Spectra Engineering MX800AB Repeater/Base Station User Manual 5 Align Test
Spectra Engineering PTY LTD Repeater/Base Station 5 Align Test
Contents
Section 5
5. Alignment and Testing
The MX800 test and alignment procedures are divided into two main sections. The first
section is a transceiver level procedure which assumes that the radio is fitted with working
modules. The second section contains the individual module test procedures.
5.1. Transceiver Setup, Calibration and Alignment
This section explains how to setup, calibrate and align the complete MX800 Base Station.
A number of procedures are required to fully initialise the MX800. The following test
equipment will be needed:
1.0 MXTOOLS (MX800 Base Station Programming Utility)
2.0 MXTOOLS User Manual
3.0 RF Test Set (HP 8920) or equivalent
4.0 CRO (Cathode Ray Oscilloscope)
5.0 RF Power Meter (Watts)
6.0 RF Signal Generator
7.0 Multimeter
8.0 +13.8 VDC @ 15 amp power supply
The order of some, but not all, of the procedures is important to ensure correct setup of the
radio. The order of the procedures as described is recommended and those that are critical
are mentioned. If the radio has been previously setup and the dealer intends to recalibrate
and align the radio then steps 5.1.1, 5.1.2 and 5.1.3 can be ignored as the model number,
serial number, configuration and channel information will have already been loaded.
5.1.1. Sending Model Number and Serial Number to the Radio
The model number is entered or updated using MXTOOLS. To edit the model number
select 'Radio Model Number', under the 'Setup' menu. This brings up a dialog box that
the dealer can then enter the model number, according to the configuration of the radio.
(Refer to the MXTOOLS User Manual for additional help)
The dealer cannot alter the serial number as this is factory set.
5.1.2. Sending Configuration Information
Firstly the configuration file for the radio needs to be setup. Using MXTOOLS the
configuration information needs to be filled out on the Configuration Screen. This
information needs to be saved to a configuration file. If an existing radio already contains
the desired configuration then this configuration can be downloaded and saved. This
configuration information then needs to be 'Sent to the MX800'. (Refer to the MXTOOLS
User Manual for additional help) A warning message will appear that indicates that the
MX800 Base Station has not yet been calibrated, this may be ignored.
Once the configuration information has been sent then all of the programmable parameters
within the MX800 Base Station are initialized.
5.1.3. Sending Channel Information
The channel information setup is similar to that of the configuration. The channel
frequencies, subtones and other parameters are setup in the Channel Screen in
MXTOOLS. At this stage it is not necessary to set the values of the digital
potentiometers. This will be done in the following procedures. After entering in the
channel details this information then needs to be saved to a file. If another radio already
contains the desired frequencies then these can be downloaded from that radio and saved
to a file. The digital potentiometer values from one radio to the next will differ so it is
advisable to save the information in a new channel file and not save over the top of any
backup copies of existing radios. The saved channel information is then sent to the
MX800. (Refer to the MXTOOLS User Manual for additional help)
After sending the configuration and channel information the MX800 is fully programmed
and will now operate. Without sending both the configuration and channel information
the radio will not function, and thus the following procedures will not be able to be
completed.
Note: The buttons for sending and loading of channel information may be disabled if
MXTOOLS did not successfully 'Connect to MX800'. If this is the case simply choose to
'Connect to the Radio' after the configuration information is sent.
5.1.4. Setting Alignment Channel
When setting up the radio it is recommended that all measurement and adjustments are
done on a channel that is in the center of the frequency spread of the channels. This
minimizes any errors due to frequency changing. Alternatively if the frequency spread of
the channels is too large then you may wish to calibrate and align every channel. (In most
cases this will not be necessary.) Both individual and group alignment will be covered.
The channel may be selected via the Channel Screen in MXTOOLS using the software
channel select or in hardware via the internal channel dip switch or via the rear channel
select. (Refer to section 2.2.2.3 for additional help.) This channel will then be used when
performing the following procedures.
5.1.5. Power Calibration
Power calibration affects the forward and reflected power meters on the Diagnostics
Screen as well as the low forward power trip point for the MX800. This procedure
requires a power meter and the relevant leads to connect the transmitter output to the
meter. Power calibration is done using MXTOOLS via the Calibration Screen. To
complete the power calibration follow the instructions that MXTOOLS provides. (Refer
to the MXTOOLS User Manual for additional help.)
Once power calibration has been completed the configuration information must be sent
again. Check that the low forward power trip point is set correctly. The calibration
affects the low forward power trip point and thus the configuration information must be
sent to update it according to the new calibration information.
