Raypak Raytherm 133 4001 Users Manual 6000.59 New RP2100
133-4001 to the manual 87754a62-441f-47db-ad19-25c61610373a
2015-02-02
: Raypak Raypak-Raytherm-133-4001-Users-Manual-443483 raypak-raytherm-133-4001-users-manual-443483 raypak pdf
Open the PDF directly: View PDF .
Page Count: 44

$%% !#%
$%#&% $
CATALOG NO. 2000.50AH Effective: 06-27-11 Replaces: 09-16-10 P/N 240035 Rev. 35
This manual should be maintained in legible condition and kept adjacent to the heater or in a safe place for future
reference.
:/07>G
%D;0
(%% * &$$
• Do not try to light any appliance.
• Do not touch any electrical switch; do not use any phone in your building.
• Immediately call your gas supplier from a neighbor's phone. Follow the gas
supplier's instructions.
• If you cannot reach your gas supplier, call the fire department.
(# Improper installation, adjustment, alteration, service or maintenance can
cause property damage, personal injury or loss of life. Refer to this manual.
Installation and service must be performed by a qualified installer, service agency or
the gas supplier.
#* &#$%* Do not store or use gasoline or other flammable vapors and
liquids or other combustible materials in the vicinity of this or any other appliance. To
do so may result in an explosion or fire.
Installation and service must be performed by a qualified installer, service agency or
the gas supplier.
#,D?30=8F
0,?492
:470=>

2
Rev. 35 reflects the following:
Changes to: Certifications on page 6, Flow chart on page 34
Additions: Canadian Installation Code references on pages 6, 8 and 24 , adjustment procedure for two-stage Robertshaw
gas valve (including Fig. 47) on pages 31-32.
Deletions: None

(#$
Pay Attention to These Terms 4
%%
#'"&!%
#%% $
#%*!$
Type H1 - Mechanical Modulating 6
Type H2 - Motorized Modulating 6
Type H3 - 2-Stage Controls 6
Type H4 - On-Off Controls 6
Type H5 - Mechanical Modulating 6
Type H9 - 4-Stage 6
$%%
Installation Codes 6
Installation Base 7
Clearances 7
Outdoor Boilers 8
High-Wind Conditions (Outdoor Units Only)8
Combustion and Ventilation Air
(Indoor Units Only) 8
Venting 9
Indoor Installations 10
Vent Piping 13
Vent Damper Installation 15
Plumbing 16
Gas Supply Connections 16
%# $
Economaster Controls 21
Electronic Ignition 21
Operating Controls 21
Limit Controls 23
%# % $
$%#%&!
Before Start-Up 25
General 25
%%$
3
Filling System - Heating Boilers 25
Ethylene Glycol Systems -
Heating Boilers 25
Initial Start-Up - Pump And Motor 25
For Models with Automatic Gas Valves 28
After Start-Up 28
Standing Pilot Checkout
Procedure 28
Intermittent Pilot System
Checkout (S8600) 28
Inspections 29
Burners 29
Controls 29
Suggested Inspection Schedule 29
( C #$
Models 181 to 401 30
Operation 30
Start-Up (S8600M) 30
Blower Adjustment 30
Visual Inspection 30
Electrical 30
Flame Roll-Out Safety Switch 31
Service 31
Burner Tray Removal 31
Gas Valve Removal 31
Main Burner and Orifice Removal 31
Pilot Removal 32
Combustion Fan Removal 32
%# &$ %
Service 38
Repair Section 38
#!%!#%$
(##%*

4
# Indicates the presence of immediate hazards which will cause severe
personal injury, death or substantial property damage if ignored.
(# Indicates the presence of hazards or unsafe practices which could cause
severe personal injury, death or substantial property damage if ignored.
&% Indicates the presence of hazards or unsafe practices which could cause
minor personal injury or product or property damage if ignored.
% Indicates special instructions on installation, operation, or maintenance which
are important but not related to personal injury hazards.
# Make sure the gas on which the heater
will operate is the same type as that specified on the
heater rating plate.
(# Should overheating occur or the gas
supply valve fail to shut, do not turn off or disconnect
the electrical supply to the heater. Instead, shut off
the gas supply at a location external to the heater.
(# Do not use this heater if any part has
been under water. Immediately call a qualified
service technician to inspect the heater and to
replace any part of the control system and any gas
control which has been under water.
(# To minimize the possibility of improper
operation, serious personal injury, fire, or damage to
the heater:
• Always keep the area around the heater free of
combustible materials, gasoline, and other
flammable liquids and vapors.
• Heater should never be covered or have any
blockage to the flow of fresh air to the heater.
(# # !# ! $%
This product contains chemicals known to the
State of California to cause cancer, birth defects or
other reproductive harm.
(# Risk of electrical shock. More than one
disconnect switch may be required to de-energize
the equipment before servicing.
&% This heater requires forced water
circulation when the burner is operating. See
minimum and maximum flow rates. Severe damage
will occur if the heater is operated without proper
water flow circulation.
&% Operation of this heater in low
temperature systems requires special piping.
Harmful internal condensation will occur if the inlet
water temperature does not exceed 105°F. Warranty
claims will be denied when condensation occurs.
&% If this heater is to be installed above
radiation level, it must be provided with a low water
cut-off device at the time of heater installation.
&% If this heater is to be installed in a
negative or positive pressure equipment room, there
are special installation requirements. Consult factory
for details.
(#$H!,D??09?4:9?:%30>0%0=8>
(# This unit contains refractory ceramic
fiber (RCF) insulation in the combustion chamber.
RCF, as manufactured, does not contain respirable
crystalline silica. However, following sustained
exposure to very high temperatures (>2192F), the
RCF can transform into crystalline silica
(cristabolite). The International Agency for Research
on Cancer (IARC) has classified the inhalation of
crystalline silica (cristabolite) as carcinogenic to
humans.
When removing the burners or heat exchangers,
take precautions to avoid creating airborne dust and
avoid inhaling airborne fibers. When cleaning spills,
use wet sweeping or High Efficiency Particulate Air
(HEPA) filtered vacuum to minimize airborne dust.
Use feasible engineering controls such as local
exhaust ventilation or dust collecting systems to
minimize airborne dust. Wear appropriate personal
protective equipment including gloves, safety
glasses with side shields, and appropriate NIOSH
certified respiratory protection, to avoid inhalation of
airborne dust and airborne fiber particles.

5
%%
The model number of a boiler can be found on the
Sales Order and the boiler's rating plate. The example
below identifies what the characters of the model num-
ber represent.
MODEL NUMBER EXAMPLE:
H 3 - 0 5 1 4 A
Series
Model Size
Representative of approximate MBTUH input
(Model 0514 has input of 511,500 BTUH)
Firing Mode
1 Mechanical Modulation
2 Motorized Modulation
3 2-Stage Firing
4 On-Off Firing
5 Low Temperature Mechanical Modulation
9 4-Stage Firing
Application
H = Heating Boiler
Boiler rating plate showing model number

$%%
9>?,77,?4:9:/0>
The installation must conform with these instructions
and the latest editions of the National Fuel Gas Code
ANSI Z223.1, the National Electric Code ANSI/NFPA
70 and local codes. In Canada installations must con-
form with the current CAN/CSA B149 and the
Canadian Electrical Code CSA C22.1 C.E.C. Part 1
(C22.1). All boiler installations must conform to ASME
boiler code. Hot water pipes must be installed with
minimum clearances to combustible material as
required by code.
6
#'"&!%
On receipt of the equipment, visually check for exter-
nal damage to the carton or the shipping crate. If either
is damaged, make a note on the Bill of Lading and
report the damage to the Carrier immediately. Remove
the boiler from the carton or the shipping crate.
On occasion, items are shipped loose. Be sure that
you receive the number of packages indicated on the
Bill of Lading.
When ordering parts, you must specify the Model and
Serial Number of the boiler. When ordering under war-
ranty conditions, you must also specify the date of
installation.
Raypak recommends that this manual be reviewed
thoroughly before installing your Raypak boiler. If there
are any questions which this manual does not answer,
please contact the factory or your local Raypak repre-
sentative.
Claims for shortages and damages must be filed with
carrier by consignee. Permission to return goods must
be factory authorized and are subject to a stocking
charge.
Purchased parts are subject to replacement only
under the manufacturer's warranty. Debits for defec-
tive replacement parts will not be accepted and will be
replaced in kind only per our standard warranties.
#%% $
The Raypak hydronic boilers are design certified and
tested under the latest requirements of the American
National Standard, ANSI Z21.13. Each boiler has been
constructed and pressure tested in accordance with
the requirements of Section IV of the American Society
of Mechanical Engineers Code, and factory fire tested.
All models are National Board approved. Temperature
and pressure gauge is standard. Model 0133 has a 4-
pass heat exchanger, 1 tube per pass. Models
0181-1826 have 2-pass heat exchangers, 5 tubes first
pass, 4 tubes second pass. Models 2100-4001 have
2-pass heat exchangers, 9 tubes per pass. Models
926-4001 have optional single-pass heat exchangers
with cast iron headers only.
All units are CSA-certified for low-lead content
(<.25%).
#%*!$
%D;00.3,94.,7
:/@7,?492:/07>
Central heating boiler with 150°-210°F mechanical
modulating gas valve(s). The number of valves varies
with the model size.
%D;0:?:=4E0/
:/@7,?492:/07>
Central heating boiler with a motorized modulating gas
valve. Modulating controller optional.
%D;0$?,20:9?=:7>
:/07>
Central heating boiler with single 2-stage gas valve
and optional 2-stage controller.
%D;0 9 11:9?=:7>
:/07>
Central heating boiler with on-off firing.
%D;00.3,94.,7
:/@7,?492:/07>
Central heating boiler with 110°-170°F mechanical
modulating gas valve(s).
%D;0$?,20:/07>
Central heating boiler with 4-stage firing. Controller
optional.

9>?,77,?4:9,>0
The boiler should be mounted on a level, non-com-
bustible surface. Boiler must not be installed on
carpeting. The boiler can be installed on a combustible
surface only when a suitable floor shield base is pro-
vided. Raypak offers an optional floor shield base
which can be factory installed on all indoor models
except Model 133; the Model 133 floor shield base is
shipped loose and must be installed by the contractor.
Do NOT use the shipping crate base as an installation
base.
In addition, the boiler shall be installed such that the
gas ignition system components are protected from
water (dripping, spraying, rain, etc.) during appliance
operation and service (circulator replacement, control
replacement, etc.).
7
70,=,9.0>
% The boiler should be located in an area
where water leakage will not result in damage to the
area adjacent to the appliance or to the structure.
When such locations cannot be avoided, it is
recommended that a suitable drain pan, adequately
drained, be installed under the appliance. The pan
must not restrict air flow.
Boiler Model No. Base Part No. Boiler Model No. Base Part No.
926*
1083*
1178*
1287*
1414*
1571*
1758*
962
1125
1223
1336
1468
1631
1826
001749
058313
058314
058315
058316
056199
056200
056201
056202
133
182/181
260/261
330/331
400/401
514
624
724
824
054597
054598
054599
054600
054601
058378
058379
059233
059234
059235
059236
059237
059238
059239
Table B: Combustible Floor Shield Ordering
Information
* Models with factory-installed floor shield as standard.
BOLD type indicates Low NOx models.
Fig. 2: Alternate Method for Providing a Non-
Combustible Base
MODEL
133 181 to
401
514 to
824
926 to
1826
2100 to
4001
Table C: Clearances from Combustible Surfaces
All dimensions are in inches.
Derived from National Fuel Gas Code, Table 6.2.3(a)
*Vent includes factory-supplied drafthood and does not include field-
supplied vent systems above the drafthood. On Models 2100-4001
drafthood is built into boiler.
% For Models 2100-4001, a factory-installed
floor shield is standard. Table B provides the floor
shield ordering information for other models.
% Combustible floor shield is required when
boiler is to be installed on a combustible surface. (See
ordering information in Table B.)
% Servicing Clearances: Provide at least 24"
(Models 133-1826), 48" (Models 2100-4001) in front of
unit for removal and servicing of the Controls & Burner
Tray. Provide at least 18" on side opposite water
connections for deliming of Heat Exchanger Tubes.

