4R44E 5R55E ZIP IN
2017-10-30
: Sonnax 4R44E-5R55E-Zip-In 4R44E-5R55E-ZIP-IN 2172 instructions part uploads
Open the PDF directly: View PDF .
Page Count: 10
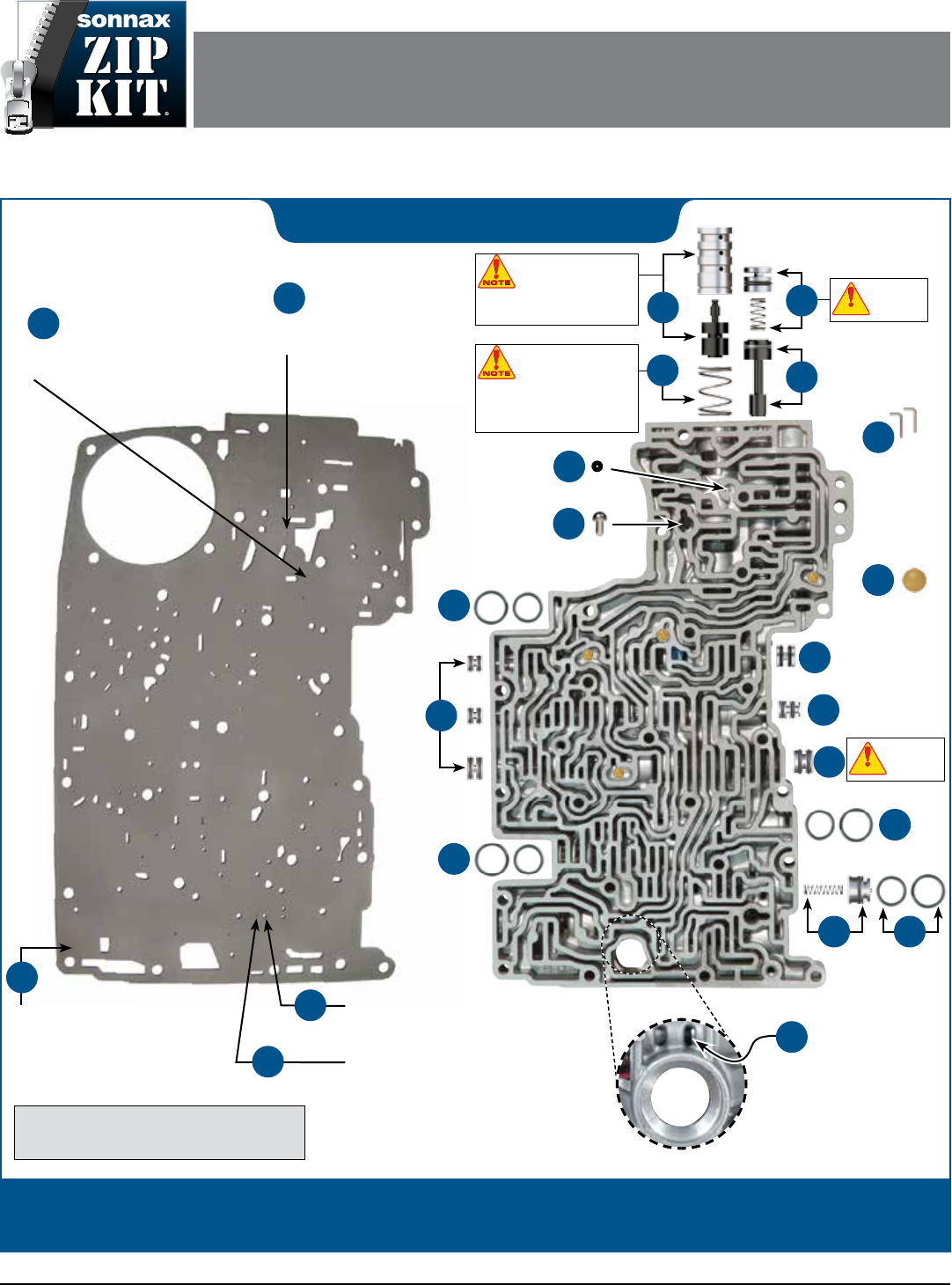
PART NUMBER 4R44E-5R55E-ZIP QUICK GUIDE
4A
4B
6C
5
5
5
8
8
8
4E
4D
8
Separator Plate Valve Body
5
Plastic
Checkball
Shown in
4 places.
2
Balance Pressure Regulator
Drill to .055" diameter.
Line-to-Converter Release
Drill to .062" diameter.
6A
OD Servo Apply
Drill to .072" diameter.
6B
TCC Modication
Drill to .062" diameter. Insert
aluminum plug & peen in place.
6C
TCC Modication
Drill to .110" diameter.
6D
TCC Modication
Remove smallest inboard
spring through casting
port on reverse side of
valve body.
7
1
NOTE: See pages 1–2 in separate Installation
and Testing Booklet for installation tips and
additional optional modications
NOTE: Kit now
includes OE ratio
boost assembly to re-
store OE pressure curve.
NOTE: Increased
strength spring is
optional, to provide
moderately increased
pressure.
1
4C
CAUTION:
See note
on page 2.
CAUTIONCAUTION
CAUTIONCAUTION
CAUTION:
See note
on page 2.
CAUTIONCAUTION
CAUTIONCAUTION
3
©2017 Sonnax Industries, Inc. 4R44E-5R55E-ZIP-Guide_C 10-26-17
800-843-2600 • 802-463-9722 • F: 802-463-4059 • www.sonnax.com Page 1
FORD 4R44E, 4R55E, 5R44E, 5R55E
ZIP KIT
Parts are labeled here in order of installation. See other side of sheet for details on Zip Kit contents.
In addition to general rebuilding tips and technical information, the technical booklet included in this kit contains vacuum
testing and additional repair options for higher mileage units or for repairing specic complaints which are beyond the
scope of this kit.
installation Diagram

FORD 4R44E, 4R55E, 5R44E, 5R55E ZIP KIT Quick Guide
Zip Kit Contents & Installation Steps
Step Replace OE Boost Assembly
NOTE: Kit now includes OE ratio boost assembly to restore OE
pressure curve. Increased strength spring is optional, to provide
moderately increased pressure.
NOTE: For rmer shifts and signicantly increased line pressure, use
Sonnax increased ratio boost valve kit 37947-03K, sold separately.
Packaging Pocket 1
• Valve • Sleeve • Spring
Step Replace OE FWD Modulator Valve
NOTE: Insert PTFE seal in valve groove and size in bore rst.
Packaging Pocket 2
• Forward Modulator Valve • PTFE Seal
Step Replace OE Solid Plug
CAUTION: If OE end plug has relief orices and tabs, DO NOT
INSTALL this Sonnax O-ringed end plug and spring. Reuse OE
end plug. Reference page 1, step 3 of Installation Booklet for details.
CAUTION: Included spring is OPTIONAL and provides rmer
forward engagement. Remove if drive test proves forward
engagement is too harsh.