5.1.6. RSSI Calibration
The RSSI calibration is used to calibrate the RSSI meter on the MXTOOLS Diagnostics
Screen. The procedure requires an RF signal generator and the relevant leads to connect
the signal generator to the RF input of the MX800 Base Station. RSSI calibration is done
via the MXTOOLS Calibration Screen. To complete the RSSI calibration follow the
instructions that MXTOOLS provides. (Refer to the MXTOOLS User Manual for
additional help.)
5.1.7. Temperature Calibration
The temperature calibration is used to calibrate the temperature meter on the MXTOOLS
Diagnostics Screen and the temperature controlled switch/alarm points. The procedure requires
dummy cable for SKB on the micro controller having a 2045 ohm resistor between pins 4 and 6
of this connector on the MX800 Base Station. Temperature calibration is done
via the MXTOOLS Calibration Screen. To complete the temperature calibration follow the
instructions that MXTOOLS provides. (Refer to the MXTOOLS User Manual for
additional help.)
5.1.8. TX Power Setup
The transmitter power setup is used to set the correct power for each channel. This can
be done on a per channel basis or all channels can be set at once. Power setup is done
using the Channel Screen in MXTOOLS. To complete this test the transmitter output
needs to be connected to a power meter.
To set all channels at once select the 'Lock Data' option on the Channel Screen. Click On
the alignment channel to bring up the Channel Edit Screen and allow editing of the
channel parameters,
Note.' If the 'Lock Data' option is selected then any changes made
to the current channel are duplicated on all channels.
Select the 'Continuous Update' option on the Channel Edit Screen. This allows real time
updating of the potentiometer values to the radio. Thus any changes made will be
immediately reflected in the radio. Alter the Transmit Power potentiometer until the
power meter reads the required output power. Choose 'OK' to accept the changes made
and then from the Channel Screen choose 'Send Data to MX800'. This then saves the
changes that you have made to the radio.
To calibrate each channel individually make sure the 'Lock Data' option is not selected
and repeat the above procedure for each channel.
5.1.9. Peak Deviation and Modulation Balance Alignment
This procedure is used to set the peak deviation and modulation balance for each channel.
This can be done on a per channel basis or all channels can be set at once. The alignment
done using the Channel Screen in MXTOOLS. To carry out this procedure the
demodulated output of the transmitter output needs to be connected to a CRO or some
other piece of equipment giving a visual display of the demodulated output. IF Bandwidth
of the RF test set should be set at 20kHz or greater (230kHz on the HP 8920) and
deemphasis should be off. The audio filters should be set at <20Hz HPF and 15kHz LPF.
To alter all channels at once use the 'Lock Data' option as described in the power setup
procedure. The correct peak deviation is dependent on whether the radio is narrow,
medium or wide band and also whether the CTCSS option is installed. The following
table specifies the peak deviation in each case.
Bandwidth CTCSS Option Peak Deviation (Hz)
narrow (12.SkHz spacing) YES 2150
NO 2400
medium (20kHz spacing-US) YES 4300
NO 4800
wide (25kHz spacing) YES 4300
NO 4800
Table 1 - Peak Deviation Settings
The setting of the peak deviation is done at 1 kHz for the standard build and 400Hz for the
E1A build. If the board is an EIA build this is noted on the motherboard. The modulation
balance for both builds is done at 400Hz. The transmitter modulating audio for this test is
connected to the WB/DC-FM input with JMP8 set to I-2. This input is located on the rear
of the MX800, on the Line I/O connector pin 13 of the DB15F connector. (Refer to
section 6.1.1 for additional help.)
Procedure
i) Disable the CTCSS if present. This is either done through the digital input port at
the rear or temporarily disabling it in the Channel Information Screen.
ii) PTT transmitter.
iii) Set the transmitter modulation frequency to lkHz, +10dBm, injected in through
the WB/DCFM input with JMP8 set to 1-2.
iv) Adjust the VCO Deviation digital potentiometer using MXTOOLS until the
correct deviation is obtained. (See Table 1- Peak Deviation)
v) Set the transmitter modulation frequency to 400Hz, +10dBm, injected in through
the WB/DCFM input.
vi) Adjust the Reference Deviation digital potentiometer until the top of the
waveform is flat. If the waveform top droops increase the level (see Figure 1) and
if it peaks reduce the level (see Figure 2).
vii) Set the transmitter modulation frequency to either 400Hz / lkHz depending on the
build, +10dBm, injected in through the WB/DCFM input.
viii) Repeat steps iv) through to vii) until the correct peak deviation and modulation
balance is obtained.
