Sea Breeze Mini Split Air Conditioning Systems 12A23Ygx Users Manual 950 0027 REV F
2015-02-06
: Sea-Breeze Sea-Breeze-Mini-Split-Air-Conditioning-Systems-12A23Ygx-Users-Manual-527141 sea-breeze-mini-split-air-conditioning-systems-12a23ygx-users-manual-527141 sea-breeze pdf
Open the PDF directly: View PDF .
Page Count: 20

INSTALLATION
INSTRUCTIONS
MINI-SPLIT
AIR CONDITIONING SYSTEMS
FOR MODELS:
9A23YGX
12A23YGX
12A23ZGX
18A23ZGX
950-0027-REV-F 12-14-06

- -
1
Table of contents
Model Numbers…………………………………………………………………………………………………2
Unit Parts and Features………………………………………………………………………………………3
Installation Dimension Diagram………………………………………………………………………………5
Safety Warnings…………………………………………………………………………………………………7
Selection of Installation Location………………………………………………………………………………8
Indoor Unit Installation…………………………………………………………………………………………9
Outdoor Unit Installation………………………………………………………………………………………12
Testing…………………………………………………………………………………………………………14
Warranty………………………………………………………………………………………………………17
Specifications…………………………………………………………………………………………………18
Troubleshooting Chart………………………………………………………………………………………19

