Hk ESC 20A Manual
User Manual: Pdf
Open the PDF directly: View PDF .
Page Count: 9
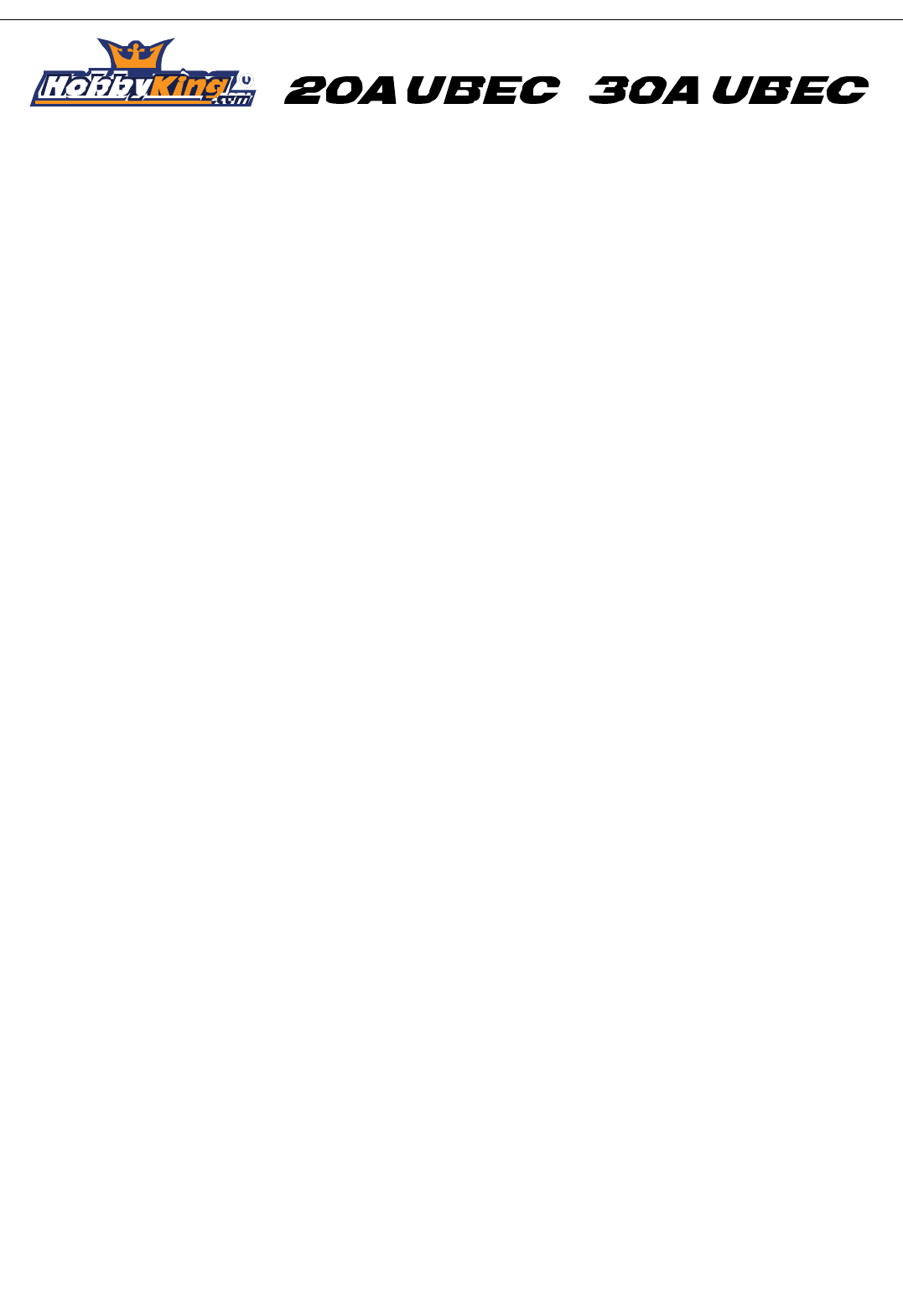
USER MANUAL
Dear customers:
Thank you for using the smart power electric speed controller (ESC) for brushless motor designed and
produced by HobbyKing.com. Wrong use and operation may cause personal injuries and damages on the
equipment due to the strong power at the starting of the product. We strongly recommend customers to read the
specification carefully before using the product and operate the product strictly in accordance with the
operating provisions. We assume no responsibilities generated from the application of the product, including
but not limited to liabilities for damage of incidental losses or indirect losses. Meanwhile, we assume no
responsibilities generated from the disassembly and modification by users themselves and assume no
responsibilities caused by products from the third party.
We have the right to alter products including appearance, performance parameter and operating requirement
without advanced notice. We make no guarantee, declaration or promise on whether the product is suitable for
specific purpose of users.
I. The main properties of electric speed controller for brushless motor
● Use powerful and high-performance MCU processor. The users can set function of use according to their
requirements. It fully reflects the smart property of our products as a unique advantage.
● Support unlimited rotate speed of brushless motor
● Support the function of fixed speed
● Delicate circuit design with strong anti-interference
● The starting mode can be set. The response speed of throttle is very quickly and with very stable linear of
speed regulation. It can be used in fixed wing aircraft and helicopter
● Threshold values of low-voltage protection can be set.
● With internal SBEC, the operating power to start steering engine is strong and the power dissipation is
small.
● Multi protection function: protection for abnormal input voltage/ protection for low battery/ protection for
overheat/protection of lowing power when lost of signals from throttle
● Good safety performance under energization: the motor will not start at the time of power on regardless of
the location of pull rod of throttle in controller.
● Protection for overheat: the output power will lesson to half when the temperature reaches 100 during the℃
operation of ESC. The output power will automatic recover when the temperature is under 100℃
● Supports with operation setting for all controller and setting of programming panels
● Set alarm sound. And judge the working situation after power on.
● The company has completed intellectual property on the product. The product can be continuingly updated
and upgraded. The product can be made to customers’ requirements.
