Siemens 21 115532 001 Users Manual JFR Instruction Manual_10 07 08
21-115532-001 JFR-Instruction-Manual-10-09-08
21-115532-001 to the manual 69bb9fd6-63c5-40d7-a3e0-908d71ad7cb5
2015-02-05
: Siemens Siemens-21-115532-001-Users-Manual-410621 siemens-21-115532-001-users-manual-410621 siemens pdf
Open the PDF directly: View PDF .
Page Count: 28

Installation / Operation / Maintenance
Instructions
JFR Distribution
Step Voltage Regulator
21-115532-001 PR4018-06
SUPERCEDES
21-115532-001
PR4018-05
October 08

TABLE OF CONTENTS
Page
INTRODUCTION
Inspection for Damage in Shipment................... 2
Storage Prior To Installation ............................. 2
Physical Considerations ................................... 3
Line Terminals and Connections ....................... 3
Electrical Considerations.................................. 3
Installation Diagrams........................................ 4
Protective Measures ........................................ 5
Control Connections ........................................ 5
Connection Diagrams
Straight Design ................................................ 6
Inverted Design................................................ 7
Series Transformers Design ............................. 8
Placing the Regulator in Service
Before Connecting ...........................................9
Connecting ...................................................... 9
Switching On-Line............................................ 9
Checking Regulator Operation .......................... 9
Removing the Regulator From Service.............10
Maintenance
General Instructions........................................11
Operational Checks.........................................11
Periodic Inspection..........................................12
Page
Special Features
Polarized Disconnect Switch
and Hinged Control Panel......................................... 13
Remote Mounting of Control Equipment ..................... 13
Vari-AMPTM Position Indicator................................... 13
Operation at Less Than Rated Voltage......................... 14
Forced Air Cooling ................................................... 15
Subbase Assembly..................................................15
Parts List
Major Components ................................................... 16
Position Indicator ................................................... 17
Type TLG Dial Switch............................................. 18
Type TLG Quick Break Mechanism ........................... 19
Type TLF Dial Switch ............................................... 20
Type TLF Quick Break Mechanism............................21
Bypass Arresters.....................................................22
Bushings.................................................................23
For Emergency Service Call:
1-877-742-3309
Siemens Energy, Inc.
THESE INSTRUCTIONS DO NOT PURPORT TO COVER ALL DETAILS OR VARIATIONS IN EQUIPMENT, NOR TO PROVIDE FOR EVERY
POSSIBLE CONTINGENCY TO BE MET IN CONNECTION WITH INSTALLATION, OPERATION OR MAlNTENANCE. SHOULD FURTHER INFOR-
MATION BE DESIRED OR PROBLEMS ARISE WHICH ARE NOT COVERED SUFICIENTLY FOR THE PURCHASER’S PURPOSES, THE MATTER
SHOULD BE REFERRED TO YOUR SIEMENS ENERGY, INC. REPRESENTATIVE.
THE CONTENTS OF THIS INSTRUCTION MANUAL SHALL NOT BECOME PART OF OR MODIFY ANY PRIOR OR EXISTING AGREEMENT,
COMMITMENT OR RELATIONSHIP. THE SALES CONTRACT CONTAINS THE ENTIRE OBLIGATION OF SIEMENS ENERGY, INC. THE
WARRANTY CONTAINED IN THE CONTRACT BETWEEN THE PARTIES IS THE SOLE WARRANTY OF SIEMENS ENERGY, INC. ANY
STATEMENTS CONTAINED HEREIN DO NOT CREATE NEW WARRANTIES OR MODIFY THE EXISTING WARRANTY.

INTRODUCTION
Page 1
Type JFR single-phase step-voltage regulators are designed
to give dependable service and to make installation, operation
and maintenance as simple as possible.
Technology advances, especially in the realm of the control
apparatus, make it efficient to provide a separate instruction
manual for the Accu/StatTM control provided with this JFR
Regulator. For specific control information, refer to the
Accu/StatTM control manual included with the regulator.
QUALIFIED PERSON
FOR THE PURPOSE OF THIS MANUAL AND PRODUCT
LABELS, A QUALIFIED PERSON IS ONE WHO IS FAMILIAR
WITH THE INSTALLATION, CONSTRUCTION AND OPERA-
TION OF THE EQUIPMENT, AND THE HAZARDS INVOLVED.
IN ADDITION, HE HAS THE FOLLOWING QUALIFICATIONS:
(a) Is trained and authorized to de-energize, clear, ground and
tag circuits and equipment in accordance with established
safety practices.
(b) Is trained in the proper care and use of protective
equipment such as rubber gloves, hard hat, safety glasses
or face shields, flash clothing, etc., in accordance with
established safety practices.
(c) Is trained in rendering first aid.
Distinctive signal words (DANGER, WARNING, CAUTION) are
used in this instruction book to indicate degrees of hazard
that may be encountered by the user. For the purpose of this
manual and product labels these signal words are defined
below.
DANGER Indicates an imminently hazardous situation
which, if not avoided, will result in death or
serious injury
WARNING Indicates a potentially hazardous situation,
which, if not avoided, could result in death or
serious injury.
CAUTION Indicates a potentially hazardous situation
which, if not avoided, may result in minor or
moderate injury.
Hazardous Voltage. Death or serious injury from
electrical shock, burns will result from misuse.
To prevent:
Do not service or touch until you have de-energized
high voltage, grounded all terminals and turned off
control voltage. Grounding terminals with line to
ground capacitors may produce a small arc.
Only qualified personnel should work on or around
this equipment after becoming thoroughly familiar
with all warnings, safety notices, instructions and
maintenance procedures contained herein.
The successful and safe operation of this
equipment is dependent upon proper handling,
installation, operation and maintenance.

