED markers, see “Active Markers” on page 39.
1.7 Polaris Vicra System Software
The following software is included on the Polaris Vicra CD. You can also download the software
from the NDI Support Site at: http://support.ndigital.com.
NDI CAPI Sample A sample program written for Windows, and the source code for the program.
This program provides an example of how to write programs to operate the Polaris Vicra System.
NDI ToolBox Use this program to configure, upgrade, troubleshoot, and test the Polaris Vicra
System. For more information, see the NDI ToolBox online help.
Note NDI 6D Architect application software is located on the CD that accompanies the developer kit.
1.8 Component Parts List
The following is a list of components that are available with the Polaris Vicra System:.
Note Additional components are available to support the Polaris Vicra System. Contact NDI for further details, or visit
the Support site at http://support.ndigital.com.
Table 1-1 Component Parts List
Item Part Number
Polaris Vicra Position Sensor 8800788.xxx.yyy
Polaris Host USB Converter
(incorporating 4.5 m communications
cable)
8800810.001
Polaris Host USB Converter
(incorporating 8 m communications
cable)
8800810.002
Polaris Vicra Power Adapter 4100139
Power Cord 7500010 (North America)
or
7500012 (France/Belgium/Germany)
Universal Serial Bus (USB) A-B cable
2 m
2600596
Polaris Vicra CD 1800042
Polaris Vicra User Guide IL-1070100
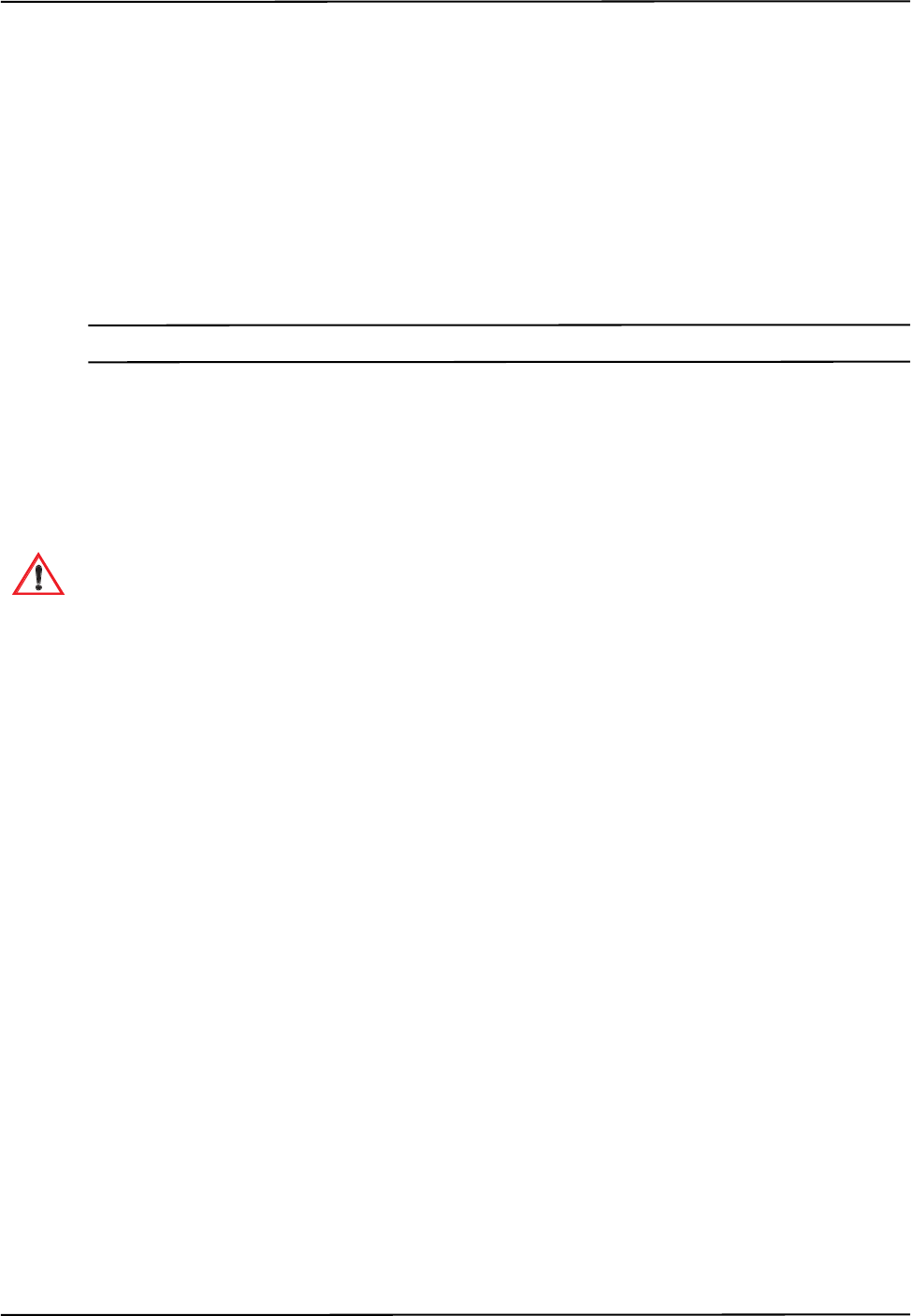
Setting Up the Polaris Vicra System
Polaris Vicra User Guide - Revision 2 15
2 Setting Up the Polaris Vicra System
2.1 Unpacking the Polaris Vicra System
The Polaris Vicra System is shipped with a Position Sensor, a Host USB Converter, a power adapter,
cables, the Polaris Vicra CD, and documentation.
When unpacking the Polaris Vicra System, be sure to handle all system components with care. Keep
the packaging in good condition; you will need to use it if the system ever needs to be returned to
NDI for repair.
Note See “Return Procedure” on page 77 for instructions on returning your system to NDI.
2.2 Polaris Vicra System Operating Environment
In order for the Polaris Vicra System to operate correctly, the system must be set up in an
environment that meets the following criteria:
Warnings
Read the following warnings before using the Polaris Vicra System, to avoid the risk of personal
injury.
1. Do not use the Polaris Vicra System in the presence of flammable materials such as
anaesthetics, solvents, cleaning agents, and endogenous gases. Flammable materials may
ignite, causing personal injury or death.
2. Do not protect or shield either the Position Sensor or tools with methods not approved by
NDI. Non-approved methods will interrupt the optical path and degrade the performance
of the system. Reliance on data provided by a Position Sensor without an uninterrupted
optical path may lead to inaccurate conclusions. If your application involves personal
safety, inaccurate conclusions increase the possibility of personal injury.
3. Radio frequency communications equipment, including portable and mobile devices, may
affect the Polaris Vicra System and result in personal injury.
4. Do not use cables or accessories, other than those listed in this guide. The use of other
cables or accessories may result in increased emissions and/or decreased immunity of the
Polaris Vicra System and may result in personal injury.
5. Do not incorporate non-NDI components with the Polaris Vicra System. The accuracy of
results produced by applications that incorporate non-NDI components with the Polaris
Vicra System is unknown. If your application involves personal safety, reliance on these
results may increase the possibility of personal injury.
6. Do not attempt to bypass the grounding prong on the power cord by using a three-prong to
two-prong adapter. The system must be properly grounded to ensure safe operation.
Failure to do so presents an electric shock hazard.
Warning!
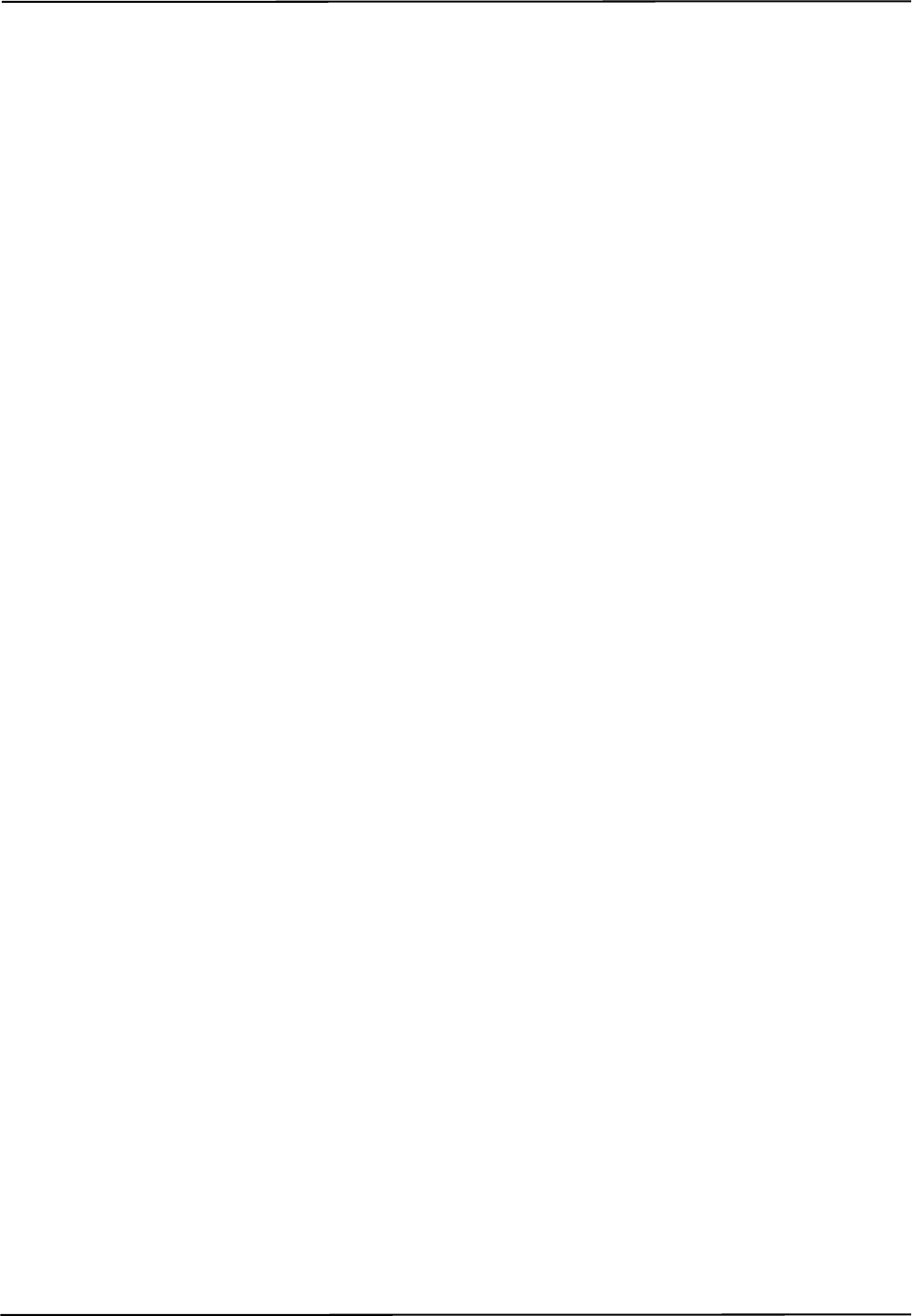
Setting Up the Polaris Vicra System
16 Polaris Vicra User Guide - Revision 2
7. Do not immerse any part of the Polaris Vicra System or allow fluid to enter the equipment.
If fluids enter any part of the system they may damage it and present a risk of personal
injury.
8. Do not sterilize the Polaris Vicra Position Sensor as this may cause irreversible damage to
its components. Reliance on data provided by a damaged Position Sensor may lead to
inaccurate conclusions. If your application involves personal safety, these inaccurate
conclusions increase the possibility of personal injury.
9. Do not use the Position Sensor without inspecting it for cleanliness and damage both
before and during a procedure. Reliance on data provided by an unclean or damaged
Position Sensor may lead to inaccurate conclusions. If your application involves personal
safety, inaccurate conclusions increase the possibility of personal injury.
10. Do not use the Polaris Vicra System for absolute measurements; the system is designed for
relative measurements only. Treating measurements as absolute may result in an incorrect
interpretation of results. If your application involves personal safety, these incorrect
interpretations increase the possibility of personal injury.
11. Do not obstruct the normal flow of air around the Position Sensor (for example, draping
or bagging the Position Sensor). Doing so will affect the Position Sensor's operational
environment, possibly beyond its recommended thresholds. Reliance on data provided by
a Position Sensor that is outside of recommended thresholds may lead to inaccurate
conclusions. If your application involves personal safety, inaccurate conclusions increase
the possibility of personal injury.
Cautions
Caution! Read the following cautions before using the Polaris Vicra System to prevent the risk of damage to
the system.
1. Make sure that the mains power is disconnected before connecting or disconnecting cables.
Failure to do so may cause damage to the equipment.
2. Always place the Position Sensor on a rigid support system. If not supported, the Position
Sensor may fall which will affect the calibration and damage the Position Sensor.
Operating Environment
• There must be a clear line of sight between the Position Sensor and the tools to be tracked.
The tools must be inside the characterized measurement volume. Refer to Figure 3-2 on
page 27 for the dimensions of the characterized measurement volume.
• Make sure that sources of background IR light in the 800 nm to 1100 nm range (e.g.
sunlight, some operating room lights) are minimized. The Position Sensor is sensitive to IR
light. Since the Position Sensor functions by detecting IR light reflected from, or emitted by,
markers, other sources of IR light can interfere with the Polaris Vicra System.
• Make sure that there are no large reflective surfaces within the field of view (described on
page 26). For example, the gantry for a magnetic resonance imaging (MRI) machine has a
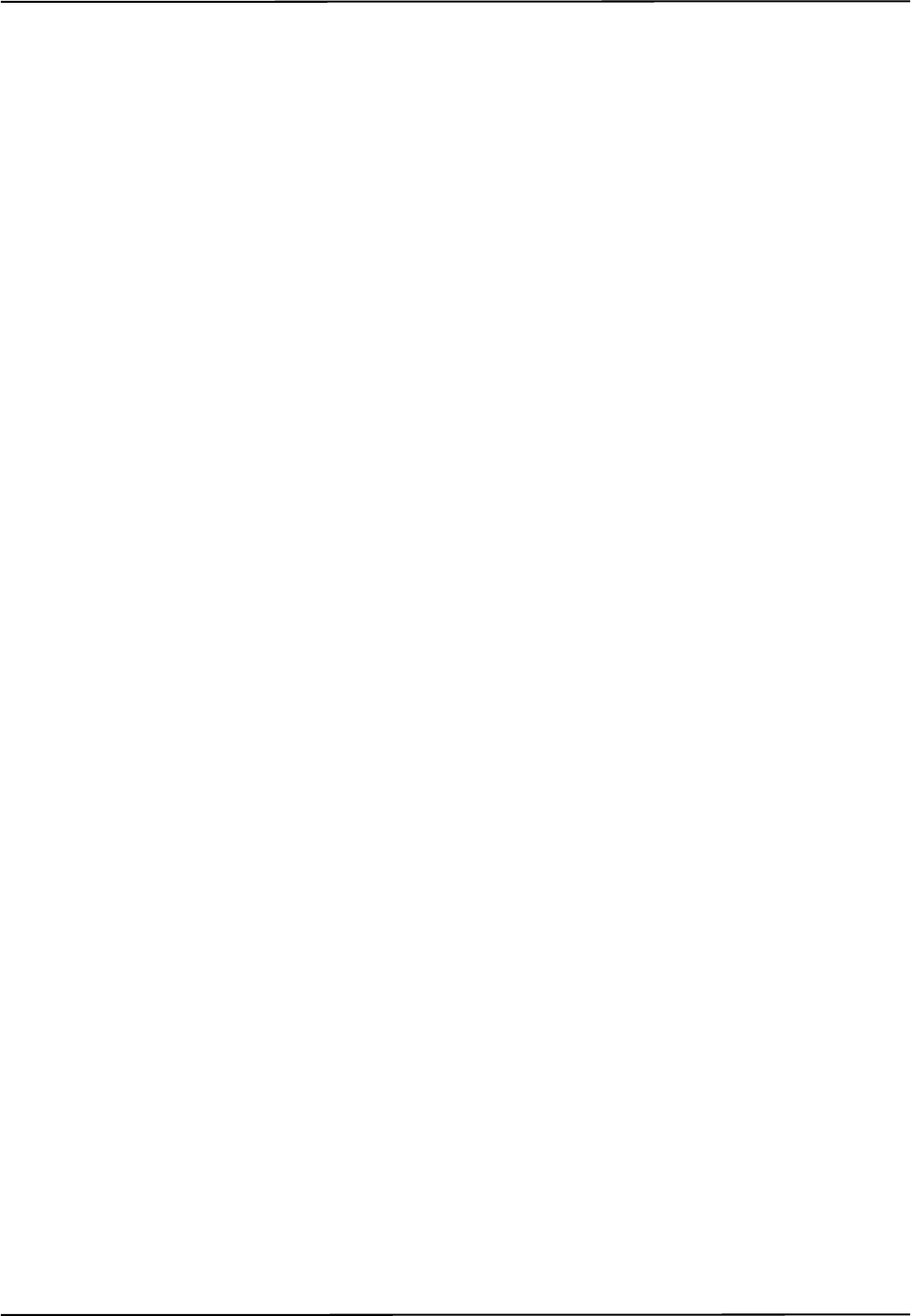
Setting Up the Polaris Vicra System
Polaris Vicra User Guide - Revision 2 17
large reflective surface. It can be draped with non-reflective material to eliminate
reflections.
• Make sure that the tools do not have flat reflective surfaces. Certain tool shapes and surfaces
can cause reflections that may interfere with the Polaris Vicra System. For more
information, see the “Polaris Tool Design Guide”.
• The system requires a warm-up time from storage temperature to operating temperature
equivalent to 10 minutes plus one minute for every 1°C of difference between storage
temperature and operating temperature. (If the temperature difference is within 5°C, the
warm-up time will be 10 minutes.)
For example, if the system is stored at -10°C and moved to a location at +30°C, the warm-
up time will be 10 minutes, plus an additional 40 minutes to account for the difference in
temperature.
• The operating environment is as close as possible to 20ºC. The Polaris Vicra System is
characterized at 20ºC and is therefore most accurate at this temperature.
• If the system is to be used in an MRI environment, contact NDI for information on response
of the system.
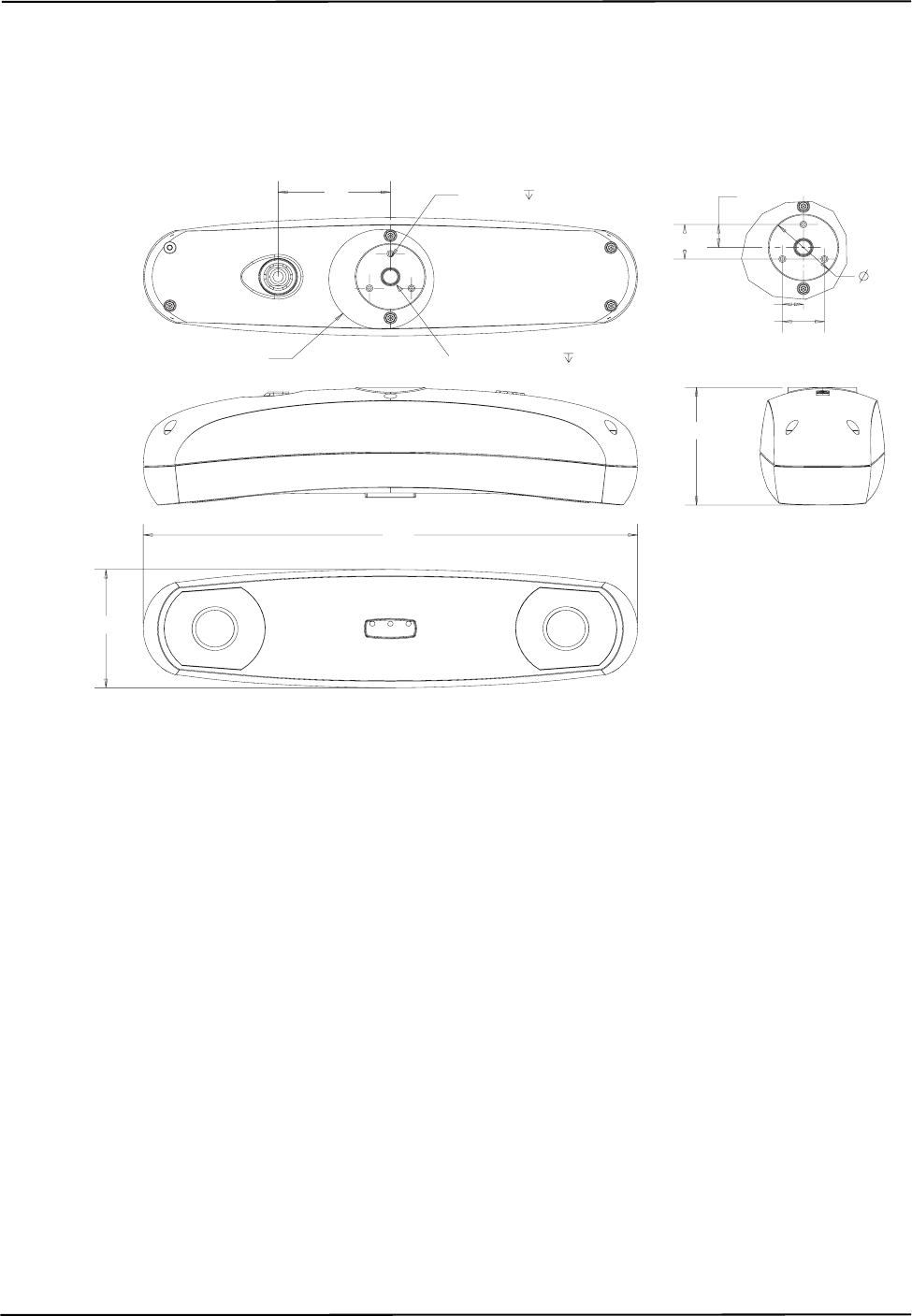
Setting Up the Polaris Vicra System
18 Polaris Vicra User Guide - Revision 2
2.3 Mounting the Position Sensor
The Position Sensor is mounted via a built-in 1/4” thread tripod mount, or 3 (user supplied) M3 x 0.5
mm pitch x 9 mm screws. Figure 2-1 shows the Position Sensor dimensions and mounting
arrangement.
Figure 2-1 Position Sensor Mounting Details
273
See Detail A
69
69
62 M3x0.5x9
3 Places
Thread 1/4-20x10
13.43
20.14
11.63
23.25
Detail A
37.
85
All dimensions in mm
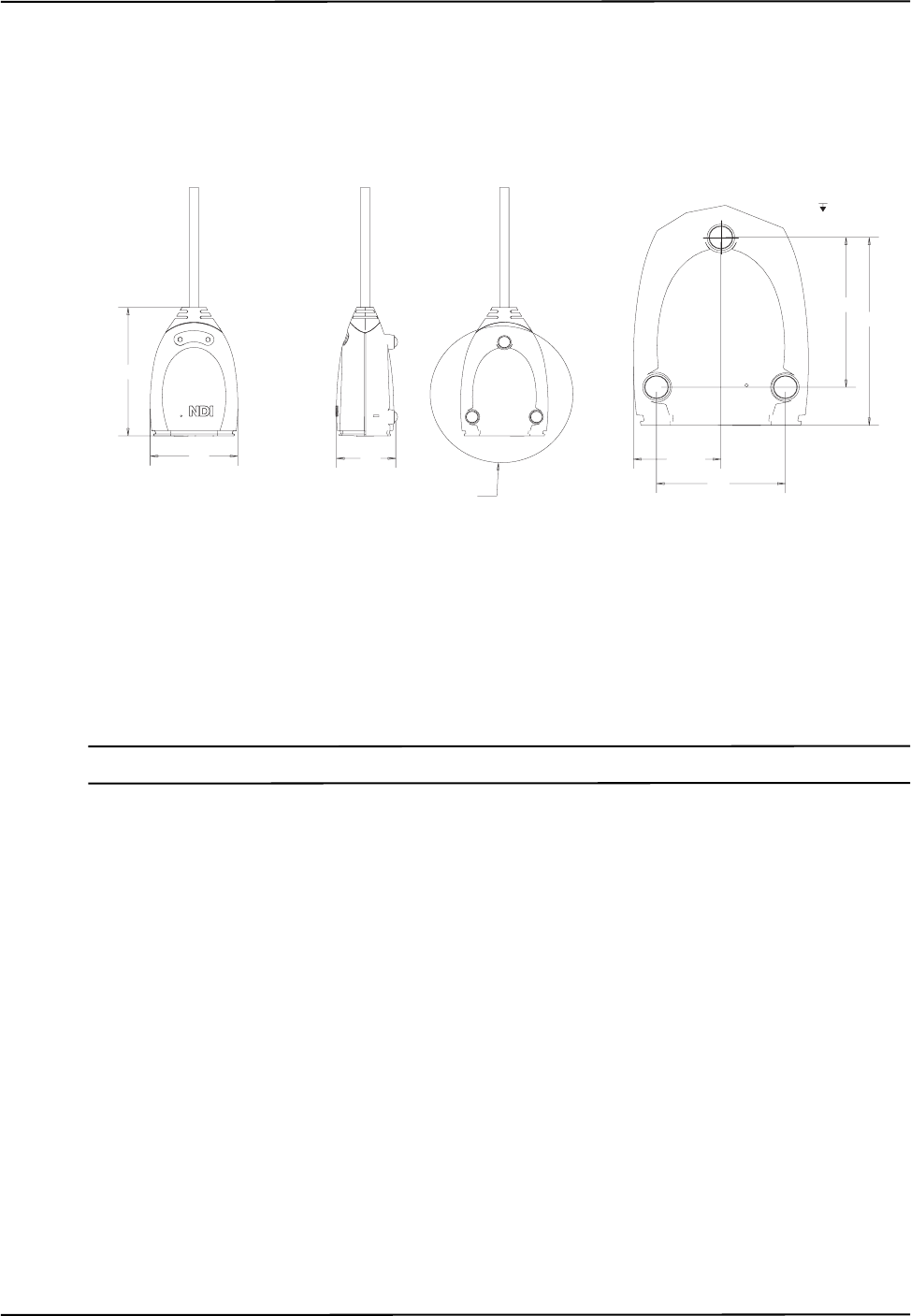
Setting Up the Polaris Vicra System
Polaris Vicra User Guide - Revision 2 19
2.4 Mounting the Host USB Converter
The Host USB Converter can be free-standing or may be mounted via M6 x 1 mm pitch x 4 mm
deep threaded holes located in the three mounting feet. Figure 2-2 shows the Host USB Converter
mounting arrangement, with dimensions.
Figure 2-2 Host USB Converter Mounting Details
2.5 Connecting the Hardware
Note It is good practise to disconnect the mains power before connecting or disconnecting cables.
1. Connect the Position Sensor cable (attached to the Host USB Converter) to the connector
located on the back of the Position Sensor. Align the red marking on the Position Sensor
connector with the red marking on the cable connector (the double keys of the connectors
should be aligned).
2. Connect the USB cable B plug and power adapter cable to the Host USB Converter, as shown in
Figure 2-3.
3. Locate the top and bottom cable covers in place on the Host USB Converter. Secure the covers
with the thumbscrew, as shown in Figure 2-3.
88
57 40
See Detail A
28.53
42
Detail A
51 6
4
M6x1x3
3Places
All dimensions in mm
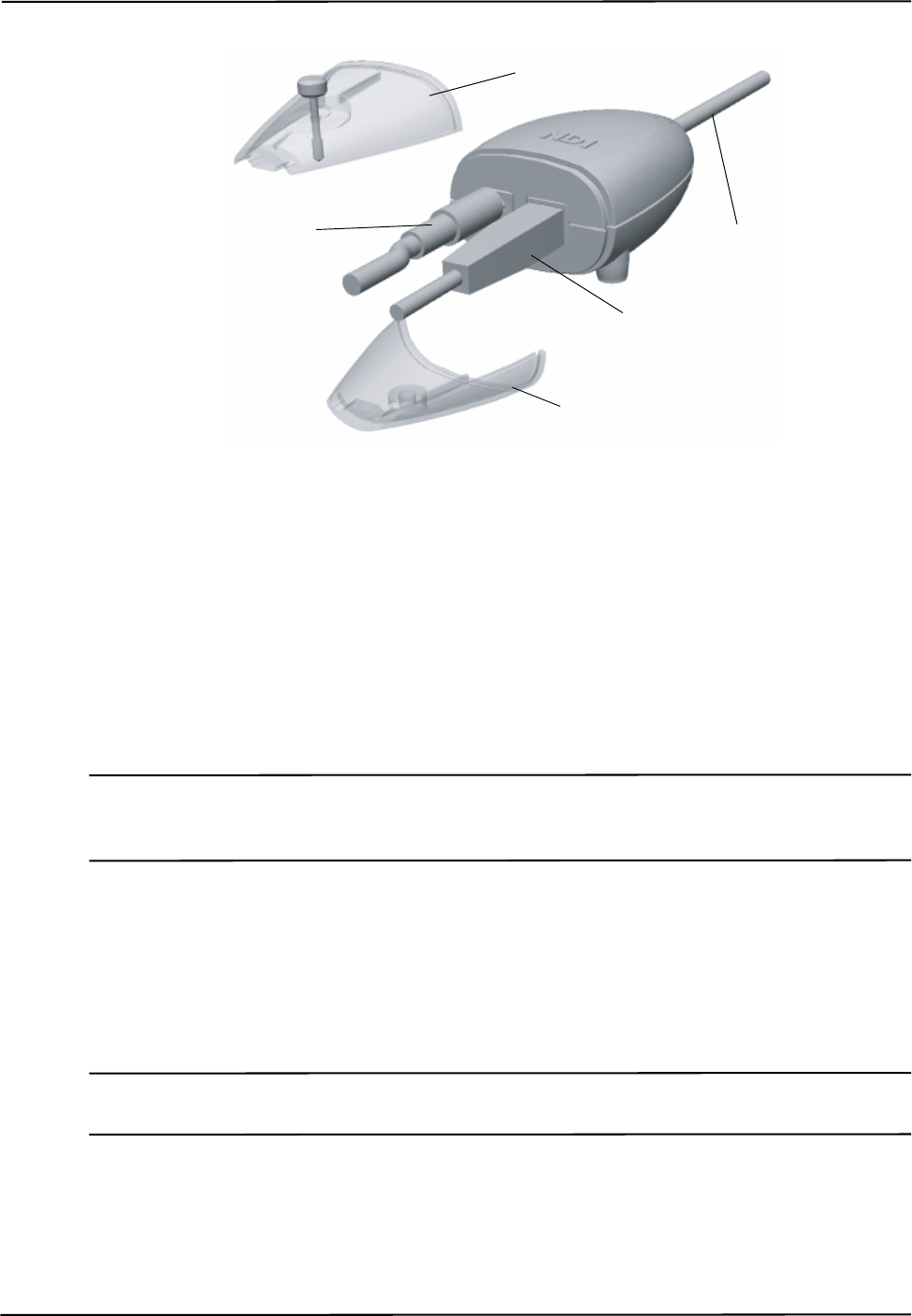
Setting Up the Polaris Vicra System
20 Polaris Vicra User Guide - Revision 2
Figure 2-3 Connecting Cables to the Host USB Converter
4. Plug the USB cable A plug into the host computer.
5. Make sure all the cables are connected firmly, and placed where they will not be stressed,
stepped on, or bent.
6. Plug the power cable into the power adapter and plug the power cable into the power mains and
turn on the mains.
The Polaris Vicra System will begin a diagnostic evaluation. During this evaluation, the LEDs on
the Position Sensor will flash. When the diagnostic evaluation is complete, the Position Sensor will
emit two tones and the power LED on the Position Sensor will light.
Note The Position Sensor initially communicates to the host computer at 9600 baud. If you are using the NDI ToolBox
application it will increase the baud rate as high as possible. If you are using your own application, the baud rate
can be set using the “COMM” API command. Refer to the “Polaris Application Program Interface Guide”.
2.6 Installing the Software
The NDI software is located on the Polaris Vicra CD. You can also download the software from the
NDI Support Site at
http://support.ndigital.com.
Note The Polaris Vicra CD does not contain NDI 6D Architect. That software application is located on the CD that
accompanies the developer kit.
NDI Combined API Sample
To install NDI Combined API Sample, copy the contents of the “CombinedAPISample” folder from
the Polaris Vicra CD onto the host computer.
Top Cable Cover
Bottom Cable Cover
Power Adapter
Cable
USB Cable
Position Sensor
Cable
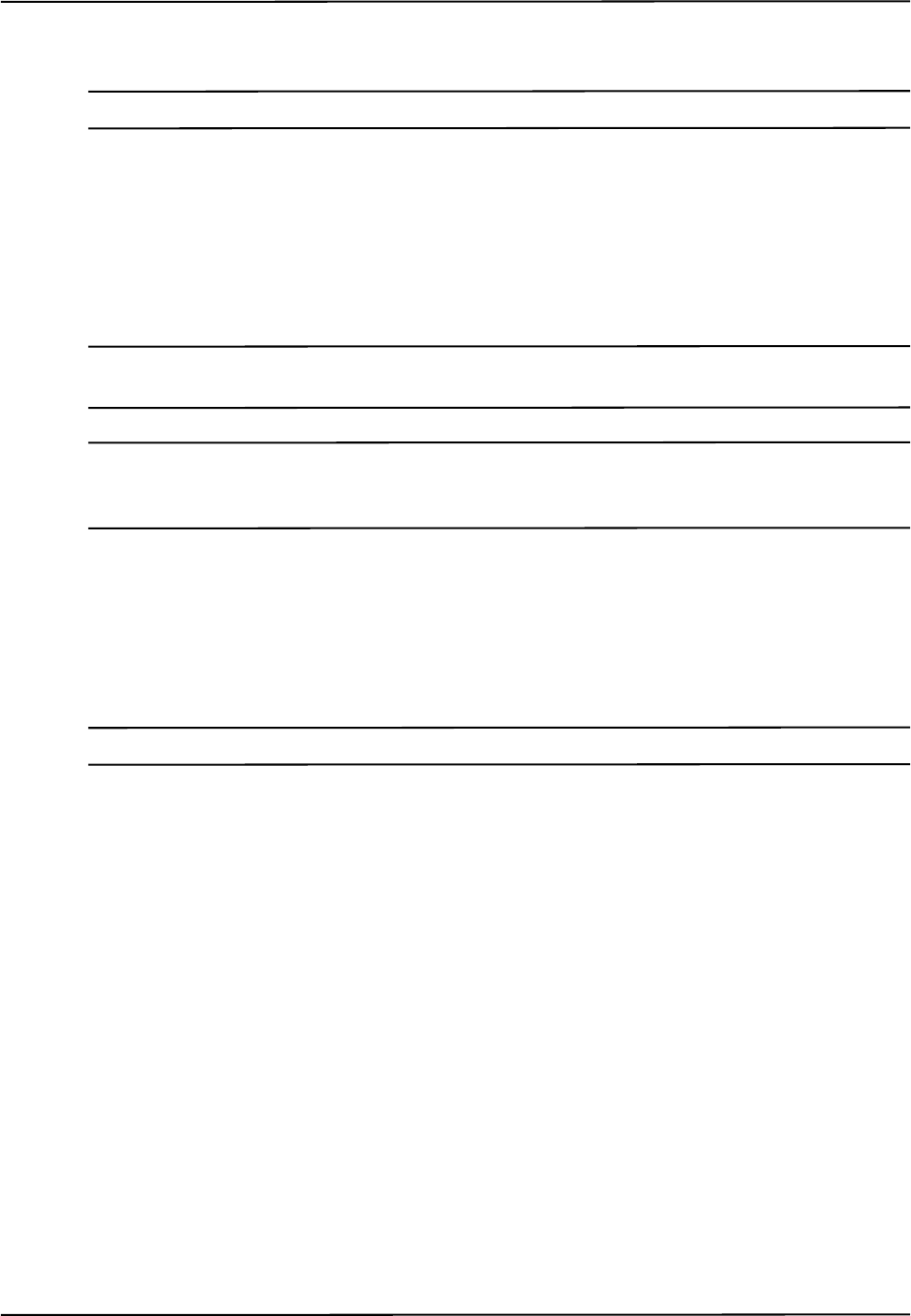
Setting Up the Polaris Vicra System
Polaris Vicra User Guide - Revision 2 21
NDI ToolBox (Windows Installation)
Note For information on Linux support, refer to “Linux Support” on page 22.
To install NDI ToolBox: Follow the on-screen instructions from the auto-run window that appears
when you insert the Polaris Vicra CD into the drive. Alternatively, on the Polaris Vicra CD, browse
to Windows\ToolBox\ directory and double-click install.exe.
Once you start the installation from the install page, a wizard appears. Follow the on-screen
instructions to complete the process. The default installation location is
C:\Program Files\Northern Digital Inc.\ToolBox
Note The installation of NDI ToolBox also includes installing the drivers for the Host USB Converter. The default
installation location is C:\Program Files\Northern Digital Inc.\ToolBox\USB Driver.
Note The NDI ToolBox installation includes a Java virtual machine (VM) for Windows and Linux systems. The Java VM
included in the NDI ToolBox installation is fully compatible with NDI ToolBox. Other versions of Java VM may
cause NDI ToolBox to exhibit unusual or unpredictable behaviour.
2.7 Installing the USB Drivers (Windows)
The Windows driver model consists of two parts; low-level USB and high-level virtual serial port. It
appears as a Windows serial port, COMx (where x is enumerated) and emulates a standard PC serial
port such that the Host USB Converter may be communicated with as a standard RS-232 device.
Note For information on Linux support, refer to “Linux Support” on page 22.
When you first connect the NDI Host USB Converter to the host computer, you will need to install
drivers for the Host USB Converter. There are two sets of drivers for the Host USB Converter:
• the first set of drivers enables the Host USB converter to work with the host computer
• the second set of drivers sets up the USB port where the Host USB Converter is connected
to emulate a serial port
Driver Location
If you have already installed NDI ToolBox, the USB drivers were installed as part of that
installation. By default, the drivers are located at C:\Program Files\Northern Digital Inc\ToolBox\
USB Driver. (See “NDI ToolBox (Windows Installation)” on page 21.)
The drivers are also located on the Polaris Vicra CD in the USB Driver folder.
Installing the USB Drivers
1. When you first connect the Host USB Converter to the host computer, the Found New
Hardware wizard will begin automatically.
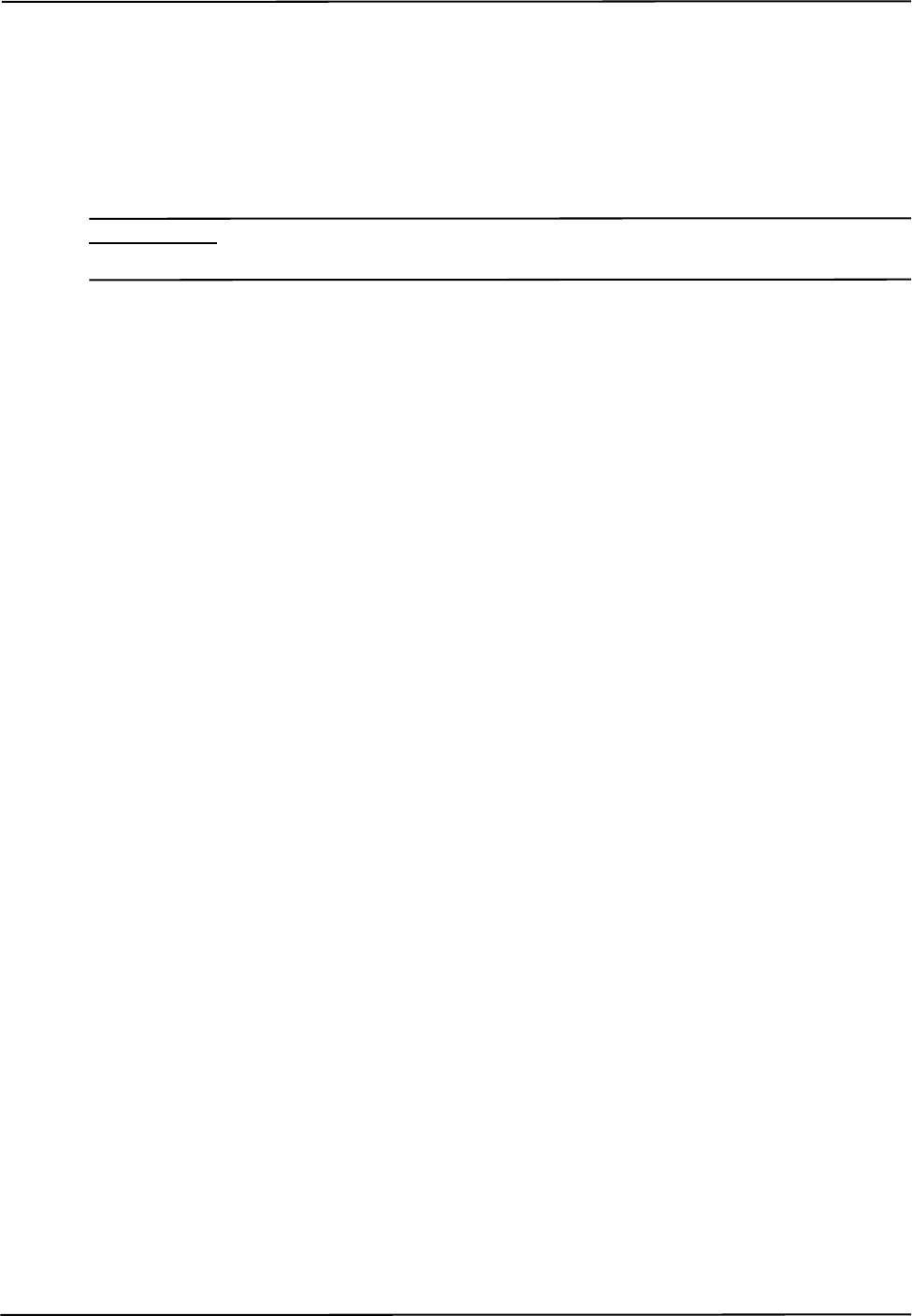
Setting Up the Polaris Vicra System
22 Polaris Vicra User Guide - Revision 2
2. When prompted, select the option that allows you to specify the drivers’ location. (“Install from
a specific list or location” in Windows XP, “Search for a suitable driver” in Windows 2000.)
3. Browse to the folder containing the drivers, either on the host computer or on the Polaris Vicra
CD. Windows will automatically select the correct drivers from the folder.
4. Click Next and Finish as required to complete the installation.
Note Windows XP only: After you have selected the folder containing the USB drivers, a warning may appear,
indicating that the drivers have not passed Windows Logo testing. Click “Continue Anyway”.
5. Once the first set of drivers is installed, the Found New Hardware Wizard will launch a
second time. Follow steps 2 to 4 above to install the second set of drivers.
6. The system will now appear to be connected through a virtual COM port.
Host USB converters are interchangeable on the same USB port, without having to re-install drivers
or losing the COM port previously established.
The Windows COM number assigned can be changed after installation as follows:
1. Launch Device Manager
2. Navigate to Ports (COM & LPT)
3. Right click on the Host USB Converter
4. Select the Properties pop-up menu
5. Select the Port Settings tab
6. Click on the Advanced Settings button
7. From the dialog box that is displayed, select the Com Port Number drop down field
8. Reassign the COM port as necessary
9. Select OK to save the changes
Windows will remember this mapping even if the Host USB Converter is unplugged from the USB
port. When the Host USB Converter is reconnected to the host computer, the COM port mapping
will be re-established (if it is plugged into the same USB port).
2.8 Linux Support
Introduction
This section provides information on Linux support for the Polaris Vicra System and covers the
following:
•USB Drivers
• NDI ToolBox
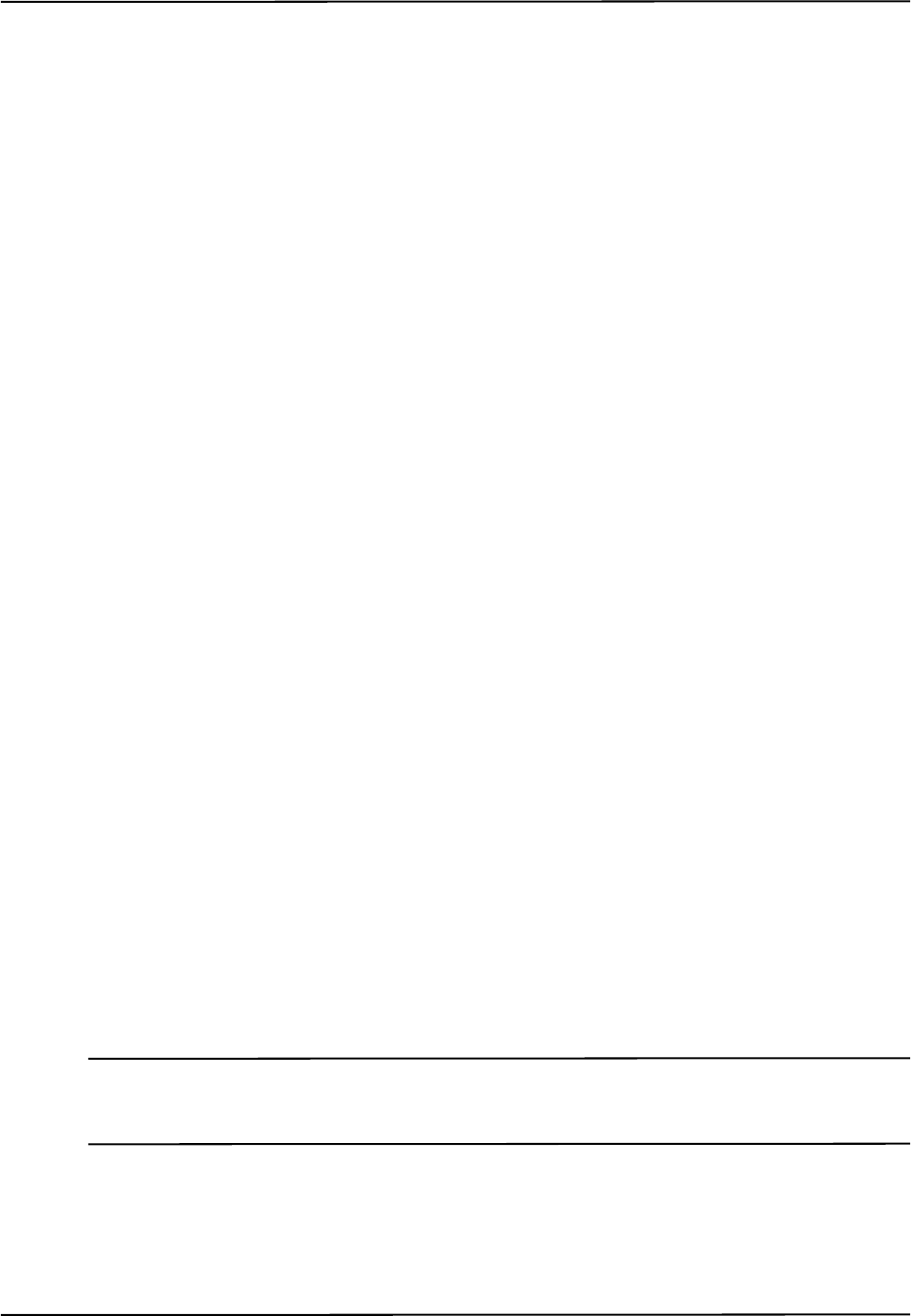
Setting Up the Polaris Vicra System
Polaris Vicra User Guide - Revision 2 23
Installing the USB Drivers
The Linux driver model is a kernel level driver that supports the USB to serial conversion. It appears
as a Linux device file “/dev/ttyUSBx” (where x is enumerated) and emulates a standard PC serial
port such that the USB device may be communicated with as a standard RS-232 device. NDI has
provided a patch to the 2.6.8 kernel driver source files.