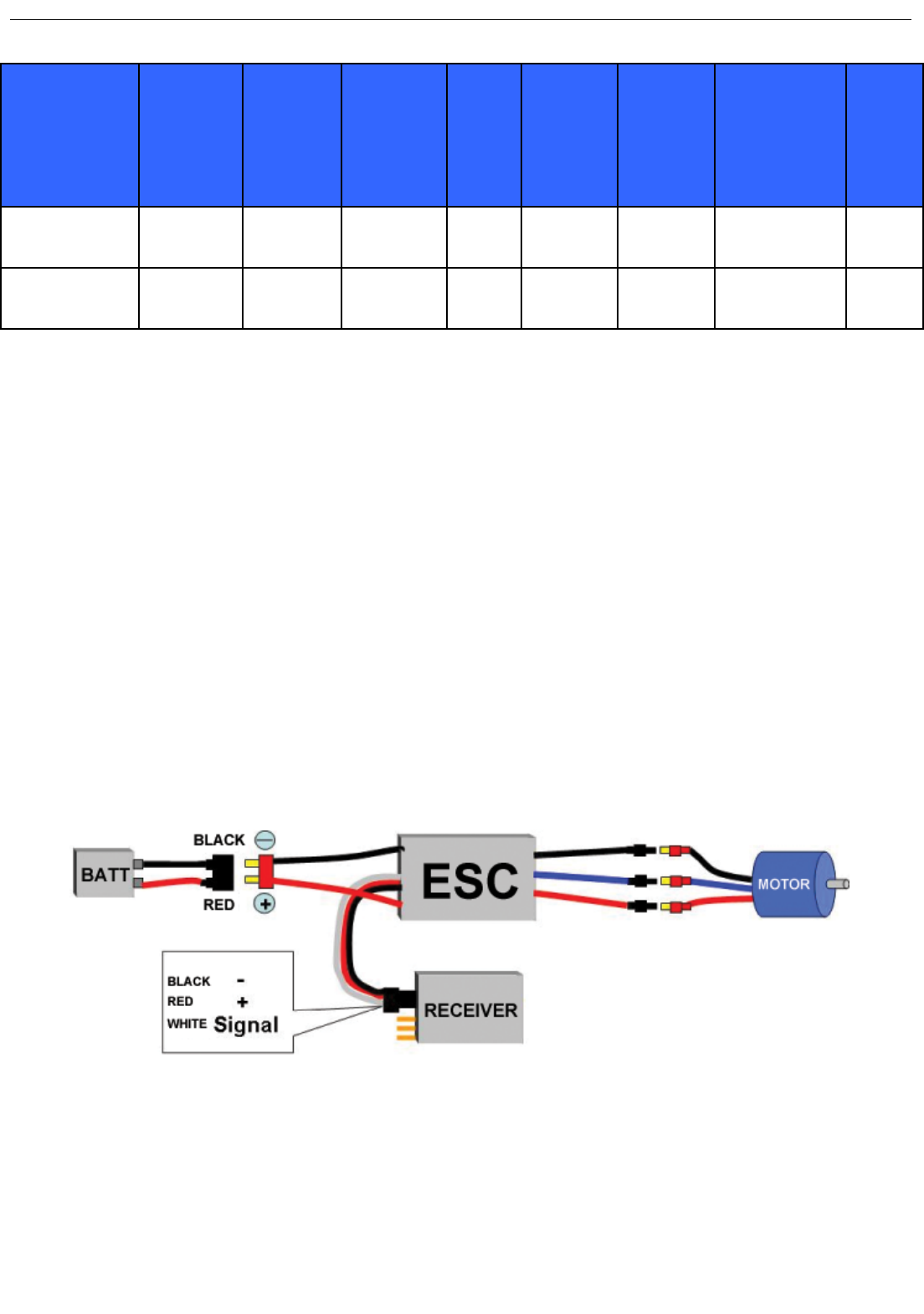
The product standard of ESC
Standard
(A)sust
ained
current
(10s)
(A)max
instantane
ous
current
(V/A)
Output
BEC
BEC
mode
Number
of
battery/lit
hium
battery
Number
of
battery/ni
ckel-
hydrogen
battery
mm
Size(width*len
gth*height)
g
weight
HK20A UBEC 20A 25A 5.5V/3A-
1A
SBEC/
UBEC 2-4Lipo 5-12NC 54*26*11 30
HK3A UBEC 30A 40A 5.5V/3A-
1A
SBEC/
UBEC 2-4Lipo 5-12NC 54*26*11 32
Notice:
1) The ESC with SBEC supply steering engine with switching power. The output voltage is 5.5V. The
load current of steering engine is 4A. At the moment of 2 seconds can reach 8A.
2) The ESC with UBEC supply steering engine with linear power. The output voltage is 5.5v. The load
current is 1A.
3) OPTO means that there is no BEC inside ESC. The steering engine and receiver shall be supplied
with power separately.
4) Customized BEC can be made according to customers’ requirements.
5) Customized ESC can be made according to customers’ requirements.
II. The introduction of the connection in the ESC
In order to avoid short circuit and leakage, the joint are connected by thermal shrinkable pipe to ensure
insulation.
Battery Pack Black Red White Motor
III. The function of electric speed controller for brushless motor
1. Reset to factory default
2. Battery types set(Lipo or NiMh/NiCd)
3. Brake set (yes/no)
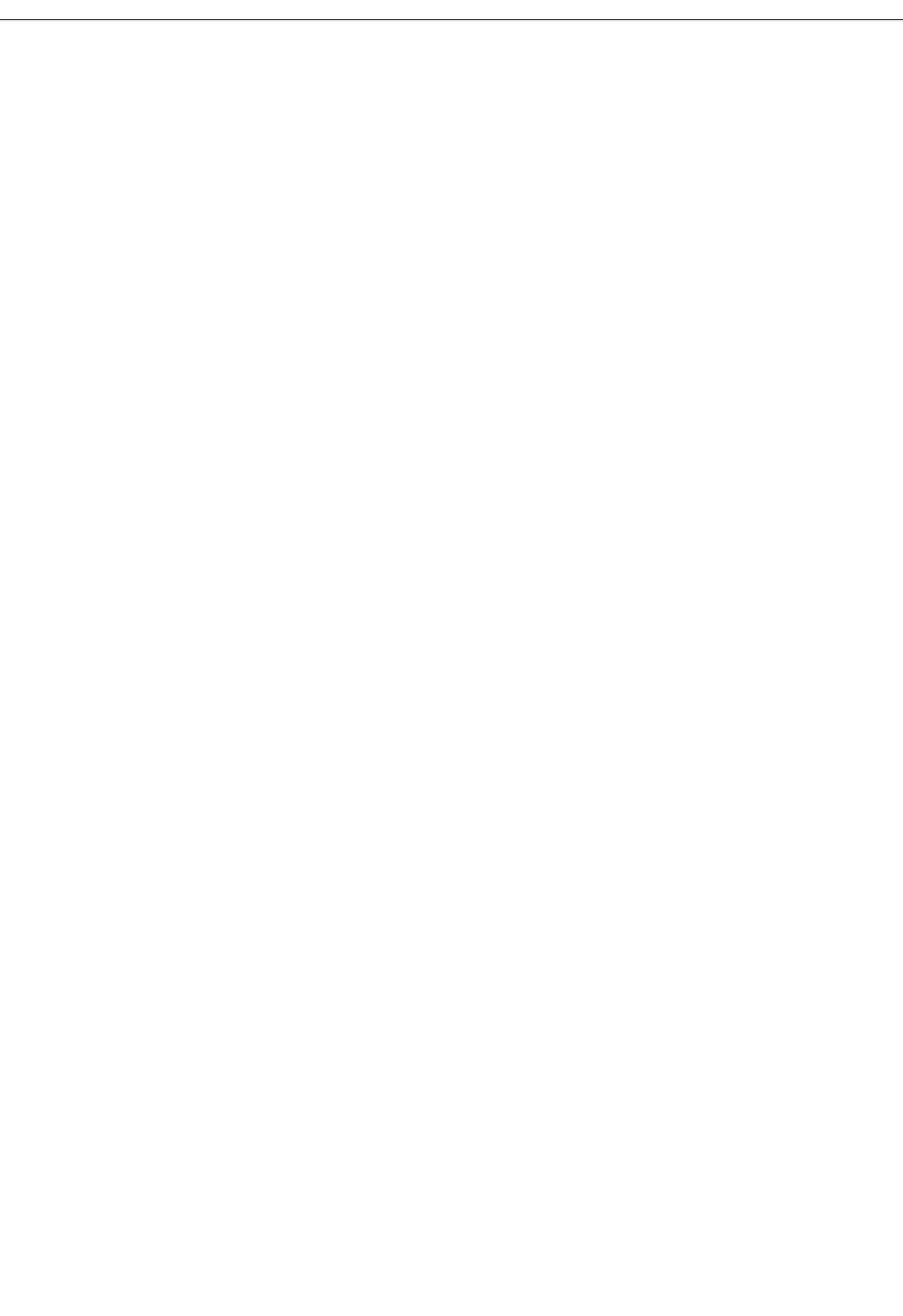
4. Threshold set of protection for low voltage (set a protective value for low voltage)
5. Motor entrance angle set (improve the service efficiency of ESC and the stability in the starting)
6. Accelerated startup set (used in precise gear box and application of helicopter)
7. Helicopter mode (used in application of helicopter)
8. Steering motor (clockwise/anticlockwise)
9. Operating frequency set
10. Protection mode under low voltage (reduces power or halts immediately)
VI. The operation steps of programming in ESC for brushless motor.
Push the pull rod of throttle in the ESC to the highest position to make the ESC enter the setting mode and
then turn on the ESC.
Remark: the ESC enters the setting mode when the pull rod of throttle in the ESC is pushed to the highest
position; the ESC enters the working mode when the pull rod of throttle in the ESC is pushed to the lowest
position.
