SunPower 110884 Advanced Tracking Controller User Manual TMAC Operator s Manual
SunPower Corporation Advanced Tracking Controller TMAC Operator s Manual
SunPower >
Users Manual
1.0
TMAC Tracker Controller Operations ......................................................................................................... 3
1.1
Overview.................................................................................................................................................. 3
1.2
Safety Procedures ................................................................................................................................... 4
1.2.1
Radio Frequency Safety................................................................................................................... 4
1.2.2
Electric Static Discharge .................................................................................................................. 4
1.2.3
Shock Hazards ................................................................................................................................. 4
1.3
Pre-Commissioning Steps ....................................................................................................................... 5
1.3.1
Installing the Mitty
©
Application ........................................................................................................ 5
1.3.2
Identifying Coordinator TMAC Units................................................................................................. 7
1.3.3
Numbering TMAC Nodes In A Network ........................................................................................... 8
1.3.4
Setting Inclinometer Offset............................................................................................................... 8
1.4
Setting Parameters and Verifying Functionality ...................................................................................... 9
1.4.1
Setting System Parameters ............................................................................................................. 9
1.5
Commissioning Procedure .................................................................................................................... 16
1.5
Remote Access ..................................................................................................................................... 20
1.5.1
Overview of Control Interface and Capabilities.............................................................................. 20
1.5.2
Accessing the TMAC Admin Server............................................................................................... 20
1.5.2.1
Logging In .................................................................................................................................. 20
1.5.2.2
Viewing Customer Site Information............................................................................................ 22
1.5.2.3
Viewing Network Information .....................................................................................................25
1.5.2.4
Viewing TMAC Unit Information................................................................................................. 26
1.5.2.5
Using the Graph ......................................................................................................................... 28
1.5.2.6
Viewing System Status .............................................................................................................. 32
1.5.2.7
Viewing Controller Events.......................................................................................................... 34
1.5.2.8
Sending Remote Updates..........................................................................................................36
1.5.2.9
Viewing Recent Updates............................................................................................................ 38
1.5.2.10
Viewing Alerts .......................................................................................................................... 39
1.5.2.11
Viewing and Managing Customer Information......................................................................... 42
1.5.2.12
Viewing and Managing Site Information .................................................................................. 44
1.5.2.13
Viewing and Managing Network Information ........................................................................... 48
1.5.2.14
Viewing and Managing Units Information ................................................................................ 50
1.5.2.15
Viewing Messages ................................................................................................................... 52
1.5.2.16
Viewing Message Types .......................................................................................................... 54
1.5.2.17
Viewing and Managing User Information ................................................................................. 55
Appendix A:
Message Types .......................................................................................................................... 58
A.1
System Status: (101) ............................................................................................................................. 58
A.2
Inclinometer Status (102) ...................................................................................................................... 59
A.3
Wireless 1 Status (103) ......................................................................................................................... 60
A.4
Wireless 2 Status (104) ......................................................................................................................... 61
A.5
Wireless 3 Status (105) ......................................................................................................................... 62
A.6
Operating System Status (106) ............................................................................................................. 63
A.7
GPS Status (107) .................................................................................................................................. 63
A.8
A/D Status (108) .................................................................................................................................... 64
A.9
DIO Status (109).................................................................................................................................... 64
A.10
Motor Status (110) ............................................................................................................................. 65
A.11
Settings 1 Status (114) ...................................................................................................................... 66
A.12
Settings 2 Status (115) ...................................................................................................................... 67
A.13
Server Status (116)............................................................................................................................ 67
A.14
Tracker Status (117) .......................................................................................................................... 68
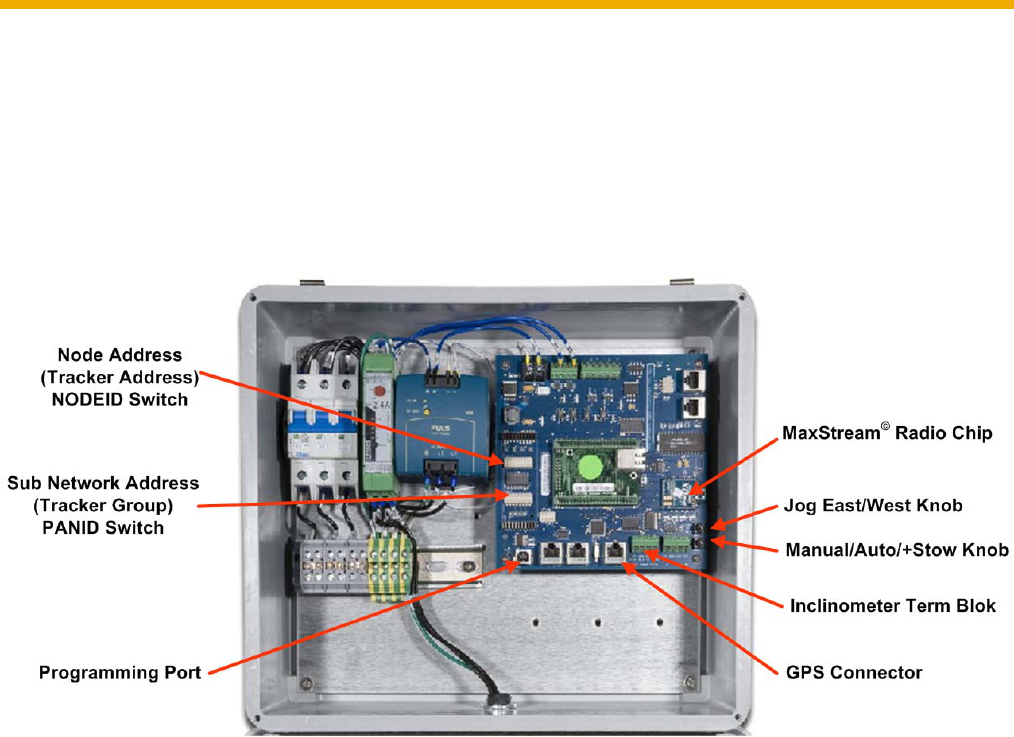
1.0 TMAC Tracker Controller Operations
1.1 Overview
The Tracker Monitoring and Control (“TMAC”) Advanced Tracker Controller controls the extension of the drive
unit, which changes the rotation of the torque tubes and the position of the modules. By optimizing the angle of
incidence between the sun and the modules, the system captures as much as 35% more sunlight than non-
tracking solar electric systems.
The TMAC controller has full remote control capability that allows for stowing in adverse weather condition,
equipment monitoring, and system optimization.
Here is an inside view of the TMAC controller:
TMAC Tracker Controller
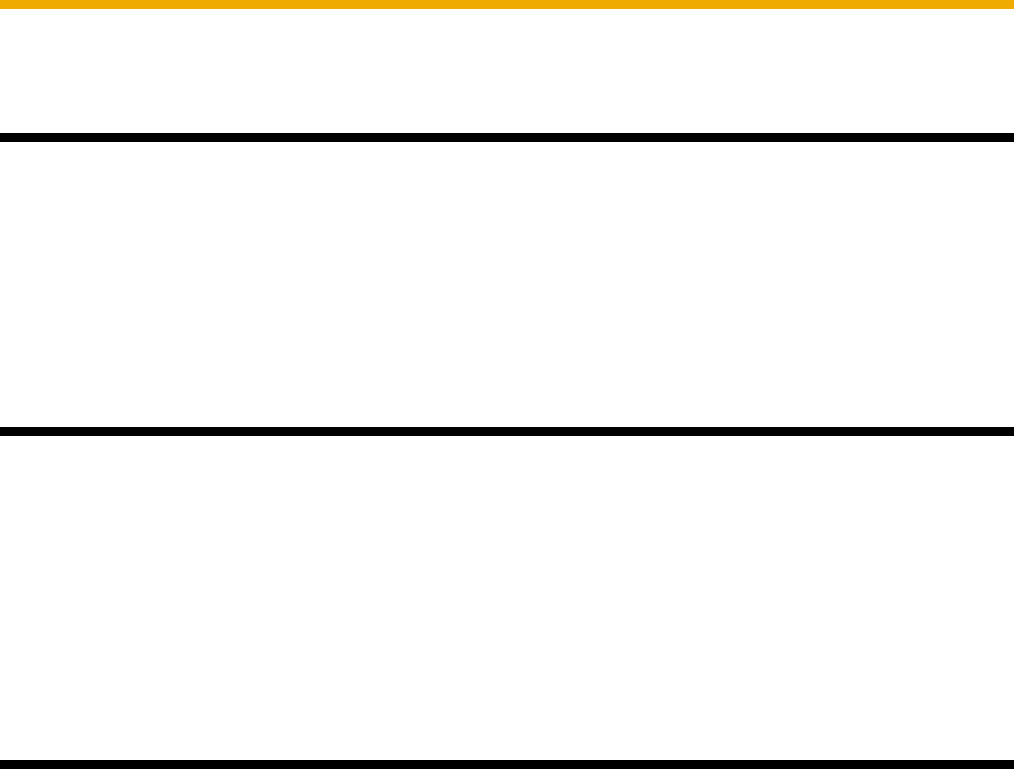
1.2 Safety Procedures
Important! All personnel must adhere to the following safety procedures when working on the TMAC controller.
These operating instructions are for use by qualified personnel only.
1.2.1 Radio Frequency Safety
• The design of the TMAC controller complies with the updated standard for safety levels with respect to human
exposure to Radio Frequency (RF) signals adopted by the Federal Communications Commission (FCC) in
August 1996. The hybrid standard consists of the existing standards of the Institute of Electrical and Electronic
Engineering (IEEE) and the American National Standards Institute (ANSI), and its guidelines are published by
the National Council of Radiation Protection (NCRP).
• Currently, the TMAC controller product is in the process of complying with the requirements of the FCC Radio
Frequency Emission Guidelines and for FCC certification.
1.2.2 Electric Static Discharge
Warning! Static buildup and electrical discharge can damage the TMAC controller.
The avoid static buildup or discharge into the equipment:
• Before touching or connecting a laptop to the TMAC controller, SunPower recommends to discharge the
laptop and yourself by simultaneously holding your laptop and grounding yourself to a metal service that is
connected to the earth ground.
• Use a grounding strap when working on the TMAC control board.
• Use a grounding mat when working on the TMAC controller.
1.2.3 Shock Hazards
Warning! Lethal voltage is present in the TMAC control box. Use appropriate Personal Protection Equipment
(PPE) when working on the equipment.
• The TMAC controller is designed to operate at 380 VAC–480 VAC 3-Phase power. Other voltages are not
compatible.
• The TMAC controller is designed with finger guards to protect the user from electrical shock. However,
SunPower requires that all personnel working on the equipment wear rubber insulating gloves.
• Ensure you avoid shocking the components on the controller circuit board.
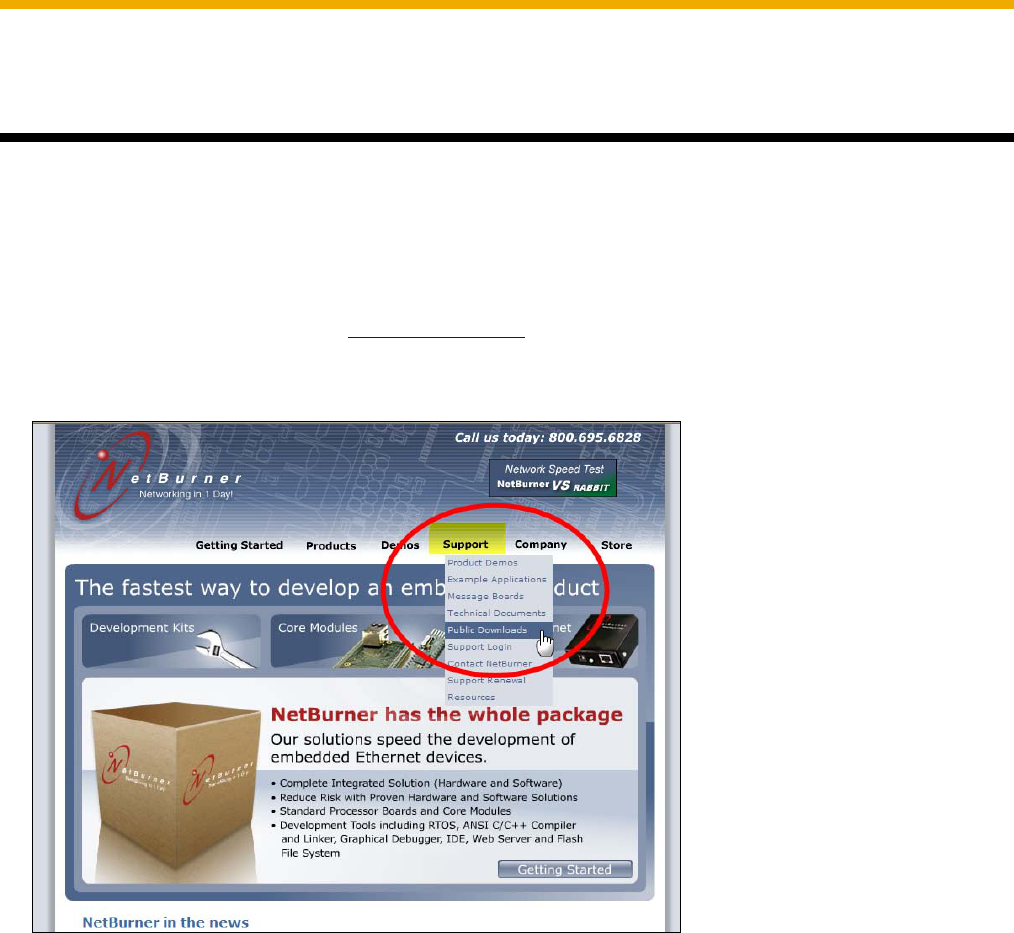
1.3 Pre-Commissioning Steps
To ensure proper and efficient commissioning of each TMAC controller installed in a site, perform the pre-
commissioning steps in this section.
1.3.1 Installing the Mitty© Application
To access the TMAC controller locally, the laptop you connect must have the Multi-Threaded TTY (“Mitty
©
”)
application installed. The Mitty application—an RS-232 serial terminal program developed by Microsoft
®
and
modified by Netburner
®
—is used as the main command prompt controller page.
To download a free copy of the Mitty application:
1. Navigate to the NetBurner website www.netburner.com
2. On the NetBurner home page, hover your mouse over the Support tab.
3. Click Public Downloads in the Support tab drop-down menu (Fig. 1).
Fig. 1
4. On the Public Downloads page, locate the NetBurner RS-232 Terminal Program in the NetBurner Utilities
section and click the Download application link (Fig. 2).
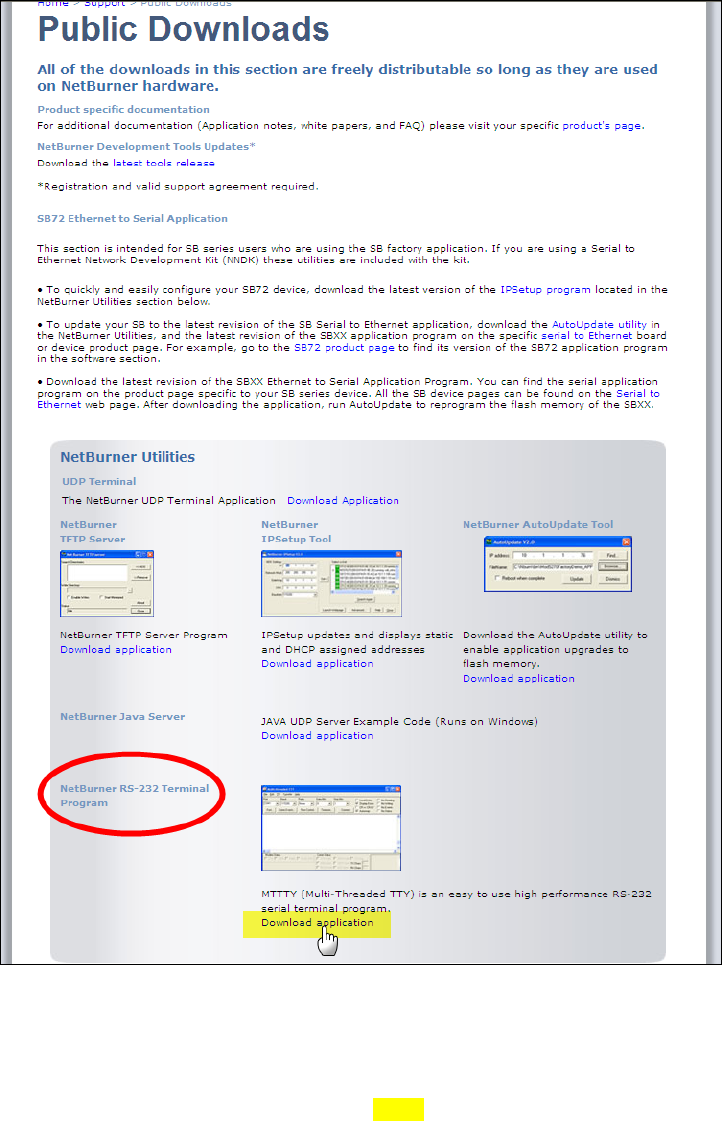
Fig. 2
5. Click Run in the File Download window to automatically install the program.
6. The Mitty application icon should appear on your desktop.
To start the Mitty application, refer to Section 1.4.1.
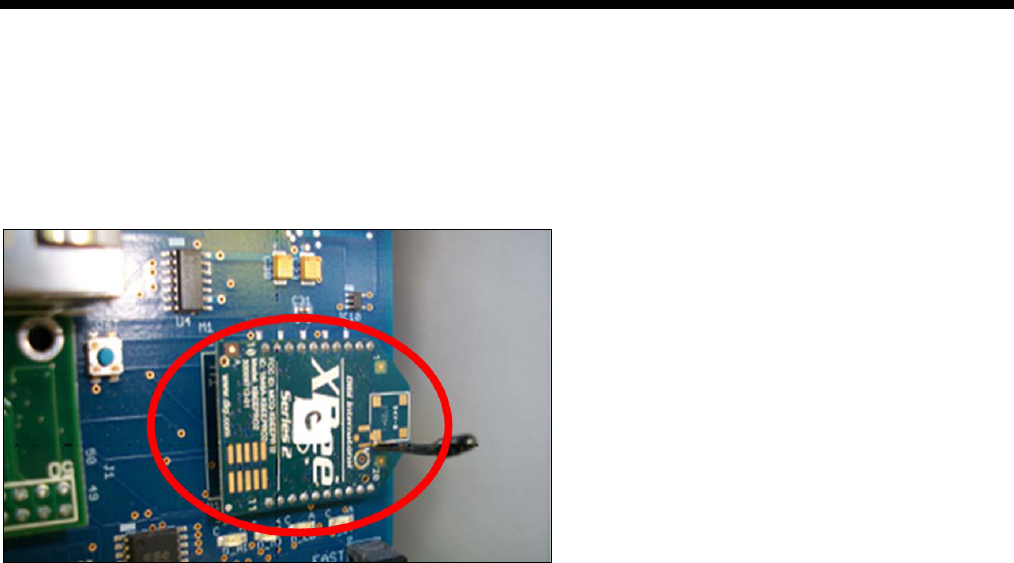
1.3.2 Identifying Coordinator TMAC Units
Refer to the project plans to identify which TMAC unit is assigned to function as the “coordinator”—that is, the
TMAC node designated to manage the flow of communications for its associated network. The coordinator TMAC
unit is hard-wired with Ethernet cable to a site network access point, typically located at the closest inverter
station.
Verify that the coordinator TMAC unit has the specially labeled MaxStream
©
radio chip (Fig. 3). If an incorrect
radio chip is installed, remove it and replace with the special coordinator chip.
Fig. 3
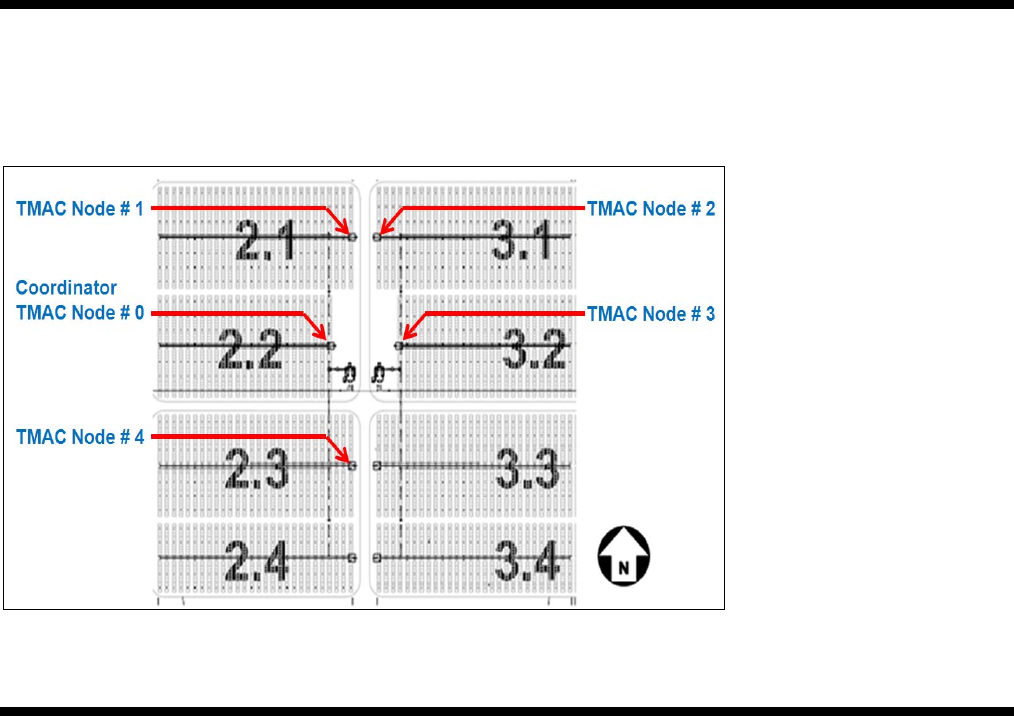
1.3.3 Numbering TMAC Nodes In A Network
Each TMAC unit in a network must be identified by a node number that is a digit from 0 to 9. By default, the
coordinator TMAC unit is always assigned node number 0. Assign a node number to each noncoordinator TMAC
unit by numbering each of the controller box locations NWÆSE. Refer to the following sample diagram for
illustration.
TMAC Node Numbering sample diagram
1.3.4 Setting Inclinometer Offset
After you install the controller and before verifying the east and west limits the system inclinometer offset must be
set for a flat PV array. After completing the offset adjustment the east and west limits can be verified.
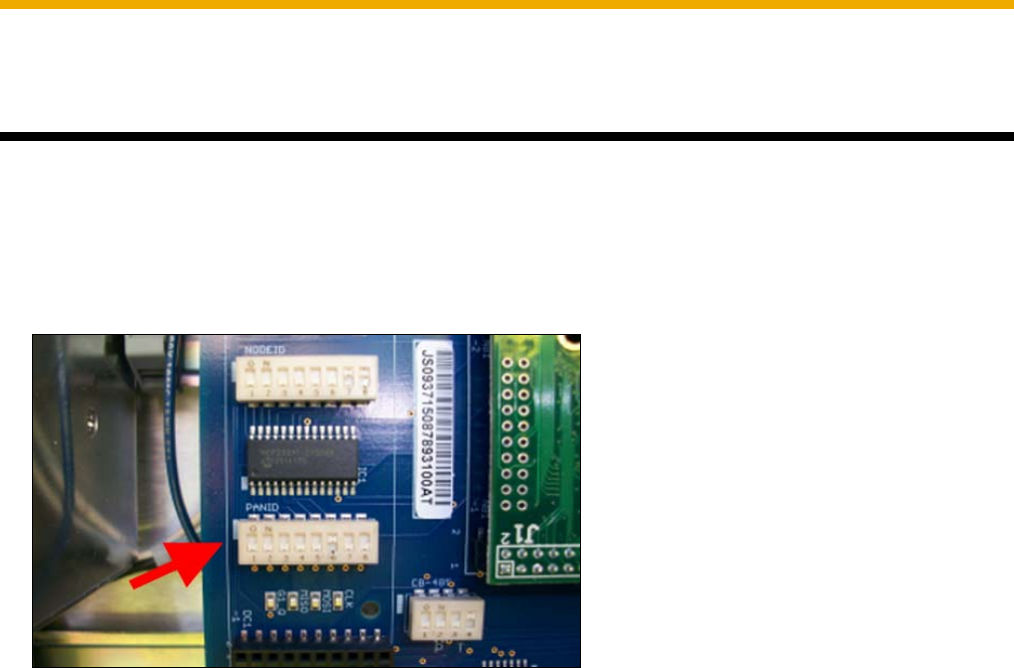
1.4 Setting Parameters and Verifying Functionality
You must enter all of the parameters and perform all the verifications for each TMAC controller on the site. This
data is stored in non-volatile memory within the TMAC memory.
1.4.1 Setting System Parameters
To set the system parameters for each TMAC controller:
1. Power down the controller.
2. Refer to the project plans for the Sub Network Address Pan ID.
3. Configure the Sub Network Address PANID Switch (Fig. 4):
Fig. 4
• On the coordinator TMAC unit, set the binary switches to 00000000 (that is, all switches are down).
• For noncoordinator TMAC units, refer to the following table for the binary switch position.
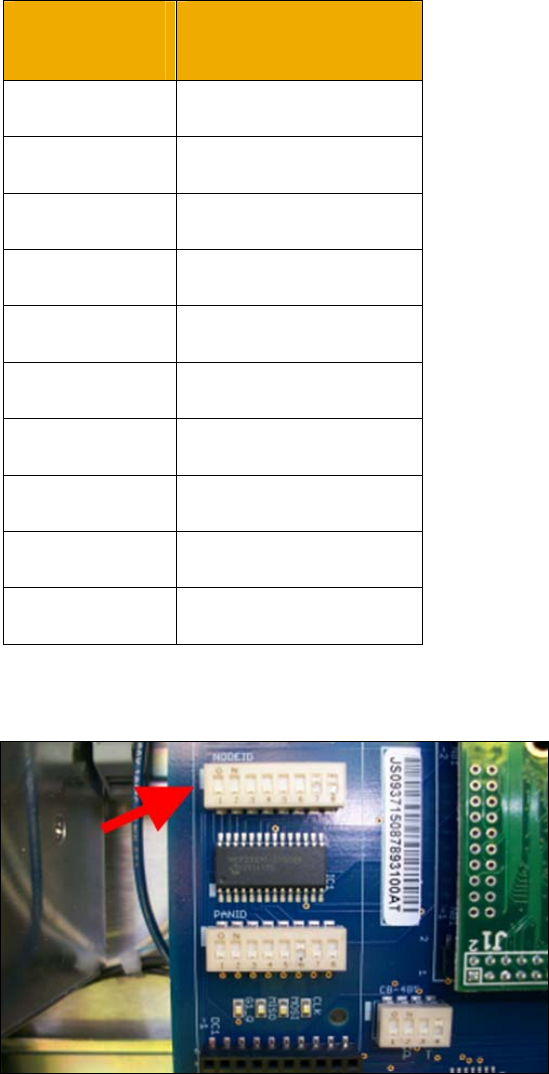
Decimal
(Node Number) Binary Switch Position
1 00000001
2 00000010
3 00000011
4 00000100
5 00000101
6 00000110
7 00000111
8 00001000
9 00001001
10 00001010
5. Configure the Node Address NODEID Switch (Fig. 5):
Fig. 5
• On the coordinator TMAC unit, set the binary switches to 00000000.