Packaging Pocket 3
• Forward Modulator End Plug • O-Ring, Large • Spring
Step Replace OE End Plugs
4A. Reverse Modulator O-Ringed End Plug
Packaging Pocket 4
• End Plug • O-Rings, Medium (3) 1 Extra
4B. 2-3/3-4 Shift Valve O-Ringed End Plug
Packaging Pocket 5
• End Plug • O-Rings, Small (2)
4C. 1-2/2-3 Shift Valve O-Ringed End Plug
NOTE: Reuse OE plunger valve inside plug.
Packaging Pocket 6
• End Plug • O-Rings, Medium (3) 1 Extra
4D.
Converter Reg. Valve O-Ringed End Plug & Spring
Packaging Pocket 7
• End Plug • O-Ring, Large • Spring, Install only if OE is damaged
4E. O-Ringed End Plugs
Packaging Pocket 8
• End Plug, Large • O-Rings, Large (2)
• End Plugs, Small (2) • O-Rings, Small (4)
1
2
3
CAUTIONCAUTION
CAUTIONCAUTION
CAUTIONCAUTION
CAUTIONCAUTION
4
Step
Replace OE Checkballs, EPC
Limit Valve & Lube Orice Plug
Packaging Pocket 9
• Plastic Checkballs (4) • EPC Limit Valve, Reuse OE Spring
• Lube Orifice Plug • "L" Pins (2), Extra, for lost/missing OE pins
Step
Drill Separator Plate in
Locations & Diameters Given
Packaging Pocket 10
6A. Balance Line Orifice Modification Drill Bit
Drill Bit, .055" dia.
6B. OD Servo Apply Orifice Modification Drill Bit
Drill Bit, .072" dia.
6C. Line-to-Converter & TCC Modification
Drill Bit & Plug
NOTE: Drill two orices and install and peen plug into plate as
shown on page 1.
• Drill Bit, .062" dia. • Aluminum Plug .062"
6D. TCC Modification Drill Bit
Drill Bit, .110" dia.
Step TCC Modication
NOTE: Remove smallest inboard cooler bypass spring
through idicated casting port.
Step
Replace OE Solenoid O-Rings
Packaging Pocket 11
• O-Rings, Small (4) • O-Rings, Large (4)
Extra O-Rings for End Plugs in Step 4
Packaging Pocket 12
• O-Rings, Small (2)
• O-Rings, Large (2)
5
6
7
8
©2017 Sonnax Industries, Inc. 4R44E-5R55E-ZIP-Guide_C 10-26-17
800-843-2600 • 802-463-9722 • F: 802-463-4059 • www.sonnax.com Page 2
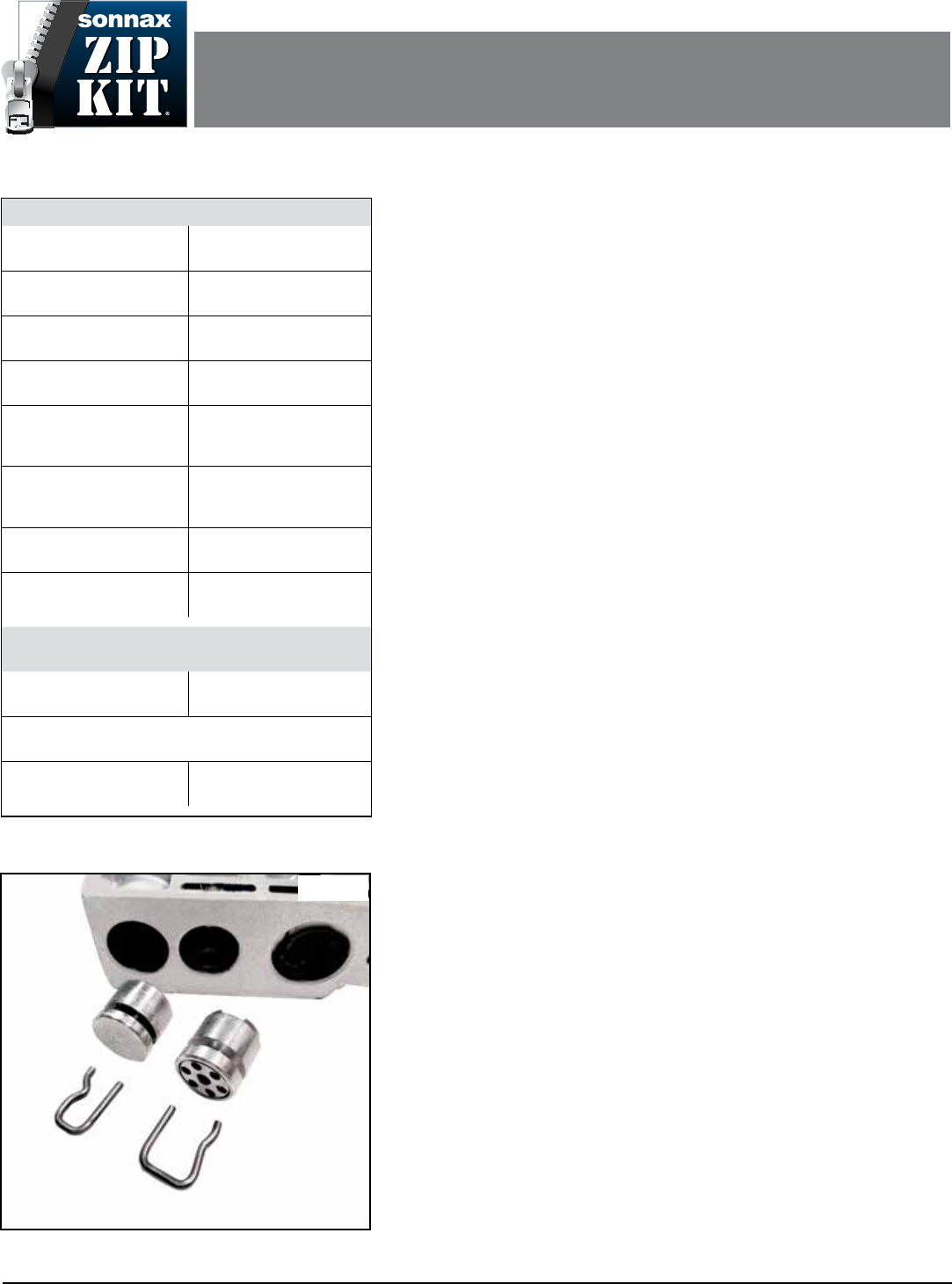
Valve Body Rebuild Tips
& Techniques
Bore-by-bore tips for removal, installation, options and checks of valve body
components. The detailed steps below correlate to the quick guide steps.
1. Replace OE Boost Assembly
Kit now includes an OE ratio boost assembly to restore OE pressure curve. The
increased strength spring is optional, and will provide moderately increased pressure
(approximately 5 psi in Drive and 6 psi in Reverse). For firmer shifts and significantly
increased line pressure, use Sonnax increased ratio boost valve kit 37947-03K, sold
separately. This increased ratio kit is NOT recommended for smaller 4-cylinder
applications, or if testing determines that the Sonnax EPC and engagement control
kit 37947-11K (sold separately) is necessary and installed.
