1272 3 Liberty Elv280 Curves 1 User Manual
510 3 Liberty Elv280Hv Curves 510_3_Liberty ELV280HV Curves
516 3 Liberty Elv290 Curves 516_3_Liberty ELV290 Curves
540 3 Liberty Elv290Hv Curves 540_3_Liberty ELV290HV Curves
717 3 Liberty Ev280Hv Curves 717_3_Liberty EV280HV Curves
768 2 Liberty Ev250 Curves 768_2_Liberty EV250 Curves
User Manual: Pump 1272 3 Liberty Elv280 Curves
Open the PDF directly: View PDF .
Page Count: 7
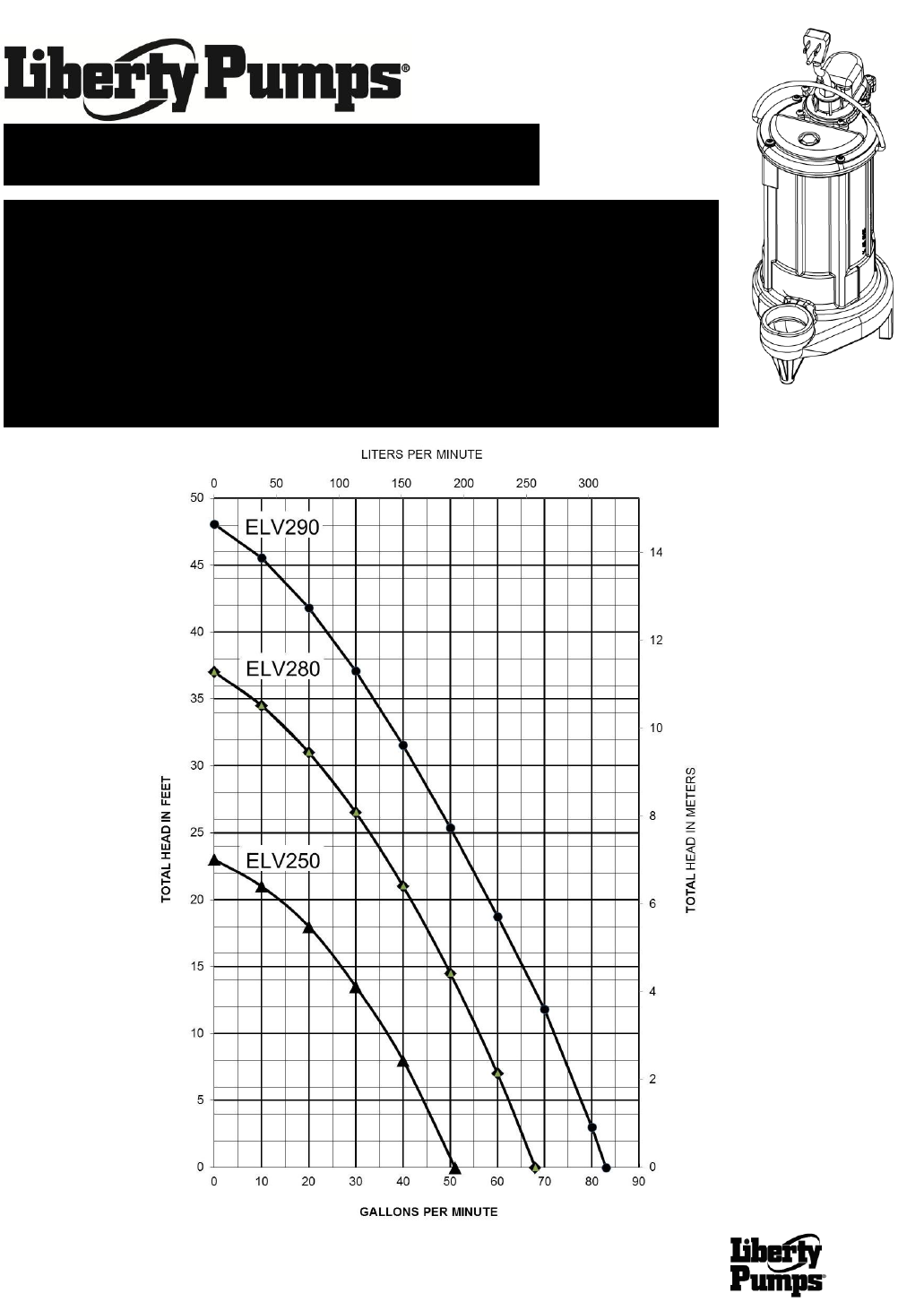
ELV_ P1 R1/24/2012 ©Copyright 2012 Liberty Pumps Inc. All rights reserved. Specifications subject to change without notice.
