TB8100 Service Manual TB8000/TB8100_Service_Manual/TB8100_Service_Manual
TB8000/TB8100_Service_Manual/TB8100_Service_Manual TB8100_Service_Manual
TB8000/TB8100_Service_Manual/TB8100_Service_Manual TB8100_Service_Manual
User Manual: Pdf TB8000/TB8100_Service_Manual/TB8100_Service_Manual
Open the PDF directly: View PDF .
Page Count: 156 [warning: Documents this large are best viewed by clicking the View PDF Link!]
- Service Manual
- Tait Contact Information
- Contents
- Preface
- 1 Safety and Servicing Information
- 2 Reciter Circuit Description
- 3 Reciter Servicing
- 4 Power Amplifier Circuit Description
- 5 Power Amplifier Servicing
- 5.1 Disassembly and Reassembly
- 5.2 PCB Connecting Links
- 5.3 Replacing the 6W PCB
- 5.4 Replacing the 60W PCB
- 5.5 Replacing the 60W RF Power Transistor
- 5.6 Replacing the Control PCB
- 5.7 Replacing the Low Pass Filter/Directional Coupler PCB
- 5.8 Replacing the Interconnect PCBs
- 5.9 Replacing the Splitter/Combiner PCBs
- 6 Power Management Unit Circuit Description
- 7 Power Management Unit Servicing
- 8 Control Panel Circuit Description
- 9 Control Panel Servicing
- 10 Subrack Servicing
- Glossary

MB8100-00-00-812
Issue 1
April 2004
TB8100 base station
Service Manual

2TB8100 Service Manual
© Tait Electronics Ltd April 2004
Tait Contact Information
Tait Radio Communications http://www.taitworld.com
Corporate Head Office
New Zealand
Tait Electronics Ltd
P.O. Box 1645
Christchurch
New Zealand
E-mail: info@taitworld.com
We b s ite: http://www.taitworld.com
Technical Support:
E-mail: support@taitworld.com
We b s i t e : http://support.taitworld.com
Tait North America
Regional Head Office - United States of
America
Tait North America Inc.
E-mail: usa@taitworld.com
Canada
Tait North America Inc.
E-mail: canada@taitworld.com
Latin America
Tait Latin America
E-mail: latinamerica@taitworld.com
Tait Europe
Regional Head Office - United Kingdom
Tait Mobile Radio Ltd
E-mail: teusales@tait.co.uk
Tait North Asia
Regional Head Office - Hong Kong
Tait Mobile Radio (Hong Kong) Ltd
E-mail: hongkong@taitworld.com
Beijing
Tait Mobile Radio (Hong Kong) Ltd
E-mail: beijing@taitworld.com
Tait South Asia
Regional Head Office - Singapore
Tait Electronics (Far East) Pte Ltd
E-mail: singapore@taitworld.com
Thailand
Tait Mobile Radio Ltd
E-mail: thailand@taitworld.com
Oceania
New Zealand
Tait Communications Ltd
E-mail: headoffice@tcl.tait.co.nz
Australia
Tait Electronics (Aust) Pty Ltd
E-mail: australia@taitworld.com
Note: For the addresses and phone numbers
of the above regional offices refer to the
TaitWorld website.

TB8100 Service Manual 3
© Tait Electronics Ltd April 2004
Contents
Tait Contact Information . . . . . . . . . . . . . . . . . . . . . . . . . . . . . . . . . . . . . 2
Preface . . . . . . . . . . . . . . . . . . . . . . . . . . . . . . . . . . . . . . . . . . . . . . . . . 9
Scope of Manual. . . . . . . . . . . . . . . . . . . . . . . . . . . . . . . . . . . . . . . . . . . . . . . . . 9
Enquiries and Comments . . . . . . . . . . . . . . . . . . . . . . . . . . . . . . . . . . . . . . . . . . 9
Updates of Manual and Equipment . . . . . . . . . . . . . . . . . . . . . . . . . . . . . . . . . . . 9
Copyright. . . . . . . . . . . . . . . . . . . . . . . . . . . . . . . . . . . . . . . . . . . . . . . . . . . . . . 9
Disclaimer . . . . . . . . . . . . . . . . . . . . . . . . . . . . . . . . . . . . . . . . . . . . . . . . . . . . . 9
Associated Documentation . . . . . . . . . . . . . . . . . . . . . . . . . . . . . . . . . . . . . . . . 10
Typographical Conventions. . . . . . . . . . . . . . . . . . . . . . . . . . . . . . . . . . . . . . . . 10
Publication Record. . . . . . . . . . . . . . . . . . . . . . . . . . . . . . . . . . . . . . . . . . . . . . 11
1 Safety and Servicing Information. . . . . . . . . . . . . . . . . . . . . . . . . . . . 13
1.1 Personal Safety . . . . . . . . . . . . . . . . . . . . . . . . . . . . . . . . . . . . . . . . . . . . 13
Lethal Voltages. . . . . . . . . . . . . . . . . . . . . . . . . . . . . . . . . . . . . . . . . . 13
Explosive Environments . . . . . . . . . . . . . . . . . . . . . . . . . . . . . . . . . . . 13
Beryllium Oxide . . . . . . . . . . . . . . . . . . . . . . . . . . . . . . . . . . . . . . . . 14
Proximity to RF Transmissions . . . . . . . . . . . . . . . . . . . . . . . . . . . . . . 14
High Temperatures . . . . . . . . . . . . . . . . . . . . . . . . . . . . . . . . . . . . . . 14
1.2 Equipment Safety . . . . . . . . . . . . . . . . . . . . . . . . . . . . . . . . . . . . . . . . . . 15
ESD Precautions . . . . . . . . . . . . . . . . . . . . . . . . . . . . . . . . . . . . . . . . 15
Aerial Load . . . . . . . . . . . . . . . . . . . . . . . . . . . . . . . . . . . . . . . . . . . . 15
1.3 Identifying Screw Types . . . . . . . . . . . . . . . . . . . . . . . . . . . . . . . . . . . . . 16
Torx Recess Head Screws. . . . . . . . . . . . . . . . . . . . . . . . . . . . . . . . . . 16
Allen Recess Head UNC Screws. . . . . . . . . . . . . . . . . . . . . . . . . . . . . 16
Pozidriv Recess Head Screws . . . . . . . . . . . . . . . . . . . . . . . . . . . . . . . 16
1.4 Recommended Tools . . . . . . . . . . . . . . . . . . . . . . . . . . . . . . . . . . . . . . . 18
1.5 Replacing Components . . . . . . . . . . . . . . . . . . . . . . . . . . . . . . . . . . . . . . 18
Surface Mount Devices. . . . . . . . . . . . . . . . . . . . . . . . . . . . . . . . . . . . 18
Leaded Components. . . . . . . . . . . . . . . . . . . . . . . . . . . . . . . . . . . . . . 19
Cased Mica Capacitors . . . . . . . . . . . . . . . . . . . . . . . . . . . . . . . . . . . . 19
1.6 Regulatory Information. . . . . . . . . . . . . . . . . . . . . . . . . . . . . . . . . . . . . . 19
1.7 PCB Information . . . . . . . . . . . . . . . . . . . . . . . . . . . . . . . . . . . . . . . . . . 20
2 Reciter Circuit Description . . . . . . . . . . . . . . . . . . . . . . . . . . . . . . . . 21
2.1 Digital Circuitry . . . . . . . . . . . . . . . . . . . . . . . . . . . . . . . . . . . . . . . . . . . 22
Digital IF . . . . . . . . . . . . . . . . . . . . . . . . . . . . . . . . . . . . . . . . . . . . . . 22
Digital Signal Processor (DSP). . . . . . . . . . . . . . . . . . . . . . . . . . . . . . . 22
Reduced Instruction Set Computer (RISC). . . . . . . . . . . . . . . . . . . . . 25
40MHz Digital Clock. . . . . . . . . . . . . . . . . . . . . . . . . . . . . . . . . . . . . 27
2.2 Reference Switch . . . . . . . . . . . . . . . . . . . . . . . . . . . . . . . . . . . . . . . . . . 28
Synthesizer. . . . . . . . . . . . . . . . . . . . . . . . . . . . . . . . . . . . . . . . . . . . . 28
VCXO . . . . . . . . . . . . . . . . . . . . . . . . . . . . . . . . . . . . . . . . . . . . . . . 28
4TB8100 Service Manual
© Tait Electronics Ltd April 2004
Reference Switch. . . . . . . . . . . . . . . . . . . . . . . . . . . . . . . . . . . . . . . . 30
2.3 Receiver RF Circuitry . . . . . . . . . . . . . . . . . . . . . . . . . . . . . . . . . . . . . . 31
Front End . . . . . . . . . . . . . . . . . . . . . . . . . . . . . . . . . . . . . . . . . . . . . 31
Mixer . . . . . . . . . . . . . . . . . . . . . . . . . . . . . . . . . . . . . . . . . . . . . . . . 31
IF Circuitry . . . . . . . . . . . . . . . . . . . . . . . . . . . . . . . . . . . . . . . . . . . . 33
Synthesizer . . . . . . . . . . . . . . . . . . . . . . . . . . . . . . . . . . . . . . . . . . . . 33
VCO. . . . . . . . . . . . . . . . . . . . . . . . . . . . . . . . . . . . . . . . . . . . . . . . . 34
AGC . . . . . . . . . . . . . . . . . . . . . . . . . . . . . . . . . . . . . . . . . . . . . . . . . 34
2.4 Exciter RF Circuitry. . . . . . . . . . . . . . . . . . . . . . . . . . . . . . . . . . . . . . . . 35
Frequency Control Loop . . . . . . . . . . . . . . . . . . . . . . . . . . . . . . . . . . 35
Synthesizer . . . . . . . . . . . . . . . . . . . . . . . . . . . . . . . . . . . . . . . . . . . . 38
VCO. . . . . . . . . . . . . . . . . . . . . . . . . . . . . . . . . . . . . . . . . . . . . . . . . 38
Exciter Control Circuit . . . . . . . . . . . . . . . . . . . . . . . . . . . . . . . . . . . 39
2.5 System Interface PCBs . . . . . . . . . . . . . . . . . . . . . . . . . . . . . . . . . . . . . . 40
2.6 Power Supply . . . . . . . . . . . . . . . . . . . . . . . . . . . . . . . . . . . . . . . . . . . . . 43
3 Reciter Servicing . . . . . . . . . . . . . . . . . . . . . . . . . . . . . . . . . . . . . . . 51
3.1 Disassembly and Reassembly . . . . . . . . . . . . . . . . . . . . . . . . . . . . . . . . . . 52
Identifying the Reciter . . . . . . . . . . . . . . . . . . . . . . . . . . . . . . . . . . . . 52
Screw Torque Settings . . . . . . . . . . . . . . . . . . . . . . . . . . . . . . . . . . . . 54
Removing the Covers . . . . . . . . . . . . . . . . . . . . . . . . . . . . . . . . . . . . 54
Removing the Front and Rear Panels . . . . . . . . . . . . . . . . . . . . . . . . . 54
Refitting the Front and Rear Panels . . . . . . . . . . . . . . . . . . . . . . . . . . 55
Refitting the Covers . . . . . . . . . . . . . . . . . . . . . . . . . . . . . . . . . . . . . 56
3.2 Replacing the Digital PCB . . . . . . . . . . . . . . . . . . . . . . . . . . . . . . . . . . . 56
3.3 Replacing the System Interface PCB . . . . . . . . . . . . . . . . . . . . . . . . . . . . 59
3.4 Replacing the RF PCB. . . . . . . . . . . . . . . . . . . . . . . . . . . . . . . . . . . . . . 61
4 Power Amplifier Circuit Description . . . . . . . . . . . . . . . . . . . . . . . . . 67
4.1 Microprocessor Control Circuitry . . . . . . . . . . . . . . . . . . . . . . . . . . . . . . 68
Diagnostics and Alarms. . . . . . . . . . . . . . . . . . . . . . . . . . . . . . . . . . . . 68
PA-Key. . . . . . . . . . . . . . . . . . . . . . . . . . . . . . . . . . . . . . . . . . . . . . . 69
Foldback . . . . . . . . . . . . . . . . . . . . . . . . . . . . . . . . . . . . . . . . . . . . . . 69
Shutdown . . . . . . . . . . . . . . . . . . . . . . . . . . . . . . . . . . . . . . . . . . . . . 71
Calibration . . . . . . . . . . . . . . . . . . . . . . . . . . . . . . . . . . . . . . . . . . . . 71
Power Control. . . . . . . . . . . . . . . . . . . . . . . . . . . . . . . . . . . . . . . . . . 71
Fan Control. . . . . . . . . . . . . . . . . . . . . . . . . . . . . . . . . . . . . . . . . . . . 72
Power Supplies . . . . . . . . . . . . . . . . . . . . . . . . . . . . . . . . . . . . . . . . . 72
Temperature Monitoring . . . . . . . . . . . . . . . . . . . . . . . . . . . . . . . . . . 72
Ambient Air Temperature Sensor . . . . . . . . . . . . . . . . . . . . . . . . . . . . 73
4.2 RF Circuitry . . . . . . . . . . . . . . . . . . . . . . . . . . . . . . . . . . . . . . . . . . . . . 73
6W PCB . . . . . . . . . . . . . . . . . . . . . . . . . . . . . . . . . . . . . . . . . . . . . . 73
60W PCB . . . . . . . . . . . . . . . . . . . . . . . . . . . . . . . . . . . . . . . . . . . . . 73
Low Pass Filter and Directional Coupler PCB . . . . . . . . . . . . . . . . . . . 74
Splitter and Combiner PCBs. . . . . . . . . . . . . . . . . . . . . . . . . . . . . . . . 74
Interconnect PCBs. . . . . . . . . . . . . . . . . . . . . . . . . . . . . . . . . . . . . . . 74
TB8100 Service Manual 5
© Tait Electronics Ltd April 2004
5 Power Amplifier Servicing . . . . . . . . . . . . . . . . . . . . . . . . . . . . . . . . 77
5.1 Disassembly and Reassembly . . . . . . . . . . . . . . . . . . . . . . . . . . . . . . . . . . 78
Identifying the PA . . . . . . . . . . . . . . . . . . . . . . . . . . . . . . . . . . . . . . . 78
Screw Torque Settings . . . . . . . . . . . . . . . . . . . . . . . . . . . . . . . . . . . . 80
Removing the Airflow Duct and Cover . . . . . . . . . . . . . . . . . . . . . . . 80
Removing the Front Panel . . . . . . . . . . . . . . . . . . . . . . . . . . . . . . . . . 80
Refitting the Front Panel . . . . . . . . . . . . . . . . . . . . . . . . . . . . . . . . . . 82
Refitting the Cover and Airflow Duct. . . . . . . . . . . . . . . . . . . . . . . . . 82
5.2 PCB Connecting Links . . . . . . . . . . . . . . . . . . . . . . . . . . . . . . . . . . . . . . 83
5.3 Replacing the 6W PCB . . . . . . . . . . . . . . . . . . . . . . . . . . . . . . . . . . . . . 83
5.4 Replacing the 60W PCB. . . . . . . . . . . . . . . . . . . . . . . . . . . . . . . . . . . . . 85
5.5 Replacing the 60W RF Power Transistor . . . . . . . . . . . . . . . . . . . . . . . . 87
5.6 Replacing the Control PCB . . . . . . . . . . . . . . . . . . . . . . . . . . . . . . . . . . 89
5.7 Replacing the Low Pass Filter/Directional Coupler PCB . . . . . . . . . . . . . 91
5.8 Replacing the Interconnect PCBs . . . . . . . . . . . . . . . . . . . . . . . . . . . . . . 92
5.9 Replacing the Splitter/Combiner PCBs . . . . . . . . . . . . . . . . . . . . . . . . . . 93
6 Power Management Unit Circuit Description . . . . . . . . . . . . . . . . . . . 99
6.1 Microprocessor Control Circuitry . . . . . . . . . . . . . . . . . . . . . . . . . . . . . 101
6.2 AC Module . . . . . . . . . . . . . . . . . . . . . . . . . . . . . . . . . . . . . . . . . . . . . 104
6.3 DC Module . . . . . . . . . . . . . . . . . . . . . . . . . . . . . . . . . . . . . . . . . . . . . 106
7 Power Management Unit Servicing . . . . . . . . . . . . . . . . . . . . . . . . . .113
7.1 Safety Precautions . . . . . . . . . . . . . . . . . . . . . . . . . . . . . . . . . . . . . . . . . 113
Personal Safety . . . . . . . . . . . . . . . . . . . . . . . . . . . . . . . . . . . . . . . . . 113
Equipment Safety . . . . . . . . . . . . . . . . . . . . . . . . . . . . . . . . . . . . . . . 114
Replacing Components Connected To The Mains . . . . . . . . . . . . . . 114
7.2 Disassembly and Reassembly . . . . . . . . . . . . . . . . . . . . . . . . . . . . . . . . . 115
Mechanical Overview. . . . . . . . . . . . . . . . . . . . . . . . . . . . . . . . . . . . 115
Identifying the PMU . . . . . . . . . . . . . . . . . . . . . . . . . . . . . . . . . . . . 116
Screw Torque Settings . . . . . . . . . . . . . . . . . . . . . . . . . . . . . . . . . . . 118
Removing the Top and Bottom Covers . . . . . . . . . . . . . . . . . . . . . . 118
Removing the Front and Rear Panels . . . . . . . . . . . . . . . . . . . . . . . . 118
Disconnecting the AC and DC Modules . . . . . . . . . . . . . . . . . . . . . . 119
Reconnecting the AC and DC Modules . . . . . . . . . . . . . . . . . . . . . . 119
Refitting the Front and Rear Panels . . . . . . . . . . . . . . . . . . . . . . . . . 122
Refitting the Top and Bottom Covers. . . . . . . . . . . . . . . . . . . . . . . . 122
7.3 Replacing the Plug-in Cards . . . . . . . . . . . . . . . . . . . . . . . . . . . . . . . . . 123
7.4 Replacing the Auxiliary Power Supply PCB. . . . . . . . . . . . . . . . . . . . . . 126
8 Control Panel Circuit Description . . . . . . . . . . . . . . . . . . . . . . . . . . .131
8.1 Control Circuitry . . . . . . . . . . . . . . . . . . . . . . . . . . . . . . . . . . . . . . . . . 133
8.2 Audio Circuitry . . . . . . . . . . . . . . . . . . . . . . . . . . . . . . . . . . . . . . . . . . 133
8.3 Power Save. . . . . . . . . . . . . . . . . . . . . . . . . . . . . . . . . . . . . . . . . . . . . . 133
6TB8100 Service Manual
© Tait Electronics Ltd April 2004
8.4 Power Supply . . . . . . . . . . . . . . . . . . . . . . . . . . . . . . . . . . . . . . . . . . . . 134
9 Control Panel Servicing . . . . . . . . . . . . . . . . . . . . . . . . . . . . . . . . . .135
9.1 Identifying the Control Panel . . . . . . . . . . . . . . . . . . . . . . . . . . . . . . . . 136
9.2 Screw Torque Settings . . . . . . . . . . . . . . . . . . . . . . . . . . . . . . . . . . . . . 136
9.3 Replacing the PCB. . . . . . . . . . . . . . . . . . . . . . . . . . . . . . . . . . . . . . . . 136
9.4 Replacing the Speaker . . . . . . . . . . . . . . . . . . . . . . . . . . . . . . . . . . . . . 139
10 Subrack Servicing . . . . . . . . . . . . . . . . . . . . . . . . . . . . . . . . . . . . . .143
Glossary . . . . . . . . . . . . . . . . . . . . . . . . . . . . . . . . . . . . . . . . . . . . . . . .149

TB8100 Service Manual 7
© Tait Electronics Ltd April 2004
List of Illustrations
Figure 1.1 Typical Antistatic Bench Set-up. . . . . . . . . . . . . . . . . . . . . . . . . . . . . . . 15
Figure 1.2 Identifying Torx Screws . . . . . . . . . . . . . . . . . . . . . . . . . . . . . . . . . . . . 16
Figure 1.3 Identifying Pozidriv and Philips Screws and Screwdrivers . . . . . . . . . . . . 17
Figure 2.1 Reciter High Level Block Diagram . . . . . . . . . . . . . . . . . . . . . . . . . . . . 21
Figure 2.2 Reciter Digital Circuitry Block Diagram . . . . . . . . . . . . . . . . . . . . . . . . 24
Figure 2.3 Reciter RISC Functional Block Diagram . . . . . . . . . . . . . . . . . . . . . . . . 27
Figure 2.4 Reciter External Reference Block Diagram . . . . . . . . . . . . . . . . . . . . . . 29
Figure 2.5 Reciter Receiver RF Circuitry Block Diagram. . . . . . . . . . . . . . . . . . . . 31
Figure 2.6 Reciter Receiver Synthesizer Block Diagram . . . . . . . . . . . . . . . . . . . . . 32
Figure 2.7 Comparison of VCXO and VCO Modulation Responses . . . . . . . . . . . . 36
Figure 2.8 Reciter Exciter Synthesizer Modulator Block Diagram . . . . . . . . . . . . . . 37
Figure 2.9 Reciter System Interface PCB Block Diagram . . . . . . . . . . . . . . . . . . . . 41
Figure 2.10 Reciter Power Supply Block Diagram . . . . . . . . . . . . . . . . . . . . . . . . . . 44
Figure 2.11 Identifying the Circuitry on the Digital and System Interface PCBs . . . . . 47
Figure 2.12 Identifying the Circuitry on the RF PCB . . . . . . . . . . . . . . . . . . . . . . . . 49
Figure 3.1 Identifying the Reciter PCBs. . . . . . . . . . . . . . . . . . . . . . . . . . . . . . . . . 53
Figure 3.2 Removing the Front and Rear Panels. . . . . . . . . . . . . . . . . . . . . . . . . . . 55
Figure 3.3 Replacing the Digital and System Interface PCBs . . . . . . . . . . . . . . . . . . 57
Figure 3.4 Reconnecting the Flexible Connectors. . . . . . . . . . . . . . . . . . . . . . . . . . 58
Figure 3.5 Replacing the RF PCB . . . . . . . . . . . . . . . . . . . . . . . . . . . . . . . . . . . . . 62
Figure 3.6 Reciter Mechanical Assembly . . . . . . . . . . . . . . . . . . . . . . . . . . . . . . . . 65
Figure 4.1 PA High Level Block Diagram. . . . . . . . . . . . . . . . . . . . . . . . . . . . . . . . 67
Figure 4.2 PA Control, RF and Power Supply Circuitry Block Diagram . . . . . . . . . 70
Figure 4.3 Identifying the Circuitry on the PA PCBs . . . . . . . . . . . . . . . . . . . . . . . 75
Figure 5.1 Identifying the PA PCBs . . . . . . . . . . . . . . . . . . . . . . . . . . . . . . . . . . . . 79
Figure 5.2 Removing the Airflow Duct, Cover and Front Panel . . . . . . . . . . . . . . . 81
Figure 5.3 PCB Connecting Links . . . . . . . . . . . . . . . . . . . . . . . . . . . . . . . . . . . . . 83
Figure 5.4 Replacing the 6W PCB . . . . . . . . . . . . . . . . . . . . . . . . . . . . . . . . . . . . 84
Figure 5.5 Replacing the 60W PCB. . . . . . . . . . . . . . . . . . . . . . . . . . . . . . . . . . . . 86
Figure 5.6 Replacing the 60W RF Power Transistor . . . . . . . . . . . . . . . . . . . . . . . 88
Figure 5.7 Replacing the Control PCB . . . . . . . . . . . . . . . . . . . . . . . . . . . . . . . . . 90
Figure 5.8 Replacing the LPF/Directional Coupler PCB. . . . . . . . . . . . . . . . . . . . . 92
Figure 5.9 Replacing the Splitter/Combiner PCBs . . . . . . . . . . . . . . . . . . . . . . . . . 94
Figure 5.10 PA Mechanical Assembly - Sheet 1 . . . . . . . . . . . . . . . . . . . . . . . . . . . . 97
Figure 5.11 PA Mechanical Assembly - Sheet 2 . . . . . . . . . . . . . . . . . . . . . . . . . . . . 98
Figure 6.1 PMU High Level Block Diagram. . . . . . . . . . . . . . . . . . . . . . . . . . . . . 100
Figure 6.2 PMU Microprocessor Functional Block Diagram . . . . . . . . . . . . . . . . . 102
Figure 6.3 PMU AC Module Block Diagram . . . . . . . . . . . . . . . . . . . . . . . . . . . . 104
Figure 6.4 PMU DC Module Block Diagram . . . . . . . . . . . . . . . . . . . . . . . . . . . . 106
Figure 6.5 Identifying the Circuitry on the AC Module PCBs. . . . . . . . . . . . . . . . 109
Figure 6.6 Identifying the Circuitry on the DC Module PCBs. . . . . . . . . . . . . . . . 111
Figure 7.1 Identifying the PMU PCBs . . . . . . . . . . . . . . . . . . . . . . . . . . . . . . . . . 117
Figure 7.2 Disconnecting the AC and DC Modules . . . . . . . . . . . . . . . . . . . . . . . 120
Figure 7.3 Reconnecting the AC and DC Modules. . . . . . . . . . . . . . . . . . . . . . . . 121
Figure 7.4 Replacing the Plug-in Cards . . . . . . . . . . . . . . . . . . . . . . . . . . . . . . . . 124
Figure 7.5 Replacing the Auxiliary Power Supply PCB. . . . . . . . . . . . . . . . . . . . . 126
Figure 7.6 PMU Mechanical Assembly - Sheet 1 . . . . . . . . . . . . . . . . . . . . . . . . . 129
8TB8100 Service Manual
© Tait Electronics Ltd April 2004
Figure 7.7 PMU Mechanical Assembly - Sheet 2 . . . . . . . . . . . . . . . . . . . . . . . . . . 130
Figure 8.1 Control Panel High Level Block Diagrams. . . . . . . . . . . . . . . . . . . . . . . 132
Figure 9.1 Replacing the Control Panel PCB . . . . . . . . . . . . . . . . . . . . . . . . . . . . . 137
Figure 9.2 Reconnecting the Flexible Connector . . . . . . . . . . . . . . . . . . . . . . . . . . 138
Figure 9.3 Replacing the Speaker . . . . . . . . . . . . . . . . . . . . . . . . . . . . . . . . . . . . . 139
Figure 9.4 Control Panel Mechanical Assembly . . . . . . . . . . . . . . . . . . . . . . . . . . . 141
Figure 10.1 Front Panel Mechanical Assembly . . . . . . . . . . . . . . . . . . . . . . . . . . . . . 145
Figure 10.2 Subrack Mechanical Assembly . . . . . . . . . . . . . . . . . . . . . . . . . . . . . . . . 146
Figure 10.3 Cable Identification . . . . . . . . . . . . . . . . . . . . . . . . . . . . . . . . . . . . . . . 147

TB8100 Service Manual 9
© Tait Electronics Ltd April 2004
Preface
Scope of Manual
This manual contains information on servicing TB8100 base station system
equipment. It also provides circuit descriptions and mechanical assembly
drawings for each module.
Enquiries and Comments
If you have any enquiries regarding this manual, or any comments,
suggestions and notifications of errors, please contact Technical Support
(refer to “Tait Contact Information” on page 2).
Updates of Manual and Equipment
In the interests of improving the performance, reliability or servicing of the
equipment, Tait Electronics Ltd reserves the right to update the equipment
or this manual or both without prior notice.
Copyright
All information contained in this manual is the property of Tait Electronics
Ltd. All rights are reserved. This manual may not, in whole or in part, be
copied, photocopied, reproduced, translated, stored, or reduced to any
electronic medium or machine-readable form, without prior written
permission from Tait Electronics Ltd. All trade names referenced are the
service mark, trademark or registered trademark of the respective
manufacturers.
Disclaimer
There are no warranties extended or granted by this manual. Tait
Electronics Ltd accepts no responsibility for damage arising from use of the
information contained in the manual or of the equipment and software it
describes. It is the responsibility of the user to ensure that use of such
information, equipment and software complies with the laws, rules and
regulations of the applicable jurisdictions.

