Senstar E4EM0101 ultraWave bistatic transmitter User Manual E4DA0402
Senstar Corporation ultraWave bistatic transmitter E4DA0402
Senstar >
Users manual

Product
Guide
µltraWave™
Microwave Detection Sensor
E4DA0402-001 Rev A
March 25, 2011
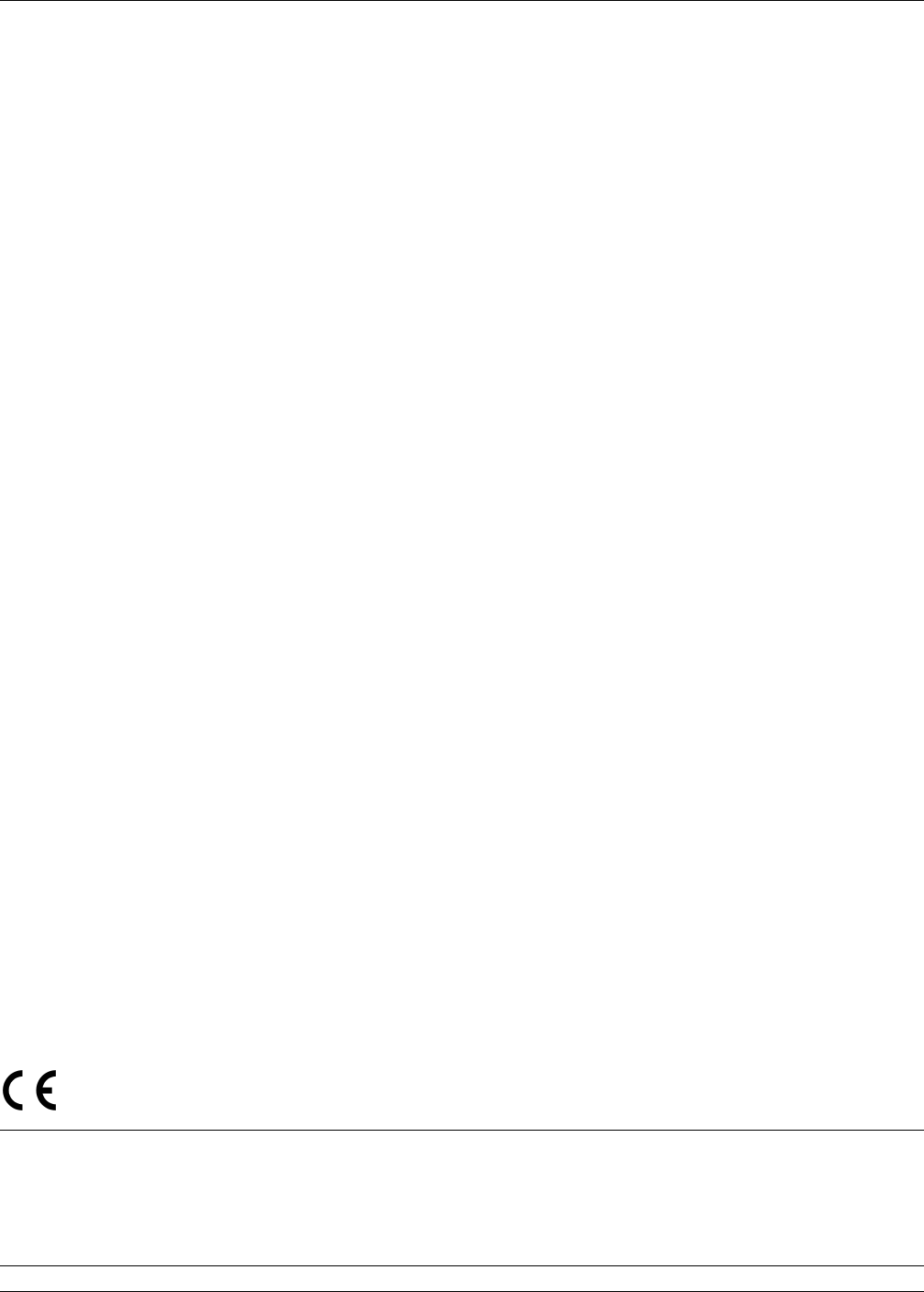
µltraWave Product Guide
Senstar Corporation
Website: www.senstar.com
Email address: info@senstar.com
E4DA0402-001 Rev A
March 25, 2011
Senstar and the Senstar logo are registered trademarks, and µltraWave and Silver Network are trademarks of Senstar
Corporation. Product names and Company names included in this document are used only for identification purposes and are
the property of, and may be trademarks of, their respective owners. Copyright © 2011, Senstar Corporation. All rights reserved.
Printed in Canada.
The information provided in this guide has been prepared by Senstar Corporation to the best of its ability. Senstar Corporation
is not responsible for any damage or accidents that may occur due to errors or omissions in this guide. Senstar Corporation is
not liable for any damages, or incidental consequences, arising from the use of, or the inability to use, the software and
equipment described in this guide. Senstar Corporation is not responsible for any damage or accidents that may occur due to
information about items of equipment or components manufactured by other companies. Features and specifications are
subject to change without notice. Any changes or modifications to the software or equipment that are not expressly approved by
Senstar Corporation void the manufacturer’s warranty, and could void the user’s authority to operate the equipment.
The figures included in this document are for illustration purposes only, and may differ from the actual equipment.
Senstar Corporation’s Quality Management System is ISO 9001:2008 registered.
Compliance:
Canada: Industry Canada Identification Number: transmitter 1454B-E4EM0101; receiver 1454B-E4EM0201
This device complies with Industry Canada license-exempt RSS standard(s). Operation is subject to the following two
conditions: (1) This device may not cause harmful interference, and (2) this device must accept any interference received,
including interference that may cause undesired operation.
Ce dispositif est conforme aux normes CNR d’Industrie Canada applicables aux appareils radio exempts de licence. Son
fonctionnement est sujet aux deux conditions suivantes : 1) le dispositif ne doit pas produire de brouillage préjudiciable; et 2) il
doit accepter tout brouillage reçu, y compris un brouillage susceptible de provoquer un fonctionnement indésirable.
USA: FCC Identification Number: transmitter 15T-E4EM0101; receiver 15T-E4EM0201
FCC Certification - This device complies with part 15 of the FCC Rules. Operation is subject to the following two conditions: (1)
This device may not cause harmful interference, and (2) this device must accept any interference received, including
interference that may cause undesired operation.
This equipment has been tested and found to comply with the limits for a Class B digital device, pursuant to Part 15 of the FCC
Rules. These limits are designed to provide reasonable protection against harmful interference in a residential installation. This
equipment generates, uses and can radiate radio frequency energy and, if not installed and used in accordance with the
instructions, may cause harmful interference to radio communications. However, there is no guarantee that interference will not
occur in a particular installation. If this equipment does cause harmful interference to radio or television reception, which can be
determined by turning the equipment off and on, the user is encouraged to try to correct the interference by one or more of the
following measures:
• Reorient or relocate the receiving antenna.
• Increase the separation between the equipment and receiver.
• Connect the equipment into an outlet on a circuit different from that to which the receiver is connected.
• Consult the dealer or an experienced radio/TV technician for help.
Europe:
This device complies with ETSI standard EN 300 440 for European operation
The use of shielded cables is required for compliance.
Service statement - We ensure that our products are correctly applied to achieve the maximum benefits for the end-user. We
work hand-in-hand with our customers and remain accessible through all stages of a project - from concept to deployment to
long-term support. We provide design assistance, site surveys, installation support, comprehensive documentation, training,
post-installation annual calibration and maintenance visits, electronics and software extended warranty, rapid factory repair
service and on-call/emergency service. Contact Senstar Corporation to inquire about how a package can be customized for
your unique applications.
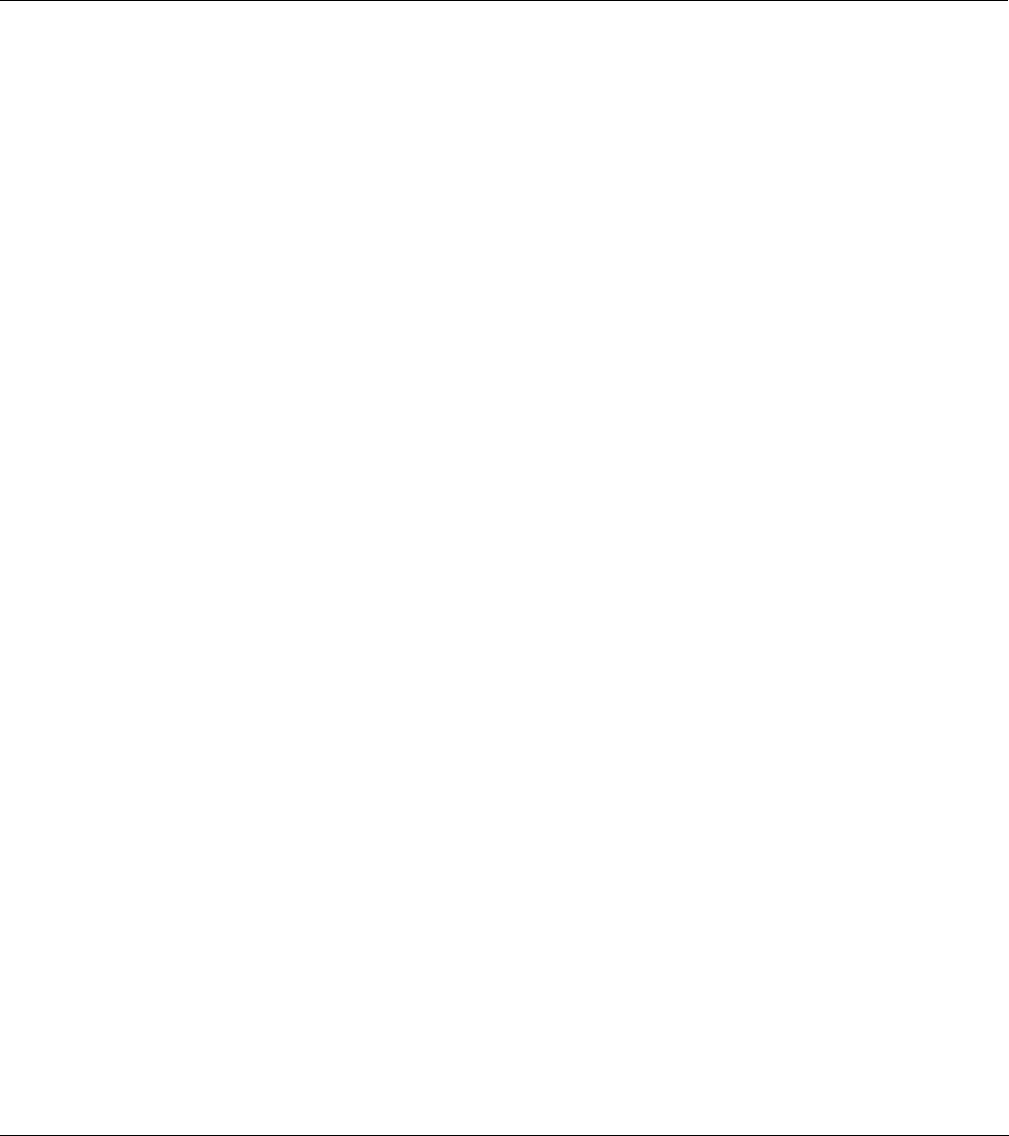
µltraWaveProductGuide Page1
Table of contents
1 System planning - - - - - - - - - - - - - - - - - - - - - - - - - - - - - - - - - - - - - - - 3
Site planning - - - - - - - - - - - - - - - - - - - - - - - - - - - - - - - - - - - - - - 4
Site design - - - - - - - - - - - - - - - - - - - - - - - - - - - - - - - - - - - - - - - - - - - 4
Zone placement - - - - - - - - - - - - - - - - - - - - - - - - - - - - - - - - - - - - - - - - 5
Zone length - - - - - - - - - - - - - - - - - - - - - - - - - - - - - - - - - - - - - - - - - - 5
Zone height - - - - - - - - - - - - - - - - - - - - - - - - - - - - - - - - - - - - - - - - - - 5
Microwave offsets - - - - - - - - - - - - - - - - - - - - - - - - - - - - - - - - - - - - - - - 6
Mounting heights - - - - - - - - - - - - - - - - - - - - - - - - - - - - - - - - - - - - - - - 7
Power and ground requirements - - - - - - - - - - - - - - - - - - - - - - - - - - - - - 8
Alarm data communications - - - - - - - - - - - - - - - - - - - - - - - - - - - - - - - - 8
Network wiring - - - - - - - - - - - - - - - - - - - - - - - - - - - - - - - - - - - - - - - - 8
Relay contact ratings - - - - - - - - - - - - - - - - - - - - - - - - - - - - - - - - - - - - - 9
Cable ports - - - - - - - - - - - - - - - - - - - - - - - - - - - - - - - - - - - - - - - - - - - 9
Mounting posts/surfaces - - - - - - - - - - - - - - - - - - - - - - - - - - - - - - - - - - 9
Foundation - - - - - - - - - - - - - - - - - - - - - - - - - - - - - - - - - - - - - - - - - - 10
2 Installation - - - - - - - - - - - - - - - - - - - - - - - - - - - - - - - - - - - - - - - - - - 11
Mounting the μltraWave units - - - - - - - - - - - - - - - - - - - - - - - - - - - 12
Post-mounting procedure - - - - - - - - - - - - - - - - - - - - - - - - - - - - - - - - - 12
Post-mount alignment - - - - - - - - - - - - - - - - - - - - - - - - - - - - - - - - - - - 13
Surface-mounting - - - - - - - - - - - - - - - - - - - - - - - - - - - - - - - - - - - - - 14
Surface mounting procedure - - - - - - - - - - - - - - - - - - - - - - - - - - - - - - 14
Surface-mount alignment - - - - - - - - - - - - - - - - - - - - - - - - - - - - - - - - - 15
Transmitter/receiver wiring connections - - - - - - - - - - - - - - - - - - - - - - -15
Relay contact ratings - - - - - - - - - - - - - - - - - - - - - - - - - - - - - - - - - - - - 16
Auxiliary input - - - - - - - - - - - - - - - - - - - - - - - - - - - - - - - - - - - - - - - - 16
Cable ports - - - - - - - - - - - - - - - - - - - - - - - - - - - - - - - - - - - - - - - - - - 16
Making the I/O wiring connections - - - - - - - - - - - - - - - - - - - - - - - - - - 17
Enclosure tamper switch - - - - - - - - - - - - - - - - - - - - - - - - - - - - - - - - - 17
Transmitter/Receiver grounding - - - - - - - - - - - - - - - - - - - - - - - - - - - - - 17
Power supply connection - - - - - - - - - - - - - - - - - - - - - - - - - - - - - - 17
Local power supply - - - - - - - - - - - - - - - - - - - - - - - - - - - - - - - - - - - - - 17
Silver Network wiring connections - - - - - - - - - - - - - - - - - - - - - - - - 18
Silver Network specifications - - - - - - - - - - - - - - - - - - - - - - - - - - - - - - - 18
Silver Network connections - - - - - - - - - - - - - - - - - - - - - - - - - - - - - - - - 19
3 Setup and calibration - - - - - - - - - - - - - - - - - - - - - - - - - - - - - - - - - - - 21
Connecting the UCM - - - - - - - - - - - - - - - - - - - - - - - - - - - - - - - - 22
Setting the transmitter/receiver Frequency Pair - - - - - - - - - - - - - - - - 23
Receiver setup - - - - - - - - - - - - - - - - - - - - - - - - - - - - - - - - - - - - - 23
Specify the Auxiliary I/O control mode - - - - - - - - - - - - - - - - - - - - - 24
Auxiliary (Aux) inputs - - - - - - - - - - - - - - - - - - - - - - - - - - - - - - - - 24
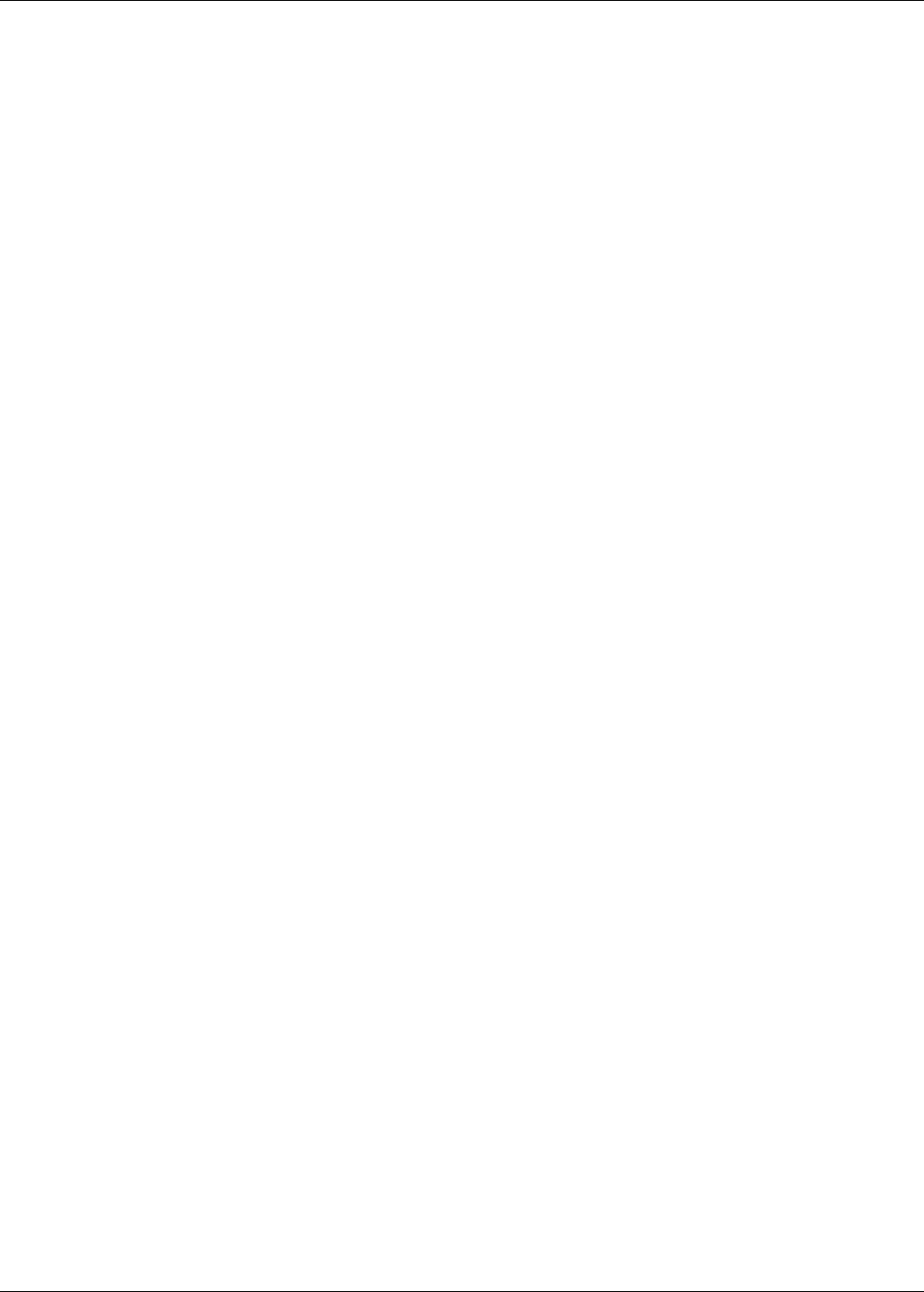
Page2µltraWaveProductGuide
Input configuration procedure (Remote control mode) - - - - - - - - - - - - - - 25
Output relays - - - - - - - - - - - - - - - - - - - - - - - - - - - - - - - - - - - - - 25
Output relay setup (Local control mode) - - - - - - - - - - - - - - - - - - - - - - - 25
Output relay setup (Remote control mode) - - - - - - - - - - - - - - - - - - - - - - 25
Setting the receiver’s address - - - - - - - - - - - - - - - - - - - - - - - - - - - 26
a Specifications - - - - - - - - - - - - - - - - - - - - - - - - - - - - - - - - - - - - - - - - - 27
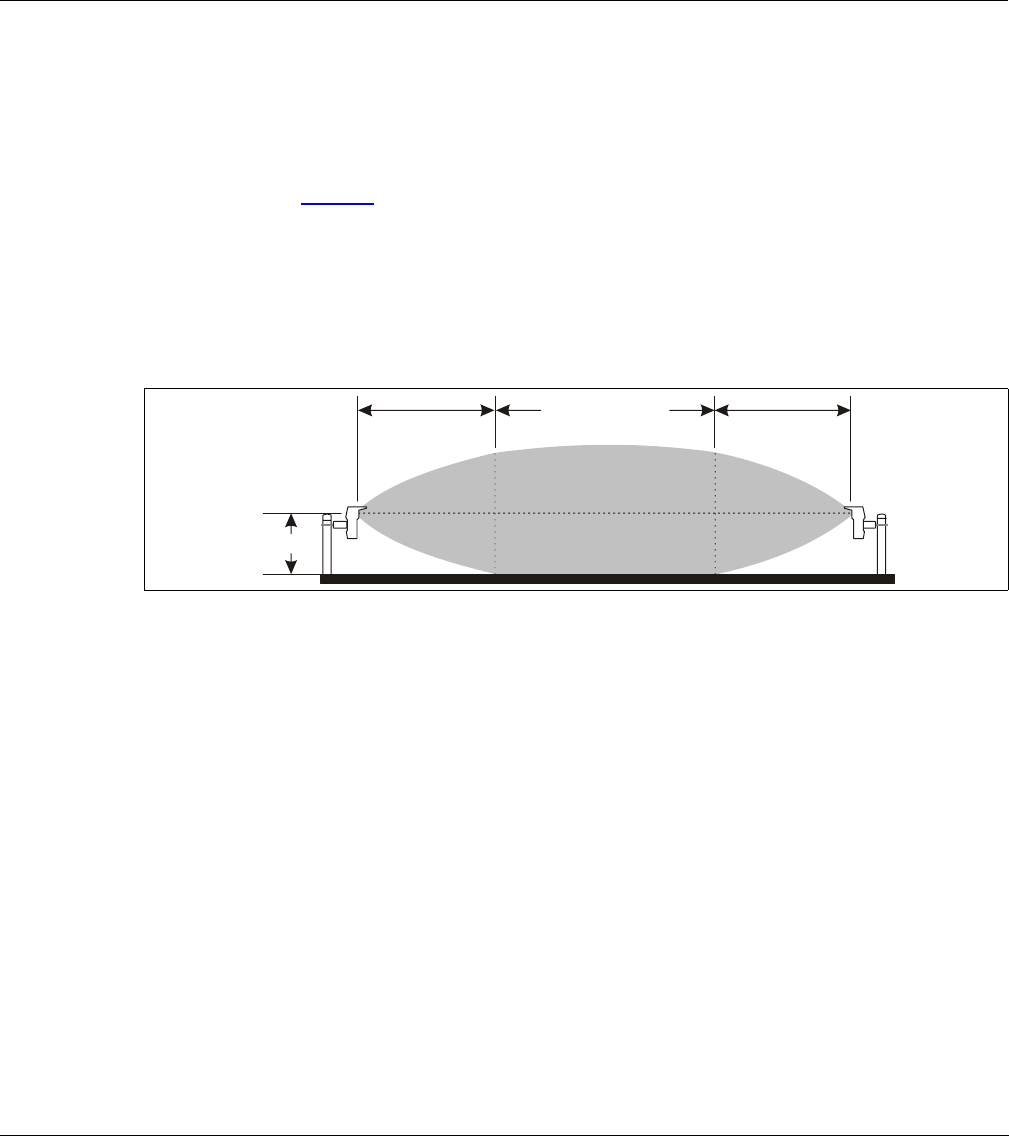
µltraWaveProductGuide Page 3
1 System planning
The μltraWave Microwave Detection Sensor is designed for exterior perimeter intrusion detection
applications. μltraWave consists of a microwave transmitter and receiver, which detect motion in a
defined area (see Figure 1). The transmitter sends microwave signals to the receiver, and any
motion in the detection zone causes a variation in the received signal strength. The signal
variations are detected and processed by the receiver, which declares an intrusion alarm when the
received signal meets the criteria for a valid target.
