SCHUNK Intec 03777V2 Sensor with radio interface User Manual RSS R1 T2
SCHUNK Intec, Inc Sensor with radio interface RSS R1 T2
Contents
- 1. manual model 0377717
- 2. manual model 8705401
manual model 0377717
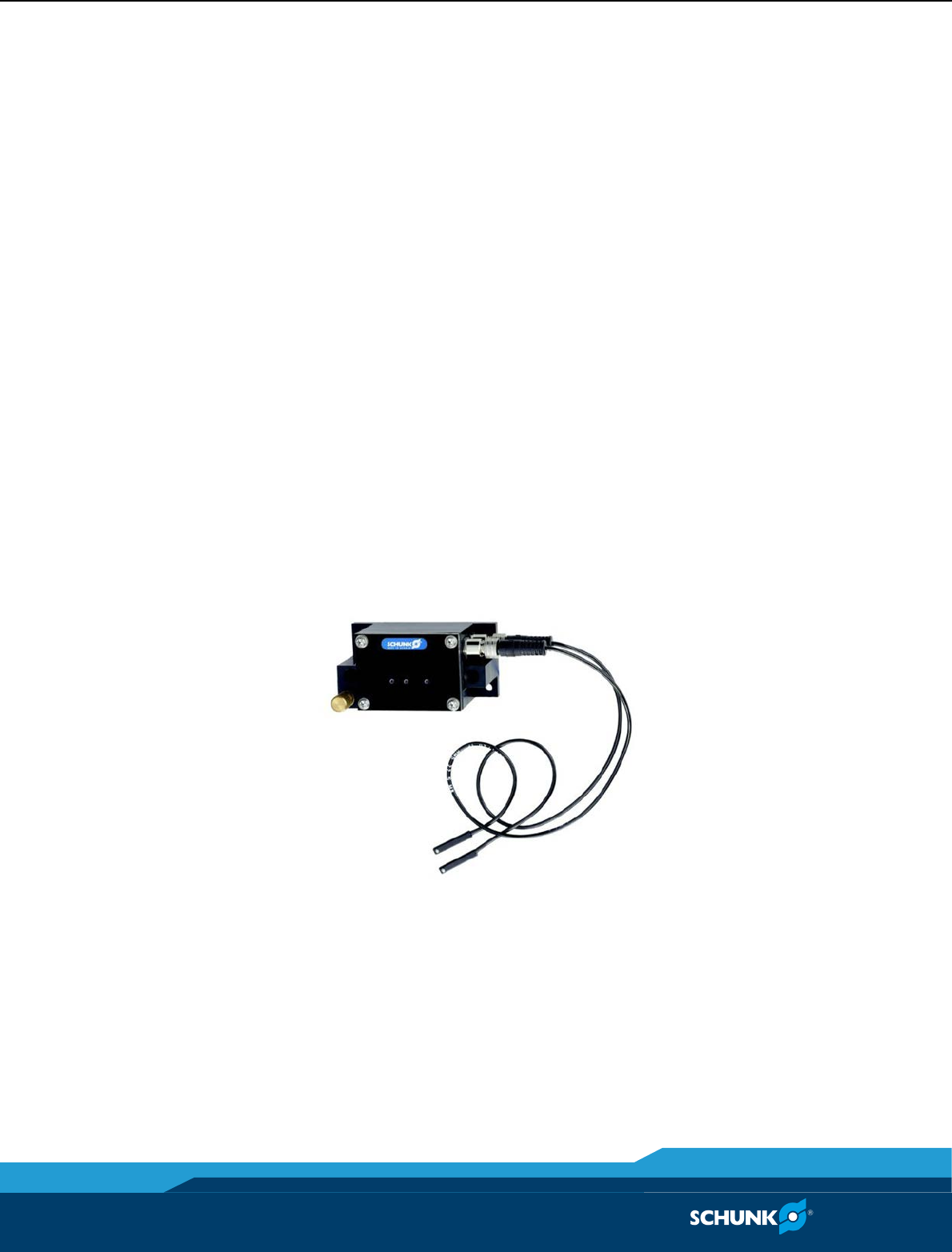
Translation of the original manual
Radio sensor system RSS
Receiver RSS R1, Transmitter RSS T2‐US/CA
Id. Nr. 8705401
Frequenz 868,3 MHz
FCC/IC‐Zertifizierung für den Betrieb in USA und Kanada.
Assembly and Operating Manual
Superior Clamping and Gripping
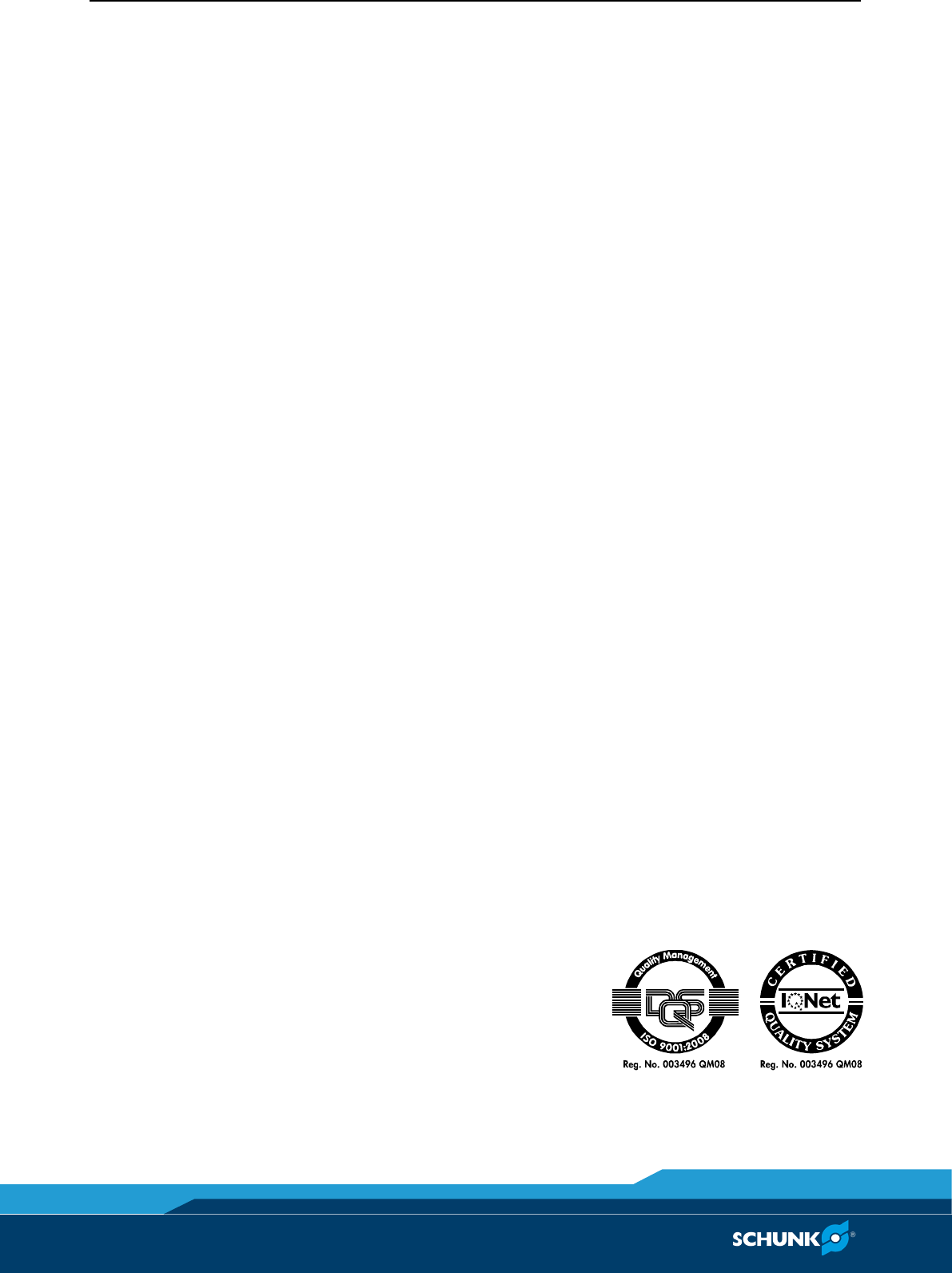
Imprint
2 02.02_preliminary|Id. Nr. 8705401 |en
Imprint
Copyright:
This manual remains the copyrighted property of SCHUNK GmbH & Co. KG. It is solely
supplied to our customers and operators of our products and forms part of the product.
This documentation may not be duplicated or made accessible to third parties, in particu‐
lar competitive companies,
without our prior permission.
Technical changes:
We reserve the right to make alterations for the purpose of technical improvement.
Document number: 0389449
Edition: 02.02_preliminary |01/08/2016|en
© SCHUNK GmbH & Co. KG
All rights reserved.
Dear customer,
congratulations on choosing a SCHUNK product. By choosing SCHUNK, you have opted for
the highest precision, top quality and best service.
You are going to increase the process reliability of your production and achieve best
machining results – to the customer's complete satisfaction.
SCHUNK products are inspiring.
Our detailed assembly and operation manual will support you.
Do you have further questions? You may contact us at any time – even after purchase.
Kindest Regards
Yours SCHUNK GmbH & Co. KG
Spann‐ und Greiftechnik
Bahnhofstr. 106 – 134
D‐74348 Lauffen/Neckar
Tel. +49‐7133‐103‐0
Fax +49‐7133‐103‐2399
info@de.schunk.com
www.schunk.com
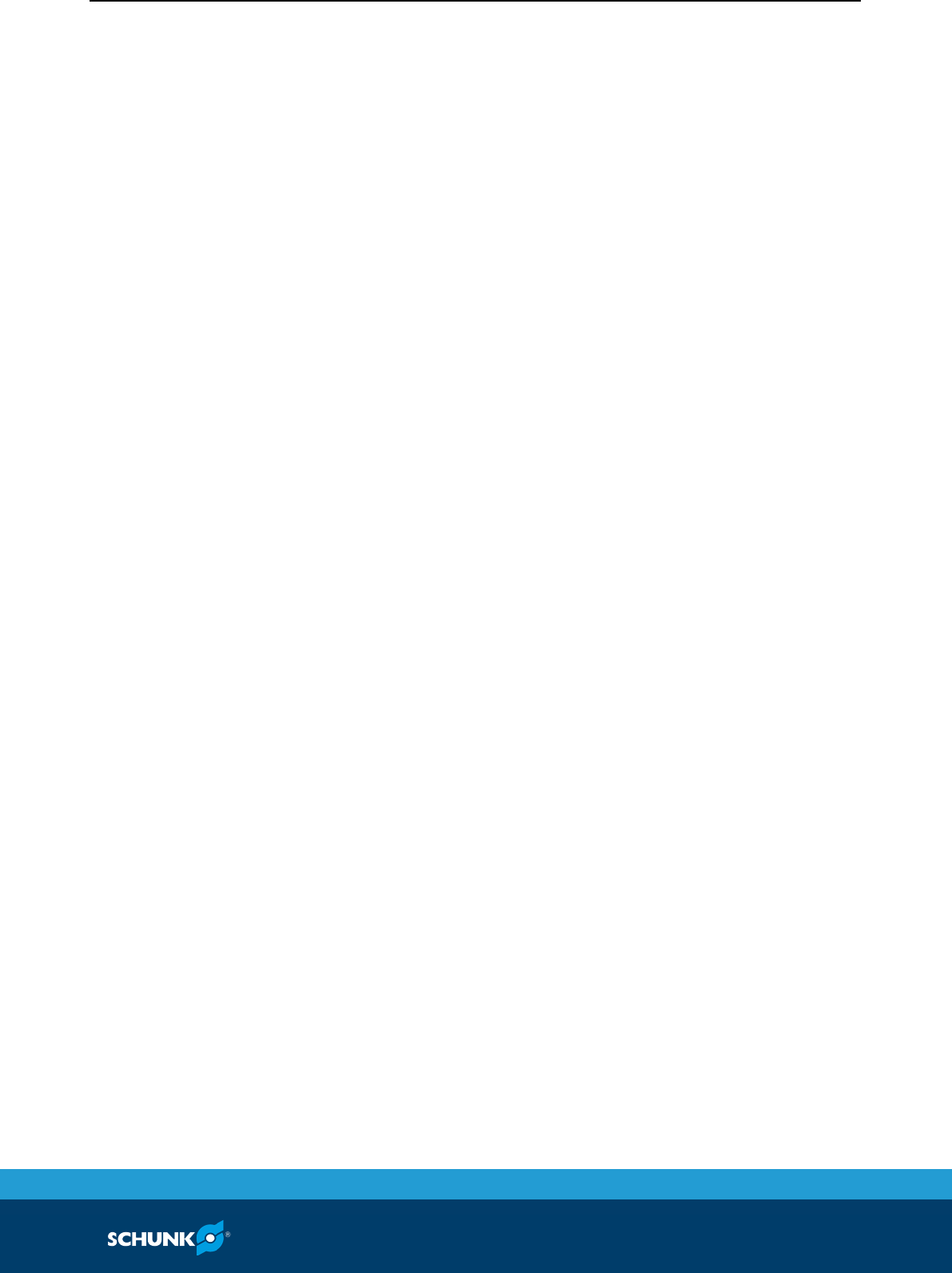
Table of contents
02.02_preliminary|Id. Nr. 8705401 |en
3
Table of contents
1
About this manual .................................................................................................... 5
1.1
Presentation of Warning Labels ............................................................................... 5
1.2
Applicable documents .............................................................................................. 5
2
Basic safety notes .................................................................................................... 6
2.1
Intended use ............................................................................................................. 6
2.2
Environmental and operating conditions ................................................................. 6
2.3
Product safety........................................................................................................... 7
2.3.1
Protective equipment ................................................................................... 7
2.3.2
Constructional changes ................................................................................. 7
2.4
Personnel qualification ............................................................................................. 7
2.5
Notes on particular risks ........................................................................................... 8
3
Warranty ................................................................................................................. 10
4
Scope of delivery ..................................................................................................... 11
5
Accessories .............................................................................................................. 12
6
Technical data ......................................................................................................... 13
6.1
Technical Data RSS‐R1 ............................................................................................ 13
6.2
Technical data ‐ RSS T2 ........................................................................................... 14
6.3
Information on radio link and range ...................................................................... 14
7
Assembly ................................................................................................................. 16
7.1
Assembly of the transmitter RSS T2 ....................................................................... 16
7.2
Assembly and electrical connection of the RSS R1 receiver .................................. 16
8
Start‐up ................................................................................................................... 18
8.1
General information on commissioning ................................................................. 18
8.2
Programming the transmitter to the receiver ....................................................... 18
8.3
Testing the antenna position ................................................................................. 19
8.4
Adjusting the watchdog time at the receiver ........................................................ 19
9
Functional description ............................................................................................. 20
9.1
RSS‐R1 ..................................................................................................................... 20
9.1.1
LED ............................................................................................................... 20
9.1.2
Measuring jacks ........................................................................................... 21
9.1.3
General discription ...................................................................................... 22
9.1.4
Function description delivery condition ..................................................... 23
9.1.5
Status definition .......................................................................................... 24
9.1.6
Time response ............................................................................................. 25
9.1.7
Function of the DIP switches ...................................................................... 25
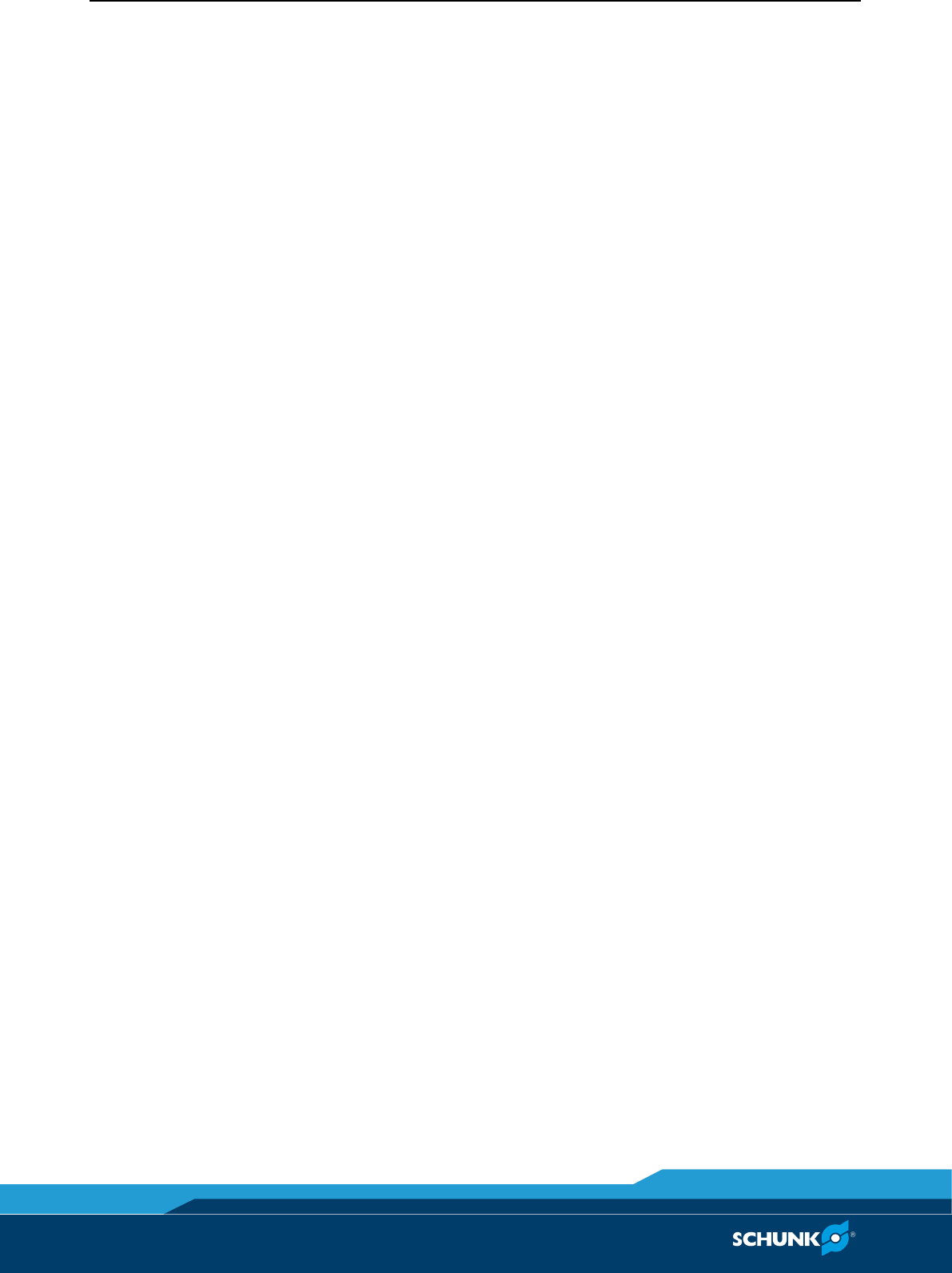
Table of contents
4 02.02_preliminary|Id. Nr. 8705401 |en
9.1.8
Delete transmitter ID .................................................................................. 26
9.1.9
Signaling the distance between signals or the signal strength................... 27
9.1.10
Setting the limit value for battery monitoring ............................................ 28
9.1.11
Setting the output behaviour...................................................................... 28
9.1.12
Teaching the limit value (teaching threshold) ............................................ 28
9.1.13
Setting the watchdog time .......................................................................... 29
9.1.14
Function of the DIP 5 Extension of the reception range during the learning
procedure .................................................................................................... 29
9.1.15
Manual setting of transmitter ID (programming) ....................................... 30
9.1.16
Output behaviour of the watchdog ............................................................ 31
9.1.17
Software block diagram .............................................................................. 31
9.2
RSS‐T2‐US/CA ......................................................................................................... 31
9.2.1
Operation .................................................................................................... 31
9.2.2
Operating mode .......................................................................................... 32
9.2.3
LED ‐ Display ................................................................................................ 32
10
Maintenance and care ............................................................................................. 33
11
Information FCC certification ................................................................................... 34
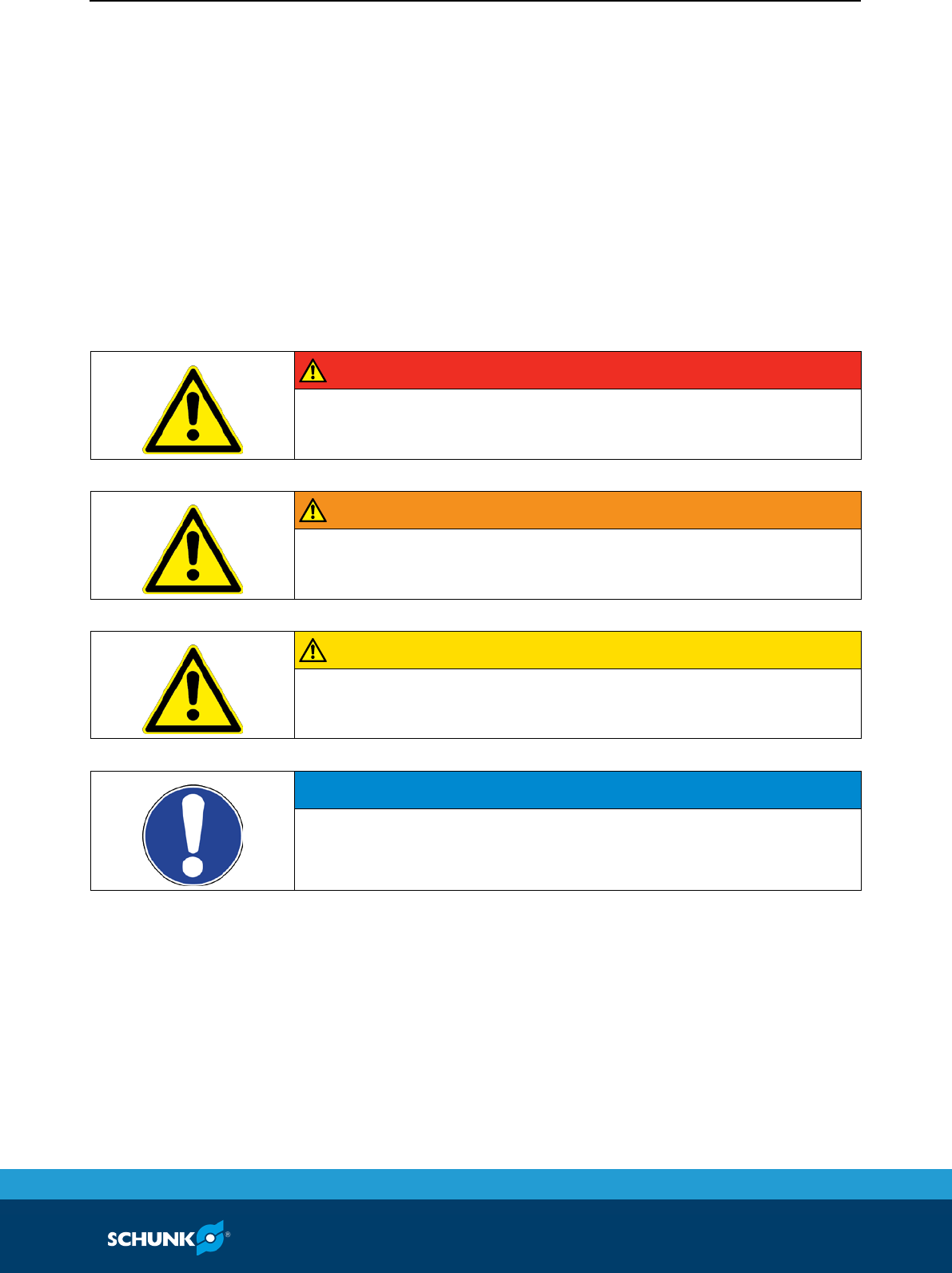
About this manual
02.02_preliminary|Id. Nr. 8705401 |en
5
About this manual
This instruction is an integral part of the product and contains im‐
portant information for a safe and proper assembly, commission‐
ing, operation, maintenance and help for easier trouble shooting.
