UBS Axcera CU0TD-5 200 Watt UHF Digital Transmitter User Manual
UBS-Axcera 200 Watt UHF Digital Transmitter
User Manual
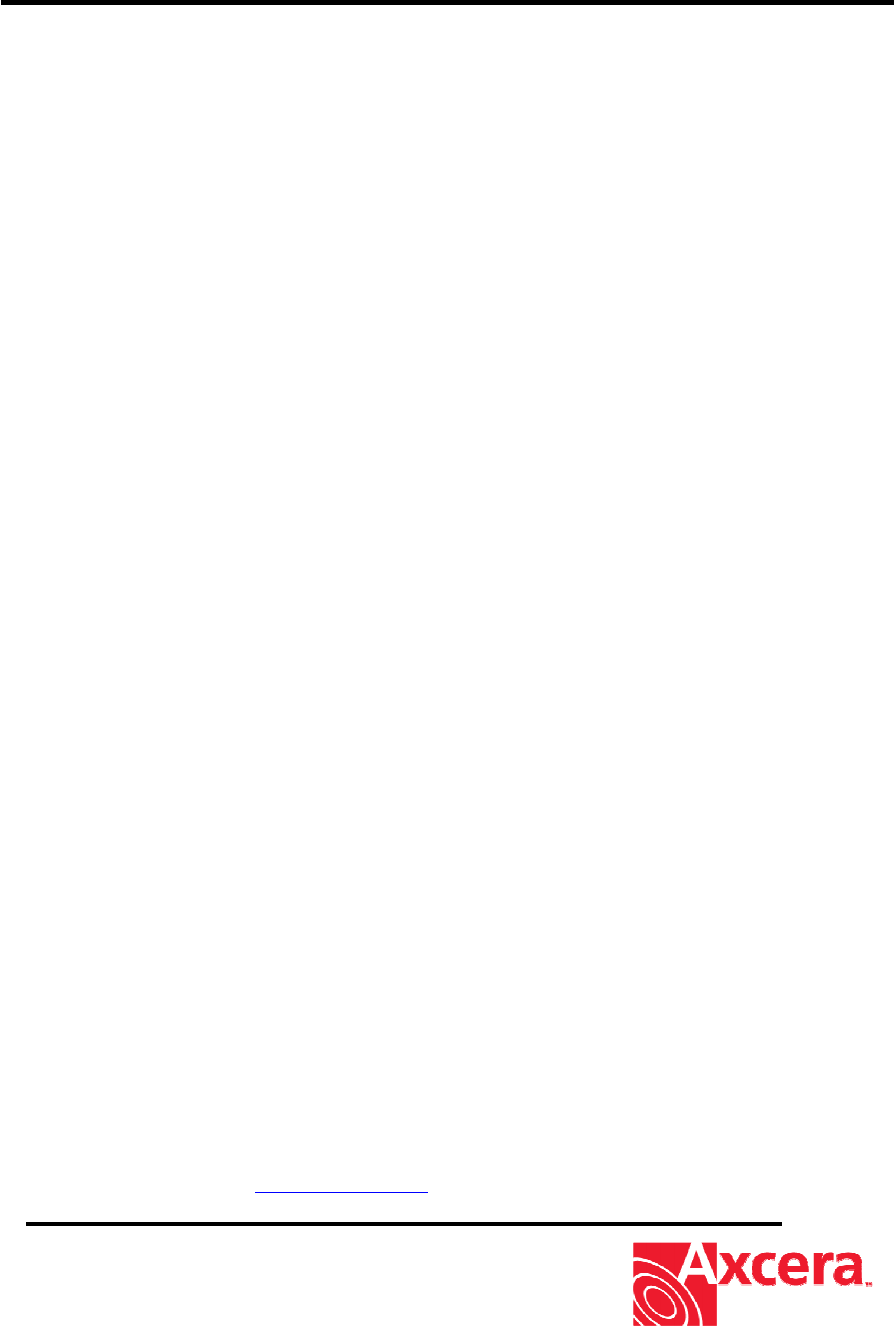
Instruction Manual
Innovator,
CU0TD-1/CU0RD-1, 5 Watt –
CU4TD/CU4RD, 2500 Watt
UHF, ATSC Transmitter/
Regenerative Translator
Axcera, LLC
103 Freedom Drive • P.O. Box 525 • Lawrence, PA 15055-0525, USA
Phone: 724-873-8100 • Fax: 724-873-8105
www.axcera.com • info@axcera.com
RESTRICTIONS ON USE, DUPLICATION OR DISCLOSURE
OF PROPRIETARY INFORMATION
This document contains information proprietary to Axcera, to its affiliates or to a third party to
which Axcera may have a legal obligation to protect such information from unauthorized
disclosure, use or duplication. Any disclosure, use or duplication of this document or any of the
information herein for other than the specific purpose for which it was disclosed by Axcera is
expressly prohibited, except as Axcera may otherwise agree in writing. Recipient by accepting this
document agrees to the above stated conditional use of this document and this information
disclosed herein.
Copyright © 2011, Axcera, LLC
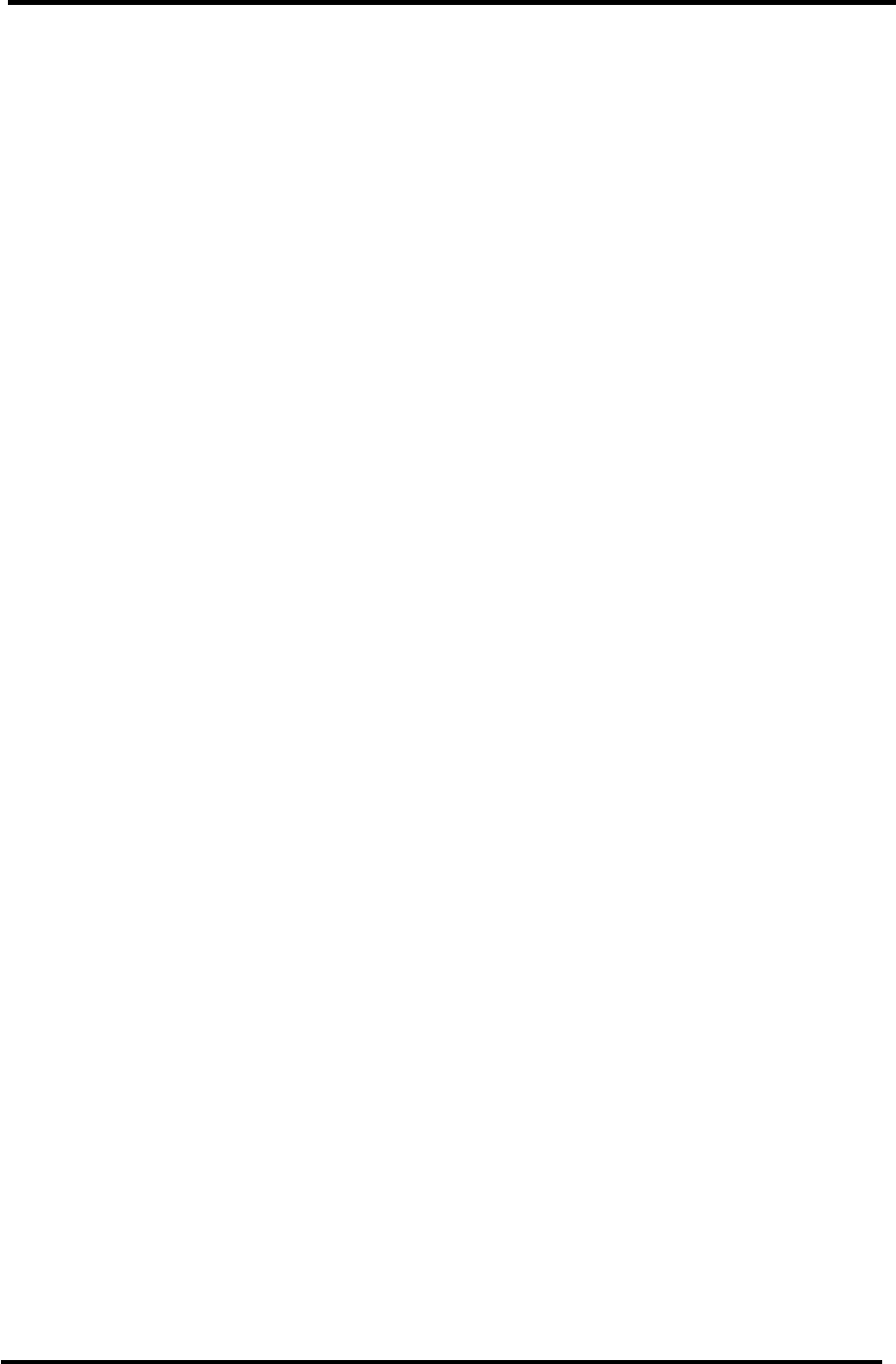
Innovator CU0TD-1/CU0RD-1 – CU4TD/CU4RD Table of Contents
ATSC Transmitter/Regenerative Translator
Instruction Manual, Rev. 1 i 10/19/11
Table of Contents
Introduction ......................................................................................................1
Manual Overview ............................................................................................1
Axcera Numbering System Explanation .............................................................1
Assembly Designators .....................................................................................2
Safety ...........................................................................................................2
Contact Information........................................................................................3
Return Material Procedure ...............................................................................3
Limited One Year Warranty for Axcera Products..................................................4
System Description ..........................................................................................11
Optional Dual Exciter System w/Axciter Modulator Trays ................................14
Unpacking, Installation and Maintenance ............................................................17
Unpacking ...................................................................................................17
Installation ..................................................................................................17
Drawer Slide Installation ............................................................................18
AC Input Connections .......................................................................................19
Input and Output Connections ...........................................................................20
J11 Power Monitoring Connections .....................................................................22
Maintenance ................................................................................................24
Initial On Site Turn On Procedure.......................................................................27
Typical System Operating Parameters ................................................................28
Typical Problems, Indications and Causes in CU0TD/RD-2 or -3 Drawer ..................29
LCD Display and Front Panel LED Indicators ........................................................29
System Remote Connections to J12....................................................................31
LCD Front Panel Screens...................................................................................32
Operation Screens ........................................................................................34
Set Up Screens ............................................................................................41
(Optional) Innovator CXB Series Web Ethernet Interface Kit (1313100)..................49
(Optional) Innovator CXB Series SNMP Ethernet Interface (1313079).....................54
Circuit Descriptions of Boards in the CU0TD/RD-1 thru CU0TD/RD-5 Systems .........55
(A1) 8 VSB Demodulator Board (1308275) ......................................................55
Overview..................................................................................................55
Microcontroller Functions............................................................................55
Jumper and DIP Switch Settings..................................................................55
(A2) Digital Modulator (1316332) ...................................................................56
SMPTE-310 or ASI input.............................................................................56
Channel Coder ..........................................................................................56
Analog Output Section ...............................................................................56
Pilot Frequency Generation.........................................................................56
Voltage Requirements................................................................................57
(A5) ALC Board, Innovator CX Series (1315006 or 1308570) .............................57
(A6) Amplifier Assembly (1309621) – Used in the CU0TD/RD-1..........................59
(A6-A1) 2 Stage UHF Amplifier Board, 24V (1309608) ...................................59
(A6) Amplifier Assembly (1315008 used w/External Axciter Drawer or 1312566
used in all other applications) – Used in the CU0TD/RD-2 and CU0TD/RD-3...... 59
(A6-A1) 2 Stage UHF Amplifier Board (1308784) ..........................................59
(A6-A2) RF Module Pallet, Philips, High Output (1309580)..............................60
(A6) Amplifier Assembly w/878 devices (1312191) – Used in the CU0TD/RD-4 &
CU0TD/RD-5 ................................................................................................60
(A6-A1) 1 Watt UHF Amplifier Module (1310282) ..........................................60
(A6-A2) BL871 Single Stage Amplifier Board (1311041).................................60
(A6-A3) Dual 878 Pallet Assembly (1313170 or 1310138) ..............................61
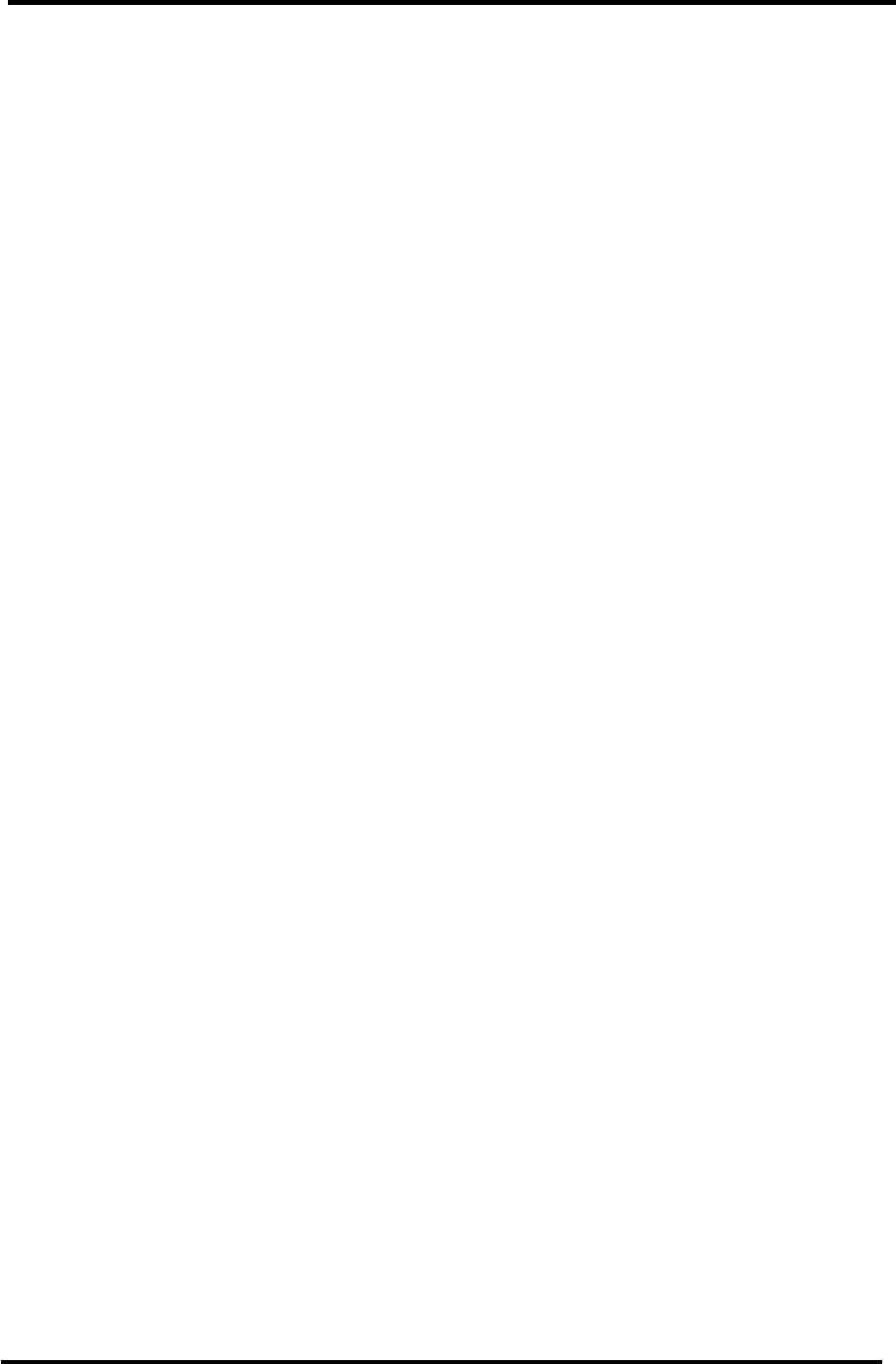
Innovator CU0TD-1/CU0RD-1 – CU4TD/CU4RD Table of Contents
ATSC Transmitter/Regenerative Translator
Instruction Manual, Rev. 1 ii 10/19/11
(A6) Amplifier Assembly w/888A devices (1316132 used w/External Axciter Drawer
or 1315381 used in all other applications) – Used in the CU0TD/RD-4 & CU0TD/RD-
5 ................................................................................................................61
(A6-A1) 1 Watt UHF Amplifier Module (1315730) ..........................................61
(A6-A2) BLF881 Single Stage Amplifier Board (1314882) ...............................61
(A6-A3) Dual BLF888A Pallet Assembly (1315347) ........................................62
(A6-A5) DC/DC Converter Board (1315335) .................................................62
(A7) Output Detector Board (1308685 or 1312207 in the CU0TD/RD-2 thru
CU0TD/RD-5)...............................................................................................62
(A8) Control Card, Innovator CX (1312543) .....................................................62
(A9 & A10) Power Supplies used in CU0TD/RD-1 thru CU0TD/RD-5 and Driver for
CU1TD/RD-1 & higher power..........................................................................63
Circuit Description of External System Metering Board which is only used in
Transmitters with multiple external Amplifier Drawers ..........................................64
(A5) System Metering Board (1312666) ..........................................................64
Circuit Descriptions of Boards in the external ATSC Amplifier Drawers ....................65
(A7) Amplifier Control Board (1315011 or 1312260) .........................................65
(A10) Current Metering Board (1309130) ........................................................65
(A5) 2 Way Splitter Board (1313158), in Amplifier Drawer w/two Dual 888A Pallets
..................................................................................................................66
(A5) 4 Way Splitter Board (1308933), in multiple pallet amplifier drawer ............66
(A1-A4) 878A Amplifier Pallets (1314098, 1313170 or 1310138)........................66
Or (A1-A2) Dual 888A Amplifier Pallets (1314173) Used in two pallet Amplifier
Drawer (CB005715) ......................................................................................66
(A1-A4) 888A Amplifier Pallets (1315347) Used in three pallet Amplifier Drawers .66
(A6) 2 Way Combiner Board (1313155), in amplifier drawer w/two Dual 888A
Pallets.........................................................................................................67
(A6) 4 Way Combiner Board (1312368), in two pallet amplifier drawer ...............67
(A8 & A9) One, two & three pallet Amplifier Drawer Power Supplies ....................67
System Set Up Procedure ...................................................................................1
ALC Board Set-Up, Forward and Reflected Power Calibration for CU0TD/RD-1 thru
CU0TD/RD-5 Systems .....................................................................................2
Forward and Reflected Power Calibration of a CU1TD/RD-1 and Higher Power
Systems with one or more External Amplifier Drawers.........................................3
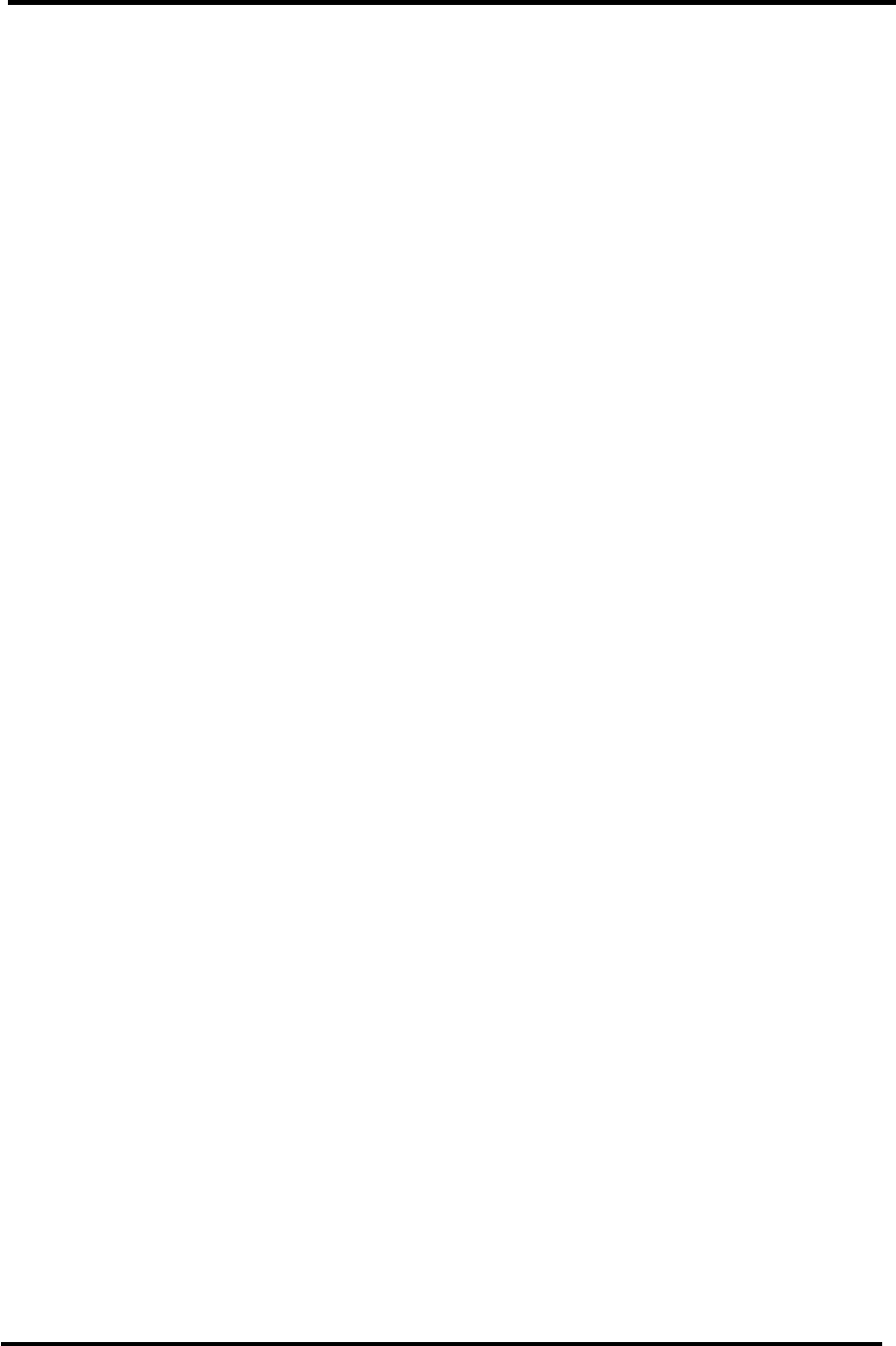
Innovator CU0TD-1/CU0RD-1 – CU4TD/CU4RD Introduction
ATSC Transmitter/Regenerative Translator
Instruction Manual, Rev. 1 1
Introduction
Manual Overview
This manual contains the description of the Innovator CU0TD-1/CU0RD-1 –
CU4TD/CU4RD Transmitter/Regenerative Translator and the circuit descriptions of the
boards, which make up the system. The manual also describes the installation, setup
and alignment procedures for the system. Appendix A of this manual contains the
system level drawings for the Innovator CU0TD-1/CU0RD-1 – CU4TD/CU4RD ATSC
Transmitter/Regenerative Translator System that was purchased. NOTES: Information
and drawings on the Axciter Digital Modulator, if part of your system, are contained in
the separate Axciter Instruction Manual. Information and drawings on the Universal
Modulator Drawer and Adaptive Precorrector Drawer, if part of your system, are
contained in the separate Universal Modulator Drawer and Adaptive Precorrector Drawer
Instruction Manuals. If your system contains dual exciters with a remote interface panel
and Exciter control panel, information and drawings on the system and panels are
contained in the separate remote interface panel instruction manual. Information on the
K-Tech Receiver or Signal Converter, if part of your system, is contained in the separate
manufacturers supplied manuals.