8
% The boiler shall be installed in a space large
in comparison to the size of the boiler. Large space
is defined as having a volume at least sixteen (16)
times the total volume of the boiler.
Table D: Reduction of Clearances to Protected
Surfaces
Derived from National Fuel Gas Code, Table 6.2.3(b)
@?/::=:470=>
These boilers are design certified for outdoor installa-
tion. Boilers must not be installed under an overhang
within three (3) feet from the top on the boiler. Three
(3) sides must be open in the area under the over-
hang. Roof water drainage must be diverted away
from the boilers with the use of gutters.
The point from where the flue products exit the boiler
must be a minimum of four (4) feet below, four (4) feet
horizontally from or one (1) foot above any door, win-
dow or gravity inlet to a building. The top surface of the
boiler shall be at least three (3) feet above any forced
air inlet, or intake ducts located within ten (10) feet hor-
izontally.
423(49/:9/4?4:9> @?/::=
&94?> 97D
In areas where high winds are frequent, it may be nec-
essary to locate the boiler a minimum of 3' from high
vertical walls, or install a wind break so the boiler is not
in direct wind current.
:8-@>?4:9,9/'09?47,?4:94=
9/::=&94?> 97D
The boiler must have both combustion and ventilation
air. Minimum requirements for net free air supply
openings are 12 inches from ceiling for ventilation and
12 inches from the floor for combustion air as outlined
in Z223.1 - latest edition or the current CAN/CSA
B149, as well as any local codes that may
have jurisdiction.
Fig. 3: Minimum Distances to Building Openings from
Where Flue Products Exit the Boiler

9
a. All Air From Inside The Building:
Each opening shall have a minimum net free
square inches as noted in Table E.
b. All Air From Outdoors:
When air is supplied directly from outside of build-
ing, each opening shall have a minimum net free
square inches as noted in Table F.
&% Combustion air must not be
contaminated by corrosive chemical fumes which
can damage the boiler and void the warranty.
Model Sq. Inches Model Sq. Inches
133 136 1125 1125
182/181 181 1223 1223
260/261 264 1336 1337
330/331 334 1468 1467
400/401 399 1631 1630
514 512 1826 1826
624 627 2100 2100
724 726 2500 2499
824 825 3001 3000
962 962 3500 3500
4001 4000
Model Sq. Inches Model Sq. Inches
133 34 1125 282
182/181 46 1223 306
260/261 66 1336 335
330/331 84 1468 367
400/401 100 1631 408
514 128 1826 457
624 157 2100 525
724 182 2500 625
824 207 3001 750
962 241 3500 875
4001 1000
Table E: Minimum Net Free Air from Inside Building
Table F: Minimum Net Free Air from Outside Building
'09?492
@?/::=9>?,77,?4:9>
:/07
1. Remove the front (4) screws.
2. Line up outdoor top vent opening over heater vent
opening.
3. Lower outdoor top onto unit lining up slots in the
outdoor top with screw holes in jacket top.
4. Reinstall (5) screws to secure jacket top and out-
door top to unit.
:/07>
Outdoor Top Installation
Fig. 4: Installing Outdoor Top—Model 133
(Part of heater)
Fig. 5: Installing Outdoor Top—Models 181-401 & 182-
400

10
1. Remove jacket top panel.
2. Remove and discard inner stack adapter panel.
3. Install jacket top panel.
4. Insert tabs of outdoor top into keyholes located on
jacket top panel (4 places). See Detail A.
5. Snap tabs on outdoor top into the locked position
of the keyhole so the top will not pull out. See
Detail B.
:/07>
1. Lower outdoor top onto unit. Position top so it is
centered on unit from side to side and front to rear.
2. Tighten the (4) screws (as indicated in Fig. 8) until
they come in contact with the unit jacket top, then
evenly tighten all (4) screws to secure to unit.
:/07>
Boilers are shipped with outdoor vent terminal factory
installed.
9/::=9>?,77,?4:9>
:/07
1. Shut-off main electrical power switch to boiler.
2. Turn heater manual switch located in upper control
panel to the "OFF" position.
3. Shut-off gas supply and water supply to the boiler.
4. Mount drafthood on boiler and attach with the
sheet metal screws provided. Drafthood should be
positioned with the vent sensor located on the
front left side (see next page).
5. Remove plastic plug from left side of boiler jacket
and install the plastic grommet provided.
6. Route flue sensor wire harness through the grom-
met installed in Step 5.
7. Remove door and locate wire from roll-out sensor
to high limit with the male/female connector.
8. Disconnect male/female connector and attach to
the 2 wires from drafthood vent sensor harness.
Outdoor Top
(Shipped Loose with Heater)
Detail A Detail B
Fig. 6: Installing Outdoor Top—Models 181-401 & 182-
400
Fig. 7: Installing Outdoor Top—Models 514–824
JACKET TOP
FASTENING
SCREW
Fig. 8: Installing Outdoor Top Detail—Models 514–824

11
Fig. 9: Indoor Installation—Model 133
:/07>
9/::=$?,.69>?,77,?4:9
1. Remove the louvered jacket top by removing four
(4) #10 flathead screws.
2. If originally installed, remove outdoor top from the
louvered jacket top.
3. Place the inner stack adapter panel over the flue
collector inside the heater. Make sure the flanged
side of the flue opening is up.
4. Turn the stack (drafthood) upside down and set it
down bottom side up.
5. Turn the jacket top panel (removed in step 1)
upside down and place it over the stack.
6. Attach the three (3) mounting brackets to the stack
using the screws provided and the holes that are
pre-drilled in the stack. Make sure the brackets
are positioned with the flange near the top side
of the stack (see Fig. 10). Caution must be
taken not to over tighten and strip the screw
threads.
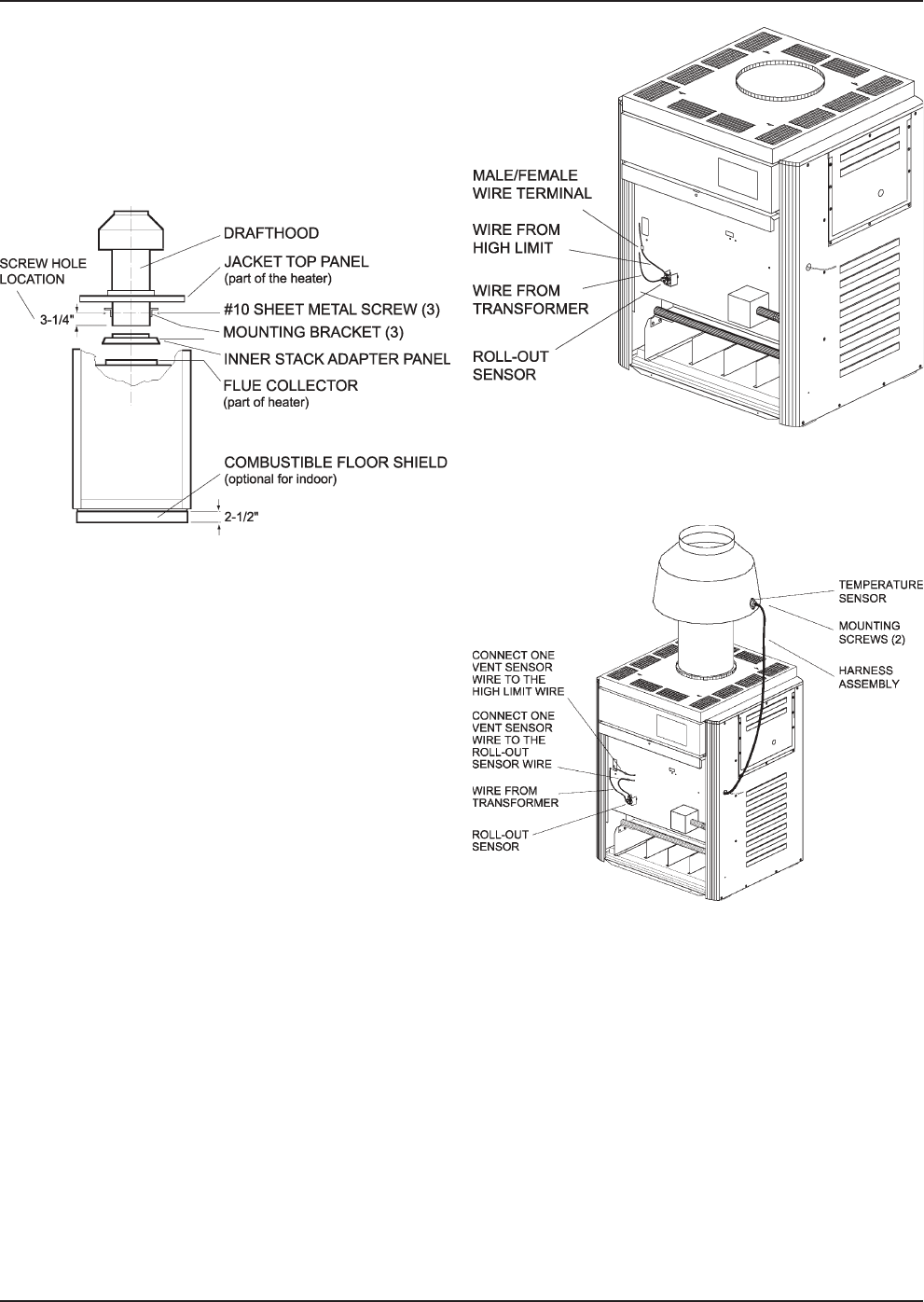
12
7. Turn the assembled stack and jacket top, rightside
up. The jacket top will be trapped between the
brackets and the top of the stack. Place the stack
over the inner stack adapter panel flanged hole
and lower the louvered jacket top panel back into
its original position. Reinstall the four (4) #10 flat-
head screws removed in step 1 above.
:/07>
1. Shut-off main electrical power switch to boiler.
2. Turn heater manual switch located in upper control
panel to the "OFF" position.
3. Shut-off gas supply and water supply to the boiler.
4. Mount drafthood on top of boiler as shown in Fig.
12. Drafthood should be positioned with the vent
sensor located on the front right side as shown.
5. Remove plastic plug from left side of boiler jacket
and install plastic grommet provided.
6. Route flue sensor wire harness through the grom-
met installed in Step 5.
7. Remove door and locate wire from roll-out sensor
to high limit with the male/female connector.
8. Disconnect male/female connector and attach to
the 2 wires from drafthood vent sensor harness.
Fig. 10: Indoor Installation—Models 181-401 & 182-400
Fig. 11: Boiler Before Drafthood Installation—Models
181-401 & 182-400
Fig. 12: Boiler After Drafthood Installation—Models
181-401 & 182-400
:/07>
Locate and assemble as shown in Fig. 13. Secure with
screws supplied in envelope in carton.