The transmitter and receiver units are housed in weatherproof enclosures. Each enclosure
contains electronic circuitry and an antenna. Both units can be wired to report enclosure tamper
alarms.
Site planning & design
The amount of site preparation required depends on the level of security. High security
applications require more stringent specifications than do applications where only a beam-break
alarm is required. Use the following definitions to determine the level of security required:
• High Security Zone - detection of an intruder stomach-crawling parallel to the beam.
• Medium Security Zone - detection of an intruder crawling on hands and knees.
• Low Security Zone - detection of an upright walking intruder (beam-break alarm).
The physical specifications for a high security detection zone are:
• maximum transmitter/receiver separation distance of 100 m (328 ft.)
• terrain must be level to grade ± 7.5 cm (3 in.)
• terrain covered with a 10 cm (4 in.) layer of crushed stone (2 cm {0.75 in.} max.) or a paved
zone free of vegetation
Figure 1 µltraWave microwave detection sensor
partial coverage
mounting height
full coverage
detection zone partial coverage
beam centerline
offset area offset area
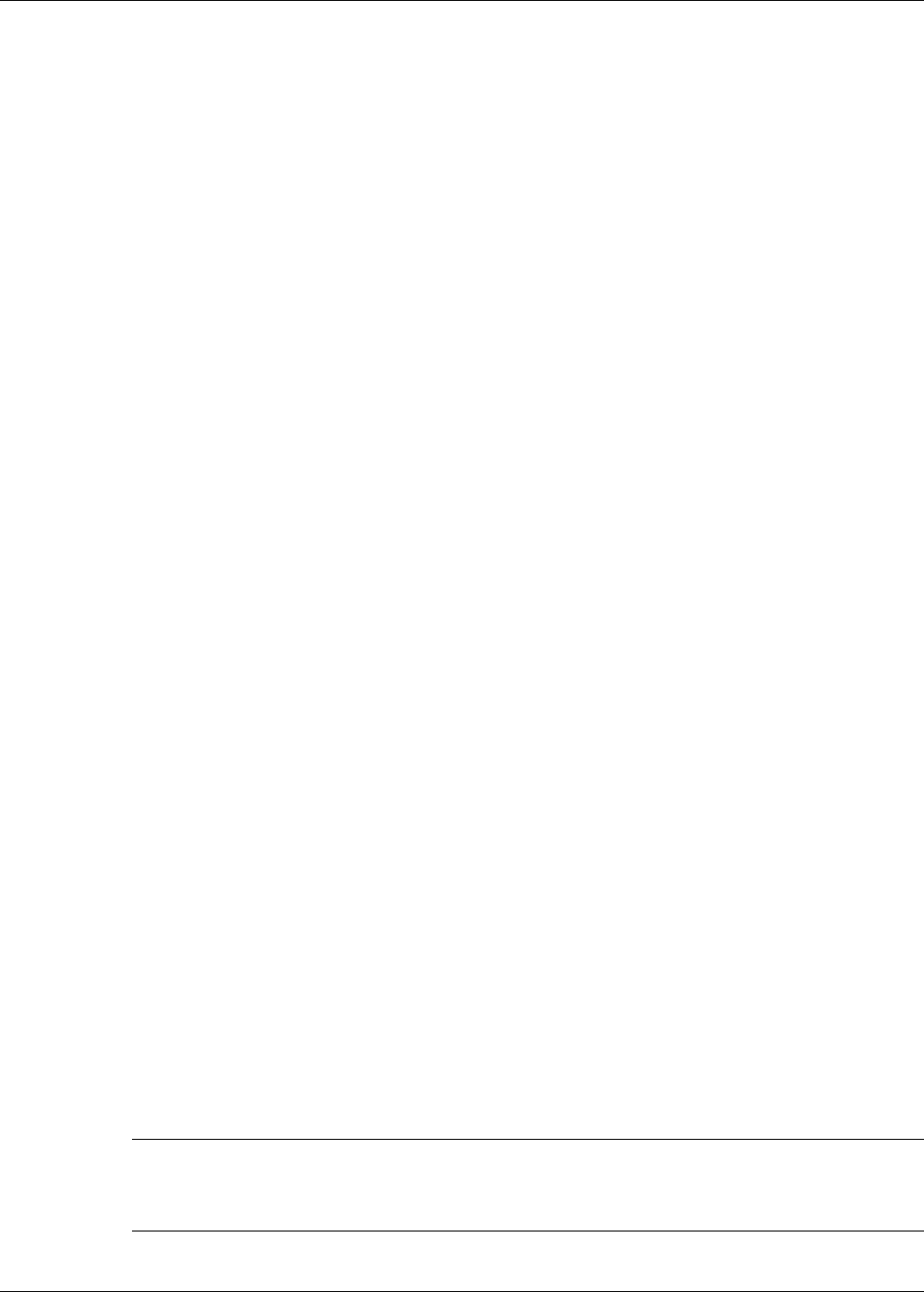
Site planning & design
Page 4 µltraWaveProductGuide
Site planning
Conduct a site survey in which you note the physical features of the zone and surrounding area.
Include accurate measurements on a detailed drawing. The following is a list of rules to follow
when planning a microwave zone:
• Line of sight - A direct, unobstructed line of sight is required between the transmitter and
receiver.
• Depressions and deviations in terrain - Drainage ditches and gullies must be avoided or
filled in. These depressions can allow undetected access by an intruder, and occasional
water flow can cause nuisance alarms. Significant deviations from level grade can result in
gaps in the detection zone and detection shadows. Gaps and detection shadows create
unmonitored areas in the zone.
• Vegetation - Trees, bushes, shrubs, tall grass and weeds within the detection zone will
increase the sensor’s nuisance alarm rate and reduce the probability of detection,
especially when the vegetation is wet with rain or dew.
• Objects - Any objects (posts, light standards, stored material, parked vehicles, etc.) within
the detection zone can result in gaps in the microwave field and detection shadows.
• Ensure that there is adequate separation from any object that could be used to jump over
or bridge the detection zone (e.g., fences, trees, storage sheds, etc.).
• Motion - Movement within the detection zone can cause nuisance alarms (trees, brush,
shrubs, weeds, etc.).
The detection zone must not include water, which can cause nuisance alarms when moving
(e.g., puddles, ponds, streams, lakes).
The detection zone must be fenced in to prevent nuisance alarms caused by animals (cats,
dogs, rabbits, deer, livestock, etc.).
The motion of metallic objects (vehicles, buildings, fences, materials, etc.) that are close to the
detection zone can produce nuisance alarms.
• Ground surface - The type of ground surface in the detection zone affects the sensor’s
operation:
Crushed stone is the optimum ground cover. Crushed stone disperses rain and helps to
prevent the formation of puddles. In addition, microwave energy reflects off the rocks,
thereby increasing the zone’s sensitivity.
Paved surface - A paved surface is recommended for detection zones that require snow
removal. Accumulated snow changes the characteristics of the detection zone and can provide
cover for a burrowing intruder.
Other acceptable surfaces for medium and low security applications include closely mowed
grass (7.5 cm {3 in.} or less) and hard-packed dirt or clay.
Site design
Prepare detailed site drawings for the μltraWave system after completing the site survey. Include
dimensions, elevations and the locations of any objects noted during the survey. Once the site
drawings are complete, carefully plot each microwave zone. Zone placement, zone length, and
offsets are critical factors in the design of a microwave sensor system.
Note The Universal Configuration Module includes a tool that calculates
microwave offsets, mounting heights, beam width, and clearance
requirements, based on zone lengths. Use the UCM design tool
when planning an μltrawave zone.
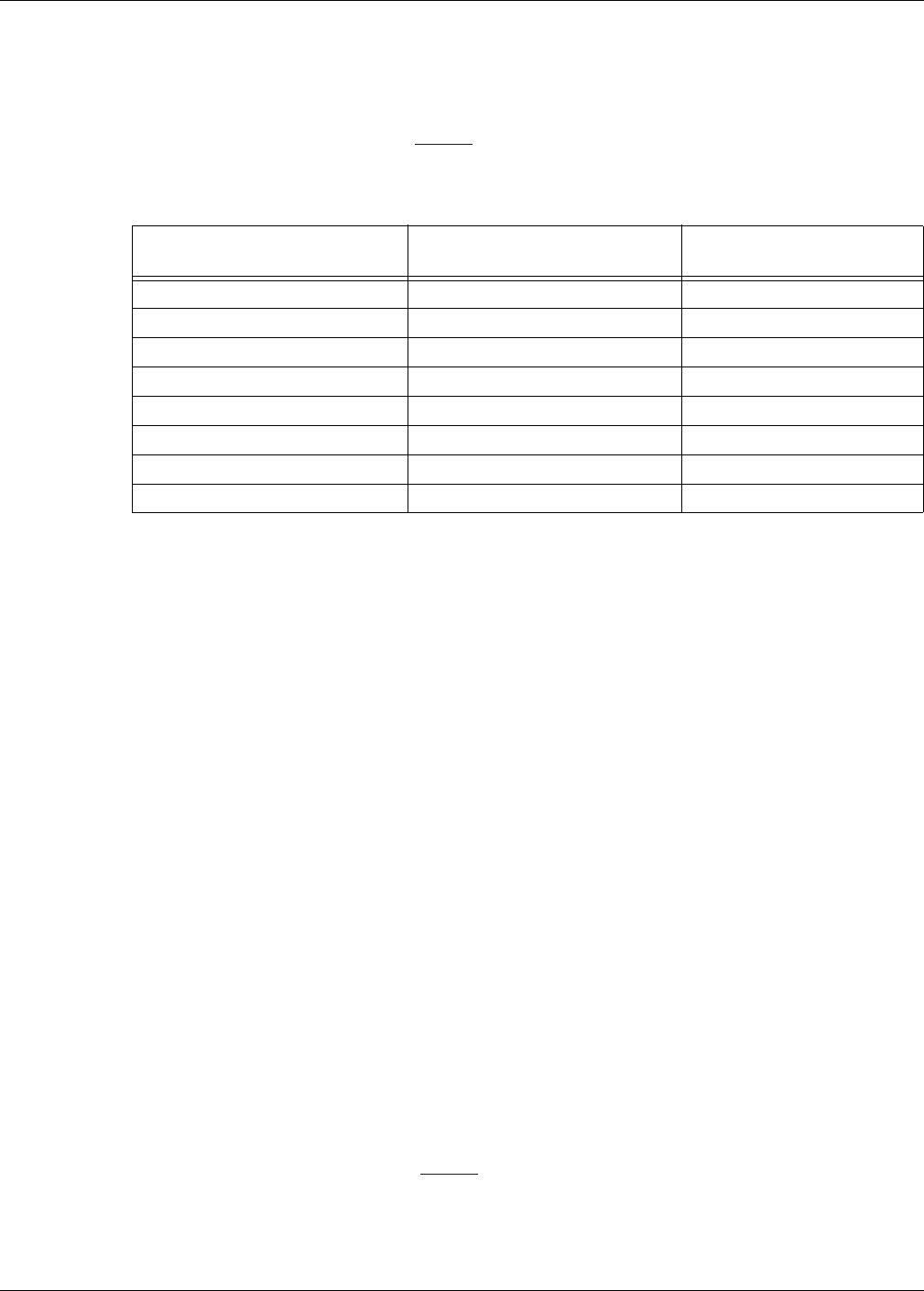
Site planning & design
µltraWaveProductGuide Page 5
Zone placement
The μltrawave system requires a long, flat, detection zone free of obstacles and depressions. The
minimum distance between the beam centerline and any object (fences, buildings, vehicles, trees,
bushes, shrubs, etc.) is outlined in Tabl e 1 . Separation distances are based on typical conditions
and can vary depending on site conditions including zone length, unit mounting height, ground
cover, type of obstacle, etc. The following separation distances are minimum values. Increase the
separation distance between the beam centerline and any objects whenever possible.
You can calculate the required minimum clearance between the beam centerline and an object by
using the following formula:
(transmitter/receiver separation) X 0.02 = (min. distance between beam centerline and object)
The formula can also be used to calculate the maximum separation between the transmitter and
receiver when you know the available clearance between the beam centerline and the nearest
object:
(transmitter/receiver separation) = (min. distance between beam centerline and object) / 0.02
Zone length
The optimum length of each zone depends on several factors:
• the required level of security
• physical constraints (terrain, trees, fences, buildings, etc.)
• available space for the detection zone
For a high security zone, the maximum zone length is 90 m (295 ft.) and the maximum distance
between the transmitter and receiver is 100 m (328 ft.).
For a medium security zone, the maximum zone length is 140 m (459 ft.) and the maximum
distance between the transmitter and receiver is 150 m (492 ft.).
For a low security zone, the maximum zone length is 200 m (656 ft.) and the maximum distance
between the transmitter and receiver is 200 m.
Zone height
The height of the microwave field is approximately equal to the minimum distance between the
beam centerline and an object (see Table 1 ) plus the unit mounting height. For applications that
require additional zone height it is possible to stack two or more units on one mounting post.
Stacking μltrawave sensors is described in application note E4DA0109.
transmitter/receiver separation min. required clearance
(beam centerline to object) midpoint zone width
30 m (98 ft.) 0.6 m (2 ft.) 1.2 m (4 ft.)
50 m (164 ft.) 1.0 m (3.3 ft.) 2.0 m (6.6 ft.)
75 m (246 ft.) 1.5 m (5 ft.) 3 m (10 ft.)
90 m (295 ft.) 1.8 m (6 ft.) 3.6 m (12 ft.)