Axcera Numbering System Explanation
The Axcera numbering system is explained as follows. The following example is for a
CU0TC-3 Transmitter system.
C – CX Series
U – UHF Frequency Band
0 or X - Number of external Power Amplifier drawers
T - Transmitter, L - Echo cancelling repeater, R - Regenerative translator
C - COFDM (DVB-T/H/T2), I - ISDB-T, D - ATSC, No letter or blank means analog.
-3 = 50W or (861 devices), -2 = 30W or (861 devices with smaller power supply), -1 =
3W or 5W depending on the modulation. -4 = 888A. For ATSC there is also a -5 at
150W output but it is the same as the -4.
The following example is for a power amplifier drawer CUBP888A-4.
1 | 2 | 3 | 4 | 5 | - | 6 | - | 7 |
C U B P 888A - 4
Position Chars Description
1 1 Transmitter Line (C=CX, 6=6X, H=HX)
2 1 or 2 Frequency Band (U=UHF, HV=HB VHF, LV=LB VHF, etc.)
3 1 Version (ex. A-line, B-line, etc. - typically matches
transmitter model version)
4 1 Use (E=Exciter/Driver, P=PA)
5 up to 4 Transistor number (might need to abbreviate)
6 1 or 2 Number of transistors in final output stage
7 up to 4 Additional field to include other important info
(ex. distinguish bet single or N+1 supplies, or other things
not covered in the number
CUBP888A-4: Line C, Frequency UHF, Version B, Use PA, Transistor Number
888A, number of transistors in final output stage 4.
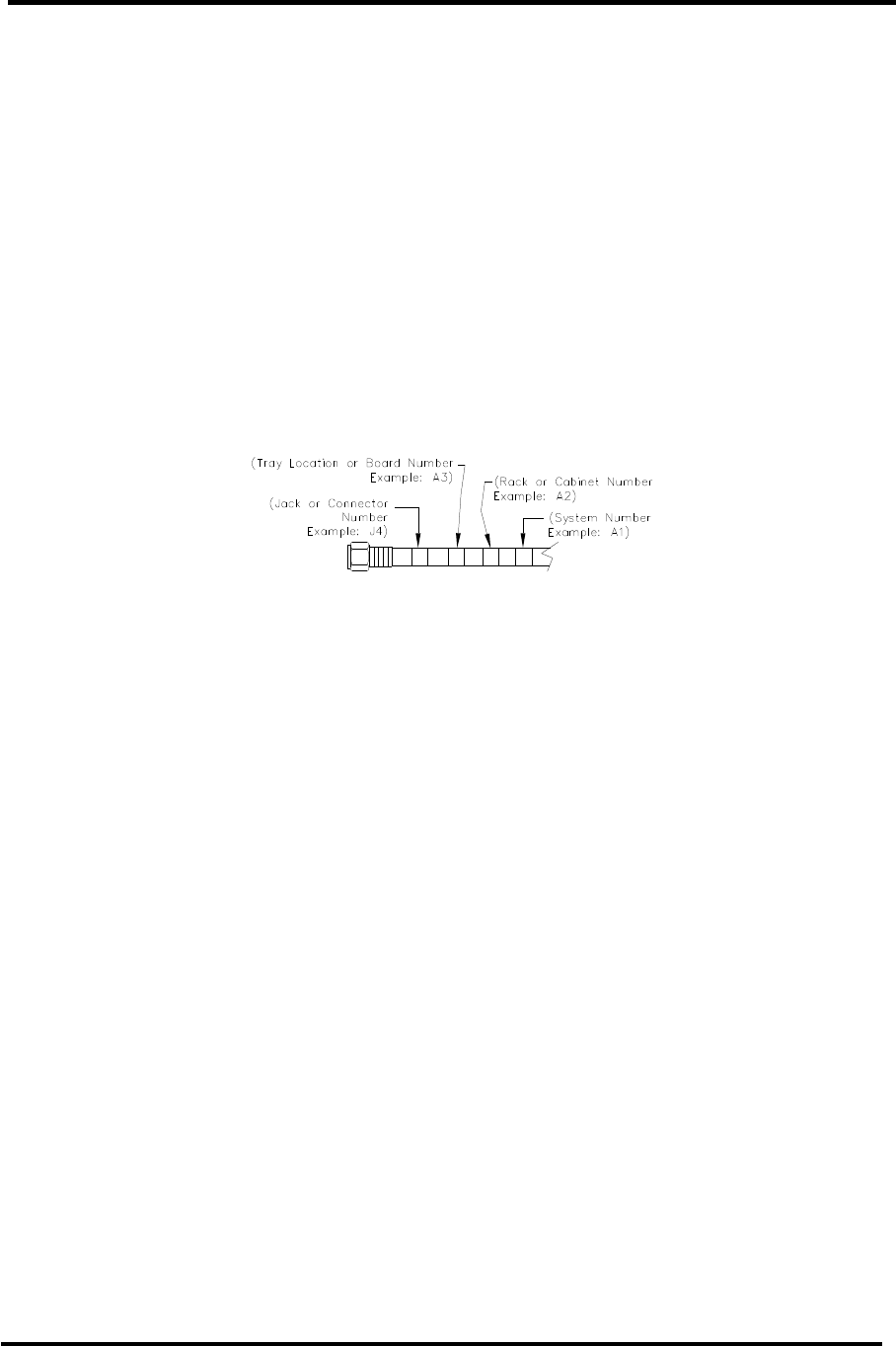
Innovator CU0TD-1/CU0RD-1 – CU4TD/CU4RD Introduction
ATSC Transmitter/Regenerative Translator
Instruction Manual, Rev. 1 2
Assembly Designators
Axcera has assigned assembly numbers, Ax designations such as A1, where x=1,2,3…etc,
to all assemblies, modules, and boards in the system. These designations are referenced
in the text of this manual and shown on the block diagram and interconnect drawings
provided in Appendix A.
The cables that connect between the boards within a drawer or assembly and that
connect between the drawers, racks and cabinets are labeled using markers. Figure 1 is
an example of a marked cable. There may be as few as two or as many as four Markers
on any one cable. These markers are read starting farthest from the connector. If there
are four Markers, the marker farthest from the connector is the system number such as
system 1 or translator 2. The next or the farthest Marker is the rack or cabinet “A”
number on an interconnect cable or the board “A” number when the cable is within a
drawer. The next number on an interconnect cable is the Drawer location or Board “A”
number. The marker closest to the connector is the jack or connector “J” number on an
interconnect cable or the jack or connector “J” number on the board when the cable is
within a drawer.
4 3 2 1
Marker Identification Drawing
Safety
The Innovator CU0TD-1/CU0RD-1 – CU4TD/CU4RD ATSC Transmitter/Regenerative
Translator systems manufactured by Axcera are designed to be easy to use and repair
while providing protection from electrical and mechanical hazards. Please review the
following warnings and familiarize yourself with the operation and servicing procedures
before working on the system.
Hazardous Accessibility – Axcera has made attempts to provide appropriate
connectors, wiring and shields to minimize hazardous accessibility.
Circuit Breakers and Wiring – All circuit breakers and wire are UL and CE certified and
are rated for maximum operating conditions.
Single Point Breaker or Disconnect - The customer should provide a single point
breaker or disconnect at the breaker box for the main AC input connection to the
transmitter.
Transmitter Ratings - The transmitter ratings are provided in the text of this manual
along with voltage and current values for the equipment.
Protective Earthing Terminal – A main protective earthing terminal is provided for
equipment required to have protective earthing.
Read All safety Instructions – All of the safety instructions should be read and
understood before operating this equipment.
Retain Manuals – The manuals for the system should be retained at the system site for
future reference. Axcera provides two manuals for this purpose; one manual can be left
at the office while the other can be kept at the site.
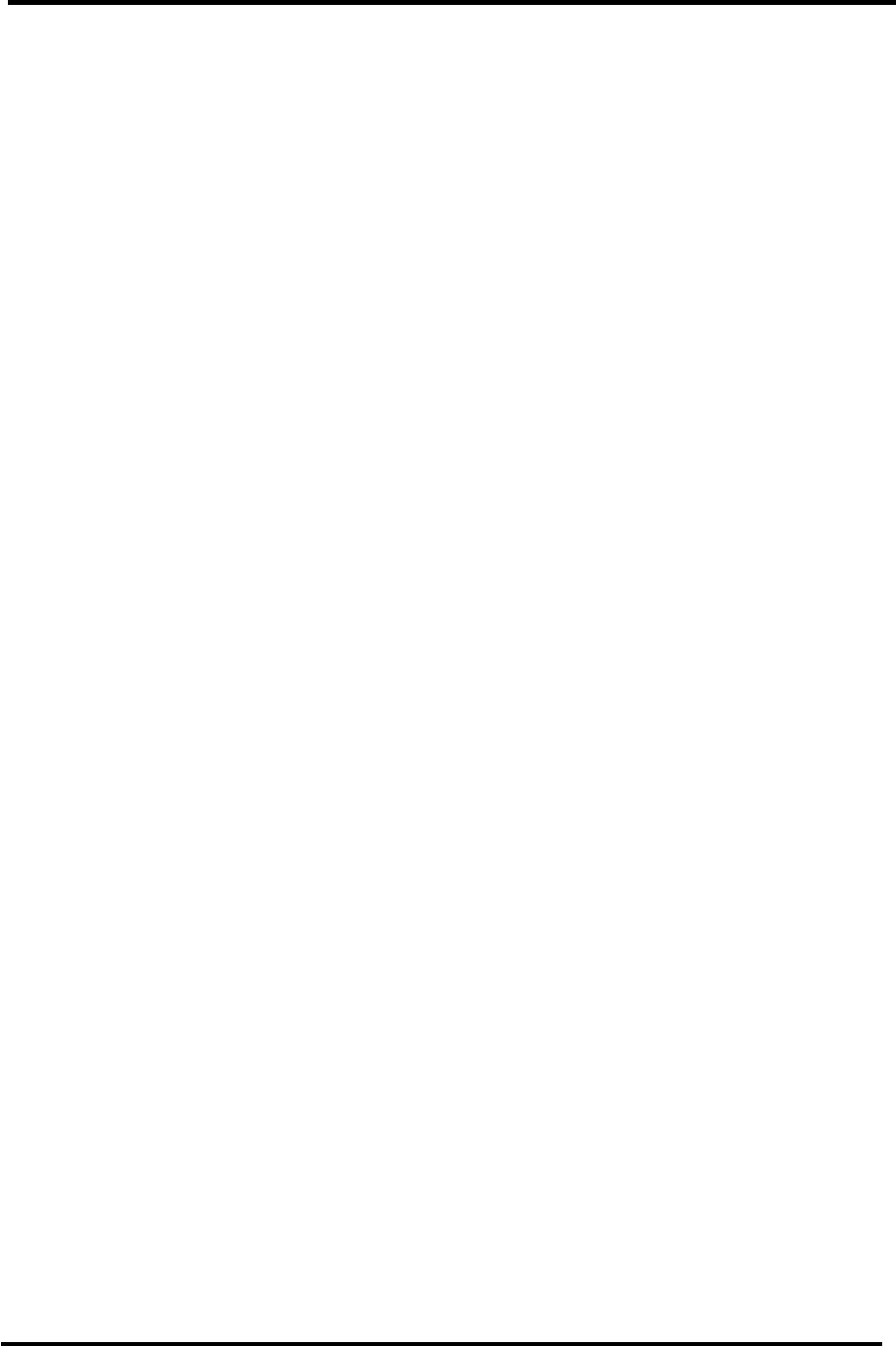
Innovator CU0TD-1/CU0RD-1 – CU4TD/CU4RD Introduction
ATSC Transmitter/Regenerative Translator
Instruction Manual, Rev. 1 3
Heed all Notes, Warnings, and Cautions – All of the notes, warnings, and cautions
listed in this safety section and throughout the manual must be followed.
Follow Operating Instructions – All of the operating and use instructions for the
system should be followed.
Cleaning – Unplug or otherwise disconnect all power from the equipment before cleaning.
Do not use liquid or aerosol cleaners. Use only a damp cloth for cleaning.
Ventilation – Openings in the cabinet and module front panels are provided for
ventilation. To ensure the reliable operation of the system, and to protect the unit from
overheating, these openings must not be blocked.
Servicing – Do not attempt to service this product yourself until becoming familiar with
the equipment. If in doubt, refer all servicing questions to qualified Axcera service
personnel.
Replacement Parts – When replacement parts are used, be sure that the parts have the
same functional and performance characteristics as the original part. Unauthorized
substitutions may result in fire, electric shock, or other hazards. Please contact the
Axcera Technical Service Department if you have any questions regarding service or
replacement parts.
Contact Information
The Axcera Field Service Department can be contacted by PHONE at 724-873-8100 or by
FAX at 724-873-8105.
Before calling Axcera, please be prepared to supply the Axcera technician with answers to
the following questions. This will save time and help ensure the most direct resolution to
the problem.
1. What are your Name and the Call Letters for the station?
2. What are the model number and type of system?
3. Is the system digital or analog?
4. How long has the system been on the air? (Approximately when was the system
installed?)
