Sensors and Software NG250 Ground Penetrating Radar System User Manual NogginGold Manual
Sensors & Software Inc. Ground Penetrating Radar System NogginGold Manual
Users Manual
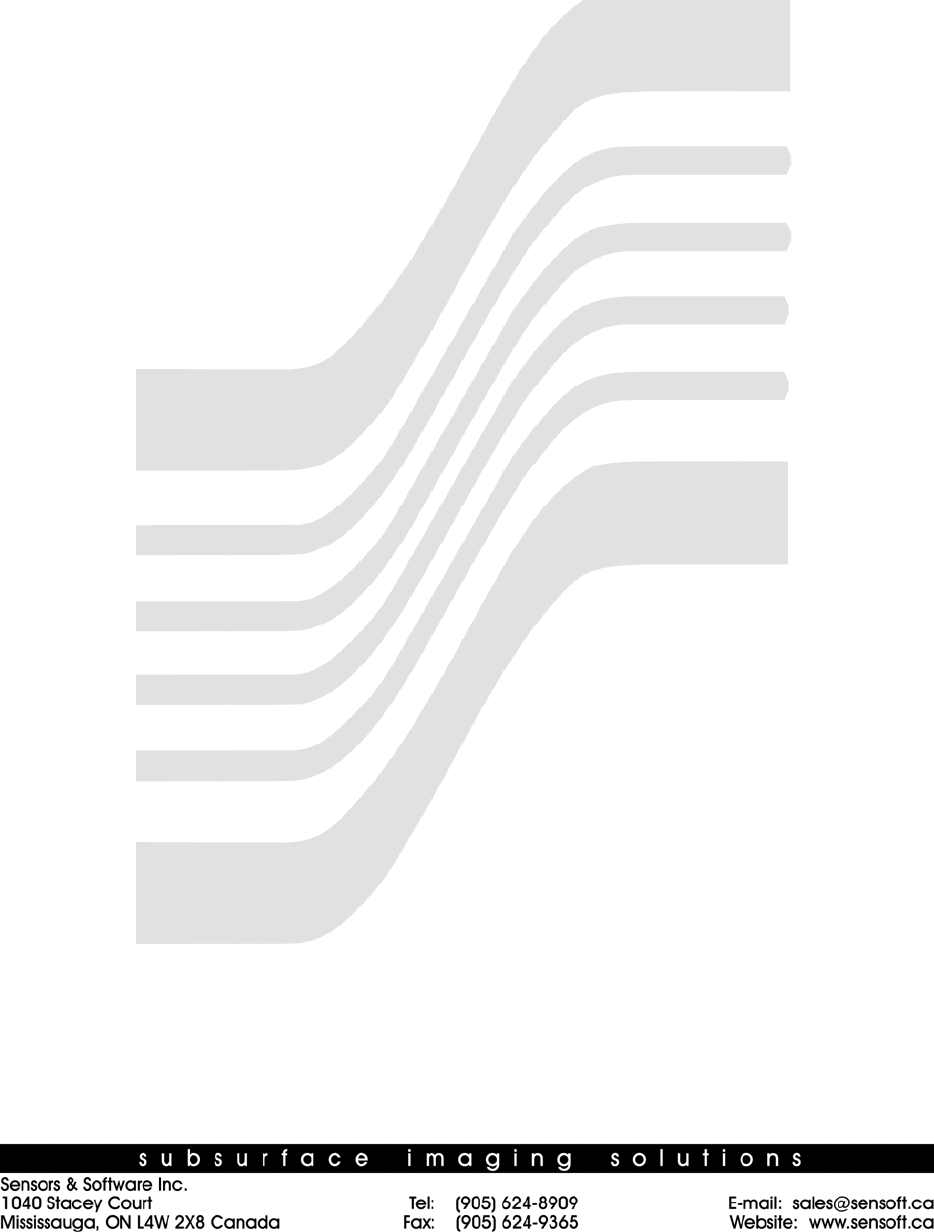
User’s Guide
Copyright 2011 Sensors & Software Inc. 1999-00273-09
Noggin


S
ENSORS
& S
OFTWARE
I
NC
. P
RODUCT
L
ICENCE
, C
OPYRIGHT
, L
IABILITY
AND
W
ARRANTY
I
NFORMATION
Important
Please read this document carefully before removing the
SOFTWARE
PRODUCT
storage media from their protective cover
or assembling the
HARDWARE
PRODUCT
. By removing the storage media or assembling the hardware, you are agreeing
to be bound by the terms of this agreement. If you do not agree to the terms of this agreement, promptly contact Sen-
sors & Software, Inc. at the address indicated at the end of this document.
Definition
The word
PRODUCT
as used herein defines any tangible item sold by Sensors & Software, Inc. and may be comprised
of
HARDWARE
PRODUCT
which consists of physical objects and
SOFTWARE
PRODUCT
which means computer programs,
codes and related support materials.
Software Product Licence Agreement
In order to preserve and protect its rights under the applicable laws, Sensors & Software, Inc. (hereafter S&S) does not
sell any rights to its Software product. Rather, S&S grants the right to use its software, diskettes (or other storage
media) and documentation (hereafter collectively called
SOFTWARE
PRODUCT
) by means of a
SOFTWARE
PRODUCT
licence. You acknowledge and agree that S&S retains worldwide title and rights to all its software and that the
SOFT-
WARE PRODUCT
contains proprietary materials protected under copyright, trademark and trade secret laws.
Grant of Software Product Licence
In consideration of payment of the licence fee which is the price you pay for the
SOFTWARE
PRODUCT
and your agree-
ment to abide by the terms and conditions of this Licence Agreement, S&S grants to you, the Licensee, a non-exclu-
sive right to use the
SOFTWARE
PRODUCT
under the following conditions:
You may:
•use the
SOFTWARE
PRODUCT
on a single workstation owned, leased or otherwise controlled by you
• copy the
SOFTWARE
PRODUCT
for backup purposes in support of your use of the product on a single workstation
You may not:
• copy, distribute or sell copies of the
SOFTWARE
PRODUCT
or accompanying written materials, including modified or
merged
SOFTWARE
PRODUCT
to others
• sell, licence, sublicence, assign or otherwise transfer this licence to anyone without the prior written consent of
S&S
• modify, adapt, translate, decompile, disassemble or create derivative works based on the
SOFTWARE
PRODUCT
Termination
This licence is effective until terminated. You may terminate the licence at any time by returning the
SOFTWARE
PROD
-
UCT
and all copies to S&S. The licence will automatically terminate without notice by S&S if you fail to comply with any
terms or conditions of this agreement. Upon termination, you agree to return all copies of the
SOFTWARE
PRODUCT
to
S&S.
Update Policy
S&S may create, from time to time, updated versions of its
SOFTWARE
PRODUCT
. At its option, S&S will make such
updates available to licencees who have paid the update fee.
Product Warranty, Limited Remedy and Limited Liability
S&S warrants the
PRODUCT
to be free from defect in material and workmanship under normal use for a period of one
year (365 days) from the date of shipment. Any third party computer systems or other items not manufactured directly
by S&S purchased with any
PRODUCT
or independently from S&S are subject to the original manufacturer's warranty
and not the responsibility of S&S.
S&S makes no other warranties including, but not limited to, any implied warranty of merchantability or fitness for a
particular purpose. If this product is defective within the warranty period stated above, your exclusive remedy shall be,
at S&S’s option to replace or repair the S&S product or refund the purchase price of the S&S product. Except where
prohibited by law, S&S will not be liable for any loss or damage arising from this S&S product, whether direct, indirect,
special, incidental or consequential regardless of the legal theory asserted.

All statements, technical information, and recommendations related to S&S products are based on information
believed to be reliable, but the accuracy or completeness is not guaranteed. Before using this product, you must eval-
uate it and determine if it is suitable for your intended application. You assume all risks and liability associated with
such use. Any statements related to the product which are not contained in S&S current publications, or any contrary
statements contained on your purchase order shall have not force or effect unless expressly agreed upon, in writing,
by an authorized officer of S&S.
S&S warrants the diskettes or other storage media on which the
SOFTWARE
PRODUCT
is furnished to be free from
defects in material and workmanship under normal use for a period of ninety (90) days from the date of purchase as
evidenced by a copy of your invoice.
Except as specified above, any
SOFTWARE
PRODUCT
is provided "as is" without warranty of any kind, either expressed
or implied, including, but not limited to, the use or result of use of the product in terms of correctness, accuracy, reliabil-
ity, currentness or otherwise. The entire risk as to the results and performance of the
PRODUCT
is assumed by you. If
the
PRODUCT
is defective or used improperly, you, and not S&S or its dealers, distributors, agents, or employees,
assume the entire cost of all necessary servicing, repair or correction.
S&S's entire liability and your exclusive remedy for
SOFTWARE
PRODUCT
shall be, at S&S's option, either
• the replacement of any diskette or hardware components which do not meet S&S's Limited Warranty and which
are returned to S&S postage prepaid with a copy of the receipt, or
• if S&S is unable to deliver a replacement diskette which is free of defects in material or workmanship, Licensee
may terminate this agreement and have the licence fee refunded by returning all copies of the
SOFTWARE
PRODUCT
postage prepaid with a copy of the receipt.
If failure of any
PRODUCT
resulted from accident, abuse or misapplication, S&S shall have no responsibility to replace
the
SOFTWARE
PRODUCT
, refund the licence fee, or replace or repair the
HARDWARE
PRODUCT
.
Do not tamper with any
PRODUCT
.
PRODUCT
contains no user serviceable parts. If tampering is evident in S&S’s
opinion, warranty is void and null.
No oral or written information or advice given by S&S, its dealers, distributors, agents or employees shall create a war-
ranty or in any way increase the scope of this warranty and you may not rely on any such information or advice.
Neither S&S nor anyone else who has been involved in the creation, production or delivery of the
PRODUCT
shall be lia-
ble for any direct, indirect, special, exemplary, incidental or consequential damages, claims or actions including lost
information, lost profits, or other damages arising out of the use or inability to use this
PRODUCT
even if S&S has been
advised of the possibility of such damages.
This warranty gives you specific rights. You may have other rights which vary from province to province, territory to ter-
ritory and certain limitations contained in this limited warranty may not apply to you.
General
pulseEKKO
®
, Noggin
®
, SpiView
®
, Conquest
®
and SnowScan
®
are registered trademarks of S&S. No right, licence, or
interest to such trademarks is granted hereunder with the purchase of the
PRODUCT
or the
SOFTWARE
PRODUCT
licence.
Governing Law
In the event of any conflict between any provision in this licence agreement and limited warranty and any applicable
provincial legislation, the applicable provincial legislation takes precedence over the contravening provision. This
agreement shall be governed and construed in accordance with the laws of the Province of Ontario, Canada.
Serviceability
Should any term of this agreement be declared void or not enforceable by any court of competent jurisdiction, the
remaining terms shall remain in full effect.
Waiver
Failure of either party to enforce any of its rights in this agreement or take action against any other party in the event of
a breach of this agreement shall not be considered a waiver of the right to subsequent enforcement of its rights or
actions in the event of subsequent breaches by the other party.

Acknowledgement
You acknowledge that you have read this agreement, understand it and agree to be bound by its terms and conditions.
You further agree that this agreement is the complete and exclusive statement of agreement between the parties and
supersedes all proposals or prior agreements oral or written between the parties relating to the subject matter of this
agreement.
Should you have any questions concerning this agreement, please contact in writing:
Sensors & Software Inc.
1040 Stacey Court
Mississauga, Ontario
Canada L4W 2X8
Tel:(905) 624-8909
Fax:(905) 624-9365
E-mail: sales@sensoft.ca
pulseEKKO, Noggin, SpiView, SnowScan, Conquest, SmartCart, SmartHandle, Conquest for Windows, EKKO_View, EKKO_Mapper,
EKKO_3D and EKKO_Pointer are Trademarks of Sensors & Software Inc.


SmartCart Table of Contents i
Table of Contents
1 General Overview
. . . . . . . . . . . . . . . . . . . . . . . . . . . . . . . . . . . . . . . . . . . . . . . .1
2 Assembling the SmartCart
. . . . . . . . . . . . . . . . . . . . . . . . . . . . . . . . . . . . . . . .2
2.1 Configuring the SmartCart for a Different Noggin System
. . . . . . . . . . . .8
2.2 Adding GPS to the SmartCart
. . . . . . . . . . . . . . . . . . . . . . . . . . . . . . . . . . .9
3 Digital Video Logger
. . . . . . . . . . . . . . . . . . . . . . . . . . . . . . . . . . . . . . . . . . . . .10
3.1 Running a DVL Detached from a Smart System
. . . . . . . . . . . . . . . . . . .13
4 Noggin
. . . . . . . . . . . . . . . . . . . . . . . . . . . . . . . . . . . . . . . . . . . . . . . . . . . . . . . . . . .14
4.1 Overview of Noggin Menu Options
. . . . . . . . . . . . . . . . . . . . . . . . . . . . . .14
4.1.1 Run. . . . . . . . . . . . . . . . . . . . . . . . . . . . . . . . . . . . . . . . . . . . . . . . . . . . . .14
4.1.2 Demo . . . . . . . . . . . . . . . . . . . . . . . . . . . . . . . . . . . . . . . . . . . . . . . . . . . .14
4.1.3 Noggin Setup . . . . . . . . . . . . . . . . . . . . . . . . . . . . . . . . . . . . . . . . . . . . . .14
4.1.4 Transfer All Buffers. . . . . . . . . . . . . . . . . . . . . . . . . . . . . . . . . . . . . . . . . .14
4.1.4.1 Copy Internal to Removable. . . . . . . . . . . . . . . . . . . . . . . . . . . . .15
4.1.5 Delete All Buffers . . . . . . . . . . . . . . . . . . . . . . . . . . . . . . . . . . . . . . . . . . .15
4.1.6 Transfer Setup . . . . . . . . . . . . . . . . . . . . . . . . . . . . . . . . . . . . . . . . . . . . .15
4.1.7 Return. . . . . . . . . . . . . . . . . . . . . . . . . . . . . . . . . . . . . . . . . . . . . . . . . . . .15
4.1.8 Noggin Screen Overview . . . . . . . . . . . . . . . . . . . . . . . . . . . . . . . . . . . . .15
4.1.9 Section A - Data Parameters . . . . . . . . . . . . . . . . . . . . . . . . . . . . . . . . . .16
4.1.10 Section B - Data Display . . . . . . . . . . . . . . . . . . . . . . . . . . . . . . . . . . . . .17
4.1.10.1 Depth Lines . . . . . . . . . . . . . . . . . . . . . . . . . . . . . . . . . . . . . . . . .17
4.1.10.2 Battery Voltage Indicator . . . . . . . . . . . . . . . . . . . . . . . . . . . . . . .17
4.1.10.3 Start of Section Indicator . . . . . . . . . . . . . . . . . . . . . . . . . . . . . . .17
4.1.10.4 Fiducial Markers . . . . . . . . . . . . . . . . . . . . . . . . . . . . . . . . . . . . . .18
4.1.11 Section C - Menu . . . . . . . . . . . . . . . . . . . . . . . . . . . . . . . . . . . . . . . . . . .18
4.2 Noggin Menu Options
. . . . . . . . . . . . . . . . . . . . . . . . . . . . . . . . . . . . . . . . .19
4.2.1 Exit . . . . . . . . . . . . . . . . . . . . . . . . . . . . . . . . . . . . . . . . . . . . . . . . . . . . . .19
4.2.2 Print Menu . . . . . . . . . . . . . . . . . . . . . . . . . . . . . . . . . . . . . . . . . . . . . . . .19
4.2.3 View Menu . . . . . . . . . . . . . . . . . . . . . . . . . . . . . . . . . . . . . . . . . . . . . . . .21
4.2.4 Calib (Calibration) Menu. . . . . . . . . . . . . . . . . . . . . . . . . . . . . . . . . . . . . .21
4.2.4.1 Hyperbola Matching . . . . . . . . . . . . . . . . . . . . . . . . . . . . . . . . . . . . . . . . .22
4.2.4.2 Identifying Air Reflections. . . . . . . . . . . . . . . . . . . . . . . . . . . . . . .24

ii Table of Contents SmartCart
4.2.4.3 Target of Known Depth. . . . . . . . . . . . . . . . . . . . . . . . . . . . . . . . .25
4.2.4.4 Selecting a Media. . . . . . . . . . . . . . . . . . . . . . . . . . . . . . . . . . . . .26
4.2.4.5 Input a Velocity Value . . . . . . . . . . . . . . . . . . . . . . . . . . . . . . . . . .26
4.2.5 Depth Menu . . . . . . . . . . . . . . . . . . . . . . . . . . . . . . . . . . . . . . . . . . . . . . .27
4.2.6 Gain Menu . . . . . . . . . . . . . . . . . . . . . . . . . . . . . . . . . . . . . . . . . . . . . . . .27
4.2.7 Start Menu . . . . . . . . . . . . . . . . . . . . . . . . . . . . . . . . . . . . . . . . . . . . . . . .28
4.2.8 Stop Menu . . . . . . . . . . . . . . . . . . . . . . . . . . . . . . . . . . . . . . . . . . . . . . . .28
4.2.9 Filter Menu . . . . . . . . . . . . . . . . . . . . . . . . . . . . . . . . . . . . . . . . . . . . . . . .28
4.3 Noggin Data Acquisition
. . . . . . . . . . . . . . . . . . . . . . . . . . . . . . . . . . . . . . .29
4.3.1 Collecting Data using the Odometer . . . . . . . . . . . . . . . . . . . . . . . . . . . .29
4.3.1.1 Reducing Data Quality by Moving too Fast . . . . . . . . . . . . . . . . .30
4.3.1.2 Backing up the System to Pinpoint Target Positions . . . . . . . . . .30
4.3.2 Collecting Data in Free Run Mode . . . . . . . . . . . . . . . . . . . . . . . . . . . . . .31
4.3.2.1 Controlling Data Collection Speed in Free Run Mode . . . . . . . . .31
4.3.2.2 Noggin Speed In Free Run Mode. . . . . . . . . . . . . . . . . . . . . . . . .31
4.3.2.3 Positions in Free Run Mode . . . . . . . . . . . . . . . . . . . . . . . . . . . . .31
4.3.3 Collecting Data using the Trigger (or B) Button . . . . . . . . . . . . . . . . . . . .32
4.3.4 Noggin Data Screens . . . . . . . . . . . . . . . . . . . . . . . . . . . . . . . . . . . . . . . .32
4.3.5 Saving Data . . . . . . . . . . . . . . . . . . . . . . . . . . . . . . . . . . . . . . . . . . . . . . .33
4.3.6 Deleting Data . . . . . . . . . . . . . . . . . . . . . . . . . . . . . . . . . . . . . . . . . . . . . .33
4.3.7 Special Buttons During Data Acquisition . . . . . . . . . . . . . . . . . . . . . . . . .33
4.3.7.1 Fiducial Markers . . . . . . . . . . . . . . . . . . . . . . . . . . . . . . . . . . . . . .33
4.3.7.2 Background Subtraction Filter . . . . . . . . . . . . . . . . . . . . . . . . . . .33
4.3.8 Error Messages . . . . . . . . . . . . . . . . . . . . . . . . . . . . . . . . . . . . . . . . . . . .34
4.4 Noggin Setup
. . . . . . . . . . . . . . . . . . . . . . . . . . . . . . . . . . . . . . . . . . . . . . . .35
4.4.1 Editing DVL Settings . . . . . . . . . . . . . . . . . . . . . . . . . . . . . . . . . . . . . . . .35
4.4.2 Default Settings . . . . . . . . . . . . . . . . . . . . . . . . . . . . . . . . . . . . . . . . . . . .35
4.4.3 Time and Date . . . . . . . . . . . . . . . . . . . . . . . . . . . . . . . . . . . . . . . . . . . . .35
4.4.4 Save Data Mode. . . . . . . . . . . . . . . . . . . . . . . . . . . . . . . . . . . . . . . . . . . .35
4.4.5 Units Used . . . . . . . . . . . . . . . . . . . . . . . . . . . . . . . . . . . . . . . . . . . . . . . .36
4.4.6 Odometer Markers . . . . . . . . . . . . . . . . . . . . . . . . . . . . . . . . . . . . . . . . . .36
4.4.7 Odometer Calibration . . . . . . . . . . . . . . . . . . . . . . . . . . . . . . . . . . . . . . . .36
4.4.8 Cart Direction . . . . . . . . . . . . . . . . . . . . . . . . . . . . . . . . . . . . . . . . . . . . . .37
4.4.9 Trigger Method . . . . . . . . . . . . . . . . . . . . . . . . . . . . . . . . . . . . . . . . . . . . .37
4.4.10 Odometer Number . . . . . . . . . . . . . . . . . . . . . . . . . . . . . . . . . . . . . . . . . .38
4.4.11 Label Size. . . . . . . . . . . . . . . . . . . . . . . . . . . . . . . . . . . . . . . . . . . . . . . . .38
4.4.12 Noggin System. . . . . . . . . . . . . . . . . . . . . . . . . . . . . . . . . . . . . . . . . . . . .39
4.4.13 Station Interval . . . . . . . . . . . . . . . . . . . . . . . . . . . . . . . . . . . . . . . . . . . . .39
4.4.14 Plot Interval . . . . . . . . . . . . . . . . . . . . . . . . . . . . . . . . . . . . . . . . . . . . . . .42

SmartCart Table of Contents iii
4.4.15 Linear Gain. . . . . . . . . . . . . . . . . . . . . . . . . . . . . . . . . . . . . . . . . . . . . . . .42
4.4.16 Arrow Reference . . . . . . . . . . . . . . . . . . . . . . . . . . . . . . . . . . . . . . . . . . .43
4.4.17 Window Zooming . . . . . . . . . . . . . . . . . . . . . . . . . . . . . . . . . . . . . . . . . . .43
4.4.18 GPS Setup Menu . . . . . . . . . . . . . . . . . . . . . . . . . . . . . . . . . . . . . . . . . . .44
4.4.19 Transfer Rate . . . . . . . . . . . . . . . . . . . . . . . . . . . . . . . . . . . . . . . . . . . . . .47
4.4.20 Reset Counter . . . . . . . . . . . . . . . . . . . . . . . . . . . . . . . . . . . . . . . . . . . . .47
4.5 Noggin File Management
. . . . . . . . . . . . . . . . . . . . . . . . . . . . . . . . . . . . . .48
4.5.1 Transferring Noggin Data to a PC using the Removable Drive . . . . . . . .48
4.5.2 Copying Noggin Data from the Internal Drive to the Removable Drive . .49
4.5.3 Transferring Noggin Data to a PC using the Optional PXFER Cable. . . .49
4.5.4 Viewing Noggin Data Files using Win_SpiView . . . . . . . . . . . . . . . . . . . .49
4.5.5 Deleting all Buffer Files on the DVL . . . . . . . . . . . . . . . . . . . . . . . . . . . . .49
4.6 Transfer Setup
. . . . . . . . . . . . . . . . . . . . . . . . . . . . . . . . . . . . . . . . . . . . . . .49
4.7 Advanced Topics
. . . . . . . . . . . . . . . . . . . . . . . . . . . . . . . . . . . . . . . . . . . . .50
4.7.1 How Depth is Determined . . . . . . . . . . . . . . . . . . . . . . . . . . . . . . . . . . . .50
5 Noggin
. . . . . . . . . . . . . . . . . . . . . . . . . . . . . . . . . . . . . . . . . . . . . . . . . . . . . . . . . . .51
5.1 Overview of Noggin Menu Options
. . . . . . . . . . . . . . . . . . . . . . . . . . . . . .51
5.1.1 Line. . . . . . . . . . . . . . . . . . . . . . . . . . . . . . . . . . . . . . . . . . . . . . . . . . . . . .51
5.1.2 Grid. . . . . . . . . . . . . . . . . . . . . . . . . . . . . . . . . . . . . . . . . . . . . . . . . . . . . .51
5.1.3 Setup . . . . . . . . . . . . . . . . . . . . . . . . . . . . . . . . . . . . . . . . . . . . . . . . . . . .52
5.1.4 File Management . . . . . . . . . . . . . . . . . . . . . . . . . . . . . . . . . . . . . . . . . . .52
5.1.5 Run without Saving Data . . . . . . . . . . . . . . . . . . . . . . . . . . . . . . . . . . . . .52
5.1.6 Utilities . . . . . . . . . . . . . . . . . . . . . . . . . . . . . . . . . . . . . . . . . . . . . . . . . . .52
5.1.7 Set Storage Drive . . . . . . . . . . . . . . . . . . . . . . . . . . . . . . . . . . . . . . . . . . .53
5.1.8 Return. . . . . . . . . . . . . . . . . . . . . . . . . . . . . . . . . . . . . . . . . . . . . . . . . . . .53
5.2 Noggin Data Acquisition
. . . . . . . . . . . . . . . . . . . . . . . . . . . . . . . . . . . . . . .54
5.2.1 Replaying or Overwriting Data . . . . . . . . . . . . . . . . . . . . . . . . . . . . . . . . .54
5.2.2 Screen Overview . . . . . . . . . . . . . . . . . . . . . . . . . . . . . . . . . . . . . . . . . . .55
5.2.3 Section A – Position Information . . . . . . . . . . . . . . . . . . . . . . . . . . . . . . .55
5.2.4 Section B - Data Display . . . . . . . . . . . . . . . . . . . . . . . . . . . . . . . . . . . . .55
5.2.4.1 Depth Lines . . . . . . . . . . . . . . . . . . . . . . . . . . . . . . . . . . . . . . . . .56
5.2.4.2 Fiducial Markers . . . . . . . . . . . . . . . . . . . . . . . . . . . . . . . . . . . . . .56
5.2.5 Section C - Menu . . . . . . . . . . . . . . . . . . . . . . . . . . . . . . . . . . . . . . . . . . .56
5.2.6 Gain . . . . . . . . . . . . . . . . . . . . . . . . . . . . . . . . . . . . . . . . . . . . . . . . . . . . .57

iv Table of Contents SmartCart
5.2.7 Collecting Data using the Odometer . . . . . . . . . . . . . . . . . . . . . . . . . . . .58
5.2.7.1 Reducing Data Quality by Moving too Fast . . . . . . . . . . . . . . . . .58
5.2.7.2 Backing up the Smart System to Pinpoint Target Positions . . . . .59
5.2.8 Collecting Data in Free Run Mode . . . . . . . . . . . . . . . . . . . . . . . . . . . . . .59
5.2.8.1 Controlling Data Collection Speed in Free Run Mode . . . . . . . . .60
5.2.8.2 Noggin Speed in Free Run Mode . . . . . . . . . . . . . . . . . . . . . . . . .60
5.2.8.3 Positions in Free Run Mode . . . . . . . . . . . . . . . . . . . . . . . . . . . . .60
5.2.9 Collecting Data using the Trigger (or B) Button . . . . . . . . . . . . . . . . . . . .60
5.2.10 Noggin Data Screens . . . . . . . . . . . . . . . . . . . . . . . . . . . . . . . . . . . . . . . .61
5.2.11 Calib. (Calibration) Menu . . . . . . . . . . . . . . . . . . . . . . . . . . . . . . . . . . . . .62
5.2.11.1 Hyperbola Matching . . . . . . . . . . . . . . . . . . . . . . . . . . . . . . . . . . .62
5.2.11.2 Identifying Air Reflections. . . . . . . . . . . . . . . . . . . . . . . . . . . . . . .64
5.2.11.3 Target of Known Depth. . . . . . . . . . . . . . . . . . . . . . . . . . . . . . . . .65
5.2.12 Error Messages . . . . . . . . . . . . . . . . . . . . . . . . . . . . . . . . . . . . . . . . . . . .66
5.3 Noggin Setup
. . . . . . . . . . . . . . . . . . . . . . . . . . . . . . . . . . . . . . . . . . . . . . . .67
5.3.1 System Parameters . . . . . . . . . . . . . . . . . . . . . . . . . . . . . . . . . . . . . . . . .67
5.3.1.1 Depth . . . . . . . . . . . . . . . . . . . . . . . . . . . . . . . . . . . . . . . . . . . . . .67
5.3.1.2 Velocity . . . . . . . . . . . . . . . . . . . . . . . . . . . . . . . . . . . . . . . . . . . . .68
5.3.1.3 Depth Units. . . . . . . . . . . . . . . . . . . . . . . . . . . . . . . . . . . . . . . . . .68
5.3.1.4 Noggin System . . . . . . . . . . . . . . . . . . . . . . . . . . . . . . . . . . . . . . .68
5.3.1.5 Stacks . . . . . . . . . . . . . . . . . . . . . . . . . . . . . . . . . . . . . . . . . . . . . .69
5.3.1.6 Linear Time Gain . . . . . . . . . . . . . . . . . . . . . . . . . . . . . . . . . . . . .70
5.3.1.7 Position Units . . . . . . . . . . . . . . . . . . . . . . . . . . . . . . . . . . . . . . . .70
5.3.2 Cart Parameters. . . . . . . . . . . . . . . . . . . . . . . . . . . . . . . . . . . . . . . . . . . .71
5.3.2.1 Cart Direction . . . . . . . . . . . . . . . . . . . . . . . . . . . . . . . . . . . . . . . .71
5.3.2.2 Trigger Method . . . . . . . . . . . . . . . . . . . . . . . . . . . . . . . . . . . . . . .71
5.3.2.3 Auto Start . . . . . . . . . . . . . . . . . . . . . . . . . . . . . . . . . . . . . . . . . . .72
5.3.2.4 Arrow Offset . . . . . . . . . . . . . . . . . . . . . . . . . . . . . . . . . . . . . . . . .72
5.3.2.5 Trip Menu . . . . . . . . . . . . . . . . . . . . . . . . . . . . . . . . . . . . . . . . . . .72
5.3.2.6 Transfer Rate . . . . . . . . . . . . . . . . . . . . . . . . . . . . . . . . . . . . . . . .72
5.3.2.7 Odometer Number . . . . . . . . . . . . . . . . . . . . . . . . . . . . . . . . . . . .73
5.3.3 Line Parameters. . . . . . . . . . . . . . . . . . . . . . . . . . . . . . . . . . . . . . . . . . . .74
5.3.3.1 Start Position . . . . . . . . . . . . . . . . . . . . . . . . . . . . . . . . . . . . . . . .74
5.3.3.2 Line Direction . . . . . . . . . . . . . . . . . . . . . . . . . . . . . . . . . . . . . . . .74
5.3.3.3 Station Interval . . . . . . . . . . . . . . . . . . . . . . . . . . . . . . . . . . . . . . .75
5.3.3.4 Plot Interval. . . . . . . . . . . . . . . . . . . . . . . . . . . . . . . . . . . . . . . . . .78
5.3.4 Grid Parameters. . . . . . . . . . . . . . . . . . . . . . . . . . . . . . . . . . . . . . . . . . . .79
5.3.4.1 Grid Type . . . . . . . . . . . . . . . . . . . . . . . . . . . . . . . . . . . . . . . . . . .79
5.3.4.2 Survey Format . . . . . . . . . . . . . . . . . . . . . . . . . . . . . . . . . . . . . . .81
5.3.4.3 Grid Dimensions. . . . . . . . . . . . . . . . . . . . . . . . . . . . . . . . . . . . . .83
5.3.4.4 Line Spacing. . . . . . . . . . . . . . . . . . . . . . . . . . . . . . . . . . . . . . . . .83
5.3.5 GPS Parameters . . . . . . . . . . . . . . . . . . . . . . . . . . . . . . . . . . . . . . . . . . .85
5.3.6 Set Defaults . . . . . . . . . . . . . . . . . . . . . . . . . . . . . . . . . . . . . . . . . . . . . . .89
5.4 Noggin File Management
. . . . . . . . . . . . . . . . . . . . . . . . . . . . . . . . . . . . . .90

SmartCart Table of Contents v
5.4.1 Transferring Noggin Data to a PC using the Removable Drive . . . . . . . .90
5.4.2 Copying Noggin Data from the Internal Drive to the Removable Drive . .91
5.4.3 Transferring Noggin Data to a PC using the PXFER Cable . . . . . . . . . . .91
5.4.4 Viewing Data Files on the External Computer . . . . . . . . . . . . . . . . . . . . .91
5.4.5 Deleting Data on the DVL. . . . . . . . . . . . . . . . . . . . . . . . . . . . . . . . . . . . .91
5.5 Noggin Utilities
. . . . . . . . . . . . . . . . . . . . . . . . . . . . . . . . . . . . . . . . . . . . . . .92
5.5.1 Time and Date . . . . . . . . . . . . . . . . . . . . . . . . . . . . . . . . . . . . . . . . . . . . .92
5.5.2 Odometer Calibration . . . . . . . . . . . . . . . . . . . . . . . . . . . . . . . . . . . . . . . .92
5.5.3 Upgrade . . . . . . . . . . . . . . . . . . . . . . . . . . . . . . . . . . . . . . . . . . . . . . . . . .93
5.5.4 System Information . . . . . . . . . . . . . . . . . . . . . . . . . . . . . . . . . . . . . . . . .93
5.5.5 DVL Recording Space . . . . . . . . . . . . . . . . . . . . . . . . . . . . . . . . . . . . . . .93
5.5.6 Transfer Mode . . . . . . . . . . . . . . . . . . . . . . . . . . . . . . . . . . . . . . . . . . . . .93
6 Troubleshooting
. . . . . . . . . . . . . . . . . . . . . . . . . . . . . . . . . . . . . . . . . . . . . . . . .94
6.1 Power Supply
. . . . . . . . . . . . . . . . . . . . . . . . . . . . . . . . . . . . . . . . . . . . . . . .94
6.2 System Communications
. . . . . . . . . . . . . . . . . . . . . . . . . . . . . . . . . . . . . .94
6.3 System Overheating
. . . . . . . . . . . . . . . . . . . . . . . . . . . . . . . . . . . . . . . . . .95
6.4 DVL Problem
. . . . . . . . . . . . . . . . . . . . . . . . . . . . . . . . . . . . . . . . . . . . . . . .95
6.5 Noggin Problem
. . . . . . . . . . . . . . . . . . . . . . . . . . . . . . . . . . . . . . . . . . . . . .95
6.6 Creating a Test Line for Data Quality
. . . . . . . . . . . . . . . . . . . . . . . . . . . .96
6.7 Contacting Sensors & Software Inc.
. . . . . . . . . . . . . . . . . . . . . . . . . . . . .96
7 Care and Maintenance
. . . . . . . . . . . . . . . . . . . . . . . . . . . . . . . . . . . . . . . . . . .97
7.1 Battery Care
. . . . . . . . . . . . . . . . . . . . . . . . . . . . . . . . . . . . . . . . . . . . . . . . .97
7.2 DVL Internal Battery
. . . . . . . . . . . . . . . . . . . . . . . . . . . . . . . . . . . . . . . . . .97
7.3 Cable Care
. . . . . . . . . . . . . . . . . . . . . . . . . . . . . . . . . . . . . . . . . . . . . . . . . .97
7.4 Skid Pads
. . . . . . . . . . . . . . . . . . . . . . . . . . . . . . . . . . . . . . . . . . . . . . . . . . .98
7.5 Storage Cases
. . . . . . . . . . . . . . . . . . . . . . . . . . . . . . . . . . . . . . . . . . . . . . .99
7.6 Spare Parts
. . . . . . . . . . . . . . . . . . . . . . . . . . . . . . . . . . . . . . . . . . . . . . . . . .99