These instructions are based on the Linux 2.6.8 kernel. The following changes are captured in the
ftdi.patch file.
In the directory /usr/src/linux-2.6.8-24/drivers/usb/serial:
1. ftdi_sio.c - added NDI Host USB Converter Product ID (PID) to supported devices tables,
added aliasing of 19.2K baud for the Host USB Converter to use 1.2Mbaud as required by NDI
ToolBox.
2. ftdi_sio.h - added the define for the USB PID for the Host USB Converter.
Apply the patch to an unmodified kernel as follows:
1. logon as root user.
2. cd /usr/src/linux-2.6.8-24.
3. patch -p1 < ftdi.patch.
4. rebuild the kernel following the instructions specific to the kernel.
5. the NDI Host USB Converter when connected will appear as "/dev/ttyUSBx", where 'x' is the
part number.
Host USB converters are interchangeable on the same USB port, without having to re-install drivers
or losing the device file enumeration previously established.
NDI ToolBox
Install NDI ToolBox as follows:
1. On the Polaris Vicra CD, browse to Linux/ToolBox/install.bin.
2. Follow the on-screen instructions to complete the process. The default installation location is
<user_account>/ToolBox.
3. The installation of NDI ToolBox also downloads the kernel patch file to apply to drivers for the
Host USB Converter. The default download location is <user_account>/ToolBox/kernel-2.6.8-
usb-patch.
Note The NDI ToolBox download includes a Java virtual machine (VM) for Windows and Linux systems. The Java VM
included in the NDI ToolBox download is fully compatible with NDI ToolBox. Other versions of Java VM may
cause NDI ToolBox to exhibit unusual or unpredictable behaviour.
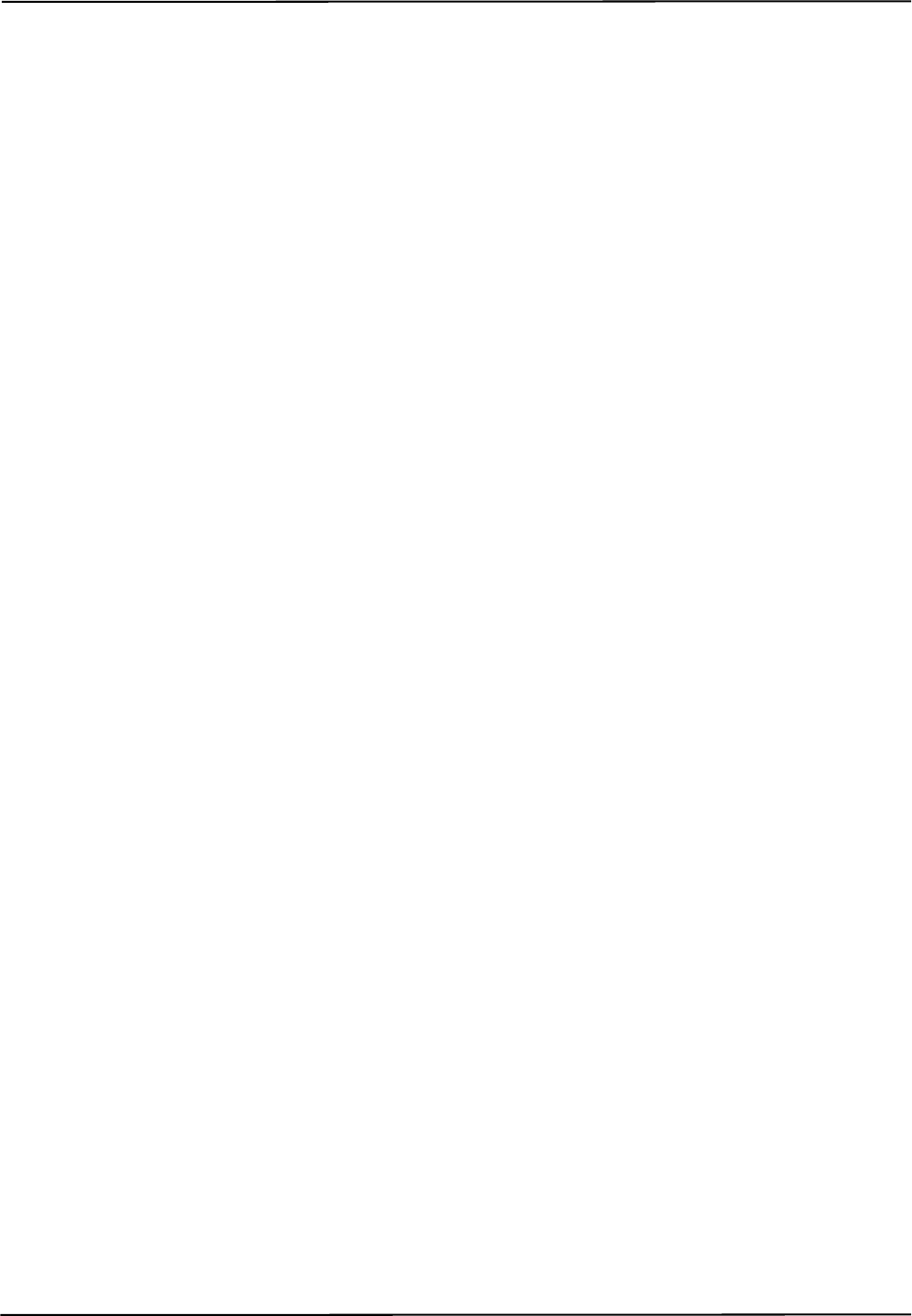
Setting Up the Polaris Vicra System
24 Polaris Vicra User Guide - Revision 2
2.9 Keyed Features
In addition to the base configuration, certain options are available as keyed features for the Polaris
Vicra System. For example the ability to use multiple versions of firmware is a keyed feature. For
information on current keyed features and how to purchase them, please contact your nearest NDI
location. See Contact Information on page 4 for your nearest NDI location.
Refer to NDI ToolBox application software online help for details on retrieving your current system
configuration and for installing additional keyed features.
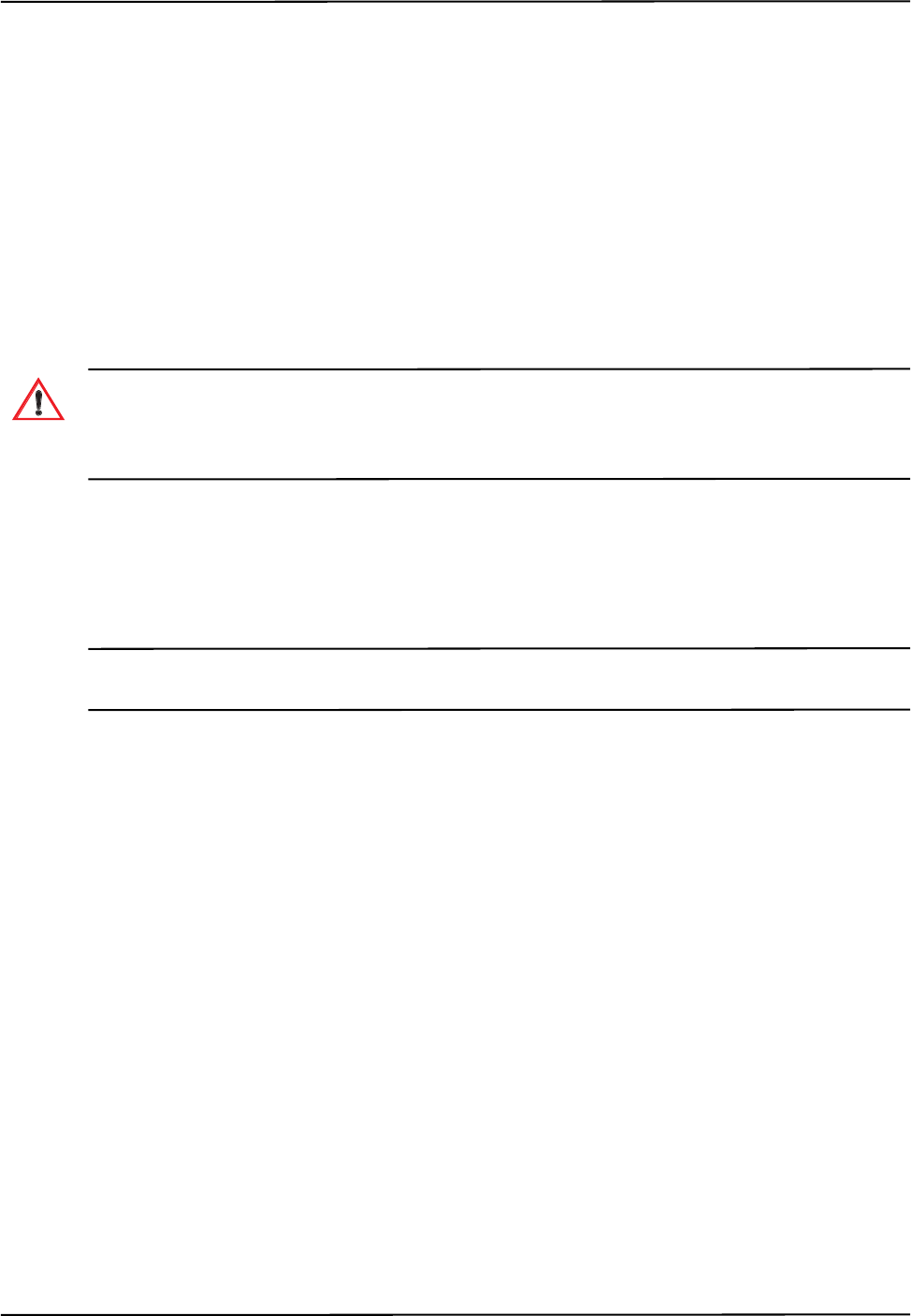
How the Polaris Vicra System Works
Polaris Vicra User Guide - Revision 2 25
3 How the Polaris Vicra System Works
3.1 Introduction
This chapter provides details on how the Polaris Vicra System works. The information is not
absolutely necessary in order to use the system, but it can help increase your technical understanding
of the system. For information on how to use the system, refer to “Using the Polaris Vicra System”
on page 41.
3.2 Information Returned by the Polaris Vicra System
Do not use the Polaris Vicra System for absolute measurements; the system is designed for relative
measurements only. Treating measurements as absolute may result in an incorrect interpretation of results. If
your application involves personal safety, these incorrect interpretations increase the possibility of personal
injury.
When the Polaris Vicra System is tracking tools, it returns information about those tools to the host
computer. The system by default returns:
•the position of each tool’s origin, given in mm, in the coordinate system of the Position
Sensor (see “Global Coordinate System” on page 26)
Note Transformations with respect to a reference tool (described on page 36), and transformations for a probe with a
tool tip offset (described on page 35) are calculated using application software such as NDI ToolBox.
•the orientation of each tool, given in quaternion format. The quaternion values are rounded
off, so the returned values may not be normalized
•an error value for each tool transformation. This RMS value, given in mm, is the result of
the least squares minimization between the marker geometry in the tool definition file and
the tool’s measured marker positions
•the status of each tool, indicating whether the tool is out-of-volume, partially out-of-
volume, or missing. It also indicates whether the port handle corresponding to each tool is
enabled and initialized. For more information on port handles, see the “Polaris Application
Program Interface Guide”
•the frame number corresponding to each tool transformation
•the system status, which includes some of the system errors described in “Tracking Errors
and Flags” on page 49
If requested, the system can also return:
• tracking errors and flags (described in “Tracking Errors and Flags” on page 49). (Some
tracking errors and flags are returned by default.
• marker status information, such as whether a particular marker was used to calculate a tool
transformation
Warning!
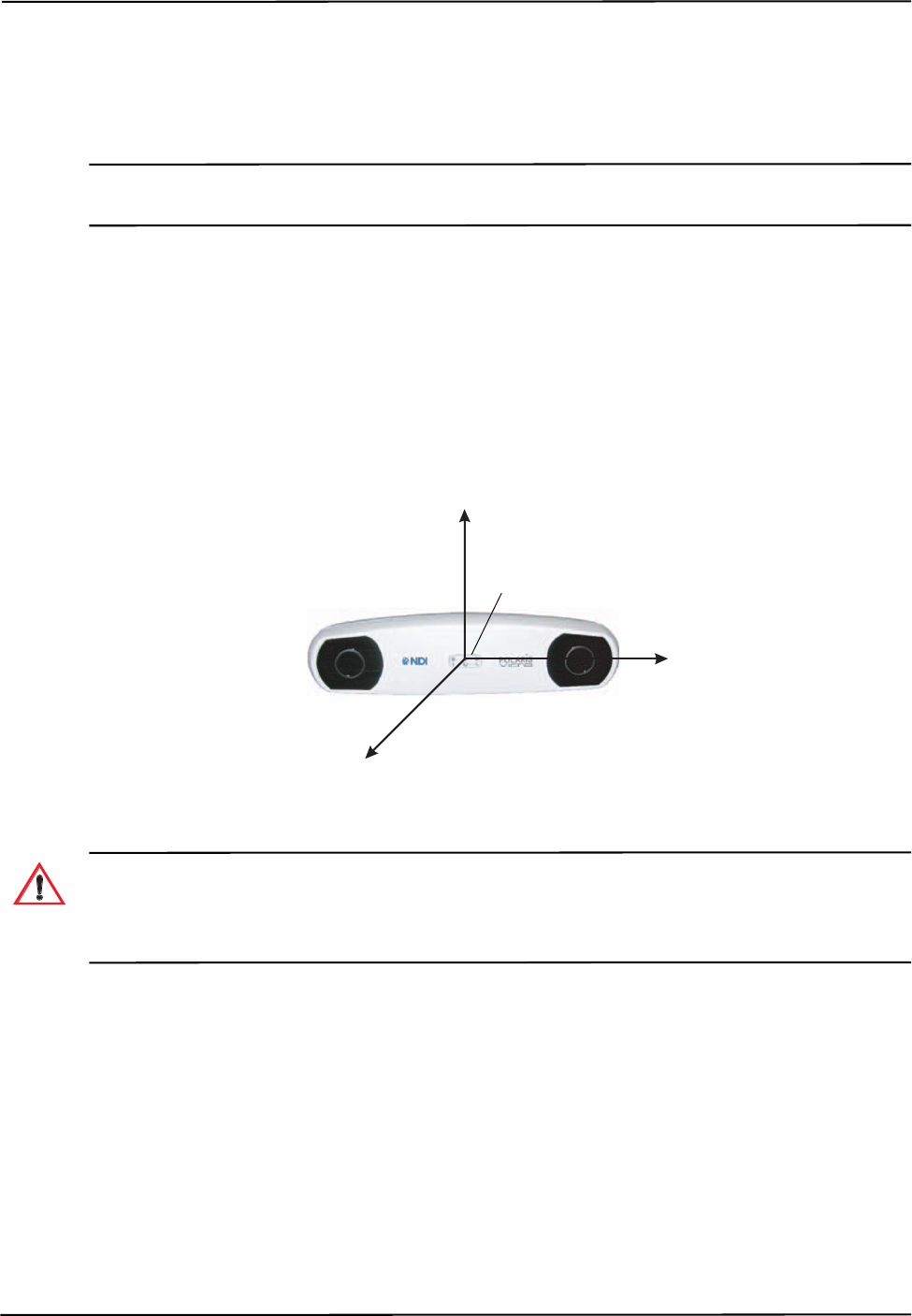
How the Polaris Vicra System Works
26 Polaris Vicra User Guide - Revision 2
• transformations for tools that are outside of the characterized measurement volume
• positions of stray passive markers
NDI ToolBox displays most of this returned information (except for the port handle information).
Note For information on the API commands used to request tracking information from the Polaris Vicra System, see
the “Polaris Application Program Interface Guide”.
3.3 Global Coordinate System and Measurement Volume
Global Coordinate System
The Polaris Vicra Position Sensor uses a coordinate system with an origin located at the Position
Sensor and axes aligned as shown in Figure 3-1. This global coordinate system is defined during
manufacturing and cannot be changed.
Figure 3-1 Position Sensor Global Coordinate System
Do not use the Polaris Vicra System for absolute measurements; the system is designed for relative
measurements only. Treating measurements as absolute may result in an incorrect interpretation of results. If
your application involves personal safety, these incorrect interpretations increase the possibility of personal
injury.
The Polaris Vicra System will report the transformations of tools in the global coordinate system.
However, if you are using a reference tool, software can calculate and report transformations in the
local coordinate system of the reference tool. For more information on reference tools, see
“Reference Tool” on page 36.
Field of View and Characterized Measurement Volume
The field of view is the total volume in which the Polaris Vicra System can detect a marker,
regardless of accuracy.
-x
-y
-z
Origin
Warning!
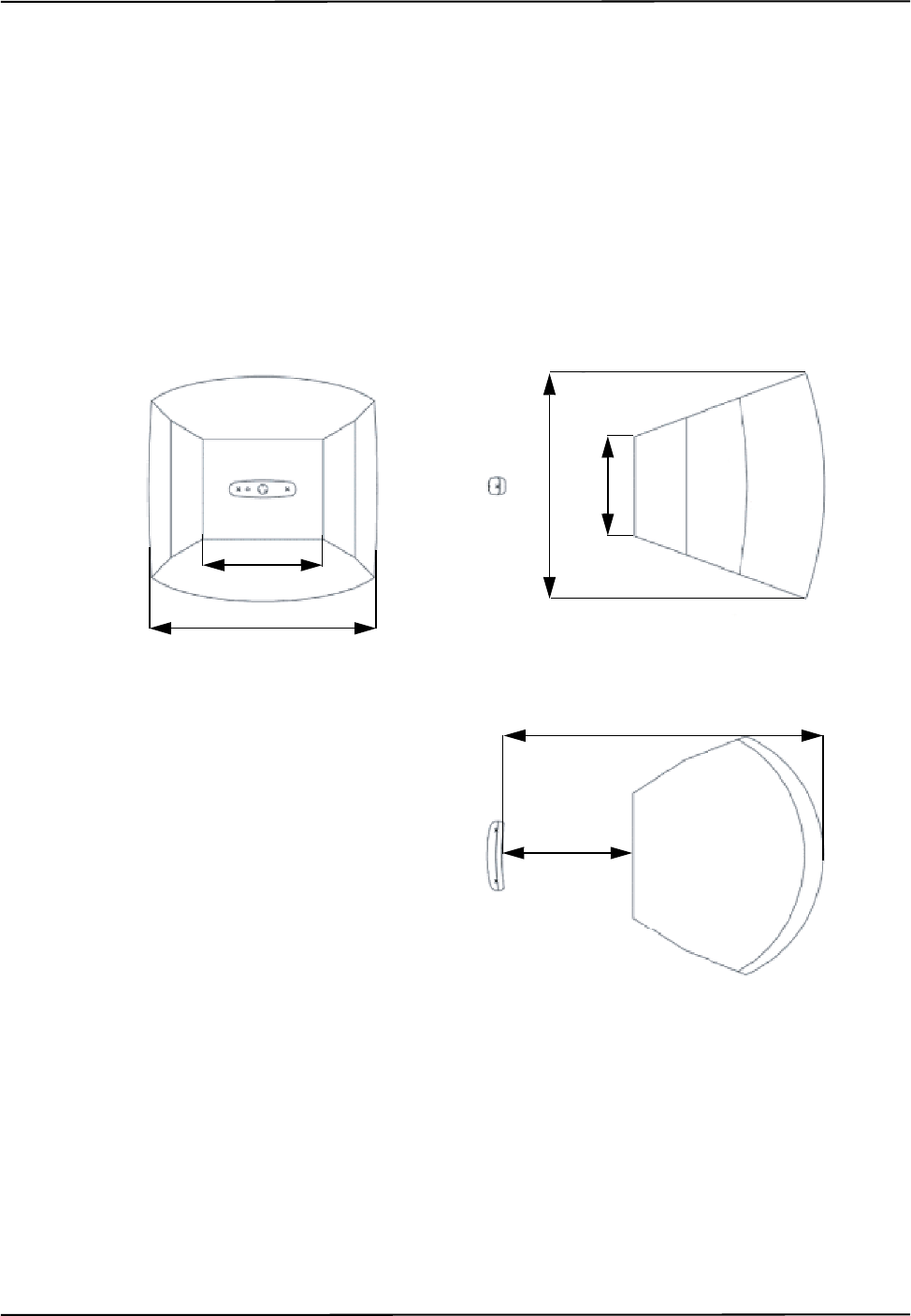
How the Polaris Vicra System Works
Polaris Vicra User Guide - Revision 2 27
The characterized measurement volume is a subset of the field of view. It is the volume where
data was collected and used to characterize the Polaris Vicra System Position Sensor. The
dimensions of the characterized measurement volume are illustrated in Figure 3-2.
Within the characterized measurement volume, the Polaris Vicra System can measure a single
marker with an accuracy of 0.25 mm RMS. The accuracy of measurements reported outside the
Polaris Vicra characterized measurement volume is unknown. The Polaris Vicra System is
specifically designed to NOT report these measurements; however, you can request such
information by applying additional API commands to application software. You enable this
additional functionality at your own discretion. The Position Sensor’s performance is determined
using the calibration methodology described in Appendix A on page 85.
Figure 3-2 Characterized Measurement Volume
Out of Volume and Partially Out of Volume
A tool is flagged as out of volume if all of its markers are outside of the characterized measurement
volume, but the system can still detect the tool.
By default, the Polaris Vicra System reports tools with markers that are outside of the characterized
measurement volume as MISSING. You can tell the Polaris Vicra System to report the
1336 mm
557 mm
491 mm
887 mm
392 mm
Top View
Side View
Front View
938 mm
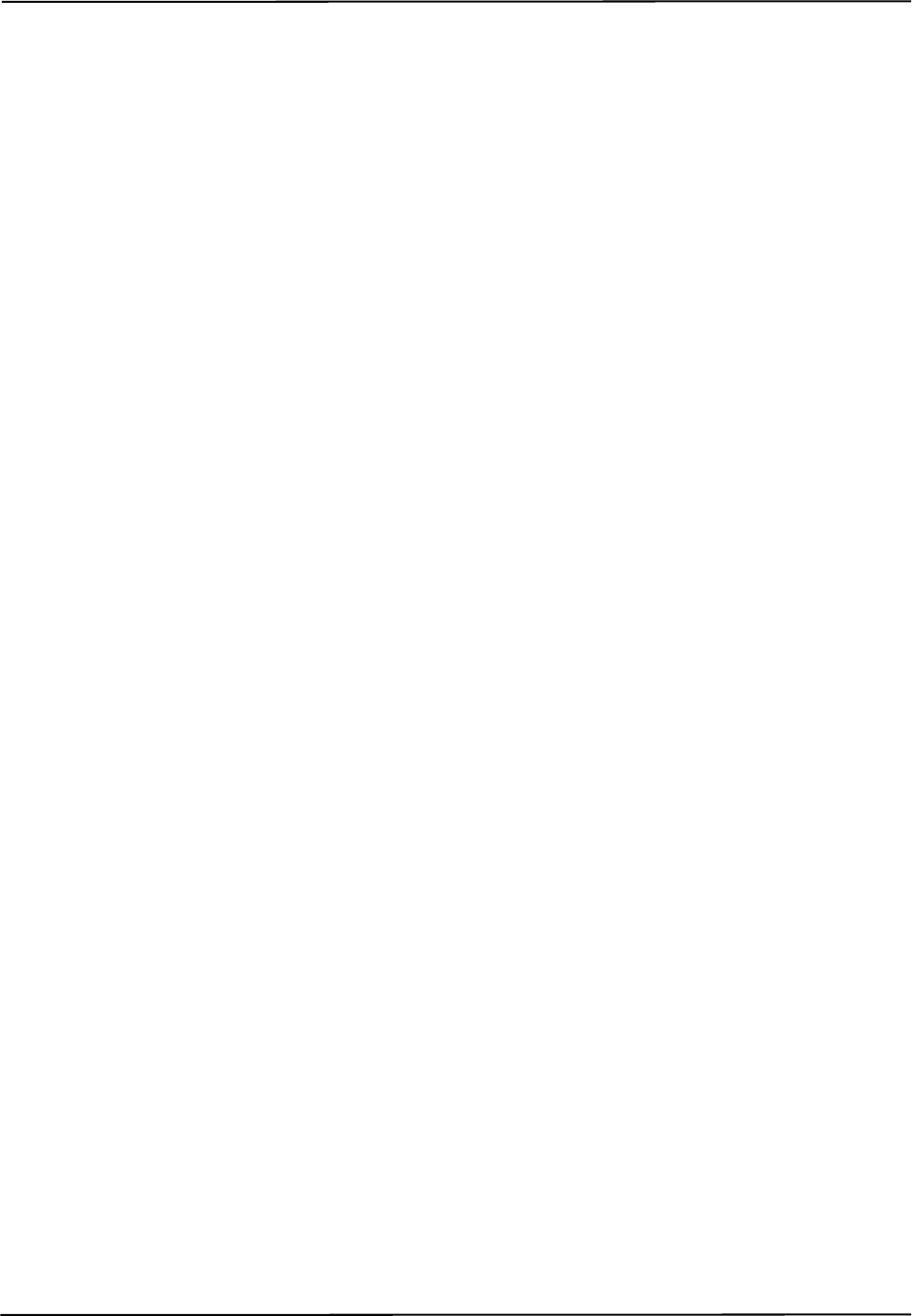
How the Polaris Vicra System Works
28 Polaris Vicra User Guide - Revision 2
transformations of these tools using reply option 0x0800 with the BX or TX command. See the
“Polaris Application Program Interface Guide” for details.
A tool is flagged as partially out of volume if:
• less than the minimum number of markers (a parameter in the tool definition file) are inside
the characterized measurement volume, and
• at least one marker on the tool is inside the characterized measurement volume
For example, consider a five-marker tool, with three markers inside the characterized measurement
volume and two markers outside the volume. If the minimum number of markers is set to 3, the tool
is considered to be inside the volume. If the minimum number of markers is set to 4 or 5, the tool
will be flagged as partially out of volume.
3.4 Marker Detection and Tool Tracking
Detecting Markers
The Position Sensor detects active and passive markers using different methods. Active markers are
triggered by a 20 Hz “chirp” signal emitted by the Position Sensor illuminators, which causes the
active markers to emit IR for the integration time. (The chirp signal is only a trigger.)
To detect passive markers, the Position Sensor’s illuminators flood the surrounding area with IR for
the whole integration time by flashing at 20 Hz (similar to the flash on a camera). The passive
sphere markers have a retro-reflective coating that reflects the IR directly back to the Position
Sensor instead of scattering it.
For both active and passive markers, the Position Sensor collects IR for a period of time called the
integration time. This acts like an electronic shutter. The system makes automatic adjustments to
the integration time so that the intensity of the brightest IR detected is set to a maximum value, and
the intensity of all other IR detected falls below this value. This process is called dynamic range
control.
The system distinguishes between potential marker data and background IR using a value called the
trigger level. The trigger level is the minimum IR intensity considered to be valid marker data.
Background IR that falls below the trigger level is rejected by the Position Sensor. The trigger level
generally increases with integration time; see “Setting the Infrared Light Sensitivity” on page 54 for
more details.
Acquiring and Tracking Tools
When the Polaris Vicra System first begins tracking a tool, or whenever a tool goes missing, it must
“acquire” the tool. (For information on why a tool goes missing, see “Missing and Disabled
Transformations” on page 48.) To acquire tools, the Polaris Vicra System first measures the
positions of all the visible markers.
IR light hits the Charge Coupled Devices (CCDs) in the Position Sensor. If the system is unable to
detect individual IR sources, or has detected more IR sources than it can process, it will report an
error, see “Tracking Errors and Flags” on page 49. Otherwise, the system will calculate the position
of the IR sources.
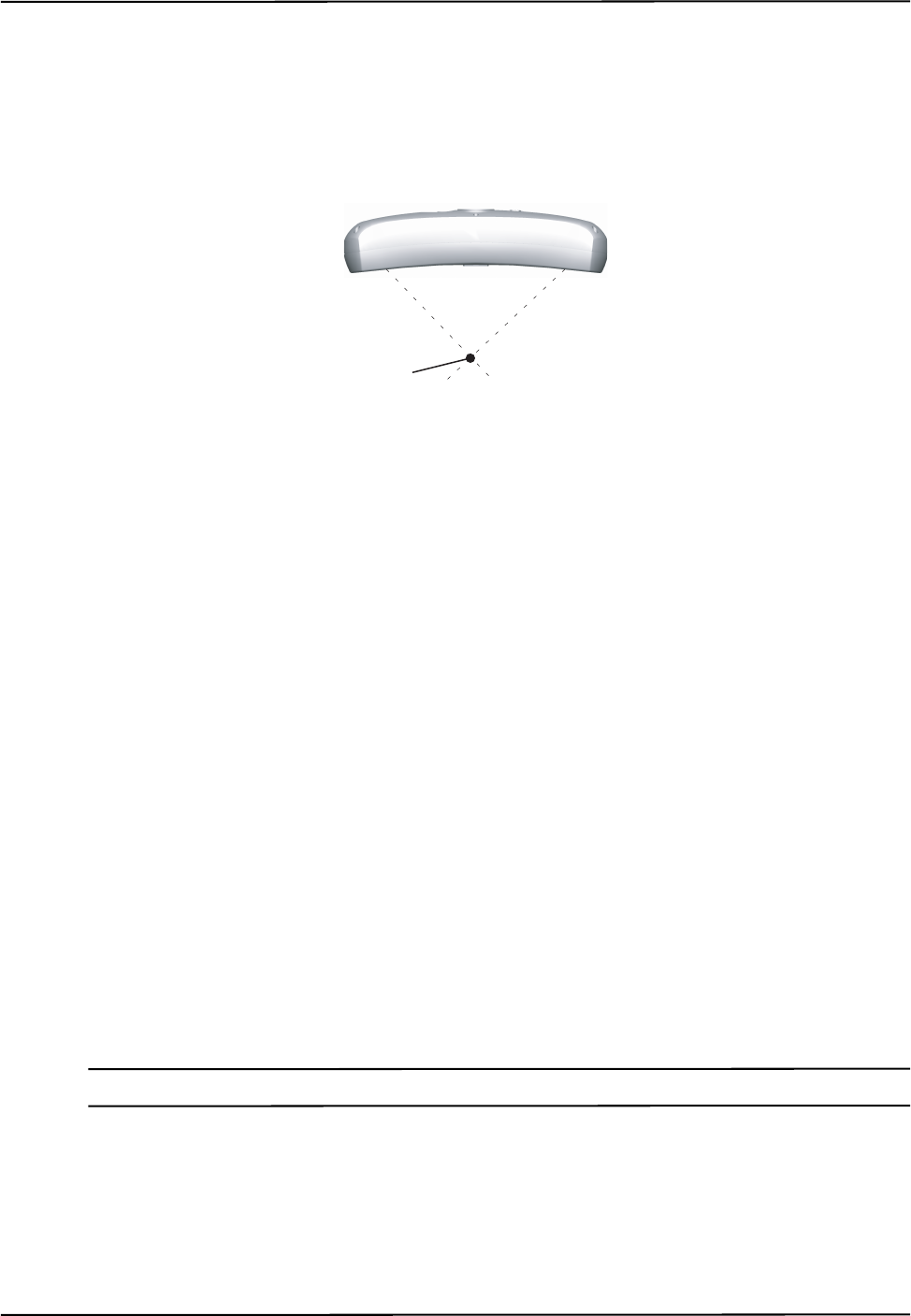
How the Polaris Vicra System Works
Polaris Vicra User Guide - Revision 2 29
To determine the position of an IR source, the Position Sensor calculates a line between the source
of IR and each sensor (displayed as dotted lines in Figure 3-3). Where the lines cross each other, the
Polaris Vicra System calculates the line separation. (The distance between the lines.) (In a
theoretical case the lines will intersect exactly, but in the modelled “real world” case they will be
apart.) If the line separation at this point is less than a predefined limit, the Polaris Vicra System
considers the point to be a possible marker position. Otherwise, the point is discarded.
Figure 3-3 Determining a Marker Position
Once the system has measured the positions of all the markers, it calculates the segment length (the
distance between two markers) for each pair of markers, and the angle between each segment. It
compares this data with the marker geometry data in each tool definition file (described on page 31),
to determine which markers belong to which tool. The unique geometry requirements, described in
the “Polaris Tool Design Guide”, allow the Polaris Vicra System to distinguish between tools. Any
markers that are not part of a tool are considered stray markers (this may include phantom markers).
See “Stray Marker Reporting” on page 37 for more details on stray markers and phantom markers.
The Polaris Vicra System has “acquired” a tool once it has matched the minimum number of
markers (a parameter in the tool definition file) for the tool and can calculate a transformation for
the tool. Once a tool has been acquired, the Position Sensor tracks it using a predictive algorithm.
Three Marker Lock On
If the “3 marker lock on” option is enabled in the tool definition file, the Polaris Vicra System will
acquire and track the tool as long as it can detect at least three markers. The system will not report
the transformations unless the minimum number of markers is used to calculate the transformation.
For example, consider a four-marker tool with the “3 marker lock on” option enabled. If the system
can only detect three of the markers on the tool, it will continue to track that tool but will only report
transformations if the minimum number of markers is set to 3. If the minimum number of markers is
set to 4, the system will continue to track the tool in the background, but will report the tool as
MISSING. Selecting 3 marker lock on in this case will result in the tool transformations being
reported faster, once the minimum number of markers becomes visible, because the system does not
have to spend time re-acquiring the tool.
Note For more details on the “3 marker lock on” option, see the “Polaris Tool Design Guide”.
Marker
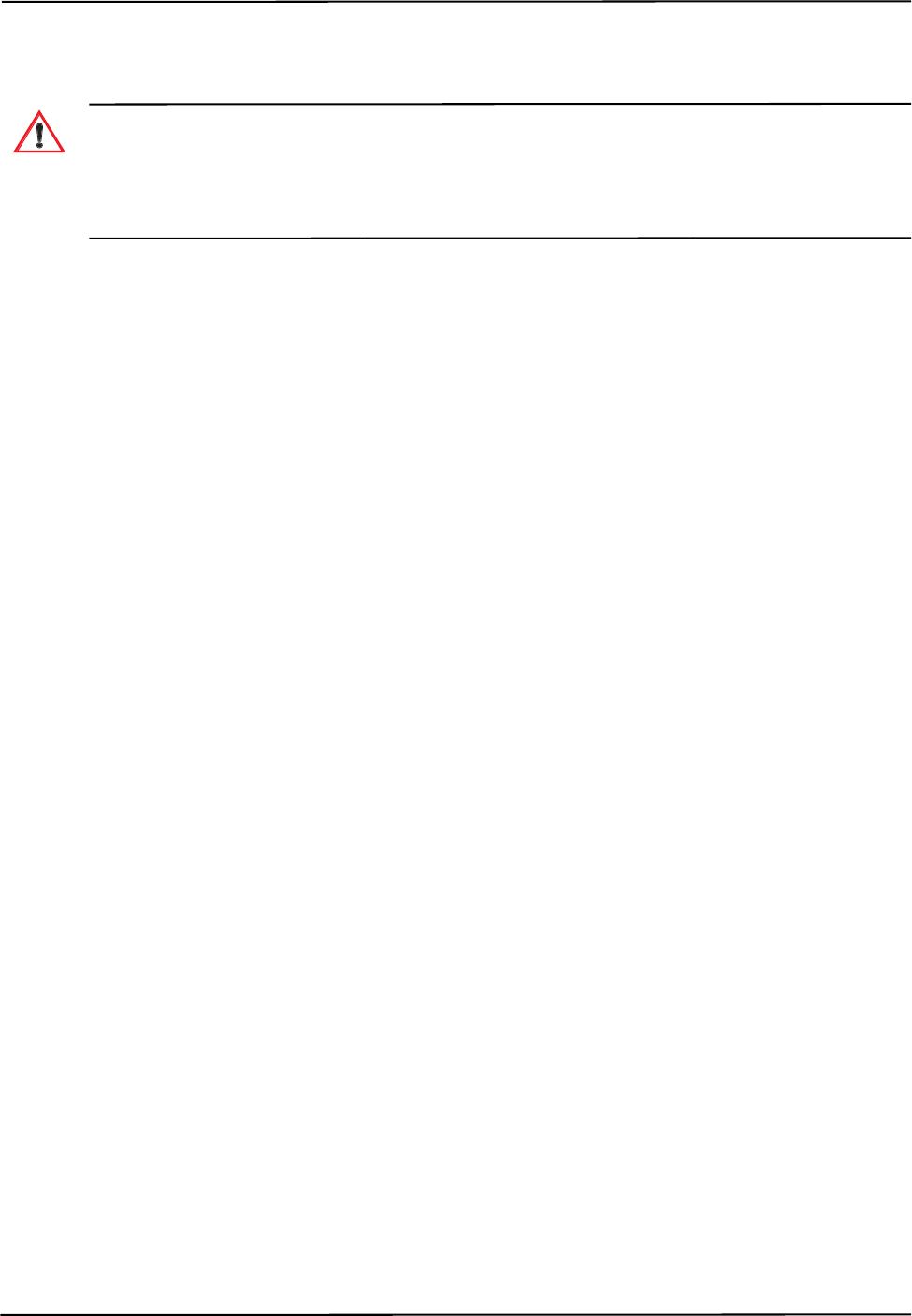
How the Polaris Vicra System Works
30 Polaris Vicra User Guide - Revision 2
3.5 Polaris Vicra System Tools
Do not use a wireless tool whose design does not conform to the Polaris Vicra System's unique geometry
constraints. When a Polaris Vicra System attempts to track more than one wireless tool in the measurement
volume, these unique geometry constraints ensure that they are distinguishable from each other. Reliance on
data produced by two indistinguishable tools can lead to inaccurate conclusions. If your application involves
personal safety, these inaccurate conclusions increase the possibility of personal injury.
Tools used with the Polaris Vicra System are wireless, and incorporate either active or passive
markers. The system can track up to six tools at a time. The Position Sensor tracks tools based on
marker geometry, which is specified in the tool definition file for each tool. A tool definition file
must be loaded before the Polaris Vicra System can track its associated tool. For more information
on tool definition files, see “Tool Definition File” on page 31.
Tools are available from NDI for use with the Polaris Vicra System. Contact NDI for more details.
Tool Characteristics
Tools used with the Polaris Vicra System have the following characteristics:
• A 5DOF (five degrees of freedom) tool has between three and six markers. All the markers
on a 5DOF tool are collinear. The Polaris Vicra System will report the 3D position and 2D
orientation of a 5DOF tool.
• A 6DOF (six degrees of freedom) tool has between three and six markers that are not
collinear. The Polaris Vicra System will report the 3D position and 3D orientation of a
6DOF tool.
• The geometry of each tool must follow the unique geometry constraints. Tools must have
different marker geometries from one another, so the Position Sensor can distinguish
between them. A marker geometry that is the mirror image of another tool’s marker
geometry is not considered unique. For more details on unique geometry constraints and
marker geometry, see the “Polaris Tool Design Guide”.
• A multi-faced tool (which is also 6DOF) can have up to six faces, totalling a maximum of
20 markers. Each face on a tool is treated as a separate rigid body which complies with the
following constraints:
• It has a maximum of eight markers
• It complies with the unique geometry constraints
• It has a different marker geometry from the other faces on the tool.
• Each tool has its own local coordinate system This is defined during the tool
characterization process, and is often dependent on the tool’s intended use.
Multi-Faced Tool Tracking
When the Polaris Vicra System is tracking a multi-faced tool, it tracks only one face at a time. The
face being tracked is returned with reply option 0x0002 of the BX and TX commands, and is
reported in NDI ToolBox (see the online help in NDI ToolBox for more details).
Warning!
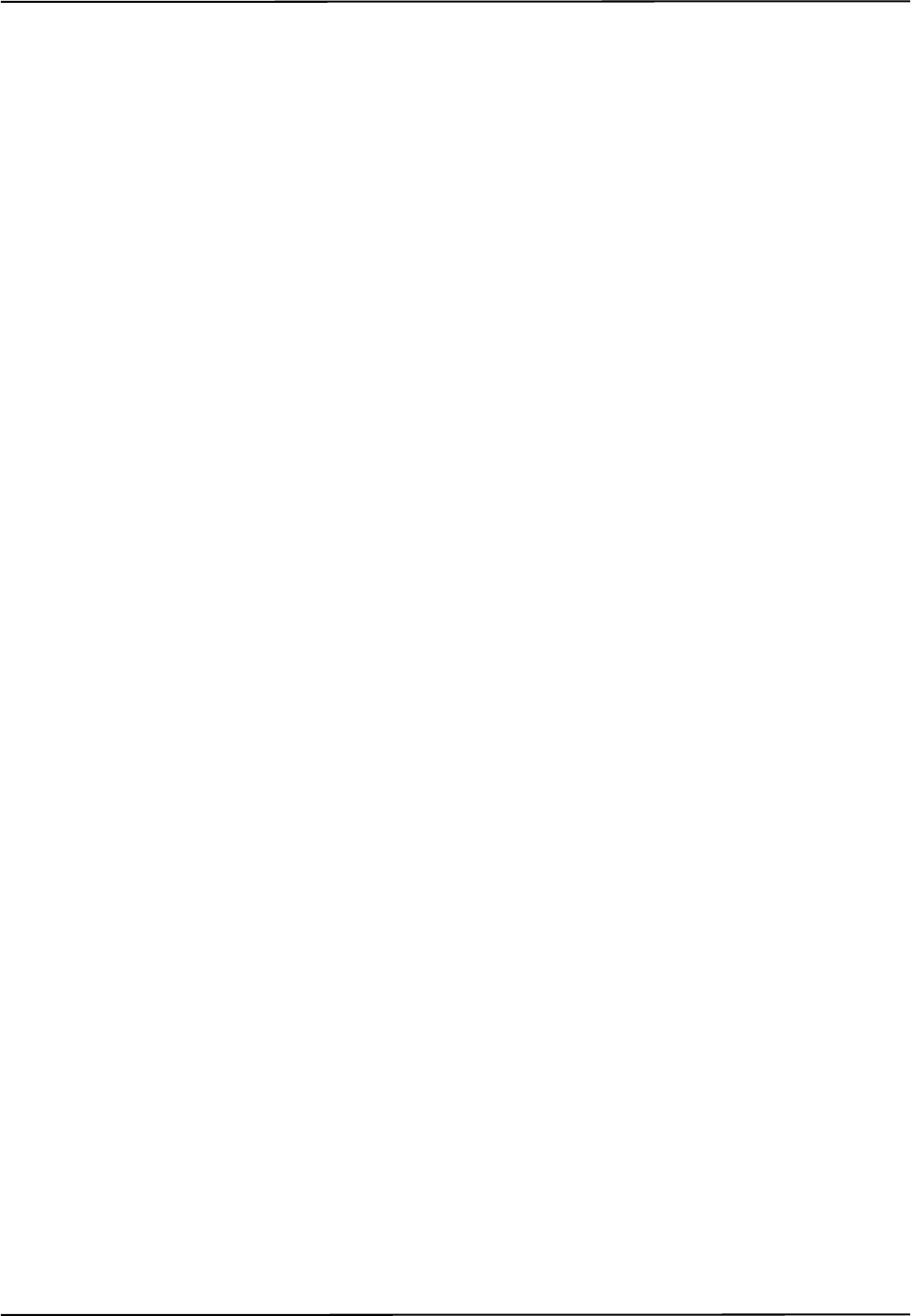
How the Polaris Vicra System Works
Polaris Vicra User Guide - Revision 2 31
Each face is assigned a face normal in the tool definition file (described on page 31). The face
normal is a vector pointing in the same direction as the tool face, to let the Polaris Vicra System
know the direction each tool face is facing. The system will track the face most directly oriented to
the Position Sensor (i.e. the face with the smallest angle between the face normal and the sensors in
the Position Sensor). If the minimum number of markers are not visible on the face most directly
oriented to the Position Sensor, the system will attempt to track another face.
The system has a hysteresis of 2° when determining whether to switch faces. The system will
determine the angle between the sensors and each face of the tool. If the face with the smallest angle
is 2° smaller than the current face’s angle, the system will switch to the new face.
3.6 Tool Definition File
A tool definition file (formatted as .rom) describes a tool to the Position Sensor. The information
stored in the tool definition file includes the geometry of the tool's markers, the tool’s manufacturing
data, information on marker and face normals, groups and faces definitions, and the parameters used
to track tools. For more information on the parameters used to track tools, see Tool Tracking
Parameters below.
A tool definition file must be loaded into the system (by the host computer) before the Polaris Vicra
System can track its associated tool. If the Polaris Vicra System is measuring the positions of stray
markers (described in “Stray Marker Reporting” on page 37), at least one tool definition file must be
loaded in order for the Position Sensor illuminators to emit IR light.
Tool definition files can be created in NDI 6D Architect. The procedure used to create a tool
definition file is called tool characterization. For more information on tool characterization, see the
“Polaris Tool Design Guide” and the “NDI 6D Architect User Guide”.
3.7 Tool Tracking Parameters
The following tool tracking parameters are specified in the tool definition file (described on page
31).The flow chart on page 34 describes how the Polaris Vicra System uses the tool tracking
parameters to determine which markers to use to calculate a tool transformation, and when to return
a transformation.
For information on how to change the tool tracking parameters and what values to use, see the
“Polaris Tool Design Guide” and the “NDI 6D Architect User Guide”.
Maximum 3D Error
The maximum 3D error parameter specifies the maximum allowable 3D error for each marker on
the tool. The maximum 3D error is the difference between the measured and expected location of a
marker on a tool. The expected location of a marker on a tool is specified in the tool definition file
(described on page 31).
If the 3D error for a particular marker is greater than the specified maximum 3D error value, the data
from that marker will be not be used to determine the tool transformation.
