Trane Round In Out Catalogue VAV PRC011M EN (03/2015)
2015-04-02
: Trane Trane-Round-In-Round-Out-Catalogue-684310 trane-round-in-round-out-catalogue-684310 trane pdf
Open the PDF directly: View PDF .
Page Count: 158 [warning: Documents this large are best viewed by clicking the View PDF Link!]
- Introduction
- Table of Contents
- Features and Benefits
- Agency Certifications
- Model Number Descriptions
- Single-Duct VAV Terminal Units
- Model Number Descriptions
- Dual-Duct VAV Terminal Units
- DDC Controls
- Tracer UC400 and UC210 Programmable BACnet Controllers
- Trane LonMark™ DDC VAV Controller (VV550)
- Direct Digital Controller—Unit Control Module (UCM4)
- Air-Fi™ Wireless System
- Wireless Receiver/Wireless Zone Sensor
- DDC Zone Sensor
- CO2 Wall Sensor and Duct CO2 Sensor
- DDC Zone Sensor with LCD
- Zone Occupancy Sensor
- Factory or Field Mounted Auxiliary Temperature Sensor
- Factory Mounted Discharge Air Temperature Sensing Matrix
- Two-Position Water Valve
- Proportional Water Valve
- VAV Piping Package
- Differential Pressure Transducer
- Transformers
- Trane Non-Spring Return Actuator
- Trane Spring Return Actuator
- VariTrane™ DDC Retrofit Kit
- Retrofit Kit Actuator
- Static Pressure Controller
- Electric Heater Silicon-Controlled Rectifier (SCR)
- Pneumatic Controls
- Controls Specifications
- Application Considerations
- VAV System
- Control Types
- Flow Measurement and Control
- Reheat Options
- Insulation
- Acoustics
- Duct Design
- Best Practices
- Unit Conversions
- Additional VAV System and Product References
- VAV Systems Air Conditioning Clinic
- Intelligent Variable Air — An EarthWise System from Trane for chilled-water applications
- Intelligent Variable Air — An EarthWise System from Trane for packaged DX applications
- Rooftop VAV Systems Applications Engineering Manual
- Chilled-Water VAV Systems Applications Engineering Manual
- Acoustics in Air Conditioning Applications Engineering Manual
- VariTrac™ catalog

VariTrane™ Products
Single Duct/Dual Duct Units
VDD, VCC, VCW, VCE
March 2015 VAV-PRC011M-EN
RA
EA
OA PA
supply
fan
cooling
coilvariable-
speed drive
thermostat
VAV
box
SA
Variable-Air-Volume (VAV) System
Product Catalog

© 2015 Trane All rights reserved VAV-PRC011M-EN
Introduction
VariTrane™ variable-air-volume (VAV) units lead the industry in quality and reliability and are
designed to meet the specific needs of today’s applications. This generation of VariTrane units
builds upon the history of quality and reliability and expands the products into the most complete
VAV offering in the industry.
Single-duct units provide an economical energy-savings system solution. This is the most
common type of VAV unit.
Dual-duct units have two air valves. One heating valve and one cooling air valve modulate
simultaneously to provide occupant comfort. This option is also used with system concepts which
use one valve for maintaining and monitoring 100% ventilation air.
Copyright
This document and the information in it are the property of Trane, and may not be used or
reproduced in whole or in part without written permission. Trane reserves the right to revise this
publication at any time, and to make changes to its content without obligation to notify any person
of such revision or change.
Trademarks
All trademarks referenced in this document are the trademarks of their respective owners.
Revision History
VAV-PRC011M-EN (033 Mar 2015)
Updated for Air-Fi™ wireless project.
VCCF VCEF VCWF

VAV-PRC011M-EN 3
Table of Contents
Introduction . . . . . . . . . . . . . . . . . . . . . . . . . . . . . . . . . . . . . . . . . . . . . . . . . . . . . . 2
Features and Benefits . . . . . . . . . . . . . . . . . . . . . . . . . . . . . . . . . . . . . . . . . . . . . . 6
Construction . . . . . . . . . . . . . . . . . . . . . . . . . . . . . . . . . . . . . . . . . . . . . . . . . . . 6
Indoor Air Quality (IAQ) Features . . . . . . . . . . . . . . . . . . . . . . . . . . . . . . . . . . 7
Tracer Building Automation System . . . . . . . . . . . . . . . . . . . . . . . . . . . . . . . . 7
Trane VAV Systems - Proven Performance . . . . . . . . . . . . . . . . . . . . . . . . . 11
Indoor Air Quality Management During Construction . . . . . . . . . . . . . . . . . 11
Agency Certifications . . . . . . . . . . . . . . . . . . . . . . . . . . . . . . . . . . . . . . . . . . . . . . 12
American Society of Heating, Refrigerating and Air-conditioning Engineers
(ASHRAE) . . . . . . . . . . . . . . . . . . . . . . . . . . . . . . . . . . . . . . . . . . . . . . . . . . . . . 12
Air Conditioning and Refrigeration Institute (AHRI) . . . . . . . . . . . . . . . . . . . 12
Underwriter’s Laboratory (UL) 1995 . . . . . . . . . . . . . . . . . . . . . . . . . . . . . . . 12
National Fire Protection Association . . . . . . . . . . . . . . . . . . . . . . . . . . . . . . . 13
Model Number Descriptions . . . . . . . . . . . . . . . . . . . . . . . . . . . . . . . . . . . . . . . . 14
Single-Duct VAV Terminal Units . . . . . . . . . . . . . . . . . . . . . . . . . . . . . . . . . . . . 17
Selection Procedure . . . . . . . . . . . . . . . . . . . . . . . . . . . . . . . . . . . . . . . . . . . . 17
General Data . . . . . . . . . . . . . . . . . . . . . . . . . . . . . . . . . . . . . . . . . . . . . . . . . . 19
Performance Data . . . . . . . . . . . . . . . . . . . . . . . . . . . . . . . . . . . . . . . . . . . . . . 21
Electrical Data . . . . . . . . . . . . . . . . . . . . . . . . . . . . . . . . . . . . . . . . . . . . . . . . . 39
Dimensional Data . . . . . . . . . . . . . . . . . . . . . . . . . . . . . . . . . . . . . . . . . . . . . . 51
Mechanical Specifications . . . . . . . . . . . . . . . . . . . . . . . . . . . . . . . . . . . . . . . 60
Model Number Descriptions . . . . . . . . . . . . . . . . . . . . . . . . . . . . . . . . . . . . . . . . 65
Dual-Duct VAV Terminal Units . . . . . . . . . . . . . . . . . . . . . . . . . . . . . . . . . . . . . . 66
Selection Procedure . . . . . . . . . . . . . . . . . . . . . . . . . . . . . . . . . . . . . . . . . . . . 66
General Data . . . . . . . . . . . . . . . . . . . . . . . . . . . . . . . . . . . . . . . . . . . . . . . . . . 68
Performance Data . . . . . . . . . . . . . . . . . . . . . . . . . . . . . . . . . . . . . . . . . . . . . . 69
Dimensional Data . . . . . . . . . . . . . . . . . . . . . . . . . . . . . . . . . . . . . . . . . . . . . . 74
Mechanical Specifications . . . . . . . . . . . . . . . . . . . . . . . . . . . . . . . . . . . . . . . 76
DDC Controls . . . . . . . . . . . . . . . . . . . . . . . . . . . . . . . . . . . . . . . . . . . . . . . . . . . . 79
Tracer UC400 and UC210 Programmable BACnet Controllers . . . . . . . . . . 79
Trane LonMark™ DDC VAV Controller (VV550) . . . . . . . . . . . . . . . . . . . . . . 88
Direct Digital Controller—Unit Control Module (UCM4) . . . . . . . . . . . . . . . 97
Air-Fi™ Wireless System . . . . . . . . . . . . . . . . . . . . . . . . . . . . . . . . . . . . . . . 101
Wireless Receiver/Wireless Zone Sensor . . . . . . . . . . . . . . . . . . . . . . . . . . 103
DDC Zone Sensor . . . . . . . . . . . . . . . . . . . . . . . . . . . . . . . . . . . . . . . . . . . . . 104

4 VAV-PRC011M-EN
Table of Contents
CO2 Wall Sensor and Duct CO2 Sensor . . . . . . . . . . . . . . . . . . . . . . . . . . . . 105
DDC Zone Sensor with LCD . . . . . . . . . . . . . . . . . . . . . . . . . . . . . . . . . . . . . 106
Zone Occupancy Sensor . . . . . . . . . . . . . . . . . . . . . . . . . . . . . . . . . . . . . . . . 107
Factory or Field Mounted Auxiliary Temperature Sensor . . . . . . . . . . . . . 108
Factory Mounted Discharge Air Temperature Sensing Matrix . . . . . . . . . 108
Two-Position Water Valve . . . . . . . . . . . . . . . . . . . . . . . . . . . . . . . . . . . . . . 109
Proportional Water Valve . . . . . . . . . . . . . . . . . . . . . . . . . . . . . . . . . . . . . . . 110
VAV Piping Package . . . . . . . . . . . . . . . . . . . . . . . . . . . . . . . . . . . . . . . . . . . 111
Differential Pressure Transducer . . . . . . . . . . . . . . . . . . . . . . . . . . . . . . . . . 112
Transformers . . . . . . . . . . . . . . . . . . . . . . . . . . . . . . . . . . . . . . . . . . . . . . . . . 113
Trane Non-Spring Return Actuator . . . . . . . . . . . . . . . . . . . . . . . . . . . . . . . 114
Trane Spring Return Actuator . . . . . . . . . . . . . . . . . . . . . . . . . . . . . . . . . . . 115
VariTrane™ DDC Retrofit Kit . . . . . . . . . . . . . . . . . . . . . . . . . . . . . . . . . . . . 116
Retrofit Kit Actuator . . . . . . . . . . . . . . . . . . . . . . . . . . . . . . . . . . . . . . . . . . . 116
Static Pressure Controller . . . . . . . . . . . . . . . . . . . . . . . . . . . . . . . . . . . . . . . 117
Electric Heater Silicon-Controlled Rectifier (SCR) . . . . . . . . . . . . . . . . . . . 118
Pneumatic Controls . . . . . . . . . . . . . . . . . . . . . . . . . . . . . . . . . . . . . . . . . . . . . . 121
3011 Pneumatic Volume Regulator . . . . . . . . . . . . . . . . . . . . . . . . . . . . . . . 121
3501 Pneumatic Volume Regulator . . . . . . . . . . . . . . . . . . . . . . . . . . . . . . . 122
Pneumatic Damper Actuator . . . . . . . . . . . . . . . . . . . . . . . . . . . . . . . . . . . . 123
Reversing Relay . . . . . . . . . . . . . . . . . . . . . . . . . . . . . . . . . . . . . . . . . . . . . . . 123
Signal Limiter . . . . . . . . . . . . . . . . . . . . . . . . . . . . . . . . . . . . . . . . . . . . . . . . 125
Controls Specifications . . . . . . . . . . . . . . . . . . . . . . . . . . . . . . . . . . . . . . . . . . . 134
Direct Digital Controls (DDC) . . . . . . . . . . . . . . . . . . . . . . . . . . . . . . . . . . . . 134
Pneumatic Controls . . . . . . . . . . . . . . . . . . . . . . . . . . . . . . . . . . . . . . . . . . . . 135
Options . . . . . . . . . . . . . . . . . . . . . . . . . . . . . . . . . . . . . . . . . . . . . . . . . . . . . . 136
DDC Retrofit Kit (VRTO) . . . . . . . . . . . . . . . . . . . . . . . . . . . . . . . . . . . . . . . . 136
Retrofit Kit Options . . . . . . . . . . . . . . . . . . . . . . . . . . . . . . . . . . . . . . . . . . . . 136
Other Options Available . . . . . . . . . . . . . . . . . . . . . . . . . . . . . . . . . . . . . . . . 137
Application Considerations . . . . . . . . . . . . . . . . . . . . . . . . . . . . . . . . . . . . . . . . 138
VAV System . . . . . . . . . . . . . . . . . . . . . . . . . . . . . . . . . . . . . . . . . . . . . . . . . . 138
Control Types . . . . . . . . . . . . . . . . . . . . . . . . . . . . . . . . . . . . . . . . . . . . . . . . 142
Flow Measurement and Control . . . . . . . . . . . . . . . . . . . . . . . . . . . . . . . . . 146
Reheat Options . . . . . . . . . . . . . . . . . . . . . . . . . . . . . . . . . . . . . . . . . . . . . . . 148
Insulation . . . . . . . . . . . . . . . . . . . . . . . . . . . . . . . . . . . . . . . . . . . . . . . . . . . . 150
Acoustics . . . . . . . . . . . . . . . . . . . . . . . . . . . . . . . . . . . . . . . . . . . . . . . . . . . . 150

VAV-PRC011M-EN 5
Table of Contents
Duct Design . . . . . . . . . . . . . . . . . . . . . . . . . . . . . . . . . . . . . . . . . . . . . . . . . . 153
Best Practices . . . . . . . . . . . . . . . . . . . . . . . . . . . . . . . . . . . . . . . . . . . . . . . . . 154
Unit Conversions . . . . . . . . . . . . . . . . . . . . . . . . . . . . . . . . . . . . . . . . . . . . . . 155
Additional VAV System and Product References . . . . . . . . . . . . . . . . . . . . 156

6 VAV-PRC011M-EN
Features and Benefits
Construction
UL-listed products
Safety and reliability are vital in commercial construction. All VariTrane™ units are listed in
accordance with UL -1995 as terminal units. This listing includes the VAV terminal with electric
heaters. Additionally, all insulation materials pass UL 25/50 smoke and flame safety standards.
AHRI Certified Performance
All VariTrane units are AHRI certified. AHRI 880 guarantees the pressure drop, flow performance,
and acoustical performance provided is reliable and has been tested in accordance with industry
accepted standards. AHRI 885 uses AHRI 880 performance and applies accepted industry methods
to estimate expected “NC” sound levels within the occupied space.
Casing Design
Interlocking Panels—VariTrane products are manufactured in Trane’s state-of-the-art facility in the
U. S. The interlocking panels are designed using integral I-beam construction technology. This
minimizes deformation and creates tremendous product rigidity. An additional benefit is a smooth
unit exterior with few exposed screws—ideal for exposed ceiling applications. VariTrane units are
designed for use in systems that operate up to 5" w.c. of inlet pressure.
Metal Encapsulated Edges—All VariTrane units are complete
with encapsulated edges to arrest cut fibers and prevent
insulation erosion into the airstream. This is the standard of
care in applications concerned with fiberglass erosion or
projects with either double-wall or externally wrapped duct
work.
The Trane Air Valve—is at the heart of VariTrane terminal
units. This is where airflow is measured and controlled.
Repeatability and ruggedness is vital. VariTrane products are
the most rugged and reliable available.
18-gage Cylinder—limits deformation or damage during shipment and job site handling, and
provides even airflow distribution across the flow ring for unmatched airflow measurement
accuracy.
Continuously Welded Seam — an automated weld process creates the highest quality continuous
seam, which is “right” every time. The welded seam improves air valve rigidity and creates
consistent and repeatable airflow across the flow measurement device. The result is a truly round
cylinder, with no flat spots caused by lower quality crimping and riveting technologies.
Flow Ring—The Trane flow ring is time tested to perform under the
most demanding conditions. Additionally, Trane’s patented flow ring
is recessed within the air valve cylinder to reduce the potential for
damage during job site handling and installation.

VAV-PRC011M-EN 7
Features and Benefits
External Shaft—This simple design provides controller flexibility and is designed to facilitate
actuator field replacement.
Position Indicator—The position indicator shows current air valve position to aid in system
commissioning. Many times this can be seen from the floor without climbing a ladder.
External Actuator—This feature increases serviceability, control system compatibility, and actuator
clutch access for simplified commissioning.
Indoor Air Quality (IAQ) Features
The oil embargo of the early 1970s created an energy crisis, which resulted in tighter buildings, and
reduced ventilation rates. A fallout issue of tighter building construction was poor indoor air
quality. This heightened IAQ awareness. IAQ issues have been featured in publications from the
smallest towns to the largest cities. System design should consider applicable ventilation and IAQ
standards.(See your local Trane Sales Engineer or visit www.trane.com for additional information).
Good indoor air quality results from units and systems which:
• Provide the required amount of ventilation air to each zone during all operating conditions
• Limit particulates from entering occupied spaces
VariTrane units are designed with simplified access and a full line of insulation options including:
Matte-faced—Typical industry standard with reduced first cost.
Closed-cell—This insulation has an R-value and performance equivalent to matte-faced insulation.
The main difference is the reduction of water vapor transmission. Closed-cell is designed for use
in installations with a high chance of water formation. (It has been used to coat the exterior of chiller
evaporator barrels for many years.)
Foil-faced—A fiberglass insulation with a thin aluminum coating on the air stream side to prevent
fibers from becoming airborne. The aluminum lining is acceptable for many applications, however
it is not as rugged as double-wall.
Double-wall—Premium insulation often used in many health care applications with insulation
locked between metal liners. This eliminates the possibility for insulation entering the airstream
and allows for unit interior wipe-down as needed.
VariTrane VAV units are the most prepared IAQ units in the industry. The end result is a reliable
product designed for peak performance, regardless of job site conditions or handling.
Tracer Building Automation System
Tracer™ Building Automation System assures comfort within your building
Building controls have a bigger job description than they did a few years ago. It’s no longer enough
to control heating and cooling systems and equipment. Sophisticated buildings require smarter
technology that will carry into the future. Tracer controls provide the technology platform – mobile,
easy-to-use, cloud-based, scalable and open - for the next generation of data-driven, technology-
enabled services that are creating high performance buildings.
With a Trane Tracer Building Automation System, you’ll:
• Reduce operating costs through energy management strategies
• Consistently provide occupant comfort
• Enjoy reliable operation with standard, pre-engineered and pretested applications
• Easily troubleshoot and monitor either on site or from a remote location
• Reduce installation time and simplify troubleshooting
Whether factory-mounted or field-installed, Trane offers a wide range of controllers to suit virtually
any application. These units are compatible with a variety of building types and can be used for new

8 VAV-PRC011M-EN
Features and Benefits
construction or renovation. Through extensive usability testing internally and with building
operators, we’ve designed our controls for real world ease of use.
(Additional control options and sequence-of-operations are located in the “Controls” section.)
Tracer BACnet Controllers
Trane now offers a full line of programmable BACnet® controllers designed for simple integration
into any system which can communicate via the BACnet protocol. These controllers are factory-
commissioned and shipped ready to be installed.
Tracer VV550 LonTalk Controllers
Trane VAV UCM Controller
Note: One of many Trane DDC Control Options which are factory-installed, wired, calibrated, and
fully tested before shipment.
Trane DDC controllers provide Trane-designed solid-state electronics intended specifically for VAV
temperature control in space comfort applications. DDC control capabilities include:
UC210 BACnet Controller UC400 BACnet Controller
LonTalk controller
Trane offers a full line of LonTalk® controllers designed for
simple integration into ANY system which can communicate
via the LONMARK® Space Comfort Control (SCC) protocol.
These controllers are also completely factory-commissioned
(see Ta bl e , p. 10).
Trane VAV UCM DDC Controller
DDC (communicating electronic)—DDC
controllers provide system-level data used to
optimize overall SYSTEM performance.
Variables such as occupied/unoccupied,
minimum and maximum cfm and
temperature, valve position, ventilation
fraction, etc. are available on a simple twisted-
shielded wire pair. For additional information,
see “Industry Issues: Energy Efficiency”.

VAV-PRC011M-EN 9
Features and Benefits
• Pressure-independent (PI) operation—Provides airflow required by the room thermostat to
maintain occupant comfort. The controller automatically adjusts valve position to maintain
required airflow. Minimum and maximum airflow is factory-set and field-adjustable.
• Factory-set airflow and temperature setpoints
Air-Fi Wireless System
For more detailed information on Air-Fi™ Wireless systems and devices, see:
• BAS-SVX40*: Air-Fi™ Wireless Installation, Operation, and Maintenance
• BAS-PRD021*-: Air-Fi™ Wireless Product Data Sheet
• BAS-SVX55*: Air-Fi™ Wireless Network Design Best Practices
Air-Fi Wireless Communications Interface (WCI)
Air-Fi Wireless Communication Sensor
Wireless Zone Sensor Set
A factory-installed Air-Fi Wireless Communications Interface
(WCI) provides wireless communication between the Tracer™
SC, Tracer unit controllers and optionally, Air-Fi Wireless
Communication sensors. The Air-Fi WCI is the perfect
alternative to a Trane BACnet® wired communication link.
Eliminating the communication wire between terminal
products, space sensors, and system controllers has
substantial benefits:
• Reduced installation time and associated risks.
• Completion of projects with fewer disruptions.
• Easier and more cost-effective re-configurations,
expansions, and upgrades.
The WCS communicates wirelessly to a Tracer unit controller
that has an Air-Fi WCI installed. A WCS is an alternative to a
wired sensor when access and routing of communication
cable are issues. It also allows flexible mounting and
relocation.
The Trane wireless zone sensor set (sensor and receiver)
communicates wirelessly to a Tracer unit controller. The Trane
wireless zone sensor set is an alternative to a wired sensor
when access and routing of communication cable are issues.
It also allows flexible mounting and relocation.
Note: The Trane wireless zone sensor set is not compatible
with an Air-Fi™ wireless system.

10 VAV-PRC011M-EN
Features and Benefits
Pneumatic Controller
Binary Input Controller
Integration Options (Interfacing with other control systems) - Trane offers the following ways to
interface with other control systems.
1. Use Trane LONMARK®, factory-commissioned VAV controllers
2. Use Trane BACnet® factory-commissioned VAV controllers.
Factory-installed vs. Factory-commissioned
The terms factory-installed and factory-commissioned are often used interchangeably. Trane takes
great pride in being the industry leader in factory-commissioned DDC controllers. Table , p. 10
differentiates these concepts.
Factory-commissioned controllers provide the highest quality and most reliable units for your VAV
system. Additional testing verifies proper unit operation including occupied/unoccupied airflow,
temperature setpoints, communication link functionality, and output device functionality. The
benefits of factory-commissioning are standard on VariTrane™ terminal units with Trane DDC
controls. This means that factory-commissioned quality on VariTrane VAV units is now available
on ANY manufacturer’s control system that can communicate using the LonMark® Space Comfort
Control (SCC) protocol or using BACnet® communication protocol. (See Controls section for
complete listing of variables which are communicated.)
Pneumatic—Pneumatic controllers provide proven reliability
and performance. A full line of options provide:
• Highest quality PVR available, which maximizes space
temperature control.
Pressure-independent operation
•All VariTrane
™ pneumatic controllers use the patented flow
sensor input to provide the most accurate performance
available.
Binary Input Controller
Binary Input Controllers are system level controllers design to
communicate with the VAV boxes via external binary inputs
using the Trane Comm4 standard with VAV units that have VAV
UCM DDC controllers installed. This non-programmable
controller satisfies critical requirements for systems that do
not need the full functionality of a true Building Automation
System (BAS).
Table 1. Factory-installed vs. factory-commissioned
Factory-installed Factory-
commissioned
Transformer installed (option) X X
Wires terminated in reliable/consistent setting X X
Controller mounted X X
Electric heat contactors and fan relay wired X X
Testing of electric heat contactors and fan relay X
Controller addressing and associated testing X

VAV-PRC011M-EN 11
Features and Benefits
Trane VAV Systems - Proven Performance
Trane is the industry leader in VAV systems, including factory-commissioned controls and
integration with other control systems. This leadership began with customers seeking the most
reliable VAV products in the industry. The solution was factory-commissioned controls (see
Factory-installed vs. Factory-commissioned). Since then, it has blossomed to include optimized
system control strategies.
Control strategies are often made more complicated than necessary. VariTrane DDC controls
simplify control strategies by pre-engineering control logic and sequencing into the controller. This
information is available via a twisted-shielded wire pair or wireless communication, and accessible
via a Trane Tracer™ SC. Data is easily accessed via a computer workstation.
Optimized system control strategies, such as ventilation optimization, fan-pressure optimization,
and optimal start/stop, are pre-engineered in VariTrane unit-level DDC controllers and the Tracer
SC building automation system.
This allows a Trane VAV system to meet or exceed the latest ASHRAE 90.1 Energy Efficiency
standards. Pre-engineered controls allow consistent, high quality installations which are very
repeatable. The end result is PROVEN control strategies you can rely on to perform. For more
information on these and other control strategies, contact your local Trane Sales Office, or visit
www.trane.com.
• Purchasing VAV controllers and VAV hardware from a single manufacturer provides a single
contact for all HVAC system related questions
Indoor Air Quality Management During Construction
Minimum & Maximum airflows settings (occupied/unoccupied) X
Minimum & Maximum temperature setpoints (occupied/unoccupied) X
Minimum ventilation requirements X
Thumbwheel enable/disable X
Heating offset X
Trane Air-Fi™ wireless communications modules (WCI) X X
Pre-wired duct temperature sensor X X
Pre-wired water valve harness X X
Wireless zone sensor receiver X
Wireless zone sensor
Trane Air-Fi™ Wireless Communications Sensor (WCS)
Table 1. Factory-installed vs. factory-commissioned (continued)
Factory-installed Factory-
commissioned
LEED wrap option is a pressure sensitive
covering that prevents contamination of the
VAV box during the construction phase. It is
utilized to seal all openings without
constraining the installation process.

12 VAV-PRC011M-EN
Agency Certifications
There are numerous regulations and standards in the industry that determine the construction and
performance parameters for VAV terminal units. Some of the more important of those standards
and regulations are listed below, along with a brief description of what each one addresses.
American Society of Heating, Refrigerating and Air-conditioning
Engineers (ASHRAE)
ASHRAE - 41.1
ASHRAE - 41.2
ASHRAE - 41.3
These standards specify methods for temperature measurement (41.1), laboratory airflow
measurement (41.2), and pressure measurement (41.3). While none of these standards specifically
discusses VAV air terminals, they discuss topics that are aspects of terminal box systems.
Therefore, some engineers will include these standards in their specifications as a primer on
accepted measurement techniques.
ASHRAE - 62
This standard specifies the minimum ventilation rates and indoor air quality that are acceptable for
occupied spaces.
ASHRAE - 111
This standard calls out procedures to be followed for testing and balancing HVAC systems. It
includes descriptions of the equipment used, procedures followed, and field changes that must be
made when a system is balanced.
Air Conditioning and Refrigeration Institute (AHRI)
AHRI 880 - 2011
This standard sets forth classifications, performance testing requirements, and test results
reporting requirements for air terminal units. The standard contains very detailed procedures that
are to be followed for the testing and certification program associated with this standard. This is
one of the most commonly referenced standards in the VAV terminal unit industry. The AHRI-880
certification program is designed to police the accuracy of documented performance for terminal
units. The certification program requires a sampling of at least four units be tested annually. The
tested units are chosen at random by AHRI and sent to an independent laboratory for the testing.
The performance is tested at one specific operating condition. The operating characteristics tested
include discharge and radiated sound power (for the damper and, in the case of fan-powered
boxes, the fan), wide-open damper pressure drop, and fan motor amp draw. VariTrane terminal
units are certified according to AHRI-880.
AHRI 885-2008
This document provides a procedure to estimate sound pressure levels in an occupied space. The
standard accounts for the amount of sound pressure in the space due to the VAV air terminal,
diffusers and their connecting low pressure ductwork. While sound generated from the central
system fan and ductwork may be a significant factor in determining the sound pressure level in the
room, this standard does not address those factors. It focuses solely on the VAV terminal and items
downstream of it. This standard is related to AHRI-880 by using sound power determined using
AHRI-880 methodology as a starting point for the AHRI-885 procedure.

VAV-PRC011M-EN 13
Agency Certifications
Underwriter’s Laboratory (UL) 1995
Underwriter’s Laboratory is an independent testing agency that examines products and
determines if those products meet safety requirements. Equipment manufacturers strive to meet
UL guidelines and obtain listing and classifications for their products because customers recognize
UL approval as a measure of a safely designed product. VariTrane™ VAV air terminals are listed per
UL-1995, Heating and Cooling Equipment. The terminals are listed as an entire assembly.
National Fire Protection Association (NFPA)
NFPA 70
This standard is also known as the National Electrical Code (NEC). The Code gives standards for
installation of wiring and electrical equipment for most types of commercial and residential
buildings. It is often referred to in VAV air terminal specifications when fan-powered boxes, electric
heat or electric controls are included.
NFPA 90A
This standard does not speak directly to VAV air terminals but does discuss central system
considerations pertaining to a fire and/or smoke condition. The standard discusses safety
requirements in design and construction that should be followed to keep the air-handling system
from spreading a fire or smoke. The standard specifies practices that are intended to stop fire and
smoke from spreading through a duct system, keep the fire-resistive properties of certain building
structures (fire walls, etc.) intact, and minimize fire ignition sources and combustible materials.

14 VAV-PRC011M-EN
Digit 1, 2 — Unit Type
VC = VariTrane™ Single Duct
Digit 3—Reheat
C = Cooling Only
E = Electric Heat
W = Hot Water Heat
Digit 4—Development Sequence
F= Sixth
Digit 5, 6—Primary Air Valve
04 = 4" inlet (225 cfm)
05 = 5" inlet (350 cfm)
06 = 6" inlet (500 cfm)
08 = 8" inlet (900 cfm)
10 = 10" inlet (1400 cfm)
12 = 12" inlet (2000 cfm)
14 = 14" inlet (3000 cfm)
16 = 16" inlet (4000 cfm)
24 = 24" x 16" inlet (8000 cfm)
Digit 7, 8, 9—Not Used
000= N/A
Digit 10, 11—Design Sequence
** = Factory Assigned
Digit 12, 13, 14, 15—Controls
DD00 Trane Actuator Only and
Enclosure
DD01= UCM4 Cooling Only Control
DD02= UCM4 N.C. On/Off Hot Water
DD03= UCM4 Prop. Hot Water
DD04= UCM4 Staged On/Off E-Heat
DD05= UCM4 Pulse Width MOD E-Heat
DD07= UCM4 N.O. On/Off Hot Water
DD11= VV550 DDC Controller - Cooling
Only
DD12= VV550 DDC Ctrl to operate N.C.
On/Off water valve
DD13= VV550 DDC Ctrl to operate Prop
water valve
DD14= VV550 DDC Ctrl - On/Off Electric
Heat
DD15= VV550 DDC Ctrl w/Pulse Width
Modulation
DD16= VV550 DDC Controller -
Ventilation Flow
DD17= VV550 DDC Ctrl to operate N.O.
On/Off Water Valve
DD19= VV550 DDC Controller with Flow
Tracking
DD20= VV550 DDC Vent Flow cntrl to
operate N.C. water valve
DD21= VV550 DDC - Vent Flow w/ On/Off
Elec Heat
DD22= VV550 DDC Vent Flow cntrl to
operate prop water valve
DD23= VV550 DDC- Basic plus- Local
(Electric heat- PWM) Remote
(Staged EH)
DD24= VV550 DDC-Basic plus- Local
(Water heat- Modulating)
Remote (Water- N.C. 2 position)
DD25= VV550 DDC-Basic plus- Local
(Water heat- Modulating)
Remote (Water- N.O. 2 position)
DD26= VV550 DDC-Basic plus- Local
(Water heat- N.O. 2-position)
Remote (Water- Modulating)
DD27= VV550 DDC-Basic plus- Local
(Water heat- N.C. 2-position)
Remote (Water- Modulating)
DD28= VV550 DDC-Basic plus- Local
(Water heat- N.O. 2-position)
Remote (Water- N.O. 2-position)
DD29= VV550 DDC-Basic plus- Local
(Water heat- N.C. 2-position)
Remote (Water- NC 2-position)
DD30= VV550 DDC-Basic plus- Local
(Water heat- N.O. 2-position)
Remote (Water- N.C. 2-position)
DD31= VV550 DDC-Basic plus- Local
(Water heat- N.C. 2-position)
Remote (Water- N.O. 2-position)
DD32= VV550 DDC-Basic plus- Local
(Electric heat- Staged) Remote
(Staged EH)
DD33= VV550 DDC Vent Flow cntrl to
operate N.O. On/Off water valve
DD41= UC400 DDC-Basic (No water or
electric heat)
DD42= UC400 DDC-Basic (Water heat-
N.C.- 2 position)
DD43= UC400 DDC-Basic (Water heat-
Modulating)
DD44= UC400 DDC-Basic (Electric heat-
staged)
DD45= UC400 DDC-Basic (Electric heat-
PWM)
DD46= UC400 DDC Ventilation flow-
cooling only
DD47= UC400 DDC-Basic (Water heat-
N.O.- 2 position)
DD49= UC400 DDC-Flow Tracking
(Cooling only)
DD50= UC400 DDC-Ventilation Flow
(Water heat- N. C.- 2 position)
DD51= UC400 DDC-Ventilation Flow
(Electric heat- staged)
DD52= UC400 DDC-Ventilation Flow
(Water heat- Modulating)
DD53= UC400 DDC-Basic plus- Local
(Electric heat- PWM) Remote
(Staged EH)
DD54= UC400 DDC-Basic plus- Local
(Water heat- Modulating)
Remote (Water- N.C. 2 position)
DD55= UC400 DDC-Basic plus- Local
(Water heat- Modulating)
Remote (Water- N.O. 2 position)
DD56= UC400 DDC-Basic plus- Local
(Water heat- N.O. 2-position)
Remote (Water- Modulating)
DD57= UC400 DDC-Basic plus- Local
(Water heat- N.C. 2-position)
Remote (Water- Modulating)
DD58= UC400 DDC-Basic plus- Local
(Water heat- N.O. 2-position)
Remote (Water- N.O. 2-position)
DD59= UC400 DDC-Basic plus- Local
(Water heat- N.C. 2-position)
Remote (Water- N.C. 2-position)
DD60= UC400 DDC-Basic plus- Local
(Water heat- N.O. 2-position)
Remote (Water- N.C. 2-position)
DD61= UC400 DDC-Basic plus- Local
(Water heat- N.C. 2-position)
Remote (Water- N.O. 2-position)
DD62= UC400 DDC-Basic plus- Local
(Electric heat- Staged) Remote
(Staged EH)
DD63= UC400 DDC-Ventilation Flow
(Water heat- N.O. 2-position)
DD65= UC400 Basic
(Electric Heat Modulating SCR)
DD66= UC400 Basic plus-Local
(Electric heat-Modulating SCR)
Remote (Staged EH)
DD67= UC400 Ventilation Flow
(Electric heat-Modulating SCR)
DD71= UC210 DDC-Basic (No water or
electric heat)
DD72= UC210 DDC-Basic (Water heat-
N.C.- 2 position)
DD73= UC400 DDC-Basic (Water heat-
Modulating)
DD74= UC210 DDC-Basic (Electric heat-
staged)
DD75= UC210 DDC-Basic (Electric heat-
PWM)
DD76= UC210 DDC Ventilation flow-
cooling only
DD77= UC210 DDC-Basic (Water heat-
N.O.- 2 position)
DD79= UC210 DDC-Flow Tracking
(Cooling only)
DD80= UC210 DDC-Ventilation Flow
(Water heat- N. C.- 2 position)
DD81= UC210 DDC-Ventilation Flow
(Electric heat- staged)
DD82= UC210 DDC-Ventilation Flow
(Water heat- Modulating)
DD83= UC210 DDC-Basic plus- Local
(Electric heat- PWM) Remote
(Staged EH)
DD84= UC210 DDC-Basic plus- Local
(Water heat- Modulating)
Remote (Water- N.C. 2 position)
DD85= UC210 DDC-Basic plus- Local
(Water heat- Modulating)
Remote (Water- N.O. 2 position)
DD86= UC210 DDC-Basic plus- Local
(Water heat- N.O. 2-position)
Remote (Water- Modulating)
DD87= UC210 DDC-Basic plus- Local
(Water heat- N.C. 2-position)
Remote (Water- Modulating)
DD88= UC210 DDC-Basic plus- Local
(Water heat- N.O. 2-position)
Remote (Water- N.O. 2-position)
DD89= UC210 DDC-Basic plus- Local
(Water heat- N.C. 2-position)
Remote (Water- N.C. 2-position)
DD90= UC210 DDC-Basic plus- Local
(Water heat- N.O. 2-position)
Remote (Water- N.C. 2-position)
DD91= UC210 DDC-Basic plus- Local
(Water heat- N.C. 2-position)
Remote (Water- N.O. 2-position)
Model Number Descriptions

VAV-PRC011M-EN 15
Model Number Descriptions
DD92= UC210 DDC-Basic plus- Local
(Electric heat- Staged) Remote
(Staged EH)
DD93= UC210 Ventilation Flow
(Water heat- N.O. 2-position)
DD95= UC210 Basic
(Electric HeatModulating SCR)
DD96= UC210 Basic plus-Local
(Electric heat-Modulating SCR)
Remote (Staged EH)
DD97= UC210 Ventilation Flow
(Electric heat-Modulating SCR)
ENCL= Shaft Only in Enclosure
ENON= Shaft Out Side for Electric Units
FM00= Other Actuator and Control
FM01= Trane Supplied Actuator, Other
Ctrl
PC00= N.C. Actuator and Linkage Only
PC04= N.C. with DA Stat, 3000 Series
PC05= N.C. with RA STAT, 3000 Series
PCSS= Normally Closed Special
PN00= N.O. Actuator and Linkage Only
PN04= N.O. 3000 Series, DA STAT
PN05= N.O. 3000 Series, RA STAT
PN11= Auto Dual Min.
PN32= N.O. PNEU Constant Vol.
PN34= N.O. 3000 Series Constant
Vol.,RA STAT
PNON= Shaft Out Side for Pneumatic
Units
PNSS= Normally Open Special
N.C .= Normally-closed
N.O. = Normally-opened
DA Stat = Direct-acting pneumatic t-stat
(by others)
RA Stat = Reverse-acting pneumatic
t-stat (by others)
PN = Pneumatic
FM = Factory installation of customer-
supplied controller
PVR = Pneumatic Volume Regulator
Digit 16—Insulation
A = 1/2" Matte-faced
B = 1" Matte-faced
D = 1" Foil-faced
F = 1" Double-wall
G = 3/8" Closed-cell
Digit 17 & 18—Not Used
00 = N/A
Digit 19—Outlet Plenum
(Connection is Slip & Drive)
0= None
A = 1 Outlet RH
B = 1 Outlet END
C = 1 Outlet LH
D = 2 Outlets, 1 RH, 1 END
E = 2 Outlets, 1 LH, 1 END
F = 2 Outlets, 1 RH, 1 LH
H = 3 Outlets, 1 LH, 1 RH, 1 END
J = 4 Outlets, 1 LH, 1 RH, 2 END
Note: See unit drawings for outlet sizes/
damper information.
Digit 20—Not Used
0= N/A
Digit 21—Water Coil
0= None
1= 1-Row
2= 2-Row
3= 3-Row
4= 4-Row
A= 1-Row Premium
B = 2-Row Premium
C = 3-Row Premium
D = 4-Row Premium
Digit 22—Electrical Connections
F = Flippable (can be flipped in the
field for LH or RH connections
- VCEF only)
L = Left (Airflow hitting you in the
face)
R = Right (Airflow hitting you in the
face)
0 = Opposite side connection – coil
and control (VCWF only)
Note: VCCF, VCWF can be flipped in field
for opposite-hand connection
Digit 23—Transformer
0= None
1 = 120/24 volt (50 VA)
2 = 208/24 volt (50 VA)
3 = 240/24 volt (50 VA)
4 = 277/24 volt (50 VA)
5 = 480/24 volt (50 VA)
6 = 347/24 Volt (50 VA)
7 = 380/24 Volt (50 VA)
8 = 575/24 Volt (50 VA)
Note: For VCEF units with transformers
the VA depends on the staging,
control, and contactor type
(ranges are 50 VA to 75 VA, for 1
and 3 phase)
Digit 24—Disconnect Switch
0= None
W= With
Note: VCCF, VCWF – Toggle Disconnect;
VCEF – Door Interlocking Power
Disconnect
Digit 25—Power Fuse
0= None
W= With
Digit 26—Electric Heat Voltage
0= None
A = 208/60/1
B = 208/60/3
C = 240/60/1
D = 277/60/1
E = 480/60/1
F = 480/60/3
G = 347/60/1
H = 575/60/3
J = 380/50/3
K = 120/60/1
Digit 27 - 29—Electric Heat kW
000= None
010 = 1.0 kW
015 = 1.5 kW
460 = 46.0 kW
Note: 0.5 to 8.0 kW – ½ kW increments
8.0 to 18.0 kW – 1 kW increments
18.0 to 46.0 kW – 2 kW increments
Digit 30—Electric Heat Stages
0 = None
1 = 1 Stage
2 = 2 Stages Equal
3 = 3 Stages Equal
Digit 31—Electrical Heat
Contactors
0 = None
1 = 24-volt magnetic
2 = 24-volt mercury
3 = PE with magnetic
4= PE with mercury
5 = SCR heat UC400/UC210
6 = SCR heat FMTD/ENCL/DD00
A = 24-volt mercury (left hand)
B = 24-volt mercury (right hand)
C = PE with mercury (left hand)
D = PE with mercury (right hand)
Digit 32 & 33—Not Used
00 = N/A
Digit 34—Actuator
0= Standard
A = Spring Return (Normally Open)
B = Spring Return (Normally Closed)
C = Belimo Actuator
Digit 35—Sensor Options
0 = Standard (Wired)
1 = Factory Mounted Wireless
Receiver (Sensor Accessory)
2 = Wireless Communications
Interface
3 = Trane Air-Fi Wireless
Communications Interface
Digit 36—Pre-Wired Factory
Solutions
0 = None
1 = Factory Mounted DTS
2 = HW Valve Harness
3 = Both DTS & HW Valve Harness
4 = Averaging DTS factory installed
in unit (Required for
UC210/UC400 with SCR heat)
Digit 37—Bottom Access with Cam
Locks
0 = None
1 = Access Left Side Terminal Unit
2 = Access Right Side Terminal Unit
3 = Access Left Side Terminal Unit
with Water Connection on Right
4 = Access Right Side Terminal Unit
with Water Coil Connection on
Left

16 VAV-PRC011M-EN
Model Number Descriptions
Digit 38—Piping Package
0= None
A = 2-way Automatic Balancing
B = 3-way Automatic Balancing
Digit 39—Water Valve
0= None
1 = Proportional, HW Valve, 0.7 Cv
2 = Proportional, HW Valve, 2.7 Cv
3 = Proportional, HW Valve, 6.6 Cv
4 = Proportional, HW Valve, 8.0Cv
Digit 40—Flow Rate
0= None
A = 0.5 gpm (0.03 l/s)
B = 1.0 gpm (0.06 l/s)
C = 1.5 gpm (0.09 l/s)
D = 2.0 gpm (0.13 l/s)
E = 2.5 gpm (0.16 l/s)
F = 3.0 gpm (0.19 l/s)
G = 3.5 gpm (0.22 l/s)
H = 4.0 gpm (0.25 l/s)
J = 4.5 gpm (0.28 l/s)
K = 5.0 gpm (0.31 l/s)
L = 5.5 gpm (0.35 l/s)
M = 6.0 gpm (0.38 l/s)
N = 6.5 gpm (0.41 l/s)
P = 7.0 gpm (0.44 l/s)
Q = 7.5 gpm (0.47 l/s)
R = 8.0 gpm (0.50 l/s)
S = 9.0 gpm (0.57 l/s)
T = 10.0 gpm (0.63 l/s)
U = 11.0 gpm (0.69 l/s)
V = 12.0 gpm (0.76 l/s)
W = 13.0 gpm (0.82 l/s)
X = 14.0 gpm (0.88 l/s)
Y = 15.0 gpm (0.95 l/s)
Z = 16.0 gpm (1.01 l/s)
1 = 17.0 gpm (1.07 l/s)
2 = 18.0 gpm (1.14 l/s)
3 = 19.0 gpm (1.20 l/s)
4 = 20.0 gpm (1.26 l/s)
5 = 21.0 gpm (1.32 l/s)
6 = 22.0 gpm (1.39 l/s)
7 = 23.0 gpm (1.45 l/s)

VAV-PRC011M-EN 17
Single-Duct VAV Terminal Units
The features of the single-duct VAV terminal units are described by the product categories shown
in bold. Within each category the available options are listed.
Selection Procedure
This section describes the catalog selection of single-duct VAV terminal units with specific
examples. A computer selection program is also available to aid in selection of VAV terminal units.
Selection of single-duct VAV terminal units can involve three elements:
• Air valve selection
• Heating coil selection (if required)
• Acoustics controls
Air Valve Selection
The wide-open static pressure and airflows are found in the performance data section of the
catalog. To select an air valve, locate the required design cooling airflow for your terminal unit type
and find the smallest air valve size that has a pressure drop equal to or lower than the maximum
wide-open static pressure requirement.
Selection Example: Cooling Only VCCF Terminal Unit
Design cooling airflow: 1700 cfm
Maximum wide open Air pressure drop: 0.25 in. wg
Minimum cooling airflow: 850 cfm
From the performance data charts, select a valve size 12, which has a wide-open static pressure
drop of 0.01 in. wg
Check the minimum and maximum cfm desired with the minimum and maximum cfm allowed in
the table in the general data section. The maximum setting of 1700 cfm is within the acceptable
range. The desired minimum setting of 850 cfm is acceptable for the cooling only box desired. Note
that if an electric reheat box was selected, the minimum cfm would be dependent upon the kW of
the electric heater. (See Electric Heat Unit Selection.)
Heating Coil Selection (If required)
First, determine the amount of heat required to meet space and downstream duct heat losses from
a load calculation.
Hot Water Heat
Select a hot water coil sufficient to meet the design heat loss.
Example:
VCWF, Hot Water Unit Heat, Size 12 (See Air Valve Selection)
Heating airflow: 850 cfm
Hot water flow: 1.0 gpm
Design Heat Loss: Q =25 MBh
Select hot water coil from the coil performance table in the Performance Data section of the catalog.
Selection:
A one-row coil is sufficient to meet design conditions. From the Hot Water Coil Capacity Data of the
Performance Data Section, a one-row coil for a size 12 air valve will operate at the above conditions
as follows:
Coil Capacity: 25.17 MBh
Water pressure drop: 0.72 ft WPD

18 VAV-PRC011M-EN
Single-Duct VAV Terminal Units
Air pressure drop (APD) of the hot water coil is included in the chart preceding the hot water coil
performance data section.
APD = 0.35 in. wg
Electric Heat
Determine the kW required to meet zone design heat loss.
kW=MBh / 3.414
MBh=Design Heat Loss
Select the nearest available kW with voltage and steps desired from the electric heater kW guideline
table in the Performance Data section of the catalog.
Example
VCEF, Electric Unit Heat, Size 12 (See Air Valve Selection)
Heating airflow: 850 cfm
Voltage: 277/60/1 VAC
Design Heat Loss: Q=25 MBh
kW=Q/3.414
kW=25/3.414
kW=7.3
Selection:
Select 7.5 kW from the electric heat table in the voltage and stages required. The table shows the
minimum cfm allowable for the kW selected. The static pressure requirement is shown as 0.06 in.
wg for this example with a design cooling flow of 1700 cfm.
Check Leaving Air Temperature:
T is the primary entering air temperature 55°F for this example.
Decide if leaving air temperature of 82.8°F is satisfactory for your application.
Acoustics
The acoustical data found in the "Performance Data" section of the VAV catalog is used to make a
determination of the amount of noise the terminal unit will generate. Locate the table for the VAV
terminal unit of interest. Sound power data and an equivalent NC level for an AHRI 885-2008
transfer function is listed.
Example
VCCF, Cooling-Only Terminal Unit, Size 10 (See air Valve Selection)
Cooling Airflow: 1100 cfm
Maximum inlet static pressure: 1.5 in. wg
Interpolation gives sound power data of:
The NC level above is determined by using either the catalog’s AHRI 885-2008 mineral fiber for
radiated sound transfer function for the conditions shown in the acoustics table. A different transfer
function could be applied as conditions dictate.
LAT Q
1.085 CFM×
-------------------------------------T+=
LAT 3414 7.5×
1.085 850×
-----------------------------------55 82.8=+=
Octave Band 2 3 4 5 6 7 NC
Disch Sound Power 68686565 605728
Rad Sound Power 63 58 54 47 39 32 29

VAV-PRC011M-EN 19
Single-Duct VAV Terminal Units
The maximum NC level is NC-29. If the maximum NC level was exceeded, it would have been
necessary to reselect the next larger unit size.
Computer Selection
The advent of personal computers has served to automate many processes that were previously
repetitive and time-consuming. One of those tasks is the proper scheduling, sizing, and selection
of VAV terminal units. Trane has developed a computer program to perform these tasks. The
software is called the Trane Official Product Selection System (TOPSS™).
The TOPSS program will take the input specifications and output the properly sized VariTrane™ VAV
terminal unit along with the specific performance for that size unit.
The program has several required fields, denoted by red shading in the TOPSS screen, and many
other optional fields to meet the criteria you have. Required values include maximum and
minimum airflows, control type, and model. If selecting models with reheat, you will be required
to enter information to make that selection also. The user is given the option to look at all the
information for one selection on one screen or as a schedule with the other VAV units on the job.
The user can select single-duct, dual-duct, and fan-powered VAV boxes with the program, as well
as most other Trane products, allowing you to select all your Trane equipment with one software
program.
The program will also calculate sound power data for the selected terminal unit. The user can enter
a maximum individual sound level for each octave band or a maximum NC value. The program will
calculate acoustical data subject to default or user supplied sound attenuation data.
Schedule View
The program has many time-saving features such as: 1) Copy/Paste from spreadsheets like
Microsoft® Excel; 2) Easily arranged fields to match your schedule; and 3) Time-saving templates
to store default settings.
The user can also export the Schedule View to Excel to modify and put into a CAD drawing as a
schedule. Specific details regarding the program, its operation, and how to obtain a copy of it are
available from your local Trane sales office.
General Data
Table 2. Primary airflow control factory settings - I-P
Control Type Air Valve Size
(in.) Maximum Valve
Cfm Maximum Controller
Cfm Minimum Controller
Cfm Constant Volume Cfm
Direct Digital Control/
UCM
4
5
6
225
350
500
25-225
40-350
60-500
0,25-225
0,40-350
0,60-500
25-225
40-350
60-500
8
10
12
900
1400
2000
105-900
165-1400
240-2000
0,105-900
0,165-1400
0,240-2000
105-900
165-1400
240-2000
14
16
24 x 16
3000
4000
8000
320-3000
420-4000
800-8000
0,320-3000
0,420-4000
0,800-8000
320-3000
420-4000
800-8000
Pneumatic with
Volume Regulator
4
5
6
225
350
500
38-225
63-350
73-500
0,38-225
0,63-350
0,73-500
38-225
63-350
73-500
8
10
12
900
1400
2000
134-900
215-1400
300-2000
0,134-900
0,215-1400
0,300-2000
134-900
215-1400
300-2000
14
16
24 x 16
2887
3789
7745
408-2887
536-3789
1096-7745
0,408-2887
0,536-3789
0,1096-7745
408-2887
536-3789
1096-7745

20 VAV-PRC011M-EN
Single-Duct VAV Terminal Units
Table 3. Primary airflow control factory settings - SI
Control Type Air Valve
Size (in.) Maximum Valve L/s Maximum Controller
L/s Minimum Controller
L/s Constant Volume L/
s
Direct Digital Control/
UCM
4
5
6
106
165
236
12-106
19-165
28-236
0,12-106
0,19-165
0,28-236
12-106
19-165
28-236
8
10
12
425
661
944
50-425
77-661
111-944
0,50-425
0,77-661
0,111-944
50-425
77-661
111-944
14
16
24 x 16
1416
1888
3776
151-1416
198-1888
378-3776
0,151-1416
0,198-1888
0,378-3776
151-1416
198-1888
378-3776
Pneumatic with
Volume Regulator
4
5
6
106
165
236
18-106
30-165
35-236
0,18-106
0,30-165
0,35-236
18-106
30-165
35-236
8
10
12
425
661
944
63-425
102-661
141-944
0,63-425
0,102-661
0,141-944
63-425
102-661
141-944
14
16
24 x 16
1363
1788
3656
193-1363
253-1788
517-3656
0,193-1363
0,253-1788
0,517-3656
193-1363
253-1788
517-3656
Note: Maximum airflow must be greater than or equal to minimum airflow.