SmartCart Table of Contents vi
Appendix A Noggin Data file Format
. . . . . . . . . . . . . . . . . . . . . . . . . . .A-1
Appendix B Health & Safety Certification
. . . . . . . . . . . . . . . . . . . . . . . B-1
Appendix C GPR Emissions, Interference and Regulations
. . . . . .C-1
C-1 FCC Regulations (USA)
. . . . . . . . . . . . . . . . . . . . . . . . . . . . . . . . . . . . . . . . . C-2
C-2 ETSI Regulations for the EC (European Community)
. . . . . . . . . . . . . . . C-6
C-3 Industry Canada Regulations
. . . . . . . . . . . . . . . . . . . . . . . . . . . . . . . . . . . . . C-7
Appendix D Instrument Interference
. . . . . . . . . . . . . . . . . . . . . . . . . . . .D-1
Appendix E Safety Around Explosive Devices
. . . . . . . . . . . . . . . . . . .E-1
Appendix F Using the PXFER Cable and WinPXFER Software
. . . F-1
F1 Transferring Data to a PC using the PXFER Cable
. . . . . . . . . . . . . . . . . F-1
F1.1 Connecting the Digital Video Logger to a PC
. . . . . . . . . . . . . . . . . . . . . . . F-1
F1.2 PXFER Cable Types
. . . . . . . . . . . . . . . . . . . . . . . . . . . . . . . . . . . . . . . . . . . F-2
F1.3 Installing and Running the WinPXFER Program
. . . . . . . . . . . . . . . . . . . . F-3
F1.4 Setting the DVL to the PXFER Cable Type
. . . . . . . . . . . . . . . . . . . . . . . . . F-4
F1.5 Transferring Noggin Data Buffer Files
. . . . . . . . . . . . . . . . . . . . . . . . . . . . . F-4
F1.6 Exporting Noggin Data
. . . . . . . . . . . . . . . . . . . . . . . . . . . . . . . . . . . . . . . . . . F-5
F2 Transferring Noggin PCX Files to an External PC using WinPXFER
.
F-6
Appendix G GPR Glossaries
. . . . . . . . . . . . . . . . . . . . . . . . . . . . . . . . . . .G-1
G-1 Basic GPR Terms
. . . . . . . . . . . . . . . . . . . . . . . . . . . . . . . . . . . . . . . . . . . . . . . .G-1
G-2 Common GPR Terms
. . . . . . . . . . . . . . . . . . . . . . . . . . . . . . . . . . . . . . . . . . . .G-2
G-3 Advanced GPR Terms
. . . . . . . . . . . . . . . . . . . . . . . . . . . . . . . . . . . . . . . . . . .G-3
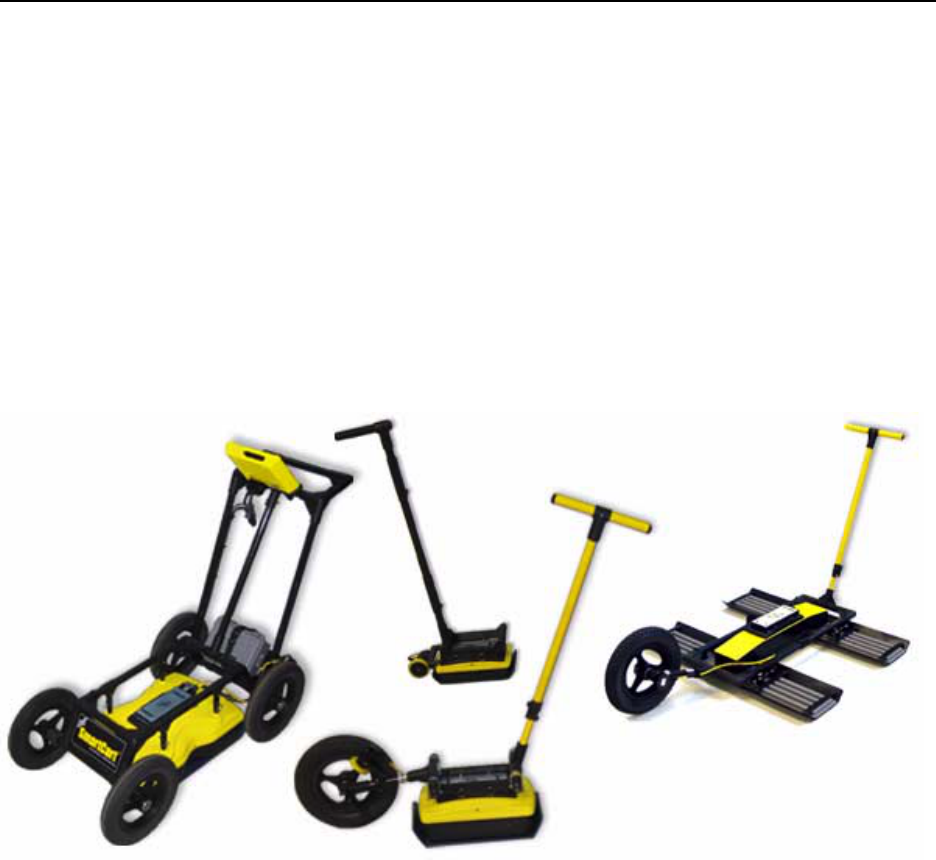
Noggin 1-General Overview
1
1 General Overview
Noggins are completely self-contained Ground Penetrating Radar (GPR) systems. Once the unit
has been assembled into its deployment configuration and powered up you can be carrying out a
GPR survey in less than a minute. There are several different Noggin configurations available:
the SmartCart, SmartHandle, SmartTow and the Rock Noggin.
This manual describes the assembly of each Noggin configuration, how to set survey parameters
and how to run the system to collect data in lines or grids.
Each Smart System’s Digital Video Logger (DVL) comes with the embedded software to acquire
data and replay data files. Data management software allows the data to be transferred to an
external computer for further processing and/or plotting.
Figure: 1-1 Noggin configurations
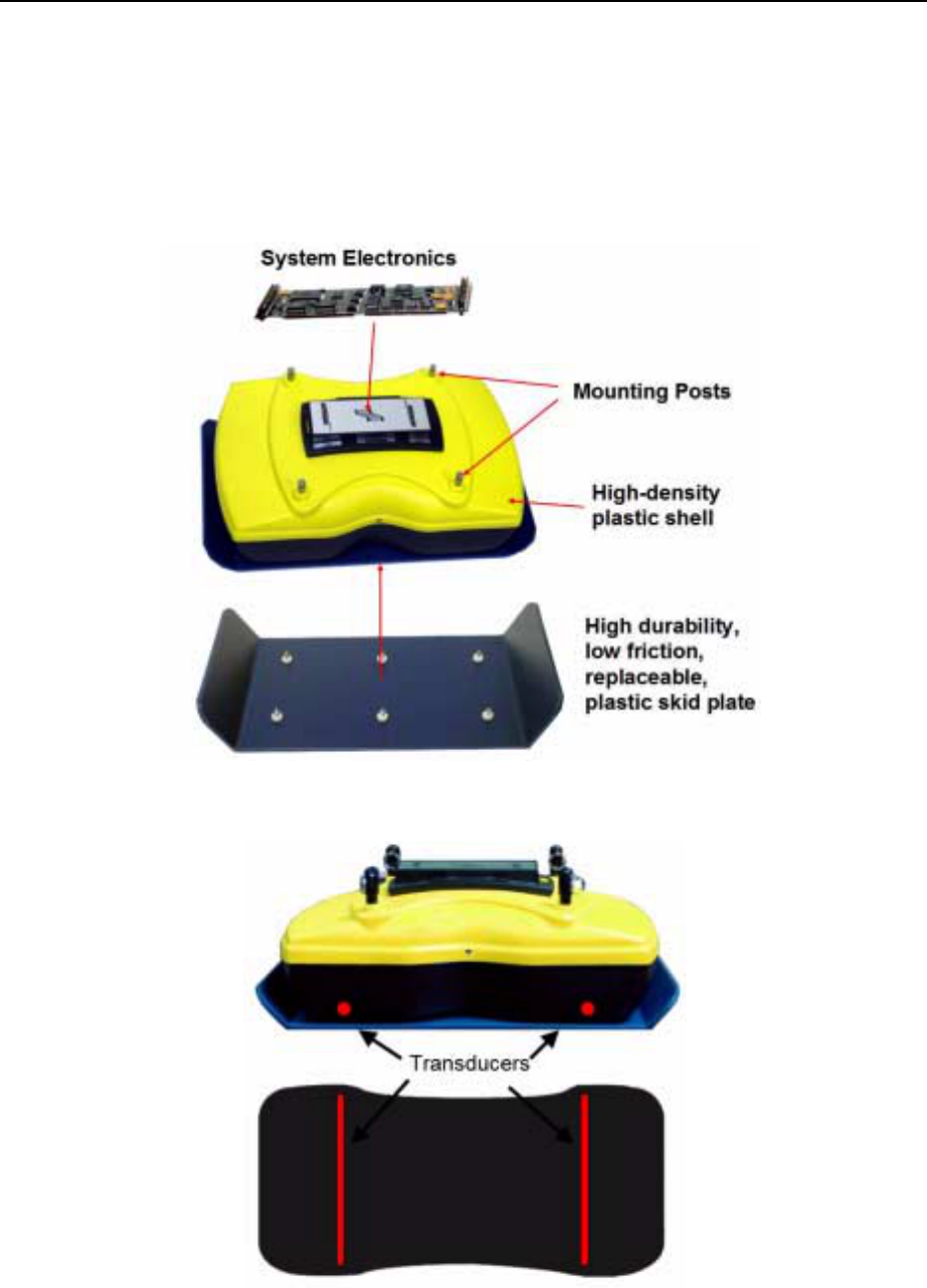
2-Noggin Components Noggin
2
2 Noggin Components
The Noggin family of GPR systems consists of the Noggin 100, 250, 500 and 1000.
The basic configuration and key components of the Noggin 250, 500 and 1000 are shown in
Figure 2-1 and Figure 2-2. The key components of the Noggin 100 are shown in Figure 2-3.
Figure: 2-1 Noggin components
Figure: 2-2 Location of the Noggin transducers
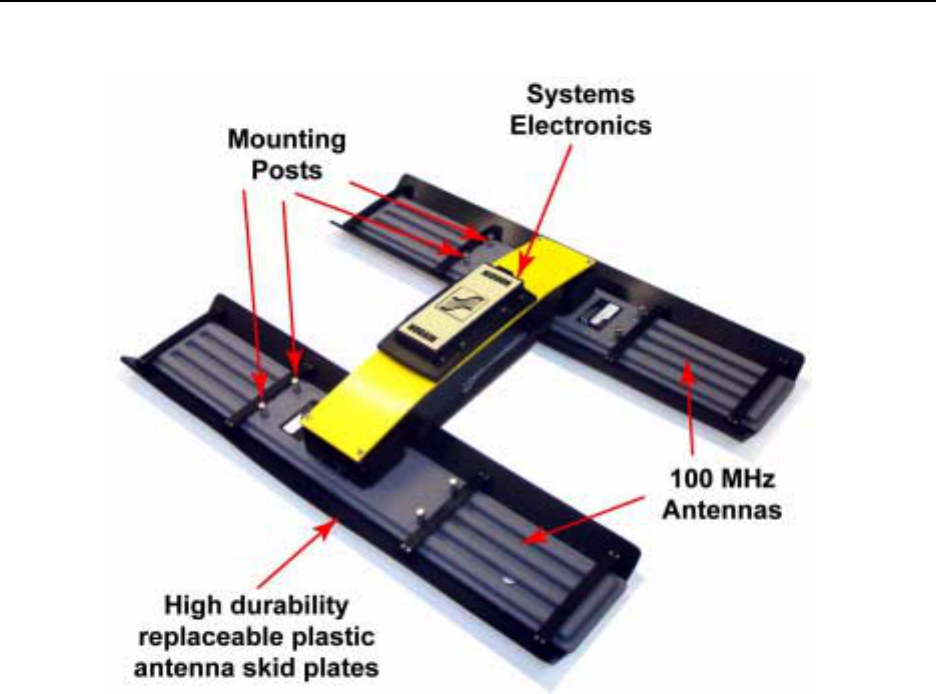
Noggin 2-Noggin Components
3
Figure: 2-3 Noggin 100 components
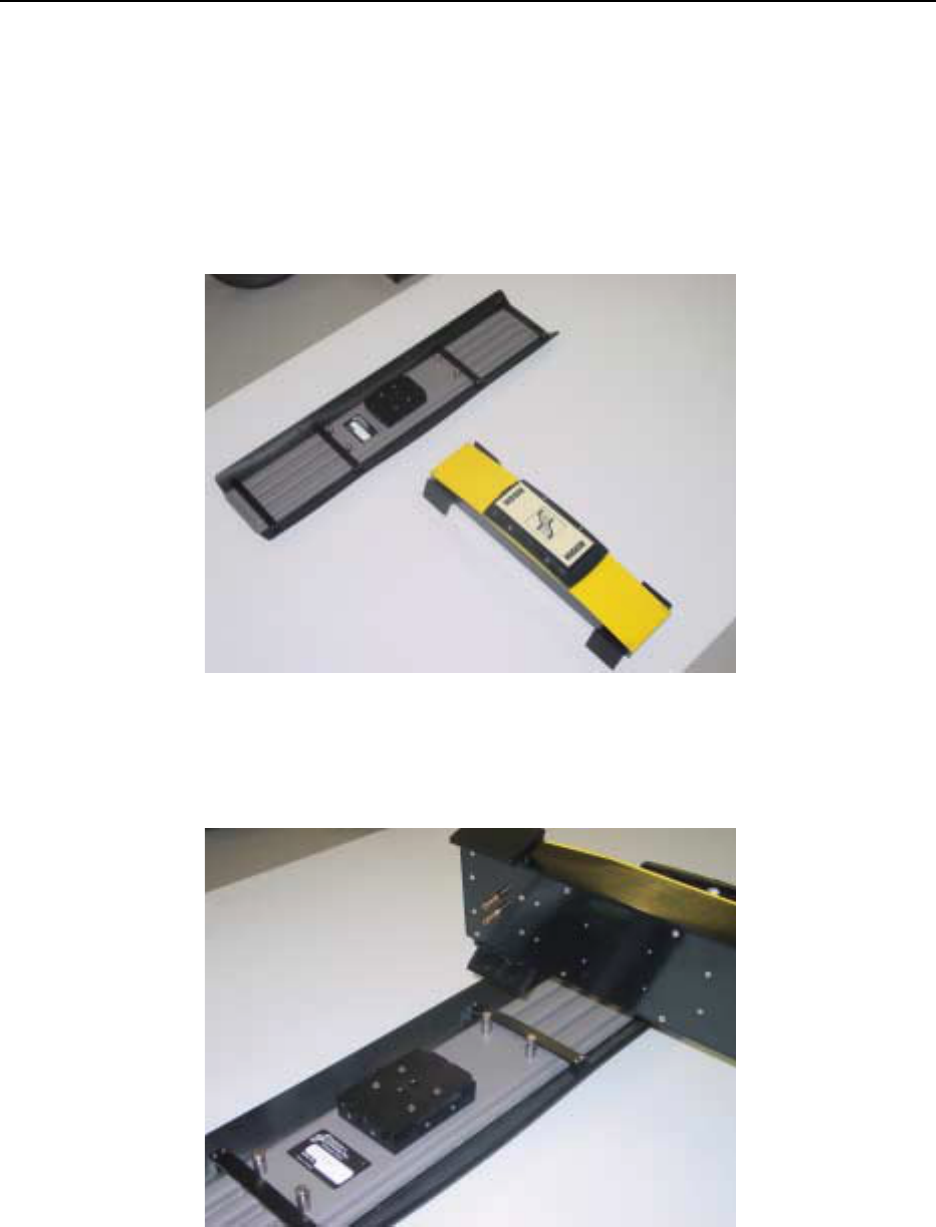
3-Noggin 100 Assembly Noggin
4
3 Noggin 100 Assembly
Unlike the higher frequency Noggins, the Noggin 100 comes with the antennas and electronics
as separate units that need to be assembled.
To assemble, space the 100 MHz antennas about 0.5 meters apart with the mounting blocks
facing up.
Figure: 3-1 Noggin 100 assembly of electronics to antenna.
Place one end of the Noggin 100 electronics module over one of the antennas and press
downward until it is seated.
Figure: 3-2 Connecting the electronics to the 100 MHz antenna. The 2 brass sockets in the bottom of the electronics
mate with the 2 brass pins in the antenna mounting block.
Secure using the electronics to the antenna using the 2 plastic latches.
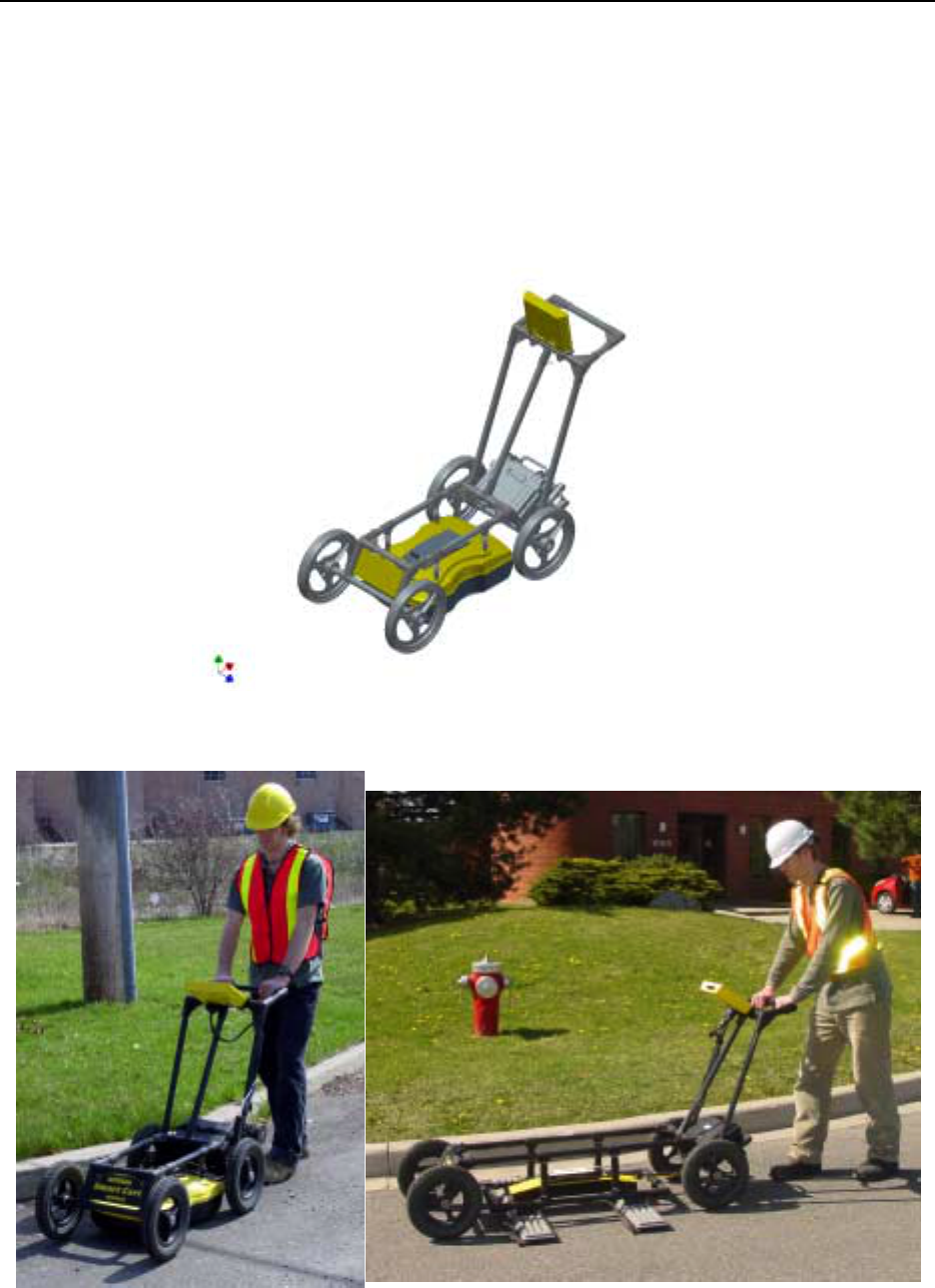
4-SmartCart Assembly Noggin
6
4 SmartCart Assembly
The SmartCart can be configured for operation with all Noggins (100, 250, 500 and 1000).
The fully-assembled Noggin 250 in the SmartCart configuration is shown in Figure 5-1. The
system is shown in field operation in Figure 5-2. Follow the directions below to assemble the
configuration.
Figure: 4-1 Fully assembled SmartCart with a Noggin 250.
Figure: 4-2 Noggin 250 SmartCart (left) and Noggin 100 SmartCart (right) in operation.
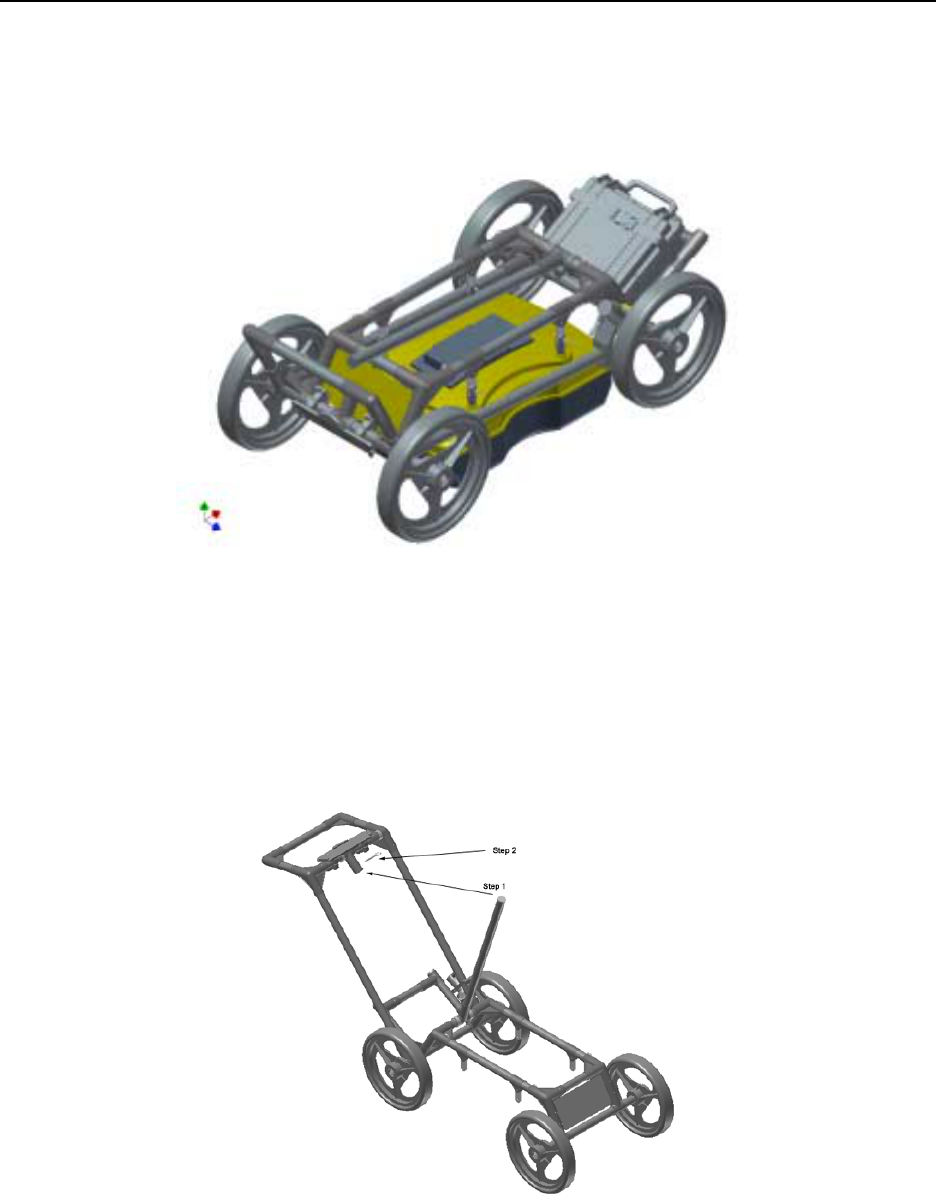
Noggin 4-SmartCart Assembly
7
4.1 Unfold the Handle
The Noggin SmartCart comes folded for transportation and storage (Figure 4-3).
Figure: 4-3 SmartCart in collapsed position.
To unfold the SmartCart, refer to Figure 4-4. Pull the ring to remove the handle Clevis pin from
the handle support arm. Raise the handle support arm and then the handle and place the open
end of the T-shaped tube on the handle onto the end of the support arm (Step 1). Then lock the
handle into position by lining up the hole in the support arm with the hole in the T-shaped tube
and inserting the handle Clevis pin (Step 2). When folding the SmartCart back up always ensure
the handle folds down before the handle support arm.
Figure: 4-4 SmartCart set up.
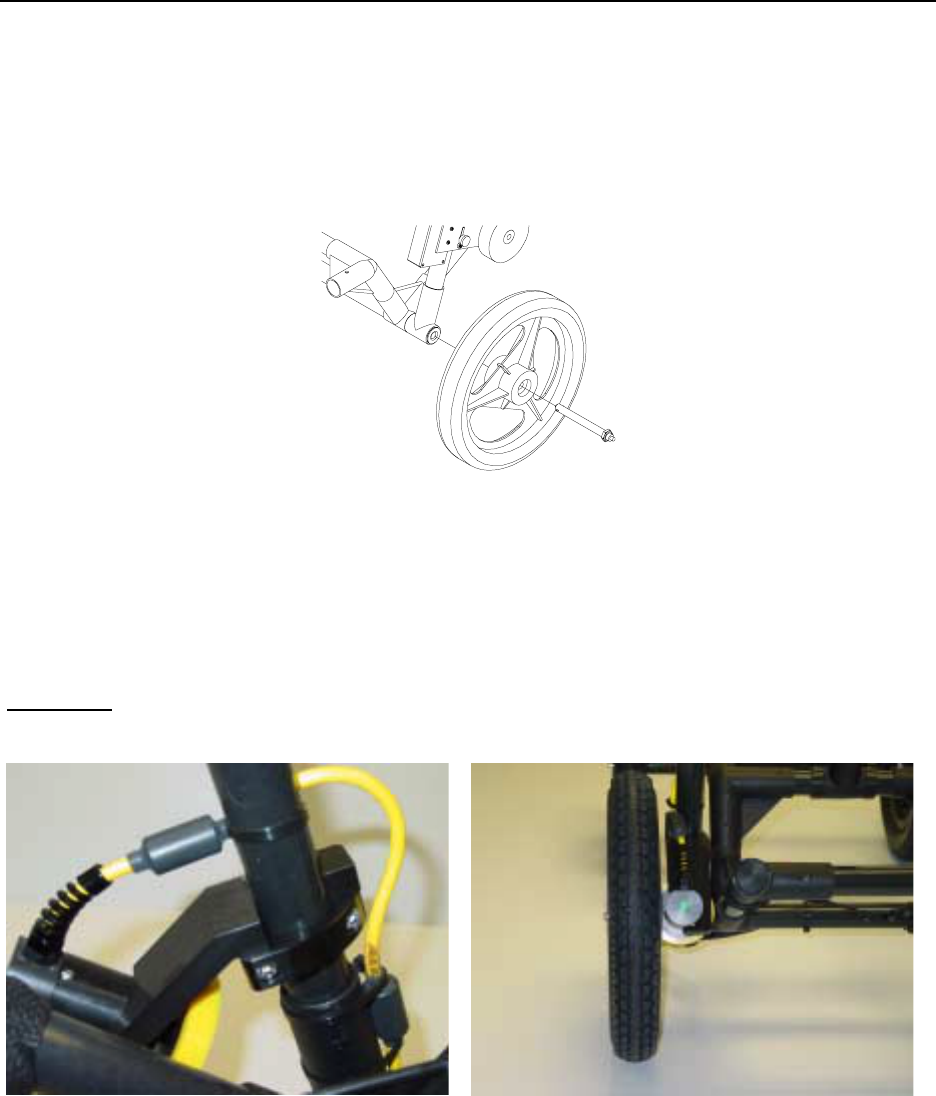
4-SmartCart Assembly Noggin
8
4.2 Attach Wheels
The SmartCart may have been shipped without the wheels attached or they may have been
removed for storage. If this is the case, find the axle for each wheel, press the button on the end
of the axle, and insert the axle through the wheel and into the SmartCart frame (Figure 4-5).
Figure: 4-5 Attaching the wheel.
With the system unfolded, make sure the small odometer wheel makes good contact with the
side of the cart wheel.
If the odometer contact with the wheel is too loose, the odometer wheel may slip, resulting in
erroneous position measurements. If the odometer wheel seems loose, use a ¼ inch Allen
(hexagonal) wrench to loosen the screws on the side of the odometer and pivot the entire
odometer unit until the small odometer wheel makes good contact with the side of the cart wheel
(Figure 4-6). Then tighten the screws to lock the odometer wheel in this position.
Figure: 4-6 If the odometer wheel does not make good contact with the wheel, use a hexagonal wrench to loosen the
2 screws (left) and pivot the odometer outward so when the wheel is attached the odometer rolls continuously (right).
After this has been done, it will be necessary to re-calibrate the odometer (Section 12.5.2
Odometer Calibration).
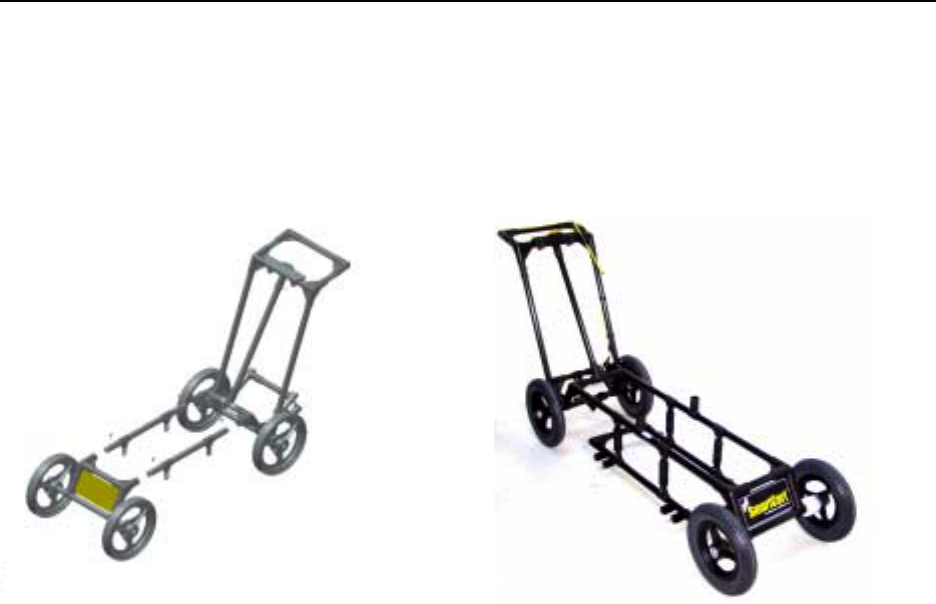
Noggin 4-SmartCart Assembly
9
4.3 Attaching Separation Bars to the SmartCart
The Noggin SmartCart can be configured to carry a Noggin 100, 250, 500 or 1000 system. Each
system has a unique set of separation bars used to attach the Noggin to the SmartCart and
suspend it over the surface (Figure 4-7).
Figure: 4-7 The separation bars are attached to the SmartCart to carry the Noggin. Each Noggin system (100, 250,
500 and 1000) has a unique set of separation bars; the Noggin 250 separation bars are shown on the left and Noggin
100 separation bars on the right.
The separation bars are attached to the SmartCart by four thumb screws.
Changing the support arms should only be done after the DVL and battery have been
detached from the SmartCart, otherwise the back half of the cart may fall to the ground
and be damaged.
Aligning the thumb screws and the support arm is very important. If the hole and insert
are not perfectly aligned, the thumb screw will bind after only half a turn and will damage
the insert by cross-threading it. As well, if the thumb screw is forced to turn it will also be
damaged. If this occurs, the only way to correct this problem is to then run a 10-32 tap
through the insert to re-tap the hole.
4.3.1 Separation Bar Assembly
Depending on the Noggin system, it may be necessary to assemble the separation bars before
attaching them to the SmartCart. For details, see the separate document “Noggin SmartCart
Separation Bar Assembly”.
Noggin 100
Noggin 250
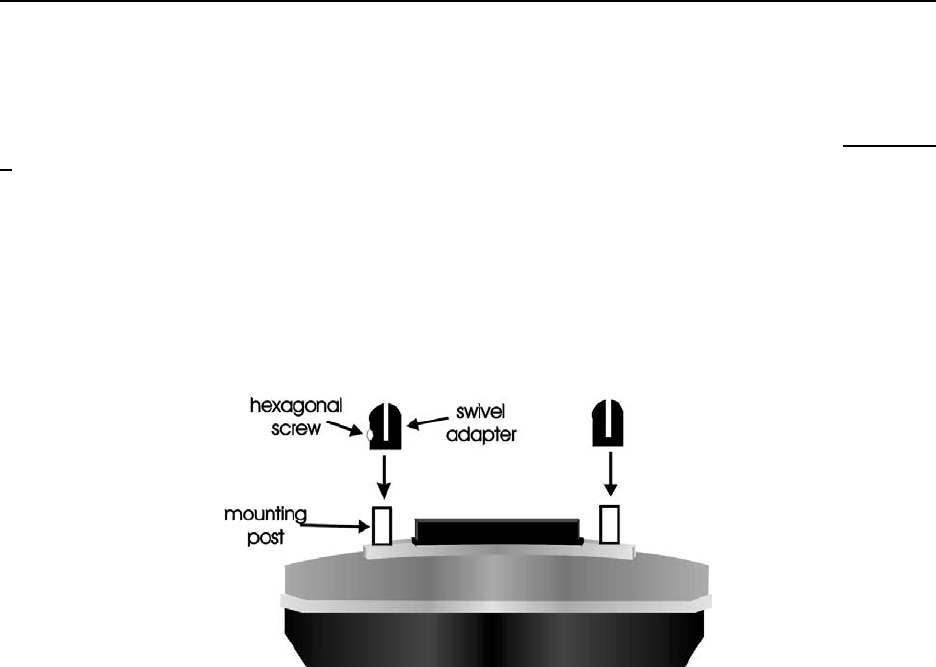
4-SmartCart Assembly Noggin
10
4.4 Attaching the Swivel Adapters (Noggin 250, 500 & 1000)
Before the Noggin 250, 500 or 1000 can be attached to the SmartCart, the 4 swivel adapters
(with attached Clevis pins) must be attached to the mounting posts on the Noggin (see Figure 2-
1). The swivel adapters may have been attached to the Noggin at the factory. If not, follow the
instructions below.
Set the swivel adapter down on the post. It may be necessary to loosen the Allen (hexagonal)
screw before the swivel adapter will slide down into the proper position. This can be done using
the 1/8” Allen (hexagonal) wrench provided. Now, tighten each screw and then loosen ¼ turn so
that the swivel adapters are firmly attached to the post but can still rotate. DO NOT OVER-
TIGHTEN!
Figure: 4-8 Attaching the swivel adapters to the Noggin.
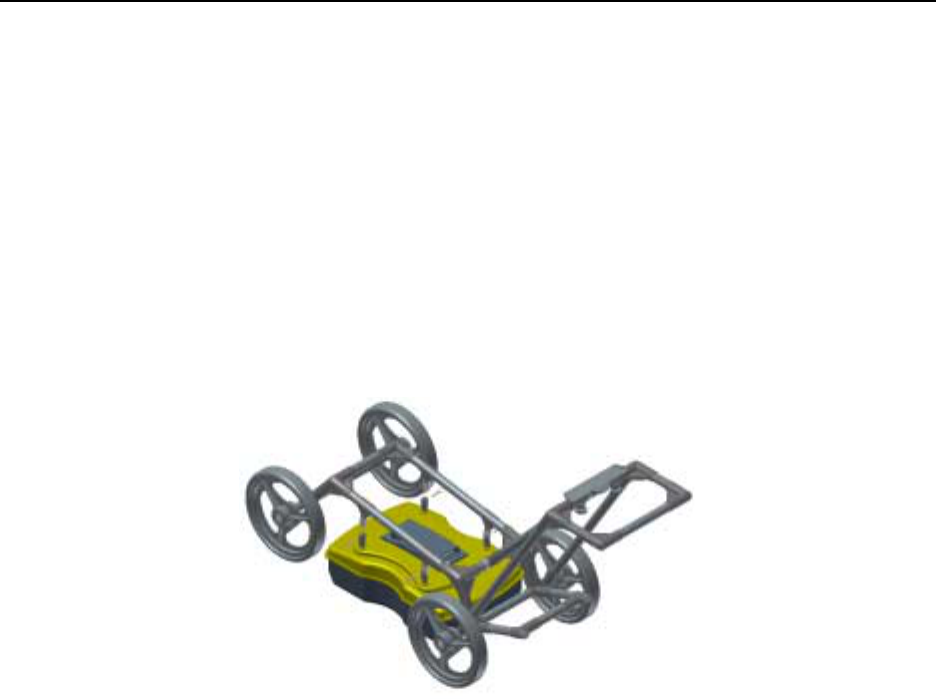
Noggin 4-SmartCart Assembly
11
4.5 Attaching the Noggin to the SmartCart
The Noggin is attached to the cart with the long axis of the Noggin unit parallel to the wheels on
the cart (see Figure 4-9 and Figure 4-10). Ensure the 37 socket female electrical receptacle on
the Noggin faces the back of the cart so that the cable on the cart will reach the receptacle.
4.5.1 Noggin 250
Remove the Clevis pins from the swivel adapters. Now, on the bottom of the cart, locate the 4
oval, moveable hangers suspended from the frame of the cart (see Figure 4-9). Notice that each
hanger has a hole in it. To attach the Noggin 250 to the cart, place each hanger into the slot on
the top of the swivel adapters, line up the holes and insert the Clevis pin.
Figure: 4-9 Attaching the Noggin 250 to the SmartCart.
Connect the 37 pin end of the Noggin-to-DVL cable to the receptacle on the Noggin and secure
this attachment with the latch.
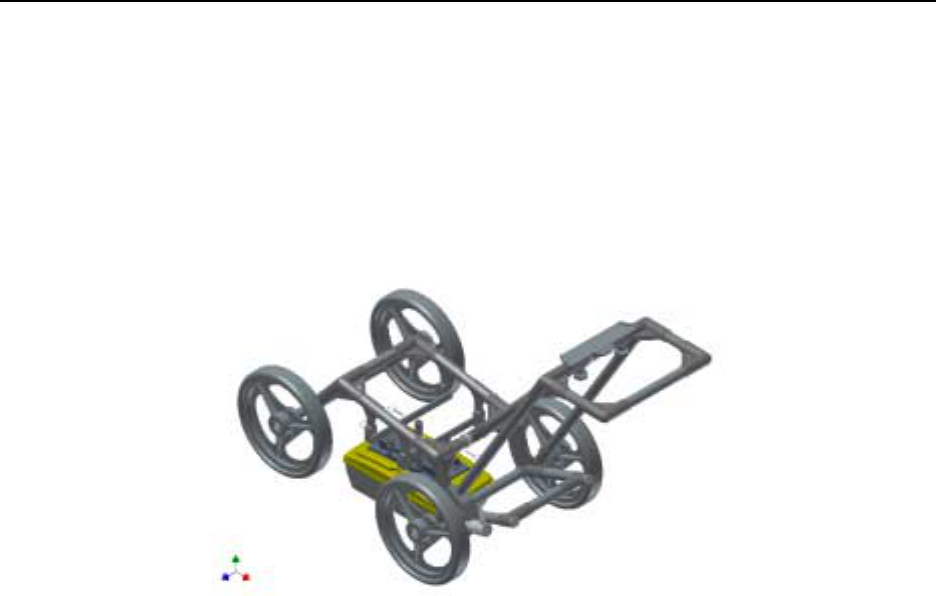
4-SmartCart Assembly Noggin
12
4.5.2 Noggin 500 & Noggin 1000
Remove the Clevis pins from the swivel adapters. Now, on the bottom of the cart, locate the two,
flat, moveable crossbars suspended from the frame of the cart.
Notice that each crossbar has 2 holes, one on each side. To attach the Noggin 500 to the cart,
place the crossbars into the slots on the top of the swivel adapters, line up the holes and insert
the Clevis pins (Figure 4-10).
Figure: 4-10 Attaching the Noggin 500 and Noggin 1000 to the cart.
Connect the 37 pin end of the Noggin-to-DVL cable to the receptacle on the Noggin and secure
this attachment with the latch.
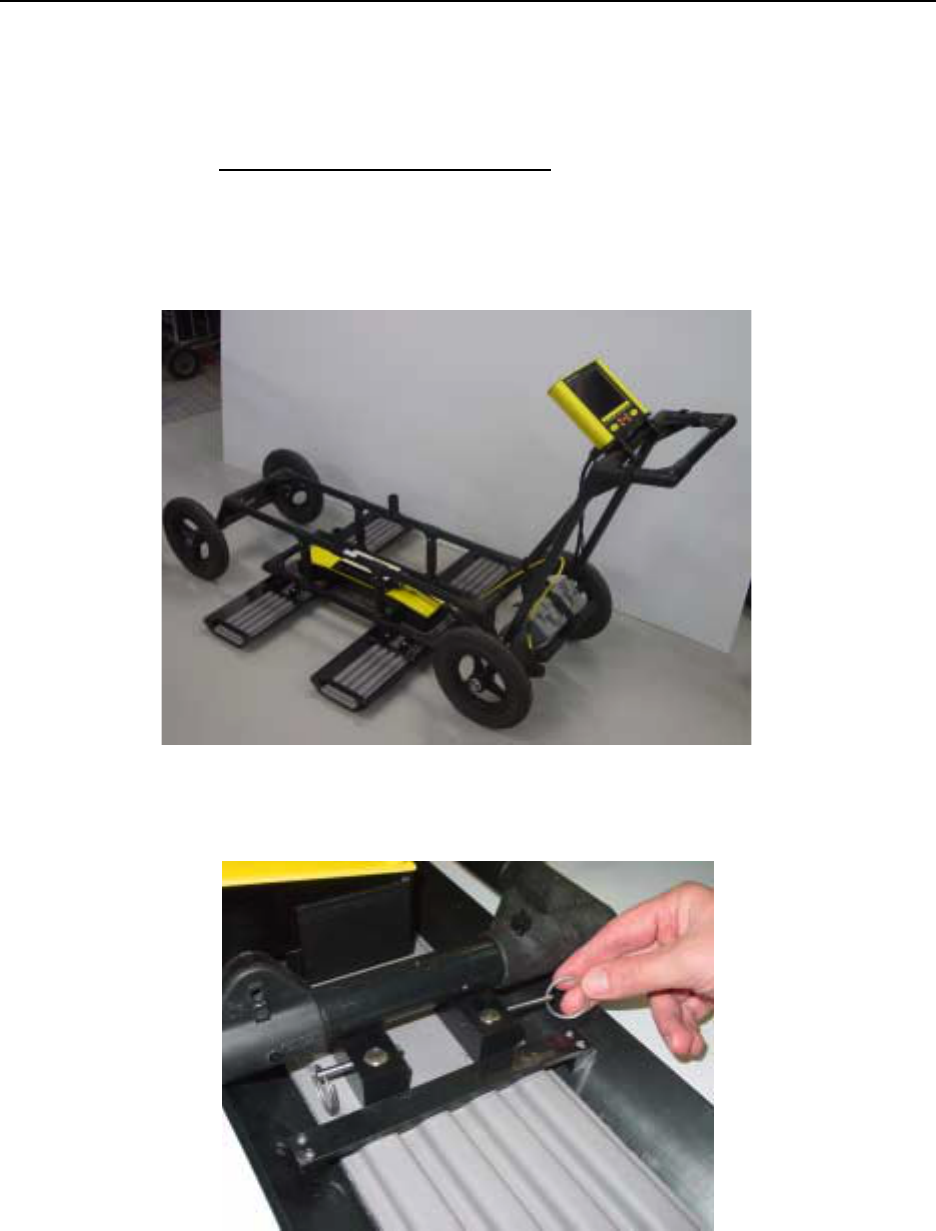
Noggin 4-SmartCart Assembly
13
4.5.3 Noggin 100
Unlike the higher frequency Noggins, the Noggin 100 comes with the antennas and electronics
as separate units that need to be assembled. Assemble the Noggin 100 electronics and
antennas as shown in Section 3 Noggin 100 Assembly.
Place the SmartCart over the Noggin 100, aligning the antenna post blocks on the frame with the
antenna mounting posts on the 100 MHz antennas. Ensure the 37 socket cable connection on
the Noggin 100 electronics faces the back (handle end) of the SmartCart.
Figure: 4-11 Place the SmartCart over the Noggin 100 system with the 8 antenna mounting posts inserted in the post
blocks. The 37 socket receptacle
Figure: 4-12 Secure the SmartCart Separation Bars to the Noggin 100 by inserting the pins into each of the 8 post
blocks.
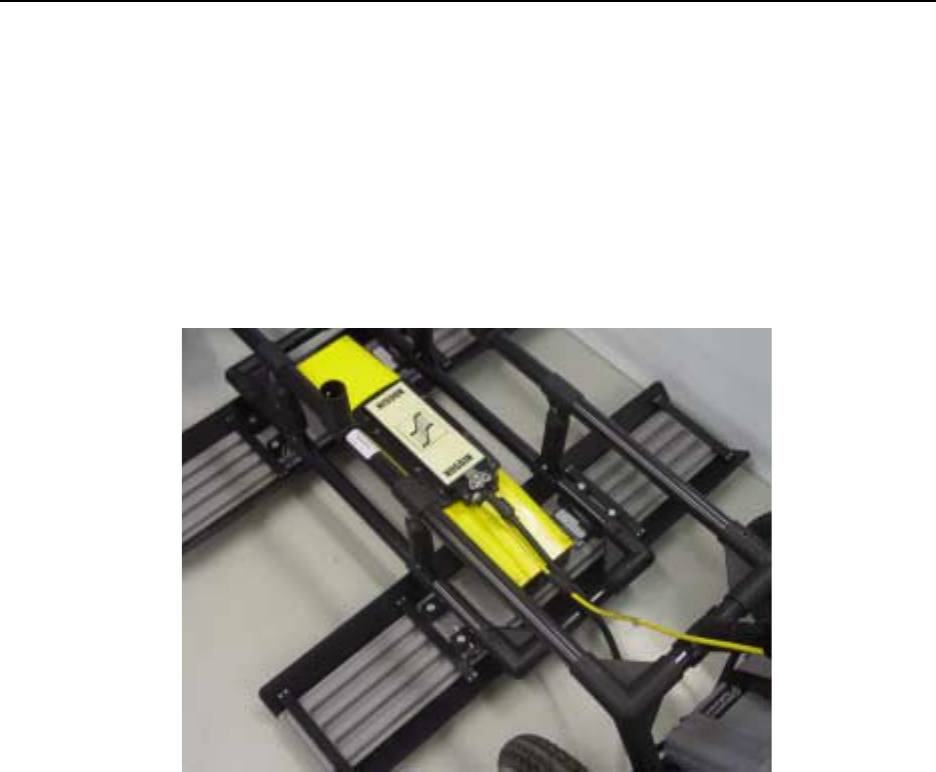
4-SmartCart Assembly Noggin
14
Connect the 37 pin end of the Noggin-to-DVL cable to the receptacle on the Noggin 100
electronics and secure this attachment with the latch.
The cable should have a little slack to reduce any stresses on the cable during data collection.
Ensure that the cable does not sag and contact the electronics or antennas as this will cause
noise in the data.
Connect the yellow odometer cable to the receptacle on the Noggin end of the Noggin-to-DVL
cable. This may require use of a short odometer extension cable. Use the velcro straps to route
the cable along the frame, keeping it away from the electronics and the the antennas.
Figure: 4-13 Connecting the Noggin-to-DVL cable to the Noggin 100 electronics. After this connection is made, con-
nect the yellow odometer cable to the round receptacle.
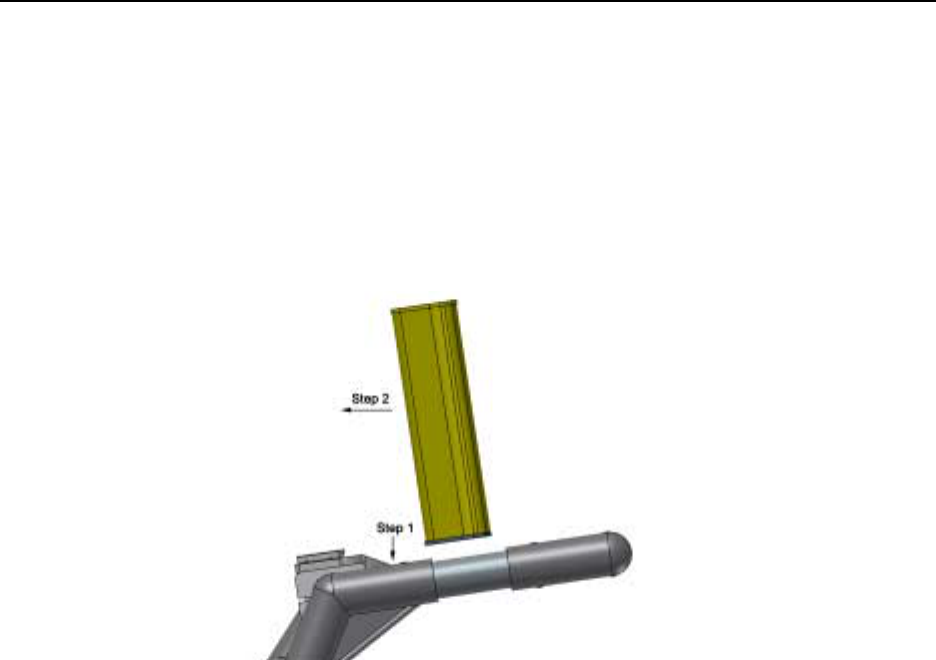
Noggin 4-SmartCart Assembly
15
4.6 Attach the Digital Video Logger (DVL)
The bottom of the Digital Video Logger is designed to slide onto the support shelf attached to the
SmartCart (Figure 4-14). Line up the bottom of the DVL with the shelf and slide it back onto the
shelf. Push the DVL back far enough so that the flexible clip on the front of the shelf catches and
holds the DVL firmly in place. Wiggle the DVL to make sure it is firmly snapped in before letting
go of the unit. To remove the DVL from the SmartCart, flex the clip downward as the DVL is slid
forward off of the shelf.
Figure: 4-14 Attaching the digital video logger (DVL). Step 1: Depress flexible clip. Step 2: Slide DVL onto shelf.
The DVL can be pivoted to adjust the view angle. If it is difficult to pivot the DVL, slightly loosen
the hand screws on the bottom of the support shelf.
Once the DVL is in place, attach the cable with the 37-socket female D-connector to the 37-pin
receptacle on the back of the Digital Video Logger. This attachment can be secured with the
latch.
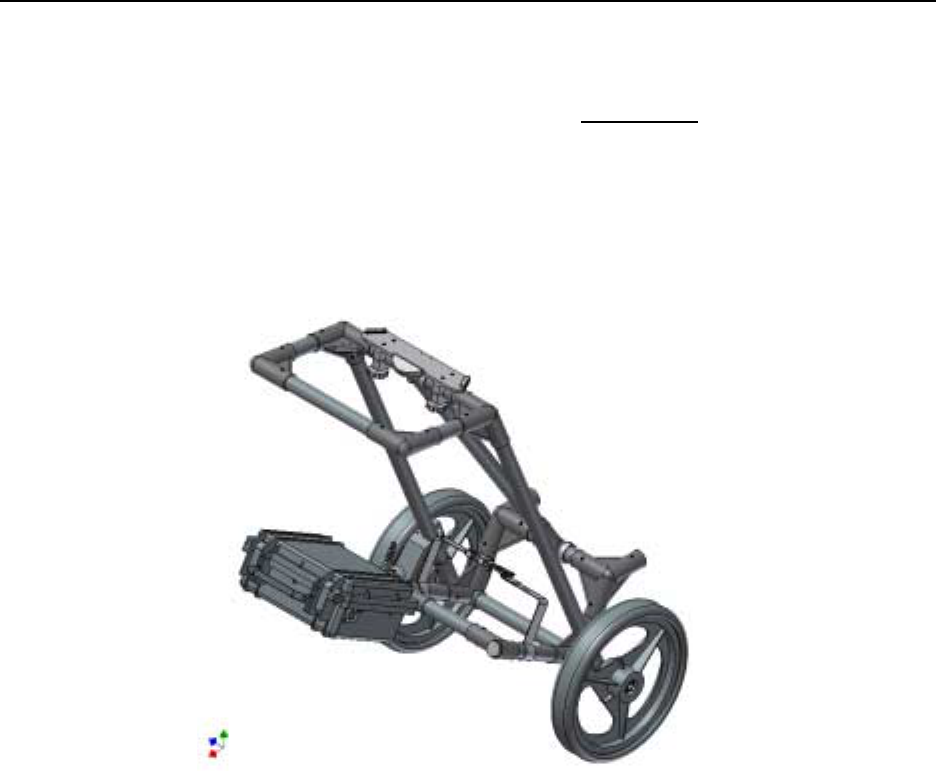
4-SmartCart Assembly Noggin
16
4.7 Attach the Battery Unit
The batteries usually used with the SmartCart are shown in Figure 10-1.
Set the battery unit onto the lower inclined shelf on the back of the SmartCart (see Figure 4-15).
The handle on the battery unit should be accessible from the back of the cart with the cable
receptacle on the right. The battery unit should rest in this area without moving. To secure the
battery onto the cart, put the straps provided over the battery unit and lock into place with the
plastic buckle. Tighten the straps if necessary.
Figure: 4-15 The SmartCart battery.
Note the battery mass forms part of the overall cart balance which enables users to raise the
front wheels with a minimum amount of force. This allows users to easily change direction and
assure the rear wheels are always in contact with the ground.
With the SmartCart completely assembled, connect the round 4-pin battery cable to the
receptacle on the side of the battery.
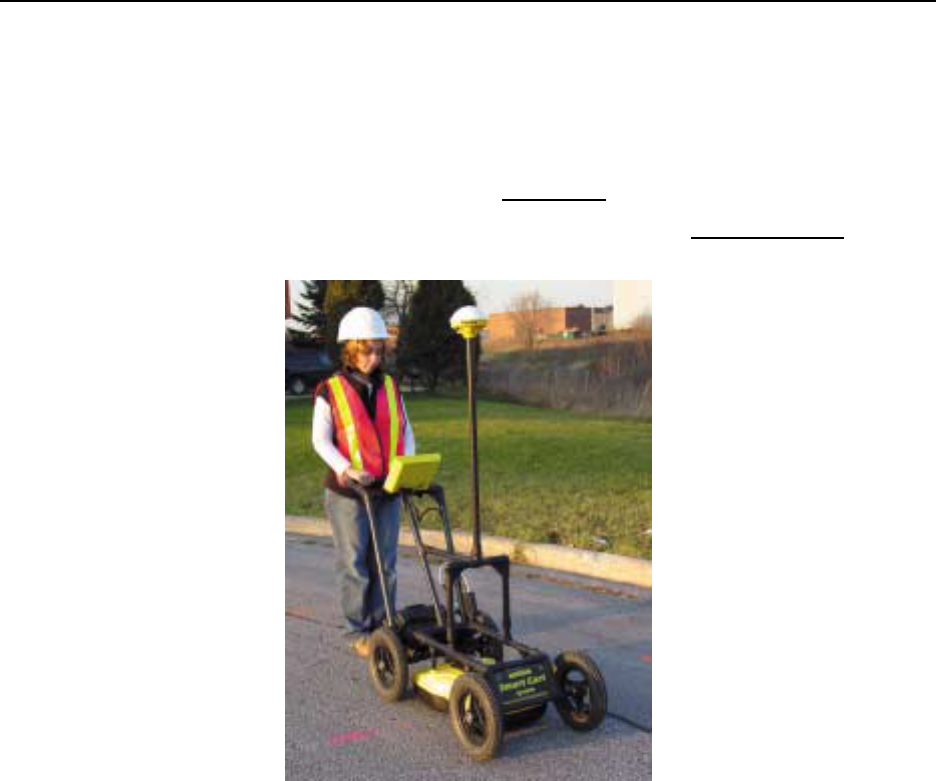
Noggin 4-SmartCart Assembly
17
4.8 Adding GPS Mount to the SmartCart
The SmartCart has an optional bracket designed to hold a Trimble or Novatel GPS (see Figure 4-
16). This bracket can be modified by the user to hold other types of GPS units.
Any GPS unit with a serial output can be attached to the serial port on the back of the DVL and
GPS information logged during data collection (see Section 8 ).
For more details about configuring the GPS with a Noggin system, see Section 12.3.5 .
Figure: 4-16 SmartCart system with the optional GPS mounting bracket.
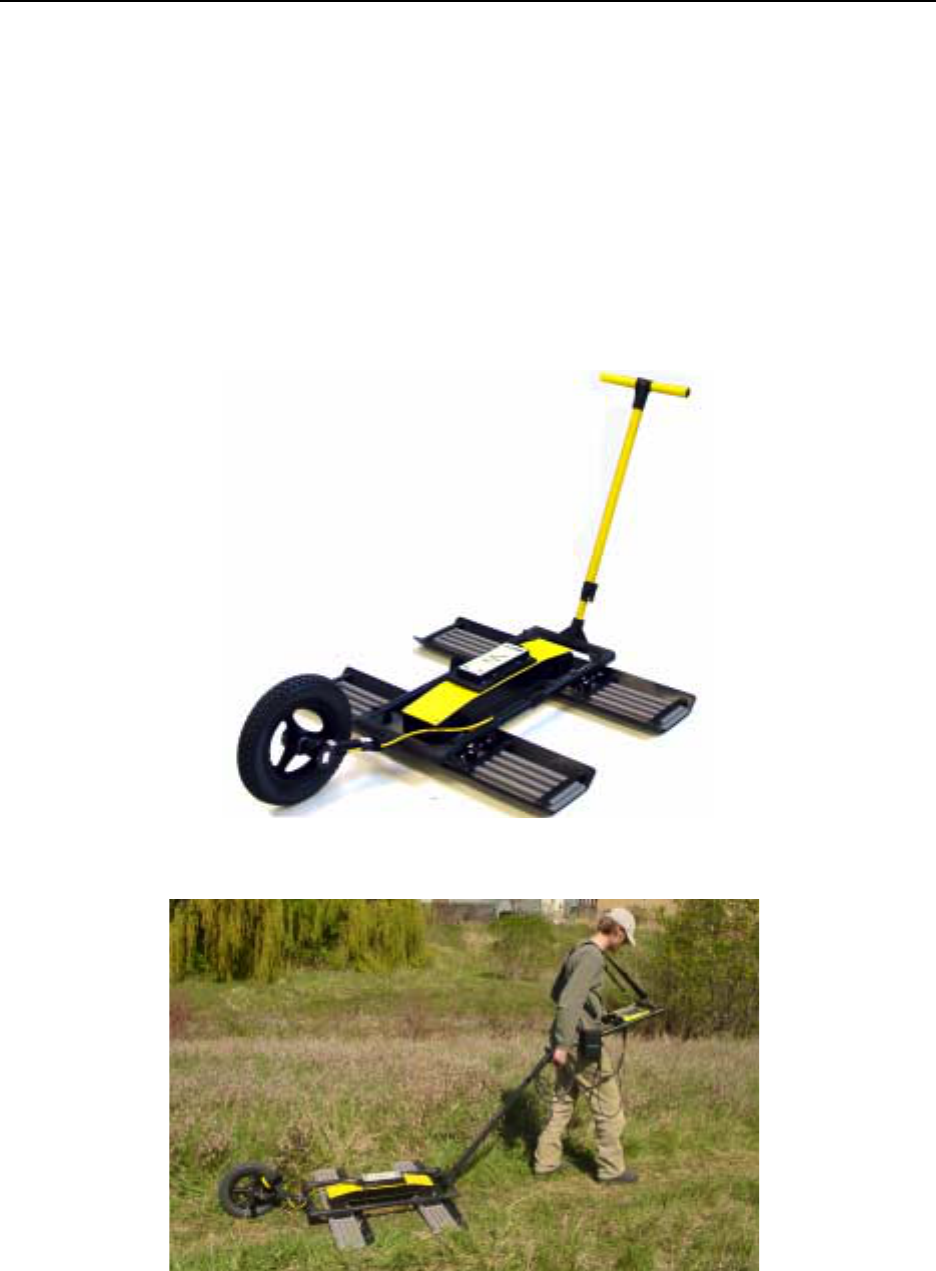
5-SmartTow Assembly Noggin
18
5 SmartTow Assembly
All Noggins (100, 250, 500 and 1000) can be operated in the SmartTow configuration.
5.1 Noggin 100
The fully-assembled Noggin 100 in the SmartTow configuration is shown in Figure 5-1. The
system is shown in field operation in Figure 5-2. Follow the directions below to assemble the
configuration.
Figure: 5-1 Noggin 100 SmartTow configuration.
Figure: 5-2 Noggin 100 SmartTow configuration in use. Note the belt battery for power and DVL carrier for conve-
niently carrying the DVL in the field. The cable runs from the electronics housing and up the handle secured by velcro
straps.
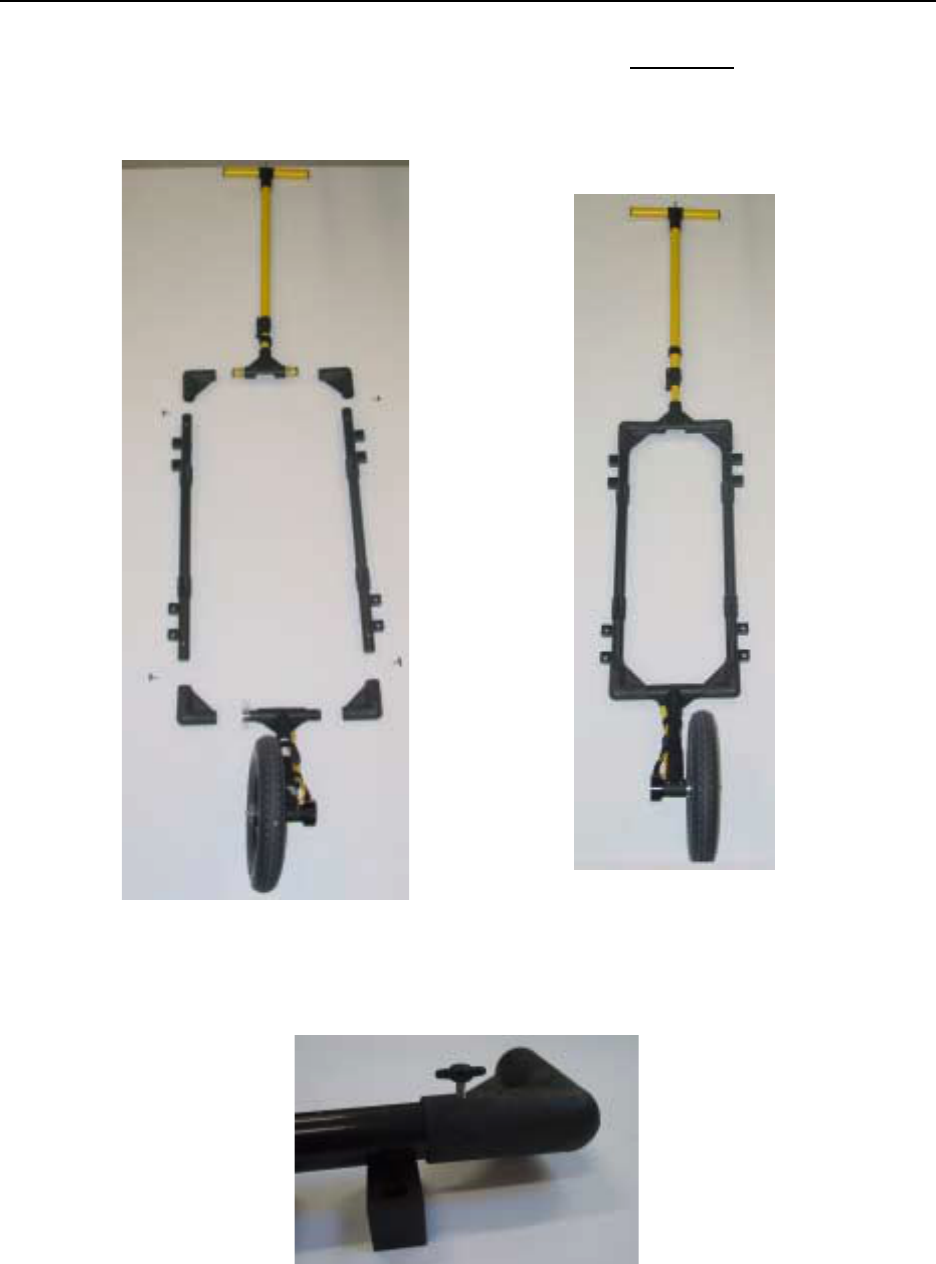
Noggin 5-SmartTow Assembly
19
Assemble the Noggin 100 electronics and antennas as shown in Section 3 .
The parts for the Noggin 100 SmartTow frame are shown in .
Figure: 5-3 The Noggin 100 SmartTow frame parts (left) and assembled (right). Ensure the antenna post blocks face
outward before assembling. The pieces are connected using the 4 thumb screws as shown in the figure below. The
Handle and Big Wheel odometer are not connected to the frame with thumb screws but held in place once the anten-
nas are attached.
Figure: 5-4 Close-up of thumbscrews used to assemble the Noggin 100 SmartTow frame. Be careful not to strip the
threads!
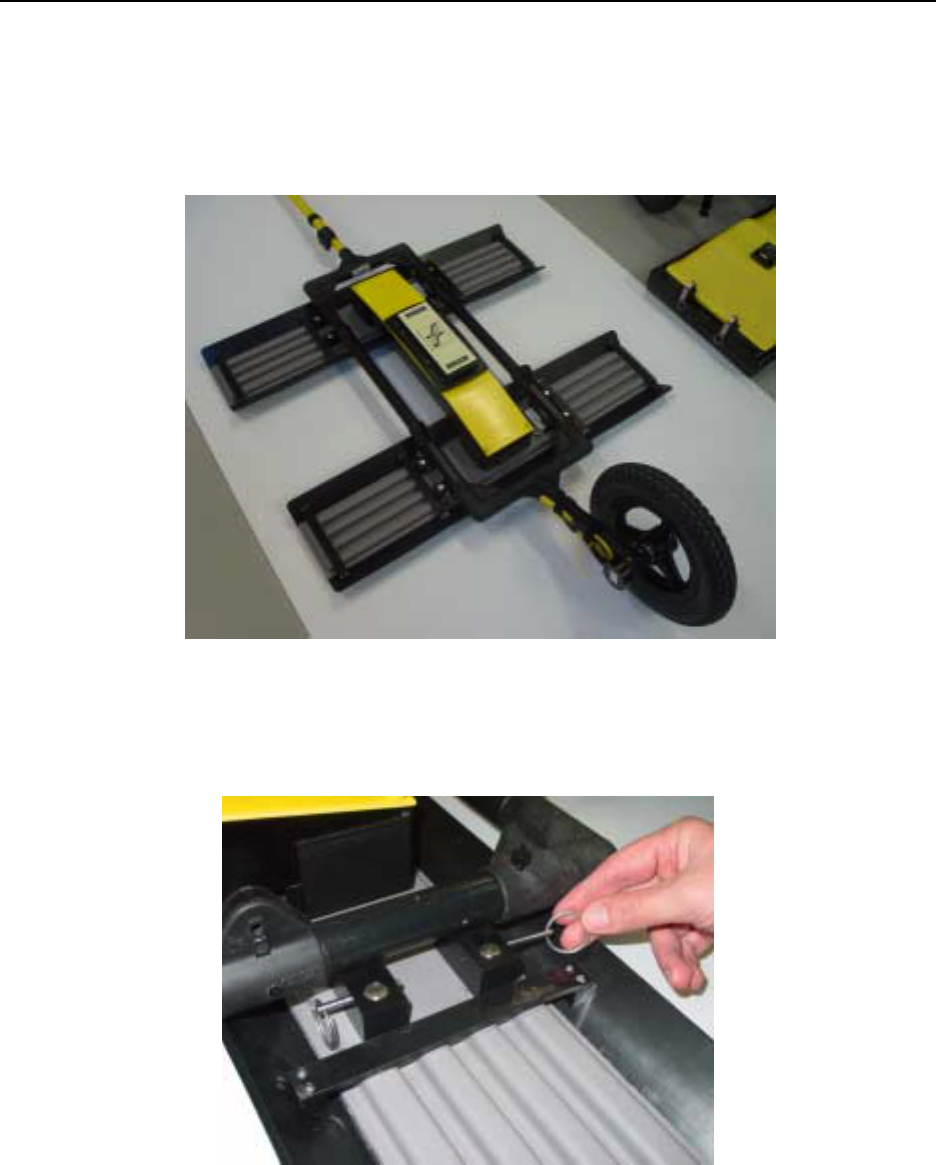
5-SmartTow Assembly Noggin
20
Place the SmartTow frame over the Noggin 100, aligning the antenna post blocks on the frame
with the antenna mounting posts on the 100 MHz antennas. Ensure the 37 socket cable
connection on the Noggin 100 electronics faces the handle end of the frame and NOT the
odometer end.
Figure: 5-5 Place the SmartTow frame over the Noggin 100 system with the 8 antenna mounting posts inserted in the
post blocks.
Figure: 5-6 Secure the SmartTow frame to the Noggin 100 by inserting the metal pins into each of the 8 post blocks.
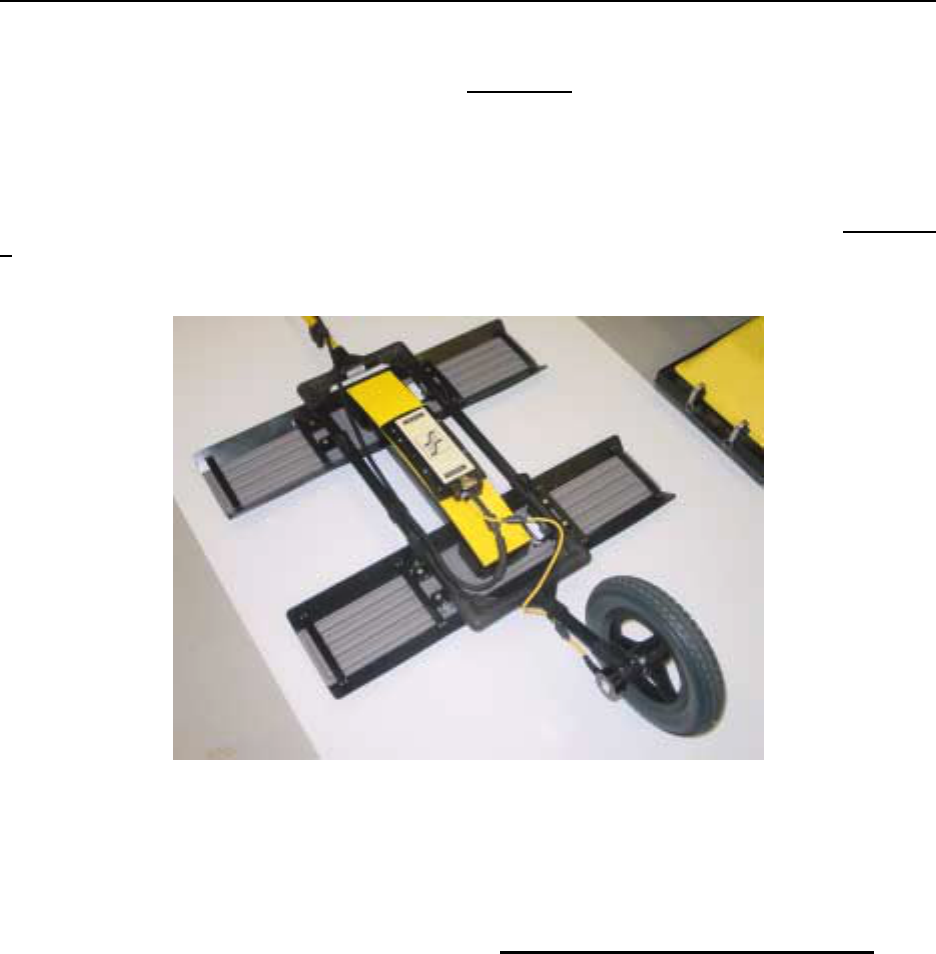
Noggin 5-SmartTow Assembly
21
Latch the 37 pin end of the Noggin-to-DVL cable to the receptacle on the Noggin 100 and use the
velcro straps to secure the cable to the handle (Figure 5-7). The cable should have a little slack
to reduce any stresses on the cable during data collection. Ensure that the cable does not sag
and contact the electronics or antennas as this will cause noise in the data.
Connect the yellow odometer cable to the receptacle on the Noggin end of the Noggin-to-DVL
cable. This may require use of a short odometer extension cable. Use the velcro straps to route
the cable along the frame, keeping it away from the electronics and the the antennas (Figure 5-
7).
Figure: 5-7 Connect the Noggin-to-DVL cable to the Noggin 100 electronics with the latch. The yellow odometer
cable connects to the small round receptacle on the back of the Noggin-to-DVL cable. The odometer cable may need
to have the odometer extension cable added to it to reach the connection.
Latch the other end of the Noggin-to-DVL cable to the back of the DVL.
With the SmartTow completely assembled, connect the round 4-pin battery cable to the
receptacle on the SmartCart battery and then go to Section 10 Powering Up the System.
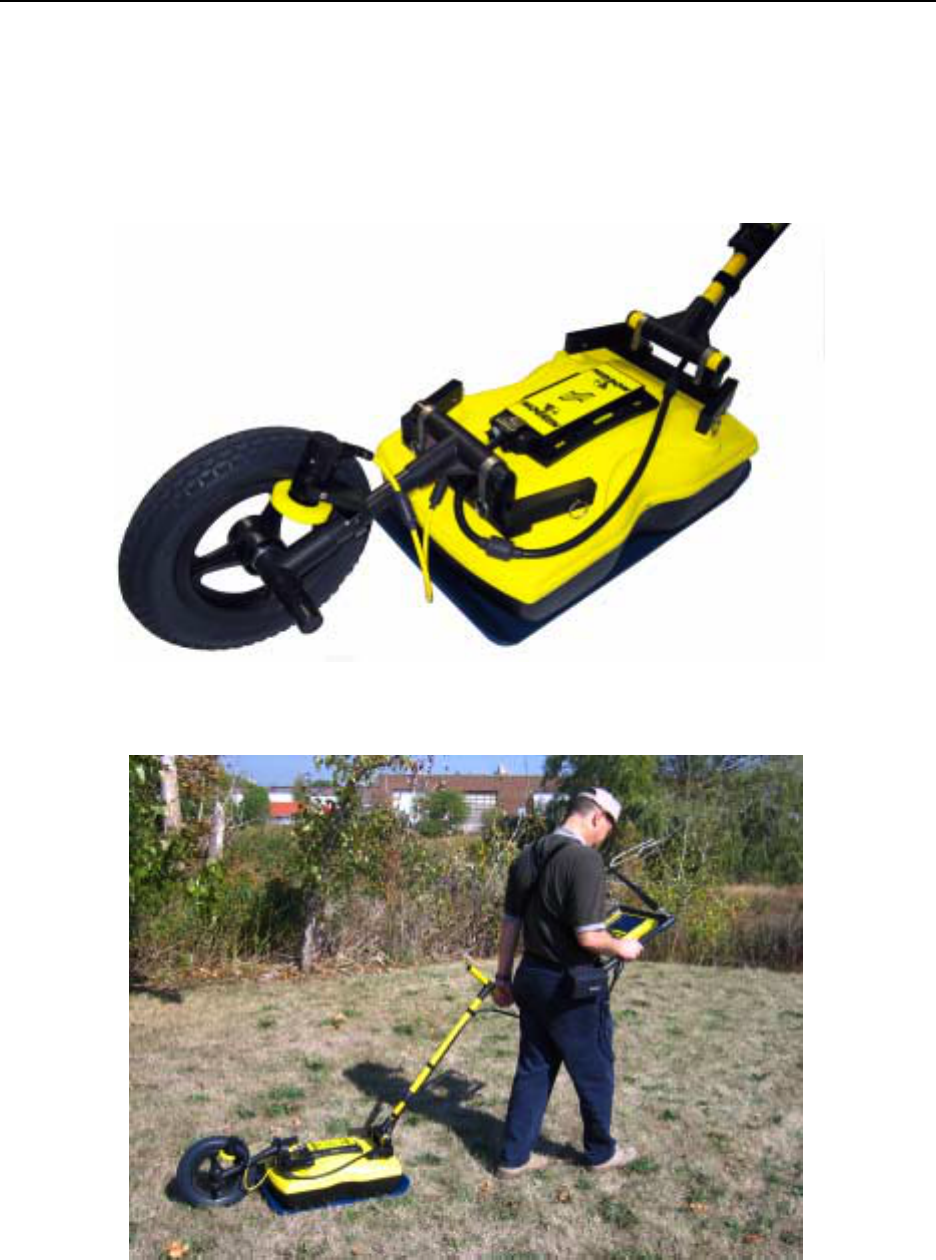
5-SmartTow Assembly Noggin
22
5.2 Noggin 250
The fully-assembled Noggin 250 in the SmartTow configuration is shown in Figure 5-1. The
system is shown in field operation in Figure 5-2. Follow the directions below to assemble the
configuration.
Figure: 5-8 Noggin 250 SmartTow system
Figure: 5-9 Noggin 250 SmartTow in operation. Note the belt battery used to power the system.
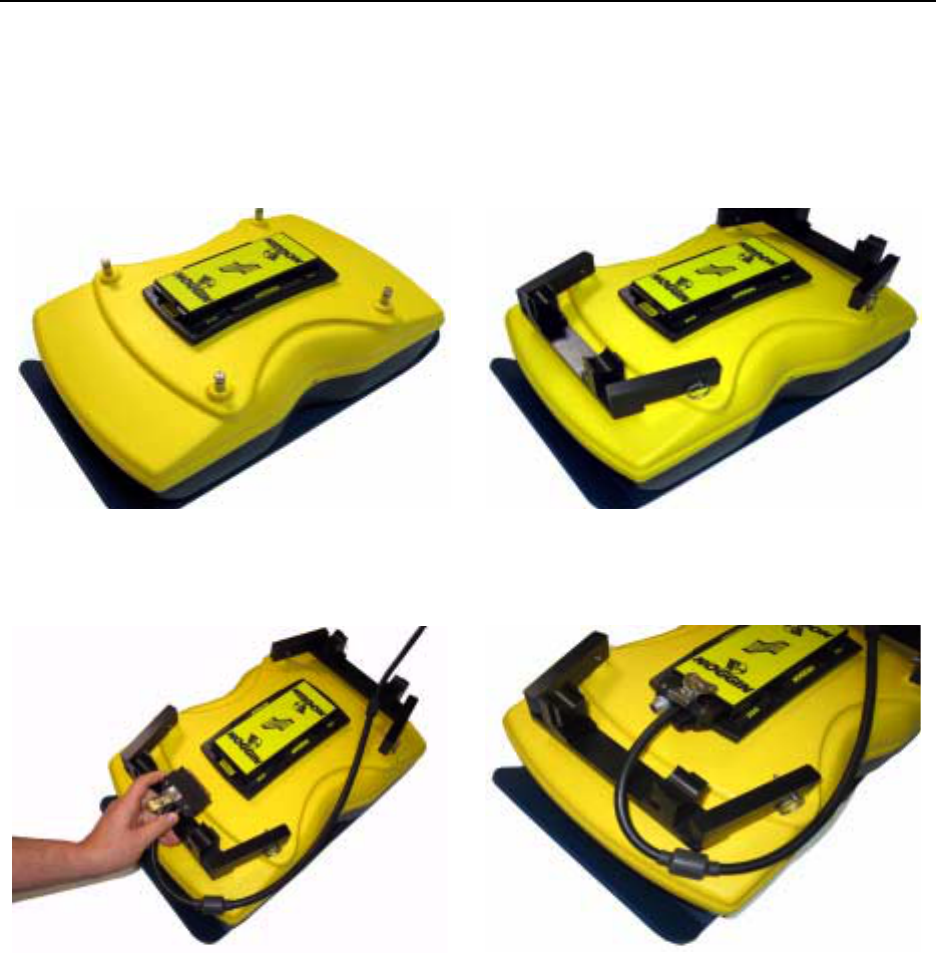
Noggin 5-SmartTow Assembly
23
Attach one of the SmartTow Bracket Assemblies to the two front mounting posts on the Noggin
250 and secure with the metal pins.
Attach the second SmartTow Bracket Assembly to the two back mounting posts on the Noggin
250 and secure with the metal pins.
Connect the large black cable to the Noggin 37-pin female connector and latch into place,
ensuring the cable lies on top of the back SmartTow Bracket Assembly.
The large odometer wheel attaches to the back SmartTow Bracket closest to the Noggin
connector. Orient the odometer so the small yellow wheel is on the upper rim of the large wheel.
Secure the odometer T-bar with the U-brackets and pins. Make sure that the black cable turns to
the front of the Noggin so it does not interfere with the odometer wheel.
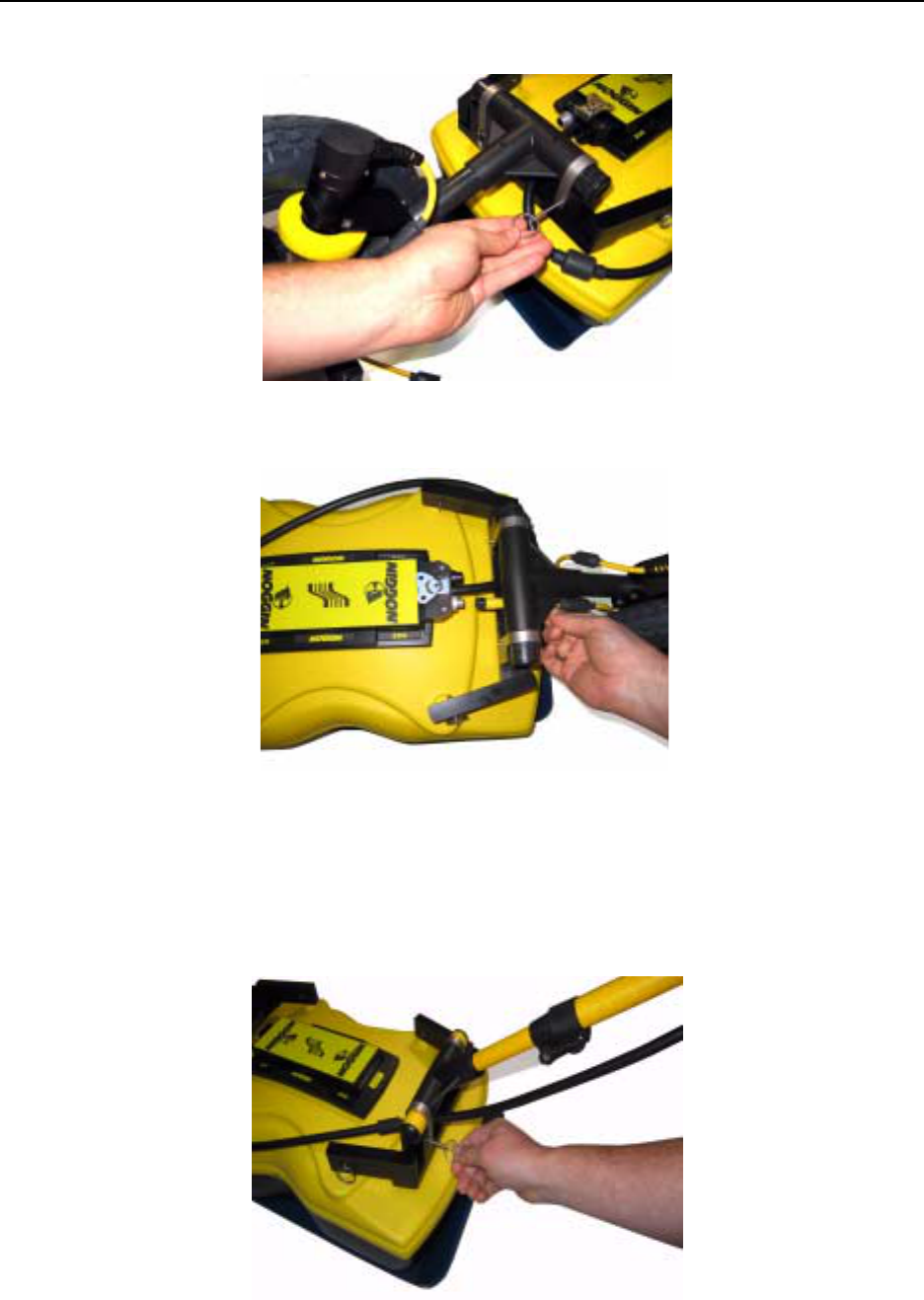
5-SmartTow Assembly Noggin
24
The yellow cable from the odometer connects to the receptacle on the connector to the Noggin.
Odometer calibration is critical for accurate data images. Odometer calibration instructions are
available in Section 12.5.2 Odometer Calibration.
Attach the handle to the front SmartTow Bracket Assembly with the U-brackets and pins. The
black cable should lie between the SmartTow Bracket and the handle. Secure the cable along
the side of the handle using 2 or 3 Velcro straps.
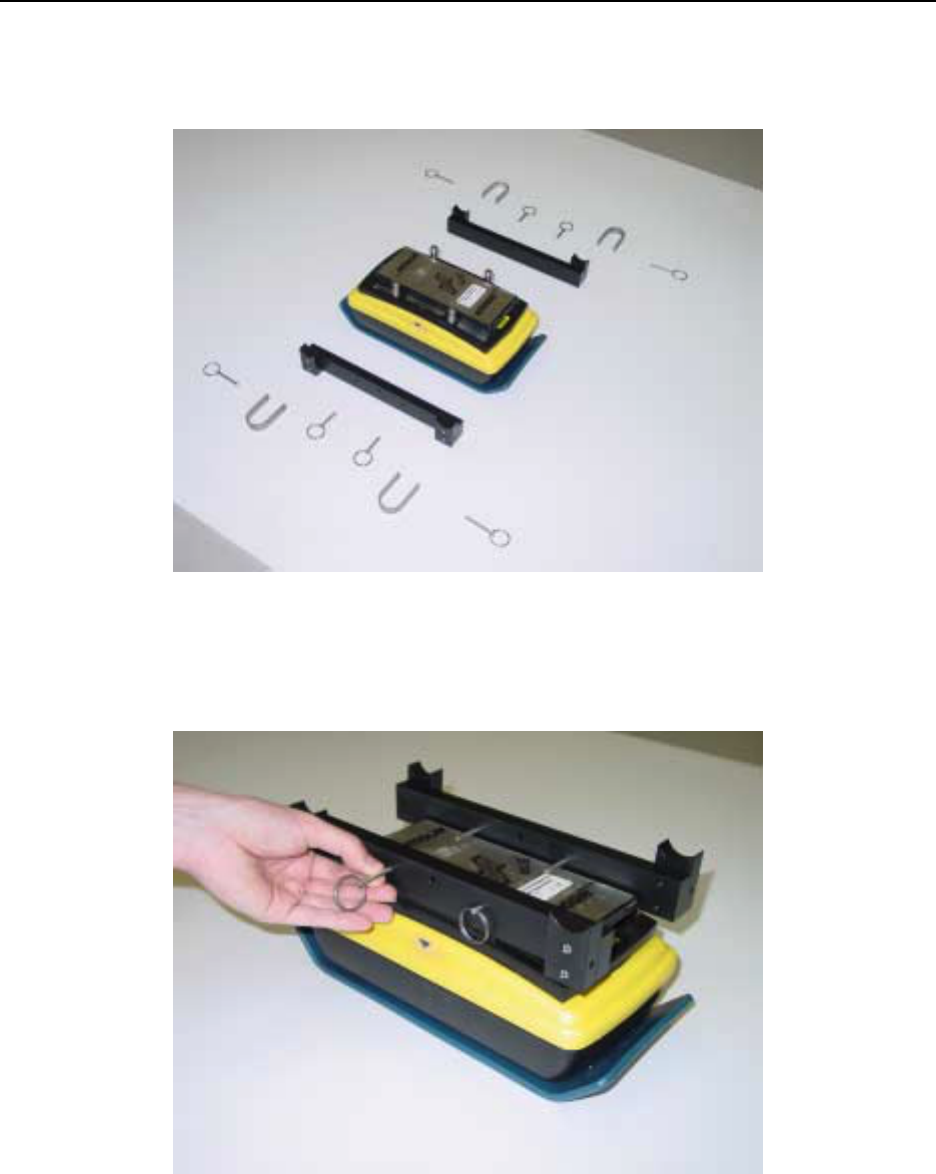
5-SmartTow Assembly Noggin
26
The parts for the Noggin 500/100 SmartTow Brackets are shown below.
Align the two holes on one of the SmartTow Brackets with the two mounting posts on one side of
the Noggin, press down firmly and secure with the short metal pins. Then attach the second
SmartTow bracket to the other side of the Noggin and secure with the short metal pins.
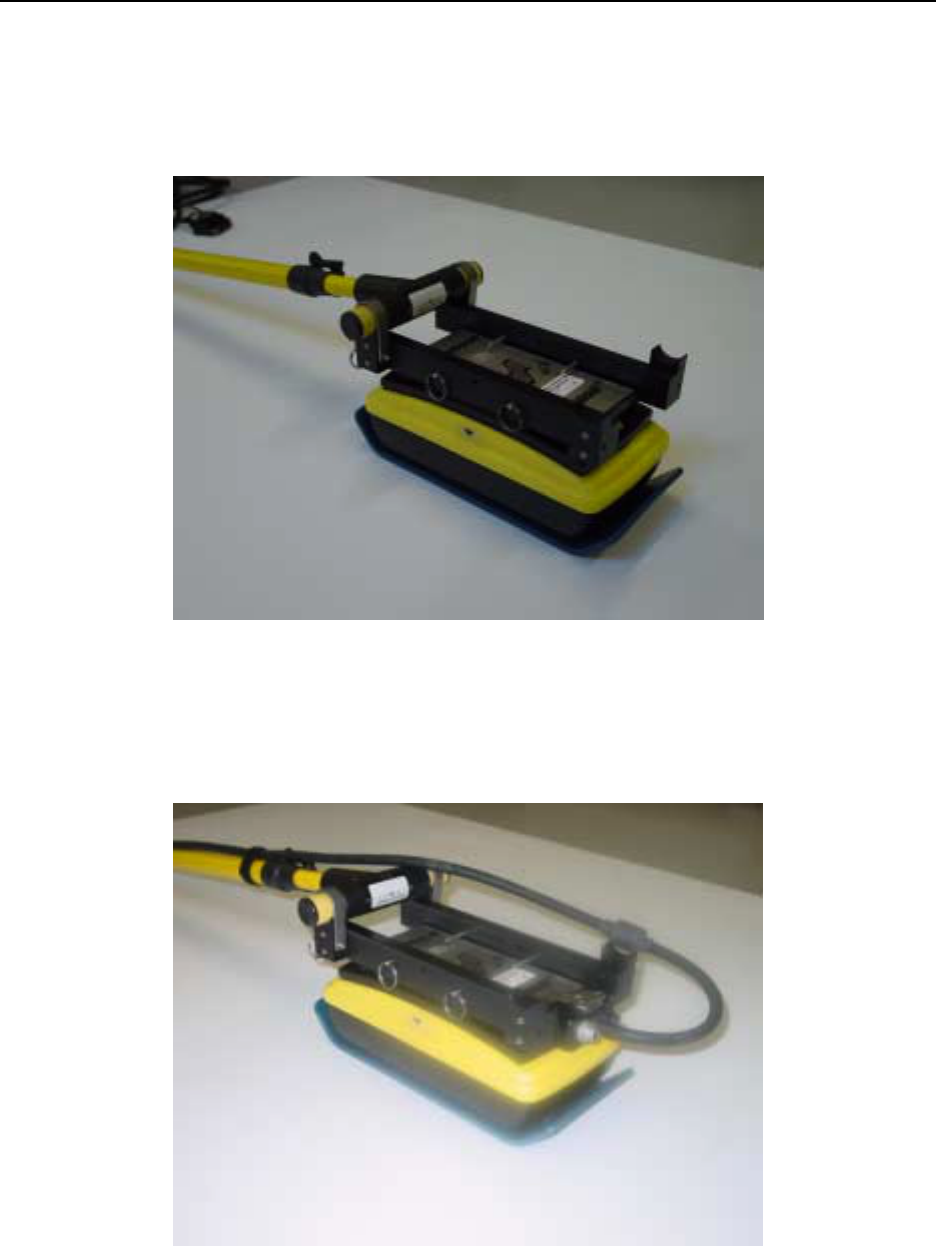
Noggin 5-SmartTow Assembly
27
Attach the handle to the front of the SmartTow Brackets with the U-brackets and log metal pins.
The handle should be attached on the end of the Noggin away from the 37 socket cable
connection.
Connect the large black Noggin-to-DVL cable to the 37-socket connector on the Noggin and latch
into place, ensuring the cable is looped to provide some slack and it is routed along the top of the
SmartTow bracket. Secure the cable to the bracket and along the side of the handle using 2 or 3
Velcro straps.
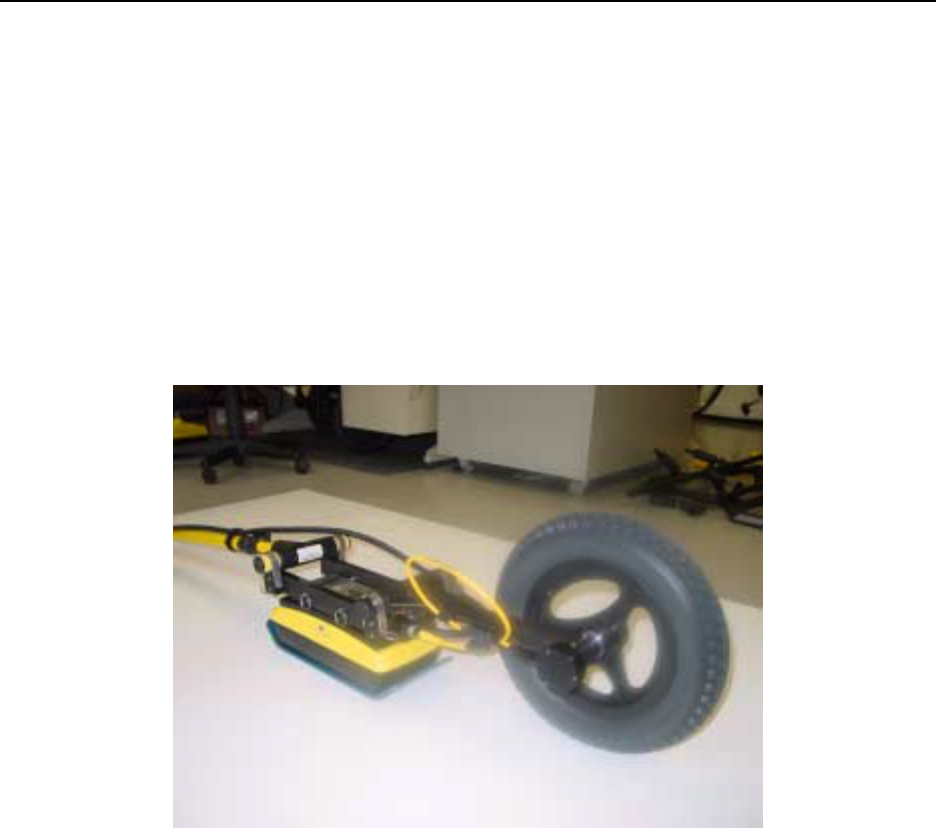
5-SmartTow Assembly Noggin
28
The large odometer wheel attaches on the end of the Noggin with the 37-socket connector. Use
the U-brackets and log metal pins to secure the odometer T-bar to the SmartTow Brackets.
Orient the odometer so the black thumbscrew on the T-bar is facing upwards and the yellow
odometer cable is on the same side of the odometer wheel as the odometer receptacle on the
Noggin cable connection.
Make sure that the black Noggin-to-DVL cable turns to the front of the Noggin so it does not
interfere with the odometer wheel.
Then connect the yellow odometer cable to the receptacle on the connector to the Noggin. Loop
the odometer cable so it does not interfere with the rotation of the odometer wheel and use velcro
straps to secure it to the T-bar.
Odometer calibration is critical for accurate data images. Odometer calibration instructions are
available in Section 12.5.2 Odometer Calibration.
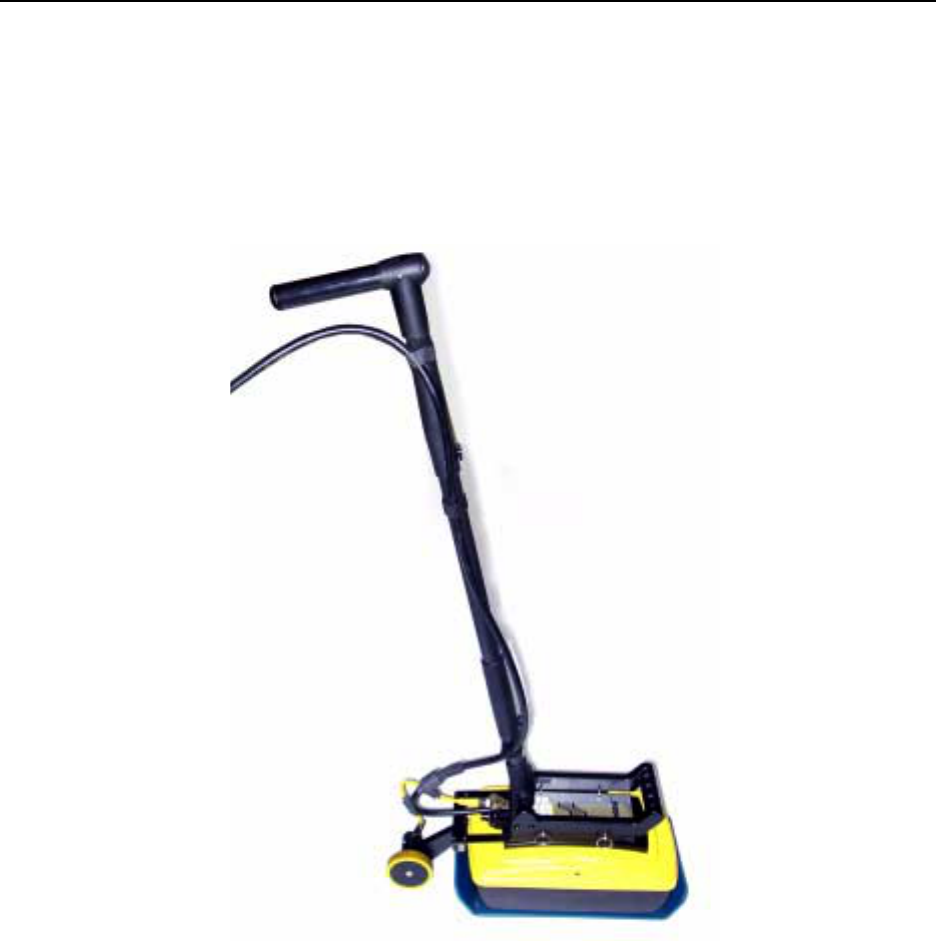
Noggin 6-SmartHandle Assembly (Noggin 500 & 1000 only)
29
6 SmartHandle Assembly (Noggin 500 & 1000 only)
The Noggin 500 and 1000 can be operated in the SmartHandle configuration.
The fully assembled Noggin 500 SmartHandle system is shown in Figure 6-1. The Noggin 1000
SmartHandle system looks very similar.
Figure: 6-1 Noggin 500 SmartHandle system.
Normally the SmartHandle system is used in the “push” configuration shown in Figure 6-1. In
some situations the “pull” configuration may be a more desirable. Figure 6-7 shows the
SmartHandle system in this configuration.
Note that most Noggin SmartHandle systems come from the factory partially assembled with the
odometer bracket, Noggin-to-DVL cable and the handle base already attached to the Noggin
unit.
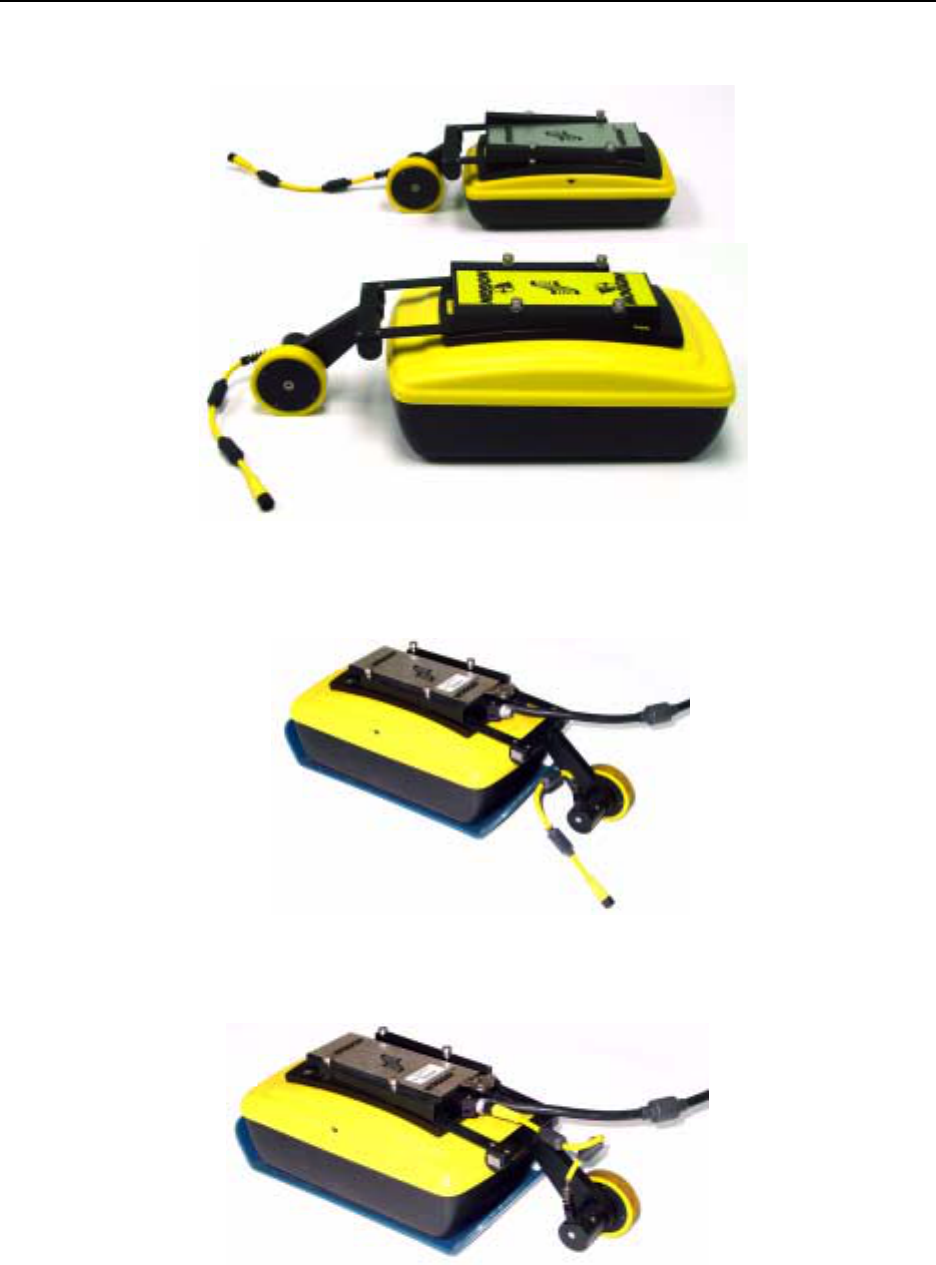
6-SmartHandle Assembly (Noggin 500 & 1000 only) Noggin
30
Figure: 6-2 Slide the Noggin odometer bracket over the four, silver mounting posts for both the Noggin
1000 (top) and Noggin 500 (bottom).
Figure: 6-3 Connect the 37 pin connector on the Noggin-to-DVL cable to the 37 socket receptacle on the
Noggin unit by tightening the latch.
Figure: 6-4 On the Noggin-to-DVL cable, note the round receptacle on the back of the connector that
attaches to the Noggin unit. Connect the yellow odometer cable to this round receptacle.
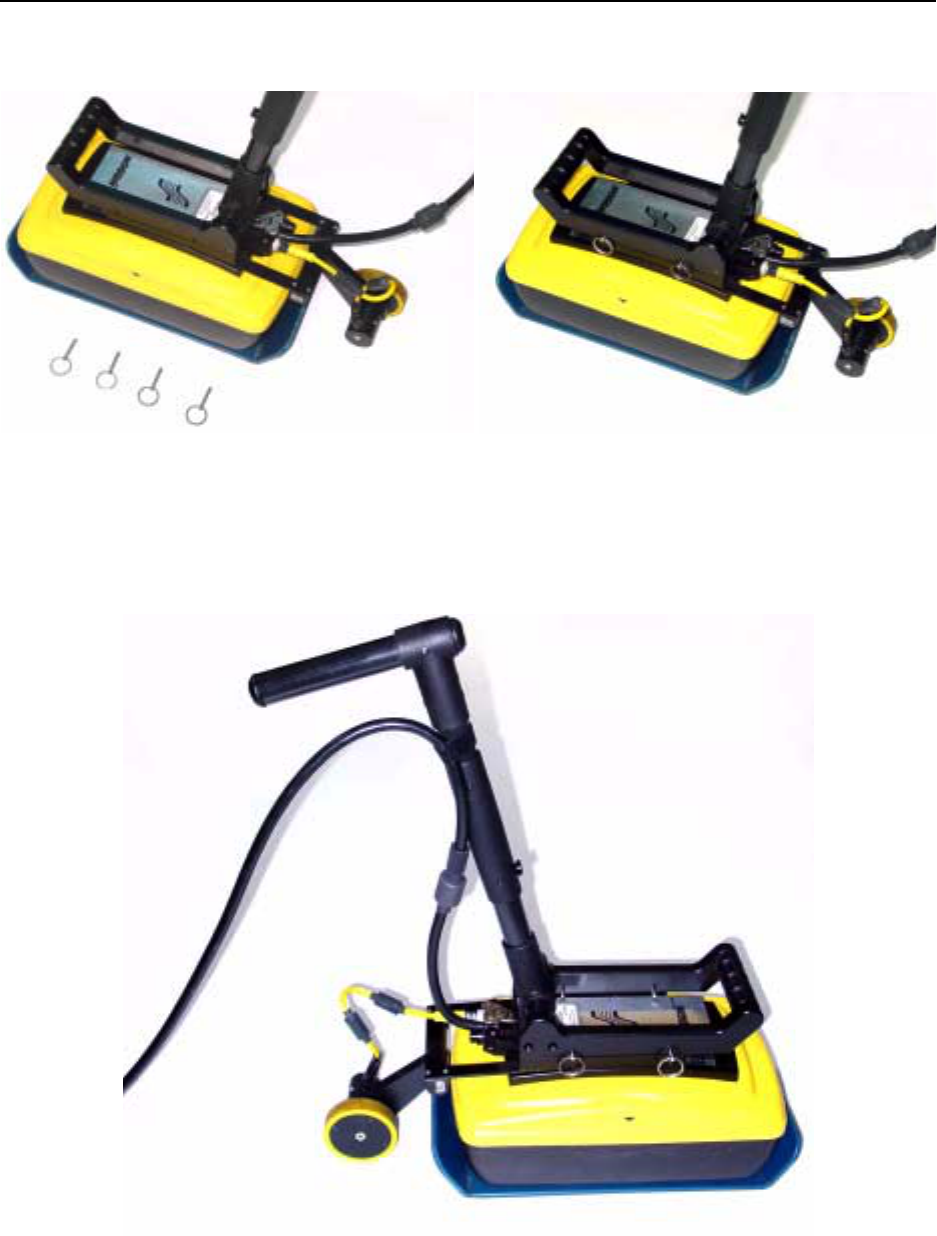
Noggin 6-SmartHandle Assembly (Noggin 500 & 1000 only)
31
Figure: 6-5 Press the handle base straight down onto the four, silver mounting posts. The handle base
should be pushed all the way down onto the odometer bracket. Insert the four quick release pins to secure
the handle.
Figure: 6-6 The full-length SmartHandle is shown in Figure 6-1. The SmartHandle can be shortened by
removing the center handle section using the thumb-screws. Use the Velcro straps to secure the cable
onto the SmartHandle, ensuring there is excess cable near the connection at the Noggin to allow the
SmartHandle to pivot up and down without straining the cable.
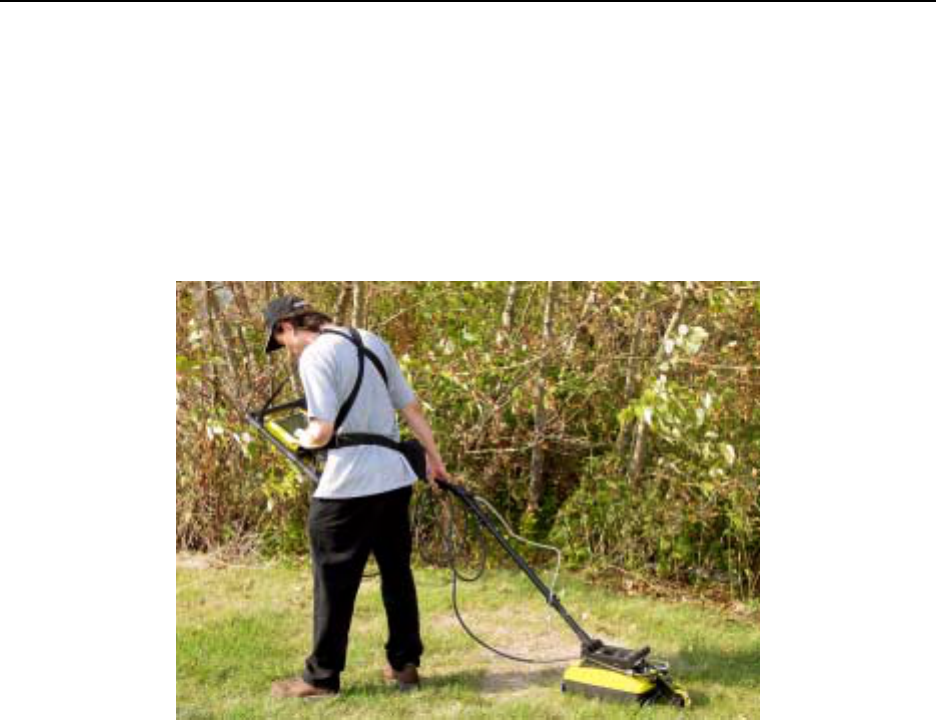
6-SmartHandle Assembly (Noggin 500 & 1000 only) Noggin
32
6.1 SmartHandle “Pull” Configuration
In some situations, conditions may dictate that pushing the SmartHandle system (Figure 6-1) is
not practical. An alternative configuration is to pull the SmartHandle system (Figure 6-7). To do
this, remove the 4 quick-release pins that hold the handle to the Noggin system, remove the
handle by pulling straight up and rotate the handle so that it faces the other direction. Then push
the handle down onto the Noggin as far as it will go and replace the 4 quick-release pins.
Figure: 6-7 In conditions where pushing the SmartHandle is difficult, it is possible to turn the handle
around and pull the system as shown.
6.2 Cable Connections
The DVL to Noggin cable is a Y-shaped cable with 3 connections; one to the Noggin sensor, one
to the DVL and one to the power supply (battery or AC).
Noggin Connection: The first connection was done in Figure 6-3 above, that is, the 37-pin
connector on the cable was attached to the 37-socket connector on the Noggin. A latch was
used to secure this connection.
From the Noggin, the DVL to Sensor Cable runs up the side of the SmartHandle. Use the Velcro
straps to secure the cable to the SmartHandle ensuring there is some slack in the cable near the
connection at the Noggin so, as the handle is pivots up and down there is no strain on the
connection (Figure 6-6).
DVL Connection: The second connection from the DVL to Sensor Cable is to the DVL. One end
of the Y-shaped cable has a 37-socket connector. This end plugs into the 37-pin connector on the
back of the DVL.
Power Connection: The third connection on the SmartHandle cable attaches to a power supply.
The round, 4-pin connector attaches to the battery. This configuration usually uses a belt battery.
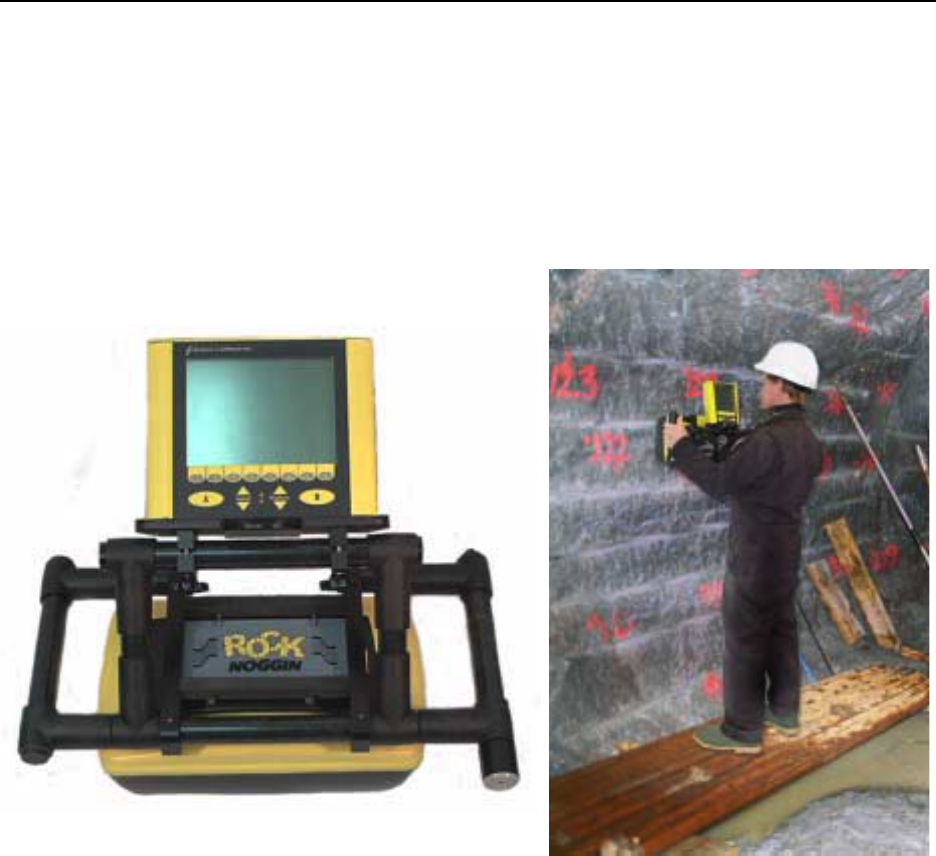
Noggin 7-Rock Noggin Assembly (Noggin 500 & 1000 only)
33
7 Rock Noggin Assembly (Noggin 500 & 1000 only)
Assembly of the Rock Noggin system for both the Noggin 500 and the Noggin 1000 is described
in this section.
The Rock Noggin 500 system is shown in Figure 7-1. The Rock Noggin 1000 system looks very
similar when assembled.
Figure: 7-1 The Rock Noggin system (left) and in use (right).
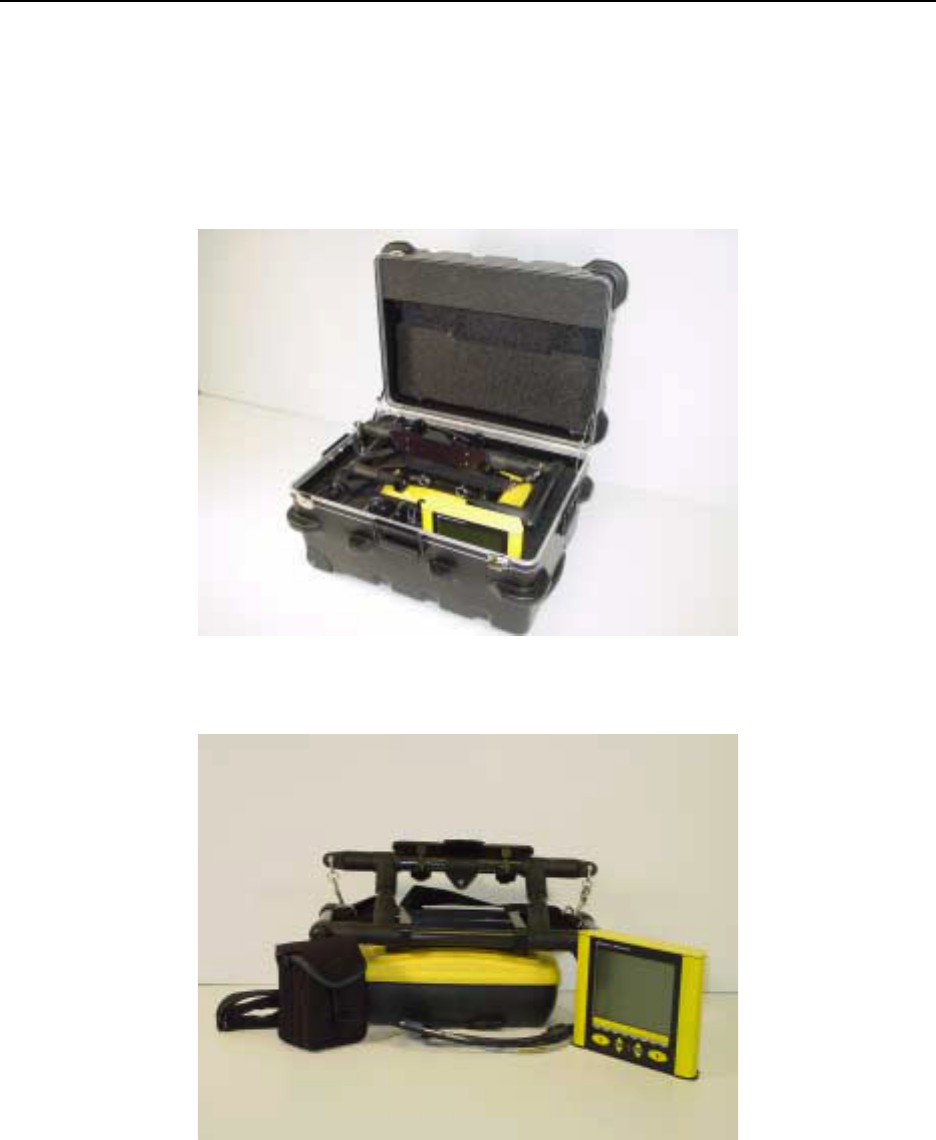
7-Rock Noggin Assembly (Noggin 500 & 1000 only) Noggin
34
The Rock Noggin shipping case contains the complete Rock Noggin system (see Figure 7-2).
Rock Noggin systems are shipped from the factory partially assembled with the frame and DVL-
to-Noggin cable already attached to the Noggin unit (see Figure 7-3). If your system is already
partially assembled, skip to Figure 7-11. Detailed assembly starts at Figure 7-4. A fully
assembled Rock Noggin system is shown in Figure 7-15
Figure: 7-2 A Rock Noggin system in its shipping case.
Figure: 7-3 The Rock Noggin system components after removal from the shipping case. From left to right are the
belt battery, the Noggin already attached to the frame and the Digital Video Logger (DVL). The system comes
partially assembled. To continue with assembly from this point, see Figure 7-11 and later.
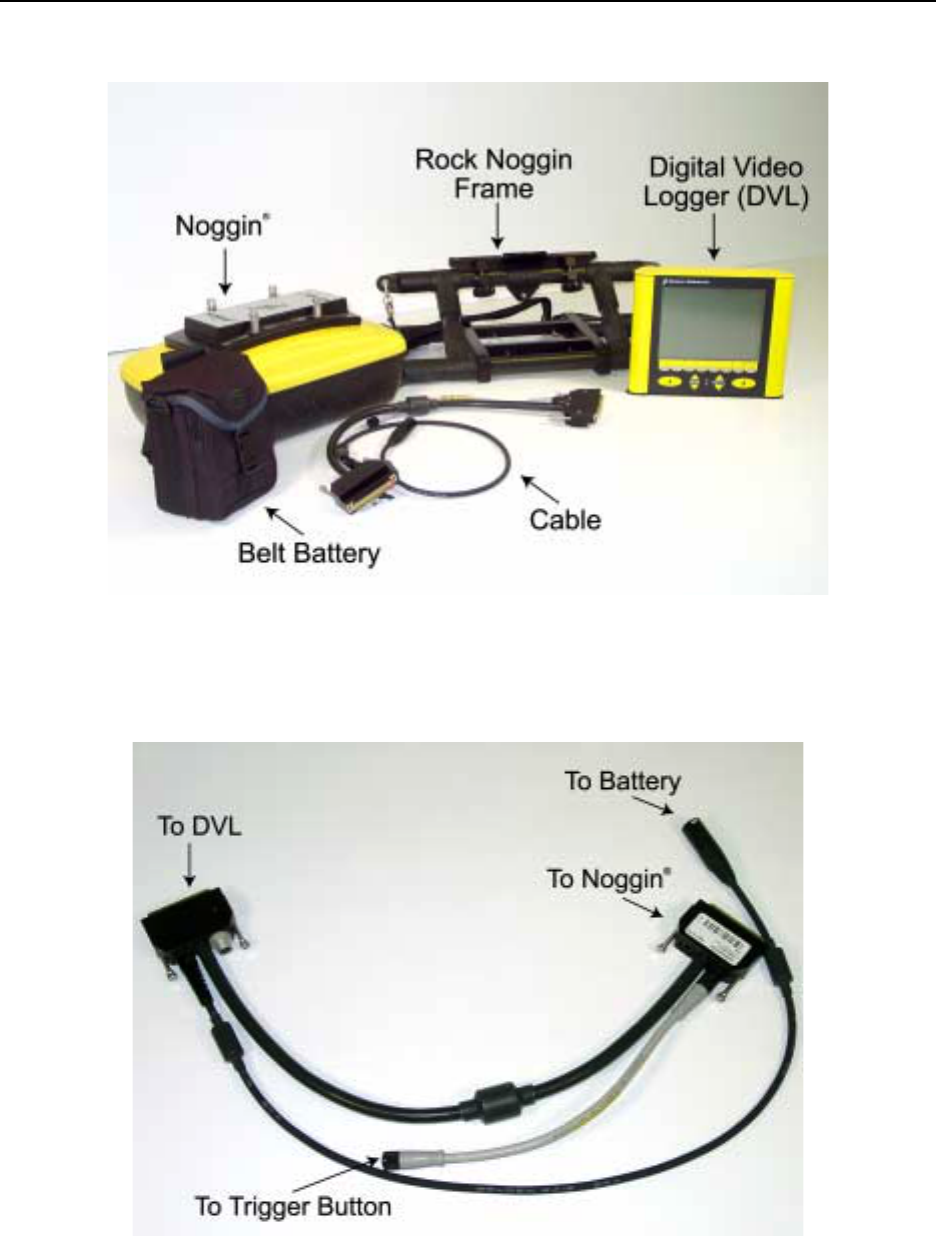
Noggin 7-Rock Noggin Assembly (Noggin 500 & 1000 only)
35
Figure: 7-4 The Rock Noggin system disassembled into its basic components and ready for assembly. From left
to right are the belt battery, the Noggin, the cable (in front), the frame and the Digital Video Logger (DVL). More
details of each component are given in the figures below.
Figure: 7-5 The Rock Noggin cable. The 4 connections are for the Noggin, the Digital Video Logger (DVL), the
trigger button and the battery.
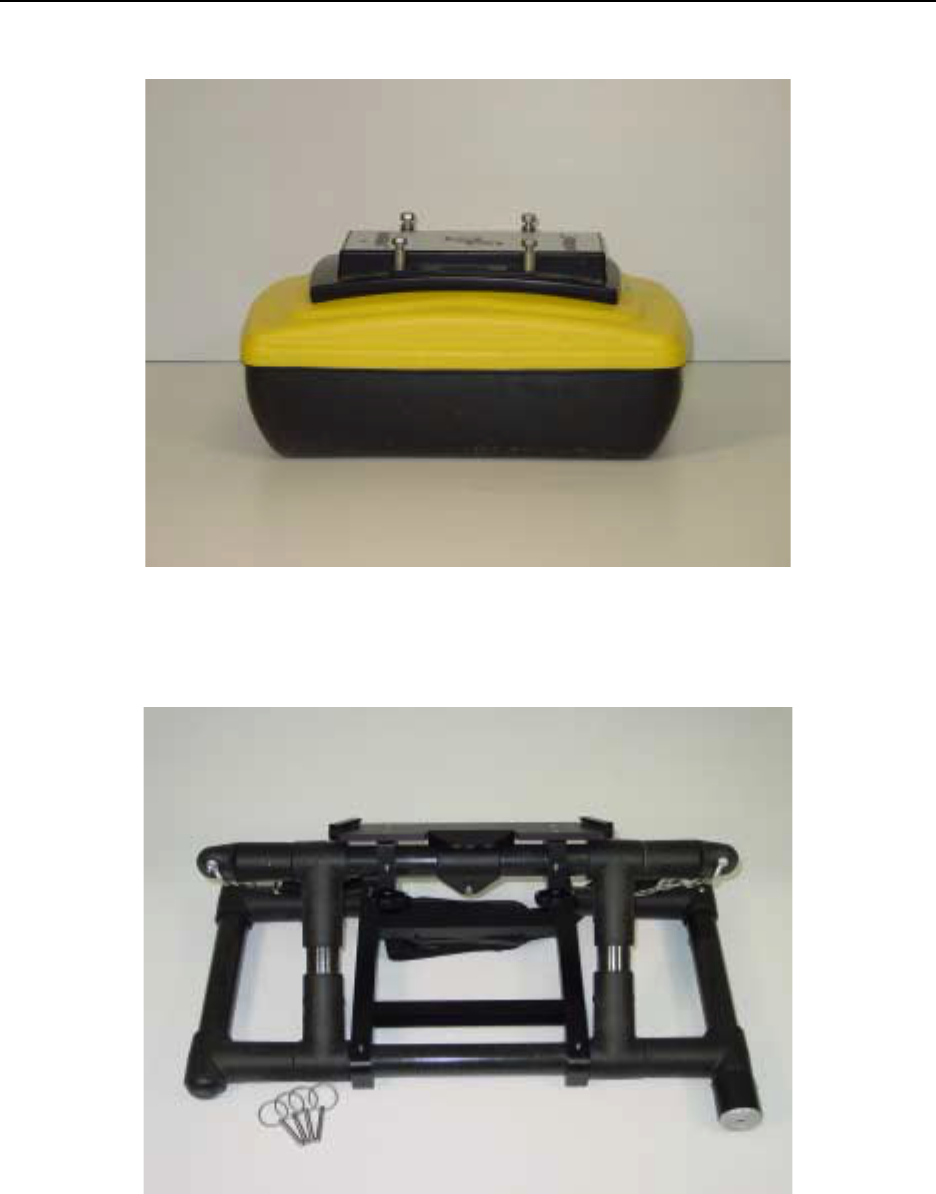
7-Rock Noggin Assembly (Noggin 500 & 1000 only) Noggin
36
Figure: 7-6 The Noggin used with the Rock Noggin can be either a Noggin 500 (shown here) or a Noggin 1000.
The connections are identical for both systems. The 4 silver mounting posts visible here are used when attaching
the frame to the Noggin (see Figure 7-8).
Figure: 7-7 The Rock Noggin frame. On the bottom of the right handle, note the grey speaker that is used to
sound an audible tone as data are collected. Also, on the underside of the right handle, note that Smart button (not
visible in this view) used to collect data. The frame is attached to the Noggin using the 4 clevis pins shown (see
below). The Digital Video Logger (DVL) clips onto the shelf at the top of the frame (see Figure 7-11).
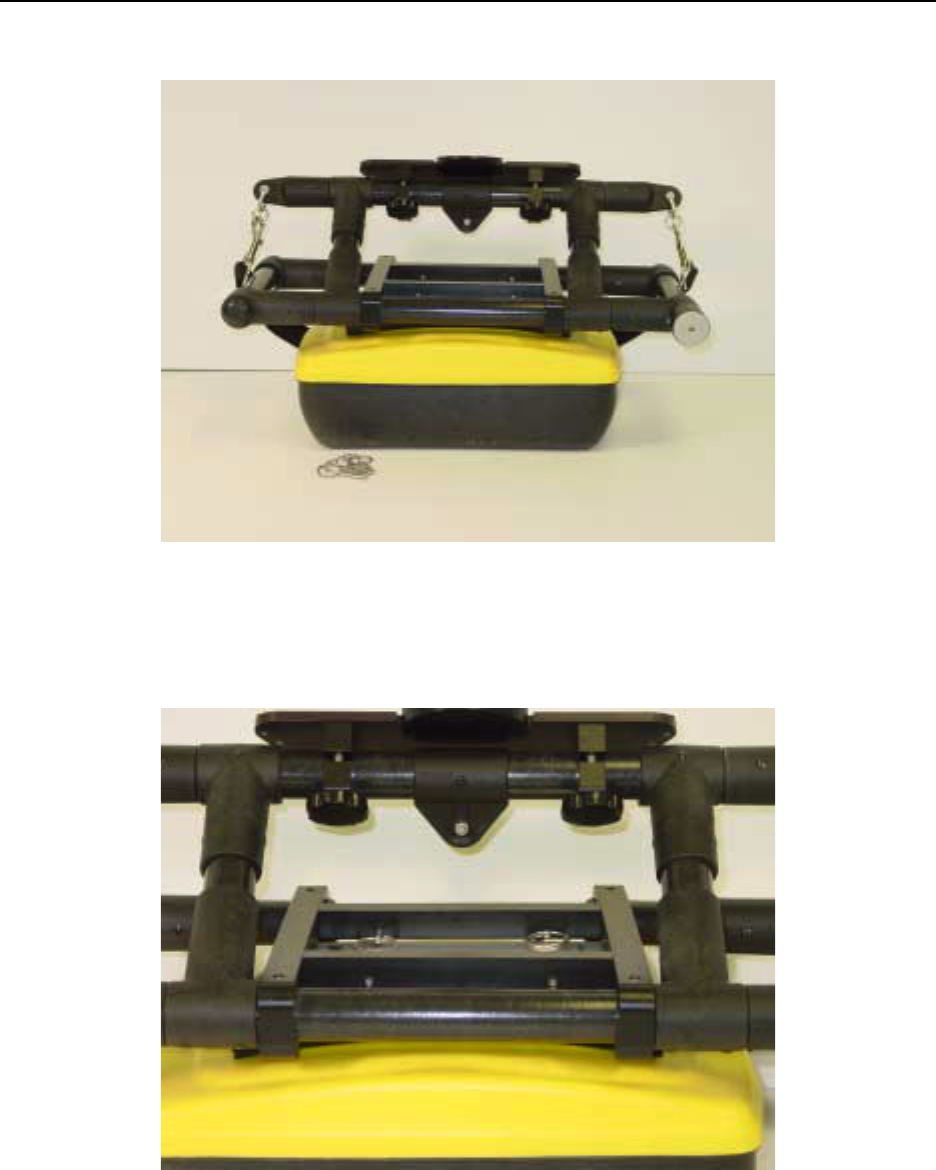
Noggin 7-Rock Noggin Assembly (Noggin 500 & 1000 only)
37
Figure: 7-8 Using the 4 holes on the bottom of the Rock Noggin frame, place the frame on the 4 mounting posts
on the top of the Noggin (shown in Figure 7-6). Push the frame down until it cannot go any further. The Noggin
should be oriented such that the 37 socket receptacle on the Noggin is on the same side as the Smart button on
the frame.
Figure: 7-9 Secure the frame to the Noggin by pushing the 4 clevis pins into the holes on the frame as shown.
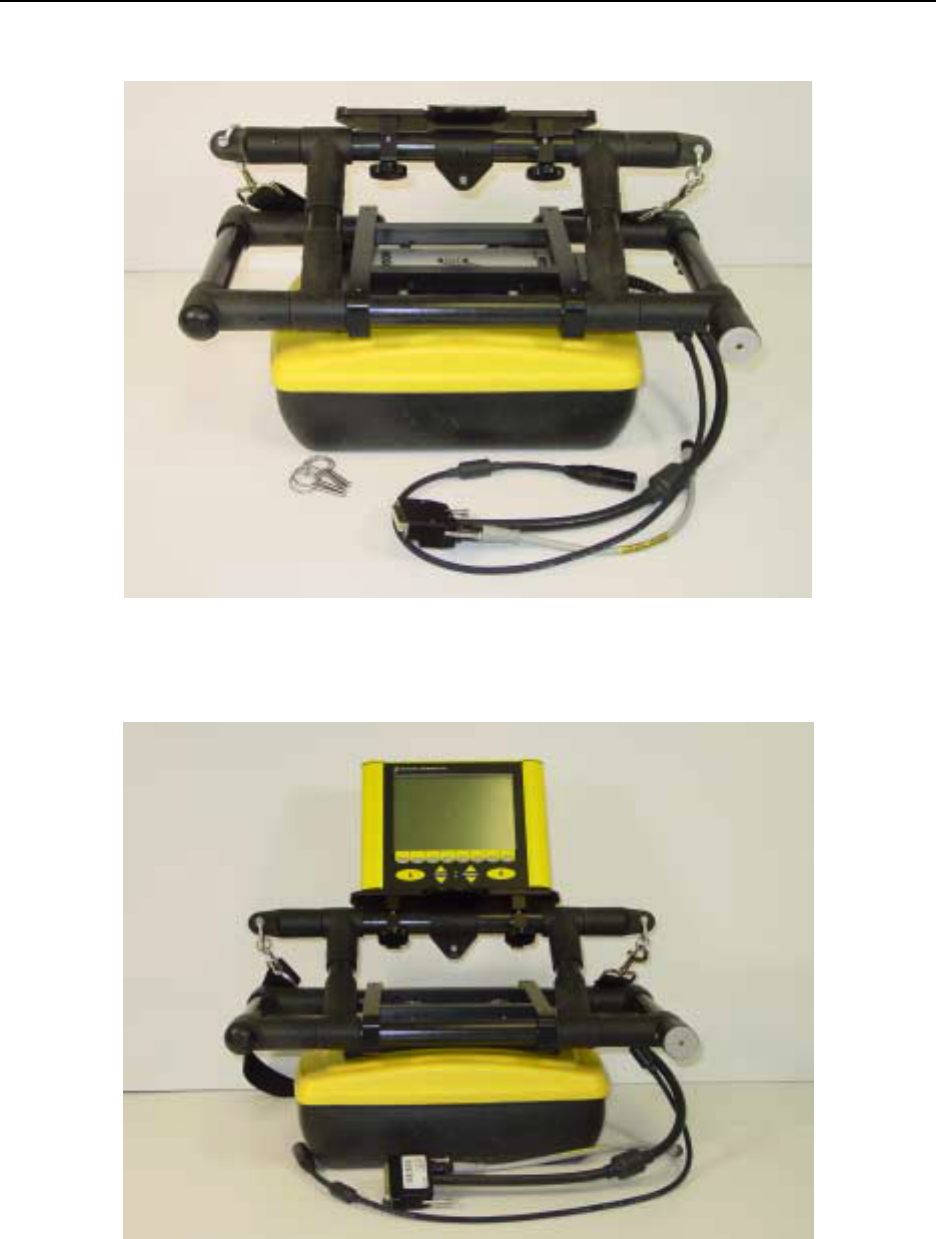
7-Rock Noggin Assembly (Noggin 500 & 1000 only) Noggin
38
Figure: 7-10 Attach the end of the cable with the 37 pin (male) connection to the Noggin. Use a slotted
screwdriver to tighten the connection.
Figure: 7-11 Attach the Digital Video Logger to the frame.
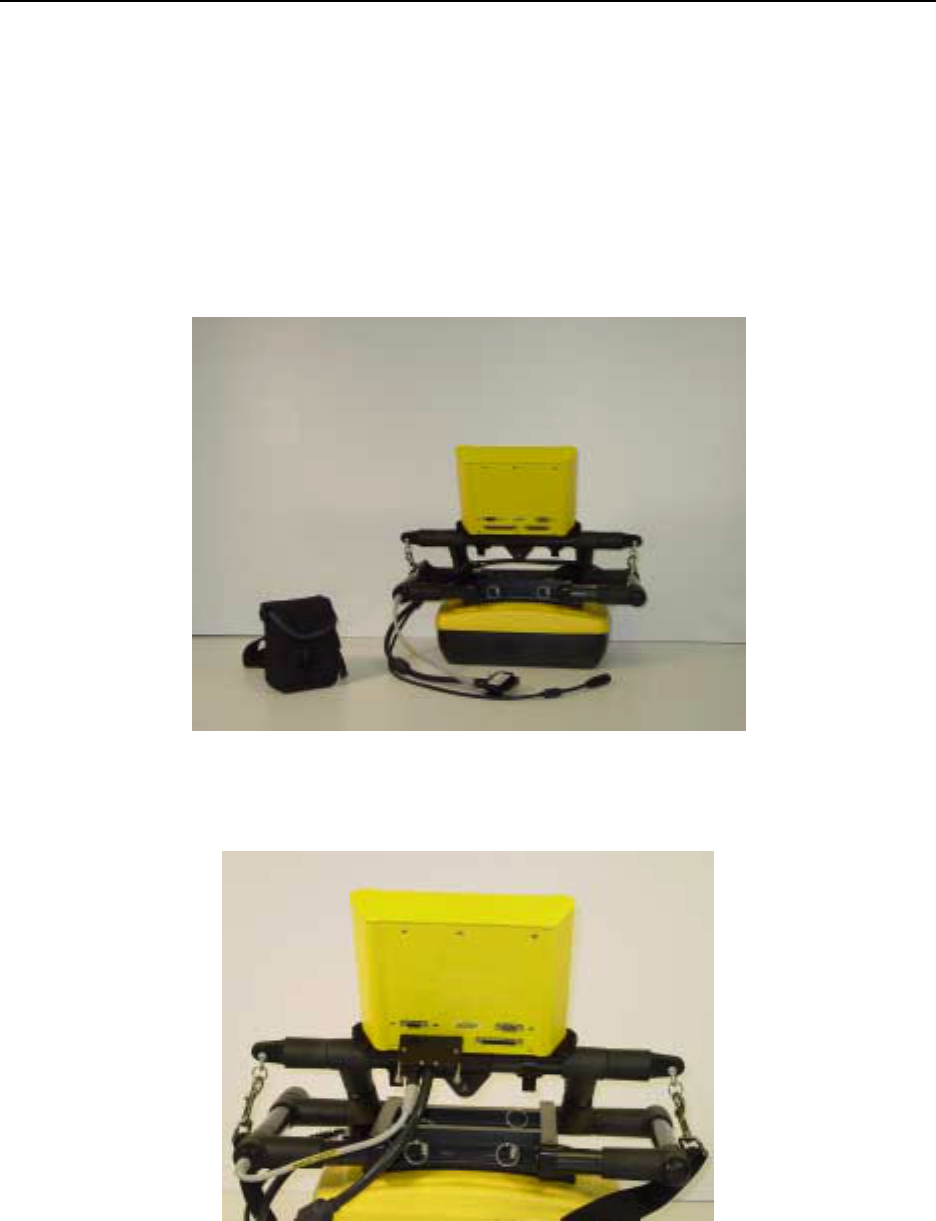
Noggin 7-Rock Noggin Assembly (Noggin 500 & 1000 only)
39
Attach the Digital Video Logger (DVL): The bottom of the Digital Video Logger is designed to
slide onto the support shelf attached to the Rock Noggin frame (see Figure 7-11). Line up the
bottom of the Digital Video Logger with the shelf and slide it back onto the shelf. Push the Digital
Video Logger back far enough so that the flexible clip on the front of the shelf catches and holds
the Digital Video Logger firmly in place. Wiggle the DVL to make sure it is firmly snapped in
before letting go of the unit. (To remove the Digital Video Logger from the Rock Noggin frame,
this clip must be flexed downward as the DVL is slid forward off of the shelf.
The two handscrews on the bottom of the DVL shelf can be loosened to allow the DVL to be
rotated to a different position on the Rock Noggin frame.
Figure: 7-12 Connect the end of the grey cable to the receptacle on the handle at the back of the frame. This
receptacle is adjacent to the Smart button.
Figure: 7-13 Attach the end of the cable with the 37 socket (female) connection to the back of the Digital Video
Logger (DVL). Use a slotted screwdriver to tighten the connection.
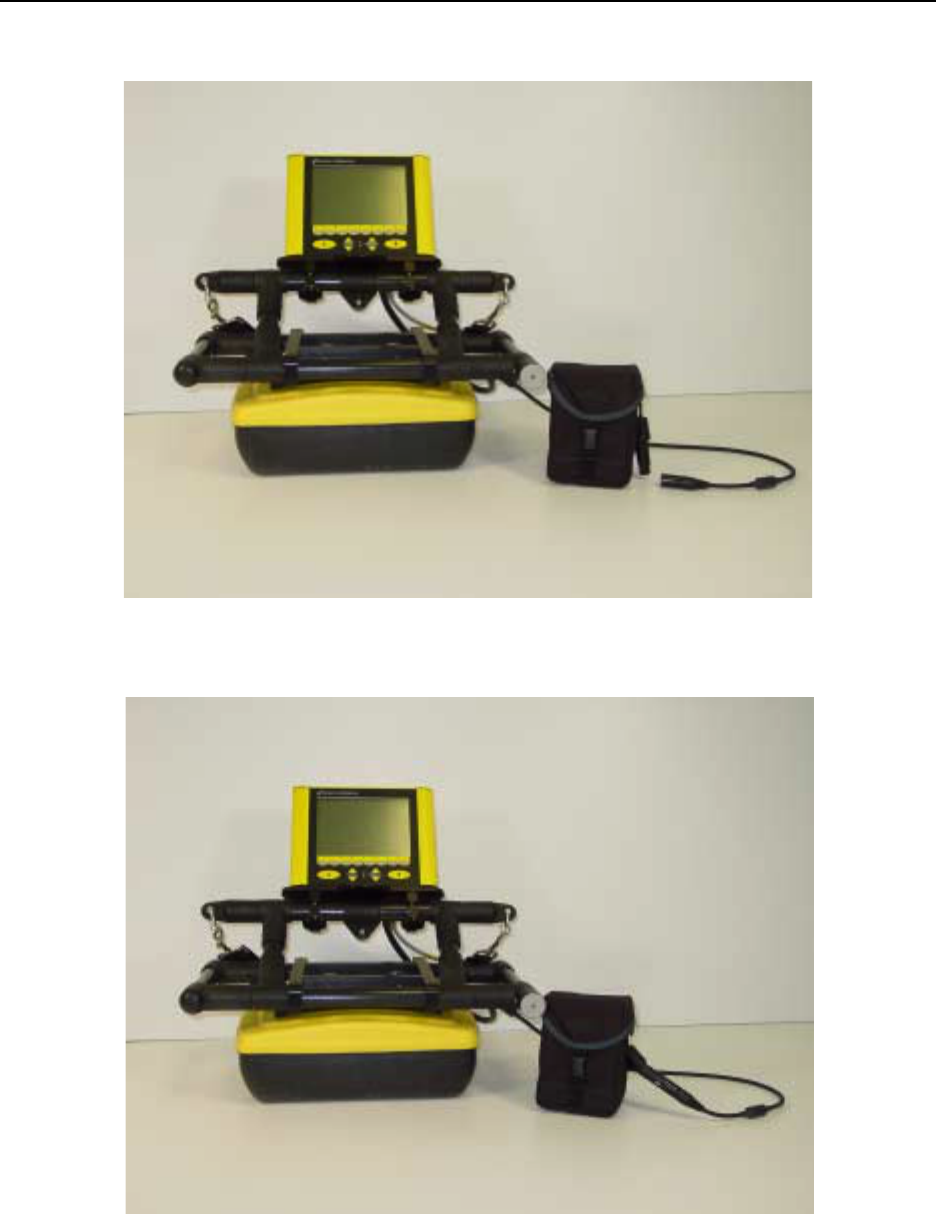
7-Rock Noggin Assembly (Noggin 500 & 1000 only) Noggin
40
Figure: 7-14 The last connection on the cable is a cylindrical, 4 pin connector for the battery.
Figure: 7-15 The Rock Noggin system is now completely assembled and ready to be turned on.
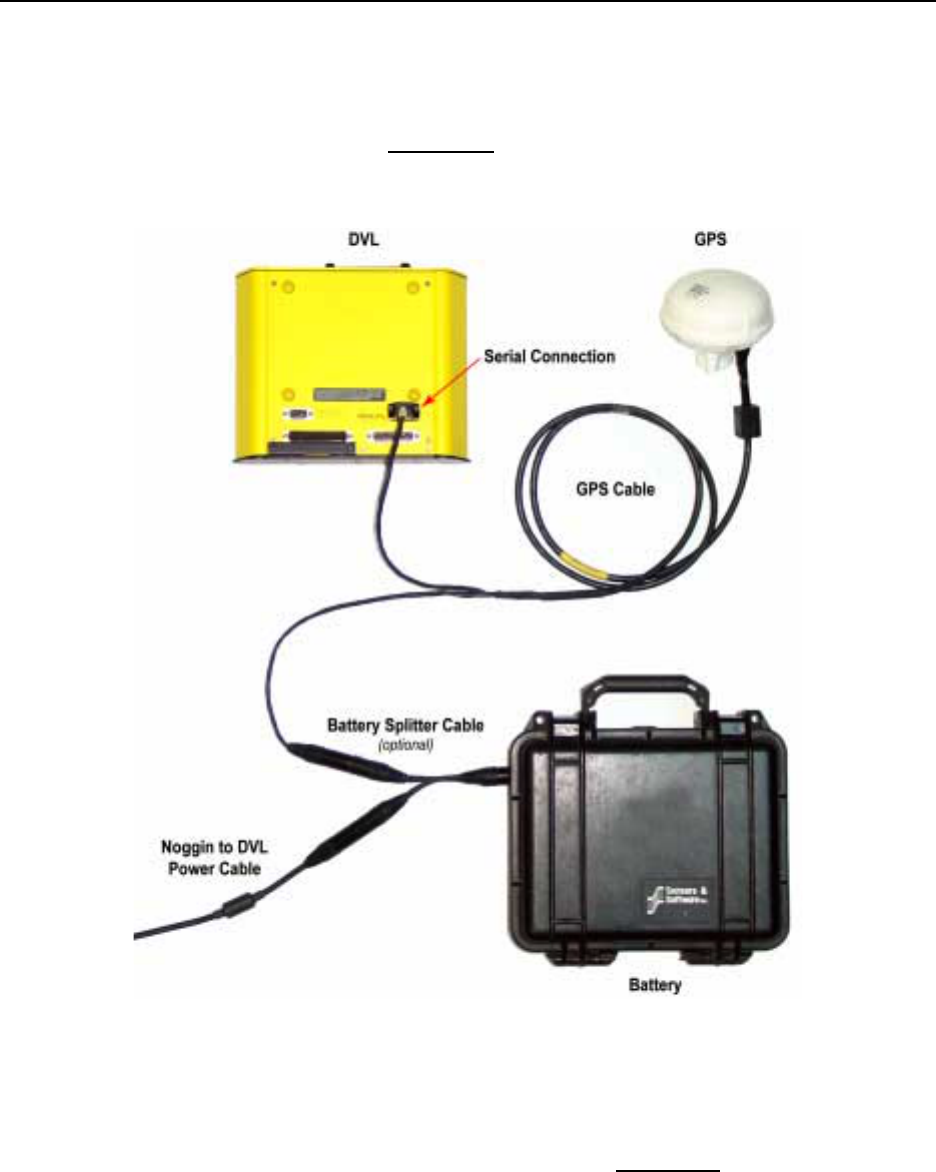
Noggin 8-Connecting GPS
41
8 Connecting GPS
For all Noggin configurations, a GPS with a serial output cable can be attached directly to the 9-
pin serial port on the back of the DVL (Figure 8-1). The DVL can be configured to read in the
GPS data and store it along with the GPR data (Section 12.3.5 GPS Parameters).
Figure: 8-1 GPS connect to the back of the DVL using a serial connection. GPS supplied with IceMap come with a
battery splitter cable to power the GPS from the IceMap battery.
The GPS requires power. User-supplied GPS’s will need to be powered using a separate battery.
GPS supplied by Sensors & Software come with a battery splitter cable to allow the 12 Volt
system battery to power both the Noggin system and the GPS (Figure 8-1).
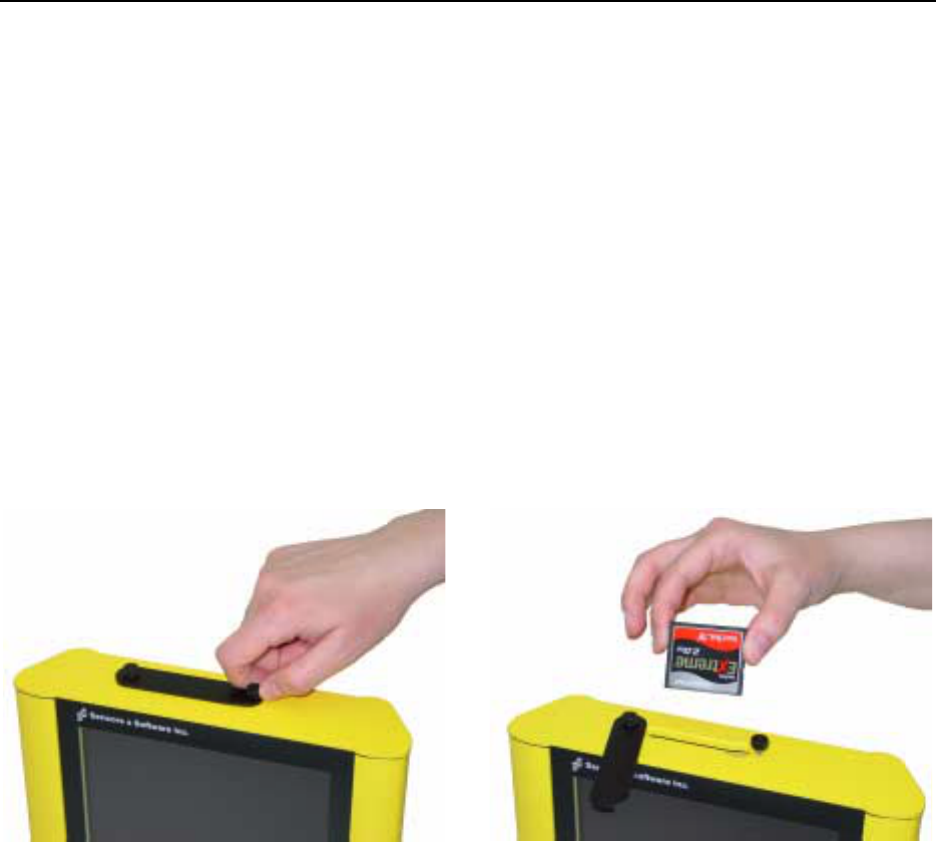
9-Digital Video Logger (DVL) Noggin
42
9 Digital Video Logger (DVL)
Data acquisition is controlled by the Digital Video Logger (DVL). The DVL has software to set
survey parameters, collect, display and store data.
9.1 Compact Flash Drive
The DVL has both an internal and a removable compact flash drive. The DVL firmware resides
on the internal drive. Data can be saved to either the internal or removable drive (Figure 9-1).
The removable compact flash drive is accessible by opening the door on the top of the DVL.
Ensure the DVL is powered down before removing or inserting the compact flash drive.
Loosen the finger screws on the top of the DVL, swing the door open and press the button to
eject the drive.
Figure: 9-1 The DVL has a removable compact flash drive for data storage.
The DVL comes with a removable compact flash drive but the user has the option to purchase
additional drives for data storage. It is best to purchase an industrial grade compact flash drive.
Normal compact flash drives work but the higher the transfer rates and temperature ranges the
better. The DVL can use cards up to a maximum of 2 GB in size. Sandisk, PSI-APRO,
SimpleTech, Kingston, Viking, and Pretech are a few manufactuers of compact flash drives.
These are widely available in consumer electronics stores.
To transfer data from the removable drive to a PC the user will need to purchase a card reader
(Figure 12-17). These are widely available in consumer electronics stores.
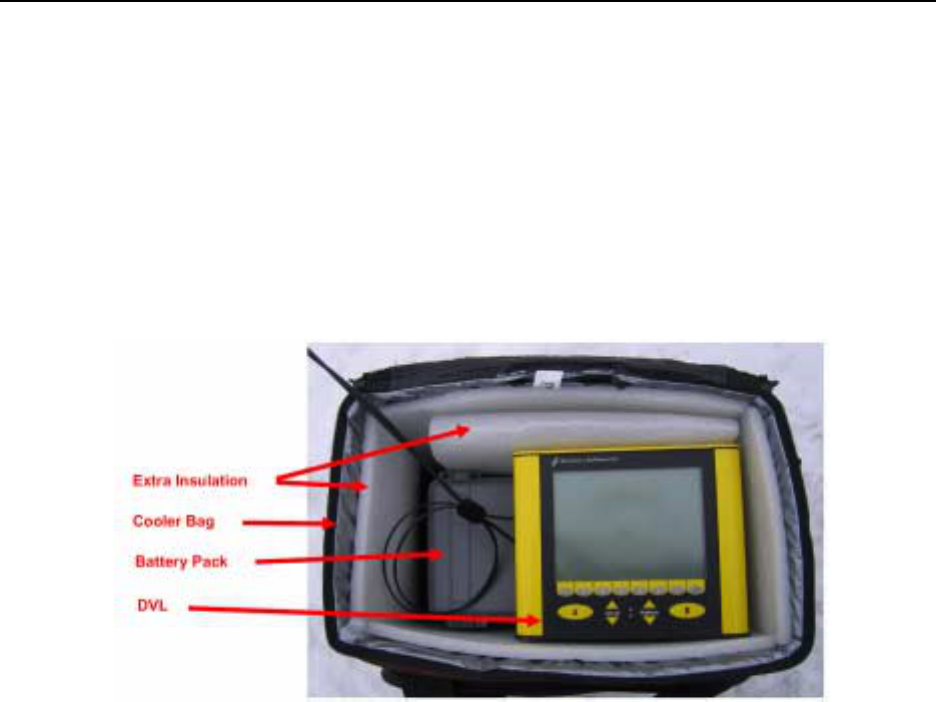
Noggin 9-Digital Video Logger (DVL)
43
9.2 DVL Temperatures
It is very important that the DVL only be operated when it can be kept warmer than -10 C
otherwise sensitive electronic components including the LCD screen may freeze. Never
start the DVL after it has been exposed to cold temperatures.
If the DVL will be operating in temperatures below -10 C, it should be kept in a wind-proof box
insulated with styrofoam or textiles and heated with hand-warmer packs, if necessary. If possible,
start the DVL in a warm temperature before placing it in the box. If the protective box is properly
insulated, the DVL can usually generate enough heat to keep itself warm.
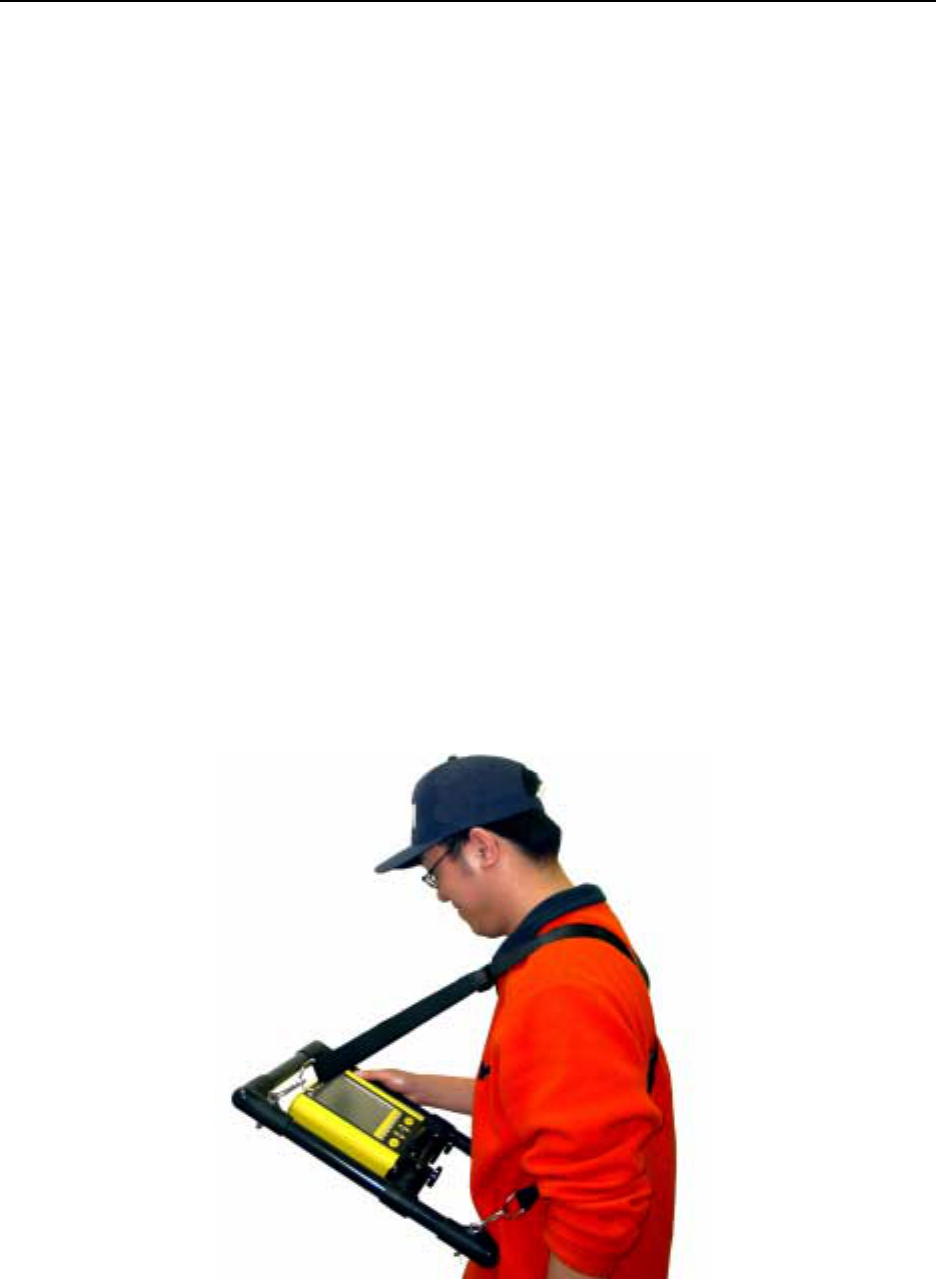
9-Digital Video Logger (DVL) Noggin
44
9.3 Running a DVL Detached from a Smart System
When collecting data with a Smart System, the DVL is powered by the system battery. It is
possible to detach the DVL from the Smart System and use it away from the system to review
data. There are 2 ways to power the DVL away from the Smart System:
1) The optional DVL to Power Supply Cable allows the user to power the DVL away
from the Smart System using the system battery. As shown in Figure 9-2, the cable
connects the battery to the 9-socket connector on the back of the DVL.
2) To avoid having to use the system battery to power the DVL, an optional AC power
supply is available. This, when combined with the DVL II to Power Supply Cable,
allows the user to power the DVL away from the Smart System using AC power. As
shown in Figure 9-3, the AC power supply connects to the DVL II to Power Supply
Cable which connects to the 9 socket connector on the back of the DVL.
9.4 DVL Carrier
For convenience during data acquisition, especially when using the SmartTow and SmartHandle
configurations, the DVL can be carried using the optional DVL Carrier shown in Figure 9-2.
The bottom of the DVL is designed to slide onto the support shelf on the DVL Carrier. Line up the
bottom of the DVL with the shelf and slide it back onto the shelf. Push the DVL back far enough
so that the flexible clip on the front of the shelf catches and holds the DVL firmly in place. Wiggle
the DVL to make sure it is firmly snapped in before letting go of the unit. To remove the DVL from
the DVL Carrier, flex the clip downward as the DVL is slid forward off of the shelf.
Figure: 9-2 The DVL and control module can be attached to the optional DVL Carrier for hands-free operation. The
DVL can be adjusted to optimize the view angle.
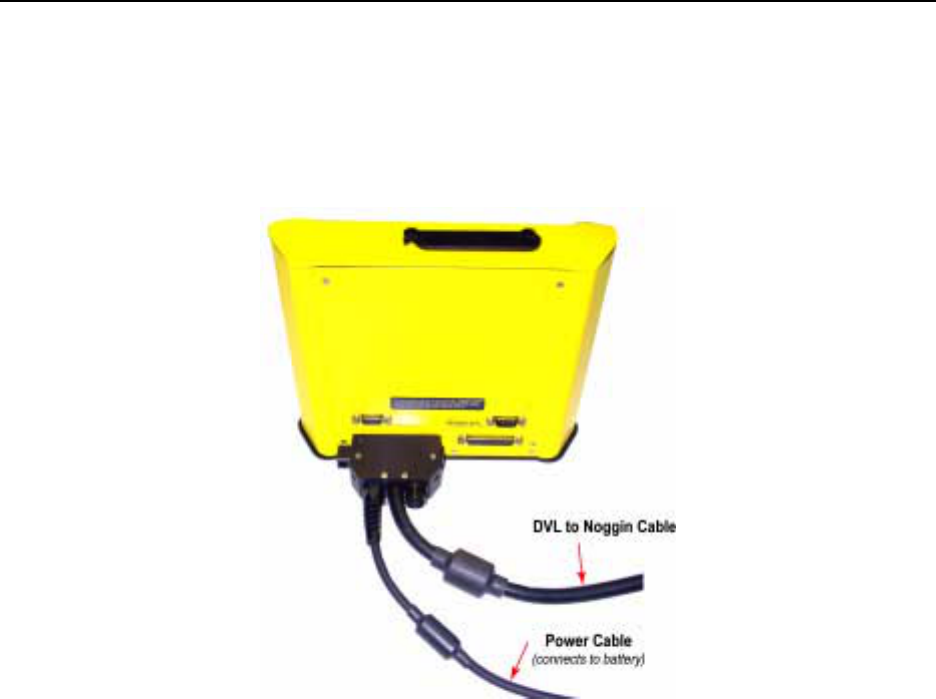
Noggin 9-Digital Video Logger (DVL)
45
9.5 Connecting the DVL to the Smart System
Attach the end of the DVL-to-Noggin cable with the 37-socket female D-connector to the 37-pin
receptacle on the back of the DVL. This attachment can be secured by tightening the latch.
Figure: 9-3 The DVl-to-Noggin cable connects to the back of the DVL.
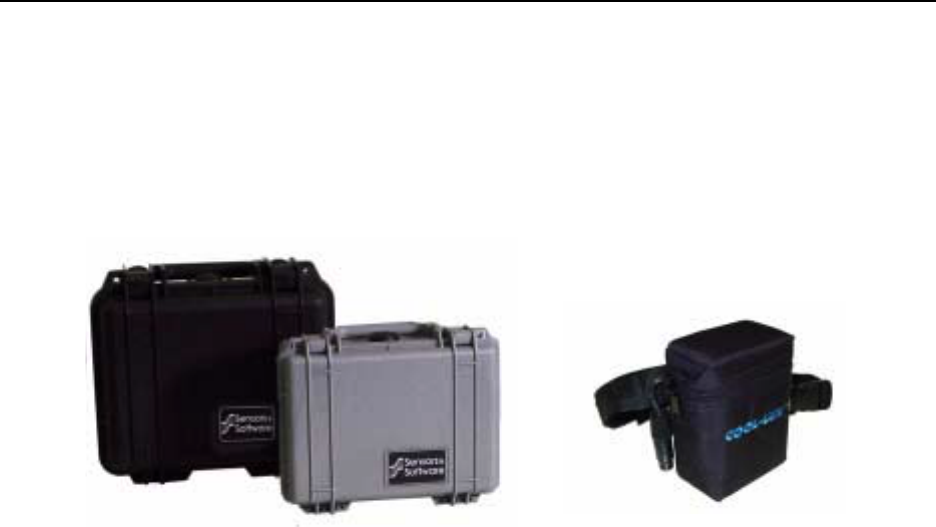
10-Powering Up the System Noggin
46
10 Powering Up the System
Once all the cable connections are made between the Noggin, the Digital Video Logger (DVL)
and any accessories like odometers and GPS’s, the final step is to connect the system to a 12
volt power source, typically one of the batteries shown in Figure 10-1.
Figure: 10-1 Batteries for Noggin Smart Systems: SmartCart batteries (left) and belt battery (right).
Connect the round 4-pin battery cable on the Noggin-to-DVL cable to the receptacle on the side
of the battery.
The upper red LED light on the DVL panel should be lit. If the battery voltage is low, the light will
flash for about 30 seconds and go out. If the light flashes or does not appear, check the
connections and make sure the battery is fully charged. (See Section 14.1: P.115 for more
information on battery care.)
The voltage indicator can be helpful for identifying when the battery needs to be recharged. If the
battery voltage drops too low the DVL will cease to operate.
The front of the DVL is shown in Figure 10-2. To start the system, press any button on the front
panel. The lower red LED on the front panel should illuminate.
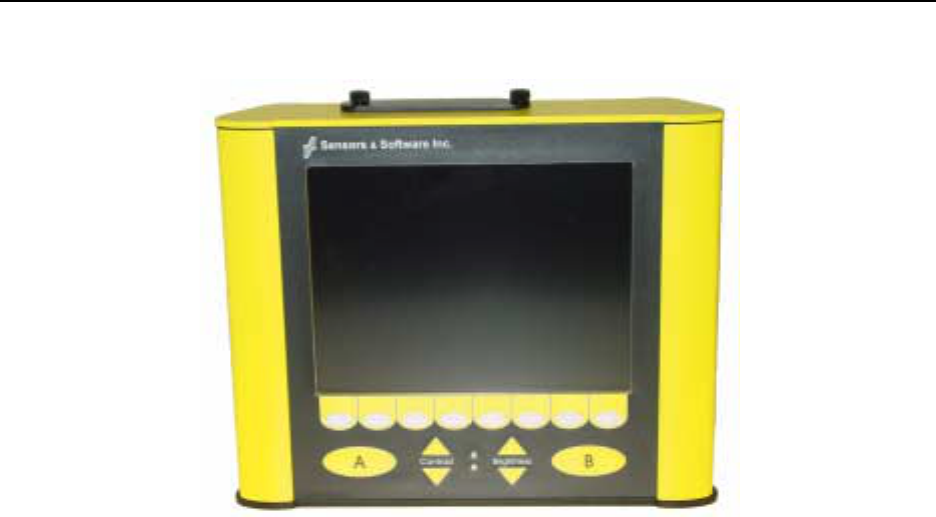
Noggin 10-Powering Up the System
47
Figure: 10-2 Digital Video Logger (DVL) face
At this stage, the Noggin unit will still be powered down. Once Noggin action is requested (see
later menu items), the DVL will enable power to the Noggin. If the Noggin is receiving power, the
red LED light on the connector to the Noggin will be illuminated.
The water-resistant membrane keypad has a number of buttons that can be pressed to perform
various tasks.
Menu Buttons: The yellow buttons labelled 1 to 8 correspond to menu choices that appear listed
on the screen or along the bottom of the screen when the Digital Video Logger is turned on.
In addition, there are two general-purpose buttons labeled A and B. All buttons are DVL
application dependent and roles change. The operation will be self-explanatory from the display
screen.
Screen: The DVL screen is a grayscale LCD selected for its wide temperature range and
visibility in sunlight. Visibility can be a major problem with viewing GPR data displays outdoors
and considerable effort has been expended on getting a readily visible outdoor display.
Brightness: The yellow Brightness control arrows are used to increase and decrease the screen
brightness. For example, increasing the Brightness setting may improve the visibility of the
screen when in a dark area. Note, however, that increasing the screen brightness also increases
battery consumption so don’t use a bright screen unless necessary.
Contrast: The yellow Contrast control arrows are used to increase and decrease the screen
contrast. For example, increasing the Contrast setting may improve the visibility of the screen on
a bright, sunny day. Increasing the Contrast can also be useful to see weaker features on the
screen. Adjusting the contrast has little effect on battery consumption.
Temperature sensors within the DVL automatically compensate the screen setting so that
manual adjustments of Brightness and Contrast should seldom be needed after initial setup.
Once the Digital Video Logger powers up, the Main Menu is displayed with 4 choices:
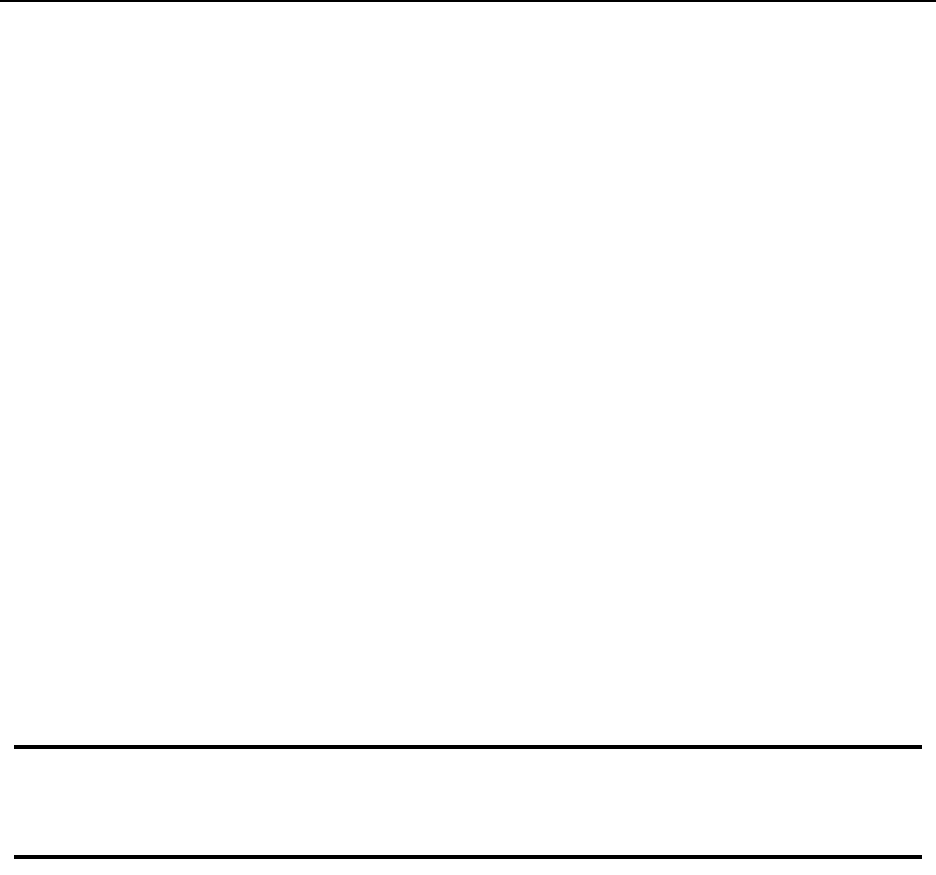
10-Powering Up the System Noggin
48
A – LOCATE & MARK
B – SURVEY & MAP
1 – CONTACT US
3 - SWITCH MENU
5 – POWER OFF
12.1 V 38°C 02-0181-03??
100°F
• Pressing the A button enters Locate & Mark mode (see Section 11: P.49).
• Pressing the B button enters Survey & Map mode (see Section 12: P.67).
• Pressing the 1 button displays contact information for Sensors & Software Inc.
• Pressing the 3 button switches the menu for use with older Noggin and Nogginplus sys-
tems (these are systems with a Yellow or Silver Noggin sticker on top of the electronics
housing). For details on using this menu system, see the Smart Systems manual.
• Pressing the 5 button will turn the DVL off.
This screen also displays the following information:
•Battery Voltage: The system will shut down when the battery voltage reaches about
10.2 Volts (see Section 14.1: P.115 for more details on the battery).
•Temperature: The internal temperature of the DVL is displayed on this screen in Cel-
sius and Fahrenheit.
•Software Version: The version of the software loaded on the DVL.
When the Noggin Smart System is not being used, do not leave the battery plugged in.
The system draws about 0.1 amps even when it is powered off and this will gradually drain
the battery.
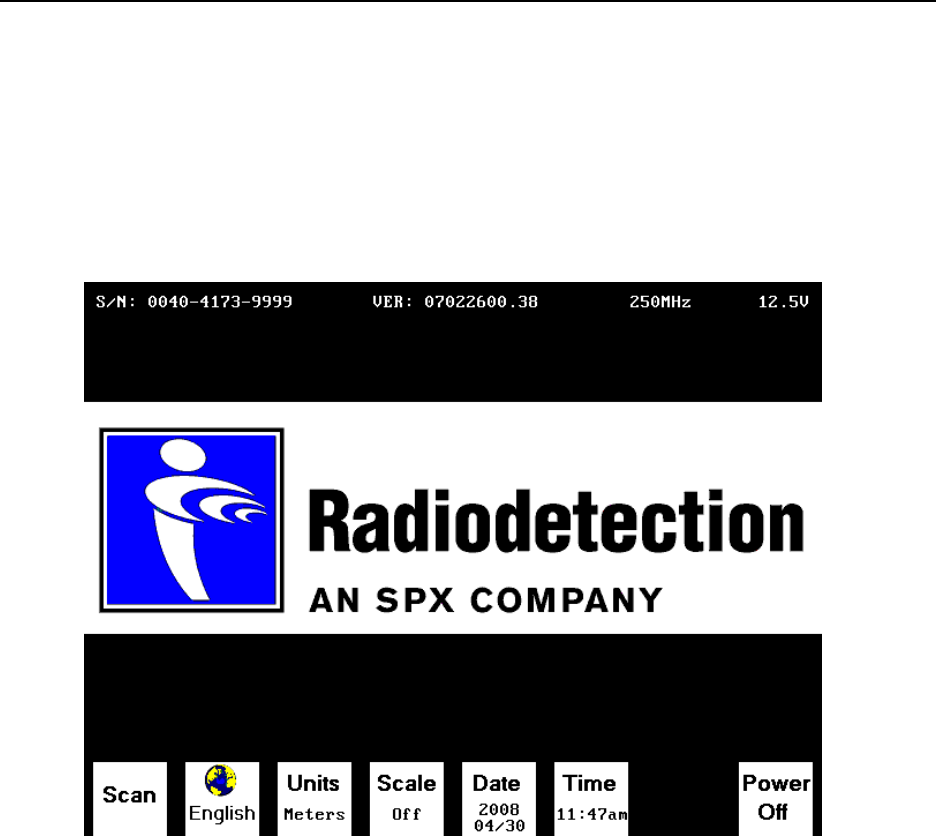
Noggin 11-Locate & Mark Mode
49
11 Locate & Mark Mode
Selecting Locate & Mark from the main menu will display the System Settings screen.
11.1 System Settings Screen
11.1.1 Scan
Press the Scan button to start scanning (see Section 3.3).
11.1.2 Language
Select the language for the menus. Current options are English or Icons. This section generally
uses the English menus. See Section 3.7?? for a chart showing all the equivalent icons.
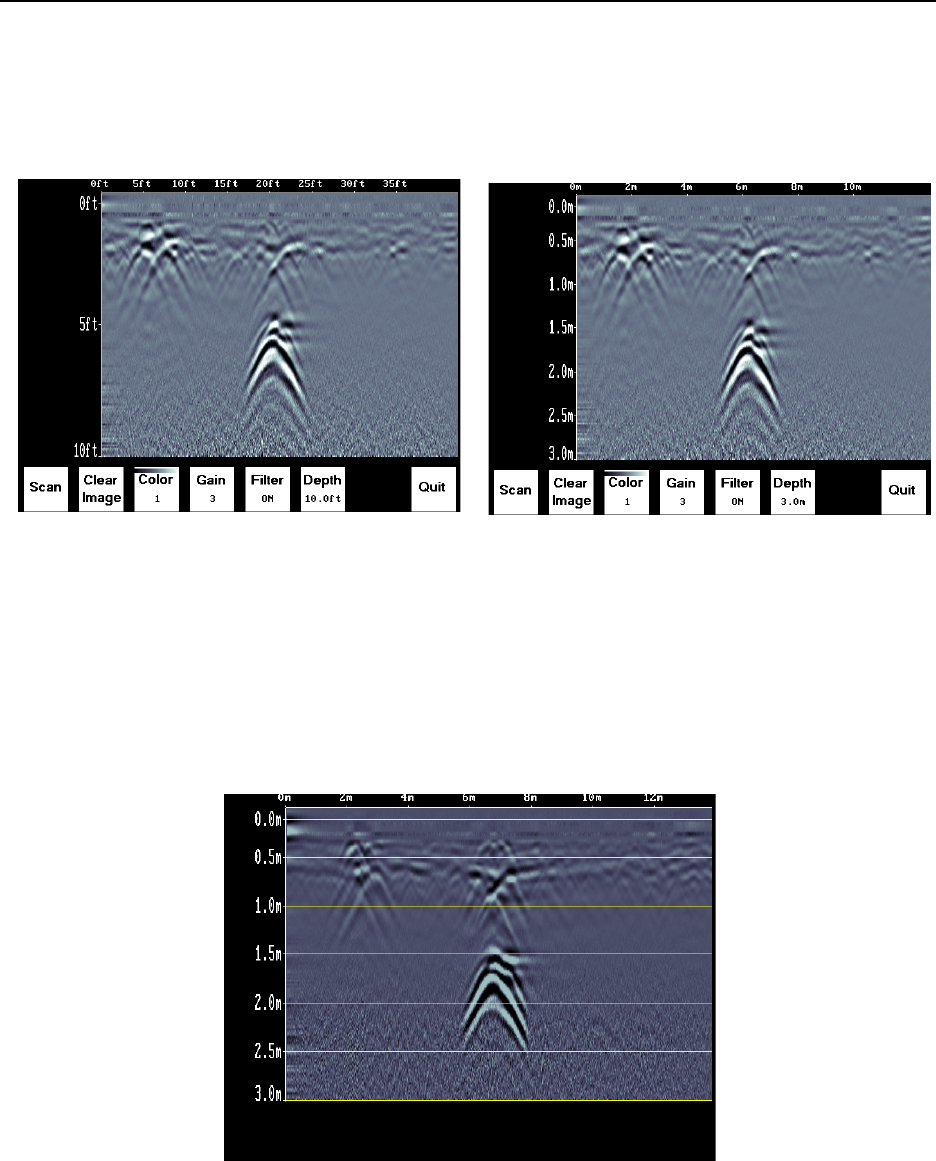
11-Locate & Mark Mode Noggin
50
11.1.3 Units
Units for the Position Axis, Depth Axis and Depth Indicator can be either Meters or Feet.
11.1.4 Scale
The Scale button toggles to four different Scale options:
1) Lines means Depth Lines are plotted on the data image to assist with determining
the depth of targets (also see Section 3.3).
2) Text means Depth Values are plotted in the center of the data image every 8
metres or 26 feet:
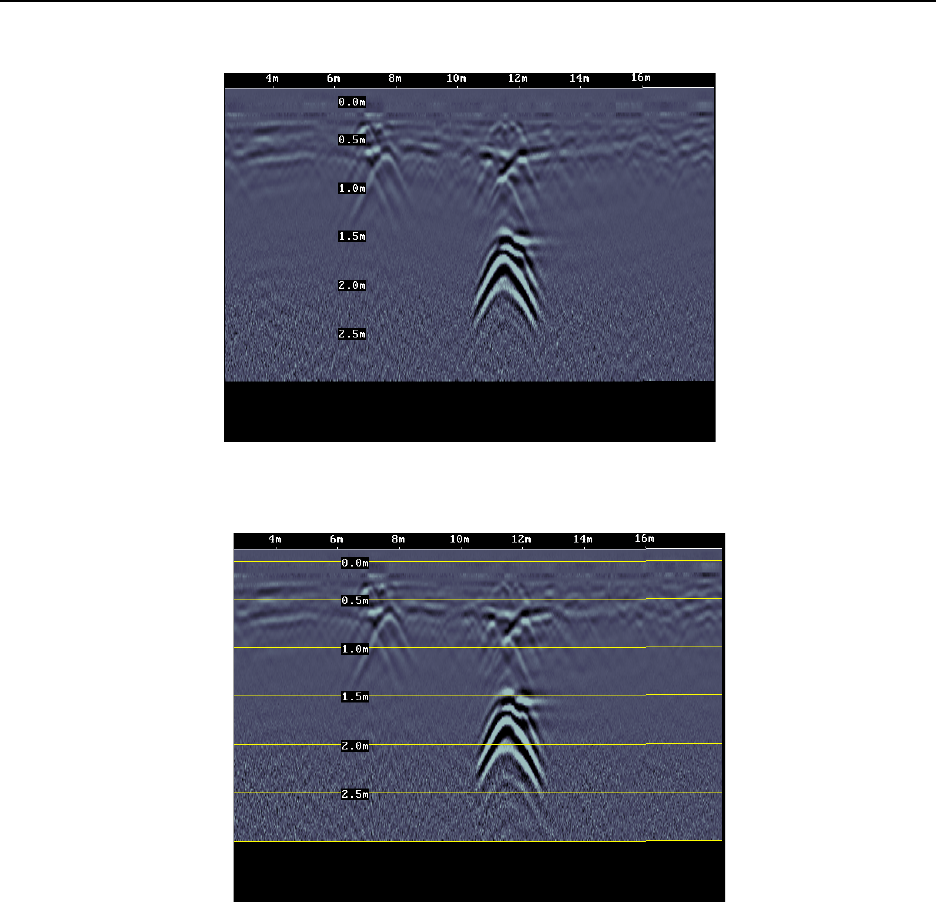
Noggin 11-Locate & Mark Mode
51
3) Both means both Depth Lines and Values are plotted on the data image:
4) Off means no Depth Lines and Values are plotted on the data image.
11.1.5 Date
Opens the Date Screen to change the current date (see Section 3.5). Images are saved with this
date.
11.1.6 Time
Opens the Time Screen to change the current date (see Section 3.5). Images are saved with this
time.
11.1.7 Power Off
Opens a sub-menu to confirm powering off the system. There is also an option to restore the
system to factory default settings.