100 m (328 ft.) 2.0 m (6.6 ft.) 4.0 m (13.2 ft.)
125 m (410 ft.) 2.5 m (8.2 ft.) 5.0 m (16.4 ft.)
150 m (492 ft.) 3.0 m (10 ft.) 6.0 m (19.7 ft.)
200 m (656 ft.) 4.0 m (13.2 ft.) 8.0 m (26.3 ft.)
Table 1 Unit separation/minimum clearance
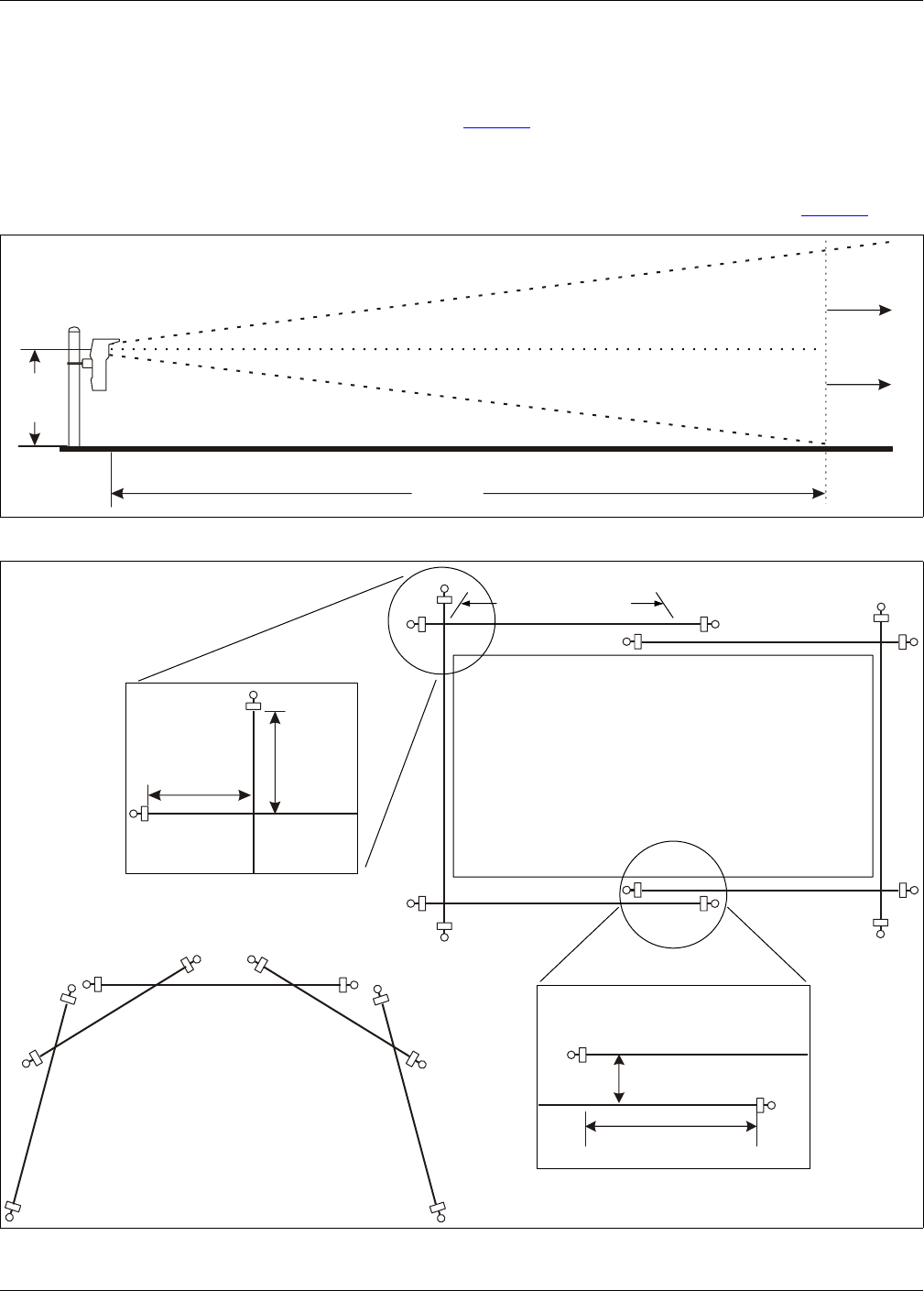
Site planning & design
Page 6 µltraWaveProductGuide
Microwave offsets
The areas immediately above and below the transmitter and receiver antennas are not exposed to
the microwave energy. A microwave offset is used to prevent this unmonitored area from being
vulnerable to undetected intrusions (see Figure 2). Offsets prevent intruders from crawling under
or jumping over a microwave unit to gain undetected access to the protected area. The offset
distances in the example drawings are based on a 100 m separation between the transmitter and
receiver and a mounting height of 55 cm (21.5 in.) beam centerline to ground. As the mounting
height increases a longer offset is necessary. Different types of offsets are shown in Figure 3.
Figure 2 Offset area
Figure 3 Offset arrangement examples
partial coverage
partial coverage
beam centerline full
coverage
detection
zone
required offset
5 m
(16.4 ft.)
55 cm
(21.5 in.)
5 m
(16.4 ft.)
detection zone
protected area
beam
centerline
corner offset
55 cm (21.5 in.) mounting height
basket weave layout
for odd shaped perimeters
1 m (3.3 ft.)
10 m (32.8 ft.)
parallel offset
55 cm (21.5 in.) mounting height
T
R
5 m
(16.4 ft.)
T
R
R
R
R
R
R
R
T
T
T
T
T
T
T
T
T
T
T
T
R
R
R
T
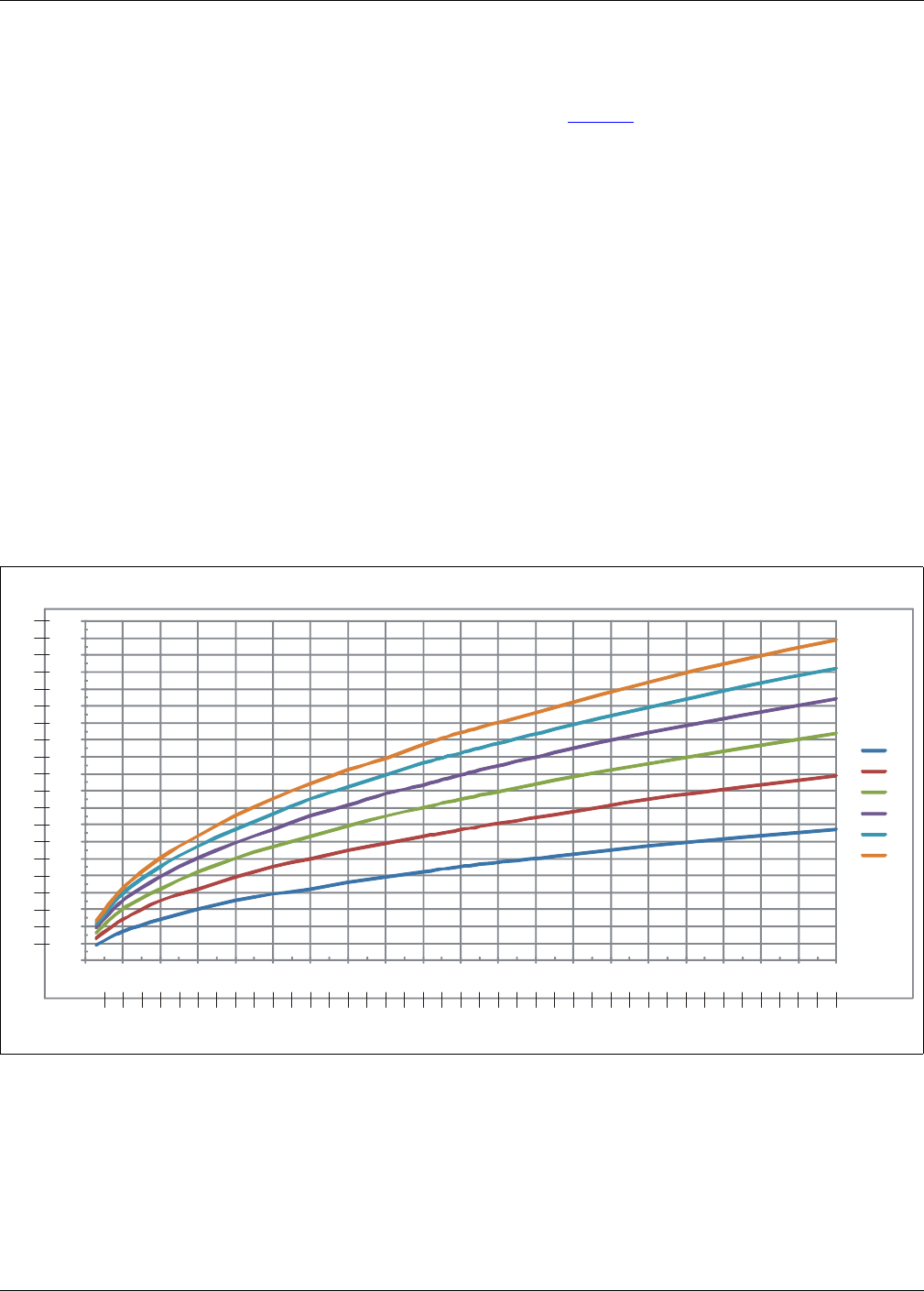
Site planning & design
µltraWaveProductGuide Page 7
Mounting heights
The recommended method for determining the μltraWave unit mounting height is to use the UCM
design tool. However, the mounting height chart (see Figure 4) can also be used to determine the
optimal mounting height for the transmitter and receiver. The horizontal axis of the chart
represents the separation distance between the transmitter and receiver. The vertical axis
represents the height of the transmitter and receiver from the center of the antenna to the
ground’s surface.
The node curves (N1, N2, N3, N4, N5 and N6) indicate the recommended locations for
coordinating distance (horizontal axis) to mounting height (vertical axis). Coordinate lines that
meet on the node curves provide the highest received signal strength. Avoid the mounting height
and distance coordinates between the node curves. For high security applications, a mounting
height at N1 will provide optimum system operation.
Example:
The distance between the transmitter and receiver is 85 m (279 ft.). Locate this distance on the
height chart's horizontal axis. Plot a vertical line from this distance point across the node curves.
These height measurements represent the best theoretical mounting heights for this example.
They are 50 cm (20 in.) for the N1 curve, 70 cm (28 in.) for the N2 curve, 87 cm (34 in.) for the N3
curve, etc.
Figure 4 Mounting height chart
0
10
20
30
40
50
60
70
80
90
100
110
120
130
140
150
160
170
180
190
200
0 10 20 30 40 50 60 70 80 90 100 110 120 130 140 150 160 170 180 190 200
N1
N2
N3
N4
N5
N6
33 66 98 131 164 197 230 263 295 328 361 394 427 459 492 525 558 591 623 656 feet
meters
cminches
79
75
71
67
63
59
55
51
47
43
39
35
32
28
24
20
16
12
8
4
mount
i
ng
h
e
i
g
h
t
transmitter/receiver se
p
aration
N1
N2
N3
N4
N5
N6
Node
curves
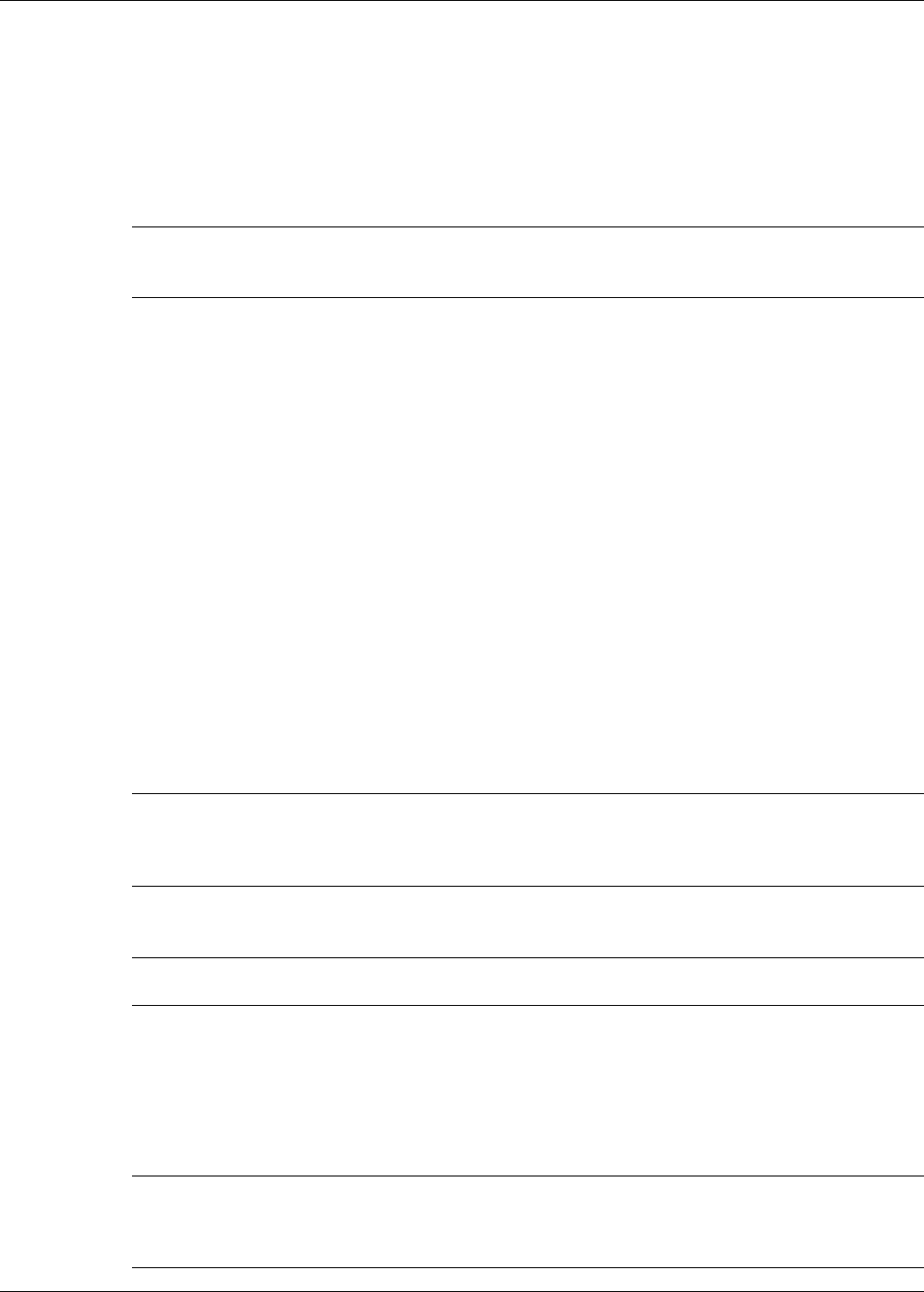
Site planning & design
Page 8 µltraWaveProductGuide
Power and ground requirements
The μltraWave sensor system consumes 4 W maximum. Both the transmitter and receiver can
operate on a wide range of input voltages (12 to 48 VDC). The required gauge of the power cable
depends on the power supply capacity, the number of μltraWave units being powered and the
lengths of the power cable runs. In locations where AC power may not be stable or reliable, an
uninterruptable power supply (UPS) should be used for primary power. Each μltraWave unit
requires a nearby connection to a low resistance earth ground.
Alarm data communications
Alarm monitoring is site specific and depends on whether you are using relay output alarm
communications (Local control mode) or network based alarm communications (Remote control
mode). Each unit has two user-configurable Form C relay outputs. In Local control mode, the
receiver’s two outputs can be configured to signal alarm, Tx comm link fail, enclosure tamper
(transmitter and receiver unit) input power fail, hardware faults (transmitter and receiver unit)
and system fail (fail-safe operation). The transmitter unit’s two outputs can be configured to signal
enclosure tamper, input power fail, hardware faults and system fail (fail-safe operation). Each
receiver unit also includes an auxiliary (Aux) input. The Aux input is not used in Local control
mode.
To communicate on the Silver Network, a network interface card (NIC) must be installed on the
receiver PCB. There are five variants of the NIC available: EIA-422, multimode fiber optic,
singlemode fiber optic, mixed media EIA-422 and multimode, and mixed media EIA-422 and
singlemode. For network based systems (Remote control mode) alarm data is carried over the
network cables and the relays are available as output control points from the security management
system. The transmitter’s tamper notification is transmitted to the receiver unit, which notifies the
security management system of a tamper condition. In Remote control mode the receiver’s Aux
input can be used to report the status of an auxiliary security device to the head end. The
transmitters Aux input is not used in Remote control mode.
Network wiring
Transmission media/maximum separation distances between μltraWave receivers using network
communications:
• EIA-422 copper wire - 1.2 km (0.75 mi.)
• Multimode fiber optic cable - 2.2 km (1.4 mi.) - 2 fibers per Channel
• Singlemode fiber optic cable - 10 km (6.2 mi.) - 2 fibers per Channel
Note Senstar recommends installing a low resistance (5Ω or less) earth
ground at each unit. Consult the local electrical codes for grounding
information.
Note It is possible to use relay output alarm communications and setup
a Silver Network for maintenance purposes. This enables remote
calibration, maintenance and diagnostic access to your μltrawave
units from a central control facility.
Note A network interface card must be installed on the receiver PCB to
enable network communications.
Note Senstar strongly recommends the use of low capacitance
shielded twisted pair data cable for EIA-422,
62.5/125 multimode fiber optic cable, and
9/125 singlemode fiber optic cable.