• For noncoordinator TMAC units, refer to the following table for the binary switch position.
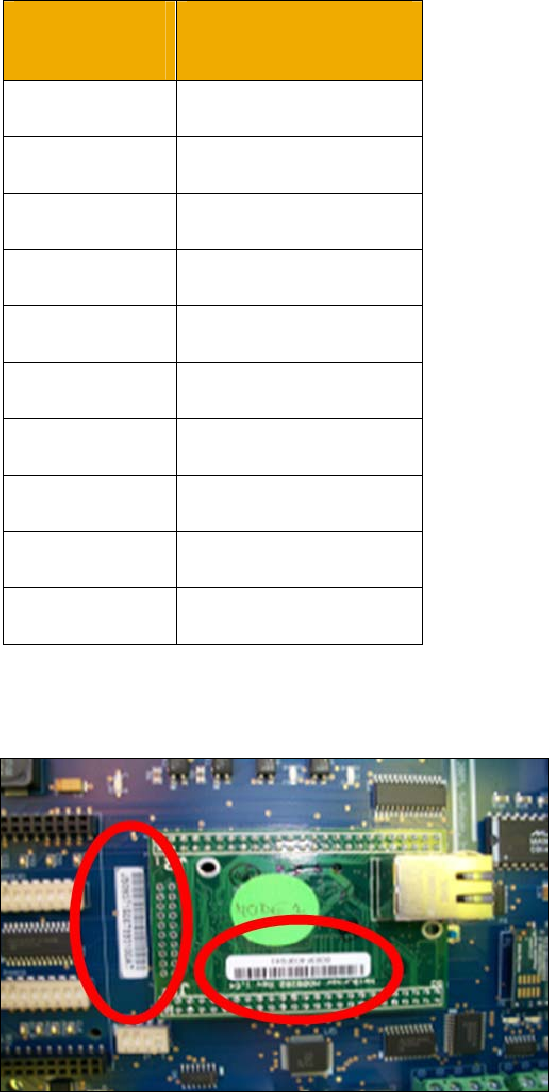
Decimal
(Node Number) Binary Switch Position
1 00000001
2 00000010
3 00000011
4 00000100
5 00000101
6 00000110
7 00000111
8 00001000
9 00001001
10 00001010
6. Record the controller’s Mac address and the PCB Number on the commissioning form (Fig. 6). The Mac
address and the PCB number are used to assign the controller to a site on the TMAC Admin Server.
Fig. 6
7. Power up the controller.
8. Use the USB A to USB B cable assembly to connect the laptop to the controller through the Programming
Port.
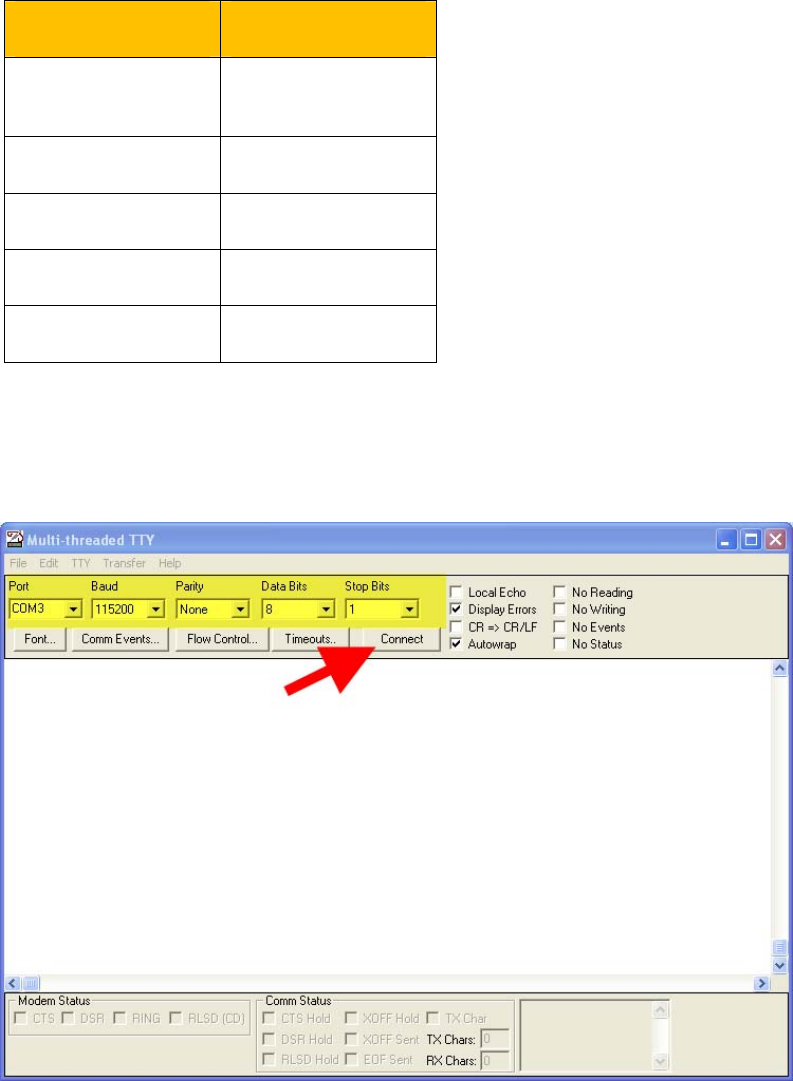
9. Start the Mitty application.
10. The Multi-threaded TTY screen opens.
a. If not already entered, select the following values in the respective fields:
Field Value
Port The COM Port you
use in your computer
Baud 115200
Parity None
Data Bits 8
Stop Bits 1
Important! To find the COM port number, open the Device Manager window on your laptop. Click Start, right-
click My Computer, select Properties, click Hardware in the System Properties dialog box, and click Device
Manager. If you’re unable to get a port in the Multi-threaded TTY screen, restart the Mitty application and look for
a new port in the Port drop-down list. Instructions on fixing the changing port issue is soon to be released.
b. Click Connect.
Multi-threaded TTY screen
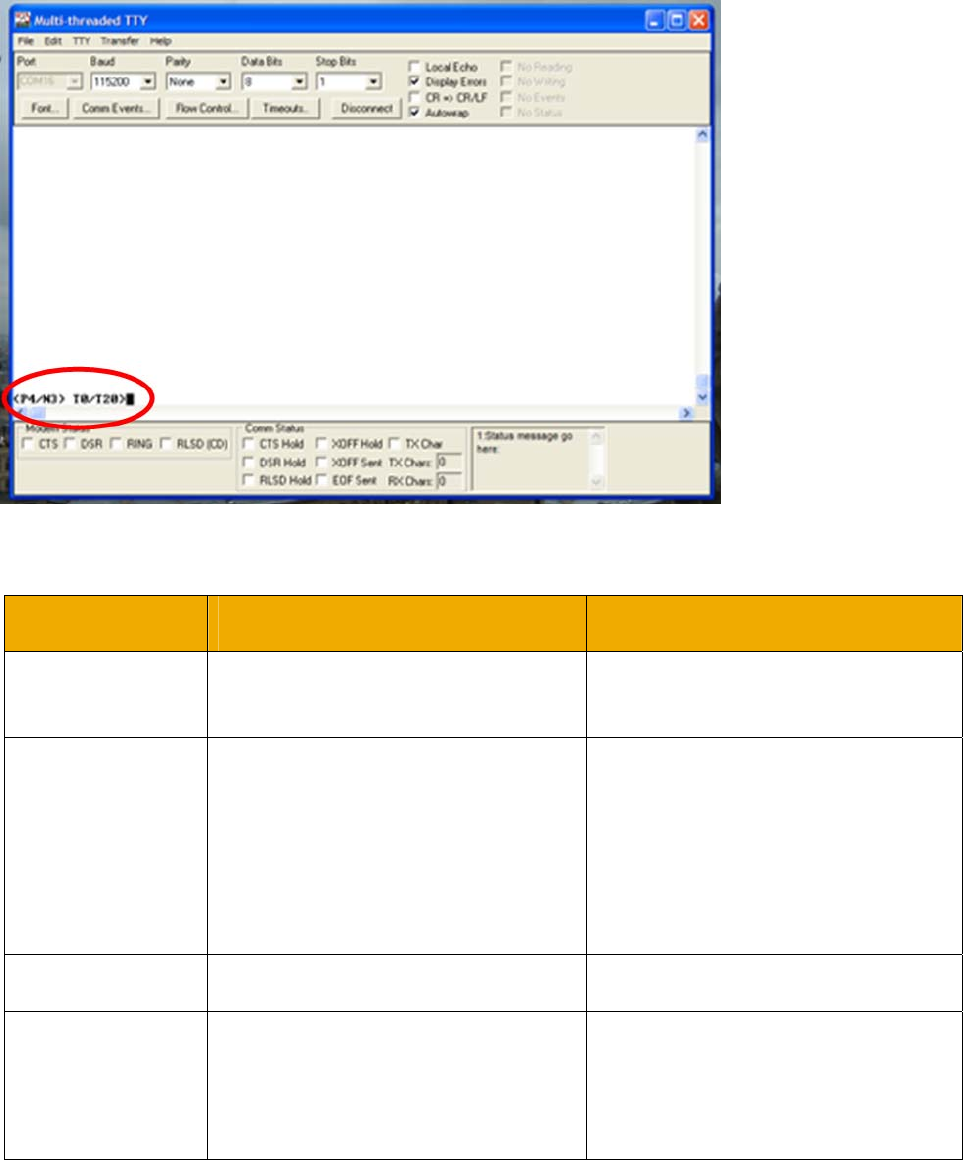
11. In the bottom left of the screen, a prompt appears (Fig. 7). The prompt indicates the Sub Network and Node ID
being accessed, and the software programmed into the TMAC unit.
Fig. 7
12. Enter the following site parameters in any sequence:
Parameter Description Value
Mount Refers to the side of the array on which
the drive unit is installed
• Enter spmw for WEST Mount
• Enter spme for EAST Mount.
Ground Coverage
Ratio (GCR)
(East/West)
The percentage of total ground surface
taken up by the system when viewed
from above with the modules flat. A
smaller GCR means that modules are
proportionally farther apart. GCR should
typically be in the range of 0.35 for a
ground-mounted system, and 0.50 for
an elevated system.
Enter spe.5 for a GCR of 0.50
GCR (North/South) (Not used at this time)
Stow Position
(East/West) A programmable position. This
represents the number of degrees at
which the modules are positioned and
at which they remain overnight and
during bad weather.
• Enter spsp5 (5° west bound Stow)
• Enter spsp-5 (5° east bound Stow)
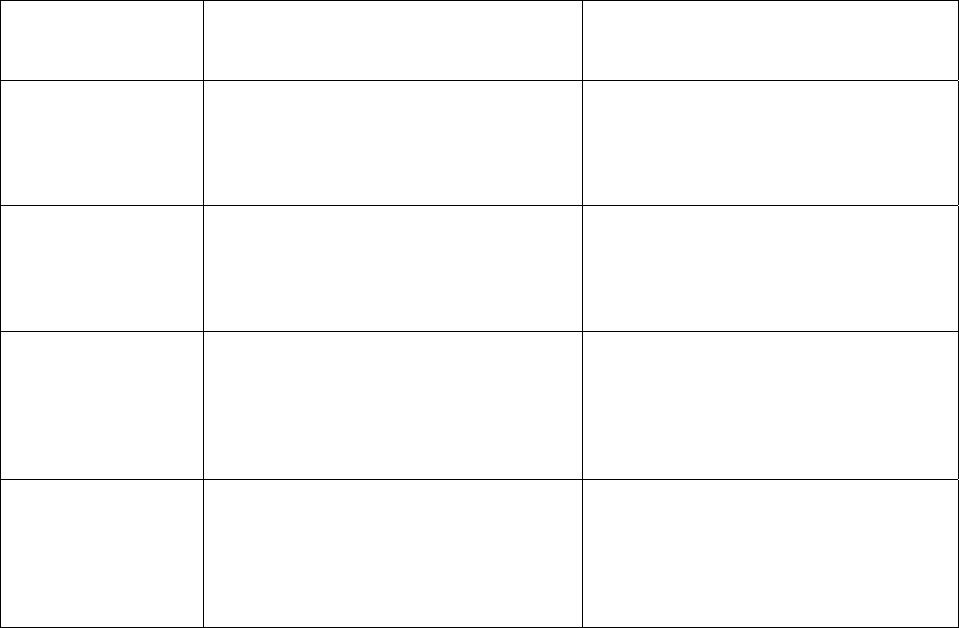
Stow Position
(North/South) (Not used at this time)
North/South
Torque Tube Slope The slope of the fully installed torque
tubes. The value is positive when the
south end of the array is lower than the
north.
• Enter t1p5 (5° sloping to the South)
• Enter t1p-5 (5°sloping to the North)
East/West Site
Slope The E–W slope of the site on which the
system is installed. The value is positive
when the drive strut slopes downward
toward the east.
• Enter t1r5 (5° sloping to the East)
• Enter t1r-5 (−5° sloping to the West)
North/South
Misalignment The number of degrees by which the
torque tube alignment is off from true
N–S. If the value is positive, the tube
alignment is clockwise from true N–S
when assessed from overhead.
• Enter t1y5 (5° to the East)
• Enter t1y-5 (5° to the West)
Inclinometer
Calibration
The difference between the controller
inclinometer reading and the digital level
measurement for the tilt angle. This
offset is expressed as a numerical value
(after the space).
Enter m1o 5
Important! The coordinator TMAC units are equipped with a GPS device that will automatically set the longitude,
latitude, and time for all controllers on the subnetwork.
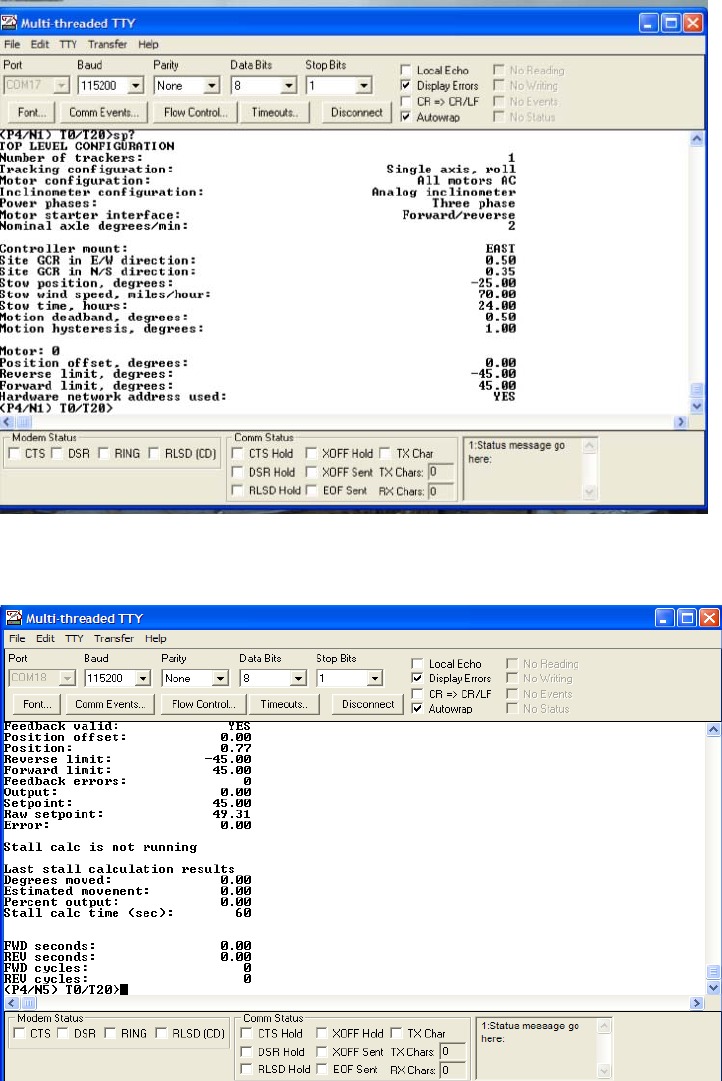
13. Verify that all the entered data parameters are correct.
a. To verify all site parameters, enter “SP?” (Fig. 8).
Fig. 8
b. To verify tracker status (Fig. 9), enter “TS?”.
Fig. 9
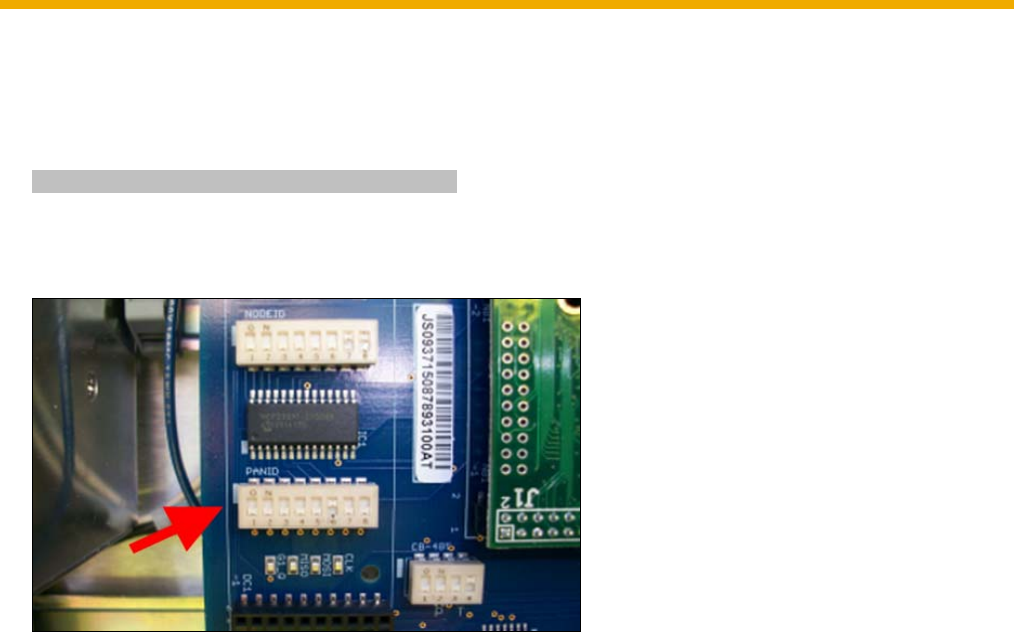
14. To store the data parameters in the non-volatile memory, enter “fw” and press the Return Key.
15. To test the entered data:
a. Power down the controller.
b. Wait 10 seconds before powering the controller back up.
c. Check the data parameters in the Multi-threaded TTY screen (refer to Step 12).
1.5 Commissioning Procedure
Warning! Lethal voltage is present in the TMAC control box. All personnel must use appropriate PPE when
performing steps that require work on the TMAC controller.
To commission the TMAC controller:
1. Verify voltage on line side of breaker/disconnect.
2. Refer to the project plans for the Sub Network Address Pan ID or the address of the group of TMAC units that
include the controller to be commissioned.
3. Configure the Sub Network Address PANID Switch (Fig. 10).
Fig. 10
• On the coordinator TMAC unit (Node 0), set the binary switches to 00000000—that is, all switches are
down.
• For the other TMAC nodes, refer to the following table for the binary switch position.
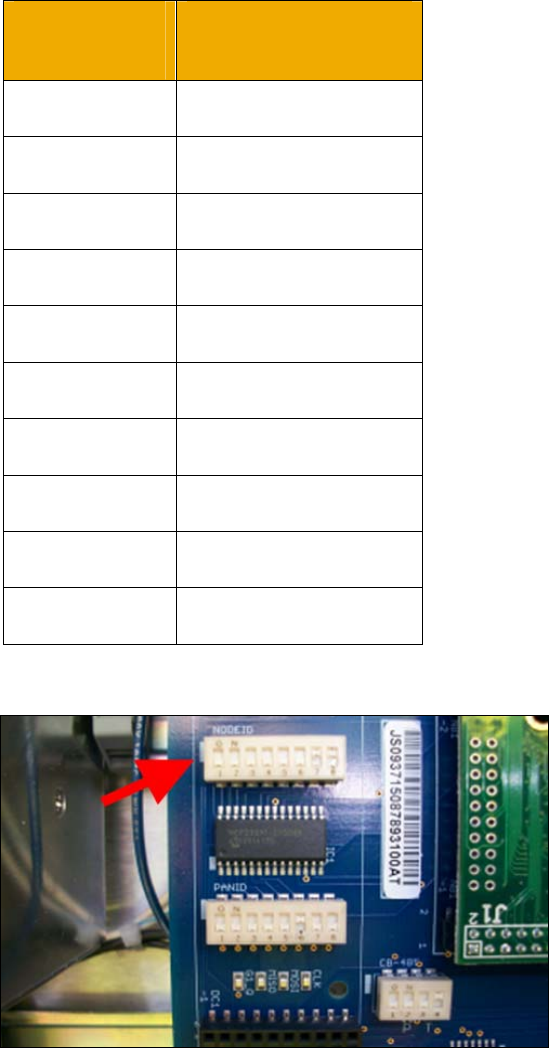
Decimal
(Node Number) Binary Switch Position
1 00000001
2 00000010
3 00000011
4 00000100
5 00000101
6 00000110
7 00000111
8 00001000
9 00001001
10 00001010
4. Configure the Node Address NODEID Switch (Fig. 10).
Fig. 10
• On the coordinator TMAC unit (Node 0), set the binary switches to 00000000.
• For the other TMAC nodes, refer to the following table for the binary switch position.
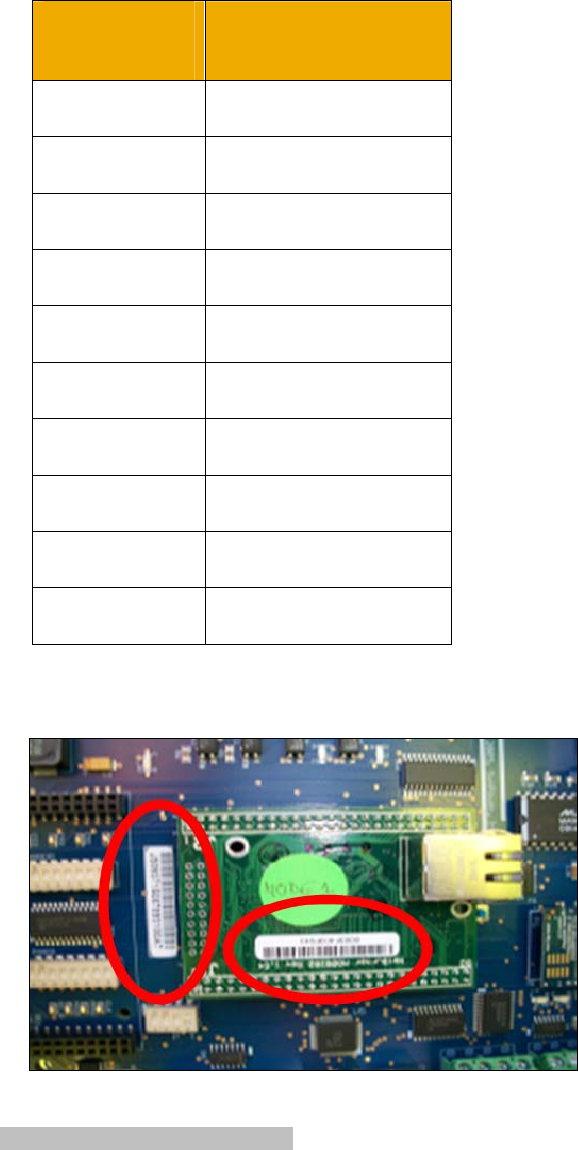
Decimal
(Node Number) Binary Switch Position
1 00000001
2 00000010
3 00000011
4 00000100
5 00000101
6 00000110
7 00000111
8 00001000
9 00001001
10 00001010
5. Record the controller’s Mac address and the PCB Number on the commissioning form (Fig. 11). The Mac
address and the PCB number are used to assign the controller to a site on the TMAC Admin Server.
Fig. 11
6. Close the breaker/disconnect.
7. Use the USB A to USB B cable assembly to connect the laptop to the controller through the Programming
Port.