Before using the product, read and note the instructions, especial‐
ly the chapter "Basic safety notes".
Presentation of Warning Labels
To make risks clear, the following signal words and symbols are
used for safety notes.
DANGER
Danger for persons!
Non‐observance will inevitably cause irreversible injury or death.
WARNING
Dangers for persons!
Non‐observance can lead to irreversible injury and even death.
CAUTION
Dangers for persons!
Non‐observance can cause minor injuries.
NOTICE
Material damage!
Information about avoiding material damage.
Applicable documents
• General terms of business *
• Catalog data sheet of the purchased product *
The documents marked with an asterisk (*) can be downloaded on
our homepage www.schunk.com.
1
1.1
1.2
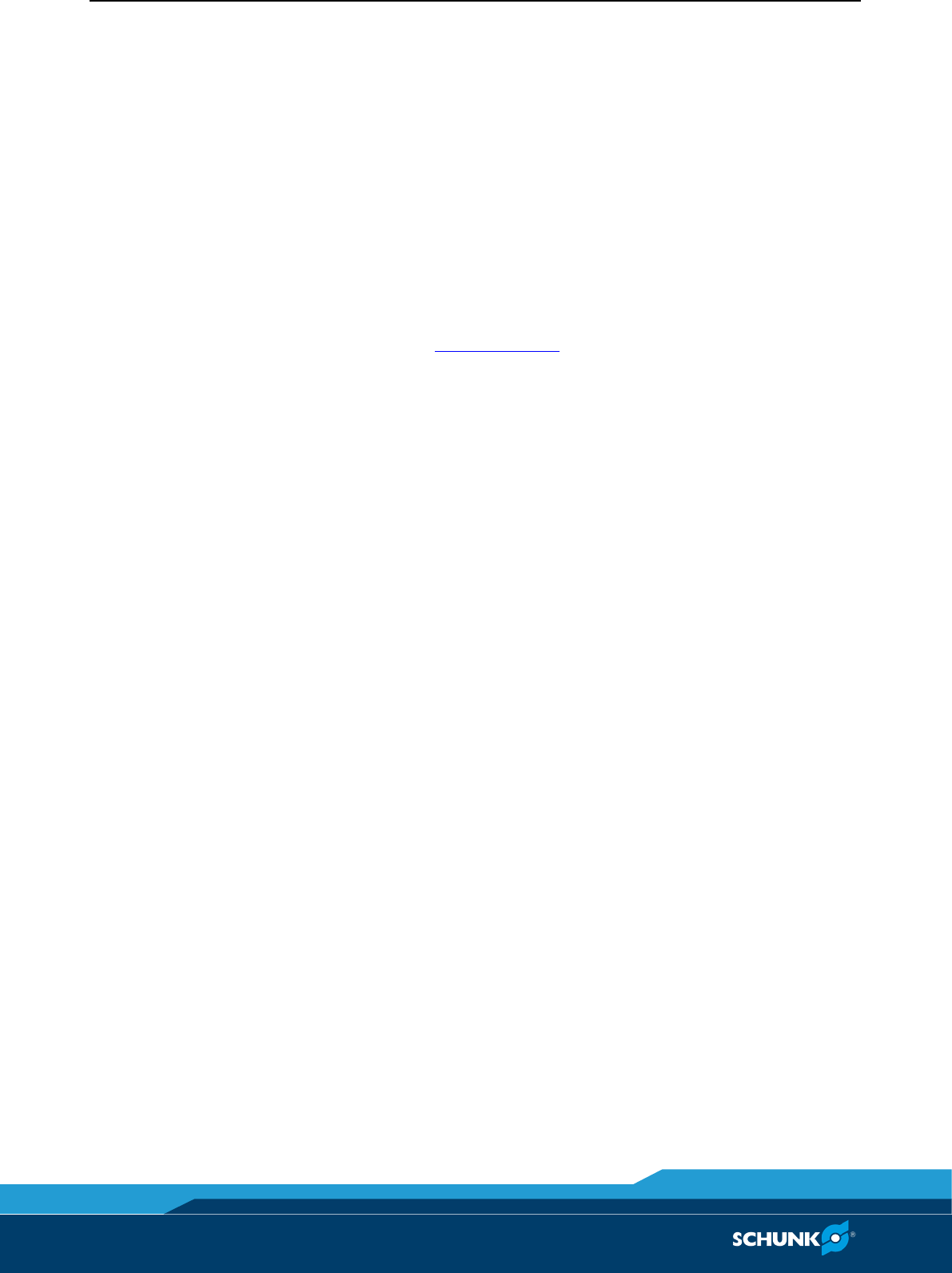
Basic safety notes
6 02.02_preliminary|Id. Nr. 8705401 |en
Basic safety notes
Intended use
The RSS radio system serves to transmit the sensor states via a ra‐
dio link from the transmitter unit to the receiver in the switching
cabinet.
The product is intended for installation in a machine/system. The
requirements of the applicable guidelines must be observed and
complied with.
The product may be used only in the context of its defined applica‐
tion parameters ( 6, Page 13).
The product is designed for industrial use.
To use this unit as intended, it is also essential to observe the
technical data and installation and operation notes in this manual
and to comply with the maintenance intervals.
Environmental and operating conditions
• Make sure that the product has a sufficient size for the applica‐
tion.
• Make sure that the environment is free from splash water and
vapors as well as from abrasion or processing dust.
• The radio link established by the system can experience tempo‐
rary or permanent interference through external influences. As
a result, the states of the sensors are not updated at the re‐
ceiver for the duration of the interference. The interference is
only reported by the receiver after the watchdog time has
lapsed. Ensure that such interferences cannot cause any dam‐
age. Adjust the watchdog time to a time suitable for your pro‐
cess.
• In the 868.3 MHz range, the system does not comply with the
EMC regulation for interference immunity to incoming radio
waves. Losses of radio telegrams may occur in this range. Dis‐
turbances become more likely if the antenna is further than 25
cm away from the receiver. The application must therefore be
tested each time before being integrated.
• The radio switch receiver must not be used in combination with
devices that are directly or indirectly used to safeguard the
health or life of per‐sons, or devices which, when in operation,
could cause danger to persons, animals or property! This is due
2
2.1
2.2
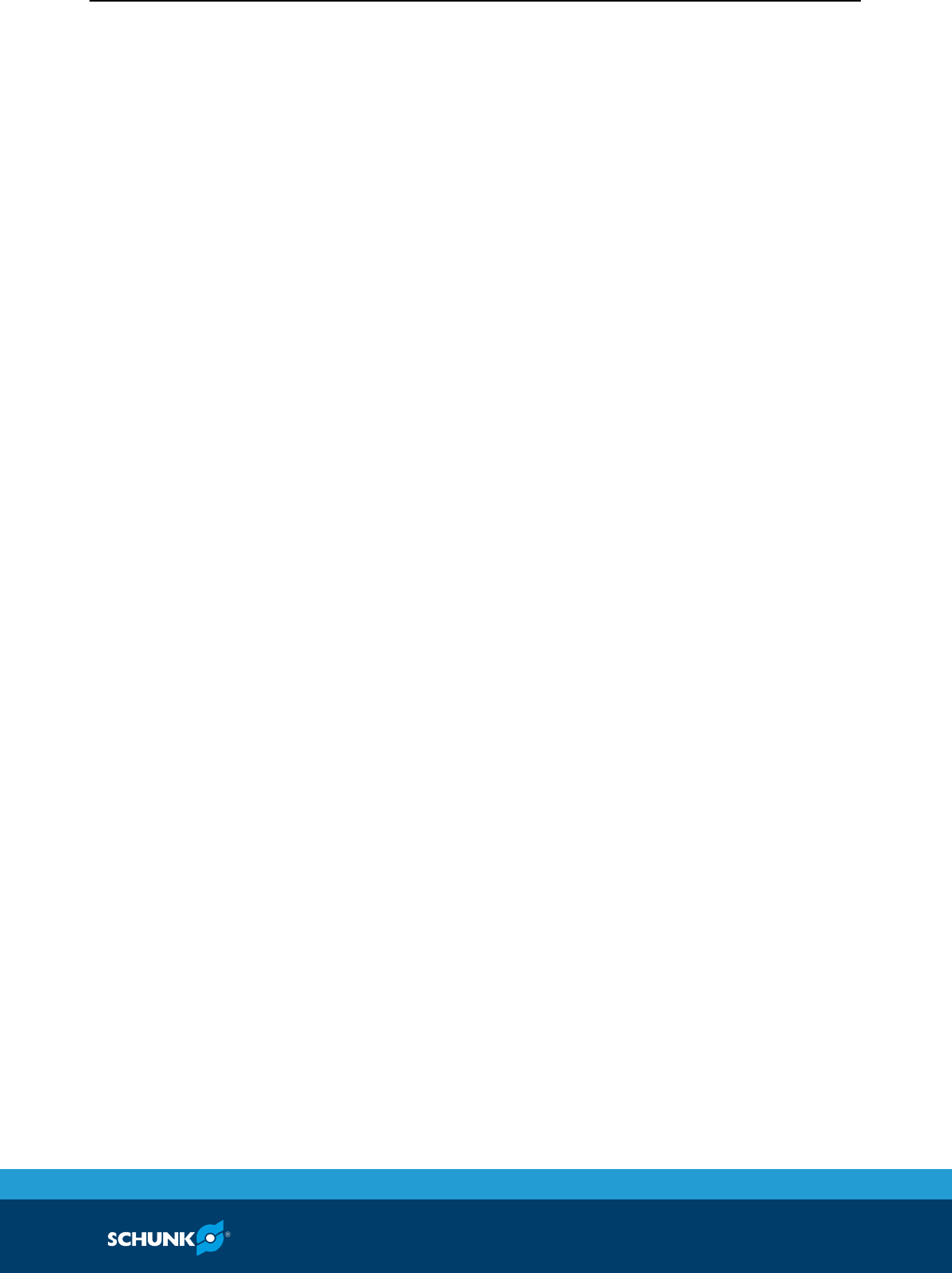
Basic safety notes
02.02_preliminary|Id. Nr.
8705401 |en
7
to the radio switch receiver’s classification as “Class 2 Equip‐
ment” in accordance with ETSI EN 301 489‐3 V1.4.1 (2202‐08)
“Specific conditions for short‐range devices (SRD)”.
• The time between evaluable telegrams must be at least 50ms.
Product safety
Dangers arise from the product, if:
• the product is not used in accordance with its intended pur‐
pose.
• the product is not installed or maintained properly.
• the safety and installation notes are not observed.
Avoid any manner of working that may interfere with the function
and operational safety of the product.
Wear protective equipment.
NOTE
More information is contained in the relevant chapters.
Protective equipment
Provide protective equipment per EC Machinery Directive.
Constructional changes
Making constructional changes
Modifications, constructional changes and subsequent work, e.g.
additional threads, drill holes and safety devices may impair the
operation and safety or damage the product.
• Constructional changes may only be done with SCHUNK's per‐
mission.
Personnel qualification
Inadequate qualifications of the personnel
If the personnel working with the product is not sufficiently quali‐
fied, the result may be serious injuries and significant property
damage.
• All work may only be performed by qualified personnel.
• Before working with the product, the personnel must have read
and understood the complete assembly and operating manual.
2.3
2.3.1
2.3.2
2.4
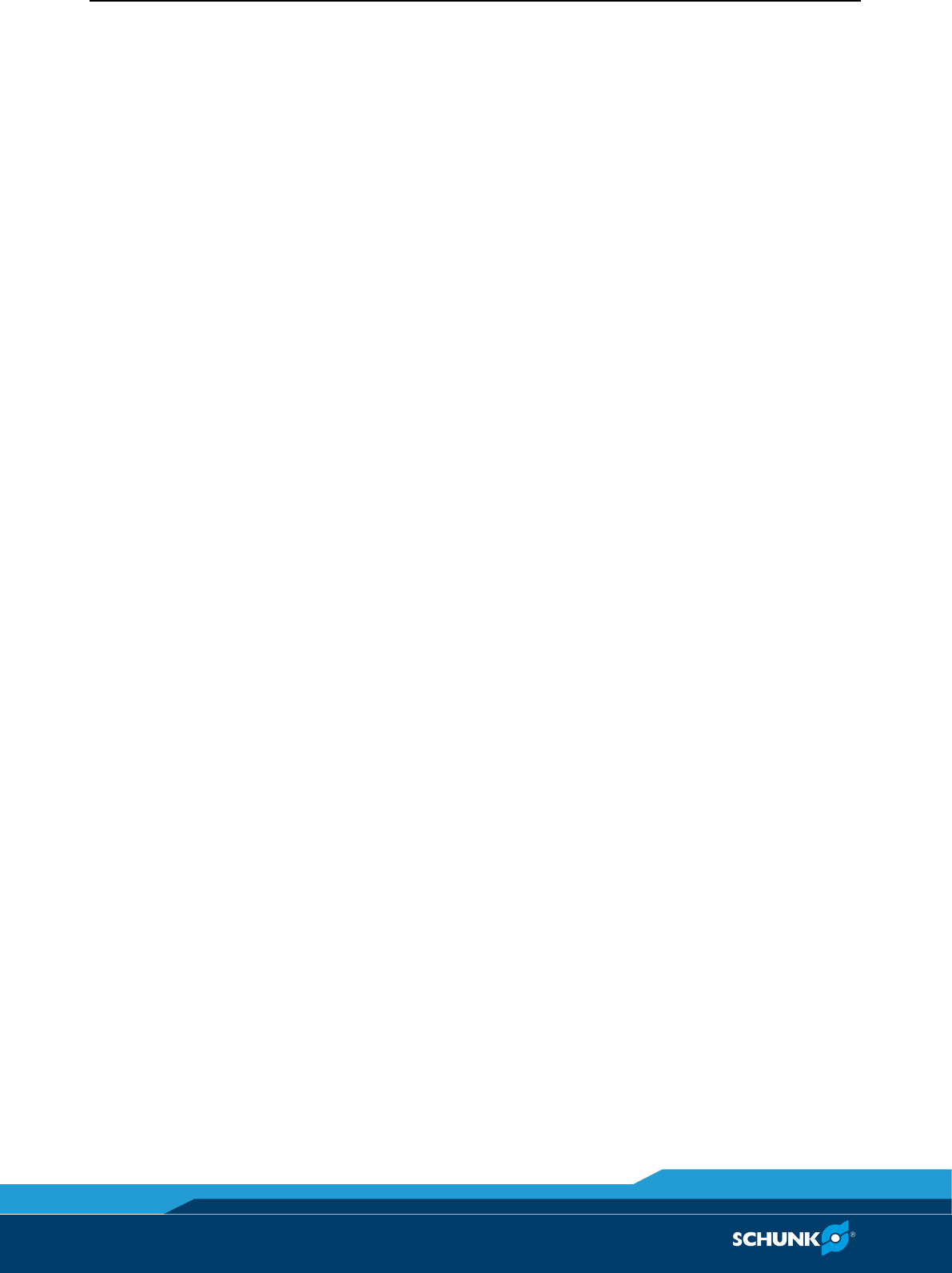
Basic safety notes
8 02.02_preliminary|Id. Nr. 8705401 |en
• Observe the national safety regulations and rules and general
safety instructions.
The following personal qualifications are necessary for the various
activities related to the product:
Due to their technical training, knowledge and experience, trained
electricians are able to work on electrical systems, recognize and
avoid possible dangers and know the relevant standards and regu‐
lations.
Pneumatics specialists have been trained for this particular area of
responsibility and know the relevant standards and regulations.
Hydraulic specialists have been trained for this particular area of
responsibility and knows the relevant standards and regulations.
Due to its technical training, knowledge and experience, qualified
personnel is able to perform the delegated tasks, recognize and
avoid possible dangers and knows the relevant standards and reg‐
ulations.
Instructed persons were instructed by the operator about the del‐
egated tasks and possible dangers due to improper behaviour.
Due to its technical training, knowledge and experience, service
personnel of the manufacturer is able to perform the delegated
tasks and to recognize and avoid possible dangers.
Notes on particular risks
Generally valid:
• Remove the energy supplies before installation, modification,
maintenance, or adjustment work.
• Make sure that no residual energy remains in the system.
• Do not move parts by hand when the energy supply is connect‐
ed.
• Do not reach into the open mechanism or the movement area
of the module.
• Perform maintenance, modifications, and additions outside of
the danger zone.
• For all work, secure the unit against accidental operation.
• Take a precautionary approach by maintenance and disassem‐
bly.
• Only specially trained staff should disassemble the module.