13
Fig. 13: Drafthood Installation—Models 514–824
:/07>
Locate and assemble as shown in Fig. 14. Secure with
screws supplied in envelope in carton.
:/07>
These models have built-in drafthoods. For proper
operation, the drafthood outlet must be connected to
the venting system.
'09?!4;492
Vent piping the same size or larger than the drafthood
outlet is recommended, however, when the total vent
height is at least 10 ft. (drafthood relief opening to vent
terminal), the vent pipe size may be reduced as spec-
ified in Chapter 10 of the latest edition of the National
Fuel Gas Code, ANSI Z223.1.
As much as possible, avoid long horizontal runs of
vent pipe and too many elbows. If installation requires
horizontal non-vertical runs, the vent pipe must have a
minimum of 1/4 inch per foot rise and should be sup-
ported at not more than 5 ft. intervals. Plumbers tape,
criss-crossed, will serve to space both horizontal and
vertical piping.
Gas vents supported only by the flashing and extend-
ing above the roof more than 5 ft. should be securely
guyed or braced to withstand snow and wind loads.
We recommend the use of insulated vent pipe spacers
through the roof and walls.
For protection against rain or blockage by snow, the
vent pipe must terminate with a vent cap which com-
plies with the local codes or, in the absence of such
codes, to the latest edition of the National Fuel Gas
Code, ANSI Z223.1.
The discharge opening must be a minimum of 2 ft. ver-
tically from the roof surface and at least 2 ft. higher
than any part of the building within 10 ft.
Vent stack shall be at least 5 ft. in vertical height above
the drafthood outlet. The vent cap location shall have
a minimum clearance of 4 feet horizontally from, and
in no case above or below, unless a 4-foot horizontal
distance is maintained, from electric meters, gas
meters regulators and relief equipment.
The weight of the vent stack or chimney must not rest
on boiler drafthood. Support must be provided in com-
pliance with applicable codes. The boiler top and
drafthood must be readily removable for maintenance
and inspection. Vent pipe should be adequately sup-
ported to maintain proper clearances from combustible
construction.
Fig. 14: Drafthood Installation—Models 962–1826
(# Indoor boilers require a drafthood
that must be connected to a vent pipe and properly
vented to the outside. Failure to follow this
procedure can cause fire or fatal carbon monoxide
poisoning.
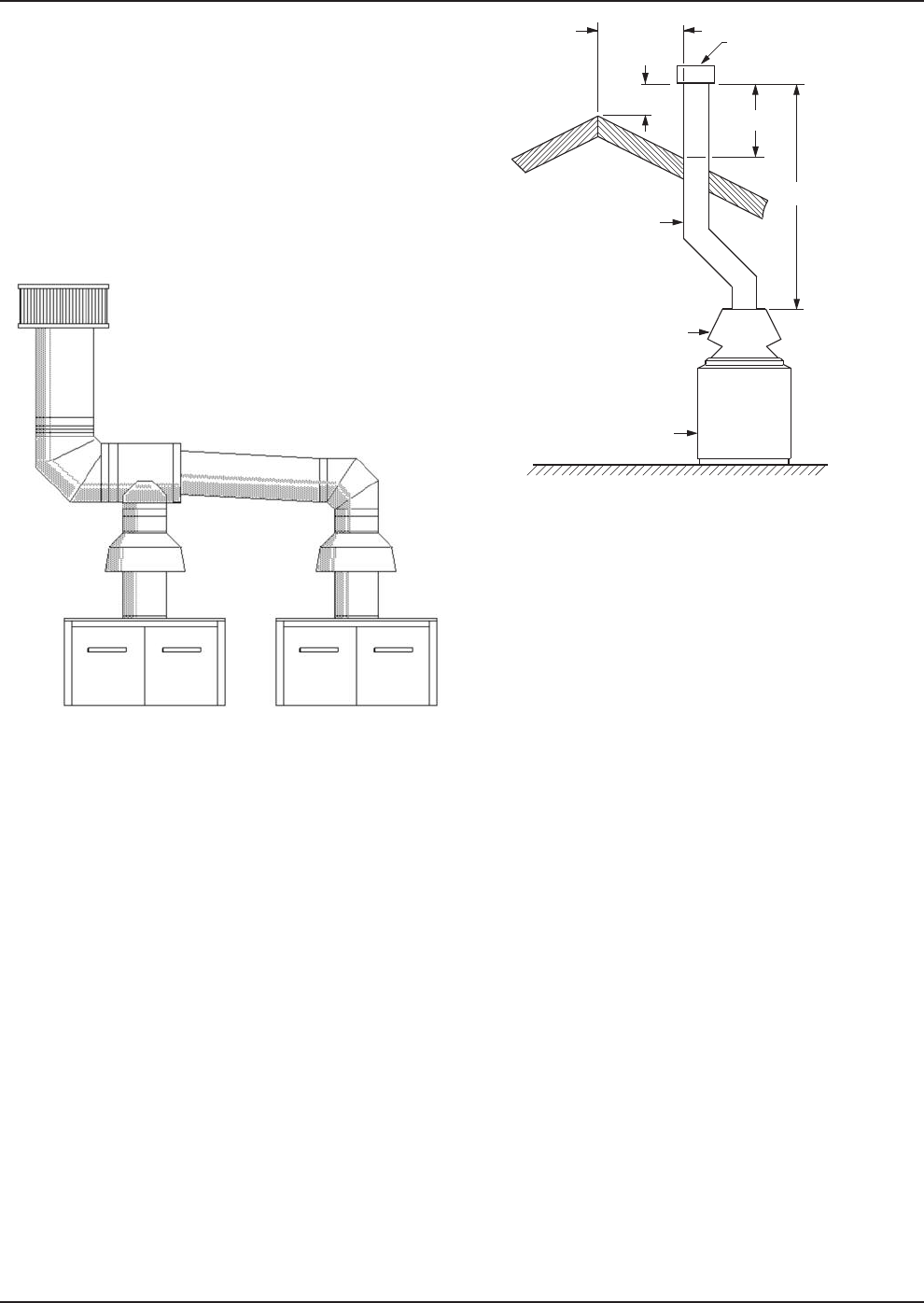
14
Type "B" double-wall or equivalent vent pipe is recom-
mended. However, single-wall metal vent pipe may be
used as specified in the latest edition of the National
Fuel Gas Code ANSI Z223.1.
Manifolds that connect more than one boiler to a com-
mon chimney must be sized to handle the combined
load. Consult available guides for proper sizing of the
manifold and the chimney. At no time should the area
be less than the area of the largest outlet.
At the time of removal of an existing boiler, the follow-
ing steps shall be followed with each appliance
remaining connected to the common venting system
placed in operation, while the other appliances remain-
ing connected to the common venting system are not
in operation.
(a) Seal any unused openings in the common venting
system.
(b) Visually inspect the venting system for proper size
and horizontal pitch and make sure there is no
blockage or restriction, leakage, corrosion and
other deficiencies which could cause an unsafe
condition.
(c) As much as possible, close all building doors and
windows and all doors between the space in which
the appliances remaining connected to the com-
mon venting system are located and other spaces
of the building. Turn on clothes dryers and any
appliance not connected to the common venting
system. Turn on any exhaust fans, such as range
Fig. 15: Common Venting
hoods and bathroom exhausts, so they will oper-
ate at maximum speed. Do not operate a summer
exhaust fan. Close fireplace dampers.
(d) Place in operation the appliance being inspected.
Follow the lighting instructions. Adjust thermostat
so appliance will operate continuously.
(e) Test for spillage at the drafthood relief opening
after 5 minutes of main burner operation. Use the
flame of a match or candle, or smoke from a ciga-
rette, cigar or pipe.
(f) After it has been determined that each appliance
remaining connected to the common venting sys-
tem properly vents when tested as outlined above,
return doors, windows, exhaust fans, fireplace
dampers and any other gas burning appliance to
their previous conditions of use.
(g) Any improper operation of the common venting
system should be corrected so that the installation
conforms with the latest edition of the National
Fuel Gas Code, ANSI Z223.1. When re-sizing any
portion of the common venting system, the com-
mon venting system should be re-sized to
approach the minimum size as determined using
the appropriate tables in Part 11 of the National
Fuel Gas Code, ANSI Z223.1.
For special venting applications that require reduced
vent sizes and through-the-wall venting, the Type D
Induced Draft Assembly can be used. Consult the fac-
tory or your local Raypak representative.
5' MIN
2' MIN
10' OR LESS
2' MIN
VENT CAP
VENT PIPE
DRAFT HOOD
HEATER
Fig. 16: Venting Clearances

15
'09?,8;0=9>?,77,?4:9
:/07>%3=:@23
(30=0#0<@4=0/
:.,?4:9
The vent damper must be located in the vent so that it
serves only the appliance for which it is intended.
If improperly installed, a hazardous condition, such as
an explosion or carbon monoxide poisoning, could
result. Make certain that it is mounted in an accessible
location at least 6 inches from any combustible mate-
rial or the heat exchanger, and that the position
indicator is in a visible location.
The vent damper must be installed after the appliance
drafthood, as close to the drafthood as practicable,
and without modification of the drafthood.
On vertical vents, the vent damper may be mounted
with the actuator in any position. On horizontal vents,
do not mount the actuator either directly above or
directly below the vent pipe; mount the vent damper
actuator to the side of the vent.
The vent damper is set up for a continuous pilot sys-
tem. If the vent damper is installed on an Intermittent
Pilot or Direct Spark Ignition equipped system, the
energy savings of the vent damper can be improved
by plugging the hole in the vent damper blade using
the knockout plug, Part No. 105612R, provided in the
parts envelope.
DO NOT plug the hole if installing the vent damper on
a continuous pilot system as this will create a hazard.
Fig. 17: Vent Damper Installation (Model 133 Drafthood
Shown)
(# Do not use thermally actuated vent
dampers on a modulating boiler. To do so may result
in asphyxiation. Use only a mechanically actuated
vent damper device that is electrically interlocked
with the modulating boiler operation.
HORIZONTAL INSTALLATION
TO BOILER D80B TO CHIMNEY
NO
NO
YES
YES
VERTICAL
INSTALLAT IO N TO CHIMNEY
VENT DAMPER
TO BOILER
INSTALL VENT DAMPER
WITH ACTUATOR TO
SIDES OF VENT ONLY.
DO NOT MOUNT ABOVE
OR BELOW VENT.
FLOW >
ACTUATOR MAY BE
INSTALLED IN ANY
POSITION ON VERTICAL
PIPE
????? ?????? ??????? ?????????? ?? ??? ?? ???????? ?????????? ?? ???? ?????
D80B
N. O. N. C.
END
SWITCH
C.
1K2
1K1
R
1K3
12345
1R
BLACK ORANGE RED YELLOW BLUE
THERMOSTAT OR
CONTROLLER
LIMIT OPTIONAL LIMIT
LOCATION
TRANSFORMER
DUAL VALVE
COMBINATION
GAS CONTROL OR
IGNITION SYSTEM
1
1
L1
L2
(HOT)
POWER SUPPLY PROVIDE DISCONNECT MEANS AND OVERLOAD PROTECTION AS REQUIRED
Fig. 18: Horizontal/Vertical Vent Damper Installation
Fig. 19: Vent Damper General Wiring Diagram

16
&% Install the vent damper to service only
the single appliance for which it is intended. if
improperly installed, a hazardous condition, such as
an explosion or carbon monoxide poisoning, could
result.
'09?,8;0=
:=8,7 ;0=,?4:9$@88,=D
For safe, efficient operation, the vent damper and all
flue product carrying areas of the appliance must be
checked annually, with particular attention given to
deterioration from corrosion or other sources. Check
vent damper operation as follows:
1. When the boiler is off, check that the vent damper
position indicator points to the closed position. (See
figure below.)
2. Turn the thermostat or controller up to call for heat
and check that the vent damper indicator points to the
open position. (See figure below.)
3. Turn the thermostat or controller down again and
check that the vent damper position indicator returns
to the closed position.
% The vent damper must be inspected at least
once a year by a trained, experienced service
technician. The name of the person who originally
installed your vent damper is shown on the
installation label. Damper must be in open position
when boiler main burners are operating.
Damper Position Indicator
Damper Open Damper Closed
Fig. 20: Vent Damper Position Indicator
EFFIKAL® RVGP
Fig. 21: Connection Diagram for Effikal® Vent Damper
!7@8-492
,>$@;;7D:990.?4:9>
Gas piping must have a sediment trap ahead of the
boiler gas controls, and a manual shut-off valve locat-
ed outside the heater jacket. All gas piping should be
tested after installation in accordance with local codes.
% Do not use teflon tape on gas line pipe
thread. A flexible sealant approved for the fuel being
used is recommended.
Fig. 22: Plumbing

