HY GAIN T 2XDX ROTATOR
User Manual: Pdf HY-GAIN--T-2XDX-ROTATOR
Open the PDF directly: View PDF .
Page Count: 35

TAILTWISTER-D
ROTATOR SYSTEM
INCLUDING THE DCU-1 "PATHFINDER"
DIGITAL CONTROL UNIT
ORDER NO.
303-D - 120 VAC 50/60 Hz
303-D-2 - 220 VAC 50/60 Hz
NOTICE:
All rights in this publication are reserved. No part of the
publication may be reproduced in any manner whatsoever
without the expressed written permission of Hy-Gain.
TABLE OF CONTENTS
Page CHAPTER 1 - Installation and Operation .....................................................................................1-1
Section 1. Components of the T2X-D...............................................…................................................. 1-1
General.............................................................……............................................................................... 1-1
Section 2. Specifications........................................…......….....……...................................................... 1-2
Section 3. Precautions...............................................….......................................................................... 1-4
Section 4. Installation Preparations..............................…....................................................................... l-5
Types of Installations............................................................................…….......................................... 1-5
Precautions...................................................................................................……................................... 1-8
Section 5. Wiring and Check-Out.......................................................................…................................ 1-9
Section 6. Installing the Rotator.............................................................................….......................... 1-11
Inside Tower Mount.................................................................................................…….................... 1-11
Outside Tower Mount................................................................................................…....…............... 1-13
Mast Mount...............................................................................................................…….................... 1-13
Section 7. Optional Accessory Kits ...............................................................................….................. 1-14
Section 8. Operation of DCU-1 Pathfinder Control Unit............:..............................……………….. 1-15
Precautions..................................................................................................................……................. 1-15
Normal Operation ......................................................................................................…….................. 1-15
Computer Operation.........................................................................................................……............ 1-16
Section 9. Troubleshooting..............................................................................................…................. 1-18
Ground Wires...............................................................................................................……..................1-19
Antenna Motion ...........................................................................................................……................ 1-19
Lack of Power..............................................................................................................……..................1-19
Checking the Control Unit Voltages............................................................................……................. 1-20
Checking the Rotator Resistances from the Ground..................................………………………....... 1-20
Section 10. Disassembly of the Rotator Unit....................................………………....….................... 1-21
Spur Gear Assembly ....................................................................................................……................ 1-22
Section 11. Reassembly of the Rotator.........................................................................….................... 1-23
Section 12. T2X Rotator Replacement Parts....................................................................................... 1-24
Section 13. DCU-1 Control Unit Block Diagrams.................................................……….…………..1-29
Section 14. DCU-1 Control Unit Replacement Parts List................................................…………… 1-30
Section 15. How To Get Factory Service.................................................................…........................ 1-32
Warranty ............................................................ .................................................…........................ 1-33
LIST OF ILLUSTRATIONS
1. Front View .............................…………………............................................................................... 1-3
2. Back View...........................................................…………………...…............................................ 1-3
3. Rotator Mounted Inside .................................................................…………………........................ 1-5
4. Rotator Mounted on Tower Top Plate ………………...................................................................... 1-6
5. Pole Mounted Rotator..................................................…………………......................................... 1-7
6. Control Cable Connector Attachments .................................................……………….................... 1-9
7. DCU-1 Display ...............................................................………………….................................... 1-10
8. Rotator Mounting in a Tower....................................................................…………………........... 1-11
9. Rotator Mounting with (optional) Lower Mast Support.………………........................................ 1-14
10. Wiring Guide ........................................................................................……………....................... 1-15
11. Command Set..........................................................................................................……………..... 1-16
12. Sample Program............................................................................……………............................... 1-17
13. Spur Gear Assembly .......................................................................................…………................ 1-22
14. Inside View of T2X Rotator.............................................................................……………............ 1-25
15. BrakeAssembly and Terminal Board Wiring Detail........................………….............................. 1-26
16. T2X Rotator-Illustrated Parts Breakdown ......................…………............................................... 1-28
17. Front Panel PCB, Block Diagram.............................…….............................................………..... 1-29
18. Control PCB and External Components, Block Diagram…………………….................. 1-29
LIST OF TABLES
Table Pag
e
1 Control Cable...................................................................................................... 1-9
2 Troubleshooting..................................................................................................1-18
3 Control Unit Voltages........................................................................................ 1-20
4 Rotator Resistances............................................................................................1-20
CHAPTER 1 INSTALLATION AND
OPERATION
Section 1. Com
p
onents of the Tailtwister - D
General Descri
p
tion
The Tailtwister - D rotator system consists of an
extra heavy duty rotator and the new DCU-1
"Pathfinder" digital control unit. The rotator is
designed to be mounted on a plate inside a
communications tower, and is attached to a
vertical steel antenna mast. This is the
recommended mounting method. The DCU-1
control unit must be installed indoors and
connected to the rotator by an 8 conductor cable.
The Tailtwister-D rotator system consists of the
following main components:
P/N 5137701 T2X Rotator Assembly
P/N 870804 DCU-1 Control Unit Assembly (120
VAC)
P/N 870842 DCU-1 Assembly Control Unit (220
VAC)
The DCU-1 "Pathfinder" digital control unit fea-
tures 6 memory presets, automatic brake delay (8
seconds), automatic motor slowdown (last 5
degrees), automatic motor control on startup,
programmable center of rotation, full circle
analog display of current and target bearings,
digital display of current and target bearings,
automatic display blanking of target bearings ( 30
seconds ), automatic display blanking (30
minutes), RS-232 control with pass-through, and
an 8 pin socket for the control cable.
The Tailtwister rotator features low temperature
operation (-30 deg. F/ -34 deg. C, a weatherproof
AMP connector with gold-plated contacts, an im-
proved high-strength steel drive gear, RF beads
on the potentiometer lines, wedge brake, and safe
26 volt operation.
The rotator unit must be connected to the control
unit with an 8-wire cable. You may assemble
your own cable from the information supplied in
this manual, or you may purchase pre-assembled
cables from a dealer.
It is recommended that you use this rotator
system with compatible antennas and towers. For
example, the maximum antenna size for this
system is 20 sq. ft. (1.86 sq. m). Therefore, if you
anticipate using antennas near this limit, the
tower system should also be rated for wind areas
of this magnitude. If you are considering
antennas with long booms and/or long elements,
do not exceed the Effective Moment specification
of 3400 ft. lb. (470 Kg. m.). EM is defined as the
antenna turning radius times weight. Antennas
with long booms and elements have much more
angular momentum and exert more torque on
rotator systems than antennas with shorter booms
and equal areas.
O
p
tions:
The optional heavy-duty lower mast support kit
must be used if you elect to use a mast mount
(see Figures 5 and 9). The part number for this
kit is 51467 10. When using the lower mast
support, the antenna size is restricted to 10
square feet of wind area. The "inside tower
mount" configuration is recommended (see
Figure 3).

Section 2. Specifications

DCU.1 Di
g
ital Control Unit:
Siz
Control Unit
Display:
Type
Scale
Display Life
Memory Presets
Rotation Center Brake
Delay
Front Panel
Controls
Rear Panel
Items
8.5"x4.3"x9.0" (WxHxD)
(21.6x 11.0 x22.8 cm)
Gas Plasma, Amber filter
5 degree (Analog), 1 degree (Digital) Target
Bearing ( 30 seconds)
Total ( 30 minutes after no activity) 30,000
to 40,000 hours
6, independently programmable User
selectable, 0 - 360 degrees 8 seconds,
fixed
-momentary reverse direction on startup
-automatic stop if no rotator movement detected in 8 seconds -motor
pulse (half-cycle)on last 5 degrees before stop,
1 Knob ( 24 pos. digital encoder) - sets
target bearing
- sets center of rotation in calibrate mode 6
Memory Preset (pushbuttons)
1 Start Rotation (pushbutton) -also starts
EPC (calibration) 1 Stop Rotation
(pushbutton)
1 Display (pushbutton)
- turns on display after blanking - enters
calibration mode
1 8-pin socket (rotor cable) 1 RS-232
Host (DB9F)
1 RS-232 Ext. (DB9M)
1 ground terminal (1/4"-20) 1 fuse
holder
1 Power Cord, 3 wire ,
Section 3. Precautions
Towers and antennas require caution during erec-
tion and placement! Extreme care must be taken
during erection so that metal tower and antenna
parts DO NOT contact power lines, even if the
p
arts sli
p
, rotate, retract, fall or fracture!