2. Replace OE Forward Modulator Valve
By positioning the manual valve furthest into the bore, air pressure can be used to blow
the modulator valve out. If there is any visible wear or ridge in the bore, buff this area
with Scotch-Brite™ placed on a twisted wire and inserted into drill. Install the PTFE
seal onto the Sonnax valve. Invert the valve and push into the bore just far enough to
size the PTFE seal. After sizing the seal, install the OE forward modulator spring into
the end of the Sonnax valve and install into the bore (illustrated in Quick Guide).
3. Replace OE Solid Plug
If OE end plug has relief orifices and tabs (Figure 1), DO NOT INSTALL the
included Sonnax O-ringed end plug and spring. Reuse the OE end plug. If the
OE end plug is solid, discard and replace with the Sonnax O-ringed end plug and
optional spring if desired.
Optional Step: Seal the “L” pin circuits at the forward and reverse modulator valve
bores (inboard at bores in steps 3 and 4). These locate and hold plugs which separate
and seal oil circuits. As the valves toggle, the plugs become loose and allow fluid to
pass around them. It is suggested to vacuum test the area for severe wear first (reference
page 7) to determine if refurbishing the bore is a better option. The following sealant
process requires cure time, so time must be allowed. Using Permatex® Surface Prep
Activator #24163 or a similar product, clean the middle plug and “L” pin area from
both sides and through the open bore. Air dry, then drip a small amount of Loctite®
609 or 3M #04732 sealant into the “L” pin opening. This must have a cure time to
hold properly. Epoxy is not suggested, as it is permanent. Loctite can be heated to
allow removal. To remove plugs once sealed, heat the area until the sealant melts, then
air dry. Flat stone the valve body surface and clean well to remove surface imprints.
4. Replace OE End Plugs
a. Most plugs require two O-rings and have a tapped hole to allow for easy
removal in the future. To install, lube the plug, slip on the O-rings and roll
the plug on a clean surface to seat the O-rings. Verify that the valves and
springs are in their original positions and install the end plugs with the tapped
hole facing out. Extra O-rings are supplied in case an O-ring is torn during
installation.
Torque Specifications
Band Adjuster Lock Nut
35 to 45 ft-lb
Transmission Oil Pan Bolt
115 to 133 in-lb
Converter Housing-to-Case
27 to 39 ft-lb
Converter-to-Flywheel
22 to 30 ft-lb
Extension Housing-to-Case
27 to 39 ft-lb
Oil Pump-to-Cnvtr Housing
16 to 21 ft-lb
Manual Lever Inner Nut
30 to 40 ft-lb
Manual Lever Outer Nut
30 to 40 ft-lb
Oil Cooler Line-to-
Connector Nut
18 to 23 ft-lb
Oil Cooler Line-to-
Connector 5/16" Tube Nut
26 to 32 ft-lb
Transmission-to-Engine
28 to 38 ft-lb (Except 3.0L)
33 to 44 ft-lb (3.0L)
Low-Reverse Servo
Cover Bolt
106 to 124 in-lb
Center Support-to-Case Bolt
80 to 115 in-lb
Separator Plate Bolt
53 to 71 in-lb
TR Sensor
71 to 98 in-lb
Valve Body-to-Case Bolt
71 to 98 in-lb
Recommended Fluid & Capacities
Mercon V (XT-5-QM) ATF
4R44E 2WD, 2.3L
9.9 Qts (9.4L)
4R44E 2WD, 3.0L
10.0 Qts (9.5L)
4R44E 4WD
10.4 Qts (9.8L)
5R55E 2WD
10.0 Qts (9.5L)
5R55E 4WD
10.3 Qts (9.8L)
Figure 1
Solid OE
End Plug
OE End Plug
with
Relief Orifices
and Tabs
Forward Modulator Valve OE End Plugs
FORD 4R44E, 4R55E, 5R44E, 5R55E
ZIP KIT
PART NUMBER 4R44E-5R55E-ZIP INSTALLATION & TESTING BOOKLET
©2017 Sonnax Industries, Inc. 4R44E-5R55E-ZIP-Booklet_C 10-26-17
800-843-2600 • 802-463-9722 • F: 802-463-4059 • www.sonnax.com Page 1
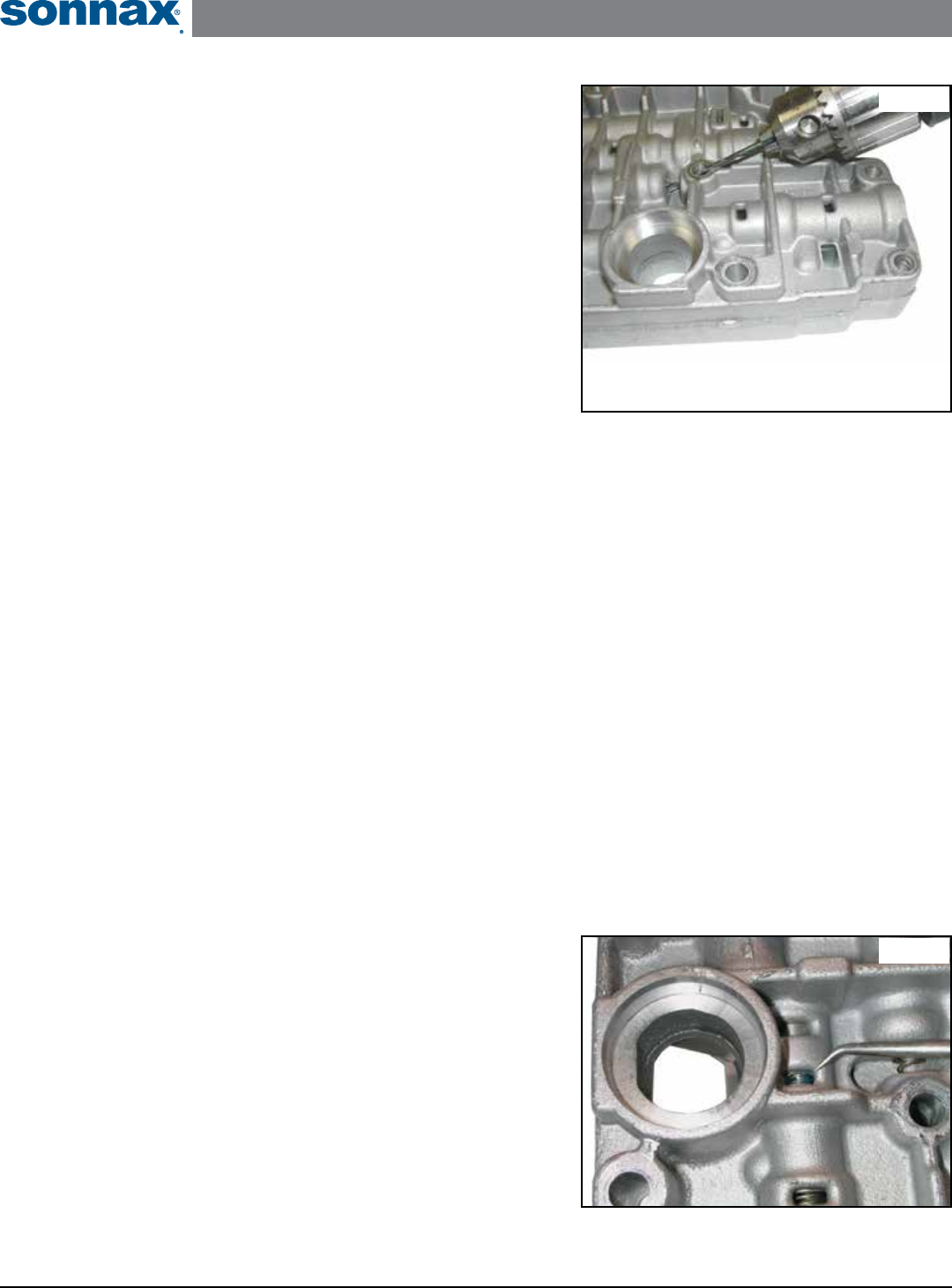
4R44E-5R55E ZIP KIT Installation & Testing Booklet
10-26-17 4R44E-5R55E-ZIP-Booklet_C ©2017 Sonnax Industries, Inc.
