PEERLESS Boiler Manual L0308220
User Manual: PEERLESS PEERLESS Boiler Manual PEERLESS Boiler Owner's Manual, PEERLESS Boiler installation guides
Open the PDF directly: View PDF .
Page Count: 32

Pinnacle T"
Gas Boilers
If the information in this manual is not
followed exactly, a fire or explosion may
result causing property damage, personal
injury or loss of life.
-Do not store or use gasoline or other
flammable vapors and liquids in the vicinity
of this or any other appliance.
- WHATTO DO IFYOU SMELL GAS
•Do not try to light any appliance.
• Do not touch any electrical switch;
do not use any phone in your building.
• Immediately call your gas supplier from
a neighbor's phone. Follow the gas
supplier's instructions.
• If you cannot reach your gas supplier,
call the fire department.
- Installation and service must be performed
by a qualified installer, service agency or
the gas supplier.
Installation,
Operation
Maintenance
Manual
p=E_Lr=-ss"
PINNACLE"
mOH EFFICIENCY STAINLSSS _TE_L BOMLER

3 Sizes 27 to 199 MBH Input 92% AFUE
Three Sizes Available
•PI80 27to80MBHInputModulation
•PI 140 -46 to 140 MBH Input Modulation
•PI 199 -66 to 199 MBH Input Modulation
Fully Modulating Burner for Maximum Efficiency
• 92% AFUE Energy Star JEfficient
Natural or LP Gas
Direct Vent
• Sealed Combustion
• No Chimney Required -Horizontal or Vertical Venting
• Uses Standard Schedule 40 PVC Plastic Pipe for Venting
•ConceTitric PVC or V1000 Aluminum Vent Kits Available
Compact, Light-Weight Design
• Installation Flexibility
•Z_'ro Cl_!aran_? to Combustibles
• Lightweight Des_n (75 to 111 lbs.) & Small Footprint
Stainless Steel Construction
•High Grad<" Stainless StPeI Burner and Heat Exchanger
Safe Operation
• Honeywell Gas Valve and Venturi System
• State oJ:the-Arf Control Board with LED Light Indicator
•Spark Ignition
Quiet Operation
• As Quiet as Most Home Appliances
Comprehensive Warranty
• One-Year Parts & Labor Warranty
•Lin_ited. 12-Year Warranty on the Heat Exchanger
• See Below_lbr Warranty Description
Environmentally Friendly
•Low Emissions
As an ENERGY STAR" Partr_er Peerless Healer Company has delermined
that thi8 producl meel_ Ihe ENERGY STAR gwdelin es for energy efficiency
•Honeywell Gas Valve
• Burner Fan
•High Limit Temperature Control
• 30 PSI Sol-ely RelieJ Valve
• Combination Temperature-Pressure Gauge
• 3" PVC Screened Air Intake Terminal and
Exhatlsl Terminal
• 3" V1000 Aluminunl Outside Venl Termination Kit
•3" Concemcic PVC Venl Terminalion Kil
• Ad.]uslable Steel Boilt, r Slartd
Pt_erless l h,cltt'i Company is pleased to o[]-er one ql ttle most comprehensive w_rrrulty piogranls in t!2e industry. T/t(, P{,t,d(,ss
Pitlllacl_h slttilllt!ss steel boiler calT_es a fitU oHe yeQr warrcItllt.] o11 tilt" t,ltlir(" boils'r: Pt!url_'ss lvJU pttrchase all _lddiitollQ! II'(IKI'(UII{t
,,sl
tllat ('over.s Iclbor.lbr r_'l)lat'irlg tcatTanled parts.lioln the! 31"" day thro_lgh th_'.llrst y('_u qlh'r iHsiclllalion, prolqctt'd lh(' it,¢ut(mt!l
r%qi.strilliotl ccuH is l't'llutled. 111additiotL Pt'(,d¢'ss Q[lt!ra o lilniled, pm rated. 12 yt'(u w(ullmlg oil tilt? ]l('_lt cxch(mgt'r ol llu'
PifuItl{'l(' I)Oil('E [PIPt' [llld It,ll-year ('xtetld('(t Ii_€.lrr(ltlti{'F. oil ])Qrt.¢_ a/id l[ll)ol ill(l!] [lINo t){' !'}lH'('_KI.v;t'[I. Wllis SllllllIl(lQ] i.s ilol (I
spt?c{]ic u,ancmtg. Pk!tzse corlslllt Pt'edess [It*¢ller (onlpany Jbr conq_lea, It,al'l'glllig il{!()rnttlliolL
Peerless Heater Company *231 North Walnut Street •Boyertown, PA 19512 1021 *610-307-2153 • www.peerless-heater.com
FA9 PI RI _I 0i 75M)
Ps,'_r/,d mLI _

1.
USING THIS MANUAL 1
A. INSTALLATION SEQUENCE ............. 1
B. SPECIAL ATTENTION BOXES ........... 1
PREINSTALLATION
A. ACCESSIBILITY CLEARANCES .......... 2
B. CLEARANCE FROM COMBUSTIBLE
CONSTRUCTION ..................... 2
C. LIQUEFIED PETROLEUM (LP) GAS ....... 2
D. INSTALLATION SURVEY ............... 2
E. PLANNING THE LAYOUT ............... 2
A. BOILER SUPPLY, RETURN AND
CONTROLS ......................... 4
B. CIRCULATOR SIZING .................. 5
C. SAFETY RELIEF VALVE ................ 5
D. PIPING FOR ZONED SYSTEMS .......... 6
E. EXPANSION TANK .................... 7
E INDIRECT-FIRED WATER HEATER ........ 7
G. FREEZE PROTECTION ................. 7
4, GAS PIPING " ........
A. GENERAL .......................... 10
B. EXHAUST VENT/AIR INLET VENT
LOCATION ......................... 10
C. EXHAUST VENT INSTALLATION ........ 10
D. AIR INLET VENT INSTALLATION ........ 11
E. EXTENDED VENT LENGTHS WITH
4" PIPE ............................ 14
E CONDENSATE ...................... 14
G. BOILER REMOVAL FROM COMMON
VENTING SYSTEM ................... 14
6. ELECTRICAL
A. WIRING ........................... 15
B. ZONED SYSTEM WIRING ............. 15
C. SEQUENCE OF OPERATION ........... 17
A. COMPLETING THE INSTALLATION ...... 18
B. LIGHTING/OPERATING INSTRUCTIONS . .19
C. CONTROL DESCRIPTIONS ............. 20
D. CHECK-OUT PROCEDURE ............. 20
A. SHUT-DOWN ...................... 21
B. BOILER FAULT CODES ................ 22
C. BOILER FAULT CONDITIONS ........... 22
A. GENERAL (WITH BOILER IN USE) ....... 24
B. WEEKLY (WITH BOILER IN USE) ........ 24
C. ANNUALLY (BEFORE START OF
HEATING SEASON) .................. 24

Follow the installation instructions provided in this
manual in the order shown. The order of these
instructions has been set in order to provide the installer
with a logical sequence of steps that will minimize
potential interferences and maximize safet F during
boiler installation.
Indicates a condition or hazard which will cause
severe personal injury, death or major property
damage.
Throughout this manual you will see special attention
boxes intended to supplement the instructions and make
special notice of potential hazards. These categories
mean, in the judgment of Peerless Heater Company:
Indicates a condition or hazard which may cause
severe personal injury, death or major property
damage.
Indicates a condition or hazard which will or can
cause minor personal injury or property damage.
Indicates special attention is needed, but not directly
related to potential personal injury or property
damage.

Read carefully, study these instructions before beginnin 9 work
This boiler must be installed by a qualified contractor.
The boiler warranty can be voided if the boiler is not installed, maintained and serviced correctly.
Boiler can be installed at high altitude with no burner adjustments. LP equipped boilers must not be installed at
elevations above 7,000 feet.
The equipment must be installed in accordance with those installation requirements of the authority having
jurisdiction or, in the absence of such requirements, to the current edition of the National Fuel Gas Code, ANSI
Z223.1/NFPA 54 and/or CAN/CGA B149 Installation Codes.
Where required by the authority having jurisdiction, the installation must conform to American Society of Mechanical
Engineers Safety Code for Controls and Safety Devices for Automatically Fired Boilers, ANSI/ASME CSD-1.
I_,! If_,T0(H:(.,'_"]I:] I! / li'd [H I d_'l; f'_1L_[_ :_
The following are the recommended minimum
accessibility clearances between boiler and adjacent wall
or other appliances.
1. 16" from right side or left side of boiler.
2. 15" from top of boiler.
3. 4" from front of boiler.
4. Provide clearance for annual inspection of vent pipe
and condensate connections.
[Igl ! [oll J=1;I 1:1DI "J:ili ;(o] I :l I hV_ll._lliC-r__
The following LP requirements from the Uniform
Mechanical Code, section 304.6, may be in effect in
your geographic area:
"Liquefied petroleum gas burning appliances shall
not be installed in a pit, basement or similar location
where heavier-than-air gas might collect. Appliances
so fueled shall not be installed in an above-grade
under-floor space or basement unless such location
is provided with an approved means for removal of
unburned gas."
Jill Ih_l.'lllf:lll/:_l/[O]L_l F.'lll;iVJ:li'
The design of this boiler is certified for closet installation
with the following clearances:
I. 0" from left side, right side, rear, top, bottom, front
and combustible construction.
2. O" from vent pipe and combustible construction.
3. This boiler is design certified for use on combustible
floors.
:11 I'J IL_ _IL_Ib_[€'l i /-"I= I I/;V.'o]ll
Do not install this boiler on carpeting. Boiler
installation on carpeting is a fire hazard.
Liquefied Petroleum (LP) is heavier than air and may
collect or "pool" in a low area in the event of a leak
from defective equipment. This gas may then ignite,
resulting in a fire or explosion.
For new and existing installations, a Water Installation
Survey is available from Peerless Heater Company. The
survey will provide information on how a hot water
boiler works with your specific system and will provide
an overview of hot water system operation in general.
You can also use this survey to locate system problems
which will have to be corrected. To obtain copies of the
Water Installation Survey, contact your Peerless
representative.
Prepare sketches and notes of the layout to minimize the
possibility of interferences with new or existing
equipment, piping, venting and wiring. Review
limitations on vent pipe, vent terminal, and air inlet pipe
locations in Section 5, Venting.
Boiler is certified as an indoor appliance. Do not
install boiler outdoors or locate where it will be
exposed to freezing temperatures.
2