Antenna position mechanisms (towers and
rotators) must be placed so that if they fail, the
parts of the antenna system cannot contact power
lines, be a hazard to individuals, or endanger
property.
Metal towers must be grounded properly at the
tower location before the tower is erected. This is
to minimize electrical hazard and the possibility
of lightning damage. DO NOT bury bare
aluminum wires or stakes in the ground. Use
copper or copper-clad ground stakes. The service
entrance ground should be checked. The
household convenience outlet should be the 3-
prong type (grounded back to the service
entrance
)
.
The DCU-1 Control Unit is not weatherproof and
must be located in a house or other protected
location. Do not allow the ambient temperature
to exceed 130°F. Connect a ground wire to the
1/4"-20 terminal on the back of the DCU-1.
NOTE: This equipment has been tested and found
to comply with the limits for a Class B digital
device, pursuant to part 15 of the FCC Rules.
These limits are designed to provide reasonable
protection against harmful interference in a
residential installation. This equipment generates,
uses and can radiate radio frequency energy and
if not installed and used in accordance with the
instructions, may cause harmful interference to
radio communications. However, there is no
guarantee that interference will not occur in a
particular installation. If this equipment does
cause harmful interference to radio or television
reception, which can be determined by turning
the equipment off and on, the user is encouraged
to try to correct the interference by one or more
of the followin
g
measures:
- Reorient or relocate the receiving antenna.
- Increase the separation between the
equiment and receiver.
- Connect the equipment into an outlet on a
circuit different from that to which the
receiver is connected.
- Consult the dealer or an experienced
radio/TV technician for help.
The Tailtwister-D rotator system has been
carefully designed and manufactured to give
many years of trouble-free service when
carefully and professionally installed. It
consists of the strongest and best commercially
available components. This product is
manufactured in the U.S.A.

Section 4. Installation Pre
p
arations
T
yp
es of installations:
There are three general types of rotator
installations (see Figures 3, 4, and 5 ).
1. The recommended installation is an "inside"
tower mount with a thrust bearing or bushing
to provide vertical and horizontal support.
The thrust bearing should mount on the top
surface of the tower and should fit the size of
mast
y
ou are usin
g
.
The rotator shelf should be at least three (3) feet
below the thrust bearing. If a single antenna is
mounted on the mast, it should be no more than
one (1) foot above the thrust bearing. The thrust
bearing should be of commercial manufacture
and should properly fit the tower that it is
attached to. If your installation follows these
guidelines, this rotator system will easily handle
an antenna system of 20 sq. ft. wind area or EM
of 3400 ft. lb.
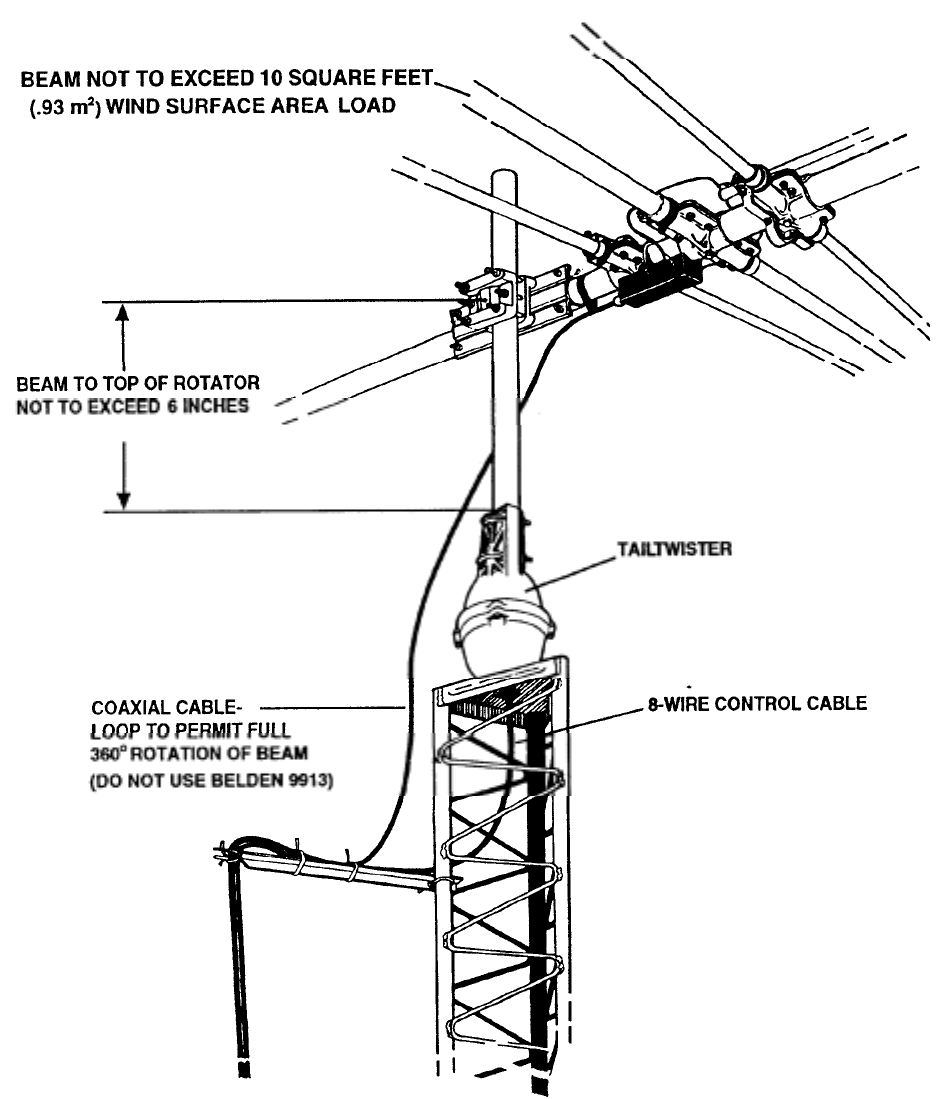
2. An "outside" tower mount may be used when
the rotator unit will not fit within the tower, or
there is no rotator shelf provided. In this
installation, the rotor mounts on a flat plate at
the top of the tower. There is no thrust
bearing.
In this application, it is extremely important that
the antenna is mounted no more than six (6)
inches above the top of the rotator. If these
guidelines are followed, the rotator system will
easily handle a single antenna with a 10 sq. ft.
wind area or EM of 1500 ft. lb.