INTRODUCTION
Page 2
INSPECTION FOR STORAGE PRIOR TO
DAMAGE IN SHIPMENT INSTALLATION
Check each item with the shipping manifest immediately
upon receipt of the regulator. Make a thorough visual in-
spection of the regulator. Check for evidence of damage
attributable to mishandling in shipment. Should any short-
age or damage be found, notify the local agent of the carrier
making the delivery and make appropriate notation on the
freight bill. Any damage or shortage that is not noted on the
freight bill becomes the recipients responsibility. A claim
should be made immediately with the carrier. Please also
notify your Siemens representative as soon as possible.
Assure that the control compartment enclosure is tightly
closed, and regulator tank is sealed.

INTRODUCTION
Page 3
PHYSICAL CONSIDERATIONS
• Handling. Type JFR regulators are designed to be lifted
either by a forklift at the base or by use of lifting hooks
on the side of each tank. Each JFR regulator is provided
with either 2 or 4 lifting hooks on the side of each tank.
The number of hooks has been established to provide a
margin of safety. Use all supplied lifting hooks when
lifting.
• Location. Type JFR regulators are designed for outdoor
installation. Any regulator may be platform or pedestal
mounted. Regulators provided with hanger brackets are
suitable for pole mounting. When the regulator is to be
installed in a substation on a pedestal it is recom-
mended that a minimum elevation to the live connection
be established, as required by applicable codes.
Elevation. When the regulator will be used at an elevation
above 1000 meters (3300 feet) the kVA rating must be de-
rated per ANSI C57.15 to assure operating temperature
limits are not exceeded.
LINE TERMINALS AND
CONNECTIONS
Type JFR voltage regulators are routinely equipped with line
bushing terminals per the following criteria.
Nameplate Line Current
Rating Conductor Size Range
or Threaded Stud Size
50A to 300A #2 to 477 MCM
301A to 668A #2 to 800 MCM
669A to 1200A 1.125- 12 UNF-2A
1201 A to 2000A 1.500- 12 UNF-2A
Clamp type terminals for use through 668 ampere are
capable of accepting an aluminum or copper conductor.
Tank grounding provision consists of a 0.5-13NC tapped
hole in a steel pad for regulators rated to 300 amperes.
Above 300 ampere ratings, a stainless steel pad with two
0.5-13NC tapped holes is provided.
ELECTRICAL CONSIDERATIONS
Type JFR regulators are commonly installed using any of
four electrical configurations.
• One regulator in single-phase application. (Figure 4A)
• Three regulators in wye on a grounded-neutral three-
phase system. (Figure 4D)
• Two regulators in open delta on a three-phase
ungrounded system. (Figure 4B)
• Three regulators in closed delta on a three-phase
ungrounded system. (Figure 4C)
Each of the four alternatives, when complete with switching
provisions, will take the electrical configuration as shown
on the next page.
The descriptions 'S', 'L', and 'SL' are embossed into the cover
for user convenience at time of installation.
Improper use of lifting provisions can cause death,
serious injury, or equipment damage.
To prevent:
Do not use cover lifting eyes to lift complete unit.
Cover lifting eyes are for untanking only.
WARNING
Hazardous voltage present at the line terminals of the
bushings on the cover of the regulator.
Will cause serious injury or death.
To prevent:
De-energize the regulator before servicing.

INTRODUCTION
INSTALLATION DIAGRAMS
Connection of two single phase JFR regulators in open
delta on a three phase, ungrounded line.
Connection of one single phase JFR regulator on single
phase line.
Connection of three JFR regulators in closed
delta on three phase, ungrounded system. Connection of three single phase JFR regulators in
wye on a three phase, grounded neutral system.
Open Delta
Closed Delta Wye Connected
Single Phase
4C)
Page 4