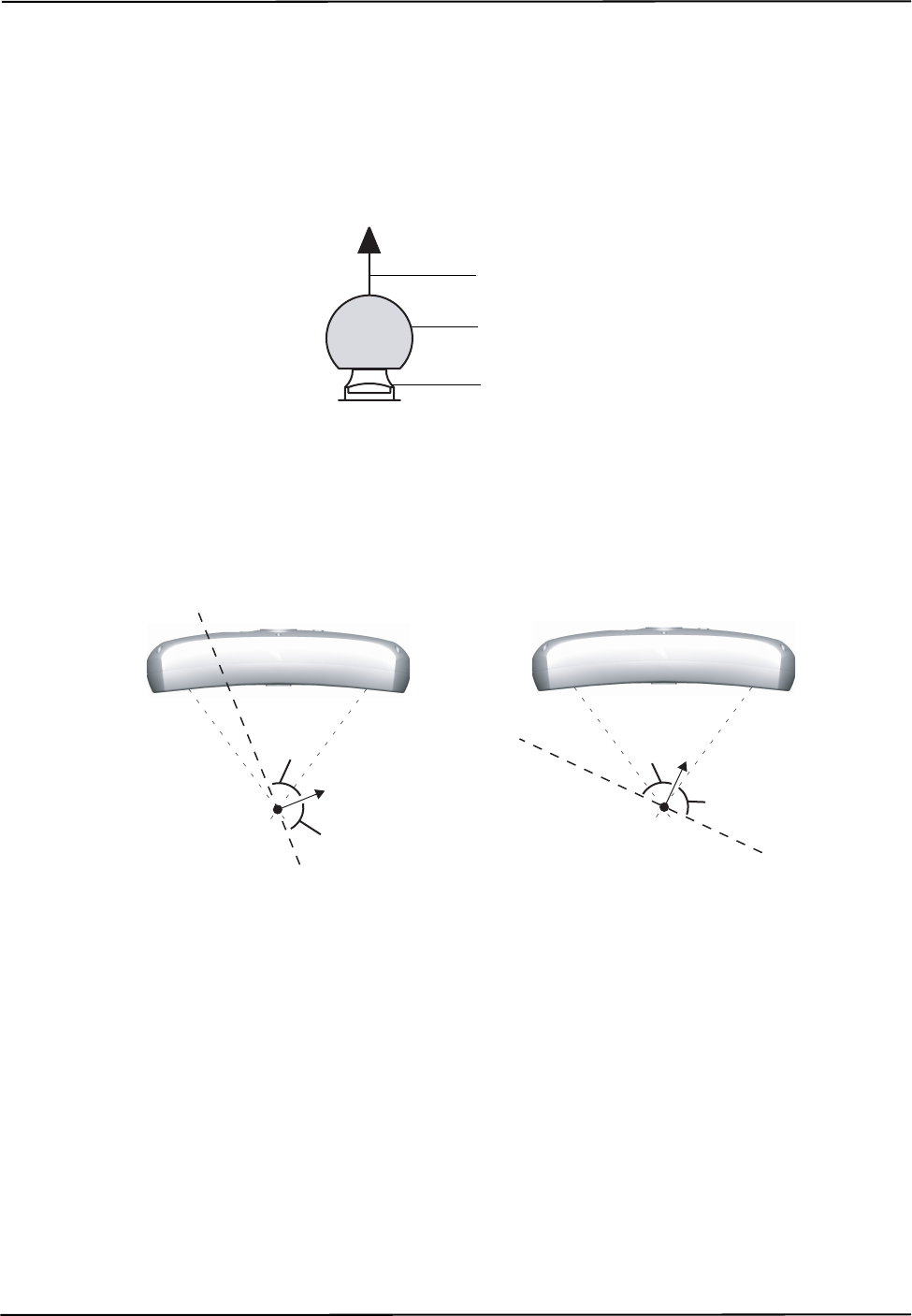
How the Polaris Vicra System Works
32 Polaris Vicra User Guide - Revision 2
Maximum Marker Angle
The maximum marker angle parameter specifies the maximum allowable angle between a marker
and each sensor on the Position Sensor. The default maximum marker angle for passive sphere
markers is 90º and for active markers it is 60°. Each marker has an associated normal vector, which
is defined in the tool definition file. A marker normal is a vector of length 1, and points in the same
direction as the marker, as illustrated in Figure 3-4.
Figure 3-4 Marker With Marker Normal
The Polaris Vicra System uses the marker normal to determine whether the maximum marker angle
has been exceeded. The system measures the angle between the marker normal and each sensor, in
both the Position Sensor’s xy- and yz-planes. (The Position Sensor’s coordinate system is described
in “Global Coordinate System” on page 26.) The Position Sensor then compares these measured
angles to the maximum marker angle, as illustrated in Figure 3-5.
Figure 3-5 Maximum Marker Angle
If the angle between a marker normal and a sensor is greater than the specified maximum marker
angle, the data from that marker will be not be used to determine the tool transformation.
The further a marker is from the Position Sensor, the smaller the angle it can be turned and still be
within the maximum marker angle.
Minimum Number of Markers
The minimum number of markers parameter specifies the minimum number of markers that the
Position Sensor must use in the calculation of a tool transformation in order to return the
Marker Normal
Passive Sphere Marker
NDI Mounting Post
Marker Normal
Marker Normal
Max Marker Angle
Max Marker Angle Max Marker Angle
Max Marker Angle
The angle between the marker normal
and the left sensor is greater than the
maximum marker angle.
The angle between the marker normal
and each sensor is less than the
maximum marker angle.
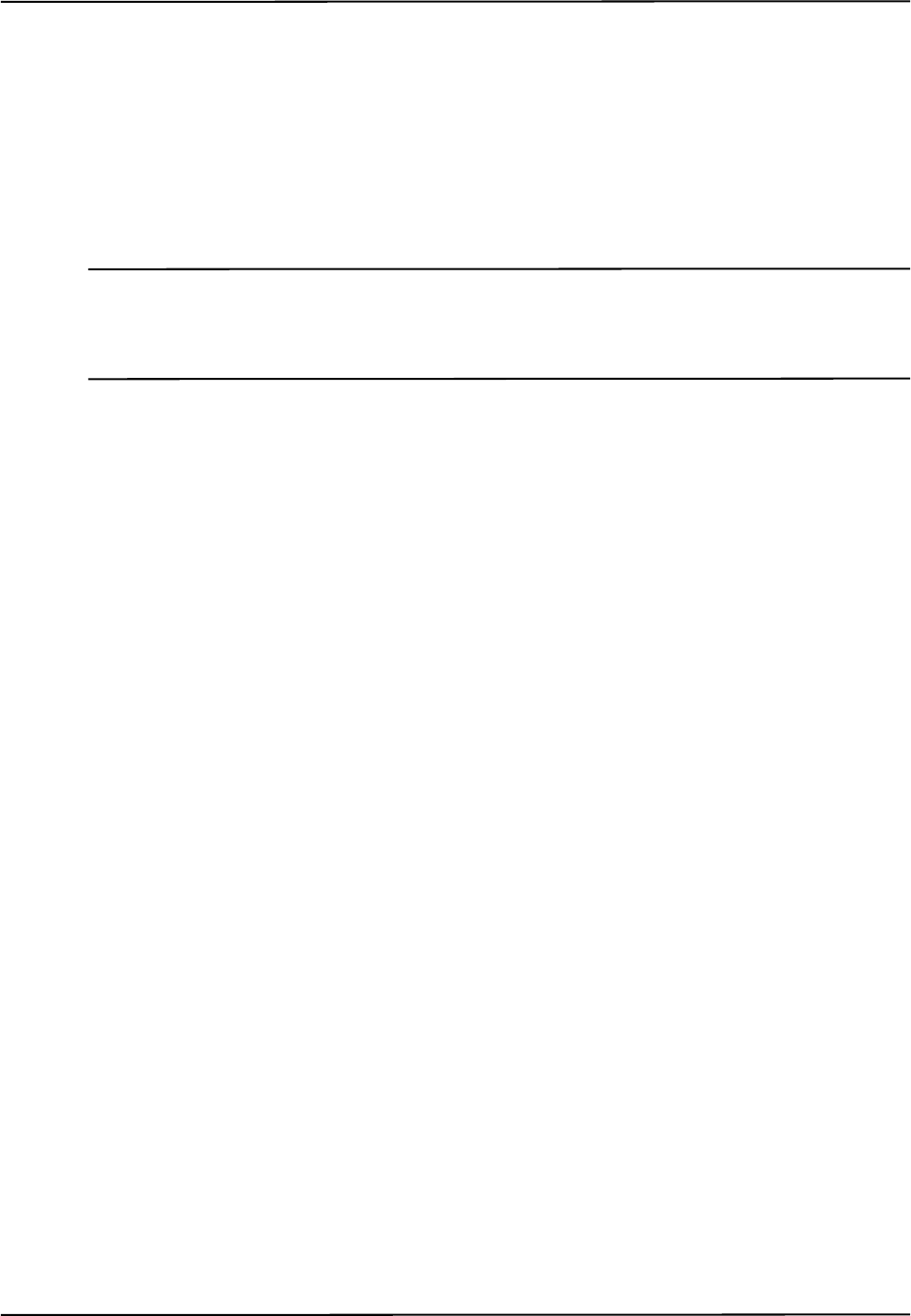
How the Polaris Vicra System Works
Polaris Vicra User Guide - Revision 2 33
transformation. If fewer markers than the minimum number of markers are used in the calculations,
then the tool will be reported as MISSING.
For example, consider a four-marker tool that has three markers inside the characterized
measurement volume, and one marker outside of the characterized measurement volume. If the
minimum number of markers parameter is set to 3, the Polaris Vicra System will report
transformations for the tool (as long as the other tool tracking parameters are satisfied). If the
minimum number of markers parameter is set to 4, the Polaris Vicra System will report the tool as
MISSING.
Note You can tell the Polaris Vicra System to report the positions of tools that have less than the minimum number of
markers inside the characterized measurement volume by using reply option 0x0800 with the TX or BX command.
This may reduce the accuracy of the transformations. See the “Polaris Application Program Interface Guide” for
details.
Minimum Spread
The minimum spread parameters specify the minimum size 3D box that must contain all the
markers used in the calculation of a tool transformation. The length, width, and height of this box
must be greater than the specified Minimum Spread 1, Minimum Spread 2 and Minimum Spread 3
parameters, respectively, or else the system will not return a transformation.
This setting is optional. For more details on the minimum spread parameter, see the “Polaris Tool
Design Guide”.
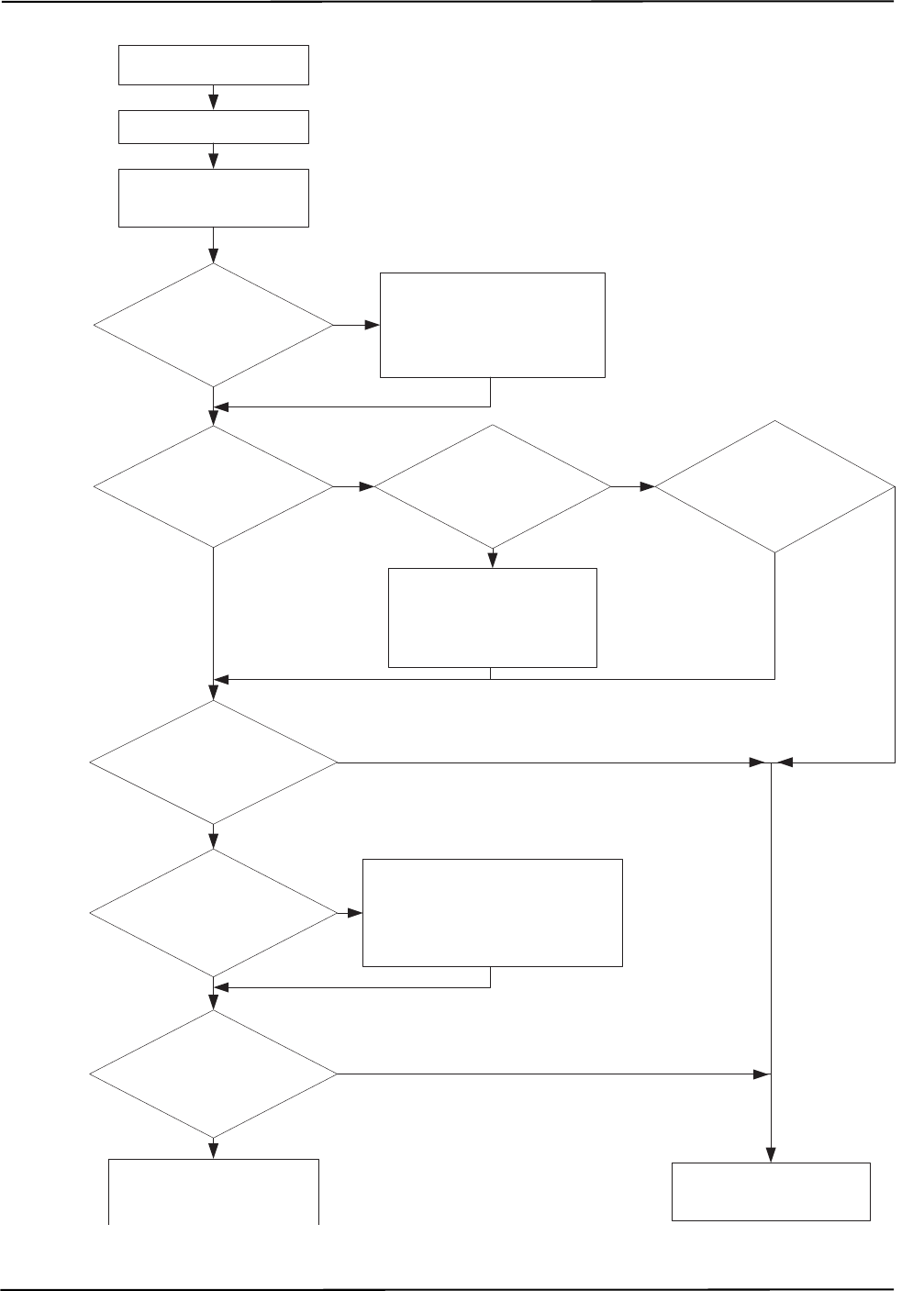
How the Polaris Vicra System Works
34 Polaris Vicra User Guide - Revision 2
Figure 3-6 Flowchart of Tool Tracking Parameters Use
Flash illuminators on
Position Sensor
Measure positions of
markers
Calculate tool
transformation using at
least 3 markers
Are all
markers within the
max. marker
angle?
Ignore markers that are outside
of the max. marker angle &
calculate tool transformation
using at least 3 markers
Are
all markers
inside the characterized
measurement
volume?
Can the
system calculate a
tool transformation without
the out-of-volume
markers?
Is reply option
0x0800 used with BX or TX
command?
Ignore the out-of-volume
markers &
calculate tool transformation
using at least 3 markers
Were
the min. number of
markers used to calculate
a transformation?
Are all markers
within the max.
3D error?
Are the spread
parameters satisfied?
Ignore markers that are greater than
the max. 3D error
&
Calculate tool transformation using at
least the min. number of markers.
Return tool transformation &
status and error information Return MISSING &
status and error information
yes
no
yes
yes
yes
yes
yes
no no
yes
no
no
no
no
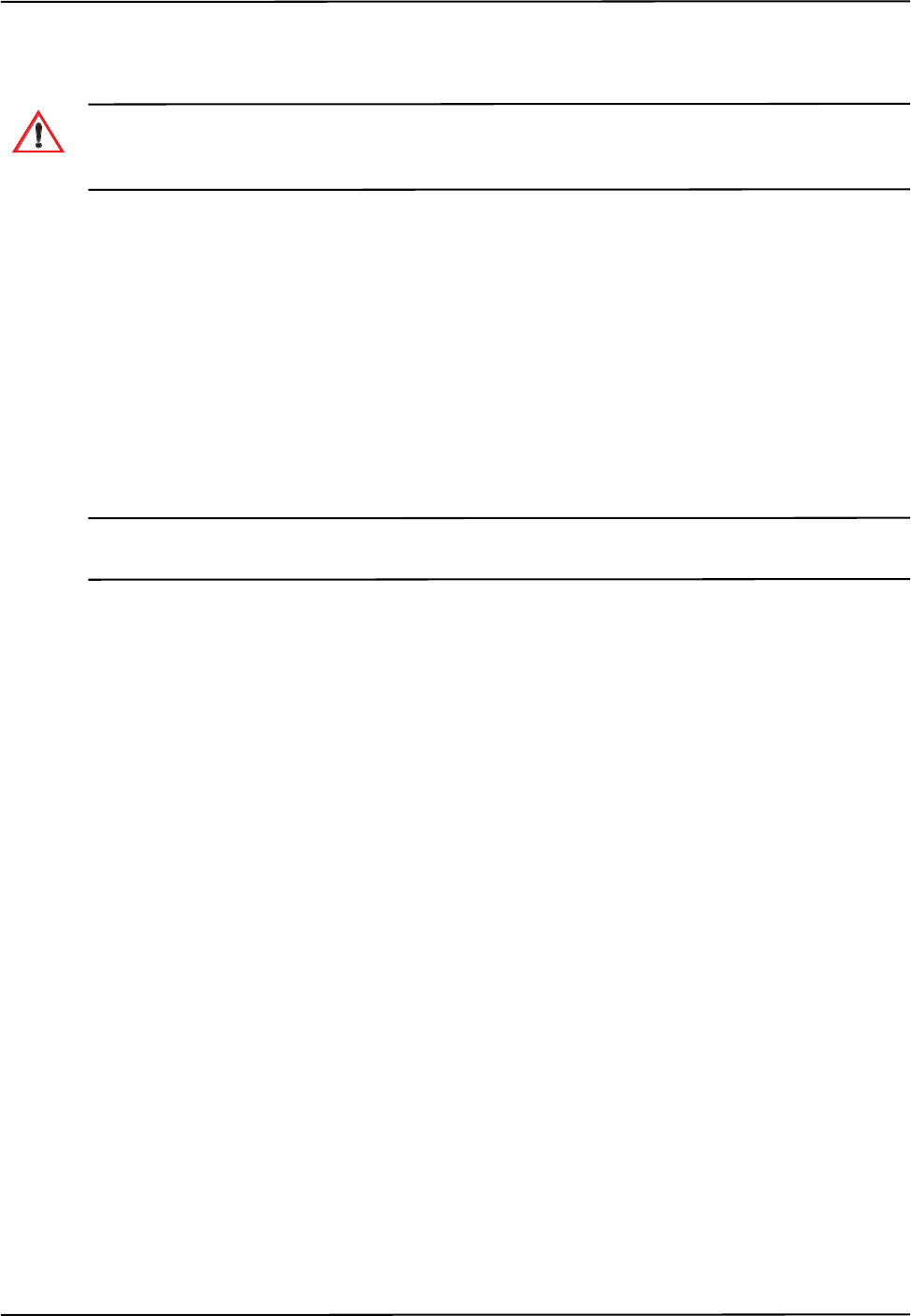
How the Polaris Vicra System Works
Polaris Vicra User Guide - Revision 2 35
3.8 Tool Tip Offset
Do not use a tool with a tip without first performing a pivot procedure to verify the tip offset. Reliance on data
produced by a tool with an inaccurate tip offset may lead to inaccurate conclusions. If your application involves
personal safety, these inaccurate conclusions increase the possibility of personal injury.
The origin of a tool is defined as part of the tool’s local coordinate system in the tool definition file.
When the Position Sensor tracks a tool, it reports the transformations of the origin of the tool.
In certain circumstances, it is useful to track a point on the tool other than the tool’s origin. In
particular, it is useful to track the location of the tip of a probe. It is possible to define the tool’s
origin at the tip of the probe; however, if the tool is later bent, the origin will no longer be located at
the tip.
NDI recommends determining the tool tip offset of the tool, prior to each use. The tool tip offset is
the vector between the tip of the tool and the origin of the tool. Application software can apply the
tool transformations reported by the Polaris Vicra System to the tool tip offset, in order to determine
the location of the tool tip.
Note The Polaris Vicra System always tracks the origin of the tool. It is the application software, not the Polaris Vicra
System, that calculates the location of the tool tip.
Determining the tool tip offset prior to each use ensures that the location of the tool tip is known as
accurately as possible.The tool tip offset can be determined either by using a calibrator, or by
performing a pivoting procedure.
Using a Calibrator
A calibrator is a rigid body that incorporates three or more markers and a clamping mechanism. The
clamping mechanism allows another tool (usually a probe) to be clamped into place. An example of
a calibrator is illustrated in Figure 3-7. To use a calibrator to determine the tool tip offset of a probe,
clamp the probe in place on the calibrator. The origin of the calibrator is defined at the point where
the tool tip will rest. The Polaris Vicra System can then measure the positions of the probe’s origin
and the calibrator’s origin. The application software compares these measurements to determine the
tool tip offset of the probe.
Warning!
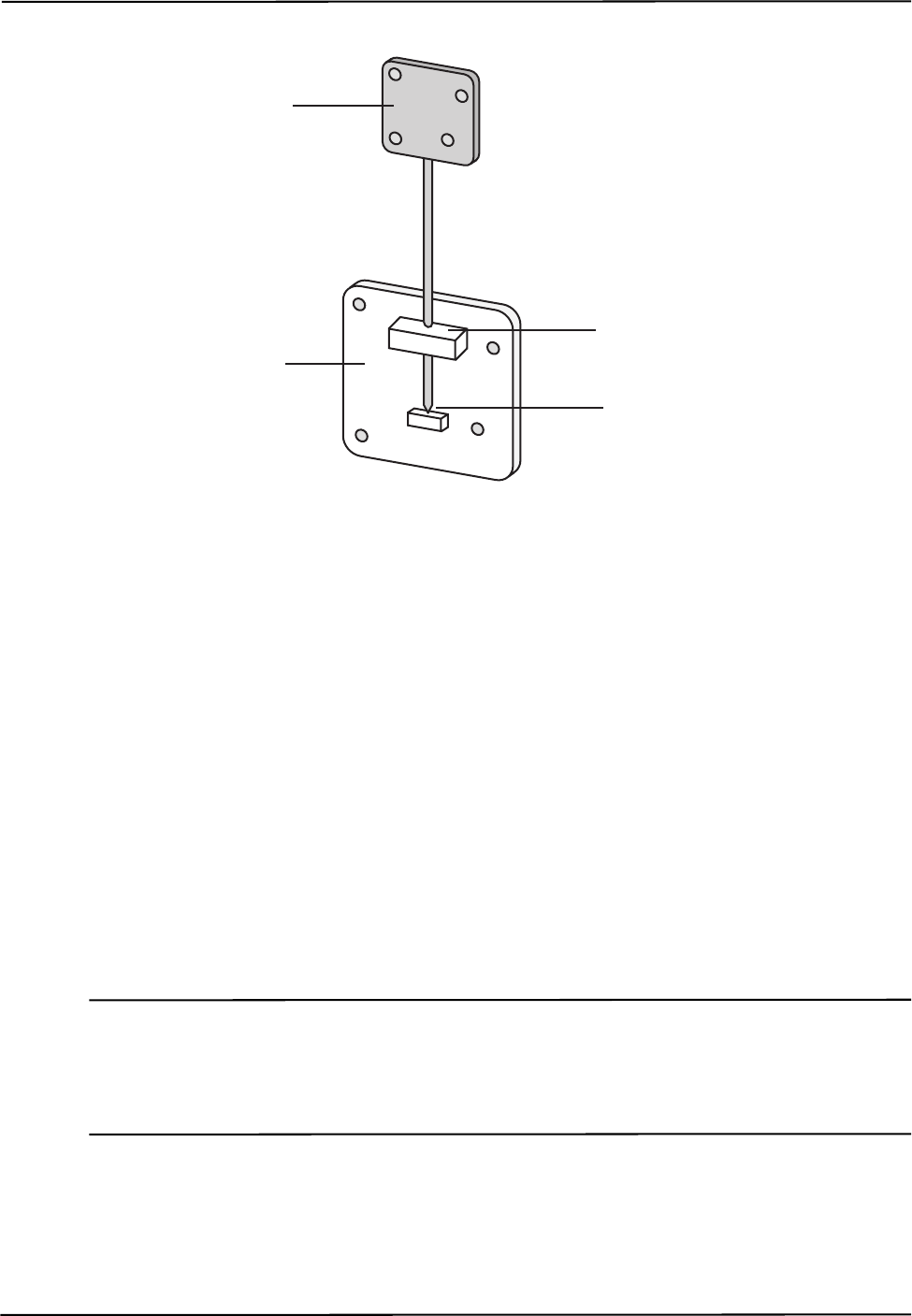
How the Polaris Vicra System Works
36 Polaris Vicra User Guide - Revision 2
Figure 3-7 Sample Calibrator
Pivoting
You can also determine the tool tip offset using a process called pivoting, using either NDI ToolBox
or NDI 6D Architect software. During the pivoting procedure, the Polaris Vicra System will
measure the positions of the markers while you pivot the tool. The software collects this data, and
uses it to determine the tool tip offset. Instructions on how to pivot a tool are detailed in
“Determining the Tool Tip Offset” on page 45. In addition the procedure is also detailed in the “NDI
6D Architect User Guide” and online help, and in the NDI ToolBox online help.
3.9 Reference Tool
A reference tool is a tool whose local coordinate system is used as the global coordinate system in
which other tools are tracked. The Polaris Vicra System tracks all the tools, including the reference
tool, and reports the transformations in the coordinate system of the Position Sensor (described on
page 26). Software (such as NDI ToolBox) then calculates and reports the positions and orientations
of all other tools with respect to the position and orientation of the reference tool.
Note Use a reference tool to ensure minimal drift in the measurements produced; specifically, drift caused by time,
settling and/or temperature.
It is the application software, not the Polaris Vicra System, that calculates the tool transformations with respect
to the reference tool.
For example, in neurosurgery the reference tool can be attached to the patient’s head. Then a
registration procedure is performed that defines the reference tool’s position relative to the patient’s
head. From then on, if either the patient’s head or the Position Sensor shifts, the measurements are
Probe
Calibrator
Clamp Probe in Place
Place Tool Tip at Origin
of Calibrator
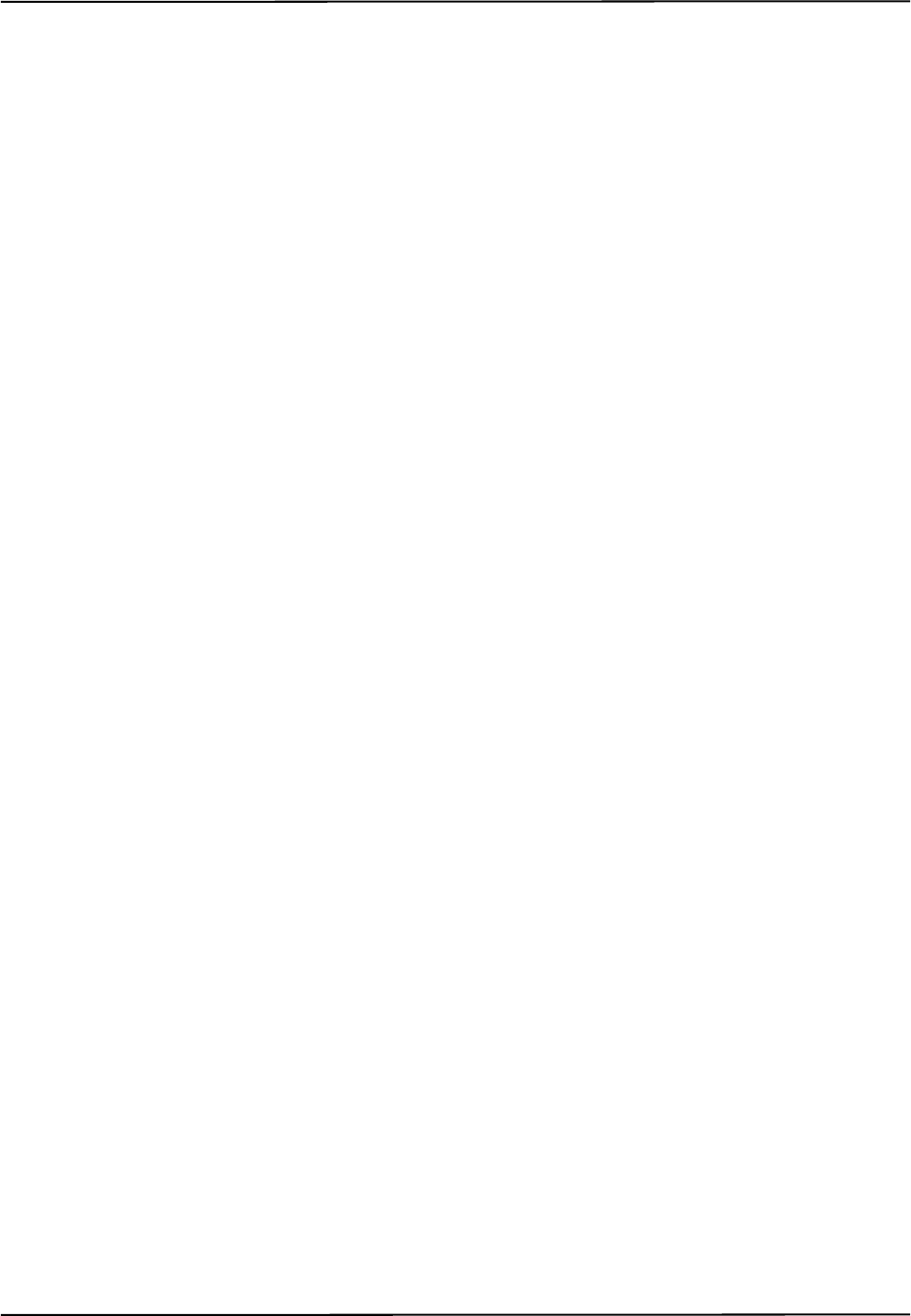
How the Polaris Vicra System Works
Polaris Vicra User Guide - Revision 2 37
not affected since they are reported with respect to the patient’s head (the reference tool) and not
with respect to the Position Sensor.
If the Polaris Vicra cannot track the reference tool (for example, if the reference tool is occluded),
then the software will not be able to calculate the transformations of other tools with respect to the
reference tool.
3.10 Stray Marker Reporting
A stray marker is a marker that is not part of a rigid body. For example, by placing stray markers on
a patient’s chest, the markers may be used to gate/track the patient’s breathing in order to time
radiation therapy.
If the stray marker reporting functionality is enabled, the Polaris Vicra System will report tool
transformations, as well as 3D data (position only, no orientation information) for up to 50 markers
that are not used in tool transformations (including phantom markers, described below). It is then
necessary to eliminate phantom markers within the application software, and verify that the stray
markers are within the characterized measurement volume.
It is important to be aware of the potential hazards associated with using the stray marker reporting
functionality. The hazards are as follows:
• An external IR source, for example, an IR transmitter or incandescent light, may be
identified as a stray marker. The position of a stray marker may be incorrectly identified and
return incorrect data.
• No marker identification is possible from frame to frame. It is therefore the user’s
responsibility to devise a method to keep track of which 3D position belongs to which
marker in which they are interested.
• A stray marker does not have any angular position to know if marker normals are being
exceeded.
• There are no built in checks to determine if the 3D result is a real marker or a phantom
marker, generated by other IR sources or markers in view of the Position Sensor. The system
tries to reject markers by the use of the line separation qualifier, but if several markers are in
a line parallel to the horizontal plane of the Position Sensor, phantom markers may still be
generated that are within the line separation qualifier.
• Partial occlusion cannot be detected, or compensated for. The partial occlusion is not
detected by the Position Sensor, but the user may be able to detect the apparent shift if the
marker position can be constrained in the application software. For example, the marker
position has to be constrained along a vector and its position relative to another marker is
supposed to be fixed within some tolerance.
To enable the stray marker reporting functionality, use the 0x1000 reply option with the BX or TX
command. This reply option returns out-of-volume information along with the 3D data. See the
“Polaris Application Program Interface Guide” for details.
In order for the Position Sensor to measure stray markers, a tool definition file must be loaded, and
the associated port handle must be initialized and enabled, even if no tools are being tracked. The
Position Sensor illuminators emit IR light only when a tool definition file is loaded.
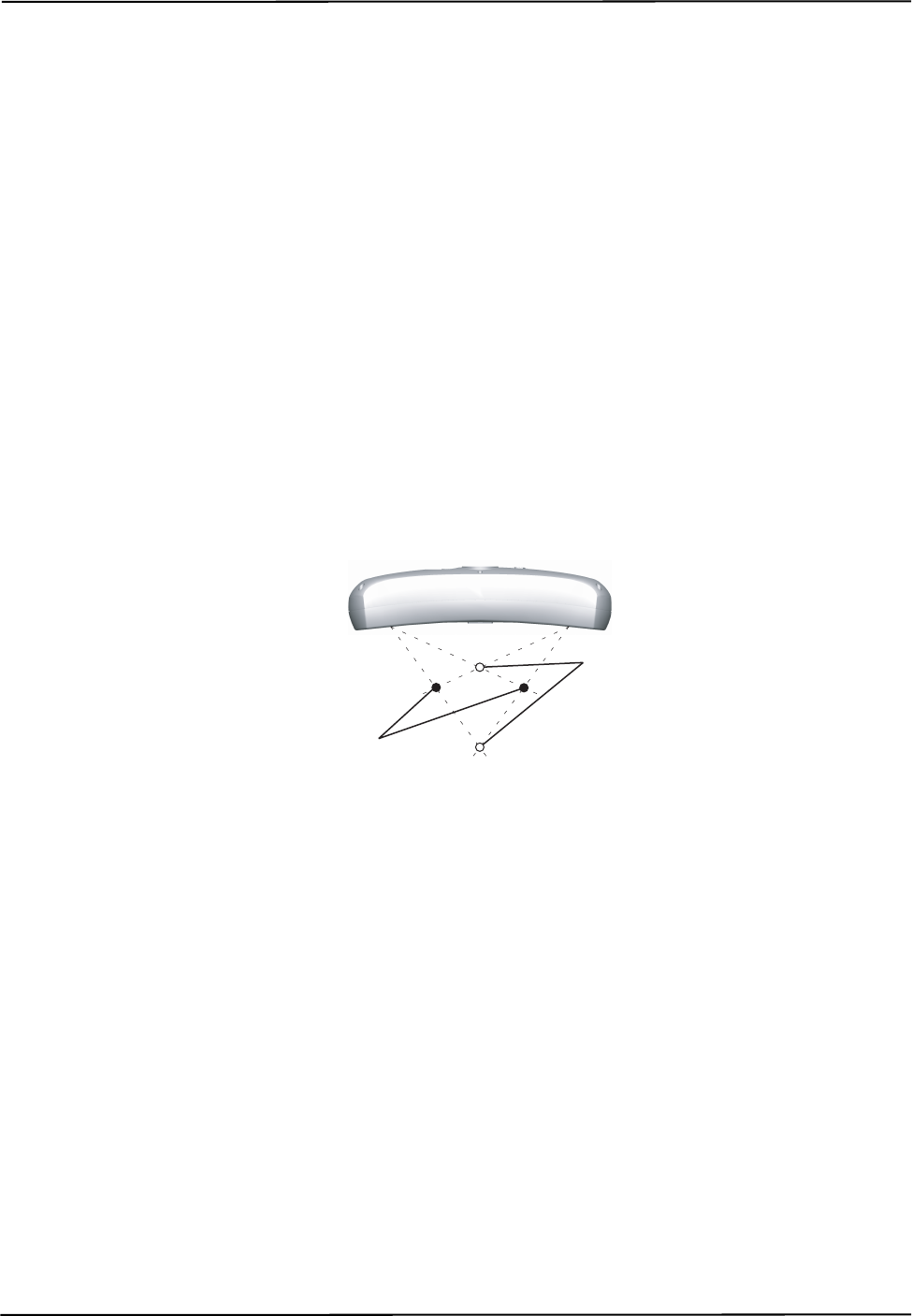
How the Polaris Vicra System Works
38 Polaris Vicra User Guide - Revision 2
3.11 Phantom Markers
Phantom markers are the result of the calculation that the Polaris Vicra System uses to determine the
position of a source of IR. They appear, and are reported as, markers but they do not actually exist;
they are phantom markers.
To determine the position of a source of IR, the Position Sensor calculates a line between the source
of IR and each sensor (displayed as dotted lines in Figure 3-8). Where the lines cross each other, the
Polaris Vicra System calculates the line separation (the distance between the lines). If the line
separation at this point is less than a predefined limit, the Polaris Vicra System considers the point to
be a possible marker position.
Phantom markers are reported when the imaginary lines calculated from the sensors intersect in
more than one place with a line separation less than a predefined limit. This generally occurs when
two or more markers are in the same plane as the sensors. For example, in the case of two coplanar
markers, there will be four mathematical solutions, as illustrated in Figure 3-8. Two are the actual
marker locations and two are the phantom marker locations. One phantom marker will usually be
closer to the Position Sensor than the actual markers and the other phantom marker will be farther
away from the Position Sensor than the actual markers.
The number of phantom markers increases with the number of coplanar markers. When there are n
coplanar markers, there will be up to n • (n - 1) phantom markers.
Figure 3-8 Phantom Markers
When the stray marker reporting functionality is not enabled, the Polaris Vicra System can eliminate
phantom marker solutions. The system matches the marker position solutions to the known marker
geometry of the tools, as described in “Marker Detection and Tool Tracking” on page 28. The
unused solutions are phantom markers, reflections, or other IR sources, and are not reported by the
system.
When the stray marker reporting functionality is enabled, it is necessary to eliminate the reported
phantom markers using application software.
3.12 Passive Sphere Markers
NDI passive sphere markers have a retro-reflective coating that reflects IR light back to its source
instead of scattering it. The IR light from the Position Sensor illuminators reflects off the passive
markers directly back to the sensors.
The Polaris Vicra System can report the positions of passive markers individually, and calculate the
position and orientation of tools that incorporate them. The measured position is the centre of the
marker. When a passive sphere marker is attached to an NDI mounting post, the centre of the sphere
is located at the top of the mounting post.
Phantom Markers
Real Markers
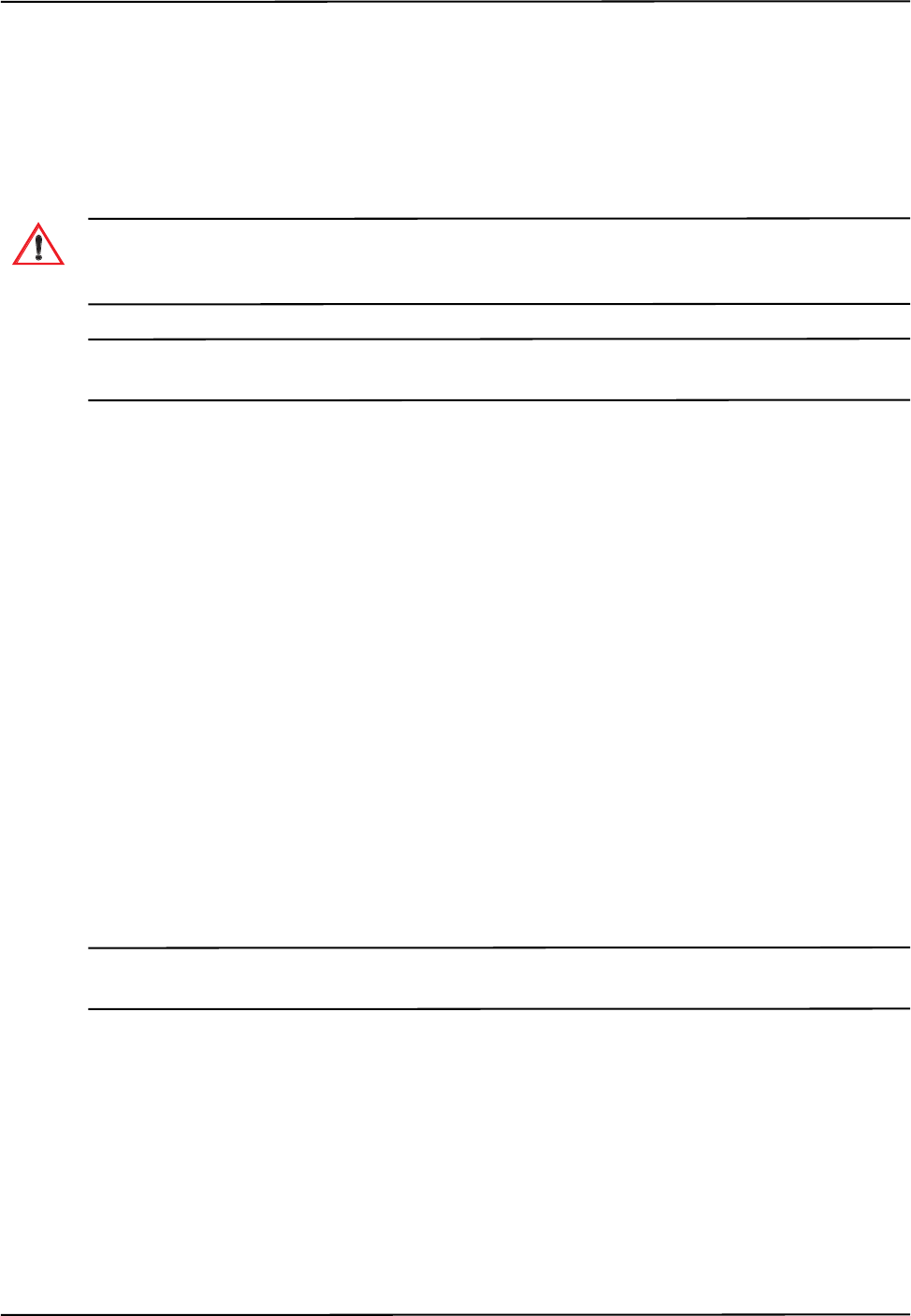
How the Polaris Vicra System Works
Polaris Vicra User Guide - Revision 2 39
The passive markers can only be sterilized one time. NDI does not recommend that a passive marker
be used if it has been sterilized more than once, as multiple cycles of sterilization may adversely
affect the marker's performance. Testing has shown that there is no significant degradation in the
performance of these markers after one cycle of ETO, STERRAD 100S, or STERIS SYSTEM 1
sterilization. The passive markers cannot be autoclaved. Pre-sterilized passive sphere markers are
also available; contact NDI for details.
Do not use markers without inspecting them for cleanliness and damage both before and during a procedure.
Reliance on data produced by unclean or damaged markers may lead to inaccurate conclusions. If your
application involves personal safety, inaccurate conclusions increase the possibility of personal injury.
Caution! Do not handle the passive sphere markers with bare hands as this will leave residue from skin that affects the
marker's reflectivity. Take care not to drop or scuff the markers, as this also affects the reflectivity of the markers.
3.13 Active Markers
Active markers are physically smaller than passive sphere markers. They consist of an Infrared
Light Emitting Diode (IRED) mounted on a ceramic base. The Position Sensor codes (“chirps”) the
IR pulses emitted from its illuminators. These coded IR pulses are received by the IR receiver on the
tool which then activates the IREDs. The Position Sensor receives the IR emitted by the IREDs and
processes it in the same manner as passive tool reflections.
Active markers are mounted in active wireless tools. The ceramic base allows them to be sterilised
by auto-claving as required. The power for active wireless tools is supplied by battery. For detailed
information on active markers and active wireless tools, refer to the “Polaris Tool Design Guide”.
3.14 Filter Spectral Response
The lenses on the Position Sensor filter out visible light, allowing only certain amounts of light at
specific frequencies to pass through to the CCDs. The CCDs are sensitive only to light below certain
frequencies. The result is a band pass filter from 800 nm to 1100 nm. Environmental light in this
range can affect the performance of the Polaris Vicra System. The more intense the environmental
light in this range, the higher the probability that it will interfere with the system.
Note It is important to reduce environmental IR, to prevent interference with the system. Some operating room lights
may emit IR.
The amount of light at various frequencies that passes through the lenses to the CCDs, and then is
detected by the CCDs, as illustrated in Figure 3-9.
Warning!
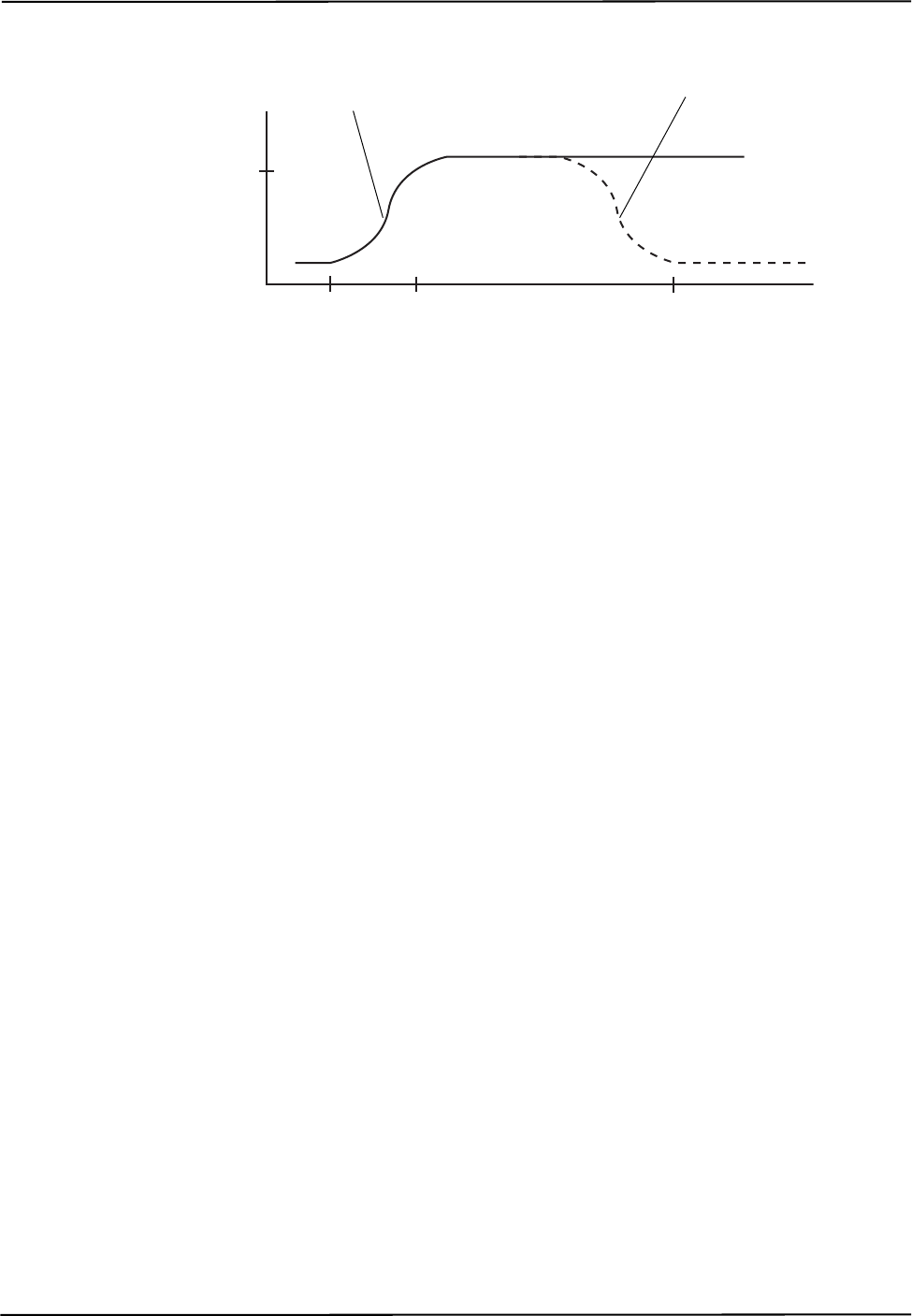
How the Polaris Vicra System Works
40 Polaris Vicra User Guide - Revision 2
Figure 3-9 Filter Spectral Response
3.15 Data Transmission Rate
The Polaris Vicra System can achieve an internal tool transformation update rate of 20 Hz. The host
update rate (the rate at which the host computer receives data) is dependent on the following factors:
Baud Rate The baud rate specifies how fast data is transferred from the system to the host computer.