11-Locate & Mark Mode Noggin
52
11.1.8 System Information
The top of the Systems Setting Screen displays the serial number of the GPR sensor, the
software version number, the GPR Sensor frequency (in MHz) and the current battery voltage.
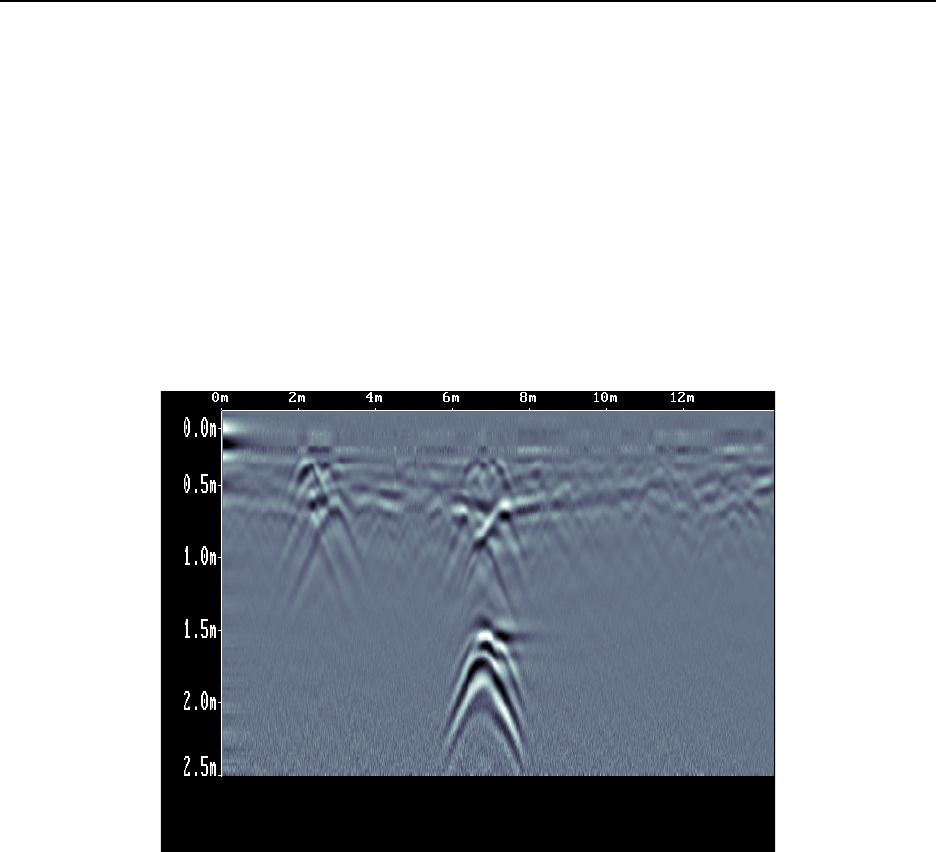
Noggin 11-Locate & Mark Mode
53
11.2 Scanning Screen
After pressing the Scan button, wait a few seconds for the vertical depth scale to appear on the
right side of the screen, and then push the Cart forward.
A cross-sectional image of the ground scrolls onto the screen from the right to left. The position
is displayed on the horizontal axis at the top while the depth is displayed on the vertical axis. The
position and depth axes units are meters or feet depending on the units set in the Systems
Setting Screen (Section 3.2).
If the Scale or Both option is selected (Section 3.2), horizontal depth lines appear on the image to
assist with determining the depth of targets.
Approximately 16 meters or 50 feet of data is displayed on one screen. If the survey line
exceeds this distance the image will scroll off the left side of the screen.
To save the current screen image to file, press the Camera button on the Display Unit. The
image number appears on the bottom of the screen with a message to press any button to
continue.
A message will appear on the screen if there is no Compact Flash card in the Display Unit.
Images are only saved when a card is present.
Pressing any of the number buttons on the Display Unit marked 1 to 8 while scanning adds a
numbered marker at the current position.
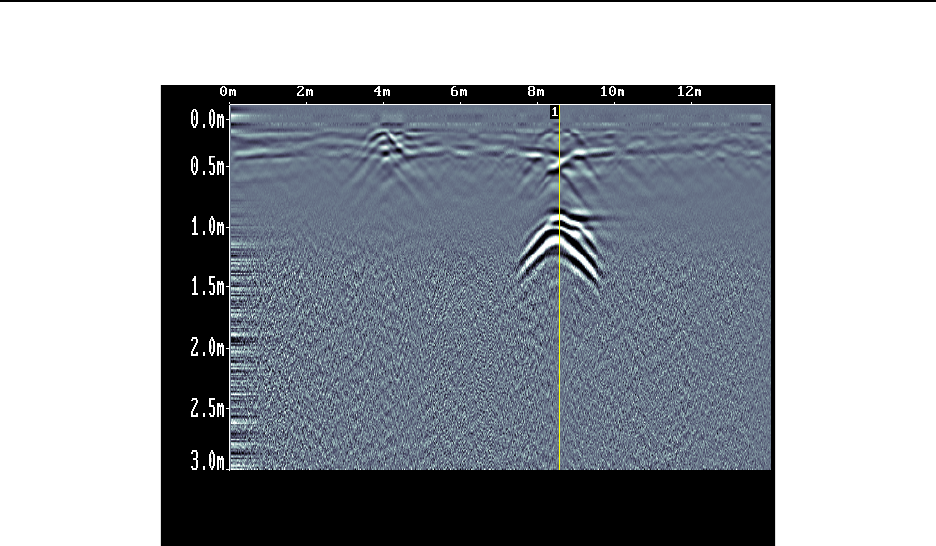
11-Locate & Mark Mode Noggin
54
Pressing the Pause button opens the Image Settings Screen to change the current Color Palette,
Depth, Filter and Gain (see Section 3.5).
Stopping and pulling the cart backwards along the same path automatically opens the Locating
Screen (See Section 3.4) used to pinpoint the position and depth of a target.
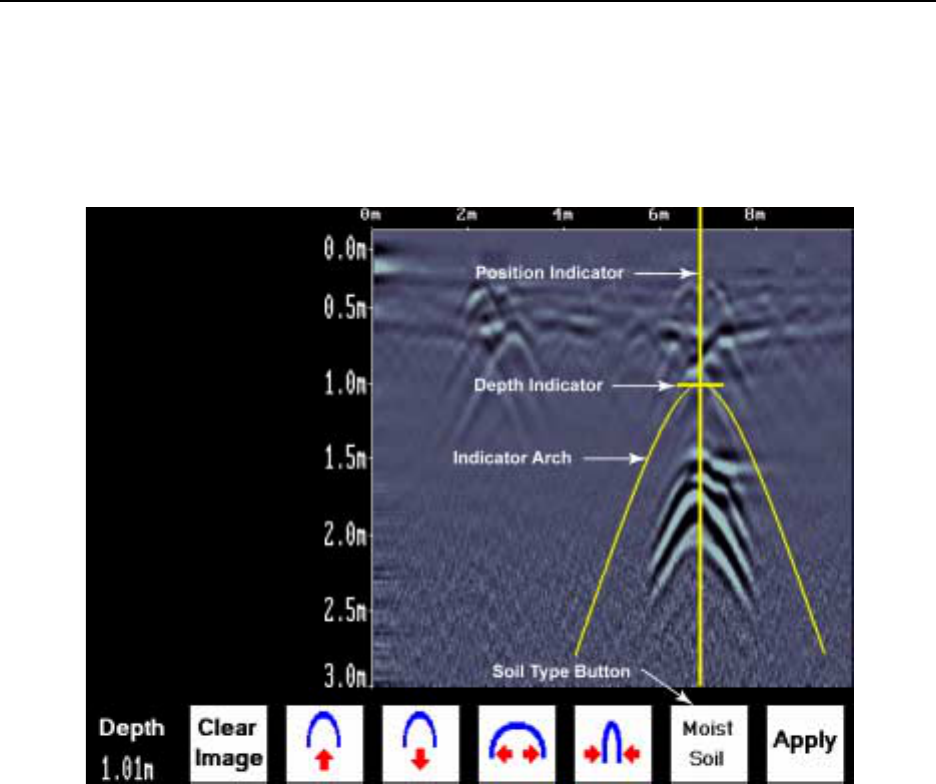
Noggin 11-Locate & Mark Mode
55
11.3 Locating Screen
The Locating Screen is accessed by stopping and pulling the cart backwards while scanning.
The cursor moves over the image and menu options appear at the bottom of the screen.
11.3.1 Locating Cursor
The Cursor consists of 3 parts:
Position IndicatorVertical cross-hair is tied to the odometer and corresponds to the location at the
center of the GPR sensor. As the cart is pulled backwards, the Position
Indicator moves to indicate the current location of the cart in the image.
Depth Indicator Horizontal cross-hair found at the peak of the soil type indicator arch indicating
the depth. The Depth Indicator moves up or down using the Arch Up and Down
buttons.
Indicator Arch Idealized representation of a typical pipe-like target response observed on the
GPR image. The width of the arch is controlled by soil type setting. The soil
type setting is changed using the Arch buttons. Increasing the soil type makes
the indicator arch wider while decreasing the soil type makes it narrower.
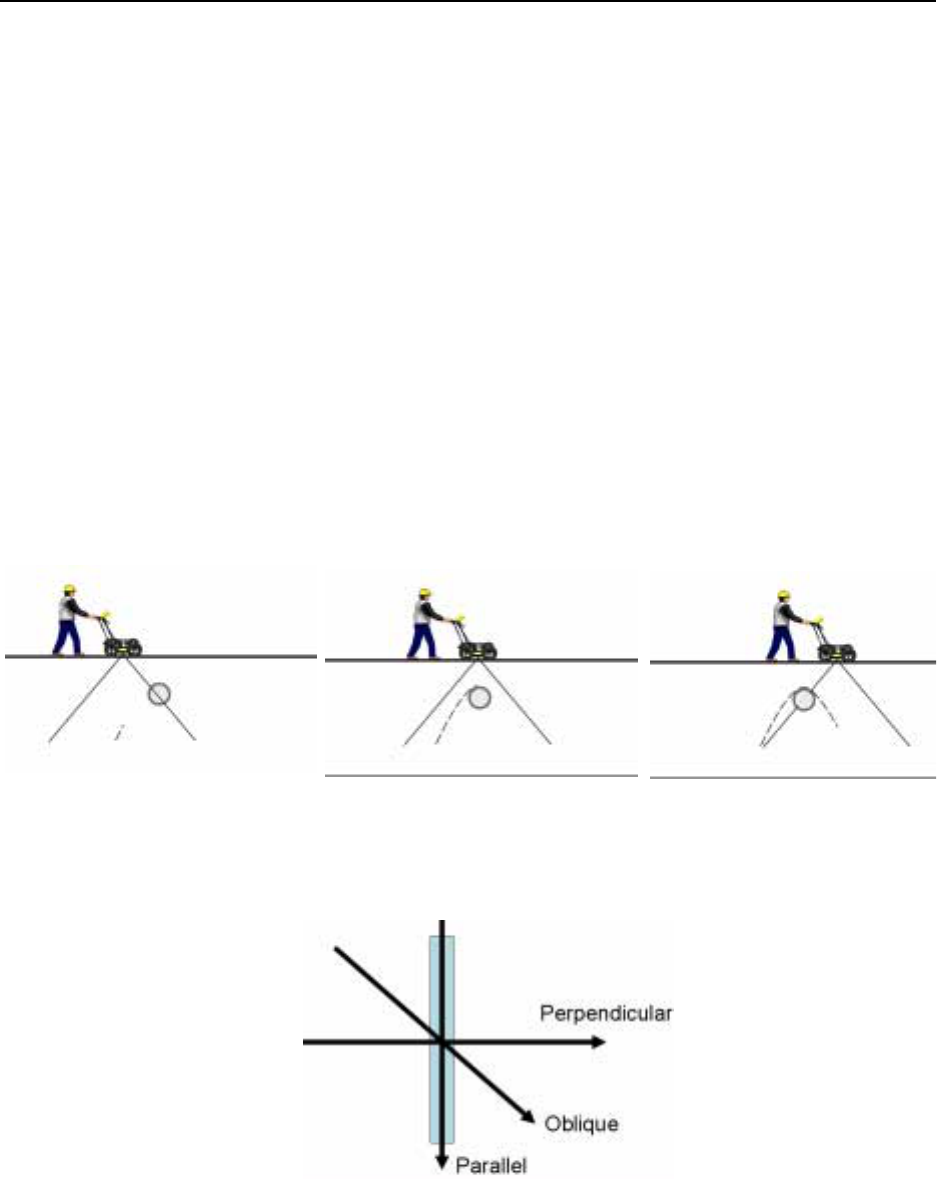
11-Locate & Mark Mode Noggin
56
11.3.2 Soil Type
To obtain an accurate depth axis and depth estimations of targets in the GPR image, a Soil Type
Calibration must be performed. Soil Type Calibration can be done 3 ways:
1) Matching the shape of a target arch,
2) Using a target at a known depth, or
3) Using the moisture level of the soil.
11.3.2.1 Matching a Target Arch
Targets like pipes, cables, buried artefacts, tree roots and rocks generate arch-shaped responses
on the GPR image.
Arches occur because GPR energy does not travel into the ground as a pencil-thin beam but
more like a 3D cone. Reflections can appear on the record even though the object is not directly
below the GPR sensor. Thus, the GPR sensor "sees" the pipe before and after going over top of
it and forms an arch-shaped response on the image.
Cross long, linear targets like pipes or cables at a 90 degree angle to produce a target arch
suitable for the soil type calibration. The depth estimation of a target will be incorrect if the soil
type calibration is done on a target arch produced at an oblique angle (smaller that 90 degrees).
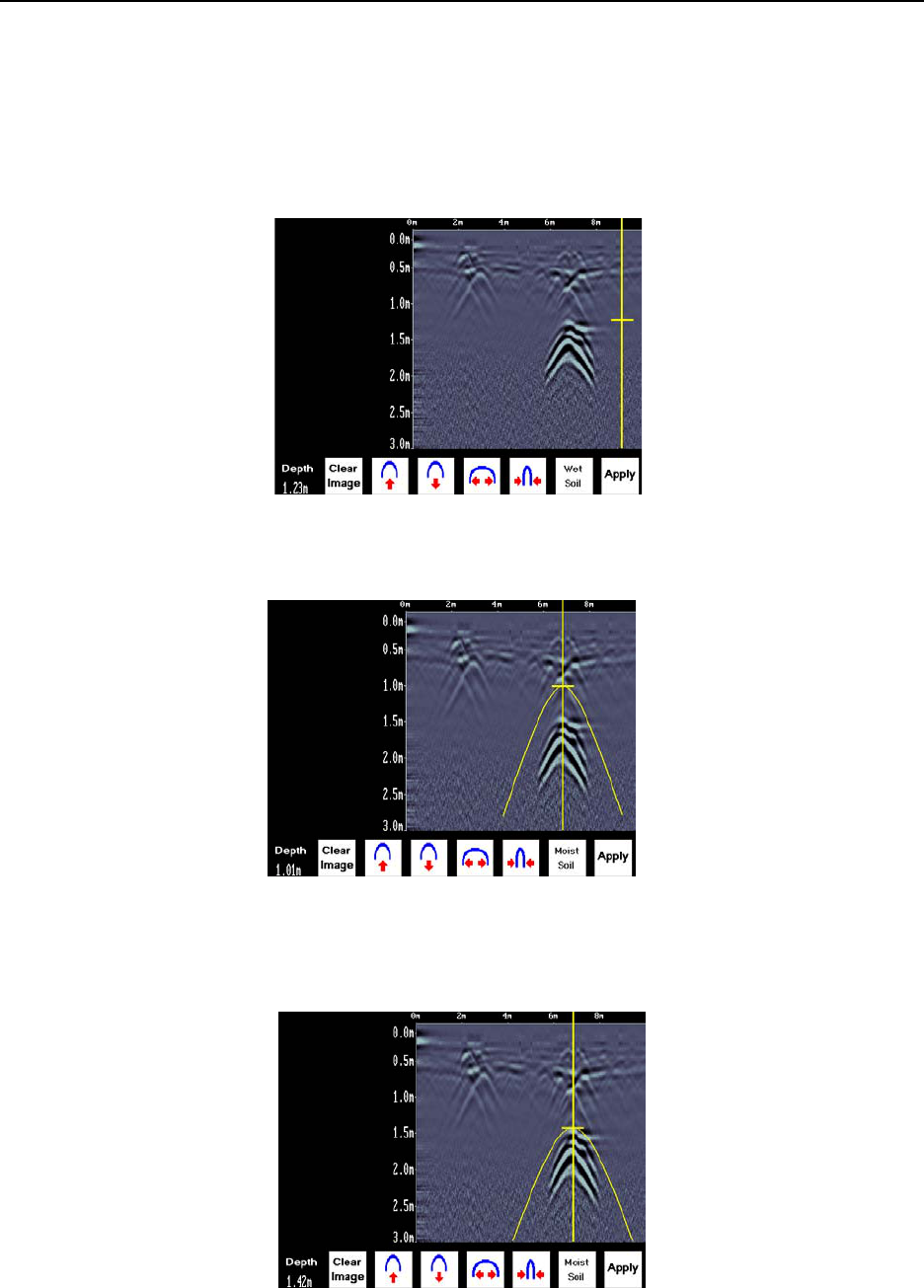
Noggin 11-Locate & Mark Mode
57
To determine the Soil Type using a Target Arch:
1) With a target arch visible on the image, back the cart up until the Position Indicator
is centered on the target arch in the GPR image; preferably one with long tails because this
provides the most accurate soil type calibration.
2) As you slow down and stop, the Indicator Arch will appear on the data image.
3) Use the Up and Down Arrows to move the Indicator Arch shallower or deeper in
the GPR image respectively, until it lies overtop of the target arch.
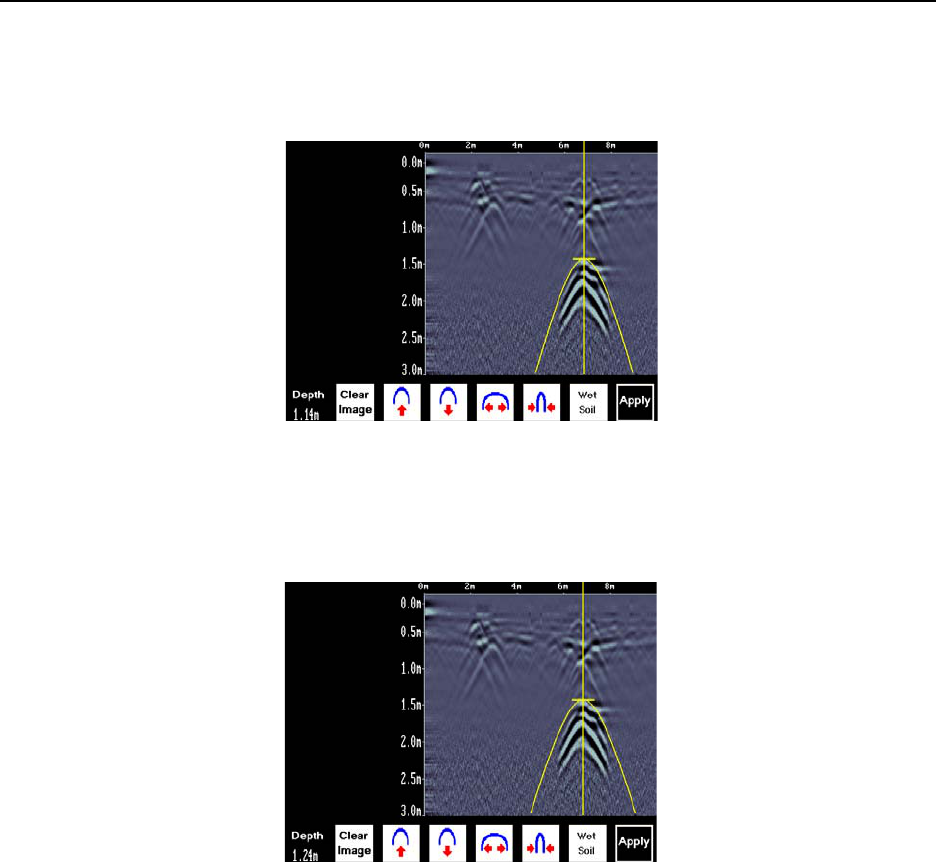
11-Locate & Mark Mode Noggin
58
4) Press the Soil Type button and toggle through the five different soil types to find
the one that roughly fits the shape of the Indicator Arch to the shape of the Target Arch.
5) Use the Wide and Narrow Arch buttons to change the shape of the Indicator Arch
to match the shape of the Target Arch on the GPR image. The depth of the target is indicated on
the bottom left.
6) Press the Apply button to save the Soil Type and update the Depth Axis on the
Scanning Screen. The Depth axis can now be used to estimate the depth of targets while
scanning in the area.
11.3.2.2 Target at Known Depth
If there are no suitable arches visible in the image to perform the Target Arch Matching described
above, there may be a target of known depth in the area being scanned.
To determine the Soil Type using a target at known depth:
1) With the target response visible on the image, use the Up and Down Arrows to
move the Depth Indicator (and Indicator Arch) until it lies on top of the GPR response of the
known target.
2) Use the Wide and Narrow Arch buttons to change the shape of the Indicator Arch
until the depth of the target, displayed in red above the menu, is correct.
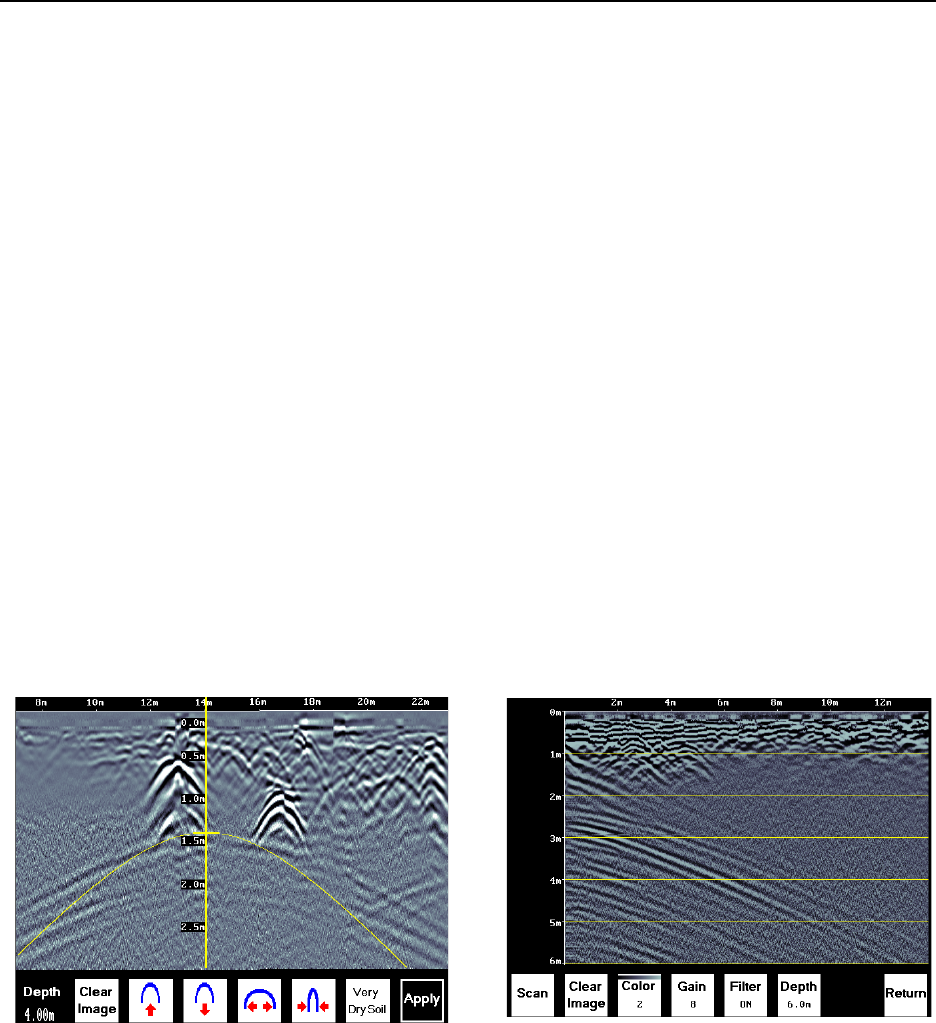
Noggin 11-Locate & Mark Mode
59
3) Once the depth is matched, save the Soil Type value by pressing the Save button.
11.3.2.3 Soil Moisture
If a good target arch or a target of known depth is not available, the user will have to estimate the
Soil Type. The soil type is most strongly affected by water so the soil type options relate to the
amount of water in the soil.
Change the soil type by pressing the Soil Moisture button until the option that best describes the
soil in the area is displayed. The options are Very Dry, Dry, Moist, Wet and Very Wet Soil.
11.3.3 Identifying Air Wave Reflections
Some arches in the image can be caused by objects that are not in the subsurface, such as
posts, fences, overhead wires and even trees.
An important part of understanding the data image is learning to recognize these unwanted "air"
targets and differentiate them from the targets in the ground.
One way of identifying air reflections is to use the target arch method described above. However,
arches from above-ground objects are wider than objects in the ground and out of the range of
the maximum Soil Type.
Therefore, if the widest Indicator Arch is still not wide enough to match the target arch, the target
arch is from on object in the air, not the ground.
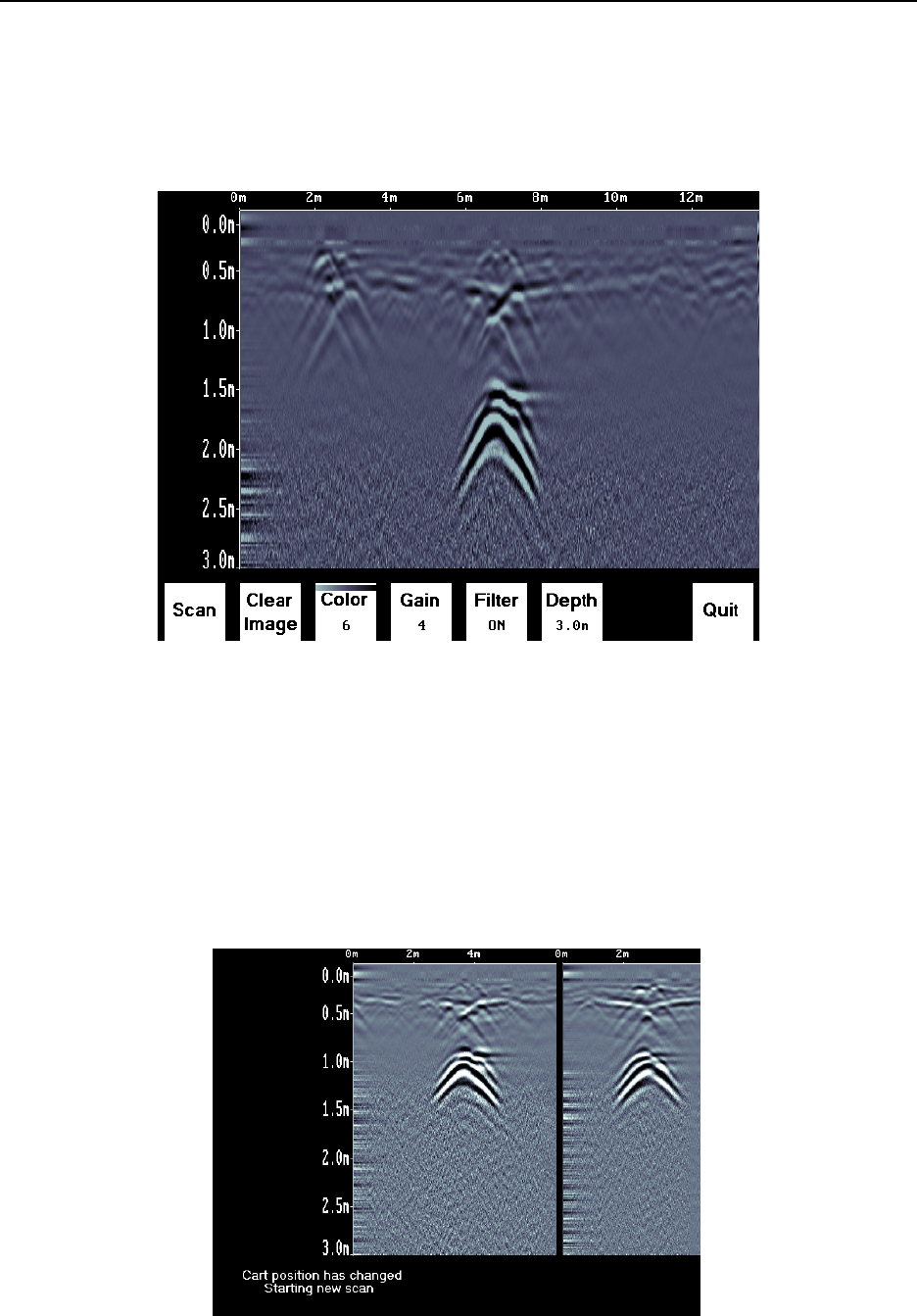
11-Locate & Mark Mode Noggin
60
11.4 Image Settings Screen
The Image Settings Screen is accessed by pressing the Pause (||) button while in the Scanning
Screen or the Locating Screen. Menu options appear along the bottom of the screen:
11.4.1 Scan
To exit from the Image Settings Screen and resume Scanning, press the Scan button or the
Pause (||) button again (to unPause). The Scanning Screen returns at the current location with
the position information preserved.
If, while paused in the Image Settings Screen, the cart has moved more than a few centimeters,
when scanning is restarted, a gap called a Position Break will appear in the image. The position
break is also indicated by a message on the bottom of the screen and the Position Axis along the
top of the data image resetting to zero.
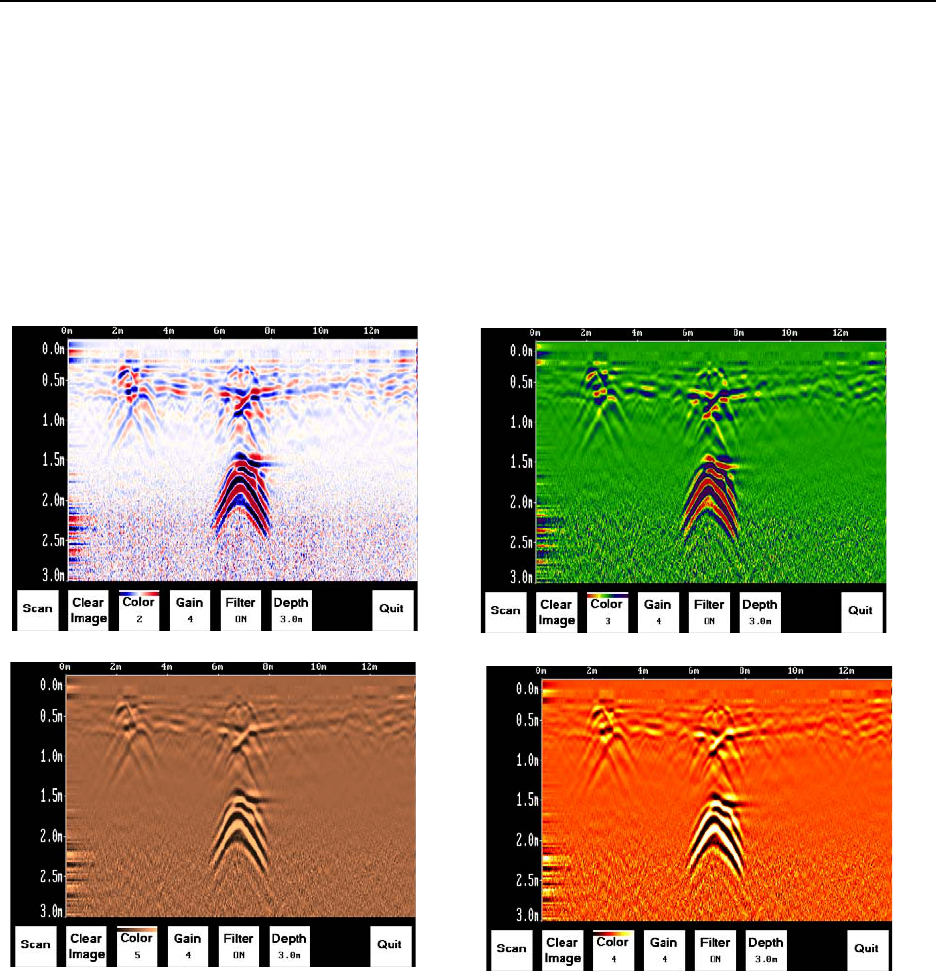
Noggin 11-Locate & Mark Mode
61
11.4.2 Clear Image
Deletes the current data image on the display.
11.4.3 Color
GPR images are displayed in colors corresponding to a color palette. In general, stronger GPR
signals appear in stronger colors. A number of different color palettes are available to display the
image. Some color palettes may show the target better than others.
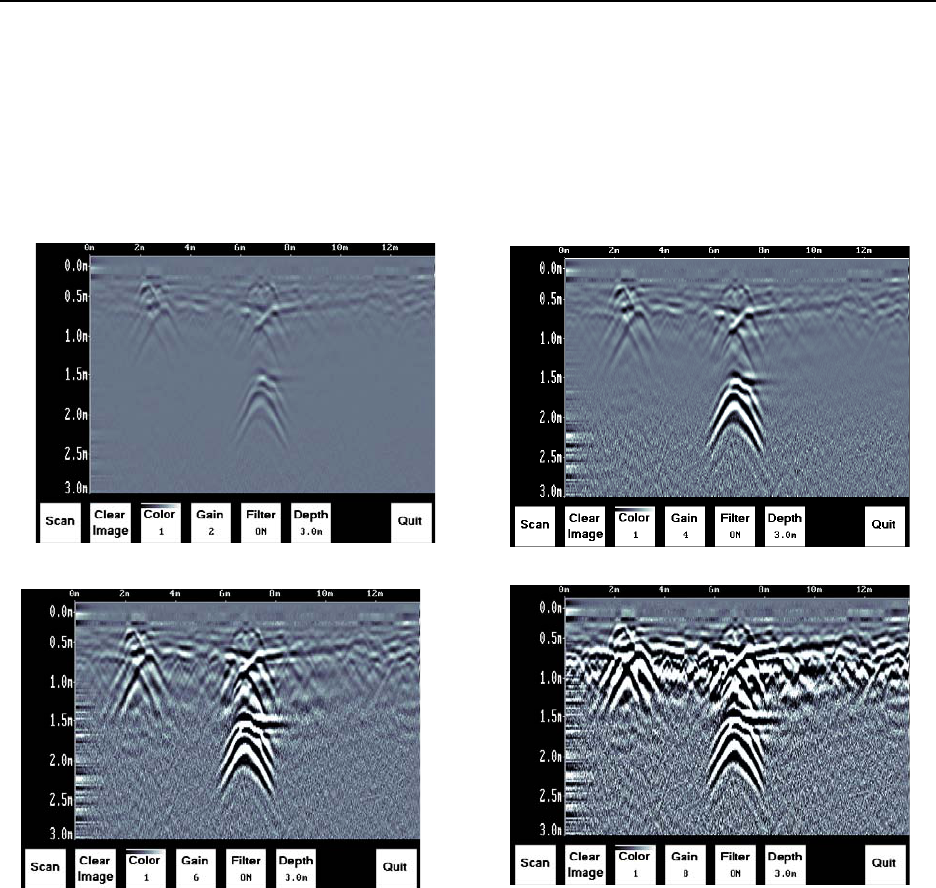
11-Locate & Mark Mode Noggin
62
11.4.4 Gain
Since GPR signals are absorbed by the material being scanned, deeper targets have weaker
signals. Gain acts like an audio volume control, amplifying the signals and making deeper
targets appear stronger in the image. The Gain varies from 1 to 9 with 1 being no gain and 9
being the maximum gain.
As the Gain changes, the current image on the display updates so it is not necessary to re-collect
an image with a different gain setting. Use the lowest gain setting that shows the targets. Try to
avoid over-gaining as understanding the image may become more difficult.
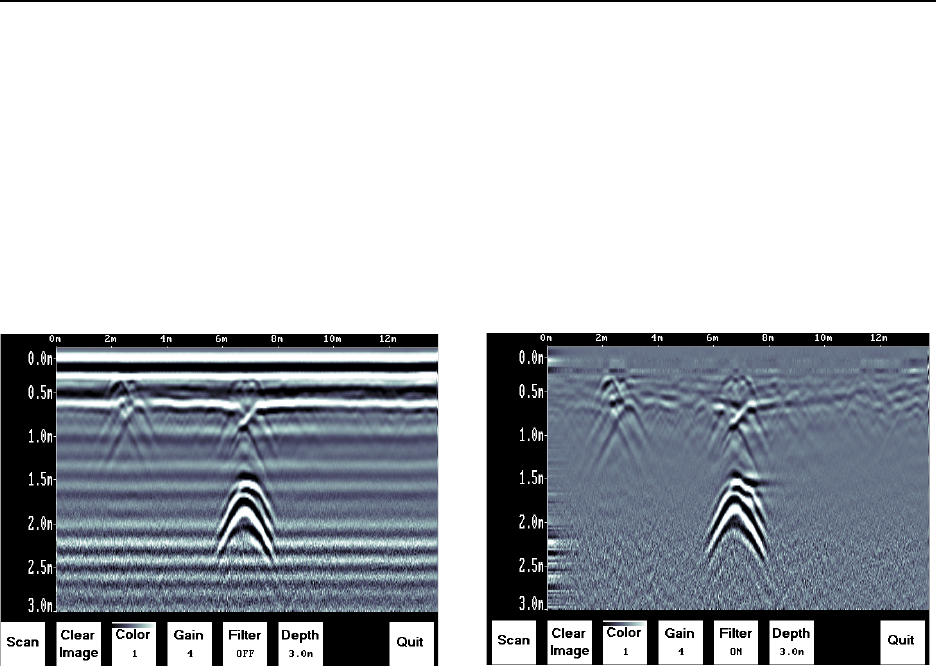
Noggin 11-Locate & Mark Mode
63
11.4.5 Filter
The filter has the effect of removing flat-lying reflections in the image and enhancing the dipping
reflections and arches usually caused by targets. It can also assist in identifying very shallow
targets that might be masked by the strong signals at the top of the image.
The Filter defaults to ON, so if you are looking for a layer or other flat-lying target, turn the Filter
OFF.
The image below shows the same scan with the Filter OFF and ON.
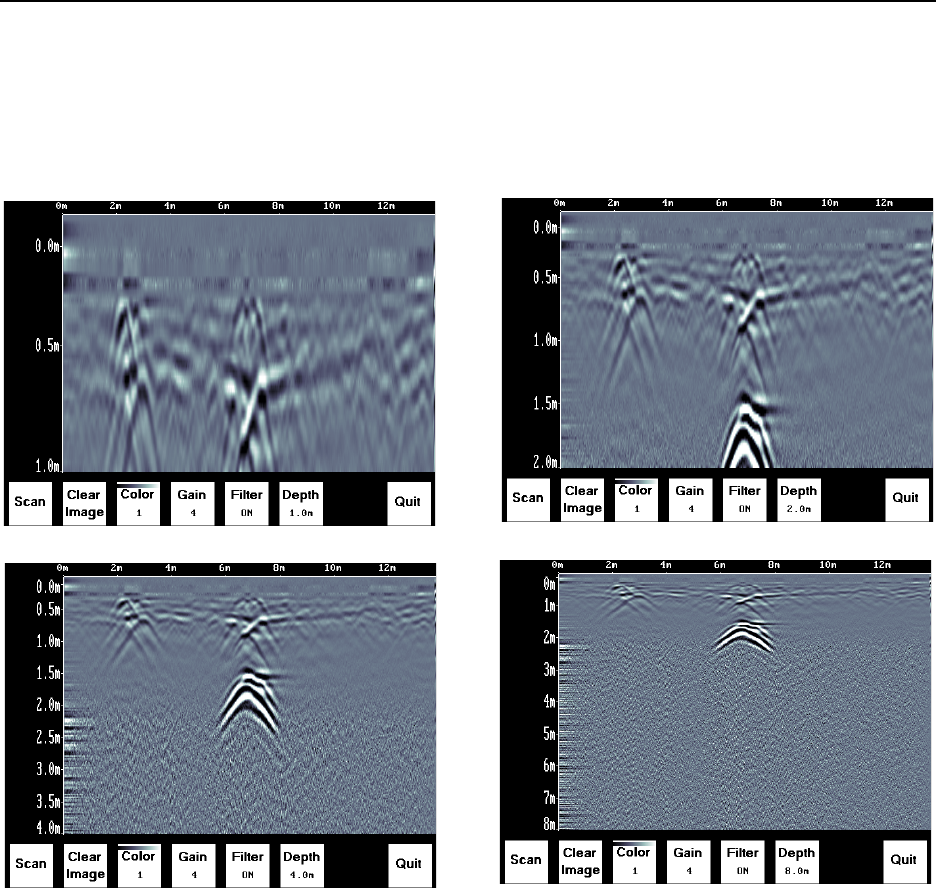
11-Locate & Mark Mode Noggin
64
11.4.6 Depth
The depth setting is an estimate of the total depth displayed on the Scanning Screen based on
the current Soil Type setting. The depth setting ranges from 1 to 8 meters.
The system always collects data to a depth of approximately 8 meters but the Depth setting on
this menu determines how much of the data is displayed on the screen. It is possible to scan with
a Depth setting of, say 2 meters, pause scanning and then increase the depth setting to re-
display the image to look for deeper targets.
11.4.7 Quit
Exits the Scanning and Image Settings Screens and returns to the Systems Settings Screen.
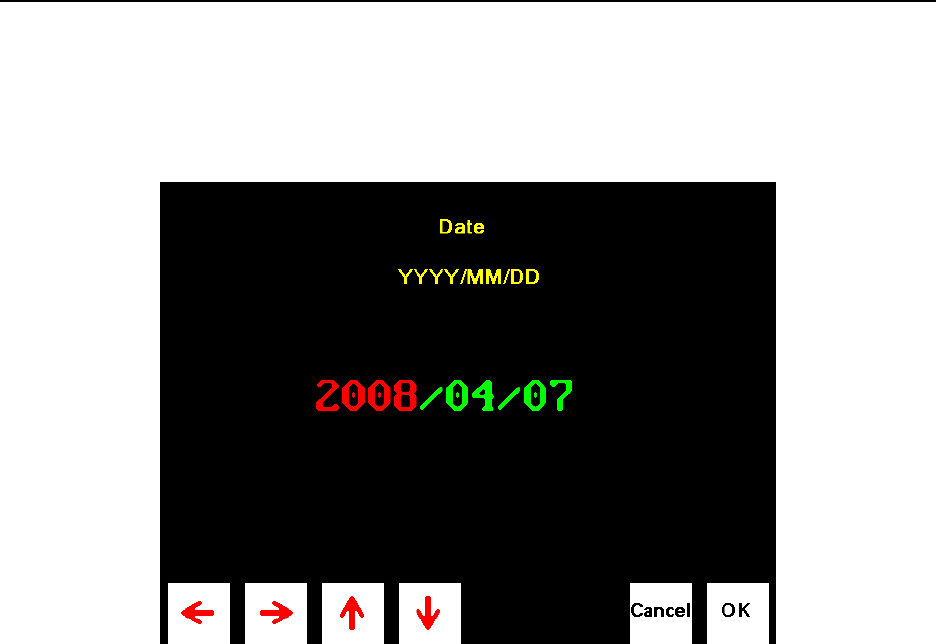
Noggin 11-Locate & Mark Mode
65
11.5 Changing the Date and Time
From the System Settings Screen, select the Date option. The Time option is similar.
Use the Left and Right Arrow buttons to highlight the number to change in red.
Increase the number using the Up Arrow and decrease the number using the Down Arrow.
Pressing OK saves the new date or time and exits the screen.
Pressing Cancel exits the screen without saving the date or time.