VAV-PRC011M-EN 21
Single-Duct VAV Terminal Units
Performance Data
Table 4. Air pressure drop - in. wg (I-P)
Inlet Size Airflow Cfm Cooling Only Hot Water
1-row coil Hot Water
2-row coil Hot Water
3-row coil Hot Water
4-row coil Electric Heat
04
50
100
150
225
0.01
0.01
0.01
0.01
0.01
0.02
0.03
0.06
0.01
0.02
0.03
0.06
0.01
0.03
0.08
0.16
0.01
0.04
0.10
0.22
0.01
0.01
0.01
0.02
05
100
200
300
350
0.01
0.01
0.01
0.02
0.01
0.05
0.09
0.12
0.03
0.08
0.17
0.22
0.03
0.13
0.27
0.35
0.04
0.18
0.36
0.47
0.01
0.01
0.02
0.02
06
100
250
350
500
0.01
0.05
0.10
0.22
0.02
0.11
0.22
0.45
0.03
0.17
0.32
0.63
0.03
0.20
0.35
0.64
0.04
0.26
0.47
0.85
0.01
0.05
0.11
0.23
08
200
400
600
900
0.01
0.02
0.04
0.08
0.03
0.10
0.20
0.40
0.05
0.17
0.34
0.69
0.07
0.24
0.49
0.97
0.09
0.32
0.64
1.28
0.01
0.02
0.05
0.11
10
500
800
1100
1400
0.01
0.01
0.01
0.01
0.07
0.15
0.27
0.42
0.12
0.26
0.44
0.66
0.17
0.38
0.66
0.99
0.22
0.51
0.88
1.32
0.01
0.02
0.03
0.05
12
800
1200
1600
2000
0.01
0.01
0.01
0.01
0.10
0.19
0.31
0.45
0.19
0.35
0.55
0.79
0.22
0.42
0.69
1.01
0.28
0.56
0.91
1.34
0.01
0.03
0.05
0.08
14
1500
2000
2500
3000
0.01
0.01
0.01
0.01
0.10
0.16
0.22
0.30
0.23
0.36
0.51
0.69
0.34
0.54
0.79
1.09
0.44
0.72
1.05
1.45
0.01
0.01
0.01
0.01
16
2000
2500
3000
4000
0.01
0.01
0.01
0.01
0.11
0.16
0.22
0.35
0.30
0.46
0.65
1.14
0.39
0.57
0.78
1.29
0.52
0.76
1.04
1.72
0.01
0.02
0.02
0.03
24 x 16
4000
5500
6500
8000
0.08
0.16
0.23
0.36
0.40
0.70
0.95
*
0.66
*
*
*
0.97
1.73
2.38
3.62
1.29
2.30
3.17
4.83
0.15
0.30
0.44
0.69
Notes:
1. Hot water coil pressure drops are for the entire unit, not just the coil. To calculate the hot water coil only pressure drop, subtract the cooling only
pressure drop from the other pressure drop.
2. * indicated "not recommended"

22 VAV-PRC011M-EN
Single-Duct VAV Terminal Units
Table 5. Air pressure drop - Pa (SI)
Inlet Size Airflow (L/s) Cooling Only Hot Water
1-row coil Hot Water
2-row coil Hot Water
3-row coil Hot Water
4-row coil Electric Heat
04
25
50
70
105
3
3
3
3
3
4
7
15
3
4
7
15
2.5
7.5
20
40
2.5
10
25
55
3
3
3
3
05
45
95
140
165
3
3
3
4
3
12
22
29
6
21
41
54
7.5
32
67
87
10
45
90
117
3
3
5
6
06
45
120
165
235
3
13
26
55
4
29
55
112
7
43
79
155
7.5
50
87
159
10
65
117
212
3
14
27
57
08
95
190
280
420
3
4
9
21
8
25
49
99
13
43
83
169
17
60
122
242
22
80
159
319
3
6
12
28
10
235
375
520
660
3
3
3
3
16
37
67
104
29
63
110
165
42
95
164
247
55
127
219
329
3
5
9
13
12
375
565
755
940
3
3
3
3
24
47
76
111
47
88
138
195
55
105
172
252
70
139
227
334
3
7
13
19
14
700
945
1180
1415
3
3
3
3
26
40
56
74
55
89
127
171
85
135
197
272
110
179
262
361
3
3
3
3
16
940
1180
1415
1885
3
3
3
3
28
40
54
87
73
114
162
284
97
142
194
321
130
189
259
428
3
4
5
8
24 x 16
1885
2600
3070
3775
20
40
57
90
100
176
236
341
165
279
366
513
242
431
593
902
321
573
790
1203
38
76
110
172
Notes:
1. Hot water pressure drops are for the entire unit, not just the coil. To calculate the hot water coil only pressure drop, subtract the cooling only
pressure drop from the other pressure drop.
ABCD HF
EJ
A,B,C III
I, II III, IV IV
I, II I, II
OUTL H
J
D,E,F
N/A
I, II
I, II
N/A
I, II
I, II
N/A
I, II
I, II
I, II, III
N/A
I, II, III
II, III, IV
I
II, III, IV
III, IV
I, II
III, IV
OUTLET AVAILABILITY CHART - SEE OUTL CONVERSION FOR NOMINALØ
VALV 4
OUTL CONVERSION CHART
NOMINALØ
5" (127 mm)
6" (152 mm)
8" (203 mm)
10" (254 mm)
IV
56
SYMBOL
II
III
I
81012
OUTLET PLENUM
ARRANGEMENTS
(TOP VIEW)

VAV-PRC011M-EN 23
Single-Duct VAV Terminal Units
Table 6. Integral outlet plenum air pressure drop - in. wg (I-P)
Inlet
Size Outlet
Configuration Outlet (in.)
Diameter
Airflow (Cfm)
50 100 150 200 250 350 400 500 600 800 900 1100 1200 1400 1600 2000
4,5,6
4,5,6 A,C 5
6
0.02
0.01
0.07
0.03
0.15
0.07
0.26
0.13
0.41
0.20
0.80
0.37
1.04
0.48
1.63
0.74
8,10
10
12
AC
8
10
10
0.04
0.01
0.06
0.02
0.03
0.11
0.04
0.06
0.14
0.05
0.08
0.23
0.08
0.12
0.33
0.12
0.17
0.58
0.21
0.29
0.74
0.27
0.37
1.11
0.41
0.54
1.33
0.48
0.64
1.81
0.66
0.86 1.11 1.71
4,5,6
4,5,6
8
B
5
6
8
0.01
0.01
0.03
0.01
0.08
0.01
0.15
0.03
0.01
0.23
0.04
0.01
0.48
0.07
0.02
0.64
0.10
0.02
1.02
0.15
0.03 0.05 0.07 0.09
10
10
12
B
8
10
10
0.02
0.01
0.04
0.01
0.02
0.07
0.01
0.04
0.09
0.01
0.05
0.14
0.02
0.08
0.20
0.02
0.11
0.35
0.04
0.19
0.44
0.06
0.24
0.65
0.08
0.36
0.76
0.10
0.43
1.03
0.13
0.58 0.76 1.17
4,5,6
4,5,6 D,E 5
6
0.01
0.01
0.01
0.01
0.02
0.01
0.04
0.01
0.05
0.01
0.09
0.01
0.12
0.02
0.17
0.03
8
8
8
D, E
5
6
8
0.06
0.02
0.01
0.09
0.03
0.01
0.18
0.05
0.01
0.23
0.07
0.01
0.35
0.11
0.01
0.49
0.15
0.01
0.85
0.26
0.01
1.06
0.32
0.01
10
10
10
D, E
6
8
10
0.02
0.01
0.01
0.04
0.01
0.01
0.07
0.01
0.01
0.10
0.02
0.01
0.15
0.02
0.01
0.22
0.04
0.01
0.38
0.06
0.02
0.48
0.08
0.02
0.72
0.12
0.03
0.85
0.14
0.04
1.16
0.19
0.05
12
12 D, E 8
10
0.01 0.02
0.01
0.03
0.01
0.05
0.02
0.07
0.02
0.12
0.04
0.15
0.05
0.23
0.07
0.28
0.08
0.38
0.11
0.49
0.14
0.77
0.21
4,5,6
4,5,6,8 F6
5
0.01
0.01
0.01
0.03
0.03
0.06
0.05
0.10
0.08
0.16
0.16
0.30
0.21
0.38
0.32
0.58 0.83 1.43 1.78
8,10
8,10 F6
8
0.05
0.01
0.08
0.02
0.14
0.04
0.18
0.06
0.27
0.09
0.37
0.13
0.61
0.23
0.76
0.29
1.08
0.43
1.26
0.52
1.66
0.71
10
12
12
F
10
8
10
0.01 0.01
0.02
0.01
0.02
0.04
0.02
0.02
0.05
0.02
0.03
0.07
0.03
0.04
0.10
0.04
0.07
0.17
0.06
0.08
0.21
0.08
0.12
0.31
0.11
0.14
0.37
0.13
0.18
0.50
0.16
0.64
0.21
0.98
0.30
4,5,6
4
5
6
H
5
6
6
6
0.01
0.01
0.01
0.01
0.01
0.01
0.01
0.01
0.01
0.01
0.01
0.01
0.01
0.01
0.01
0.01
0.01
0.01
0.03
0.01
0.01
0.04
0.01
0.06
0.01
8
8
8
H
5
6
8
0.03
0.01
0.01
0.05
0.01
0.01
0.09
0.02
0.01
0.11
0.03
0.01
0.18
0.04
0.01
0.25
0.06
0.01
0.43
0.10
0.02
0.54
0.13
0.03
10
10
10
H
6
8
10
0.01
0.01
0.01
0.02
0.01
0.01
0.04
0.01
0.01
0.05
0.01
0.01
0.08
0.01
0.01
0.11
0.02
0.01
0.18
0.03
0.01
0.22
0.03
0.01
0.32
0.05
0.01
0.38
0.05
0.01
0.50
0.07
0.01
12
12 H8
10
0.01
0.01
0.01
0.01
0.02
0.01
0.03
0.01
0.04
0.01
0.06
0.02
0.08
0.02
0.11
0.03
0.13
0.03
0.17
0.05
0.21
0.06
0.32
0.09
10
12
12
J
5
5
6
0.02 0.02
0.03
0.01
0.05
0.06
0.02
0.06
0.08
0.03
0.09
0.12
0.04
0.13
0.17
0.06
0.23
0.30
0.11
0.29
0.38
0.14
0.43
0.57
0.21
0.51
0.68
0.25
0.70
0.92
0.35
1.20
0.45
1.87
0.71

24 VAV-PRC011M-EN
Single-Duct VAV Terminal Units
Table 7. Integral outlet plenum air pressure drop - Pa (SI)
Inlet Size Outlet
Configuration Outlet (mm)
Diameter
Airflow (L/s)
25 50 70 95 120 165 190 235 280 375 420 520 565 660 755 940
4,5,6
4,5,6 A,C 127
152
4
3
17
8
37
18
66
32
102
49
199
93
260
120
405
185
8,10
10
12
AC
203
254
254
914
3
27
5
8
36
10
15
56
13
19
81
21
29
145
30
42
185
53
73
277
67
91
330
101
134
451
120
159
164
214 277 427
4,5,6
4,5,6
8
B
127
152
203
3
3
8
3
20
4
36
6
3
58
10
3
119
19
5
158
24
6
254
37
8111923
10
10
12
B
203
254
254
6
3
9
3
5
17
3
10
22
3
12
35
4
19
49
6
28
86
11
48
109
14
61
161
20
90
190
24
107
257
33
145 188 292
4,5,6
4,5,6 D,E 127
152
3
3
3
3
6
3
9
3
13
3
23
3
29
4
42
6
8
8
8
D, E
127
152
203
15
5
3
23
7
3
44
13
3
57
17
3
87
26
3
123
37
3
211
64
3
264
81
3
10
10
10
D, E
152
203
254
6
3
3
9
3
3
18
3
3
24
4
3
37
6
3
54
9
3
95
16
4
120
20
5
179
30
8
213
35
9
289
48
12
12
12 D, E 203
254
3
3
6
3
7
3
12
4
17
6
30
10
38
12
57
17
69
20
94
27
123
34
193
52
4,5,6
4,5,6,8 F152
127
3
3
4
7
8
15
14
25
21
39
40
74
52
95
81
145 206 355 444
8,10
8,10 F152
203
13
3
19
5
35
10
45
14
66
22
92
31
153
56
189
72
269
108
315
129
414
177
10
12
12
F
254
203
254
33
5
3
4
9
4
5
11
5
7
18
7
10
25
9
17
43
16
21
53
19
29
78
27
34
92
31
45
124
41
159
51
244
75
4,5,6
4
5
6
H
127
152
152
152
3
3
3
3
3
3
3
3
3
3
3
3
3
3
3
3
3
3
7
3
3
9
3
15
3
8
8
8
H
127
152
203
8
3
3
12
3
3
22
6
3
29
7
3
44
11
3
62
15
3
108
26
5
136
33
6
10
10
10
H
152
203
254
4
3
3
5
3
3
10
3
3
13
3
3
19
3
3
27
4
3
45
6
3
56
8
3
81
12
3
95
14
3
126
18
3
12
12 H203
254
3
3
3
3
4
3
6
3
9
3
15
4
19
5
27
7
32
9
42
11
53
15
80
22
10
12
12
J
127
127
152
46
7
3
11
14
5
15
19
7
23
29
11
33
42
15
58
75
28
73
95
35
108
142
53
128
168
63
173
229
86
299
113
467
178

VAV-PRC011M-EN 25
Single-Duct VAV Terminal Units
Table 8. Heating capacity (MBh) - inlet size 04, 05, 06 (I-P)
Water
Pressure
Drop (ft)
Airflow (cfm)
Rows gpm 50 100 150 200 250 300 350 400 450 500
1-Row
Capacity
MBH
0.5 0.48 4.33 5.97 7.09 7.97 8.73 9.39 9.98 10.50 10.97 11.39
1.0 1.61 4.64 6.61 8.02 9.19 10.21 11.13 11.96 12.72 13.43 14.10
1.5 3.27 4.75 6.85 8.39 9.68 10.83 11.87 12.83 13.72 14.55 15.34
2.0 5.44 4.81 6.98 8.59 9.95 11.17 12.29 13.32 14.28 15.19 16.05
2.5 8.07 4.85 7.06 8.71 10.12 11.39 12.55 13.63 14.65 15.61 16.51
2-Row
Capacity
MBH
1.0 0.57 5.54 9.39 12.19 14.31 15.98 17.33 18.46 19.40 20.22 20.92
2.0 1.96 5.70 9.96 13.27 15.93 18.12 19.97 21.56 22.93 24.15 25.22
3.0 4.08 5.75 10.16 13.66 16.54 18.95 21.01 22.80 24.37 25.77 27.03
4.0 6.87 5.78 10.26 13.87 16.86 19.39 21.57 23.47 25.16 26.67 28.02
5.0 10.31 5.80 10.33 14.00 17.06 19.66 21.92 23.90 25.66 27.24 28.66
3-Row
Capacity
MBH
1.0 0.82 6.00 10.53 13.96 16.62 18.75 20.48 21.93 23.15 24.20 25.11
2.0 2.82 6.12 11.04 15.02 18.31 21.07 23.42 25.46 27.24 28.82 30.22
3.0 5.83 6.19 11.21 15.39 18.91 21.93 24.54 26.83 28.86 30.67 32.30
4.0 9.78 6.29 11.30 15.58 19.23 22.37 25.12 27.55 29.72 31.67 33.44
5.0 14.64 6.35 11.35 15.70 19.42 22.65 25.49 28.00 30.26 32.30 34.15
4-Row
Capacity
MBH
1.0 1.08 6.46 11.64 15.80 19.08 21.72 23.88 25.67 27.18 28.47 29.58
2.0 3.68 6.50 12.09 16.85 20.88 24.33 27.31 29.90 32.17 34.19 35.99
3.0 7.58 6.51 12.24 17.19 21.50 25.25 28.55 31.47 34.08 36.42 38.54
4.0 12.70 6.52 12.34 17.37 21.81 25.72 29.19 32.29 35.08 37.61 39.91
5.0 18.97 6.53 12.47 17.47 21.99 26.00 29.58 32.80 35.70 38.34 40.76
Notes:
1. Fouling Factor = 0.00025 °F·ft²·h/Btu
2. Capacity based on 55°F entering air temperature and 180°F entering water temperature.
Table 9. Heating capacity (MBh) - inlet size 08 (I-P)
Water
Pressure
Drop (ft)
Airflow (cfm)
Rows gpm 105 200 300 400 500 600 700 800 900
1-Row
Capacity
MBH
0.5 0.64 7.05 9.19 10.80 12.04 13.04 13.87 14.58 15.19 15.72
1.0 2.14 7.82 10.61 12.78 14.56 16.11 17.50 18.72 19.82 20.81
1.5 4.37 8.12 11.18 13.63 15.70 17.51 19.13 20.60 21.97 23.22
2.0 7.25 8.28 11.49 14.10 16.33 18.31 20.09 21.73 23.24 24.63
2.5 10.76 8.37 11.68 14.40 16.74 18.83 20.73 22.47 24.09 25.60
2-Row
Capacity
MBH
2.5 0.39 10.83 17.05 21.63 25.03 27.66 29.78 31.53 33.00 34.26
4.0 0.94 11.12 17.89 23.11 27.13 30.33 32.97 35.18 37.08 38.72
6.0 2.00 11.29 18.39 24.03 28.45 32.05 35.05 37.60 39.81 41.74
8.0 3.42 11.37 18.66 24.52 29.17 32.99 36.20 38.95 41.34 43.45
10.0 5.21 11.43 18.83 24.83 29.62 33.58 36.93 39.81 42.33 44.55
12.0 7.35 11.46 18.94 25.04 29.94 34.00 37.44 40.42 43.02 45.33

26 VAV-PRC011M-EN
Single-Duct VAV Terminal Units
3-Row
Capacity
MBH
2.5 0.53 11.95 19.51 25.34 29.76 33.26 36.09 38.44 40.43 42.15
4.0 1.24 12.18 20.28 26.82 31.97 36.16 39.65 42.61 45.15 47.38
6.0 2.62 12.31 20.74 27.71 33.32 37.98 41.91 45.29 48.23 50.83
8.0 4.45 12.37 20.97 28.17 34.04 38.95 43.13 46.75 49.93 52.75
10.0 6.73 12.41 21.11 28.46 34.49 39.56 43.91 47.68 51.01 53.97
12.0 9.45 12.44 21.21 28.66 34.80 39.98 44.44 48.33 51.76 54.83
4-Row
Capacity
MBH
2.5 0.66 13.02 22.00 29.26 34.89 39.37 43.03 46.06 48.63 50.84
4.0 1.55 13.18 22.72 30.80 37.33 42.73 47.25 51.12 54.45 57.37
6.0 3.23 13.25 23.13 31.69 38.78 44.76 49.87 54.31 58.19 61.63
8.0 5.48 13.29 23.33 32.14 39.53 45.83 51.27 56.02 60.22 63.97
10.0 8.26 13.32 23.46 32.42 40.00 46.50 52.14 57.10 61.51 65.45
12.0 11.56 13.34 23.54 32.61 40.31 46.95 52.74 57.85 62.39 66.47
Notes:
1. Fouling Factor = 0.00025 °F·ft²·h/Btu
2. Capacity based on 55°F entering air temperature and 180°F entering water temperature.
Table 9. Heating capacity (MBh) - inlet size 08 (I-P) (continued)
Water
Pressure
Drop (ft)
Airflow (cfm)
Rows gpm 105 200 300 400 500 600 700 800 900
Table 10. Heating capacity (MBh) - inlet size 10 (I-P)
Water
Pressure
Drop (ft)
Airflow (cfm)
Rows gpm 200 300 400 500 600 700 800 900 1000 1200 1400
1-Row
Capacity
MBH
0.7 1.60 11.99 14.16 15.95 17.43 18.69 19.77 20.73 21.58 22.35 23.68 24.79
1.0 2.97 12.82 15.36 17.40 19.18 20.78 22.19 23.46 24.61 25.66 27.52 29.11
1.5 6.04 13.53 16.42 18.80 20.87 22.72 24.41 26.01 27.48 28.85 31.30 33.47
2.0 10.03 13.92 17.00 19.58 21.85 23.90 25.78 27.52 29.14 30.69 33.54 36.08
2.5 14.87 14.16 17.37 20.08 22.48 24.66 26.67 28.54 30.30 31.95 35.02 37.83
2-Row
Capacity
MBH
2.5 1.09 19.51 25.67 30.49 34.36 37.55 40.24 42.54 44.53 46.27 49.20 51.56
4.0 2.60 20.19 27.00 32.50 37.06 40.92 44.24 47.12 49.66 51.92 55.78 58.97
6.0 5.55 20.58 27.78 33.72 38.72 43.02 46.76 50.06 52.99 55.62 60.17 63.98
8.0 9.54 20.78 28.19 34.36 39.61 44.15 48.13 51.66 54.82 57.67 62.62 66.80
10.0 14.53 20.90 28.44 34.76 40.16 44.86 48.99 52.67 55.98 58.97 64.19 68.61
3-Row
Capacity
MBH
2.5 1.31 21.72 29.21 35.21 40.10 44.18 47.62 50.58 53.15 55.40 59.18 62.24
4.0 3.11 22.32 30.49 37.27 42.99 47.89 52.13 55.85 59.15 62.08 67.12 71.29
6.0 6.59 22.65 31.22 38.48 44.71 50.13 54.90 59.14 62.93 66.35 72.30 77.31
8.0 11.26 22.82 31.60 39.10 45.61 51.31 56.37 60.89 64.97 68.67 75.14 80.64
10.0 17.10 22.92 31.82 39.48 46.16 52.04 57.28 61.99 66.25 70.12 76.94 82.76
4-Row
Capacity
MBH
2.5 1.76 23.85 32.84 40.21 46.29 51.39 55.70 59.39 62.59 65.39 70.06 73.79
4.0 4.13 24.36 34.08 42.37 49.48 55.64 61.02 65.75 69.95 73.70 80.13 85.45
6.0 8.67 24.71 34.75 43.58 51.31 58.13 64.19 69.61 74.49 78.91 86.62 93.13
8.0 14.72 24.81 35.09 44.18 52.23 59.40 65.83 71.63 76.89 81.69 90.13 97.34
10.0 22.23 24.85 35.29 44.55 52.79 60.18 66.84 72.88 78.38 83.42 92.34 100.00
Notes:
1. Fouling Factor = 0.00025 °F·ft²·h/Btu
2. Capacity based on 55°F entering air temperature and 180°F entering water temperature.

VAV-PRC011M-EN 27
Single-Duct VAV Terminal Units
Table 11. Heating capacity (MBh) - inlet size 12 (I-P)
Water
Pressure
Drop (ft)
Airflow (cfm)
Rows gpm 300 500 700 900 1100 1300 1500 1700 1900 2000
1-Row
Capacity
MBH
1.0 0.62 17.04 20.87 23.79 26.07 27.94 29.51 30.85 32.03 33.06 33.52
2.0 2.17 19.32 24.45 28.47 31.86 34.91 37.59 39.99 42.15 44.11 45.02
3.0 4.53 20.21 25.94 30.55 34.52 38.04 41.21 44.15 46.87 49.37 50.55
4.0 7.68 20.69 26.75 31.70 36.01 39.88 43.40 46.64 49.63 52.44 53.80
5.0 11.57 20.99 27.26 32.43 36.97 41.07 44.82 48.29 51.53 54.55 56.00
2-Row
Capacity
MBH
3.5 0.66 28.44 39.44 47.27 53.16 57.79 61.53 64.63 67.25 69.49 70.50
5.0 1.29 29.38 41.51 50.49 57.46 63.05 67.66 71.55 74.88 77.77 79.08
8.0 3.14 30.24 43.48 53.63 61.74 68.40 74.01 78.81 82.98 86.65 88.32
11.0 5.76 30.65 44.43 55.18 63.88 71.13 77.28 82.59 87.24 91.36 93.25
14.0 9.12 30.89 44.99 56.11 65.18 72.79 79.28 84.92 89.88 94.29 96.32
17.0 13.23 31.05 45.37 56.73 66.06 73.91 80.65 86.51 91.69 96.30 98.43
3-Row
Capacity
MBH
3.5 0.83 31.05 44.01 53.46 60.67 66.37 71.00 74.84 78.09 80.88 82.14
5.0 1.60 31.90 46.06 56.81 65.27 72.13 77.82 82.64 86.78 90.39 92.02
8.0 3.86 32.66 47.95 59.97 69.73 77.85 84.73 90.66 95.84 100.40 102.50
11.0 7.02 33.02 48.84 61.51 71.93 80.70 88.22 94.76 100.51 105.63 107.98
14.0 11.05 33.22 49.37 62.41 73.24 82.42 90.33 97.25 103.37 108.84 111.36
17.0 15.95 33.36 49.72 63.02 74.11 83.57 91.76 98.94 105.32 111.02 113.66
4-Row
Capacity
MBH
3.5 1.00 35.26 51.81 64.24 73.81 81.37 87.49 92.55 96.80 100.42 102.03
5.0 1.92 35.98 53.92 68.04 79.36 88.62 96.32 102.84 108.43 113.28 115.48
8.0 4.58 36.60 55.77 71.49 84.57 95.61 105.05 113.23 120.40 126.73 129.63
11.0 8.28 36.88 56.61 73.10 87.04 98.99 109.35 118.43 126.47 133.64 136.95
14.0 12.98 37.04 57.09 74.03 88.49 100.99 111.91 121.55 130.14 137.85 141.41
17.0 18.68 37.16 57.41 74.64 89.45 102.31 113.62 123.64 132.60 140.68 144.43
Notes:
1. Fouling Factor = 0.00025 °F·ft²·h/Btu
2. Capacity based on 55°F entering air temperature and 180°F entering water temperature.

28 VAV-PRC011M-EN
Single-Duct VAV Terminal Units
Table 12. Heating capacity (MBh) - inlet size 14 (I-P)
Water
Pressure
Drop (ft)
Airflow (cfm)
Rows gpm 600 1000 1400 1800 2200 2600 3000 3400 3800 4000
1-Row
Capacity
MBH
2.0 1.13 25.34 32.22 37.40 41.72 45.32 48.41 51.10 53.46 55.57 56.85
3.0 2.35 26.92 34.91 41.07 46.22 50.79 54.84 58.45 61.69 64.63 66.45
4.0 3.96 27.78 36.42 43.21 48.99 54.07 58.64 62.86 66.70 70.22 72.41
5.0 5.96 28.33 37.39 44.60 50.81 56.32 61.29 65.82 70.06 74.00 76.46
6.0 8.33 28.71 38.06 45.58 52.10 57.92 63.21 68.06 72.55 76.73 79.40
7.0 11.06 28.98 38.56 46.31 53.06 59.12 64.65 69.75 74.48 78.90 81.68
2-Row
Capacity
MBH
5.0 1.02 39.00 56.35 68.54 77.63 84.71 90.41 95.11 99.07 102.45 104.46
9.0 3.13 40.70 60.53 75.32 86.87 96.21 103.96 110.52 116.17 121.09 124.04
13.0 6.33 41.38 62.27 78.23 90.95 101.40 110.19 117.72 124.26 130.01 133.49
17.0 10.61 41.75 63.23 79.87 93.27 104.38 113.79 121.91 129.00 135.28 139.08
21.0 15.96 41.99 63.85 80.92 94.76 106.31 116.14 124.66 132.13 138.76 142.78
23.0 19.02 42.07 64.08 81.32 95.33 107.05 117.04 125.71 133.33 140.09 144.21
3-Row
Capacity
MBH
5.0 1.24 43.53 64.87 80.32 92.01 101.18 108.59 114.70 119.86 124.26 126.87
7.0 2.33 44.48 67.50 84.86 98.44 109.38 118.41 126.02 132.52 138.16 141.52
9.0 3.74 45.01 69.01 87.53 102.29 114.38 124.48 133.09 140.53 147.04 150.94
11.0 5.46 45.35 69.98 89.27 104.85 117.73 128.61 137.94 146.05 153.19 157.50
13.0 7.50 45.59 70.67 90.51 106.67 120.14 131.59 141.46 150.09 157.71 162.33
15.0 9.84 45.76 71.18 91.44 108.04 121.96 133.84 144.14 153.17 161.18 166.03
15.0 9.84 45.76 71.18 91.44 108.04 121.96 133.84 144.14 153.17 161.18 166.03
19.0 15.42 46.00 71.88 92.73 109.97 124.53 137.04 147.95 157.57 166.14 171.35
21.0 18.67 46.09 72.14 93.20 110.67 125.47 138.22 149.36 159.20 167.98 173.33
23.0 22.21 46.16 72.35 93.59 111.26 126.26 139.21 150.54 160.57 169.53 174.99
4-Row
Capacity
MBH
5.0 1.46 47.78 73.53 92.70 107.32 118.79 128.02 135.61 141.95 147.33 150.50
7.0 2.72 48.59 76.19 97.71 114.80 128.67 140.13 149.78 158.02 165.13 169.37
9.0 4.35 49.02 77.66 100.56 119.18 134.57 147.51 158.56 168.11 176.46 181.47
11.0 6.33 49.29 78.59 102.40 122.04 138.48 152.47 164.52 175.02 184.27 189.85
13.0 8.66 49.48 79.23 103.69 124.05 141.26 156.01 168.81 180.04 189.97 195.99
15.0 11.33 49.64 79.71 104.64 125.55 143.34 158.68 172.05 183.84 194.32 200.69
17.0 14.35 49.71 80.07 105.37 126.71 144.96 160.76 174.59 186.83 197.74 204.39
19.0 17.70 49.80 80.35 105.95 127.63 146.25 162.42 176.63 189.24 200.51 207.39
21.0 21.38 49.86 80.58 106.42 128.38 147.30 163.79 178.31 191.22 202.79 209.87
23.0 25.40 49.92 80.78 106.81 129.01 148.18 164.93 179.72 192.89 204.71 211.95
Notes:
1. Fouling Factor = 0.00025 °F·ft²·h/Btu
2. Capacity based on 55°F entering air temperature and 180°F entering water temperature.

VAV-PRC011M-EN 29
Single-Duct VAV Terminal Units
Table 13. Heating capacity (MBh) - inlet size 16 (I-P)
Water
Pressure
Drop (ft)
Airflow (cfm)
Rows gpm 600 1000 1400 1800 2200 2600 3000 3400 3800 4000
1-Row
Capacity
MBH
2.0 1.25 32.86 40.56 46.53 51.24 55.14 58.43 61.26 63.73 65.91 66.90
3.0 2.59 35.44 44.58 51.72 57.88 63.13 67.69 71.71 75.30 78.52 80.01
4.0 4.37 36.88 46.94 54.96 61.77 67.89 73.31 78.17 82.55 86.54 88.40
5.0 6.56 37.79 48.47 57.10 64.53 71.08 77.08 82.54 87.51 92.07 94.22
6.0 9.15 38.43 49.55 58.62 66.50 73.50 79.83 85.69 91.11 96.12 98.48
7.0 12.13 38.90 50.34 59.76 67.98 75.33 82.01 88.14 93.85 99.20 101.74
8.0 15.50 39.26 50.96 60.64 69.13 76.76 83.73 90.13 96.07 101.63 104.31
2-Row
Capacity
MBH
5.0 1.08 54.27 73.74 87.13 96.97 104.54 110.57 115.52 119.66 123.18 124.76
7.0 2.04 56.31 78.10 93.71 105.54 114.88 122.47 128.80 134.16 138.78 140.87
9.0 3.29 57.49 80.68 97.71 110.87 121.41 130.09 137.39 143.64 149.07 151.53
11.0 4.82 58.26 82.39 100.40 114.50 125.90 135.38 143.41 150.32 156.36 159.10
13.0 6.64 58.80 83.61 102.34 117.13 129.19 139.27 147.86 155.28 161.80 164.76
15.0 8.73 59.20 84.53 103.81 119.14 131.70 142.26 151.29 159.12 166.01 169.16
17.0 11.10 59.51 85.24 104.96 120.71 133.69 144.62 154.01 162.18 169.38 172.67
19.0 13.75 59.76 85.82 105.88 121.99 135.30 146.55 156.23 164.67 172.13 175.55
21.0 16.67 59.96 86.29 106.65 123.04 136.63 148.14 158.07 166.75 174.43 177.95
23.0 19.86 60.13 86.68 107.28 123.92 137.75 149.49 159.63 168.51 176.37 179.98
3-Row
Capacity
MBH
5.0 1.33 61.29 85.48 102.45 115.01 124.69 132.40 138.70 143.95 148.40 150.39
7.0 2.48 63.23 90.09 109.84 125.00 137.04 146.85 155.04 161.98 167.96 170.65
9.0 3.98 64.32 92.75 114.23 131.08 144.70 155.97 165.49 173.65 180.74 183.95
11.0 5.80 65.01 94.49 117.14 135.17 149.91 162.24 172.73 181.80 189.73 193.33
13.0 7.95 65.50 95.71 119.21 138.10 153.68 166.80 178.04 187.80 196.38 200.30
15.0 10.42 65.85 96.62 120.76 140.31 156.53 170.28 182.10 192.42 201.51 205.68
15.0 10.42 65.85 96.62 120.76 140.31 156.53 170.28 182.10 192.42 201.51 205.68
19.0 16.32 66.35 97.88 122.93 143.42 160.58 175.22 187.91 199.04 208.91 213.44
21.0 19.73 66.52 98.33 123.71 144.55 162.06 177.05 190.06 201.50 211.66 216.33
23.0 23.46 66.67 98.71 124.37 145.51 163.31 178.58 191.87 203.57 213.98 218.78
4-Row
Capacity
MBH
5.0 1.58 68.18 97.68 118.67 134.16 146.01 155.34 162.90 169.14 174.39 176.72
7.0 2.93 69.98 102.65 127.23 146.24 161.34 173.61 183.79 192.38 199.73 203.02
9.0 4.67 70.95 105.42 132.20 153.46 170.73 185.04 197.09 207.41 216.34 220.38
11.0 6.79 71.56 107.19 135.42 158.23 177.03 192.81 206.25 217.86 228.00 232.60
13.0 9.27 71.98 108.41 137.68 161.62 181.55 198.43 212.93 225.53 236.60 241.66
15.0 12.12 72.28 109.31 139.35 164.14 184.95 202.68 218.00 231.39 243.21 248.62
17.0 15.33 72.53 110.00 140.64 166.09 187.59 206.01 221.99 236.02 248.45 254.15
19.0 18.89 72.69 110.54 141.66 167.65 189.70 208.68 225.21 239.76 252.70 258.64
21.0 22.80 72.84 110.98 142.50 168.93 191.44 210.88 227.86 242.86 256.21 262.36
23.0 27.07 73.01 111.35 143.19 169.99 192.89 212.71 230.08 245.45 259.17 265.50
Notes:
1. Fouling Factor = 0.00025 °F·ft²·h/Btu
2. Capacity based on 55°F entering air temperature and 180°F entering water temperature.

30 VAV-PRC011M-EN
Single-Duct VAV Terminal Units
Table 14. Heating capacity (MBh) - inlet size 16x24 (I-P)
Water
Pressure
Drop (ft)
Airflow (cfm)
Rows gpm 800 1200 1800 2400 3000 3600 4200 4800 5400 6000 6600 7200 8000
1-Row
Capacity
MBH
2.0 1.38 39.61 46.73 54.59 60.43 65.04 68.79 71.91 74.56 76.83 78.80 80.54 82.07 83.86
3.0 2.84 43.29 51.67 61.73 69.73 76.28 81.81 86.54 90.65 94.26 97.47 100.33 102.90 105.96
4.0 4.78 45.36 54.73 65.89 75.29 83.20 90.01 95.95 101.20 105.88 110.09 113.89 117.34 121.49
5.0 7.16 46.70 56.73 68.87 78.98 87.87 95.62 102.48 108.60 114.12 119.12 123.68 127.87 132.94
6.0 9.97 47.63 58.14 71.00 81.78 91.23 99.70 107.26 114.07 120.25 125.89 131.07 135.85 141.68
7.0 13.21 48.32 59.18 72.59 83.93 93.85 102.80 110.92 118.28 124.99 131.15 136.84 142.11 148.57
8.0 16.87 48.85 59.99 73.84 85.62 95.98 105.26 113.80 121.61 128.76 135.35 141.46 147.14 154.13
2-Row
Capacity
MBH
5.0 1.14 68.34 86.06 103.98 116.13 124.98 131.76 137.14 141.53 145.20 148.31 151.00 153.35 156.05
7.0 2.14 71.52 91.72 113.08 128.18 139.51 148.38 155.56 161.50 166.53 170.85 174.61 177.91 181.76
9.0 3.45 73.37 95.09 118.70 135.79 148.87 159.26 167.77 174.89 180.97 186.22 190.82 194.88 199.64
11.0 5.05 74.57 97.33 122.50 141.04 155.40 166.93 176.45 184.48 191.36 197.35 202.61 207.29 212.78
13.0 6.94 75.42 98.93 125.26 144.87 160.21 172.62 182.94 191.68 199.20 205.78 211.58 216.75 222.83
15.0 9.13 76.05 100.13 127.34 147.80 163.91 177.03 187.97 197.28 205.33 212.38 218.62 224.20 230.78
17.0 11.59 76.54 101.06 128.97 150.11 166.84 180.53 191.99 201.77 210.26 217.70 224.31 230.22 237.21
19.0 14.34 76.94 101.81 130.29 151.98 169.23 183.38 195.28 205.46 214.30 222.08 228.99 235.19 242.54
21.0 17.38 77.26 102.42 131.38 153.53 171.21 185.76 198.02 208.54 217.69 225.75 232.93 239.37 247.01
23.0 20.69 77.52 102.94 132.29 154.83 172.87 187.77 200.34 211.14 220.56 228.88 236.28 242.93 250.84
3-Row
Capacity
MBH
5.0 1.41 77.68 99.68 122.22 137.52 148.61 157.05 163.71 169.12 173.61 177.40 180.66 183.49 186.73
7.0 2.64 80.85 105.82 132.77 151.99 166.44 177.75 186.88 194.42 200.77 206.21 210.92 215.06 219.86
9.0 4.22 82.64 109.38 139.13 160.98 177.78 191.18 202.14 211.32 219.13 225.87 231.77 236.97 243.05
11.0 6.15 83.78 111.70 143.37 167.09 185.61 200.55 212.91 223.34 232.29 240.06 246.90 252.96 260.08
13.0 8.41 84.58 113.33 146.40 171.50 191.33 207.46 220.90 232.33 242.17 250.77 258.37 265.13 273.10
15.0 11.02 85.17 114.54 148.68 174.85 195.68 212.76 227.07 239.29 249.87 259.14 267.35 274.69 283.36
15.0 11.02 85.17 114.54 148.68 174.85 195.68 212.76 227.07 239.29 249.87 259.14 267.35 274.69 283.36
19.0 17.21 85.98 116.23 151.86 179.57 201.89 220.36 235.97 249.38 261.06 271.36 280.52 288.75 298.50
21.0 20.80 86.27 116.83 153.02 181.30 204.18 223.18 239.28 253.15 265.27 275.96 285.50 294.07 304.25
23.0 24.71 86.51 117.34 153.99 182.76 206.11 225.55 242.07 256.34 268.82 279.86 289.72 298.59 309.15
4-Row
Capacity
MBH
5.0 1.69 87.07 113.91 141.48 159.95 173.12 182.96 190.61 196.72 201.76 205.92 209.47 212.53 216.01
7.0 3.14 90.21 120.68 154.09 177.94 195.75 209.55 220.57 229.58 237.11 243.50 249.00 253.78 259.29
9.0 4.99 91.90 124.47 161.53 188.97 210.07 226.81 240.43 251.75 261.32 269.52 276.66 282.92 290.19
11.0 7.25 92.96 126.89 166.40 196.37 219.87 238.81 254.42 267.55 278.76 288.45 296.93 304.43 313.17
13.0 9.89 93.68 128.56 169.83 201.67 226.97 247.60 264.78 279.34 291.86 302.76 312.34 320.86 330.84
15.0 12.91 94.21 129.79 172.37 205.63 232.35 254.32 272.74 288.46 302.05 313.94 324.44 333.79 344.81
17.0 16.31 94.61 130.73 174.34 208.72 236.56 259.61 279.06 295.72 310.19 322.90 334.17 344.24 356.14
19.0 20.08 94.92 131.46 175.89 211.19 239.94 263.88 284.18 301.64 316.85 330.25 342.17 352.85 365.49
21.0 24.23 95.18 132.06 177.16 213.21 242.72 267.41 288.41 306.55 322.39 336.39 348.86 360.06 373.35
23.0 28.74 95.39 132.56 178.22 214.89 245.05 270.37 291.98 310.69 327.08 341.59 354.54 366.19 380.04
Notes:
1. Fouling Factor = 0.00025 °F·ft²·h/Btu
2. Capacity based on 55°F entering air temperature and 180°F entering water temperature.

VAV-PRC011M-EN 31
Single-Duct VAV Terminal Units
Hot Water Reheat Coil Notes (I-P)
1. Fouling Factor = 0.00025
2. Capacity based on 55°F entering air temperature and 180°F entering water temperature. Refer
to correction factors found in Table 15, p. 31 and Ta b l e 16, p. 31 for different entering
conditions.
3. The following equations may be used in calculating Leaving Air Temperature (LAT) and Water
Temperature Difference (WTD).
4. For premium coils (.020” wall), side pressure drop increasesx 17% and water velocity increases
7% for fixed GPM.
Table 15. Temperature correction factors for water pressure drop (ft)
Average Water Temperature
Correction Factor
200
0.970
190
0.985
180
1.000
170
1.020
160
1.030
150
1.050
140
1.080
130
1.100
120
1.130
110
1.150
Table 16. Temperature correction factors for coil capacity (MBH)
Entering Water Minus Entering Air
Correction Factor
40
0.32
50
0.40
60
0.48
70
0.56
80
0.64
100
0.80
125
1.00
140
1.12
150
1.20
160
1.28
180
1.44
200
1.60
Table 17. Coil only-water weights
Inlet
Size
1-Row Coil 2-Row Coil 3-Row Coil 4-Row Coil
Internal
Volume Operating
Weight Internal
Volume Operating
Weight Internal
Volume Operating
Weight Internal
Volume Operating
Weight
(in3) (gal) (lbs) (in3) (gal) (lbs) (in3) (gal) (lbs) (in3) (gal) (lbs)
04 9.37 0.041 5.3 23.68 0.102 6.9 33.52 0.145 23 43.08 0.186 24
05 9.37 0.041 5.3 23.68 0.102 6.9 33.52 0.145 23 43.08 0.186 24
06 9.37 0.041 5.3 23.68 0.102 6.9 33.52 0.145 23 43.08 0.186 24
08 12.78 0.055 5.5 35.47 0.154 9.0 48.89 0.212 24 61.92 0.268 26
10 19.06 0.083 7.7 48.83 0.211 11.7 68.84 0.298 32 88.28 0.382 36
12 30.05 0.130 10.7 67.34 0.292 15.5 98.89 0.428 41 129.54 0.561 45
14 51.21 0.222 13.9 94.27 0.408 19.8 148.04 0.641 51 200.27 0.867 55
16 58.62 0.254 16.2 109.09 0.472 23.3 170.64 0.739 56 230.43 0.998 61
24x16 66.03 0.286 20.4 123.91 0.536 29.8 193.24 0.837 76 260.59 1.128 82
LAT EAT MBH 921.7×
Cfm
--------------------------------------
+=
WTD EWT LWT 2MBH×
Gpm
------------------------
=–=

32 VAV-PRC011M-EN
Single-Duct VAV Terminal Units
Table 18. Heating capacity (kW) - inlet size 04, 05, 06 (SI)
Water
Pressure
Drop (kPa)
Airflow (L/s)
Rows L/s 24 47 71 94 118 142 165 189 212 236
1-Row
Capacity
MBH
0.03 1.44 1.27 1.75 2.08 2.34 2.56 2.75 2.92 3.08 3.21 3.34
0.06 4.80 1.36 1.94 2.35 2.69 2.99 3.26 3.50 3.73 3.94 4.13
0.09 9.78 1.39 2.01 2.46 2.84 3.17 3.48 3.76 4.02 4.27 4.49
0.13 16.25 1.41 2.05 2.52 2.92 3.27 3.60 3.90 4.19 4.45 4.70
0.16 24.13 1.42 2.07 2.55 2.97 3.34 3.68 4.00 4.29 4.57 4.84
2-Row
Capacity
MBH
0.06 1.70 1.62 2.75 3.57 4.19 4.68 5.08 5.41 5.69 5.93 6.13
0.13 5.86 1.67 2.92 3.89 4.67 5.31 5.85 6.32 6.72 7.08 7.39
0.19 12.18 1.69 2.98 4.00 4.85 5.55 6.16 6.68 7.14 7.55 7.92
0.25 20.53 1.69 3.01 4.06 4.94 5.68 6.32 6.88 7.37 7.82 8.21
0.32 30.83 1.70 3.03 4.10 5.00 5.76 6.42 7.00 7.52 7.98 8.40
3-Row
Capacity
MBH
0.06 2.46 1.76 3.09 4.09 4.87 5.49 6.00 6.43 6.78 7.09 7.36
0.13 8.43 1.79 3.23 4.40 5.37 6.17 6.87 7.46 7.98 8.45 8.86
0.19 17.42 1.81 3.28 4.51 5.54 6.43 7.19 7.86 8.46 8.99 9.47
0.25 29.24 1.84 3.31 4.57 5.64 6.56 7.36 8.07 8.71 9.28 9.80
0.32 43.76 1.86 3.33 4.60 5.69 6.64 7.47 8.21 8.87 9.47 10.01
4-Row
Capacity
MBH
0.06 3.23 1.89 3.41 4.63 5.59 6.37 7.00 7.52 7.97 8.34 8.67
0.13 10.99 1.90 3.54 4.94 6.12 7.13 8.00 8.76 9.43 10.02 10.55
0.19 22.66 1.91 3.59 5.04 6.30 7.40 8.37 9.22 9.99 10.67 11.29
0.25 37.95 1.91 3.62 5.09 6.39 7.54 8.55 9.46 10.28 11.02 11.70
0.32 56.70 1.91 3.65 5.12 6.45 7.62 8.67 9.61 10.46 11.24 11.95
Note: Refer to the Hot Water Reheat & Coil Notes (SI) at the end of the Performance Data section for fouling factors and LAT/WTD calculating equations.
Table 19. Heating capacity (kW) - inlet size 08 (SI)
Water
Pressure
Drop (kPa)
Airflow (L/s)
Rows L/s 50 94 142 189 236 283 330 378 425
1-Row
Capacity
kW
0.03 1.92 2.07 9.19 10.80 12.04 13.04 13.87 14.58 15.19 15.72
0.06 6.41 2.29 10.61 12.78 14.56 16.11 17.50 18.72 19.82 20.81
0.09 13.05 2.38 11.18 13.63 15.70 17.51 19.13 20.60 21.97 23.22
0.13 21.67 2.43 11.49 14.10 16.33 18.31 20.09 21.73 23.24 24.63
0.16 32.16 2.45 11.68 14.40 16.74 18.83 20.73 22.47 24.09 25.60
2-Row
Capacity
kW
0.16 1.17 3.17 17.05 21.63 25.03 27.66 29.78 31.53 33.00 34.26
0.25 2.80 3.26 17.89 23.11 27.13 30.33 32.97 35.18 37.08 38.72
0.38 5.97 3.31 18.39 24.03 28.45 32.05 35.05 37.60 39.81 41.74
0.50 10.24 3.33 18.66 24.52 29.17 32.99 36.20 38.95 41.34 43.45
0.63 15.57 3.35 18.83 24.83 29.62 33.58 36.93 39.81 42.33 44.55
0.76 21.96 3.36 18.94 25.04 29.94 34.00 37.44 40.42 43.02 45.33

VAV-PRC011M-EN 33
Single-Duct VAV Terminal Units
3-Row
Capacity
kW
0.16 1.57 3.50 19.51 25.34 29.76 33.26 36.09 38.44 40.43 42.15
0.25 3.71 3.57 20.28 26.82 31.97 36.16 39.65 42.61 45.15 47.38
0.38 7.82 3.61 20.74 27.71 33.32 37.98 41.91 45.29 48.23 50.83
0.50 13.31 3.63 20.97 28.17 34.04 38.95 43.13 46.75 49.93 52.75
0.63 20.13 3.64 21.11 28.46 34.49 39.56 43.91 47.68 51.01 53.97
0.76 28.25 3.65 21.21 28.66 34.80 39.98 44.44 48.33 51.76 54.83
4-Row
Capacity
kW
0.16 1.98 3.82 22.00 29.26 34.89 39.37 43.03 46.06 48.63 50.84
0.25 4.62 3.86 22.72 30.80 37.33 42.73 47.25 51.12 54.45 57.37
0.38 9.67 3.88 23.13 31.69 38.78 44.76 49.87 54.31 58.19 61.63
0.50 16.38 3.90 23.33 32.14 39.53 45.83 51.27 56.02 60.22 63.97
0.63 24.68 3.90 23.46 32.42 40.00 46.50 52.14 57.10 61.51 65.45
0.76 34.55 3.91 23.54 32.61 40.31 46.95 52.74 57.85 62.39 66.47
Note: Refer to the Hot Water Reheat & Coil Notes (SI) at the end of the Performance Data section for fouling factors and LAT/WTD calculating equations.
Table 19. Heating capacity (kW) - inlet size 08 (SI) (continued)
Water
Pressure
Drop (kPa)
Airflow (L/s)
Rows L/s 50 94 142 189 236 283 330 378 425
Table 20. Heating capacity (kW) - inlet size 10 (SI)
Water
Pressure
Drop (kPa)
Airflow (L/s)
Rows L/s 94 142 189 236 283 330 378 425 472 566 661
1-Row
Capacity
kW
0.04 4.79 3.51 4.15 4.67 5.11 5.48 5.80 6.08 6.33 6.55 6.94 7.26
0.06 8.89 3.76 4.50 5.10 5.62 6.09 6.50 6.88 7.21 7.52 8.06 8.53
0.09 18.06 3.97 4.81 5.51 6.12 6.66 7.15 7.62 8.05 8.45 9.17 9.81
0.13 29.97 4.08 4.98 5.74 6.40 7.00 7.55 8.06 8.54 9.00 9.83 10.58
0.16 44.45 4.15 5.09 5.88 6.59 7.23 7.82 8.37 8.88 9.36 10.26 11.09
2-Row
Capacity
kW
0.16 3.24 5.72 7.52 8.93 10.07 11.01 11.79 12.47 13.05 13.56 14.42 15.11
0.25 7.77 5.92 7.91 9.53 10.86 11.99 12.96 13.81 14.55 15.22 16.35 17.28
0.38 16.59 6.03 8.14 9.88 11.35 12.61 13.70 14.67 15.53 16.30 17.63 18.75
0.50 28.51 6.09 8.26 10.07 11.61 12.94 14.11 15.14 16.07 16.90 18.35 19.58
0.63 43.44 6.13 8.34 10.19 11.77 13.15 14.36 15.44 16.40 17.28 18.81 20.11
3-Row
Capacity
kW
0.16 3.92 6.36 8.56 10.32 11.75 12.95 13.96 14.82 15.58 16.24 17.34 18.24
0.25 9.29 6.54 8.94 10.92 12.60 14.03 15.28 16.37 17.33 18.20 19.67 20.89
0.38 19.70 6.64 9.15 11.28 13.10 14.69 16.09 17.33 18.44 19.45 21.19 22.66
0.50 33.67 6.69 9.26 11.46 13.37 15.04 16.52 17.85 19.04 20.12 22.02 23.63
0.63 51.10 6.72 9.33 11.57 13.53 15.25 16.79 18.17 19.42 20.55 22.55 24.26
4-Row
kW
MBH
0.16 5.26 6.99 9.63 11.78 13.57 15.06 16.32 17.41 18.34 19.17 20.53 21.63
0.25 12.35 7.14 9.99 12.42 14.50 16.31 17.88 19.27 20.50 21.60 23.48 25.04
0.38 25.92 7.24 10.18 12.77 15.04 17.04 18.81 20.40 21.83 23.13 25.39 27.29
0.50 44.01 7.27 10.28 12.95 15.31 17.41 19.29 20.99 22.54 23.94 26.42 28.53
0.63 66.45 7.28 10.34 13.06 15.47 17.64 19.59 21.36 22.97 24.45 27.06 29.31
Refer to the Hot Water Reheat & Coil Notes (SI) at the end of the Performance Data section for fouling factors and LAT/WTD calculating equations.