Page 2 800-843-2600 • 802-463-9722 • F: 802-463-4059 • www.sonnax.com
TIME TESTED • INDUSTRY TRUSTED
4. Replace OE End Plugs (continued)
b. The OE “U”-shaped retainer is used to hold the plug into the casting, and
should be inserted into the plug groove between the two O-rings. The outer
plug groove will protrude from the bore and is used to help retain the OE
solenoid bracket.
c. Remove the plug between the EPC solenoid and the 1-2/2-3 shift valve. e
plug may not come out easily after removing the “U”-shaped retainer. A rod
(.125" dia.) can be inserted into the opposite bore (113, page 7) to drive out
the plug. After the plug is removed, push the shift valve to the bottom of
the bore and retain it with a screwdriver. Install the small OE plunger valve
into the Sonnax O-ringed plug before installing into the bore. e large OE
“U”-shaped retainer should be installed with the longer leg closest to the
manual valve.
d. Pull out the “L” pin near the solenoid. e OE plug can be dicult to remove.
With a strong needle-nose pliers, turn the plug and hit it with the tip of your
pliers. Continue this until the spring drives out the plug. If the OE plug
will not come out, you must also remove the inner “L” pin retainer. You will
then have to drill an access hole to drive out the valves (Figure 2). A new
spring is supplied for the inner coast clutch valve in case the OE is damaged
during this process. Use the needle nose pliers to install the Sonnax end plug
(O-ring only) by holding the small nub. Twist while inserting the plug until
the O-ring is inboard of the “L” pin retainer port.
e. ese three plugs seal shift solenoid oil. e two smaller end plugs use four
small O-rings. e larger end plug is .630" in diameter, and uses two large
O-rings.
5. Replace OE Checkballs, EPC Limit Valve
& Lube Orice Plug
Replace the four OE checkballs with the new Torlon® balls included, ensuring prop-
er location. Replace the OE lube orifice. Replace the OE EPC relief valve with the
Sonnax domed relief, reusing the OE spring. The TCC relief and the EPC relief
springs are interchangeable. Two replacement “L” pins are included in case originals
are lost or damaged.
6. Drill Separator Plates
a. Drill the pressure regulator balance orice to .055" dia. with included drill. To
prevent ashing, start the drill on one side and then nish from the opposite. It’s
always best to taper the orice holes when done with a larger drill.
b. Drill the overdrive servo apply orice to .072" dia. with included drill. is
will supply rmer 4th in 4R units and rmer 5th and 2nd in 5R units. Later
5R55E units are already this size.
c. Drill line pressure circuit to converter feed orice in the plate to .062" dia.
with included drill. Late-model 5R55E units are already this size. Drill the
indicated converter clutch orice to .062" dia., then insert the included .062"
aluminum plug and peen in place to close o the hole.
d. Drill the TCC exhaust hole to .110" dia. with included drill.
Figure 2
For bore 109 valve removal, drill .110" hole, entering
at bolt and exiting into spring pocket of bore 109.
This allows rod to drive out the valve.
Figure 3
7. TCC Modication
Remove the smallest spring from the cooler bypass
valve bore. is spring can be pulled out from the
lower side of the casting, through the slot next to the
lter inlet (Figure 3).
8. Replace OE Solenoid O-Rings
Replace small and large O-rings from the four
indicated solenoids (see Quick Guide). Lube the
O-ringed solenoid snout prior to bore installation.

4R44E-5R55E ZIP KIT Installation & Testing Booklet
©2017 Sonnax Industries, Inc. 4R44E-5R55E-ZIP-Booklet_C 10-26-17
800-843-2600 • 802-463-9722 • F: 802-463-4059 • www.sonnax.com Page 3
TIME TESTED • INDUSTRY TRUSTED
Figure 4
If there is a hole
here, use includ-
ed EPC relief tee and
OE spring. If there is
no hole here, you
must use blow-off end
plug at forward
modulator valve
(Figure 5). End plug
installs here. Figure 5
This plate and part number
does not have an EPC relief
hole (Figure 3) and must be
used with OE part # 3L5Z-
7M203-JA end plug relief. Figure 6
4R44E Plate
5R55E Plate:
has
bathtub checkball,
ahead of bolt hole.
Rebuilding Cautions
• Do not combine aftermarket parts or procedures
with this kit.
• Do not drill line-to-lube through the casting at the
pressure regulator valve.
• Do not use a stronger pressure regulator valve
spring or shim than the ones supplied.
• Do not remove springs or block reverse engagement
control valve.
Troubleshooting Tips
ese tips are not about common problems such as blown gaskets or dirty valve
bodies. ese only include valve body problems not visible during a rebuild.
No/Slow Reverse
• The SSA solenoid must be turned on, allowing flow through the solenoid, or
direct clutch will not apply until EPC rises to 20 psi. The direct clutch psi
will then slowly rise following EPC until clutch holds.
• Always install new servo pistons. Both servos are charged on the release side
in reverse.
• Inspect the center support sleeve, sealing rings and direct drum sleeve for cracks.
• Ensure the vehicle has line rise, as reverse will not engage until line is 120 psi.
Delayed Reverse & Forward
e separator plate must be aligned with pins. If not, the bolt threads will separate
the case from the plate, causing a line pressure leak.
Servo Covers Blown Out of Case
Inspect for causes of high line psi such as pressure regulator bore or boost sleeve
wear, or line booster valve stuck inboard.
Servo Rubber Separated/Blown Off
is often occurs from pre-assembly damages, so inspect carefully before install-
ing. e rubber lip separation occurs from heat and high pressure. Both servos are
pushed toward the cover in reverse, so check for cause of high line pressure.
No 2nd, 1-2 Slide or Soft 2nd
Gear Starts
• Air test the rectangular circuit five openings in from
EPC solenoid. No cross leakage should be visible!
• Look for bore wear at the forward modulation
valve (repaired by 37947-11K
,
not included in this
Zip Kit), This valve controls the servo apply rate.
• If the plug that lives in the middle of OE assembly
(repaired by 37947-11K, not included in this Zip Kit),
is loose and bore leaks, a poor 1-2 and/or 2-3 results.
No 2nd or 4th, Erratic Direct
Clutch, No Upshift
e solenoid regulator valve is likely out of position.