Figure 4 Rotator Mounted on Tower
To
p
Plate
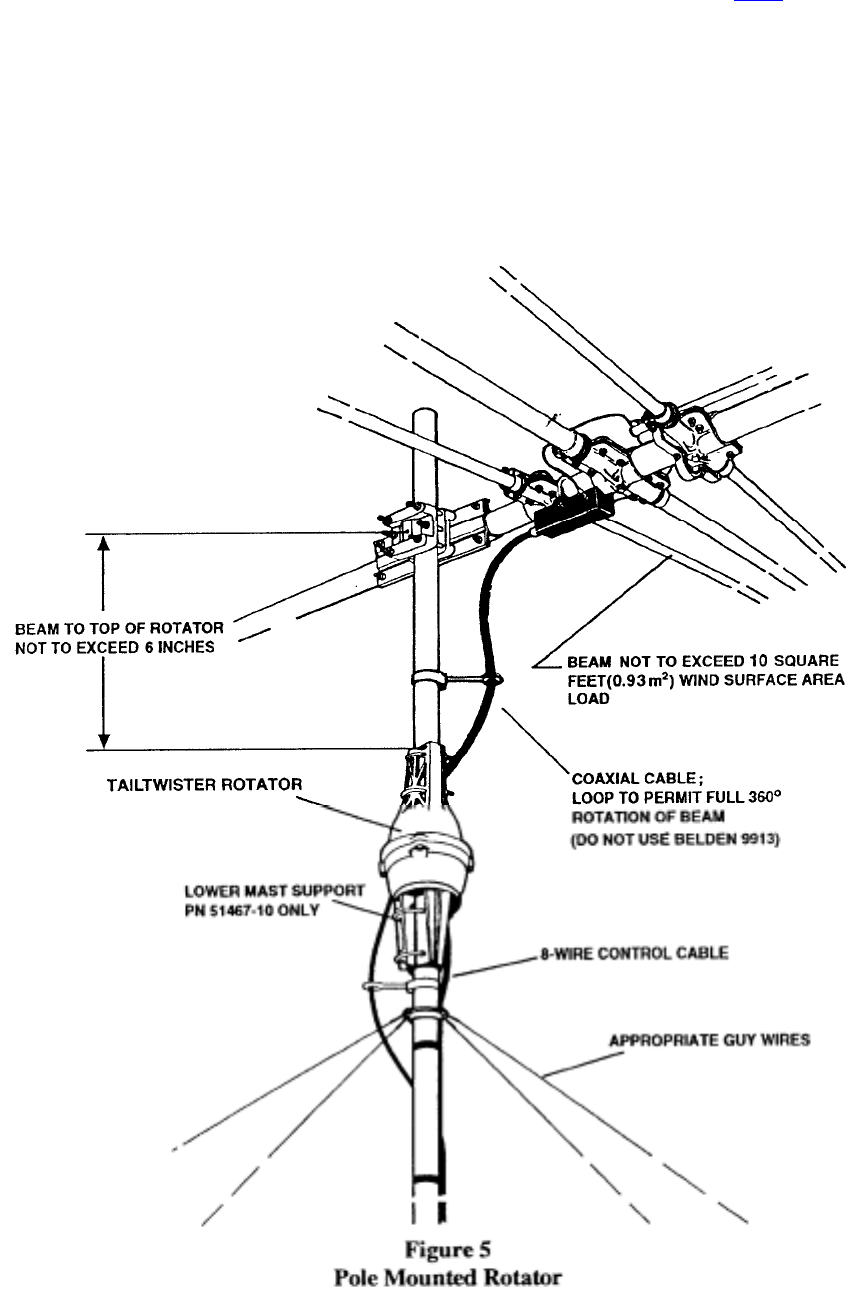
If these guidelines are followed, the rotator system
will easily handle a single antenna with a 10 sq. ft.
wind area or EM of 1500 ft. lb. Ensure that the
mast is also rated for this load!
There are variations of mounting which fall
generally into one of the above categories. For
example, the rotator may be mounted much lower
in the tower than described. In this case, more than
one mast bearing may be required.
3.A telescoping or other type mast may also be
used. This installation requires the optional
"Heavy Duty Lower Mast Support Kit". In this
application, it is extremely important that the
antenna is mounted no more than six (6) inches
above the top of the rotator.
Precautions
1. Unbalanced weight: Weight should be as
closely balanced as possible. Unbalanced
weight in an antenna creates a bending
moment of force which is concentrated on the
mast at the point where it is clamped to the
rotator.
2. Wind Pressure: Balanced wind pressure
against the antenna system produces a
bending force on the mast which can cause the
same stresses as unbalanced weight. To
minimize these forces, a thrust bearing should
be used where possible, the antenna should be
as close to the top of the tower as possible and
the rotator shelf should be as low as
p
ossible.
3. Unbalanced Wind: If the antenna has unequal
wind areas and element spacings on each side
of the mast attachment point, it could produce
torque on the support mast. This is similar to
the principle of a weather vane. If the
unbalance is high enough or the wind velocity
is high enough, this could prevent rotation or
could damage the limit switches. To minimize
this effect, the antenna should be designed for
minimum mast torque or "torque
compensators" added to produce minimum
mast torque.
4. Mast Binding: If the antenna support mast
binds within the tower due to ice accumulation
or other reasons
,
this could
p
revent rotation.
5. Extreme Cold: If the ambient temperature is at
or below -30 degrees F, this could prevent
rotation. If no movement is detected within 8
seconds of pressing "START", then the rotator
will stop.
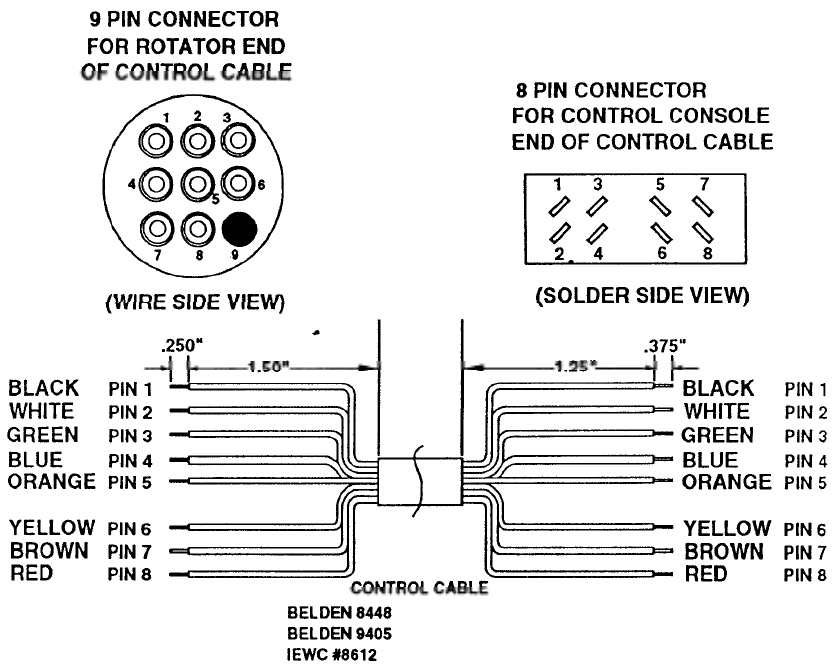
Section 5. Wiring and Check-Out
Wirin
g
and Check-Out
1. Determine the length of control cable
required and find the wire gauge (size)
required from Table 1.
Maximum Gauge for Gauge for
'CAUTION
Shorts between terminals or grounded leads
may damage the rotator. Check the numbered
pins on each connector with an Ohmmeter. Pin 1 is
connected to pin. l: etc
125' (38 m) 200'
(61 m) 300' (91 m)
Recommended
Cables Belden 8448
Belden 9405 IEWC
#8612
NOTE: The specifications call for heavier gauge
wire in two locations. Leads #1 and #2 must be
heavier
g
au
g
e and less total lead resistance.
2. Assemble the rotator cable as shown in
Fi
g
ure 6
,
or
p
urchase a
p
re-assembled cable.
#18 (1.19 mm) #20 (.97 mm)
#16
(
1.42 mm
)
#18
(
1.19
TABLE 1
3. Temporarily attach the 6 screws, 5/16" - 18 x
15/8", to the bottom of the rotor unit. These
will be used to support the rotator during
bench-testin
g
.
4. With the rotator sitting in the upright position
and connected to the control unit by the 8-
wire cable; plug the control unit power cord
into a receptacle. At this time, the rotator
brake wedge may momentarily release and
re-engage. This is normal.
Figure 6 Control Cable Connector
Attachments

5. The DCU-1 display should look similar to the
display shown in Figure 7. The numeric
display in the lower left corner indicates the
current bearing of your rotator. The numeric
display in the lower right corner indicates the
target bearing. If both displays read a steady
"000", disconnect your control cable and
check the cable wirin
g
with an ohmmeter.
NOTE: After approximately 30 to 45 seconds of
inactivity, the target digital and analog displays
will blank (disappear). After 30 minutes of
inactivity, the entire display will blank. Push the
"DISPLAY" button to return normal dis
p
la
y
.
6. If the current bearing display shows a number
between "001" and "359", then proceed. Twist
the knob marked with the two (2) arrows
The target bearing display should change
along with the inner circle tick mark. Using
the knob, select a target bearing at least 30
degrees from the current bearing. Push the
"START" button. The brake in the rotator
should release, the rotator will turn a few
degrees in the opposite direction, reverse
direction, then turn to the target bearing.
During the last 5 degrees, the rotator will slow
down to half speed, then stop on or close to
the target bearing. The brake solenoid will
"hum" for 8 seconds, then the brake will
engage. During rotation, the outer circle tick
mark will move to the new bearing.
8. Decide on the mechanical center of rotation at
this time. For example, if you would like to
rotate from East to West through South, then
South (180 degrees) is your center of rotation.
The center of rotation can be selected as any
bearing between "000" and "359". Press "DIS-
PLAY" and hold until the letters "CAL"
appear in the center of the display. The rotator
should automatically turn to the mechanical
center of rotation. When it has reached this
position, the letters "SET" should appear in
the center of the display. Twist the knob until
the desired center of rotation is displayed in
the lower right corner.