10 TB8100 Service Manual
© Tait Electronics Ltd April 2004
Associated Documentation
TB8100 Installation and Operation Manual.
TB8100 Installation Guide (a subset of the Installation and Operation
Manual.).
TB8100 Specifications Manual.
TB8100 Service Kit and Alarm Center User’s Manuals and online Help.
TB8100 Calibration Kit User’s Manual and online Help.
Technical notes are published from time to time to describe applications for
Tait products, to provide technical details not included in manuals, and to
offer solutions for any problems that arise.
All available TB8100 product documentation is provided on the CD
supplied with the base station1. Updates may also be published on the Tait
support website.
Typographical Conventions
Within this manual, four types of alerts are given to the reader: Warning,
Caution, Important and Note. The following paragraphs illustrate each type
of alert and its associated symbol.
Warning!! This alert is used when there is a potential risk
of death or serious injury.
Caution This alert is used when there is a risk of minor or
moderate injury to people.
Important This alert is used to warn about the risk of equipment dam-
age or malfunction.
Note This alert is used to highlight information that is required to
ensure procedures are performed correctly.
1. Technical notes are only available in PDF format from the Tait support
website. Consult your nearest Tait Dealer or Customer Service Organisa-
tion for more information.

TB8100 Service Manual 11
© Tait Electronics Ltd April 2004
Publication Record
Issue Publication Date Description
1 April 2004 first release
12 TB8100 Service Manual
© Tait Electronics Ltd April 2004

TB8100 Service Manual Safety and Servicing Information 13
© Tait Electronics Ltd April 2004
1 Safety and Servicing Information
This chapter contains general information on safety and servicing
procedures for the TB8100 base station system (BSS) modules:
■reciter
■power amplifier (PA)
■power management unit (PMU)
■control panel.
You will find specific safety and servicing information about individual
modules and procedures in the appropriate chapters.
1.1 Personal Safety
Lethal Voltages
Warning!! The PMU contains voltages that may be lethal.
Refer to the ratings label on the rear of the
module.
The TB8100 BSS must be installed so that the rear of the PMU is located
in a service access area.
Disconnect the mains IEC connector and wait for five minutes for
the internal voltages to self-discharge before dismantling. The AC
power on/off switch does not isolate the PMU from the mains. It
breaks only the phase circuit, not the neutral.
The PMU should be serviced only by qualified technicians. All servicing
should be carried out only when the PMU is powered through a mains
isolating transformer of sufficient rating. We strongly recommend that
the mains power to the whole of the repair and test area is supplied via an
earth leakage circuit breaker.
Explosive Environments
Warning!! Do not operate TB8100 BSS equipment near
electrical blasting caps or in an explosive atmos-
phere. Operating the equipment in these envi-
ronments is a definite safety hazard.

14 Safety and Servicing Information TB8100 Service Manual
© Tait Electronics Ltd April 2004
Beryllium Oxide
Caution The termination resistors used in the 100W power
amplifier contain some beryllium oxide. This sub-
stance is perfectly harmless in its normal solid form,
but can become a severe health hazard when it has
been reduced to dust. For this reason the termina-
tion resistors should not be broken open, mutilated,
filed, machined, or physically damaged in any way
that can produce dust particles. You should safely
dispose of all used or obsolete components accord-
ing to your local regulations.
Proximity to RF Transmissions
Do not operate the transmitter when someone is standing within 90cm (3ft)
of the antenna. Do not operate the transmitter unless you have checked that
all RF connectors are secure.
High Temperatures
Take care when handling a PMU or PA which has been operating recently.
Under extreme operating conditions (+60°C [+140°F] ambient air
temperature) or high duty cycles the external surfaces of the PMU and PA
can reach temperatures of up to +80°C (+176°F).
Caution The magnetics and power devices attached to the
heatsink in the PMU get hot when they are operat-
ing. Take care when working on a PMU that has
been in recent use.
Caution Touching high-power RF components or circuits
can cause serious burns. We strongly recommend
you do not touch any RF components or tracks in
the PA while it is transmitting.

TB8100 Service Manual Safety and Servicing Information 15
© Tait Electronics Ltd April 2004
1.2 Equipment Safety
ESD Precautions
Important This equipment contains devices which are susceptible to
damage from static charges. You must handle these devices
carefully and according to the procedures described in the
manufacturers’ data books.
We recommend you purchase an antistatic bench kit from a reputable
manufacturer and install and test it according to the manufacturer’s
instructions. Figure 1.1 shows a typical antistatic bench set-up.
You can obtain further information on antistatic precautions and the dangers
of electrostatic discharge (ESD) from standards such as ANSI/ESD
S20.20-1999 or BS EN 100015-4 1994.
Aerial Load
The TB8100 BSS equipment has been designed to operate safely under a
wide range of aerial loading conditions. However, we strongly recommend
that the transmitter should always be operated with a suitable load to prevent
damage to the transmitter output power stage.
Figure 1.1 Typical Antistatic Bench Set-up
common point ground
(building ground or
mains ground via 1M
ohm series resistor)
conductive wrist strap dissipative rubber
bench mat

16 Safety and Servicing Information TB8100 Service Manual
© Tait Electronics Ltd April 2004
1.3 Identifying Screw Types
Torx Recess Head Screws
Torx recess head screws are the standard type of screw used in all TB8100
equipment, although Pozidriv and Allen recess head screws are also used in
a few special applications.
Figure 1.2 below shows a typical Torx recess head screw (actual hardware
may differ slightly from this illustration due to variations in manufacturing
techniques).
Allen Recess Head UNC Screws
Allen recess head 4-40 UNC thread screws are used to secure the RF power
transistors in the TB8100 power amplifier and cannot be interchanged with
M3 screws (refer to Figure 5.10 on page 97).
Pozidriv Recess Head Screws
Pozidriv recess head screws are used in TB8100 equipment in a few special
applications. It is important that you use the correct type and size
screwdriver to avoid damaging the screw head.
It is particularly important that you do not use Philips screwdrivers on
Pozidriv screw heads as the tapered driving flutes of the Philips screwdriver
do not engage correctly with the parallel-sided slots in the Pozidriv screw
head. This can result in considerable damage to the screw head if the
screwdriver tip turns inside the recess.
Figure 1.2 Identifying Torx Screws
“star” shaped recess with
six internal notches

TB8100 Service Manual Safety and Servicing Information 17
© Tait Electronics Ltd April 2004
Note If you find you need excessive downwards pressure to keep the
screwdriver tip in the Pozidriv screw head, you are probably using
the wrong type or size screwdriver.
Figure 1.3 below shows the main differences between typical Pozidriv and
Philips screw heads and screwdriver tips (actual hardware may differ slightly
from these illustrations due to variations in manufacturing techniques).
Figure 1.3 Identifying Pozidriv and Philips Screws and Screwdrivers
internal notches
Pozidriv Philips
no special markings
“star” markings
between slots
slots with parallel sides
slots with tapered sides
driving flutes with
parallel sides
driving flutes with
tapered sides
ridges between
driving flutes

18 Safety and Servicing Information TB8100 Service Manual
© Tait Electronics Ltd April 2004
1.4 Recommended Tools
It is beyond the scope of this manual to list every tool that a service
technician should carry. However, the tools specifically required for
servicing TB8100 BSS equipment are listed in the table below. You can also
obtain the TBA0ST2 tool kit from your nearest Tait Dealer or Customer
Service Organisation. It contains the basic tools needed to install, tune and
service TB8100 BSS equipment.
1.5 Replacing Components
Ensure that any replacement components are of the same type and
specifications as the originals. This will prevent the performance and safety
of the TB8100 equipment from being degraded.
Surface Mount Devices
Important Surface mount devices (SMDs) require special storage, han-
dling, removal and replacement techniques. This equip-
ment should be serviced only by an approved Tait Dealer or
Customer Service Organisation equipped with the neces-
sary facilities. Repairs attempted with incorrect equipment
or by untrained personnel may result in permanent damage.
If in doubt, contact your nearest Tait Dealer or Customer
Service Organisation.
Driver/
Spanner Size Location / Function
Tor x T 8 a
a. Included in the TBA0ST2 tool kit.
M2.5 securing the SMA connector to the reciter and PA
front panel
Tor x T 1 0 aM3 all M3 screws
Tor x T 2 0 aM4 all M4 screws
Pozidriv PZ3 M6 DC input terminals on the PMU
3/32in Allen
key
4-40 UNC securing the RF power transistors to the PA heatsink
5.5mm AFaM3 securing the speaker to the control panel chassis
11mm AF securing the BNC/TNC connectors to the reciter rear
panel

TB8100 Service Manual Safety and Servicing Information 19
© Tait Electronics Ltd April 2004
Leaded Components
Whenever you are doing any work on the PCB that involves removing or
fitting components, you must take care not to damage the copper tracks or
pads. The two satisfactory methods of removing components from plated-
through hole (PTH) PCBs are detailed below.
Desoldering Iron
Method This method requires the use of a desoldering station.
1. Place the tip over the lead and, as the solder starts to melt, move the
tip in a circular motion.
2. Start the suction and continue the movement until three or four
circles have been completed.
3. Remove the tip while continuing suction to ensure that all solder is
removed from the joint, then stop the suction.
4. Before pulling the lead out, ensure it is not stuck to the plating.
5. If the lead is still not free, resolder the joint and try again.
Note The desoldering iron does not usually have enough heat to desol-
der leads from the ground plane. Additional heat may be applied
by holding a soldering iron on the tip of the desoldering iron (this
may require some additional help).
Component Cutting
Method 1. Cut the leads on the component side of the PCB.
2. Heat the solder joint sufficiently to allow easy removal of the lead
by drawing it out from the component side: do not use undue force.
3. Fill the hole with solder and then clear with solderwick.
Cased Mica Capacitors
Cased mica capacitors can be removed by heating the top with a heavy-duty
soldering iron and gently lifting the capacitor off the PCB with a
solder-resistant spike or equivalent. Make sure that the solder at the tab
solder joint is melted or removed before attempting to lift the capacitor.
1.6 Regulatory Information
Any modifications you make to this equipment which are not authorised by
Tait Electronics Ltd may invalidate your compliance authority’s approval to
operate the equipment.

20 Safety and Servicing Information TB8100 Service Manual
© Tait Electronics Ltd April 2004
1.7 PCB Information
All PCBs are identified by a unique 10 digit IPN (internal part number)
which is printed onto the PCB (usually on the top side), as shown in the
example below.
The last two digits of this number define the issue status, which starts at 01
and increments through 02, 03, 04 etc. as the PCB is updated.
Information on individual PCBs is published in PCB Information Packages.
This information consists of:
■parts lists
■grid reference indexes
■PCB layouts
■schematics (circuit diagrams).
Contact your nearest Customer Service Organisation for more details on the
availability of PCB Information Packages (refer to “Tait Contact
Information” on page 2).

TB8100 Service Manual Reciter Circuit Description 21
© Tait Electronics Ltd April 2004
2 Reciter Circuit Description
The reciter comprises three PCBs: an RF, a digital, and an optional system
interface PCB. These PCBs are mounted on a central chassis/heatsink.
Figure 2.1 below shows the configuration of the main circuit blocks, and the
main inputs and outputs for power, RF and control signals. The locations
of the main circuit blocks on the PCBs are shown in Figure 2.11 on page 47
and Figure 2.12 on page 49.
Figure 2.1 Reciter High Level Block Diagram
DSP
CODEC
CODEC
CODEC
40MHz
Clock
Receiver
Exciter
Synthesizer
Subsystem
Reference
Frequency
Subsystem
Digital
Receiver
Power
Supply
Power
Supply
RISC
DSP/RISC
CODECs
IF
12.8MHz
Ref.
RF I/P
28VDC I/P
28V
28V 5V
3.3V
9.3V
RF O/P +
PA Key Audio
System
Control Bus System I/O
Digital
Receiver
Audio &
RSSI
Control &
Communications
Control &
Communications
Modulation
& Frequency
Control
Control &
Communications
External
Reference
Frequency
(if used)
RF PCB Digital PCB
System
Interface
PCB
22 Reciter Circuit Description TB8100 Service Manual
© Tait Electronics Ltd April 2004
2.1 Digital Circuitry
Refer to Figure 2.2 on page 24.
Digital IF
The heart of the digital IF system is the 14-bit analogue-to-digital converter
(ADC). This is a high-speed device, with a multi-staged “pipeline”
architecture, which is clocked and outputs samples at 40MSPS
(megasamples per second). The analogue IF input of the ADC is a
differential structure, and the output is via a 14-bit parallel bus.
The band-limited 70.1MHz IF signal is sub-sampled by the ADC at
40MSPS. The sub-sampling results in images of the input signal appearing
at other frequencies so that the ADC behaves in a similar fashion to a mixer.
The digital output therefore contains information in the form of images,
which can be digitally processed to extract one of the many signals. The
lowest frequency image for the 70.1MHz IF and 40MHz clock is at
9.9MHz.
The digital downconverter (DDC) digitally downconverts the desired image
(9.9MHz) to baseband. This is achieved by digital mixing with a
numerically controlled oscillator (NCO). The mixing process is done using
in-phase and quadrature methods to achieve image rejection, and allows
channel filtering to be applied before the signal is passed to the digital signal
processor (DSP) for demodulation. The digital channel filtering also
decimates the sample rate down to 50kSPS (kilosamples per second) for the
DSP.
Digital Signal Processor (DSP)
The DSP is responsible for software processing of digitised signals in the
receiver and transmitter. The processing word width is 16-bit fixed point.
There are 96 kilobytes of on-chip program memory, and 64 kilobytes of
on-chip data memory. Although no external memory is used, the external
memory interface is connected to the DDC for initialisation and
configuration.
Transmit Functions The DSP performs the following transmit functions:
■CTCSS and DCS sub-audible signal generation
■CWID generation
■pip tone generation
■audio filtering: including removal of sub-audible components, pre-
emphasis and low pass filtering
■signal path switching
■signal level adjustment
TB8100 Service Manual Reciter Circuit Description 23
© Tait Electronics Ltd April 2004
■peak FM deviation limiting
■FM signal generation by controlling the dual point modulator
■calibration parameter estimation
■line level monitoring.
Receive Functions The DSP performs the following receive functions:
■detection of CTCSS and DCS signalling
■audio filtering: including removal of sub-audible components, de-
emphasis and low pass filtering
■signal path switching
■signal level adjustment
■FM demodulation of the base band signal
■RSSI measurement for monitoring and RSSI signal voltage output
■SINAD measurement
■measurement and detection for control of the audio mute
■calibration parameter estimation
■line level monitoring.
Serial Ports The DSP has three synchronous serial ports. Serial port 1 is connected to
the DDC and receives base band samples. Serial port 2 is connected to the
three CODECs (encoder/decoder). Serial port 3 is not used.
CODECs The three CODECs provide the audio frequency analogue interface to the
reciter. There are six analogue input and six analogue output paths. The
sample rate on all paths is 25kSPS and the sampling resolution is 16 bits.
The CODEC inputs are as follows:
■two input signals from the frequency control loop (FCL)
■balanced line input
■unbalanced line input
■microphone input
■synthesizer loop control voltage.
The CODEC outputs are as follows:
■VCO voltage control line
■VCXO voltage control line
■balanced line output
■unbalanced line output
■speaker output
■RSSI voltage indicator.

24 Reciter Circuit Description TB8100 Service Manual
© Tait Electronics Ltd April 2004
Figure 2.2 Reciter Digital Circuitry Block Diagram
RSSI
Process
Loopback
Crosspoint
Switch
FM
Demodulation
Rx Audio
Processor
DDCADC
Rx
Crosspoint
Switch
Interface
(serial
port)
CODECs
& Signal
Conditioning
Interface
(RISC/
DSP)
Tx
Crosspoint
Switch
DSP
Frequency
Control Loop
Section
Tx Audio
Processor
Signalling
Processor
Audio & DC
Measurement
Noise
Mute
serial port
Interface
(RISC/
DSP)
RISC
serial port
CODECs
& Signal
Conditioning
serial port
CODECs
& Signal
Conditioning
serial port
Tx VCO
Tx
Synthesiser
Tx VCXO
RF
Frequency
Control Loop
Section
RF PCBDigital PCB
Control Panel PCB
Digital Signal
Paths
DSPDigital IF
System Interface PCB
Speaker
Microphone
Programming Port
LEDs and Switches
RSSI
Balanced Audio Output
Unbalanced Audio Output
Balanced Audio Input
Discrete I/O & SIO Bus
Unbalanced Audio Input
VCO Modulation
VCXO Modulation
VCO Control Feedback
FCL I
FCL Q
40MHz Clock
40MHz Clock
70.1MHz IF
from RF PCB 40MSPS
TB8100 Service Manual Reciter Circuit Description 25
© Tait Electronics Ltd April 2004
Reduced Instruction Set Computer (RISC)
Refer to Figure 2.3 on page 27.
Hardware and I/O The RISC processor engine is a Samsung S3C3410X processor with a
40MHz external clock. It has 4 megabytes of flash memory containing the
following:
■bootloader
■application code
■DSP code
■non-volatile data
■2 megabytes of RAM for run-time variables.
The discrete digital inputs and outputs are as follows:
■chip select signals to synthesizers
■out-of-lock signals from synthesizers
■external reference detection
■internal/external reference selection
■Rx Gate output
■Tx Relay output
■reciter hex switch
■reciter alarm LED
■DIP switch for manufacturing testing
■debug LEDs
■fan good input
■flash programming voltage control.
The RISC has the following serial interfaces:
■asynchronous serial port for communication with the Service Kit
software and CCTM
■serial peripheral interface (SPI) for programming the synthesizers
■SPI for communication with the system interface PCB
■I2C for communication with the control panel and other modules in the
subrack.
Responsibilities The RISC communicates with the DSP’s shared memory via a host port
interface. It loads the DSP code and monitors and controls the following
DSP operations:
■receive path
■transmit path
■crosspoint switches
■power supplies
■PA Key output.
26 Reciter Circuit Description TB8100 Service Manual
© Tait Electronics Ltd April 2004
The RISC controls the frequency generation subsystem. It detects an
external reference source and selects internal or external reference. It also
programs, and handles out-of-lock signals for, the following synthesizers:
■12.8MHz external reference synthesizer
■40MHz digital clock synthesizer
■receiver synthesizer
■exciter synthesizer.
The RISC communicates with the control panel via I2C bus to:
■read the button states
■read the microphone PTT state
■control the LEDs
■turn the speaker amplifier on and off
■turn the microphone amplifier on and off.
The following signals go via the control panel for signal conditioning:
■Service Kit communication via the RS-232 interface
■fan-good indication (front panel fans).
Note that the volume control on the control panel is analogue only and is
not controlled by the RISC.
The RISC communicates with the other modules in the subrack via I2C in
order to:
■verify that they are present
■write configuration settings
■read their current status.
The RISC subsystem communicates with the system interface PCB via SPI
to:
■set input and output gains
■mute and unmute outputs
■read digital inputs
■write digital outputs.
The Rx Gate and Tx Relay lines go via the system interface PCB for signal
conditioning.

TB8100 Service Manual Reciter Circuit Description 27
© Tait Electronics Ltd April 2004
40MHz Digital Clock
The 40MHz synthesized digital clock is situated on the digital PCB. It is
used to drive the entire digital circuitry.
The 40MHz frequency synthesizer is implemented using an Integer_N-
based phase locked loop (PLL) IC. The PLL is a negative feedback loop,
which continuously monitors and maintains the 40MHz VCXO to a fixed
frequency and constant phase relationship with respect to a 12.8MHz
reference. The 40MHz VCXO oscillator is electrically tuned using two
varactors. The oscillator output is buffered before being distributed to the
digital circuitry.
Figure 2.3 Reciter RISC Functional Block Diagram
Reciter
Status
External
Reference
Detect/
Select
RISC
40MHz
Clock
Synthesizers
Flash
RAM
DSP
System
Control
Bus
System
Interface
PCB
Interrupt
Interrupt
Main Loop
Debug LEDs
DIP Switch
SPI SPI
Chip Selects Chip Selects
Lock Detects
Lock Detects
Detect 10MHz or
12.8MHz External
System I/O
System Control Bus
to BSS Modules &
Control Panel
10MHz or
12.8MHz
12.8MHz
Internal TCXO
Rx L.O.
Ex L.O.
12.8MHz
40MHz
Select
Address, Data, Control
Flash Programming Voltages
Alarm LEDs
IC
2
UART
Fan Good
SPI
Select
Rx Gate
Tx Relay
Tx Key
Hex Switch
Test
Digital PCB
RF PCB
- ARM 7 Processor
- Drivers
- SPI
- UART
- Timers
- Watchdog
- Discrete I/O
- Interrupts

28 Reciter Circuit Description TB8100 Service Manual
© Tait Electronics Ltd April 2004
2.2 Reference Switch
Refer to Figure 2.4 on page 29.
Synthesizer
The external reference synthesizer consists of a programmable frequency
synthesizer IC, a 12.8MHz VCXO, and a stable 10MHz or 12.8MHz
reference frequency supplied to the reciter externally via a BNC connector
on the rear panel.
The synthesizer uses a phase-locked loop to lock the 12.8MHz VCXO to
the external reference frequency. The synthesizer IC receives the divider
and control information from the RISC processor via a 3-wire serial bus
(clock, data and enable). When the data bits are latched in, the synthesizer
processes incoming signals from the 12.8MHz VCXO feedback buffer
(fvcxofb) and the external reference buffer (fref).
A transistor is used as a unity gain 12.8MHz VCXO feedback buffer for the
prescaler within the synthesizer IC.
The 10MHz or 12.8MHz externally supplied reference is detected, buffered
and divided down to the 100kHz divider reference within the synthesizer
IC. The same divider reference is maintained by dividing the 12.8MHz
VCXO feedback buffered signal using the programmable dividers of the
synthesizer IC. Phase lock is achieved when both divider references have
the same phase and frequency content (i.e. their difference is zero or DC).
This is achieved by the digital phase detector (part of the synthesizer IC),
which compares both divider references and delivers an error signal. A
±1mA charge pump circuit (also part of the synthesizer IC) and the passive
loop filter circuit convert this error signal to a DC voltage (0 to 3V) to tune
the 12.8MHz VCXO for correction. A loop filter with a bandwidth of
180Hz further filters the VCO control line reference side bands and
spurious signals.
Note The VCXO frequency increases as the control line voltage
increases.
VCXO
The VCXO is implemented by using a varactor to linearly tune a 12.8MHz
crystal unit over a specified frequency range. The frequency range provided
will cover frequency drifts due to calibration, the temperature tolerance of
the crystal unit, and the frequency stability of the externally supplied
reference.