INTRODUCTION
Page 5
PROTECTIVE MEASURES
Bypass Arrester. All JFR regulators are equipped with a
properly sized arrester, connected externally between the 'S'
and 'L' line terminals. The arrester is provided to protect the
series winding of the regulator from line surges. By itself, the
bypass arrester does not provide lightning protection for the
regulator.
Lightning Protection. The number of lightning arresters used
will be a discretionary decision on the part of the user,
considering such factors as isokeraunic level and degree of
risk of damage to be accepted. The minimum recommended
lightning protection consists of a properly sized arrester
between the 'S' or 'L' bushing and ground on a single phase
or a wye connected system. A delta connection system
requires the use of two arresters to accomplish minimum
protection levels. Additional protection can be obtained with
the use of arresters at both the 'S' and 'L' terminals in single
phase or wye systems and on all three terminals on a delta
system.
For best results, install lightning arresters on the mounting
lugs adjacent to the bushings near the top of the tank. The
lugs are 0.5 - 13NC located on 2.5 inch centers. Ground the
arrester(s) and the regulator tank solidly to the same ground
connection. Be careful to keep the ground lead connections
as short as possible.
Thru Fault. Type JFR regulators are rated under condition of
thru-faults per ANSI C57.15.
The user is advised to provide for additional source imped-
ance, bus sectionalizing or other means of limiting the avail-
able thru-fault current if these criteria are exceeded at the
installation.
CONTROL CONNECTIONS
Many regulators can be used at several different nominal
system voltages. It is therefore necessary to assure that the
regulator is properly connected at the 19 pin upper terminal
block for the system voltage on which the particular regulator
will be used.
Figure 5A
For this purpose, it is necessary to use the nameplate
drawing and control diagram found in the control enclosure.
1. Refer to the Nameplate. The P2 column indicates the
correct connection for lead P2 based on the system
voltage. Using the applicable control diagram, the
terminal designation of the nameplate can be cross
referenced to the proper terminal on the 19-pin terminal
block.
2. Depending on the regulator, there may be a second
nameplate column indicating that lead U2 should also be
connected. If so, the U2 column indicates the correct
connection for lead U2 based on the system voltage
Using the applicable control diagram, the “U” terminal
designation of the nameplate can be cross referenced to
the proper terminal on the 19-pin terminal block.
3. For regulator equipped with fans for forced-air cooling,
another set of connections will be shown.
NOTE Matters specifically relating to the Accu/StatTM
control used in conjunction with the regulator are
not included in this manual. Refer to the
appropriate control instruction manual.

CONNECTION DIAGRAMS
STRAIGHT DESIGN (ANSI TYPE A)
S L SL
SOURCE
LOAD
Typical arrangement of windings and connections of
Type “A” JFR regulators.
Note: Straight design units may or may not be
equiped with a balance winding. Refer to
regulator nameplate.
Schematic diagram of a typical Type “A” JFR regulator with fan
power circuit U3-U5.
Note: Other typical motor supply configurations below.
Wiring diagram of a typical Type “A” regulator showing
both internal and external connections without fan power.
Page 6

CONNECTION DIAGRAMS Page 7
S L LOAD
SOURCE
SL
INVERTED DESIGN (ANSI TYPE B)
L
S
SL
Wiring diagram of a typical Type “B” regulator
showing both internal and external connections.
Schematic diagram of a typical Type “B” JFR
regulator utilizing single potential source for motor
and control circuit.
Typical arrangement of windings and connections of
Type “B” JFR regulators.
Note: Inverted design units may or may not be
equiped with a balance winding. Refer to
regulator nameplate.
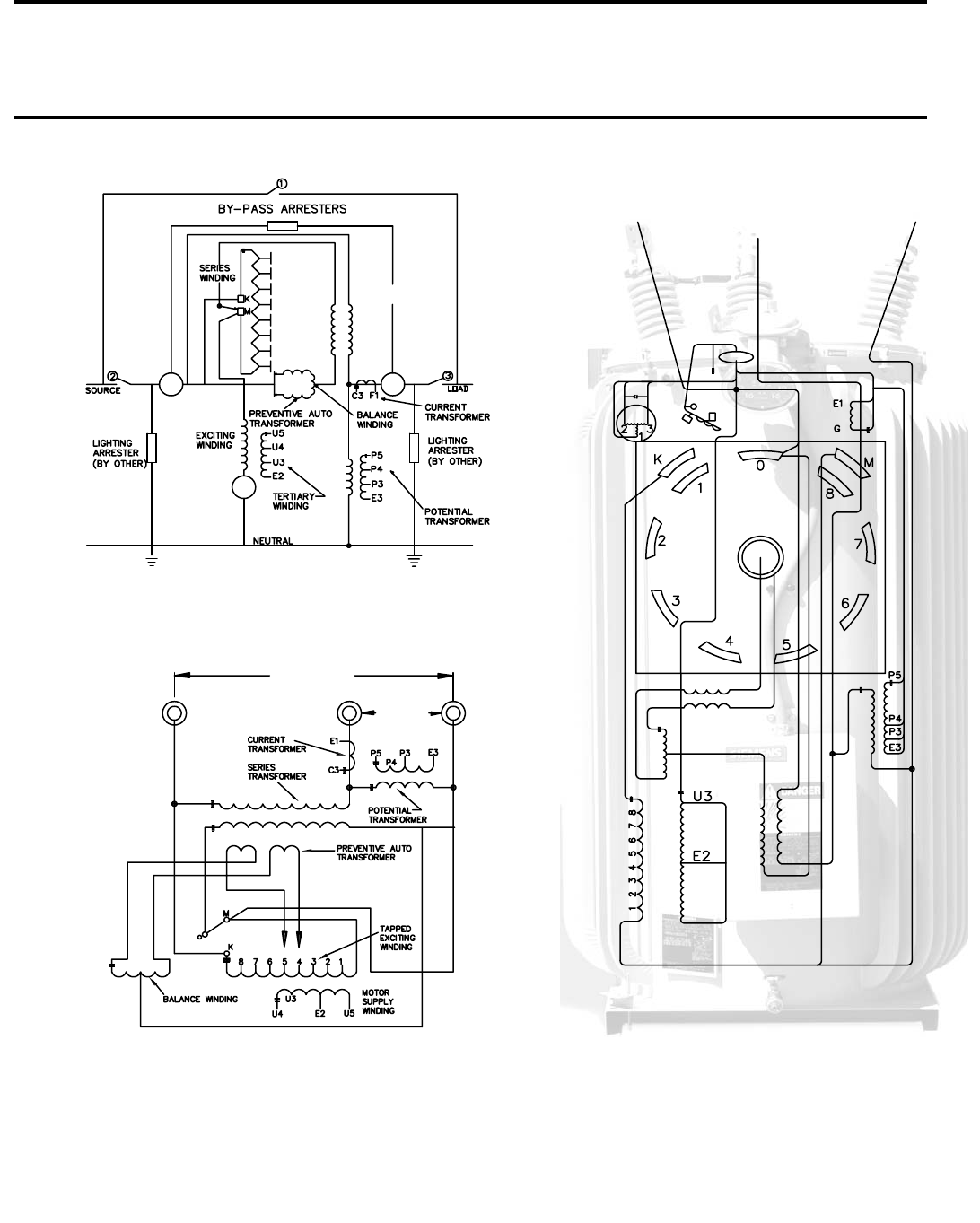
Wiring diagram of a typical regulator with series transformer
showing both internal and external connections.
S L
SL
CONNECTION DIAGRAMS
Page 8
S L SL
LOAD
SOURCE
Schematic diagram of a typical regulator with series
transformer with fan power U3-U5.
*Note: Exciting Winding may not be fully tapped.
R
e
f
e
r
to
r
egu
l
ato
r n
a
m
ep
l
ate
.
SERIES TRANSFORMER DESIGN
Typical arrangement of windings and connections of
Series JFR regulators, without fan power.
Note: Series Transformer design units may or may
not be equiped with a balance winding.
Refer to regulator nameplate.