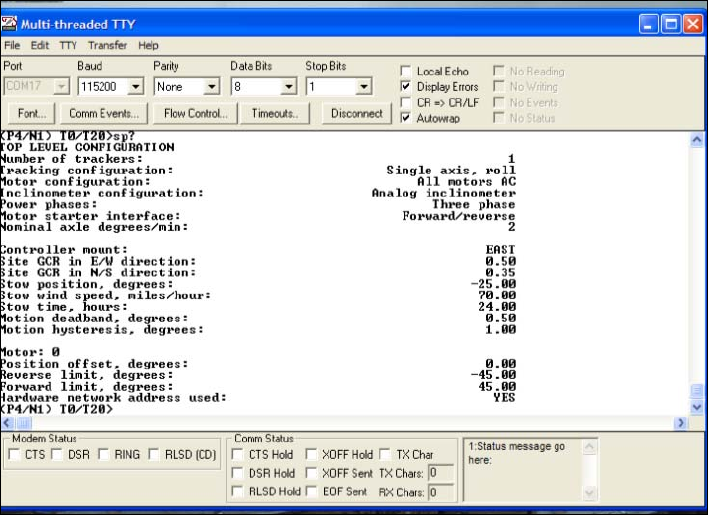
8. Start the Mitty application.
9. In the Multi-threaded TTY screen, enter “SP?” to check the site parameters.
Multi-threaded TTY screen
10. Adjust if necessary tracker mounting, Check motor direction with in manual mode.
11. Using the TMAC controller in manual mode move the array to Flat.
12. Adjust inclinometer offset.
13. Verify East and West limit switches
14. Verify and adjust GCR
15. Verify and adjust Stow
16. Verify and adjust Site Slope
17. Verify and adjust Torque Tube Slope
18. Verify and adjust North/South Misalignment
19. Verify all setting and Program Memory by entering “fw” press Return
20. Set mode switch to “Auto”
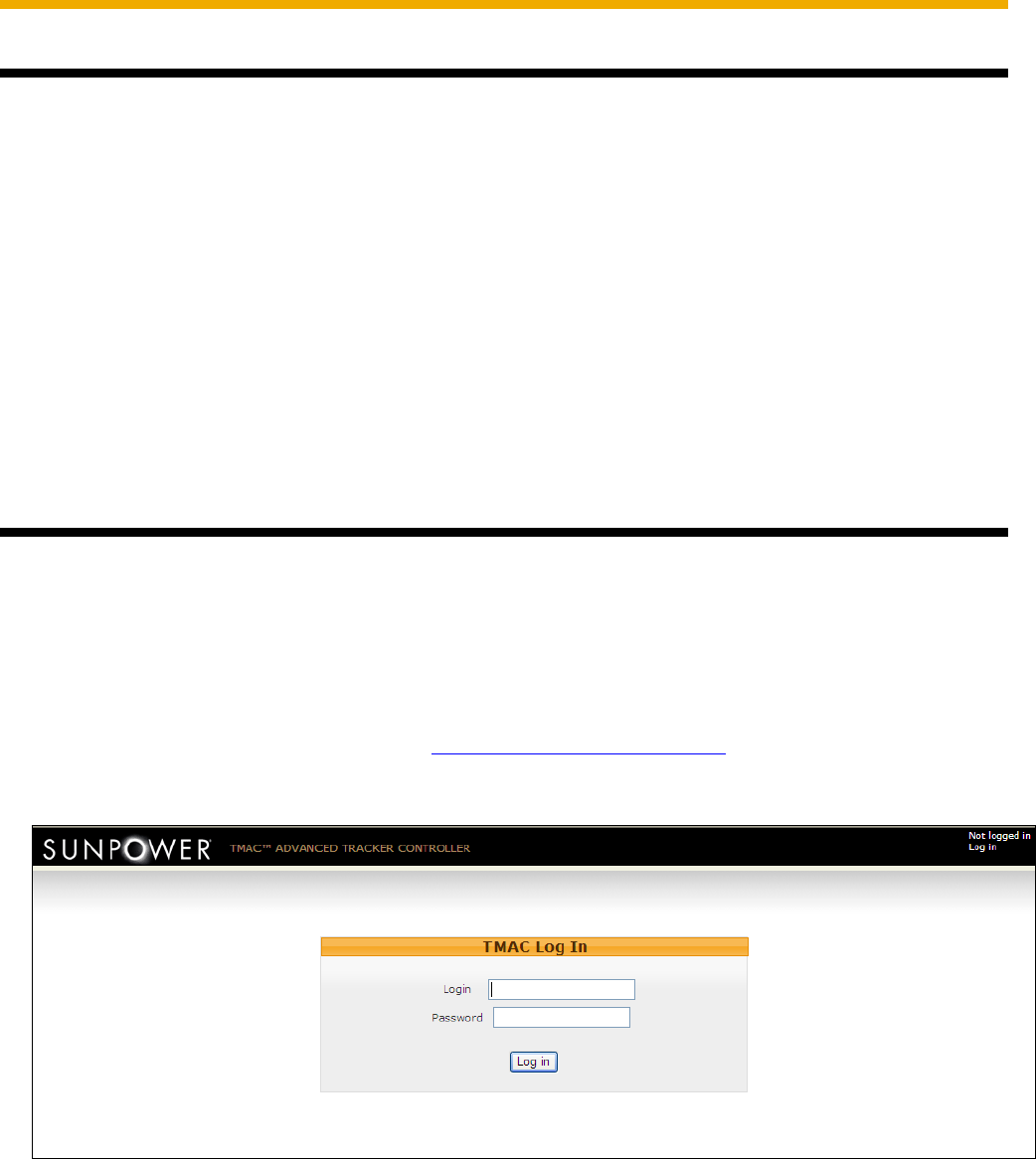
1.5 Remote Access
1.5.1 Overview of Control Interface and Capabilities
Remote access to the TMAC controller enables better control of the entire network. By accessing the TMAC
Admin Server, you can perform the following tasks:
• Stowing the array
• Checking array status
• Accessing weather data
• Accessing temperature readings for each TMAC controller
• Carrying out advanced control functions with outside data
• Performing advanced maintenance functions
• Generating email reports
Note. Most of these functions are add-ons and chargeable to our customers.
1.5.2 Accessing the TMAC Admin Server
To access the TMAC Admin Server, you need login information. Contact the Engineering Department to have an
account set up for you.
1.5.2.1 Logging In
To log in to the server:
1. Navigate to the TMAC Admin Server website http://tmac.sunpowermonitor.com
2. On the TMAC Log In page, enter your username and password in the Login and Password fields,
respectively and click Log in.
TMAC Log In page
Note. Passwords are case sensitive.
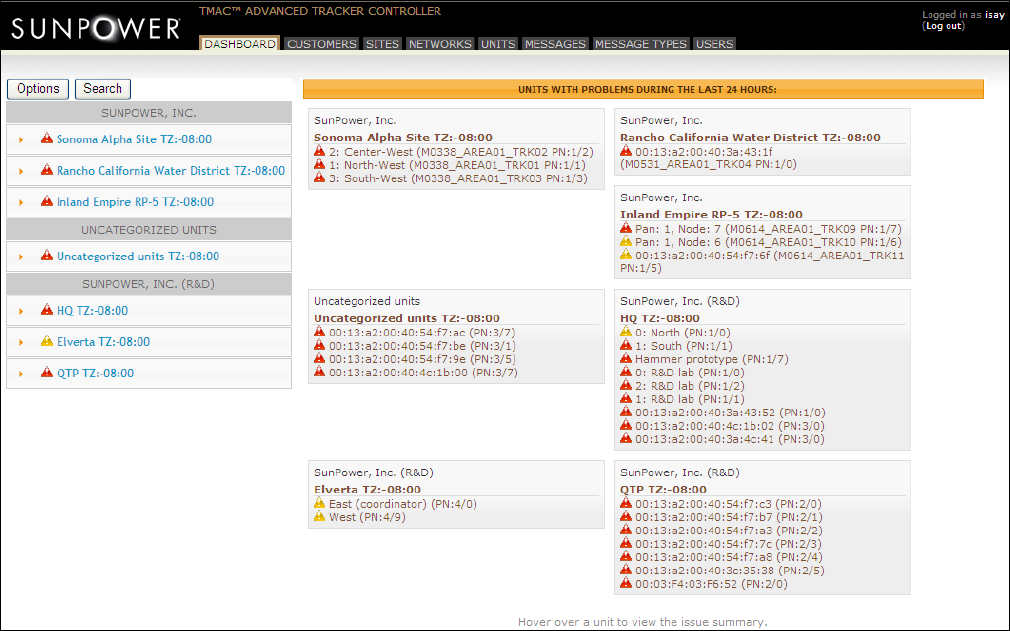
3. The TMAC Dashboard page appears. This page is the TMAC main page.
TMAC Dashboard page
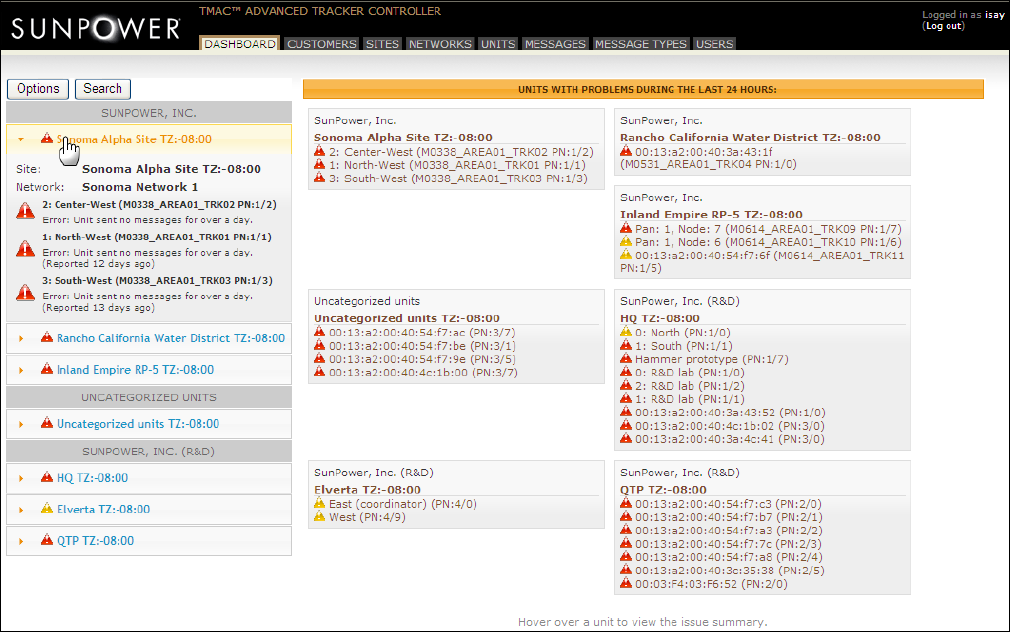
1.5.2.2 Viewing Customer Site Information
To view customer site information on the TMAC Dashboard page:
1. In the list on the left side of the page, click the name of the customer site you want to view (Fig. 11).
Fig. 11
2. In the collapsed pane below the customer site name, click the site name link to view the site-level details to the
right (Fig. 12).
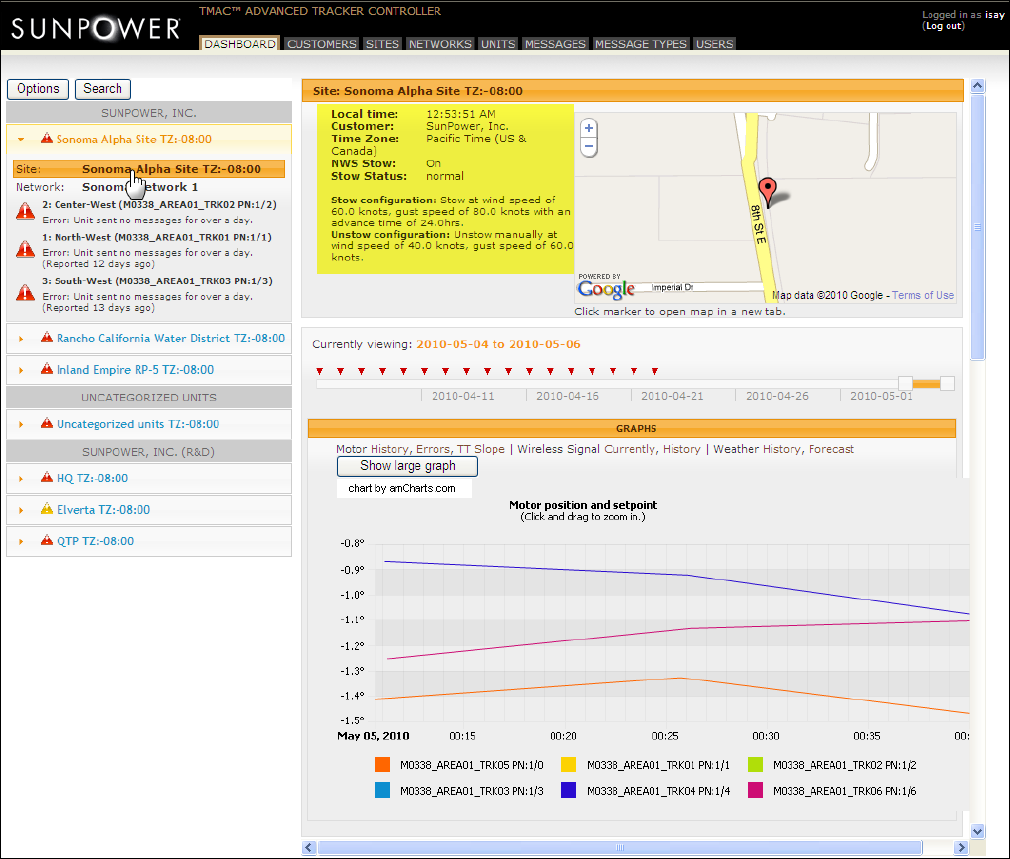
Fig. 12
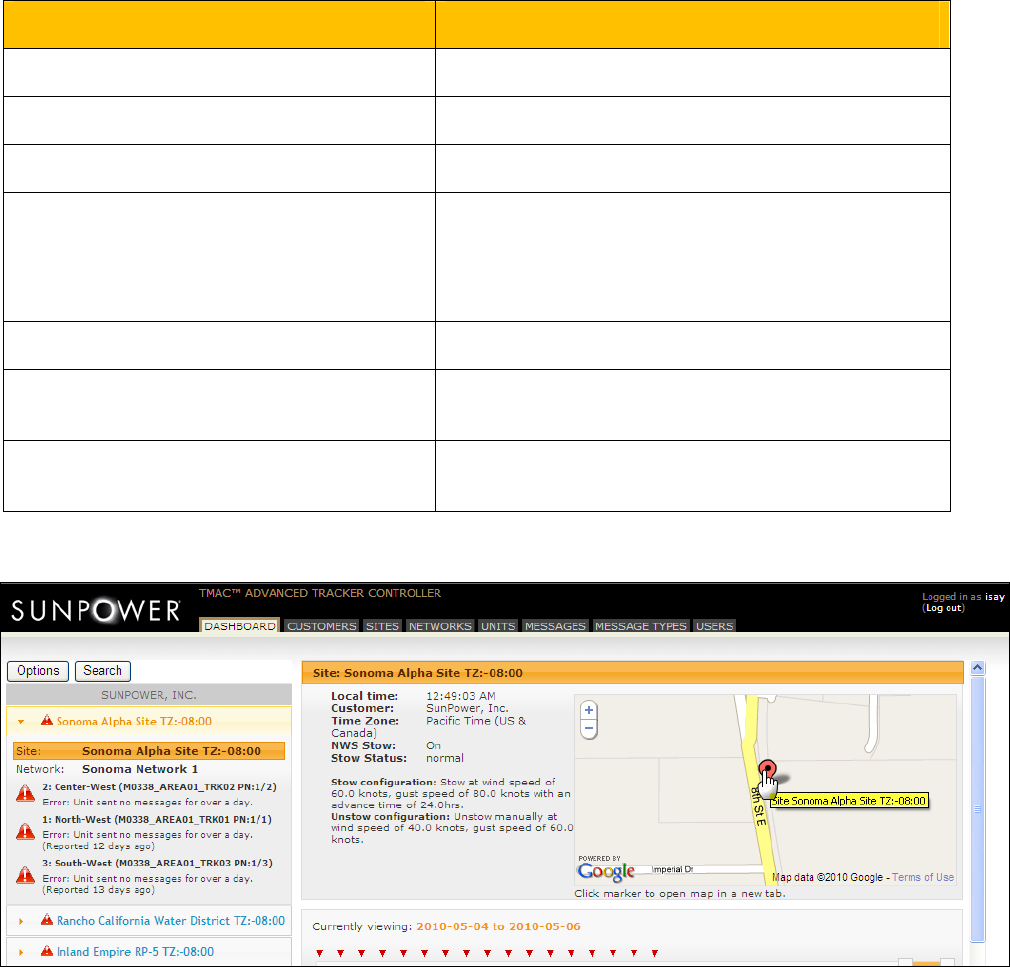
3. View the customer site information:
Information Description
Local time Real-time, 12-hour format local time with AM/PM
Customer Name of the customer
Time Zone The time zone in text
NWS Stow The National Weather Service Stow Enable indicator—
ON indicates NWS is enabled; OFF, disabled.
The stow and unstow perimeters are defined in the
Stow and Unstow Configuration retrospect.
Stow Status
Stow Configuration Defines at what perimeters the tracker controller will
stow the panels
Unstow configuration Defines at what perimeters the tracker controller will
allow the panels to resume normal operations
4. To view the site location map in a separate window, click the marker on the map (Fig. 13).
Fig. 13

1.5.2.3 Viewing Network Information
On the TMAC Dashboard page, you can view network information for a customer site:
1. In the list on the left side of the page, click the name of the customer site you want to view.
2. In the collapsed pane below the customer site name, click the network name link to view the network details to
the right (Fig. 14).
Fig. 14
3. View the network information:
Information Description
Local time Real-time, 12-hour format local time with AM/PM
Customer Name of the customer
Site The customer site name
Note. The customer site name is an active link. Click to
view the customer site information (refer to Section
1.5.2.2).
Time Zone The time zone in text
PAN ID The tracker group address used by the network
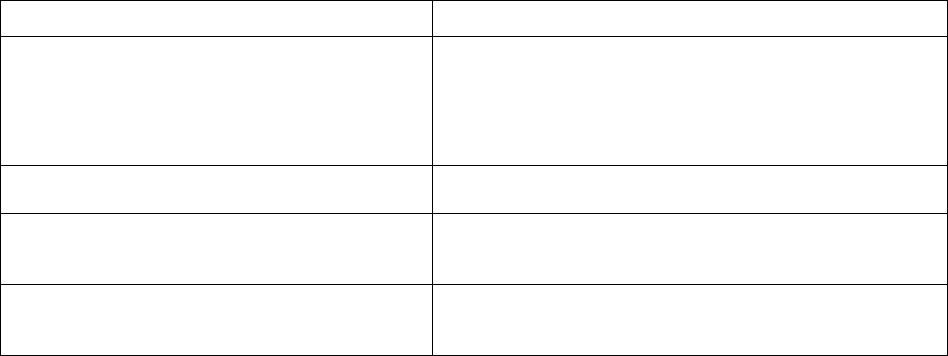
communication
NWS Stow The National Weather Service Stow Enable indicator—
ON indicates NWS is enabled; OFF, disabled.
The stow and unstow perimeters are defined in the
Stow and Unstow Configuration retrospect.
Stow Status Current system status: stowed/tracking/backtracking
Stow Configuration Defines at what perimeters the tracker controller will
stow the panels
Unstow configuration Defines at what perimeters the tracker controller will
allow the panels to resume normal operations
1.5.2.4 Viewing TMAC Unit Information
On the TMAC Dashboard page, you can view detailed information on each TMAC unit installed at the customer
site:
1. In the list on the left side of the page, click the name of the customer site you want to view.
2. In the collapsed pane below the customer site name, click the TMAC unit link to view the unit details to the
right (Fig. 15).
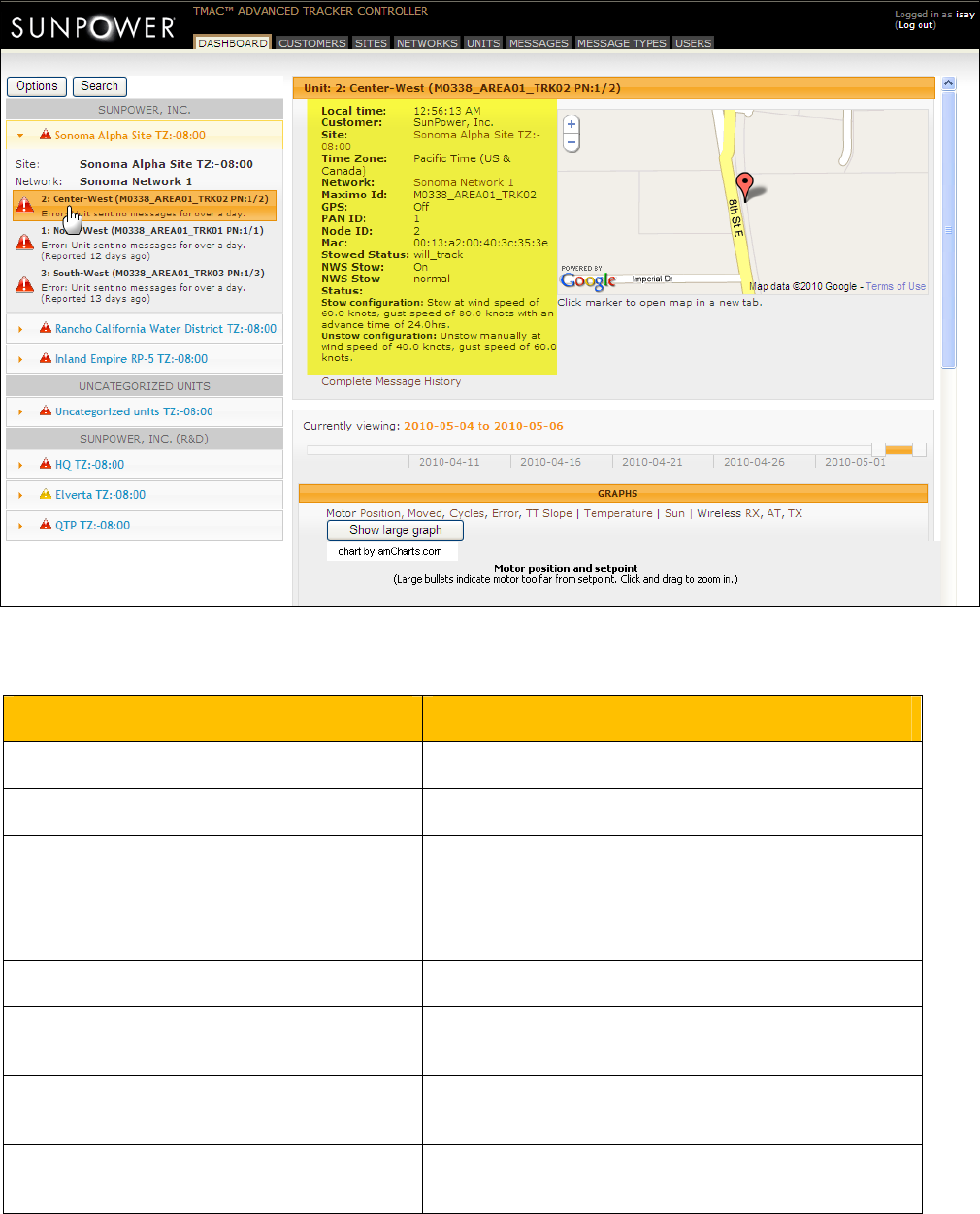
Fig. 15
3. View the TMAC unit information:
Information Description
Local time Real-time, 12-hour format local time with AM/PM
Customer Name of the customer
Site The customer site name
Note. The customer site name is an active link. Click to
view the customer site information (refer to Section
1.5.2.2).
Time Zone The time zone in text
Network The name of the network to which the TMAC unit
belongs
Maximo ID The description or name of the Tracker used as
identifier for reporting in Maximo
GPS GPS is enabled when a GPS receiver and antenna is
installed
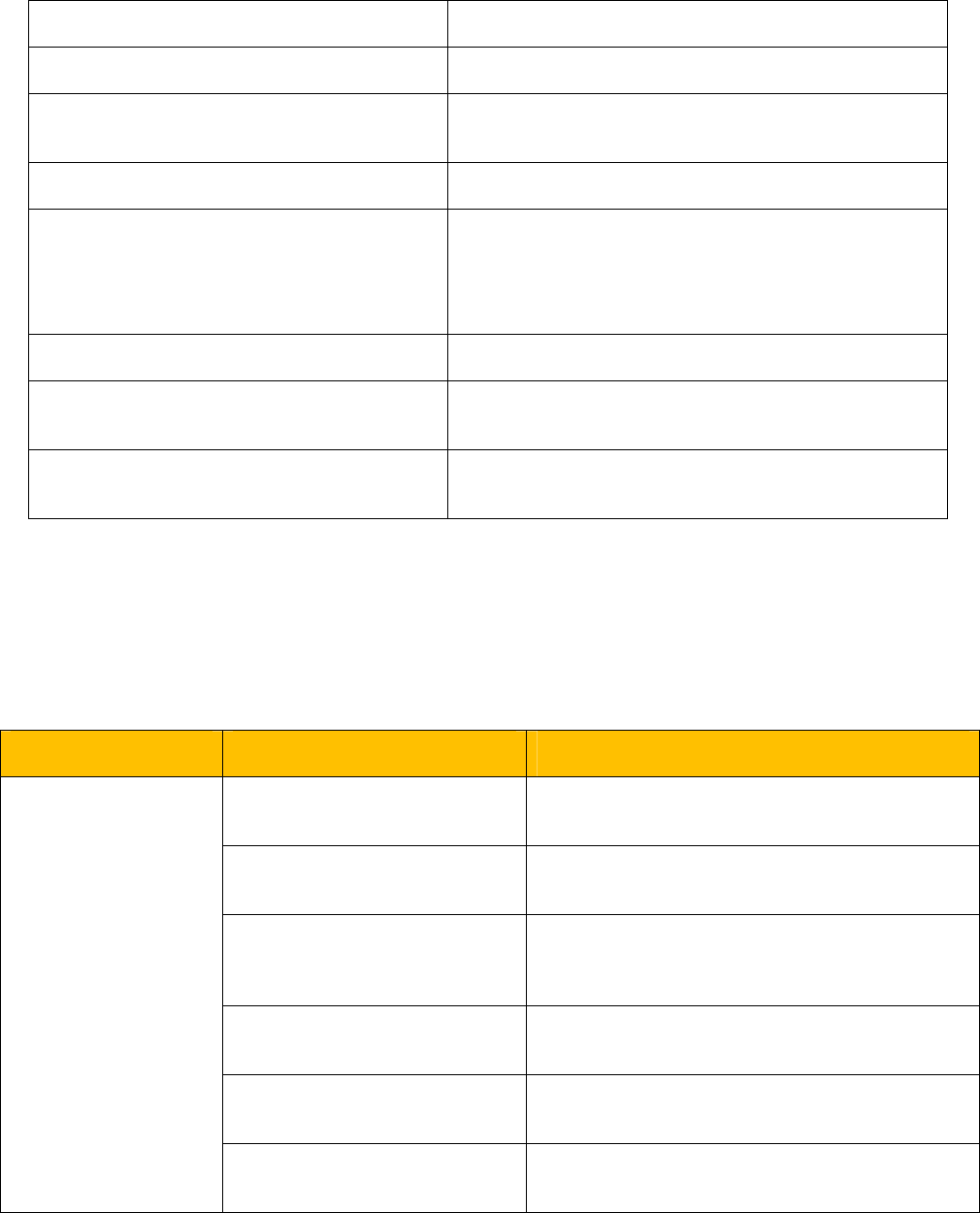
PAN ID The tracker group address
Node ID The individual tracker network address
Mac This address is programmed at the factory in the
network interface and cannot be changed
Stowed Status Current system status: stowed/tracking/backtracking
NWS Stow The National Weather Service Stow Enable indicator—
ON indicates NWS is enabled; OFF, disabled.
The stow and unstow perimeters are defined in the
Stow and Unstow configuration retrospect.
NWS Stow Status Indicates system stow status based on NWS forecast
Stow Configuration Defines at what perimeters the tracker controller will
stow the panels
Unstow configuration Defines at what perimeters the tracker controller will
allow the panels to resume normal operations
4. To view graphic and error reports for the selected TMAC unit, use the graph. To use the graph, refer to
Section 1.5.2.5.
