7400 Service Manual Tennant Rider Floor Scrubber
2018-06-13
: Sweepscrub Tennant-7400-Rider-Floor-Scrubber-Service-Manual tennant-7400-rider-floor-scrubber-service-manual 2760 file product_file
Open the PDF directly: View PDF .
Page Count: 322 [warning: Documents this large are best viewed by clicking the View PDF Link!]
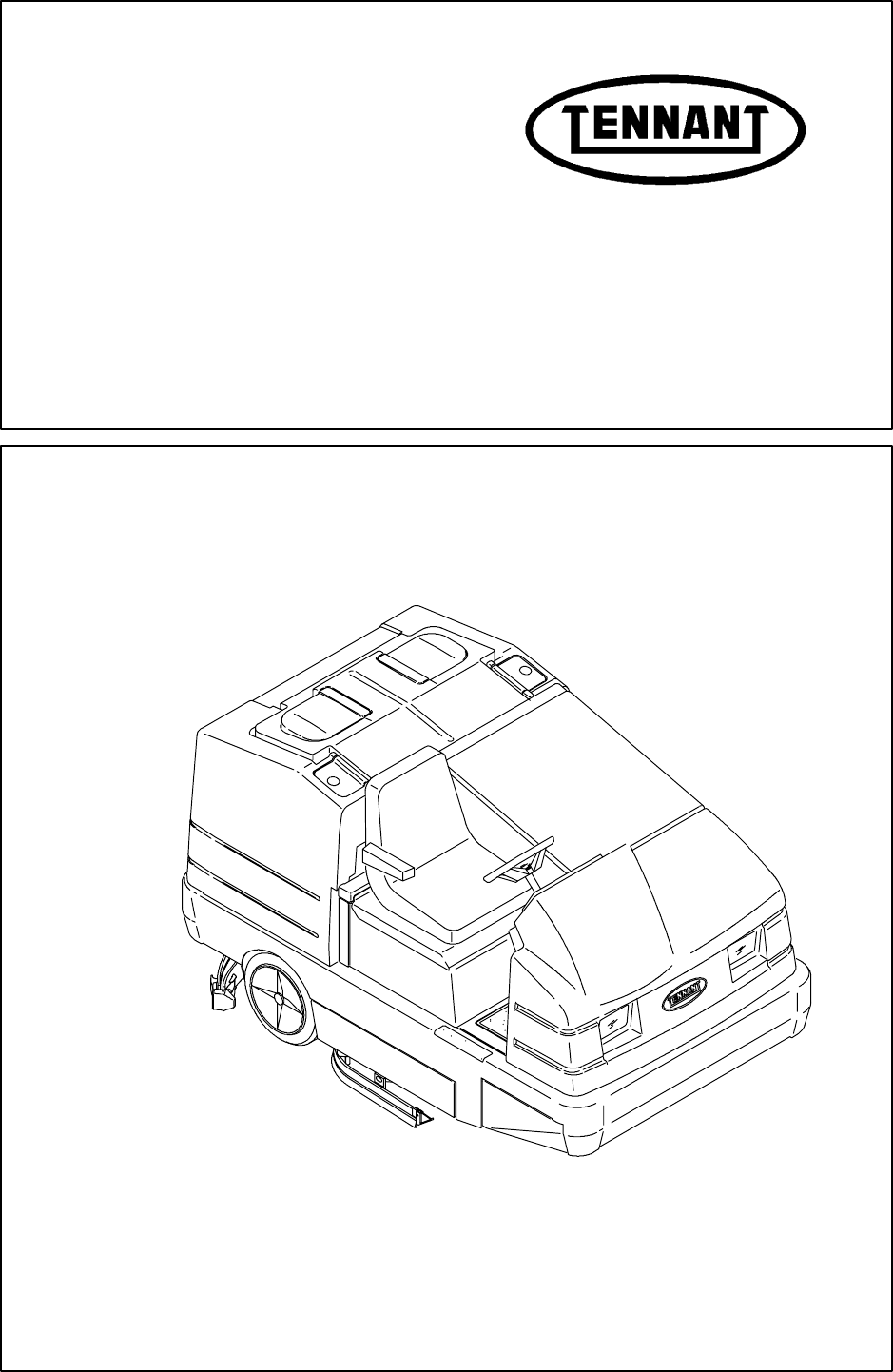
7400
Service Manual
MM428
Rev. 04 (3--02)
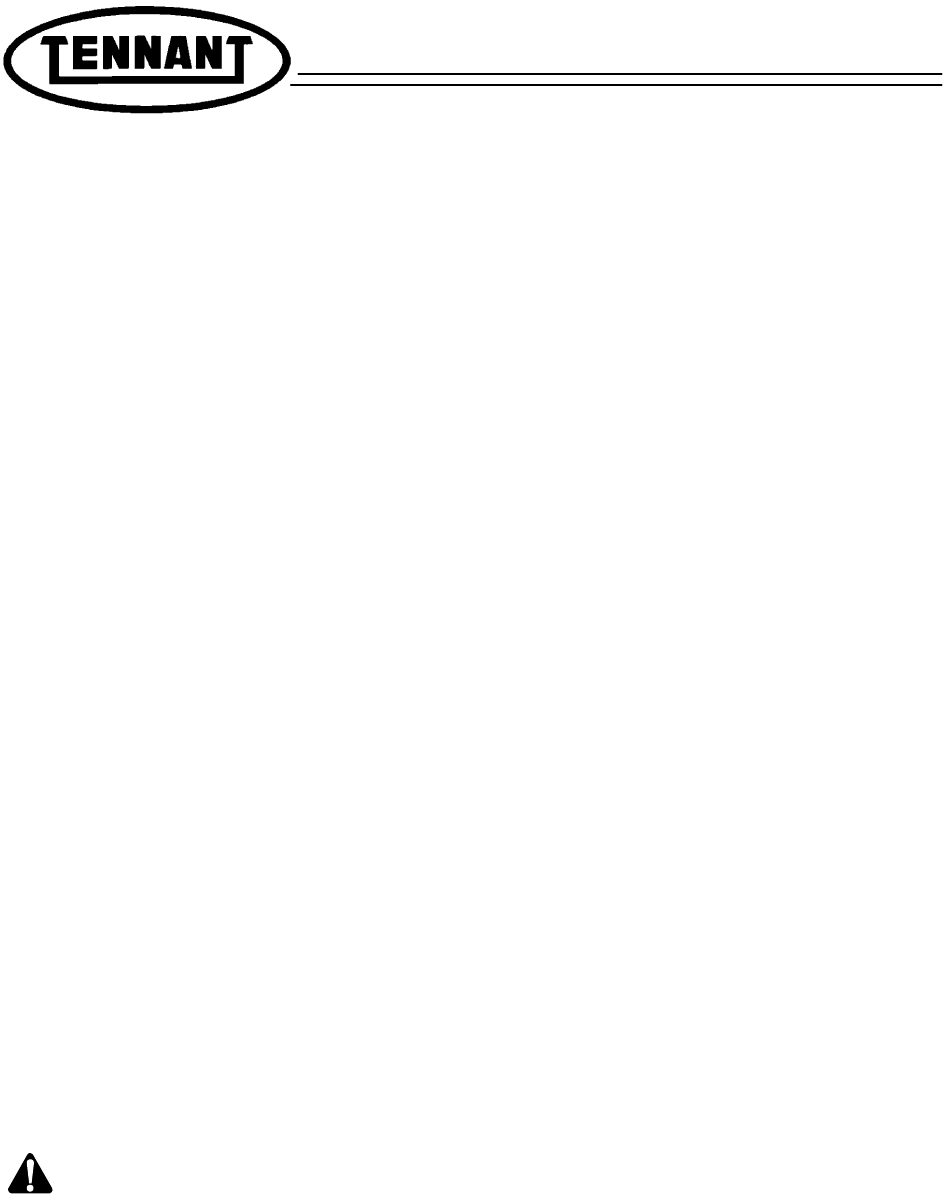
This service manual is intended to be an aid for the disassembly and reassembly of your TENNANT
Model 7400.
This manual is organized into seven major groups: General Information, Chassis, Scrubbing, Electrical,
Hydraulics, Engine--G/LPG and Engine--D.
General Information: Machine transport, machine jacking, machine storage, machine specifications, and
machine maintenance chart.
Chassis: Tire/wheel replacement, brake adjustment and replacement, chassis lubrication, steering
adjustment and replacement.
Scrubbing: Scrubber head repair/replacement, brush repair/replacement. squeegee repair/replacement,
and scrubber troubling shooting.
Electrical: Battery maintenance and replacement, instrument panel replacement, and electrical
troubleshooting.
Hydraulics: Valve replacement/repair, motor replacement/repair, cylinder replacement/repair, pump
replacement/repair, filter replacement, and hydraulics troubleshooting.
Engine -- G/LPG: Air filter replacement, oil changing, cooling system maintenance/repair, fuel system
maintenance/repair, governor adjustment/repair, engine repair, engine troubleshooting, and engine
repairs.
Engine -- D: Air filter replacement, oil changing, cooling system maintenance/repair, fuel system
maintenance/repair, governor adjustment/repair, engine repair, engine troubleshooting, and engine
repairs.
Manual Number -- MM428
Revision: 04
Published: 3--02
CALIFORNIA PROPOSITION 65 WARNING:
Engine exhaust from this product contains chemicals known to the State of
California to cause cancer, birth defects, or other reproductive harm.
Copyright E1996, 1998, 2001, 2002 TENNANT, Printed in U.S.A.

GENERAL INFORMATION
1-1
7400 MM428 (6--01)
CONTENTS
Page
SAFETY PRECAUTIONS 1--3..............
SPECIFICATIONS 1--6....................
GENERAL MACHINE
DIMENSIONS/CAPACITIES 1--6......
GENERAL MACHINE PERFORMANCE1--6
POWER TYPE 1--7.....................
STEERING 1--7........................
HYDRAULIC SYSTEM 1--8..............
BRAKING SYSTEM 1--8................
TIRES 1--8.......................
MACHINE DIMENSIONS 1--9...............
MAINTENANCE 1--10.....................
MAINTENANCE CHART / G/LP 1--10.....
MAINTENANCE CHART / DIESEL 1--12..
PUSHING, TOWING, AND
TRANSPORTING THE MACHINE 1--14...
PUSHING OR TOWING
THE MACHINE 1--14.................
TRANSPORTING THE MACHINE 1--15...
MACHINE JACKING 1--17...............
STORING MACHINE 1--18..............
HARDWARE INFORMATION 1--19..........
STANDARD BOLT TORQUE CHART 1--19
METRIC BOLT TORQUE CHART 1--19...
BOLT IDENTIFICATION 1--19............
THREAD SEALANT AND LOCKING
COMPOUNDS 1--19.................
HYDRAULIC FITTING INFORMATION1--20
HYDRAULIC TAPERED PIPE FITTING (NPT)
TORQUE CHART 1--20..............
HYDRAULIC TAPERED SEAT FITTING (JIC)
TORQUE CHART 1--20..............
HYDRAULIC O--RING FITTING TORQUE
CHART 1--20......................

GENERAL INFORMATION
1-2 7400 MM428 (6--01)

GENERAL INFORMATION
1-3
7400 MM428 (6--01)
SAFETY PRECAUTIONS
The following precautions are used throughout
this manual as indicated in their description:
WARNING: To warn of hazards or
unsafe practices which could result in
severe personal injury or death.
FOR SAFETY: To identify actions which
must be followed for safe operation of
equipment.
The machine is suited to sweep disposable
debris. Do not use the machine other than
described in this Operator Manual. The machine
is not designed for use on public roads.
The following information signals potentially
dangerous conditions to the operator or
equipment:
FOR SAFETY:
1. Do not operate machine:
-- Unless trained and authorized.
-- Unless operator manual is read and
understood.
-- If it is not in proper operating
condition.
-- In flammable or explosive areas unless
designed for use in those areas.
-- In areas with possible falling objects
unless equipped with overhead guard.
2. Before starting machine:
-- Check for fuel, oil, and liquid leaks.
-- Keep sparks and open flame away
from refueling area.
-- Make sure all safety devices are in
place and operate properly.
-- Check brakes and steering for proper
operation.
3. When starting machine:
-- Keep foot on brake and directional
pedal in neutral.
4. When using machine:
-- Use brakes to stop machine.
-- Go slow on inclines and slippery
surfaces.
-- Use care when reversing machine.
-- Do not carry passengers on machine.
-- Always follow safety and traffic rules.
-- Report machine damage or faulty
operation immediately.
5. Before leaving or servicing machine:
-- Stop on level surface.
-- Set parking brake.
-- Turn off machine and remove key.
6. When servicing machine:
-- Avoid moving parts. Do not wear loose
jackets, shirts, or sleeves.
-- Block machine tires before jacking
machine up.
-- Jack machine up at designated
locations only. Block machine up with
jack stands.
-- Use hoist or jack of adequate capacity
to lift machine.
-- Wear eye and ear protection when
using pressurized air or water.
-- Disconnect battery connections before
working on machine.
-- Avoid contact with battery acid.
-- Avoid contact with hot engine coolant.
-- Allow engine to cool.
-- Keep flames and sparks away from
fuel system service area. Keep area
well ventilated.
-- Use cardboard to locate leaking
hydraulic fluid under pressure.
-- Use Tennant supplied or approved
replacement parts.
WARNING: Engine emits toxic gases.
Severe respiratory damage or
asphyxiation can result. Provide
adequate ventilation. Consult with your
regulatory authorities for exposure
limits. Keep engine properly tuned.
WARNING: Flammable materials can
cause an explosion or fire. Do not use
flammable materials in tank(s).
WARNING: Flammable materials or
reactive metals can cause explosion or
fire. Do not pick up.
WARNING: Moving belt and fan. Keep
away.
WARNING: Strong Vacuum. Keep Away
From Fan Inlet When Fan Is Running.
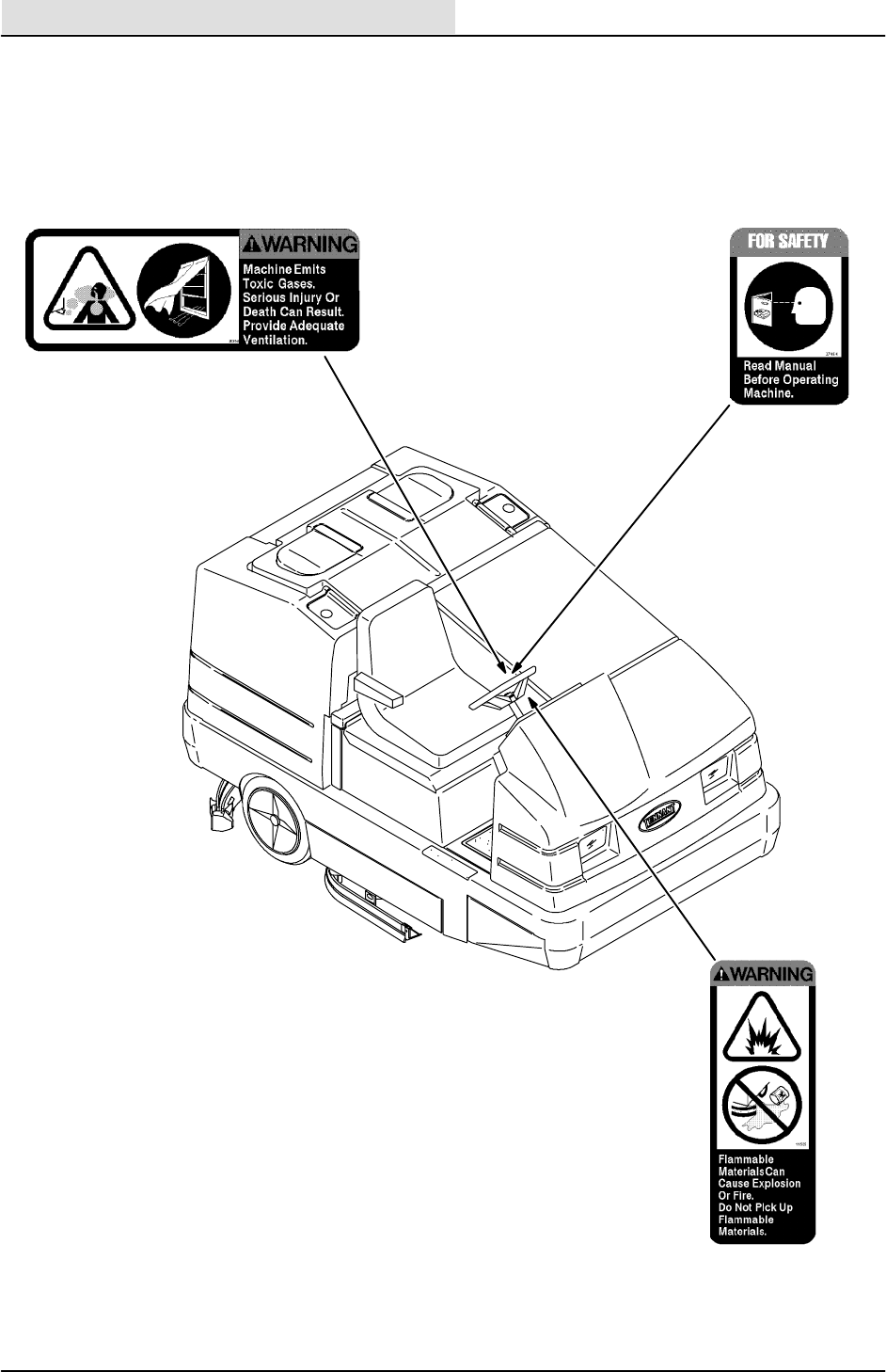
GENERAL INFORMATION
1-4 7400 MM428 (6--01)
The following safety labels are mounted on the
machine in the locations indicated. If these or any
labels become damaged or illegible, install a new
label in its place.
EMISSIONS LABEL -- LOCATED ON THE SIDE
OF THE OPERATOR COMPARTMENT.
10783
FOR SAFETY LABEL -- LOCATED ON THE
SIDE OF THE OPERATOR COMPARTMENT.
FLAMMABLE SPILLS LABEL -- LOCATED ON
THE SIDE OF THE OPERATOR
COMPARTMENT.

GENERAL INFORMATION
1-5
7400 MM428 (6--01)
FAN AND BELT LABEL -- LOCATED ON THE
ENGINE COMPARTMENT LINTEL.
10783
STRONG VACUUM LABEL -- LOCATED ON
THE VACUUM FAN HOUSING.
FLAMMABLE MATERIALS LABEL -- LOCATED
NEXT TO THE SOLUTION TANK COVERS AND
ON THE DETERGENT TANK.

GENERAL INFORMATION
1-6 7400 MM428 (6--01)
SPECIFICATIONS
GENERAL MACHINE DIMENSIONS/CAPACITIES
Item Dimension/capacity
Length 2460 mm (97 in)
Width 1525 mm (60 in)
Width with optional side brush 1590 mm (62.5 in)
Height 1475 mm (58 in)
Height with overhead guard 2045 mm (80.5 in)
Main scrub brush diameter 280 mm (11 in)
Main scrub brush length 1140 mm (45 in)
Side scrub brush diameter (option) 410 mm (16 in)
Squeegee width 1525 mm (60 in)
Scrubbing path width 1140 mm (45 in)
Scrubbing path width with optional side brush 1450 mm (57 in)
Debris tray volume capacity 42L(1.5 ft
3)
Solution tank 265 L (70 gal)
Recovery tank 272 L (72 gal)
Detergent tank (option) 25 L (6.7 gal)
Total capacity with ESt(option) 397 L (105 gal)
GVWR 2087 kg (4600 lb)
GENERAL MACHINE PERFORMANCE
Item Measure
Maximum forward speed 12.9 kmh (8 mph)
Maximum reverse speed 6.4 kmh (4 mph)
Minimum aisle turn width 3190 mm (125.5 in)
Minimum turning radius, right 2660 mm (104.75 in)
Minimum turning radius, left 2030 mm (79.75 in)
Maximum rated incline for scrubbing 6_
Maximum rated incline for transport of machine 8_

GENERAL INFORMATION
1-7
7400 MM428 (6--01)
POWER TYPE
Engine Type Ignition Cycle Aspiration Cylinders Bore Stroke
Kubota
V1505--B (E)
Piston Diesel 4Natural 478 mm
(3.07 in)
78.4 mm
(3.08 in)
Displacement Net power, governed Net power, maximum
1500 cc (91.4 cu in) 24.6 kw (34 hp) @ 2400 rpm 27.2 kw (37.5 hp) @
3000 rpm
Fuel Cooling system Electrical system
Diesel
Fuel tank: 42 L (11.2 gal)
Water/ethylene glycol
antifreeze
12 V nominal
Total: 7.5 L (2 gal) 37 A alternator
Radiator: 3.8 L (1 gal)
Idle speed, no load (Fast) governed speed, under
load
Engine lubricating oil
without filter
950 +50 rpm 2400 +50 rpm 6 L (6.35 qt)
SAE--CC/CD rated
engine oil
Engine Type Ignition Cycle Aspiration Cylinders Bore Stroke
Ford VSG 1.3 Piston Distributorless-
type spark
4Natural 474 mm
(2.91 in)
75 mm
(2.97 in)
Displacement Net power, governed Net power, maximum
1300 cc (79 cu in) 23.2 kw (32 hp) @ 2400 rpm 39.5 kw (53 hp) @
4000 rpm
Fuel Cooling system Electrical system
Gasoline, 87 octane
minimum, unleaded.
Fuel tank: 42 L (11.2 gal)
Water/ethylene glycol
antifreeze
12 V nominal
LPG,
F
l
t
k
1
5
k
(
3
3
l
b
)
Total: 7.5 L (2 gal) 50 A alternator
Fuel tank: 15 kg (33 lb) Radiator: 3.8 L (1 gal)
Idle speed, no load (Fast) governed speed, under
load
Firing order
1350 + 250 rpm 2400 + 50 rpm 1--2--4--3,
counterclockwise
rotation
Spark plug gap Valve clearance, cold Engine lubricating oil
with filter
1 mm (0.04 in) 0.20 mm (0.008 in) intake
0.50 mm (0.002 in) exhaust
3.3 L (3.5 qt) 10W30
SAE--SG/SH

GENERAL INFORMATION
1-8 7400 MM428 (6--01)
STEERING
Type Power source Emergency steering
Front wheel, hydraulic cylinder
and rotary valve controlled
Hydraulic accessory pump Manual
HYDRAULIC SYSTEM
System Capacity Fluid Type
Hydraulic reservoir 38 L (10 gal) TENNANT part no. 65869 -- above 7_C(45_F)
Hydraulic total 74 L (19.5 gal) TENNANT part no. 65870 -- below 7_C(45_F)
BRAKING SYSTEM
Type Operation
Service brakes Mechanical drum brakes (2), one per rear wheel,
cable actuated
Parking brake Utilize service brakes, cable actuated
TIRES
Location Type Size Pressure
Front (1) Solid 460 x 130 mm (5 x 18 in) --
Rear (2) Solid 460 x 130 mm (5 x 18 in) --

GENERAL INFORMATION
1-9
7400 MM428 (6--01)
1327 mm
(52.25 in)
2460 mm
(97 in)
2045 mm
(80.5 in)
1475 mm
(58 in)
1525 mm
(60 in)
1260 mm
(49.6 in)
1610 mm
(63.4 in)
1483 mm
(58.4 in)
1686 mm
(66.4 in)
10919
MACHINE DIMENSIONS

GENERAL INFORMATION
1-10 7400 MM428 (6--01)
MAINTENANCE
1
2
3
4
5
6
7
8
10
11 12
9
5
13
13
13
13
MAINTENANCE CHART / G/LP
Interval Key Description Procedure
Lubricant/
Fluid
No. of
Service
Points
Daily 4Engine air filter Check indicator -- 1
y
g
Empty dust cap -- 1
4Engine crankcase Check oil level EO 1
8Rear Squeegee Check for damage and wear -- 1
q
g
Check deflection -- 1
11 Side Squeegees Check for damage and wear -- 2
10 Scrub brushes Check for damage and wear -- 1
7Recovery tank Clean -- 1
7Recovery tank, EStmode Clean EStfilter -- 1
5Solution tank, EStmode Clean -- 1
50 Hours 10 Scrub brushes Rotate end-for-end or front-to-
rear
-- 1
100 Hours 6Radiator Clean core exterior -- 1
Check coolant level WG 1
4Engine crankcase Change oil and filter element EO 1
13 Cover seals Check for damage and wear -- 4
4Engine Check fan belt tension -- 1
g
Check and adjust idle speed -- 1
Check and adjust idle mixture -- 1
3Hydraulic fluid reservoir Check fluid level HYDO 1
-- Tires Check for damage -- 3
8Rear squeegee Check leveling -- 1
8Rear squeegee casters Lubricate SPL 2

GENERAL INFORMATION
1-11
7400 MM428 (6--01)
Interval Key Description Procedure
Lubricant/
Fluid
No. of
Service
Points
100 Hours 10 Scrub brush idlers Lubricate SPL 2
10 Scrub head skirts Check for damage and wear -- 2
-- Side brush skirt Check for damage and wear -- 1
200 Hours 6Radiator hoses and clamps Check for tightness and wear -- 2
4Engine fan belt Check tension -- 1
2 Parking brake Check adjustment -- 1
2Brake pedal Check and adjust travel -- 1
1Front wheel
support bearings
Lubricate SPL 2
400 Hours 9Rear wheel bearings Check, lubricate, and adjust SPL 2
4Engine Clean or replace and adjust -- 4
g
p
j
spark plugs
HCheck and adjust valve -- 8
j
clearance
Check and adjust idle speed -- 1
Check and adjust carburetor -- 1
j
idle mixture
Replace PCV valve. Clean PCV -- 1
p
hoses, tubes, and fittings
Fuel filter, gasoline -- 1
800 Hours 3Hydraulic reservoir Replace filler cap -- 1
y
Replace suction strainer -- 1
Change hydraulic fluid HYDO 1
4Hydraulic fluid filter Change filter element -- 1
-- Hydraulic hoses Check for wear and damage -- All
6 Cooling system Flush WG 1
1Propelling motor HTorque shaft nut -- 1
1Front wheel HTorque wheel nuts -- 1
12 Battery HClean and tighten battery cable -- 1
y
g
y
connections
NOTE: Also check procedures indicted (H) after
the first 50-hours of operation.
NOTE: More frequent intervals may be required
in extremely dusty conditions.
LUBRICANT/FLUID
EO Engine oil, SAE--SG/SH rated....
HYDO Tennant or approved hydraulic fluid.
WG Water and permanent-type ethylene glycol anti-freeze, --34_C(--30_F)...
SPL Special lubricant, Lubriplate EMB grease (TENNANT part no. 01433--1)...
DW Distilled water....
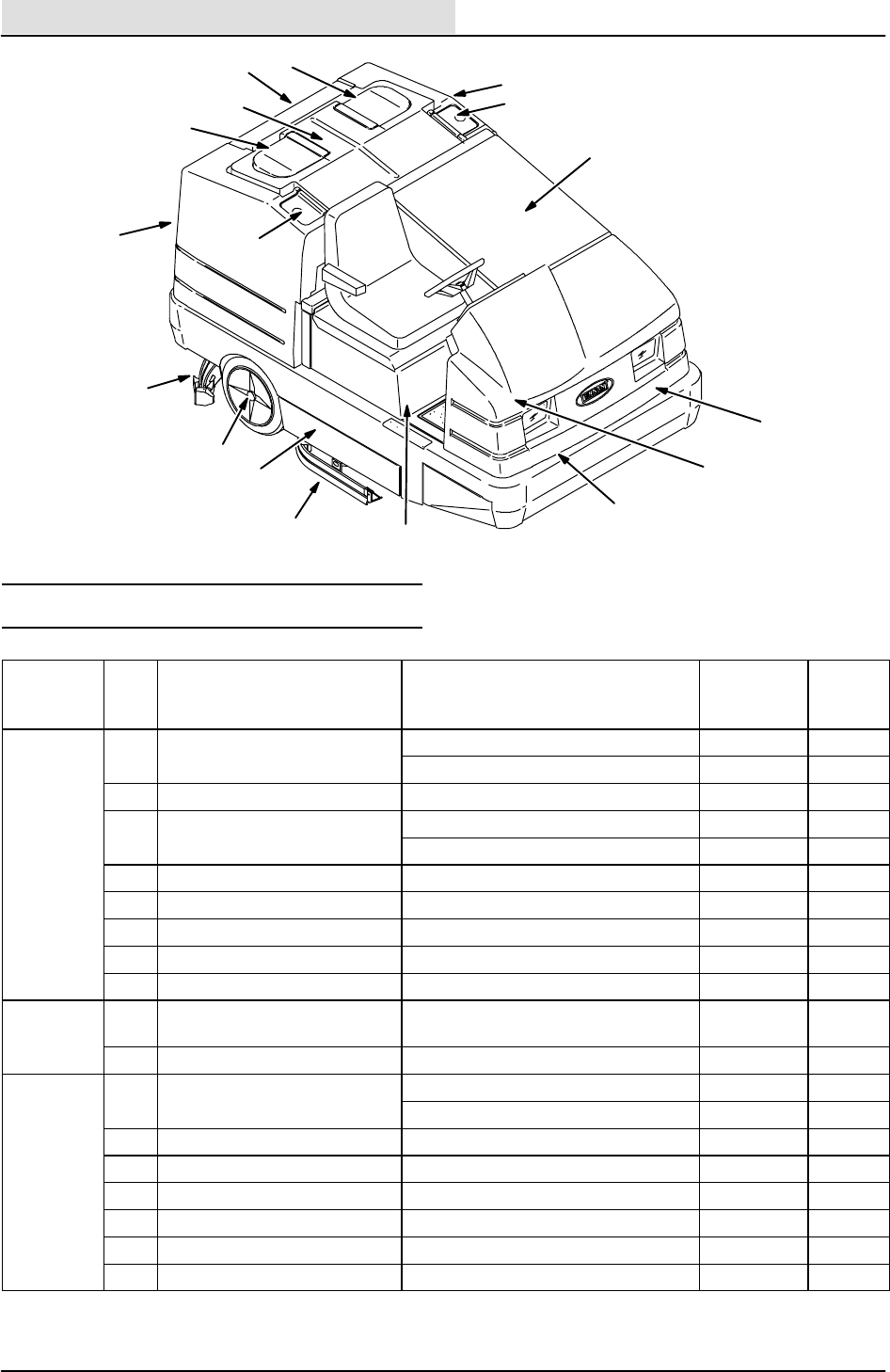
GENERAL INFORMATION
1-12 7400 MM428 (6--01)
1
2
3
4
5
6
7
8
10
11 12
9
5
13
1
3
13
13
09076
MAINTENANCE CHART / DIESEL
Interval Key Description Procedure
Lubricant/
Fluid
No. of
Service
Points
Daily 4Engine air filter Check indicator -- 1
y
g
Empty dust cap -- 1
4Engine crankcase Check oil level EO 1
8Rear Squeegee Check for damage and wear -- 1
q
g
Check deflection -- 1
11 Side Squeegees Check for damage and wear -- 2
10 Scrub brushes Check for damage and wear -- 1
7Recovery tank Clean -- 1
7Recovery tank, EStmode Clean EStfilter -- 1
5Solution tank, EStmode Clean -- 1
50 Hours 10 Scrub brushes Rotate end-for-end or front-to-
rear
-- 1
4Fuel pipes and clamps Check for tightness and wear -- 1
100 Hours 6Radiator Clean core exterior -- 1
Check coolant level WG 1
4Engine crankcase Change oil and filter EO 1
4Engine fan belt Check tension -- 1
3Hydraulic fluid reservoir Check fluid level HYDO 1
-- Tires Check for damage -- 3
8Rear squeegee Check leveling -- 1
8Rear squeegee casters Lubricate SPL 2

GENERAL INFORMATION
1-13
7400 MM428 (6--01)
Interval Key Description Procedure
Lubricant/
Fluid
No. of
Service
Points
100 Hours 13 Cover seals Check for damage and wear -- 4
10 Scrub brush idlers Lubricate SPL 2
10 Scrub head skirts Check for damage and wear -- 2
-- Side brush skirt Check for damage and wear -- 1
200 Hours 6Radiator hoses and clamps Check for tightness and wear -- 2
2 Parking brake Check adjustment -- 1
2Brake pedal Check and adjust travel -- 1
1Front wheel Lubricate SPL 2
support bearings
400 Hours 9Rear wheel bearings Check, lubricate, and adjust SPL 2
4Fuel filter Replace cartridge -- 1
6 Cooling system Flush WG 1
800 Hours 3Hydraulic reservoir Replace filler cap -- 1
y
Replace suction strainer -- 1
Change hydraulic fluid HYDO 1
4Hydraulic fluid filter Change filter element -- 1
-- Hydraulic hoses Check for wear and damage -- All
1Propelling motor HTorque shaft nut -- 1
1Front wheel HTorque wheel nuts -- 1
12 Battery HClean and tighten battery cable -- 1
y
g
y
connections
NOTE: Also check procedures indicted (H) after
the first 50-hours of operation.
NOTE: More frequent intervals may be required
in extremely dusty conditions.
LUBRICANT/FLUID
EO Engine oil, SAE--CC/CD rated....
HYDO Tennant Company or approved hydraulic fluid.
WG Water and permanent-type ethylene glycol anti-freeze, --34_C(--30_F)...
SPL Special lubricant, Lubriplate EMB grease (TENNANT part no. 01433--1)...
DW Distilled water....

GENERAL INFORMATION
1-14 7400 MM428 (6--01)
PUSHING, TOWING, AND TRANSPORTING
THE MACHINE
PUSHING OR TOWING THE MACHINE
If the machine becomes disabled, it can be
pushed from the front or rear, but towed only from
the rear.
The propelling pump has a bypass valve to
prevent damage to the hydraulic system when the
machine is being pushed or towed. This valve
allows a disabled machine to be moved for a very
short distance and at a speed to not exceed 1.6
kp/h (1 mph). The machine is NOT intended to be
pushed or towed a long distance or at a high
speed.
ATTENTION! Do not push or tow
machine for a long distance and without
using the bypass valve, or the machine
hydraulic system may be damaged.
Turn the bypass valve 90_from the normal
position before pushing or towing the machine.
The illustration shows the bypass valve in the
pushing or towing position.

GENERAL INFORMATION
1-15
7400 MM428 (6--01)
TRANSPORTING THE MACHINE
1. Position the rear of the machine at the
loading edge of the truck or trailer.
2. If the loading surface is not horizontal or is
higher than 380 mm (15 in) from the ground,
use a winch to load machine.
If the loading surface is horizontal AND is
380 mm (15 in) or less from the ground, the
machine may be driven onto the truck or
trailer.
3. To winch the machine onto the truck or
trailer, attach the winching chains in the
holes at the bottom of the rear bumper.
If the machine has the optional rear tie down
brackets, attach the winching chains to
them.
4. Turn the bypass valve 90_from the normal
position before winching the machine onto
the truck or trailer. See PUSHING OR
TOWING THE MACHINE section of this
manual. Make sure the machine is centered.
FOR SAFETY: When loading machine
onto truck or trailer, use winch. Do not
drive the machine onto the truck or
trailer unless the loading surface is
horizontal AND is 380 mm (15 in) or less
from the ground.

GENERAL INFORMATION
1-16 7400 MM428 (6--01)
5. Position the machine onto the truck or trailer
as far as possible. If the machine starts to
veer off the centerline of the truck or trailer,
stop and turn the steering wheel to center
the machine.
6. Set the parking brake and block the machine
tires. Tie down the machine to the truck or
trailer before transporting.
The front tie down locations are in the holes
at the bottom of the front bumper. If the
machine has the optional tie down brackets,
use them to tie down the machine.
The rear tie down locations are in the holes
at the bottom of the rear bumper. If the
machine has the optional rear tie down
brackets, use them to tie down the machine.
7. If the loading surface is not horizontal or is
higher than 380 mm (15 in) from the ground,
use a winch to unload machine.
If the loading surface is horizontal AND is
380 mm (15 in) or less from the ground, the
machine may be driven off the truck or
trailer.
FOR SAFETY: When unloading machine
off truck or trailer, use winch. Do not
drive the machine off the truck or trailer
unless the loading surface is horizontal
AND 380 mm (15 in) or less from the
ground.

GENERAL INFORMATION
1-17
7400 MM428 (6--01)
MACHINE JACKING
Empty the recovery and the solution tanks before
jacking the machine.You can jack up the machine
for service at the designated locations. Use a
hoist or jack that will support the weight of the
machine. Always stop the machine on a flat, level
surface and block the tires before jacking the
machine up.
FOR SAFETY: Before leaving or
servicing machine; stop on level
surface, set parking brake, turn off
machine and remove key.
The front jacking location is the left front corner of
the machine frame.
The rear jacking locations are the two rear
corners of the machine frame.
FOR SAFETY: When servicing machine,
block machine tires before jacking
machine up.
FOR SAFETY: When servicing machine,
jack machine up at designated locations
only. Block machine up with jack
stands.

GENERAL INFORMATION
1-18 7400 MM428 (6--01)
STORING MACHINE
When storing the machine for extended periods of
time, the following procedures must be followed to
lessen the chance of rust sludge, or other
undesirable deposits from forming.
1. Drain and clean the solution and recovery
tanks.
2. EStmachines: Run clean water through
the solution system and the EStsolution
pump.
3. Raise the rear squeegee and the scrub
head.
4. Park the machine in a cool, dry area.
5. Remove or charge the battery every three
months.

GENERAL INFORMATION
1-19
7400 MM428 (6--01)
HARDWARE INFORMATION
The following charts state standard plated
hardware tightening ranges for normal assembly
applications. Decrease the specified torque by
20% when using a thread lubricant. Do not
substitute lower grade hardware for higher grade
hardware. If higher grade hardware than specified
is substituted, tighten only to the specified
hardware torque value to avoid damaging the
threads of the part being threaded into, as when
threading into speed nuts or weldments.
STANDARD BOLT TORQUE CHART
Thread
Size
SAE Grade 5
Torque ft lb
(Nm)
SAE Grade 8
Torque ft lb
(Nm)
0.25 in 7--10 (9--14) 10--13 (14--38)
0.31 in 15--20 (20--27) 20--26 (27--35)
0.38 in 27--35 (37--47) 36--47 (49--64)
0.44 in 43--56 (58--76) 53--76 (72--103)
0.50 in 65--85 (88--115) 89--116
(121--157)
0.62 in 130--170
(176--231)
117--265
(159--359)
0.75 in 215--280
(291--380)
313--407
(424--552)
1.00 in 500--650
(678--881)
757--984
(1026--1334)
NOTE: Decrease torque by 20% when using a
thread lubricant.
METRIC BOLT TORQUE CHART
Thread
Size
Class 8.8
Torque ft lb
_Nm)
Class 10.9
Torque ft lb
(Nm)
M4 2(3) 3(4)
M5 4(5) 6(8)
M6 7(9) 10 (14)
M8 18 (24) 25 (34)
M10 32 (43) 47 (64)
M12 58 (79) 83 (112)
M14 94 (127) 133 (180)
M16 144 (195) 196 (265)
M20 260 (352) 336 (455)
M24 470 (637) 664 (900)
NOTE: Decrease torque by 20% when using a
thread lubricant.
Exceptions to the above chart:
Check the machine for exceptions!
BOLT IDENTIFICATION
Identification
Grade Marking
Specification and
Grade
SAE--Grade 5
SAE--Grade 8
ISO--Grade 8.8
ISO--Grade 10.9
01395
THREAD SEALANT AND LOCKING
COMPOUNDS
Thread sealants and locking compounds may be
used on this machine. They include the following:
Locktite 515 sealant -- gasket forming
material. TENNANT Part No. 75567,15 oz
(440 ml) cartridge.
Locktite 242 blue -- medium strength thread
locking compound. TENNANT Part No.
32676, 0.5 ml tube.
Locktite 271 red -- high strength thread
locking compound. TENNANT Part No.
19857, 0.5 ml tube.

GENERAL INFORMATION
1-20 7400 MM428 (6--01)
HYDRAULIC FITTING INFORMATION
HYDRAULIC TAPERED PIPE FITTING (NPT)
TORQUE CHART
NOTE: Ratings listed are when using teflon
thread seal.
Size Minimum
Torque
Maximum
Torque
1/4 NPT 10 ft lb (14 Nm) 30 ft lb (41 Nm)
1/2 NPT 25 ft lb (34 Nm) 50 ft lb (68 Nm)
3/4 NPT 50 ft lb (68 Nm) 100 ft lb (136
Nm)
HYDRAULIC TAPERED SEAT FITTING (JIC)
TORQUE CHART
Tibe O.D.
(in)
Thread Size Maximum
Torque
0.25 0.44--20 9ftlb(12Nm)
0.38 0.56--18 20 ft lb (27 Nm)
0.50 0.75--16 30 ft lb (41 Nm)
0.62 0.88--14 40 ft lb (54 Nm)
0.75 1.12--12 70 ft lb (95 Nm)
1.0 1.31--12 90 ft lb (122 Nm)
HYDRAULIC O--RING FITTING TORQUE
CHART
Tube
O.D.
(in)
Thread
Size
Minimum
Torque
Maximum
Torque
0.25 0.44--20 6ftlb(8Nm) 9ftlb
(12 Nm)
0.38 0.56--18 13 ft lb
(18 Nm)
20 ft lb
(27 Nm)
*10 ft lb
(14 Nm)
12 ft lb
(16 Nm)
0.50 0.75--16 20 ft lb
(27 Nm)
30 ft lb
(41 Nm)
*21 ft lb
(28 Nm)
24 ft lb
(33 Nm)
0.62 0.88--14 25 ft lb
(34 Nm)
40 ft lb
(54 Nm)
0.75 1.12--12 45 ft lb
(61 Nm)
70 ft lb
(95 Nm)
1.0 1.31--12 60 ft lb
(81 Nm)
90 ft lb
(122 Nm)
NOTE: Do not use sealant on o--ring threads.
*Aluminum bodied components

CHASSIS
2-1
7400 MM428 (12--98)
CONTENTS
Page
CHASSIS 2-3............................
SEAT 2-3................................
TO REMOVE SEAT ASSEMBLY 2-3.....
TO REPLACE SEAT ASSEMBLY 2-3.....
OPERATOR SEAT 2-4.................
STATIC DRAG CHAIN 2-4.................
BRAKES AND TIRES 2-5..................
SERVICE BRAKES 2-5.................
TO REPLACE BRAKE SHOES 2-5.......
REAR TIRES AND WHEELS 2-7........
TO REPACK REAR WHEEL
BEARINGS 2-7.....................
FRONT TIRE AND WHEEL, AND
WHEEL SUPPORT 2-9.................
TO REPLACE FRONT DRIVE MOTOR 2-9
TO REPLACE FRONT WHEEL
HOUSING PIVOT BEARINGS 2-11...

CHASSIS
2-2 7400 MM428 (12--98)

CHASSIS
2-3
7400 MM428 (12--98)
INTRODUCTION
This section includes information on the main
chassis related components for example the seat,
steering, brakes, and tires.

CHASSIS
2-4 7400 MM428 (12--98)
SEAT
The seat assembly is adjustable forward and
backward on the 7400.
TO REMOVE SEAT ASSEMBLY
FOR SAFETY: Before Leaving Or
Servicing Machine; Stop On Level
Surface, Set Parking Brake, Turn Off
Machine And Remove Key.
1. Tilt the seat assembly forward and engage
theproprod.
2. Remove the four hex screws and nuts
holding the seat assembly hinge to the seat
support.
3. Slide the prop rod to the opening in the slot
and remove.
4. Remove the seat assembly from the
machine.
TO REPLACE SEAT ASSEMBLY
FOR SAFETY: Before Leaving Or
Servicing Machine; Stop On Level
Surface, Set Parking Brake, Turn Off
Machine And Remove Key.
1. Position the seat assembly on the seat
support.
2. Reinstall the four hex screws and nuts.
Tighten to 18 -- 24Nm (15 -- 20 ft lb).
3. Slide the seat prop rod through large hole in
slot.
4. Lower the seat.

CHASSIS
2-5
7400 MM428 (12--98)
OPERATOR SEAT
The operator seat is a fixed back style with a
forward-backward adjustment.
Adjust: Pull the lever out, slide the seat
backward or forward to the desired position and
release the lever.
Lift: Pull up on the seat mounting plate until the
seat mount locks up.
Lower: Pull on the release lever and lower the
seat mounting plate.
STATIC DRAG CHAIN
A static drag chain prevents the buildup of static
electricity in the machine. The chain is attached to
the machine with a hex screw by the scrub head
torque tube mount bearing.
Make sure the chain is touching the floor at all
times.

CHASSIS
2-6 7400 MM428 (12--98)
BRAKES AND TIRES
SERVICE BRAKES
The mechanical service brakes are located on the
rear wheels. The brakes are operated by the foot
brake pedal.
Check the brake adjustment every 200 hours of
operation.
TO REPLACE BRAKE SHOES
FOR SAFETY: Before Leaving Or
Servicing Machine; Stop On Level
Surface, Set Parking Brake, Turn Off
Machine And Remove Key.
1. Drain the solution and recovery tanks.
2. Make sure the parking brake is not engaged.
3. Remove floor plate from the operators
compartment.
4. Loosen the jam nuts on the brake cable turn
buckle. Rotate the turn buckle to loosen the
tension on the brake cable.
5. Jack up one rear corner of the machine.
Place jack stands under machine.
FOR SAFETY: Block machine tires
before jacking machine up. Jack
machine up at designated locations
only. Block machine up with jack
stands.
6. Remove the hub cap from the center of the
tire and wheel assembly.
7. Remove the cotter pin, slotted nut, flat
washer, and bearing cone.
8. Remove the tire and wheel assembly from
the machine.
9. Remove the two springs holding the brake
shoes together. Remove the old brake
shoes.
10. Position the new brake shoes on the brake
mounting plate.
11. Reattach the two brake springs to the new
brake shoes.
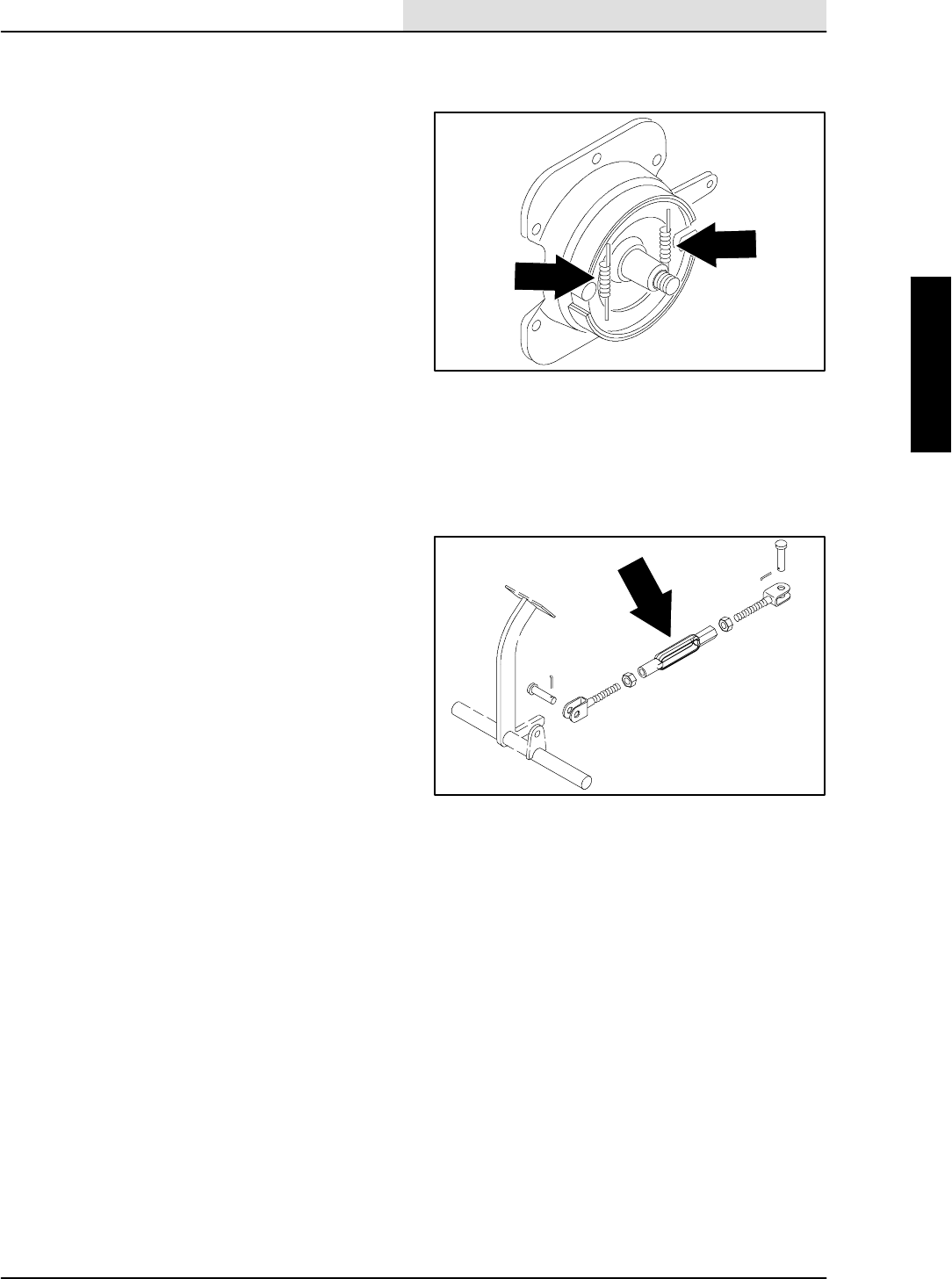
CHASSIS
2-7
7400 MM428 (12--98)
12. Pack the wheel bearings with Lubriplate
EMB grease.
13. Slide the tire and wheel assembly on the
axle.
14. Slide the outer bearing, flat washer and nut
on the shaft.
15. Tighten nut with hand wrench until wheel
binds, then back nut off to nearest hole.
16. Insert a new cotter pin through nut and hole.
17. Spin the tire and wheel assembly. The tire
should spin freely.
18. Reinstall the hub cap in the center of the
wheel.
19. Lower the machine.
NOTE: Always replace brake shoes in sets.
20. Repeat the procedure on the other wheel.
21. Rotate the brake cable turn buckle until the
brake cable is tight or until the brake pedal
travels 25--50 mm (1--2 in) before engaging
brakes.
22. Tighten the brake cable turn buckle jam
nuts.
23. Reinstall the floor plate in the operators
compartment.
24. Operate the machine and check the brakes
for proper operation.

CHASSIS
2-8 7400 MM428 (12--98)
REAR TIRES AND WHEELS
The standard machine rear tires are
semi--pneumatic.
Inspect the rear wheel bearings for seal damage,
and repack and adjust every 1600 hours of
operation. Use Lubriplate EMB grease
(TENNANT part no. 01433--1).
TO REPACK REAR WHEEL BEARINGS
FOR SAFETY: Before Leaving Or
Servicing Machine; Stop On Level
Surface, Set Parking Brake, Turn Off
Machine And Remove Key.
1. Drain the solution and recovery tanks.
2. Make sure the parking brake is not engaged.
3. Remove floor plate from the operators
compartment.
4. Loosen the jam nuts on the brake cable turn
buckle. Rotate the turn buckle to loosen the
tension on the brake cable.
5. Jack up one rear corner of the machine.
Place jack stands under machine.
FOR SAFETY: Block machine tires
before jacking machine up. Jack
machine up at designated locations
only. Block machine up with jack
stands.
6. Remove the hub cap from the center of the
tire and wheel assembly.
7. Remove the cotter pin, slotted nut, flat
washer, and bearing cone.
8. Remove the tire and wheel assembly from
the machine.
9. Pack the wheel bearings with Lubriplate
EMB grease.
10. Slide the tire and wheel assembly on the
axle.
11. Slide the outer bearing, flat washer and nut
on the shaft.

