Tyco Safety Software House RMXIC Proximity Card Reader HID iClass compatible User Manual rm1 ICP quick install
Tyco Safety Products / Software House Proximity Card Reader HID iClass compatible rm1 ICP quick install
Contents
- 1. USERS MANUAL
- 2. users manual
USERS MANUAL
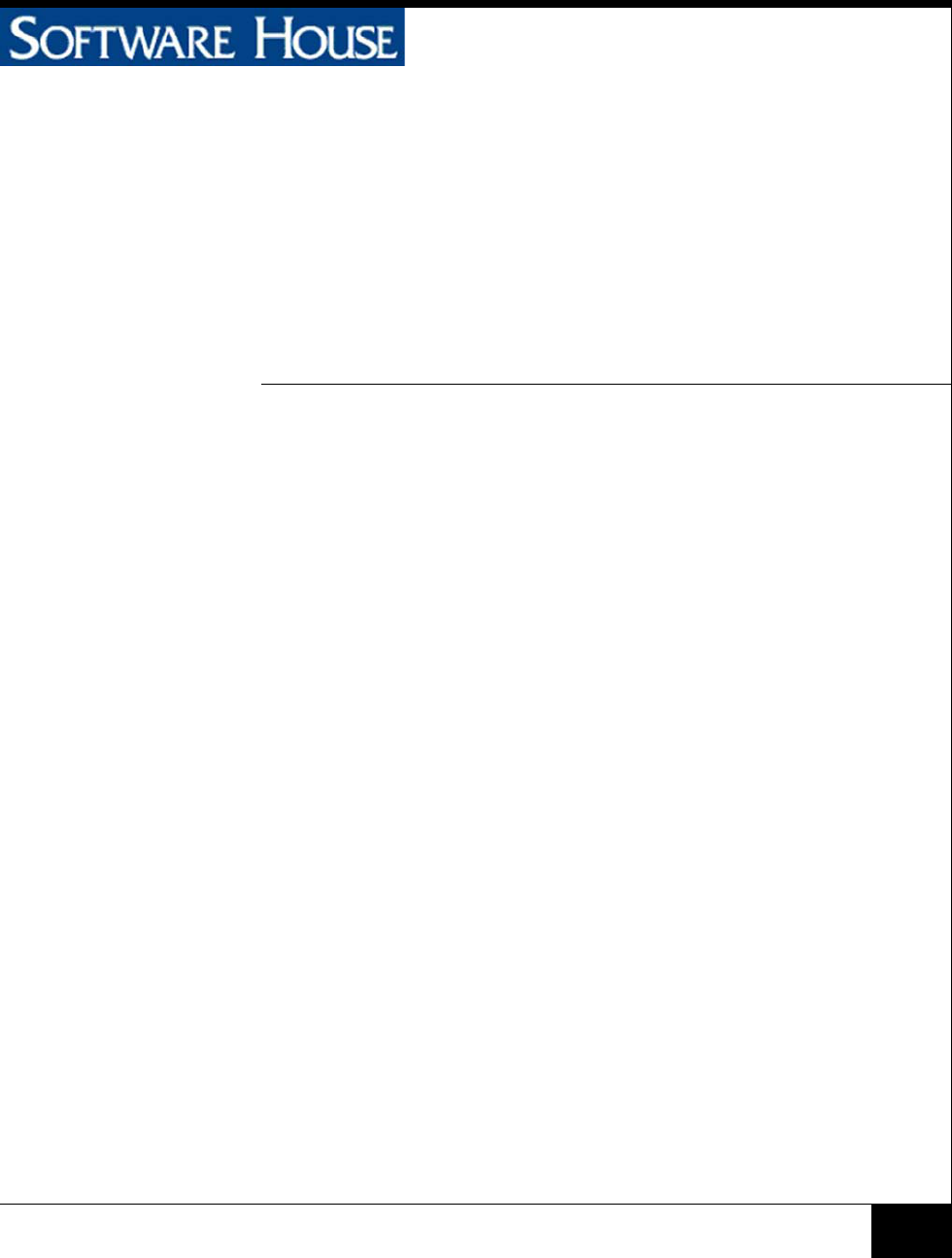
1
RM-iC Series
Quick Start
Installation Guide
Version B.0
Part Number UM-068
December 2004
PRODUCT
OVERVIEW
The RM-iC series readers provide an enclosed RM-4 board and attached iCLASS read
head, available in the following styles:
RM1-IC - enclosed RM-4 and attached iCLASS read head
RM2-IC - enclosed RM-4 with keypad and attached iCLASS read head
RM2L-IC - enclosed RM-4 with keypad, LCD display, and attached iCLASS read
head
The RM-iC Quick Start Installation Guide provides a synopsis of installation and
connection information for RM-IC series readers. Refer to the RM-4/RM-4E Technical
Manual for in-depth technical and installation information.
Specifications The following specifications apply to all RM-iC series readers:
Power: 12VDC, 300 mA
Cable: Beldon 9841
Cable distance from iSTAR or apC: 4,000 ft
Temperature: 32° F to 140° F (0°C to 60°C)
Qualified on 26 bit, 35 bit, 37 bit and 32 bit Mifare serial number card formats
Standards RM1-IC series readers are Underwriters Laboratories Inc.(UL), Listed to Standard UL
294, Access Control System Units, Fifth Edition.