5. What are the symptoms being exhibited by the system? Include the current front
panel LCD readings and what the status LED is indicating on the front panel of
the drawer. If possible, include the LCD readings before the problem occurred.
Return Material Procedure
To insure the efficient handling of equipment or components that have been returned for
repair, Axcera requests that each returned item be accompanied by a Return Material
Authorization Number (RMA#). The RMA# can be obtained from any Axcera Field
Service Engineer by contacting the Axcera Field Service Department at 724-873-8100 or
by Fax at 724-873-8105. This procedure applies to all items sent to the Field Service
Department regardless of whether the item was originally manufactured by Axcera.
When equipment is sent to the field on loan, the RMA# is included with the unit. The RMA#
is intended to be used when the unit is returned to Axcera. In addition, all shipping
material should be retained for the return of the unit to Axcera.
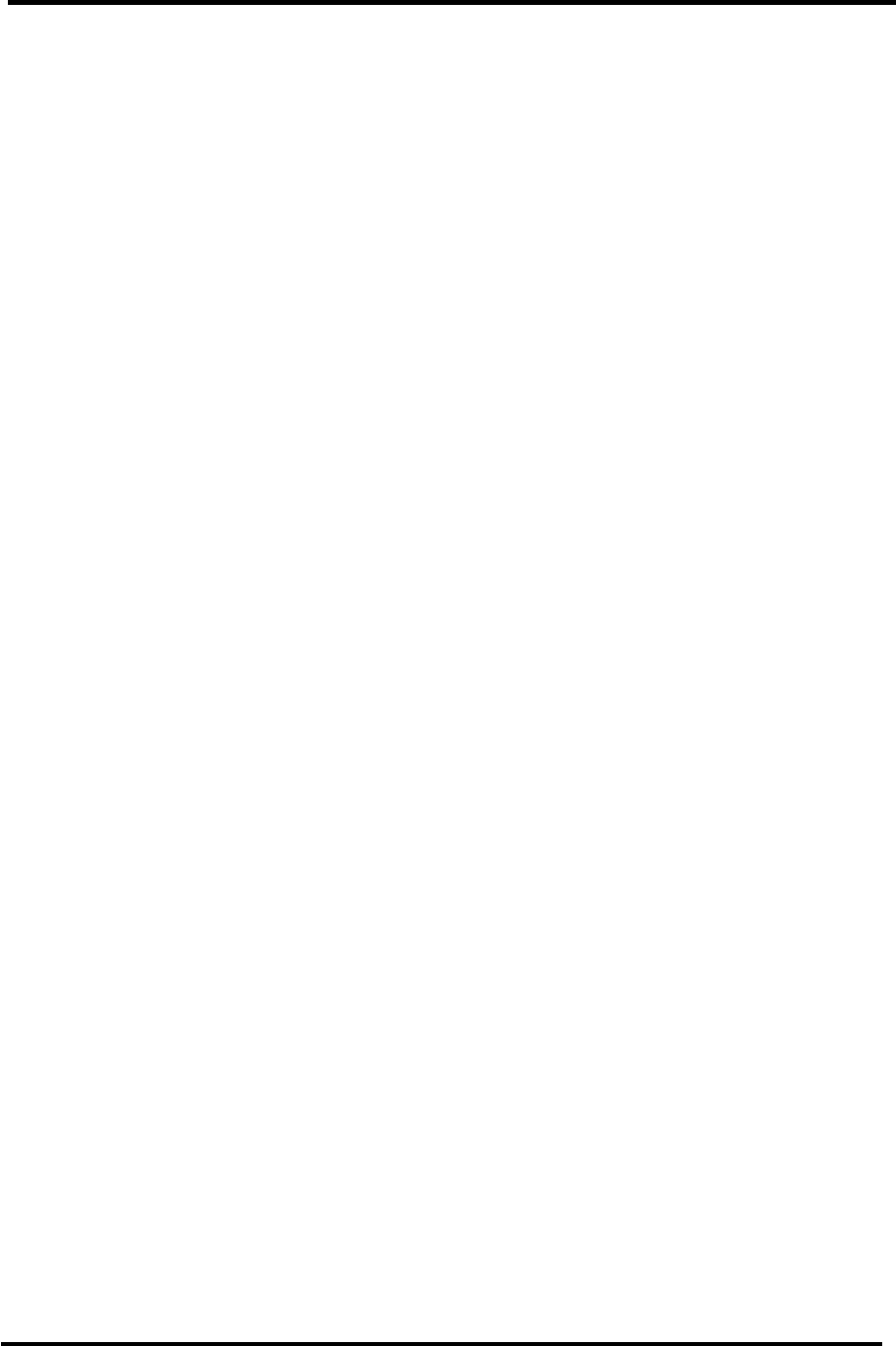
Innovator CU0TD-1/CU0RD-1 – CU4TD/CU4RD Introduction
ATSC Transmitter/Regenerative Translator
Instruction Manual, Rev. 1 4
Replacement assemblies are also sent with the RMA# to allow for the proper routing of the
exchanged hardware. Failure to close out this type of RMA# will normally result in the
customer being invoiced for the value of the loaner item or the exchanged assembly.
When shipping an item to Axcera, please include the RMA# on the packing list and on the
shipping container. The packing slip should also include contact information and a brief
description of why the unit is being returned.
Please forward all RMA items to:
Axcera, LLC
103 Freedom Drive
P.O. Box 525
Lawrence, PA 15055-0525 USA
For more information concerning this procedure, call the Axcera Field Service Department
at 724-873-8100.
Axcera can also be contacted through e-mail at info@axcera.com and on the Web at
www.axcera.com.
Limited One Year Warranty for Axcera Products
Axcera warrants each new product that it has manufactured and sold against defects in
material and workmanship under normal use and service for a period of one (1) year
from the date of shipment from Axcera's plant, when operated in accordance with
Axcera's operating instructions. This warranty shall not apply to tubes, fuses, batteries,
bulbs or LEDs.
Warranties are valid only when and if (a) Axcera receives prompt written notice of
breach within the period of warranty, (b) the defective product is properly packed and
returned by the buyer (transportation and insurance prepaid), and (c) Axcera
determines, in its sole judgment, that the product is defective and not subject to any
misuse, neglect, improper installation, negligence, accident, or (unless authorized in
writing by Axcera) repair or alteration. Axcera's exclusive liability for any personal
and/or property damage (including direct, consequential, or incidental) caused by the
breach of any or all warranties, shall be limited to the following: (a) repairing or
replacing (in Axcera's sole discretion) any defective parts free of charge (F.O.B. Axcera’s
plant) and/or (b) crediting (in Axcera's sole discretion) all or a portion of the purchase
price to the buyer.
Equipment furnished by Axcera, but not bearing its trade name, shall bear no warranties
other than the special hours-of-use or other warranties extended by or enforceable
against the manufacturer at the time of delivery to the buyer.
NO WARRANTIES, WHETHER STATUTORY, EXPRESSED, OR IMPLIED, AND NO
WARRANTIES OF MERCHANTABILITY, FITNESS FOR ANY PARTICULAR
PURPOSE, OR FREEDOM FROM INFRINGEMENT, OR THE LIKE, OTHER THAN AS
SPECIFIED IN PATENT LIABILITY ARTICLES, AND IN THIS ARTICLE, SHALL
APPLY TO THE EQUIPMENT FURNISHED HEREUNDER.
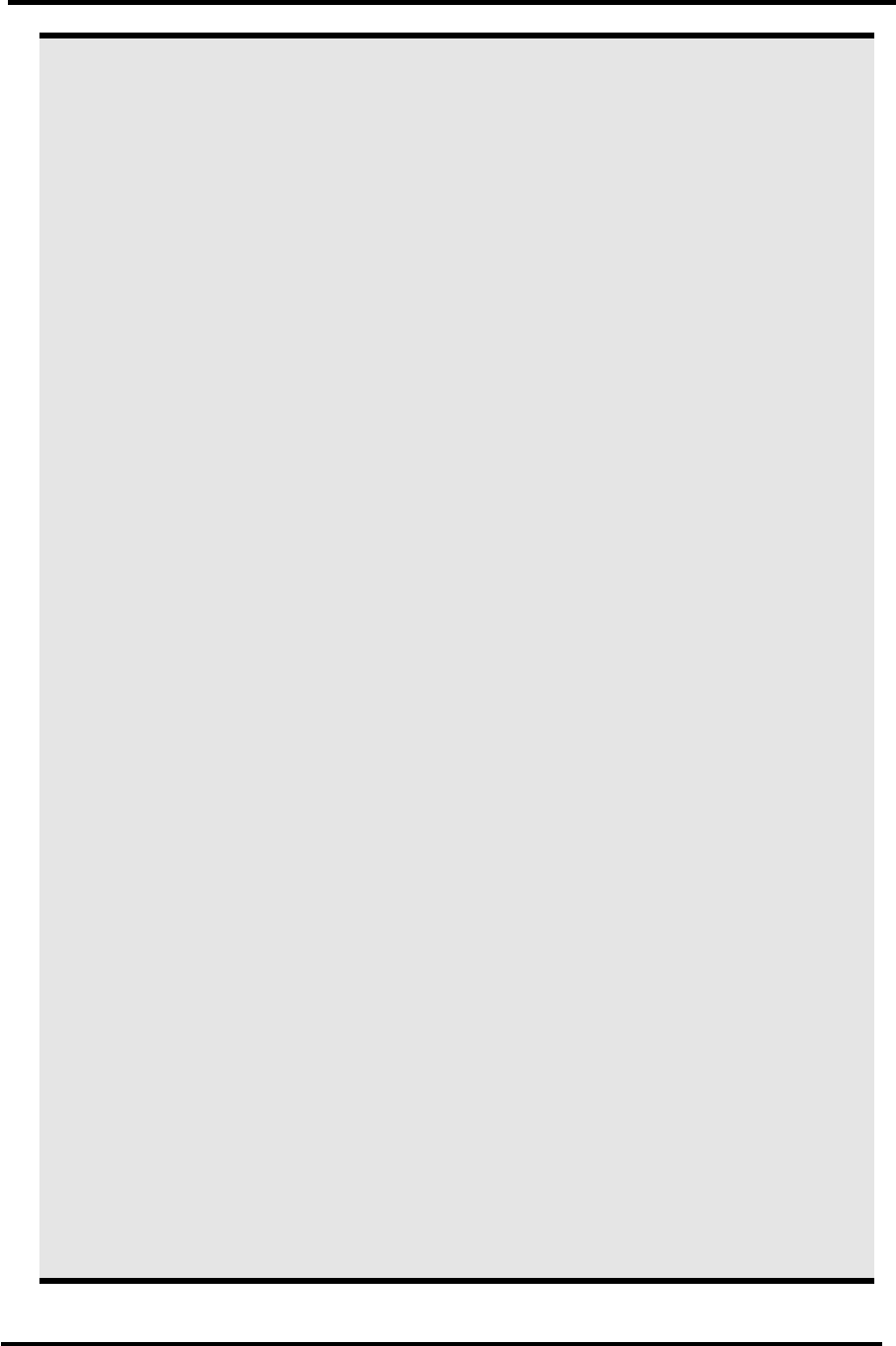
Innovator CU0TD-1/CU0RD-1 – CU4TD/CU4RD Introduction
ATSC Transmitter/Regenerative Translator
Instruction Manual, Rev. 1 5
WARNING!!!
HIGH VOLTAGE
DO NOT ATTEMPT TO REPAIR OR TROUBLESHOOT THIS EQUIPMENT UNLESS
YOU ARE FAMILIAR WITH ITS OPERATION AND EXPERIENCED IN
SERVICING HIGH VOLTAGE EQUIPMENT. LETHAL VOLTAGES ARE PRESENT
WHEN POWER IS APPLIED TO THIS SYSTEM. IF POSSIBLE, TURN OFF
POWER BEFORE MAKING ADJUSTMENTS TO THE SYSTEM.
RADIO FREQUENCY RADIATION HAZARD
MICROWAVE, RF AMPLIFIERS AND TUBES GENERATE HAZARDOUS RF
RADIATION THAT CAN CAUSE SEVERE INJURY INCLUDING CATARACTS,
WHICH CAN RESULT IN BLINDNESS. SOME CARDIAC PACEMAKERS MAY BE
AFFECTED BY THE RF ENERGY EMITTED BY RF AND MICROWAVE
AMPLIFIERS. NEVER OPERATE THE TRANSMITTER SYSTEM WITHOUT A
PROPERLY MATCHED RF ENERGY ABSORBING LOAD OR THE ANTENNA
ATTACHED. KEEP PERSONNEL AWAY FROM OPEN WAVEGUIDES AND
ANTENNAS. NEVER LOOK INTO AN OPEN WAVEGUIDE OR ANTENNA.
MONITOR ALL PARTS OF THE RF SYSTEM FOR RADIATION LEAKAGE AT
REGULAR INTERVALS.
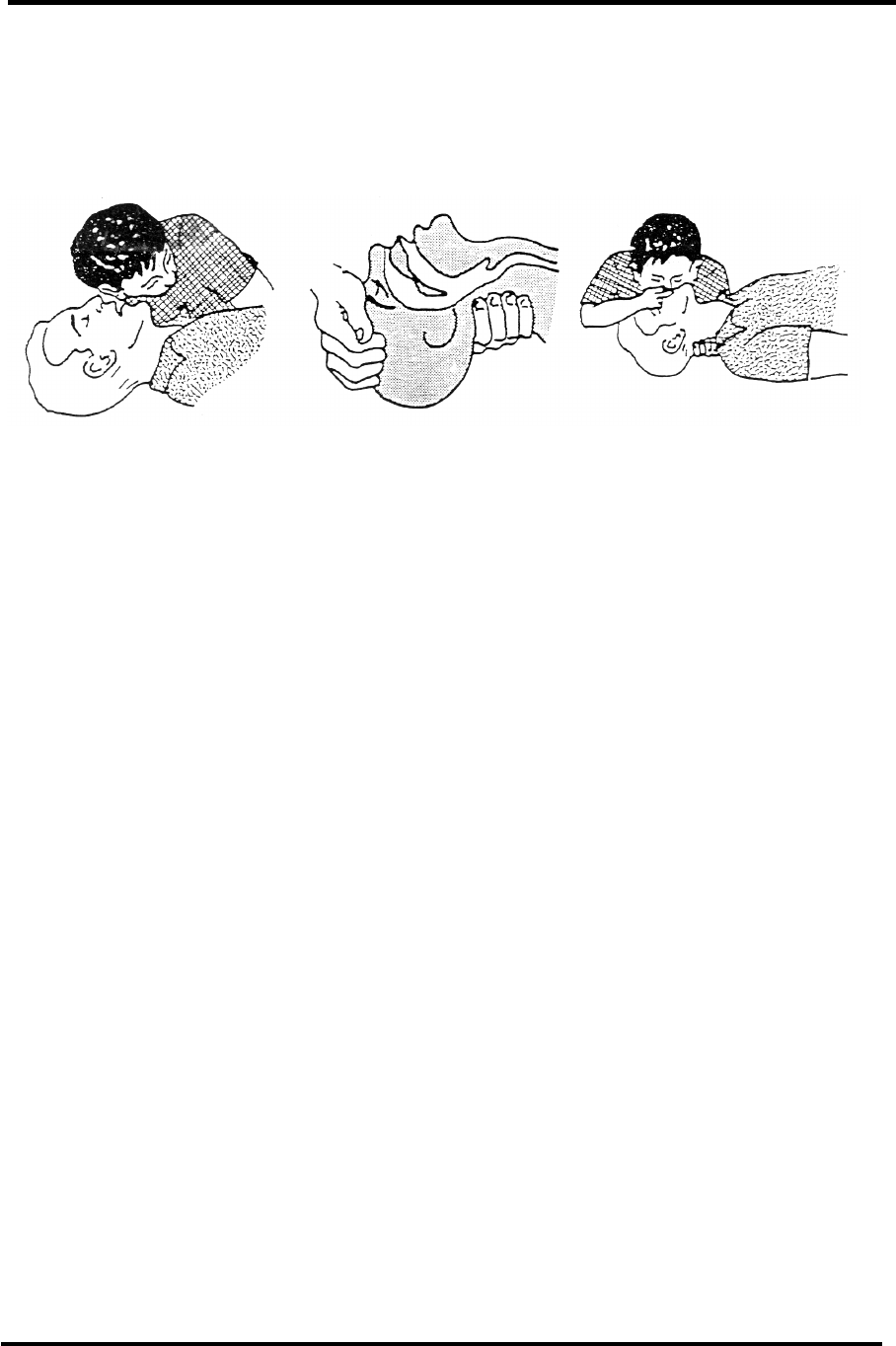
Innovator CU0TD-1/CU0RD-1 – CU4TD/CU4RD Introduction
ATSC Transmitter/Regenerative Translator
Instruction Manual, Rev. 1 6
EMERGENCY FIRST AID INSTRUCTIONS
Personnel engaged in the installation, operation, or maintenance of this equipment are
urged to become familiar with the following rules both in theory and practice. It is the
duty of all operating personnel to be prepared to give adequate Emergency First Aid and
thereby prevent avoidable loss of life.
RESCUE BREATHING
1. Find out if the person is
breathing.
You must find out if the
person has stopped breathing.
If you think he is not
breathing, place him flat on
his back. Put your ear close to
his mouth and look at his
chest. If he is breathing you
can feel the air on your
cheek. You can see his chest
move up and down. If you do
not feel the air or see the
chest move, he is not
breathing.
2. If he is not breathing,
open the airway by tilting his
head backwards.
Lift up his neck with one
hand and push down on his
forehead with the other. This
opens the airway. Sometimes
doing this will let the person
breathe again by himself.
3. If he is still not breathing,
begin rescue breathing.
-Keep his head tilted
backward. Pinch nose shut.
-Put your mouth tightly over
his mouth.
-Blow into his mouth once
every five seconds
-DO NOT STOP rescue
breathing until help arrives.
LOOSEN CLOTHING - KEEP
WARM
Do this when the victim is
breathing by himself or help
is available. Keep him as
quiet as possible and from
becoming chilled. Otherwise
treat him for shock.
BURNS
SKIN REDDENED: Apply ice cold water to
burned area to prevent burn from going
deeper into skin tissue. Cover area with a
clean sheet or cloth to keep away air. Consult
a physician.