1. Place boiler on a level surface (Note: An optional
boiler stand is available. Contact your Peerless
Dish-ibutor. )
2. Locate boiler to allow for ease of vent pipe
installation and heating system piping.
Boiler must be set on a levei surface so condensate
does not back up inside the boiler.
3. Install boiler in an area with a floor drain or install in
a suitable drain pan.
3

2.
3.
4.
5.
Size the supply and return to suit the system. Refer
to Figure I. Refer also to the I-B=R Installation
Guide No. 2000 and the Peerless Water Survey for
additional guidance during water piping installation.
The boiler incorporates a pressure switch in the
Outlet Manifold. This switch will not let the boiler
operate without a minimum of 10 PSI on system.
Refer to Figure ] for suggested controls and
components location in the near boiler piping.
In older hydronic systems where sediment may exist,
install a basket strainer to prevent particles from
returning to boiler.
Install this boiler so that the gas ignition system
components are protected from water {dripping,
spraying, etc.) during appliance operation and
service {circulator replacement, condensate trap,
control replacements, etc.)
6
7.
8.
If this boiler and distribution system is used in
conjunction with a refrigeration system, i_Jipe the
chilled medium in parallel with the boiler and install
the proper valve to prevent the chilled medium from
entering the boiler
When the boiler is connected to heating coils
located in air handling units where they may be
exposed to refrigerated air circulation, install flow
control valves or other automatic means to prevent
gravity circulation of the boiler water during the
cooling cycle.
If the boiler is installed above radiation level, provide
a low water cutoff device at the time of boiler
installation.
All piping must be properly supported. See Figure 1.
SYSTEM
_ (_F_jt_(_) _RGE & BALANCE VALVE _UP=PLY__
_ I_ BACK rL_,4 pREVeNTER ._.
_ I_) LOW pRESSURE FIED (15 _ NQIqI_L}
_ I_ EXPANSION T&_
t _I)Alll VEtlT (Mi rco bubbler Air
Etimtnltol" Recmer_led)
• _ DRAIN VALVE
_ TEMPERATURE I pRESSURE GAEE
tITE_$U I_PLIEOBYC_ITRACTOR CONNECT TO _OILER SUPPLY I_IT
SYSTEM F_ I_
_VltCH
CD_N _
E:o_JST E
_ rl/KET
CONNECT TO BOILER RETURN COLD
_.L pe._= _U=T E _m_lU.V _ttW'a_T[It
_IU_R HO
¢OL_
_l_ONt
NOTE: I_I U_R CONNECTIONS
ARE I I/i" N_T
LEfT _I_ VI{W
Figure 1: Supply and Return Near Boiler Piping
4

:! [e.]l:T_eJW'_'ll[e]H _'t[rAh_[€
The boiler heat exchanger does have a pressure drop
which must be allowed for in determining circulator sizing
Using the chart in Figure 2, the pressure drop for each
boiler model is as follows:
PI-80 -- 8 feet of head at 8 GPM flow rate
PI-140 - 11 feet of head at 14 GPM flow rate
PI 199 18 feet of head at 19.9 GPM flow rate
Refer to Figure 2 for recommended circulator sizing.
[-*'_ .[_'_1==ill5"dlzf=ll!l=l= kVl_,NAvJ
The safety relief valve is factory insta[led into the right
side boiler manifold.
Pipe the discharge of safety relief valve to prevent
injury in the event of pressure relief. Pipe the
discharge to a drain. Provide piping that is the same
size as the safety relief valve outlet.
F
R
I
C
T
I
O
N
F
E
E
T
H
E
A
D
21-
20-
19-
18-
17-
16-
15-
14-
13-
12-
11-
10-
9
8
7
6
5
4
3
2
1
n , ,n n n
1 23 45 678910 11 12 13 14 15 16 17 18 19 20 21 22 23
FLOW IN GALLONS PER MINUTE
PI-80
P1-140
P1-199
IIIIIIII
TACO P/N GRUNDFOS P/N
007(1) 15-42 F SPD-2
0010(1) 26-64 F
0011 (1) 26-96 F
1) THE RECOMMENDED CIRCULATORS ARE BASED ON 1 GPM PER 10,000 BTU/HR W/20 ° At
Figure 2: Circulator Sizing

DJ I;JI;,]l_[cl I;[e):_(e]K_l:_D][_A'd_liil:lL'd<
I. See Figures 3 and 4 for basic zoned system layouts.
2. If required, provide means to isolate and drain each
zone separately
ZONE
VALVES
TO SYSTEM
ZONE ZONE ZONE
521
D_z
l
ET_Z (3-
CONNECT TO
BOILER
SUPPLY
FROM SYSTEM
ZONE ZONE ZONE
1 2 5
BALANCING
VALVES
-, I I
CONNECT TO
BOILER
RETURN
Figure 3: Zone Piping with Zone Valves
TO SYSTEM
ZONE ZONE ZONE
5 2 1
FROM SYSTEM
ZONE ZONE ZONE
1 2 5
FLOW
CONTROL/
VALVES _" ZONE
RCULATORS
CONNECT
TO BOILER
SUPPLY
CONNECT TO
BOILER
RETURN
Figure 4: Zone Piping with Circulators
6

:_"mI=:t::l::P:,l:_I;,I:{oleeI:T_J/[O]_
i. Consult the tank manufacturer's instructions for
specific information relating to tank installation. Size
the expansion tank for the required system volume
and capacity.
2. Expansion tanks are available with built-in fill valves
and check valves for reducing supply water pressure
and maintaining minimum system pressure. Check
the design features of the tank and provide valves as
necessary. Boiler system requires 12 PSI minimum.
Refer back to Figure 1 for typical expansion tank piping.
I_ I1_,_ID]I ;t:[kl I_ = I;t :1D]iTA_I'-_I/ :1:!1 : I=Lr-'_nl=1:
If the boiler is to be used in conjunction with an indirect-
fired water heater, refer to Figure 4 for typical piping.
Follow the instructions provided by the water heater
manufacturer. Pipe the water heater as a separate zone.
For new or existing systems that must be freeze-
protected:
Use only inhibited propylene glycol solutions of up to
50% by volume with water. Ethylene glycol is toxic
and can attack gaskets and seals used in hydronic
systems.
1.
2.
3.
4.
Glycol in hydronic applications is specially
formulated for this purpose. It includes inhibitors
which prevent the glycol from attacking metallic
system components. Make certain that the system
fluid is checked for the correct glycol concentration
and inhibitor level.
The antifreeze solution should be tested at least once
a year and as recommended by the antifreeze
manufacturer.
Antifreeze solutions expand more than water. For
example, a 50% by volume solution expands 4.8%
in volume for a temperature increase from 32 ° F to
180 ° E while water expands 3% with the same
temperature rise. Allowance must be made for this
expansion in system design.
For more information, consult the Peerless Water
Installation Survey and the antifreeze manufacturer.
FROM
BOILER
SUPPLY
TO
BOILER
RETURN
BALANCING
VALVE
II
7
[3-
I
BALANCING
VALVE
SUPPLY
TO TANK
INDIRECT-FIRED
WATER HEATER
f
SUPPLY TO
SYSTEM
RETURN FROM
SYSTEM
HOT DOMESTIC
WATER SUPPLY
COLD DOMESTIC
WATER SUPPLY
Figure 5: Typical Piping with Indirect-Fired Water Heater