TB8100 Service Manual Reciter Circuit Description 29
© Tait Electronics Ltd April 2004
Figure 2.4 Reciter External Reference Block Diagram
/R
/N
10 or 12.8MHz
External Reference
Internal Reference
12.8MHz TCXO
Programmable
Reference Divider
Programmable
VCO Divider
Phase
Detector
Charge
Pump
fref
fVCOfb
Software
Register
External Reference
Detector
Lock
Detect
RISC
8/9
Prescaler
Frequency Synthesizer IC
Loop
Filter
External Reference
12.8MHz VCO
Clock
Data
Chip Select/Latch Enable
Serial Bus
External
Reference
Buffer
12.8MHz VCXO
Feedback Buffer
Reference Switch
Ext_Ref_Det
Ext_Ref_Lock_Detect
Digital Switch
OFF / ON
ON / OFF
RF Switch
Ext_Ref_Ctrl
Buffer
Buffer
FCL Reference
Receiver Synthesizer
Reference
Digital Clock
Synthesizer Reference
Internal/External Reference Clock Branch
30 Reciter Circuit Description TB8100 Service Manual
© Tait Electronics Ltd April 2004
Reference Switch
The reference switch consists of the external reference detector, the
hardware switch, and the digital switch.
External Reference
Detector A discrete NPN dual transistor pair is used as a low level signal detector. The
Syn_Ref_Det signal has a high logic level when the externally supplied
signal has the correct level.
Hardware Switch The hardware switch is implemented using a discrete dual transistor pair.
When the switch is off (default), it powers up the internal reference
12.8MHz TCXO and shuts down the external reference 12.8MHz VCXO.
When the switch is on, it powers up the external reference 12.8MHz
VCXO and shuts down the internal reference 12.8MHz TCXO.
Digital Switch The digital switch is controlled by the RISC, which processes the
Syn_Ref_Det and Lock Detect signals from the external reference
synthesizer. The RISC controls the hardware switch using the
Syn_Ref_Ctrl signal. The hardware switch is on if the Syn_Ref_Det and
Lock Detect signals have a high logic level for a set time. In all other
conditions the hardware switch is off.
Internal/External
Reference Clock
Branch
A complementary emitter follower, using NPN/PNP dual transistors, forms
two clock buffer branches which distribute the internal or external
references to the rest of the system. The branches provide a reasonable drive
level at low impedance.

TB8100 Service Manual Reciter Circuit Description 31
© Tait Electronics Ltd April 2004
2.3 Receiver RF Circuitry
Front End
The incoming signal from the BNC connector is fed through a triplet helical
filter, followed by a simple low pass network which attenuates harmonics
and spurious responses from the preceding filter. The signal is then
amplified and passed through a low pass filter which provides immunity to
interference from higher frequency out-of-band signals. Automatic gain
control (AGC) is provided at this point by a PIN diode attenuator. The
signal is now amplified again in a second RF amplifier, and is then fed
through a band pass filter and 6dB pad to the mixer.
Mixer
The RF signal from the front end is converted down to the 70.1MHz IF by
a high level (+17dBm local oscillator) mixer. The voltage controlled
oscillator (VCO) generates a level of 20dBM which is fed to the mixer
through a 3dB attenuator pad. A diplexer terminates the IF port of the
mixer in 50Ω, thus ensuring a good match for all mixing products, as well
as enhancing the linearity. The post-mixer buffer amplifier compensates for
the insertion loss of the crystal filter, and any excess gain is reduced by the
following 5dB attenuator pad.
Figure 2.5 Reciter Receiver RF Circuitry Block Diagram
Band Pass
Filter 1
Band Pass
Filter 2
RF
Amplifier 1
RF
Amplifier 2
Low Pass
Filter
PIN
Attenuator 6dB Pad
5dB
Pad
AGC Control AGC Detector
Mixer
Local Oscillator
Diplexer
Post-mixer
Buffer
Crystal
Filter
IF
Amplifier
Anti-alias
Filter
IF Output
RF In

32 Reciter Circuit Description TB8100 Service Manual
© Tait Electronics Ltd April 2004
Figure 2.6 Reciter Receiver Synthesizer Block Diagram
/R
/N
12.8MHz
Reference
Oscillator
Receiver VCO
Programmable
Reference Divider
Programmable
VCO Divider
Phase
Detector
Lock Detect
Output
Charge
Pump
fref
fVCOfb
Software
Register
VCO Feedback
Attenuator
Lock Detect
Circuitry
64/65
Prescaler
Frequency Synthesizer IC
Loop
Filter VCO
LNA
Buffer
Harmonic
Filter
Fixed Slope
Attenuator Final
Driver
+20dBm LO
Clock
Data
Chip Select/Latch Enable
Serial Bus

TB8100 Service Manual Reciter Circuit Description 33
© Tait Electronics Ltd April 2004
IF Circuitry
The signal from the mixer is fed to the IF amplifier through a 4-pole crystal
filter which provides protection from strong off-channel signals. The IF
amplifier is a two-transistor design with voltage and current feedback, which
provides sufficient gain to drive the digital receiver. The 70.1MHz signal is
finally passed to the analogue-to-digital converter (ADC) in the digital
receiver via an anti-alias filter. This filter prevents IF noise at frequencies
other than 70.1MHz, generated in the amplifier, from being sampled by the
ADC at other Nyquist zones.
Synthesizer
The receiver synthesizer consists of a programmable frequency synthesizer
IC, the receiver VCO, and a stable known reference.
The synthesizer uses a phase-locked loop to lock the receiver VCO to a
stable known frequency reference. The synthesizer IC receives the divider
and control information from the RISC processor via a 3-wire serial bus
(clock, data and enable). When the data bits are latched in, the synthesizer
processes the incoming signals from the VCO feedback signal (fvcofb) and
the reference oscillator (fref).
The VCO feedback attenuator is a resistive divider that terminates the VCO
feedback signal in a fixed low impedance (50Ω). This attenuates the VCO
RF level down to a level suitable for the RF prescaler (within the synthesizer
IC).
A 12.8MHz temperature controlled crystal oscillator (TCXO) is used as the
internal reference oscillator. When the TCXO is active, the receiver
synthesizer is locked to an “internal reference mode” (by default).
Alternatively, a phase-locked 12.8MHz voltage controlled crystal oscillator
(VCXO) can be used as the external reference oscillator. When the VCXO
is active, the receiver synthesizer is locked to an “external reference mode”.
In operation only one oscillator is active at any given time. Refer to
“Reference Switch” on page 28 for details on the phase-locked 12.8MHz
external reference oscillator.
The reference oscillators are buffered, branched, and divided down to the
6.25kHz (default) or 5kHz divider reference within the synthesizer IC. The
same divider reference is maintained by dividing the VCO feedback signal
using the prescaler and programmable dividers of the synthesizer IC. Phase
lock is achieved when both divider references have the same phase and
frequency content (i.e. their difference is zero or DC). This is achieved by
the phase detector (part of the synthesizer IC), which compares both divider
references and delivers an error signal. A ±4mA charge pump circuit (also
part of the synthesizer IC) and the active loop filter circuit convert this error
signal to a DC voltage (0 to 22V1) to tune the VCO for correction. The
1. The normal lock range is between 3V and 16V.

34 Reciter Circuit Description TB8100 Service Manual
© Tait Electronics Ltd April 2004
loop filter has a bandwidth of 150Hz and filters the VCO control lines,
reference side bands and spurious signals.
Note The VCO frequency increases as the control line voltage increases.
VCO
The receiver VCO consists of a high Q VCO, low noise amplifier, harmonic
filter, fixed slope attenuator, and a final driver. Refer to Figure 2.6 on
page 32.
High Q VCO The VCO BJT transistor operates in a common collector Colpitts oscillator,
and uses a shorted quarter-wave ceramic coaxial resonator. The open end
of the resonator is terminated by a combination of a high Q trimmer and
varactor diodes. This forms a high Q resonator which is both mechanically
and electronically tunable. Mechanical tuning is possible by adjusting the
trimmer. Changes in the control voltage from the loop filter are applied to
the varactors to facilitate electronic tuning. The oscillator has a drive level
of +7dBm ±1dB.
Low Noise Amplifier An N-channel dual gate MOSFET is used as a broad band matched Class A
low noise amplifier. It has internal self-bias circuitry, and delivers an output
of +12dBm (nominal) before entering compression.
Harmonic Filter The VCO has a high second harmonic content. A third order low pass
elliptic filter is used to attenuate this content. It has an insertion loss of
0.5dB with 10dB of attenuation at the second harmonics.
Fixed Slope
Attenuator and
Final Driver
A silicon-based BJT transistor is used as a broad band matched Class A final
driver to drive the +20dBm local oscillator port of the mixer. This circuit
delivers 20dB ±1dB of gain for a +3dBm fixed input level. To maintain a
fixed input level, a fixed slope attenuator is introduced at the input to the
final driver so that the attenuation rate (slope) decreases with an increase in
frequency. The slope attenuator has 8dB of attenuation at the bottom of
the band and a slope of –1dBattn /100MHz.
The VCO frequency spans from either 370–410MHz, 400–450MHz or
470–510MHz according to the product type (refer to “Identifying the
Reciter” on page 52). The VCO is tuned to either 70.1MHz below (low
side injection) or above (high side injection) to produce the 70.1MHz IF
signal at the output of the mixer.
AGC
The AGC is used to prevent the ADC from being overloaded by strong
interfering signals present at the receiver antenna port. The AGC loop
consists of a PIN diode attenuator, AGC buffer, and detector. The pick-off
TB8100 Service Manual Reciter Circuit Description 35
© Tait Electronics Ltd April 2004
point for the AGC is the output of the post-mixer buffer. The input signal
to the AGC is buffered, amplified and then detected. The detected DC
voltage is buffered and fed to PIN_CTRL to control the attenuation of the
PIN attenuator.
To prevent overload of the ADC, the peak level at its input should not
exceed 0dBm. This corresponds to –30dBm at the antenna connector, and
approximately –22dBm at the AGC pick-off point. The AGC operates over
a range of approximately 11dB.
The AGC circuit can be enabled or disabled using the Service Kit
(Configure > Base Station > Channel Profiles > General tab).
2.4 Exciter RF Circuitry
Refer to Figure 2.8 on page 37.
Frequency Control Loop
Audio modulation of the exciter synthesizer is implemented in the
frequency control loop (FCL). It uses a three-point modulation scheme
involving the FCL_VCXO and VCO signals.
The FCL consists of reference oscillators, clock buffers, twisted ring counter
phase detectors, low pass filters (LPFs), ADCs, the FCL processor and
digital-to-analogue converters (DACs).
Reference
Oscillators Modulation to the FCL_VCXO reference oscillator requires the use of the
FCL_VCXO_CTRL and SYN_VCO_MOD signals to apply:
■a constant DC offset to the FCL_VCXO signal until it achieves
frequency lock to the internal referenced TCXO;
■frequency modulation to the FCL_VCXO and VCO simultaneously
from the transmit audio signal; the transmit audio signal has a range of 0
to 3kHz.
The modulated signal from the VCXO is attenuated by the bandwidth of
the loop filter in the low pass filter (i.e. 150Hz). To obtain flat modulation
across the audio band, the VCO is also modulated simultaneously to obtain
a composite high pass filter response. Figure 2.7 shows the relationships
between the frequency modulation gain characteristics of the VCXO and
VCO.
Clock Buffers The TCXO and VCXO signals are squared up and buffered as digital
signals using hex inverters.

36 Reciter Circuit Description TB8100 Service Manual
© Tait Electronics Ltd April 2004
Twisted Ring
Counter The VCXO and TCXO signals are phase shifted and multiplied by XOR
(exclusive_or) logic. This is achieved using a twisted ring counter, which
also divides both signals by four.
Low Pass Filter There are two output signals from the twisted ring counter. Both signals
have the sum and difference frequency contents of the TCXO and VCXO
signals, but there is a 90° phase difference between them.
I and Q low pass filters capture the difference frequency contents down to
DC and integrate them to form two triangular waves, which are 90° out of
phase with each other. This frequency is equal to a quarter of the difference
frequency content of the TCXO and VCXO signals.
The in-phase triangle frequency is referred to as “I channel” and the
quadrature-phase triangle frequency is referred to as “Q channel”.
ADC The I_Q channel triangular analogue waveforms are sampled and
transformed to digits using a 16-bit ADC with a signal-to-noise ratio of
75dB.
FCL Processor and
DAC The FCL processor runs a DSP-based algorithm which takes the digitised
signals, I_Q and transmit audio, and compares them to the transmit
modulation calibration data.
Using the compared results it attempts to lock FCL_VCXO to the TCXO,
as well as modulate the FCL_VCXO and VCO signals to achieve
modulation flatness across the transmit audio and VCO RF bands.
The FCL processor achieves this by sending the digitised modulation code
through a16-bit DAC. Here the code is translated to analogue signals which
modulate FCL_VCXO and the VCO. The DAC has a signal -to-noise ratio
of 70dB.
Figure 2.7 Comparison of VCXO and VCO Modulation Responses
VCXO VCO
150Hz
Gain
Frequency
3kHz
linear relationship
proportianal to the RF
frequency and
FCL_GAIN, measured
during calibration
non-linear relationship,
determined by
CalVcoGain_Corrected,
calculated from the
calibration data
0

TB8100 Service Manual Reciter Circuit Description 37
© Tait Electronics Ltd April 2004
Figure 2.8 Reciter Exciter Synthesizer Modulator Block Diagram
ADC
ADC
DAC
DAC
Delay
Delay
FM
Demodulator
VcoMod
Digitised Tx Audio
IntGain
DSP based FCL Processor
VcxoScale
TripleScale
TripleScale
PresTriDemod
FclFreqOffset (DC value)
FclMidPoint
(DC value)
Integrator
VcxoScale
Q Channel
I Channel
/4
/R
/N
Divide by 4
LPF
LPF
FCL_I
FCL_Q
I-Q Exclusive OR Gate
Twisted Ring Counter
Digital Clock
Buffer
Digital Clock
Buffer
12.8MHz FCL
VCXO Oscillator
12.8MHz
Reference
Oscillator
VCXO Modulation
+ DC Offset
Exciter VCO
Programmable
Reference Divider
Programmable
VCO Divider
Digital Clock
Buffer
Phase
Detector
Charge
Pump
fref
fVCOfb
Software
Register
VCO Feedback
Attenuator
Exciter Control
Circuit
64/65
Prescaler
Frequency Synthesizer IC
Loop
Filter
Varicap
Diodes
VCO
LNA
Buffer
Harmonic
Filter
Fixed Slope
Attenuator
10dB
Pad
Final
Driver
Fixed
Attenuator
+11dBm
to PA
Ex_Key
PA_Key
FCL_VCXO_CTRL
SYN_VCO_MOD
Frequency Control Loop
Clock
Data
Chip Select/Latch Enable
Serial Bus
Lock Detect
Output
Lock Detect
Circuitry

38 Reciter Circuit Description TB8100 Service Manual
© Tait Electronics Ltd April 2004
Synthesizer
The exciter synthesizer consists of a programmable frequency synthesizer
IC, the exciter VCO, and a modulatable frequency reference.
The synthesizer uses a phase-locked loop to lock the exciter VCO to a
modulatable frequency reference. The synthesizer IC receives the divider
and control information from the RISC processor via a 3-wire serial bus
(clock, data and enable). When the data bits are latched in, the synthesizer
processes the incoming signals from the VCO feedback signal (fvcofb) and
the reference oscillator (fref).
The VCO feedback attenuator is a resistive divider that terminates the VCO
feedback signal in a fixed low impedance (50Ω). This attenuates the VCO
RF level down to a level suitable for the RF prescaler (within the synthesizer
IC).
The FCL_VCXO reference oscillator is modulated by the FCL. The FCL
itself is locked to an internal reference 12.8MHz TCXO. When the TCXO
is active, the exciter synthesizer is locked to an “internal reference mode”
(by default). Alternatively, the FCL is locked to a phase locked 12.8MHz
external reference oscillator. When this external oscillator is active, the
exciter synthesizer is locked to an “external reference mode”. In operation
only one reference oscillator is active at any given time. Refer to
“Reference Switch” on page 28 for details on the phase-locked 12.8MHz
external reference oscillator.
The FCL_VCXO reference oscillator is buffered and divided down to the
6.25kHz (default) or 5kHz divider reference within the synthesizer IC. The
same divider reference is maintained by dividing the VCO feedback signal
using the prescaler and programmable dividers of the synthesizer IC. Phase
lock is achieved when both divider references have same phase and
frequency content (i.e. their difference is zero or DC). This is achieved by
the phase detector (part of the synthesizer IC), which compares both divider
references and delivers an error signal. A ± 4mA charge pump circuit (also
part of the synthesizer IC) and the active loop filter circuit convert this error
signal to a DC voltage (0 to 22V1) to tune the VCO for correction. The
loop filter has a bandwidth of 150Hz and filters the VCO control lines,
reference side bands and spurious signals.
Note The VCO frequency increases as the control line voltage increases.
VCO
The exciter VCO consists of a high Q VCO, modulation based on varicap
diodes, low noise amplifier, harmonic filter, fixed slope attenuator, final
driver and a 10dB fixed attenuator.
1. The normal lock range is between 3V and 16V.
TB8100 Service Manual Reciter Circuit Description 39
© Tait Electronics Ltd April 2004
High Q VCO The VCO BJT transistor operates in a common collector Colpitts oscillator,
and uses a shorted quarter-wave ceramic coaxial resonator. The open end
of the resonator is terminated by a combination of a high Q trimmer and
varactor diodes. This forms a high Q resonator which is both mechanically
and electronically tunable. Mechanical tuning is possible by adjusting the
trimmer. Changes in the control voltage from the loop filter are applied to
the varactors to facilitate electronic tuning. The oscillator has a drive level
of +7dBm ±1dB.
Modulation Based
on Varicap Diodes Modulation on the VCO is provided by an auxiliary varicap-based control
circuit which provides a modulation gain of 5kHz/Vp.
Low Noise Amplifier An N-channel dual gate MOSFET is used as a broad band matched Class A
low noise amplifier. It has internal self-bias circuitry and delivers an output
of +12dBm (nominal) before entering compression.
Harmonic Filter The VCO has a high second harmonic content. A third order low pass
elliptic filter is used to attenuate this content. It has an insertion loss of
0.5dB with 10dB of attenuation at the second harmonics.
Fixed Slope
Attenuator, Final
Driver and 10dB
Fixed Attenuator
To provide a drive of +20dBm, a silicon-based BJT transistor is used as a
broad band matched Class A final driver. This circuit delivers 20dB ±1dB
of gain for a +3dBm fixed input level. To maintain a fixed input level, a
fixed slope attenuator is introduced at the input to the final driver so that the
attenuation rate (slope) decreases with an increase in frequency. The slope
attenuator has 8dB of attenuation at the bottom of the band and a slope of
–1dBattn /100MHz. A 10dB fixed resistive pad attenuator provides a signal
level of +11dBm ±2dB to the input port of the PA, providing better reverse
isolation.
The VCO frequency spans from either 400–440MHz, 440–480MHz or
470–520MHz according to the product type (refer to “Identifying the
Reciter” on page 52).
Exciter Control Circuit
This circuit powers up and shuts down the exciter final driver in a controlled
manner. During transient adjacent channel power and cyclic keying, the
exciter needs to power up and shut down in a specified time sequence. The
exciter control circuit uses Ex_Key to power up or shut down the VCO final
driver, and PA_Key to power up or shut down the PA driver.

40 Reciter Circuit Description TB8100 Service Manual
© Tait Electronics Ltd April 2004
2.5 System Interface PCBs
The reciter can be fitted with an optional system interface PCB which
provides the links between the reciter’s internal circuitry and external
equipment. This PCB is securely mounted to the reciter’s chassis and is
connected to the digital PCB with a flexible connector. The system
interface PCB is fitted with industry-standard connectors and several
standard types are available for different applications.
The circuitry on the system interface PCB provides additional signal
processing so that the outputs meet standard system requirements. It also
enables the PCB to identify itself to the reciter control circuitry.
The system interface PCB is removable, which makes it possible to change
the application of a reciter by removing one type of PCB and fitting another.
Only one system interface PCB can be fitted to a reciter at any one time.
The following section provides an overview of all the system interface
circuitry. However, not all the circuitry described here will be fitted to any
particular system interface PCB. The different types of PCB and their main
features are listed in the following table. Refer also to Figure 2.9 on
page 41.
Note This section provides details on the system interface PCBs availa-
ble at the time of publication. Other types may be developed for
future applications.
System Interface PCB
Feature Standard Isolated
Isolated
E & M TaitNet
balanced audio non-isolated isolated isolated isolated
unbalanced audio ✓✓✓✓
RSSI ✓✓✓
Rx Gate ✓✓✓✓
Tx Key ✓✓✓✓
digital inputs 10 10 6 1
digital outputs 2 2 2 3
Tx relay output ✓✓✓
auxiliary power ✓✓✓✓
opto-coupled input ✓
opto-coupled output ✓
third-party connector ✓✓✓✓
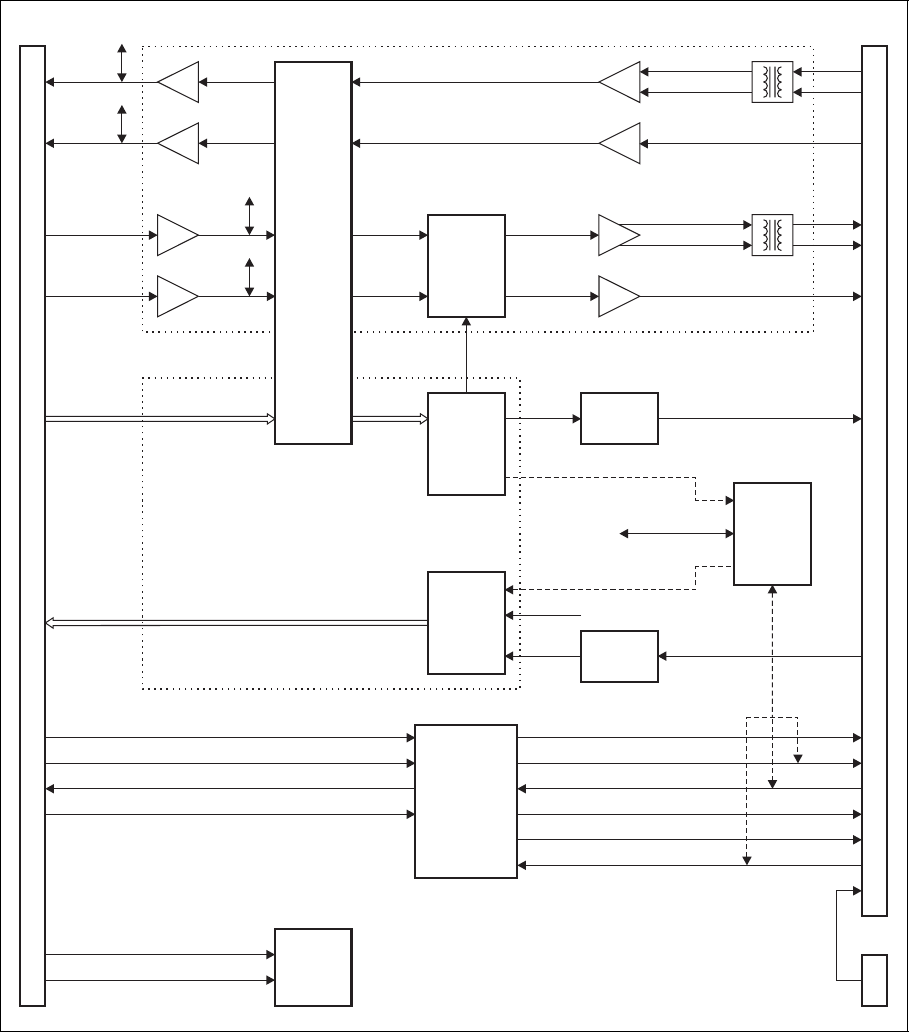
TB8100 Service Manual Reciter Circuit Description 41
© Tait Electronics Ltd April 2004
Connections to the
Reciter The system interface PCB has two connections to the reciter: a 40-way
flexible connection, and a high-speed connection.
The 40-way connection is essential to the system interface PCB’s operation.
It provides power and communications from the reciter, along with all the
other system interface inputs and outputs.
The high-speed connection is only used on system interface PCBs which
require a high rate data connection to the reciter processor.
Figure 2.9 Reciter System Interface PCB Block Diagram
Power
Supply
Digital
Inputs
Digital
Outputs
Third-party
Connector
Mutes
SIPOs*
PISOs*
Conventional
Signalling
Interface
System Interface Identification
Third-party Audio
RSSIRSSI
Rx GateRx Gate
Tx KeyTx Key
Tx RelayTx Relay
Opto-coupled Output
Opto-coupled Input
Audio I/O
Digital Sub-system
Control
SIO BusSIO Bus
SIO Bus
Digipots
Third-party
I/O
Third-party
I/O
Third-party
I/O
Third-party
I/O
External Interface
Reciter Interface
Auxiliary
Power
Balanced Audio Input
Balanced Audio Output
Unbalanced Audio Input
Unbalanced Audio Output
*SIPO = Serial In, Parallel Out
PISO = Parallel In, Serial Out
# transformers not fitted to
standard system interface PCB
#
#
42 Reciter Circuit Description TB8100 Service Manual
© Tait Electronics Ltd April 2004
Balanced Audio
Output The balanced audio output is a 600Ω audio interface. The output level can
be set over the range –20dBm to +10dBm, for 60% modulation. The
output level can be set with a resolution of 0.1dB. This output may be
either transformer isolated or just AC coupled.
Unbalanced Audio
Output The unbalanced audio output should only be used with high impedance
loads (>10kΩ). The output level can be set over the range 0.3Vpp to
3.0Vpp, for 60% modulation. The output level can be set with a resolution
of 0.1Vpp. This output is AC coupled.
Balanced Audio
Input The balanced audio input is a 600Ω audio interface. The input level can be
set over the range –20dBm to +10dBm, for 60% modulation. The input
level can be set with a resolution of 0.1dB. This input may be either
transformer isolated or just AC coupled.
Unbalanced Audio
Input The unbalanced audio input is a high impedance input (>10kΩ). The input
level can be set over the range 0.3Vpp to 3.0Vpp, for 60% modulation. The
input level can be set with a resolution of 0.1Vpp. This input is AC
coupled.
RSSI The RSSI output is DC coupled and provides a voltage proportional to the
received signal strength with a user-defined characteristic.
Rx Gate The Rx Gate output is an open collector output. The transistor is on when
a valid signal is received. The maximum current rating of this output is
100mA. The maximum voltage that should be applied to this output is 30V.
Tx Key The Tx Key input has a high input threshold guaranteed to be >5V. The
low input threshold is 2V. A low input keys the transmitter.
Digital Inputs The digital inputs have 5V logic thresholds and are active low. The
maximum external pull-up voltage on these inputs is 20V.
Digital Outputs The digital outputs are open collector outputs. The maximum current
rating of these outputs is 100mA. The maximum voltage that should be
applied to these outputs is 30V.
Tx Relay Driver
Output The Tx relay driver output is an open collector output. The maximum
current rating of this output is 250mA. The maximum voltage that should
be applied to this output is 30V.
Opto-coupled
Keying Input This input operates in parallel with the Tx Key input. Although it has the
same functionality as the Tx Key input, it is electrically isolated. The input
may be driven with a voltage in the range ±10V to ±60V. The input
current is regulated to 10mA.
TB8100 Service Manual Reciter Circuit Description 43
© Tait Electronics Ltd April 2004
Opto-coupled Gate
Output This output operates in parallel with the Rx Gate output. Although it has
the same functionality as the Rx Gate output, it is electrically isolated. The
maximum output current is 120mA. The maximum voltage that should be
applied across this output is ±350V.
Third-party
Connector The third-party connector provides access to audio, keying, gating and
digital I/O signals to allow the integration of third-party modules such as
scramblers.
Power Supplies The system interface PCB is powered via the 40-way flexible connection to
the reciter.
2.6 Power Supply
The reciter is designed to operate from the +28V regulated supply provided
by the PMU. The nominal +28V supply enters the reciter digital PCB and
passes through an overcurrent and overvoltage protection section before
being distributed. The protected +28V output supplies the control
comparators, fan switch, and main regulators. There is one regulator on the
digital PCB and another on the RF PCB.
RF PCB The main regulator is a switched mode converter that has two outputs: the
flyback portion generates +8.5V, and the buck portion generates +5.3V.
The +8.5V supply is regulated to +8.0V for reticulation to the RF circuits,
either directly, or via switching circuits used in power saving modes. The
+8.5V supply is also used to power the analogue sections of the system
interface PCB (via the digital PCB).
The +5.3V supply is regulated to +3.3V to power the RF synthesizers.
The RF PCB has a charge pump converter that generates +23V from both
the +5.3V and +8.5V supplies. This is used to supply the active loop filters
of the RF synthesizers. The +8.5V output and the +5.3V supply to the
charge pump can be switched as part of the power saving modes.
Digital PCB The main regulator is a switched mode converter that has two outputs: the
flyback portion generates +5.3V, and the buck portion generates +3.3V.
The +5.3V output supplies the op amps associated with the CODECs and
is distributed with regulators: +5V for the ADC, +5V for the system, and
+3V for the 40MHz clock circuitry. The +5.3V and +5V regulated
supplies can be switched as part of the power saving modes.