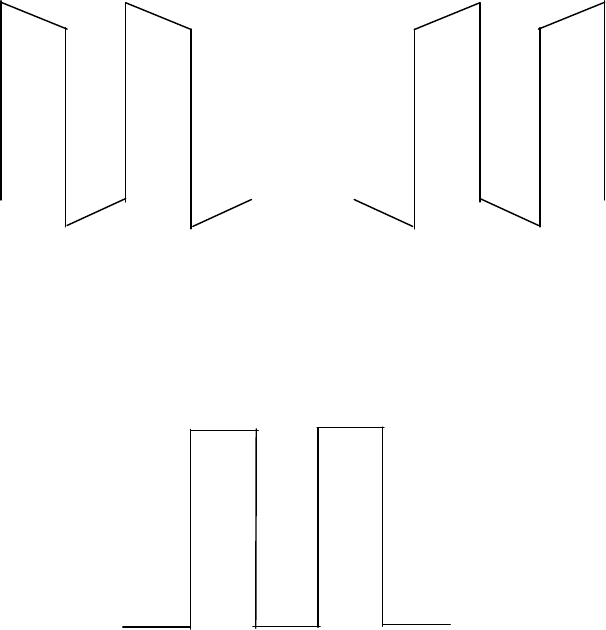
Examples of incorrect, observed waveforms are as follows:
Figure 5-1 - Under (increase level) Figure 2 -Over (decrease level)
The waveform when correctly aligned should look as follows:
Figure 3 - Correctly Aligned Waveform
Choose 'OK' to accept the changes made and then from the Channel Screen choose 'Send
Data to MX800'. This then saves the changes that you have made to the radio.
After balancing and setting the correct peak deviation is necessary to align the reference
oscillator and re-check the deviation alignment, as the reference oscillator alignment
affects the deviation. This may require running through the deviation alignment again
after the oscillator alignment procedure.
5.1.10. TX Center Frequency Alignment
The reference oscillator alignment is used to set the correct center frequency for each
channel. This can be done on a per channel basis or all channels can be set at once.
Oscillator alignment is done using a digital potentiometer adjustment through the Channel
Screen in MXTOOLS. To carry out this procedure the transmitter output needs to be
connected to a RF test set displaying the frequency error. This procedure should be done
after the deviation alignment procedure has been done. Transmitter modulation should be
disabled.
To alter all channels at once use the 'Lock Data'•ption as described in the power setup
procedure. Alter the Reference Oscillator Frequency potentiometer until the channel is
"on frequency". Choose 'OK' to accept the changes made and then from the Channel
Screen choose 'Send Data to MX800'. This then saves the changes that you have made to
the radio.
To calibrate each channel individually make sure the 'Lock Data' option is not selected
and repeat the above procedure for each channel.
5.1.11.TX Line Input Level and Nominal Deviation Alignment
There are three manual potentiometers associated with the TX deviation on the
motherboard. These are set by injecting the correct audio levels and adjusting the
potentiometers. The transmitter modulating audio is to be connected to either the WB/DC-
FM input or the TX VF input as described in the procedures.
The required nominal deviation is dependent on whether the radio is narrow, medium or
wide. The following table lists the required level for each case:
Bandwidth FM Deviation (kHz)
narrow (12.5kHz spacing) 1.5
medium (20kHz spacing-US) 3.0
wide (25kHz spacing) 3.0
Table 2 - Nominal Deviation
The first potentiometer sets the TX Limiter Gain. The transmitter modulating audio for
this test is connected to the WB/DC-FM input with JMP8 set to 1-2. This input is located
on the rear of the MX800, on the Line I/O connector pin 13 of the DB 15F connector.
(Refer section 6.1,1 for additional help,)
Procedure
i) PTT the transmitter.
ii) Set the transmitter modulation frequency to lkHz, at 1V pk-pk injected in the
WB/DC-FM input.
iii) Adjust TX Limiter gain RV2 to obtain to obtain the nominaI deviation. (See
.Table 2 - Nominal Deviation)
The second potentiometer sets the TX VF line input level. The transmitter modulating
audio for this test is connected to the TX VF input. This input is located on the rear of the
MX800, on the Line I/O connector pin 9 of the DB15F connector. (Refer section 5.1.I for
additional help.)