At lower baud rates, the host computer may not receive tool transformations at 20 Hz.
API command reply length The more data the system must return with every transformation, the
slower the host update rate. The amount of data returned with each transformation increases as you
track more tools and select more options.
Application speed The host transmission rate can vary according to how often the application asks
for data, and how often the graphical user interface (in particular, graphics) need to be updated.
3.16 Serial Port Emulation
The Host USB Converter emulates a standard PC serial port, such that the host application may
communicate with the Polaris Vicra System as if it was a standard RS-232 device. A feature of this
is that the following modem status bits are used as follows:
• The Data Set Ready (DSR) will be set when the Host USB Converter senses that a Position
Sensor is connected (power must also be connected to the Host USB converter).
• The Ring Indicator (RI) will be set when a fault condition is showing on the Host USB
Converter error indicator.
If your operating system cannot set the serial port rate directly to 1.2 Mbaud, an aliased 19200 baud
rate is provided to enable you to run at the higher speed. Do not use the COMM API command’s
baud rate selection of “2” (in this case COMM 2xxxx) but instead use a selection of “7” (COMM
7xxxx).
800 nm 880 nm 1100 nm
90 %
Light Wavelength
Amount of Light
Amount of Light
Passing Through
Lenses to CCDs
Amount of Light
Detected by CCDs
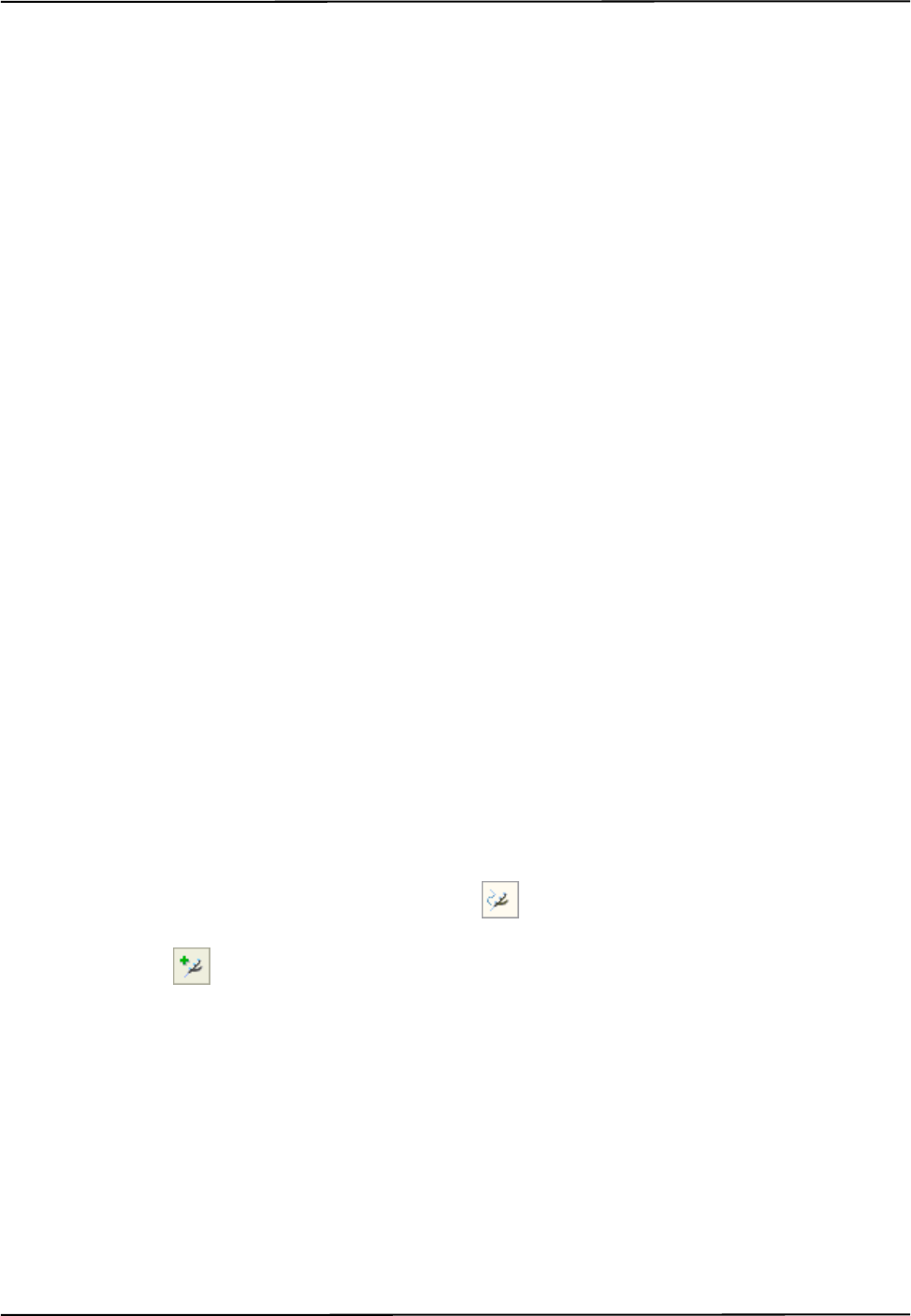
Using the Polaris Vicra System
Polaris Vicra User Guide - Revision 2 41
4 Using the Polaris Vicra System
This chapter is intended as a tutorial to demonstrate the basic functionality of the Polaris Vicra
System using NDI ToolBox. The tutorial is designed for first time users of the system to:
• set up the system to track tools
• observe error and information flags while tracking tools
• track using a reference tool
• pivot a tool to determine the tool tip offset
For more detailed information on NDI ToolBox, refer to the NDI ToolBox online help.
4.1 Getting Started: Tracking Tools
This section describes how to set the system up to track tools.
To Set Up the System
1. Set up and connect the hardware, as described in “Connecting the Hardware” on page 19.
2. Install the drivers for the Host USB Converter, as described in “Installing the USB Drivers
(Windows)” on page 21.
3. Open NDI ToolBox.
4. If NDI ToolBox does not automatically connect to the system, select File > Connect to >
(COMx) (For further details on installing the software, refer to “Installing the Software” on
page 20.)
To Track Tools
In NDI ToolBox:
1. If the tool tracking utility is not open, click to open it.
2. Click to load the tool definition files for the tools you want to track.
3. In the dialog that appears, browse to the desired tool definition file(s). Hold down Ctrl and click
to select more than one file.
4. Click Open.
Once a tool definition file has been loaded, the Polaris Vicra System will automatically attempt
to track the tool.
5. Move the tool throughout the characterized measurement volume, making sure the markers on
the tool face the Position Sensor.
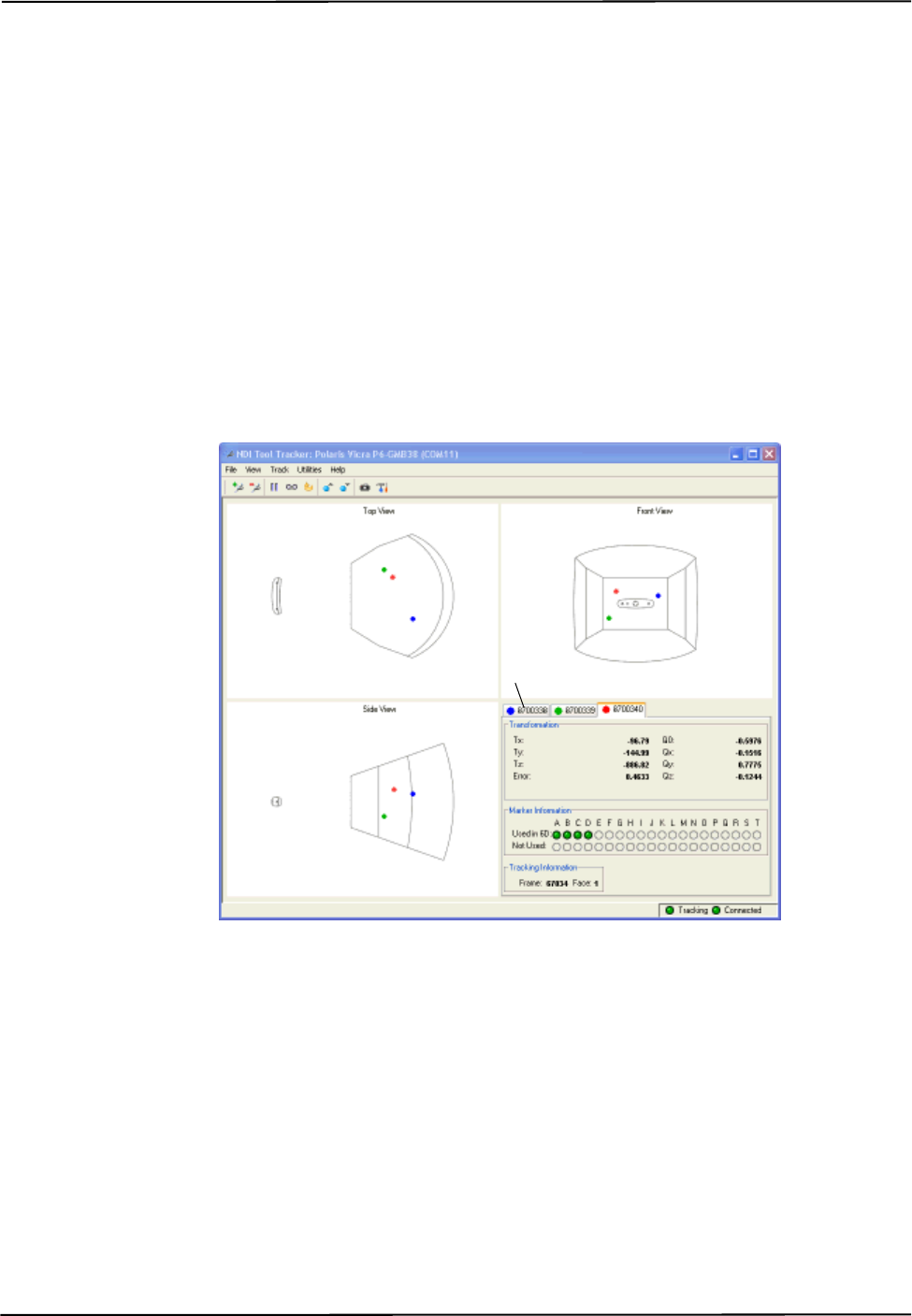
Using the Polaris Vicra System
42 Polaris Vicra User Guide - Revision 2
As you move the tool, the symbol representing the tool in the graphical representation will move
to reflect the tool’s position.
4.2 Information and Error Flags
This section describes how to trigger some of the most common flags. Tracking errors, warnings,
and marker information for each tool are displayed in the bottom right section of the tool tracking
utility.
To View Information and Error Flags
1. Set up the system to track tools, as described in “Getting Started: Tracking Tools” on page 41.
2. For each loaded tool definition file, there is a tab in the bottom right section of the tool tracking
utility. Select a tab to display tracking information for a particular tool.
Figure 4-1 Tool Tracking Window
“Partially Out of Volume” and “Out of Volume” flags:
Move the tool to the edge of the characterized measurement volume.
As you move the tool to the edge of the volume (some markers are in the volume and some out),
NDI ToolBox will display the message “Partially Out of Volume.” Once the tool is completely
outside of the volume (all markers are outside the volume), NDI ToolBox will display the message
“Out of Volume.”
Select a tab to display
tracking information for
a particular tool
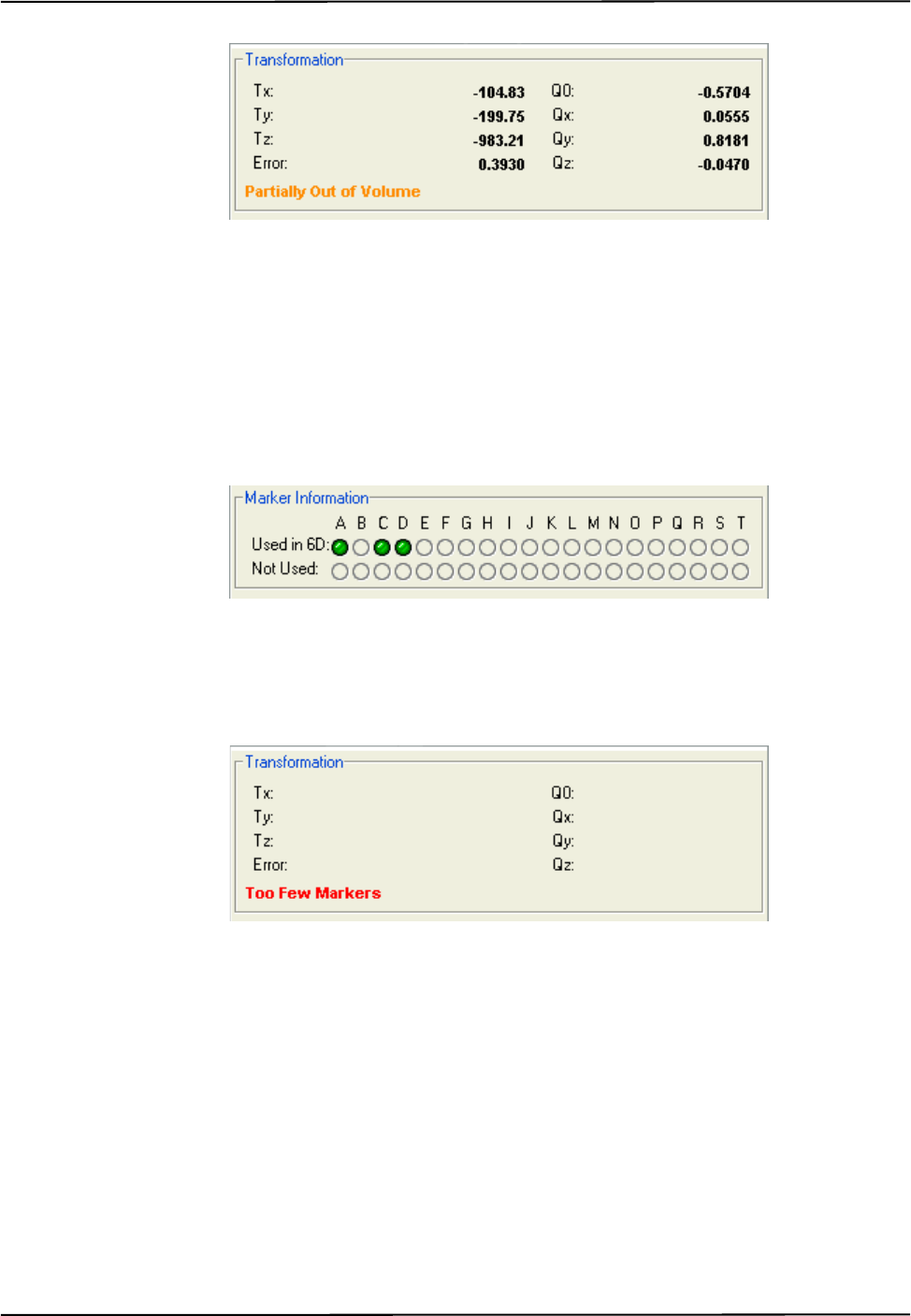
Using the Polaris Vicra System
Polaris Vicra User Guide - Revision 2 43
Figure 4-2 Partially Out of Volume Flag
“Too Few Markers” flag:
1. Position the tool inside the characterized measurement volume, with the markers facing the
Position Sensor.
2. Cover one or more markers, without touching them.
The Position Sensor will no longer be able to detect the covered markers.
Figure 4-3 Markers Information Pane - Missing Marker
If the Position Sensor cannot detect the minimum number of markers, NDI ToolBox will display
the message “Too Few Markers” and will not report a transformation.
Figure 4-4 Transformation Pane - Too Few Markers
“Exceeded Maximum Marker Angle” flag:
1. Position the tool inside the characterized measurement volume, with the markers facing the
Position Sensor.
2. Turn the tool gradually until the markers are no longer facing the Position Sensor.
Once a marker has exceeded the maximum marker angle, NDI ToolBox will display a blue
indicator in the Not Used section of the marker information.
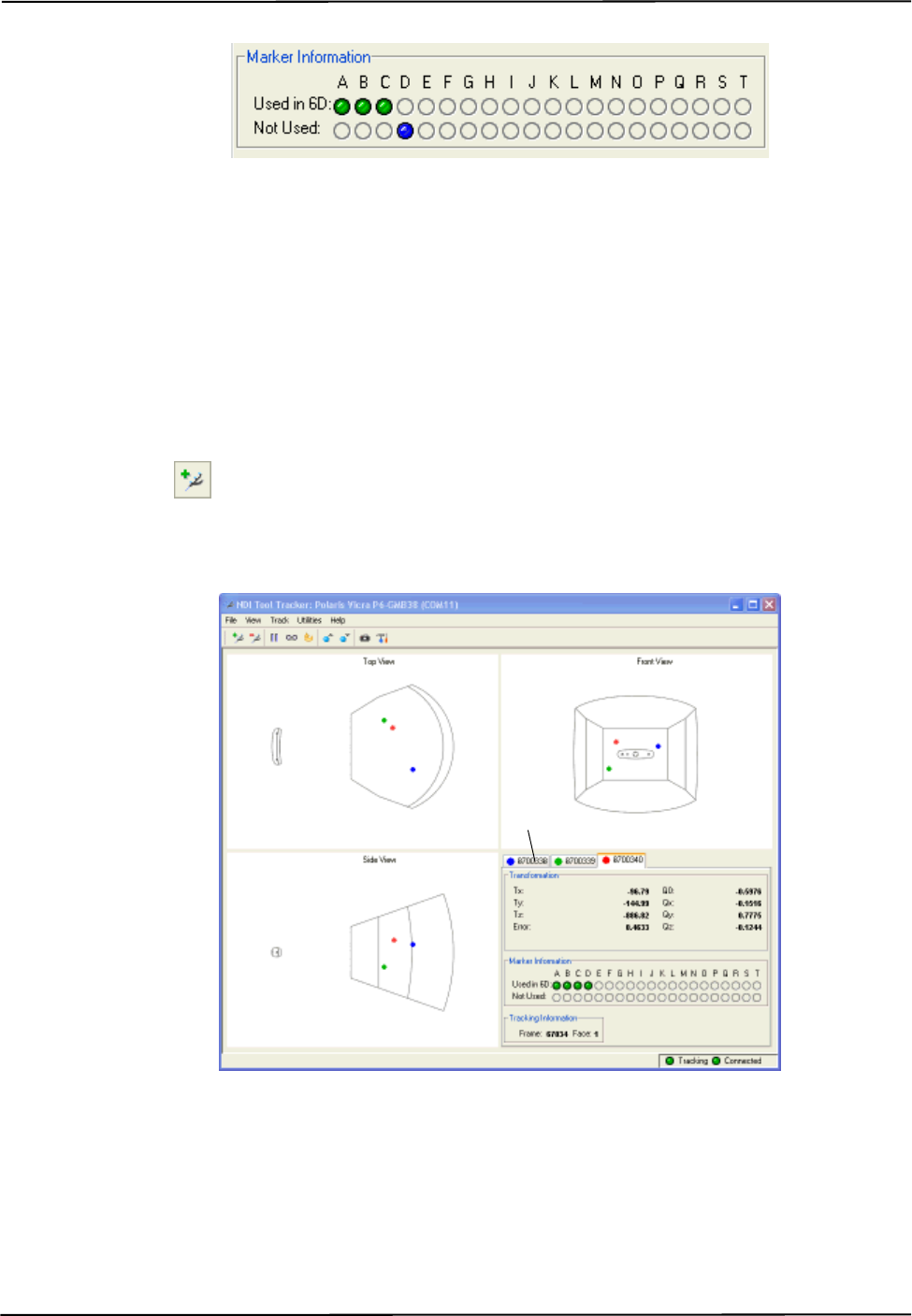
Using the Polaris Vicra System
44 Polaris Vicra User Guide - Revision 2
Figure 4-5 Markers Information Pane - Exceeded Max Marker Angle
4.3 Setting a Tool as Reference
This section describes how to set a tool as reference. When you set a tool as reference, all the other
tools will be tracked with respect to the reference tool.
To Set a Tool as Reference
1. Set up the system to track tools, as described in “Getting Started: Tracking Tools” on page 41.
2. Click to load tool definition files for at least two tools.
3. For each loaded tool definition file, there is a tab in the bottom right section of the tool tracking
utility. Select the tab corresponding to the tool you want to set as reference.
Figure 4-6 Selecting a Reference Tool
4. Right click on the tool tab, then select Global Reference.
The reference tool will appear as a square in the graphical display. The other tools will be
displayed inside a square, that is the colour of the reference tool. The positions and orientations
of other tools will now be reported in the local coordinate system of the reference tool.
Select the tab for the
tool you want to set
as reference.
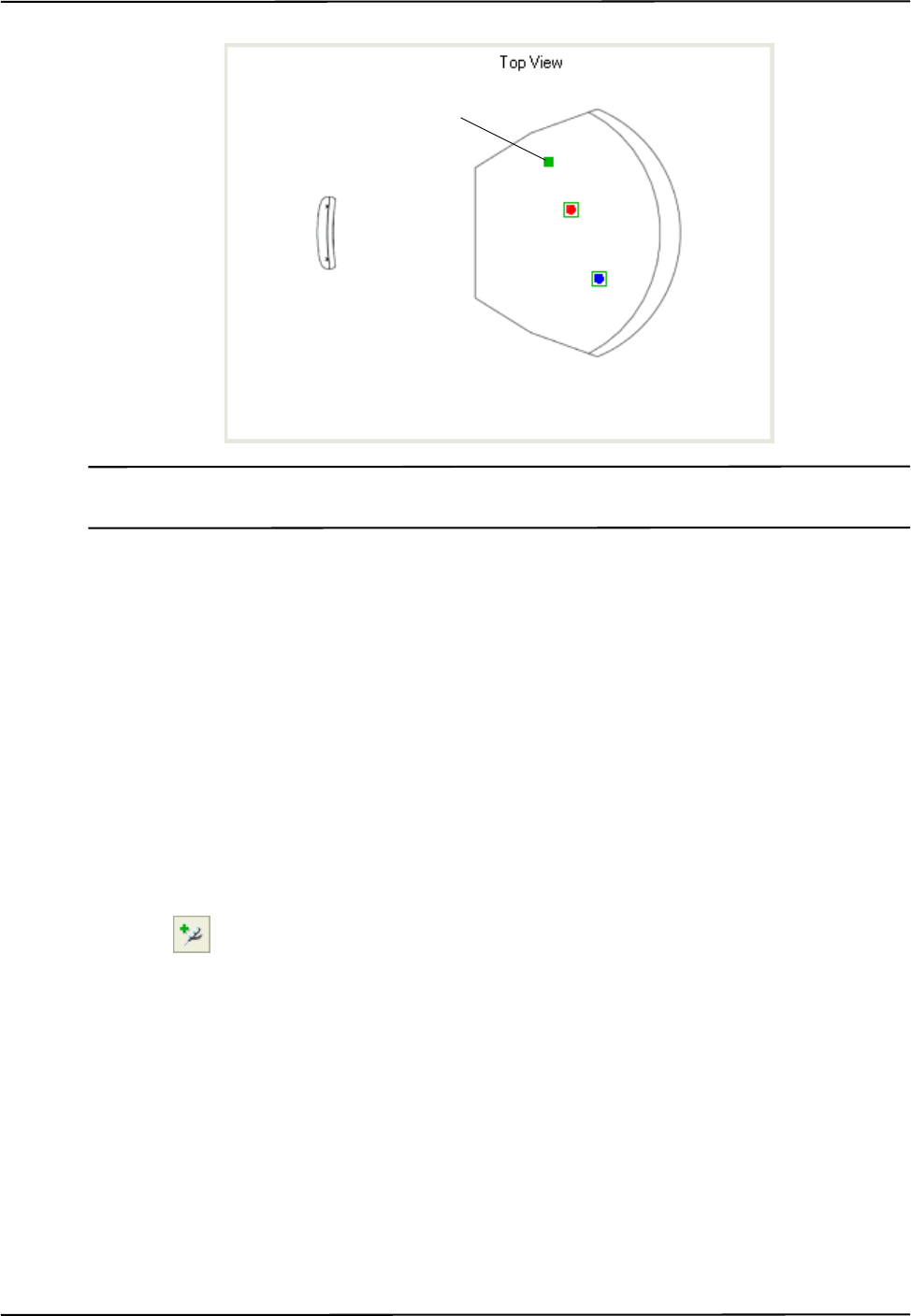
Using the Polaris Vicra System
Polaris Vicra User Guide - Revision 2 45
Note The Polaris Vicra System still calculates the tool transformations in the coordinate system of the Position Sensor.
The NDI ToolBox software then calculates and reports the tool transformations with respect to the reference tool.
4.4 Determining the Tool Tip Offset
This section describes how to determine the tool tip offset of a probe or pointer tool by pivoting.
Once NDI ToolBox has calculated the tool tip offset, it can report the position of the tip of the tool,
instead of the position of the origin of the tool. See “Tool Tip Offset” on page 35 for more details.
To Set Up the System to Pivot
You will need a divot in which to rest the tool tip while you pivot the tool. The size and shape of the
divot must match the tool tip, to ensure that the tip does not move. For example, a probe with a
1 mm ball tip requires a hemispherical divot with a 1 mm diameter in which to pivot.
1. Set up the system to track tools, as described in “Getting Started: Tracking Tools” on page 41.
2. Click to load a tool definition file for the probe or pointer tool.
3. For each loaded tool definition file, there is a tab in the bottom right section of the tool tracking
utility. Select the tab corresponding to the tool you want to pivot.
Reference Tool
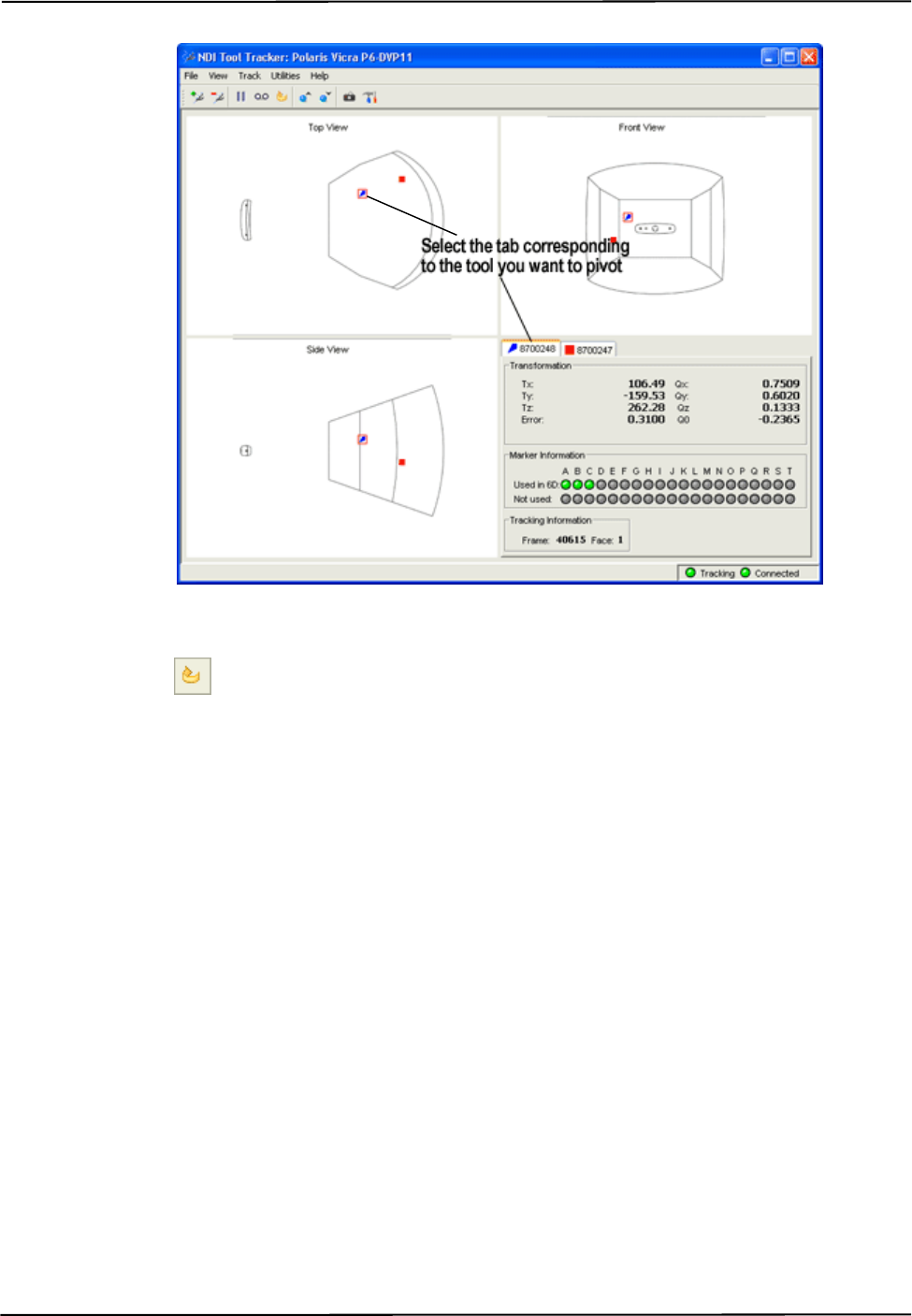
Using the Polaris Vicra System
46 Polaris Vicra User Guide - Revision 2
Figure 4-7 Selecting a Tool to Pivot
4. Click to open the Pivot dialog.
5. Select a start delay of about 5 seconds and a duration of about 20 seconds.
To Pivot the Tool
1. Place the tool tip in the divot.
2. Ensure that the tool is within the characterized measurement volume, and will remain within the
volume throughout the pivoting procedure.
3. Click Start Collection in the Pivot tool dialog.
4. Pivot the tool in a cone shape, at an angle of 30º to 60º from the vertical.
a) Keep the tool tip stationary, and ensure that there is a line of sight between the markers on
the tool and the Position Sensor throughout the pivoting procedure.
b) Pivot the tool slowly until the specified pivot duration time has elapsed.
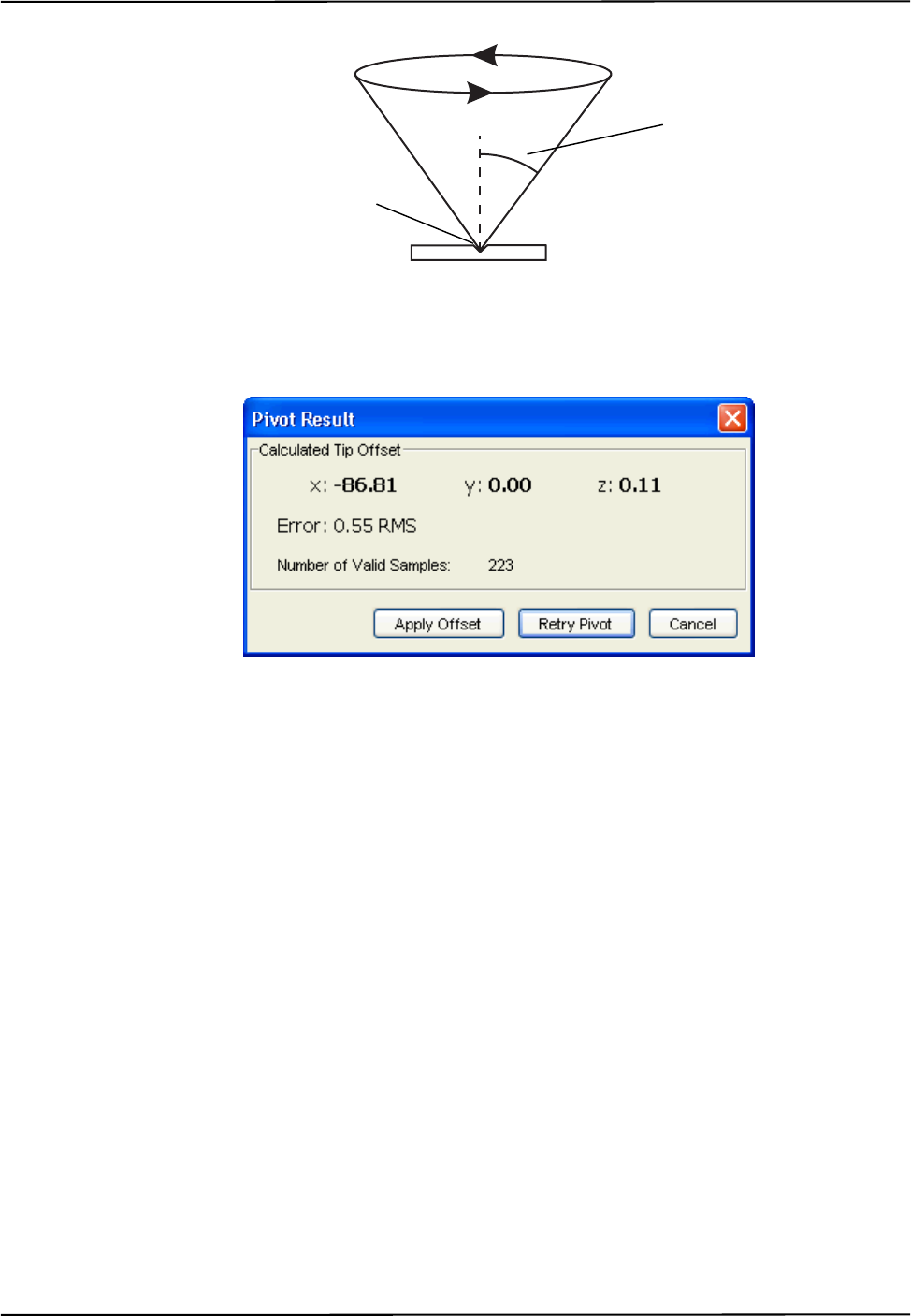
Using the Polaris Vicra System
Polaris Vicra User Guide - Revision 2 47
Figure 4-8 Pivoting Technique
When the pivot is complete, the Pivot Result dialog appears. Click Apply Offset to report the
position of the tip of the tool.
Figure 4-9 Pivot Result Dialog
Divot
30° to 60°

Error Flags and Codes
48 Polaris Vicra User Guide - Revision 2
5 Error Flags and Codes
This chapter lists error flags that the Polaris Vicra System may return, and what each one means. It
also lists the LED and audio indications output by the Position Sensor.
5.1 Missing and Disabled Transformations
Normally, the Polaris Vicra System reports a position, orientation, and error value for every
transformation. If the system cannot return a transformation, it will report the tool as MISSING or
DISABLED.
Missing Transformations
The system reports a tool as MISSING if it cannot calculate a transformation for the tool. The
system may be unable to calculate a transformation if:
• the system cannot detect the minimum number of markers
• less than the minimum number of markers are inside the characterized measurement
volume. By default, the Polaris Vicra System only reports the transformation of markers and
tools inside the characterized measurement volume. You can tell the Polaris Vicra System to
report the positions of markers outside the characterized measurement volume, using reply
option 0x0800 with the TX or BX command. See the “Polaris Application Program
Interface Guide” for details. See “Tool Tracking Parameters” on page 31 for a description of
this parameter.
• less than the minimum number of markers are within the maximum marker angle or the
maximum 3D error
• the spread parameters are not satisfied
• there is a system error (described on page 49)
Disabled Transformations
The system reports a tool as DISABLED if the port handle corresponding to the tool was not
enabled, has been disabled, or is unoccupied. A port handle is unoccupied if it has been allocated,
but you have not yet associated a tool definition file with that port handle. See the “Polaris
Application Program Interface Guide” for more details on port handles.
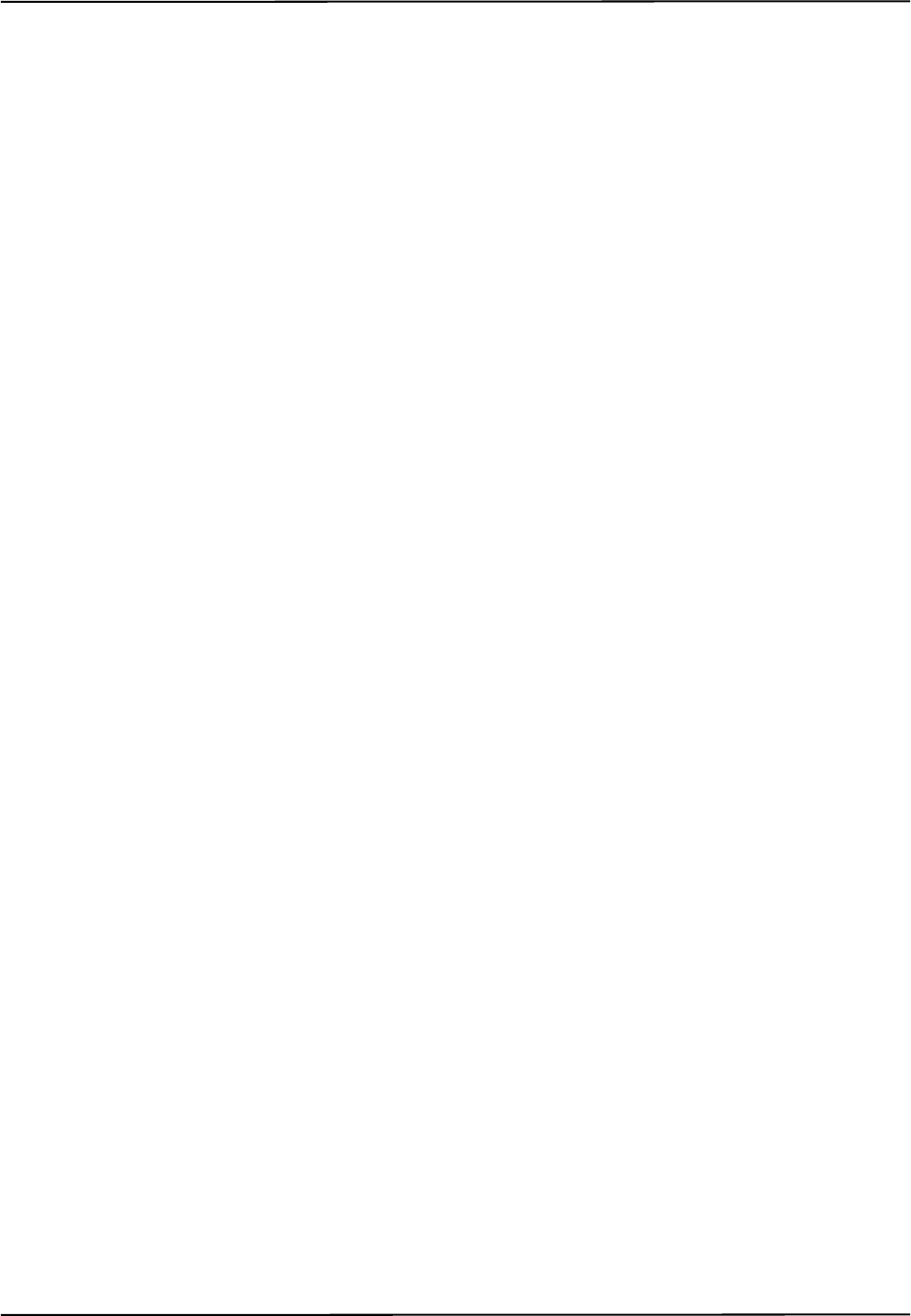
Error Flags and Codes
Polaris Vicra User Guide - Revision 2 49
5.2 Tracking Errors and Flags
Many of the following errors and flags are displayed in NDI ToolBox. They are all returned with the
TX and BX commands (using reply options 0x0001 and 0x0002).
System status flags
System Communication Synchronization Error indicates communication problems between internal
sub-components of the system.
Diagnostic Pending Indicates a change in any of the alerts flags. The flag is persistent until the alerts
parameter are read. Reading the alerts parameter automatically clears the flag. By default
transformation data is not returned when this flag is set.
Temperature System is out of specified operating temperature range or not yet warmed up. By
default transformation data is not returned when this flag is set. The flag will automatically be
cleared as soon as the system is back in the specified operating temperature range.
Port status flags
Out of Volume The out of volume flag is set for a marker or tool that is completely outside of the
characterized measurement volume, but can still be detected by the system. The flag is set regardless
of whether the reply option 0x0800 for the TX or BX command is used. (Reply option 0x0800
enables the reporting of the positions of tools and markers that are outside of the characterized
measurement volume. See the “Polaris Application Program Interface Guide” for details.)
Partially Out of Volume The partially out of volume flag is set for a tool if less than the minimum
number of markers are inside the characterized measurement volume, and at least one marker on the
tool is inside the characterized measurement volume. See “Tool Tracking Parameters” on page 31
for a description of the minimum number of markers parameter.
Algorithm Limitations Indicates that during parts of the algorithm used for 2D/3D/6D calculations a
limitation has been detected (for example buffer full). This does not mean that an error occurred or
that the tools will not track properly.
If the flag is transient, i.e. it comes on for only a few frames during the beginning of tracking or
during a disruption of the scene (blocking/unblocking), no actions need to be taken.
If the flag persists and the tool does not track, changing the scene (removing tools and/or markers)
or simply re-arranging the scene should resolve the problem.
IR Interference Indicates that one of the sensors has detected an object that is bright enough to be
considered a marker but is too large. (For example, this flag can be triggered by two passive sphere
markers being close together.) This may not affect tracking in which case it can be ignored. If one or
more tools do not track and the flag persists the scene should be examined for the root cause of the
flag (for example by taking a video capture with NDI ToolBox).
Processing Exception Indicates that an exception has been detected in the firmware. Transformation
data will be invalid as long as the flag persists. The system may self-recover from this condition,
depending on the scene. The flag typically comes on when the system is overloaded, ie it cannot
handle the scene. Remove some tools and/or markers from the scene to prevent this flag from being
triggered.
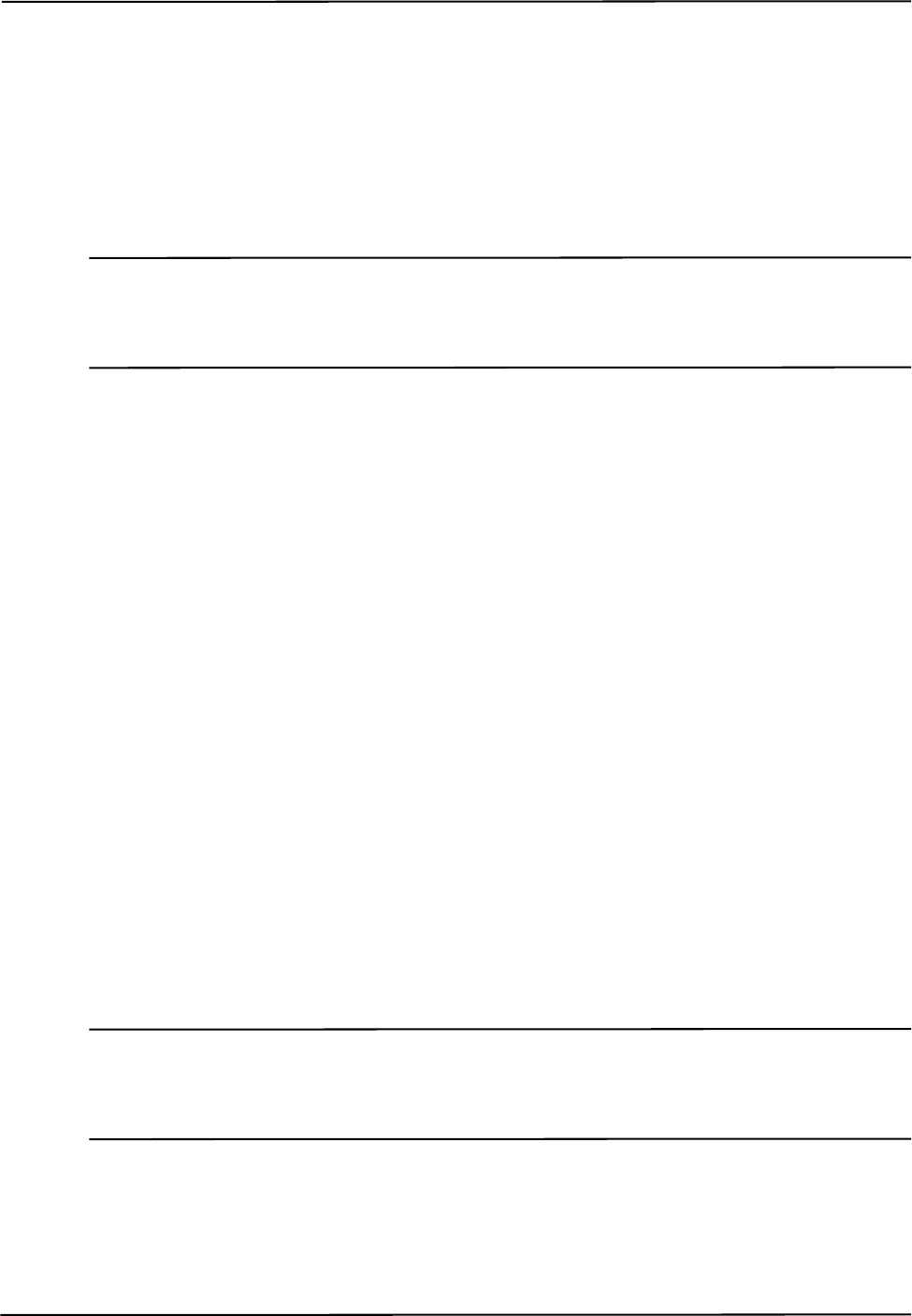
Error Flags and Codes
50 Polaris Vicra User Guide - Revision 2
Fell Behind While Processing Indicates that the system cannot keep up with processing the data.