PLACING THE REGULATOR IN SERVICE
Page 9
The following checks will be useful in assuring the regulator is
ready for use. The list cannot be all inclusive; careful at-
tention on the part of a qualified operator remains imperative.
BEFORE CONNECTING
• Check oil level at oil sight window. If low, add sufficient oil
(ASTM D-3487 Type II) to bring to desired level.
• Check oil dielectric strength per ASTM D 877. If found
below 25kV, oil should be changed or reconditioned.
Reference ANSI C57.106-2002. Note: Oil tests are not
required for new equipment.
• Perform insulation power factor test per ANSI C57.15.
Maximum value is 2.0%.
• Verify from the nameplate that the unit is connected for the
proper output voltage, motor voltage and control panel
voltage.
• Assure that the regulator is on the neutral tap position.
This should be accomplished by observing the position
indicator pointer and by powering the control from a 120V
external source and observing the NeutraliteTM to be
illuminated.
BEFORE CONNECTING
• Identify 'S', 'L' and 'SL' bushings on the cover. Make elec-
trical connections per the appropriate installation diagrams,
page 4, first connecting 'SL' bushing.
• Set Vari-AmpTM limits on position indicator, if necessary.
See Page 11.
• Set Accu/StatTM Control as desired. See Accu/StatTM
instruction manual.
SWITCHING “ON-LINE”
• Improper by-pass operation will result in explosion
and fire hazard. Will cause serious injury, death or
equipment damage.
• Do NOT place into service unless tap-changer is in
neutral position AND control panel is properly
disabled.
Improper By-Pass operation will
result in explosion and fire hazard.
Will cause serious injury, death or
equipment damage.
To Prevent:
Do NOT install OR remove from
service unless Tap Changer is in
neutral position AND Control Panel
is properly disabled to prevent tap
changes while in By-Pass
configuration. Read Operators
Manual before attempting to By-
Pass this Regulator.
Follow instructions to place into service:
1. Place the Auto/Manual switch in the By-Pass position
2. Place the Raise/Lower switch in "Off"
3. Make certain regulator is in neutral (N) position
4. Turn voltage power source switch to "Off"
5. Remove power fuse
6. Close, sequentially, the source and load switches
7. Open the bypass switch
8. Visually observe that bypass circuit has opened
9. Replace power fuse
10. Place voltage power source switch to "Normal."
CHECKING REGULATOR OPERATION
1. Refer to applicable Accu/StatTM Control instruction
manual.)Turn the Tap Control switch to MANUAL.
2. Run the tapchanger in the lower direction, at least until
the control is observed to go out of band "LOW".
3. Turn the Tap Control switch to AUTO. After a time delay,
the regulator will return to an "IN" band condition.
4. Turn the Tap Control switch to MANUAL.
5. Run the tapchanger in the raise direction, at least until the
control is observed to go out of band "HIGH".
6. Turn the Tap Control switch to AUTO. After a time delay,
the regulator will return to an "IN" band condition.