Trained electrician
Pneumatics specialist
Hydraulic specialist
Qualified personnel
Instructed person
Service personnel of
the manufacturer
2.5
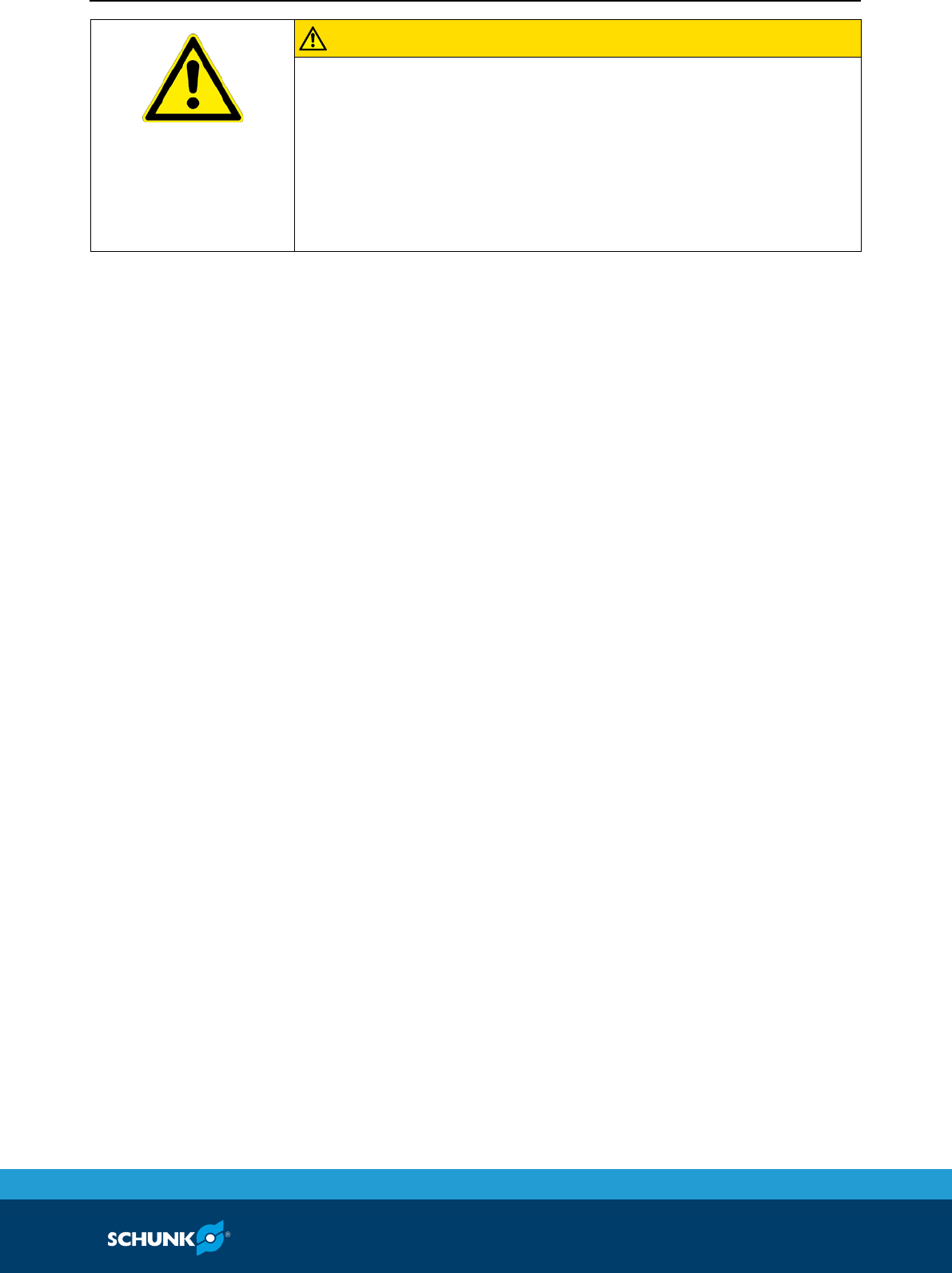
Basic safety notes
02.02_preliminary|Id. Nr.
8705401 |en
9
CAUTION
Possible risk of injury due to electrostatic energy!
Components or assembly groups may become electrostatically
charged. When touched, the electrostatic discharge can trigger a
startle response, which can result in injuries.
• The operator must ensure that all components and assembly
groups are included in the local equipotential bonding in line
with the applicable regulations.
NOTE
• The equipotential bonding must be installed by a specialist
electrician in line with the applicable regulations, paying partic‐
ular attention to the actual conditions in the working environ‐
ment.
•
The effectiveness of the equipotential bonding must be verified
by a specialist electrician through regular safety measurements.
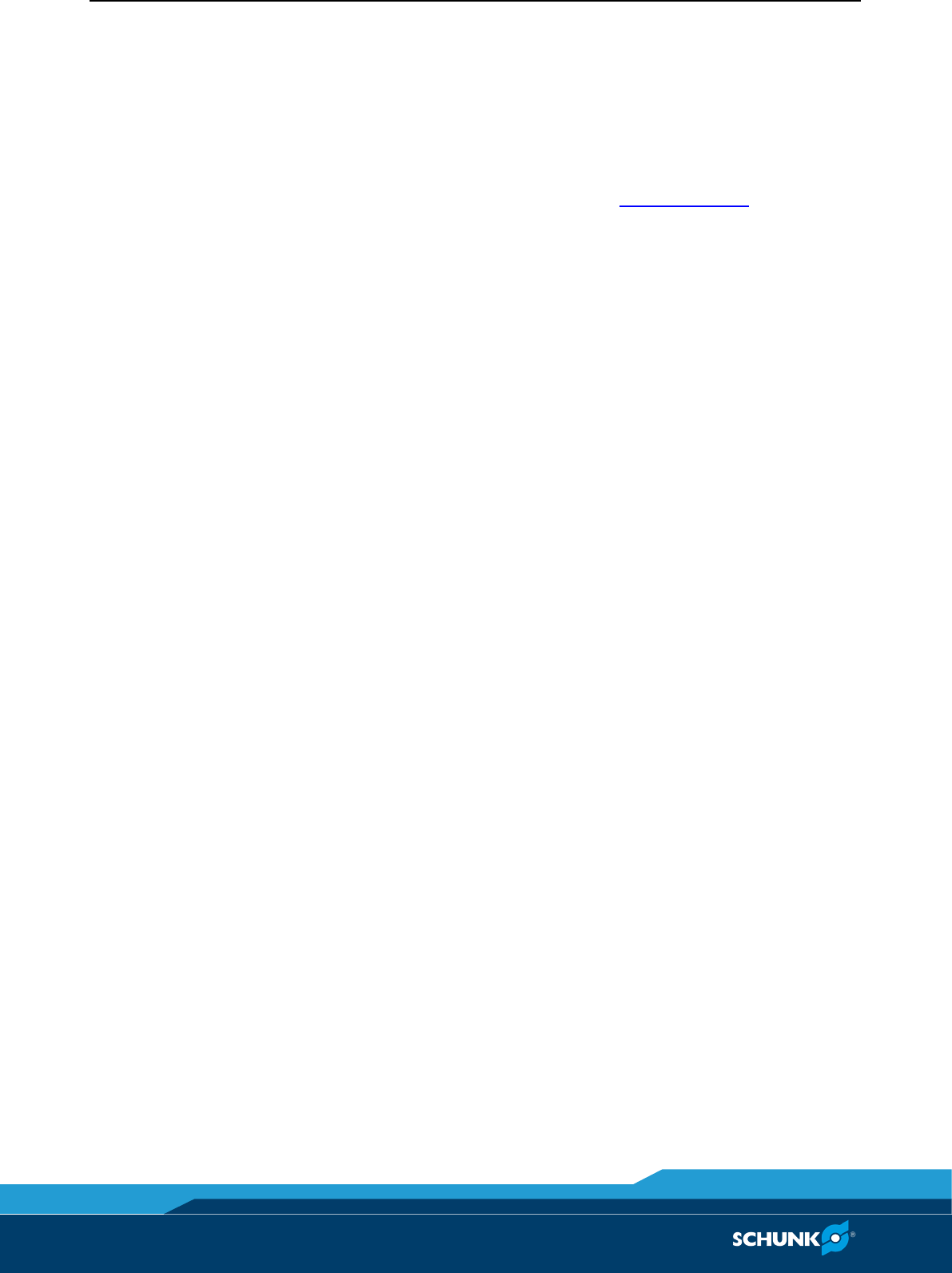
Warranty
10 02.02_preliminary|Id. Nr. 8705401 |en
Warranty
If the product is used as intended, the warranty is valid for 24
months from the ex‐works delivery date under the following con‐
ditions:
• Intended use in 1‐shift operation
• Observe the applicable documents ( 1.2, Page 5)
• Observe the ambient conditions and operating conditions Link
Ungebungs‐ und Einsatzbedingungen
Parts touching the workpiece and wearing parts are not included
in the warranty.
The warranty of the battery is valid for 36 months from the deliv‐
ery date to the production facility if used appropriately.
3
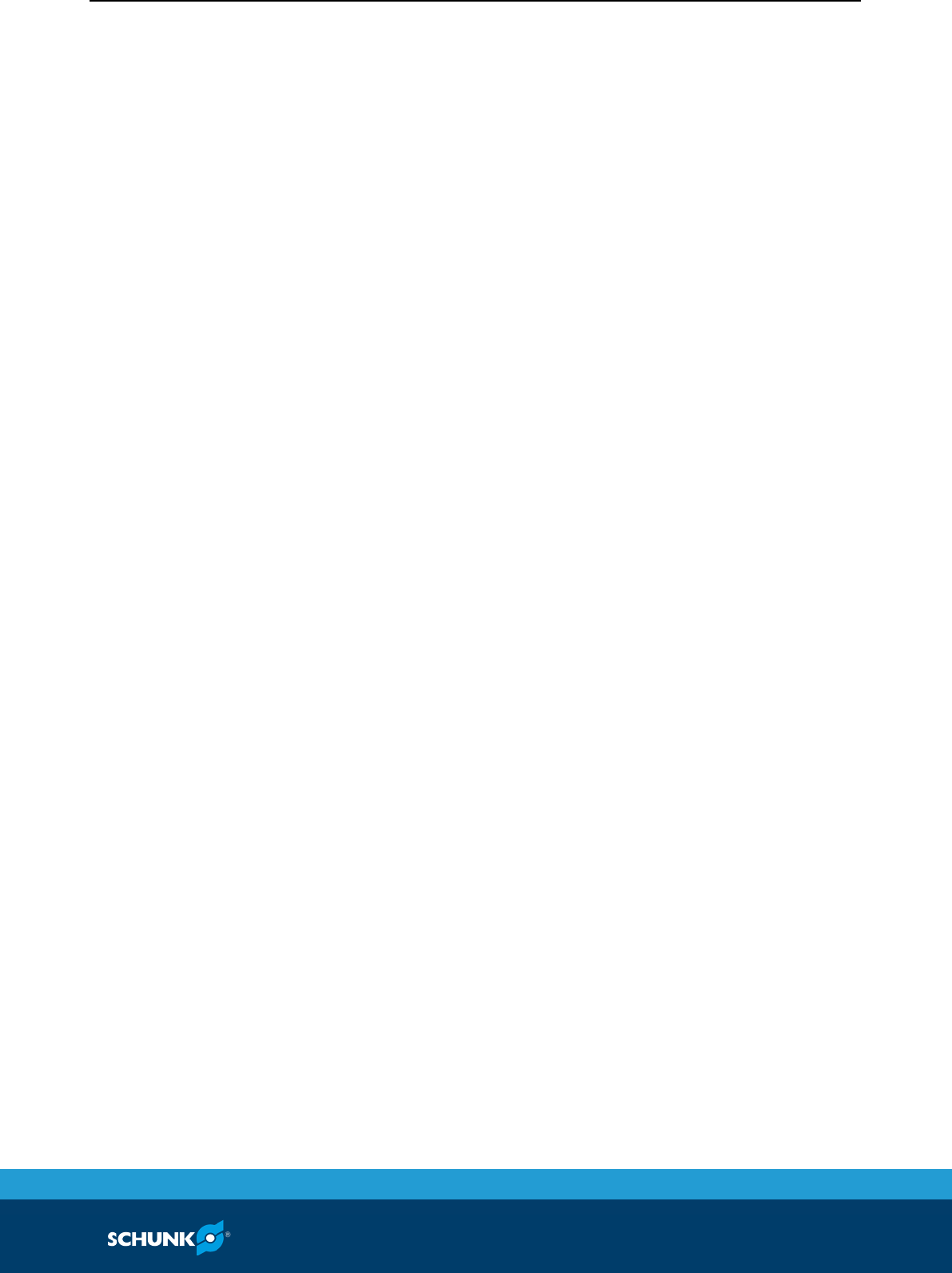
Scope of delivery
02.02_preliminary|Id. Nr. 8705401 |en
11
Scope of delivery
The scope of delivery includes
• RSS radio sensor system with FCC/IC certification Receiver R1,
transmitter T2‐US/CA in the version ordered
• Accessory pack
4
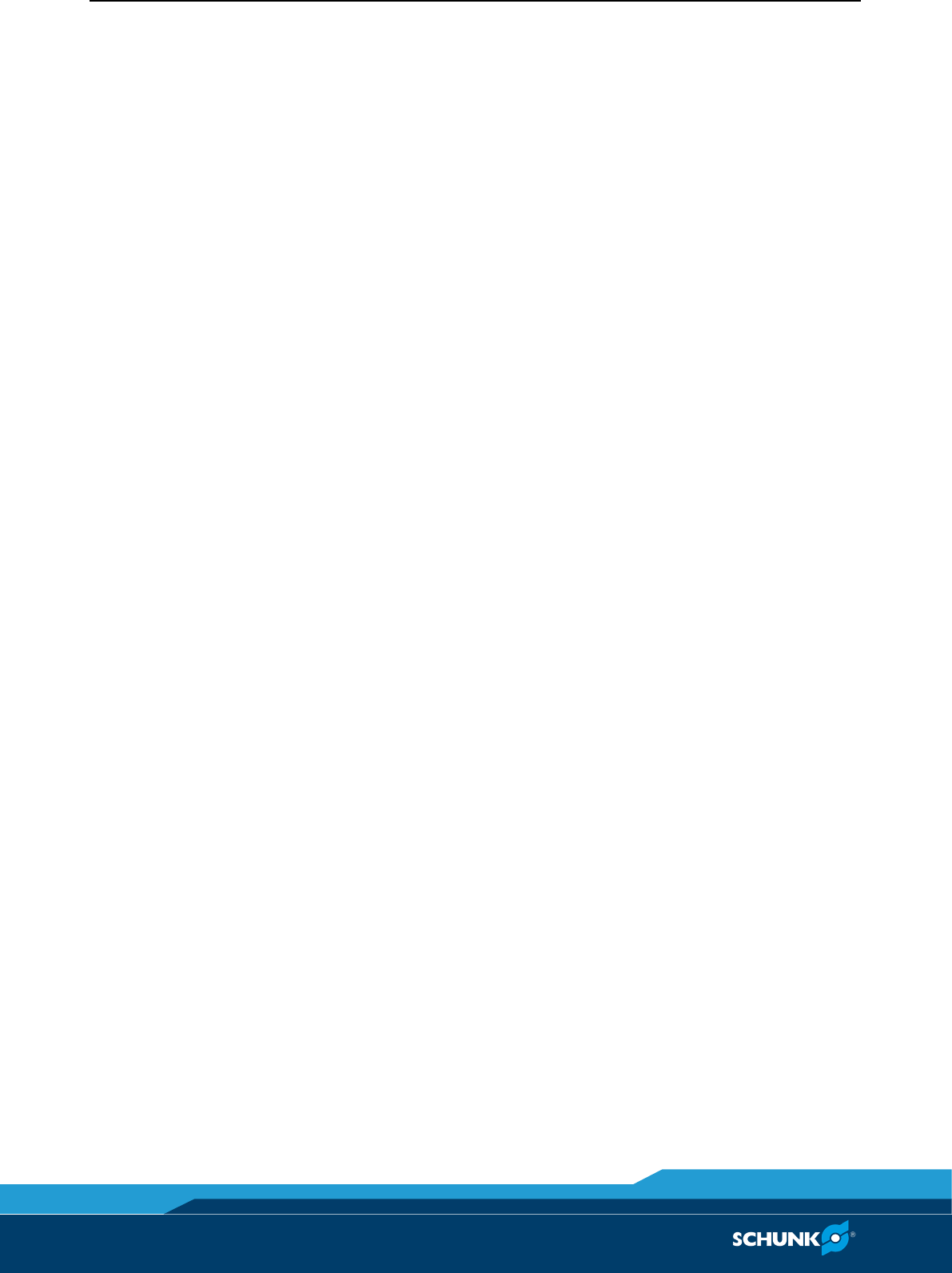
Accessories
12 02.02_preliminary|Id. Nr. 8705401 |en
Accessories
The following accessories, which must be ordered separately, are
required for the product:
• Sensors: 2 pieces per gripper
– either RMS 80 plus specific adapter kit of gripper
– or RMS 22
– or other sensors for normally open contact, without own
power consumption
• Radio transmitter: One RSS T2 transmitter is required per 2
sensors
• Radio receiver: One RSS T2 radio transmitter is required per
RSS R1 radio receiver
• Antenna: One RSS‐R‐A antenna per radio receiver
A wide range of accessories are available for this product
For information about which accessories can be used with the ap‐
propriate product version see catalog.
5
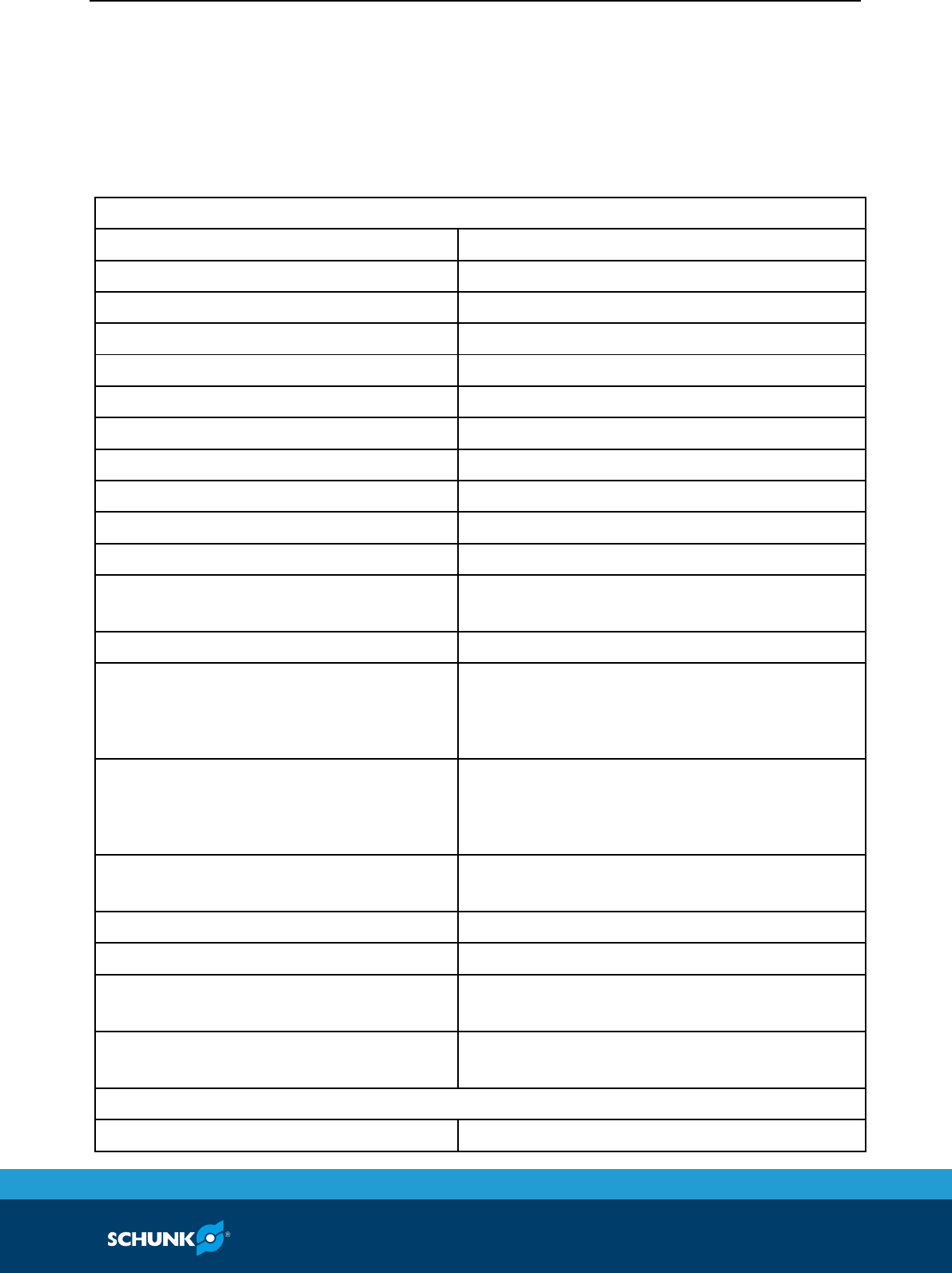
Technical data
02.02_preliminary|Id. Nr. 8705401 |en
13
Technical data
More technical data are included in the catalog data sheet. Which‐
ever is the latest version.