2.
3.
4.
5.
6.
Size and install the gas supply piping properly in
order to provide a supply of gas sufficient to meet
the maximum demand without exceeding a pressure
drop greater than .5" W.C. between the meter and
the boiler.
Determine the volume of gas to be provided to the
boiler in cubic feet per hour. To obtain this value,
divide the Btu per hour rating (on the boiler rating
label) by the heating value of the gas in Btu per
cubic feet. Obtain the heating value of the gas from
the gas supplier. As an alternative, use Table 1 or 2
on the next page to obtain the volume of gas to be
provided to the boiler.
Use the value obtained above as the basis for piping
sizing. Size the gas piping in accordance with Table 3
for natural gas. Consult the National Fuel Gas Code
ANSI Z223.5/NFPA 54 and/or CAN/CGA B149 for
other sizing options and LP gas pipe sizes.
Locate the drop pipe adjacent to, but not in front of
the boiler.
Install a sediment trap. See Figure 6. Locate a tee in
the drop pipe at same elevation as the gas inlet
connection to the boiler. Extend the drop pipe to a
pipe cap.
Install a ground joint union ahead of the gas control
assembly to permit servicing of the control. Install a
service valve as shown in Figure 6.
Use a pipe joint sealing compound that is resistant to
the action of liquefied petroleum gas. A non-resistant
compound may lose sealing ability in the presence of
this gas, resulting in a gas leak and fire or explosion
potential.
7. Check piping for leaks prior to placing the boiler in
operation.
Use an approved gas detector, a non-corrosive leak
detection fluid or other leak detection method. If
leaks are found, turn off all gas flow and repair as
necessar_
When checking for leaks, do not use matches,
candles, open flames or other methods that provide a
source of ignition. This can ignite a gas leak,
resulting in fire or explosion.
8. The gas piping connection to the boiler must be a
minimum of 3/4 pipe size. Boiler is provided with a
3/4 x I/2 pipe reducer. Do not remove the reducer.
SERVICE VALVE---J_"-_
O.J. UNION _
SEDIMENT TRAP
FLOOR LINE_
I
_ JACKET
Figure 6: Gas Connection to Boiler
9. Disconnect the boiler and its individual shut-off valve
from the gas supply piping system during any
pressure testing of that system at test pressure in
excess of i/2 psig (3.5 kPa). Remove the mounting
screws of the flanged gas connection on the gas
valve, and disconnect flange from valve.
Do not subject the gas valve to more than 112 psi
pressure. Doing so may damage the valve.
Isolate the boiler from the gas supply piping system
by closing its individual service valve during any
pressure testing of the gas supply piping system at
test pressure equal to or less than 1/2 psig (3.5 kPa).
10. Check for proper supply pressures to boiler at
sediment trap location. Remove pipe cap and
provide fittings as required. Minimum permissible
supply pressure (Inches Water Column):
Natural Gas 3.7"
LP Gas 3.7"
Maximum permissible supply pressure to the boiler
(Inches Water Column):
Natural Gas 13.5"
LP Gas 13.5"
11. Maintain a minimum distance of 10 feet between a
gas pressure regulator and boiler.
12. Gas line must be properly purged of air to allow for
normal main burner ignition.
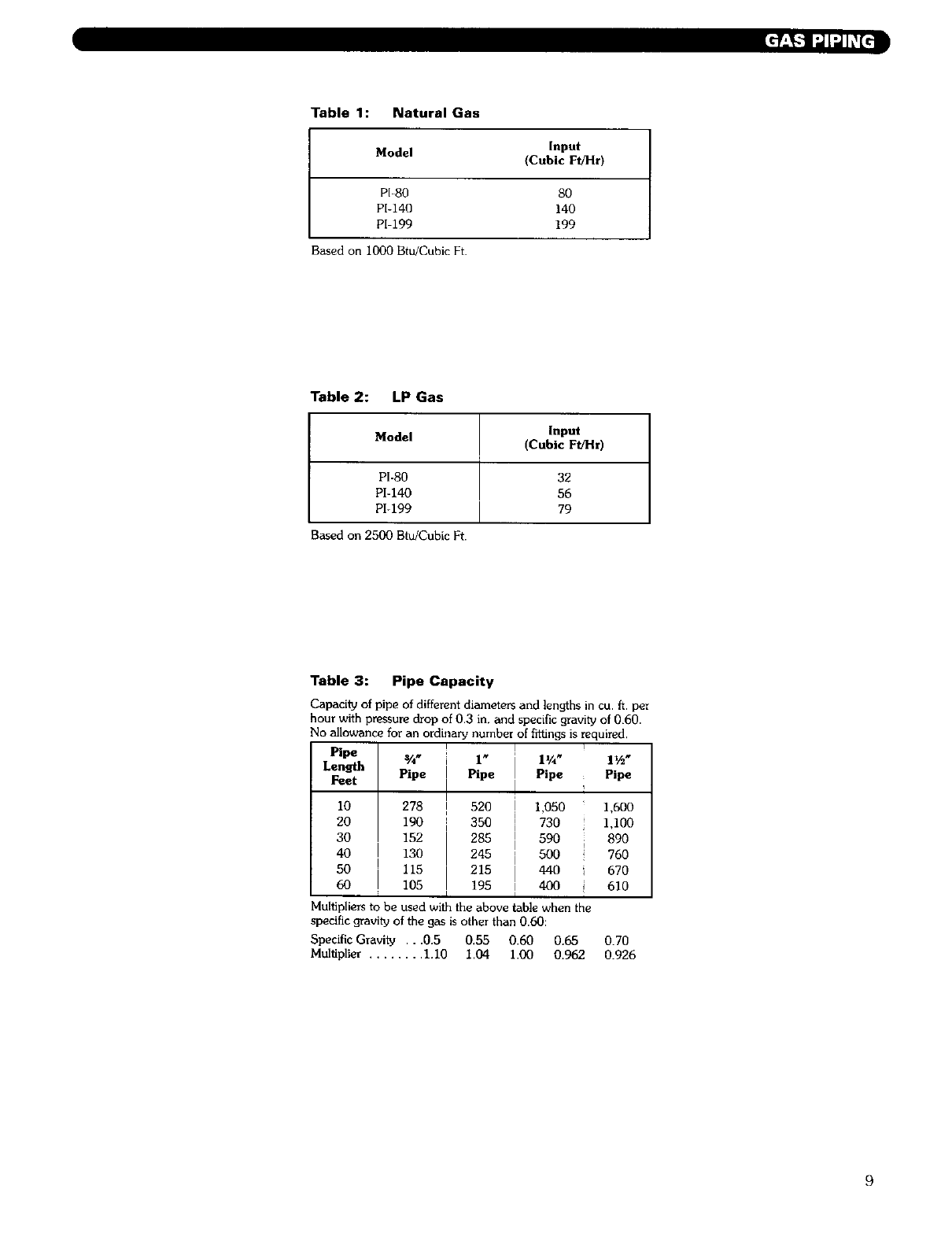
Table 1: Natural Gas
Model Input
(Cubic Ft/Hr)
PI-80 80
Pb140 140
PI 199 199
Based on 1000 Btu/Cubic Ft.
Table 2: LP Gas
Model Input
(Cubic Ft/Hr)
PI-80 32
PI-140 56
PI-199 79
Based on 2500 Blu/Cubic Ft.
Table 3: Pipe Capacity
Capacity of pipe of different diameters and lengths in cu. ft. per
hour with pressure drop of 0.3 in. and specific gravity of 0.60.
No allowance for an ordinary number of fiVdngs is required.
Pipe
Length
Feet
3/'4"*
Pipe
I
1# 1¼" 1½"
IPipe Pipe Pipe
10 278 520 I 1,050
20 190 i 350 730
30 152 285 590
40 130 245 500
50 115 215 440
60 105 195 400
Multipliers to be used wi_ the above _b_ when the
specific gravity of me gas is other than 0.60:
Specific Gravity . . .0.5 0.55 0.60 0.65
Multiplier ........ 1.10 1.04 1.00 0.962
1,600
1,100
890
760
i 670
J 610
0.70
0.926
9

r,_1 [€-I=b,_I=h_±_.
Install vent system in accordance with these
instructions and with Part 7, V_'nting of Equipment,
National Fuel Gas Code, ANSI Z223.1/NFPA 54,
CAN/CGA B149, or applicable provisions of the local
building codes•
2. Boiler is a direct vent appliance. The boiler vent is
listed as Category IV.
rA |vivhl ;t ii ,,
This vent system will operate with a positive
pressure in the vent pipe, Do not connect vent
connectors serving appliances vented by natural
draft into any portion of mechanical draft systems
operating under positive pressure.
2 Determine air inlet vent location
a Provide I foot clearance between bottom of vent
and ground level and normal snow lines.
3 Refer to venting diagrams (Figures 7 through 12) for
typical sidewall and vertical vent/air inlet piping.
a. Maintain distances between air inlet, vent. and
exhaust vent as indicated in Figures 7, 8, and 11.
Do not space the air inlet vent and exhaust vent
greater than 6 feet apart•
b. When sidewall venting multiple 3" concentric vent
kits, the vent kits must remain in a horizontal
plane and placed no closer than 8" center to
center• Also refer to instructions provided with
vent kit.
c. When sidewall venting multiple VI000 vent kits
refer to instructions provided with vent kit.
Flue gases will condense as they exit the vent
termination. This condensate can freeze on exterior
building surfaces which may cause discoloration of
these surfaces.
i. Determine exhaust vent location,
a. Vent is approved for 0" clearance to combustible
constr_ction.
b. Provide 3 feet clearance above any forced air
inlet within 10 feet.
C.
d,
e.
Provide 1 foot clearance below, I foot beside, or
1 foot above any door, window, or gravity air
inlet into any building•
Provide I foot clearance between bottom of vent
terminal and ground level and normal snow lines•
Provide 4 feet horizontal clearance from, and in
no case above or below, unless a 4 foot
horizontal distance is maintained, from electric
meters, gas meters, regulators and relief
equipment.
Do not locate vent terminal over public walkways
where condensate could create a nuisance or
hazard.
g.
h.
i.
When adjacent to a public walkway, locate vent
terminal at least 7 feet above grade.
Do not locate directly under roof overhangs to
prevent icicles from forming.
Provide 3 foot clearance from inside corner of
adjacent walls•
I.
2.
3.
4.
5.
6.
7.
8.
For minimum and maximum vent pipe lengths refer
to Table 4,
Use only 3" PVC, CPVC, or ABS solid schedule 40
or 80 material for exhaust vent, 4" PVC, CPVC, or
ABS solid schedule 40 or 80 pipe is also approved
under special conditions; see Section E, Extended
Vent Lengths with 4" Pipe, in this section for details,
FOAM CORE PIPING IS NOT APPROVED•
Vent connection is located on rear of boiler and is
marked "exhaust outlet".
Alljoints must be properly cleaned, primed, and
cemented, Use only approved cement and primer for
PVC, CPVC and ABS materials. Cement must
conform to ASTM D-2564 (PVC) or D2235 (ABS).
Remove all burrs and debris from joints and fittings.
Horizontal lengths must slope back to boiler
connection not less than 1/4" per foot to allow
codensate to flow back to boiler•
A screened 3" straight coupling is provided with
boiler for use as a vent termination• Optional vent
terminations approved for use with the Pinnacle
boiler are 3" concentric KGAVT0601CVT Vent Kit
and V1000 Vent Kit. Both are available from a
Peerless Distributor.
Vent piping must be supported at 4 ft. intervals to
prevent sagging. The boiler is not intended as a
support means for vent.
I0

ivl _ _lih_[€]
i]. f-'ll;t h_llllitill_ll Ih_t-'tP-1!l!-'_l / [l]_
I. For minimum and maximum pipe length rpfer to
Table 4.
2 Use same material as noted in Section C for exhaust
vent
3 Air inlet pipe connections is located in the rear of
boiler and is marked "air inlet" Connection is a slip
fit. No sealant is required.
4. All joints and fittings are to be assembled as per
instructions for vent pipe in Section C.
5 A screened inlet air tee is provided with boiler, to be
used as an outside termination.
6. Provide same suport means as noted for exhaust
vent in Section C.
Table 4: Minimum/Maximum Vent Length
Total Combined **Equivalent Length of 3 _
Exhaust Vent Plus 3 _ Air Inlet Vent
Boiler
Model *Minimum Length *Maximum Length
All 16 feet 85 feet
*Lengths are the combined added lengths of the exhaust
vent and air inlet vent.
**Include equivalent length of fittings as follows:
3" 90 degree elbow = 5 equivalent feet
3" 45 degree elbow - 3 equivalent feet
3" concenlric vent kit = 3 equivalent feet
3" air inlet tee = 0 feet
3" VI000 vent kit = 0 feet
Refer to Venting Diagram Figures 7 through 12 for Sidewall
and Vertical Venting arangements.
11