34 VAV-PRC011M-EN
Single-Duct VAV Terminal Units
Table 21. Heating capacity (kW) - inlet size 12 (SI)
Water
Pressure
Drop (kPa)
Airflow (L/s)
Rows L/s 142 236 330 425 519 613 708 802 897 944
1-Row
Capacity
kW
0.06 1.86 4.99 6.12 6.97 7.64 8.19 8.65 9.04 9.39 9.69 9.82
0.13 6.48 5.66 7.17 8.34 9.34 10.23 11.02 11.72 12.35 12.93 13.20
0.19 13.55 5.92 7.60 8.95 10.12 11.15 12.08 12.94 13.74 14.47 14.82
0.25 22.94 6.06 7.84 9.29 10.55 11.69 12.72 13.67 14.55 15.37 15.77
0.32 34.58 6.15 7.99 9.50 10.83 12.04 13.14 14.15 15.10 15.99 16.41
2-Row
Capacity
kW
0.22 1.97 8.34 11.56 13.85 15.58 16.94 18.03 18.94 19.71 20.37 20.66
0.32 3.85 8.61 12.17 14.80 16.84 18.48 19.83 20.97 21.94 22.79 23.17
0.50 9.38 8.86 12.74 15.72 18.09 20.05 21.69 23.10 24.32 25.39 25.89
0.69 17.20 8.98 13.02 16.17 18.72 20.85 22.65 24.21 25.57 26.77 27.33
0.88 27.27 9.05 13.19 16.44 19.10 21.33 23.24 24.89 26.34 27.63 28.23
1.07 39.55 9.10 13.30 16.63 19.36 21.66 23.63 25.35 26.87 28.22 28.85
3-Row
Capacity
kW
0.22 2.48 9.10 12.90 15.67 17.78 19.45 20.81 21.93 22.89 23.70 24.07
0.32 4.80 9.35 13.50 16.65 19.13 21.14 22.81 24.22 25.43 26.49 26.97
0.50 11.53 9.57 14.05 17.58 20.44 22.82 24.83 26.57 28.09 29.43 30.04
0.69 20.97 9.68 14.31 18.03 21.08 23.65 25.85 27.77 29.46 30.96 31.65
0.88 33.04 9.74 14.47 18.29 21.46 24.15 26.47 28.50 30.30 31.90 32.64
1.07 47.68 9.78 14.57 18.47 21.72 24.49 26.89 29.00 30.86 32.54 33.31
4-Row
Capacity
kW
0.22 2.99 10.33 15.18 18.83 21.63 23.85 25.64 27.12 28.37 29.43 29.90
0.32 5.74 10.55 15.80 19.94 23.26 25.97 28.23 30.14 31.78 33.20 33.84
0.50 13.68 10.73 16.34 20.95 24.78 28.02 30.79 33.18 35.28 37.14 37.99
0.69 24.74 10.81 16.59 21.42 25.51 29.01 32.05 34.71 37.06 39.17 40.14
0.88 38.81 10.86 16.73 21.70 25.93 29.60 32.80 35.62 38.14 40.40 41.44
1.07 55.82 10.89 16.82 21.88 26.21 29.99 33.30 36.24 38.86 41.23 42.33
Note: Refer to the Hot Water Reheat & Coil Notes (SI) at the end of the Performance Data section for fouling factors and LAT/WTD calculating equations.

VAV-PRC011M-EN 35
Single-Duct VAV Terminal Units
Table 22. Heating capacity (kW) - inlet size 14 (SI)
Water
Pressure
Drop (kPa)
Airflow (L/s)
Rows L/s 283 472 661 849 1038 1227 1416 1604 1793 1888
1-Row
Capacity
kW
0.13 3.37 7.43 9.44 10.96 12.23 13.28 14.19 14.97 15.67 16.29 16.66
0.19 7.02 7.89 10.23 12.04 13.54 14.88 16.07 17.13 18.08 18.94 19.47
0.25 11.85 8.14 10.67 12.66 14.36 15.85 17.18 18.42 19.55 20.58 21.22
0.32 17.81 8.30 10.96 13.07 14.89 16.50 17.96 19.29 20.53 21.69 22.41
0.38 24.89 8.41 11.16 13.36 15.27 16.97 18.52 19.95 21.26 22.49 23.27
0.44 33.04 8.49 11.30 13.57 15.55 17.33 18.95 20.44 21.83 23.12 23.94
2-Row
Capacity
kW
0.32 3.05 11.43 16.52 20.09 22.75 24.83 26.50 27.87 29.03 30.03 30.61
0.57 9.35 11.93 17.74 22.07 25.46 28.20 30.47 32.39 34.04 35.49 36.35
0.82 18.93 12.13 18.25 22.93 26.66 29.72 32.29 34.50 36.42 38.10 39.12
1.07 31.73 12.24 18.53 23.41 27.33 30.59 33.35 35.73 37.81 39.65 40.76
1.33 47.69 12.30 18.71 23.71 27.77 31.16 34.04 36.53 38.72 40.67 41.85
1.45 56.86 12.33 18.78 23.83 27.94 31.37 34.30 36.84 39.07 41.06 42.26
3-Row
Capacity
kW
0.32 3.70 12.76 19.01 23.54 26.97 29.65 31.82 33.62 35.13 36.42 37.18
0.44 6.96 13.04 19.78 24.87 28.85 32.06 34.70 36.93 38.84 40.49 41.48
0.57 11.17 13.19 20.22 25.65 29.98 33.52 36.48 39.01 41.19 43.09 44.24
0.69 16.33 13.29 20.51 26.16 30.73 34.50 37.69 40.43 42.80 44.90 46.16
0.82 22.40 13.36 20.71 26.53 31.26 35.21 38.56 41.46 43.99 46.22 47.57
0.95 29.40 13.41 20.86 26.80 31.66 35.74 39.23 42.24 44.89 47.24 48.66
0.95 29.40 13.41 20.86 26.80 31.66 35.74 39.23 42.24 44.89 47.24 48.66
1.20 46.10 13.48 21.07 27.18 32.23 36.50 40.16 43.36 46.18 48.69 50.22
1.33 55.80 13.51 21.14 27.31 32.43 36.77 40.51 43.77 46.66 49.23 50.80
1.45 66.38 13.53 21.20 27.43 32.61 37.00 40.80 44.12 47.06 49.68 51.29
4-Row
Capacity
kW
0.32 4.36 14.00 21.55 27.17 31.45 34.82 37.52 39.74 41.60 43.18 44.11
0.44 8.13 14.24 22.33 28.64 33.65 37.71 41.07 43.90 46.31 48.40 49.64
0.57 12.99 14.37 22.76 29.47 34.93 39.44 43.23 46.47 49.27 51.72 53.18
0.69 18.92 14.45 23.03 30.01 35.77 40.59 44.68 48.21 51.29 54.00 55.64
0.82 25.88 14.50 23.22 30.39 36.36 41.40 45.72 49.47 52.76 55.68 57.44
0.95 33.87 14.55 23.36 30.67 36.80 42.01 46.50 50.42 53.88 56.95 58.82
1.07 42.88 14.57 23.47 30.88 37.13 42.48 47.11 51.17 54.75 57.95 59.90
1.20 52.89 14.60 23.55 31.05 37.40 42.86 47.60 51.77 55.46 58.76 60.78
1.33 63.91 14.61 23.62 31.19 37.63 43.17 48.00 52.26 56.04 59.43 61.51
1.45 75.91 14.63 23.67 31.30 37.81 43.43 48.34 52.67 56.53 59.99 62.12
Note: Refer to the Hot Water Reheat & Coil Notes (SI) at the end of the Performance Data section for fouling factors and LAT/WTD calculating equations.

36 VAV-PRC011M-EN
Single-Duct VAV Terminal Units
Table 23. Heating capacity (kW) - inlet size 16 (SI)
Water
Pressure
Drop (kPa)
Airflow (L/s)
Rows L/s 283 472 661 849 1038 1227 1416 1604 1793 1888
1-Row
Capacity
kW
0.13 3.74 9.63 11.89 13.64 15.02 16.16 17.12 17.95 18.68 19.32 19.61
0.19 7.76 10.39 13.07 15.16 16.96 18.50 19.84 21.02 22.07 23.01 23.45
0.25 13.06 10.81 13.76 16.11 18.10 19.90 21.49 22.91 24.19 25.36 25.91
0.32 19.60 11.08 14.21 16.74 18.91 20.83 22.59 24.19 25.65 26.98 27.61
0.38 27.34 11.26 14.52 17.18 19.49 21.54 23.40 25.11 26.70 28.17 28.86
0.44 36.27 11.40 14.75 17.51 19.92 22.08 24.04 25.83 27.50 29.07 29.82
0.50 46.33 11.51 14.94 17.77 20.26 22.50 24.54 26.42 28.16 29.79 30.57
2-Row
Capacity
kW
0.32 3.22 15.90 21.61 25.54 28.42 30.64 32.41 33.86 35.07 36.10 36.56
0.44 6.10 16.50 22.89 27.46 30.93 33.67 35.89 37.75 39.32 40.67 41.28
0.57 9.83 16.85 23.64 28.64 32.49 35.58 38.12 40.27 42.10 43.69 44.41
0.69 14.42 17.07 24.15 29.43 33.56 36.90 39.67 42.03 44.06 45.82 46.63
0.82 19.84 17.23 24.50 29.99 34.33 37.86 40.82 43.33 45.51 47.42 48.29
0.95 26.10 17.35 24.77 30.42 34.92 38.60 41.69 44.34 46.63 48.65 49.58
1.07 33.19 17.44 24.98 30.76 35.38 39.18 42.39 45.14 47.53 49.64 50.61
1.20 41.09 17.51 25.15 31.03 35.75 39.65 42.95 45.79 48.26 50.45 51.45
1.33 49.81 17.57 25.29 31.25 36.06 40.04 43.42 46.33 48.87 51.12 52.15
1.45 59.35 17.62 25.40 31.44 36.32 40.37 43.81 46.78 49.38 51.69 52.75
3-Row
Capacity
kW
0.32 3.96 17.96 25.05 30.03 33.71 36.54 38.80 40.65 42.19 43.49 44.08
0.44 7.42 18.53 26.40 32.19 36.63 40.16 43.04 45.44 47.47 49.22 50.01
0.57 11.89 18.85 27.18 33.48 38.42 42.41 45.71 48.50 50.89 52.97 53.91
0.69 17.35 19.05 27.69 34.33 39.61 43.93 47.55 50.62 53.28 55.60 56.66
0.82 23.77 19.20 28.05 34.94 40.47 45.04 48.88 52.18 55.04 57.55 58.70
0.95 31.16 19.30 28.32 35.39 41.12 45.88 49.90 53.37 56.39 59.06 60.28
0.95 31.16 19.30 28.32 35.39 41.12 45.88 49.90 53.37 56.39 59.06 60.28
1.20 48.77 19.44 28.69 36.03 42.03 47.06 51.35 55.07 58.33 61.22 62.55
1.33 58.98 19.50 28.82 36.26 42.36 47.50 51.89 55.70 59.05 62.03 63.40
1.45 70.12 19.54 28.93 36.45 42.64 47.86 52.34 56.23 59.66 62.71 64.12
4-Row
Capacity
kW
0.32 4.71 19.98 28.63 34.78 39.32 42.79 45.53 47.74 49.57 51.11 51.79
0.44 8.76 20.51 30.08 37.29 42.86 47.28 50.88 53.86 56.38 58.53 59.50
0.57 13.96 20.79 30.90 38.74 44.97 50.04 54.23 57.76 60.79 63.40 64.59
0.69 20.28 20.97 31.41 39.69 46.37 51.88 56.51 60.45 63.85 66.82 68.17
0.82 27.71 21.09 31.77 40.35 47.36 53.21 58.15 62.40 66.10 69.34 70.82
0.95 36.23 21.18 32.04 40.84 48.10 54.20 59.40 63.89 67.81 71.28 72.86
1.07 45.81 21.26 32.24 41.22 48.68 54.98 60.37 65.06 69.17 72.81 74.48
1.20 56.46 21.30 32.40 41.52 49.13 55.60 61.16 66.00 70.27 74.06 75.80
1.33 68.16 21.35 32.53 41.76 49.51 56.11 61.80 66.78 71.17 75.09 76.89
1.45 80.90 21.40 32.63 41.96 49.82 56.53 62.34 67.43 71.94 75.96 77.81
Note: Refer to the Hot Water Reheat & Coil Notes (SI) at the end of the Performance Data section for fouling factors and LAT/WTD calculating equations.

VAV-PRC011M-EN 37
Single-Duct VAV Terminal Units
Table 24. Heating capacity (kW) - inlet size 16x24 (SI)
Water
Pressure
Drop (kPa)
Airflow (L/s)
Rows L/s 378 566 849 1133 1416 1699 1982 2265 2548 2831 3115 3398 3775
1-Row
Capacity
kW
0.13 4.11 11.61 13.70 16.00 17.71 19.06 20.16 21.08 21.85 22.52 23.09 23.60 24.05 24.58
0.19 8.50 12.69 15.14 18.09 20.44 22.36 23.98 25.36 26.57 27.63 28.57 29.40 30.16 31.05
0.25 14.27 13.29 16.04 19.31 22.07 24.38 26.38 28.12 29.66 31.03 32.26 33.38 34.39 35.61
0.32 21.39 13.69 16.63 20.18 23.15 25.75 28.02 30.03 31.83 33.44 34.91 36.25 37.47 38.96
0.38 29.81 13.96 17.04 20.81 23.97 26.74 29.22 31.44 33.43 35.24 36.89 38.41 39.81 41.52
0.44 39.50 14.16 17.34 21.27 24.60 27.50 30.13 32.51 34.66 36.63 38.44 40.10 41.65 43.54
0.50 50.42 14.32 17.58 21.64 25.09 28.13 30.85 33.35 35.64 37.74 39.67 41.46 43.12 45.17
2-Row
Capacity
kW
0.32 3.40 20.03 25.22 30.47 34.03 36.63 38.61 40.19 41.48 42.55 43.47 44.25 44.94 45.73
0.44 6.41 20.96 26.88 33.14 37.57 40.89 43.49 45.59 47.33 48.81 50.07 51.17 52.14 53.27
0.57 10.31 21.50 27.87 34.79 39.80 43.63 46.68 49.17 51.26 53.04 54.57 55.92 57.11 58.51
0.69 15.10 21.85 28.52 35.90 41.33 45.54 48.92 51.71 54.07 56.08 57.84 59.38 60.75 62.36
0.82 20.76 22.10 28.99 36.71 42.46 46.95 50.59 53.61 56.17 58.38 60.31 62.01 63.52 65.31
0.95 27.28 22.29 29.34 37.32 43.32 48.04 51.88 55.09 57.82 60.18 62.24 64.07 65.71 67.63
1.07 34.65 22.43 29.62 37.80 43.99 48.90 52.91 56.27 59.13 61.62 63.80 65.74 67.47 69.52
1.20 42.87 22.55 29.84 38.18 44.54 49.60 53.74 57.23 60.21 62.81 65.09 67.11 68.93 71.08
1.33 51.94 22.64 30.02 38.50 44.99 50.18 54.44 58.03 61.12 63.80 66.16 68.26 70.15 72.39
1.45 61.84 22.72 30.17 38.77 45.38 50.66 55.03 58.71 61.88 64.64 67.08 69.25 71.20 73.51
3-Row
Capacity
kW
0.32 4.23 22.77 29.21 35.82 40.30 43.55 46.03 47.98 49.56 50.88 51.99 52.95 53.78 54.73
0.44 7.89 23.70 31.01 38.91 44.54 48.78 52.09 54.77 56.98 58.84 60.43 61.82 63.03 64.43
0.57 12.62 24.22 32.06 40.78 47.18 52.10 56.03 59.24 61.93 64.22 66.20 67.92 69.45 71.23
0.69 18.37 24.55 32.74 42.02 48.97 54.40 58.78 62.40 65.46 68.08 70.36 72.36 74.14 76.22
0.82 25.15 24.79 33.21 42.91 50.26 56.07 60.80 64.74 68.09 70.97 73.49 75.72 77.70 80.04
0.95 32.92 24.96 33.57 43.57 51.24 57.35 62.35 66.55 70.13 73.23 75.95 78.35 80.50 83.04
0.95 32.92 24.96 33.57 43.57 51.24 57.35 62.35 66.55 70.13 73.23 75.95 78.35 80.50 83.04
1.20 51.44 25.20 34.06 44.51 52.63 59.17 64.58 69.15 73.09 76.51 79.53 82.21 84.62 87.48
1.33 62.17 25.28 34.24 44.85 53.14 59.84 65.41 70.13 74.19 77.74 80.88 83.67 86.18 89.17
1.45 73.87 25.35 34.39 45.13 53.56 60.40 66.10 70.94 75.13 78.78 82.02 84.91 87.51 90.60
4-Row
Capacity
kW
0.32 5.06 25.52 33.38 41.46 46.88 50.74 53.62 55.86 57.65 59.13 60.35 61.39 62.29 63.31
0.44 9.39 26.44 35.37 45.16 52.15 57.37 61.41 64.64 67.28 69.49 71.36 72.97 74.38 75.99
0.57 14.93 26.93 36.48 47.34 55.38 61.57 66.47 70.46 73.78 76.58 78.99 81.08 82.92 85.04
0.69 21.66 27.24 37.19 48.77 57.55 64.44 69.99 74.56 78.41 81.70 84.54 87.02 89.22 91.78
0.82 29.55 27.46 37.68 49.77 59.10 66.52 72.56 77.60 81.87 85.54 88.73 91.54 94.03 96.96
0.95 38.58 27.61 38.04 50.52 60.27 68.09 74.53 79.93 84.54 88.52 92.01 95.08 97.83 101.05
1.07 48.75 27.73 38.31 51.09 61.17 69.33 76.08 81.78 86.67 90.91 94.63 97.94 100.89 104.37
1.20 60.03 27.82 38.53 51.55 61.89 70.32 77.34 83.28 88.40 92.86 96.79 100.28 103.41 107.11
1.33 72.42 27.89 38.70 51.92 62.48 71.14 78.37 84.53 89.84 94.48 98.59 102.24 105.52 109.42
1.45 85.91 27.96 38.85 52.23 62.98 71.82 79.24 85.57 91.05 95.86 100.11 103.90 107.32 111.38
Note: Refer to the Hot Water Reheat & Coil Notes (SI) at the end of the Performance Data section for fouling factors and LAT/WTD calculating equations.

38 VAV-PRC011M-EN
Single-Duct VAV Terminal Units
Hot Water Reheat Coil Notes (SI)
1. Fouling Factor = 0.00025
2. Capacity based on 12°C entering air temperature and 82°C entering water temperature. Refer
to correction factors found in Table 15, p. 31 and Ta b l e 16, p. 31 for different entering
conditions.
3. The following equations may be used in calculating Leaving Air Temperature (LAT) and Water
Temperature Difference (WTD).
LAT = EAT + (kW x 0.83 / L/s)
WTD = EWT - LWT = (kW / (4.19) L/s)
4. For premium coils (.020” wall), side pressure drop increases x 17% and water velocity increases
7% for fixed GPM.
Table 25. Temperature correction factors for water pressure drop (kPa)
Average Water Temperature
Correction Factor
93
0.970
88
0.985
82
1.000
77
1.020
71
1.030
66
1.050
60
1.080
54
1.100
49
1.130
43
1.150
Table 26. Temperature correction factors for coil capacity (kW)
Entering Water Minus Entering Air
Correction Factor
22
0.32
28
0.40
33
0.48
39
0.56
44
0.64
56
0.80
69
1.00
78
1.12
83
1.20
89
1.29
100
1.45
111
1.61
Table 27. Coil only-water weights (SI)
1-Row Coil 2-Row Coil 3-Row Coil 4-Row Coil
Inlet
Size
Internal
Volume
(cm3)
Internal
Volume
(liter)
Operating
Weight
(kg)
Internal
Volume
(cm3)
Internal
Volume
(liter)
Operating
Weight
(kg)
Internal
Volume
(cm3)
Internal
Volume
(liter)
Operating
Weight
(kg)
Internal
Volume
(cm3)
Internal
Volume
(liter)
Operating
Weight
(kg)
04 153.6 0.154 2.421 388.0 0.388 3.12 549.3 0.549 10.44 705.9 0.706 10.90
05 153.6 0.154 2.421 388.0 0.388 3.12 549.3 0.549 10.44 705.9 0.706 10.90
06 153.6 0.154 2.421 388.0 0.388 3.12 549.3 0.549 10.44 705.9 0.706 10.90
08 209.4 0.209 2.477 581.3 0.580 4.099 801.1 0.801 10.90 1014.8 1.015 11.80
10 312.4 0.312 3.487 800.1 0.799 5.294 1128.1 1.128 14.53 1446.7 1.447 16.34
12 492.5 0.493 4.853 1103.0 1.101 7.026 1620.6 1.621 18.61 2122.8 2.123 20.43
14 839.1 0.839 6.309 1545.0 1.542 8.965 2425.9 2.426 23.15 3281.9 3.282 24.97
16 960.6 0.961 7.337 1788.0 1.784 10.57 2796.3 2.796 25.42 3776.1 3.776 27.69
24x16 1082.0 1.082 9.273 2030.0 2.027 13.53 3166.6 3.167 34.50 4270.3 4.270 37.23

VAV-PRC011M-EN 39
Single-Duct VAV Terminal Units
Electrical Data
Table 28. VCEF electric coil kW guidelines - minimum to maximum
Single-Phase Voltage Three-Phase Voltage
Inlet Size Stages 120V 208V/240V 277V 347V 480V 208V 480V 575V(a) 380V/50 Hz
04
1
2
3
1.0
1.0
1.0
1.0
1.0
1.0
1.0
1.0
1.0
1.0
1.0
-
1.0
-
-
1.0
1.0
1.0
1.0
1.0
-
-
-
-
1.0
1.0
-
05
1
2
3
1.0-2.5
1.0-2.5
1.0-2.5
1.0-2.5
1.0-2.5
1.0-2.5
1.0-2.5
1.0-2.5
1.0-2.5
1.0-2.5
1.0-2.5
1.5-2.5
1.0-2.5
2.0-2.5
2.5
1.0-2.5
1.0-2.5
1.0-2.5
1.0-2.5
1.0-2.5
2.5
1.5-2.5
1.5-2.5
-
1.0-2.5
1.0-2.5
2.0-2.5
06
1
2
3
1.0-4.0
1.0-4.0
1.0-4.0
1.0-4.0
1.0-4.0
1.0-4.0
1.0-4.0
1.0-4.0
1.0-4.0
1.0-4.0
1.0-4.0
1.5-4.0
1.0-4.0
2.0-4.0
2.5-4.0
1.0-4.0
1.0-4.0
1.0-4.0
1.0-4.0
1.0.4.0
2.5-4.0
1.5-4.0
1.5-4.0
4.0
1.0-4.0
1.0-4.0
2.0-4.0
08
1
2
3
1.0-5.0
1.0-5.0
1.0-5.0
1.0-7.0
1.0-7.0
1.0-7.0
1.0-7.0
1.0-7.0
1.0-7.0
1.0-7.0
1.0-7.0(b)
1.5-7.0
1.0-7.0
1.5-7.0
2.5-7.0
1.0-7.0
1.0-7.0
1.0-7.0
1.0-7.0
1.0-7.0
2.5-7.0
1.5-7.0
1.5-7.0
3.5-7.0(a)
1.0-7.0
1.0-7.0
1.5-7.0
10
1
2
3
1.0-5.0
1.0-5.0
1.0-5.0
1.0-9.0
1.0-9.0
1.0-9.0
1.0-11.0
1.0-11.0
1.0-11.0
1.0-11.0
1.0-11.0
1.5-11.0
1.0-11.0
1.0-11.0
1.5-11.0
1.0-11.0
1.0-11.0
1.0-11.0
1.0-11.0
1.0-11.0
1.5-11.0
1.5-11.0
1.5-11.0
2.5-11.0
1.0-11.0
1.0-11.0
1.5-11.0
12
1
2
3
1.0-5.0
1.0-5.0
1.0-5.0
1.0-9.0
1.0-9.0
1.0-9.0
1.0-13.0
1.0-13.0
1.0-13.0
1.0-16.0
1.0-16.0
1.5-16.0
1.0-16.0
1.0-16.0
1.5-16.0
1.0-15.0
1.0-15.0
1.0-15.0
1.0-16.0
1.0-16.0
1.5-16.0
1.5-15.0
1.5-15.0
2.0-15.0
1.0-16.0
1.0-16.0
1.5-16.0
14
1
2
3
1.0-5.0
1.0-5.0
1.0-5.0
1.0-9.0
1.0-9.0
1.0-9.0
1.0-13.0
1.0-13.0
1.0-13.0
1.0-16.0
1.0-16.0
1.5-16.0
1.0-22.0
1.0-22.0
1.5-22.0
1.0-15.0
1.0-15.0
1.0-15.0
1.0-22.0
1.0-22.0
1.5-22.0
1.5-22.0
1.5-22.0
2.0-22.0
1.0-22.0
1.0-22.0
1.5-22.0
16
1
2
3
1.0-5.0
1.0-5.0
1.0-5.0
1.0-9.0
1.0-9.0
1.0-9.0
1.0-13.0
1.0-13.0
1.0-13.0
1.0-16.0
1.0-16.0
1.5-16.0
1.0-22.0
1.0-22.0
1.5-22.0
1.0-15.0
1.0-15.0
1.0-15.0
1.0-30.0
1.0-30.0
1.5-30.0
1.5-30.0
1.5-30.0
2.0-30.0
1.0-26.0
1.0-26.0
1.5-26.0
24 x 16
1
2
3
1.5-5.0
1.5-5.0
1.5-5.0
1.0-9.0
1.0-9.0
1.0-9.0
1.0-13.0
1.0-13.0
1.0-13.0
1.0-16.0
1.0-16.0
1.5-16.0
1.0-22.0
1.0-22.0
1.5-22.0
1.5-15.0
1.5-15.0
1.5-15.0
1.0-34.0
1.0-34.0
1.5-34.0
1.5-42.0
1.5-42.0
2.0-42.0
1.0-26.0
1.0-26.0
1.5-26.0
Notes:
1. Coils available with 24-volt magnetic or mercury contactors, load carrying P.E switches, and P.E. switch with magnetic or mercury contactors.
2. Available kW increments are by 0.5 kW from 1.0 to 8.0 kW, by 1.0 kW from 9.0 to 18.0 kW, and by 2.0 kW from 18.0 to 46.0 kW.
3. Each stage will be equal in kW output.
4. All heaters contain an auto-thermal cutout and a manual-reset cutout.
5. The current amp draw for the heater elements is calculated by the formula at the end of this section.
6. The maximum allowable kW is based on the largest kW possible per a voltage and the minimum airflow per an inlet size and kW.
7. SCR not available with 575V.
(a) No 5.5 kW available.
(b) No 6.5 kW available.

40 VAV-PRC011M-EN
Single-Duct VAV Terminal Units
Table 29. Minimum and maximum airflow per inlet size and kW
I-P SI
Inlet size kW Min Heat cfm Max cfm Min L/s Max L/s
4 1.0 83 225 39 106
5
1.0
1.5
2.0
2.5
83
124
166
175
350
350
350
350
39
59
78
82
165
165
165
165
6
1.0
1.5
2.0
2.5
3.0
3.5
4.0
83
124
166
175
210
245
280
500
500
500
500
500
500
500
39
59
78
82
99
115
132
236
236
236
236
236
236
236
8
1.0
1.5
2.0
2.5
3.0
3.5
4.0
4.5
5.0
5.5
6.0
6.5
7.0
121
157
175
187
210
245
280
315
349
384
419
454
489
900
900
900
900
900
900
900
900
900
900
900
900
900
57
74
82
88
99
115
132
148
165
181
198
214
231
425
425
425
425
425
425
425
425
425
425
425
425
425
10
1.0
1.5
2.0
2.5
3.0
3.5
4.0
4.5
5.0
5.5
6.0
6.5
7.0
7.5
8.0
9.0
10.0
11.0
165
165
190
215
240
265
290
315
349
384
419
454
489
524
559
629
699
769
1400
1400
1400
1400
1400
1400
1400
1400
1400
1400
1400
1400
1400
1400
1400
1400
1400
1400
78
78
90
101
113
125
137
149
165
181
198
214
231
247
264
297
330
363
661
661
661
661
661
661
661
661
661
661
661
661
661
661
661
661
661
661
12
1.0 - 7.5
8.0
9.0
10.0
11.0
12.0
13.0
14.0
15.0
16.0
524
559
629
699
769
839
909
978
1048
1118
2000
2000
2000
2000
2000
2000
2000
2000
2000
2000
247
264
297
330
363
396
429
462
495
528
944
944
944
944
944
944
944
944
944
944

VAV-PRC011M-EN 41
Single-Duct VAV Terminal Units
14
1.0 - 9.0
10.0
11.0
12.0
13.0
14.0
15.0
16.0
17.0
18.0
20.0
22.0
685
731
769
839
909
978
1048
1118
1188
1258
1398
1538
3000
3000
3000
3000
3000
3000
3000
3000
3000
3000
3000
3000
323
345
363
396
429
462
495
528
561
594
660
726
1416
1416
1416
1416
1416
1416
1416
1416
1416
1416
1416
1416
16
1.0 - 12.0
13.0
14.0
15.0
16.0
17.0
18.0
20.0
22.0
24.0
26.0
28.0
30.0
920
951
978
1048
1118
1188
1258
1398
1538
1677
1817
1957
2097
4000
4000
4000
4000
4000
4000
4000
4000
4000
4000
4000
4000
4000
434
449
462
495
528
561
594
660
726
792
858
924
990
1888
1888
1888
1888
1888
1888
1888
1888
1888
1888
1888
1888
1888
16 x 24
1.0 - 22.0
24.0
26.0
28.0
30.0
32.0
34.0
36.0
38.0
40.0
42.0
1688
1755
1817
1957
2097
2236
2376
2516
2656
2796
2935
8000
8000
8000
8000
8000
8000
8000
8000
8000
8000
8000
797
828
858
924
990
1055
1121
1187
1253
1319
1385
3776
3776
3776
3776
3776
3776
3776
3776
3776
3776
3776
Table 29. Minimum and maximum airflow per inlet size and kW (continued)
I-P SI
Inlet size kW Min Heat cfm Max cfm Min L/s Max L/s
Table 30. Discharge air reset parameter setup
I-P SI
Inlet
Size kW
Reset Min/
Max Local
Heat
Range
Nom Reset
Min Local
Heat Setting
(cfm)
Nom Reset
Max Local
Heat Setting
(cfm)
Max Discharge
Air Temp Reset
(Setpoint &
Max) ∆T
Reset
Min/Max
Local Heat
Range
Nom Reset
Min Local
Heat Setting
(cfm)
Nom Reset
Max Local
Heat Setting
(cfm)
Max Discharge
Air Temp Reset
(Setpoint &
Max) ∆T
4 1.0 25 - 112 25 83 38 12 - 53 12 39 21
5
1.0
1.5
2.0
2.5
40 - 175
40 - 175
40 - 175
40 - 175
40
40
40
40
83
124
166
140
38
38
38
45
19 - 83
19 - 83
19 - 83
19 - 83
19
19
19
19
39
59
78
66
21
21
21
25
6
1.0
1.5
2.0
2.5
3.0
3.5
4.0
60 - 250
60 - 250
60 - 250
60 - 250
60 - 250
60 - 250
60 - 250
60
60
60
60
60
60
60
83
124
166
175
210
245
250
38
38
38
45
45
45
45
28 - 118
28 - 118
28 - 118
28 - 118
28 - 118
28 - 118
28 - 118
28
28
28
28
28
28
28
39
59
78
82
99
115
118
21
21
21
25
25
25
25

42 VAV-PRC011M-EN
Single-Duct VAV Terminal Units
8
1.0
1.5
2.0
2.5
3.0
3.5
4.0
4.5
5.0
5.5
6.0
6.5
7.0
105 - 450
105 - 450
105 - 450
105 - 450
105 - 450
105 - 450
105 - 450
105 - 450
105 - 450
105 - 450
105 - 450
105 - 450
105 - 450
105
105
105
105
105
105
105
105
105
105
105
105
105
121
157
175
187
210
245
280
315
349
384
419
454
489
26
30
36
42
45
45
45
45
45
45
45
45
45
50 - 213
50 - 213
50 - 213
50 - 213
50 - 213
50 - 213
50 - 213
50 - 213
50 - 213
50 - 213
50 - 213
50 - 213
50 - 213
50
50
50
50
50
50
50
50
50
50
50
50
50
57
74
82
88
99
115
132
148
165
181
198
214
231
14
17
20
23
25
25
25
25
25
25
25
25
25
10
1.0
1.5
2.0
2.5
3.0
3.5
4.0
4.5
5.0
5.5
6.0
6.5
7.0
7.5
8.0
9.0
10.0
11.0
165 - 700
165 - 700
165 - 700
165 - 700
165 - 700
165 - 700
165 - 700
165 - 700
165 - 700
165 - 700
165 - 700
165 - 700
165 - 700
165 - 700
165 - 700
165 - 700
165 - 700
165 - 700
165
165
165
165
165
165
165
165
165
165
165
165
165
165
165
165
165
165
165
165
190
215
240
265
290
315
349
384
419
454
489
524
559
629
699
700
19
29
33
37
39
42
43
45
45
45
45
45
45
45
45
45
45
45
78 - 331
78 - 331
78 - 331
78 - 331
78 - 331
78 - 331
78 - 331
78 - 331
78 - 331
78 - 331
78 - 331
78 - 331
78 - 331
78 - 331
78 - 331
78 - 331
78 - 331
78 - 331
78
78
78
78
78
78
78
78
78
78
78
78
78
78
78
78
78
78
78
78
90
101
113
125
137
149
165
181
198
214
231
247
264
297
330
330
11
16
18
20
22
23
24
25
25
25
25
25
25
25
25
25
25
25
12
1.0
1.5
2.0
2.5
3.0
3.5
4.0
4.5
5.0
5.5
6.0
6.5
7.0
7.5
8.0
9.0
10.0
11.0
12.0
13.0
14.0
15.0
16.0
240 - 1000
240 - 1000
240 - 1000
240 - 1000
240 - 1000
240 - 1000
240 - 1000
240 - 1000
240 - 1000
240 - 1000
240 - 1000
240 - 1000
240 - 1000
240 - 1000
240 - 1000
240 - 1000
240 - 1000
240 - 1000
240 - 1000
240 - 1000
240 - 1000
240 - 1000
240 - 1000
240
240
240
240
240
240
240
240
240
240
240
240
240
240
240
240
240
240
240
240
240
240
240
524
524
524
524
524
524
524
524
524
524
524
524
524
524
559
629
699
769
839
909
978
1000
1000
6
9
12
15
18
21
24
27
30
33
36
39
42
45
45
45
45
45
45
45
45
45
45
113 - 472
113 - 472
113 - 472
113 - 472
113 - 472
113 - 472
113 - 472
113 - 472
113 - 472
113 - 472
113 - 472
113 - 472
113 - 472
113 - 472
113 - 472
113 - 472
113 - 472
113 - 472
113 - 472
113 - 472
113 - 472
113 - 472
113 - 472
113
113
113
113
113
113
113
113
113
113
113
113
113
113
113
113
113
113
113
113
113
113
113
247
247
247
247
247
247
247
247
247
247
247
247
247
247
264
297
330
363
396
429
462
472
472
3
5
7
8
10
12
13
15
17
18
20
22
23
25
25
25
25
25
25
25
25
25
25
Table 30. Discharge air reset parameter setup (continued)
I-P SI
Inlet
Size kW
Reset Min/
Max Local
Heat
Range
Nom Reset
Min Local
Heat Setting
(cfm)
Nom Reset
Max Local
Heat Setting
(cfm)
Max Discharge
Air Temp Reset
(Setpoint &
Max) ∆T
Reset
Min/Max
Local Heat
Range
Nom Reset
Min Local
Heat Setting
(cfm)
Nom Reset
Max Local
Heat Setting
(cfm)
Max Discharge
Air Temp Reset
(Setpoint &
Max) ∆T

VAV-PRC011M-EN 43
Single-Duct VAV Terminal Units
14
1.0
1.5
2.0
2.5
3.0
3.5
4.0
4.5
5.0
5.5
6.0
6.5
7.0
7.5
8.0
9.0
10.0
11.0
12.0
13.0
14.0
15.0
16.0
17.0
18.0
20.0
22.0
320 - 1500
320 - 1500
320 - 1500
320 - 1500
320 - 1500
320 - 1500
320 - 1500
320 - 1500
320 - 1500
320 - 1500
320 - 1500
320 - 1500
320 - 1500
320 - 1500
320 - 1500
320 - 1500
320 - 1500
320 - 1500
320 - 1500
320 - 1500
320 - 1500
320 - 1500
320 - 1500
320 - 1500
320 - 1500
320 - 1500
320 - 1500
320
320
320
320
320
320
320
320
320
320
320
320
320
320
320
320
320
320
320
320
320
320
320
320
320
320
320
685
685
685
685
685
685
685
685
685
685
685
685
685
685
685
685
731
769
839
909
978
1048
1118
1188
1258
1398
1500
5
7
9
11
14
16
18
21
23
25
28
30
32
34
37
41
43
45
45
45
45
45
45
45
45
45
45
151 - 708
151 - 708
151 - 708
151 - 708
151 - 708
151 - 708
151 - 708
151 - 708
151 - 708
151 - 708
151 - 708
151 - 708
151 - 708
151 - 708
151 - 708
151 - 708
151 - 708
151 - 708
151 - 708
151 - 708
151 - 708
151 - 708
151 - 708
151 - 708
151 - 708
151 - 708
151 - 708
151
151
151
151
151
151
151
151
151
151
151
151
151
151
151
151
151
151
151
151
151
151
151
151
151
151
151
323
323
323
323
323
323
323
323
323
323
323
323
323
323
323
323
345
363
396
429
462
495
528
561
594
660
708
3
4
5
6
8
9
10
11
13
14
15
17
18
19
20
23
24
25
25
25
25
25
25
25
25
25
25
Table 30. Discharge air reset parameter setup (continued)
I-P SI
Inlet
Size kW
Reset Min/
Max Local
Heat
Range
Nom Reset
Min Local
Heat Setting
(cfm)
Nom Reset
Max Local
Heat Setting
(cfm)
Max Discharge
Air Temp Reset
(Setpoint &
Max) ∆T
Reset
Min/Max
Local Heat
Range
Nom Reset
Min Local
Heat Setting
(cfm)
Nom Reset
Max Local
Heat Setting
(cfm)
Max Discharge
Air Temp Reset
(Setpoint &
Max) ∆T

44 VAV-PRC011M-EN
Single-Duct VAV Terminal Units
16
1.0
1.5
2.0
2.5
3.0
3.5
4.0
4.5
5.0
5.5
6.0
6.5
7.0
7.5
8.0
9.0
10.0
11.0
12.0
13.0
14.0
15.0
16.0
17.0
18.0
20.0
22.0
24.0
26.0
28.0
30.0
420 -2000
420 -2000
420 -2000
420 -2000
420 -2000
420 -2000
420 -2000
420 -2000
420 -2000
420 -2000
420 -2000
420 -2000
420 -2000
420 -2000
420 -2000
420 -2000
420 -2000
420 -2000
420 -2000
420 -2000
420 -2000
420 -2000
420 -2000
420 -2000
420 -2000
420 -2000
420 -2000
420 -2000
420 -2000
420 -2000
420 -2000
420
420
420
420
420
420
420
420
420
420
420
420
420
420
420
420
420
420
420
420
420
420
420
420
420
420
420
420
420
420
420
920
920
920
920
920
920
920
920
920
920
920
920
920
920
920
920
920
920
920
951
978
1048
1118
1188
1258
1398
1538
1677
1817
1957
2000
3
5
7
9
10
12
14
15
17
19
21
22
24
26
27
31
34
38
41
43
45
45
45
45
45
45
45
45
45
45
45
198 - 891
198 - 891
198 - 891
198 - 891
198 - 891
198 - 891
198 - 891
198 - 891
198 - 891
198 - 891
198 - 891
198 - 891
198 - 891
198 - 891
198 - 891
198 - 891
198 - 891
198 - 891
198 - 891
198 - 891
198 - 891
198 - 891
198 - 891
198 - 891
198 - 891
198 - 891
198 - 891
198 - 891
198 - 891
198 - 891
198 - 891
198
198
198
198
198
198
198
198
198
198
198
198
198
198
198
198
198
198
198
198
198
198
198
198
198
198
198
198
198
198
198
434
434
434
434
434
434
434
434
434
434
434
434
434
434
434
434
434
434
434
449
462
495
528
561
594
660
726
792
858
924
944
2
3
4
5
6
7
8
9
9
10
11
12
13
14
15
17
19
21
23
24
25
25
25
25
25
25
25
25
25
25
25
Table 30. Discharge air reset parameter setup (continued)
I-P SI
Inlet
Size kW
Reset Min/
Max Local
Heat
Range
Nom Reset
Min Local
Heat Setting
(cfm)
Nom Reset
Max Local
Heat Setting
(cfm)
Max Discharge
Air Temp Reset
(Setpoint &
Max) ∆T
Reset
Min/Max
Local Heat
Range
Nom Reset
Min Local
Heat Setting
(cfm)
Nom Reset
Max Local
Heat Setting
(cfm)
Max Discharge
Air Temp Reset
(Setpoint &
Max) ∆T

VAV-PRC011M-EN 45
Single-Duct VAV Terminal Units
Note: For VCEF units, Discharge Air Reset Enable is not compatible with legacy design LH and RH
units. This feature can only be enabled with the (F) flippable orientation units with centrally
located electric heat rack. Additionally, SCR heat, BACnet controls and averaging temp
sensing matrix must be selected to enable this energy efficiency feature.
16 x 24
1.0
1.5
2.0
2.5
3.0
3.5
4.0
4.5
5.0
5.5
6.0
6.5
7.0
7.5
8.0
9.0
10.0
11.0
12.0
13.0
14.0
15.0
16.0
17.0
18.0
20.0
22.0
24.0
26.0
28.0
30.0
32.0
34.0
36.0
38.0
40.0
42.0
800 - 4000
800 - 4000
800 - 4000
800 - 4000
800 - 4000
800 - 4000
800 - 4000
800 - 4000
800 - 4000
800 - 4000
800 - 4000
800 - 4000
800 - 4000
800 - 4000
800 - 4000
800 - 4000
800 - 4000
800 - 4000
800 - 4000
800 - 4000
800 - 4000
800 - 4000
800 - 4000
800 - 4000
800 - 4000
800 - 4000
800 - 4000
800 - 4000
800 - 4000
800 - 4000
800 - 4000
800 - 4000
800 - 4000
800 - 4000
800 - 4000
800 - 4000
800 - 4000
800
800
800
800
800
800
800
800
800
800
800
800
800
800
800
800
800
800
800
800
800
800
800
800
800
800
800
800
800
800
800
800
800
800
800
800
800
1688
1688
1688
1688
1688
1688
1688
1688
1688
1688
1688
1688
1688
1688
1688
1688
1688
1688
1688
1688
1688
1688
1688
1688
1688
1688
1688
1755
1817
1957
2097
2236
2376
2516
2656
2796
2935
2
3
4
5
6
7
7
8
9
10
11
12
13
14
15
17
19
20
22
24
26
28
30
32
34
37
41
43
45
45
45
45
45
45
45
45
45
378 - 1782
378 - 1782
378 - 1782
378 - 1782
378 - 1782
378 - 1782
378 - 1782
378 - 1782
378 - 1782
378 - 1782
378 - 1782
378 - 1782
378 - 1782
378 - 1782
378 - 1782
378 - 1782
378 - 1782
378 - 1782
378 - 1782
378 - 1782
378 - 1782
378 - 1782
378 - 1782
378 - 1782
378 - 1782
378 - 1782
378 - 1782
378 - 1782
378 - 1782
378 - 1782
378 - 1782
378 - 1782
378 - 1782
378 - 1782
378 - 1782
378 - 1782
378 - 1782
378
378
378
378
378
378
378
378
378
378
378
378
378
378
378
378
378
378
378
378
378
378
378
378
378
378
378
378
378
378
378
378
378
378
378
378
378
797
797
797
797
797
797
797
797
797
797
797
797
797
797
797
797
797
797
797
797
797
797
797
797
797
797
797
828
858
924
990
1055
1121
1187
1253
1319
1385
1
2
2
3
3
4
4
5
5
6
6
7
7
8
8
9
10
11
12
13
14
16
17
18
19
21
23
24
25
25
25
25
25
25
25
25
25
Table 30. Discharge air reset parameter setup (continued)
I-P SI
Inlet
Size kW
Reset Min/
Max Local
Heat
Range
Nom Reset
Min Local
Heat Setting
(cfm)
Nom Reset
Max Local
Heat Setting
(cfm)
Max Discharge
Air Temp Reset
(Setpoint &
Max) ∆T
Reset
Min/Max
Local Heat
Range
Nom Reset
Min Local
Heat Setting
(cfm)
Nom Reset
Max Local
Heat Setting
(cfm)
Max Discharge
Air Temp Reset
(Setpoint &
Max) ∆T

46 VAV-PRC011M-EN
Single-Duct VAV Terminal Units
Minimum Circuit Ampacity (MCA) Equation
• MCA = heater amps x 1.25
Maximum Over Current Protection (MOP) Equation
• MOP = heater amps
• However since MOP is less than or equal to MCA, then choose next fuse greater than MCA.
• Units without electric reheat would use smallest fuse sizing.
Standard Fuse Sizes: 15, 20, 25, 30, 35, 40, 45, 50, and 60.
Example–For MOP of Single-Duct Unit
A model VCEF, electric reheat unit size 14 has 480/3 phase 15 kW electric reheat with 2 stages.
15 kW – 480/3 heater
15x1000/480x1.73=18.06
MCA = 18.06 x 1.25 = 22.58 amps. Since MOP is less than or equal to MCA, then MOP = 25.
Useful Formulas
kW = 1214 X L/s X ATD
ATD = kW / 1214 X L/s
kW Cfm ATD×
3145
--------------------------------
=
3φamps kW 1000×
PrimaryVoltage 3×
------------------------------------------------------------------
=
ATD kW 3145×
Cfm
-------------------------------
=
1φamps kW 1000×
PrimaryVoltage
----------------------------------------------------
=

VAV-PRC011M-EN 47
Single-Duct VAV Terminal Units
Table 31. Discharge sound power (dB)1, 2, 4Perf
Inlet
Size
(in)
0.5" Inlet Pressure
Ps51.0" Inlet Pressure
Ps51.5" Inlet Pressure
Ps32.0" Inlet Pressure
Ps53.0" Inlet Pressure
Ps5
Cfml/s234567234567234567234567234567
4
80 38 65 61 46 44 40 37 66 65 53 51 47 46 68 70 61 60 60 56 69 73 67 66 64 61
120 57 686449484341726955534947 727364605755737671686360
150 71 686449494542737056545149757461585553757665615856767672686461
225 106 73 68 54 54 50 49 78 75 61 59 55 54 81 81 68 64 61 59 80 82 73 69 65 63
5
130 61 605645434138636252504847 656861595855677269666360
200 94 635948474340676556535049 707164615856697370676361
250 118 65 61 49 49 44 42 70 67 57 55 52 50 71 70 61 57 55 54 73 73 64 60 58 57 73 75 72 69 63 61
350 165 67 63 54 53 48 47 74 69 59 57 53 53 78 76 67 62 59 58 78 78 73 69 64 63
6
200 94 605746444138646355524947 667064605855687472676360
300 142 64 60 48 48 44 41 67 65 56 53 50 48 71 71 65 61 58 56 72 75 72 69 64 62
400 189 65 60 51 49 44 42 71 67 58 55 51 50 73 71 63 59 56 55 74 73 66 61 58 57 76 76 73 68 63 62
500 236 69 64 55 53 49 47 73 69 61 58 53 53 77 75 69 63 60 59 79 78 73 69 64 63
8
350 165 61 57 48 45 44 40 64 64 54 51 50 53 68 71 62 58 58 60 71 76 71 66 63 61
520 245 63 59 51 48 45 42 66 66 57 53 52 56 71 74 65 61 60 66 73 76 72 66 65 66
700 330 65 60 54 51 48 44 69 67 60 56 53 57 71 71 63 59 58 60 73 74 67 62 61 64 75 77 74 68 66 69
900 425 68 63 57 56 52 49 72 68 62 59 56 57 77 75 69 64 62 65 79 78 74 68 67 68
10
550 260 59 54 53 51 45 40 64 62 58 57 53 48 70 68 65 66 62 58 72 71 70 71 66 62
820 387 62 57 55 51 46 42 67 64 61 60 55 52 72 70 66 66 62 60 75 74 70 70 66 63
1100 519 66 60 58 54 49 46 71 67 64 61 56 53 75 70 67 66 61 57 76 72 68 68 63 60 78 75 73 71 67 64
1400 661 70 63 62 58 53 51 75 68 65 62 57 54 79 74 70 66 63 60 80 77 73 70 67 64
12
800 378 59 54 52 49 47 41 64 61 57 55 55 52 71 69 65 63 63 61 72 71 68 67 67 64
1200 566 61 56 54 50 49 43 67 64 60 57 57 55 73 71 67 63 64 62 77 75 71 68 68 66
1600 755 64 59 58 53 52 46 69 66 62 58 57 56 73 71 66 61 62 60 75 73 69 64 65 63 78 77 73 69 69 66
2000 944 68 62 61 56 56 51 73 69 65 61 60 59 78 75 70 65 65 64 81 77 74 69 69 67
14
1100 519 58 53 51 46 44 39 64 61 57 54 53 51 69 72 66 62 61 59 72 73 71 67 66 63
1600 755 61 56 55 49 46 41 67 62 60 56 54 51 71 71 67 63 62 61 74 76 72 67 67 64
2100 991 64 60 59 52 49 44 69 66 63 57 54 52 72 69 66 61 59 58 73 72 69 64 62 61 76 74 73 68 67 64
3000 1416 70 66 67 57 55 52 75 71 68 61 58 58 80 77 72 66 64 61 81 78 75 70 69 66
16
1400 661 57 53 51 47 46 40 63 61 58 55 55 51 69 72 67 63 63 62 72 76 73 69 67 66
2100 991 60 56 55 51 49 43 66 63 60 57 55 52 71 71 68 64 64 61 73 76 73 70 68 66
2800 1321 64 61 61 54 51 48 69 66 64 58 57 54 72 69 67 62 61 60 72 72 70 65 64 63 75 74 73 70 69 65
4000 1888 71 68 68 63 57 54 74 71 70 63 61 59 78 76 73 68 65 64 80 77 76 72 70 67
24
x
16
2700 1274 71 68 61 58 54 50 75 72 67 65 62 58 77 76 73 71 68 65 78 78 76 75 72 69
4000 1888 73 71 65 62 58 54 77 76 71 68 65 61 81 80 77 75 72 68 82 82 80 78 76 72
5300 2501 72 71 67 64 61 58 78 77 75 71 67 63 80 80 78 75 71 68 81 83 81 78 74 70 84 85 84 81 78 74
6000 2832 71 71 68 65 62 60 78 77 76 72 68 65 82 83 83 79 75 71 84 86 86 82 79 75
7500 3540 70 71 70 67 63 63 79 77 77 73 70 68 83 84 88 81 76 73 85 87 90 84 80 76
8000 3776 70 71 71 68 64 64 79 77 78 74 71 69 83 84 89 82 77 74 85 87 91 85 81 77
Notes:
1. All data are measured in accordance with Industry Standard ARI 880-2011.
2. All sound power levels, dB re: 10-12 Watts.
3. Data in this column constitute AHRI 880-2011 Standard Rating Conditions
4. Where Ps is the inlet static pressure minus discharge static.
5. Application ratings are outside the scope of the certification program.