RM-iC series readers must be installed within a protected premise in accordance with
the National Electrical Code (ANSI/NFPA 70), local codes, and the authorities having
jurisdiction.
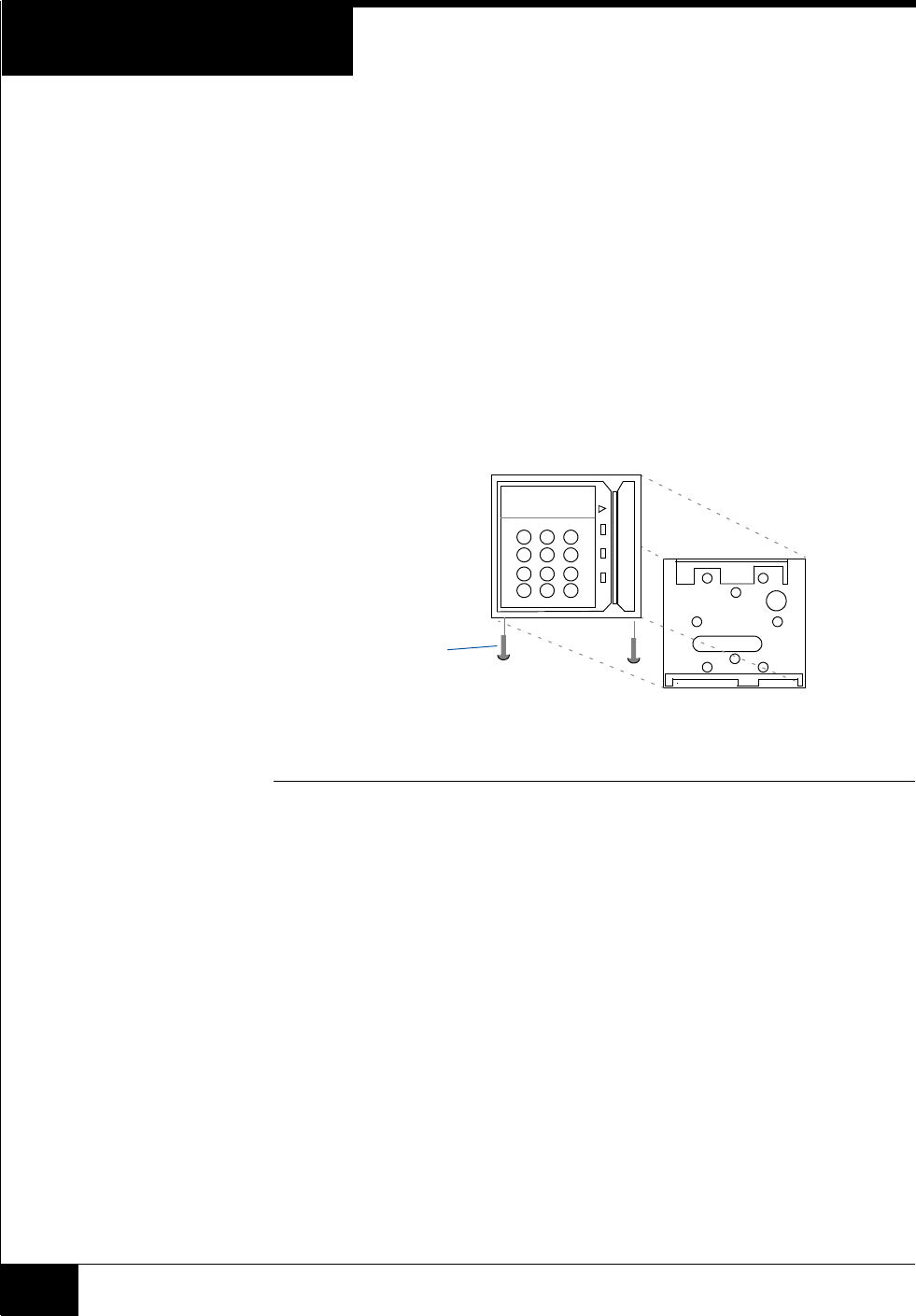
Installation
2
INSTALLATION Installing an RM-iC series reader involves:
1. Installing the mount plate
2. Wiring the components
3. Grounding and shielding the wire bus
4. Setting the RM-4 address
5. Installing the ARM-1 relay board
6. Installing the heater kit.
Installing the Mount
Plate
Figure 1 shows RM-iC standard housing and mount plates. All RM-iC series readers
conform to the same housing and mount plate dimensions.
FIGURE 1. Standard Housing and Mount Plate
Figure 2 shows mount plate dimensions.