With SSB solenoid removed, the end of the casting to
edge of the long aluminum plug will measure 1.720"
when “L” pin is installed properly.
No Coast Clutch Pressure
• Inspect the bore plug for wear at the TCC regulator
valve. Sonnax TCC regulator sleeve kit 37947–09K
(not included in this Zip Kit) eliminates the leak
and bore plug here.
• The bore for the coast clutch shift valve wears out.
Insert the valve: no side-to-side movement should
be visible.
Separator Plate & Relief Valve Information
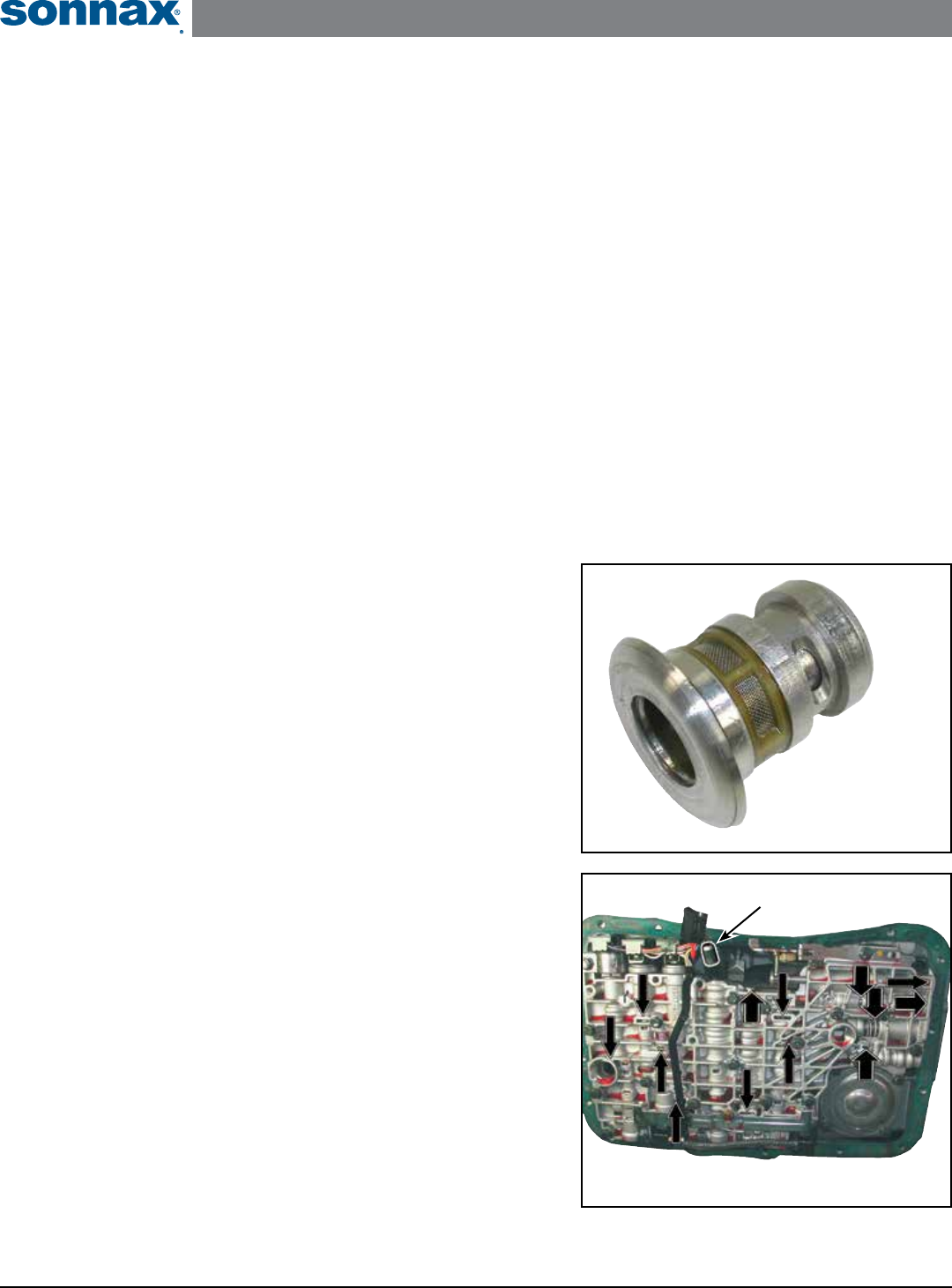
4R44E-5R55E ZIP KIT Installation & Testing Booklet
10-26-17 4R44E-5R55E-ZIP-Booklet_C ©2017 Sonnax Industries, Inc.
Page 4 800-843-2600 • 802-463-9722 • F: 802-463-4059 • www.sonnax.com
TIME TESTED • INDUSTRY TRUSTED
Troubleshooting Tips (continued)
No Overdrive Servo Apply psi
• The coast clutch shift valve may be out of position, the bore worn severely or
the dumbbell-shaped valve (opposite bore from the TCC modulator) is not
being retained correctly.
• This “L” pin falls out of position easily.
• Timing valve may be stuck toward the end plug or the spring is not on
center, which causes it to coil bind.
• Kickdown valve may be stuck or spring missing.
No OD Servo Release
(No Overdriven 2nd in 5R & No 4th in 4R)
Mismatched separator plate at 5R/4R identication (Figure 6).
OD Band Failure, No Overdrive Release psi
e 3-4 shift valve may not be positioned due to a loose SSC solenoid. Bracket must
hold it in ush.
Broken Bands, No EPC Blow-Off, EPC psi Too High
Relief Tee near the pressure regulator is not opening or mismatched plate without a
hole here and no relief used at forward modulator end plug. e EPC spring bore
is often tapered, which alters spring operation. e Sonnax EPC and engagement
control kit 37947-11K (not included in this Zip Kit) addresses this problem.
Low EPC, Soft Shifts, Slip in 3rd
Multiple EPC leakage points. Use the Sonnax EPC and engagement control kit
37947-11K (not included in this Zip Kit), which address this entire circuit. Good
maximum EPC is 125-130 psi in OD and maximum of 144 in reverse. EPC should
not drop more that 15 psi during TCC apply.
Low EPC Pressure & No Lockup Control
If TCC modulator valve sticks, EPC will only obtain about 65 psi.
Flare on 2-3 Shift, 4R (3-4 on 5 Speed)
e servo pin bore is worn on the intermediate servo, or the spring on the piston is
too strong.
No 3rd or 4th
e 2-3 shift valve spring is missing or installed wrong. Also, the 1-2 shift valve
should stroke during wet air test (WAT) at the rectangular circuit ve openings in
from EPC solenoid.
TCC Applied Prematurely, Harsh Shifts
If the solenoid is restricted or grounded, the TCC valve can stroke and apply the
converter clutch.
Poor Converter Charge, Delayed Engagements
e balance spool or innermost bore for the pressure regulator is worn out.
Shift Solenoids
It is very rare to have a shift solenoid problem on these
units. It’s more common to have a loss of solenoid oil
psi due to loose end plugs.