SKIN BLISTERED OR FLESH CHARRED:
Apply ice cold water to burned area to
prevent burn from going deeper into skin
tissue.
Cover area with clean sheet or cloth to keep
away air. Treat victim for shock and take to
hospital.
EXTENSIVE BURN - SKIN BROKEN: Cover
area with clean sheet or cloth to keep away
air. Treat victim for shock and take to
hospital.
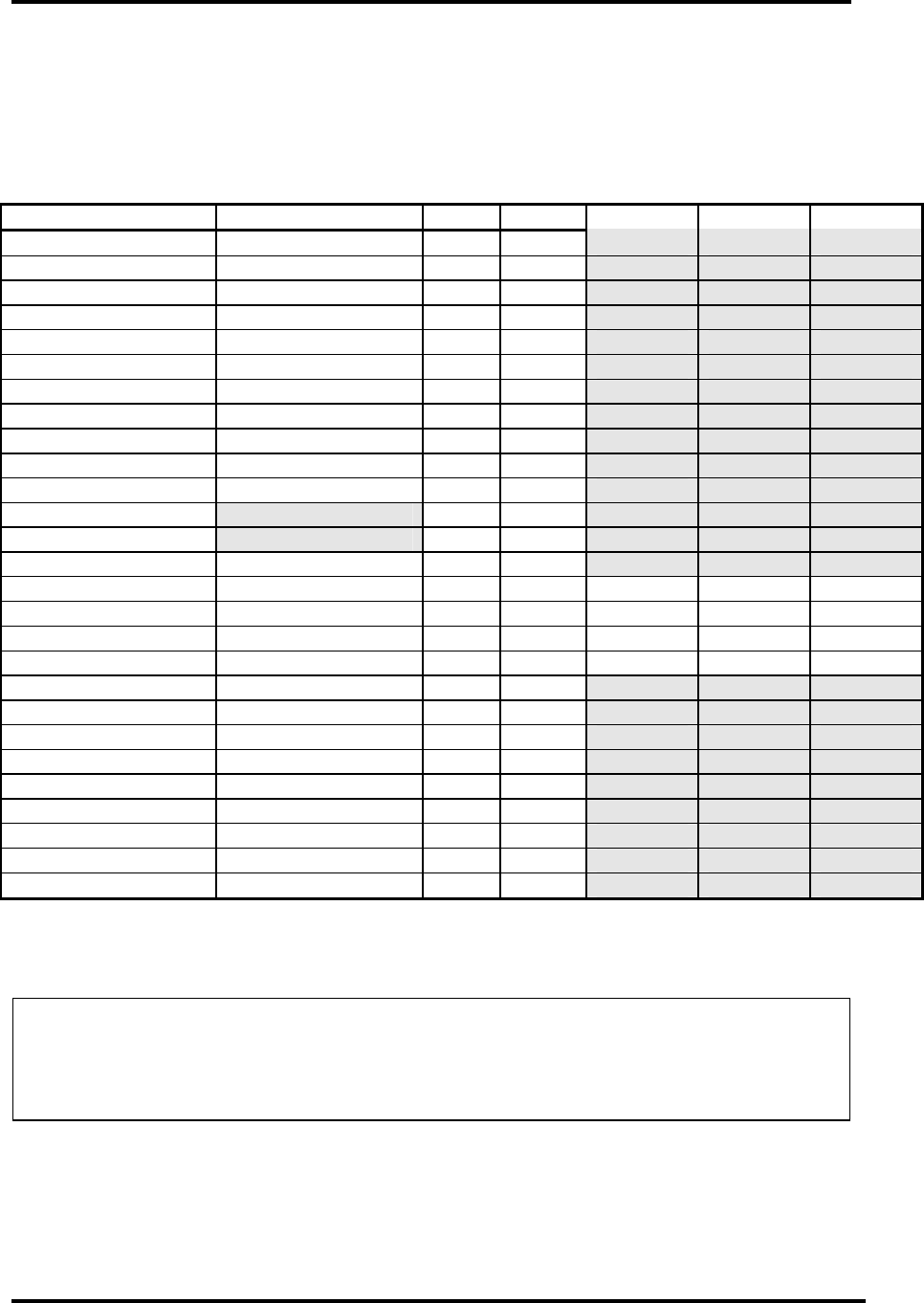
Innovator CU0TD-1/CU0RD-1 – CU4TD/CU4RD Introduction
ATSC Transmitter/Regenerative Translator
Instruction Manual, Rev. 1 7
dBm, dBw, dBmV, dBµ
µµ
µV, & VOLTAGE
EXPRESSED IN WATTS
50 Ohm System
WATTS PREFIX dBm dBw dBmV dBµV VOLTAGE
1,000,000,000,000 1 TERAWATT +150
+120
100,000,000,000 100 GIGAWATTS +140
+110
10,000,000,000 10 GIGAWATTS +130
+100
1,000,000,000 1 GIGAWATT +120
+ 99
100,000,000 100 MEGAWATTS +110
+ 80
10,000,000 10 MEGAWATTS +100
+ 70
1,000,000
1 MEGAWATT + 90 + 60
100,000
100 KILOWATTS + 80 + 50
10,000 10 KILOWATTS + 70 + 40
1,000 1 KILOWATT + 60 + 30
100 1 HECTROWATT + 50 + 20
50
+ 47 + 17
20
+ 43 + 13
10
1 DECAWATT + 40 + 10
1
1 WATT + 30 0 + 77 +137 7.07V
0.1
1 DECIWATT + 20 - 10 + 67 +127 2.24V
0.01 1 CENTIWATT + 10 - 20 + 57 +117 0.707V
0.001 1 MILLIWATT 0 - 30 + 47 +107 224mV
0.0001 100 MICROWATTS - 10 - 40
0.00001
10 MICROWATTS - 20 - 50
0.000001
1 MICROWATT - 30 - 60
0.0000001 100 NANOWATTS - 40 - 70
0.00000001 10 NANOWATTS - 50 - 80
0.000000001 1 NANOWATT - 60 - 90
0.0000000001 100 PICOWATTS - 70 -100
0.00000000001 10 PICOWATTS - 80 -110
0.000000000001 1 PICOWATT - 90 -120
TEMPERATURE CONVERSION
°
°°
°F = 32 + [(9/5) °
°°
°C]
°
°°
°C = [(5/9) (°
°°
°F - 32)]
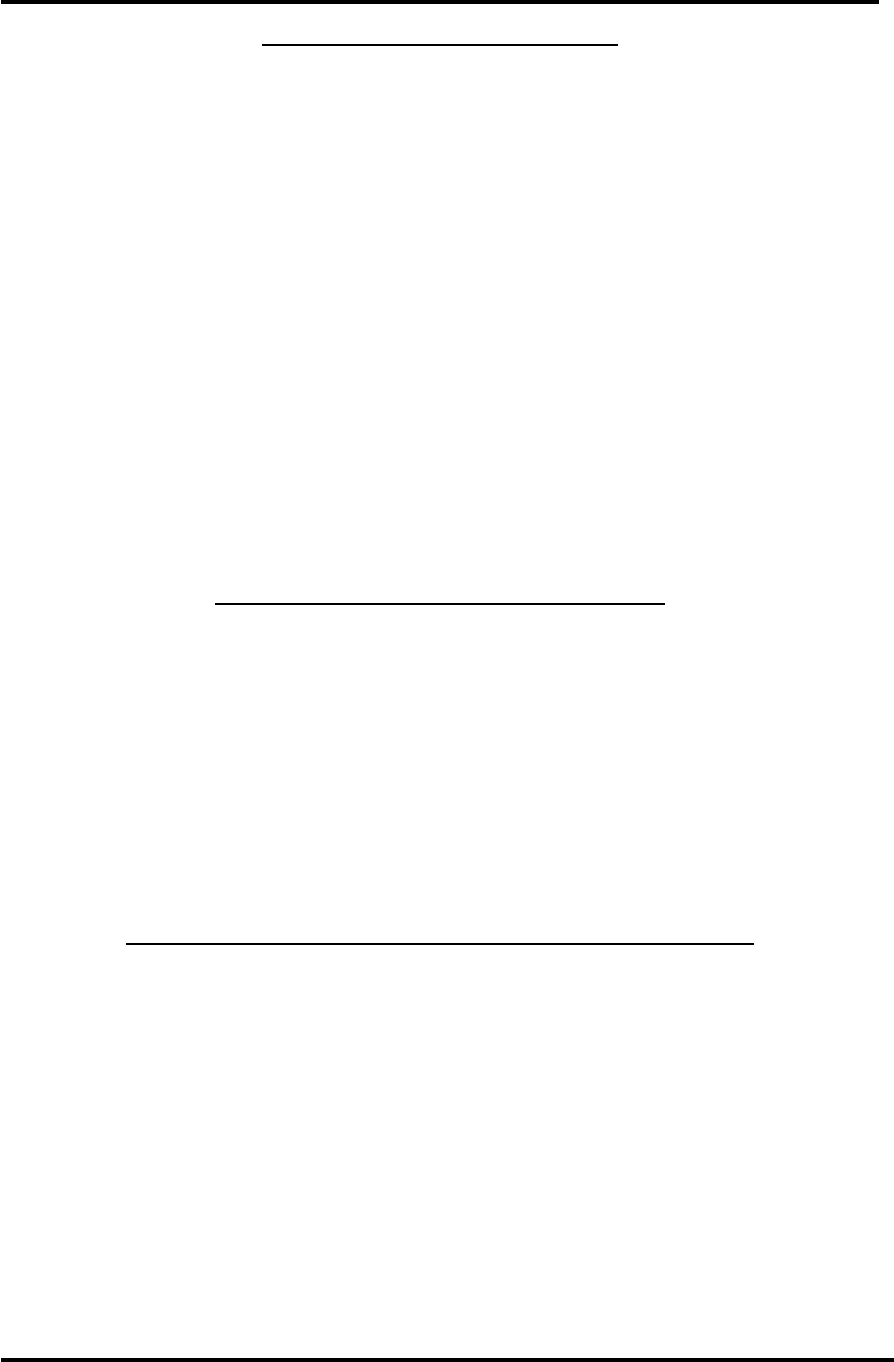
Innovator CU0TD-1/CU0RD-1 – CU4TD/CU4RD Introduction
ATSC Transmitter/Regenerative Translator
Instruction Manual, Rev. 1 8
USEFUL CONVERSION FACTORS
TO CONVERT FROM TO MULTIPLY BY
mile (US statute) kilometer (km) 1.609347
inch (in) millimeter (mm) 25.4
inch (in) centimeter (cm) 2.54
inch (in) meter (m) 0.0254
foot (ft) meter (m) 0.3048
yard (yd) meter (m) 0.9144
mile per hour (mph) kilometer per hour(km/hr) 1.60934
mile per hour (mph) meter per second (m/s) 0.44704
pound (lb) kilogram (kg) 0.4535924
gallon (gal) liter 3.7854118
U.S. liquid
(One U.S. gallon equals 0.8327 Canadian gallon)
fluid ounce (fl oz) milliliters (ml) 29.57353
British Thermal Unit watt (W) 0.2930711
per hour (Btu/hr)
horsepower (hp) watt (W) 746
NOMENCLATURE OF FREQUENCY BANDS
FREQUENCY RANGE DESIGNATION
3 to 30 kHz VLF - Very Low Frequency
30 to 300 kHz LF - Low Frequency
300 to 3000 kHz MF - Medium Frequency
3 to 30 MHz HF - High Frequency
30 to 300 MHz VHF - Very High Frequency
300 to 3000 MHz UHF - Ultrahigh Frequency
3 to 30 GHz SHF - Superhigh Frequency
30 to 300 GHz EHF - Extremely High Frequency
LETTER DESIGNATIONS FOR UPPER FREQUENCY BANDS
LETTER FREQ. BAND
L 1000 - 2000 MHz
S 2000 - 4000 MHz
C 4000 - 8000 MHz
X 8000 - 12000 MHz
Ku 12 - 18 GHz
K 18 - 27 GHz
Ka 27 - 40 GHz
V 40 - 75 GHz
W 75 - 110 GHz
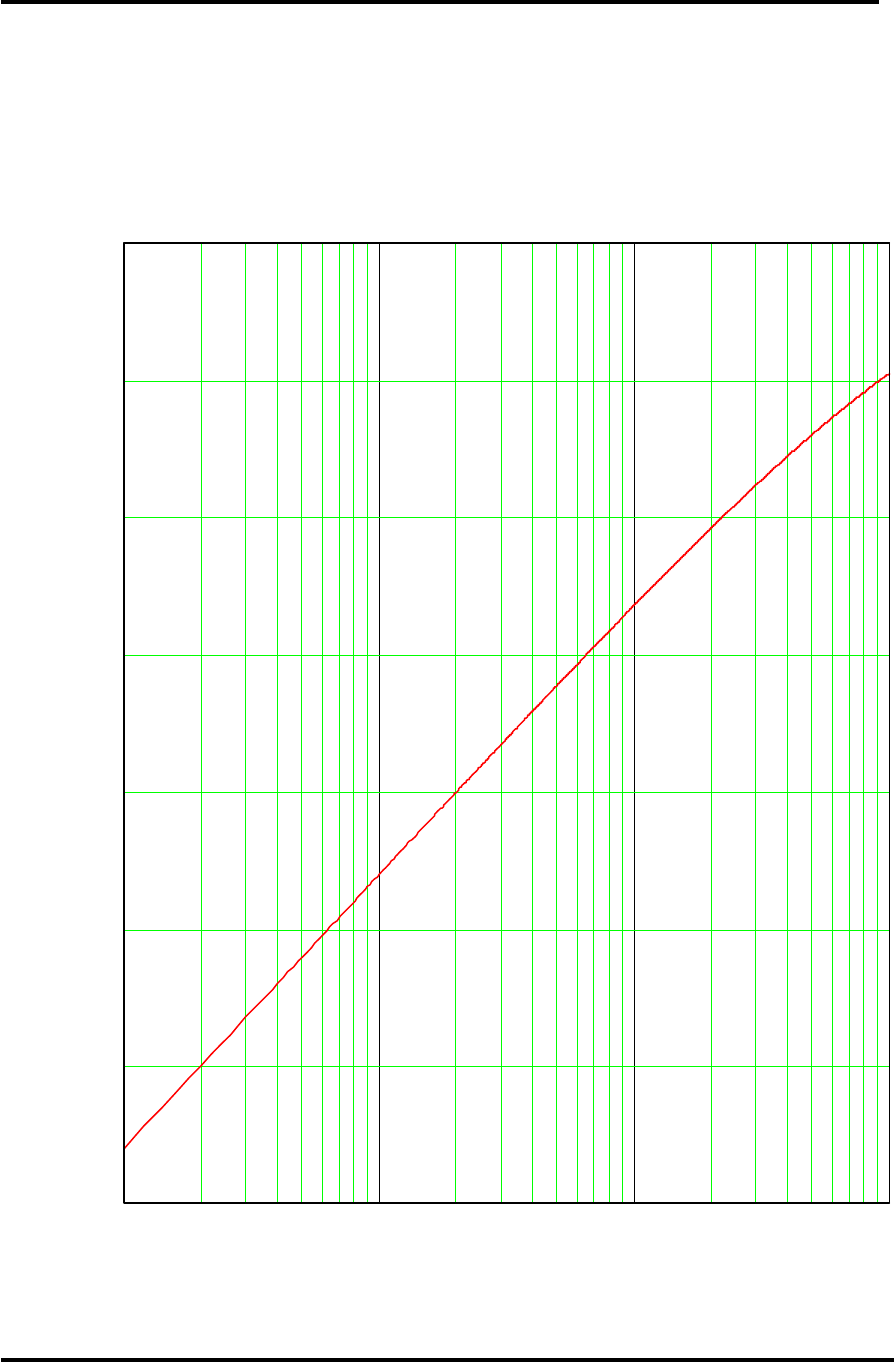
Innovator CU0TD-1/CU0RD-1 – CU4TD/CU4RD Introduction
ATSC Transmitter/Regenerative Translator
Instruction Manual, Rev. 1 9
RETURN LOSS VS. VSWR
1.001 1.01 1.1 2.0
VSWR
0
-
10
-
20
-
30
-
40
-
50
-
60
-
70
R
E
T
U
R
N
L
O
S
S
dB
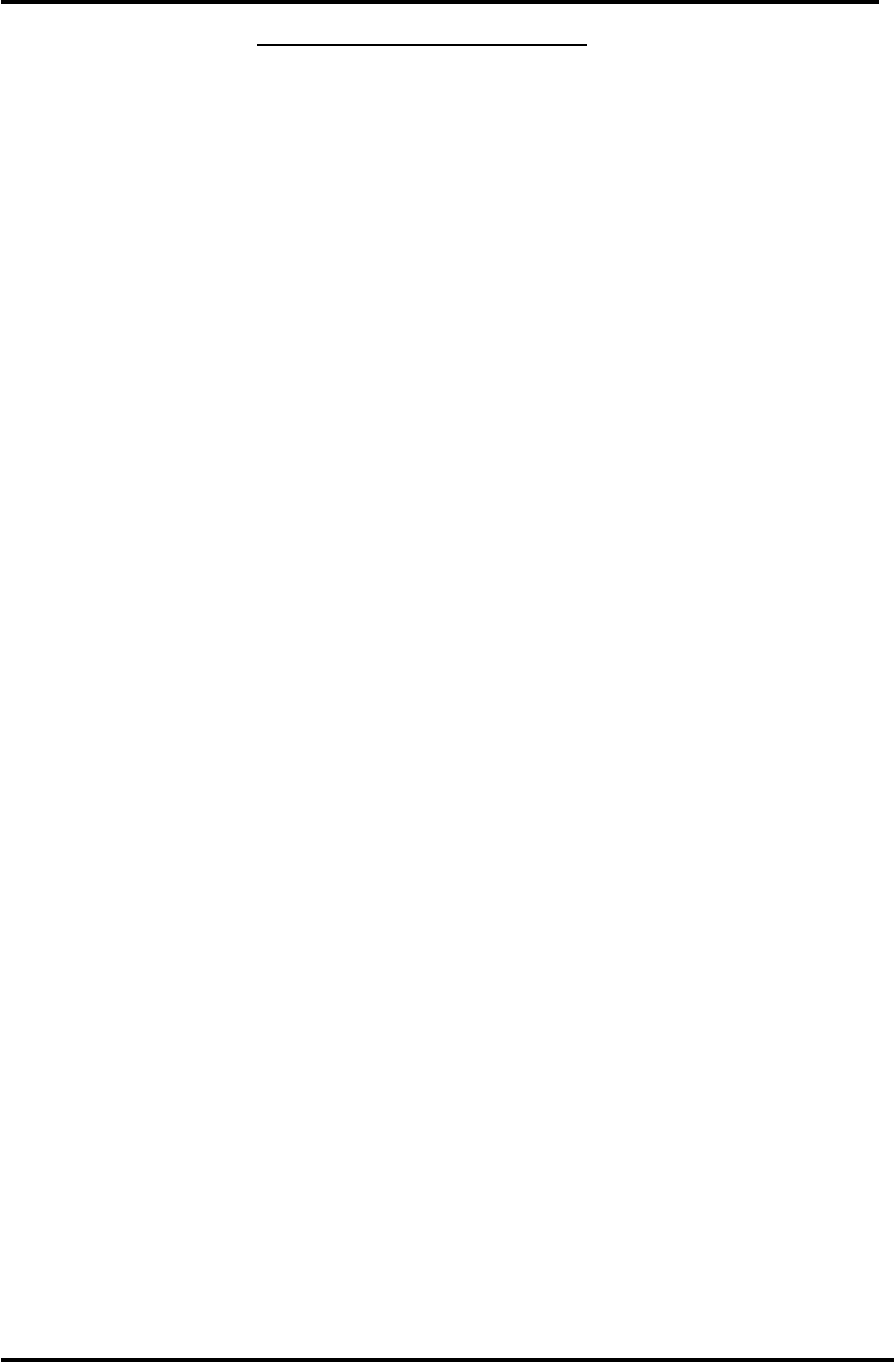
Innovator CU0TD-1/CU0RD-1 – CU4TD/CU4RD Introduction
ATSC Transmitter/Regenerative Translator
Instruction Manual, Rev. 1 10
ABBREVIATIONS/ACRONYMS
AC: Alternating Current
AFC: Automatic Frequency
Control
ALC: Automatic Level Control
AM: Amplitude Modulation
AGC: Automatic Gain Control
ATSC: Advanced Television
Systems Committee (Digital)
AWG: American Wire Gauge
B/D: Block Diagram
BER: Bit Error Rate
BW: Bandwidth
COFDM: Coded Orthogonal Frequency
Division Multiplexing
modulation scheme.