Standard Housing
Standard
mount plate
Housing
screws
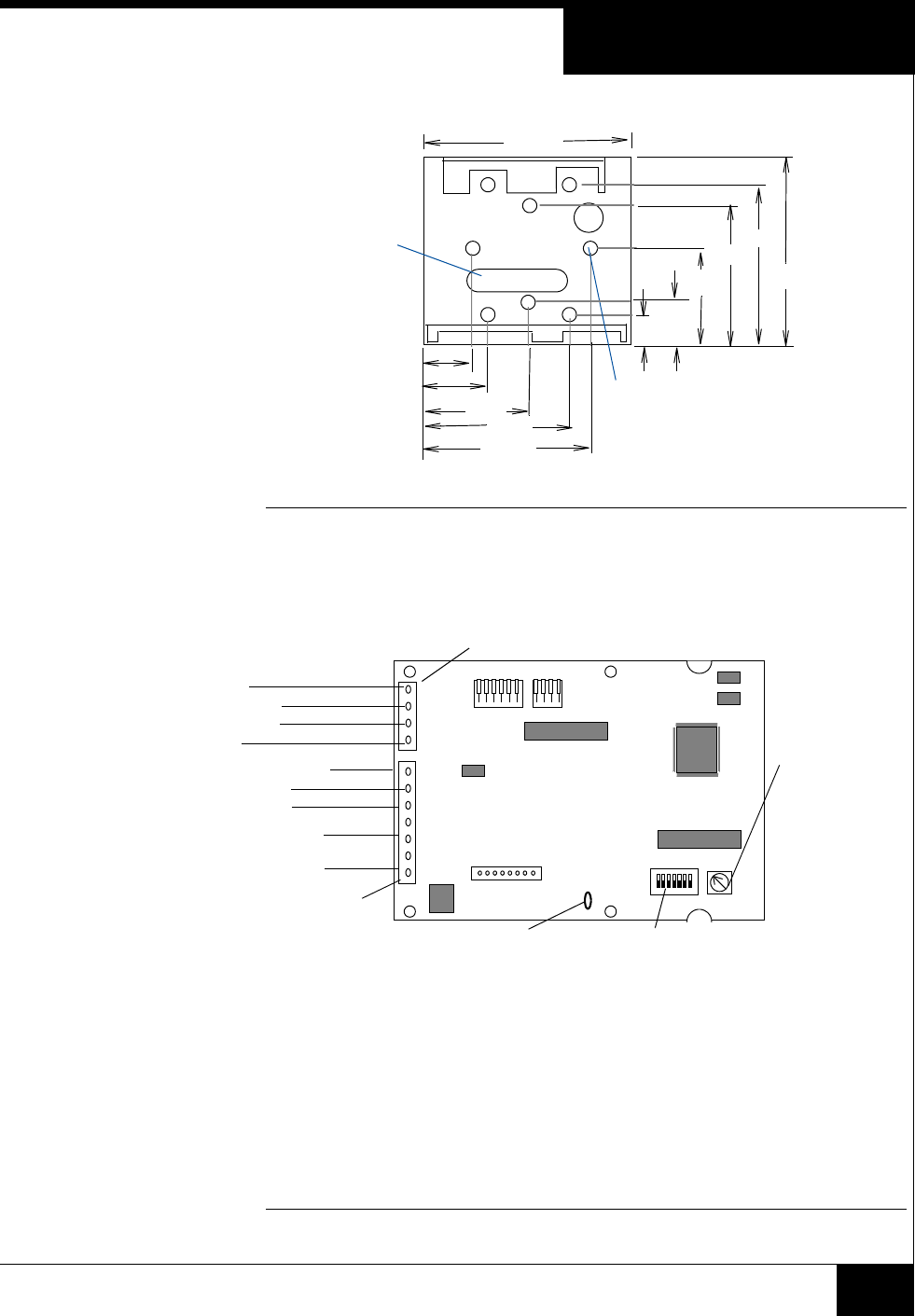
Installation
3
FIGURE 2. Mount Plate Dimensions
Wiring the Components Figure 3 shows RM-4 wiring.
FIGURE 3. RM-4 Wiring Requirements
Wiring
access
1.29"
.83"
2.47"
3.66"
2.73"
1.54"
5.45"
4.94"
4.11"
1.82"
3.92"
3.64"
8x
Mounting hole
0.156" Thru, 0.280” Countersink
1
J2
P1
P5
J5
SW3
SW1
1
1
1
4
SW1-
Address
switch
6
7
8
+12V Relay Power
Relay 1 Drive
Relay 2 Drive
(Pin 4 &5) Input 1
(Pin 6 & 7) Input 2
P1- Reader
port wiring
+12V
TXD/RXD+
TXD/RXD-
GND
P5 Door Inputs
and Outputs J5- Chassis
ground wiring
Position 1 Magnetic Off
Wiegand On
Position 2 LCD Off
No LCD On
Position 3 LED (normal) Off
Ext. bi-color On
Position 4 Tamper (normal) Off
Tamper (bypass) On
Position 5 EOL terminate Off
Not terminated On
Position 6 LED (normal) Off
J4-3 wire-or
red and green On
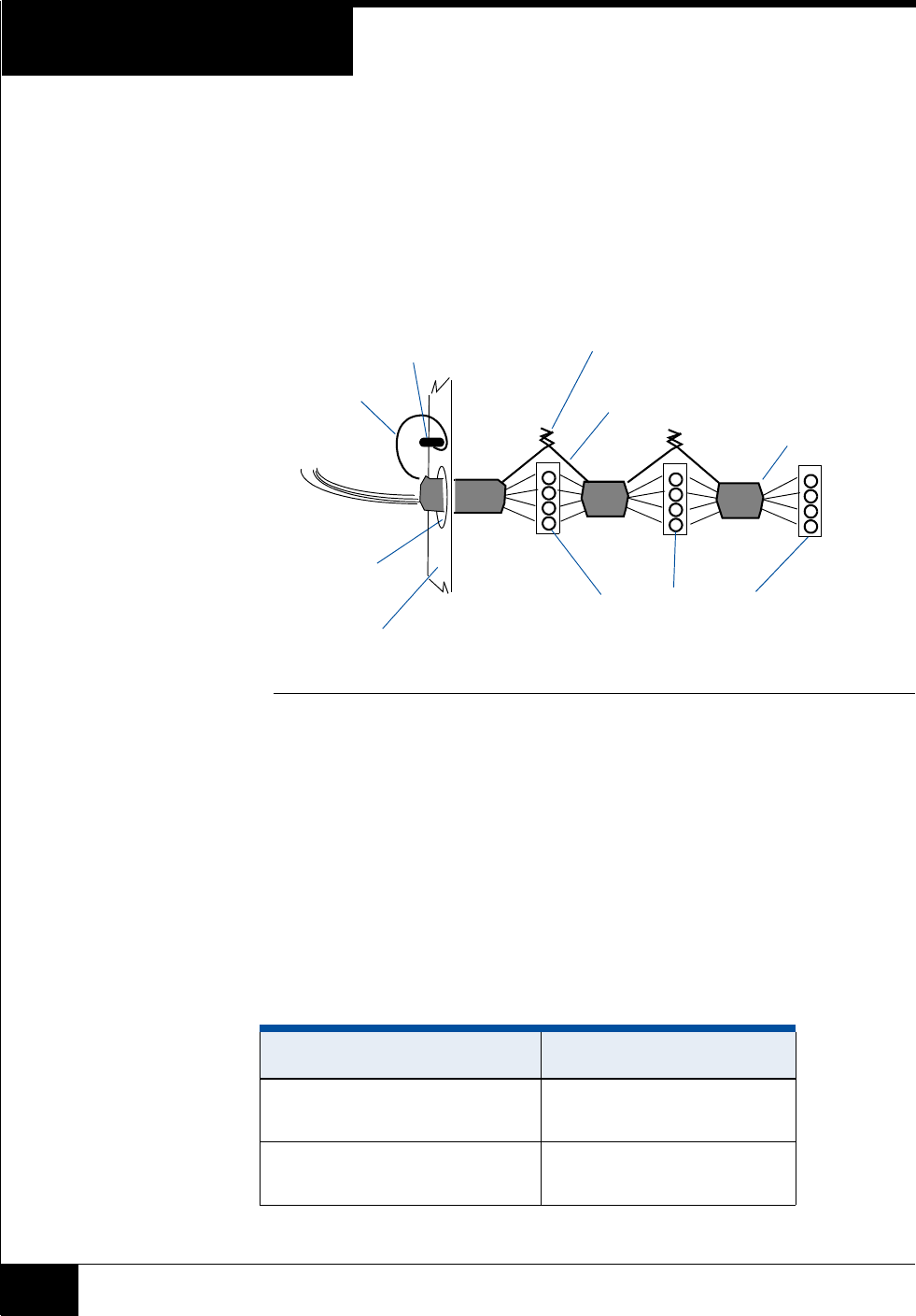
Installation
4
Grounding and
Shielding
When bus wiring more than one RM-iC reader (Figure 4 ):
1. Attach the shields along the bus together (insulate each connection). Snip off the
shield wire at the end of the bus.
2. Attach the shield to the ground at only one point, the ground stud inside the cabinet
adjacent to the knockout.
3. Attach a local earth ground (18 or 22 gauge) wire to the J5 component.
FIGURE 4. Reader Shield Wiring
Setting Module
Address and
EOL Termination
To set the module address, set SW1 (16 position rotary switch) to a number from one to
eight. Every RM-iC series reader on a bus must have a unique address.
To set EOL termination, set SW3, position 5 to the On (closed) position if the module is
the last unit in the bus. If the module is not last, SW3, position 5 should be Off (open).
Installing the ARM-1
Relay
Two ARM-1 relay components can be connected to the RM-iC series reader through the
P5 connector (Table 1 ). P5-1 is the common pin for either ARM. P5-2 is the output
drive for the first relay. P5-3 is the output drive for the second relay.