Press the "START" button and hold until the
rotator starts to turn. The rotator will automat-
ically find both limit switches and set up the
calibration for the center of rotation you
selected. During this time, the letters "EPC"
will be displayed for "End Point Calibration".
When this process is finished, the "EPC" will
disappear, and the rotator is ready for use. If
you wish, you may re-calibrate the rotator
system at any time.
9. You may set the memory presets at this time
or at any time after the rotator system has
been installed. To store a bearing into a
memory location, select a target bearing with
the knob then press and hold the appropriate
memory location button until the letters
"PRE" lights up. You may use previously
stored memory presets and the knob to select
new bearings.
7. You may wish to repeat step 6 to confirm
operation over a wide range of bearings. If the
"STOP" button is depressed during rotation,
rotation will stop and the brake wil I engage 8
seconds later. If the operation is consistent,
proceed to the next step.
10. Rotate the system to the center of rotation.
You are now ready to install the rotator
s
y
stem in
y
our tower or on
y
our mast.
Figure 7 DCU-
1 Display 1-10
3. Attach the control cable to the rotator connector
as before. Using the DCU-1 control unit, turn
the rotator and observe rotator movement. If
everything works properly, secure the cable to
the tower using proper strain-relief techniques.
6. Turn the rotator using the DCU-1 control.
Observe mast movement throughout full 360
degree rotation. If any binding occurs, reposition
the rotator on the flat plate and retighten the
mounting bolts.
4. Assemble the mast to the rotator using the U-
bolts, nuts, lockwashers, and clamp plate as
shown in Figure 8. Apply a coating of heavy-
duty motor oil or grease to the threads of the
stainless steel bolts and U-bolts to prevent seiz-
in
g
. Do not ti
g
hten at this time.
5. Center the mast within the tower thrust bearing
and secure the thrust bearing to the mast. Turn
the mast by hand to check for binding within the
tower. Adjust the thrust bearing if required. If
no binding occurs, then tighten the rotator U-
bolts to secure the mast to the rotator. Install
and tighten the center mast bolt at this time. See
Figure 8.
7. Position the rotator to the center of rotation using
the DCU-1 control unit. Attach the directional
antenna so that it points the same direction. The
coaxial cable should be attached to the mast and
tower so that the rotator can freely move in both
directions to the ends of rotation. The coaxial
cable should be flexible enough to permit
rotation without damage. Do NOT use Belden
9913 cable in this rotation loop!
CAUTION:
Do not use masts with an O.D. less than 17/8"
with a thrust bearing! It is important that the
rotator does not try to turn the mast
eccentrically within the top thrust bearing.
Outside Tower:
Mast mount:
The rotator is mounted to the top surface of a
tower, see Figure 4, by means of six (6) bolts
furnished in the hardware kit. Use the following
p
rocedure:
1. Position the rotator on the top surface of the
tower or other support structure and attach by
means of six (6) bolts and lockwashers. The
top of the tower must be cut out to allow the
connecting 8-wire cable with connector to
pass through the plate. If a new hole must be
made, use the template in the back of this
manual. Ti
g
hten the six
(
6
)
bolts.
2. Attach the control cable to the rotator
connector as before. Using the DCU-1 control
unit, turn the rotator and observe rotator
movement. If everything works properly,
secure the cable to the tower using proper
strain-relief techni
q
ues.
3. Assemble the mast to the rotator using the U-
bolts, nuts, lockwashers, and clamp plate as
shown in Figure 4. Apply a coating of heavy-
duty motor oil or grease to the threads of the
stainless steel bolts and U-bolts to prevent
seizin
g
. Ti
g
hten all bolts securel
y
.
4. Position the rotator to the center of rotation
using the DCU-1 control unit. Attach the
directional antenna so that it points the same
direction. The coaxial cable should be
attached to the mast and tower so that the
rotator can freely move in both directions to
the ends of rotation. The coaxial cable should
be flexible enough to permit rotation without
damage. Do NOT use Belden 99.13 cable in
this rotation loop!
The rotator is mounted to a vertical mast, see
Figures 5 and 9, by means of four (4) bolts and
the optional lower mast support, PIN 5146710.
Use the following procedure:
l. Attach the rotator to the lower mast support
by means of four (4) bolts, nuts and
lockwashers. Tighten the four (4) bolts.
Attach this assembly to the top of the mast as
shown in Fi
g
ure 5. Ti
g
hten all bolts securel
y
.
2. Attach the control cable to the rotator
connector as before. Using the DCU-1 control
unit, turn the rotator and observe rotator
movement. If everything works properly,
secure the cable to the mast using proper
strain-relief techniques.
3. Assemble the top mast to the rotator using the
U-bolts, nuts, lockwashers, and clamp plate
as shown in Figure 8. Apply a coating of
heavyduty motor oil or grease to the threads
of the stainless steel bolts and U-bolts to
prevent seizing. Tighten all bolts securely.
4. Position the rotator to the center of rotation
using the DCU-1 control unit. Attach the
directional antenna so that it points the same
direction. The coaxial cable should be
attached to the mast and tower so that the
rotator can freely move in both directions to
the ends of rotation. The coaxial cable should
be flexible enough to permit rotation without
daniage. Do NOT use Belden 9913 cable in
this rotation loo
p
!
NOTE: Belden 9913 Coax has a solid center
conductor and an air-space dielectric. It is not
flexible enou
g
h to use in a rotation loo
p
.
CAUTION:
This rotator is designed for vertical
operation with the bell-shaped housing
pointing straight up. Do not mount this unit
either horizontally or upside down.
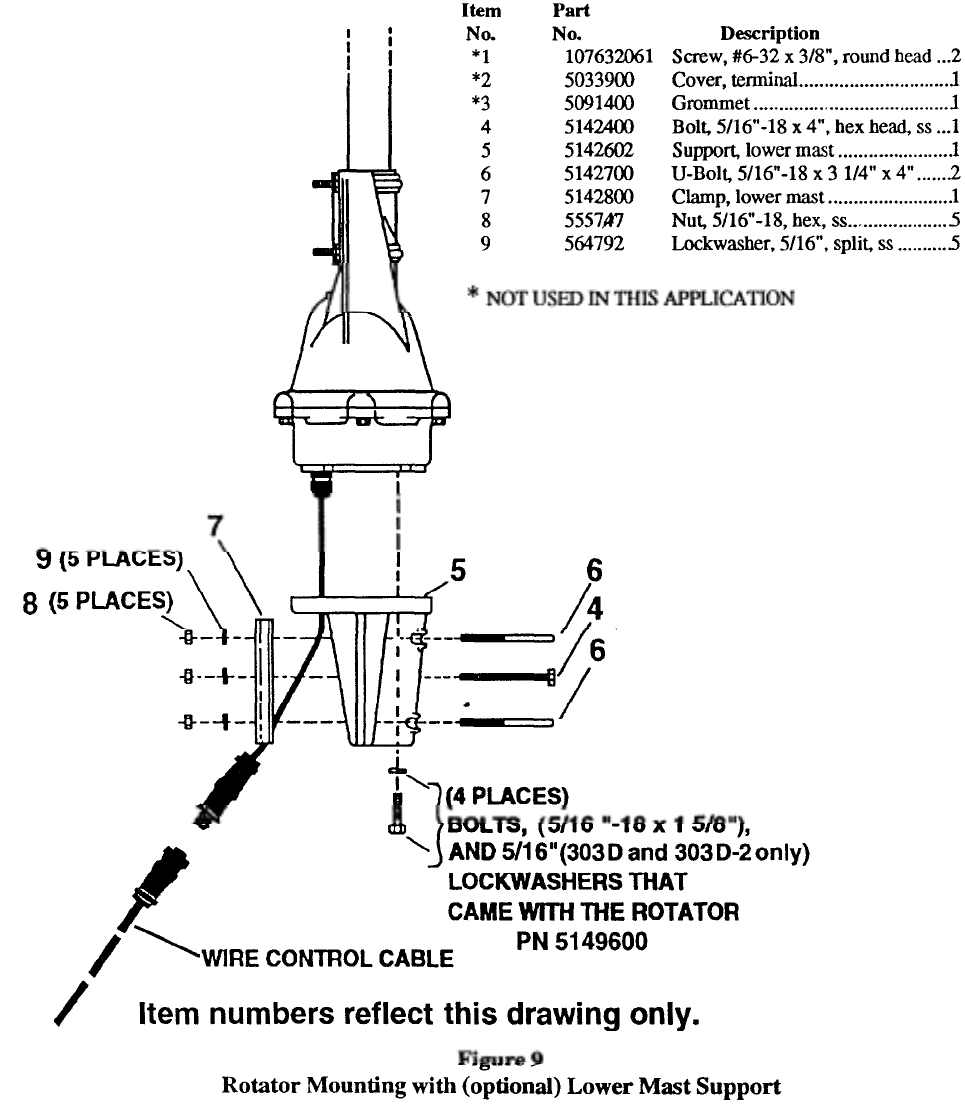
Section 7. O
p
tional Accessor
y
Optional Heavy-Duty Lower Mast Support
Kit PN 5146710
This kit contains a heavy-duty lower mast
support and the necessary hardware to facilitate
mounting the rotator on a mast.