CHASSIS
2-9
7400 MM428 (12--98)
12. Tighten nut with hand wrench until wheel
binds, then back nut off to nearest hole.
13. Insert a new cotter pin through nut and hole.
14. Spin the tire and wheel assembly. The tire
should spin freely.
15. Reinstall the hub cap in the center of the
wheel.
16. Lower the machine.
17. Repeat the procedure on the other wheel.
18. Rotate the brake cable turn buckle until the
brake cable is tight or until the brake pedal
travels 25--50 mm (1--2 in) before engaging
brakes.
19. Tighten the brake cable turn buckle jam
nuts.
20. Reinstall the floor plate in the operators
compartment.
21. Operate the machine and check the rear
wheels for proper operation.

CHASSIS
2-10 7400 MM428 (12--98)
FRONT TIRE AND WHEEL SUPPORT
The front wheel support pivots the front wheel.
The support has one grease fitting for the
bearings. The front wheel support bearings must
be lubricated every 200 hours of operation. Use
Lubriplate EMB grease
(TENNANT part no. 01433--1).
Torque the front wheel nuts to 142 -- 156 Nm
(105 -- 115 ft lb) after the first 50-hours of
operation, and every 800 hours thereafter.
Torque the front wheel hub nut to (375 ft lb)
TO REPLACE FRONT DRIVE MOTOR
FOR SAFETY: Before Leaving Or
Servicing Machine; Stop On Level
Surface, Set Parking Brake, Turn Off
Machine And Remove Key.
1. Engage parking brake, block rear tires.
2. Jack up front of machine. Use jack stands to
support machine.
FOR SAFETY: Block machine tires
before jacking machine up. Jack
machine up at designated locations
only. Block machine up with jack
stands.
3. Remove the front tire and wheel assembly.
4. Remove the cotter pin and slotted nut from
the front wheel drive motor shaft.
5. Use a puller to remove the drive hub from
the tapered shaft of the drive motor.
6. Remove and plug the hydraulic hoses
leading to the front wheel drive motor.
NOTE: Observe hydraulic cleanliness
requirements when opening hydraulic lines.
7. Remove the four drive motor mounting bolts.
8. Slide the motor out of front wheel housing.

CHASSIS
2-11
7400 MM428 (12--98)
9. Remove the hydraulic fittings from the old
motor and install in the new motor in the
same orientation.
10. Slide the new motor in the front wheel
housing. Note the orientation of the motor.
11. Reinstall the four socket--head screws.
Torque to 90 -- 117 Nm (70 -- 85 ft lb).
12. Reconnect the hydraulic hoses to the drive
motor.
NOTE: Make sure the square key is in place on
the shaft of the new motor.
13. Mount the drive hub to tapered motor shaft.
Tighten slotted nut to 500 Nm (375 ft lb).
Install the cotter pin.
14. Install the front tire. Torque the front wheel
nuts to 142 -- 156 Nm (105 -- 115 ft lb).
15. Remove jack stands and lower machine.
16. Operate the machine and check the front
drive motor for any leaks.

CHASSIS
2-12 7400 MM428 (12--98)
TO REPLACE FRONT WHEEL HOUSING
PIVOT BEARINGS
1. Engage parking brake, block rear tires.
2. Disconnect the battery cables from the
battery.
3. Jack up front of machine. Use jack stands to
support machine.
FOR SAFETY: Block machine tires
before jacking machine up. Jack
machine up at designated locations
only. Block machine up with jack
stands.
4. Remove the front tire and wheel assembly.
5. Remove and plug the hydraulic hoses
leading to the front wheel drive motor.
NOTE: Observe hydraulic cleanliness
requirements when opening hydraulic lines.
6. Remove the hydraulic hose clamp from the
top of the wheel housing.
7. Remove the one 3/4 in. hex screw attaching
the rod end of steering cylinder to the front
wheel housing. Retain the spacer.
8. Remove the cotter pin and large slotted nut
from the top of the pivot pin.
9. Loosen the two M10 socket head bolts
holding the pivot pin to the machine frame.
NOTE: Use a floor jack to support the wheel
housing before removing the pivot pin. The wheel
housing and drive motor assembly is very heavy.
10. Remove the pivot pin from the bottom of the
wheel support.
NOTE: Do not loose the thrust washer from on
top of the wheel housing.
11. Remove the wheel housing and drive motor
assembly out of the main frame.
12. Use a steel punch and hammer to drive the
old bearing cups out of the wheel housing.

CHASSIS
2-13
7400 MM428 (12--98)
13. Install a new set of bearing cups in the
wheel housing. Use a large press or a punch
and hammer to install the cups.
14. Pack the new bearing cones with Lubriplate
EMB grease. Coat the bearing cups with
grease.
15. Position the new bearing cones in the wheel
housing.
16. Position the thrust washer on top of the
upper bearing cone.
17. Position the wheel housing back in the
machine.
18. Slide the large pivot pin up through hole in
the machine frame. Thread castle nut on the
top of the pivot pin. Tighten to 34 -- 40 Nm
(25 -- 30 ft lb). Check the wheel housing for
play. If pin is not seated, tap with rubber
mallet and re--torque castle nut.
NOTE: The wheel housing should rotate with a
slight amount of drag.
19. Torque the top socket screw with a hand
torque wrench to 100 -- 115 Nm
(73--85 ft lb).
20. Tighten the castle nut to the next slot and
insert the cotter pin. Torque not to exceed
100 Nm (75 ft lb).
21. Check the casting to see if it rocks or binds.
If it does, loosen top socket screw, move the
casting to seat the bearings, and re--tighten
the socket screw to 100 -- 115 Nm
(73--85 ft lb).
22. Tighten the lower socket screw to
100 -- 115 Nm (73--85 ft lb).
23. Reinstall rod end of steering cylinder to the
top of the wheel housing using the 3/4 in. x
3--1/4 in. hex screw,nyloc nut, and four flat
washers. Tighten to 270 -- 300 Nm
(200 -- 220 ft lb).

CHASSIS
2-14 7400 MM428 (12--98)
24. Reconnect the hydraulic hoses to the drive
motor.
25. Reinstall the hose clamp to the top of the
wheel housing. Tighten M8 hex screws to
18.5 -- 24Nm (15 -- 20 ft lb).
26. Install the front tire. Torque the front wheel
nuts to 142 -- 156 Nm (105 -- 115 ft lb)
27. Re--connect battery cables, start engine, run
propelling in both directions, check for leaks.
28. Remove jack stands, lower machine to the
ground.

SCRUBBING
3-1
7400 MM428 (9--01)
CONTENTS
Page
INTRODUCTION 3-3...................
SOLUTION TANKS 3-4....................
TO REMOVE LH SOLUTION TANK 3-4...
TO INSTALL LH SOLUTION TANK 3-5...
TO REMOVE RH SOLUTION TANK 3-6..
TO INSTALL RH SOLUTION TANK 3-7...
RECOVERY TANK 3-8....................
TO REMOVE RECOVERY TANK 3-8.....
TO INSTALL RECOVERY TANK 3-11.....
SCRUB HEAD 3-13.......................
TO REPLACE MAIN SCRUB
BRUSHES 3-13.....................
CHECKING AND ADJUSTING SCRUB
BRUSH PATTERN 3-14..............
TO REPLACE MAIN BRUSH IDLER
SHAFT BEARINGS 3-16.............
TO REMOVE MAIN BRUSH DRIVE
MOTOR MOUNT PLATE 3-18........
TO INSTALL MAIN BRUSH DRIVE
MOTOR MOUNT PLATE 3-19........
TO REPLACE OPTIONAL SIDE
BRUSH 3-20.......................
SQUEEGEES 3-21........................
TO REPLACE REAR SQUEEGEE
LIFT CABLE 3-21...................
TO REPLACE REAR SQUEEGEE
CENTERING SPRINGS 3-22.........
TO REMOVE REAR SQUEEGEE
FRAME 3-23.......................
TO INSTALL REAR SQUEEGEE
FRAME 3-23.......................
SQUEEGEE BLADES 3-24................
REAR SQUEEGEE 3-24................
TO REPLACE OR ROTATE REAR
SQUEEGEE BLADES 3-24...........
TO ADJUST REAR SQUEEGEE
BLADE DEFLECTION 3-25...........
TO LEVEL THE REAR SQUEEGEE 3-26.
SIDE SQUEEGEES 3-27...............
TO REPLACE SIDE SQUEEGEE
BLADES 3-27.......................
TO REPLACE SIDE BRUSH
SQUEEGEE 3-28...................
SIDE BRUSH SKIRT 3-28...............
VACUUM FAN 3-29.......................
TO REMOVE VACUUM FAN 3-29........
TO INSTALL VACUUM FAN 3-30........
TO REPLACE VACUUM IMPELLER 3-31.

SCRUBBING
7400 MM428 (12--98)
3-2

SCRUBBING
3-3
7400 MM428 (12--98)
INTRODUCTION
When the scrubbing mode is used, water flows
from the solution tank through the solution valve
to the two cylindrical scrub brushes. The brushes
scrub the floor. As the machine is moved forward
the squeegee wipes the dirty solution off the floor,
which is then picked up and drawn into the
recovery tank by the vacuum fan. There are three
settings on the solution flow----high, low, and off.

SCRUBBING
3-4 7400 MM428 (12--98)
SOLUTION TANKS
The two solution tanks hold the clean water and
detergent mixture that will be applied to the floor
for the scrubbing operation. There is a LH and a
RH solution tank. They are connected by a large
diameter solution line.
TO REMOVE LH SOLUTION TANK
FOR SAFETY: Before Leaving Or
Servicing Machine; Stop On Level
Surface, Set Parking Brake, Turn Off
Machine And Remove Key.
1. Empty the solution and recovery tanks.
2. Open the engine side door and engine
cover.
3. Unlatch the rear radiator cover panel and tilt
it open.
4. Disconnect the wires going to the float
switch at the back of the LH solution tank.
5. Remove the two hex screws from the rear
tank bracket where it attaches to the LH
solution tank.
6. Remove the one hex screw from the rear,
lower corner of the LH tank. This hex screw
is located near the left hand taillight.
7. Go to the front of the LH solution tank.
Disconnect the solution cross--over line from
the bottom, front of the LH solution tank.
NOTE: Access the the clamp on the cross--over
line is made easier by removing the two vacuum
hoses leading to the recovery tank.
8. Remove the two M8 hex screws from the
front of the LH solution tank near the engine
alternator.
9. The LH solution tank can now be lifted up
and out of the machine frame.

SCRUBBING
3-5
7400 MM428 (12--98)
TO INSTALL LH SOLUTION TANK
FOR SAFETY: Before Leaving Or
Servicing Machine; Stop On Level
Surface, Set Parking Brake, Turn Off
Machine And Remove Key.
1. Position the LH solution tank back in the
machine frame.
NOTE: Be careful not to pinch hydraulic hoses or
electrical wires during this procedure.
2. Reinstall the two M8 hex screws in the front
of the LH solution tank near the engine
alternator. Leave hardware loose for now.
3. Reinstall the two M8 hex screws in the top,
rear of the LH solution tank in the rear tank
bracket. Leave hardware loose for now.
4. Reinstall the one M8 hex screw in the rear,
bottom of the LH solution tank near the LH
taillight.
5. Tighten the five M8 hex screws to
18 -- 24 Nm (15 -- 20 ft lb).
6. Reconnect the solution cross--over line at
the bottom of the tank.
NOTE: Reconnect the vacuum hoses if removed
earlier.
7. Reconnect the wires to the float switch at
the back of the LH solution tank.
8. Close the rear radiator cover panel and
latch.
9. Close the engine side door and engine
cover.
10. Fill the LH solution tank with water and
check for leaks.

SCRUBBING
3-6 7400 MM428 (12--98)
TO REMOVE RH SOLUTION TANK
FOR SAFETY: Before Leaving Or
Servicing Machine; Stop On Level
Surface, Set Parking Brake, Turn Off
Machine And Remove Key.
1. The RH solution tank can only be removed
after the LH solution and recovery tanks
have been removed. See TO REMOVE LH
SOLUTION TANK and TO REMOVE
RECOVERY TANK instructions.
2. Remove the one hex screw from the rear,
lower corner of the RH tank. This hex screw
is located under the frame, above the drain
cap.
3. Place the operators seat in the raised
position and engage the prop rod.
4. Remove the two M8 hex screws from the
front, right corner of the RH solution tank
where it attaches to the seat support.
5. Disconnect any solution lines still attached to
the RH solution tank.
6. The RH solution tank can now be lifted up
and out of the machine frame.

SCRUBBING
3-7
7400 MM428 (12--98)
TO INSTALL RH SOLUTION TANK
FOR SAFETY: Before Leaving Or
Servicing Machine; Stop On Level
Surface, Set Parking Brake, Turn Off
Machine And Remove Key.
1. Position the RH solution tank back in the
machine frame.
NOTE: Be careful not to pinch hydraulic hoses or
electrical wires during this procedure.
2. Reinstall the one M8 hex screw in the rear,
bottom of the RH solution tank. This hex
screw is located under the frame, above the
drain cap. Leave hardware loose for now.
3. Reinstall the two M8 hex screws from the
front, right corner of the RH solution tank
where it attaches to the seat support. Leave
hardware loose for now.
4. Reconnect any solution lines that were
disconnected from the RH solution tank.
5. The remain RH solution tank hardware will
be installed during the recovery tank
installation. See TO INSTALL RECOVERY
TANK and TO INSTALL LH SOLUTION
TANK instructions.

SCRUBBING
3-8 7400 MM428 (12--98)
RECOVERY TANK
The recovery tank holds the used water and
detergent solution pulled off the floor by the
squeegee and scrubbing vacuum fan.
TO REMOVE RECOVERY TANK
FOR SAFETY: Before Leaving Or
Servicing Machine; Stop On Level
Surface, Set Parking Brake, Turn Off
Machine And Remove Key.
1. Empty the solution and recovery tanks.
2. Place the operators seat in the raised
position and engage the prop rod.
3. Remove the LH solution tank. See TO
REMOVE LH SOLUTION TANK
instructions.
4. Disconnect the vacuum and squeegee
hoses from the front of the recovery tank.
5. Remove the two hex screws holding the
demister cover on the recovery tank.
Remove the demister cover.
6. If the machine is equipped with an overhead
guard, it must be removed in order to
remove the tank lintel.
NOTE: The engine hood must be supported in the
open position before the next step can be
completed.
7. Remove the clips on the bottom of the
engine hood gas springs. Remove the gas
springs from the ball studs on the support
channel.
8. Remove the hex screws holding the support
channel to the tank lintel and hood lintel.
Remove the support channel from the
machine.

SCRUBBING
3-9
7400 MM428 (12--98)
9. Remove the solution and recovery tank drain
caps from the rear of the machine.
10. Remove the three hex screws holding the
tank drain cover to the machine. Remove
the cover.
11. Remove the hex screws holding the tank
lintel to the frame, recovery tank, RH
solution tank, and seat support. Remove the
lintel from the machine.
12. Mark, disconnect, and plug the three
hydraulic hoses leading to the engine fan
hydraulic motor.
NOTE:Observe hydraulic cleanliness
requirements when opening hydraulic lines.
13. Disconnect the solution line at the front of
the recovery tank if the machine is equipped
with the auto--fill option.
14. Disconnect the wires leading to the float
switch that is located at the front, right
corner of the recovery tank.
NOTE: Machines equipped with ES will have two
switches on the float assembly.
15. Disconnect the solution hose at the back of
the tank if the machine is equipped with the
EStoption.
16. Unplug the main electrical harness from the
EStpump at the rear of the tank.
17. Remove the EStpump and cap assembly
from the recovery tank.
18. Remove the one hex screw and two nyloc
nuts holding the radiator assembly to the
back of the recovery tank. Leave the black
mount plate attached to the recovery tank.
Do not disconnect the hoses from the
radiator.

SCRUBBING
3-10 7400 MM428 (12--98)
19. Carefully pull the radiator assembly back
and out of the way of the recovery tank. Let
the radiator assembly lean against the oil
cooler.
20. Remove the two M8 hex screws attaching
the rear tank bracket to the RH solution tank
21. Remove the one M8 hex screw under the
rear of the tank, just above the drain cap.
22. Carefully push the recovery tank forward, lift
it up, and remove it from the machine.
NOTE: An overhead hoist or two people must be.
used when lifting the recovery tank out of the
machine frame.

SCRUBBING
3-11
7400 MM428 (12--98)
TO INSTALL RECOVERY TANK
FOR SAFETY: Before Leaving Or
Servicing Machine; Stop On Level
Surface, Set Parking Brake, Turn Off
Machine And Remove Key.
NOTE: An overhead hoist or two people must be
used when positioning the recovery tank back in
the machine frame.
1. Position the recovery tank back in the
machine frame.
NOTE: Be careful not to pinch hydraulic hoses or
electrical wires during this procedure.
2. Reinstall the tank lintel in the machine.
Reinstall the six M8 hex screws. Leave the
hardware loose for now.
3. Reconnect the solution line at the front of
the recovery tank if machine is equipped
with the auto fill option.
4. Reconnect the float switches at the front of
the recovery tank to the main harness. See
schematic in the ELECTRICAL section.
5. Carefully pivot the radiator assembly back in
position on the rear of the recovery tank.
Reinstall the hardware and tighten to
18 -- 24 Nm (15 -- 20 ft lb).
6. Plug the EStpump back in the main
harness. See schematic in the
ELECTRICAL section.
7. Reinstall the hardware in the rear tank
bracket where it attaches to the RH solution
tank.
8. Reinstall the one M8 hex screw under the
rear of the tank, just above the drain cap.
9. Reinstall the support channel to the tank
lintel and hood lintel. Reinstall the four M8
hex screws.
10. Tighten the all of the M8 hex screws to
18 -- 24 Nm (15 -- 20 ft lb).

SCRUBBING
3-12 7400 MM428 (12--98)
11. Reinstall the engine hood gas springs on the
ball studs on the support channel. Reinstall
the two clips.
12. Reconnect the hydraulic hoses to the engine
fan motor. See schematic in the
HYDRAULIC section.
NOTE:Observe hydraulic cleanliness
requirements when opening hydraulic lines.
13. Reinstall the demister cover on the recovery
tank. Reinstall the two M8 hex screws and
tighten to 18 -- 24 Nm (15 -- 20 ft lb).
14. Reinstall the LH solution tank. See TO
INSTALL LH SOLUTION TANK instructions.
15. Reconnect the two vacuum hoses to the
front of the recovery tank.
16. Reinstall the overhead guard if it was
removed earlier.
17. Reinstall the tank drain cover to the rear of
the tanks. Reinstall the hardware and tighten
to 18 -- 24 Nm (15 -- 20 ft lb).
18. Reinstall the solution and recovery tank
drain covers.
19. Partially fill the recovery tank with water and
check for any leaks and for proper operation
of the float switches.

SCRUBBING
3-13
7400 MM428 (12--98)
SCRUB HEAD
The scrub head contains the two cylindrical
brushes, hydraulic motors, brush idler plate, brush
wrap, and side squeegees. Water from the
solution tank flows to the center of of the scrub
head brush wrap and is spread evenly in front of
the scrub brushes.
TO REPLACE MAIN SCRUB BRUSHES
1. Place the main scrub brushes in the raised
position.
FOR SAFETY: Before Leaving Or
Servicing Machine; Stop On Level
Surface, Set Parking Brake, Turn Off
Machine And Remove Key.
2. Open the RH brush door.
3. Pull back on the front ball joint locking collar
on the leveling rod. Remove the leveling rod
from the front ball stud.
4. Remove the two hair pins from the brush
wrap attachment pins.
5. Remove the M12 hex screw holding the
brush idler plate arm to the lift tube.
6. Remove the idler plate and side squeegee
assembly from the machine.
NOTE: Thread the mounting bolt into the idler arm
removal hole if you are having trouble removing
the idler arm.
7. Pull the two main brushes off the drive
plugs.
6. Line up the drive end of the new or rotated
brushes with the brush drive plugs. The
cylindrical scrub brushes must be installed
with the V-patterns on the brushes pointing
towards each other. Slide the brushes onto
the brush drive plugs.
8. Reinstall the idler plate and side squeegee
assembly in the machine.
NOTE: Lift up on the brush wrap slightly when
installing the idler plate in the machine so the
attachment pins line up with the holes in the plate.

SCRUBBING
3-14 7400 MM428 (12--98)
9. Align the two pins on the lift tube with the
two holes in the brush idler plate arm.
10. Reinstall the M12 hex screw in the brush
idler plate arm. Tighten to 64 -- 83 Nm
(47 -- 61 ft lb).
NOTE: Apply a small amount of grease to the
threads on the bolt and in the tube.
11. Reinstall the two hair pins in the brush wrap
attachment pins.
12. Reconnect the front of the leveling rod to the
ball stud.
13. Close the RH brush door and operate the
machine. Check the main brushes for proper
operation.
CHECKING AND ADJUSTING SCRUB BRUSH
PATTERN
1. Apply chalk, or some other material that will
not easily blow away, to a smooth, level
floor.
2. Raise the scrub head. Position the scrub
head over the chalked area.
3. Set the parking brake.
4. Lower the scrub head for 15 to 20 seconds
while keeping the scrub head in one spot in
the chalked area.
NOTE: If chalk or other material is not available,
allow the brushes to spin on the floor for two
minutes. A polish mark will remain on the floor.
5. Raise the scrub head, release the parking
brake, and drive the machine away from the
chalked area.
6. Observe the width of the brush pattern. If
the brush patterns have parallel sides and
are the same width, the brushes do not need
taper adjustment.
If one or both of the brush patterns are
tapered, the scrub head will have to be
adjusted to straighten the brush pattern.
10355
10652

SCRUBBING
3-15
7400 MM428 (12--98)
7. Loosen the three scrub head mounting bolts
on the idler or drive side of the scrub head.
Move the scrub head up to decrease the
pattern width on that side of the scrub head.
Move the scrub head down to increase the
pattern width on that side of the scrub head.
Tighten the mounting bolts and check the
pattern again and readjust if necessary.
The brush patterns should be the same
width. If one is narrower then the other, the
scrub head needs to be leveled from front to
rear.
8. Lengthen or shorten the leveling rods on
both sides of the scrub head. Lengthening
the rods will increase the rear brush pattern
width. Shortening the rods will will increase
the front brush pattern.
10653

SCRUBBING
3-16 7400 MM428 (12--98)
TO REPLACE MAIN BRUSH IDLER SHAFT
BEARINGS
1. Place the main scrub brushes in the raised
position.
FOR SAFETY: Before Leaving Or
Servicing Machine; Stop On Level
Surface, Set Parking Brake, Turn Off
Machine And Remove Key.
2. Open the RH brush door.
3. Pull back on the front ball joint locking collar.
Remove the leveling rod from the front ball
stud.
4. Remove the two hair pins from the brush
wrap attachment pins.
5. Remove the M12 hex screw holding the
brush idler plate arm to the lift tube.
6. Remove the idler plate and side squeegee
assembly from the machine.
NOTE: For better access to the shaft and
bearings----remove the C--clip and brush arm from
the idler plate.
7. Turn the idler plate and side squeegee
assembly over. Remove the cotter pins,
castle nuts, and washers from the idler
plugs.
8. Use a puller to remove the idler plugs from
the tapered shafts. Remove and retain the
square key.
9. Remove the retaining rings from both ends
of the idler shafts.
10. Use a press to remove the tapered shafts
from the idler plate. Push the shafts out
toward the direction of the idler plugs.
NOTE: Use a small amount of heat in the area of
the bearings to help break the loctite loose.
11. Use a press to remove the bearing from the
tapered end of the idler shaft.
12. Use a press to remove the bearing from the
bearing housing in the idler plate. Discard
the old bearings.
13. Use a press to install a new bearing in the
bearing housing on the outside of the idler
plate. The open face of the bearing points in.
Use green loctite #680 on the outer diameter
of the bearing before pressing in place.

SCRUBBING
3-17
7400 MM428 (12--98)
14. Use a press to install a new bearing on the
tapered shaft. The open face of the bearing
points in. Reinstall the retaining ring on the
tapered shaft next to the bearing.
15. Reinstall the tapered shaft and bearing in
the bearing housing on the inside of the
idler plate. Use green loctite #680 on the
outer diameter of the bearing before
pressing in place.
16. Reinstall the retaining ring on the flat end of
the tapered shaft on the outside of the idler
plate.
17. Reinstall the square key on the tapered
shaft. Put a small amount of grease on the
taper.
18. Reinstall the idler plugs, washers, and castle
nuts. Hold the plug from turning and tighten
the castle nut down hard until the slot in the
nut lines up with the hole in the shaft. Install
a new cotter pin.
19. Reinstall the brush arm and C clip if they
were removed earlier.
20. Reinstall the idler plate and side squeegee
assembly in the machine.
NOTE: Lift up on the brush wrap slightly when
installing the idler plate in the machine so the
attachment pins line up with the holes in the plate.
21. Align the two pins on the lift tube with the
two holes in the brush idler plate arm.
22. Reinstall the M12 hex screw in the brush
idler plate arm. Tighten to 64 -- 83 Nm
(47 -- 61 ft lb).
NOTE: Apply a small amount of grease to the
threads on the bolt and in the tube.
23. Reinstall the two hair pins in the brush wrap
attachment pins.
24. Reconnect the front of the leveling rod to the
ball stud.
25. Close the RH brush door and operate the
machine. Check the main brushes for proper
operation.

SCRUBBING
3-18 7400 MM428 (12--98)
TO REMOVE MAIN BRUSH DRIVE MOTOR
MOUNT PLATE
1. Place the main scrub brushes in the raised
position.
FOR SAFETY: Before Leaving Or
Servicing Machine; Stop On Level
Surface, Set Parking Brake, Turn Off
Machine And Remove Key.
2. Open the LH brush door.
3. Remove the front ball joint on the leveling
rod from the machine frame.
4. Remove the two hair pins from the brush
wrap attachment pins.
5. Remove the M12 hex screw holding the
brush arm to the lift tube.
6. Remove the three hex screws holding the
side squeegee assembly to the motor mount
plate. Remove the side squeegee assembly.
NOTE: For better access to the hydraulic drive
motors----remove the C--clip and brush arm from
the motor plate.
7. Mark, disconnect, and plug the three
hydraulic hoses leading to the main brush
drive motors.
NOTE:Observe hydraulic cleanliness
requirements when opening hydraulic lines.
8. Remove the motor mount plate assembly
from the machine.

SCRUBBING
3-19
7400 MM428 (12--98)
TO INSTALL MAIN BRUSH DRIVE MOTOR
MOUNT PLATE
FOR SAFETY: Before Leaving Or
Servicing Machine; Stop On Level
Surface, Set Parking Brake, Turn Off
Machine And Remove Key.
1. Position the motor plate assembly back in
the machine.
NOTE: Lift up on the brush wrap slightly when
installing the motor plate in the machine so the
attachment pins line up with the holes in the plate.
2. Reinstall the two hair pins in the brush wrap
attachment pins.
3. Reconnect the hydraulic hoses to the brush
motors. See schematic in HYDRAULICS
section.
4. Reinstall the brush arm and C clip if they
were removed earlier.
5. Align the two pins on the lift tube with the
two holes in the brush motor plate arm.
6. Reinstall the M12 hex screw in the brush
motor plate arm. Tighten to 64 -- 83 Nm
(47 -- 61 ft lb).
NOTE: Apply a small amount of grease to the
threads on the bolt and in the tube.
7. Reinstall the front of the leveling rod ball
joint to the machine frame.
NOTE:Observe hydraulic cleanliness
requirements when opening hydraulic lines.
8. Reinstall the side squeegee assembly to the
motor plate. Tighten the three hex screws to
37 -- 48 Nm (26 -- 34 ft lb).
9. Close the LH brush door and operate the
machine. Check the main brush motors for
proper operation.

SCRUBBING
3-20 7400 MM428 (12--98)
TO REPLACE OPTIONAL SIDE BRUSH
FOR SAFETY: Before Leaving Or
Servicing Machine; Stop On Level
Surface, Set Parking Brake, Turn Off
Machine And Remove Key.
1. Rotate the side brush by hand until the
spring clips are visible through the window in
the side brush motor mount plate.
2. Reach in through the opening in the top of
the side brush guard, through the mount
plate window, and pinch the spring clips
together.
3. Drop the brush off the drive hub. Remove
the brush from the machine.
4. Position the new side brush under the
machine.
5. Lift the side brush and line up the hub in the
brush with the motor drive plug. Snap the
brushupinplace.
6. Operate the machine and check the side
brush for proper operation.

SCRUBBING
3-21
7400 MM428 (12--98)
SQUEEGEES
The squeegee channels water into the vacuum
fan suction. The front blade channels the water,
and the rear blade wipes the floor.
There are two types of squeegee blades
available; one for smooth surfaces is standard on
the machine, and one for rough surfaces is an
option.
The side squeegees control water spray and
channel water into the path of the rear squeegee.
Check the side squeegees for damage and wear
daily.
TO REPLACE REAR SQUEEGEE LIFT CABLE
1. Open the debris tray latch and swing the
squeegee assembly out for better access.
2. Start engine, lower rear squeegee, shut off
engine.
FOR SAFETY: Before Leaving Or
Servicing Machine; Stop On Level
Surface, Set Parking Brake, Turn Off
Machine And Remove Key.
3. Remove the cotter pin and clevis pin from
the squeegee lift cable where it attaches to
the squeegee frame assembly.
4. Remove the cotter pin and clevis pin from
the squeegee lift cable where it attaches to
the squeegee lift bellcrank located near the
lift cylinder.
5. Remove the clevis pin holding the cable
roller to the frame. Remove the roller.
6. Remove and discard the old squeegee lift
cable.
7. Position the new cable in the machine.
Reinstall one end to the squeegee lift
bellcrank located near the lift cylinder.
Re--use the clevis and cotter pin.
8. Reinstall the other end to the squeegee pivot
frame assembly. Re--use the clevis and
cotter pin.
9. Reinstall the cable roller and clevis pin in the
frame.
10. Start the machine and raise the squeegee.
Swing the squeegee assembly back in.
Check the lift cable for proper operation.

SCRUBBING
3-22 7400 MM428 (12--98)
TO REPLACE REAR SQUEEGEE
CENTERING SPRINGS
1. Open the debris tray latch and swing the
squeegee assembly out for better access.
2. Start engine, lower rear squeegee, shut off
engine.
FOR SAFETY: Before Leaving Or
Servicing Machine; Stop On Level
Surface, Set Parking Brake, Turn Off
Machine And Remove Key.
3. Loosen the jam nuts on the squeegee down
pressure spring rods. This will relax the
tension on the springs.
4. Remove the nyloc nuts from the squeegee
rod ball joints where they are connected to
the debris tray.
NOTE: Remove both the upper and lower nuts on
one side. Do one side at a time.
5. Remove and discard the old squeegee
centering spring.
6. Position a new squeegee centering spring
on the upper and lower ball joint studs.
7. Reinstall the two nyloc nuts and tighten to
37 -- 48 Nm (26 -- 34 ft lb).
8. Repeat this procedure on the other side if
needed.
9. Start the machine and raise the squeegee.
Swing the squeegee assembly back in.
Check the centering springs for proper
operation.

SCRUBBING
3-23
7400 MM428 (12--98)
TO REMOVE REAR SQUEEGEE FRAME
1. Open the debris tray latch and swing the
squeegee assembly out for better access.
2. Start engine, lower rear squeegee, shut off
engine.
FOR SAFETY: Before Leaving Or
Servicing Machine; Stop On Level
Surface, Set Parking Brake, Turn Off
Machine And Remove Key.
3. Remove vacuum hose from squeegee
frame.
4. Remove the cotter pin and clevis pin from
the squeegee lift cable where it attaches to
the squeegee frame assembly.
5. Loosen the jam nuts on the squeegee down
pressure spring threaded rods. This will
relax the tension on the springs.
6. Remove the four hex screws and nuts
holding the squeegee frame to the squeegee
lift assembly.
7. Remove the squeegee frame from the
machine.
TO INSTALL REAR SQUEEGEE FRAME
FOR SAFETY: Before Leaving Or
Servicing Machine; Stop On Level
Surface, Set Parking Brake, Turn Off
Machine And Remove Key.
1. Position the squeegee frame back under the
lift assembly.
2. Reinstall the four hex screws and nuts.
Tighten to 37 -- 48 Nm (26 -- 34 ft lb).
3. Re--connect the squeegee lift cable to the
frame assembly. Re--use the clevis and
cotter pin.
4. Re--apply tension on the down pressure
springs using the threaded rods and jam
nuts.
5. Reinstall the vacuum hose on the squeegee
frame.
6. Start the machine and raise the squeegee.
Swing the squeegee assembly back in.

SCRUBBING
3-24 7400 MM428 (12--98)
SQUEEGEE BLADES
REAR SQUEEGEE
Check the squeegee blades for damage and wear
daily. Rotate or replace either of the squeegee
blades if the leading edge is torn or worn half-way
through the thickness of the blade.
The rear squeegee has two squeegee blades.
Each blade has four wiping edges. To use them
all, start with one wiping edge. To use the next
wiping edge, rotate the blade end-for-end. To use
the next wiping edge, rotate the top edges down,
bottom edges up. To use the last edge, rotate the
blade end-for-end.
Replace any worn or damaged squeegee blades.
TO REPLACE OR ROTATE REAR
SQUEEGEE BLADES
1. Make sure the squeegee is raised off the
floor.
2. Shut the engine off and set the parking
brake.
FOR SAFETY: Before Leaving Or
Servicing Machine; Stop On Level
Surface, Set Parking Brake, Turn Off
Machine And Remove Key.
3. Open the retaining band clamp and remove
the squeegee blade.
4. Replace or rotate the squeegee blade to
allow a new edge to face the front of the
machine.
5. Place the squeegee blade over the pins of
the squeegee frame.
6. Position the retaining band over the
squeegee blade. Latch the retaining band
clamp.
7. Adjust the squeegee blade leveling and
deflection. See TO ADJUST REAR
SQUEEGEE BLADE DEFLECTION or TO
LEVEL THE REAR SQUEEGEE
instructions.

SCRUBBING
3-25
7400 MM428 (12--98)
TO ADJUST REAR SQUEEGEE BLADE
DEFLECTION
Deflection is the amount of curl the squeegee
blade has when the machine travels forward with
the squeegee lowered to the floor. The best
deflection is when the squeegee wipes the floor
just dry with a minimum amount of deflection.
1. Lower the squeegee and drive the machine
forward.
2. Shut off the engine and set the machine
parking brake.
FOR SAFETY: Before Leaving Or
Servicing Machine; Stop On Level
Surface, Set Parking Brake, Turn Off
Machine And Remove Key.
3. Look at the deflection over the full length of
the squeegee blade. The correct amount of
deflection for the rear squeegee blade is
15 to 20 mm (0.50 to 0.75 in). The front
slotted squeegee blade should contact the
floor with a slight deflection, 5 mm (0.13 to
0.25 in).
4. To adjust the amount of deflection, unlock
the height adjustment knobs on the two
squeegee casters by sliding the locking
bracket off to the side.
NOTE: If the locking brackets won’t slide over, lift
up the end of the squeegee to pick the caster up
off the floor slightly. Then slide the locking bracket
over.
5. Turn the adjustment knob clockwise to
decrease deflection, turn the adjustment
knob counter-clockwise to increase the
deflection. Be sure to turn the knobs the
same number of turns.
6. Start the engine and drive the machine
forward again to check the squeegee blade
deflection. Readjust the squeegee blade
deflection if necessary.
7. Slide the locking brackets back to lock the
height adjustment knobs.
8. Raise the squeegee when finished.
10918
15 to
20 mm
(0.50 to
0.75 in)
5mm
(0.13 to
0.25 in)

SCRUBBING
3-26 7400 MM428 (12--98)
TO LEVEL THE REAR SQUEEGEE
Leveling of the squeegee assures even contact
over the length of the squeegee blade with the
surface being scrubbed. Make sure this
adjustment is done on an even, level floor.
1. Lower the squeegee and drive the machine
forward.
2. Shut off the engine and set the machine
parking brake.
FOR SAFETY: Before Leaving Or
Servicing Machine; Stop On Level
Surface, Set Parking Brake, Turn Off
Machine And Remove Key.
3. Look at the deflection over the full length of
the squeegee blade.
4. If the deflection is not the same over the full
length of the blade, loosen the locking nut on
the two rear squeegee balljoints.
NOTE: The rear squeegee links should be
adjusted so there is 11 inches from the center
lines of the two ball joints.
5. Turn the balljoint adjustment nut clockwise,
from the rear of the machine, to increase the
deflection at the ends of the squeegee. Turn
the balljoint adjustment nut
counter-clockwise, from the rear of the
machine, to decrease the deflection at the
ends of the squeegee blade.
6. Tighten the locking nuts.
7. Start the engine and drive the machine
forward again to check the squeegee blade
deflection.
8. Readjust the squeegee blade deflection if
necessary.
11.00 in.

SCRUBBING
3-27
7400 MM428 (12--98)
SIDE SQUEEGEES
The side squeegees control water spray and
channel water into the path of the rear squeegee.
Check the side squeegees for damage and wear
daily. Replace the side squeegee blades
whenever they become damaged or lose their
shape or resilience. Replace the squeegee
deflectors whenever they become worn.
TO REPLACE SIDE SQUEEGEE BLADES
1. Raise the scrub head.
2. Shut off the engine and set the machine
parking brake.
FOR SAFETY: Before Leaving Or
Servicing Machine; Stop On Level
Surface, Set Parking Brake, Turn Off
Machine And Remove Key.
3. Remove the cotter pin, clevis pin, deflector,
and the retainer bracket from the front of the
side squeegee.
4. Pull the squeegee blade out the front of the
squeegee frame.
5. Slide the new squeegee blade onto the
frame.
NOTE: Lubricating the squeegee frame where
the squeegee makes contact will make it easier to
install the squeegee blade.
6. Replace the retainer bracket, deflector,
clevis pin, and cotter pin.
7. Repeat for the side squeegee on the other
side of the scrub head.
00000

SCRUBBING
3-28 7400 MM428 (12--98)
TO REPLACE SIDE BRUSH SQUEEGEE
FOR SAFETY: Before Leaving Or
Servicing Machine; Stop On Level
Surface, Set Parking Brake, Turn Off
Machine And Remove Key.
1. Raise the side brush.
2. Shut off the engine and set the parking
brake.
FOR SAFETY: Before leaving or
servicing machine; stop on level
surface, set parking brake, turn off
machine and remove key.
3. Remove the side brush guard.
4. Remove the retainer clip from the end of the
squeegee.
5. Pull the squeegee blade out the front of the
squeegee frame.
6. Slide the new squeegee blade onto the
frame.
NOTE: Lubricating the squeegee frame where
the squeegee makes contact will make it easier to
install the squeegee blade.
7. Install the retainer clip on the end of the
squeegee.
8. Install the side brush guard.
SIDE BRUSH SKIRT
The side brush skirt is located behind the
squeegee blade. Check the skirt for wear and
damage every 100 hours of operation.

SCRUBBING
3-29
7400 MM428 (12--98)
VACUUM FAN
The vacuum fan, when activated, creates a
vacuum in the recovery tank. Water is pulled from
the rear squeegee to the recovery tank through a
vacuum hose. The vacuum fans impeller is driven
with a high speed hydraulic motor.
TO REMOVE VACUUM FAN
FOR SAFETY: Before Leaving Or
Servicing Machine; Stop On Level
Surface, Set Parking Brake, Turn Off
Machine And Remove Key.
1. Open the engine cover, engine side door,
and the front cover.
2. Loosen the hose clamp and remove the
vacuum hose leading from recovery tank to
the center of the vacuum fan housing.
3. Mark, disconnect, and plug the four
hydraulic hoses going to the vacuum fan
NOTE:Observe hydraulic cleanliness
requirements when opening hydraulic lines.
4. Remove three M10 hex screws, washers,
and nyloc nuts holding vacuum fan to
mounting brackets.
5. Remove the vacuum fan assembly from the
machine.

SCRUBBING
3-30 7400 MM428 (12--98)
TO INSTALL VACUUM FAN
FOR SAFETY: Before Leaving Or
Servicing Machine; Stop On Level
Surface, Set Parking Brake, Turn Off
Machine And Remove Key.
1. Position the vacuum fan assembly back in
the machine
2. Align the three mounting holes in the
vacuum fan housing with the three rubber
isolators in the mounting brackets. Reinstall
the three M10 hex screws, washers, and
nyloc nuts. Tighten to 18 -- 24 Nm
(13 -- 18 ft lb).
3. Reconnect the hydraulic hoses to the
vacuum fan motor. See schematic
in HYDRAULIC section.
4. Reinstall vacuum hose from recovery tank to
vacuum fan housing. Hand tighten clamps.
5. Start the engine and turn on the vacuum fan.
Check for leaks and proper operation.

SCRUBBING
3-31
7400 MM428 (12--98)
TO REPLACE VACUUM IMPELLER
FOR SAFETY: Before Leaving Or
Servicing Machine; Stop On Level
Surface, Set Parking Brake, Turn Off
Machine And Remove Key.
1. Remove the vacuum fan from the machine.
See TO REMOVE VACUUM FAN
instructions.
2. Place the vacuum fan assembly in a vice or
some other holding device.
3. Remove the six hex screws holding the front
housing to rear housing. Remove the front
housing.
NOTE: Mark the front housing in relation to the
rear housing so it is re--assembled correctly.
4. Remove crown nut on impeller shaft. Slide
impeller off shaft.
NOTE: Remove and save the key and any shims
that are on the motor shaft, under the impeller.
5. Install the shims, key, new fan impeller, and
crown nut. Tighten nut to 34 -- 47 Nm
(25 -- 35 ft lb).
NOTE: Be sure the square key is on the motor
shaft. Super gluing the key to the shaft helps keep
it in place when installing the impeller.
NOTE: Use a small amount of blue loctite 242 on
the motor shaft threads.
6. Reinstall the front housing on the rear
housing. Reinstall the six hex screws and
tighten to 22 -- 27 Nm (16 -- 20 ft lb).
NOTE: Tennant part no. 57543 plastic shims must
be used for proper fan to housing clearance.
Remove these shims after housing hardware has
been tightened.
7. Reinstall the vacuum fan assembly in the
machine. See TO INSTALL VACUUM FAN
instructions.

SCRUBBING
3-32 7400 MM428 (12--98)

ELECTRICAL
4-1
7400 MM428 (9--01)
CONTENTS
Page
INTRODUCTION 4-3.........................
BATTERY 4-4............................
TO REPLACE BATTERY 4-5............
INSTRUMENT PANEL 4-6.................
TO REPLACE INSTRUMENT PANEL 4-6.
TO DISASSEMBLE INSTRUMENT
PANEL 4-7.........................
TO REASSEMBLE INSTRUMENT
PANEL 4-8.........................
TO REPLACE MACHINE RELAY 4-9.....
TO REPLACE CIRCUIT BREAKER 4-10..
GAS/LPG ELECTRICAL
SCHEMATIC 4-11...................
GAS/LPG ELECTRICAL
SCHEMATIC 4-12...................
DIESEL ELECTRICAL SCHEMATIC 4-13.
DIESEL ELECTRICAL SCHEMATIC 4-14.
GAS/LPG WIRE HARNESS GROUP 4-15.
GAS/LPG WIRE HARNESS GROUP
(OPTIONS) 4-18....................
DIESEL WIRE HARNESS GROUP 4-19..
DIESEL WIRE HARNESS GROUP
(OPTIONS) 4-22....................
ELECTRICAL 4-11...........................
DIAGNOSTICS 4-23.....................
OPERATING MODES 4-24................
NORMAL MODE 4-25.................
SCRUB BUTTON 4-25..............
SQUEEGEE BUTTON 4-26.........
DETERGENT 4-27.................
EStBUTTON 4-27................
OVERFLOW FLOAT 4-27...........
MANUAL MODE 4-28.................
EStBUTTON 4-28................
SIDE BRUSH BUTTON 4-28........
SQUEEGEE BUTTON 4-28.........
ENGINE BUTTON 4-28.............
SCRUB BUTTON 4-28..............
DETERGENT BUTTON 4-28........
INPUT DISPLAY MODE 4-29...........
ERROR DISPLAY MODE 4-30..........
EStLED 4-30.....................
SIDE BRUSH LED 4-31.............
SQUEEGEE LED 4-31..............
SCRUB LED 4-32..................
DETERGENT LED 4-32.............
PRESSURE ADJUST MODE 4-33......
SCRUB BUTTON 4-33..............
RESET SCRUB PRESSURES 4-34.....
TROUBLESHOOTING 4-35...............
INSTRUMENT PANEL DOES NOT
POWER UP (SCHEMATIC) 4-36.....
INSTRUMENT PANEL DOES NOT
POWER UP (FLOW CHART) 4-37...
Page
SCRUB BRUSH WILL NOT TURN ON
AND/OR DOWN (SCHEMATIC) 4-38.
SCRUB BRUSH WILL NOT TURN ON
AND/OR DOWN (FLOW CHART) 4-39
SQUEEGEE AND VACUUM FAN NOT
TURNING ON AND GOING DOWN
(SCHEMATIC) 4-41..............
SQUEEGEE AND VACUUM FAN NOT
TURNING ON AND GOING DOWN
(FLOW CHART) 4-42............
SIDE BRUSH WILL NOT TURN ON AND
GO DOWN (SCHEMATIC) 4-44......
SIDE BRUSH WILL NOT TURN ON
ANDGODOWN(FLOWCHART) 4-45
WATER VALVES NOT OPERATING
(SCHEMATIC) 4-47................
WATER VALVES NOT OPERATING
(FLOW CHART) 4-48...............
HEAD LIGHTS WILL NOT TURN ON
(SCHEMATIC) 4-49.................
HEAD LIGHTS WILL NOT TURN ON
(FLOW CHART) 4-50...............
EStPUMP NOT WORKING
(SCHEMATIC) 4-51................
EStPUMP NOT WORKING
(FLOW CHART) 4-52...............
REVERSE LIGHT OR ALARM NOT
WORKING (SCHEMATIC) 4-54......
REVERSE LIGHT OR ALARM NOT
WORKING (FLOW CHART) 4-55.....
DETERGENT METERING PUMP IS NOT
OPERATING (SCHEMATIC) 4-57....
DETERGENT METERING PUMP IS NOT
OPERATING (FLOW CHART) 4-58...
ALTERNATOR / BATTERY WARNING
LIGHT STAYS ON WHEN ENGINE
IS RUNNING (SCHEMATIC) 4-59.
ALTERNATOR / BATTERY WARNING
LIGHT STAYS ON WHEN ENGINE
IS RUNNING (FLOW CHART) 4-60
ALTERNATOR / BATTERY WARNING
LIGHT WILL NOT TURN ON
(SCHEMATIC) 4-61..............
ALTERNATOR / BATTERY WARNING
LIGHT WILL NOT TURN ON
(FLOW CHART) 4-62............
ENGINE TEMPERATURE LIGHT WILL
NOT TURN ON OR OFF
(SCHEMATIC) 4-63..............
ENGINE TEMPERATURE LIGHT WILL
NOT TURN ON (FLOW CHART) 4-64
ENGINE TEMPERATURE LIGHT WILL
NOT TURN OFF (FLOW CHART) 4-64

ELECTRICAL
4-2 7400 MM428 (9--01)
Page
HYDRAULIC (HIGH) PRESSURE
INDICATOR LIGHT WILL NOT TURN
ON OR OFF (SCHEMATIC) 4-65..
HYDRAULIC (HIGH) PRESSURE
INDICATOR LIGHT WILL NOT TURN
ON (FLOW CHART) 4-66........
HYDRAULIC (HIGH) PRESSURE
INDICATOR LIGHT WILL NOT TURN
OFF (FLOW CHART) 4-66.......
ENGINE OIL PRESSURE WARNING
LIGHT WILL NOT TURN ON OR
OFF (SCHEMATIC) 4-67.........
ENGINE OIL PRESSURE WARNING
LIGHT WILL NOT TURN ON
(FLOW CHART) 4-68.............
ENGINE OIL PRESSURE WARNING
LIGHT WILL NOT TURN OFF
(FLOW CHART) 4-68.............
RECOVERY TANK FULL LIGHT WILL
NOT TURN ON OR OFF
(SCHEMATIC) 4-69...............
RECOVERY TANK FULL LIGHT WILL
NOT TURN ON (FLOW CHART) 4-70.
RECOVERY TANK FULL LIGHT WILL
NOT TURN OFF (FLOW CHART) 4-70
FUEL GAUGE (GAS AND DIESEL)
(SCHEMATIC) 4-71.................
FUEL GAUGE (GAS AND DIESEL)
(FLOW CHART) 4-72................
FUEL GAUGE (LPG) (SCHEMATIC) 4-73.
FUEL GAUGE (LPG) (FLOW CHART) 4-74

ELECTRICAL
4-3
7400 MM428 (12--98)
INTRODUCTION
The machine electrical system consists of the
battery, relays, instrument panels, and related
components. This section includes information on
these components and their troubleshooting.

ELECTRICAL
4-4 7400 MM428 (12--98)
BATTERY
The battery used in the machine is a low
maintenance battery. It has been constructed with
special materials and has extra electrolyte to
reduce or eliminate maintenance. Its design
reduces electrolyte loss and contamination. Do
not add water, remove the battery vent plugs, or
check the battery specific gravity. For specific
instructions, see the battery label.
Do not allow the battery to remain in discharged
condition for any time. Do not operate the
machine if the battery is in poor condition or
discharged beyond 80%, specific gravity below
1.120.
Periodically clean the top surface of the batteries
and the terminals, and check for loose
connections. Use a strong solution of baking
soda and water. Brush the solution sparingly over
the battery tops, terminals, and cable clamps. Do
not allow any baking soda solution to enter the
batteries. Use a wire brush to clean the terminal
posts and the cable connectors. After cleaning,
apply a coating of clear battery post protectant to
the terminals and the cable connectors. Keep the
tops of the batteries clean and dry.
Keep all metallic objects off the top of the
batteries, which may cause a short circuit.
Replace any worn or damaged wires.
The electrolyte level in regular non--sealed
batteries can be checked. The level must always
be above the battery plates. Never add acid to the
batteries, only distilled water. Keep the battery
caps on the batteries always except when adding
water or taking hydrometer readings.
FOR SAFETY: When Servicing Machine,
Avoid Contact With Battery Acid.

ELECTRICAL
4-5
7400 MM428 (12--98)
Using a hydrometer to measure the specific
gravity is a way to determine the charge level and
condition of the batteries. If one or more of the
battery cells test lower than the other battery cells
(0.050 or more), the cell is damaged, shorted, or
is about to fail.
NOTE: Do not take readings immediately after
adding distilled water. If the water and acid are not
thoroughly mixed, the readings may not be
accurate. Check the hydrometer readings against
the following chart to determine the remaining
battery charge level:
SPECIFIC GRAVITY BATTERY
at 27_C(80_F) CHARGE
1.260 -- 1.280 100% Charged
1.230 -- 1.250 75% Charged
1.200 -- 1.220 50% Charged
1.170 -- 1.190 25% Charged
1.110 -- 1.160 Discharged
NOTE: If the readings are taken when the battery
electrolyte is any temperature other than 27_C
(80_F), the reading must be temperature
corrected. Add or subtract to the specific gravity
reading 0.004, 4 points, for each 6_C(10_F)
above or below 27_C(80_F).
TO REPLACE BATTERY
FOR SAFETY: Before Leaving Or
Servicing Machine; Stop On Level
Surface, Set Parking Brake, Turn Off
Machine And Remove Key.
1. Raise the seat support and engage the prop
rod.
2. Disconnect the negative then the positive
battery cables.
3. Remove the battery hold down bracket from
the machine.
4. Tilt the battery and lift it out of the machine.
5. Clean the cables and the posts on the new
battery and install back in the machine.
6. Reinstall the battery hold down bracket.
7. Reconnect the positive then the negative
battery cables and close the seat support.