Pump Specifications
ELV Series Submersible Sump Pump
with OilTector Control
ELV250 1/3 hp
ELV280 1/2 hp
ELV290 3/4 hp

ELV_ P2 R1/24/2012 ©Copyright 2012 Liberty Pumps Inc. All rights reserved. Specifications subject to change without notice.
ELV280 Dimensional Data
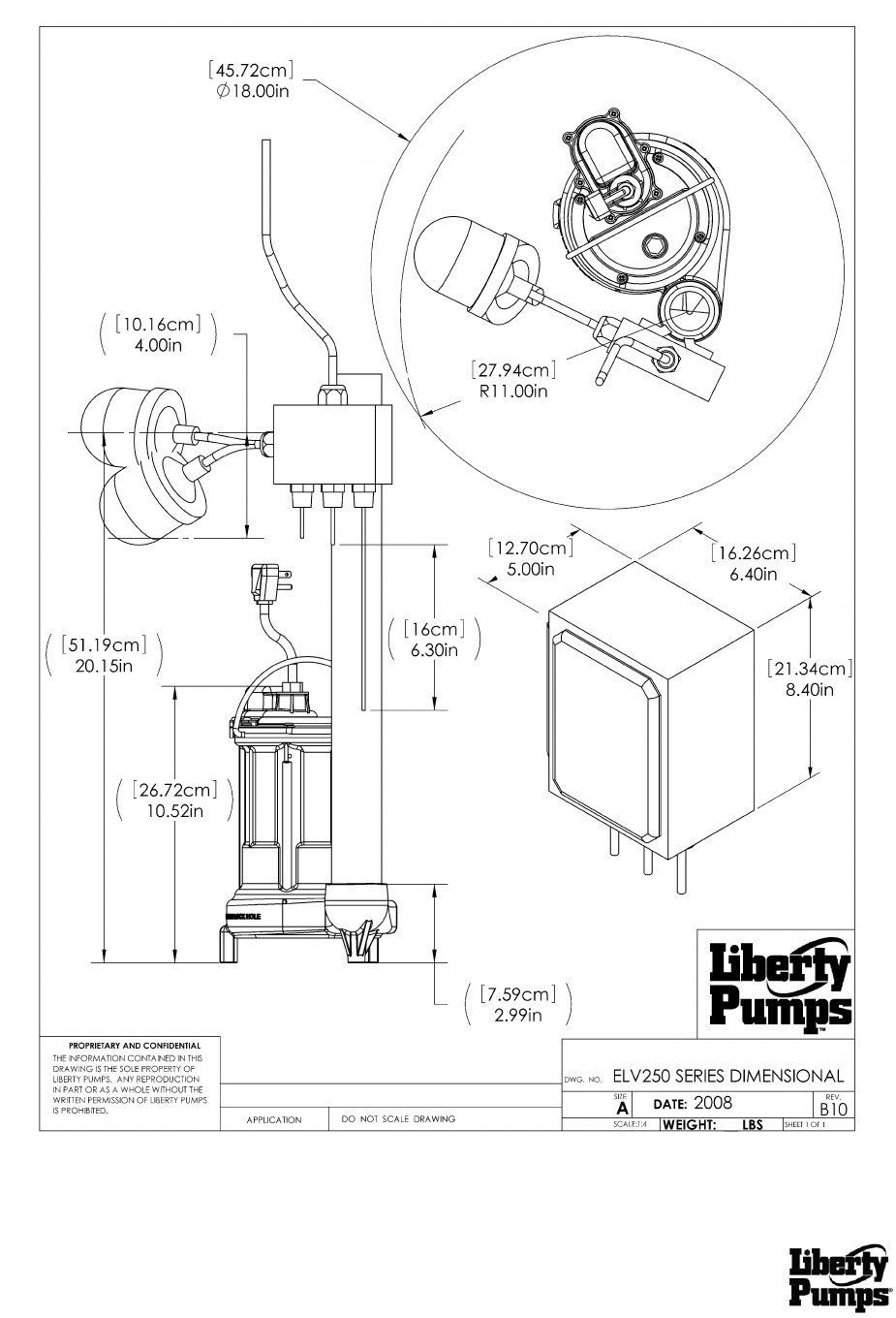
ELV_ P3 R1/24/2012 ©Copyright 2012 Liberty Pumps Inc. All rights reserved. Specifications subject to change without notice.