CAUTION:
When the rotator is installed using the
lower mast support kit, the antenna size
must be restricted to 10 square feet (0.93 sq.
m.) of wind surface area.

Section S. Operation of DCU-1 Control Unit
O
p
eration of DCU-1 Control Unit
Precautions:
1.Thermal Protection: If the rotator fails to turn
after 4 or 5 minutes of continuous operation,
the thermal switch has come into play. This
protective device in the transformer assembly
automatically shuts off power if the
transformer becomes too hot. It will
automatically reset after approximately 10
minutes.
2. Display Protection: The gas-plasma display
will be turned off during periods of inactivity
to extend its useful life. After approximately
30 to 45 seconds of inactivity, the target
digital and analog displays will blank
(disappear). After 30 minutes of inactivity, the
entire display will blank. Push the
"DISPLAY" button to return normal dis
p
la
y
.
3. Brake Wedge Protection: The brake wedge
will only engage after waiting eight seconds
after removing power from the motor. This
allows large antenna systems to coast to a
complete stop before engaging the brake. Even
if the "STOP" button is pressed, the system
will still wait eight (8) seconds before
dropping the brake. The brake will
immediately engage if AC power is
disconnected from the control unit.
Normal O
p
eration
The numeric display in the lower left corner and
the outer circle tick mark always indicates the
current bearing of your rotator. The numeric
display in the lower right corner and the inner
circle tick mark indicates the target bearing. This
display is also used during calibration to select
the center of rotation. The center alpha-numeric
display is used during the calibrate routine and to
indicate memory preset selections. The tick marks
may fluctuate between two marks if the rotator is
moving in the wind and the digital bearing ends
with "2" or "T'.
To move the rotator to a new bearing, either the
knob, memory presets, or a combination of these
may be used to select the new bearing. To start
rotation to this new bearing, press "START". The
brake in the rotator will release, the rotator will
turn a few degrees in the opposite direction,
reverse direction, then turn to the target bearing.
During the last 5 degrees, the rotator will slow
down to half speed, then stop on or close to the
target bearing. The brake solenoid will stay on for
8 seconds, then the brake will engage. During
rotation, the outer circle tick mark will move to
the new bearing.
If the "STOP" button is pressed during rotation,
rotation will stop and the brake will engage 8
seconds later.
To store a bearing into a memory location, select
a target bearing with the knob then press and hold
the appropriate memory location button until the
letters "PRE" light up. These pre-sets are stored
in nonvolatile memory and will stay in memory
even if the unit loses power. You may use
previously stored memory presets and the knob to
select new bearin
g
s to store.
NOTE: The rotator may end up a few degrees off
the desired target bearing. This is because the
brake wedge locks into place every six (6)
degrees. This should not cause any problems in
m
os
t HF
a
n
d
V
HF in
s
t
a
ll
a
ti
o
n
s.
Com
p
uter O
p
eration
The DCU-1 may be controlled from your
computer via a RS-232 cable connection. The
rear panel has two (2) RS-232 connectors. The
connector marked "HOST" is a DB9 female
connector and should be directly connected to the
host computer. Do not use a null-modem
connection. The connector marked "EXT" is a
DB9 male connector and should be connected to
other ham equipment such as a modem, TNC, or
radio interface unit. If the "EXT" connector is not
attached to other equipment, it should be
terminated with the supplied plug. The supplied
termination plug shorts DTR,DSR and DCD
(Pins 4, 6, 1) together and RTS and CTS (Pins 7
and 8
)
to
g
ether.
The cable which is attached to the computer and
to the DCU-1 should have a DB9 male connector
at one end and either a DB9 female or DB25
female connector at the other end. The
connections should be straight through, e.g. pin 1
to pin 1, pin 2 to pin 2, etc if both ends have 9 pin
connectors. If a DB25 female connector is used
to attach to the computer's COMI or COM2 port,
use the wiring guide shown in Figure 10. You
may also purchase a pre - assembled cable from
Hy-Gain to connect your computer to the DCU-1.
Order either DCU-9P or DCU-25P cable
assemblies.
Figure 11
Command Set
Signal Name DB9 pin DB25 pin
DCD Data Carrier Detect 1 8
RX Receive Data 2 3
TX Transmit Data 3 2
DTR Data Terminal Ready 4 20
GND Signal Ground 5 7
DSR Data Set Ready 6 6
RTS Request to Send 7 4
CTS Clear to Send 8 5
RI Ring Indicator 9 22
Figure 10
Wiring Guide
Command: Result:
API***; Sets Target Bearing in
DCU-1 (***is a three digit number between 000 and 359)
AM1; Starts Rotation to Target Bearing
Resets system after any previous
command

A sample BASIC program is shown in Figure 12
which can be used to control operation of the
DCU-1. Other software vendors may also include
the ability to directly control the DCU-1 from
within a lo
gg
in
g
or ri
g
control
p
ro
g
ram.
The commands are similar to those used by Ken-
wood in controlling radio operations. A summary
of unique commands is shown in Figure 11. The
COM port should be used at 4800 baud with No
parity, 8 data bits, 1 stop bit and ASCII mode.
This is usuall
y
shown as "4800
,
N
,
8
,
1
,
ASC".
After a command is sent to the DCU-1, all other
motor and brake operation is automatic. There are
no provisions at this time to send current bearing
information back to the com
p
uter.
You may wish to check with our Customer
Service Dept. from time to time in order to obtain
the latest firmware u
pg
rades.

Section 9. Troubleshooting
Troubleshootin
g
CAUTION: This unit has been thoroughly tested
and cycled before shipment. Follow the
connector wiring carefully between the rotator
and the DCU- I control box. Pin #1 must attach to
Pin #1, etc... Incorrect wiring will burn out the
rotator
p
otentiometer and void the warrant
y
.
The DCU-I control box is designed to be used
ONLY with Hy-Gain HAM-IV and T-2X rotator
systems. Do not t r y to use this control on other
s
y
stems!
Problem Possible Cause
Antenna Bearing doesn't match display Mast slipped in rotator clamp
Antenna slipped on mast
DCU-1 Calibration not performed
Current Bearing changes randomly Potentiometer broken or burned-up
or does no change at all Shorts or opens in control cable
Extremel
y
hi
g
h RF field near rotator
DCU-I MPU or A/D failure
Tower or DCU-I not grounded
Antenna Bearing changes by itself Brake wedge failure
DCU-1 MPU failure
Current Bearing changes +/- less than 3 degrees Antenna rocking in high winds
Potentiometer dirty or poor connection
High RF field near rotator
Long (200') control cable
Rotator unable to reach target bearing Temperature less than -30 degrees F
Broken teeth in gears
Shorts or opens in control cable
Thermal cut-out in power transformer
Mast bindin
g
in tower
Old motor-start capacitor
High winds, high wind area
Control cable wire size too small
DCU-I MPU failure
Rotator slow to reach target bearing Temperature between -30 and 0 degrees F
Broken teeth in gears
Mast bindin
g
in tower
Old motor-start capacitor
High winds, high wind area
Table 2
Ground Wires Lack of Power
Most operational difficulties with rotators are
traceable to broken, shorted, grounded or
miswired control cables. Time spent on
assembling, routing and protecting the control
cable will lead to a long trouble-free rotator life.
Unintentional grounds on cable leads can burn
out the line fuse in the DCU-1 control box, the
A/D IC, or the potentiometer in the rotator. If pin
#3 or pin #7 is grounded, it shorts out part of the
potentiometer so that as rotation progresses to the
other end, the full DC voltage is applied across a
decreasing portion until current becomes so high
that the potentiometer burns out. Note also that
any grounds may put an overload on the power
transformer which could cause the line fuse to
blow.