1) Connect the battery pack to the ESC. After two seconds, a beep shows that the ESC enters the setting mode.
The menu of setting mode is a cycle model. Each function corresponds to one corresponding musical tone.
Each musical tone will ring out for four times continuously. During the four periods when music rings, push the
pull rod of throttle in the ESC to the lowest position. Then the motor will give out a beep to inform that
corresponding parameters have been stored, and the ESC enters the working mode.
2) Repeat the above operation to set various functions you need.
Remark: Can also set with programming panels (optional accessories ). Refer to specification of
programming panels for setting method.
1. Brake: turn on/turn off
Turn on: the propeller stops immediately when the throttle works under the smallest position.
Turn off: the propeller stops naturally when the throttle works under the smallest position.
2. Battery types: LiPo or NiCd/NiMh
NiCd/NiMh- set protection point for NiCad/NiMh.
Lipo-set protection point for Lipo and detect numbers of battery automatically in the battery pack.
Remark: the choice of NiCad/NiMh battery will make the ESC automatically set the cutoff value of voltage
at 65% of factory defaults. The cutoff value can be modified through the function of protection
for low voltage in case of changes. Once the battery pack of NiCad/NiMh connects to the power,
the ESC will read its initial voltage. The voltage will used as a reference value for cutoff value of
voltage.
3. Protection function of low voltage: low/middle/high
1) In case of Ni-xx battery pack: the cutoff value of voltage is 50%/65%/65% of the initial voltage of
battery pack under low/middle/high threshold value.
2) In case of Li-xx battery pack: the number of batteries can be calculated automatically. Users need not to
set anything except the types of battery. The ESC provides three optional gears for protection point of low
voltage: low(2.8V)/middle(3.0V)/high(3.2V)
For example: the protection cutoff voltage for low voltage is 11.2V as low /12.0V as middle/12.8V as high
in case of Li-po battery pack with four batteries and voltage at 14.8V.
4. Recover to factory default setting.
1) The factory default setting of ESC:
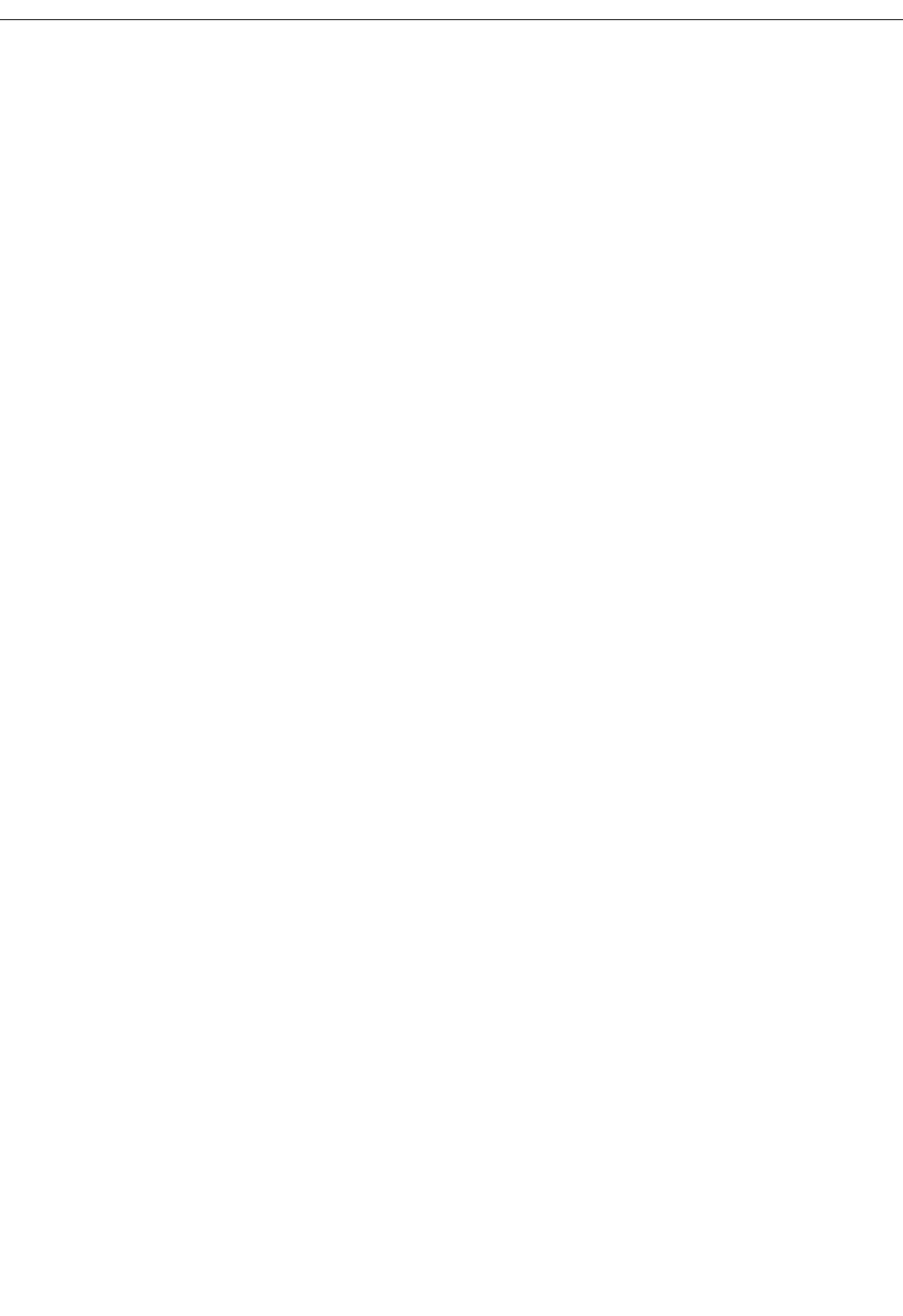
2) The brake: off
3) The types of battery: Lipo battery with automatic detection.