ACM module
RS-485 connector on a reader
Knockout
Twist shield wires together and insulate
(do not ground)
Ground stud
(bus configuration)
Shield wire
Enclosure/cabinet
Shield wire Snip off shield
wire at end of
bus
TABLE 1. ARM-1 Wiring
Module Wiring
ARM-1 Relay P2-1 to RM P5-1
P2-2 to RM P5-2
ARM-2 Relay P2-1 to RM P5-1
P2-2 to RM P5-3
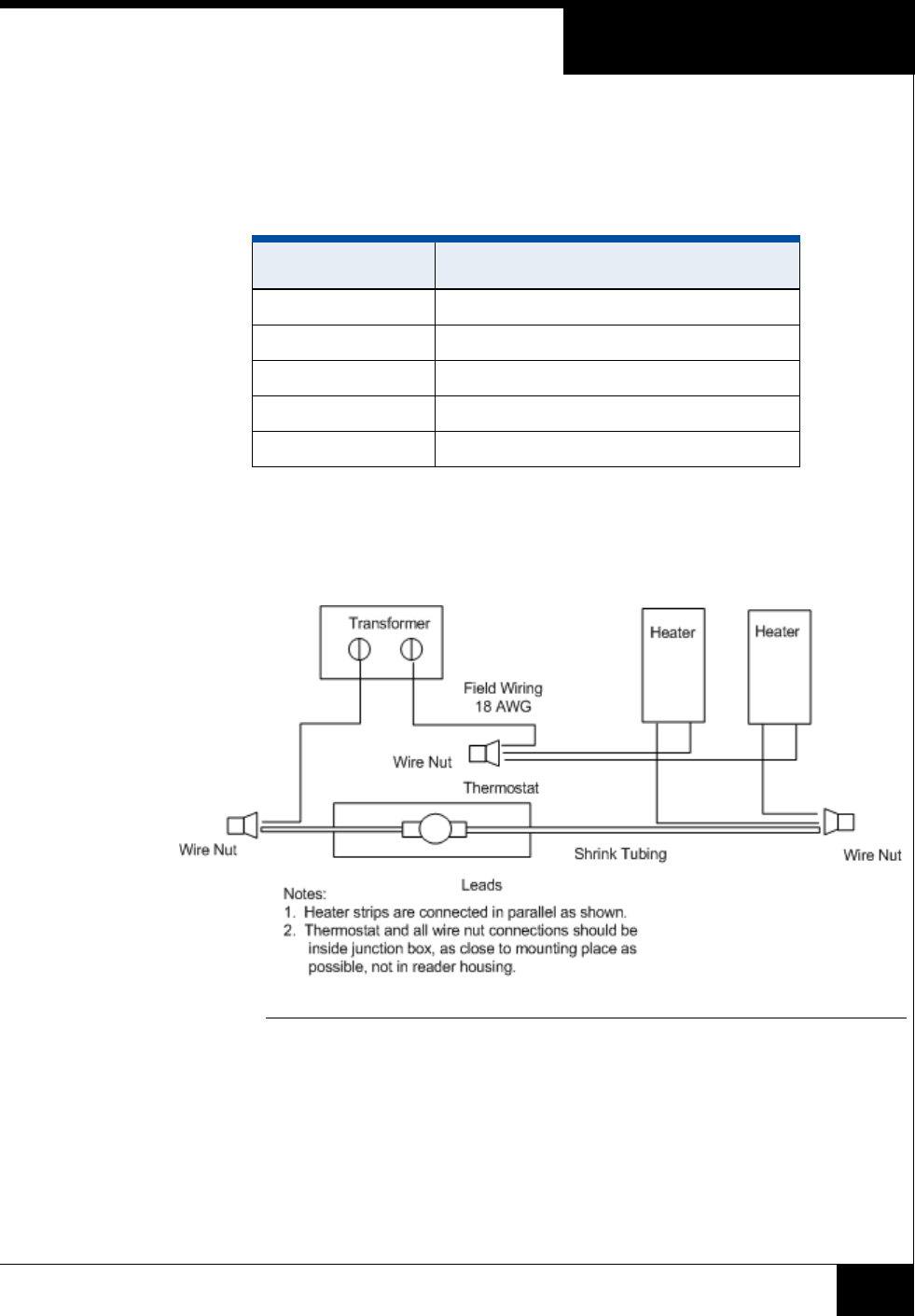
Installation
5
Installing the Heater RM-iC readers require a heater kit in environments where temperatures exceed 5 ° C.
The heater kit contains the following parts:
Part # 130-915A is supplied without a transformer. A UL Listed Class 2 transformer
rated output 12 VAC, 40 VA is required to proper installation.
Figure 5 shows RM/heater wiring.
FIGURE 5. RM/Heater Wiring
TABLE 2. Heater Parts
Quantity Description
1 Transformer 12 VAC 40VA
2 Heater Strips
1 Thermostat (turns on at 40 ° F
3 Wire nuts
2 6-32x1/4 screws to mount thermostat to RM plate.