44 Reciter Circuit Description TB8100 Service Manual
© Tait Electronics Ltd April 2004
Figure 2.10 Reciter Power Supply Block Diagram
Polyswitch
+ Zener
DSP Low
Regulator
2.5V
3V
Lock-out
Circuit*
3V
Regulator
3.3V
Regulator
8V
Regulator
Power
Switch
Power
Switches
Charge
Pump
Power
Switch
Power
Switch
Protection
Circuit
Linear 5V
Regulator
Dual SMPS
Regulator
Dual SMPS
Regulator
Comparators
Fan
Switch
Filter
Filter
5V
Regulator
Filter
5V
Regulator
Switch Filter
+28V
+28V 5.3V
8.5V 23V
8.5V to SIF
8V
8VEX
8VRX
3.3V
PWD_EX
PWD_RX
PWD_ON
+28V
+28V SD
5.3V
3.3V
Control
PWR_GOOD
PWD_ON
PWD_RX
5V to SIF
Digital 5.3V
To Fan
+28V to RF PCB
RF PCB
Digital PCB
*To prevent DSP latch-up
SIF = system interface PCB
Analogue 5.3V
Analogue 5V
Analogue
3V
System 5V
Digital 3.3V
Analogue 3.3V
Analogue 3.3V
2.5V
3.3V to SIF
TB8100 Service Manual Reciter Circuit Description 45
© Tait Electronics Ltd April 2004
The +3.3V output is distributed to the remaining circuitry and to the
+2.5V regulator for the DSP. These are switched as part of the power saving
modes. The +3.3V output is also supplied to the system interface PCB via
a protection circuit.
46 Reciter Circuit Description TB8100 Service Manual
© Tait Electronics Ltd April 2004

TB8100 Service Manual Reciter Circuit Description 47
© Tait Electronics Ltd April 2004
Figure 2.11 Identifying the Circuitry on the Digital and System Interface PCBs
bsystem interface PCB
cCODECs
dSRAM
eRISC JTAG connector (factory use only)
fflash memory
gRISC
hDSP
iDSP JTAG connector (factory use only)
jmain digital system
1) power supply
1! digital IF and clock
1@ DDC
1# ADC
1$ 40MHz digital clock
1% 70.1MHz IF
1^ 12.8MHz reference
1& audio
1* high speed data connector
1( third-party connector
UHF (H band) reciter shown fitted
with isolated system interface PCB
b
c
d
f
g
h
j
1)
1!
1@
1#
1$
1%
1^
1&
1*
e
i
1(
48 Reciter Circuit Description TB8100 Service Manual
© Tait Electronics Ltd April 2004

TB8100 Service Manual Reciter Circuit Description 49
© Tait Electronics Ltd April 2004
Figure 2.12 Identifying the Circuitry on the RF PCB
bexternal reference input
cmixer and post-mixer buffer
dreceiver VCO
ereceiver VCO trimmer
fIF tuning elements
greceiver synthesizer
hIF
iTCXO
jaudio buffers
1) exciter VCO
1! exciter VCO trimmer
1@ exciter synthesizer
1# exciter RF output
1$ FCL
1% FCL buffers
1^ power supply
1& external reference switch/internal VCXO reference
1* AGC
1( front end 1
2) front end first helicals
2! front end 2
2@ front end second helicals
2# receiver RF input
Note:
In order to show as much of the circuitry as possible in the
photograph, the SMD shields have been removed.
UHF (H band) reciter shown
b
c
d
e
f
g
h
1$
1^
1&
1*
1(
2)
2!
2@
i
j
1)
1!
1@
1#
1%
2#
50 Reciter Circuit Description TB8100 Service Manual
© Tait Electronics Ltd April 2004

TB8100 Service Manual Reciter Servicing 51
© Tait Electronics Ltd April 2004
3 Reciter Servicing
Important This equipment contains devices which are susceptible to
damage from static charges. Refer to “ESD Precautions”
on page 15 for more information on antistatic procedures
when handling these devices.
This chapter provides information on how to identify, remove and replace
the main mechanical parts and individual PCBs.
Figure 3.6 on page 65 identifies the main mechanical parts, and Figure 3.1
on page 53 identifies the individual PCBs. “Identifying the Reciter” on
page 52 explains how to identify the model and hardware configuration of
a reciter from its product code.
Note For the sake of simplicity and clarity, the instructions and illustra-
tions in this chapter refer to a UHF (H band) reciter fitted with an
isolated system interface PCB. However, the same basic proce-
dures and techniques apply to other models of reciter and system
interface PCB.

52 Reciter Servicing TB8100 Service Manual
© Tait Electronics Ltd April 2004
3.1 Disassembly and Reassembly
Identifying the Reciter
You can identify the model and hardware configuration of a reciter by
referring to the product code printed on a label on the rear panel. The
meaning of each character in the product code is explained in the table
below.
Note This explanation of reciter product codes is not intended to sug-
gest that any combination of features is necessarily available in any
one reciter. Consult your nearest Tait Dealer or Customer Service
Organisation for more information regarding the availability of
specific models and options.
Product Code Description
TBAXXXX-XXXX 4 = reciter
TBA4XXX-XXXX 0 = default
TBA4XXX-XXXX Frequency Band and Sub-band
B2 = 136MHz to 156MHz
B3 = 148MHz to 174MHz
C2 = 174MHz to 193MHz
C3 = 193MHz to 225MHz
H1 = 400MHz to 440MHz
H2 = 440MHz to 480MHz
H3 = 470MHz to 520MHz
K2 = 762MHz to 870MHza
a. The actual frequency coverage in this band is:
Transmit: 762MHz to 776MHz, and 850MHz to 870MHz
Receive: 792MHz to 824MHz
TBA4XXX-XXXXSystem Interface PCB
000 = no system interface PCB fitted
0A0 = standard
0B0 = isolated
0C0 = isolated E & M
0T1 = TaitNet
TBA4XXX-XXXX0 = default

TB8100 Service Manual Reciter Servicing 53
© Tait Electronics Ltd April 2004
Figure 3.1 Identifying the Reciter PCBs
digital PCB
UHF (H band) reciter shown
fitted with isolated system
interface PCB; RF PCB shown
with shields removed for clarity
system interface PCBRF PCB

54 Reciter Servicing TB8100 Service Manual
© Tait Electronics Ltd April 2004
Screw Torque Settings
The recommended torque settings for the screws and nuts used in the reciter
are as follows:
Removing the Covers
1. Remove the M3 Torx screws securing the covers to the heatsink, and
to the front and rear panels. Lift off the covers.
Removing the Front and Rear Panels
The circled numbers in the following instructions refer to Figure 3.2.
1. Remove the four M2.5 Torx screws b securing the SMA connector
to the heatsink and to the front panel.
2. Desolder the centre pin of the SMA connector c from the RF PCB
and remove the connector.
3. Remove the two M3 Torx screws d securing the handle to the
heatsink.
4. Remove the M3 screw e securing the front panel to the heatsink,
and remove the front panel.
5. If necessary, remove the two M3 screws securing the fan duct f to
the heatsink.
6. Remove the vent guard clip g from the rear panel.
7. Remove the two M3 Torx screws h securing each rear panel to the
heatsink. If you want to remove the rear panel on the RF side, first
unplug the coaxial cables from the RF PCB.
Location / Function Torque Driver/
Spanner Size
■securing the side covers to the
heatsink and front and rear panels
■securing the front and rear panels to
the heatsink
■securing the handle to the front
panel
■securing the PCBs to the heatsink
0.5N·m / 4.5lbf·in T10 M3
securing the SMA connector to the
front panel
0.3N·m / 2.5lbf·in T8 M2.5
securing the BNC/TNC connectors to
the rear panel
1.7N·m / 15lbf·in 11mm AF

TB8100 Service Manual Reciter Servicing 55
© Tait Electronics Ltd April 2004
Refitting the Front and Rear Panels
The circled numbers in the following instructions refer to Figure 3.2.
1. If removed previously, refit the fan duct f to the heatsink and secure
with the two M3 Torx screws.
2. Refit the front panel and secure to the heatsink with the M3 Torx
screw e.
3. Secure the handle to the heatsink with the two M3 Torx screws d.
Figure 3.2 Removing the Front and Rear Panels
front view rear view
RF side
RF sidedigital side
b
c
d
e
f
h2 for each
rear panel
g

56 Reciter Servicing TB8100 Service Manual
© Tait Electronics Ltd April 2004
4. Secure the SMA connector to the heatsink and front panel with the
four M2.5 Torx screws b.
5. Resolder the centre pin of the SMA connector c to the RF PCB.
6. Refit the rear panel to the heatsink and secure with the two M3 Torx
screws h. If you have removed the rear panel on the RF side,
reconnect the coaxial cables to the RF PCB.
7. Refit the vent guard clip g.
Refitting the Covers
1. Slide each cover into place over the front and rear panels. Make sure
the holes in the covers line up with the threaded holes in the heatsink
and front and rear panels.
2. Press the covers firmly into place and secure with the M3 Torx screws.
Note The covers are not interchangeable. Each cover must be fitted to
the correct side and in the correct orientation.
3.2 Replacing the Digital PCB
Important You must reprogram and recalibrate the reciter after replac-
ing the digital PCB. Refer to “Reprogramming and Rec-
alibration” on page 59.
Refer to Section 3.1 “Disassembly and Reassembly” for details on removing
and refitting the covers and front and rear panels. The circled numbers in
the following instructions refer to Figure 3.3.
Removal 1. Remove the digital side cover and the front panel.
2. Disconnect the flexible connectors to the system interface PCB b
and RF PCB c from their respective sockets on the digital PCB.
3. Disconnect the 70.1MHz IF d and 12.8MHz reference e coaxial
cables.
4. Remove the M3 Torx screws securing the PCB to the heatsink.
5. Carefully lift the PCB upwards off the locating pins f and remove it
from the heatsink, feeding the coaxial cables and flexible connector
through the slot in the PCB. Take care not to dislodge the flexible
connector from its socket on the RF PCB.

TB8100 Service Manual Reciter Servicing 57
© Tait Electronics Ltd April 2004
Figure 3.3 Replacing the Digital and System Interface PCBs
b
f
d
e
c
f
g
g

58 Reciter Servicing TB8100 Service Manual
© Tait Electronics Ltd April 2004
Refitting 1. To refit the PCB, follow the removal instructions in reverse order.
Important Make sure the insulator sheet is correctly positioned and flat
on the heatsink. Although this sheet is an electrical insula-
tor, it is also thermally conductive and must allow the PCB
to sit as flat as possible to provide effective heatsinking.
Operating the reciter without the insulator sheet in
place will result in permanent damage to the digital
or system interface PCBs.
Important Make sure the flexible connectors are correctly positioned
and latched in their sockets, as shown in Figure 3.4.
Note Before tightening the screws, press the PCB down over the locat-
ing pins so that it is firmly seated against the heatsink. Then
tighten the M3 Torx screws to the correct torque, working from
the centre of the PCB to the edges.
Figure 3.4 Reconnecting the Flexible Connectors
flexible connector inserted
straight into socket
blue stripe on same
side as latch
latch pushed fully down
at both ends

TB8100 Service Manual Reciter Servicing 59
© Tait Electronics Ltd April 2004
Reprogramming
and Recalibration If you have replaced the digital PCB, you will have to reprogram and
recalibrate the reciter as described in the table below.
3.3 Replacing the System Interface PCB
Important You must reprogram and recalibrate the reciter after replac-
ing the system interface PCB. Refer to “Reprogramming
and Recalibration” on page 60.
Refer to Section 3.1 “Disassembly and Reassembly” for details on removing
and refitting the covers and front and rear panels. The circled numbers in
the following instructions refer to Figure 3.3 on page 57.
Removal 1. Remove the digital side cover and rear panel.
2. Disconnect the flexible connector to the digital PCB b from the
socket on the system interface PCB.
3. Remove the M3 Torx screws securing the PCB to the heatsink.
4. Carefully lift the PCB upwards off the locating pins g and remove it
from the heatsink.
Procedure Details
■reprogram the product code
■reprogram the reciter type
reprogram this information into the reciter
using the Calibration Kit software; refer to
the Calibration Kit documentation for more
details
reprogram the feature licence keys
(if necessary)
you will need to reprogram new feature
licence keys into the reciter to re-enable any
software features that were previously
enabled; you will need to use the Service Kit
software to do this; contact your nearest
Tait Customer Service Organisation for
further details about obtaining feature
licence keys
replace the serial number label the serial number of the reciter will change
to the number already programmed into the
replacement digital PCB; stick the new serial
number label onto the rear panel
■calibrate the exciter
■calibrate the RSSI
■calibrate the audio
■adjust the receiver lock band
(switching range)
■tune the receiver
■adjust the exciter lock band
carry out these procedures in the order
shown using the Calibration Kit software;
refer to the Calibration Kit documentation
for more details

60 Reciter Servicing TB8100 Service Manual
© Tait Electronics Ltd April 2004
Refitting 1. To refit the PCB, follow the removal instructions in reverse order.
Important Make sure the insulator sheet is correctly positioned and flat
on the heatsink. Although this sheet is an electrical insula-
tor, it is also thermally conductive and must allow the PCB
to sit as flat as possible to provide effective heatsinking.
Operating the reciter without the insulator sheet in
place will result in permanent damage to the digital
or system interface PCBs.
Important Make sure the flexible connector is correctly positioned and
latched in its socket, as shown in Figure 3.4 on page 58.
Note Before tightening the screws, press the PCB down over the locat-
ing pins so that it is firmly seated against the heatsink. Then
tighten the M3 Torx screws to the correct torque, working from
the centre of the PCB to the edges.
Reprogramming
and Recalibration If you have replaced the system interface PCB, you will have to reprogram
and recalibrate the reciter. The actual procedures required will depend on
whether or not the replacement PCB is the same type as the original, as
shown in the table below.
PCB Type Procedure Details
when the replacement
system interface PCB is
a different type from
the original
■reprogram the product code
■reprogram the reciter type
reprogram this information into the reciter
using the Calibration Kit software; refer to
the Calibration Kit documentation for more
details
calibrate the audio carry out this procedure using the Calibration
Kit software; refer to the Calibration Kit
documentation for more details
when the replacement
system interface PCB is
the same type as the
original
calibrate the audio carry out this procedure using the Calibration
Kit software; refer to the Calibration Kit
documentation for more details

TB8100 Service Manual Reciter Servicing 61
© Tait Electronics Ltd April 2004
3.4 Replacing the RF PCB
Important You must recalibrate the reciter after replacing the RF PCB.
Refer to “Recalibration” on page 63.
Refer to Section 3.1 “Disassembly and Reassembly” for details on removing
and refitting the covers and front and rear panels. Unless otherwise
indicated, the circled numbers in the following instructions refer to
Figure 3.5.
Removal 1. Remove both covers and the front panel.
2. Disconnect the flexible connector to the digital PCB c from its
socket on the digital PCB (refer to Figure 3.3 on page 57).
3. Disconnect the 70.1MHz IF d and 12.8MHz reference e coaxial
cables from their sockets on the digital PCB (refer to Figure 3.3).
4. Disconnect the RF input b and external reference c coaxial cables
from their sockets on the RF PCB.
5. Remove the M3 Torx screws securing the PCB to the heatsink.
6. Carefully lift the PCB upwards off the locating pins d and remove it
from the heatsink, feeding the coaxial cables and flexible connector
through the slot in the heatsink.
Refitting 1. Make sure that the 70.1MHz IF and 12.8MHz reference coaxial
cables are secure in their sockets on the bottom of the RF PCB.
2. Make sure that the flexible connector is correctly positioned and
latched in its socket on the bottom of the RF PCB (refer to
Figure 3.4 on page 58).
3. Refit the PCB, following the removal instructions in reverse order.
Note Before tightening the screws, press the PCB down over the locat-
ing pins so that it is firmly seated against the heatsink. Then
tighten the M3 Torx screws to the correct torque, working from
the centre of the PCB to the edges.

62 Reciter Servicing TB8100 Service Manual
© Tait Electronics Ltd April 2004
Figure 3.5 Replacing the RF PCB
b
d
c
d

TB8100 Service Manual Reciter Servicing 63
© Tait Electronics Ltd April 2004
Recalibration If you have replaced the RF PCB, you will have to recalibrate the reciter as
described in the table below.
Important Do not adjust the IF.
Procedure Details
■calibrate the exciter
■calibrate the RSSI
■adjust the receiver lock band
(switching range)
■tune the receiver
■adjust the exciter lock band
carry out these procedures in the order
shown using the Calibration Kit software;
refer to the Calibration Kit documentation
for more details
64 Reciter Servicing TB8100 Service Manual
© Tait Electronics Ltd April 2004

TB8100 Service Manual Reciter Servicing 65
© Tait Electronics Ltd April 2004
Figure 3.6 Reciter Mechanical Assembly
Description IPN
b70.1MHz IF and 12.8MHz reference coaxial cables 219-02849-XX
cflexible connector 219-02850-XX
dRF input coaxial cable 219-02851-XX
eexternal reference coaxial cable 219-02852-XX
fSMA connector 240-02155-XX
gvent guard clip 303-50108-XX
hhandle 308-01065-XX
iheatsink 308-13148-XX
jRF side cover 316-06795-XX
1) front panel 316-06796-XX
1! digital side cover 316-06797-XX
1@ rear panel - digital side; changes according to the
system interface PCB fitted:
standard, isolated, isolated E & M
Tai tN e t
none
316-06798-XX
316-06799-XX
316-06802-XX
1# fan duct 316-06804-XX
1$ rear panel - RF side 316-06805-XX
1% M3x6mm countersunk Torx screw 345-40460-XX
1^ M3x8mm pan head Torx screw with spring & flat
washers
345-40470-XX
1& M2.5x8mm pan head Torx screw 345-40490-XX
1* M3x12mm pan head Torx Taptite screw 349-02065-XX
1( 4–40 UNC screw lock 354-01043-XX
2) thermally conductive insulator sheet 362-01120-XX
2! RF PCB
2@ digital PCB
2# system interface PCB
Note:
The characters XX in an IPN (Tait Internal Part Number)
stand for the issue number of the part. Only the latest
issue of each part will normally be available for ordering
as spare or replacement parts.
b
c
c
e
d
f
g
h
i
j
1)
1!
1@
1#
1$
1%
1%
1%
1%
1%
1^
1^
1&
1*
1(
2)
2!
2@
2#
1^
x14
x4
x2
x2
x16
x2
x11
x2
x4
x24
x8
66 Reciter Servicing TB8100 Service Manual
© Tait Electronics Ltd April 2004

TB8100 Service Manual Power Amplifier Circuit Description 67
© Tait Electronics Ltd April 2004
4 Power Amplifier Circuit Description
The TB8100 power amplifier (PA) is a modular design with the circuitry
divided between separate PCBs. These PCBs are assembled onto a heatsink
in different configurations in different models.
Figure 4.1 below shows the configuration for a 100W PA, along with the
main inputs and outputs for power, RF and control signals. The 100W PA
consists of:
■a 6W PCB
■two quadrature-combined 60W PCBs
■a splitter PCB and a combiner PCB
■a low pass filter and directional coupler PCB
■a control PCB.
The configuration of the 50W PA is similar, but it uses only one 60W PCB
and does not require the splitter or combiner PCBs. The 5W PA does not
use the 60W, splitter or combiner PCBs.
RF interconnect PCBs are also used in some configurations to connect the
PCBs together. The type of interconnect PCB used depends on the
configuration of the PA. Figure 5.1 on page 79 shows the different
configurations for the 5W, 50W and 100W PAs.
The locations of the main circuit blocks on the PCBs are shown in
Figure 4.3 on page 75.
Figure 4.1 PA High Level Block Diagram
6W
PCB
Control PCB
60W
PCB
60W
PCB
Ambient Air
Temperature
Sensor
PCB
Splitter
PCB
Combiner
PCB
Low-Pass
Filter
&
Directional
Coupler
PCB
RF I/P +
PA Key RF O/P
28VDC
I/P
DC
DC
DC
RF RF RF RF
RF RF
Control &
Monitor
Control &
Monitor
Control &
Monitor
System
Control
Bus

68 Power Amplifier Circuit Description TB8100 Service Manual
© Tait Electronics Ltd April 2004
4.1 Microprocessor Control Circuitry
Refer to Figure 4.2 on page 70.
The PA has a microprocessor which performs the following functions:
■monitors the operating conditions of the PA
■controls the RF power level
■reports faults (by generating alarms)
■takes preventative action to protect the PA under fault conditions.
The alarms and diagnostics are accessed through I2C bus messages via the
reciter, control panel and Service Kit software.
There are no manual adjustments in the PA because all the calibration
voltages and currents required to control and protect the PA are monitored
by the microprocessor. The software also automatically detects the PA
configuration and controls the PA accordingly.
Diagnostics and Alarms
The diagnostic functions and alarms monitored by the PA include:
■the temperature of the 6W PCB
■the temperatures of 60W PCB 1 (50W and 100W PAs) and 60W
PCB 2 (100W PA)
■the ambient temperature of the intake air1
■forward and reverse power
■load VSWR
■the transmit current of the 6W driver transistor
■the transmit current of the final transistors on 60W PCB 1 (50W and
100W PAs) and 60 W PCB 2 (100W PA)
■the current imbalance between the final transistors on 60W PCBs 1 and
2 (100W PA)
■the supply voltage
■the summary alarm.
Most alarms have two thresholds. The first threshold activates the alarm and
is usually set by the user via the Service Kit software. The second threshold
defines the limit of operation of the PA and the software will either foldback
the RF transmit power or suspend transmission until the fault condition is
recovered. The values for the second threshold are set in the factory and
cannot be changed. In all instances there is a small amount of hysteresis
between the value at which the alarm, foldback or shutdown activates and
the value at which the alarm or shutdown is cleared.
1. Ambient temperature is defined as the temperature of the air at the intake
to the cooling fan.