ELECTRICAL
4-6 7400 MM428 (12--98)
INSTRUMENT PANEL
The instrument panel consists of a circuit board, a
touch panel, and a water/dust resistant plastic
enclosure. Its touch panel controls various
machine functions, while its indicator lights keep
the operator informed on machine performance.
TO REPLACE INSTRUMENT PANEL
FOR SAFETY: Before Leaving Or
Servicing Machine; Stop On Level
Surface, Set Parking Brake, Turn Off
Machine And Remove Key.
1. Raise the seat support and engage the prop
rod.
2. Remove the battery cables from the battery.
3. Put the steering wheel in the lowest position.
4. Open the front cover on the machine.
5. Remove four M5 pan head screws holding
the instrument panel to the dash panel.
6. Pull the instrument panel back away from
machine.
7. Loosen the allen head screw in center of
wire harness plug. Disconnect the harness.
8. Remove instrument panel from machine.
9. Install the new instrument panel back on the
dash panel with the four M5 pan head
screws and washers. Hand tighten snug.
10. Push the main harness plug back in the
instrument panel.
NOTE: Slot in panel must line up with notch on
plug. Hand tighten the allen head screw.
11. Close the front cover.
12. Reconnect the battery cables and lower the
seat support.
13. Start the machine and check for proper
operation.

ELECTRICAL
4-7
7400 MM428 (12--98)
TO DISASSEMBLE INSTRUMENT PANEL
1. Remove panel from machine. See TO
REPLACE INSTRUMENT PANEL
instructions.
2. Place the instrument panel face down and
remove the twelve larger pan head screws
from the back.
3. The touch panel case can now be separated
from the outer case and new O-ring gasket
installed if necessary.
4. To disassemble the touch panel case further,
remove the four smaller pan head screws
from the center of case box.
5. Remove the case box from the circuit board
/ touch panel assembly.
6. The O--ring and connector gaskets can now
be replaced in the case box if necessary.
7. Remove the eight pan head screws, unplug
the flat connector and ground strap, remove
the touch panel from the circuit board.
8. Any burned-out lamps can now be changed
by turning them 1/4 turn counterclockwise
and lifting out.
9. To replace the hour meter, unplug the two
wires and remove the two pan head screws.

ELECTRICAL
4-8 7400 MM428 (12--98)
TO REASSEMBLE INSTRUMENT PANEL
1. Position the circuit board over the touch
panel. Feed the flat connector from panel
through the slot in board, plug it in and
reconnect the ground strap.
2. Reinstall the eight pan head screws and
lightly hand tighten.
3. Turn the circuit board assembly over and
place it back in the case box.
4. Reinstall the four smaller pan head screws
in center of case box. Lightly hand tighten.
5. Reinstall the touch panel case on the outer
case.
6. Reinstall the twelve pan head screws and
lightly hand tighten.
7. The instrument panel is now ready to be
reinstalled in the machine. See TO
REPLACE INSTRUMENT PANEL
instructions.

ELECTRICAL
4-9
7400 MM428 (12--98)
TO REPLACE MACHINE RELAY
FOR SAFETY: Before Leaving Or
Servicing Machine; Stop On Level
Surface, Set Parking Brake, Turn Off
Machine And Remove Key.
1. Raise the seat support and engage the prop
rod.
2. Remove the battery cables from the battery.
3. Open the front cover on the machine.
4. Locate the relays at the front of the
operators compartment, near the hydraulic
steering motor.
5. Lift up on the relay to harness locking tab.
6. Pull the harness plug out of the relay.
7. Remove the pan screw holding the relay to
the operators compartment. Remove and
discard the old relay.
8. Position the new relay on the operators
compartment.
9. Reinstall the pan screw holding the relay to
the operators compartment.
10. Reconnect the harness plug in the relay.
See schematic in the ELECTRICAL section.
11. Reconnect the battery cables to the battery.
12. Lower the seat support.
13. Close the front cover on the machine.
14. Start and operate the machine, checking for
proper operation.

ELECTRICAL
4-10 7400 MM428 (12--98)
TO REPLACE CIRCUIT BREAKER
FOR SAFETY: Before Leaving Or
Servicing Machine; Stop On Level
Surface, Set Parking Brake, Turn Off
Machine And Remove Key.
1. Raise the seat support and engage the prop
rod.
2. Remove the battery cables from the battery.
3. Open the front cover on the machine.
4. Locate the circuit breakers at the front of the
operators compartment, near the hydraulic
steering motor.
5. Remove and retain the rubber boot on the
front of the circuit breaker
6. Disconnect the electrical wires on the back
of the circuit breaker.
7. Remove the steel retaining ring holding the
circuit breaker to the dash panel. Remove
the circuit breaker.
8. Position the new circuit breaker in the
mounting hole on the dash panel.
9. Install the retaining ring on the new circuit
breaker. Push the ring on all the way to the
bottom of the circuit breaker.
10. Reconnect the wires to the back of the
circuit breaker. See schematic in the
ELECTRICAL section.
11. Reconnect the battery cables to the battery.
12. Lower the seat support.
13. Close the front cover on the machine.
14. Start and operate the machine, checking for
proper operation.

ELECTRICAL
4-11
7400 MM428 (6--01)
18A/ORA
1E/RED
1/RED
15B/BLU
13E/BLK
19B/BLU
72C/YEL
71C/YEL
72C/YEL
23C/GRY
PIN 20
TIED TO ENG.
OIL PRESS.
PIN 9
SCRUB BR.
MUST BE ON
5 SEC. DELAY
ES PUMP RUNS
30 SEC.
5 SEC. DELAY
1MIN.TOVAC
FAN SHUT--OFF
42B/YEL
42A/YEL42/YEL
56/ORA
3
5
13
10
7
8
17
14
15
4
1
9
18
20
19A/BLU
13R/BLK
13M/BLK
13K/BLK
13D/BLK
13G/BLK
23C/GRY
23C/GRY
23B/GRY 23/GRY
27/PUR
26/BRN
58/BLU
60/GRN
18T/ORA
RECOVERY
TANK
SOLUTION
TANK
S--18 N.C.H.O.
S--17 N.O.H.C.
13F/BLK
72B/GRY
18U/ORA
71B/YEL
ELEC.
SPARK
CONT.
COOLANT TEMP.
SENSOR
67/ORA
10K OHMS
VAR. RELUCTANCE
SENSOR
64/BRN
65/BLU
66/GRN
68/BRN T
13PP/BLK
70/GRN
PLUGS
12
11
10
9
8
7
6
4
3
2
13N/BLK
FILTER SWITCH
S--14
HYDRAULIC
M6
LIGHTS
85 86 LP CLOSES BELOW
40 PSI
M7
REVERSE
85 86
83/BRN
10/GRY
15/BLU
CB--1
15A
36/GRN
35/BRN
13H/BLK
14/GRN
18A/ORA
N.C.H.O.
N.C.H.O.
GAS--DIESEL
13P/BLK
13B/BLK
C
S--4 OIL SWITCH
15A/BLU
FUEL PUMP
10A/GRY
M2
STARTER RELAY
M1
S--6
18A/
ORA
18A/
ORA
71C/YEL
18C/ORA
18/ORA
8730
FLOW SWITCH
15/
BLU
M4 8685
28/YEL
C
M5 57/GRN
5.0A
S--15
23A/GRY
ES PUMP
MTR
DETERGENT METERING
85 86
REVERSE
RECOVERY TANK
S--8
S--1
M322/
YEL
8685 M3
1E/
RED
CB--6
19/BLU
A
2/
ORA
C
IGNITION
SWITCH
S--3
CB--5
43/BLU
13L/BLK
13J/BLK
55A MAX.
CHARGE
1C/RED
1D/RED
2/ORA
A
L2
1B/RED
5/YEL
18D/ORA
12V
540 C.C.A.
20A/BLU
20/BLU
10/GRY
4/YEL
84/GRN
86/PUR
HG
FEDC
B
A
CLOSES AT225
°F
ELECTRONIC
INSTRUMENT
PANEL
COOLANT TEMP
SENDER
FUEL SENDER
SE--1
SE--2
HORN BUTTON
15A
HORN
17
50
BATT.
30
19
ACC
START
SENSE
GOV
CONTROL
THROTTLE
ACTUATOR
13A/BLK
STARTER MOTOR
13/BLK
B
A
TTER
Y
ALTERNATOR
GND
OUT
1A/RED
STARTER RELAY
M1 MTR
SHEET 1
GAS/LPG ELECTRICAL SCHEMATIC

ELECTRICAL
4-12 7400 MM428 (6--01)
SHEET 2
GAS/LPG ELECTRICAL SCHEMATIC

ELECTRICAL
4-13
7400 MM428 (6--01)
8/GRN
FU--1
40A
13Q/BLK
GLOW PLUGS
MAGNETIC
PICKUP
7/YEL
72C/GRY
71C/YEL
84/GRN
86/PUR
18C/ORA
THROTTLE
ACTUATOR
23C/GRY
PIN 20
TIED TO ENG.
OIL PRESS.
PIN 9
SCRUB BR.
MUST BE ON
5 SEC. DELAY
ES PUMP RUNS
30 SEC.
5 SEC. DELAY
1MIN.TOVAC
FAN SHUT--OFF
42A/YEL42/YEL
56/ORA
3
5
13
10
7
8
17
14
15
4
1
9
18
20
19A/BLU
13R/BLK
13K/BLK
13D/BLK
13G/BLK
23C/GRY
23C/GRY
23B/GRY 23/GRY
27/PUR
26/BRN
58/BLU
60/GRN
RECOVERY
TANK
SOLUTION
TANK
S--18 N.C.H.O.
S--17 N.O.H.C.
13N/BLK
FILTER SWITCH
S--14
HYDRAULIC
M6
LIGHTS
85 86
M7
REVERSE
85 86
83/BRN
10/GRY
15/BLU
15A
CB--1
15A
CB--5
15A
CB--5
15A
36/GRN
35/BRN
13H/BLK
14/GRN
18A/ORA
N.C.H.O.
GAS--DIESEL
13P/BLK
13B/BLK
C
S--4 OIL SWITCH15A/BLU
FUEL PUMP
10A/GRY
M2
STARTER RELAY
M1
18A/
ORA
18A/
ORA
18/ORA
8730
FLOW SWITCH
15/
BLU
M4 8685
28/YEL
M5 57/GRN
5.0A
S--15
23A/GRY
ES PUMP
MTR
DETERGENT METERING
85 86
REVERSE
RECOVERY TANK
S--8
S--1
M3
22/
YEL
8685 M3
1E/
RED CB--6
19/BLU
A
2/
ORA
C
IGNITION
SWITCH
S--3
CB--5
43/BLU
13L/BLK
13J/BLK
55A MAX.
CHARGE
1C/RED
1D/RED
2/ORA
A
L2
1B/RED
5/YEL
12V
540 C.C.A.
20A/BLU
20/BLU
10/GRY
4/YEL
HG
FEDC
B
A
CLOSES AT
225
°
F
ELECTRONIC
INSTRUMENT
PANEL
COOLANT TEMP
SENDER
FUEL SENDER
SE--1
SE--2
HORN BUTTON
15A
HORN
17
50
BATT.
30
19
ACC
START
SENSE
GOV
CONTROL
13A/BLK
STARTER MOTOR
13/BLK
BATTERY
ALTERNATOR
GND
OUT
1A/RED
STARTER RELAY
M1
1/RED MTR
SHEET 3
DIESEL ELECTRICAL SCHEMATIC

ELECTRICAL
4-14 7400 MM428 (6--01)
SHEET 4
DIESEL ELECTRICAL SCHEMATIC

ELECTRICAL
4-15
7400 MM428 (6--01)
13H/BLK
13H/BLK
96/GRY
96B/GRY
46/BRN
46C/BRN
BRN
BLK
RED
62E/BRN
13II/BLK
89B/ORA
13J/BLK
13M/BLK
13F/BLK
13N/BLK
13TT/BLK
13P/BLK
13B/BLK
1D/RED
1A/RED
1C/RED
AC
CIRCUIT 2
CIRCUIT 1
25D/GRY
25D/GRY
BA
25A/GRY
AB
EH
E
46C/BRN WATER
VALV E
CONTROL
42A/YEL
CC
BB
VIEW B--B
WATER CONTROL
SWITCH
36/GRN
13R/BLK
43/BLU
RED
GRN
BLK
BRN
BLK
RED
MAIN PANEL
96/GRY
95/BLU
95/BLU
5/YEL
5/YEL
4/YEL
SIDE BRUSH
VALV E LOW
OPTION
SOLUTION
SWITCHES
OPTION
R.H. TAIL--LIGHT
SEE MAIN SCRUB VALVE
HYD. FILTER SWITCH
OPTIONS
REC TANK -- INNER SWITCH
NO C
NC
62D/BRN
13HH/BLK
89A/ORA
BACK--UP
ALARM
ES PUMP
AUTO FILL
ROT. LIGHT
SEE OPTIONS
SEE OPTIONS
DETERGENT PUMP
28/YEL
13J/BLK
13K/BLK
13R/BLK
13F/BLK
18C/ORA
71C/YEL
CBA
10/GRY
42/YEL
62A/YEL
CBA
AB
ABC
A
B
1E/RED
HORN
1/RED
TO
BATTERY
STARTER
TO MAIN
HARNESS
85/BLU
83/BRN
84/GRN
86/PUR
72C/YEL 18D/ORA
13E/BLK
71C/YEL 1D/RED
20D/BLU
20/BLU
10A/GRY
10/GRY
VIEW C--C
GOVERNOR
CONTROL VIEW F--F
KEY SWITCH
ALTERNATOR
WATER
TEMPERATURE
SENDER
13A/BLK
SEE
OPTIONS
FUEL
SENDER
42A/YEL
13L/BLK
1/RED
BATTERY
GAS AND DIESEL
LOCATION
TO
ENGINE
13/BLK
13P/BLK
14/GRN
FUEL PUMP
HORN
SWITCH
15B/BLU
13B/BLK
86/PUR
84/GRN
13M/BLK
D.I.S. ENGINE
HARNESS
ACTUATOR
OIL
PRESSURE
SWITCH
L.P.
SWITCH
72C/YEL
13X/BLK
13Y/BLK
13DD/BLK
13G/BLK
GOVERNOR
CONTROL
L.H. HEADLIGHT
62B/YEL
62A/YEL
13DD/BLK
13CC/BLK
13CC/BLK
R.H. HEADLIGHT
62/YEL
FF
17
19
30
50
L.H. TAIL--LIGHT
RELAYS
LOWHIGH
REVERSE
FLOW
SWITCH
SIDE BRUSH VALVE
OPTION
DIODE
BRAKE SWITCH
OPTION
DA
HE
CIRCUIT BREAKERS
WATER CONTROL
SWITCH
C
AB
1
SHEET 5
GAS/LPG WIRE HARNESS GROUP

ELECTRICAL
4-16 7400 MM428 (6--01)
18U/BLK
30
85
86
87
87A
VIEW A--A
RELAYS
M2 FUEL PUMP
M3 INSTRUMENT PANEL
M4 HYD. SOLENOIDS
M5 ES PUMP
M6 HEADLIGHTS
M7 REVERSE
21B/GRY
25/GRY
72C/YEL
71C/YEL
70/GRN
13PP/BLK
18T/ORA
68/BRN
68/BRN
67/ORA
66/GRN
65/BLU
VIEW G--G
UNIVERSAL
ELECTRONIC
SPARK CONTROL
UNIVERSAL
ELECTRONIC
SPARK CONTROL
66/GRN
65/BLU
VARI BL E
RELUCTANCE
SENSOR
70/GRN
64/BRN
COOLANT
SENSOR
71B/YEL
72B/GRY
DISTRIBUTORLESS
IGNITION
COIL
D.I.S. ENGINE
HARNESS TO MAIN
HARNESS
13F/BLK
18C/ORA
71C/YEL
72C/YEL
AC
GG
12
11
10
9
8
7
6
5
4
3
2
1
B
1F/RED
92/PUR
18/ORA
18C/ORA
20/BLU
4/YEL
65/GRY
65A/GRY
22/YEL
4A/YEL
1C/RED
59/BRN
59A/BRN
20C/BLU
CIRCUIT
BREAKERS
CB--1 IGNITION
CB--2 ES PUMP
CB--3 HEADLIGHTS
CB--4 BACK--UP ALARM
CB--5 HORN
CB--6 INSTRUMENT PANEL (5.0A)
CB--7 SCRUB SOLENOIDS
CB--8 SIDE BRUSH SOLENOIDS AND
WATER VALVES
CB--3
MAIN
HARNESS
CB--1CB--2CB--4
CB--5CB--6CB--7CB--8
20B/BLU
20A/BLU
24/PUR
25A/GRY
1E/RED
21A/GRY
21/GRY
DIODE
ASSY
19B/BLU
13D/BLK
AB
AB
10A/GRY
92/PUR
M5 M6 M7M2 M3 M4
93/ORA62/YEL
58/BLU19A/BLK
65/GRY
57/GRN
66/BRN
59/BRN
60/GRN
14/GRN
15A/BLU
18A/ORA
18A/ORA
22/YEL
19/BLU
18A/ORA
23B/GRY
1F/RED
18A/ORA
21/GRY
23C/GRY 23C/GRY 23C/GRY
2345 7
MAIN
HARNESS
SECTION B--B
85 COIL+
86 COIL --
30 COMMON CONTACT
87 N.O. CONTACT
87A N.C. CONTACT
B
B
AA
2
4
SHEET 6
GAS/LPG WIRE HARNESS GROUP

ELECTRICAL
4-17
7400 MM428 (6--01)
MAIN INSTRUMENT
PANEL SOCKET
REAR VIEW
SV2
24B/PUR
12
18
24
23
22
21
20
19
13 7
6
5
4
3
2
1
24B/PUR
48/GRY
47/BRN
24B/PUR
24B/PUR
45/GRY
AB
AB
BA
BA
24B/PUR
46A/BRN
AB
A
B
AB
AB
A
B
25C/GRY
AB
A
B
46A/BRN
A
B
AB
SV7 46A/BRN
24B/PUR
SCRUB VALVE
BLOCK
MAIN
HARNESS
51C/PUR
SV5
SV1SV6
SV4
SV3
HYDRAULIC SOLENOID VALVES
SV--1 SCRUB BRUSH ON
SV--2 VACUUM FAN ON
SV--3 SQUEEGEE DOWN
SV--4 DOWN PRESS. PROPORTIONAL VALVE
SV--5 SCRUB BRUSH DOWN
SV--6 SIDE BRUSH ON
SV--7 SCRUB BRUSH UP -- HOLD
58/BLU
83/BRN
1A/RED
21B/GRY
13S/BLK
13T/BLK
13U/BLK
45/GRY
60/GRN
46/BRN
48/GRY
15/BLU
2/ORA
42/ORA
51/PUR
47/BRN
28/YEL
56/YEL
36/GRN
35/BRN
52/YEL
43/BLU
57/GRN
26/BRN
23/GRY
13A/BLK
1B/RED
2/ORA
E
S
EXC
L2
B
P
CONN. A.SOC. NO.
24
23
22
21
20
19
18
17
16
15
14
13
12
11
10
9
8
7
6
5
4
3
2
1
CONNECTOR WIRIN
G
MANDO
ALTERNATOR
60559
TO
MAIN
HARNESS
TO
ENGINE
BLOCK
BA
SHEET 7
GAS/LPG WIRE HARNESS GROUP
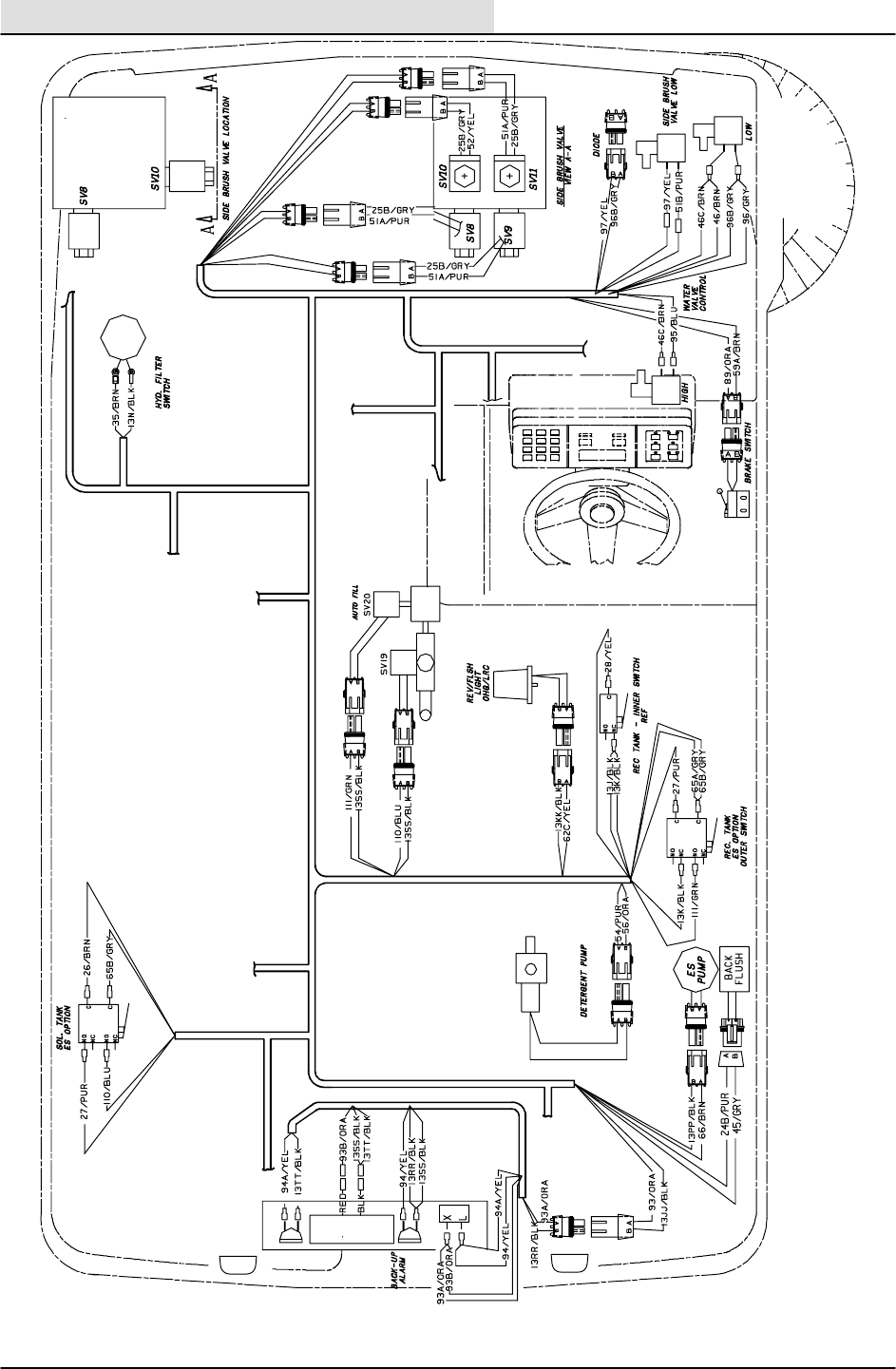
ELECTRICAL
4-18 7400 MM428 (6--01)
SHEET 8
GAS/LPG WIRE HARNESS GROUP (OPTIONS)

ELECTRICAL
4-19
7400 MM428 (6--01)
13DD/BLK
43/BLU 1D/RED
1C/RED
1A/RED
62A/YEL
BRN
BLK
RED
62E/BRN
13II/BLK
89B/ORA
WATER CONTROL
SWITCH
CIRCUIT 2
CIRCUIT 1
25A/GRY
AB
BA
MAGNETIC
PICK--UP
13Y/BLK 72E/GRN
GLOW PLUGS
8/GRN
7/YEL
8/GRN
7A/YEL
7/YEL
TO
MAIN
HARNESS 1D/RED
20D/BLU
20/BLU
10A/GRY
10/GRY
AC
17
19
30
50
BA
25D/GRY
AB
E H
E
46C/BRN
13H/BLK
13H/BLK
WATER
VALV E CONTROL
CC
BB
VIEW B--B
WATER CONTROL
SWITCH
36/GRN
13R/BLK
RED
GRN
BLK
BRN
BLK
RED
MAIN PANEL
96/GRY
25D/GRY
95/BLU
95/BLU
5/YEL
96/GRY
96B/GRY
46/BRN
46C/BRN
5/YEL
4/YEL
SIDE BRUSH
VALV E LOW
OPTION
SOLUTION SWITCHES
R.H. TAIL--LIGHT
SEE MAIN SCRUB VALVE
HYD. FILTER SWITCH
OPTIONS
REC TANK -- INNER SWITCH
NO C
NC
62D/BRN
13HH/BLK
89A/ORA
BACK--UP
ALARM ES PUMP
AUTO FILL
ROT. LIGHT
SEE OPTIONS
SHEET 12
DETERGENT PUMP
28/YEL
13J/BLK
13K/BLK
13M/BLK
13J/BLK
13R/BLK
10/GRY
42/YEL
62A/YEL
CBA
ABC
1E/RED
HORN
1/RED
TO
BATTERY
STARTER
85/BLU
83/BRN
84/GRN
86/PUR
72C/YEL 18D/ORA
13E/BLK
71C/YEL
VIEW C--C
GOVERNOR CONTROL
VIEW F--F
KEY SWITCH
ALTERNATOR
WATER
TEMPERATURE
SENDER
13A/BLK
FUEL
SENDER
42A/YEL
13L/BLK
1/RED
BATTERY
GAS AND DIESEL
LOCATION
TO
ENGINE
13/BLK
13P/BLK
14/GRN
FUEL PUMP
HORN
SWITCH
15B/BLU
13B/BLK
86/PUR
84/GRN
ACTUATOR
OIL
PRESSURE
SWITCH
13N/BLK
13X/BLK
13TT/BLK
13P/BLK
13B/BLK
13Y/BLK
13G/BLK
GOVERNOR
CONTROL
L.H. HEADLIGHT
62B/YEL
13DD/BLK
13CC/BLK
13CC/BLK
R.H. HEADLIGHT
62/YEL
FF
L.H. TAIL--LIGHT
RELAYS
LOW
HIGH
REVERSE
FLOW
SWITCH
SIDE BRUSH
VALV E
OPTION
DIODE
BRAKE SWITCH
OPTION
DA
HE
CIRCUIT BREAKERS
C
A B
1
SHEET 9
DIESEL WIRE HARNESS GROUP

ELECTRICAL
4-20 7400 MM428 (6--01)
30
85
86
87
87A
21B/GRY
25/GRY
1F/RED
92/PUR
18/ORA
18C/ORA
20/BLU
4/YEL
65/GRY
65A/GRY
22/YEL
4A/YEL
1C/RED
59/BRN
59A/BRN
20C/BLU
CIRCUIT
BREAKERS
CB--1 IGNITION
CB--2 ES PUMP
CB--3 HEADLIGHTS
CB--4 BACK--UP ALARM
CB--5 HORN
CB--6 INSTRUMENT PANEL (5.0A)
CB--7 SCRUB SOLENOIDS
CB--8 SIDE BRUSH SOLENOIDS AND
WATER VALVES
CB--3
MAIN
HARNESS
CB--1CB--2CB--4
CB--5CB--6CB--7CB--8
20B/BLU
20A/BLU
24/PUR
25A/GRY
1E/RED
21A/GRY
21/GRY
VIEW A--A
ROTATED
DIODE
ASSY
19B/BLU
13D/BLK
A
B
AB
RELAYS
M2 FUEL PUMP
M3 INSTRUMENT PANEL
M4 HYD. SOLENOIDS
M5 ES PUMP
M6 HEADLIGHTS
M7 REVERSE
10A/GRY
92/PUR
M5 M6 M7M2 M3 M4
93/ORA62/YEL
58/BLU
19A/BLK
65/GRY
57/GRN
66/BRN
59/BRN
60/GRN
14/GRN
15A/BLU
18A/ORA
18A/ORA
22/YEL
19/BLU
18A/ORA
23B/GRY
1F/RED
18A/ORA
21/GRY
23C/GRY 23C/GRY 23C/GRY
234567
MAIN
HARNESS
SECTION B--B
85 COIL+
86 COIL --
30 COMMON CONTACT
87 N.O. CONTACT
87A N.C. CONTACT
BB
AA
2
SHEET 10
DIESEL WIRE HARNESS GROUP

ELECTRICAL
4-21
7400 MM428 (6--01)
SV2
24B/PUR
24B/PUR
48/GRY
47/BRN
24B/PUR
24B/PUR
45/GRY
AB
AB
BA
B
A
24B/PUR
46A/BRN
AB
A
B
AB
A
B
AB
A
B
25C/GRY
AB
AB
46A/BRN
A
B
AB
SV7 46A/BRN
24B/PUR
SCRUB VALVE
BLOCK
MAIN
HARNESS
51C/PUR
SV5
SV1SV6
SV4
SV3
HYDRAULIC SOLENOID VALVES
SV--1 SCRUB BRUSH ON
SV--2 VACUUM FAN ON
SV--3 SQUEEGEE DOWN
SV--4 DOWN PRESS. PROPORTIONAL VALVE
SV--5 SCRUB BRUSH DOWN
SV--6 SIDE BRUSH ON
SV--7 SCRUB BRUSH UP -- HOLD
MAIN INSTRUMENT
PANEL SOCKET
REAR VIEW
12
18
24
23
22
21
20
19
13 7
6
5
4
3
2
1
58/BLU
83/BRN
1A/RED
21B/GRY
13S/BLK
13T/BLK
13U/BLK
45/GRY
60/GRN
46/BRN
48/GRY
15/BLU
2/ORA
42/ORA
51/PUR
47/BRN
28/YEL
56/YEL
36/GRN
35/BRN
52/YEL
43/BLU
57/GRN
26/BRN
23/GRY
13A/BLK
1B/RED
2/ORA
E
S
EXC
L2
B
P
CONN. A.
SOC. NO.
24
23
22
21
20
19
18
17
16
15
14
13
12
11
10
9
8
7
6
5
4
3
2
1
CONNECTOR WIRING
MANDO
ALTERNATOR
60559
TO
MAIN
HARNESS
TO
ENGINE
BLOCK
SHEET 11
DIESEL WIRE HARNESS GROUP
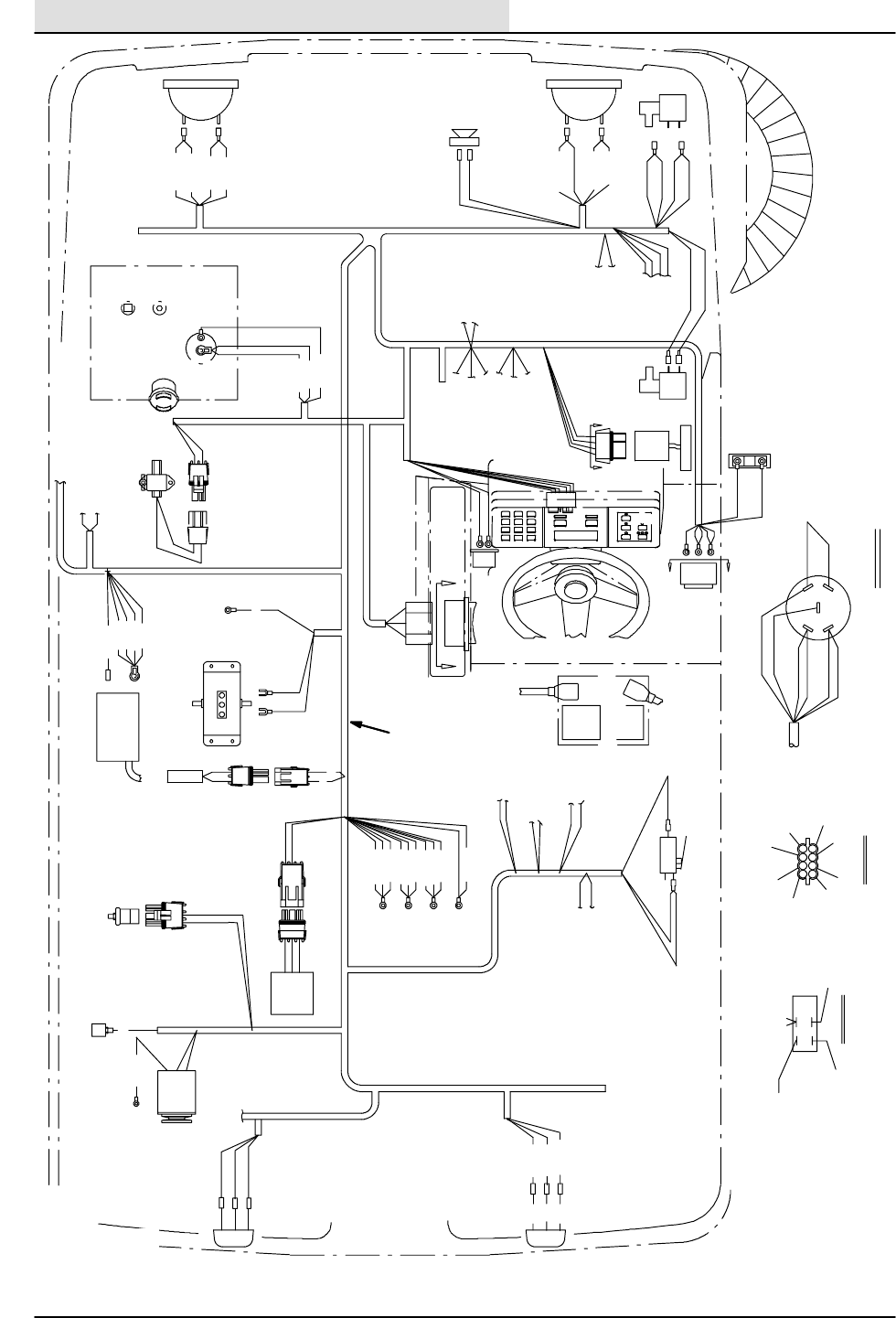
ELECTRICAL
4-22 7400 MM428 (6--01)
13DD/BLK
43/BLU 1D/RED
1C/RED
1A/RED
62A/YEL
BRN
BLK
RED
62E/BRN
13II/BLK
89B/ORA
WATER CONTROL
SWITCH
CIRCUIT 2
CIRCUIT 1
25A/GRY
AB
BA
MAGNETIC
PICK--UP
13Y/BLK 72E/GRN
GLOW PLUGS
8/GRN
7/YEL
8/GRN
7A/YEL
7/YEL
TO
MAIN
HARNESS 1D/RED
20D/BLU
20/BLU
10A/GRY
10/GRY
AC
17
19
30
50
BA
25D/GRY
AB
E H
E
46C/BRN
13H/BLK
13H/BLK
WATER
VALV E CONTROL
CC
BB
VIEW B--B
WATER CONTROL
SWITCH
36/GRN
13R/BLK
RED
GRN
BLK
BRN
BLK
RED
MAIN PANEL
96/GRY
25D/GRY
95/BLU
95/BLU
5/YEL
96/GRY
96B/GRY
46/BRN
46C/BRN
5/YEL
4/YEL
SIDE BRUSH
VALV E LOW
OPTION
SOLUTION SWITCHES
R.H. TAIL--LIGHT
SEE MAIN SCRUB VALVE
HYD. FILTER SWITCH
OPTIONS
REC TANK -- INNER SWITCH
NO C
NC
62D/BRN
13HH/BLK
89A/ORA
BACK--UP
ALARM ES PUMP
AUTO FILL
ROT. LIGHT
SEE OPTIONS
SHEET 12
DETERGENT PUMP
28/YEL
13J/BLK
13K/BLK
13M/BLK
13J/BLK
13R/BLK
10/GRY
42/YEL
62A/YEL
CBA
ABC
1E/RED
HORN
1/RED
TO
BATTERY
STARTER
85/BLU
83/BRN
84/GRN
86/PUR
72C/YEL 18D/ORA
13E/BLK
71C/YEL
VIEW C--C
GOVERNOR CONTROL
VIEW F--F
KEY SWITCH
ALTERNATOR
WATER
TEMPERATURE
SENDER
13A/BLK
FUEL
SENDER
42A/YEL
13L/BLK
1/RED
BATTERY
GAS AND DIESEL
LOCATION
TO
ENGINE
13/BLK
13P/BLK
14/GRN
FUEL PUMP
HORN
SWITCH
15B/BLU
13B/BLK
86/PUR
84/GRN
ACTUATOR
OIL
PRESSURE
SWITCH
13N/BLK
13X/BLK
13TT/BLK
13P/BLK
13B/BLK
13Y/BLK
13G/BLK
GOVERNOR
CONTROL
L.H. HEADLIGHT
62B/YEL
13DD/BLK
13CC/BLK
13CC/BLK
R.H. HEADLIGHT
62/YEL
FF
L.H. TAIL--LIGHT
RELAYS
LOW
HIGH
REVERSE
FLOW
SWITCH
SIDE BRUSH
VALV E
OPTION
DIODE
BRAKE SWITCH
OPTION
DA
HE
CIRCUIT BREAKERS
C
A B
1
SHEET 12
DIESEL WIRE HARNESS GROUP (OPTIONS)

ELECTRICAL
4-23
7400 MM428 (12--98)
DIAGNOSTICS
The Model 7400 has an on--board diagnostic
system. Each time the control board is powered
up, it performs a self test. If the self test passes,
the “OK” light is illuminated.
This trouble shooting section describes the
different operating modes that are available, how
to enter that mode, and a detail description of how
that mode works.

ELECTRICAL
4-24 7400 MM428 (12--98)
OPERATING MODES
The Model 7400 has 6 different operating modes.
The machine operator can access each mode by
pressing various buttons on the control panel,
holding them, and turning on the key. The
common operating modes are detailed in the
following charts.
Operating Modes Entry Sequence
(how to activate)
Normal Mode;Normal operation.
More info pages 4--25 thru 4--27
Default (when key is turned on)
Manual Mode; Manually operate discrete
functions without interlocks.
More info page 4--28
1. Push and hold the ES button
2. Turn on the key
3. Hold the ES button until the maintenance light
comes on.
4. Release the ES button
Input Display Mode; Display the state of floats,
limit switches, and sensors.
More info page 4--29
1. Push and hold the Squeegee button
2. Turn on the key
3. Hold the Squeegee button until the maintenance
light comes on.
4. Release the Squeegee button
Error Display Mode; Display the cause of a
self--test failure.
More info pages 4--30 thru 4--32
1. Push and hold the Detergent button
2. Turn on the key
3. Hold the Detergent button until the maintenance
light comes on.
4. Release the Detergent button
Pressure Adjust Mode; Adjust the pressure
levels for the three down pressure settings.
More info page 4--33
1. Push and hold the Side Brush button
2. Turn on the key
3. Hold the Side Brush button until the
maintenance light comes on.
4. Release the Side Brush button
Reset Scrub Pressures; Return the down
pressure settings to the factory defaults.
More info page 4--34
1. Push and hold the Scrub button
2. Turn on the key
3. Hold the scrub button
4. Wait for the maintenance light
5. While holding the Scrub button, press and hold
the Side Brush button
6. Wait for the maintenance light to go out
7. Release the Scrub and Side Brush buttons
8. Turn the key off
9. Restart the machine

ELECTRICAL
4-25
7400 MM428 (12--98)
Operating Mode Entry Sequence
(how to activate)
Normal Mode;Normal operation. Default (when key is turned on)
NORMAL MODE
The purpose of the normal mode is for the general
operation of the machine. The machine will
normally start in this mode. What follows is a brief
description of each of the operations in the normal
mode.
SCRUB BUTTON
The purpose of the scrub button is to turn the
scrubbing operations on and off and adjust the
scrubbing down pressure. Pressing the scrub
button while the scrubbing operation is currently
inactive will initiate the following actions:
1. The engine speed will be set to high.
2. If the machine is not in reverse, the main
brushes will turn on and lower. The down
pressure setting will be the same used
during the last scrub cycle. The solution will
flow at the high or low rate according to the
water position switch.
3. If the machine is in reverse, the brushes will
stay up until reverse is no longer sensed.
4. If the side brush LED is on, the side brush will
turn on and lower. The down pressure
setting will be the same used during the last
scrub cycle.
5. The vacuum fan will turn on.
6. If the machine is not in reverse, the squeegee
will lower.
7. If the machine is in reverse, the squeegee will
stay up until reverse is no longer sensed.
8. If any of the detergent LED’s are active, the
water valves are turned on, and the machine
is not in reverse, the detergent pump will
run. The detergent pump will run at its slow
rate if one LED is on. The detergent pump
will run at its fast rate if two LED’s are on.

ELECTRICAL
4-26 7400 MM428 (12--98)
SCRUB BUTTON (continued)
If the operator pushes and holds the scrub button,
the pressure settings will begin to scroll. The
pressure settings displayed after releasing the
scrub button will become the new default down
pressure setting.
If the scrub function was active and the operator
pushes, then releases the scrub button, the
following actions will take place:
1. The main brushes will turn off and rise.
2. The side brush will turn off and rise.
3. The solution flow will turn off.
4. The detergent pump will turn off.
5. A delay will pass, and then the squeegee will
rise.
6. Another small delay will pass and the vacuum
fan will turn off.
SQUEEGEE BUTTON
Pressing the squeegee button will start or stop the
water pickup operation. If the operator presses
the squeegee button while the squeegee LED is
currently not illuminated will cause the following
actions:
1. The squeegee LED will be illuminated.
2. The squeegee will drop and the vacuum fan
will turn on, if the machine is not in reverse.
If the machine goes into reverse while the
squeegee is active, the squeegee will rise.
Pressing the squeegee button while the squeegee
LED is on will cause the following actions:
1. The squeegee LED will turn off.
2. The squeegee will raise.
3. There will be a 30 second delay.
4. The vacuum fan will turn off.

ELECTRICAL
4-27
7400 MM428 (12--98)
DETERGENT
Pressing the detergent button will cause the
detergent display to scroll through its three
modes. The detergent pump will run only if the
main scrub brushes are active and the solution
switch is on.
DOff (all LED’s off) -- detergent pump off.
DLow (left LED is on) -- detergent pump on low.
DHigh (both LED’s are on) -- detergent pump
on high.
EStBUTTON
Pressing the EStbutton will enable or disable
the EStsystem. The EStsystem will draw
water from the recovery tank, through a filter and
pump it into the solution tank. If the operator has
turned on the EStsystem, and the recovery tank
EStfloat reads a full tank, the EStpump will
begin to run. The EStpump will continue to run
for about 30 seconds after the EStfloat
becomes uncovered.
OVERFLOW FLOAT
In order for the recovery tank float to become
active, it must be consistently in the up position
for at least 10 seconds. If the scrub or vacuum fan
are active and the tank full float becomes active,
the following actions will occur:
1. The overflow light will begin to blink.
2. A one minute delay will pass.
3. The overflow light will stop blinking and stay
on.
4. The Scrub and Squeegee functions will be
canceled.

ELECTRICAL
4-28 7400 MM428 (12--98)
Operating Mode Entry Sequence
(how to activate)
Manual Mode; Manually operate discrete
functions without interlocks.
1. Push and hold the EStbutton
2. Turn on the key
3. Hold the EStbutton until the maintenance
light comes on.
4. Release the EStbutton
MANUAL MODE
The purpose of the manual mode is to allow the
operator to exercise individual functions on the
machine.
NOTE: This mode disregards the effects of
various interlocks. Do not scrub with the
machine in this mode.
FOR SAFETY: When Servicing Machine,
AvoidMovingParts.DoNotWear
Loose Jackets, Shirts, Or Sleeves.
After entering the Manual Mode, the control
buttons assume the following functions:
EStBUTTON
Pressing the EStbutton will toggle the ESt
pump on or off. In the on position, the EStpump
will run regardless of the state of the floats.
SIDE BRUSH BUTTON
Pressing the Side Brush button will turn on and
lower the side brush. If the main brush is off, the
side brush will use the low pressure setting.
SQUEEGEE BUTTON
Pressing the Squeegee button will turn on the
vacuum fan and lower the squeegee. Reverse is
ignored.
ENGINE BUTTON
Pressing the Engine button will toggle the engine
between high and low speed.
SCRUB BUTTON
Pressing the Scrub button will turn on and lower
the main scrub head. Holding the Scrub button
while scrub is active will cause the down pressure
to scroll.
DETERGENT BUTTON
Pressing the Detergent button will cause the
detergent LED’s to scroll. If no LED’s are on, the
detergent pump will be off. If one LED is
illuminated, the detergent pump will run in low
speed. If both LED’s are on, the detergent pump
will run in high speed.

ELECTRICAL
4-29
7400 MM428 (12--98)
Operating Mode Entry Sequence
(how to activate)
Input Display Mode; Display the state of floats,
limit switches, and sensors.
1. Push and hold the Squeegee button
2. Turn on the key
3. Hold the Squeegee button until the maintenance
light comes on.
4. Release the Squeegee button
INPUT DISPLAY MODE
In this mode, the operator can observe whether or
not inputs to the panel are operating as intended.
In the Input Display Mode, the segments of the
gas gauge display the state of each input. If an
input is open, the controller turns off the segment
associated with that input. If an input is shorted to
ground, the controller turns on the segment
associated with that input.
The operation of the Input Display Mode is as
follows:
DSEGMENT 0 -- Rightmost segment of the
gas gauge. This segment displays the state
of the ES float. This segment will illuminate
when this input is shorted to ground.
DSEGMENT 1 -- Second segment from the
right of the gas gauge. This segment
displays the state of the recovery tank float.
This segment will be illuminated when this
input is shorted to ground.
DSEGMENT 2 -- Third segment from the right
of the gas gauge. This segment displays the
state of the reverse input. This segment will
be illuminated when this input is shorted to
ground.
DSEGMENT 3 -- Forth segment from the right
of the gas gauge. This segment displays the
state of the forward input. This segment will
be illuminated when this input is shorted to
ground.
DENGINE TEMPERATURE LIGHT -- In the
Input Display Mode, the engine temperature
light will blink until the engine reaches
operating temperature.

ELECTRICAL
4-30 7400 MM428 (12--98)
Operating Mode Entry Sequence
(how to activate)
Error Display Mode; Display the cause of a
self--test failure.
1. Push and hold the Detergent button
2. Turn on the key
3. Hold the Detergent button until the maintenance
light comes on.
4. Release the Detergent button
ERROR DISPLAY MODE
Each time the operator starts the machine, the
panel will run a self test on each output. If the
panel passes the diagnostic, the “OK” indicator is
illuminated. If the panel fails, a code is stored in a
non volatile (preserved even after power down)
memory. If the machine passes the diagnostic on
the next startup cycle, the panel preserves the
last failed code. In the Error Display Mode, the
operator can obtain the error code stored after the
last startup diagnostic failure. When the machine
is in this mode, the LED’s on the operators panel
will indicate which system experienced the failure.
If the operator pushes the button associated with
an illuminated LED, segments on the gas gauge
will indicate which output failed and what type of
failure occurred.
The operation of the Error Display Mode is as
follows:
EStLED
Problem with the EStoutput. If the operator
pushes the headlight button in this mode, the
panel will display one of the following codes:
DSEGMENT 0 -- Rightmost segment of the gas
gauge. This segment would indicate that the
output was shorted to ground when the
controller was expecting it to be open.
DSEGMENT 0, 1 -- First and second segments
from the right of the gas gauge. These
segments would indicate that the output was
open when the controller was trying to short
it to ground.

ELECTRICAL
4-31
7400 MM428 (12--98)
SIDE BRUSH LED
Problem with the side brush or side brush
actuator outputs. If the operator pushes the side
brush button in this mode, the panel would display
one of the following codes:
DSEGMENT 0 -- Rightmost segment of the gas
gauge. This segment would indicate that the
side brush actuator output was shorted to
ground when the controller was expecting it
to be open.
DSEGMENT 0, 1 -- First and second segments
from the right of the gas gauge. These
segments would indicate that the side brush
actuator output was open when the
controller was trying to short it to ground.
DSEGMENT 2 -- Third segment from the right of
the gas gauge. This segment would indicate
that the side brush motor output was shorted
to ground when the controller was expecting
it to be open.
DSEGMENT 2, 3 -- Third and forth segments
from the right of the gas gauge. These
segments would indicate that the side brush
motor output was open when the controller
was trying to short it to ground.
SQUEEGEE LED
Problem with the squeegee actuator or vacuum
fan motor outputs. If the operator pushes the
squeegee button in this mode, the panel would
display one of the following codes:
DSEGMENT 0 -- Rightmost segment of the gas
gauge. This segment would indicate that the
squeegee actuator output was shorted to
ground when the controller was expecting it
to be open.
DSEGMENT 0, 1 -- First and second segments
from the right of the gas gauge. These
segments would indicate that the squeegee
actuator output was open when the
controller was trying to short it to ground.
DSEGMENT 2 -- Third segment from the right of
the gas gauge. This segment would indicate
that the vacuum fan motor output was
shorted to ground when the controller was
expecting it to be open.
DSEGMENT 2, 3 -- Third and forth segments
from the right of the gas gauge. These
segments would indicate that the vacuum
fan motor output was open when the
controller was trying to short it to ground.

ELECTRICAL
4-32 7400 MM428 (12--98)
SCRUB LED
Problem with the main brush actuator or motor
outputs. If the operator pushes the scrub button in
this mode, the panel would display one of the
following codes:
DSEGMENT 0 -- Rightmost segment of the gas
gauge. This segment would indicate that the
main brush actuator output was shorted to
ground when the controller was expecting it
to be open.
DSEGMENT 0, 1 -- First and second segments
from the right of the gas gauge. These
segments would indicate that the main brush
actuator output was open when the
controller was trying to short it to ground.
DSEGMENT 2 -- Third segment from the right of
the gas gauge. This segment would indicate
that the main brush motor output was
shorted to ground when the controller was
expecting it to be open.
DSEGMENT 2, 3 -- Third and forth segments
from the right of the gas gauge. These
segments would indicate that the main brush
motor output was open when the controller
was trying to short it to ground.
DETERGENT LED
Problem with the headlight or detergent pump
outputs. If the operator pushes the detergent
button in this mode, the panel would display one
of the following codes:
DSEGMENT 0 -- Rightmost segment of the gas
gauge. This segment would indicate that the
detergent pump output was shorted to
ground when the controller was expecting it
to be open.
DSEGMENT 0, 1 -- First and second segments
from the right of the gas gauge. These
segments would indicate that the detergent
pump output was open when the controller
was trying to short it to ground.
DSEGMENT 2 -- Third segment from the right of
the gas gauge. This segment would indicate
that the headlight output was shorted to
ground when the controller was expecting it
to be open.
DSEGMENT 2, 3 -- Third and forth segments
from the right of the gas gauge. These
segments would indicate that the headlight
pump output was open when the controller
was trying to short it to ground.

ELECTRICAL
4-33
7400 MM428 (12--98)
Operating Mode Entry Sequence
(how to activate)
Pressure Adjust Mode; Adjust the pressure
levels for the three down pressure settings.
1. Push and hold the Side Brush button
2. Turn on the key
3. Hold the Side Brush button until the
maintenance light comes on.
4. Release the Side Brush button
PRESSURE ADJUST MODE
When the machine is in this mode, the operator
can adjust the down pressures for the main and
side brushes. When the operator adjusts down
pressure number 3, pressures 1 and 2 are
automatically calculated and stored. The operator
may make independent adjustments to pressures
1 and 2 after storing number 3. These
adjustments will influence only the currently
displayed setting.
The operator can change the pressure settings by
pressing and holding the scrub button. When the
side brush is inactive and the main brush is
active, the operator can adjust the down pressure
for the main brush. When the side brush and main
brush are active, the operator can adjust the
down pressure for the side brush.
To store the new down pressure settings, turn off
the Side Brush and Scrub Panel LEDs on the
touch panel. Then turn off the key switch.
The operation of the Pressure Adjust Mode is as
follows:
SCRUB BUTTON
Pressing the Scrub button will start the normal
scrub sequence. When scrub is active the
following controls and displays take on alternate
functions.
DGAS GAUGE -- The gas gauge in the pressure
adjust mode displays the relative down
pressure of the main (when the side brush is
inactive) or the side brush (when the side
brush is active).
DSQUEEGEE BUTTON -- Holding the squeegee
button will decrease the down pressure.
DDETERGENT BUTTON -- Holding the
detergent button will increase the down
pressure.
NOTE: To return to the factory brush pressure
settings, run RESET SCRUB PRESSURES from
the Diagnostics menu.