ELV250 Dimensional Data
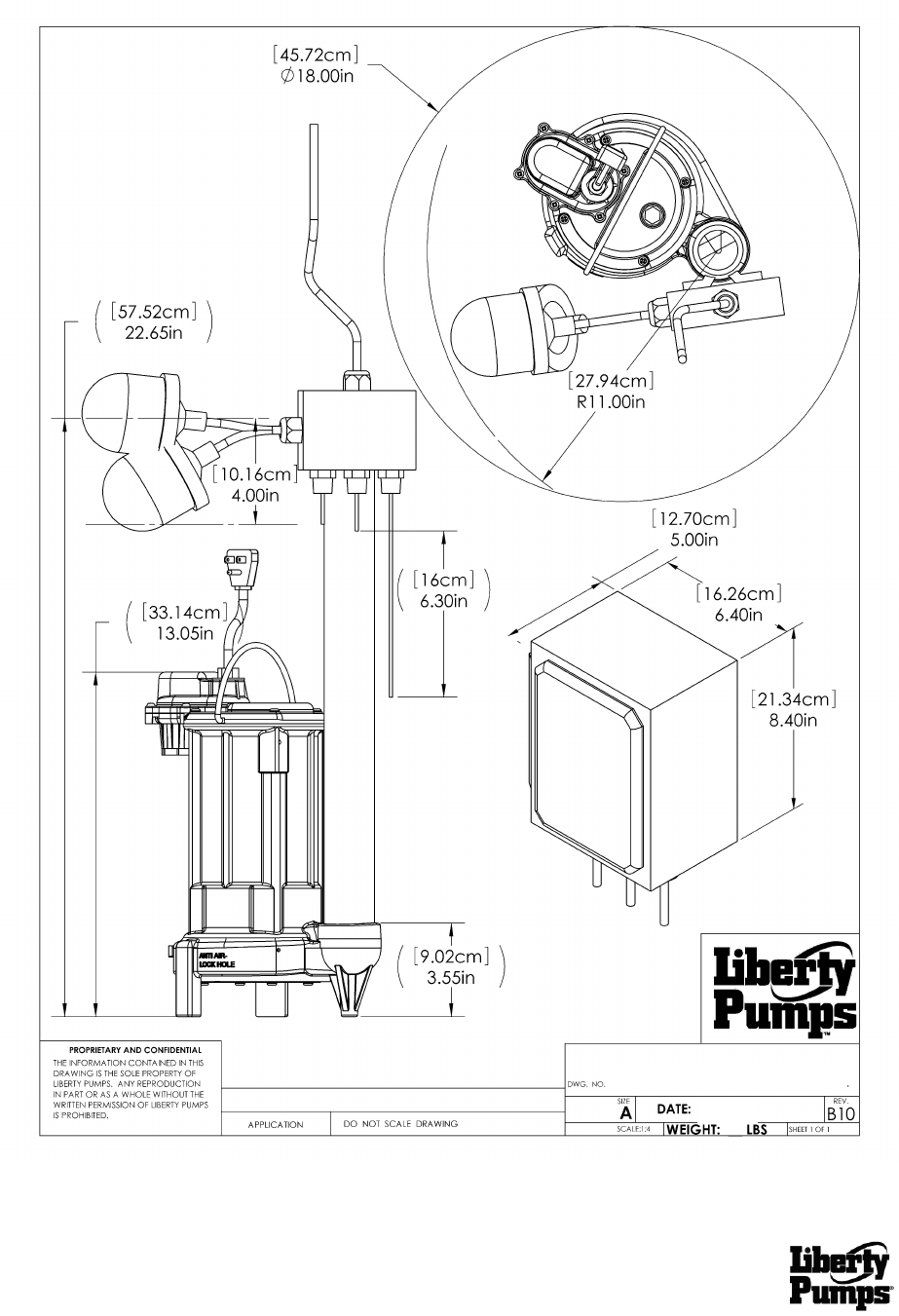
ELV_ P4 R1/24/2012 ©Copyright 2012 Liberty Pumps Inc. All rights reserved. Specifications subject to change without notice.