DIAGRAMS FOR SIDEWALL VENTING
BOILER
OT&P
_j===_
_"TS_EWW
EXTERIOR
WALL
ST_mHT
CcuPUNG --. --
1" MIN.
_INTAKE
_12"_
BOILER
3" EXHAUST
R_"T _OZ ViEW
T_E {VERTICAL_ COUPLING TEE (VErtiCAL)
FRONTeLEVAT_N
qMULTIPLeVENTS)
EXTERIOR
WALL
1" MIN, EXHAUST
.... STRAIGHT
_INTAKE
SlDEE_EVAXl0N
**IMPORTANT NOTE: All vent pipes must be glued, properly
supported, and the exhaust must be pitched minimum of a
1/4" per foot back to the boiler (to allow drainage of
condensate).
Figure 7: 3" Sidewall Vent with Tee (Intake) b
Coupling (Exhaust)
**IMPORTANT NOTE: All vent pipes must be glued, properly
supported, and the exhaust must be pitched minimum of a
1/4" per foot back to the boiler (to allow drainage of
condensate).
Figure 8: 3 _Sidewall Vent with Tee (Intake) 8"
Coupling (Exhaust)
BOILER
OT&P
RIGHT SIDE ViEW
INTAKE3"
coupu_
eX_XUSTOUTLETEXHAUST
EXTERIOR
WALL
VI000
VENT KIT
BOILER
OT&P
RIGHT SIDE V_EW
EXTERIOR
WALL
--IMFOR_ANT _NTAKE LEG
MUST WE FACI_ Up**
"_r--_INTAKE
ST_,aHr EXHA T
¢_pu,o US
**IMPORTANT NOTE: All vent pipes must be glued, properly
supported, and the exhaust must be pitched minimum of a
i/4" per foot back to the boiler (to allow drainage of
condensate).
Figure 9: 3 _Sidewall Vent with VlOOO Kit
**IMPORTANT NOTE: All vent pipes must be glued, properly
supported, and the exhaust must be pitched minimum of a
1/4" per foot back to the boiler (to allow drainage of
condensate).
Figure 10:3 _Sidewall Vent with 3 _Concentric
Vent Kit (KGAVT06OICVT)
12

DIAGRAMS FOR VERTICAL VENTING
STRAIGHT COUPLING
_J
MAINTAIN12", (18" FORCANADA),_
MINIMUMCLEARANCEABOVE
NORMALSNOW LINES.
It
BO/LER
O T&P
RIGHT S_DE_IEW
3,,
INTAKE
STRA_HT
COUPUNG rJ
3"
EXHAUST
ex_ust OUTU_T
,, 24"
MIN.
MAINTAIN 12_, (18" FOR CANADA),_ I "",
DO NOT EXTEND MORE THAN
24" ABOVE ROOF LINE.
BOILER
m
OT&P
R_HT SlOEVIEW
3,,
fNTAKE
STRAIGHT
COUpLiNG
3"
_T _TL_r EXHAUST
*'_[MPORTANT NOTE: All vent pipes must be glued, properly
supported, and the exhaust must be pitched minimum of a
1/4" per foot back to the boiler (to allow drainage of
condensate).
Figure 1 1: 3" Roof Vent with Tee (Intake) 6'
Coupling (Exhaust)
**IMPORTANT NOTE: All vent pipes must be glued, properly
supported, and the exhaust must be pitched minimum of a
1/4" per foot back to the boiler (to allow drainage of
condensate).
Figure 12: 3""Roof Vent with 3" Concentric
Vent Kit (KGAVTO6OICVT)
13

:lq -'_lll :_ l *] :ie] LvA:ib,_llllq:lL_LcJlIbl_i_ji/'Ev-m;JI;J:
2.
3.
The connection of air inlet vent and exhaust vent at
boiler must remain 3" and each vent must extend
from boiler a minimum of 15 equivalent feet before
transitioning to 4" vent
The maximum length shown in Table 4 can be
increased by using 4" PVC, CPVC, or ABS solid
schedule 40 or 80 pipe.
Use a 4" x 3" reducing coupling to transition to
4" vent•
4. The maximum combined *equivalent length of 4"
air inlet vent plus 4" exhaust vent must not exceed
125 feet•
* Equivalent Length of 4" Piping:
4" 90 degree elbow - 3 feet
4" 45 degree elbow - I foot
4" air inlet tee = 0 feet
5. Use the same pipe sizes for air inlet vent and
exhaust vent.
6. To use the VI000 Vent Kit or 3" Concentric Vent Kit
transition 4" pipe to 3" pipe at exit point of building.
I;4 [_o) L_I u_] :IL'_l+,."f'.*_lII
I.
2.
4+
5.
6.
7.
This boiler is a high efficiency unit that produces
condensate.
The rear of the boiler has a plastic hose for
connection of a 5/8" size plastic tubing.
Slope condensate tubing down and away from boiler
into a drain pan or condensate neutralizing filter.
Condensate has a low PH level; check with local
codes or ordinances before connecting to drain.
Do not expose condensate line to freezing
temprature.
Use only plastic tubing as a condensate drain line.
To allow for proper drainage on large horizontal
runs, a second line vent may be required and tubing
size may need to increase to i".
A condensate removal pump is required ifboiler is
below drain•
At the time of removal of an existing boiler, follow these
steps with each appliance remaining connected to the
common venting system placed in operation, while the
other appliances remaining connected to the common
venting system are not in operation:
a. Seal any unused openings in the common venting
system•
b. Visually inspect the venting system for proper size
and horizontal pitch and determine there is no
blockage or restriction, leakage, corrosion and other
deficiencies which could cause an unsafe condition.
C. Insofar as is practical, close all building doors and
windows and all doors belween the space in which
the appliances remaining connected to the common
venting system are located and other spaces of the
building• Turn on any clothes dryers and any
appliance not connected to common venting system.
Turn on any exhaust fans, such as range hoods and
bathroom exhausts, so they will operate at maximum
speed. Do not operate a summer exhaust fan+ Close
fireplace dampers.
d+ Place in operation the appliance being inspected•
Follow the lighting instructions. Adjust thermostat so
appliance will operate continuously•
e. Test for spillage at the draft hood relief opening after
5 minutes of main burner operation• Use the flame
of a match or candle, or smoke from a cigarette,
cigar, or pipe.
f. After it has been determined that each appliance
remaining connected to the common venting system
properly vents when tested as outlined above, return
doors, windows, exhaust fans, fireplace dampers and
any other gas-burning appliance to their previous
conditions of use.
g. Any improper operation of the common venting
system should be corrected so that the installation
conforms with the National Fuel Gas Code, ANSI
Z223.1/NFPA 54 and/or CAN/CGA B149. When
resizing any portion of the common venting system,
the common venting system should be resized to
approach minimum size as determined using the
appropriate tables located in the Chapter "Sizing of
Category I Venting Systems" of the National Fuel
Gas Code, ANSI Z223.J/NFPA 54.
14