CUBP888A-4: Line C, Frequency
UHF, Version B, Use PA,
Transistor Number 888A,
number of transistors in final
output stage 4.
DC: Direct Current
D/A: Digital to Analog
DSP: Digital Signal Processing
DTV: Digital Television
dB: Decibel
dBm: Decibel referenced to
1 milliwatt
dBmV: Decibel referenced to
1 millivolt
dBw: Decibel referenced to 1 watt
FEC: Forward Error Correction
FM: Frequency Modulation
FPGA: Field Programmable Gate
Array
Hz: Hertz
I/C: Interconnect
ICPM: Incidental Carrier Phase
Modulation
I/P: Input
IF: Intermediate Frequency
LED: Light emitting diode
LSB: Lower Sideband
LDMOS: Lateral Diffused Metal Oxide
Semiconductor Field Effect
Transistor
MPEG: Motion Pictures Expert
Group
NTSC: National Television
Systems Committee (Analog)
O/P: Output
PLL: Phase Locked Loop
PCB: Printed Circuit Board
QAM: Quadrature Amplitude
Modulation
RD: Regenerative
Translator, Digital
SMPTE: Society of Motion Picture
and Television Engineers
TD: Transmitter, Digital
VSB: Vestigial Side Band
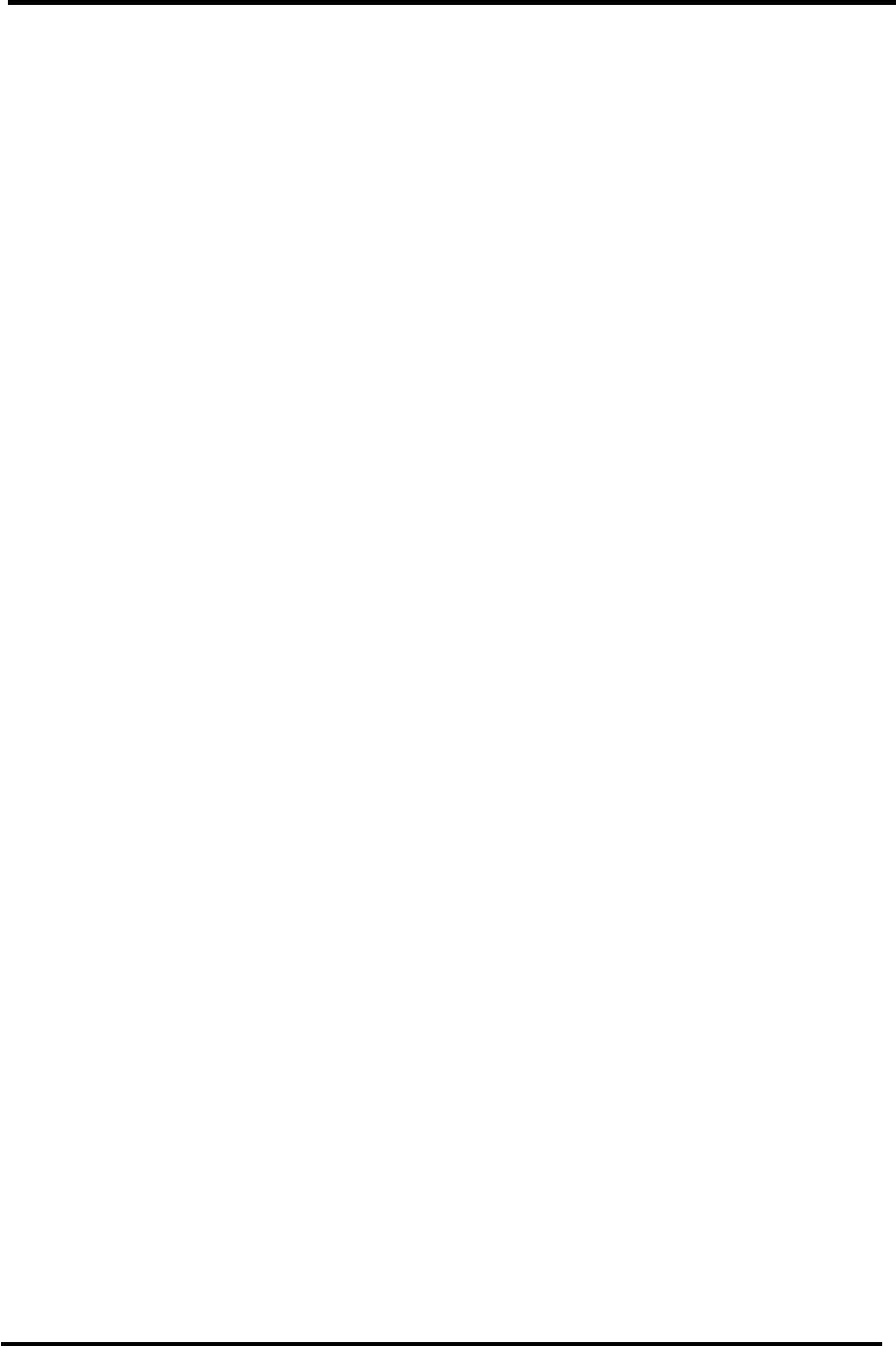
Innovator CU0TD-1/CU0RD-1 – CU4TD/CU4RD System Description
ATSC Transmitter/Regenerative Translator
Instruction Manual, Rev. 1 11
System Description
The Innovator CX Series Systems are of two different types. They are either
Regenerative Translators, example: CU3RD, or DTV Transmitters, example:
CU3TD. The Regenerative Translator (RD) accepts an RF On Channel signal (-79
to –8 dBm) and converts it to a DTV RF On Channel output signal. If an optional
preamp is present in your system it connects to the output of the receive antenna
and amplifies the weak signal approximately 20 dB. The DTV System (TD) takes
a SMPTE-310 Input and converts it to a DTV RF On Channel output signal. The
SMPTE-310 input can be from an ASI to S310 converter, a K-Tech Receiver
Drawer, an Axciter Drawer, a Universal Modulator Drawer or any other SMPTE-
310 source. The output power level of either configuration is at 5, 30, 50, 100 or
150 Watts ATSC using a single drawer, at 250, 400 or 750 Watts ATSC using an
additional single amplifier drawer, at 1400 Watts ATSC with two Amplifier
drawers, at 2100 Watts ATSC with three Amplifier drawers, or at 2500 Watts
ATSC with four Amplifier drawers.
The Innovator CX Series system provides linear and nonlinear correction
capability for the transmission path as well as internal test sources that are used
during initial system installation. If your system contains the Optional Internal
GPS Kit, the output of the GPS Antenna connects to the J5 TNC connector on the
rear panel of the CXB drawer. This kit supplies 10 MHz and 1 pps references for
use in the CXB drawer.
The CU0TD-1 thru CU0TD-5 Innovator CX Series systems and the same drawer
used as driver for higher power transmitter systems contain the Digital Modulator
w/Power Conditioner (1309629) that is made up of (A2) the Digital Modulator
Board (1304883) and (A22) the Power Conditioner Board (1309404). The drawer
also contains (A3) the IF Precorrector Board (1308796), (A4) the Frequency Agile
Upconverter (1309695), and (A6) the Amplifier Assembly. The (A7) Output
Detector Board (1312207), (A8) the Innovator CX Control Board (1312543), (A9)
the +5V, ±12V Power Supply and (A10) the +24V/+28V/+32V/+39V/+48VDC
Power Supply are also contained in the drawer. To make the system a
regenerative translator, the RD kit (1310182) supplies the (A1) 8 VSB
Demodulator Board (1308275) to the drawer.
The type of (A6) Amplifier Assembly used in the drawer changes as the output
power of the system changes. The Amplifier Assembly (1309621) is used in
CU0TD/RD-1 systems, the Amplifier Assembly (1312566) is used in CU0TD/RD-2
and CU0TD/RD-3 systems and the Amplifier Assembly (1312191) is used in
CU0TD/RD-4 and CU0TD/RD-5 systems and the Amplifier Assembly (1315009) is
used in CU0TD/RD-4 and CU0TD/RD-5 systems with Axciters. The Amplifier
Assembly (1315381) is used in the CUBE888A-2 and the CUBE888A-2 w/8 VSB
Demodulator Board drawers. Also part of the amplifier assemblies are an ALC
Board (1315006, used with Axciter systems or 1308570, used with all other
systems).
The (A10) Power Supply Assembly also changes as the output power of the
system changes. A +24V Power Supply is used in CU0TD/RD-1 systems, a
+28V/300W Power Supply is used in CU0TD/RD-2 Systems, a +36V/600W Power
Supply operating at 30V is used in CU0TD/RD-3 systems and a +48V/1100W
Power Supply operating at 48V is used in CU0TD/RD-4 and CU0TD/RD-5
systems.
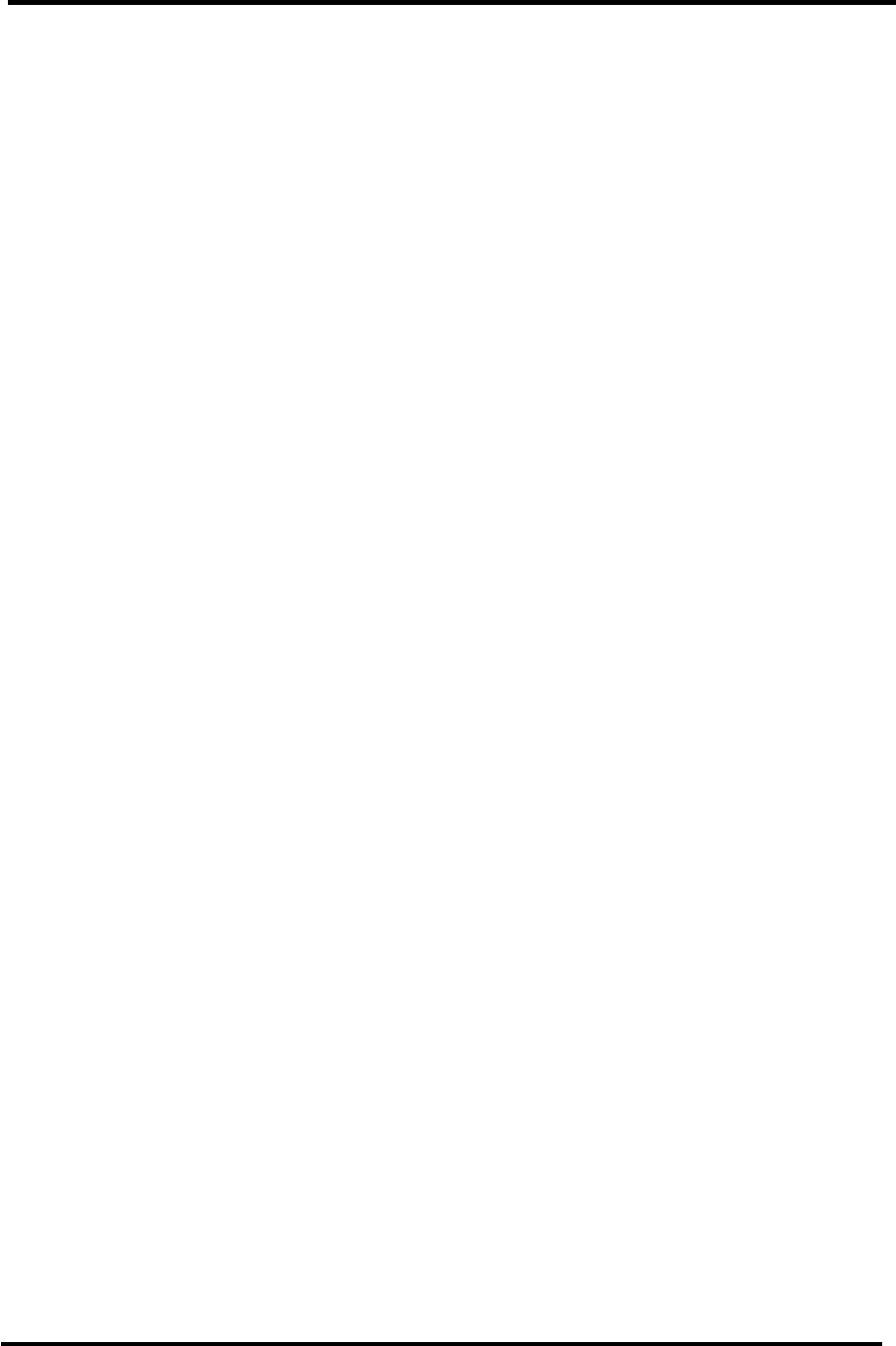
Innovator CU0TD-1/CU0RD-1 – CU4TD/CU4RD System Description
ATSC Transmitter/Regenerative Translator
Instruction Manual, Rev. 1 12
When configured as an ATSC Transmitter (TD), the SMPTE-310 input at (J1),
from an ASI to S310 converter, a KETCH Receiver, an Axciter Drawer or any
other SMPTE-310 source, connects directly to the input jack (J42) on the (A2)
Digital Modulator Board (1304883). When configured to operate as a
Regenerative Translator (RD), the DTV ON Channel RF Input at (J1), (-8 to -79
dBm) connects to the Tuner Input Jack on (A1) the 8 VSB Modulator Board
(1308275) supplied with the (RD) kit. The 8 VSB Modulator Board (1308275)
converts the DTV input to a SMPTE-310 output at (J13) that connects to the input
jack (J42) on the (A2) Digital Modulator Board (1304883) in systems without an
Axciter drawer. The IF output of the 8 VSB modulator board connects to J2 on
the IF pre-corrector board (1308796). The IF Pre-Corrector Board provides ALC,
automatic or manual, gain control of the IF level. The board also supplies pre-
correction Response, In Phase and Quadrature Non-Linear adjustments. The
board has the circuitry for ALC Fault, Input Fault and Modulation Fault monitoring
and indications. The IF from the IF precorrector board is connected to the digital
upconverter board (1309695) at J6.
In regenerative translator systems with an Axciter, the DTV ON Channel RF Input
at (J1), (-8 to -79 dBm) connects to the Tuner Input Jack on (A1) the 8 VSB
Modulator Board (1308275). The SMPTE-310 output of the board at J13 is wired
to J2 on the rear panel of the drawer. The SMPTE-310 is cabled to the SMPTE-
310 input jack J27 on the Axciter drawer. The digital IF output of the Axciter at
J40 is cabled to J3 on the CU0RD-3 drawer that is wired to J6 on the digital
upconverter board. The rest of the drawer operates the same for both the RD
and the TD systems.
The digital upconverter takes the 44 MHz or 36 MHz IF signal and converts it to a
TV channel frequency in the range of 54-860 MHz. The RF on channel signal is
fed to the ALC Board, Innovator CX Series (1308570), which is used to control
the drive power to the RF amplifier chain in the CU0TD/RD-1, CU0TD/RD-2,
CU0TD/RD-3, CU0TD/RD-4 and CU0TD/RD-5 Transmitter/Translators. In a
CU0TD/RD-2 or CU0TD/RD-3, the RF is connected to the (A6) Amplifier Assembly
(1312566) that is made up of (A6-A1) the 2 Stage UHF Amplifier Board
(1308784) and (A6-A2) the RF Module Pallet w/Philips transistors (1300116).
The assembly has approximately 36 dB of gain. The amplified output at
approximately +38 dBm connects to the (A7) Output Detector Board (1308685 or
1312207) which provides forward (2V=100%) and reflected (2V=25%) power
samples to the CU Control Board (1312543) for metering and monitoring
purposes. An output power sample is also supplied to the front panel sample
jack J15, which is a 50 Ohm BNC type. The typical sample value in a CU50 is
approximately 60dB down from the output power level of the drawer. The RF
output is cabled to J2 the “N” connector RF output jack on the rear panel of the
drawer. In CU0TD/RD-1, CU0TD/RD-2, CU0TD/RD-3, CU0TD/RD-4 and
CU0TD/RD-5 systems the output connects to a digital mask filter, low pass filter
and then the antenna for your system. In CU1TD/RD-1, CU1TD/RD-2, and
CU1TD/RD-3 systems, the RF output, from the driver drawer, is connected to J1
on the rear panel of the amplifier drawer. The RF is cabled to J1 on the Amplifier
Heatsink Assembly in the amplifier drawer. In CU2TD/RD and higher power
systems the RF is connected to a splitter and then to the inputs of the amplifier
drawers.