ELV290 Dimensional Data
ELV290 SERIES DIMENSIONAL
2011
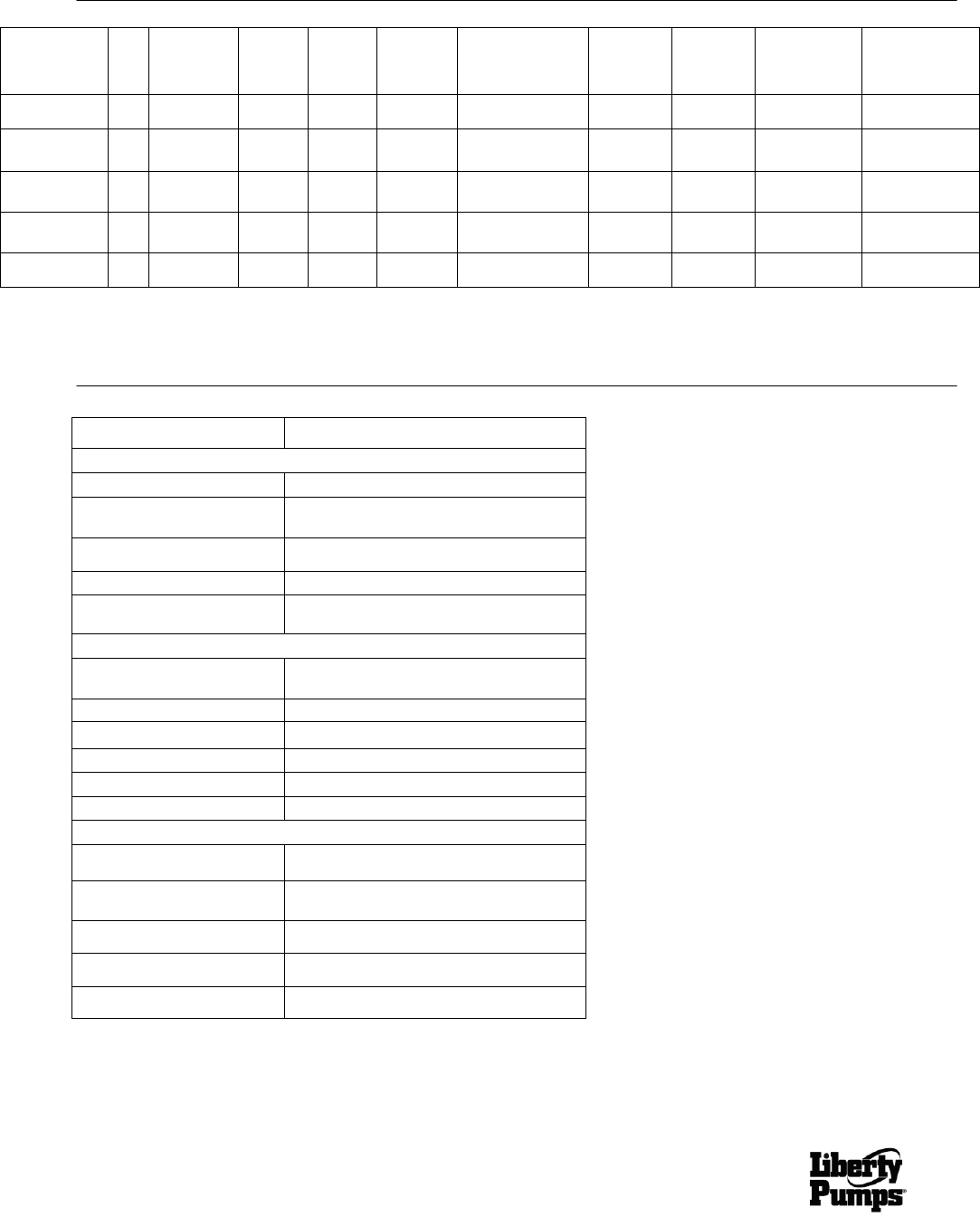
ELV_ P5 R1/24/2012 ©Copyright 2012 Liberty Pumps Inc. All rights reserved. Specifications subject to change without notice.