TB8100 Service Manual Power Amplifier Circuit Description 69
© Tait Electronics Ltd April 2004
A red LED visible from the front panel of the PA will light to indicate a
summary alarm.
For a more detailed description of alarms and diagnostics refer to the Service
Kit User’s Manual or on-line help.
PA-Key
The PA is keyed by a +8VDC signal which is superimposed on the RF
signal on the coaxial input cable.
The key-up sequence requires the RF input (+11dBm) to be turned on and
stable before the PA is keyed on. When the PA is keyed off, the RF input
is turned off only when the key-down sequence is complete.
Foldback
The PA control circuitry will reduce the RF output power to Pmin when
any one of the following fault conditions occurs:1
■the temperature of the 6W PCB, 60W PCB 1 or 60W PCB 2 exceeds
the maximum allowable temperature
■the supply voltage drops to between 24 and 26VDC or rises to between
30 and 32VDC
■the load VSWR is ≥10:1 (foldback is deactivated when the VSWR
<5:1)
■the transmit current of the 6W driver transistor, 60W final transistor 1
or 60W final transistor 2 exceeds the maximum allowable current.
Pmin is defined as follows:
1. The accuracy of the measurement of the parameter values is subject to the
tolerances listed in the Specifications Manual.
Model Pmin
5W 1W
50W 5W
100W 10W
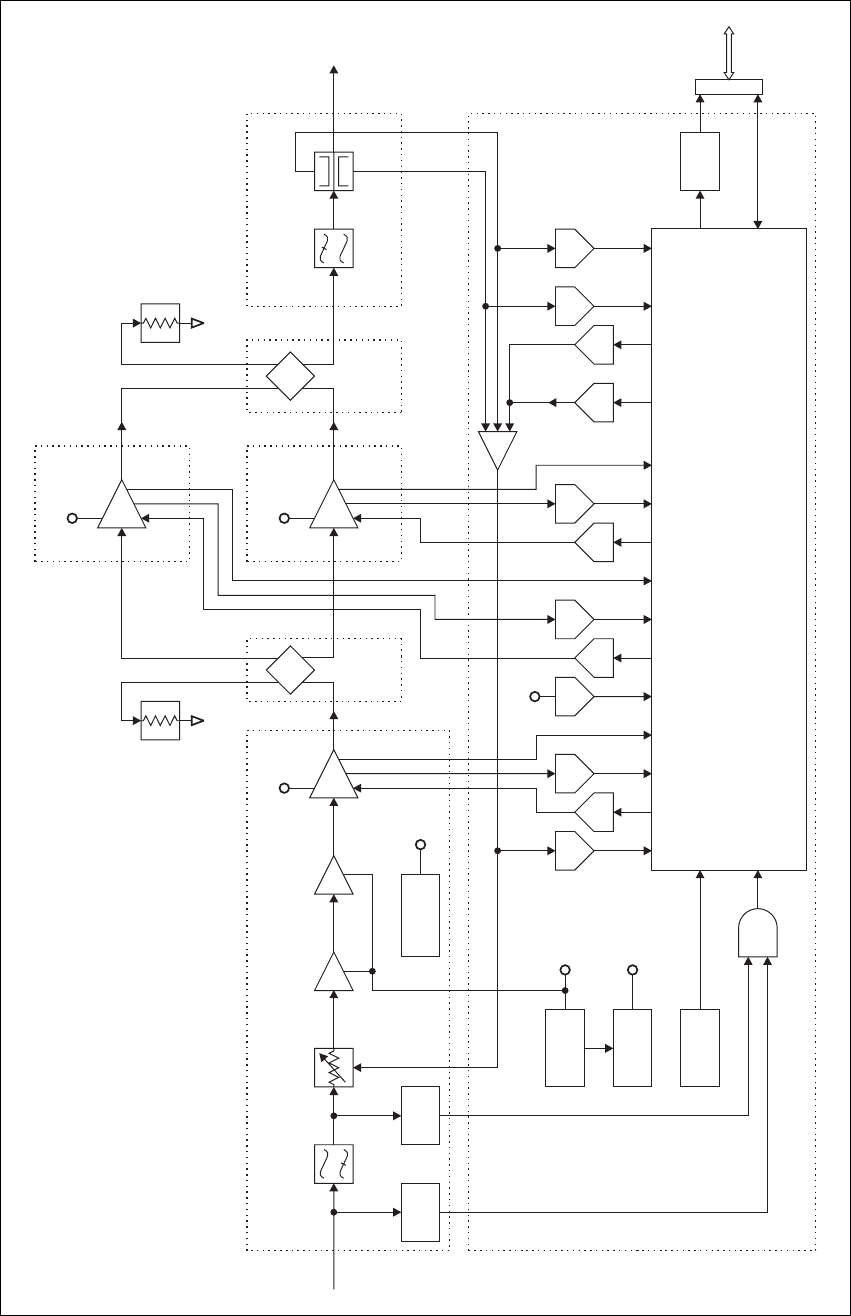
70 Power Amplifier Circuit Description TB8100 Service Manual
© Tait Electronics Ltd April 2004
Figure 4.2 PA Control, RF and Power Supply Circuitry Block Diagram
60W
High Pass
Filter
Directional
Coupler
Low Pass
Filter
PIN
Attenuator
100mW
Gain Block
Final
6W PCB
Control PCB
LPF/Directional Coupler PCB
Microprocessor
60W
PCB
60W
PCB
Combiner
PCB
Splitter
PCB
Driver
6W
50
Load
Ω50
Load
Ω
1W
Pre-driver
RF In RF Out
RF
Block
RF
Detect
DACDACDACDACDAC
ADCADC ADC ADC ADC ADC ADC
AND
power control
driver current
driver temperature
final 2 drive current
final 1 drive current
driver bias
final 2 bias
final 2 temperature
final 1 temperature
final 1 bias
RF power setting
transient wave shape
forward power
reverse power
ambient air temperature
+10V Power
Supply
+5V Power
Supply
Fan
Buffer
-3V Power
Supply
+2.5V Power
Supply
+10V
-3V
PA_KEY I C
2
System
Control
Bus
+28V
+28V
60W
Final
+28V
This drawing shows the
circuitry for the 100W PA.

TB8100 Service Manual Power Amplifier Circuit Description 71
© Tait Electronics Ltd April 2004
Shutdown
The PA software will prevent transmission under the following conditions:
■the following calibration procedures were not completed successfully:
■6W driver transistor, 60W final transistor 1 or 60W final
transistor 2 bias
■detector bias
■supply voltage
■output power
■the supply voltage drops below 24VDC or exceeds 32VDC
■the transmit current of the 6W driver and 60W final transistors does not
reduce to a safe level after foldback
■the configuration of the PA is invalid.
Calibration
You can calibrate the bias currents and output power settings of the 6W
driver and 60W final transistors using the Calibration Kit software.
However, this calibration is only required if components in the RF signal
path have been altered.
Power Control
The PA has a power control circuit which keeps the output power constant
and protects the PA from VSWR mismatch conditions. The control circuit
monitors forward and reverse power and these measurements are used to:
■determine forward and reverse power
■keep the output power constant
■foldback the power under mismatch conditions
■calculate VSWR.
The power level is set by requesting the power level in Watts via an I2C bus
message. The minimum size of a power step is 1W and the range of output
power settings is:
The forward power, reverse power and load VSWR measurements may also
be requested via I2C bus messages.
Model Output Power Range
5W 1 to 5W
50W 5 to 50W
100W 10 to 100W
72 Power Amplifier Circuit Description TB8100 Service Manual
© Tait Electronics Ltd April 2004
The foldback loop is analogue until the VSWR reaches 10:1, at which point
the microprocessor initiates foldback.
The microprocessor and control loop are also used to shape the RF signal
envelope during key-on and key-off transients.
Fan Control
The fan is supplied from a +24V controlled supply on pin 13 of the IDC
connector (ground is on pin 14). The status of the fan supply voltage is
dependent on the operating temperature of the PA. The fan is turned on
when the PA operating temperature exceeds the user-defined thresholds set
using the Service Kit software. The fan remains on until the operating
temperature of the PA falls to 5°C below the threshold temperature.
The fan is also turned on for 30 seconds before an ambient temperature
measurement is taken. This is necessary as the ambient temperature sensor
requires airflow to perform an accurate temperature measurement.
Power is supplied to the fan via the 16-way ribbon cable from the PA to the
subrack interconnect PCB. From there it is fed through the control panel
to the fan. If two PAs are fitted in a subrack, either PA will turn on the fan
when required.
Power Supplies
The PA operates off a single +28VDC external power supply. The normal
range of operation is +26 to +30VDC. If the supply voltage falls to
between +24 and +26VDC or rises to between +30 and +32VDC, the PA
will reduce its output power to foldback levels. If the supply voltage falls
below +24VDC or rises above +32VDC, the PA will cease transmission
(shutdown).
The PA also has four internal power supplies to produce –3, +2.5, +5 and
+10VDC.
Temperature Monitoring
The PA monitors the temperatures of the 6W PCB, 60W PCB 1 and 60W
PCB 2. The operating temperatures can be requested via an I2C bus
message.
If any PCB reaches the designated maximum temperature, the PA software
will report an alarm via the I2C bus. The maximum temperature thresholds
may be set using the Service Kit software. In addition to activating alarms,
the PCB temperatures are also used to activate the PA fan, and power
foldback. The foldback thresholds are set in the factory and cannot be

TB8100 Service Manual Power Amplifier Circuit Description 73
© Tait Electronics Ltd April 2004
adjusted by the user. A recovery hysteresis of 5°C is applied to all
temperature thresholds.
Ambient Air Temperature Sensor
The PA ambient air temperature sensor PCB may be fitted in one of two
positions. It is inserted through the appropriate slot in the control PCB and
plugs into a 3-way connector. The sensor PCB is positioned between the
heatsink fins and requires forced airflow to perform an accurate
measurement.
Note You must fit the sensor PCB in the correct location to ensure that
the temperature of the airflow over the sensor is nearest the ambi-
ent temperature of the air at the intake to the cooling fan.
Figure 5.1 on page 79 shows the correct location of the sensor
PCB in each model of PA.
4.2 RF Circuitry
Refer to Figure 4.2 on page 70.
6W PCB
The 11dBm (±2dB) RF input is fed to the variable PIN diode attenuator
which provides power control. From the PIN diode attenuator the signal is
fed via a 100mW gain block and a 1W gain stage to a 6W transistor where
it is amplified to the final output level of 6W. This 6W transistor forms the
output stage of the 5W PA and is the driver stage for the 50W and 100W
PAs.
The gain block and 1W transistor operate off a +10V switched supply,
while the 6W driver transistor operates off a +28V supply.
The 6W PCB also has circuitry to monitor the drain current and
temperature of the 6W transistor, and the presence of an RF input signal.
60W PCB
The output from the 6W PCB is fed to the 60W final transistor which
amplifies the signal to an output power of 60W. The 60W transistor
operates off a +28V supply.
The 60W PCB also has circuitry to monitor the drain current and
temperature of the 60W transistor.
74 Power Amplifier Circuit Description TB8100 Service Manual
© Tait Electronics Ltd April 2004
Low Pass Filter and Directional Coupler PCB
The output from the 60W PCB is fed to the RF output connector via a low
pass filter (LPF), to attenuate harmonics, and a dual directional coupler.
The directional coupler senses forward and reverse power which is rectified
and passed to the control circuitry for metering, alarm and power control.
The directional coupler is on the output side of the LPF to measure true
output power.
Splitter and Combiner PCBs
In the 100W PA the output from the 6W PCB is split through a 3dB hybrid
coupler on the splitter PCB to drive two 60W PCBs in quadrature. The
outputs from these two PCBs are then combined by another 3dB hybrid
coupler on the combiner PCB before being fed to the LPF/directional
coupler PCB.
Interconnect PCBs
Because of the modular design of the PA, interconnect PCBs are used in
certain models to connect PCBs that are physically separated on the
heatsink. They have no components and their only function is to link two
parts of the circuit together. The interconnect PCBs are shown in
Figure 5.1 on page 79.

TB8100 Service Manual Power Amplifier Circuit Description 75
© Tait Electronics Ltd April 2004
Figure 4.3 Identifying the Circuitry on the PA PCBs
bRF output
clow pass filter/directional coupler PCB
ddirectional coupler
elow pass filter
fcontrol PCB
gpower supply
hambient air temperature PCB
i28VDC power feed
j60W PCB
1) microprocessor
1! 6W PCB temperature sense
1@ 6W driver transistor drain current sense
1# I2C signal filtering
1$ RF input (obscured)
1% 28VDC input
1^ 6W PCB
1& pre-driver transistor
1* 6W driver transistor
1( termination resistor (50Ω load)
2) splitter PCB
2! 60W PCB temperature sense
2@ 60W final transistor
2# 60W PCB
2$ 60W final transistor drain current sense
2% combiner PCB
2^ termination resistor (50Ω load)
Note:
This drawing shows a 100W UHF (H band) PA. The configuration of
the 5W and 50W PAs is shown in Figure 5.1 on page 79.
d
e
h
f
j
1)
1!
1@
1#
b
1$
c
g
1%
1^
1&
1*
1(
2)
2!
2@
2#
2$
2%
2^
i
76 Power Amplifier Circuit Description TB8100 Service Manual
© Tait Electronics Ltd April 2004

TB8100 Service Manual Power Amplifier Servicing 77
© Tait Electronics Ltd April 2004
5 Power Amplifier Servicing
Caution The termination resistors used in the 100W power
amplifier contain some beryllium oxide. This sub-
stance is perfectly harmless in its normal solid form,
but can become a severe health hazard when it has
been reduced to dust. For this reason the termina-
tion resistors should not be broken open, mutilated,
filed, machined, or physically damaged in any way
that can produce dust particles. You should safely
dispose of all used or obsolete components accord-
ing to your local regulations.
Caution Touching high-power RF components or circuits
can cause serious burns. We strongly recommend
you do not touch any RF components or tracks in
the PA while it is transmitting.
Caution The TB8100 power amplifier (PA) weighs between
4.8kg and 5.8kg. Take care when handling the PA
to avoid personal injury.
Important This equipment contains devices which are susceptible to
damage from static charges. Refer to “ESD Precautions”
on page 15 for more information on antistatic procedures
when handling these devices.
The TB8100 PA is a modular design with the circuitry divided between
separate PCBs which are assembled in different configurations in different
models.
This chapter provides information on how to identify, remove and replace
the main mechanical parts and individual PCBs.
Figure 5.10 on page 97 and Figure 5.11 on page 98 identify the main
mechanical parts, and Figure 5.1 on page 79 identifies the individual PCBs
and shows how they are configured in different models. “Identifying the
PA” on page 78 explains how to identify the model and hardware
configuration of a PA from its product code.
Note Unless otherwise noted, the instructions and illustrations in this
chapter refer to a 100W UHF (H band) PA. However, the same
basic procedures and techniques apply to other models of PA.

78 Power Amplifier Servicing TB8100 Service Manual
© Tait Electronics Ltd April 2004
5.1 Disassembly and Reassembly
Identifying the PA
You can identify the model and hardware configuration of a PA by referring
to the product code printed on labels on the heatsink and rear of the cover.
The meaning of each character in the product code is explained in the table
below.
Note This explanation of PA product codes is not intended to suggest
that any combination of features is necessarily available in any one
PA. Consult your nearest Tait Dealer or Customer Service
Organisation for more information regarding the availability of
specific models and options.
Product Code Description
TBAXXXX-XXXX 7 = 5W
8 = 50W
9 = 100W
TBAXXXX-XXXX 0 = default
TBAXXXX-XXXX Frequency Band and Sub-band
B1 = 136MHz to 174MHz
C0 = 174MHz to 225MHz
H0 = 400MHz to 520MHz
K2 = 762MHz to 870MHza
a. The actual frequency coverage in this band is 762MHz to 776MHz, and 850MHz to
870MHz.
TBAXXXX-XXXX 0 = default
TBAXXXX-XXXX 0 = default
TBAXXXX-XXXX 0 = default
TBAXXXX-XXXX0 = default

TB8100 Service Manual Power Amplifier Servicing 79
© Tait Electronics Ltd April 2004
Figure 5.1 Identifying the PA PCBs
b6W PCB g5W interconnect PCB
c60W PCB h50W interconnect PCB
dlow pass filter/directional coupler PCB isplitter PCB
econtrol PCB jcombiner PCB
fambient air temperature sensor PCB
5W PA
50W PA
100W PA
f
f
f
b
g
e
under
shield
d
e
under
shield
d
b
h c
b
e
c
cd
j
i

80 Power Amplifier Servicing TB8100 Service Manual
© Tait Electronics Ltd April 2004
Screw Torque Settings
The recommended torque settings for the screws used in the PA are as
follows:
Removing the Airflow Duct and Cover
The circled numbers in the following instructions refer to Figure 5.2.
Airflow Duct
(100W PA Only) 1. Remove the M3 Torx screw b securing the P-clip and DC input
cable to the airflow duct.
2. Remove the M3 Torx screws c securing the airflow duct to the
heatsink. Lift the airflow duct off the heatsink.
Cover 1. Remove the M3 Torx screws securing the cover to the heatsink and
to the front panel.
2. Remove the two M3 Torx screws securing the N-type connector to
the cover d.
3. Carefully lift the cover straight up off the heatsink, being careful not
to put any strain on the N-type connector.
Removing the Front Panel
The circled numbers in the following instructions refer to Figure 5.2.
1. Disconnect the +28VDC power feed by desoldering the feedthrough
capacitor from the metal strap e soldered to the 6W PCB.
2. Remove the four M2.5 Torx screws f securing the SMA connector
to the heatsink and to the front panel.
3. Desolder the centre pin of the SMA connector g from the 6W PCB
and remove the connector.
4. Remove the M3 Torx screws securing the front panel to the heatsink
and remove the panel.
Location / Function Torque Driver Size
secure the RF power transistors to
the heatsink
0.6N·m / 5.0lbf·in 3/32in
Allen key
4–40 UNC
secure the SMA connector to the
front panel
0.3N·m / 2.5lbf·in T8 M2.5
M3 screws are used in all other
locations
0.5N·m / 4.5lbf·in T10 M3

TB8100 Service Manual Power Amplifier Servicing 81
© Tait Electronics Ltd April 2004
Figure 5.2 Removing the Airflow Duct, Cover and Front Panel
b
c
d
x3 on other side
f
g
e
x4

82 Power Amplifier Servicing TB8100 Service Manual
© Tait Electronics Ltd April 2004
Refitting the Front Panel
The circled numbers in the following instructions refer to Figure 5.2 on
page 81.
1. Refit the front panel and secure it to the heatsink with the M3 Torx
screws.
2. Insert the SMA connector through the front panel and secure it to the
heatsink and front panel with the four M2.5 Torx screws f.
3. Resolder the centre pin of the SMA connector g to the 6W PCB.
4. Resolder the +28VDC feedthrough capacitor to the metal strap e
soldered to the 6W PCB.
Refitting the Cover and Airflow Duct
The circled numbers in the following instructions refer to Figure 5.2 on
page 81.
Cover 1. Slide the cover into place on the heatsink. Make sure the cover is
seated correctly between the heatsink and N-type connector.
2. Secure the cover with the M3 Torx screws.
Note Fit the two screws d securing the N-type connector to the cover
first, followed by the screws securing the cover to the heatsink.
Airflow Duct
(100W PA Only) 1. Slide the airflow duct into place on the heatsink and secure with the
M3 Torx screws.
2. Secure the DC input cable to the airflow duct with the P-clip and M3
To r x s c r e w b.

TB8100 Service Manual Power Amplifier Servicing 83
© Tait Electronics Ltd April 2004
5.2 PCB Connecting Links
There are two types of link used to connect individual PCBs in the PA:
■RF links b are used to carry RF signals from one PCB to another
■bridging links c are used to carry control signals from one PCB to
another.
Figure 5.3 shows typical examples of both types of links.
5.3 Replacing the 6W PCB
Important There is heatsink compound between the PCB and the
heatsink under certain components. Any objects caught in
the heatsink compound underneath the PCB which pre-
vent effective heatsinking may cause these components to
fail.
Important If you replace the 6W PCB, you must recalibrate the PA
bias using the Calibration Kit software. Refer to the Cali-
bration Kit documentation for more details.
Refer to Section 5.1 “Disassembly and Reassembly” for details on removing
and refitting the cover and front panel. The circled numbers in the
following instructions refer to Figure 5.4 on page 84. Figure 5.4 shows a
50W UHF (H band) PA. The exact number and location of links may differ
in other models.
Removal 1. Remove the cover and front panel.
2. Remove the bridging links b connecting the PCB to the control
PCB.
Figure 5.3 PCB Connecting Links
bc

84 Power Amplifier Servicing TB8100 Service Manual
© Tait Electronics Ltd April 2004
3. If necessary, desolder the +28VDC power feed wire c.
4. Desolder the RF links d connecting the PCB to any adjacent PCBs.
5. Remove the M3 Torx screws securing the PCB to the heatsink.
6. Carefully lift the PCB directly upwards off the locating pins e and
remove it from the heatsink.
Refitting 1. Ensure the heatsink and bottom of the PCB are clean. Remove any
old heatsink compound.
2. Apply a thin layer of fresh heatsink compound to the bottom of the
PCB underneath Q103 f, D200 g and AT100 h (if fitted). Use as
little as possible, while still covering the whole of the mounting area
of each component.
3. Refit the PCB, following the removal instructions in reverse order.
Note Before tightening the screws, press the PCB down over the locat-
ing pins so that it is firmly seated against the heatsink. Then
tighten the M3 Torx screws to the correct torque.
4. Refit the front panel and cover.
Figure 5.4 Replacing the 6W PCB
b
c
d
f
g
h
e
e

TB8100 Service Manual Power Amplifier Servicing 85
© Tait Electronics Ltd April 2004
5.4 Replacing the 60W PCB
Important There is heatsink compound between the RF power tran-
sistor and the heatsink. You may need to carefully prise the
transistor away from the heatsink with a small screwdriver.
Any objects caught in the heatsink compound underneath
the transistor which prevent effective grounding and/or
heatsinking may cause the transistor to fail.
Important If you replace the 60W PCB, you must recalibrate the PA
bias using the Calibration Kit software. Refer to the Cali-
bration Kit documentation for more details.
Refer to Section 5.1 “Disassembly and Reassembly” for details on removing
and refitting the cover. The circled numbers in the following instructions
refer to Figure 5.5 on page 86.
Removal 1. Remove the cover.
2. Remove the bridging links b connecting the PCB to the control
PCB.
3. Desolder the +28VDC power feed wire c.
4. Desolder the RF links d connecting the PCB to any adjacent PCBs.
5. Remove the 4-40 UNC Allen screws e securing the RF power
transistor f to the heatsink.
6. Remove the M3 Torx screws securing the PCB to the heatsink.
7. Carefully lift the PCB directly upwards off the locating pins g and
remove it from the heatsink.
Refitting the Same
PCB and Transistor Use the following instructions if you are fitting the same 60W PCB and RF
power transistor, and haven’t disturbed any of the solder joints around the
transistor.
1. Ensure the heatsink and bottom of the transistor are clean. Remove
any old heatsink compound.
2. Apply a thin layer of fresh heatsink compound to the bottom of the
transistor. Use as little as possible, while still covering the whole of
the mounting area of the transistor.
3. Refit the PCB, following the removal instructions in reverse order.
Note Before tightening the screws, press the PCB down over the locat-
ing pins so that it is firmly seated against the heatsink. Then
tighten the M3 Torx screws to the correct torque.

86 Power Amplifier Servicing TB8100 Service Manual
© Tait Electronics Ltd April 2004
4. Progressively tighten each 4–40 UNC screw, alternating from side to
side, to the correct torque. Retorque the screws after eight hours of
operation.
5. Refit the cover.
Refitting a New PCB
and Transistor Use the following instructions if you are fitting a new 60W PCB, a new RF
power transistor, or have disturbed any of the solder joints around the
transistor.
1. Remove any old heatsink compound from the heatsink.
2. Refit the PCB, following the removal instructions in reverse order.
Note Before tightening the screws, press the PCB down over the locat-
ing pins so that it is firmly seated against the heatsink. Then
tighten the M3 Torx screws to the correct torque.
3. Fit the new RF power transistor as described in the “Refitting”
section of “Replacing the 60W RF Power Transistor” on page 87.
4. Refit the cover.
Figure 5.5 Replacing the 60W PCB
b
c
d
d
f
e
d
g
g

TB8100 Service Manual Power Amplifier Servicing 87
© Tait Electronics Ltd April 2004
5.5 Replacing the 60W RF Power Transistor
Important If you do not follow these procedures correctly, the transis-
tor may fail because of poor heatsinking.
Important Do not apply too much heat or pressure to the PCB pads
and tracks as you may damage them or lift them from the
PCB. This will permanently damage the PA.
Important Insulated gate FET transistors are susceptible to damage
from static charges, due to their extremely high input resist-
ance. To avoid possible damage to the device during han-
dling, testing or actual operation, we recommend you fol-
low these procedures: avoid unnecessary handling; when
handling the device, pick it up by the cap, not the leads; do
not insert or remove the device while the power is on;
avoid contact with non-conductive plastic or non-conduc-
tive styrofoam.
Important If you replace an RF power transistor, you must recalibrate
the PA bias using the Calibration Kit software. Refer to the
Calibration Kit documentation for more details.
Refer to Section 5.1 “Disassembly and Reassembly” for details on removing
and refitting the cover. The circled numbers in the following instructions
refer to Figure 5.6 on page 88.
Removal 1. Remove the cover.
2. Remove the two 4–40 UNC Allen recess head screws b securing the
transistor to the heatsink.
3. Desolder and remove the two ground tags c.
4. Desolder the transistor tabs d by heating them with a soldering iron
and then carefully lifting them away from the PCB with a screwdriver
or thin stainless steel spike. When the tabs are completely free of the
PCB, remove the transistor.
5. Remove any excess solder from the PCB pads with solder wick.
6. Remove any old heatsink compound from the heatsink.
Refitting 1. Lightly tin the underside of the transistor tabs. Remove any excess
solder to leave a thin, even layer of solder on the tabs.
2. Apply a small amount of heatsink compound (Dow-Corning 340 or
equivalent) to the transistor mounting surface. Use as little as possible

88 Power Amplifier Servicing TB8100 Service Manual
© Tait Electronics Ltd April 2004
to provide a very thin, but even, film over the entire mounting
surface.
3. Place the transistor on the PCB in the correct orientation and ensure
the tabs are flush with the surface.
Important Make sure the heatsink compound is clean. Any objects
caught in the heatsink compound underneath the transistor
which prevent effective heatsinking may cause the transistor
to fail.
4. Refit the two ground tags and secure the transistor to the heatsink
with the two 4–40 UNC screws. Progressively tighten each screw,
alternating from side to side, to the correct torque.
5. Solder the ground tags and transistor tabs to the PCB. While
soldering the transistor tabs, gently press down on them with a
ceramic trimming tool to ensure they are as close as possible to the
pads on the PCB.
6. Retorque the 4–40 UNC screws after eight hours of operation.
7. Refit the cover.
Figure 5.6 Replacing the 60W RF Power Transistor
d
db c

TB8100 Service Manual Power Amplifier Servicing 89
© Tait Electronics Ltd April 2004
5.6 Replacing the Control PCB
Important You must reprogram and recalibrate the PA after replacing
the control PCB. Refer to “Reprogramming and Recali-
bration” on page 90.
Refer to Section 5.1 “Disassembly and Reassembly” for details on removing
and refitting the cover and front panel. The circled numbers in the
following instructions refer to Figure 5.7 on page 90.
Removal 1. Remove the cover and front panel.
2. Remove the ambient air temperature sensor PCB b.
3. Remove the bridging links c connecting the PCB to any adjacent
PCBs.
4. Desolder the RF links d connecting the PCB to any adjacent PCBs.
You may need to move the +28V power feed wire e out of the way
first.
5. Remove the M3 Torx screws securing the PCB to the heatsink.
6. Carefully lift the PCB directly upwards off the locating pins f and
remove it from the heatsink.
Refitting 1. To refit the PCB, follow the removal instructions in reverse order.
Important When refitting the ambient air temperature sensor PCB,
make sure that it fits properly into the correct hole provided
in the heatsink (refer to Figure 5.7). You must fit the sensor
PCB in the correct location to ensure that the temperature
of the airflow over the sensor is nearest the ambient temper-
ature of the air at the intake to the cooling fan. The sensor
PCB must not come into contact with the metal of the
heatsink fins. Note that you may feel some resistance as you
push the sensor PCB through the slot in the foam dust seal
located under the control PCB.
Note Before tightening the screws, press the PCB down over the locat-
ing pins so that it is firmly seated against the heatsink. Then
tighten the M3 Torx screws to the correct torque.