Technical Data RSS‐R1
Recipient
ID number
0377700
Receiver frequency [MHz]
868.3
Nominal voltage [VDC]
24
min. voltage [V]
10
Max. voltage [V]
30
max. current on contact per channel [mA]
500
Protocol
Enocean Standard
Short‐circuit‐proof
yes
IP rating
20
Assembly type
Snapping on DIN rail (EN50022)
Dimensions
Assembly drawing
Connection technology
CAGE CLAMP® connection 0.08...2.5 mm²
WAGO Multi Connection System Series 722
Housing material
Polycarbonate
Ambient temperature [°C]
Min.
Max.
0
55
Stocking temperature [°C]
Min.
Max.
‐25
+75
Electromagnetic compatibility (EMC)
CE compliant to EMC Directive 89/336/EEC and
R&TTE
Interference signals
EN 61000‐6‐4
Radiated interference
EN 61000‐6‐2
Further standards
ETSI EN 301 489‐1 (09/01), ETSI EN 301 489‐3
(11/01), ETSI EN 300 220‐1 (09/00)
Transmission license En Ocean
Receiver RCM 100
CETECOM test report 2_3041‐01‐02/02
DAR test report P0ZNNP1P
Antenna
ID number
0377730
6
6.1
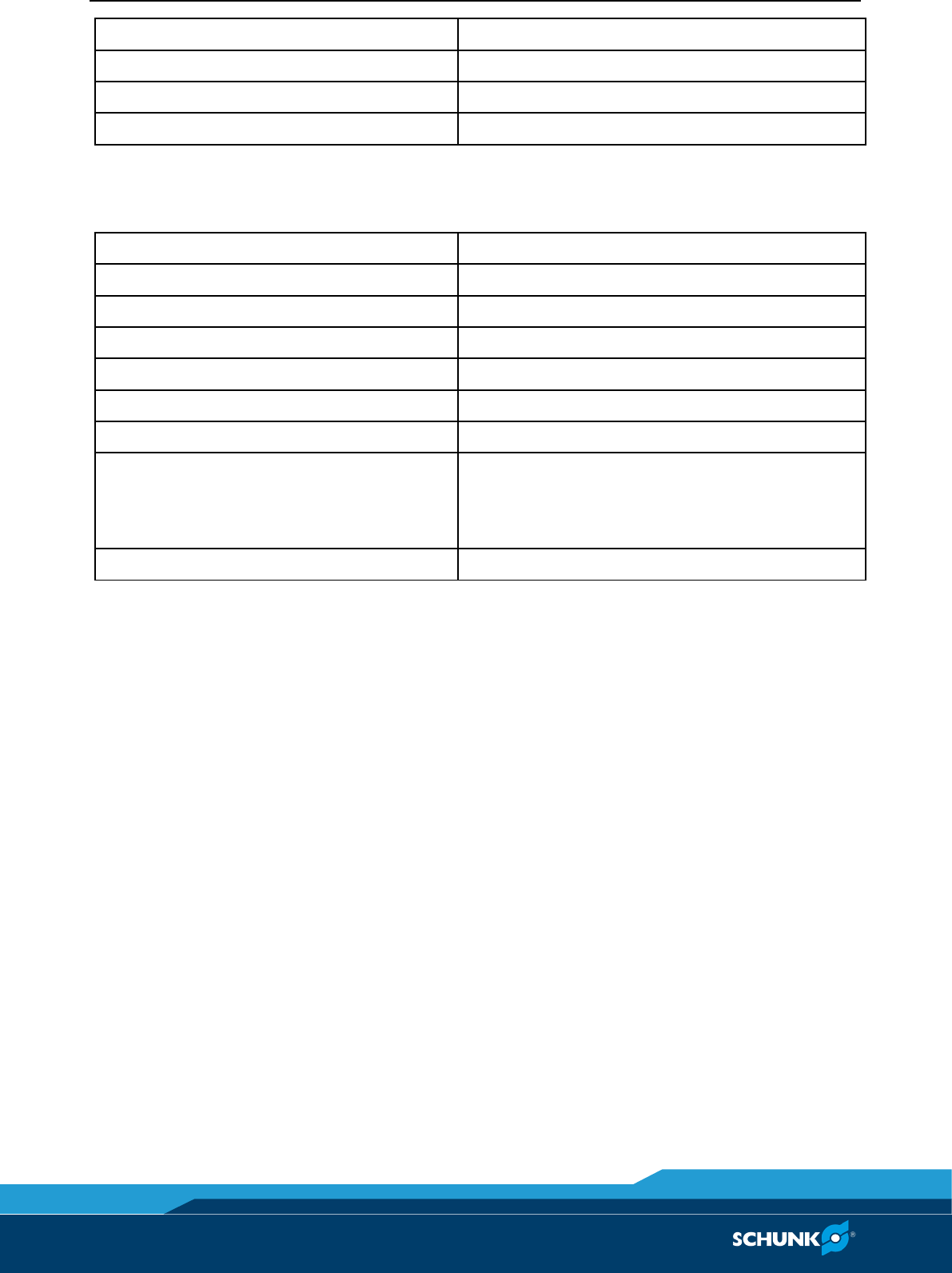
Technical data
14 02.02_preliminary|Id. Nr. 8705401 |en
Assembly
Magnetic base
Cable length [m]
2
Connection at the cable end
SMA Mini
Application
Connection at the receiver RSS‐R1
Technical data ‐ RSS T2
ID number
0377717
Transmission frequency [MHz]
868.3
Sensor connection
2x M8
Integrated power supply
Lithium battery
Housing material
PUR
Protocol
Enocean Standard
IP rating
67
Ambient temperature [°C]
Min.
Max.
0
50
Weight [kg]
0.16
Information on radio link and range
The transmitter sends telegrams with 868 MHz to the receiver. The
receiver checks the incoming telegrams and uses them to control
its outputs.
This radio link is principally prone to interferences by other radio
systems or systems emitting radio signals. For reasons of availabil‐
ity, the presence of systems emitting radio waves – such as wire‐
less or mobile phones or PCs – in the immediate proximity of the
transmitter is to be avoided. We recommend observing a mini‐
mum air distance of at least one meter between receiver and in‐
terference source or between transmitter and interference source.
Since the radio signals represent electromagnetic waves, the signal
is damped on its route to the receiver. This means, the signal
strength decreases with increasing distance between transmitter
and receiver. Thus, the radio range is limited. In particular, the
range will also be significantly limited in case of irradiation above
400 MHz.
It must also be noted that the radio range is reduced by materials
between transmitter and receiver. For the practical application,
6.2
6.3
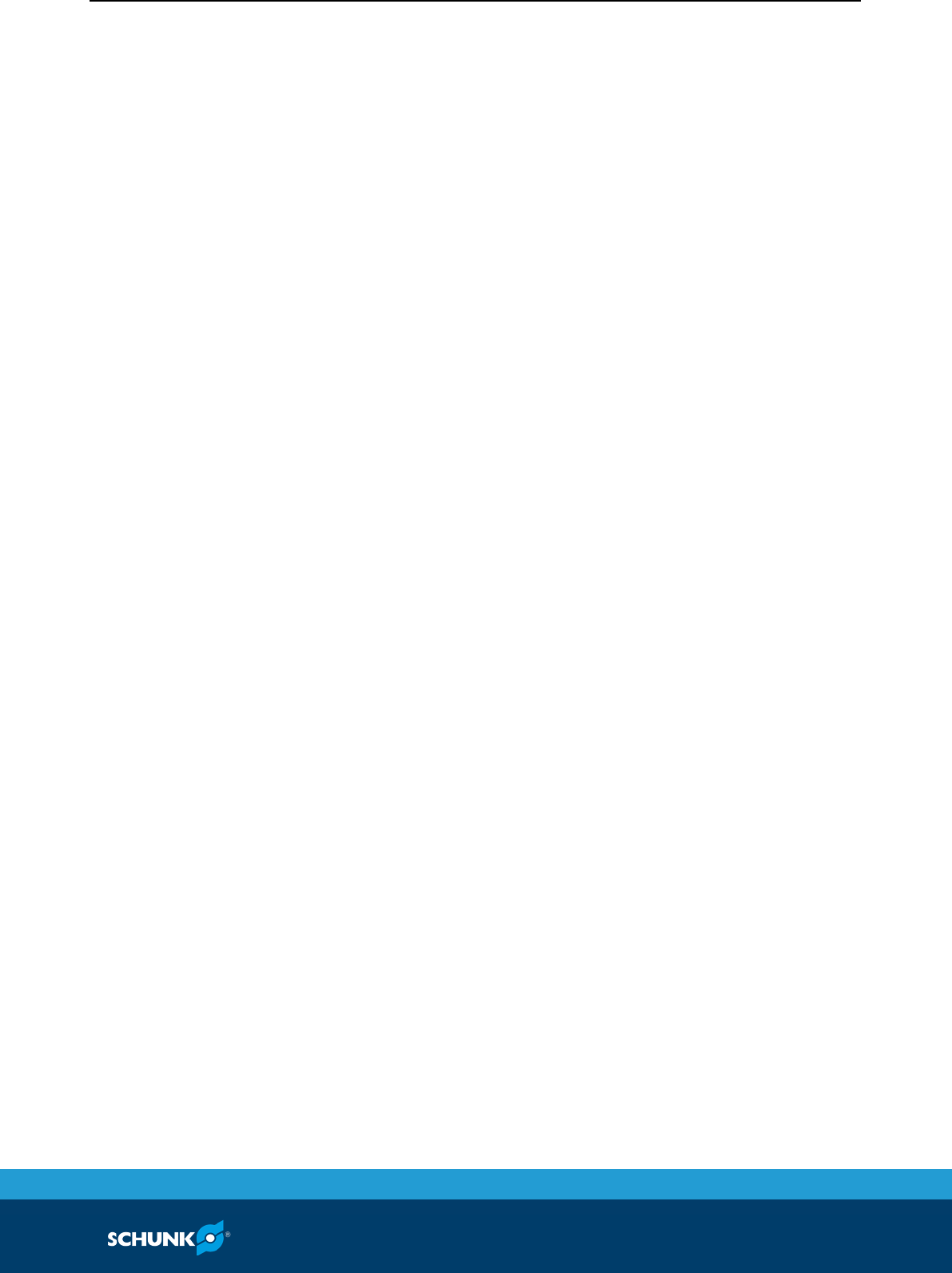
Technical data
02.02_preliminary|Id. Nr. 8705401 |en
15
this means that the construction materials used in buildings and
facilities (machines) play an important role for the evaluation of
the radio range. Some reference values that can be used to esti‐
mate the range are:
• Line of sight
– Typically 30 m range
• Concrete or brick walls
– Typically 20 m range
• Steel‐reinforced concrete walls
– Typically 10 m range
• Fire protection walls, elevator shafts ..
– Can be considered blockages.
• Turning centres
– The radio waves penetrate to the outside through various
slots and especially through the viewing glasses. It is difficult
here to make an exact statement on the range. Based on
our experience, a range of at least 3 m must be expected.
• Cordless telephone at a distance of less than 1m
– Range approx. 25 cm
The distance from the receiver to other transmitting devices also
radiating high‐frequency signals (computers, video systems, etc.)
should be at least 0.5 m.
Using the receiving strength LED (SI) to our receiver it is easy to
decide whether the system provides secure transmission for the
intended location or if strong interferences are present.
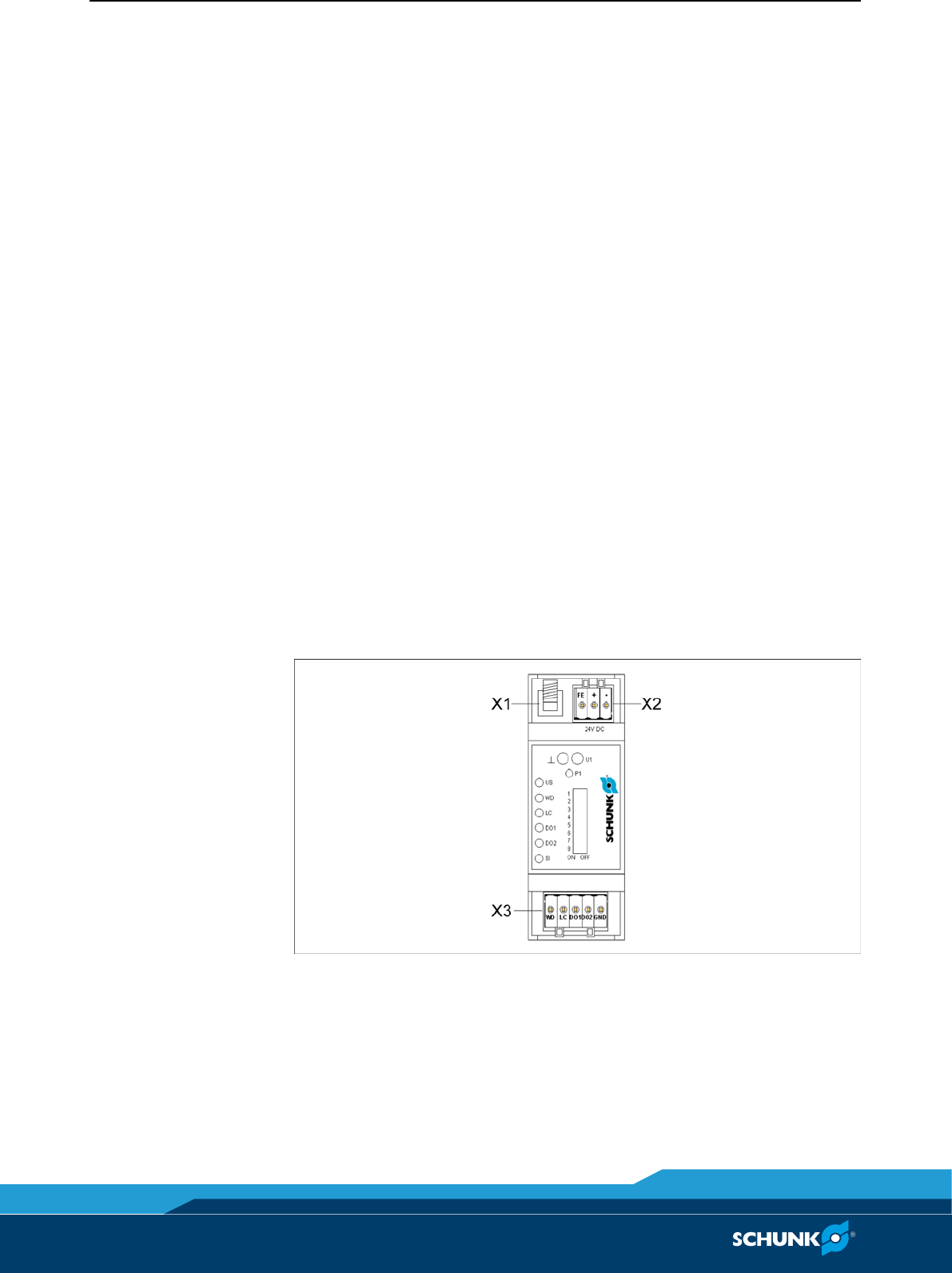
Assembly
16 02.02_preliminary|Id. Nr. 8705401 |en
Assembly
Assembly of the transmitter RSS T2
1 Install the housing in a suitable position next to the sensor fas‐
tening using two screws M4.
2 ‐ Install the sensor (closer) at the gripper.
3 Fasten the M8 sensor plugs with screws to the transmitter.
4 For adjustment of the sensors the magnetic brackets of the
transmitter can be plugged into ‘test mode‘ position. Now you
can see the individual sensors’ status on the LEDs. Position the
sensors at a suitable position and finally screw the magnetic
switch onto the ‚normal mode‘ position.
5 Never leave the magnetic bracket in ‘test mode‘ position, oth‐
erwise the battery of the transmitter will be discharged within
a few days!
NOTE
Always use closers. Otherwise the system cannot recognize a
changing status of the sensors, i.e. if a sensor is open while the
signal of another sensor changes.
Assembly and electrical connection of the RSS R1 receiver
1 Mount the receiver in a switching cabinet located less then 10
m from the transmitter by snapping it onto a DIN track
(EN50022).
2 Connect the receiver:
Antenna socket X1:
‐ SMA socket for external antenna (we recommend our RSS‐R‐
7
7.1
7.2
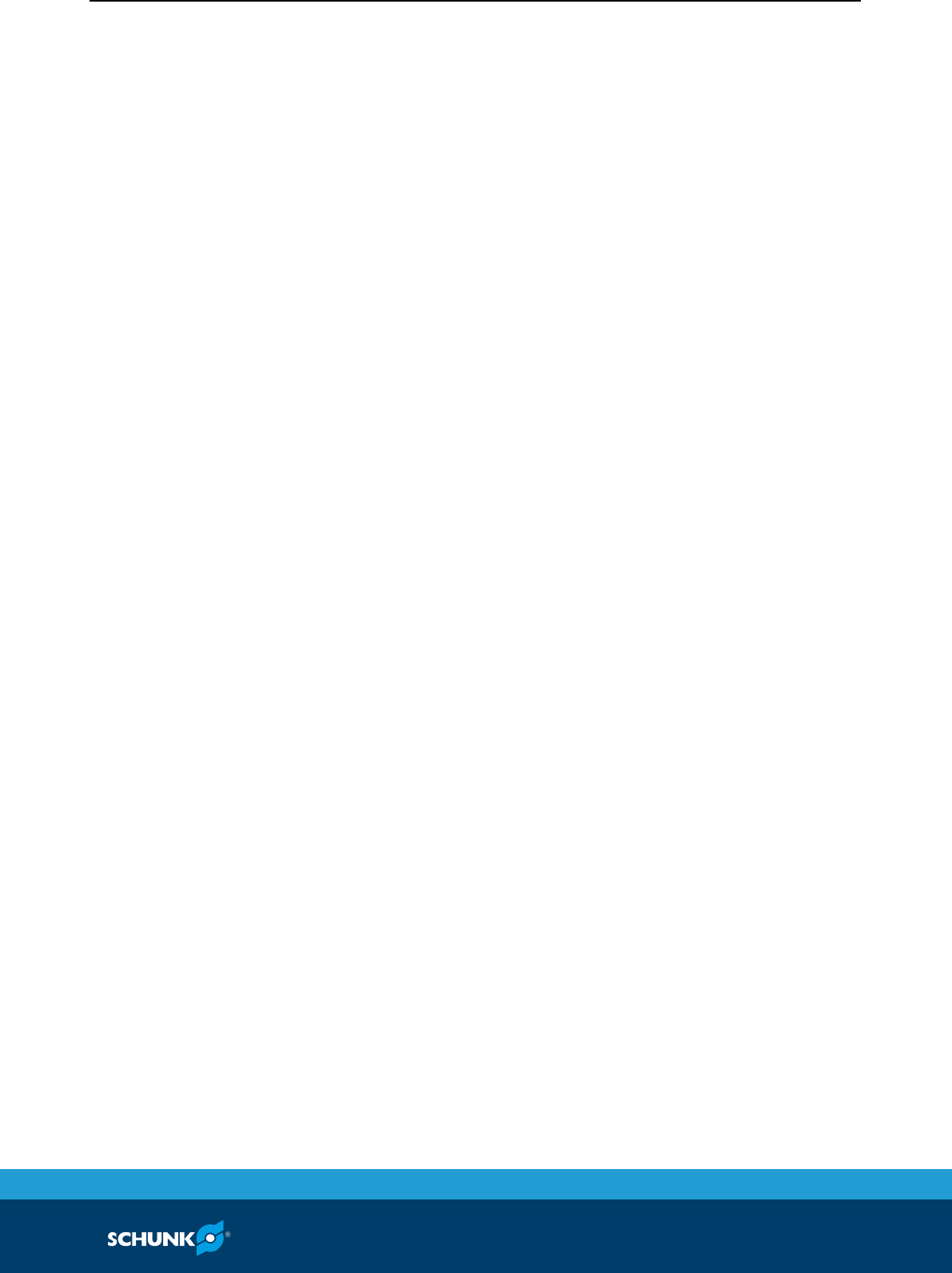
Assembly
02.02_preliminary|Id. Nr. 8705401 |en
17
A antenna, ID No. 0377730)
Connector X2:
‐ X2.1 FE Function ground
‐ X2.2 + Supply DC 24DCV+external
‐ X2.3 ‐ Supply DC 24V‐external
Connector X3:
‐ X3.1 WD Output watchdog, high signal, if radio IO
‐ X3.2 LC Output limit value, high signal, if battery IO, i.e. has
still more than 1 week capacity remaining.