REMOVING THE REGULATOR FROM SERVICE
Page 10
SWITCHING “OFF LINE”
• Improper by-pass operation will result in explosion and
fire hazard. Will cause serious injury, death or
equipment damage.
• Do NOT remove from service unless tap-changer is in
neutral position AND control panel is properly
disabled.
• If the regulator being removed is in a closed delta bank,
it is necessary to bypass and isolate all regulators in
the bank.
Improper By-Pass operation will result
in explosion and fire hazard.
Will cause serious injury, death or
equipment damage.
To Prevent:
Do NOT install OR remove from
service unless Tap Changer is in
neutral position AND Control Panel is
properly disabled to prevent tap
changes while in By-Pass
configuration. Read Operators
Manual before attempting to By-Pass
this Regulator.
Follow instructions to remove from service:
1. Place the Auto/Manual switch in the By-Pass position
2. Place the Raise/Lower switch in "Off"
3. Make certain regulator is in neutral (N) position. If
independent checks of the position indicator and
NeutraliteTM indicator do not confirm the neutral position,
bypassing must not be attempted. In such event, de-
energize the system to remove the regulator from service
4. Turn voltage power source switch to "Off"
5. Remove power fuse
6. After assuring the voltage regulator is on neutral, close the
bypass switch
7. Open sequentially, the load and source switches
8. (a) For a single phase or grounded wye connection, make
sure that the high voltage disconnect switches are opened
(b) For a closed delta connection, be sure all regulators in
the bank are bypassed and isolated
9. Exercise appropriate care in the removal of the regulator.
High voltage will still be present at the bypass switch and
the source and load switch terminals. Remove the ground
connection last.

MAINTENANCE
Pa
g
e 11
GENERAL INSTRUCTIONS
This manual does not represent an exhaustive survey of
maintenance steps necessary to ensure safe operation of
the regulator. Particular applications may require further pro-
cedures. Should further information be desired or should
particular problems arise which are not covered sufficiently
for the purchaser’s purposes, the matter should be referred
to the local Siemens sales representative.
OPERATIONAL CHECKS
Basic regulator operation can be checked while the regulator
remains in service. The output voltage can be monitored from
the control panel display under the <METER> menu on the
“Vld” screen.
• Check the calibration by following the steps in the Basic
Troubleshooting section of the Accu/Stat control panel
instruction manual.
• Run the tapchanger several steps in one direction in the
manual mode until the output voltage is outside of the
bandwidth. Return the control to automatic mode. After the
predetermined time delay, the tapchanger motor will be
observed to return the output voltage in-band. Repeat this
operation, running the tapchanger in the opposite direction.
• Check the Vari-AmpTM limit switches by attempting to run the
tapchanger beyond the position to which the switches are
set. The limit switches should function to open the circuit.
Note: If the limit switch is set at the maximum 10% range and
fails to function, the tapchanger will stall against a mechanical
stop. The motor is designed to stall continuously without
damage.
WARNING
Failure to properly maintain the regulator can result in
serious injury, death, or equipment damage. The
instructions contained herein should be carefully
reviewed, understood and followed.
To prevent:
The following maintenance procedures should be
performed regularly:
1. Operational checks.
2. Periodic inspection.
Hazardous voltages. Will cause serious injury, death, or
equipment damage.
To prevent:
Always de-energize and ground the equipment before
maintenance requiring access to high voltage parts.
CAUTION
Operation of the regulator at extreme tap positions
could produce line voltages outside of operating limits
that could result in property damage.
To prevent:
Operate the regulator only to judiciously determined
voltage extremes.
WARNING
Regulator may have High Internal Pressure. Can cause
serious injury, death, or equipment damage.
To prevent:
Use pressure relief valve to vent regulator before
untanking.
WARNING
The use of unauthorized parts in the repair of the
equipment, tampering by unqualified personnel, or faulty
repair and adjustments can result in dangerous conditions
which can cause serious injury, death, or equipment
damage.
To prevent:
Follow all safety instructions contained herein, and contact
your local Siemens sales representative for replacement
parts.

MAINTENANCE
Page 12
PERIODIC INSPECTION
A sample of oil from the regulator should be subjected to
dielectric breakdown test, per ASTM D-877. If found below
25kV, the oil should be changed or reconditioned. Refer to
ANSI C57.106-2002. Other tests, especially Neutralization
Number, Interfacial Tension and Power Factor are also useful
and may be preferred by particular users.
The oxidation inhibitor in the oil will be depleted over a period
of a few years and should be replaced. The inhibitor is 2, 6-
ditertiary-butyl-para-cresol (DBPC) at a concentration level of
0.2 to 0.3%.
The time interval between internal inspections will depend
upon frequency of tapchanger operation and the load on the
regulator. Regulators subjected to numerous overloads and a
high load factor may require more frequent inspections than
those carrying normal loads. While internal inspection is not a
necessity, preventive maintenance inspections will help assure
the continuity of service.
To untank a JFR regulator, proceed as folllows:
1. Remove the regulator from service as described on
Page10.
2. Place the regulator in a position where energized
overhead lines will not interfere.
3. Operate pressure relief valve to vent regulator before un-
tanking
4. Remove the mounting bolts holding the control box onto
the main tank.
5. Remove all cover bolts.
6. The regulator can now be pulled from the main tank by the
cover lifting eyes.
When inspecting, check to be certain all hardware and con-
nections are tight. The principal point of the internal inspection will
be the condition of the arcing contacts on the tapchanger. Since
numerous factors influence the rate of contact tip wear, no one
criteria can be stated to recommend when a contact should be
changed.
The following figure shows the possible condition of contact wear
after a period of operation. If the contact surface is less than 1/8
inch wide, the contact should be replaced. (See the Figure below)
Contacts, both movable and stationary, show normal burning and wear
once placed in service. If for any reason A1 dimensions exceed 4/5 of
A, the stationary contact should be replaced. (See the Figure below)
• UPPER FILTER PRESS SEALING
If cover top cap is removed, make certain the cap is properly
sealed when replaced on cover. Siemens recommends applying
pipe sealant (Loctite PST or equivalent) around the threads of the
adapter. Furthermore, it is recommended that the seal be tested by
applying 5 psig pressure through the pressure relief valve fitting for
5 minutes, with no loss in pressure. Failure to assure seal may
allow moisture to be pulled into the unit during a cool-down cycle.
• FAN MAINTENANCE
Cooling fans (if equipped), require minimum attention. Fans with
plain sleeve bearings or Oil-Lite sleeve bearings should be oiled at
least once a year with SAE 10-W engine oil which does not thicken
in cold weather. Oil must be added to sleeve bearings before
starting motor for the first time after installation.
Fans equipped with ball bearing motors are packed with grease
before shipment and should be greased at least once a year with a
soda-soap, ball-bearing grease of medium consistency furnished
by a reliable supplier.
A
A
1
Hazardous voltages. Will cause serious injury, death, or
equipment damage.
To prevent:
Always de-energize and ground the equipment before
maintenance requiring access to high voltage parts.

