PTS Installation Instructions
Pts Installation Instructions PTS_Installation_Instructions PTS_Installation_Instructions 1271 file instruction uploads sonnax-dev
Pts Installation Instructions PTS_Installation_Instructions PTS_Installation_Instructions 1274 file instruction uploads sonnax-dev
Pts Installation Instructions PTS_Installation_Instructions PTS_Installation_Instructions 1263 file instruction uploads sonnax-dev
Pts Installation Instructions PTS_Installation_Instructions PTS_Installation_Instructions 1277 file instruction uploads sonnax-dev
Pts Installation Instructions PTS_Installation_Instructions PTS_Installation_Instructions 1276 file instruction uploads sonnax-dev
2016-05-23
: Sonnax Pts Installation Instructions PTS_Installation_Instructions 1267 file instruction uploads
Open the PDF directly: View PDF .
Page Count: 2
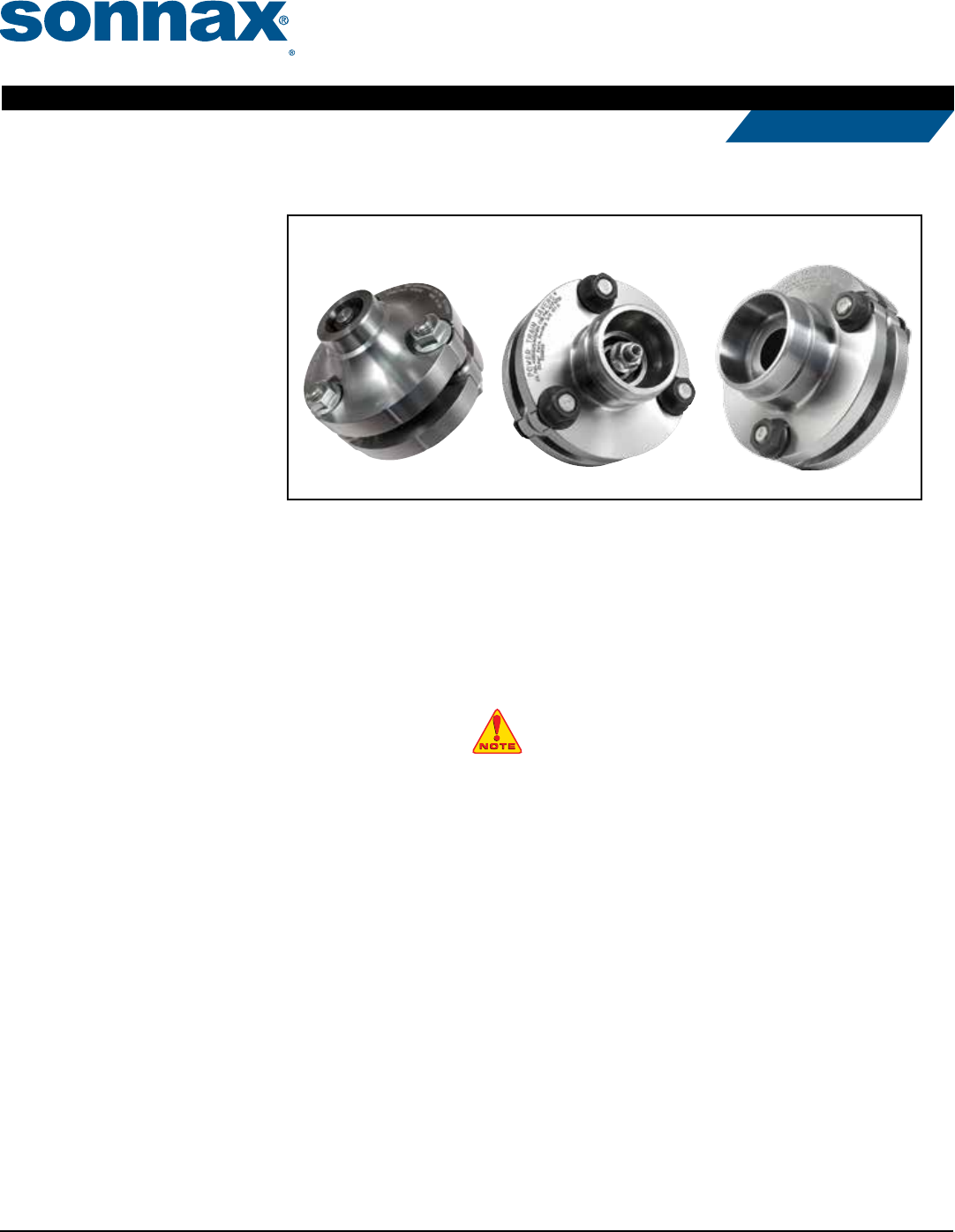
P
OWER
T
RAIN
S
AVERS
ADVANCED DRIVELINE PROTECTION SYSTEM
Instructions
©2016 Sonnax Industries, Inc. PTS_Instructions 05-23-16
800-843-2600 • 802-463-9722 • F: 802-463-4059 • www.sonnax.com Page 1
Power Train Savers®
Light, Medium & Heavy Duty
Light Duty Medium Duty Heavy Duty
Welding Procedure for PTS Installation
Preparation of Driveshaft
All loose or thick scale, rust, moisture, grease, paint or other
foreign material that would prevent proper welding or produce
objectionable fumes should be removed to within 2" of weld
location. e repair area should be prepared by machining or
grinding to remove any burrs or surface defects and to ensure
squareness of tube ends.
