I Mop XXL Service Manual Tennant Xl Walk Behind Floor Scrubber
Tennant-I-Mop-Xxl-Walk-Behind-Floor-Scrubber-Service-Manual tennant-i-mop-xxl-walk-behind-floor-scrubber-service-manual tennant-i-mop-xxl-walk-behind-floor-scrubber-service-manual 2844 file product_file sweepscrub 3:
2018-06-13
: Sweepscrub Tennant-I-Mop-Xl-Walk-Behind-Floor-Scrubber-Service-Manual tennant-i-mop-xl-walk-behind-floor-scrubber-service-manual 2758 file product_file
Open the PDF directly: View PDF .
Page Count: 64
- i-mop xxl – ServiceManual
- SUMMARY
- CHAPTER 1 – GENERAL INFORM
- CHAPTER 2 – SAFETY
- CHAPTER 3 – MACHINE DESCRIPTION
- CHAPTER 4 – SCHEDULED MAINTENANCE
- CHAPTER 5 – I-MOP BRUSHMOTOR REPLACEMENTINSTRUCTIONS
- CHAPTER 6 – I-MOP MAGNETIC VALVE REPLACEMENTINSTRUCTIONS
- CHAPTER 7 – I-MOP MAINBOARD ASSEMBLY INSTRUCTIONS
- CHAPTER 8 – I-MOP MAIN LEVER REPLACEMENT
- CHAPTER 9 – I-MOP DASHBOARD ASSEMBLYINSTRUCTIONS
- CHAPTER 10 – I-MOP TUBES REPLACEMENT INSTRUCTIONS
- CHAPTER 11 – I-MOP VACUUM MOTOR REPLAC
- CHAPTER 12 – I-MOP WHEEL AND WHEEL SUPPORTREPLACEMENT
- CHAPTER 13 – I-MOP FILTER AND DEFLECTORREPLACEMENT INSTRUCTIONS
- CHAPTER 14 – SQUEEGEE WHEELS CLEANING
- CHAPTER 15 – WATER SAFE INTERVAL ADJUSTMENT
- CHAPTER 16 – ELECTRICAL SCHEME
- CHAPTER 17 – BATTERIES
- CHAPTER 18 – CHARGER
- CHAPTER 19 – REPAIR FLOW CHART
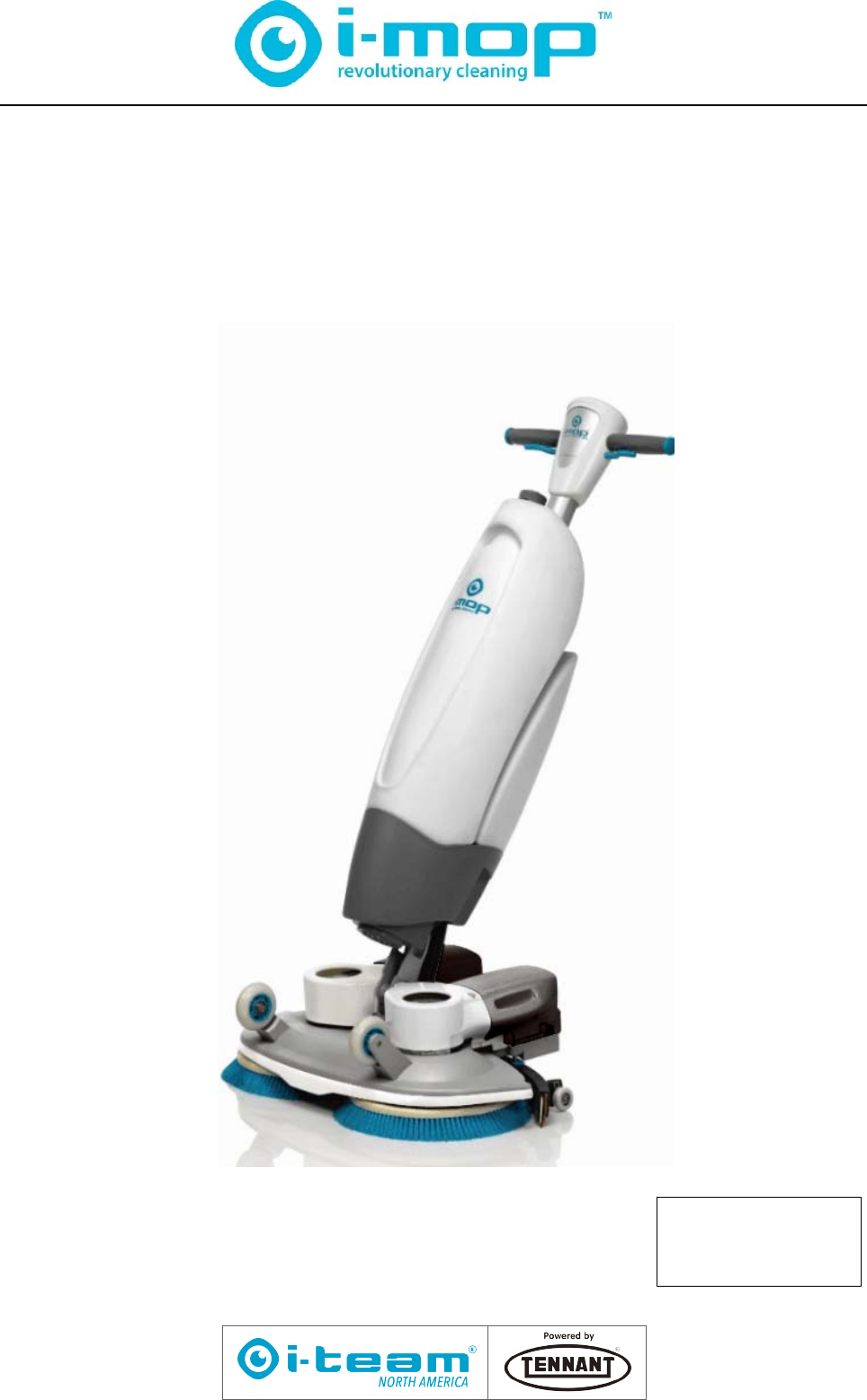
1
/
64
i-mop xxl – Service
Manual
Jan.2018
Warning: read the
instructions before
using the machine