‐ X3.3 DO1 Output 1, sensor signal 1, Low, if sensor actuated.
‐ X3.4 DO2 Output 2, sensor signal 2, Low, if sensor actuated.
‐ X3.5 GND Reference ground for the outputs
3 Mount the antenna on the top of the switching cabinet using
the magnetic base.
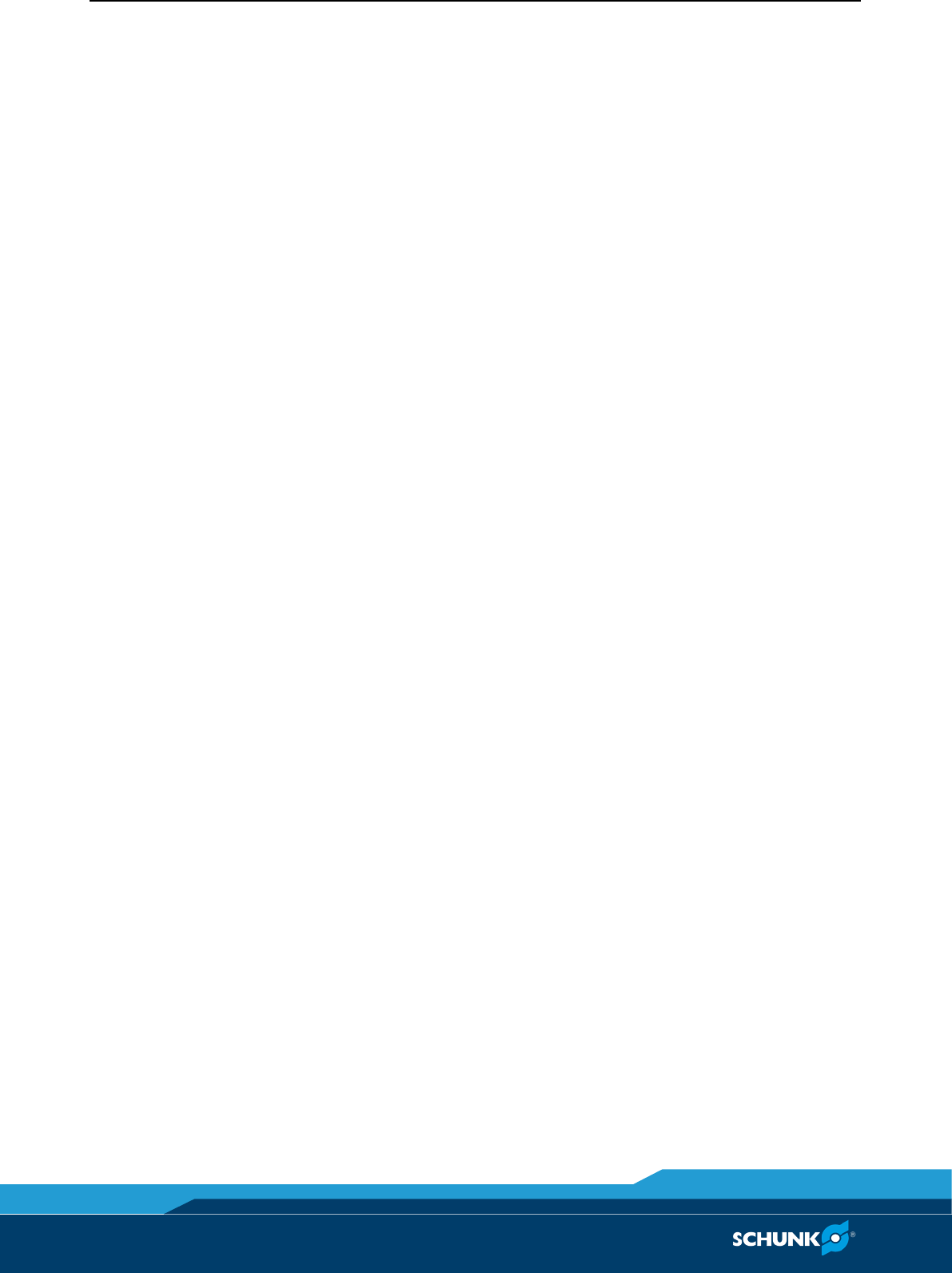
Start‐up
18 02.02_preliminary|Id. Nr. 8705401 |en
Start‐up
General information on commissioning
Before commissioning, please check the device for any transport
damages. Do not start up the device if it is mechanically damaged.
Please read this assembly and operating manual carefully and ob‐
serve the technical information as well as the legal requirements
relevant to your country.
NOTE
The components are equipped with electronic elements which
could be destroyed in case of an electrostatic discharge. When
handling the components, it must be ensured that environment
(persons, workstation and packaging) are proper
ly grounded. Do
not touch conductive elements.
Notes on installation
When installing the antenna and antenna cable assembly group, it
is imperative to avoid any proximity to sources with transient dis‐
turbances such as fluorescent tubes with a faulty starter, frequen‐
cy converters or power cables. They could result in interrupted
communication and therefore lead to incorrect initial states.
Notes on connecting the antenna
Only use suitable antennas (e.g. WAGO 758‐910 incl. 2.5 m RG174
connection cable and SMA connector; see accessories). The an‐
tenna must be fixed on a plate with the minimum dimensions of
25 cm x 25 cm. The antenna and the antenna cable must be at
least 30 cm away from sources of interference and the antenna
must be at least 35 cm away from the next wall at the side. The
antenna cable must under no circumstances be bent sharply as
this could result in permanent damage to the antenna cable
(RG174 bending radius > 15 mm).
Preconditions for commissioning
The voltage supply must be applied and the external antenna must
be connected prior to commissioning.
Programming the transmitter to the receiver
1 Switch DIP 1 to ‘on’ and immediately back to ‘off’.
2 to energize the sensor from the transmitter.
8
8.1
8.2
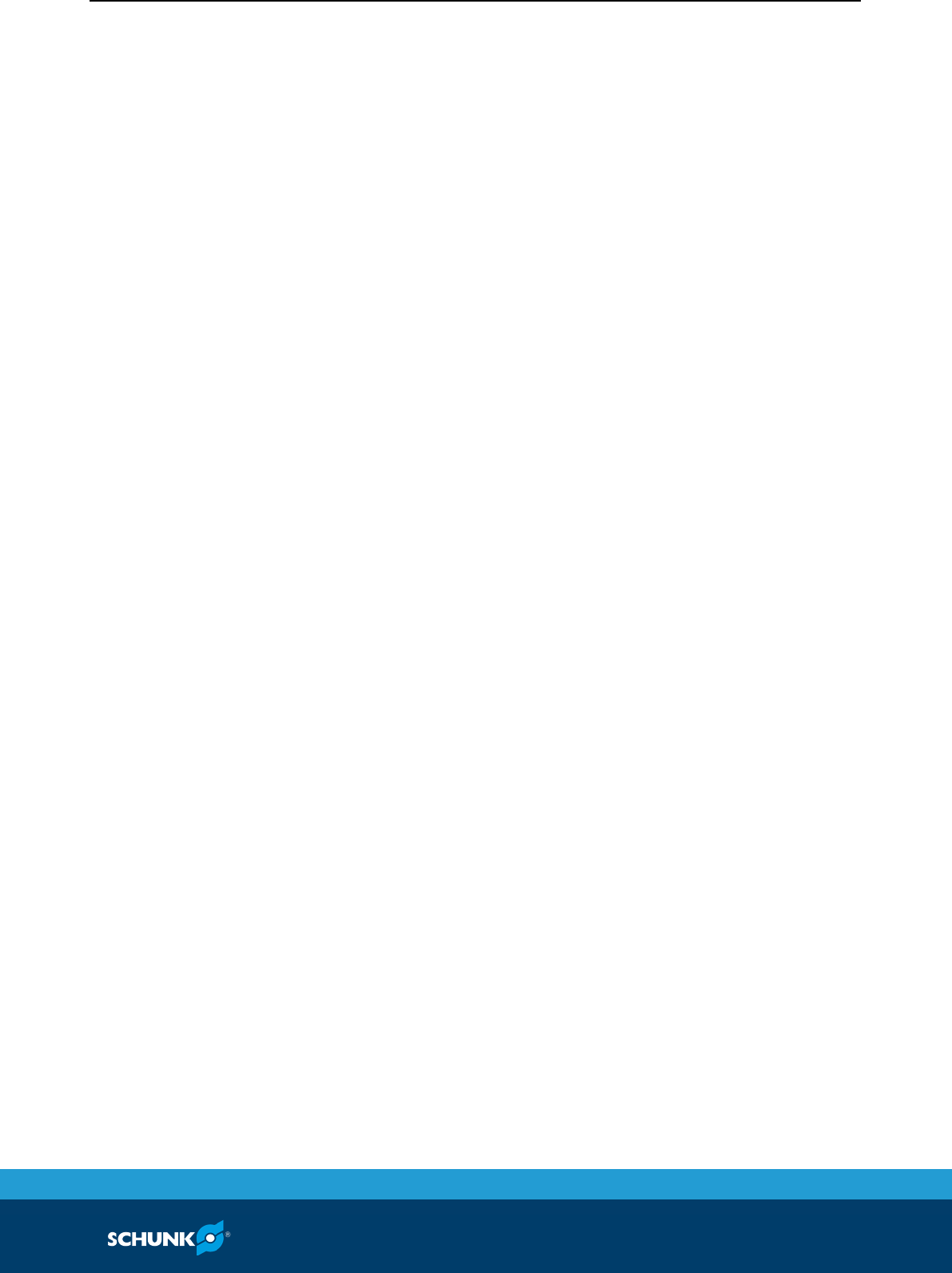
Start‐up
02.02_preliminary|Id. Nr. 8705401 |en
19
3 Wait for 15 seconds.
4 Now, the receiver should indicate the condition of the sensors
by means of the LEDs. Anymore the WD LED lights up briefly
approx. every 10 seconds.
5 Please try a second time if the learning procedure has failed.
Ideally, no second RSS system should radio in the immediate
vicinity during the learning phase.
Testing the antenna position
1 Observe the LED ‘SI’. This LED signals the current quality of the
radio link. This LED should preferably light up or blink green.
2 If necessary, move the antenna closer to the transmitter or
reposition the antenna to avoid any solid obstacles between
antenna and transmitter.
Adjusting the watchdog time at the receiver
1 Adjust watchdog time to best suit your process. The transmit‐
ter transmits a presence signal every second to monitor the
transmission path. If no signal is received for longer than the
set watchdog time, the 'WD' LED lights up until the next signal
is received. The 'WD' output then signals through 0 VDC the
down‐time of the transmission path.
2 Switch Dip 4 to on.
3 Turn the potentiometer clockwise to extend the time. The set
time can be determined from the flash rate of the WD LED.
With DIP 8 switched off, the time can be varied between 0 and
one second. SCHUNK recommends setting the time to 15 sec‐
onds with DIP 8 switched on.
4 Switch DIP 4 to 'off' (leave DIP 8 in the selected position!).
8.3
8.4
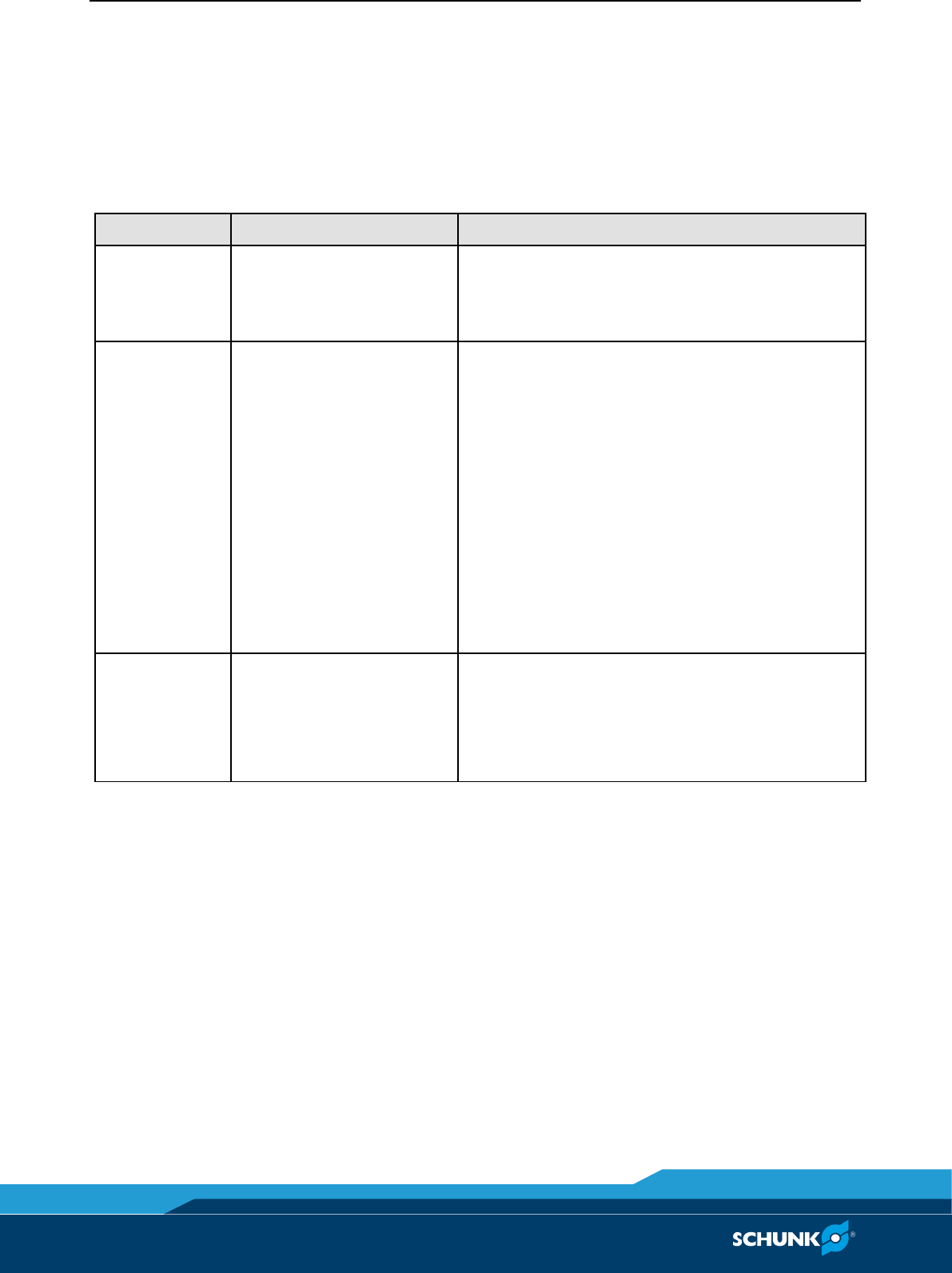
Functional description
20 02.02_preliminary|Id. Nr. 8705401 |en
Functional description
RSS‐R1
LED
LED color
Status
Meaning
US (green)
Off
On
Status of voltage supply
• No voltage supply present
• 24 V DC OK
WD (red)
Off / Flash
0.5 Hz blinking
2 Hz
On
Status system check and operating mode
• Operating status active (reception active)
“Flashing” of 15 ms indicates reception of a
“taught” telegram
• Learning status
• Missing assignment; Sensor must be
“taught“
• Watchdog addressed (non‐saving), neither
of 2 data telegrams of the taught sensor
were received within the monitoring time.
(The output behaves inversely.)
LC (yellow)
Off
On
0.5 Hz blinking
Status of limit value message (MIN indicator)
• Limit value fallen below ‐ output LOW
• Limit value not reached ‐ output HIGH
• Learning mode active via DIP3 and DIP4
9
9.