4) The cutoff value under low voltage: middle (3.0V/65%)
5) The angle of entrance in motor: automatic
6) Setting for accelerated startup: smooth
7) The setting Mode for helicopter: off
8) The frequency of working: 8kHz
9) Protection mode under low voltage: reduce power
5. The angle of entrance in motor: automatic/low/high
Automatic-the ESC detect the most suitable angle of entrance in motor automatically.
Low (7-22 degree) – suitable for the setting of most motors with inner rotor
High (22-30 degree)-suitable for the setting of most motors with outer rotor and 6 poles or more than poles
Under most cases, the automatic angle of entrance is suitable for all motors. However, in order to increase
efficiency, we recommend using low angle of entrance in motors with 2 poles (generally inner rotor), and using
high angle of entrance in motors with 6 and more than 6 poles (generally outer rotor). We can set a high angle
of entrance for motors with higher rotate speed. Some motors need special angle of entrance. We recommend
using the angle of entrance recommended by motor producers or automatic detected angle of entrance in case of
uncertainty.
Remark: please debug the motor on the ground after successfully altering the angle of entrance in motor.
Setting for accelerated startup: provide rapid accelerated start up with linear throttle response.
Ultra smooth startup: the lag time of throttle response between the starting and highest speed is 1.5 seconds.
The setting mode can prevent the precision gear/gearing dropping under momentary load. The setting mode is
recommended to use in fixed wing model with gear box or helicopter.
Smooth startup: the lag time of throttle response between the starting and highest speed is 1 second. The
setting mode is recommended to use in fixed wing model with gear box or helicopter.
Accelerated startup: there is no lag time of throttle response between the starting and highest speed. The
setting mode is recommended to use in fixed wing model with direct drive.
6. The Mode for helicopter: (use in application of helicopter)
Turn off the helicopter
Helicopter 1: the lag time of throttle response between the starting and highest speed is 5 seconds. However,
if the throttle is turned off after startup, the next startup will commence in common mode.
Helicopter 1: the lag time of throttle response between the starting and highest speed is 15 seconds. However,
if the throttle is turned off after startup, the next startup will commence in common mode.
Remark: once working under mode for helicopter, the brake and types of protection under low voltage will
be reset automatically to mode of no brake and reduce power mode separately regardless of previous setting of
ESC.
7. Steering motor (clockwise/anticlockwise)
In most cases, the clockwise and anticlockwise rotation of motor can be realized by exchanging any two lines
among the three output lines in the ESC connected to the motor. The direction of rotation can be changed by
altering the setting value on the ESC in case that the wire connected to motor has been directly welded on the
ESC.
8. Operating frequency: 8kHz / 16kHz
8 kHz-the Operating frequency for motor with 2 poles, for example inner rotor
16 kHz-the Operating frequency for motor with poles more than 2, for example outer rotor
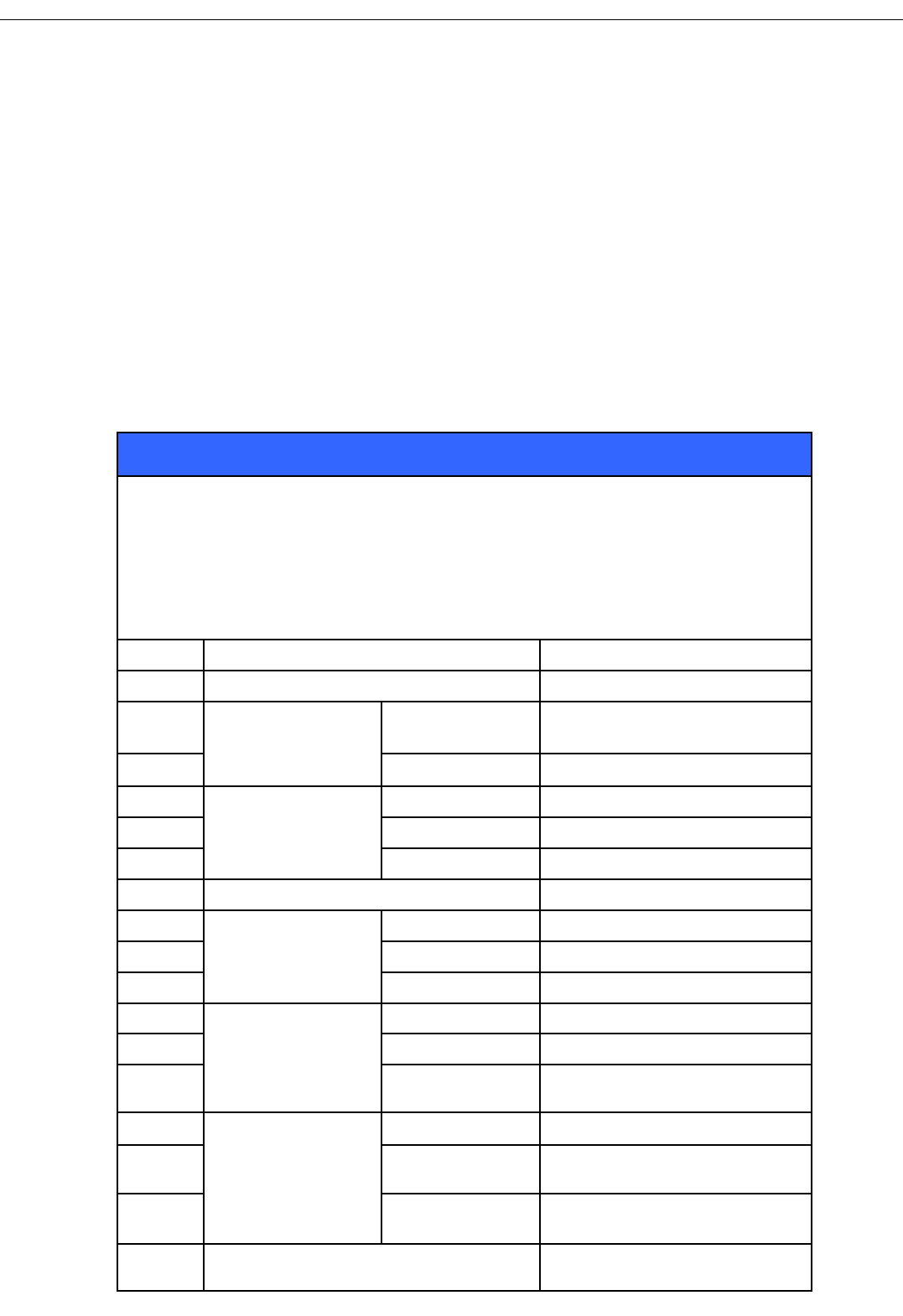
Although the operating frequency of 16 kHz can provide strong power for fixed wing or helicopter, the
default setting is 8 kHz for there are louder RF noise under the operating frequency of 16 kHz.