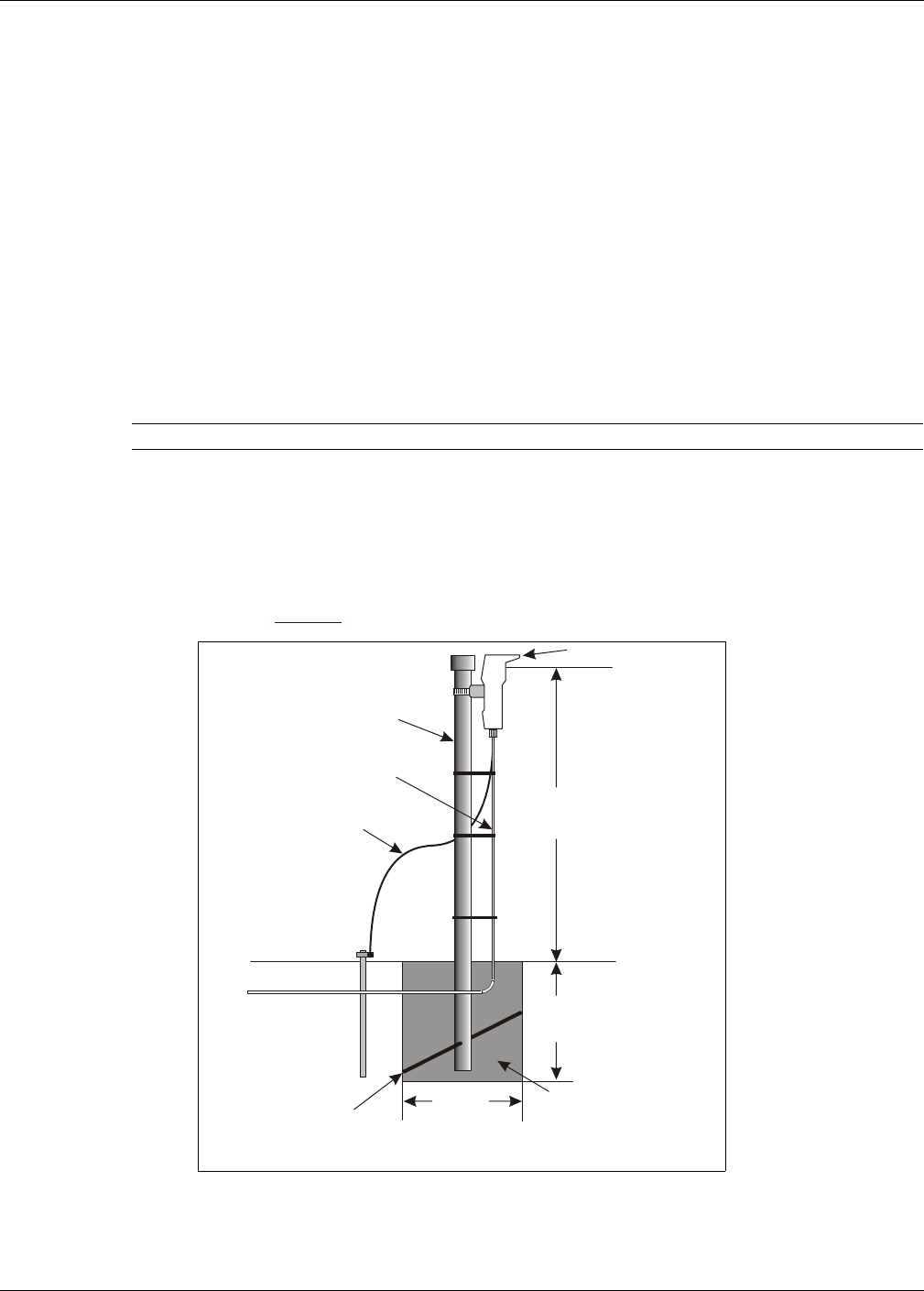
Site planning & design
µltraWaveProductGuide Page 9
Relay contact ratings
The dry contact relays are single pole, double throw, Form C, latching, rated for 30 V @ 1 A max.
In Remote control mode, you can configure the relays as latching (ON by command, OFF by
command), in flash mode (ON-OFF-ON-OFF, etc. by command, then OFF by command), or pulse
mode (ON for a period, then OFF). For flash and pulse modes, the relay Active/Inactive times are
selectable. In Local control mode the relays remain active for the event’s duration or for the
selectable Hold Time, whichever is longer.
Cable ports
Each μltraWave unit includes two 22 mm (0.875 in.) cable ports. The post-mounting kit
(E4KT0300) includes two compression glands for cable sizes 5 mm to 6.4 mm (3/16 in. to 1/4 in.)
and two alternate compression glands for cable sizes 11 mm to 13 mm (7/16 in. to 1/2 in.). If
required, the enclosure can be fitted with 13 mm (1/2 in.) conduit, in place of the compression
glands.
Mounting posts/surfaces
The μltraWave units mount easily on posts with an outside diameter ranging between 4.8 cm and
11.4 cm (1.875 in. and 4.5 in.). The posts must be plumb, firmly set in the ground, and unable to
rotate or move. For areas where the ground freezes, the posts must be protected against potential
frost heaving. A 2.5 m (8 ft.) post is generally used with 91 cm (3 ft.) of the post buried in a
concrete footing. Figure 5 is an illustration of a post-mounted μltraWave unit.
Note Conduit and conduit fittings are not included.
Figure 5 Post installation and unit mounting
4.8 to 11.4 cm post
power and alarm
wiring in conduit
ground wire
ground rod
µltraWave unit
mounting height from
center of antenna to ground
ground level
buried conduit
to alarm panel
& power supply
rebar
through post 61 cm
(2 ft.) concrete footing
91 cm *
(3 ft.)
Consult the local construction codes for information about using
concrete footings in ares where ground freezing occurs.
*
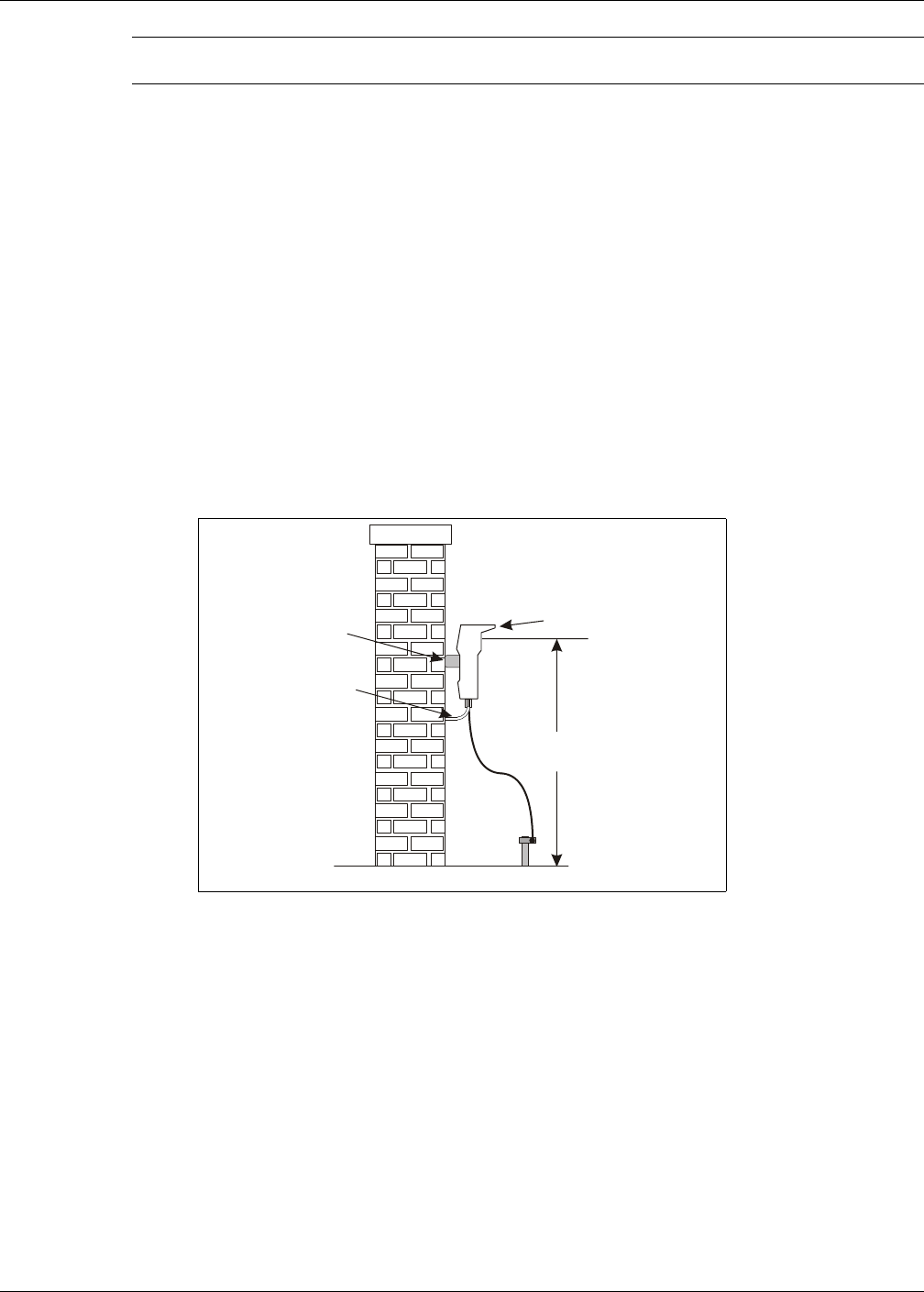
Site planning & design
Page 10 µltraWaveProductGuide
Foundation
The foundation for the mounting posts in normal soil should be at least 91 cm (3 ft.) deep and
61 cm (2 ft.) in diameter. If soil conditions are such that a non-shifting foundation is questionable,
then a larger footing is required. In areas where ground freezing can cause frost heaving, use a
truncated pyramid base foundation.
When the foundation concrete cures, there is a possibility of it pulling away from the post,
thereby, allowing the post to rotate. Installing a length of rebar through the post in the concrete
foundation will prevent any rotation.
Surface-mount applications
The post-mount bracket can also be used to mount an μltraWave unit on a fixed stable surface. The
hardware required for fastening the bracket to the surface is not included. If you are considering a
surface mount application, the transmitter receiver alignment must be carefully planned, as the
mounting bracket cannot be adjusted in the horizontal plane for surface mount applications.
Note Senstar recommends hiring a local fencing contractor to install
the μltraWave mounting posts.
Figure 6 Surface mounting example
power and alarm
wiring in conduit
ground wire
ground rod
µltraWave unit
mounting height from
center of antenna to ground
ground level
mounting
bracket

µltraWaveProductguide Page 11
2 Installation
The μltraWave transmitter and receiver units are almost identical, with only minor differences in
component layout. Figure 7 shows an μltraWave receiver and illustrates the unit’s features. The
receiver’s diagnostic activity LEDs are listed in Tab le 2 .
Figure 7 µltraWave receiver PCB
LED # Description LED # Description
D37 POWER LED ON = DC input Power ON D6 RXA LED ON = receiving A-side network comm
D35 ALARM LED ON = sensor alarm D7 TXA LED ON = transmitting A-side network comm
D34 DOOR LED ON = enclosure tamper condition D8 RXB LED ON = receiving B-side network comm
D33 MEMEORY LED ON = internal memory fault D9 TXB LED ON = transmitting B-side network comm
D36 POWER FAIL LED ON = power rail fault D10 FAULT A LED ON = A-side communication fault
D37 RESERVED D11 FAULT B LED ON = B-side communication fault
D31 RESERVED D12 NETWORK POWER LED ON = NIC power ON
D30 UCM ACTIVE LED ON = UCM connected D13 BOOT LED ON = NIC initialization failure
D24 ALARM LED ON = sensor alarm (default) D16 POWER LED ON = input power fault
D25 SUPERVISION LED ON = supervision alarm
Table 2 µltraWave diagnostic activity LEDs
center of antenna
USB port (connect UCM PC)
diagnostic activity LEDs
NIC mounting hardware (X 3)
T1 expansion header (for NIC)
power fault LED
T3 power input connection
T6 input/output connections
relay active LEDs
T4 bypass tamper header
S1 tamper switch
PCB earth ground connection
22 mm cable entry ports
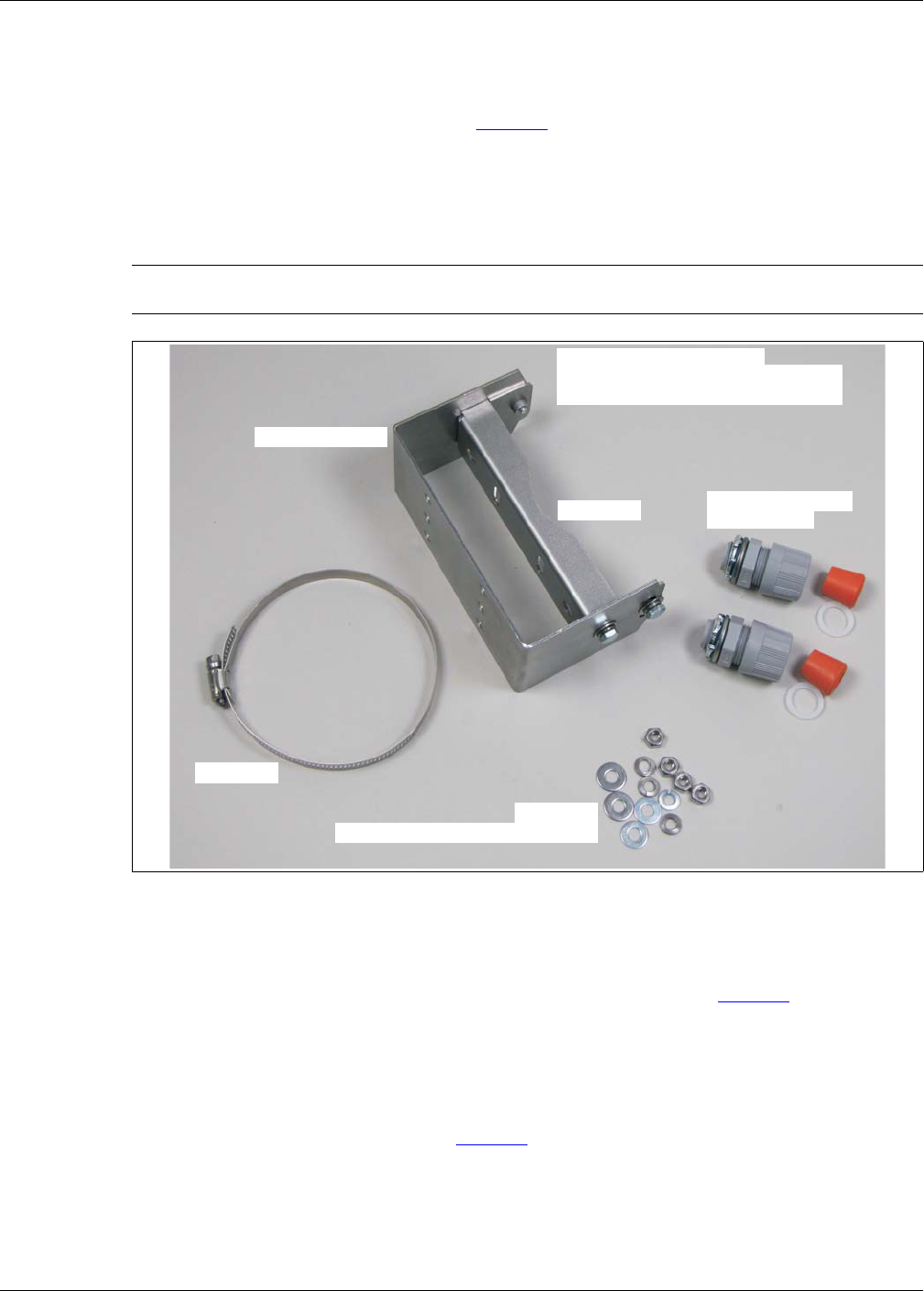
Page 12 µltraWaveProductguide
Mounting the µltraWave units
Mount the transmitter and receiver units on their respective posts, using the hardware provided in
the post-mounting kit (p/n E4KT0300, see Figure 8 ). The mounting height of the transmitter and
receiver units is measured from the center of the antenna to the ground’s surface. As an alignment
aid, the cover over the antenna includes an embossed X-pattern, that indicates the center of the
antenna.The μltraWave units can also be mounted on a wall or other flat stable surface. Both the
transmitter and receiver units must be mounted at the same height above ground. After mounting,
the two units must be aligned to point directly at each other.
Post-mounting procedure
1. Using an 11 mm (7/16 in.) wrench and the supplied hardware (hex nut, lock washer, flat
washer - X4) attach the mounting bracket to the μltraWave unit (see Figure 9 ).
2. Pass the gear clamp through the slots in the post collar.
3. Using an 11 mm wrench and the supplied hardware (bolt, lock washer, flat washer - X4) attach
the post collar to the mounting bracket.
4. Wrap the gear clamp around the post and measure the mounting height of the μltraWave unit
from the center of the antenna (see Figure 8 ) to the ground’s surface.
5. Aim the μltraWave unit at the second mounting post, and using an 8 mm (5/16 in.) nut driver
or socket, tighten the gear clamp with the μltraWave unit at the specified height.
6. Measure and verify the mounting height.
7. Repeat for the second μltraWave unit.
Note Senstar recommends hiring a local fencing contractor to install
the μltraWave mounting posts.
Figure 8 Mounting hardware/alignment aid
mounting bracket
post collar
gear clamp
E4KT0300 post-mounting kit
hardware
Each µltraWave unit includes one set of
the following hardware components:
compression glands
and alternates
mounting bracket to µltraWave unit
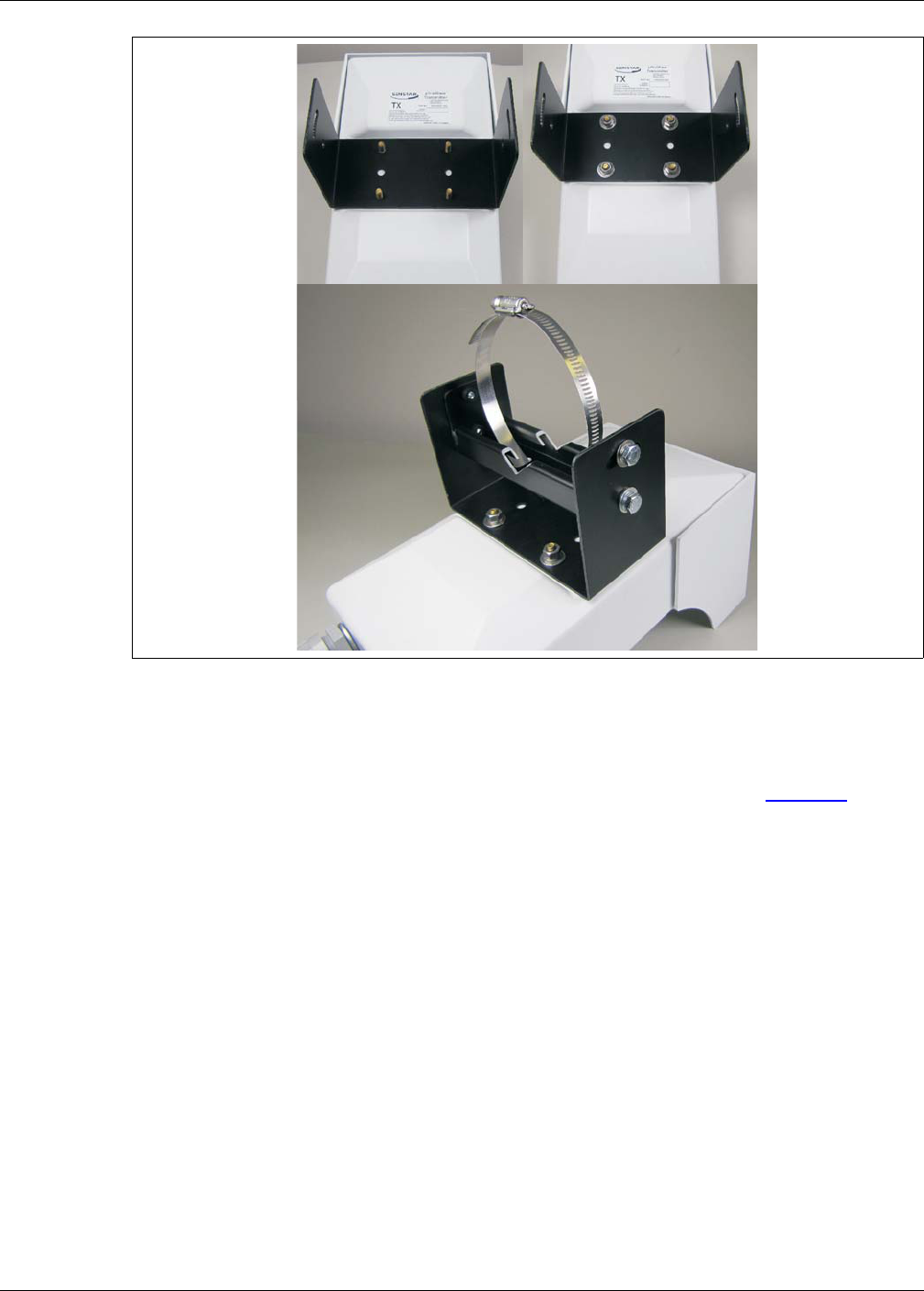
µltraWaveProductguide Page 13
Post-mount alignment
For optimal performance, ensure that the μltraWave transmitter and receiver are aimed directly
toward each other, and that the mounting height is correct for both units (see Figure 10 ).