InstallallelectricalwiringinaccordancewiththeNational Electrical Code and local requirements.
This unit when installed must be electrically grounded in accordance with the requirements of the authority
having jurisdiction or, in the absence of such requirements, with the current edition of the National Electrical
Code, ANSI/NFPA 70.
r_,11i_A_il;th_[=
1,
2.
3.
4.
:m _[e]L'_l::le]t*.."b'd.,.']lll::l_'JI|vA_il;th,_[{
5.
6.
7.
Refer to Figures 13 and 14 for power supply
connection to boiler. Use #14 AWG size wire.
Connect boiler to a separate, permanently live
electrical supply line with a fused switch. 120 volts,
60 HZ, 15 amp service.
The boiler electrical connection is located on the left
side of unit.
The boiler is supplied with a burner service switch.
When refering to Figures 13 and 14, wire the burner
service switch in the (HOT) line to boiler.
Wires in the electrical J Box have been labeled at the
factory. Do not remove labels.
Connect the supply line (HOT) wire to the black wire
and supply line (GROUND) to the white wire. Boiler
control board is polarity sensitive. If polairty is
reversed, boiler control will not sense main burner
flame.
Connect building service ground (green wire), and
boiler ground (green wire) to green ground screw
located in boiler J Box.
The Building System Ground must be inspected by a
qualified Electrician.
8. For connection to system circulator and room
thermostat refer to Figures 13 and 14. Thermostat
anticipator setting is 0.56 amp.
9. The boiler control board and factory wiring are
shown in Figure 17.
See Figure 15 for typical wiring with zone valves. See
Figure 16 for typical wiring with zone circulators. When
wiring a zoned heating system, follow all applicable
codes, ordinances and regulations.
Do not power zone valves directly from the boiler
transformer. Doing so will greatly reduce the life of
the transformer. Use a separate transformer sized to
handle the total of all zone valve electrical loads.
GP.J:EN (GROUNO)
WHITE
DRY PUMP RELAy
RED RED
NORMALLY OPEN
_ERHOSTAT
CONNECTION
GREEN
BLACK
tj GROUND
SCREW
ELECTRICAL
SWITCH JUNCTION BOX
120V 60 HZ
RED (NOT USED)
NORMALLY OPEN
THERHO_I'AT
CONNECTION
G GRAY
OG_ WH_E __
(NEUTRAL)•BLACK
(HOT)
GREEN --
(GROUNO)•_
GROUND
SCREW
ELECTR[CAL
SW_CH JUNCtiON BOX
120V 60 HZ
Figure 13: Connection Wiring with Circulator Relay Figure 14: Connection Wiring without
Circulator Relay
15
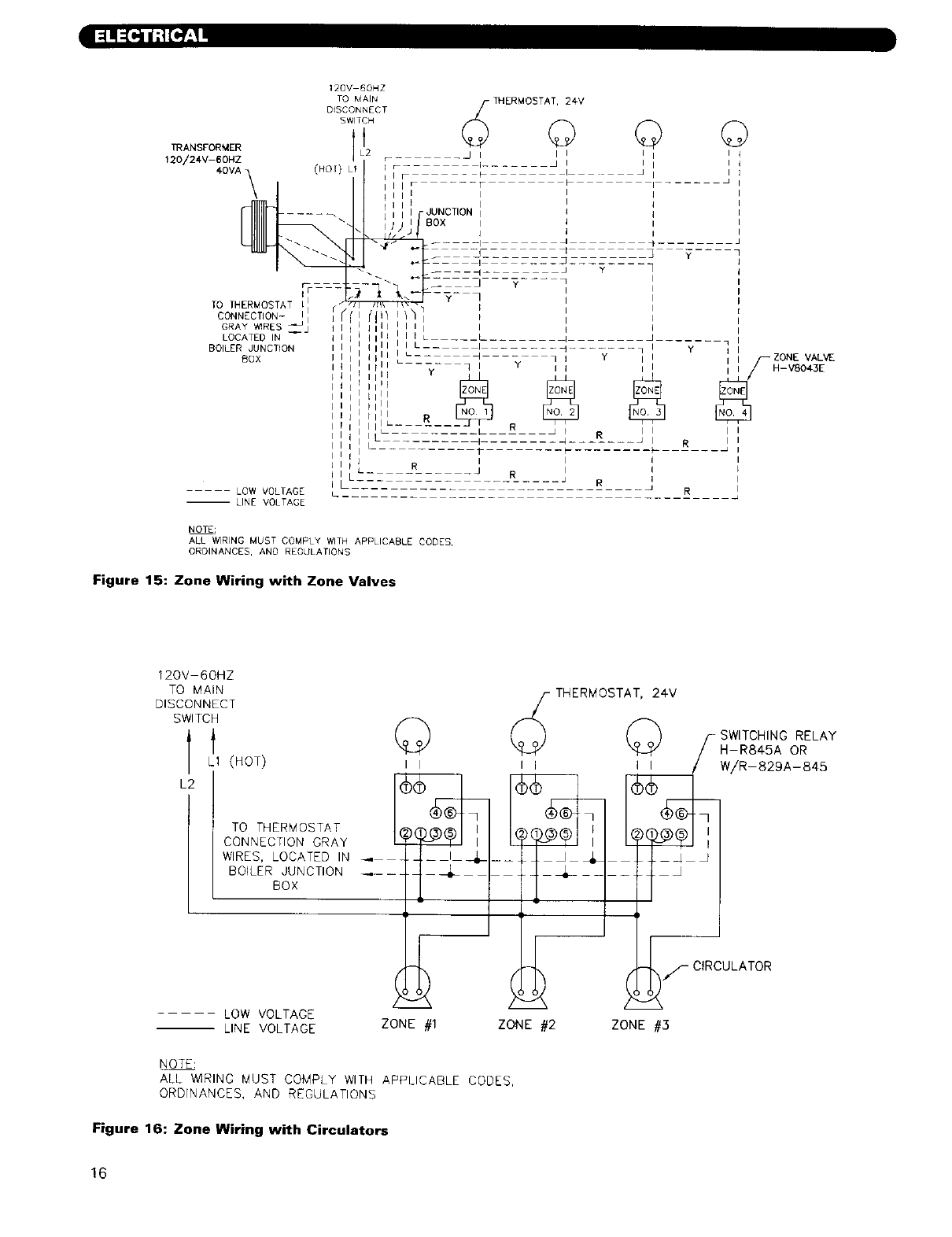
1T_ANSFORMER
120/24V--60HZ
40VA_
TO THERMOSTAT
CONNECTION-
GRAY raRES
LOCATED IN
BOILER JUNCTION
BOX
LOW VOLTAGE
-- LINE VOLTAGE
120V-60HZ
TO MAIN
DISCONNECT
SWITCH
t
i
(HOT) [ I r
iIr
(_THERMOBTA(_V
J I
I
I
I
JUNCllON I
BOX I
J
I
J
I
I I
j I
I
I
I
I
I
I
]
J
I
I
I
I
J R
© ©
I I I
I I I
J I I
I
I
I
I
I
I
4
Y
Y
Y ] Y ! ZONE VALVE
_" H-V8043E
R I I I I
J I R I I
I I
RI I
I
NOT£_
ALL WlRING MUST COMPLY WITH APPLICABLE CODES,
ORDINANCES, AND REGULATIONS
Figure 15: Zone Wiring with Zone Valves
120V-60HZ
TO MAIN
DISCONNECT
SWITCH
TO THERMOSTAT
CONNECTION GRAY
BOILER JUNCTION .....
BOX
_ "/_ '_CULATOR
LOW VOLTAGE
LINE VOLTAGE ZONE #1 ZONE #2 ZONE #3
THERMOSTAT, 2€V
{_ /- SWITCHING RELAY
/H-R845A OR
/W/R-829A-845
NOTE:
ALL WIRING MUST COMPLY WITH APPLICABLE CODES,
ORDINANCES, AND REGULATIONS
Figure 16: Zone Wiring with Circulators
16

=ilit::[_i+_[o,7'iTili
INLET TEMP
PROBE
t20 VAC
CDNBUSTION BLOWER
GAS VALVE
FLAME ROD
PRESSURE SWITCH
PROVE AIR
SPARK {]LIT V
_ CIRC. pUMP
THERM[] DISC TEMP. SWITC_ 210 DEGREE
WATER PRESSURE SWITCH
ECO WATER/ HIGH LIMIT
120 VAC
24 VAC
(_ 1_0 VAC
LINE _II_T
Figure 17: Boiler Control Board Factory Wiring
.[ ."]:loll J:1L_[I.] =[o] :11o]'] :1t#,.31/ [m]i
1,
2.
3.
4.
When power is first applied to the control, the
control will initially run through a self-diagnostic
routine, and then go into its operating mode. The
green LED light will pulse in a dim to bright
sequence indicating a normal operating mode. If
there is no call for heat, the control will go into the
idle state.
If the thermostat is calling for heat, the control will
apply power to the circulator pump. If the control
determines the appliance water temperature is below
the temperature dial set point value less the
switching differential, the control will initiate a
heating cycle.
The control then performs selected system diagnostic
checks. If all checks are successfully passed, a 5
second pre-purge cycle is initiated (blower on max
speed).
When the pre-purge period is complete, power is
applied to the spark ignitor for a 6 second trial for
ignition. If a flame is not verified during the trial-for-
ignition, the gas valve is immediately closed, and the
control will return to step 2. If after three trials a
flame is not verified, the control will go into lockout
mode. If a flame is confirmed, the control enters the
heating mode.
5. When water temperature reaches the temperature
dial set point plus i0 ° F (or if the thermostat call-for-
heat is satisfied), the gas valve is closed and the
control enters a 4 second post-purge (blower on max
speed). NOTE: IF THE THERMOSTAT IS STILL
CALLING FOR HEAT, THE CIRCULATOR PUMP
WILL CONTINUE TO RUN UNTIL THE
THERMOSTAT CALL FOR HEAT IS SATISFIED.
6.
7.
When post-purge is complete, the control enters the
idle state while continuing to monitor temperature
and the state of other system devices. If a call-for-
heat is received, the control will automatically return
to step 2 and repeat the entire operating cycle.
During the idle state and heat state, if the control
detects an improper operating condition for external
devices such as the high-limit switch, the green LED
on the control will flash an error code sequence.
During the call for heat the boiler control board will
continually monitor the return and supply water
temps in relation to the temperature dial set point
and the differential switch setting. The control board
will use this input to modulate the blower speed. The
blower coupled with the gas valve venturi system will
modulate the premix air/gas input to the burner. The
gas valve and venturi system provide the optimum
gas/air ratio through the full burner modulation.
17