ELECTRICAL
4-34 7400 MM428 (12--98)
Operating Mode Entry Sequence
(how to activate)
Reset Scrub Pressures; Return the down
pressure settings to the factory defaults.
1. Push and hold the Scrub button
2. Turn on the key
3. Hold the Scrub button
4. Wait for the maintenance light
5. While holding the Scrub button, press and hold
the Side Brush button
6. Wait for the maintenance light to go out
7. Release the Scrub and Side Brush buttons
8. Turn the key off
9. Restart the machine
RESET SCRUB PRESSURES
When the machine goes into this mode, the
controller replaces the current brush down
pressure settings with factory defaults. To initiate,
follow the entry sequence (how to activate). The
pressures will automatically reset.

ELECTRICAL
4-35
7400 MM428 (12--98)
TROUBLESHOOTING
The following troubleshooting section is organized
with the section of the electrical schematic that
pertains to that particular problem first, followed
by the flow chart.

ELECTRICAL
4-36 7400 MM428 (12--98)
1/RED
19B/BLU
1
13D/BLK
23/GRY
CB--1
15A
18A/
ORA
18/ORA
8730
5.0A
M3
22/
YEL
8685 M3
1E/
RED
CB--6
19/BLU
IGNITION
SWITCH
S--3
20A/BLU
20/BLU
ELECTRONIC
INSTRUMENT
PANEL
17
50
BATT.
30
19
ACC
13/BLK
BATTERY
22 13S/BLK
INSTRUMENT PANEL
DOES NOT POWER UP
(SCHEMATIC)
OPERATION:
--KEY SWITCH ACTIVATES
M3 AND M4
--M3 CONTACT SUPPLIES
14VDC TO INSTRUMENT
PANEL (PIN 1)
BATTERY
LINE
SWITCHED
LINE

ELECTRICAL
4-37
7400 MM428 (12--98)
INSTRUMENT PANEL
DOES NOT POWER UP
(FLOW CHART)
NO
TURN KEY ON
ENGINE NEED NOT BE RUNNING
REMOVE M3 RELAY
WORKS
PROBLEM
SOLVED
INSTALL NEW M3
RELAY
CHECK FOR BAT.
VOLTAGE AT M3
(PIN 85) 18A/ORA
BATTERY
VOLTAGE
VOLTAGE
CHECK FOR BAT.
VOLTAGE AT KEY
SWITCH 20/BLU
NO
VOLTAGE VOLTAGE
20/BLUE,
18/ORA, OR
CB--1 ARE OPEN
CHECK FOR BAT.
VOLTAGE AT KEY
SWITCH 1D/RED
NO
VOLTAGE
VOLTAGE
DOES NOT
WORK
REPLACE KEY
SWITCH
1D/RED IS OPEN
FROM BATTERY
TO KEY SWITCH
CHECK FOR BAT.
VOLTAGE AT M3
(PIN 30) 22/YEL
NO VOLTAGE
WIRE 22/YEL,
CB--6, OR
1E/RED ARE OPEN
BATTERY
VOLTAGE
OPEN
REPLACE DIODE OR
REPAIR OPEN WIRES
DISCONNECT INSTRUMENT
PANEL
CHECK CONTINUITY OF:
23/GREY FROM M3 (PIN 87)
TO (PIN 1) OF PANEL
13S/BLACK FROM (PIN 22)
OF PANEL TO BAT. NEG.
OK
REPLACE
INSTRUMENT
PANEL
GOOD
CONTINUITY
OPEN WIRE
REPAIR OR REPLACE
OPEN WIRES
OPERATION:
--KEY SWITCH ACTIVATES
M3 AND M4
--M3 CONTACT SUPPLIES
14VDC TO INSTRUMENT
PANEL (PIN 1)
CHECK CONTINUITY OF
WIRES 19/BLU AND 13D/
BLK AND CHECK DIODE
AT M3 (PIN 86) 19/BLU

ELECTRICAL
4-38 7400 MM428 (12--98)
24/
PUR
21/GRY
21B/
GRY 47/BRN
48/GRY
46A/BRN
46A/BRN
46/
BRN
24B/PUR
24B/PUR
24B/PUR
24B/PUR
24B/PUR
SV--7 SCRUB BR.
UP HOLD VALVE
SV--3 SQUEEGEE
DOWN VALVE
CB--7
24B/PUR
21B/GRY
SV--2 VAC FAN
ON VALVE
SV--6 SIDE BR.
ON VALVE
SV--4 SCRUB BR. DN. FORCE
PROP. VALVE
SV--5 SCRUB BR.
DOWN VALVE
45/GRY
46A/BRN
21 (8 SEC
DELAY)
11 (4 SEC
16
19
2
15 AMP
SV--1 SCRUB BR.
ON VALVE
87
30
M4
1F/RED
OPERATION:
--SCRUB IS SELECTED ON
TOUCH PANEL
--SCRUB SOLENOIDS ARE
TURNED ON
--HEAD WILL LOWER,
BRUSHES WILL SPIN
SCRUB BRUSH WILL NOT
TURN ON AND/OR DOWN
(SCHEMATIC)
813R/BLK
36/GRN
FLOW SWITCH
S--15
REVERSE
1/RED
19B/BLU
1
13D/BLK
23/GRY
CB--1
15A
18A/
ORA
18/ORA
8730
5.0A M3
22/
YEL
8685 M3
1E/
RED
CB--6
19/BLU
IGNITION
SWITCH
S--3
20/BLU
ELECTRONIC
INSTRUMENT
PANEL
17
50
BATT.
30
19
ACC
13/BLK
BATTERY
22 13S/BLK
13T/BLK
13U/BLK
13Y/BLK
23
24
DELAY)
8685M4
19A/BLU

ELECTRICAL
4-39
7400 MM428 (12--98)
46/BRN IS OPEN
FROM PANEL PIN TO
SOLENOID WITHOUT
VOLTAGE
OPERATION:
--SCRUB IS SELECTED ON
TOUCH PANEL
--SCRUB SOLENOIDS ARE
TURNED ON
--HEAD WILL LOWER,
BRUSHES WILL SPIN
SCRUB BRUSH WILL NOT
TURN ON AND/OR DOWN
(FLOW CHART)
PANEL IS POWERED UP
KEY IS ON
ENGINE IS OFF
CAN THE SCRUB BUTTON
BE TURNED ON AND OFF ?
NO
REPLACE TOUCH
PANEL FACE
STILL NOT TURNING
ON/OFF
REPLACE INSTRUMENT
PANEL
YES
ENGINE IS ON
ACTIVATE SQ. / VAC BUTTON
DOES THE SQUEEGEE GO DOWN
AND VAC FAN TURN ON ?
YES
NO
IS THE REC TANK
LIGHT ON ? YES
DRAIN THE TANK
NO
ENGINE IS OFF
KEY IS ON
SCRUB SELECTED
ALL 24/PUR WIRES, 21B/GRY
21/GRY, 1F/RED, OR M4
CONTACTS ARE OPEN
DISCONNECT SOLENOIDS
CHECK VOLTAGE AT SV--1,
SV--5, SV--7, AND SV--4
FROM 24/PUR TO GROUND
VOLTAGE
NO
WIRE 24/PUR
FROM CB--7 TO
SOLENOIDS SV--1,
SV--5, SV--7, OR
SV--4 IS OPEN
VOLTAGE
ENGINE IS OFF
KEY IS ON
SCRUB SELECTED
DISCONNECT SOLENOIDS
CHECK VOLTAGE AT SV--1,
SV--5, AND SV--7
FROM 24/PUR TO 46/BRN
VOLTAGE ON AT LEAST
ONE SOLENOID
NO VOLTAGE
AT ALL SOLENOIDS
SOLENOID STILL DISCONNECTED
TURN KEY SW. OFF THEN ON
DOES THE ” OK” LIGHT COME ON ? YES
WIRE 46/BRN IS OPEN
FROM PANEL (PIN 19)
NO
DISCONNECT INST. PANEL
CHECK CONTINUITY OF
WIRE 46/BRN FROM INST.
PANEL HARNESS (PIN 19)
TO GROUND
OPEN
REPLACE INST.
PANEL
CONTINUED ON
NEXT PAGE CONTINUITY
WIRE 46/BRN IS
SHORTED TO
GROUND

ELECTRICAL
4-40 7400 MM428 (12--98)
CONTINUED FROM
PREVIOUS PAGE
KEY ON
ENGINE OFF
SCRUB SELECTED
SV--4 DISCONNECTED
CHECK VOLTAGE AT SV--4
FROM 24/PUR TO 48/BRN
NO VOLTAGE
SOLENOID STILL
DISCONNECTED
TURN KEY OFF, THEN ON
DOES THE ”OK” LIGHT COME ON ?
NO YES
WIRE48/GRYISOPEN
FROM SV--4 TO INST.
PANEL (PIN 16)
KEY IS OFF
DISCONNECT INSTRUMENT PANEL
CHECK CONTINUITY FROM 48/GRY
TO GROUND
OPEN CONTINUITY
REPLACE PANEL WIRE 48/GRY IS
SHORTED TO GROUND
VOLTAGE
CHECK TO SEE IF ALL
FOUR SOLENOIDS ARE
O N -- -- U S E M A G N E T I S M
TEST ON SV--1, SV--5,
SV--7, AND SV--4
ALL ON ONE OR
MORE NOT
ACTIVATED
REPLACE BAD SOLENOID
HYDRAULIC
PROBLEM
>2VOLTS

ELECTRICAL
4-41
7400 MM428 (12--98)
SQUEEGEE AND VACUUM FAN NOT
TURNING ON AND GOING DOWN
(SCHEMATIC)
OPERATION:
--SQ/VAC IS SELECTED ON
TOUCH PANEL
--WITH MACHINE IN FWD
OF NEUT., SV--3 AND SV--2
ARE TURNED ON
--SQ. LOWERS AND VAC
TURNS ON
24/
PUR
21/GRY
21B/
GRY 47/BRN
48/GRY
46A/BRN
46A/BRN
46/
BRN
24B/PUR
24B/PUR
24B/PUR
24B/PUR
24B/PUR
SV--7 SCRUB BR.
UP HOLD VALVE
SV--3 SQUEEGEE
DOWN VALVE
CB--7
24B/PUR
21B/GRY
SV--2 VAC FAN
ON VALVE
SV--4 SCRUB BR. DN. FORCE
PROP. VALVE
SV--5 SCRUB BR.
DOWN VALVE
45/GRY
46A/BRN
21 (8 SEC
DELAY)
16
19
2
15 AMP
SV--1 SCRUB BR.
ON VALVE
87
30
M4
1F/RED
813R/BLK
36/GRN
FLOW SWITCH
S--15
REVERSE
1/RED
19B/BLU
1
13D/BLK
23/GRY
CB--1
15A
18A/
ORA
18/ORA
8730
5.0A M3
22/
YEL
8685 M3
1E/
RED
CB--6
19/BLU
IGNITION
SWITCH
S--3
20/BLU
ELECTRONIC
INSTRUMENT
PANEL
17
50
BATT.
30
19
ACC
13/BLK
BATTERY
22 13S/BLK
13T/BLK
13U/BLK
13Y/BLK
23
24
11 (4 SEC
DELAY)
8685M4
19A/BLU

ELECTRICAL
4-42 7400 MM428 (12--98)
CHECK REVERSE INPUT
--DISCONNECT INSTRUMENT
PANEL
--TURN ENGINE ON, MACHINE
IN REVERSE
--CHECK CONTINUITY AT THE
INSTR. PANEL (PIN 8) FROM
36/GRN TO GROUND
ELECTRONICS OK
SEE HYDRAULIC
TROUBLESHOOTING
DOES THE SQ. AND/OR
VAC TURN ON/OFF WITH THE
SQ/VAC BUTTON NOW ?
CAN THE SQ/VAC TOUCH
PANEL BUTTON
BE TURNED ON AND OFF?
SQUEEGEE AND VACUUM FAN NOT
TURNING ON AND GOING DOWN
(FLOW CHART)
OPERATION:
--SQ/VAC IS SELECTED ON
TOUCH PANEL
--WITH MACHINE IN FWD
OF NEUT., SV--3 AND SV--2
ARE TURNED ON
--SQ. LOWERS AND VAC
TURNS ON
PANEL IS POWERED UP
KEY IS ON
ENGINE IS RUNNING
NO
YES
REPLACE TOUCH
PANEL FACE
STILL DOES
NOT WORK
REPLACE INST.
PANEL
GO INTO ”MANUAL MODE”
THE OUTPUTS WILL TURN
ON REGARDLESS OF THE
INPUTS
--TURN KEY OFF
--PUSH AND HOLD ”ES”
BUTTON
--TURN KEY ON
--KEEP HOLDING ”ES” BUT-
TON UNTIL THE MAINTE-
NANCE LIGHT COMES ON
--RELEASE ”ES” BUTTON
NO
CHECK VOLTAGE AT SV--3
FROM 24P/PUR TO GRND. AND
SV--2 FROM 24/PUR TO GRND.
VOLTAGE
NO
VOLTAGE
--MANUAL MODE
--ENGINE OFF
--KEY ON
--SQ/VAC SELECTED
”ON”
ARE SV--2 AND SV--3
TURNED ON ? (USE
MAGNETIZED TEST)
NO
YES
DISCONNECT HYD.
COILS
CHECK VOLTAGE
ACROSS BOTH COILS,
SV--2 FROM 24/PUR TO
45/GRY AND SV--3 FROM
24/PUR TO 47/BRN
VOLTAGE
NO
VOLTAGE
CONTINUED ON
NEXT PAGE
REPLACE HYD. COIL
THAT WILL NOT TURN
ON----RE--TEST SYSTEM
24/PUR, 21/GRY,
CB--7, OR M--4
CONTACTS ARE
OPEN
YES
IS THE REC TANK
FULL LIGHT ON ?
YES
DRAIN TANK AND
RE--TEST
NO
OPEN
CONTINUITY
REPLACE THE
PANEL
36/GRN, 13R/BLK, OR
S--15 ARE OPEN
NOTE: S--15 IS
CLOSED IN REVERSE

ELECTRICAL
4-43
7400 MM428 (12--98)
REMOVE THE SHORT
TO GROUND ON
47/BRN AND/OR
45/GRY
COILS STILL
DISCONNECTED
CONTINUED FROM
PREVIOUS PAGE
--TURN KEY OFF THEN ON
IS THE ”OK” LIGHT ON ?
NO
YES
WIRE 47/BRN OR
WIRE 45/GRY
ARE OPEN
KEY OFF
PANEL
DISCONNECTED
CHECK CONTINUITY OF
47/BRN AND 45/GRY TO
GROUND
OPEN
CONTINUITY
--RECONNECT PANEL
--KEY OFF THEN ON
DOES THE ”OK” PANEL
LIGHT COME ON ?
YESNO
RE--TEST
SYSTEM
REPLACE
INSTRUMENT PANEL

ELECTRICAL
4-44 7400 MM428 (12--98)
CIRCUIT 1
CIRCUIT 2
S10
46C/BRN
46B/BRN
25/
GRY
21/GRY
51A/PUR
51A/PUR
51/PUR51C/PUR
S10
97/YEL
25B/GRY
25B/GRY
25B/GRY
25B/GRY
SV--11 SIDE BR.
UP HOLD VALVE
SV--12 LOW
WATER VALVE
SV--13 HIGH
WATER VALVE
95/BLU
96/GRY
21A/
GRY
15 AMP
CB--8
51B/PUR
SV--14 SIDE BR.
WATER VALVE
SV--10 SIDE BR. DN. FORCE
PROP. VALVE
25C/GRY
SV--9 SIDE BR.
OUT VALVE
SV--8 SIDE BR.
DOWN VALVE
SV--6 SIDE BR.
ON VALVE
52/YEL
51A/PUR
6 (3 SEC. DELAY)
12
87
30
M4
1F/RED
SIDE BRUSH WILL NOT TURN ON
AND GO DOWN
(SCHEMATIC)
OPERATION:
--MACHINE MUST BE IN
SCRUB MODE
--SIDE BRUSH BUTTON IS
ACTIVATED AND WILL
TURN ON AND LOWER
SIDE BRUSH
-- S V -- 6 , S V -- 9 , S V -- 8 , S V -- 1 0 ,
AND SV--11 WILL BE ON
813R/BLK
36/GRN
FLOW SWITCH
S--15
REVERSE
1/RED
19B/BLU
1
13D/BLK
23/GRY
CB--1
15A
18A/
ORA
18/ORA
8730
5.0A M3
22/
YEL
8685 M3
1E/
RED
CB--6
19/BLU
IGNITION
SWITCH
S--3
20/BLU
ELECTRONIC
INSTRUMENT
PANEL
17
50
BATT.
30
19
ACC
13/BLK
BATTERY
22 13S/BLK
13T/BLK
13U/BLK
13Y/BLK
19
23
24
8685M4
19A/BLU

ELECTRICAL
4-45
7400 MM428 (12--98)
51/PUR IS OPEN
FROM PANEL (PIN
12) TO SOLENOID
WITHOUT VOLTAGE
25/GRY, 21A/GRY, OR
CB--8 IS OPEN FROM
SOLENOID TO M--4
(PIN 87)
GO TO SCRUB
TROUBLESHOOTING
FLOW CHART FIRST
REPLACE TOUCH
PANEL FACE
CAN THE SCRUB AND SIDE
BRUSH BUTTONS BE TURNED
ON AND OFF
SIDE BRUSH WILL NOT TURN ON
AND GO DOWN
(FLOW CHART)
OPERATION:
--MACHINE MUST BE IN
SCRUB MODE
--SIDE BRUSH BUTTON IS
ACTIVATED AND WILL
TURN ON AND LOWER
SIDE BRUSH
-- S V -- 6 , S V -- 9 , S V -- 8 , S V -- 1 0 ,
AND SV--11 WILL BE ON
PANEL IS POWERED UP
KEY IS ON
ENGINE IS RUNNING
NO
YES
STILL DOES
NOT WORK
REPLACE INST.
PANEL
--ENGINE ON
ACTIVATE THE SCRUB BUTTON
DO THE SCRUB FUNCTIONS TURN ON ?
YESNO
--ENGINE OFF
--KEY ON
--SCRUB SELECTED
--SIDE BRUSH SELECTED
CHECK VOLTAGE AT SV--6, SV--8, SV--9,
SV--10, AND SV--11 FROM 25/GRY TO
GROUND
VOLTAGE
NO VOLTAGE
ON ANY OR
ALL
--ENGINE OFF
--KEY ON
--SCRUB SELECTED
--SIDE BRUSH SELECTED
--ALL FOUR SOLENOIDS DISCONNECTED
CHECK VOLTAGE ACROSS SOLENOIDS
SV--6, 8, 9, AND 11 FROM 25/GRY TO 51 PUR
CONTINUED ON
NEXT PAGE
VOLTAGE ACROSS
ALL FOUR SOLENOIDS
VOLTAGE ACROSS
AT LEAST ONE SOLENOID
NO VOLTAGE
ON ALL FOUR
--SOLENOIDS STILL DISCONNECTED
--TURN KEY OFF, THEN ON
DOES THE ”OK” LIGHT COME ON ? YES
NO
51/PUR IS OPEN
FROM PANEL TO ALL
FOUR SOLENOID
--DISCONNECT INSTRUMENT PANEL
CHECK CONTINUITY OF 51/PUR FROM
INSTR. PANEL (PIN 12) TO GROUND
OPEN
CONTINUITY
REPLACE INST.
PANEL
WIRE 51/PUR IS
SHORTED TO
GROUND

ELECTRICAL
4-46 7400 MM428 (12--98)
--KEY OFF
PANEL DISCONNECTED
CHECK CONTINUITY FROM
52/YEL TO GROUND
WIRE 52/YEL IS OPEN
FROM SV--10 TO
INSTR. PANEL (PIN 6)
--KEY ON
--ENGINE OFF
--SCRUB AND SIDE BRUSH ON
--SV--10 DISCONNECTED
CHECK VOLTAGE AT SV--10 FROM
25/GRY TO 52/YEL
CONTINUED FROM
PREVIOUS PAGE
NO VOLTAGE
VOLTAGE
WITH SOLENOID STILL DISCONNECTED----
TURN KEY OFF, THEN ON
DOES THE :OK” LIGHT COME ON ?
NO YES
WIRE 52/YEL
IS SHORTED
TO GROUND
CONTINUITYOPEN
REPLACE INSTRUMENT
PANEL
CHECK TO SEE IF ALL SOLENOIDS
ARE TURNING ON
USE THE MAGNETIC TEST
ONE OR
MORE OFF
REPLACE BAD
SOLENOIDS
ALL SOLENOIDS
ON
HYDRAULIC PROBLEM
SEE TROUBLESHOOTING
>2VOLTS

ELECTRICAL
4-47
7400 MM428 (12--98)
WATER VALVES NOT OPERATING
(SCHEMATIC) OPERATION:
--SCRUB FUNCTIONS MUST
BE ON
--WATERSWITCHINPOSITION#1
TURNS ON SV--12 LOW WATER
VALVE AND SV--14 SIDE BRUSH
VALVE
--WATERSWITCHINPOSITION#2
TURNS ON SV--12, SV--14, AND
SV--13 (HIGH WATER VALVE)
CIRCUIT 1
CIRCUIT 2
S10
46C/BRN
46B/BRN
25/
GRY
21/GRY
51A/PUR
51A/PUR
51/PUR51C/PUR
S10
97/YEL
25B/GRY
25B/GRY
25B/GRY
25B/GRY
SV--11 SIDE BR.
UP HOLD VALVE
SV--12 LOW
WATER VALVE
SV--13 HIGH
WATER VALVE
95/BLU
96/GRY
21A/
GRY
15 AMP
CB--8
51B/PUR
SV--14 SIDE BR.
WATER VALVE
SV--10 SIDE BR. DN. FORCE
PROP. VALVE
25C/GRY
SV--9 SIDE BR.
OUT VALVE
SV--8 SIDE BR.
DOWN VALVE
SV--6 SIDE BR.
ON VALVE
52/YEL
51A/PUR
6 (3 SEC. DELAY)
12
87
30
M4
1F/RED
813R/BLK
36/GRN
FLOW SWITCH
S--15
REVERSE
1/RED
19B/BLU
1
13D/BLK
23/GRY
CB--1
15A
18A/
ORA
18/ORA
8730
5.0A M3
22/
YEL
8685 M3
1E/
RED
CB--6
19/BLU
IGNITION
SWITCH
S--3
20/BLU
ELECTRONIC
INSTRUMENT
PANEL
17
50
BATT.
30
19
ACC
13/BLK
BATTERY
22 13S/BLK
13T/BLK
13U/BLK
13Y/BLK
19
23
24
8685M4
19A/BLU

ELECTRICAL
4-48 7400 MM428 (12--98)
TROUBLESHOOT THE
SCRUB FUNCTION
AND SIDE BRUSH
FUNCTION FIRST
ACTIVATE SCRUB AND SIDE BRUSH
DO THEY BOTH TURN ON AND COME DOWN ?
WATER VALVES NOT OPERATING
(FLOW CHART) OPERATION:
--SCRUB FUNCTIONS MUST
BE ON
--WATERSWITCHINPOSITION#1
TURNS ON SV--12 LOW WATER
VALVE AND SV--14 SIDE BRUSH
VALVE
--WATERSWITCHINPOSITION#2
TURNS ON SV--12, SV--14, AND
SV--13 (HIGH WATER VALVE)
PANEL IS POWERED UP
KEY IS ON
ENGINE IS RUNNING
YES NO
--ENGINE RUNNING
--SCRUB AND SIDE BRUSH ON
--WATERSWITCHONPOSITION#2
--SV--14, SV--12, AND SV--13 DISCONNECTED
CHECK FOR VOLTAGE AT SV--14 FROM
97/YEL TO GROUND
CHECK FOR VOLTAGE AT SV--12 FROM
96/GRY TO GROUND
CHECK FOR VOLTAGE AT SV--13 FROM
95/BLU TO GROUND
NO VOLTAGE ON ANY
WIRES 97/YEL, 96/GRY, 95/BLU
25/GRY, OR SWITCH S--10 ARE
OPEN FROM CB--8 TO SOLENOID
WITH NO VOLTAGE
VOLTAGE ON
ALL SOLENOIDS
--KEY ON, ENGINE OFF
--SOLENOIDS STILL DISCONNECTED
--SCRUB AND SIDE BRUSH ON
CHECK VOLTAGE AT SV--14 FROM
97/YEL TO 51B/PUR
CHECK VOLTAGE AT SV--12 FROM
96/GRY TO 46B/BRN
CHECK VOLTAGE AT SV--13 FROM
95/BLU TO 46C/BRN
NO VOLTAGE ON ANY
VOLTAGE ON
ALL SOLENOIDS
REPLACE ANY VALVE
NOT OPERATING
--IF SV--14 IS NO VOLTAGE
WIRE 51B/PUR FROM SV--14 TO
(PIN 12) IS OPEN
--IF SV--12 IS NO VOLTAGE
WIRE 46B/BRN FROM SV--12 TO
(PIN 19) IS OPEN
--IF SV--13 IS NO VOLTAGE
WIRE 46C/BRN FROM SV--13 TO
(PIN 19) IS OPEN

ELECTRICAL
4-49
7400 MM428 (12--98)
13S/BLK
13T/BLK
13Y/BLK
62E/BRN
62D/BRN
62B/YEL
62A/YEL
59A/BRN
59/
BRN
20B/
BLU
62C/YEL
ELECTRONIC
INSTRUMENT
PANEL
M6
8730
BRAKE SWITCH
S--11
REV/FLSH LIGHT LRC
89/ORG
CB--3
13HH/
BLK
13II/
BLK
13DD/BLK
13CC/BLK
13KK/BLK
62/YEL
89A/ORA
89B/ORA
15 AMP
TAIL LHT L.H.
TAIL LHT R.H.
HEADLIGHT L.H.
HEADLIGHT R.H.
15
20
23C/GRY 60/GRN
M6
LIGHTS
85 86
CB--1
15A
IGNITION
SWITCH
S--3 20A/BLU
20/BLU
17
50
BATT.
30
19
ACC
START
15B/BLU
15/BLU
14/GRN
18A/ORA 13P/BLK
13B/BLK
S--4 OIL SWITCH
15A/BLU
FUEL PUMP
10A/GRY
M2
HEAD LIGHTS WILL NOT TURN ON
(SCHEMATIC) OPERATION:
--(PIN 15) TO GROUND BY OIL
PRESSURE SWITCH TURNS ON M6
1/RED 13/BLK
BATTERY
22
13U/BLK
23
24
18A/ORA
1
23/GRY
18A/
ORA
8730
5.0A
M3
22/
YEL
8685 M3
1E/
RED
CB--6
19/BLU 13D/BLK
1E/
RED
1D/RED

ELECTRICAL
4-50 7400 MM428 (12--98)
-- P O W E R O F F
--DISCONNECT PANEL
IS 60/GRN SHORTED
TO GROUND ?
WIRES 15/BLU, 13B/BLK, OR S--4 ARE
OPEN, OR ENGINE OIL PRESSURE
IS LOW
DISCONNECT M6 AND CHECK
CONTINUITY OF 60/GRN
FROM M6 (PIN 86) TO INSTR.
PANEL (PIN 20)
CHECK VOLTAGE ON M6 AT
(PIN 30) FROM 59/BRN TO
GROUND
REMOVE M6 RELAY
CHECK VOLTAGE AT M6
(PIN 85) FROM 23C/GRY
TO GROUND
HEAD LIGHTS WILL NOT TURN ON
(FLOW CHART) OPERATION:
--(PIN 15) TO GROUND BY OIL
PRESSURE SWITCH TURNS ON M6
PANEL IS POWERED UP
KEY IS ON
ENGINE IS RUNNING
VOLTAGE
NO VOLTAGE
CHECK VOLTAGE AT M6 (PIN 87)
FROM 59/BRN TO GROUND VOLTAGE
NO VOLTAGE
WIRE 20B/BLU IS OPEN FROM
KEY SWITCH TO CB--3
CHECK VOLTAGE AT HEAD LIGHTS
FROM 62/YEL TO 13CC/BLK OR
FROM 62A/YEL TO 13DD/BLK
HEAD LIGHT IS BAD
62/YEL, 62A/YEL,
13CC/BLK, OR 13DD/
BLK ARE OPEN
VOLTAGENO VOLTAGE
REPLACE M6 RELAY
WORKS
PROBLEM SOLVED
NO LIGHTS
VOLTAGE
WIRE 23C/GRY IS OPEN
FROM M6 (PIN 85) TO
M3 (PIN 87)
IS THE ENGINE OIL PRESSURE
WARNING LIGHT ”ON” ON THE
INSTRUMENT PANEL ?
NO VOLTAGE
NO
YES
CONTINUITY
OPEN
REPAIR 60/GRN DOES ”OK” LIGHT COME
ON WHEN KEY IS
TURNED ON ?
NO
YES
GROUND AT (PIN 15)
REPLACE INSTR.
PANEL
--DISCONNECT THE INSTR. PANEL
--START ENGINE
CHECK FOR GROUND ON 15/BLU
AT INSTR. PANEL ON (PIN 15)
NO
15/BLU, S--4, OR 13B/BLK
IS OPEN
REPLACE INSTR.
PANEL
NO
YES
REPAIR 60/GRN

ELECTRICAL
4-51
7400 MM428 (12--98)
5 SEC. DELAY
ES PUMP RUNS
30 SEC.
5 SEC. DELAY
1MIN.TOVAC
FAN SHUT--OFF
3
10
4
13K/BLK
23C/GRY
27/PUR
26/BRN
RECOVERY
TANK
SOLUTION
TANK
S--18 N.C.H.O.
S--17 N.O.H.C.
N.C.H.O.
28/YEL
M5
57/GRN
ES PUMP
85 86
RECOVERY TANK
S--8
IGNITION
SWITCH
S--3
13J/BLK
1D/RED
20A/BLU
20/BLU
ELECTRONIC
INSTRUMENT
PANEL
17
50
BATT.
30
19
ACC
START
66/BRN 13PP/BLK
AUTO FILL
65/GRY
CB--2
ES PUMP
M5
20A/
BLU 8730
15 AMP
MTR
EStPUMP NOT WORKING
(SCHEMATIC) OPERATION:
-- I F E S tIS SELECTED ON PANEL AND
--S--17 AND S--18 CLOSE FOR 5 SECONDS
--M5 RELAY WILL ACTIVATE, TURNING ON
PUMP
13T/BLK
13Y/BLK
15
CB--1
15A
15B/BLU
15/BLU
14/GRN
18A/ORA 13P/BLK
13B/BLK
S--4 OIL SWITCH
15A/BLU
FUEL PUMP
10A/GRY
M2
1/RED 13/BLK
BATTERY
22
13U/BLK
23
24
18A/ORA
1
23/GRY
18A/
ORA
87
30 M3
22/
YEL
8685 M3
1E/
RED
19/BLU 13D/BLK
13S/BLK
23/GRY
15/BLU

ELECTRICAL
4-52 7400 MM428 (12--98)
DISCONNECT INSTR. PANEL
--CHECK FOR CONTINUITY
AT INSTR. PANEL FROM
26/BRN (PIN 3) TO GROUND STILL NOT
WORKING IN
MANUAL MODE
CAN THE ES PUMP TOUCH
PANEL BUTTON BE
TURNED ON/OFF
EStPUMP NOT WORKING
(FLOW CHART) OPERATION:
-- I F E S tIS SELECTED ON PANEL AND
--S--17 AND S--18 CLOSE FOR 5 SECONDS
--M5 RELAY WILL ACTIVATE, TURNING ON
PUMP
PANEL IS POWERED UP
KEY IS ON
ENGINE IS RUNNING
NO
YES REPLACE TOUCH
PANEL FACE
STILL DOES
NOT WORK
REPLACE INST.
PANEL
GO INTO ”MANUAL MODE”
THE OUTPUTS WILL TURN ON
REGARDLESS OF THE INPUTS
--TURN KEY OFF
--PUSH AND HOLD ”ES” BUTTON
--TURN KEY ON
--KEEP HOLDING ”ES” BUTTON
UNTIL THE MAINTENANCE LIGHT
COMES ON
--RELEASE ”ES” BUTTON
NO
YES DOES THE ES PUMP TURN
ON AND OFF WITH THE ES
BUTTON NOW ?
INPUT OUTPUT
REPLACE M5
CHECK VOLTAGE AT
M5 (PIN 30) FROM 65/GRY
TO GROUND
NO VOLTAGE
CHECK VOLTAGE AT M5
(PIN 85) FROM 23C/GRY
TO GROUND
VOLTAGE
20A/BLU, CB--2, OR 65/GRY
ARE OPEN FROM M5 (PIN 30)
TO KEY SWITCH
CONTINUED ON
NEXT PAGE
23C/GRY IS OPEN FROM
M5 (PIN 85) TO M3 (PIN 87)
CHECK FLOAT
INPUT
KEY
OFF
NO
YES
26/BRN, S--17, 27/PUR,
S--18, OR 13K/BLK
OPEN
KEY ON
PANEL CONNECTED
GO TO INPUT MODE
APPLY AND RE-
MOVE GROUND TO
(PIN 3) BY CLOSING
S--17 AND S--18
YES
NO
REPLACE PANEL
SYSTEM O.K.
VOLTAGE
NO VOLTAGE

ELECTRICAL
4-53
7400 MM428 (12--98)
WIRE 66/BRN OR
13PP/BLK ARE
OPEN
57/GRN IS OPEN FROM
(PIN 4) ON INSTR. PAN-
EL TO (PIN 86)
CONTINUED FROM
PREVIOUS PAGE
VOLTAGE
NO VOLTAGE
WITH ES ON AND
MACHINE IN
MANUAL MODE
CHECK VOLTAGE AT M5 (PIN 87)
FROM WIRE 66/BRN TO GROUND
WITH ES ON AND
MACHINE IN
MANUAL MODE
CHECK VOLTAGE AT ES PUMP
FROM 66/BRN TO 13PP/BLK
NO VOLTAGE VOLTAGE
MOTOR BAD
WITH M5 REMOVED
TURN KEY ON, THEN OFF
IS ”OK” LIGHT ON ?
NO YES
PANEL DISCONNECTED
POWER OFF
M5 REMOVED
REPLACE PANEL
NO
YES
REMOVE SHORT TO
GROUND ON 57/GRN
CHECK CONTINUITY
FROM 57/GRN TO
GROUND

ELECTRICAL
4-54 7400 MM428 (12--98)
23C/GRY
8
18
13R/BLK
58/BLU
M7
REVERSE
85 86
36/GRN
18A/
ORA
87
30
FLOW SWITCH
5.0A
S--15 REVERSE
M3
22/
YEL
86
85
M3
CB--6
13RR/BLK
13JJ/BLK
93A/ORA
93/ORA
20C/
BLU 92/PUR M7
8730
CB--4 94/YEL
93B/ORA
15 AMP
BACK--UP ALARM UNIT
FLASHER
REVERSE LIGHT OR ALARM
NOT WORKING
(SCHEMATIC)
OPERATION:
--GROUND AT (PIN 8) WHEN
MACHINE IS IN REVERSE
--TURNS ON M7
--SUPPLIES POWER TO BACK--UP
ALARM/LIGHT
ELECTRONIC
INSTRUMENT
PANEL
ES PUMP
MTR
13T/BLK
13Y/BLK
22
13U/BLK
23
24
13S/BLK
IGNITION
SWITCH
S--3
1D/RED
20A/BLU
20/BLU
17
50
BATT.
30
19
ACC CB--1
15A
1/RED 13/BLK
BATTERY
1
23/GRY
19/BLU 13D/BLK

ELECTRICAL
4-55
7400 MM428 (12--98)
M7 STILL REMOVED
TURN KEY OFF THEN
ON, IS ”OK LIGHT ON?
REPAIR OR REPLACE WIRES
93A/ORA, 93B/ORA, OR
94/YEL
CHECK VOLTAGE AT M7
(PIN 85) FROM 23C/GRY
TO GROUND
CHECK CONTINUITY OF WIRES
93/ORA, 93A/ORA, 93B/ORA,
AND 94/YEL
CHECK FOR VOLTAGE FROM
ALARM OR LIGHTS WORK-
ING WIRE OR 13JJ BLK,
13RR/BLK TO BATT POSITIVE
CHECK THE VOLTAGE
FROM THE ALARM OR
LIGHT NOT WORKING TO
GROUND
REVERSE LIGHT OR ALARM
NOT WORKING
(FLOW CHART)
OPERATION:
--GROUND AT (PIN 8) WHEN
MACHINE IS IN REVERSE
--TURNS ON M7
--SUPPLIES POWER TO BACK--UP
ALARM/LIGHT
PANEL IS POWERED UP
KEY IS ON
ENGINE IS RUNNING
NO
YES
DOES THE BACK--UP ALARM
OR LIGHT WORK
VOLTAGE
NO VOLTAGE
93/ORA, 93B/ORA, 94/YEL
OR FLASHER ARE OPEN
KEY ON
REPLACE M7
STILL NOT
WORKING
REMOVE M7 AND CHECK
VOLTAGE AT M7 (PIN 30)
FROM 92/PUR TO GROUND
NO VOLTAGE
VOLTAGE
92/PUR, 20C/BLU, OR
CB--4 ARE OPEN
NO VOLTAGE
23C/GRY IS OPEN VOLTAGE
VOLTAGE
REPLACE BAD ALARM
OR FLASHER LIGHT
NO VOLTAGE
REPAIR OR REPLACE
13JJ/BLK OR 13RR/BLK
OPEN
CONTINUED ON
NEXT PAGE
OK
YES
NO
POWER OFF
DISCONNECT PANEL
CHECK CONTINUITY ON
WIRE 58/BLU TO GROUND
NOYES
REPLACE
PANEL
58/BLU IS SHORTED
TO GROUND, RE-
PAIR AND REPLACE

ELECTRICAL
4-56 7400 MM428 (12--98)
REPLACE INSTR.
PANEL
36/GRN, 13R/BLK, OR S--15
ARE OPEN AND IN REVERSE
GO INTO ”INPUT” MODE
IS THE 3RD SEGMENT FROM
THE RIGHT TURNING ON WITH
THE MACHINE RUNNING AND IN
REVERSE ?
CONTINUED FROM
PREVIOUS PAGE
DISCONNECT INSTR. PANEL WITH ENGINE
RUNNING AND MACHINE IN REVERSE
CHECK CONTINUITY AT INSTR. PANEL
CONNECTOR (PIN 8) FROM 36/GRN TO
GROUND WHEN MACHINE IS RUNNING
CONTINUITY
NO CONTINUITY
YES
NO
--DISCONNECT PANEL
-- P O W E R O F F
CHECK CONTINUITY
OF 58/BLU
REPLACE INSTR.
PANEL
CONTINUITY OPEN
REPAIR 58/BLU

ELECTRICAL
4-57
7400 MM428 (12--98)
56/ORA 9
23A/GRY MTR
DETERGENT METERING
DETERGENT METERING
PUMP IS NOT OPERATING
(SCHEMATIC)
OPERATION:
--PANEL DETERGENT BUTTON IS
ACTIVE IN LOW OR HIGH POSITION
--MACHINE IS IN SCRUB MODE
--DETERGENT PUMP WILL BE TURNED
ON WITH A PULSE WIDTH MODULATED
SIGNAL
18A/
ORA
87
30
5.0A
M3
22/
YEL
86
85 M3
CB--6
ELECTRONIC
INSTRUMENT
PANEL
13T/BLK
13Y/BLK
22
13U/BLK
23
24
13S/BLK
IGNITION
SWITCH
S--3
1D/RED
20/BLU
17
50
BATT.
30
19
ACC CB--1
15A
1/RED 13/BLK
BATTERY
1
23/GRY
19/BLU 13D/BLK

ELECTRICAL
4-58 7400 MM428 (12--98)
REPAIR AND
REPLACE
56/ORA
23A/GRY IS OPEN
FROM PUMP TO
M3 (PIN 87)
VERIFY THAT THE SCRUBBING
SYSTEM IS FUNCTIONING
IS 46/BRN AT INSTR. PANEL (PIN 19)
GOING LOW AND TURNING ON
SV--1, SV--5, AND SV--7 ?
--IN MANUAL MODE
--KEY ON, ENGINE OFF
CHECK VOLTAGE AT
PUMP FROM WIRE 23A/
GRY TO 56/ORA
GO INTO ”MANUAL MODE”
THE OUTPUTS WILL TURN ON
REGARDLESS OF THE INPUTS
--TURN KEY OFF
--PUSH AND HOLD ”ES” BUTTON
--TURN KEY ON
--KEEP HOLDING ”ES” BUTTON
UNTIL THE MAINTENANCE LIGHT
COMES ON
--RELEASE ”ES” BUTTON
ENGINE DOES NOT HAVE TO BE
RUNNING
DETERGENT METERING
PUMP IS NOT OPERATING
(FLOW CHART)
OPERATION:
--PANEL DETERGENT BUTTON IS
ACTIVE IN LOW OR HIGH POSITION
--MACHINE IS IN SCRUB MODE
--DETERGENT PUMP WILL BE TURNED
ON WITH A PULSE WIDTH MODULATED
SIGNAL
PANEL IS POWERED UP
KEY IS ON
ENGINE IS RUNNING
REPLACE TOUCH
PANEL FACE
STILL DOES
NOT WORK
REPLACE INST.
PANEL
NO
CAN THE DETERGENT
METERING AND TOUCH
PANEL SWITCHES BE
TURNED ON AND OFF ?
YES
DOES THE DETERGENT METERING
PUMP TURN ON AND OFF WITH
THE TOUCH PANEL SWITCH ?
NO
YES
SCRUB
INPUTS DISCONNECT DETERGENT
PUMP
CHECK VOLTAGE AT DETERGENT
PUMP FROM 23A/GRY TO GROUND
VOLTAGE
NO VOLTAGE
YES
NO
TROUBLESHOOT
SCRUB BRUSH
SYSTEM FIRST
NO VOLTAGE
VOLTAGE
REPLACE
PUMP
-- P O W E R O F F
--PANEL DISCONNECTED
CHECK CONTINUITY OF 56/ORA
FROM PANEL (PIN 9) TO PUMP
OPEN
CONTINUITY
REPLACE INST.
PANEL
DETERGENT METERING
TESTS OUT O.K.

ELECTRICAL
4-59
7400 MM428 (12--98)
1E/RED
1/RED
14
IGNITION
SWITCH
S--3
55A MAX.
CHARGE
1D/RED
2/ORA
L2
1B/RED
12V
540 C.C.A.
ELECTRONIC
INSTRUMENT
PANEL
17
50
BATT.
30
19
ACC
START
SENSE
13A/BLK
STARTER MOTOR
13/BLK
BATTERY
ALTERNATOR
GND
OUT
1A/RED
STARTER RELAY
M1 MTR
ALTERNATOR / BATTERY WARNING LIGHT
STAYS ON WHEN ENGINE IS RUNNING
(SCHEMATIC)
OPERATION:
--CONNECTION L2 ON ALTERNATOR
GOES TO BATTERY POSITIVE WHEN ALTER-
NATOR IS TURNED ON
--BATTERY POSITIVE AT (PIN 14) TURNS OFF
THE ALTERNATOR / BATTERY INDICATOR
18A/
ORA
87
30
M3
22/
YEL
86
85
M3
20/BLU
CB--1
15A
19/BLU
1
23/GRY
13D/BLK
5.0A
CB--6
1E/RED
13T/BLK
13Y/BLK
22
13U/BLK
23
24
13S/BLK

ELECTRICAL
4-60 7400 MM428 (12--98)
DISCONNECT INSTR.
PANEL, THEN RECONNECT
IF LIGHT STILL ON----REPLACE
INSTR. PANEL
WIRE 2/ORA IS
SHORTED TO BATTERY
POSITIVE
--ENGINE RUNNING
--PANEL DISCONNECTED
CHECK VOLTAGE OF WIRE
2/ORA AT (PIN 14) OF INSTR.
PANEL
DISCONNECT WIRE 2/ORA
AT THE ALTERNATOR
TOUCH WIRE 2/ORA TO WIRE 1B/RED
AT THE ALTERNATOR
DOES THE ALTERNATOR LIGHT TURN
OFF ?
ALTERNATOR / BATTERY WARNING LIGHT
STAYS ON WHEN ENGINE IS RUNNING
(FLOW CHART)
OPERATION:
--CONNECTION L2 ON ALTERNATOR
GOES TO BATTERY POSITIVE WHEN ALTER-
NATOR IS TURNED ON
--BATTERY POSITIVE AT (PIN 14) TURNS OFF
THE ALTERNATOR / BATTERY INDICATOR
ENGINE RUNNING
CHECK VOLTAGE FROM L2
AT ALTERNATOR TO GROUND VOLTAGE
NO VOLTAGE
KEY ON
ENGINE OFF
YES
NO
TIGHTEN ALTERNATOR BELT
IF NECESSARY
REPLACE ALTERNATOR
DOES LIGHT TURN OFF ?
NO
VOLTAGE
NO VOLTAGE
WIRE2/ORAISOPEN

ELECTRICAL
4-61
7400 MM428 (12--98)
ALTERNATOR / BATTERY WARNING
LIGHT WILL NOT TURN ON
(SCHEMATIC)
OPERATION:
--CONNECTION L2 ON ALTERNATOR
GOES TO BATTERY POSITIVE WHEN ALTER-
NATOR IS TURNED ON
--BATTERY POSITIVE AT (PIN 14) TURNS OFF
THE ALTERNATOR / BATTERY INDICATOR
1E/RED
1/RED
14
IGNITION
SWITCH
S--3
55A MAX.
CHARGE
1D/RED
2/ORA
L2
1B/RED
12V
540 C.C.A.
ELECTRONIC
INSTRUMENT
PANEL
17
50
BATT.
30
19
ACC
START
SENSE
13A/BLK
STARTER MOTOR
13/BLK
BATTERY
ALTERNATOR
GND
OUT
1A/RED
STARTER RELAY
M1 MTR
18A/
ORA
87
30
M3
22/
YEL
86
85
M3
20/BLU
CB--1
15A
19/BLU
1
23/GRY
13D/BLK
5.0A
CB--6
1E/RED
13T/BLK
13Y/BLK
22
13U/BLK
23
24
13S/BLK

ELECTRICAL
4-62 7400 MM428 (12--98)
ALTERNATOR IS SHORTED
L2 TO BATTERY POSITIVE
OR WIRE 2/ORA IS SHORTED
TO BATTERY POSITIVE
ALTERNATOR / BATTERY WARNING
LIGHT WILL NOT TURN ON
(FLOW CHART)
OPERATION:
--CONNECTION L2 ON ALTERNATOR
GOES TO BATTERY POSITIVE WHEN ALTER-
NATOR IS TURNED ON
--BATTERY POSITIVE AT (PIN 14) TURNS OFF
THE ALTERNATOR / BATTERY INDICATOR
KEY ON
ENGINE OFF
REMOVE 2/ORA FROM
ALTERNATOR (PIN L2)
GROUND WIRE 2/ORA
DOES THE LIGHT
TURN ON ?
NO
YES
OPEN
REPAIR AND REPLACE
2/ORA
CONTINUITY
REPLACE LAMP L8
INSIDE THE PANEL
CHECK CONTINUITY 2/ORA
FROM ALTERNATOR TO
(PIN 14)

ELECTRICAL
4-63
7400 MM428 (12--98)
543/BLU COOLANT TEMP
SENDER
SE--2
ELECTRONIC
INSTRUMENT
PANEL
ENGINE TEMPERATURE LIGHT
WILL NOT TURN ON OR OFF
(SCHEMATIC)
OPERATION:
--225 DEGREE F. SE--2 =<80 OHMS
--COOLANT LIGHT TURNS ON
13T/BLK
13Y/BLK
22
13U/BLK
23
24
13S/BLK
1/RED
IGNITION
SWITCH
S--3
1D/RED
12V
540 C.C.A.
17
50
BATT.
30
19
ACC
START
13/BLK
BATTERY
18A/
ORA
87
30 M3
22/
YEL
86
85
M3
20/BLU
CB--1
15A
19/BLU
1
23/GRY
13D/BLK
5.0A
CB--6
1E/RED

ELECTRICAL
4-64 7400 MM428 (12--98)
ENGINE TEMPERATURE LIGHT
WILL NOT TURN ON
(FLOW CHART)
OPERATION:
--225 DEGREE F. SE--2 =<80 OHMS
--COOLANT LIGHT TURNS ON
DOES THE LIGHT TURN
ON MOMENTARILY AT POWER UP ?
YES
NO
REPLACE LAMP L2
INSIDE PANEL
RETEST
REPLACE INSTR. PANEL
STILL NOT
TURNING ON AT
POWER UP
DISCONNECT SE--2 AND GROUND
WIRE 43/BLU
DOES LIGHT TURN ON ?
YES
NO
WIRE 43/BLU IS
OPEN FROM (PIN 5) TO SE--2
IF ENGINE TEMP IS LESS
THAN 225 DEGREES
REPLACE SE--2
SYSTEM IS OK
ENGINE TEMPERATURE LIGHT
WILL NOT TURN OFF
(FLOW CHART)
OPERATION:
--225 DEGREE F. SE--2 =<80 OHMS
--COOLANT LIGHT TURNS ON
KEY ON
ENGINE OFF
DISCONNECT SE--2
LIGHT STILL ON
LIGHT TURNS OFF
POWER OFF
DISCONNECT PANEL
DISCONNECT SE--2
CHECK CONTINUITY
43/BLU TO GROUND
OPEN
CONTINUITY
REPLACE INSTR. PANEL
WIRE 43/BLU IS
GROUNDED
IF ENGINE TEMP IS LESS
THAN 225 DEGREES
REPLACE SE--2
SYSTEM IS OK

ELECTRICAL
4-65
7400 MM428 (12--98)
7
13N/BLK
FILTER SWITCH
S--14
HYDRAULIC
35/BRN
OPERATION:
--WHEN S--14 CLOSES, LIGHT
TURNS ON
--THIS LIGHT IS AN OPTION
HYDRAULIC (HIGH) PRESSURE INDICATOR
LIGHT WILL NOT TURN ON OR OFF
(SCHEMATIC)
ELECTRONIC
INSTRUMENT
PANEL
13T/BLK
13Y/BLK
22
13U/BLK
23
24
13S/BLK
1/RED
IGNITION
SWITCH
S--3
1D/RED
12V
540 C.C.A.
17
50
BATT.
30
19
ACC
START
13/BLK
BATTERY
18A/
ORA
87
30 M3
22/
YEL
86
85
M3
20/BLU
CB--1
15A
19/BLU
1
23/GRY
13D/BLK
5.0A
CB--6
1E/RED