2
/
64
SUMMARY
CHAPTER 1 – GENERAL INFORMATION ....................................................................................................... 4
1.1 CONVENTIONS ................................................................................................................................... 4
1.2 WORKING ON THE MACHINE............................................................................................................ 4
1.3 TRANSPORTING THE MACHINE ....................................................................................................... 4
1.4 OTHER REFERENCE MANUALS ....................................................................................................... 4
CHAPTER 2 – SAFETY..................................................................................................................................... 5
2.1 SYMBOLS USED ................................................................................................................................. 5
2.2 GENERAL INSTRUCTIONS ................................................................................................................ 5
CHAPTER 3 – MACHINE DESCRIPTION ........................................................................................................ 7
3.1 TECHNICAL CHARACTERISTICS ...................................................................................................... 7
3.2 DESCRIPTION ..................................................................................................................................... 8
CHAPTER 4 – SCHEDULED MAINTENANCE ............................................................................................... 12
4.1 SCHEDULED MAINTENANCE PLAN ............................................................................................... 12
CHAPTER 5 – I-MOP BRUSHMOTOR REPLACEMENT INSTRUCTIONS................................................... 13
CHAPTER 6 – I-MOP MAGNETIC VALVE REPLACEMENT INSTRUCTIONS .............................................. 19
CHAPTER 7 – I-MOP MAINBOARD ASSEMBLY INSTRUCTIONS…….……………….................................. 22
CHAPTER 8 – I-MOP MAIN LEVER REPLACEMENT ….................................................................................29
CHAPTER 9 – I-MOP DASHBOARD ASSEMBLY INSTRUCTIONS…………………..................................... 34
CHAPTER 10 – I-MOP TUBES REPLACEMENT INSTRUCTIONS............................................................... 38
1.Brushtubereplacement–WATERCHANNELØ4MM.................................................................................... 38
2.Maintubereplacement–TRANSPARENTWATERCHANNELØ6MM............................................................... 41
3.Internaltubereplacement–WATERCHANNELØ6MM................................................................................. 45
CHAPTER 11 – I-MOP VACUUM MOTOR REPLACEMENT......................................................................... 47
CHAPTER 12 – I-MOP WHEEL AND WHEEL SUPPORT REPLACEMENT ................................................. 50
1. Wheelreplacement.................................................................................................................................... 50
2. Wheelsupportreplacement........................................................................................................................ 50
CHAPTER 13 – I-MOP FILTER AND DEFLECTOR REPLACEMENT INSTRUCTIONS............................... 54
CHAPTER 14 – SQUEEGEE WHEELS CLEANING………………………. ...................................................... 55

3
/
64
CHAPTER 15 – WATER SAFE INTERVAL ADJUSTMENT ........................................................................... 56
CHAPTER 16 – ELECTRICAL SCHEME........................................................................................................ 57
CHAPTER 17 – BATTERIES .......................................................................................................................... 58
DATASHEET ............................................................................................................................................ 58
ASSEMBLY INSTRUCTIONS .................................................................................................................. 59
CHAPTER 18 – CHARGER ............................................................................................................................ 62
DATASHEET ............................................................................................................................................ 62
REFERENCE STANDARDS .................................................................................................................... 62
CHAPTER 19 – REPAIR FLOW CHART ........................................................................................................63

4
/
64
CHAPTER 1 – GENERAL INFORMATION
1.1CONVENTIONS
All references to forward, backward, front, rear, right, left indicated in this manual shall be considered as
referred to the operator in the working position with the hands on the handle and the sticker facing the
direction of travel.
1.2WORKINGONTHEMACHINE
WARNING!
Do not work close to the machine, without adequate fixed safety supports.
1.3TRANSPORTINGTHEMACHINE
WARNING!
Before transporting the machine with a conveyance, make sure that:
All the tanks are empty and removed from the machine
The batteries are extracted from the machine
The machine is securely fastened in accordance with the means of transportation (air, sea, road etc.)
1.4OTHERREFERENCEMANUALS
The following manuals are available from the manufacturer:
User and Maintenance Manual

5
/
64
CHAPTER 2 – SAFETY
The following symbols are used to indicate potential hazardous conditions. Always read this information with
attention and take any precautions necessary to protect the people and things.
2.1SYMBOLSUSED
DANGER!
Indicates a danger with risk, possibly even deadly for the user.
WARNING!
Indicates a potential risk of injury to persons or damage to devices.
CAUTION!
Indicates a caution or a note on key functions or on useful features. Pay careful attention to text blocks
indicated by this symbol.
&
Indicates a note on key functions or on useful features.
CONSULTATION
Indicates the need to consult the User Manual before carrying out any operation.
2.2GENERALINSTRUCTIONS
Specific cautions and warnings are described below to highlight the potential dangers of damage to the
machine and/or people.
DANGER!
Before carrying out any maintenance/repair, remove the batteries as described in user manual.
This machine should only be used by properly trained and authorized personnel.
Do not operate this machine in environments where there are harmful, hazardous, flammable, and/or
explosive powders, liquids or vapors.
Keep sparks, flames and incandescent material, away from the batteries.
When charging the batteries, perform the operation only in well ventilated areas and away from
naked flames.
Remove all jewelry when working with electrical components.