l,_ll [iI* ] lviI:l I::l / IL'_[ci i l I= IIb.'ff.-'lI'_I ! i!'_l /1*]i
1.
2.
3.
4.
5.
6.
7.
Confirm that all water, gas and electricity are
turned off.
Verify that water piping, venting, gas piping and
electrical wiring and components are installed
properly. Refer back to previous sections of these
instructions as well as equipment manufacturer's
instructions as necessary.
Fill the boiler and system with water, making certain
to vent all air from all points in the system. To check
water level in the system, open and close each vent
in the system. Water should exit from each vent
when it is opened.
The pressure reducing valve on the fill line will
typically allow the system to be filled and pressurized
to 12 PSI. Consult the valve and expansion tank
manufacturer for more specific information.
Check joints and fittings throughout the system for
leaks. If leaks are found, drain the system and repair
as required.
Connect a manometer at the sediment trap location.
Refer to Figure 6. Remove pipe cap and provide
fittings as required.
Confirm that the gas supply pressure to the boiler is
above the minimum and below the maximum values
for the gas being used. See the end of Section 4 for
these values. If a supply pressure check is required
isolate the boiler and gas valve before performing
the pressure check. If the supply pressure is too high
or too low, contact the gas supplier.
8. Adjust set point temperature and differential settings
as follows:
a. Temperature Adjustment: A potentiometer
located on the control board is used to adjust the
set point temperature on the boiler appliance.
This can be set between 70 and 210 degrees.
b. Temperature Differential Adjustment: A "DIP"
switch is located on the control board.
Depending upon the configuration of the "DIP"
switch, the differential selection is 6, 12, 20, or
30. See the figure below for further detail.
NOTE: the differential adjustment is the value below
the set point, when the burner will fire. (Example:
190 degrees set point, 30 degrees differential, burner
will not fire until return water drops below 160
degrees and will modulate the flame until 200
degrees is reached, then post purge and idle state
will be achieved. If at any point "IT is satisfied, the
cycle will be interrupted by post purge and idle
state.
9. Turn on electricity and gas to boiler. Check to see if
LED light is illuminated on control board.
10. Light the boiler by following the Lighting/Operating
Instructions in this section. The initial ignition may
require several tries as the piping is purged of air.
11. Use the sequence of operation description and
Figure 17 in Section 6 (Electrical) to follow light-off
and shutdown sequences and to assist in diagnosing
problems. If the boiler does not function properly,
consult Section 8, Troubleshooting.
CK
1 2
CK
I2
CK CK
1 2 1 2
Differential Dip Switch Adjustments
18

:H I [of: / i h_[€_Lo]:,1:1:f,_'t/ IL_[€'l IL_I,.i Ii:1ILO,]li [o]L_F:
FOR YOUR SAFETY READ BEFORE OPERATING
WARNING: If you do not follow these instructions exactly, a fire or explosion may
result, causing property damage, personal injury or loss of life.
A. This applianca does not have a pilot. It is equipped
with an ignition device which automatically lights the
burner. Do not try to light the burner by hand,
B. BEFORE OPERATING smell all around the appliance
area for gas. Be sure to smell next to the floor
because some gas is heavier than air and will settle
on the floor.
WHAT TO DO IF YOU SMELL GAS
•Do not try to light any appliance.
Do not touch any electric switch; do not use any
phone in your building.
•Immediately call your gas supplier from a neighbor's
phone. Follow the gas suppliers' instructions.
C,
D.
If you cannot reach your gas supplier, call the
fire department.
Use only your hand to turn the gas control knob. Never
use tools. If the handle will not turn by hand, don't try
to repair it, call a qualified service technician. Force or
attempted repair may result in a fire or explosion.
Do not use this appliance if any part has been under
water. Immediately call a qualified service technician to
inspect the appliance and to replace any part of the
control system and any gas control which has been
under water,
OPERATING INSTRUCTIONS
1. STOP! Read the safety information above.
2. Set the thermostat to lowest setting.
3. Turn off all electric power to the appliance.
4. This appliance is equipped with an ignition device
which automatically lights the burner. Do not try to light
the burner by hand.
Combination
Gas Control
/
Gas Shutoff
Valve
5. Remove front cover.
6. Turn gas shutoff valve clockwise to "off". Handle will be
vertical, do not force.
7. Wait five (5) minutes to clear out any gas. If you then
smell gas, STOP! Follow "B" in the safety information
above on this label. If you don't smell gas, go to next
step.
8. Turn gas shutoff valve counterclockwise to "on".
Handle will be horizontal
9. Install Front Cover.
10. Turn on all electric power to appliance.
11. Set thermostat to desired setting.
12. If the appliance will not operate, follow the instructions
"To Turn Off Gas To Appliance" and call your service
technician or gas suppllier.
TO TURN OFF GAS TO APPLIANCE
1. Set the thermostat to lowest setting.
2. Turn off all electric power to the appliance if service is
to be performed.
3. Remove front cover.
4. Turn gas shutoff valve clockwise to "off". Handle will be
vertical. Do not force.
5. Install front cover.
19

[a,,]il[_o] L_IIii;{o] nilI.] :;(.."_o.];t I:,inId[o] L__
See Figure 19 for Location of these devices.
1. SUPPLY WATER TEMPERATURE THERMISTOR
Senses supply water temperature from boiler Shuts
down main burner gas upon reaching i0 degrees
over control board set point. As supply temperature
falls, boiler ignition will restart.
2. RETURN WATER TEMPERATURE THERMISTOR -
Senses return water temperature from system. As
thermistor senses a drop in return water temperature
below the control board set point minus the
differential set point, boiler ignition sequence begins.
3. WATER HIGH LIMIT SWITCH -Senses supply
water temperature and shuts down main burner gas
upon reaching limit set point. Boiler control will go
into lockout mode upon activation of high limit.
4. WATER PRESSURE SWITCH - Senses boiler water
system pressure and shuts down main burner gas
when pressure falls to 8 PSI. Boiler contiol will go
into lockout mode upon activation of water pressure
switch.
5.
6,
AIR PRESSURE SWITCH -Senses burner manifold
pressure and prevents ignition sequence activation if
blower is not operating.
THERMODISC TEMPERATURE SWITCH - Senses
combustion chamber outside surface temperature
and shuts down main burner gas upon reaching set
point of 210 °E Boiler control will go into lockout
mode upon reaching set point. This is a manually
resetable switch.
Ira1 [_:l:[_[_ellli I:J;{elq=llllJ:!
1. After starting the boiler, be certain all controls are
working properly. Check to be sure that boiler will
shut down on action of water temperature reaching
control board temperature set point.
2. To check operation of the ignition system safety
shut-off features:
a. Turn gas supply off.
3.
4,
5.
6.
7.
8.
9.
b. Set thermostat or controller above room
temperature to call for heat.
c Ignition sequence should try 3 times before going
into lockout mode.
d Turn gas supply on.
e. Reset by turning 120V power supply off then on.
f. Observe boiler operation through one complete
cycle.
Low Water Cut-Off (if used) - Consult the
manufacturer's instructions for the low water cut-off
operational check procedure.
Check the system to make sure there are no leaks or
overfilling problems which might cause excessive
make-up water to be added. Make-up water causes
liming in the boiler.
Check the expansion tank and automatic fill valve (if
used) to confirm that they are operating correctly. If
either of these components causes high pressure in
the system, the boiler relief valve will weep or open,
allowing fresh water to enter the system.
Check the general condition of the system including
piping support, joints, etc. Check cleanliness of the
radiators, baseboard units and!or convectors. Clean
them to the extent possible. If radiators do not heat
evenly, vent any remaining air from them.
Review operation with end-user.
Complete the Warranty Card and submit it to
Peerless Heater Company.
Hang the Installation, Operation and Maintenance
Manual in an accessible position near the boilen
2O

