Work Method Statement Demolition Manual V1.2 Ref 324
User Manual: Pdf
Open the PDF directly: View PDF .
Page Count: 3
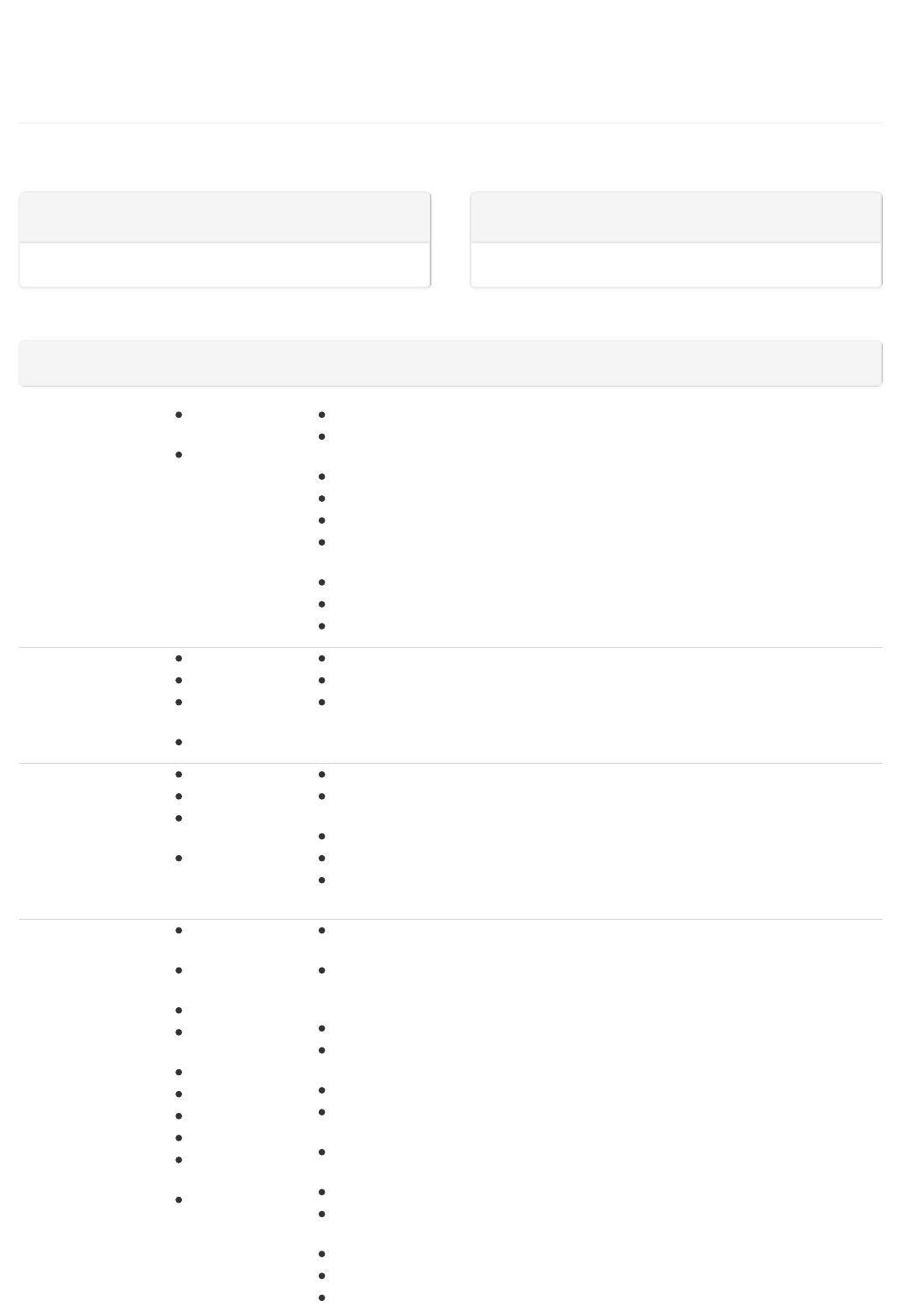
version 1.2
Project / Location: All Jobs
Safe Work Method Statement
Activity / Task: Demolition - ManualDemolition - Manual
Scott Bartley PlumbingScott Bartley Plumbing 43 KELVIN PDE
PICNIC POINT, NSW 2213
0418 204 151
scott@scottbartleyplumbing.com.au
Company:Company: Scott Bartley Plumbing
Signed by: Tanya Bartley Date: 03/08/2017
Principal Contractor:Principal Contractor: Modum Pty Ltd
Accepted by: Date:
StepsSteps Potential HazardsPotential Hazards Controls / Responsible Person(s)Controls / Responsible Person(s)
1. Access to site Slips, trips, falls and
accessibility.
