Manual
User Manual: Pdf
Open the PDF directly: View PDF .
Page Count: 9
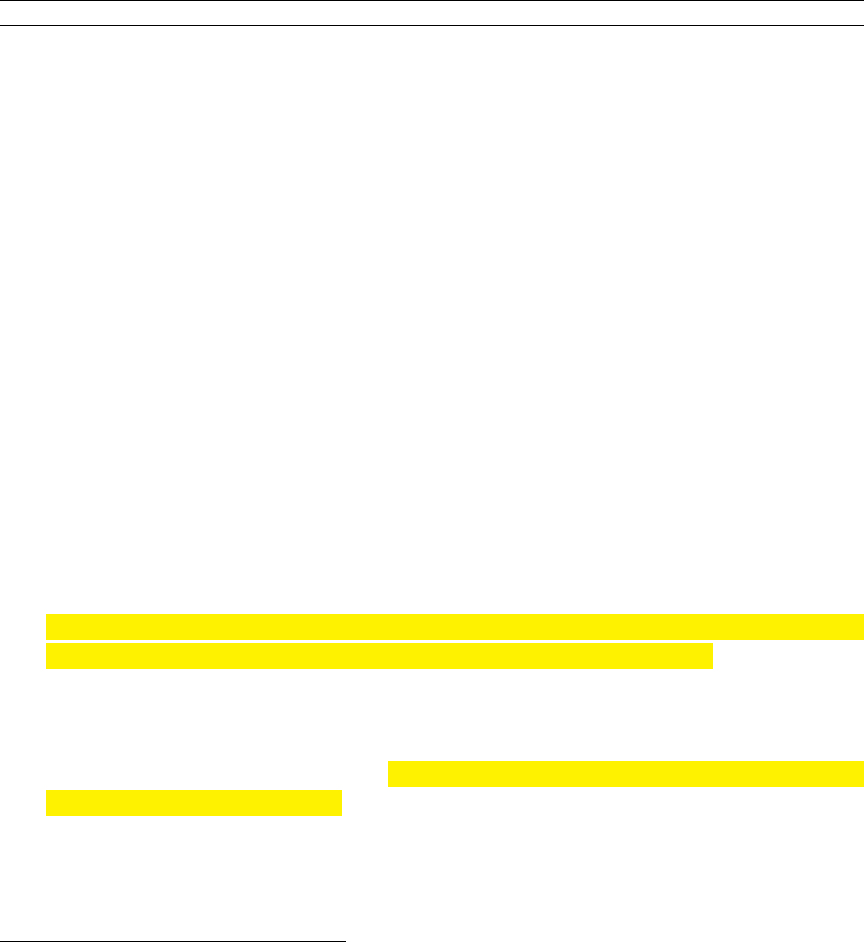
Manual for GRANDproto35 operation
Jacques Davida, Junhua Gub, Olivier Martineau-Huynha, David Martina, Patrick
Naymana, Vincent Voisina
aLPNHE, Universit´e Pierre et Marie Curie, Universit´e Paris Diderot, CNRS/IN2P3, Paris,
France.
bNational Astronomical Observatories of China, Chinese Academy of Science, Beijing 100012,
P.R. China.
1 Introduction
In this document we give details needed to set up, run and maintain the GRAND-
proto35 acquisition, and (tentatively) fix possible issues.
2 The Front-End Unit
Here we give a brief description of the structure of the Front-End Unit and provide
informations needed to make sure it runs in a proper state and identify possible
problems if should be encountered.
2.1 Unit Set-Up
The unit should be fixed to the corresponding antenna pole as shown in Fig. 1:
the front pannel is vertical, with the pressure valve facing ground.
2.2 Connections
Connections to the Front-End Units should be carried out in the following order:
i) First connect the three outputs of the antenna to the associated inputs ANT X,
ANT Y,ANT Z of the Front End Units with the three dedicated coax cables.
Make sure here that you connect the 75Ω F-type connector end (the thinner one),
and not the 50Ω one (thicker). Inversion would destroy the plug. Also since the
12 V DC power supply to the antenna LNAs is provided through these cables, it
is in principle safer to plug/unplugg them only when the Front-End Unit power
is off.
ii) Then connect the GPS antenna. By no means should the GPS antenna be con-
nected when the power is on. This may destroy the GPS unit inside the board
(see section 2.3.2) and make it unusable. The GPS antenna should preferably
be placed above ground. A magnet inside the GPS antenna allows to fix it to a
close-by metalic surface.