The CU1TD/RD-1 ATSC system is made up of a Driver Drawer and a 250 Watt
ATSC Amplifier Drawer. The driver drawer connects to the 250 Watt Amplifier
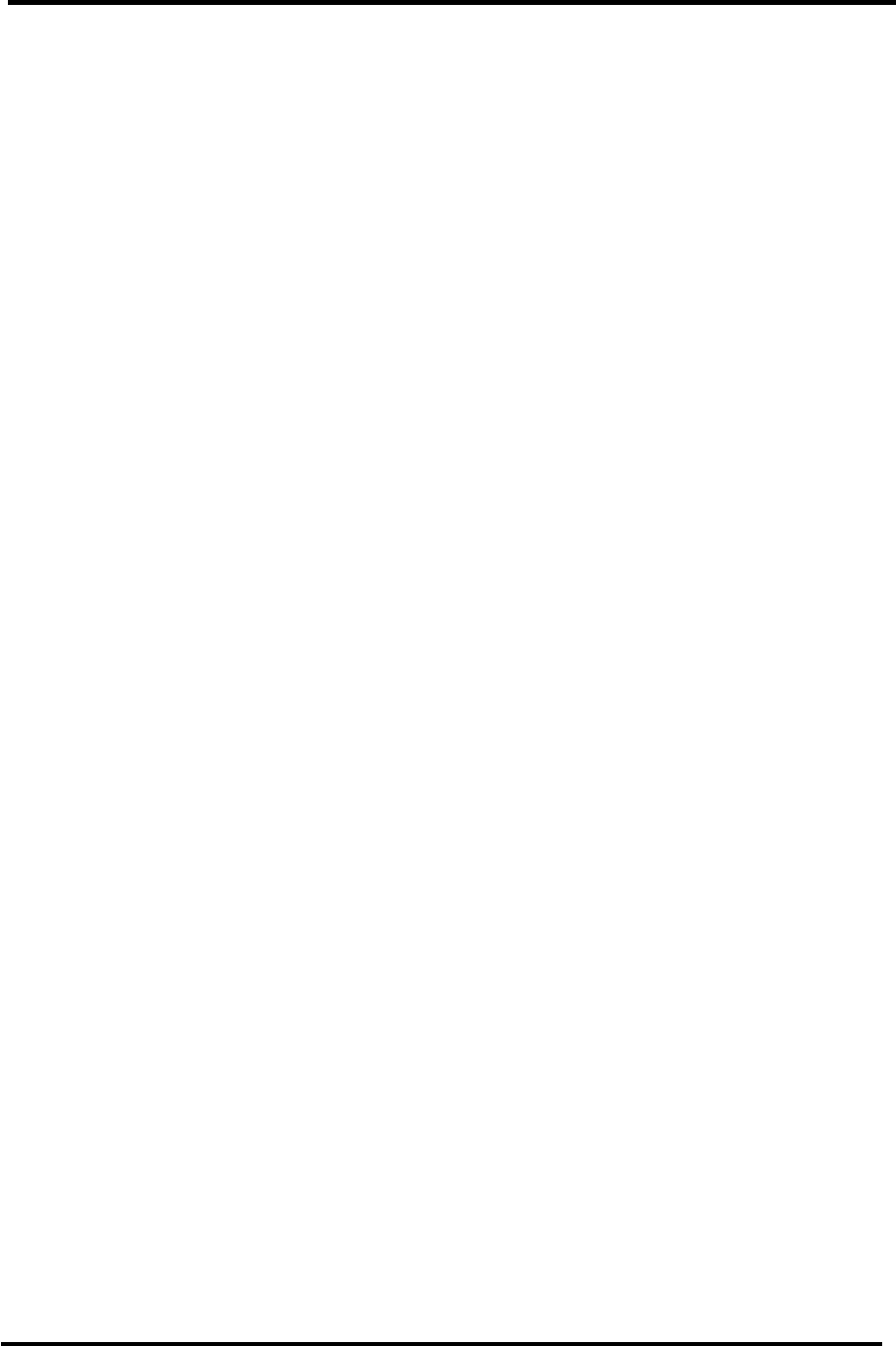
Innovator CU0TD-1/CU0RD-1 – CU4TD/CU4RD System Description
ATSC Transmitter/Regenerative Translator
Instruction Manual, Rev. 1 13
drawer and supplies the needed drive level to produce the 250 Watts output of
the system. The control and operating parameters of the 250 Watt Amplifier
Drawer are displayed on the LCD Screen on the driver drawer. In the 250 Watt
amplifier drawer, the RF input signal is at J1 on the rear panel of the drawer that
is cabled to J1 on the amplifier pallet. In a standard 250 Watt amplifier drawer, a
single +42VDC power supply provides the operating voltages, through the
current metering board, to the amplifier pallet. In a N+1 250 Watt amplifier
drawer, two +42VDC power supplies are diode-ord and provide the operating
voltages, through the current metering board, to the amplifier pallet. If one
power supply should malfunction, the other power supply will maintain the
necessary voltage to provide the 250 Watts output. The amplified output of the
pallet, which has approximately 15 dB gain, is connected to J2 the 7/16” (1.1cm)
Din RF output jack of the drawer. An output detector board supplies a forward
and a reflected power sample to the amplifier control board for metering and
monitoring purposes.
The standard CU1TD/RD-2 ATSC system is made up of a driver drawer and a 400
Watt Amplifier Drawer. The driver drawer output connects to the 400 Watt
Amplifier drawer and supplies the needed drive level to produce the 400 Watts
output of the system. The control and operating parameters of the 400 Watt
Amplifier Drawer are displayed on the LCD Screen on the driver drawer. In the
400 Watt Amplifier Drawer, the input RF signal at J1, located on the rear panel of
the drawer, is fed to J1 on the Splitter Board, which supplies two outputs, one to
each 888 amplifier pallet. Each amplifier pallet has approximately 14 dB gain.
The amplified outputs of the pallets are combined in the 2 Way combiner board
whose output is at J1. The RF is connected to J2 the 7/16” (1.1cm) Din RF
output jack located on the rear panel of the drawer. The 2 way combiner board
supplies a forward and a reflected power sample to the amplifier control board for
metering and monitoring purposes. In a 400 Watt amplifier drawer, the typical
sample value at J6, a 50Ω BNC jack located on the front panel of the drawer, is
approximately 65dB down from the output power level of the drawer.
The CU500 ATSC system w/two dual 888 pallets and Axciter is made up of a
CU30 w/Axciter Drawer and a 500 Watt Amplifier Drawer w/two dual 888 pallets.
The CU30 w/Axciter is used as a driver that connects to the CU500 Amplifier
drawer and supplies the needed drive level to produce the 500 Watts output of
the system. The control and operating parameters of the 500 Watt Amplifier
Drawer are displayed on the LCD Screen on the CU30 Drawer. In the CU500, the
input RF signal at J1, located on the rear panel of the drawer, is fed to J1 on the
2 Way Splitter Board, which supplies two outputs, one to each 888 amplifier
pallet. Each amplifier pallet has approximately 16 dB gain. The amplified
outputs of the pallets are combined in the 2 Way combiner board whose output is
at J1. The RF is connected to J2 the 7/16” (1.1cm) Din RF output jack located on
the rear panel of the drawer. The 2 way combiner board supplies a forward and
a reflected power sample to the amplifier control board for metering and
monitoring purposes. In a CU500, the typical sample value at J6, a 50Ω BNC
jack located on the front panel of the drawer, is approximately 65dB down from
the output power level of the drawer.
The CU1TD/RD-3, 750 Watt ATSC system is made up of a driver drawer and a
750 Watt Amplifier Drawer. The output of the driver drawer connects to the
Amplifier drawer and supplies the needed drive level to produce the 750 Watts
output of the system. The control and operating parameters of the amplifier
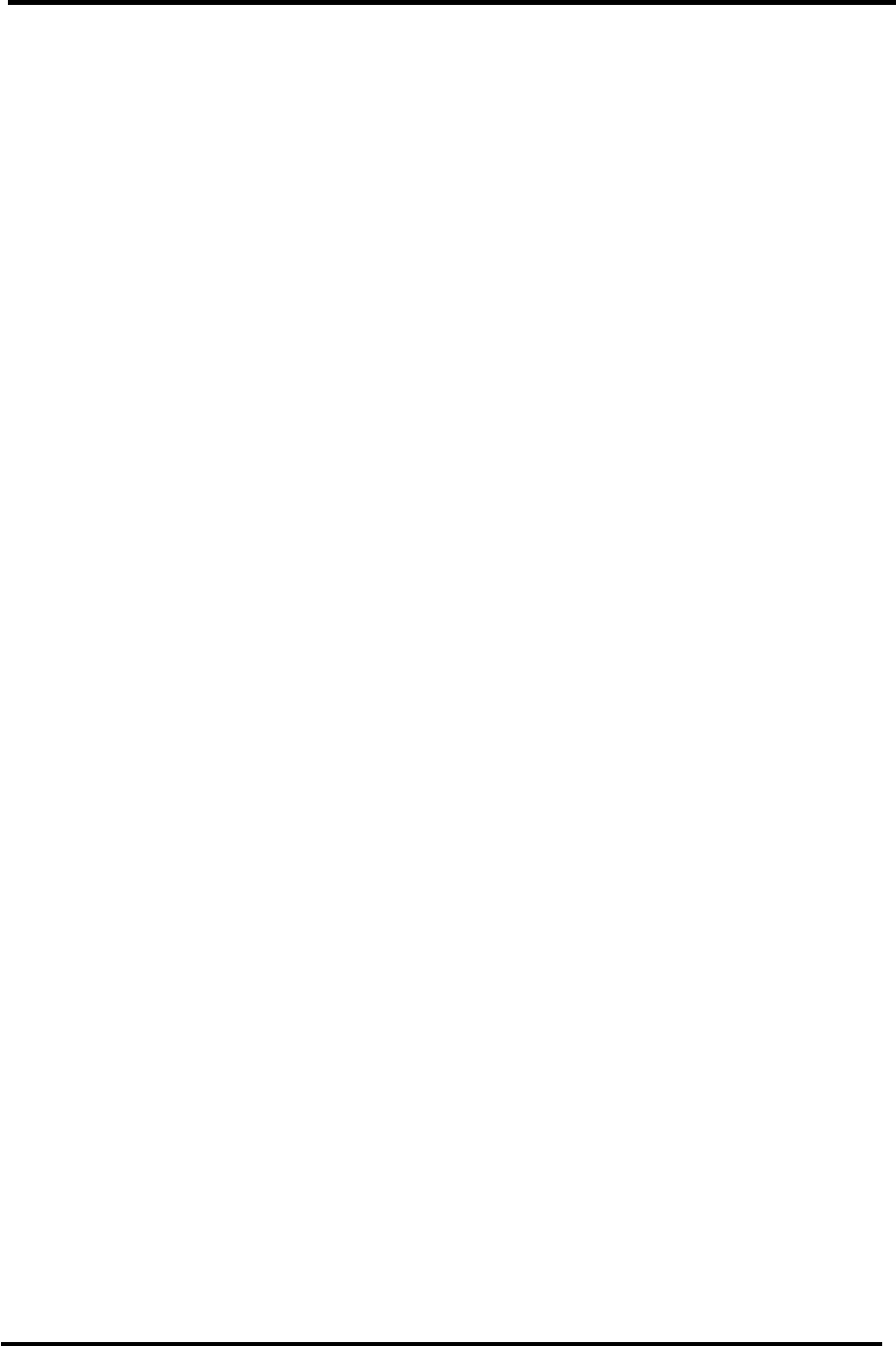
Innovator CU0TD-1/CU0RD-1 – CU4TD/CU4RD System Description
ATSC Transmitter/Regenerative Translator
Instruction Manual, Rev. 1 14
drawer are displayed on the LCD Screen on the driver drawer. In the amplifier
drawer the input RF signal at J1, located on the rear panel of the drawer, is fed to
J1 on the 4 Way Splitter Board, which supplies four outputs, one to each 888A
amplifier pallet. Each amplifier pallet has approximately 15 dB gain. The
amplified outputs of the pallets are combined in the 4 Way combiner board whose
output is at J1. The RF is connected to J2 the 7/16” (1.1cm) Din RF output jack
located on the rear panel of the drawer. The 4 way combiner board supplies a
forward and a reflected power sample to the amplifier control board for metering
and monitoring purposes. The typical sample value at J6, a 50Ω BNC jack
located on the front panel of the drawer, is approximately 65dB down from the
output power level of the drawer.
In higher power systems, multiple amplifier drawers are used along with splitters
and combiners to produce the desired output. A System Metering Board
(1312666) provides forward, reflected, overtemperature and other parameters to
the exciter/driver drawer from the external power amplifier chain. The
CU2TD/RD is made up of a driver drawer, a two way splitter, two amplifier
drawers and a two way combiner with a reject load. The reject load provides
isolation protection of the operating power amplifier if the other amplifier fails.
One–half the power of the operating amplifier drawer connected to the combiner
will be dissipated by the reject load with the other half of the power going to the
output filters and the antenna. The CU3TD/RD is made up of a driver drawer, a
three way splitter, three amplifier drawers and a three way combiner with reject
load. The CU4TD/RD is made up of a driver drawer, a four way splitter, four
amplifier drawers and a four way combiner with reject load. The reject loads in
the multi-amplifier systems have thermal switches connected to them which
monitor the temperature of the load and provide the overtemperature fault, if it
occurs, through the system metering board to the exciter/driver drawer.
The On Channel RF output of the amplifier drawer either connects directly to the
digital mask filter and low pass filter and then to the antenna in single amplifier
systems or to a combiner, the digital mask filter, low pass filter, output coupler
and finally to the antenna in multiple amplifier systems. The output coupler
provides a forward and a reflected power sample to the system metering board
which detects the samples and supplies the forward and reflected power levels to
the exciter/driver drawer for use in the metering circuits.
Optional Dual Exciter System w/Axciter Modulator Trays
The typical optional Dual Exciter System contains a Remote Interface Unit, two
Axciter modulators, two CXB Exciter/Driver Assemblies, an Exciter Output
Routing Switch, a power amplifier tray, a pre filter coupler, a low pass filter, a
digital bandpass filter, a post filter coupler and an output coupler. The system
also contains two Axciter relays, two 2 way splitters, a signal routing board and
two system metering boards which generate forward and a reflected power
samples for metering purposes in the exciter/driver assemblies.
The Remote Interface Unit monitors that state of the exciters and provides
automatic exciter switching based on current conditions and operator inputs. The
two exciters are configured as either the main On-Air exciter or the back-up
exciter. Either exciter can be used as the selected main exciter and the other
exciter functions in a backup role if it is not faulted.
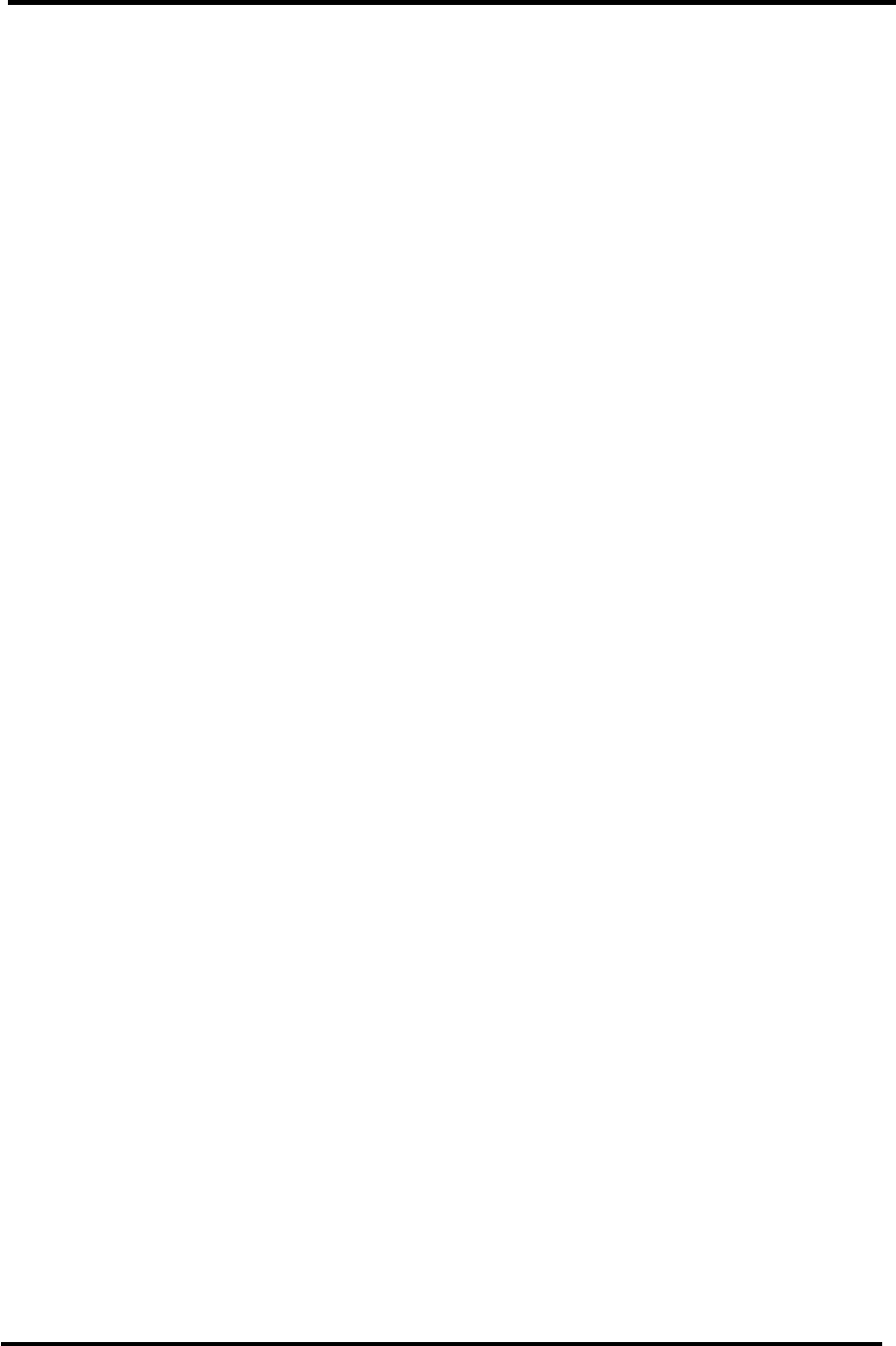
Innovator CU0TD-1/CU0RD-1 – CU4TD/CU4RD System Description
ATSC Transmitter/Regenerative Translator
Instruction Manual, Rev. 1 15
NOTE: Information and drawings on the Axciter Modulator Drawer are
contained in the separate Axciter Instruction Manual.