48 VAV-PRC011M-EN
Single-Duct VAV Terminal Units
Table 32. Radiated sound power (dB)1, 2, 4
Inlet
Size
(in)
0.5" Inlet Pressure
Ps51.0" Inlet Pressure
Ps51.5" Inlet Pressure
Ps32.0" Inlet Pressure
Ps53.0" Inlet Pressure
Ps5
Cfml/s234567234567234567234567234567
4
80 38 48 45 40 33 31 23 48 47 43 37 34 25 48 51 53 47 43 35 46 52 60 54 48 42
120 57 474540333023494845383427 505154464236515460524742
150 71 474541353024514946393528525250433933525355474337515661534842
225 106 52 49 44 40 35 30 57 54 49 43 39 33 60 59 57 48 45 39 59 61 63 54 49 44
5
130 61 474435292421484541353025 484850453933485158514540
200 94 484538322522494743373226 505252453935505558514540
250 118 48 44 40 34 27 23 50 48 45 38 33 27 52 50 49 42 37 31 52 53 53 44 40 35 53 56 60 52 44 40
350 165 51 47 44 38 31 26 55 51 47 41 35 31 59 56 55 47 41 37 56 58 60 51 44 40
6
200 94 524638312522504743363126 525152433833515559504440
300 142 52 48 41 33 25 22 55 50 46 38 32 27 56 53 53 44 38 35 57 57 60 50 44 39
400 189 55 49 44 36 28 24 56 53 48 40 33 28 58 54 51 43 37 32 59 56 55 46 40 35 59 58 60 50 43 40
500 236 55 49 47 40 32 27 59 54 51 43 36 31 62 59 57 47 41 36 63 60 61 52 44 40
8
350 165 46 42 38 31 27 22 48 45 43 36 35 27 54 52 53 42 41 36 56 58 64 52 46 42
520 245 49 43 41 35 31 24 51 48 47 39 37 29 55 54 54 45 43 38 56 57 63 51 47 44
700 330 50 46 44 38 34 26 54 51 50 42 38 34 57 54 53 45 42 36 58 57 57 48 45 39 60 59 62 52 48 44
900 425 56 49 50 44 37 29 59 53 53 46 41 35 62 59 57 49 46 39 63 61 62 53 49 44
10
550 260 48 44 42 32 25 24 52 49 48 40 31 26 55 55 53 47 39 32 58 58 59 50 44 38
820 387 53 47 43 36 28 25 57 52 49 41 33 27 60 58 55 48 40 33 62 61 60 52 44 38
1100 519 58 50 46 39 30 27 61 55 51 43 35 29 63 59 54 47 39 32 64 61 57 50 42 35 67 63 61 53 45 39
1400 661 62 53 49 42 34 30 66 58 54 46 38 33 69 63 58 51 43 37 71 65 63 55 46 41
12
800 378 49 46 40 33 27 27 54 51 46 39 34 29 58 58 53 46 42 35 59 62 59 51 47 40
1200 566 54 48 43 35 29 27 59 54 48 41 35 30 64 61 55 48 43 37 66 64 60 52 47 42
1600 755 60 53 47 38 32 30 63 58 50 42 37 32 66 62 54 46 40 36 68 64 57 49 43 39 71 66 61 53 48 43
2000 944 63 58 52 42 37 34 67 62 54 45 40 38 72 68 58 50 45 42 75 68 61 54 50 45
14
1100 519 47 46 36 30 24 23 53 53 42 36 32 27 57 61 52 43 40 35 60 64 60 48 43 38
1600 755 52 49 39 32 24 23 56 54 45 38 32 26 60 63 52 44 39 35 63 67 60 49 43 40
2100 991 55 52 43 35 27 25 59 57 48 40 33 28 61 61 51 43 37 32 63 64 55 46 40 36 65 67 61 50 44 40
3000 1416 63 59 51 42 34 31 65 64 54 44 36 34 68 68 57 48 41 37 69 69 60 52 45 41
16
1400 661 50 47 38 32 26 23 54 54 45 40 35 29 60 62 53 47 43 38 63 66 61 52 47 43
2100 991 51 49 41 35 28 24 56 54 47 41 36 30 61 61 55 49 44 39 64 66 60 53 48 43
2800 1321 56 54 45 38 31 27 59 56 49 43 37 32 60 60 53 46 41 36 62 62 56 49 44 39 65 65 61 54 49 44
4000 1888 61 60 55 45 38 32 63 63 56 47 41 36 67 66 59 51 46 41 69 66 62 55 50 45
24
x
16
2700 1274 65 63 53 45 38 30 70 65 60 52 45 37 71 69 66 59 51 45 72 71 69 62 54 50
4000 1888 67 67 57 48 40 32 71 71 64 55 48 41 74 75 69 61 54 48 76 77 72 65 58 52
5300 2501 67 66 58 49 42 35 74 75 69 57 49 42 75 76 72 61 53 46 76 77 74 64 56 50 78 79 76 67 60 53
6000 2832 68 66 59 51 44 37 74 75 69 58 50 43 77 78 75 65 57 51 79 80 77 68 61 54
7500 3540 69 67 61 54 48 42 75 74 70 59 51 45 78 80 78 66 58 52 80 81 79 69 62 55
8000 3776 69 67 62 55 49 44 75 74 70 59 52 46 79 81 79 67 59 52 80 82 80 70 63 56
Notes:
1. All data are measured in accordance with Industry Standard AHRI 880-2011.
2. All sound power levels, dB re: 10-12 Watts.
3. Data in this column constitute AHRI 880-2011 Standard Rating Conditions
4. Where Ps is the inlet static pressure minus discharge static.
5. Application ratings are outside the scope of the certification program.

VAV-PRC011M-EN 49
Single-Duct VAV Terminal Units
Table 33. Sound noise criteria (NC)
Discharge1,2,4 Radiated1,2,4
Inlet
Size (in)
Inlet Pressure (Ps)3,5 Inlet Pressure (Ps)3,5
CFM l/s 0.5” 1.0” 1.5” 2.0” 3.0” 0.5” 1.0” 1.5” 2.0” 3.0”
4
80 38 21 25 31 34 -- 16 27 35
120 57 25 30 34 38 -- 19 28 35
150 71 25 32 35 38 38 -- 20 24 30 36
225 106 32 38 44 45 18 23 32 38
5
130 61 -- 21 28 33 -- -- 24 33
200 94 19 25 32 34 -- 16 26 33
250 118 21 28 31 34 37 -- 19 23 27 35
350 165 24 33 38 40 18 21 30 35
6
200 94 -- 21 29 34 -- 16 26 34
200 142 18 23 31 35 15 20 27 35
400 189 18 26 31 33 37 18 22 25 30 35
500 236 23 28 35 39 21 25 32 36
8
350 165 -- 23 31 37 -- 16 27 39
520 245 17 25 34 37 -- 21 28 38
700 330 18 26 31 34 38 18 24 27 32 37
900 425 21 27 36 39 24 27 32 37
10
550 260 -- 19 26 30 15 22 27 34
820 387 -- 22 29 33 16 23 30 35
1100 519 17 25 29 31 35 20 25 28 32 36
1400 661 21 27 33 37 25 30 34 38
12
800 378 -- 17 27 29 -- 20 27 34
1200 566 -- 21 29 34 16 23 31 35
1600 755 15 23 29 32 36 22 27 32 34 37
2000 944 19 27 34 36 27 32 39 42
14
1100 519 -- 18 31 32 -- 21 31 35
1600 755 -- 19 30 36 17 23 33 38
2100 991 17 24 28 31 33 20 26 31 34 38
3000 1416 24 30 37 38 28 34 39 40
16
1400 661 -- 18 31 36 -- 23 32 37
2100 991 -- 20 30 36 17 23 31 37
2800 1321 18 24 27 31 33 23 25 30 32 36
4000 1888 26 30 36 37 30 33 37 37
24 x 16
2700 1274 26 31 35 38 33 36 41 45
4000 1888 30 35 40 43 38 43 47 50
5300 2501 30 37 40 44 46 37 47 49 50 52
6000 2832 30 37 44 47 37 47 51 53
7500 3540 30 37 45 49 38 46 55 56
8000 3776 30 37 45 49 38 46 56 57
Notes:
1. "--" represents NC levels below NC 15.
2. NC Values are calculated using modeling assumptions based on AHRI 885-2008-02 Addendum.
3. Data at 1.5" inlet pressure constitute AHRI 880-2011 Standard Rating Conditions
4. Where Ps is the inlet static pressure minus discharge static.
5. Data at 0.5", 1.0", 2.0"& 3.0" are application ratings, these ratings are outside the scope of the certification program.

50 VAV-PRC011M-EN
Single-Duct VAV Terminal Units
Table 34. AHRI 885-2008 discharge transfer function assumptions
Octave Band
23 4 567
Small Box (< 300 cfm)
Medium Box (300-700 cfm)
Large Box (> 700 cfm)
-24
-27
-29
-28
-29
-30
-39
-40
-41
-53
-51
-51
-59
-53
-52
-40
-39
-39
Notes: Add to terminal unit sound power to determine discharge sound pressure in the space.
1. “—” represents NC levels below NC 15.
2. NC Values are calculated using current Industry Standard AHRI 885-2008. Radiated Transfer Function obtained from Appendix E, Type 2 Mineral Fiber
Insulation.
3. Where Ps is inlet static pressure minus discharge static pressure.
4. Application ratings are outside the scope of the Certification Program.
Table 35. AHRI 885-2008 radiated transfer function assumptions
Octave Band
234567
Type - Mineral Fiber -18 -19 -20 -26 -31 -36
Notes: Select the ceiling type which most closely represents the application. Next, add to terminal unit sound power to determine radiated sound
pressure in the space.
1. “—” represents NC levels below NC 15.
2. NC Values are calculated using current Industry Standard AHRI 885-2008. Radiated Transfer Function obtained from Appendix E, Type 2 Mineral Fiber
Insulation.
3. Where Ps is inlet static pressure minus discharge static pressure.
4. Application ratings are outside the scope of the Certification Program.

VAV-PRC011M-EN 51
Single-Duct VAV Terminal Units
Dimensional Data
NOTES:
1. Air inlet centered in unit front panel.
2. Outlet combinations to remote diffusers have
optional integral balancing dampers. (See
specification sheet.)
3. Outlet connections are centered in plenum panel.
4. Plenum not available with size 14 & 16 units.
5. Minimum of 1.5 duct diamenters of straight duct
required at inlet for proper flow reading.
6. Allow 36" (914 mm) on control side for servicing.
7. Weights are an estimation and will vary based on
selected options, insulation type, etc.
8. Unit is field convertible from a left-hand connection
(shown) to right-hand by rotating unit.
ABCD FEHJ
OUTLET PLENUM
ARRANGEMENTS
(TOP VIEW)
11.50" [292mm]
13.50" [343mm]
15.50" [394mm]
9.50" [241mm]
L/s
CFM
225
350
500
900
1400
2000
08
12
10
06
05
04
VALV
425
661
994
106
165
236
13.00" [330mm]
12.00" [305mm]
11.00" [279mm]
11.50" [292mm]
INLET SIZE
(NOMINAL Ø)
8" [203mm]
10" [254mm]
12" [305mm]
4" [104mm]
5" [127mm]
6" [152mm]
CL H
14.00" [356mm]
E
11.50" [292mm]
14.00" [356mm]
15.50" [394mm]
W
12.50" [318mm]
18.50" [470mm]
11.50" [292mm]
38 [17]
30 [14]
22 [10]
LBS
21 [9.5]
WT
SYMBOL NOMINALØ
IV
III
I
II
10" [254mm]
8" [203mm]
6" [152mm]
5" [127mm]
OUTL CONVERSION CHART
D,E,F
J
H
A,B,C
OUTLET AVAILABILITY CHART - SEE OUTL CONVERSION FOR NOMINALØ
OUTL
VALV
I, II, III
N/A
I, II, III
N/AN/A
I, II
I, II
I, II
4I, II
I, II
I, II
5
N/A
I, II
I, II
I, II
6III
8
III, IV
III, IV
12
II, II
II, III, IV
II, III, IV
10
III, IV IV
20.50" [521mm]14" [356mm]14 3000 1416 14.00" [356mm] 19.50" [495mm] NA 46 [21]
24.50" [622mm]16" [406mm]16 4000 1888 15.00" [381mm] NA 51 [23]
28.50" [724mm]
16X24"
24RT 8000 3776 18.00" [457mm] NA 70 [32]
[406mm x 610MM]
[KGS]
4.25" [108mm]
2.75" [70mm]
3.25" [83mm]
2.25" [57mm]
Z
2.75" [70mm]
2.25" [57mm]
A (h) B (w)
10.00" [254mm]
12.00" [305mm]
14.00" [356mm]
18.00" [457mm]
8.00" [203mm]
19.00" [483mm]
17.00" [432mm]
14.00" [356mm]
11.00" [279mm]
10.00" [250mm]
23.00" [584mm]
27.00" [686mm]
SINGLE-DUCT COOLING ONLY WITH OPTIONAL OUTLET PLENUM (VCCF)
SIZE 04 &05
6.50” (165MM)
4.00”
(102MM)
AIRFLOW
C
Z
AIR
VALVE
FLOW RING TUBING
CONTROL BOX
(PNEU. CONTROLS AREA)
14.60”
(371MM)
1.00”
(25.4MM)
SLIP & DRIVE
CONNECTION
DISCHARGE
DIMENSIONS (BXA)
AIRFLOW
L
E
ARRANGEMENT “H”
1.50” (38 MM) FLANGE
TOP VIEW
W5.50”
(140MM)
H
9.50”
(241MM)
BACK VIEW

52 VAV-PRC011M-EN
Single-Duct VAV Terminal Units

VAV-PRC011M-EN 53
Single-Duct VAV Terminal Units
SINGLE DUCT HOT WATER W/PLENUM (VCWF)
CONTROL BOX
(PNEU. CONTROLS
AREA)
SLIP & DRIVE
CONNECTION
COIL ACCESS
76mm x 178mm
[3.00" x 7.00"]
C
L
H
W
SIZE 04 & 05
5.75" [146mm]
4.00"
[102 mm]
14.60"
[371 mm]
5.50"
[140 mm]
9.50"
[241 mm]
BACK VIEW
TOP VIEW
04,05,06 - 7.70" [196 mm]
ALL OTHERS - 7.40" [188 mm]
E
AIR FLOW
OUTLET AVAILABILITY CHART - SEE OUTL CONVERSION FOR NOMINALØ
A,B,C
H
OUTL
J
VALV
D,E,F
N/A N/A N/A
III
I, II
45
III, IV
6
IV
81012
I, II I, II
I, II I, II I, II I, II, III II, III, IV III, IV
I, II I, II I, II
I
N/A I, II
I, II, III II, III, IV III, IV
4. Plenum not available w/sizes 14 & 16 units.
3. Outlet connections are centered in plenum panel.
optional integral balancing dampers (See
7. Weights are an estimation and will vary
based on selected options, insulation type, etc.
6. Allow 36" [914mm] on control side for servicing.
5. Minimum of 1.5 duct diameters of straight
2. Outlet combinations to remote diffusers have
1. Air inlet is centered in unit front panel.
specification sheet.)
duct required for proper flow reading.
CUSTOMER NOTES:
(TOP VIEW)
ARRANGEMENTS
A B C D
OUTLET PLENUM
HFE J handedness of coil connection is determined
8. Coil furnished with stub sweat connections.
by facing air stream.
FLOW RING
TUBING
Z
DISCHARGE
DIMENSIONS(BxA)
ARRANGEMENT "H"
1.50" (38 mm) FLANGE
2.75" [70mm]
2.25" [57mm]
2.75" [70mm]
3.25" [83mm]
4.25" [108mm]
2.25" [57mm]
6" [152mm]23650006
16" [406mm]
14" [356mm]
12" [305mm]
10" [254mm]
8" [203mm]08
12
10
14
16
24RT
1888
1416
3776
3000
4000
8000
900
1400
2000
661
994
425
16X24"
11.50" [292mm]
13.50" [343mm]
15.50" [394mm]
19.50" [495mm]
11.00" [279mm]
12.00" [305mm]
13.00" [330mm]
14.00" [356mm]
15.00" [381mm]
18.00" [457mm]
15.50" [394mm]
12.50" [318mm]
18.50" [470mm]
20.50" [521mm]
24.50" [622mm]
28.50" [724mm]
INLET SIZE
(NOMINAL Ø)
5" [127mm]
4" [104mm]
05
04
VALV L/s
CFM
225
350 165
106
C
9.50" [241mm]
11.50" [292mm]
L
11.50" [292mm]
HW
27.00" [686mm]
23.00" [584mm]
19.00" [483mm]
17.00" [432mm]
14.00" [356mm]
11.00" [279mm]
18.00" [457mm]
14.00" [356mm]
12.00" [305mm]
10.00" [254mm]
14.00" [356mm]
14.00" [356mm]
NA
NA
NA 71 [32]
95 [43]
62 [28]
40 [18]
51 [23]
30 [14]
10.00" [254mm]8.00" [203mm]
A (h)
Z
11.50" [292mm]
B (w) ELBS
27 [12]
[KGS]
WT
NOMINALØ
8" [203mm]
6" [152mm]
5" [127mm]
OUTL CONVERSION CHART
10" [254mm]
IV
SYMBOL
I
III
II
humidity, external insulation around the heating
the unit is to be installed in a location with high
9. Coils are provided without internal insulation. If
coil should be installed as required.
(shown) to right-hand by rotating unit.
10. Unit is field convertible from a left-hand connection
11. Add 1.75" for 3 or 4 row coils. 1 or 2 row shown.
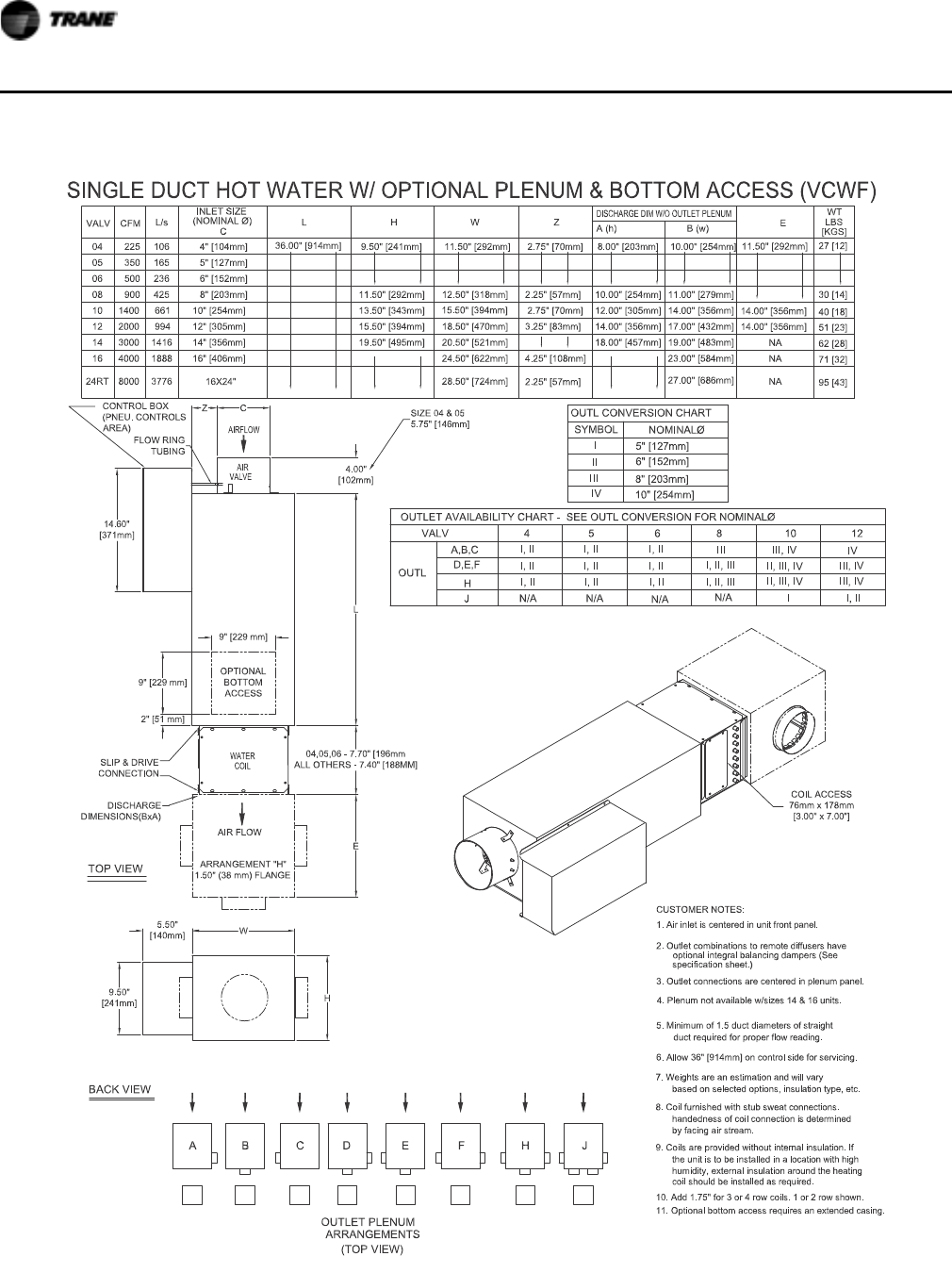
54 VAV-PRC011M-EN
Single-Duct VAV Terminal Units

VAV-PRC011M-EN 55
Single-Duct VAV Terminal Units
Use port at the bottom for inlet and top for outlet on
single row coils. For multirow coils, always plumb in
counter flow orientation. Water inlet always on the
airflow downstream side of the hot water coil. Water
outlet always on the upstream side of the hot water
coil. See drawings below for reference.

56 VAV-PRC011M-EN
Single-Duct VAV Terminal Units
[25mm]
3
[79mm]
OUTLET
64
/
7
"
1
AIR FLOW
B
[198mm]
7
32
/"
INLET
A
[86mm]
3
[29mm]
1
64
9
/"
"
C
AIR FLOW
W
[25mm]
1"
AB
INLET
OUTLET
3
[79mm]
64
/
7
"
[86mm]
32
13
3/"
[198mm]
13
7
32
/"
AIR FLOW
[29mm]
1
64
9
/"
AccessPanel
AccessPanel
W
13
32
/"
13
stream. L.H. Coil connections shown, R.H. opposite.
Location of coil connections is determined by facing air1.
CUSTOMER NOTES:
2. Coil furnished with stub sweat connections.
08
10
12
14
INLT
04
05
06
COIL INFORMATION FOR 2 ROW COIL ASSY
CONNECTION
7
/
8
"[22mm] O.D.
7
/
8
"[22mm] O.D.
B CA
1400 661
3000
2000 994
1416
SECOND
LITERS
900
350
500
225
per
165
425
236
CFM
106 [206mm]
/
8"
8
1
3.
Coil height and width is dependent upon unit height4.
and width.
Access Panel is standard.5.
16
16 x 24
4000
8000
1888
3776 [22mm] O.D.
[22mm] O.D.
7
/
8
/
78
"
"
COIL
[206mm]
8
8
1
/"
[206mm]
8
8
1
/"
[257mm]
8
10 /
1
"
[308mm]
8
12
1
/"
[359mm]
8
14 /
1
"
[460mm]
8
18 /
1
"
[460mm]
8
18 /
1
"
[460mm]
/
8
18
1
"
10" [254mm]
10" [254mm]
10" [254mm]
11" [279mm]
14" [356mm]
17" [432mm]
19" [483mm]
23" [584mm]
27" [686mm]
[22mm] O.D.
[22mm] O.D./
78
/
78
"
"
[413mm]
[311mm]
[260mm]
[210mm]
[191mm]
10
16
12
8
/
4
1
/
4
/
14
"
"
1
/
1
4
"
"
6"
[191mm]"
6
[191mm]"
6
[413mm]
"
1
16 /
4
[413mm]
"
1
16 /
4
W
[210mm]
8/
14
"
8
1
/
4
[210mm]
"
8
1
/
4
[210mm]
"
4
/
1
4
/
1
4
/
1
8
8
1
1
8
1
[210mm]
[210mm]
[210mm]
4
/
4
/"
"
/
4
"
8
8
1
1
8
1
[210mm]
[210mm]
[210mm]
4
/
4
/"
"
/
4
"
7
7
7
[22mm] O.D.
[22mm] O.D.
[22mm] O.D.
8
/
8
/"
"
/
8
"
LEFT HAND RIGHT HAND
Use port at the bottom for inlet and top for outlet on
single row coils. For multirow coils, always plumb in
counter flow orientation. Water inlet always on the
airflow downstream side of the hot water coil. Water
outlet always on the upstream side of the hot water
coil. See drawings below for reference.

VAV-PRC011M-EN 57
Single-Duct VAV Terminal Units
C
10"
[254mm]
13
/"
[86mm]
3
32
AIR FLOW
/
7
13 32
[198mm]
"
AccessPanel
[72mm]
27
OUTLET
2
32
/"
A
INLET
D
INLET
B
/
7
13 32
[198mm]
"
A
AccessPanel
13
/"
[86mm]
3
32
[72mm]
27
2
32
/"
OUTLET
AIR FLOW
10"
[254mm]
B
AIR FLOW
stream. L.H. Coil connections shown, R.H. opposite.
Location of coil connections is determined by facing air1.
CUSTOMER NOTES:
2. Coil furnished with stub sweat connections.
3.
Coil height and width is dependent upon unit height4.
and width.
Access Panel is standard.5.
[206mm]
[206mm]
[206mm]
[257mm]
[308mm]
[359mm]
[460mm]
[460mm]
[460mm]
COIL INFORMATION FOR 3 ROW COIL ASSY
16 x 24
16 4000
8000
05 350
10
12
14
08
06
1400
3000
2000
900
500
04
INLT CFM
225
8
/
[400mm]
4
/
15
15
1888
3776 [400mm]
[400mm]
"
"
34
/
34
1
18
181
8
/"
8
/"
5
11
15
9
CONNECTION
[22mm] O.D.
165
661
994
1416
425
236
SECOND
106
LITERS
per
7"
8
5
7
5
COIL
[146mm]
4
/
[298mm]
[248mm]
[196mm]
[146mm]
3"
"
"
/4
3
3
/4
"
/4
/
34
3"
[146mm]
3/
3
4"
"
A
88
/
1
1
14
181
12
8
/
"
8
/"
"
101
1
8 /
8
/"
8"
1
1
8"
/8
"
B
19" [483mm]
27" [686mm]
23" [584mm]
10" [254mm]
10" [254mm]
10" [254mm]
11" [279mm]
14" [356mm]
17" [432mm]
C
[22mm] O.D.
78"
[22mm] O.D.
78"
[22mm] O.D.
78"
[22mm] O.D.
78"
[22mm] O.D.
78"
[22mm] O.D.
78"
[22mm] O.D.
78"
[22mm] O.D.
78"
[22mm] O.D.
78"
[22mm] O.D.
78"
[22mm] O.D.
78"
[22mm] O.D.
78"
[22mm] O.D.
78"
[22mm] O.D.
78"
[22mm] O.D.
78"
[22mm] O.D.
78"
[22mm] O.D.
78"
[22mm] O.D.
78"
[22mm] O.D.
78"
[22mm] O.D.
78"
[22mm] O.D.
78"
[22mm] O.D.
78"
[22mm] O.D.
78"
[22mm] O.D.
78"
[22mm] O.D.
78"
[22mm] O.D.
78"
[22mm] O.D.
78"
[22mm] O.D.
78"
[22mm] O.D.
78"
[22mm] O.D.
78"
[22mm] O.D.
78"
[22mm] O.D.
78"
[22mm] O.D.
78"
[22mm] O.D.
78"
[22mm] O.D.
78"
/
/
/
/
/
/
/
/
/
/
/
/
/
/
/
/
/
/
/
/
/
/
/
/
/
/
/
/
/
/
/
/
/
/
/
//
D
5
3[92mm]
"
8
/
[92mm]
5/
38"
[92mm]
5/
38"
[92mm]
5/
38"
[92mm]
5/
38"
[92mm]
5/
38"
[92mm]
5/
38"
[92mm]
5/
38"
[92mm]
5/
38"
LEFT HAND RIGHT HAND
Use port at the bottom for inlet and top for outlet on
single row coils. For multirow coils, always plumb in
counter flow orientation. Water inlet always on the
airflow downstream side of the hot water coil. Water
outlet always on the upstream side of the hot water
coil. See drawings below for reference.

58 VAV-PRC011M-EN
Single-Duct VAV Terminal Units
AIR FLOW
C
AIR FLOW
D
10"
[254mm]
AIR FLOW B
/
32
[198mm]
7
13
"
AccessPanel
[86mm]
3
"
32
/
13
[94mm]
32
"
OUTLET
23
3
/
A
INLET
[94mm]
32
"
23
3
/
B
/
32
[198mm]
7
13
"
AccessPanel
[86mm]
3
"
32
/
13
A
INLET
OUTLET
10"
[254mm]
stream. L.H. Coil connections shown, R.H. opposite.
Location of coil connections is determined by facing air1.
CUSTOMER NOTES:
2. Coil furnished with stub sweat connections.
Coil height and width is dependent upon unit height4.
and width.
Access Panel is standard.5.
[206mm]
[206mm]
[206mm]
[257mm]
[308mm]
[359mm]
[460mm]
[460mm]
[460mm]
COIL INFORMATION FOR 4 ROW COIL ASSY
16 x 24
16 4000
8000
05 350
10
12
14
08
06
1400
3000
2000
900
500
04
INLT CFM
225
8
/
[413mm]
4
/
16
161888
3776 [413mm]
[413mm]
"
"
14
/
14
1
18
181
8
/"
8
/"
6
12
16
10
CONNECTION
[22mm] O.D.
165
661
994
1416
425
236
SECOND
106
LITERS
per
7"
8
6
8
6
COIL
[158mm]
4
/
[311mm]
[260mm]
[210mm]
[158mm]
1"
"
"
/4
1
1
/4
"
/4
/
14
1"
[158mm]
1/
1
4"
"
A
88
/
1
1
14
181
12
8
/
"
8
/"
"
101
1
8 /
8
/"
8"
1
1
8"
/8
"
B
19" [483mm]
27" [686mm]
23" [584mm]
10" [254mm]
10" [254mm]
10" [254mm]
11" [279mm]
14" [356mm]
17" [432mm]
C
[22mm] O.D.
78"
[22mm] O.D.
78"
[22mm] O.D.
78"
[22mm] O.D.
78"
[22mm] O.D.
78"
[22mm] O.D.
78"
[22mm] O.D.
78"
[22mm] O.D.
78"
[22mm] O.D.
78"
[22mm] O.D.
78"
[22mm] O.D.
78"
[22mm] O.D.
78"
[22mm] O.D.
78"
[22mm] O.D.
78"
[22mm] O.D.
78"
[22mm] O.D.
78"
[22mm] O.D.
78"
[22mm] O.D.
78"
[22mm] O.D.
78"
[22mm] O.D.
78"
[22mm] O.D.
78"
[22mm] O.D.
78"
[22mm] O.D.
78"
[22mm] O.D.
78"
[22mm] O.D.
78"
[22mm] O.D.
78"
[22mm] O.D.
78"
[22mm] O.D.
78"
[22mm] O.D.
78"
[22mm] O.D.
78"
[22mm] O.D.
78"
[22mm] O.D.
78"
[22mm] O.D.
78"
[22mm] O.D.
78"
[22mm] O.D.
78"
/
/
/
/
/
/
/
/
/
/
/
/
/
/
/
/
/
/
/
/
/
/
/
/
/
/
/
/
/
/
/
/
/
/
/
//"
8
3/
5[92mm]
"
8
3/
5[92mm]
"
8
3/
5[92mm]
"
8
3/
5[92mm]
"
8
3/
5[92mm]
"
8
3/
5[92mm]
"
8
3/
5[92mm]
"
8
3/
5[92mm]
/8"[92mm]
35
D
3.
LEFT HAND RIGHT HAND
Use port at the bottom for inlet and top for outlet on
single row coils. For multirow coils, always plumb in
counter flow orientation. Water inlet always on the
airflow downstream side of the hot water coil. Water
outlet always on the upstream side of the hot water
coil. See drawings below for reference.

VAV-PRC011M-EN 59
Single-Duct VAV Terminal Units

60 VAV-PRC011M-EN
Single-Duct VAV Terminal Units
Mechanical Specifications
Single-Duct Terminal Units
Casing
22-gage galvanized steel.
Agency Listing
Unit is UL and Canadian UL Listed as a room air terminal unit. Control # 9N65. AHRI 880 Certified.
Insulation
1/2" (12.7 mm) Matte-faced Insulation—Interior surface of unit casing is acoustically and thermally
lined with ½-inch, 1.5 lb/ft3 (12.7 mm, 24.0 kg/m3) composite density glass fiber with a high-density
facing. Insulation R-Value is 1.9. Insulation is UL listed and meets NFPA-90A and UL 181 standards.
There are no exposed edges of insulation (complete metal encapsulation).
1" (25.4 mm) Matte-faced Insulation—Interior surface of unit casing is acoustically and thermally
lined with 1-inch, 1.0 lb/ft3 (25.4 mm, 16.0 kg/m3) composite density glass fiber with a high-density
facing. Insulation R-Value is 3.85. Insulation is UL listed and meets NFPA-90A and UL 181 standards.
There are no exposed edges of insulation (complete metal encapsulation).
1" (25.4 mm) Foil-faced Insulation— Interior surface of unit casing is acoustically and thermally
lined with 1-inch, 1.0 lb/ft3 (25.4 mm, 16.0 kg/m3) density glass fiber with foil facing. Insulation R-
Value is 3.85. Insulation is UL listed and meets NFPA-90A and UL 181 standards and bacteriological
standard ASTM C 665. There are no exposed edges of insulation (complete metal encapsulation).
1" (25.4 mm) Double-wall Insulation—Interior surface of unit casing is acoustically and thermally
lined with a 1-inch, 1.0 lb./ft3 (25.4 mm, 16.0 kg/m3) composite density glass fiber with high-density
facing. Insulation R-value is 3.85. Insulation is UL listed and meets NFPA-90A and UL 181 standards.
Insulation is covered by interior liner made of 26-gage galvanized steel. All wire penetrations are
covered by grommets. There are no exposed edges of insulation (complete metal encapsulation).
3/8" (9.5 mm) Closed-cell Insulation—Interior surface of the unit casing is acoustically and
thermally lined with 3/8-inch, 4.4 lb/ft3 (9.5 mm, 70.0 kg/m3) closed-cell insulation. Insulation is UL
listed and meets NFPA-90A and UL 181 standards. Insulation has an R-Value of 1.4. There are no
exposed edges of insulation (complete metal encapsulation).
Primary Air Valve
Air Valve Round—The primary air inlet connection is an 18-gage galvanized steel cylinder sized to
fit standard round duct. A multiple-point, averaging flow sensing ring is provided with balancing
taps for measuring +/-5% of unit cataloged airflow. An airflow-versus-pressure differential
calibration chart is provided. The damper blade is constructed of a closed-cell foam seal that is
mechanically locked between two 22-gage galvanized steel disks. The damper blade assembly is
connected to a cast zinc shaft supported by self-lubricating bearings. The shaft is cast with a
damper position indicator. The valve assembly includes a mechanical stop to prevent over-
stroking. At 4.0 in. wg, air valve leakage does not exceed 1% of cataloged airflow.
Air Valve Rectangular—Inlet collar is constructed of 22-gage galvanized steel sized to fit standard
rectangular duct. An integral multiple-point, averaging flow-sensing ring provides primary airflow
measurement within +/-5% of unit cataloged airflow. Damper is 22-gage galvanized steel. The
damper blade assembly is connected to a cast zinc shaft supported by self-lubricating bearings.
The shaft is cast with a damper position indicator. The valve assembly includes a mechanical stop
to prevent over-stroking. At 3.0 in. wg air valve leakage does not exceed 6% of maximum airflow.
VCCF - Cooling Only VCWF - With Hot Water Coil VCEF - With Electric Coil

VAV-PRC011M-EN 61
Single-Duct VAV Terminal Units
Outlet Conection
Slip & Drive Connection—Terminal units come standard with slip & drive connection.
Outlet Plenum—A sheet metal, insulated box with circular opening(s) is attached to main unit
discharge at the factory. Circular opening(s) are centered on unit plenum to accept round ductwork
connections.
Outlet Plenum with Balancing Dampers—A sheet metal, insulated box with circular opening(s) is
factory- connected to the main unit. The circular opening(s) with balancing damper(s) are centered
on the unit plenum to accept round ductwork connections.
Hot Water Coils
All hot water coils are factory-installed on the discharge outlet. Full fin collars provided for accurate
fin spacing and maximum fin-tube contact. The 3/8" (9.5 mm) OD seamless copper tubes are
mechanically expanded into the fin collars. Coils shall be subjected to a pressure decay test at 450
psig for a minimum of 45 seconds. Coils shall then be evacuated and charged with a helium gas
mixture and pressurized to 150 psig. While pressurized with the helium gas mixture, the coil shall
be checked with a gas analyzer to detect helium leaks. Alternatively, the coil shall be subjected to
a final air-under-water leak test at 300 psig.
1-Row Hot Water Coils— The 1-row coil has 144 aluminum fins per foot. Full fin collars provided
for accurate fin spacing and maximum fin-tube contact. Coil connections are left-hand. Right-hand
connections are optional. Coils are assembled with either 3/8" or 7/8" (22.2 mm) OD braze
connections.
2-Row Hot Water Coils— The 2-row coil has 144 aluminum per foot. Coils are assembled with
headers that provide 7/8" (22.2 mm) OD braze connections. Right-hand connections are optional.
3-Row Hot Water Coils—The 3-row coil has 120 aluminum fins per foot. Coils are assembled with
headers that provide 7/8" (22.2 mm) OD braze connections. Right-hand connections are optional.
4-Row Hot Water Coils—The 4-row coil has 120 aluminum fins per foot. Coils are assembled with
headers that provide 7/8" (22.2 mm) OD braze connections. Right-hand connections are optional.
Electric Heat Coils
The electric heater is a factory-provided and -installed, UL recognized resistance open-type heater
with airflow switch. It also contains a disc-type automatic pilot duty thermal primary cutout, and
manual reset load carrying thermal secondary device. Heater element material is nickel-chromium.
The heater terminal box is provided with 7/8" (22 mm) knockouts for customer power supply.
Terminal connections are plated steel with ceramic insulators.
Electric Heat Options
Silicon-Controlled Rectifier (SCR)—Optional electric heat control that provides modulation. Allows
use of energy efficient dual max algorithm with selection of UC210 or UC400 controls. See “Single-
Duct: SCR Modulation of Electric Heat,” p. 84 for detailed description of dual max algorithm
function.
Electric Heat Transformer—Optional transformer is an integral component of heater control panel
(dependent on unit load requirements) to provide 24 VAC for controls. There is 19 VA available for
controls.
Magnetic Contactor—Optional electric heater 24V contactor for use with direct digital controls.
Mercury Contactor—Optional electric heater 24V contactor for use with direct digital controls.
P.E. Switch with Magnetic Contactor—This optional switch and magnetic contactor is for use with
pneumatic controls.
P.E. Switch with Mercury Contactor—This optional switch and mercury contactor is for use with
pneumatic controls.

62 VAV-PRC011M-EN
Single-Duct VAV Terminal Units
Airflow Switch— An air pressure device designed to disable the heater. This is standard on single-
duct with electrical reheat units.
Line Fuse—An optional safety fuse located in the line of power of the electric heater to prevent
power surge damage to the electric heater.
Disconnect Switch—A optional factory-provided door interlocking disconnect switch on the heater
control panel disengages primary voltage to the terminal.
Unit Controls Sequence of Options
Unit controller continuously monitors zone temperature against its setpoint and varies primary
airflow as required to meet zone setpoints. Airflow is limited by minimum and maximum position
setpoints. Upon further call for heat after the air valve reaches the minimum airflow setting, any
hot water or electric heat associated with the unit is enabled.
Direct Digitals Controls
DDC Actuator—Trane 3-wire, 24-VAC, floating-point quarter turn control actuator with linkage
release button. Actuator has a constant drive rate independent of load, a rated torque of 35 in-lb,
a 90-second drive time, and is non-spring return. Travel is terminated by end stops at fully-opened
and -closed positions. An integral magnetic clutch eliminates motor stall.
DDC Actuator - Belimo — LMB24-3-T TN 3-wire, 24 VAC/DC, floating-point, quarter turn actuator
with linkage release button. Actuator has constant drive rate independent of load, rated torque 45
in-lb, 95 sec drive time, and non-spring return. Travel terminated by end stops at fully-opened and
-closed positions. Internal electronic control prevents motor stall when motor reaches end stops.
Direct Digital Controller—Microprocessor based terminal unit controller provides accurate,
pressure-independent control through the use of a proportional integral control algorithm and
direct digital control technology. The controller, named Unit Control Module (UCM), monitors zone
temperature setpoints, zone temperature and its rate of change, and valve airflow using a
differential pressure signal from the pressure transducer. Additionally, the controller can monitor
either supply duct air temperature or CO2 concentration via appropriate sensors. Controller
enclosure has 7/8"(22 mm) knockouts for remote control wiring. Trane DDC zone sensor is required.
DDC Zone Sensor—The UCM controller senses zone temperature through a sensing element
located in the zone sensor. In addition to the sensing element, zone sensor options may include an
externally-adjustable setpoint, communications jack for use with a portable edit device, and an
override button to change the individual controller from unoccupied to occupied mode. The
override button has a cancel feature that will return the system to unoccupied. Wired zone sensors
utilize a thermistor to vary the voltage output in response to changes in the zone temperature.
Wiring to the UCM controller must be 18- to 22-awg. twisted pair wiring. The setpoint adjustment
range is 50–88ºF (10–31°C). Depending upon the features available in the model of sensor selected,
the zone sensor may require from a 2-wire to a 5-wire connection. Wireless zone sensors report the
same zone information as wired zone sensors, but do so using radio transmitter technology.
Therefore with wireless, wiring from the zone sensor to the UCM is unnecessary.
Digital Display Zone Sensor with Liquid Crystal Display (LCD)—Digital display zone sensor
contains a sensing element, which signals the UCM. A Liquid Crystal Display (LCD) displays
setpoint or space temperature. Sensor buttons allow user to adjust setpoints, and allow space
temperature readings to be turned on or off. Digital display zone sensor also includes a
communication jack for use with a portable edit device, and an override button to change UCM from
unoccupied to occupied. Override button cancel feature returns system to unoccupied mode.
System Communications— The Controller is designed to send and receive data from a Tracer™SC
or other Trane controllers. Current unit status conditions and setpoints may be monitored and/or
edited via this data communication feature. The network type is a twisted wire pair shielded serial
communication.

VAV-PRC011M-EN 63
Single-Duct VAV Terminal Units
Pneumatic Controls
Normally Open Actuator—Pneumatic 3-8 psig (20-55 kPa) spring-range pneumatic actuator.
Normally-Closed Actuator—Pneumatic 8 -13 psig (55-90 kPa) spring-range pneumatic actuator.
3011 Pneumatic Volume Regulator (PVR)—The regulator is a thermostat reset velocity controller,
which provides consistent air delivery within 5% of cataloged flow down to 18% or less of unit
cataloged cfm, independent of changes in system static pressure. Factory-calibrated, field-
adjustable setpoints for minimum and maximum flows. Average total unit bleed rate, excluding
thermostat, is 28.8 scim at 20 psig (7.87 ml/min at 138 kPa) supply.
Control Options
Transformer (VCCF, VCWF)—A 50-VA transformer is factory-installed in an enclosure with 7/8” (22
mm) knockouts to provide 24 VAC for controls.
Disconnect Switch (VCCF, VCWF)—A toggle disconnect disengages primary power to terminal.
Fuse (VCCF, VCWF)—Optional fuse is factory-installed in the primary voltage hot leg.
Hot Water Valves
Two-Position Valve—The valve is a field-adaptable, 2-way or 3-way configuration and ships with
a cap to be field-installed when configured as a 2-way valve. All connections are National Pipe
Thread (NPT). valve body is forged brass with stainless steel stem and spring. Upon demand, the
motor strokes the valve. When actuator drive stops, a spring returns valve to its fail-safe position.
Flow Capacity – 4.00 Cv
Overall Diameter – ½" NPT
Close-off Pressure – 25 psi (172 kPa)
Flow Capacity – 5.0 Cv
Overall Diameter – 3/4" NPT
Close-off Pressure – 20 psi (138 kPa)
Flow Capacity – 8.0 Cv
Overall Diameter – 1" NPT
Close-off Pressure – 17 psi (117 kPa)
Maximum Operating Fluid Temperature – 200ºF (93ºC)
Maximum system pressure – 300 psi (2067 kPa)
Electrical Rating – 7 VA at 24 VAC, 6.5 Watts, 50/60 Hz
Proportional Water Valve—The valve is a field-adaptable, 2-way or 3-way configuration and ships
with a cap over the bottom port. This configures the valve for 2-way operation. For 3-way operation,
remove the cap. The valve is designed with an equal percentage plug. The intended fluid is water
or water and glycol (50% maximum glycol). The actuator is a synchronous motor drive. The valve
is driven to a predetermined position by the UCM controller using a proportional plus integral
control algorithm. If power is removed, the valve stays in its last position. The actuator is rated for
plenum applications under UL 94-5V and UL 873 standards.
Pressure and Temperature Ratings – The valve is designed and tested in full compliance with ANSI
B16.15 Class 250 pressure/temperature ratings, ANSI B16.104 Class IV control shutoff leakage, and
ISA S75.11 flow characteristic standards.
Flow Capacity – 0.7 Cv, 2.7 Cv, 6.6 Cv, 8.0 Cv
Overall Diameter – ½" NPT
Maximum Allowable Pressure – 300 psi (2068 kPa)
Maximum Operating Fluid Temperature – 200ºF (93°C)
Maximum Close-off Pressure – 60 psi (379 kPa)
Electrical Rating – 3VA at 24 VAC
8” plenum rated cable with AMP Mate-N-Lok connector. This connector is designed to mate with

64 VAV-PRC011M-EN
Single-Duct VAV Terminal Units
the optional factory mounted valve harness to make electrical connection quick and simple (120”
plenum rated cable with quick connect tabs for control board interface).