90 Power Amplifier Servicing TB8100 Service Manual
© Tait Electronics Ltd April 2004
Reprogramming
and Recalibration If you have replaced the control PCB, you will have to reprogram and
recalibrate the PA as described in the table below.
Figure 5.7 Replacing the Control PCB
bc
ce
dd
b
d f
f
100W PA
5/50W PA
Procedure Details
■reprogram the product code
■reprogram the PA type
reprogram this information into the PA using
the Calibration Kit software; refer to the
Calibration Kit documentation for more
details
replace the serial number labels the serial number of the PA will change to
the number already programmed into the
replacement control PCB; stick the new
serial number labels onto the heatsink and
rear panel
■calibrate the stage bias
■calibrate the forward and reverse
detector bias voltages
■calibrate the PA output power
carry out these procedures using the
Calibration Kit software; refer to the
Calibration Kit documentation for more
details

TB8100 Service Manual Power Amplifier Servicing 91
© Tait Electronics Ltd April 2004
5.7 Replacing the Low Pass Filter/Directional Coupler
PCB
Important If you replace the LPF/directional coupler PCB, you must
recalibrate the detector bias voltages and PA output power
using the Calibration Kit software. Refer to the Calibration
Kit documentation for more details.
Refer to Section 5.1 “Disassembly and Reassembly” for details on removing
and refitting the cover. The circled numbers in the following instructions
refer to Figure 5.8 on page 92.
Removal 1. Remove the cover.
2. Desolder the two tabs and remove the shield lid.
3. Remove the bridging links b connecting the PCB to the control
PCB.
4. Desolder the RF links c connecting the PCB to any adjacent PCBs.
5. Remove the M3 Torx screws securing the N-type connector to the
heatsink.
6. Desolder and remove the N-type connector, leaving the ground plate
d soldered in place on the shield wall.
7. Remove the M3 Torx screws securing the PCB to the heatsink.
8. Carefully lift the PCB directly upwards off the locating pins e and
remove it from the heatsink.
Refitting 1. Refit the PCB onto the heatsink, ensuring it is correctly positioned
on the locating pins.
2. Secure the PCB to the heatsink with the M3 Torx screws and tighten
to the correct torque.
3. If the ground plate d is already soldered to the shield wall:
■fit the N-type connector and tighten the two M3 Torx screws to
the correct torque
■solder the N-type connector to the PCB.
If the ground plate is not already soldered to the shield wall:
■fit the ground plate and N-type connector to the heatsink,
ensuring that the tab on the ground plate fits through the slot in
the shield wall
■tighten the two M3 Torx screws to the correct torque
■solder the N-type connector to the PCB
■solder the tag on the ground plate to the inside of the shield wall.

92 Power Amplifier Servicing TB8100 Service Manual
© Tait Electronics Ltd April 2004
Note In both cases make sure that the ground plate sits flat against the
base of the N-type connector, otherwise the cover may not fit cor-
rectly.
4. Replace the RF links c and bridging links b.
5. Refit the shield lid and resolder the two tabs.
6. Refit the cover.
Note If you are fitting a new PCB, make sure that the RF input tab f
is left in place for a 5W or 50W PA, and removed for a 100W PA.
If you have to remove the tab, cut it off cleanly with a sharp cut-
ting tool (such as tin snips or a guillotine).
5.8 Replacing the Interconnect PCBs
Refer to Section 5.1 “Disassembly and Reassembly” for details on removing
and refitting the cover.
Removal 1. Remove the cover.
2. Desolder the RF links connecting the PCB to any adjacent PCBs.
You may need to move the +28VDC power feed wire out of the way
first.
3. Remove the M3 Torx screws securing the PCB to the heatsink.
Figure 5.8 Replacing the LPF/Directional Coupler PCB
b
c
d
e
f
100W PA 5W and 50W PA

TB8100 Service Manual Power Amplifier Servicing 93
© Tait Electronics Ltd April 2004
4. Carefully lift the PCB directly upwards off the locating pins and
remove it from the heatsink.
Refitting 1. To refit the PCB, follow the removal instructions in reverse order.
Note Before tightening the screws, press the PCB down over the locat-
ing pins so that it is firmly seated against the heatsink. Then
tighten the M3 Torx screws to the correct torque.
5.9 Replacing the Splitter/Combiner PCBs
Important There is heatsink compound between the termination resis-
tors and the heatsink. You may need to carefully prise the
resistors away from the heatsink with a small screwdriver.
Any objects caught in the heatsink compound underneath
the resistors which prevent effective grounding and/or
heatsinking may cause the resistors to fail. There is also
heatsink compound between the PCB and the heatsink
under the splitter and combiner devices. Any objects
caught in the heatsink compound underneath the PCB
which prevent effective heatsinking may cause these com-
ponents to fail.
Important Do not apply too much heat or pressure to the PCB pads
and tracks as you may damage them or lift them from the
PCB. This will permanently damage the PA.
Refer to Section 5.1 “Disassembly and Reassembly” for details on removing
and refitting the cover. The circled numbers in the following instructions
refer to Figure 5.9 on page 94.
Removal 1. Remove the cover.
2. Desolder the RF links b connecting the PCB to any adjacent PCBs.
3. Desolder the tab of the termination resistor c and carefully lift it
away from the PCB with a screwdriver or thin stainless steel spike.
4. Desolder the termination resistor ground tag(s) d and carefully lift
away from the PCB with a screwdriver or thin stainless steel spike.
5. Remove the 4-40 UNC Allen screw(s) e securing the termination
resistor to the heatsink and carefully remove the resistor and ground
tag(s).
6. Remove the M3 Torx screws securing the PCB to the heatsink.

94 Power Amplifier Servicing TB8100 Service Manual
© Tait Electronics Ltd April 2004
7. Carefully lift the PCB directly upwards off the locating pins f and
remove it from the heatsink.
Refitting 1. Ensure the heatsink and bottom of the PCB are clean. Remove any
old heatsink compound.
2. Apply a thin layer of fresh heatsink compound (Dow-Corning 340 or
equivalent) to the bottom of the PCB underneath the splitter or
combiner. Use as little as possible, while still covering the whole of
the mounting area of the component.
3. Refit the PCB onto the heatsink, ensuring it is correctly positioned
on the locating pins.
4. Secure the PCB to the heatsink with the M3 Torx screws and tighten
to the correct torque.
5. Apply a small amount of heatsink compound to the termination
resistor mounting surface. Use as little as possible to provide a very
thin, but even, film over the entire mounting surface.
6. Place the resistor on the heatsink and ensure the tab is flush with the
surface of the PCB.
Figure 5.9 Replacing the Splitter/Combiner PCBs
e
d
Splitter Combiner
b
b
f
f
b
b
c
eecd
d

TB8100 Service Manual Power Amplifier Servicing 95
© Tait Electronics Ltd April 2004
Important Make sure the heatsink compound is clean. Any objects
caught in the heatsink compound underneath the resistor
which prevent effective heatsinking may cause it to fail.
7. Refit the ground tag(s) and secure the resistor to the heatsink with the
4–40 UNC screw(s). If there are two screws, progressively tighten
each screw, alternating from side to side, to the correct torque.
8. Solder the ground tag(s) and resistor tab to the PCB. While soldering
the resistor tabs, gently press down on them with a ceramic trimming
tool to ensure they are as close as possible to the pads on the PCB.
9. Retorque the 4–40 UNC screws after eight hours of operation.
10. Refit the cover.
96 Power Amplifier Servicing TB8100 Service Manual
© Tait Electronics Ltd April 2004

TB8100 Service Manual Power Amplifier Servicing 97
© Tait Electronics Ltd April 2004
Figure 5.10 PA Mechanical Assembly - Sheet 1
Description IPN
bDC input feedthrough capacitor 012-04100-07
cDC power link 051-00640-XX
dDC input cable - 5/50W
DC input cable - 100W
219-02854-XX
219-02855-XX
ebridging links 240-00020-61
fN-type connector 240-02100-64
gSMA connector 240-02155-20
hP-clip 303-50107-XX
ihandle 308-01065-XX
jheatsink - 5/50W
heatsink - 100W
308-13144-XX
308-13145-XX
1) front panel - 5/50W
front panel - 100W
316-06815-XX
316-06817-XX
1! LPF/directional coupler shield lid 319-01247-XX
1@ N-type connector ground plate 319-01249-XX
1# LPF/directional coupler shield lid spring contacts 319-01259-XX
1$ M3x6mm countersunk Torx screw 345-40460-XX
1% M3x8mm pan head Torx screw + spring/flat washers 345-40470-XX
1^ M2.5x8mm pan head Torx screw 345-40490-XX
1& M3x10mm pan head Torx Taptite screw 349-02066-XX
1* 4–40x5/16 UNC Allen recess head screw 349-20460-XX
1( 3mm solder tag - short 356-00010-01
2) 3mm solder tag - long 356-00010-03
2! 4mm right-angle solder tag 356-00010-74
2@ RF link 356-01080-XX
2# ground tag for 60W RF power transistor 356-01081-XX
2$ metal strap for feedthrough capacitor 356-01082-XX
2% insulating washer for feedthrough capacitor 362-00010-51
2^ dust seal for ambient air temperature sensor PCB 362-01036-XX
2& control PCB
2* 6W PCB
2( LPF/directional coupler PCB
3) 60W PCB
3! ambient air temperature sensor PCB
3@ combiner PCB
3# splitter PCB
3$ bridging link PCB
50W interconnect PCB*
5W interconnect PCB*
*Not shown in this drawing. Refer to Figure 5.1 on
page 79.
Note:
The characters XX in an IPN (Tait Internal Part Number)
stand for the issue number of the part. Only the latest
issue of each part will normally be available for ordering
as spare or replacement parts.
Note:
This drawing shows a 100W PA. Any differences
between the 100W, 5W and 50W PAs are indicated in
the description of the parts.
1#
1!
2(
e
2&
3)
3$
2)
1%
f
j
1@
1$
b
1)
1$
2!
2%
i
1&
h
d
1^
g2^
2$
3#
2*
1%
1*
1(
3)
2#
1*
3! 2@
c
3@
1*1(
1&
x2
x4
x3 each side
x5 100W
x4 5/50W
x2
x4
x2
x2
x2
x2

98 Power Amplifier Servicing TB8100 Service Manual
© Tait Electronics Ltd April 2004
Figure 5.11 PA Mechanical Assembly - Sheet 2
Description IPN
bcover - 5/50W
cover - 100W
303-03070-XX
303-03071-XX
cP-clip 303-50107-XX
dairflow duct centre panel 316-06818-XX
eairflow duct side panel 316-06819-XX
fM3x6mm countersunk Torx screw 345-40460-XX
gM3x10mm pan head Torx Taptite screw 349-02066-XX
Note:
The characters XX in an IPN (Tait Internal Part Number)
stand for the issue number of the part. Only the latest
issue of each part will normally be available for ordering as
spare or replacement parts.
c
g
d
b
f
e
f
e
x26 100W
x24 5/50W
x3 each side

TB8100 Service Manual Power Management Unit Circuit Description 99
© Tait Electronics Ltd April 2004
6Power Management Unit Circuit
Description
The TB8100 power management unit (PMU) provides stable, low-noise
28VDC outputs to power the TB8100 BSS. The PMU is made up of a
number of individual PCBs and cards which comprise two main modules,
the AC module and the DC module. The standby power supply card and
auxiliary power supply PCB are optional.
The AC module accepts an input of 115/230VAC 50/60Hz nominal, and
the DC module accepts an input of 12, 24 or 48VDC1 nominal (depending
on the model). Both modules provide the following outputs:
■28VDC high current (PA)
■28VDC low current (reciter)
■13.65, 27.3 or 54.6VDC low current (with the optional auxiliary power
supply PCB).
The PMU is available in three main configurations:
■AC PMU (AC input only)
■DC PMU (DC input only)
■AC and DC PMU (both the AC and DC modules are fitted to allow both
AC and DC inputs).
If both the AC and DC modules are fitted, the PMU uses the AC input by
default, and provides battery back-up by operating from the DC input if the
AC input is interrupted. The changeover from AC to DC input, and from
DC back to AC input, is breakless. This allows the base station to operate
without interruption.
The optional standby power supply card allows efficient use of the DC input
at low power requirements. The optional auxiliary power supply PCB
provides output voltages which are different from the 28VDC required by
the TB8100 BSS. It can also be used to trickle-charge batteries.
Figure 6.1 on page 100 shows the configuration for an AC and DC PMU,
along with the main inputs and outputs for power and control signals. The
table which follows shows which PCBs and cards are fitted in each module.
The locations of the main circuit blocks on the PCBs are shown in
Figure 6.5 on page 109 and Figure 6.6 on page 111.
1. Because the DC module is designed to run from a battery, there will be a
minimum start-up voltage when operating on DC only (refer to the
TB8100 Specifications Manual for more details).

100 Power Management Unit Circuit Description TB8100 Service Manual
© Tait Electronics Ltd April 2004
Figure 6.1 PMU High Level Block Diagram
PFC
Circuitry
PFC
Control
Card
DC Input
Filter
Card
DC
Control
Card
Auxiliary
Power Supply
PCB*
Battery
Control
Card
Standby
Power Supply
Card*
HVDC Control &
Microprocessor
Card
HVDC Circuitry
DC Converter PCB
28V
28V
28V O/P (PA)
System
Control Bus
28V O/P (Reciter)
AC I/P
115/230V
50/60Hz 400VDC
DC I/P
12V
28V 13.8V O/P
*optional
AC Converter PCB
AC Module
DC Module
DC I/P
12/24/48V
DC O/P
13.65/27.3/54.6V

TB8100 Service Manual Power Management Unit Circuit Description 101
© Tait Electronics Ltd April 2004
6.1 Microprocessor Control Circuitry
The microprocessor on the HVDC control card monitors and controls the
operation of the PMU. If any of the monitored conditions exceeds its
normal range of values, the microprocessor will generate an alarm and take
appropriate action, depending on the configuration of the PMU. The
software also automatically detects the PMU configuration and controls the
PMU accordingly.
The alarms and diagnostic functions are accessed through I2C bus messages
on the system control bus via the reciter, control panel and Service Kit
software.
The microprocessor also calibrates the output voltage to the required
specification. This information is stored in EEPROM memory during
factory run-up. The output voltage of an uncalibrated PMU is 26.5VDC.
Figure 6.2 on page 102 shows the control signal and power connections to
and from the microprocessor. These are described in more detail in the
paragraphs which follow.
PCB and Card Name AC PMU DC PMU AC and DC PMU
DC converter PCB fitted fitted
DC input filter card fitted fitted
DC control card fitted fitted
battery control card fitted fitted
standby power supply cardaoptional optional
AC converter PCB fitted fittedbfitted
HVDC control and microprocessor card fitted fittedcfitted
PFC control card fitted fitted
auxiliary power supply PCBdoptional optional optional
a. You must fit the appropriate model card to match the DC input voltage of the PMU (i.e. 12, 24 or 48VDC nominal).
b. Only the current sense and output filter circuitry is placed on this PCB when it is fitted to a DC PMU.
c. Only the feedback and microprocessor circuitry is placed on this card when it is fitted to a DC PMU.
d. The output voltage is dependent on the model of PCB - there is a different model PCB for each output voltage (i.e.
13.65, 27.3 or 54.6VDC).

102 Power Management Unit Circuit Description TB8100 Service Manual
© Tait Electronics Ltd April 2004
AC Converter The microprocessor can enable or disable the AC converter if the user needs
to test the DC module and battery back-up by simulating a failure of the AC
mains input.
The microprocessor monitors the output voltage and current, the
temperature of the AC module heatsink, and whether the AC mains input
is within the specified range.
DC Converter The microprocessor controls the on/off function of the DC converter. It
also controls the mode of operation of the DC converter: normal mode,
hysteresis mode1, or deep sleep mode. Refer to “Hysteresis Mode” on
page 107 for details on hysteresis mode, and to “Standby Power Supply”
below for details on deep sleep mode.
Figure 6.2 PMU Microprocessor Functional Block Diagram
R
5V Supply
Flash
Programming
Supply
AC
Converter
DC
Converter
Auxiliary
Power
Supply*
Microprocessor
Temperature
28V
Data
Run
Voltage Sense
Current Sense
Fan
Current Sense
Microprocessor
Supply
Temperature
Mains
Input
PA
Output
Reciter
Output
Auxiliary
Output
Battery
Input Battery
Supply
On/Off
Standby
Power
Supply*
Hysteresis Mode
Shutdown
Standby Supply
Present
Low Battery
Alarm On
*optional
Summary
Alarm On
Vpp
Vpp Enable
Fan Supply On
I C
2Signals
Fan
Output
Summary Alarm
Output
Low Battery
Alarm Output
I C Port
2
Run
Data
Standby Supply Isolate
Mains OK
Shutdown
I
V
0V
0V
0V
1. A type of “sleep” mode available when the standby power supply card is not
fitted.
TB8100 Service Manual Power Management Unit Circuit Description 103
© Tait Electronics Ltd April 2004
The microprocessor monitors the battery input voltage and the temperature
of the DC module heatsink. It also identifies the model of DC converter
fitted to the DC module (i.e 12, 24 or 48V nominal input).
Standby Power
Supply The microprocessor detects whether this power supply is fitted, and disables
it when the AC mains supply is operating.
The output from this power supply can be isolated from the reciter output
to maintain power to the microprocessor when battery capacity is low. The
low battery threshold is set with the Service Kit software.
This power supply is also used to maintain power to the microprocessor
when the PMU is in deep sleep mode and the DC converter is switched off.
Deep sleep mode is configured with the Service Kit software and can only
function if the load on the PMU reciter output is <10W.
If the power supply is not fitted, the microprocessor is powered by an
internal 5V power supply derived from the main PA output.
Auxiliary Power
Supply The microprocessor controls the on/off function for this power supply. The
actual operation of the power supply is set with the Service Kit software:
■on only when AC mains is present
■controlled by Task Manager.
The microprocessor detects when the power supply is operating. It also
detects which model of power supply is fitted (12, 24 or 48V), whether the
power supply is operating or not.
Front Panel Fan The microprocessor measures the current drawn by the PMU fan mounted
in the front panel. It protects the fan driver circuitry from overload or short
circuit by switching the fan off for five seconds, and then switching it on
again. The microprocessor will continue to try running the fan indefinitely.
If the fan has failed, the reciter sends an alarm to the Service Kit.
I2C Communications The microprocessor controls the I2C communications between the PMU
and the base station system.
The current source used by the I2C lines as active pull-up resistors is housed
on the microprocessor PCB.

104 Power Management Unit Circuit Description TB8100 Service Manual
© Tait Electronics Ltd April 2004
6.2 AC Module
The AC module accepts an input of 115/230VAC 50/60Hz nominal, and
provides two regulated 28VDC outputs: high current for the PA, and low
current for the reciter.
The main circuit blocks are shown in Figure 6.3 below, and are described in
more detail in the paragraphs which follow.
EMC Filter,
Protection, and AC
Switch
The AC input is fed first to an EMC filter consisting of two common-mode
and two differential-mode filters. The input voltage is monitored, and if it
is within the specified voltage range, a “mains OK” signal is sent to the
microprocessor via an opto-coupler. If the mains input voltage is outside the
specified range, the power factor stage is inhibited to protect the AC
converter from damage.
An MOV is fitted between line and phase to clamp low energy noise on the
line. A 10A fuse is also fitted for additional safety. If the fuse blows, it
disconnects the PMU from the mains. Inrush current control is provided by
a high power resistor, which is bypassed by a relay when the PMU is
powered up.
Power Factor
Correction (PFC) The filtered AC input is fed to this boost power supply where the active
power factor correction circuit converts it to the regulated 400VDC output.
This stage is fully protected from overload and short circuit by the power
supply control circuitry.
PFC Control The control circuitry for the boost power supply is located on the PFC
control card which plugs into the AC converter PCB. This circuitry is
designed to achieve a power factor of near unity. The power supply for the
Figure 6.3 PMU AC Module Block Diagram
EMC Filter,
Protection,
& AC Switch
Power Factor
Correction
(PFC)
High Voltage
to DC
(HVDC)
System
Interface
and
Fan Control
PFC Control HVDC Control
Current Sense
and
Output Filter
Interface to
DC Module Microprocessor
AC I/P
115/230V
50/60Hz
DC
Control &
Monitor
28VDC O/P
(PA)
28VDC O/P
(Reciter)
System
Control Bus
Fan
TB8100 Service Manual Power Management Unit Circuit Description 105
© Tait Electronics Ltd April 2004
PFC control circuitry is derived from the secondary winding on the main
boost choke.
High Voltage to DC
(HVDC) The regulated 400VDC from the PFC circuitry is converted to a regulated
28VDC output using a forward converter.
The forward converter transformer provides galvanic isolation between the
input and output. The primary is switched between 400V and 0V via two
power MOSFETs.
The output from the transformer is rectified and filtered before being fed to
a current sense resistor.
HVDC Control This secondary control circuitry consists of a voltage and current amplifier,
which provides a combined error signal. This error signal is fed via an opto-
coupler to the PWM (pulse width modulation) controller IC, which is part
of the primary control circuitry.
The power supply for the HVDC control circuitry is derived from the
secondary winding on the main transformer. The HVDC control circuitry
is located on a separate card which plugs into the AC converter PCB.
Current Sense and
Output Filter The current sense resistor provides the current output level to the
microprocessor for monitoring purposes and to supply data to the Service
Kit software. The current output level is also used by the analogue current
control loop to limit the maximum output current.
After the current shunt the regulated 28VDC output is split and filtered to
provide two DC outputs: a high current output for the PA, and a low
current output for the reciter. The high current output is electronically
protected, and the low current output is protected by a 2.5A self-resetting
fuse.
The low current output for the reciter is normally supplied by the standby
power supply. If this card is not fitted, the high current PA output is also
supplied to the low current reciter output via a diode.
The current sense and output filter circuitry is also used by the DC converter
to provide a common output stage for the PMU.
Microprocessor
Control The microprocessor is located on the HVDC control card and is referenced
to the output (secondary side) of the converter. The microprocessor is used
by both the AC and DC modules and is fitted to all PMU models.
The microprocessor controls the output voltage to the fan via a MOSFET
and dropping resistor to provide the 24VDC output.