11-Locate & Mark Mode Noggin
66
11.6 English and Equivalent Icons
11.6.1 System Settings Screen Menu
11.6.2 Locating Screen Menu
11.6.3 Image Settings Screen Menu
11.6.4 Date and Time Menus
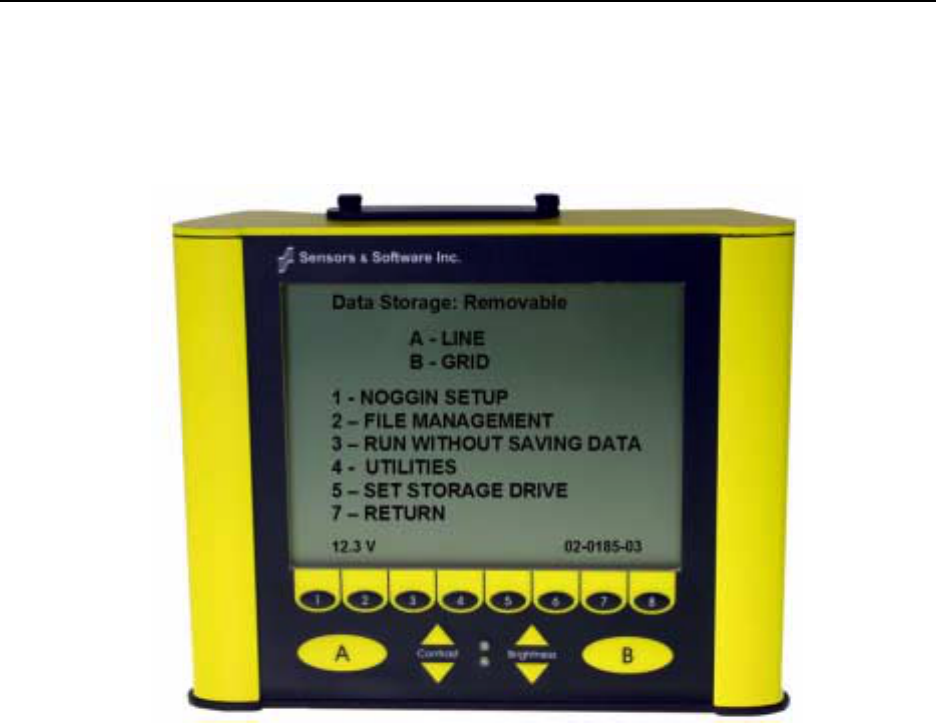
Noggin 12-Survey & Map Mode
67
12 Survey & Map Mode
The Survey & Map main menu has the following choices:
12.1 Survey & Map Menu
12.1.1 Line
Survey lines collected with the Noggin are saved as digital data files that can be viewed on the
DVL or exported to an external computer for processing and plotting. Sensors & Software
programs like EKKO_View, EKKO_Mapper and EKKO_3D are available to process and display
the data.
Pressing the A button from the main Noggin menu takes the user to Line data collection. This
menu allows the user to select a project number and line number to save each data file to.
Data files from the same area can be organized and saved under a project number selected by
the user. As each individual line is collected, it is given a line number. These line numbers are
usually in sequential order but this is up to the user.
12.1.2 Grid
Survey lines collected with the Noggin are saved as digital data files that can be viewed on the
DVL or exported to an external computer for processing and plotting.
Pressing the B button from the main Noggin menu takes the user to Grid data collection.