ELV-Series Electrical Data
MODEL
HP
VOLTAGE
PHASE
FULL
LOAD
AMPS
LOCKED
ROTOR
AMPS
THERMAL
OVERLOAD
TEMP
STATOR
WINDING
CLASS
CORD
LENGTH
FT
DISCHARGE
AUTOMATIC
ELV290
3/4
115
1
10.4
24
120˚C/ 248˚F
B
25
1 1/2
YES W/
CONTROL
ELV290HV
3/4
208-230
1
5.3
13
105˚C/ 221˚F
B
25
1 1/2
YES W/
CONTROL
ELV280
1/2
115
1
8.5
23
105˚C/ 221˚F
B
25
1 1/2
YES W/
CONTROL
ELV280HV
1/2
208-230
1
4.6
12.5
105˚C/ 221˚F
B
25
1 1/2
YES W/
CONTROL
ELV250
1/3
115
1
5.2
8
105˚C/ 221˚F
B
25
1 1/2
YES W/
CONTROL
ELV-Series Technical Data
IMPELLER
VORTEX ENGINEERED POLYMER
SOLIDS HANDLING SIZE
ELV250
½”
ELV280, ELV280HV,
ELV290, ELV290HV
¾”
PAINT
POWDER COAT
MAX LIQUID TEMP
60˚C/ 140˚F
MAX STATOR TEMP
CLASS B
130˚C/ 266˚F
THERMAL OVERLOAD
ELV250, ELV280,
ELV280HV, ELV290HV
105˚C/ 221˚F
ELV290
120˚C/ 248˚F
MOTOR HOUSING/ VOLUTE
CLASS 25 CAST IRON
SHAFT
STAINLESS
HARDWARE
STAINLESS
ORINGS
BUNA N
SHAFT SEAL
ELV250
ENGINEERED DOUBLE LIP WITH
STAINLESS STEEL SPRINGS
ELV280 & ELV280HV
ELV290 & ELV290HV
UNITIZED CERAMIC CARBON
ELV250
23 LBS
ELV280, ELV280HV,
ELV290, ELV290HV
30 LBS
MIN. SUMP SIZE
Ø18” X 30”
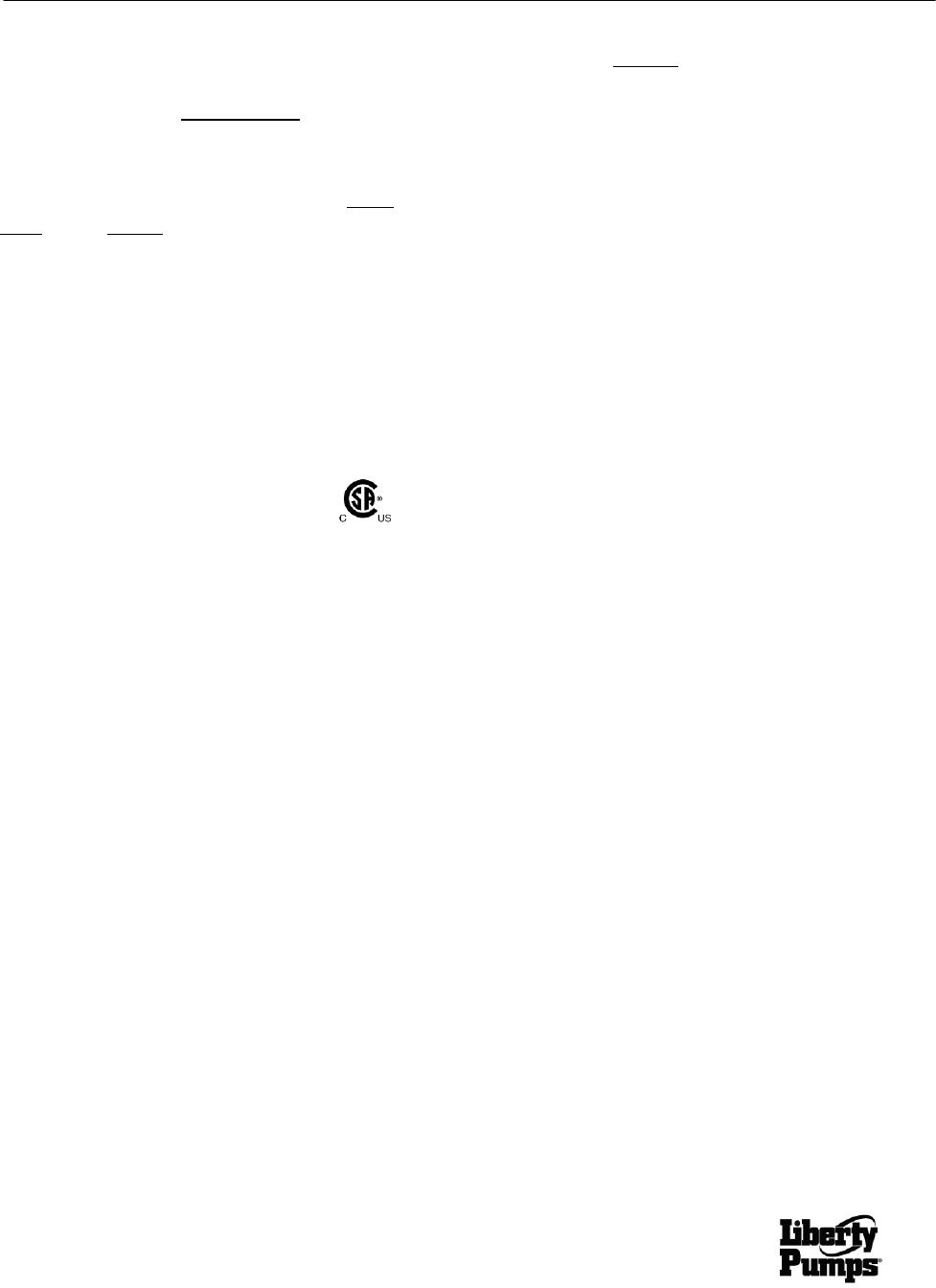
ELV_ P6 R1/24/2012 ©Copyright 2012 Liberty Pumps Inc. All rights reserved. Specifications subject to change without notice.
ELV-Series Specifications
1.01 GENERAL:
The contractor shall provide labor, material, equipment, and incidentals required to provide (QTY) centrifugal pumps as
specified herein. The pump models covered in this specification are ELV Series single phase pumps. The pump furnished for this
application shall be model ______________as manufactured by Liberty pumps.
2.01 OPERATING CONDITIONS:
Each submersible pump shall be rated for ____hp, _____ volts, single phase, 60 Hz, & 3450 RPM. The unit shall produce
_____G.P.M. at ______ feet of total dynamic head.
The submersible pump shall be capable of handling water with _____ solid handling capability. The submersible pump shall have
a shut-off head of ____ feet and a maximum flow of _____ GPM @ 5 feet of total dynamic head.
The pump shall be controlled with:
The manual pump is connected to a control which has the ability to prevent oil from being pumped from the vault. This same
control unit will activate an alarm when an oil “film” is detected or when a high water condition exits. The system will continue to
monitor and remove water from the vault even if an oil condition is detected.