- -
2
Model Numbers
Air Conditioning
Indoor Unit 9A23YIGX
SYSTEM MODEL
9A23YGX Outdoor Unit 9A23YOGX
9,000 BTU 115 VAC
13 SEER
Indoor Unit 12A23YIGX
SYSTEM MODEL
12A23YGX Outdoor Unit 12A23YOGX
12,000 BTU 115 VAC
13 SEER
Indoor Unit 12A23ZIGX
SYSTEM MODEL
12A23ZGX Outdoor Unit 12A23ZOGX
12,000 BTU 208-230 VAC
13 SEER
Indoor Unit 18A23ZIGX
SYSTEM MODEL
18A23ZGX Outdoor Unit 18A23ZOGX
18,000 BTU 208-230 VAC
13 SEER
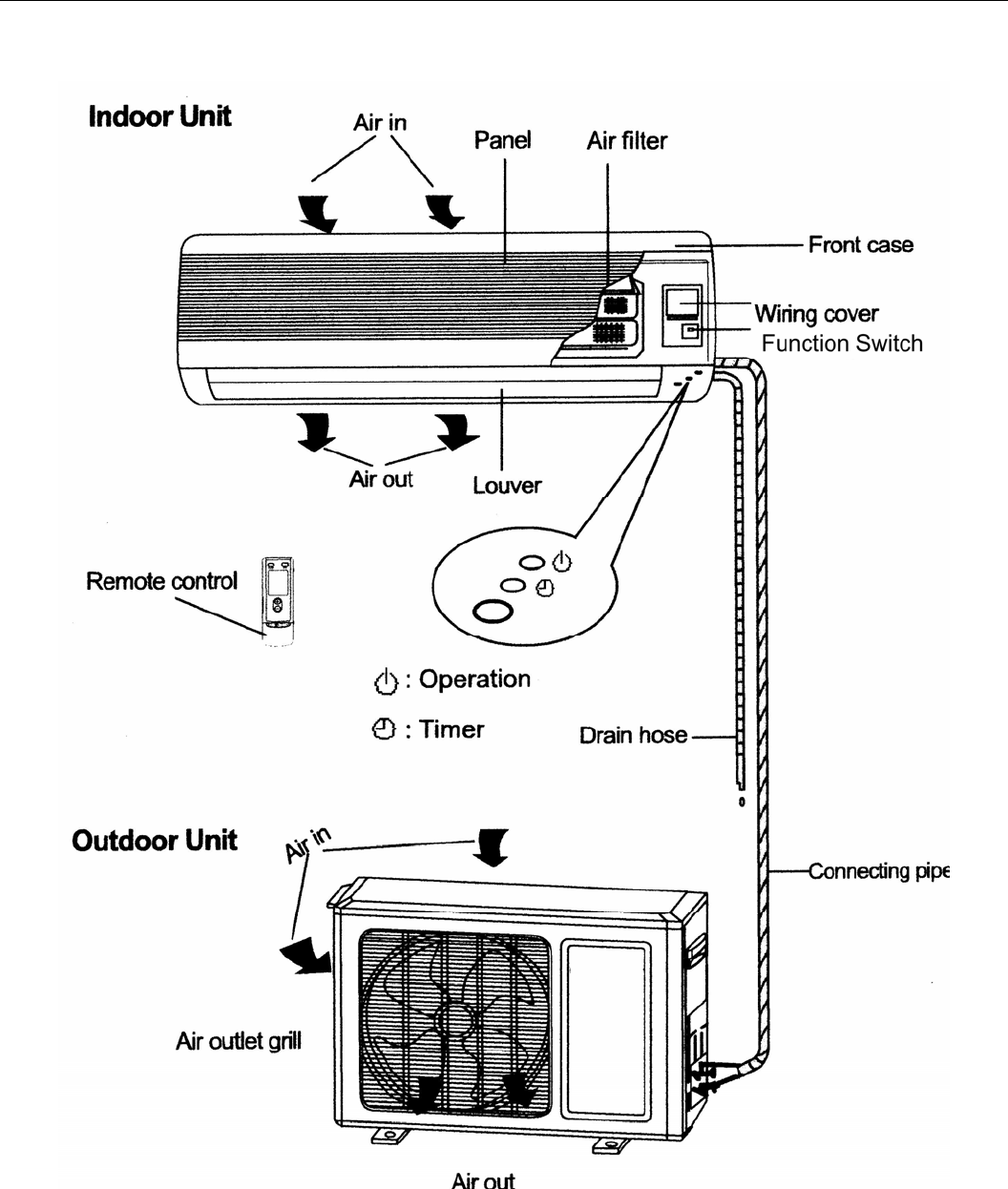
- -
3
Unit Parts & Features
(Models 9A23YGX, 12A23YGX, 12A23ZGX)
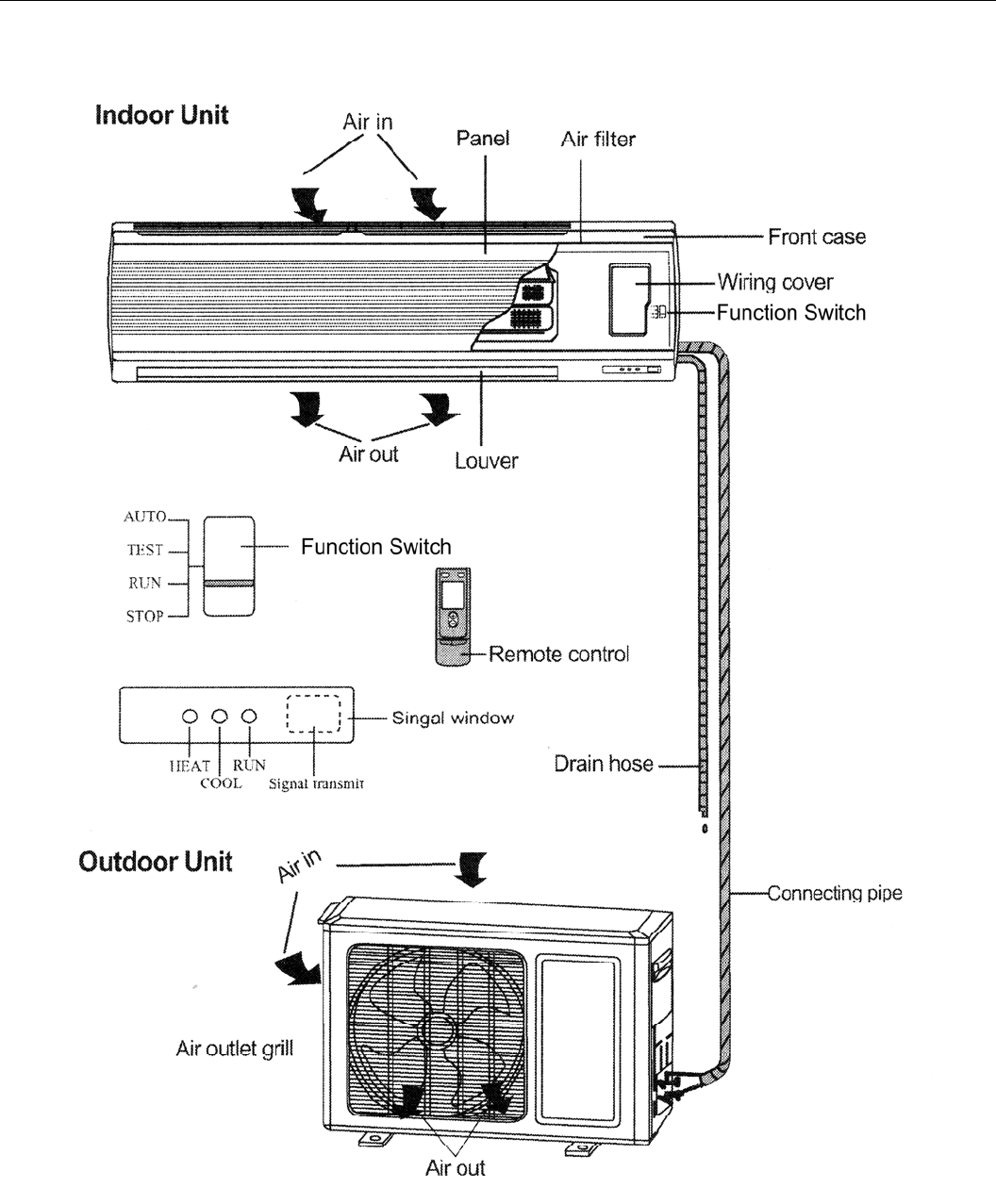
- -
4
Unit Parts & Features (Cont)
(Model 18A23ZGX)

- -
5
Installation Dimension Diagram
(Models 9A23YGX, 12A23YGX, 12A23ZGX)
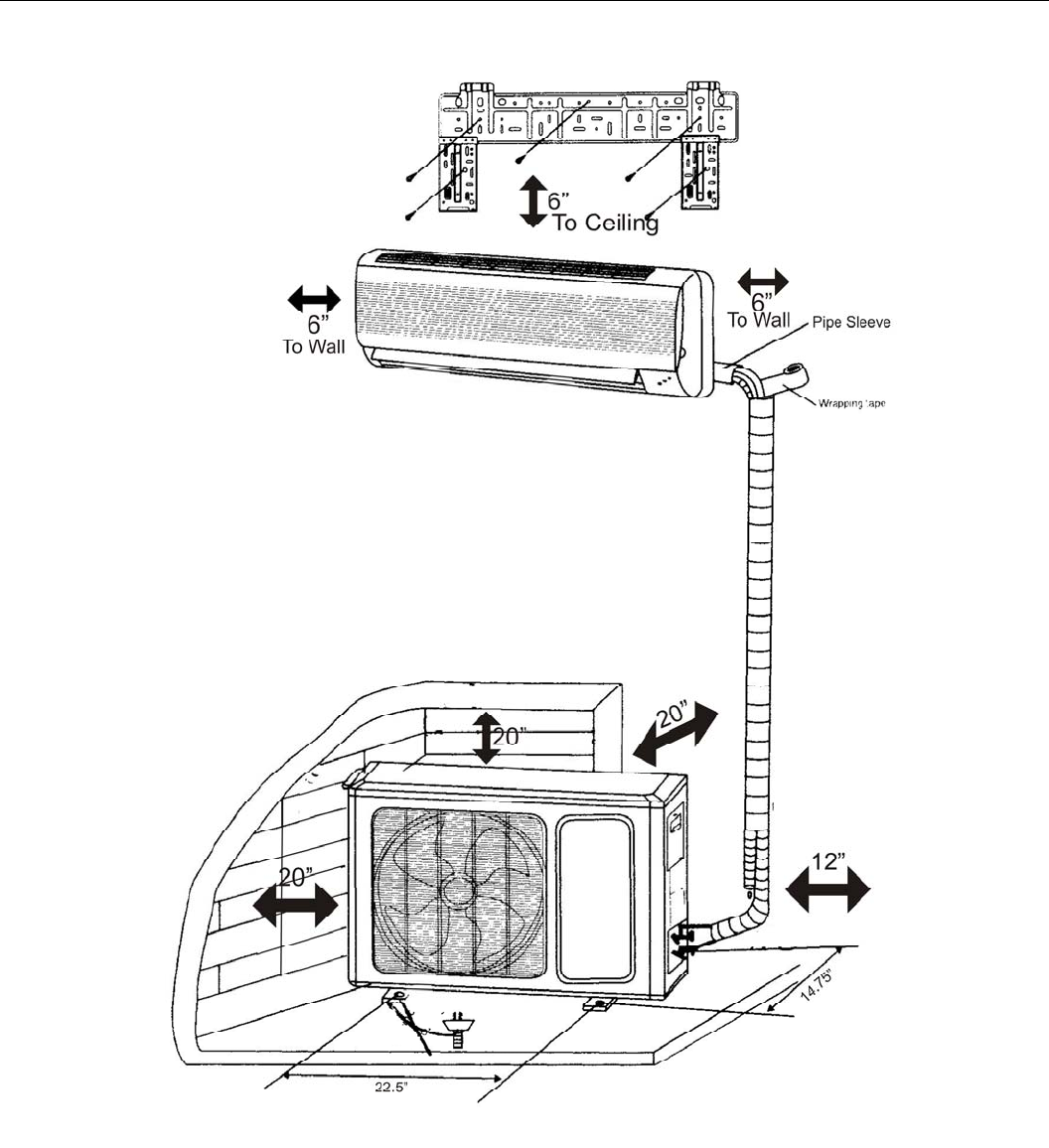
- -
6
Installation Dimension Diagram
(Model 18A23ZGX)

- -
7
Safety Warnings
• Use Copper Wires only for Power Supply
• Risk of electric shock can cause injury or death. Disconnect all electric power supplies before servicing or
installation
• Do not use excessive torque on flare nuts during connection of the refrigeration tubes, or service valve on
discharge line may be damaged.
• Do not install indoor unit in damp or wet locations.
• Electrical installation must be done by a qualified technician according to the instruction manual and in
accordance with local electrical standards.
• Certified Power supply conductors must be used.

- -
8
Selecting of Installation Locations
Indoor Unit:
• Intake and outlet should not be obstructed.
• The wall the unit is to be mounted on should allow for a clear hole for the condensation drain and the refrigeration
lines.
• The wall the unit is mounted on should be strong enough to bear the weight and vibration of the unit.
• Allow for proper clearances around the unit - see installation dimension diagram (page 5 and page 6).
• Location should allow easy access for maintenance and removal of air filter.
• Position unit and remote control at least 3 feet from electric appliances such as televisions, radios, etc.
• Keep unit and remote out of direct sunlight and/or florescent lighting and away from any excessive heat source,
steam, or flammable materials.