12-Survey & Map Mode Noggin
68
Grid collection involves collecting data in an organized pattern over an area. This type of data
acquisition allows the GPR data to be presented as plan maps with the EKKO_Mapper software
or 3D volumes with the EKKO_Mapper 3D software.
For inexperienced surveyors, laying out a grid with straight lines and all the corners at 90
degree angles can be difficult. Sensors & Software provides a product called EasyGrid to
make laying out an accurate grid simple. Contact Sensors & Software for more details.
The Grid menu allows the user to select a grid number and line number to save each data file to.
Before the data acquisition on a grid begins, the user must define the size of the area to be
surveyed, the direction of the survey lines and line spacing. The details of the grid survey are
specified in the Grid Setup menu option (Section 12.3.4: P.97).
12.1.3 Setup
There are many background setup parameters related to the Noggin Smart Systems operation
for line and grid surveys that can be edited. This menu allows the user to display and change
various settings for different aspects of the Smart system (see Section 12.3: P.84). The user can
also reset all the parameters to the factory default settings.
12.1.4 File Management
The File Management menu allows the user to delete data from the DVL and copy data from the
internal compact flash drive to the removable compact flash drive.
The Export options in this menu require the use of the optional PXFER cable and WinPXFER
software so this menu is not required for users transferring Noggin data using the removable
compact flash drive. This type of data transfer is described in Appendix F.
12.1.5 Run without Saving Data
This option allows the user to go straight into data acquisition. This feature is to allow a “quick
look” at the data in the area. The data collected when in this mode are NOT saved and cannot be
reviewed later or exported. Data that scrolls off the edge of the screen is gone and cannot be
reviewed.
If a GPS receiver is attached to the DVL, GPS information can be logged to a file even when the
Noggin data are not being saved (see Section 12.3.5: P.103).
12.1.6 Utilities
This menu has utility programs to:
a) Change the Date and Time on the DVL (see Section 12.5.1: P.110)
b) Calibrate the odometer (see Section 12.5.2: P.110),
c) Use the optional PXFER cable and the WinPXFER software installed on a PC
to transfer upgraded firmware to the DVL (see Section 12.5.3: P.111),
d) List or print or transfer system information to assist Sensors & Software in
troubleshooting problems with your system (see Section 12.5.4: P.111) and

Noggin 12-Survey & Map Mode
69
e) Determine how much space is left on the DVL (see Section 12.5.5: P.111).
f) For the optional PXFER cable used to transfer data from the DVL to a PC, set
the PXFER Transfer Mode to Normal or Turbo (see Section 12.5.6: p.111)
12.1.7 Set Storage Drive
This setting controls how data are saved on the DVL. The available options are:
1) Internal: If this setting is selected, the data are saved to the internal compact flash
drive in the DVL.
2) Removable: If this setting is selected, the data are saved to the removable compact
flash drive accessible by opening the door at the top of the DVL (see Figure 9-1).
12.1.8 Return
This button will return the user to main menu.

12-Survey & Map Mode Noggin
70
12.2 Data Acquisition
Selecting the Line, Grid or Run without Saving Data options from the main Noggin menu will start
data acquisition. The Run without Saving Option goes straight to data acquisition while the Line
and Grid options require the user to select a project number, file number and press Run before
data acquisition begins.
If the Auto Start option is set to ON (see Section 12.3.2.3: p.90 for details) the system will
automatically boot up and be ready for data acquisition. If Auto Start is set to OFF the user must
press the Start button to boot up the system.
After acquisition has started, the Start button disappears and a Stop button (used to halt
acquisition) appears on the right. A Gain button is also visible as well as the current Depth
setting and equivalent Time Window length in nanoseconds (see Figure 12-1).
Data acquisition begins by pressing the Start button on the DVL.
When the Start button is pressed for the first time after the unit is turned on, the Noggin will boot
up (this can take up to 30 seconds depending on the software version of the Noggin). During this
time the system is self-calibrating and measuring such factors as temperature and battery
voltage.
Once this boot up has been completed, data acquisition can begin. For subsequent lines there is
only a short delay before data acquisition can begin.
Data acquisition is done by moving the Smart System along the survey line. During data
acquisition, the Gain button is dynamic and the screen display of the signal sensitivity can be
changed on the go (see Section 12.2.6: P.73).
When the survey line is completed, press the Stop button to stop data acquisition. At this point
no more data can be collected without starting a new line.
12.2.1 Replaying or Overwriting Data
Immediately after a data file has been collected and the Stop button pressed, the data file can be
replayed by pressing the left and right arrow buttons to the scroll the data to the left and right. As
well, during data replay, the data can be enlarged or “zoomed” by pressing the Zoom button and
changing the zoom factor. For example, zooming 2 times on data with a depth setting of 5.0
metres will show the first 2.5 metres of data on the screen.
Any data file that has been collected can be replayed at any time by selecting the file number and
selecting Run. The user then has the option to View, Overwrite or Delete the data file.
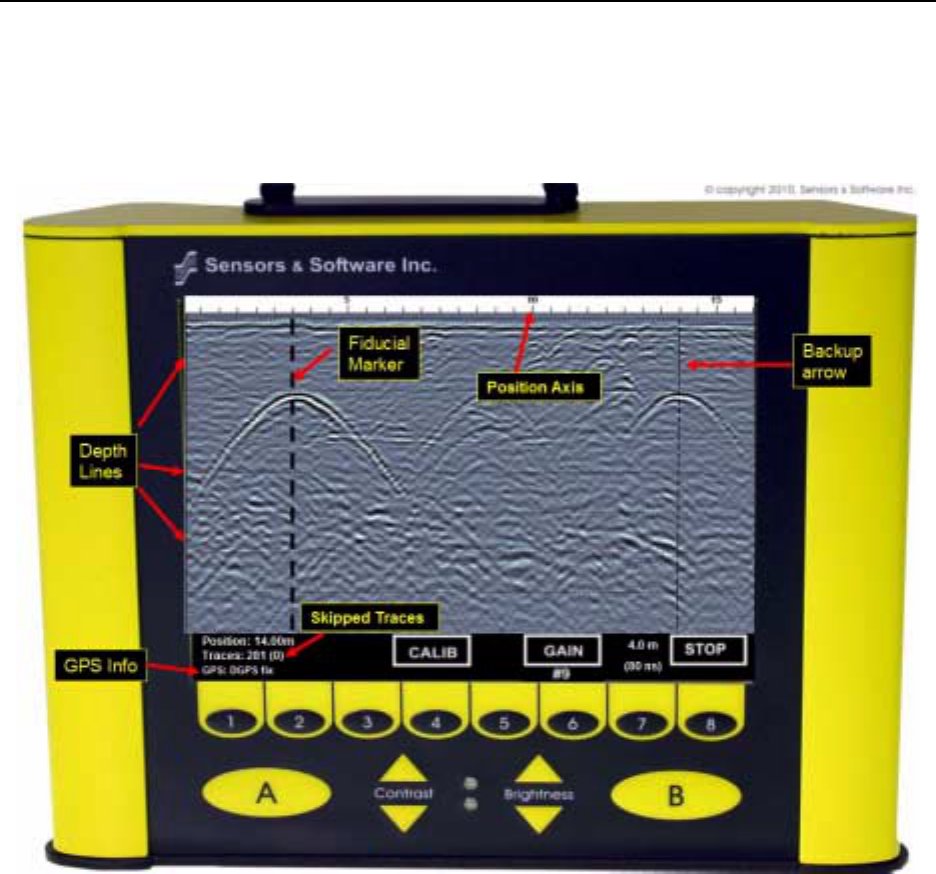
Noggin 12-Survey & Map Mode
71
12.2.2 Screen Overview
The data acquisition screen is shown in Figure 12-1. It is divided into 3 sections.
Figure: 12-1 Noggin Data Acquisition Screen
The Noggin screen is shown in Figure 12-1. It is divided into 3 sections. The top section provides
positioning information. The center section contains the actual data and the bottom section
contains the menu.
12.2.3 Position Information
The top section contains horizontal spatial positioning information in feet or metres depending on
the position units setting (see Position Units on page 88)

12-Survey & Map Mode Noggin
72
12.2.4 Data Display
This section contains the actual data collected or replayed. The section also contains the Depth
Lines and any Fiducial Markers the user enters. See the sections below for more details.
12.2.4.1 Depth Lines
Depth lines are horizontal lines indicating the estimated depth. They are very useful for getting
depth estimates to features of interest in the data.
The Depth Lines are controlled by the current velocity value as well as the depth selected. See
Depth on page 84 on changing the depth setting and for more details on how depths are
determined.
To display the correct depth, it is the responsibility of the user to calibrate the system to
the correct velocity of the material (see Section 12.2.11: P.79 on how to calibrate the
system). Once a velocity value has been determined see Velocity on page 85 on how to
change the velocity setting.
Note that it is possible to change the depth units between metres and feet (see Position Units on
page 88).
12.2.4.2 Fiducial Markers
A fiducial marker is a dotted vertical line placed on the data section at a specific position during
data acquisition. Adding these markers during data acquisition is useful for recording significant
positions or the positions of surface objects encountered during the survey.
A fiducial marker is activated by pressing the A button on the keypad during data acquisition. As
well, when using the backup arrow (Section 12.2.7: P.74) fiducial markers can be added at the
current arrow location by pressing the A button.
The position and name of the object encountered at each marker can be recorded in a field
notebook. The fiducial marker is written to the trace header of the next trace to be collected.
Fiducial markers are numbered sequentially (F1, F2 etc.). When the data are transferred to a PC
and reviewed, these markers can assist with data interpretation.
If a GPS receiver is attached to the DVL, a file containing GPS information can be saved. In
Fuducial Tagging mode, whenever a fiducial marker is added to the data, a line of GPS
information will be added to the GPS file (see Section 12.3.5: P.103)
12.2.5 Section C - Menu
The bottom section (Section C) contains the user menu selection and current program settings.
This includes:
1) The total depth (and time window) to the bottom of the data image in Section B (see
Section 12.3.1: P.84),
2) The Gain button and current Gain setting (see Section 12.2.6: P.73),
3) GPS information (if GPS receiver attached, see below and Section 12.3.5: P.103),
4) The current position based on the current triggering device (see Trigger Method on
page 89) and Station Interval (see Section 12.3.3.3: p.93),

Noggin 12-Survey & Map Mode
73
5) The Repeat Trace Number which indicates when the system is being moved too fast
(see Section 12.2.7: P.74) and
6) The Calib button for calibrating the velocity setting (see Section 12.2.11: P.79).
If a GPS receiver is attached to the DVL (see Section 12.3.5: P.103) a message will appear in the
bottom left corner of the menu indicating whether the GPS data is successfully being logged.
The possible messages are:
1) GPS: DGPS fix means differential GPS data are currently being logged.
2) GPS: GPS fix means standard GPS data are currently being logged.
3) GPS: fix not valid means GPS data are NOT currently being logged. This is usually
because GPS satellites are not available.
4) GPS: No Input means the GPS receiver is not operating properly. Check the settings
and test the system (see Section 12.3.5: P.103).
5) GPS: No GGA means the GPS receiver is not outputting a GGA NMEA string that
the DVL requires (see Section 12.3.5: P.103).
12.2.6 Gain
During data acquisition, the Gain setting can be changed by pressing the Gain button until the
desired setting appears. This can be done while the instrument is collecting data; there is no
need to stop first.
The signals that the Noggin system collects from the ground can be very weak, especially from
deeper objects. To see these weak signals it is necessary to amplify or apply “gain” to them.
The Gain setting controls how much the signal is amplified. It varies from 1 to 9 with 1 the lowest
and 9 the highest. In general, if the target is relatively shallow (1-2 metres) a low gain value can
be used. If the target is deeper or if the screen seems to be blank or speckled in the lower part of
the data section, increase the gain setting. Remember, however, that if the Noggin signal is not
penetrating to the maximum depth setting, even the maximum gain setting will not show any
data.
Figure 12-2 shows the effect of the gain setting. The data on the left has a gain of 1 incrementing
to the right up to a gain of 9.
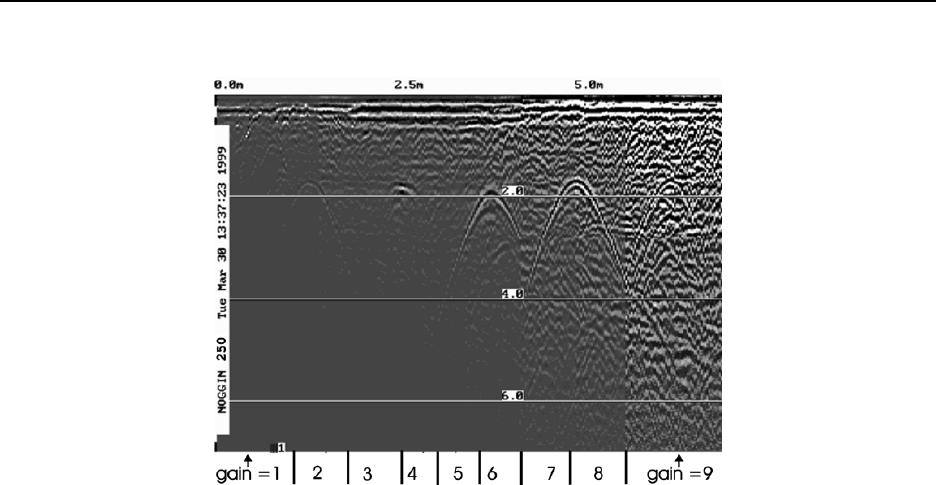
12-Survey & Map Mode Noggin
74
Figure: 12-2 Effects of the Gain setting
Note that the gain setting is only for data display. The data are always saved without any
gain applied. It is not possible to collect Noggin data with an “incorrect” gain setting.
If the user finds that they are always using very high or very low gain settings to see the data
adequately, the user may want to adjust the Linear Gain setting under Setup (see Linear Time
Gain on page 88).
12.2.7 Collecting Data using the Odometer
As the Smart System moves, the odometer triggers the system to collect a data trace at fixed
distance intervals. This interval is called the “station interval”. For the Noggin 250, the normal
station interval is 5 centimeters (about 2 inches). For the Noggin 500, the normal station interval
is 2.5 centimeters (about 1 inch). For the Noggin 1000, the normal station interval is 1.0
centimeter (about 0.48 inch). The station interval can be changed to a longer or short distance in
the Setup (see Station Interval on page 93).
Each data trace is plotted as a vertical strip on the screen (see Figure 12-1). The width of this
strip can be changed to 1, 2, 4, or 8 pixels (see Plot Interval on page 96). The normal trace width
for Noggin 250 traces is 2 pixels while the normal width for Noggin 500 and Noggin 1000 systems
is 1 pixel.
The odometer units that appear across the top of the screen can be set to either metres or feet
(see Depth Units on page 85).
Smart Systems can normally collect data at a very fast walking pace. However, if the system is
moved too quickly, data quality is reduced (see below).
During data acquisition, the current odometer position value (in the current units, either metres or
feet) is written to the lower left corner of the screen (see Figure 12-1).
Note that Smart systems can be configured to collect data either by pushing the system (forward)
or pulling the system (reverse). See Cart Direction on page 89 about changing the direction of
data acquisition.