EPC Circuit Testing
e most eective method to isolate the EPC circuit is
to perform an wet air test with uid while the body is
still bolted to the case. is can be done in the vehicle
or at the bench. A quick test adapter can be made from
an old 4R/5R EPC solenoid. e coil housing and
valve will be removed and a plug or epoxy used to seal
the inboard circuit (Figure 7).
Supply 40-60 psi of air into the adapter. No leaks
should be visible at the locations shown in Figure 8.
Any leakage is reduction of EPC pressure and line rise
while in operation. Remember, though, as operating
temperature increases, valve clearance and the ow rate
(viscosity) of ATF increase. You can duplicate hot uid
at the bench by lling the case and valve body with
solvent, then bolt up and test with the adapter.
Figure 7
Old 4R/5R
EPC Solenoid
Figure 8
“Tired” valve bodies leak at any
or all of these locations.
40-60 psi supplied to modied EPC solenoid/tool.
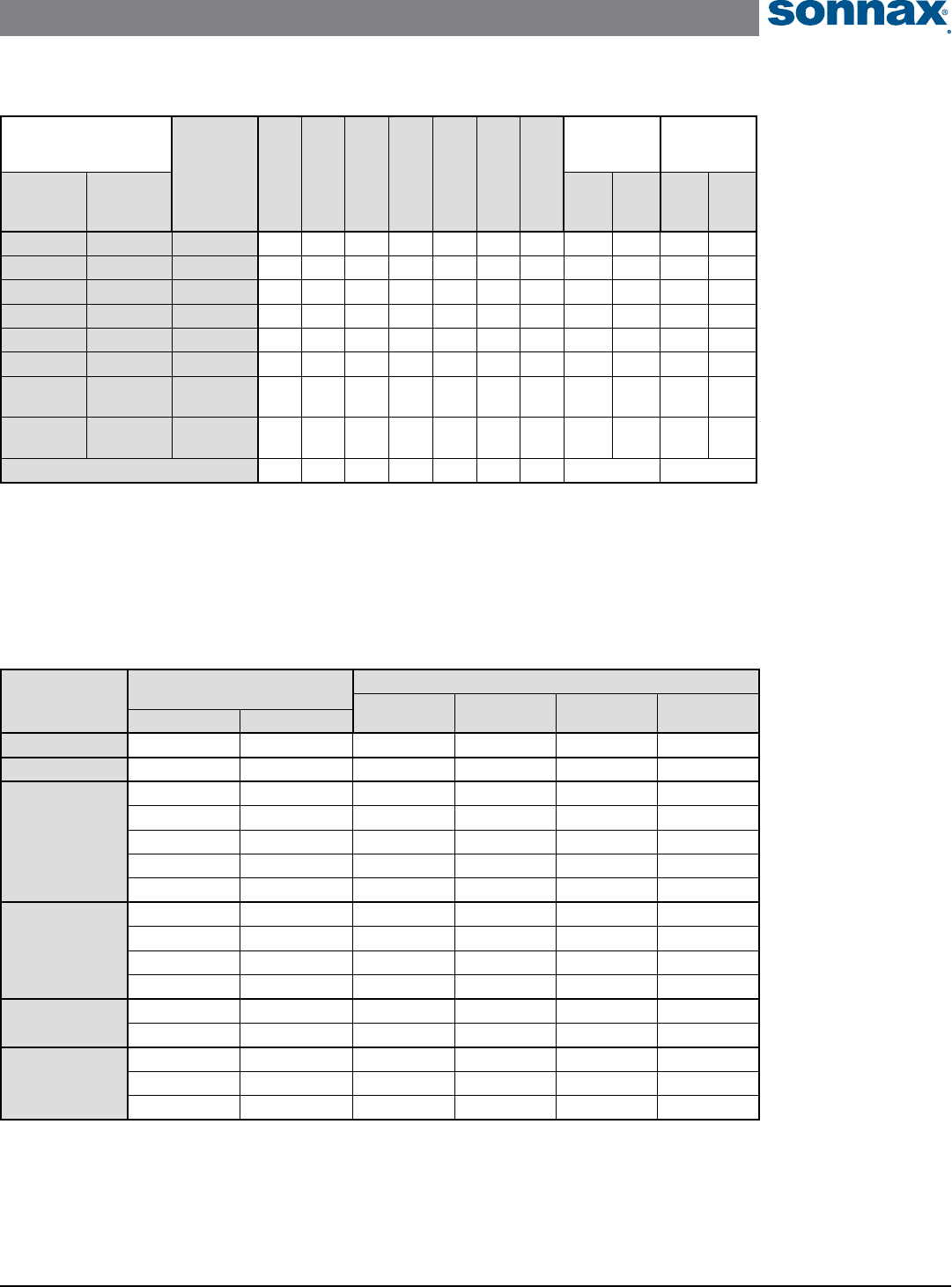
4R44E-5R55E ZIP KIT Installation & Testing Booklet
©2017 Sonnax Industries, Inc. 4R44E-5R55E-ZIP-Booklet_C 10-26-17
800-843-2600 • 802-463-9722 • F: 802-463-4059 • www.sonnax.com Page 5
TIME TESTED • INDUSTRY TRUSTED
Apply Component Chart
GEAR
Shifter
Position
Front Band
Intermediated
Band
Reverse Band
Coast Clutch
‘95-‘96
Coast Clutch
‘97-‘00
Direct Clutch
Forward Clutch
Front
One-Way
Clutch
Reverse
One-Way
Clutch
4R44E/
4R55E 5R55E
Drive
Coast
Drive
Coast
Reverse Reverse Reverse A A* A H OR†
1st 1st
Overdrive
A* A H OR†H OR
2nd
Overdrive
A A OR OR H OR
2nd 3rd
Overdrive
A A* A* A H OR†OR OR
3rd 4th
Overdrive
A* A* A A H OR†OR OR
4th 5th
Overdrive
A A A OR OR OR OR
Manual 2
Position
Manual 2
Position 2A A A A H OR OR OR
Manual 1
Position
Manual 1
Position 1A A A A H OR H OR
Planetary Component FRS FS RP FRS FRS FS FR FRS RP
Figure 9
A = Applied
H = Holding
OR = Overrunning
* = Applied, TCS on
† = Ineffective, TCS on
FRS = Front Sun Gear
FS = Forward Sun Gear
RP = Reverse Planet Assembly
FR = Forward Ring Gear
Apply Component Chart Key:
Solenoid Apply Chart
Transmission
Range Selector
Lever Position
Powertrain Control Module
(PCM) Gear Commanded
Shift Solenoids
SSA SSB SSC SSD/CCS
4R44E/4R55E 5R55E
Park/Neutral Park/Neutral Park/Neutral On Off Off Off
Reverse Reverse Reverse On Off Off Off
Overdrive
(TCS Off)
1 1 On Off Off Off
2 On Off On Off
2 3 On On Off Off
3 4 Off Off Off Off
4 5 Off Off On Off
Overdrive
(TCS On)
1 1 On Off Off Off
2 On Off On On*
2 3 On On Off On*
3 4 Off Off Off On
Manual 2nd 2 3 On On Off On
3A4AOff Off Off On
Manual 1st
1 1 On Off Off On
2AOn Off On On
2A* On On Off On
Figure 10
A = When a manual pull-in occurs above calibrated speed, the transmission will not downshift
until the vehicle speed drops below this calibrated speed.