9. Protection mode under low voltage: reduce power/ halt immediately
Reduce power- the ESC will reduce the output power of motor when reaches default protection threshold
for low voltage (recommend)
Halt immediately-the ESC will cut off the output power of motor when reaches default protection threshold
for low voltage
V. The order and introduction of circle menu under programming mode
● Turn on ESC- push the throttle to the highest position-connect the ESC to battery- wait two second-enter
programming mode
After enter programming mode, the following beeps will give out in accordance with the following circuit.
After certain warning tone, push the throttle to the lowest position during the four beeps.
Confirm and reserve the setting.
The introduction for the setting of programming
The setting of programming :( the five following warning tone is as follows.)
A= - beep- short sound
B= beep-beep-beep 3 three continuing sounds
C=~beep gradual changing sound+beep
D= beep low sound↘
E= beep-- long sound
music1 throttle A-A-A-A
music2 brake B-B-B-B
music3 types of battery
nickel-hydrogen
battery C-C-C-C
music4 lithium battery D-D-D-D
music5 protection
threshold for low
voltage
low E-E-E-E
music6 middle AA-AA-AA-AA
music7 high BB-BB-BB-BB
music8 Recover to factory default setting CC-CC-CC-CC
music9
Angle of entrance
Automatic DD-DD-DD-DD
music10 Low EE-EE-EE-EE
music11 High AAA-AAA-AAA-AAA
music12
Startup of motor
Ultra smooth BBB-BBB-BBB-BBB
music13 Smooth CCC-CCC-CCC-CCC
music14 Accelerated
startup DDD-DDD-DDD-DDD
music15
Mode for
helicopter
Turn off EEE-EEE-EEE-EEE
music16 The helicopter
mode 1 AAAA-AAAA-AAAA-AAAA
music17 The helicopter
mode 2 BBBB-BBBB-BBBB-BBBB
music18 The pros and cons setting of motor
rotation CCCC-CCCC-CCCC-CCCC
Turn on the remote
control and push the
pull rod of throttle
to the lowest
positionp
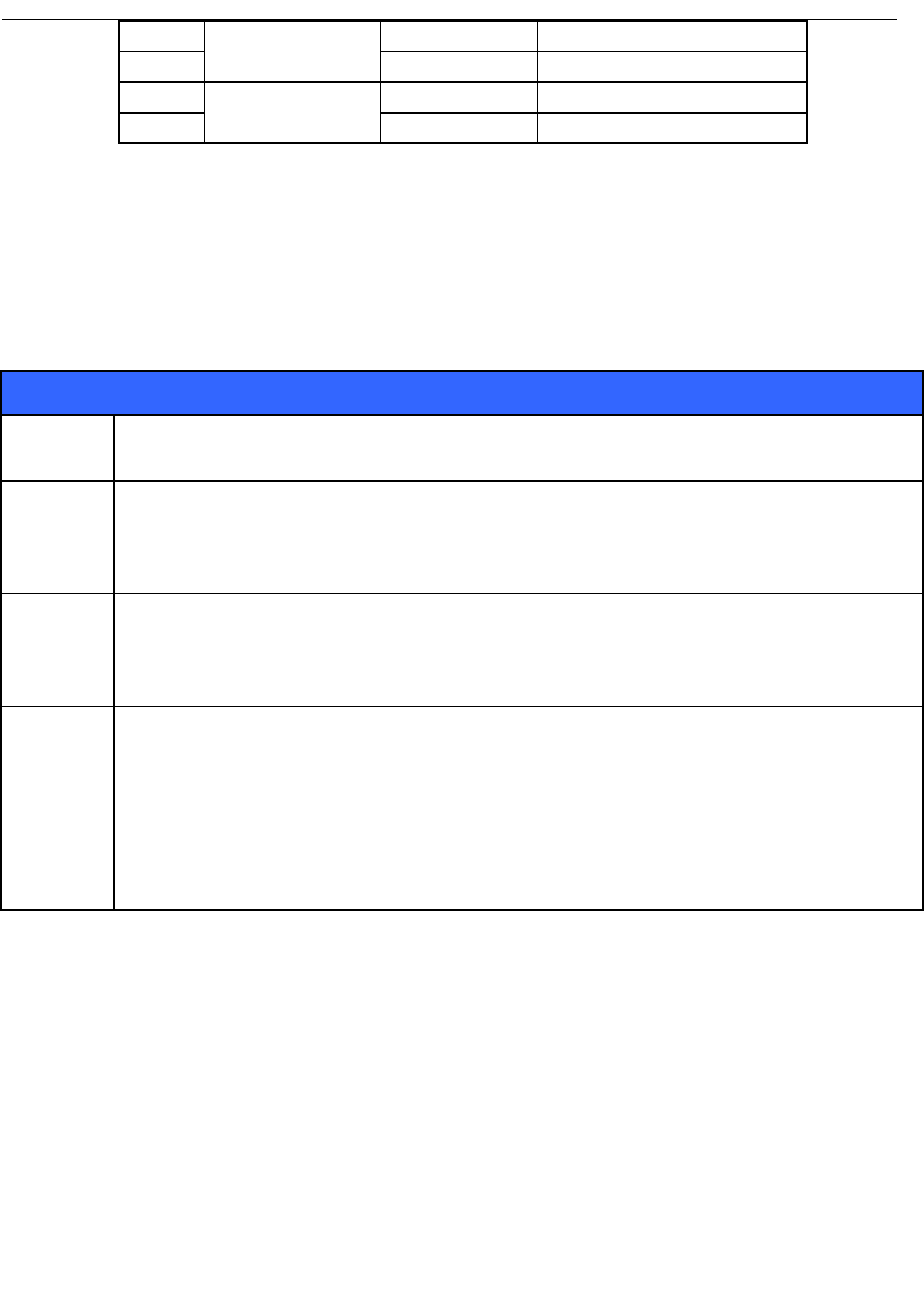
music19 PWM frequency of
motor
8K DDDD-DDDD-DDDD-DDDD
music20 16K EEEE-EEEE-EEEE-EEEE
music21 Protection mode
under low voltage
Reduce power AD-AD-AD-AD
music22 cutoff output AE-AE-AE-AE
● The warning tone: the warning tone is set as audible sound to help users judge abnormal condition after turn
on the power.