3.01 CONSTRUCTION:
Each centrifugal sump pump shall be equal to the Certified ELV-Series pumps as manufactured by Liberty Pumps,
Bergen NY. The castings shall be constructed of class 25 cast iron. The motor housing shall be oil filled to dissipate heat. Air filled
motors shall not be considered equal since they do not properly dissipate heat from the motor. All mating parts shall be machined
and sealed with a Buna-N o-ring. All fasteners exposed to the liquid shall be stainless steel. The motor shall be protected on the
top side with sealed cord entry plate with molded pins to conduct electricity eliminating the ability of water to enter internally
through the cord. The motor shall be protected on the lower side with a unitized ceramic/carbon seal with stainless steel housings
and spring or engineered double lip seal with stainless steel springs. The pump shall be furnished with stainless steel handle.
4.01 ELECTRICAL POWER CORD
The submersible pump shall be supplied with a 25 feet of multiconductor power cord. It shall be cord type YELLOW
UL 16-3 SJEOOW 300V 105°C, capable of continued exposure to the pumped liquid. The power cord shall be sized for the rated
full load amps of the pump in accordance with the National Electric Code. The power cable shall not enter the motor housing
directly but will conduct electricity to the motor by means of a water tight compression fitting cord plate assembly, with molded pins
to conduct electricity. This will eliminate the ability of water to enter internally through the cord, by means of a damaged or wicking
cord.
5.01 MOTORS
Single phase motors shall be oil filled, permanent split capacitor, class B insulated NEMA B design, rated for continuous duty. At
maximum load the winding temperature shall not exceed 130 degrees C unsubmerged. Since air filled motors are not capable of
dissipating heat they shall not be considered equal. The pump motor shall have an integral thermal overload switch in the
windings for protecting the motor. The capacitor circuit shall be mounted internally in the pump.
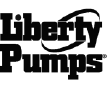
ELV_ P7 R1/24/2012 ©Copyright 2012 Liberty Pumps Inc. All rights reserved. Specifications subject to change without notice.
6.01 BEARINGS AND SHAFT
An upper sleeve and lower ball bearing shall be required. The lower ball bearing shall be a single ball / race type bearing. Both
bearings shall be permanently lubricated by the oil, which fills the motor housing. The motor shaft shall be made of 300 or 400
series stainless steel.
7.01 SEALS
The pump shall have a unitized carbon / ceramic seal with stainless steel housings and spring, or engineered double lip seal with
stainless steel springs. The motor plate / housing interface shall be sealed with a Buna-N o-ring.
8.01 IMPELLER
The impeller shall be vortex style made of an engineered polymer, with pump out vanes on the back shroud to keep debris away
from the seal area. It shall be threaded to the motor shaft.
9.01 CONTROLS
The control unit has three probes and a float ball switch. The pump will activate when the middle probe contacts water, and will
remain on until the first, longest probe no longer is in contact with water. A high water alarm is activated when third or shortest
probe contacts water. The system will ignore a small film of oil, however larger volumes of oil will be detected when the alarm
probe does not detect water and the float ball activates. The system will continue to operates, removing water not oil from the
vault even when oil has been detected.
10.01 PAINT
The exterior of the casting shall be protected with powder coat paint.
11.01 SUPPORT
The pump shall have cast iron support legs, enabling it to be a free standing unit.
12.01 SERVICEABILITY
Components required for the repair of the pump shall be shipped within a period of 24 hours.
13.01 TESTING
The pump shall have a ground continuity check and the motor chamber shall be Hi-potted to test for electrical integrity, moisture
content and insulation defects. The motor and volute housing shall be pressurized, and an air leak decay test is performed to
ensure integrity of the motor housing. The pump shall be run, voltage current monitored, and the tester checks for noise or other
malfunction.
14.01 QUALITY CONTROL
The pump shall be manufactured in an ISO 9001 certified Facility.
15.01 WARRANTY
Standard limited warranty shall be 3 years.