Email address: martineau@lpnhe.in2p3.fr (Olivier Martineau-Huynh)
Preprint submitted to Elsevier April 19, 2018

Figure 1: Front (left) and bottom (right) views of a GRANDproto35 Front-End unit casing once
fixed to an antenna pole.
G
iii) Then connect the optical fiber (which can however be plugged/unplugged at any
time, with no risk of damage).
iv) Finally plug the power cable. Nominal value of the power supply should be 15 V,
but values between xx and xx are still OK. A green LED on the front panel
just below the power plug allows to check if the board is powered on.
2.3 Front-end board description
A picture of the board is shown in figure 2. It can be divided in 4 functionnal
sections: analog, digitial, communication and power supply.
2.3.1 Analog part
The description of the analog part of the board is given in details in [1] (in French).
Here we just give a brief overview.
The analog part lies in the top-left corner of the board. Signal input to the board
is done for each of the three channels through an MMCX 75Ω jack connected to the
corresponding F-type connector. From top to bottom we have X, Y and Z channels.
The signal is adapted to a 50Ω impedance thanks to a dedicated amplifier placed just
after the connector, then fed into the 30-100 MHz filters tagged KR ELECTRONICS.
Signal is finally processed through a power detector AD8310 [2], which acts as an
envelop detector. The power detector runs in differential mode. Its common mode
voltage has a nominal value of 0.9 V adjusted thanks to a potentiometer (blue square,
just above the filter). It can be measured between ground and the test point shown
on Fig. 2 To Be Done.
The analog section also provides the power supply to the LNAs placed inside the
antenna nut through a bias-tee system connected to the MMCX plugs. This means
that in normal operation, a 12 V DC voltage is applied to the input plugs, which the
2
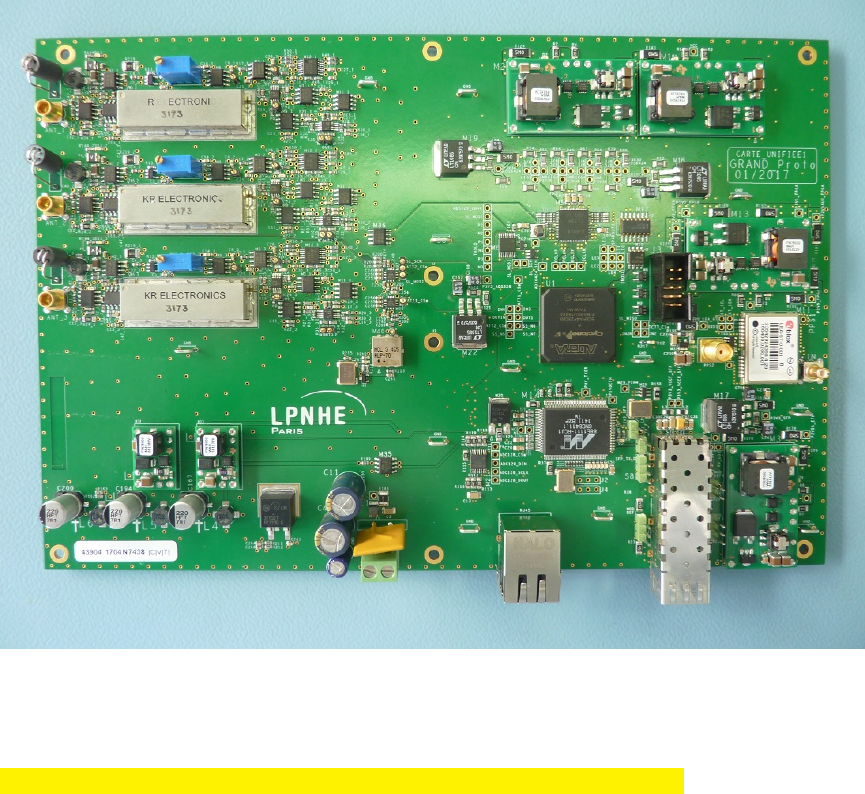
Figure 2: Picture of the GRANDproto35 Front-End unit board. TO BE UPDATED.
user should be aware of when performing tests on a powered board. The LNAs power
supply can be switched on and off by the user (see section 3.3.2).
In addition to this, the analog part includes a trigger section, where the signals at the
output of the filters are compared to threshold values. A trigger flag is generated and
sent to the FPGA (see section 2.3.2) if one channel exceeds it. Note that there are
six independant trigger channels, with two polarities for each of the three channels.
The user can activate/inhibit independantly each of these trigger channels and set
their respective threshold values (see section 3.3.3).