106 Power Management Unit Circuit Description TB8100 Service Manual
© Tait Electronics Ltd April 2004
System Interface
and Fan Control The system interface circuitry consists of the I2C lines, fan power, and alarm
outputs, which are fed to the system control bus connector on the front
panel. There is high frequency filtering on all lines.
The microprocessor also monitors the current drawn by the PMU fan and
protects it from overload or short circuit.
Interface to DC
Module This interface consists of the connectors which connect the AC module to
the DC module. Although there is no circuitry involved this interface, it is
included in the block diagram to illustrate the interconnection between the
AC and DC modules.
6.3 DC Module
The DC module accepts an input of 12, 24 or 48VDC nominal, and
provides two regulated 28VDC outputs: high current for the PA, and low
current for the reciter.
The main circuit blocks are shown in Figure 6.4 below, and are described in
more detail in the paragraphs which follow.
Figure 6.4 PMU DC Module Block Diagram
EMC Filter
and
Protection
DC Power
Converter
(DCDC)
DC Control
Battery
Control
Standby
Power
Supply*
Auxiliary
Power
Supply*
Interface to
AC Module
DC I/P
12/24/48V
Control &
Monitor
DC
*optional
DC O/P
13.65/27.3/54.6V
TB8100 Service Manual Power Management Unit Circuit Description 107
© Tait Electronics Ltd April 2004
EMC Filter and
Protection The DC input is fed first to an EMC filter consisting of bus bars, an e-core
transformer, and capacitors. These components are located on the DC
input filter card, which is connected to the DC converter PCB via the bus
bars and soldered tabs.
The protection is provided by an anti-parallel diode, which prevents damage
from reverse polarity input voltage. External series protection (e.g. fuse or
circuit breaker) must be provided by the user.
DC Power Converter
(DCDC) In this stage the filtered DC input is fed to a push-pull converter which
converts the DC input voltage to a regulated DC output voltage.
The DC voltage is fed to a high frequency transformer which provides
galvanic isolation between input and output via two pairs of power
MOSFETS on the primary winding.
The output from this transformer is rectified and filtered before being fed to
the current sense and output filter circuitry on the AC converter PCB.
DC Control This secondary control circuitry consists of a voltage amplifier, which
provides a reference voltage and error signal. This error signal is fed via an
opto-coupler to the PWM controller IC, which is part of the primary
control circuitry.
The power supply for the DC control circuitry is provided by the battery
control card. The DC control circuitry is located on a separate card which
plugs into the DC converter PCB.
Hysteresis Mode When the DC control circuitry receives a “hysteresis enable” signal from the
microprocessor, it changes the regulation to a hysteric method (hysteresis
mode). Hysteresis mode is used in sleep mode to improve the efficiency of
the DC converter under light loads. Sleep mode is configured with the
Service Kit software and can only function if the load on the PMU is <10W.
In hysteresis mode the DC converter is switched off when the output
voltage reaches the maximum threshold, and on again when the voltage
reaches the minimum threshold. The thresholds are set in hardware at the
factory.
While the DC converter is switched on, the output capacitors are charged.
When the DC converter is switched off, the output capacitors are
discharged by the load connected to the PMU. The discharge time varies
in proportion to the load. The longer the discharge time, the greater the
efficiency of the PMU, as less power is drawn from the battery.
Battery Control The battery control circuitry monitors the DC input voltage from the
battery. If the voltage is within the specified range, power is supplied to the
control circuitry and optional standby power supply (if fitted). Protection is
provided against the wrong input voltage being supplied.
108 Power Management Unit Circuit Description TB8100 Service Manual
© Tait Electronics Ltd April 2004
The battery input voltage is also provided as a digital signal to the
microprocessor via opto-coupler circuitry. This provides isolation between
battery ground and microprocessor ground.
The battery control circuitry also prevents deep discharge of the battery by
removing the load from the battery if the voltage falls below a minimum
threshold. This threshold is independent of the microprocessor threshold,
which is set by the user with the Service Kit software.
Another function of the battery control circuitry is to provide the
microprocessor with information to identify which DC module is fitted to
the PMU (i.e. 12, 24 or 48V).
The battery control circuitry is located on a separate card which plugs into
the DC converter PCB.
Standby Power
Supply The optional standby power supply is a high efficiency, low power DC
converter which operates in parallel with the main DC converter.
This converter provides a low power output to the reciter, and can also
operate when the main DC converter is shut down (i.e. deep sleep mode).
It is protected from overload and short circuit.
The circuitry for the standby power supply is located on a separate card
which plugs into the DC converter PCB.
Auxiliary Power
Supply The optional auxiliary power supply uses a high power version of the circuit
design used in the standby power supply. It operates from the AC power
supplied to the PMU. The mode of operation is controlled with the Service
Kit software.
The circuitry for the auxiliary power supply is located on a separate PCB
which is mounted on the heatsink of the DC module. The PCB is
connected to the AC converter PCB via an 8-way cable.
The main function of this power supply is to provide a controlled 13.65,
27.3 or 54.6VDC output (depending on model), as the main output for the
TB8100 base station system is 28VDC. However, because the converter is
voltage and current regulated, it can also be used to trickle-charge batteries.
The output voltage is set in the factory to the required float voltage, so the
batteries can remain connected at all times.
Interface to AC
Module This interface consists of the connectors which connect the DC module to
the AC module. Although there is no circuitry involved this interface, it is
included in the block diagram to illustrate the interconnection between the
DC and AC modules.

TB8100 Service Manual Power Management Unit Circuit Description 109
© Tait Electronics Ltd April 2004
Figure 6.5 Identifying the Circuitry on the AC Module PCBs
bEMC filter, protection and AC switch
cpower factor correction (PFC)
dPFC control
ehigh voltage to DC converter
f28VDC input from the DC converter PCB
gcurrent sense and output filter
h28VDC output for PA
i28VDC output for reciter
j28VDC output to auxiliary power supply PCB
1) microprocessor control
1! AC and DC voltage and current control
1@ HVDC control
1# fuse (10A 250V)
1$ AC mains input
Note:
In order to show as much of the circuitry as possible in the
photograph, the heatsinks and the components normally
attached to them are not fitted, and the plug-in cards are not
plugged in.
b
c
d
e
g
i
h
h
1)
1!
1@
1$
f
j
1#
110 Power Management Unit Circuit Description TB8100 Service Manual
© Tait Electronics Ltd April 2004

TB8100 Service Manual Power Management Unit Circuit Description 111
© Tait Electronics Ltd April 2004
Figure 6.6 Identifying the Circuitry on the DC Module PCBs
bDC input
cauxiliary power supply
dDC power converter
eDC control
foutput to the current sense and output filter circuitry on the
AC converter PCB
gbattery control
hcurrent transformer
istandby power supply
jEMC filter and protection
Note:
In order to show as much of the circuitry as possible in the
photograph, the heatsinks and the components normally
attached to them are not fitted, and the plug-in cards are not
plugged in.
b
c
d
e
f
g
h
i
j
12V DC module shown
112 Power Management Unit Circuit Description TB8100 Service Manual
© Tait Electronics Ltd April 2004

TB8100 Service Manual Power Management Unit Servicing 113
© Tait Electronics Ltd April 2004
7 Power Management Unit Servicing
This chapter provides information on how to identify, remove and replace
the main mechanical parts, plug-in cards, and auxiliary power supply PCB.
7.1 Safety Precautions
Personal Safety
Warning!! The PMU contains voltages that may be lethal.
Refer to the ratings label on the rear of the
module.
The TB8100 BSS must be installed so that the rear of the PMU is located
in a service access area.
Disconnect the mains IEC connector and wait for five minutes for
the internal voltages to self-discharge before dismantling. The AC
power on/off switch does not isolate the PMU from the mains. It
breaks only the phase circuit, not the neutral.
The PMU should be serviced only by qualified technicians. All servicing
should be carried out only when the PMU is powered through a mains
isolating transformer of sufficient rating. We strongly recommend that
the mains power to the whole of the repair and test area is supplied via an
earth leakage circuit breaker.
Caution The magnetics and power devices attached to the
heatsink in the PMU get hot when they are operat-
ing. Take care when working on a PMU that has
been in recent use.
Caution The PMU can weigh up to 6.4kg (14.1lb). Take care
when handling the PMU to avoid personal injury.

114 Power Management Unit Servicing TB8100 Service Manual
© Tait Electronics Ltd April 2004
Equipment Safety
Important This equipment contains devices which are susceptible to
damage from static charges. Refer to “ESD Precautions”
on page 15 for more information on antistatic procedures
when handling these devices.
Important Insulated gate FET transistors are susceptible to damage
from static charges, due to their extremely high input resist-
ance. To avoid possible damage to the device during han-
dling, testing or actual operation, we recommend you fol-
low these procedures: avoid unnecessary handling; when
handling the device, pick it up by the cap, not the leads; do
not insert or remove the device while the power is on;
avoid contact with non-conductive plastic or non-conduc-
tive styrofoam.
Replacing Components Connected To The Mains
To maintain operator safety and protection against fire, you must replace
components connected to the mains supply (e.g. fuse [10A 250V], X & Y
capacitors, filter chokes, etc.) and those that are critical to maintain isolation
(optocouplers, transformers, etc.) only with their new, original equivalent.
To maintain performance levels we strongly recommend that you apply this
policy to every component that is replaced.

TB8100 Service Manual Power Management Unit Servicing 115
© Tait Electronics Ltd April 2004
7.2 Disassembly and Reassembly
Mechanical Overview
The TB8100 PMU is made up of a number of individual PCBs and cards
which comprise two main modules, the AC module and the DC module.
The standby power supply card and auxiliary power supply PCB are
optional.
The PMU is available in three main hardware configurations:
■AC PMU (AC input only)
■DC PMU (DC input only)
■AC and DC PMU (both the AC and DC modules are fitted to allow both
AC and DC inputs).
The table below provides an overview of the major mechanical differences
between these three configurations.
Figure 7.6 on page 129 and Figure 7.7 on page 130 identify the main
mechanical parts. Figure 7.1 on page 117 identifies the individual PCBs and
cards, and shows how they are configured in an AC and DC PMU.
“Identifying the PMU” on page 116 explains how to identify the model and
hardware configuration of a PMU from its product code.
Note For the sake of simplicity and clarity, the instructions and illustra-
tions in this chapter refer to the AC and DC PMU. However, the
AC PMU and DC PMU can be disassembled and reassembled
using the same basic procedures and techniques.
Part/Assembly
PMU Configuration
AC PMU DC PMU AC and DC PMU
AC module standard module fitted AC converter PCB is mounted on
special brackets which also cover
the holes normally covered by the
AC module heatsinks; only the
current sense and output filter
circuitry is placed on the PCB
standard module fitted
DC module not fitted standard module fitted standard module fitted
shield fitted not fitted fitted
front and rear
panels
fitted with blanking plates
to cover the holes normally
covered by the DC module
heatsinks
fitted fitted
top and bottom
covers
fitted fitted fitted

116 Power Management Unit Servicing TB8100 Service Manual
© Tait Electronics Ltd April 2004
Identifying the PMU
You can identify the model and hardware configuration of a PMU by
referring to the product code printed on a label on the rear panel. The
meaning of each character in the product code is explained in the table
below.
Note This explanation of PMU product codes is not intended to suggest
that any combination of features is necessarily available in any one
PMU. Consult your nearest Tait Dealer or Customer Service
Organisation for more information regarding the availability of
specific models and options.
Product Code Description
TBAXXXX-XXXX 3 = PMU
TBA3XXX-XXXX 0 = default
TBA3XXX-XXXX 0 = AC module not fitted
A = AC module fitted
TBA3XXX-XXXX 0 = DC module not fitted
1 = 12V DC module fitted
2 = 24V DC module fitted
4 = 48V DC module fitted
TBA3XXX-XXXX 0 = standby power supply card not fitted
1 = 12VDC standby power supply card fitted
2 = 24VDC standby power supply card fitted
4 = 48VDC standby power supply card fitted
TBA3XXX-XXXX 0 = auxiliary power supply PCB not fitted
1 = 12VDC auxiliary power supply PCB fitted
2 = 24VDC auxiliary power supply PCB fitted
4 = 48VDC auxiliary power supply PCB fitted
TBA3XXX-XXXX 0 = default
TBA3XXX-XXXX0 = default

TB8100 Service Manual Power Management Unit Servicing 117
© Tait Electronics Ltd April 2004
Figure 7.1 Identifying the PMU PCBs
standby power supply card
battery control card
auxiliary power supply PCB
DC converter PCB
PFC control card
AC converter PCB
AC converter PCB
DC converter PCB
HVDC control and
microprocessor card
DC control card
bottom view
top view
AC and DC PMU shown

118 Power Management Unit Servicing TB8100 Service Manual
© Tait Electronics Ltd April 2004
Screw Torque Settings
The recommended torque settings for the screws used in the PMU are as
follows:
Removing the Top and Bottom Covers
1. Remove the four M3 Torx screws securing the top cover to the front
and rear panels. Lift off the top cover.
Note If the top cover is difficult to
move, we suggest you lift one
end of the cover away from the
end panel with a flat-blade
screwdriver. The cover should
then be loose enough to lift off.
2. Turn the PMU over and remove
the four M3 Torx screws securing
the bottom cover to the front and
rear panels. Lift off the bottom
cover.
Removing the Front and Rear Panels
1. Remove the M4 Torx Taptite screw securing the front panel to the
AC converter PCB.
2. Remove the five M4 Torx Taptite screws securing the front panel to
the heatsinks and shield. Slide the front panel off the heatsinks.
3. Remove the M4 Torx Taptite screw securing the rear panel to the AC
converter PCB.
Location / Function Torque Driver Size
■securing the front and rear panels to
the heatsinks
■securing the AC and DC converter
PCBs to the heatsinks
■securing the bus bars to the DC
converter PCB
2.0N·m / 18lbf·in T20 M4
■securing the top and bottom covers
to the front and rear panels
■securing the handle to the front
panel
■securing the DC input filter card to
the bus bars
0.5N·m / 4.5lbf·in T10 M3
securing the 500W DC transformer
primary wires into their terminals
1.8N·m / 16lbf·in flat blade

TB8100 Service Manual Power Management Unit Servicing 119
© Tait Electronics Ltd April 2004
4. Remove the five M4 Torx Taptite screws securing the rear panel to
the heatsinks and shield.
5. Loosen the rear panel slightly and remove the fibreglass DC input
insulator from behind the DC input terminals. Slide the rear panel
off the heatsinks.
Disconnecting the AC and DC Modules
Unless otherwise indicated, the circled numbers in the following
instructions refer to Figure 7.2 on page 120.
1. As shown in Figure 7.3 on page 121, rotate the PMU so that the DC
module f is on top of the AC module g and unplug the 12-way rib-
bon cable h from the DC converter PCB.
2. Unfold the DC module from on top of the AC module, and place it
end-to-end with the AC module, as shown in Figure 7.2.
3. Unplug the 28VDC cable b from the DC converter PCB.
4. If fitted, unplug the 8-way cable c from the auxiliary power supply
PCB. Remove the cable from the retaining clips d.
Note These connectors have locking tabs. You must disengage the
locking tab before you can remove the plug from the socket.
5. Slide the plastic grommet e out of the shield f. Unplug the mains
input connector g from the AC converter PCB and remove the
shield.
Reconnecting the AC and DC Modules
Unless otherwise indicated, the circled numbers in the following
instructions refer to Figure 7.3 on page 121.
1. If previously removed, reconnect the 28VDC cable b, 12-way rib-
bon cable c, and 8-way cable d (if fitted) to the AC converter PCB
and feed them through the plastic grommet e.
2. Reconnect the mains input connector to the AC converter PCB (as
shown in Figure 7.2 on page 120), then insert the plastic grommet
holding the cables into the hole in the shield.
3. As shown in Figure 7.2, place the AC and DC modules end-to-end
and reconnect the 28VDC cable b and 8-way cable c (if fitted).
Position the 12-way ribbon cable h between the two modules so that
it will still be accessible when the AC module is folded on top of the
DC module.

120 Power Management Unit Servicing TB8100 Service Manual
© Tait Electronics Ltd April 2004
4. Fold the AC module f on top of the DC module g, ensuring that
the cables and shield i are correctly positioned. Make sure that none
of the cables is pinched between the modules and/or shield.
5. Reconnect the 12-way ribbon cable h to the DC converter PCB.
Figure 7.2 Disconnecting the AC and DC Modules
AC module DC module
bcddfe
g
h

TB8100 Service Manual Power Management Unit Servicing 121
© Tait Electronics Ltd April 2004
Figure 7.3 Reconnecting the AC and DC Modules
ce
b
d
f
i
g
h

122 Power Management Unit Servicing TB8100 Service Manual
© Tait Electronics Ltd April 2004
Refitting the Front and Rear Panels
1. Hold the two modules firmly together and fit the front panel over the
heatsinks. Ensure that the shield remains in place. You may find it
easier to fit the front panel while the PMU is lying on its side. This
way the shield is held in place between the heatsinks.
2. Refit and tighten the five M4 Torx Taptite screws to secure the front
panel to the heatsinks and shield.
Note Make sure that all connectors are correctly located in their respec-
tive holes in the panel before fully tightening the screws.
3. Refit and tighten the M4 Torx Taptite screw securing the front panel
to the AC converter PCB.
4. Fit the rear panel over the heatsinks.
5. Slide the fibreglass DC input
insulator in behind the DC input
terminals. Make sure it fits into the
slot in the PCB b and is correctly
located on its mounting tabs in the
rear panel c.
6. Refit and tighten the five M4 Torx
Taptite screws to secure the rear
panel to the heatsinks and shield.
Note Before fully tightening the
screws, make sure that all con-
nectors, switches and the fibre-
glass insulator are correctly
located in their respective holes
in the panel.
7. Refit and tighten the M4 Torx Taptite screw securing the rear panel
to the AC converter PCB.
Refitting the Top and Bottom Covers
1. Refit the bottom cover over the front and rear panels and secure with
the four M3 Torx screws.
Note The bottom cover cannot be fitted to the top of the PMU as the
mounting holes in the cover will not align with the holes in the
front and rear panels.
2. Turn the PMU over and align the top cover over the front and rear
panels. Carefully slide the cover down until the locating tabs engage
with the bottom cover. Ensure that the fibreglass DC input insulator
sits inside the top cover.
bc

TB8100 Service Manual Power Management Unit Servicing 123
© Tait Electronics Ltd April 2004
3. Push the top cover down firmly and secure with the four M3 Torx
screws.
Note Both the top and bottom covers are symmetrical and can be fitted
in either orientation.
7.3 Replacing the Plug-in Cards
Important You must reprogram the PMU if you fit a replacement
HVDC and microprocessor card, or change the configura-
tion of the PMU. Refer to “Reprogramming” on
page 125.
Important The HVDC and microprocessor card normally fitted to a
DC PMU does not have the HVDC circuitry fitted. Do
not fit this type of card to a PMU with an AC mod-
ule or the AC module will be damaged. You can,
however, safely fit a card with the HVDC circuitry to any
model of PMU.
Important The DC input voltage of a replacement standby power sup-
ply card must match the DC input voltage of the DC mod-
ule (i.e 12VDC, 24VDC or 48VDC nominal). Fitting a
card with the wrong input voltage may damage the DC
module.
Important We strongly recommend that you use the TB8100 card
remover1, as shown in Figure 7.4 on page 124. A flat-blade
screwdriver may reach too far through the slot and damage
the components on the card.
Refer to Section 7.2 “Disassembly and Reassembly” for details on removing
and refitting the top and bottom covers and front panel.
Removal - Method 1 This procedure applies to the standby power supply and PFC control cards.
The procedure for removing the other cards is described in Method 2 below.
1. Remove the top cover.
2. Insert the card remover into the slot in the AC or DC converter PCB
b and push down c to lift the nearest plug out of its socket (refer to
Figure 7.4).
1. The card remover is included in the TBA0ST2 tool kit, which is available
from your nearest Tait Dealer or Customer Service Organisation. It is also
available separately as part number 220-02034-01.

124 Power Management Unit Servicing TB8100 Service Manual
© Tait Electronics Ltd April 2004
3. Repeat this procedure at the other end of the card.
4. When all plugs are free of their sockets, slide the card out from the
groove in the heatsink.
Figure 7.4 Replacing the Plug-in Cards
b
c
d
e
g
f
g

TB8100 Service Manual Power Management Unit Servicing 125
© Tait Electronics Ltd April 2004
Removal - Method 2 This procedure applies to the DC control, battery control, and HVDC and
microprocessor cards.
1. Remove the top and bottom covers and front panel.
2. Insert the card remover between the card and the edge of the AC or
DC converter PCB d and push down e to lift the nearest plug out
of its socket (refer to Figure 7.4).
3. Insert the card remover into the slot near the other end of the card
and push down to lift the plug out of its socket. On the longer
HVDC and microprocessor card, repeat this procedure for each slot
along the length of the card, working from the front to the rear of the
PMU.
4. When all plugs are free of their sockets, slide the card out from the
groove in the heatsink.
Refitting 1. Insert the top of the card into the groove in the heatsink f.
2. Align the plugs on the card with their matching sockets on the AC or
DC converter PCB.
3. Press the card down firmly at each end g so that each plug fits
correctly into its matching socket. There should be an audible
“click” when each plug is fully inserted. On the longer HVDC and
microprocessor card, you may need to use both hands to press evenly
along its length.
4. Refit the front panel and covers as necessary.
Reprogramming If you have replaced the HVDC and microprocessor card, you will have to
reprogram the PMU as described in the table below.
If you have changed the configuration of the PMU by fitting or removing a
standby power supply card, you will have to reprogram the PMU as
described in the table below.
Procedure Details
reprogram the product code reprogram this information into the PMU
using the Calibration Kit software; refer to
the Calibration Kit documentation for more
details
replace the serial number label the serial number of the PMU will change to
the number already programmed into the
replacement HVDC and microprocessor card;
stick the new serial number label onto the
rear panel

126 Power Management Unit Servicing TB8100 Service Manual
© Tait Electronics Ltd April 2004
There is no need for any recalibration when any of the plug-in cards is fitted,
removed or replaced.
7.4 Replacing the Auxiliary Power Supply PCB
Important You must reprogram the PMU if you change its configura-
tion by fitting or removing an auxiliary power supply PCB.
Refer to “Reprogramming” on page 127.
Refer to Section 7.2 “Disassembly and Reassembly” for details on removing
and refitting the top and bottom covers and rear panel. The circled numbers
in the following instructions refer to Figure 7.5.
Procedure Details
reprogram the product code use the Calibration Kit software to
reprogram the PMU with the product code
which corresponds to the new configuration
of the PMU; for more details refer to
“Identifying the PMU” on page 116, and to
the Calibration Kit documentation
Figure 7.5 Replacing the Auxiliary Power Supply PCB
cb

TB8100 Service Manual Power Management Unit Servicing 127
© Tait Electronics Ltd April 2004
Removal 1. Remove the top and bottom covers and rear panel.
2. Unplug the loom b from the auxiliary power supply PCB.
3. Remove the two M4 Torx Taptite screws c securing the PCB to the
heatsink.
Refitting 1. Position the PCB as shown in Figure 7.5 and secure with the two M4
Torx Taptite screws c.
2. Reconnect the loom b.
3. Replace the rear panel and top and bottom covers.
Reprogramming If you have changed the configuration of the PMU by fitting or removing
an auxiliary power supply PCB, you will have to reprogram the PMU as
described in the table below.
There is no need for any recalibration when this PCB is fitted, removed or
replaced.
Procedure Details
reprogram the product code use the Calibration Kit software to
reprogram the PMU with the product code
which corresponds to the new configuration
of the PMU; for more details refer to
“Identifying the PMU” on page 116, and to
the Calibration Kit documentation
128 Power Management Unit Servicing TB8100 Service Manual
© Tait Electronics Ltd April 2004

TB8100 Service Manual Power Management Unit Servicing 129
© Tait Electronics Ltd April 2004
Figure 7.6 PMU Mechanical Assembly - Sheet 1
Description IPN
bcurrent transformer 053-00028-XX
cE-core choke 069-00010-40
dclamp for E-core choke 069-00010-41
eAC mains input connector 219-02843-XX
fE-core choke PCB 220-02023-XX
g4mm bus bar terminal 240-04030-44
hretaining clip (holds device against heatsink) 303-50040-XX
ihandle 308-01065-XX
jheatsink 308-13146-XX
1) heatsink insulator 309-01051-XX
1! DC input insulator 309-01052-XX
1@ bottom cover 316-06811-XX
1# front panel 316-06812-XX
1$ rear panel 316-06813-XX
1% top cover 316-06814-XX
1^ shield 319-01246-XX
1& M6x12mm pan head Pozidriv screw 345-00070-05
1* M3x6mm countersunk Torx screw 345-40460-XX
1( M3x8mm pan head Torx Taptite screw 349-00020-36
2) M4x12mm pan head Torx Taptite screw 349-02058-XX
2! M3x10mm pan head Torx Taptite screw 349-02066-XX
2@ wire retaining clip (if 40W aux. PS PCB fitted) 357-01051-XX
2# plastic grommet 360-02026-XX
2$ M3 T03 insulator bush 362-00010-11
2% 10mm ID insulator bush with shoulder 362-00011-XX
2^ seal (when 40W aux. PS PCB not fitted) 362-01122-XX
2& AC converter PCB
2* PFC control card
2( HVDC control and microprocessor card
3) DC converter PCB
3! DC input filter card
3@ DC control card
3# battery control card
Not Shown in this Drawing
12-way ribbon cable between AC and DC modules 219-02629-XX
8-way cable for auxiliary power supply PCB 219-02844-XX
28VDC cable between AC and DC modules 219-02846-XX
thermally conductive insulator sheet 16x22mm 362-01116-XX
thermally conductive insulator sheet 130x22mm 362-01117-XX
Note:
The characters XX in an IPN (Tait Internal Part Number)
stand for the issue number of the part. Only the latest
issue of each part will normally be available for ordering
as spare or replacement parts.
Note:
This drawing shows an AC and DC PMU. Those parts
fitted only to an AC PMU or a DC PMU are shown in
sheet 2.
1*
1%
1!
1$
2^
j
2&
2*
2)
2(
j
1@
1*
2# 1^
e
2)
i
2!
1# 2@
j
b
2)
2%
1)
h
3#
2)
jc3)
d
1&
1(
f
3!
3@
2$
x4
x7 each
module
x4
x5 each end
x3
x2
gx3
x2
x2 per
transformer
x1 per
heatsink
x2
x2
x3
x2
x2

130 Power Management Unit Servicing TB8100 Service Manual
© Tait Electronics Ltd April 2004
Figure 7.7 PMU Mechanical Assembly - Sheet 2
Description IPN
DC PMU
bAC converter PCB mounting bracket 302-05268-XX
cheatsink insulator 309-01051-XX
dM4x12mm pan head Torx Taptite screw 349-02058-XX
eAC converter PCB (current sense and output filter
circuitry only)
fPFC control card
gHVDC control and microprocessor card (feedback and
microprocessor circuitry only)
AC PMU
hDC input insulator 309-01052-XX
irear panel 316-06813-XX
jAC blanking plate 316-06836-XX
1) M4x12mm pan head Torx Taptite screw 349-02058-XX
1! seal (when 40W aux. PS PCB not fitted) 362-01122-XX
Note:
The characters XX in an IPN (Tait Internal Part Number)
stand for the issue number of the part. Only the latest
issue of each part will normally be available for
ordering as spare or replacement parts.
b
c
d
e
f
g
c
b
x4
h
1)
i
1!
j
DC PMU
This drawing shows the assembly of the
AC module when it is fitted to a DC PMU.
AC PMU
This drawing shows the blanking plates fitted to
the front and rear panels in an AC PMU. These
plates cover the holes normally covered by the
DC module heatsinks.
x4 each end
x2
each end