6
/
64
WARNING!
Before performing any maintenance/repair, carefully read all the instructions relevant to the
maintenance/repair.
Do not use the machine for purposes other than those listed in the user manual. Only use
accessories recommended by the manufacturer.
Always protect the machine from sun, rain, and other weather conditions, both when on and off, this is
to avoid the risk of electrical shock. Store the machine indoors
Do not use the machine as a means of transport.
Do not leave the machine unattended without making sure that the machine itself cannot move
independently.
Do not use the machine in particularly dusty environments.
Do not use the machine on ramps or inclinations greater than 6%.
Do not knock shelves or scaffolding, especially if there is a danger of falling objects.
Do not let any object penetrate the openings of the machine. Do not use the machine if the openings
are blocked; keep the openings of the machine free of dust, lint, hair and any other foreign body that
can reduce air flow.
Do not remove or alter the plates affixed to the machine by the manufacturer.
The usage temperature of the machine must be between 0°C and +40 °C.
The storage temperature of the machine must be between 0°C and +40 °C.
The humidity must be between 30% and 95%.
Do not tamper with the protections in place for the machine, for any reason.
Do not wash the machine with direct jets of water or pressure or with corrosive substances.
Before working on the electrical components wear ESD gloves to avoid the electrostatic discharge
(ESD), which may result in damage to components on the PCB.
Before using the external battery charger appliance, make sure that the frequency and voltage as
indicated on the machine's registration plate match the mains voltage.
Do not charge the batteries if the power cord or plug are damaged.
Do not smoke when charging the batteries.
To reduce the risk of fire, electric shock, or injury, do not leave the machine connected to the mains
when unattended. Disconnect the machine from the socket when not being used and before
maintenance.
Keep the power cord away from hot surfaces.
Take the necessary measures to ensure that hair, jewelry and/or other loose parts cannot be
caught by any moving parts of the machine.
If replacing parts, ask a Dealer or Authorized Retailer for Original Spare Parts (OSP).
When the machine is used correctly in accordance with the terms of use, the vibrations of the
machine will not cause any dangerous situations. The level of the vibrations are well within the legal
limits.
When transferring the machine with temperatures below freezing point, be careful because the water
in the tanks or hoses may freeze and seriously damage the machine.
Only use the brushes supplied with the machine and those specified in User Manual. The use of
other brushes can compromise your safety, and might damage the machine.
When it is necessary to tilt the machine for maintenance, remove the batteries first.
When the machine reaches the end of the lifecycle, please take care of proper removal and
disposal, due to the possible presence inside of toxic and poisonous materials (e.g. Batteries, PCB
etc.) These materials are subject to regulations which provide for the disposal at designated
appropriate centers in the area.
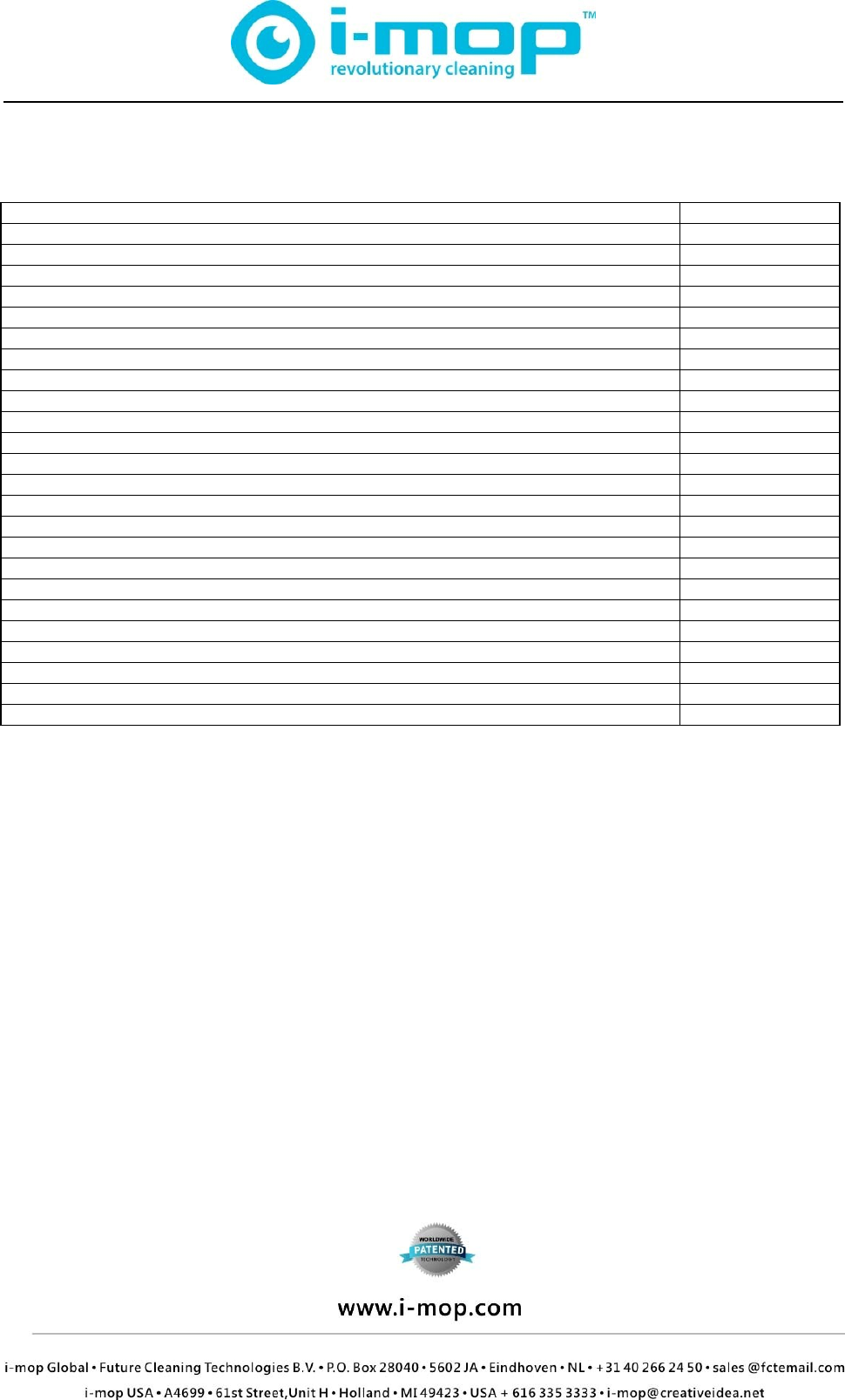
7
/
64
CHAPTER 3 – MACHINE DESCRIPTION
3.1TECHNICALCHARACTERISTICS
DESCRIPTION
V
ALUES
Voltage 24 V
Washed track 64 cm
Vacuum 5.8 kPa
Solution tank capacit
y
5L
Recovery
t
ank capacity 5L
Disc brush speed 350 rpm
Number of disc brushes 2
Disc brush pressure 24.6 kg
Maximum floor slope for using the machine 6%
No. of batteries 2
Built-in battery charger No
Theoretical hourly yield 2300 m2
Estimated hourly yield 1700 m2
A
utonom
y
70 min
Width of machine passage 64 cm
Machine body dimensions, with squeegee and brush (length x height x width) 43x124x69 cm
Machine weight empty (without batteries, with empty tanks) 21 kg
Machine weight heavy (with batteries, with a full tank) 35.3 kg
Disc brush motor 170 W (x2)
Vacuum motor 180 W
Construction standards CE
Protection class IP2X
Sound pressure level A in the operating position 76 dB(A)
Sound power level A 74 dB(A)

8
/
64
3.2DESCRIPTION
Control panel and controls
1. A l u m i n u m Dashboard
2. Battery charger status in graphic scale
3. Light indication of the brush working
4. Light indication of the vacuum working
5. Select switch
6. Water safe button
7. Light indication of the interval flow rate working
1
2
3
4
5
6
7

9
/
64
External view
1. Handle
2. Lever
3. Squeegee
4. Brushes
5. Solution tank
6. Transport handle
1
2
5
6
3
4

10
/
64
7. Recovery tank
8. Left battery
9. Right battery
10. Transport wheels
11. Brush motors
9
7
8
10
11

11
/
64
Internal view
1. Vacuum motor filter
2. Transparent plastic deflector
3. Vacuum hose
2
3
1