Antenna Motion
Frequently the slight motion of the antenna array
in gusts of wind is due more to the natural
flexing of the elements and mast than to actual
play in the rotator mechanism. A slight amount
of "play" is built into the rotator to avoid binding
due to environmental chan
g
es.
If the antenna rotation is slow or sluggish or hard
to start, check for proper voltages on pins #1,2,5,
and 6 (See Table 3). If the voltages are correct,
the 130 - 156 MFD capacitor may be old. If your
unit is more than 5 years old, try replacing this
capacitor. Also, if your cable run is over 200 feet,
make sure that you are using the proper wire size.
See Table 1. For cable runs over 300 feet, you
may wish to move the motor capacitor to the
tower. This allows you to run only 6 wires from
the control to the rotator, so that you can reduce
wire resistance by doubling up wires or using
fewer, heavier wires.
If the electrical circuit is working, then check for
mechanical problems. Look for mast binding or
thrust bearing misalignment if you have ex-
perienced strong winds recently. If the
temperature is less than -30 dog. F (-34 dog. C),
the rotator will be very sluggish or may not run at
all! This is normal. Do not try to rotate with the
DCU-1 control if temperatures are below -30 dog.
F !
If the antenna actually rotates in high winds, this
is usually just the mast slipping in the rotator or
the antenna slipping on the mast. For large
antennas, it is often necessary to drill a 5/16"
hole through the rotator clamping plate and mast
and pin them together with the bolt provided.
Also, if possible, pin the antenna to the mast with
appropriate hardware. If slipping is suspected,
return the rotator to an end of rotation limit and
visuall
y
check antenna ali
g
nment.
Checkin
g
the Control Unit Volta
g
es
To check the control unit voltages, first remove
the rotator control cable from the DCU-1 control
box, then plug the line cord into a 110 VAC outlet.
With no connections, the front panel display
should read "180" on the current display and
"000" on the target bearing displays. Check for the
followin
g
volta
g
es on the 8
p
in connector:
NOTE:
You have 8 seconds after pressing "START" to
make each measurement. The DCU-1 checks
for movement, and after 8 seconds without
movement, it stops trying to rotate. You may
wish to make
y
our meter connections with
Pin #'s Ambient State Press "START" (see note)
1-2 0 30 VAC
1-5 0 30 VAC
1-6 0 0
4-8 0 0
3-7 + 5.0 VDC + 5.0 VDC
Checking the Rotator Resistances
from the
g
round
Table 3
You may possibly avoid bringing the rotator down
from the tower by making electrical resistance
checks on the control cable. Disconnect the
control cable from the control box. Check for the
followin
g
resistances:
Description
Brake Solenoid Pin #'s
1-2 Approximate Resistance (ohms)
0.75+ cable resistance
1/2 Motor Winding 1 - 8 2.5 +cable resistance
1/2 Motor Winding 1-4 2.5 +cable resistance
1/2 Motor Winding + switch 1-6 2.5 +cable resistance
Entire Motor 4-8 4.5 + cable resistance
Right Limit Switch 5-8 0 +cable resistance
Left Limit Switch 4-6 0 + cable resistance
Entire Pot 3-7 500 + cable resistance
Pot Arm to + End 1-3 0 to 500 ( 0 at full CCW)
Pot Arm to - End 1-7 0 to 500
(
500 at full CCW
)
Table 4
Section 10. Disassembl
y
of the Rotator
DISASSEMBLY OF THE ROTATOR
In order to service the rotator, the unit must be
disassembled. We recommend the following pro-
cedure:
1. Set the rotator on a flat surface.
2. Remove the four (4) screws and carefully raise
the top casting to expose the potentiometer
and drive mechanism.
3. Carefully remove upper ball bearing retaining
ring. Keep it circular and lay it on clean
paper.
4. See that the potentiometer strip is clean and
not burned at either end and that the arm is
clean at the point of contact. Use only fine
rou
g
e cloth to
p
olish the contact arm.
5. If the drive ring happens to be near the end
of rotation, hold the unit horizontal, operate
the spur gear to rotate the mechanical stop on
the drive ring away from the area of the limit
switch. See that the mechanical stop lever
(which is positioned between the two limit
switches) will open each electrical contact
before it hits the corresponding mechanical
stop. Also, see that the stop lever has not
been deformed and that the electrical
contacts are clean and uncorroded.
Rotate the top spur gear several revolutions
to determine that the motor and its bearings
are operating freely. Look for broken teeth in
any of the gears.
6. Lift the motor and brake mechanism out of
the brake housing. Carefully remove the ball
bearing retainer and place it on a clean piece
of
p
a
p
er.
7. Remove the ring gear from the motor base.
This is accomplished by first pulling up on
the side opposite the gear train. Then raise
the entire ring slightly upward with the side
away from the gear train so that it will slide
out from under the
g
ears.
8. Examine the teeth in the brake casting. Ex-
amine closely for evidence of broken or
worn teeth.
9. To remove the potentiometer, remove the hex
nuts and unsolder the leads. The mounting
stug are integral to the motor and bell. In
replacing the pot, be sure the connections are
on the side which overhan
g
s the motor.
10. To replace the motor, first remove the pot per
step 9, then unsolder the black motor lead
from the solder lug, the red lead from the
inside left limit switch lug and the blue lead
from inside the right switch lug. The
fastenings holding the motor on the studs
may then be removed and the motor pulled
up and out. In replacing a motor, be sure to
see that the round hole in the motor is next
to the limit switch. Use a double locknut on
this stud near the limit switch to provide
clearance for the leads. Use special
internal/external lockwasher over the stud
that works in the slotted hole in the motor.
Be sure that the pinion is snug against the
spur gear before tightening this fastener over
the slot.

SPUR GEAR ASSEMBLY
PLACE THE OPENING FOR
ELECTRICAL LEADS TO THE
RIGHT.
Figure 13 Spur Gear
Assembl
y
The numbers within circles on this illustration are
sequence-of-assembly numbers; their only func-
tion is to indicate which part should be
positioned on the gear shaft in a particular
sequence.
Item Numbers are used to identify a particular
item by Part Number and Description. The Item
Numbers listed correspond to the Item Numbers
used in the Rotator Parts List in the rear of the
manual.
Sequence Numbers 7, 9, and 10 (PN 5011200-1)
are identical spur gears with rather small pinion
g
ears attached to the bottom side.
Sequence Number 6 (PN 5011100-1) is a spur
gear with a rather long pinion gear attached to the
bottom side.
Sequence Number 3 consists of two (2) spur
gears (PN 5010700-1) "sandwiched" together.
There is no pinion gear on this spur gear.
Sequence Numbers 1 and 8 are identical flat
washers.
The pinion gears for this application are always
orientated on the shafts with the pinion gear side
"down".
When assembling the gears and their associated
components on both shafts, follow the numerical
se
q
uence shown.
Section 11. Reassembl
y
of the Rotator
REASSEMBLY OF THE ROTATOR
It is assumed in the following instructions that
the brake mechanism is assembled and
operative. The motor and gear train along with
the potentiometer and the limit switches are
likewise assembled
,
wired and o
p
erative.
4. Clean the inner portion of the housing and
apply a small amount of grease to the ball
race. Then, carefully insert one ball bearing
assembly with the fringed rim up and
a
g
ainst the outer ed
g
e of the castin
g
.
It is not likely that the brake wedge will be
exactly positioned in relation to the teeth in the
brake housing to permit proper assembly unless
the brake mechanism is retracted. For this
reason, it is necessary to operate the brake
mechanism electrically during Step 8 of the
assembl
y
of the rotator unit.
1. See that a small amount of low temperature,
high quality, light weight grease is
conservatively distributed around the ball
bearings, ring gear and spur gears. Only an
even film of grease is desirable
(approximately one thimbleful of grease
should be used to lubricate a completely dry
rotator). Excessive grease will only run out
during high temperatures or cause power
loss during low temperatures.
2. Rotate the upper spur gear until the inwardly
protruding mechanical stop on the ring gear
touches the channel shaped stop lever. This
action will push it far enough to the left to
just open the left hand limit switch contact
(it is assumed that the rotator is viewed
from the side of the limit switch). This
situation represents the extreme clockwise
end of rotation. The potentiometer arm must
then be rotated to extreme clockwise
position against the top stop.