Preheat
Preheating of the PTS is not necessary and should not be done.
Weld at room temperature (68°F/20°C). e driveline tube can be
preheated if needed.
Welder Settings
All welders are dierent. Some may have to be adjusted higher
or lower to produce the same amperage. e following are
average settings:
• Voltage: 19-21 • Amperage: 195-200
Weld Procedure
e welding process will be ux cored arc welding (FCAW) pro-
cess, semi-automatic using an E4801 T-9 CH electrode with a
75/25% shielding gas. Use only stringer beads with a radial direc-
tion of travel. e driveline should be mounted on rollers and
rotated to maintain a at or horizontal welding position with a
controlled rate of weld deposit.
• Slag or ux remaining after a pass must be removed before
applying the next pass. Similarly, cracks or blowholes which
appear on the surface of any pass must be removed before de-
positing the next pass.
• Care must be used to prevent the containment or trapping of
slag, the formation of voids or root porosity.
• Weld geometry must be free from undercut, cold laps and poor
transitions, and must be consistent with acceptable weld proles.
Cooling of Driveline
e best method is to air-cool welds slowly at room temperature.
Do not rush the cooling process by quenching the welds with cool-
ant or water, as this can cause stress cracks not noticeable to the eye.
Installation
IMPORTANT: A qualied driveline technician must install the
Power Train Saver.
e Power Train Saver (PTS) should normally be installed directly
in front of the forward dierential, on the weld yoke end of the
shaft (Figure 1 driveshaft “A”).
In some cases, when the driveshaft angles and RPM exceed manu-
facturer specications, the PTS can be installed ahead of the car-
rier bearing (Figure 1 driveshaft “B”).
In either case, the PTS must be installed on the weld yoke end
of the driveshaft.
1. Check PTS part number. Cut and discard the appropriate
portion of driveshaft based on the PTS being installed us-
ing the dimensions shown in Figure 1, then machine tube
ends square.
2. Align the timing marks on the outside diameter of the PTS
and install the Torque Fuses® according to the instructions
packed with the fuse set. e nuts must be tightened to the
torque specication given.
3. Install the PTS into the longer section of the driveshaft.
Make sure the PTS is square with the tube and tack weld
it in place.