Exciter 1 consists of the (A4) Axciter Modulator Tray, the (A2) Axciter Relay, the
(A1) Exciter/Driver Assembly Exciter 1, the (A3) system metering board and the
(A5) 2 way splitter.
Exciter 2 consists of the (A14) Axciter Modulator Tray, the (A12) Axciter Relay,
the (A11) Exciter/Driver Assembly Exciter 2, the (A13) system metering board
and the (A15) 2 way splitter.
Each of the exciter/driver assemblies typically contains (A3) the Downconverter
Board (1311103), (A4) the Frequency Agile Upconverter board (1309695), (A6)
the Amplifier Assembly (1315008), (A7) the Output Metering Detector Board
(1312207), (A8) the Innovator CX Control Board (1312543), (A9) the +5V, ±12V
Power Supply and (A10) the +48VDC Power Supply. NOTE: If your system
contains 888A amplifier devices, the Amplifier Assembly may be (1315381).
The SMPTE-310 inputs connect to the rear panels of the (A4 & A14) Axciter
modulator Drawers at the BNC connectors J27. The ASI Inputs, if option is
present, connect to the ASI BNC input jacks J33 on the rear panels of the
Drawers. The Optional External 10MHz reference inputs connect to J9 on the rear
panels of the Axciter modulator trays. The Axciter modulator tray converts the
ASI input into a digital IF signal at 44 MHz. The IF is connected to the digital
upconverter board (1309695) that takes the 44 MHz IF signal and converts it to a
TV channel frequency in the range of 54-860 MHz. The RF on channel signal is
fed to the ALC Board, Innovator CXB Series (1308570), which is used to control
the drive power to the RF amplifier chain in the Transmitter. The RF is connected
to the (A6) Amplifier Assembly (1315008) that is made up of (A6-A1) the 2 Stage
UHF Amplifier Board (1308784) and the (A6-A2) the RF Module Pallet (1309580).
The assembly also contains the (A6-A3) ALC Board (1315006). In systems that
contain 888A amplifier devices, the RF is connected to the (A6) Amplifier
Assembly (1315381) that is made up of (A6-A1) the 1 Watt Amplifier Board
(1315730), and the (A6-A2) the BLF881 Amplifier Board (1314882) and (A6-A3)
the Dual 888A Amplifier Pallet (1315347). The assembly also contains the (A6-
A3) ALC Board (1315006 for systems that contain an Axciter or 1308570 for all
other systems). The assembly has approximately 40 dB of gain. The amplified
output at approximately +50 dBm connects to the (A7) Output Detector Board
(1312207) which provides forward and reflected power samples to the CU Control
Board (1312543) for metering and monitoring purposes. An output power
sample is also supplied to the front panel sample jack J15, which is a 50 Ohm
BNC type. The typical sample value is approximately 60dB down from the output
power level of the tray. The RF output is cabled to J9 the “N” connector RF
output jack on the rear panel of the tray. The RF outputs of the Exciter/driver
trays connect to (A20) the Exciter Output Routing Switch. The control panel
selects which exciter/driver output is connected to J1 on the Power Amplifier
Tray. The control and operating parameters of the Amplifier Tray are displayed
on the LCD Screen located on the selected ON Air exciter/driver tray. In the
CU500/600 tray, the input RF signal at J1, located on the rear panel of the tray,
is fed to J1 on the 4 Way Splitter Board, which supplies four outputs, one to each
amplifier pallet. Each amplifier pallet has approximately 14 dB gain. The
amplified outputs of the pallets are combined in the 4 Way combiner board whose
output is at J1. The RF is connected to J2 the 7/16” (1.1cm) Din RF output jack
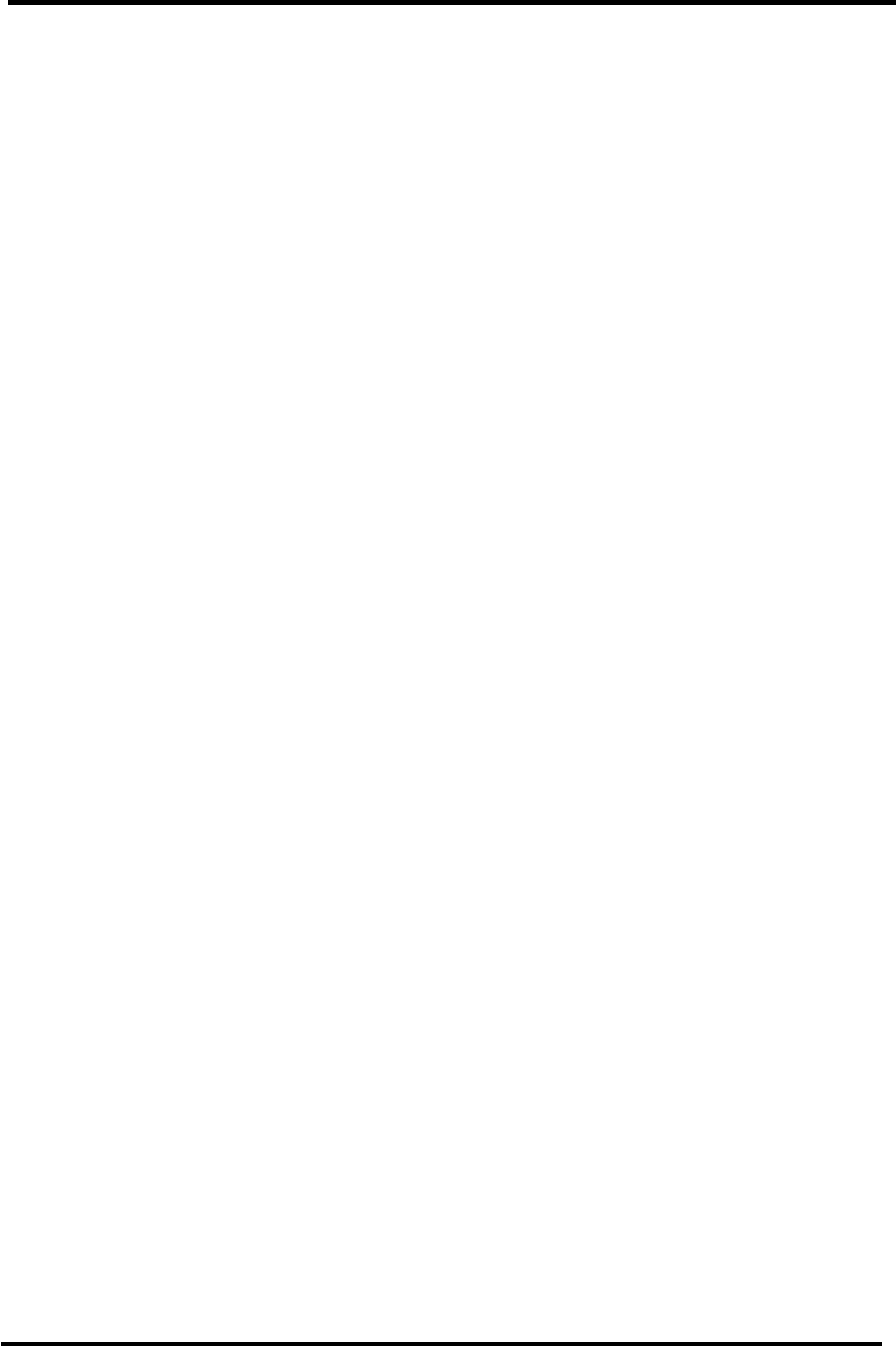
Innovator CU0TD-1/CU0RD-1 – CU4TD/CU4RD System Description
ATSC Transmitter/Regenerative Translator
Instruction Manual, Rev. 1 16
located on the rear panel of the tray. The 4 way combiner board supplies a
forward and a reflected power sample to the amplifier control board for metering
and monitoring purposes. In a CU500/600, the typical sample value at J6, a 50Ω
BNC jack located on the front panel of the tray, is approximately 65dB down from
the output power level of the tray. The On Channel RF output of the amplifier
tray is connected to the (A32) pre filter coupler that provides a pre filter forward
sample to a coaxial switch located in (A27) the Remote Interface Assembly. The
output of the pre filter coupler connects through the (A36) a low pass filter, to
(A35) the digital mask filter, the (A37) post filter coupler, the (A37) output
coupler and then to the antenna for your system. The post filter coupler provides
forward and reflected post filter power samples that connect to a coaxial switch
located in (A27) the Remote Interface Assembly. The forward and reflected
power samples are directed to the ON Air exciter by using the remote interface
panel to make the selection. Also included in the system is the Signal Routing
Board (1310948) which controls the RS-485 data connections between the dual
Exciter/Driver Assemblies and the power amplifier tray. Using a relay, which is
controlled by the (A27) remote interface module, connections between the
Exciters and the power amplifier tray are made. Exciter 1 can communicate with
the Power Amplifier Tray or Exciter 2 can communicate with the Power Amplifier
Tray both will not communicate at the same time. Each of the CXB exciters has
an Ethernet controller and a separate Ethernet port that will need wired to the
customer's network
Pre-Filter Sample (Non-Linear Distortion)
The pre-filter sample from the (A32) coupler connects to (A27) the remote
interface module which controls to which exciter the sample connects. The
sample connects to J1, on the (A2 or A12) Axciter relay, in the On Air exciter.
The (A2) relay is controlled by the (A4) Axciter Modulator in exciter 1 and the
(A12) relay is controlled by the (A14) Axciter Modulator in exciter 2 through jack
J7 on the tray. The selected output of the relay at J3, either the Pre or Post filter
sample, connects to the rear panel of the (A1 or A11) exciter/driver assembly at
the BNC Jack J4 that is connected to the downconverter board in the tray for use
in the adaptive equalization process in the Axciter system.
Post-Filter Sample (Linear Distortion)
A forward power sample, after-filtering, from the (A37) coupler at the output of
the DTV filter connects to (A27) the remote interface module which controls to
which exciter the sample connects. The forward sample from the selected On Air
exciter connects to the (A5 or A15) 2 way splitter. One output of the splitter
connects to the system metering board (A3 or A13) for use in the metering and
control circuits in the exciter. The other output of the splitter connects the post
filter forward sample to J2 on the (A2 or A12) Axciter relay in the selected On Air
Exciter. The post filter forward power sample is connected to J2, on the (A2 or
A12) Axciter relay located in the exciter that is selected as ON Air. The (A2)
relay is controlled by the (A4) Axciter Modulator and the (A12) relay is controlled
by the (A14) Axciter Modulator through jack J7 on the tray. The selected output
of the relay, either the Pre or Post filter sample, connects to the rear panel of the
(A1 or A11) driver/amplifier chassis assembly at the BNC Jack J4 that is
connected to the downconverter board for use in the adaptive equalization
process in the Axciter system.
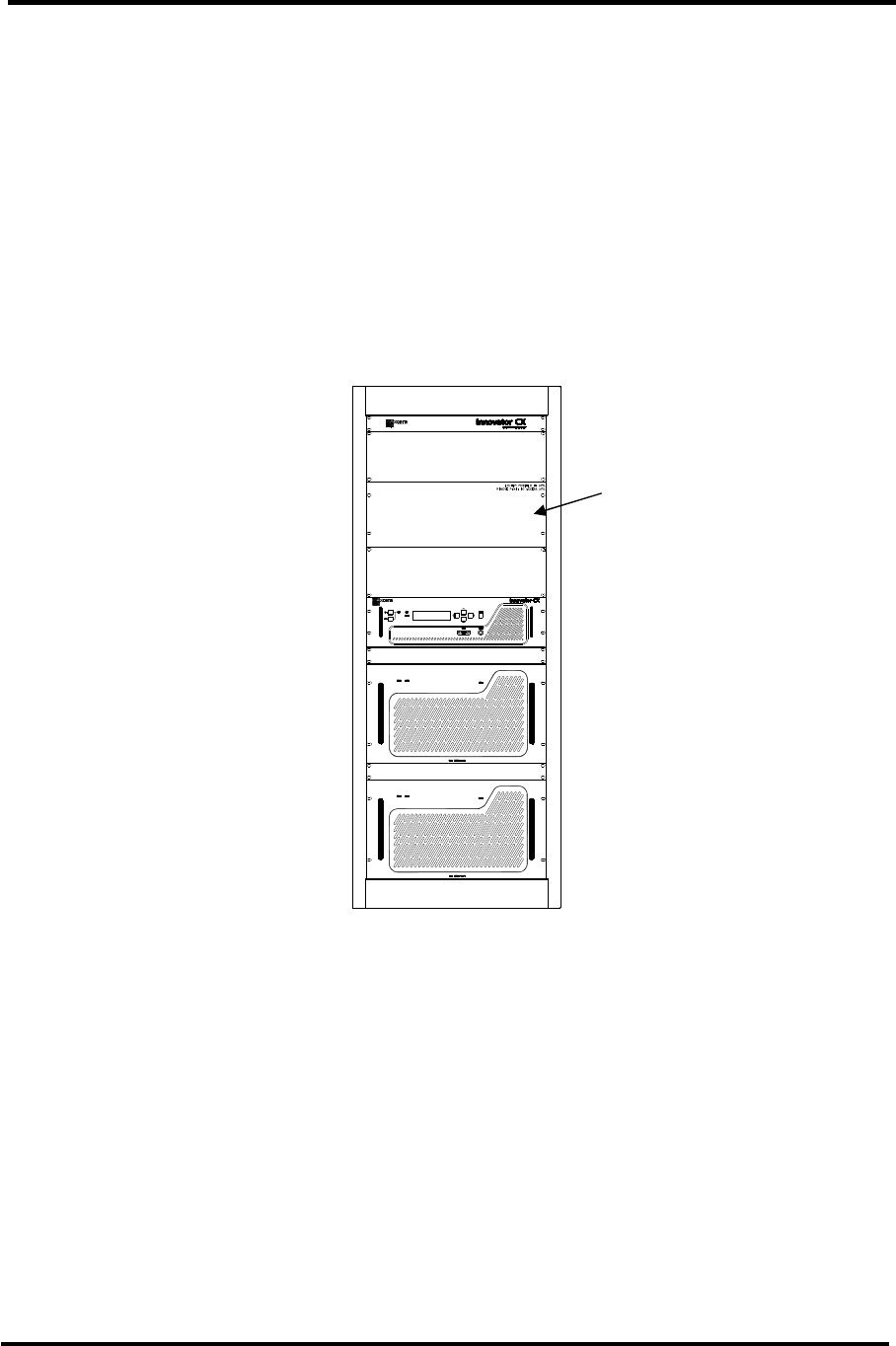
Innovator CU0TD-1/CU0RD-1 – CU4TD/CU4RD Unpacking, Installation &
ATSC Transmitter/Regenerative Translator Maintenance
Instruction Manual, Rev. 1 17
Unpacking, Installation and Maintenance
Unpacking
Axcera certifies that upon leaving our facility all equipment was undamaged and in proper
working order. It is imperative that all packages be inspected immediately upon arrival to
verify that no damage occurred in transit to the site. Inspect all packages for exterior
damage and make note of any dents, broken seals, or other indications of improper
handling. Carefully open each package and inspect the contents for damage. Verify that
all materials are enclosed as listed on the packing slip. Report any shortages to Axcera.
In the event any in transit damage is discovered, report it to the carrier. Axcera is not
responsible for damage caused by the carrier. If the equipment is not going to be
installed immediately, return all items to their original packaging for safe storage. Save
all packing material for future use. If equipment is ever removed from the site, the
original packaging will ensure its safe transport.
Figure 1: CU2TD Front View Typical Racking Plan
Installation
The Innovator CX Series transmitters are designed for simple installation. Expensive test
equipment is not required for installation and set up and to keep a system operational. An
information decal, with Voltage Range, Current Range, Manufacturer, Model and ratings is
attached to the rear panel of the stand alone drawer or if mounted in a cabinet, to the top
of the frame above the door facing the rear of the cabinet. Prior to installing the product,
review the following items. Check that they been installed, tested and/or inspected.