This flag comes on when the system is overloaded. Remove some tools and/or markers from the
scene to prevent this flag from being triggered.
Data Buffer Limitations The systems' internal data buffers cannot hold all incoming data. This flag
comes on when the scene is overloaded or, in rare cases, if the scene is arranged in an unfavourable
way (many markers lined up in a horizontal line).
Re-arranging the scene or removing tools/markers will remove this flag.
Note This flag is different from "Algorithm limitations" as "Data buffer limitations" means that real raw data is lost. In
the case of the "Algorithm limitations" flag the system has all raw data, but does not have enough buffer to
process it. Both flags are very scene dependent and are independent of each other, however both typically only
come on in heavily loaded scenes.
Tool information flags
Bad Transformation Fit Indicates that although enough markers are visible, the tool transformation
could not be calculated due to fit constraints.
Not Enough Acceptable Markers for Transformation The system does not have enough "good"
markers to calculate a transformation for this tool.
IR Interference This flag is a combination of the "IR interference" and "Data buffer limitation" flags
in the port status flags. It is kept for backward compatibility with Polaris. NDI recommends that
instead you use the port status flags.
Fell Behind While Processing This is a copy of the flag "Fell behind while processing" in the port
status flags. It is kept for backward compatibility with Polaris. NDI recommends that instead you
use the port status flags.
Processing exception This is a copy of the flag "Processing exception" in the port status flags. It is
kept for backward compatibility with Polaris. NDI recommends that instead you use the port status
flags.
Marker Information
The marker information returned with option 0x0002 of the TX and BX commands are 4-bit
numbers that indicate if and how a marker was used in the tool transformation or, if it was not used,
it provides an indication why it was rejected for the tool transformation. For a detailed explanation
of the marker information see the “Polaris API Guide” (TX and BX commands).
Note If option 0x0008 (3D position of markers on tools) is used, NDI recommends that you use the 3D information only
in combination with the marker information reported in option 0x0002. Option 0x0008 will report all markers
associated with a tool, regardless of individual marker status. The marker information can provide further
indication about the "quality" of the reported 3D position.
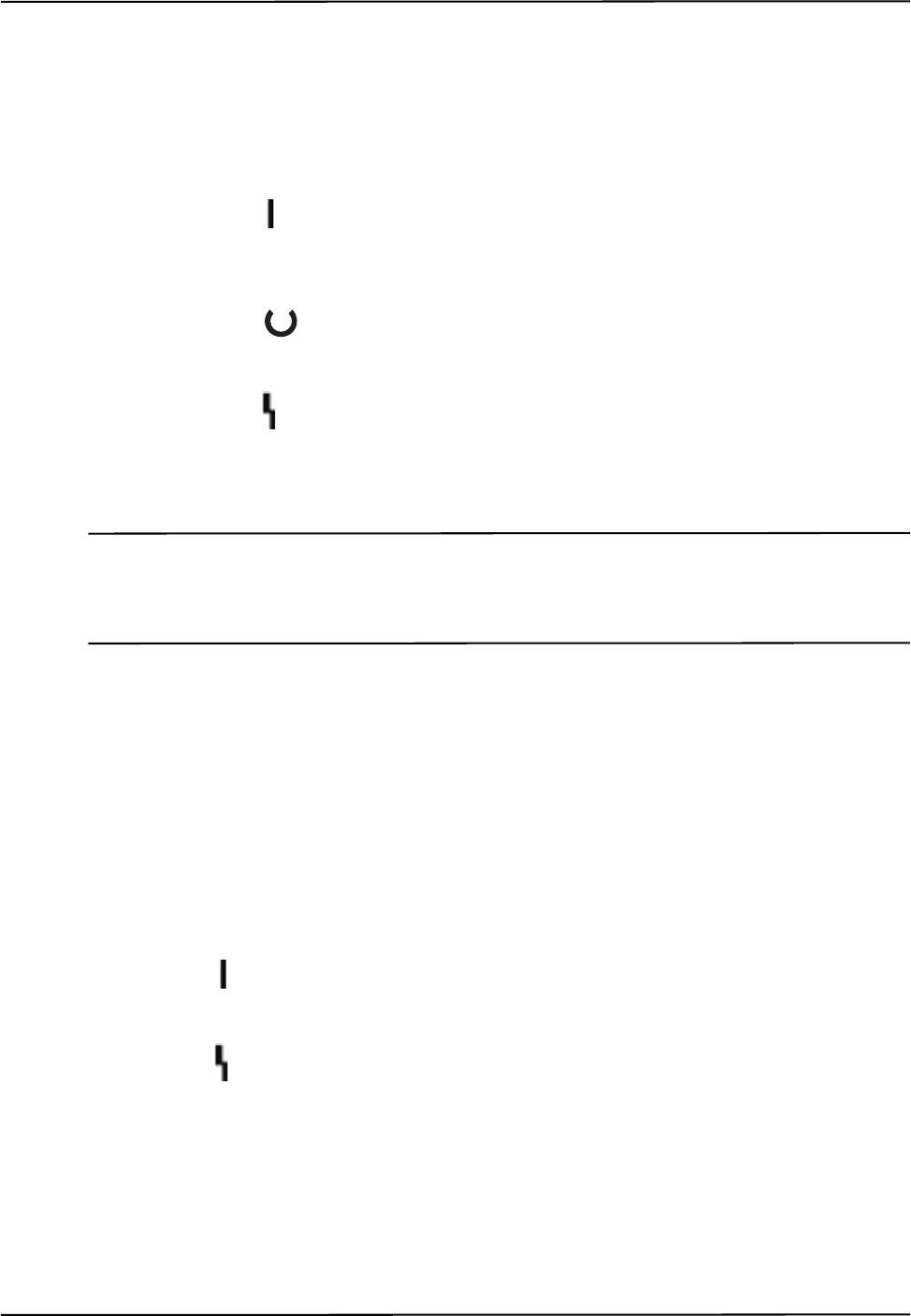
Error Flags and Codes
Polaris Vicra User Guide - Revision 2 51
5.3 Polaris Vicra System LEDs and Audio Codes
The Polaris Vicra System components are equipped with LEDs and audio codes to communicate the
system status.
Position Sensor LEDs
•Power LED :
Flashes green during system warm-up.
Steady green when system is ready for use.
•Status LED :
Steady green when the communications connection is available.
•Error LED :
Lights steady amber if a critical error is detected (Position Sensor must be returned to NDI).
Flashes amber if a non-critical error is detected (for example, a firmware update is not
completed).
Note If a non-critical error is detected (error LED is flashing), refer to the NDI ToolBox application to further diagnose
the fault. (The nature of the error is described on the NDI ToolBox initial page.) If you are using your own
applications, use the GET command to read the “Info.StatusAlert” parameter to check the alert status. Refer to
the “Polaris Application Program Interface Guide” for further information.
Position Sensor Audio Codes
Two tones are emitted by the Position Sensor after it has been powered up or reset and has
completed initialization. You can disable this feature using the NDI ToolBox software.
If the host computer does not send a command to the system within a given time, the Position Sensor
will emit two quick tones every three seconds. (This feature is an application watchdog and is set by
the API command HWCDOG.)
Host USB Converter LEDs
•Power :
Lights green when power is being supplied to the Host USB Converter.
•Error :
Lights amber when the Host USB Converter has detected a fault.
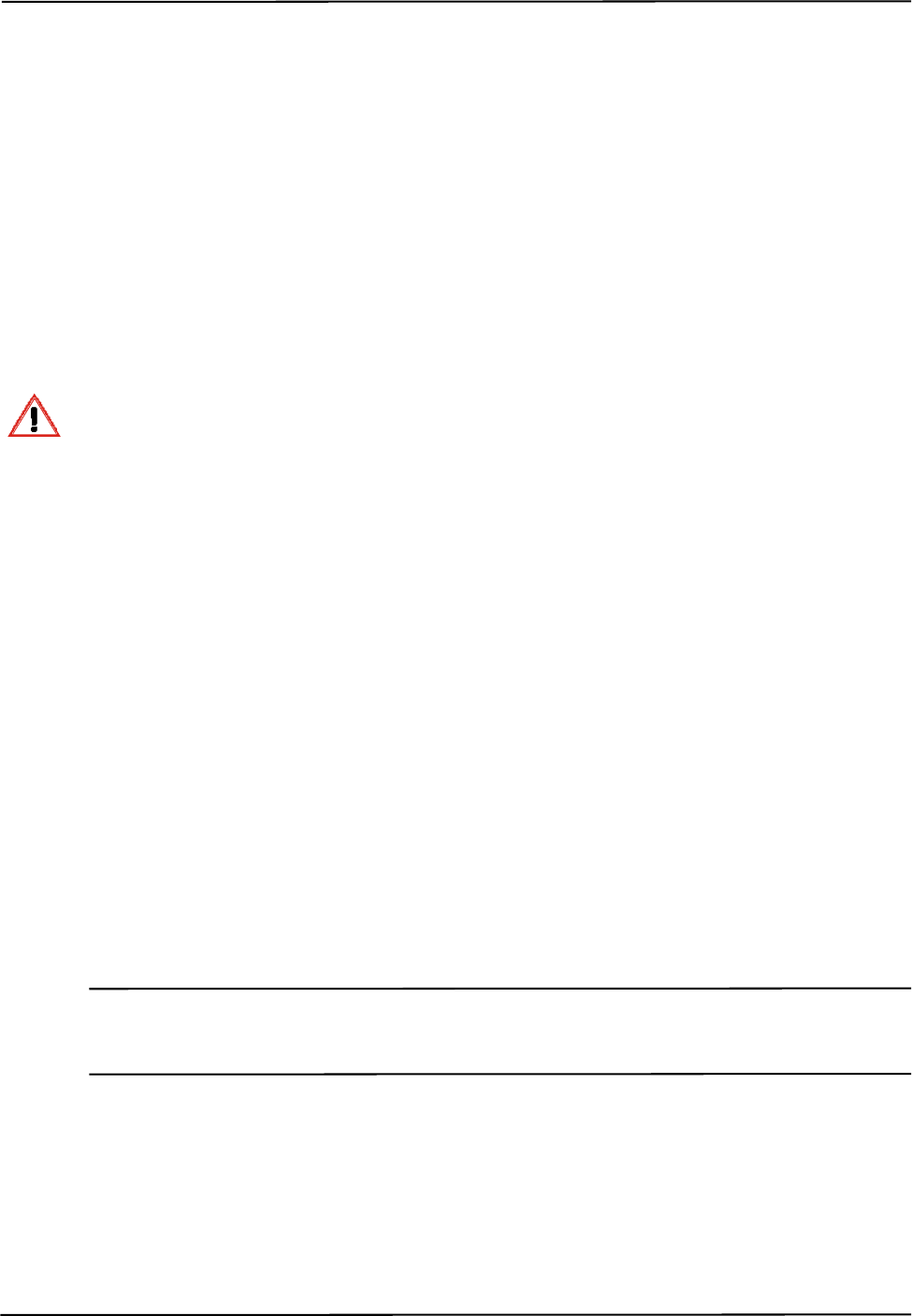
Maintenance
52 Polaris Vicra User Guide - Revision 2
6 Maintenance
User maintenance of the Polaris Vicra System is limited to the following procedures:
1. Cleaning the Position Sensor
2. Care of cables and connectors
The Position Sensor is the only system unit that requires special consideration. The power adapter
and Host USB Converter can be cleaned by following standard procedures.
Maintenance Warnings
Before doing any maintenance on the Polaris Vicra System, read the following warnings:
1. All user maintenance must be done by appropriately trained personnel. Individual
components of the Polaris Vicra System contain no user-serviceable parts. Maintenance by
untrained personnel may present an electric shock hazard.
2. Do not use the Position Sensor without inspecting it for cleanliness and damage both
before and during a procedure. Reliance on data provided by an unclean or damaged
Position Sensor may lead to inaccurate conclusions. If your application involves personal
safety, inaccurate conclusions increase the possibility of personal injury.
3. Do not immerse any part of the Polaris Vicra System or allow fluid to enter the equipment.
If fluids enter any part of the system they may damage it and present a risk of personal
injury.
4. Do not sterilize the Polaris Vicra Position Sensor as this may cause irreversible damage to
its components. Reliance on data provided by a damaged Position Sensor may lead to
inaccurate conclusions. If your application involves personal safety, these inaccurate
conclusions increase the possibility of personal injury.
6.1 Position Sensor
Regularly inspect the Position Sensor for cleanliness. The Position Sensor and particularly the
illuminator filters and lenses, should be cleaned only when necessary. The frequency of cleaning
must be determined by the user. This may include “in-use” cleaning.
Caution! Use only 70% isopropanol and a lens cleaning solution formulated for multi-coated lenses (for example, AR66) to
clean the Position Sensor. Other fluids may cause damage to the illuminator filters. Do not use any paper
products for cleaning. Paper products may cause scratches on the illuminator filters.
To clean the Position Sensor, follow the procedure detailed below:
1. Remove dust from each illuminator filter and lens, using a photographic lens duster (brush).
Gently wipe the surface in one direction only, by pulling the brush across the surface.
2. Gently wipe the illuminator filters and lenses with disinfectant wipes containing 70%
isopropanol. Continue cleaning the remainder of the Position Sensor, taking care not to wipe
Warning!
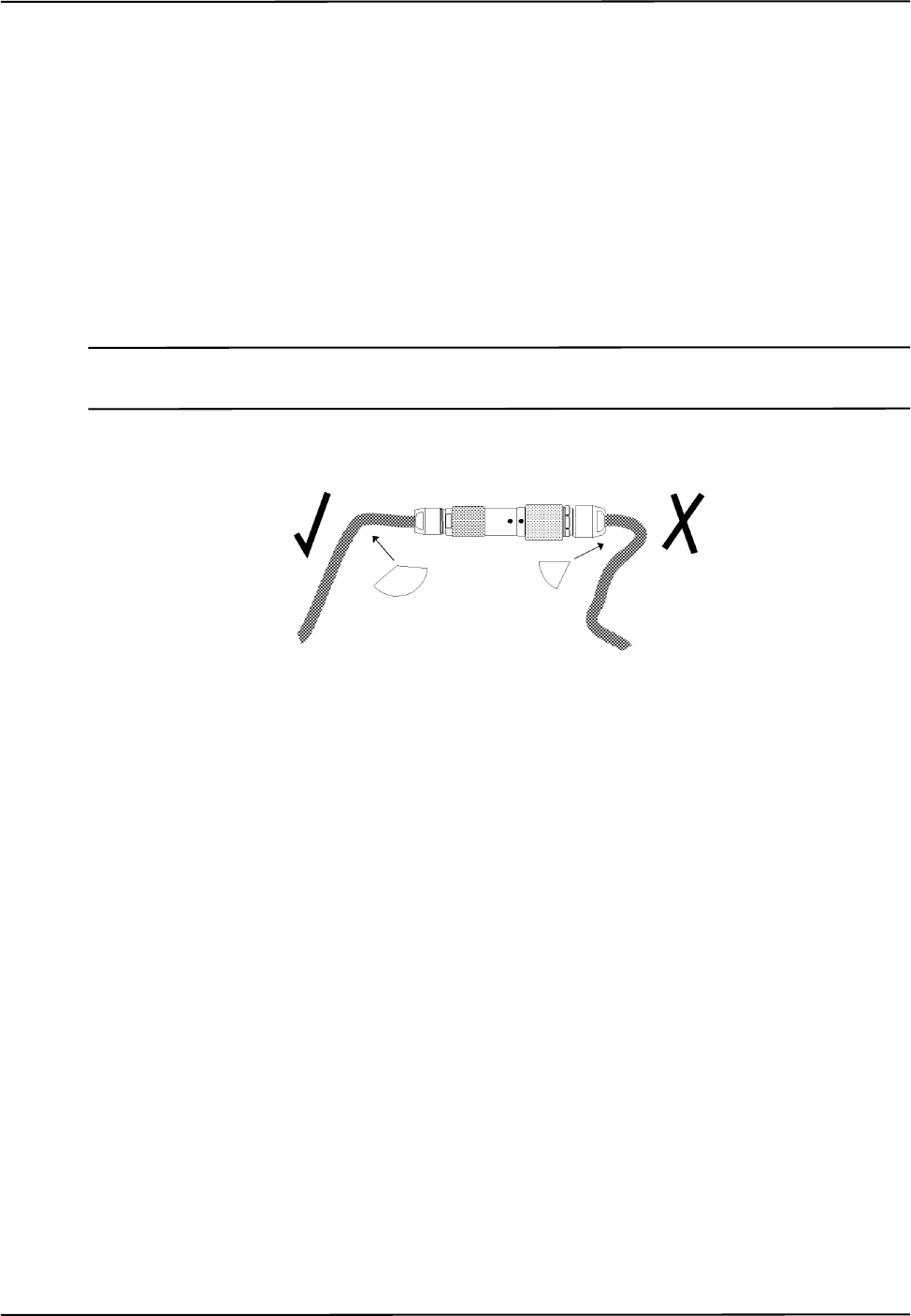
Maintenance
Polaris Vicra User Guide - Revision 2 53
debris from the Position Sensor case onto the illuminator filters or lenses. Avoid prolonged
contact between the wipes and the Position Sensor.
3. Clean the illuminator filters and lenses, using a commercial lens cleaning solution formulated
for multi-coated lenses (for example, AR66) and a clean knitted microfibre optical cleaning
cloth (for example, Hitecloth). Avoid prolonged contact between the lens cleaner and the
illuminator filters and lenses.
6.2 Cables and Connectors
To avoid damage to cables, make sure the cables are not bent at sharp angles.
Caution! Make sure that mains power is disconnected before connecting or disconnecting cables. Failure to do so may
cause damage to the equipment.
Figure 6-1 How to Avoid Stressed Cables
The Polaris Vicra System incorporates a number of different connectors:
• self-locking circular connector
• USB connector
• jack connector
Handle the connectors with care, paying particular attention to the points detailed below:
• Pull connections apart by gripping the connector. Do not pull them apart by tugging on the
cable as this can damage the connecting cable and connector pins.
• Do not leave cable connectors where they will get damaged, particularly on the floor, where
they can easily be stepped on or rolled over by heavy equipment.
• Do not put heavy objects on cables or cable connectors.
• Never force a connection.
• On LEMO connectors, make sure that the red dots on the connectors are lined up with each
other before connection (the double keys of the connector should be aligned).
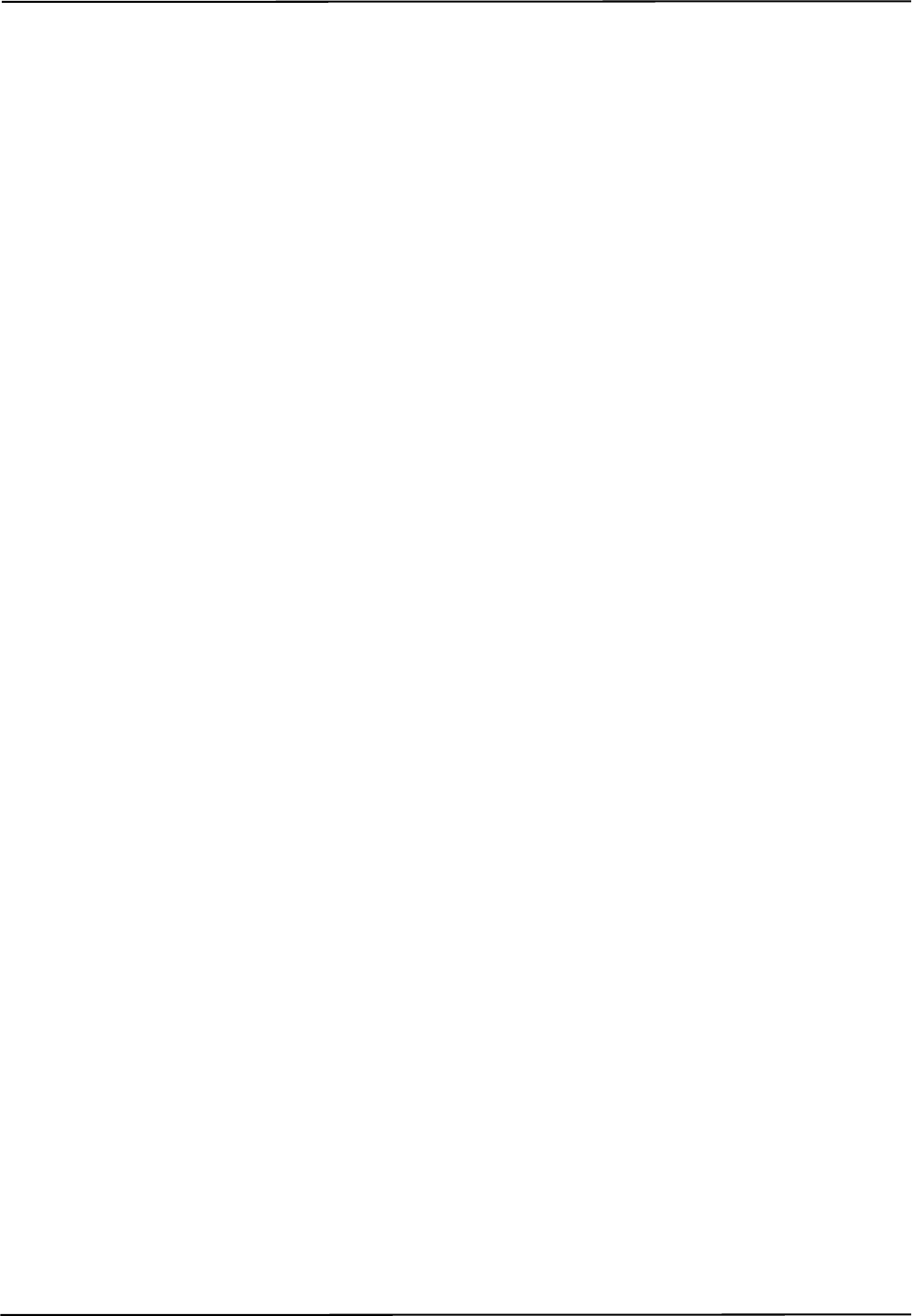
Setting the Infrared Light Sensitivity
54 Polaris Vicra User Guide - Revision 2
7 Setting the Infrared Light Sensitivity
7.1 IR Light Sensitivity Levels
The IR light sensitivity level determines how sensitive the Polaris Vicra System is to IR light.
Background IR Light
Background IR light is IR light that is not reflected (passive) or emitted (active) from a marker, but
is detected by the Polaris Vicra Position Sensor. Background IR light can be direct (light bulbs,
sunlight) or indirect (reflections off shiny surfaces or draping). In particular, IR light in the 800 nm
to 1100 nm range can interfere with the Polaris Vicra System’s ability to track tools. For example,
some types of operating room lights emit IR light that is detected as background IR.
The IR light sensitivity level controls the Polaris Vicra System’s ability to tolerate background IR
light.
Trigger Level and Integration Time
The integration time is the time in which the Polaris Vicra Position Sensor collects IR light.
The trigger level is the minimum IR light intensity considered to be valid marker data. The Polaris
Vicra System uses the trigger level to distinguish between marker data and background IR light. IR
light that falls below the trigger level is rejected by the Position Sensor. The trigger level increases
with the integration time. In general, as the sensitivity level increases, so does the trigger level.
During operation, the Polaris Vicra System makes adjustments to the integration time so that the
intensity of the brightest IR light detected is set to a maximum value, and the intensity of all other IR
light detected falls below this value. Changing the sensitivity level does not change this maximum
value. Thus, when the sensitivity level changes, the integration time does not change but the trigger
level does.
The relationship between trigger level and integration time for each sensitivity level is illustrated in
Figure 7-1.
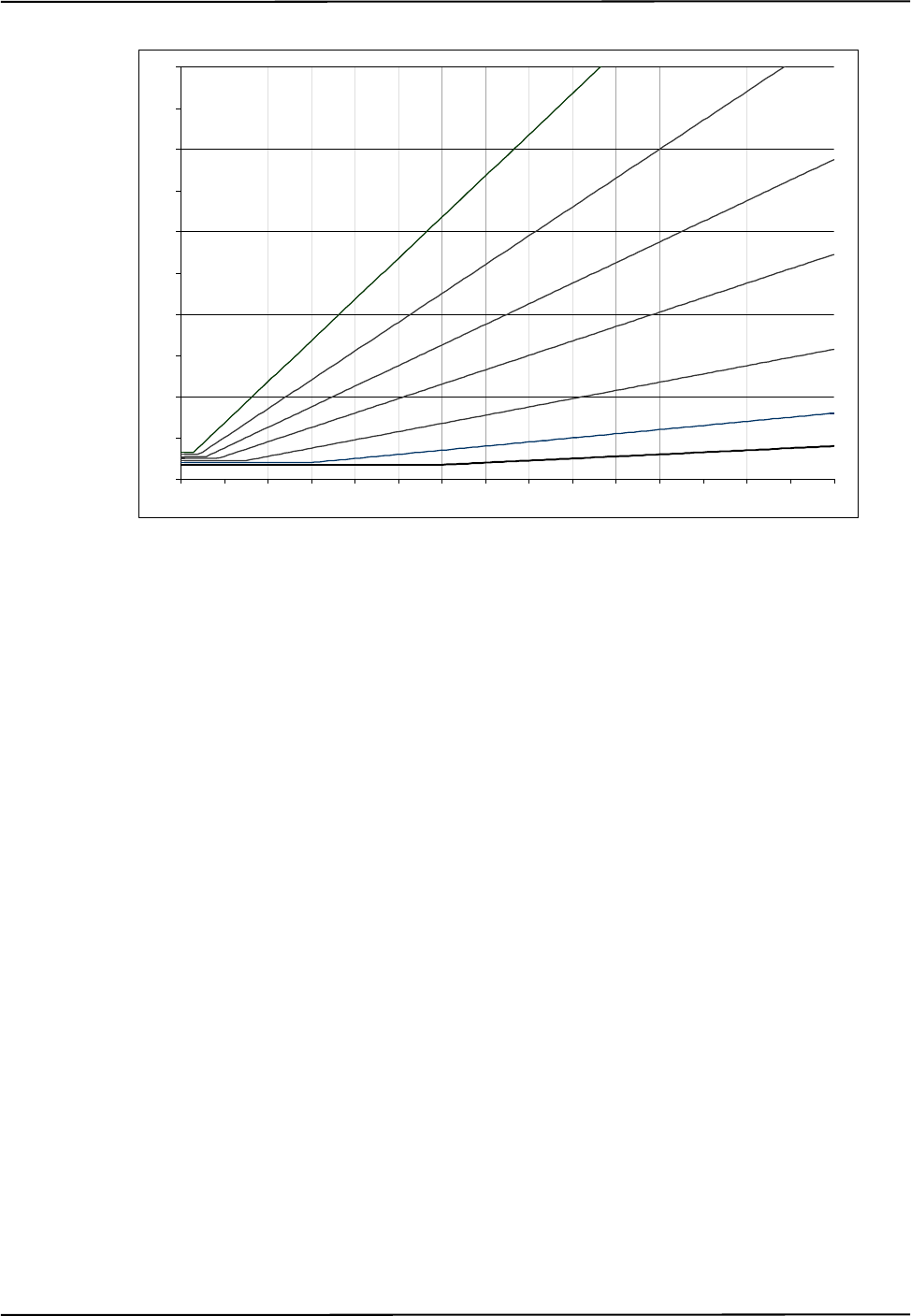
Setting the Infrared Light Sensitivity
Polaris Vicra User Guide - Revision 2 55
Figure 7-1 Infrared Light Sensitivity Levels
Sensitivity Levels
There are seven sensitivity levels; with each increasing level number, the ability of the system to
tolerate background IR light increases. Increasing the sensitivity level makes the system
performance more robust in the presence of background IR light; however, it increases the chance
that a tool cannot be tracked properly because it may have a marker that is not bright enough. Low
marker brightness can be caused by, for example, the surface of a marker becoming partially
occluded by fluids or other materials, thus reducing the reflectivity of the marker.
Level 4 is the default sensitivity level for the Polaris Vicra System and should work well in most
situations.
7.2 Changing the Sensitivity Level
Checking for Background IR Light
If a tool is tracking intermittently or not tracking at all, check the IR interference flag in the port
status and in the tool information returned with the BX or TX command. If the IR interference flag
is intermittently or constantly on for any of the tools, there may be background IR present.
Alternatively, you can check for the “Interference” flag in the tool tracking utility of NDI ToolBox,
or use the image capture utility in NDI ToolBox to capture images of the IR detected by the system.
0
10
20
30
40
50
60
70
80
90
100
0 100 200 300 400 500 600 700 800 900 1000 1100 1200 1300 1400 1500
Trigger Level (% of maximum)
Integration Time (µs)
2
1
3
4
5
6
7
1 -7 represent
sensitivity levels
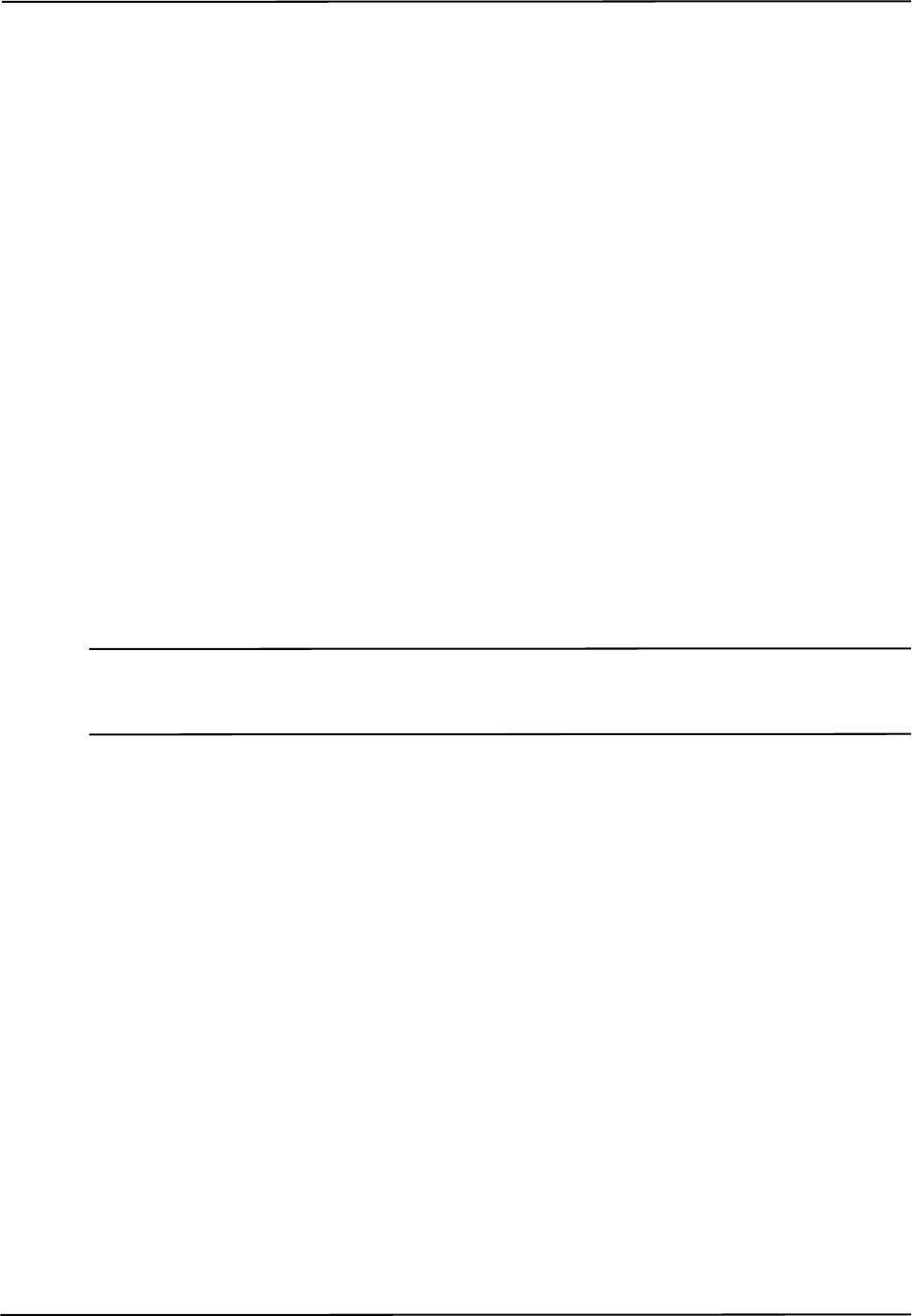
Setting the Infrared Light Sensitivity
56 Polaris Vicra User Guide - Revision 2
Choosing a Sensitivity Level
Choose a sensitivity level of 5, 6 or 7 if:
• If the "IR Interference" flag in the Port Status flags is on persistently
AND
• tools don't track
AND
• re-arranging the scene doesn't help.
Choose a sensitivity level of 3, 2 or 1 if:
• If a tool doesn't track
AND
• all markers are clearly in view AND clean
AND
• no other error flags are giving any indication for why the tool is not tracking
(NDI experience shows that there should not be any reason for going to a level lower than 4.)
Note The sensitivity levels do NOT change the way centroid extraction is performed and therefore can NOT solve
tracking problems with tools embedded in background IR. Sensitivity level adjustment only helps when tool and
background IR are in different physical locations.
Use the default sensitivity level 4 unless the system is experiencing interference from background
IR light. If the system is experiencing such interference, check the environment for causes (for
example, reflections). If it is not possible to eliminate the source of the background IR light, then
start with a low sensitivity level and increase the level until the tools track reliably.
The system may actually be tracking a tool even when the tool’s IR interference flag is on. You
should still increase the sensitivity level, since the behaviour of the system in this case is dependent
on the setup. (For example, moving the tool to another part of the measurement volume may prevent
it from being tracked properly.)
Changing the Sensitivity Level
You can change the IR sensitivity of the Polaris Vicra System using either NDI ToolBox or the
SENSEL command.
The NDI ToolBox software can be used to select a sensitivity level, and to program a sensitivity
level as the default setting in the Position Sensor memory.
The SENSEL command is used to temporarily select a sensitivity level. The level set using the
SENSEL command persists until a RESET or INIT command is issued. The SENSEL command can
also be used to query the currently active level. For more information on the SENSEL command, see
the “Polaris Application Program Interface Guide”.
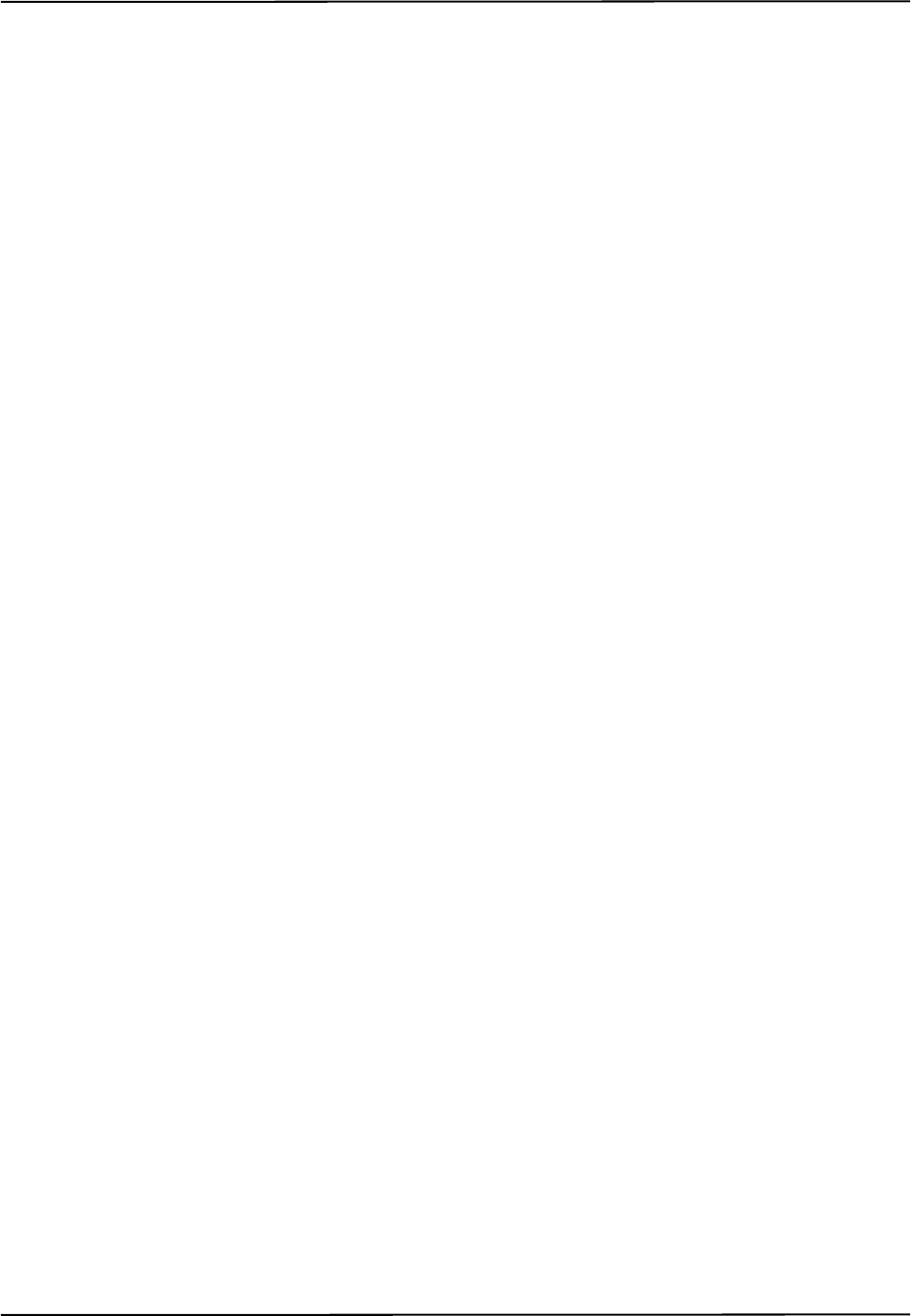
Calibration and Firmware
Polaris Vicra User Guide - Revision 2 57
8 Calibration and Firmware
8.1 Checking the Calibration of the Polaris Vicra System
The Position Sensor is calibrated at NDI, using the methodology described in Appendix A. Over
time, it is possible for the Position Sensor to lose calibration. A periodic calibration check should be
performed on the Position Sensor. The frequency of the calibration check depends on the specific
application and environment in which the Position Sensor is used.
If the Position Sensor begins to lose calibration, it may lose the ability to track some tools before
others. This is due to the various constraints used by the Polaris Vicra System, which make certain
tool designs more sensitive to loss of calibration than others. For example, consider a tool that has
several similar segment lengths or similar angles between segments, or has segment lengths similar
to those of another tool. An out-of-calibration Position Sensor may not be able to determine which
markers belong to which tool, because the segment lengths will be measured less accurately. In this
case, the system will report the tools as missing. (See “Marker Detection and Tool Tracking” on
page 28 and the “Polaris Tool Design Guide” for details on segment lengths and angles.)
NDI’s Accuracy Assessment Kit can be used as an aid in determining whether a Position Sensor is
performing acceptably for the user’s application. For all calibration procedures, return the Position
Sensor to NDI. This practice ensures that all calibrations are conducted in accordance with
procedures established specifically for the Polaris Vicra Position Sensor. See “Return Procedure” on
page 77 for instructions on returning equipment to NDI.
Line Separation and Calibration
The Position Sensor line separation (described on page 28) can sometimes be an indication that a
Position Sensor is out of calibration, but is not necessarily the best indicator and cannot always
detect calibration loss. For example, suppose one of the sensors was to shift towards the centre of the
Position Sensor while maintaining its horizontal alignment. In this case, the Position Sensor would
be out of calibration without any change in line separation, and the reported position of the tool
would be shifted.
If the Position Sensor is measuring high line separation values, it may be an indication of loss of
calibration. Line separation alone should not, however, be used as a test for calibration loss.
Bump Sensor
The bump sensor detects when the Position Sensor has been bumped above a shock limit broadly
equivalent to a 200 mm to 254 mm drop onto a vinyl tiled concrete surface. A bump can cause the
system to lose calibration; however, it is not the only cause of calibration loss. Checking the bump
sensor status should be part of your regular calibration check.
You can use the GET command to check the bump sensor status. The bump status is indicated in bit
0x00200000 of the “Info.Status.Alerts” parameter. You can also check the bump sensor status using
NDI ToolBox.
Because a bump can affect the calibration of the Position Sensor, the system will not report
transformations if the bump sensor has detected a bump, unless:
• the bump sensor has been cleared, or
• reply option 0x0800 is used with the TX or BX command.
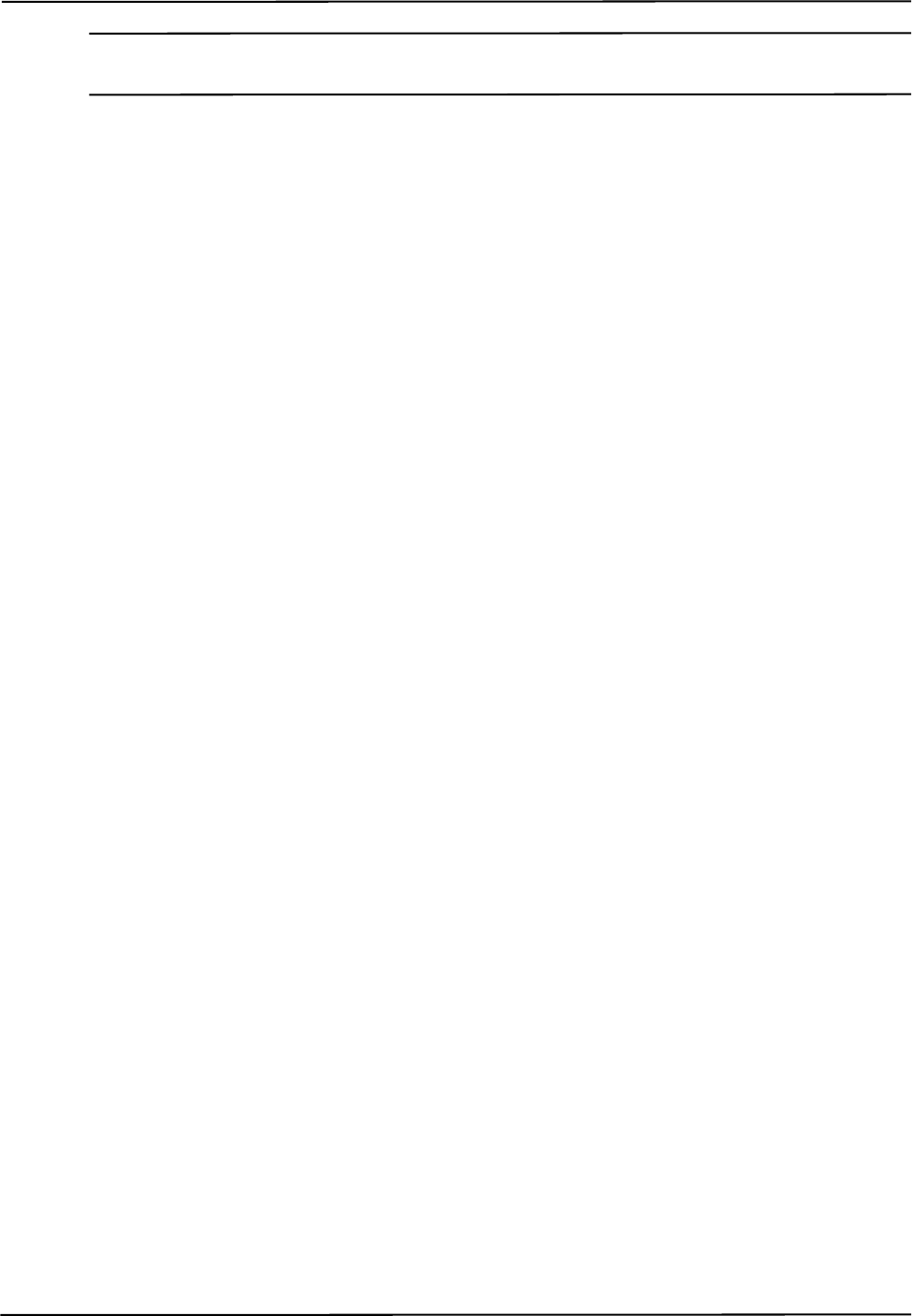
Calibration and Firmware
58 Polaris Vicra User Guide - Revision 2
Note See the “Polaris Application Program Interface Guide” for details on checking and clearing the bump sensor, and
using the TX, BX and GET commands.
If a bump has been detected, NDI recommends that you perform an accuracy assessment procedure
with the NDI Accuracy Assessment Kit (AAK), to ensure that the Position Sensor is still calibrated.
For information on the accuracy assessment procedure and AAK, contact NDI.
8.2 Updating the Firmware
The Polaris Vicra System’s firmware is stored in an EPROM flash memory device in the Position
Sensor. The latest firmware can be downloaded from the NDI Support Site at
http://support.ndigital.com.
Update the Polaris Vicra System’s firmware using NDI ToolBox. (See the NDI ToolBox online help
for further information.)
The system incorporates a safe boot loader that will perform verification of the control firmware in
the Position Sensor's memory prior to loading and executing it. It has been included to provide a
fall back if a future control firmware upgrade fails. A field firmware upgrade could fail, due to
communication or power faults. In these cases, the Position Sensor will still be able to start up by
running the safe boot loader. This will provide minimal support, to allow the user to retry the
control firmware upgrade.

Approvals
Polaris Vicra User Guide - Revision 2 59
9 Approvals
The Polaris Vicra System (consisting of a Position Sensor, Model P6, Power Adapter and a Host
USB Converter), qualifies for the following approvals.
9.1 Optical Radiation Safety
The Polaris Vicra Position Sensor has been assessed against the IEC Standard 60825-1 and the
Euronorm EN60825-1 and found not to pose a potential hazard to the eye under any foreseeable
viewing condition.
Note The Polaris Vicra System emits IR light that may interfere with IR controlled devices, such as operating room
tables. It is recommended that you test the Polaris Vicra System if you intend to use it in an environment where
other IR controlled devices are in use.
Table 9-1 Electrical Safety
Standard Description
EN60601-1 (1990) Second Edition plus
A1:93, A2:95, A12:93 and Corr:94
Medical Electrical Equipment Part I: General
Requirements for Safety
CAN/CSA-C22.2 No. 601.1-M90
(R2001)
Medical Electrical Equipment Part I: General
Requirements for Safety
UL 60601-1, First Edition, dated April 25,
2003.
Medical Electrical Equipment Part I: General
Requirements for Safety
Table 9-2 Electromagnetic Compatibility
Standard Description
CISPR 11/EN55011
FCC Part 15, Class B
Class B, Group 2, ISM Equipment
IEC60601-1-2:2001 Medical Electrical Equipment, Part 1: General Requirements
for Safety—Collateral Standard: Electro-Magnetic
Compatibility - Requirements and Tests.