1.5.2.5 Using the Graph
On the TMAC Dashboard page, you can view the following level-specific graphs:
Level Graph Description
Motor History Plots motor position against programmed setpoint
values for each tracker in the site
Motor Errors Plots the differential between motor position and
setpoint values for each tracker in the site
Wireless Signal Currently Plots current minimum, maximum, and average
signal strength values (in dB) for each tracker in
the site
Wireless Signal History Plots historical signal strength values (in dB) for
each tracker in the site
Weather History Plots historical temperature, wind speed, and gust
speed values
Site-level
Weather Forecast Plots temperature and wind-speed forecast for the
next three days
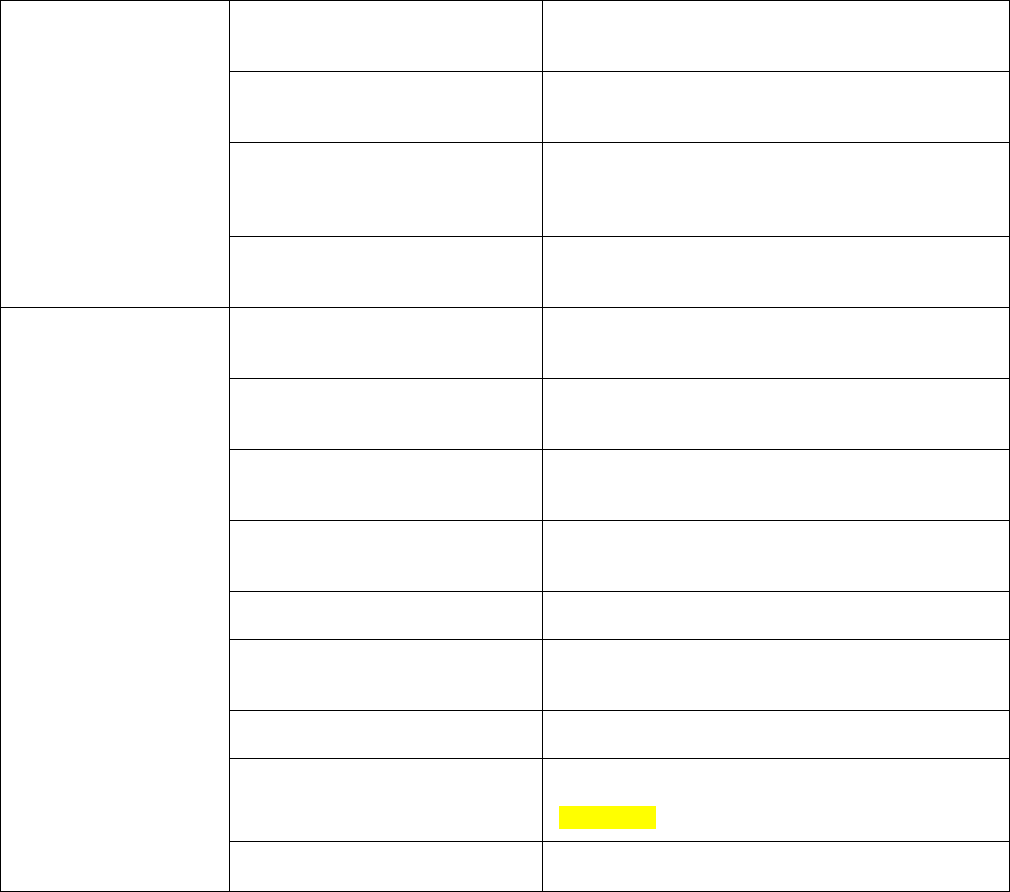
Motor History Plots motor position against programmed setpoint
values for each tracker within the network
Motor Errors Plots the differential between motor position and
setpoint values for each tracker within the network
Wireless Signal Currently Plots current minimum, maximum, and average
signal strength values (in dB) for each tracker
within the network
Network-level
Wireless Signal History Plots historical signal strength values (in dB) for
each tracker within the network
Motor Position Plots the tracker’s motor position against
programmed setpoint values
Motor Moved Plots the amount of time the tracker motor is
running in forward and reverse
Motor Cycles Plots the number of times the tracker motor is
switched on and off
Motor Error Plots the differential between the tracker’s motor
position and setpoint values
Temperature Plots the tracker enclosure temperature over time
Sun Plots the position of the sun in both tracker and
world frame throughout the day
Wireless RX Plots the quality of received data
Wireless AT (Wireless Communication Status: AT)
[description]
TMAC unit-level
Wireless TX Plots the quality of transmitted data
To illustrate, perform the following steps to view the graphed motor position and setpoint values for a TMAC
unit—for example, Unit: 00:13:a2:00:40:3a:43:1f (M0531_AREA01_TRK04 PN:1/0) installed at Rancho California
Water District TZ:-08:00—over the last three days.
1. In the list on the left side of the TMAC Dashboard page, click Rancho California Water District TZ:-08:00.
2. In the collapsed pane below the customer site name, click 00:13:a2:00:40:3a:43:1f (M0531_AREA01_TRK04
PN:1/0).
3. View the Motor Position graph—the default graph view— for Unit: 00:13:a2:00:40:3a:43:1f
(M0531_AREA01_TRK04 PN:1/0) (Fig. 16).
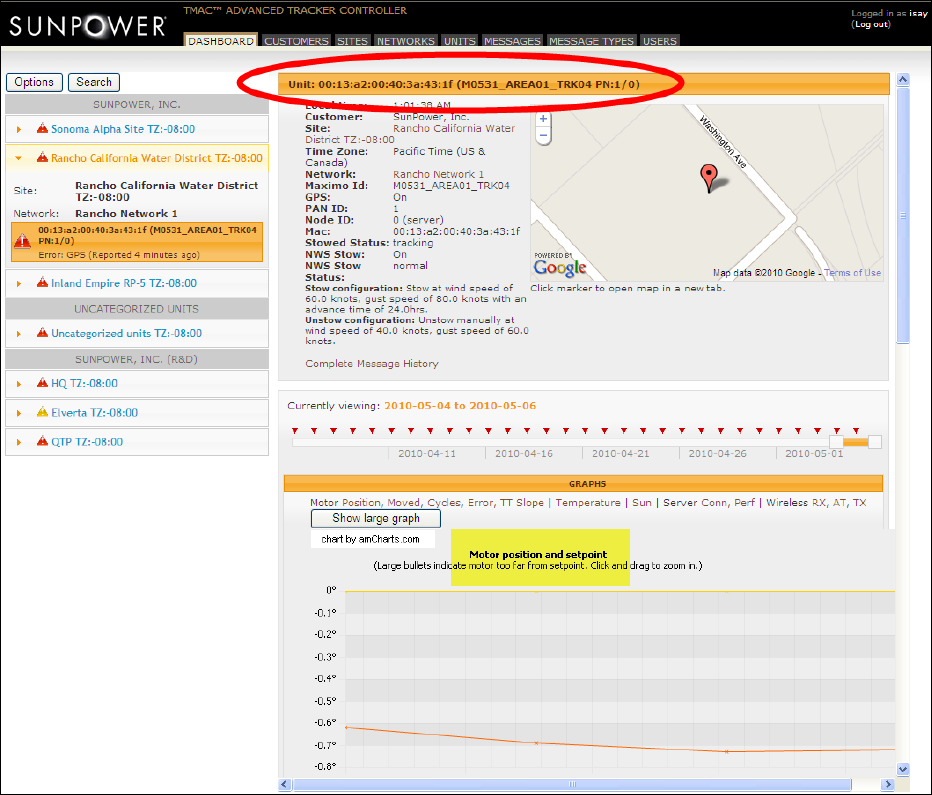
Fig. 16
4. To view older data, move the slider above the Graphs title bar. To view data a day or two days at a time
instead of the maximum three, decrease the width of the slider.
Important! You can view older data only if available. Small red triangles appear over the slider bar to indicate
available older data.
If you want to view graph data for non-TMAC specific parameter such as temperature forecast for the next three
days, select either the site- or network-level view and then click the Weather Forecast graph link (Fig. 17). Hover
over interval points in the graph line to view the data details.
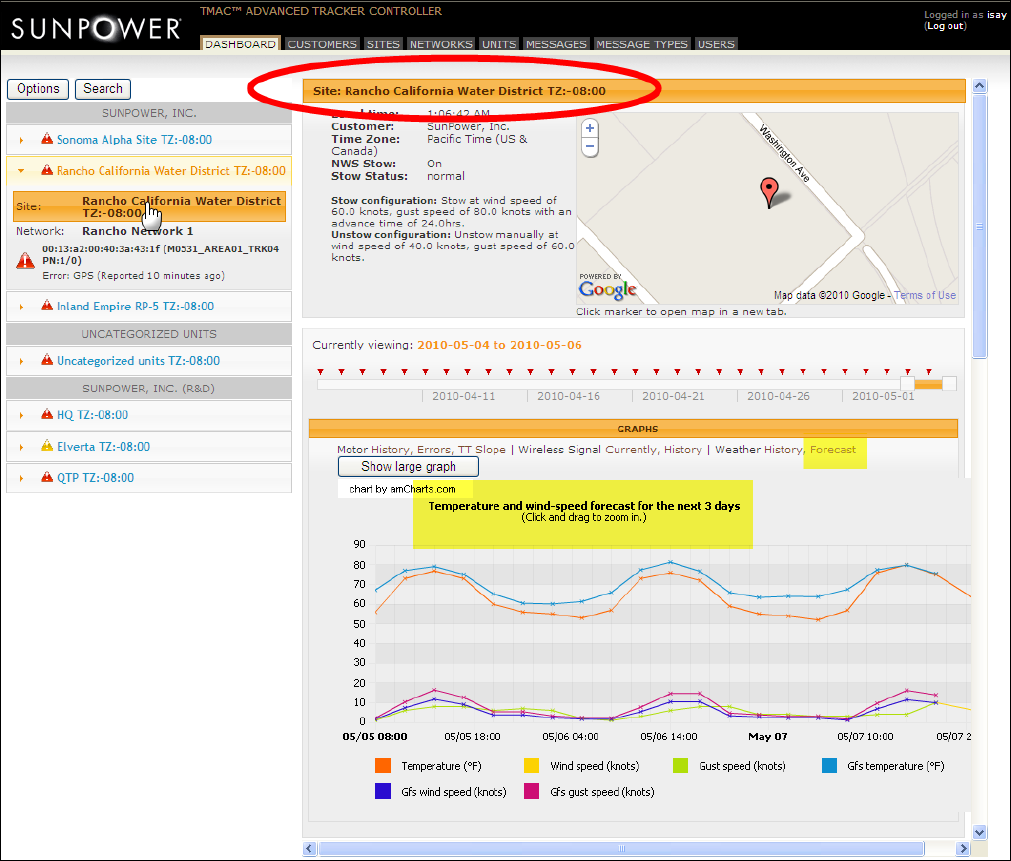
Fig. 17
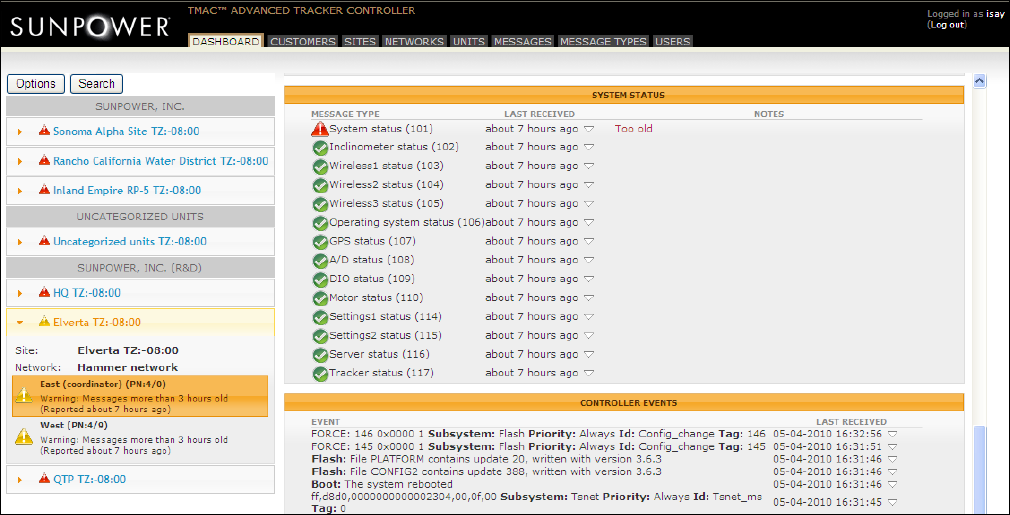
1.5.2.6 Viewing System Status
On the TMAC Dashboard page, you can view system status details for each TMAC unit.
1. Perform the steps in Section 1.5.2.4 to open the unit-level page for the TMAC controller you want to view.
2. Scroll down the unit-level page. The SYSTEM STATUS section (below the GRAPHS section) lists message
types and when each was last received (Fig. 18). Refer to Appendix A for full description of the message
types.
Fig. 18
3. To view the details of a message type—for example, System status (101), click the Arrow_down button under
the LAST RECEIVED column to collapse the selected row (Fig. 19).
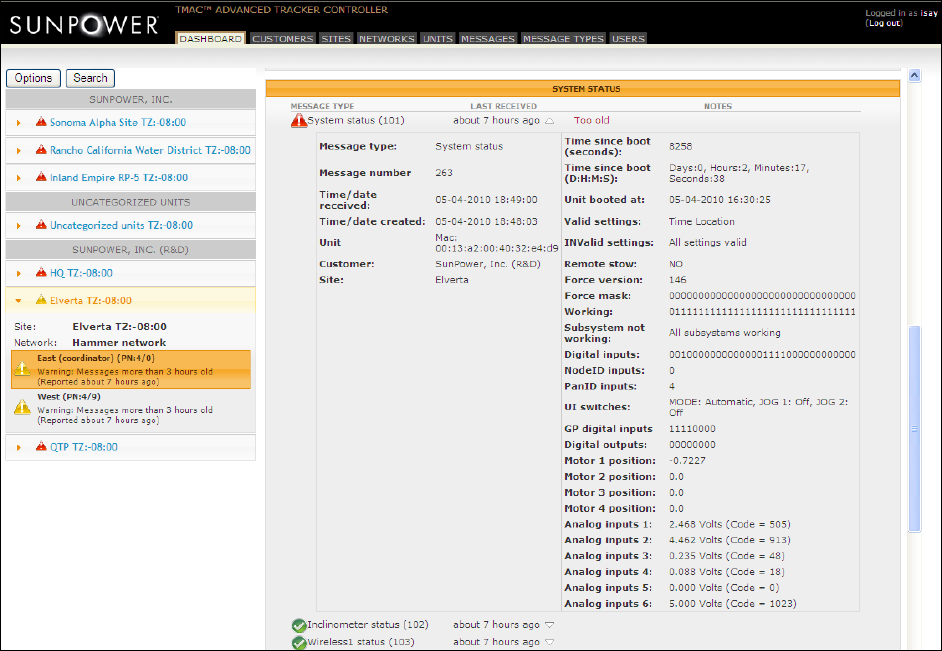
Fig. 19
4. Click the Arrow_up button to hide the details.
5. Perform Steps 3–4 to view the details of other message types.
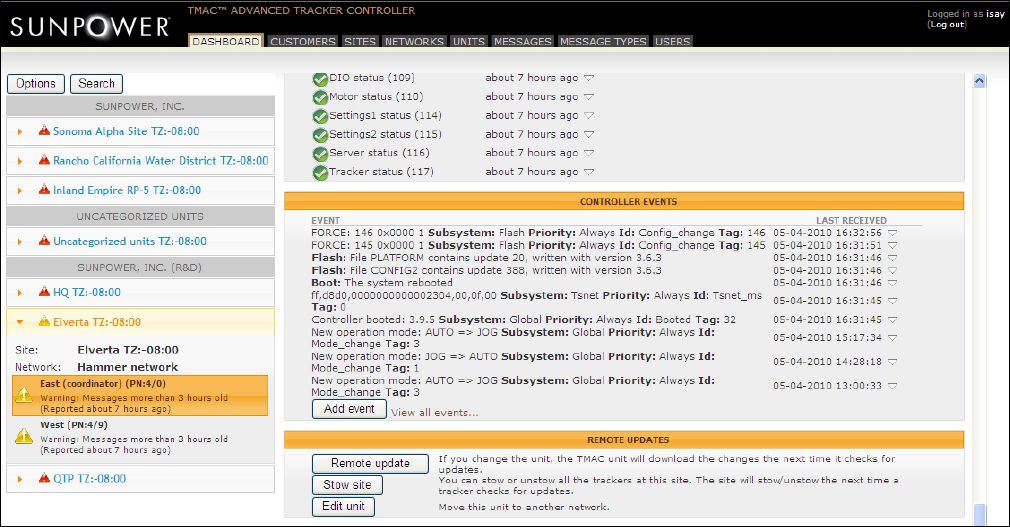
1.5.2.7 Viewing Controller Events
On the TMAC Dashboard page, you can view details of controller events for each TMAC unit.
1. Perform the steps in Section 1.5.2.4 to open the unit-level page for the TMAC controller you want to view.
2. Scroll down the unit-level page. The CONTROLLER EVENTS section lists controller events and when each
was last received (Fig. 20).
Fig. 20
3. To view the details of a controller event—for example, the event report at the top of the list, click the
Arrow_down button under the LAST RECEIVED column to collapse the row (Fig. 21).
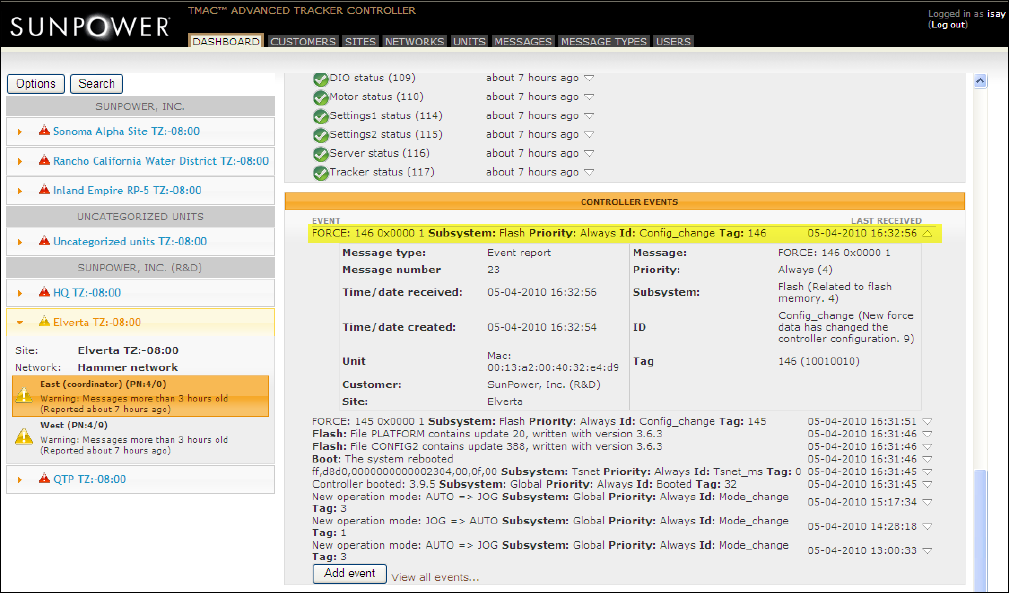
Fig. 21
4. Click the Arrow_up button to hide the details.
5. Perform Steps 3–4 to view the details of other controller events.
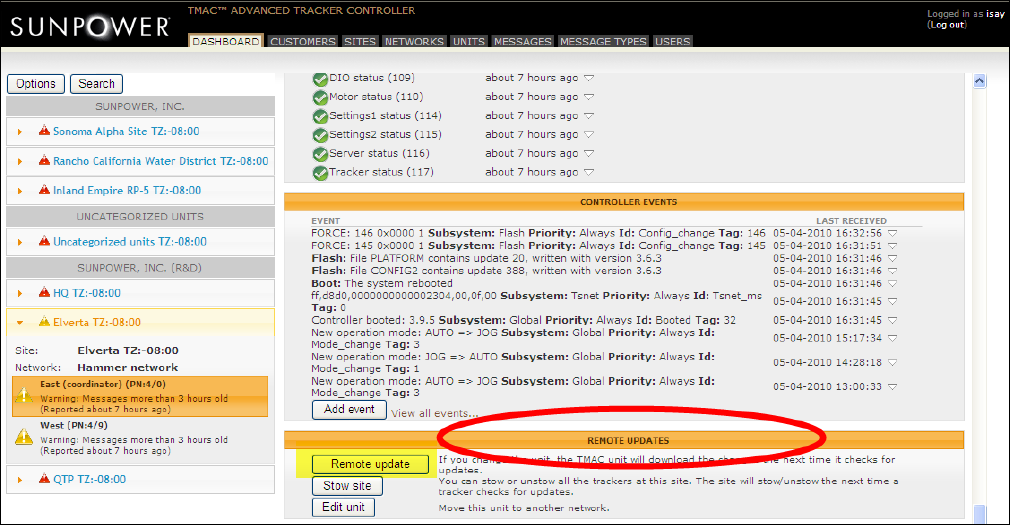
1.5.2.8 Sending Remote Updates
On the TMAC Dashboard page, you can send remote updates for each TMAC unit.
1. Perform the steps in Section 1.5.2.4 to open the unit-level page for the TMAC controller you want to view.
2. Scroll down the unit-level page. The REMOTE UPDATES section contains the Remote update button that
enables you to send commands to the TMAC controller and enter values in the commissioning form (Fig. 22).
Fig. 22
3. Click Remote update.
4. A screen appears (Fig. 23).
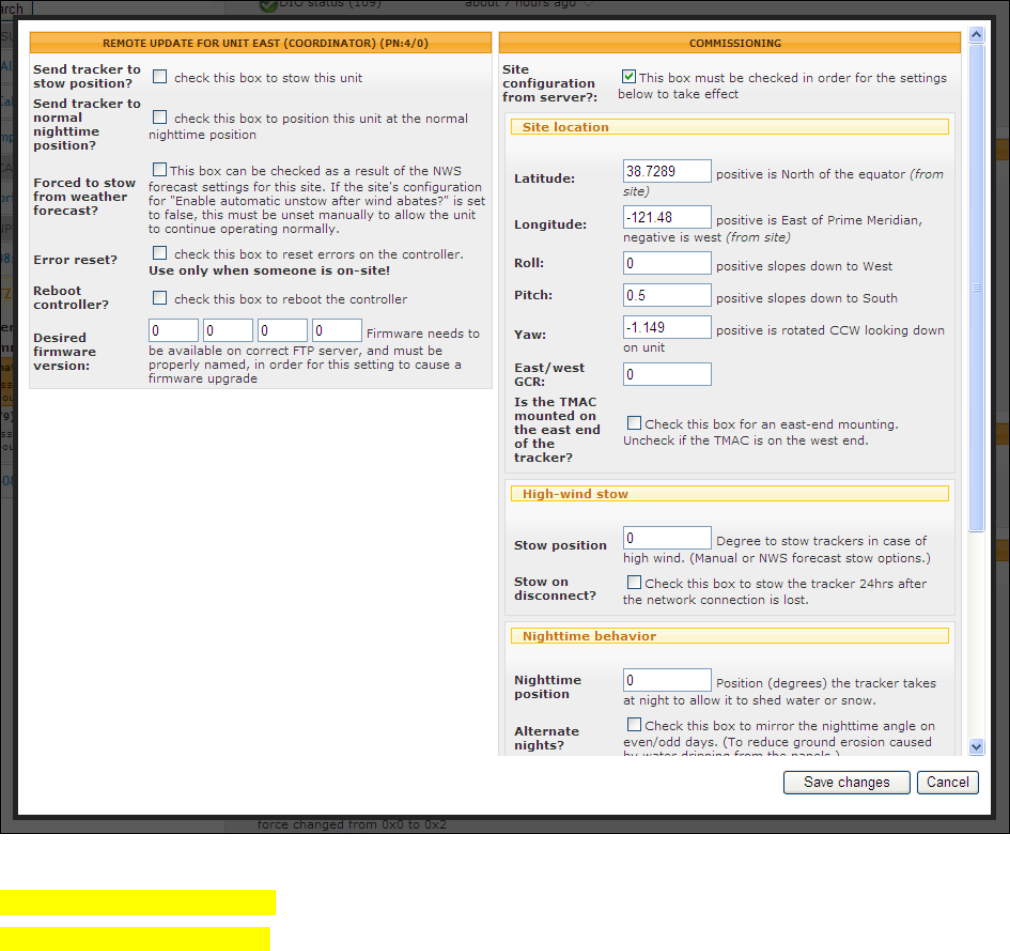
Fig. 23
• REMOTE UPDATE section:
• COMMISSIONING section:
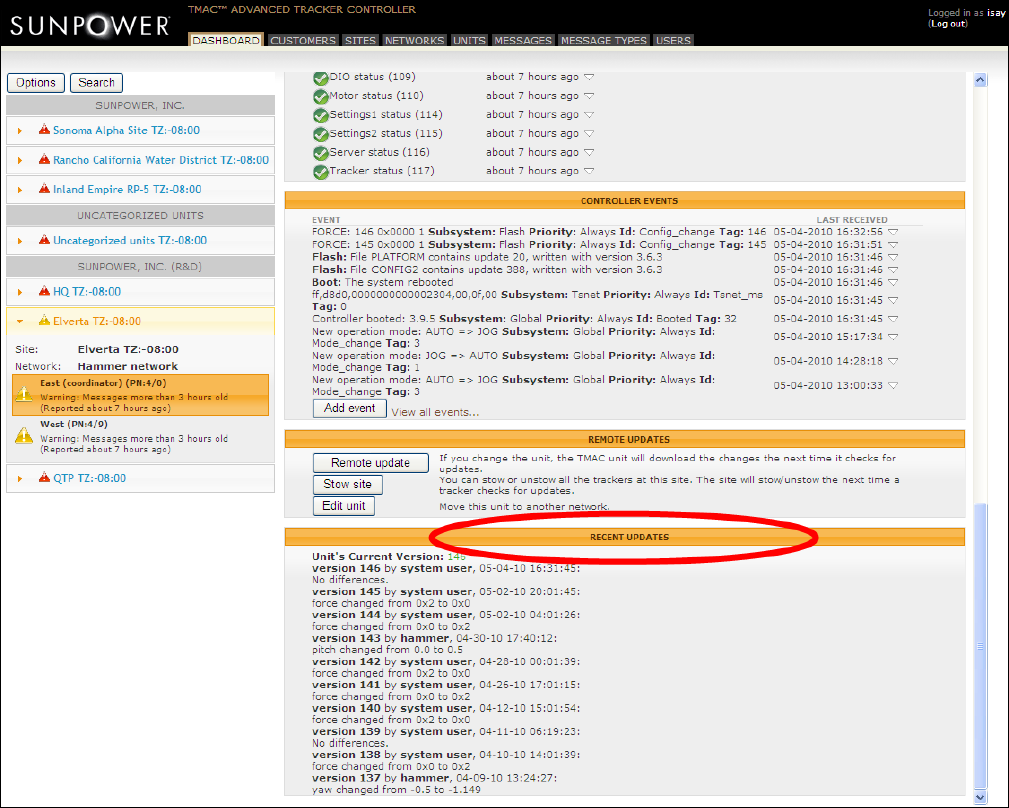
1.5.2.9 Viewing Recent Updates
On the TMAC Dashboard page, you can view recent updates sent remotely to each TMAC unit.
1. Perform the steps in Section 1.5.2.4 to open the unit-level page for the TMAC controller you want to view.
2. Scroll down the unit-level page. The RECENT UPDATES section lists the updates on remote commands sent
to the TMAC controller (Fig. 24).