12
/
64
CHAPTER 4 – SCHEDULED MAINTENANCE
The service life of the machine and its maximum safety of operation are guaranteed by careful and regular
maintenance.
WARNING!
See the chapter GENERAL INFORMATION AND SAFETY.
The Scheduled Maintenance Plan is detailed as below. The frequency specified may be subject to change
depending on particular work conditions, to be defined by the maintenance manager.
The maintenance instructions, listed in the following Scheduled Maintenance Plan, are described in following
chapters describing maintenance/replacement procedures.
4.1SCHEDULEDMAINTENANCEPLAN
OPERATION
DAILY OPERATION OR
AFTER USING THE
MACHINE
MONTHLY OR EVERY
100 HOURS
EVERY SI
X
MONTHS
OR EVERY 400
HOURS
Squeegee cleaning ⱱ
Clean disc brush ⱱ
Charge batteries ⱱ
Check vacuum filter ⱱ
Clean transparent
plastic deflector ⱱ
Clean squeegee wheels ⱱ
Check/replace
squeegee blades ⱱ
Clean filter for the
detergent solution (or
washing water) ⱱ
Clean nozzles ⱱ
Check tightening of
screws and nuts ⱱ (1)(2)
(1): and after the first 8 hours of operation
(2): maintenance to be carried out by an US Group Authorized Service Centre

13
/
64
CHAPTER 5 – I-MOP BRUSHMOTOR REPLACEMENT
INSTRUCTIONS
1. Disassemble the two BRUSH MOTOR COOLING COVERs by removing the 4 SCREWS EJOT DELTA
PT 50X14, then remove the two BRUSH MOTOR COOLING COVERs
2. Disconnect the cables that are protected with the HEAT SHRINKBALE TUBE and unsolder the cables or
cut them
3. Remove the 6pcs SCREW WN 5451 50X14 EJOT DELTA
4. Remove the 2pcs COVER BRUSH MOTOR SCREW
,
13-1 13-2
13-413-3
13-6
13-5

14
/
64
5. Remove 2pcs COUNTER SUNK BOLT M5X18.5 at the center of the motor shaft
6. Remove the2pcs DRIVING WHEEL BOTTOM
7. Remove the BRUSH UNIT BOTTOM PART by unscrewing 13pc SCREWS SOCKET HEAD CAP
M5X10 with attention to the LOCTITE 222
8. Remove the BRUSH UNIT BOTTOM PART
9. Remove the BRUSH MOTOR HELICAL GEARS
14-2
14-1
14-4
14-3
14-5

15
/
64
10. Remove the BRUSH MOTOR FIXATION RUBBER and the BRUSH MOTOR SUPPORT RUBBER
11. Remove the DRIVING WHEEL TOP from the shaft of the BRUSH MOTOR HELICAL GEARS if needed
with an extractor / pulley lifter
12. Remove the SUPPORT DISC GEARBOX SIDE
Puller Lifter
See toolbox
13. Remove the BRUSH MOTOR CONSTRUCTION RING by loosening the 4 SCREWS COUNTER
SUNK M6X16
14. Put the BRUSH MOTOR CONSTRUCTION RING on the BRUSH MOTOR HELICAL GEARS and block
it with 4 SCREWS COUNTER SUNK M6X16 dipped in LOCTITE 222
15-215-1
15-3 15-4
15-5

16
/
64
15. Put the DRIVING WHEEL TOP on the shaft of the BRUSH MOTOR HELICAL GEARS
16. Put the BRUSH MOTOR SUPPORT RUBBER in the upper side of the BRUSH MOTOR HELICAL
GEARS by pushing it close to the flange
17. Put the BRUSH MOTOR FIXATION RUBBER in the lower side of the BRUSH MOTOR HELICAL
GEARS and block it together with the BRUSH MOTOR SUPPORT RUBBER matching the pins and the
holes of the two gaskets
18. Put the 2 BRUSH MOTORS HELICAL GEARS on the BRUSH MOTOR CONSTRUCTION COVER
19. The proper connections are as follows: red wire - red wire for the left brush motor and red wire - black
wire for the right brush motor.
16-1
16-2
16-4
16-3

17
/
64
LEFT RIGHT
20. Put the BRUSH UNIT PROTECTOR on the BRUSH MOTOR CONSTRUCTION COVER and close
everything with the BRUSH UNIT BOTTOM PART
21. Block the BRUSH UNIT BOTTOM PART with the SCREWS SOCKET HEAD CAP M5X10 dipped in the
LOCTITE 222
22. Put the DRIVING WHEEL BOTTOM, with attention to the side of mounting, on the DRIVING WHEEL
TOP
23. Fasten 2pcs COUNTER SUNK BOLT M5X18.5 at the center of the motor shaft
24. Put the two COVER BRUSH MOTOR SCREW
17-217-1
17-417-3
17-6
17-5

18
/
64
25. Fasten 3pcs EJOT SCREW 50X14 each side to fix the COVER BRUSH MOTOR SCREW
26. Adjust the cables in the correct position and re-assemble the BRUSH MOTOR CONSTRUCTION
COVER by fastening 2 SCREWS EJOT on each side
18-2
18-1
18-3
18-5
18-4

19
/
64
CHAPTER 6 – I-MOP MAGNETIC VALVE REPLACEMENT
INSTRUCTIONS
1. WARNING! Wear gloves when you touch electrical components to avoid ESD.
2. Remove the 4 SCREWS M4X12 CROSS HEAD and open the MOTOR UNIT TOP
3. Remove the 2 SCREWS EJOT DELTA PT 50X14 and extract the ASSY MAGNETIC VALVE
4. Unplug the PCB MAGNETIC VALVE & VAC MOTOR CONNECTION, the cables of the ASSY
MAGNETIC VALVE are the external ones. If needed remove the SCREW PARKER 2.9X16
5. Remove the VALVE COUPLINGS and the CHANNELS Ø6 MM from the ASSY MAGNETIC VALVE
6. Replace the ASSY MAGNETIC VALVE
19-3
19-2
19-1
19-519-4
19-6

20
/
64
7. Put the MAGNETIC VALVE COUPLING on the WATER CHANNEL Ø6 MM, then connect it to the
ASSY MAGNETIC VALVE, Block the TRANSPARENT WATER CHANNEL Ø6 MM on the ASSY
MAGNETIC VALVE with the MAGNETIC VALVE COUPLING
8. Insert the transparent exhausting hose to the copper tube head.
20-2
20-1
20-3
20-4

21
/
64
9. Close the MOTOR UNIT COVER with attention to not press the cables or the hoses
10. Screw the MOTOR UNIT TOP on the MOTOR UNIT COVER with 4 SCREWS CROSS HEAD M4X12
21-2
21-1

22
/
65
CHAPTER 7 – I-MOP MAINBOARD ASSEMBLY INSTRUCTIONS
1. WARNING! Wear gloves when you touch electrical components to avoid ESD damage.
See Toolbox
2. Disassemble the two BRUSH MOTOR COOLING COVERS by removing the 4 SCREWS EJOT DELTA
PT 50X14, then remove the two BRUSH MOTOR COOLING COVERs
3. Disconnect the cables that are protected with the HEAT SHRINK TUBING and unsolder the cables or cut
them
4. Disconnect MAIN LEVER COVER and MAIN LEVER HOUSING by removing 8 screw EJOT DELTA PT
50X14
22-1
22-3
22-2
22-5
22-4