17
Table G: Maximum Equivalent Pipe Length
A minimum of 7" W.C. and a maximum of 10.5" W.C.
upstream pressure, under load and no-load condi-
tions, must be provided for natural gas, or a minimum
of 12" W.C. and a maximum of 13" for propane.
,>!=0>>@=0#02@7,?:=
The gas pressure regulator is preset nominally at 4"
W.C. for natural gas, and 11" W.C. for propane.
Between the gas valve and the burners is a 1/8" pipe
plug. The pressure at this point, taken with a manome-
ter, should be about 3.7" W.C. for natural gas and
10.5" W.C. for propane. Low NOx models should be
3.9" W.C., natural gas only. If an adjustment is need-
ed, turn adjustment screw clockwise to increase
pressure, or counter-clockwise to decrease pressure.
For boilers with mechanical modulation gas valves
(Type H1 and H5) or two-stage gas valves (Type H3),
the gas pressure regulator is preset and sealed, and
not field adjustable. Pressure tap is provided on the
outlet side of the gas valve for measurement of gas
pressure in the manifold.
'09?492:14,;3=,28,>
:8;:909?>
Gas valves that are equipped with a gas bleed must be
vented to the outdoors as required by the National
Fuel Gas Code. Under NO circumstances shall bleed
lines terminate in the gas utilization equipment flue or
exhaust system.
090=,7
Boiler should be located so that any water leaks will
not cause damage to any adjacent areas or structures.
See piping diagrams for proper water connections for
the type of boiler and system.
!@8;$070.?4:9
In order to ensure proper hydraulics in your hydronic
heating system, adequate pump size must be select-
ed. We recommend that the pump be sized for 20°F
Delta T whenever possible. (Delta T is the temperature
Fig. 23: Bleed Line Connection Location
&% The boiler and its manual shut-off valve
must be disconnected from the gas supply during
any pressure testing of that system at test pressures
in excess of 1/2 PSIG. Dissipate test pressure in
the gas supply line before reconnecting the boiler
and its manual shut-off valve to gas supply line.
FAILURE TO FOLLOW THIS PROCEDURE MAY
DAMAGE THE GAS VALVE. OVER PRESSURED
GAS VALVES ARE NOT COVERED BY
WARRANTY. The boiler and its gas connections
shall be leak tested before placing the appliance in
operation. Use soapy water for leak test do NOT use
open flame.
*Low NOx units not available for propane.
Bleed Line
Connection
Vent Line
Connection

18
RDHRDHLEDOM
SIZE GPM T P FT GPM T P FT CONN GPM T P FT GPM T P FT CONN
133* 22 10 14.7 10 22 3.3 1-1/4"
182/181 45 7 9.2 20 15 1.8 1-1/2"
260/261 45 10 9.4 20 22 1.9 1-1/2"
330/331 45 12 9.6 20 28 1.9 1-1/2"
400/401 45 15 9.8 20 33 2.0 1-1/2"
514 90 9 9 40 21 1.8 2"
624 90 12 9.5 40 26 1.9 2"
724 90 13 10 40 30 2.0 2"
824 90 15 10.5 40 34 2.1 2"
926 90 17 11 40 38 2.2 2 1/2" 200 8 9.7 90172.13"
962 90 18 11 40 40 2.2 2 1/2" 200 8 9.7 90 18 2.1 3"
1083 90 20 12 45 40 3.1 2 1/2" 200 9 10.3 90 20 2.3 3"
1125 90 21 12 47 40 3.3 2 1/2" 200 9 10.3 90202.33"
1178 90 22 12.5 49 40 3.8 2 1/2" 200 10 11 90 21 2.4 3"
1223 90 22 12.5 51 40 4.0 2 1/2" 200 10 11 90 22 2.4 3"
1287 90 24 13.2 53 40 4.5 2 1/2" 200 11 11.7 90 23 2.5 3"
1336 90 24 13.2 55 40 4.9 2 1/2" 200 11 11.7 90 24 2.5 3"
1414 90 26 14 58 40 5.8 2 1/2" 200 12 12.290 26 2.7 3"
1468 90 27 14 61 40 6.4 2 1/2" 200 12 12.290 27 2.7 3"
1571 90 29 14.5 65 40 7.5 2 1/2" 200 13 13 90 29 2.8 3"
1631 90 30 14.5 68 40 8.3 2 1/2" 200 13 13 90 30 2.8 3"
1758 90 32 15.4 73 40 10.0 2 1/2" 200 14 14.7 90 32 3 3"
1826 90 34 15.4 76 40 10.8 2 1/2" 200 15 14.7 90 33 3 3"
2100 200 17 14.8 90 39 3.2 3" 400 9 18 180 19 4 4"
2500 200 21 15.8 103 40 4.4 3" 400 10 18.8 180 23 4.1 4"
3001 200 25 16.7 124 40 6.7 3" 400 12 19.5 180 27 4.3 4"
3500 200 29 17.5 145 40 9.5 3" 400 14 20.5 180 32 4.5 4"
4001 200 33 18.7 166 40 13.0 3" 400 16 21.5 180 36 4.7 4"
MAXIMUM AND MINIMUM FLOW RATES
2-PASS HEAT EXCANGER 1-PASS HEAT EXCHANGER
NIMXAMNIMXAM
GPM Flow rates limited by maximum acceptable velocity through heat exchanger tubes. May be increased by 10% for closed heating
systems.
* 4 Pass Heat Exchanger
BOLD TYPE indicates Low NOx models.
difference between the inlet and outlet water when the
boiler is firing at full rate). For some boilers, the Delta
T is more than 20°F (22°-33°F) at the recommended
flow rates.
00/B,?0=#02@7,?:=
We recommend that a feedwater regulator be installed
and set at 12 PSIG minimum pressure. Install a check
valve or back flow device upstream of the regulator,
with a manual shut-off valve. Leave the valve open.
!4;492H0,?492:470=>
We recommend that all high points be vented and that
purge valves and a bypass valve be installed. A boiler
installed above radiation level must be provided with a
low water cut-off device. The boiler, when used in con-
junction with a refrigeration system, must be installed
so that the chilled medium is piped in parallel with the
boiler with appropriate valves to prevent the chilled
medium from entering the boiler.
#0.:8809/0/!@=20,941:7/>1:=
%D;4.,7D/=:94.$D>?08::6@;>
The boiler piping system of a hot water heating boiler
connected to heating coils located in air handling units
where they may be exposed to refrigerated air circulat-
ing, must be equipped with flow control valves or other
automatic means to prevent gravity circulation of the
boiler water during the cooling cycle.
%08;0=,?@=0!=0>>@=0,@20
The temperature & pressure gauge is standard equip-
ment on all hydronic heating and hot water supply
boilers. All temperature & pressure gauges are factory
mounted in the in/out header except for residential
boilers, Models 133 and 181-401. On these models
the temperature & pressure gauge is shipped loose for
field installation, and located in the outlet water con-
nection. All fittings required to mount gauge to piping
system are supplied by others.
Table H: Maximum and Minimum Flow Rates

19
CONTROLLER SENSOR
(LESS THAN 4-STAGE)
CONTROLLER SENSOR
(4-STAGE OR MODULATION)
5’ MAX
5’ MAX
Fig. 24: Single Boiler Primary/Secondary Piping—Models 133–4001
Note: Expansion tanks (supplied by others) should be installed per manufacturer's instructions.

20
MAXIMUM OF 12”OR
4 PIPE DIAMETERS
CONTROLLER
SENSOR
5’ MAX
Reverse return piping is a proper method of manifolding multiple boiler hook-ups to ensure balanced flow through each boiler. Valves on
supply and return are needed to isolate any boiler, as required.
Fig. 25: Multiple-Boiler– Reverse Return Hook-Up—Models 133–4001

21
%# $
.:9:8,>?0=:9?=:7>
The Economaster II is an electronic device that allows
the operator to set the desired time for the pump to run
after the boiler shuts off. The time is factory-set at 7
minutes and it can be re-adjusted in the field anywhere
from 3 to 10 minutes.
In a conventional system, when the aquastat is satis-
fied, the main gas valve closes, but the pump
continues operating. With the energy-conserving
Economaster II the boiler pump is programmed to con-
tinue running for an optimum period of time in order to
absorb the residual heat from the combustion chamber
and use it in the system. The pump then shuts off until
the next call for heat is received from the aquastat.
70.?=:94.294?4:9
The intermittent ignition device conserves energy by
automatically extinguishing the pilot when desired
temperature is reached. When additional heat is need-
ed, the pilot re-ignites electrically, eliminating the fuel
costs of maintaining a constant pilot. To ensure safe
operation, the gas valve cannot open until the pilot
relights and is proven.
All units are shipped with lockout ignition module as
standard.
% Pump will come on when power is first
applied to boiler.
Fig. 26: Economaster PCB
;0=,?492:9?=:7>
:/0>,9/0.3,94.,7:/@7,?4:9
Models 133-1826 with mechanical modulating controls
have one or more Robertshaw (Invensys) Unitrol 7000
Series hydraulic snap-on thermostatic combination
gas valves. These dual-seat combination valves have
the pressure regulator and 24 volt operator built-in.
The hydraulic actuator will throttle the boiler input to
adjust the firing rate and meet the required load. This,
in effect, prevents costly fuel consumption, as com-
pared to an on-off cycling boiler.
The valve has a remote capillary bulb immersed in a
well, at the header outlet, to maintain a constant outlet
water temperature. When multiple valves are fur-
nished, they can be staged to give greater flexibility of
control. Standard factory setting is at position 5.
Consult the dial setting tag attached to the control for
your desired temperature. See sample tag drawings
below.
INVENSYS
INVENSYS
Fig. 27: Sample Tags
Low Temp. Range High Temp. Range
% No external control of the valve position is
possible.

22
Fig. 29: Mechanical Modulating Valve
MODULATING VALVES
W/ BUILT-IN REGULATOR
Fig. 28: Mechanical Modulating Valve Location
:/0:?:=4E0/:/@7,?4:9
The design uses a motorized valve which varies posi-
tion based upon an external controller that
communicates with the gas valve actuator, through a
3-wire 0-135 ohm wiper circuit. Minimum fire is 20%
of rate. The actuator runs on 120V power, and takes
26 seconds to go from fully closed to fully open.
Raypak offers a single-boiler digital controller which
drives the actuator; see controller options B-40 and
B-41 (includes outdoor reset). For systems with mul-
tiple boilers, see controller options B-45 through
B-47. For a field-supplied controller with a 4-20 mA
signal, see option B-35.
-
Fig. 30: Single Stage Tankstat
:/0$?,204=492
The boiler will fire at low fire when there is closure
across the stage 1 contacts. Thereafter, it will fire at
high fire when there is closure across the stage 2
contacts. Numerous staged controllers are available.
:/0 9 114=492
The boiler will fire at full fire when there is closure
across the TH contacts. Numerous mechanical
staged controllers are available (see Fig. 37), as well
as digital controllers offering additional features. A
typical wiring diagram for a mid-size H4 unit is shown
on page 35; this basic layout applies to most other
firing modes as well.
:/0$?,204=492
The boiler will fire at lowest setting when there is clo-
sure across the stage 1 contacts. Thereafter, it will
fire at increasing rates when there is closure across
the contacts for additional stages. Loss of closure
across stage 1 will shut down the entire boiler imme-
diately. Numerous digital controllers are available.
(:/0>
Connections for Tankstats in WH modes are shown in
Figs. 30 and 31.