1
9.1.1
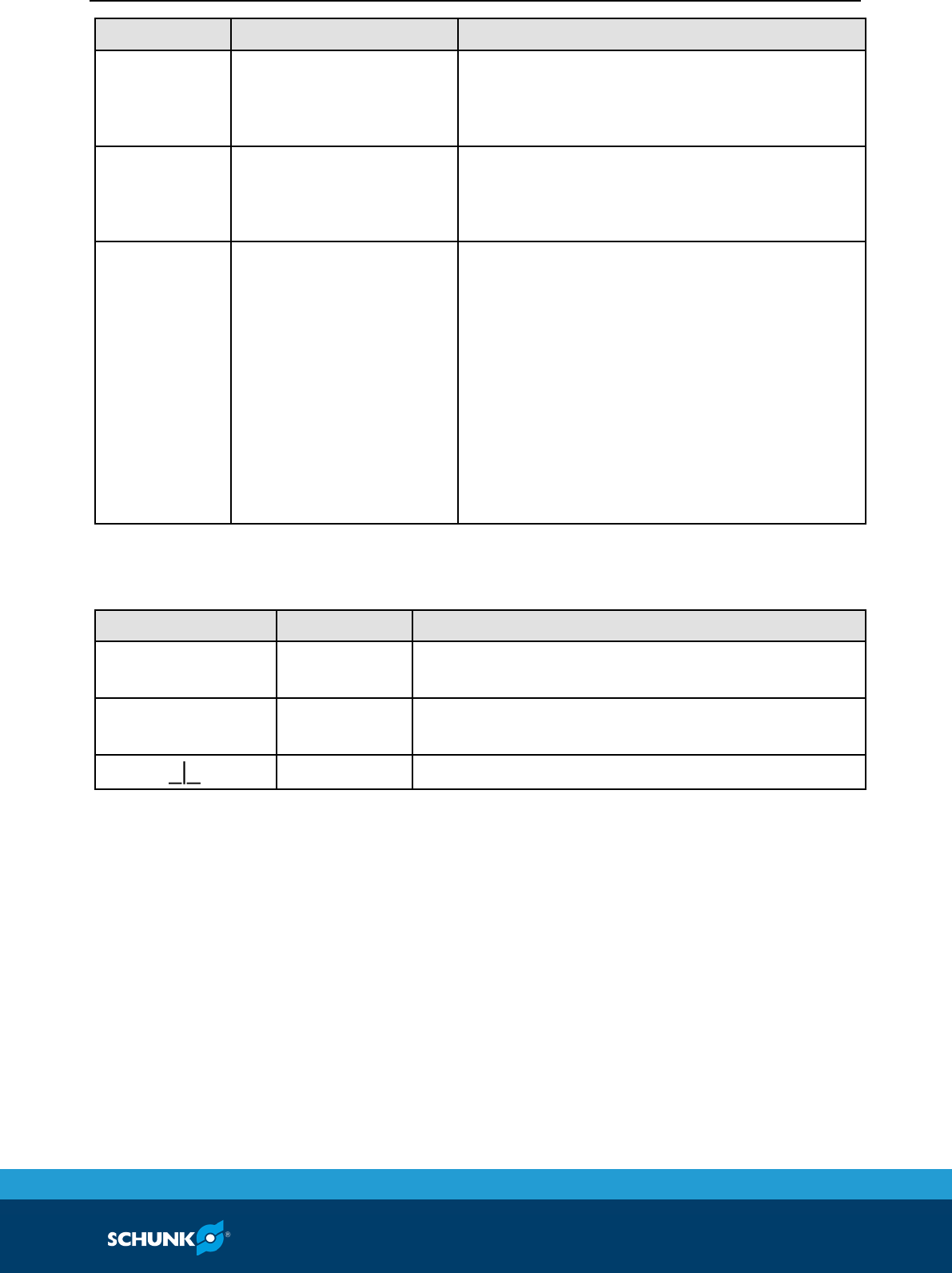
Functional description
02.02_preliminary|Id. Nr. 8705401 |en
21
LED color
Status
Meaning
DO1 (yellow)
Off
On
Status of Sensor 1
• Status 0 output LOW
• Status 1 output HIGH
DO2 (yellow)
Off
On
Status of Sensor 2
• Status 0 output LOW
• Status 1 output HIGH
SI
(yellow/
red)
LED green continuous
light
LED green blinking
LED orange continuous
light
LED orange blinking
LED red continuous light
LED red blinking
Indication of the signal strength
Signal optimal
Signal excellent
Signal good
Signal medium
Signal poor
Signal critical
Definition of ‘blinking’: 200 ms on and 200 ms
off, alternating
Measuring jacks
Designation
Type
Meaning
P1
Potentiometer
Adjustment of time and limit value (value accepted
with DIP switch)
U1
Jack
Measuring jack to adjust the watchdog and limit
values ac‐cording to voltage diagram
Jack
Reference potential
9.1.2
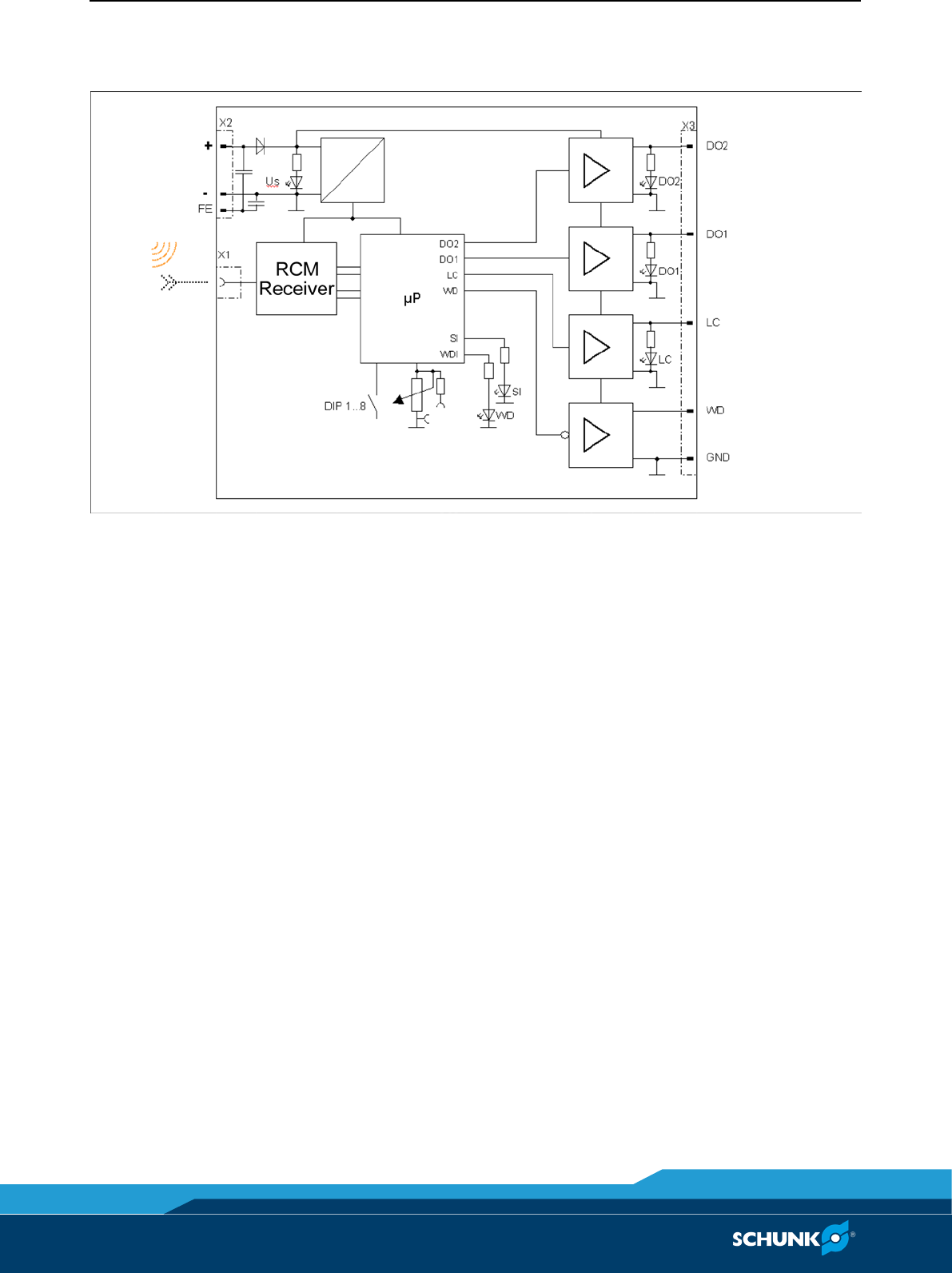
Functional description
22 02.02_preliminary|Id. Nr. 8705401 |en
General discription
Block diagram of the receiver
A supply voltage of 12 – 24 VDC is required to operate the radio
receiver. The connection is established using Cage Clamp® con‐
nectors. An external magnetic antenna for the frequency range of
868 MHz is required to receive the radio telegrams.
The radio receiver is based on the EnOcean radio receiver RCM
121, whose received data is processed with a downstream micro‐
controller.
The program in the microcontroller can be divided into the learn‐
ing mode and the operating mode.
Learning mode
In the learning mode (activated by DIP 1 ON/OFF), the ID of a de‐
tected EnOcean telegrams is stored in the receiver and the learn‐
ing mode is automatically closed. If no valid telegram of a trans‐
mitter is received in the learning mode, this is signaled as a faulty
status after 15 s. Alternatively, at Status of “INACTIVE” the trans‐
mitter ID can be taught manually by actuating the DIP switches 3
and 4 (simultaneously).
9.1.3
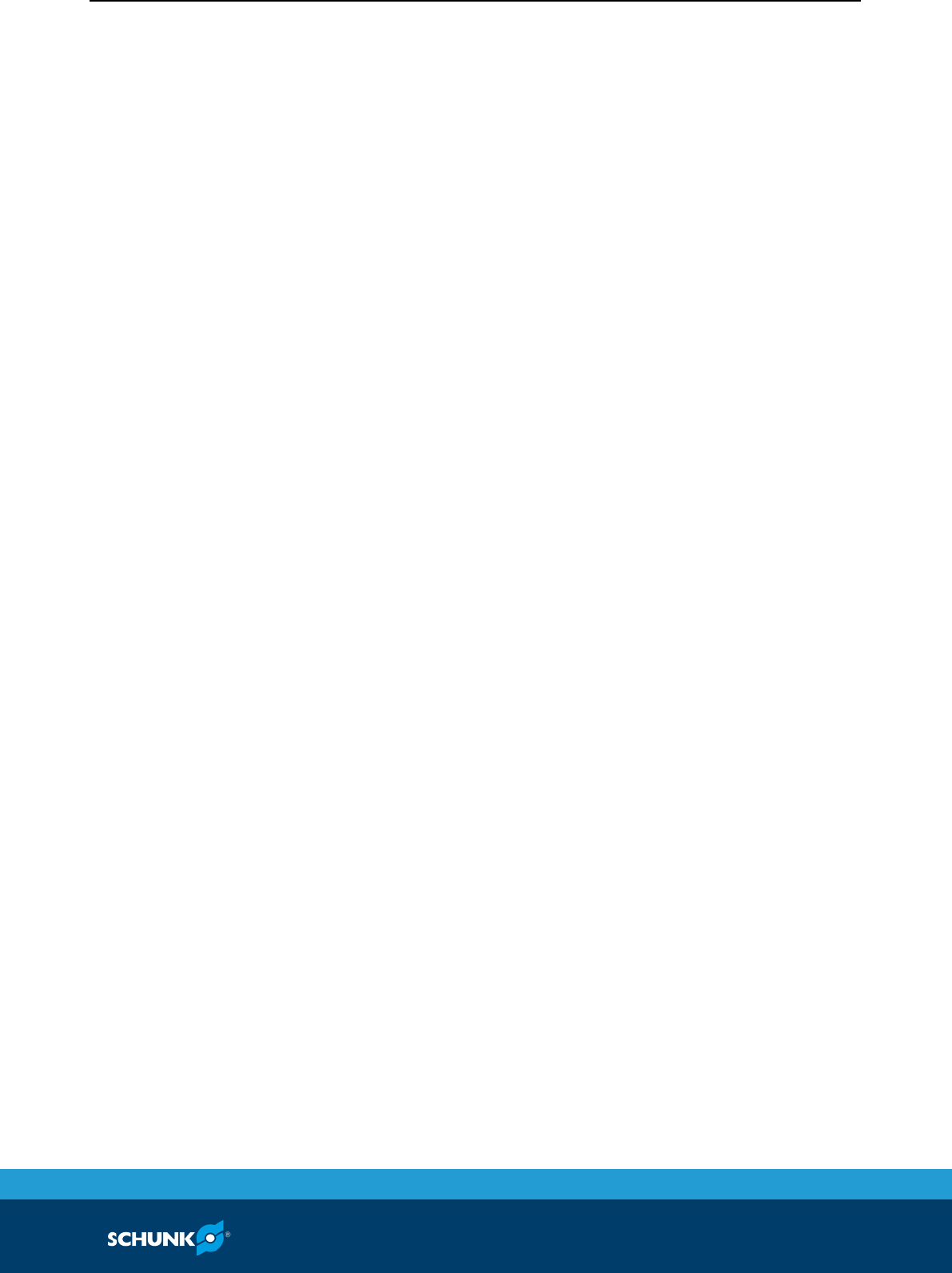
Functional description
02.02_preliminary|Id. Nr. 8705401 |en
23
The adjustment of the monitoring time and the limit value is done
by specifying default values or adjustments with the potentiome‐
ter based on a diagram. The diagrams and the DIP switches are de‐
scribed in the following chapters.
Operating mode
In the operating mode, the receiver monitors the incoming signals
of the transmitter with the watchdog function. The watchdog LED
(WD) indicates each incoming telegram of the taught transmitter
by blinking briefly. When the watchdog time set is exceeded, the
WD LED signals an error by staying lit continuously; the WD output
switches to the LOW status.
The LEDs and Outputs DO1 and DO2 directly indicate the status of
the two‐channel sensor. The level control monitors the current
battery status for an adjustable limit value with each telegram.
When the limit value is fallen short of, the output switches to the
LOW status and the LED is OFF.
The signal strength of incoming telegrams is indicated by blinking
codes of the SI LED; this allows an optimum radio connection to be
established already during commissioning.
Function description delivery condition
After first switching on the voltage supply, the receiver module is
in the “INACTIVE” mode. For the commissioning, the ID of a
transmitter needs to be “LEARNING”.
NOTE
A transmission needs to be activated at the transmitter during the
“Learning phase”. During the learning phase, telegrams from
EnOcean sensors are evaluated on STM basis. The transmitter with
the largest signal strength is trained.
N
one or only a few transmissions of other transmitters should
therefore take place in the reception range of the module to pre‐
vent faulty teaching.
9.1.4
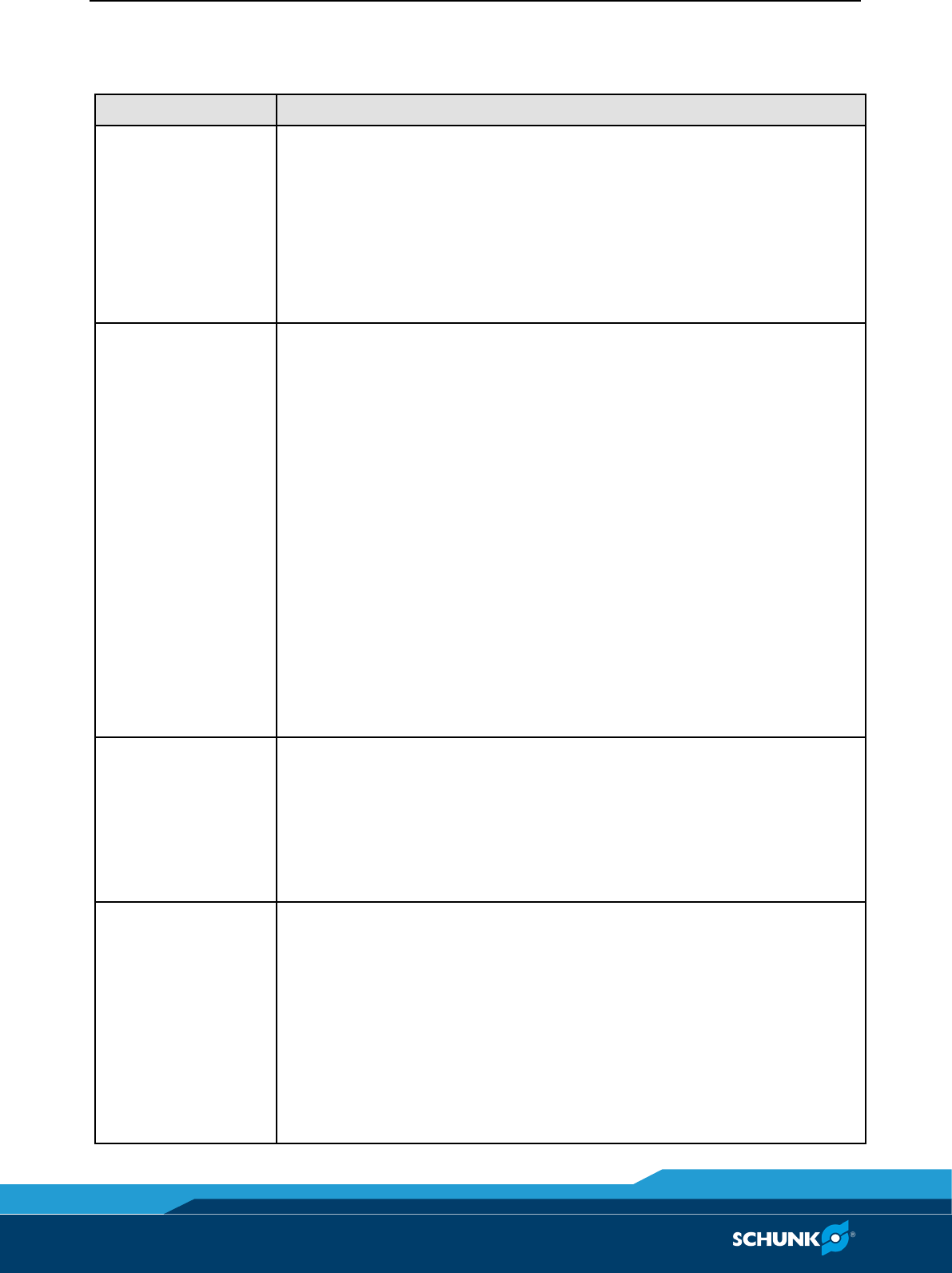
Functional description
24 02.02_preliminary|Id. Nr. 8705401 |en
Status definition
Status
Description
INACTIVE
During commissioning, the switching actuator signals a missing as‐
signment (status: inactive) to the sensor by a blinking watchdog LED
(2Hz).
No ID of a sensor has been “learned" yet.
The “inactive” status can be restored by switching on the DIP switch
“Delete ID” if no ID has been learned within the 15‐second learning
time following actuation.
LEARNING
In the learning mode, the receiving range is reduced to approx. 5 m
(if DIP 5 = OFF) to exclude the learning of other receivers as much
as possible.
To teach a new radio sensor, the “learn switch” (DIP 1) must be ac‐
tuated on the receiver. The learning status is signalled by a slow (0.5
Hz) blinking watchdog LED. The DIP switch should be reset immedi‐
ately.
After a telegram has been received from a transmitter, its ID is
stored in the receiver, safe from power failures, and the learning
mode is subsequently exited.
In the learning mode, each received (detected) signal of any ID is
indicated on the SI LED. The signal strength of a telegram is indicated
until the next telegram is received.
If no new sensor is learned w
ithin 15 seconds, the switching actuator
returns to the “active” or “inactive” status.
ACTIVE
In the “active” status, the switching actuator monitors all IDs re‐
ceived and compares them with the ID learned. If the sensor is de‐
tected as "assigned", the data bytes received (Data_Byte 0…3) are
processed and output.
In the operating status “active”, only signals from taught transmit‐
ters are indicated on the SI and WD LED.
System moni‐toring
/ WATCHDOG
The system check is only switched on in the "active" state. A timer
(watchdog abbrev. WD) is used to monitor whether new data tele‐
grams of the taught sensor have been received within the system
time set. The system time can be adjusted with the system check
potentiometer or the DIP switch.
If the time between two telegrams is greater than the monitoring
time, the system LED signals this fact with a continuous light. The
associated output of the system monitoring (output WD) switches to
the LOW status. The status outputs of the sensor maintain the last
9.1.5
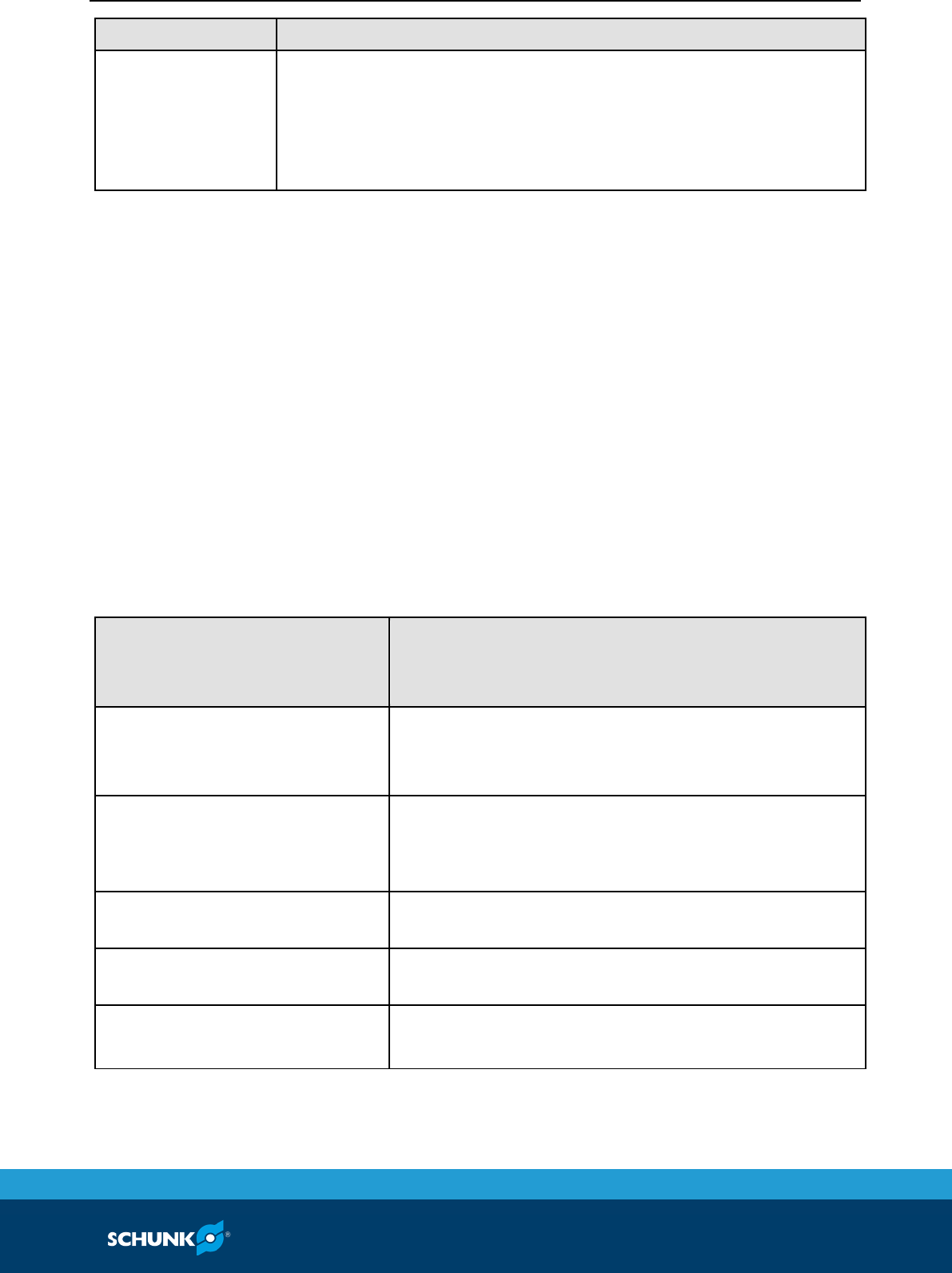
Functional description
02.02_preliminary|Id. Nr. 8705401 |en
25
Status
Description
status.
The output behaviour with addressed system monitoring is non‐
saving. When the WD is addressed, the last value of the signal
strength is not saved (SI LED); the current signal strength of the
taught sensor continues to be evaluated.
Time response
The time lag between measurable telegrams must be at least 50
ms.