VAV-PRC011M-EN 65
Digit 1, 2, 3—Unit Type
VDD= VariTrane™ dual-duct
Digit 4—Development Sequence
F= Sixth
Digit 5, 6—Primary Air Valve
05 = 5" inlet (350 cfm)
06 = 6" inlet (500 cfm)
08 = 6" inlet (900 cfm)
10 = 10" inlet (1400 cfm)
12 = 12" inlet (2000 cfm)
14 = 14" inlet (3000 cfm)
16 = 16" inlet (4000 cfm)
Digit 7, 8—Secondary Air Valve
05 = 5" inlet (350 cfm)
06 = 6" inlet (500 cfm)
08 = 8" inlet (900 cfm)
10 = 10" inlet (1400 cfm)
12 = 12" inlet (2000 cfm)
14 = 14" inlet (3000 cfm)
16 = 16" inlet (4000 cfm)
Digit 9—Not Used
0= N/A
Digit 10, 11—Design Sequence
** = Factory Assigned
Digit 12, 13, 14, 15—Controls
DD00= Trane Actuator Only
DD01= UCM4 Cooling Only Control
DD08= UCM4 Dual Duct
Constant Volume
DD11= VV550 DDC Controller -
Cooling Only
DD18= VV550 DDC Controller w
Constant Volume
DD41= UC400 DDC-Basic (No water or
electric heat)
DD48= UC400 DDC-Basic (Constant
Volume)
DDSS= Digital Special
ENON= Shaft Out Side for Electric
Units
FM00= Other Actuator and Control
FM01= Trane Supplied Actuator, Other
Ctrl
PC03= NC Heating Valve, N.O. Cooling
Valve
PCSS= Normally Closed Special
PN08= N.O. Heat/Cool Actuators &
Linkage Only
PN09= N.O. Heating, N.O. Cooling,
w/PVR’s
PN10= N.O. Heating, N.O. Cooling,
w/PVR’s (CV DISCH)
PNON= Shaft Out Side for Pneumatic
Units
PNSS= Normally Open Special
Notes:
N.C. = Normally-closed
N.O. = Normally-opened
DA Stat = Direct-acting pneumatic t-stat
(by others)
RA Stat = Reverse-acting pneumatic t-stat
(by others)
PN = Pneumatic
FM = Factory installation of customer-
supplied controller
PVR = Pneumatic Volume Regulator
Digit 16—Insulation
A = 1/2" Matte-faced
B = 1" Matte-faced
D = 1" Foil-faced
F = 1" Double-wall
G = 3/8" Closed-cell
Digit 17—Not Used
0= N/A
Digit 18—Not Used
0= N/A
Digit 19—Outlet Plenum (Connection
is slip & drive)
0 = none
A = 1 outlet–RH
B = 1 outlet–END
C = 1 outlet–LH
D = 2 outlets–1 RH, 1 END
E = 2 outlets–1 LH, 1 END
F = 2 outlets–1 RH, 1 LH
G = 2 outlets - END
H = 3 outlets–1 LH, 1 RH, 1 END
J = 4 outlets–1 LH, 1 RH, 2 END
Note: See unit drawings for outlet sizes/
damper information.
Digit 20—Not Used
0= N/A
Digit 21—Not Used
0= N/A
Digit 22—Not Used
0= N/A
Digit 23—Transformer
0= None
1 = 120/24 volt (50 VA)
2 = 208/24 volt (50 VA)
3 = 240/24 volt (50 VA)
4 = 277/24 volt (50VA)
5 = 480/24 volt (50 VA)
6 = 347/24 volt (50 VA)
7 = 575/24 volt (50 VA)
Digit 24—Disconnect Switch
0= None
W = With Toggle
Digit 25—Power Fuse
0= None
W= With
Digit 26—Not Used
0= N/A
Digit 27—Not Used
0= N/A
Digit 28—Not Used
0= N/A
Digit 29—Not Used
0= N/A
Digit 30—Not Used
0= N/A
Digit 31—Not Used
0= N/A
Digit 32—Not Used
0= N/A
Digit 33—Special Options
0= None
X = Varies - Factory Assigned
Digit 34—Not Used
Blank
Digit 35—Wireless Sensor
0 = Sensor/Receiver Standard
1 = Wireless Sensor/Receiver
Mounted
Note: All sensors selected in accessories
Digit 36—Duct Temp Sensor
0= None
1 = With Duct Temp Sensor
Model Number Descriptions

66 VAV-PRC011M-EN
Dual-Duct VAV Terminal Units
Dual-duct units have two air valves. One heating valve and one cooling air valve modulate
simultaneously to provide occupant comfort. These systems were popular prior to the energy crisis
of the early 1970s. Popularity is increasing with system concepts which use one valve for
maintaining and monitoring 100% ventilation air.
The features of the dual-duct VAV terminal units are described by the product categories shown in
bold. Within each category the options available are listed
Selection Procedure
This section describes the catalog selection of dual-duct VAV terminal units with specific examples.
A computer selection program is also available to aid in selection of VAV terminal units.
Selection of dual-duct VAV terminal units can involve two elements:
• Air valve selection
• Acoustics
Air Valve Selection
The wide-open static pressure and airflows are found in the performance data section of the
catalog. To select the air valves, locate the required design cooling and heating airflows for your
terminal unit type and find their vertical intersection, with the smallest air valve size that has a
pressure drop equal to or lower than the maximum wide-open static pressure requirement.
Example:
VDDF Terminal Unit Design cooling airflow: 1000 cfm
Maximum wide-open Air pressure drop: 0.25 in. wg
Minimum cooling airflow: 500 cfm
Design heating airflow: 1000 cfm
Maximum wide-open Air pressure drop: 0.25 in. wg
Minimum heating airflow: 400 cfm
From the performance data charts, select a valve size 10 for cooling, which has a wide-open static
pressure drop of 0.09 in. wg. Select a size 10 for heating, which has a wide-open static pressure drop
of 0.09 in. wg.
Check the minimum and maximum cfm desired with the minimum and maximum cfm allowed in
the table in the general data section. The maximum setting of 1000 cfm is within the acceptable
range. The desired minimum setting of 500 cfm is acceptable for the unit desired.
Figure 1. Dual duct terminal unit

VAV-PRC011M-EN 67
Dual-Duct VAV Terminal Units
Acoustics
The acoustical data found in the “Performance Data” section of the VAV catalog is used to make
a determination of the amount of noise the terminal unit will generate. Locate the table for the VAV
terminal unit of interest. Sound power data and an equivalent NC level for an AHRI 885-2008
transfer function is listed.
Example:
VDDF, Cooling-Only Terminal Unit, Size 10 cooling, Size 10 heating (See air Valve Selection)
Cooling Airflow: 1000 cfm
Max. inlet static pressure: 1.5 in. wg
Heating Airflow: 1000 cfm
Max. inlet static pressure: 1.5 in. wg
Interpolation gives sound power data of:
The NC level above is determined by using either the catalog’s AHRI 885-2008 (mineral fiber for
radiated sound) transfer function for the conditions shown in the acoustics table. A different
transfer function could be applied as conditions dictate.
The maximum NC level is NC-40. If the maximum NC level was exceeded, it would have been
necessary to reselect the next larger unit size.
Computer Selection
The advent of personal computers has served to automate many processes that were previously
repetitive and time-consuming. One of those tasks is the proper scheduling, sizing, and selection
of VAV terminal units. Trane has developed a computer program to perform these tasks. The
software is called the Trane Official Product Selection System (TOPSS™).
The TOPSS program will take the user’s input specifications and output the properly sized
VariTrane™ VAV terminal unit along with the specific performance for that size unit.
The program has several required fields, denoted by red shading in the TOPSS program, and many
other optional fields to meet the criteria you have. Required values include maximum and
minimum airflows, control type, and model. If selecting models with reheat, you will be required
to enter information to make that selection also. The user is given the option to look at all the
information for one selection on one screen or as a schedule with the other VAV units on the job.
The user can select single-duct, dual-duct, and fan-powered VAV boxes with the program, as well
as most other Trane products, allowing you to select all your Trane equipment with one software
program.
The program will also calculate sound power data for the selected terminal unit. The user can enter
a maximum individual sound level for each octave band or a maximum NC value. The program will
calculate acoustical data subject to default or user supplied sound attenuation data.
Schedule View: The program has many time-saving features such as: 1) Copy/Paste from
spreadsheets like Microsoft® Excel; 2) Easily arranged fields to match your schedule; and 3) Time-
saving templates to store default settings The user can also export the Schedule View to Excel to
modify and put into a CAD drawing as a schedule. Details regarding the program, its operation, and
how to obtain a copy of it are available from your local Trane sales office.
Octave Band 234567NC
Disch. Sound Power 83 72 69 67 66 60 39
Rad. Sound Power 69 63 57 54 47 40 34

68 VAV-PRC011M-EN
Dual-Duct VAV Terminal Units
General Data
Table 36. Primary airflow control factory settings (per valve) - I-P
Control Type Air Valve Size
(in.) Maximum Valve
Cfm Maximum
Controller Cfm Minimum Controller Cfm Constant Volume
Unit Cfm
Direct Digital Control/
UCM
5
6
8
10
12
14
16
350
500
900
1400
2000
3000
4000
40-350
60-500
105-900
165-1400
240-2000
320-3000
420-4000
0,40-350
0,60-500
0,105-900
0,165-1400
0,240-2000
0,320-3000
0,420-4000
40-700
60-1000
105-1800
165-2800
240-4000
320-6000
420-8000
Pneumatic with Volume
Regulator
5
6
8
10
12
14
16
350
500
900
1400
2000
2885
3785
63-350
73-500
134-900
215-1400
300-2000
408-2885
536-3785
0,63-350
0,73-500
0,134-900
0,215-1400
0,300-2000
0,408-2885
0,536-3785
63-700
73-1000
134-1800
215-2800
300-4000
408-5770
536-7570
Table 37. Primary airflow control factory settings (per valve)-SI
Control Type Air Valve Size
(in.) Maximum Valve
L/s Maximum
Controller L/s Minimum Controller L/s Constant Volume
Unit L/s
Direct Digital Control/
UCM
5
6
8
10
12
14
16
165
236
425
661
944
1416
1888
19-165
28-236
50-425
77-661
111-944
151-1416
198-1888
0,19-165
0,28-236
0,50-425
0,77-661
0,111-944
0,151-1416
0,198-1888
19-330
28-472
50-850
77-1321
111-1888
151-2832
198-3776
Pneumatic with Volume
Regulator
5
6
8
10
12
14
16
165
236
425
661
944
1362
1787
30-165
35-236
63-425
102-661
141-944
193-1362
253-1787
0,30-165
0,35-236
0,63-425
0,102-661
0,141-944
0,193-1362
0,253-1787
30-330
35-472
63-850
102-1321
141-1888
193-2723
253-3573
Note: Maximum airflow must be greater than or equal to minimum airflow.

VAV-PRC011M-EN 69
Dual-Duct VAV Terminal Units
Performance Data
Table 38. Air pressure drop-in. wg (l-P)
Inlet Size Airflow Cfm VDDF
05
100
200
300
350
0.01
0.02
0.04
0.06
06
100
250
350
500
0.01
0.08
0.17
0.38
08
200
400
600
900
0.01
0.04
0.10
0.24
10
500
800
1100
1400
0.02
0.05
0.10
0.17
12
800
1200
1600
2000
0.01
0.03
0.06
0.10
14
1500
2000
2500
3000
0.04
0.07
0.12
0.19
16
2000
2500
3000
4000
0.03
0.04
0.06
0.10
Note: Pressure drops are per air valve
Table 39. Air pressure drop-Pa (SI)
Inlet Size Airflow L/s VDDF
05
45
95
140
165
3
5
11
15
06
45
120
165
235
3
21
42
93
08
95
190
280
420
3
11
25
59
10
235
375
520
660
5
13
26
42
Note: Pressure drops are per air valve

70 VAV-PRC011M-EN
Dual-Duct VAV Terminal Units
12
375
565
755
940
3
8
15
24
14
700
945
1180
1415
9
18
30
46
16
940
1180
1415
1885
6
10
14
25
Note: Pressure drops are per air valve
Table 39. Air pressure drop-Pa (SI) (continued)
Table 40. Integral outlet plenum air pressure drop-in. wg (I-P)
Outlet Diameter
(in.) Airflow
(Cfm)
Integral Outlet Configurations
A,C B D,E F G H J
5
100
200
300
350
0.06
0.23
0.50
0.67
0.05
0.19
0.44
0.60
0.02
0.09
0.19
0.26
0.03
0.09
0.18
0.24
-
-
-
-
0.01
0.03
0.08
0.12
-
-
-
-
6
100
250
350
500
0.04
0.20
0.38
0.74
0.03
0.17
0.32
0.63
0.01
0.07
0.13
0.25
0.01
0.06
0.11
0.21
-
-
-
-
0.01
0.04
0.08
0.15
-
-
-
-
8
200
400
600
900
0.11
0.28
0.50
0.88
0.02
0.10
0.25
0.59
0.01
0.03
0.07
0.15
0.01
0.04
0.09
0.22
0.01
0.02
0.05
0.11
0.01
0.02
0.04
0.09
0.01
0.01
0.02
0.03
10
500
800
1100
1400
0.07
0.19
0.35
0.56
0.08
0.19
0.34
0.52
0.02
0.04
0.07
0.11
0.03
0.08
0.15
0.24
-
-
-
-
0.01
0.02
0.04
0.07
-
-
-
-
Table 41. Integral outlet plenum air pressure drop-Pa (SI)
Outlet Diameter
(mm) Airflow
(L/s)
Integral Outlet Configurations
A,C B D,E F G H J
127
50
100
140
165
16
58
124
166
12
48
109
148
6
23
49
65
7
22
46
60
-
-
-
-
3
8
21
30
-
-
-
-
152
50
120
165
235
9
51
95
185
8
43
80
158
3
17
32
62
3
15
27
51
-
-
-
-
3
10
19
36
-
-
-
-
203
95
190
280
420
27
71
125
219
6
26
62
147
2
8
18
39
3
10
24
54
3
6
13
27
3
5
10
22
3
2
4
8
254
235
375
520
660
18
46
87
140
20
47
84
131
5
11
18
27
7
19
36
59
-
-
-
-
3
6
11
17
-
-
-
-

VAV-PRC011M-EN 71
Dual-Duct VAV Terminal Units
ABCD FEGH
NOMINALØ
127 mm (5")
152 mm (6")
203 mm (8")
254 mm (10")
OUTL CONVERSION CHART
SYMBOL
II
III
IV
I
OUTLET AVAILABILITY CHART-SEE OUTL CONVERSION FOR NOMINALØ
A,B,C
H
OUTL
J
VALV
D,E,F
N/A
0505 0606 0808 1010
I, II N/A
G
I, II, III
N/A
I, II N/A
N/A
I, II, III
I, II, III
II, III
N/A
N/A
I, II, III
III, IV
II, III, IV III, IV
III, IV
III
III
J
OUTLET PLENUM
ARRANGEMENTS
(TOP VIEW)
Table 42. Discharge sound power (dB)1, 2, 4
Inlet
Size
(in)
0.5" Inlet Pressure
Ps51.0" Inlet Pressure
Ps51.5" Inlet Pressure
Ps32.0" Inlet Pressure
Ps53.0" Inlet Pressure
Ps5
Cfml/s234567234567234567234567234567
5
130 61 544642413633595249484643 615554555552615759616158
200 94 605046454236645652514744 686159585652686262636257
250 118 63 52 49 47 45 39 67 57 54 53 50 45 70 62 58 57 53 50 72 64 61 60 57 53 72 66 65 64 63 57
350 165 70 58 53 51 49 43 73 62 59 56 55 49 78 69 65 63 60 55 80 71 69 68 65 59
6
200 94 594946454235645552504743 686058585651676162626256
300 142 66 54 50 48 46 39 69 60 58 54 52 46 75 66 63 61 58 53 75 68 66 65 63 57
400 189 69 57 53 50 46 40 75 64 61 57 55 49 77 66 63 61 58 53 79 69 66 63 60 55 81 72 70 68 65 59
500 236 67 56 54 50 44 41 77 67 63 58 55 50 85 73 69 66 63 57 86 75 74 71 67 61
8
350 165 64 54 51 50 48 39 70 61 58 57 55 45 73 66 64 64 62 53 73 68 68 68 66 58
520 245 67 56 54 54 52 44 75 64 61 61 58 51 81 72 69 68 65 56 81 73 72 72 69 60
700 330 69 58 56 55 53 46 77 66 63 62 61 54 81 71 69 67 64 58 85 74 72 70 68 60 87 79 76 74 71 62
900 425 71 61 59 56 52 46 78 68 65 64 62 56 86 76 73 72 69 62 91 81 79 76 73 66
12
800 378 70 59 55 53 51 46 78 67 64 62 61 57 83 75 71 69 67 64 83 77 73 71 69 68
1200 566 74 61 56 53 51 46 83 71 64 62 60 56 89 79 73 70 68 65 89 82 77 73 72 69
1550 732
1600 755 74 64 58 55 53 48 84 72 65 62 60 56 90 77 69 68 65 61 92 81 73 71 69 65 94 84 77 75 72 70
2000 944 76 66 61 57 55 50 84 74 67 63 61 56 95 82 74 72 69 65 97 87 78 76 72 69
14
1100 519 70 60 57 57 57 50 79 69 65 65 65 61 84 76 73 71 71 69 84 78 76 73 73 75
1600 755 72 62 57 57 56 50 80 70 65 65 66 60 88 78 74 72 72 70 89 82 77 76 74 74
2100 991 74 65 60 59 58 51 82 72 66 66 66 60 86 76 70 70 70 65 89 79 73 73 72 70 90 83 78 76 75 74
3000 1416 78 68 63 64 63 55 85 75 69 70 69 61 91 82 76 75 74 70 94 86 80 77 76 75
16
1400 661 69 60 57 56 59 54 78 69 67 64 66 63 84 77 73 70 70 72 85 80 77 73 71 76
2100 991 70 61 57 58 60 53 79 70 66 65 66 63 87 78 74 72 72 71 89 82 78 76 73 76
2800 1321 72 64 59 60 62 54 79 71 66 67 67 63 84 76 70 70 71 68 87 78 74 72 72 71 91 83 79 76 75 75
3000 1416
4000 1888 75 67 63 67 67 59 82 74 69 71 71 64 90 81 76 75 75 71 93 85 80 77 76 75
Notes:
1. All data are measured in accordance with Industry Standard AHRI 880-2011.
2. All sound power levels, dB re: 10-12 Watts.
3. Data in this column constitute AHRI 880-2011 Standard Rating Conditions
4. Where Ps is the inlet static pressure minus discharge static.
5. Application ratings are outside the scope of the certification program.

72 VAV-PRC011M-EN
Dual-Duct VAV Terminal Units
Table 43. Radiated sound power (dB)1, 2, 4
Inlet
Size
(in)
0.5" Inlet Pressure
Ps51.0" Inlet Pressure
Ps51.5" Inlet Pressure
Ps32.0" Inlet Pressure
Ps53.0" Inlet Pressure
Ps5
Cfml/s234567234567234567234567234567
5
130 61 514433282424524638342930 524843433939484946484747
200 94 534636312523565042373129 575248443939565451494646
250 118 55 49 39 33 27 24 58 52 44 39 33 29 59 55 48 42 37 35 59 56 50 45 41 39 59 58 54 51 47 46
350 165 60 53 45 37 31 26 62 57 48 42 36 31 64 60 53 48 42 40 65 63 58 52 47 45
6
200 94 524535292423554841342827 585147413634565349454240
300 142 57 50 40 34 26 23 59 53 45 38 31 27 62 57 50 44 37 34 61 59 55 49 43 39
400 189 58 51 42 34 28 24 63 58 49 42 35 29 64 60 52 45 37 31 65 60 54 47 40 35 66 63 58 51 44 39
500 236 58 52 45 36 31 27 66 60 51 42 37 30 69 65 57 50 43 37 71 67 60 55 46 41
8
350 165 56 49 40 34 28 25 60 55 47 41 33 28 63 59 53 46 39 35 62 61 55 49 44 40
520 245 57 52 44 37 31 26 64 58 51 44 37 30 68 64 57 50 43 36 67 66 60 54 46 41
700 330 60 55 47 40 34 28 66 61 52 46 39 32 69 64 57 51 43 36 71 67 59 53 45 39 73 72 64 58 49 44
900 425 60 56 48 41 37 31 67 64 55 48 43 36 73 70 61 55 48 43 76 74 66 60 52 46
12
800 378 61 51 45 39 32 22 66 59 50 45 38 31 70 64 57 50 44 39 71 67 60 52 47 44
1200 566 64 54 48 41 36 25 71 62 52 47 42 34 75 69 59 52 47 42 77 72 64 55 50 47
1550 732 65 57 47 42 40 28 73 64 53 47 46 36 81 72 61 53 49 45 83 75 65 56 52 48
1600 755 78 68 58 50 47 41
2000 944 66 59 48 44 45 35 75 66 54 48 48 40 85 74 62 53 51 47 88 79 67 57 53 50
14
1100 519 58 50 43 39 33 23 67 58 52 45 40 34 72 66 60 51 45 40 72 68 64 53 48 46
1600 755 61 53 44 40 36 24 69 60 53 47 42 32 76 68 61 53 47 41 79 73 66 55 49 46
2100 991 63 55 46 42 40 27 71 62 53 47 44 35 76 66 57 50 47 39 78 69 61 52 48 43 82 73 66 56 51 46
3000 1416 66 60 50 46 49 36 75 66 55 50 50 40 85 73 61 54 52 47 88 77 66 57 53 48
16
1400 661 57 50 46 43 37 25 65 58 52 48 42 34 73 66 60 50 45 42 72 70 64 53 46 47
2100 991 59 53 48 46 42 28 67 60 54 50 47 36 75 68 62 53 49 45 78 73 66 56 49 48
2800 1321 74 66 58 53 52 44
3000 1416 61 56 50 50 48 33 69 62 54 52 52 40 78 69 61 55 53 47 83 74 66 58 53 51
4000 1888 65 61 54 54 59 43 71 65 58 55 60 49 83 72 63 58 59 54 89 76 66 61 58 55
Notes:
1. All data are measured in accordance with Industry Standard AHRI 880-2011.
2. All sound power levels, dB re: 10-12 Watts.
3. Data in this column constitute AHRI 880-2011 Standard Rating Conditions
4. Where Ps is the inlet static pressure minus discharge static.
5. Application ratings are outside the scope of the certification program.

VAV-PRC011M-EN 73
Dual-Duct VAV Terminal Units
Table 44. Sound noise criteria (NC)
Discharge1,2,4 Radiated1,2,4
Inlet
Size (in) Inlet Pressure (Ps)3,5 Inlet
Size (in) Inlet Pressure (Ps)3,5
CFM l/s 0.5” 1.0” 1.5” 2.0” 3.0” CFM l/s 0.5” 1.0” 1.5” 2.0” 3.0”
5
130 61 -- -- 16 21
5
130 61 -- -- 16 20
200 94 -- 20 25 25 "200 94 -- 18 22 25
250 118 19 24 28 30 30 250 118 17 20 24 25 28
350 165 28 32 38 41 350 165 22 26 30 33
6
200 94 -- 16 21 20
6
200 94 -- 16 21 23
300 142 19 23 30 30 "300 142 19 21 26 30
400 189 23 30 33 35 38 400 189 20 27 30 30 33
500 236 20 33 43 44 500 236 20 30 36 38
8
350 165 16 24 28 28
8
300 142 17 24 28 31
520 245 20 30 38 38 500 236 20 27 34 37
700 330 23 33 38 43 46 700 330 24 31 34 38 44
900 425 25 34 44 51 900 425 25 34 42 46
10
550 260 16 26 32 32
10
500 236 20 25 30 34
820 387 20 30 39 39 800 378 22 29 36 39
1100 519 24 33 39 43 46 1100 519 22 31 36 39 43
1400 661 28 35 46 50 1400 661 24 35 43 47
12
800 378 21 32 38 38
12
650 307 24 30 35 38
1200 566 27 38 46 46 1100 519 27 36 42 44
1550 732 1550 732 29 39 49 52
1600 755 27 39 47 50 52 1600 755 45
2000 944 29 39 54 56 2000 944 30 42 54 58
14
1100 519 21 33 39 39
14
900 425 20 31 38 39
1600 755 24 34 45 46 1500 708 24 34 43 47
2100 991 27 37 42 46 47 2100 991 26 36 43 45 51
3000 1416 32 41 48 52 3000 1416 30 42 54 58
16
1400 661 20 32 39 41
16
1200 566 20 29 39 42
2100 991 21 33 43 46 2000 944 22 31 42 45
2800 1321 24 33 39 43 48 2800 1321 40
3000 1416 3000 1416 25 34 45 52
4000 1888 28 37 47 51 4000 1888 31 36 52 60
Notes:
1. "--" represents NC levels below NC 15.
2. NC Values are calculated using modeling assumptions based on AHRI 885-2008-02 Addendum.
3. Data at 1.5" inlet pressure constitute AHRI 880-2011 Standard Rating Conditions
4. Where Ps is the inlet static pressure minus discharge static.
5. Data at 0.5", 1.0", 2.0"& 3.0" are application ratings. These ratings are outside the scope of the certification program.
Table 45. AHRI 885-2008 radiated transfer function assumptions
Octave Band
23 4 5 6 7
Type 2- Mineral Fiber Insulation
Total dB reduction
-18
-18
-19
-19
-20
-20
-26
-26
-31
-31
-36
-36
Notes: Subtract from terminal unit sound power to determine radiated sound pressure in the space.
1. NC Values are calculated using modeling assumptions based on AHRI 885-2008.
2. Where DPs is inlet static pressure minus discharge static pressure.
3. Application ratings are outside the scope of the Certification Program.
Table 46. AHRI 885-2008 discharge transfer function assumptions
Octave Band
23456 7
Small Box (<300 Cfm)
Medium Box (300-700 Cfm)
Large Box (>700 Cfm)
-24
-27
-29
-28
-29
-30
-39
-40
-41
-53
-51
-51
-59
-53
-52
-40
-39
-39
Notes: Subtract from terminal unit sound power to determine discharge sound pressure in the space.
1. NC Values are calculated using modeling assumptions based on AHRI 885-2008.
2. Where DPs is inlet static pressure minus discharge static pressure.
3. Application ratings are outside the scope of the Certification Program.

74 VAV-PRC011M-EN
Dual-Duct VAV Terminal Units
Dimensional Data
COOLING
CONTROL BOX
HEATING
CONTROL BOX
H
W
14.00"
[356 mm]
L
SLIP & DRIVE
CONNECTION
14.60"
[371 mm]
C D
AIR
VALVE
COOLING
AIR
VALVE
HEATING
AIRFLOW
ARRANGEMENT "H"
1.50" [38 mm] FLANGE
9.50"
[241 mm]
FLOW RING
TUBING
FLOW RING
TUBING
DISCHARGE
DIMENSIONS
(BxA)
TOP VIEW
BACK VIEW SIDE VIEW
15.50"
[394 mm]
4.00"
[102 mm]
21.50"
[546 mm]
5.40"
[137 mm]
DUAL-DUCT WITH OUTLET PLENUM (VDDF)
12" [305mm]
OUTL CONVERSION CHART
6" [152mm]
5" [127mm]
10" [254mm]
8" [203mm]
INLET SIZE (NOMINAL Ø)
II
III
IV
SYMBOL
I
06 900
08
10
08
08
2000
1400
1400
900
INLET
05
05
06
350
500
500
CFM
236
425
661
425
425
165
236
165
L/s
OUTL
NOMINALØ
6" [152mm]
8" [203mm]
10" [254mm]
5" [127mm] A,B,C
D,E,F
J
H
VALV
I, II
N/A
I, II
0505
I, II, III
24.00" [610mm]
22.00" [559mm]
LW
I, II, III
N/A
I, II, III
0606
II, III
II, III, IV
I, II, III
N/A
0808
III, IV
III, IV
III
III,IV
1010
N/A
DISCHARGE DIMENSIONS
20.00" [508mm]
14.00" [356mm]
AB
WT
55 [25]
58 [26]
61 [28]
56 [25]
57 [26]
[kg]
54 [24]
LBS
A CB D E F JH
(TOP VIEW)
ARRANGEMENTS
OUTLET PLENUM
G
GIII
N/AN/AN/A
06
06
05
10
08
10
12
08
12
59 [27]
661200010
12 2000 994
60 [27]
12
14" [356mm]
14 3000 1416
81 [37]
14
16 1888400016
16" [406mm] 83 [38]
COOL HEAT HEATCOOL
4000
3000
2000
1400
350
500
350
900
900
1400
900
500
COOL HEAT
1888
1416
994
994
236
236
165
425
661
661
994
425
COOL HEAT
16" [406mm]
14" [356mm]
8" [203mm]
10" [254mm]
5" [127mm]
6" [152mm]
8" [203mm]
10" [254mm]
12" [305mm]
20.00" [508mm]
8.00" [203mm]
7.00" [178mm]
7.00" [178mm]
10.00" [254mm]
CD
10.00" [254mm]
7.00" [178mm]
7.00" [178mm]
8.00" [203mm]
8.00" [203mm]
9.00" [229mm]
28.00" [711mm]
40.00" [1016mm]
H
15.50" [394mm]
21.50" [546mm]
54 [24]
54 [24]
1. Outlet combinations to remote diffusers have
optional integral balancing dampers (see
specification sheet).
2. Outlet connections are centered in plenum panel.
duct required for proper flow reading.
3. Minimum of 1.5 duct diameters of straight
4. Allow 36" [914mm] on control side for servicing
based on selected options, insulation type, etc.
5. Weights are an estimation and will vary
should be equal discharge size (A x B).
of unit before first runout & inside of the duct
6. Allow 48" [1219] of straight duct downstream

VAV-PRC011M-EN 75
Dual-Duct VAV Terminal Units
COOLING
CONTROL BOX
PNEUMATIC
CONTROLS
AREA (SEE
NOTES)
HEATING
CONTROL BOX
PNEUMATIC
CONTROLS
AREA (SEE
NOTES)
H
W
12.50"
[318 mm]
L
14.60"
[371 mm]
AB
AIR
VALVE
COOLING
AIR
VALVE
HEATING
AIRFLOW
DISCHARGE OUTLET
9.50"
[241 mm]
FLOW RING
TUBING
TOP VIEW
BACK VIEW SIDE VIEW
4.00"
[102 mm]
C
5.40"
[137 mm]
SEE CHART ABOVE
FLOW
RING
FLOW RING TUBING
CONNECTS TO HEATING
SIDE CONTROL
DISCHARGE IS CENTERED
ON BACK OF UNIT.
54 [24]
54 [24]
21.50" [546mm]
15.50" [394mm]
H
40.00" [1016mm]
28.00" [711mm]
9.00" [229mm]
8.00" [203mm]
8.00" [203mm]
7.00" [178mm]
7.00" [178mm]
10.00" [254mm]
BA
10.00" [254mm]
7.00" [178mm]
7.00" [178mm]
8.00" [203mm]
12" [305mm]
10" [254mm]
8" [203mm]
6" [152mm]
5" [127mm]
10" [254mm]
8" [203mm]
14" [356mm]
16" [406mm]
HEATCOOL
425
994
661
661
425
165
236
236
994
994
1416
1888
HEATCOOL
500
900
1400
900
900
350
500
350
1400
2000
3000
4000
COOL HEATHEATCOOL
83 [38]
16" [406mm]16 4000 188816
14 81 [37]
1416300014 14" [356mm]
12 60 [27]
994200012
10 2000 661 59 [27]
12
08
12
10
08
10
05
06
06
LBS
54 [24]
[kg]
57 [26]
56 [25]
61 [28]
58 [26]
55 [25]
WT
W
L
22.00" [559mm]
24.00" [610mm]
L/s
165
236
165
425
425
661
425
236
CFM
500
500
350
06
05
05
INLET
900
1400
1400
2000
08
08
10
08
90006
INLET SIZE (NOMINAL Ø)
8" [203mm]
10" [254mm]
5" [127mm]
6" [152mm]
12" [305mm]
DUAL-DUCT WITH OUTLET PLENUM (VDDF)
2. No control box provided for the following options:
ENON, PNON, DD00 and Pneumatic controls.
1. See mechanical specifications for general unit clearances.
12" [305mm]
6" [152mm]
5" [127mm]
10" [254mm]
8" [203mm]
14" [356mm]
16" [406mm]
C

76 VAV-PRC011M-EN
Dual-Duct VAV Terminal Units
Mechanical Specifications
Dual-Duct Terminal Unit
Model VDDF
Casing
22-gage galvanized steel.
Hanger brackets provided.
Agency Listing
The unit is UL and Canadian UL. Listed as a room air terminal unit. Control # 9N65.
AHRI 880 Certified.
Insulation
1/2" (12.7 mm) Matte-faced Insulation—The interior surface of the unit casing is acoustically and
thermally lined with ½-inch, 1.5 lb/ft3 (12.7 mm, 24.0 kg /m3) composite density glass fiber with a
high-density facing. The insulation R-Value is 1.9. The insulation is UL listed and meets NFPA-90A
and UL 181 standards. There are no exposed edges of insulation (complete metal encapsulation).
1" (25.4 mm) Matte-faced Insulation—The interior surface of the unit casing is acoustically and
thermally lined with 1-inch, 1.0 lb/ft3 (25.4 mm, 16.0 kg /m3) composite density glass fiber with a
high-density facing. The insulation R-Value is 3.85. The insulation is UL listed and meets NFPA-90A
and UL 181 standards. There are no exposed edges of insulation (complete metal encapsulation).
1" (25.4 mm) Foil-faced Insulation—The interior surface of the unit casing is acoustically and
thermally lined with 1-inch, 1.0 lb/ft3 (25.4 mm, 16.0 kg /m3) density glass fiber with foil facing. The
insulation R-Value is 3.85. The insulation is UL listed and meets NFPA-90A and UL 181 standards
as well as bacteriological standard ASTM C 665. There are no exposed edges of insulation
(complete metal encapsulation).
1" (25.4 mm) Double-wall Insulation—The interior surface of the unit casing is acoustically and
thermally lined with a 1-inch, 1.0 lb./ft3 (25.4 mm, 16.0 kg/m3) composite density glass fiber with
high-density facing. The insulation R-value is 3.85. The insulation is UL listed and meets NFPA-90A
and UL 181 standards. An interior liner made of 26-gage galvanized steel covers the insulation. All
wire penetrations are covered by grommets. There are no exposed edges of insulation (complete
metal encapsulation).
3/8" (9.5 mm) Closed-cell Insulation—The interior surface of the unit casing is acoustically and
thermally lined with 3/8-inch, 4.4 lb/ft3 (9.5 mm, 70.0 kg/m3) closed cell insulation. The insulation
is UL listed and meets NFPA-90A and UL 181 standards. The insulation has an R-Value of 1.4. There
is complete metal encapsulation.
Primary Air Valves
Table 47. Air valve combinations available
Air Valve Size in. (mm)
Cooling Cataloged Airflow cfm
(L/s)
Cooling
Air Valve Size in. (mm)
Heating Catalog Airflow cfm
(L/s)
Heating
05 (127) 350 (165) 05 (127) 350 (165)
06 (152) 500 (236) 05 (127) 350 (165)
06 (152) 500 (236) 06 (152) 500 (236)
08 (203) 900 (425) 06 (152) 500 (236)
08 (203) 900 (425) 08 (203) 900 (425)

VAV-PRC011M-EN 77
Dual-Duct VAV Terminal Units
Air Valve Round — The primary air inlet connection is an 18-gage galvanized steel cylinder sized
to fit standard round duct. A multiple-point, averaging flow sensing ring is provided with balancing
taps for measuring +/-5% of unit cataloged airflow.
An airflow-versus-pressure differential calibration chart is provided. The damper blade is
constructed of a closed-cell foam seal that is mechanically locked between two 22-gage galvanized
steel disks. The damper blade assembly is connected to a cast zinc shaft supported by self-
lubricating bearings. The shaft is cast with a damper position indicator. The valve assembly
includes a mechanical stop to prevent over-stroking. At 4.0 in. wg, air valve leakage does not exceed
1% of cataloged airflow.
Outlet Connection
Slip & Drive Connection—Terminal units come standard with slip & drive connection.
Outlet Plenum/Attenuator—A sheet metal, insulated plenum/attenuator with circular opening(s)
is attached to the discharge of the main unit at the factory. The circular opening(s) are centered on
the unit plenum to accept round ductwork connections.
Outlet Plenum/Attenuator with Balancing Dampers—A sheet metal, insulated plenum/attenuator
with circular opening(s) is factory-connected to the main unit. The circular opening(s) with
balancing damper(s) are centered on the unit plenum to accept round ductwork connections.
Unit Controls Sequence of Operation
Unit controller continuously monitors zone temperature against its setpoint and varies primary
airflow as required to meet zone setpoints. Airflow is limited by minimum and maximum position
setpoints.
Direct Digital Controls
DDC Actuator—Trane 3-wire, 24-VAC, floating-point quarter turn control actuator with linkage
release button. Actuator has a constant drive rate independent of load, a rated torque of 35 in-lb,
a 90-second drive time, and is non-spring return. Travel is terminated by end stops at fully-opened
and -closed positions. An integral magnetic clutch eliminates motor stall.
DDC Actuator - Belimo — LMB24-3-T TN 3-wire, 24 VAC/DC, floating-point, quarter turn actuator
with linkage release button. Actuator has a constant drive rate independent of load, a rated torque
of 45 in-lb, a 95 second drive time, and is non-spring return. Travel is terminated by end stops at
fully-opened and -closed positions. Internal electronic control prevents motor stall when motor
reaches end stops.
Direct Digital Controller—The microprocessor based terminal unit controller provides accurate,
pressure-independent control through the use of a proportional integral control algorithm and
direct digital control technology. The controller, named the Unit Control Module (UCM), monitors
zone temperature setpoints, zone temperature and its rate of change, and valve airflow using a
10 (254) 1400 (661) 08 (203) 900 (425)
10 (254) 1400 (661) 10 (254) 1400 (661)
12 (305) 1400 (944) 08 (203) 900 (425)
12 (305) 2000 (944) 10 (254) 1400 (661)
12 (305) 2000 (944) 12 (305) 2000 (944)
14 (356) 3000 (1416) 14 (356) 3000 (1416)
16 (406) 4000 (1888) 16 (406) 4000 (1888)
Table 47. Air valve combinations available (continued)
Air Valve Size in. (mm)
Cooling Cataloged Airflow cfm
(L/s)
Cooling
Air Valve Size in. (mm)
Heating Catalog Airflow cfm
(L/s)
Heating
05 (127) 350 (165) 05 (127) 350 (165)

78 VAV-PRC011M-EN
Dual-Duct VAV Terminal Units
differential pressure signal from the pressure transducer. Additionally, the controller can monitor
either supply duct air temperature or CO2 concentration via appropriate sensors. The controller is
provided in an enclosure with 7/8" (22 mm) knockouts for remote control wiring. A Trane UCM zone
sensor is required.
DDC Zone Sensor—The UCM controller senses zone temperature through a sensing element
located in the zone sensor. In addition to the sensing element, zone sensor options may include an
externally-adjustable setpoint, communications jack for use with a portable edit device, and an
override button to change the individual controller from unoccupied to occupied mode. The
override button has a cancel feature that will return the system to unoccupied. Wired zone sensors
utilize a thermistor to vary the voltage output in response to changes in the zone temperature.
Wiring to the UCM controller must be 18 to 22 awg. twisted pair wiring. The setpoint adjustment
range is 50–88ºF (10–31°C). Depending upon the features available in the model of sensor selected,
the zone sensor may require from a 2-wire to a 5-wire connection. Wireless zone sensors report the
same zone information as wired zone sensors, but do so using radio transmitter technology.
Therefore with wireless, wiring from the zone sensor to the UCM is unnecessary.
Digital Display Zone Sensor with Liquid Crystal Display (LCD)—The digital display zone sensor
contains a sensing element, which sends a signal to the UCM. A Liquid Crystal Display (LCD)
displays setpoint or space temperature. Sensor buttons allow the user to adjust setpoints, and
allow space temperature readings to be turned on or off. The digital display zone sensor also
includes a communication jack, for use with a portable edit device, and an override button to
change the UCM from unoccupied to occupied. The override button has a cancel feature, which
returns the system to unoccupied mode.
System Communications—The Controller is designed to send and receive data from a Tracer™ SC
or other Trane controllers. Current unit status conditions and setpoints may be monitored and/or
edited via this data communication feature. The network type is a twisted wire pair shielded serial
communication.
Pneumatic Controls
Normally-Open Actuator—Pneumatic 3 to 8 psig (20 to 55 kPa) spring-range pneumatic actuator.
Normally-Closed Actuator—Pneumatic 8 to 13 psig (55 to 90 kPa) spring-range pneumatic actuator.
3011 Pneumatic Volume Regulator (PVR)—The regulator is a thermostat reset velocity controller,
which provides consistent air delivery within 5% of cataloged flow down to 18% or less of unit
cataloged cfm, independent of changes in system static pressure. Factory-calibrated, field-
adjustable setpoints for minimum and maximum flows. Average total unit bleed rate, excluding
thermostat, is 28.8 scim at 20 psig (7.87 mL/min at 138 kPa) supply.
3501 Pneumatic Volume Regulator (PVR)—The 3501 regulator is a linear reset volume controller.
This PVR is used to maintain a constant volume of airflow from the dual-duct unit when constant
volume control is used. Average total unit bleed rate, excluding thermostat, is 43.2 scim at 20 psig
(11.8 mL/min at 138 kPa) supply.
Control Options
Tr a n s fo rm e r — The 50-VA transformer is factory-installed in an enclosure with 7/8" (2 mm)
knockouts to provide 24 VAC for controls.
Disconnect Switch – A toggle disconnect disengages primary power to the terminal.
Fuse – Optional fuse is factory-installed in the primary voltage hot leg.

VAV-PRC011M-EN 79
DDC Controls
Tracer UC400 and UC210 Programmable BACnet Controllers
The Tracer™ UC400 and UC210 controllers are programmable general purpose BACnet®,
microprocessor-based, Direct Digital Controllers (DDC). When factory installed on Trane (Variable
Air Volume) VAV terminal units, they are factory downloaded with appropriate VAV programs and
configuration settings. Trane VAV units have been made with either pneumatic, analog electronic,
or microprocessor controls (DDC VAV). UC400 is not an option on Dual Duct.
The Tracer UC400 or UC210 controller can be configured from the factory with three different
application programs: Space Temperature Control (STC), Ventilation Flow Control (VFC), and Flow
Tracking Control (FTC).
The Tracer UC400 or UC210 controller programmed for STC modulates a VAV's damper blade
based on a zone temperature, measured airflow, and setpoints to continuously control conditioned
air delivery to the space. The volume of incoming air is monitored and the damper adjusts to
provide accurate control independent of the duct pressure. The damper modulates between
operator setpoints depending on space conditions. Additionally, fan and heat outputs may be
energized depending on the application.
The Tracer UC400 or UC210 controller configured for VFC can be applied to a VAV terminal and used
to temper cold outdoor air (OA) that is brought into a building for ventilation purposes. The
tempered air is intended to supply an air-handling unit (AHU), which provides comfort control to
the zones it is serving. The VAV terminal supplies the correct amount of ventilation air, and when
reheat is added, tempers the ventilation air to reduce the load on the air handler by sensing the
discharge air temperature of the VAV unit and controlling its long-term average to the discharge
air temperature setpoint.
The Tracer UC400 or UC210 controller can be configured for FTC and has two VAV units with Tracer
UC400 or UC210 controllers working together to provide flow tracking control. One Tracer UC400
or UC210 controller is configured from the factory with the Space temperature program and the
other is downloaded with the FTC program. The STC airflow output is bound to the flow tracking
controller airflow setpoint input. The flow tracking controller adds the configured airflow tracking
offset (positive or negative) to the airflow setpoint (communicated airflow setpoint) and controls
the airflow to this setpoint.
The Tracer UC400 or UC210 controller is BTL compliant with BACnet, an open standard building
automation protocol. It meets the Application Specific Controller (ASC) profile per ASHRAE 135-
2004. This allows the Tracer UC400 controller to integrate with other BACnet systems.
Available Inputs
Inputs include a twisted/shielded communication link, zone sensor, duct temperature sensors
(optional), Occupancy Sensor (optional), Discharge Air Temperature (DAT) and/or Supply Air
Temperature (SAT), CO2 sensor, and 24 VAC power. In addition to the points used for the VAV
application, the spare inputs and outputs on the Tracer UC400 controller may be used for ancillary
control, which can be programmed using Tracer TU Tracer Graphical Programming 2 (TGP2).
Note: For more information on using spare points, see BAS-SVX20*-EN Tracer UC400
Programmable Controller Installation, Operation, and Maintenance.
General Features and Benefits
Assured Accuracy
• Proportional-plus-integral control loop algorithm for determining required airflow needed to
control room temperature. Airflow is limited by active minimum and maximum airflow
setpoints.
• Pressure-independent (PI) operation that automatically adjusts valve position to maintain
required airflow. In certain low-flow situations or in cases where the flow measurement has
failed, the DDC controller will operate in a pressure-dependent (PD) mode of operation.