SPECIAL FEATURES Page 13
POLARIZED DISCONNECT SWITCH VARI-AMPTM POSITION INDICATOR
(JACK PLUG) AND HINGED
CONTROL PANEL
The Accu/StatTM control panel is hinged and may be re-
moved completely from the regulator control box by
removing the wing nuts on the polarized jack plug and
pulling the jack from its fixed position. This will
automatically de-energize the control. It is not necessary
to bypass or de-energize the regulator to remove the
control.
A spring-loaded shorting bar in the plug automatically
short circuits the current transformer secondary when
the jack is removed.
REMOTE MOUNTING
OF CONTROL
EQUIPMENT
The Accu/StatTM control may be remotely mounted.
Remote cable is available in standard lengths of 18, 25
and 30 feet incorporating oil and moisture resistant,
color-coded conductors.
The Vari-AmpTM feature provides a method of operating the
regulator at increased load by decreasing the range of op-
eration. It provides operator flexibility by allowing the range of
regulation to be adjusted in 1¼ percent increments. The
various regulation ranges together with the corresponding
current capacities for standard regulators are listed on the
next page. All that is necessary to adjust the range of
regulation anywhere from ±5 percent to ±10 percent is to
turn the adjusting knobs until the proper range of regulation
is shown on the side of the position indicator. The upper and
lower limits need not be the same.
It is not necessary to remove the regulator from service to
make this adjustment. The switches are, however, in the
motor power circuit so the motor should not be running while
the switches are being set.

SPECIAL FEATURES
VARI-AMPTM RANGE AND CURRENT RATINGS AVAILABLE
±10% ±8 3/4% ±7 1/2% ±6 1/4% ±5%
10-02.5-050.0 200 220 240 270 320
10-02.5-075.0 300 330 360 405 480
10-02.5-100.0 400 440 480 540 640
10-02.5-167.0 668 668 668 668 668
10-02.5-250.0 1000 1000 1000 1000 1000
10-02.5-333.0 1332 1332 1332 1332 1332
11-02.5-416.3 1665 1665 1665 1665 1665
10-05.0-050.0 100 110 120 135 160
10-05.0-100.0 200 220 240 270 320
10-05.0-167.0 334 367 401 451 534
10-05.0-250.0 500 550 600 668 668
10-05.0-333.0 668 668 668 668 668
11-05.0-416.3 835 835 835 835 835
10-07.6-038.1 50 55 60 68 80
10-07.6-057.2 75 83 90 102 120
10-07.6-076.2 100 110 120 135 160
10-07.6-114.3 150 165 180 203 240
10-07.6-167.0 219 241 263 296 351
10-07.6-250.0* 328/347 361/381 394/416 443/468 525/555
10-07.6-333.0* 437/463 481/509 524/556 590/625 668/668
10-07.6-416.3* 546/578 601/636 656/668 668/668 668/668
10-07.6-500.0 656 668 668 668 668
10-07.6-667.0 875 875 875 875 875
11-07.6-889.0 1167 1167 1167 1167 1167
10-13.8-069.0 50 55 60 68 80
10-13.8-138.0 100 110 120 135 160
10-13.8-207.0 150 165 180 203 240
10-13.8-276.0 200 220 240 270 320
10-14.4-072.0 50 55 60 68 80
10-14.4-144.0 100 110 120 135 160
10-14.4-288.0 200 220 240 270 320
10-14.4-333.0 231 254 277 312 370
10-14.4-432.0 300 330 360 405 480
10-14.4-576.0 400 440 480 540 640
11-14.4-720.0 500 550 600 668 668
10-14.4-833.0 578 636 668 668 668
10-19.9-100.0 50 55 60 68 80
10-19.9-200.0 100 110 120 135 160
10-19.9-333.0 167 184 201 226 268
10-19.9-400.0 200 220 240 270 320
10-19.9-667.0 335 368 402 452 536
11-19.9-833.0 418 459 502 565 668
Units with catalog number starting with:
10 are self cooled
11 are forced-air cooled
Regulators can be modified at factory for 50
Hz operation with appropriate de-rating of
voltage.
*Capable of carrying current corresponding
to rated kVA when operated at 7200/12470
volts ground wye.
OPERATION AT LESS
THAN
RATED VOLTAGE
JFR regulators may be operated at less
than the voltage for which they were de-
signed. All system voltages for which
control system taps have been provided
are shown on the nameplate. When this
is to be accomplished it may be neces-
sary to reconnect particular leads at the
upper 19-pin terminal block as illustrated
on page 5. When operating the regulator
at reduced voltage it must be noted that
the regulator carries a maximum current
rating which rules regardless of the
voltage (see table at right). It may
therefore be necessary to operate the
regulator at less than its nameplate kVA
rating.
Page 14