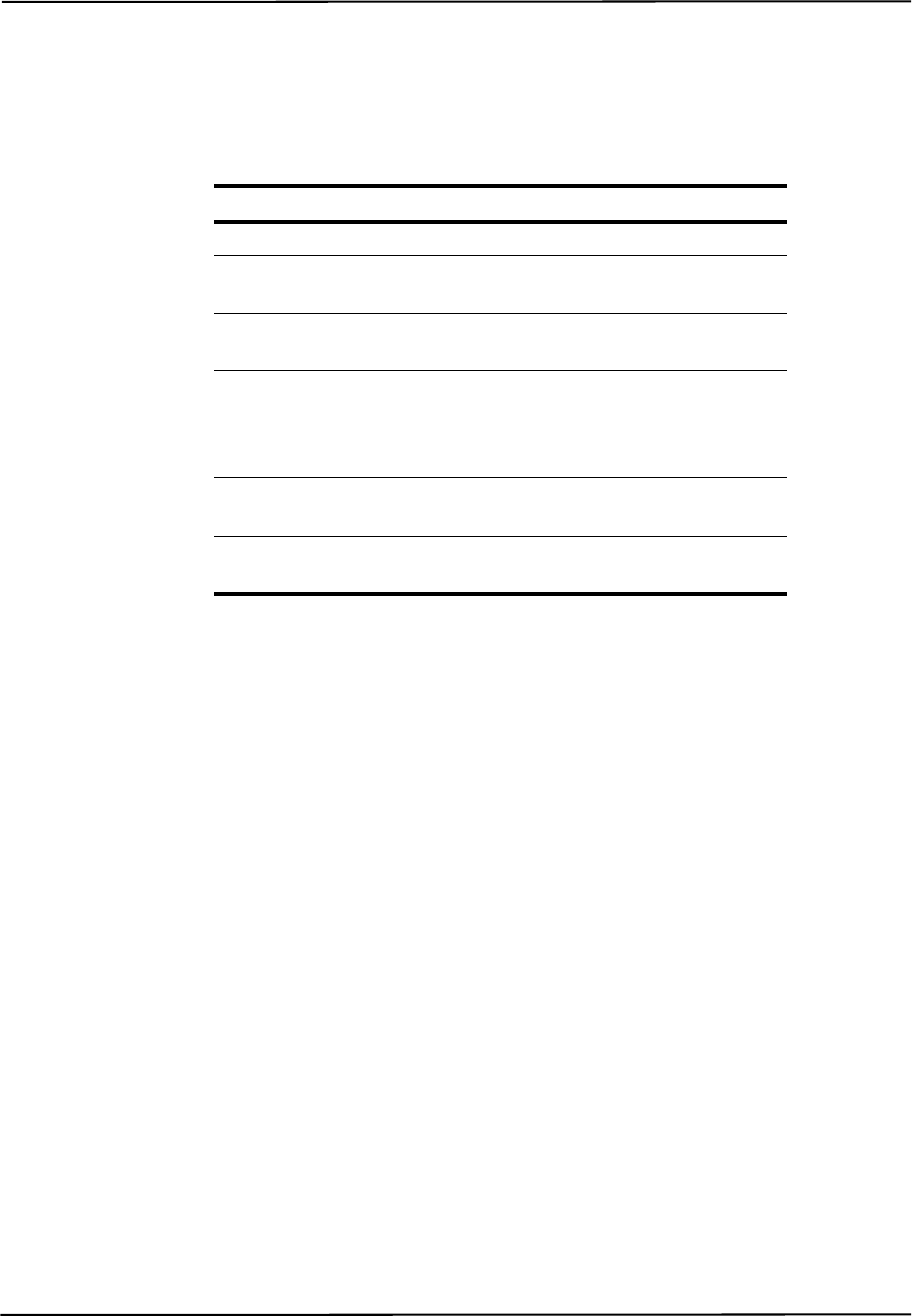
Classifications
60 Polaris Vicra User Guide - Revision 2
10 Classifications
Table 10-1 Classifications
Classification Description
Electric shock protection Class I - no applied parts
Degree of Protection from
electric shock
Not classified
Degree of Protection against
ingress of solids and liquids
Position Sensor designed to
IP 54
Flammable atmosphere Not suitable for use in the
presence of a flammable
anaesthetic mixture with air,
oxygen or nitrous oxide
Mode of operation Continuous when supplied by
mains
Method of sterilization or
disinfection
Not suitable for sterilization
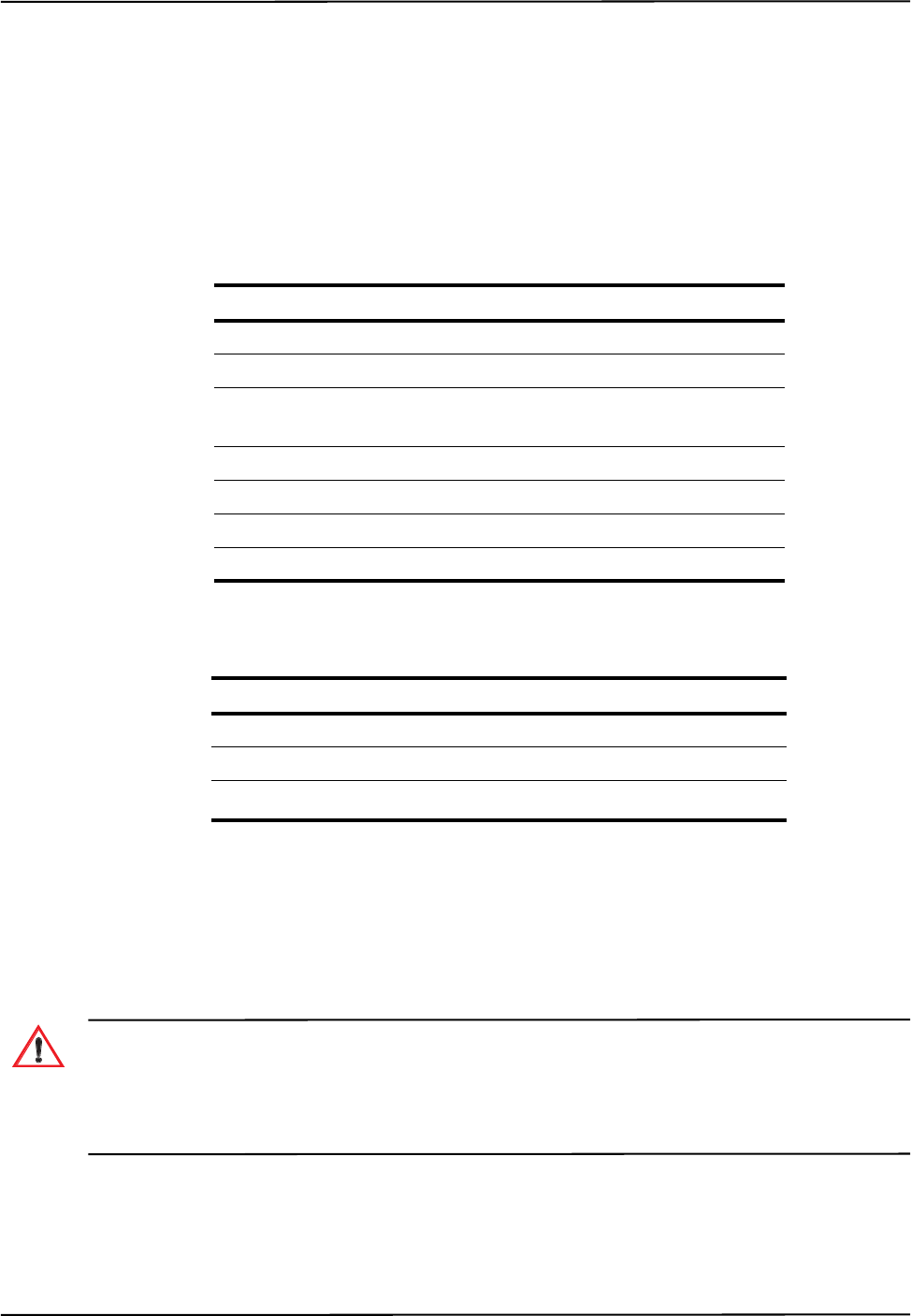
Technical Specifications
Polaris Vicra User Guide - Revision 2 61
11 Technical Specifications
This chapter provides technical specifications on each of the system units.
11.1 Position Sensor
The system requires a warm-up time from storage temperature to operating temperature equivalent
to 10 minutes plus one minute for every 1°C of difference between storage temperature and
operating temperature. (If the temperature difference is within 5°C, the warm-up time will be 10
minutes.)
For example, if the system is stored at -10°C and moved to a location at +30°C, the warm-up time
will be 10 minutes, plus an additional 40 minutes to account for the difference in temperature.
Do not transport or store the Position Sensor outside the recommended storage temperature range, as this may
cause the system to go out of calibration. Reliance on data provided by an out of calibration Position Sensor may
lead to inaccurate conclusions and may cause personal injury. A calibration procedure must be performed
before using the Position Sensor after it has been transported or stored outside the recommended storage
temperature range.
Table 11-1 Position Sensor - Technical Specifications
Specification Value
Dimensions 273 mm x 69 mm x 69 mm
Weight <1 kg
Mounting 1/4” thread tripod mount, or 3
M3 x 0.5 mm x 9 mm screws
Host Interface USB (1.1 and 2.0 compatible)
Maximum Update Rate 20 Hz
Input Voltage 26 VDC
Power Consumption 13.5 W (approx.)
Table 11-2 Position Sensor - Operating Environmental Conditions
Environmental Condition Value
Atmospheric Pressure 70 kPa to 106 kPa
Relative Humidity 30% to 75%
Temperature +10oC to +30oC (See note below)
Warning!
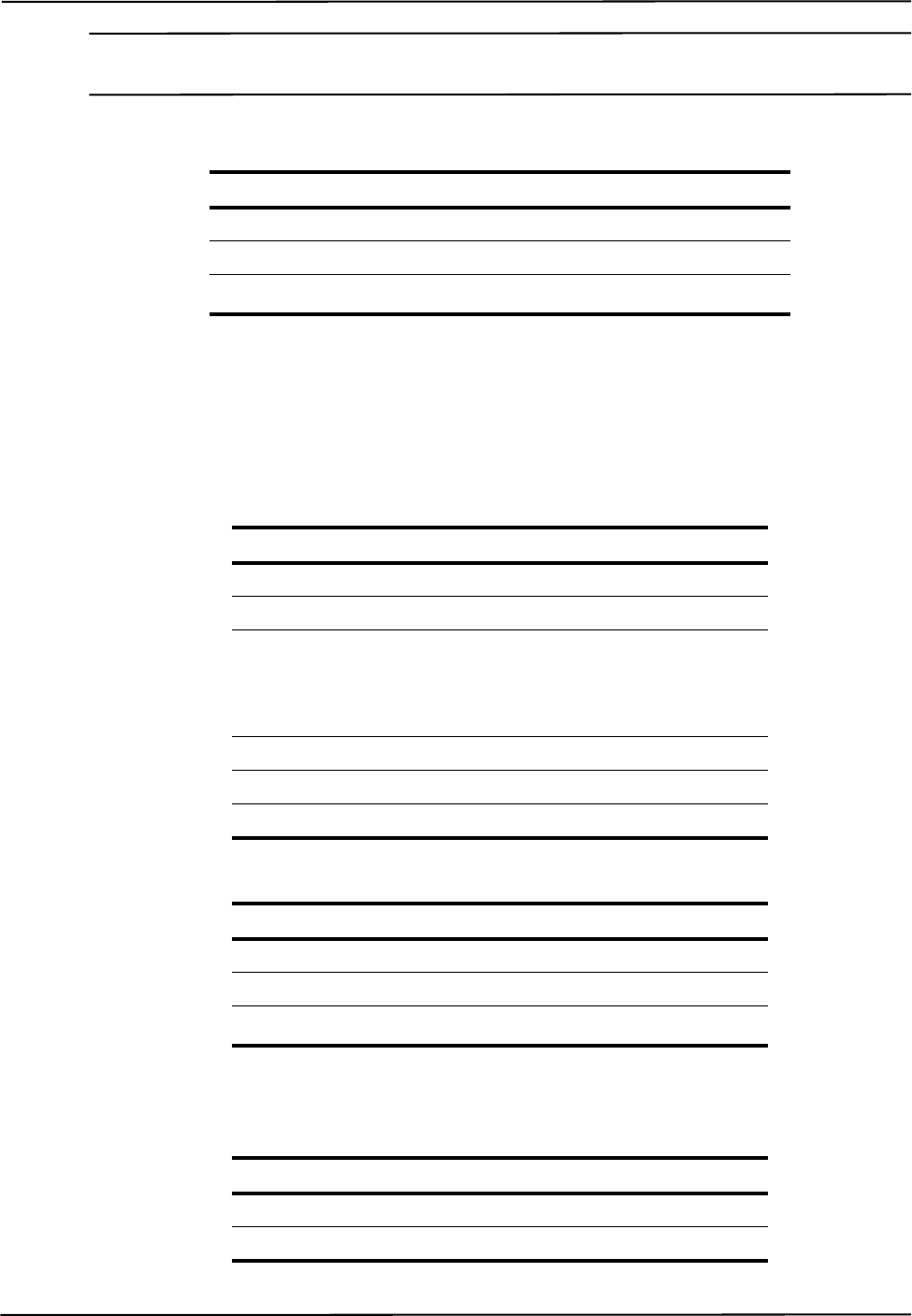
Technical Specifications
62 Polaris Vicra User Guide - Revision 2
Caution! To ship the Polaris Vicra System, repack it in the original containers with all the supplied protective packaging.
The provided packaging is designed to prevent damage to the equipment.
11.2 Host USB Converter
Table 11-3 Position Sensor - Transportation and Storage Environmental Conditions
Specification Value
Atmospheric Pressure 50 kPa to 106 kPa
Relative Humidity 10% to 90% non-condensing
Temperature -10oC to +50oC
Table 11-4 Host USB Converter - Technical Specifications
Specification Value
Dimensions 88 mm x 57 mm x 39 mm
Weight 0.35 kg
Mounting Free standing or secured via
internal threads (M6 x 1mm
pitch 3 mm depth) in (three)
mounting feet
Input Voltage 24 VDC
Output Voltage 26 VDC
Power Consumption <2 W
Table 11-5 Host USB Converter - Operating Environmental Conditions
Environmental Condition Value
Atmospheric Pressure 70 kPa to 106 kPa
Relative Humidity 30% to 75%
Temperature +10oC to +30oC
Table 11-6 Host USB Converter - Transportation and Storage Environmental Conditions
Specification Value
Atmospheric Pressure 50 kPa to 106 kPa
Relative Humidity 10% to 90% non-condensing

Technical Specifications
Polaris Vicra User Guide - Revision 2 63
11.3 Power Adapter
Temperature -10oC to +50oC
Table 11-6 Host USB Converter - Transportation and Storage Environmental Conditions
Specification Value
Table 11-7 Power Adapter - Technical Specifications
Specification Value
Dimensions 125 mm x 62 mm x 32 mm
Weight 0.37 kg
Mounting Free standing
Input Voltage 100 VAC to 240 VAC, 50/60 Hz
Output Voltage 24 VDC @ 2.1 A
Power Consumption 48 W (max.) (24 W typical)
Table 11-8 Power Adapter - Operating Environmental Conditions
Environmental Condition Value
Atmospheric Pressure 70 kPa to 106 kPa
Relative Humidity 30% to 75%
Temperature +10oC to +30oC
Table 11-9 Power Adapter - Transportation and Storage Environmental Conditions
Specification Value
Atmospheric Pressure 50 kPa to 106 kPa
Relative Humidity 10% to 90% non-condensing
Temperature -10oC to +50oC
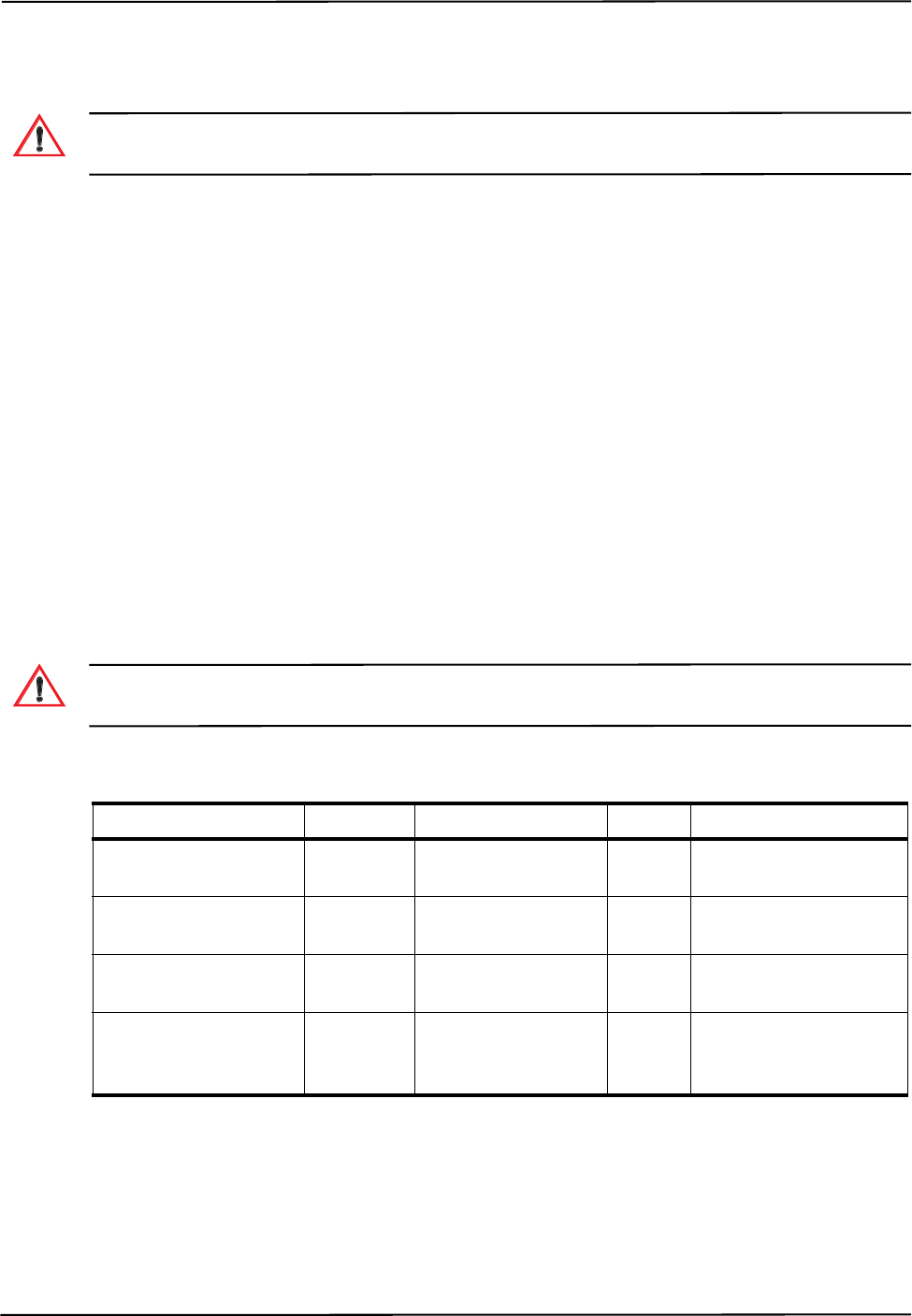
Electromagnetic Compatibility
64 Polaris Vicra User Guide - Revision 2
12 Electromagnetic Compatibility
Radio frequency communications equipment, including portable and mobile devices, may affect the Polaris Vicra
System and result in personal injury.
12.1 Electrostatic Discharge
Care should be taken to mitigate the production of electrostatic charges, to avoid any damage to the
equipment that could cause incorrect data to be returned, (possibly resulting in personal injury).
These measures can include, but are not limited to, appropriate air conditioning, humidification,
conductive floor coverings, attire.
It is not a good practice to use the Polaris Vicra System either adjacent to, or stacked with, other
equipment. Check that the Polaris Vicra System is operating normally if it is used either adjacent to,
or stacked with, other equipment.
12.2 Cables and Accessories
The following table lists the cables and accessories that may be used with the Polaris Vicra System
while still maintaining compliance to the emissions and immunity requirements of IEC60601-1-
2:2001.
Use of cables or accessories, other than those listed in the following table, may result in increased emissions
and/or decreased immunity of the Polaris Vicra System and may result in personal injury.
Warning!
Warning!
Table 12-1 Cables and Accessories That Maintain Compliance
Name NDI P/N Type Shield Notes
Cable AC Line Cord,
Medical Grade
7500010 North American No Mains to Power Adapter
Cable AC Line Cord 7500012 France/Belgium/
Germany
No Mains to Power Adapter
USB cable 2600596 USB, A-B male,
double shielded, 2 m
Yes Computer to Host USB
Converter
Power Adapter 4100139 Switch Mode, 100-
240 VAC input, 24
VDC, 40 W output
NA NA
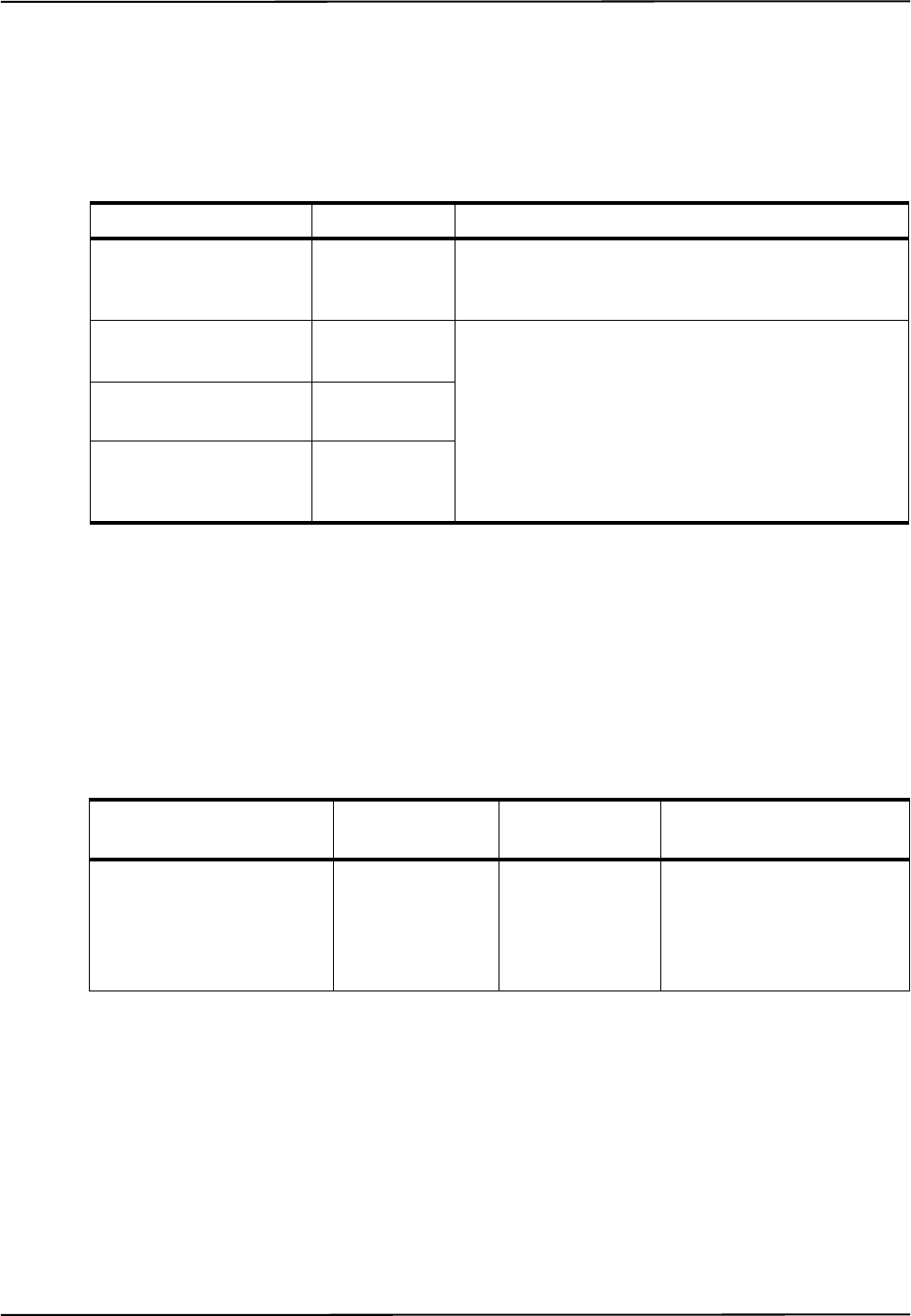
Electromagnetic Compatibility
Polaris Vicra User Guide - Revision 2 65
12.3 Guidance and Manufacturer's Declaration - Electromagnetic Emissions
The Polaris Vicra System meets the electromagnetic environments listed below. The customer or the
user of the Polaris Vicra System should ensure that it is only used in such an environment.
12.4 Guidance and Manufacturer’s Declaration - Electromagnetic Immunity
The Polaris Vicra System is intended for use in an environment that meets the requirements outlined
by the manufacturer’s declaration for electromagnetic immunity (See Table 12-3 on page 65). The
customer or the user of the Polaris Vicra System should ensure that it is only used in such an
environment.
Table 12-2 Manufacturer’s Declaration for Electromagnetic Emissions
Emissions Test Compliance Electromagnetic Environment Guidance
RF emissions
CISPR11
Group 2 The Polaris Vicra System must emit electromagnetic
energy in order to perform all its intended functions.
Nearby electronic equipment may be affected.
RF emissions
CISPR11
Class B The Polaris Vicra System is suitable for use in all
establishments, including domestic establishments
and those directly connected to the public low-
voltage power supply network that supplies buildings
used for domestic purposes
Harmonic emissions
IEC61000 3-2
Class A
Voltage fluctuations/
flicker emissions
IEC61000-3-3
Complies
Table 12-3 Electromagnetic Immunity
Immunity Test IEC 60601 Test
Level Compliance Level Electromagnetic
Environment - Guidance
Electrostatic discharge
(ESD)
IEC 61000-4-2
±6 kV contact
±8 kV air
±6 kV contact
±8 kV air
Observe precautions when
connecting or disconnecting
cables at ports identified
with the ESD warning
symbol
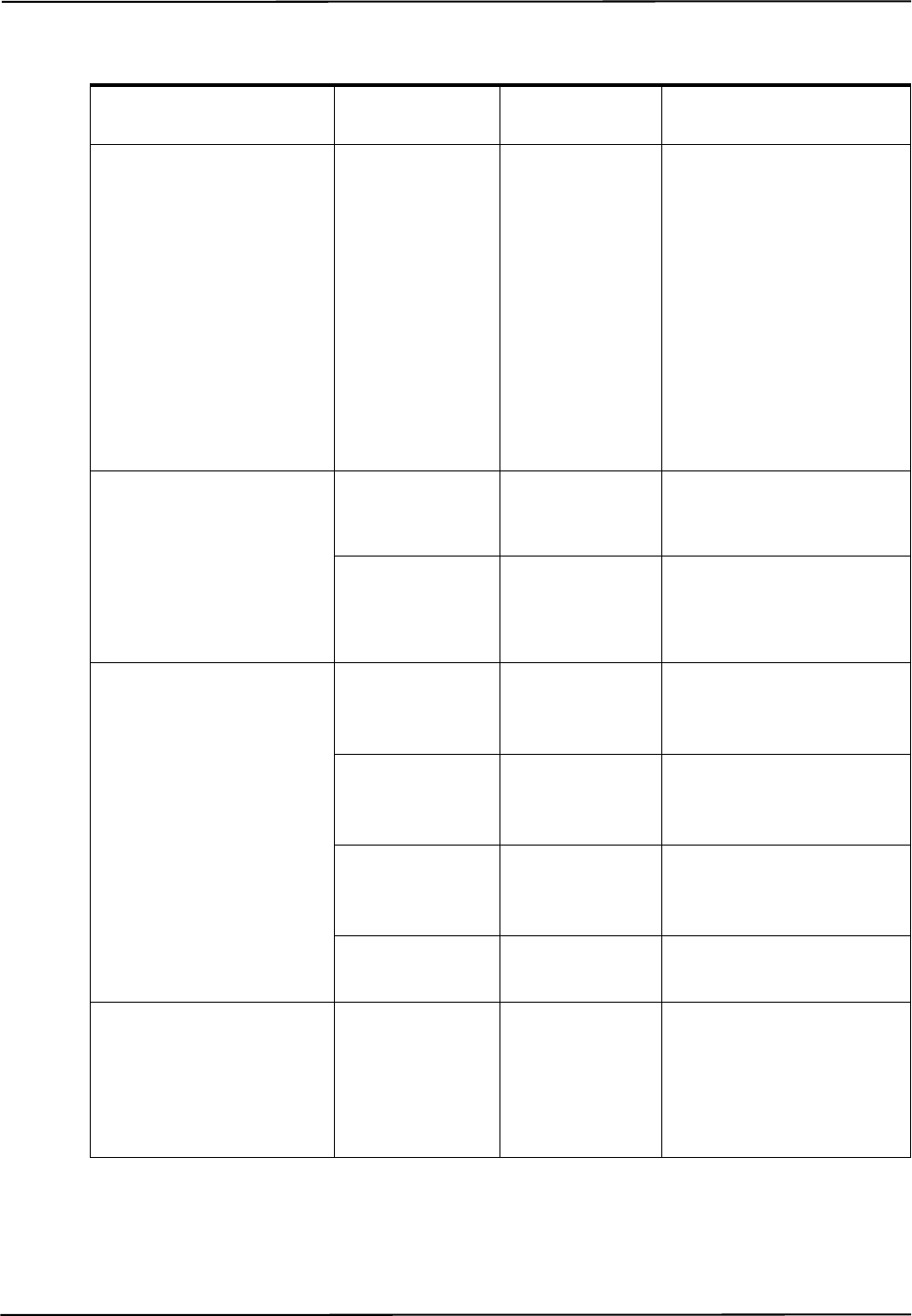
Electromagnetic Compatibility
66 Polaris Vicra User Guide - Revision 2
Electrical Fast Transient
(EFT)/burst IEC 61000-4-4
±2 kV for power
supply lines.
±1 kV for I/O
lines
±2 kV for power
supply lines.
±1 kV for I/O
lines
Care must be taken to route
all patient-coupled cables
away from high power, high
current or other cables or
sources that may induce
electrical fast transients into
the patient-coupled cables.
If such interference is
suspected, the cables should
be re-routed and/or the
source of the interference
shielded or otherwise
isolated.
Surge
IEC 61000-4-5
±1 kV different-
ial mode
±1 kV
differential mode
±2 kV common
mode
±2 kV common
mode
Dips/Interruptions/
Variations on power supply
input
IEC 61000-4-11
<5% Ut for 0.5-
cycles
<5% Ut for 0.5-
cycles
40% Ut for 5-
cycles
40% Ut for 5-
cycles
70% Ut for 25-
cycles
70% Ut for 25-
cycles
<5% Ut for 5 sec <5% Ut for 5 sec
Power frequency
(50/60Hz) magnetic field
IEC 61000-4-8
3 A/m 3 A/m Power frequency magnetic
fields should be at levels
characteristic of a typical
location in a typical
commercial or hospital
environment.
Table 12-3 Electromagnetic Immunity (Continued)
Immunity Test IEC 60601 Test
Level Compliance Level Electromagnetic
Environment - Guidance
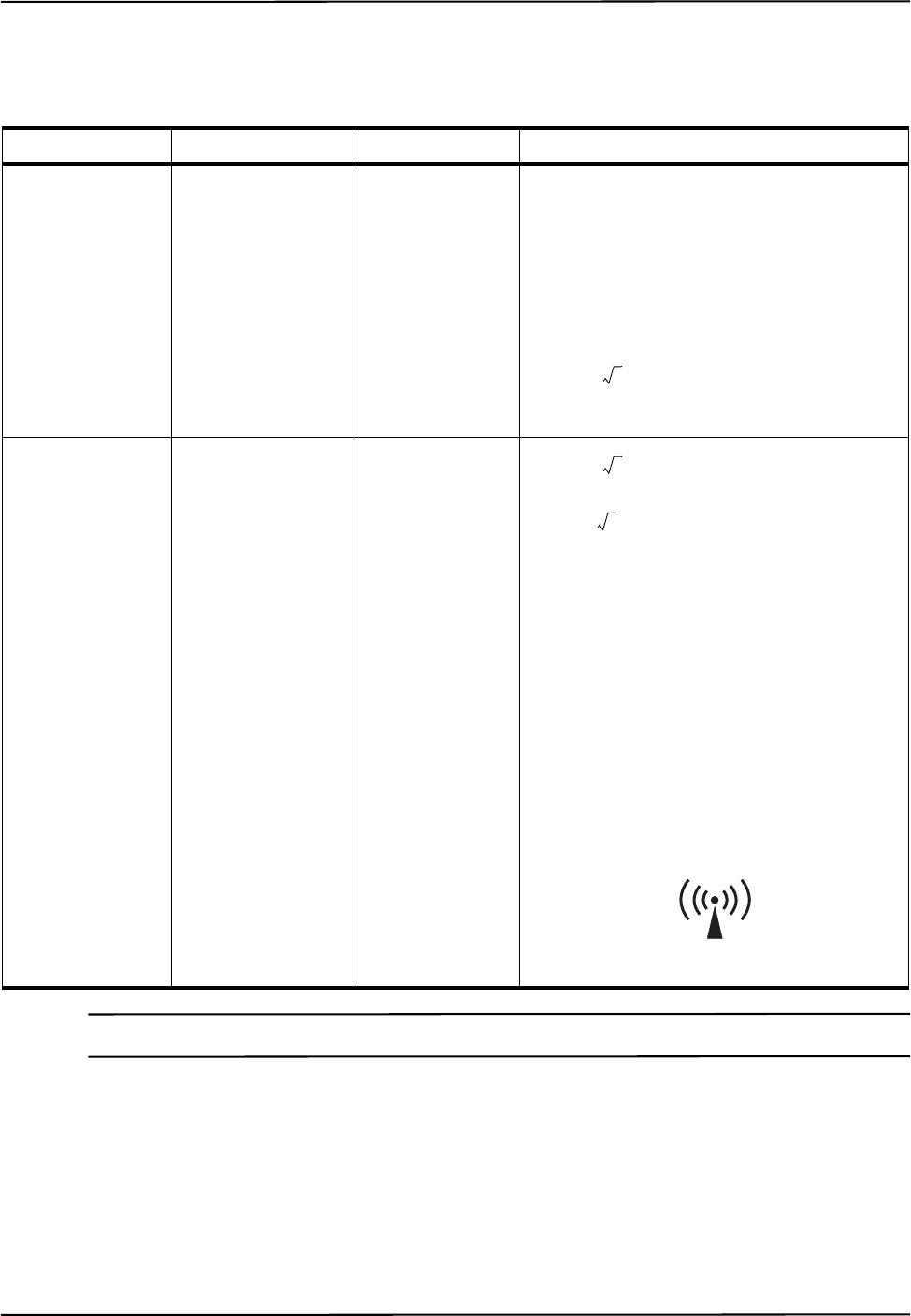
Electromagnetic Compatibility
Polaris Vicra User Guide - Revision 2 67
Note Ut is the AC mains voltage prior to the application of the test level.
a - Field strengths from fixed transmitters, such as base stations for radio (cellular/cordless)
telephones and land mobile radios, amateur radio, AM and FM radio broadcast and TV broadcast,
cannot be accurately predicted. To assess the electromagnetic environment due to fixed RF
transmitters, an electromagnetic site survey should be considered. If the measured field strength in
the location where the Polaris Vicra System is used exceeds the applicable RF compliance level
above, observe the system to verify normal operation. If abnormal performance is observed,
additional measures may be necessary, such as re-orienting or relocating the Polaris Vicra System.
Table 12-4 Electromagnetic Immunity - Not Life Supporting
Immunity Test IEC 60601 Test Level Compliance Level Electromagnetic Environment - Guidance
Portable and mobile RF communications
equipment should be used no closer to any
part of the Polaris Vicra System, including
cables, than the recommended separation
distance calculated from the equation
applicable to the frequency of the transmitter.
Conducted RF
IEC 61000-4-6
3 Vrms
150 kHZ to 80 MHz
3 V Recommended separation distance:
See Table 12-5 on page 68
Radiated RF
IEC 61000-4-3
3 V/m
80 MHz to 2.5 GHz
3 V/m 80 MHz to 800 MHz
800 MHz to 2.5 GHz
where 'P' is the maximum output power
rating of the transmitter in watts (W)
according to the transmitter manufacturer and
'd' is the recommended separation distance in
metres.
Field strengths from fixed RF transmitters, as
determined by an electromagnetic site
surveya, should be less than the compliance
level in each frequency rangeb. Interference
may occur in the vicinity of equipment
marked with the following symbol:
See Table 12-5 on page 68.
d3.5
3
-------
P=
d3.5
3
-------
P=
d7
3
---
P=

Electromagnetic Compatibility
68 Polaris Vicra User Guide - Revision 2
b - Over the frequency range of 150 kHz to 80 MHz, field strengths should be less than 3 V/m.
Note At 80 MHz and 800 MHz, the higher frequency range applies.
These guidelines may not apply to all situations. Electromagnetic propagation is affected by absorption and
reflection from structures, objects, and people. If an electromagnetic interference is suspected, it is the
responsibility of the user to assess the electromagnetic environment in their location.
12.5 Recommended Separation Distances
The Polaris Vicra System is intended for use in an electromagnetic environment in which radiated
RF disturbances are controlled. The customer or the user of the Polaris Vicra System can help
prevent electromagnetic interference by maintaining a minimum distance between portable and
mobile RF communications equipment (transmitters) and the Polaris Vicra System, as recommended
below according to the maximum output power of the communications equipment.
For transmitters rated at a maximum output power not listed above, the recommended separation
distance (d) in metres (m) can be estimated using the equation applicable to the frequency of the
transmitter, where P is the maximum output power rating of the transmitter in watts (W) according
to the transmitter manufacturer.
Note At 80 MHz and 800 MHz, the higher frequency range applies.
These guidelines may not apply to all situations. Electromagnetic propagation is affected by absorption and
reflection from structures, objects, and people.
12.6 RF Emissions
This device complies with Part 15 of the FCC rules. Operation is subject to the following two
conditions:
1. This device may not cause harmful interference and,
Table 12-5 Recommended Separation Distances
Rated maximum output power
of transmitter (watts)
Separation distance according to frequency of transmitter (metres)
150kHz to 80MHz 80 MHz to 800 MHz 800 MHz to 2.5 GHz
0.01 0.117 0.117 0.233
0.1 0.369 0.369 0.737
1.0 1.17 1.17 2.33
10 3.69 3.69 7.38
100 11.67 11.67 23.33
d3.5
3
-------
P= d 3.5
3
-------
P= d 7
3
---
P=
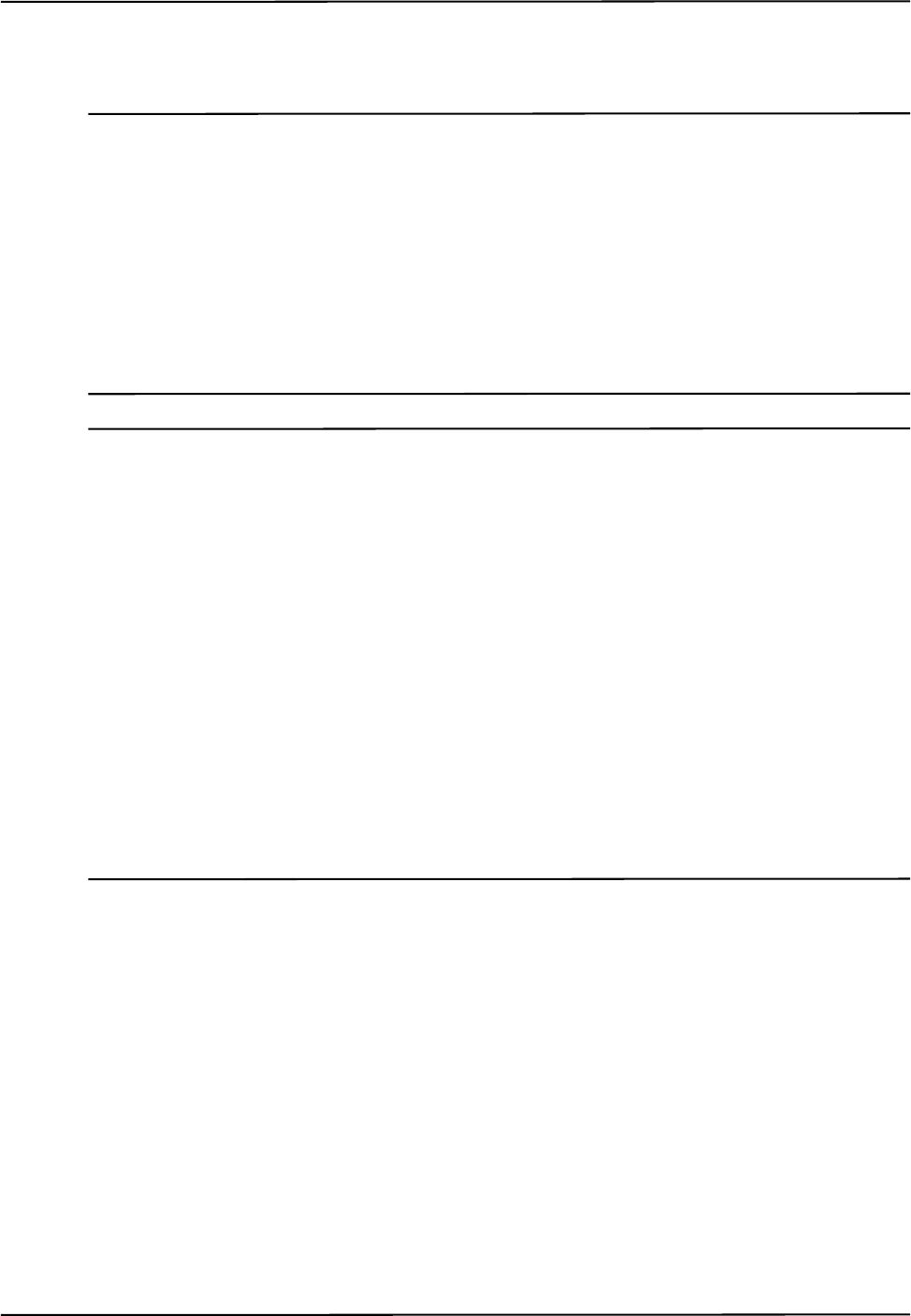
Electromagnetic Compatibility
Polaris Vicra User Guide - Revision 2 69
2. This device must accept any interference received, including interference that may cause
undesired operation.
Note This equipment has been tested and found to comply with the limits for a Class B digital device, pursuant to Part
15 of the FCC Rules. These limits are designed to provide reasonable protection against harmful interference in a
residential installation. This equipment generates, uses and can radiate radio frequency energy and, if not
installed and used in accordance with the instructions, may cause harmful interference to radio communications.
However, there is no guarantee that interference will not occur in a particular installation. If this equipment does
cause harmful interference to radio or television reception, which can be determined by turning the equipment off
and on, the user is encouraged to try to correct the interference by one or more of the following measures:
-- Reorient or relocate the receiving antenna.
-- Increase the separation between the equipment and receiver.
-- Connect the equipment into an outlet on a circuit different from that to which the receiver is connected.
-- Consult the dealer or an experienced radio/TV technician for help.
Notes CE Mark: This is a Class B product. In a domestic environment, this product may cause radio interference, in
which case the user may be required to take adequate measures.
Changes or modifications not expressly approved by Northern Digital Inc. could void the user’s authority to
operate the equipment.
To satisfy FCC and IC RF exposure requirements for mobile transmitting devices, a separation distance of 20 cm
or more should be maintained between the antenna of this device and persons during device operation. To
ensure compliance, operations at closer than this distance is not recommended.
The antenna used for this transmitter must not be co-located in conjunction with any other antenna or
transmitter.
Industry Canada Compliance Statement: This class B digital apparatus meets the requirements of the Canadian
Interference-Causing Equipment Regulations.
Avis de Conformité à la réglementation d’Industrie Canada: Cet appareil numerique de la classe B respecte
toutes les exigences du réglement sur le materiel brouilleur du Canada.
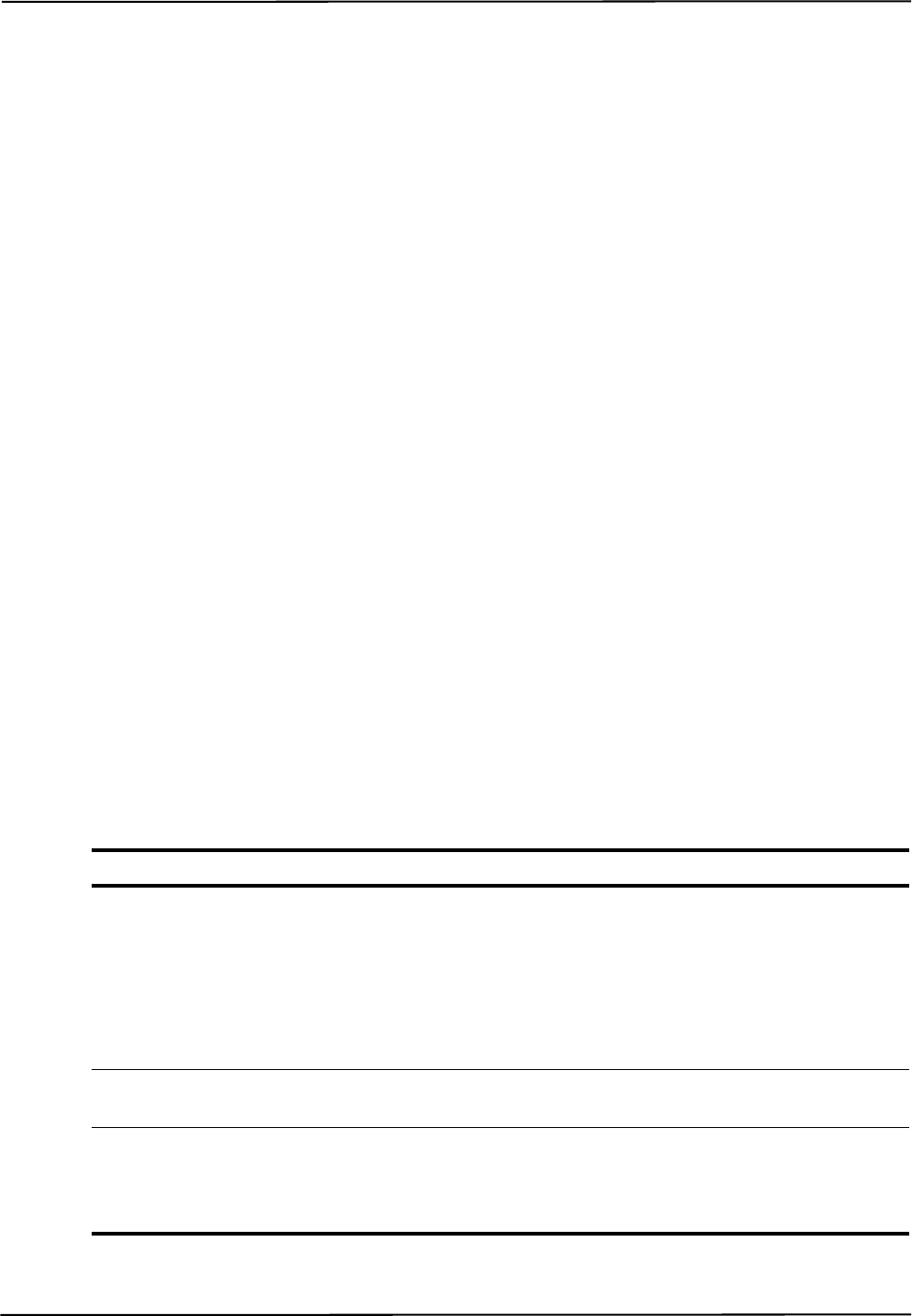
Troubleshooting
70 Polaris Vicra User Guide - Revision 2
13 Troubleshooting
13.1 Introduction
This section provides possible solutions to common problems and answers some frequently asked
questions. For further information regularly check the NDI Support Site at:
http://support.ndigital.com
If you cannot find the answer to your question here or on the support site, contact NDI at the address
shown at the front of this guide.