Outdoor Unit
• Allow sufficient ventilation around the unit - see installation dimension diagram (page 5 and page 6).
• The air intake and outlet should not be obstructed.
• Position unit so that noise and outlet airflow will not inconvenience neighbors.
• Position unit on a solid foundation. Location should be able to withstand the full weight and vibration of the unit.
• Installation should not be performed in the following locations exposed to: machine oil, flammable or corrosive
gases, high - frequency waves (i.e. from radio equipment, medical equipment, etc.)
Both Indoor and Outdoor Units:
Installation of Either unit in the following locations may cause malfunction. Locations exposed to:
• machine oil
• flammable or corrosive gasses
• high frequency waves (i.e. from radio equipment, medical equipment, etc.)

- -
9
Indoor Unit Installation
Install the Rear Panel (mounting plate)
Always mount rear panel horizontally.
Hold the rear panel on the wall where you want the unit to be located and ensure that it is level using a plumb line or
level. Once leveled, mark the screw locations on the wall.
Fasten the rear panel to the wall at the location marked using the screws supplied with the unit.
Insure that the panel has been mounted firmly to withstand the weight of the unit, with the weight being evenly
distributed by each screw.
Install the Piping Hole
• Select the location for the piping hole - either left-positioned or right-positioned (see installation dimension
diagram on page 5 and page 6).
• Make piping hole in the wall approximately 2.5 inches in diameter at a slight downward slant (this ensures proper
drainage).
• Insert a piping-hole sleeve in the hole (i.e. PVC pipe) to prevent the connection piping and wiring from being
damaged
Install Drainage Hose Extension (optional)
• Drainage hose extension is included with unit, for use if attached drainage line is not long enough for your
application.
• Please note that the extension can be installed after existing drainage pipe is fed through wall later in the
installation process, if it is determined later that it is necessary.
• Do not wrench or bend drainage hose or extension.
Wire the Indoor Unit.
• Note: All electrical wiring must be done by a qualified technician in accordance with local electrical codes.
• A separate circuit breaker must be provided.
• AC power for the indoor unit is provided by the power cable that runs between the outdoor unit and the indoor unit.
• If a disconnect switch is required for the indoor unit, it must be properly rated. (see specifications)
MODEL
INTERCONNECTING
WIRE GAUGE
POWER
SUPPLY WIRE
GAUGE
Min
CIRCUIT
AMAPCITY
Max
CIRCUIT
BREAKER
Max
FUSE SIZE
9A23YGX 16 AWG 14 AWG 10 AMP 15 AMP 15 AMP
12A23YGX 16 AWG 14 AWG 11.6 AMP 20 AMP 20 AMP
12A23ZGX 16 AWG 14 AWG 5.4 AMP 15 AMP 15 AMP
18A23ZGX 16 AWG 14 AWG 10.5 AMP 20 AMP 20 AMP
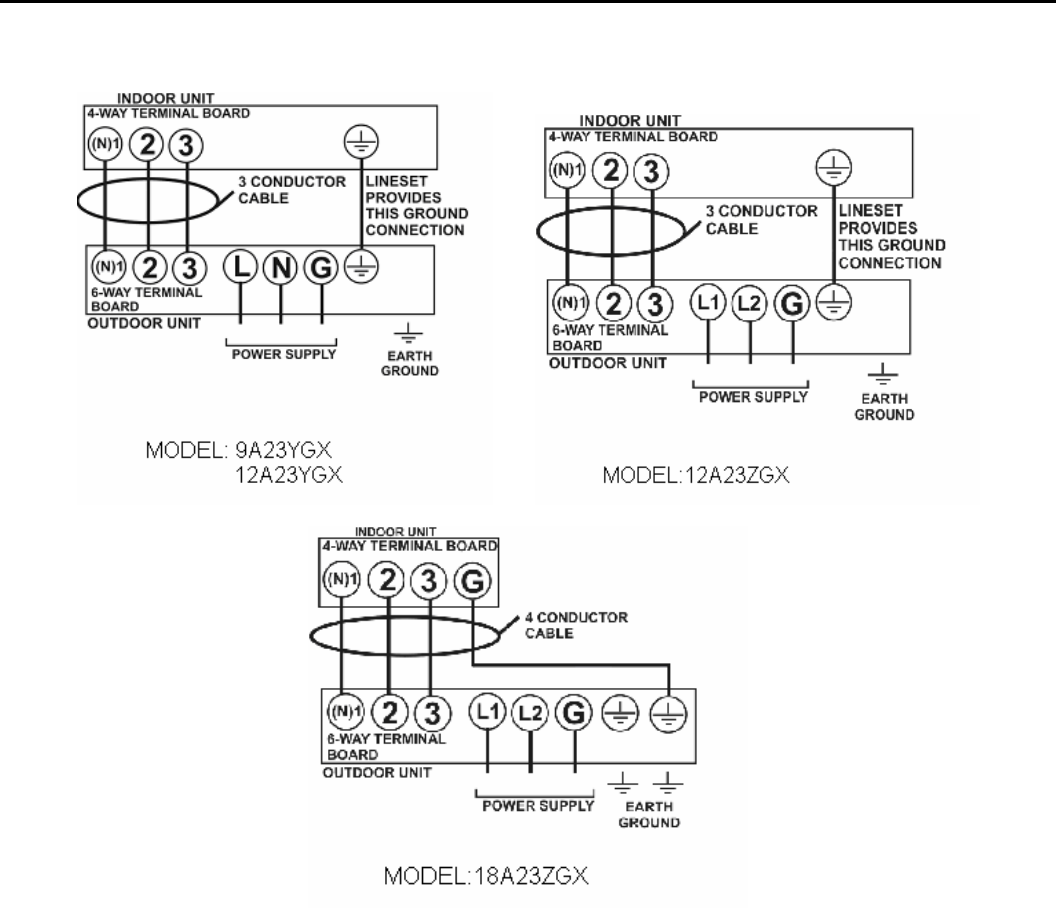
- -
10
Indoor Unit Installation (Cont)
Terminal Board Diagram
NOTE:
Power Connection cable is provided in the installation kit (sold separately). If the cable is not of sufficient length, it will be
necessary to purchase cable for this purpose.