23
484?:9?=:7>
,9@,7#0>0?423484?
All models except 133 are equipped with a manual
reset high limit. Set the manual limit to its maximum
set point.
@?:#0>0?423484?
Set the auto limit(s) to 30-40 °F above the desired
operating temperature and 5-10°F below the Manual
High Limit setting.
Fig. 32: Manual Reset High Limit
7:B$B4?.3
This dual purpose control shuts off the boiler in the
case of a pump failure or low water condition. It is
mounted and wired in series to the main gas valve.
Standard on all models except the 133.
% Flow switch will not operate if flow is less
than 12 gpm.
Fig. 33: Flow Switch
!47:?$,10?D
All standard boiler models 181-4001 employ electron-
ic devices which close the main gas valve within 8/10
of a second whenever the pilot flame is interrupted.
Pilot flame is automatically lit when the device is pow-
ered. Unit performs its own safety check and opens
the main valve only after the pilot is proven to be lit.
Fig. 34: Safety Control
Fig. 31: 2-Stage Tankstat

24
%#
% $
This boiler is normally wired for 120 Volts. The voltage
is indicated on the tie-in leads. Consult the wiring dia-
gram shipped with the boiler in the instruction packet.
The "TH" leads are for the remote tank control connec-
tion. 24 Volts are supplied to this connection through
the boiler transformer.
DO NOT attach line voltage to the "TH" leads on mod-
els 133-1826. Before starting boiler check to ensure
proper voltage to boiler and pump.
The boiler must be electrically grounded in accordance
with National Electrical Code ANSI/NFPA No 70, or
with CSA C22.1 C.E.C. Part 1 in Canada.
NOTES:
1. Field install ground to inside of junction box.
2. If any of the original wire as supplied with the boil-
er must be replaced, it must be replaced with
105°C wire or its equivalent.
&% Label all wires prior to disconnection
when servicing controls. Wiring errors can cause
improper and dangerous operation. Verify proper
operation after servicing.
# $ +# Make sure
electrical power to the heater is disconnected to
avoid potential serious injury or damage to
components.
:B(,?0=@? 11 ;?4:9,7
The probe-type low water cut-off automatically shuts
down burner whenever water level drops below the
probe for more than 2 seconds. A 30-second time
delay prevents premature lockout due to temporary
conditions such as power failure or air pockets.
Fig. 35: Low Water Cut-Off
423,9/:B,>!=0>>@=0
$B4?.30> ;?4:9,7
These switches sense either high or low gas pres-
sures and automatically shut down burners if abnormal
pressures exist.
Fig. 36: Gas Pressure Switch
% The High Gas Pressure Switch is standard
on Models 3001-4001

25
$%#%&!
01:=0$?,=?&;
Safe lighting and other performance criteria were met
with the gas manifold and control assembly provided
on the boiler when the boiler underwent tests specified
in the latest edition of ANSI Z21.13 Standard.
090=,7
Before lighting up a new installation, water should be
flowing through the boiler. Regulator should be set to
minimum 12 PSI.
477492$D>?080,?492
:470=>
Fill system with water. Purge all air from the system
using purge valve sequence. After system is purged of
air, lower system pressure. Open valves for normal
system operation. Fill system through feed pressure.
Manually open air vent on the compression tank until
water appears, then close vent.
&% Propane gas is heavier than air and
sinks to the ground. Exercise extreme care in light-
ing boiler in confined areas.
&% Pump must be off to check oil in bearing
assembly. Do not run pump without water in system.
MECHANICAL
MODULATING
GAS VALVES WITH
REGULATOR
T & P GAUGE
(NOT SHOWN)
INLET
HI-LIMIT
Fig. 37: General Location of Controls
?3D70907D.:7$D>?08>
0,?492:470=>
Fill through filler opening on the top on the Air-X Tank
to solution desired. Always maintain solution level in
sight glass.
94?4,7$?,=?&;!@8;,9/
:?:=
Many pumps are now direct-drive. They have no cou-
pler or bearing assembly. These pumps do not require
lubrication. Others require SAE-30 non-detergent oil to
lubricate both the motor and the bearing assembly.
Check pump motor for type before attempting to oil.
Clean dust and lint from pump and motor. Check pump
coupler and tighten if necessary. Flush system before
putting into operation to ensure that foreign material
does not damage pump seals.
% Raypak recommends the use of Ethylene
Glycol solution only.

26
1. Set the thermostat to lowest setting.
2. Turn off all electric power to the appliance.
3. Remove boiler door.
4. Push in gas control knob slightly and turn clock-
wise to “OFF”. Do not force.
5. Replace boiler door panel.
1. STOP! Read the safety information above on
this label.
2. Set the thermostat to lowest setting.
3. Turn off all electric power to the appliance.
4. Remove boiler door panel.
5. Push in gas control knob slightly and turn
clockwise to “OFF”.
NOTE: Knob cannot be turned from “PILOT” to “OFF”
unless knob is pushed in slightly. Do not force.
6. Wait five (5) minutes to clear out any gas. Then
smell for gas, including near the floor. If you
smell gas, STOP! Follow “B” in the safety in-
formation above on this label. If you don’t smell
gas, go to next step.
7. Locate pilot mounted
on the right side of the
burner tray, and right
of first burner.
8. Turn knob on gas control
counter-clockwise
to "PILOT"
9. Push in control knob all the way and hold in .
Immediately light the pilot with a match. Continue
to hol d t he control k nob in for about one (1 ) minute
after the pilot is lit. Release knob and it will pop
back up. Pilot should remain lit. If it goes out, re-
peat steps 5 through 9.
• If knob does not pop up when released, stop
and immediately call your service technician
or gas supplier.
• If the pilot will not stay lit after several tries,
turn the gas control knob to “OFF” and call
your service technician or gas supplier.
10. Stand to the side of the boiler and turn the gas
control knob counter-clockwise to "ON".
11 Replace boiler door panel.
12. Turn on all electric power to the appliance.
13 Set the thermostat to the desired setting.
PILOT THERMO-
BURNER COUPLE
A. This appliance has a pilot which must be lighted
by hand. When lighting the pilot, follow these
instructions exactly.
B. BEFORE LIGHTING smell all around the appli-
ance area for gas. Be sure to smell next to the
floor because some gas is heavier than air and
will settle on the floor.
WHAT TO DO IF YOU SMELL GAS
• Do not try to light any appliance.
• Do not touch any electric switch; do not use
any phone in your building.
• Immediately call your gas supplier from a
neighbor’s phone. Follow the gas supplier’s
instructions.
• If you cannot reach your gas supplier, call
the fire department.
C. Use only your hand to push in or turn the gas
control knob. Never use tools. If the knob will
not push in or turn by hand, don’t try to repair it,
call a qualified service technician. Force or at-
tempted repair may result in a fire or explosion.
D. Do not use this appliance if any part has been
under water. Immediately call a qualified
service technician to inspect the appliance and
to replace any part of the control system and
any gas control which has been under water.
WARNING: If you do not follow these instructions exactly, a fire or explosion may
result causing property damage, personal injury or loss of life.
START-UP
LIGHTING INSTRUCTIONS FOR BOILERS WITH STANDING PILOT. For Models 133, 182, 260, 330 & 400
GAS CONTROL
KNOB SHOWN
IN "OFF"
POSITION
GAS INLET
GAS CONTROL
KNOB SHOWN
IN "OFF"
POSITION
GAS INLET
TO TURN OFF GAS TO APPLIANCE
LIGHTING INSTRUCTIONS
FOR YOUR SAFETY READ BEFORE LIGHTING

27
LIGHTING INSTRUCTIONS FOR BOILERS WITH ELECTRONIC IGNITION (IID)
For Models with Manual Gas Valves
FOR YOUR SAFETY READ BEFORE OPERATING
WARNING: If you do not follow these instructions exactly, a fire or explosion may result causing
property damage, personal injury or loss of life.
A. This appliance is equipped with an ignition device which
automatically lights the pilot. Do not try to light the pilot
by hand.
B. BEFORE OPERATING smell all around the appliance
area for gas. Be sure to smell next to the floor because
some gas is heavier than air and will settle on the floor.
WHAT TO DO IF YOU SMELL GAS
* Do not try to light any appliance.
* Do not touch any electric switch; do not use any phone
in your building.
* Immediately call your gas supplier from your neighbor’s
phone. Follow the gas supplier’s instructions.
* If you cannot reach your gas supplier, call the fire de-
partment.
C. Use only your hand to push in or turn the gas control
knob. Never use tools. If the knob will not push in or turn
by hand, do not try to repair it, call a qualified service
technician. Force or attempted repair may result in a fire
or explosion.
D. Do not use this appliance if any part has been under
water. Immediately call a qualified service technician to
inspect the appliance and to replace any part of the
control system and any gas control which has been
under water.
OPERATING INSTRUCTIONS
For Honeywell gas valve: Turn gas control knob
counter-clockwise from “OFF” until it
stops. Push in gas control knob and continue
rotating counter-clockwise to “ON”
position. Make sure knob rests against stop.
For Honeywell gas valve (Models 40# only):
Turn gas control knob counter-clockwise to “ON”.
9. Replace boiler door panel.
10. Turn on all electrical power to the appliance.
11. Set thermostat to desired setting.
12. If the appliance will not operate, follow the instructions
“To Turn Off Gas To Appliance” and call your service
technician or gas supplier.
HONEYWELL
GAS CONTROL
KNOB SHOWN
IN "ON" POSITION
GAS INLET
ROBERTSHAW
GAS CONTROL
KNOB SHOWN
IN "ON" POSITION
GAS INLET
TO TURN OFF GAS TO APPLIANCE
1. Set the thermostat to the lowest setting.
2. Turn off all the electrical power to the appliance if service
is to be performed.
3. Remove door panel.
4. For Robertshaw gas valve: Turn gas control knob
clockwise to “OFF”.
For Honeywell gas valve (all models except 40#):
Turn gas control knob clockwise to “OFF”.
Make sure knob rests against stop.
For Honeywell gas valve (Models 40# only):
Push in gas control knob slightly and turn clockwise
to “OFF”.
5. Replace heater door panel.
GAS CONTROL KNOB
SHOWN IN "ON"
POSITION
GAS INLET
1. STOP! Read the safety information above.
2. Set the thermostat on the lowest setting.
3. Turn off all electrical power to the appliance.
4. This appliance is equipped with an ignition device which
automatically lights the pilot. Do not try to light the pilot
by hand.
5. Remove boiler door panel.
6. For Robertshaw gas valve: Turn gas control knob
clockwise to “OFF”.
For Honeywell gas valve (all models except 40#):
Turn gas control knob clockwise to “OFF".
Make sure knob rest against stop.
For Honeywell gas valve (Models 40# only):
Push in gas control knob slightly and turn clockwise
to “OFF”. Knob cannot be turned to “OFF”
unless knob is pushed in slightly. Do not force.
7. Wait five (5) minutes to clear out any gas. Then smell
for gas, including near the floor. If you smell gas, STOP!
Follow “B” in the safety information above. If
you do not smell gas, go to the next step.
8. For Robertshaw gas valve: Turn gas control knob
counter-clockwise to “ON”.