3. Secure the upper bell housing upside down
by the mast support in a vise with the open
end of the "V" toward the bench. The boss,
which drives the potentiometer arm that is
located in the bottom part of the housing,
will then be to the left of center.
5. Grasp the operating mechanism by the flat
base, steady the ring gear, invert the
mechanism and lower it into the housing. In
doing this, note that the serrated portion of
the potentiometer arm must engage the
driving boss in the housing and that the
three driving bosses on the ring gear must
engage into the mating recesses in the top
rousing. This situation will result automat-
ically if the previous instructions have been
followed.
6. Clean the exposed bearing race and apply a
film of grease. Then apply the top bearing
assembly to the race with the rim
downward.
7. Clean the brake housing. Lower the brake
housing into place so that the assembly
holes will appriximately line up with the
threaded holes in the bell housing. Do not
mechanically force an exact alignment of
these holes without electrically retracting
the brake mechanism.
8. Connect control unit pins 1 and 2 only to the
corresponding pins on the rotator while it
remains clamped in the vise. Momentarily
operate the "Brake Release". This will permit
the brake housing to freely rotate the exact
alignment of the holes. With the brake
retracted, secure the upper mast support
(bell) to the lower brake housing. Tighten
finger tight. With the brake retracted, tighten
all four (4) bolts in an alternate pattern to
approximately 85 inch-pounds of torque.
Recheck the brake to make sure that it
operates freely.
It is suggested that all eight wires be
connected from the control box while the
rotator is still on the bench and that its
complete operation be checked.
Section 12. T2X Rotator Re
p
lacement
ITEM
PART
NO. NO. DESCRIPTION QTY
101 5137701 Rotator with connector................................................................................1
102 5136201 Upper Mast support (Bell Casting) .............................................................1
103 5136301 Brake Housing ...........................:................................................................1
104 5033501 Ball Bearings (Unit 1)................................................................................98
Ball Bearings (Unit 2) ...............................................................................40
105 5011300 Bearing Retainer (Unit 1) ............................................................................1
Bearing Retainer (Unit 2) ............................................................................1
106 5136401 Casting, Brake Support ...............................................................................1
107 5011200 Gear and Pinion ...........................................................................................3
108 5011100 Gear and Pinion ...........................................................................................1
109 560084 Spacer, Small Gear ......................................................................................1
110 5037800 Spacer, Large Gear ......................................................................................1
111 5112000 Washer .....................................;,.................................................................3
112 5010700 Gear, Final Spur ..........................................................................................2
113 5037900 Bushing, Gear ..............................................................................................1
114 5136101 Gear, High-Strength Drive (Ring Gear) ....................................................... 1
115 5037000 Base Casting and Gear Shaft Assembly.......................................................1
116 5012200 Plate, Motor Mounting.................................................................................1
117 5137600 Motor and Pinion (brass)......................................_.......................................1
118 5023100 Potentiometer ...............................................................................................1
119 5009900 Solenoid (Brake) ..........................................................................................1
120 5010401 Latch, Brake.................................................................................................1
121 5010500 Spring, Latch................................................................................................2
122 5010600 Pin, Latch .....................................................................................................2
123 5028204 Retainer, Latch Pin.......................................................................................2
124 5011400 Spring, Extension.........................................................................................2
125 5009800 Links, Connecting ........................................................................................2
126 380626 Pin, Connecting Link ...................................................................................1
127 350885 Washer, Connecting Link ............................................................................1
128 5151401 Wedge, Brake...............................................................................................1
129 5011700 Support, Brake Wedge .................................................................................1
130 5010000 Pin, Solenoid ................................................................................................1
131 5010101 Spacer, Solenoid ..........................................................................................3
132 5028206 Pin, Retaining. .............................................................................................2
133 179894 Mounting plate, drilled.................................................................................1
134 510680 Screw, #6 x 3/8", torx ..................................................................................2
135 509711 Bolt, 5/16-18 x 2", Hex Head, SS................................................................6
136 555747 Nut, Hex, 5/16"-18, SS ................................................................................6
137 564792 Lockwasher, Split, 5/16", SS .......................................................................6
138 450590 Strain relief, Heyco ......................................................................................1
139 610215 Cable, 2 # 16, 6 # 18 ............................................................................... A/R
140 5149600 Bolt, Hex Head, 5/16"-18 x 15/8", SS ........................................................6
141 650179 Receptacle, AMP .........................................................................................1
142 5147800 Nut, Hex, 5/16"-18, SS ................................................................................5
143 567115 Lockwasher, Split, 1/4"..............................................................................11
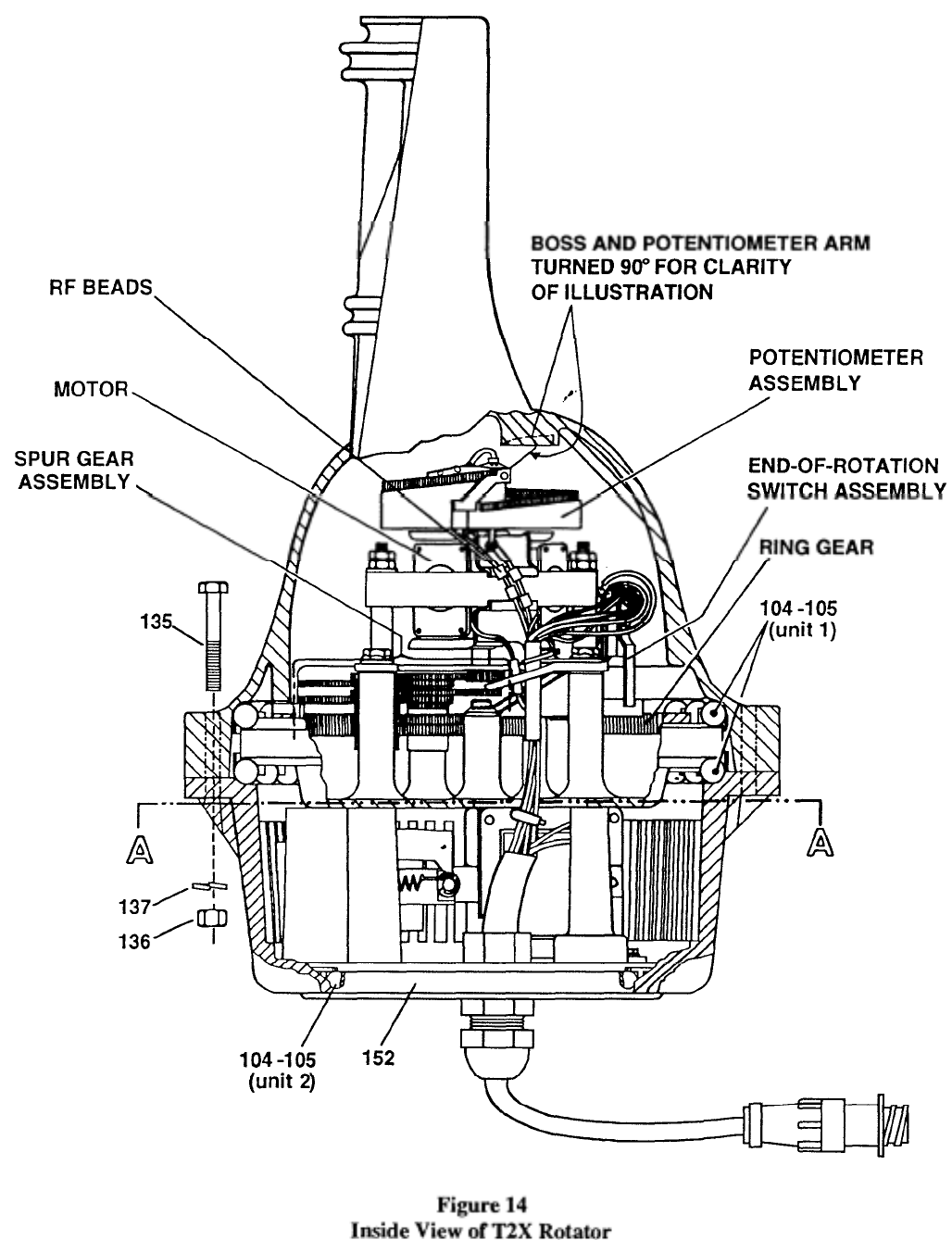

d 123; ATTACH AFTER ITEM 122 IS
INSTALLED THROUGH ITEMS 129
AND 120 (2 PLACES)
Figure 15 Brake
Assembl
y
Detail
T
2
X Rotator Re
p
lacement Parts
(
Continued
)
ITEM
PART
NO. NO. DESCRIPTION QTY
144 650291 Contact, AMP ..............................................................................................8
145 5112300 Flatwasher, 3/8" ...........................................................................................3
146 5112200 Flatwasher, 3/16" .........................................................................................4
147 5105600 Screw, Thread Cutting, #10-24 x-1/2" .........................................................6
148 5104700 Lockwasher, Internal/External #8 ................................................................1
149 5067000 Arm, Pivot....................................................................................................1
150 5113100 Nut, Hex, #6-32............................................................................................2
151 _Nut, Hex, #8-32............................................................................................4
152 5136401 Casting, Break Support................................................................................1
153 5009600 Clamp, Spring ..............................................................................................2
154 567115 Lockwasher, Split, 1/4"................................................................................4
155 120006001 Lockwasher, External, #6.............................................................................2
156 567135 Lockwasher, Internal, #8..............................................................................3
157 102720521 Screw, 1/4"-20 x 3 1/4"................................................................................4
158 5146110 Assembly, End Of Rotation ..... °..................................................................1
159 5031100 Lug, Solder...................................................................................................2
5142210 Kit, Accessory..............................................................................................1
160 5137000 Plate, Mast Clamp....................................................................................1
161 5136900 U-Bolt, 5/16"-18 x 3 1/4" x 4"................................................................2
140 5149600 Bolt, Hex Head, 5/16"-18 x 15/8", SS ....................................................6
162 5142400 Bolt, Hex Head, 5/16"-18 x 31/2", SS .....................................................1
136 555747 Nut, Hex, 5/16"-18, SS ............................................................................5