Do not splice cable.

- -
11
Indoor Unit Installation (Cont)
Prepare refrigeration Lines
• Refrigeration Lines and wiring can be routed from the indoor unit several different ways using the cut-out access
pieces on the back of the unit.
• Bend the refrigeration lines carefully to the position needed to align with the drilled piping hole.
Hang Indoor Unit
• Bundle the refrigeration lines, drainage hose, and wiring conduit attached to
the indoor unit and wrap them securely for enough length to extend through the
piping hole to the exterior of the building. (Note: leave remainder unwrapped to
allow for remaining step in installation of the outdoor unit and connecting the
indoor unit to the outdoor unit.)
• Carefully push bundled lines through the piping hole.
• Hang the unit on the wall by hooking the mounting slots of the unit over the
upper tabs of the rear panel.
• Check to make sure the: unit is properly secured - it should feel firmly attached
to the wall, and you should not be able to slide it to the right or left.

- -
12
Outdoor unit Installation
Connect Refrigeration Lines to Bundled Lines from Indoor Unit
• Use standard A/C practices to attach the connection pipes to the proper pipes of the bundled lines coming
through the wall from the indoor unit.
• Tighten the flare nut of the connection pipes using a spanner and torque
wrench. (see diagram)
• Note: Do not over-tighten flare nuts, or the connection may be damaged.
Insulate/Bundle Refrigeration Lines and Wiring
• Individually insulate all refrigeration lines and condensation drainage hose to
ensure that they do not sweat. This will help to maintain the unit at its proper capacities.
• Once all lines have been properly insulated, bundle the refrigeration lines with the wiring conduit and wrap
securely to complete the run to the outdoor unit.
• Note: The condensation drainage hose should be left free of the bundled lines in order to drain properly.
Install Outdoor Condensation Drainage Hose (Heat Pump Models only)
• When the heat pump unit is heating or defrosting, wastewater forms in
the outdoor unit. This can be drained off using the outdoor drain elbow
and hose provided.
• Insert the drain elbow into the hole on the base plate as shown.
• Join the drain hose to the elbow and turn so that the water drains to the
desired location.

- -
13
Outdoor Unit Installation (Cont)
Position Outdoor unit
• Review page 5 for assistance in selecting location for outdoor unit.
• Make sure unit is positioned solidly and level on its foundation. Use leveling feet if necessary.
• If possible affix unit to foundation using proper hardware.
Connect refrigeration lines to Outdoor Unit
• Remove caps on outdoor unit
• Use standard A/C practices to attach the refrigeration lines bundled in step 2 to the
outdoor unit.
• Tighten the flare nut of the connection pipes using a spanner and torque wrench.
(see diagram)
• Note: Do not over-tighten flare nuts, or the connection may be damaged.
Wire the outdoor unit
• Refer to page 9 for proper wire sizes
• Refer to page 10 for wiring diagrams.

- -
14
Testing
Notes
• Installation MUST be complete prior to testing.
• System MUST be tested prior to operation.
Leakage Test
• Use standard A/C practices to properly check refrigeration tubes and connections for any leaks prior to system
start up.
Air Purging and Pressure Test
• Remove bonnet (cover) of gas valve on outdoor unit.
• Charge system with Nitrogen to 100 PSI and check for leaks. Evacuate Nitrogen.
• Connect the gas valves of a vacuum gauge, vacuum pump, and outdoor unit
(see diagram). Start the vacuum pump and allow to run for at least 30 minutes at
a level of 500 microns or less.
• Shut off the vacuum and continue to monitor vacuum gauge for another 15
minutes. The pressure should not rise above 800 microns.
• lf a vacuum of 500 microns cannot be obtained, or if it rises above 800 microns
during the l5-minute monitoring period, pressurize the system with nitrogen and
look for leaks. Repair any leaks that are found and repeat the vacuum testing.
• Close the valves to the vacuum pump and gauge and disconnect from the
outdoor unit.
• Tighten bonnet (cover) of gas valve and open gas and liquid valves completely.