1. Measure and verify the mounting heights of both units.
2. If required, loosen the transmitter’s gear clamp slightly, and then carefully aim the transmitter
directly at the receiver.
3. Tighten the transmitter’s gear clamp.
4. If required, loosen the receiver’s gear clamp slightly, and then carefully aim the receiver
directly at the transmitter.
5. Tighten the receiver’s gear clamp.
6. If required, loosen the four bolts that attach the post collar to the mounting bracket and aim
the units (in the vertical axis) toward each other. Re-tighten the bolts.
Figure 9 Post-mounting procedure
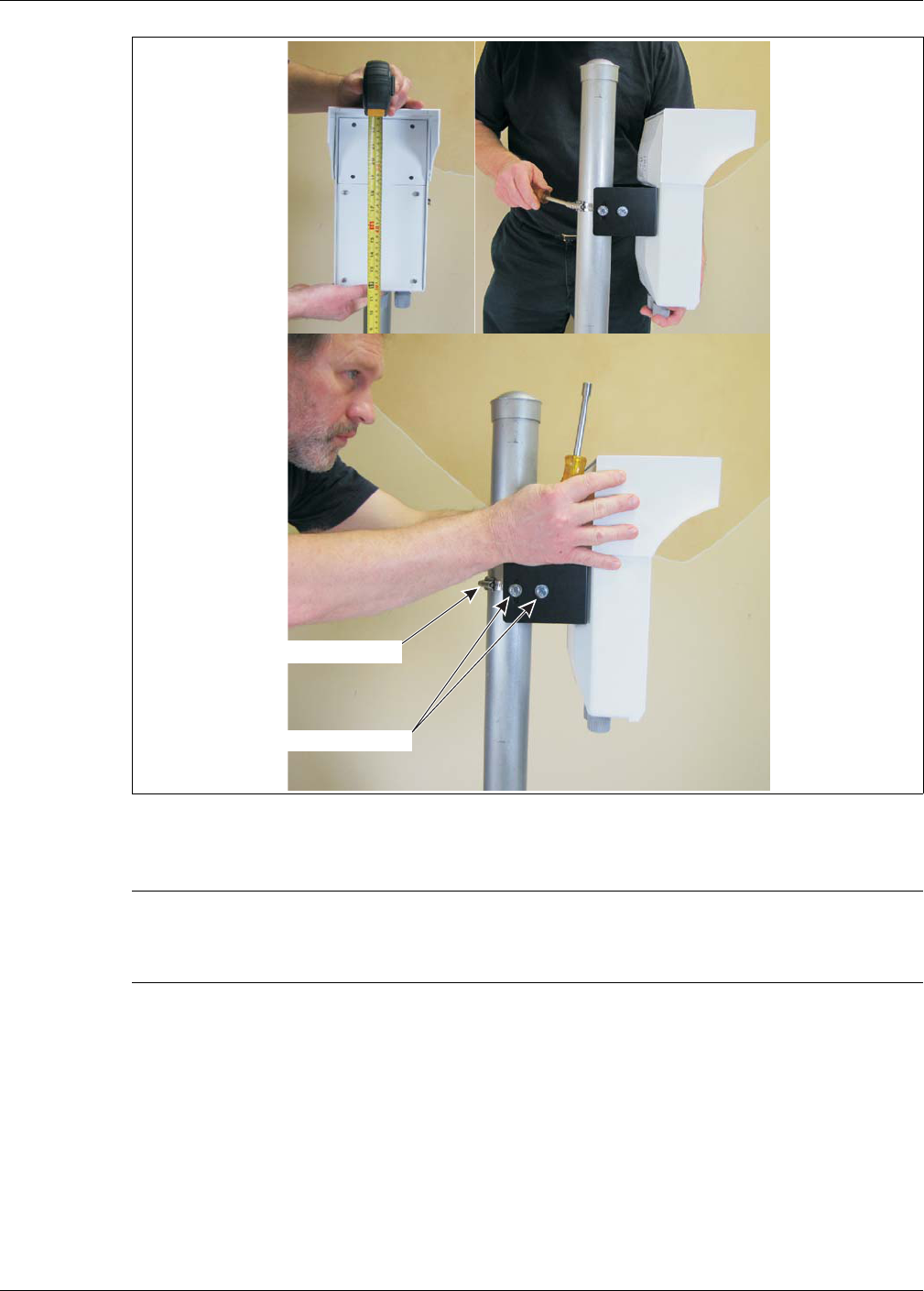
Page 14 µltraWaveProductguide
Surface-mounting
The μltraWave mounting bracket can be used to surface mount the transmitter and/or receiver.
The mounting bracket is attached to the μltraWave unit, and then to the post collar. The post
collar is rotated 180º so the flat side is facing outward toward the mounting surface. Customer-
supplied hardware is used to attach the collar to the mounting surface.
Surface mounting procedure
1. Using an 11 mm (7/16 in.) wrench and the supplied hardware (hex nut, lock washer, flat
washer - X4) attach the mounting bracket to the μltraWave unit.
Figure 10 µltraWave alignment
CAUTION For surface mount applications, the two mounting surfaces
must face toward each other. Surface mounted μltraWave units
cannot be rotated in the horizontal axis. If required, use shims
to adjust the horizontal alignment of surface mounted units.
horizontal adjustment
vertical adjustment
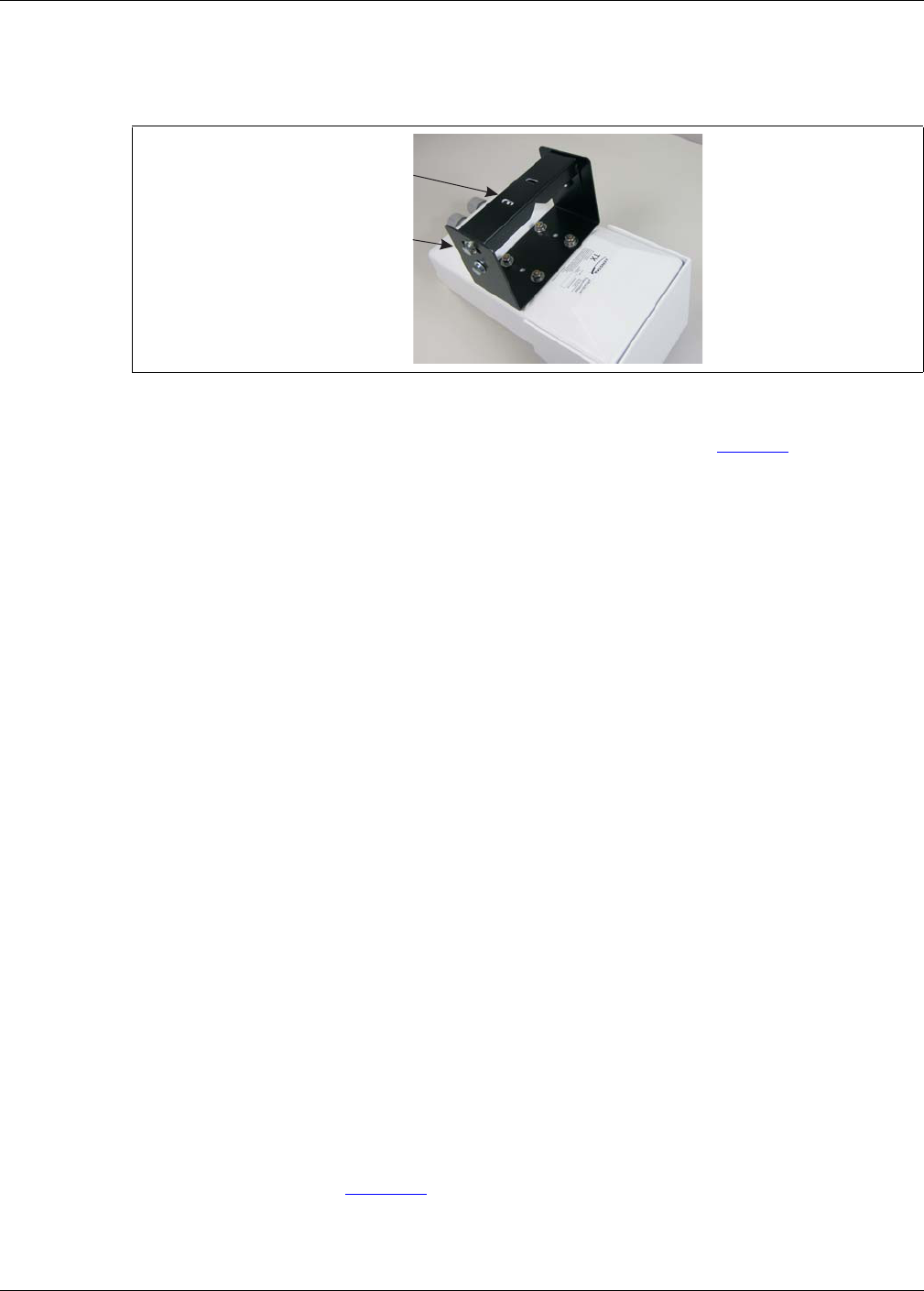
µltraWaveProductguide Page 15
2. Using an 11 mm (7/16 in.) wrench and the supplied hardware (bolt, lock washer, flat washer -
X4) attach the post collar to the mounting bracket with the flat side of the collar to the
outside.
3. Hold the μltraWave unit against the mounting surface and measure the mounting height of
the unit from the center of the antenna to the ground’s surface (see Figure 8 ). Mark the
mounting surface at the centers of the two slots in the post collar.
4. Drill two holes in the mounting surface.
5. Remove the post collar from the mounting bracket, and use appropriate fasteners to attach
the post collar to the mounting surface.
6. Re-attach the mounting bracket and μltraWave unit to the post collar.
7. Measure and verify the mounting height.
8. Mount the second μltraWave unit.
Surface-mount alignment
To ensure optimal performance, it is critical that the μltraWave transmitter and receiver are aimed
directly toward each other, and that the mounting height is correct for both units.
1. Verify the mounting heights of both units.
2. If required, loosen the mounting hardware on the post collars, and install shims so that the
μltraWave transmitter and receiver point directly at each other (horizontal adjustment).
3. Tighten the mounting hardware.
4. If required, loosen the four bolts attaching the post collar to the mounting bracket and aim
the units toward each other (in the vertical axis). Re-tighten the bolts.
Transmitter/receiver wiring connections
The μltraWave wiring connections are made on removable terminal blocks. The screw terminals
accept wire sizes from 12 to 24 AWG, with a 6.4 mm (0.25 in.) strip length. Remove the terminal
blocks to make the wiring connections. Reinstall the blocks after the connections are complete,
and verified. The DC power input is made on T3 and the input/output connections are made on
T6. The Aux input is available only through Remote control mode when using network
communications. Refer to Figure 12 for an illustration of the μltraWave wiring connections.
Figure 11 µltraWave alignment
post collar
mounting bracket
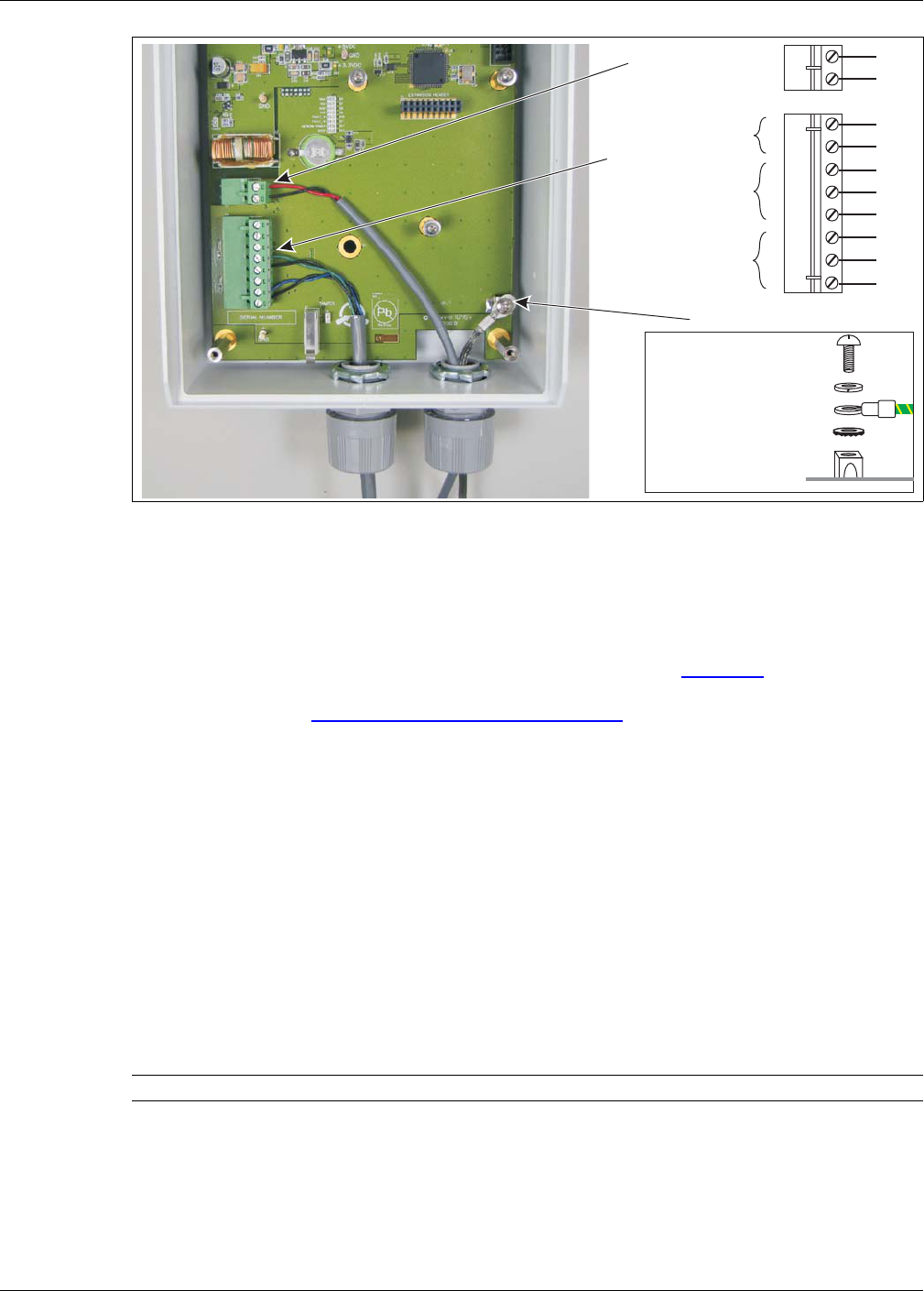
Page 16 µltraWaveProductguide
T3 - power input
The μltraWave units require 12 to 48 VDC to operate. Pin 1 is negative and pin 2 is positive.
T6 - inputs/outputs
T6 connects to output 1, output 2 and an auxiliary (Aux) input (see Figure 12 for connection
details). In Local control mode each output is configured via the UCM to report user-specified
alarm conditions (see Alarm data communications on page 8). The Aux input is not used in Local
control mode.
In Remote control mode the outputs are used by the security management system as output
control points. The Receiver’s Aux input is available to report the status of an auxiliary security
device. The Aux input on the transmitter is not used.
Relay contact ratings
The dry contact relays are single pole, double throw, Form C, latching, rated for 30 V @ 1 A max.
Auxiliary input
In Remote control mode, the receiver’s AUX input is a voltage sensing input. The receiver
determines the input’s status via an internal reference voltage, and the configuration of the
contact closures and supervision resistors. Any change in the input’s status is reported to the host
security management system.
Cable ports
Each μltraWave unit includes two 22 mm (0.875 in.) cable ports fitted with compression glands.
Remove the compression glands, pull the cables through the glands and into the enclosure. Then
replace the compression glands. After making the wiring connections, hand-tighten the
compression glands to provide weather protection and strain relief.
Figure 12 Transmitter/receiver wiring connections
Note The contact closure input to the AUX input must be voltage-free.