80 VAV-PRC011M-EN
DDC Controls
• When combined with the patented Trane Flow ring and pressure transducer, flow is repeatable
to +/- 5% accuracy across the Pressure Independent (PI) flow range. (See Valve/Controller
Airflow Guidelines section).
• Improved 2-Point Air Balancing is available – Assures optimized flow-sensing accuracy across
the operating range. This provides a more accurate airflow balancing method when compared
to typical single-point flow correction air balancing.
• Analog input resolution of +/- 1/8°F within the comfort range maximizes zone temperature
control yielding excellent comfort control.
Reliable Operation
• Built for life – Trane products are designed to stand the test of time, with a proven design life
that exceeds 20 years.
• Fully factory tested – fully screened and configured at the factory. All features are tested
including fan and reheat stage energization, air valve modulation, and controller inputs and
outputs.
Safe Operation
• All components, including the controller, pressure transducer, transformer, etc. are mounted
in a NEMA 1 sheet metal enclosure and are tested as an assembly to UL1995 standards. The
result is a rugged and safe VAV, controller, and thus, overall unit.
• When in PI-mode, EH is disabled when the sensed flow is below the minimum required.
• HW coil VAV units in ventilation flow control (VFC) have a Freeze protection algorithm to protect
the water coil and the internal space from water damage. This is accomplished by driving the
water valve to maximum position on alarm conditions.
System-Level Optimization
Trane controllers are designed to integrate into Trane Tracer™ Building Automation Systems and
leverage clear and clean unit-controller related data for system level control decisions. Integrating
a Trane VV550 controller into a Tracer SC Control System provides the next step in building system
control.
Specifically, system-level decisions on how to operate all components can be made. Energy
efficient optimization strategies like Static Pressure Optimization, Ventilation Reset, and CO2
Demand-controlled Ventilation can be employed with the simple press of a button. The end-result
is the most efficient and reliable building control system available.
Simplified Installation
Factory Commissioned Quality – All Trane DDC VAV controllers are factory-commissioned. This
means that the DDC boards are powered and run-tested with your specific sequence parameters.
They are connected to a communication link to make sure that information and diagnostic data
function properly. Before any VariTrane™ VAV unit ships they must pass a rigorous quality control
procedure. You can be assured that a Trane VAV unit with Trane DDC VAV controls will work right
out of the crate.
Zone sensor air balance – When applied to a Trane zone sensor with thumb-wheel and on/cancel
buttons, a balancing contractor can drive the primary air valve to maximum or minimum airflow
from the sensor to determine the point of calibration to be used (maximum will result in optimum
performance). The flow reading can then be calibrated from the sensor, without the use of
additional service tools. (Non-LCD versions)
Tenant-Finish Heat Mode – In some office projects, the building is being constructed as tenants are
being identified. Tenant-finish heat mode is designed for applications when a given floor has not
been occupied. The main AHU system is used for heat and because the internal furnishings are not
complete, the sensors have not been installed. In this case, the primary valve drives open using

VAV-PRC011M-EN 81
DDC Controls
the heat of the main AHU to keep plumbing lines from freezing. When available, the operation of
the VAV unit fan (series or parallel) remains unaffected.
Controller Flexibility
• 24 VAC binary input that can be configured as a generic input or as occupancy input. When the
DDC controller is operating with a Tracer ™ SC, the status of the input is provided to Tracer for
its action. In stand-alone operation and when configured for an occupancy input, the input will
control occupancy status of the DDC controller.
• Auxiliary temperature analog input configured for an auxiliary temperature sensor. When
sensor is mounted in the supply air duct, the value of the input is used as status-only by Tracer
SC if Tracer SC is providing a supply air temperature to the DDC controller. Otherwise, the input
will be used for determining heating/cooling control action of the VAV unit. When the auxiliary
temperature sensor is located in the discharge of the unit, and attached to a Trane Tracer SC
BAS, additional test sequencing and reporting is available to maximize VAV system capabilities
and simplify system commissioning.
• Dual-duct support with two DDC controllers. One DDC controller controls the cooling air valve
and the other controller controls the heating air valve. With constant-volume sequences, the
discharge air volume is held constant by controlling discharge air volume with the heating
Controller.
• Tracer™ UC400 or UC210 Programmable BACnet® Controller certified performance ensures
that a Trane VAV with controller will provide state-of-the-art, consistent open communication
protocol for integration with the industry’s latest (Non-Trane) building automation control
systems, including Johnson Control, Andover, Siemens, Honeywell, etc.
•CO
2 demand controlled ventilation enables a HVAC system to adjust ventilation flow based on
the measured CO2 concentration in the zone. Trane demand controlled ventilation strategies
are pre-defined for simplified application and can be easily customized to meet the needs of a
specific system.
Trane DDC VAV Controller Logic with UC210 or UC400 Controls
Control Logic
Direct Digital Control (DDC) controllers are today’s industry standard. DDC controllers share
system-level data to optimize system performance (including changing ventilation requirements,
system static pressures, supply air temperatures, etc.). Variables available via a simple twisted-
shielded wire pair include occupied/unoccupied status, minimum and maximum airflow setpoints,
zone temperature and temperature setpoints, air valve position, airflow cfm, fan status (on or off),
fan operation mode (parallel or series), reheat status (on or off), VAV unit type, air valve size,
temperature correction offsets, flow correction values, ventilation fraction, etc.
With the advent of Tracer UC400 open protocol, the most reliable VAV controller is now available
for ANY system. Gone are the days of being locked into a single supplier. Trane DDC controllers
provide Trane-designed solid-state electronics intended specifically for VAV applications including:
1. Space Temperature Control
2. Ventilation Flow Control (100% outside air applications)
3. Flow Tracking Space Pressurization Control (New feature)

82 VAV-PRC011M-EN
DDC Controls
Note: Flow sensor DP (in. wg) is measured at the flow ring to aid in system balancing and commissioning. See “Valve/Controller
Airflow Guidelines” in each section for unit performance.
Space Temperature Control
Space temperature control applications are where Trane emerged as an industry leader in quality
and reliability. This did not occur overnight and has continued to improve as our controller and
control logic has improved over time. STC employs controller logic designed to modulate the
supply airstream and associated reheat (either local or remote) to exactly match the load
requirements of the space.
Additionally, minimum and maximum airflow and specific controller sequence requirements are
pre-programmed to ensure that appropriate ventilation standards are consistently maintained.
When connected to a Trane Tracer™ SC control system, trend logging, remote alarming, etc. are
available to fully utilize the power and capabilities of your systems.
General Operation-Cooling
In cooling control action, the DDC controller matches primary airflow to cooling load. The DDC
controller will automatically change over to heating control action if the supply air temperature is
above a configured/editable setpoint. When the supply air temperature is less than 10 degrees
below this setpoint, the controller will automatically switch to cooling control action. The DDC
controller first chooses the Tracer SC -provided supply air temperature value to use for auto
changeover. If this is not available, it uses the temperature provided by the optional auxiliary
temperature sensor (must be installed for inlet temperature monitoring). If this is also not available,
it uses the heating/cooling mode assigned by Tracer SC or the DDC controller’s service tool.
General Operation-Heating and Reheat
In heating control action, the DDC controller matches primary airflow to heating load. The DDC
controller will automatically change over to heating control action if the supply air temperature is
above a configured/editable setpoint. When the supply air temperature is less than 10 degrees
below this setpoint, the controller will automatically switch to cooling control action. The DDC
controller first chooses the Tracer SC-provided supply air temperature value to use for auto
changeover. If this is not available, it uses the temperature provided by the optional auxiliary
temperature sensor (must be installed for inlet temperature monitoring). If this is also not available,
it uses the heating/cooling mode assigned by Tracer SC or the DDC controller’s service tool.
When heat is added to the primary air, the air is considered reheated. Reheat can be either local
(integral to the VAV unit in the form of an electric coil or hot water coil) or remote (typically existing
Figure 2. Flow sensor single vs. airflow delivery
0.01
0.1
1
5
10 100 1,000 10,000
Cfm
Flow Sensor DP (In. wg)
4" 12"
10"
8"6"
5" 14" 16"

VAV-PRC011M-EN 83
DDC Controls
wall fin radiation, convector, etc.) or any combination of local and remote. The operating
characteristics of the four basic types of VariTrane DDC terminal reheat are discussed.
Single-Duct: On/Off Hot Water Reheat
Three stages of on/off hot water reheat are available. Two-position water valves complete the HW
reheat system and are either fully opened or fully closed. The heating minimum airflow setpoint
is enforced during reheat.
Stage 1 energizes when the space temperature is at or below the heating setpoint. When the zone
temperature rises above the active heating setpoint by 0.5°F (0.28°C), stage 1 is de-energized. Stage
2 energizes when the space temperature is 1°F (0.56°C) or more below the active heating setpoint,
and is de-energized when the space temperature is 0.5°F (0.28°C) below the active heating setpoint.
Stage 3 energizes when the zone temperature is 2°F (1.11°C) or more below the active heating
setpoint, and de-energizes when the space temperature is 1.5°F (0.83°C) below the active heating
setpoint. When reheat is de-energized, the cooling minimum airflow setpoint is enforced.
Single-Duct: Proportional Hot Water Reheat
Proportional hot water reheat uses 3-wire, floating-point-actuator technology.
When the space temperature drops below the active heating setpoint, the air valve open to the
Airflow Setpoint Reset Minimum Local Heat and the reheat valve modulates to maintain space
temperature at the active heating setpoint. Control of the water valve uses a separate proportional
plus integral control loop, and its position is dependent on the degree that the space temperature
is below the active heating setpoint and the amount of time that the space temperature has been
below the active heating setpoint.
If the discharge air temperature reaches the Discharge Air Temperature Design Setpoint, the air
valve opens further and modulates between Airflow Setpoint Reset Minimum Local Heat and
Airflow Setpoint Reset Maximum Local Heat to maintain space temperature at the active heating
setpoint, while the water valve modulates to maintain discharge air temperature at the Discharge
Air Temperature Design Setpoint. If the air valve reaches Airflow Setpoint Reset Maximum Local
Heat, the water valve opens further and modulates to maintain space temperature at the active
heating setpoint, while the air valve remains at Airflow Setpoint Reset Maximum Local Heat.
An additional on/off remote heat output is available and energized when the water valve is driven
100% open and de-energized when the water valve reaches 50% open.
In the event that the DAT sensor fails, or is not connected, when the space temperature drops below
the active heating setpoint, the air valve open to the Airflow Setpoint Minimum Local Heat and the
water valve modulates to maintain space temperature at the active heating setpoint.
When reheat is de-energized, the cooling Airflow Minimum Setpoint is enforced.
Single-Duct: On/Off Electric Reheat
One, two, or three stages of staged electric reheat are available. The heating minimum airflow
setpoint is enforced during reheat.
Stage 1 is energized when the space temperature falls below the active heating setpoint and
minimum airflow requirements are met. When the zone temperature rises above the active heating
setpoint by 0.5°F (0.28°C), stage 1 is de-energized. Stage 2 energizes when the space temperature
is 1°F (0.56°C) or more below the active heating setpoint, and is de-energized when the space
temperature is 0.5°F (0.28°C) below the active heating setpoint. Stage 3 energizes when the zone
temperature is 2°F (1.11°C) or more below the active heating setpoint, and de-energizes when the
space temperature is 1.5°F (0.83°C) below the active heating setpoint. When reheat is de-energized,
the cooling minimum airflow setpoint is enforced.
Single-Duct: Pulse-Width Modulation of Electric Heat
One to three stages of pulse-width modulation of electric heat are available. Energizing for a
portion of a three-minute time period modulates the electric heater. This allows for closer matching

84 VAV-PRC011M-EN
DDC Controls
of heating capacity to the heating load, resulting in more stable temperature control. The heating
minimum airflow setpoint is enforced during reheat.
The amount of reheat supplied is dependent on both the degree that the space temperature is
below the active heating setpoint and the time that the space temperature has been below the
active heating setpoint. If not already off, reheat de-energizes when the zone temperature rises
more than 0.5°F (0.28°C) above the heating setpoint.
The Stage 1 “on” time is proportional to the amount of reheat required. For example, when 50%
of stage 1 capacity is required, reheat is on for 90 seconds and off for 90 seconds. When 75% of
stage 1 capacity is required, reheat is on for 135 seconds and off for 45 seconds. When 100% of
stage 1 capacity is required, reheat is on continuously.
Stage 2 uses the same “on” time logic as stage 1 listed above, except stage 1 is always energized.
For example, when 75% of unit capacity is required, stage 1 is energized continuously, and stage
2 is on for 90 seconds and off for 90 seconds. When reheat is de-energized, the cooling minimum
airflow setpoint is activated. Caution: Care should be taken when sizing electric heaters. Discharge
air temperatures should not exceed between 100°F and 110°F, with a temperature between 85°F and
95°F being optimal for space temperature control. If too hot of air is delivered to the space through
ceiling-mounted diffusers, and then leaves the space through ceiling-mounted return-air grilles,
the buoyancy of this hot air will tend to cause some of the air to bypass from the supply-air diffusers
to the return-air grilles, resulting in uneven air distribution and possible comfort complaints. To
prevent stratification, the warm air temperature should not be more than 20°F (6.7°C) above zone
air temperature. (See Diffuser, “D”, section for additional application details).
Single-Duct: SCR Modulation of Electric Heat
SCR is a heat controller that controls a single stage electric heater proportional to an analog signal.
The analog output signal is proportional to the amount of reheat required. Typically with SCR heat,
the heater is turned on and off on a very short cycle time to provide proportional control of heat
output. This allows for closer matching of heating capacity to the heating load, resulting in more
stable temperature control.
When the space temperature drops below the active heating setpoint, the air valve open to the
Airflow Setpoint Reset Minimum Local Heat and the SCR controls the electric heater to maintain
space temperature at the active heating setpoint. SCR control is dependent on the degree that the
space temperature is below the active heating setpoint and the amount of time that the space
temperature has been below the active heating setpoint.
If the discharge air temperature reaches the Discharge Air Temperature Design Setpoint, the air
valve opens further and modulates between Airflow Setpoint Reset Minimum Local Heat and
Airflow Setpoint Reset Maximum Local Heat to maintain space temperature at the active heating
setpoint, while the SCR controls the electric heater to maintain discharge air temperature at the
Discharge Air Temperature Design Setpoint. If the air valve reaches Airflow Setpoint Reset
Maximum Local Heat, the SCR controls the electric heater to maintain space temperature at the
active heating setpoint, while the air valve remains at Airflow Setpoint Reset Maximum Local Heat.
Reheat de-energizes when the space temperature rises more than 0.5°F (0.28°C) above the heating
setpoint. When reheat is de-energized, the cooling Airflow Minimum Setpoint is enforced.
Ventilation Control
Ventilation control enhances the usability of Trane DDC controllers in more select applications that
require measurement of outside air (ventilation). Ventilation control is designed for use with
constant volume single-duct VAV units which modulate the primary damper and associated reheat
to maintain an average constant discharge air temperature. The reheat is modulated to provide
discharge air temperature consistent with AHU supply air temperature (typically 50º–60ºF). This is
critical to ensure that ASHRAE Standard 62.1 ventilation standards are attained, consistently
maintained, and monitored. When connected to a Tracer™ building automation control system,
trend logging, remote alarming, etc. is available. In fact, the Trane Tracer Control System can

VAV-PRC011M-EN 85
DDC Controls
provide unmatched “peace of mind” by calling/paging the appropriate person(s) when specific
alarms occur.
Flow Tracking Control
This enhanced VAV DDC controller feature allows two Trane VV550 controllers to coordinate
modulation simultaneously. This allows a specific CFM offset to be maintained. The CFM offset
provides pressurization control of an occupied space, while maintaining the comfort and energy
savings of a VAV system. A flow tracking system in a given zone consists of a standard Space
Comfort Control VAV (see B) unit plus a single-duct, cooling-only, exhaust VAV unit (see C). As the
supply VAV unit modulates the supply airflow through the air valve to maintain space comfort, the
exhaust box modulates a similar amount to maintain the required CFM differential. This is a simple,
reliable means of pressurization control, which meets the requirements of the majority of zone
pressurization control applications. Typical applications include:
• School and University laboratories
• Industrial laboratories
• Hospital operating rooms
• Hospital patient rooms
• Research and Development facilities
•And many more…
The CFM offset is assured and can be monitored and documented when connected to a Trane
Tracer Building Automation System. Flow Tracking Control is designed to meet most pressurization
control projects. If an application calls for pressure control other than flow tracking, contact your
local Trane Sales Office for technical support.
Figure 3. How does it operate?
B
A
C
Exhaust
Communication link
Supply VAV To other VAVs or
Main Control Panel
How Does It Operate?
T
Primary Air
from Main
AHU
Occupied Space

86 VAV-PRC011M-EN
DDC Controls
Tracer UC210 and Tracer UC400 Programmable BACnet Controllers
The Tracer™ UC210 and Tracer UC400 are programmable controllers available on Varitrane VAV
boxes which provide accurate airflow and room temperature control. The controller can operate
in pressure-independent or pressure-dependent.
The UC210 and UC400 monitor zone temperature, temperature set point, and flow rate. The
controller also accepts a discharge air temperature sensor and accepts a supply air temperature
from the building controller. hen used with a Tracer SC or other BACnet® building controller zone
grouping, system set points and unit diagnostics can be obtained. Also factory commissioning of
parameters is specified by the engineer. (See “Factory-installed vs. Factory-commissioned,” p. 10
for more details).
Specifications
Supply Voltage
24 VAC, 50/60 Hz
Maximum VA Load
No Heat or Fan
• 13VA for cooling box only (includes temperature sensors, flow sensor, occupancy input and air
valve).
• Additional power needed for other devices and power sensors. See IOM VAV-SVX008*-EN for
details.
•Fan: 6VA
•Proportional water valve: 4VA
•2 position water valve: 6.5VA
•Staged electric: 10VA (magnetic contactor) each stage
Binary Inputs
Occupancy. Tracer UC400 also has two additional generic binary inputs.
Binary Outputs
Fan Start, Air valve Open, Air Valve Closed, Heat (Water valve open/closed or staged heat)
The Tracer UC400 also has two generic relays outputs.
Universal Analog Inputs
CO2 and one generic analog input.
Temperature Inputs
Discharge, Zone Temperature, and Zone Set Point.
Tracer UC400 also has two generic temperature inputs.
UC210 BACnet Controller UC400 BACnet Controller

VAV-PRC011M-EN 87
DDC Controls
Operating Environment
32 to 140°F, (0 to 60°C)
5% to 95% RH, Non-condensing
Storage Environment
-40 to 180°F (-40 to 82.2°C),
5% to 95%RH, Non-Condensing
Physical Dimensions
Width: 5.5" (139.7 mm)
Length: 4.5" (69.85 mm)
Height: 2.0" (44.45 mm)
Connections
• UC210: 1/4 tabs and removable screw terminals
• UC400: Removable screw terminals
Communications
BACnet® MS/TP
Heat Staging
Staged electric, SCR electric, proportional or two-position hot water or pulse-width modulation.

88 VAV-PRC011M-EN
DDC Controls
Trane LonMark™ DDC VAV Controller (VV550)
This LonMark™ certified controller uses the Space Comfort Controller (SCC) profile to exchange
information over a LonTalk™ network. Networks with LonMark certified controllers provide the
latest open protocol technology. Being LonMark certified guarantees that owners and end-users
have the capability of adding Trane products to other “open” systems and relieves owners of the
pressure and expense of being locked into a single DDC supplier. The Trane VV550 VAV controller
with VariTrane VAV units can be applied to more than just Trane systems. When a customer buys
a Trane VAV unit with Trane DDC controller, they take advantage of:
• Factory-commissioned quality
• Knowing they have selected the most reliable VAV controllers in the industry
• Trane as a single source to solve any VAV equipment, or system-related issues
• The most educated and thorough factory service technicians in the controls industry
• Over 150 local parts centers throughout North America that can provide what you need, when
you need it.
Don’t let your existing controls supplier lock you out of the most recognized name in VAV system
control in the industry. Specify Trane open-protocol systems.
The features of this controller are explained below.
General Features and Benefits
Assured Accuracy
• Proportional-plus-integral control loop algorithm for determining required airflow needed to
control room temperature. Airflow is limited by active minimum and maximum airflow
setpoints.
• Pressure-independent (PI) operation that automatically adjusts valve position to maintain
required airflow. In certain low-flow situations or in cases where the flow measurement has
failed, the DDC controller will operate in a pressure-dependent (PD) mode of operation.
• When combined with the patented Trane Flow ring and pressure transducer, flow is repeatable
to +/- 5% accuracy across the Pressure Independent (PI) flow range. (See Valve/Controller
Airflow Guidelines section).
• Improved 2-Point Air Balancing is available – Assures optimized flow-sensing accuracy across
the operating range. This provides a more accurate airflow balancing method when compared
to typical single-point flow correction air balancing.
• Analog input resolution of +/- 1/8°F within the comfort range maximizes zone temperature
control yielding excellent comfort control.
Reliable Operation
• Built for life – Trane products are designed to stand the test of time, with a proven design life
that exceeds 20 years.
• Fully factory tested – fully screened and configured at the factory. All features are tested
including fan and reheat stage energization, air valve modulation, and controller inputs and
outputs.
Safe Operation
• All components, including the controller, pressure transducer, transformer, etc. are mounted
in a NEMA 1 sheet metal enclosure and are tested as an assembly to UL1995 standards. The
result is a rugged and safe VAV, controller, and thus, overall unit.
• When in PI-mode, EH is disabled when the sensed flow is below the minimum required.

VAV-PRC011M-EN 89
DDC Controls
• HW coil VAV units in ventilation flow control (VFC) have a Freeze protection algorithm to protect
the water coil and the internal space from water damage. This is accomplished by driving the
water valve to maximum position on alarm conditions.
System-Level Optimization
Trane controllers are designed to integrate into Trane Tracer SC and leverage clear and clean unit-
controller related data for system level control decisions. Integrating a Trane VV550 controller into
a Tracer SC Control System provides the next step in building system control.
Specifically, system-level decisions on how to operate all components can be made. Energy
efficient optimization strategies like Static Pressure Optimization, Ventilation Reset, and CO2
Demand-controlled Ventilation can be employed with the simple press of a button. The end-result
is the most efficient and reliable building control system available.
Simplified Installation
Factory Commissioned Quality – All Trane DDC VAV controllers are factory-commissioned. This
means that the DDC boards are powered and run-tested with your specific sequence parameters.
They are connected to a communication link to make sure that information and diagnostic data
function properly. Before any VariTrane VAV unit ships they must pass a rigorous quality control
procedure. You can be assured that a Trane VAV unit with Trane DDC VAV controls will work right
out of the crate.
Zone sensor air balance – When applied to a Trane zone sensor with thumb-wheel and on/cancel
buttons, a balancing contractor can drive the primary air valve to maximum or minimum airflow
from the sensor to determine the point of calibration to be used (maximum will result in optimum
performance). The flow reading can then be calibrated from the sensor, without the use of
additional service tools. (Non-LCD versions)
Tenant-Finish Heat Mode – In some office projects, the building is being constructed as tenants are
being identified. Tenant-finish heat mode is designed for applications when a given floor has not
been occupied. The main AHU system is used for heat and because the internal furnishings are not
complete, the sensors have not been installed. In this case, the primary valve drives open using
the heat of the main AHU to keep plumbing lines from freezing. When available, the operation of
the VAV unit fan (series or parallel) remains unaffected.
Controller Flexibility
• 24 VAC binary input that can be configured as a generic input or as occupancy input. When the
DDC controller is operating with Tracer SC, the status of the input is provided to Tracer for its
action. In stand-alone operation and when configured for an occupancy input, the input will
control occupancy status of the DDC controller.
• Auxiliary temperature analog input configured for an auxiliary temperature sensor. When
sensor is mounted in the supply air duct, the value of the input is used as status-only by Tracer
SC if Tracer SC is providing a supply air temperature to the DDC controller. Otherwise, the input
will be used for determining heating/cooling control action of the VAV unit. When the auxiliary
temperature sensor is located in the discharge of the unit, and attached to a Trane SC BAS,
additional test sequencing and reporting is available to maximize VAV system capabilities and
simplify system commissioning.
• Dual-duct support with two DDC controllers. One DDC controller controls the cooling air valve
and the other controller controls the heating air valve. With constant-volume sequences, the
discharge air volume is held constant by controlling discharge air volume with the heating
Controller.
• LonMark certified performance ensures that a Trane VAV with controller will provide state-of-
the-art, consistent open communication protocol for integration with the industry’s latest (Non-
Trane) building automation control systems, including Johnson Control, Andover, Siemens,
Honeywell, etc.

90 VAV-PRC011M-EN
DDC Controls
•CO
2 demand controlled ventilation enables a HVAC system to adjust ventilation flow based on
the current CO2 concentration in the zone. Trane demand controlled ventilation strategies are
pre-defined for simplified application and can be easily customized to meet the needs of a
specific system.
Trane DDC VAV Controller Logic with VV550 Controls
Control Logic
Direct Digital Control (DDC) controllers are today’s industry standard. DDC controllers share
system-level data to optimize system performance (including changing ventilation requirements,
system static pressures, supply air temperatures, etc.). Variables available via a simple twisted-
shielded wire pair include occupied/unoccupied status, minimum and maximum airflow setpoints,
zone temperature and temperature setpoints, air valve position, airflow cfm, fan status (on or off),
fan operation mode (parallel or series), reheat status (on or off), VAV unit type, air valve size,
temperature correction offsets, flow correction values, ventilation fraction, etc.
With the advent of LonMark open protocol, the most reliable VAV controller is now available for
ANY system. Gone are the days of being locked into a single supplier. Trane DDC controllers
provide Trane-designed solid-state electronics intended specifically for VAV applications including:
4. Space Temperature Control
5. Ventilation Flow Control (100% outside air applications)
6. Flow Tracking Space Pressurization Control (New feature)
Note: Flow sensor DP (in. wg) is measured at the flow ring to aid in system balancing and commissioning. See “Valve/Controller
Airflow Guidelines” in each section for unit performance.
Space Temperature Control
Space temperature control applications are where Trane emerged as an industry leader in quality
and reliability. This did not occur overnight and has continued to improve as our controller and
control logic has improved over time. STC employs controller logic designed to modulate the
supply airstream and associated reheat (either local or remote) to exactly match the load
requirements of the space.
Additionally, minimum and maximum airflow and specific controller sequence requirements are
pre-programmed to ensure that appropriate ventilation standards are consistently maintained.
When connected to a Trane Tracer SC control system, trend logging, remote alarming, etc. are
available to fully utilize the power and capabilities of your systems.
Figure 4. Flow sensor single vs. airflow delivery
0.01
0.1
1
5
10 100 1,000 10,000
Cfm
Flow Sensor DP (In. wg)
4" 12"
10"
8"6"
5" 14" 16"

VAV-PRC011M-EN 91
DDC Controls
General Operation-Cooling
In cooling control action, the DDC controller matches primary airflow to cooling load. The DDC
controller will automatically change over to heating control action if the supply air temperature is
above a configured/editable setpoint. When the supply air temperature is less than 10 degrees
below this setpoint, the controller will automatically switch to cooling control action. The DDC
controller first chooses the Tracer SC -provided supply air temperature value to use for auto
changeover. If this is not available, it uses the temperature provided by the optional auxiliary
temperature sensor (must be installed for inlet temperature monitoring). If this is also not available,
it uses the heating/cooling mode assigned by Tracer SC or the DDC controller’s service tool.
General Operation-Heating and Reheat
In heating control action, the DDC controller matches primary airflow to heating load. The DDC
controller will automatically change over to heating control action if the supply air temperature is
above a configured/editable setpoint. When the supply air temperature is less than 10 degrees
below this setpoint, the controller will automatically switch to cooling control action. The DDC
controller first chooses the Tracer SC -provided supply air temperature value to use for auto
changeover. If this is not available, it uses the temperature provided by the optional auxiliary
temperature sensor (must be installed for inlet temperature monitoring). If this is also not available,
it uses the heating/cooling mode assigned by Tracer SC or the DDC controller’s service tool.
When heat is added to the primary air, the air is considered reheated. Reheat can be either local
(integral to the VAV unit in the form of an electric coil or hot water coil) or remote (typically existing
wall fin radiation, convector, etc.) or any combination of local and remote. The operating
characteristics of the four basic types of VariTrane DDC terminal reheat are discussed.
Single-Duct: On/Off Hot Water Reheat
Three stages of on/off hot water reheat are available. Two-position water valves complete the HW
reheat system and are either fully opened or fully closed. The heating minimum airflow setpoint
is enforced during reheat.
Stage 1 energizes when the space temperature is at or below the heating setpoint. When the zone
temperature rises above the active heating setpoint by 0.5°F (0.28°C), stage 1 is de-energized. Stage
2 energizes when the space temperature is 1°F (0.56°C) or more below the active heating setpoint,
and is de-energized when the space temperature is 0.5°F (0.28°C) below the active heating setpoint.
Stage 3 energizes when the zone temperature is 2°F (1.11°C) or more below the active heating
setpoint, and de-energizes when the space temperature is 1.5°F (0.83°C) below the active heating
setpoint. When reheat is de-energized, the cooling minimum airflow setpoint is enforced.
Single-Duct: Proportional Hot Water Reheat
Proportional hot water reheat uses 3-wire, floating-point-actuator technology.
The heating minimum airflow setpoint is enforced during reheat. The water valve opens as space
temperature drops below the heating setpoint. A separate reheat proportional-plus-integral
control loop from that controlling airflow into the room is enforced.
Water valve position is dependent on the degree that the space temperature is below the active
heating setpoint and the time that the space temperature has been below the active heating
setpoint. If not already closed, the water valve fully closes when the zone temperature rises above
the active heating setpoint by 0.5 °F (0.28 °C).
An additional on/off remote heat output is available and energized when the proportional value is
driven 10% open and de-energized when the proportional valve reaches 50% open.
When reheat is de-energized, the cooling minimum airflow setpoint is enforced. Again, these
reheat devices can be either local or remote.

92 VAV-PRC011M-EN
DDC Controls
Single-Duct: On/Off Electric Reheat
One, two, or three stages of staged electric reheat are available. The heating minimum airflow
setpoint is enforced during reheat.
Stage 1 is energized when the space temperature falls below the active heating setpoint and
minimum airflow requirements are met. When the zone temperature rises above the active heating
setpoint by 0.5°F (0.28°C), stage 1 is de-energized. Stage 2 energizes when the space temperature
is 1°F (0.56°C) or more below the active heating setpoint, and is de-energized when the space
temperature is 0.5°F (0.28°C) below the active heating setpoint. Stage 3 energizes when the zone
temperature is 2°F (1.11°C) or more below the active heating setpoint, and de-energizes when the
space temperature is 1.5°F (0.83°C) below the active heating setpoint. When reheat is de-energized,
the cooling minimum airflow setpoint is enforced.
Single-Duct: Pulse-Width Modulation of Electric Heat
One to three stages of pulse-width modulation of electric heat are available. Energizing for a
portion of a three-minute time period modulates the electric heater. This allows for closer matching
of heating capacity to the heating load, resulting in more stable temperature control. The heating
minimum airflow setpoint is enforced during reheat.
The amount of reheat supplied is dependent on both the degree that the space temperature is
below the active heating setpoint and the time that the space temperature has been below the
active heating setpoint. If not already off, reheat de-energizes when the zone temperature rises
more than 0.5°F (0.28°C) above the heating setpoint.
The Stage 1 “on” time is proportional to the amount of reheat required. For example, when 50%
of stage 1 capacity is required, reheat is on for 90 seconds and off for 90 seconds. When 75% of
stage 1 capacity is required, reheat is on for 135 seconds and off for 45 seconds. When 100% of
stage 1 capacity is required, reheat is on continuously.
Stage 2 uses the same “on” time logic as stage 1 listed above, except stage 1 is always energized.
For example, when 75% of unit capacity is required, stage 1 is energized continuously, and stage
2 is on for 90 seconds and off for 90 seconds. When reheat is de-energized, the cooling minimum
airflow setpoint is activated. Caution: Care should be taken when sizing electric heaters. Discharge
air temperatures should not exceed between 100°F and 110°F, with a temperature between 85°F and
95°F being optimal for space temperature control. If too hot of air is delivered to the space through
ceiling-mounted diffusers, and then leaves the space through ceiling-mounted return-air grilles,
the buoyancy of this hot air will tend to cause some of the air to bypass from the supply-air diffusers
to the return-air grilles, resulting in uneven air distribution and possible comfort complaints. To
prevent stratification, the warm air temperature should not be more than 20°F (6.7°C) above zone
air temperature. (See Diffuser, “D”, section for additional application details).
Ventilation Control
Ventilation control enhances the usability of Trane DDC controllers in more select applications that
require measurement of outside air (ventilation). Ventilation control is designed for use with
constant volume single-duct VAV units which modulate the primary damper and associated reheat
to maintain an average constant discharge air temperature. The reheat is modulated to provide
discharge air temperature consistent with AHU supply air temperature (typically 50º–60ºF). This is
critical to ensure that ASHRAE Standard 62.1 Ventilation standards are attained, consistently
maintained, and monitored. When connected to a Trane Building Automation System control
system, trend logging, remote alarming, etc. is available. In fact, the Trane Tracer Control System
can provide unmatched “peace of mind” by calling/paging the appropriate person(s) when specific
alarms occur.
Flow Tracking Control
This enhanced VAV DDC controller feature allows two Trane VV550 controllers to coordinate
modulation simultaneously. This allows a specific CFM offset to be maintained. The CFM offset
provides pressurization control of an occupied space, while maintaining the comfort and energy

VAV-PRC011M-EN 93
DDC Controls
savings of a VAV system. A flow tracking system in a given zone consists of a standard Space
Comfort Control VAV (see B) unit plus a single-duct, cooling-only, exhaust VAV unit (see C). As the
supply VAV unit modulates the supply airflow through the air valve to maintain space comfort, the
exhaust box modulates a similar amount to maintain the required CFM differential. This is a simple,
reliable means of pressurization control, which meets the requirements of the majority of zone
pressurization control applications. Typical applications include:
• School and University laboratories
• Industrial laboratories
• Hospital operating rooms
• Hospital patient rooms
• Research and Development facilities
•And many more…
The CFM offset is assured and can be monitored and documented when connected to a Trane
Tracer Building Automation System. Flow Tracking Control is designed to meet most pressurization
control projects. If an application calls for pressure control other than flow tracking, contact your
local Trane Sales Office for technical support.
LONMARK Direct Digital Controller—Unit Control Module (VV550)
Figure 5. How does it operate?
B
A
C
Exhaust
Communication link
Supply VAV To other VAVs or
Main Control Panel
How Does It Operate?
T
Primary Air
from Main
AHU
Occupied Space
The Trane LONMARK® direct digital controller Unit Control Module (DDC-
UCM) is a microprocessor-based terminal unit with non-volatile memory
which provides accurate airflow and room temperature control of Trane and
non-Trane VAV air terminal units. provides a simple open protocol to allow
integration of Trane VAV units and controls into other existing control
systems. The UCM can operate in pressure-independent or pressure-
dependent mode and uses a proportional plus integral control algorithm.

94 VAV-PRC011M-EN
DDC Controls
The controller monitors zone temperature setpoints, zone temperature and its rate of change and
valve airflow (via flow ring differential pressure). The controller also accepts an auxiliary duct
temperature sensor input or a supply air temperature value from Tracer™ SC. Staged electric heat,
pulse width modulated electric heat, proportional hot water heat or on/off hot water heat control
are provided when required. The control board operates using 24-VAC power. The Trane LONMARK
DDC-UCM is also a member of the Trane Integrated Comfort™ systems (ICS) family of products.
When used with a Trane Tracer SC or other Trane controllers, zone grouping and unit diagnostic
information can be obtained. Also part of ICS is the factory-commissioning of parameters specified
by the engineer (see “Factory-installed vs. Factory-commissioned,” p. 10 for more details).
Note: Trane LONMARK® DDC-UCM controllers can also take advantage of factory-commissioned
quality on non-Trane systems through LONMARK open protocol.
Specifications
Supply Voltage
24 VAC, 50/60 Hz
Maximum VA Load
No Heat or Fan
8 VA (Board, Transducer, Zone Sensor, and Actuator)
Note: If using field-installed heat, 24 VAC transformer should be sized for additional load.
Output Ratings
Actuator Output:24 VAC at 12 VA
1st Stage Reheat:24 VAC at 12 VA
2nd Stage Reheat:24 VAC at 12 VA
3rd Stage Reheat:24 VAC at 12 VA
Binary Input
24 VAC, occupancy or generic.
Auxiliary Input
Can be configured for discharge or primary air temperature sensor.
Operating Environment
32 to 140°F, (0 to 60°C)
5% to 95% RH, Non-condensing
Storage Environment
-40 to 180°F (-40 to 82.2°C),
5% to 95%RH, Non-Condensing
Physical Dimensions
Width: 5.5" (139.7 mm)
Length: 4.5" (69.85 mm)
Height: 2.0" (44.45 mm)
Connections
1/4" (6.35 mm) Stab Connections
Communications
LONMARK – Space Comfort Control (SCC) profile with FTT-10 transceiver.
22 awg. unshielded level 4 communication wire.
Heat Staging
Staged electric, proportional or two-position hot water or pulse-width modulation.

VAV-PRC011M-EN 95
DDC Controls
Table 48, p. 95 provides an input listing for Tracer VV550/551 VAV controllers, and Table 49, p. 95
provides an output listing for Tracer VV550/551 VAV controllers. Table 50, p. 96 provides the
configuration properties for the controller. The content of the lists conforms to both the LonMark
SCC functional profile 8500 and the LonMark node object.
Table 48. Input listing
Input description Input SNVT type
Space temperature nviSpaceTemp SNVT_temp_p
Setpoint nviSetpoint SNVT_temp_p
Occupancy, schedule nviOccSchedule SNVT_tod_event
Occupancy, manual command nviOccManCmd SNVT_occupancy
Occupancy sensor nviOccSensor SNVT_occupancy
Application mode nviApplicMode SNVT_hvac_mode
Heat/cool mode input nviHeatCool SNVT_hvac_mode
Fan speed command nviFanSpeedCmd SNVT_switch
Auxiliary heat enable nviAuxHeatEnable SNVT_switch
Valve override nviValveOverride SNVT_hvac_overid
Flow override nviFlowOverride SNVT_hvac_overid
Emergency override nviEmergOverride SNVT_hvac_emerg
Source temperature nviSourceTemp SNVT_temp_p
Space CO2 nviSpaceCO2 SNVT_ppm
Clear alarms/diagnostics nviRequest(a) SNVT_obj_request
Air flow setpoint input nviAirFlowSetpt SNVT_flow
(a) Part of the node object
Table 49. Output listing
Output description Output SNVT type
Space temperature nvoSpaceTemp SNVT_temp_p
Unit status, mode nvoUnitStatus SNVT_hvac_status
Effective setpoint nvoEffectSetpt SNVT_temp_p
Effective occupancy nvoEffectOccup SNVT_occupancy
Heat cool mode nvoHeatCool SNVT_hvac_mode
Setpoint nvoSetpoint SNVT_temp_p
Discharge air temperature nvoDischAirTemp SNVT_temp_p
Space CO2 nvoSpaceCO2 SNVT_ppm
Effective air flow setpoint nvoEffectFlowSP SNVT_flow
Air flow nvoAirFlow SNVT_flow
File table address nvoFileDirectory(a) SNVT_address
Object status nvoStatus(a) SNVT_obj_status
Alarm message nvoAlarmMessage SNVT_str_asc
(a) Part of the node object.

96 VAV-PRC011M-EN
DDC Controls
Table 50. Configuration properties
Configuration property
description Configuration property SNVT type SCPT reference
Send heartbeat nciSndHrtBt SNVT_time_sec SCPTmaxSendTime (49)
Occ temperature setpoints nciSetpoints SNVT_temp_setpt SCPTsetPnts (60)
Minimum send time nciMinOutTm SNVT_time_sec SCPTminSendTime (52)
Receive heartbeat nciRecHrtBt SNVT_time_sec SCPTmaxRcvTime (48)
Location label nciLocation SNVT_str_asc SCPTlocation (17)
Local bypass time nciBypassTime SNVT_time_min SCPTbypassTime (34)
Manual override time nciManualTime SNVT_time_min SCPTmanOverTime (35)
Space CO2 limit nciSpaceCO2Lim SNVT_ppm SCPTlimitCO2 (42)
Nominal air flow nciNomFlow SNVT_flow SCPTnomAirFlow (57)
Air flow measurement gain nciFlowGain SNVT_multiplier SCPTsensConstVAV (67)
Minimum air flow nciMinFlow SNVT_flow SCPTminFlow (54)
Maximum air flow nciMaxFlow SNVT_flow SCPTmaxFlow (51)
Minimum air flow for heat nciMinFlowHeat SNVT_flow SCPTminFlowHeat (55)
Maximum air flow for heat nciMaxFlowHeat SNVT_flow SCPTmaxFlowHeat (37)
Minimum flow for standby nciMinFlowStdby SNVT_flow SCPTminFlowStby (56)
Firmware major version nciDevMajVer(a) n/a SCPTdevMajVer (165)
Firmware minor version nciDevMinVer(a) n/a SCPTdevMinVer (166)
Flow offset for tracking applications nciFlowOffset SNVT_flow_f SCPToffsetFlow (265)
Local heating minimum air flow nciMinFlowUnitHt SNVT_flow SCPTminFlowUnitHeat (270)
Minimum flow for standby heat nciMnFlowStbyHt SVNT_flow SCPTminFlowStbyHeat(263)
(a) Part of the node object.

VAV-PRC011M-EN 97
DDC Controls
Direct Digital Controller—Unit Control Module (UCM4)
The controller also accepts an auxiliary duct temperature sensor input or a supply air temperature
value from Tracer™ SC. Staged electric heat, pulse width modulated electric heat, proportional hot
water heat or on/off hot water heat control are provided when required. The control board operates
using 24-VAC power. The Trane DDC-UCM is a member of the Trane Integrated Comfort™ systems
(ICS) family of products. When used with a Trane Tracer SC building management controller or
other Trane controllers, zone grouping and unit diagnostic information can be obtained. Also part
of ICS is the factory-commissioning of parameters specified by the engineer (see “Factory-installed
vs. Factory-commissioned,” p. 10 for more details).
Specifications
Supply Voltage
24 VAC, 50/60 Hz
Maximum VA Load
No Heat or Fan
12 VA (Board, Transducer, Zone Sensor, and Actuator)
Note: If using field-installed heat, 24 VAC transformer should be sized for additional load.
Output Ratings
Actuator Output: 24 VAC at 12 VA
1st Stage Reheat: 24 VAC at 12 VA
2nd Stage Reheat: 24 VAC at 12 VA
3rd Stage Reheat: 24 VAC at 12 VA
Binary Input
24 VAC
Auxiliary Input
Can be configured for an optional 2–10 VDC CO2 sensor, or auxiliary temperature sensor.
Operating Environment:
32 to 140°F, (0 to 60°C)
5% to 95% RH, Non-condensing
Storage Environment
-40 to 180°F (-40 to 82.2°C),
5% to 95%RH, Non-Condensing
Physical Dimensions
Width: 5.5" (139.7 mm)
Length: 2.8" (69.85 mm)
Height: 1.8" (44.45 mm)
The Trane direct digital controller Unit Control
Module (DDC-UCM) is a microprocessor-based
terminal unit with non-volatile memory which
provides accurate airflow and room temperature
control of Trane VAV air terminal units. The UCM can
operate in a pressure-independent or a pressure-
dependent mode and uses a proportional plus
integral control algorithm. The controller monitors
zone temperature setpoints, zone temperature and its
rate of change and valve airflow (via flow ring
differential pressure).

98 VAV-PRC011M-EN
DDC Controls
Connections
1/4" (6.35 mm) Stab Connections
Communications
RS-485; Stranded wire, twisted pair, shielded, copper conductor only, 18–20 awg
Fan Control
• Series fan: On unless unoccupied and min. flow has been released.
• Parallel fan: On when zone temperature is less than heating setpoint plus fan offset. Off when
zone temperature is more than heating setpoint plus fan offset plus 0.5°F (0.28°C).
Heat Staging
Staged electric or hot water proportional or pulse-width modulation
Trane DDCVAV Controller Logic - UCM 4
DDC controllers are today’s industry standard. DDC controllers provide system-level data used to
optimize system performance. Variables such as occupied/unoccupied status, minimum and
maximum airflow setpoints, temperature and temperature setpoints, valve position, fan status (on
or off, and mode of operation: series or parallel), reheat status (on or off), box type and air valve
size, temperature correction offsets, flow correction values, ventilation fraction, etc. are available
on a simple twisted-shielded wire pair.
Trane DDC controllers provide Trane-designed, solid-state electronics intended specifically for VAV
temperature control in space comfort applications. DDC control capabilities include:
• Proportional plus integral control loop algorithm for determining required airflow needed to
control room temperature. Airflow is limited by active minimum and maximum airflow
setpoints.
• Pressure-independent (PI) operation, which automatically adjusts valve position to maintain
required airflow. In certain low-flow situations or in cases where the flow measurement has
failed, the DDC controller will operate in a pressure-dependent (PD) mode of operation.
• Cooling and heating control action of air valve. In cooling control action, the DDC controller
matches cooling airflow to cooling load. In heating control action, the DDC controller matches
the heating airflow to control heating load. The DDC controller will automatically change over
to cooling control action if the supply air temperature is below the room temperature and will
automatically change over to heating control action if the supply air temperature is 10°F or more
above the room temperature. If the supply air temperature is between the room temperature
and the room temperature plus 10°F, then the DDC controller will provide the active minimum
airflow. The DDC controller first chooses the Tracer™ SC -supplied supply air temperature value
to use for auto changeover. If this is not available, it uses the temperature provided by the
optional auxiliary temperature sensor. If this is also not available, it uses the heating/cooling
mode assigned by Tracer SC or the DDC controller’s service tool (Everyware™or Rover™ V4).
• Multiple reheat control options including staged electric, staged hot-water (normally on or
normally off), proportional hot-water, slow pulsed width modulation, electric, and SCR electric.
Modulating reheat options utilize a separate reheat proportional-plus-integral control loop
from that controlling airflow into the room. Staged reheat options utilize a control algorithm
based on heating setpoint and room temperature.
• 24 VAC binary input that can be configured as a generic input or as occupancy input. When the
DDC controller is operation with Tracer SC, the status of the input is provided to Tracer SC for
its action. In stand-alone operation and when configured for an occupancy input, the input will
control occupancy status of the DDC controller.
• Auxiliary temperature analog input that can be configured for an auxiliary temperature sensor
or a 2-to-10 VDC CO2 sensor. When sensor is mounted in the supply air duct and configured for
temperature, the value of the input is used as status-only by Tracer SC if Tracer SC is providing
a supply air temperature to the DDC controller. Otherwise, the input will be used for

VAV-PRC011M-EN 99
DDC Controls
determining control action of the DDC controller. When configured for a CO2 sensor, the value
of the input is used as a status-only input by Tracer SC.
• Dual-duct support with two DDC controllers. One DDC controller controls the cooling air valve
and the other controller controls the heating air valve. With constant-volume sequences, the
discharge air volume is held constant by controlling discharge air volume with the heating
UCM.
Note: Flow sensor DP (in. wg) is measured at the flow ring to aid in system balancing and commissioning. See “Valve/Controller
Airflow Guidelines” in each section for unit performance.
DDC Remote Heat Control Options
When heat is added to the primary air at the VAV unit before it enters the zone, the air is said to
be reheated. The operating characteristics of the four basic types of VariTrane DDC terminal reheat
are discussed.
Single-Duct: On/Off Hot Water Reheat
Three stages of on/off hot water reheat are available. The water valves used are 2-position and are
either fully-opened or fully-closed. The heating minimum airflow setpoint is enforced during
reheat.
Stage 1 energizes when the space temperature is at or below the heating setpoint. When the zone
temperature rises above the active heating setpoint by 0.5°F (0.28°C), stage 1 is de-energized. Stage
2 energizes when the space temperature is 1°F (0.56°C) or more below the active heating setpoint,
and is de-energized when the space temperature is 0.5°F (0.28°C) below the active heating setpoint.
Stage 3 energizes when the zone temperature is 2°F (1.11°C) or more below the active heating
setpoint, and de-energizes when the space temperature is 1.5°F (0.83°C) below the active heating
setpoint. When reheat is de-energized, the cooling minimum airflow setpoint is enforced.
Single-Duct: Proportional Hot Water Reheat
Proportional hot water reheat uses 3-wire, floating-point-actuator technology.
When the space temperature drops below the active heating setpoint, the air valve open to the
Airflow Setpoint Reset Minimum Local Heat and the reheat valve modulates to maintain space
temperature at the active heating setpoint. Control of the water valve uses a separate proportional
plus integral control loop, and its position is dependent on the degree that the space temperature
Figure 6. Flow sensor signal vs. airflow delivery
0.01
0.1
1
5
10 100 1,000 10,000
Cfm
Flow Sensor DP (In. wg)
4" 12"
10"
8"6"
5" 14" 16"

100 VAV-PRC011M-EN
DDC Controls
is below the active heating setpoint and the amount of time that the space temperature has been
below the active heating setpoint.
If the discharge air temperature reaches the Discharge Air Temperature Design Setpoint, the air
valve opens further and modulates between Airflow Setpoint Reset Minimum Local Heat and
Airflow Setpoint Reset Maximum Local Heat to maintain space temperature at the active heating
setpoint, while the water valve modulates to maintain discharge air temperature at the Discharge
Air Temperature Design Setpoint. If the air valve reaches Airflow Setpoint Reset Maximum Local
Heat, the water valve opens further and modulates to maintain space temperature at the active
heating setpoint, while the air valve remains at Airflow Setpoint Reset Maximum Local Heat.
An additional on/off remote heat output is available and energized when the water valve is driven
100% open and de-energized when the water valve reaches 50% open.
When reheat is de-energized, the cooling Airflow Minimum Setpoint is enforced.
Single-Duct: On/Off Electric Reheat
Three stages of staged electric reheat are available. The heating minimum airflow setpoint is
enforced during reheat.
Stage 1 is energized when the space temperature falls below the active heating setpoint and
minimum airflow requirements are met. When the zone temperature rises above the active heating
setpoint by 0.5°F (0.28°C), stage 1 is de-energized. Stage 2 energizes when the space temperature
is 1°F (0.56°C) or more below the active heating setpoint, and is de-energized when the space
temperature is 0.5°F (0.28°C) below the active heating setpoint. Stage 3 energizes when the zone
temperature is 2°F (1.11°C) or more below the active heating setpoint, and de-energizes when the
space temperature is 1.5°F (0.83°C) below the active heating setpoint. When reheat is de-energized,
the cooling minimum airflow setpoint is enforced.
Single-Duct: Pulse-Width Modulation of Electric Heat
Electric heat is modulated by energizing for a portion of a three-minute time period. One of two
stages can be used. This allows for closer matching of heating capacity to the heating load,
resulting in more stable temperature control. The heating minimum airflow setpoint is enforced
during reheat.
The amount of reheat supplied is dependent on both the degree that space temperature is below
the active heating setpoint and the time that the space temperature has been below the active
heating setpoint. If not already off, reheat de-energizes when the zone temperature rises more than
0.5°F (0.28°C) above the heating setpoint.
The Stage 1 “on” time is proportional to the amount of reheat required. For example, when 50%
of stage 1 capacity is required, reheat is on for 90 seconds and off for 90 seconds. When 75% of
stage 1 capacity is required, reheat is on for 135 seconds and off for 45 seconds. When 100% of
stage 1 capacity is required, reheat is on continuously.
Stage 2 uses the same “on” time logic as stage 1 listed above, except stage 1 is always energized.
For example, when 75% of unit capacity is required, stage 1 is energized continuously, and stage
2 is on for 90 seconds and off for 90 seconds. When reheat is de-energized, the cooling minimum
airflow setpoint is enforced.

VAV-PRC011M-EN 101
DDC Controls
Air-Fi™ Wireless System
Quantity of WCIs per Network
Each Trane wireless network can have a total of 31 WCIs (30 member WCIs plus 1 coordinator WCI).
Each network requires one WCI to function as network coordinator.
Quantity of Networks per Tracer SC
A Tracer SC can support up to 8 wireless networks.
Automatic Network Formation
When a WCI is connected to a Tracer SC, it is auto-assigned as the coordinator. To enable the
coordinator, Tracer SC must be configured for wireless communication. The coordinator WCI
opens the network to allow all WCIs having matching addresses to automatically join the network.
If no Tracer SC is present, a centrally located WCI must be designated to act as the coordinator. You
can manually set the coordinator WCI so all WCIs having matching addresses automatically join
the network.
Air-Fi™ Wireless Communication Sensors (WCS)
Two wireless communication sensors are available:
• Digital display model (WCS-SD)
• Base model with no exposed display or user interface (WCS-SB)
Optional: in most applications, one WCS will be used per WCI acting as a router. However, up to
6 WCS’s can be associated to a single BACnet DDC VAV unit.
Wireless Zone Sensors and Wired Zone Sensors
Systems using Air-Fi™ can be wed with WCS or wired sensors. Our previous line of wireless zone
sensors are not compatible with Air-Fi™ WCIs.
Systems using Wireless Comm can also use wired zone sensors.
Wireless Communications Interface (WCI)
The Trane® Wireless Communication Interface (WCI) enables
wireless communication between system controls, unit
controls, and wireless sensors for the new generation of Trane
control products. The WCI works with BACnet DDC VAV unit
controllers and replaces the need for communication wire in
all system applications.
Note: See BAS-SVX40*-EN, Installation, Operation and
Maintenance, Air-Fi Wireless Comm for more
information.

102 VAV-PRC011M-EN
DDC Controls
Dimensions
Specifications
Operating Temperature
-40 to 158ºF (-40 to 70ºC)
Storage temperature
-40 to 185ºF (-40 to 85°C)
Storage and operating humidity range
5% to 95% relative humidity (RH), non-condensing
Voltage
24 Vac/Vdc nominal ± 10%. If using 24 Vac, polarity must be maintained.
Receiver power consumption
<2.5 VA
Housing material
Polycarbonate/ABS (suitable for plenum mounting), UV protected, UL 94: 5 VA flammability rating
Mounting
3.2 in (83 mm) with 2 supplied mounting screws
Range
Open range: 2,500 ft (762 m) with packet error rate of 2%
Indoor: Typical range is 200 ft (61 mm); actual range is dependent on the environment. See BAS-
SVX55 for more detail.
Note: Range values are estimated transmission distances for satisfactory operation. Actual
distance is job specific and must be determined during site evaluation. Placement of WCI
is critical to proper system operation. In most general office space installations, distance is
not the limiting factor for proper signal quality. Signal quality is effected by walls, barriers,
and general clutter. For more information is available at http://www.trane.com.
Output power
North America: 100 mW
2.896 in (73.55 mm)
0.118 in
(3.00 mm)
4.677 in (118.8 mm)
3.385 in (86.0 mm)
2.480 in (63.0 mm)
R0.71 in
(R1.80 mm) TYP
0.236 in
(6.0 mm)
1.344 in (34.14 mm)
1.419 in (36.03 mm)
0.650 in (16.50 mm)
2.62 in (66.55 mm)

VAV-PRC011M-EN 103
DDC Controls
Radio frequency
2.4 GHz (IEEE Std 802.15.4-2003 compliant) (2405–2480 MHz, 5 MHz spacing)
Radio channels
16
Address range
Group 0–8, Network 1–9
Mounting
Fits a standard 2 in. by 4 in. junction box (vertical mount only). Mounting holes are spaced 3.2 in.
(83 mm) apart on vertical center line. Includes mounting screws for junction box or wall anchors
for sheet-rock walls. Overall dimensions: 2.9 in. (74 mm) by 4.7 in. (119 mm)
Wireless protocol
ZigBee PRO—ZigBee Building Automation Profile, ANSI/ASHRAE Standard 135-2008 Addendum
q (BACnet™/ZigBee)
Wireless Receiver/Wireless Zone Sensor
Specifications
Power Requirements
Receiver: 24 V nominal AC/DC ± 10% < 1VA
Zone Sensor: (2) AA lithium batteries
Sensor Operating Environments
32 to 122°F, (0 to 50°C)
5 to 95%RH, Non-condensing
Receiver Operating Environments
-40 to 158°F, (-40 to 70°C)
5 to 95%RH, Non-condensing
Storage Environment—Sensor/Receiver
-40 to 185°F, (-40 to 85°C)
5 to 95%RH, Non-condensing
Mounting
Receiver: Suitable for mounting above or below ceiling grid. Requires 24 V power. Factory installed
receiver comes mounted to the VAV unit with power provided by associated unit controller
transformer. Field installed option provided with associated wire harness for similar power and
communication connection.
Sensor: Mounts to a 2x4 handi-box or directly to the wall by attaching the backplate and then
snapping the sensor body into place.
The wireless zone sensor system eliminates the
wiring problems associated with VAV temperature
sensors. It provides the flexibility to move zone
sensors after the occupants have revised the space
floor plan layout. The zone sensor houses the space
temperature sensor, local setpoint adjustment thumb
wheel, OCCUPIED/UNOCCUPIED button, battery life,
signal strength indicators, and spread spectrum
transmitter. Works with all Trane VAV DDC unit
controllers.