UV light / weather
exposure.
Site specific induction. By: Scott Bartley PlumbingBy: Scott Bartley Plumbing
All “workers” to register before entering the site; to read the General Construction Safety Plan
signage; and to read the Site Specific Risk Assessment form. By: Scott Bartley PlumbingBy: Scott Bartley Plumbing
Tool box talk to highlight any WHS concerns relative to the site By: Scott Bartley PlumbingBy: Scott Bartley Plumbing
Ensure that site and work place access is unobstructed. By: Scott Bartley PlumbingBy: Scott Bartley Plumbing
Ensure all weather access to work areas. By: Scott Bartley PlumbingBy: Scott Bartley Plumbing
Wear appropriated PPE - hat, long sleeves, sun screen, sunglasses and fluids and reduce exposure
where possible. By: Scott Bartley PlumbingBy: Scott Bartley Plumbing
Provision of designated waste areas. By: Principal ContractorBy: Principal Contractor
Storage of materials in designated areas By: Scott Bartley PlumbingBy: Scott Bartley Plumbing
Regular site clean ups. By: Scott Bartley PlumbingBy: Scott Bartley Plumbing
2. Unloading plant,
equipment and
tools
Manual task injuries
Slips, trips and falls.
Proximity of other
“workers”.
Public access.
Team lifting and carrying. By: Scott Bartley PlumbingBy: Scott Bartley Plumbing
Training of “workers” in correct lifting and carrying methods. By: Scott Bartley PlumbingBy: Scott Bartley Plumbing
Unload and move the equipment to designated area to keep footpath / work place access clear.
By: Scott Bartley PlumbingBy: Scott Bartley Plumbing
3. Setting up
equipment
Manual task injuries
Slips, trips and falls.
Proximity of other
“workers”.
Public access.
Set up in a clear area and maintain a clear travel path. By: Scott Bartley PlumbingBy: Scott Bartley Plumbing
Training of “workers” in setting up of electrical leads and power tools and pneumatic tools. By:By:
Scott Bartley PlumbingScott Bartley Plumbing
Ensure proper use of all safety guards provided. By: Scott Bartley PlumbingBy: Scott Bartley Plumbing
Ensure that all power tools and electrical leads have current tagging. By: Scott Bartley PlumbingBy: Scott Bartley Plumbing
Ensure that all power tools are attached to a residual current device [RCD]. By: Scott BartleyBy: Scott Bartley
PlumbingPlumbing
4. Stripping of
external cladding
Slips, trips, falls and
accessibility
UV light / weather
exposure
Electrocution
Hazardous
materials
Exposure to dust
Exposure to noise
Manual task injuries
Cuts and abrasions.
Proximity of other
“workers”.
Public access.
Assess the site conditions and conduct a Site Specific Risk Assessment before commencing. By:By:
Principal ContractorPrincipal Contractor
Identify that the electrical service has been isolated and that ‘tiger tails’ are in place as protection
from overhead wires and points of attachment before commencing installation work. By: PrincipalBy: Principal
ContractorContractor
Provide “Demolition in Progress” and “Restricted Access” warning signage. By:By:
Establish a “No access area” to work areas by barricading to prevent access to the area of work.