28
:=:/07>B4?3@?:8,?4.
,>',7A0>
423?4929>?=@.?4:9>
1. Close all gas valves. Turn off electrical power sup-
ply. Wait five (5) minutes.
2. Open manual pilot valve. Turn on electrical power.
Pilot is automatically lighted.
3. Open main gas valve.
4. Set temperature controls to desired temperature.
%:$3@?:B9
Close all manual gas valves. Turn off electrical power.
1?0=$?,=?&;
$?,9/492!47:?30.6:@?
!=:.0/@=0
1. Turn on pilot gas supply, light pilot, and check pilot
tubing connections for leakage. With main burner
in operation, paint tubing connections with a rich
PILOT
VALVE CONTROL
SHOWN IN THE MAIN GAS SHUT-OFF
"ON" POSITION VALVE SHOWN IN
THE "ON"
POSITION
GAS INLET
Fig. 38: Shut Off Valve
Fig. 39: Ignition Module
soap and water solution. Bubbles indicate a gas
leak.
2. Adjust pilot to obtain a normal flame enveloping
3/8 to 1/2 inch [9.5 to 12.5 mm] of the thermocou-
ple or generator tip.
3. Place system in operation, and:
a. Check for satisfactory ignition of main burner.
b. Make certain the pilotstat "holds in", and that
shutdown occurs within 2-1/2 minutes after the
pilot flame is extinguished.
c. Observe operation for at least three cycles to
be sure the system is functioning normally.
9?0=84??09?!47:?$D>?08
30.6:@?
$
1. Turn on power to the ignition systems and turn gas
supply off.
2. Check ignition module as follows:
a. Set the thermostat or controller above room
temperature to call for heat.
b. Watch for continuous spark at the pilot burner.
c. Time the spark operation. Time must be with-
in the lockout timing period (15 or 90
seconds).
d. Turn thermostat down to end call for heat and
wait 60 seconds on lockout models before
beginning step 3.
3. Turn on gas supply.
4. Set thermostat or controller above room tempera-
ture to call for heat.
5. Systems should start as follows:
a. Spark will turn on and pilot gas valve will open
Pilot with
Burner Flame
Standing Pilot
Fig. 40: Pilot Flame Should Engulf Thermocouple

29
at once. Pilot burner should ignite after gas
reaches the pilot burner.
b. Spark ignition should cut-off when pilot flame
is established.
c. Main gas valve should open and main burner
should ignite after gas reaches the burner
port.
9>;0.?4:9>
@=90=>
Clean main burners and air louvers of dust, lint and
debris. Keep boiler area clear and free from com-
bustibles and flammable liquids. Do not obstruct the
flow of combustion and ventilation air. Make visual
check of burner and pilot flame. Yellow flame indicates
clogging of air openings. Lifting or blowing flame indi-
cates high gas pressure. Low flame indicates low gas
pressure.
Fig. 41: Typical Main Burner Flame
Modulating burner flame varies in height from approximately 1/4"
at low fire to approximately 4" at high fire.
Fig. 42: Pilot Burner Flame (IID Units)
Fig. 43: Pilot Burner Flame (Standing Pilot Units)
:9?=:7>
Check all controls to see that they are operational. To
check electronic safety (IID Models), turn off main
burner. Observe pilot burner when shutting off pilot
gas. Ignition spark should go on. Main gas valve will
also drop out.
To check high limit switch, turn dial setting down to a
point slightly below the temperature of the water leav-
ing the heater. The reset button should snap out and
the burner should shut-off. Reset dial to 30°F to 40°F
above desired operating temperature, and push reset
button. Burner should light.
$@220>?0/9>;0.?4:9
$.30/@70
The boiler should be inspected on the first and third
months after initial start-up and then on an annual
basis. If problems are found, refer to Troubleshooting
Guide for additional directions.
1. Remove top of heater and inspect heat exchanger
for soot and examine venting system.
2. Remove rear header and inspect for scale
deposits, and/or accelerated erosion.
*3. Inspect pilot and main burner flame and firing rate.
*4. Inspect and operate all controls and gas valve.
*5. Visually inspect system for water leaks.
*6. a. Oil pump motor and bearing assembly, if oil
cups are provided.
b. Disconnect pump from header and check condi-
tion of pump impeller. Check condition of bearing
by attempting to move impeller from side to side.

30
Replace any parts showing wear.
c. Check pump coupler for wear and vibration.
7. Check flow switch paddle.
8. Clean room air intake openings to ensure ade-
quate flow of combustion and ventilation air.
9. Keep boiler area clear and free from combustible
materials, gasoline, and other flammable vapors
and liquids.
*Should be checked monthly. (Takes approximately
15 minutes).
( ) #$H
:/07>?:
The boilers are certified and tested under the latest
edition of the ANSI Z21.13 standards for hot water
boilers.
The boiler should be installed to meet the latest edition
of all local codes, the National Fuel Gas Code Z223.1
and the National Electrical Code, ANSI/NFPA 70.
&% Combustion air must not be
contaminated by corrosive chemical fumes which
can damage the boiler and void the warranty.
SEE DETAIL VIEW A
DETAIL A
Fig. 44: Burner Detail
;0=,?4:9
On call for heat, the ignition system, consisting of an
electronic spark module, and gas pilot system is ener-
gized. Providing pilot is proven, blower will start
running, the main gas valve will open and the boiler
will operate. When the operating control is satisfied the
boiler will shut down.
$?,=?&;$
1. Turn on power to the boiler with gas supply off.
2. Check ignition module as follows:
a. Set the thermostat or controller to call for heat.
b. Watch for continuous spark at the pilot burner.
c. Check the ignition spark operation. Time must
be within the lockout timing period (90 sec-
onds).
d. Turn control down to end call for heat and wait
60 seconds before beginning step 3.
3. Turn on gas supply.
4. Set controller to call for heat.
5. System should start as follows:
a. Spark will turn on and pilot gas valve will open.
b. Main valve and blower will be powered after
pilot flame signal is proven.
c. Heater will operate until call for heat is satis-
fied.
7:B0=/5@>?809?
The blower is set for optimal operation. If adjustment is
needed, see Fig. 46.
'4>@,79>;0.?4:9
Flame can be observed through the slot opening
above the plenum. Flame color is blue and evenly
spread on the top surface of the burner. At least every
three months a visual inspection should be made of
the burners. In case flame lifting is observed, check
gas pressure on manifold and static pressure in
plenum. Gas pressure in manifold should be 3.9" W.C.
and static pressure in plenum should be greater than
0.5" W.C.
70.?=4.,7
Be sure that electrical service to the boiler has proper
overload fuse or circuit breaker protection and wire

31
size, and connections which comply with all applicable
codes.
7,80#:77 @?$,10?D$B4?.3
The boiler is equipped with a cut-off device to prevent
flame roll-out in the event the heat exchanger
becomes blocked. This is a "manual reset" type roll-
out switch, that must be reset by a service technician
after any over temperature conditions have been fixed.
Excessive restriction in the heat exchanger flue pas-
sage may cause the switch to disable the boiler.
$0=A4.0
@=90=%=,D#08:A,7
Fig. 45: Flame Roll-Out Safety Switch
1. Shut-off main electrical power switch to heater.
2. Shut-off gas upstream of heater.
3. Remove front door.
4. Disconnect gas line from gas valve.
5. Remove (2) screws that mount burner tray to the
base of the unit, and (2) screws that secure gas
valve to jacket.
6. Disconnect wires that terminate at gas valve.
7. Unscrew (4) screws that secure the control box.
8. Disconnect pilot wire from the ignition module.
9. Disconnect wire harness from the combustion
blower.
10. Carefully slide out the burner tray assembly.
11. Reverse above procedure to re-install.
,>',7A0/5@>?809?#:-0=?>3,B
9A09>D>$0=40>$?,20,>
',7A0B4?3$:709:4/',7A0
1. Turn the heater off.
2. Remove the 3/8” nut or the #10 Torx screw.
3. Lift solenoid valve up, keeping the wires connect-
ed to the solenoid valve.
4. If only low fire adjustment is needed, go to Step 9.
5. Using a 3/8” wrench, carefully remove the alu-
minum cap that was under the solenoid
valve-count # of turns when removing the cap.
Be careful not to drop the cylinder (weight) or the
small spring that is under the cap –see Fig. 47.
6. Remove the spring and store in a safe place.
BURNER
BURNER
HOLD-
DOWN
BRACKET
GAS
VALVE
COMBUSTION
AIR BLOWER
AIR SHUTTER
ADJUSTMENT
Fig. 46: Low NOx Burner Tray Assembly
% Attach a manometer and check the manifold
pressures –both high fire and low fire– before
making any adjustments.
Fig. 47: 2-Stage Gas Valve Adjustment (Invensys)

32
5. Pull the pilot bracket slightly, then drop and pull
downwards and outwards.
6. Reverse above procedure to re-install. Make sure
the pilot bracket is all the way up on the pilot side,
see drawing below.
:8-@>?4:9,9#08:A,7
1. Remove burner tray. See Burner Tray Removal
procedure.
2. Remove (4) screws that mount the combustion
blower to the manifold assembly.
3. Reverse above procedure to re-install.
7. Using an Allen wrench, turn the screw clockwise to
increase or counterclockwise to decrease high fire
manifold pressure –see Fig. 47.
8. Install the spring, weight and aluminum cap –tight-
en the cap using same # of turns as was used in
removing the cap.
9. For low fire adjustment, tighten the aluminum cap
to increase and loosen to decrease low fire mani-
fold pressure.
10. Install 2-stage solenoid valve and turn heater on,
check manifold pressures.
11. Repeat steps 3 to 10 until correct manifold pres-
sures are obtained.
12. Secure 2-stage solenoid valve by tightening the
3/8” nut or #10 Torx screw.
,>',7A0#08:A,7
1. Remove burner tray. See Burner Tray Removal
procedure.
2. Disconnect, pilot tubing from gas valve.
3. Turn vertical gas pipe from manifold slightly and
unscrew gas valve.
4. Reverse above procedure to re-install.
,49@=90=,9/ =414.0
#08:A,7
1. Remove burner tray. See Burner Tray Removal
procedure.
2. Remove pilot. See Pilot Removal procedure.
3. Remove (8) total screws from the hold-down
brackets, front and rear of tray.
4. Remove (8) total screws from the left and right
sides of the manifold assembly. Detach the mani-
fold assembly from the burner tray assembly.
5. Remove burners by raising the bracket on the
back end of the burners up and out of their slots.
6. Use a long ½” socket wrench to remove orifices
from the gas manifold.
7. Remove burners by raising the bracket on the
back end of the burners up and out of their slots.
8. Reverse above procedure to re-install.
!47:?#08:A,7
1. Disconnect pilot tubing from gas valve.
2. Remove (4) screws from control box. Open the
control box.
3. Remove the pilot wire from the ignition wire.
4. Remove (2) screws that mount the pilot bracket to
the air manifold assembly.
Fig. 48: IID Pilot
FOR HEATERS
MADE IN OR AFTER
AUGUST 2001
Fig. 49: Pilot Removal

33
NOTE: Before troubleshooting, familiarize yourself with the start-up and checkout
procedure.
Check line voltage power, low voltage transformer, limit controller, thermostat
(controller) and wiring.
Pull ignition lead and check spark at module.
If spark Okay:
• Check ignition cable, ground wiring, ceramic insulator and gap, and correct.
• Check boot of the ignition cable for signs of melting or buckling. Take protective
action to shield cable and boot from excessive temperatures.
If not, replace module.
• Check that all manual gas valves are open, supply tubing and pressures are
good, and pilot burner orifice is not blocked.
• Check electrical connections between module and pilot operator on gas control.
• Check for 24 Vac across PV-MV/PV terminals on module. If voltage is
okay, replace gas control; if not, replace module.
NOTE: If S8600H goes into lockout, reset system. Lockout is used on propane
models.
• Check continuity of ignition cable and ground wire.
• Clean flame rod.
• Check electrical connections between flame rod and module.
• Check for cracked ceramic flame rod insulator.
• Check that pilot flame covers flame rod and is steady and blue.
• Adjust pilot flame.
• If problem persists, replace module.
• Check for 24 Vac across MV-MV/PV terminals. If no voltage, replace module.
• Check electrical connections between module and gas control. If okay, replace
gas valve or gas control operator, i.e. pilot gas valve, flow switch, etc.
NOTE: IF S8600H goes into lockout, reset system.
• Check continuity of ignition cable and ground wire.
NOTE: If ground is poor or erratic, shutdowns may occur occasionally even though
operation is normal at the time of checkout.
• Check that pilot flame covers flame rod and is steady and blue.
• If checks are okay, replace module.
• Check for proper thermostat (controller) operation.
• Remove MV lead at module; if valve closes, re-check temperature
controller and wiring; if not, replace gas valve.
START
TURN GAS SUPPLY OFF.
TURN T H ERMOSTAT
(CONTROLLER) TO CALL
FOR HEAT
POWER TO MODULE
(24 V NOMINAL)
YES
SPARK ACROSS
IGNITER/SENSOR GAP
YES
TURN GAS SUPPLY ON
PILOT BURNER LIGHTS?
YES
SPARK STOPS WHEN
PILOT IS LIT?
YES
MAIN BURNER LIGHTS?
YES
SYSTEM RUNS UNTIL
CALL FOR HEAT ENDS?
YES
CALL FOR HEAT ENDS
SYSTEM SHUTS OFF?
YES
TROUBLESHOOTING
ENDS
NO
NO
NO
NO
NO
NO
NO
%# &$ %
70.?=4.,7H70.?=:94.294?4:9
9?0=84??09?!47:?$D>?08
:90DB077$
(#H ' % For qualified
technicians ONLY.
% Some heaters may be equipped with an
ignition module that shuts off pilot gas if pilot fails to
light. To reset, interrupt power to heater.