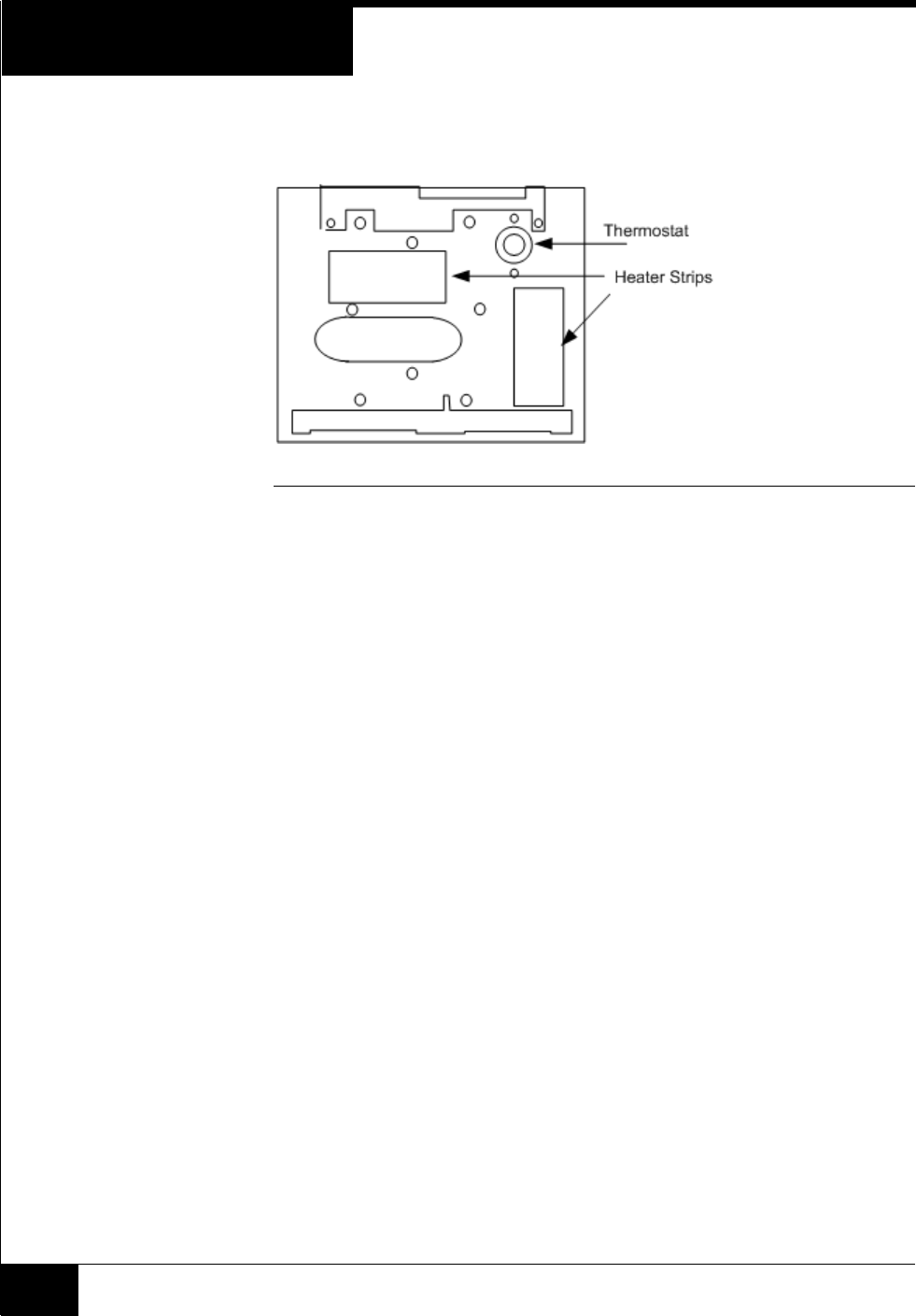
Testing with apC or iSTAR hardware
6
Figure 6 shows RM installation
.
FIGURE 6. RM Installation
Heater Strip Application
To apply the heater strip:
1. Clean the attachment surface of the back plate with a solvent such as alcohol (use all
required precautions when handling solvents).
2. Carefully remove the release film from the adhesive.
3. Locate the heater on the clean surface of the back plate.
4. Gently roll in place to remove air bubbles.
5. Allow to remain for 72 hours before use for maximum adhesion.
Air gaps or bubbles under the heater cause localized overheating and possible heater
burnout. Also, application of adhesives at temperatures below 50 D is not
recommended.
TESTING WITH APC
OR ISTAR
HARDWARE
To test an RM-iC series reader with an apC or iSTAR:
1. Measure the supply voltage to the RM-4.
The voltage can be measured between pin 1 (+12 Volt supply) and pin 4 (ground) on
the P4 connector. The voltage must be +12 Volts (+/-5%).
2. Check the RM-iC reader address setting.
The RM-iC must be set to an unused address when connected to the apC or iSTAR.
Use rotary switch SW1 to set the reader address.