Provide a ‘spotter’ where necessary. By: Scott Bartley PlumbingBy: Scott Bartley Plumbing
Identify any products or materials that may contain asbestos [ACM]. By: Scott Bartley PlumbingBy: Scott Bartley Plumbing
Ensure that the scaffolding is safe and erected by a qualified Scaffolder before commencing. By:By:
Principal ContractorPrincipal Contractor
Ensure that the scaffolding and edge protection is in place before commencing. By: Scott BartleyBy: Scott Bartley
PlumbingPlumbing
Correct use of ladder. By: Scott Bartley PlumbingBy: Scott Bartley Plumbing
Use appropriate PPE - safety glasses, footwear, noise / hearing protection, dust protection
[disposable], gloves and hard hats. By: Scott Bartley PlumbingBy: Scott Bartley Plumbing
Training of “workers” in the safe use of hand tools and power tools By: Scott Bartley PlumbingBy: Scott Bartley Plumbing
Systematic safe removal of materials. By: Scott Bartley PlumbingBy: Scott Bartley Plumbing
Team lifting and carrying. By: Scott Bartley PlumbingBy: Scott Bartley Plumbing
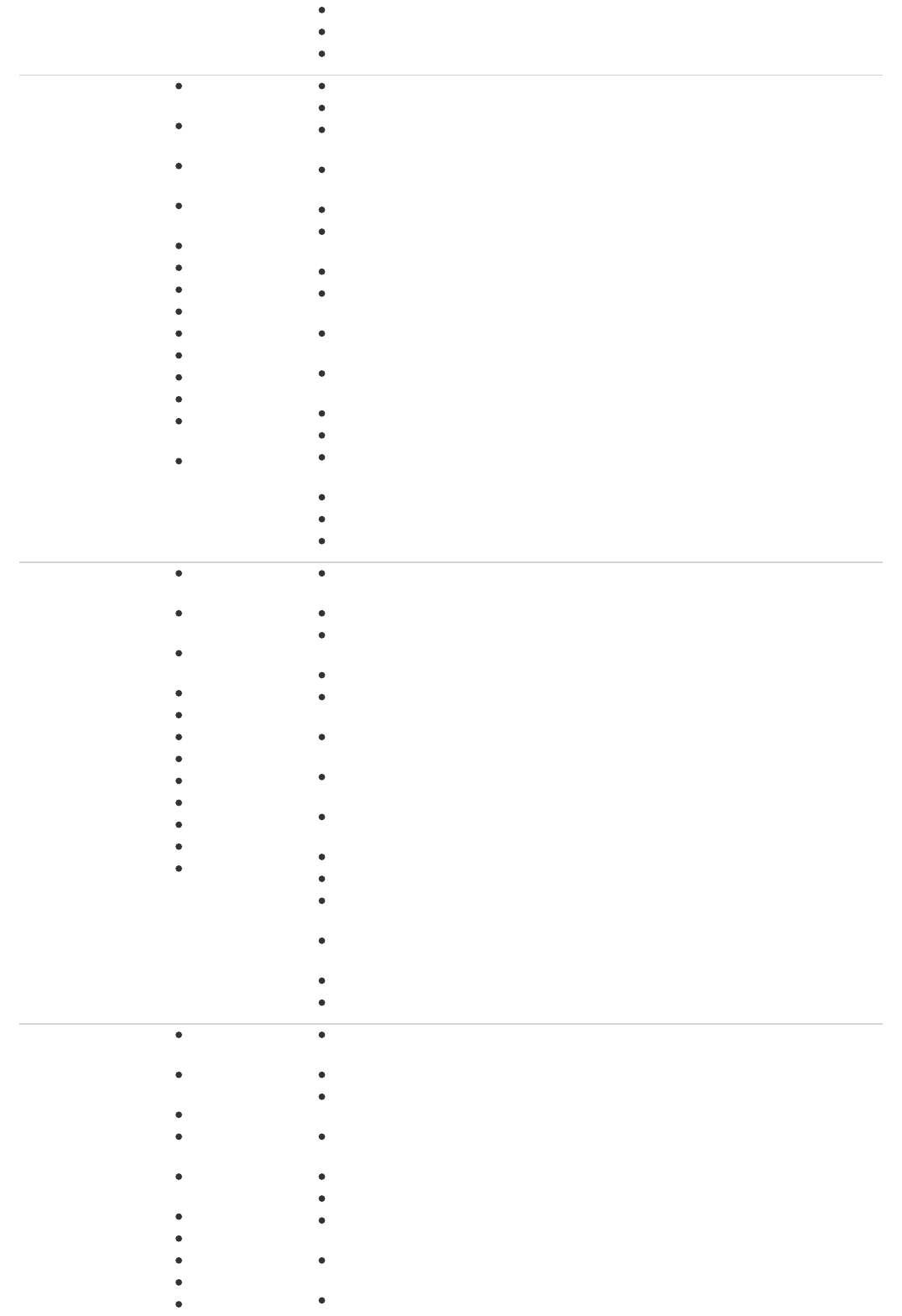
Storage of materials in designated waste areas By: Scott Bartley PlumbingBy: Scott Bartley Plumbing
Regular site clean ups. By:By:
Ensure materials are not stored on roof surface or scaffold. By: Scott Bartley PlumbingBy: Scott Bartley Plumbing
5. Demolishing of
ground floor by
hand
Slips, trips, falls and
accessibility.
UV light / weather
exposure.
Hazardous
materials.
Identification of
services.
Electrocution.
Gas explosions.
Falling objects.
Exposure to dust.
Exposure to noise.
Manual task injuries
Heavy lifting.
Cuts and abrasions.
Proximity of other
“workers”.
Public access.
Assess the site conditions and conduct a Site Specific Risk Assessment before commencing. By:By:
Identify any products or materials that may contain asbestos [ACM]. By: Scott Bartley PlumbingBy: Scott Bartley Plumbing
Identify services and make sure all electrical, gas, water and sewerage services have been isolated
or safely relocated before commencing. By: Scott Bartley PlumbingBy: Scott Bartley Plumbing
Use Licensed Electrician and Plumber to isolate, disconnect and relocate existing services. By:By:
Principal ContractorPrincipal Contractor
Provide “Demolition in Progress” and “Restricted Access” warning signage. By:By:
Establish a “No access area” to work areas by barricading to prevent access to the area of work.
Provide a spotter where necessary. By: Scott Bartley PlumbingBy: Scott Bartley Plumbing
Monitor air quality. By: Scott Bartley PlumbingBy: Scott Bartley Plumbing
Ensure that all exposed openings and voids in the floor are guard railed or covered. By: ScottBy: Scott
Bartley PlumbingBartley Plumbing
Use appropriate PPE – safety glasses, footwear, noise / hearing protection, dust protection
[disposable], gloves, and hard hats. By: Scott Bartley PlumbingBy: Scott Bartley Plumbing
Training of “workers” in the safe use of pneumatic and electrical power tools. By: Scott BartleyBy: Scott Bartley
PlumbingPlumbing
Systematic safe removal of materials. By: Scott Bartley PlumbingBy: Scott Bartley Plumbing
Team lifting and carrying. By: Scott Bartley PlumbingBy: Scott Bartley Plumbing
Provide shade cloth around work area and wet down dust as required to prevent wind borne dust.
By: Scott Bartley PlumbingBy: Scott Bartley Plumbing
Storage of materials in designated waste areas By: Scott Bartley PlumbingBy: Scott Bartley Plumbing
Regular site clean ups. By:By:
Ensure all exposed nails are removed. By: Scott Bartley PlumbingBy: Scott Bartley Plumbing
6. Demolishing
brickwork by
hand
Slips, trips, falls and
accessibility.