ELECTRICAL
4-66 7400 MM428 (12--98)
DOES THE LIGHT TURN
ON MOMENTARILY AT
POWER UP ?
OPERATION:
--WHEN S--14 CLOSES, LIGHT
TURNS ON
--THIS LIGHT IS AN OPTION
HYDRAULIC (HIGH) PRESSURE
INDICATOR LIGHT WILL NOT TURN ON
(FLOW CHART)
YES
NO
REPLACE LAMP L5
INSIDE PANEL,
THEN RETEST
DOES THE LIGHT TURN
ON MOMENTARILY AT
POWER UP ?
NO
REPLACE INSTR. PANEL
DISCONNECT S--14 AND
GROUND WIRE 35/BRN
DOES THE LIGHT COME
ON ?
YES NO
WIRE 35/BRN IS OPENREPLACE S--14
--DISCONNECT S--14
--DISCONNECT INSTR.
PANEL
CHECK CONTINUITY
35/BRN TO GROUND
OPERATION:
--WHEN S--14 CLOSES, LIGHT
TURNS ON
--THIS LIGHT IS AN OPTION
HYDRAULIC (HIGH) PRESSURE
INDICATOR LIGHT WILL NOT TURN OFF
(FLOW CHART)
YES
NO
KEY ON
ENGINE OFF
DISCONNECT S--14
DOES LIGHT TURN
OFF ?
IF HYDRAULIC SYSTEM OK
REPLACE S--14
POWER OFF
OPEN
CONTINUITY
REPLACE INSTR. PANEL
35/BRN IS SHORTED
TO GROUND
REPAIR AND RE-
PLACE 35/BRN

ELECTRICAL
4-67
7400 MM428 (12--98)
OPERATION:
--(PIN 15) IS PULLED TO GROUND
WHEN OIL PRESSURE IS HIGH ENOUGH
--OIL LIGHT TURNS OFF
ENGINE OIL PRESSURE WARNING
LIGHT WILL NOT TURN ON OR OFF
(SCHEMATIC)
5 SEC. DELAY
ES PUMP RUNS
30 SEC.
5 SEC. DELAY
1MIN.TOVAC
FAN SHUT--OFF
3
10
4
13K/BLK
23C/GRY
27/PUR
26/BRN
RECOVERY
TANK
SOLUTION
TANK
S--18 N.C.H.O.
S--17 N.O.H.C.
N.C.H.O.
28/YEL
M5
57/GRN
ES PUMP
85 86
RECOVERY TANK
S--8
IGNITION
SWITCH
S--3
13J/BLK
1D/RED
20/BLU
ELECTRONIC
INSTRUMENT
PANEL
17
50
BATT.
30
19
ACC
START
13T/BLK 13Y/BLK
15
CB--1
15A
15B/BLU
15/BLU
14/GRN
18A/ORA 13P/BLK
13B/BLK
S--4 OIL SWITCH
15A/BLU
FUEL PUMP
10A/GRY
M2
1/RED 13/BLK
BATTERY
22
13U/BLK
23
24
18A/ORA
1
23/GRY
18A/
ORA
8730
M3
22/
YEL
86
85 M3
1E/
RED
19/BLU 13D/BLK
13S/BLK
23/GRY
15/BLU

ELECTRICAL
4-68 7400 MM428 (12--98)
(PIN 15) IS GROUNDED
CHECK OIL PRESSURE
SWITCH OPERATION
DOES OIL LIGHT TURN
ON MOMENTARILY AT
POWER UP ?
OPERATION:
--(PIN 15) IS PULLED TO GROUND
WHEN OIL PRESSURE IS HIGH ENOUGH
--OIL LIGHT TURNS OFF
ENGINE OIL PRESSURE WARNING
LIGHT WILL NOT TURN ON
(FLOW CHART)
YES
NO
REPLACE LAMP L1
INSIDE PANEL
STILL NOT TURNING
ON AT POWER UP
REPLACE INSTR. PANEL
DISCONNECT OIL PRESSURE
SWITCH S--4
GROUND WIRE 15/BLU
DOES LIGHT SHUT OFF ?
OPERATION:
--(PIN 15) IS PULLED TO GROUND
WHEN OIL PRESSURE IS HIGH ENOUGH
--OIL LIGHT TURNS OFF
ENGINE OIL PRESSURE WARNING
LIGHT WILL NOT TURN OFF
(FLOW CHART)
YES
NO
KEY ON
ENGINE OFF
REPLACE OIL PRESSURE LIGHT
WIRE 15/BLU IS OPEN
FROM OIL PRES-
SURE SWITCH TO
(PIN 15)

ELECTRICAL
4-69
7400 MM428 (12--98)
OPERATION:
--IF S--8 CLOSES, THE RECOVERY TANK
IS FULL
--THE RECOVERY TANK LIGHT COMES ON
--SCRUB , SQUEEGEE, AND VACUUM FAN
TURNS OFF
RECOVERY TANK FULL LIGHT
WILL NOT TURN ON OR OFF
(SCHEMATIC)
5 SEC. DELAY
1MIN.TOVAC
FAN SHUT--OFF
10
4
23C/GRY
N.C.H.O.
28/YEL
M5
57/GRN
ES PUMP
85 86
RECOVERY TANK
S--8
IGNITION
SWITCH
S--3
13J/BLK
1D/RED
20/BLU
ELECTRONIC
INSTRUMENT
PANEL
17
50
BATT.
30
19
ACC
START
13T/BLK 13Y/BLK
15
CB--1
15A
15B/BLU
15/BLU
14/GRN
18A/ORA 13P/BLK
13B/BLK
S--4 OIL SWITCH
15A/BLU
FUEL PUMP
10A/GRY
M2
1/RED 13/BLK
BATTERY
22
13U/BLK
23
24
18A/ORA
1
23/GRY
18A/
ORA
8730 M3
22/
YEL
86
85 M3
1E/
RED
19/BLU 13D/BLK
13S/BLK
23/GRY
15/BLU

ELECTRICAL
4-70 7400 MM428 (12--98)
-- P O W E R O F F
--DISCONNECT INSTR. PANEL
DISCONNECT S--8
CHECK CONTINUITY FROM WIRE
28/YEL TO GROUND
IF THE LIGHT IS STILL
NOT TURNING ON MO-
MENTARILY AT POWER
UP----REPLACE THE PANEL
OPERATION:
--IF S--8 CLOSES, THE RECOVERY TANK
IS FULL
--THE RECOVERY TANK LIGHT COMES ON
--SCRUB , SQUEEGEE, AND VACUUM FAN
TURNS OFF
RECOVERY TANK FULL LIGHT
WILL NOT TURN ON
(FLOW CHART)
YES
NO
DOES THE LIGHT TURN ON
MOMENTARILY AT POWER UP ?
REPLACE LAMP L4
INSIDE THE PANEL
DISCONNECT S--8 GROUND WIRE
28/YEL DOES THE LIGHT TURN ON ?
YES NO
WIRE 28/YEL IS OPEN
FROM S--8 TO PANEL
(PIN 10)
WHEN RECOVERY TANK
IS FULL, S--8 IS NOT CLOSING
OR 13J/BLK IS OPEN
OPERATION:
--IF S--8 CLOSES, THE RECOVERY TANK
IS FULL
--THE RECOVERY TANK LIGHT COMES ON
--SCRUB , SQUEEGEE, AND VACUUM FAN
TURNS OFF
RECOVERY TANK FULL LIGHT
WILL NOT TURN OFF
(FLOW CHART)
DISCONNECT S--8
DOES THE LIGHT TURN OFF ?
YES NO
RECOVERYTANKISFULL
SYSTEM OK, OR
S--8 IS SHORTED
OPEN CONTINUITY
REPLACE INSTR.
PANEL
WIRE 28/YEL IS
GROUNDED

ELECTRICAL
4-71
7400 MM428 (12--98)
42A/YEL
42/YEL
13 GAS--DIESEL
13L/BLK
FUEL SENDER
SE--1
OPERATION:
--S--6 IS NOT ON MACHINE
--SE--1 GREATER THE 90 OHMS=FULL TANK
--SE--1 LESS THAN 10 OHMS=EMPTY TANK
FUEL GAUGE (GAS AND DIESEL)
(SCHEMATIC)
4
23C/GRY M5
57/GRN
ES PUMP
85 86
IGNITION
SWITCH
S--3
1D/RED
20/BLU
ELECTRONIC
INSTRUMENT
PANEL
17
50
BATT.
30
19
ACC
START
13T/BLK 13Y/BLK
15
CB--1
15A
15B/BLU
15/BLU
14/GRN
18A/ORA 13P/BLK
13B/BLK
S--4 OIL SWITCH
15A/BLU
FUEL PUMP
10A/GRY
M2
1/RED 13/BLK
BATTERY
22
13U/BLK
23
24
18A/ORA
1
23/GRY
18A/
ORA
8730
M3
22/
YEL
8685 M3
1E/
RED
19/BLU 13D/BLK
13S/BLK
23/GRY
15/BLU

ELECTRICAL
4-72 7400 MM428 (12--98)
42/YEL IS SHORTED
TO GROUND
-- P O W E R O F F
--DISCONNECT SE--1
--DISCONNECT INSTR. PANEL
CHECK CONTINUITY OF WIRE
42A/YEL TO GROUND
GROUND 42A/YEL AT SE--1
IS GAUGE FULL ON ?
REPLACE INSTR.
PANEL
IF GAUGE IS INACCURATE
REPLACE THE FLOAT
DISCONNECT 42A/YEL AT SE--1
IS GAUGE FULL ON ?
OPERATION:
--S--6 IS NOT ON MACHINE
--SE--1 GREATER THE 90 OHMS=FULL TANK
--SE--1 LESS THAN 10 OHMS=EMPTY TANK
FUEL GAUGE (GAS AND DIESEL)
(FLOW CHART)
YES
NO
KEY ON
ENGINE OFF
NO YES
GAUGE STILL
WAY OFF
REPLACE INSTR.
PANEL
REPLACE INSTR.
PANEL
OPEN CONTINUITY
CHECK CONTINUITY
OF 42/YEL
OK
OPEN
REPAIR 42/YEL

ELECTRICAL
4-73
7400 MM428 (12--98)
OPERATION:
--S--6ISOPEN=GAUGEISOFF
--S--6 IS CLOSED = LEFT 2 SEGMENTS OF
GAUGE FLASH
--SE--1 IS NOT ON MACHINE
FUEL GAUGE (LPG)
(SCHEMATIC)
42B/YEL
42/YEL
13
13M/BLK
LP CLOSES BELOW
40 PSI
N.C.H.O.
S--6
C
4
23C/GRY M5
57/GRN
ES PUMP
85 86
IGNITION
SWITCH
S--3
1D/RED
20/BLU
ELECTRONIC
INSTRUMENT
PANEL
17
50
BATT.
30
19
ACC
START
13T/BLK 13Y/BLK
15
CB--1
15A
15B/BLU
15/BLU
14/GRN
18A/ORA 13P/BLK
13B/BLK
S--4 OIL SWITCH
15A/BLU
FUEL PUMP
10A/GRY
M2
1/RED 13/BLK
BATTERY
22
13U/BLK
23
24
18A/ORA
1
23/GRY
18A/
ORA
8730
M3
22/
YEL
8685 M3
1E/
RED
19/BLU
13D/BLK
13S/BLK
23/GRY
15/BLU

ELECTRICAL
4-74 7400 MM428 (12--98)
42/YEL IS SHORTED
TO GROUND
-- P O W E R O F F
--DISCONNECT PANEL
--DISCONNECT S--6
CHECK CONTINUITY OF
42B/YEL TO GROUND
-- P O W E R O F F
CHECK CONTINUITY OF 42B/YEL
FROM S--6 TO PANEL (PIN 13)
IF SYSTEM IS NOT
WORKING PROPERLY----
REPLACE S--6
GROUND 42B/YEL AT S--6
IS GAUGE FLASHING ?
OPERATION:
--S--6ISOPEN=GAUGEISOFF
--S--6 IS CLOSED = LEFT 2 SEGMENTS OF
GAUGE FLASH
--SE--1 IS NOT ON MACHINE
FUEL GAUGE (LPG)
(FLOW CHART)
YES
NO
KEY ON
ENGINE OFF
DISCONNECT S--6
IS GAUGE OFF ?
NO
YES
OPEN CONTINUITY
REPLACE INSTR.
PANEL
REPAIR 42 /YEL
CONTINUITY
OPEN
REPLACE INSTR.
PANEL

HYDRAULICS
5-1
7400 MM428 (6--01)
CONTENTS
Page
HYDRAULIC FLUID RESERVOIR 5-3..........
HYDRAULIC FLUID 5-3......................
HYDRAULIC HOSES 5-4.....................
TO REPLACE DIRECTIONAL PEDAL
CENTERING SPRING 5-5.................
TO REPLACE DIRECTIONAL
CONTROL CABLE 5-7....................
TO ADJUST CENTERING SPRING 5-9.....
TO REPLACE PROPEL PUMP 5-10...........
TO REPLACE ACCESSORY PUMP 5-12.......
TO REPLACE STEERING CYLINDER 5-14.....
TO REPLACE HYDRAULIC STEERING
VALVE 5-15..............................
TO REPLACE MAIN HYDRAULIC VALVE 5-16..
TO REPLACE SIDE BRUSH HYDRAULIC
VALVE 5-18..............................
TO REPLACE SOLENOID VALVE
CARTRIDGE 5-20........................
TO REPLACE ENGINE COOLING FAN
HYDRAULIC MOTOR 5-22.................
TO REPLACE MAIN SCRUB BRUSH
HYDRAULIC MOTORS 5-24...............
TO REPLACE SCRUB HEAD ASSEMBLY
LIFT CYLINDER 5-27.....................
TO REPLACE OPTIONAL SIDE BRUSH
HYDRAULIC MOTOR 5-28.................
TO REPLACE OPTIONAL SIDE BRUSH
LIFT CYLINDER 5-29.....................
TO REPLACE OPTIONAL SIDE BRUSH
SWING CYLINDER 5-30...................
TO REPLACE SQUEEGEE LIFT
CYLINDER 5-31..........................
TO REPLACE VACUUM FAN HYDRAULIC
MOTOR 5-32.............................
HYDRAULIC SCHEMATIC 5-35...............
HYDRAULIC HOSE GROUP 5-37.............
HYDRAULIC HOSE GROUP/SIDE BRUSH
OPTION 5-38............................
TROUBLESHOOTING 5-39...................
ENGINE FAN CIRCUIT (SCHEMATIC) 5--40.
ENGINE FAN SLOW OR DOESN’T RUN
(FLOW CHART) 5--41..................
ENGINE FAN MOTOR SHAFT SEAL
LEAKS (FLOW CHART) 5--42...........
MAIN BRUSH ON CIRCUIT
(SCHEMATIC) 5--44...................
MAIN BRUSHES DO NOT TURN ON
(FLOW CHART) 5--45..................
MAIN BRUSHES DO NOT TURN OFF
(FLOW CHART) 5--46..................
Page
MAIN BRUSHES DO NOT LOWER
(FLOW CHART) 5--49..................
MAIN BRUSH LIFT CIRCUIT
(SCHEMATIC) 5--50...................
MAIN BRUSH LOWER CIRCUIT
(SCHEMATIC) 5--48...................
MAIN BRUSHES DO NOT RAISE
(FLOW CHART) 5--51..................
MAIN BRUSHES DO NOT STAY UP
(FLOW CHART) 5--52..................
SCRUB FAN CIRCUIT
(SCHEMATIC) 5--54...................
SCRUB FAN DOES NOT TURN ON
(FLOW CHART) 5--55..................
SCRUB FAN DOES NOT TURN OFF
(FLOW CHART) 5--56..................
SCRUB FAN MOTOR SHAFT SEAL
LEAKS (FLOW CHART) 5--57...........
MAIN BRUSH ON CIRCUIT
(SCHEMATIC) 5--58...................
SIDE BRUSH DOES NOT TURN ON
(FLOW CHART) 5--59..................
SIDE BRUSH DOES NOT TURN OFF
(FLOW CHART) 5--60..................
SIDE BRUSH EXTEND CIRCUIT
(SCHEMATIC) 5--62...................
SIDE BRUSH DOES NOT GO OUT
(FLOW CHART) 5--63..................
SIDE BRUSH DOES NOT GO IN
(FLOW CHART) 5--64..................
SIDE BRUSH LOWER CIRCUIT
(SCHEMATIC) 5--66...................
SIDE BRUSH DOES NOT STAY UP
(FLOW CHART) 5--67..................
SIDE BRUSH DOES NOT RAISE
(FLOW CHART) 5--68..................
SIDE BRUSH DOES NOT LOWER
(FLOW CHART) 5--69..................
SQUEEGEE LIFT CIRCUIT
(SCHEMATIC) 5--70...................
SQUEEGEE DOES NOT LOWER
(FLOW CHART) 5--71..................
SQUEEGEE DOES NOT RAISE
(FLOW CHART) 5--72..................
SQUEEGEE DOES NOT STAY UP
(FLOW CHART) 5--73..................
STEERING CIRCUIT (SCHEMATIC) 5--74...
EATON HYDRAULICS REPAIR
MANUAL 5--75........................

HYDRAULICS
5-2 7400 MM428 (12--98)

HYDRAULICS
5-3
7400 MM428 (12--98)
INTRODUCTION
The hydraulic system consists of the propel pump,
accessory pump, control valve, drive motors,
steering cylinder, and vacuum fan motor.

HYDRAULICS
5-4 7400 MM428 (12--98)
HYDRAULIC FLUID RESERVOIR
The reservoir is located in the front left corner of
the machine.
Mounted on top of the reservoir is a filler cap with
a built-in breather and fluid level dipstick. Replace
the cap every 800 hours of operation.
Check the hydraulic fluid level at operating
temperature every 100 hours of operation. Make
sure the hopper is down when checking hydraulic
fluid level. The end of the dipstick is marked with
FULL and ADD levels to indicate the level of
hydraulic fluid in the reservoir.
Lubricate the filler cap gasket with a film of
hydraulic fluid before putting the cap back on the
reservoir.
ATTENTION! Do not overfill the
hydraulic fluid reservoir or operate the
machine with a low level of hydraulic
fluid in the reservoir. Damage to the
machine hydraulic system may result.
Drain and refill the hydraulic fluid reservoir with
new hydraulic fluid every 800 hours of operation.
The hydraulic fluid filter is located at the bottom of
the engine compartment. Replace the filter
element every 800 hours of operation.
The reservoir has a built-in strainer outlet that
filters hydraulic fluid before it enters the system.
Replace the strainer every 800 hours of operation.
HYDRAULIC FLUID
The quality and condition of the hydraulic fluid
play a very important role in how well the machine
operates. Tennant’s hydraulic fluid is specially
selected to meet the needs of Tennant machines.
Tennant’s hydraulic fluids provide a longer life for
the hydraulic components. There are two fluids
available for different temperature ranges:
Tennant part no. Ambient Temperature
65869 above 7_C(45_F)
65870 below 7_C(45_F)

HYDRAULICS
5-5
7400 MM428 (12--98)
The higher temperature fluid has a higher
viscosity and should not be used at the lower
temperatures. Damage to the hydraulic pumps
may occur because of improper lubrication.
The lower temperature fluid is a thinner fluid for
colder temperatures.
If a locally-available hydraulic fluid is used, make
sure the specifications match Tennant hydraulic
fluid specifications. Using substitute fluids can
cause premature failure of hydraulic components.
European manufactured machines are filled with
locally available hydraulic fluids. Check the label
on the hydraulic fluid reservoir.
ATTENTION! Hydraulic components
depend on system hydraulic fluid for
internal lubrication. Malfunctions,
accelerated wear, and damage will result
if dirt or other contaminants enter the
hydraulic system.
HYDRAULIC HOSES
Check the hydraulic hoses every 800 hours of
operation for wear or damage.
Fluid escaping at high pressure from a very
small hole can be almost invisible, and can cause
serious injuries.
See a doctor at once if injury results from
escaping hydraulic fluid. Serious infection or
reaction can develop if proper medical treatment
is not given immediately.
FOR SAFETY: When servicing machine,
use cardboard to locate leaking
hydraulic fluid under pressure.
If you discover a fluid leak, contact your
mechanic/supervisor.

HYDRAULICS
5-6 7400 MM428 (12--98)
TO REPLACE DIRECTIONAL PEDAL
CENTERING SPRING
FOR SAFETY: Before Leaving Or
Servicing Machine; Stop On Level
Surface, Set Parking Brake, Turn Off
Machine And Remove Key.
1. Pivot the operators seat to the open position
and engage the prop rod.
2. Disconnect the battery cables and remove
the battery.
3. Locate the pedal centering spring on the
right side of the accessory pump.
4. Remove the nyloc nut holding the centering
spring balljoint to directional control arm on
the propel pump.
5. Loosen the large jam nut holding the
centering spring to the propel bracket.
6. Remove the spring assembly from bracket
and position it up in the seat support area for
disassembly access.
7. Remove the ball joint and jam nuts.
8. Unscrew the centering spring assembly from
the directional control cable. Discard the old
spring.
NOTE: The cable will have to be held to keep it
from turning
9. Thread a new centering spring assembly all
the way back on the directional control
cable. Leave 1/4 in. of threads showing on
the larger diameter threads on the cable.
10. Install two 1/4 in. jam nuts on the end of the
cable. Tighten one to the centering spring
housing and the other one to the balljoint.
Leave 1/16 in. between the two jam nuts.
11. Use the large jam nut to lock the centering
spring assembly in place.

HYDRAULICS
5-7
7400 MM428 (12--98)
12. Reinstall the spring assembly balljoint back
in the directional control arm. Tighten the
nyloc nut to 11 -- 14 Nm (7 -- 10 ft lb).
13. Reinstall the battery and reconnect the
battery cables.
14. Jack up the front of the machine.
FOR SAFETY: Block machine tires
before jacking machine up. Jack
machine up at designated locations
only. Block machine up with jack stands
15. Check neutral centering of pump by starting
machine and observing front tire for any
rotation. If tire is rotating See TO ADJUST
CENTERING SPRING instructions.
16. Once the neutral centering has been set,
remove the jack stands, lower the machine,
and close the operators seat.

HYDRAULICS
5-8 7400 MM428 (12--98)
TO REPLACE DIRECTIONAL CONTROL
CABLE
FOR SAFETY: Before Leaving Or
Servicing Machine; Stop On Level
Surface, Set Parking Brake, Turn Off
Machine And Remove Key.
1. Pivot the operators seat to the open position
and engage the prop rod.
2. Disconnect the battery cables and remove
the battery.
3. Locate the pedal centering spring on the
right side of the accessory pump.
4. Remove the hex screw and nyloc nut
holding the centering spring balljoint to
directional control arm on the propel pump.
Retain the two steel sleeves.
5. Loosen the large jam nut holding the
centering spring to the propel bracket.
6. Remove the spring assembly from the
mount bracket and position it up in the seat
support area for disassembly access.
7. Remove the ball joint and jam nuts.
8. Unscrew the centering spring assembly from
the directional control cable. Retain the old
centering spring.
NOTE: The cable will have to be held to keep it
from turning
9. Remove the two hex screw holding the floor
plate in the operators compartment. Remove
the floor plate.
10. Remove the clamp holding the directional
cable to the operators compartment.
11. Reach in through the floor plate opening and
remove the nyloc nut holding the directional
control cable ball joint to the forward reverse
pedal arm. Pull the directional control cable
ball joint out of the pedal arm.
12. Loosen the large jam nut on the directional
control cable. Drop the cable out of the slot.
Remove the cable from the machine.

HYDRAULICS
5-9
7400 MM428 (12--98)
13. Install the old centering spring assembly all
the way back on the new directional control
cable. Leave 1/4 in. of threads showing on
the larger diameter threads on the cable.
14. Install two 1/4 in. jam nuts on the end of the
cable. Tighten one to the centering spring
housing and the other one to the balljoint.
Leave 1/16 in. between the two jam nuts.
15. Reinstall the centering spring/directional
cable assembly back in the machine.
16. Use the large jam nut to lock the centering
spring assembly in place on the mount
bracket.
17. Reinstall the spring assembly balljoint back
on the directional control arm. Reinstall the
hex screw, two steel sleeves, and nyloc nut.
Tighten to 11 -- 14 Nm (7 -- 10 ft lb).
18. Reach in through the floor plate opening and
reinstall the cable ball joint in the forward
reverse pedal arm. Reinstall the nyloc nut
and tighten to 11 -- 14 Nm (7 -- 10 ft lb).
19. Use the large jam nut to lock the directional
cable in place on the mount bracket.
20. Reinstall the cable clamp that holds the
directional cable to the operators
compartment.
21. Reinstall the battery and reconnect the
battery cables.
22. Jack up the front of the machine.
FOR SAFETY: Block machine tires
before jacking machine up. Jack
machine up at designated locations
only. Block machine up with jack
stands.
23. Check neutral centering of pump by starting
machine and observing front tire for any
rotation. If tire is rotating See TO ADJUST
CENTERING SPRING instructions.
24. Once the neutral centering has been set,
remove the jack stands, lower the machine,
and close the operators seat.

HYDRAULICS
5-10 7400 MM428 (12--98)
TO ADJUST CENTERING SPRING
FOR SAFETY: Before Leaving Or
Servicing Machine; Stop On Level
Surface, Set Parking Brake, Turn Off
Machine.
1. Jack up the front of the machine.
FOR SAFETY: Block machine tires
before jacking machine up. Jack
machine up at designated locations
only. Block machine up with jack stands
2. Check the neutral centering of the pump by
starting the machine and observing the front
tire for any rotation.
3. If tire is rotating, shut off the engine. Pivot
the operators seat to the open position and
engage the prop rod.
4. Locate the centering spring adjustment
bracket on the right side of the accessory
pump. Loosen the two M6 hex screws on
top of the bracket.
5. Loosen the two jam nuts on the hex screw
that is used to move the adjustment bracket
back and forth.
6. Start the machine and observe the front tire
for any rotation. If the tire is rotating in
either direction, move the adjustment
bracket backward or forward until rotation
stops. Re--tighten the two jam nuts. Shut off
the engine.
7. Once all the rotation has been eliminated,
tighten the two M6 hex screws that hold the
two brackets together. Tighten to
11 -- 1 4 N m ( 7 -- 1 0 f t l b ) .
8. Lower the operators seat.
9. Remove the jack stands and lower the
machine to the ground.

HYDRAULICS
5-11
7400 MM428 (12--98)
TO REPLACE PROPEL PUMP
FOR SAFETY: Before Leaving Or
Servicing Machine; Stop On Level
Surface, Set Parking Brake., Turn Off
Machine And Remove Key.
1. Pivot the operators seat to the open position
and engage the prop rod.
2. Disconnect the battery cables and remove
the battery.
NOTE: The battery tray can also be removed for
better access to the propel pump
3. Remove the detergent tank and the rubber
sound flap from the machine.
4. Disconnect the tension spring leading from
the directional spring bracket to the brush
wrap.
5. Remove the two hex screws holding the
accessory pump to the propel pump.
6. Lift the directional spring bracket up far
enough to allow accessory pump removal.
NOTE: The main suction line to the accessory
pump is held, by plastic ties, in a bundle of hoses
near the main valve. Remove the plastic ties to
gain slack in the suction line to ease pump
removal.
7. The accessory pump can now be pulled out
of the propel pump. Do not disconnect the
hydraulic hoses leading to the accessory
pump.
8. Mark, remove, and plug the hydraulic hoses
leading to the propel pump.
NOTE: Observe hydraulic cleanliness
requirements when opening hydraulic lines.
9. Remove the one socket screw holding the
propel pump directional arm and hub to the
pump shaft. Remove the hub and arm from
the pump.
NOTE: The pump shaft is tapered so the hub may
need to be removed with a puller.
10. Remove the two hex screws holding the
propel pump to the engine bellhousing.

HYDRAULICS
5-12 7400 MM428 (12--98)
11. Pull the propel pump out of the bellhousing
and drive coupler. Remove the pump from
the machine.
12. Remove the fittings from the old propel
pump and install in the new pump in the
same orientation.
13. Place grease on the splines of the new
pump and install back in the machine.
14. Reinstall the two hex screws and washers.
Use a small amount of blue loctite 242 on
the threads. Tighten to 31 -- 40 Nm
(27 -- 35 ft lb).
15. Reinstall the propel pump directional arm
and hub to the pump shaft. Reinstall the
socket screw. Tighten to 18 -- 24 Nm
(15 -- 20 ft lb).
16. Reconnect the hydraulic hoses to the propel
pump. See the schematic in this section.
17. Reinstall the accessory pump in the back of
the propel pump. Make sure the O--ring is in
place on the accessory pump.
18. Place the directional spring bracket back on
the flange of the accessory pump.
19. Reinstall the two hex screws and washers.
Use a small amount of blue loctite 242 on
the threads. Tighten to 31 -- 40 Nm
(27 -- 35 ft lb).
20. Reconnect the tension spring to the brush
wrap and directional spring bracket.
21. Reinstall the detergent tank in the seat
support area.
22. Reinstall the battery and reconnect the
battery cables.
23. Start the machine. Check the propel pump
for leaks and proper operation.

HYDRAULICS
5-13
7400 MM428 (12--98)
TO REPLACE ACCESSORY PUMP
FOR SAFETY: Before Leaving Or
Servicing Machine; Stop On Level
Surface, Set Parking Brake., Turn Off
Machine And Remove Key.
1. Pivot the operators seat to the open position
and engage the prop rod.
2. Disconnect the battery cables and remove
the battery.
3. Remove the detergent tank from the
machine.
4. Disconnect the tension spring leading from
the directional spring bracket to the brush
wrap.
5. Mark, remove, and plug the hydraulic hoses
leading to the accessory pump.
NOTE: Observe hydraulic cleanliness
requirements when opening hydraulic lines.
6. Remove the two hex screws holding the
accessory pump to the propel pump.
7. Lift the directional spring bracket up far
enough to allow accessory pump removal.
8. The accessory pump can now be pulled
back out of the propel pump. Remove the
accessory pump from the machine.
9. Remove the fittings from the old accessory
pump and install in the new pump in the
same orientation.
10. Place grease on the splines of the new
pump and install back in the machine.
11. Position the accessory pump back in the
propel pump. Make sure the O--ring is in
place on the accessory pump.

HYDRAULICS
5-14 7400 MM428 (12--98)
12. Reinstall the two hex screws and washers.
Use a small amount of blue loctite 242 on
the threads. Place the directional spring
bracket back under the bolt heads. Tighten
to 31 -- 40 Nm (27 -- 35 ft lb).
13. Reconnect the hydraulic hoses to the
accessory pump. See the schematic in this
section.
14. Reconnect the tension spring to the brush
wrap and directional spring bracket.
15. Reinstall the detergent tank in the seat
support area.
16. Reinstall the battery and reconnect the
battery cables.
17. Start the machine. Check the accessory
pump for leaks and proper operation.
TO REPLACE STEERING CYLINDER
FOR SAFETY: Before Leaving Or
Servicing Machine; Stop On Level
Surface, Set Parking Brake., Turn Off
Machine And Remove Key.
1. Turn the steering wheel to the left and open
the machine front cover.
2. Mark, remove, and plug the two hydraulic
hoses leading to the steering cylinder.
NOTE: Observe hydraulic cleanliness
requirements when opening hydraulic lines.

HYDRAULICS
5-15
7400 MM428 (12--98)
3. Remove the clamp holding the drive motor
hoses to the drive motor casting. Move the
hoses to gain access to steering cylinder
attachment hardware.
4. Remove the large hex screw and nyloc nut
holding the rod end of the steering cylinder
to drive motor casting. Retain the spacer
under the ball end.
5. Remove the large hex screw and nyloc nut
holding the piston end of the steering
cylinder to the machine frame.
6. Remove the steering cylinder from the
machine.
7. Remove the fittings from the old cylinder and
install in the new cylinder in the same
orientation.
8. Position new cylinder and balljoint assembly
back in the machine with rod end pointed
toward the drive motor casting.
9. Reinstall the hex screw, spacer, and nyloc
nut in the rod end of the steering cylinder
and through the drive motor casting. Tighten
to 271 Nm (200 ft lb).
10. Reinstall the hex screw and nyloc nut in the
piston end of the steering cylinder and
through the machine frame. Tighten to
271 Nm (200 ft lb).
11. Reconnect the hydraulic hoses to the
steering cylinder. See schematic in this
section.
12. Reinstall the clamp holding the drive motor
hoses to the front casting. Tighten the
hardware to 18 -- 24 Nm (15 -- 20 ft lb).
13. Start the machine and operate the steering.
Check for any leaks and proper operation.
Close the front cover.

HYDRAULICS
5-16 7400 MM428 (12--98)
TO REPLACE HYDRAULIC STEERING VALVE
FOR SAFETY: Before Leaving Or
Servicing Machine; Stop On Level
Surface, Set Parking Brake, Turn Off
Machine And Remove Key.
1. Open the machine front cover.
2. Mark, remove, and plug the five hydraulic
hoses leading to the steering control valve.
NOTE: Observe hydraulic cleanliness
requirements when opening hydraulic lines.
3. Remove the four M6 hex screws holding the
steering control valve to the steering
column.
4. Pull the steering valve out of the steering
column and remove it from the machine.
5. Remove the hydraulic fittings from old
control valve and install in the new valve in
the same orientation.
6. Install the new steering valve back in the
machine. Position the ports in the same
orientation as the old valve. Reinstall the
four M6 hex screws and tighten to
8--10Nm(5--7ftlb).
7. Reconnect hydraulic hoses to steering valve.
See schematic in this section.
8. Start the machine and operate the steering.
Check for any leaks and proper operation.

HYDRAULICS
5-17
7400 MM428 (12--98)
TO REPLACE MAIN HYDRAULIC VALVE
FOR SAFETY: Before Leaving Or
Servicing Machine; Stop On Level
Surface, Set Parking Brake., Turn Off
Machine And Remove Key.
1. Raise the operators seat, engage the prop
rod, and disconnect the battery cables from
the battery.
2. Open the machine front cover, engine cover,
and side door. Remove the side door from
the machine.
3. If the machine is an LPG, remove the LP
tank from the cradle.
4. Locate the main hydraulic valve under the
vacuum fan. Disconnect the 7 electrical
solenoids on the main valve from the main
harness.
5. Mark, remove, and plug the hydraulic hoses
leading to the main hydraulic valve.
NOTE: Observe hydraulic cleanliness
requirements when opening hydraulic lines.
6. Remove the three M8 hex screws holding
the main valve to the machine frame.
7. The main valve can now be removed from
the machine.
8. Remove the hex screws holding the main
valve to the mount bracket.
9. Remove hydraulic fittings from the old valve
and install in the new valve in the same
orientation.
10. Reinstall the mount bracket on the new
valve. Reinstall the three M8 hex screws
and washers. Tighten to 18 -- 24 Nm
(15 -- 20 ft lb).

HYDRAULICS
5-18 7400 MM428 (12--98)
11. Position the new valve back in the machine.
Reinstall the three M8 hex screws and
washers. Tighten to 18 -- 24 Nm
(15 -- 20 ft lb).
12. Reconnect the hydraulic hoses to the main
valve. See schematic in this section.
13. Reconnect the 7 electric solenoids to the
main harness. See ELECTRICAL section.
14. Reinstall the LP tank.
15. Reinstall the engine side door.
16. Reconnect the battery cables and close the
operators seat.
17. Start the machine and check the main valve
for any leaks.

HYDRAULICS
5-19
7400 MM428 (12--98)
TO REPLACE SIDE BRUSH HYDRAULIC
VALVE
FOR SAFETY: Before Leaving Or
Servicing Machine; Stop On Level
Surface, Set Parking Brake., Turn Off
Machine And Remove Key.
1. Raise the operators seat, engage the prop
rod, and disconnect the battery cables from
the battery.
2. Open the machine front cover, engine cover,
and side door. Remove the side door from
the machine.
3. If the machine is an LPG, remove the LP
tank from the cradle.
4. Locate the side brush hydraulic valve under
the LP/gas tank cradle. Disconnect the 4
electrical solenoids from the main harness.
5. Mark, remove, and plug the hydraulic hoses
leading to the side brush valve.
NOTE: Observe hydraulic cleanliness
requirements when opening hydraulic lines.
6. Remove the three M8 hex screws holding
the side brush valve to the LP tank cradle.
7. The side brush valve can now be removed
from the machine.
8. Remove hydraulic fittings from the old valve
and install in the new valve in the same
orientation.
NOTE: Observe hydraulic cleanliness
requirements when opening hydraulic lines.
9. Position the new valve back in the machine.
Reinstall the three M8 hex screws and
washers. Tighten to 18 -- 24 Nm
(15 -- 20 ft lb).
C5
C8
P5
P6
DR2
C7 C6

HYDRAULICS
5-20 7400 MM428 (12--98)
10. Reconnect the hydraulic hoses to the side
brush valve. See schematic in this section.
NOTE: Observe hydraulic cleanliness
requirements when opening hydraulic lines.
11. Reconnect the 4 electric solenoids to the
main harness. See ELECTRICAL section.
12. Reinstall the LP tank.
13. Reinstall the engine side door.
14. Reconnect the battery cables and close the
operators seat.
15. Start the machine and check the side brush
valve for any leaks.

HYDRAULICS
5-21
7400 MM428 (12--98)
TO REPLACE SOLENOID VALVE CARTRIDGE
FOR SAFETY: Before Leaving Or
Servicing Machine; Stop On Level
Surface, Set Parking Brake, Turn Off
Machine And Remove Key.
1. Raise the operators seat, engage the prop
rod, and disconnect the battery cables from
the battery.
2. Open the machine front cover, engine cover,
and side door. Remove the side door from
the machine.
3. If the machine is an LPG, remove the LP
tank from the cradle.
4. Locate and identify the cartridge to be
removed. Unplug the solenoid from the main
harness.
5. Remove the hex nut and rubber O--ring from
the cartridge stem.
NOTE: The port marked SV--4 on the main valve
and the port marked SV--10 on the side brush
valve contain an extra washer on the cartridge
stem between the top nut and O--ring.
6. Slide the electrical coil and rubber o--ring off
the stem.
NOTE: Oil will run out of valve when the
cartridge is removed.
7. Loosen and unscrew the cartridge stem out
of the valve body.
NOTE: Observe hydraulic cleanliness
requirements when opening hydraulic lines.
8. Install a new or rebuilt cartridge stem back in
the port. Tighten to 47 Nm (35 ft lb).
NOTE: Make sure the new cartridge had an
O--ring installed and oiled.
9. Slip the O--ring and coil back over the stem.

HYDRAULICS
5-22 7400 MM428 (12--98)
10. Install the 0--ring and hex nut on the stem
and tighten to 170 Ncm (15 in lb).
11. Reconnect the coil to the main harness. See
schematic in Electrical section.
12. Reinstall the LP tank.
13. Reinstall the engine side door.
14. Reconnect the battery cables and close the
operators seat.
15. Start the machine and check the side brush
valve for any leaks.

HYDRAULICS
5-23
7400 MM428 (12--98)
TO REPLACE ENGINE COOLING FAN
HYDRAULIC MOTOR
FOR SAFETY: Before Leaving Or
Servicing Machine; Stop On Level
Surface, Set Parking Brake, Turn Off
Machine And Remove Key.
1. Open the engine cover and side door.
2. Remove the hose from the vacuum fan and
recovery tank.
3. Remove the air cleaner hose from the air
cleaner and carburetor.
4. Mark, disconnect, and plug the three
hydraulic hoses going to the fan motor.
NOTE: Observe hydraulic cleanliness
requirements when opening hydraulic lines.
5. Remove the hydraulic fittings from the fan
motor. Note the orientation of the fittings for
proper reassembly in the new motor.
6. Reach in through the fan blades and remove
the four M6 hex screws holding the fan
blade to the motor hub. Set the fan blade
down in the fan air chamber.
7. Remove the 5/16 in. nut and washer holding
the fan blade hub to the motor shaft.
Remove the hub from the shaft. Retain the
square key from the motor shaft.
NOTE: The fan blade hub is on a tapered shaft
and may need to be pried off the motor.
8. Remove the two M10 hex screws and nyloc
nuts holding the fan motor to the mount
bracket. Remove the fan motor from the
machine.
9. Install the new fan motor on the mount
bracket. Reinstall the M10 hex screws and
nyloc nuts (nylocs positioned on the motor
side). Tighten to 37 -- 48 Nm (26 -- 34 ft lb).
NOTE: The notch in the mount bracket is for the
motor fitting.
10. Install the square key on the fan motor shaft.
NOTE: A small amount of super glue helps keep
the key in place when installing the fan hub.

HYDRAULICS
5-24 7400 MM428 (12--98)
11. Install the fan hub on the motor shaft.
Reinstall the 5/16 in. nut and tighten to
18 -- 24 Nm (15 -- 20 ft lb).
NOTE: Make sure key is in place on motor shaft.
12. Reinstall the fan blade back on the fan hub.
The deep side of the fan blade points to the
back of the machine. Reinstall the four M6
hex screws and tighten to 7.9 -- 9.9 Nm
(6 -- 7 ft lb).
13. Reinstall the hydraulic fittings in the fan
motor in the same orientation as they were
removed.
14. Reconnect the hydraulic hoses to the fan
motor. See schematic in this section.
15. Reinstall the air cleaner hose and vacuum
fan hose.
16. Reconnect the engine cover outer gas
spring to lower ball.
17. Start machine and check for leaks. Check
the engine fan for proper rotation. (air blows
out the back of machine).

HYDRAULICS
5-25
7400 MM428 (12--98)
TO REPLACE MAIN SCRUB BRUSH
HYDRAULIC MOTORS
1. Place the main scrub brushes in the raised
position.
FOR SAFETY: Before Leaving Or
Servicing Machine; Stop On Level
Surface, Set Parking Brake, Turn Off
Machine And Remove Key.
2. Open the LH brush door.
3. Remove the front ball joint on the leveling
rod from the machine frame.
4. Remove the two hair pins from the brush
wrap attachment pins.
5. Remove the three hex screws holding the
side squeegee assembly to the motor mount
plate. Remove the side squeegee.
6. Remove the M12 hex screw holding the
brush idler plate arm to the lift tube.
NOTE: For better access to the hydraulic drive
motors----remove the C--clip and brush arm from
the motor plate.
7. Mark, disconnect, and plug the three
hydraulic hoses leading to the main brush
drive motors.
NOTE:Observe hydraulic cleanliness
requirements when opening hydraulic lines.
8. Remove the motor mount plate assembly
from the machine.
9. Turn the motor plate assembly over.
Remove the cotter pins, castle nuts, and
washers from the drive plugs.
10. Use a puller to remove the drive plug from
the brush motors. Remove and retain the
square key.
11. Remove the steel hydraulic tube running
between the brush drive motors.

HYDRAULICS
5-26 7400 MM428 (12--98)
12. Remove the four hex screws holding each
brush motor to the motor plate.
NOTE: Make sure to note the orientation of the
motor and fittings before removing the motors
from the plate.
13. Remove the fittings from the old motor and
install in the new motor in the same
orientation.
14. Install the new brush motor and fittings in
the motor plate in the same orientation as
the old motor.
15. Reinstall the four hex screws and tighten to
37 -- 48 Nm (26 -- 34 ft lb).
16. Reinstall the steel hydraulic tube running
between the brush drive motors.
NOTE:Observe hydraulic cleanliness
requirements when opening hydraulic lines.
17. Reinstall the square key on the tapered
motor shaft. Put a small amount of grease
on the taper of the shaft.
18. Reinstall the drive plugs, washers, and
castle nuts. Hold the plug from turning and
tighten the castle nut down to 37 -- 48 Nm
(26 -- 34 ft lb) and then until the slot in the
nut lines up with the hole in the shaft. Install
a new cotter pin.
19. Position the motor plate assembly back in
the machine.
NOTE: Lift up on the brush wrap slightly when
installing the motor plate in the machine so the
attachment pins line up with the holes in the plate.
20. Reinstall the two hair pins in the brush wrap
attachment pins.
21. Reconnect the hydraulic hoses to the brush
motors. See schematic in this section.
NOTE:Observe hydraulic cleanliness
requirements when opening hydraulic lines.
22. Reinstall the brush arm and C--clip to the
motor plate if they were removed earlier.
23. Align the two pins on the lift tube with the
two holes in the brush arm.

HYDRAULICS
5-27
7400 MM428 (12--98)
24. Reinstall the M12 hex screw in the brush
arm. Tighten to 64 -- 83 Nm (47 -- 61 ft lb).
NOTE: Apply a small amount of grease to the
threads on the bolt and in the tube.
25. Reinstall the front of the leveling rod ball
joint to the machine frame.
26. Reinstall the side squeegee assembly to the
motor plate. Tighten the three hex screws to
37 -- 48 Nm (26 -- 34 ft lb).
27. Close the LH brush door and operate the
machine. Check the main brush motors for
proper operation.

HYDRAULICS
5-28 7400 MM428 (12--98)
TO REPLACE SCRUB HEAD ASSEMBLY
LIFT CYLINDER
1. Start the engine and drop the main scrub
brushes down until they just touch the floor.
FOR SAFETY: Before Leaving Or
Servicing Machine; Stop On Level
Surface, Set Parking Brake, Turn Off
Machine And Remove Key.
2. Jack up the front of the machine and install
jack stands under the frame.
FOR SAFETY: Block machine tires
before jacking machine up. Jack
machine up at designated locations
only. Block machine up with jack
stands.
3. Go under the machine on the LH side.
4. Locate the lift cylinder on the left side of the
front scrub brush.
5. Mark, disconnect, and plug the two hydraulic
hoses going to the lift cylinder.
6. Remove the two cotter pins and clevis pins.
7. Remove the lift cylinder from the machine.
8. Remove the hydraulic fittings from the lift
cylinder and install in the new cylinder in the
same orientation.
9. Install the new cylinder in the machine.
NOTE: The rod end of the cylinder points down.
10. Reinstall the upper and lower clevis and
cotter pins.
11. Reconnect the hydraulic hoses to the new
lift cylinder. See schematic in this section.
12. Remove the jack stands and lower the
machine.
13. Start the machine and check the scrub head
lift cylinder for proper operation.

HYDRAULICS
5-29
7400 MM428 (12--98)
TO REPLACE OPTIONAL SIDE BRUSH
HYDRAULIC MOTOR
1. Remove the side brush. See TO REPLACE
OPTIONAL SIDE BRUSH instructions in the
SCRUBBING section.
FOR SAFETY: Before Leaving Or
Servicing Machine; Stop On Level
Surface, Set Parking Brake, Turn Off
Machine And Remove Key.
2. Remove the four hex screws holding the
side brush guard to the machine frame.
3. Remove the hex screw holding the side
brush drive hub to the side brush motor.
Remove the drive hub from the motor.
4. Mark, disconnect, and plug the two hydraulic
hoses going to the side brush motor.
NOTE:Observe hydraulic cleanliness
requirements when opening hydraulic lines.
5. Remove the four hex screws holding the
side brush motor to the mount plate.
6. Lift the motor straight up, tilt back, and
remove it from the side brush assembly.
NOTE: Make sure to note the orientation of the
motor to the mount plate.
7. Remove the hydraulic fittings from the old
motor and install in the new motor in the
same orientation.
8. Position the new motor back in the side
brush assembly.
9. Reinstall the four hex screws and tighten to
37 -- 48 Nm (26 -- 34 ft lb).
10. Reconnect the hydraulic hoses to the motor.
See schematic in this section.
11. Reinstall the drive hub, washers, and hex
screw. Tighten to 18 -- 24 Nm (15 -- 20 ft lb).
12. Reinstall the side brush. See TO REPLACE
OPTIONAL SIDE BRUSH instructions.
13. Reinstall the side brush guard to the
machine frame. Tighten the four hex screws
to 37 -- 48 Nm (26 -- 34 ft lb).
14. Operate the machine and check the side
brush for proper operation.

HYDRAULICS
5-30 7400 MM428 (12--98)
TO REPLACE OPTIONAL SIDE BRUSH LIFT
CYLINDER
1. Remove the side brush. See TO REPLACE
OPTIONAL SIDE BRUSH instructions.
2. Remove the four hex screws holding the
side brush guard to the machine frame.
3. Remove the side brush hydraulic motor. See
TO REPLACE OPTIONAL SIDE BRUSH
HYDRAULIC MOTOR instructions.
FOR SAFETY: Before Leaving Or
Servicing Machine; Stop On Level
Surface, Set Parking Brake, Turn Off
Machine And Remove Key.
4. Mark, disconnect, and plug the two hydraulic
hoses going to the lift cylinder.
NOTE:Observe hydraulic cleanliness
requirements when opening hydraulic lines.
5. Remove the two cotter pins and clevis pins
holding the lift cylinder to the side brush
assembly. Remove the lift cylinder from the
machine.
NOTE: Make sure to note the orientation of the
cylinder to the mount plate.
6. Remove the hydraulic fittings from the old
cylinder and install in the new cylinder in the
same orientation.
7. Position the new cylinder back in the side
brush assembly.
8. Reconnect the hydraulic hoses to the
cylinder. See schematic in this section.
9. Reinstall the side brush motor in the
machine. See TO REPLACE OPTIONAL
SIDE BRUSH HYDRAULIC MOTOR
instructions.
10. Reinstall the side brush. See TO REPLACE
OPTIONAL SIDE BRUSH instructions in the
SCRUBBING section.
11. Reinstall the side brush guard to the
machine frame. Tighten the four hex screws
to 37 -- 48 Nm (26 -- 34 ft lb).
12. Operate the machine and check the side
brush lift cylinder for proper operation.

HYDRAULICS
5-31
7400 MM428 (12--98)
TO REPLACE OPTIONAL SIDE BRUSH
SWING CYLINDER
FOR SAFETY: Before Leaving Or
Servicing Machine; Stop On Level
Surface, Set Parking Brake, Turn Off
Machine And Remove Key.
1. Open the front cover on the machine.
2. Locate the swing cylinder down in front of
the operators compartment.
3. Mark, disconnect, and plug the two hydraulic
hoses going to the swing cylinder.
NOTE:Observe hydraulic cleanliness
requirements when opening hydraulic lines.
4. Remove the cotter pin and clevis pin holding
the rod end of the swing cylinder to the
threaded sleeve and ball joint assembly.
5. Remove the cotter pin and clevis pin holding
the other end of the swing cylinder to the
machine frame.
6. Pull the swing cylinder back out of the
threaded sleeve and remove it from the
machine.
7. Remove the hydraulic fittings from the old
cylinder and install in the new cylinder in the
same orientation.
8. Position the new cylinder back in the side
brush assembly. Position the rod end of the
cylinder back in the threaded sleeve first,
then install the clevis and cotter pin in the
other end.
9. Reinstall the clevis and cotter pin in the rod
end of the swing cylinder and through the
hole in the threaded sleeve.
10. Reconnect the hydraulic hoses to the
cylinder. See schematic in this section.
11. Operate the machine and check the side
brush swing cylinder for proper operation.

HYDRAULICS
5-32 7400 MM428 (12--98)
TO REPLACE SQUEEGEE LIFT CYLINDER
1. Open the debris tray latch and swing the
squeegee assembly out for better access.
2. Start engine, lower rear squeegee, shut off
engine.
FOR SAFETY: Before Leaving Or
Servicing Machine; Stop On Level
Surface, Set Parking Brake, Turn Off
Machine And Remove Key.
3. Mark, disconnect, and plug the two hydraulic
hoses going to the squeegee lift cylinder.
NOTE:Observe hydraulic cleanliness
requirements when opening hydraulic lines.
4. Remove the snap retaining ring from the pin
on the debris tray at piston end of the
cylinder.
NOTE: The cylinder pin DOES NOT have a snap
ring grove.
5. Remove the cotter pin and clevis pin from
the rod end of lift cylinder and squeegee lift
bellcrank.
6. The cylinder can now be pulled up and off
the pin and removed from the machine.
7. Remove the hydraulic fittings from the old
cylinder and install in the new cylinder in the
same orientation.
8. Position new cylinder back in the machine.
Place the hole in the piston end of the
cylinder on the pin on the debris tray.
Reinstall the snap ring retainer on the pin.
NOTE: The cylinder pin DOES NOT have a snap
ring grove.
9. Align the hole in rod end of the cylinder with
the hole in squeegee lift bellcrank. Reinstall
the clevis and cotter pin.
10. Reconnect the hydraulic hoses to the
squeegee lift cylinder. See schematic in this
section.
11. Start the machine and raise the squeegee.
Swing the squeegee assembly back in.
Check the lift cylinder for proper operation.