T6
T3
1
2
3
4
5
6
7
8
1
2
NC
COM
NO
NC
COM
NO
-
+
-
+
ground connection details
machine screw
lock washer
ground wire
external tooth washer
PCB ground connection
PCB
power input
(12 to 48 VDC)
input/output
connections
AUX input
output 1
output 2
(Remote control mode)
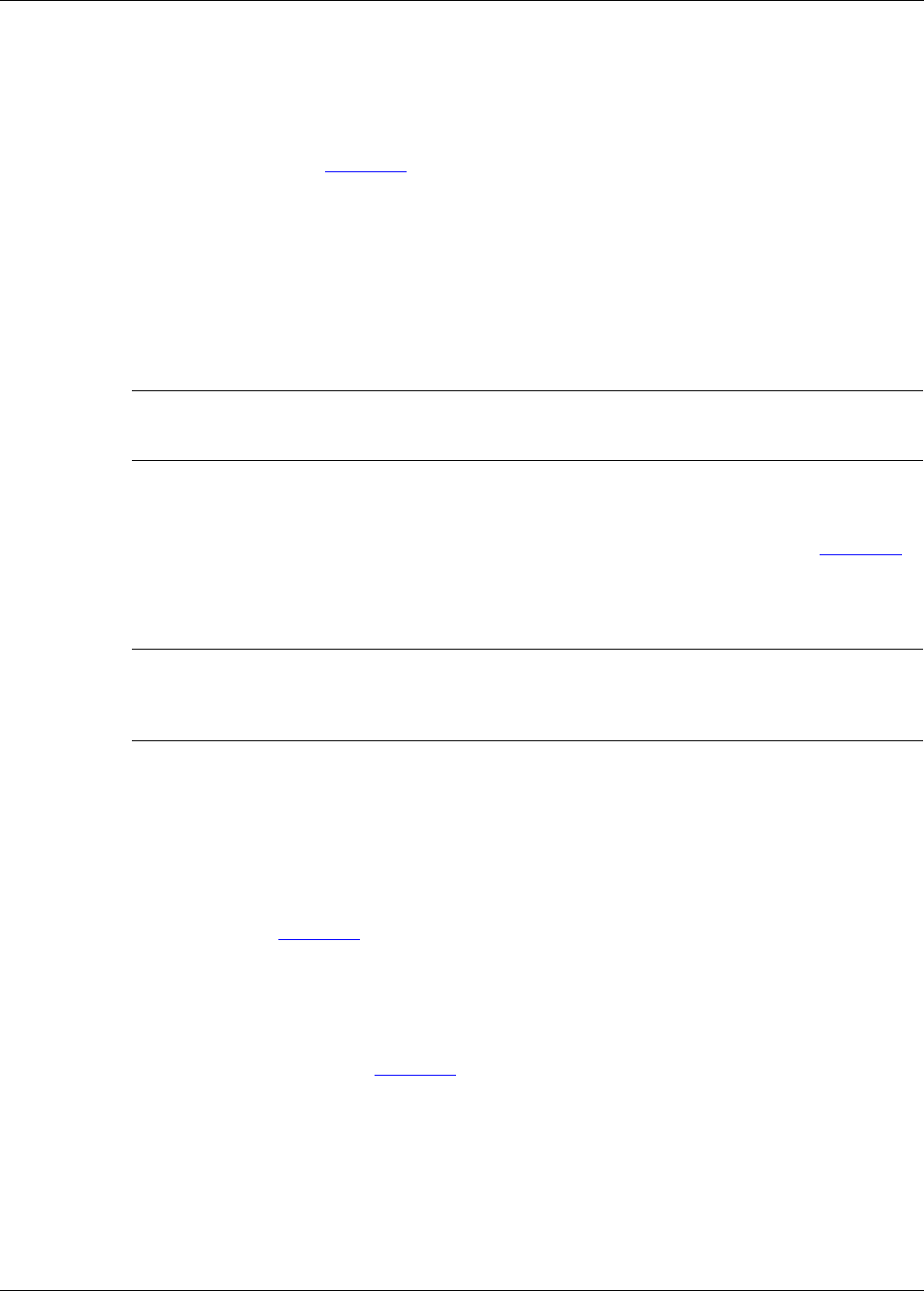
µltraWaveProductguide Page 17
Making the I/O wiring connections
1. Pull the data cable into the enclosure.
2. Prepare the data cable - strip length = 6.4 mm (0.25 in.).
3. Remove the terminal block from T6, make the wiring connections, and then replace the
terminal block (see Figure 12 ).
Enclosure tamper switch
Each μltraWave unit includes a mechanical tamper switch (closed = secure, open = tamper) to
indicate if the enclosure cover is removed. Placing a shunt on header T2 overrides the tamper
switch (shunt ON = secure).
Transmitter/Receiver grounding
1. Connect an approved ground wire to a properly installed ground rod at the μltraWave unit’s
installation location.
2. Connect the ground wire to the ground lug on the transmitter/receiver PCB (see Figure 12 ).
Power supply connection
When a central low voltage power supply is being used for primary power, it should be powered
from an uninterruptible AC power source.
• To power the system from a central source, run the power distribution cable around the
perimeter and tap off to each μltraWave unit. Use a minimum 14 gauge wire for power runs
up to 1.2 km (4000 ft.). For longer runs use 12 gauge wire.
•At each μltraWave unit, splice the power cable to a lighter gauge pigtail that is approximately
30 cm (12 in.) long. Connect the negative lead to T3-1 (-) and connect the positive lead to
T3-2 (+) (see Figure 12 ).
Local power supply
To use a local DC power supply outdoors, the power supply must be installed in its own
weatherproof enclosure. The local supply can be mounted on the same post as the μltraWave unit
to keep the wire runs to a minimum. Connect the negative lead to T3-1 (-) and connect the
positive lead to T3-2 (+) (see Figure 12 ).
Note Senstar recommends using a low resistance (5Ω or less) earth ground
connection at each unit. Consult the local electrical codes for
additional grounding information.
WARNING! DO NOT bring AC mains power into the μltraWave enclosure. If a
local power supply is being used, it must be installed in its own
weatherproof enclosure. Consult the local electrical code for
information about the connection of AC mains to your power supply.
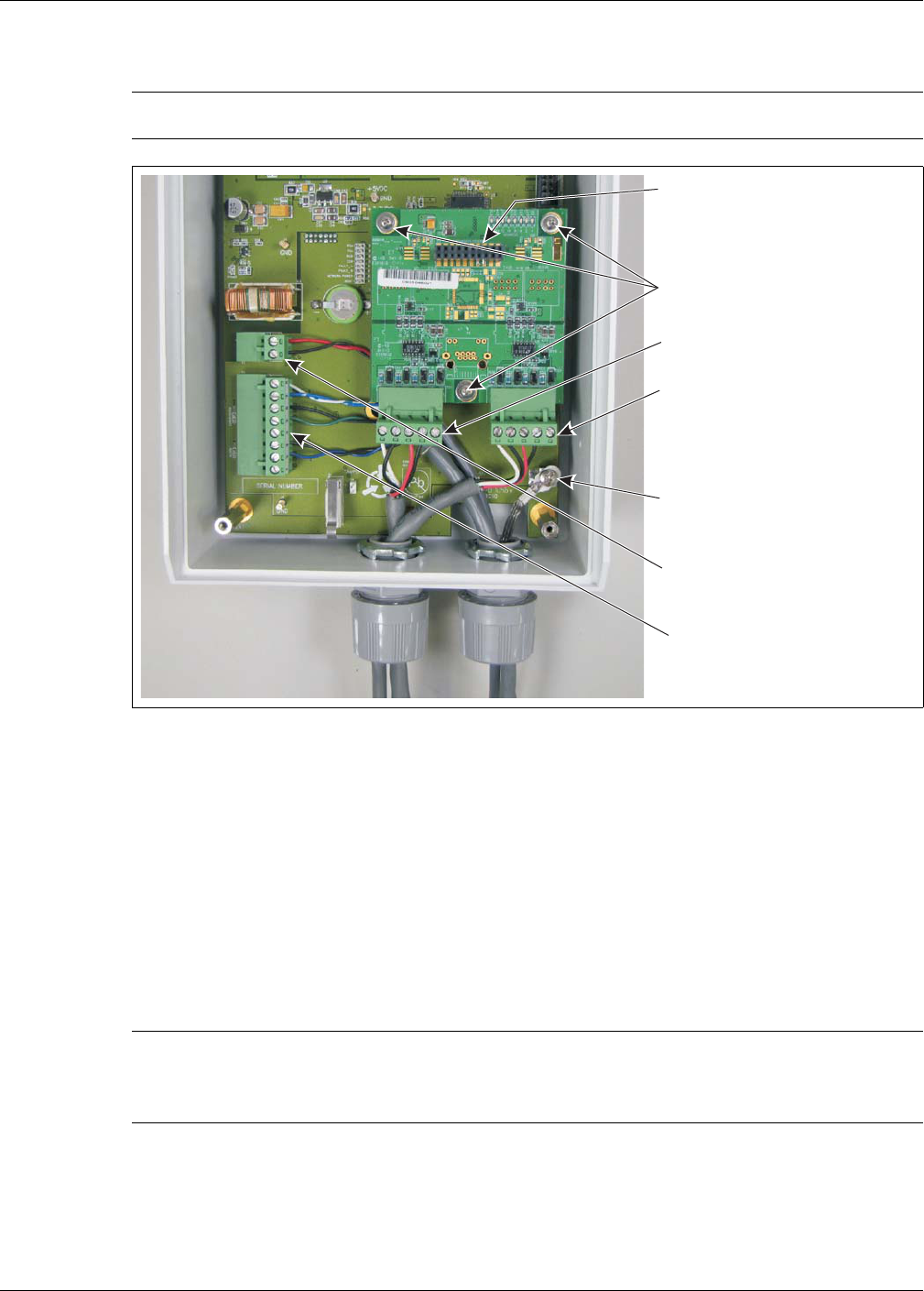
Page 18 µltraWaveProductguide
Silver Network wiring connections
Silver Network specifications
• Data rate - fixed 57.6 k bps
• Maximum 32 devices spread over up to 4 independent network loops
• Two communication Channels (Side A, Side B)
• Network termination - not required
• Transmission media/maximum separation distances between μltraWave receivers:
EIA-422 copper wire - 1.2 km (0.75 mi.)
Multimode fiber optic cable - 2.2 km (1.4 mi.) - 2 fibers per Channel
Singlemode fiber optic cable - 10 km (6.2 mi.) - 2 fibers per Channel
Note A network interface card must be installed on the μltraWave
receiver to enable network communications.
Figure 13 Receiver unit Silver Network wiring connections
Note Senstar strongly recommends the use of low capacitance
shielded twisted pair data cable for EIA-422,
62.5/125 multimode fiber optic cable, and
9/125 singlemode fiber optic cable.
B-side data path connections *
ground connection
T3 power input (see Figure 10)
(12 to 48 VDC)
T6 input/output (see Figure 10)
AUX input
output 1
output 2
A-side data path connections *
NIC mounting hardware (X 3)
T1 expansion header (solder side)
plug into T1 on PCB
use single point grounding
connect one end of the shield, trim
back the other end and leave it
disconnected
*
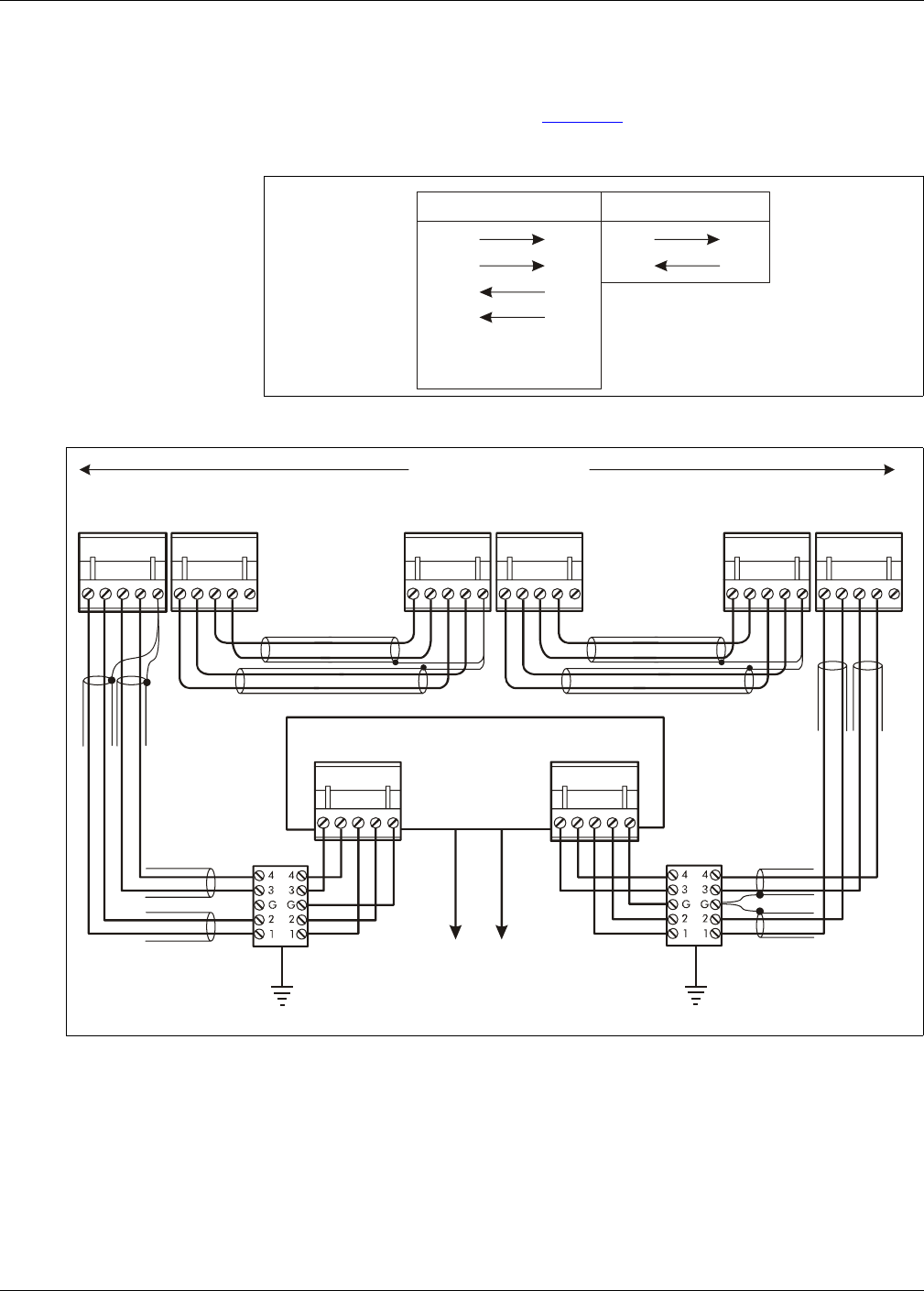
µltraWaveProductguide Page 19
Silver Network connections
The following connection diagrams illustrate an EIA-422 based Silver Network, a fiber optic based
Silver Network and a mixed media Silver Network. Figure 14 shows the network connections and
data flow directions for the EIA-422 and fiber optic communication options:
Figure 14 Silver Network connections
Figure 15 Silver Network EIA-422 wiring diagram
TXA+
TXA-
RXA+
RXA-
GND
RXB+
RXB-
TXB+
TXB-
TXA
RXA
RXB
TXB
EIA-422 Fiber Optic
(use single point
grounding, connect only
one side of shield)
11
223344
55
RXB+
RXB-
GND
TXB+
TXB-
RXA+
RXA-
GND
TXA+
TXA-
11
223344
55
12345 12345
11
223344
55
12345 1234512345 12345
RXB+
RXB-
GND
TXB+
TXB-
RXA+
RXA-
GND
TXA+
TXA-
RXB+
RXB-
GN
D
TXB+
TXB-
RXA+
RXA-
GND
TXA+
TXA-
RXA+
RXA-
GND
TXA+
TXA-
12345
RXB+
RXB-
GND
TXB+
TXB-
12345
maximum 32 devices
max. distance between devices = 1.2 km (3/4 mile)
first receiver second receiver last receiver
shield shield
shield shield
shield
shield
NOTE: Use single point grounding - connect one end of the shield, trim the other end and leave it disconnected.