Fig. 24
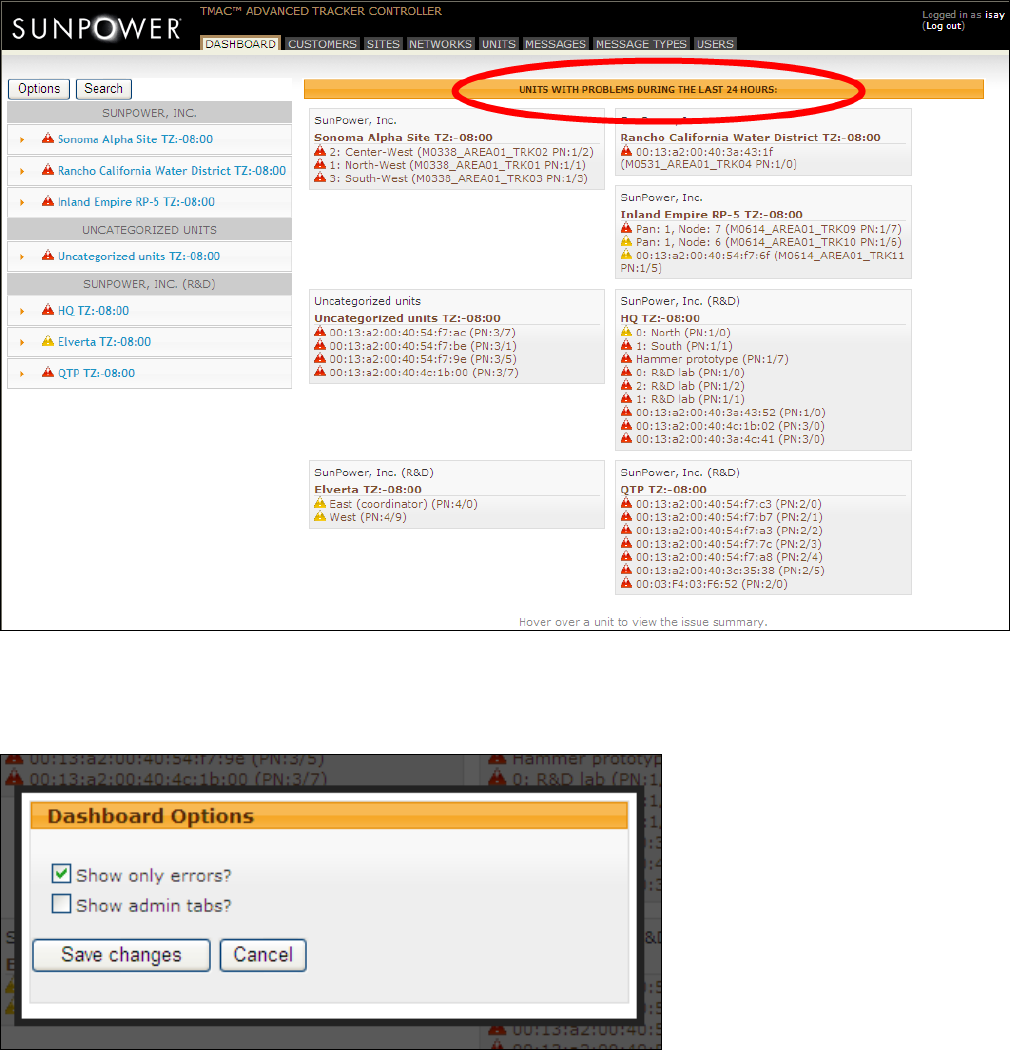
1.5.2.10 Viewing Alerts
If there are TMAC units with problems during the last 24 hours, the TMAC Dashboard page displays the alerts by
default.
TMAC Dashboard page
To see only the customer sites that have alerts, click the Options button below the SunPower logo. In the
Dashboard Options window, select the Show only errors? check box and click Save changes (Fig. 25).
Fig. 25
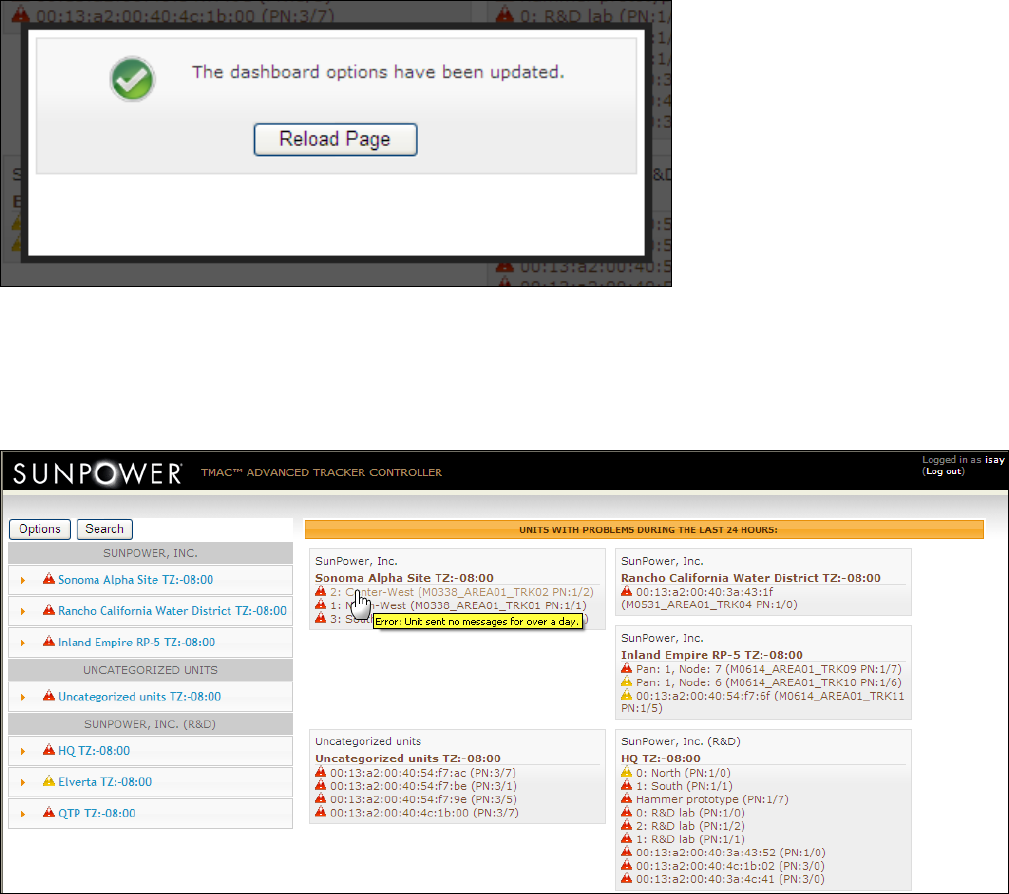
Click Reload Page in the confirmation window (Fig. 26).
Fig. 26
Important! To see all customer sites on the TMAC Dashboard page, click Options and clear the Show only
error? check box before saving the changes and reloading the page.
To view the issue summary, hover over the unit name (Fig. 27).
Fig. 27
Click the unit name link to open the unit-level view. Note that the graph does not show data for the unit with the
issue (Fig. 28).
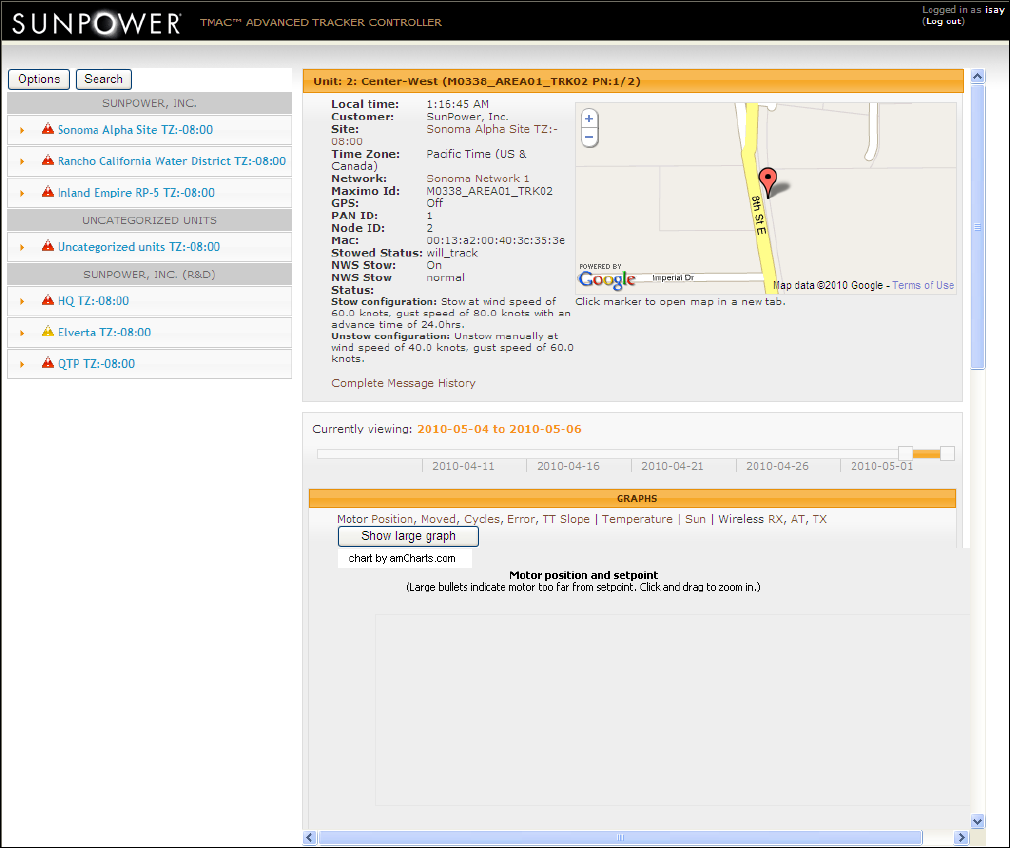
Fig. 28
Important! In the site-level view for a customer site where a unit has an issue, the graph will also not show any
data.
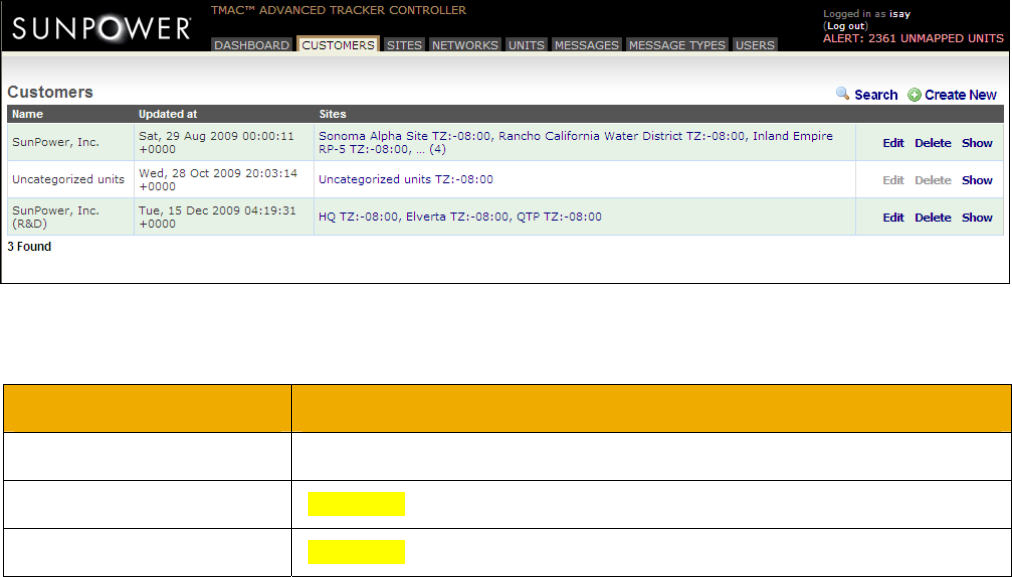
1.5.2.11 Viewing and Managing Customer Information
To view, edit, or delete customer information, click the CUSTOMERS tab (Fig. 29).
Fig. 29
The Customers page lists customer details in columns:
Column Description
Name The customer name…
Updated at [description]
Sites [description]
• To view customer information, click Show in the selected customer details row. The Show Customer window
opens (Fig. 30). Click Close or the X button to close the window.
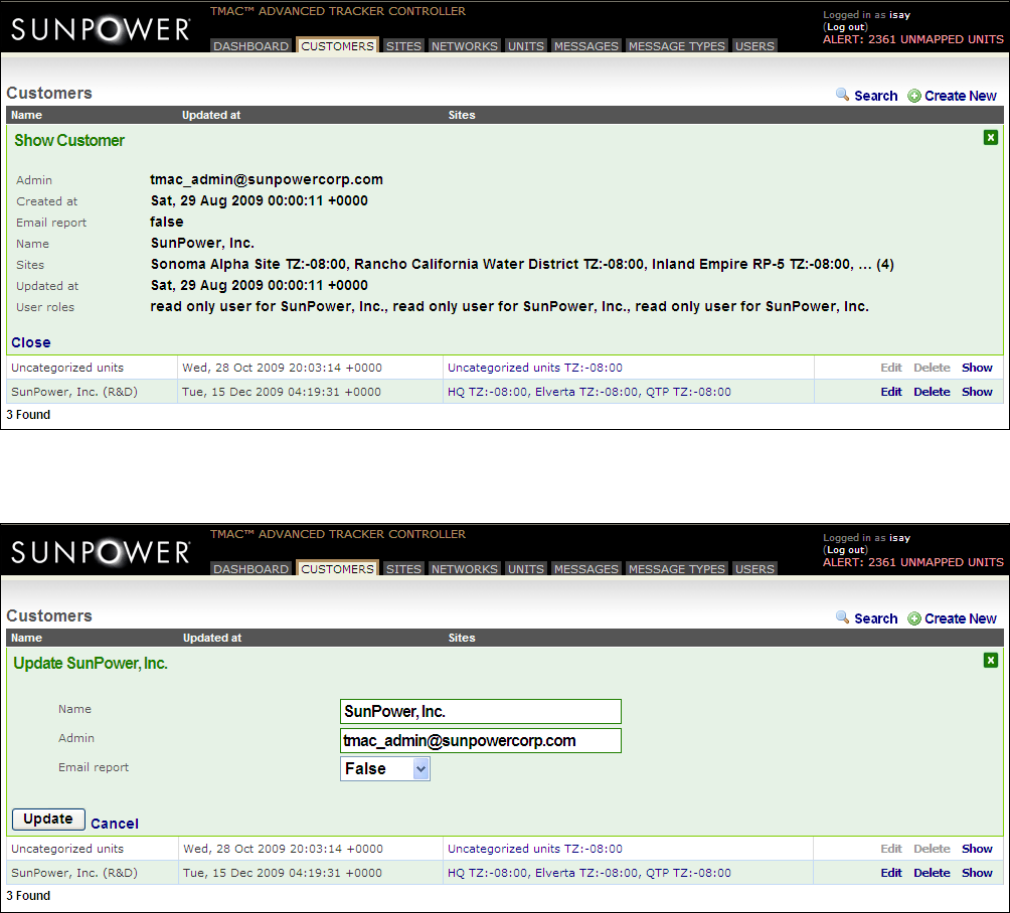
Fig. 30
• To change customer information details, click Edit. The Update [Customer name] window opens (Fig. 31).
Fig. 31
a. Enter or select new values in the Name, Admin, and Email report fields.
b. Click Update to save the changes. Click Cancel or the X button to close the window.
• To delete customer information profile, click Delete. Click OK in the confirmation window.
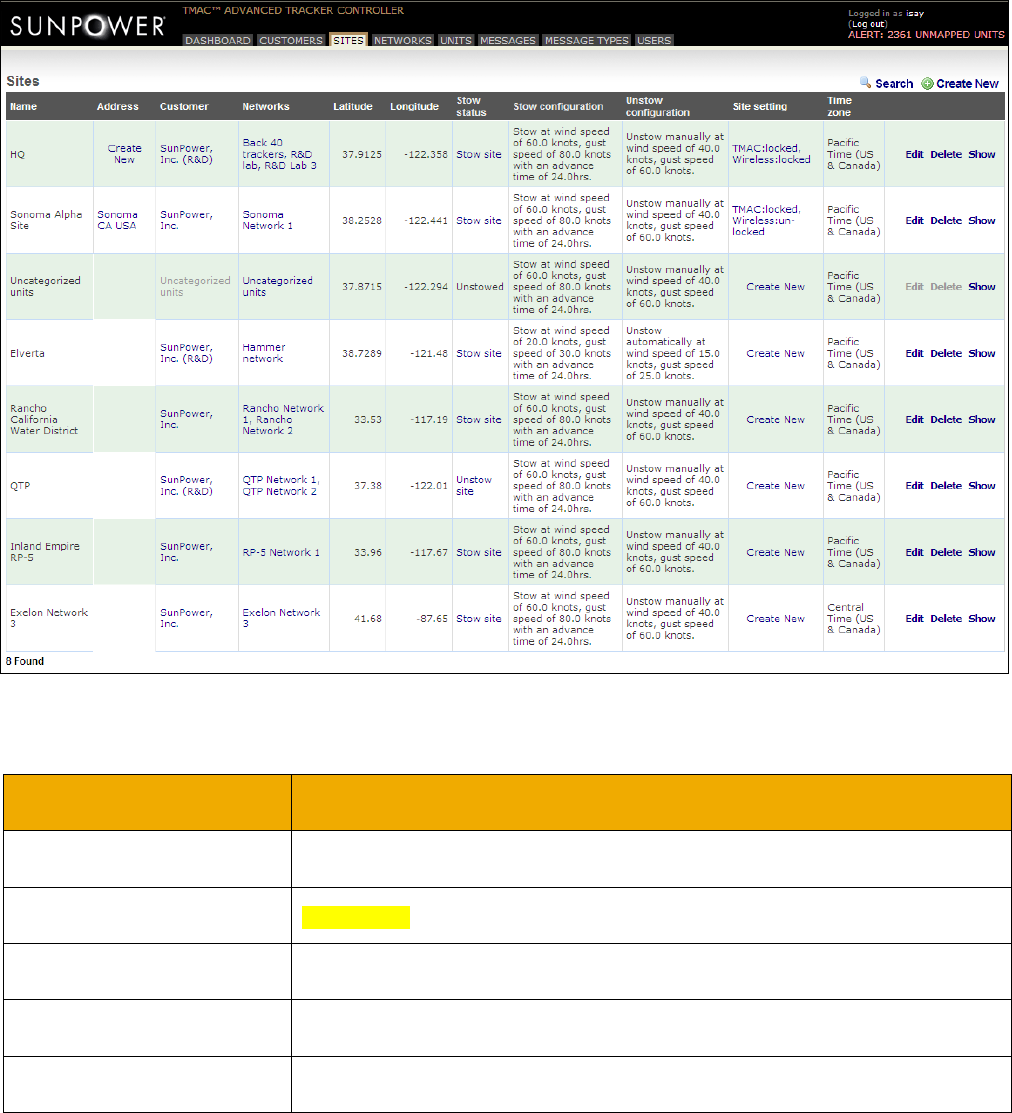
1.5.2.12 Viewing and Managing Site Information
To view, edit, or delete site information, click the SITES tab (Fig. 32).
Fig. 32
The Sites page lists site details in columns:
Column Description
Name The site name…
Address [description]
Customer [description]
Networks [description]
Latitude [description]
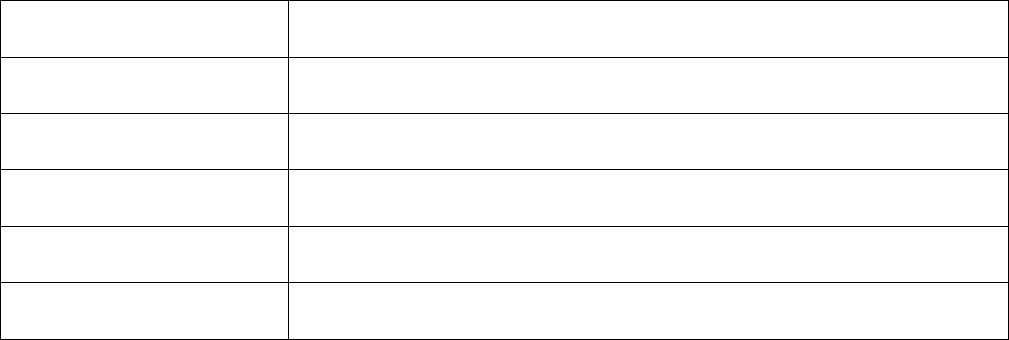
Longitude [description]
Stow status [description]
Stow configuration [description]
Unstow configuration [description]
Site setting [description]
Time zone [description]
• To view information for a site, click Show in the selected site details row. The Show Site window opens (Fig.
33). Click Close or the X button to close the window.
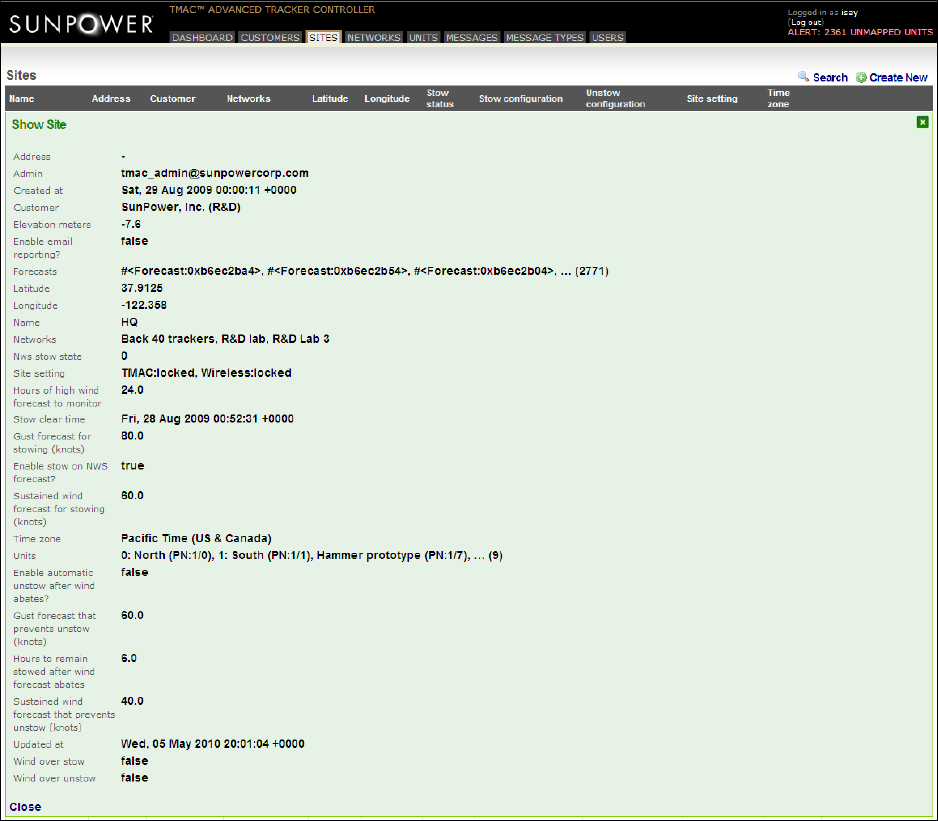
Fig. 34
• To change customer site information details, click Edit. The Update [Site name] window opens (Fig. 35).
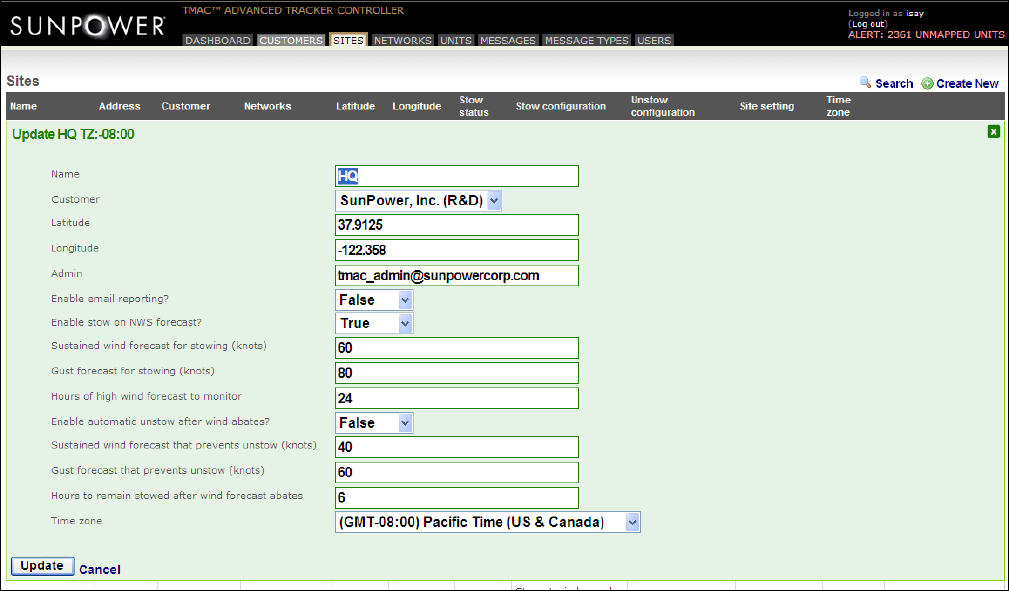
Fig. 35
a. Enter or select new values in the fields.
b. Click Update to save the changes. Click Cancel or the X button to close the window.
• To delete customer site profile, click Edit. Click OK in the confirmation window.
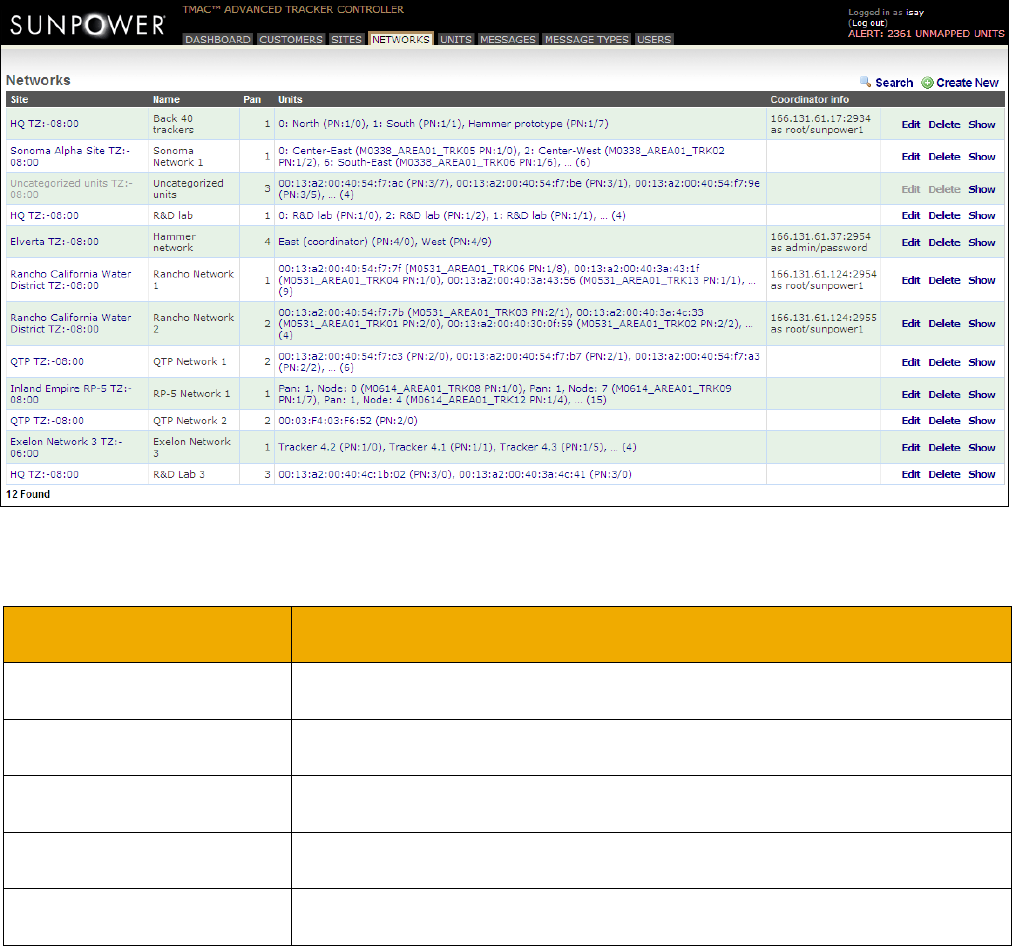
1.5.2.13 Viewing and Managing Network Information
To view, edit, or delete network information, click the NETWORKS tab (Fig. 36).