23
/
65
5. Cut the cable tie fixed to the 8-pin connector of UTP cable and HOT SHRINK TUBING fixed to the
grounding wire, then pull out the 8-pin connector from MAIN PCB.
6. Remove the 11 screws of the MAIN PCB which fix the terminal of the wires for the battery, brush motor
and main wires to vacuum motor housing.
c
23-2
23-1
23-4
23-3
23-7
23-6
23-5

24
/
65
7. Take the MACHINE BATTERY CONTROL PCB ASSY out of the MAIN LEVER COVER by removing
10 SCREWS EJOT DELTA PT 25X10
8. Block the POWER CABLE 3 WIRES with a CABLE TIE 3X15 to the MAIN LEVER COVE
9. Put the cables through the MACHINE BATTERY CONTROL PCB ASSY following the scheme of the
pictures below
10. Block the MACHINE BATTERY CONTROL PCB ASSY to the MAIN LEVER COVER with 10 SCREWS
EJOT DELTA PT 25X10
24-2
24-1
24-4
24-3
24-5 24-6

25
/
65
11. Fix the four input cables to the MACHINE BATTERY CONTROL PCB ASSY following the scheme of the
pictures below
12. Fix the seven output cables to the MACHINE BATTERY CONTROL PCB ASSY following the scheme of
the pictures below
13. Put a small piece of HEAT SHRINK TUBING through the UTP CABLE, then joint the connector to the
MACHINE BATTERY CONTROL PCB ASSY, block the UTP CABLE with a CABLE TIE 3X15, remove
the residue of tie via diagonal cutting pliers
25-225-1
25-4 25-5
25-3
25-7
25-6

26
/
65
14. Block the UTP CABLE with a CABLE TIE 3.5X30, , remove the residue of the cable tie with a diagonal
cutting pliers.
15. Put a small piece of HEAT SHRINK TUBING around the ESD CABLE and bend it with an angle of 90°,
16. Shrink the HEAT SHRINK TUBING with a hair-dryer/hot air gun
17. Block the HEAT SHRINK TUBING with a drop of LOCTITE 502
18. Add the 3pcs Thermal Conductive Pad 14X17X2 MM onto the HEAT SINKS
26-1 26-2
26-3 26-4
26-6
26-7 26-8
26-5

27
/
65
19. Add 4 pieces of insulating tape onto the MAIN LEVER HOUSING
20. Add the whole preassembly on the MAIN LEVER HOUSING centering the BRISH MOTORS HELICAL
GEARS on their own seats
21. Turn the MAIN LEVER HOUSING and close the MAIN LEVER UNIT ASSY with the MAIN LEVER
COVER, paying attention not to damage the mini USB on the main board while screwing it with 8
screw EJOT DELTA PT 50X14
27-1 27-2
27-3 27-4
27-5 27-6

28
/
65
22. Close the opening on the MAIN LEVER COVER with the USB UPDATE SLOT COVER and 1 SCREW
COUNTER SUNK M1.7X6
Special screw
driver in Toolbox
28-1

29
/
65
CHAPTER 8 – I-MOP MAIN LEVER REPLACEMENT
1. Remove the 6 pcs EJOT SCREW 50X14 which fixed the two COVER BRUSH MOTOR SCREW, then
remove the 2pcs COVER BRUSH MOTOR SCREW
2. Remove the 2pcs COUNTER SUNK BOLT M5X18.5 at the center of brush motor shaft
3. Remove the DRIVING WHEEL BOTTOM
4. Remove the BRUSH UNIT BOTTOM PART by unscrewing the SCREWS SOCKET HEAD CAP
M5X10 while paying attention to the LOCTITE 222 that was used.
5. Remove the BRUSH UNIT BOTTOM PART
29-1 29-2
29-3
29-4
29-5 29-6

30
/
65
6. Remove the 2 BRUSH UNIT HINGE SUPPORTS from the CHASSIS HINGE
7. Remove the CHASSIS HINGE from the centering hole of the MAIN LEVER HOUSING while unscrewing
the SCREW COUNTER SUNK M4X12 previously dipped in the LOCTITE 222
8. Remove from both sides the SCREW COUNTER SUNK M4X12 previously dipped in the LOCTITE 222
9. Remove the 2 MAIN LEVER SUPPORT PLATES on the side of the MAIN LEVER HOUSING by
unscrewing the 2 SCREWS COUNTER SUNK M3X8 previously dipped in the LOCTITE 222.
30-1 30-2
30-3 30-4
30-5 30-6

31
/
65
10. Turn the MAIN LEVER HOUSING and open the MAIN LEVER UNIT ASSY removing the MAIN LEVER
COVER unscrewing the 8 SCREWS EJOT DELTA PT 50X14
11. Replace the MAIN LEVER HOUSING
12. Recompose everything putting the 2 MAIN LEVER SUPPORT PLATES on the side of the MAIN LEVER
HOUSING and block it with 2 SCREWS COUNTER SUNK M3X8 dipped in the LOCTITE 222
13. Put the CHASSIS HINGE in the centering hole of the MAIN LEVER HOUSING
14. Block the CHASSIS HINGE with 1 SCREW COUNTER SUNK M4X12 dipped in the LOCTITE 222
31-1 31-2
31-3 31-4
31-5 31-6

32
/
65
15. Put the 2 BRUSH UNIT HINGE SUPPORTS from the 2 sides of the MAIN LEVER HOUSING
16. Put the BRUSH UNIT PROTECTOR on the BRUSH MOTOR CONSTRUCTION COVER and close
everything with the BRUSH UNIT BOTTOM PART
17. Block the BRUSH UNIT BOTTOM PART with the SCREWS SOCKET HEAD CAP M5X10 dipped in the
LOCTITE 222
18. Put the DRIVING WHEEL BOTTOM, with attention to the side of mounting, on the DRIVING WHEEL
TOP
32-1
32-2 32-3
32-4 32-5

33
/
65
19. Fasten the 2pcs COUNT SUNK SCREW M5X18.5 to fix the two DRIVING WHEEL TOP
20. Put on 2pcs COVER BRUSH MOTOR SCREW
21. Fasten 3pcs EJOT SCREW 50x14 to fix COVER BRUSH MOTOR SCEW each side
22. Add the WASHER AXIS MAIN LEVER that will be the spacer between the HINGE CARDAN TOP UNIT
and the MAIN LEVER HOUSING
23. Put the ASSY HING CARDAN on the MAIN LEVER HOUSING and block it with 2 SCREWS COUNTER
SUNK M4X12 dipped in the LOCTITE 222
33-1 33-2
33-3
33-4
33-5 33-6