1. Fail to enter working mode after turn on the power: the routine of throttle has not been set yet.
2. Continuing beeps: the pull rod of throttle is not in the lowest position
3. There is a short pause after a beep: the ESC can not detect normal throttle signals from receiver.
4. There is a pause of one second after a beep: the voltage of battery pack is out of acceptable limit (once
the battery is connected, the ESC will carry out a self-checking and check the voltage of battery.)
VI.The smart protection functions of ESC.
The introduction of the protection function in the ESC for brushless motor
Types of
protection Descriptions of protection
Protection
for startup
If the motor fails to startup normally in two seconds after push the throttle to start, the ESC will
cut off the motor. The throttle shall be reset to commence a restart. Possible reasons: there is a
disconnection or poor contact in wiring between the ESC and motor. The propeller is stemmed by
other objects. The speed reduction gear is badly blocked.
Protection
for
temperature
When the working temperature in the ESC is higher than 100 , the ESC will reduce the output℃
power automatically to commence protection, but will reduce the output power to 40% of full
power to reserve some power for motor and avoid crash landing instead of turning off all output
power. The ESC will recover to max power as the temperature falls.
Protection
for lost of
throttle
signals
The ESC will reduce the output power to motor when the ESC detect that there are 2 seconds’ lost
of throttle signals. If there another 2 seconds’ lost of throttle signals, the ESC will cut off motor
automatically. If the throttle signals recover during the reduction of output power of motor, the
ESC will recover control of throttle at once. In this method, in the case of momentary lost of
signals (within 2 seconds), the ESC will not commence the protection of throttle. Only when the
control signals have been lost for a long time, the ESC will commence protection. However, the
ECS will reduce the output power gradually instead of cutting off output power immediately so
that the players will have certain period to rescue the machine. It has both safety and practicability.
VII.The routine of throttle shall be set at the first time turn on the ESC.
The feature of HobbyKing ESC is to set best routine of throttle according to different transmitters. The
ESC can obtain most stable throttle linear response through the total routine of throttle in transmitters. The
objective is let the ESC to obtain and remember the output signals of throttle in transmitters. The operation
needs to be carried for one time. Please repeat the operation when change transmitters.
Notice: must to check carefully whether polarities of all connector assembly are correct and whether the
installation is firm before connect the battery pack during the using to avoid damages to the ESC due to
incorrect connection between polarities or short cut.
The operation when use the ESC for the first time is as follows:
● The normal startup procedure of the ESC is as follows:
Turn on the remote
control and push the
pull rod of throttle
to the lowest
positionp
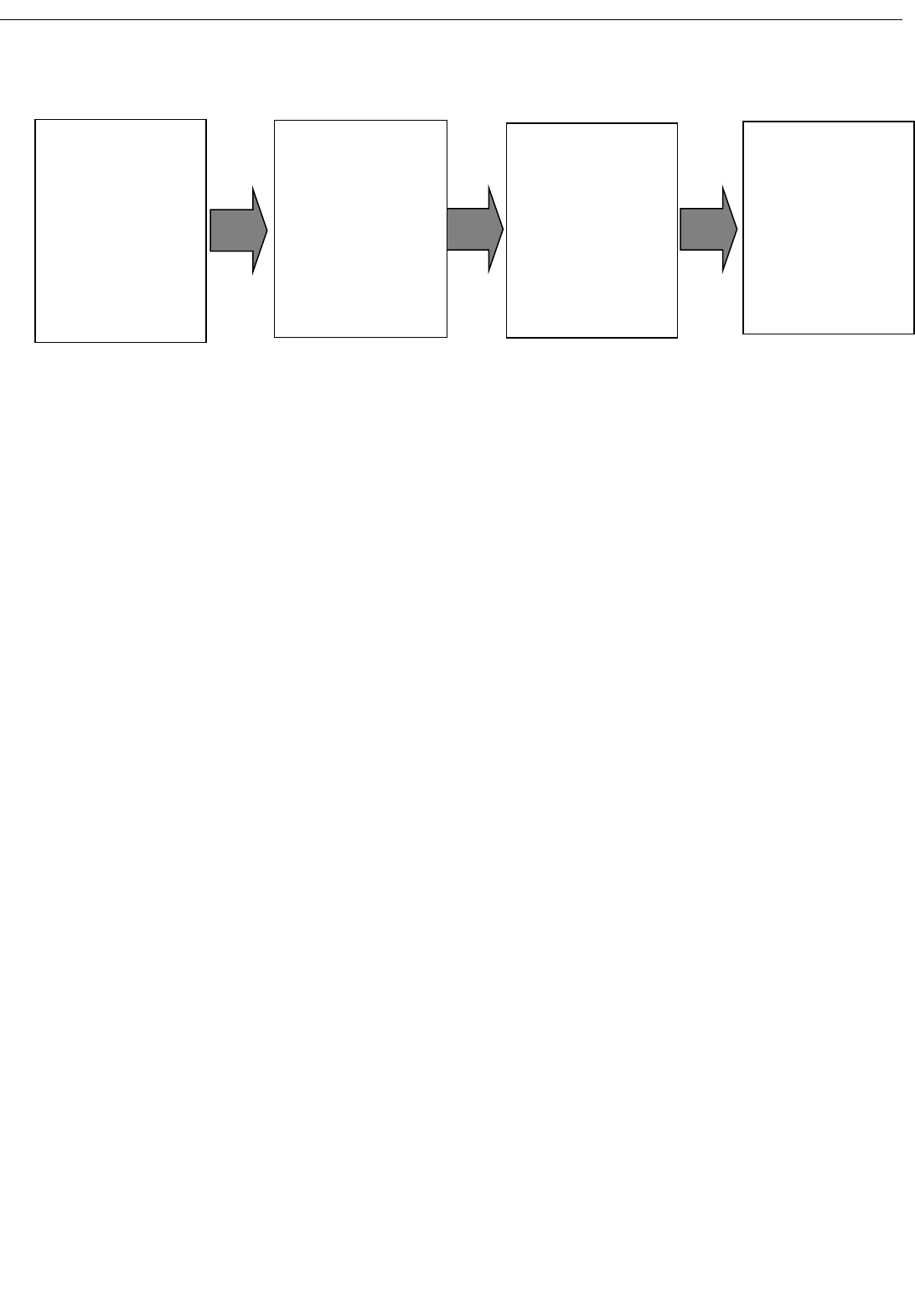
Remark: if the motor suddenly stops when your model airplane are flying, you shall immediately push the
pull rod of throttle to the lowest position and then push to the high position. Then the motor will restart. You
shall land the model airplane immediately with throttle controlled with a lower position.