Fig. 36
The Networks page lists network details in columns:
Column Description
Site The name…
Name [description]
Pan [description]
Units [description]
Coordinator info [description]
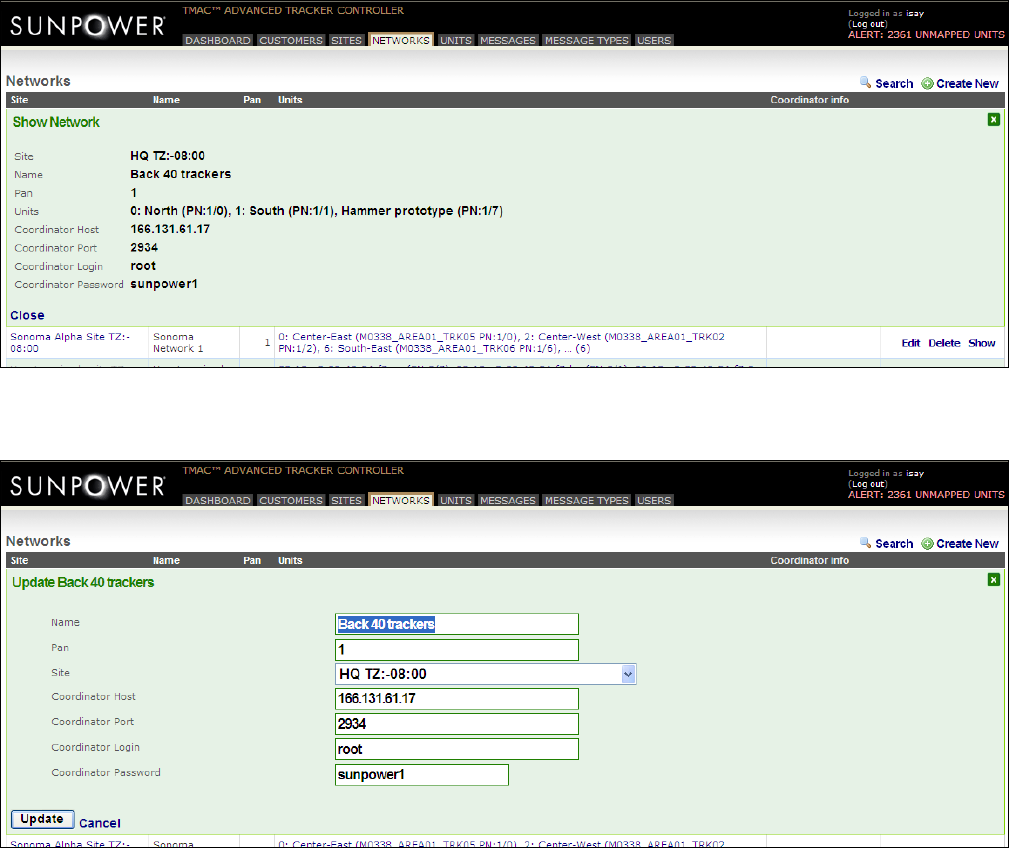
• To view the network information, click Show in the selected network details row. The Show Network window
opens (Fig. 37). Click Close or the X button to close the window.
Fig. 37
• To change network information details, click Edit. The Update [Network name] window opens (Fig. 38).
Fig. 38
a. Enter or select new values in the fields.
b. Click Update to save the changes. Click Cancel or the X button to close the window.
• To delete a network profile, click Delete. Click OK in the confirmation window.
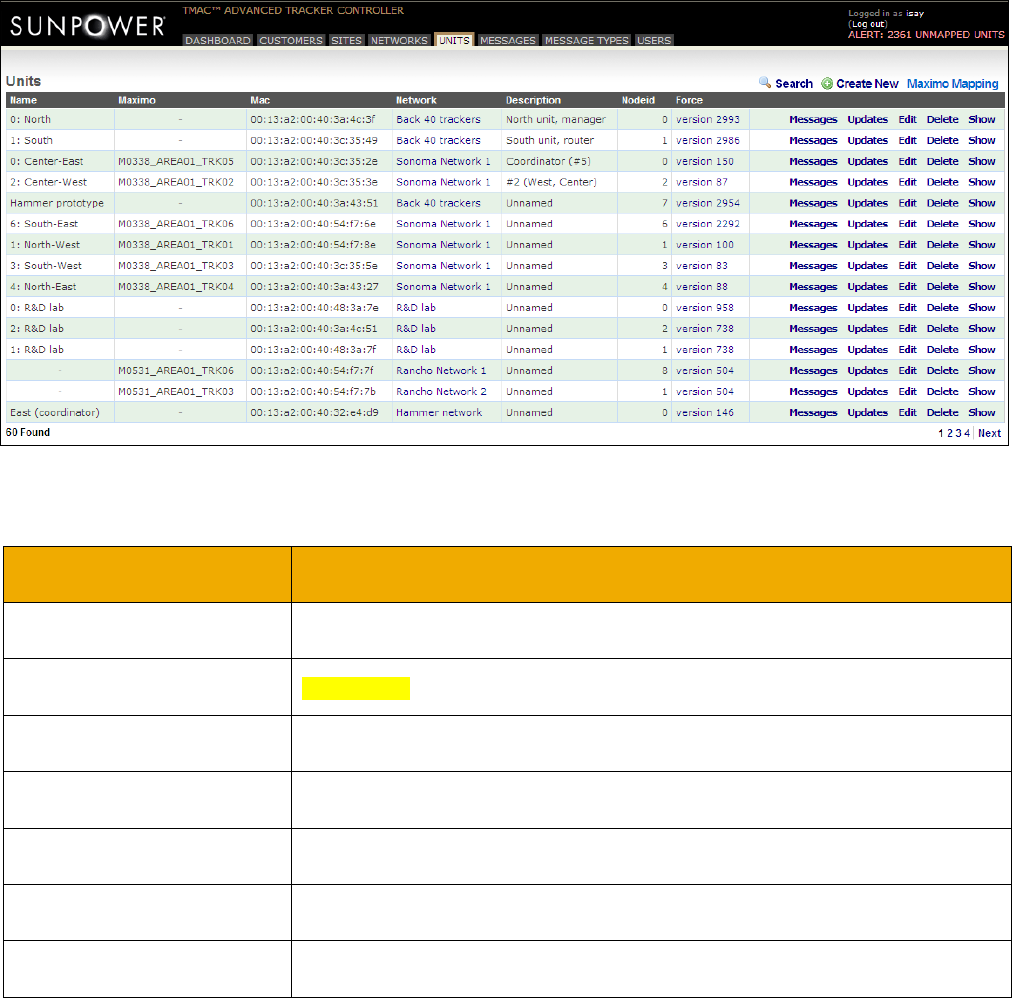
1.5.2.14 Viewing and Managing Units Information
To view all the TMAC units in the field, and edit, or delete TMAC controller information, click the UNITS tab (Fig.
39).
Fig. 39
The Units page lists TMAC unit details in columns:
Column Description
Name The name…
Maximo [description]
Mac [description]
Network [description]
Description [description]
Nodeid [description]
Force [description]
• To view information on a TMAC unit, click Show in the selected TMAC unit details row. The Show Unit
window opens (Fig. 40). Click Close or the X button to close the window.
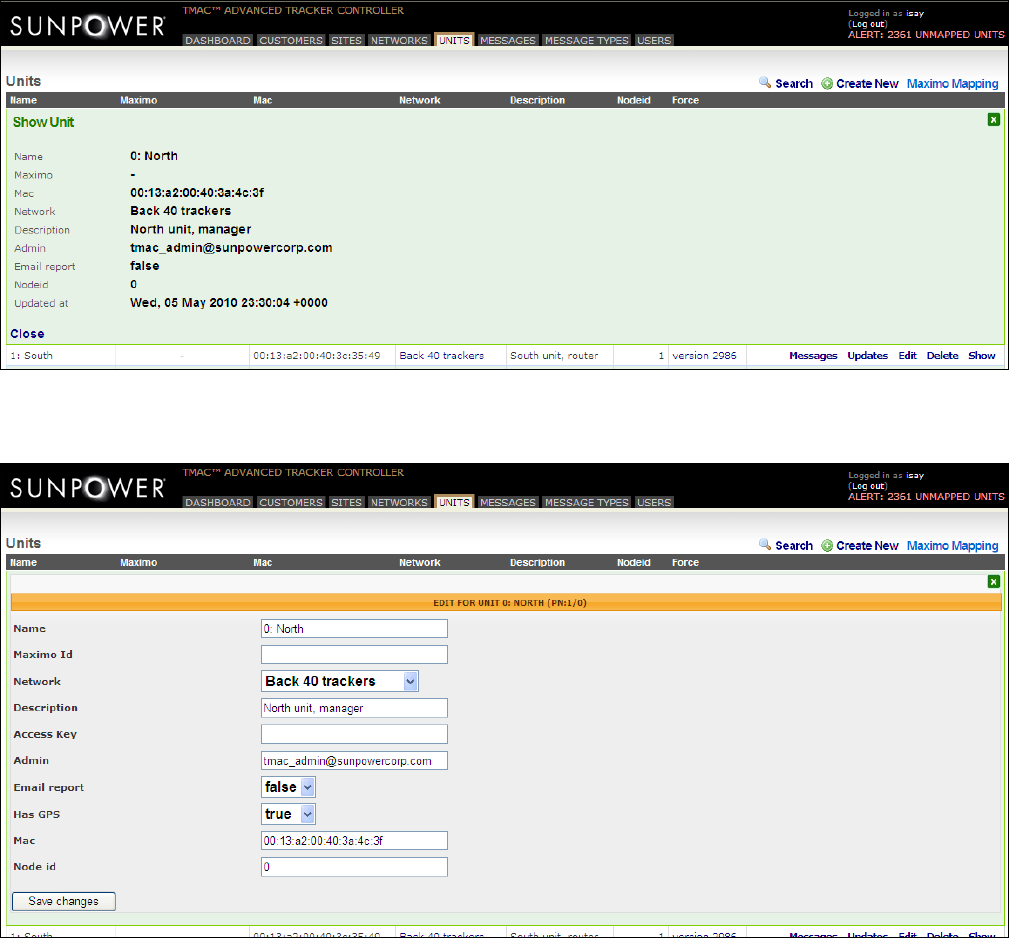
Fig. 40
• To change unit information details, click Edit. The Edit for unit [Unit name] window opens (Fig. 41).
Fig. 41
a. Enter or select new values in the fields.
b. Click Save changes.
• To delete a unit profile, click Delete. Click OK in the confirmation window.
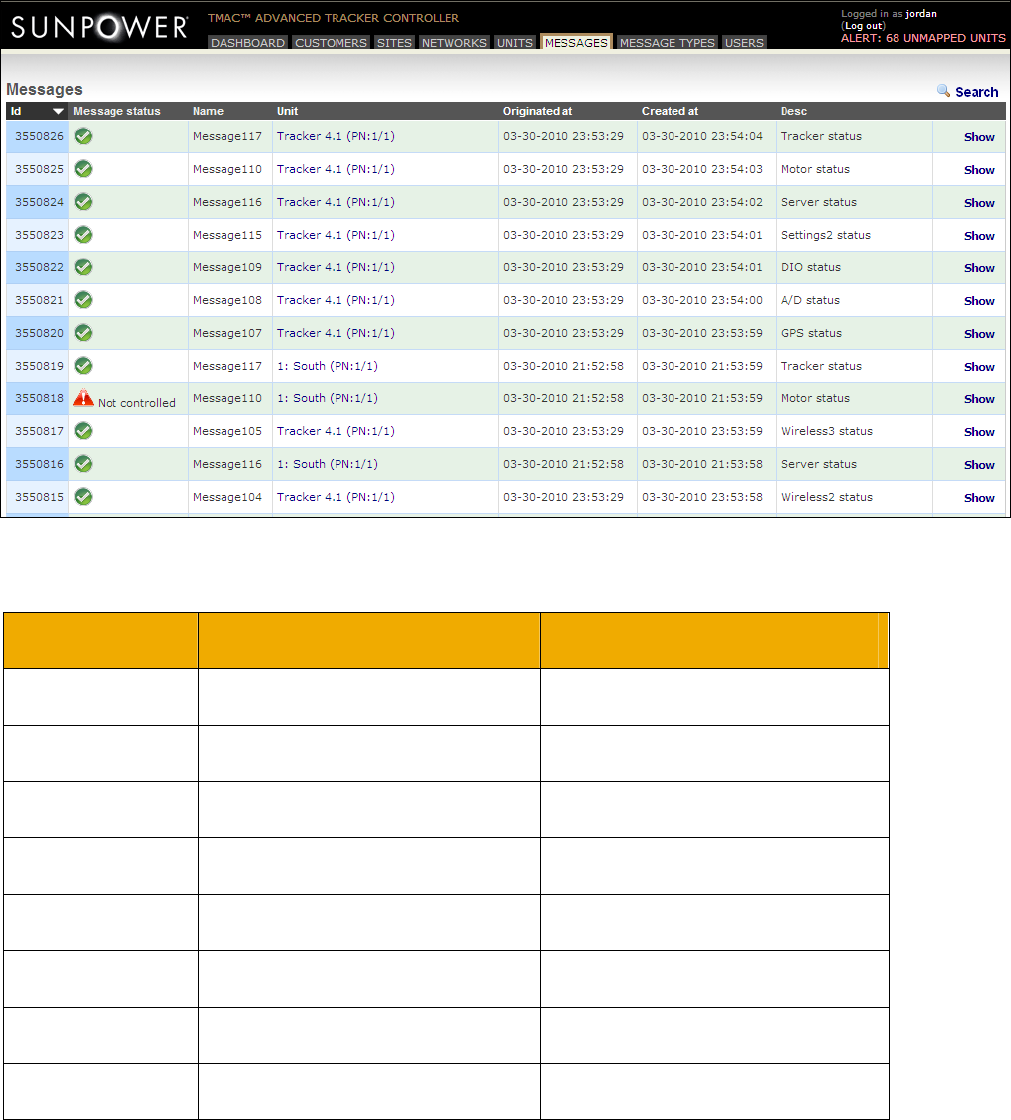
1.5.2.15 Viewing Messages
To view messages, click the MESSAGES tab (Fig. 42).
Fig. 42
The following table lists the descriptions of each message number.
Message Number Short Description Full Description
109 DIO Status See Appendix A
111 Flash messages See Appendix A
104 Wireless2 messages See Appendix A
113 Boot messages See Appendix A
105 Wireless3 messages See Appendix A
114 Settings1 messages See Appendix A
112 Event messages See Appendix A
110 Motor messages See Appendix A
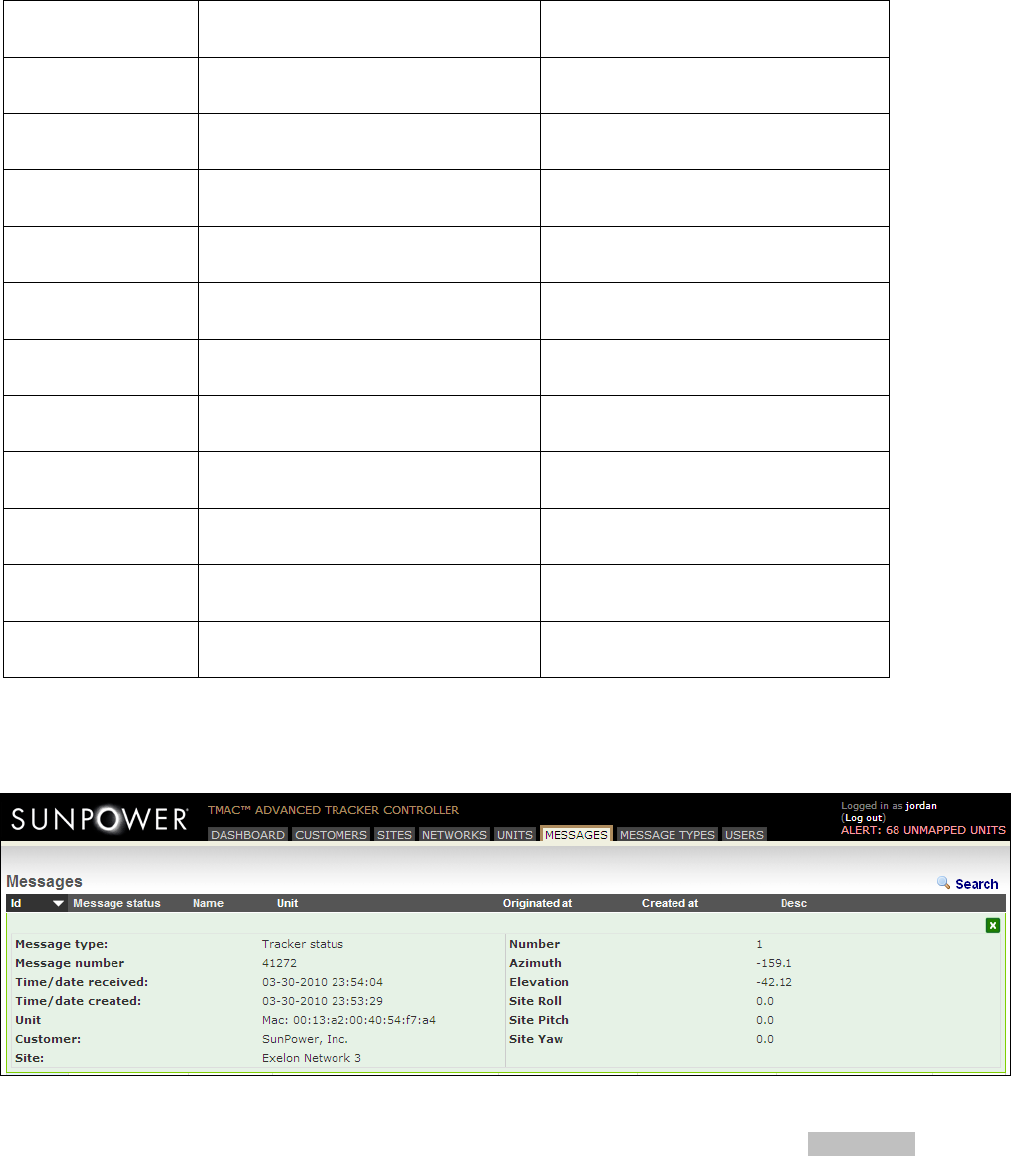
116 Server messages See Appendix A
106 Operating system messages See Appendix A
115 Settings2 messages See Appendix A
107 GPS messages See Appendix A
117 Tracker messages See Appendix A
102 Inclinometer messages See Appendix A
Test messages See Appendix A
112 Event messages See Appendix A
108 A/D messages See Appendix A
101 System messages See Appendix A
SCADA messages See Appendix A
103 Wireless1 messages See Appendix A
• To view the details of a message, click Show. A pop-up window opens and displays the details (Fig. 43). Refer
to Appendix A for a full description of message types.
Fig. 43
• To search for a specific message, click Search in the upper right of the table. Enter the [message ID] into the
Search Terms field that opens and click Search (Fig. 34). Click Reset to return to the unfiltered message list.
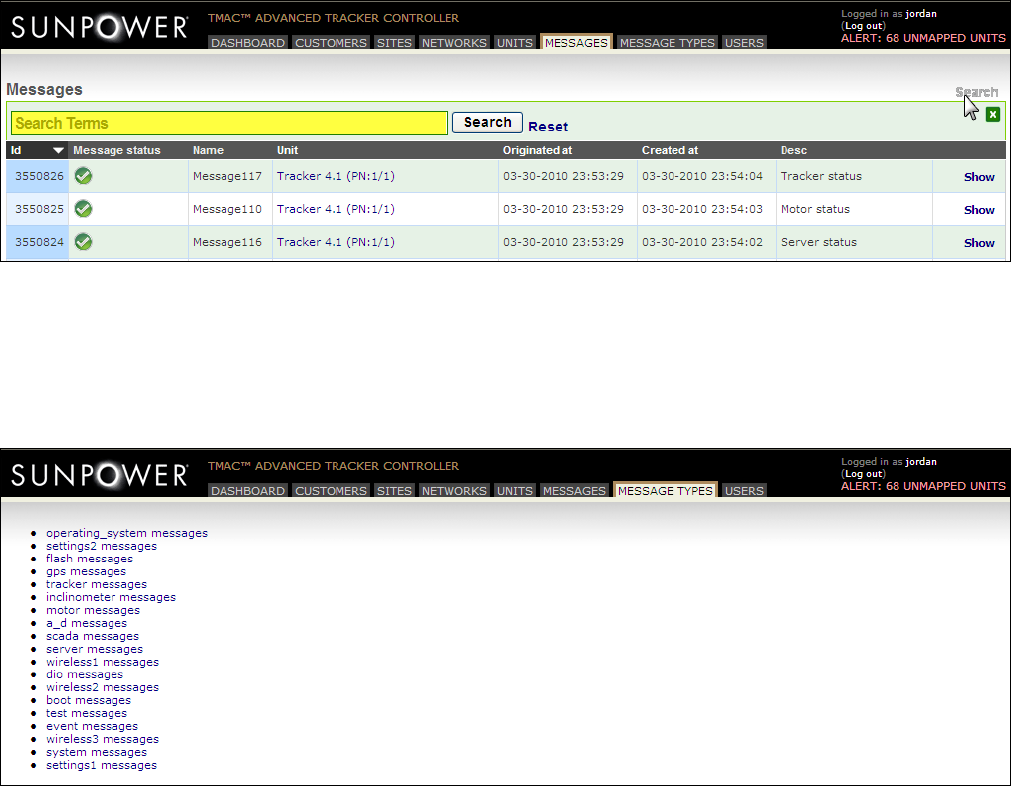
Fig. 43
1.5.2.16 Viewing Message Types
To view the list of message types, click the MESSAGE TYPES tab (Fig. 44).
Fig. 44
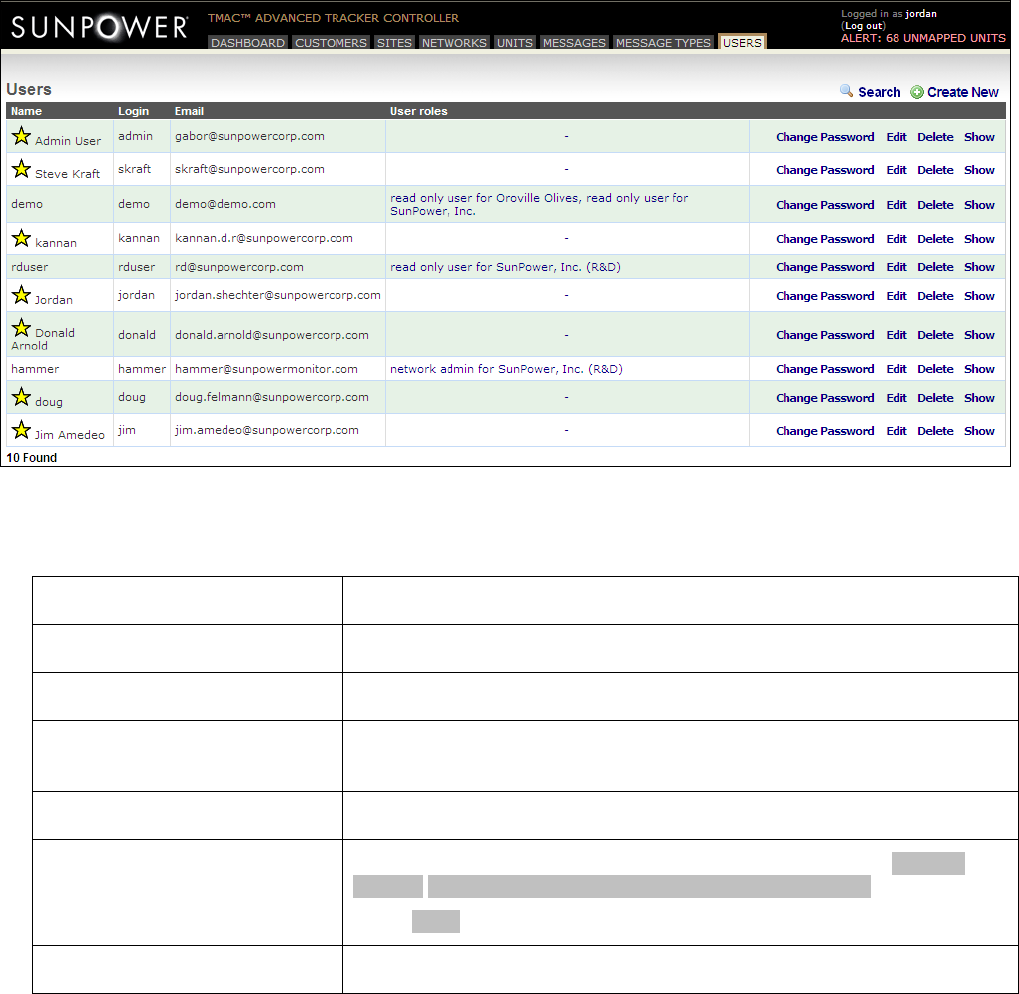
1.5.2.17 Viewing and Managing User Information
To view, edit, or delete user information, click the USERS tab (Fig. 45).
Fig. 45
• To create a new user, click Create New in the upper right of the table. In the Create User window, enter or
select values in the following fields (Fig. 46):
Name Enter the user’s name or user role.
Login Enter the login username.
Email Enter the email address of the user.
Password and Password
confirmation Enter and re-enter the user password.
Admin Select True or False.
User roles Select from the Customer dropdown list the customer name to which
account the user will be given access/assigned permission.
Enter [value] in the Role field.
Create Another
• To view user information, click Show. The Show User window opens (Fig. 36). Click Close or the X button to
close the window.