Hazardous
materials.
Identification of
services.
Electrocution.
Gas explosions.
Falling objects.
Exposure to dust.
Exposure to noise.
Manual task injuries
Heavy lifting.
Cuts and abrasions.
Proximity of other
trades.
Assess the site conditions and conduct a Risk Assessment before commencing. By: Scott BartleyBy: Scott Bartley
PlumbingPlumbing
Provide “Demolition in Progress” and “Restricted Access” warning signage. By: Principal ContractorBy: Principal Contractor
Establish a “No access area” to work areas by barricading to prevent access to the area of work.
Provide a spotter where necessary. By: Scott Bartley PlumbingBy: Scott Bartley Plumbing
Identify any products or materials that may contain asbestos [ACM]. By:By:
Identify services and ensure all electrical, gas, water and sewerage services have been isolated or
safely relocated before commencing. By:By:
Use Licensed Electrician and Plumber to isolate, disconnect and relate existing services. By:By:
Principal ContractorPrincipal Contractor
Use appropriate PPE - safety glasses, footwear, noise / hearing protection, dust protection
[disposable], gloves, and hard hats. By: Scott Bartley PlumbingBy: Scott Bartley Plumbing
Training of “workers” in safe use of pneumatic and electrical power tools. By: Scott BartleyBy: Scott Bartley
PlumbingPlumbing
Systematic safe removal of materials. By: Scott Bartley PlumbingBy: Scott Bartley Plumbing
Team lifting and carrying By: Scott Bartley PlumbingBy: Scott Bartley Plumbing
To upper floor areas provide a shute for materials into designated waste area as required. Provide
a spotter where necessary. By: Scott Bartley PlumbingBy: Scott Bartley Plumbing
Monitor air quality. Provide shade cloth around work area and wet down dust as required to
prevent wind borne dust. By: Scott Bartley PlumbingBy: Scott Bartley Plumbing
Storage of materials in designated waste areas By: Scott Bartley PlumbingBy: Scott Bartley Plumbing
Regular site clean ups. By:By:
7. Stripping of
existing roof
frame and
covering
Slips, trips, falls and
accessibility.
UV light / weather
exposure.
Fall from height.
Hazardous
materials.
Identification of
services.
Electrocution.
Gas explosions.
Falling objects.
Exposure to dust.
Exposure to noise.
Assess the site conditions including the weather and conduct a Site Specific Risk Assessment
before commencing. By: Scott Bartley PlumbingBy: Scott Bartley Plumbing
Identify any products or materials that may contain asbestos. By:By:
Identify services and ensure all electrical, gas, water and sewerage services have been isolated or
safely relocated before commencing. By:By:
Use Licensed Electrician and Plumber to isolate, disconnect and relate existing services. By:By:
Principal ContractorPrincipal Contractor
Training of “workers” in safe working at heights. By: Scott Bartley PlumbingBy: Scott Bartley Plumbing
Provide “Demolition in Progress” and “Restricted Access” warning signage. By: Principal ContractorBy: Principal Contractor
Establish a “No access area” below overhead work areas by barricading to prevent access to the
area of work. Provide a ‘spotter’ where necessary. By: Scott Bartley PlumbingBy: Scott Bartley Plumbing
Ensure that the scaffolding and edge protection is in place before commencing. By: Scott BartleyBy: Scott Bartley
PlumbingPlumbing
Correct use of ladder By: Scott Bartley PlumbingBy: Scott Bartley Plumbing
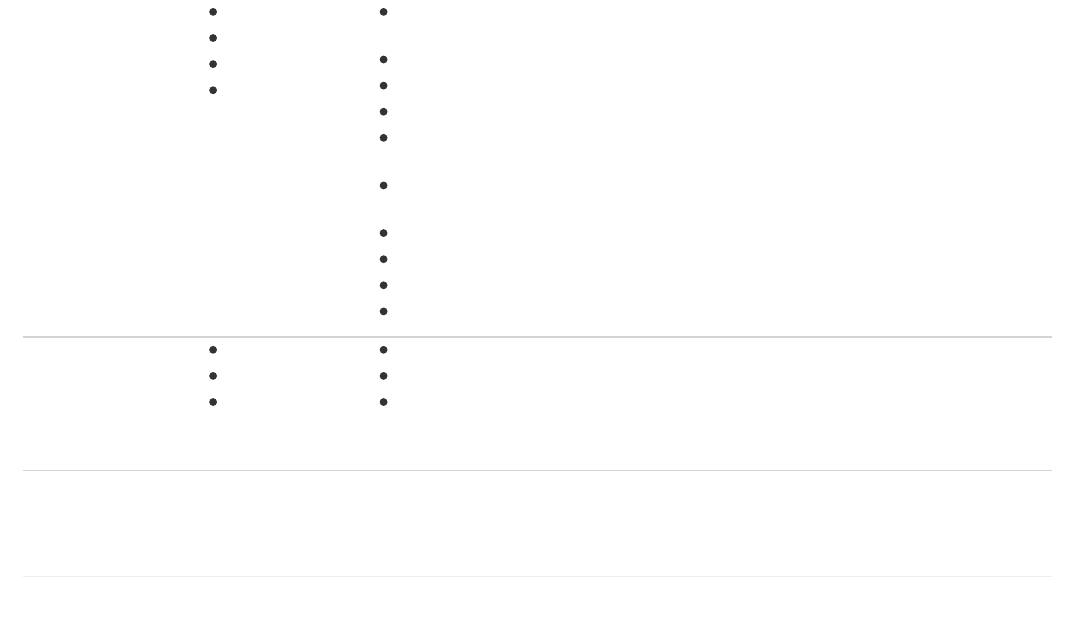
Manual task injuries
Heavy lifting.
Cuts and abrasions.
Proximity of other
trades
Use appropriate PPE - safety glasses, footwear, noise / hearing protection, dust protection
[disposable], gloves and hard hats. By: Scott Bartley PlumbingBy: Scott Bartley Plumbing
Training of “workers” in the safe use of hand tools and power tools. By: Scott Bartley PlumbingBy: Scott Bartley Plumbing
Systematic safe removal of materials. By: Scott Bartley PlumbingBy: Scott Bartley Plumbing
Team lifting and carrying. By: Scott Bartley PlumbingBy: Scott Bartley Plumbing
Provide a shute for materials into designated waste area as required. Provide a spotter where
necessary. By: Principal ContractorBy: Principal Contractor
Provide shade cloth / mesh around work area and wet down dust as required to prevent wind
borne dust. By:By:
Storage of materials in designated waste areas By: Scott Bartley PlumbingBy: Scott Bartley Plumbing
Regular site clean ups. By: Principal ContractorBy: Principal Contractor
Ensure all roof tarps are tied down and not weighted with tiles. By: Scott Bartley PlumbingBy: Scott Bartley Plumbing
Ensure materials are not stored on the roof or scaffold. By:By:
8. Site clean up on
completion of
work
Manual task injuries
Exposure to dust
Exposure to
hazardous
substances
Remove any temporary barricades if no longer required By: Scott Bartley PlumbingBy: Scott Bartley Plumbing
Place all rubbish / debris in designated waste storage area By: Scott Bartley PlumbingBy: Scott Bartley Plumbing
Leave site / work area in a clean and tidy condition By: Scott Bartley PlumbingBy: Scott Bartley Plumbing
Person responsible for ensuring compliance with SWMS:Person responsible for ensuring compliance with SWMS: SCOTT BARTLEY
Person responsible for reviewing SWMS control measures:Person responsible for reviewing SWMS control measures: SCOTT BARTLEY
Document Updated: 03/08/2017