Procedure
i) PTT the transmitter.
ii) Set the transmitter modulation frequency to lkHz, at nominal line input level (-
10dBm is default level) injected in through the TX VF input.
iii) Adjust TX VF gain RV4 to obtain to obtain the nominal deviation. (See Table 2 -
Nominal Deviation.)
The third potentiometer sets the TTR Gain.
Procedure
i) Remove TX PTT.
ii) Enable the repeater. The repeater may be enabled by turning on switch 4, of
DIP2, inside the radio. Alternatively the repeater may be enabled/disabled via the
repeater enable pin 8 of the Line I/O connector. The polarity of the repeater
enable function is dependent on how the internal LIFUISEN jumper is set (JMP9).
iii) Set the receiver modulation frequency to I kHz and the FM deviation to that
specified in Table 2 - Nominal Deviation, for the particular RF receive frequency
of the test channel.
iv) Adjust TTR Deviation RV3 to obtain to obtain the same deviation as input to the
RX. (See Table 2 - Nominal Deviation.)
Note: The test channel must be programmed as a repeater channel so this potentiometer can be
setup. If not then temporarily alter the channel settings using the Channel Edit Screen in
MXTOOLS.
5.l.l2 RX Line Output Level Adjustment
The fourth potentiometer sets the RX Line output level.
Procedure
i) Disable the repeater (switch SW4/DIP2 OFF).
ii) Using a 600ohm termination monitor RX line output level. Tl•is output is located
on the rear of the MX800, on the Line I/O connector pin 9 of the DBI 5F.
iii) Set the receiver modulation frequency to I kHz and the FM deviation to nominal
for the particular RF receive frequency of the test channel.
iv) Adjust Line Output level RV5 to obtain nominal line output level (-10dBm is the
default level).
5.1.12.TX VF Loop Back Level
Under control of the TX VF Loopback Control line (LIFUSEN) the TX line input may be
looped back to the RX Line output. The fifth potentiometer sets the loop-back level.
Procedure
Enable the TX VF loopback using JMP9.
Set the transmitter modulation frequency to lkHz, -10dBm, injected in through
the TX VF input.
Adjust RV7 to obtain a RX Line output level of-10dBm.
Resore JMP9
5.1.13.Mute Threshold Setting
The Mute Threshold Setting is used to set the level at which the mute opens.
§ Force the mute open using the Remote Screen in MXTOOLS.
§ Inject the correct RF frequency into the receiver for the test channel.
§ Set the receiver modulation frequency to I kHz at nominal deviation.
§ Alter the amplitude of the RF signal until the RX audio has an 8dB SINAD.
§ Set the mute back to normal using the Remote Screen in MXTOOLS.
§ Adjust the mute level potentiometer, RV6, until the mute opens then wind it back until it just
closes.
5.2. Module Level Test Procedures
The following alignment and testing procedures are based upon using a working
transceiver as the test environment. It is also assumed that test fixtures to the radio are
available to exercise control lines and monitor outputs and that a PC with MXTOOLS is
connected to the radio.
There are four modules in the Mxg00 - the Exciter, Receiver, Power Amplifier and Micro
Controller. The Exciter and the Receiver have VCO daughter boards. Receiver and
Exciter VCOs are identical.
5.2.1. Exciter Module
Test Equipment:
§ Tested MX800 with Exciter removed
§ Tested TX VCO board (in wanted band)
§ PC with MXTOOLS software
§ RF Communications test set
§ Multimeter
§ Oscilloscope
§ +13.8VDC power supply
Preliminaries:
* Program upper, middle and lower frequencies of band (refer section 5.4 for band
split details) into 3 channels in MXTOOLS channel screen ( Note that 'Continuous
Update Enabled' on the MXTOOLS channel screen should be ticked for these
tests).
¯ Remove top cover from Exciter module under test and fit known working VCO
tuned for the band to be tested.
¯ Connect Exciter to working Micro Controller via 16-way ribbon cable.
¯ Disconnect Exciter RF drive output CN 1 from PA.
Procedure:
1. Switch DC power on and check that the output voltage on pin 1 of IC5 is 5V +/- 0.2V
and that the output voltage on pin 1 of IC3 and IC8 is 8V +/-0.2V. Assert PTT and
check that the 8V is switched through to SKU-3.
2. Check reference oscillator signal on center pin pad of CN3 is > 3V pk-pk.
3. Select mid channel. Connect comms test set RF input port to CN 1. Assert PTT and
check that Lock Detect (LD) on SKD-16 goes high indicating that the loop is locked.