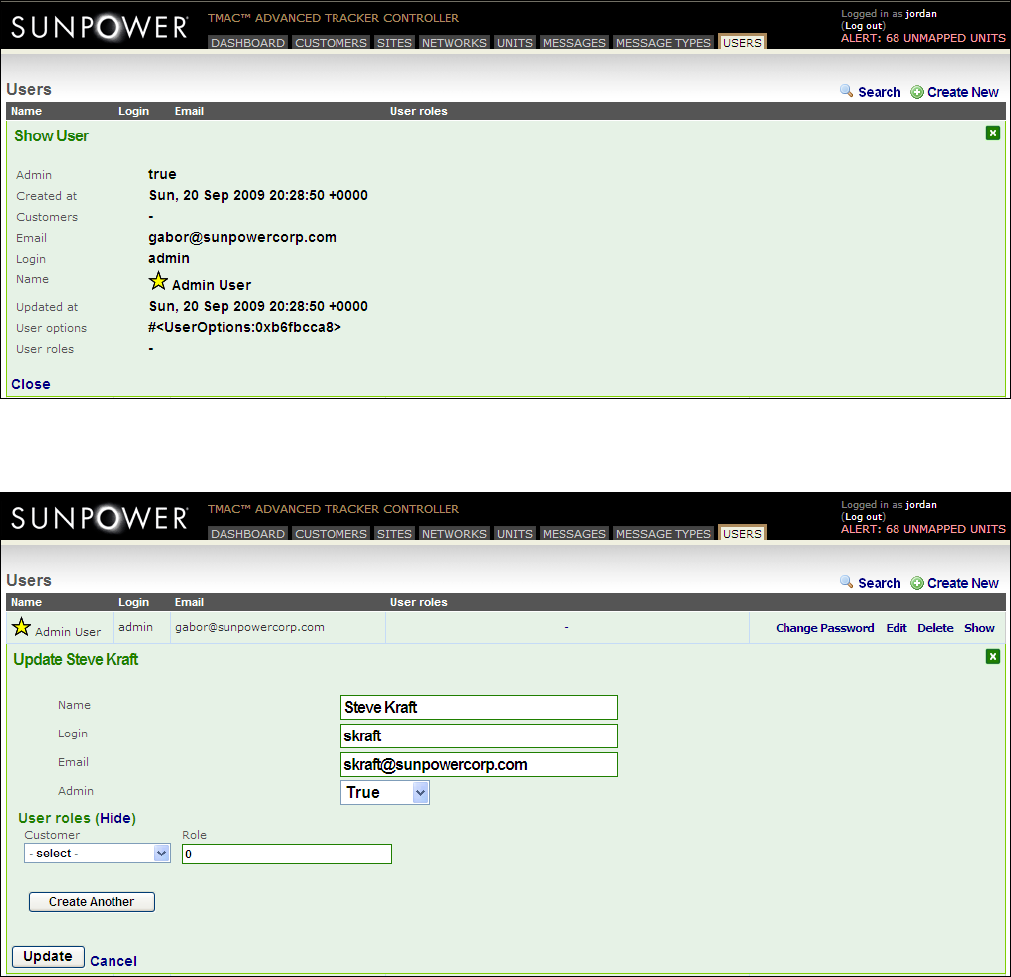
Fig. 46
• To change user information details, click Edit. The Update [User name] window opens (Fig. 47).
Fig. 47
• To change user passwords, click Change Password. The Change password for user [User name] window
opens (Fig. 48).
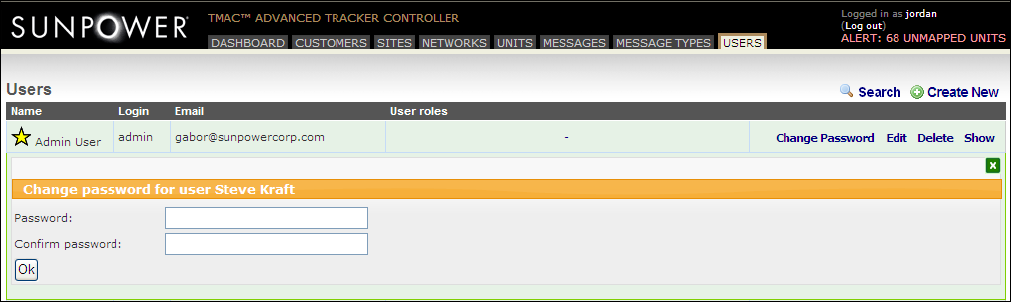
Fig. 48
a. Enter the new password and re-enter to confirm.
b. Click Ok.
• To delete a user profile, click Delete. Click OK in the confirmation window.
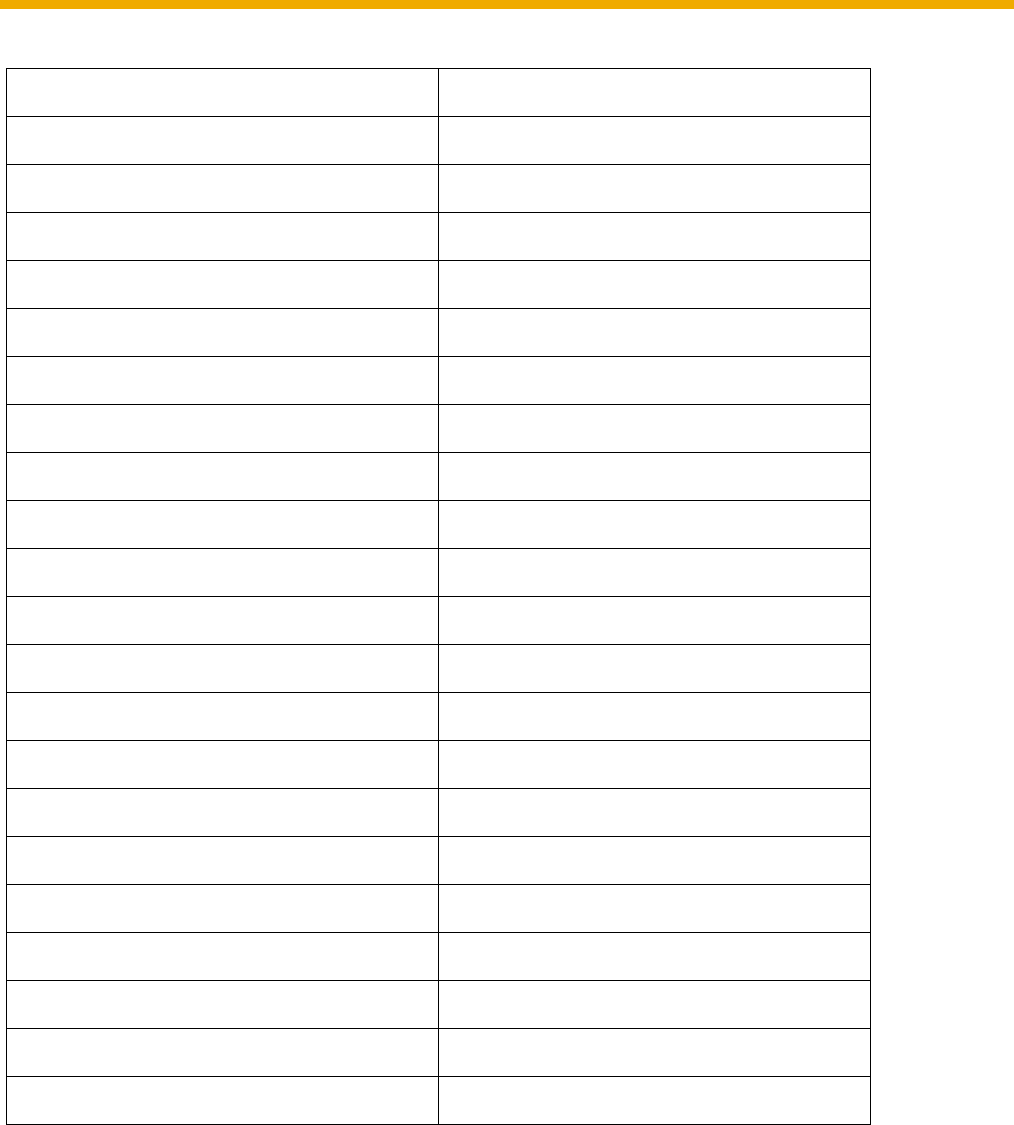
Appendix A: Message Types
A.1 System Status: (101)
Message type System status
Message number 12957
Time/date received 03-15-2010 15:54:49
Time/date created 03-15-2010 15:53:58
Unit Mac: 00:13:a2:00:40:3c:35:61
Customer SunPower, Inc.
Site Exelon Network 3
Time since boot (seconds) 964038
Time since boot (D:H:M:S) Days:11,Hours:3,Minutes:47,Seconds:18
Unit booted at 03-04-2010 11:06:40
Valid settings Time Location
Invalid settings All settings valid
Remote stow NO
Force version 4
Force mask 00000000000000000000000000000000
Working 00000000000011111111111111111111
Subsystem not working All subsystems working
Digital inputs 11000000000000001111000000000000
NodeID inputs 0
PanID inputs 3
UI switches MODE:Automatic,JOG1: Off,JOG2: Off
GP digital inputs 11110000
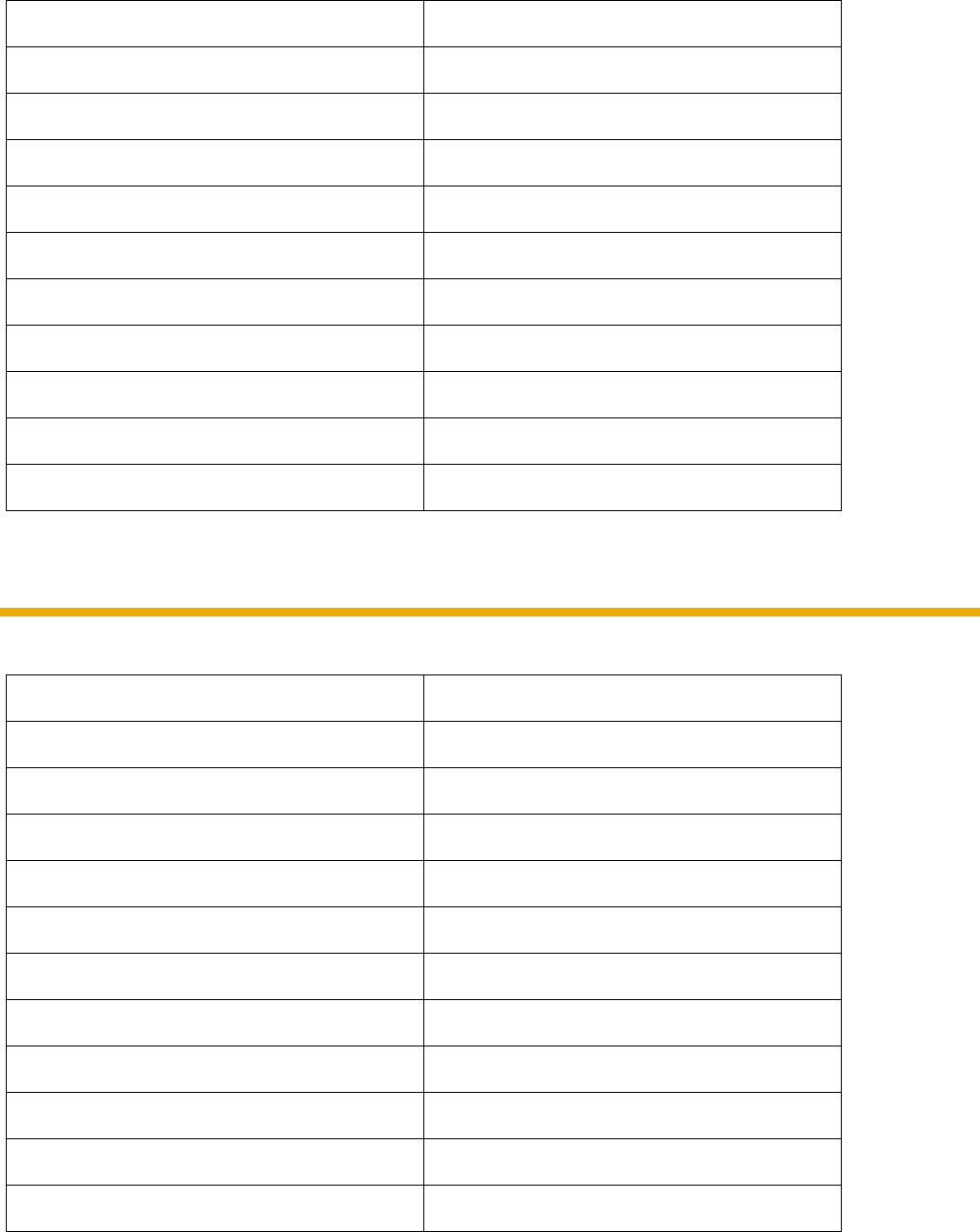
Digital outputs 00000000
Motor1 position −44.44
Motor2 position 0.0
Motor3 position 0.0
Motor4 position 0.0
Analog inputs 1 2.542 Volts (Code=520)
Analog inputs 2 1.085 Volts (Code=222)
Analog inputs 3 0.523 Volts (Code=107)
Analog inputs 4 0.083 Volts (Code=17)
Analog inputs 5 1.119 Volts (Code=229)
Analog inputs 6 0.904 Volts (Code=185)
A.2 Inclinometer Status (102)
Message type Inclinometer status
Message number 12960
Time/date received 03-15-2010 15:54:52
Time/date created 03-15-2010 15:54:00
Unit Mac: 00:13:a2:00:40:3c:35:61
Customer SunPower, Inc.
Site Exelon Network 3
Number 0
Reading valid VALID
Reading, +/- 180 −44.91
Reading, 0-360 0.0
Temperature 0.0 C, 32.0 F
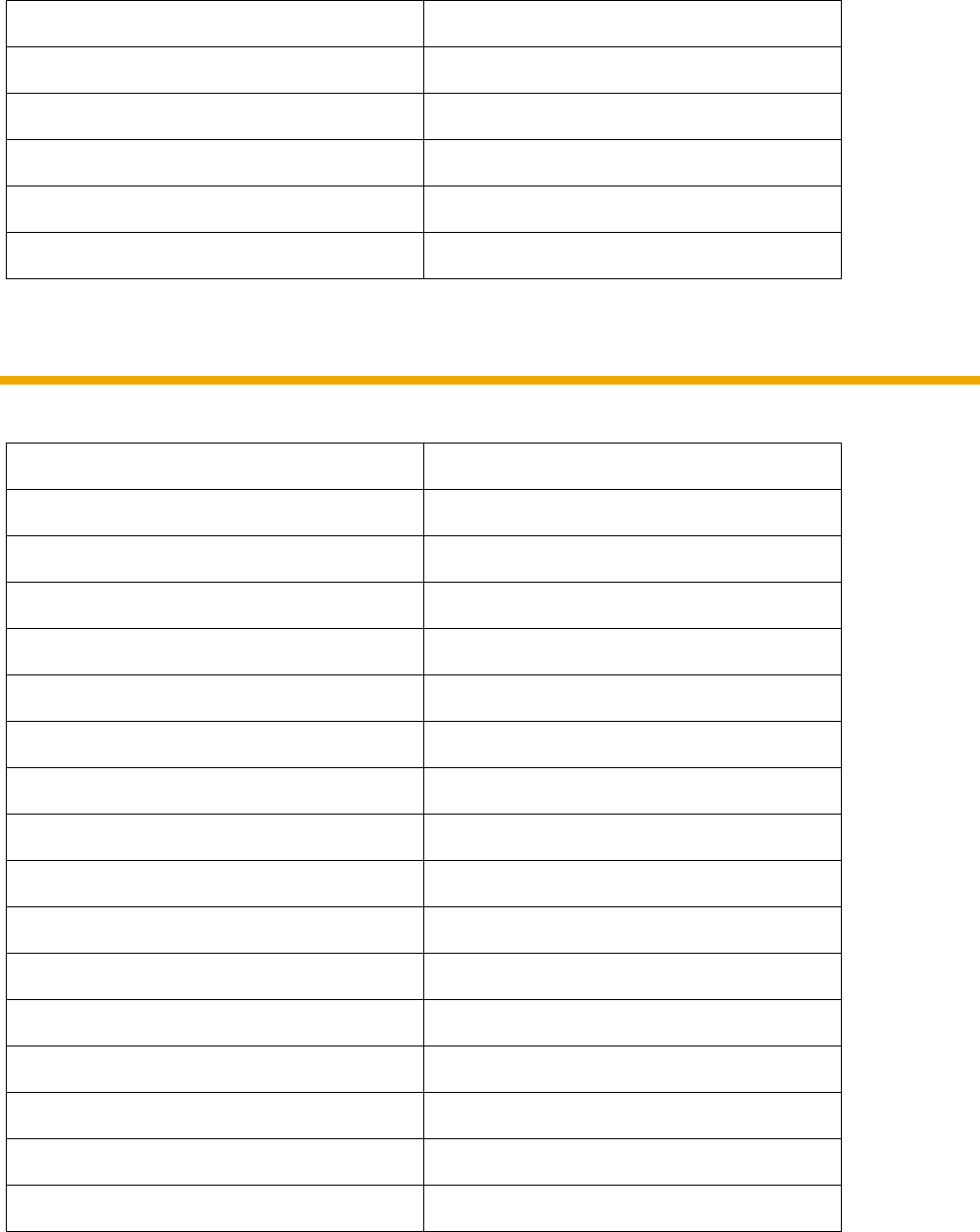
Maximum temperature −999.0 C, −1766.2 F
Minimum temperature 999.0 C, 1830.2 F
Power supply voltage 0.0
Attempts 61647190
Updates 61647190
Failures 0
A.3 Wireless 1 Status (103)
Message type Wireless1 status
Message number 13030
Time/date received 03-15-2010 16:55:04
Time/date created 03-15-2010 16:54:22
Unit Mac: 00:13:a2:00:40:3c:35:61
Customer SunPower, Inc.
Site Exelon Network 3
Wireless MAC 00:13:a2:00:40:3c:35:61
Address 0 (0x0)
Network 45995 (0xb3ab)
Rx: OK 28951
Rx: Out of frame 22
Rx: Bad checksum 0
Rx: Unknown packet ID 0
Rx: AT OK 57097
Rx: AT timeout 1
Rx: AT error 0
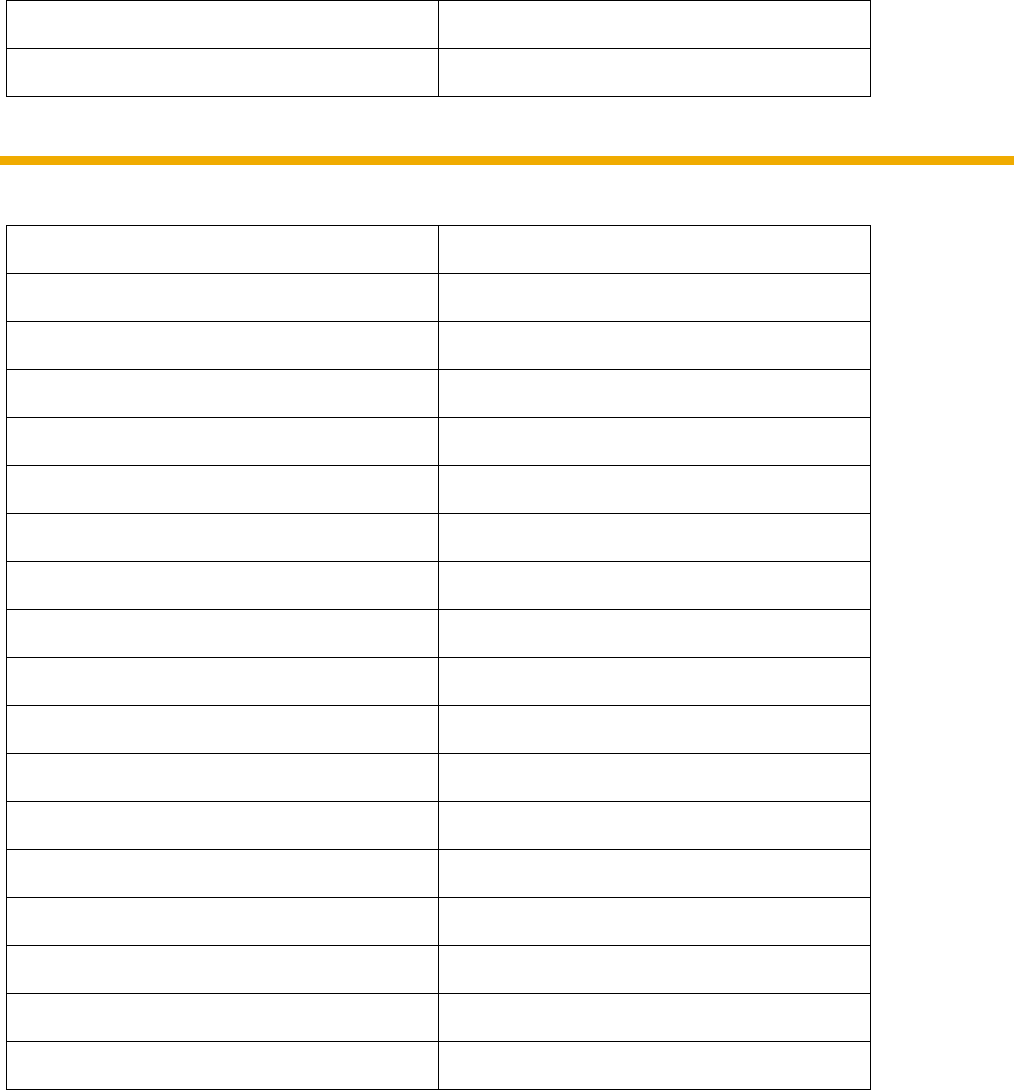
Rx: AT invalid command 0
Rx: AT invalid parameter 0
A.4 Wireless 2 Status (104)
Message type Wireless2 status
Message number 13031
Time/date received 03-15-2010 16:55:05
Time/date created 03-15-2010 16:54:22
Unit Mac: 00:13:a2:00:40:3c:35:61
Customer SunPower, Inc.
Site Exelon Network 3
Tx: attempts 6800
Tx: OK 6800
Tx: failures 0
Tx: characters 176608
Tx: retries 0
# of decibel measurements 122
Average decibel measurement −75
Minimum decibel measurement −89
Maximum decibel measurement −60
Wireless chip firmware version 2.1.6.4
Wireless chip hardware version 6724 (0x1a44)
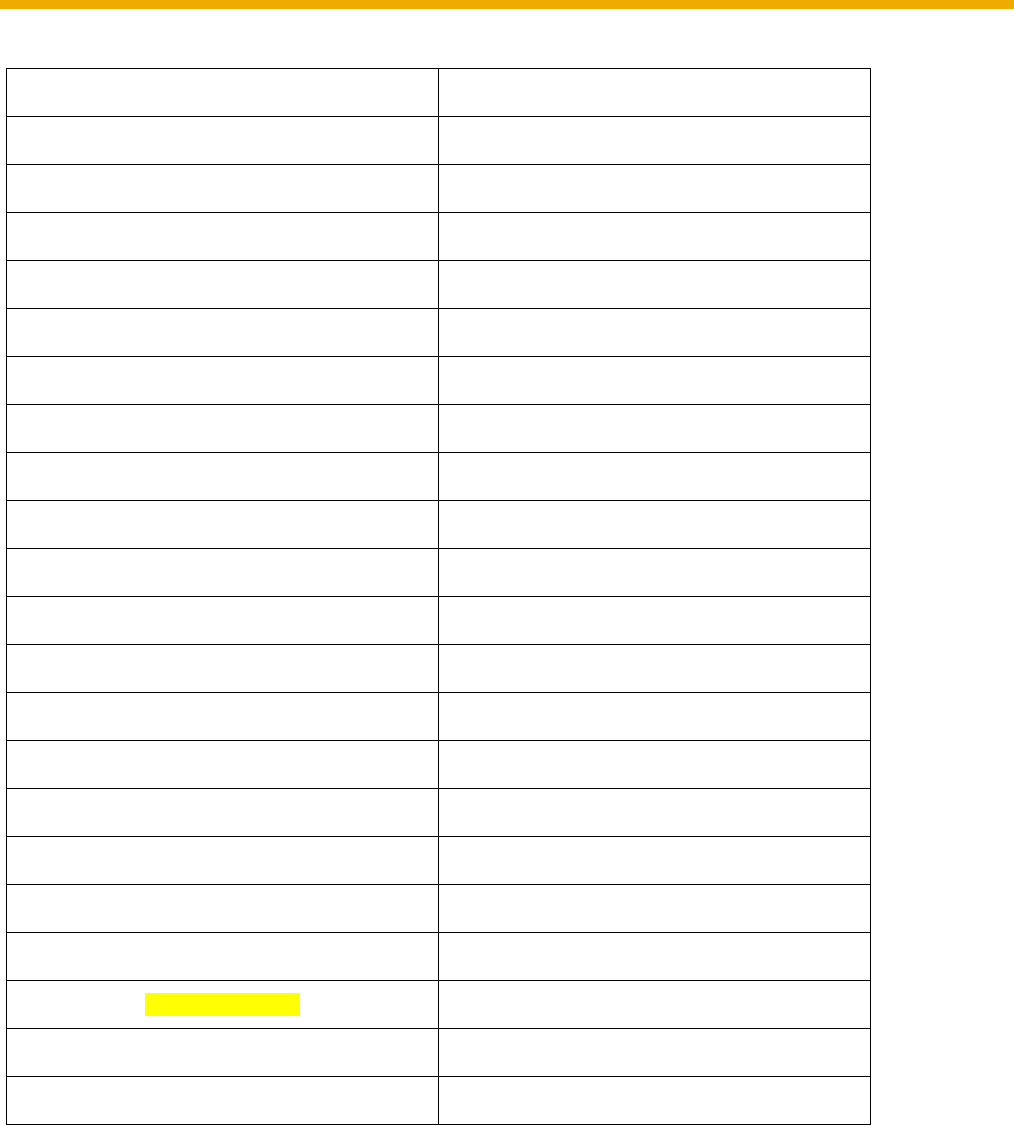
A.5 Wireless 3 Status (105)
Message type Wireless3 status
Message number 13032
Time/date received 03-15-2010 16:55:06
Time/date created 03-15-2010 16:54:22
Unit Mac: 00:13:a2:00:40:3c:35:61
Customer SunPower, Inc.