Noggin 12-Survey & Map Mode
75
The odometer should be periodically re-calibrated to ensure accuracy. The procedure for re-
calibrating the odometer is described in Section 12.5.2: P.110.
12.2.7.1 Reducing Data Quality by Moving too Fast
On the lower part of the data acquisition screen, beside the current total number of traces
collected is the total number of traces skipped.
If the Smart System is being used with the odometer and is moved too quickly for the Noggin
system to keep up, traces are skipped and the quality of the survey is reduced. The skipped
traces do not actually create gaps in the data but rather, the last trace that was collected properly
is repeated. The Skipped Traces number displays the total number of skipped traces. If this
number exceeds 0 this is due to moving the system too quickly. To eliminate this either slow
down the system speed, decrease the number of Stacks or reduce the Depth setting (see Section
12.3.1: P.84).
If the system is moved too fast, after the data survey line is complete, the DVL will indicate the
total number of traces that were “skipped”. The user then has the option to Autofix the data. The
Autofix process replaces any repeated traces in the data with interpolated traces. While this
process does not solve the problem of skipping traces, it will make the data traces look less
“blocky”.
If the number of traces skipped is a significant percentage of the total number of traces collected,
i.e. 10% or more, the operator should slow down, decrease the number of Stacks or reduce the
Depth setting (see Section 12.3.1: P.84).
12.2.7.2 Backing up the Smart System to Pinpoint Target Positions
The odometer also allows the user to stop the Smart System in the middle of a survey line and
back up. When this is done, an arrow and vertical line appear on the data image and move back
along the image as the system moves backwards (see Figure 12-1). This makes it possible to
correlate a target in the data image to an exact location on the ground. Once the arrow lines up
with the target, mark the ground at the centre point of the Noggin.
When the system is moved forward again to continue with the survey, the Smart system does not
start collecting data again until you reach the position where you stopped at. This feature is
useful for producing a continuous data image even if the system is backed up during the survey
line.
Note that it is not possible to back up and have the arrow indicator move more than one screen.
The physical position corresponding to the Back-up arrow is the centre of the Noggin. This
position can be changed from the centre of the Noggin to any other position. See Arrow Offset on
page 90 on changing the Arrow Offset value.
12.2.8 Collecting Data in Free Run Mode
It is possible to change the triggering method from the odometer and have the Noggin system run
in Free Run (or continuous mode) (see Trigger Method on page 89). This means that the system
collects data even if it is not moving. This option is useful for collecting data when using the
odometer wheel is not practical.

12-Survey & Map Mode Noggin
76
When the Smart System is used in Free Run mode, it is up to the user to keep track of
positioning by some other method, for example, a measuring tape, using fiducial markers (see
Fiducial Markers on page 72) or GPS (see Section 12.3.5: P.103).
In this mode, data collection is dependent on two factors,
1) the speed that the Noggin system is collecting data and
2) the speed the Noggin system is moving.
12.2.8.1 Controlling Data Collection Speed in Free Run Mode
In Free Run mode the user can control the speed the Noggin collects data by increasing or
decreasing the number of stacks (for more details on Stacking, see Stacks on page 86).
Increasing the number of Stacks has the effect of slowing down the data collection speed of the
Noggin system. Decreasing the number of Stacks has the effect of speeding up the data
collection speed Noggin system. The user can also control the speed of the Noggin data
collection by adjusting a time delay between data collection points. Note that any time delay
more than 0.0 seconds causes the system to emit a beeping sound as the data trace is collected.
12.2.8.2 Noggin Speed in Free Run Mode
In Free Run mode, the speed the Noggin moves determines the distance between sample points
on the ground (station interval). This type of data collection requires experimenting with the
number of stacks and time delay (see Trigger Method on page 89) and practicing to find a
satisfactory speed for the Noggin. Moving too quickly may result in under-sampling the data
making it more difficult to interpret. Moving too slowly may result in over-sampling the data. This
stretches the data image making it more difficult to interpret. As well, maintaining a uniform
speed is important for minimizing image distortion.
12.2.8.3 Positions in Free Run Mode
Each data trace is plotted as a vertical strip on the screen (see Plot Interval on page 96). In Free
Run mode the station interval is not fixed so each screen of data can represent any ground
distance. This means that the position values displayed in Section A at the top of the data image
(see Section 12.2.3: P.71) are not correct.
When running the system in Free Run mode it is best to set the units (see Position Units on page
88) to metres and the Station Interval (see Section 12.3.3.3: p.93) to a value of 1.0 metre. Then
the position values appearing on the top of the data image can be interpreted as trace numbers
and not an absolute position.
12.2.9 Collecting Data using the Trigger (or B) Button
It is possible to change the triggering method from the odometer and have the Noggin system
only collect data when the Trigger button (or B button on the DVL) is pressed (see Section
12.2.9: P.76). This option is useful for collecting data when using the odometer wheel is not
practical.
After the user selects this option (see Trigger Method on page 89), a menu appears to select the
number of stacks for each trace. Generally, the more stacks the better the data quality (for more
details on Stacking, see Stacks on page 86).

Noggin 12-Survey & Map Mode
77
In Trigger Button mode, the system “beeps” as each trace is collected. The length of the beep
will depend on the number of stacks (the more stacks, the longer it takes to collect a trace and
therefore the longer the beep).
When the Smart System is used in Trigger Button Mode, it is up to the user to keep track of
positioning by some other method, for example, using a measuring tape, fiducial markers (see
Fiducial Markers on page 72) or GPS (see Section 12.3.5: P.103).
Since data collection only occurs by the user pressing the trigger button, usually a fewer number
of traces are collected in this mode compared to odometer triggering mode or Free Run mode
(see above). Therefore, it is often useful to increase the trace width to 4 or 8 pixels so that the
data are more easily seen on the DVL screen (see Plot Interval on page 96).
12.2.10 Noggin Data Screens
Total Distance Per Screen
The total distance that can be displayed on one screen varies depending on the Noggin system,
Station Interval and Plot Interval (see Section 12.3.3.4: p.96). As the Station Interval increases,
the distance between data traces increases and the total distance per screen increases. As the
Plot Interval increases, the total distance per screen decreases.
Noggin 100
For the Noggin 100, each trace is normally 2 pixels wide. Since the screen is 640 pixels wide,
each screen has 320 traces. When the station interval is set to Normal (10 centimetres or 4
inches), each screen displays 32 metres or 105 feet of data.??
Noggin 250
For the Noggin 250, each trace is normally 2 pixels wide. Since the screen is 640 pixels wide,
each screen has 320 traces. When the station interval is set to Normal (5 centimetres or 1.92
inches), each screen displays 16.0 metres or 52.5 feet of data.
Noggin 500
For the Noggin 500, each trace is normally 1 pixel wide. Since the screen is 640 pixels wide,
each screen has 640 traces. When the station interval is set to Normal (2.5 centimetres or 0.96
inches), each screen displays 16.0 metres or 52.5 feet of data.
Noggin 1000
For the Noggin 1000, each trace is normally 1 pixel wide. Since the screen is 640 pixels wide,
each screen has 640 traces. When the station interval is set to Normal (1.0 centimetres or 0.48
inches), each screen displays 6.4 metres or 25.7 feet of data.
Total Data Distance on the DVL
For more details on total distances and Station Intervals see Section 12.3.3.3: p.93.
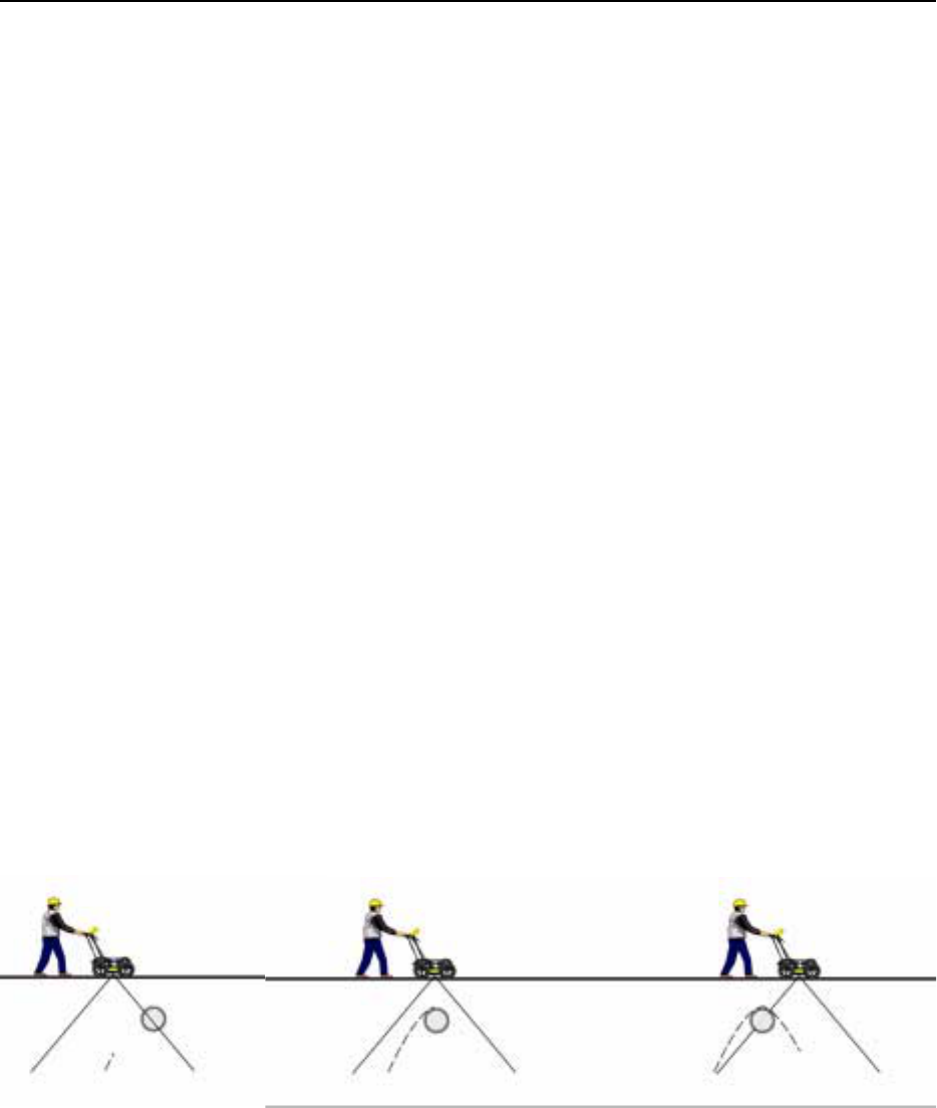
Noggin 12-Survey & Map Mode
79
12.2.11 Calib. (Calibration) Menu
Noggin systems can be used to scan into many different materials including soil, rock, concrete,
snow, ice and wood. The radio wave emitted by a Noggin system will travel at different velocities
depending on the material being scanned. The depth value (see Section 12.3.1: P.84) and on
Depth Lines (see Section 12.2.4: P.72) are only accurate if the system has been properly
calibrated to determine the velocity of the material being scanned. See Depth on page 84 for
more details about how depth is calculated.
The Calibration function is a tool for determining the velocity of the material being scanned. A
velocity value can be input directly (see Section 12.3.1.2: p.85) or determined in one of two
different ways depending on the situation:
1) Hyperbola matching
2) Target of known depth
Note that unlike the Calibration with Noggin systems (see Section 12.2.11: P.79), the
Noggin Calibration does NOT automatically update the velocity value in the software. In
the Noggin calibration, once a velocity is determined, the user must enter it into the
System Parameters (see Velocity on page 85).
12.2.11.1Hyperbola Matching
The most accurate way of determining the velocity of the material being scanned is to use the
hyperbola-fitting method because it extracts the velocity using data collected in the area. This
method may not work in all situations because it depends on having a good quality hyperbola (or
inverted U) in the data.
A hyperbola is the characteristic GPR response from a small point target like a pipe, rock or even
a tree root. This phenomenon occurs because radar energy does not radiate as a pencil-thin
beam but more like a 3D cone. Reflections can appear on the record even though the object is
not directly below the radar system. Thus, the radar system “sees” the pipe before and after
going over top of it and forms a hyperbolic reflection.
Figure: 12-3 Hyperbolas in the data result from the conical shape of the GPR energy as it goes into the ground. Tar-
gets, like pipes, are detected as the GPR approaches them (left), passes over them (middle) and after it has passed by
them (right) because the GPR energy propagates both in front and behind the instrument.
If the hyperbola has long tails on it, we can match the shape of the hyperbola and determine the
velocity of the material in the area.
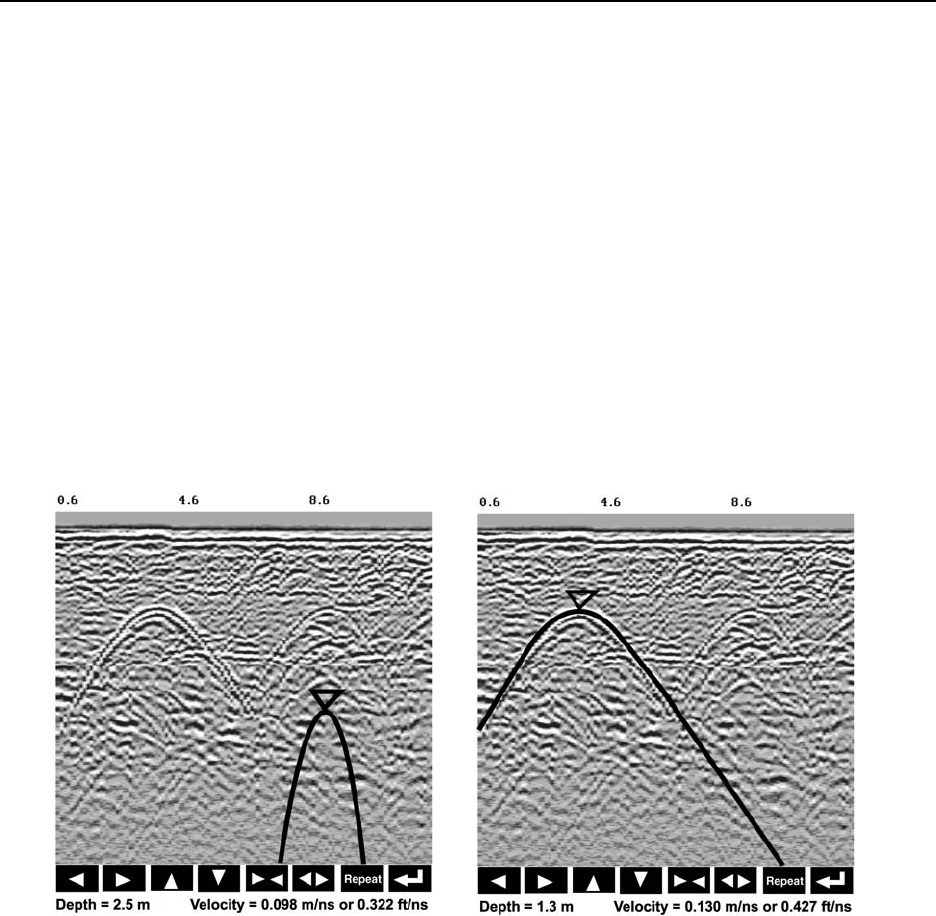
12-Survey & Map Mode Noggin
80
With the hyperbola visible on the DVL screen, select the hyperbola (
∩
) button. This will
superimpose a hyperbola on the data. This hyperbola can be moved up (!), down ("), left (#)
and right ($) using the appropriate arrow buttons. The goal is move the hyperbola until it lies on
top of the hyperbola in the data (see Figure 12-4). Then, the user can adjust the width of the
hyperbola to make it wider (#$) or narrower ($#) until the shape of the hyperbola matches the
shape of the hyperbola in the data. After matching the hyperbola, the velocity value is displayed
and now can be entered under the System Parameters (see Velocity on page 85).
Pressing the up, down left, right, wider and narrow buttons once makes a very small change in
the position or width of the hyperbola. These buttons must sometimes be pressed many times to
move the hyperbola to the correct position or width. To speed up the movement of the hyperbola,
use the REPEAT button. For example, to move the hyperbola up a long distance, press the up
button (!) followed by the REPEAT button. The hyperbola will then start moving upward without
having to press any more buttons. When it gets close to the desired location press any button to
stop it and then use the up, down, left and right buttons to fine-tune the position. The REPEAT
button can also be used after pressing the wider (#$) or narrower ($#) button.
(a) (b)
Figure: 12-4 Hyperbola matching to extract velocity. After pressing the CALIB button a hyperbola
appears on the screen (a). This hyperbola should be moved overtop of a hyperbola in the data using
the arrow keys. It can then be widened or narrowed to match the shape of the hyperbola in the data (b).
When the hyperbola shapes match, the velocity is extracted and displayed. The user can then use this
velocity value for surveys done in the area.
In Noggin mode, hyperbola Matching calibration can be done during data acquisition and also
while viewing previously collected data.
If units are metres then depths will appear in metres and velocities in metres per nanosecond (m/
ns). If units are feet then depths will appear in feet and velocities in feet per nanosecond (ft/ns).
To change units see Depth Units on page 85.
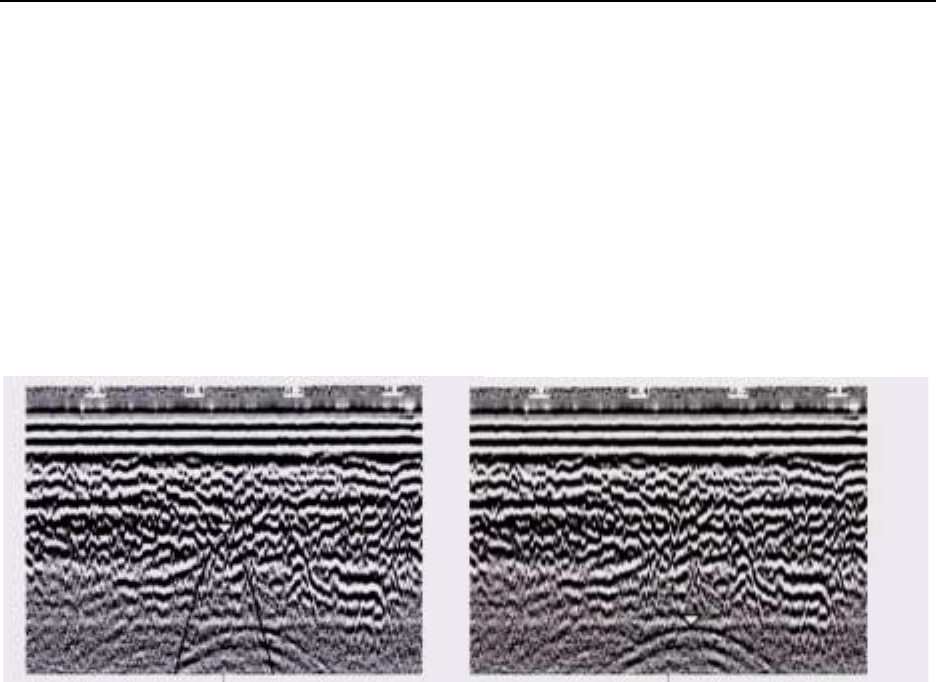
Noggin 12-Survey & Map Mode
81
12.2.11.2Identifying Air Reflections
Some hyperbolic reflections can also be caused by objects not in the subsurface such as fences,
overhead wires and, in some conditions, even large trees.
An important part of data interpretation is learning to recognize these unwanted “air” events and
differentiate them from the desired subsurface events. Good field notes are indispensable for
helping identify unwanted events on the data.
One way of identifying air reflections is to use the hyperbola fitting method. If the object is in air,
the radar velocity will be 0.3 m/ns or 0.984 ft/ns and will be much faster than if it is in the ground
(v ~ 0.1 m/ns or 0.328 ft/ns).
Figure: 12-5 Hyperbola matching can be used to identify reflections from objects that are not in the subsurface but
are from objects above ground. If the hyperbola matching velocity is near the speed of light (0.3 m/ns or 0.984 ft/ns)
then the hyperbola was caused by surface object like a overhead wire, tree, etc. After matching the hyperbola (right),
the “depth” value displayed on the bottom of the screen is really a measure of how far from the survey line the object is.
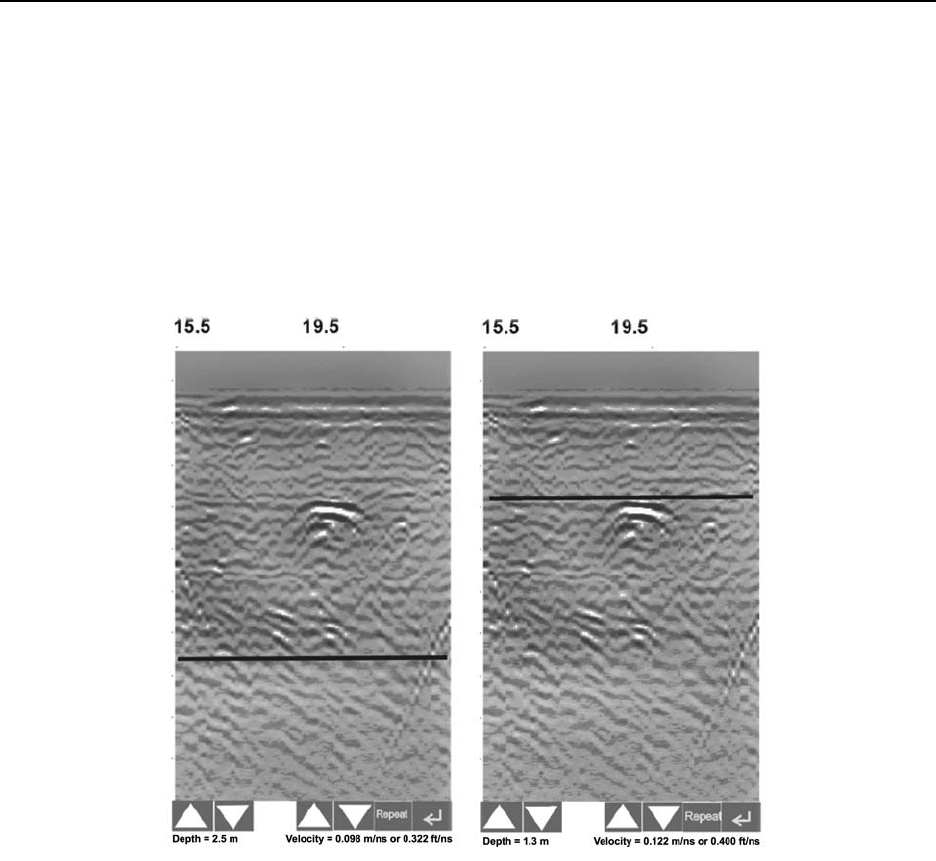
12-Survey & Map Mode Noggin
82
12.2.11.3Target of Known Depth
If there are no suitable hyperbolas visible in the data to perform the Hyperbola Matching
described above, it may be the situation that there is a target of known depth in the area being
scanned. If this is the case, selecting the button with the circle with a horizontal line through it will
superimpose a horizontal line on the data. This line can then be moved up or down until it lies on
top of the Noggin response to the known target. Then, the user can adjust the velocity value up
or down until the known target depth is correct. Once the depth is matched, the current velocity
value is the one used for all subsequent data acquisition.
(a) (b)
Figure: 12-6 Using a target of known depth to extract velocity. After selecting CALIB, choosing the
known depth button (a circle with a horizontal line through it) will superimpose a horizontal line on the
data (a). Using the depth buttons, this line can then be moved up or down until it lies on top of the
Noggin response to the known target (b). Then, the user can use the velocity buttons to adjust the
velocity value up or down until the known target depth is correct. Once the depth is matched, the
velocity value should be used for all subsequent data acquisition.
If units are metres then depths will appear in metres and velocities in metres per nanosecond (m/
ns). If units are feet then depths will appear in feet and velocities in feet per nanosecond (ft/ns).
To change units see Depth Units on page 85.

Noggin 12-Survey & Map Mode
83
12.2.12 Error Messages
If an error occurs during data acquisition, an error message will appear in the bottom left section
of the data acquisition screen. Note the message number, exit the program and turn off the
Digital Video Logger.
Make sure the cables are not damaged and that all cable connections are tightly secured.
Sometimes vibrations cause the cable connections to loosen just a bit and break contact and this
can cause errors. Disconnecting cables and reconnecting them may provide a better contact
and solve the problem. Also check and make sure the battery is adequately charged. Turn the
Digital Video Logger back on and try running the system again.
For more information on Troubleshooting the system, see Section 13: P.112.

12-Survey & Map Mode Noggin
84
12.3 Noggin Setup
Pressing the number 1 on the main menu selects the Setup item. Setup lists the various
parameters that can be edited. These parameters are organized under the following headings:
1 - System Parameters
2 - Cart Parameters
3 - Line Parameters
4 - Grid Parameters
5 – GPS Parameters
6 – Set Defaults
To select a setting to edit, press the corresponding number button. Then use the numbered
buttons to select the new setting. It is also possible to change all the settings back to the factory
default settings by pressing the 6 button (labelled Set Defaults).
The SETUP options are outlined below.
12.3.1 System Parameters
The System Parameters settings allow the user to view and modify settings specific to the data
collection of the Noggin system. This includes the type of Noggin system, the desired depth of
investigation, the velocity of the material being surveyed, the units of depth and position, the
number of stacks and the amount of linear gain.
12.3.1.1 Depth
The depth setting is how deep the radar will try to probe in to the subsurface. It is important to
realize that the depth setting is an estimated value that is dependent on the velocity of the
material being probed.
Ground penetrating radar systems record the time for a radio wave to travel to a target and back.
They do not measure the depth to that target directly. The depth to a target is calculated based
on the velocity at which the wave travels to the target and back. It is calculated as:
D = V x T/2
Where D is Depth (m)
V is Velocity (m/ns)
T is Two-way travel time (ns)
The Depth units can be changed to metres, feet or time in nanoseconds. For details, see Depth
Units below in this section.
It is important to remember that just because the Depth setting is set to a certain value, it
does not necessarily mean that the Noggin is able to penetrate to that depth and collect
data. For example, if the Depth setting is 5 metres but the material penetration is only 3
metres the last 2 metres of the image will not contain subsurface information. Some
materials will absorb the Noggin signal and limit penetration to less than the selected
depth.
If the depth setting is deeper than the Noggin signals penetrate, the data in the lower part of the
data screen will look blank or speckled rather than signal with continuity.
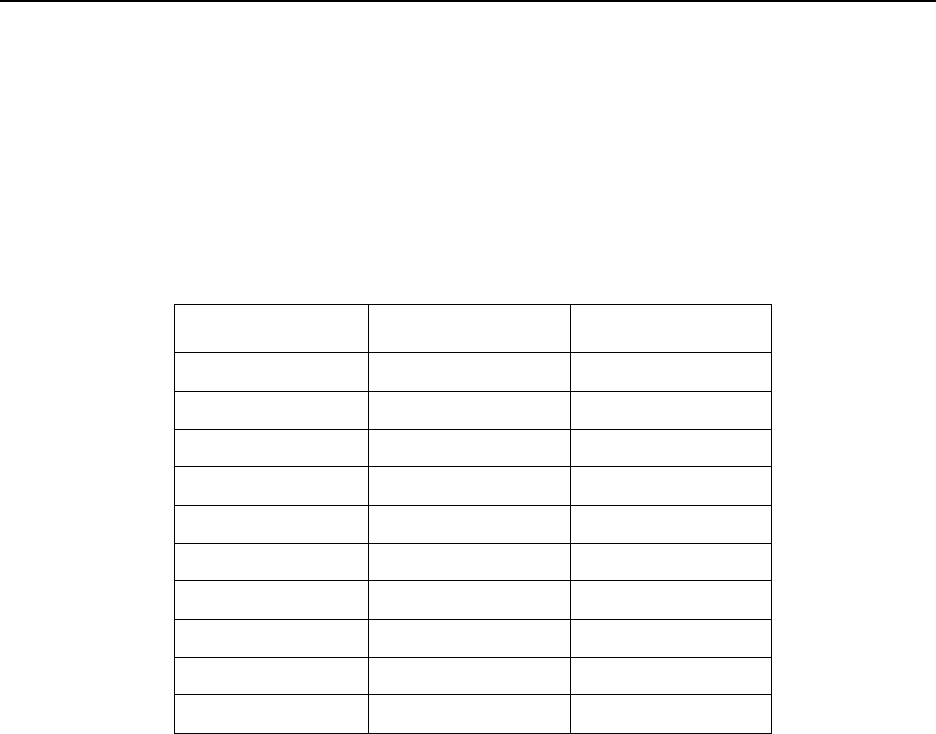
Noggin 12-Survey & Map Mode
85
12.3.1.2 Velocity
The wave velocity depends on the properties of the material. The Noggin software allows the
user to input a velocity, which changes the total time window collected by the system.
See Section 12.2.11: P.79 for a discussion about determining velocity.
A table of typical radar velocities in various materials is given below. If in doubt, use a value of
0.10 m/ns. This is a good average velocity that will provide a good estimate of depth in most
situations.
If units are metres then velocities will appear in metres per nanosecond (m/ns). If units are feet
then velocities will appear in feet per nanosecond (ft/ns). To change units see Depth Units on
page 85.
The Noggin will accept units in metres/nanosecond or feet/nanosecond depending on the Depth
Units setting.
12.3.1.3 Depth Units
This is the setting for the units of the horizontal depth lines that appear on the screen. The
available settings are metres, feet or nanoseconds (ns). If nanoseconds are selected the “depth”
lines (see Section 12.2.2: P.71) are actually time lines.
1) metres
2) feet
3) nanoseconds
12.3.1.4 Noggin System
The Noggin System should be set to the type of Noggin currently in use on the Smart System.
The Noggins available are: 1) Noggin 100
2) Noggin 250
Material Velocity (m/ns) (ft/ns)
Air 0.300 1.000
Ice 0.170 0.558
Dry Soil 0.130 0.427
Dry Rock 0.120 0.394
Soil 0.100 0.328
Wet Rock 0.100 0.328
Concrete 0.100 0.328
Pavement 0.100 0.328
Wet Soil 0.065 0.213
Water 0.033 0.108
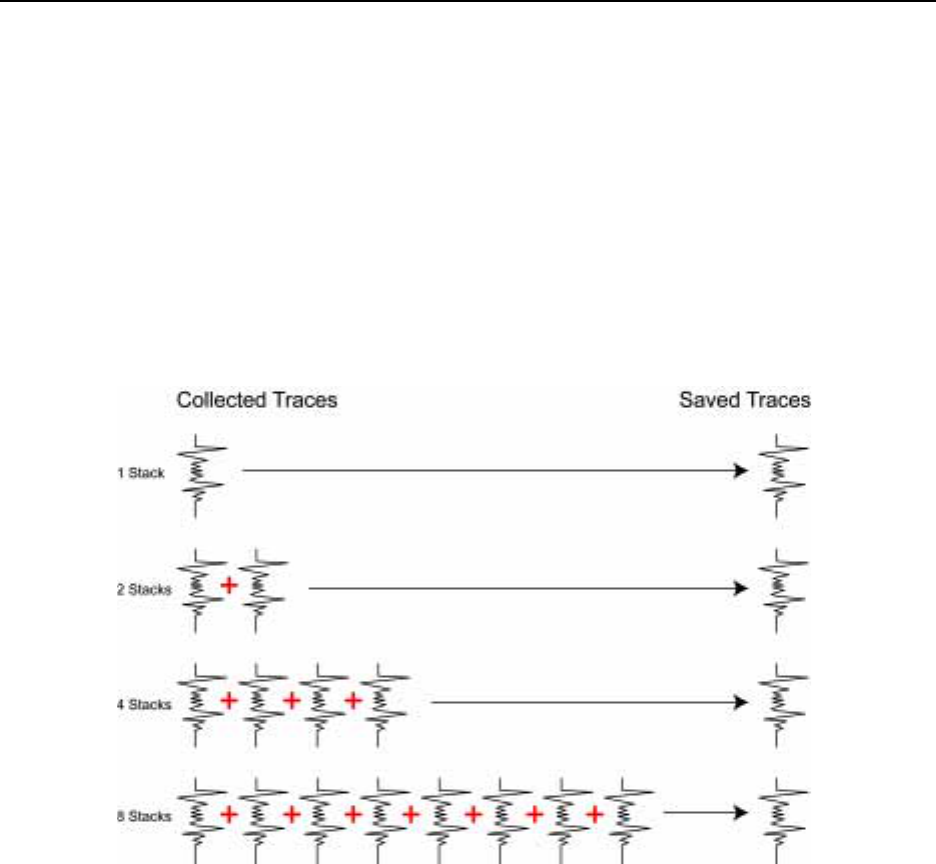
12-Survey & Map Mode Noggin
86
3) Noggin 500
4) Noggin 1000
12.3.1.5 Stacks
Some materials tend to absorb radar signals and limit penetration. These materials are said to
be lossy. When collecting data in lossy areas or areas with a lot of radio frequency noise, one
way of increasing data quality is to collect more than one trace at each survey position, average
them and save the averaged trace. This is known as “stacking”. Data quality improves because
the noise, which is usually random (like white noise on a TV screen with no station in the area),
tends to zero when averaged. Consequently, the usable signal is easier to see. This is known as
increasing the “signal-to-noise ratio”.
Figure: 12-7 The concept of stacking data. At each data location point, the trace is collected multiple times. These
traces are averaged together to calculate the trace that is actually saved. Stacking improves the data quality by
increasing the signal to noise ratio.
The amount of Stacking can vary from 1 to 2048 by factors of 2.
While stacking improves data quality, it also forces the user to slow down survey production. The
more stacks the longer it takes to collect data at each survey position. Therefore, it is important to
find the lowest number of stacks that still reveal the target adequately. For most surveys, stacking
4 times is suitable.
See the warning in Section 12.2.7 Collecting Data using the Odometer about losing data if the
Smart System is moving too quickly for the odometer to keep up.
Increasing Data Quality with DynaQ
If the Trigger Method (Section 12.3.2.2 Trigger Method) is set to odometer, one of the options
for Stacking is DynaQ.

Noggin 12-Survey & Map Mode
87
DynaQ is an advanced, patented technology that dynamically adjusts stacking as the system
movement speed varies. In most situations, moving the system at a comfortable speed stacks
enough to generate data of good quality. In situations where target resolution or maximum
penetration depth is critical, moving slower increases the number of stacks and increases the
data quality.
As the system moves during data collection, the DVL screen displays a DynaQ scale bar from L
(Low) to H (high) to indicate data with enhanced signal-to-noise are being attained??.
Figure: 12-8 When collecting data with an odometer, stacking can be set to DynaQ so the number of stacks for each
trace is dynamically adjusted depending on the speed the system is moving. Moving the system slower increases the
number of stacks and increases data quality. The number of stacks is indicated on the DynaQ scale bar from Low (L)
to High (H).
The DynaQ information for each data line is written to the header (.HD) file.

12-Survey & Map Mode Noggin
88
12.3.1.6 Linear Time Gain
As described in Section 12.2.6: P.73, the weak signals must be amplified or “gained” to see them
on the display. The Gain button described in Section 12.2.6: P.73 can be set to a value from 1 to
9 depending on the amount of gain required (1 is lowest gain, 9 is highest gain).
There is also a second level of gain available to the user and that is the Linear Gain setting. The
default Linear Gain setting of 2.0 is usually adequate for most ground conditions, however, if
advanced users find that they are surveying in areas where high Gain button settings are always
required to see data, it may be advantageous to increase the Linear Gain setting. Conversely, if
the user finds that low Gain button values work to see the data, it may be useful to decrease the
Linear Gain setting.
For the experienced user, the setting indicates the gain increases per nanosecond.
The Linear Gain setting can vary from 0.0 to 5.0 in steps of 0.5.
12.3.1.7 Position Units
This is the setting for the position units used by the odometer. The available options are:
1) metres (default)
2) feet

Noggin 12-Survey & Map Mode
89
12.3.2 Cart Parameters
The Cart Parameters settings allow the user to view and modify settings specific to the Smart
System. This includes the direction the Noggin will move to collect data, whether or not the
odometer is active and whether Auto Start is on or off.
12.3.2.1 Cart Direction
This setting determines whether data are collected as the Noggin is pushed forward or pulled in
reverse. The back up arrow (see Section 12.2.7: P.74) will work in the direction opposite to this
setting. The available options are:
1) Push (default)
2) Pull
12.3.2.2 Trigger Method
This setting determines the method used to trigger the Smart System to collect data at each data
collection point. The available options are:
1) Odometer
2) Free Run
3) Button
Trigger with Odometer: Selecting this option means that the Smart System will be triggered to
collect data using the input from the currently selected odometer (see Odometer Number below).
See Section 12.2.7: P.74 for more details about data acquisition with an odometer.
When collecting data with an odometer, data quality can be increased using the DynaQ stacking
option (Section 12.3.1.5 Stacks).
Free Run Operation: Selecting this option means that the Smart System runs continuously in
time, independent of any other triggering device (see Section 12.2.8: P.75). When continuous
operation is selected, two other menus appear to select the number of stacks and time delay
between data traces. These options allow the user to control the speed of the data acquisition.
The user can control the speed the Noggin collects data by increasing or decreasing the number
of stacks (for more details on Stacking, see Stacks on page 86). Increasing the number of Stacks
has the effect of slowing down the data collection speed of the Noggin system. Decreasing the
number of Stacks has the effect of speeding up the data collection speed of the Noggin system.
The second menu to appear prompts the user to input the time delay, in seconds, between each
data collection point. To run the system as quickly as possible, set this value to 0.0 seconds. For
a longer time delay, use the buttons to set the value. Note that any time delay longer than zero
(0.0) seconds causes the Smart System to emit a beeping sound to indicate data collection is
taking place.
The number of stacks and time delay should be set to values that, when combined with speed
the Noggin is moving at, provide an appropriate station interval. This may take a little
experimenting to determine the optimal values for stacks, time delay and the actual speed the
Noggin is moving at.
Trigger with Button: Selecting this means that the Smart System will be triggered to collect data
by pressing the trigger button (if the Smart System has a trigger button) or the B button on the
DVL (see Section 12.2.9: P.76).

12-Survey & Map Mode Noggin
90
After the user selects this option, a menu appears to select the number of stacks for each trace
(for more details on Stacking, see Stacks on page 86).
Note that when data are collected in Trigger Button mode, the Smart System will emit a beeping
sound after the button is pressed to indicate data collection is taking place.
12.3.2.3 Auto Start
If the Auto Start option is set to ON, after the user presses Run to collect a data line, the system
will automatically boot up and be ready for data acquisition, rather than having the Start button
appear. This prevents the user from having to press the Start button at the start of every new
line. This setting is especially useful when collecting numerous lines as occurs when
collecting grid data. If Auto Start is set to OFF the user must press the Start button to begin
data acquisition for each line.
12.3.2.4 Arrow Offset
Section 12.2.7: P.74 describes the Back-up Arrow that appears when the Smart System is
backed up. The Back-up Arrow allows the user to pinpoint the exact ground position
corresponding to a target response on the data image. The Arrow Offset value is used to change
the physical position that corresponds to the Back-up Arrow. If the Arrow Reference value is set
to the default value of zero (0.0) metres, the Back-up arrow position corresponds with the centre
point of the Noggin.
However, the Arrow Offset value can be changed so that the Back-up Arrow corresponds to a
position at any offset from the centre of the Noggin. For example, setting the Arrow Offset value
to +0.25 metres moves the Back-up Arrow to line up with a position 25 centimetres in front of the
Noggin centre point (on the Noggin 500 SmartCart this roughly corresponds to the front axle).
Setting the Arrow Reference value to -0.25 metres moves the Back-up Arrow to line up with a
position 25 centimetres in behind the Noggin centre point (on the Noggin 500 SmartCart this
roughly corresponds to the back axle). In this way, the Arrow Offset value can be changed to
correspond with any position desired by the user.
One reason the user may want to change the Arrow Offset value is to ensure that the Noggin
does not cover the actual target location. This makes it easier to spray paint a mark or put a flag
on the ground where the target occurs.
Positive values correspond to positions in front of the Noggin and negative values are positions
behind the Noggin. Note that the Arrow Offset value is always expressed in metres regardless of
the settings of the other units.
12.3.2.5 Trip Menu
The software records the total distance the system has travelled. This value is displayed but
cannot be changed.
The software also records a distance that can be reset by the user. To reset the distance counter,
move to the Reset Counter option and press the Zero button.
12.3.2.6 Transfer Rate
Transfer Rate is a variable from 1 to 8 that corresponds to the speed of the data transfer from the
Noggin to the DVL. A value of 8 provides the fastest transfer speed while a value of 1 is the
slowest.

Noggin 12-Survey & Map Mode
91
For standard Smart Systems the Transfer Rate value must be set to 8.
The Transfer Rate value will only be decreased for systems with data cables longer than
standard lengths. Please contact Sensors & Software before changing the Transfer Rate on your
system.
12.3.2.7 Odometer Number
Noggin Smart Systems can take input from several different odometers.
It is very important that the user selects and calibrates the odometer appropriate for their
Smart System.
When Odometer Number is selected, the user is prompted to select the odometer that is being
used with the Smart System.
If a SmartCart System is being used, select one of the two SmartCart odometers (usually #1).
If a SmartHandle system is being used, select one of the two SmartHandle odometers (usually
#1).
If the system is being towed behind a vehicle and using the transmission odometer to trigger the
system, select one of the two Vehicle odometers (usually #1).
The odometers labelled Other are to be used in future configurations.
The number after the odometer is the current Odometer Calibration value for that odometer. To
calibrate the odometer, see Section 12.5.2: P.110.