Finaly an internal calibration system is also included in this analog part: its core is
a 66.666 MHz quartz oscillator (placed at the center of the board), which generates a
sine wave. Its amplitude can be moderated thanks to two attenuators, with attenua-
tion values adjustable by the user (see section 3.3.2). When the user uses the DAQ in
calibration mode, the input of the signal treatment chain detailed above is switched
from the MMCX connector input to this calibration signal.
2.3.2 Digital part
The digital treatment of the signal is detailed in [3]. It is performed on the right
part of the card, starting with a 4-channels ADC [4] running at a nominal frequency of
3
50 MHz, ajustable up to 100 MHz through the FPGA firmware. The ADC continously
digitizes the signal coming from the three analog channels. The 4th ADC channel is
used in calibration mode to digitize the signal at the output of the quartz oscillator.
The digital signal of each of the four channels is buffered in a circular register inside
the FPGA. When one trigger is received (see previous section), a subset of length
2×OFFSET (where OFFSET is a parameter set by the user at run start) is saved for
each of the four channels to form one event. A GPS time-tag is also requested to the
uBlox GPS unit[5] and embeded in the event header and sent to the board output
(see section 2.3.3).
2.3.3 Communication
Communication with the DAQ computer is done through a Marvell interface chip,
using the GEDEK Communication Engine. Messages are exchanged using UDP pro-
tocol. Either a standard ethernet plug can be used, or optical transfer through an
SFP connector (see FIg. 2). A jumper placed just below the Marvell chip allows to
switch from one to the other (left: ethernet plug, right: optical). The latter is the
standard communication system in GRANDproto35 operation, with a bi-modal SFP
(λ1= 1310 nm & λ2= 1550 nm) allowing down (data) and upstream (commands)
communication on a single fiber.
The Front-End Unit is identified through a unique MAC adress given by a specific
chip (Dallas DS2502). At boot time, IP adresses of all units are identically set to
192.168.1.18 by default. A software program however allows to map each MAC adress
to an IP adress of format 192.168.1.1xx (see section 4.1) where xx is the Front-End
unit ID, ranging between 01 and 35. This IP adress is used for any further commu-
nication with the DAQ PC, whose IP should be 192.168.1.1 within a local network.
2.3.4 Power supply
The nominal power supply of the Front-End Unit is 15 V DC, and standard power
consumption is ∼10W in normal run conditions. In standard operation at Ulastai,
this DC voltage is provided by the external AC/DC converter installed at the pod
level. There is also an internal AC/DC converter fixed on the internal side of the
Front-End unit casing, but it is not used.
A re-armable fuse is installed at the input of the board power supply (yellow thing
on Fig. 2). It will disrupt power supply in case a current surge is detected (level ?).
It is re-armed after power cycling.
DC voltages of +4 V and -3.3 V are generated by DC-DC converters located on small
mezanines placed at 3 corners of the board.
2.3.5 Board control
There are several tools to check that the board is in a proper state and identify
possible issues.
TO BE COMPLETED WITH INPUT FROM LPNHE COLLEAGUES.
4
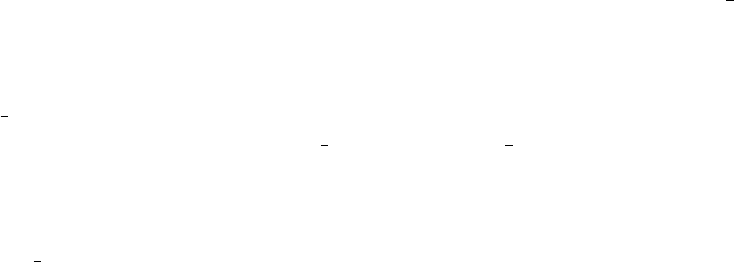
3 Data acquisition & communication with board
3.1 General structure
The DAQ has a multi-layer structure. At the core of it is a very basic system of
formated words exchanges between the front-end units and the PC. These are briefly
described in section 3.3, and in more details in [3].
One of the central element of the DAQ system is a C program, called TREND server,
which runs on the DAQ PC and collects data sent by the Front-End units on a given
port of the PC (by defaut 1235 for slow-control data, and 1236 for antenna data).
This is the ”ear” of the DAQ. It is complemented by its ”mouth”, a program called
send message which issues commands to the Front-End units on another port (by
default 1234). Note here that TREND server and send message do not communicate
with each other. This is a built-in feature of the DAQ system, which directly derives
from the fact that the DAQ is based on socket communication in UDP protocol. It
also means that there is no straightforward way to guarantee that a command issued
by send message is indeed received and executed by the Front-End Unit.