Network Interface Unit
lightning
arrestors lightning
arrestors
to Network Manager
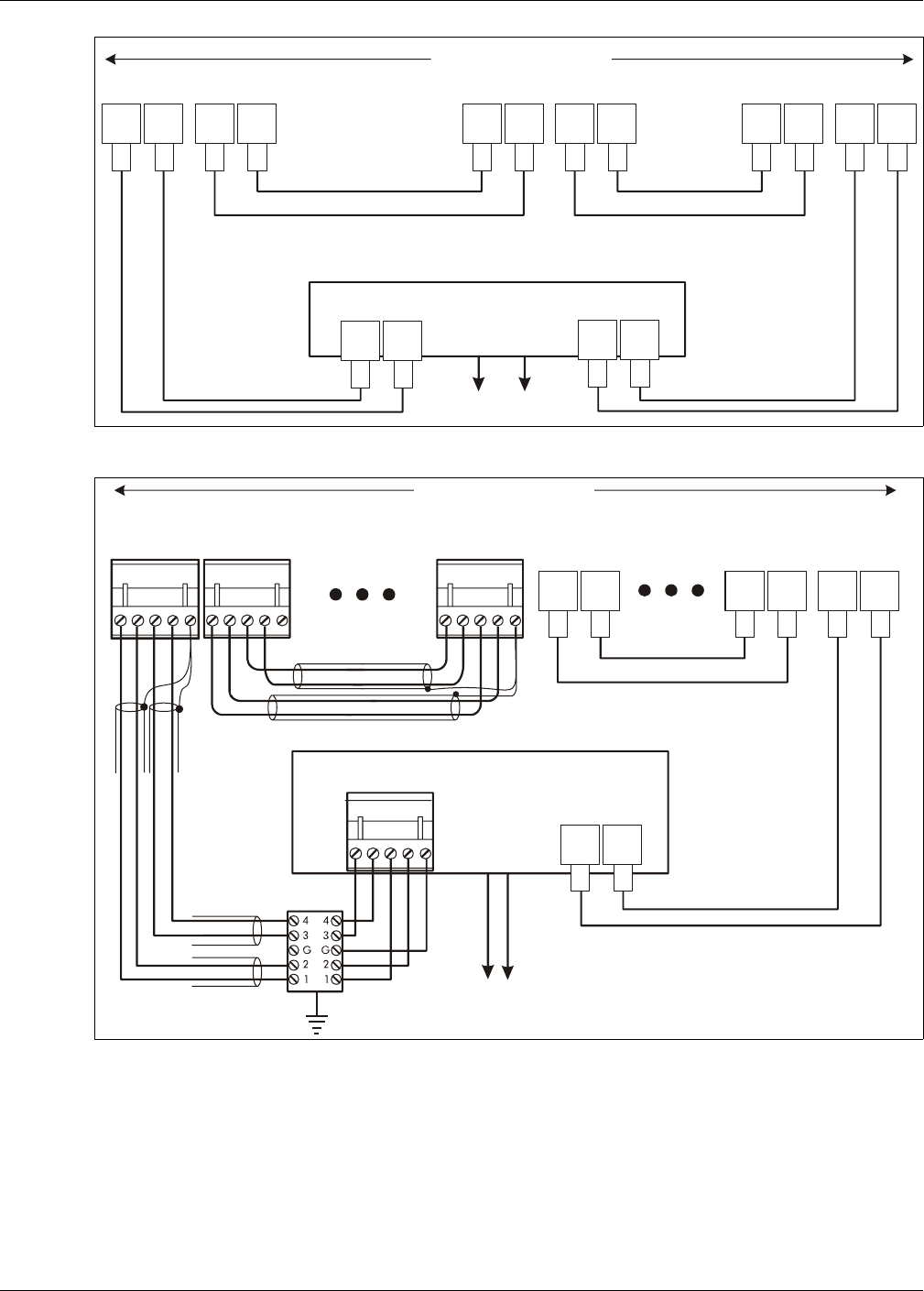
Page 20 µltraWaveProductguide
Figure 16 Silver Network fiber optic wiring diagram
Figure 17 Mixed media EIA-422/fiber optic wiring diagram
TXB RXBTXA RXA
TXB RXB TXA RXA
TXB RXBTXA RXA TXB RXBTXA RXA
maximum 32 devices
first receiver second receiver last receiver
Network Interface Unit
to Network Manager
maximum distance between devices
multimode fiber optic = 2.2 km (1.4 miles)
singlemode fiber optic = 10 km (6.2 miles)
TXA RXA
TXB RXB TXB RXBTXA RXA
11
223344
55
RXB+
RXB-
GND
TXB+
TXB-
RXA+
RXA-
GND
TXA+
TXA-
1
234
5
1234512345 12345
RXA+
RXA-
GND
TXA+
TXA-
RXB+
RXB-
GND
TXB+
TXB-
12345
maximum 32 devices
first receiver second receiver last receiver
Network Interface Unit
to Network Manager
maximum distance between devices:
multimode fiber optic = 2.2 km (1.4 miles)
singlemode fiber optic = 10 km (6.2 miles)
EIA-422 wire = 1.2 km (3/4 mile)
lightning
arrestors
shield
shield
shield
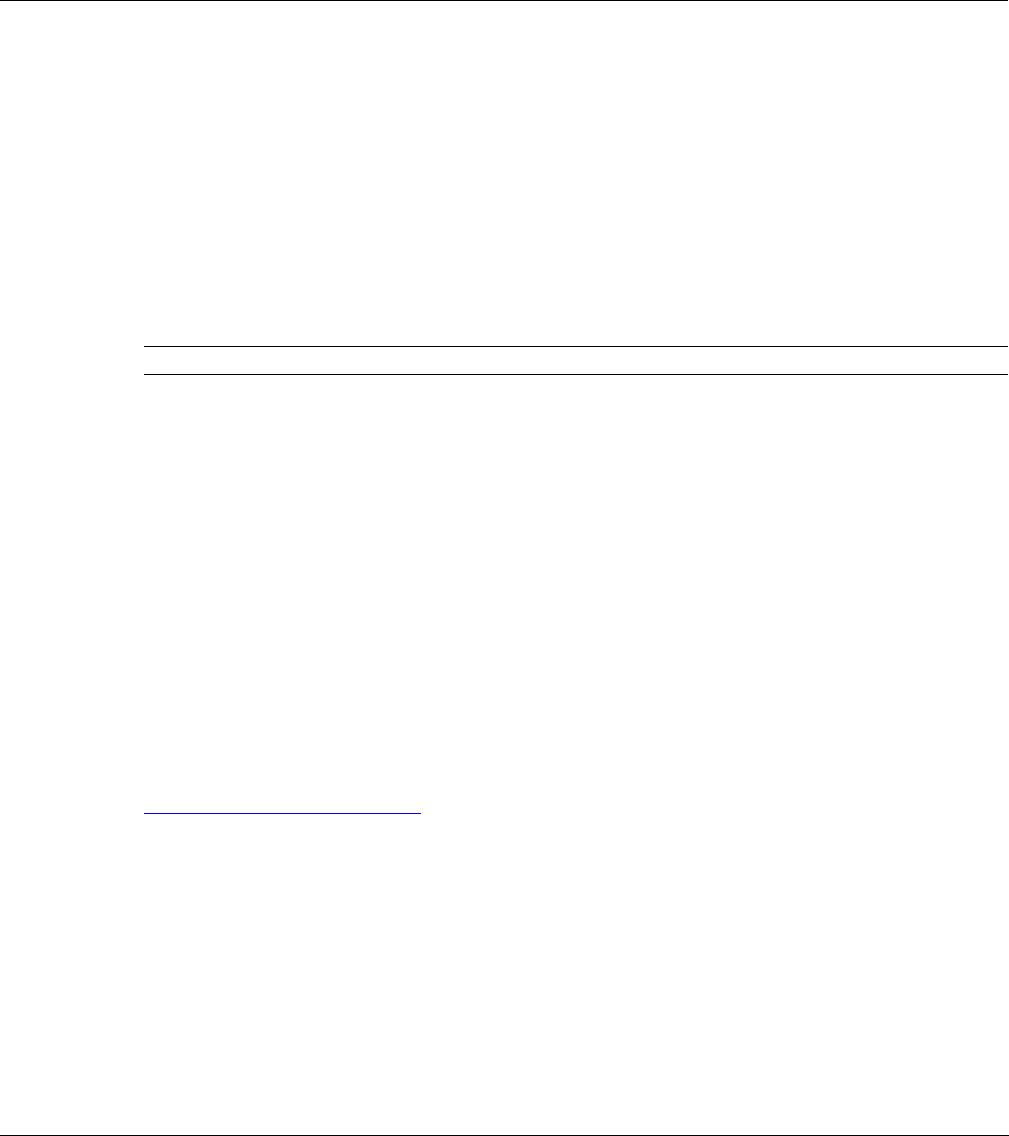
µltraWaveProductguide Page 21
3 Setup and calibration
μltraWave setup and calibration is done using Senstar’s Universal Configuration Module (UCM).
The UCM is a window-based software application that performs the calibration, setup,
maintenance and diagnostic functions for Senstar’s line of intrusion detection sensors. The UCM
connects directly to the μltraWave unit via USB. Network based μltraWave receivers can also
connect remotely via the Silver Network Manager.
Senstar recommends that the initial calibration be done at the μltraWave unit using a direct USB
connection to the UCM. An enclosure tamper condition must exist to enable UCM communication
via a USB connection.
The μltraWave receiver setup requires the following configuration settings:
•specify the Locale - FCC for North American applications, ETSI for European applications
(transmitter and receiver settings must match)
•specify the Frequency Pair (transmitter and receiver settings must match)
• enter the Transmitter Serial Number
•set the detection Thresholds (velocity response)
(use the UCM design tool to calculate the optimum detection Thresholds)
The μltraWave transmitter setup requires the following configuration settings:
•specify the Locale - FCC for North American applications, ETSI for European applications
(transmitter and receiver settings must match)
•specify the Frequency Pair (transmitter and receiver settings must match)
Once the μltraWave transmitter and receiver are properly installed and configured, you can
calibrate the receiver unit. On the receiver’s UCM Status tab, select the recalibrate button and the
μltraWave receiver will auto-calibrate to provide the best possible received signal strength (see
Receiver calibration on page 26).
Note Consult the online help for detailed information on UCM operation.
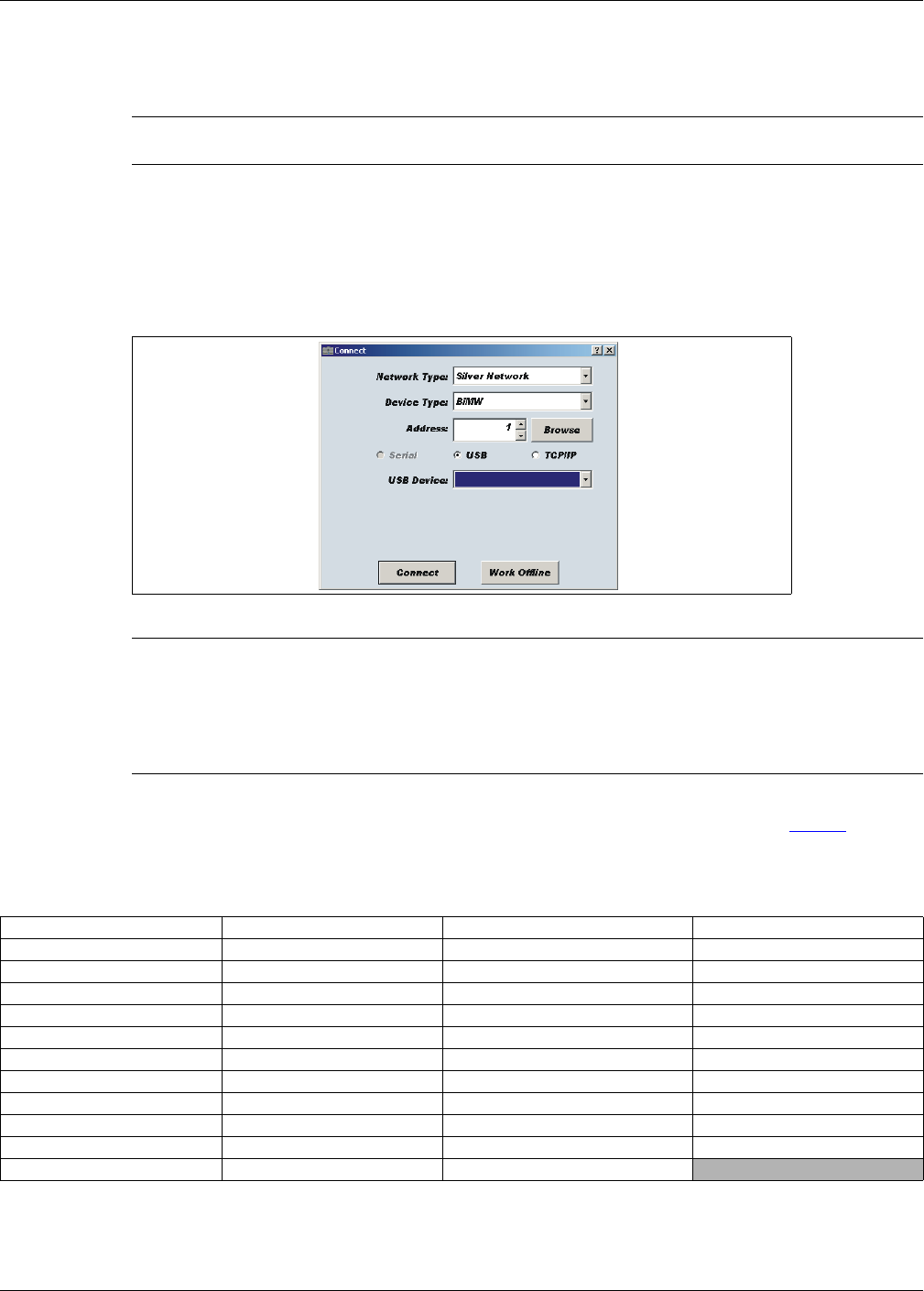
Setup
Page 22 µltraWaveProductguide
Setup
Connecting the UCM
1. Remove the lower cover from the μltraWave enclosure and use a USB cable to connect the
UCM computer to T2 on the transmitter PCB.
2. Start the UCM application and establish a connection.
The μltraWave Microwave Detection Sensor complies with FCC standard 15.245 for North
American operation, and with ETSI standard EN 300 440 for European operation. Tabl e 3 includes
the European countries in which the standard is recognized (CEPT group of nations with the EU
members listed in parenthesis). If the country in which you are installing the μltraWave is not
included in the table, contact the local Certification Authority before installing the system.
3. Select the Config tab and specify the Locale.
Note μltraWave setup and calibration must be performed by a qualified
technician.
Figure 18 Connecting the UCM
Note The first time the UCM connects to the transmitter/receiver units, you
are prompted to select the sensor’s Locale (FCC for North American
operation, or ETSI for European operation). Make the selection
based on the country in which the unit is installed. The μltraWave will
not operate until both the transmitter and receiver have the Locale
specified.
Albania France (EU) Montenegro Switzerland
Andorra Georgia Netherlands (EU) Turkey
Austria (EU) Germany (EU) Norway Ukraine
Azerbaijan Greece (EU) Poland (EU) United Kingdom (EU)
Belarus Hungary (EU) Portugal (EU) Vatican
Belgium (EU) Iceland the former Yugoslav Republic Bosnia and Herzegovina
Ireland (EU) Romania (EU) Bulgaria (EU) Italy (EU)
Russian Federation Croatia Latvia (EU) San Marino
Cyprus (EU) Liechtenstein Serbia Czech Republic (EU)
Lithuania (EU) Slovakia (EU) Denmark (EU) Luxembourg (EU)
Slovenia (EU) Estonia (EU) Malta (EU) Spain (EU)
Finland (EU) Moldava Sweden (EU)
Table 3 European nation groups
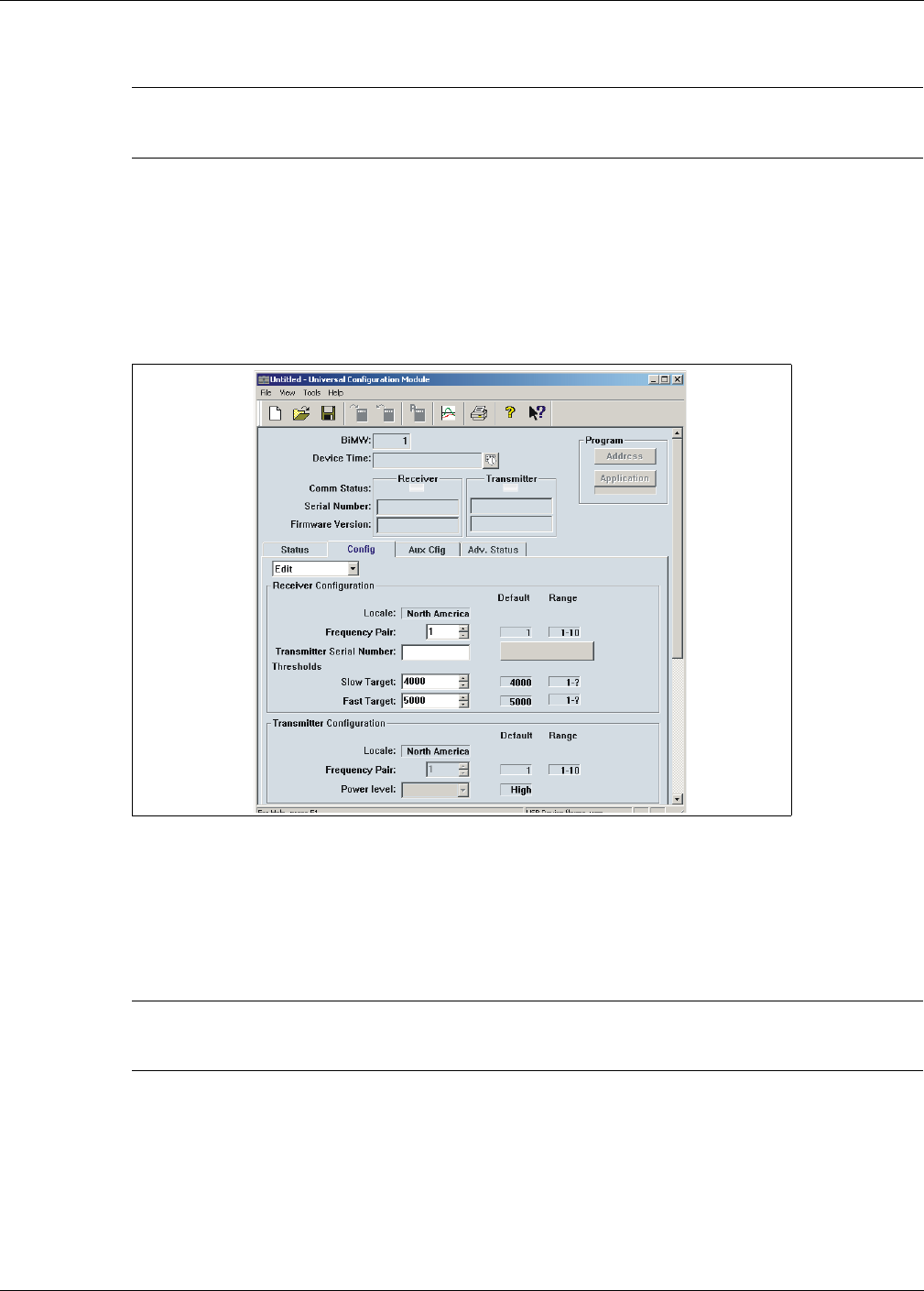
Setup
µltraWaveProductguide Page 23
Setting the transmitter/receiver Frequency Pair
1. Connect the UCM to the transmitter unit.
2. On the μltraWave main menu, select the Config tab.
3. In the Frequency Pair field, use the arrows to specify the Frequency Pair that will be used for
this μltraWave sensor (transmitter and receiver).
4. Download the configuration change to the transmitter unit.
5. Repeat this procedure for the receiver unit.
Receiver setup
Once the transmitter and receiver units are installed, aligned and set to the correct frequency pair,
the receiver can be setup and calibrated.
1. Connect the UCM computer to the receiver PCB.
2. Verify the Locale and Frequency Pair settings.
3. In the Transmitter Serial Number field, enter the serial number for the paired transmitter unit.
4. Specify the Thresholds (Slow Target and Fast Target settings). Use the UCM design tool to
calculate the optimal detection Thresholds.
5. Save the configuration and download the configuration changes to the receiver unit.
Note Both the transmitter and receiver must use the same Frequency Pair.
If there are other nearby μltraWave sensors, they must be set to
different Frequency Pairs.
Figure 19 UCM Config tab
Note During the receiver calibration process, the transmitter and receiver
units must not be moved, and nothing may interfere with the
microwave signal (i.e., nobody walks between or near the units).

Setup
Page 24 µltraWaveProductguide
Specify the Auxiliary I/O control mode
This section details the procedures for configuring the outputs and input for Local control and
Remote control operation.
1. Select the Aux Cfig tab.
2. Use the Aux Control arrow to specify the control mode (Local or Remote).
3. Select the Download button to save the configuration changes to the μltraWave unit.
Auxiliary (Aux) inputs
In Remote Control mode, the receiver’s Aux input is a voltage sensing input that is used to report
the status of an auxiliary device to the host computer. The receiver determines the input’s status
via an internal reference voltage, and the configuration of the contact closures and supervision
resistors. Input contact closures MUST be voltage-free. You define the input as normally open
(NO) or normally closed (NC) with single resistor supervision, dual resistor supervision, or
unsupervised. The Filter Window parameter allows you to set the time period for which an input
must be active, before the receiver reports an event. Tab le 4: includes the selectable Remote
Control input wiring configurations, and Ta bl e 5 : includes the selectable supervision resistor
values.