System Testing
• Before testing the system, ensure that cut-off valves of the connection pipes are opened and that all debris (such
as packing scraps, thrums, etc.) are clear from the unit.
• Switch on power to the system and press the ''ON/OFF'' button on the remote
control to activate the indoor unit.
• Press ''MODE'' button repeatedly, taking a moment on each setting to ensure
that system functions in all modes. (Note: HEAT mode will function only on
heat pump models)
• If the remote control is lost, emergency run operation can be initiated by
pressing the button in the upper right corner of the indoor unit under the cover
panel. (see diagram)
Installation Verification
• Have both units been securely and firmly installed?
• Are all piping connections secured?
• Have the refrigeration lines been sufficiently insulated?
• Have you verified the length of the connection pipes and the refrigerant capacity?
• Have you conducted all leakage and system tests?
• Does the unit drain properly?
• Are all electrical connections in compliance with local standards?
• Has the unit been properly grounded?
• Is the power cord as specified?
• Are all air inlets and outlets free from obstruction?

- -
15
Testing (Cont)
Test operation
Before test operation
• Do not switch on power before installation is complete.
• Verify that all electrical connections are connected properly.
• Verify that valves of the line set have been opened.
• Remove all construction materials such as boxes, packaging, etc from
operating area of the units.
Manual operation (18,000 BTU) units only
• Turn on power.
• Verify that both units have power, using a DVM check between terminals
1 and 3 on indoor unit for line voltage. If no line voltage is present, STOP. Check connections and wiring between
indoor and outdoor unit. Verify that unit has been connected as the proper wiring indicates.
• Press “ON/OFF” button on remote.
• Press “MODE” button to verify operation of all functions. Unit may take up to 4 min. to change modes.
If remote control is lost:
• Open the front panel.
• Turn function switch to “AUTO” for automatic operation (Factory preset to 81 deg.F.) Unit will operate in all
necessary modes to maintain this temperature.
• Turn function switch to “TEST” to operate unit in cool mode. (Unit will operate at last set temperature).
• Turn function switch to “RUN” mode. This mode allows use of remote control for all functions and will be the
normal setting for the function switch.
• Turn function switch to “STOP”. This function stops all unit functions.
H andling sw itch
AUTO
TEST
RUN
STOP

- -
16
Testing (Cont)
IF UNIT FAILS TO OPERATE PROPERLY
ISSUE CHECK
Unit will not operate
Verify that Red "Power" light is illuminated.
Verify that line voltage is present between terminals 1 and 3 of indoor unit.
Turn unit on with remote. (you should hear a "Beep" from indoor unit). Allow
3-4 min. for unit to restart.
Turn unit to "Test" mode. Verify that cooling function works (allow 3-4 min.
for unit to restart.)
Compressor will not operate
Turn unit to Cool mode. Allow 3-4 min for compressor timer to operate.
Check for line voltage between pins 1 and 2 of indoor unit. If no voltage is
present please call technical support.
The unit vibrates during operation Is the indoor unit firmly attached to the wall?
Is the front cover closed properly?
Inefficient Cooling (heating)
Was the refrigerant leakage test performed with good results?
Are the air flow grills (inlet and outlet free from obstructions?)
Was refrigerant added as necessary?
Appearance of water or condensation. Were refrigerant lines completely covered with insulation?
Is condensate drain routed properly (downward)?
- -
17
WARRANTY
SEA BREEZE AIR warrants the accompanying split air conditioner or heat pump system to be free of
defects in material and workmanship for the applications specified in the operation manual and
installation manual for a period of one (1) year on parts and five (5) years on compressor, valid from
the date of original retail purchase in the United States or Canada. Labor is not covered under
warranty.
If the unit exhibits a defect in normal use and is determined to be within the warranty period, SEA
BREEZE AIR will, at its option, either repair or replace the unit free of charge within a reasonable
time after the unit is returned.
This warranty DOES NOT cover:
z Damage, accidental or otherwise, to the unit while in possession of the consumer that is not a
result of a defect in material in workmanship.
z Damage caused by consumer misuse, tampering, or failure to follow all care and maintenance
instructions in the manuals.
z Damage to the finish of the case or other parts caused by water.
z Damage caused by repairs or alterations to the unit by anyone other than a qualified technician.
z Filter.
z Freight and Insurance cost for the warranty service.
Warranty Activation Card must be completed and sent in to activate the warranty for the
accompanying unit.