However a third layer of code, which consists of shell scripts, is in charge of properly
starting relevent processes, and sending appropriate commands in a timely manier so
that all runs smoothly. This third layer is also supposed to send notifications to the
user in case things go wrong. The user in principle only accesses this layer.
TO BE COMPLETED/CORRECTED ONCE WE HAVE CONVERGED
TO A STABLE DAQ SYSTEM.
3.2 Acquisition modes
The different types of acquisition are the following:
3.2.1 Pattern mode
Here we request that the ADC generates a specific 12-bits pattern which can be:
i) zeros, a series of 8 null bits.
ii) ones, a series of 8 ”1” bits, corresponding to a numeric value of 4095.
iii) toggle, corresponding to an alternance between sequences ’010101010101’ and
’101010101010’, equal to numeric values of 1365 and 2730 respectively.
iv) deskew, corresponding to a sequence ’110011001100’, equal to a numeric value
of 819.
v) sync, corresponding to a sequence ’111111000000’, equal to a numeric value of
4032.
A soft trigger is issued, resulting in the Front-End Unit sending one event only. This
mode allows to check that the digital section of the unit works properly.
5

3.2.2 Calibration mode
Here the signal processed by the Front-End unit is the sine wave from the calibrator
(see section 2.3.1). Again a soft trigger is issued, but usually repeated several times in
a single acquisition, resulting in a run composed of several event (typically 1000). This
mode allows to test that the analog part of the board works properly, and moreover
to calibrate the response of the DAQ chain, as the amplitude of the input signal is
known here.
3.2.3 Physics mode
This is the standard acquisition mode for cosmic-ray detection. Here the input of
the Front-End unit is the antenna signals, and the acquisition is triggered by them,
with ajustable threshold values (see section 3.3.3). The run will go on (and data will
flow) as long as no other command is issued.
3.2.4 Minimal bias mode
This mode differs from the previous only by the fact that acquisition is triggered
by a soft trigger, again looped for 1000 times to collect a large enough statistics.
This allows to record a baseline signal at a given instant, and is used for monitoring
purposes.
3.2.5 Slow control
This mode allows to record the slow control information of the Front-End (namely:
voltage of the 3 LNAs, voltage at the unit input, absolute value of the +3V and -4V
DC levels, temeprature, trigger rates of the six channels).
3.3 Configuration files
The parameters defining an acquistion are written in configuration files (.cfg ex-
tension). These files are readable through a standard text editor. They are also
read and passed to the DAQ by the send message program. We detail below these
parameters and configuration files for the various type of runs.
3.3.1 TRENDADC message
Each parameter of a TRENDADC message corresponds to the configuration of
the ADC (see details in [4]). Only the word with adress 0xa (corresponding to the
register 2 of the ADC) differs for the pattern mode, where its value depends on the
type of pattern chosen (see section 3.2.1), while it is 0 otherwise.
3.3.2 TRENDDAQ message
The main parameters of the DAQ are defined in the TRENDDAQ word. They
are:
-DAQon, a boolean which switches acquisition on and off.
-AntOn, a 3-bit-pattern switching on and off the output of channels X,Y and Z.
It is set to 0 in calibration or pattern mode, and 7 (all channels on) in standard
operation for the other modes.
6

-EnOSC, a boolean switching on and off the calibration oscillator. It is 1 in cali-
bration mode, 0 otherwise.
-Offst, a scalar corresponding to half the trace length, in sample units. Default
value is 90, corresponding to a 3.6 µs trace for a 50 MHz sampling rate.
-EnablePD, a 3-bit-pattern switching on and off the power detectors of channels
X,Y and Z. Its default value is 7.
-DisLNA, a 3-bit-pattern switching off or on the LNAs of channels X,Y and Z. The
default value for this parameter is 7 (all LNAs off). It is also set to this value in
calibration or pattern mode, and 0 in standard operation for the other modes.
-Attr1 and Attr2 are the values for the 2 attenuators of the calibrator. Their value
range between 0 (full attenuation) and 127 (no attenuation). These values do not
matter for modes others than calibration.
3.3.3 TRENDTRIG message
In the TRENDTRIG message, we define the parameters relative to the trigger.
Most important for the user are:
-ST, a boolean sending a soft trigger order to the Front-End unit.