HYDRAULICS
5-33
7400 MM428 (12--98)
TO REPLACE VACUUM FAN HYDRAULIC
MOTOR
FOR SAFETY: Before Leaving Or
Servicing Machine; Stop On Level
Surface, Set Parking Brake, Turn Off
Machine And Remove Key.
1. Remove the vacuum fan from the machine.
See TO REMOVE VACUUM FAN
instructions in the SCRUBBING section.
2. Place the vacuum fan assembly in a vice or
some other holding device.
3. Remove the six hex screws holding the front
housing to the rear housing. Remove the the
front housing.
NOTE: Mark the front housing in relation to the
rear housing so it can be re--assembled correctly.
4. Remove the crown nut on the impeller shaft.
Slide the impeller off the shaft.
NOTE: Remove and save the key and any shims
that are on the motor shaft, under the impeller.
5. Turn the housing over and remove the four
nyloc nuts and washers from the motor
mount plate. Remove the motor mount plate
from the housing.
NOTE: Note the orientation of hydraulic motor and
fittings for proper re--assembly.
6. Remove the four flat head screws and nyloc
nuts holding the hydraulic motor to the
mount plate. Remove the old motor.
7. Install the new motor on the plate. Reinstall
the flat head screws. Tighten to 9 -- 13 Nm
(7 -- 10 ft lb).
8. Remove the hydraulic fittings from the old
motor and install in the new motor in the
same orientation.

HYDRAULICS
5-34 7400 MM428 (12--98)
9. Reinstall the motor and mounting plate on
the rear housing. Reinstall the four nyloc
nuts and tighten to 16 -- 22 Nm
(12 -- 16 ft lb).
NOTE: Be sure the square key is on the motor
shaft. Super gluing the key to the shaft helps keep
it in place when installing the impeller.
10. Turn the housing over and reinstall shims,
key, fan impeller, and crown nut. Tighten nut
to 34 -- 47 Nm (25 -- 35 ft lb).
NOTE: Use a small amount of blue loctite 242 on
the motor shaft threads.
11. Reinstall the front housing on the rear
housing. Reinstall the six hex screws and
tighten to 22 -- 27 Nm (16 -- 20 ft lb).
NOTE: Tennant part no. 57543 plastic shims must
be used for proper fan to housing clearance.
Remove these shims after housing hardware has
been tightened.
12. Reinstall the vacuum fan assembly in the
machine. See TO INSTALL VACUUM FAN
instructions in the SCRUBBING section.

HYDRAULICS
5-35
7400 MM428 (6--01)
AB C D EFGH I
HYDRAULIC SCHEMATIC

HYDRAULICS
5-36 7400 MM428 (6--01)
S-- 14
ABCD GHI
F
E
HYDRAULIC SCHEMATIC

HYDRAULICS
5-37
7400 MM428 (6--01)
M3
P7
G1
T3
T1
M1
T4
C3
C1
C2
C4
T2
R
E
P
L
T
T5
IN
OUT
P3
DR1
P2 M2 P1
Scrub
Brush
Motors
Steering
Valve
Control Valve
Front
Reservoir
Vac Fan
Wheel
Drive
Motor
Flow
Sensor
Switch
Cooling
Fan
Motor
Scrub Head
Lift Cylinder
Rear
SqueegeeLift
Cylinder
Pump
Cooler
Filter
2
3
4
5
6
7
8
9
10
1
11
12
13
14
15
16
17
18
19
20 21
22
23
24
25
26
1
1
1
1
7
HYDRAULIC HOSE GROUP

HYDRAULICS
5-38 7400 MM428 (6--01)
M3
G3
G1
T3
T1
M1
T4
C3
C1
C2
C4
P6
C7
C8
T2
T5
DR2
C5
C6
P5
P3
DR1
P2 M2 P1
SIDE
BRUSH
VALVE
VACUUM FAN
MOTOR
MAIN CONTROL
VALVE
SIDE
BRUSH
MOTOR
SIDE
BRUSH
LIFT CYL
SIDE BRUSH
SWING CYL
HYDRAULIC HOSE GROUP / SIDE BRUSH OPTION

HYDRAULICS
5-39
7400 MM428 (12--98)
TROUBLESHOOTING
The following troubleshooting section is organized
with the section of the hydraulic schematic
pertaining to that particular problem first, followed
by the flow chart.

HYDRAULICS
5-40 7400 MM428 (12--98)
ENGINE
FAN
STRAINER
T
E
P
R
L
RV7
1160
RV3
3 PSI
RV6
85
PSI
M
2400
RPM
3.7 GPM
PSI
ENGINE FAN CIRCUIT
(SCHEMATIC)
PRESSURE
RETURN
SUCTION
CASE DRAIN
PRESSURE READINGS BASED
ON 150 F
400 PSI
3.7GPM
x

HYDRAULICS
5-41
7400 MM428 (12--98)
MOTOR INLET
FLOW OK?
REPAIR OR
REPLACE MOTOR
REPAIR OR
REPLACE STEERING
CONTROL
PUMP OUTLET
FLOW OK?
PLUMBING OK?
REPAIR OR
REPLACE PLUMBING
YES NO
NO
REPAIR OR
REPLACE PUMP
ENGINE FAN SLOW OR DOESN’T RUN
(FLOW CHART)
YES NO
STEERING INLET
PRESSURE OK?
NO YES

HYDRAULICS
5-42 7400 MM428 (12--98)
MOTOR CASE
PRESSURE OK?
< 25 PSI
REPAIR OR
REPLACE MOTOR
REPAIR OR
REPLACE CASE DRAIN
PLUMBING & MOTOR
YES NO
ENGINE FAN MOTOR SHAFT SEAL LEAKS
(FLOW CHART)

HYDRAULICS
5-43
7400 MM428 (12--98)

HYDRAULICS
5-44 7400 MM428 (12--98)
MAIN
BRUSHES
STRAINER FILTER
RV1
RV2
P3 DR1
C1
C2
G5
C4
C3
G4
M3
M2
T5
T2
T4
T1
M1
T3
G1
P1P2
G2
P7
RV3
3 PSI
8.5 GPM
2500
PSI
2500
PSI SV01
SV02
SV06
SV04
SV05
SV07
SV03
PR1
300
PSI
S.BR.
OPT
MAIN BRUSH ON CIRCUIT
(SCHEMATIC)
PRESSURE
RETURN
SUCTION
CASE DRAIN
PRESSURE READINGS BASED
ON 150 F
xx
LEVEL #1 800 PSI
LEVEL #2 1000 PSI
LEVEL #3 1300 PSI
8.4 GPM
LEVEL #1 400 PSI
LEVEL #2 550 PSI
LEVEL #3 700 PSI
8.3 GPM

HYDRAULICS
5-45
7400 MM428 (12--98)
SV1 STEM
MAGNETIZED?
CHECK
ELECTRICAL SYSTEM
REPAIR OR
REPLACE MOTOR
PLUMBING OK?
SV1 STEM
CARTRIDGE
SHIFTING OK?
REPAIR OR
REPLACE SV1
STEM CARTRIDGE
YES
NO
PUMP OUTLET
FLOW OK?
MAIN BRUSHES DO NOT TURN ON
(FLOW CHART)
YES NO
MOTOR INLET
FLOW OK?
NO
YES
REPAIR OR
REPLACE
PLUMBING
NO
YES
REPAIR OR
REPLACE
PUMP
YES
RV1 RELIEF
CARTRIDGE OK?
2500 PSI
NO
REPAIR OR REPLACE
RV1 RELIEF
CARTRIDGE
NO

HYDRAULICS
5-46 7400 MM428 (12--98)
SV1 STEM
MAGNETIZED?
CHECK
ELECTRICAL SYSTEM
SV1 STEM
CARTRIDGE
SHIFTING OK?
REPAIR OR
REPLACE SV1
STEM CARTRIDGE
YES NO
MAIN BRUSHES DO NOT TURN OFF
(FLOW CHART)
NO

HYDRAULICS
5-47
7400 MM428 (12--98)

HYDRAULICS
5-48 7400 MM428 (12--98)
MAIN BRUSH LIFT
LOWER
MAIN
BRUSHES
STRAINER
RV1
RV2
P3 DR1
C1
C2
G5
C4
C3
G4
M3
M2
T5
T2
T4
T1
M1
T3
G1
P1P2
G2
P7
RV3
3 PSI
8.5 GPM
2500
PSI
2500
PSI SV01
SV02
SV06
SV04
SV05
SV07
SV03
PR1
300
PSI
S.BR.
OPT
MAIN BRUSH LOWER CIRCUIT
(SCHEMATIC)
x
PRESSURE
RETURN
SUCTION
CASE DRAIN
PRESSURE READINGS BASED
ON 150 F
LEVEL #1 350 PSI
LEVEL #2 500 PSI
LEVEL #3 650 PSI

HYDRAULICS
5-49
7400 MM428 (12--98)
SV4, SV5 & SV7
STEMS
MAGNETIZED?
CHECK
ELECTRICAL SYSTEM
SV7 STEM
CARTRIDGE
SHIFTING OK?
REPAIR OR REPLACE
PR1 STEM
CARTRIDGE
C3 PORT
PRESSURE OK?
460 -- 730 PSI
SV5 STEM
CARTRIDGE
SHIFTING OK?
YES
NO
MAIN BRUSHES DO NOT LOWER
(FLOW CHART)
YES NO
G5 PORT
PRESSURE OK?
300 PSI
NO
YES
G4 PORT
PRESSURE OK?
460 -- 730 PSI
NO
REPAIR OR REPLACE
SV7 STEM
CARTRIDGE
NO
YES
REPAIR OR REPLACE
SV5 STEM
CARTRIDGE
NO
REPLACE
SV4 STEM
CARTRIDGE

HYDRAULICS
5-50 7400 MM428 (12--98)
MAIN BRUSH LIFT
UP
MAIN
BRUSHES
STRAINER
RV1
RV2
P3 DR1
C1
C2
G5
C4
C3
G4
M3
M2
T5
T2
T4
T1
M1
T3
G1
P1P2
G2
P7
RV3
3 PSI
3.7 GPM
2500
PSI
2500
PSI SV01
SV02
SV06
SV04
SV05
SV07
SV03
PR1
300
PSI
S.BR.
OPT
MAIN BRUSH LIFT CIRCUIT
(SCHEMATIC)
PRESSURE
RETURN
SUCTION
CASE DRAIN
PRESSURE READINGS BASED
ON 150 F
300 PSI
1.0 GPM WHILE MOVING
x
(2.0 -- 3.0 SEC)

HYDRAULICS
5-51
7400 MM428 (12--98)
SV5
STEM
MAGNETIZED?
CHECK
ELECTRICAL SYSTEM
LIFT
CYLINDER
SEALS OK?
OR1
ORIFICE
PLUGGED?
C3 PORT
PRESSURE OK?
< 25 PSI
PLUMBING
OK?
YES NO
MAIN BRUSHES DO NOT RAISE
(FLOW CHART)
YES NO
G5 PORT
PRESSURE OK?
300 PSI
NO
YES
SV5 STEM
CARTRIDGE
SHIFTING OK?
NO
REPLACE LIFT
CYLINDER
NO
YES
REPAIR OR
REPLACE
PLUMBING
REPAIR OR
REPLACE OR1
ORIFICE
REPAIR OR
REPLACE PR1
STEM CARTRIDGE
NO
YES
REPAIR OR
REPLACE SV5
STEM CARTRIDGE
NO

HYDRAULICS
5-52 7400 MM428 (12--98)
SV7 STEM
CARTRIDGE
MAGNETIZED?
CHECK
ELECTRICAL
SYSTEM
REPAIR OR
REPLACE
PLUMBING
LIFT
CYLINDER
SEALS OK?
SV7 STEM
CARTRIDGE
SHIFTING & SEAT OK?
REPAIR OR
REPLACE SV7 STEM
CARTRIDGE
YES NO
NO
REPLACE
LIFT
CYLINDER
MAIN BRUSHES DO NOT STAY UP
(FLOW CHART)
YES NO
PLUMBING
OK?
NO YES

HYDRAULICS
5-53
7400 MM428 (12--98)

HYDRAULICS
5-54 7400 MM428 (12--98)
STRAINER FILTER
VACUUM FAN
RV1
RV2
P3 DR1
C1
C2
G5
C4
C3
G4
M3
M2
T5
T2
T4
T1
M1
T3
G1
P1P2
G2
P7
RV3
3 PSI
6.7 GPM
2500
PSI
2500
PSI SV01
SV02
SV06
SV04
SV05
SV07
SV03
PR1
300
PSI
S.BR.
OPT
SCRUB FAN CIRCUIT
(SCHEMATIC)
PRESSURE
RETURN
SUCTION
CASE DRAIN
PRESSURE READINGS BASED
ON 150 F
1700 PSI
6.3 GPM
11,000 +/-- 1000 RPM
x

HYDRAULICS
5-55
7400 MM428 (12--98)
SV2 STEM
MAGNETIZED?
CHECK
ELECTRICAL SYSTEM
REPAIR OR
REPLACE MOTOR
PLUMBING OK?
SV2 STEM
CARTRIDGE
SHIFTING OK?
REPAIR OR
REPLACE SV2
STEM CARTRIDGE
YES
NO
PUMP OUTLET
FLOW OK?
SCRUB FAN DOES NOT TURN ON
(FLOW CHART)
YES NO
MOTOR INLET
FLOW OK?
NO
YES
REPAIR OR
REPLACE
PLUMBING
NO
YES
REPAIR OR
REPLACE
PUMP
YES
RV2 RELIEF
CARTRIDGE OK?
2500 PSI
NO
REPAIR OR REPLACE
RV2 RELIEF
CARTRIDGE
NO

HYDRAULICS
5-56 7400 MM428 (12--98)
SV2 STEM
MAGNETIZED?
CHECK
ELECTRICAL SYSTEM
SV2 STEM
CARTRIDGE
SHIFTING OK?
REPAIR OR
REPLACE SV2
STEM CARTRIDGE
YES NO
SCRUB FAN DOES NOT TURN OFF
(FLOW CHART)
NO
ROTOR
SPEED
< 200 RPM
SYSTEM
NORMAL
NO YES

HYDRAULICS
5-57
7400 MM428 (12--98)
MOTOR CASE
PRESSURE OK?
< 25 PSI
REPAIR OR
REPLACE MOTOR
REPAIR OR
REPLACE CASE DRAIN
PLUMBING & MOTOR
YES NO
SCRUB FAN MOTOR SHAFT SEAL LEAKS
(FLOW CHART)

HYDRAULICS
5-58 7400 MM428 (12--98)
MAIN
BRUSHES
STRAINER FILTER
RV1
RV2
P3 DR1
C1
C2
G5
C4
C3
G4
M3
M2
T5
T2
T4
T1
M1
T3
G1
P1P2
G2
P7
RV3
3 PSI
8.5 GPM
2500
PSI
2500
PSI SV01
SV02
SV06
SV04
SV05
SV07
SV03
PR1
300
PSI
S.BR.
OPT
MAIN BRUSH ON CIRCUIT
(SCHEMATIC)
PRESSURE
RETURN
SUCTION
CASE DRAIN
PRESSURE READINGS BASED
ON 150 F
xx
LEVEL #1 800 PSI
LEVEL #2 1000 PSI
LEVEL #3 1300 PSI
8.4 GPM
LEVEL #1 400 PSI
LEVEL #2 550 PSI
LEVEL #3 700 PSI
8.3 GPM

HYDRAULICS
5-59
7400 MM428 (12--98)
SV6 STEM
MAGNETIZED?
CHECK
ELECTRICAL SYSTEM
REPAIR OR
REPLACE MOTOR
PLUMBING OK?
SV6 STEM
CARTRIDGE
SHIFTING OK?
REPAIR OR
REPLACE SV6
STEM CARTRIDGE
YES
NO
PUMP OUTLET
FLOW OK?
SIDE BRUSH DOES NOT TURN ON
(FLOW CHART)
YES NO
MOTOR INLET
FLOW OK?
NO
YES
REPAIR OR
REPLACE
PLUMBING
NO
YES
REPAIR OR
REPLACE
PUMP
YES
RV2 RELIEF
CARTRIDGE OK?
2500 PSI
NO
REPAIR OR REPLACE
RV2 RELIEF
CARTRIDGE
NO

HYDRAULICS
5-60 7400 MM428 (12--98)
SV6 STEM
MAGNETIZED?
CHECK
ELECTRICAL SYSTEM
SV6 STEM
CARTRIDGE
SHIFTING OK?
REPAIR OR
REPLACE SV6
STEM CARTRIDGE
YES NO
SIDE BRUSH DOES NOT TURN OFF
(FLOW CHART)
NO
BRUSH
SPEED
<10RPM
SYSTEM
NORMAL
NO YES

HYDRAULICS
5-61
7400 MM428 (12--98)

HYDRAULICS
5-62 7400 MM428 (12--98)
SIDE BRUSH
LIFT
SIDE BRUSH
EXTEND
UP
EXTEND
SIDE BRUSH
OPTION
STRAINER
RV1
RV2
P3 DR1
C1
C2
G5
C4
C3
G4
M3
M2
T5
T2
T4
T1
M1
T3
G1
P1P2
G2
P7
DR2
C7
C8
C5
C6
P6 P5 G6
SV09
SV11
SV08
SV10
PR2
300
PSI
100--
800
PSI
RV3
3 PSI
SC1
8.5 GPM
2500
PSI
2500
PSI SV01
SV02
SV06
SV04
SV05
SV07
SV03
PR1
300
PSI
S.BR.
OPT
SIDE BRUSH EXTEND CIRCUIT
(SCHEMATIC)
PRESSURE
RETURN
SUCTION
CASE DRAIN
PRESSURE READINGS BASED
ON 150 F
(WITH MAIN BRUSHES ON)
x
300 PSI
1.0 GPM WHILE MOVING

HYDRAULICS
5-63
7400 MM428 (12--98)
SV9
STEM
MAGNETIZED?
CHECK
ELECTRICAL SYSTEM
CYLINDER
LINKAGE & SEALS
OK?
REPAIR OR REPLACE
PR2 PRESSURE
CONTROL CARTRIDGE
DR2 PORT
PRESSURE OK?
< 25 PSI
PLUMBING
OK?
YES
NO
SIDE BRUSH DOES NOT GO OUT
(FLOW CHART)
YES NO
C5 PORT
PRESSURE OK?
300 PSI
NO
YES
SV9 STEM
CARTRIDGE
SHIFTING OK?
NO
REPAIR
CYLINDER LINKAGE
OR SEALS
NO
YES
REPAIR OR
REPLACE
PLUMBING
NO
REPAIR OR REPLACE
SV9 STEM
CARTRIDGE

HYDRAULICS
5-64 7400 MM428 (12--98)
SV9
STEM
MAGNETIZED?
CHECK
ELECTRICAL SYSTEM
CYLINDER
LINKAGE &
SEALS OK?
OR2
ORIFICE
PLUGGED?
C6 PORT
PRESSURE OK?
< 25 PSI
PLUMBING
OK?
YES NO
SIDE BRUSH DOES NOT GO IN
(FLOW CHART)
YES NO
C5 PORT
PRESSURE OK?
300 PSI
NO
YES
SV9 STEM
CARTRIDGE
SHIFTING OK?
NO
REPAIR CYLINDER
LINKAGE
OR SEALS
NO
YES
REPAIR OR
REPLACE
PLUMBING
REPAIR OR
REPLACE OR2
ORIFICE
SC1 SHUTTLE
CHECK CARTRIDGE
SHIFTING OK?
NO
YES
REPAIR OR
REPLACE SV9
STEM CARTRIDGE
NO
REPAIR OR REPLACE
PR2 PRESSURE
CONTROL CARTRIDGE
REPAIR OR REPLACE
SHUTTLE CHECK
CARTRIDGE
YES NO

HYDRAULICS
5-65
7400 MM428 (12--98)

HYDRAULICS
5-66 7400 MM428 (12--98)
SIDE BRUSH
LIFT
SIDE BRUSH
EXTEND
DOWN
RETRACT
SIDE BRUSH
OPTION
STRAINER
RV1
RV2
P3 DR1
C1
C2
G5
C4
C3
G4
M3
M2
T5
T2
T4
T1
M1
T3
G1
P1P2
G2
P7
DR2
C7
C8
C5
C6
P6 P5 G6
SV09
SV11
SV08
SV10
PR2
300
PSI
100--
800
PSI
RV3
3 PSI
SC1
8.5 GPM
2500
PSI
2500
PSI SV01
SV02
SV06
SV04
SV05
SV07
SV03
PR1
300
PSI
S.BR.
OPT
SIDE BRUSH LOWER CIRCUIT
(SCHEMATIC)
PRESSURE
RETURN
SUCTION
CASE DRAIN
PRESSURE READINGS BASED
ON 150 F
(WITH MAIN BRUSHES ON)
x
LEVEL #1 210 PSI
LEVEL #2 270 PSI
LEVEL #3 320 PSI
1.0 GPM WHILE MOVING

HYDRAULICS
5-67
7400 MM428 (12--98)
SV11 STEM
CARTRIDGE
MAGNETIZED?
CHECK
ELECTRICAL
SYSTEM
REPAIR OR
REPLACE
PLUMBING
LIFT
CYLINDER
SEALS OK?
SV11 STEM
CARTRIDGE
SHIFTING & SEAT OK?
REPAIR OR
REPLACE SV11 STEM
CARTRIDGE
YES NO
NO
REPLACE
LIFT
CYLINDER
SIDE BRUSH DOES NOT STAY UP
(FLOW CHART)
YES NO
PLUMBING
OK?
NO YES

HYDRAULICS
5-68 7400 MM428 (12--98)
SV8
STEM
MAGNETIZED?
CHECK
ELECTRICAL SYSTEM
LIFT CYLINDER
LINKAGE & SEALS
OK?
OR2
ORIFICE
PLUGGED?
DR2 PORT
PRESSURE OK?
< 25 PSI
PLUMBING
OK?
YES NO
SIDE BRUSH DOES NOT RAISE
(FLOW CHART)
YES NO
C5 PORT
PRESSURE OK?
300 PSI
NO
YES
SV8 STEM
CARTRIDGE
SHIFTING OK?
NO
REPAIR LINKAGE
OR REPLACE
LIFT CYLINDER
NO
YES
REPAIR OR
REPLACE
PLUMBING
REPAIR OR
REPLACE OR2
ORIFICE
NO
YES
REPAIR OR
REPLACE SV8
STEM CARTRIDGE
NO
SC1 SHUTTLE
CHECK CARTRIDGE
SHIFTING OK?
REPAIR OR REPLACE
PR2 PRESSURE
CONTROL CARTRIDGE
REPAIR OR REPLACE
SHUTTLE CHECK
CARTRIDGE
YES NO

HYDRAULICS
5-69
7400 MM428 (12--98)
SV8, SV10 & SV11
STEMS
MAGNETIZED?
CHECK
ELECTRICAL SYSTEM
SV11 STEM
CARTRIDGE
SHIFTING OK?
REPAIR OR REPLACE
PR2 PRESSURE
CONTROL CARTRIDGE
C7 PORT
PRESSURE OK?
> 200 PSI
SV8 STEM
CARTRIDGE
SHIFTING OK?
YES
NO
SIDE BRUSH DOES NOT LOWER
(FLOW CHART)
YES NO
C5 PORT
PRESSURE OK?
300 PSI
NO
YES
G6 PORT
PRESSURE OK?
> 200 PSI
NO
REPAIR OR REPLACE
SV11 STEM
CARTRIDGE
NO
YES
REPAIR OR REPLACE
SV8 STEM
CARTRIDGE
NO
REPLACE
SV10 STEM
CARTRIDGE

HYDRAULICS
5-70 7400 MM428 (12--98)
SQUEEGEE LIFT
UP
STRAINER
RV1
RV2
P3 DR1
C1
C2
G5
C4
C3
G4
M3
M2
T5
T2
T4
T1
M1
T3
G1
P1P2
G2
P7
RV3
3 PSI
3.7 GPM
2500
PSI
2500
PSI SV01
SV02
SV06
SV04
SV05
SV07
SV03
PR1
300
PSI
S.BR.
OPT
SQUEEGEE LIFT CIRCUIT
(SCHEMATIC)
PRESSURE
RETURN
SUCTION
CASE DRAIN
PRESSURE READINGS BASED
ON 150 F
x
350 PSI
1.0 GPM WHILE MOVING

HYDRAULICS
5-71
7400 MM428 (12--98)
SV3 STEM
MAGNETIZED?
CHECK
ELECTRICAL SYSTEM
REPAIR OR REPLACE
PC1 PILOT
CHECK CARTRIDGE
TV1
ORIFICE
PLUGGED?
SV3 STEM
CARTRIDGE
SHIFTING OK?
REPAIR OR
REPLACE SV3
STEM CARTRIDGE
YES
NO
LIFT
CYLINDER SEALS
OK?
SQUEEGEE DOES NOT LOWER
(FLOW CHART)
YES NO
PC1 PILOT
CHECK CARTRIDGE
SHIFTING OK?
NO YES
CLEAN OR
REPLACE
ORIFICE
NO YES
REPLACE
LIFT
CYLINDER
NO

HYDRAULICS
5-72 7400 MM428 (12--98)
SV3 STEM
MAGNETIZED?
CHECK
ELECTRICAL SYSTEM
REPAIR OR REPLACE
PC1 PILOT
CHECK CARTRIDGE
TV1
ORIFICE
PLUGGED?
SV3 STEM
CARTRIDGE
SHIFTING OK?
REPAIR OR
REPLACE SV3
STEM CARTRIDGE
YES NO
LIFT
CYLINDER SEALS
OK?
SQUEEGEE DOES NOT RAISE
(FLOW CHART)
YES NO
PC1 PILOT
CHECK CARTRIDGE
SHIFTING OK?
NO YES
CLEAN OR
REPLACE
ORIFICE
NO YES
REPLACE
LIFT
CYLINDER
NO

HYDRAULICS
5-73
7400 MM428 (12--98)
REPAIR OR
REPLACE
PLUMBING
LIFT
CYLINDER
SEALS OK?
PC1 PILOT CHECK
CARTRIDGE
SHIFTING & SEAT OK?
REPAIR OR
REPLACE PC1 PILOT
CHECK CARTRIDGE
NO
REPLACE
LIFT
CYLINDER
SQUEEGEE DOES NOT STAY UP
(FLOW CHART)
YES NO
PLUMBING
OK?
NO YES

HYDRAULICS
5-74 7400 MM428 (12--98)
STEERING SYSTEM
STRAINER
PROPEL SYSTEM
T
E
P
R
L
RV7
1160
RF
RV3
3 PSI
RV5
4000
PSI
RV6
85
PSI
M
2400
RPM
RV4
4000
PSI
S--15
3.7 GPM
PSI
STEERING CIRCUIT
(SCHEMATIC)
PRESSURE
RETURN
SUCTION
CASE DRAIN
PRESSURE READINGS BASED
ON 150 F
x
750 PSI (STATIONARY)
850 PSI (TURNING)
1500 PSI (HELD AT STOP ON STEERING WHEEL)
3.7 GPM

No. 7-623
July,1995
Eaton®
Medium Duty Piston Pump
Repair Information
Model 70142 / 70144, 20.3 cm3/r [1.24 in3/r] Displacement
and 70145, 23.6 cm3/r [1.44 in3/r] Displacement
Variable Displacement Piston Pump design code 01 02
with Valve Plate

22
Model 70142 / 70144 and 70145
Introduction
Table of Contents
Introduction....................................................................................................... 2
Identification...................................................................................................... 3
Required Tools .................................................................................................. 3
Exploded View Drawing ..................................................................................... 4 & 5
Parts List ........................................................................................................... 6 & 7
Disassembly and Inspection.............................................................................. 8
Reassembly ....................................................................................................... 9
Appendix A: ....................................................................................................... 10
Appendix B: ....................................................................................................... 11
Fault-Logic Trouble Shooting ............................................................................ 12 - 16
Start-up Procedure ............................................................................................ 17
Introduction
This manual provides service information for the Eaton Models 70142 / 70144 and 70145 Variable
Displacement Piston Pumps. Step by step instructions for the complete disassembly, inspection, and
reassembly of the pump are given. The following recommendations should be followed to insure successful
repairs.
Remove the pump from the application.
Cleanliness is extremely important.
Clean the port areas thoroughly before disconnecting the hydraulic lines.
Plug the pump ports and cover the open hydraulic lines immediately after they're disconnected.
Drain the oil and clean the exterior of the pump before making repairs.
Wash all metal parts in clean solvent.
Use compressed air to dry the parts. Do not wipe them dry with paper towels or cloth.
The compressed air should be filtered and moisture free.
Always use new seals when reassembling hydraulic pumps.
For replacement parts and ordering information refer to parts list 6-632.
Lubricate the new rubber seals with a petroleum jelly (vaseline) before installation.
Torque all bolts over gasketed joints, then repeat the torquing sequence to make-up for gasket
compression.
Verifying the accuracy of pump repairs on an authorized test stand is essential.

33
Model 70142 / 70144 and 70145
Identification and
Tools Required
Identification Numbers
Stamped on each unit.
A- Product Number Discription
70142 = Piston Pump (20.3 cm3/r [1.24 in3/r]) with Gerotor
70144 = Piston Pump (20.3 cm3/r [1.24 in3/r]) without Gerotor
70145 = Piston Pump (23.6 cm3/r [1.44 in3/r]) with or without Gerotor
78113 = Tandem Piston Pumps (20.3 cm3/r [1.24 in3/r]) no Gear Pump
78114 = Tandem Piston Pumps (20.3 cm3/r [1.24 in3/r]) with Gear Pump
78115 = Tandem Piston Pumps (23.6 cm3/r [1.44 in3/r]) no Gear Pump
78116 = Tandem Piston Pumps (23.6 cm3/r [1.44 in3/r]) with Gear Pump
ABC D
Single Pump - Product Number
7 0 1 4 2 - R A A - 0 1
Required Tools
7/16 in. Hex Key (Allen)
9/16 in. End Wrench
1 in. End Wrench
9/16 in. Socket
1/2 in. Socket
Internal Retaining Ring Pliers (straight .090 tip)
External Retaining Ring Pliers (straight .070 tip)
O-ring Pick
Torque Wrench (135.6 N.m [100 lbf.ft] capacity)
Hammer (soft face)
Light Petroleum Jelly
Seal Driver
Arbor Press
Testers Initials
Day of Month
(two digits)
Month (two digits)
Serial Number Code:
B 93 01 31 JB
Revision level
of parts list.
Last two digits
of year built.
( 93 for 1993 etc.)
Tandem Pumps - Product Number
7 8 1 1 3 - R A B - 0 1
ABCD
B- Rotation,
R = Righthand,
L = Lefthand
C- Sequential Letters
D- Design Code Number

44
3-1 3
6
Date Code and
Assembly Number Location
5
4
1
Shaft assembly for
rear pump of tandem.
Shaft assembly for
single pump
or front pump
of tandem.
50
50-1
51
51-1
1
7
7
8
8
8
8
910
10
910
10
11
11
13
13
14 15
15 16
17
17
22
23
24 25
30
29
48
12
6
Model 70142 / 70144 and 70145
Parts
Drawing - Figure 1-1
Right Side
Left Side

55
Model 70142 / 70144 and 70145
2
2-1 2-2
26
26
21
20
18
1919-1
19
19-1
18
27
27
28
28
37
37
(K4-4)
2-1 2-2
26
26
21
20
18
19
19-1
19
19-1
18
2
27A
27B
28A
49-1
49
49-2
49-3
49-4
49-5
37
35
36
49-1
49
49-2
49-3
49-4
49-5
34
34-1
32
(K2-1)
K2-2
K2-3
32
(K3-1)
31
(K3-2)
33
(K3-3)
K3
K2
32
(K4-1)
K4-2
K4-3
K4
K1-1
32
(K2-2)
K2-3
K2-4
K1
46
46
No
Groove
design code
02
design code
01
design code
02

66
Model 70142 / 70144 and 70145
Parts List
Item Qty. Description
1 1 Drive Shaft
2 1 Backplate Assembly
3 1 Housing Assembly
4 1 Rotating Kit Assembly
5 1 Camplate
6 1 Washer
+ 7 1 Retaining Ring
+ 8 2 Retaining Ring
9 1 Thrust Bearing
10 2 Bearing Race
+ 11 1 Shaft Seal, Drive
+ 12 1 Housing Gasket
13 2 Needle Bearing
+ 14 1 O-ring, 3.175 mm Dia. x 31.75 mm ID. [.125 in. Dia. x 1.25 in. ID.]
15 2 Washer
+ 16 1 Shaft Seal, Trunnion
17 4 Screw, Pan Head
18 2 Spring
19 2 Plug Assembly
+ 19-1 2 O-ring, 2.38 mm Dia. x 22.23 mm ID. [.0937 in. Dia. x .875 in. ID.]
20 1 Relief Valve for Port “C”
21 1 Relief Valve for Port “D”
22 1 Inner Race
23 1 Seal Cover
24 1 Trunnion Cover
25 1 Cover, O-ring
26 2 Dowel Pin
27 2 Cap Screws, 5/16-18, 50.8 mm [2 in.] Long
28 2 Cap Screws, 5/16-18, 63.5 mm [2.5 in.] Long
29 1 Key, Drive Shaft
30 1 Key, Camplate Trunnion
31 1 Cover Plate (In K3 kit)
+ 32 1 O-ring (In K1, K2, K3 & K4 kit)
33 2 Cap Screws, Cover Plate (In K3 kit)
34 1 Plug Assembly
+ 34-1 1 O-ring, 2.21 mm Dia. x 16.36 mm ID. [.087 in. Dia. x .644 in. ID.]
+ 35 1 Molded O-ring
36 1 Charge Pump Adaptor
37 1 Gerotor set and coupler sub-assembly
6.9 cm3/r [.42 in3/r] displacement, 6.35 mm [.25 in ] width
13.8 cm3/r [.84 in3/r] displacement, 12.7 mm [.5 in] width
37 1 9 tooth coupler (In K4 kit)
46 1 Mounting Bracket, Square shaped
46 1 Mounting Bracket, “V” shaped
48 1 Valve Plate

77
Model 70142 / 70144 and 70145
Parts List
Item Qty. Description
49 1 Dump Valve sub-assembly
+ 49-1 1 Retaining Ring
49-2 1 Separator Plug
49-3 1 Separator
+ 49-4 1 O-ring, 1.59 mm Dia. x 9.53 mm I.D. [.0625 in. Dia. x .375 in. I.D.]
+ 49-5 1 O-ring, 2.46 mm Dia. x 19.18 mm I.D. [.097 in. Dia. x .755 in. I.D.]
49 1 Plug Assembly
49-5 1 O-ring, 2.46 mm Dia. x 19.18 mm I.D. [.097 in. Dia. x .755 in. I.D.]
50 1 Plug Assembly
+ 50-1 1 O-ring, 1.98 mm Dia. x 11.89 mm ID. [.078 in. Dia. x .468 in. ID.]
51 1 Plug Assembly
+ 51-1 1 O-ring, 1.98 mm Dia. x 11.89 mm ID. [.078 in. Dia. x .468 in. ID.]
Mounting Kits
K1 1 Tandem Piston Pump Mounting Kit
K1-1 1 35T Coupler, 36.8 mm [1.45 in.] long
K1-2 1 O-ring, 1.59 mm Dia. x 101.6 mm ID. [.0625 in. Dia. x 4 in. ID.]
K1-3 2 Cap Screws
K1-4 2 Washer
K2 1 Gear Pump Mounting Kit
K2-1 1 O-ring, 1.59 mm Dia. x 82.55 mm ID. [.0625 in. Dia. x 3.25 in. ID.]
K2-2 2 Washer
K2-3 2 Cap Screws
K3 1 Cover Plate Kit
K3-1 1 O-ring, 1.59 mm Dia. x 82.55 mm ID. [.0625 in. Dia. x 3.25 in. ID.]
K3-2 1 Cover Plate
K3-3 2 Cap Screws
K4 1 Gear Pump Mounting Kit with Coupler
K4-1 1 9T Coupler
K4-2 1 O-ring, 1.59 mm Dia. x 101.6 mm ID. [.0625 in. Dia. x 4 in. ID.]
K4-3 2 Cap Screws
K4-4 2 Washer
Seal Repair Kit
70142-938 Seal Repair Kit for 70142, 70144 and 70145 piston pump.
Legend + Included in seal repair kit.

88
Model 70142 / 70144 and 70145
Disassembly
8Remove housing gasket from housing or backplate.
9To remove rotating kit assembly from housing, first
remove pump from vise holding the rotating kit assembly in
position. Lower pump so that the shaft end (flange end) is up.
Set the rear of housing onto table with housing flat and rotating
kit assembly at rest on table. Hole in table for protruding shaft
is required. Remove by lifting the housing and shaft from
rotating kit assembly.
Refer to Appendix B for disassembly and Inspection of rotating
kit.
10 Remove retaining ring from the front of housing. Press the
shaft, shaft seal or spacer, and washer from housing. Remove
retaining ring, thrust washer, thrust bearing, second thrust
washer, and second retaining ring from shaft.
11 To remove camplate from housing, remove the two screws
from both sides of housing (four total) retaining seal cover and
trunnion cover. Remove seal cover, shaft seal, washer, and
bearing from housing. Remove trunnion cover, o-ring cover, o-
ring, washer, inner race, and bearing from housing. Slide the
camplate over to one side and remove thru the back side of
housing.
Camplate Inspection:
• The finish on the piston shoe surfaces of the camplate
should show no signs of scoring.
Housing Inspection:
• Check the bearing (press fit) in front of housing. If
needles remain in cage, move freely, and setting at the
dimension shown in figure 1-4, removal not required.
1.78 mm
[.07 in.]
Numbered End Flange End of Housing
Figure 1-4
12 Discard the shaft seal, gaskets, and o-rings from all
assemblies. Replace with new seals upon reassembly.
Disassembly
The following instructions apply to a variable displacement
piston pump with or without a gerotor charge pump. A tandem
pump assembly should be separated into individual pumps
before disassembly.
1Position the pump into a protected jaw vise, clamping onto
the outer portion of the flange, with the input drive shaft down.
Remove the four cap screws retaining charge pump adapter or
backplate.
No gerotor charge pump skip to step 6.
2Lift the charge pump adapter assembly straight up off
backplate, shaft, and gerotor. Gerotor may stay in adapter or on
backplate.
3Remove o-ring from charge pump adapter.
4Remove outer gerotor ring from either the charge pump
adapter or the inner gerotor ring.
Refer to Appendix A for disassembly and inspection of charge
pump adapter assembly.
5Remove the inner gerotor ring and coupler assembly from
shaft.
6Lift backplate straight up off of shaft and housing. Remove
valve plate from backplate or from rotating kit assembly, still in
housing.
7From backplate remove dump valve assembly or plug
assembly, and relief valve assemblies. Note: Mark the relief
valve in relationship to the cavity it was removed, for
reassembly purposes.
Backplate Inspection:
• Check the bearing (press fit) in backplate. If needles
remain in cage, move freely, and setting is at the dimension
shown in figure 1-3, removal not required.
• Check roll pin in backplate. If tight and set to the
dimension shown in figure 1-3, removal not required.
2.79 mm
[.110 in.]
1.91 mm
[.075 in.]
Numbered End
Figure 1-3

99
Model 70142 / 70144 and 70145
Reassembly
Reassembly
1All parts should be cleaned and critical moving parts
lubricated before reassembly.
2If necessary, press new bearing in housing to dimension
shown in figure 1-4 with the numbered end of bearing outward.
3Starting with the camplate, insert camplate into the housing
with the long trunnion side down and to the appropriate side of
linkage on the machine.
4 On the short trunnion side of camplate install bearing
(bearing with numbered side to the inside of pump), bearing
race (race with chamfer toward inside of pump), washer, o-ring,
o-ring cover, trunnion cover, and retain with two screws.
Torque screws 4.1 to 5.4 N.m [36 to 48 lbf.in].
5 On the long trunnion side of camplate install bearing
(bearing with numbered side to the inside of pump), washer,
trunnion shaft seal, seal cover, and retain with two screws.
Torque screws 4.1 to 5.4 N.m [36 to 48 lbf.in].
6To install shaft, place exterior retaining ring, thrust race,
thrust bearing, second thrust race, and second retaining ring
onto shaft. Position washer and shaft seal or spacer onto shaft.
7Install shaft assembly into front of housing: For units with
spacer, retain with interior retaining ring and go on to step 8.
For units with shaft seal, seat seal into position with seal driver
and retain with interior retaining ring.
Refer to Appendix B for reassembly of rotating kit assembly.
8With flange end of housing up, position rotating kit
assembly onto shaft and into housing. Align the spline within
the piston block with shaft internal spline. Make sure piston
block is engaged fully to put piston shoes in contact with
camplate. Check all parts for proper position before proceeding.
9Clamp pump assembly in a protected jaw vise with the
open end of the housing up. Install gasket and two dowel pins
onto housing.
10 If necessary, press new bearing and roll pin in backplate to
dimension shown in figure 1-3. Bearing installed with the
numbered end outward. Roll pin installed with split oriented
away from bearing.
11 Install new o-ring on relief valves. Install relief valve in its
original cavity in backplate that it was removed. Torque 128 to
142 N.m [95 to 105 lbf.ft.]
12 Install new o-ring on dump valve or plug. Install dump
valve or plug into backplate. Torque dump valve or plug to 36.6
to 40.7 N.m [ 27 to 30 lbf.ft]
13 Apply a small amount of petroleum jelly to the steel side of
valve plate to hold in place for installation. Aligning the index
pin, place the valve plate in position onto the backplate, with
steel side against backplate.
14 Install backplate assembly onto housing assembly. Making
sure valve plate and gasket stay in place.
No gerotor charge pump, skip to step 17.
15 Install inner gerotor and coupler assembly. The coupler has
a "V" groove on one end and this end of coupler should enter
backplate first. Lubricate inner gerotor.
Refer to Appendix A for reassembly of Charge relief valve in
adapter plate.
16 Install o-ring and outer gerotor ring onto adapter plate.
Lubricate both o-ring and outer gerotor ring to hold in position
during assembly of adapter plate. Install adapter plate onto
backplate. Make sure o-ring and gerotor ring stay in place.
17 Retain backplate and adapter plate (when used) with four
cap screws, Torque 23 to 27 N.m [17 to 20 lbf.ft].
18 Install new o-rings on all plugs. Install plugs into housing.
Torque 9/16 in. - 18 plug 28 to 32 N.m [21 to 24 lbf.ft].
19 Refer to start-up procedures on page 17.

1010
Model 70142 and 70145
Appendix A - Charge Pump Adapter Assembly
36-4
36-3 36-1
36-2
Gerotor Ring
Pocket
(See chart for
depth)
Bearing
36-4a
36-3a or 3b
36-2a
Configuration for
6.9 to 1.3 bar
[100 to 150 lbf/in
2
]
Charge Relief Valve
36
Charge Pump
Suction Port
Pressure Check Port or
Remote Charge Port
Configuration for
13.8 to 17.2 bar [200 to 250 lbf/in
2
] or
17.2 to 20.7 bar [250 to 300 lbf/in
2
]
Charge Relief Valve
Reassembly - Charge Pump Adapter Assembly
1If necessary, press new bearing in adapter assembly. The
bearing to dimension shown in figure 1-2 with the numbered
end of bearing outward and closest to mounting flange.
2Install cup poppet or pin poppet, spring, and spring
retainer into charge pump adapter. Torque retainer 6.8 to 9.5
N.m [5 to 7 lbf.ft.]
Numbered End
Gerotor Pocket
2.41 mm
[.095 in.]
Flange
Figure 1-2
Disassembly - Charge Pump Adapter Assembly
1Remove spring retainer, spring, and poppet from adapter
assembly.
Inspection:
• Inspect the charge pump relief valve seat inside the
charge pump adapter. Check to insure that seat is smooth and
free of burrs or other defects.
• Inspect the charge pump relief valve spring.
• Inspect the bearing inside the charge pump adapter.
The bearing needles must remain in the bearing cage and
bearing at dimension shown in figure 1-2.
• Inspect the gerotor pocket inside the charge pump
adapter assembly. It should not be scored excessively.
Item Qty. Description
36 1 Charge Pump Adapter Assy.
36-11 Bearing (press fit)
36-21 Poppet, Cup
36-2a 1 Poppet, Pin
36-31 Spring, Tappered
36-3a 1 Spring, "Light Green" *
36-3b 1 Spring, "Pink" **
36-41 Spring Retainer
36-4a 1 Spring Retainer
*200 to 250 lbf/in2
**250 to 300 lbf/in2
Gerotor Pocket Depth
Displacement Depth of Pocket
cm3/r [in3/r] mm [in.]
6.9 [.42] 6.35 [.25]
13.8 [.84] 12.7 [.50]

1111
Model 70142 / 70144 and 70145
Appendix B -
Rotating Kit Assembly
4-1
4-2 4-3
4-5
4-4
4-6 4-7 4-8
4-9
4-7
4
Item Qty. Description
4-19 Piston assemblies
4-21 Spider
4-31 Spider Pivot
4-41 Retainer
4-51 Piston Block
4-63 Pins
4-72 Washer
4-81 Spring
4-91 Retaining Ring
Disassembly - Rotating Kit Assembly
Disassembly of rotating assembly is required for inspection
only.
1Remove the nine piston assemblies, spider, and spider
pivot from piston block.
Inspection:
• Examine the O.D. of the pistons for finish condition.
They should not show wear or deep scratches. Inspect the
shoes for a snug fit on the ball end of the pistons and a flat
smooth surface that comes in contact with the camplate. Do not
lap piston shoes.
• Examine the spider for wear in the pivot area.
• Examine the pivot to insure smoothness and no signs
of wear.
• Inspect the piston block surface that makes contact
with valve plate. This surface should be smooth and free of
deep scratches. Do not lap piston block.
• The pistons should move freely in the piston block
bore. If not free moving, examine the bore for scoring or
contamination.
2To inspect pins and spring Caution should be taken in
removing spring. The spring is highly compressed and the
retaining ring should not be removed without compressing the
spring safely.
The following parts are required to disassemble the piston
block:2 ea. 5/16 in. I.D. x 15/16 in. O.D. flat washers
1 ea. 5/16 in. x 2-7/8 in. N.C. cap screw, and
1 ea. 5/16 in. N.C. nut
To remove spring, place one of the flat washers over the 5/16
in. x 2-7/8 in. cap screw. Put cap screw through the center of
the piston block and apply the second washer. Let washer rest
on the three pins and retain with nut. Turning nut and
compressing spring inside the block. Use a pair of retaining ring
pliers and remove the internal retaining ring. Remove nut, bolt,
and the two washers from block. Removing the washer, spring,
second washer, three pins, and pin keeper at the same time.
Reassembly - Rotating Kit Assembly
1To reassemble the rotating kit assembly complete the
following: Compress the pin keeper and install in the spline of
the piston block. Install the three pins with head end to the
inside of the block and position in the special grooves of the
piston block spline.
2Install the washer, spring, and second washer into the
piston block. Use the two 5/16 in. I.D. washers, nut, and 5/16
in. x 2-7/8 in. cap screw to compress the spring and retain with
retaining ring. Remove the nut, cap screw, and the two
washers.
3Install the pivot onto the three pins, spider on the pivot,
and piston assemblies thru the spider and into piston block,
resting on spider.

1212
1
Inspect
?
Repair
or
Replace
Defective
Action
Step
Comment
Number
Decision
Solution
Symptom:
Gauges Recommended
Inlet vacuum gauge: 207 bar to 0 bar [30 lbf/in2 to 30 inHg]
System pressure gauge: 700 bar [10,000 lbf/in2]
Charge pressure gauge: 0 to 50 bar [0 to 600 lbf/in2]
Case pressure gauge: 0 to 25 bar [0 to 300 lbf/in2]
Explanatory
Diagram
Model 70142 / 70144 and 70145
Fault - Logic
Trouble Shooting
This fault - logic trouble shooting guide is a diagnostic aid in
locating transmission problems.
Match the transmission symptoms with the problem statements
and follow the action steps shown in the box diagrams. This will
give expedient aid in correcting minor problems eliminating
unnecessary machine down time.
Following the fault - logic diagrams are diagram action
comments of the action steps shown in the diagrams. Where
applicable, the comment number of the statement appears in
the action block of the diagrams.
Recommended Gauge Locations
Figure 3-1
Pressure Ports
Tee in line to check System
Pressure
Charge Pump Suction Port
Tee in line to check Inlet Vacuum
Drain Port
Tee in line to check Case
Pressure
Auxiliary Port
Check Charge Pressure

1313
Model 70142 / 70144 and 70145
Fault - Logic
Trouble Shooting
Inspect
Servo Control
(If used)
OK
12
Inspect
External Control
Linkage
Defective
Repair
or
Replace
Defective
Repair
or
Replace
Symptom: Neutral Difficult or Impossible to Find
Inspect
Heat
Exchanger OKOK OK
456
Check
Oil Level in
Reservoir
Fill to
Proper
Level
DefectiveBelow Level
Repair
or
Replace
Check
System
Pressure
Reduce
System
Load
High
OK 9
Inspect
Charge Relief
Valve
OK 11
Inspect
Charge
Pump 13
Inspect
Motor 12
Inspect
Inlet Screen
or Filter
Replace
Clogged
OK 8
Check
Charge
Pressure
10
Low OK
OK
Replace
Pump &
Motor
Inspect
Dump Valve
(If used)
OK 7
Inspect Heat
Exchanger
By-Pass Valve
(If used)
OK
Defective
Repair
or
Replace
Defective
Repair
or
Replace
Defective
Repair
or
Replace
Defective
Repair
or
Replace
Defective
Repair
or
Replace
Symptom: System Operating Hot

1414
Model 70142 / 70144 and 70145
Fault - Logic
Trouble Shooting
Inspect
Servo Control
(If used)
OK OK
123
Inspect
External Control
Linkage
Defective
Repair
or
Replace
Inspect
System Relief
Valves
Defective
Repair
or
Replace
Defective
Repair
or
Replace
Symptom: Operates in One Diection Only
Inspect
Servo Control
(If used) OKOK OK
27
Defective
Repair
or
Replace
Inspect
Motor
12
Replace
Clogged
Check
Charge
Pressure
10
Low OK
Inspect
Dump Valve
(If used)
Replace
Pump &
Motor
Defective
Repair
or
Replace
Inspect
Inlet Screen
or Filter OK
OK OK
813
Defective
Repair
or
Replace
Inspect
Charge Relief
Valve
11
Inspect
Charge
Pump
Defective
Repair
or
Replace
Defective
Repair
or
Replace
Symptom: System Response Sluggish

1515
Model 70142 / 70144 and 70145
Fault - Logic
Trouble Shooting
Check External
Control
Linkage OKOK OK
417
Check
Oil Level in
Reservoir
Fill to
Proper
Level
DefectiveBelow Level
Repair
or
Replace
Check
System
Pressure
OK 9
Inspect
Charge Relief
Valve
OK 11
Inspect
Charge
Pump 13
Inspect
Motor 12
Inspect
Inlet Screen
or Filter
Replace
Clogged
OK 8
Check
Charge
Pressure
10
Low OK
OK
Replace
Pump &
Motor
Inspect
Servo Control
(If used)
OK 2
Inspect
Dump Valve
(If used)
OK
Defective
Repair
or
Replace
Defective
Repair
or
Replace
Defective
Repair
or
Replace
Defective
Repair
or
Replace
Defective
Repair
or
Replace
High
Reduce
System
Load
Symptom: System Will Not Operate In Either Direction

1616
11 Inspect Charge Relief Valve for:
a. improper charge relief pressure setting *
b. damaged or broken spring
c. poppet valve held off seat
12 Inspect Motor for:
a. disconnected coupling
13 Inspect Charge Pump for:
a. broken or missing drive key
b. damaged or missing o-ring
c. excessive gerotor clearance
d. galled or broken gerotor set
* System/Charge Relief Valve
Pressure Settings for
Eaton’s Variable Displacement
Controlled Piston Pumps
Inlet Vacuum 6 inHg max.
Case Pressure 25 lbf/in2 maximum
Charge Pressure 100 to 150 lbf/in2 Standard
200 to 250 lbf/in2 Optional
250 to 300 lbf/in2 Optional
System Pressure 5000 lbf/in2 maximum
3000 lbf/in2 continuous
The high pressure relief valves are all factory preset and cannot
be readjusted.
The pressure setting and assembly number is stamped on each
high pressure relief valve cartridge.
Valve Identification Example:
32060-IA 5000
Relief Valve Setting
Relief Valve Assembly Number
Model 70142 / 70144 and 70145
Fault - Logic
Trouble Shooting
Diagram Action Step Comments
1Inspect External Control Linkage for:
a. misadjusted or disconnected
b. binding, bent, or broken
c. misadjusted, damaged or broken neutral return spring
2Inspect Servo Control Valve for: (if used)
a. proper inlet pressure
b. misadjusted, damaged or broken neutral return spring
c. galled or stuck control spool
d. galled or stuck servo piston
3Inspect System Relief Valves * for:
a. improper pressure relief setting
b. damaged or broken spring
c. valve held off seat
d. damaged valve seat
4Check Oil Level in Reservoir:
a. consult owner/operators manual for the proper type
fluid and level
5Inspect Heat Exchanger for:
a. obstructed air flow (air cooled)
b. obstructed water flow (water cooled)
c. improper plumbing (inlet to outlet)
d. obstructed fluid flow
6Inspect Heat Exchanger By-Pass Valve for: (if used)
a. improper pressure adjustment
b. stuck or broken valve
7Inspect Dump Valve for: (if used)
a. held in a partial or full open position
8Inspect Inlet Screen or Filter for:
a. plugged or clogged screen or filter element
b. obstructed inlet or outlet
c. open inlet to charge pump
9Check System Pressure:
a. See figure 3-1 for location of pressure gauge
installation.
b. consult owner/operators manual for maximum system
relief valve settings
10 Check Charge Pressure:
a. See figure 3-1 for location of pressure gauge
installation.
b. consult owner/operators manual for maximum charge
relief valve settings

1717
Model 70142 / 70144 and 70145
Start-up Procedure
When initially starting a new or a rebuilt transmission system, it
is extremely important that the start-up procedure be followed.
It prevents the chance of damaging the unit which might occur
if the system was not properly purged of air before start-up.
1After the transmission components have been properly
installed, fill the pump housing at least half full with filtered
system oil. Connect all hydraulic lines and check to be sure they
are tight.
2Install and adjust all control linkage.
3Fill the reservoir with an approved oil that has been filtered
through a 10 micron filter. Refer to Eaton Hydraulics Technical
Data sheet number 3-401 titled Hydraulic Fluid
Recommendations.
4Gasoline or L.P. engines: remove the coil wire and turn the
engine over for 15 seconds. Diesel engines: shut off the fuel
flow to the injectors and turn the engine over for 15 seconds.
5Replace the coil wire or return the fuel flow to the injectors.
Place the transmission unit in the neutral position, start the
engine and run it at a low idle. The charge pump should
immediately pick up oil and fill the system. If there is no
indication of fill in 30 seconds, stop engine and determine the
cause.
6After the system starts to show signs of fill, slowly move
pump camplate to a slight cam angle. Continue to operate
system slowly with no load on motors until system responds
fully.
7Check fluid level in the reservoir and refill if necessary to
the proper level with an approved filtered oil.
8Check all line connections for leaks and tighten if
necessary.
9The machine is now ready to be put into operation.
10 Frequent filter changes are recommended for the first two
changes after placing the machine back into operation. Change
the first filter in 3-5 hours and the second at approximately 50
hours approx. hours. Routinely scheduled filter changes are
recommended for maximum life of the hydraulic system.