34
/
65
CHAPTER 9 – I-MOP DASHBOARD ASSEMBLY
INSTRUCTIONS
17. WARNING! Wear gloves when you touch electrical components in order to avoid ESD damage.
SEE TOOLBOX
18. Put the PCB CONTROL UNIT on the TOP HOUSING CONTROL UNIT
19. Fix the TOP HOUSING CONTROL UNIT with 1 SCREW PARKER 2.9X16
20. Have LOCTITE 401 to fix the rubber to the micro switch, then fix it to the REAR HOUSING CONTROL
UNIT
34-1
34-2 34-3
34-4

35
/
65
21. Assemble the quick connector by putting the cables in the connector following the scheme below
22. Fix the esd wire of top board onto the hole of the INLET TUBE with a SCREW CROSS HEAD M4X12
23. Assemble the spring onto the new POWER SWITCH CONTROL UNIT (in blue)
Spring
24. Put the REAR HOUSING CONTROL UNIT onto the tube while inserting the POWER SWITCH
CONTROL UNIT (blue) together with the spring in its seat by moving the HANDLE CONTROL UNIT
until you find the correct positioning on the POWER SWITCH CONTROL UNIT itself.
35-1 35-2
35-3
35-4
35-5
35-6

36
/
65
9. Close the INLET TUBE ASSY with the FRONT HOUSING CONTROL UNIT
25. Cover the cable with a piece of heat shrink tubing Ø8 – Ø4 long enough to wrap a portion of the grey
sheath that covers the cable.
26. Connect the PCB CONTROL UNIT with the connector that was created.
27. Complete the other connections of the PCB CONTROL UNIT
36-1 36-2 36-3
36-4
36-5 36-6
36-7

37
/
65
30. Close the HOUSING CONTROL UNIT with the TOP HOUSING CONTROL UNIT and put two sleeves to
the two holes
31. Fix the top aluminum dashboard via two screws
32. Add the Rubber Block for water flow adjustment to the board
33. Put the TURNING BUTTON onto the pin and lock it with 1 SCREW SOCKET HEAD M3X8
37-1 37-2
37-4
37
-
3

38
/
65
CHAPTER 10 – I-MOP TUBES REPLACEMENT INSTRUCTIONS
1. Brushtubereplacement–WATERCHANNELØ4MM
1.1. Remove the 6pcs EJOT SCREW 50 X14
1.2. Remove the 2pcs COVER BRUSH MOTOR SCREW
1.3. Remove the COUNTER SUNK BOLT M5X18.5
1.4. Remove the DRIVING WHEEL BOTTOM
1.5. Remove the BRUSH UNIT BOTTOM PART by unscrewing the SCREWS SOCKET HEAD
CAP M5X10 doing attention to the LOCTITE 222
1.6. Remove the BRUSH UNIT BOTTOM PART
38-1
38-2
38-3 38-4
38-5 38-6

39
/
65
1.7. Remove the WATER CHANNEL Ø4 MM from the WATER COUPLING BRUSH MOTOR and from
the BRUSH MOTOR SUPPORT RUBBER after having cut the CABLE TIE 3.X15
1.8. Replace the WATER CHANNEL Ø4 MM
1.9. Re-assemble the group putting the WATER CHANNEL Ø 4 MM in the BRUSH MOTOR
SUPPORT RUBBER and block it with a CABLE TIE 3X15
1.10. Put the WATER CHANNEL Ø 4 MM in the WATER COUPLING BRUSH MOTOR
39
-
1
39-2
39-3 39-4
39-5 39-6

40
/
65
1.11. Put the BRUSH UNIT PROTECTOR onto the BRUSH MOTOR CONSTRUCTION COVER and
close everything with the BRUSH UNIT BOTTOM PART
1.12. Block the BRUSH UNIT BOTTOM PART with the SCREWS SOCKET HEAD CAP M5X10 dipped
in the LOCTITE 222
1.13. Put the DRIVING WHEEL BOTTOM, with attention to the side of mounting, on the DRIVING
WHEEL TOP
1.14. Fasten 2pcs COUNTER SUNK M5X18.5 to fix 2pcs DRIVING WHEEL BOTTOM
1.15. Add 2pcs COVER BRUSH MOTOR SCREW
40-1 40-2
40-3 40-4
40-5 40-6

41
/
65
1.16. Fasten 3pcs EJOT SCREW 50X14 each side to fix 2pcs COVER BRUSH MOTOR
2. Maintubereplacement–TRANSPARENTWATERCHANNELØ6MM
2.1. Remove the 6pcs EJOT SCREW 50 X14
2.2. Remove the 2pcs COVER BRUSH MOTOR SCREW
2.3. Remove the COUNTER SUNK BOLT M5X18.5
2.4. Remove the DRIVING WHEEL BOTTOM
41-1
41-2 41-3
41-4 41-5

42
/
65
2.5. Remove the BRUSH UNIT BOTTOM PART by unscrewing the SCREWS SOCKET HEAD
CAP M5X10 doing attention to the LOCTITE 222
2.6. Remove the BRUSH UNIT BOTTOM PART
2.7. Remove the WATER CHANNEL Ø6 MM from the WATER COUPLING BRUSH MOTOR
2.8. Remove the 4 SCREWS COUNTER SUNK M6X12 and open the MOTOR UNIT TOP
2.9. Remove the MAGNETIC VALVE COUPLINGS from the ASSY MAGNETIC VALVE and remove the
WATER CHANNELS Ø6 MM from the ASSY MAGNETIC VALVE
2.10. Pull the WATER CHANNEL Ø6 MM and extract it completely
2.11. Replace the WATER CHANNEL Ø6 MM
42-1 42-2
42-3 42-4
42-5 42-6

43
/
65
2.12. Put the TRANSPARENT WATER CHANNEL Ø6 MM on the ASSY MAGNETIC VALVE
2.13. Lock the TRANSPARENT WATER CHANNEL Ø6 MM on the ASSY MAGNETIC VALVE with the
MAGNETIC VALVE COUPLING
2.14. Put the WATER CHANNEL Ø6 MM through the MOTOR UNIT TOP until it comes out on the other
side
2.15. Put the WATER CHANNEL Ø6 MM in the CONSTRUCTION COVER SEAL
2.16. Put the WATER CHANNEL Ø6 MM in the WATER COUPLING BRUSH MOTOR
43-1
43-2
43-3 43-4

44
/
65
2.17. Close everything with the BRUSH UNIT BOTTOM PART
2.18. Lock the BRUSH UNIT BOTTOM PART with the SCREWS SOCKET HEAD CAP M5X10 dipped
in the LOCTITE 222
2.19. Put the DRIVING WHEEL BOTTOM, with attention to the side of mounting, on the DRIVING
WHEEL TOP
2.20. Fasten 2pcs COUNTER SUNK M5X18.5 to fix 2pcs DRIVING WHEEL BOTTOM
2.21. Add 2pcs COVER BRUSH MOTOR SCREW
44-1 44-2
44-4
44-3
44-5 44-6