3. Check the RM-4 for communications to the apC or iSTAR.
4. Check the supervised inputs.
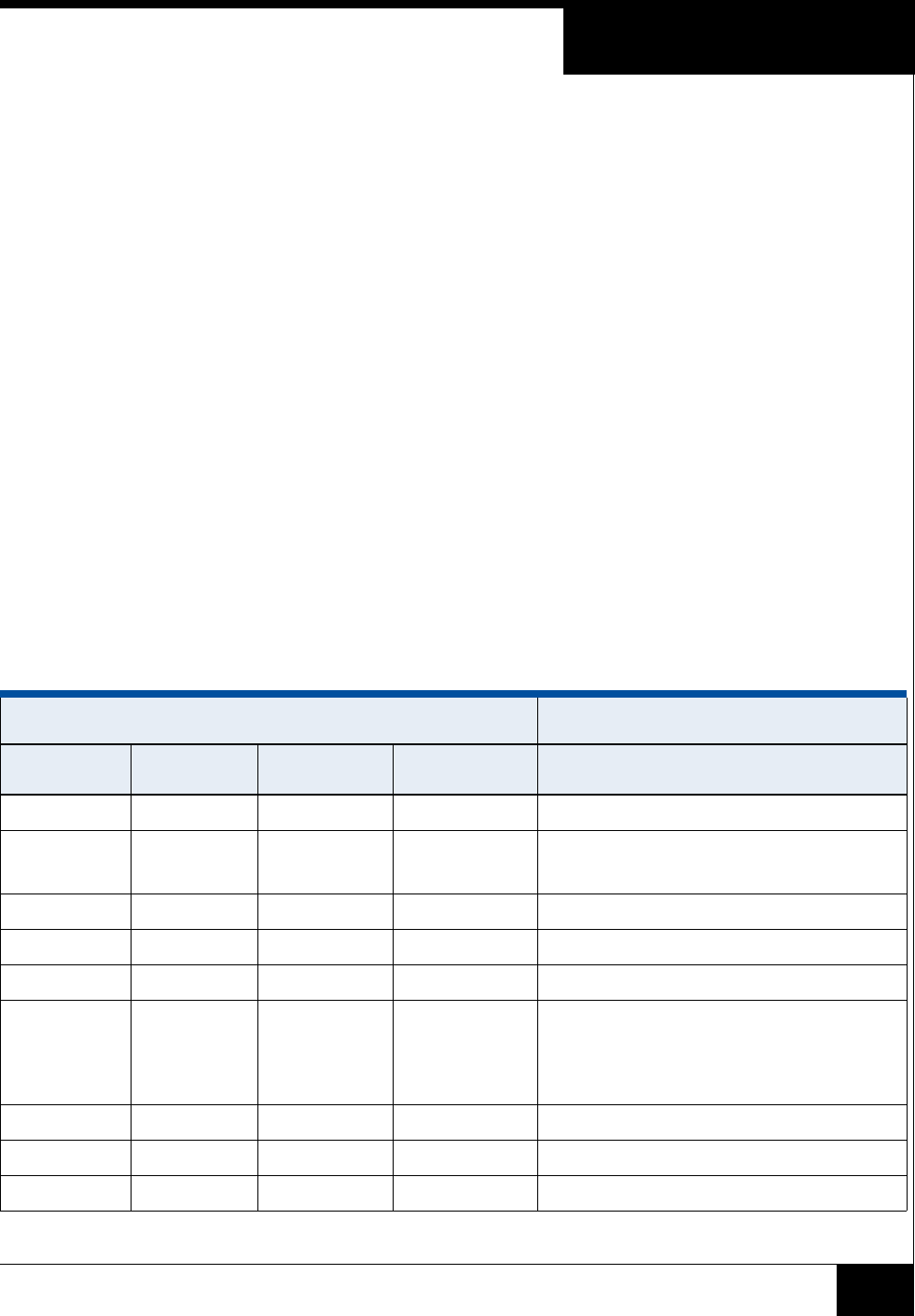
Testing with iSTAR PRO Hardware
7
With no switches or resistors connected to the supervised input 1 and 2 lines, the C•
CURE 800/8000 Monitoring Program should report inputs as “Open Loop”. When
you connect the 1,000-ohm resistor to the input terminals, the C• CURE 800/8000
Monitoring Program should report that the input as “Deactivated”. Supervised
inputs #1 is found at pins 4 and 5 of P5. Supervised input #2 is found at pins 6 and 7
of P5.
5. Check the outputs.
The outputs can be functionally tested by using the “momentary activate” feature in
the C• CURE 800/8000 Monitoring Program. When the outputs are momentarily
activated, the signal will change state for a few seconds. A 1,000 ohm resistor and an
LED can be connected to the output to obverse the functionality. Connect the
resistor to pin 1 of P5 (+12V). Connect anode of the LED to the resistor and connect
the cathode to pin 2 of P5 for output #1 and to pin 3 of P5 for output #2.
6. Check the reader interface.
The reader interface can only be tested with the reader chosen for the installation.
Reading a card will cause the display to show “Access Granted” or “Access
Denied”, depending upon the clearance of the card.
TESTING WITH
ISTAR PRO
HARDWARE
Use the iSTAR Pro S4 switch, positions 5 through 8, to test RM-iC class readers.
Table 3 shows S4 settings for Positions 5 through 8.