SPECIAL FEATURES Page 15
FORCED AIR COOLING
Certain regulators may be equipped for forced-air cooling and
include fans mounted on the radiators. The fans are usually
automatically controlled by means of the change in oil
temperature (see Connection Diagram). The thermometer
located in the top transformer oil contains two identical
switches which control fan operation when fan control switch is
in “Auto” position.
SUBBASE ASSEMBLY
Subbase assemblies are available in 4-inch high increments
from 21 through 49 inches for most JFR regulators. The
proper height is selected by picking the elevation that will
provide required clearance from foundation to the live part of
the regulator bushing.
The switches are normally set to start the fans at 65°C and to
stop them at 55°C top oil temperature, but may be adjusted
plus or minus 5°C.
A thermal overload relay is mounted on each fan motor. Any
fan that develops trouble will be automatically disconnected
from the line without affecting the other fans of the system.
One fan can be removed from the radiators without affecting
the operation of the others. When fans are out of service,
care must be exercised to prevent overloading the regulator.

PARTS LIST
Page 16
MAJOR COMPONENTS PARTS LIST
Instructions For Ordering Part
When ordering parts give the quantity of parts required, the
regulator serial number, parts list item number, complete
description, and method of shipping. State whether for
emergency repair, maintenance, spare part, etc.
A
ll shipments will be made F.O.B Factory
Item
01-11 Description
5050A Control Compartment Gasket
5079 Position Indicator
5081 Main Cover Gasket
5083 Pressure Relief Valve
5084 Terminal Box Gasket
5085 Nameplate
5087 Sampling Device
5088 Grounding Lug Terminal (not shown)
5092 Terminal Block Clamp
5094B Terminal Block Studs
5095 Terminal Block Gasket
5246 Motor Capacitor TLG
5287 Motor Capacitor TLF
17 Drain Valve
80 Oil Sight Glass
81A Oil Sight Gauge Gasket
90A Bolts - Stainless Steel

PARTS LIST
TYPE TLG DIAL SWITCH
Item
01-11 Description
5320 Panel
5317A Reversing Main Shaft
5321 Main Stationary Contacts
5322 Reversing Stationary Contact R
5323 Reversing Stationary Contact L
5324 Neutral Stationary Contact
5325 Collector Ring
5326 Collector Hub
5327 Reversing Switch Arm
Item
01-11 Description
5328A Reversing Switch Finger Assembly
5328B Reversing Switch Hub Finger Assembly
5329 Drive Arm
5330 Hub Finger Support
5331 Ring Finger Support
5332 Main Moving Finger Assembly
5333 Hub Finger Assembly
5334 Ring Finger Assembly
5336 Phenolic Drive Pin
Page 17

PARTS LIST
Page 18
TYPE TLG QUICK BREAK MECHANISM
Item
01-11 Description
5201G Mounting Frame Assembly
5202 Motor
5207 Drive Spring Assembly
5212 Latch Assembly
5213 Latch Spring (not shown)
5214 Latch Pin (not shown)
*5216A Reversing Switch Drive Arm - Phenolic
*5216B Reversing Switch Drive Arm - Phenolic
*5216C Rev. Switch Drive Arm – Glass Phenolic
5217 Interlock Disk And Drive Assembly
5229 Main Shaft w/Sleeve Bearing
5231 Motor Mounting Bracket
5233A Operation Counter Switch Assembly
5234 Roller Chain Position Indicator
5237 Reversing Switch Shaft
Item
01-11 Description
5238 Reversing Switch Assembly
5240 Spring
5241 Spring Tube
5242 Position Indicator Drive Mechanism
5243A Neutral Switch
5244 Index Plate
5245A Motor Sprocket
5246 Capacitor for Motor
5247 Sprocket Assembly
5248 Main Drive Chain Assembly
5250 Drive Pin
5273 Phenolic S
p
acer
5600 Flexible Shaft
5600A Flexible Shaft O-Ring

PARTS LIST
TYPE TLF DIAL SWITCH
FIGURE 20A
Item
01-11 Description
5351 Panel
5352 Stationary Contact
5353 Neutral Stationary Contact
5354 Stationary Contact - LH
5355 Stationary Contact - RH
5356 Collector Ring
5357 Shaft Assembly
5358A Main Finger Assembly (each)
5359 Contact Finger Assembly Collector Ring
5360A Contact Finger Assembly Collector Hub
Item
01-11 Description
5363 Drive Plate
5364 Contact Finger Assembly - Rev. Switch
5365 Contact Support Assembly
5366 Reversing Drive Pin
5367 Reversing Shaft
5368 Spacer
5369 Contact Finger Support
5370 Contact Finger Support
5373 Reversing Switch Stop
Page 19