Please pay attention to the following safety information when using.
● Never disassemble any electro components in the ESC by yourself, or permanent damages or lost of
information will occur.
● Check the setting of receiver. Do not install propeller or small driving gear on motor if you haven’t confirm
that the setting of receiver is correct when test the ESC and motor for the first time.
● Do not use cracked or broken battery pack.
● Do not use battery pack easily get overheat.
● Do not use short-cut battery.
● Do not use cable insulation material against standards.
● Do not use cable connector against standards.
● The number of battery or servo system shall not exceed the rules for ESC.
● The voltage of battery shall not exceed the scope of working voltage of ESC.
● Pay attention to the polarities of battery. Wrong polarities will damage the ESC.
● Be sure that the ESC will not use in manned craft or other manned machines.
● Do not place the ESC in moist or over exposure.
● Do not take out battery when the motor is working, for the generated large peak current will damage the ESC.
● Do not pack anything outside the ESC. Install the ESC in places with good ventilation and heat dissipation as
far as possible.
The second group
sound means the
situation of brake.
(One beep to the
open of brake, two
beeps to the close of
brake). The
preparation of the
ESC is completed.
The first group
sound means that
the number of
battery in battery
pack connected to
the ESC (three
beeps to three
batteries, four beeps
to four batteries.)
Turn on the remote
control and push the
pull rod of throttle
to the lowest
positionp
Connect battery
pack with the ESC,
the ESC will give
out two group
sounds to present
that the ESC enters
working mode when
the ESC is
electrified for the
first time.
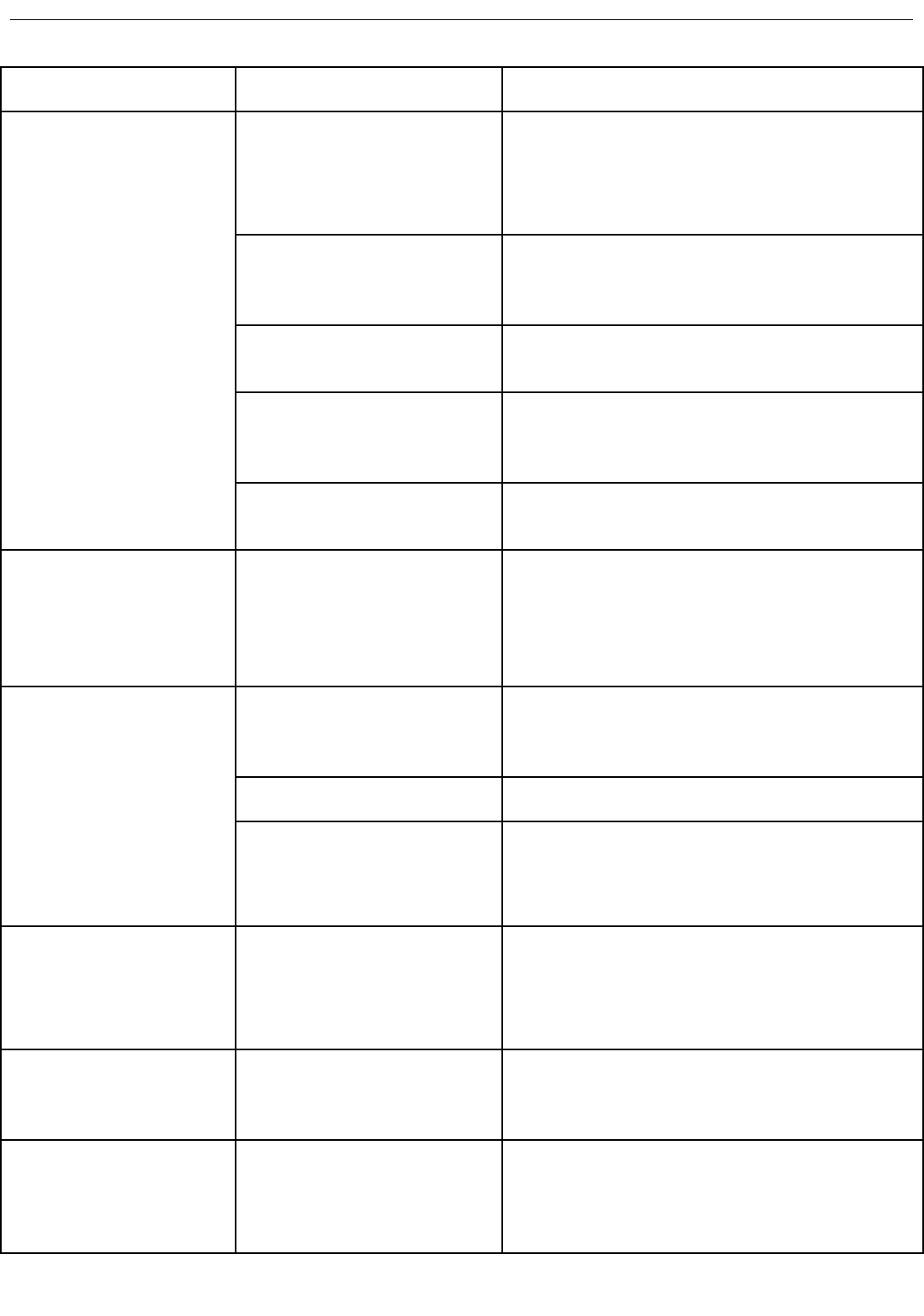
VIII.Handling of common problems
Problems Possible reasons Solutions
After power on, the motor
fails to work and there is
no music. The servo
system fails to work and
switch on.
There is a poor contact
between battery pack and
ESC.