* = Model and calibration dependent.
Apply Component Chart Key:

4R44E-5R55E ZIP KIT Installation & Testing Booklet
10-26-17 4R44E-5R55E-ZIP-Booklet_C ©2017 Sonnax Industries, Inc.
Page 6 800-843-2600 • 802-463-9722 • F: 802-463-4059 • www.sonnax.com
TIME TESTED • INDUSTRY TRUSTED
Solenoid & Bolt Locations
Install bolts in sequence indicated by numbers. Colors indicate bolt lengths, see chart for details.
Bolt
Color Code Bolt Lengths No. Bolts
Required
Red 20mm 4
Green 30mm 1
Yellow 35mm 2
Blue 40mm 16
Orange 45mm 4
Purple 55mm 1
Bore Valve Springs O.D. Wire
Dia.
Free
Length
Coils Color
101 Forward Control .338" .032" .665"-
-.775" 6.5 White
102 Pressure Regulator, Outer .745" .055" 1.065" 4 Plain/Lt. Purp.
102 Pressure Regulator, Inner .412" .032" 1.135" 9.5 Lt. Green
103 Forward Modulator .236" .026" .738" 14 White
103 EPC Boost .293" .040" 1.210" 12 Orange
105 Reverse Modulator, Outer .210" .018" 1.080" 10.5 Plain
105 Reverse Modulator, Inner .210" .018" 1.080" 10.5 Plain
106 2-3/3-4 Shift .275" .030" 1.052" 13 Plain
107 1-2/2-3 Shift .284" .033" .730" 7 Lt. Purple
108 Solenoid Regulator .218" .030" .830" 8.5 Yellow
109 TCC Regulator, Inner .187" .028" .720" 12 White
27
13
10
1
20 28
23
16 8
4
5
9
17 19
21
11
7
6
14
22
12
24 26
25
15
18
23
Shift Solenoid B (SSB) 22–48 ohms
EPC Solenoid 3.1–5.7 ohms
Coast Clutch Solenoid
(CCS/SSD) 22–48 ohms
TCC Solenoid 8.9–16 ohms
Shift Solenoid C (SSC) 22–48 ohms Shift Solenoid A (SSA) 22–48 ohms
Bore Valve Springs O.D. Wire
Dia.
Free
Length
Coils Color
109 TCC Regulator, Outer .285" .040" .787" 9.5 Orange
109 Coast Clutch. Bottom Bore .222" .023" .840" 9.5 Red
110 TCC Modulator .238" .023" 1.230" 11.5 White/Yellow
111 Thermal Outer, Big .575" .042" 1.045" 4.5 White
111 Thermal, Middle .264" .026" 1.232" 13.5 Lt. Green
111 Inner Limit (smallest) .200" .018" .840" 12 Blue
112 3-4/4-5 Shift .280" .032" 1.162" 12 Plain
113 Throttle Downshift .263" .028" .700" 6.5 Orange
114 Manual Low .320" .032" .985" 7.5 Yellow
115 Kickdown .262" .028" .670" 7 Orange
N/A Steel EPC Relief Tee .292" .040" .982" 13.5 Plain
N/A Plastic TCC Relief Tee .292" .040" .982" 13.5 Plain
OE Spring Identification Chart
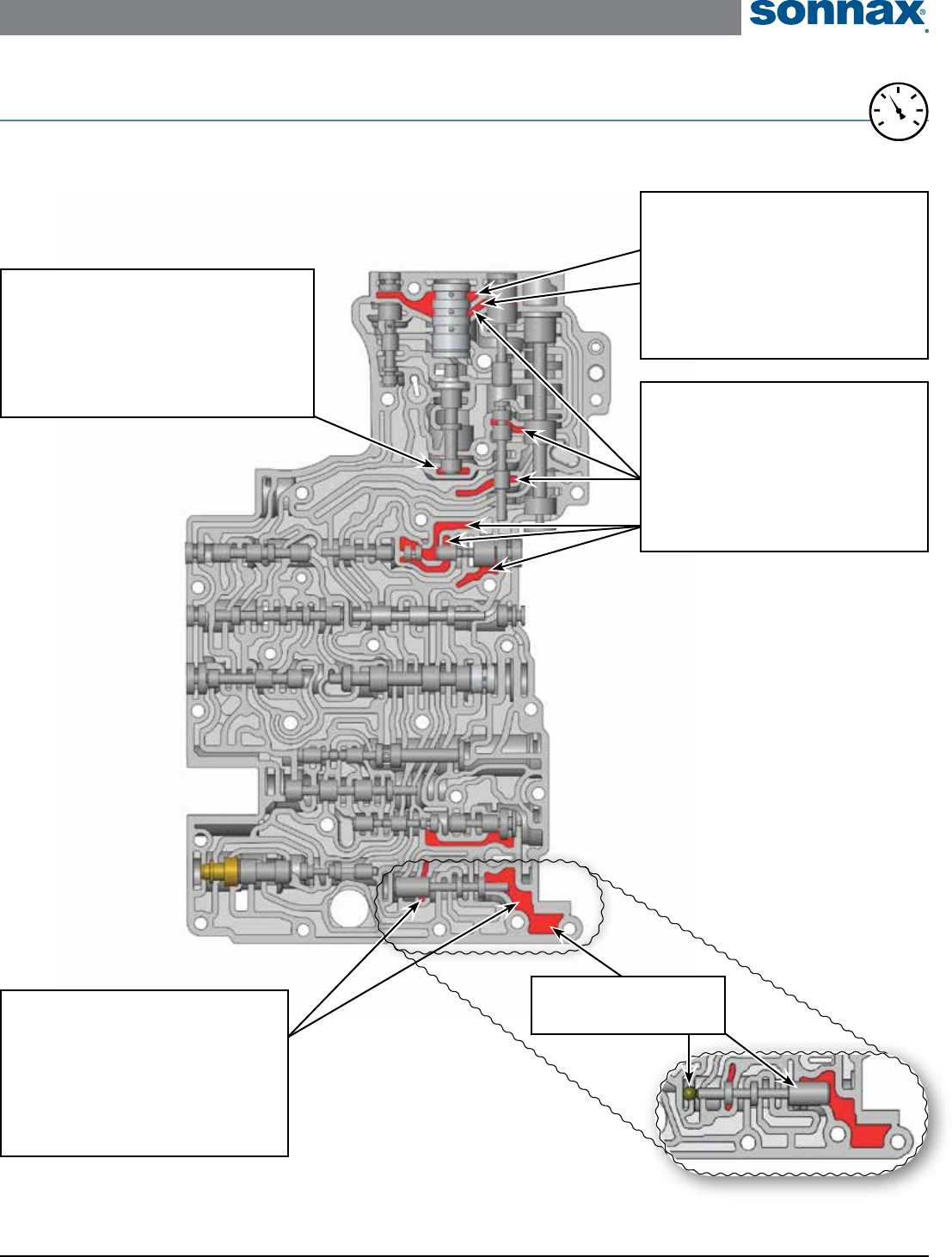
4R44E-5R55E ZIP KIT Installation & Testing Booklet
©2017 Sonnax Industries, Inc. 4R44E-5R55E-ZIP-Booklet_C 10-26-17
800-843-2600 • 802-463-9722 • F: 802-463-4059 • www.sonnax.com Page 7
TIME TESTED • INDUSTRY TRUSTED
Critical Wear Areas & Vacuum Test Locations
NOTE: OE valves are shown in rest position and should be tested in rest position unless otherwise indicated. Test locations are pointed
to with an arrow. Springs are not shown for visual clarity. Low vacuum reading indicates wear and Sonnax parts noted for replacement.