The majority of problems that may occur with the Polaris Vicra System can be grouped into one of
the following categories:
• A system hardware failure (for example a faulty Position Sensor or cable)
• A tool error (for example, dirty markers)
• Environmental conditions (for example, incidental IR light)
• User error (for example, obscuring the optical path)
Certain faults may be indicated by system LEDs or audio tones, or by means of error messages in
NDI ToolBox application software. These indications and messages are detailed in the following
paragraphs.
13.2 System Indications
The LED indicators on the Position Sensor and Host USB Converter provide a visual indication of
system status. In addition the Position Sensor emits audio tones that provide an audible indication of
system status. Refer to table 13-1 below to interpret the system visual and audio indications.
Table 13-1 System Visual and Audio Indications
Indication Meaning Action
Position Sensor: Power
LED is off
Position Sensor voltage
out of range
1. Refer to Figure 13-1. If necessary
proceed to 2 below.
2. Check for green power LED on Host
USB Converter. If lit, check/replace the
Position Sensor. If not lit, check/replace
the power adapter, cables and Host USB
Converter
Position Sensor: Power
LED is flashing
Normal indication during
warm-up
No action required
Position Sensor: Error
LED is flashing
A recoverable system fault
has been detected
Refer to the NDI ToolBox error message
and table 13-2. (If you are using your own
application, use the “Info.Status.Alert”
parameter in the GET command)
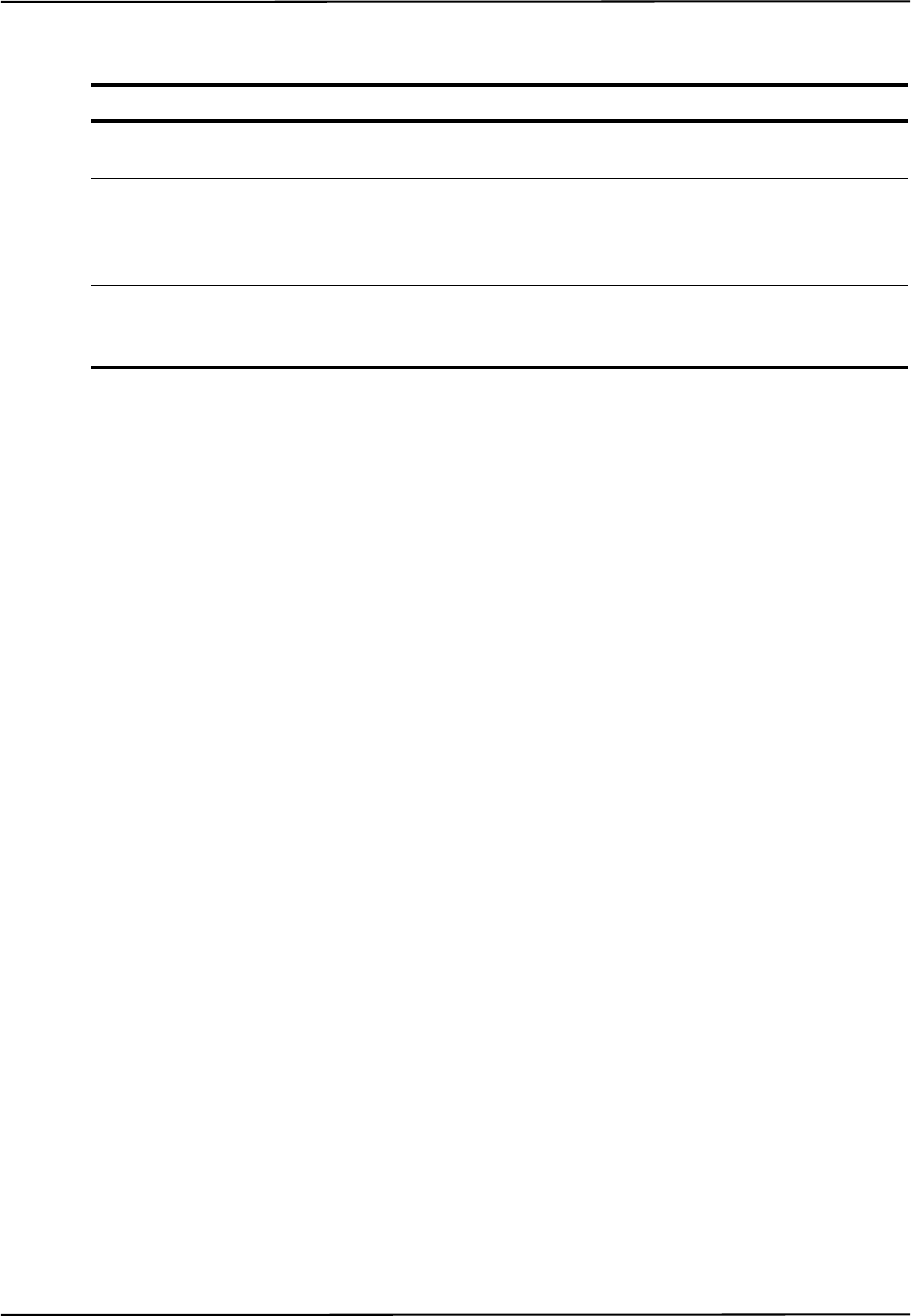
Troubleshooting
Polaris Vicra User Guide - Revision 2 71
Position Sensor: Error
LED is lit
A non-recoverable system
fault has been detected
Replace the Position Sensor
Position Sensor: two
audio tones emitted
Normal indication when
power is initially applied
to the system or the system
is reset
No action required
Host USB Converter:
Error LED is lit
A fault has been detected
by the Host USB
Converter
Refer to Figure 13-1 for action
Table 13-1 System Visual and Audio Indications (Continued)
Indication Meaning Action
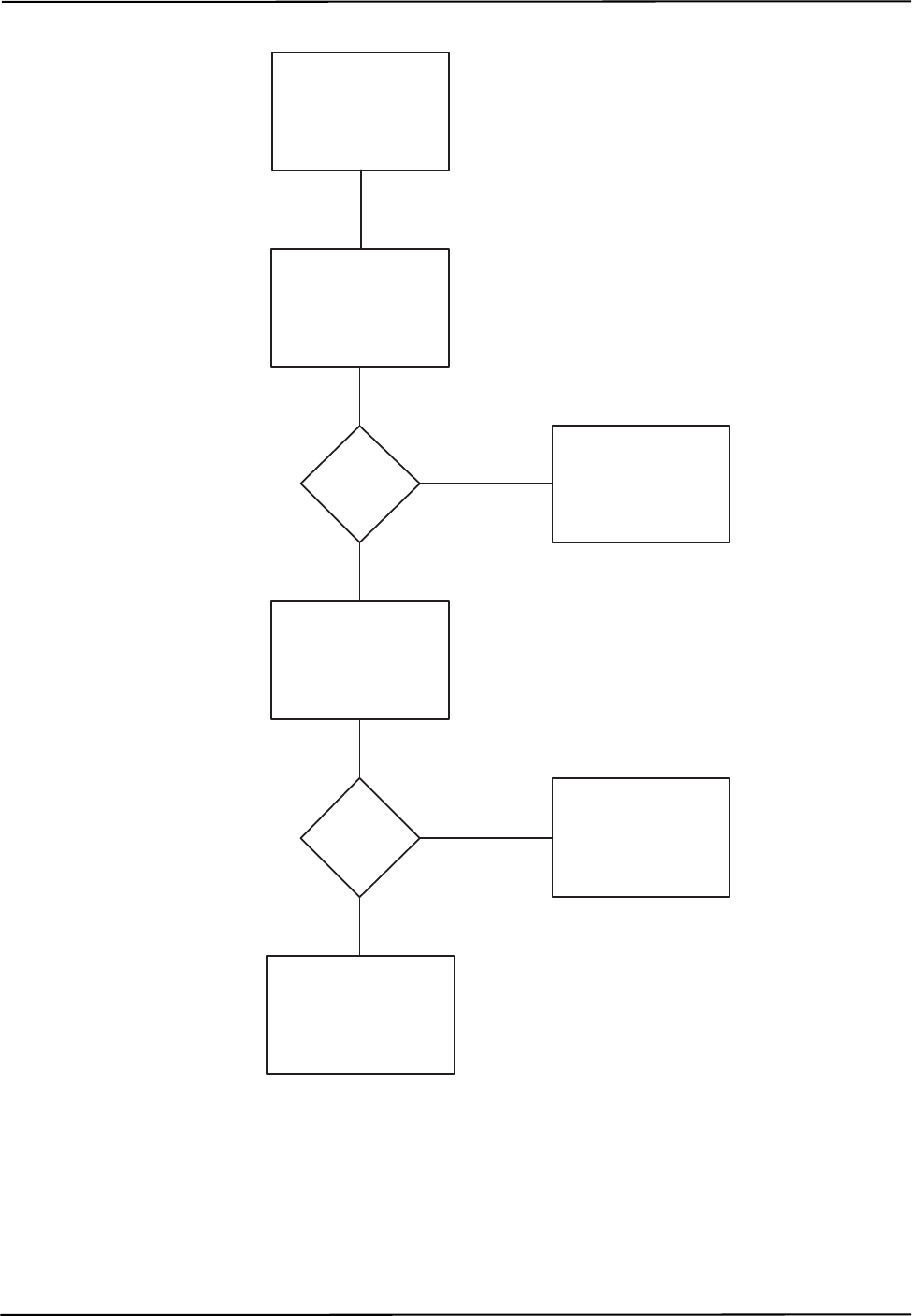
Troubleshooting
72 Polaris Vicra User Guide - Revision 2
Figure 13-1 Host USB Converter - Error LED Fault Chart
13.3 NDI ToolBox Error Messages
The NDI ToolBox application software displays a box around the appropriate icon and an associated
error message in the status message area for a number of possible system fault conditions. The
Host USB Converter
Error LED is lit
Turn system mains power
off for 10 seconds, then
turn back on
Does
Error
LED go
off?
Fault Cleared
Disconnect Position
Sensor
Does
Error
LED go
off?
Replace Position
Sensor
Check/Replace:
1. Power Adapter
2. Host USB Converter
Yes
No
Yes
No
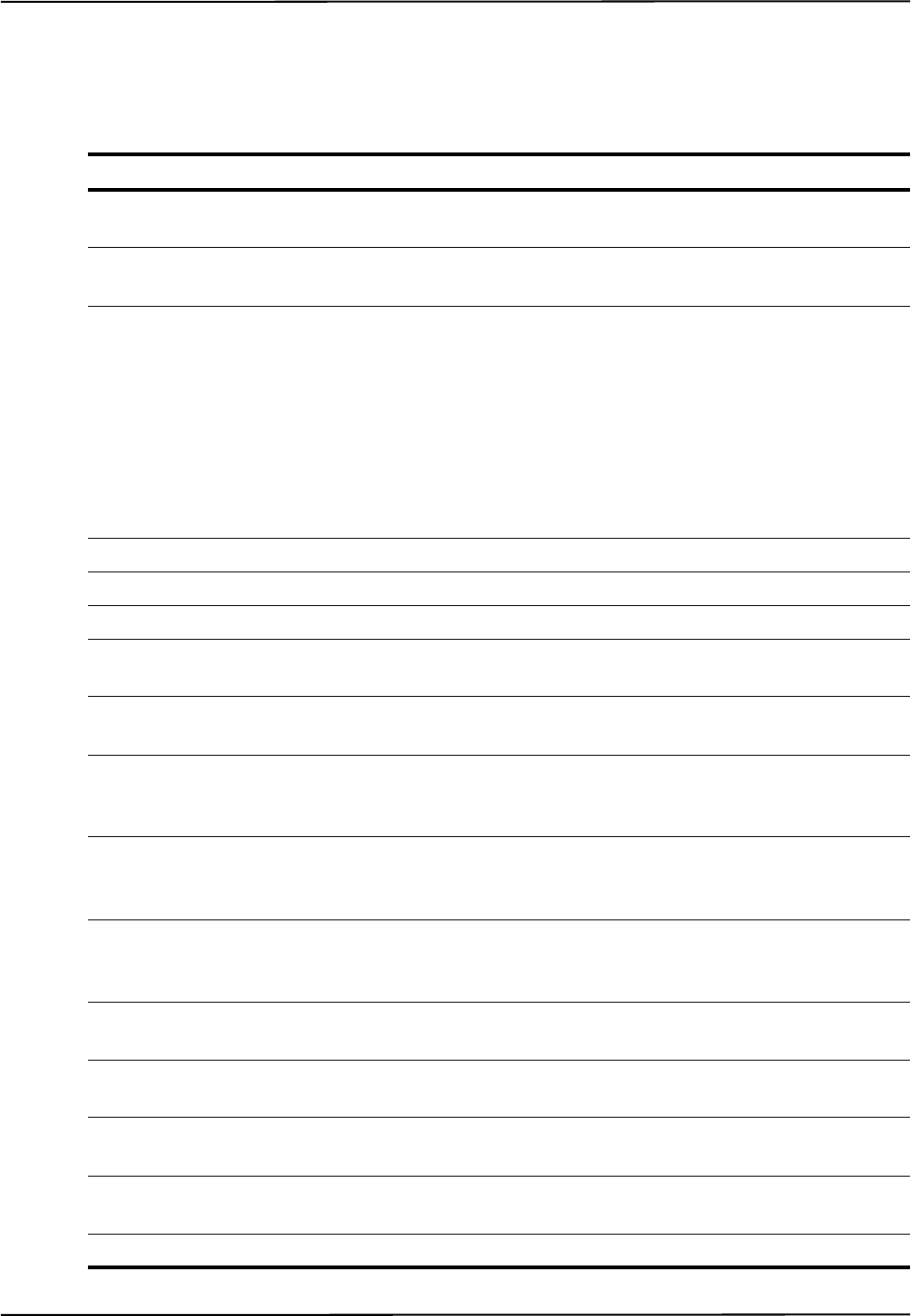
Troubleshooting
Polaris Vicra User Guide - Revision 2 73
messages should be read in conjunction with the system LED and audio indications shown in Table
13-1. A list of error messages that may be displayed in NDI ToolBox is shown in Table 13-2
Table 13-2 NDI ToolBox Error Messages
ToolBox Icon ToolBox Message Action
Hardware “Unable to initialize the system” and “Non-
recoverable memory fault. Return for service”
Replace Position Sensor
Hardware “Unable to initialize the system” and “Sensor
calibration fault. Return for service”
Replace Position Sensor
Hardware “Power fault. Check power supply, USB converter
and cables”
1. Refer to Figure 13-1. I
necessary proceed to 2 below.
2. Check for green power LED
on Host USB Converter. If lit,
check/replace the Position
Sensor. If not lit, check/
replace the power adapter,
cables and Host USB
Converter
Hardware “Sensor hardware fault. Return for service” Replace Position Sensor
Hardware “Illuminator hardware fault. Return for service” Replace Position Sensor
Hardware “Illuminator hardware fault. Return for service” Replace Position Sensor
Hardware “Cable fault. Check USB converter and cables” Check/replace Host USB
Converter
Hardware “Incompatible firmware versions” and “System
programming fault. Firmware update required”
Reload/update firmware
Hardware “Unable to initialize the system” and
“Recoverable memory error. Check settings and
save”
Reload/update firmware
Bump status “Bump detector battery fault. Return for service” Replace Position Sensor or be
aware that bumps will not be
detected
Bump status “Serious bump detected. Accuracy assessment
recommended”
System accuracy assessment
recommended. Contact NDI
for details.
Temperature “Internal temperature above calibrated operating
range”
Allow Position Sensor to cool
down
Temperature “Internal temperature below calibrated operating
range”
Allow Position Sensor to
reach operating range
Temperature “Temperature compensation fault. Return for
service”
Replace Position Sensor
No icon “Control firmware missing or corrupted” and
“Unable to initialize the system”
Reload/update firmware
No icon “Internal flash memory is full” Replace Position Sensor
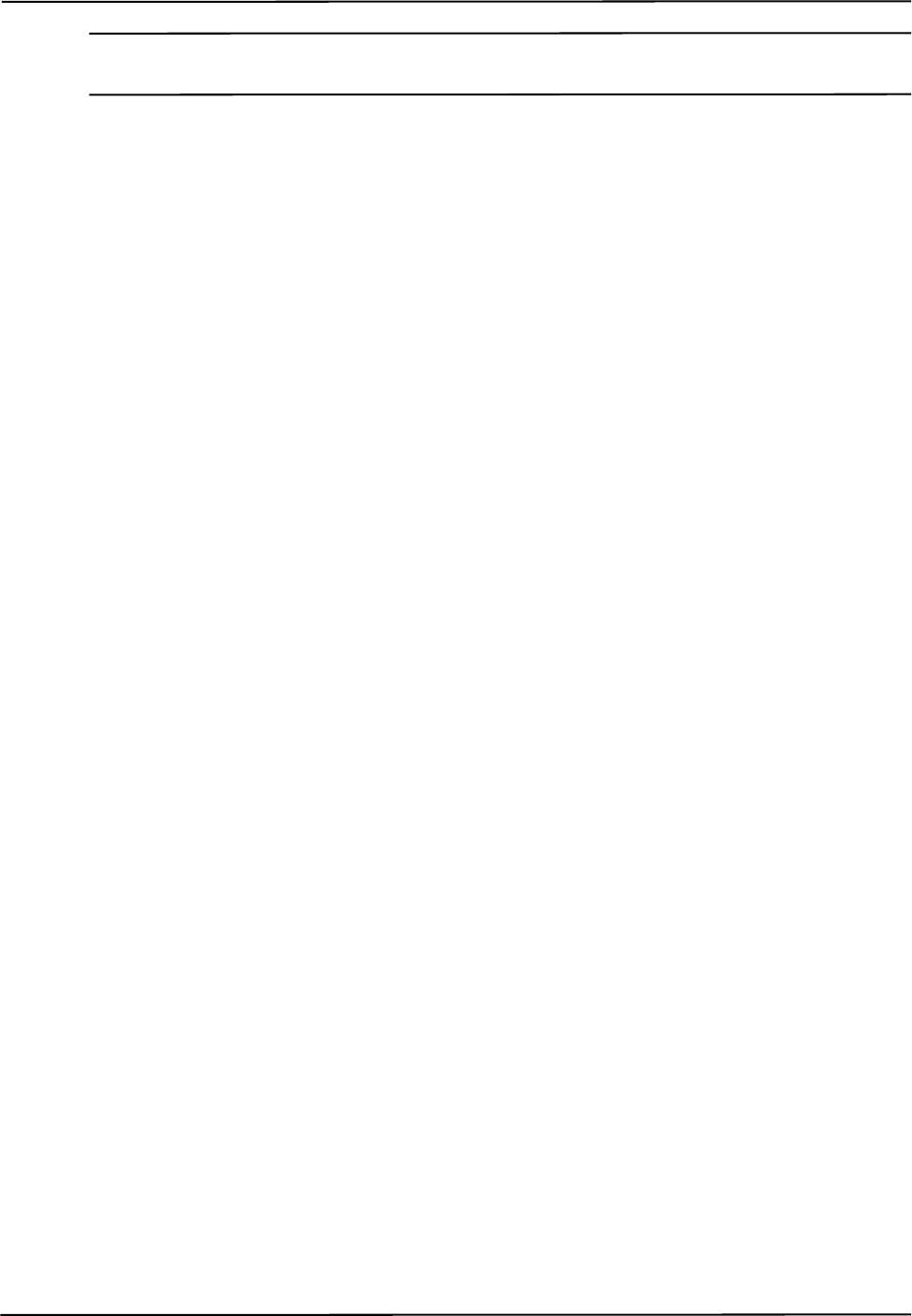
Troubleshooting
74 Polaris Vicra User Guide - Revision 2
Note If you are using your own applications, use the GET command to read the “Info.StatusAlert” parameter to check
the alert status. Refer to the “Polaris Application Program Interface Guide” for further information.
13.4 Common Problems
The following paragraphs lists specific problems and a possible solution.
The tool is inside the measurement volume, but the software reports that the tool is
partially out of volume
This may mean that less than the minimum number of markers (a parameter in the tool definition
file) are inside the characterized measurement volume, but at least one marker on the tool is inside
the characterized measurement volume.
For example, consider a four-marker tool, whose minimum number of markers parameter is set to 4.
If three of the tool’s markers are inside the characterized measurement volume, and the other marker
is outside the characterized measurement volume, the Polaris Vicra System will continue to track the
tool, but the accuracy is unknown, and the tool will be reported as partially out of volume.
The system doesn’t track tools at the back of the characterized measurement volume
If the system will track at the front of the measurement volume but not at the back, the Position
Sensor may be damaged, or calculating high line separation values. For more details on line
separation, see “Marker Detection and Tool Tracking” on page 28. You can check the line separation
values using the 3D command. See the “Polaris Application Program Interface Guide” for details.
Other IR-based devices are not working properly
Using the Polaris Vicra System in the same room as other IR-based devices may cause these other
devices to malfunction. The Position Sensor’s illuminators flood the surrounding area with IR light,
which could saturate other IR receiving devices, preventing them from properly receiving other IR
signals.
It may be possible to synchronize other devices with the Polaris Vicra System, so that IR signals
from the other devices are not being emitted at the same time as the illuminators emit IR. Contact
NDI Technical Support for details or visit the support site at http://support.ndigital.com.
The Polaris Vicra System is tracking some tools, but not others
As the Position Sensor begins to lose calibration, it may lose the ability to track some tools before
others. This is due to the various algorithm constraints used by the Polaris Vicra System, which
make certain tool designs more sensitive to loss of calibration than others. Consider, for example, a
tool that has several similar segment lengths or similar angles between segments, or has segment
lengths similar to those of another tool. The out-of-calibration Position Sensor may not be able to
determine which markers belong to which tool, and so will report the tools as missing. (See “Marker
Detection and Tool Tracking” on page 28 and the “Polaris Tool Design Guide” for details on
segment lengths and angles.)
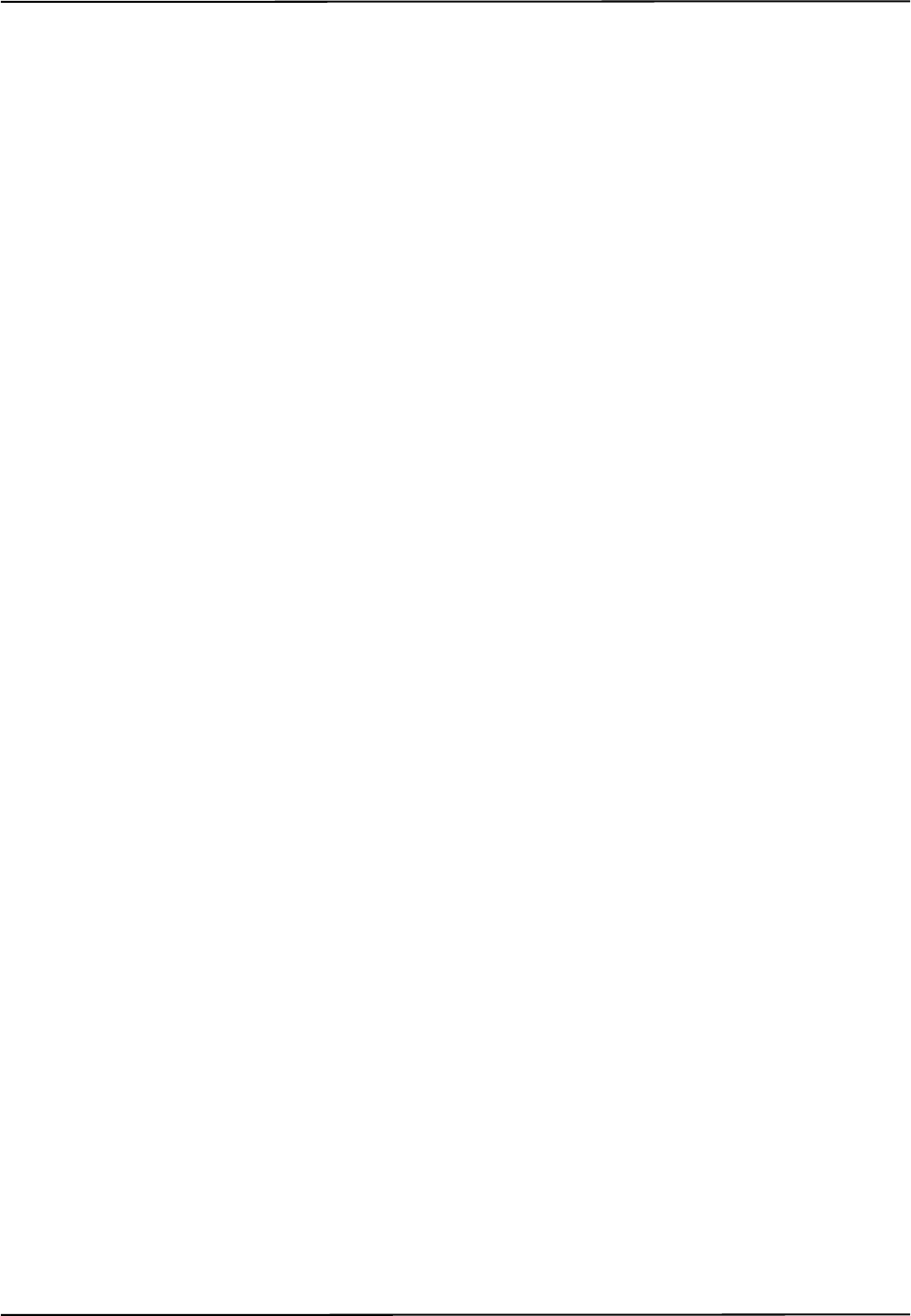
Troubleshooting
Polaris Vicra User Guide - Revision 2 75
See “Checking the Calibration of the Polaris Vicra System” on page 57 for more details about
calibration.
Reflections and other IR Sources
Reflections and other IR sources may cause markers to become “lost” in the background IR light.
These reflections and sources should be eliminated or minimised as much as possible. Reflections
occur when IR light from the illuminators is reflected off surfaces such as:
• drapes - ensure that drapes are placed such the reflections are minimised
• reflective surfaces - minimise reflective surfaces in the environment
• tools - design and manufacture tools in non-reflective materials. Refer to the “Polaris Tool
Design Guide” for further information.
Other sources of IR light, such as operating room lights, should be considered when positioning the
system in order to minimise interference from such devices.
What happens if the markers are partially blocked from the view of the Position
Sensor?
The Polaris Vicra System requires a clear line-of-sight to the markers. Anything that interferes with
the line-of-sight can reduce the measurement accuracy. The magnitude of the errors that are caused
by partial occlusion of the markers depends on the number of markers, the geometry of the tool, and
the severity of the occlusion. Errors caused by partial occlusion can have exactly the same
magnitude for active and passive tools. However, there is more opportunity to partially occlude the
passive markers because they are larger than active markers.When designing a new tool, it is
important to consider the effect of partial occlusion on its accuracy. The values used for these
parameters will also depend on the design of the tool. The best value is usually determined through
experimentation. See the “Polaris Tool Design Guide” for further information on tool design.
Why is the tool reported as missing?
A tool may be reported as missing if:
• it has been rotated so that too few markers are visible to the Position Sensor
• the tool is no longer in the field of view
• the tool is damaged, for instance if it is bent
• the condition of the makers has deteriorated, for instance scuffed, or occluded with foreign
matter.
The Position Sensor seems too warm
The Position Sensor will be warm to the touch during normal use. If the temperature goes out of
range an error message will be shown in NDI ToolBox application software.
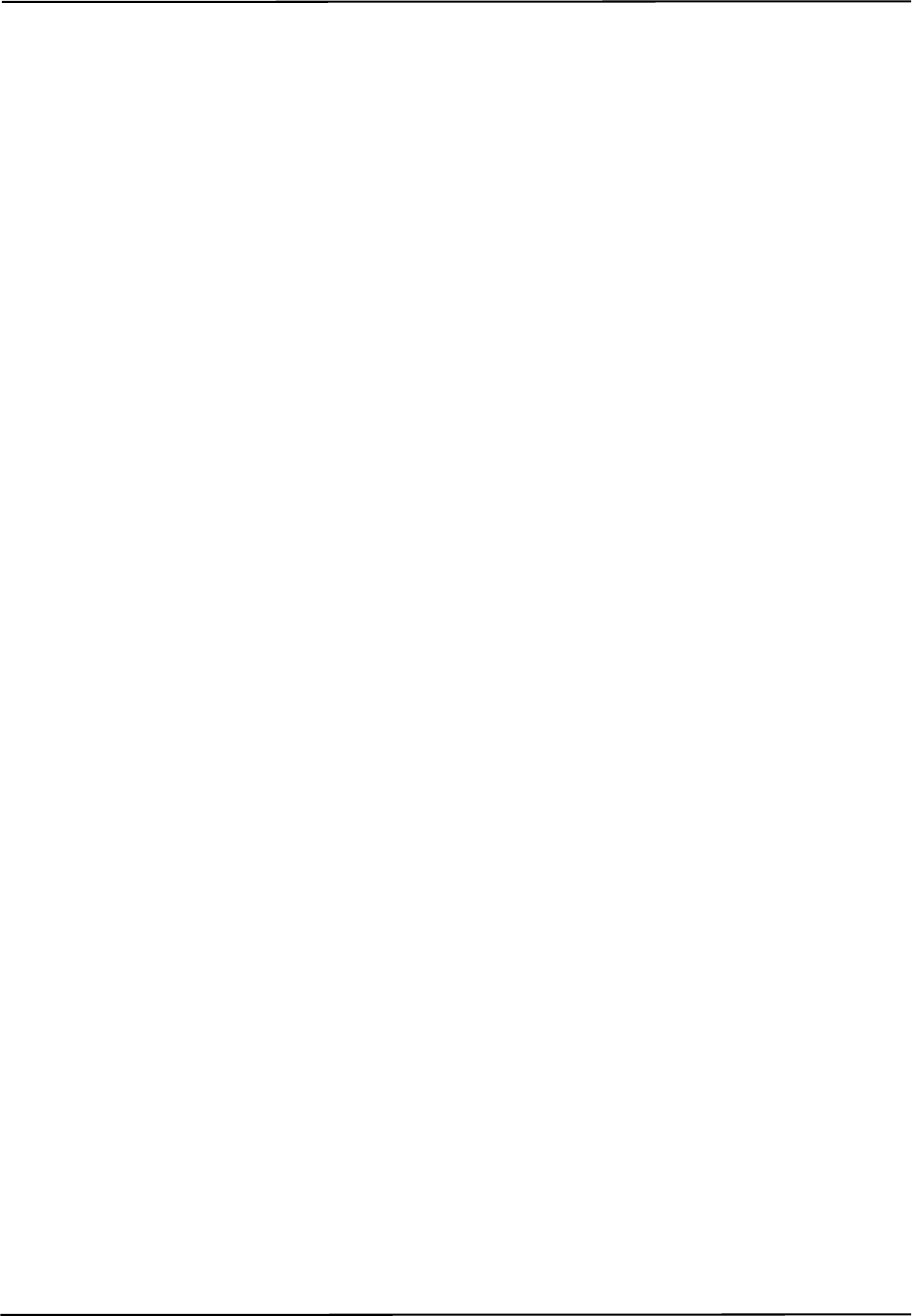
Troubleshooting
76 Polaris Vicra User Guide - Revision 2
The Virtual Serial Port cannot be opened
If you cannot open the virtual serial port, check the system connections, the Host USB Converter
and the host PC USB port.

Return Procedure and Warranty
Polaris Vicra User Guide - Revision 2 77
14 Return Procedure and Warranty
14.1 Return Procedure
In the event that you need to return equipment to NDI for repairs, you will need to fill out a Return
Materials Authorization (RMA) request form at the NDI Support Site at http://support.ndigital.com.
NDI will contact you with RMA information and shipping instructions. Any materials you are
returning to NDI should be shipped in their original packaging.
You are responsible for the shipping costs of returning equipment to NDI, whether or not the
equipment is covered under warranty. When the equipment is received at NDI, it will be inspected to
determine whether the required repair is covered under warranty. NDI can provide you with a quote
of repair costs either before or after repairs have been made. If the equipment is covered under
warranty, NDI will pay the return shipping costs. If the equipment is not covered under warranty,
you are required to pay the return shipping costs.
14.2 Warranty
Unless otherwise agreed to in writing by NDI, the warranty is as follows, and applies only to the
original purchaser.
Note This warranty is also posted on the NDI Support Site at http://support.ndigital.com.
Hardware
NDI warrants to the Buyer that NDI’s hardware product(s) will be free from defects in material and
workmanship only for a period twelve (12) months from the date such product(s) is/are shipped
from NDI to the Buyer.
This warranty does not apply to product(s) normally consumed in Buyer’s operations or which have
a normal life inherently shorter than the above-stated warranty period. Without limiting the
generality of the foregoing, the following products shall have the following warranty periods:
Software
NDI’s software product(s) is/are licensed and provided “as is, where is” without warranty of any
kind. NDI makes no warranties, express or implied, that the functions contained in the software
product(s) will meet the Buyer’s requirements or that the operation of the programs contained
therein will be error free.
product or components thereof which are re-chargeable batteries . . . 90 days from shipment
infrared emitting diode (IRED) markers or product(s) which contain
IRED markers (other than illuminators on Position Sensors) . . . . . . . 90 days from shipment
single use, disposable reflective (passive-type) markers . . . . . . . . . . . prior to first use but no more
than 90 days from shipment
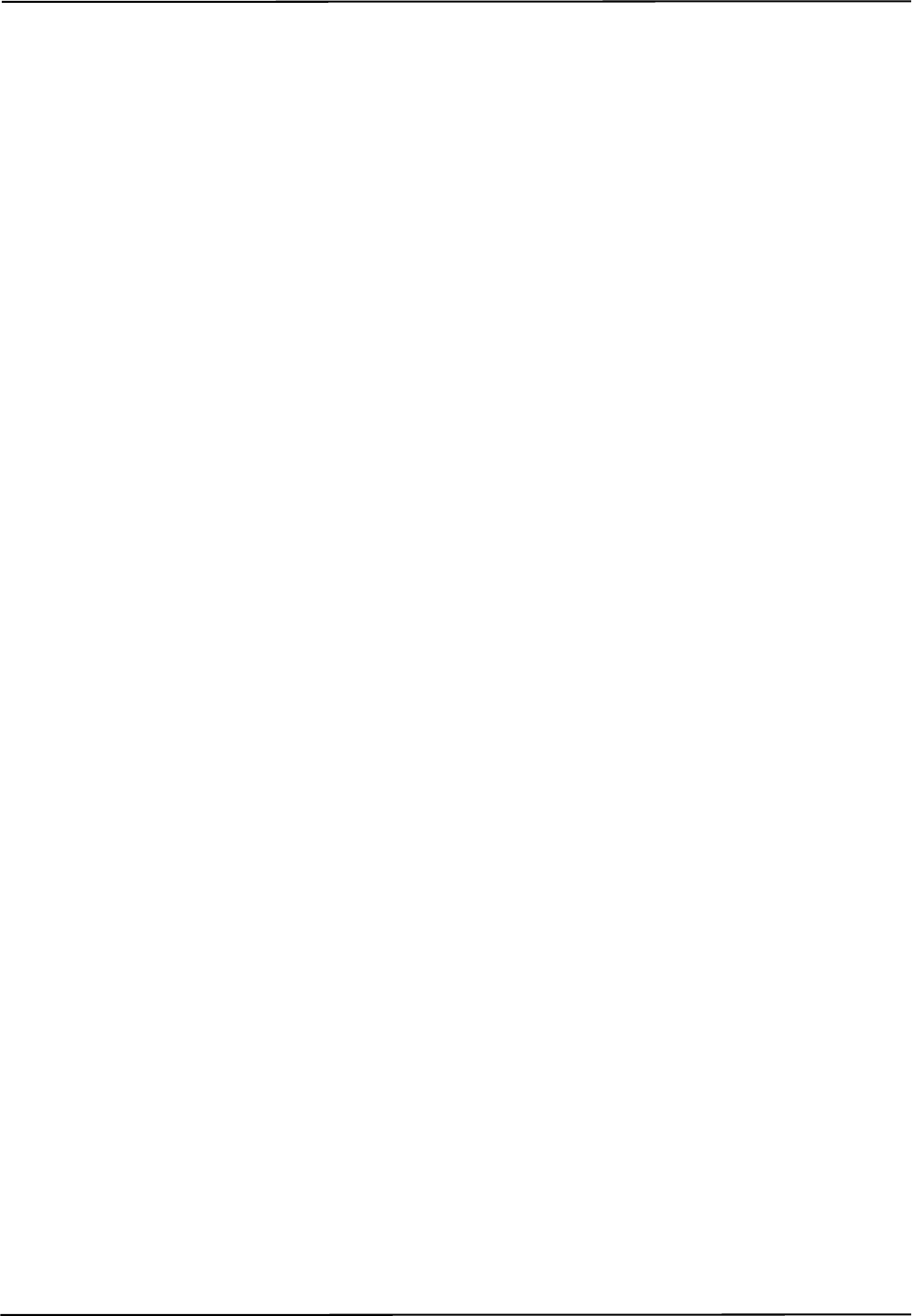
Return Procedure and Warranty
78 Polaris Vicra User Guide - Revision 2
General Provisions Applicable to Warranty
NDI’s obligations under this warranty shall be limited to repairing or replacing (at NDI’s option) the
product(s), EXW (Incoterms 2000) NDI’s plant (Waterloo, Ontario, Canada). Any original parts
removed and/or replaced during any repair process shall become the property of NDI. This warranty
shall apply only to the original Buyer [being that person or legal entity which has contracted directly
with NDI for the supply of the product(s)]. Repair work shall be warranted on the same terms as
stated herein except such warranty shall be for a period of sixty (60) days or for the remainder of the
unexpired warranty period, whichever is longer. In respect of any product(s) supplied hereunder
which are manufactured by others, NDI gives no warranty whatsoever, and the warranty given by
such manufacturers, if any, shall apply.
The obligations of NDI set forth in this warranty are conditional upon proper transportation,
shipping, handling, storage, installation, use, maintenance and compliance with any applicable
recommendations of NDI. Without limiting the generality of the foregoing, this warranty shall not
apply to defects or damage resulting from: fire; misuse; abuse; accident; neglect; improper
installation; improper care and/or maintenance; lack of care and/or maintenance; customer supplied
software interfacing; modification or repair which is not authorized by NDI; power fluctuations;
operation of hardware product(s) outside of environmental specifications; improper site preparation
and maintenance; permitting any substance whatsoever to contaminate or otherwise interfere with
optics; and any other cause beyond the control of NDI. The obligations set forth in this warranty are
further conditional upon the Buyer promptly notifying NDI of any defect and, if required, promptly
making the product(s) available for correction. NDI shall be given reasonable opportunity to
investigate all claims and no product(s) shall be returned to NDI without NDI first providing the
Buyer with a return material authorization number and shipping instructions. All product(s) returned
to NDI shall be packaged in the containers originally used by NDI to ship the product(s) to the
Buyer.
NDI, for itself, its agents, contractors, employees, providers, and for any parent or subsidiary of
NDI, expressly disclaims all warranties, express or implied, including, without limitation, of
merchantability or fitness for a particular purpose.
The foregoing warranty is the entire warranty of NDI. NDI neither assumes nor authorizes any
person, purporting to act on its behalf, to modify or to change this warranty, or any other warranty or
liability concerning the product(s).
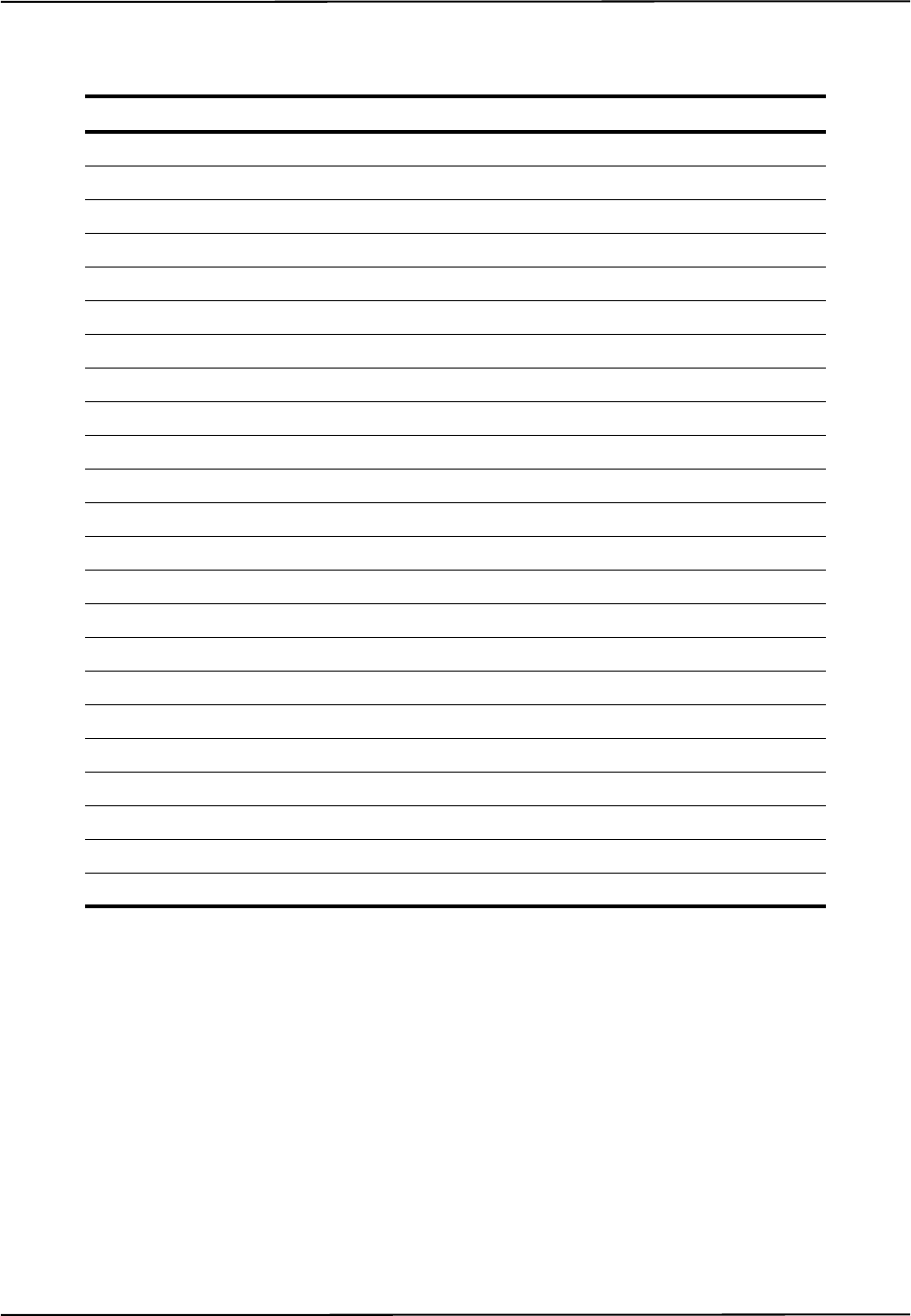
Abbreviations and Acronyms
Polaris Vicra User Guide - Revision 2 79
15 Abbreviations and Acronyms
Acronym or Abbreviation Definition
5DOF 5 Degrees Of Freedom
6DOF 6 Degrees Of Freedom
AAK Accuracy Assessment Kit
API Application Program Interface
CCD Charge Coupled Device
CRC Cyclic Redundancy Check
DSR Data Set Ready
EMC Electromagnetic Compatibility
EMI Electromagnetic Interference
EPROM Erasable Programmable Read Only Memory
FCC Federal Communications Commission
IC Industry Canada
IR Infrared Light
IRED InfraRed Light Emitting Diode
LED Light Emitting Diode
MRI Magnetic Resonance Imaging
NDI Northern Digital Inc.