45
/
65
2.22. . Fasten 3pcs EJOT SCREW 50X14 each side to fix 2pcs COVER BRUSH MOTOR
3. Internaltubereplacement–WATERCHANNELØ6MM
3.1. Remove the 4 SCREWS COUNTER SUNK M6X12 and open the MOTOR UNIT TOP
3.2. Remove the MAGNETIC VALVE COUPLING from the MAGNETIC VALVE ASSY and remove the
WATER CHANNELS Ø6 MM from the MAGNETIC VALVE ASSY
3.3. Remove the MAGNETIC VALVE COUPLING from the ANGLE METAL CONNECTOR and remove
the WATER CHANNEL Ø6 MM from the ANGLE METAL CONNECTOR
3.4. Replace the WATER CHANNEL Ø6 MM
45-1
45-2 45-3
45-4

46
/
65
3.5. Put the WATER CHANNEL Ø6 MM on the ASSY MAGNETIC VALVE and on the ANGLE METAL
CONNECTOR and block it with the MAGNETIC VALVE COUPLINGS
3.6. Close the MOTOR UNIT COVER with attention not pressing the cables or the hoses in between.
3.7. Screw the MOTOR UNIT TOP on the MOTOR UNIT COVER with 4 SCREWS CROSS HEAD
M4X12
46-1 46-2
46-3

47
/
65
CHAPTER 11 – I-MOP VACUUM MOTOR REPLACEMENT
1. WARNING! Wear gloves when you touch electrical components to avoid ESD damage.
2. Remove the 4 SCREWS M4X12 CROSS HEAD and open the MOTOR UNIT TOP
3. Remove the 2 SCREWS EJOT DELTA PT 50X14 and extract the ASSY MAGNETIC VALVE
4. Remove the MAGNET TOP UNIT 40X20X10MM, the put a steel tool such as wrench there to hold the
vacuum unit to the brush unit
5. Unscrew the 8 SCREWS EJOT DELTA PT 50X14
6. Open the MOTOR UNIT COVER extracting the POWER CABLES 2 WIRES
7. Extract the VACUUM MOTOR GROUP
8. Unplug the DOMEL VACUUM CLEANER MOTOR of the POWER CABLES 3 WIRES with attention to
not extract the POWER CABLES2 WIRES from the VACUUM MOTOR SEALING SUPPORT
9. Replace the DOMEL VACUUM CLEANER MOTOR
47-1 47-2 47-3
47-4 47-5
47-6 47-7

48
/
65
10. Put the other side of the cables through the VACUUM MOTOR SEALING SUPPORT
11. Put the VACUUM MOTOR SEALING SUPPORT on the DOMEL VACUUM CLEANER MOTOR
12. Fit the whole VACUUM MOTOR GROUP in the MOTOR UNIT COVER
13. Fit the VACUUM MOTOR GROUP in the MOTOR COVER UNIT with attention to have the UTP
CABLE in the correct position together with the WATER CHANNEL Ø6 MM and the POWER CABLE
2 WIRES
48-1 48-2
48-3
48-4 48-5
48-6

49
/
65
14. Put the POWER CABLES 2 WIRES in the MOTOR UNIT COVER
15. Close the group with 8 SCREWS EJOT DELTA PT 50X14
16. Take away the steel tool such as a wrench then put the MAGNET TOP UNIT 40X20X10MM there
17. Close the MOTOR UNIT COVER with attention not to press the cables or the hoses in between
18. Screw the MOTOR UNIT TOP on the MOTOR UNIT COVER with 4 SCREWS CROSS HEAD M4X12
49-1 49-2
49-3 49-4
49-5 49-6 49-7

50
/
65
CHAPTER 12 – I-MOP WHEEL AND WHEEL SUPPORT
REPLACEMENT
1. Wheelreplacement
1.1. Put the SHAFT TRANSPORT CASTOR( 72.0027.1) one the work table , then put the
TRANSPORT CASTOR (72.0029.2/797)
1.2. then locate the TRANPORT WHEEL PILLA (left or right), . Add NUT M5 NYLON/M5 (04.0048.0) on
it, then use wrench to fix them together tightly
2. Wheelsupportreplacement
2.1. Remove the 6pcs EJOT SCREW 50X14
2.2. Remove the 2pcs COVER BRUSH MOTOR SCREW
50-1 50-2
50-3
50-5
50-6
50-4

51
/
65
2.3. Remove 2pcs COUNT SUNK SCREW M5X18.5 at the center of brush motors
2.4. Remove the DRIVING WHEEL BOTTOM
2.5. Remove the BRUSH UNIT BOTTOM PART by unscrewing the SCREWS SOCKET HEAD CAP
M5X10 with attention to the LOCTITE 222
2.6. Remove the BRUSH UNIT BOTTOM PART
2.7. Remove the TRANSPORT WHEEL PILLAR from his own seat on the BRUSH MOTOR
CONSTRUCTION COVER by unscrewing the 2 SCREWS COUNTER SUNK M6X16 with
attention that they have been dipped in the LOCTITE 222
2.8. Replace the TRANSPORT WHEEL PILLAR and put the 2 SCREWS COUNTER SUNK M6X16 after
having them dipped in the LOCTITE 222
51-1
51-2
51-451-3
51-5 51-6

52
/
65
2.9. Put the BRUSH UNIT PROTECTOR on the BRUSH MOTOR CONSTRUCTION COVER and close
everything with the BRUSH UNIT BOTTOM PART
2.10. Lock the BRUSH UNIT BOTTOM PART with the SCREWS SOCKET HEAD CAP M5X10 dipped
in the LOCTITE 222
2.11. Put the DRIVING WHEEL BOTTOM, with attention to the side of mounting, on the
DRIVING WHEEL TOP
2.12. Fast the 2pcs COUNT SUNK SCREW M5X18.5 to fix the 2pcs DRIVING WHEEL TOP
2.13. Put on the 2pcs COVER BRUSH MOTOR SCREW
52-1 52-2
52-3 52-4
52-5 52-6

53
/
65
2.14. Fasten 3pcs EJOT SCREW 50X14 to fix the COVER BRUSH MOTOR SCREW each side
53-1

54
/
65
CHAPTER 13 – I-MOP FILTER AND DEFLECTOR
REPLACEMENT INSTRUCTIONS
1. replace the filter cassette inside dirty tank
2. Put the TRANSPARENT PLASTIC DEFLECTOR DIRTY TANK on his seat on the TANK HOLDER
REAR, recognizable from the O-RING around the lips of the DIRT COMPARTMENT SEAL
54-1 54-2