137 564792 Lockwasher, Split, 5/16", SS .................................................................11
870598 Parts Pack, Connector..................................................................................1
163 650181 Plug, 9 pin ................................................................................................1
164 650180 Receptacle shell........................................................................................ l
165 650293 Contact.....................................................................................................8
166 640077 Plug, 8 pin ................................................................................................1
167 890014 Ferrite bead, Type 73 ................................................................. ..............4
168 Grease, Special Kit (Quantity for one overhaul).......................................... 1

Figure 16 T2X Rotator - Blustrated Parts
Breakdown

Section 14. DCU-1 Control Unit Re
p
lacement Parts
Part
No.
870804
Description Qty
DCU-1 Assembly, 120 V......................................................................1
870842 DCU-1 Assembly, 220 V........................................................................1
1034403 Fuse 3 Amp 3 AG (120 VAC).-.:...........................................................1
(710053) Fuse 1 AMP 5 x 20 mm (220 VAC)........................................................ 1
1056300 Fuse Holder (120 VAC...........................................................................1
(710054) Fuse Holder 5/20 mm (220 VAC............................................................1
105632051 6-32 x 5/16 screw............................................................................…....2
150078 Front overlay, printed.............................................................................1
150624-3 Label, "TELEX"....................................................................................1
171131 Spacer, transformer assy. .......................................................................4
350979 Clip, capacitor.......................................................................................1
450431 Strain Relief (120 VAC)........................................................................1
(450403) Strain Relief (220 VAC) ........... ..........................................................1
450433 Hole plug (l 10 VAC only) .....................................................................1
450614 Filter Display, printed ............................................................................1
470677 Backing plate, switch..............................................................................3
46002 RD Connector, 2 pin, red..............................................................................2
47138P2 Contact, connector .................................................................................4
500157 Screw, 10-24 x 2"...................................................................................4
500326 Screw, 4-40 x 5/16"...............................................................................7
5022500 Terminal, solder.....................................................................................1
506325 Screw, 1/4"-20 x 3/4" ............................................................................1
5086100 Power Cord (120 VAC) ..........................................................................1
(5079800) Power Cord (220 VAC) ..........................................................................1
5112400 Flat Washer. 128 I.D................................................................................
5113100 Nut, 6-32, hex .......................................................................................5
5141100 Rotator Housing, Top cover....................................................................1
5141200 Rotator Housing, bottom cover................................................................1
5151501 Capacitor 130-156 MFD.........................................................................1
5152700 Bumper (rubber feet).............................................................................4
520057 Screw, 6-32 x 3/81', (black) ....................................................................8
53432116 Knob.....................................................................................................1
53433015 Knob-cap...............................................................................................1
550029 Wing nut, 1/4"-20 .................................................................................1
554071 Nut, 10-24, hex .....................................................................................8
556960 Nut, 1/4"-20, hex...................................................................................1
567110 Lockwasher, 1/4", internal ....................................................................2
567120 Flat washer, 1/4" ...................................................................................2
567125 Lockwasher, No. 10 internal...................................................................8
640076 Socket, 8 pin (Part of 870849 Wire Assembly) .......................................1
640084 Cable Assembly, 10 wire, 7 inch ...........................................................1
640085 Cable Assembly, 6 wire, 7 inch ..............................................................1
810138 Key pad, 3 button...................................................................................3
51401-031 Screw, 4-40 x 1/4", socket head..............................................................3

DCU-1 Control Unit Re
p
lacement Parts List
Item
No
Part
No. Description Qt
y
870806 Transformer Assembl
y
,
(
120 VAC
)
........................................................... 1
1073501 Transformer Assembly, (220 VAC)........................................................... 1
870807 PCB Assembly, front panel........................................................................ l
870808 PCB Assembly, control................................................................................1
8800102114 Connector D, 9 pin, male (Part of 870848 Wire Assembly) ..................... 1
8800102132 Connector D, 9
p
in, female
(
Part of 870848 Wire Assembl
y)
.................. 1
8800102463 Hardware , D Connector .............................................................................2
880394 Chassis, Assembl
y
.....................................................................................1
Section 15. Parts-Pack Parts List
Accessor
y
Kit PN 5142210
Item Part
No. No. Description Qt
y
147 110820035 1/4"-20 x 1 1/4 Hex......................................................................................5
144 5011500 Mast Clamp.................................................................................................. l
145 5038200 U-type Bolt...................................................................................................3
145 5050200 Flatwasher....................................................................................................4
148 554099 1/4"-20 hex nut.............................................................................................5
149 561177 1/4"
,
s
p
lit lockwasher..................................................................................9
Connector Parts Pack PN 870598
Item
Part
No. No. Description Qty
176 650181 Plu
g,
Am
p
....................................................................................................1
177 650180 Shell, Amp ...................................................................................................1
178 650293 Contact, socket.............................................:...............................................8
179 640077 Plu
g
, 8
p
in....................................................................................................1
DCU-1 Parts Pack
,
120V
,
870805
1034403Fuse, 3 AMP, 3 AG.............................................................................2
640077 Plug, 8 pin ............................................................................................1
870844 DCU Termination Assembly ................................................................1
DCU-1 Parts Pack
,
220V
,
870843
710053 Fuse, 1 AMP, 5 x 20 mm .....................................................................2
640077 Plug, 8 pin ..........................................................................................1
870844 DCU Termination Assembly (plug)......................................................1
Section 16. How to Get Factory Service
If service is required, the unit must be packed
securel
y
and sent
p
re
p
aid to:
Hy-Gain
308 Industrial Park Road
Starkville, MS 39759 USA
Ph: (662) 323-9538
Fax: (662) 323-6551
For units that are in warranty, no charge will be
made for any repair work required. Include a copy
of your sales receipt. For out-of-warranty units, call
the Warranty Service Department for prices.
The price includes rebuilding the unit, replacing all
defective and/or worn parts, and return freight char-
ges. Hy-Gain reserves the right to change prices at
its option. When returning items for repair, a check
or money order for the repair charges must be
included. Be sure to include your name, address,
zip code, and telephone number. Also, give a brief
descri
p
tion of the
p
roblem.

CLEARANCE HOLES TO BE 11/32"(.87 CM)
Tower Drilling Template
This information is believed correct, but no warranty is given or implied and no
liability is assumed by Hy-Gain as to its accuracy or completeness. Changes
may be made from time to time so that the user should verify all factors that
may be critical. This information is not to be construed as authorizing or
advising use of any patented invention.