Check that the power control volts on SKD-4 is > 10V ancl that the RF output on CN 1
is >300roW. In the channel screen on MXTOOLS adjust the power digipotentiometer
slider to 0 and check that the power control volts on SKD-4 goes to 0 and that the RF
power out drops to <lmW. Set digipotentiometer slider back to mid position.
4. Select lowest channel. Assert PTT, check that LD goes high and check that the VCO
tuning volts on SKD-14 is > 2V. Select highest channel. Assert PTT, check that LD
goes high and check that the VCO tuning volts on SKD-14 is <18V. Check that RF
output is >300mW in both cases.
5. Select mid channel. Assert PTT, note RF output carrier frequency and check that by
adjusting the Reference Oscillator Frequency digipotentiometer slider on the
MXTOOLS channel screen that the carrier frequency can be adjusted + and - 3ppm of
the nominal frequency.
6. Select mid channel. Assert PTT carry out steps 4.2.1.1 and 4.2.1.2 of the TX VF
alignment procedure below to check the function of the VCO and Reference oscillator
modulation inputs.
5.2.2. Receiver Module
Test Equipment:
§ Tested MX800 with Receiver removed
§ Tested RX VCO board (in wanted band)
§ PC with MXTOOLS software
§ RF Communications test set
§ Spectrum analyser with tracking generator
§ Multimeter
§ High frequency (89.545MHz) pick up loop.
§ Oscilloscope
§ +13.8VDC power supply
Preliminaries:
¯ Program upper, middle and lower frequencies of band (refer section 5.4 for band
split details) into 3 channels in MXTOOLS channel screen ( Note that 'Continuous
Update Enabled' on the MXTOOLS channel screen should be ticked for these
tests).
¯ Remove top cover from Receiver module under test and fit known working VCO
tuned for the band to be tested ( refer section 4.5).
¯ Connect Receiver to working Micro Controller via 16-way ribbon cable.
Procedure:
The test procedure for the Receiver is divided into the front end alignment and the IF
alignment procedures
Front End Alignment:
I. Switch DC power on. Check that the output voltage on pin I of IC8 is 5V +/- 0.2V,
on pin 1 oflC2 is 8V +/-0.2V, on output of IC9 (on C66) is 8V +/- 0.2V and on pin 1
oflC3 is 9V +/- 0.2V.
2. Remove jumper E and D. Install jumper C. Connect tracking generator output to CN1
and spectrum analyser input to CN4. Set tracking generator to sweep the band.
Adjust A4, A 10 and A 16 for a symmetrical passband around the band center
frequency. Check that the gain over the band is 12dB and that the ripple is <+/-
1.5dB. Check that the attenuation at the first IF image is >50dB.
3. Remove jumper C and I. Install jumper E and H. Connect tracking generator output
to CN4 and spectrum analyser input to CN5. Set tracking generator to sweep the
band. Adjust B4, B10 and B16 for a symmetrical passband around the band center
frequency. Check that the maximum loss over the band is < 3dB and that the
attenuation at the first IF image is >50dB.
4. Remove jumper E. Install jumper D. Connect spectrum analyser input to CN5 and
tracking generator output to CN1. Set tracking generator to sweep the band. Check
for symmetrical passband around band center frequency. Check that the gain over the
band is 10dB and that the ripple is <l.5dB. Remove Jumper H. Install Jumper J.
IF Alignment:
1. Select the mid channel. Check that LD on SKD-16 goes high indicating that the
synthesizer is in lock. Remove S3 (0gl local oscillator connection to mixer) and
solder a 500 coax test lead across C60 position ( note C60 position is near a retaining
screw and C60 is not fitted). Connect a comms test set to this lead and check that RF
local oscillator power is +17dBm +/- 2dB. Measure local oscillator frequency, this
should be Frx-90MHz(45 MHz for A2,A3 modules). Using a non metallic trimmer tool carefully
adjust the TCXO (X2) frequency until the correct frequency is obtained. Remove the test lead and
solder S3 back in position.
2. Place the high frequency pick up loop in close proximity. to IC1 in order to pick up the
second IF oscillator frequency ( note do not probe directly on the chip as test lead
capacitance will affect oscillator frequency). Adjust CT1 for 89.545MHz (44.545 MHz for A2,A3
models).
3. Inject an RF signal at -80dBm (unmodulated) at Frx into CN5 (Jumper I out, Jumper
J in). Measure DC voltage at VF output SKD-3, adjust L14 for 2.5VDC on this point.