- -
18
MINI-SPLIT SPECIFICATIONS
Model 9A23YGX 12A23YGX 12A23ZGX 18A23ZGX
Function COOLING COOLING COOLING COOLING
Rated Voltage 115V 115V 208-230V 208V-230 V
Rated Frequency 60HZ 60HZ 60HZ 60HZ
Total Capacity (BTU/Hr) 9000 12000 12000 18000
SEER 13 13 13 13
Power Input (W) 800 960 960 1610
Rated Input (W) 900 1100 1100 2200
Rated Current (A) 7.82 9.56 5 11.4
Air Flow Volume (CFM) 350 388 483 706
Circuit Breaker Size (A) 15 20 15 20
Minimum Circuit Ampacity (A) 10 11.6 5.4 10.5
Dehumidifying Volume (pt/h) 4.2 4.2 4.2 6.3
Model of Indoor Unit 9A23YIGX 12A23YIGX 12A23ZIGX 18A23ZIGX
Fan Motor Speed (r/min) (L/M/H) 1100/1200/1300 1100/1200/1300 1350/1450/1550 1200/1300/1400
Output of Fan Motor (w) 20 20 20 25
Input of Heater (w) N/A N/A N/A N/A
Fan Motor Capacitor (uF) 4 4 1 3.5
Fan Motor RLA(A) 0.17 0.17 0.09 0.4
Fan Type-Piece Cross flow fan -1 Cross flow fan – 1 Cross flow fan – 1 Cross flow fan – 1
Diameter-Length (in) 3.5X28.5 3.5X28.5 3.5X28.5 4.2X35
Evaporator Aluminum fin-copper tube Aluminum fin-copper tube Aluminum fin-copper tube Aluminum fin-copper tube
Pipe Diameter (in) 0.275 0.275 0.275 0.275
Row-Fin Gap(in) 3-.062/2-.060 3-.062/2-.060 3-.062/2-.060 2-.055
Coil length (l) x height (H) x coil width (L)(in) 28.7X15.75X1.57 28.7X15.75X1.57 28.7X15.75X1.57 35.5X15X1
Swing Motor Model MP24EA MP24EA MP24EA MP24GA
Output of Swing Motor (w) 1.5 1.5 1.5 2
Fuse (A) 3.15A 3.15A 3.15A 3.15A
Sound Pressure Level dB (A) 38/41/45 39/42/46 40/43/47 48/50/52
Dimension (W/D/H)(in) 35.7X11.4X7.67 35.7X11.4X7.67 35.7X11.4X7.67 46.37X12.8X8.9
Dimension of Package (W/D/H)(in) 42X15X13 42X15X13 42X15X13 50X16X13
Indoor unit
Net Weight /Gross Weight (LB) 26.5/33 26.5/33 26.5/33 38.5/53
Model of Outdoor Unit 9A23YOGX 12A23YOGX 12A23ZOGX 18A23ZOGX
Compressor Model Panasonic 2P14S126B1Y Panasonic 2P16S126B1P Panasonic 2P15S236A1H Hitachi SL253SN-C7EU
Compressor Type Rotary Rotary Rotary Hermetic motor compressor
L.R.A. (A) 49 54 26 39
Compressor RLA(A) 7.5 8.8 4.1 7.6
Compressor Power Input(w) 855 750 930 1685
Overload Protector Build in Build in Build in Internal Inherent Protector
Throttling Method Capillary Capillary Capillary Capillary
Compressor Start Capacitor (uF) 40 45 30 50
Starting Method Capacitor Capacitor Capacitor Capacitor
Working Temp Range (degF) 23-109 23-109 23-109 23-109
Condenser Aluminum fin-copper tube Aluminum fin-copper tube Aluminum fin-copper tube Aluminum fin-copper tube
Pipe Diameter (in) 0.375 0.375 0.375 0.375
Rows-Fin Gap(in) 2-.062 2-.062 2-.062 2-.055
Coil length (l) x height (H) x coil width (L)(in) 30.75X20X1.73 30.75X20X1.73 30.75X20X1.73 26.88X32X1.73
Fan Motor Speed (rpm) 885 885 920 780