The power is off.
Clean the plugs again or change plugs. Check and
confirm the polarities of wiring.
The polarities of connection
between receiver and signal
wires of ESC are wrong
Check the signal wire to ensure the polarities are
correct.
The welding is not firm so a
poor contact easy happens. Weld the connecting line for the second time.
The wiring polarities of
batteries are wrong.
Check the battery pack and exchange battery
pack with full voltage in accordance with
standards.
Other quality problems in
ESC Change ESC
After power on, there is
sound that ESC
automatically check the
number of batteries, but
the motor fails to work.
The ESC fails to set routine of
throttle.
Reset the routine of throttle.
The ESC work
successfully, but motor
fails to work. There is no
music.
After power on of ESC
,motor fails to work and
gives out warning
tone(two bees and short
pause)
There is a poor contact or
welding between ESC and
motor.
Check the end of connector or change connector
or weld the wiring of motor again.
Bad motor Change motor
Protection for low voltage in
ESC. The voltage of battery is
out of acceptable limit.
Check the voltage of battery group, change with
battery group of full voltage.
After power on, motor
fails to work but gives out
warning tone(one beep
and short pause
There is no output signal of
throttle in receiver.
Check and confirm the connection between signal
wire and throttle in receiver is correct.
Check the transmitters and receivers to ensure
that there are output signals.
After power on, motor
fails to work and gives out
continuing beeps
The pull rod of throttle is not
in the lowest position
Push the pull rod of throttle to the lowest position
and reset the routine of throttle.
After power on, motor
fails to work and gives out
two long beeps and then
two short beeps
ESC enters programming
mode due to wrong pros and
cons setting of throttle
channel.
Adjust the pros and cons setting of throttle
channel according to the specification of remote
control.
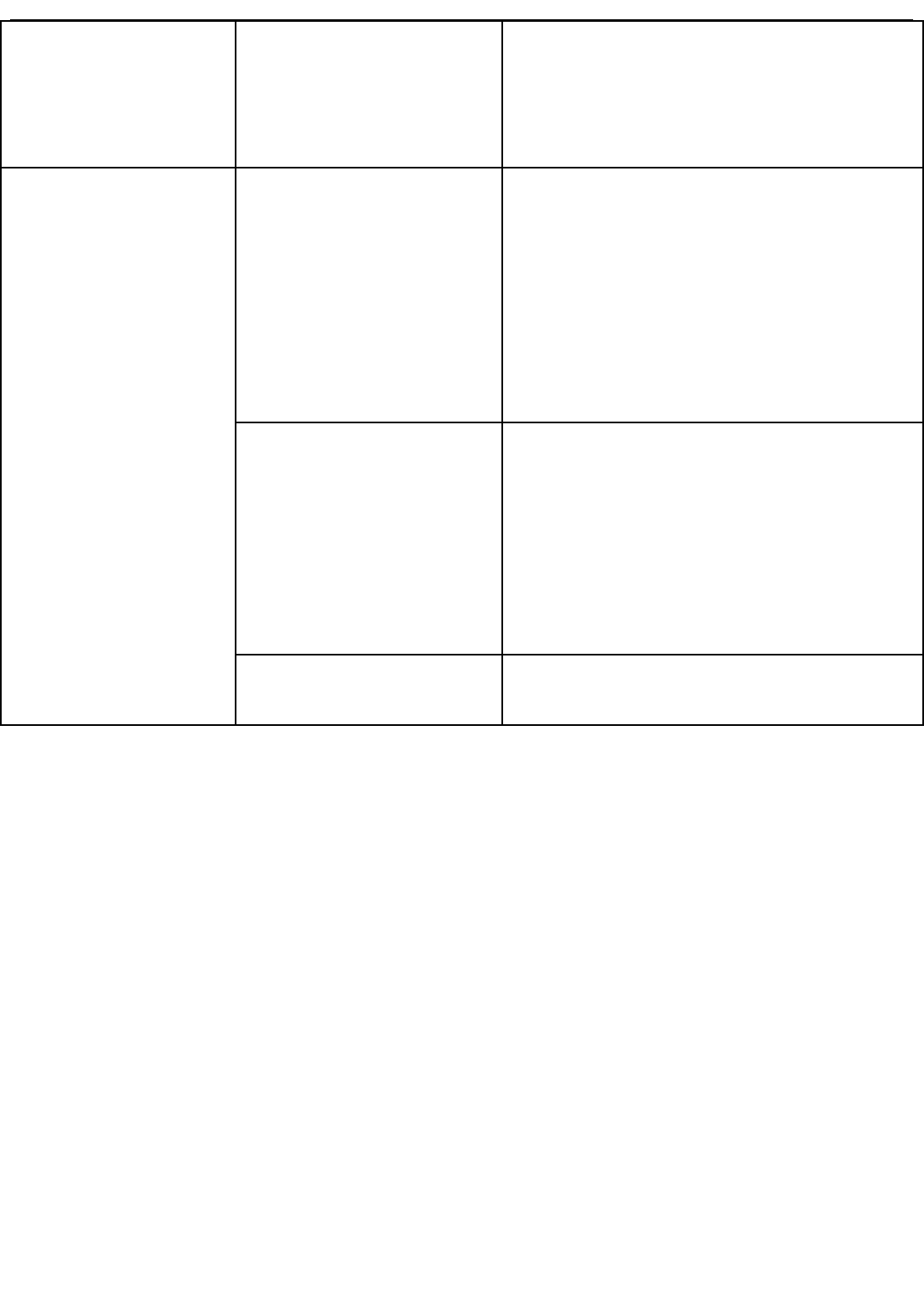
The motor is in a inverted
running
The order of wiring between
motor and ESC is wrong
1. Alter any two connection line among three
connection line between ESC and motor
2. Change direction by changing the rotation
setting of motor directly with remote control or
programming panels.
The motor stops in the
flying.
The voltage of battery is lower
than default protection
threshold for low voltage, and
the protection mode for low
voltage is cut off.
1. Set the protection threshold for low voltage
correctly. Fly with battery of full voltage. The
protection mode for low voltage is set in mode of
reduces power (default mode). Please land your
model airplane in time if you find reduction of
power during the flying.
2. Control the model airplane flying in the scope
of remote control
3. Pay attention to the voltage of battery in
remote control. Please land the model airplane in
time if there is large reduction in voltage.
Lost of throttle signals
1. Check the operation of remote control is
correct.
2. Check if the remote control is suitable to
receiver.
3. Please try restarting to recover normal
operation if there is strong electromagnetic
interference in the operating environment. If the
problem occurs again and again, please change
flying site for there is too strong interference
from outside environment in this flying site.
Poor contact in wiring.
Check the connection between plug of battery
pack, output line of battery and connection line of
motor is reliable.