1818
Model 70142 / 70144 and 70145
Notes

1919
Model 70142 / 70144 and 70145
Notes

Form No. 7-623
November, 1993
Copyright Eaton Corporation, 1993
All Rights Reserved
Printed in USA
Eaton Corporation
15151 Hwy. 5
Eden Prairie, MN 55344
Telephone 612/937-9800
Fax 612/937-7130
Hydraulics Division Eaton Ltd.
Glenrothes, Fife
Scotland, KY7 4NW
Telephone 44/592-771-771
Fax 44/592-773-184
Hydraulics Division
Order parts from number 6-632 Parts Information booklet.
Each order must include the following information.
1. Product and/or Part Number
2. Serial Code Number
3. Part Name
4. Quantity

No. 7-118
May, 1999
Char-Lynn®
Disc Valve Motor
4000 Series
Geroler® Motors Std., Whl. and Brgl.-004 Std. and Whl.-006
Repair Information

2
4000 Series Char-Lynn Motors
Retainer,
Front
(Flange)
Retainer, Front
(C Flange)
Housing, Bearing
Screw,
Cap
Screw, Cap Screw, Cap
Valve Housing Inner
Face
Seal
Outer
Face
Seal
Spring
Piston Shuttle
Seal
Balance
Ring
Valve
Valve
Plate
Valve
Drive
Geroler
Drive
Seal
Seal
Seal
Seal
Seal
Seal
Seal
Seal
Seal
Geroler
Geroler
Geroler
Shaft
Face
Seal
Bearingless Motor
Mounting Flange
Bearing Housing
Wheel Motor Back-up
Washer
(if supplied)
O-ring
Poppet
Spring
Spring
Sleeve, Dash Pot
Sleeve, Dash Pot
Shaft
Seal
Shuttle (Two Way)
Shuttle Valve
Location when
Applicable Dust
Seal
Dust
Seal Seal
Guard
Shaft and
Bearing Kit
(1-1/4 inch Straight)
Shaft and
Bearing Kit
(1-5/8 inch Tapered)
Shaft and Bearing Kit
(1-1/4 inch
14 Tooth Splined)
Plug
Assembly
Plug
Assembly
Plug Assembly
Plug Assembly
Check
Valve
Plug
Assembly
Ball Plug
Key
Nut
Key
Retainer
Spring

3
4000 Series Char-Lynn Motors
Tools required for disassembly and reassembly
— Torque wrench (68 Nm [600 lb-in] capacity)
— 300 to 400 mm [12 to 16 inch] breaker bar
— 3/4 inch and 1/2 inch sockets
— Small screwdriver (150 to 200 mm [6 to 8 inch] long,
6 mm [.25 inch] blade)
— 3/16 inch Hex Key
— Hydraulic press — 1335 N [300 lbf]
— Shaft face seal (-004) installation tool 600468
— Shaft face seal (-006) installation tool 600421-2
*— Bullet (600463) for 1-1/4 inch diameter shafts
— Shaft seal installation tool (2 -1/4 inch socket)
— Torq wrench required for eight mounting flange
screws (replacement screws or -006 design)
No. E10
The following tools are not necessary for disassembly
and reassembly but are extremely helpfull
— Alignment studs (2), see dimensions below
*Available by special order, contact Eaton Corp.,
Hydraulics Division Service Dept.
200 mm [8 inch]
Approx. 13 [.5]
6,3 [.25] Grind Flat Spots on Each Side
11 mm [7/16 inch] Dia. Steel Rod
25 mm
[1 inch]
7/16-20 UNF
Wheel motor and bearingless motor repair information on page 9 and 10.
Shuttle valve and seal guard repair information on page 10.
Seal guard reference on page 10.
Tools

4
4000 Series Char-Lynn Motors
Disassembly
Cleanliness is extremely important when repairing a hydraulic motor.
Work in a clean area. Before disconnecting the lines, clean port area of
motor thoroughly. Use a wire brush to remove foreign material and
debris from exterior joints of motor. Check shaft and keyway. Use
600 grit paper/cloth to remove all nicks, burrs, and sharp edges that
might damage the shaft seals when installing retainer on shaft and
bearing assembly. Before starting disassembly procedures, drain oil
from inside of motor.
1 Place motor in a vise with output shaft down. Clamp across edge
of mounting flange, not on housing (see Figure 1). Excessive
clamping pressure will cause distortion. When clamping, use some
protective device on vise, such as special soft jaws, pieces of hard
rubber or board.
Although not all drawings show the motor in a vise, it is recom-
mended that you keep the motor in the vise during disassembly.
Follow the clamping procedures explained throughout the manual.
2 Remove 4 bolts from the valve housing.
3 Lift valve housing straight up. If done carefully, the springs and
balance ring subassembly will remain on valve for easy removal.
4 Carefully remove the following from the valve housing:
1 seal, 82,3 mm [3.24 inch] I.D.
1 seal, 8,9 mm [.35 inch] I.D.
2 check valve plug assemblies (plug, seal, spring, ball) 1 plug (case
drain) with seal.
5 Remove 2 balance ring springs.
6 Remove balance ring subassembly.
7 Remove inner and outer face seals from the balance ring.
8 Lift off valve.
Figure 1
Figure 2
Plug
Assembly Valve
Housing
Check
Plug
Assembly Seal
Seal
Figure 3
Spring Balance Ring
Valve
Figure 4
Inner
Face
Seal Outer Face Seal

5
4000 Series Char-Lynn Motors
Disassembly
9 Remove valve plate.
10 Remove 88,6 mm [3.49 inch] I.D. seal from valve plate (see
Figure 5).
11 Remove valve drive (see Figure 5).
12 Remove Geroler. Retain rollers in outer Geroler ring if they are
loose.
13 Remove 2 seals from Geroler, 1 seal on each side of Geroler.
14 Remove drive.
15 Remove 88,6 mm [3.49 inch] I.D. seal from bearing housing.
17 Remove shaft seal, back-up ring (if used) and dust seal from flange.
Use a small screwdiver to remove dust seal. Do not damage bore of
flange.
16 Use a stud remover or vise grips to remove studs (earlier models
only). Clamp bearing housing in vise as shown in Figure 7. Loosen 8
screws. Remove screws, washers (discard washers, as they are not
required for reassembly), and mounting flange (see Figure 8).
Valve
Plate Seal Seal
Valve Drive
Figure 5
Figure 6
Seal Seal
Geroler Drive
Figure 7
Figure 8
Shaft
Seal Back-up
Ring
Mounting
Flange
Dust
Seal
Figure 9

6
4000 Series Char-Lynn Motors
Reassembly
Check all mating surfaces. Replace any parts that have scratches or
burrs that couId cause leakage. Clean all metal parts in clean solvent.
Blow dry with air. Do not wipe with cloth or paper towel because lint
or other matter could get into the hydraulic system and cause damage.
Do not use a coarse grit papers/cloth or try to file or grind motor parts.
Check around the keyway and chamfered area of the shaft for burrs,
nicks, or sharp edges that can damage the seals when reassembling
the retainer.
Note: Lubricate all seals (prior to installation) with petroleum jelly
such as Vaseline®. Use new seals when reassembling the motor.
21 Place bearing housing on smooth flat surface with largest open end
of housing up. Apply petroleum jelly to shaft face seal. Install seal in
seal seat. Seat seal properly in groove (see Figure 11). A damaged or
improperly installed shaft face seal could cause internal lubrication
loss and subsequent parts wear.
22 Install shaft and bearing assembly in bearing housing (see Figure
12). Do not damage seal in bore of housing. You may need a press to
install shaft and bearing assembly.
18 Remove shaft and bearing assembly. You may need a press to
remove shaft and bearing assembly (see Figure 10).
19 Remove shaft face seal from bore of bearing housing (see Figure
10). Do not damage bore of bearing housing.
Note: Individual parts of the shaft and bearing assembly are not sold
separately and must be replaced as a unit.
Disassembly
Bearing Housing
Shaft and
Bearing
Assembly
Seal
Shaft Face Seal
Figure 10
Figure 11
Seal
Driver Seal
Tube
Seal
Seat
Bearing
Housing
Seal
Face
Seal
Note: Shaft face seal installation tool is available by special order.
Contact Eaton Corporation, Hydraulics Division (Service Department).
600468 (-004) 600421-2 (-006).
Figure 13
Shaft
Face
Seal
Seal
Flange
Shaft and
Bearing
Assembly
Back-up Ring Dust Seal Lip
Shaft Seal
Figure 12
Bearing
Housing
Shaft and
Bearing
Assembly

7
4000 Series Char-Lynn Motors
27 Lubricate threads of 8 screws with a film of light oil. Install and
finger tighten screws. Clamp bearing housing in vise. Torque screws
to 6 Nm [50 lb-in] in sequence (see Figure 14). Then final torque to 34
Nm [300 lb-in], in sequence. Install key (when used) in keyway of
shaft.
Note: Full torque 34 Nm [300 lb-in] on one bolt at a time can
damage bolt or retainer.
29 Pour a small amount of light oil inside the output shaft.
30 Apply a light film of petroleum jelly on 88,6 mm [3.49 inch] I.D.
seal. Install seal in bearing housing.
31 Install drive in output shaft (insert longer splined end of drive first),
(see parts drawing on page 2).
32 To help in the reassembly procedure, it is recommended using two
alignment studs (see special tools page 3) diagonally opposed in the
four bolt holes of the bearing housing.
33 Apply petroleum jelly on 2 seals, 9,3 mm [.25 inch] I.D. Install seals
(1 on each side of Geroler) in case drain grooves of Geroler.
Note: Installation at this point involves 3 steps in timing the motor.
Timing determines the direction of rotation of the output shaft.
Timing parts include:
1. Geroler
2. Valve drive
3. Valve Plate
4. Valve
23 Apply petroleum jelly to 88,6 [3.49] ID seal. Install seal in seal
groove of bearing housing (see Figure 13).
24 Use a small press, if available, to install dust seal in retainer. Metal
side of dust seal must face toward flange, as shown in Figure 13. If a
press is not available, use a plastic or rubber hammer to tap dust seal
in place.
25 Install 92,1 [3.62] ID seal, back-up ring and shaft seal in retainer.
Flat or smooth side of shaft seal must face toward retainer as shown in
Figure 13. Apply petroleum jelly to inside diameter of shaft seal (after
installing seal).
26 Before installing retainer, place a protective sleeve of bullet (see
note below) over shaft. Grease inside diameter of dust and shaft seals.
To prevent damage to seals, install retainer over shaft with a twisting
motion. Do not cut or distort shaft seal. Damage to shaft seal will
cause external leakage.
Note: Bullet 600463 for 1-1/4 inch diameter shafts available by
special order through Eaton Hydraulics Division service department.
Figure 14
1
2
3
4
5
67
8
Figure 15
28 Reposition motor in vise with output shaft down. Clamp across
edges of retainer as shown in Fig. 15.
Rotate Valve Clockwise
1/2 Tooth to Engage Spline
Valve
Valve
Plate
Alignment
Ref. Only
Note: Case Drain Holes (2)
Proper Alignment Shown Case Drain
Hole
Do Not Use
as a drain
hole Pressure
Relief Hole
Anyone of 6 Ports
Open to Outside
of Valve
Largest Open
Pocket
Geroler
Figure 16 Timing Alignment
Timing Step No. 1 — Locate largest open pocket in Geroler. Then
mark location of pocket on outside edge of Geroler (see Figure 16).
34 Align case drain hole and pressure relief hole in Geroler with case
drain hole and pressure relief hole in bearing housing. Install Geroler
on bearing housing (see Figure 16). Retain rollers in outer Geroler ring
if they are loose.
35 Install valve drive in Geroler.
Reassembly

8
4000 Series Char-Lynn Motors
Reassembly
36 Apply a light film of petroleum jelly on 88,6 mm [3.49 inch] I.D.
seal. Install seal in valve plate.
37 Align case drain hole in valve plate with case drain hole in Geroler.
Install valve plate (seal side toward Geroler) on Geroler as shown in
Figure 16.
Timing Step No. 2 — Locate slot opening in valve plate which is in
line with largest open pocket of Geroler (see Figure 16).
38 Use the following procedure for installing the valve on the valve
plate.
Timing Step No. 3 — Locate any one of the side openings of the
valve that goes through to the face of the valve. Line up this side
opening in the valve with open slot of valve plate that is in line with
largest open pocket of Geroler. Rotate valve clockwise (1/2 spIine
tooth) to engage valve with the valve drive spline, alignment reference
shown in Figure 17 (above). This procedure provides standard timing
when pressurized as shown in Figure 17.
39 Apply clean grease on balance ring assembly springs. Install
springs in 2 holes located inside bore face of valve housing (see
Figure 18).
41 Apply a light film of petroleum jelly on 82,3 mm [3.24 inch] I.D.
seal. Install seal in outside seal groove of valve housing.
42 Apply petroleum jelly on inner and outer face seals. Install seals on
balance ring as shown in Figure 19.
Important: Install face seals in the positions shown in Figure 19 or
the motor will not operate properly. Do not force or bend these face
seals. Any damage to these seals will affect the operation of the
motor.
43 Align 2 pins of balance ring with 2 spring holes in valve housing as
shown in Figure 20 . Install balance ring in valve housing.
40 Apply a light film of petroleum jelly on 8,9 mm [.35 inch] I.D. seal.
Install seal in case drain groove of valve housing.
Figure 19
Balance Ring
Pin Inner Seal Outer Seal
Valve
Housing
Seal
Figure 18
Seal
Balance Ring
Spring
Clockwise
Rotation
Counter
Clockwise
Rotation
Figure 17
Figure 20
Figure 21

9
4000 Series Char-Lynn Motors
Wheel Motors
Reassembly 45 Install and finger tighten 2 bolts (or studs for earlier models)
opposite alignment studs. Remove alignment studs and install
remaining bolts (or studs and 4 nuts for earlier models). Torque bolts
(or nuts) to 85 Nm[750 lb-in], in sequence (see Figure 23).
46 Install 2 check plug assemblies (ball, spring, plug with seal). Also
install case drain plug with seal, parts shown in Figure 22 (plug torque
shown in Figure 24).
A different bearing housing is used on wheel
motors (see Figure 24). Other than this, the
parts are the same as the standard motor and
the same disassembly and reassembly
procedures apply.
Bearingless Motors
This motor is the same as the standard without the shaft/bearing
assembly, bearing housing and retainer. The mounting flange replaces
the bearing housing (see Figure 25). Follow same disassembly and
reassembly procedures as rear section of standard motor.
Important: Loctite® information for bearingless motor on page 10.
44 Insert your finger through port of housing. Apply pressure to side
of balance ring assembly. Hold ring in position until valve housing is
in place (see Figure 21). Align case drain hole in housing with case
drain hole in valve plate. Install valve housing against valve plate (see
Figure 22).
Note: After installing valve housing on valve plate, check between
body parts of motor for unseated seals.
Figure 22
Check Plug
Assembly
Bolt Plug Assembly
Key Seal
Shaft
Seal
Retainer
Dust
Seal
Nut
Cap ScrewBackup Ring
Figure 24
Figure 25
Drive Seal Seal
O-ring
Seal
Mounting
Flange
Figure 23
1
3
4
2
7/16-20 Drain
Plug Torque to
17 Nm [150 lb-in]
(lubricated threads)
Check Plug
Torque to
7-14 Nm
[60-120 lb-in]
(lubricated threads)

10
4000 Series Char-Lynn Motors
Important: This motor requires Loctite in threaded holes of
mounting flange.
Follow these procedures:
Adequate Loctite penetration and sealing depend highly on cleanliness
and dryness of threads. Use a non-petroleum base solvent to clean
excess oil from threads of flange after disassembly. You may need to
use a tap to clean threads of excess old Loctite. After you have fully
reassembled the motor, apply 2 to 3 drops of Loctite no. 290 at top of
threaded holes (see Figure 26).
Note: Allow Loctite 5 minutes for thread penetration before installing
motor on gear case.
Reassembly
Figure 26
Attention:
Do not use
more than
3 drops of
Loctite on
threaded
portion.
Motors with Shuttle
and, or Seal Guard
Piston
Poppet
Dash
Pot
Plug/O-ring
S/A (9/16-18)
Torque to
41 Nm [360 lb-in]
(Lubricated Thread)
Enlarged
Parts
Drawing
Plug/O-ring*
S/A (9/16-18)
Torque to
23 Nm [200 lb-in]
(Lubricated
Thread)
Plug/O-ring
S/A (3/8-24)
Torque to
5 Nm [50 lb-in]
(Lubricated
Thread)
*Plug/O-ring S/A must be removed and
drain line added for shuttle valve operation.
Plug/
O-ring
S/A
Optioal
Seal Guard
Dash
Pot
Spring
Spring
Poppet

11
4000 Series Char-Lynn Motors
Char-Lynn
®
Product number
Eaton Corp. Hydraulics Div.
Eden Prairie, MN 55344
Product Number
109 0000 000
110 0000 000
111 0000 000
Product Line
Identification
Number
Product
Identification
Number
Engineering
Change
Code
Week of
Year 01
Thru 52
Last
Number
of Year
Date Code
00 0
For more detailed information contact Eaton Corp. Hydraulics
Division 15151 Highway 5 Eden Prairie, MN 55344.
Specifications and performance data, Catalog No. 11-878.
Replacement part numbers and kit information — Parts
Information No. 6-126.
Each Order Must Include the Following:
How to Order Replacement Parts
1. Product Number
2. Date Code
3. Part Name
4. Part Number
5. Quantity of Parts
Product Numbers—4000 Series Motors
Use digit prefix —109-, 110-, or 111- plus four digit number from charts
for complete product number—Example 111-1057.
Orders will not be accepted without three digit prefix.
109-1100 -1101 -1102 -1103 -1104 -1105 -1106 -1212
1-1/4 inch Straight
Standard
SAE
B-Mount
Standard
SAE
C-Mount
Displ. cm
3
/r [ in
3
/r] Product Number
ShaftMounting 130
[ 7.9] 160
[ 9.9] 205
[12.5] 245
[15.0] 310
[19.0] 395
[24.0] 495
[30.0]
110
[ 6.7] 625
[38.0]
109-1114 -1115 -1116 -1117 -1118 -1119 -1120 —
Ports
1-5/8 Inch
Tapered 110-1081 -1082 -1083 -1084 -1085 -1086 -1087 1116
111-1033 -1034 -1035 -1036 -1037 -1038 -1039 -1062
1-1/16 O-ring
Bearingless
Wheel
Motor
1-1/4 Inch
14 T Splined
111-1057
1-1/16 O-ring
1-1/16 O-ring
1-1/16 O-ring -1215
—
-1117
-1063
109-1184 -1185 -1227 -1224 -1225 -1189 -1190 —40 mm Straight G 3/4 (BSP) —
111-1052 -1053 -1054 -1055 -1056 -1057 -1058 —
G 3/4 (BSP) —
110-1074 -1075 -1076 -1077 -1078 -1079 -1080 —
1-1/4 inch Straight 1-1/16 O-ring -1122
110-1088 -1089 -1090 -1091 -1092 -1093 -1094 —
1-1/4 Inch
14 T Splined 1-1/16 O-ring —
109-1001 -1054 -1002 -1003 -1055 -1056 -1057 —
3/4 inch Split Flange —
109-1011 -1062 -1012 -1013 -1063 -1064 -1065 —
3/4 inch Split Flange —
110-1001 -1040 -1002 -1003 -1041 -1042 -1043 —
3/4 inch Split Flange —
110-1006 -1044 -1007 -1008 -1045 -1046 -1047 —
3/4 inch Split Flange —
110-1011 -1048 -1012 -1013 -1049 -1050 -1051 —
3/4 inch Split Flange —
111-1044 -1015 -1045 -1046 -1016 -1017 -1018 —
3/4 inch Split Flange —
1-5/8 Inch
Tapered
109-1107 -1108 -1109 -1110 -1111 -1112 -1113 —
1-1/16 O-ring —
109-1006 -1058 -1007 -1008 -1059 -1060 -1061 —
3/4 inch Split Flange —
109-1191 -1192 -1193 -1194 -1195 -1196 -1197 —
1-1/2 Inch
17 T Splined G 3/4 (BSP) —
110-1108 -1109 -1110 -1111 -1112 -1113 -1125 —
40 mm Straight G 3/4 (BSP) —

Copyright Eaton Corporation 1981, 1992, 1995, 1997 and 1999
All Rights Reserved
Printed in USA
Form No. 7-118
Disc Valve Motors
4000 Series Motors
Sumitomo Eaton
Hydraulic Company Ltd.
Ooi-Cho Kameoka-Shi
621-0017 Kyoto
Japan
Telephone: [+81] 771-22-9601
Fax: [+81] 771-29-2020
Eaton Corporation
Hydraulics Division
15151 Hwy. 5
Eden Prairie, MN 55344
Telephone: 612/937-7254
Fax: 612/937-7130
Eaton Ltd.
7th Floor, Woo Duk Building
832-2 Yeoksam-Dong, Kangnam-Ku
Soeul 135-750
Korea
Telephone: [+82] 2-557-0595
Fax: [+82] 2-557-1634
Eaton Ltd.
Hydraulics Division
Glenrothes, Fife
Scotland, KY7 4NW
Telephone: [+44] (0)1592-771-771
Fax: [+44] (0)1592-773-184
Eaton Hydraulics (Shanghai) Co. Ltd.
388 Aidu Road, Waigaogiao FTZ
Pudong New Area
Shanghai 200137
Peoples Republic of China
Telephone: [+86] 21-5046 0758
Fax: [+86] 21-5046 0767
Eaton B.V.
Boeing Avenue 11
1119 PC Schiphol-Rijk
The Netherlands
Telephone: [+31] (0)20-655 6776
Fax: [+31] (0)20-655 6800
Jining Eaton Hydraulic Co. Ltd.
6 Ji Da Road
Jining City
Shandong Province 272131
Peoples Republic of China
Telephone: [+86] 537-2221288
Fax: [+86] 537-2221557
Sumitomo Eaton Hydraulic Co.
8 Temasek Blvd.
42-01 Suntec Tower Three
Singapore 03988
Telephone: [+65] 832-7727
Fax: [+65] 832-7733
www.eatonhydraulics.com
ISO-9001 CERTIFICATED FIRM
DET NORSKE VERITAS INDUSTRY BV, THE NETHERLANDS
ACCREDITED BY
THE DUTCH COUNCIL
FOR CERTIFICATION
Reg. No. 24
Qualitiy System Certified
Products in this catalog are manufactured
in an ISO-9001-certified site.









No. 7-310
January, 1995
Char-Lynn®
Power Steering
2 Series
Steering Control Unit 001
Repair Information
TE
LR
P

2
Dust
Seal
Housing Quad
Seal
Thrust
Bearing
Sleeve
Spool
Pin
Centerin
Springs
Bearing Race (2)
O-ring
Seal
O-ring
Seal
Wear
Plate
Drive
Gerotor
Spacer
Manual Steering
Relief Valve
O-ring
O-ring
O-ring
O-ring Seal
Ring
End
Cap
Cap
Screw
(7)
Plug
Plug
Check
Ball
Spring
Retaining
Ring
Power Steering
2 Series
Steering Control Units
Tools Required
• 10 mm Socket
• 7/8 in. Socket
• Torque Wrench (18 Nm [160 lb-in] Capacity)
• Small Blade Screwdriver

3
Power Steering
2 Series
Steering Control Units
Disassembly
Cleanliness is extremely important when repairing hydraulic
Steering Control Units (SCU). Work in a clean area. Before
disconnecting the hydraulic lines, clean the port area of the
SCU. Before disassembly, drain the oil, then plug the ports and
thoroughly clean the exterior of the SCU. During repairs,
always protect machined surfaces.
1 Remove the seven cap screws and disassemble the SCU as
shown in Figure 1.
2 Remove the plug and manual steering check as shown in
Figure 1.
Note: The manual steering check may be a check ball or a
check/relief valve.
3 Slide the spool and sleeve from the housing (see Figure 2).
4 Remove the thrust bearing and bearing races.
5 Remove the quad seal.
6 Using a small blade screwdriver, carefully pry the dust seal
from the housing.
Important: Do not damage the dust seal seat.
O-ring
Seal
O-ring
Seal
Wear
Plate Drive
Gerotor
Seal
Ring
Spacer
Manual Steering
Check/Relief Valve
O-ring
O-ring O-ring
End
Cap
Cap
Screw
(7)
Figure 1
Plug
Dust
Seal
Housing Quad
Seal
Thrust
Bearing
Bearing Race (2)
Spool and Sleeve
Figure 2

4
Power Steering
2 Series
Steering Control Units
7 Remove the pin that holds the spool and sleeve together
(see Figure 3).
8 Carefully slide the spool out of the sleeve. The springs
and retaining ring will stay with the spool as it's removed.
Reassembly
Check all mating surfaces. Replace any parts with
scratches or burrs that could cause leakage. Wash all
metal parts in clean solvent. Blow them dry with pressur-
ized air. Do not wipe parts dry with paper towels or cloth
as lint in a hydraulic system will cause damage.
Note: Always use new seals when reassembling
hydraulic steering control units. Refer to parts list 6-323
for seal kit part numbers, replacement parts, and
ordering information.
Important: During reassembly lubricate the new seals
with a petroleum jelly such as Vaseline®. Also lubricate
machined surfaces and bearings with clean hydraulic
fluid.
9 Remove the retaining ring and springs.
Caution: The centering springs are under tension. Remove
the retaining ring carefully.
10 Install the quad seal:
• Put one of the bearing races and sleeve into
the housing.
• Together, the housing and bearing race create
a groove into which the quad seal will be
installed.
• Hold the bearing race tightly against the input
end of the housing by pushing on the gerotor
end of the sleeve.
• Fit the quad seal into its seat through the input
end of the housing. Be sure the seal is not
twisted.
• Remove the sleeve and bearing race.
Centering
Springs and
Spacers
Sleeve
Pin
Spool
Figure 3
Spring
Retaining
Ring

5
Power Steering
2 Series
Steering Control Units
20 Lubricate and install a new o-ring seal in the groove in
the housing.
21 Install the wear plate and align the holes in the wear
plate with threaded holes in the housing.
Note: The holes in the wear plate are symmetrical.
22 Install the drive, be sure the slot in the drive engages
the pin.
23 Lubricate and install a new o-ring seal in the groove in
the wear plate.
24 Install the gerotor and align the screw holes.
25 Lubricate and install a new o-ring seal in the groove in
the gerotor ring.
26 Lubricate and install a new o-ring and seal ring in the
groove in the gerotor star.
27 Install the spacer.
28 Install end cap and seven cap screws. Tighten cap screws,
in a crisscross pattern, to 16 -18 Nm [140 -160 lb-in].
29 Remove the SCU from the vise.
30 Install the relief valve/check or check ball and plug. Use
a new o-ring and tighten the plug to 17 Nm [150 lb-in].
Quad Seal
Figure 4
Dust Seal Thrust Bearing
and Race (2)
Figure 5
11 Lubricate and install the dust seal (see Figure 4 for
correct seal orientation).
12 Install the centering springs in the spool. It is best to
install the two flat pieces first. Next, install the curved
pieces, three at a time.
13 Fit the retaining ring over the centering springs.
14 Apply a light coating of clean hydraulic fluid to the
spool and slide it into the sleeve. Be sure the centering
springs fit into the notches in the sleeve.
15 Install the pin (see Figure 3).
16 Apply a light coating of petroleum jelly to the inner
edge of the dust and quad seals.
17 Put the thrust bearing and races into the housing. The
thrust bearing goes between the two races (see Figure 2).
18 Apply a light coating of clean hydraulic fluid to the
spool and sleeve assembly and slide it into the housing.
Important: Do not damage the dust or quad seals.
19 Clamp the housing in a vise as shown in Figure 5. Use
just enough clamping force to hold the housing securely.

6
System
Product Numbers 2 Series (Standard — 69 Bar [1000 PSI])
Product Numbers 2 Series (High Pressure — 103 Bar [1500 PSI])
Ports Relief Valve
Setting
Bar [PSI] 31 [1.9] 39 [2.4] 63 [3.8] 74 [4.5] 100 [6.1]51 [3.1]
Displacement cm
3
/r [in
3
/r] and Product Number
291-1001-001None 291-1002-001 291-1003-001 291-1004-001 291-1005-001 291-1006-001
291-1001-04140 [ 580] 291-1002-041 291-1003-041 291-1004-041 291-1005-041 291-1006-041
291-1001-05150 [ 725] 291-1002-051 291-1003-051 291-1004-051 291-1005-051 291-1006-051
291-1001-06163 [ 914] 291-1002-061 291-1003-061 291-1004-061 291-1005-061 291-1006-061
291-1001-07170 [1015] 291-1002-071 291-1003-071 291-1004-071 291-1005-071 291-1006-071
293-4001-001None 293-4002-001 293-4003-001 293-4004-001 293-4005-001 293-4006-001
293-4007-001None 293-4008-001 293-4009-001 293-4010-001 293-4011-001 293-4012-001
Open
Center
Non-
Load
Reaction
Power
Beyond
Non-
Load
Reaction
Dynamic
Signal
Load
Sensing
9/16 Inch
Plug-O (4)
9/16 Inch
Plug-O (5)
9/16 Inch
Plug-O (5)
9/16 -18
Inch
SAE (4)
9/16 -18
Inch
SAE (5)
9/16 -18
Inch
SAE (5)
None
40 [ 580]
50 [ 725]
63 [ 914]
70 [1015]
None
40 [ 580]
50 [ 725]
63 [ 914]
70 [1015]
None
40 [ 580]
50 [ 725]
63 [ 914]
70 [1015]
291-1007-001 291-1008-001 291-1009-001 291-1010-001 291-1011-001 291-1012-001
291-1007-041 291-1008-041 291-1009-041 291-1010-041 291-1011-041 291-1012-041
291-1007-051 291-1008-051 291-1009-051 291-1010-051 291-1011-051 291-1012-051
291-1007-061 291-1008-061 291-1009-061 291-1010-061 291-1011-061 291-1012-061
291-1007-071 291-1008-071 291-1009-071 291-1010-071 291-1011-071 291-1012-071
291-5001-001 291-5002-001 291-5003-001 291-5004-001 291-5005-001 291-5006-001
291-5001-041 291-5002-041 291-5003-041 291-5004-041 291-5005-041 291-5006-041
291-5001-051 291-5002-051 291-5003-051 291-5004-051 291-5005-051 291-5006-051
291-5001-061 291-5002-061 291-5003-061 291-5004-061 291-5005-061 291-5006-061
291-5001-071 291-5002-071 291-5003-071 291-5004-071 291-5005-071 291-5006-071
291-5007-001 291-5008-001 291-5009-001 291-5010-001 291-5011-001 291-5012-001
291-5007-041 291-5008-041 291-5009-041 291-5010-041 291-5011-041 291-5012-041
291-5007-051 291-5008-051 291-5009-051 291-5010-051 291-5011-051 291-5012-051
291-5007-061 291-5008-061 291-5009-061 291-5010-061 291-5011-061 291-5012-061
291-5007-071 291-5008-071 291-5009-071 291-5010-071 291-5011-071 291-5012-071
291-1001-121None 291-1002-121 291-1003-121 291-1004-121 291-1005-121 291-1006-121
291-1001-081 80 [1160] 291-1002-081 291-1003-081 291-1004-081 291-1005-081 291-1006-081
291-1001-091 90 [1305] 291-1002-091 291-1003-091 291-1004-091 291-1005-091 291-1006-091
291-1001-101100 [1450] 291-1002-101 291-1003-101 291-1004-101 291-1005-101 291-1006-101
293-4001-121None 293-4002-121 293-4003-121 293-4004-121 293-4005-121 293-4006-121
293-4007-121None 293-4008-121 293-4009-121 293-4010-121 293-4011-121 293-4012-121
Open
Center
Non-
Load
Reaction
Power
Beyond
Non-
Load
Reaction
Dynamic
Signal
Load
Sensing
9/16 Inch
Plug-O
(4)
9/16 Inch
Plug-O
(5)
9/16 Inch
Plug-O (5)
9/16 -18
Inch
SAE
(4)
9/16 -18
Inch
SAE
(5)
9/16 -18
Inch
SAE (5)
None
80 [1160]
90 [1305]
100 [1450]
None
80 [1160]
90 [1305]
100 [1450]
None
80 [1160]
90 [1305]
100 [1450]
291-1007-121 291-1008-121 291-1009-121 291-1010-121 291-1011-121 291-1012-121
291-1007-081 291-1008-081 291-1009-081 291-1010-081 291-1011-081 291-1012-081
291-1007-091 291-1008-091 291-1009-091 291-1010-091 291-1011-091 291-1012-091
291-1007-101 291-1008-101 291-1009-101 291-1010-101 291-1011-101 291-1012-101
291-5001-121 291-5002-121 291-5003-121 291-5004-121 291-5005-121 291-5006-121
291-5001-081 291-5002-081 291-5003-081 291-5004-081 291-5005-081 291-5006-081
291-5001-091 291-5002-091 291-5003-091 291-5004-091 291-5005-091 291-5006-091
291-5001-101 291-5002-101 291-5003-101 291-5004-101 291-5005-101 291-5006-101
291-5007-121 291-5008-121 291-5009-121 291-5010-121 291-5011-121 291-5012-121
291-5007-081 291-5008-081 291-5009-081 291-5010-081 291-5011-081 291-5012-081
291-5007-091 291-5008-091 291-5009-091 291-5010-091 291-5011-091 291-5012-091
291-5007-101 291-5008-101 291-5009-101 291-5010-101 291-5011-101 291-5012-101
Power Steering
2 Series Steering Control Units

7
Power Steering
2 Series
Steering Control Units

Copyright Eaton Corporation, 1991, and 1995
All Rights Reserved
Printed in USA
Form No. 7-310
Char-Lynn
®
Eaton Corp. Hydraulics Div.Hydraulics Div.
Eden Prairie, MN 55344
Product number
000 0000 000
000
Product Number
000 0000 000
Product Line
Identification
Number
Product
Identification
Number
Engineering
Change
Code
Week of
Year
01 Thru 52
Last Number(s)
of Year
Date Code
00 00
Relief Valve Pressure Code
00 = None
04 = 40 Bar [ 580 PSI]
05 = 50 Bar [ 725 PSI]
06 = 63 Bar [ 914 PSI]
07 = 70 Bar [1015 PSI]
08 = 80 Bar [1160 PSI]
09 = 90 Bar [1305 PSI]
10 = 100 Bar [1450 PSI]
Each Order Must Include the Following:
How to Order Replacement Parts
1. Product Number
2. Date Code
3. Part Name
4. Part Number
5. Quantity of Parts
For More Detailed Information Contact Eaton Corp. Hydraulics
Division 15151 Highway 5 Eden Prairie, MN 55344.
Specifications and performance data, Catalog No. 11-872
Replacement part numbers and kit information — Parts
Information No. 7-310.
Power Steering
2 Series
Steering Control Units
Eaton Corporation
Hydraulics Division
15151 Hwy. 5
Eden Prairie, MN 55344
Telephone 612/937-9800
Fax 612/937-7130
Eaton Ltd.
Hydraulics Division
Glenrothes, Fife
Scotland, KY7 4NW
Telephone 01-592-771-771
Fax 01-592-773-184
Eaton GmbH
Hydraulics Products
Am Schimmersfeld 7
40880 Ratingen, Germany
Telephone 02102-406-830
Fax 02102-406-800
ISO-9001 CERTIFICATED FIRM
DET NORSKE VERITAS INDUSTRY BV, THE NETHERLANDS
ACCREDITED BY
THE DUTCH COUNCIL
FOR CERTIFICATION
Reg. No. 24
Quality System Certified
Products in this catalog are manufactured
in an ISO-9001-certified site.

ENGINE--GAS/LP
6-1
7400 MM428 (3--02)
CONTENTS
Page
INTRODUCTION 6-3......................
LUBRICATION 6-4.....................
ENGINE OIL 6-4....................
COOLING SYSTEM 6-4................
ENGINE FAN BELT 6-5..............
AIR INTAKE SYSTEM 6-5..............
AIR FILTER INDICATOR 6-5.........
AIR FILTER 6-5.....................
TO REPLACE AIR FILTER
ELEMENT 6-6...................
FUEL SYSTEM -- GASOLINE 6-7........
FUEL FILTER 6-7...................
CARBURETOR 6-7.................
FUEL SYSTEM -- LPG 6-8..............
LP FUEL TANKS 6-10...............
TO CHANGE AN LPG FUEL
TANK 6-12......................
FUEL FILTER LOCK 6-14............
VAPORIZER-REGULATOR 6-14......
CARBURETOR 6-14................
OIL PRESSURE SWITCH 6-14.......
LPG FUEL TROUBLESHOOTING 6-15
CYLINDER HEAD 6-15.................
VALVE TAPPET CLEARANCE 6-15...
CRANKCASE VENTILATION
SYSTEM 6-15...................
GOVERNOR
TROUBLESHOOTING 6-16.......
GOVERNOR 6-24.....................
TO ADJUST GOVERNOR 6-24.......
DIGITAL CONTROLLER SET--UP 6-25
IGNITION SYSTEM 6-26...............
SPARK PLUGS 6-26................
TO REPLACE SPARK PLUGS 6-26...
FORD DISTRIBUTORLESS IGNITION
SYSTEM 6-27......................
SYNOPSIS 6-27....................
ENGINE TEMPERATURE 6-27.......
RUN MODE 6-28...................
SERVICING AND TESTING 6-28.....
“FAILURE MODE OF DIS”
IGNITION HARNESS 6-29........
FORD DIS IGNITION 6-30...........
ENGINE COOLANT SENSOR 6-31......
TO REPLACE ENGINE
ALTERNATOR 6-32.................
TO REPLACE ENGINE STARTER 6-34...
TO REMOVE ENGINE 6-35.............
TO INSTALL ENGINE 6-38..............
TO PURGE AIR FROM RADIATOR 6-40..
GAS ENGINE SERVICE MANUAL
FORD VSG--411/413
TENNANT Part Number 38978

ENGINE--GAS/LP
6-2 7400 MM428 (12--98)

ENGINE--GAS/LP
6-3
7400 MM428 (12--98)
INTRODUCTION
This section includes repair information on the
engine and related systems, such as fuel,
electrical, and drive belts.

ENGINE--GAS/LP
6-4 7400 MM428 (12--98)
LUBRICATION
ENGINE OIL
Check the engine oil level daily. Change the
engine oil and oil filter every 100 hours of machine
operation. Use 10W30 SAE--SG/SH rated engine
oil.
Fill the engine with oil to the level indicated on the
oil dipstick. The engine oil capacity is 3.3 L
(3.5 qt) including the oil filter.
COOLING SYSTEM
Check the radiator coolant level every 100 hours
of operation. Use clean water mixed with a
permanent-type, ethylene glycol antifreeze to a
-- 3 4 _C(--30_F) rating.
FOR SAFETY: When Servicing Machine,
Avoid Contact With Hot Engine Coolant.
ATTENTION! Never pour cold water or
cold antifreeze into the radiator of an
overheated engine. Allow the engine to
cool down to avoid cracking the
cylinder head or block. Keep the engine
running while adding water.
Check the radiator hoses and clamps every 200
hours of operation. Tighten the clamps if they are
loose. Replace the hoses and clamps if the hoses
are cracked, harden, or swollen.
Check the radiator core exterior and hydraulic
cooler fins for debris every 100 hours of
operation. Blow or rinse all dust, which may have
collected on the radiator, in through the grille and
radiator fins, opposite the direction of normal air
flow. The grille and hydraulic cooler open for
easier cleaning. Be careful not to bend the cooling
fins when cleaning. Clean thoroughly to prevent
the fins becoming encrusted with dust. Clean the
radiator and cooler only after the radiator has
cooled to avoid cracking.
FOR SAFETY: When Servicing Machine,
Wear Eye And Ear Protection When
Using Pressurized Air Or Water.
Flush the radiator and the cooling system every
800 hours of operation, using a dependable
cleaning compound.

ENGINE--GAS/LP
6-5
7400 MM428 (12--98)
ENGINE FAN BELT
The engine fan belt is driven by the engine
crankshaft pulley and drives the alternator pulley.
Proper belt tension is 13 mm (0.50 in) from a
forceof4to5kg(8to10lb)appliedatthe
mid-point of the longest span.
Check and adjust the belt tension every 100 hours
of operation.
AIR INTAKE SYSTEM
AIR FILTER INDICATOR
The air filter indicator shows when to clean or
replace the air filter element. Check the indicator
daily. The indicator’s red line will move as the air
filter element fills with dirt. Do not clean or replace
the air filter element until the red line reaches 5
kPa (20 in H2O) and the ”SERVICE WHEN RED”
window is filled with red. The indicator’s red line
may return to a lower reading on the scale when
the engine shuts off. The red line will return to a
correct reading after the engine runs for a while.
Reset the air filter indicator by pushing the reset
button on the end of the indicator after cleaning or
replacing the air filter element.
AIR FILTER
The engine air filter housing has a dust cap and a
dry cartridge-type air filter element. Empty the
dust cap daily. The air filter must be replaced
whenever the filter element is damaged or has
been cleaned three times.
Service the air filter element only when the air
filter indicator shows restriction in the air intake
system. Do not remove the air filter element from
the housing unless it is restricting air flow.

ENGINE--GAS/LP
6-6 7400 MM428 (12--98)
TO REPLACE AIR FILTER ELEMENT
FOR SAFETY: Before Leaving Or
Servicing Machine: Stop On Level
Surface, Set The Parking Brake, Turn Off
Machine And Remove Key.
1. Open the engine cover and side door.
2. Unscrew the clamp ring on the filter.
3. Remove the dust cap.
4. Empty the dust cap.
5. Remove the filter wing nut.
6. Pull the filter element out of the filter
housing.
7. Clean the interior of the air cleaner housing
with a camp cloth. Clean the element
housing sealing surfaces.
8. Using an air hose, direct dry, clean air
maximum 205 kPa (30 psi) up and down
pleats on the inside of the filter. Do not rap,
tap, or pound dust out of the element.
FOR SAFETY: When Servicing Machine,
Wear Eye And Ear Protection When
Using Pressurized Air Or Water.
9. After cleaning the air filter element, inspect it
for damage by placing a bright light inside.
The slightest rupture requires replacement
of the filter. Clean and inspect the seals on
the ends of the element. They should be
unbroken and flexible. Remember to replace
the element after cleaning it three times.
10. Install the new or cleaned filter element so
the fins on the element are at the intake end
of the air cleaner. Be careful not to damage
the fins. Make sure the element is seating
evenly. Tighten the element wing nut.
11. Install the dust cap with the arrows pointing
up. Tighten the clamp ring to hold it in place.
Check all intake hose connections for leaks
or abrasions.
12. Reset the air filter restriction indicator.
13. Close the access doors.

ENGINE--GAS/LP
6-7
7400 MM428 (2--94)
FUEL SYSTEM -- GASOLINE
FUEL FILTER
The fuel filter trap fuel contaminants. The filter is
located on the fuel line going into the carburetor.
Replace the filter elements every 400 hours of
operation.
CARBURETOR
The carburetor has two basic adjustments. Those
adjustments are idle fuel mixture and idle speed.
Check and adjust idle fuel mixture and idle speed
every 100 hours of operation.
FOR SAFETY: When Servicing Machine,
Keep Flames And Sparks Away From
Fuel System Service Area. Keep Area
Well Ventilated.
The idle speed is controlled by a screw located on
the side of the carburetor next to the throttle
linkage. Increase the engine speed by turning the
screw clockwise. Decrease the engine speed by
turning the screw counter--clockwise. Idle speed is
800 to 900 rpm for gasoline, and 900 to 1000 for
LPG, with no power to the electronic governor.

ENGINE--GAS/LP
6-8 7400 MM428 (12--98)
FUEL SYSTEM -- LPG
The liquid withdrawal LPG fuel system has
up of five components: the LPG fuel tank,
pressure relief valve, fuel filter lock,
vaporizer-regulator, and the carburetor.
Liquid LPG fuel flows from the LPG tank, under its
own pressure, to the pressure relief valve. Usually
this valve is closed, preventing LPG fuel from
escaping into the atmosphere. The valve opens to
relieve pressure if the fuel pressure exceeds
system limits. From the pressure relief valve, the
liquid LPG fuel flows to the fuel filter lock.
The fuel filter lock filters unwanted tank scale and
deposits out of the LPG fuel. The fuel filter lock
also stops the flow of LPG fuel when the engine is
not operating. The oil pressure switch controls the
fuel filter lock. When the engine oil pressure
is 35 kPa (5 psi) or greater, the oil pressure switch
permits an electrical current to open the fuel filter
lock which allows LPG fuel to flow on to the
vaporizer-regulator. The oil pressure switch is
bypassed when the engine is being started,
allowing LPG fuel to flow.
The vaporizer section of the vaporizer-regulator
converts the liquid LPG fuel into a gaseous LPG
fuel. From the vaporizer section, the gaseous
LPG fuel is sent to the primary regulator section
of the vaporizer-regulator. The primary regulator
section reduces the pressure of the LPG fuel. The
secondary regulator section reduces the LPG fuel
pressure to the level required by the carburetor.
From the vaporizer-regulator, the LPG fuel is sent
to the carburetor where it is finally metered into
the air flow sent to the engine combustion
chamber.
Never operate an LPG powered machine if the
LPG fuel system is leaking, or if any component in
the fuel system is malfunctioning. Operating the
machine under either of these conditions may
cause a fire or explosion.

ENGINE--GAS/LP
6-9
7400 MM428 (12--98)
Check for frosting. If frosting occurs on or near
any LPG component, there is a possible LPG fuel
leak or malfunctioning component.
To locate the leak, apply a soapy water solution to
the suspected area. Watch for bubbles forming in
this suspected area. This area may have an LPG
fuel leak. Repair or replace the part. Use Loctite
brand Stainless Steel PST thread sealant when
reassembling. Aging or high humidity does not
affect this epoxy-type sealant. Be sure to follow
application directions and apply proper torque
when reconnecting fittings. Never bypass safety
components except to test. If they are defective,
replace them before operating the machine.
Frosting does not occur before the engine
reaches operating temperature. Check after
engine reaches operating temperature.
Check routings of all LPG hoses. Keep them
away from sharp edges, exhaust manifolds, or
other hot surfaces. Check for signs of abrasion or
deterioration. Replace worn or damaged hoses.

ENGINE--GAS/LP
6-10 7400 MM428 (12--98)
LP FUEL TANKS
The LPG fuel tanks should be inspected for sharp
dents, gouges, leaks, and broken protecting rings
whenever the tanks are refilled. All tank valves
must be inspected for leaks using a soap solution.
Valves must also be checked for dirt, paint, or
other debris in the valve openings. The following
specific checks must also be made:
Filler Valve -- Check the valve for proper
functioning and the presence of the
handwheel. Valve must be closed except
during filling.
Liquid Service Valves -- Check the valve
for proper functioning and presence of the
handwheel. The valve must be closed
except when in service.
Tank Service Valve Coupling -- Check for
proper functioning, thread condition, and
damaged or missing washers or o-rings.

ENGINE--GAS/LP
6-11
7400 MM428 (12--98)
Safety Relief Valve -- Check for damage.
Check for the presence of the relief valve
elbow and the proper direction of the elbow.
If the rain cap is missing, check for foreign
matter and replace the rain cap. Do not
tamper with the relief valve setting.
Magnetic Liquid Level Gauge -- Check the
operation against the maximum filling point
as determined by weight.
An LPG fuel tank with any of the stated defects
must be removed from service and be repaired or
destroyed accordingly.
If an LPG fuel tank is damaged or leaking, it
should be removed to a designated safe area. Do
not attempt to make repairs to the tank,
regardless of condition. Qualified personnel must
make repairs or disposal.
The care an LPG fuel tank receives has a direct
bearing on how long that tank can be used safely.
LPG fuel tanks must not be dropped or dragged
across any surface. To move LPG fuel tanks, use
a hand truck or roll the tank on its foot ring while it
is being held in a position slightly off the vertical.
Whether the storage is inside or outside, fuel
tanks should not be stored near combustible
materials or high temperature sources such as
ovens and furnaces, since the heat may raise the
pressure of the fuel to a point where the safety
relief valves would function. Store the tanks in a
way that if the safety relief valves do function,
they will relieve vapor and not liquid.