34
For Service Technicians
START BOILER
RENRUB TOLIP FISTHGIL RENRUB TOLIP FI
THGIL TON SEODTON OD SRENRUB NIAM TUB
ELPUOCOMREHT KCEHCV 42 ROF KCEHC
AT GAS VALVE
IF NO 24 V IF 24 V: IF O.K. IF DEFECTIVE
CHECK TRANSFORMER OUPUT REPLACE
ECALPER ECALPER EVLAV SAGV 42 ROF
GAS VALVE THERMOCOUPLE
IF NO IF 24 V:
24V:
REPLACEPROBLEM IN
TRANSFORMER LIMIT
CIRCUITS
70.?=4.,7H$?,9/492!47:? (#H ' % For qualified
technicians ONLY.
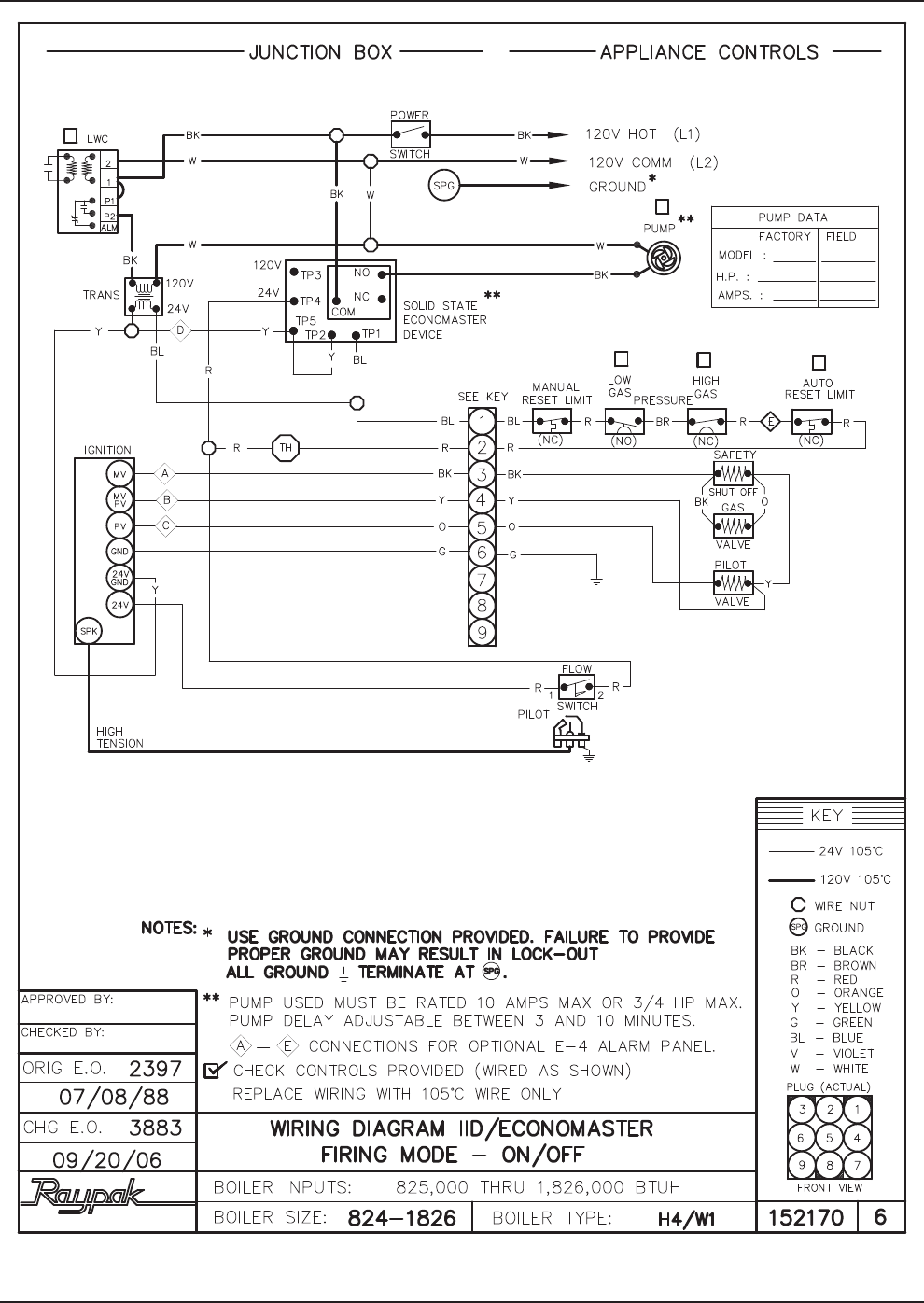
35
TYPICAL ON-OFF INTERMITTENT IGNITION
CONTROL WIRING DIAGRAM

36
MECHANICAL PROBLEM
When boiler is turned on nothing
happens.
Thermostat in "ON" position causes
relay and pump to operate, but boiler
does not fire.
Continuous shut down of manual reset
high limit.
Sooting
CAUTION-Soot may be combustible.
Wet down and exercise caution when
cleaning.
Continuous shut down of low water cut-
off or flow switch.
Low flame.
Outer jacket very hot (blistered paint).
POSSIBLE CAUSE
Pilot is not lit………………………………
No power to the boiler…………………...
Bad transformer………………………….
Inoperative thermostat…………………..
Inoperative toggle switch………………..
Inoperative relay………………………….
Main gas valve is closed……………….
Plugged bleed line on gas valve or
gas pressure regulator…………………..
Broken pump coupler……………………
Shutdown by low water cut-off,
caused by air……………………………..
Gas valve defective………………………
Temperature setting too low…………….
Low water flow……………………………
Interrupted pump operation……………..
Modulating control set too high………..
Mechanical modulating control…………
Air starvation……………………………..
Condensation……………………………..
Toxic fumes which cause a chemical
reaction with copper tubes or destroy
combustion……………………………….
Improper venting…………………………
Insufficient system flow………………….
Low water due to leaking………………..
Air in system………………………………
Line strainer dirty…………………………
Lime in heat exchanger…………………
Gas supply………………………………..
Insects or debris clogging burners..........
Burner intake ports low gas pressure….
Venting or combustion air……………….
Broken refractory…..…………………….
CORRECTIVE ACTION
Light pilot. (Standing pilot models)
Check the circuit breaker, outdoor con-
troller, etc., upstream of boiler.
If power to Leads L1 and L2 of trans-
former, but no power on 24V side, re-
place.
Jum p er t hermostat . Replac e wit h new if
boiler fires.
If power to toggle switch, but not
through switch, replace.
If power to relay, but not operating,
replace.
Open valve.
Loosen bleed line and clean.
Replace coupler. Inspect bearing as-
sembly, and if frozen, lubricate or re-
place.
Bleed air from system.
Check for power to gas valve. If valve
has power but will not open, check vent
tube for blockage. If clear, replace
valve.
Reset high limit to higher temperature.
Check system water pumps.
Check pump oil if necessary.
Reset modulator to a lower setting.
Check and replace if necessary.
Refer to installation instructions regard-
ing combustion air requirements.
Set bypass valve to prevent boiler inlet
temperature from dropping below
105 °F.
Remove all sources of fumes, such as
freon, chloride, or isolate the boiler.
Follow recommended vent installation
instructions.
Check pumps and piping.
Inspect for leakage and repair.
Inspect for leakage and repair. Install
an automatic air vent.
Clean.
Ream tubes.
Debris in gas line (pipe dope, rocks,
etc.). Gas line too small.
Improperly sized gas meter.
Gas regulator adjustment.
Clean burners.
Adjust gas pressure.
Refer to installation instructions regard-
ing combustion air requirement.
Replace refractory panels.

37
!@8;>
,47@=0%:!@8;
1. Pump not properly primed.
2. Wrong direction of rotation.
3. Speed too low.
4. Total head too high.
#0/@.0/,;,.4?D9/ =0,/
1. Air pockets or leaks in suction line.
2. Clogged impeller.
3. Foot valve strainer too small or clogged.
4. Excessive suction lift (over 15 ft.).
5. Insufficient positive suction head (for hot water).
6. Total head more than that for which pump is
intended.
7. Excessively worn impeller and wearing rings.
#,;4/(0,= 1:@;7492
1. Misalignment or a bent shaft.
2. Sagging motor mounts (over-oiling).
!@8;:>0>!=480
1. Air leaks in suction line.
2. Excessive amount of air in water.
3. Water seal in stuffing box not functioning.
4. Excessive suction lift and pump operating too
near shut-off point.
A0=7:,/0/=4A492&94?
1. Head much lower than that for which pump is
designed.
2. Speed too high or higher than that contemplated.
0.3,94.,7%=:@-70>,9/:4>0
1. Misalignment.
2. Excessive suction lift or vapor binding (hot
water).
3. Bent shaft and/or damaged bearings.
4. Suction and discharge piping not properly sup-
ported and anchored.
Fig. 50: Tube Cleaning Procedure

38
RAYPAK TUBE CLEANING KIT
Extension Pieces (5) Auger with Carbide Tip Wire Brush
P/N 052871F - 5/8 DIA. P/N 052870F - 7/8 DIA.
$0=A4.0
#0;,4=$0.?4:9
%@-070,9492!=:.0/@=0
Establish a regular inspection schedule, the frequency
depending on the local water condition and severity of
service. Do not let the tubes clog up solidly. Clean out
deposits over 1/16" in thickness.
The boiler may be cleaned from the side opposite the
water connections as shown, without breaking pipe
connections. It is preferable, however, to remove both
headers for better visibility through the tubes and to be
sure the residue does not get into the system.
Note that you do not remove the top pan or the heat
exchanger generally. After reaming with the auger,
mount the wire brush and clean out the debris remain-
ing in the tubes. Another method is to remove the heat
exchanger, ream tubes and immerse heat exchanger
in noninhibited de-scale solvent.
@=90=%=,D#08:A,7
1. Shut-off power and gas supply to the boiler.
Disconnect union(s) and pilot tubing, then loosen
and remove burner hold-down screws.
2. Disconnect wires at gas valve and slide burner
tray out.
,>',7A0#08:A,7
1. Shut-off gas supply to the boiler. Remove gas pip-
ing to gas valve inlet.
2. Disconnect wires, pilot tubing and bleed line, if
required.
3. Turn vertical gas pipe from manifold slightly and
unscrew gas valve.
4. Reverse above procedure to re-install.
,49@=90=9/ =414.0#08:A,7
1. Remove screws and burner hold-down bracket.
Fig. 51: Raypak Tube Cleaning Kit
COMBINATION FLAME SENSOR/
IGNITER AND PILOT BURNER
Fig. 52: Typical Burner Tray Illustrated