For specic vacuum test information, refer to individual part instructions included in kits and available at www.sonnax.com.
20
25
15
0
10
5
30
VACUUM
TEST
*Part numbers with an asterisk (*) are included in this Zip Kit. Other part numbers are available separately.
Pressure Regulator Valve
• Delayed engagement due to poor converter ll
• High/Low line pressure
• Low cooler ow at idle
• Overheated converters
Replace with Sonnax Part No.
37947-05K Requires 37947-TL5
TCC Modulator Valve
• No TCC apply
• Code 1741
• Low cooler ow
• Poor converter ll & delayed engagements
• Engine stall on Forward engagement
Replace with Sonnax Part No.
37947-07K Requires 37947-TL5
Boost Valve Assembly
• Soft shifts
• Delayed Reverse
• Low line pressure
• Poor modulator control
Replace with Sonnax Part No.
37947-01K OE Ratio
37947-03K* Increased Ratio
EPC Boost Valve,
Forward Modulator Valve
& Reverse Modulator Valve
• Poor shift quality
• Delayed Forward/no Reverse
• 2nd Gear starts
Replace with Sonnax Part No.
37947-11K Requires 37947-TL11
To vacuum test this port: invert
valve and prop outboard with a
Torlon checkball.
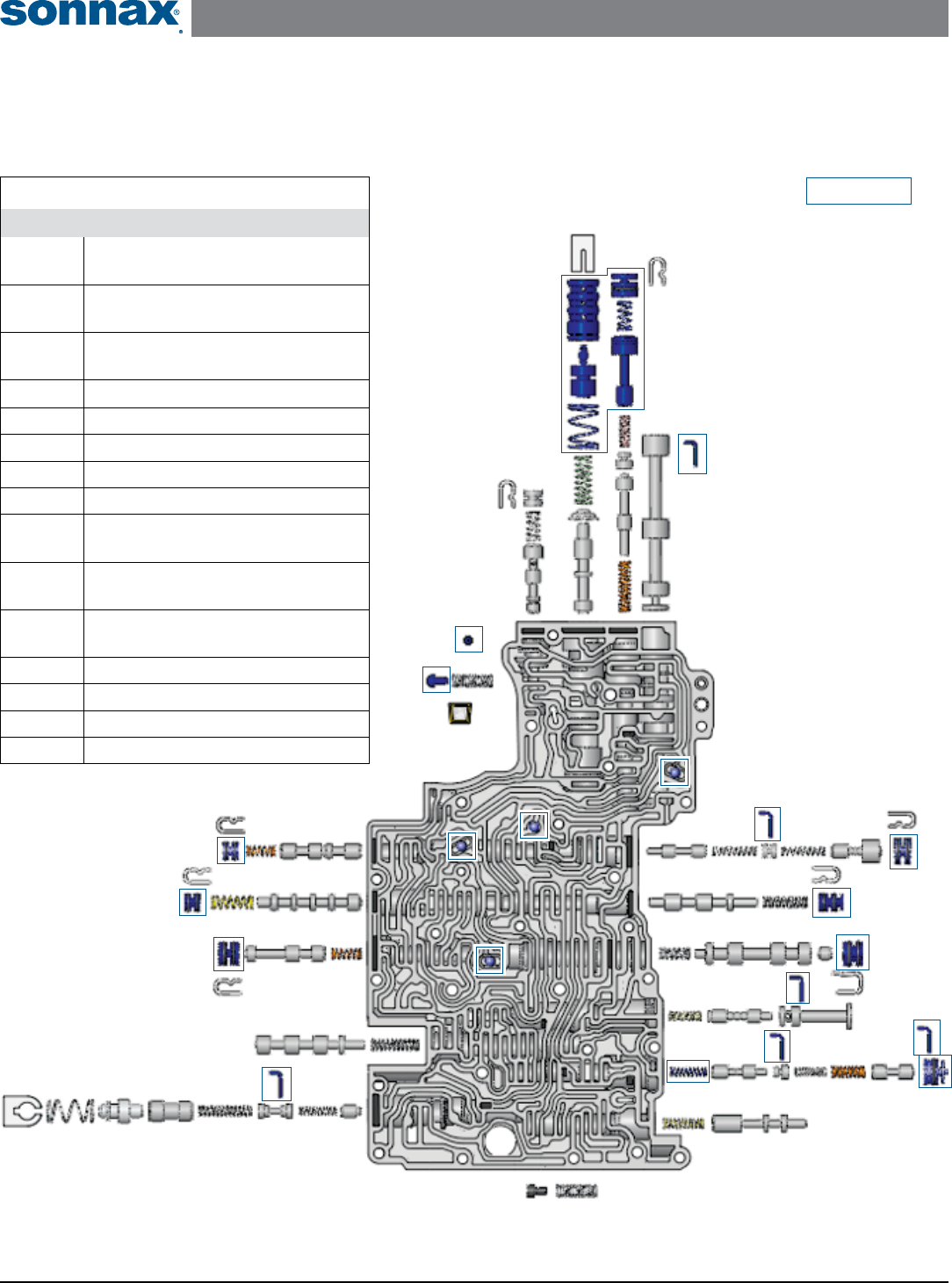
4R44E-5R55E ZIP KIT Installation & Testing Booklet
10-26-17 4R44E-5R55E-ZIP-Booklet_C ©2017 Sonnax Industries, Inc.
Page 8 800-843-2600 • 802-463-9722 • F: 802-463-4059 • www.sonnax.com
TIME TESTED • INDUSTRY TRUSTED
Valve Body Descriptions
I.D No. Description
101 Forward Engagement
Control Valve
102 Boost Valve Assembly
& Pressure Regulator Valve
103 EPC Boost Valve
& Forward Modulator Valve
104 Manual Valve
105 Reverse Modulation Valves
106 2-3 or 3-4 Shift Valve
107 1-2 or 2-3 Shift Valve
108 Solenoid Regulator Valve
109 Coast Clutch Valve
& Converter Regulator Valve
110 Converter Clutch
Modulator Valve
111 Cooler Limit Valve, Bypass Valve
& Thermostat Bypass Valve
112 3-4 or 1-2 & 4-5 Shift Valve
113 Throttle Downshift Control Valve
114 Manual Low Valve
115 Kick Downshift Control Valve
OE & Sonnax Reinstallation Valve Body Exploded View
101
102
106
105
104
103
107
108
109
110
111
115
114
113
112
Sonnax Parts
NOTE: Sonnax replacement
parts are boxed and in blue
in this diagram.
There are six “L” pins in this
OE valve body. Sonnax gives
you two new “L” pins in this
Zip Kit to replace any that
may be damaged.