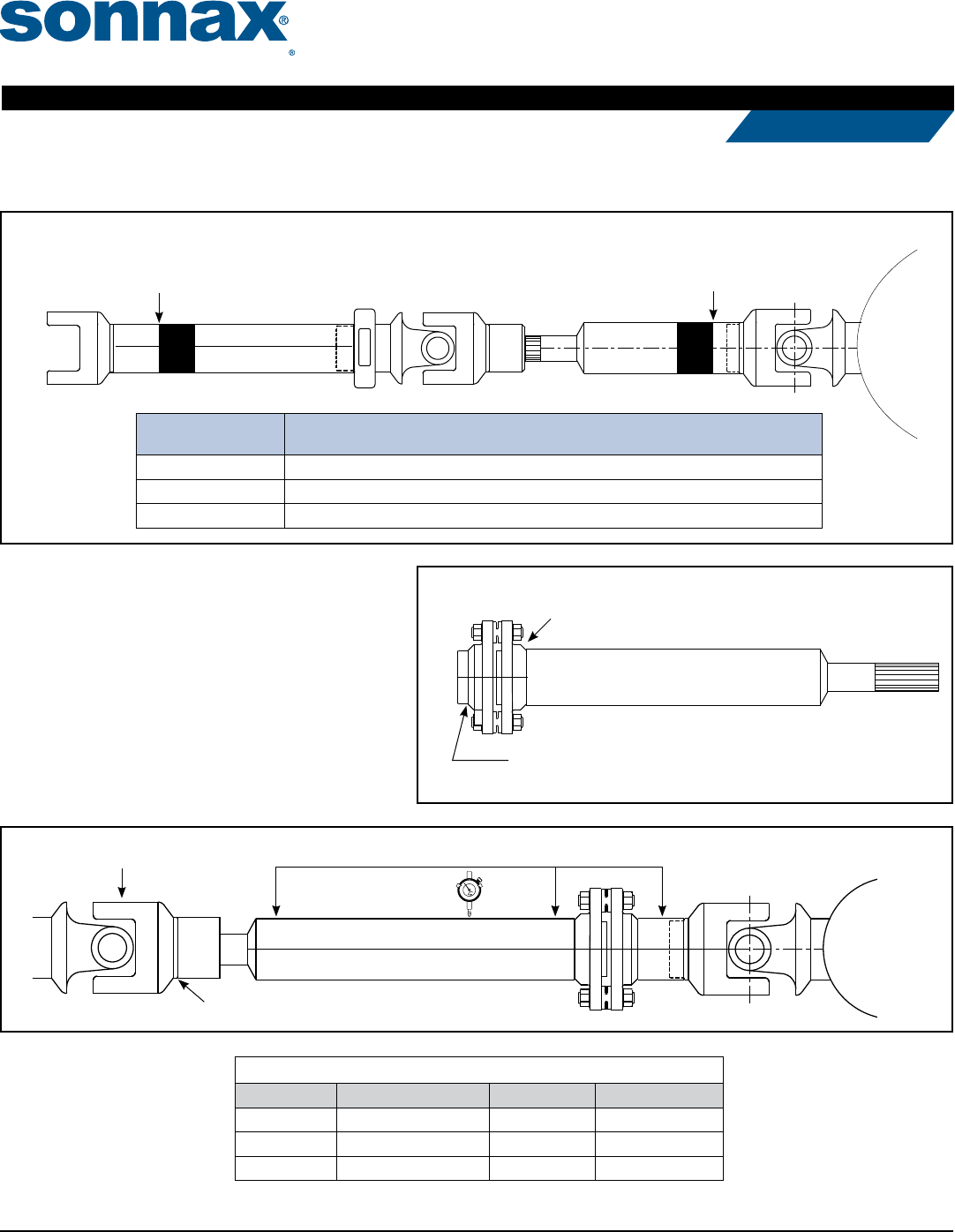
P
OWER
T
RAIN
S
AVERS
ADVANCED DRIVELINE PROTECTION SYSTEM
Instructions
POWER TRAIN SAVERS® LIGHT, MEDIUM & HEAVY DUTY
©2016 Sonnax Industries, Inc. PTS_Instructions 05-23-16
800-843-2600 • 802-463-9722 • F: 802-463-4059 • www.sonnax.com Page 2
Installation (continued)
4. Radial run out of the PTS must be .002" or less
when measured (Figure 2). Once correct positioning
has been veried, complete the weld and re-measure.
5. Tack and weld the short end of the driveshaft to the
PTS as shown in Figure 3.
6. Check the nished assembly for radial runout at the
locations shown in Figure 3. No part of the assembly
should have more than .004" radial run out.
7. Balance to within 0.2 ounce-inches on both ends of
the assembly.
Figure 3
Differential
Check Radial Runout
Tack and weld (short end).
Weld Yoke
Figure 1
BADifferential
Start cut 3.000"
from weld line.
Start cut 3.000"
from weld line.
Discarded Portion
from A or B Part Numbers
3.500" 20083B, 20120B, 25083B, 25095B, 25120B
4.505" 15095, 16134, 17180, 18134, 18259, SP138, 30083, 35083, 35095, 40083, 40180
6.000" SP165, SP197
Fuse Nut Torque Specifications
PTS Series Fuse ID Stamp Code Fuse Nut Hex Fuse Nut Torque
Light Duty 1E — 1Q 3/4"80 Ft. Lbs.
Medium Duty 0 — 13 15/16"140 Ft. Lbs.
Heavy Duty F — Z 11/8"220 Ft. Lbs.
Tack and weld
(long end).
Check radial runout
on this surface.
Figure 2