39
2. Lift burners from slotted spacer and slide from ori-
fices. Clean with a wire brush.
3. Clean orifice(s) as necessary.
!47:?#08:A,7,9/70,9492
1. Disconnect pilot tubing at pilot and sensor/igniter
wire. Remove screws holding pilot bracket to burn-
er tray.
2. Remove pilot and bracket, clean pilot of debris,
small bugs, etc., with wire or small brush.
3. Replace pilot, pilot tubing, sensor ignition wires
and check for leaks.
423484?:=%,96>?,?#08:A,7
1. Turn off electrical power.
% If the heat exchanger is sooted badly, the
burner hold-down bracket and spacer can become
distorted from direct flame impingement and this
usually necessitates replacement of these parts.
2. Remove front inspection panel.
3. Remove wires to high limit and loosen screws
holding high limit to cabinet.
4. Remove wedge clip holding sensing bulb in con-
trol well.
5. Remove high limit and install a new one.
6. Check control operation before leaving job.
0,?C.3,920=#08:A,7
1. Shut water, gas and electricity off, close valves
and relieve pressure, remove relief valve. Remove
side inspection panels.
2. Remove top holding screws.
3. Remove draft diverter, lift and remove top and flue
collector on stack type models. Remove inspec-
tion panels.
4. Loosen bolts and disconnect flange nuts on in/out
header, loosen union(s) at gas pipe, and slide boil-
er away from piping until studs clear the heater.
IN/OUT
HEADER
HIGH LIMIT
ELECTRICAL
JUNCTION BOX
REDUNDANT
SAFETY
SHUT-OFF
VALVE
MANUAL GAS VALVE
MAIN GAS VALVE
SEDIMENT TRAP
Fig. 53: Model 2100–4001 Boiler Illustration

40
5. Remove heat exchanger corner brackets.
6. Remove combustion chamber clips at the four cor-
ners of the heat exchanger.
7. Lift heat exchanger straight up using caution not to
damage refractory.
0,?C.3,920=#0>>08-7D
1. Heat exchanger water header O-rings should be
replaced with new ones.
2. Install in/out and return water headers and install
header retainer nuts and torque nuts evenly.
3. Install the four (4) corner clips between tube
sheets and refractory. Replace "V" baffles.
4. Install thermostat sensing bulbs in header wells
and replace bulb retaining clips.
5. Install inlet and return pipes in water headers
using pipe thread sealant.
6. Install water pressure relief valve, flow switch, and
low water cut-off devices if so equipped.
7. Open water supply and return shut-off valves. Fill
boiler and water piping system with water. Check
boiler and piping system for leaks at full line pres-
sure. Run system circulating pump for a minimum
of 1/2 hour with boiler off.
8. Shut down entire system and vent all radiation
units and high points in system piping. Check all
strainers for debris. Expansion tank water level
should be at the 1/4 mark and the balance of the
tank filled with air.
9. Install flue collector, jacket top and inspection pan-
els. Install top holding screws. Install draft diverter
and vent piping if so equipped.
10. If gas piping was disconnected, reconnect gas pip-
ing system and check for leakage using a soapy
solution.
11. Check for correct water pressure and water level
in the system. Make sure that system pump oper-
ates immediately on the call for heat. The system
is ready for operation.
12. Within two (2) days of start-up, recheck all air
vents and expansion tank levels.
:8-@>?4:93,8-0=#08:A,7
To remove combustion chamber you must first remove
the heat exchanger. Unbolt metal combustion cham-
ber retainer from top and remove combustion chamber
panels individually.
:9?=:7(077#0;7,.0809?
Remove top, sensing bulb and clip. Collapse well tube
at the opening with a chisel, push through into header
and remove the well through header. Insert a new well
and roll into place. If a roller is not available, solder the
well in place with silver solder.
%@-0#0;7,.0809?!=:.0/@=0
1. Remove heat exchanger from boiler following
instructions outlined under HEAT EXCHANGER
REMOVAL above.
2. Remove in/out and return headers. Remove "V"
baffle from damaged tube.
3. Remove damaged tube by cutting with a hack saw
or shearing with a chisel adjacent to each tube
sheet.
4. Collapse stub ends in tube sheets using a chisel or
screwdriver. DO NOT cut into tube sheet or mar
surface in tube hole in any way.
Fig. 54: Heat Exchanger
Fig. 55: Refractory Panels—Top View

41
5. Insert replacement tube by inserting the end with
the most fins removed in the opening of one tube
sheet. Slide tube until the opposite end clears the
other tube sheet and fit the tube into the hole.
6. Insert the tube roller into tube opening up to stop,
making certain that 1/8" of tube projects beyond
the tube sheet.
7. Attach drill to tube roller, holding it straight and
level.
8. Reverse drill motor and withdraw tube roller. If
necessary wrench out by hand.
9. DO NOT apply excessive torque during rolling
operation and avoid thinning any wall of the tube
beyond 0.015".
10. Use same procedure on opposite end.
11. Apply line pressure test. Re-roll if necessary.
12. Reinstall as outlined under HEAT EXCHANGER
RE-ASSEMBLY.
70,94927@0,>!,>>,20B,D>
Soot will clog areas behind fins and cause eventual
tube failure. Any sign of soot at base of burners or
around outer jacket indicates a need for cleaning.
1. Lift off drafthood and flue collector by removing
bolts and screws.
2. Remove "V" baffles from heat exchanger.
3. Remove burner tray.
4. Take garden hose and wash heat exchanger, mak-
ing sure soot is removed from between fins. (Avoid
excessive water against refractory).
5. Reassemble; when boiler is fired, some steam will
form from wet refractory. This is normal.
6. Correct reason for soot formation.
#!%!#%$
See separate parts sheet in instruction envelope.
Any part returned for replacement under standard
company warranties must be properly tagged with
Raypak return parts tag, completely filled in with the
heater serial number, model number, etc., and shipped
to Raypak freight prepaid. If determined defective by
Raypak and within warranty, the part will be returned in
kind or equal substitution, freight collect. Credit will not
be issued.
RAYPAK, INC.
2151 Eastman Avenue
Oxnard, CA 93030
% In extreme cases it may be necessary to
remove the heat exchanger completely for cleaning.
The simplest method is steam cleaning at a local car
wash. DO NOT WIRE BRUSH!
&% Soot is combustible, so exercise
extreme care.
% To supply the correct part it is important that
you supply the model number, serial number and
type of gas when applicable.
% Use a 3/8" heavy duty, reversible, electric
drill or larger. Proceed to expand tube until tool starts
to grab. Approximately 1/2 to 1" of the tool shank will
be visible.

42
Catalog Number: 1900.10H
Effective 08/01/10
LIMITED WARRANTY
RAYTHERM - TYPES H AND WH
Models: 133 - 4001
SCOPE
Raypak, Inc. (Raypak) warrants to the original owner that all parts of this heater which are actually manufactured by Raypak will be free from defects in
materials and workmanship under normal use and service for the specified warranty periods and subject to the conditions set forth in this Limited
Warranty. Labor charges and other costs for parts removal or reinstallation, shipping and transportation are not covered by this Limited Warranty, but
are the owner’s responsibility.
EFFECTIVE DATE
The Effective Date of this Limited Warranty is the date of original installation if properly documented; if you are not able to provide documentary proof of
the date of original installation, the Effective Date will be the date of manufacture plus 30 days.
HEAT EXCHANGER WARRANTY PERIODS
Domestic Hot Water
Five (5) years from Effective Date. Includes copper heat exchanger with bronze or cast iron waterways.
Ten (10) years from Effective Date. Includes only cupro-nickel heat exchanger with bronze or cast iron waterways.
Space Heating (Closed Loop System)
Ten (10) years from Effective Date. Includes both cupro-nickel and copper heat exchanger with bronze or cast iron waterways.
Thermal Shock Limited Warranty
Twenty (20) years from Effective Date against “Thermal Shock” (excluded, however, if caused by heater operation at large changes exceeding 150ºF
between the water temperature at intake and heater temperature, or operating at heater temperatures exceeding 230ºF).
ANY OTHER PART MANUFACTURED BY RAYPAK
One (1) year from Effective Date.
THIS LIMITED WARRANTY WILL BE VOID IF THE HEATER RATING PLATE IS ALTERED OR REMOVED.
ADDITIONAL WARRANTY EXCLUSIONS
This Limited Warranty does NOT cover units moved from their original installation location or conditions including failures or malfunctions resulting from:
1. Failure to properly install, operate or maintain the heater in accordance with our printed instructions provided;
2. Abuse, misuse, alteration, accident, fire, flood and the like;
3. Sediment or lime build-up, freezing, or other conditions causing inadequate water circulation;
4. High velocity flow exceeding heater design rates;
5. Failure of connected systems devices, such as pump or controller;
6. Use of non-factory authorized accessories or other components in conjunction with the heater system;
7. Failing to eliminate air from, or replenish water in, the connected water system;
8. Chemical contamination of combustion air or use of chemical additives to water.
REPAIR OR REPLACEMENT
At its option, Raypak will repair or replace a defective part(s) in accordance with the terms of this Limited Warranty, if it fails in normal use and service
during its specified warranty period. The failed part must first be returned to Raypak if requested, with transportation charges prepaid, and all applicable
warranty conditions found satisfied. The repair or replacement part will be warranted for only the unexpired portion of the original Limited Warranty.
Raypak makes no warranty whatsoever on parts not manufactured by it, but Raypak will apply any such warranty as may be provided to it by the parts
manufacturer.
HOW TO MAKE A WARRANTY CLAIM
You should immediately notify the original installer, supplying the model number and serial numbers of the unit, date of installation and description of the
problem. The installer must then notify his Raypak distributor for instructions regarding the claim. If either is not available please contact Service
Manager, Raypak, Inc. 2151 Eastman Avenue, Oxnard CA 93030 or call (805) 278-5300. In all cases proper authorization must first be received from
Raypak before repair or replacement of any part.
EXCLUSIVE WARRANTY-LIMITATION OF LIABILITY
The Limited Warranty is the only warranty for this product and its component parts given by Raypak. No one is authorized to make any other warranties
on Raypak’s behalf. ANY IMPLIED WARRANTIES, INCLUDING MERCHANTABILITY OR FITNESS FOR A PARTICULAR PURPOSE, SHALL NOT
EXTEND BEYOND THE APPLICABLE WARRANTY PERIODS SPECIFIED IN THIS LIMITED WARRANTY. RAYPAK’S SOLE LIABILITY WITH
RESPECT TO ANY DEFECT SHALL BE AS SET FORTH IN THIS LIMITED WARRANTY. IT IS AGREED THAT RAYPAK SHALL HAVE NO
LIABILITY WHETHER UNDER THIS LIMITED WARRANTY OR IN CONTRACT, TORT OR NEGLIGENCE OR OTHERWISE FOR CLAIMS FOR
SPECIAL, INCIDENTAL OR CONSEQUENTIAL DAMAGES (INCLUDING NO LIABILITY FOR DAMAGE FROM WATER LEAKAGE) WHICH ARE
EXPRESSLY EXCLUDED, NOTWITHSTANDING ANY FAILURE OF ESSENTIAL PURPOSE OF ANY LIMITED REMEDY. Some states do not allow
limitations on how long an implied warranty lasts, or for the exclusion of incidental or consequential damages, so the above limitation or exclusion may
not apply to you.
THIS LIMITED WARRANTY GIVES YOU SPECIFIC LEGAL RIGHTS, AND YOU MAY ALSO HAVE OTHER RIGHTS WHICH VARY FROM STATE
TO STATE.
We suggest you immediately record the model and serial number and date of original installation and retain this Limited Warranty Certificate along with
your original proof of purchase and date of installation/start-up in the event warranty service is needed.
DO NOT RETURN THIS DOCUMENT TO RAYPAK. KEEP IT WITH YOUR HEATER OR BUSINESS RECORDS.
rellatsnI fo emaN renwO fo emaN
rellatsnI fo rebmuN enohpeleT sserddA srenwO
etiS noitallatsnI noitallatsnI fo etaD
rebmuN laireS rebmuN ledoM
RAYPAK, INC., 2151 Eastman Avenue, Oxnard, CA 93030 • (805) 278-5300 FAX (800) 872-9725 www.raypak.com
43

www.raypak.com
Raypak, Inc., 2151 Eastman Avenue, Oxnard, CA 93030 (805) 278-5300 Fax (805) 278-5468
Litho in U.S.A.