55
/
65
CHAPTER 14 – SQUEEGEE WHEELS CLEANING
Part List :
72.0137.2 ,shaft squeegee castor dia.8mm,3pcs
72.0235.0 M5 washer stainless steel 5X15X1MM,6pcs
04.0048.0, NUT M5 NYLON, 6pcs
72.0138.1, height adjust plate ver.1, 3pcs
72.0238.32,SQUEEGEE CASTOR GREY DIA.8MM,3pcs
1. Use wrench to assemble SHAFT SQUEEGEE CASTOR (72.0137.2) SQUEEGEE CASTOR GREY
(72.0238.32) , M5 WASHER STAINLESS STEEL 5X15X1MM (72.0235.0) and NUT M5 NYLON
(04.0048.0) together.
2. Insert the HEIGHT ADJUSTMENT PLATE (72.0138.1) to the subassembly of step 1, then attach them
to the square hole of the squeegee, pay attention that the two blue dots need be upside. When doing the
height adjustment, the white dot need to be upside.
3. Fix the subassembly step 2 to squeegee by one M5 WASHER STAINLESS STEEL 5X15X1MM
(72.0235.0)and one NUT M5 NYLON (04.0048.0) via wrench.
55-1 55-2
55-3
55-4 55-5
55-6 55-7

56
/
65
CHAPTER 15 – WATER SAFE INTERVAL ADJUSTMENT
1. Remove the rubber block of water save internal setting
2. Adjust the position of the interval functioning moving the selector with a screw driver to the desired
position following the scheme
3. In the table the values (in seconds) of the different positions:
POSITION WATER
(
S
)
STOP
(
S
)
0 0.6 9.4
1 1.2 8.8
2 1.8 8.2
3 2.4 7.6
4 3 7
5 3.5 6.5
6 4.1 5.9
7 4.7 5.3
8 5.3 4.7
9 5.9 4.1
A
6.53.5
B 7 3
C 7.6 2.4
D 8.2 1.8
E 8.8 1.2
F 9.4 0.6
56-3
56-2
56-4
56-4
56-1

CHAPTER 16 – ELECTRICAL SCHEME
57/65
57-1

58
/
65
CHAPTER 17 – BATTERIES
DATASHEET
ModelSamsungICR18650‐GA
Voltageandcapacity
Nominal voltage 4.2 V
Nominal capacity @ 25 °C * 100% - 220 mAh
Nominal capacity @ 0°C * 80% - 1760 mAh
Nominal capacity @ -20 °C * 60% - 1320 mAh
Nominal energy @ 25 °C * 8.14 Wh
* Discharge current ≤ 1C
Cycles
80% intensit
y
of discharge 800 c
y
cles
70% intensit
y
of discharge 800 c
y
cles
50% intensit
y
of discharge 800 c
y
cles
Discharge
Continuous maximum discharge current 10
A
Continuous recommended discharge curren
t
6.45
A
Impulsive 10 s maximum curren
t
20
A
End of discharge voltage 2.75 V
Working
cond
i
t
ions
Working temperature -40 °C
–
55 °C
(do not charge when temperature is < -20 °C)
Storage temperature -40 °C
–
85 °C
Humidity (without condensation) Max 95%
Index of protection IP54
Charge
Charge voltage 4.2 V
Holding voltage 3.62 V
Maximum charge curren
t
2.15
A
Recommended charge curren
t
≤ 1.075
A
Cells
Weight of Lithium (per cell) 1.25 g
Weight of Lithium compound (per cell) 18.67 g
Number of cells (per battery) 28
Other
Maximum storage time @ 25 °C 12 months
Maximum storage time @ 60 °C 3 months
Dimensions 157 x 133 x 94 mm
Weigh
t
1.665 kg
PCB on board YES

59
/
65
ASSEMBLYINSTRUCTIONS
1. Paste the SIDE FOAM MOTOR VACUUM to the BATTERY PACK CELLS.
2. Put the BATTERY CONNECTOR FEMALE into the BATTERY PACK HOUSING BOTTOM. The BLUE
in the LEFT battery and the GREY in the RIGHT battery.
3. Screw the BATTERY CONNECTOR FEMALE to the BATTERY PACK HOUSING BOTTOM with 2
SCREW WN 5451 25X10 EJOT DELTA PT.
4. Put the BATTERY PACK CELLS into the BATTERY PACK HOUSING BOTTOM.
5. Put a piece of heat shrinkable tubing on the cables and solder the ones coming from the BATTERY
PACK CELLS to the ones coming from the BATTERY CONNECTOR FEMALE (RED with RED and
BLACK with BLACK).
59-1 59-2
59-3 59-4
59-5 59-6

60
/
65
6. Cover the soldering with the heat shrinkable tubing and heaten it to shrink it.
7. Put the fuse into its seat in the BATTERY PACK CELLS.
8. Close the ASSY BATTERY PACK with the BATTERY PACK HOUSING TOP.
9. Screw the two BATTERY PACK HOUSINGS with 4 SCREW WN 5451 25X10 EJOT DELTA PT
10. Testing procedure of Battery
Measure the Voltage of Battery via Voltage meter or Multiple meter by insert the red wire to the hole
with “+” mark and black wire to the “-” mark
A, If the reading of Voltage is with minus, this is the plus and minus was installed incorrectly
and will damage the main PCB if insert this kind of battery to machine
B. If the reading is Zero, the insert fuse is broken and need be replaced
C. If the reading is about 10V, the batter is possibly damaged via over-discharge.
60-1 60-2
60-3 60-4
60-5

D, if the reading is above 16V, the battery is OK.
61/65
61-1 61-2

62
/
65
CHAPTER 18 – CHARGER
DATASHEET
Model
Input voltage
A
C 100-240 V
Frequency 50-60 Hz
Output current 9
A
Charging voltage 29.4 V
“Float” voltage 27.4 V
Charge current 9
A
Charge features 3 phases with max time of 20 hours per absorption
Minimum capacity of the batteries 10 Ah
Thresholdcharge interrupt 0.3 Ah
A
vailable as power pack NO
Protection
Reverse polarity of the battery
(fuse in the positive lead)
Output short circui
t
Overheating
Working temperature -20 +55 °C
Humidit
y
Up to 100 °C
Weigh
t
1.125 kg
Dimensions 266 x 215 x105 mm
REFERENCESTANDARDS
Safety
EN55022:2006 + A1:2007
Emissions
EN61000-3-2:2006 + A1:2009 + A2:2009; EN61000-3-3:2008
Immunity
EN55024:201
62-1

CHAPTER 19 – REPAIR FLOW CHART
63/64
64-1
64-2

64/64
65-1
Tennant Company
PO Box 1452
Minneapolis, MN 55440
Phone: 1-800-553-8033
www.tennantco.com