-TrgEn, a 3-bit-pattern enabling the different channels. The order of the channels
in the pattern is Z-, Y-, X-, Z+, Y+, X+, where the sign stands for the polarity of
the trigger signal.
-ThXs (where X=1,2,3 is the channel, and s=+,- the polarity) is the threshold
(in mV) of the 6 trigger channels. Obviously these values are relevant only if the
corresponding bits in the TrgEn pattern are set to 1.
4 Operation
Here we describe how to start and run the GRANDproto35 setup.
4.1 Start up
- First set-up, connect and power the Front-End Unit as described in section 2.
- Issue the following command should be launched on the DAQ PC:
setAdress.sh BOARDID
Note here that BOARDID is 2 digits for ALL units (ie 01 for n◦1).
This command will call the subprocess configureGedek located in subfolder setAdress/.
This program, written in C, will attribute a dedicated IP adress 192.168.1.1xx to
each board of ID number xx. Communication of configureGedek with the board
is done through its MAC adresss stored in the dedicated file configGedek.txt.
Success in establishing the proper IP adress to a unit can be checked through a ping
command to the unit IP adress. Note that the setAdress.sh script also informs
the units about the DAQ PC ID (IP adress and MAC adress). If these 2 parameters
do not correspond to the actual values of the PC, then DAQ communication will
not be possible (see troubleshooting section).
7
- Then the status of the unit can be requested, through the following command:
slcreq.sh BOARDID
A slow-control event file should appear in the $DATADIR folder. Edit it and check
that all voltage values are correct (Voltage1=14V, Voltage2=3V, Voltage3=4V,
Voltage4 to 6= 12V) and that temeprature is also reasonable (between 10 and
50◦C). If all is OK at this stage, this means that DAQ communication with teh
board works fine and that the Unit is properly powered.
- Then launch:
pattern.sh BOARDID 3
This executes a pattern run in toggle mode (see section 3.2.1) and allows to check
that the logical section of the board is running properly.
- Then launch:
loopCalib.sh BOARDID 60 60
This execute a calibration run with a total attenuation of xx dB. Open the run
file with python script with anaData.py and check that the average value of the
signal is around a value of xx Volts, with a standard deviation not above xx Volts.
This allows to check that analog section of the board is running properly.
- Then launch:
minBias.sh BOARDID
Open the run file with python script with anaData.py and check that the aver-
age value of the signal is around a value of xx Volts, with a standard deviation
not above xx Volts. This allows to check the status of the antenna and of its
electromagnetic environment.Check also in the event header that the GPS info is
present.
- Finaly launch:
phys.sh BOARDID 60 60 60 60 1000 10000
This will start a physics run, with triggers on the X and Y channels. Monitor
the trigger rate by launching loopSLC.sh, which will request slow control data
every 10 seconds. Display the trigger rate with the anaSLC.py script.
8
4.2 Normal operation
4.3 Monitoring data
4.4 Calibration
5 Troubleshooting
Below are summarized the most frequent problems encounter on the GRAND-
proto35 setup, and how they may be solved.
•no ping: check network settings on the PC (should be local network, with IP:
192.168.1.1). Check cable and fiber connection. Cycle power on the Front-End
unit (may need to be done several times). If this does not work, go on field, and
connect directly to unit from local fiber. If this works, then the problem comes from
the fiber. If this does not work, then open the casing lid and check the Marvell leds
(see section 2.3.5): first two should be blinking, two following should be on. If not,
check that jumper is set on the right slot and that SFP is properly set in its slot.
If nothing works, switch jumper to left slot (with power off) and test connection
on field with Ethernet cable. If this works, then problems comes from the SFP
module. If this does not work then the communication module has a problem and
the unit should be brought back to lab for further test.
•no DAQ communication (ie no response to slcreq.sh): Ping Front-End
unit. Issue the command echo $DATADIR in a terminal window of the DAQ PC,
and check that the variable is indeed set to the folder where you want data to be
written. Check that IP and MAC adress of the PC actually correspond to those
given in setAdress.sh. Relaunch setIP.sh. Launch the Wireshark program.
When a SLCreq.sh command is issued, a response from the Front-End Unit should
appear in the packet traffic, with appropriate IP and MAC adresses from both
sides.
6 References
[1] J. David, Carte analogique GRANDproto35, 2017.
URL http://xxx
[2] A. Devices, AD8310 technical note, 2017.
URL http://xxx
[3] P. Nayman, DAQ for TREND, 2016.
URL http://xxx
[4] T. Instrument, ADS6426 technical note, 2013.
URL http://xxx
[5] [link].
URL http://xxx
9