104 VAV-PRC011M-EN
DDC Controls
Dimensions
DDC Zone Sensor
Specifications
Thermistor Resistance Rating
10,000 Ohms at 77°F (25°C)
Setpoint Resistance Rating
Setpoint potentiometer is calibrated to produce 500 Ohms at a setting of 70°F (21.11°C)
Electrical Connections
Terminal Block – Pressure Connections
Communications Jack – WE-616 (available for field installation)
Physical Dimensions
Width: 2.75" (69.85 mm)
Height: 4.5" (114.3 mm)
Depth: 1.0" (25.4 mm)
Receiver/Translator
Enclosure: Plastic
Height: 4.75" (120.6 mm)
Width: 2.90" (73.5 mm)
Depth: 1.08" (27.5 mm)
Sensor/Transmitter
Enclosure: Plastic
Height: 4.78" (121.4 mm)
Width: 2.90" (73.5 mm)
Depth: 1.08" (27.5 mm)
The DDC zone sensor is used in conjunction with the
Trane direct digital controller to sense the space
temperature and to allow for user adjustment of the
zone setpoint. Models with external zone setpoint
adjustments and occupied mode override
pushbuttons are available.

VAV-PRC011M-EN 105
DDC Controls
CO2 Wall Sensor and Duct CO2 Sensor
The wall- and duct-mounted carbon dioxide (CO2) sensors are designed for use with Trane DDC/
UCM control systems. Installation is made simple by attachment directly to the DDC/ UCM
controller. This allows the existing communication link to be used to send CO2 data to the higher-
level Trane control system.
Wall-mounted sensors can monitor individual zones, and the duct-mounted sensor is ideal for
monitoring return air of a given unit. Long-term stability and reliability are assured with advanced
based Non-Dispersive Infrared (NDIR) technology.
When connected to a building automation system with the appropriate ventilation equipment, the
Trane CO2 sensors measure and record carbon dioxide in parts-per-million (ppm) in occupied
building spaces. These carbon dioxide measurements are typically used to identify under-
ventilated building zones or to reduce ventilation airflow during periods of reduced occupancy to
save energy (i.e. demand-controlled ventilation).
Specifications
Measuring Range
0–2000 parts per million (ppm)
Accuracy at 77°F (25°C)
< ± (40 ppm CO2 + 3% of reading) (Wall only)
< ± (30 ppm CO2 + 3% of reading)
Recommended calibration interval
5 years
Response Time
1 minute (0–63%)
Operating Temperature
59 to 95°F (15 to 35°C) (Wall only)
23 to 113°F (-5 to 45°C)
Storage Temperature
-4 to 158°F (-20 to 70°C)
Humidity Range
0–85% relative humidity (RH)
Output Signal (jumper selectable)
4-20 mA, 0–20 mA,
0–10 VDC
Figure 7. CO2 wall sensor (L) and duct CO2 sensor (R)

106 VAV-PRC011M-EN
DDC Controls
Resolution of Analog Outputs
10 ppm CO2
Power Supply
Nominal 24 VAC
Power Consumption
<5 VA
Housing Material
ABS plastic
Dimensions
4 1/4" x 3 1/8" x 1 7/16" (Wall only)
(108 mm x 80 mm x 36 mm) (Wall only)
3 1/8" x 3 1/8" x 7 ¾"
(80 mm x 80 mm x 200 mm)
DDC Zone Sensor with LCD
Specifications
Thermistor Resistance Rating
10,000 Ohms at 77°F (25oC)
Setpoint Resistance Rating
Setpoint potentiometer is calibrated to produce 500 Ohms at a setting of 70oF (21.11oC)
Temperature Range
Displays 40 to 99oF (5 to 35oC)
With Setpoints 50 to 90oF (10 to 32oC)
Electrical Connections
Terminal Block – Pressure Connections
Communication Jack – WE – 616
4 VA maximum power input.
Physical Dimensions
Width: 2.8" (71.12 mm)
Length: 4.5" (114.3 mm)
Height: 1.1" (27.94 mm)
The DDC zone sensor with LCD has the look and functionality of the
standard Trane DDC zone sensor but has a LCD display. The sensor
includes setpoint adjustment, the display of the ambient temperature, a
communication jack, and occupied mode override pushbuttons. Also, it
can be configured in the field for either a Fahrenheit or Celsius display, a
continuous display of the setpoint and the offset of displayed
temperatures.

VAV-PRC011M-EN 107
DDC Controls
Zone Occupancy Sensor
Sensor ships with 30-minute time delay pre-set from the factory. Time delay and sensitivity can be
field-adjusted.
Specifications
Power Supply
24 VAC or 24 VDC, ± 10%
Maximum VA Load
0.88 VA @ 24 VAC,
0.72 VA @ 24 VDC
Isolated Relay Rating
1 A @ 24 VAC or 24 VDC
Operating Temperature
32 to 131°F (0 to 55°C)
Storage Temperature
-22 to 176°F (-30 to 80°C)
Humidity Range
0 to 95% non-condensing
Effective Coverage Area
1200 sq ft
Effective Coverage Radius
22 feet
Housing Material
ABS Plastic
Dimensions
3.3" dia. x 2.2" deep (85 mm x 56 mm). Protrudes 0.36" (9 mm) from ceiling when installed.
The zone occupancy sensor is ideal for spaces with intermittent occupancy.
It is connected to the Trane DDC UCM and allows the zone to shift to
unoccupied setpoints for energy savings when movement is not detected
in the space.
The zone occupancy sensor has a multi-cell, multi-tier lens with a
maximum field of view of 360°. The maximum coverage area of the sensor
is 1200 square feet with a maximum radius of 22 feet from the sensor when
mounted at 8 feet above the floor.

108 VAV-PRC011M-EN
DDC Controls
Factory or Field Mounted Auxiliary Temperature Sensor
Factory or Field Mounted Auxiliary Temperature Sensor
Sensing Element
Thermistor 10,000 Ohms @ 77°F (25°C)
Operating Environment
-4 to 221°F (-20 to 105°C), 5%-95%RH
Non-Condensing
Wiring Connection
8 ft 18 awg
Sleeving for wire leads is acrylic #5 awg grade C rated @ 155°C
Probe Dimensions
3.4" long x 5/16" diameter
(86 mm x 7.9 mm diameter)
Mounting
In any position on duct.
Mount the sensor to the duct using
#10 x ¾" (19.05 mm) sheet metal screws.
Factory Mounted Discharge Air Temperature Sensing Matrix
The auxiliary temperature sensor is used in conjunction with the Trane DDC
controller to sense duct temperature. When the DDC controller is used with
a Building Automation System, the sensor temperature is reported as status
only. When the DDC control is used as stand alone configuration and the
sensor is placed in the supply air duct, the sensor determines the control
action of the UCM in a heat/cool changeover system.
When factory mounted, the sensor is terminated. If sensor is field mounted,
it is shipped loose and is terminated in the field.
The sensing matrix consists of (2) probes factory installed in the unit reading
an average of 4 points within the unit discharge. Traditional single point
temperature sensors are more of a heat on/off indicator than an accurate
temperature due to stratification in the duct work. The new sensing matrix
provides a factory installed accurate discharge temp. Additionally, when
coupled with SCR heat and UC210 or UC400 controls, the energy efficient
dual max algorithm can be used to reduce energy costs.

VAV-PRC011M-EN 109
DDC Controls
Two-Position Water Valve
Specifications
Valve De sign
Body: Brass
Cover: Aluminum
Case: Stainless Steel
Stem: Brass, Hard Chrome Plate
“O” Ring Seals: Viton
Operating Paddle: Buna N
Valve Body Ratings
UL 873 Listed File E27743
Plenum Rated CSA C22.2 No. 139
Certified, File LR85083, Class 3221 01
Temperature Limits
200°F (93.33°C) Fluid
104°F (40°C) Ambient
Maximum Operating Pressure
300 psi (2069 kPa)
Electrical Rating
Motor Voltage – 24 VAC, 50/60 Hz
Power Consumption – 7.0 VA of 24 VAC
Valve Offerings
All valves are spring returned.
4.0 Cv – ½" (12.7 mm) O.D. NPT
5.0 Cv – ¾" (19.1 mm) O.D. NPT
8.0 Cv – 1" (25.4 mm) O.D. NPT
Cv offered (Close-off Pressure):
Cv 3.0 (25) psi (172 kPa)
Cv 4.0 (20) psi (138 kPa)
Cv 8.00 (17) psi (117 kPa)
Two-position hot water valves are used with Trane DDC/UCM controls and
analog electronic controls. Valve actuation is by a hysteresis synchronous
motor.
All valves are field-installed and convertible from three-way to two-way by
means of an included cap.

110 VAV-PRC011M-EN
DDC Controls
Proportional Water Valve
The direct digital controller uses a time-based signal to drive the motor to its proper position. When
power is removed from the valve, it remains in its last controlled position.
Specifications
Valve Design:
Ball valve construction designed for chilled/hot water or water with up to 50% glycol
Temperature Limits
32 to 201°F (0 to 94°C) Fluid
23 to 122°F (-5 to 50°C) Ambient
Rated Body Pressure
300 psi (2.06 mPa)
Maximum Actuator Close-Off Pressure
60 psi (0.4 mPa)
Electrical Rating
Motor Voltage – 24 VAC, 50/60 Hz
Power Consumption – 3.0 VA at 24 VAC
Valve Offerings
All valves are proportional control with ½" (12.7 mm) O.D. NPT connections
Cv offered:
0.7
2.7
6.6
8.0
The proportional water valve is used to provide accurate control of a hot
water heating coil to help maintain a zone temperature setpoint. The valve
is a ball design and comes in available in four different flow capacities for
proper controllability. The valves are field-adjustable for use as a two- or
three-way configuration. The valves ship in a two-way configuration with a
plug that is installed loose in the bypass port. Conversion to three-way
operation is accomplished by removing the plug from the "B" port. The valve
actuator contains a three-wire synchronous motor.

VAV-PRC011M-EN 111
DDC Controls
VAV Piping Package
Specifications
Differential Operation Pressure:
• 2519 (2-80 psid 0.5-3.0 gpm) / (3-80 psid 3.50 – 5.00 gpm)
• 2515 (3-80 psid 5.50 – 9.00 gpm)
• 2524 (3-80 psid 10.0 –17.0 gpm) / (5-80 psid 18.0 –23.0 gpm)
• ± 10% accuracy of published flow
Operating Temperature:
32° - 225°F
• Offered in both 2-way and 3-way configurations
• The Automatic Balancing Flow Control sized for the specified VAV coil
and gpm.
• Field connections are NPT with Coil connections Sweat to match the
Trane VAV water coil copper
• For 3-way configuration the connections between the ATC valve and the
supply shut off assembly are sweat to allow for field installation of hose
or piping connection between the supply and return lines.
• Included in the package are:
•P/T Ports for pressure and temperature measurement on both the
supply and return sections.
•Blow down drainable filter on the supply.
•Y-Ball Combination Mesurflo Automatic Balance Valve on the Return
side to isolate the coil
•Y-Ball Combination Strainer on the supply to isolate the coil.
• Each piping package is tagged to match the VAV terminal tag it is
specified for.
• Each piping package includes a 24v floating point control proportional
control ball valve.
• The Cv is sized to match the specified gpm/coil performance of the VAV
terminal unit. Package includes unions with sweat connections to the
coil.

112 VAV-PRC011M-EN
DDC Controls
Differential Pressure Transducer
Specifications
Input Pressure Range
0.0 to 5.0 in. wg
(Maximum input pressure 5 psig)
Operating Environment
32 to 140° F, (0 to 60°C)
5% to 95% RH, Non-Condensing
Storage Environment
-40 to 180° F, (-40 to 82.2°C)
5% to 95%RH, Non-condensing
Electrical Connections
Vin = 5.0 VDC nominal
(4.75 to 5.25 VDC acceptable)
Current Draw = 5 mA maximum
Null Voltage = 0.250 VDC ± 0.06 VDC
Span = 3.75 VDC ± 0.08 VDC
Note: Null and Span are ratio-metric with Vin
Physical Dimensions
Width: 2.5" (63.5 mm)
Length: 3.0" (76.2 mm)
Height: 1.5" (38.1 mm)
Pressure Connections
1/8" (3.175 mm) barbed tubing connections
The differential pressure transducer is used in conjunction with the Trane
direct digital controller and analog electronic controller. The pressure
transducer measures the difference between the high-pressure and low-
pressure ports of the Trane flow ring. The transducer is self-adjusting to
changes in environmental temperature and humidity.

VAV-PRC011M-EN 11 3
DDC Controls
Transformers
Specifications
Primary Voltage
120 VAC
208 VAC
240 VAC
277 VAC
347 VAC
480 VAC
575 VAC
Secondary Voltage
24 VAC
Power Rating
50 VA
Physical Dimensions
For all voltages:
The transformers will be no larger than the following dimensions:
Width: 2.63" (66.7 mm)
Length: 2.50" (63.5 mm)
Height: 2.30" (58.4 mm)
The transformer converts primary power supply voltages to the voltage
required by the direct digital controller and analog. The transformer also
serves to isolate the controller from other controllers which may be
connected to the same power source.

114 VAV-PRC011M-EN
DDC Controls
Trane Non-Spring Return Actuator
This actuator is used with DDC controls and retrofit kits. it is available with a 3-wire floating-point
control device. It is a direct-coupled over the shaft (minimum shaft length of 2.1”), enabling it to
be mounted directly to the damper shaft without the need for connecting linkage. The actuator has
an external manual gear release to allow manual positioning of the damper when the actuator is
not powered. The actuator is Underwriters Laboratories Standard 873 and Canadian Standards
associate Class 3221 02 certified as meeting correct safety requirements and recognized industry
standards.
Specifications
Actuator Design
3-wire, 24-AC floating-point control. Non-spring return.
Actuator Housing
Housing type - NEMA 1
Rotation Range
90° clockwise or counterclockwise
Electrical Rating
Power supply - 24VAC (20 to 30 VAC) at 50/60 Hz
Power Consumption - 1.8 VA maximum, Class 2
Electrical Connection
No. 6-32 screw terminals (For DD00 and FM01 control options and retrofit kits.)
6-pin female connector harness for Trane UCM (for Trane DDC controls except retrufit kits)
Manual Override
External clutch release lever
Shaft Requirement
1/2” round
2.1” length
Humidity
5% to 95% RH, Non-Condensing
Temperature Rating
Ambient operating: 32 to 125°F (0 to 52°C)
shipping and storage: -20 to 130°F (-29 to 66°C)

VAV-PRC011M-EN 11 5
DDC Controls
Trane Spring Return Actuator
Specifications
Actuator Design
24-VAC, floating-point control. Spring return
Actuator Housing
Housing Type-NEMA IP54
Rotation Range
Adjustable from 0° to 90° at 5° intervals, clockwise or counterclockwise
Electrical Rating
Power Supply – 24 VAC (19.2 to 28.8 VAC) at 50/60 Hz
Power Consumption – 4VA holding, 5VA running maximum, Class 2
Electrical Connection
6-pin female connector for Trane UCM (for Trane DDC controls)
Manual Override
Manual override key provided
Shaft requirement:
¼" to ¾" round
2.1" length
Humidity
95% RH, Non-Condensing
Temperature Rating
Ambient operating: 32 to 130°F
(0 to 54°C)
Shipping and storage: -40 to 158°F
(-40 to 70°C)
To r q u e
62 in.-lbs (7N-m)
This actuator is used with DDC controls and is a floating-point control
device. It is direct-coupled over the shaft (minimum shaft length of 2.1"),
enabling it to be mounted directly to the damper shaft without the need for
connecting linkage. The actuator is Underwriters Laboratories Standard
60730 and Canadian Standards Association C22.2 No. 24-93 certified as
meeting correct safety requirements and recognized industry standards.

116 VAV-PRC011M-EN
DDC Controls
VariTrane™ DDC Retrofit Kit
A VariTrane DDC-UCM, an electronic differential pressure transducer, and a six-pin connector with
wiring for an actuator, make up the assembly of the retrofit kit. All are housed inside a metal
enclosure. For maximum flexibility, the kit is available with one of two actuators or without an
actuator. If a kit is ordered without an actuator, ensure the actuator used has 24VAC three-wire
floating control. Other accessories are available with the retrofit kit which include zone sensors,
flow bars (used with units without a flow sensor), power transformers, control relays, and E/P
solenoid valves.
Retrofit Kit Actuator
Specifications
Actuator Design
on-off/floating-point
Actuator housing
Housing Type-NEMA type 1
Housing Material Rating- UL 94-5V
Direction of Rotation
Reverse wires terminals 2 and 3
Angle of Rotation
Max 95º, adjustable with mechanical stops
Electrical Rating
Power Supply – 24 VAC ± 20% 50/60 Hz 24 VDC ± 10%
Power Consumption – 2 W
Transformer Sizing – 3 VA (Class 2 power source)
Manual Override
External push button
The retrofit kit provides the system advantages of VariTrane DDC controls to
building owners for existing systems. The kit can be applied when
converting from pneumatic or analog controlled systems to a DDC
controlled system. The kit may be used on existing single-duct units with hot
water and electric reheat (three stages), dual-duct units, and all fan-powered
units (both series and parallel) with hot water and electric reheat (two
stages).
This actuator is available with the DDC Retrofit Kit and is a 3-terminal,
floating-point control device. It is direct-coupled over the damper shaft so
there is no need for connecting linkage. The actuator has an external manual
gear release to allow manual positioning of the damper when the actuator
is not powered. A three-foot plenum-rated cable with bare ends will be sent
separately. The actuator is listed under Underwriters Laboratories Standard
873, CSA 22.2 No. 24 certified, and CE manufactured per Quality Standard
SO9001.

VAV-PRC011M-EN 11 7
DDC Controls
Humidity
5% to 95% RH, Non-Condensing
Ambient Temperature
-22 to 122°F (-30C to 50°C)
Storage Environment
-40 to 176°F (-40 to 80°C)
To r q u e
Min 35 in.-lb (4Nm), Independent of load
Running Time
95 sec. for 0 to 35 in-lb
Noise Rating
Less than 35 dB (A)
Weight
1.2 lbs (0.55 kg)
Static Pressure Controller
Specifications
Supply Voltage
24 VAC, 60 HZ
Maximum VA Load
No more than 12 VA
Recommended Wire Size
14 – 22 AWG Stranded
Housing Material
ABS
Components
Control box
Pressure sensor
Interconnecting wire
Static pressure tap
Fits standard 2" deep x 4" x 2 1/8" utility box.
The Trane static pressure controller will sense duct static pressure and
modulate a relief device in an effort to limit maximum duct static pressure.
An analog signal from the air probe is used to compare the difference in the
duct static pressure and the duct static pressure setpoint. The relief device
can be a VariTrane terminal or any blade damper device with the
specifications stated below. See VAV-EB-64 for installation and calibration.

118 VAV-PRC011M-EN
DDC Controls
Electric Heater Silicon-Controlled Rectifier (SCR)
Specifications
• Microprocessor based burst-fire controller / SSR
• Low-voltage control
• Output status indicator
•0-100% Control Range
• Synchronized triggering output (P3)
• 20 AC Cycles Base Period
• Coupled with the averaging temperature sensing matrix and UC210 or
UC400 controls, allows use of energy efficient dual max algorithm.
Input Specifications DC Control
Supply Voltage Range (VDC) (P1) 8-28
Input Current Range [mA] 20-30
Nominal Input Impedance [Ohms] 30K
Control Voltage (a)[VDC][P4]
(a) Control voltage < 0.2 Vdc guarantees heat is turned off.
0-10
Nominal Input Impedance [ohms][P4] 20K
Output Status Functions LED
Initial Logic Supply On Flash Once
Load Voltage Missing / Load Open (W/ PLV = 0V) Flash Once Intermittently
Load Voltage Missing / Load Open (W/ PLV > 0V) Flash Twice Intermittently
General Specifications Parameters
Dielectric Strength, Input/Output/Base (50/60Hz) 4000 Vrms
Minimum Insulation Resistance (@ 500 V DC) 109 Ohm
Maximum Capacitance, Input/Output 10 pF
Ambient Operating Temperature Range -20 to 80°C
Ambient Storage Temperature Range -40 to 125 °C
Encapsulation Thermally conductive Epoxy
Input connector Header Connector 3.5mm
Output Terminals Screws and Saddle Clamps Furnished, Installed
Output Max Wire Size Output:2 x AWG 8 (3.8mm)
Output Screws Maximum Torque 20 in lbs (2.2 Nm)
Assembly Specifications
Weight (typical) 1.38 Lb (0.628 Kg.)
Heat Transfer Material Used Thermal Pad
Material Steel
Finish Nickel Plate
Torque Applied 20 in/lbs ± 10%.

VAV-PRC011M-EN 119
DDC Controls
Heat Controls
24-VAC Fan/Staged
2nd
1st
C
Fan
Load: 10 VA (MAGN)
Load: 12 VA (MERC)
Load: 6.5 VA
FAN RELAY
2
1
3
5
4
2
1
HEATER CONTROL BOX
3rd
2
3
4
5.
Damper
Actuator
Line Voltage
CW
COM
CCW
24 VAC, 50 VA
Transformer
Load: 4 VA
24-VAC to
Customer
Controls
By Others
Damper Controls
24-VAC M
Load: 4 VA
Actuator
Damper
24-VAC
Damper Controls
By Others COM
CW
CCW
M
Y
BL
NOTES:
1. Factory-installed
Field Wiring
Optional or installed by others
2.
Only available with fan-powered units.
3.
4. Located in Heater Terminal box.
Only available with dual-duct units.
5.
DD00—Available for all VariTrane Units
(Trane actuator for field-installed DDC controls)
A unit controller is not provided. The air damper actuator is provided with an integral screw terminal block.
The fan contactor (fan-powered units), 24-VAC control power transformer (optional for single- and dual-duct
units), and factory-installed electric heater contactor wires are attached to the outside of the unit for field
connection of controls. A second actuator is provided with an integral screw terminal for dual-duct units.
Located in Heater Terminal Box for electric heat on single-duct units.
Located in Control Box for cooling only and hot water heat on single-duct units.
Located in Control Box on all fan-powered units.

120 VAV-PRC011M-EN
DDC Controls
L
O
1st stage
2nd stage
3rd stage
24VAC (hot) common
CCW
COM
CW
24 VAC
Y
BL
24 VAC, 50va
Standard – (Fan-powered)
Optional – (Single-duct and Dual-duct)
Transformer
Customer-furnished
Controller
Electric
Reheat
Contactors
Hot Water
Reheat
Fan
Relay
Actuator Customer-furnished
or Trane-supplied
Trane-supplied
(Fan-powered only)
Trane-supplied
Available on all VariTrane Units
FM00 – Customer-supplied actuator and DDC controller factory-installed.
FM01 – Trane actuator and customer-supplied DDC controller factory-installed
Optional or installed by others
NOTES:
1. Factory-installed
Field Wiring
Optional
Trane-supplied
water valve
field-wired
to controller.
Airflow
Sensor
LO HI Trane-supplied
All customer furnished controllers and actuators are installed and wired per control manufacturer's specifications.
Metal control enclosure is standard.
2. NEMA-1 Enclosure provided.

VAV-PRC011M-EN 121
Pneumatic Controls
3011 Pneumatic Volume Regulator
Specifications
Differential Pressure Range
0-1 in. wg (0–249 Pa)
Minimum Setpoint Range
0-1 in. wg (0–249 Pa)
Maximum Setpoint Range
0.05 in. wg (12.5 Pa) above minimum to 1 in. wg (249 Pa) above minimum
Operating Static Pressure Range
0.25 in. wg—6.0 in. wg (62.3–1494 Pa)
Reset Pressure Span
Factory-set at 5 psig (34.5 kPa)
Field-adjustable from 0 to 10 psig
(0 to 68.9 kPa)
Reset Start Point
Field-adjustable from 0 to 10 psig
(0 to 68.9 kPa)
Main Air Pressure
15 to 30 psig (103 to 207 kPa)
Air Consumption
28.8 scim (0.472 L/m) at 20 psig (138 kPa) main air pressure
Operating Environment
40 to 120ºF (4 to 49°C)
Storage Environment
-40 to 140ºF (-40 to 60°C)
Output Sensitivity
5 psig/0.02 in. wg (34.5 kPa/5.0 Pa)
Physical Dimensions
Width: 4.5" (114.3 mm)
Length: 2.3" (58.4 mm)
Height: 3.87" (98.3 mm)
Weight: 11 oz (312 g)
The pneumatic volume regulator (PVR) is a controller that provides a
consistent airflow to the space, regardless of varying inlet duct pressure
conditions, in response to a pneumatic thermostat signal. The controller
maintains minimum and maximum airflow setpoints. The 3011 PVR can be
set to control either normally open or normally-closed air valve actuators
and can be calibrated to accept either direct-acting or reverse-acting
thermostat signals. Fixed reset control of maximum and minimum airflow
setpoints is provided.

122 VAV-PRC011M-EN
Pneumatic Controls
3501 Pneumatic Volume Regulator
This is in contrast to the 3011 PVR, which resets velocity pressure with a change in thermostat
pressure. This allows the 3501 PVR to have improved stability at low flows.
Specifications
Differential Pressure Range
0–1.0 in. wg (0–249 Pa)
Minimum Setpoint Range
0–1.0 in. wg (0–249 Pa)
Maximum Setpoint Range
Minimum to 1.0 in. wg (249 Pa)
Operating Static Pressure Range
0.25–6.0 in. wg (62.3–1494 Pa)
Reset Pressure Span
Factory-set at 5 psig (34.5 kPa)
Field-adjustable from 0 to 7 psig
(0 to 48.3 kPa)
Reset Start Point
Factory-set at 8 psig (55.2 kPa)
Field-adjustable from 0 to 10 psig
(0 to 68.9 kPa)
Main Air Pressure
15–30 psig (103 to 207 kPa)
Air Consumption
43.2 scim (0.708 L/m) at 20 psig (138 kPa) main air pressure
Operating Environment
40 to 120ºF (4 to 49°C)
Storage Environment
-40 to 140ºF (-40 to 60°C)
Output Sensitivity
5 psig/ 0.02 in. wg (34.5 kPa/ 5.0 Pa)
Physical Dimensions
Width: 4.5" (114.3 mm)
Length: 3.87" (98.3 mm)
Tubing Connections:
1/4" O.D. tubing connections
The 3501 PVR can be set to control either normally open or normally-closed
air valve actuators and can be calibrated to accept either direct-acting or
reverse-acting thermostat signals. Fixed reset control of maximum and
minimum airflow setpoints is provided. The controller is used primarily in
dual-duct constant-volume applications because of its linear output
response characteristics. The controller resets the primary air velocity
linearly with a change in thermostat pressure.

VAV-PRC011M-EN 123
Pneumatic Controls
Height: 4.1" (104.1 mm)
Weight: 12 oz (340 g)
Pneumatic Damper Actuator
Specifications
Effective Area
8 sq inches (51.6 sq cm)
Normal Rotation
100 degrees
Spring Ranges
Model 3631–5000: 8-13 psi (55.2–89.6 kPa)
Model 3631–8000: 3-8 psi (20.7–55.2 kPa)
Supply Connection
3/16" (4.8 mm) nipple for ¼" (6.4 mm) O.D. tubing
Weight
1.5 lbs (680 g)
Ambient Limits:
Operating:-20 to 120°F
(-28.889 to 48.889°C)
Shipping:-40 to 140°F (-40 to 60°C)
Reversing Relay
Specifications
Factory Setting
Contingent upon the selected control option
Generally set for 8 psig in. = 8 psig out or 9 psig in=9 psig out (55.2 kPa in. = 55.2 kPa out or 62.1
kPa in. = 62.1 kPa out)
The pneumatic actuator is designed for use on VAV terminal units in HVAC
systems. The damper actuator mounts to a standard ½" diameter shaft by a
pin and cross hold arrangement, retaining clip, and non-rotation bracket.
Two model actuators are offered with spring ranges of 3–8 psi or 8–13 psi.
Tubing Connections:
1/4" O.D. tubing connections
The pneumatic reversing relay is a proportional device that reverses the
action of the input signal. It is used to change a direct-acting signal into a
reverse-acting signal or to change a reverse-acting signal into a direct-acting
signal. This relay is used to match the operating pressure range of controlled
devices (valves, pressure switches, etc.) to the output pressure range of a
controller (such as a thermostat). The output response will always remain in
1:1 proportion to the input signal, but the relay includes the capability to bias
the output signal.

124 VAV-PRC011M-EN
Pneumatic Controls
Bias Adjustment
+/- 15 psig (103 kPa)
Main Air Pressure
15-30 psig (103–207 kPa)
Air Consumption
18 scim (0.295 L/m) at 20 psig (138 kPa) main air pressure
Operating Environment
40 to 120ºF (4°C to 49°C)
Storage Environment
-40 to 140ºF (-40 to 60°C)
Physical Dimensions
Width: 1.5" (38.1 mm)
Length: 1.5" (38.1 mm)
Height: 2.5" (63.5 mm)

VAV-PRC011M-EN 125
Pneumatic Controls
Signal Limiter
Specifications
Factory Setting
Maximum output = 8 psig (55.2 kPa) Adjustable from 2–12 psig (13.8–82.7 kPa)
Main Air Pressure
Nominal 20 psig (138 kPa) 22 psig
(152 kPa) maximum acceptable pressure
Air Consumption
10 scim (0.164 L/m) at 20 psig (138 kPa) main air pressure
Operating Environment
50 to 120ºF (10 to 48.89°C)
Physical Dimensions
Width:. 1.1" (27.94 mm)|
Length: 0.9" (22.86 mm)
Height: 0.9" (22.86 mm)
Tubing Connections
9/100" (2.3 mm) nipples
Tubing Connections:
3/16" (4.8 mm) nipples for 1/4" (6.4 mm) polyethylene tubing
The pneumatic signal limiter is a pressure limiting type device. The output
pressure from the signal limiter is not allowed to rise above the signal
limiter’s setting. Adjustments to the output pressure setting are made via a
screw on the back side of the valve.

126 VAV-PRC011M-EN
Pneumatic Controls
Remote Mounted
(Direct Acting)
(Direct Acting)
Remote Mounted
Optional or installed by others.
One Pipe
Restrictor
T-Stat Branch Pressure (kPa)
% Flow (CFM)
Water valve
CFM
Min
CFM
810
20.7
Max
100
20
(137.9)
55.2
% Flow (LPS)
Air Flow
LPS
Min
LPS
Max
100
Customer Notes:
1. Factory installed.
Restricted Leg
S
(137.9)
20
Tee
One Pipe Inset
T-Stat
S
MVolume
Regulator
T
Tee
(N.O.)
Valve
Water
15
(103.4)
(137.9)
20
T-Stat
Two Pipe
(20.69 - 55.16 kPa)
3-8 PSI S
Remote Mounted
Optional or installed by others.
Air Valve Position
T-Stat Branch Pressure (kPa)
T-Stat Branch Pressure (PSI)
100
38
20.7
55.2
13
100
89.6
Customer Notes:
Factory installed.1.
Restricted Leg
20
S
(137.9) One Pipe Inset
(Direct Acting)
T-Stat
Actuator
(137.9)
20
Restrictor
Tee One Pipe
Remote Mounted
Two Pipe
(Direct Acting)
T-Stat
S
T-Stat Branch Pressure (PSI)
313 15
69
89.6
103.4
(Normal Operation: Cooling with Hot Water Reheat)
Normally-Closed Damper, Actuator, and 3011 Pneumatic Volume Regulator
(Direct-Acting Thermostat)
PC04 – VCCF and VCWF - Single-Duct Terminal Units
With an increase in room temperature, the thermostat output pressure is increased. This signal is input for the volume regulator, which
also receives inputs from the high- and low-pressure sides of the flow ring. The volume regulator outputs a signal compensated for
changing duct pressure to the valve actuator which opens the damper and increases primary cooling flow to the space. With a
decrease in room temperature, the opposite action occurs. Minimum and maximum primary airflow settings are maintained by the
volume regulator. When the system is designed with reheat, heating stages are energized at the appropriate pressure settings.
With an increase in room temperature, the thermostat output pressure is increased and the actuator opens to increase primary
cooling airflow to the space. With a decrease in room temperature, the opposite action occurs.
PC00 – VCCF - Single-Duct Terminal Units
(Normal Operation: Cooling Only)
Normally-Closed Damper and Actuator (Direct-Acting Thermostat)
% Position (Open)
% Position (Open)

VAV-PRC011M-EN 127
Pneumatic Controls
Optional or installed by others.
Factory installed.
Limiter
Minimum
Restricted Leg
One Pipe Inset
Capped
Diverting
T-Stat Branch Pressure (PSI)
T-Stat Branch Pressure (kPa)
Min
CFM
CFM
Max
100
3810
M
T
13 15
Min
LPS
LPS
Max
3-8 PSI
100
Customer Notes:
1.
Restrictor
(20.69 - 55.16 kPa)
Valve
(N.O.)
Water
Relay
S
Tee
C
NC
NO Tee
Tee
Restrictor
Bleed
Restricted Leg Ports
With an increase in room temperature, the thermostat output pressure is decreased. This signal is input for the volume regulator, which also
receives the inputs from the high- and low-pressure sides of the flow ring. The volume regulator outputs a signal compensated for changing
duct pressure to the valve actuator which opens the damper and increases primary cooling flow to the space. With a decrease in room
temperature, the opposite action occurs. Minimum and maximum primary airflow settings are maintained by the volume regulator. When the
system is designed with reheat, heating stages are energized at the appropriate pressure settings.
T-Stat Branch Pressure (kPa)
T-Stat Branch Pressure (PSI)
Max
CFM
CFM
Min
3810 1513 Stages of Heat
LPS
Min
LPS
Max
M
Terminal Box
Electric Heater
T
Tee
With a decrease in room temperature, the thermostat output pressure is decreased. This signal is input to the volume regulator, which also
receives inputs from the high- and low-pressure sides of the flow ring. The volume regulator outputs a signal compensated for changing duct
pressure to the valve actuator, which closes the damper and decreases primary cooling flow to the space. With a further decrease in room
temperature, the auxiliary limit will override the thermostat signal, which is followed by the reheat being energized. Once the reheat has been
energized, the volume regulator will send a signal to the actuator to open to its secondary minimum. With an increase in temperature, the
opposite action occurs. Minimum and maximum airflow settings are maintained by the volume regulator. Heating stages are energized at the
appropriate pressure settings.
(Normal Operation: Cooling with Hot Water Reheat - Auto Dual Minimum)
Normally-Open Damper, Actuator, and 3011 Pneumatic Volume Regulator (Direct-Acting Thermostat)
PN11 – VCWF - Single-Duct Terminal Units
Regulator
Volume
Regulator
Volume
Restrictor
Customer Notes:
1. Factory installed.
One Pipe Inset
Restricted Leg
Tee
Optional or installed by others.
(Normal Operation: Cooling with Electric Reheat)
Normally-Open Damper, Actuator, and 3011 Pneumatic Volume Regulator (Direct-Acting Thermostat)
PN05 – VCCF and VCEF - Single-Duct Terminal Units
% Flow (CFM)
% Flow (CFM)
% Flow (LPS)
% Flow (LPS)
Two Pipe
Remote Mounted
T–Stat
(Direct Acting)
One Pipe
Remote Mounted
T–Stat
(Direct Acting)
Two Pipe
Remote Mounted
T–Stat
(Reverse Acting)
One Pipe
Remote Mounted
T–Stat
(Reverse Acting)
15
(103.4) 20
(137.9)
20
(137.9)
S
S
S
20
(137.9)
S
S
S
20
(137.9)
20
(137.9)
15
(103.4) 20
(137.9)
S
20
(137.9)

128 VAV-PRC011M-EN
Pneumatic Controls
One Pipe
Restricted Leg
(Reverse Acting)
Remote Mounted
One Pipe Inset
Factory installed.
Optional or installed by others.
T-Stat Branch Pressure (PSI)
T-Stat Branch Pressure (kPa)
100
Constant
Volume
% Flow (CFM)
Constant Volume
3810
Air Valve
20.7
55.2
69
% Flow (LPS)
13 15
1st
2nd
Stages of Heat
3rd
89.6
103.4
100
Customer Notes:
1.
Tee
20
(137.9)
S
20
(137.9)
S
MVolume
Regulator
(103.4)
Electric Heater
T
Terminal Box
Restrictor
Remote Mounted
(Reverse Acting)
(137.9)
15 20
Two Pipe
T-Stat
S
T-Stat
Two Pipe
Remote Mounted
(Direct Acting)
T-Stat
(Direct Acting)
Remote Mounted
Restricted Leg
One Pipe Inset
Factory installed.
Optional or installed by others.
T-Stat Branch Pressure (kPa)
Constant Volume
Air Flow
T-Stat Branch Pressure (PSI)
Constant
Volume
38
100
% Flow (CFM)
Water Valve
20.7
55.2
15
10 13
103.4
69
89.6
100
% Flow (LPS)
Customer Notes:
1.
20
(137.9)
S
20
(137.9)
S
MVolume
Regulator (20.69 - 55.16 kPa)
3-8 PSI
T
(N.O.)
Restrictor
Tee
Valve
Water
(103.4)
15
(137.9)
20
S
One Pipe
T-Stat
The unit shall operate to a constant volume flow regardless of changes in space temperature. The volume regulator receives the inputs from
high- and low-pressure sides of the flow ring. The volume regulator outputs a signal compensated for changing duct pressure to maintain
constant volume flow. When reheat is applied, heating stages are energized at the appropriate settings.
(Normal Operation: Cooling with Electric Reheat - Constant Volume)
Normally-Open Damper, Actuator, and 3011 Pneumatic Volume Regulator (Reverse-Acting Thermostat)
PN34 – VCEF - Single-Duct Terminal Units
The unit shall operate to a constant volume flow regardless of changes in space temperature. The volume regulator receives the inputs from
high- and low-pressure sides of the flow ring. The volume regulator outputs a signal compensated for changing duct pressure to maintain
constant volume flow. When reheat is applied, heating stages are energized at the appropriate settings.
PN32 – VCWF - Single-Duct Terminal Units
(Normal Operation: Cooling with Hot Water Reheat - Constant Volume)
Normally-Open Damper, Actuator, and 3011 Pneumatic Volume Regulator (Direct-Acting Thermostat)

VAV-PRC011M-EN 129
Pneumatic Controls
One Pipe Inset
Remote Mounted
(Direct Acting)
T-Stat Branch Pressure (PSI)
T-Stat Branch Pressure (kPa)
Air Flow
Min
CFM
38
55.2
20.7
% Flow (CFM)
CFM
Max
100
Water Valve
S
(137.9)
20
10
LPS
Min
103.4
69
89.6
% Flow (LPS)
LPS
Max
100
(137.9)
20
S
Restricted Leg
Restrictor
Tee
T-Stat
One Pipe
Regulator
MVolume
T
Tee
(20.69 - 55.16 kPa)
(N.O.)
Valve
Water
3-8 PSI
Two Pipe
(Direct Acting)
T-Stat
Remote Mounted
(103.4)
20
15
(137.9)
S
Optional or installed by others.
Customer Notes:
1.
Factory installed.
With an increase in room temperature, the thermostat output pressure is increased. This signal is input for the volume regulator, which also
receives inputs from the high- and low-pressure sides of the flow ring. The volume regulator outputs a signal compensated for changing duct
pressure to the valve actuator, which opens the damper and increases primary cooling flow to the space. With a decrease in room temperature,
the opposite action occurs. Minimum and maximum primary airflow settings are maintained by the volume regulator. When the system is
designed with reheat, heating stages are energized at the appropriate pressure settings.
T-Stat Branch Pressure (PSI)
T-Stat Branch Pressure (kPa)
100
Air Valve
38
20.7
55.2
100
Actuator
20
Two Pipe
Remote Mounted
(Reverse Acting)
T-Stat
S
(Normal Operation: Cooling Only)
Normally-Open Damper and Actuator (Reverse-Acting Thermostat)
With an increase in room temperature, the thermostat output pressure is decreased and the actuator opens to increase primary cooling
airflow to the space. With a decrease in room temperature, the opposite action occurs.
(Normal Operation: Cooling with Hot Water Reheat)
Normally-Open Damper, Actuator, and 3011 Pneumatic Volume Regulator (Direct-Acting Thermostat)
PN04 – VCCF and VCWF - Single-Duct Terminal Units
13 15
Factory installed.
Optional or installed by others.
One Pipe
T-Stat
Restricted Leg
(Reverse Acting)
Remote Mounted
One Pipe Inset
1.
Customer Notes:
20
(137.9)
S
Tee
Restrictor
(137.9)
PN00 – VCCF - Single-Duct Terminal Units
% Position (Open)
% Position (Open)

130 VAV-PRC011M-EN
Pneumatic Controls
T-Stat
One Pipe
Remote Mounted
(Reverse Acting)
One Pipe Inset
Factory installed.
Optional or installed by others.
(137.9)
T-Stat Branch Pressure (kPa)
T-Stat Branch Pressure (PSI)
100
Max
CFM
Min
CFM
% Flow (CFM)
Air Flow
3810 1315
1st
2nd
20
20.7
69
Stages of Heat
3rd
Customer Notes:
1.
S
20
(137.9)
Restrictor
Tee
Restricted Leg
T
S
MRegulator
Volume
15 20
Tee
Electric Heater
Terminal Box
Two Pipe
T-Stat
(Reverse Acting)
Remote Mounted
(137.9)
(103.4)
S
LPS
LPS
Max
Min
% Flow (LPS)
100
55.2
89.6
103.4
(Normal Operation: Cooling with Electric Reheat)
Normally-Closed Damper, Actuator, and 3011 Pneumatic Volume Regulator (Reverse-Acting Thermostat)
PC05 – VCCF and VCEF - Single-Duct Terminal Units
With an increase in room temperature, the thermostat output pressure is decreased. This signal is input for the volume regulator, which also receives
the inputs from the high- and low-pressure sides of the flow ring. The volume regulator outputs a signal compensated for changing duct pressure to
the valve actuator which opens the damper and increases primary cooling flow to the space. With a decrease in room temperature, the opposite
action occurs. Minimum and maximum primary airflow settings are maintained by the volume regulator. When the system is designed with reheat,
heating stages are energized at the appropriate pressure settings.

VAV-PRC011M-EN 131
Pneumatic Controls
T-Stat Branch Pressure (kPa)
T-Stat Branch Pressure (PSI)
Heating
% Position (Open)
38
Cooling
100
20.7
55.2
13 15
100
89.6
103.4
8 PSI Out
(55.16 kPa)
(55.16 kPa)
8 PSI In
Relay
Reversing
BS
M
Tee
Optional or installed by others.
Factory installed.
Customer Notes:
1.
Remote Mounted
Two Pipe
T-Stat
(Reverse Acting)
Restrictor
Tee
Restricted Leg
One Pipe Inset
One Pipe
Remote Mounted
(Reverse Acting)
T-Stat
Actuator Actuator
(Direct Acting)
Remote Mounted
One Pipe Inset
Optional or installed by others.
CoolingHeating
Cooling
T-Stat Branch Pressure (PSI)
T-Stat Branch Pressure (kPa)
38
55.2
20.7
CFM
% Flow (CFM)
Min
CFM
Max
100
Heating
1. Factory installed.
1513
(Direct Acting)
T-Stat
Two Pipe
Remote Mounted
Customer Notes:
103.4
89.6
100
Max
LPS
Min
LPS
% Flow (LPS)
One Pipe
Restrictor
Tee
Restricted Leg
T-Stat
B
M
Flow Ring
Actuator
Heating
LO
HI
Cooling
Flow Ring
Actuator
Regulator
Volume
HLTLO
HI
M
B
HLT
With an increase in room temperature, the thermostat pressure is decreased. The cooling valve actuator opens the damper to
increase primary cooling flow to the space, the heating valve is closed. With a decrease in room temperature, the heating valve
modulates and the cooling valve is closed.
% Position (Open)
20
(137.9)
S
20
(137.9)
S
20
(137.9)
S
(137.9)
S
20
S
(137.9)
20
S
(137.9)
20
S
(137.9)
20
Volume
Regulator
(Normal Operation: Cooling and Heating)
Normally-Open Heating Damper with Actuator and Normally-Open Cooling Damper with Actuator
(Reverse-Acting Thermostat)
PN08 – VDDF - Dual-Duct Terminal Units
PN09 – VDDF - Dual-Duct Terminal Units
(Normal Operation: Cooling and Heating)
Normally-Open Heating Damper with Actuator, Normally-Open Cooling Damper with Actuator, and
3001 Pneumatic Volume Regulator (Qty of 2) (Direct-Acting Thermostat)
With an increase in room temperature, the thermostat output pressure is decreased. This signal is input to the volume regulator,
which also receives the inputs from the high- and low-pressure from the flow ring. The volume regulator outputs a signal
compensated for changing duct pressures to the valve actuator, which opens the damper and increases primary cooling flow to the
space. With a decrease in room temperature, the opposite action occurs. Minimum and maximum primary airflow settings are
maintained by the volume regulator. If the zone temperature continues to decrease after the fan has been energized, heating stages
are energized at the appropriate pressure settings.

132 VAV-PRC011M-EN
Pneumatic Controls
T-Stat Branch Pressure (kPa)
T-Stat Branch Pressure (PSI)
Cooling
% Flow (CFM)
38
Heating
Min
CFM
CFM
Max
100
20.7
55.2
13 15
LPS
Min
LPS
Max
100
89.6
103.4
Optional or installed by others.
Factory installed.
Customer Notes:
1.
Remote Mounted
Two Pipe
T-Stat
(Direct Acting)
Restrictor
Tee
Restricted Leg
One Pipe Inset
One Pipe
Remote Mounted
(Direct Acting)
T-Stat
Actuator
Flow Ring
LO
HI
Volume
Regulator
M
B
HLT
Actuator
Flow Ring
LO
HI
Volume
Regulator
M
B
HLT
Heating Cooling
Heating Cooling
% Flow (LPS)
(Direct Acting)
Remote Mounted
One Pipe Inset
Optional or installed by others.
CoolingHeating
Cooling
T-Stat Branch Pressure (PSI)
T-Stat Branch Pressure (kPa)
38
Heating
Max
% Flow (CFM)
CFM
Min
CFM
100
20.7
55.2
1. Factory installed.
1513
(Direct Acting)
T-Stat
Two Pipe
Remote Mounted
Customer Notes:
103.4
100
Max
LPS
Min
LPS
89.6
% Flow (LPS)
Restrictor
Tee One Pipe
Restricted Leg
T-Stat
B
M
Flow Ring
Actuator
Heating
LO
HI
Cooling
Flow Ring
Actuator
Regulator
Linear
Reset
Volume
HLTLO
HI
MRegulator
Linear
Reset
Volume
B
HLT
(137.9)
20
S
(137.9)
S
20
(137.9)
S
20
(137.9)
S
20
(137.9)
20
S
S
20
(137.9)
S
20
(137.9)
S
20
(137.9)
PC03 – VDDF - Dual-Duct Terminal Units
(Normal Operation: Cooling and Heating)
Normally-Closed Heating Damper with Actuator, Normally-pen Cooling Damper with Actuator, and
3011 Pneumatic Volume Regulator (Qty of 2) (Direct-Acting Thermostat)
PN10 – VDDF - Dual-Duct Terminal Units
(Normal Operation: Cooling and Heating - Constant Volume)
Normally-Open Heating Damper with Actuator, Normally-Open Cooling Damper with Actuator, and
3501 Pneumatic Volume Regulator (Qty of 2) (Direct-Acting Thermostat)
in Discharge
With an increase in room temperature, the thermostat output pressure is increased. This signal is input to the volume regulators,
which also receives the inputs from the high- and low-pressure from the flow ring. The cooling volume regulator outputs a signal
compensated for changing duct pressure to the valve actuator, which opens the damper and increases primary cooling airflow to the
space. The heating valve is at a minimum flow. With a decrease in room temperature, the heating valve modulates in response to
signals from the heating pneumatic volume regulator, while maintaining constant volume at the discharge. The heating minimum
and maximum settings and the constant volume settings are maintained by the volume regulators.
With an increase in room temperature, the thermostat output pressure is increased. This signal is input to the volume regulators,
which also receives the inputs from the high- and low-pressure from the flow ring. The cooling volume regulator outputs a signal
compensated for changing duct pressure to the valve actuator, which opens the damper and increases primary cooling airflow to the
space. The heating valve is at a minimum flow. With a decrease in room temperature, the heating valve modulates in response to
signals from the heating pneumatic volume regulator. The heating valve is at a minimum flow. Both heating and cooling minimum
and maximum settings are maintained by the volume regulators.

VAV-PRC011M-EN 133
Pneumatic Controls
Optional or installed by others.
Customer Notes:
1. Factory installed.
(Reverse-Acting)
Remote Mounted
One Pipe Inset
(Reverse-Acting)
Remote Mounted
Tee
T-Stat Pressure (PSI)
T-Stat Pressure (kPa)
3
100
Position %
Air Valve
20.7
Stages of Heat
14
8910 12
1st
96.5
2nd
Fan On
55.2
62.1
69
82.7
100
3rd
Restricted Leg
(137.9)
20
S
T-Stat
Actuator Tee
Terminal Box
Electric Heater Fan P.E.
Tee
(N.O.)
Switch
(62.06 kPa)
9 PSI
Restrictor
One Pipe
Two Pipe
T-Stat
(103.4)
15
(137.9)
20
S
T-Stat Pressure (kPa)
T-Stat Pressure (PSI)
100
Position %
Air Valve
3
20.7
Restrictor
Customer Notes:
100
89
Fan On
1.
Switch
(N.O.)
(62.06 kPa)
9PSI
55.2
62.1
Fan
P.E.
20
OnePipeInset
Factory installed.
Optional or installed by others.
One Pipe
T-Stat
Remote Mounted
(Reverse-Acting)
Restricted Leg
S
(137.9)
Tee
Actuator
15
(103.4)
Tee
(137.9)
Two Pipe
Remote Mounted
(Reverse-Acting)
T-Stat
20
S
Position %
Position %
PN00 – VPCF, LPCF Parallel Fan-Powered Without Reheat
(Normal Operation: Cooling Only)
Normally-Open Damper and Actuator (Reverse-Acting Thermostat)
With an increase in room temperature, the thermostat output pressure is decreased and the actuator opens to
increase primary cooling airflow to the space. With a decrease in room temperature, the opposite action occurs
until the damper is fully closed. Upon a continued decrease in zone temperature below setpoint, the parallel fan
is energized.
PN00 – VPEF, LPEF Parallel Fan-Powered with Electric Heat
(Normal Operation: Cooling Only)
Normally-Open Damper and Actuator (Reverse-Acting Thermostat)
With an increase in room temperature, the thermostat output pressure is decreased and the actuator opens to increase
primary cooling airflow to the space. With a decrease in room temperature, the opposite action occurs until the damper
is fully closed. Upon a continued decrease in zone temperature below setpoint, the parallel fan is energized. If zone
temperature continues to decrease after the fan has been energized, heating stages are energized at the appropriate
pressure settings.