TB8100 Service Manual Control Panel Circuit Description 131
© Tait Electronics Ltd April 2004
8 Control Panel Circuit Description
The control panel is designed to be the link between the user and the
TB8100 BSS. The circuitry for the operation of the control panel is located
on a PCB mounted behind its front face. All communication between the
BSS and the control panel is via the system control bus. Figure 8.1 on
page 132 shows the configuration of the main circuit blocks, and the main
inputs and outputs for power, audio and control signals.
This chapter provides an overview of all the control panel circuitry1.
However, not all the circuitry described here will be fitted to any particular
control panel PCB. The different types of PCB and their main features are
listed in the following table.
1. For a description of the controls located on the control panel, refer to
“Operating Controls” in the Installation and Operation Manual.
Control Panel PCB
Feature Standard Power Save
programming port ■■
microphone socket ■
volume control knob ■
0.5W speaker ■
PTT key from microphone ■
LED indicators ■■
channel speaker button ■
channel carrier button ■
microphone channel select button ■

132 Control Panel Circuit Description TB8100 Service Manual
© Tait Electronics Ltd April 2004
Figure 8.1 Control Panel High Level Block Diagrams
IC
Translation
2
RS-232
Translation
Microphone
Pre-emphasis
& Gain Control
Speaker
Volume &
Gain Control
LEDs &
Switches
Control
Panel Type
Microphone
Connector
Speaker
Fan Inputs
RS-232
Connector
Power
Supply
Microphone Audio
System
Control Bus
Speaker
Enable
Speaker Audio
I C Bus
2
28V, GND
Fan Power & GND
Open Collector RS-232 RS-232 Bus
IC
Translation
2
RS-232
Translation
LEDs
Control
Panel Type
Fan Inputs
RS-232
Connector
Power
Supply
System
Control Bus
Full Power On
Power Save On
I C Bus
2
28V, GND
Fan Power & GND
Open Collector RS-232 RS-232 Bus
Standard Control Panel
Power Save Control Panel

TB8100 Service Manual Control Panel Circuit Description 133
© Tait Electronics Ltd April 2004
8.1 Control Circuitry
The control panel translates I2C messages into an appropriate response on
the LEDs. It also translates key inputs from the front panel membrane1 and
fan rotation inputs from both fans into appropriate I2C messages. The type
of control panel is also sent with I2C messages.
The control panel translates RS-232 from the programming port into 0V to
5V open-collector signals which feed from and drive up to seven reciters.
8.2 Audio Circuitry
This circuitry is present only on the standard control panel PCB.
The audio input level from the reciter is 1V pp for a single reciter. When
multiple reciters are connected, this input level will drop by approximately
1⁄(number of reciters), to a minimum of 167mV pp for seven reciters.
The volume of the speaker is controlled by the volume control knob. In
addition, the control panel performs gain control so that, with an input of
167mV pp, the power output into a 16Ω speaker is ≥0.5W at the maximum
position of the knob, and 0W at the minimum position of the knob. An
LED indicates when the speaker is on.
The control panel is designed to work with an electret microphone with an
input range of 80dBSPL to 115dBSPL.
8.3 Power Save
This circuitry is present only on the power save control panel PCB.
When the BSS enters power save mode, the control panel will shut down
after receiving the appropriate I2C bus message from the reciter. The power
LED flashes once every two seconds to indicate the BSS is in power save
mode.
The control panel will power up again when it receives a signal on the
RS-232 system control bus or serial port.
1. Standard control panel only.
134 Control Panel Circuit Description TB8100 Service Manual
© Tait Electronics Ltd April 2004
8.4 Power Supply
The control panel operates off a 28V (nominal) power supply provided by
the reciter. The power supply for the cooling fans mounted on the front
panel is fed through the control panel.

TB8100 Service Manual Control Panel Servicing 135
© Tait Electronics Ltd April 2004
9 Control Panel Servicing
Important This equipment contains devices which are susceptible to
damage from static charges. Refer to “ESD Precautions”
on page 15 for more information on antistatic procedures
when handling these devices.
This chapter provides information on how to identify, remove and replace
the main mechanical parts and PCB.
Figure 9.4 on page 141 identifies the main mechanical parts, and
“Identifying the Control Panel” on page 136 explains how to identify the
model of control panel from its product code.
Note For the sake of simplicity and clarity, the instructions and illustra-
tions in this chapter refer to a standard control panel. However,
the same basic procedures and techniques apply to other models.

136 Control Panel Servicing TB8100 Service Manual
© Tait Electronics Ltd April 2004
9.1 Identifying the Control Panel
You can identify the model of control panel by referring to the product code
printed on a label on the side of the chassis. The product codes are
explained in the table below.
9.2 Screw Torque Settings
The recommended torque settings for the screws and nuts used in the
control panel are as follows:
9.3 Replacing the PCB
The circled numbers in the following instructions refer to Figure 9.1.
Removal 1. Gently pull the volume knob off its shaft.
2. Disconnect the speaker plug b from the socket on the PCB.
3. Remove the M3 Torx screws c securing the PCB and D-range
connector.
4. Carefully lift and rotate the PCB away from the control panel chassis,
feeding the shaft of the volume control through the hole in the
chassis, until the PCB is standing upright d.
5. With the PCB standing upright, disconnect the flexible connector to
the keypad e.
Product Code Description
TBA201X power save
TBA202X standard
Location / Function Torque Driver/
Spanner Size
■securing the PCB
■securing the D-range connector
0.5N·m / 4.5lbf·in T10 M3
securing the speaker clamps 0.5N·m / 4.5lbf·in 5.5mm AF M3

TB8100 Service Manual Control Panel Servicing 137
© Tait Electronics Ltd April 2004
Figure 9.1 Replacing the Control Panel PCB
b
c
c
d
e
e
x4
x2

138 Control Panel Servicing TB8100 Service Manual
© Tait Electronics Ltd April 2004
Refitting 1. Withdraw the flexible connector to the keypad through the hole in
the side of the control panel chassis.
2. Refit the PCB to the chassis, feeding the speaker wire through the
hole in the PCB. Secure the PCB and D-range connector with the
M3 Torx screws.
3. Reconnect the speaker wire.
4. Insert the flexible connector into its socket on the PCB through the
hole in the side of the chassis.
Important Make sure the flexible connector is correctly positioned and
latched in its socket, as shown in Figure 9.2.
5. Refit the volume knob.
Figure 9.2 Reconnecting the Flexible Connector
flexible connector inserted
straight into socket
latch pushed fully down
at both ends

TB8100 Service Manual Control Panel Servicing 139
© Tait Electronics Ltd April 2004
9.4 Replacing the Speaker
The circled numbers in the following instructions refer to Figure 9.3.
Removal 1. Remove the PCB as described in “Replacing the PCB” on page 136.
2. Remove the M3 nuts and spring washers b and then remove the
brackets c.
3. Remove the speaker.
Refitting 1. To refit the speaker, follow the removal instructions in reverse order.
Tighten the M3 nuts to the correct torque.
Important Make sure the speaker is correctly aligned as shown in
Figure 9.3 so that the wire will fit through the slot in the
PCB (refer to Figure 9.1 on page 137).
2. Refit the PCB as described in “Replacing the PCB” on page 136.
Figure 9.3 Replacing the Speaker
b
c
x2
x2
140 Control Panel Servicing TB8100 Service Manual
© Tait Electronics Ltd April 2004

TB8100 Service Manual Control Panel Servicing 141
© Tait Electronics Ltd April 2004
Figure 9.4 Control Panel Mechanical Assembly
Description IPN
bD-range to Micromatch ribbon cable 219-02853-XX
cspeaker* 252-00011-XX
dspeaker mounting bracket* 302-05266-XX
espeaker grille cloth* 307-01024-XX
fvolume knob* 311-01054-XX
gkeypad - standard
keypad - power save
311-03116-XX
311-03115-XX
hchassis 316-06820-XX
iM3x8mm pan head Torx screw with spring & flat
washers
345-40470-XX
jM3 hex nut* 352-00010-08
1) M3 spring washer* 353-00010-12
1! control panel PCB
Note:
The characters XX in an IPN (Tait Internal Part Number)
stand for the issue number of the part. Only the latest
issue of each part will normally be available for ordering
as spare or replacement parts.
Note:
This drawing shows a standard control panel. Any
differences between the standard and power save
control panels are indicated in the description of the
parts, or as shown below:
* fitted to standard control panel only
b
c
dx2
e
f
g
h
ix4
jx2
1) x2
ix2
1!
142 Control Panel Servicing TB8100 Service Manual
© Tait Electronics Ltd April 2004

TB8100 Service Manual Subrack Servicing 143
© Tait Electronics Ltd April 2004
10 Subrack Servicing
This chapter provides information on the standard mechanical parts and
cables used in the TB8100 BSS:
■Figure 10.1 on page 145 identifies the mechanical parts used in the front
panel assembly
■Figure 10.2 on page 146 identifies the mechanical parts used in the
subrack assembly
■Figure 10.3 on page 147 identifies the cables used in single and dual base
station systems.
144 Subrack Servicing TB8100 Service Manual
© Tait Electronics Ltd April 2004

TB8100 Service Manual Subrack Servicing 145
© Tait Electronics Ltd April 2004
Figure 10.1 Front Panel Mechanical Assembly
Description IPN
bfan contact PCB 220-02028-XX
cfan:
no rotation sensor
rotation sensor
258-00011-XX
258-00014-XX
dPA fan duct 302-05264-XX
ePMU fan duct 302-05265-XX
fspring clip 303-50106-XX
gfront panel 316-06821-XX
hKC30x10mm pan head Torx PT screw 346-10030-10
iM4x40mm pan flange head Torx PT screw 346-10440-XX
jquarter-turn fastener 354-01047-XX
1) retaining washer for quarter-turn fastener 354-01048-XX
Note:
The characters XX in an IPN (Tait Internal Part Number)
stand for the issue number of the part. Only the latest
issue of each part will normally be available for ordering
as spare or replacement parts.
Note:
Fully-assembled front panels and replacement fan kits are
also available as separate products. Consult your nearest
Tait Dealer or Customer Service Organisation for details
on the availability of these products.
j
g
i
c
e
dh
c
fh
b
1)
x2
x8
x6
x2

146 Subrack Servicing TB8100 Service Manual
© Tait Electronics Ltd April 2004
Figure 10.2 Subrack Mechanical Assembly
Description IPN
bmodule retaining clamp 303-50102-XX
ccable retaining clip 303-50104-XX
dbottom guide rail 307-02052-XX
etop guide rail (also used in the bottom corners
when required)
307-02053-XX
frear blanking panel 316-06785-XX
gsubrack 318-01051-XX
hM4x10mm pan head Pozidriv screw 345-00050-07
iM3 hex nut 352-00010-08
jM3 spring washer 353-00010-12
1) receptacle for quarter-turn fastener 354-01049-XX
1! subrack ground connector 356-00010-61
1@ 9.5mm P-clip 357-00010-48
1# insulating foam 362-01037-XX
1$ insulator for interconnect PCB 362-01121-XX
1% interconnect PCB
Note:
The characters XX in an IPN (Tait Internal Part Number)
stand for the issue number of the part. Only the latest
issue of each part will normally be available for ordering
as spare or replacement parts.
Note:
Some of the parts illustrated in this diagram are also
available as part of a kit or set of parts. These kits or sets
are available as separate products. Consult your nearest
Tait Dealer or Customer Service Organisation for details
on the availability of these products.
b
c
d
ef
g
h
i
j
1)
1!
1@
1#
1$
x5
x2
x3
x3
1%

TB8100 Service Manual Subrack Servicing 147
© Tait Electronics Ltd April 2004
Figure 10.3 Cable Identification
Description IPN
bRF coaxial cable - reciter to 5/50W PA (long) 219-02859-XX
cRF coaxial cable - reciter to 5/50W PA (short) 219-02862-XX
dRF coaxial cable - reciter to 100W PA 219-02864-XX
esystem control bus ribbon cable - reciter to subrack
interconnect PCB
219-02858-XX
fsystem control bus ribbon cable - 5/50W PA to
subrack interconnect PCB
219-02861-XX
gsystem control bus ribbon cable - PMU and 5/50W
PA to subrack interconnect PCB
219-02857-XX
hsystem control bus ribbon cable - PMU and 100W
PA to subrack interconnect PCB
219-02863-XX
iDC power cable - PMU to single reciter 219-02856-XX
jDC power cable - PMU to dual reciters 219-02860-XX
1) DC power cable - PMU aux. output to single reciter
DC power cable - PMU aux. output to dual reciters
219-02895-XX
219-02896-XX
Note:
The characters XX in an IPN (Tait Internal Part Number)
stand for the issue number of the part. Only the latest
issue of each part will normally be available for ordering
as spare or replacement parts.
Note:
The cables illustrated in this diagram are also available as
part of a wiring kit. These kits are available as separate
products. Consult your nearest Tait Dealer or Customer
Service Organisation for details on the availability of
these products.
b
c
d
e
f
e
g
h
i
j
1)
dual 5/50W BSS - front view
single 100W BSS - front view
dual 5/50W BSS - rear view
148 Subrack Servicing TB8100 Service Manual
© Tait Electronics Ltd April 2004

TB8100 Service Manual Glossary 149
© Tait Electronics Ltd April 2004
Glossary
This glossary contains an alphabetical list of terms and abbreviations related
to the TB8100 base station system. For information about trunking,
mobile, or portable terms, consult the glossary provided with the relevant
documentation.
A B C D E F G H I K L N P R S T U V W
A
access level There are three different levels of access to a base station: Administrator,
User, and Read-only. The User access level has a configurable access profile;
the Administrator decides which functions that access level can carry out.
action An action is the second part of a Task Manager task. It specifies what the
base station must do when the first part (the input) becomes true.
active Digital outputs are active when the base station pulls their voltage low and
current is flowing. Digital inputs are active when external equipment is
pulling them to ground. All base station digital inputs and outputs are open
collector.
ADC Analog-to-Digital Converter. A device for converting an analog signal to a
digital signal that represents the same information.
Alarm log The alarm log is a list of the last 50 alarms that the base station generated.
This list is stored in the base station. To view it, select Monitor > Alarms >
Reported Alarms.
Alarm Center Alarm Center is a utility provided with the Service Kit that is able to receive,
store, and display alarms from any number of base stations with dial-up
connections. Participating base stations need an Alarm Reporting license.
Alarm Center also routes emailed messages to the email server.
alarm notification Alarm notification is the process by which the base station passes on
information about an alarm condition. It can notify alarms over the air, over
the line, via email, or to an Alarm Center. It can also activate a digital
output. If the Service Kit is logged on to the base station, it is automatically
notified of any alarms.
air intake
temperature The temperature of the air as measured at the PA’s air intake.
150 Glossary TB8100 Service Manual
© Tait Electronics Ltd April 2004
anti-kerchunking Anti-kerchunking is a base station configuration that discourages users from
kerchunking.
B
balanced line A balanced line has two wires carrying equal and opposite signals. It is
typically used in a line-connected base station for connecting to the
despatcher console. The system interface identifies the balanced line in as
Rx+ and Rx-, and the balanced line out as Tx+ and Tx-.
BCD BCD (binary coded decimal) is a code in which a string of four binary digits
represents a decimal number.
BSS A BSS (base station system) is a subrack containing at least one TB8100 base
station.
C
Calibration Kit The TB8100 Calibration Kit is a utility for defining the switching ranges of
the receiver and the exciter and for flattening the receiver response across its
switching range. It can also be used to calibrate various parts of the reciter
and the PA circuitry.
CCDI2 CCDI2 (computer controlled data interface version 2) is a proprietary Tait
command protocol used between computer equipment and a Tait radio.
channel A channel is:
■A frequency pair (or just a single frequency in a simplex system).
■A set of configuration information that defines the frequency pair and
other settings. Also referred to as a channel configuration. Generally,
‘channel’ has this meaning in the Service Kit.
channel profile A channel profile is a named set of configuration items relating to the base
station’s RF configuration, transmitter power output and power saving
modes. Like the signalling profile, it can be applied to any channel.
Together, these profiles define most configuration items.
channel spacing Channel spacing is the bandwidth that a channel nominally occupies. If a
base station has a channel spacing of 12.5 kHz, there must be a separation of
at least 12.5 kHz between its operating frequencies and those of any other
equipment.
channel table The channel table is the base station’s database of channel configurations. To
view it, select Configure > Base Station > Channel Table.
TB8100 Service Manual Glossary 151
© Tait Electronics Ltd April 2004
CODEC An IC which combines analog-to-digital conversion (coding) and digital-
to-analog conversion (decoding).
configuration file A configuration file consists of all the configuration settings needed for a
base station, stored as a file in the configurations folder. Configuration files
have the extension *.t8c.
connection A connection is a named group of settings that the Service Kit uses when
establishing communications with a BSS.
control bus The control bus is used for communications between modules in a base
station system. It is an I2C bus, a bi-directional two-wire serial bus which
is used to connect integrated circuits (ICs). I2C is a multi-master bus, which
means that multiple chips can be connected to the same bus, and each one
can act as a master by initiating a data transfer.
control panel The control panel is an area at the front of the BSS with buttons, LEDs and
other controls that let you interact with the BSS.
CTCSS CTCSS (continuous tone controlled squelch system), also known as PL
(private line), is a type of signalling that uses subaudible tones to segregate
groups of users.
custom action A custom action is a user-defined Task Manager action that consists of more
than one pre-defined action.
custom input A custom input is a user-defined Task Manager input that consists of a
combination of pre-defined inputs.
CWID CWID (Continuous Wave IDentification) is a method of automatically
identifying the base station using a Morse code. Continuous wave means
transmission of a signal with a single frequency that is either on or off, as
opposed to a modulated carrier.
D
DAC Digital-to-Analog Converter. A device for converting a digital signal to an
analog signal that represents the same information.
DCS DCS (digital coded squelch), also known as DPL (digital private line), is a
type of subaudible signalling used for segregating groups of users. DCS
codes are identified by a three-digit octal number, which forms part of the
continuously repeating code word. When assigning DCS signalling for a
channel, you specify the three-digit code.
de-emphasis De-emphasis is a process in the receiver that restores pre-emphasised audio
to its original relative proportions.
152 Glossary TB8100 Service Manual
© Tait Electronics Ltd April 2004
duty cycle Duty cycle is used in relation to the PA. It is the proportion of time
(expressed as a percentage) during which the PA is operated. The TB8100
PA can be operated continuously.
E
EIA Electronic Industries Alliance. Accredited by the American National
Standards Institute (ANSI) and responsible for developing
telecommunications and electronics standards in the USA.
EMC Electromagnetic Compatibility. The ability of equipment to operate in its
electromagnetic environment without creating interference with other
devices.
ETSI European Telecommunications Standards Institute. The non-profit
organisation responsible for producing European telecommunications
standards.
F
flag A flag is a programming term for a “yes/no” indicator used to represent the
current status of something. The base station has a set of system flags that
are read and set by Task Manager. There is also a separate set of flags that
you can use in your own Task Manager tasks.
frequency band The range of frequencies that the equipment is capable of operating on.
front panel The cover over the front of the BSS containing fans for the PA and PMU.
G
gating Gating is the process of opening and closing the receiver gate. When a valid
signal is received, the receiver gate opens.
H
hiccup mode Many power supplies switch off in the event of a short-circuit and try to start
again after a short time (usually after a few seconds). This “hiccup”-type of
switching off and on is repeated until the problem is eliminated.
hysteresis Hysteresis is the difference between the upper and lower trigger points. For
example, the receiver gate opens when the upper trigger point is reached,
TB8100 Service Manual Glossary 153
© Tait Electronics Ltd April 2004
but will not close until the level falls to the lower trigger point. An adequate
hysteresis prevents the receiver gate from repeatedly opening and closing
when the level is about that of the trigger point.
Hysteresis mode A mode of PMU operation designed to save power. The PMU is mainly
turned off, but switches back on intermittently to maintain output voltage
when the output current is low.
I
inactive Digital outputs are inactive if the base station is doing nothing to them.
They are floating, open collector outputs. Digital inputs are inactive when
they are open circuit.
Intercom mode Intercom mode makes it possible for the operator at the dispatch centre and
the servicing technician at the base station to communicate with each other
over the line. It connects the base station microphone to line out.
isolator An isolator is a passive two-port device which transmits power in one
direction, and absorbs power in the other direction. It is used in a PA to
prevent damage to the RF circuitry from high reverse power.
K
kerchunking Kerchunking is transmitting for a second or less without saying anything in
order to test the base station. This results in a ‘kerchunk’ sound.
L
line-controlled base
station A TB8100 is a line-controlled base station when it receives audio (sending
it out via its systems interface), transmits audio received over its systems
interface, and its transmitter is keyed via the Tx Key line.
logging on Once you are connected to a BSS, you log on to a base station. This
establishes communications between the Service Kit and a particular base
station.
N
navigation pane The navigation pane is the left-hand pane of the Service Kit application
window. It displays a hierarchical list of items. When you click an item, the
main pane displays the corresponding form.
154 Glossary TB8100 Service Manual
© Tait Electronics Ltd April 2004
0
operating range Operating range is another term for switching range.
P
PA The PA (power amplifier) is a base station module that boosts the exciter
output to transmit level.
PMU The PMU (power management unit) is a module that provides power to the
BSS.
pre-emphasis Pre-emphasis is a process in the transmitter that boosts higher audio
frequencies.
R
reciter The reciter is a module of a TB8100 base station that acts as receiver and
exciter.
reverse tone burst Reverse tone bursts can be used with CTCSS. When reverse tone bursts are
enabled, the phase of the generated tones is reversed for a number of cycles
just before transmission ceases. If the receiver is configured for reverse tone
burst, it responds by closing its gate.
RSSI RSSI (Received Signal Strength Indicator) is a level in dBm or volts that
indicates the strength of the received signal.
Run mode Run mode is the normal operating mode of the base station.
signalling profile A signalling profile is a named set of configuration items related to signalling
that can be applied to any channel. Items include subaudible signalling and
transmit timers.
S
sensitivity The sensitivity of a radio receiver is the minimum input signal strength
required to provide a useable signal.
SINAD SINAD (Signal plus Noise and Distortion) is a measure of signal quality. It
is the ratio of (signal + noise + distortion) to (noise + distortion). A SINAD
of 12dB corresponds to a signal to noise ratio of 4:1. The TB8100 can
provide an approximate SINAD value while in service by comparing the in-
TB8100 Service Manual Glossary 155
© Tait Electronics Ltd April 2004
band audio against out-of-band noise. This value should not be relied upon
to make calibrated measurements.
Sleep mode Sleep mode is a power saving state in which a part of the base station is
switched off, and then periodically switched on again.
Standby mode Standby mode is a mode of base station operation in which active service is
suspended so that special operations can be carried out, such as
programming the base station with a new configuration.
status message A status message is a set of information about the base station that can be
emailed. It identifies the base station, indicates the current operating
channel, lists the status of all alarms, and gives the current values of a number
of other monitored parameters. It also contains the alarm log.
subaudible
signalling Subaudible signalling is signalling that is at the bottom end of the range of
audible frequencies. The TB8100 base station supports CTCSS and DCS
subaudible signalling.
subtone A subtone (subaudible signalling tone) is a CTCSS tone or a DCS code.
switching range The switching range is the range of frequencies (about 10MHz) that the
equipment is tuned to operate on. This is a subset of the equipment’s
frequency band.
system flag System flags are binary indicators that are read and set by Task Manager.
Generally, they are used to disable or enable configured base station
functions.
system interface The system interface is the set of inputs to and outputs from the base station
(excluding power and RF), provided by a board inside the reciter. A range
of different boards are available for different applications.
T
TB8100 Base Station A Tait TB8100 base station consists of the equipment necessary to receive
and transmit on one channel. Generally, this means a reciter, a PA, and a
PMU. Often abbreviated to TB8100 or base station.
Talk Through
Repeater A TB8100 is a talk through repeater when its audio path is configured to
pass the audio it receives on to the transmitter.
Tas k M a na ge r Task Manager is a part of the TB8100 base station firmware that carries out
tasks in response to inputs. These tasks are formulated using the Service Kit.
156 Glossary TB8100 Service Manual
© Tait Electronics Ltd April 2004
template file A template file contains configuration information that can be used to create
a new base station configuration. Template files have the extension *.t8t.
transmit lockout The transmit lockout feature prevents the base station from transmitting for
a time once the transmit timer has expired. It is designed to prevent users
from monopolising the base station.
U
Unbalanced line An unbalanced line has one wire earthed. It is typically used for short
connections, for example, between a base station and a repeater on the same
site. The system interface identifies the wires of unbalanced lines with Rx
audio, Tx audio, and Audio Ground. Audio Ground is common to line-in
and line-out.
V
valid signal A valid signal is a signal that the receiver responds to by opening the receiver
gate. A signal is valid for example when it is stronger than a minimum level
and when it has the specified subtone.
VSWR Voltage Standing Wave Ratio (VSWR) is the ratio of the maximum peak
voltage anywhere on the line to the minimum value anywhere on the line.
A perfectly matched line has a VSWR of 1:1. A high ratio indicates that the
antenna subsystem is poorly matched.
W
Watchdog A watchdog circuit checks that the system is still responding. If the system
does not respond (because the firmware has locked up), the circuit resets the
system.