12-Survey & Map Mode Noggin
92
12.3.3 Line Parameters
The Line Parameters settings allow the user to view and modify settings specific to collecting
data as individual lines, namely, the starting position of the line and line direction.
12.3.3.1 Start Position
The Start Position is the position value at the very beginning of a line. This will usually be set to
zero (0.0). However, if the user wants a data file to start at a position other than zero, this value
can be edited.
12.3.3.2 Line Direction
The Line Direction setting specifies which direction that line will be collected, either Forward or
Reverse. Data are usually collected in a forward direction.
If data are collected in the Forward direction the position stepsize is positive, that is, the position
value of each data collection point increments positively. For example, for a Noggin 250 system,
if the Start Position is 10.0 and the Line Direction is Forward, the positions on the line will
increment 10.00, 10.05, 10.10, 10.15 ….
If data are collected in the Reverse direction the position stepsize is negative, that is, the position
value of each data collection point increments negatively. For example, for a Noggin 250 system,
if the Start Position is 10.0 and the Line Direction is Reverse, the positions on the line will
decrement 10.00, 9.95, 9.90, 9.85 ….
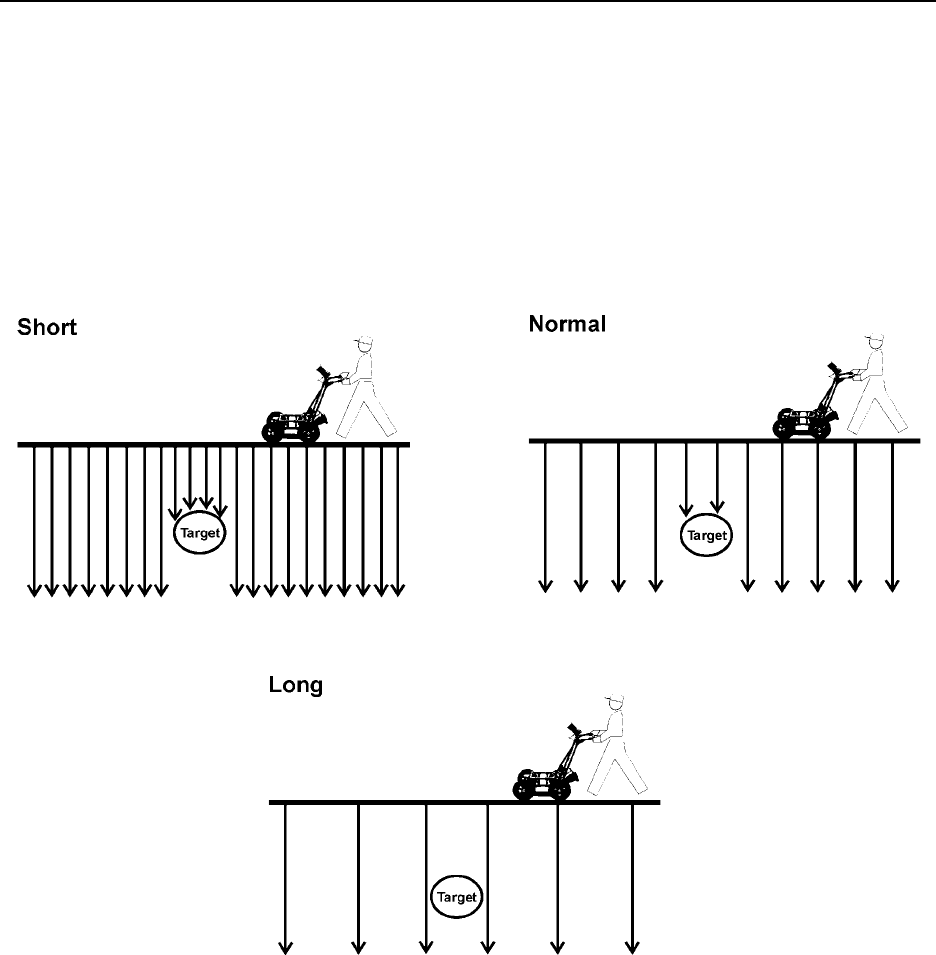
Noggin 12-Survey & Map Mode
93
12.3.3.3 Station Interval
As Smart Systems moves, the odometer triggers the system to collect a data trace at fixed
distance intervals. This interval is called the “station interval”.
The station interval can be changed to allow a longer or shorter distance between traces. For a
successful survey, it is important that several traces be collected over a target. If the target is
small, the user may want to shorten the station interval to ensure that data traces are collected
over the target. Conversely, if the target is very large or is a flat-lying feature it is probably not
necessary to collect a lot of traces over the target, in fact, sometimes this can make the target
more difficult to see in the data. In this case it may be beneficial to increase the station interval.
Figure: 12-9 The Station Interval is the distance between sample points on the ground. Be careful not
to choose a Station Interval that is larger than the smallest target to be detected.
Note that decreasing the station interval increases the data volume and increasing the station
interval reduces the data volume.
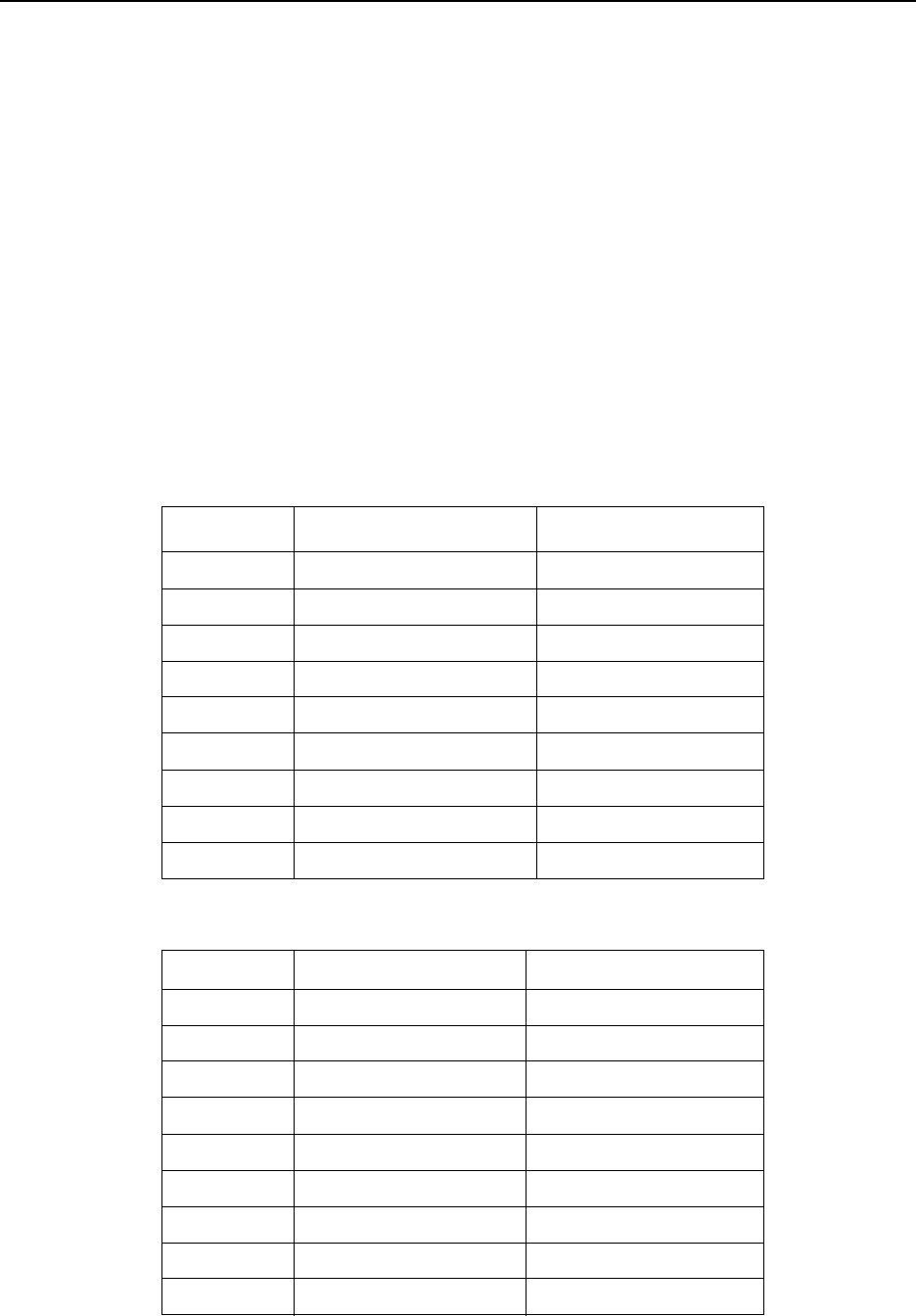
12-Survey & Map Mode Noggin
94
The choices available are:
1) Short
2) Normal
3) Long
4) X-Long
5) 10x Normal
6) 20x Normal
7) 40x Normal
8) 50x Normal
9) 100x Normal
Each choice listed will be followed by an actual value in metres or inches depending on which
units are selected and which Noggin system is being used. Here is a chart showing the station
interval for each system and setting. Note the calculations for Data per Screen assumes that the
Plot Interval is set to Normal for the particular Noggin system (Noggin 250 = 2 pixels per trace
and Noggin 500 and 1000 = 1 pixel per screen). If this assumption is not true, see the formula
after the charts for calculating this value.
N
OGGIN
250 S
YSTEM
N
OGGIN
500 S
YSTEM
Setting Station Interval Data per Screen
Short 2.5 cm or 0.96 in 8 m or 25.6 ft
Normal 5.0 cm or 1.92 in 16 m or 51.2 ft
Long 10.0 cm or 3.84 in 32 m or 102.4 ft
X-Long 25.0 cm or 9.6 in 80 m or 256 ft
Norm x10 50.0 cm or 19.20 in 160 m or 512 ft
Norm x20 100.0 cm or 38.4 in 320 m or 1024 ft
Norm x40 200.0 cm or 76.8 in 640 m or 2048 ft
Norm x50 250.0 cm or 96.0 in 800 m or 2560 ft
Norm x100 500.0 cm or 192.0 in 1600 m or 5120 ft
Setting Station Interval Data per Screen
Short 1.0 cm or 0.48 in 6.4 m or 25.6 ft
Normal 2.5 cm or 0.96 in 16 m or 51.2 ft
Long 5.0 cm or 1.92 in 32 m or 102.4 ft
X-Long 12.5 cm or 4.8 in 80 m or 256 ft
Norm x10 25 cm or 9.6 in 160 m or 512 ft
Norm x20 50 cm or 19.2 in 320 m or 1024 ft
Norm x40 100 cm or 38.4 in 640 m or 2048 ft
Norm x50 125 cm or 48.0 in 800 m or 2560 ft
Norm x100 250 cm or 96.0 in 1600 m or 5120 ft
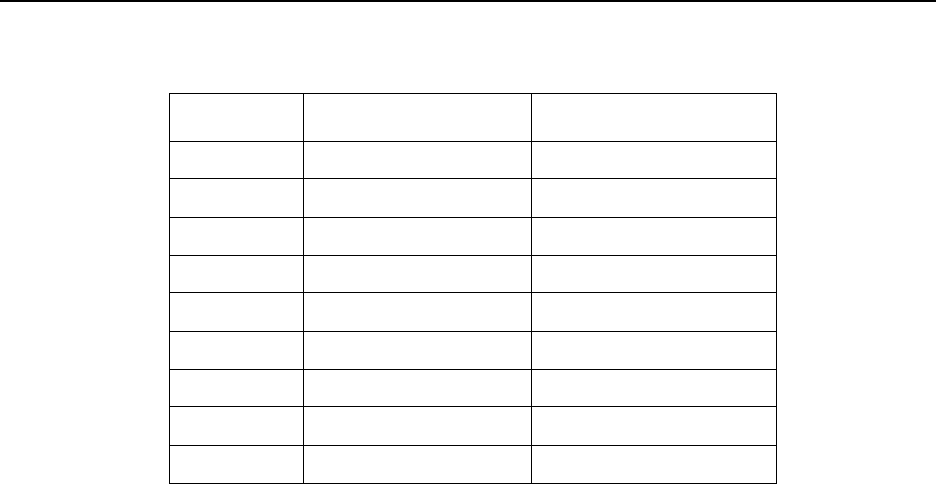
Noggin 12-Survey & Map Mode
95
N
OGGIN
1000 S
YSTEM
If the Plot Interval is not set to Normal, use the following formula to calculate the total distance
per screen:
Total Distance Per Screen = Station Interval * (640 / Plot Interval)
where: Station Interval is in metres or feet, and
Plot Interval is in Pixels.
For example, if the Station Interval is 10 centimetres (0.1 metres) and the Plot Interval is 4 pixels,
the total distance per screen is calculated as follows:
0.10 * (640 / 4) = 16.0 metres per screen
To see how much data can be collected before the DVL memory is full and data must be deleted
or downloaded, see DVL Recording Space in Section 12.5.5: P.111.
To delete Noggin data see Section 12.4.5: P.109.
Setting Station Interval Data per Screen
Short 0.5 cm or 0.24 in 3.2 m or 12.8 ft
Normal 1.0 cm or 0.48 in 6.4 m or 25.6 ft
Long 2.0 cm or 0.96 in 12.8 m or 51.2 ft
X-Long 5.0 cm or 2.4 in 32.0 m or 128 ft
Norm x10 10 cm or 4.8 in 64.0 m or 256 ft
Norm x20 20 cm or 9.6 in 128 m or 512 ft
Norm x40 40 cm or 19.2 in 256 m or 1024 ft
Norm x50 50 cm or 24.0 in 320 m or 1280 ft
Norm x100 100 cm or 48.0 in 640 m or 2560 ft
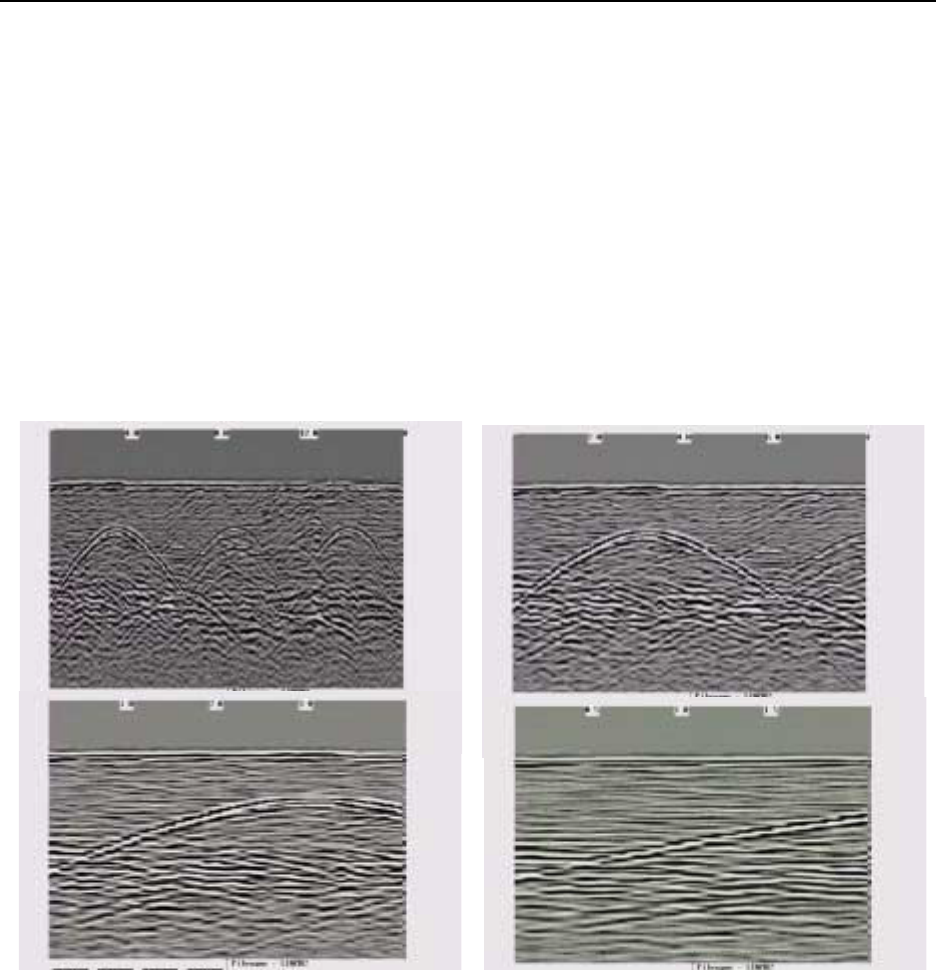
12-Survey & Map Mode Noggin
96
12.3.3.4 Plot Interval
The plot interval setting determines the width of data traces plotted to the screen. Traces can be
1, 2, 4 or 8 pixels wide.
The Normal setting for Noggin 250 systems is 2 pixels per trace and the Normal setting the
Noggin 500 and 1000 is 1 pixel per trace.
It can be useful to plot traces narrower than normal to allow more data to fit onto one screen. It
can also be useful to plot traces wider on the screen so that they are easier to see. For example,
when collecting data using the button to trigger the system (see Section 12.2.9: P.76) it is often
preferable to make each trace 4 or 8 pixels wide.
Figure: 12-10 Data traces can be plotted to the screen with a width of 1 pixel (top left), 2 pixels (top right), 4 pixels
(bottom left) or 8 pixels (bottom right). The narrower the trace width, the more data that can be plotted on one screen.
In this example, plotting the data 1 pixel wide results in 16 metres of data displayed on one screen while 2 pixels
results in 8 metres of data, 4 pixels results in 4 metres of data and 8 pixels results in 2 metres of data
Note that the Plot Interval in Noggin is strictly for display purposes on the DVL screen in real time.
The Plot Interval setting has no effect on the actual data collected and, in fact, data can be
viewed later on the DVL screen with any Plot Interval value. Similarly, data downloaded to a PC
can be plotted using any trace width.
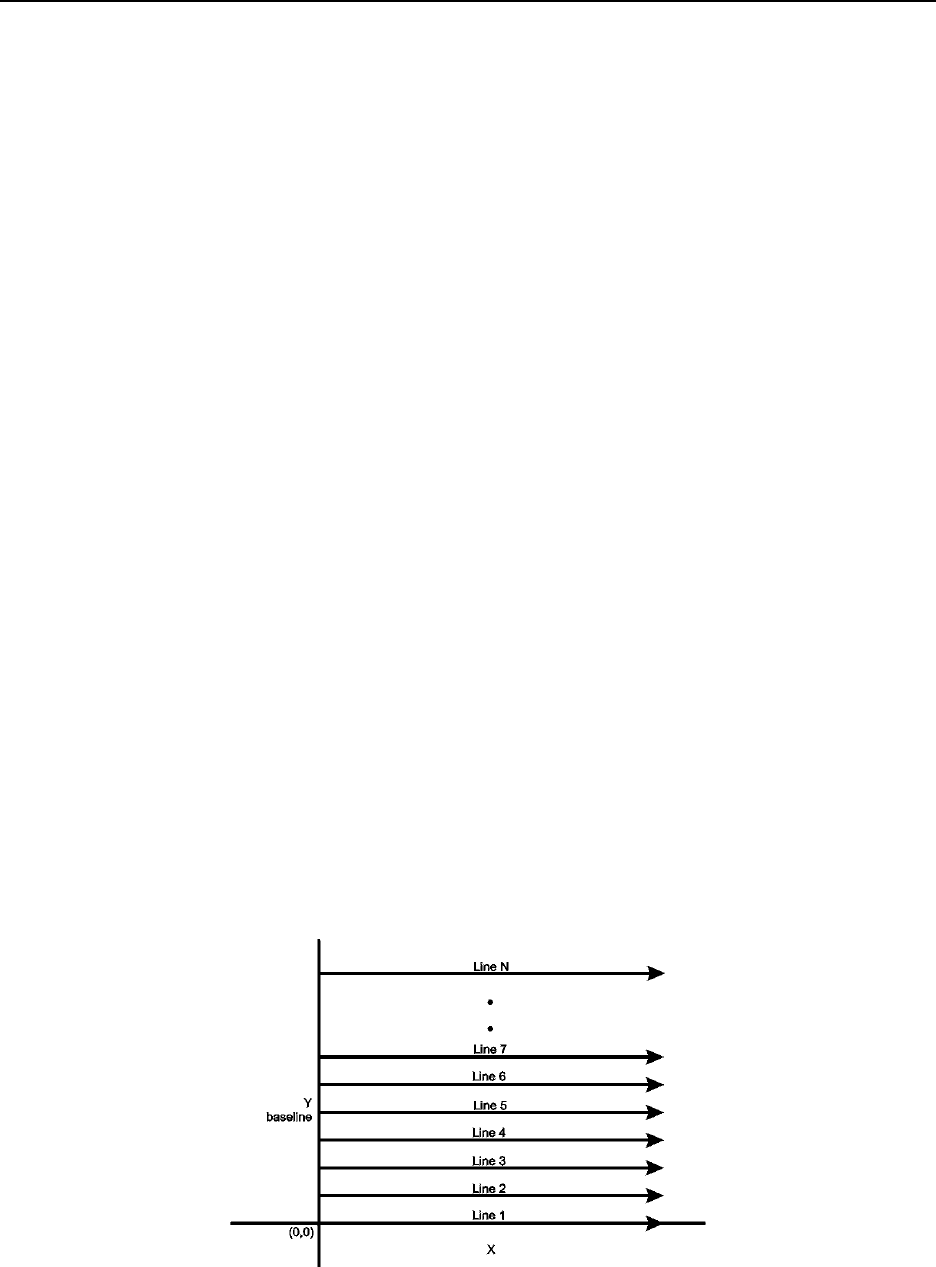
Noggin 12-Survey & Map Mode
97
12.3.4 Grid Parameters
The Grid Parameters settings allow the user to view and modify settings specific to collecting
data in organized grids. This includes the grid dimensions, line spacing, grid type and survey
format.
Data are normally collected on a grid if the user is interested in displaying the data as a 3D
volume (using the EKKO_3D software) or as a plan map (using the EKKO_Mapper and/or
EKKO_Pointer software). Producing accurate 3D volumes or plan maps is easier if the field
survey is properly designed and data are collected correctly.
Positional accuracy of each line is vital if the user wants to be able to relocate targets of interest
after the data have been processed.
For linear targets like pipes and utilities, the best GPR response occurs when the GPR survey
line crosses the target at right angles. If possible, it is always best to run GPR survey lines
perpendicular to the direction of linear targets.
For inexperienced surveyors, laying out a grid with straight lines and all corners at 90
degree angles can be difficult. Sensors & Software provides a product called EasyGrid to
make laying out an accurate grid simple. Contact Sensors & Software for more details.
12.3.4.1 Grid Type
The Grid Type asks specifically the way that the area of the grid is to be covered by the survey
lines. Survey lines can be either a set of parallel lines in the X axis direction (Figure 12-11), a set
of parallel lines in the Y axis direction (Figure 12-12), or, for complete coverage, parallel lines in
both the X and Y direction (Figure 12-13).
X Lines Only - Forward
Set up a first-quadrant XY grid. Data lines run in the X direction, distance increasing from the Y
axis baseline. Line numbers increase in the positive Y direction (see Figure 12-11). Lines must
be equally spaced. It is not critical that all the lines are the same length. However, it does make
processing easier if all the lines start at the same baseline position (usually defined as zero
(0.0)).
Figure: 12-11 Proper X Line surveying pattern. Following this pattern and starting each line from the
same baseline minimizes the data editing required to produce a spatially accurate map of GPR data.
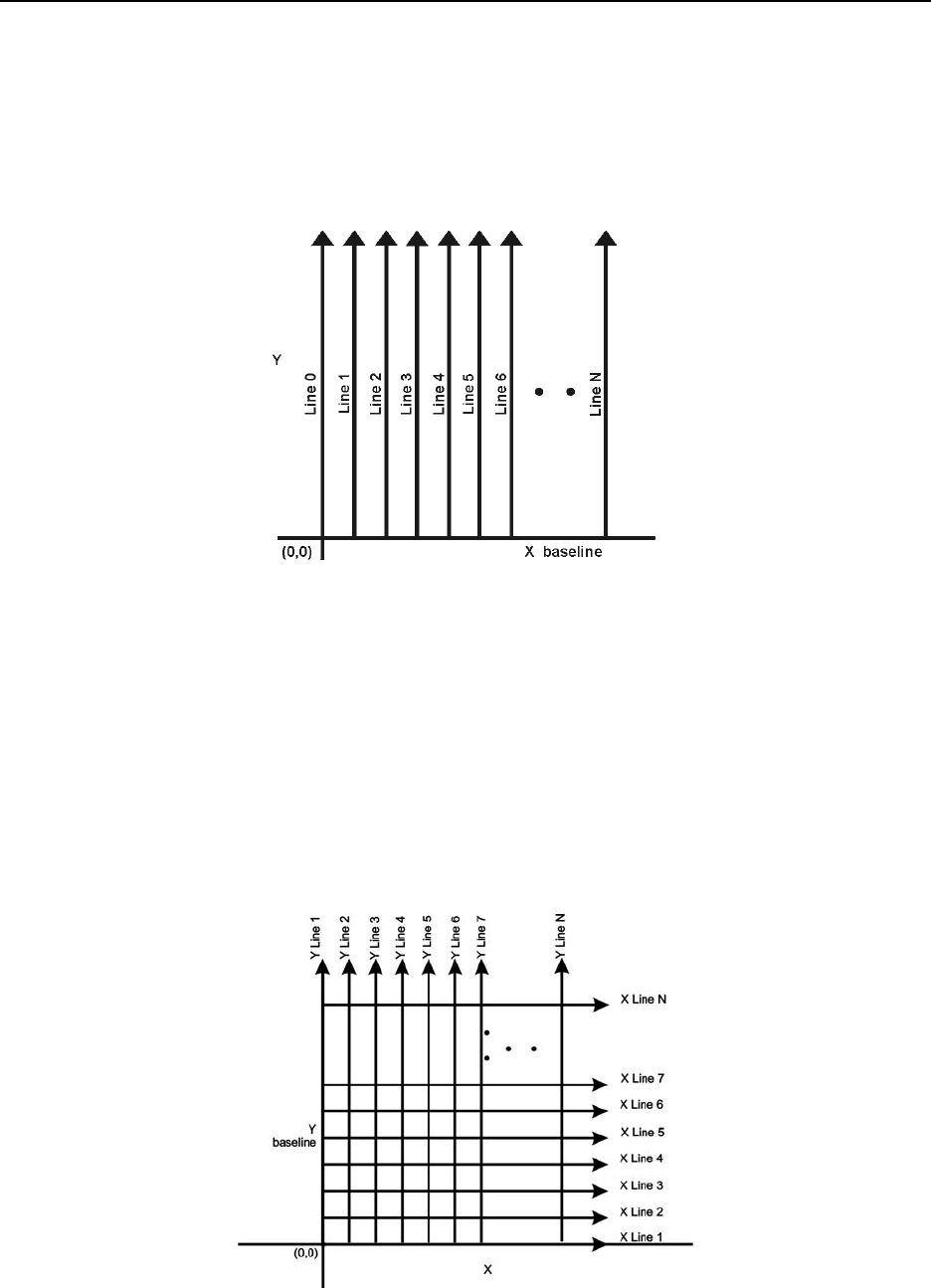
12-Survey & Map Mode Noggin
98
Y Lines Only - Forward
Set up a first-quadrant XY grid. Data lines run in the Y direction, distance increasing from the X
axis baseline. Line numbers increase in the positive X direction (see Figure 12-12). Lines must
be equally spaced. It is not critical that all the lines are the same length. However, it does make
processing easier if all the lines start at the same baseline position (usually defined as zero
(0.0)).
Figure: 12-12 Proper Y Line surveying pattern. Following this pattern and starting each line from the
same baseline minimizes the data editing required to produce a spatially accurate map of GPR data.
XY Lines - Forward
Set up a first-quadrant XY grid. X data lines run in the X direction, distance increasing from the Y
axis baseline. Line numbers increase in the positive Y direction (see Figure 12-13). Lines must
be equally spaced. Y data lines run in the Y direction, distance increasing from the X axis
baseline. Line numbers increase in the positive X direction. Lines should be equally spaced.
The line spacing of the X lines and Y lines can be different.
It is not critical that all the lines are the same lengths. However, it does make processing easier
if all the lines start at the same baseline position (usually defined as zero (0.0)).
Figure: 12-13 Proper XY grid surveying pattern. Following this pattern and starting each line from the
same baseline minimizes the data editing required to produce a spatially accurate map of GPR data.
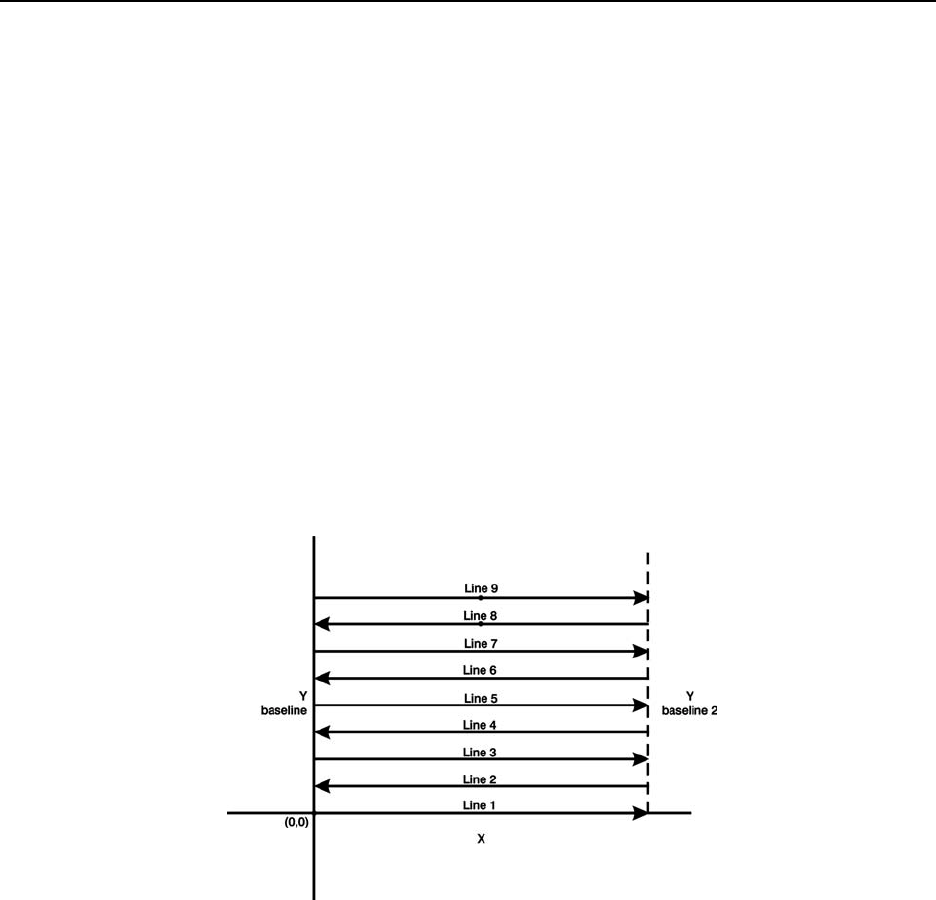
Noggin 12-Survey & Map Mode
99
12.3.4.2 Survey Format
The Survey Format specifies how the lines will be collected. The lines shown in Figure 12-11,
Figure 12-12, and Figure 12-13 are all collected in the Forward direction only. This means that
each line starts at the X or Y baseline.
When the length of the survey lines are more than about 20 metres, data acquisition speed may
be increased by collecting every second line in the reverse direction (Figure 12-14, Figure 12-15,
and Figure 12-16). This is called a Forward and Reverse survey format.
Using forward and reverse format can speed acquisition but can lead to mapping artifacts called
“herringbone” if there are positional errors. It is important that the odometer is calibrated (Section
12.5.2: P.110), the Grid Dimensions are correct (see Grid Dimensions on page 101) and that
lines are always collected starting on a baseline.
X Lines Only – Forward and Reverse
Using the Forward and Reverse survey format, X line data are collected in the pattern shown in
Figure 12-14.
Figure: 12-14 For collecting GPR data consisting of long data lines it makes more sense to follow a
forward and reverse surveying pattern. For the final data to be spatially correct with a minimum of
editing, data collected in this pattern should be on lines that extend completely from one baseline to the
other.
Y Lines Only – Forward and Reverse
Using the Forward and Reverse survey format, Y line data are collected in the pattern shown in
Figure 12-15.
When data are collected like this, it is important that lines start and end on established baselines,
otherwise, when lines are reversed to the correct orientation for the display, they may be offset
from one another.
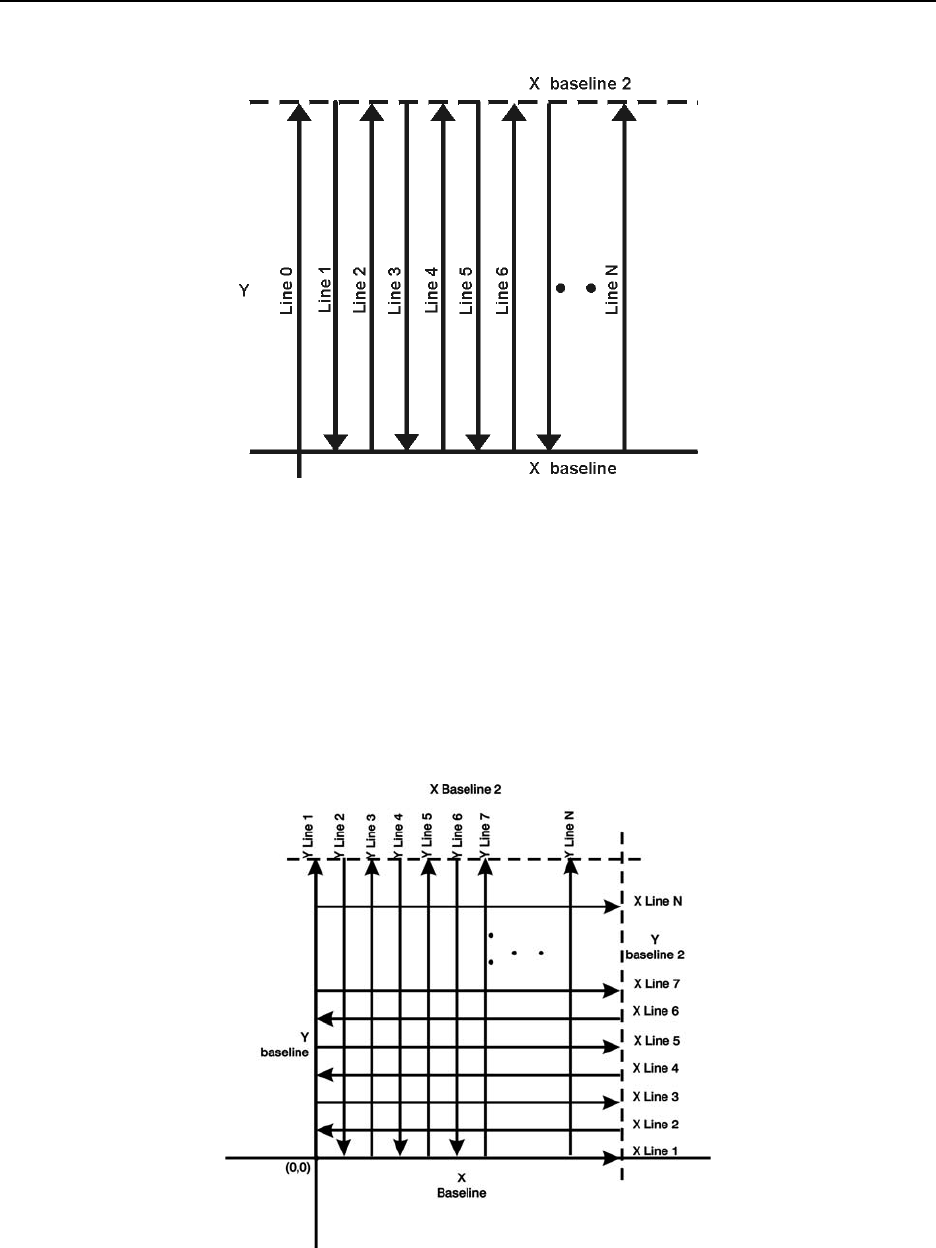
12-Survey & Map Mode Noggin
100
Figure: 12-15 For collecting GPR data consisting of long data lines it makes more sense to follow a
forward and reverse surveying pattern. For the final data to be spatially correct with a minimum of
editing, data collected in this pattern should be on lines that extend completely from one baseline to the
other.
XY Lines – Forward and Reverse
Using the Forward and Reverse survey format, XY line data are collected in the pattern shown in
Figure 12-16.
When data are collected like this, it is important that lines start and end on established baselines,
otherwise, when lines are reversed to the correct orientation for the display, they may be offset
from one another.
Figure: 12-16 For collecting GPR data on a grid consisting of long data lines, it makes more sense to
follow a forward and reverse surveying pattern. For the final data to be spatially correct with a minimum
of editing, data collected in this pattern should be on lines that extend completely from one baseline to
the other.

Noggin 12-Survey & Map Mode
101
12.3.4.3 Grid Dimensions
For grid data acquisition, the grid size needs to be specified. The user needs to input the length
of the X dimension and the length of the Y dimension. The dimensions entered are assumed to
be in the same units as the Position Units (see Section 12.3.1.7: P.88), i.e. metres or feet.
On this screen the user needs to highlight the dimension to be changed. The user can toggle
between the X and Y fields by pressing the X/Y button.
The dimension value is incremented or decremented by pressing the +Line or –Line buttons.
The dimension value will change by a value equal to the current Line Spacing in that dimension.
For example, if the Line Spacing in the X direction is 0.5 metres, the grid dimension in the X
direction will increment or decrement in 0.5 metre intervals.
Note that the maximum number of lines that can be collected in each direction is 100.
Therefore, the X and Y grid dimensions cannot be set to a value that will result in more
than 100 lines being collected.
For example, if the Line Spacing between Y lines (defined as lines parallel to the Y axis) is set to
0.25 metres, the maximum X dimension is (100-1) X 0.25 = 24.75 metres. (One is subtracted
because the first line is at position 0.0 metres.)
To increase the X dimension value, the Y line spacing must be increased. Using the example
above, if the Y Line Spacing is increased to 0.30 metres then the maximum X dimension is (100-
1) X 0.30 = 29.70 metres.
If the Grid Type is set to X Lines only or Y Lines only (see Section 12.3.4: P.97), the length of
those lines are not restricted by the Line Spacing parameter of the opposite dimension. That is
why if an X Lines only grid is selected, the X dimension can be input as a value rather than an
increment of the Y Line Spacing. Similarly, if a Y Lines only grid is selected, the Y dimension can
be input as a value rather than an increment of the X Line Spacing.
12.3.4.4 Line Spacing
For grid data acquisition, the distance between survey lines needs to be specified.
If the grid type is X Lines only (see Section 12.3.4: P.97) then the spacing between the X lines
needs to be input.
If the grid type is Y Lines only (see Section 12.3.4: P.97) then the spacing between the Y lines
needs to be input.
If the grid type is XY Lines (see Section 12.3.4: P.97) then the spacing between the X lines and Y
lines need to be input. The line spacing can be different. The user can toggle between the X line
spacing and Y line spacing fields by pressing the X/Y button.
Note that the maximum number of lines that can be collected in each direction is 100.
The calculation for determining an appropriate line spacing is complex. One has to consider
system frequency, target size and practical considerations. In general, the Noggin 250 should
have a line spacing of 0.5 metres or less, the Noggin 500 should have a line spacing of 0.25
metres or less and the Noggin 1000 should have a line spacing of 0.10 metres or less.

12-Survey & Map Mode Noggin
102
However, line spacing should really be determined by target size. In most cases the system
must pass over a target to detect it. Therefore, the line spacing needs to be on the order of the
size of the target or smaller, if practical. This can be adjusted to a larger spacing for larger targets
or targets with a linear extent. As well, these rules may have to be bent for practical purposes
like survey production rates. The fact is that a tighter line spacing takes longer to collect and this
may not be economically possible in all circumstances.

Noggin 12-Survey & Map Mode
103
12.3.5 GPS Parameters
The Global Positioning System (GPS) uses special satellites around the Earth to determine the
position of a GPS receiver located at any position on the surface of the Earth. GPS receivers can
be purchased from a number of manufacturers.
The DVL has a serial port on the back for attaching a GPS receiver. This port will accommodate
any GPS receiver that has a standard serial port output.
The GPS receiver can be set up to send one or more types of data strings to the DVL. These
strings are called NMEA-0183 strings and each contains positional or other information in
specific formats. Each type of string is specified by a 5-character prefix. There are numerous
NMEA strings but to integrate the GPS data into the Noggin data, the GPS must be sending at
least one of the following NMEA strings: GPGGA, GPGLL and GPRMC.
This feature allows GPS information to be logged while collecting Noggin data. The GPS
information may be useful for mapping where GPR surveys have been performed (see Reading
per Trace mode below) or determining where a specific target of interest is located in GPS co-
ordinates (see Fiducial Tagging mode below).
The DVL can be set up to read and log GPS information collected during data acquisition with the
Noggin system. GPS information can be logged in two different ways:
1) For every trace collected by the Noggin system, or
2) Every time the user adds a fiducial to the data by pressing the A button (see Fiducial
Markers on page 72).
This feature provides a means of logging GPS information to an independent file. Note that the
GPS information is NOT automatically integrated with the Noggin data. After data
acquisition is complete, the data can be downloaded to a PC and the EKKO_View Deluxe
software can be used to integrate the GPS data with the Noggin data.
In order for the DVL to read the GPS data string, the GPS settings for the specific GPS receiver
being used must be input into this menu. There are 4 important items that must be specified
correctly for the DVL to display the GPS strings. These items are Baud Rate, Stop Bits, Data Bits
and Parity. These are discussed in more detail below. The default values listed below are the
values that are typically used. Read the GPS Receiver User’s Guide or experiment with the
settings to find the correct ones.
Once these 4 items are set correctly you should be able to run System Test #1 and have GPS
information written to the screen.
When the logging of GPS information is enabled, during data acquisition a message will appear
in the bottom left-hand corner of the DVL screen indicating whether GPS data is successfully
being received (see Section 12.2.4: P.72).

12-Survey & Map Mode Noggin
104
Mode
There are three GPS modes available:
1) Off mode means that a GPS receiver is not connected to the DVL so no GPS
information is being logged. This should be the setting if you do not have a GPS
receiver.
2) Reading every x traces mode means that every time the Noggin collects a user-
defined number of traces of GPR data, a data string of GPS information will be added
to a file. This file has the same name as the data file i.e. LINE6, but with a GPS
extension. This file can be accessed after transferring the GPR data files to an
external PC (see Section 12.4.1: p.108).
For example, if the number of traces is set to 1, the LINE6.GPS may look like this:
Trace #1 at position 0.00
$GPGGA,134713.00,4338.221086,N,07938.421365,W,2,06,2.1,152.51,M,-35.09,M,5.0,0118*79
$GPVTG,34.0,T,,,001.4,N,002.5,K,D*70
$GPGSA,A,3,30,26,10,13,24,06,,,,,,,4.2,2.1,3.6*36
Trace #2 at position 0.05
$GPGGA,134713.00,4338.221086,N,07938.421365,W,2,06,2.1,152.51,M,-35.09,M,5.0,0118*79
$GPVTG,34.0,T,,,001.4,N,002.5,K,D*70
$GPGSA,A,3,30,26,10,13,24,06,,,,,,,4.2,2.1,3.6*36
Trace #3 at position 0.10
$GPGGA,134713.00,4338.221086,N,07938.421365,W,2,06,2.1,152.51,M,-35.09,M,5.0,0118*79
$GPVTG,34.0,T,,,001.4,N,002.5,K,D*70
$GPGSA,A,3,30,26,10,13,24,06,,,,,,,4.2,2.1,3.6*36
Trace #4 at position 0.15
$GPGGA,134713.00,4338.221086,N,07938.421365,W,2,06,2.1,152.51,M,-35.09,M,5.0,0118*79
$GPVTG,34.0,T,,,001.4,N,002.5,K,D*70
$GPGSA,A,3,30,26,10,13,24,06,,,,,,,4.2,2.1,3.6*36
Note that when the Reading per Trace option is on, it is still possible to add fiducial markers to
the GPS file. These will appear as F1, F2 etc. between the trace numbers. For example, a
portion of LINE6.GPS may look like this:
Trace #85 at position 4.20
$GPGGA,134850.00,4338.204868,N,07938.429003,W,2,06,2.1,152.60,M,-35.09,M,4.2,0118*74
$GPVTG,152.6,T,,,002.3,N,004.3,K,D*43
$GPGSA,A,3,30,26,10,13,24,06,,,,,,,4.2,2.1,3.7*37
F1
$GPGGA,134850.00,4338.204868,N,07938.429003,W,2,06,2.1,152.60,M,-35.09,M,4.2,0118*74
$GPVTG,152.6,T,,,002.3,N,004.3,K,D*43
$GPGSA,A,3,30,26,10,13,24,06,,,,,,,4.2,2.1,3.7*37
Trace #86 at position 4.25
$GPGGA,134851.00,4338.204362,N,07938.428362,W,2,06,2.1,152.40,M,-35.09,M,5.2,0118*72
$GPVTG,136.9,T,,,002.8,N,005.2,K,D*45
$GPGSA,A,3,30,26,10,13,24,06,,,,,,,4.2,2.1,3.7*37

Noggin 12-Survey & Map Mode
105
3) Fuducial Tagging mode means that whenever a fiducial marker (F1, F2 etc.) is
added to the data (see Section 12.2.4: P.72), a data string of GPS information will be
added to a file. This file has the same name as the data file i.e. LINE6, but with a
GPS extension. This file can be accessed after transferring the GPR data files to an
external PC (see Section 12.4.1: p.108).
For example, LINE6.GPS may look like this:
F1
$GPGGA,134218.00,4338.190204,N,07938.438411,W,2,05,2.6,154.60,M,-35.09,M,4.0,0118*7B
$GPVTG,356.8,T,,,000.2,N,000.4,K,D*4B
$GPGSA,A,3,30,10,13,24,06,,,,,,,,4.3,2.6,3.4*36
F2
$GPGGA,134219.00,4338.190294,N,07938.438409,W,2,05,2.6,154.45,M,-35.09,M,5.0,0118*7C
$GPVTG,1.3,T,,,000.4,N,000.7,K,D*44
$GPGSA,A,3,30,10,13,24,06,,,,,,,,4.3,2.6,3.4*36
F3
$GPGGA,134221.00,4338.190261,N,07938.438285,W,2,05,2.6,154.05,M,-35.09,M,5.2,0118*79
$GPVTG,10.0,T,,,000.2,N,000.4,K,D*72
$GPGSA,A,3,30,10,13,24,06,,,,,,,,4.3,2.6,3.4*36
F4
$GPGGA,134222.00,4338.190397,N,07938.438255,W,2,05,2.6,153.95,M,-35.09,M,5.0,0118*73
$GPVTG,9.8,T,,,000.3,N,000.5,K,D*42
$GPGSA,A,3,30,10,13,24,06,,,,,,,,4.3,2.6,3.4*36
If the GPS mode is set to Reading per Trace or Fiducial Tagging AND the Noggin is Run Without
Saving Data (see Section 12.1.5: P.68), it is still possible to log GPS data strings. Every time a
fiducial marker is added to the data (see Section 12.2.4: P.72), a data string of GPS information is
added to a file. This file is called TAGGED.GPS and can be exported and/or deleted using the
Noggin File Management (see Section 12.4: P.108).
An example of a TAGGED.GPS file is shown below.
New File 09-18-2000 13:53:38
F1
$GPGGA,134227.00,4338.190520,N,07938.438280,W,2,05,2.6,153.98,M,-35.09,M,4.6,0118*7E
$GPVTG,347.7,T,,,000.3,N,000.5,K,D*44
$GPGSA,A,3,30,10,13,24,06,,,,,,,,4.3,2.6,3.4*36
F2
$GPGGA,134228.00,4338.190238,N,07938.438286,W,2,05,2.6,153.87,M,-35.09,M,4.4,0118*75
$GPVTG,5.4,T,,,000.2,N,000.4,K,D*42
$GPGSA,A,3,30,10,13,24,06,,,,,,,,4.3,2.6,3.4*36
F3
$GPGGA,134229.00,4338.190277,N,07938.438273,W,2,05,2.6,153.76,M,-35.09,M,5.4,0118*7A
$GPVTG,23.4,T,,,000.1,N,000.2,K,D*73
$GPGSA,A,3,30,10,13,24,06,,,,,,,,4.3,2.6,3.4*36
F4
$GPGGA,134231.00,4338.190127,N,07938.438362,W,2,05,2.6,154.59,M,-35.09,M,5.0,0118*7A
$GPVTG,20.2,T,,,000.2,N,000.3,K,D*74
$GPGSA,A,3,30,10,13,24,06,,,,,,,,4.3,2.6,3.4*36
********************************************************************************
New File 09-18-2000 13:55:36
F1
$GPGGA,134259.00,4338.192453,N,07938.449096,W,2,06,2.4,153.14,M,-35.09,M,5.4,0118*75
$GPVTG,310.9,T,,,000.5,N,001.0,K,D*4A
$GPGSA,A,3,04,30,10,13,24,06,,,,,,,3.2,2.4,2.1*32
F2
$GPGGA,134301.00,4338.192559,N,07938.449176,W,2,06,2.4,153.17,M,-35.09,M,5.0,0118*7A
$GPVTG,314.4,T,,,000.6,N,001.1,K,D*41
$GPGSA,A,3,04,30,10,13,24,06,,,,,,,3.2,2.4,2.1*32
F3

12-Survey & Map Mode Noggin
106
4) GPR data out port mode means that the GPR data stream will be output to the serial
port of the DVL. This is for users who wish to read the GPR data into their own PC or
other device. Contact Sensors & Software Inc. for more details if you want to use this
option.
Note that this option slows down data acquisition speeds.
Baud Rate
The baud rate is the speed that data is sent from the GPS receiver to the serial port of the DVL.
The available options are: 2400, 4800, 9600 (default) or 19200.
Stop Bits
The available settings for Stop Bits are: 1 (default) or 2.
Data Bits
The available settings for Data Bits are: 7 or 8 (default).
Parity
The available settings for Parity are: none (default), odd or even.
End String
The GPS receiver can be set up to send one or more types of data strings to the DVL. These
strings are called NMEA-0183 strings and each contains positional or other information in
specific formats. Each type of string is specified by a 5-character prefix. There are numerous
NMEA strings but examples of three different NMEA strings (GPGGA, GPVTG and GPGSA) are
shown below.
$GPGGA,134713.00,4338.221086,N,07938.421365,W,2,06,2.1,152.51,M,-35.09,M,5.0,0118*79
$GPVTG,34.0,T,,,001.4,N,002.5,K,D*70
$GPGSA,A,3,30,26,10,13,24,06,,,,,,,4.2,2.1,3.6*36
$GPGGA,134713.00,4338.221086,N,07938.421365,W,2,06,2.1,152.51,M,-35.09,M,5.0,0118*79
$GPVTG,34.0,T,,,001.4,N,002.5,K,D*70
$GPGSA,A,3,30,26,10,13,24,06,,,,,,,4.2,2.1,3.6*36
$GPGGA,134713.00,4338.221086,N,07938.421365,W,2,06,2.1,152.51,M,-35.09,M,5.0,0118*79
$GPVTG,34.0,T,,,001.4,N,002.5,K,D*70
$GPGSA,A,3,30,26,10,13,24,06,,,,,,,4.2,2.1,3.6*36
$GPGGA,134713.00,4338.221086,N,07938.421365,W,2,06,2.1,152.51,M,-35.09,M,5.0,0118*79
$GPVTG,34.0,T,,,001.4,N,002.5,K,D*70
$GPGSA,A,3,30,26,10,13,24,06,,,,,,,4.2,2.1,3.6*36
Before using the GPS with the Noggin, the DVL software needs to know the prefix of the LAST
string being sent in each group. In the example above, three strings are being sent each time
(GPGGA, GPVTG and GPGSA). Since GPGSA is the last one being sent in each group, the End
String needs to be specified as GPGSA.
To see what the End String is for your particular GPS, run System Test #1 and note the first 5
characters on the last line after each series of strings is written to the screen. These are the 5
characters that need to be filled in under End String.

Noggin 12-Survey & Map Mode
107
The End String option allows the user to fill in the 5 character GPS prefix. Use the Left and Right
buttons to move left or right to different characters in the string. The currently selected character
will have an “^” under it. To change the letter of the current character, use the Next button to
change it to the next letter in the alphabet and the Previous button to change it to the previous
letter in the alphabet. Using these keys all 5 characters can be filled in with the necessary GPS
End String.
See the GPS Receiver User’s Guide for details on how to set up the receiver to output specific
NMEA strings or groups of NMEA strings.
System Test #1
After all the settings above have been input and the GPS receiver is attached to the serial port on
the DVL, the user can test that the DVL is receiving the GPS output by using the Test option.
If the NMEA strings are successfully being read by the DVL they will appear on the DVL screen.
This is a good time to note the prefix of the last NMEA string in the list and input it in the End
String setting above.
If the NMEA strings do not appear, check that the port settings are correct. It is also possible that
a crossover cable is required between the output cable of the GPS receiver and the serial port on
the DVL.
System Test #2
Once the GPS system is running successfully, System Test #2 can be used to graphically display
the GPS data. This screen displays the GPS Time, Latitude, Longitude and Altitude as well as
other values indicating the accuracy of the GPS reading. The GPS position is also displayed in a
square that can be Zoomed from 2 metres square to 16384 metres square.
12.3.6 Set Defaults
To reset all the parameter settings back to the factory default settings press the 6 button (labelled
Set Defaults).

12-Survey & Map Mode Noggin
108
12.4 Noggin File Management
The File Management option is available by pressing 2 from the main Noggin menu.
The File Management menu allows the user to delete data from the DVL and copy data from the
internal compact flash drive to the removable compact flash drive.
The Export options in this menu require the use of the optional PXFER cable and WinPXFER
software so this menu is not required for users transferring Noggin data using the removable
compact flash drive. These options allow the user to export Noggin data or the TAGGED.GPS file
(see Section 12.3.5: P.103) to a PC using the optional PXFER cable. This is described in
Appendix F.
12.4.1 Transferring Noggin Data to a PC using the Removable Drive
Files collected with the Noggin system are saved either to the Internal or the Removable drive on
the DVL. To transfer data collected on the removable drive to a PC, eject the compact flash drive
from the DVL and insert it into a user-supplied card reader connected to a PC. Use the Windows
Explorer program to make a new folder on the PC, read the removable drive and copy the
Noggin data files to the new folder.
If data were collected to the internal drive of the DVL (Section 12.1.7: p.69), the data can be
copied to the removable drive so it can be transferred to a PC (see Section 12.4.2: p.109).
Figure: 12-17 Noggin data files saved to the removable drive are easily transferred to a PC. First, power down the
DVL, then (i) loosen both of the finger-screws on the top of the DVL so the drive door can swing open freely. (ii) Press
the button to partially eject the compact flash drive. (iii) Remove the drive and insert it into a PC card reader (user sup-
plied). Copy the Noggin data files from the drive into a folder on the PC using the Windows Explorer program. The Win-
PXFER program can then be used to view the Noggin data.

Noggin 12-Survey & Map Mode
109
12.4.2 Copying Noggin Data from the Internal Drive to the Removable
Drive
If data were collected to the internal drive of the DVL (Section 12.1.7: p.69), the data can be
copied to the removable drive so the data transfer method described above can be used. To copy
Noggin data from the internal drive to the removable drive, from the Noggin menu select 2 - File
Management and then select 7 - Copy Internal to Removable.
12.4.3 Transferring Noggin Data to a PC using the PXFER Cable
Files collected with the Noggin system are saved to the Internal or the Removable drive on the
DVL. While the method described above, of transferring data by ejecting the removable drive, is
the usual method of data transfer, data can also be transferred to a PC using the optional PXFER
cable and the WinPXFER program. This process is described in Appendix F.
12.4.4 Viewing Data Files on the External Computer
After transferring data files to the external computer the Noggin data files can be viewed,
processed and plotted using the EKKO_View, EKKO_3D and EKKO_Mapper software.
Appendix A contains details about the file format of Noggin data.
12.4.5 Deleting Data on the DVL
After data has been successfully transferred to an external computer or if the data is longer
required, the whole Line or Grid project can be deleted from the DVL. From the File
Management main menu, select Delete Line Project or Delete Grid Project. The next screen lists
all the current projects.
To delete a project, use the up and down arrows to highlight it and then press the DEL button.
It is also possible to use the TAG button to select several projects and delete them all at once.
Use the up and down arrows to highlight the projects, the TAG button to tag each project and
then press the DEL button to delete the data from the DVL.
Before the project is deleted, the user is asked to confirm the deletion by pressing Yes or No. If
the answer to the question is No, the project is not deleted.
This menu also allows the user to delete the TAGGED.GPS file.

12-Survey & Map Mode Noggin
110
12.5 Noggin Utilities
Pressing the number 4 on the main menu selects Utilities. This menu has utility programs to
change the date and time on the DVL and also calibrate the odometer.
12.5.1 Time and Date
The date and time are saved with the data files. The DVL date and time setting can be changed
by moving to one or more of the appropriate fields and editing the current setting. The LEFT and
RIGHT arrows are used to move between fields. To change any of the numbers or months, use
the UP and DOWN arrows to increase or decrease the value. When the desired date and time
are set, press ENTER to save the changes.
12.5.2 Odometer Calibration
The odometer should be calibrated periodically to ensure accuracy.
Noggin Smart Systems can take input from several different odometers.
It is very important that the user selects and calibrates the odometer appropriate for their
Smart System.
When Odometer Calibration is selected, the user is prompted to select the odometer that is being
used with the Smart System.
If a SmartCart System is being used, select one of the two SmartCart odometers (usually #1).
If a SmartHandle system is being used, select one of the two SmartHandle odometers (usually
#1).
If the system is being towed behind a vehicle and using the transmission odometer to trigger the
system, select one of the two Vehicle odometers (usually #1).
The odometers labelled Other are to be used in future configurations.
Once an odometer is selected, the user is prompted to either 1) manually enter the odometer
calibration factor or 2) to actually calibrate the odometer over a known distance. To achieve the
highest accuracy, it is recommended that the user choose option number 2 - Odometer
Calibration.
When Odometer Calibration is selected, the user is prompted to select the length of the line to
calibrate on. There are 8 different choices in metres and 8 choices in feet. To toggle the units
between metres and feet, press the B button. Pressing the A button on this screen gives the
additional option to select a user-defined value. The user-defined value can range from 0.01 to
5000 metres or 0.01 to 26400 feet.
When the calibration distance has been selected follow the directions on the screen:
1) Set the cart at zero and press A
2) Move the cart the selected distance and press B
3) Press A to exit.
Odometer calibration values for the SmartCart odometer should be around 1080.

Noggin 12-Survey & Map Mode
111
Odometer calibration values for the SmartHandle odometer should be around 1530.
Odometer calibration values for the Vehicle odometer vary but may be around 50.
12.5.3 Upgrade
Upgrade requires the use of the optional PXFER cable so this menu is not required for users
who upgrade their DVL firmware using a removable compact flash drive.
The menu allows the user to enter Upgrade mode to update the firmware on the DVL. Selecting
Upgrade puts the DVL into listen mode to allow a software upgrade to be transferred from an
external PC to the DVL using the PXFER and WinPXFER cable. Avoid pressing this button until
the instructions in a software upgrade tell you to. Once pressed, the DVL must have the power
disconnected to exit from this menu item.
12.5.4 System Information
This option can be used to list system information that may be useful to troubleshoot a problem
with the Noggin. The information is intended for the use of Sensors & Software staff to assist in
solving a problem with the Noggin system.
System information can be listed to the screen, printed directly to an attached printer or
transferred to a PC.
To print the information to a printer, attach the printer to the parallel port of the DVL and then
press the B button.
To transfer the information file to a PC, attach the parallel XFER cable from the parallel port of the
PC to the parallel port of the DVL. Then run the WinPXFER program on the PC (see Section
12.4.1: p.108) and press the 1 button.
Sensors & Software technical staff may request that this information be sent to them. A printed
copy of the information can be faxed to Sensors & Software Inc. If the data is transferred to a
PC, the data file can be e-mailed to Sensors & Software Inc.
12.5.5 DVL Recording Space
This option shows, based on the current data collection settings, the total number of traces that
can be collected before the DVL memory is full. It also lists, based on the current Station Interval,
the total distance of data that can be collected before the DVL memory is full.
12.5.6 Transfer Mode
Transfer Mode requires the use of the optional PXFER cable so this menu is not required for
users transferring Noggin data using the removable compact flash drive. This menu allows the
user to set the transfer mode to Normal or Turbo depending on what type of PXFER cable they
have (see Appendix F).

13-Troubleshooting Noggin
112
13 Troubleshooting
Noggin Smart Systems are designed to minimize user problems; however, all electronic devices
are subject to possible failure. The following are troubleshooting hints in the likelihood of
occurrence if your Smart System fails to operate.
13.1 Power Supply
The most common problem that can occur while trying to run a system is insufficient power. The
battery may be dead or have a low voltage. If the system is being run from AC, there may be a
problem with the AC power supply or adapter.
If there is enough power to run the DVL, the upper red LED on the front of the DVL will light up
when the battery is plugged into the system. If this light is on and the DVL boots up, runs and
displays the main menu, next check that the red light on the connector to the Noggin is on. If this
light is off then there is a problem with the connection from the DVL to the Noggin. Check the
connection and this part of the cable.
If the DVL is running but the Noggin system will not run, go to the main menu and check that
battery voltage in the lower left corner is above 10.2 volts. If not, the battery needs to be
recharged or replaced for the Noggin to run (see below).
If the battery voltage is less than about 10.2 volts, the DVL may not turn on and the upper red
LED will flash or not illuminate.
Check the battery voltage with a voltmeter. Try to do this while the system is still attached to the
Smart System to get a true measure of the voltage while under load (it will be necessary to open
the SmartCart battery case or belt battery case and connect the voltmeter to the positive and
negative battery terminals). If the battery has a low voltage or seems dead, try the system with
another battery (if available), or give the battery a good 12-14 hour charge and try running the
system again.
If the battery does not charge up to 12 Volts or more, it should be replaced.
Smart System batteries are fused to protect the system. For the SmartCart system, open the
battery case and check that the 10 Amp fuse is OK. If necessary, replace it with one of the spare
fuses available inside the battery case. The smaller belt batteries available for the SmartHandle
systems are also fused. Remove the battery from padded casing and check the 5 Amp fuse.
Replace the fuse if necessary.
13.2 System Communications
If the system power supply is OK but the Noggin does not respond there may be a
communication failure between the DVL and the Noggin. This type of failure is often indicated by
a 10000 series error number like 10012.
If an error occurs, an error message will appear in the bottom left section of the Noggin screen.
EXIT the program and turn off the Digital Video Logger. Disconnect the power source to
completely shut down the system.

Noggin 13-Troubleshooting
113
Make sure the cables are not damaged and that all cable connections are tightly secured. Use a
slotted screwdriver to snug up the connections. Sometimes vibrations cause the cable
connections to loosen just a bit and break contact and this can cause errors. Disconnecting
cables and reconnecting them may provide a better contact and solve the problem. Turn the
Digital Video Logger back on and try running the system again.
If the power supply and cable are OK, the problem is likely a failure of the DVL. The DVL has no
user-serviceable parts so it will have to be returned to Sensors & Software Inc for inspection and
possible repair (see Section 13.6: P.114).
13.3 System Overheating
The Noggin systems are designed to operate to a maximum internal temperature of 70 C or 158
F. In situations of high ambient temperatures or long exposure to direct sun, this maximum
internal temperature may be exceeded and cause the system to fail. While the temperature
displayed on the DVL in the lower left corner of the main menu indicates the internal temperature
of the DVL and not the Noggin, this temperature should give an idea of whether the Noggin is
overheating.
If you suspect that the Noggin system is overheating, shut it off and give it a chance to cool down
in a shady location before trying to run it again. Placing a wet cloth on top of the Noggin may
help in cooling it down.
If the situation is such that the high temperatures or direct sun cannot be avoided, it may be a
good idea to put some sort of shade over the Noggin.
Contact Sensors & Software Inc. if the problem persists as there may be defective electronic
components that need to be replaced (see Section 13.6: P.114).
13.4 DVL Problem
While the DVL has been ruggedized as much as possible, it should be handled in much the same
way a notebook computer is. If the DVL does not power up and boot up, there may be a problem
with the CPU or the storage media. If this occurs, contact Sensors & Software Inc. (see Section
13.6: P.114).
13.5 Noggin Problem
When the Smart System is powered up and the user selects data acquisition in Noggin or Noggin
mode, the Noggin system goes through a self-calibration sequence. While the self-calibration is
occurring the user sees the words “Booting Noggin” in the lower left corner of the DVL screen.
These words are followed by a number that counts up from 1. Normally, once the count reaches
6 the text disappears and the Noggin is ready to collect data. Sometimes, however, this count
goes beyond 6 and keeps going without stopping. This indicates an internal problem with the
Noggin. No error message will be displayed on the screen and the only way to exit from the
screen is to pull out the power connection.