134 VAV-PRC011M-EN
Controls Specifications
For all VariTrane™ units, the unit controller continuously monitors the zone temperature and varies
the primary airflow as required to meet zone setpoints. Airflow is limited by adjustable minimum
and maximum setpoints.
Additionally, for series fan-powered units, the controller will start and run the fan continuously
during the occupied mode and intermittently during the unoccupied mode. Upon a further call for
heat, any hot water or electric heat associated with the unit is enabled.
For parallel fan-powered units, the controller energizes the fan upon a call for heat. Upon a further
call for heat, reheat is enabled.
Direct Digital Controls (DDC)
LONMARK Direct Digital Controller
Trane-designed LONMARK® certified controller uses the space comfort control (SCC) profile to
exchange information over a LonTalk™ Network. LonMark networks provide the latest open
protocol technology.
Direct Digital Controller
The microprocessor-based terminal unit controller provides accurate, pressure-independent
control through the use of a proportional integral control algorithm and direct digital control
technology. The UCM, monitors zone temperature setpoints, zone temperature, the rate of
temperature change, and valve airflow. With the addition of optional sensors, room occupancy or
supply duct air temperature can be monitored. The controller is provided in an enclosure with 7/
8” (22 mm) knockouts for remote control wiring. A Trane DDC zone sensor is required.
DDC Actuator
Trane 3-wire, 24-VAC, floating-point quarter turn control actuator with linkage release button.
Actuator has a constant drive rate independent of load, a rated torque of 35 in-lb, a 90-second drive
time, and is non-spring return. Travel is terminated by end stops at fully opened and closed
positions. An integral magnetic clutch eliminates motor stall.
DDC Actuator - Belimo
LMB24-3-T TN 3-wire, 24 VAC/DC, floating-point, quarter turn actuator with linkage release button.
Actuator has a constant drive rate independent of load, a rated torque of 45 in-lb, a 95 second drive
time, and is non-spring return. Travel is terminated by end stops at fully-opened and -closed
positions. Internal electronic control prevents motor stall when motor reaches end stops.
DDC Zone Sensor
The UCM controller measures zone temperature through a sensing element located in the zone
sensor. Other zone sensor options may include an externally-adjustable setpoint, communications
jack for use with a portable service tool, and an override button to change the individual controller
from unoccupied to occupied mode. The override button has a cancel feature that will return the
system to unoccupied. Wired zone sensors utilize a thermistor to vary the voltage output in
response to changes in the zone temperature. Wiring to the UCM controller must be 18 to 22 awg.
twisted pair wiring. The setpoint adjustment range is 50–88ºF (10–31°C) Depending upon the
features available in the model of sensor selected, the zone sensor may require from a 2-wire to
a 7-wire connection. Wireless zone sensors report the same zone information as wired zone
sensors, but do so using radio transmitter technology. No wiring from the zone sensor to the UCM
controller is necessary.
Digital Display Zone Sensor with Liquid Crystal Display (LCD)
The direct digital zone sensor contains a sensing element which sends a signal to the UCM. A Liquid
Crystal Display (LCD) indicates setpoint, or space temperature. Sensor buttons allow setpoint
adjust, and allow space temperature readings to be turned on or off. The digital display zone sensor
also includes a communication jack, for use with a portable edit device, and an override button to
change the UCM from unoccupied to occupied. The override button has a cancel feature, which

VAV-PRC011M-EN 135
Controls Specifications
returns the system to unoccupied mode. The digital display zone sensor requires seven wires, one
for 24-VAC power.
Pneumatic Controls
Normally-Open Actuator
Pneumatic 3 to 8 psig (20 to 55 kPa) spring-range pneumatic actuator.
Normally-Closed Actuator
Pneumatic 8 to 13 psig (55 to 90 kPa) spring-range pneumatic actuator.
3011 Pneumatic Volume Regulator (PVR)
The regulator is a thermostat reset velocity controller, which provides consistent air delivery within
5% of cataloged flow down to 15% of unit cataloged cfm, independent of changes in system static
pressure. Factory-calibrated, field-adjustable setpoints for minimum and maximum flows.
Average total unit bleed rate, excluding thermostat, is 28.8 scim at 20 psig (7.87 mL/min at 138 kPa)
supply.
3501 Pneumatic Volume Regulator (PVR)
The 3501 regulator is a linear-reset volume controller. This PVR is used to maintain a constant
volume of airflow from the dual-duct unit when constant volume control is used. Average total unit
bleed rate, excluding thermostat, is 43.2 scim at 20 psig (11.8 mL/min at 138 kPa) supply.
Considerations for Pneumatic Thermostat
Field-supplied and -installed based on chosen control options, a direct-acting or a reverse- acting,
one-pipe or two-pipe pneumatic room thermostat will control the available air valve, reheat and
fan switch to maintain room temperature setpoint. The following pneumatic control features are
available with VariTrane terminal units:
• Controls Option – PN00: Cooling with Normally-Open damper and actuator only (Reverse-
Acting Thermostat)
• Controls Option – PN04: Cooling with hot water reheat, Normally-Open damper, 3011 PVR
(Direct-Acting Thermostat)
• Controls Option – PN05: Cooling with electric reheat, Normally-Open damper, 3011 PVR
(Reverse-Acting Thermostat)
• Controls Option – PN08: Cooling and Heating, Normally-Open dampers, actuators only
(Reverse-Acting Thermostat)
• Controls Option – PN09: Cooling and Heating, Normally-Open dampers, 3011 PVR’s (Direct-
Acting Thermostat)
• Controls Option – PN10: Cooling and Heating, Normally-Open dampers, 3501 PVR’s, Dual-Duct
Constant Volume (Direct-Acting Thermostat)
• Controls Option – PN11: Cooling with hot water reheat, Normally-Open damper, 3011 PVR - Auto
Dual Minimum (Direct-Acting Thermostat) (N.O. Water Valve)
• Controls Option – PN32: Cooling with hot water reheat, Normally-Open damper, 3011 PVR -
Constant Volume (Direct-Acting Thermostat)
• Controls Option – PN34: Cooling with electric reheat, Normally-Open damper, 3011 PVR -
Constant Volume (Reverse-Acting Thermostat)
• Controls Option – PN51: Cooling with reheat, Normally-Open damper, 3011 PVR Duct Pressure
Switch (Reverse-Acting Thermostat)
• Controls Option – PN52: Cooling with reheat, Normally-Open damper, 3011 PVR - Dual Pressure
Minimum (Reverse-Acting Thermostat)
• Controls Option – PC00: Cooling Only with Normally-Closed damper - Direct-Acting Thermostat

136 VAV-PRC011M-EN
Controls Specifications
• Controls Option – PC03: Cooling and Heating, Normally-Closed heating damper, Normally-
Open cooling damper, actuators only - Direct-Acting Thermostat
• Controls Option – PC04: Cooling with hot water reheat, Normally-Closed damper, 3011 PVR -
Direct-Acting Thermostat
• Controls Option – PC05: Cooling with electric reheat, Normally-Closed damper, 3011 PVR -
Reverse-Acting Thermostat
Options
Power Fuse (cooling only and hot water units, and VDDF)
An optional fuse is factory-installed in the primary voltage hot leg.
Transformer (Standard on fan-powered, optional on VCCF, VCWF, VDDF)
The 50-VA transformer is factory-wired and installed in an enclosure with 7/8" (22 mm) knockouts
to provide 24 VAC for controls.
Wireless Zone Sensor/Receiver
Factory mounted Receiver with field mounted sensor accessory eliminates the need for the wiring
between the zone sensor and unit level controller.
Disconnect Switch (Optional on VCCF, VCWF, VDDF)
Disengages power.
DDC Retrofit Kit (VRTO)
The kit consists of a Trane DDC Unit Control Module (UCM) VAV terminal unit controller and a
pressure transducer installed in a metal enclosure. The mechanical specifications of accessories
such as DDC zone sensors, hot water valves, and transformers are found elsewhere in this section.
Retrofit Kit Options
Flow Bar Sensor
The flow bar sensor is a multiple-point, averaging, pitot tube type flow sensor. It is intended for field
installation on terminal units that have no flow measurement device. The total and static pressure
outputs of the sensor are field-piped to the high and low inputs of the pressure transducer in the
retrofit kit.
Retrofit Kit Actuator
The electric actuator is a direct-coupled type actuator that utilizes three-wire, floating-point control.
The actuator is field-installed to the damper shaft and field-wired to the controller.
Trane Actuator – Actuator is rated at 4 VA at 24 VAC. Drive time is 90 seconds with 35 in.-lb (4 N-m).
Retrofit Actuator – Actuator is rated at 3 VA at 24 VAC. Drive time is 80 to 110 seconds for 0 to 35
in.-lb (0 to 4 N-m).

VAV-PRC011M-EN 137
Controls Specifications
Other Options Available
• DDC Zone Sensors - wired or wireless
• 2-Position & Modulating Water Valves
• Control Transformer (Ships loose with mounting plate for 4x4 junction box)
• Auxiliary Temperature Sensor
• Zone Occupancy Sensors
•CO2 Sensors (Room- or duct-mounted)

138 VAV-PRC011M-EN
Application Considerations
VAV System
There are two primary types of VAV systems—single-duct and dual-duct.
Single-Duct Systems
Single-duct systems include one supply fan and a single supply duct, which is attached to each
zone. The supply fan delivers cooled air to the VAV zones in variable volumes, depending upon the
cooling requirements. The supply fan is usually designed to modulate airflow delivered to the VAV
zones.
Many VAV zones require heating as well as cooling. The supply air-handling unit provides either
no heat (cooling only), morning warm-up heat or occupied (changeover) heat. In addition, heat may
be provided at any individual VAV zone (within the zone or within the VAV terminal) by reheating
cool air provided by the central air handler.
No Heat
Central Cooling Only—In some systems, the central air handler provides only cooling and
ventilation during zone occupied periods. The supply air is maintained at a constant temperature
and the supply airflow is modulated to match the VAV airflow rate with the zone cooling
requirements.
Central Heat
Central Heat for Morning Warm-up—Many buildings cool down during the night. To be at a
comfortable temperature in the morning when the building is again occupied, heat must be added
to the spaces. Heat provided by the central air handler for morning warm-up is supplied at constant
air volume to the zones, prior to the time of occupancy. During the morning warm-up period, the
VAV terminal units must open to allow heated air to flow into the zones. In most instances very little
additional heat is needed once the building is occupied.
Central Occupied Heating-Changeover—Some buildings use the same air handler to provide
both occupied cooling and occupied heating. This is commonly referred to as a changeover system.
The system changes between heating and cooling depending on the need of the zones on the
system. In a changeover system, the operation of the VAV terminal units must also change over,
opening to provide heat in the heating mode and opening to provide cooling in the cooling mode.
RA
EA
OA PA
supply
fan
cooling
coilvariable-
speed drive
thermostat
VAV
box
SA
Variable-Air-Volume (VAV) System

VAV-PRC011M-EN 139
Application Considerations
Trane's main product in this type of application is called VariTrac™. VariTrane products can also be
used in these systems. (These types of systems are beyond the scope of this manual and are
discussed in detail in the VariTrac II Manual.
Terminal Heat
Remote Heat—In some zones of a single-duct VAV system, perimeter heating equipment, remote
from the terminal unit, is used to add heat to the zone when the cooling load is lower than the
minimum cooling capacity of the VAV terminal unit. Heat is added directly to the zone while cool
supply air continues to enter the zone at a minimum rate for zone ventilation.
Termi n a l R e heat— In some zones of a single-duct VAV system, a minimum flow of cool supply air
is reheated at the terminal unit before entering the zone. Terminal reheat can be provided by
electrical resistance heaters or by hot water coils.
Parallel Fan-Powered Heat—In some zones of a single-duct VAV system, cool supply air at
minimum flow is mixed with warm plenum air before entering the zone at a constant flow rate. A
fan in the terminal unit, in parallel with the central fan, draws air from the plenum whenever the
zone requires heat.
Series Fan-Powered Heat—In some zones of a single-duct VAV system, the airflow to the zone
is held constant, during both heating and cooling, by a terminal unit fan that is in series with the
central fan. The terminal unit fan runs continuously. When the zone requires heat, cool supply air
at minimum flow is mixed with warm, return plenum air before entering the zone.
Dual-Duct Systems
Dual-duct systems have either one or two supply fans and two duct systems. One duct system
carries heated air and the other duct system carries cooled air. Heated air and cooled air are
modulated and/or mixed at each zone in the proper proportions to control zone temperature.
Terminal reheat is not required in a dual-duct system.
Figure 8. Single-fan, dual-duct VAV system
VSD
supply
fan
central air handler cooling
coil
coil
heating 105°F (40.6°C)
dual-duct
VAV
terminal
units
EA
OA
40°F
(4.4°C)
(23.9°C)
75°F
(12.8°C)
55°F
RA

140 VAV-PRC011M-EN
Application Considerations
VariTrane VAV Terminal Units
The function of the VariTrane™ terminal unit in a VAV control zone is to vary the volumetric airflow
rate to the zone. VariTrane units are available with either microprocessor-based DDC controls or
pneumatic or analog electronic controls. Factory-installed controls are available with all types of
terminal units.
VAV Terminal Unit Types
Single-Duct
Single-duct terminal units control the volumetric flow of supply air to the space to maintain the
zone temperature at setpoint. These units are generally applied in cooling-only VAV zones that
require no heat during occupied hours. If local zone heat is necessary it can be provided either
remotely (for example, perimeter heat) or by terminal reheat (either electric or hot water coils).
Dual-Duct
Dual-duct terminal units are used in a special type of air distribution system where the main system
has both warm air and cold air separately ducted to each terminal unit. The flow of both warm air
and cool air is modulated, delivering air to the VAV zone at variable air volumes as well as variable
temperatures. Since full capacity occupied heating is always available, control of additional local
heat is not provided.
Figure 9. Single-Duct cooling only unit (L) and single-duct unit with hot water coil (R)
Figure 10. Dual-Duct terminal unit

VAV-PRC011M-EN 141
Application Considerations
Fan-Pressure Optimization
With Trane's Integrated Comfort System, the information from VAV terminal units can be used for
other energy-saving strategies. Fan-pressure optimization is the concept of reducing the supply fan
energy usage based on the position of the terminal unit dampers.
The control system allows this scenario. The system polls the VAV units for the damper position
on each unit. The supply fan is modulated until the most wide-open damper is between 85% and
95% open. The correct airflow is still being sent to the zones since the controls of the VAV units are
pressure-independent, and the fan modulates to an optimal speed and duct static pressure which
results in fan energy savings.
Ventilation Reset
The Ventilation Reset control strategy enables a building ventilation system to bring in an
appropriate amount of outdoor air per ASHRAE Standard 62.1. The basis for the strategy is
measuring airflow at each zone, calculating current system ventilation efficiency using the
multiple-zone system equations of the standard, and communicating a new outdoor airflow
setpoint to the air handler.
This strategy continually monitors the zone ventilation needs and system outdoor air intake flow,
minimizing the amount of ventilation air and increasing the energy efficiency of the system. This
ensures that the right amount of air is brought in at all times and that proper ventilation can be
documented. Trane has integrated this control ability into the VAV controls, air-handler controls,
and building controls.
For more detailed information on these energy-saving strategies, please refer to “Additional VAV
System and Product References,” p. 156 for appropriate material.
Figure 11. Optimized static-pressure control
static
pressure
sensor
P
supply
fan
RTU controller
Tracer SC
VAV boxes with
DDC controllers
VFD

142 VAV-PRC011M-EN
Application Considerations
Control Types
VAV terminal units are available with many different options. These options fall into three main
categories of controls: direct digital (DDC), pneumatic, and analog electronic. All of these control
types can be used to perform the same basic unit control functions, yet differences exist in accuracy
of performance, versatility, installed cost, operating cost, and maintenance cost.
Direct Digital Control (DDC) Systems
Benefits
Performance—DDC controls offer PI control capability. A PI control scheme is the most accurate
and repeatable control scheme available in the VAV terminal unit industry.
Versatility—DDC controls accepts software commands to determine how its outputs will be
controlled. When a control sequence must be modified, making changes to the software
instructions is easier and quicker than changing hardware.
Figure 12. Ventilation reset
OA
SA RA
VAV Controllers
• Required outdoor airflow
• Current primary airflow
• Current OA fraction
Tracer SC
• Find highest OA fraction
• Calculate current system
intake airflow (ASHRAE 62.1)
RTU controller
• Reset intake airflow
Direct digital control (DDC) systems became
available as advances in computer technology made
small microprocessors available and affordable.
Much of the hardware in DDC systems is similar to
analog electronic systems. The primary difference is
that DDC controllers allow system integration, remote
monitoring, and adjustment. The microprocessor is
programmed using software that gives the controller
a higher level of capability than either the pneumatic
or analog electronic options.

VAV-PRC011M-EN 143
Application Considerations
Operating and Maintenance Costs—DDC controls can be networked together via wired or wireless
networks to provide system-control strategies for energy savings. Multiple controllers can be
easily monitored and adjusted from a remote location. DDC controls also have system and
individual diagnostic capability.
Pneumatic Control Systems
Pneumatic control systems use compressed air through simple mechanical control devices, such
as diaphragms, springs, and levers to change an output in response to a change in a monitored
variable. With VAV terminal units, the output is typically a primary airflow and the monitored
variable is zone temperature.
Benefits
Performance—Pneumatic controls are a proven technology that is effective and has a long life
cycle.
Installed Cost—When a source of compressed air exists at the facility, pneumatics generally have
a lower installed cost than other types of controls when only a basic functionality is required.
Operating and Maintenance Costs—Pneumatics are still the most familiar control technology to
many building designers and maintenance people.
Large Installed Base—Pneumatic systems are very common in existing buildings. This eliminates
the need to purchase the most expensive piece of equipment in a pneumatic control system—the
control air compressor. Extensions to existing pneumatic systems are generally very simple and
extremely cost-effective.
Disadvantages
Performance—Pneumatic controls provide proportional-only control for VAV terminal unit
systems. This control scheme is less accurate than the more advanced control schemes. Improper
calibration of pneumatic controls leads to poor energy utilization.
Versatility—A central pneumatic control system, where each of the control zones can be monitored
and adjusted from a remote location, is extremely costly to configure and to modify.
Operating and Maintenance Costs—Pneumatics easily drift and require constant upkeep and
scheduled maintenance. Diagnostic capability for pneumatics is not available. A main compressor
which is not maintained and becomes contaminated with oil or water can pump those
contaminants into the compressed-air-distribution system. This may require costly cleaning of the
system and a possible replacement of system components.
DDC Controls Basic Information
DDC controls have become the industry standard for VAV terminal unit control systems. DDC
systems use electronic field devices such as a flow transducer, a primary air modulating damper,
and an electronic thermostat. These field devices report software instructions of how the outputs
are positioned in relation to the inputs to a controller. The VariTrane™ system uses a primary air
valve and flow transducer for both DDC systems and analog electronic systems. However, the DDC
zone sensor is different from the analog electronic thermostat.
DDC controls provide much flexibility and considerable diagnostic capability. DDC controllers can
be connected together to form a network of controllers. Once the controllers are networked, they
can be monitored for proper operation from a remote location. Commands and overrides can be
sent for groups of controllers at one time to make system-wide changes. Commands and overrides
can be sent to individual units to allow problem diagnosis, temporary shutdown, startup schedules
or other specialized changes. When integrated into a building management system, the operation
of the VAV terminal unit system can be modified to do such things, as coincide with occupancy
schedules and reduce energy charges.
DDC control of VAV terminal units is a key element in providing intelligent and responsive building
management. Precision control, flexible comfort, and after hours access are all available with the
VariTrane™ DDC control system for VAV terminal units.

144 VAV-PRC011M-EN
Application Considerations
Key features of the system include:
• An advanced unit controller
• Flexible system design
• User-friendly interaction
Pneumatic Controls Basic Information
Pneumatic controls modulate air pressure of a controller to maintain setpoint. For VAV systems,
there are two primary types of pneumatic controllers—the room thermostat and the pneumatic
volume regulator (PVR).
Room Thermostats
The most visible controller to the customer is the room thermostat. Pneumatic room thermostats
can be classified by two characteristics: the tubing connection(s) to the thermostat and the action
of the thermostat output in response to a change in the input.
Room thermostats are available in models that require a one-pipe or a two-pipe configuration. The
name is derived from the number of tubes that must run to the thermostat location. The difference
is really in the construction of the thermostats. The two-pipe thermostats have a constant pressure
supply connected via an air tube to the thermostat supply air port. The supply air travels through
the thermostat’s relays, levers, diaphragm, and bleed port to produce an output. The output line
is connected to the output port of the thermostat and extends to the controlled device. The one-
pipe thermostat has, as its name suggests, only one air line connection. The thermostat works by
opening and closing an air bleed valve. This will either decrease or increase the pressure on the
controlled device, which is connected to the same line that runs to the thermostat.
Room thermostats also can be classified by their reaction to a change in temperature. Room
thermostats classified this way are denoted as either direct-acting or reverse-acting. Direct-acting
thermostats will increase their output pressure as the temperature the thermostat measures
increases.
On the contrary, reverse-acting thermostats will decrease their output pressure as the temperature
the thermostat measures increases.
Pneumatic Volume Regulators
These controllers accept the room thermostat signal and modulate the VAV terminal unit primary
air damper. The primary air damper is controlled for an airflow setpoint that is determined by the
room thermostat. The thermostat increases the PVR’s airflow setting when the temperature in the
space is warm. On the other hand, the thermostat decreases the PVR’s airflow setting when the
temperature in the space is cold.
Figure 13. Direct-acting thermostat response (L) and direct-acting thermostat response (R)

VAV-PRC011M-EN 145
Application Considerations
Currently, VariTrane offers two models of pneumatic volume regulators in its controls offering—
the 3011 regulator (used in most applications) and the 3501 model (used in dual-duct constant-
volume applications). The primary difference is the 3501 PVR’s ability to change the velocity
pressure linearly with a change in thermostat pressure, which results in improved stability at low
flows. In contrast, the 3011 PVR resets the velocity pressure with a change in thermostat pressure.
Reset Control of Minimum and Maximum Flow—The 3011 PVR and 3501 use fixed reset control of
minimum and maximum flow settings. The primary benefit of fixed reset in a pneumatic volume
regulator is stable flow control without excessive damper movement.
Fixed Reset—A fixed reset controller operates over a thermostat signal change of 5 psi between
minimum and maximum flow, regardless of the differential pressure flow sensor signal. The
thermostat is usually set for a gain of 2.5; i.e. it produces a 2.5 psi output change per degree of space
temperature change. This control strategy provides stable flow control with the primary air valve
throttling between minimum and maximum flow over a 2°F space temperature change.
Example 1: Air valve with a 6" inlet, Pneumatic thermostat gain = 2.5 psi/degree:
Minimum Flow=0 cfm, 0.0 in. wg flow signal
Maximum Flow=680 cfm, 2.0 in. wg flow signal
2.0 in. wg signal range
The damper will modulate from zero to maximum position over a 2°F temperature change.
Bleed Port to Atmosphere—Bleeding air to the atmosphere is a normal operation for a volume
regulator. The 3011 volume regulator addresses this function with a dedicated bleed port. When air
is bled through the flow sensor, the differential pressure signal from the sensor is affected. As a
result, the flow sensor signal can be radically altered if the volume regulator is bleeding air, and
may cause excessive damper movement.
Calibration—The minimum and maximum settings are independent of each other and need to be
set only once during calibration.
Signal Configuration Flexibility—Both can be configured to work with both normally-open and
normally-closed pneumatic air valves, and both direct-acting and reverse-acting thermostats.
Pneumatic Volume Regulators

146 VAV-PRC011M-EN
Application Considerations
Flow Measurement and Control
The differential pressure signal output of the flow ring provides the terminal unit controller a
measurement of the primary airflow through the inlet. The terminal unit controller then opens or
closes the inlet damper to maintain the controller airflow setpoint
Flow Measurement
Most VAV terminal units contain a differential pressure airflow measurement device, mounted at
the primary air inlet, to provide a signal to the terminal unit controller. Numerous names exist for
the differential pressure measurement device—flow sensor, flow bar, flow ring. The differential
pressure measured at the inlet varies according to the volumetric flow rate of primary air entering
the inlet.
The total pressure and the static pressure are measurable quantities. The flow measurement
device in a VAV terminal unit is designed to measure velocity pressure. Most flow sensors consist
of a hollow piece of tubing with orifices in it. The VariTrane air valve contains a flow ring as its flow
measuring device. The flow ring is two round coils of tubing. Evenly spaced orifices in the upstream
coil are the high-pressure taps that average the total pressure of air flowing through the air valve.
The orifices in the downstream ring are low-pressure taps that average the air pressure in the wake
of flow around the tube. By definition, the measurement of static pressure is to occur at a point
perpendicular to the airflow. The low-pressure taps on the VariTrane flow ring measure a pressure
that is parallel to the direction of flow but in the opposite direction of the flow. This “wake pressure”
that the downstream ring measures is lower than the actual duct static pressure. The difference
between the “wake pressure” and the static pressure can be accounted for so that the above
relationship between flow and differential pressure remain valid. The difference also helps create
a larger pressure differential than the velocity pressure. Since the pressures being measured in VAV
terminal box applications are small, this larger differential allows transducers and controllers to
measure and control at lower flow settings than would otherwise be possible.
The average velocity of air traveling through the inlet is expressed in the equation:
Where:
Often, the density is assumed to be a constant for dry air at standard conditions (68°F (20°C)) and
sea level pressure of 14.7 psi (101.4 kPa)). These conditions yield the following commonly used
equation:
The velocity pressure is defined as the difference between the total pressure in the duct and the
static pressure in the duct:
One of the most important characteristics of a VAV terminal unit is
its ability to accurately sense and control airflow. The VariTrane
terminal unit was developed with exactly that goal in mind. The
patented, multiple-point, averaging flow ring measures the
velocity of the air at the unit primary air inlet.
FPM = Velocity of air in feet per minute
1096.5 = A constant
VP = The velocity pressure of the air expressed in inches of water
DENS = The density of the air expressed in pounds per cubic foot
FPM 1096.5 VP
DENS
------------------=
FPM 4005 VP=

VAV-PRC011M-EN 147
Application Considerations
VP = TP - SP (All units are expressed in inches of water)
The amount of air traveling through the inlet is related to the area of the inlet and the velocity of
the air:
AIRFLOW = AREA (square feet) x AVERAGE VELOCITY (feet per minute)
Accuracy
The multiple, evenly spaced orifices in the flow ring of the VariTrane terminal unit provide quality
measurement accuracy even if ductwork turns or variations are present before the unit inlet. For
the most accurate readings, a minimum of 1½ diameters, and preferably 3 diameters, of straight-
run ductwork is recommended prior to the inlet connection. The straight-run ductwork should be
of the same diameter as the air valve inlet connection. If these recommendations are followed, and
the air density effects mentioned below are addressed, the flow ring will measure primary airflow
within ±5% of unit nominal airflow.
Air Density Effects
Changes in air density due to the conditions listed below sometimes create situations where the
standard flow sensing calibration parameters must be modified. These factors must be accounted
for to achieve accuracy with the flow sensing ring. Designers, installers, and air balancers should
be aware of these factors and know of the necessary adjustments to correct for them.
Elevation
At high elevations the air is less dense. Therefore, when measuring the same differential pressure
at elevation versus sea level the actual flow will be greater at elevation than it would be at sea level.
To calculate the density at an elevation other than standard conditions (most manufacturers choose
sea level as the point for their standard conditions), you must set up a ratio between the density
and differential pressure at standard conditions and the density and differential pressure at the new
elevation.
Since the data from the manufacturer is published at standard conditions, this equation should be
solved for the differential pressure at standard conditions and the other quantities substituted to
determine the ratio for the differential pressure measured at the new conditions.
Duct Pressure and Air Temperature Variations
While changes in these factors certainly affect the density of air, most operating parameters which
VAV systems need keep these effects very small. The impact on accuracy due to these changes is
less than one half of one percent except in very extreme conditions (extreme conditions are defined
as those systems with static pressures greater than 5 in. wg (1245 Pa) and primary air temperatures
greater than 100°F (37.8°C)). Since those types of systems occur so infrequently, we assume the
effects of duct pressure and air temperature variations to be negligible.
Figure 14. Air pressure measurement orientations
ΔPS dardConditionsταν
DENSS dardConditionsταν
-----------------------------------------------------------------------------------ΔPNew Conditions
DENSNew Conditions
-------------------------------------------------------------------
=

148 VAV-PRC011M-EN
Application Considerations
Linearity
With the increase in DDC controls over pneumatic controls, the issue of linearity is not as great as
it once was. The important aspect of flow measurement versus valve position is the accuracy of
the controller in determining and controlling the flow. Our units are tested for linearity and that
position versus airflow curve is downloaded and commissioned in the factory to insure proper
control of the unit.
Reheat Options
Hot water heating coils are generally applied on VAV terminal units as reheat devices. When
applying these coils it is important to make sure that they are operating in the proper air flow and
water flow range. Either a two-way or a three-way valve controls the coils.
The most important factor when sizing valves is the coefficient of velocity or Cv. The Cv is defined
as the flow rate, in gallons of 60°F (15.56°C) water, that will pass through the valve in one minute
with a one pound pressure drop. The coefficient of velocity, which is commonly called the flow
coefficient, is an industry standard rating. Valves having the same flow coefficient rating,
regardless of manufacturer, will have the same waterside performance characteristics.
The equation that governs valve sizing is:
Where
Cv=Flow coefficient
GPM=The maximum water flow rate through the valve in gallons per minute
DP=The maximum allowable differential pressure across the valve in psi
The flow and differential pressure are generally the known quantities. The equation is solved for
the flow coefficient. The flow coefficient is then compared to the published CV values for the control
valves that are available. The control valve with the CV that is the closest, but greater than, the
calculated flow coefficient is the correct choice for the control valve. This choice will keep the valve
pressure drop below the maximum allowable valve pressure drop. The valve pressure drop should
then be checked against the coil pressure drop. If the coil pressure drop is appreciably larger than
the valve pressure drop, a valve with a smaller CV should be selected to produce a larger control
valve pressure drop. If this new valve has a pressure drop that is much larger than the maximum
allowable pressure drop for valves, the system designer should be consulted to make sure that the
system hot water pumps can deliver the water at the new conditions.
Figure 15. Hot water coil (L) & hot water valves (R)
CvGPM
ΔP
--------------
=

VAV-PRC011M-EN 149
Application Considerations
Electric Reheat
Electric heating coils are applied on VAV terminal units as terminal reheat devices. Electric heat coil
capacity is rated in kilowatts (kW). Coils are available with the total capacity divided into one, two,
or three stages.
Electric heat coils are available in single-phase or three-phase models. This refers to the type of
power source connected to the coil. Single-phase models have resistance elements internally
connected in parallel. Three- phase models have resistance elements internally connected in a
delta or a wye configuration.
The current draw for the electric coil will depend upon whether it is a single-phase coil or a three-
phase coil. The current draw is necessary for determining what size wire should be used to power
the electric coils and how big the primary power fusing should be.
The equations for current draw for these coils are:
VariTrane three-phase electric heat is available in balanced configurations. For example, a 9 kW
three-phase coil, each stage would carry 1/3 or 3 kW of the load.
It is important to note that these coils have certain minimum airflow rates for each amount of kW
heat the coil can supply to operate safely. See Figure 29, p. 40 for minimum air flow rates by unit
inlet size and electric heat kW.
The equation that relates the airflow across an electric coil to the temperature rise and the coil
change in temperature is:
Where
CFM=Minimum airflow rate across the coil
kW=The heating capacity of the electric coil
3145=A constant
DP=The maximum rise in air temperature across the coil (usually 50 degrees F (28 degrees C))
Electric heat coils are available with magnetic or mercury contactors. Magnetic contactors are less
expensive than mercury contactors. However, mercury contactors can be cycled at a more rapid
rate without failing. Mercury contactors are rated for heavier duty use and should be used in as
many applications as possible. For pneumatic applications the electric coils are available with
factory-installed pressure-electric switches.
1φamps kW 1000×
PrimaryVoltage
--------------------------------------------------
=
3φamps kW 1000×
PrimaryVoltage 3
-----------------------------------------------------------
=
CFM kW 3145×
ΔT
-------------------------------
=

150 VAV-PRC011M-EN
Application Considerations
Insulation
Matte-Faced
This type of insulation is used for typical applications. It consists of a fiberglass core covered by
a high-density skin. The dual-density construction provides good sound attenuation and thermal
performance.
Foil-Faced
This type of insulation is used in applications where there is some concern regarding airborne
contaminants entering the space, or dirt being trapped in the fibers of the insulation. The insulation
is composed of a fiberglass core laminated to a foil sheet. Foil-faced insulation will provide the
same sound attenuation performance as matte-faced insulation.
Double-Wall
This type of insulation is used in applications where there is extreme concern regarding airborne
contaminants entering the space or dirt being trapped in the fibers of the insulation. The insulation
is the same as the matte-faced insulation. However, after the insulation is installed, a second solid
wall of 26-gage steel covers the insulation. All wire penetrations of this insulation are covered by
a grommet. This type of insulation will result in higher discharge and radiated sound power.
Closed-Cell
This type of insulation is used in applications where IAQ and fibers are of primary concern. The
acoustics of the closed-cell insulation are similar to double-wall insulation. The thermal properties
are similar to fiberglass insulation. This insulation contains no fiberglass.
Acoustics
Acoustical Best Practices
Acoustics with terminal units is sometimes more confusing than it needs to be. As we know, lower
velocities within a unit leads to improved acoustical performance. Additionally, if the VAV terminal
unit has a fan, a lower RPM provides better Acoustical performance. It is as simple as that—there
are some catches, however.
Additional considerations will be discussed in more detail throughout this portion of Application
Considerations, such as unit size and type, appurtenance affects (due to insulation, attenuation,
etc.), certification, and computer modeling. Let’s take a look at the first consideration, sizing of
units.
Sizing of Units
Before blindly increasing the size of units, we must first understand what is setting the acoustics
within the space. In general, over 95% of acoustics in VAV terminal units, which set the sound
Encapsulated edges
Insulation in a VAV terminal unit is used to avoid condensation
on the outside of the unit, to reduce the heat transfer from the
cold primary air entering the unit, and to reduce the unit noise.
The VariTrane line offers four types of unit insulation. The type
of facing classifies the types of insulation. To enhance IAQ
effectiveness, edges of all insulation types have metal
encapsulated edges.

VAV-PRC011M-EN 151
Application Considerations
pressure levels and ultimately the NC within the space, is from radiated sound. This is readily
known for fan-powered units, but less commonly known for single- and dual-duct units. Radiated
sound emanates from the unit and enters the occupied space via means other than through the
supply ductwork. The most typical path is through the plenum space, then through the ceiling, then
into the occupied space. While discharge sound should never be ignored, radiated sound is the
most dominant and usually the most critical sound source.
When increasing air valve sizes, BE CAREFUL. Oversizing an air valve can adversely impact the
ability to modulate and properly control temperature in the space. In extremely oversized
situations, the air valve will operate like a two-position controlled device, with air either being “on”,
or “off”, and not really much in between. The best way to avoid this is to understand that the
minimum for most air valves is 300 FPM. This is a function of the flow sensing device and the ability
of the pressure transducer and controller to properly read and report flow. This is not manufacturer
specific, as physics applies to all. Therefore, when sizing air valves, regardless of the max cooling
velocity the minimum velocity for proper pressure independent flow is 300 FPM.
Modulation capability and range is vital for proper operation of VAV systems. With oversized units,
the unit will act as a constant volume system eliminating the energy savings and individual zone
control advantages of VAV systems. A good rule of thumb is to size cooling airflow for around 2000
FPM. VAV systems only operate at full flow when there is a maximum call for cooling in the zone.
The greatest portion of the time, an air valve will be operating at partial flows.
When sizing fan-powered units, the fan airflow range can be determined by looking at the fan-
curve. Because parallel and series fan-powered units operate at a constant fan flow, selections can
be made all the way to the lowest flow ranges of the fan curve. A good balance of performance and
cost is to select fans at 70-80% of maximum fan flow.
Insulation types
Insulation is a factor to consider when dealing with the acoustics of terminal units. Most insulation
types will provide similar acoustical results, but there are exceptions. Double-wall and closed-cell
foam insulation will generally increase your sound levels because of the increased reflective
surface area that the solid inner-wall and closed-cell construction provides. This increase in sound
will have to be balanced with the IAQ and cleanability considerations of the dual-wall and closed-
cell construction.
Placement of units
Unit placement in a building can have a significant impact on the acceptable sound levels. Locating
units above non-critical spaces (hallways, closets, and storerooms) will help to contain radiated
sound from entering the critical occupied zones.
Unit Attenuation
Terminal unit-installed attenuators are an option available to provide path sound attenuation.
Manufacturer-provided attenuators on the discharge of a terminal unit are targeted at reducing
discharge path noise and are typically a simple lined piece of ductwork. It would often be easier and
less expensive to design the downstream ductwork to be slightly longer and require the installing
contractor to include lining in it. Attenuators on the plenum inlet of fan-powered terminals are
targeted at reducing radiated path noise since the plenum opening on a fan-powered terminal unit
is typically the critical path sound source. Significant reduction in radiated path noise can result
from a well-designed inlet attenuator. The attenuation from these attenuators is due to simple
absorption from the attenuator lining and occupant line of sight sound path obstruction. Therefore,
longer attenuators and attenuators that require the sound to turn multiple corners before reaching
the occupied space provide superior results, particularly in the lower frequency bands.

152 VAV-PRC011M-EN
Application Considerations
Attenuators that are simple “cups” at the plenum inlet(s) have been shown in Trane’s acoustical
mock-up to provide no measurable reduction in sound pressure in the critical octave bands which
set the occupied space noise criteria.
Certification and Testing
Terminal units should be submitted based on the same criteria. There are several ways to ensure
this by certification and testing.
Raw unit sound data can be good measurement criteria for evaluation. In using this as a basis for
comparison, the designer needs to make sure that the information is based on the AHRI Standard
880-2011 that gives the procedure for testing.
Specifying NC or RC sound levels is a possible comparison, but the designer needs to be sure the
comparison is fair. Two options are to specify the attenuation effect on which you would like the
units to be evaluated or to specify that AHRI Standard 885-2008 transfer functions be used. The
importance of AHRI Standard 885-2008 is that it is the first AHRI Standard that specifies exact
transfer functions to be used for evaluation. Previous versions of the standard gave guidelines, but
the manufacturers could choose their own set of factors.
By using NC sound levels, it is possible to express acceptable sound levels for various types of
buildings or environments. A few examples are:
Table 51. Octave band frequencies
Octave Band Center Frequency Band Edge Frequencies
1
2
3
4
63
125
250
500
44.6-88.5
88.5-177
177-354
354-707
5
6
7
8
1000
2000
4000
8000
707-1414
1414-2830
2830-5650
5650-11300

VAV-PRC011M-EN 153
Application Considerations
Path Attenuation
Sound is generated by a terminal unit can reach the occupied space along several paths. The
terminal unit generated sound will lose energy—i.e., the energy is absorbed by path obstacles—
as it travels to the occupied space. This acoustical energy dissipation as it travels to the occupied
space is called path attenuation. The amount of energy lost along a particular path can be
quantified and predicted using the procedure outlined in AHRI-885. Each path must be considered
when determining acceptable sound power generated by a terminal unit.
The term “transfer function” is often used to describe the entire path attenuation value for each
octave band (i.e., the sum of all components of a particular path).
Examples of path attenuation include locating the terminal unit away from the occupied space,
increasing the STC (sound transmission classification) of the ceiling tile used, internally lining
ductwork, drywall lagging the ceiling tiles or enclosing the terminal unit in drywall. All of these
choices have costs associated with them that must be weighed against the benefits. Some of these
alternatives can be acoustically evaluated from application data provided in AHRI-885. Others may
require professional analysis from an acoustical consultant.
Computer Modeling
Computer modeling of acoustical paths is available to help estimate sound levels and determine
problem sources. The software used by Trane for computer modeling is called Trane Acoustics
Program (TAP™).
TAP can analyze different room configurations and materials to quickly determine the estimated
total sound levels (radiated and discharged) in a space. The Trane Official Product Selection System
(TOPSS™) can also be used to determine sound levels of terminal units. You can base selections
on a maximum sound level and enter your own attenuation factors (defaults based on AHRI-885
are also available).
Other Resources
Refer to “Additional VAV System and Product References,” p. 156 to see a list of publications to help
with the basics of acoustical theory and modeling. You can also contact your local Trane
salesperson to discuss the issue.
Duct Design
Designing cost-effective VAV duct systems is challenging. Some duct design methods result in
better pressure balance than others do. Duct shape and duct material can influence duct system
design and cost. In addition, duct layout is properly designed for optimal duct installation and
operation.
Duct Design Program
Trane has developed a computer program, VariTrane™ Duct Designer, to aid in the duct design
process. This program is used to calculate duct sizes, fitting sizes, terminal unit sizes, and pressure
drops according to the equal friction or static regain method. The duct design program can be
easily incorporated into the selection of VAV terminal units. The inputs and outputs for the program
enable VariTrane units to be selected based on the conditions you require. This makes selecting and
Concert Hall NC-22
Hospital Room NC-30
School Room NC-35
General Office NC-40
Cafeteria NC-45
Factory NC-65

154 VAV-PRC011M-EN
Application Considerations
scheduling units much easier. Contact the local sales office or the Trane C.D.S.™ department for
more details on this program.
Design Methods
The two most widely used supply duct design methods—equal friction and static regain—are
discussed below.
Equal Friction – Using this method, ducts are sized at design flow to have roughly the same static
pressure drop for every 100 feet of duct. Static pressures throughout the duct system can be
balanced at design flow using balancing dampers, but are no longer balanced at part load flows.
For this reason, equal friction duct designs are better suited for constant volume systems than for
VAV systems. If the equal friction method is used for the VAV supply duct design, the terminal units
usually require pressure-independent (PI) control capability to avoid excessive flow rates when
duct pressures are high.
In VAV systems, the ducts located downstream of the terminal unit are usually sized for equal
friction. The advantage of this design method is its simplicity. Often, calculations can be made
using simple tables and duct calculators. Drawbacks include increased higher total pressure drops
and higher operating costs.
Static Regain – In the static regain method, ducts are sized to maintain constant static pressure in
each section, which is achieved by balancing the total and velocity pressure drops of each section.
In other words, static pressure is “regained” by the loss of velocity pressure. Since the static
pressures throughout the duct system are roughly balanced at design and part load flow, static
regain duct designs can be used successfully for either constant volume or VAV systems. When the
static regain method is used for VAV systems, the system is roughly pressure balanced at design.
Advantages of the static regain method include reduced total pressure drops, lower operating
costs, and balanced pressures over a wide range of flows. The drawback of this design is the time-
consuming, iterative calculation procedure and for large systems, it is essential to have a duct
design computer program.
Best Practices
Common Mistakes
Some of the most common system or installation errors are discussed below.
Reducers at Unit Inlet
This problem is a very common issue that is seen in applications of VariTrane products. It is often
mistaken by those in the field as an unacceptably large static pressure drop through the unit. It is
also sometimes mistaken as a malfunctioning flow ring, pressure transducer (if DDC or analog
electronic controls are present) or PVR (if pneumatic controls are present).
This problem is sometimes unknowingly encountered because of the capability of the VariTrane
unit to allow greater airflow for a specific size duct than other terminal units. For example, a project
engineer specifies an 8" (203 mm) round take off from the main duct trunk to the VAV terminal unit.
The person supplying the VAV terminal unit checks the required airflow and finds that a VariTrane
unit with a 6" (152 mm) inlet will provide the specified terminal unit performance. The terminal unit
supplier submits, receives approval, and orders the 6" (152 mm) inlet unit. While this is happening,
the installing contractor has run the connecting duct from the main trunk to the terminal unit in the
specified 8" (152 mm) round. The unit arrives at the job site, and the installer notices that the 8" (203
mm) duct and the 6" (152 mm) terminal unit inlet do not match. To get the unit installed, an 8- to
6-inch reducer is placed at the inlet to the terminal unit air valve.
The reducer will cause a phenomenon called flow separation at the unit inlet. Fluid dynamics
analysis can present a detailed technical explanation of flow separation, but the characteristics
important to this discussion are the production of pressure loss and turbulence. The reducer will
have a significant static pressure drop associated with it since the air velocity is increased (i.e.,

VAV-PRC011M-EN 155
Application Considerations
static pressure is given up for increased velocity pressure). The pressure loss is sometimes
mistaken as a loss due to the function of the terminal unit. The turbulence is at its greatest just
downstream of the reducer. Unfortunately, this is the location of the flow ring at the air-valve inlet.
The reducer will cause the flow ring to give an inaccurate and inconsistent reading because of the
turbulent air.
The solutions to this situation are:
• Locate the reducer upstream of the terminal unit at least three duct diameters to eliminate flow
separation and turbulence at the unit inlet and to improve the airflow measurement accuracy.
• Consider proper sizing of the terminal unit in the duct design and account for the pressure loss
of the reducer in the central fan selection if a reducer is required. Be cautious of “oversizing”
a VAV terminal. It is good practice to make sure that the inlet duct velocity at the minimum
airflow setting is no lower than 500 feet per minute.
Improper Use of Flexible Ductwork
While flexible ductwork has many benefits, improper use can cause numerous problems in a VAV
system. Flexible ductwork causes turbulent airflow and relatively large static pressure drops.
Flexible ductwork at a primary damper inlet (i.e., the flow sensor location) may cause flow accuracy
and repeatability problems due to turbulence. The use of flexible ductwork should be primarily
limited to the downstream side of the terminal units in a VAV system. Use of flexible ductwork
upstream of terminal units should be kept to an absolute minimum. All runs of flexible ductwork
should be kept as short as possible. While most know these guidelines, the ease of installation
which flexible ductwork provides is always an enticement to push the limits of what are acceptable
practices.
Static Pressure Measurement Errors
Improper measurement techniques for static pressure can lead many to mistakenly believe that the
terminal unit is causing a large pressure drop in the system. The chief error made here is taking a
static pressure measurement in turbulent locations such as flexible ductwork or near transitions.
This produces invalid static pressure readings. Another error commonly made is trying to read the
static pressure at the same point as the flow sensing device. The inlets to VAV terminal units
produce turbulence and will give poor readings. Flow sensors with their multiple-point averaging
capability are best equipped to deal with this type of flow, while a single-point static probe is not.
Another common error is the incorrect orientation of the static pressure probe. The static pressure
is correctly measured when the probe is oriented perpendicular to the direction of airflow. The
probe, or a part of it, should never be facing the direction of airflow, because the total pressure will
influence the reading of the probe.
Unit Conversions
Table 52. Conversions of length and area
To convert From To Multiply by
Length
Length
Length
Length
In.
Ft
m
m
m
m
In.
Ft
0.0254
0.3048
39.3701
3.28084
Area
Area
Area
Area
In.2
Ft2
m2
m2
m2
m2
In.2
Ft2
0.00064516
0.092903
1550
10.7639

156 VAV-PRC011M-EN
Application Considerations
Additional VAV System and Product References
VAV Systems Air Conditioning Clinic
This clinic is designed to explain the system components, the system configurations, many of the
VAV system options and applications. A great resource for VAV system understanding.
Literature Order Number: TRG-TRC014-EN
Intelligent Variable Air —
An EarthWise System from Trane for chilled-water applications
This catalog describes Trane's EarthWise approach to chilled-water VAV systems, which includes
pre-packaged, optimized system controls to consistently deliver energy savings, interactive
operator dashboards that demonstrate real time savings, and intelligent analytics that identify
efficiency improvement opportunities, helping sustain a high level of performance for life.
Literature Order Number: APP-PRC002-EN
Intelligent Variable Air —
An EarthWise System from Trane for packaged DX applications
This catalog describes Trane's EarthWise approach to packaged DX rooftop VAV systems, which
includes pre-packaged, optimized system controls to consistently deliver energy savings,
interactive operator dashboards that demonstrate real time savings, and intelligent analytics that
identify efficiency improvement opportunities, helping sustain a high level of performance for life.
Literature Order Number: APP-PRC003-EN
Rooftop VAV Systems Applications Engineering Manual
Discusses proper design and application of packaged rooftop, VAV systems. Topics include: basic
system operation, benefits and drawbacks of a rooftop VAV system, in-depth coverage of system
components (packaged rooftop unit, VAV terminal units, air distribution system, hot water heating
system), solutions to address common design challenges (thermal zoning, ventilation, humidity
control, energy efficiency, acoustics), several system variations (cold air distribution, single-zone
VAV, air-to-air energy recovery), and common unit-level and system-level control functions
(including system optimization strategies).
Literature order Number: SYS-APM007-EN
Table 53. Conversions of velocity, pressure, and flow rate
To convert From To Multiply by
Velocity
Velocity
Ft/min
M/s
M/s
Ft/min
0.00508
196.850
Pressure
Pressure
Pressure
Pressure
Pressure
Pressure
Psi
Ft of water
In. of water
Pa
Pa
Pa
Pa
Pa
Pa
Psi
Ft of water
In. of water
6894.76
2988.98
249.082
0.000145038
0.000334562
0.00401474
Flow Rate
Flow Rate
Flow Rate
Flow Rate
Flow Rate
Flow Rate
Cfm
Cfm
Gpm
m3/s
L/s
L/s
L/s
m3/s
L/s
Cfm
Cfm
Gpm
0.4719
0.000471947
0.0630902
2118.88
2.1191
15.8503

VAV-PRC011M-EN 157
Application Considerations
Chilled-Water VAV Systems Applications Engineering Manual
Discusses proper design and application of chilled-water, VAV systems. Topics include: basic
system operation, benefits and drawbacks of a chilled-water VAV system, in-depth coverage of the
components that make up the system (VAV air-handling units, VAV terminal units, air distribution
system, chilled-water system, hot water heating system), solutions to address common design
challenges (thermal zoning, ventilation, humidity control, energy efficiency, acoustics), several
system variations (cold air distribution, single-zone VAV, air-to-air energy recovery, dual-duct VAV
systems), and common unit-level and system-level control functions (including system
optimization strategies)
Literature order Number: SYS-APM008-EN
Acoustics in Air Conditioning Applications Engineering Manual
This manual describes the basic fundamentals, behavior, measurement, and control of sound, all
directed at the design of quiet systems.
Literature Order Number: ISS-APM001-EN
VariTrac™ catalog
The catalog will help explain features and benefits of VariTrac, how the VariTrac product works,
applications for the product, and selection procedures.
Literature Order Number: VAV-PRC003-EN
ASHRAE Handbook of Fundamentals
ASHRAE Handbook of HVAC Systems and Equipment
ASHRAE Handbook of HVAC Applications
ASHRAE Handbook of Refrigeration
Web sites:
•www.ashrae.org
•www.ahrinet.org
•www.trane.com

Trane optimizes the performance of homes and buildings around the world. A business of Ingersoll Rand, the leader in
creating and sustaining safe, comfortable and energy efficient environments, Trane offers a broad portfolio of advanced
controls and HVAC systems, comprehensive building services, and parts. For more information, visit www.Trane.com.
Trane has a policy of continuous product and product data improvement and reserves the right to change design and specifications without notice.
We are committed to using environmentally
conscious print practices that reduce waste.
© 2015 Trane All rights reserved
VAV-PRC011M-EN 03 Mar 2015
Supersedes VAV-PRC011L-EN (16 Sep 2014)