Input option UCM selection Alarm relay Supervision relay R1 R2
unsupervised NO --- --- ---
single resistor
supervision NO NC 5.1 k ---
dual resistor
supervision NO NO/NC 4.3 k 820
unsupervised NC --- --- ---
single resistor
supervision NC NO 5.1 k ---
dual resistor
supervision NC NO/NC 5.1 k 820
Table 4: Selectable input configurations
R1 values (single resistor
supervision)
R1 values (double resistor
supervision)
R2 values (double resistor
supervision)
820 1.1 k 820
1 k 2.2 k 1.1 k
1.1 k 4.3 k 2.2 k
1.2 k 5.1 k 5.6 k
1.5 k 5.6 k
2.2 k
3.3 k
4.7 k
5.1 k
5.6 k
Table 5: Selectable resistor values
A
1A
S
12A
S
A
1
A
S
12A
S
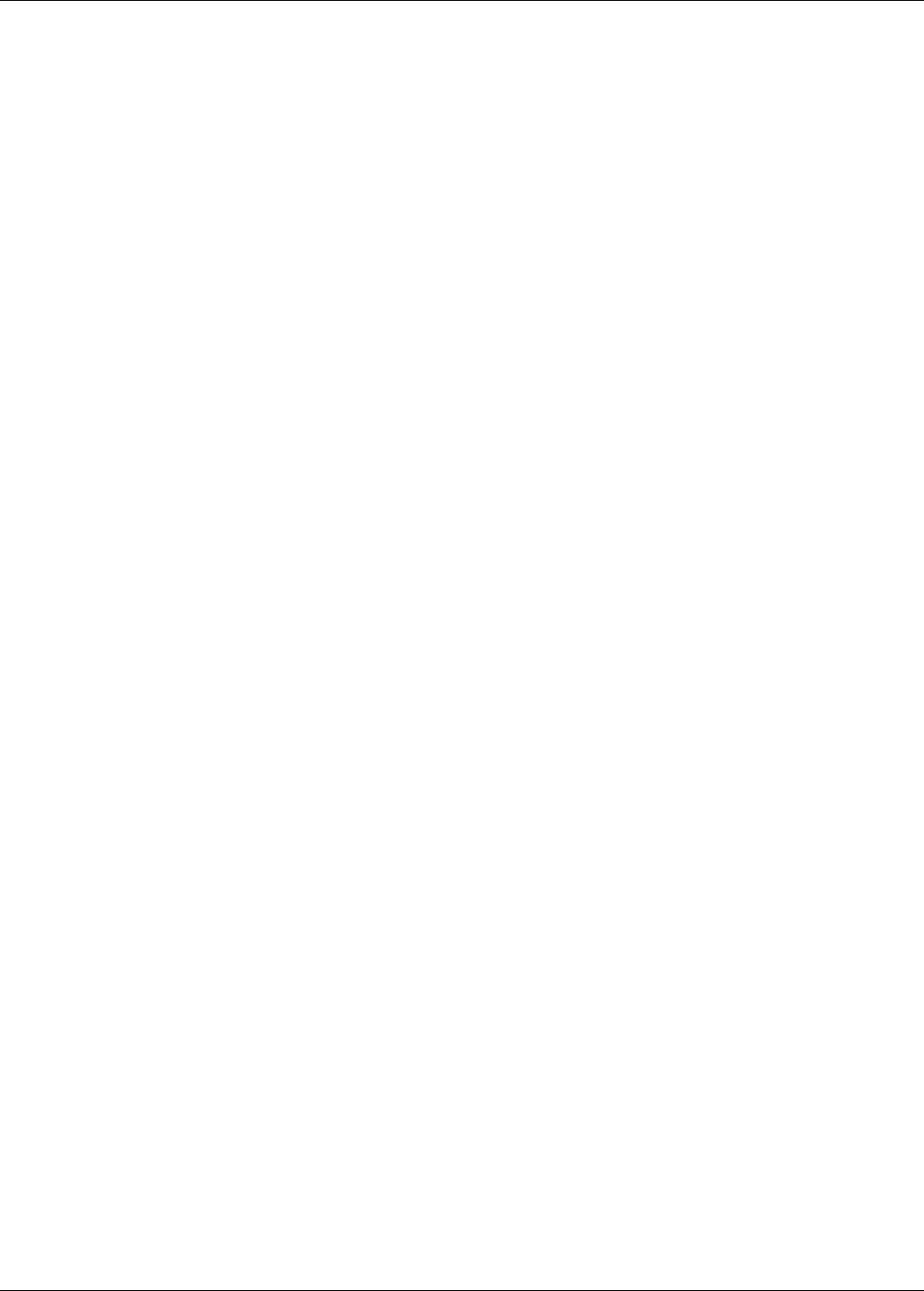
Setup
µltraWaveProductguide Page 25
Input configuration procedure (Remote control mode)
1. Select the Aux Cfig tab on the UCM window.
2. From the Supervision drop down, select the desired supervision scheme for the input.
3. Select the Resistor 1 value, if applicable.
4. Select the Resistor 2 value, if applicable.
5. Set the Noise Tolerance, if required.
6. Set the Line Drop, if required.
7. Set the Filter Window.
8. Save the UCM configuration file.
9. Select the Download button to save the configuration changes to the receiver.
Output relays
Output relay setup (Local control mode)
In Local control mode, the two relays are setup via the Local Aux Control Activation check boxes
to report alarm and supervision conditions. The relays are then controlled by the μltraWave unit to
activate on the user-specified conditions. The relays remain active for an event’s duration or for
the selectable relay Active Time, whichever is longer.
1. Use the Output selection arrows to select a relay.
2. Specify the Hold/Active Time parameter.
3. Specify the conditions from the Local Aux Control Activation field under which this relay will
activate.
4. Repeat this procedure for the other relays.
5. Save the UCM configuration file.
6. Select the Download button to save the configuration changes to the μltraWave unit.
Output relay setup (Remote control mode)
In Remote control mode, the receiver’s relays are controlled by the host computer to operate
auxiliary equipment as output control points (e.g., to activate lights, doors, sirens, CCTV
equipment, etc.). The transmitter’s relays are not used in Remote control mode. You configure the
relays response to commands from the host computer. You can configure the relays as latching
(ON by command, OFF by command) or in flash mode (ON-OFF-ON-OFF etc. by command, OFF
by command) or in pulse mode (ON for a period, then OFF). For flash and pulse modes, the ON-
OFF time duration is configurable.
1. Use the Output selection arrows to select a relay.
2. Select the type of relay Activation (latching, or flash mode, or pulse mode).
3. Select the Hold/Active Time parameter, if applicable.
4. Select the Inactive Time parameter, if applicable.
5. Repeat this procedure for the other relays.
6. Save the UCM configuration file.
7. Select the Download button to save the configuration changes to the receiver.
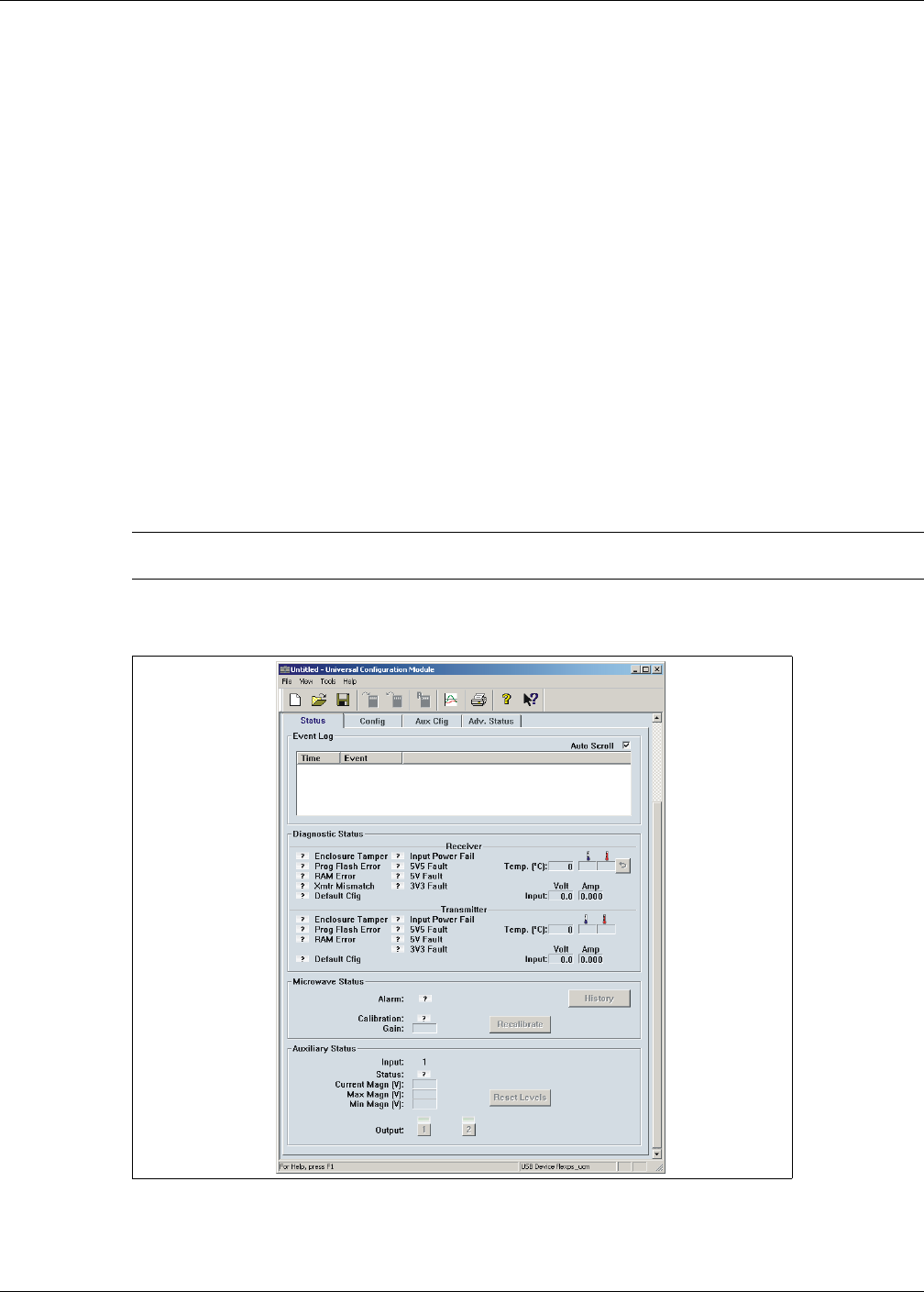
Receiver calibration
Page 26 µltraWaveProductguide
Setting the receiver’s address
The receiver address can be set only by using a direct USB connection between the UCM
computer and T3, the USB port on the receiver. Systems that do not use network communications
can use the default address of 1.
1. In the Program field select the Address button.
The change Device Address dialog displays.
2. In the Change Device Address dialog, specify the New Address for the connected receiver.
3. Select the Program button.
The new address takes effect when communications are re-established.
Receiver calibration
Once the μltraWave transmitter and receiver are setup and configured, perform the receiver
calibration.
1. On the receiver’s UCM Status tab, select the Recalibrate button.
The receiver performs a self-calibration.
Once the self-calibration is complete, the μltrawave sensor is ready to be put into service.
CAUTION Ensure that the microwave detection zone is not disturbed or
interrupted during the calibration process.
Figure 20 UCM Status tab
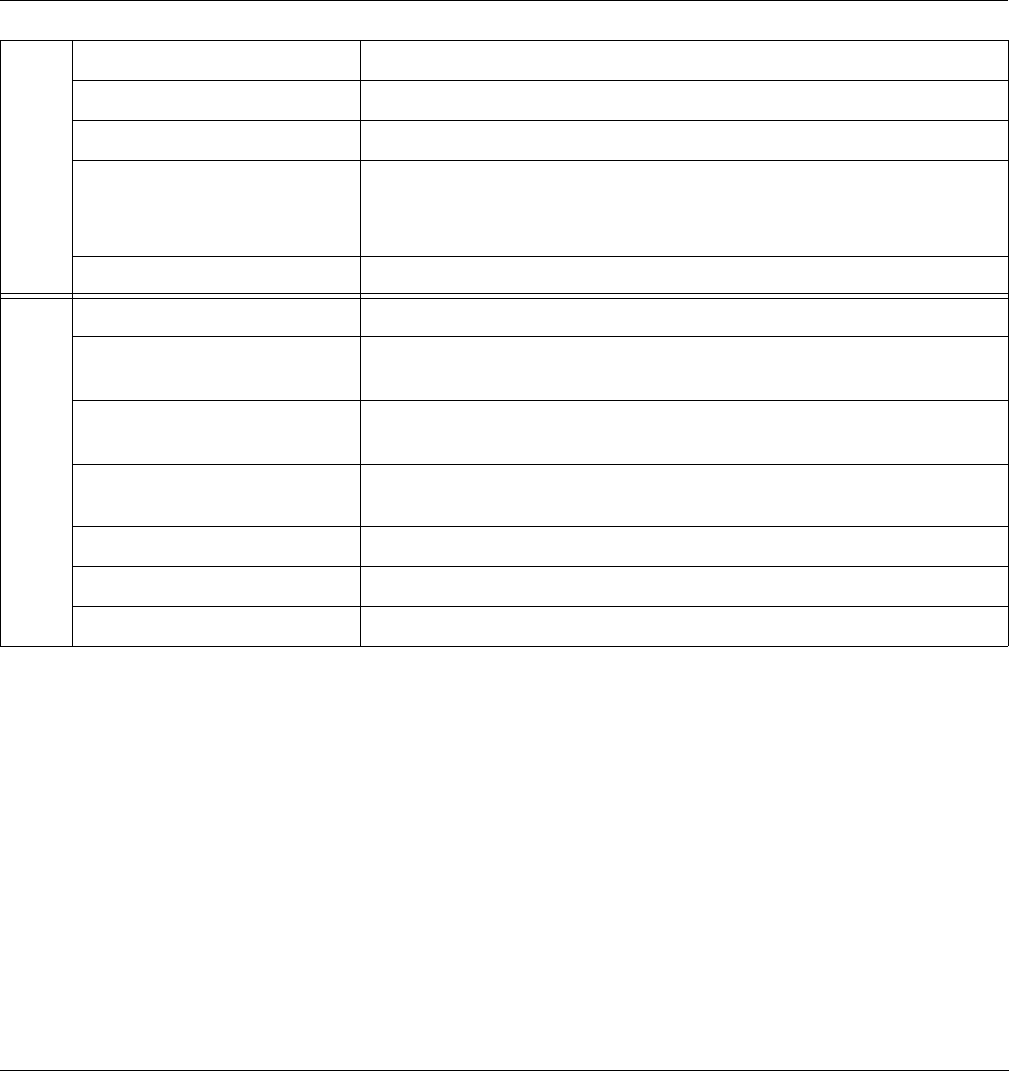
µltraWave ProductGuide Page 27
aSpecifications
General
Voltage requirements • 12 - 48 VDC
Power consumption • 4 W (maximum) (system - receiver plus transmitter)
Operating range • 3 to 200 m (10 to 656 ft.)
Dimensions
• width - 16 cm (6.25 in.)
• depth - 9 cm (3.375 in.)
• height - 31 cm (12.25 in.)
Weight • 0.9 kg (2 lbs.)
Transmitter/Receiver
Operating voltage & current • 12 - 48 VDC, 120 mA maximum
Microwave carrier frequency • ETSI - 24.150 - 24.250 GHz
• FCC - 24.075 - 24.175 GHz
Separation distance (max.) • transmitter/receiver - high security 100 m (328 ft.)
• transmitter/receiver - low security 200 m (656 ft.)
Antenna pattern • 13º (horizontal)
• 13º (vertical)
Operating temperature • -40º to +66ºC (-40º to +150º F)
Output relays (2 per unit) • 2 form C relay outputs 30 VDC @ 1 A maximum, non-inductive load
Auxiliary input (1 per unit) • voltage sensing auxiliary device input
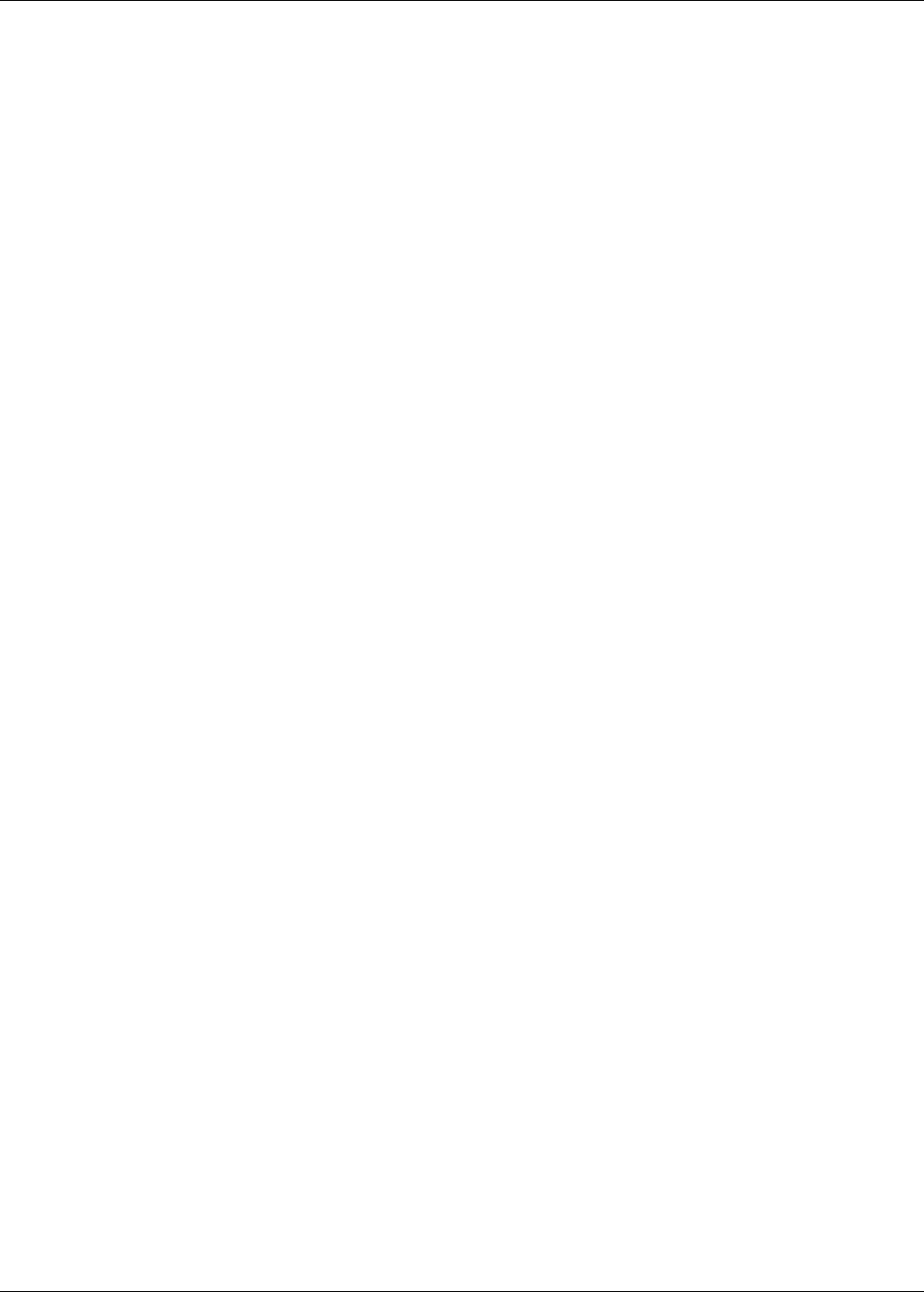
Page 28 µltraWave ProductGuide