L'W _._]: lilt _t eIolY,_J_
In the event of a shut down caused by thermodisc
temperature switch, water pressure switch or high limit
switch effecting a shut-down of the main burner and
ignition control lockout:
a. Refer to section "C. Boiler Fault Conditions," item 1.,
"Limit String Open," in this section and follow the
procedure to restart the boiler.
b. If control goes into ignition lockout mode again refer
to the Lighting/Operating Instructions, Section 7, to
properly turn off the gas to the boiler.
c. Turn off electric power to the boiler.
d. Call a qualified heating service organization or local
gas company and have the cause of the shut-down
investigated and corrected.
e. Refer to Lighting/Operating Instructions, Section 7,
to re-start boiler.
When servicing or replacing items that communicate
with the boiler water, be certain that:
•There is no pressure on the boiler.
•The boiler is not hot.
•The power is off.
When servicing all other boiler controls, be certain
that:
•The gas is off.
•The electricity is off.
Do not use this appliance if any part has been under
water. Improper or dangerous operation may result.
Immediately call a qualified service technician to
inspect the boiler and to replace any part of the
control system and any gas control which has been
under water.
Label all wires prior to disconnection when servicing
controls. Wiring errors can cause improper and
dangerous operation. Verify proper operation after
servicing.
Should overheating occur or the gas supply fail to
shut off, do not turn off or disconnect the electrical
supply to the pump.This may aggravate the problem
and increase the likelihood of boiler damage. Instead,
shut off the gas supply at a location external to the
appliance.
21
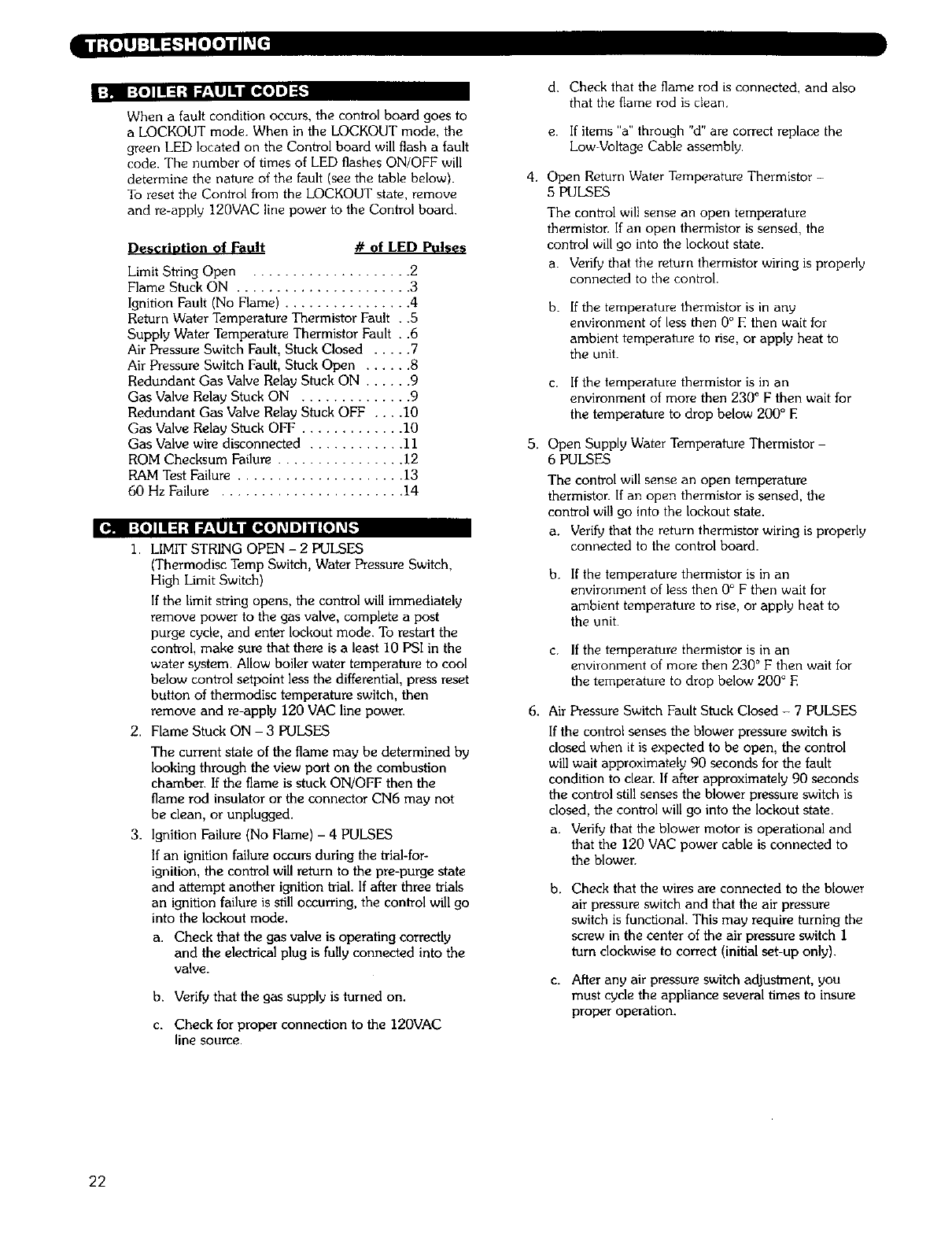
:11 I:[o]lll':l:llgL"_llRI [e,[o]e]:l.;
When a fault condition occurs, the control board goes to
a LOCKOUT mode. When in the LOCKOUT mode, the
green LED located on the Control board will flash a fault
code. The number of times of LED flashes ON/OFF will
determine the nature of the fault (see the table below).
To reset the Control from the LOCKOUT state, remove
and re-apply 120VAC line power to the Control board.
D_scfintion of Fault #of LED Pulses
Limit String Open .................... 2
Flame Stuck ON ...................... 3
Ignition Fault (No Flame) ................ 4
Return Water Temperature Thermistor Fault . .5
Supply Water Temperature Thermistor Fault . .6
Air Pressure Switch Fault, Stuck Closed ..... 7
Air Pressure Switch Fault, Stuck Open ...... 8
Redundant Gas Valve Relay Stuck ON ...... 9
Gas Valve Relay Stuck ON .............. 9
Redundant Gas Valve Relay Stuck OFF .... 10
Gas Valve Relay Stuck OFF ............. 10
Gas Valve wire disconnected ............ 11
ROM Checksum Failure ................ 12
RAM Test Failure ..................... 13
60 Hz Failure ....................... 14
*,e,]llI:{e]lll::l-'t _'_IlIII|O,[O]L'_ID]II[O]L'q_
1. LIMIT STRING OPEN - 2 PULSES
(Thermodisc Temp Switch, Water Pressure Switch,
High Limit Switch)
If the limit string opens, the control will immediately
remove power to the gas valve, complete a post
purge cycle, and enter lockout mode. To restart the
control, make sure that there is a least 10 PSI in the
water system. Allow boiler water temperature to cool
below control setpoint less the differential, press reset
buflon of thermodisc temperature switch, then
remove and re-apply 120 VAC line power.
2. Flame Stuck ON - 3 PULSES
3.
The current state of the flame may be determined by
looking through the view port on the combustion
chamber. If the flame is stuck ON/OFF then the
flame rod insulator or the connector CN6 may not
be clean, or unplugged.
Ignition Failure (No Flame) - 4 PULSES
If an ignition failure occurs during the trial-for-
ignition, the control will return to the pre-purge state
and attempt another ignition trial. If after three trials
an ignition failure is still occurring, the control will go
into the lockout mode.
a. Check that the gas valve is operating correctly
and the electrical plug is fully connected into the
valve.
b. Verify that the gas supply is turned on.
c. Check for proper connection to the 120VAC
line source.
d. Check that the flame rod is connected, and also
that the flame rod is clean.
e. If items "a" through "d" are correct replace the
Low-Voltage Cable assembly.
4. Open Return Water Temperature Thermistor -
5 PULSES
The control will sense an open temperature
thermistor If an open thermistor is sensed, the
conttol will go into the lockout state.
a. Verify that the return thermistor wiring is properly
connected to the control.
b. If the temperature thermistor is in any
environment of less then 0°Fthen wait for
ambient temperature to rise, or apply heat to
the unit.
c. If the temperature thermistor is in an
environment of more then 230 ° F then wait for
the temperature to drop below 200 ° F
5. Open Supply Water Temperature Thermistor -
6PULSES
The control will sense an open temperature
thermistor. If an open thermistor is sensed, the
control will go into the lockout state.
a. Verify that the return thermistor wiring is properly
connected to the control board.
b. If the temperature thermistor is in an
environment of less then 0° F then wait for
ambient temperature to rise, or apply heat to
the unit.
c. If the temperature thermistor is in an
environment of more then 230 ° F then wait for
the temperature to drop below 200 ° F
6. Air Pressure Switch Fault Stuck Closed - 7 PULSES
If the control senses the blower pressure switch is
closed when it is expected to be open, the control
will wait approximately 90 seconds for the fault
condition to clear. If after approximately 90 seconds
the control still senses the blower pressure switch is
closed, the control will go into the lockout state.
a. Verify that the blower motor is operational and
that the 120 VAC power cable is connected to
the blower.
b.
c.
Check that the wires are connected to the blower
air pressure switch and that the air pressure
switch is functional. This may require turning the
screw in the center of the air pressure switch I
turn clockwise to correct (initial set-up only).
After any air pressure switch adjustment, you
must cycle the appliance several times to insure
proper operation.
22

7. Air Pressure Switch Fault Stuck Open 8 PULSES
If the control senses the blower pressure switch is not
closed during the pre-purge cycle, the control will
attempt two additional pre-purge trials. If after three
pre-purge trials the control is still sensing the blower
pressure switch is not closing, the control will enter the
lockout state.
a. Check that the blower motor is off and verify that
the blower air pressure switch is functional. This
may require turning the screw in the center of the
air pressure switch in 1/4 turn counter clockwise to
correct (initial set-up only).
b. After any air pressure switch adjustment, you must
cycle the appliance several times to insure proper
operation.
8. Redundant Gas Valve/Gas Valve Relay Stuck ON 9
PULSES
If the controller senses the redundant gas valve or the
gas valve relay is stuck ON it will go into the lockout
state.
a. Check for short-circuit(s) from the 24VAC and no
continuity between CN4 pins 3 and 4.
b. If the problem persists, replace the control board.
9. Redundant Gas Valve/Gas Valve Relay Stuck OFF -
10 PULSES
If the controller senses the redundant gas valve or the
gas valve relay is stuck OFF, it will go into a lockout
state.
Replace the control board.
10.Gas Valve NOT Connected - 11 PULSES
If the controller detects that the gas valve is not
connected it will go into the lockout state.
Check the connection to the gas valve.
11.ROM Checksum Failure 12 PULSES
If the controller detects that the ROM check has failed
then it will go into a lockout state.
a. Turn the 120V power OFF then ON.
b. If the problem persists, replace the control board
12.RAM Test Failure 13 PULSES
If the controller detects that the RAM test failed it will
go into a lockout state.
a. Turn the 120V power OFF then ON.
b. If the problem persists, replace the control board,
13.60 Hz Failure 14 PULSES
If the generator, inverter, or other power source does
not provide 60Hz, then the power source must be
replaced.
a. If the power source used supplies 60Hz, turn the
120V power OFF then ON.
b. If the problem persists, replace the control board.
23