TABLE 3. S4 Diagnostic Settings
Switch Setting Description
Position 5 Position 6 Position 7 Position 8
Off Off Off Off Display status messages (auto configure on)
On On On On Display status messages
(auto configure off)
Off Off Off On Test card data
Off On Off On Reader test
Off On Off On Reader test
Off Off (2 second
LCD display)
On (1 second
LDC display)
On Off Test inputs
Off Off On On Manual output test (including readers and R/8s)
Off On Off Off Automatic ACM output test
Off On On On Automatic output test (including readers and R/8s)
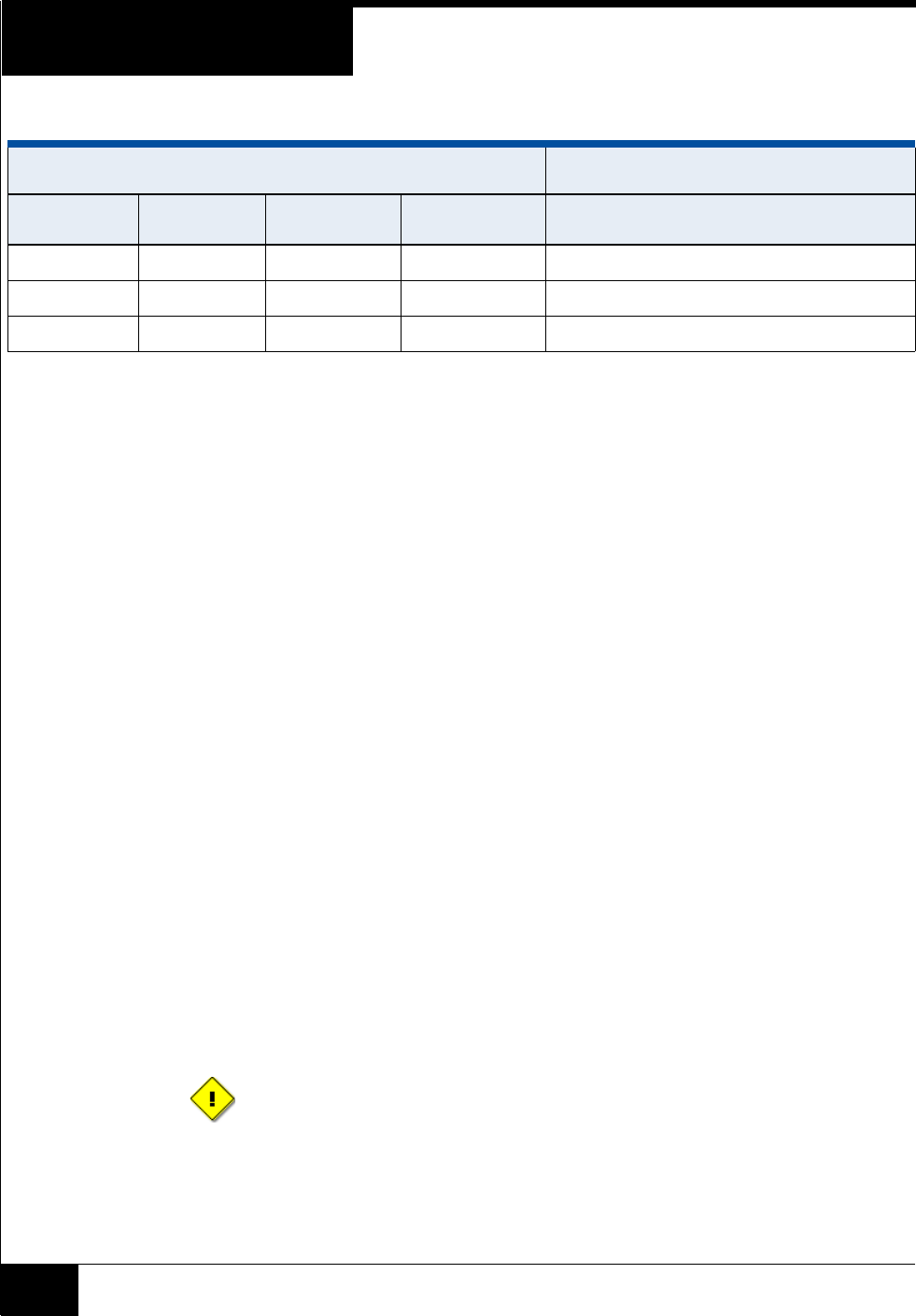
Canadian Radio Emissions Requirements
8
CANADIAN RADIO
EMISSIONS
REQUIREMENTS
This digital apparatus does not exceed the Class A limits for radio noise emissions from
digital apparatus set out in the Radio Interference Regulations of the Canadian
Department of Communications.
Le present appareil numerique n’emet pas de bruits radioelectriques depassant les
limites applicables aux appareils numeriques de la class A prescrites dans le Reglement
sur le brouillage radiolelectrique edicte par le ministere des Communications du
Canada.
FCC DIGITAL
DEVICE
LIMITATIONS
Radio and Television Interference
This equipment has been tested and found to comply with the limits for a digital
device, pursuant to Part 15 of the FCC rules. These limits are designed to provide
reasonable protection against harmful interference when the equipment is
operated in a commercial environment. This equipment generates, uses, and can
radiate radio frequency energy and, if not installed and used in accordance with
the instruction manual, may cause harmful interference to radio communications.
Operation of this equipment in a residential area is likely to cause harmful
interference, in which case the user will be required to correct the interference at
his own expense.
Operation is subject to the following two conditions: (1) This device may not cause
harmful interference, and (2) this device must accept any interference received,
including interference that may cause undesired operation.
In order to maintain compliance with FCC regulations, shielded cables must be
used with this equipment. Operation with non-approved equipment or unshielded
cables is likely to result in interference to radio and television reception.
Caution: Changes or modifications not expressly approved by the manufacturer
could void the user’s authority to operate this equipment.
On Off Off Off Ethernet/PCMCIA port and device test
On On Off Off DIMM memory test
On Off Off On Battery charger test
TABLE 3. S4 Diagnostic Settings (Continued)
Switch Setting Description
Position 5 Position 6 Position 7 Position 8