4. Inject an RF signal at -80dBm with standard modulation at Fe, x into CN5, monitor line
RX out and adjust T1 and T2 for minimum distortion. Reduce RF signal level and
check that sensitivity is better than -112dBm for 12dB SINAD.
5. Remove Jumper J and fit Jumper I. Inject an RF signal with standard modulation at
Frx into CN 1, monitor line RX out and check that sensitivity is better than -117dBm
for 12dB SINAD. Repeat test for band upper and lower frequencies.
5.2.3. Power Amplifier Module
Test Equipment:
§ Tested MX800 with PA removed
§ PC with MXTOOLS software
§ RF Power Meter
§ RF Signal Generator
§ Multimeter
§ +13.8VDC 15A power supply
Preliminaries:
* Program upper, middle and lower frequencies of band into 3 channels in
MXTOOLS channel screen. Although the PA will function over a wider
bandwidth, the nominal switching bandwidth of the PA is 10 MHz. The
recommended procedure is to center this 10MHz around the center of the user
frequencies. ( Note that 'Continuous Update Enabled' on the MXTOOLS channel
screen should be ticked for these tests)
¯ Do not connect Exciter RF drive output CN1 to PA.
Procedure:
1. Remove PA top cover. Measure resistance of thermistor between CN4-6 and CN4-4,
this should be approximately 2kfL Connect DC power lead and 10-way connector
from MX800. Connect PA RF output to RS power meter and PA RF input (CNi) to
RF signal generator.
2. Set signal generator to center frequency of PA under test and reduce RF drive level
(from signal generator) to zero. Switch DC power on and check that supply is present
on L9. Assert PTT (check that no output RF power is emitted from the PA) check that
the 13.8V supply is switched through to the Hybrid on pin adjacent to RF input and
that 5V is switched to the Hybrid on the next pin along (pins not numbered on
Hybrid).
Slowly increase RF drive level from signal generator until RF power output is
approximately 25W. Adjust trim caps CT1, CT2 and CT3 for maximum power
output. Adjust RF drive level so that RF power output is 50W and fine tune the trim
caps. Check during this process that supply current does not exceed 11A and that RF
output power does not exceed 65W.
With PA transmitting at 50W into 50fl load measure DC volts FWD power sense
CN4-8 and REFL power sense CN4-5. These voltages should be approx 2.8V and
<450mV respectively. Reduce RF drive until PA output is 10W and disconnect PA
RF output cable. Measure DC voltage on CN4-8 and CN4-5 again. These should now
both read approximately 1VDC. Remove PTT.
5.2.4. VCO Board
Test Equipment:
§ Tested MX800 with Exciter VCO removed
§ PC with MXTOOLS software
§ RF Communications test set
§ Multimeter
§ Oscilloscope
§ +13.8VDC power supply
Preliminaries:
¯ Program upper, middle and lower frequencies of band (refer section 5.4 for band
split details) into 3 channels in MXTOOLS channel screen. (Note that 'Continuous
Update Enabled' on the MXTOOLS channel screen should be ticked for these
tests)
¯ Remove top cover from Exciter module and fit VCO under test. As the TX and
RX VCOs are identical the RX VCO may also be tested in an exciter. As the
receiver VCO operates at Fp, x - 90MHz the frequencies
¯ Connect Exciter to working Micro Controller via 16-way ribbon cable.
¯ Disconnect Exciter RF drive output CN 1 from PA.
Procedure:
I. Select mid channel. Connect SKU from exciter to VCO, switch DC power on, assert
PTY and measure RF output power on VCO SKT-6. This should be 0dBm to +3dBm.
Measure RF output level on SKU-1. This should be 0dBm to +3dBm (Note that if
SKU-1 is disconnected from the exciter the loop will lose lock). Reconnect SKT and
SKU to exciter.
2. Select lower channel. Assert PTT and check that loop is locked. Adjust trim cap CT1
on VCO for 3VDC (2VDC for N2 band) on SKT- 1. Select upper channel. Check that
the loop is locked and that the voltage on SKT-1 is <18VDC.
3. The following test is not required for the RX VCO. Connect Exciter output to comms
test set. Inject l kHz tone at nominal line input level and check that Exciter RF output
is modulated and that the depth of modulation can be controlled through the
MXTOOLS channel screen.
5.2.5. Micro Controller Module
Comprehensive testing of the Micro Controller can only be carried out at the Factory. The
procedures in sections 5.1.10 to 5.1.13 provide alignment instructions for the workshop
adjustable parameters.