Site Exelon Network 3
Tx: bad state 0
Tx: packet timeout 0
Tx: route discovery 0
Tx: address discovery 0
Tx: CCA fail 0
Tx: invalid destination 0
Tx: ACK fail 0
Tx: unjoined 0
Tx: self addressed 0
Tx: address not found 0
Tx: route not found 0
Tx: unknown err 0
Tx: unknown err 0
Network resets 0
Network hardware resets 0
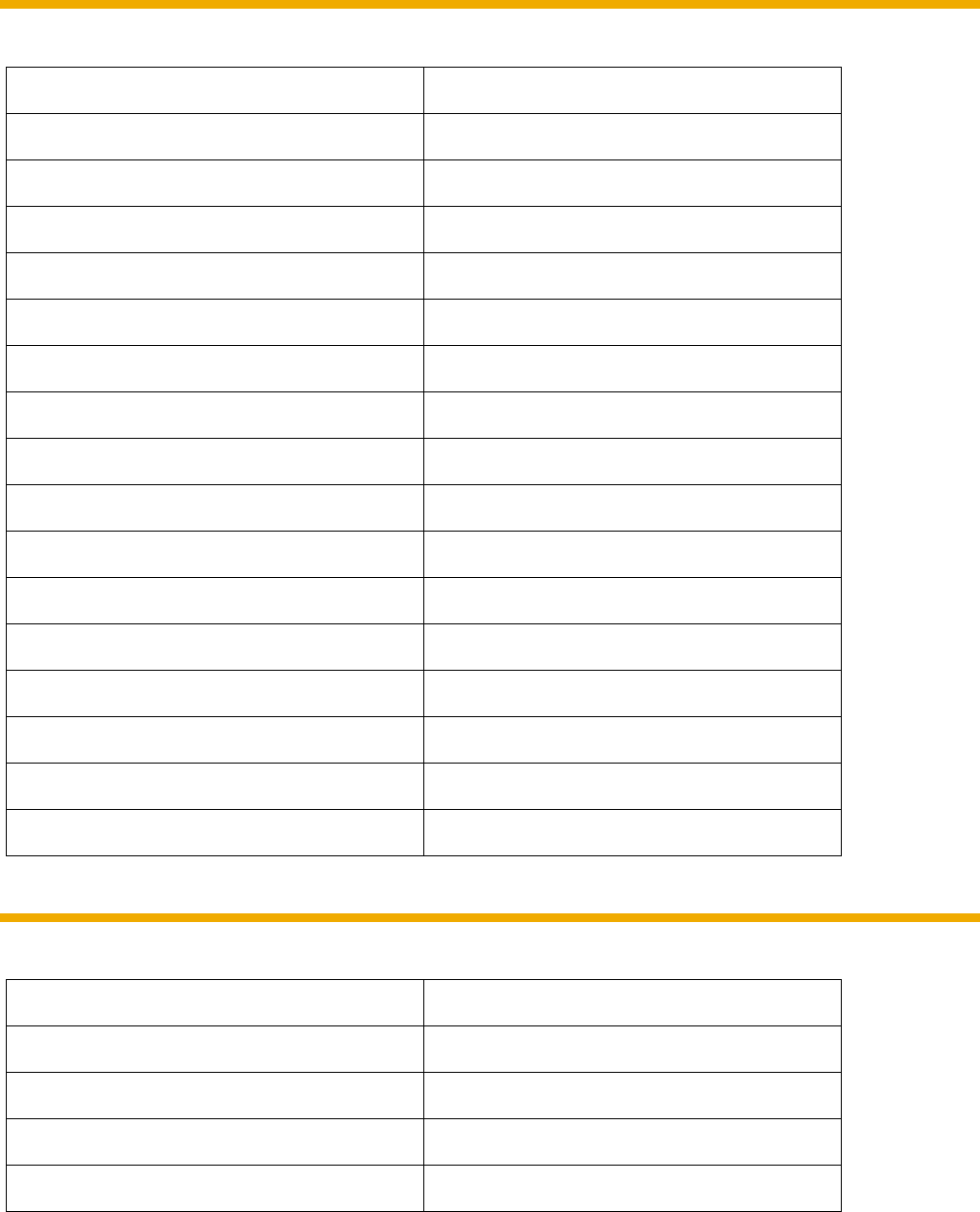
A.6 Operating System Status (106)
Message type Operating system status
Message number 13027
Time/date received 03-15-2010 16:55:02
Time/date created 03-15-2010 16:54:22
Unit Mac: 00:13:a2:00:40:3c:35:61
Customer SunPower, Inc.
Site Exelon Network 3
Ethernet MAC 00:03:f4:03:f6:41
Minimum watchdog (ticks) 37366
Minimum watchdog (seconds) 4.61
Thread Watchdog Max (seconds) 0
Firmware version 3.2.6
PCA Serial Number JS09371508789310000
Sun position valid true
Sun azimuth (earth) −66.59 (sun position is West of South)
Sun elevation (earth) 21.44 (sun is above horizon)
Enclosure temperature (deg. C) 21.94
A.7 GPS Status (107)
Message type GPS status
Message number 13033
Time/date received 03-15-2010 16:55:07
Time/date created 03-15-2010 16:54:22
Unit Mac: 00:13:a2:00:40:3c:35:61
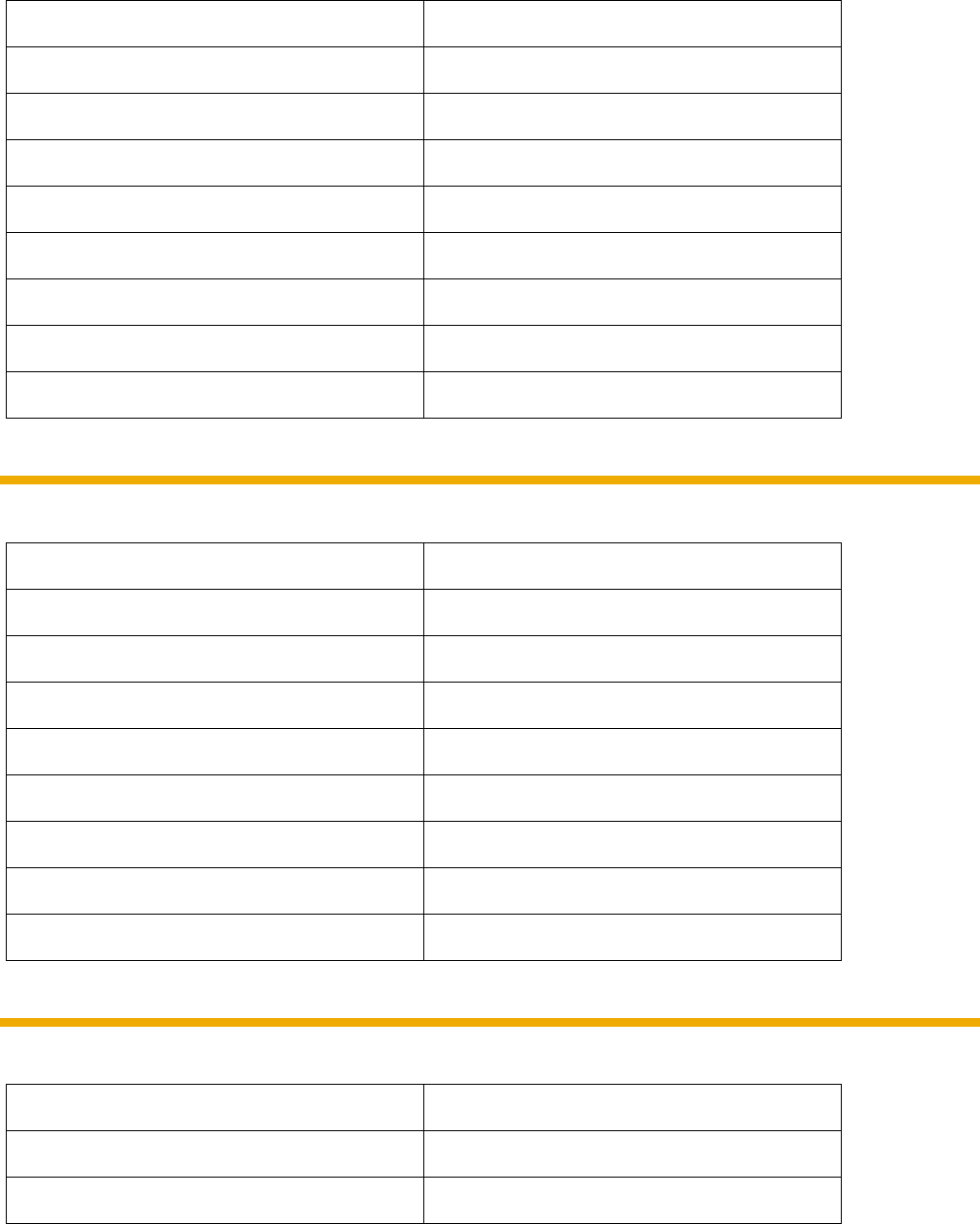
Customer SunPower, Inc.
Site Exelon Network 3
Errors 0
Total bytes 371934969
Latitude 41.68 N
Longitude −87.65 W
Receiver status A
GPS time 2010-03-15 21:54:21 UTC
UART status
A.8 A/D Status (108)
Message type A/D status
Message number 13034
Time/date received 03-15-2010 16:55:07
Time/date created 03-15-2010 16:54:22
Unit Mac: 00:13:a2:00:40:3c:35:61
Customer SunPower, Inc.
Site Exelon Network 3
Point updates 580489830
Full updates 96748305
A.9 DIO Status (109)
Message type DIO status
Message number 13035
Time/date received 03-15-2010 16:55:08
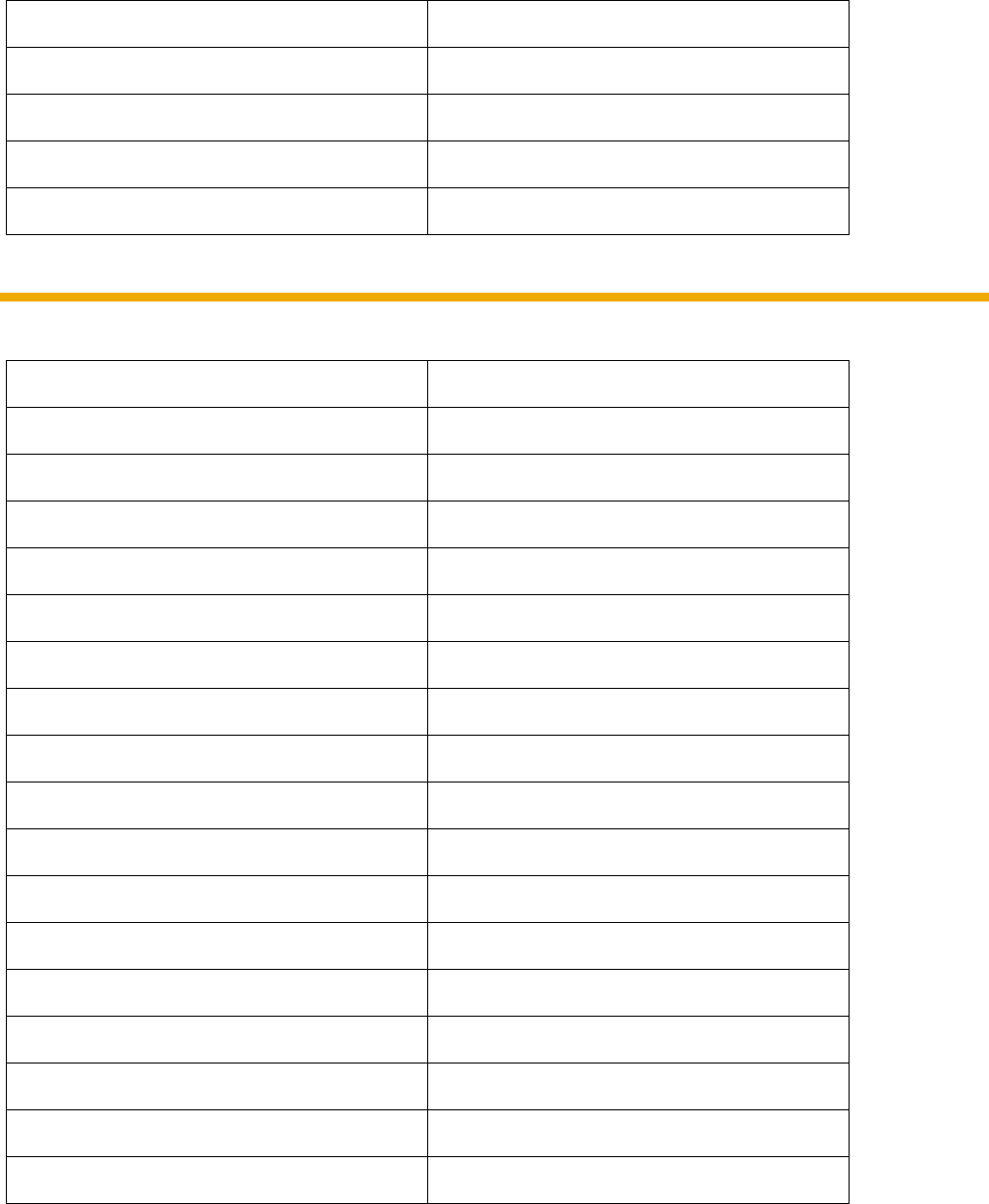
Time/date created 03-15-2010 16:54:22
Unit Mac: 00:13:a2:00:40:3c:35:61
Customer SunPower, Inc.
Site Exelon Network 3
Updates 404042
A.10 Motor Status (110)
Message type Motor status
Message number 13038
Time/date received 03-15-2010 16:55:11
Time/date created 03-15-2010 16:54:22
Unit Mac: 00:13:a2:00:40:3c:35:61
Customer SunPower, Inc.
Site Exelon Network 3
Number 0
Enabled YES
Controlled YES
Setpoint valid YES
Feedback valid YES
Actual position −29.55 degrees
Setpoint position −28.73 degrees
Position error 0.82 degrees
Output 0.0 percent
Forward limit (H/W) OK
Reverse limit (H/W) OK
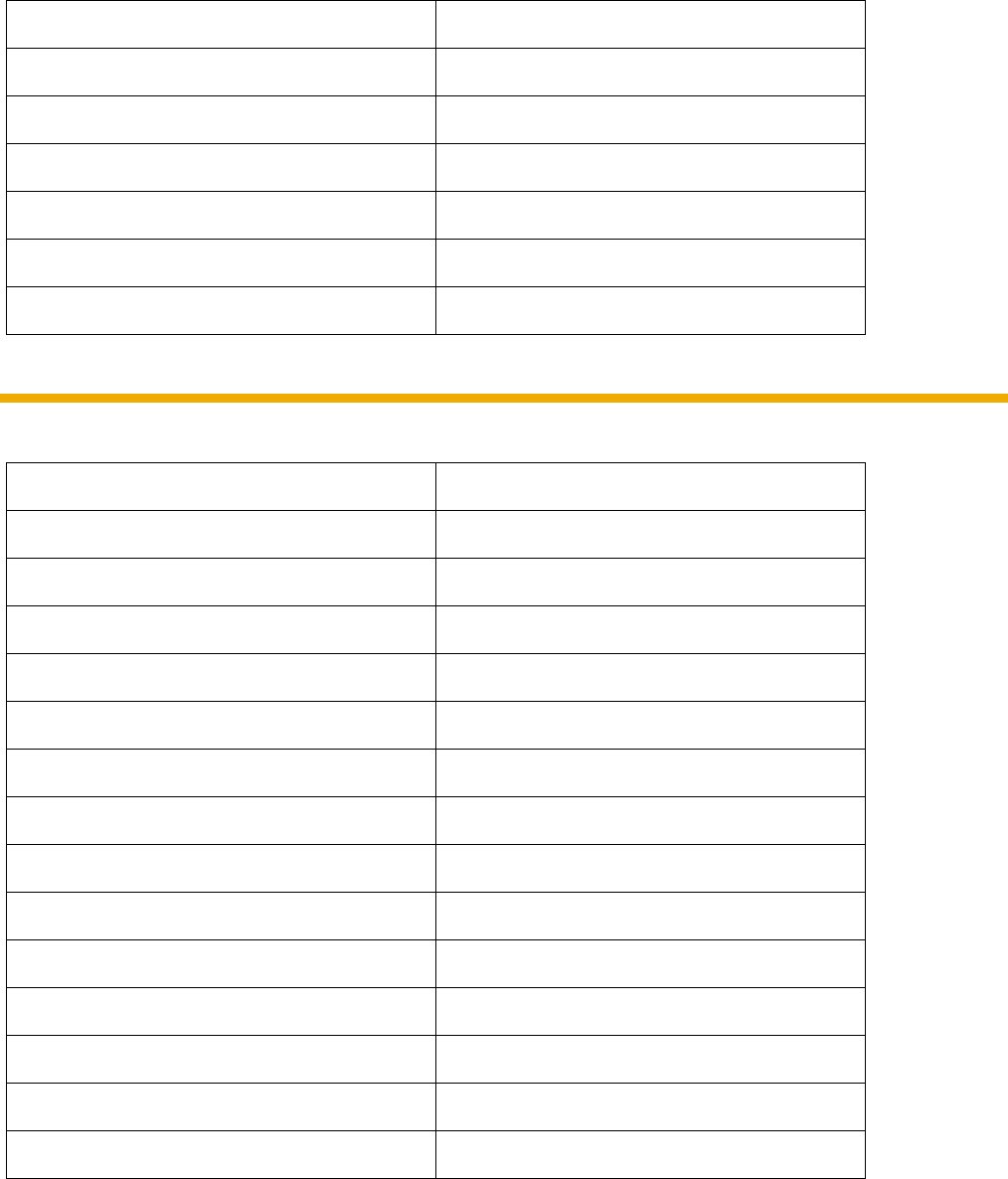
Forward limit (S/W) 45.0
Reverse limit (S/W) −45.0
Feedback errors 0
FWD seconds 676.19
REV seconds 0.0
FWD cycles 47
REV cycles 0
A.11 Settings 1 Status (114)
Message type Settings1 status
Message number 13028
Time/date received 03-15-2010 16:55:03
Time/date created 03-15-2010 16:54:22
Unit Mac: 00:13:a2:00:40:3c:35:61
Customer SunPower, Inc.
Site Exelon Network 3
Latitude 41.68
Longitude −87.65
Location source GPS (2)
Wind speed current (miles/hour) 0.0
Wind speed source Invalid (0)
Wind speed peak (over interval) 0.0
Wind speed avg (over interval) 0.0
Time source GPS (1)
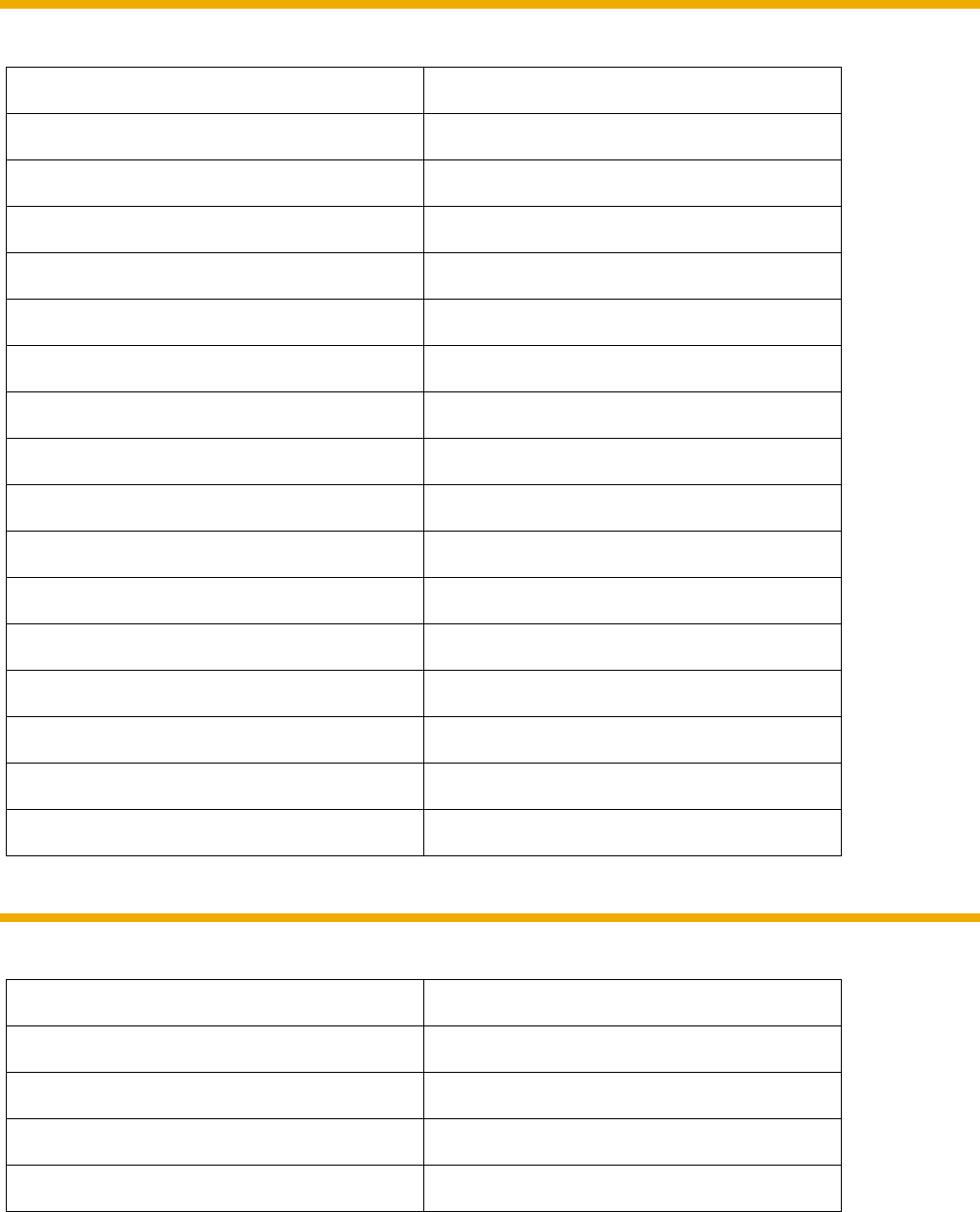
A.12 Settings 2 Status (115)
Message type Settings2 status
Message number 13036
Time/date received 03-15-2010 16:55:09
Time/date created 03-15-2010 16:54:22
Unit Mac: 00:13:a2:00:40:3c:35:61
Customer SunPower, Inc.
Site Exelon Network 3
Tracker type Single axis, roll (0)
Inclinometer type Analog (voltage) inclinometer (1)
Motor type AC motors (0)
East to west GCR 0.5
North to south GCR 0.35
Stow position 25.0
Motion deadband (in) 0.5
Motion deadband (out) 1.0
Controller mount East
Nominal degrees per minute
A.13 Server Status (116)
Message type Server status
Message number 13037
Time/date received 03-15-2010 16:55:10
Time/date created 03-15-2010 16:54:22
Unit Mac: 00:13:a2:00:40:3c:35:61
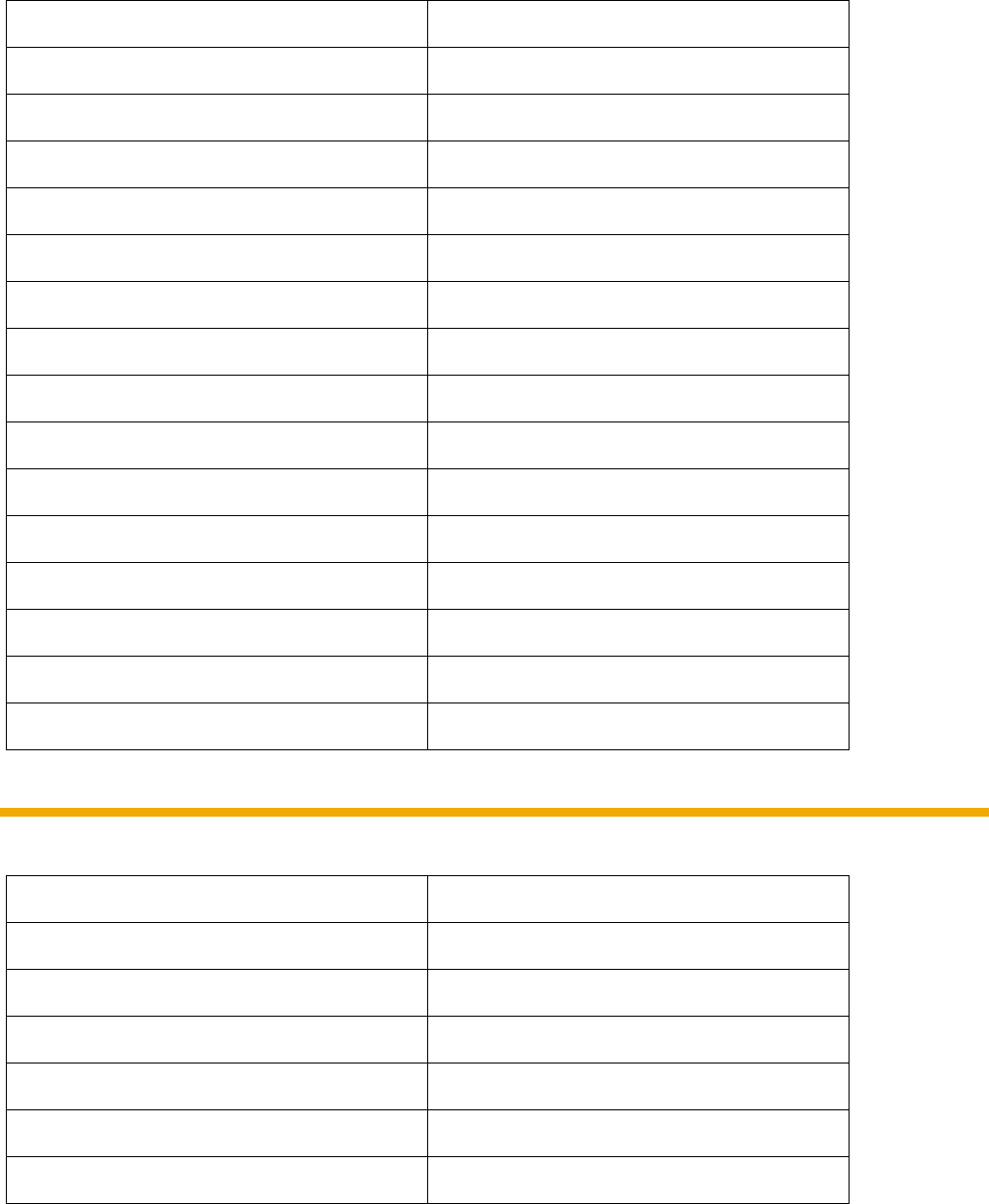
Customer SunPower, Inc.
Site Exelon Network 3
Attempts 14760
Successes 13642
Host transactions 26970
MS per host transaction 788.74
DNS OK 13949
Dns fail 811
Connect OK 26953
Connect fail 17
Bad command 0
Bad key 0
Bad status 290
Read fail 0
Write fail 17
Telnet Port 0
A.14 Tracker Status (117)
Message type Tracker status
Message number 13039
Time/date received 03-15-2010 16:55:12
Time/date created 03-15-2010 16:54:22
Unit Mac: 00:13:a2:00:40:3c:35:61
Customer SunPower, Inc.
Site Exelon Network 3
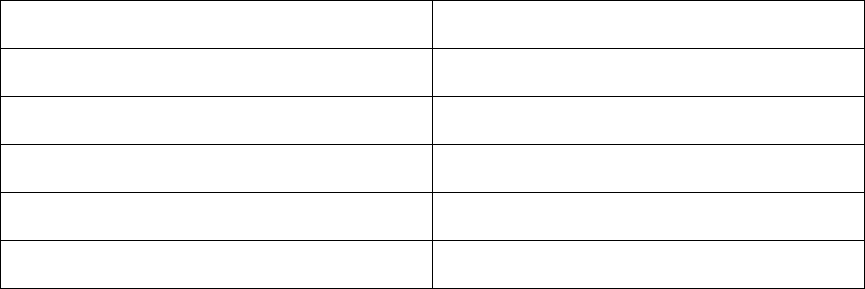
Number 1
Azimuth −66.59
Elevation 21.44
Site Roll 0.0
Site Pitch 0.0
Site Yaw 0.0