OR Operating Room
PROM Programmable Read Only Memory
RF Radio Frequency
RMA Return Materials Authorization
RMS Root Mean Square
USB Universal Serial Bus
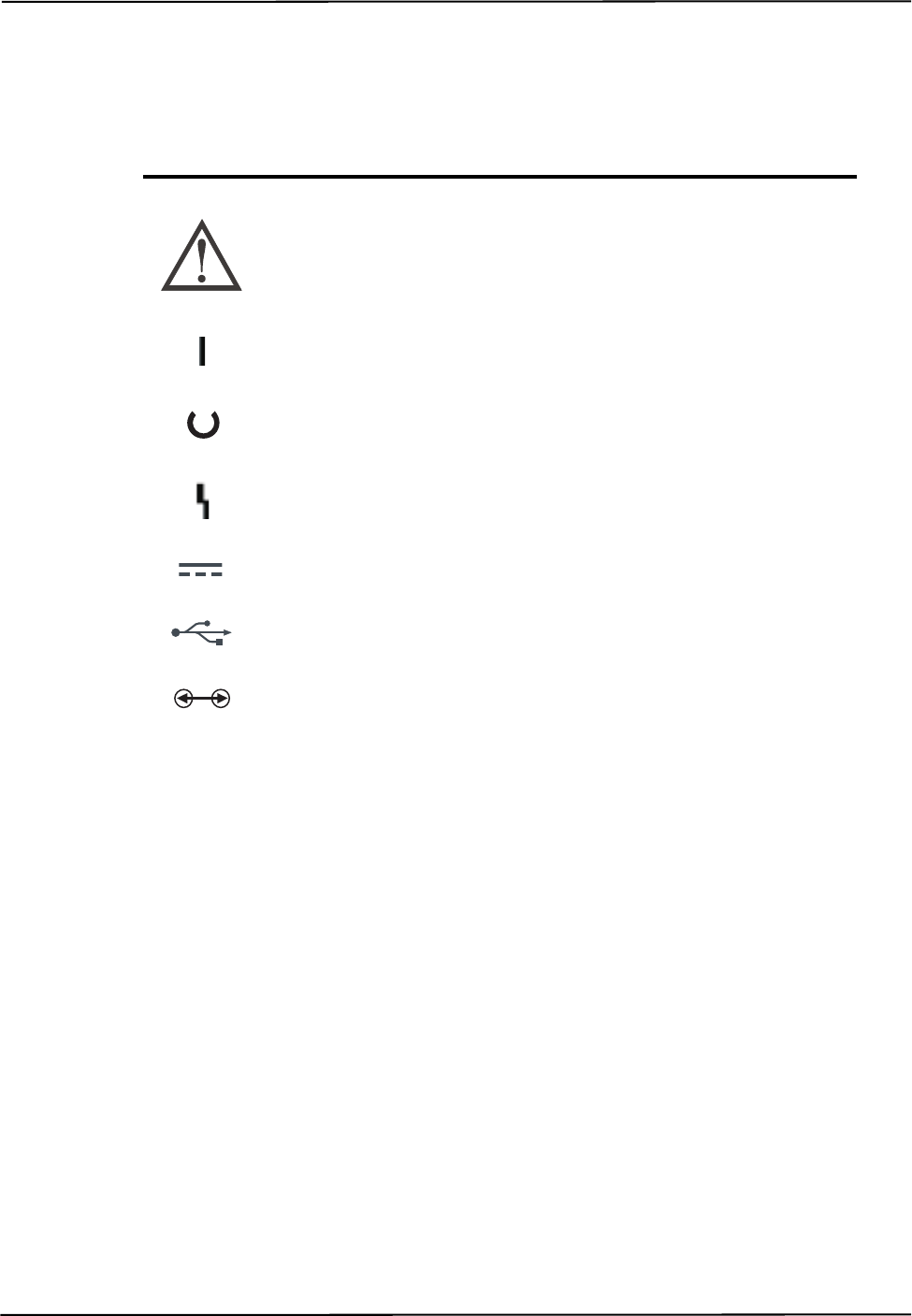
Equipment Symbols
80 Polaris Vicra User Guide - Revision 2
16 Equipment Symbols
Symbol Meaning System Components
Hardware Attention!
Consult accompanying documents.
Position Sensor
Host USB Converter
On (power: connection to the mains supply) Position Sensor
Host USB Converter
Status Position Sensor
Error Position Sensor
Host USB Converter
Direct Current Host USB Converter
USB Port Host USB Converter
Connection Port Position Sensor

Glossary
Polaris Vicra User Guide - Revision 2 81
17 Glossary
3D RMS Error
The RMS error is the square root of the sum of the squares of the measurement errors. This can be
approximated by the square root of the mean square added to the standard deviation squared of the
errors.
Calibration
Calibration is the process of establishing, under specified conditions, the relationship between
values produced by an NDI measurement system and corresponding known values established by a
device that is traceable to a national standard.
Characterized Measurement Volume
The characterized measurement volume is the volume within the detection region where accuracy is
within specified limits. NDI cannot guarantee measurement accuracy outside this region.
Faces
Tool faces are separate rigid bodies that make up a tool.
Field of View
The field of view is the total volume in which the Polaris Vicra System can track a marker,
regardless of accuracy.
Firmware
Firmware is a computer program stored in an NDI hardware device and controls the Polaris Vicra
System.
Flash EPROM
Flash Electrically Erasable Programmable Read Only Memory (EEPROM) stores control
parameters and system information within the Position Sensor. The information programmed to the
Flash EEPROM is retained even after the system is turned off.
Frame
A frame contains the measured positions of the markers in the field of view at a particular point in
time.
Global Coordinate System
The global coordinate system is the Polaris Vicra coordinate system. The global coordinate system
is used by the Polaris Vicra as a frame of reference against which tool transformations are reported.
By default, the global coordinate system's origin is set at the Position Sensor
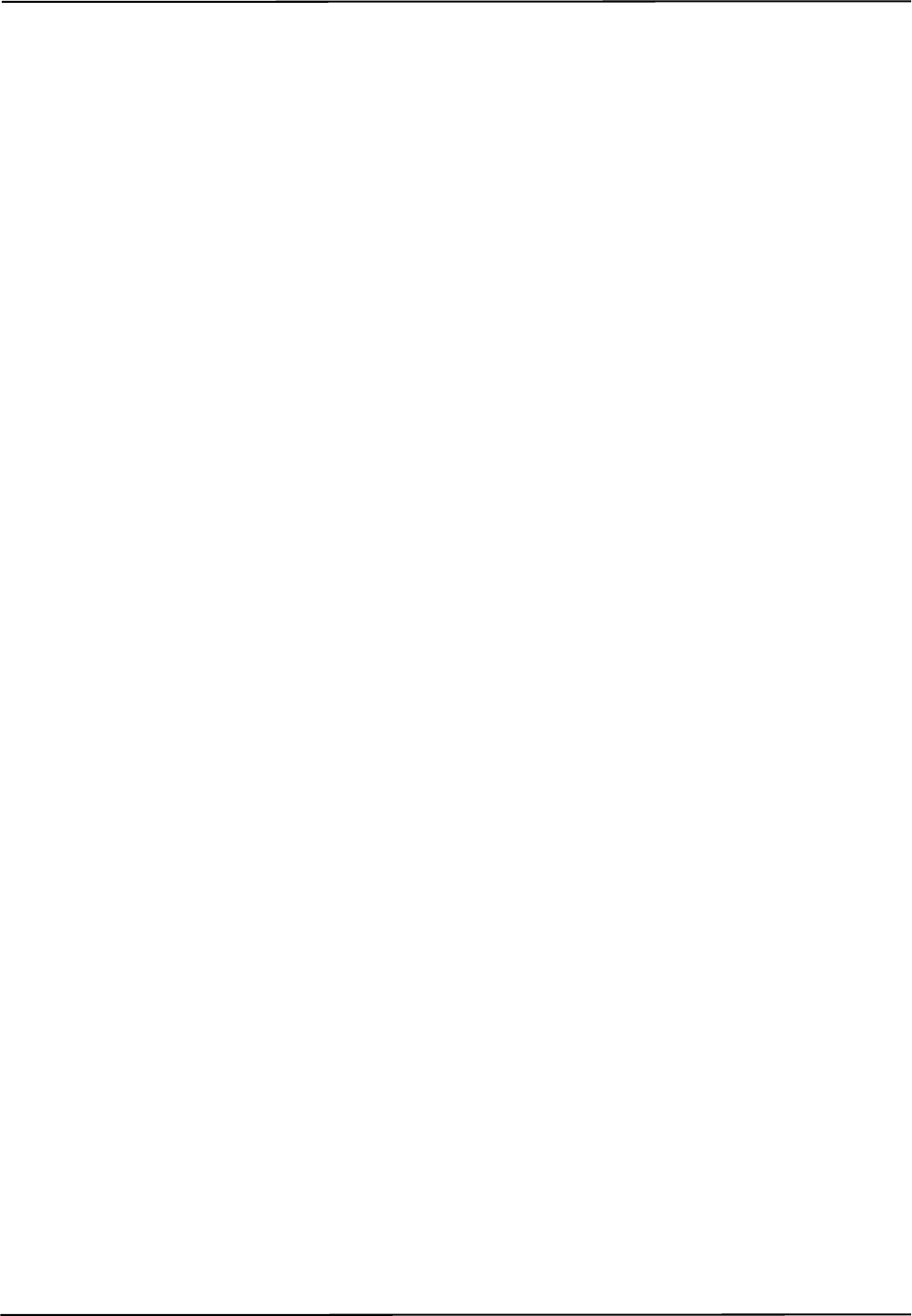
82 Polaris Vicra User Guide - Revision 2
Illuminator Ring
The illuminator ring is a ring of IR light emitting diodes that surround the sensor lenses on the
Position Sensor. These flood the area in front of the Position Sensor with IR light, which is reflected
back to the Position Sensor by the passive markers.
Line Separation
To determine the position of an IR source, the Position Sensor calculates a line between the source
of IR and each sensor. The line separation is the distance between these two lines where they cross.
Local Coordinate System
A local coordinate system is a coordinate system assigned to a specific tool or rigid body.
Maximum 3D Error
Maximum 3D error applies to individual markers. It specifies, in the tool definition file, the
maximum allowable difference between the measured and expected location of a marker on a tool or
rigid body.
Maximum Marker Angle
Maximum marker angle is used to determine if a marker will be used in the calculation of a rigid
body or tool. If the marker is determined to be farther off-angle to the Position Sensor than the
maximum marker angle, this data is not used to determine the rigid body or tool.
Passive Marker
A passive marker is a retro-reflective passive sphere that reflects IR light emitted by the Position
Sensor.
Pivoting
Pivoting is a procedure (of rotating a tool about its tip) used to determine the tool tip offset.
Position Sensor
The Position Sensor is the component of the Polaris Vicra System that provides a source of IR light
for passive markers, collects marker position data from both active and passive markers, calculates
tool transformations, and sends the results to the host computer.
Quaternion
A quaternion is a compact representation of rotations, or correspondingly, orientations in 3D space
(rather than having to use orthogonal matrices).
Reference Tool
A reference tool is a tool or rigid body whose local coordinate system is used as a frame of reference
in which other tools are reported/measured.
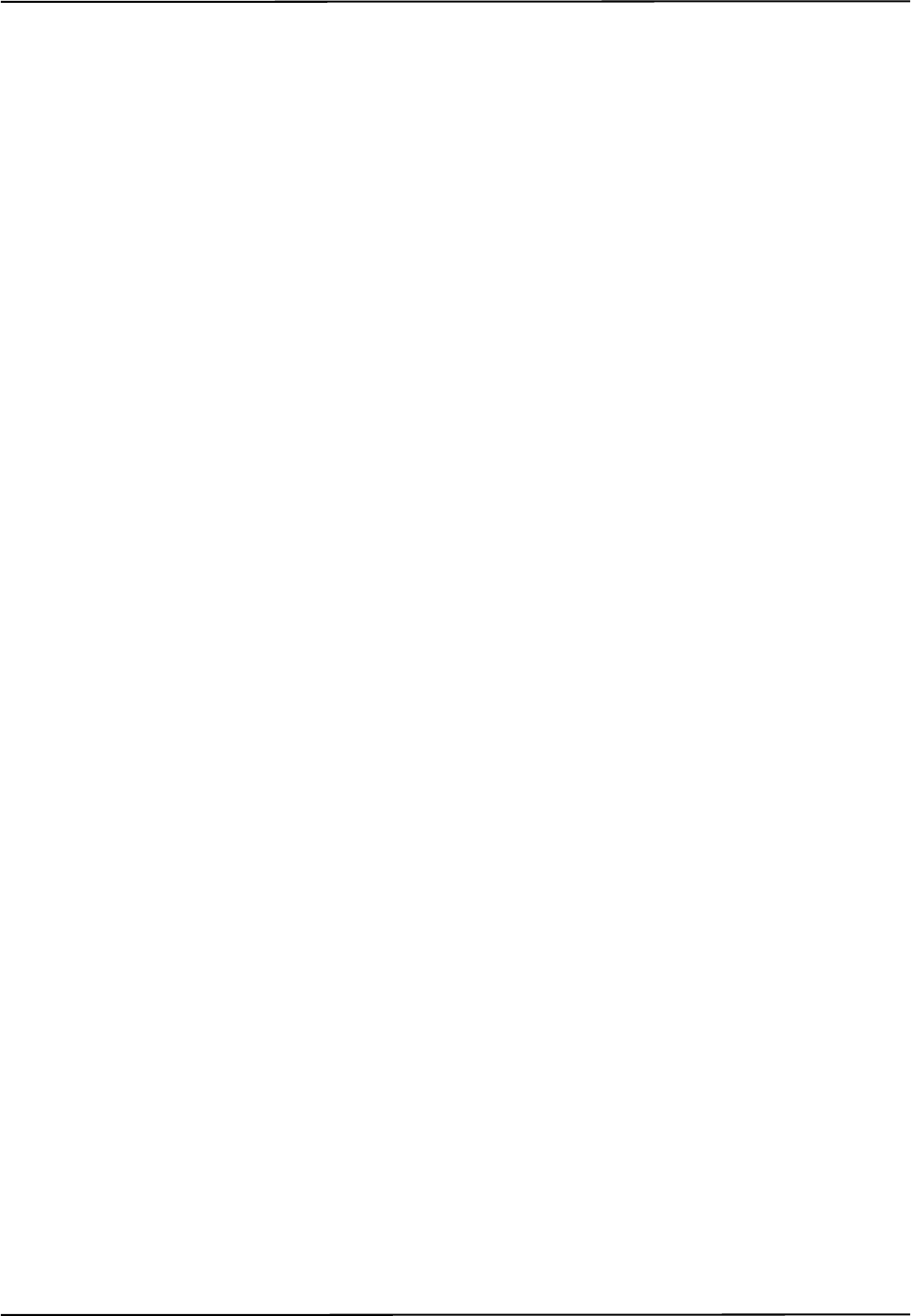
Glossary
Polaris Vicra User Guide - Revision 2 83
Rigid Body
A rigid body is an object on which three or more markers are fixed relative to one another.
Tool Definition File
A tool definition file stores information about a tool or rigid body. This includes information such as
the placement of the tool's markers, the location of its origin, and its manufacturing data. A tool
definition file is formatted as .rom for tools.
Tool Tip Offset
The tool tip offset is the vector between the tip of the tool and the tool origin.
Transformation
A transformation is a combination of translation and rotation values that describe a change of the
tool or rigid body in position and orientation.
Unique Geometry Tool
Unique geometry tools incorporate markers positioned in such a way that, when detected in the
measurement volume, the tool can be uniquely identified from other tools.
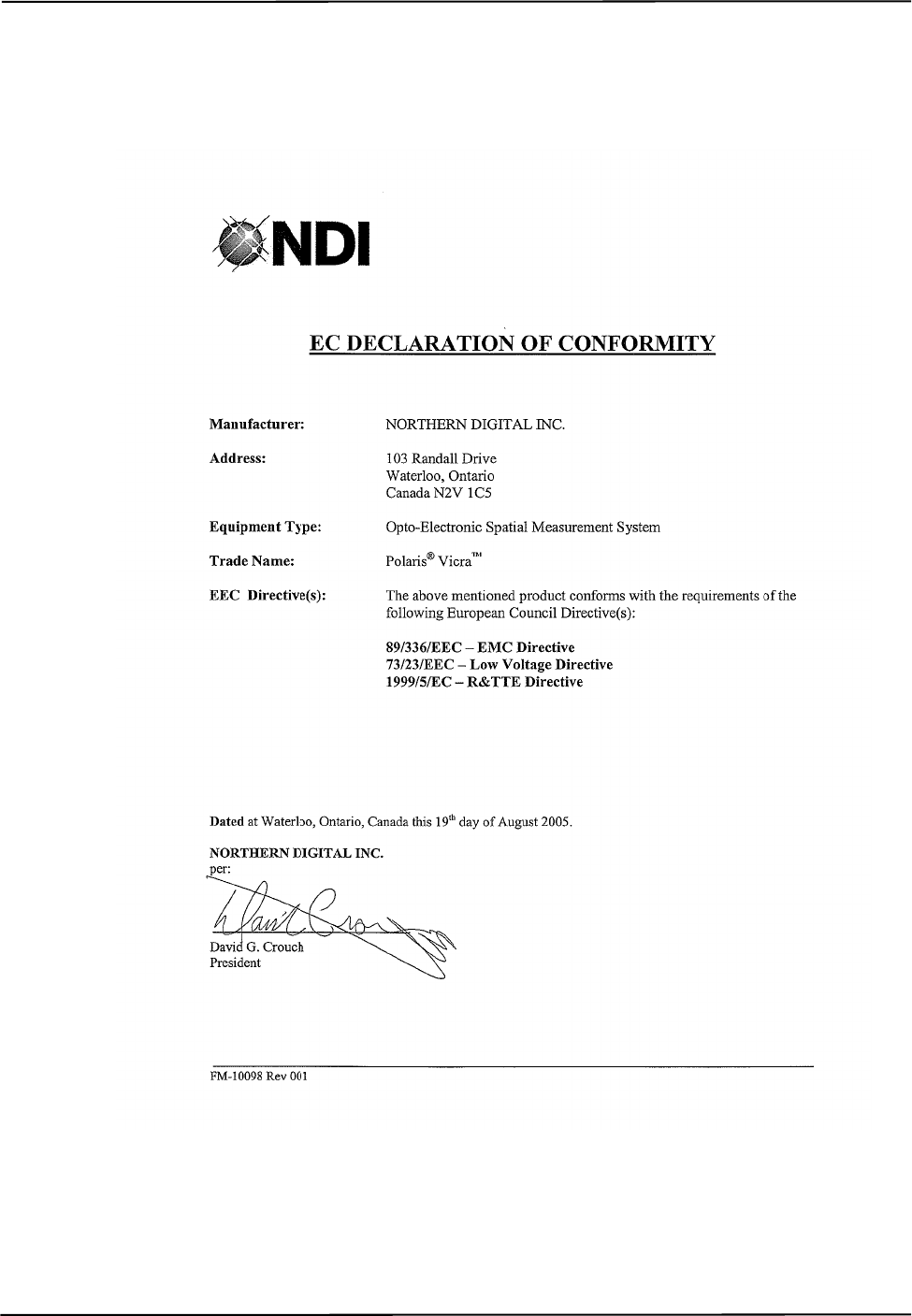
Declaration of Conformity
84 Polaris Vicra User Guide - Revision 2
18 Declaration of Conformity
Figure 18-1 is a copy of the EC Declaration of Conformity for the Polaris Vicra System.
Figure 18-1 EC Declaration of Conformity
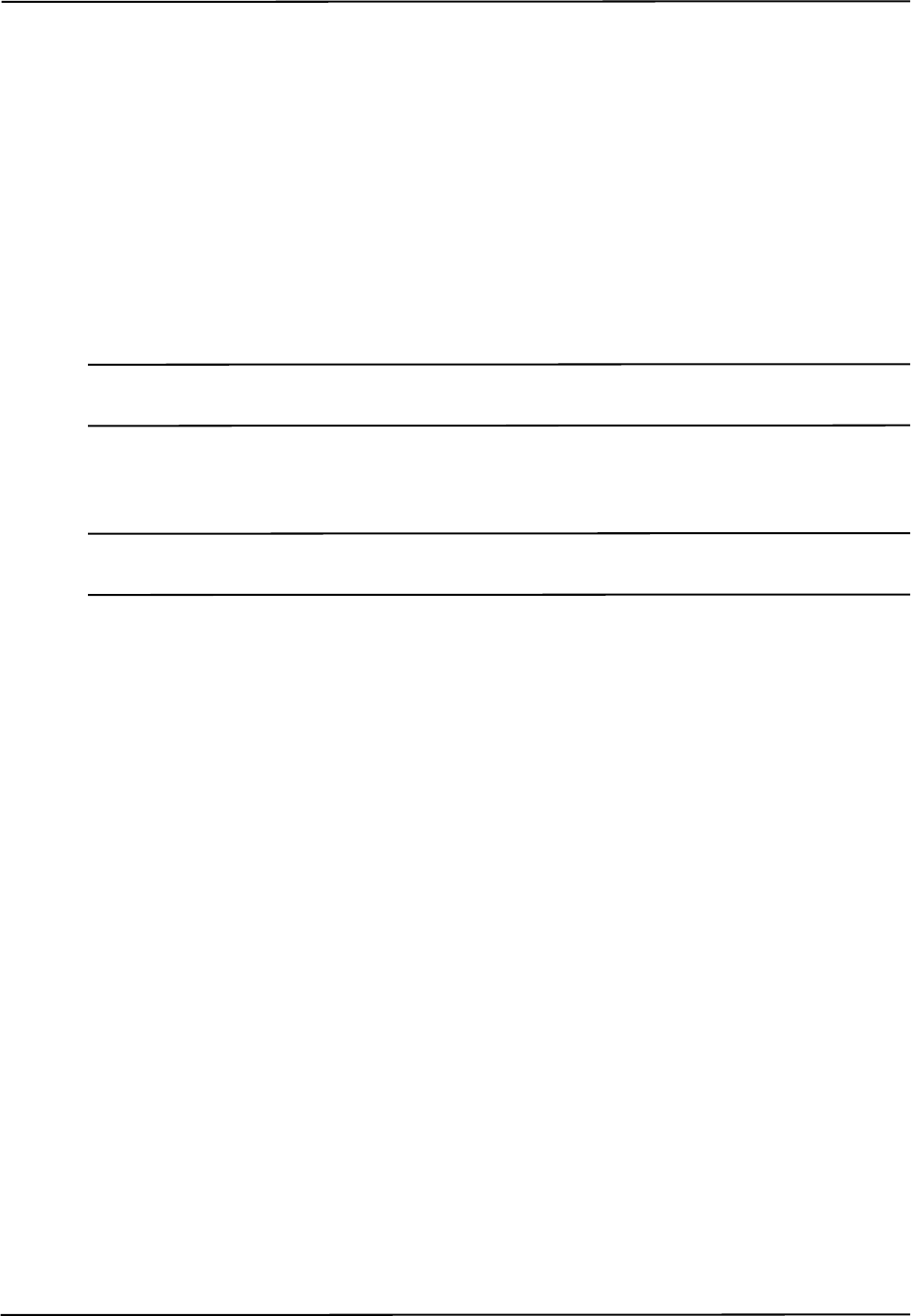
Polaris Vicra Calibration Performance and Methodology
Polaris Vicra User Guide - Revision 2 85
Appendix A Polaris Vicra Calibration Performance and Methodology
Standard industry practice dictates that all measurement and testing instruments should be
periodically calibrated to ensure they are operating within tolerances acceptable to the user and/or
the user’s customers.
The user must establish a calibration procedure and interval that is appropriate for the accuracy
requirements of their application.
The Position Sensor is a highly specialized instrument developed exclusively by NDI. For all
calibration procedures, return the Position Sensor to NDI. This practice ensures that all calibrations
are conducted in accordance with procedures established specifically for the Polaris Vicra Position
Sensor.
Note The NDI Accuracy Assessment Kit (AAK) can be used in the field as an aid to determine whether a Position
Sensor is performing acceptably for the user’s application.
If, at any time, a concern should arise that the Position Sensor is not measuring accurately, it should
be returned to NDI.
Note The calibration procedure at NDI applies to single markers and cannot be directly applied to an application that
uses tools with several markers.
A.1 Polaris Vicra Performance
The Polaris Vicra System performance is determined by a statistical analysis of the 3D Euclidean
distance error between the reported position of an NDI marker and its true position, based on
measurements taken throughout the entire Polaris Vicra System’s measurement volume. Acceptance
criteria for the Polaris Vicra System’s performance are based on the RMS values of the accuracy and
repeatability.
The 3D RMS volumetric accuracy acceptance criterion is less than or equal to 0.25 mm, based on
a single marker stepped through a statistically representative set of positions throughout the
measurement volume, using the mean of 30 samples at each position at 20°C.
The 3D RMS repeatability acceptance criterion is less than or equal to 0.20 mm, based on total
samples of a single marker stepped through a statistically representative set of positions throughout
the measurement volume, using 30 samples per position at 20°C.
A.2 Calibration Method
The following method is used to calculate the Polaris Vicra System’s accuracy and repeatability:
An NDI marker is accurately moved to each of n locations (Xi, Yi, Zi) spread throughout the
measurement volume. The mechanism that moves the marker is assumed to have an accuracy that is
at least 10 times better than the measured accuracy of the Polaris Vicra System. This assumption
allows the errors in the marker positioning to be ignored.
At each of the n locations, the Polaris Vicra System takes m readings of the marker’s 3D position
(xij, yij, zij).

Polaris Vicra Calibration Performance and Methodology
86 Polaris Vicra User Guide - Revision 2
The accuracy of the Polaris Vicra System is calculated as the RMS variation of the mean of m
readings about the true 3D location calculated across all n locations throughout the measurement
volume.
The repeatability of the Polaris Vicra System is calculated as the RMS variation of the m readings
about the average of the 3D readings at each location n. This RMS variation is calculated across all
n locations throughout the measurement volume.
3D average measurements:
3D RMS
repeatability =
xiaverage
xij
,
j1=
m
∑
m
----------------------------- ,= yiaverage
yij
,
j1=
m
∑
m
----------------------------- ,= ziaverage
zij
,
j1=
m
∑
m
----------------------------- =
3D RMS accuracy
xiaverage Xi
–()
2yiaverage Yi
–()
2ziaverage Zi
–()
2
++
i1=
n
∑
n
------------------------------------------------------------------------------------------------------------------------------------------------=
xij
,
xiaverage
–()
2yij
,
yiaverage
–()
2zij
,
ziaverage
–()
2
++
j1=
m
∑
i1=
n
∑
nm⋅
-----------------------------------------------------------------------------------------------------------------------------------------------------------------------------
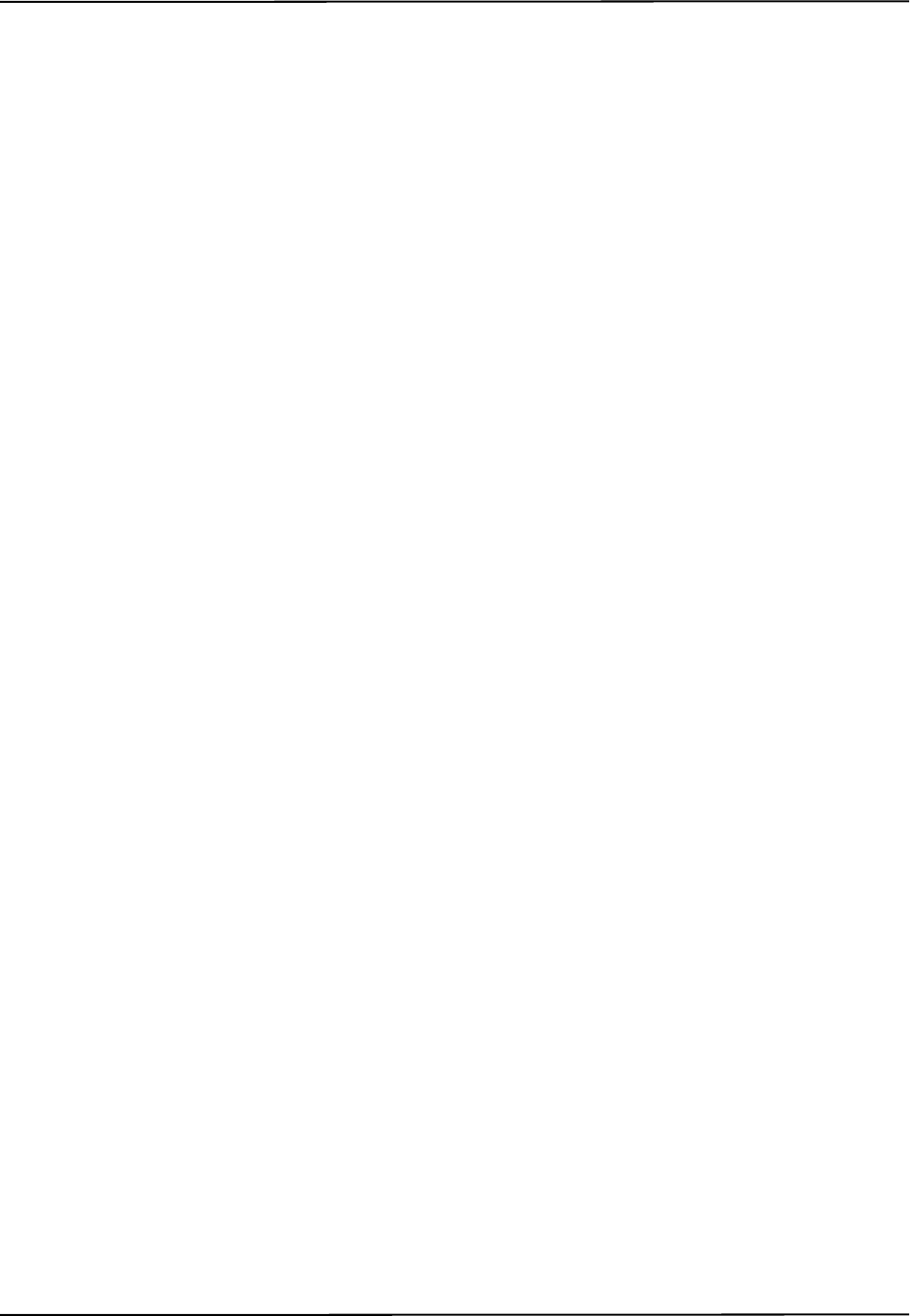
Polaris Vicra User Guide - Revision 2 87
Index
Index
Symbols
.rom file, 31
Numerics
3 marker lock on, 29
3D RMS error, 81
5DOF, 30
6D Architect
installation, 21
6DOF, 30
A
AAK, 85
accessories, 64
accuracy, 27
accuracy assessment kit, 10, 57, 58, 85
acquiring tools, 28
active wireless tools, 13
approvals, 59
audio codes, 9, 48, 51
B
background IR light, 16, 54, 55
battery, 10
baud rate, 20
boot loader, 58
bump sensor, 10
bump sensor battery, 10
C
cables, 12
connecting, 19
cables and accessories, 64
cables and connectors, 53
calibration, 57, 81, 85
calibration method, 85
calibrator, 35
CAPI Sample, 14
installing, 20
cautions, 2, 16
CCD, 28
characterization, 31
characterized measurement volume, 26, 81
classifications, 60
codes, 48
component parts list, 14
connecting hardware, 19
coordinate system
global, 26, 81
local, 30, 82
D
data transmission rate, 40
declaration of conformity, 84
decontamination policy, 77
detecting markers, 28
disabled transformations, 48
disclaimers, 3
drivers
USB, 21
E
electrical safety, 59
electromagnetic compatibility, 64
electromagnetic emissions, 65
electromagnetic immunity, 65
electrostatic discharge, 64
EMC, 79
EMI, 79
environment, 15
EPROM, 81
error, 25
maximum 3D, 82
error codes, 48
error flags, 42, 48
error indicator
Host USB Converter, 11, 51
Position Sensor, 8
errors
out of volume, 49
F
face, 81
face normal, 31
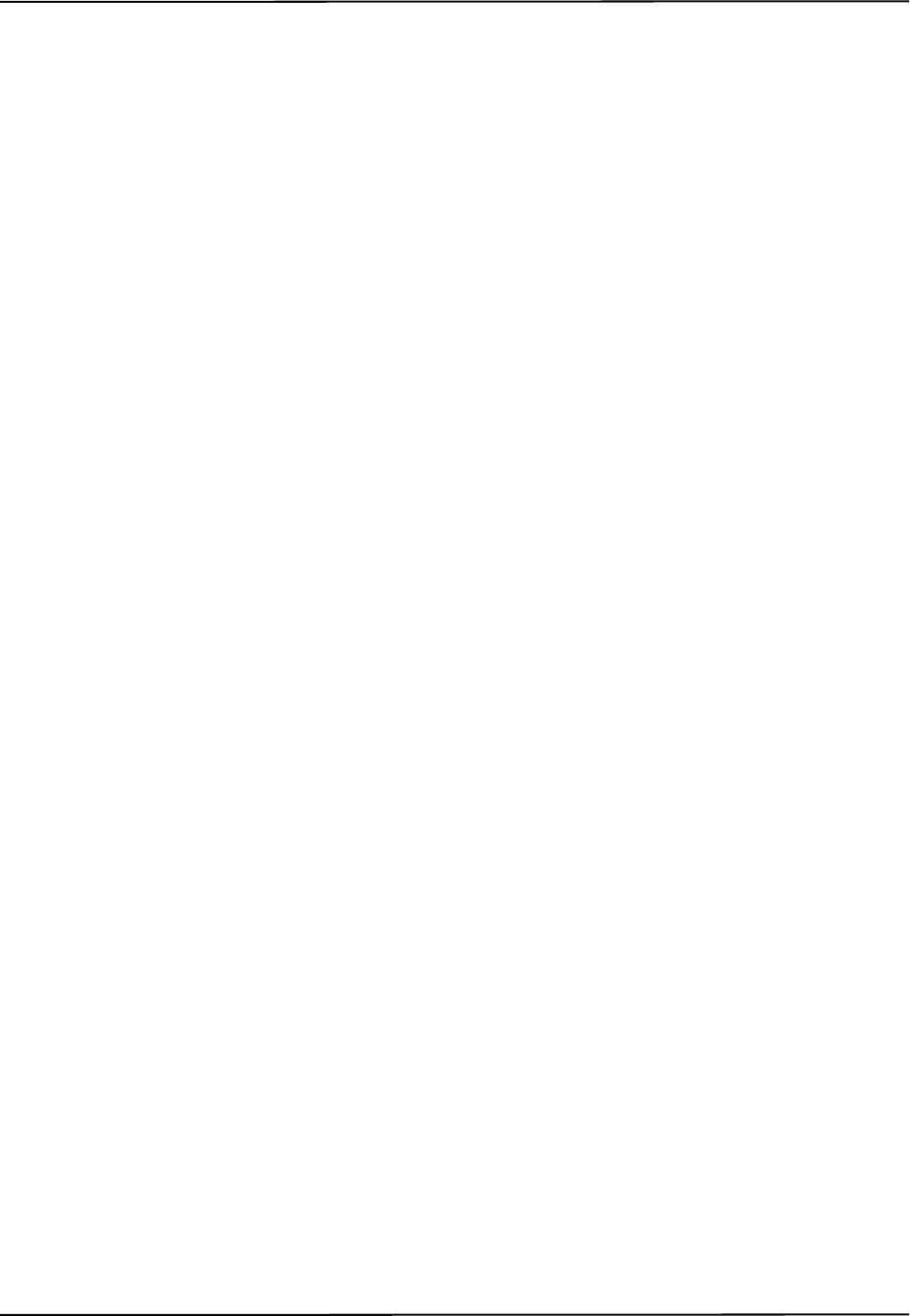
88 Polaris Vicra User Guide - Revision 2
Index
field of view, 26, 81
firmware, 81
Firmware Update Utility
installation, 21
flags, 25, 48
out of volume, 49
flash EPROM, 81
frame, 81
frame number, 25
G
geometry, 30
global coordinate system, 26, 81
H
hardware warranty, 77
host computer
specifications, 6
Host USB Converter, 11
connecting, 19
error indicator, 11
mounting, 11
operating environmental conditions, 62
part number, 14
power indicator, 11
I
illuminator filter, 8
illuminator ring, 82
illuminators, 7, 28
indicator LED, 8, 11, 51
communications, 51
error, 8, 51
power, 8, 51
status, 8
information and error flags, 42
infrared light sensitivity, 54, 55
API command SENSEL, 56
ingress protection, 10
installing
software, 20
USB drivers, 21
integration time, 28, 54
IR light, 16
IRED, 79
K
keyed features, 24
L
LED, 11
lights, 11
line of sight, 16
line separation, 29, 38, 57
Linux support, 22
local coordinate system, 30, 82
M
maintenance, 52
marker
detection, 28
passive, 82
phantom, 38
marker geometry, 30
marker Information, 50
marker normal, 32
markers, 32
stray, 37
maximum 3D error, 31, 82
maximum marker angle, 32, 82
measurement volume, 6, 26
minimum number of markers, 29, 32
minimum spread, 33
missing transformations, 48
mounting
Host USB Converter, 11
Position Sensor, 9
mounting post, 32
MRI, 17
N
NDI, 79
NDI 6D Architect
installation, 21
NDI CAPI Sample, 14
installing, 20
NDI Firmware Update Utility
installation, 21
NDI Sensitivity Utility
installation, 21
NDI ToolBox, 8, 14
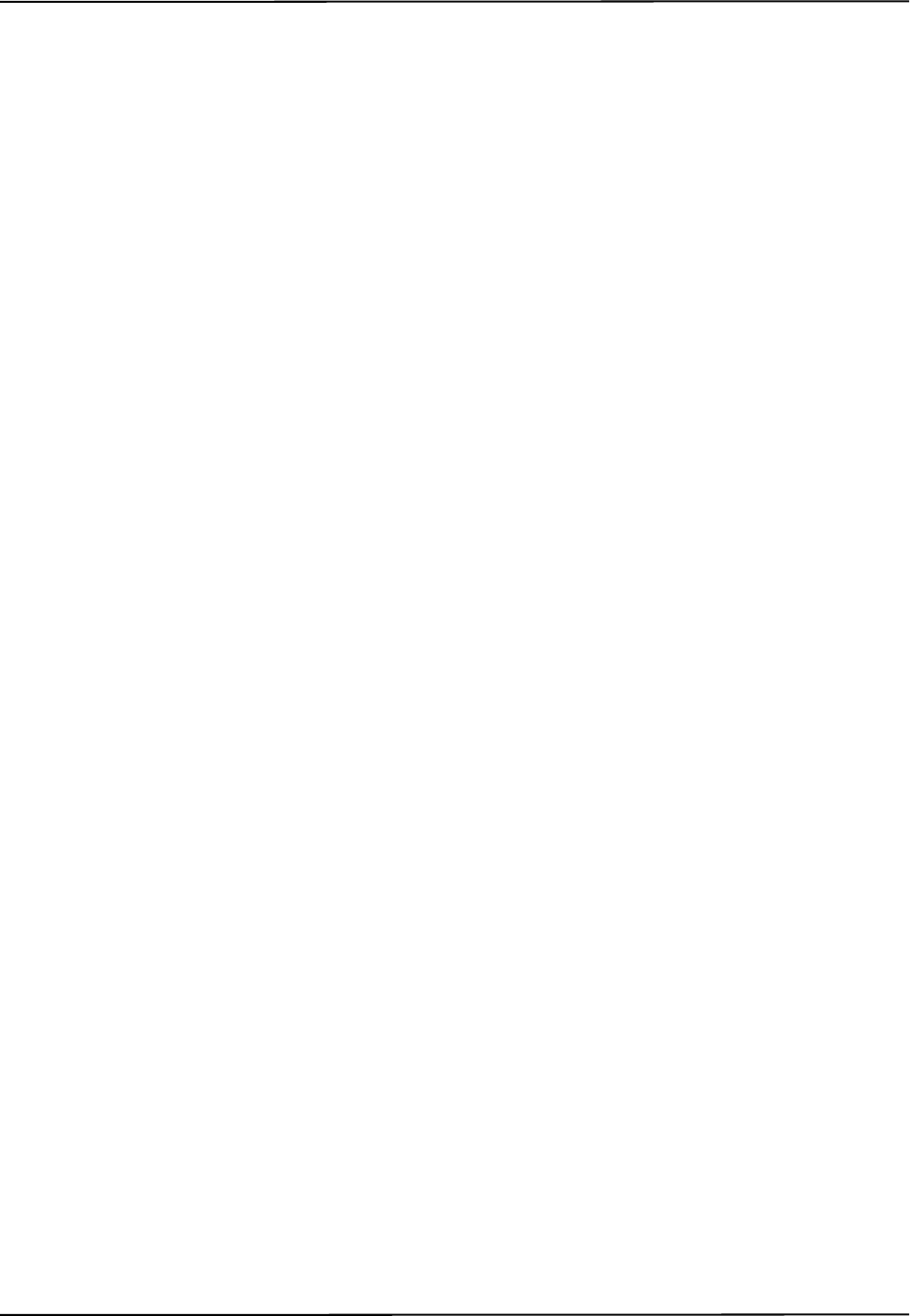
Polaris Vicra User Guide - Revision 2 89
Index
error messages, 72
installing, 21
normals
face, 31
marker, 32
O
offset, 35
operating environment, 16
operating environmental conditions
Host USB Converter, 62
Position Sensor, 61
power adapter, 63
optical radiation safety, 59
orientation of tool, 25
origin of a tool, 35
out of volume, 27, 49
overview, system, 6
P
parameter
minimum number of markers, 32
minimum spread, 33
parameters, 31, 34
maximum 3D error, 31
maximum marker angle, 32
part number
Host USB Converter, 14
position sensor, 14
Power Adapter, 14
USB cable, 14
partially out of volume, 27
parts list, 14
passive marker, 82
Passive Sphere Markers, 38
passive sphere markers, 32
sterilization, 39
passive tools, 13
phantom markers, 38
pivot, 45
pivoting, 36, 82
port status flags, 49
position of tool, 25
Position Sensor, 7, 28, 82
cleaning, 52
connector, 9
front view, 8
mounting, 9
operating environmental conditions, 61
rear view, 9
technical specifications, 61
temperature, 75
Position Sensor cable, 12
post, 32
power adapter, 12
operating environmental conditions, 63
technical specifications, 63
transportation and storage environmental con-
ditions, 63
power adapter cable, 12
power indicator
Host USB Converter, 11, 51
Position Sensor, 51
power LED, 8
Q
quaternion, 25
R
reference tool, 36, 44, 82
resolution, screen, 7
return procedure, 77
RF, 79
rigid body, 83
RMA number, 77
RMS error, 25
S
safety
electrical, 59
optical radiation, 59
screen resolution, 7
SENSEL command, 56
sensitivity to IR light, 54, 55
API command SENSEL, 56
changing the IR sensitivity level, 55
Sensitivity Utility
installation, 21
sensor, 8
separation distances, 68
set as reference, 44
setting a tool as reference, 44
software, 14
installing, 20
NDI CAPI Sample, 14
NDI ToolBox, 14
ToolBox, 56
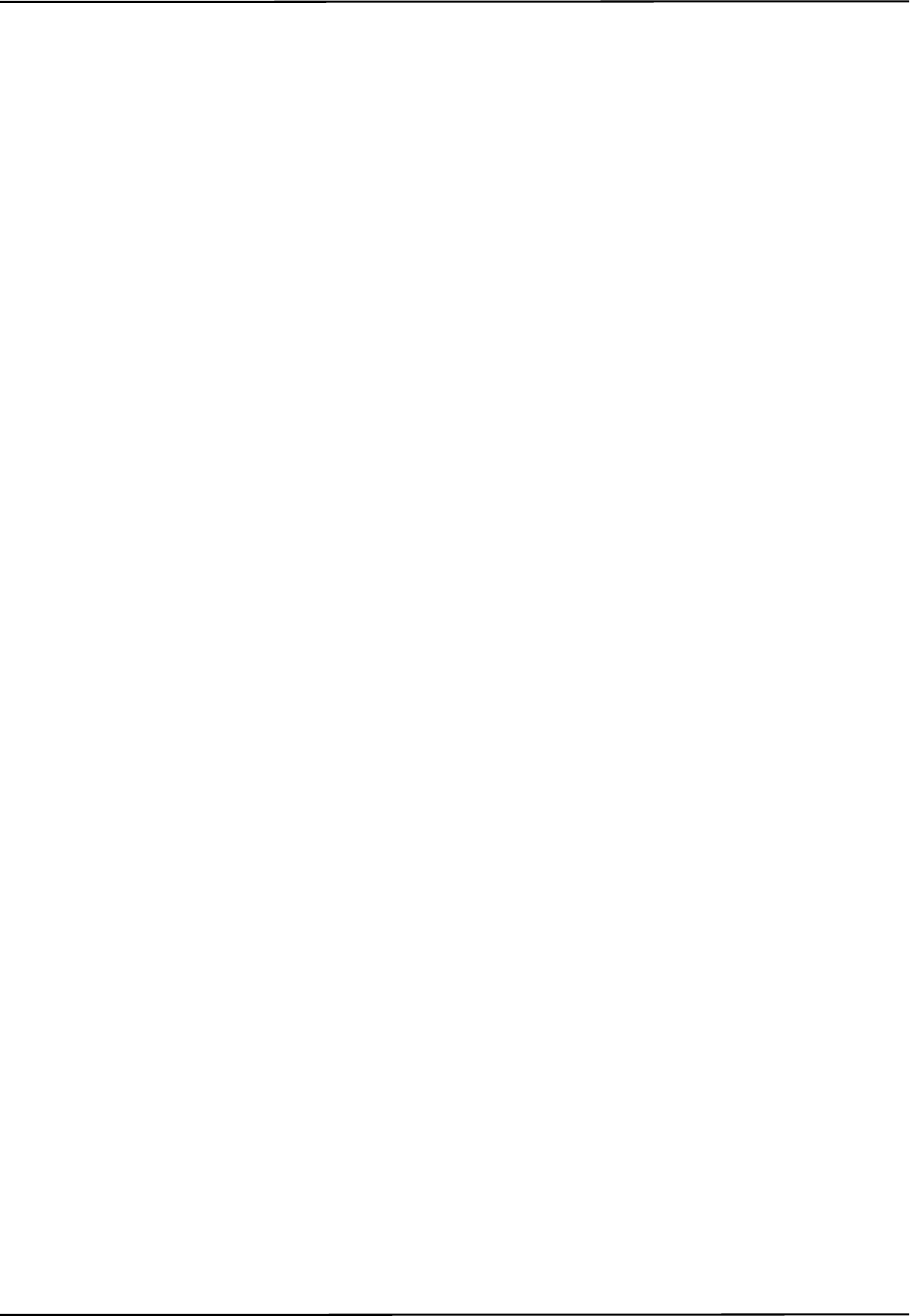
90 Polaris Vicra User Guide - Revision 2
Index
warranty, 77
specifications
host computer, 6
status
marker, 25
system, 25
tool, 25
status LED, 8
stray markers, 26, 37
strober voltage, 54
support site, 4
system indications, 70
system overview, 6
system software, 14
system status, 25
T
temperature, 17
tip offset, 35
tool definition file, 13, 31, 83
tool information flags, 50
tool tip offset, 35, 45, 83
tool tracking parameters, 31, 34
tool tracking utility, 41
ToolBox, 14, 56, 75
installing, 21
tools, 13
5DOF, 30
6DOF, 30
acquiring, 28
geometry, 30
multi-face, 30
tracking, 28
using as reference, 36, 82
tracking error, 25
tracking flags, 25
tracking tools, 28, 41
transformation, 83
transformations
out of volume, 26
transportation and storage environmental conditions
Host USB Converter, 62
Position Sensor, 62
power adapter, 63
trigger level, 28, 54
U
unique geometry, 30, 83
unpacking the system, 15
update information, 4
USB, 79
USB cable, 12
USB drivers, 21
V
virtual serial port, 76
W
warnings, 1
warranty, 77
general provisions, 78
hardware, 77
software, 77