I_T'_ l_l_o_l
IF:llc-1 =h,'_1:1;.r_*1!ilVl_l I/:nn:{o] III =1;| IL_III _--] _
General boiler observation can be performed by the
owner. If any potential problems are found, a qualified
installer or service technician/agency must be notified.
I. Remove any combustible materials, gasoline and
other flammable liquids and substances that generate
flammable vapors from the area where the boiler is
contained.
2.
3.
4.
5.
Observe general boiler conditions (unusual noises,
vibrations, etc.)
Observe operating temperature and pressure on the
combination gauge located in the supply piping on
the left side of the boiler. Boiler pressure should
never be higher than 5 psi below the rating shown
on the safety relief valve (25 psig maximum for a 30
psig rating). Boiler temperature should never be
higher than 240 °P
Check for water leaks in boiler and system piping.
Smell around the appliance area for gas. If you smell
gas. follow the procedure listed in the Lighting
Operating Instructions to shut clown appliance in
Section 7, Start-Up Procedure Part B.
:!1 ItAtl:l:l[11_'m LIiIlll;l;{o]ll:l;llh_lllj."] :1
1. Flush float-type low-water cut-off {if used) to remove
sediment from the float bowl as stated in the
manufacturer's instructions.
The following annual inspection must be performed
by a qualified service technician.
1. Check boiler room floor drains for proper
functioning.
2, Check function of the safety relief valve by
performing the following test:
a. Check valve piping to determine that it is
properly installed and supported.
b. Check boiler operating temperature and pressure.
c. Lift the t_y lever on the safety relief valve to the
full open position and hold it for at least five
seconds or until clean water is discharged,
d.
e.
f.
g.
Release the try lever and allow the valve to close.
If the valve leaks, operate the lever two or three
times to clear the valve seat of foreign matter. It
may take some time to determine if the valve has
shut completely.
If the valve continues to leak, it must be replaced
before the boiler is returned to operation.
Check that operating pressure and temperature
have returned to normal.
Check again to confirm that valve has closed
completely and is not leaking,
3. Test low-water cut-off (if used) as described by the
manufacturer.
4. Test limit as described in Section 7, Part D, "Check-
Out Procedure".
5 Test function of ignition system safety shut-off
features as described in Section 7, Part D, "Check-
Out Procedure".
When servicing or replacing components, be
absolutely certain that the following conditions are
met:
•Water, gas and electricity are off.
•The boiler is at room temperature.
•There is no pressure in the boiler.
6. Remove the top/front jacket panel and inspect for
any foreign debris that may have entered through air
inlet vent.
7.
8.
Inspect burner for deterioration. Replace if necessary.
With boiler in operation cheek that condensate is
dripping from drain hose. Cheek for any restriction in
condensate drain line.
9. Inspect exhaust vent and air inlet vents for proper
support and joint integrity. Repair as necessary. Refer
to Section 5, VENTING.
10. Inspect exhaust vent and air inlet vent terminations
for obstructions.
Leaks in the vent system will cause products of
combustion to enter structure (vent system operates
under positive pressure),
24

I_o]]ll_l=]l_,_l:::l_[-,,.'][=]_ _![[_='_ _]
PI-80
--1712 aPP_OX -- --_ _ 3e_
4 _ APe_OX --
eXMAUST DUTL_r
2132 APP'0× _
II '°'
BOILER gDILER
RE tU_C_ SU_PPtL_
--1_TS--
L_FT SIDe vIEv
35 _PeeOx -- _q
_LIEr
v_v_
_ XH_USt OUtLet
0_S _UPPL_o
•e_ox _-- _0 x
_p_l w_v
I...... ]-
i_c_ vi[v
!
PI-140/PI-199
eLBI
AP_OX _XH_US_ _UTLET
'_S SU_OL --_
LErr S_D[ V_V
32_
75 _P_X
2t3 f
,3!8
_Pp_x
I
_EL_Er
V_V£
Figure 18: Boiler Dimensions
_x_a_JST _UTLET
G_S St_PL_
SVltC_ eoo--
_kl[r
VALV_
i ,
[Nk£T _
/con_nsat[ _
H0_ 375
25

Boiler Supply/Return
Model Connection
All 1 1/4" NPT
Gas
Connection
3/4" NPT
Air Inlet Vent!
Exhaust Size
3 t,
Table 5: Pinnacle" Boiler Ratings
JI_1_ r:lel I :MIB"-{elI I ;1:_I:q.*NHI_.(L"e.
DOE Net I=B=R
Boiler Heating Ratings Seasonal
Modet Input Capacity Water Efficiency
Number MBH MBHg MBH 1,2 AFUE %
PI-80 80 74 64 92
PI-140 140 129 :112 92
PI-199 199 183 I 159 92
I Net I-B-R water ratings based on an allowance of 1 15
2 Consult factory before selecting a boiler for installations having unusual piping and pickup
requirements, such as intermittent system operation, extensive piping systems, etc.
3 Heating Capacity and Annual Fuel U{ilization Efficiency (AFUE) ratings are based on US.
Government t_'st HI Division
of qama
26
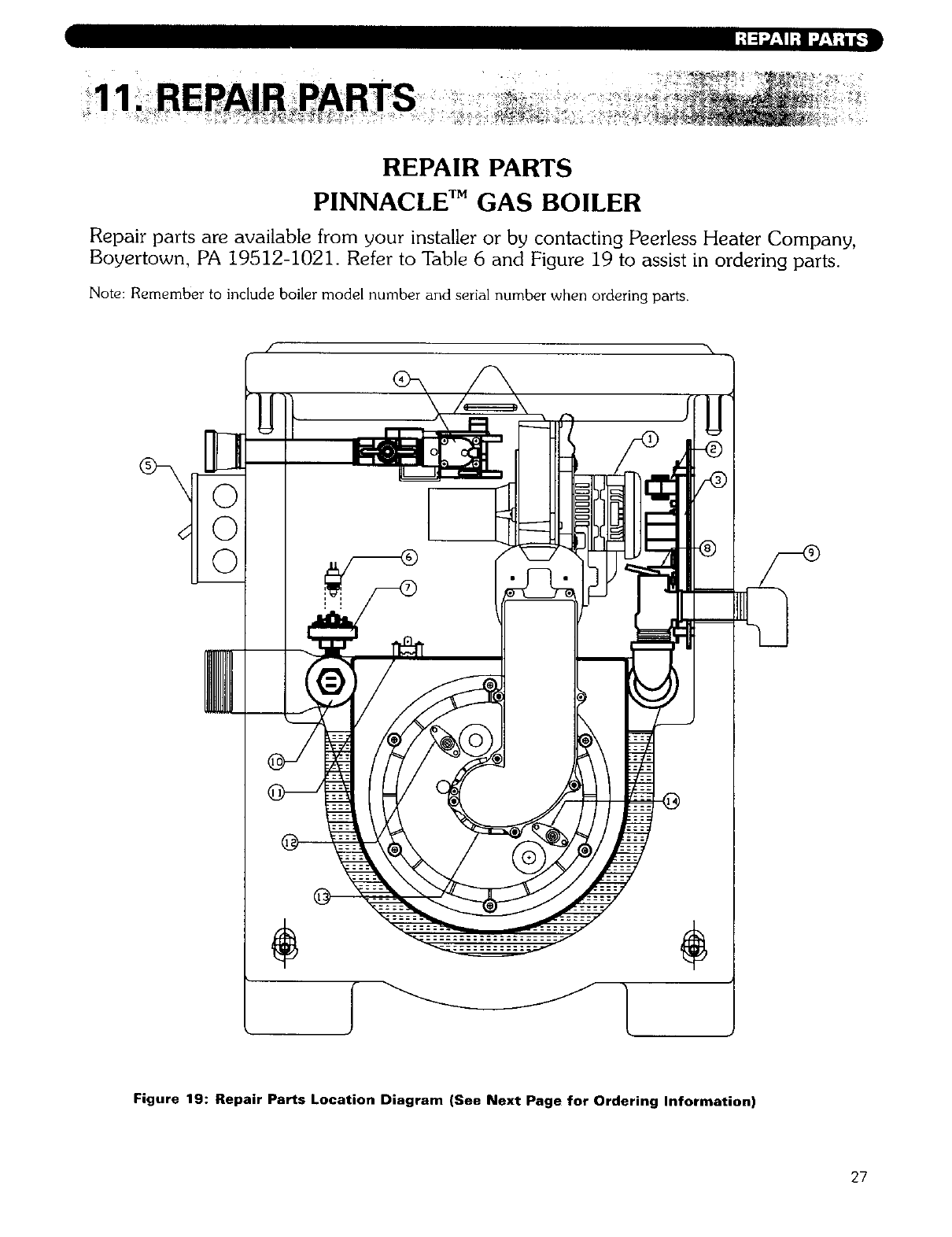
REPAIR PARTS
PINNACLE TM GAS BOILER
Repair parts are available from your installer or by contacting Peerless Heater Company,
Boyertown, PA 19512-1021. Refer to Table 6 and Figure 19 to assist in ordering parts.
Note: Remember to include boiler model number and serial number when ordering parts.
÷ ÷
Figure 19: Repair Parts Location Diagram (See Next Page for Ordering Information)
27

i;l :l'./flhl _I
Table 6: Repair Parts
I Blower 91423 91424 91425
2 Transformer
3 Control Board
4 Gas Valve
5 J/Box
6 Supply/Return Water Temperature Thermistor
7 Water Pressure Switch
8 Air Pressure Switch
I
9 { Relief Valve
l
10 High Limit Water Temperature Switch
I 1 ! Thermodisc Temperature Switch
91413 91413
91404 91405
91426 91426
!
91422 _ 91422
91427 i 91427
91428 91428
i
91430 91430
91410 ' 9i410 ]
91429 91429
91413
91406
91426
91422
91427
91428
91430
91410
9i429
. ÷
!2 ! Spark Electrode 91411 91411 91411
13 ' Main Burner (burner not vlslbie in view) i 91407 _ 91408 91409
14 Flame Sensor i 91412 | 91412 91412
28

Peerless Pinnacle T"
Stainless Steel Gas Boilers
Installation,
Operation f_
Maintenance
Manual
TO THE INSTALLER:
This manual is the property of the owner and must
be affixed near the boiler for future reference.
TO THE OWNER:
This boiler should be inspected annually by a
Qualified Service Agency.
CONTROLS
HIDivision ASME
otgama
Pr=-BRLB$S"
PINNACLE"
m m_m_r sv_amJ_s =rmaL m
PEERLESS HEATER COMPANY
231 NORTH WALNUT STREET •BOYERTOWN, PA 19512-1021 • PHONE 610-367-2153
www.peedess-heate_ corn
THE PREFERRED NU'lrINO CHOICE
©2003 Peerless Heater Company PI8008 R4 (1/03-2M)
Printed in U.S.A.