13-Troubleshooting Noggin
114
If this error occurs, power the system down, power it up again and retry data acquisition. If the
error persists, contact Sensors & Software Inc. (see Section 13.7: P.114).
13.6 Creating a Test Line for Data Quality
One of the best ways of detecting problems with the GPR system is, shortly after receiving the
system and getting comfortable with its operation, to collect a line of data at a convenient, easily
accessible location. The line does not have to be too long but 100 - 200 traces is a good guide.
This data line should be saved electronically and perhaps plotted out on paper and dated. The
test line could be collected say, every 6 months and, by reviewing the previous data, system
problems can be detected early. As well, if there is a suspected problem with the system, this test
line could be collected and compared with earlier tests.
13.7 Contacting Sensors & Software Inc.
If you develop problems with your Noggin system, contact your agent or Sensors & Software Inc.
Sensors & Software Inc.’s hours of operation are 9:00 AM to 5:00 PM Eastern Standard Time,
Monday to Friday. You can contact Sensors & Software Inc. at:
Sensors & Software Inc.
1040 Stacey Court
Mississauga, Ontario
Canada L4W 2X8
Tel: (905) 624-8909
Fax: (905) 624-9365
E-mail: sales@sensoft.ca
When contacting Sensors & Software Inc., please have the following information
available:
1) Noggin and/or DVL Serial Number.
2) Version number of the data acquisition software.
3) The error number or message appearing.
4) A brief description of when the error is happening and the operating conditions
(temperature, humidity, sunshine, system and survey setup, etc.).
5) Sensors & Software Inc. technical staff may request a copy of the System Information
file be sent to them by fax or e-mail. See Section 12.5.4: P.111 on how to view, print
and download this file.
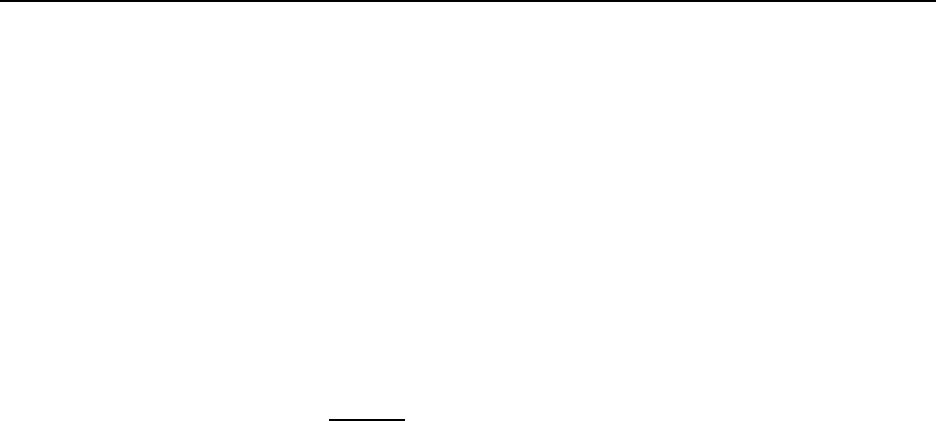
Noggin 14-Care and Maintenance
115
14 Care and Maintenance
14.1 Battery Care
Smart Systems use 12-volt sealed lead acid batteries. They are fused with a 10 Amp fuse to
protect them from short circuit damage.
The SmartCart battery unit uses contains a 9 Amp-hour battery. The battery unit should run the
Cart Noggin for 4-5 hours before recharging is necessary. If long days of data surveying are
typical, a second battery unit may be a useful item.
If batteries are maintained in a charged condition they will give long life and reliable service.
Improper use and lack of maintenance will greatly reduce their life.
Sealed lead acid batteries should NEVER be left in a discharged condition for any period of time.
Charge the batteries as soon as possible after use.
Charge batteries at room temperature whenever possible.
The Noggin and DVL contain a voltage monitoring circuit that will turn off the unit when the input
voltage drops below 10.2 volts.
If a battery has been deeply discharged or left in a discharged condition for some period of time it
may not accept charge immediately when it is connected to the charger (The fast charge LED will
not light). If the fast charge light does not come on within 6 hours the battery should be
considered damaged and should be discarded.
Do not assume that a battery that is still charging after 8 hours is nearing the end of its charge
cycle. Typical charging time for an empty battery is 12-14 hours from start of fast charge.
Ensure that the batteries are fully charged before storing. If practical, store the batteries in a cool
place, 10
o
c (a refrigerator is ideal), but make sure the temperature is not likely to drop below -
30
o
C or the electrolyte may freeze and possibly split the case.
14.2 DVL Internal Battery
If the Smart System has not been powered up for an extended period of time, the internal battery
will discharge. The dead battery causes the DVL time and date to reset to January 1, 1988 at
12:00 PM. To correct the time and date see Section 12.5.1: P.110.
To recharge the internal battery the Smart System must be powered up and left running for at
least one hour and preferably longer.
14.3 Cable Care
1) The cable connectors as well as the connectors on the Noggin and DVL need to stay
clean and free of dust and moisture. Use a brush or air spray to clean dust, lint and
other foreign particles from these connectors.
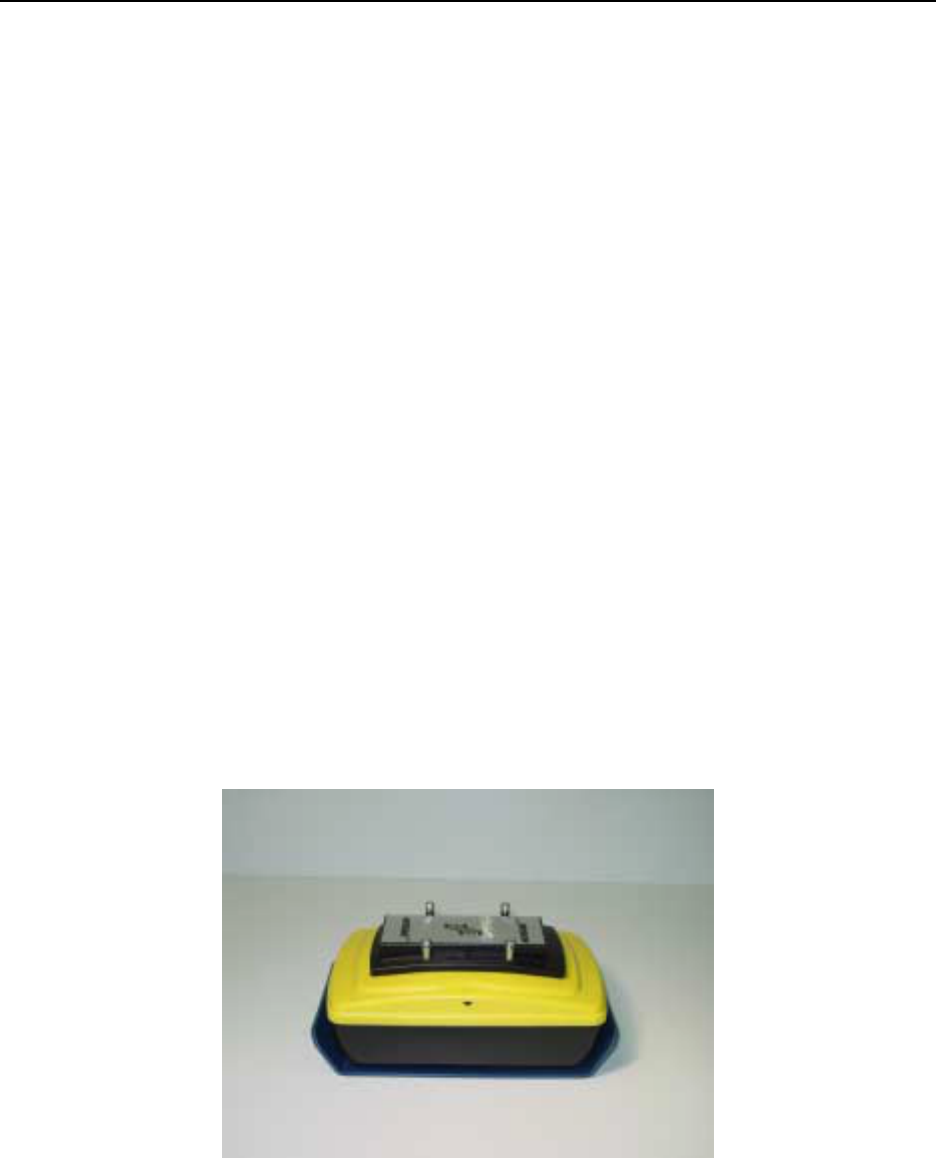
14-Care and Maintenance Noggin
116
2) When the system is not being used, make sure the connections are done up to
prevent dust and moisture from collecting inside. If the connectors are exposed,
cover them with some sort of dust cap.
3) Cables are designed to be as tough as practical.
4) Careless use of cables making them carry loads that they are not designed for can
cause internal damage.
5) Connectors are weak points in any system. With the use of this product in rough,
dusty and outdoor environments, users can minimize potential down time if they care
for cables and treat connectors with respect.
6) Cables and connectors are not designed to suspend or tow or otherwise carry the
weight of systems. They are part of the electronic circuit and should be treated
accordingly. When not in use they should be placed in their storage box.
14.4 Skid Pads
The bottom of the Noggin unit is covered with one large wear-resistant skid pad. The skid pad is
designed to protrude from the bottom of the Noggin and take the majority of the abrasive wear. If
the pad wears down enough, the less-resistant plastic housing may start to wear. If this occurs, it
is best to replace the skid pad. It is easily removed with a Phillips screwdriver and a new one can
be purchased from Sensors & Software Inc.
Note that there are two types of skid pads available. The standard type is flat and covers the
bottom of the Noggin. There is also an optional skid pad that covers the bottom of the Noggin but
also has curved edges that covers the front and back portions of the Noggin. Contact Sensors &
Software for details.
Figure: 14-1 Noggin with optional curved skid pad.

Noggin 14-Care and Maintenance
117
14.5 Storage Cases
Equipment that is transported and stored loosely is more susceptible to damage. All equipment
should be stored in its shipping case or a storage box. Sensors & Software has shipping cases
available as options for all Noggins and DVL’s.
14.6 Spare Parts
For customers working in remote areas or if downtime in the field is unacceptable, consider
buying our optional extended spares kit. This kit includes extra cables, batteries and chargers.

14-Care and Maintenance Noggin
118

Noggin Appendix A - Noggin Data file Format
A-1
Appendix A Noggin Data file Format
Noggin data consists of two files, a Header file and a Data file. The files have the same name but
different extensions. The format details of these files are given below.
Header (.HD) File:
The header file, identified by the file extension .HD, is an ASCII file. An example is shown below.
The heading identifies what each piece of information represents.
1234
Data Collected with Noggin Plus
12/10/2000
NUMBER OF TRACES = 220
NUMBER OF PTS/TRC = 156
TIMEZERO AT POINT = 31
TOTAL TIME WINDOW = 62
STARTING POSITION = 0.0000
FINAL POSITION = 10.9500
STEP SIZE USED = 0.0500
POSITION UNITS = m
NOMINAL FREQUENCY = 250.00
ANTENNA SEPARATION = 0.3048
PULSER VOLTAGE (V) = 100
NUMBER OF STACKS = 4
SURVEY MODE = Reflection
This file can be read and/or printed using any Word Processor.
Data (.DT1) File:
The data file contains as many records as there are traces. Each record in turn consists of a
header section and a data section. The header section consists of an array of 25 real*4 numbers
and a string of 28 characters which is used for annotation. The 25 element real array contains the
following information:
Item # Description
1 Trace number
2Position
3 Number of points per trace
4 Topographic data, if available
5 (not used)
6 # bytes/point (always 2 for Rev 3 firmware)
7 Time Window
8 # of stacks
9-10 reserved for GPS X position (double*8 number)
11-12 reserved for GPS Y position (double*8 number)
13-14 reserved for GPS Z position (double*8 number)
15 reserved for receiver x position

Appendix A - Noggin Data file Format Noggin
A-2
16 reserved for receiver y position
17 reserved for receiver z position
18 reserved for transmitter x position
19 reserved for transmitter y position
20 reserved for transmitter z position
21 timezero adjustment
where:point(x)= point(x+adjustment)
22 Zero flag: 0 = data okay, 1=zero data
23 (not used)
24 Time of day data collected in seconds past midnight.
25 Comment flag: 1 = comment attached.
26 - 32 Comment
The data section consists of an array of two-byte integers, one value for every data point.
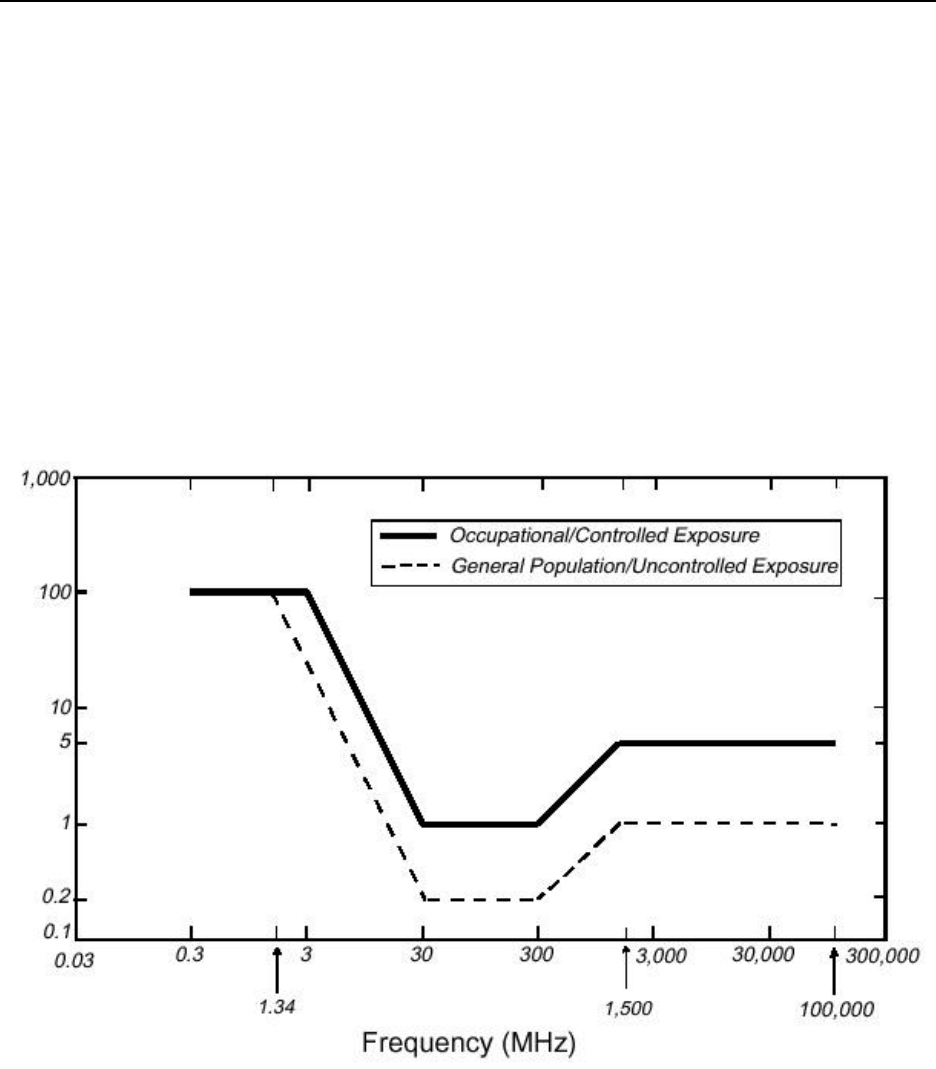
Noggin Appendix B - Health & Safety Certification
B-1
Appendix B Health & Safety Certification
Radio frequency electromagnetic fields may pose a health hazard when the fields are intense.
Normal fields have been studied extensively over the past 30 years with no conclusive epidemiol-
ogy relating electromagnetic fields to health problems. Detailed discussions on the subject are
contained in the references and the web sites listed below.
The USA Federal Communication Commission (FCC) and Occupational Safety and Health
Administration (OSHA) both specify acceptable levels for electromagnetic fields. Similar power
levels are mandated by corresponding agencies in other countries. Maximum permissible expo-
sures and time duration specified by the FCC and OSHA vary with excitation frequency. The low-
est threshold plane wave equivalent power cited is 0.2 mW/cm2 for general population over the
30 to 300 MHz frequency band. All other applications and frequencies have higher tolerances as
shown in graphically in Figure B-1.
Figure B-1: FCC limits for maximum permissible exposure (MPE) plane-wave equivalent power density mW/cm
2
.
All Sensors & Software Inc. pulseEKKO, Noggin and Conquest products are normally operated
at least 1 m from the user and as such are classified as “mobile” devices according to the FCC.
Typical power density levels at a distance of 1 m or greater from any Sensors & Software Inc.
product are less than 10
-3 mW/cm2 which are 200 to 10,000 times lower than mandated limits.
As such, Sensors & Software Inc. products pose no health and safety risk when operated in the
normal manner of intended use.
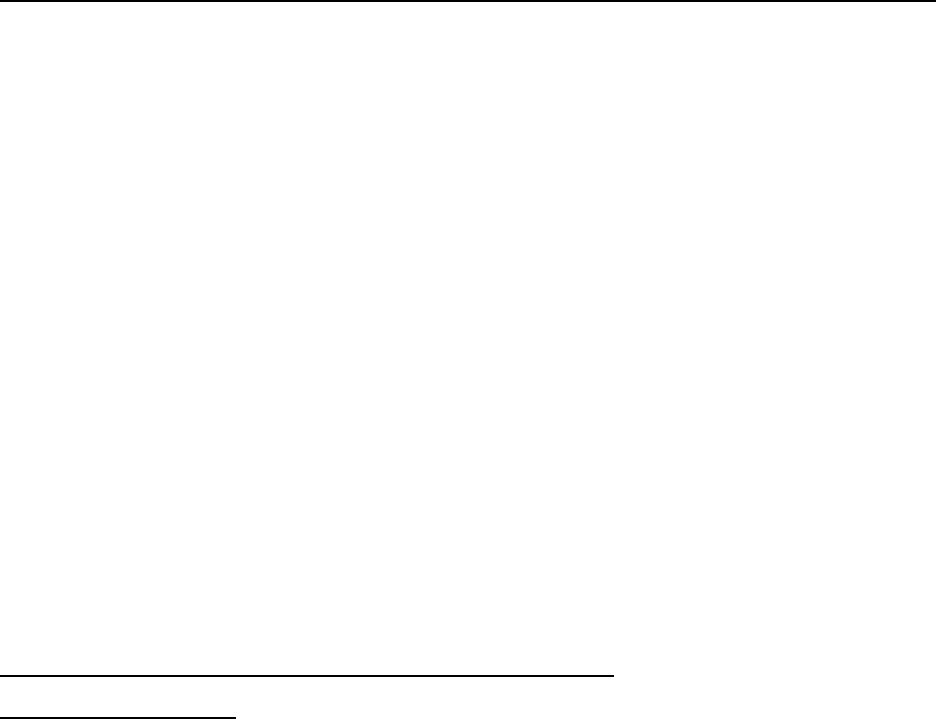
Appendix B - Health & Safety Certification Noggin
B-2
References
1. Questions and answers about biological effects and potential hazards of radio-frequency
electromagnetic field
USA Federal Communications Commission, Office of Engineering & Technology
OET Bulletin 56
(Contains many references and web sites)
2. Evaluation Compliance with FCC Guidelines for Human Exposure to Radio Frequency Elec-
tromagnetic Fields.
USA Federal Communications Commission, Office of Engineering & Technology
OET Bulletin 56
(Contains many references and web sites)
3. USA Occupational Safety and Health Administration regulations paragraph 1910.67 and
1910.263.
Web Sites
www.fcc.gov/Bureau/EngineeringTechnlogy/Documents/bulletin
www.osha-slc.gov/SLTC (see radio frequency)

Noggin Appendix C - GPR Emissions, Interference and Regulations
C-1
Appendix C GPR Emissions, Interference and Regulations
All governments have regulations on the level of electromagnetic emissions that an electronic apparatus
can emit. The objective is to assure that one apparatus or device does not interfere with any other appara-
tus or device in such a way as to make the other apparatus non-functional.
Sensors & Software Inc. extensively test their pulseEKKO, Noggin and Conquest subsurface imaging
products using independent professional testing houses and comply with latest regulations of the USA,
Canada, European Community, and other major jurisdictions on the matter of emissions.
GPR instruments are considered to be UWB (ultra-wideband) devices. The regulatory regimes worldwide
are devising new rules for UWB devices. Sensors & Software Inc. maintains close contact with the regula-
tors to help guide standard development and assure that all products conform. You should continually
monitor the "News" link on our website (www.sensoft.ca) for updates on standards.
Electronic devices have not always been designed for proper immunity. If a GPR instrument is placed in
close proximity to an electronic device, interference may occur. While there have been no substantiated
reports of interference to date, if any unusual behavior is observed on nearby devices, test if the distur-
bance starts and stops when the GPR instrument is turned on and off. If interference is confirmed, stop
using the GPR.
Where specific jurisdictions have specific GPR guidelines, these are described below.
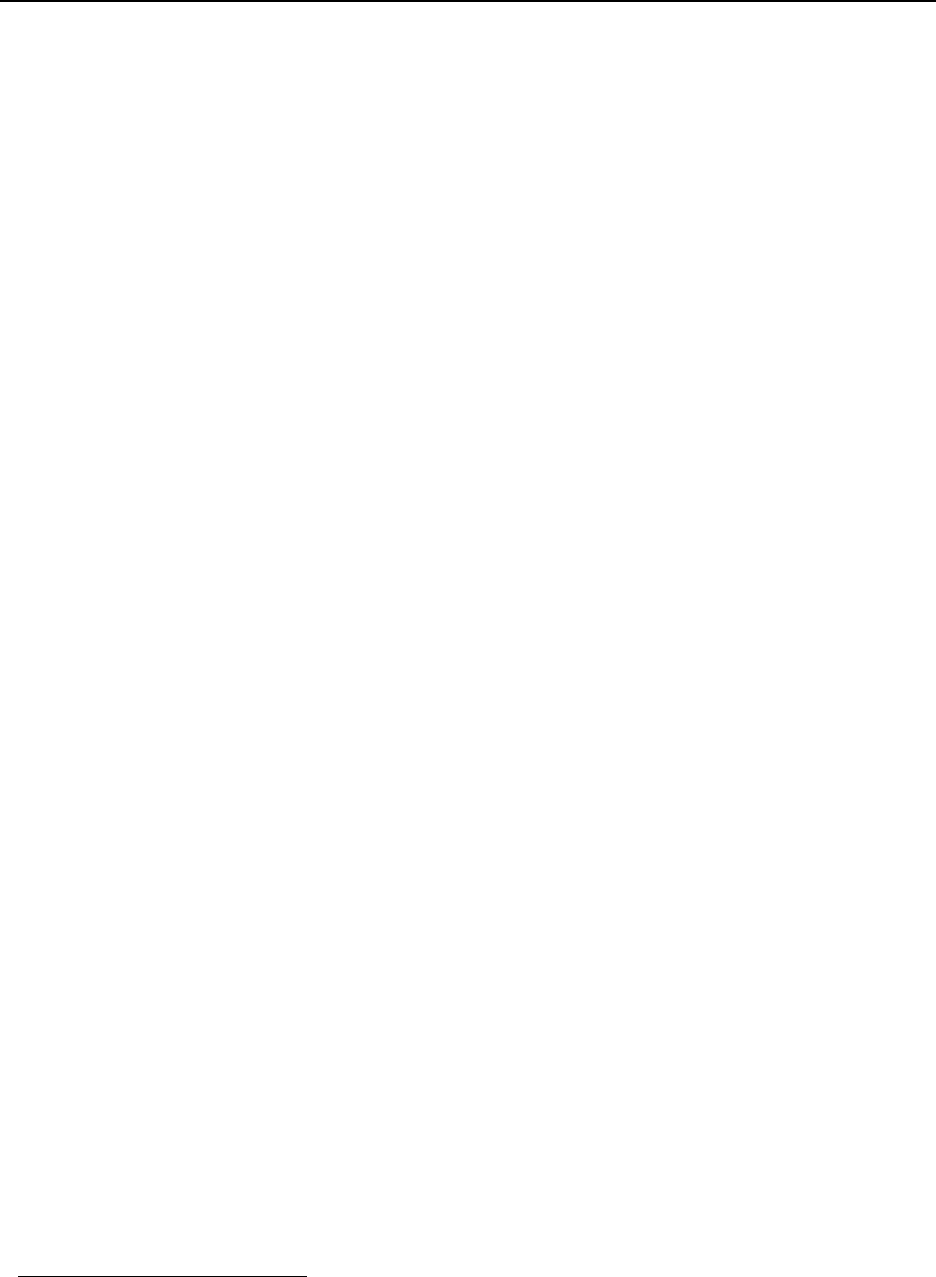
Appendix C - GPR Emissions, Interference and Regulations Noggin
C-2
C-1 FCC Regulations (USA)
This device complies with Part 15 of the USA Federal Communications Commission (FCC) Rules. Opera-
tion in the USA is subject to the following two conditions:
(1) this device may not cause harmful interference and
(2) this device must accept any interference received, including interference that may cause undesired
operation.
Part 15 – User Information
This equipment has been tested and found to comply with the limits for a Class A digital device, where
applicable, and for an ultrawide bandwidth (UWB) device where applicable, pursuant to Part 15 of the FCC
Rules. These limits are designed to provide reasonable protection against harmful interference when the
equipment is operated in a commercial environment. This equipment generates, uses and can radiate
radio frequency energy and, if not installed and used in accordance with the instruction manual, may cause
harmful interference to radio communications. Operation of this equipment in a residential area is likely to
cause harmful interference in which case the user will be required to correct the interference at his own
expense.
WARNING
Changes or Modifications not expressly approved by Sensors & Software Inc. could void the user’s author-
ity to operate the equipment.
Certification of this equipment has been carried out using approved cables and peripheral devices. The
use of non-approved or modified cables and peripheral devices constitutes a Change or Modification out-
lined in the warning above.
Operating Restrictions
Operation of this device is limited to purposes associated with law enforcement, fire fighting, emergency
rescue, scientific research, commercial mining, or construction. Parties operating this equipment must be
eligible for licensing under the provisions of Part 90 of this chapter.
FCC Interpretation of Operation Restrictions issued July 12, 2002
(FCC Order DA02-1658, paragraph 9)
The regulations contain restrictions on the parties that are eligible to operate imaging systems.
1
Under the
new regulations, GPRs and wall imaging systems may be used only by law enforcement, fire and emer-
gency rescue organizations, by scientific research institutes, by commercial mining companies, and by
construction companies. Since the adoption of the Order, we have received several inquiries from the
operators of GPRs and wall imaging systems noting that these devices often are not operated by the users
listed in the regulations but are operated under contract by personnel specifically trained in the operation of
these devices. We do not believe that the recent adoption of the UWB rules should disrupt the critical
safety services that can be performed effectively only through the use of GPRs and wall imaging systems.
We viewed these operating restrictions in the broadest of terms. For example, we believe that the limita-
tion on the use of GPRs and wall imaging systems by construction companies encompasses the inspec-
tion of buildings, roadways, bridges and runways even if the inspection finds no damage to the structure
1. See 47 C.F.R. §§15.509(b), 15.511(b), and 15.513(b)

Noggin Appendix C - GPR Emissions, Interference and Regulations
C-3
and construction does not actually result from the inspection; the intended purpose of the operation of the
UWB device is to determine if construction is required. We also believe that the GPRs and wall imaging
systems may be operated for one of the purposes described in the regulations but need not be operated
directly by one of the described parties. For example, a GPR may be operated by a private company
investigating forensic evidence for a local police department.
FCC Permitted Mode of Usage
The GPR antenna must be kept on the surface to be in compliance with FCC regulations. Use of the
antenna is not permitted if it is lifted off the surface. Use as a through-the-wall imaging device is prohib-
ited.
GPR Use Coordination
FCC regulation 15.525(c) (updated in February 2007) requires users of GPR equipment to coordinate the
use of their GPR equipment as described below:
TITLE 47--TELECOMMUNICATION
CHAPTER I--FEDERAL COMMUNICATIONS COMMISSION
PART 15_RADIO FREQUENCY DEVICES
Subpart F_Ultra-Wideband Operation Sec.
15.525 Coordination requirements.
(a) UWB imaging systems require coordination through the FCC before the equipment may be used.
The operator shall comply with any constraints on equipment usage resulting from this coordination.
(b) The users of UWB imaging devices shall supply operational areas to the FCC Office of Engineering
and Technology, which shall coordinate this information with the Federal Government through the National
Telecommunications and Information Administration. The information provided by the UWB operator shall
include the name, address and other pertinent contact information of the user, the desired geographical
area(s) of operation, and the FCC ID number and other nomenclature of the UWB device. If the imaging
device is intended to be used for mobile applications, the geographical area(s) of operation may be the
state(s) or county(ies) in which the equipment will be operated. The operator of an imaging system used
for fixed operation shall supply a specific geographical location or the address at which the equipment will
be operated. This material shall be submitted to:
Frequency Coordination Branch, OET
Federal Communications Commission
445 12
th
Street, SW, Washington, D.C.
20554
Attn: UWB Coordination
(Sensors & Software Inc. Note: The form given on the following page is a suggested format for performing
the coordination.)
(c) The manufacturers, or their authorized sales agents, must inform purchasers and users of their sys-
tems of the requirement to undertake detailed coordination of operational areas with the FCC prior to the
equipment being operated.
(d) Users of authorized, coordinated UWB systems may transfer them to other qualified users and to dif-

Appendix C - GPR Emissions, Interference and Regulations Noggin
C-4
ferent locations upon coordination of change of ownership or location to the FCC and coordination with
existing authorized operations.
(e) The FCC/NTIA coordination report shall identify those geographical areas within which the operation
of an imaging system requires additional coordination or within which the operation of an imaging system
is prohibited. If additional coordination is required for operation within specific geographical areas, a local
coordination contact will be provided. Except for operation within these designated areas, once the infor-
mation requested on the UWB imaging system is submitted to the FCC no additional coordination with the
FCC is required provided the reported areas of operation do not change. If the area of operation changes,
updated information shall be submitted to the FCC following the procedure in paragraph (b) of this section.
(f) The coordination of routine UWB operations shall not take longer than 15 business days from the
receipt of the coordination request by NTIA. Special temporary operations may be handled with an expe-
dited turn-around time when circumstances warrant. The operation of UWB systems in emergency situa-
tions involving the safety of life or property may occur without coordination provided a notification
procedure, similar to that contained in Sec. 2.405(a) through (e) of this chapter, is followed by the UWB
equipment user.[67 FR 34856, May 16, 2002, as amended at 68 FR 19751, Apr. 22, 2003]
Effective Date Note: At 68 FR 19751, Apr. 22, 2003, Sec. 15.525 was amended by revising[[Page
925]]paragraphs (b) and (e). This amendment contains information collection and recordkeeping require-
ments and will not become effective until approval has been given by the Office of Management and Bud-
get.

Noggin Appendix C - GPR Emissions, Interference and Regulations
C-5
FCC GROUND PENETRATING RADAR COORDINATION NOTICE
NAME:
ADDRESS:
CONTACT INFORMATION [CONTACT NAME AND PHONE NUMBER]:
AREA OF OPERATION [COUNTIES, STATES OR LARGER AREAS]:
FCC ID: [E.G. QJQ-NOGGIN100 FOR NOGGIN 100 SYSTEM, QJQ-NOGGIN250 FOR NOGGIN 250
SYSTEM, QJQ-NOGGIN500 FOR NOGGIN 500 SYSTEM, QJQ-NOGGIN1000 FOR NOGGIN 1000 SYS-
TEM]
EQUIPMENT NOMENCLATURE: [E.G. NOGGIN 250]
Send the information to:
Frequency Coordination Branch., OET
Federal Communications Commission
445 12
th
Street, SW
Washington, D.C. 20554
ATTN: UWB Coordination
Fax: 202-418-1944
INFORMATION PROVIDED IS DEEMED CONFIDENTIAL

Noggin Appendix C - GPR Emissions, Interference and Regulations
C-6
C-2 ETSI Regulations for the EC (European Community)
In the European Community (EC), GPR instruments must conform to ETSI (European Technical Standards
Institute) standard EN 302 066-1 v1.2.1. Details on individual country requirements for licensing are coor-
dinated with this standard. For more information, contact Sensors & Software’s technical staff.
All Sensors & Software ground penetrating radar (GPR) products offered for sale in European Community
countries or countries adhering to ETSI standards are tested to comply with EN 302 066 v1.2.1.
For those who wish to get more detailed information, they should acquire copies of the following docu-
ments available from ETSI.
ETSI EN 302 066-1 V1.2.1 (February 2008) Electromagnetic compatibility and Radio spectrum Matters
(ERM); Ground and Wall- Probing Radar applications (GPR/WPR) imaging systems; Part 1: Technical
characteristics and test methods
ETSI EN 302 066-2 V1.2.1 (February 2008) Electromagnetic compatibility and Radio spectrum Matters
(ERM); Ground and Wall- Probing Radar applications (GPR/WPR) imaging systems; Part 2: Harmonized
EN covering essential requirements of article 3.2 of the R&TTE Directive
ETSI TR 101 994-2 V1.1.2 (March 2008) Electromagnetic compatibility and Radio spectrum Matters
(ERM); Short Range Devices (SRD); Technical characteristics for SRD equipment using Ultra Wide Band
technology (UWB); Part 2: Ground- and Wall- Probing Radar applications; System Reference Document

Noggin Appendix C - GPR Emissions, Interference and Regulations
C-7
C-3 Industry Canada Regulations
Industry Canada published it regulations for ground penetrating radar (GPR) on Mar 29 2009 as part of the
RSS-220 titled 'Devices Using Ultra-Wideband (UWB) Technology'.
Industry Canada has made a unique exception for GPR by not requiring user licensing. The user does
have to comply with the following directives:
(1) This Ground Penetrating Radar Device shall be operated only when in contact with or within
1 m of the ground.
(2) This Ground Penetrating Radar Device shall be operated only by law enforcement agencies,
scientific research institutes, commercial mining companies, construction companies, and
emergency rescue or firefighting organizations.
Should the ground penetrating radar be used in a wall-penetrating mode then the following restriction
should be noted by the user:
(1) This In-wall Radar Imaging Device shall be operated where the device is directed at the wall
and in contact with or within 20 cm of the wall surface.
(2) This In-wall Radar Imaging Device shall be operated only by law enforcement agencies, sci-
entific research institutes, commercial mining companies, construction companies, and emer-
gency rescue or firefighting organizations.
Since operation of GPR is on a licence-exempt basis, the user must accept the following:
Operation is subject to the following two conditions: (1) this device may not cause interference, and (2) this
device must accept any interference, including interference that may cause undesired operation of the
device.

Noggin Appendix D - Instrument Interference
D-1
Appendix D Instrument Interference
Immunity regulations place the onus on instrument/apparatus/device manufacturers to assure
that extraneous interference will not unduly cause an instrument/apparatus/device to stop func-
tioning or to function in a faulty manner.
Based on independent testing house measurements, Sensors & Software Inc. systems comply
with such regulations in Canada, USA, European Community and most other jurisdictions. GPR
devices can sense electromagnetic fields. External sources of electromagnetic fields such as TV
stations, radio stations and cell phones, can cause signals detectable by a GPR which may
degrade the quality of the data that a GPR device records and displays.
Such interference is unavoidable but sensible survey practice and operation by an experienced
GPR practitioner can minimize such problems. In some geographic areas emissions from exter-
nal sources may be so large as to preclude useful measurements. Such conditions are readily
recognized and accepted by the professional geophysical community as a fundamental limitation
of geophysical survey practice. Such interference being present in the GPR recordings is not
considered as an equipment fault or as a failure to comply with immunity regulations.

Appendix D - Instrument Interference Noggin
D-2

Noggin Appendix E - Safety Around Explosive Devices
E-1
Appendix E Safety Around Explosive Devices
Concerns are expressed from time to time on the hazard of GPR products being used near blast-
ing caps and unexploded ordnance (UXO). Experience with blasting caps indicates that the
power of Sensors & Software Inc.’s GPR products are not sufficient to trigger blasting caps.
Based on a conservative independent testing house analysis, we recommend keeping the GPR
transmitters at least 5 feet (2m) from blasting cap leads as a precaution. Some customers do
experimental trials with their particular blasting devices to confirm with safety. We strongly rec-
ommend that GPR users routinely working with explosive devices develop a systematic safety
methodology in their work areas.
The UXO issue is more complex and standards on fuses do not exist for obvious reasons. To
date, no problems have been reported with any geophysical instrument used for UXO. Since
proximity and vibration are also critical for UXO, the best advice is to be cautious and understand
the risks.

Appendix E - Safety Around Explosive Devices Noggin
E-2
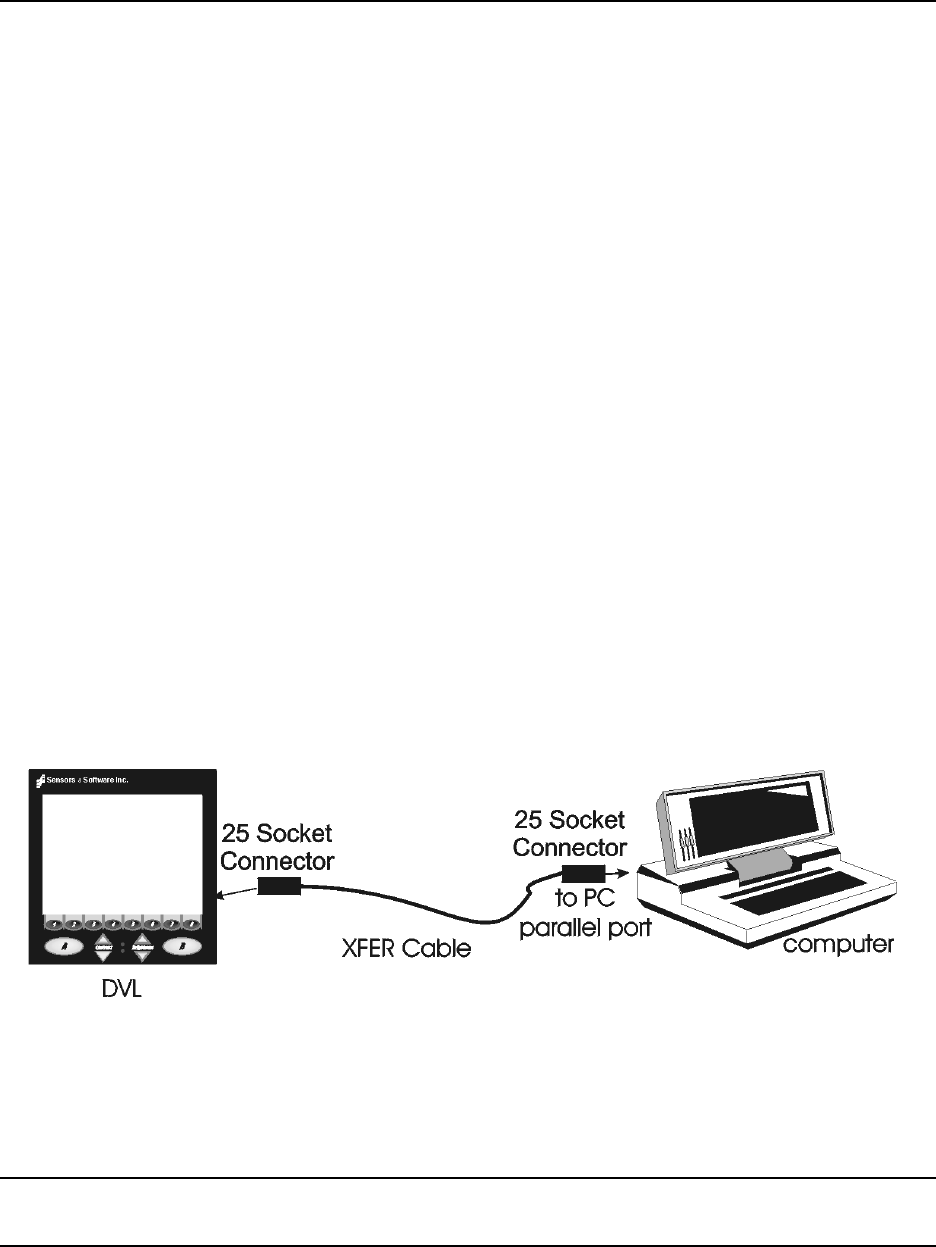
Noggin Appendix F - Using the PXFER Cable and WinPXFER Software
F-1
Appendix F Using the PXFER Cable and WinPXFER Software
F1 Transferring Data to a PC using the PXFER Cable
There are two methods available to transfer data files from the DVL to a PC. The usual method is
to save the data to the removable compact flash drive that is accessible using the door on the top
of the DVL. After powering down the DVL, this drive can be removed and inserted into a card
reader attached to a PC.
The other method of transferring data files to a PC, described in detail in this section, requires the
use of the optional PXFER cable and WinPXFER software.
There are two ways of transferring data to PC using the PXFER cable and WinPXFER. This
section describes transferring all data files to a PC. The other method is to transfer one or more
screens of data as a single PCX graphics file (see F2: p.F-6). This other type of transfer is
appropriate when the user wants to transfer a small amount of data to an external computer for
use with third-party graphics software packages like Microsoft Paint and Word.
To transfer all the data buffers from the DVL to an external computer, the computer must be
connected to the DVL using the special parallel XFER cable that is supplied with the system
(Section F1.1: p.1). Note that this is a special cable and standard 25 pin to 25 pin or Laplink
cables will not work. As well, the computer must have the WinPXFER program running on it
(Section F1.3: p.3).
F1.1 Connecting the Digital Video Logger to a PC
The Smart System comes with a separate cable called the parallel XFER cable. This cable is
designed to connect the DVL to an external computer.
Figure F-1: Parallel XFER cable (CABL0023) connections
The 2 connections that must be made before attempting to transfer data are:
1) Attach the 25 socket parallel connector to the 25 socket parallel port on back of the
Digital Video Logger, and
2) Attach the 25 socket parallel connector the parallel port of the external computer.
WARNING: To avoid damaging any of the components, turn off the DVL and computer
before making any of these connections.
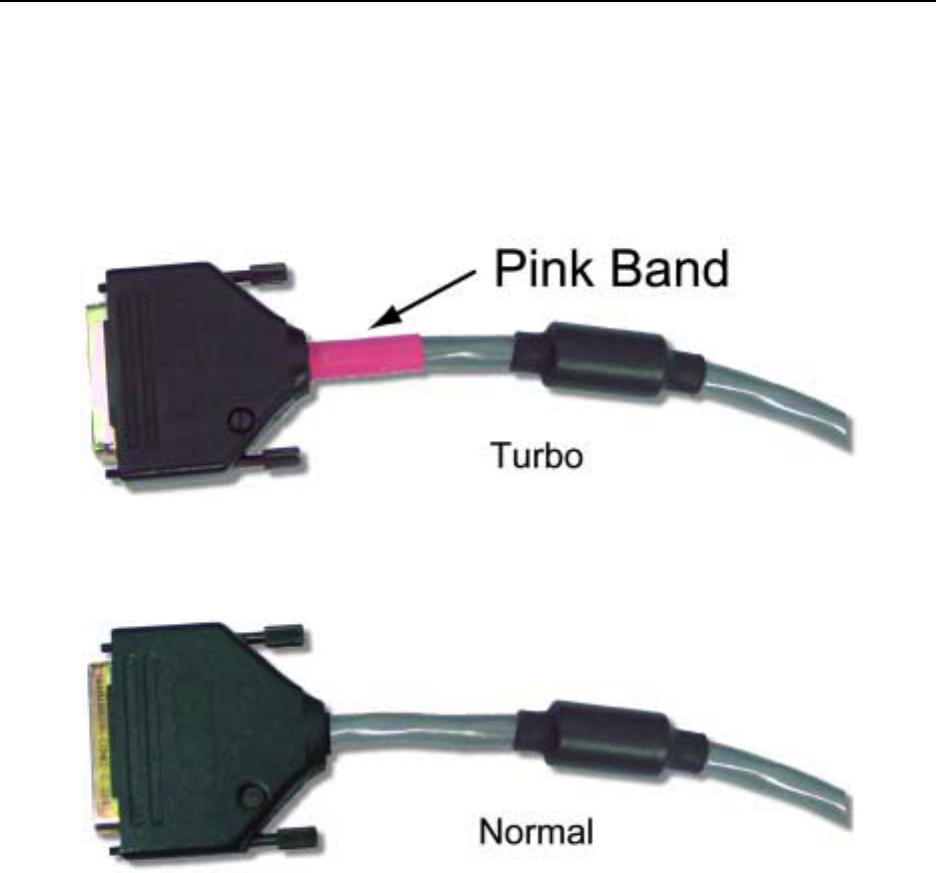
Appendix F - Using the PXFER Cable and WinPXFER Software Noggin
F-2
F1.2 PXFER Cable Types
There are two types of PXFER cable, Normal and Turbo. The Turbo PXFER cable can be identi-
fied by the pink band visible near the connector at either end. The Normal PXFER cable does
not have this pink band.
Figure F-2: Turbo PXFER cable.
Figure F-3: Normal PXFER cable.
Data transfer can only occur if the DVL is set to the correct type of cable (see F1.4: p.F-4). As
well, the WinPXFER software must be set to the correct type of cable (see F1.2: p.F-2).
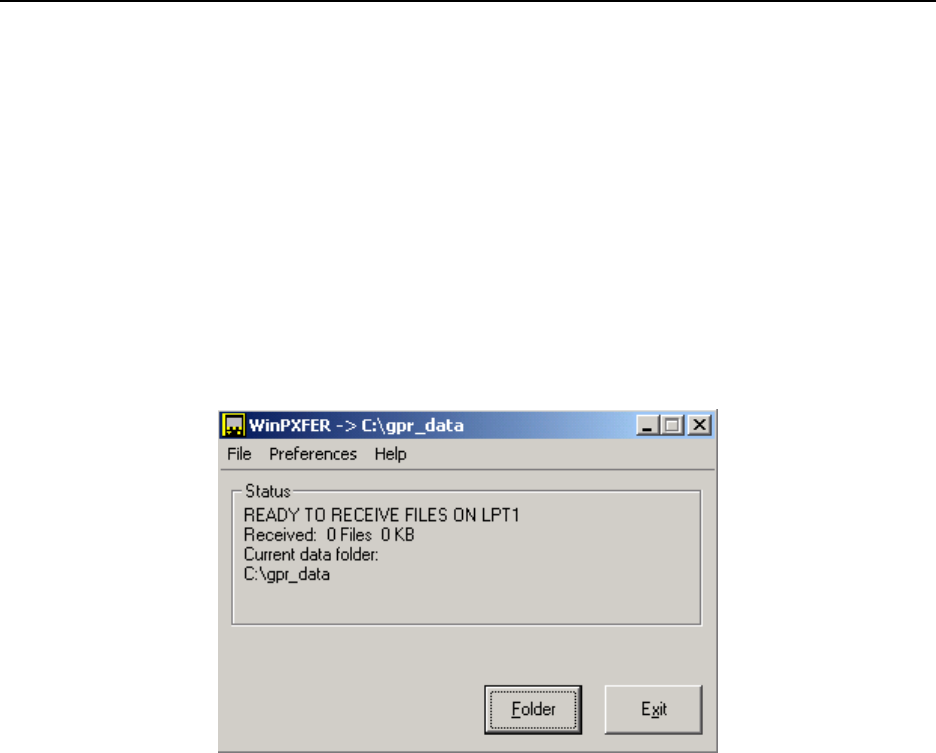
Noggin Appendix F - Using the PXFER Cable and WinPXFER Software
F-3
F1.3 Installing and Running the WinPXFER Program
The Smart system comes with a CD-ROM containing the WinPXFER program.
To install the WinPXFER program, follow the directions in the “Software Installation” document
that accompanies the CD. Briefly, running the SETUP.EXE program from the WinPXFER folder
on the CD will install WinPXFER on the computer.
Once the WinPXFER program has been installed on the computer and the user is ready to
transfer data to the computer, the WinPXFER program needs to be run. This can be done using
the WinPXFER shortcut on the Desktop, double-clicking the WinPXFER.EXE program in
Windows Explorer or pressing Start – Programs – Sensors & Software GPR and finally
WinPXFER.
Figure F-4: WinPXFER main screen
When the WinPXFER program has been run, it will display a screen as shown in Figure F-4.
This means that it is ready to receive data transferred from the DVL to the LPT port number 1.
This command assumes that the data buffers are being transferred across Parallel Port 1 (LPT1).
If using Parallel Port 2 (LPT2) or higher (LPT3, LPT4 etc.), specify the parallel port number under
the Port menu item from WinPXFER.
The name of the folder that the Noggin data will be transferred into is listed under the “Current
data folder”. In the example in Figure F-4, the data will be transferred to the C:\gpr_data folder.
The data folder can be changed by pressing the Folder button and choosing another folder.
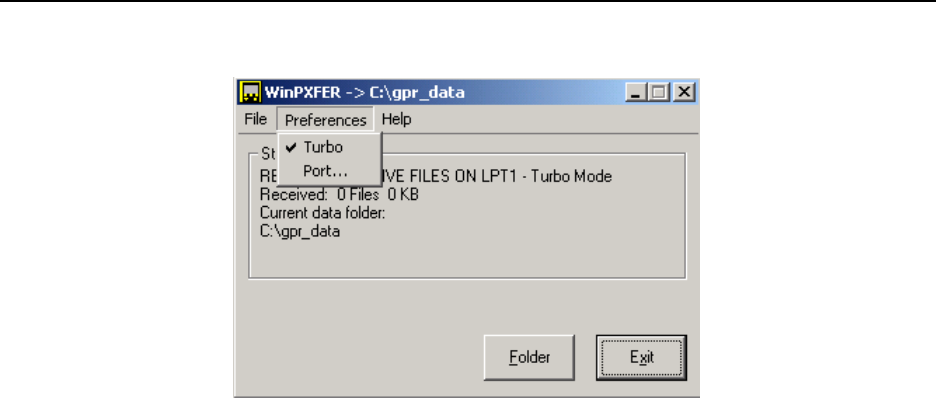
Noggin Appendix F - Using the PXFER Cable and WinPXFER Software
F-4
Figure F-5: Turbo mode under Preferences should only be checked if a Turbo PXFER cable is being
used.
It is vital that WinPXFER be configured properly for the type of PXFER cable (see F1.2: p.F-2). If
the PXFER cable is a Normal cable, the Turbo option under Preferences should NOT be checked
when attempting to transfer data. If the PXFER cable is a Turbo cable, the Turbo option under
Preferences should be checked when attempting to transfer data.
F1.4 Setting the DVL to the PXFER Cable Type
Noggin Mode: The DVL needs to be configured for the type of PXFER cable being used (see
F1.2: p.F-2). In Noggin mode, select 4 - Transfer Setup from the Noggin main menu. The
choices are Normal and Turbo.
Nogginplus Mode: The DVL needs to be configured for the type of PXFER cable being used
(see F1.2: p.F-2). In Nogginplus mode, select 4 - Utilities from the Nogginplus main menu and
then Transfer Mode. The choices are Normal and Turbo.
F1.5 Transferring Noggin Data Buffer Files
Once the parallel XFER cable is connected and the WinPXFER software is installed and running
(see above), it is now possible to transfer all data buffer files to the external computer.
On the DVL, from the main menu, select number 2 – TRANSFER ALL BUFFERS.
The data will be transferred from the DVL to the computer and saved in the current working
directory. The progress of the data transfer will be displayed on the DVL screen and the external
computer.
When the data transfer is complete, on the external computer, exit from the WinPXFER program.
Press any button on the DVL to return to the main menu.

Noggin Appendix F - Using the PXFER Cable and WinPXFER Software
F-5
F1.6 Exporting Noggin
plus
Data
Once the parallel XFER cable is connected (see above) and the WinPXFER software is installed
and running, it is now possible to export data to the external computer.
All the data in one or more Line or Grid Projects or the TAGGED.GPS file can be transferred to
an external computer. From the main File Management menu, the user selects whether to export
Line data, Grid data or the TAGGED.GPS file. If Line or Grid data is selected, the next screen
lists the current projects.
One project can be highlighted and selected for export. Use the up and down arrows to highlight
the project and then press the XFER button to transfer to the PC.
It is also possible to use the TAG button to select several projects and export them all at once.
Use the up and down arrows to highlight the projects, the TAG button to tag each project and
then press the XFER button to transfer all the projects to the PC.
The data will be transferred from the DVL to the computer and saved in a sub-folder from the
current data directory indicated on the WinPXFER program, for example, \DATA\PROJECT2.
The progress of the data transfer will be displayed on the DVL screen and the external computer.
When the data transfer is complete, exit from the WinPXFER program. Press any button on the
DVL to return to the main menu.

Noggin Appendix F - Using the PXFER Cable and WinPXFER Software
F-6
F2 Transferring One or More Noggin PCX Files to an External PC
using WinPXFER
There are two ways of using the PXFER cable and the WinPXFER software to transfer Noggin
data to an external computer. The first is to transfer one or more screens (or buffers) of data as a
single PCX graphics file. This method is described in this section. The second way of transferring
data files to an external computer is to copy all the individual SPI (PCX) files from the DVL (see
Section F1: p.1). This method is useful when the user wants to view the data on an external
computer using the Win_SpiView software.
The data transfer function can only be used after the parallel XFER cable has been
connected from the DVL to the external computer and after the WinPXFER program has
been installed on the external computer and run. Section F1: p.1 describes how to attach
the parallel XFER cable and also how to install and run the WinPXFER program.
Once WinPXFER has been run on the external computer, it is ready to receive data image files
from the Digital Video Logger.
On the Digital Video Logger, after the Print option is selected, the user must define the section to
be printed. The left edge of the page must be established first. This is done by lining up the left
edge of the Digital Video Logger screen with the edge of the plot desired. Use the arrow buttons
on the screen to move the section back and forth. A single arrow moves the image 8 pixels either
right ($), or left (#). A double arrow will move the image 640 pixels or 1 full page to the right (%)
or left (&). A single arrow with a vertical line will move the section either to the start (y#), or end
($y) of the section. If the start or end of section button is pressed, the image will page through
one screen at a time. Data scrolling can be stopped by pressing any button. Once the left edge is
in place, pressing the OK button will lock the left edge of the plot.
The right edge of the plot must now be defined the same as the left, however now using the right
edge of the Digital Video Logger screen. Note that the right edge cannot exceed the left edge.
Next, select a name for the image file from the options CART-1 to CART-4. As long as the
WinPXFER program is running on the external PC, the file will be transferred to the current
directory indicated by WinPXFER. When the data image file transfer is complete, the user will
find a data image (CART-n.PCX) file on the external computer in the current directory.
When the data transfer is complete, on the external computer, exit from the WinPXFER program.
Press any button on the DVL to return to the Noggin screen.

Noggin
G-1
Appendix G GPR Glossaries
G-1 Basic GPR Terms
alpha exponential attenuation coefficient - normal units dB/m (see attenuation)
K relative permittivity or dielectric constant
sigma electrical conductivity - normal units mS/m
v propagation velocity - normal units m/ns
dB/m decibels/metre, common unit for attenuation,
m/ns metre/nanosecond, common unit of GPR velocity, v (see nanosecond)
mS/m milli-Siemens/metre, common unit for conductivity,
ns nanosecond, normal unit of GPR time (see nanosecond)
ps picosecond = 0.001 ns =10
-12
s, occasion unit of GPR time
us microsecond = 1000ns =10
-6
s, occasion unit of GPR time
COR common offset reflection (survey type where a constant antenna separation is main-
tained).
CMP common mid-point (survey type where a transmitter and receiver antenna separation
are changed but the mid point remains constant)
GPR ground penetrating radar
EM electromagnetic (common abbreviation)
antenna Device used to couple electromagnetic energy into the ground. Sometimes called a
transducer.
antenna separation Spacing between transmitting and receiving antennas.
attenuation A reduction in signal amplitude caused by energy dissipation in the transmitting media
(see alpha).
bandwidth The range of frequencies over which a given device transmits or detects signals above
a specified amplitude or power
centre frequency Middle of the frequency band defined by a device's bandwidth
conductivity The ability of a material to conduct electrical current. In isotropic materials the recipro-
cal of resistivity. Sometimes called specific conductance. Units are siemen/m or S/m.
(Or occasionally, mhos/m). For GPR, usually expressed as mS/m. Common symbol
nanosecond 10
-9
s (One Billionth of a second)
radio wave Electromagnetic fields that travel through a material as waves and typically have oscil-
lating frequencies in the 1 GHz to 10 GHz range

Noggin
G-2
receiver (Rx) General term for electronics devices used to detect fields and translate signals into
records or displays
resolution The minimum separation of two objects before their individual responses merge into a
single response
signal amplitude A measure of the strength of the radio wave signal
station interval Spatial distance between observation points along a survey traverse line or mesh
points on a grid
step size See station interval
transmitter (Tx) General term used for electronics devices used to create propagating electromagnetic
fields
transducer Name used where GPR antenna, electronics, and shield are combined into one physi-
cal unit
sample point Signal amplitude measured at specific point in time
trace Sequence of sample points from a single GPR channel that indicate time variation of
signal amplitude
cross section Image that results from side-by-side display of a number of traces which are from adja-
cent spatial measurement position
gain Process of amplifying signals to match recording device or display dynamic range
G-2 Common GPR Terms
zone of influence The size of an area on a reflecting feature that can be uniquely resolved. (See lat-
eral resolution length).
fresnel zone See zone of influence.
range resolution length The radial distance separation between two objects that is needed so that a GPR
clearly detects two responses.
lateral resolution length The lateral separation between two objects that is needed so that a GPR clearly
detects two responses.
ringing Impulsive GPR signals can give rise to reverberating responses that oscillate for a
much longer time than the GPR pulse or wavelet. Such a response is referred to
as a "ringing" response or "ringing" for short.
hyperbola Characteristic inverted "U" GPR response from a point target. (Mathematical form
of the position-travel time response from a point target)
signal to noise ratio The ratio of GPR signal amplitude to the average noise amplitude. A large ratio
results in a larger penetration depth or detection of weaker signals.
system performance Measure of system exploration depth indicated by the ratio of transmitter output
power or voltage to receiver noise power or voltage.

Noggin
G-3
wavelet or EM pulse Impulsive GPR's emit an oscillatory electromagnetic pulse which is short in time
and space and is often referred to as a wavelet.
penetration depth The depth of a GPR wavelet can penetrate to before it is attenuated to an unde-
tectable amplitude.
air waves GPR systems can create and detect energy which travels through air above the
ground. Undesired responses from above ground targets are often called 'air
waves'.
G-3 Advanced GPR Terms
GPS global positioning system (satellite based positioning).
DMI distance measuring indicator.
stacks number of repeated measurements averaged to get resulting measurements.
reflectivity measure of amplitude returned by a target.
reflection coefficient normally named fresnel reflection coefficient and quantifies GPR signal reflection
amplitude from a flat interface between two materials.
3 dB bandwidth Range of spectrum over which the GPR signal amplitude remains above a value
equal to the (peak amplitude).
6 dB bandwidth Range of spectrum over which the GPR signal amplitude remains above a value
equal to the (peak amplitude).

Noggin
G-4