PARTS LIST
Page 20
TYPE TLF QUICK BREAK MECHANISM
Figure 21A
Item
01-11 Description
5266 Interlock Disc and Drive Sprocket Assembly
5267 Quick Break Mechanism Shaft
5275 Actuating Arm Assembly
5276 Spacer
5278 A-Frame
5285 Drive Chain for Position Indicator
5286 Motor Sprocket
5287 Motor Capacitor (may be located in control box)
5288 Actuating Disc and Sprocket
5289 Main Drive Chain
5290 Position Indicator Drive Mechanism
5291 Reversing Switch Spring Assembly
5600 Flexible Shaft
5600A Flexible Shaft O-Ring
Item
01-11 Description
5233A Counter Switch Assembly
5243B Neutral Switch
5251 Mounting Frame
5252 Motor
5256 Drive Spring Tube
5257 Drive Spring
5259 Spacer
5260 Notched Index Plate
5262 Latch
5263 Latch Spring
5264 Latch Pin
5265 Reversing Switch Drive Arm

PARTS LIST
Page 21
BYPASS ARRESTERS
Item
01-11 Description Volts
5423 Bypass Arrester Assembly 3 kV MOV 2,500, 5,000, 7,620
5425 Mounting Bracket Assembly
5423 Bypass Arrester Assembly, 3 kV MOV 12,000-13,800-14,400
5425 Mounting Bracket Assembly
5428 Bypass Arrester Assembly, 6 kV MOV 19,920
5429 Mounting Bracket Assembly
Include regulator serial number when ordering replacement parts
Figure 22B
Polymer arresters now used on voltage regulators.
Supersedes previous porcelain arresters.
Figure 22A

PARTS LIST
Page 22
Figure 23A
BUSHINGS
Item
01-11 Description kVA Volts
5400P Bushing Assembly for 15 kV 50 5000
38.1 thru 76.2 7620
69 thru 138 13,800
5400R Bushing Assembly for 15 kV 50 2500
100 5000
114.3 thru 167 7620
5400S Bushing Assembly for 15 kV 75 2500
414 13,800
5401P Bushing Porcelain for 15 kV 50 5000
38.1 thru 76.2 7620
69 thru 138 13,800
5401R Bushing Porcelain for 15 kV 50 2500
100 5000
5401S Bushing Porcelain for 15 kV 114.3 thru 167 7620
5410 Clamping Ring for 5400 and R Ratings 75 2500
5419 Clamping Ring for 5400S Rating 414 13800
5411 Cushion Spring
5418 Cap Screw
5426 Bushing Cap Line Terminal for
5430
5400P Rating
Bushing Cap Line Terminal for
5427
5400R and S Ratings
Gasket
4034 Gasket

PARTS LIST
Page 23
BUSHINGS
z
Item
01-11 Description kVA Volts
5400T Bushing Assembly 15 kV 100 thru 167 2500
167 500
250 thru 509 7620
5400U Bushing Assembly, 15 kV 207-276 13,800
5400V Bushing Assembly, 23 kV 72 thru 144 14,400
100 thru 200 19,920
5400W Bushing Assembly 15 kV 333 thru 416.3 2500
250 thru 416.3 5000
5400X Bushing Assembly, 23 kV 576 thru 833 14,400
5400Y Bushing Assembly, 23 kV 288 14,400
333 thru 400 19,920
5400YY Bushing Assembly, 15 kV 333 12,000
5400Z Bushing Assembly, 23 kV 333 thru 432 14,400
5400AB Bushing Assembly, 23 kV 667 thru 833 19,920
5400AC Bushing Assembly, 15 kV 667-889 7620
5401T Bushing Porcelain, 15 kV 100 thru 167 2500
167 5000
250 thru 509 7620
5401U Bushing Porcelain, 15 kV 207-276 13,800
5401V Bushing Porcelain, 23 kV 72 thru 144 14,400
100 thru 200 19,920
5401W Bushing Porcelain, 15 kV 250 thru 416.3 2500
250 thru 416.3 5000
5401X Bushing Porcelain, 23 kV 576 thru 833 14,400
5401Y Bushing Porcelain, 23 kV 288 14,400
333 thru 400 19,920
5401YY Bushing Porcelain, 15 kV 333 12,000
5401Z Bushing Porcelain, 23 kV 333 thru 432 14,400
5401AB Bushing Porcelain, 23 kV 667 thru 833 19,920
5401AC Bushing Porcelain, 15 kV 7620
4025 Clamping Ring for 5400T
4026 X, Z and AB Ratings
Clamping Ring for 5400U
4028
V, W (SL Bushing only),
Y and YY Ratings
Clamping Ring for 5400W
4030 Rating S and L Bushings only
Cushion Spring
4027 Gasket
4032 Gasket
4034 Gasket
4035 *Bushing Cap Line Terminal
5430 for 5400T X, YY and AB Ratings
*Bushing Cap Line Terminal for
5426 5400U, Y and Z ratings
*Bushing Cap Line Terminal
5418 for 5400V Rating Cap Screw
*Units rated 250 kVA and above, 2500 and 5000 volts are not supplied with line terminals

Siemens Energy, Inc.
P.O. Box 6289
Jackson, MS 39288-6289
Phone: 601-939-0550
Fax: 601-939-3606
ACCU/STAT, DATA/PAK, NEUTRALITE and VARI-
AMP are trademarks of Siemens Energy, Inc.
PR4018-06
PR4018-05
PR4018-04
October 08 PRINTED IN U.S.A.
s