ENGINE--GAS/LP
6-12 7400 MM428 (12--98)
Valves on empty tanks must be closed during
storage and transportation.
Similar precautions should be taken in storing
machines fitted with LPG fuel tanks. The
machines may be stored or serviced inside
buildings, provided there are no leaks in the fuel
system and the tanks are not overfilled. While
machines are being repaired inside a building, the
shut-off valve on the tank must be closed, except
when the engine has to be operated.
Changing the tank is a chance for the machine
operator to carefully check over the tank, fittings,
and the fuel lines and fittings. If abnormal wear is
detected, report the findings to the appropriate
personnel.
TO CHANGE AN LPG FUEL TANK
1. Park the machine in a designated safe area.
2. Close the tank service valve.
3. Operate the engine until it stops from lack of
fuel, then set the machine parking brake.
FOR SAFETY: Before Leaving Or
Servicing Machine: Stop On Level
Surface, Set The Parking Brake, Turn Off
Machine And Remove Key.
4. Put on gloves and remove the
quick-disconnect tank coupling.
5. Inspect the LPG fuel lines for wear or
damage.
6. Remove the empty LPG fuel tank from the
machine.
7. Check the tank for damage or wear.
8. Store the tank in a designated, safe area.
9. Select a filled LPG fuel tank and inspect it
for damage or leaks.
NOTE: Make sure the LPG fuel tank matches the
fuel system (liquid tank with liquid system).

ENGINE--GAS/LP
6-13
7400 MM428 (12--98)
10. Carefully put the LPG tank in the machine
so that the tank centering pin enters the
aligning hole in the tank collar.
NOTE: If you cannot line up the centering pin,
make sure you have the correct LPG fuel tank
and then adjust the pin locator in or out.
11. Fasten the tank hold-down clamp to lock the
tank in position.
12. Connect the LPG fuel line to the tank service
coupling. Make sure the service coupling is
clean and free of damage. Also make sure it
matches the machine service coupling.
13. Open the tank service valve slowly and
check for leaks. Close the service valve
immediately if an LPG leak is found, and tell
the appropriate personnel.
14. If no leaks are found, the engine is ready to
start.

ENGINE--GAS/LP
6-14 7400 MM428 (12--98)
FUEL FILTER LOCK
The fuel filter lock filters the LPG fuel. It also
stops the flow of LPG fuel to the engine when the
engine is not operating or when the engine oil
pressure is less than 35 kPa (5 psi).
VAPORIZER-REGULATOR
If any malfunction is found, completely
disassemble the vaporizer-regulator. Clean all the
parts in alcohol.
Inspect all the parts and replace where needed.
Carefully reassemble the vaporizer-regulator with
the seal repair kit. Check for proper operation.
CARBURETOR
If any malfunction is found, completely
disassemble the carburetor. Clean all the parts in
alcohol.
Inspect all the parts and replace where needed.
Carefully reassemble the carburetor with the seal
repair kit.
OIL PRESSURE SWITCH
The engine oil pressure switch requires no regular
maintenance. Never bypass the oil pressure
switch. The switch is a safety feature that
prevents LPG fuel from flowing when the engine
is not operating properly.

ENGINE--GAS/LP
6-15
7400 MM428 (12--98)
LPG FUEL TROUBLESHOOTING
Problem Cause Remedy
Engine will not start Outoffuel Replace fuel tank with full one
Service valve opened too quickly
-- check valve stopped fuel flow
Close service valve and reopen
slowly
Plugged fuel filter Replace filter
Kinked or restricted fuel line Straighten or replace fuel line
Engine out of tune Tune-up engine
Oil pressure switch failure Replace oil pressure switch
Fuel lock valve failure Repair or replace fuel filter lock
Vaporizer-regulator failure Repair or replace
vaporizer-regulator
Engine runs unevenly or lacks
power
Wrong type of fuel tank -- vapor
withdrawal tank
Replace vapor withdrawal tank
with liquid withdrawal tank
Plugged fuel filter Replace filter
Kinked or restricted fuel line Straighten or replace fuel line
Engine out of tune Tune-up engine
Restricted air filter Clean or replace air filter element
Vaporizer-regulator out of
adjustment
Adjust vaporizer-regulator
CYLINDER HEAD
A three-stage torque procedure should be used
when reassembling the cylinder head. Tighten the
cylinder head bolts seasonally. See Ford VSG
411/413 Engine Service Manual.
VALVE TAPPET CLEARANCE
Check and adjust the intake valve clearance to
0.22 mm (0.009 in), and the exhaust valve
clearance to 0.32 mm (0.013 in) while the engine
is cold the first 50 hours of operation and every
400 hours there after. See Ford VSG 411/413
Engine Service Manual.
CRANKCASE VENTILATION SYSTEM
Clean the crankcase ventilation hoses, tubes, and
fittings and replace the PCV valve every 400
hours of operation.

ENGINE--GAS/LP
6-16 7400 MM428 (12--98)
GOVERNOR TROUBLESHOOTING
1. The first step in this troubleshooting is to
disconnect the throttle linkage at the
carburetor and work the throttle at the
carburetor by hand.
If you can run the engine by hand and it
works with no problems, go to step four.
If the problem continues, it is not with the
governor, it is with the ignition signal fuel
systems or the engine itself.
2. Ignition Signal
The DIS engine has no distributor, but the
timing signals that drive the governor
originate from the Ignition Control input
leads. They are the Yellow Wire #71 and the
Yellow Wire #72. To test this, use the
governor test harness (TENNANT Part No.
66137). Once the harness is in place, use a
tach/dwell meter to test for the proper RPM’s
and a flat ignition signal. Test at the text plug
at either Pin C, or Pin D.
NOTE: An inductive RPM pickup won’t work for
this test.
NOTE: When checking the RPM’s at Pin C, and
Pin D, the ignition signal will be half of the total
RPM’s the engine is running at because of the
DIS system.
Your readings should be:
TOTAL READING--GAS
a. Start/Idle -- 800 RPM
b. I -- 1350¦50 RPM
c. II -- 2400¦50 RPM
TOTAL READING--LPG
a. Start/Idle -- 900 RPM
b. I -- 1350¦50 RPM
c. II -- 2400¦50 RPM

ENGINE--GAS/LP
6-17
7400 MM428 (12--98)
3. Fuel System
A common problem that has been
encountered on LPG machines is a
restricted fuel hose (a clogged fuel filter can
have the same effect).
If the governor opens the carburetor wide
open and the engine loses speed, the
problem is not in the governor. The fuel
system is at fault. The purpose of the
governor is to open the carburetor and to
bring the engine to set RPM’s depending on
where you have the speed control switch set
at.
After you have verified that the ignition
system and the fuel system are not at fault,
go to the next step.

ENGINE--GAS/LP
6-18 7400 MM428 (12--98)
(A) +
(B) --
(C) Signal
(D) Signal
(E) Actuator +
(F) Actuator --
(G) Speed
(H) Speed
High=+9VDC
Low = 0VDC
+12VDC Switched (18D/ORA)
Ground (13E/BLK)
D.I.S.
Ignition
Module (72C/YEL)
(71C/YEL)
(84/GRN)
(83/BRN)
ELECTRONIC GOVERNOR WIRING PICTORIAL
Throttle actuator
(+)
(--)
(86/PUP)
(85/BLU)
Electronic
Instrument
Panel
A
B
C
D
E
F
G
H
A
B
C
D
E
F
G
H
A BCDEF G
H
TO: HARNESS TO: GOVERNOR
TEST PLUG
NOTE: The wire colors of the test harness do not necessarily match the machine harness.

ENGINE--GAS/LP
6-19
7400 MM428 (12--98)
5. System Grounds
The wire harness grounds on the machines
with a DIS engine are routed to the stud on
the alternator, and from there, a separate
cable is routed to the bolt on the bell housing
where the battery cable is attached.
If a bad ground is present, the engine will
tend to run over speed.
The machine must have good grounds
throughout from the battery cable to the
control box.
The battery cable must be clean and tight.
There must not be a greater voltage drop
than .2 volts between Pin B, on the test
harness, the engine, the alternator, and the
battery positive terminal and the battery
negative terminal.
To do this, take your voltmeter and set it on
the DC volts scale. Then with your positive
probe, clamp it to battery positive. Then with
the negative probe, move it to the
above-stated places on the machine.
The actuator is internally isolated and does
not require that the cable be grounded.
6. Start-Up Check
With the throttle switch in the engine start
position, turn the ignition switch to the on
position. The actuator should cycle the
carburetor lever once.
NOTE: A cycle is to move from the off or idle
position to the open position and then return to
the off or idle position.
If this does not happen, the power wiring to
the control box is probably at fault or the
control box is faulty. IT IS RARE TO HAVE
A FAULTY CONTROL BOX, so proceed
with the following voltage checks BEFORE
REPLACING IT.
7. Throttle Control Switch Check
If the engine doesn’t respond to the throttle
switch control:
a. With the engine running, disconnect
Wire 86, purple wire, at the actuator.

ENGINE--GAS/LP
6-20 7400 MM428 (12--98)
b. Connect a jumper wire from the battery
terminal on the starter to the terminal
where you removed Wire 86, purple
wire, from the actuator.
The engine should come up to operating
speed. If the engine comes up to speed,
replace the throttle control switch. If the
engine doesn’t respond, go to the next step.
8. Operating Voltage
The following voltage checks are done with
the machine not running and using a Fluke
or Beckman digital multimeter and the
governor test harness.
Throttle control switch in start/idle position:
Pin A -- Battery Voltage ¦.2
Pin B -- 0 -- this is a ground
Pin C -- Battery Voltage ¦.2
Pin D -- Battery Voltage ¦.2
Pin E -- Battery Voltage ¦.2
Pin F -- Battery Voltage ¦.2
Pin G -- Battery Voltage ¦.2
PinH--3to3.5VDC
Throttle control switch in the normal sweep
position:
Pin G -- <1VDC
PinH--7to9VDC
Throttle control switch in the Litter sweep position:
Pin G -- <1VDC
Pin H -- <1VDC
The following voltage and RPM readings are at
the electric control box using the test harness with
the machine running.
NOTE: when you are testing if you should be in
the DC or AC scale on your multimeter. You will
also need your tach/dwell for the RPM checks.
The readings are taken with either a Fluke or
Beckman digital multimeter:

ENGINE--GAS/LP
6-21
7400 MM428 (12--98)
Throttle control switch in the start/idle position:
Pin C -- 675 ¦100 RPM
Pin D -- 675 ¦100 RPM
Pin E -- Battery Voltage ¦.2
PinF--6to6.5VAC
Throttle control switch in the normal sweep
position:
Pin C -- 1100 ¦25 RPM
Pin D -- 1100 ¦25 RPM
Pin E -- Battery Voltage ¦.2
PinF--6.5to7VAC
Throttle control switch in the litter sweep position:
Pin C -- 1200 ¦25 RPM
Pin D -- 1200 ¦25 RPM
Pin E -- Battery Voltage ¦.2
PinF--7to7.5VAC
If you do not get these values:
Pin A -- Check battery, wiring/connections,
and also the charging system.
Pin B -- Check all grounds.
Pin C -- Check ignition system and fuel
systems.
Pin D -- Check ignition system and fuel
systems.
Pin E -- Possible control board.
Pin F -- Possible control board.
Pin G -- Possible switch.
Pin F -- Possible switch.

ENGINE--GAS/LP
6-22 7400 MM428 (3--02)
The volt readings at the actuator with the machine
running and using a Fluke or Beckman digital
multimeter:
At the terminal where Wire 84, green wire, is
hooked to:
Start/Idle -- 6 to 6.5 VAC ¦.2
Normal -- 6.5 to 7 VAC ¦.2
Litter -- 7 to 7.5 VAC ¦.2
At the terminal where Wire 86, purple wire, is
hooked to:
Start/Idle -- 12 to 14.5 VDC ¦.2
Normal--12to14.5VDC¦.2
Litter -- 12 to 14.5 VDC ¦.2
9. Control Box Adjustment
If all the above aspects, in particular the
linkage, have been verified and the warmed
up engine either:
a. Hunts at running speed with the
accessories off.
b. Responds very sluggishly to switch
changes, an adjustment change in the
control box may be necessary.
FOR ANALOG CONTROLLERS:
Cut and remove the RTV seal on the back of
the box.
A slight adjustment of the surge screw may
be necessary to correct the conditions
mentioned above. Turn the screw
approximately 2_at a time and wait for 30
seconds to verify the change. Be careful.
Only a slight change is necessary, and the
“pot” can be broken if too much force is
used.

ENGINE--GAS/LP
6-23
7400 MM428 (3--02)
After the control throttle response is
achieved, verify that the operating speeds
are correct and adjust, if necessary. After
the speeds are reset, the surge screw may
have to be readjusted.
In general, if a new box is being installed, a
gasoline-equipped machine may require that
the sensitivity be reduced slightly.
When the sensitivity is adjusted, the run
speed should not be affected. If the
adjustment is too great, the start speed will
be affected. Verify that the start speed is
correct.
If too much sensitivity is adjusted in, the
engine will either hunt in a no load condition
or over speed severely when the speed
switch is actuated.
If too little sensitivity is adjusted in, the
engine will seem sluggish. The engine speed
will drop off when the load is increased and
not recover promptly.
The engine speed should not drop off, but
you can have the three hunts of the engine.
If, for some reason, the sensitivity
adjustment became grossly maladjusted, a
good starting point can be obtained by
rotating the pot fully counterclockwise and
then back clockwise 45_.
After the adjustments are made and verified,
reassemble the back plate and reseat the plate
with a bead of RTV to keep dust and moisture out
of the box.
FOR DIGITAL CONTROLLERS:
See TO ADJUST GOVERNOR section of
this manual.

ENGINE--GAS/LP
6-24 7400 MM428 (3--02)
GOVERNOR
The electronic governor controls engine speed.
The governor consists of an ignition control
assembly, a control box, and an actuator mounted
on the engine. The ignition control assembly and
control box regulate the actuator, which in turn
controls the throttle.
The electronic governor is factory set and is not
user serviceable.
TO ADJUST GOVERNOR
1. Raise the front of the machine and place
jack stands under the frame.
FOR SAFETY: Block machine tires
before jacking machine up. Jack
machine up at designated locations
only. Block machine up with jack
stands.
2. Start the engine and warm to operating
temperature.
3. Move the speed switch to idle, all
accessories off.
4. Move the speed switch to the fast position.
5. For ANALOG CONTROLLER: If engine
speed surges occur, turn the surge
adjustment screw (located on back of
governor control box under hole plug)
counterclockwise one-eighth of a turn.
Repeat until surges do not occur.
Replace hole plug if removed for adjustment.
6. For DIGITAL CONTROLLER: Follow the
instructions on the DIGITAL CONTROLLER
SET--UP diagram.
7. Remove the jack stands and lower the
machine.

ENGINE--GAS/LP
6-25
7400 MM428 (3--02)
rocker down
O
F
F
Set DIP switches according to
controller label, before installing
controller.
123 45 6 78
DIGITAL CONTROLLER SET -- UP

ENGINE--GAS/LP
6-26 7400 MM428 (12--98)
IGNITION SYSTEM
SPARK PLUGS
Clean or replace, and set the gap of the spark
plugs every 400 hours of operation. A wire gauge
is best for checking the spark plug gap. A flat
gauge should not be used unless the electrode
surfaces have been dressed with a small file to
get parallel surfaces between the center and side
electrode. Set the spark plug gap by bending the
side electrode. All spark plugs, new or used,
should have the gaps checked and reset if
necessary.
The proper spark plug gap is 1 mm (0.040 in).
TO REPLACE SPARK PLUGS
FOR SAFETY: Before Leaving Or
Servicing Machine: Stop On Level
Surface, Set The Parking Brake, Turn Off
Machine And Remove Key.
1. Open the engine cover and side door.
2. Remove the spark plug wires from the four
spark plugs.
NOTE: Clean any dirt from the spark plug seat
area before removing the spark plugs.
3. Remove the spark plugs from the engine
4. Clean the spark plug seat in the cylinder
head.
5. Use a new seat gasket and screw the plug
in by hand.
6. Tighten the spark plugs with a socket
wrench of the correct size.

ENGINE--GAS/LP
6-27
7400 MM428 (3--02)
FORD DISTRIBUTORLESS IGNITION SYSTEM
SYNOPSIS
This is a troubleshooting guide for the Ford
Distributorless Ignition System.
Unlike a conventional system, the Ford
Distributorless Ignition System (DIS) uses two
coils that each fire one pair of spark plugs. The
spark plugs are also fired on both the power and
exhaust stroke.
The DIS system also uses a Universal Electronic
Spark Control (UESC) module which adjusts the
timing of the engine. The degree of timing change
needed is determined by electrical and vacuum
input to the UESC, these are:
The engine harness has a separate wire for the
gas and another for the LPG machines. Make
sure you connect the correct wire for the type of
fuel being used.
ENGINE LOAD -- FROM PRESSURE
REDUCER:
Located in the intake manifold.
Minimum 21 KPA (6.22” Hg)
Maximum 101 KPA (29.91” Hg)
ENGINE TEMPERATURE
The Engine Coolant Temperature Sensor (ECTS)
located in the intake manifold water jacket sends
engine temperature information to UESC.
Minimum --39_C38_F
Maximum 112_C 232_F
When the engine is starting, at 250 RPM or less,
the timing is set at 10_before top dead center
(BTDC).

ENGINE--GAS/LP
6-28 7400 MM428 (12--98)
RUN MODE
In this mode the RPM is above 250 and the spark
advance is calculated in three sections which are
added together to maintain optimum running
condition.
The Base Spark Advance (BSA) is calculated by
the UESC module looking at speed and load
inputs.
The Spark Advance Offset Temperature (SAOT)
will change ignition timing. This is determined by
the Engine Coolant Temperature (ECT). This
allows the spark advance to be altered during cold
engine conditions.
SERVICING AND TESTING
SERVICING:
1. Every 400 hours, remove the spark plugs
and clean and adjust the electrode.
2. Clean and visually check spark plug high
tension leads and test for resistance. The
Ohm meter should read between 9,000 and
16,000 Ohms.
TESTING:
Secondary Coil Testing
Remove the four (4) spark plug wires and
measure the secondary coil resistance by
placing the meter into plug wire terminal.
1 -- 4 at the coil
2 -- 3 at the coil
On each test you should read 14,000 + 50
Ohms.
Universal Spark Control Module Diaphragm
Testing
Using a vacuum pump, apply 15” Hg to the
UESC and vacuum inlet. The diaphragm
should hold the pressure. If it fails, replace
UESC unit.
To test the sensors and wiring harness,
follow the direction on the next three pages.

ENGINE--GAS/LP
6-29
7400 MM428 (12--98)
“FAILURE MODE OF DIS” IGNITION HARNESS
The Ford DIS Universal Spark Control was
checked for “poor connection”.
The results of open leads were:
Term 11 or 12 Ignition Coil Signal Leads --
The governor received 1/2 of its intended
signal and caused the actuator to hold the
carb arm wide open. At the same time, the
engine missed due to incorrect firing of
plugs, but the speed still climbed to about
3,000--4,000 rpm. When either of these
leads were opened at the start speed, the
engine missed slightly and rose to double
the start speed or about 3,000 rpm.
Term 9 Ground -- Any failure here killed the
engine instantly or caused the engine to
slow down if it were cycled.
Term 6 & 7 Octane Selector -- Opening
these terminals retards the spark in varying
degrees. Under light to moderate load
conditions, no adverse effect will take place.
However, run-on or pre-ignition may take
place.
Term 4 & 10 Coolant Sensor -- Contrary to
previous thoughts, opening the lead doesn’t
noticeably affect the engine. The timing only
changes a few degrees.
Term 2 & 3 Crank Position Sensor --
Opening either of these leads kills the
engine quickly and it will not start.
Term 8 Power Lead -- Opening this lead kills
the engine and it will not start.
In summary, no alarming effect happens except if
the coil signal leads are interrupted. These are the
end leads on the module and if the harness has
too much tension on it, the signal will become
intermittent and cause the engine to overspeed.
The only obvious damage will probably occur to
the propelling pump, as the fan is rated for
operation to 10,000 rpm. If the acc. are on when
the lead becomes intermittent, the engine will not
develop enough power to overspeed excessively.

ENGINE--GAS/LP
6-30 7400 MM428 (12--98)
200---600
Ohms
2
3
VRS +
V R S ---
65 Blue
66 Green
Variable reluctance
sensor (crank position
sensor)
Ohms
Ohms
105,000
0
4
10
ECT1
ECT2
67 Orange
10K Ohm
70 Green
64 Brown
Engine coolant
temperature sensor in
ice water bath
See Engine Coolant
Sensor chart
1
2
6
7
OCT2
OCT1
6
6
68 Brown
Cut and ground to set octane (retard
spark advance)
18T Orange
12.6
Volts +
D . C . ---
8
9
VBatt
Power Ground
16M 16I
57
13PP Black
Ignition
switch on
13QQ Black
+
Batt
12.6 V
DC
---
11
12
0.5 --- 1.0
Ohms
CDO
(Phase
A)
CDO
(Phase
B)
852
71 Yellow
72 Gray
850A
852A
HT HT
14
HT HT
23
Distributorless
Ignition Coil
12.6
Volts +
D . C . ---
Remove the coil connector and probe
the center female terminal
To Pi n #9
FORD DIS IGNITION

ENGINE--GAS/LP
6-31
7400 MM428 (12--98)
ENGINE COOLANT SENSOR
Temperature
_C_F
Sensor (Ohms)
+.02_
Sensor & Harness
(Ohms) + .03_
-- 3 0 --- 2 2 481,000 491,000
-- 2 0 4271,000 281,000
-- 1 0 14 158,000 168,000
032 95,000 105,000
10 50 58,750 68,750
20 68 37,300 47,300
30 86 24,270 34,270
40 104 16,150 26,150
50 122 10,970 20,970
60 140 7,600 17,600
70 158 5,360 15,360
80 176 3,840 13,840
90 194 2,800 12,800
100 212 2,070 12,070
110 230 1,550 11,550
120 248 1,180 11,180
130 266 930 10,930
140 284 701 10,701
150 302 550 10,550

ENGINE--GAS/LP
6-32 7400 MM428 (12--98)
TO REPLACE ENGINE ALTERNATOR
FOR SAFETY: Before Leaving Or
Servicing Machine; Stop On Level
Surface, Set Parking Brake, Turn Off
Machine And Remove Key.
1. Raise the operators seat, engage the prop
rod, and disconnect the battery cables from
the battery.
2. Open the machine engine cover and side
door. Remove the side door from the
machine.
3. Remove the two hex screws holding the
plastic fan belt cover to the front of the
engine. Remove the cover.
4. Disconnect the wires from the back of the
alternator.
5. Remove the hex screw from the top of the
alternator.
6. Loosen the lower hex screw and nyloc nut
and push the alternator in toward the engine.
Remove the V--belt from the alternator drive
pulley.
7. Remove the hex screw and nyloc nut from
the bottom of the alternator. Remove the
alternator.
8. If the new alternator does not have a drive
pulley----remove the hex nut and washer
holding the drive pulley to the old alternator.
Install the drive pulley on the new alternator
and tighten tight.
9. Install the new alternator back in the
machine. Reinstall the lower hex screw and
nyloc nut. Leave loose for now.
10. Reinstall the hex screw in the upper arm and
the top of the alternator. Leave loose for
now.

ENGINE--GAS/LP
6-33
7400 MM428 (12--98)
11. Reinstall the V--belt on the alternator drive
pulley.
12. Pull the alternator away from the engine to
tighten the V--belt. Tighten the upper hex
screw tight.
13. Reconnect the wires to the back of the new
alternator. See schematic in the
ELECTRICAL section.
14. Reinstall the plastic belt cover to the front of
the engine. Hand tighten the hex screws
tight.
15. Reconnect the battery cables, close the
operators seat and start the machine.
16. Check the new alternator for proper
operation.

ENGINE--GAS/LP
6-34 7400 MM428 (12--98)
TO REPLACE ENGINE STARTER
FOR SAFETY: Before Leaving Or
Servicing Machine; Stop On Level
Surface, Set Parking Brake, Turn Off
Machine And Remove Key.
1. Raise the operators seat, engage the prop
rod, and disconnect the battery cables from
the battery.
2. Open the machine front cover, engine cover,
and side door. Remove the side door from
the machine.
3. If the machine is an LPG, remove the LP
tank from the cradle.
4. The vacuum fan assembly can be removed
for better access to the starter. See TO
REMOVE VACUUM FAN instructions in the
SCRUBBING section.
5. Remove the air cleaner intake tube from the
air cleaner and machine frame.
6. Reach in through the left side of the engine
and disconnect the battery cable and
electrical wires leading to the starter.
7. Reach in through the open seat support area
and remove the three M10 hex screws
holding the starter to the bellhousing.
NOTE: The bottom hex screw has a nyloc nut on
the starter side.
8. Remove the starter out through the area of
the vacuum fan and engine oil filter.
9. Position the new starter in the machine.
10. Reinstall the three M10 hex screws and one
nyloc nut. The nyloc nut goes on the bottom
hex screw. Tighten to 31 -- 40 Nm
(27 -- 35 ft lb).
11. Reconnect the battery cable and electrical
wires to the starter. See schematic in the
ELECTRICAL section.

ENGINE--GAS/LP
6-35
7400 MM428 (12--98)
12. Reinstall the air cleaner intake tube to the air
cleaner and machine frame.
13. If the vacuum fan was removed----reinstall.
See TO INSTALL VACUUM FAN
instructions in the SCRUBBING section.
14. Reconnect the battery cables to the battery
and close the operators seat.
15. If the machine is an LPG----reinstall the LP
tank.
16. Reinstall the engine side door and close the
covers.
17. Start the machine.
TO REMOVE ENGINE
FOR SAFETY: Before Leaving Or
Servicing Machine; Stop On Level
Surface, Set Parking Brake., Turn Off
Machine And Remove Key.
1. Pivot the operators seat to the open position
and engage the prop rod.
2. Disconnect the battery cables and remove
the battery.
NOTE: The battery tray can also be removed for
better access to the propel pump.
3. Remove the detergent tank and the rubber
sound flap from the machine.
4. Remove the two hex screws holding the
propel pump to the engine bellhousing
NOTE: The main suction line to the accessory
pump is held, by plastic ties, in a bundle of hoses
near the main valve. Remove the plastic ties to
gain slack in the suction line to ease pump
removal.

ENGINE--GAS/LP
6-36 7400 MM428 (12--98)
5. Remove the two hex screws holding the
hydraulic flow valve to the back, left of the
bellhousing. Do not disconnect any hydraulic
hoses.
6. Pull the propel pump out of the bellhousing
and drive coupler. Do not disconnect any
hydraulic hoses.
7. If the machine is an LPG, remove the LP
tank from the cradle.
8. Open the machine front cover, engine cover,
and side door. Remove the side door from
the machine.
9. Remove the vacuum hose from the vacuum
fan and the recovery tank.
10. The vacuum fan assembly can be removed
for better access to the engine. See TO
REMOVE VACUUM FAN instructions in the
SCRUBBING section.
NOTE: The engine hood must be supported in the
open position before the next step can be
completed.
11. Remove the clips on the bottom of the
engine hood gas springs. Remove the gas
springs from the ball studs on the support
channel.
12. Remove the hex screws holding the support
channel to the tank lintel and hood lintel.
Remove the support channel from the
machine.
13. Drain the radiator coolant.
14. Remove the radiator hoses where they
connect to the engine.
15. Drain the engine oil.
NOTE: Disconnect the engine oil drain hose from
the oil pan before lifting the engine completely out
of the machine.

ENGINE--GAS/LP
6-37
7400 MM428 (12--98)
16. Disconnect the exhaust pipe at the engine
manifold.
17. Disconnect the wire harness from all of the
engine components and place it out of the
way.
18. Disconnect the engine ground strap from
frame.
19. Disconnect the battery cable and electric
wires from the engine starter.
20. Disconnect the fuel line at the fuel pump on
a gas machine.
21. Disconnect the fuel line from the LP tank at
fuel lockoff / vaporizer on an LPG machine.
22. Using an overhead hoist, hook a chain or
strap through two or three pick--up points on
the engine. Put a slight amount of tension on
the chain.
23. Remove the three M12 hex screws and
nyloc nuts holding the motor mounts to the
rubber isolators on the machine frame.
24. Engine can now be carefully lifted out.

ENGINE--GAS/LP
6-38 7400 MM428 (12--98)
TO INSTALL ENGINE
FOR SAFETY: Before Leaving Or
Servicing Machine; Stop On Level
Surface, Set Parking Brake., Turn Off
Machine And Remove Key.
1. Using a overhead hoist, hook a chain or
strap through two or three pick--up points on
top of the engine. Carefully position the
engine back in the engine compartment.
2. Carefully Lower the engine assembly down
on the the motor mounts.
NOTE: Make sure the hoses, wire harness,
exhaust pipe, and propel pump are pulled back
out of the way when lowering the engine
assembly in place.
3. Reinstall the three M12 hex screws in the
three motor mount isolators. Tighten to
64 -- 83 Nm (50 -- 60 ft lb)
4. Reconnect the ground cable from the
bellhousing to the machine frame.
5. Reinstall the flow valve on the back, left of
the bellhousing.
6. Reconnect the battery cable and electrical
wires to the starter. See schematic in the
ELECTRICAL section.
7. Reconnect the wire harness to engine
components, alternator, governor actuator,
oil switch, temperature sender, distributor,
and ignition module. See schematic in the
ELECTRICAL section.
8. Reinstall the propel pump back in the
bellhousing. Use a small amount of blue
loctite 242 on the threads. Reinstall the two
hex screws. Tighten to 64 -- 83 Nm
(50 -- 60 ft lb).
NOTE: Make sure the splines on pump line up
with splines in coupler when installing pump.
9. Reinstall the detergent tank in the seat
support area.
10. Reinstall the battery tray and battery.
11. Reinstall the exhaust pipe back on the
manifold. Reinstall the muffler clamp and
tighten tight.

ENGINE--GAS/LP
6-39
7400 MM428 (12--98)
12. Reconnect the fuel line at the fuel pump on
a gas machine.
13. Reconnect the fuel line from the LP tank at
fuel lockoff / vaporizer on an LPG machine.
14. Fill the engine with the proper grade of oil.
15. Reinstall the radiator hoses to the engine
and fill the radiator with coolant. See TO
PURGE AIR FROM RADIATOR instructions.
16. If the vacuum fan was removed----reinstall.
See TO INSTALL VACUUM FAN
instructions in the SCRUBBING section.
17. Reinstall the vacuum hose on the recovery
tank and vacuum housing.
18. Reinstall the support channel to the tank
lintel and hood lintel. Reinstall the four hex
screws and tighten to 18 -- 24 Nm
(15 -- 20 ft lb).
19. Reinstall the engine hood gas springs on the
ball studs on the support channel. Reinstall
the two clips.
20. Reconnect the battery cables.
21. Disengage the prop rod and lower the seat.
22. Reinstall the LP tank on a LPG machine.
23. Jack up the front of the machine and place
jack stands under the frame.
FOR SAFETY: Block machine tires
before jacking machine up. Jack
machine up at designated locations
only. Block machine up with jack stands
24. Start the machine. Check the engine,
hydraulic motors, and pumps for leaks.
25. Reinstall the engine side door and close the
covers.

ENGINE--GAS/LP
6-40 7400 MM428 (12--98)
TO PURGE AIR FROM RADIATOR
FOR SAFETY: Before Leaving Or
Servicing Machine; Stop On Level
Surface, Set Parking Brake., Turn Off
Machine And Remove Key.
1. Make sure that both radiator hoses are
connected to the engine.
2. Remove the radiator cap and pour in
approximately 1--1/2 gallons of coolant.
3. Open the engine cover and side door.
4. Loosen the hose clamp on the upper
radiator hose. Thisisthehoseonthe
thermostat housing.
5. Break the hose loose from the neck of the
thermostat housing and slowly pull the hose
off the neck.
6. Keep the hose off the neck until coolant
starts to flow out of the hose.
7. Quickly place the hose back on the neck of
the thermostat housing. Re--tighten the hose
clamp.
8. Start the machine and run it to operating
temperature. Shut off the engine.
9. Let the machine cool down for and carefully
re--check the level of the radiator coolant.
There should be enough room to poor
another 1/2 gallon of coolant in. If
not----repeat steps 4 thru 8.
10. If the machine overheats----repeat steps 4
thru 8.
NOTE: There may be air trapped in one of the
radiator hoses. It might take one or two tries to
completely purge all of the air from the cooling
system.

ENGINE--DIESEL
7-1
7400 MM428 (9--01)
CONTENTS
Page
LUBRICATION 7-3........................
ENGINE OIL 7-3.......................
COOLING SYSTEM 7-3...................
ENGINE FAN BELT 7-4.................
AIR INTAKE SYSTEM 7-4.................
AIR FILTER INDICATOR 7-4............
AIR FILTER 7-4.......................
TO REPLACE AIR FILTER ELEMENT 7-5
FUEL SYSTEM 7-6.......................
FUEL FILTER 7-6......................
TO REPLACE THE FUEL FILTER
CARTRIDGE 7-6....................
FUEL LINES 7-7.......................
TO PRIME FUEL SYSTEM 7-7..........
TO REPLACE ENGINE ALTERNATOR 7-8..
TO REPLACE ENGINE STARTER 7-10.....
TO REMOVE ENGINE 7-12................
TO INSTALL ENGINE 7-14................
TO PURGE AIR FROM RADIATOR 7-16....
DIESEL ENGINE SERVICE MANUAL
KUBOTA V1505 B (E)
TENNANT Part Number 84660

ENGINE--DIESEL
7-2 7400 MM428 (12--98)

ENGINE--DIESEL
7-3
7400 MM428 (12--98)
INTRODUCTION
This section includes repair information on the
engine and related systems, such as fuel,
electrical, and drive belts.

ENGINE--DIESEL
7-4 7400 MM428 (12--98)
LUBRICATION
ENGINE OIL
Check the engine oil level daily. Change the
engine oil and oil filter every 100 hours of machine
operation. Use 10W30 SAE--CC/CD rated engine
oil.
Fill the engine with oil to the level indicated on the
oil dipstick. The engine oil capacity is 6 L (6.3 qt)
with out the oil filter.
COOLING SYSTEM
Check the radiator coolant level every 100 hours
of operation. Use clean water mixed with a
permanent-type, ethylene glycol antifreeze to a
-- 3 4 _C(--30_F) rating.
FOR SAFETY: When Servicing Machine,
Avoid Contact With Hot Engine Coolant.
ATTENTION! Never pour cold water or
cold antifreeze into the radiator of an
overheated engine. Allow the engine to
cool down to avoid cracking the
cylinder head or block. Keep the engine
running while adding water.
Check the radiator hoses and clamps every 200
hours of operation. Tighten the clamps if they are
loose. Replace the hoses and clamps if the hoses
are cracked, harden, or swollen.
Check the radiator core exterior and hydraulic
cooler fins for debris every 100 hours of
operation. Blow or rinse all dust, which may have
collected on the radiator, in through the grille and
radiator fins, opposite the direction of normal air
flow. The grille and hydraulic cooler open for
easier cleaning. Be careful not to bend the cooling
fins when cleaning. Clean thoroughly to prevent
the fins becoming encrusted with dust. Clean the
radiator and cooler only after the radiator has
cooled to avoid cracking.
FOR SAFETY: When Servicing Machine,
Wear Eye And Ear Protection When
Using Pressurized Air Or Water.
Flush the radiator and the cooling system every
400 hours of operation, using a dependable
cleaning compound.

ENGINE--DIESEL
7-5
7400 MM428 (12--98)
ENGINE FAN BELT
The engine fan belt is driven by the engine
crankshaft pulley and drives the alternator pulley.
Proper belt tension is obtained when the belt
deflects 7 to 9 mm (0.28 to 0.35 in) from a force
of 10 kg (22 lb) applied at the mid-point of the
longest span.
Check and adjust the belt tension every 100 hours
of operation.
WARNING: Moving belt and fan. Keep
away.
AIR INTAKE SYSTEM
AIR FILTER INDICATOR
The air filter indicator shows when to clean or
replace the air filter element. Check the indicator
daily. The indicator’s red line will move as the air
filter element fills with dirt. Do not clean or replace
the air filter element until the red line reaches 5
kPa (20 in H2O) and the ”SERVICE WHEN RED”
window is filled with red. The indicator’s red line
may return to a lower reading on the scale when
the engine shuts off. The red line will return to a
correct reading after the engine runs for a while.
Reset the air filter indicator by pushing the reset
button on the end of the indicator after cleaning or
replacing the air filter element.
AIR FILTER
The engine air filter housing has a dust cap and a
dry cartridge-type air filter element. Empty the
dust cap daily. The air filter must be replaced
whenever the filter element is damaged or has
been cleaned three times.
Machines with the heavy duty air filter option have
a safety element. It is inside the standard
element. Replace, do not clean this element after
the regular element has been damaged or
cleaned three times.
Service the air filter element only when the air
filter indicator shows restriction in the air intake
system. Do not remove the air filter element
unless it is restricting air flow.

ENGINE--DIESEL
7-6 7400 MM428 (12--98)
TO REPLACE AIR FILTER ELEMENT
FOR SAFETY: Before Leaving Or
Servicing Machine: Stop On Level
Surface, Set The Parking Brake, Turn Off
Machine And Remove Key.
1. Open the engine cover and side door.
2. Unscrew the clamp ring on the filter.
3. Remove the dust cap.
4. Empty the dust cap.
5. Remove the filter wing nut.
6. Pull the filter element out of the filter
housing.
7. Clean the interior of the air cleaner housing
with a camp cloth. Clean the element
housing sealing surfaces.
8. Using an air hose, direct dry, clean air
maximum 205 kPa (30 psi) up and down
pleats on the inside of the filter. Do not rap,
tap, or pound dust out of the element.
FOR SAFETY: When Servicing Machine,
Wear Eye And Ear Protection When
Using Pressurized Air Or Water.
9. After cleaning the air filter element, inspect it
for damage by placing a bright light inside.
The slightest rupture requires replacement
of the filter. Clean and inspect the seals on
the ends of the element. They should be
unbroken and flexible. Remember to replace
the element after cleaning it three times.
10. Install the new or cleaned filter element so
the fins on the element are at the intake end
of the air cleaner. Be careful not to damage
the fins. Make sure the element is seating
evenly. Tighten the element wing nut.
11. Install the dust cap with the arrows pointing
up. Tighten the clamp ring to hold it in place.
Check all intake hose connections for leaks
or abrasions.
12. Reset the air filter restriction indicator.
13. Close the access doors.

ENGINE--DIESEL
7-7
7400 MM428 (12--98)
FUEL SYSTEM -- DIESEL
The diesel fuel system is made up of five basic
components which are: fuel tank, fuel filter/water
trap, fuel pump, injection pump, and injectors.
Fuel flows from the fuel tank through the fuel filter/
water trap. The water trap-filter separates water
and impurities from the fuel. From the fuel water
trap-filter, fuel is drawn through the electric fuel
pump and pumped to the injection pump. The
injection pump pressurizes and sends fuel to the
injectors. The injectors atomize and inject proper
amounts of fuel into the combustion chamber at
the proper times. Excess fuel is returned to the
fuel tank through an overflow pipe.
FUEL FILTER
The fuel filter cartridge filters impurities from the
fuel. It is located low on the left side of the engine
block
TO REPLACE THE FUEL FILTER CARTRIDGE
FOR SAFETY: Before Leaving Or
Servicing Machine; Stop On Level
Surface, Set Parking Brake, And Turn
Off Machine.
1. Loosen the unit vent plug and open the
water trap drain to drain diesel fuel.
2. Remove the filter cartridge from the filter
head.
3. Lubricate the o-ring of the new filter
cartridge and spin it onto the filter head.
4. Bleed the fuel lines of air as described in TO
PRIME FUEL SYSTEM instructions.

ENGINE--DIESEL
7-8 7400 MM428 (12--98)
FUEL LINES
Check the fuel lines every 50 hours of operation.
If the clamp band is loose, apply oil to the screw
of the band, and securely tighten the band.
The rubber fuel lines can become worn-out
whether the engine has been used much or not.
Replace the fuel lines and clamp bands every two
years.
If the fuel lines and clamp bands are found worn
or damaged before two years’ time, replace or
repair them at once. Bleed the fuel system after
replacement of any of the fuel lines, see TO
PRIME THE FUEL SYSTEM. When the fuel lines
are not installed, plug both ends with clean cloth
or paper to prevent dirt from entering the lines.
Dirt in the lines can cause fuel injection pump
malfunction.
PRIMING FUEL SYSTEM
Typical diesel fuel systems require priming to
remove pockets of air in the fuel lines and fuel
components. This is usually required after running
out of fuel, changing fuel filter elements or
repairing a fuel system component. Air in the fuel
system prevents smooth engine operation.
This fuel system however is self-priming. The
return line comes from the top of the injector that
causes all air to escape through the return line.
TO PRIME FUEL SYSTEM
FOR SAFETY: Before Leaving Or
Servicing Machine; Stop On Level
Surface, Set Parking Brake, And Turn
Off Machine.
1. Make sure the fuel tank is full.
2. Open the air vent on top of the fuel filter.
3. Start the engine, operate it for one minute,
then stop it; or operate the starter motor in
ten-second intervals until a steady stream of
fuel flows from the vent.
4. Close the air vent and shut off the engine.
5. Clean up any fuel that was spilled during the
bleeding process.

ENGINE--DIESEL
7-9
7400 MM428 (12--98)
TO REPLACE ALTERNATOR ON DIESEL
ENGINE
FOR SAFETY: Before Leaving Or
Servicing Machine; Stop On Level
Surface, Set Parking Brake, Turn Off
Machine And Remove Key.
1. Raise the operators seat, engage the prop
rod, and disconnect the battery cables from
the battery.
2. Open the machine engine cover and side
door. Remove the side door from the
machine.
3. Remove the two hex screws holding the fan
belt cover to the front of the engine. Remove
the cover.
4. Disconnect the wires from the back of the
alternator.
5. Remove the hex screw from the top of the
alternator.
6. Loosen the lower hex screw and nyloc nut
and push the alternator in toward the engine.
Remove the V--belt from the alternator drive
pulley.
7. Remove the hex screw and nyloc nut from
the bottom of the alternator. Retain the
spacer. Remove the alternator.
8. If the new alternator does not have a drive
pulley----remove the hex nut and washer
holding the drive pulley to the old alternator.
Install the drive pulley on the new alternator
and tighten tight.
9. Install the new alternator back in the
machine. Reinstall the lower hex screw,
spacer, and nyloc nut. Leave loose for now.
10. Reinstall the hex screw in the upper arm and
the top of the alternator. Leave loose for
now.

ENGINE--DIESEL
7-10 7400 MM428 (12--98)
11. Reinstall the V--belt on the alternator drive
pulley.
12. Pull the alternator away from the engine to
tighten the V--belt. Tighten the upper hex
screw tight.
13. Reconnect the wires to the back of the new
alternator. See schematic in the
ELECTRICAL section.
14. Reinstall the belt cover to the front of the
engine. Hand tighten the hex screws tight.
15. Reconnect the battery cables, close the
operators seat and start the machine.
16. Check the new alternator for proper
operation.

ENGINE--DIESEL
7-11
7400 MM428 (12--98)
TO REPLACE STARTER ON DIESEL ENGINE
FOR SAFETY: Before Leaving Or
Servicing Machine; Stop On Level
Surface, Set Parking Brake, Turn Off
Machine And Remove Key.
1. Raise the operators seat, engage the prop
rod, and disconnect the battery cables from
the battery.
2. Open the machine front cover, engine cover,
and side door. Remove the side door from
the machine.
3. The vacuum fan assembly can be removed
for better access to the starter. See TO
REMOVE VACUUM FAN instructions in the
SCRUBBING section.
4. Remove the air cleaner intake tube from the
air cleaner and machine frame.
5. Reach in through the left side of the engine
and disconnect the battery cable and
electrical wires leading to the starter.
6. Reach in through the left side of the engine
and remove the two hex screws holding the
starter to the bellhousing.
7. Remove the starter out through the area of
the vacuum fan and engine oil filter.
8. Position the new starter in the machine.
9. Reinstall the two hex screws and tighten to
18 -- 24 Nm (15 -- 20 ft lb).
10. Reconnect the battery cable and electrical
wires to the starter. See schematic in the
ELECTRICAL section.

ENGINE--DIESEL
7-12 7400 MM428 (12--98)
11. Reinstall the air cleaner intake tube to the air
cleaner and machine frame.
12. If the vacuum fan was removed----reinstall.
See TO INSTALL VACUUM FAN
instructions in the SCRUBBING section.
13. Reconnect the battery cables to the battery
and close the operators seat.
14. Reinstall the engine side door and close the
covers.
15. Start the machine.

ENGINE--DIESEL
7-13
7400 MM428 (12--98)
TO REMOVE DIESEL ENGINE
FOR SAFETY: Before Leaving Or
Servicing Machine; Stop On Level
Surface, Set Parking Brake., Turn Off
Machine And Remove Key.
1. Pivot the operators seat to the open position
and engage the prop rod.
2. Disconnect the battery cables and remove
the battery.
NOTE: The battery tray can also be removed for
better access to the propel pump
3. Remove the detergent tank and the rubber
sound flap from the machine.
4. Remove the two hex screws holding the
propel pump to the engine bellhousing
NOTE: The main suction line to the accessory
pump is held, by plastic ties, in a bundle of hoses
near the main valve. Remove the plastic ties to
gain slack in the suction line to ease pump
removal.
5. Remove the two hex screws holding the
hydraulic flow valve to back, left of the
engine mount. Do not disconnect any
hydraulic hoses.
6. Pull the propel pump out of the bellhousing
and drive coupler. Do not disconnect any
hydraulic hoses.
7. Open the machine front cover, engine cover,
and side door. Remove the side door from
the machine.
8. Remove the vacuum hose from the vacuum
fan and the recovery tank.
9. The vacuum fan assembly can be removed
for better access to the engine. See TO
REMOVE VACUUM FAN instructions in the
SCRUBBING section.
NOTE: The engine hood must be supported in the
open position before the next step can be
completed.
10. Remove the clips on the bottom of the
engine hood gas springs. Remove the gas
springs from the ball studs on the support
channel.

ENGINE--DIESEL
7-14 7400 MM428 (12--98)
11. Remove the hex screws holding the support
channel to the tank lintel and hood lintel.
Remove the support channel from the
machine.
12. Drain the radiator coolant.
13. Remove the radiator hoses where they
connect to the engine.
14. Drain the engine oil.
NOTE: Disconnect the engine oil drain hose from
the oil pan before lifting the engine completely out
of the machine.
15. Disconnect the exhaust pipe at the engine
manifold.
16. Disconnect the wire harness from all of the
engine components and place it out of the
way.
17. Disconnect the engine ground strap from
frame.
18. Disconnect the battery cable and electric
wires from the engine starter.
19. Disconnect the fuel line at the fuel
filter/water separator on the left side of the
engine. Disconnect the small fuel return line.
20. Using an overhead hoist, hook a chain
through two pick--up points on the engine.
Put a slight amount of tension on the chain.
21. Remove the three M12 hex screws and
nyloc nuts holding the motor mounts to the
rubber isolators on the machine frame.
22. Engine can now be carefully lifted out.

ENGINE--DIESEL
7-15
7400 MM428 (12--98)
TO INSTALL DIESEL ENGINE
FOR SAFETY: Before Leaving Or
Servicing Machine; Stop On Level
Surface, Set Parking Brake., Turn Off
Machine And Remove Key.
1. Using a overhead hoist, hook a chain
through the two pick--up points on top of the
engine. Carefully position the engine back in
the engine compartment.
2. Carefully Lower the engine assembly down
on the the motor mounts.
NOTE: Make sure the hoses, wire harness,
exhaust pipe, and propel pump are pulled back
out of the way when lowering the engine
assembly in place.
3. Reinstall the three M12 hex screws in the
three motor mount isolators. Tighten to
64 -- 83 Nm (50 -- 60 ft lb)
4. Reconnect the ground cable from the
bellhousing to the machine frame.
5. Reinstall the flow valve on the back, left of
the bellhousing.
6. Reconnect the battery cable and electrical
wires to the starter. See schematic in the
ELECTRICAL section.
7. Reconnect the wire harness to engine
components, alternator, governor actuator,
oil switch, and temperature sender. See
schematic in the ELECTRICAL section.
8. Reinstall the propel pump back in the
bellhousing. Use a small amount of blue
loctite 242 on the threads. Reinstall the two
hex screws. Tighten to 64 -- 83 Nm
(50 -- 60 ft lb).
NOTE: Make sure the splines on pump line up
with splines in coupler when installing pump.
9. Reinstall the detergent tank in the seat
support area.
10. Reinstall the battery tray and battery.
11. Reinstall the exhaust pipe back on the
manifold. Reinstall the muffler clamp and
tighten tight.

ENGINE--DIESEL
7-16 7400 MM428 (12--98)
12. Reconnect the fuel line at the fuel filter/water
separator on the left side of the engine.
13. Fill the engine with the proper grade of oil.
14. Reinstall the radiator hoses to the engine
and fill the radiator with coolant. See TO
PURGE AIR FROM RADIATOR instructions.
15. If the vacuum fan was removed----reinstall.
See TO INSTALL VACUUM FAN
instructions in the SCRUBBING section.
16. Reinstall the vacuum hose on the recovery
tank and vacuum housing.
17. Reinstall the support channel to the tank
lintel and hood lintel. Reinstall the four hex
screws and tighten to 18 -- 24 Nm
(15 -- 20 ft lb).
18. Reinstall the engine hood gas springs on the
ball studs on the support channel. Reinstall
the two clips.
19. Reconnect the battery cables.
20. Disengage the prop rod and lower the seat.
21. Jack up the front of the machine and place
jack stands under the frame.
FOR SAFETY: Block machine tires
before jacking machine up. Jack
machine up at designated locations
only. Block machine up with jack stands
22. Start the machine. Check the engine,
hydraulic motors, and pumps for leaks.
23. Reinstall the engine side door and close the
covers.

ENGINE--DIESEL
7-17
7400 MM428 (12--98)
TO PURGE AIR FROM RADIATOR
FOR SAFETY: Before Leaving Or
Servicing Machine; Stop On Level
Surface, Set Parking Brake., Turn Off
Machine And Remove Key.
1. Make sure that both radiator hoses are
connected to the engine.
2. Remove the radiator cap and pour in
approximately 1--1/2 gallons of coolant.
3. Open the engine cover and side door.
4. Loosen the hose clamp on the upper
radiator hose. This is the hose on the
thermostat housing.
5. Break the hose loose from the neck of the
thermostat housing and slowly pull the hose
off the neck.
6. Keep the hose off the neck until coolant
starts to flow out of the hose.
7. Quickly place the hose back on the neck of
the thermostat housing. Re--tighten the hose
clamp.
8. Start the machine and run it to operating
temperature. Shut off the engine.
9. Let the machine cool down for and carefully
re--check the level of the radiator coolant.
There should be enough room to poor
another 1/2 gallon of coolant in. If
not----repeat steps 4 thru 8.
10. If the machine over heats----repeat steps 4
thru 8.
NOTE: There may be air trapped in one of the
radiator hoses. It might take one or two tries to
completely purge all of the air from the cooling
system.

ENGINE--DIESEL
7-18 7400 MM428 (12--98)