For small grippers, the time between 'Gripper open' and 'Gripper
closed' is considerably shorter. However, it is possible here to set a
sensor for 'Gripper open' and the other sensor for 'Gripper closed'.
As the gripper usually either opens or grips a part, but very rarely
closes completely, the system can be programmed as with cable‐
based sensors.
If the gripper now closes completely due to a missing component,
the gripper closed message comes ten seconds late.
Function of the DIP switches
Switch
Type / function / code designa‐
tion
Meaning
DIP switch 8‐pin
1 OFF / ON
Delete transmitter ID and activate teach‐in mode = ON
*
2 OFF / ON
OFF = SI LED displays distance between signals
ON = SI LED shows signal levels
Delivery state: distance between signals
3 OFF / ON
Adjust battery limit ON= ACTIVE; set transmitter ID DIP
(3+4)
4 OFF / ON
Adjust watchdog time ON= ACTIVE; set transmitter ID
(DIP 3+4)
5 OFF / ON
OFF = teaching in with reduced reception range
ON = teaching in with full reception range
9.1.6
9.1.7
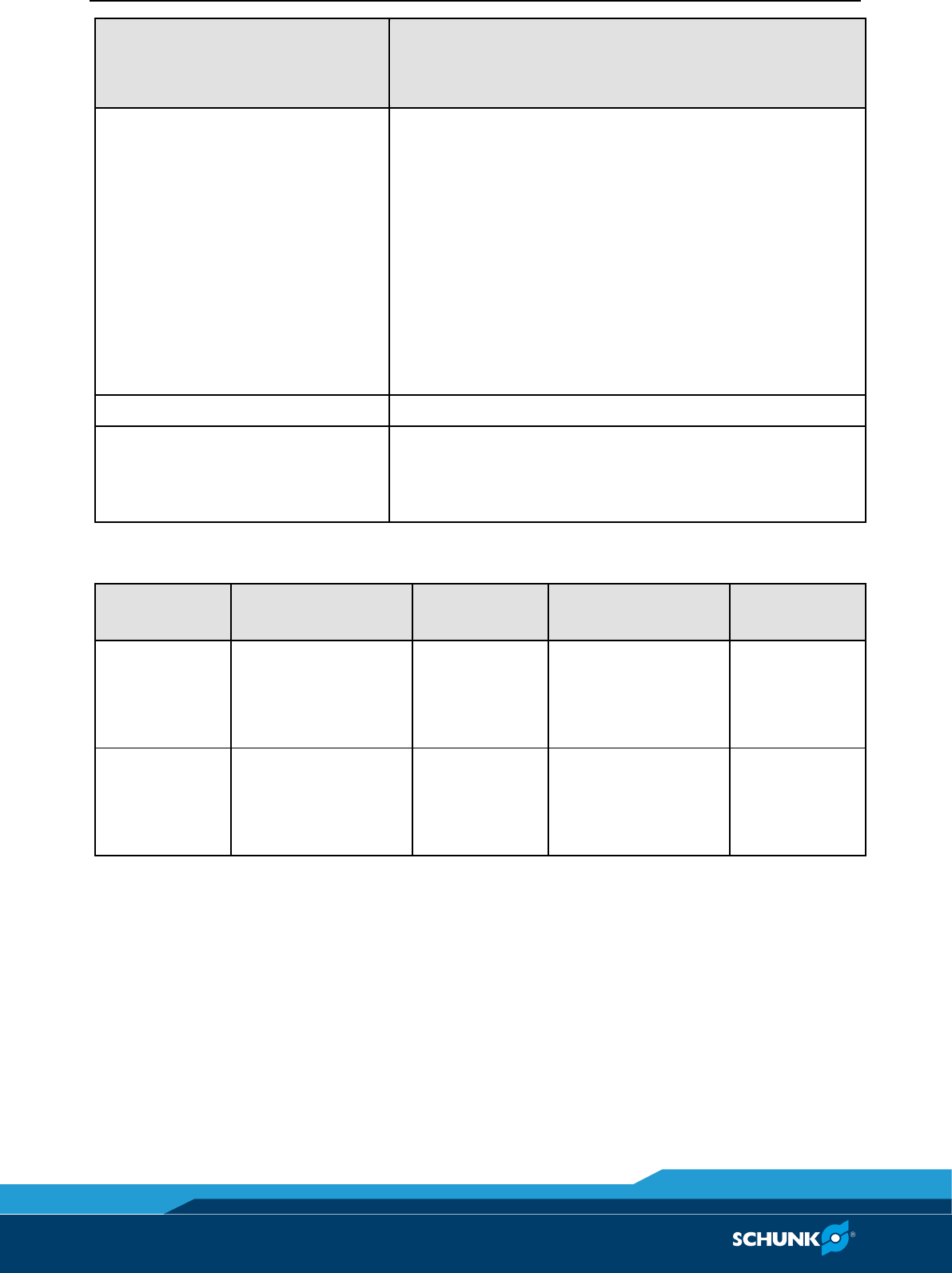
Functional description
26 02.02_preliminary|Id. Nr. 8705401 |en
Switch
Type / function / code designa‐
tion
Meaning
6 OFF / ON
OFF = DI1 is transmitted from the transmitter to the
receiver and issued on receiver output D01;
DI2 is transmitted from the transmitter to the receiver
and issued on receiver output D02.
ON = DI2 is transmitted from the transmitter to the
receiver and issued on receiver output D01;
The receiver ignores incoming radio data relating to
D01.
The receiver sets its output D02 as a negation of the
signal D02.
7 OFF / ON
Apply current battery value –0.5V as a limit *
8 OFF / ON
Setting the system time
OFF = 1 SECOND / ON = 35 SECONDS (preferred)
0‐2.5V = 0...1s / 0‐2.5V = 0...35s
*
edge‐controlled
DIP6
Transmitter
DI1
DI2
Receiver
D01
D02
OFF
0
1
0
1
0
0
1
1
0
1
0
1
0
0
1
1
ON
0
1
0
1
0
0
1
1
0
0
1
1
1
1
0
0
Delete transmitter ID
To learn a new transmitter, the DIP 1 must be momentarily
switched to “ON” (assignment function). Any previously learned
transmitter will be deleted and cannot be learned for approx. 30
minutes thereafter (☞ see list of deleted transmitters). For further
behaviour, see ☞ “Status definition / LEARNING”.
When actuating DIP 1, the ID of the transmitter last learned is
stored in a list comprising a maximum of 10 entries “List of deleted
9.1.8
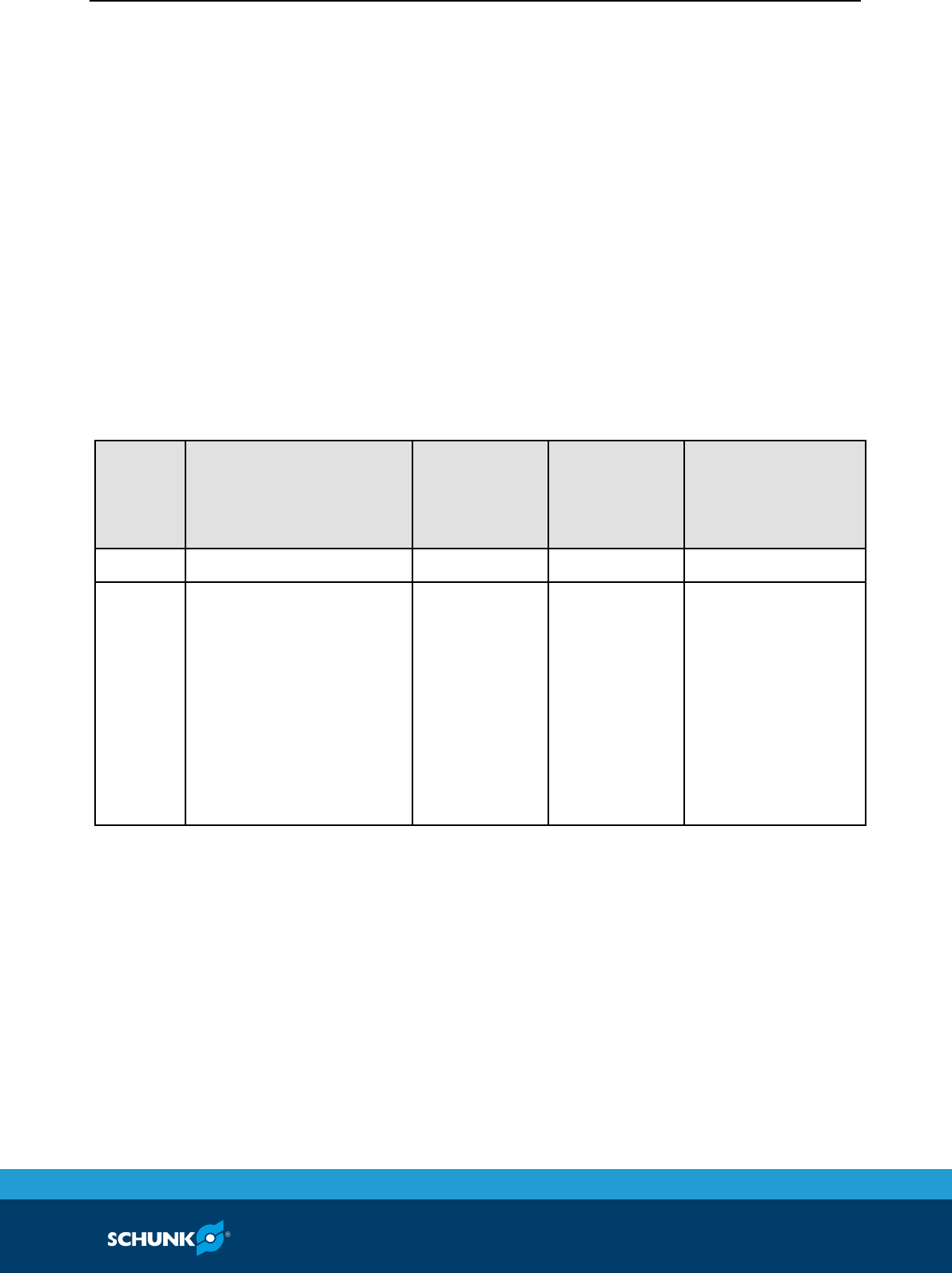
Functional description
02.02_preliminary|Id. Nr. 8705401 |en
27
transmitters”. These IDs are stored in the RAM for up to 30
minutes. The purpose of this is to prevent repeated learning for up
to 30 minutes after an incorrect learning followed by deletion.
The “list of deleted transmitters” is reset (i.e. deleted) either by
switching off the supply voltage or if no other transmitters have
been deleted for 30 minutes (retriggerable timer).
Signaling the distance between signals or the signal strength
In the as‐delivered condition (DIP 2 = “OFF”), the signal distance of
the useful signal and the noise signal is displayed by the blinking SI
LED. The ‘noise level’ is measured every 20 ms (watchdog time 0..1
s), or approx. every t = (adjusted watchdog time / 64 measure‐
ments) (watchdog time 0..35 s).
The average determination for the noise signal is carried out once
a new telegram is available.
LED
Signalling
Signal strength
Planned func‐
tional exten‐
sion
(DIP 2 = OFF)
Signal level RSSI *
(DIP2 = ON)
‐
V
SI
(green/
red)
LED green continuous
light
LED green blinking
LED green/orange blink‐
ing
LED orange/red blinking
LED red continuous light
LED red blinking
Signal optimal
Signal excel‐
lent
Signal good
Signal medium
Signal bad
Signal critical
No functionali‐
ty
> 2,5
2,43 < RSSI*1 < 2,5
2,37 < RSSI < 2,43
2,00 < RSSI < 2,37
1,60 < RSSI < 2,00
< 1,6
*
RSSI means "Received Signal Strength Indication“ and is an in‐
dicator for the received radio signal strength of wireless com‐
munication applications.
9.1.9
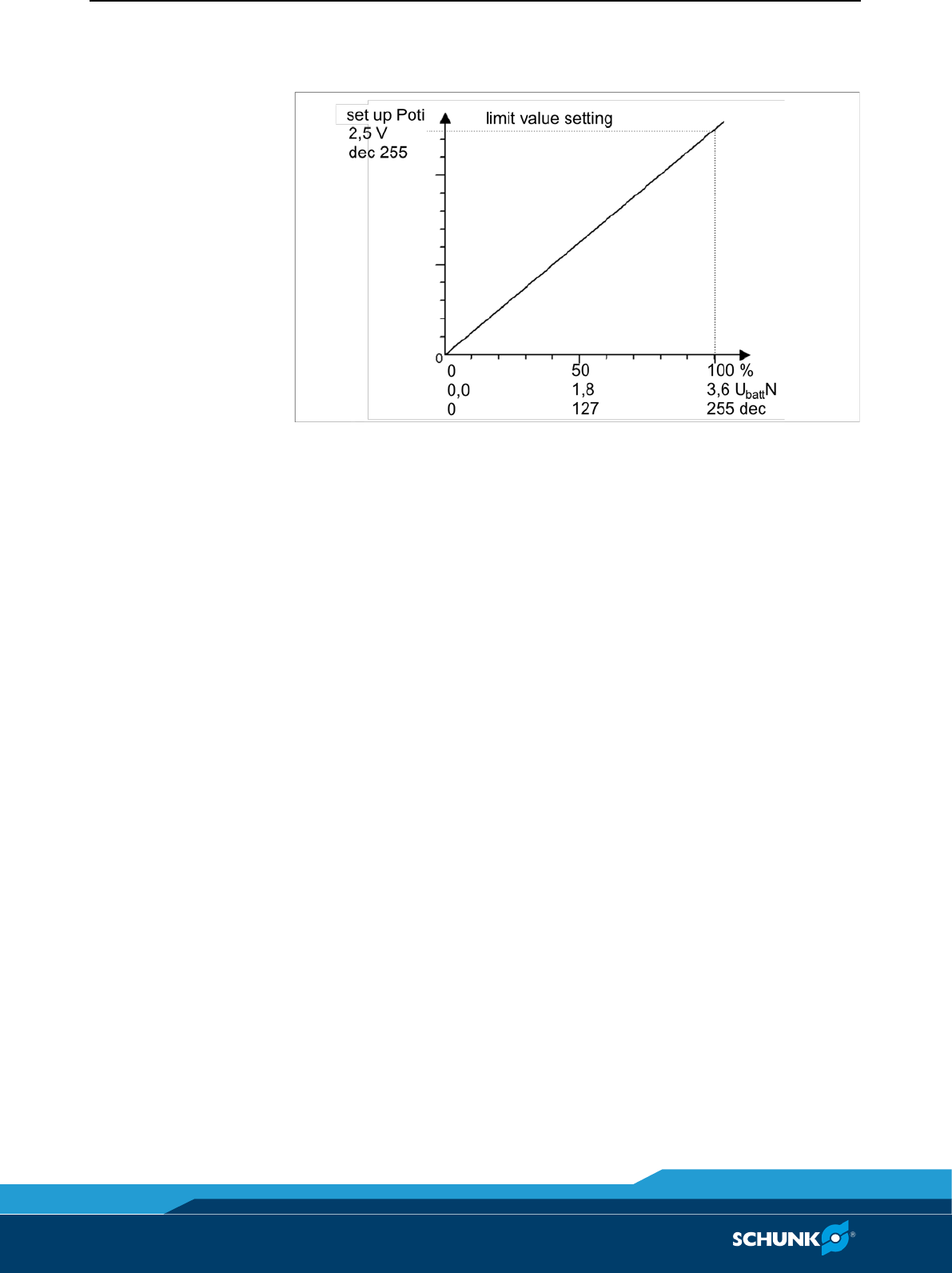
Functional description
28 02.02_preliminary|Id. Nr. 8705401 |en
Setting the limit value for battery monitoring
Limit value setting
The current potentiometer value is stored when switching on DIP
switch 3 at status of “ACTIVE” and “Watchdog”. During the setup
mode (DIP 3 ON), the LED responds directly to a changing potenti‐
ometer value.
Hint on setting the limit value to approx. 5% below the current
battery level:
1 Turn potentiometer until the LED extinguishes.
2 Set DIP 3 to OFF.
A 3‐step hysteresis (approx. 1 %) ensures a steady function of the
indicator in the limit value range.
If the DIP switch is switched back without the POTI value having
changed outside of its ‘oscillation range’, no new value is accepted
as system time or limit value (to avoid faulty operations).
Setting the output behaviour
Functional change of the output signal D01
Output D01 will not be received as at radio transmitter, but is
“NOT D02”.
Teaching the limit value (teaching threshold)
Analog value currently sent – 0.5V
The current value of the analog value minus 0.5 V is accepted as
limit value for the battery monitoring.
9.1.10
9.1.11
DIP6 = ON:
9.1.12
DIP7:
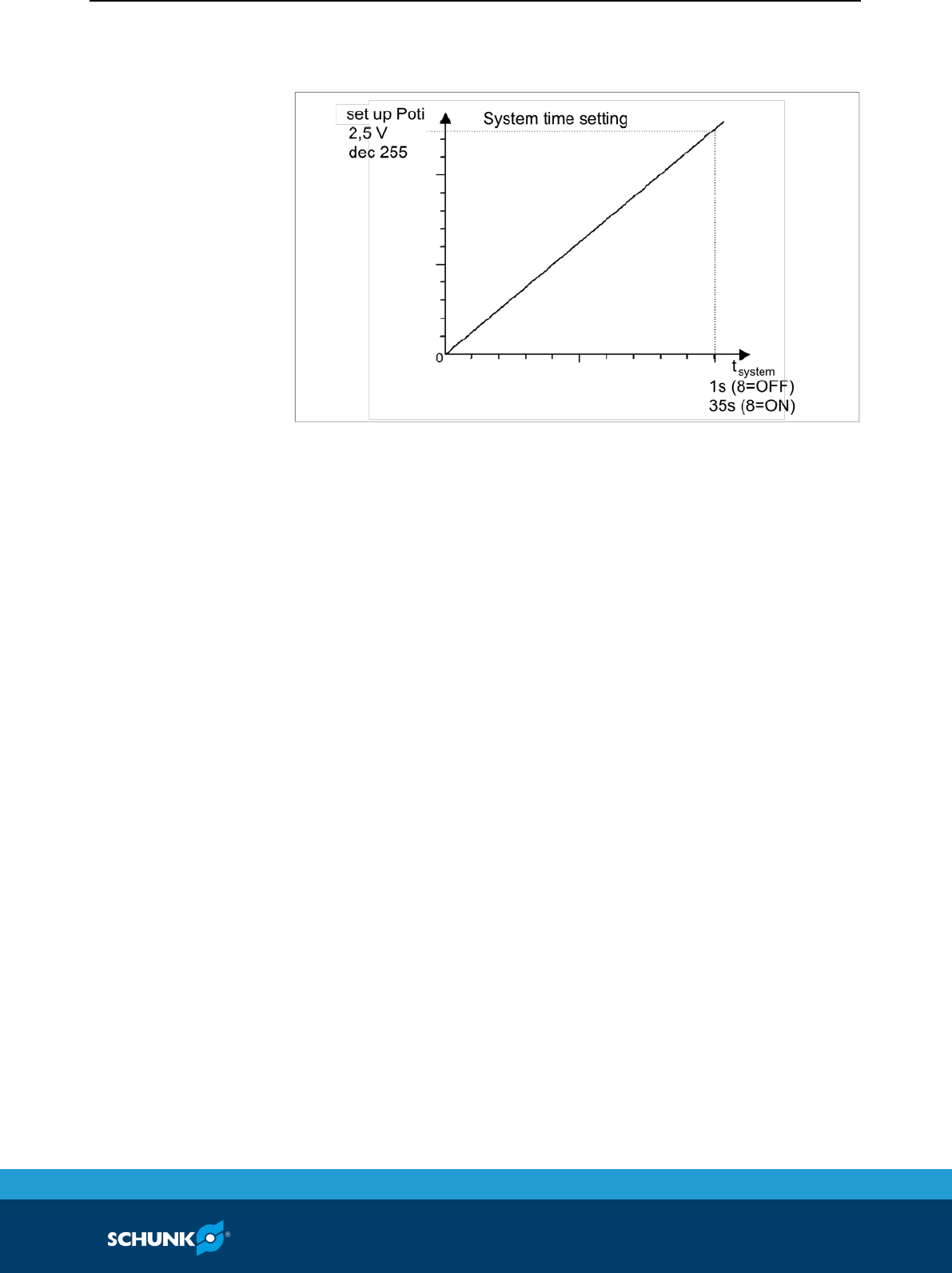
Functional description
02.02_preliminary|Id. Nr. 8705401 |en
29
Setting the watchdog time
Setting the watchdog time
The POTI value is saved by turning on of the DIP switch 4 at status
“ACTIVE” and “WATCHDOG”. During the set‐up mode (DIP 4
moved), the LED responds directly to a changing POTI value (and
DIP 8 setting) by changing the blinking frequency.