Output of Fan Motor (w) 48 48 48 60
Fan Motor RLA(A) 0.42 0.42 0.22 0.56
Fan Motor Capacitor (uF) 10 10 2 3.5
Air Flow Volume of Outdoor Unit(CFM) 1265 1265 1265 2649
Fan Type-Piece Axial fan –1 Axial fan –1 Axial fan –1 Axial fan –1
Fan Diameter (in) 15.75 15.75 15.75 18.11
Defrosting Method Auto defrost Auto defrost Auto defrost Auto defrost
Climate Type T1 T1 T1 T1
Isolation I I I I
Moisture Protection IP24 IP24 IP24 IP24
Design Pressure High (PSI) 362 362 362 362
Design Pressure Low (PSI) 145 145 145 145
Sound Pressure Level dB (A) 55 55 55 58
Sound Power Level dB (A) 65 65 65 68
Dimension (W/D/H)(in) 33.4X12.6X21.3 33.4X12.6X21.3 33.4X12.6X21.3 39.6X13.4X33.4
Dimension of Package (W/D/H)(in) 35X14X23 35X14X23 35X14X23 43X18X36
Net Weight /Gross Weight (LB) 88/99 88/99 88/99 139/150
Outdoor unit
Refrigerant Charge (LB) R22/2.2 R22/2.75 R22/2.75 R22 / 3.63
Design Length (ft) 26.25 26.25 26.25 24.6
Extra Refrigerant Charge per feet above .32 oz/ft .32 oz/ft .32 oz/ft .43 oz/ft
Outer Diameter Liquid Pipe (in) 1/4 1/4 1/4 3/8
Outer Diameter Gas Pipe (in) 1/2 1/2 1/2 5/8
Max Distance Height (ft) 16 16 16 32
Max Distance Length (ft) 32 32 32 49
Connection Pipe
Installation Kit Catalog Number LS1412GSB LS1412GSB LS1412GSB LS3858GSB
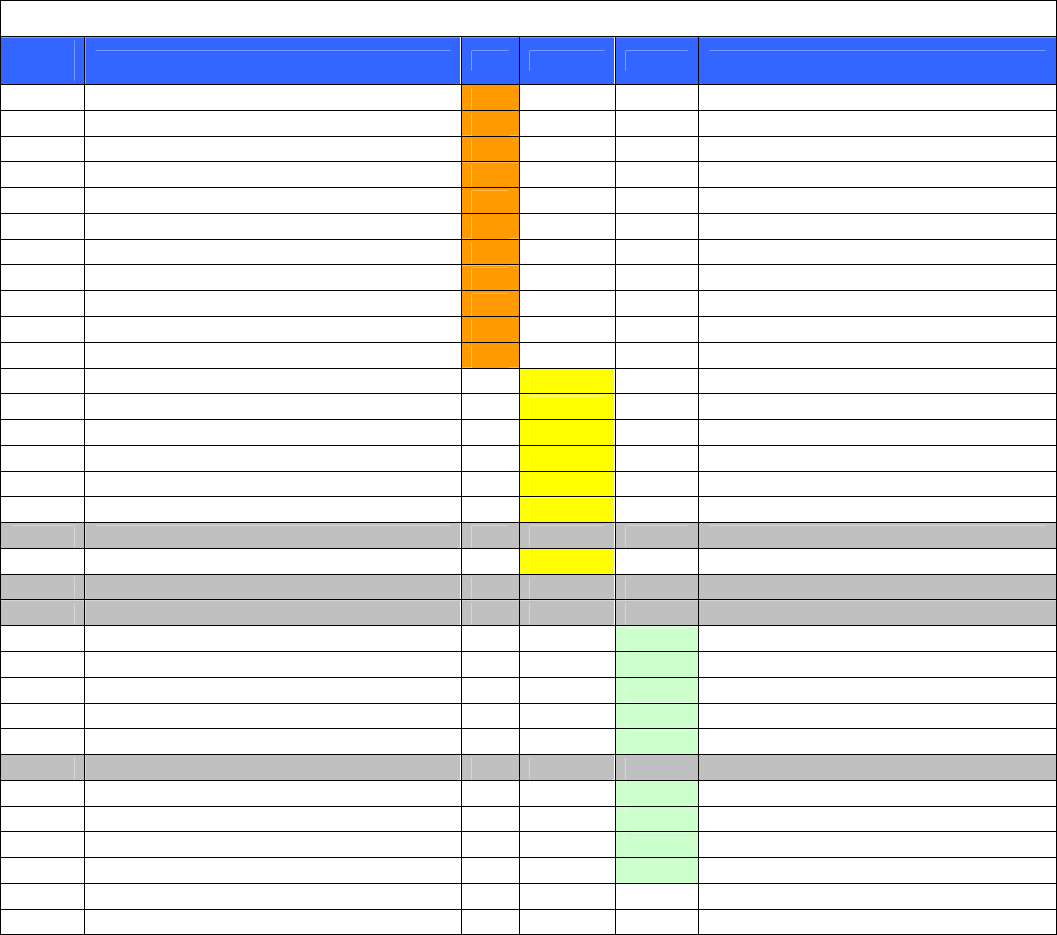
- -
19
Mini-Split Error Codes
ERROR
CODE EXPLANATION RED YELLOW GREEN NOTES
E1 High Pressure protect 1
E2 Inside Anti-Freeze Protect 2
E3 Low Pressure Protect 3
E4 Compressor Discharge protect 4 6 sec Pause before Flash Sequence
E5 low pressure over current protect 5
E6 indoor-outdoor communication Error 6
E7 Mode conflict 7
E8 high Temp protect 8
E9 cold wind protect 9
E0 AC Voltage Low 10
H6 No Indoor motor feedback 11
F1 room temp sensor open/short 1
F2 Indoor evaporator sensor open/short 2
F3 Outdoor temp sensor open/short 3
F4 Outdoor evaporator sensor open/short 4 6 sec Pause before Flash Sequence
F5 Outdoor sensor open/short 5
F6 Cooling Overload 6
F7 Unused 7
F8 Current Overload 8
F9 Unused 9
F0 Unused 10
H1 Defrost 1
H2 Static duct clean protect 2
H3 compressor overload protect 3
H4 System Abnormal 4 6 sec Pause before Flash Sequence
H5 Mode Protect 5
H6 Unused 6
H7 Synchronize fail 7
H8 Water full protect 8
H9 PTC heating Error 9
HO Heat high temp protect 10
FA Pipe Hot
FH Freeze Protect
Notes: Some Codes may not be available on some units.
Codes will flash prior to any change of state I.E. cool off, cool on, heat off, heat on, power on, etc.
Normal operation for indicator lights is as follows: Constant Red: power on, Constant Yellow: heat on,
Constant Green: cool on.
Heat Mode available for heat pump units only.