The setting occurs using the “System time setting” characteristic
curve. System time = f (DIP8 and POTI value). The acceptance oc‐
curs only when DIP 4 is switched back.
If the DIP switch is switched back without the POTI value having
changed outside of its ‘oscillation range’, no new value is accepted
as system time or limit value (to avoid faulty operations).
Function of the DIP 5 Extension of the reception range during the
learning procedure
By switching on DIP 5, the range reduction to 5 m in learning mode
can be switched off, i.e. the full reception range of the receiver is
then used for learning, e.g. in order to learn more remote trans‐
mitters with a good signal strength.
NOTE
All incoming EnOcean telegrams are (internally) transferred via the
serial inter
‐face. The response time of the receiver can thereby be
permanently reduced. (special function of the RCM121DB is not
used during this)
It is therefore imperative to switch the DIP 5 back to OFF after the
learning!
9.1.13
9.1.14
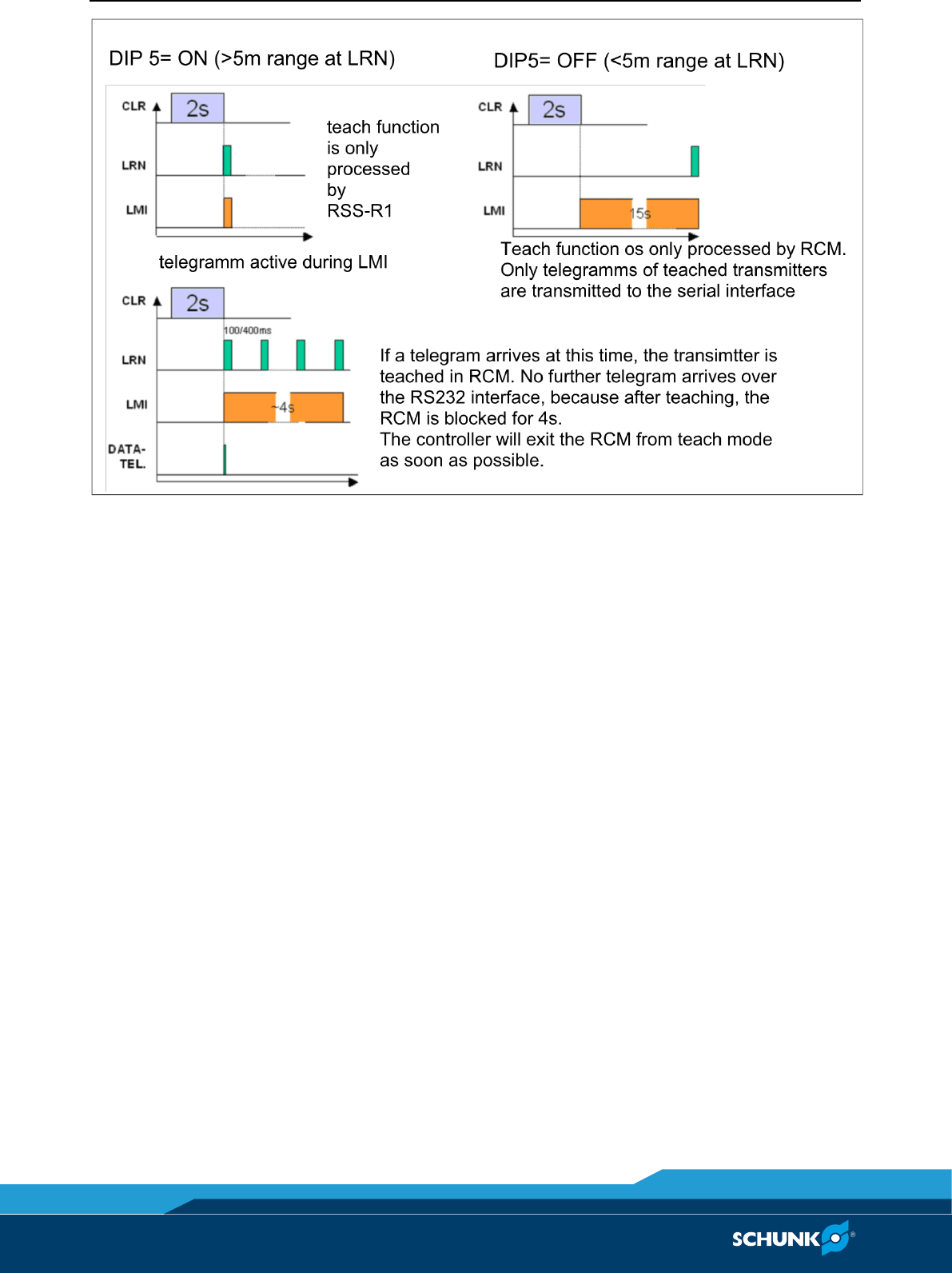
Functional description
30 02.02_preliminary|Id. Nr. 8705401 |en
Manual setting of transmitter ID (programming)
By simultaneously activating DIP3 and DIP4 at status “INACTIVE”,
the switching actuator is placed in the programming mode.
While setting the first ID byte (ID0), the LC LED (incl. output) blinks
for 10 s with 0.5 Hz. The LC LED then lights for 2 s to accept the DIP
combination.
The input of the ID bytes 1, 2 and 3 is done in the same manner,
whereby at the end (accepting ID3) the LC LED lights for 10 s to
have sufficient time to set the output DIP combination.
Example ID: 00 | 00| 09 | 88 = 00000000 | 00000000 | 00001001 |
10001000
ID3 ID2 ID1 ID0
DIP 1|2|3|4|5|6|7|8
NOTE
Observe the sequence of ID0... ID3 while teaching.
9.1.15
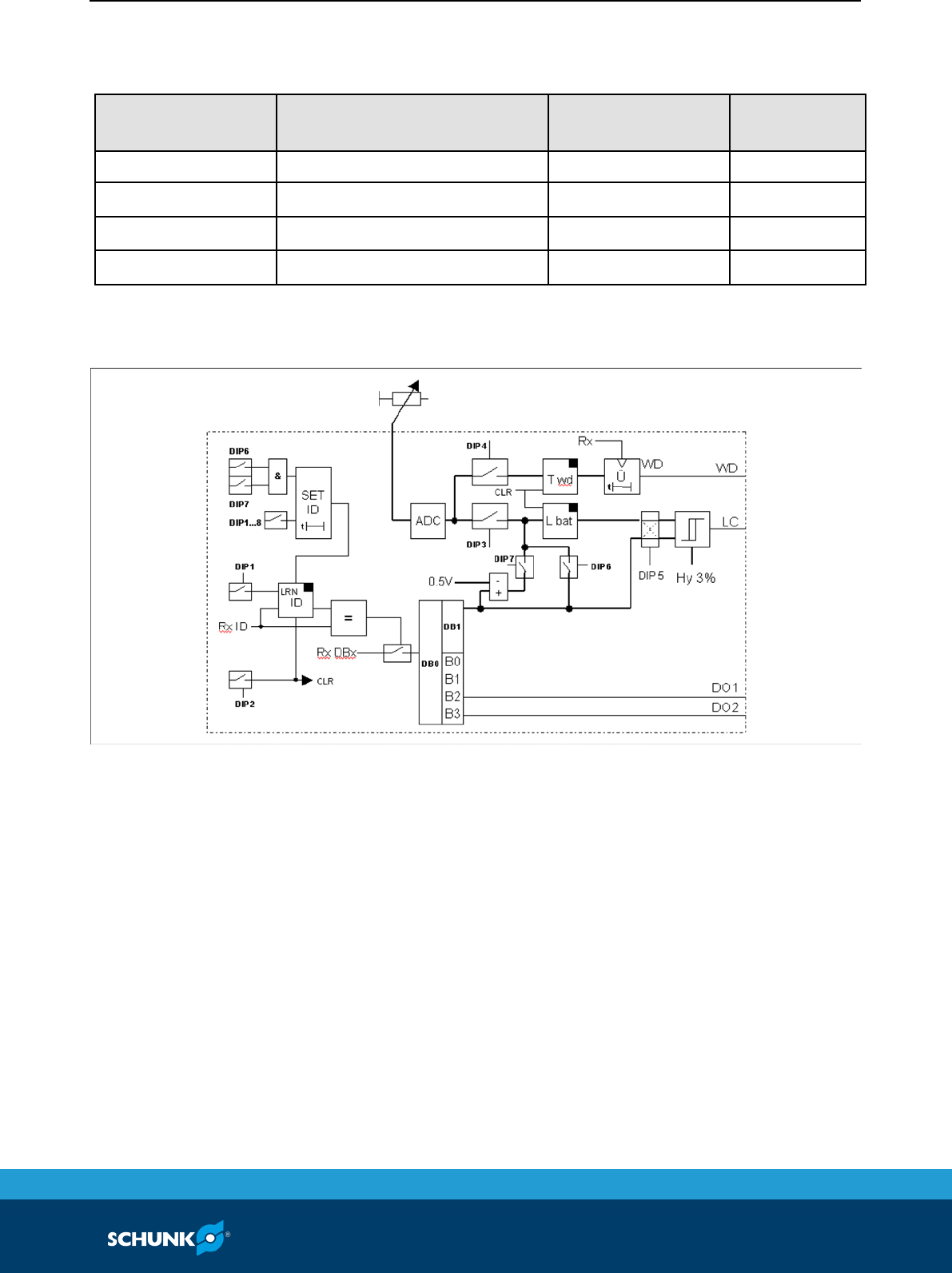
Functional description
02.02_preliminary|Id. Nr. 8705401 |en
31
Output behaviour of the watchdog
Operating mode
Possible cause
Behaviour (Output
S)
LED
Operation
Watchdog addressed
Output LOW
On
Watchdog not addressed
Output HIGH
Off
Learning
Output LOW
On
Inactive
Output LOW
On
Software block diagram
RSS‐T2‐US/CA
Operation
The transmitter module is not equipped with conventional control
elements. Two reed switches are integrated instead, which can be
operated via screw fastened magnetic brackets. Unscrew the
magnetic bracket of its present position. Screw in the magnetic
bracket into the desired position again.
If the magnetic bracket should not be screwed in somewhere, this
will correspond to the „normal mode“.
9.1.16
9.1.17
9.2
9.2.1
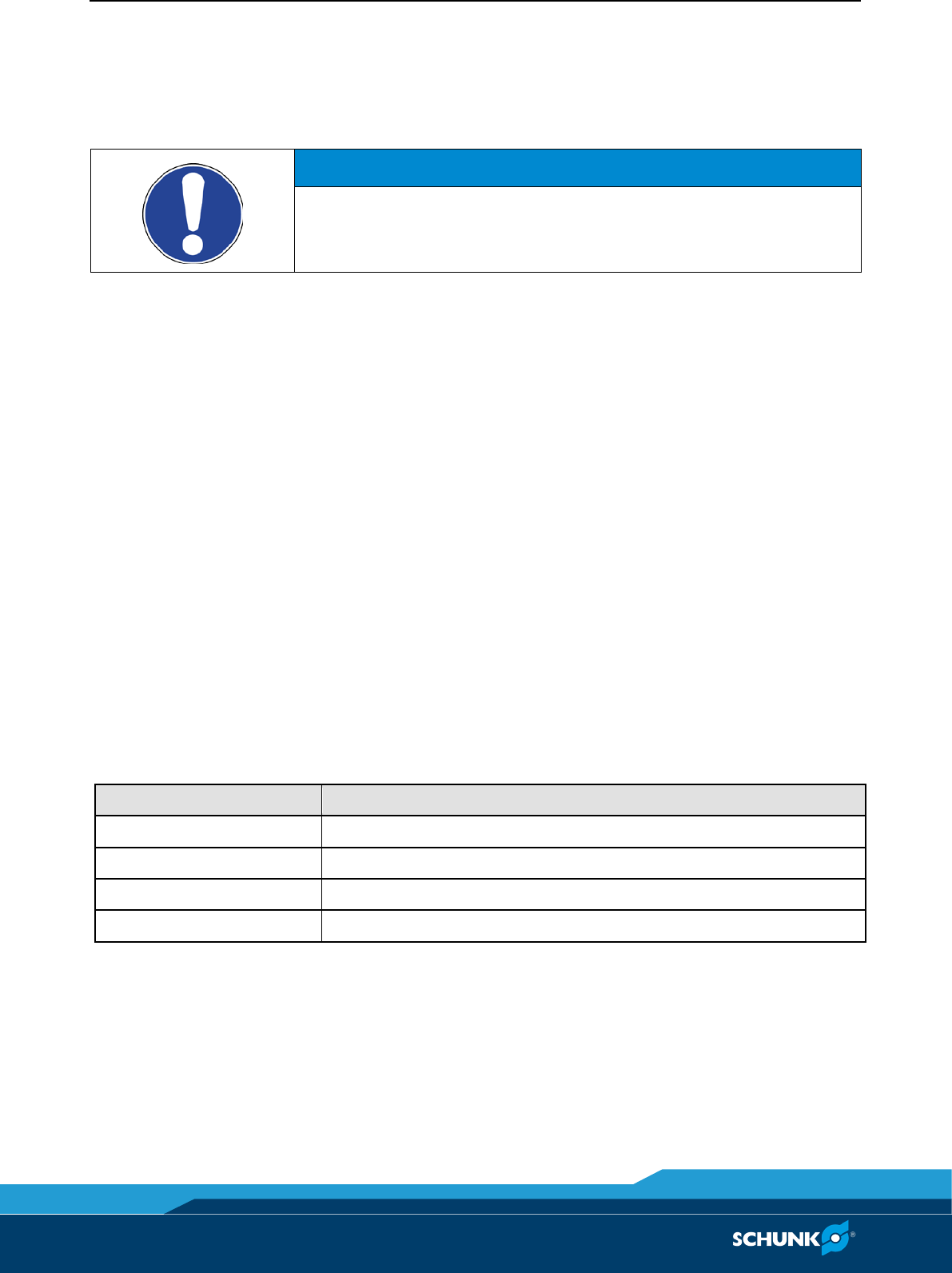
Functional description
32 02.02_preliminary|Id. Nr. 8705401 |en
The transmitter module is not equipped with control elements. It
independently sends a signal every 10 seconds. Anymore if the
state of the input is changed, it immediately sends a signal.
NOTICE
If the red LED WD lights up longer than 0,2 seconds, the radio
contact is disturbed. The adjustment work must be interrupted
and it should be checked what disturbs the radio contact.
Operating mode
Storage mode:
This is the delivery state. In this mode, the transmitter module re‐
acts to changes in the two sensor inputs with a wireless telegram,
but doesn't transmit any presence signal. This mode is used for po‐
sitioning the transmitter. The advantage here is the low energy
consumption. The life span of the battery is hardly shortened dur‐
ing positioning.
Test mode:
This mode places great load on the battery. It should only be used
for a short a time as possible!
The mode is used for adjusting the two sensors and for testing the
transmitter.
LED ‐ Display
DesignationLED
Meaning
D01 light luminous
The sensor 1 is actuated. The contact of the sensor is closed.
D02 light luminous
The sensor 2 is actuated. The contact of the sensor is closed.
D02 dark luminous
Test mode is activated and battery voltage is existing.
TX
A radiogram is sent just now.
9.2.2
9.2.3
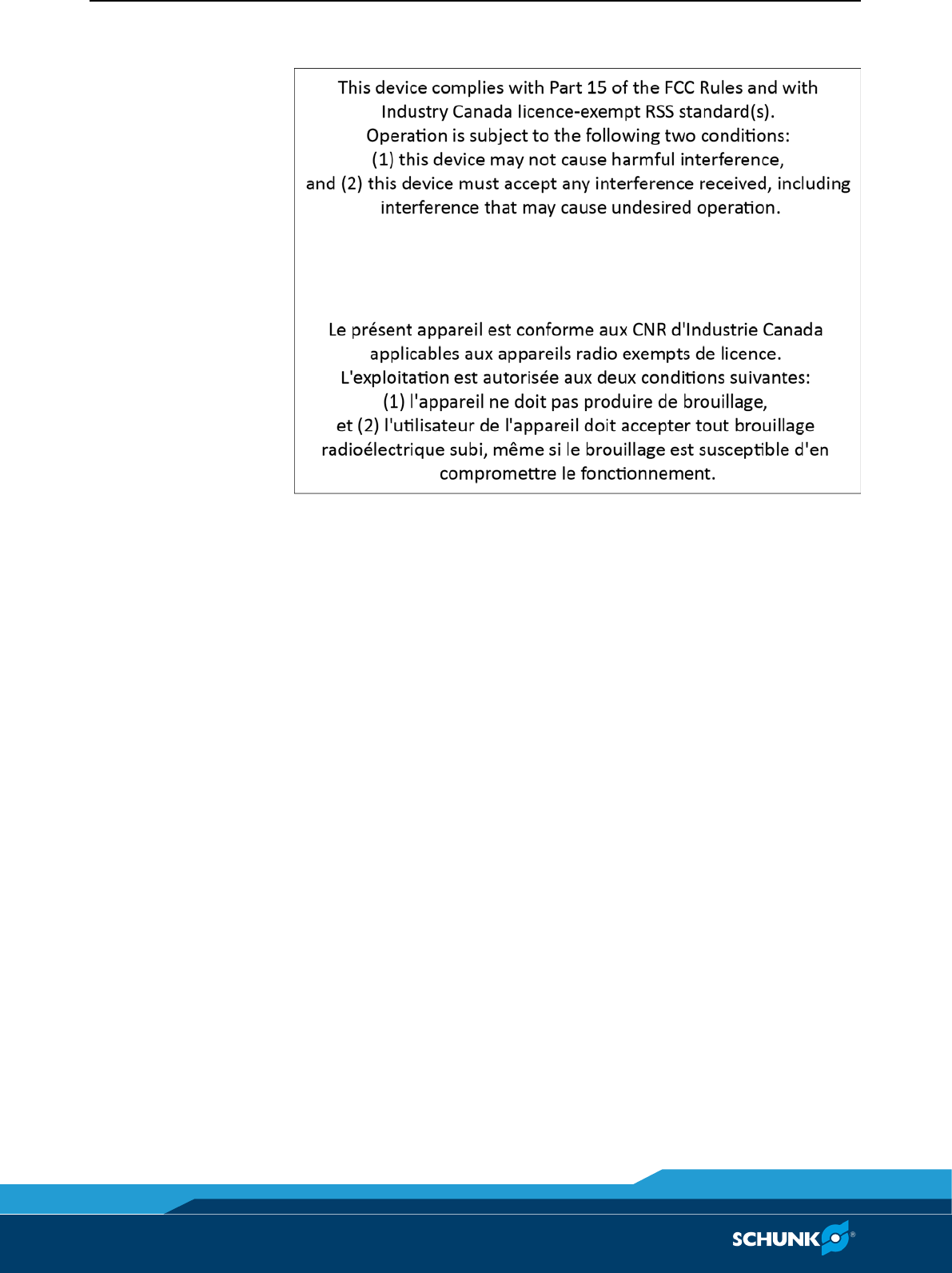
Information FCC certification
34 02.02_preliminary|Id. Nr. 8705401 |en
Information FCC certification
The RSS‐T2‐US/CA is used at grippers.
Incorrectly gripping the workpiece may cause the gripped work‐
piece to loosen itself out of the gripper fingers during movement
and to move uncontrollably. As a result there may be significant
material damage and/or serious personal injury.
To detect if the gripper fingers are positioned correctly, up to 2
reed switches can be attached to the gripper and in this way 2 po‐
sitions can be monitored. If the correct position is reached, the
signal at the sensor is changed which results in a radio signal.
To ensure there is a radio contact, cyclical sending is required eve‐
ry 10 seconds.
NOTE:
This equipment has been tested and found to comply with the lim‐
its for a Class A digital device, pursuant to Part 15 of the FCC Rules.
These limits are designed to provide reasonable protection against
harmful interference when the equipment is operated in a com‐
mercial environment.
This equipment generates, uses, and can radiate radio frequency
energy and, if not installed and used in accordance with the in‐
struction manual, may cause harmful interference to radio com‐
munications. Operation of this equipment in a residential area is
likely to cause harmful interference in which case the user will be
required to correct the interference at his own expense.
11