Building Structure
Electrical Systems
Heating and Air Conditioning
Receive Antenna or Satellite Dish and input cabling
Optional ASI to S310 Converter, if needed
Transmit Antenna and output transmission line
A1
Exciter/Driver
A2
Power Amplifier
A3
Power Amplifier
The (Optional) UPS is
located behind this blank
panel
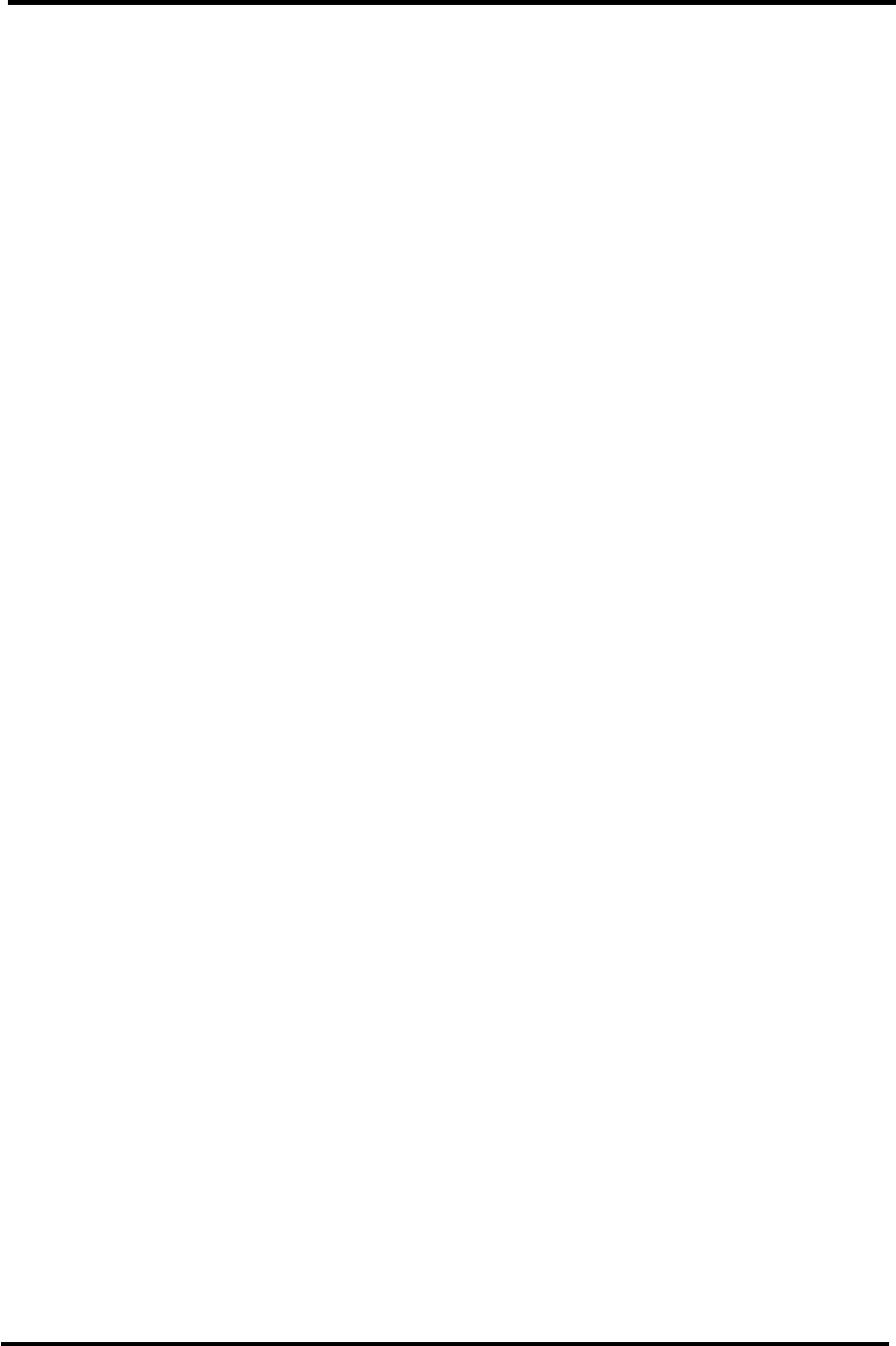
Innovator CU0TD-1/CU0RD-1 – CU4TD/CU4RD Unpacking, Installation &
ATSC Transmitter/Regenerative Translator Maintenance
Instruction Manual, Rev. 1 18
The Innovator CX Series systems are 17” (43.2cm) wide standard rack mountable
drawers. They are supplied with side mounted Drawer Slides for ease of installation and
removal. The CU0TD/RD-1, CU0TD/RD-2, CU0TD/RD-3, CU0TD/RD-4 & CU0TD/RD-5
systems are 3 RU, 5.25” (13.3cm), high. The CU1TD/RD-1, CU1TD/RD-2 & CU1TD/RD-3
systems are 9 RU, 15.75” (40cm) high, which is 3 RU, 5.25” (13.3cm) for the driver
drawer and 6 RU, 10.5” (26.7cm) for the amplifier drawer. The CU2TD/RD systems are 15
RU, 26.25” (66.7cm) high, which is 3 RU, 5.25” (13.3cm) for the driver drawer and 12 RU,
21” (53.4cm) for the two amplifier drawers. The CU3TD/RD systems are 21 RU, 36.75”
(93.3cm) high, which is 3 RU, 5.25” (13.3cm) for the driver drawer and 18 RU, 31.5”
(80cm) for the three amplifier drawers. The CU4TD/RD systems are 27 RU, 47.25”
(120cm) high, which is 3 RU, 5.25” (13.3cm) for the driver drawer and 24 RU, 42”
(106.7cm) for the four amplifier drawers. In all the systems just described, if the Axciter is
also part of the system, another 3 RU, 5.25” (13.3cm) must be added to the rack space
for the Axciter drawer. NOTE: The Optional Dual Exciter System requires an additional 4
RU, 7” (17.73cm) for mounting into the cabinet. 3 RU, 5.25” (13.3cm) for the second
Exciter/Driver drawer and an additional 1 RU, 1.75” (4.43cm) for the Exciter Switcher
panel.
Also needed for FCC compliance operation is an ATSC filter on the broadcast channel that
connects to the output of the CU0TD/RD thru CU4TD/RD systems. Space must be
provided for the ATSC filter, and in some systems, for the circulator, splitter, combiner,
reject load, and low pass filter whose dimensions will vary depending on manufacturer and
channel. Refer to the vendor supplied information included with your ATSC filter and low
pass filter for specific dimensions. Make sure that the space provided for the CX Series
equipment is sufficient and includes the circulator, splitters, combiners, reject load and
external filters. Check that any additional equipment, which is included in the system that
extends above or to the side of the mounting rack, has sufficient clearance space. Refer
to the custom racking plan for the system, if prepared, for detailed information.
Drawer Slide Installation
If the system is pre-mounted in a cabinet skip this section. Locate the drawer slides
included in the installation material for your system. See Figure 2 and the manufacturers
instructions, included with the drawer slides, for the cabinet mounting instructions of the
drawer slides. Install the left drawer slide into the left side of the cabinet (as viewed from
the rear). Allow 3 RU, 5.25” (13.3cm) of space between the drawers for a CU0TD/RD-1,
CU0TD/RD-2, CU0TD/RD-3, CU0TD/RD-4 & CU0TD/RD-5 systems. In high power systems,
allow a space of 3 RU, 5.25” (13.3cm) for the driver drawer and 6 RU, 10.5” (26.7cm) for
each of the amplifier drawers. Space must also be provided for the splitter, combiner,
ATSC filter and low pass filter, if present, whose dimensions will vary depending on the
manufacturer and the output channel. Secure the left drawer slide by connecting it to the
front and rear mounting bars using No. 10 screws and the bar nuts that have been
provided. Install the drawer slide on the right side of the cabinet (as viewed from the rear)
making sure that it is aligned with the drawer slide on the left side. Secure the slide by
connecting it to the front and rear mounting bars using No. 10 screws and the bar nuts that
have been provided. Repeat this process for any other drawers if purchased. With both
slides in place, slide the drawer or drawers into the cabinet.
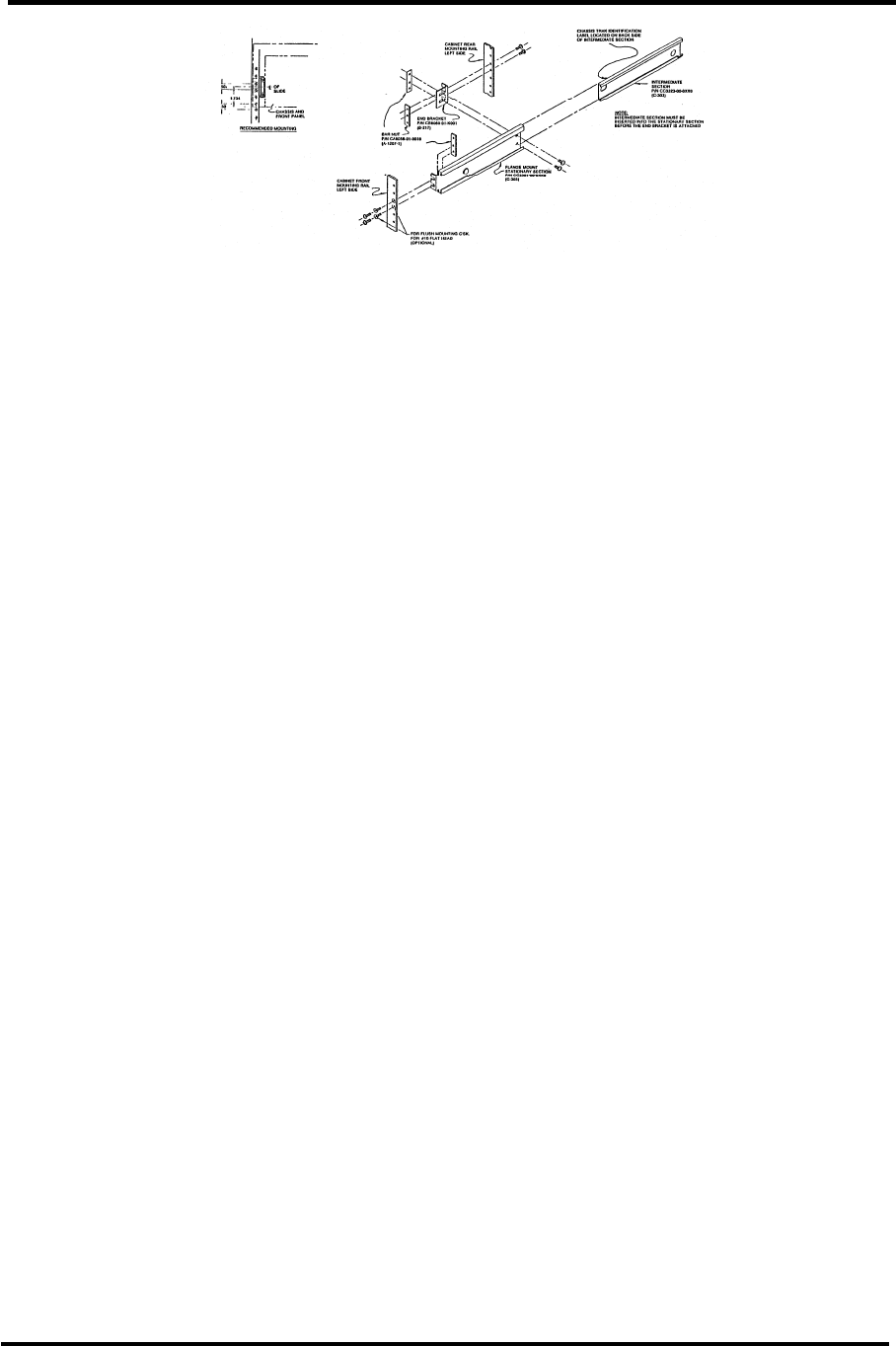
Innovator CU0TD-1/CU0RD-1 – CU4TD/CU4RD Unpacking, Installation &
ATSC Transmitter/Regenerative Translator Maintenance
Instruction Manual, Rev. 1 19
Figure 2: Cabinet Slides
AC Input Connections
The CU0TD/RD-1, CU0TD/RD-2 and CU0TD/RD-3 single drawer systems will operate with
an input voltage of 85-253VAC. The CU0TD/RD-4 single drawer systems operate on 185-
253VAC. The customer should provide a single point disconnect for the main AC input
connection to the transmitter. Check that the AC switch, located on the rear of the drawer
above the AC power jack, is OFF. Connect the AC power cord supplied with the drawer from
J6 on the rear of the drawer to the AC source. If your system has the optional ASI to S310
Converter, check that it is connected to the AC source. If your system contains an
optional preamp check that the 24VDC power supply is connected to the preamp and an
AC source.
If your system is a CU1TD/RD-1, CU1TD/RD-2 or CU1TD/RD-3, it also contains one
amplifier drawer. In CU2TD/RD and higher power systems, multiple amplifier drawers are
included. Each amplifier drawer is configured for 230 VAC operation only. Check that the
ON/OFF circuit breaker in the CU1TD/RD-1 amplifier drawer, or circuit breakers in N+1
amplifier drawers, CU1TD/RD-2 or CU1TD/RD-3, located on the rear panel on either side
of the AC power jack, are OFF. Connect the AC power cord supplied with the drawer from
J10 on the rear of the drawer to the 230 VAC source. Refer to Table 1 for the typical
voltage and current requirements for CX Systems.
If the system is mounted in a rack, an AC distribution box wired to a quad receptacle box is
used to connect the AC to the individual drawers. The AC distribution box is mounted on
the upper right side of the rack accessed through the back of the rack. The main AC input
for a C1TD-1 transmitter is, 195-253VAC, at least 10Amps, 50/60Hz. The customer should
provide a single point disconnect for the main AC input that connects to the transmitter.
The AC input lines connect inside the AC distribution box by first removing the two screws
that hold the cover plate to the front of the AC distribution box. Then connect the three
wire main AC input to the input lugs, L1 to L1, L2 to L2 and Ground to Ground. The power
amplifier drawer and the quad receptacle box connect through AC power cords directly to
the AC distribution box. The AC power to the optional receiver drawer and the
exciter/driver drawer are connected through AC power cords that plug into the quad
receptacle box.
If the system is mounted in a cabinet, an AC distribution panel is supplied to connect the AC
to the individual drawers. The AC distribution panel is mounted facing the rear of the
cabinet and accessed through the back of the cabinet. The main AC input for a CU2TD
transmitter is, 195-253VAC, at least 30Amps, 50/60Hz. The customer should provide a
single point disconnect for the main AC input that connects to the transmitter. The AC input
lines connect to the AC distribution panel by first removing the four #8 screws that hold the
cover plate to the front of the AC distribution panel. Then connect the three wire main AC
input to the input lugs located at the top left of the AC distribution panel, L1 to L1, L2 to L2
and Ground to the Ground lug on the left. The AC distribution panel in a CU2TD has three
circuit breakers that distribute the AC to the individual drawers, which are the Exciter and
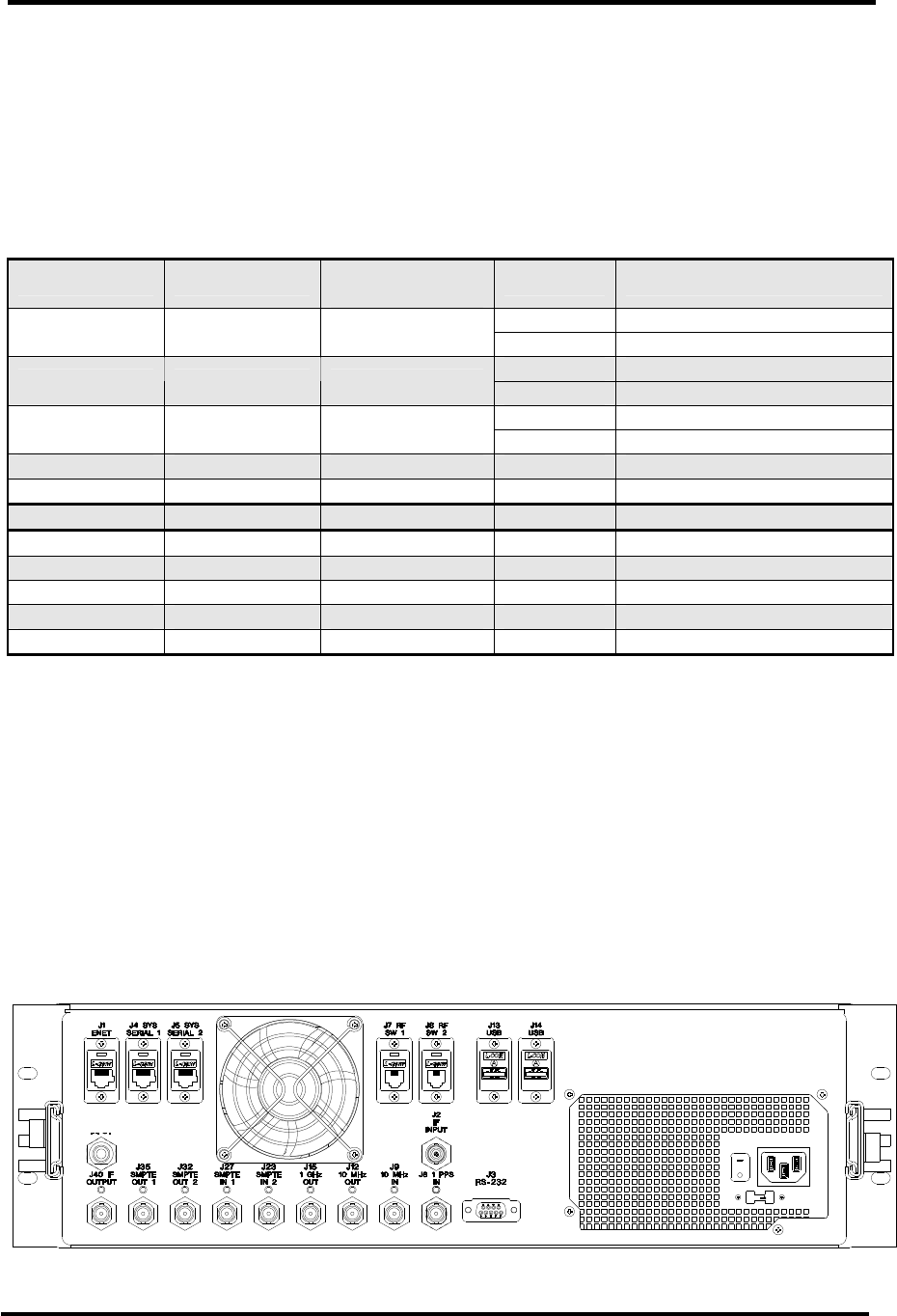
Innovator CU0TD-1/CU0RD-1 – CU4TD/CU4RD Unpacking, Installation &
ATSC Transmitter/Regenerative Translator Maintenance
Instruction Manual, Rev. 1 20
the two power amplifier drawers. The circuit breakers, which are accessed through the rear
door of the cabinet, supply the AC though AC line cords, that connect to the AC input jacks
mounted on the rear panels of the drawers. CB1 is a 30 Amp circuit breaker which supplies
the AC to the (A2), top, Power Amplifier A drawer. CB2 is a 30 Amp circuit breaker which
supplies the AC to the (A3), bottom, Power Amplifier B drawer. CB3 is a 10 Amp circuit
breaker which supplies the AC to the (A1) Exciter/Driver drawer. A maximum of four 30
Amp circuit breakers for four amplifier drawers and two 10 Amp circuit breakers for two
Exciter/Driver drawers can be installed in the AC Distribution Panel.
Table 1: CXB Series Digital Systems Typical AC Input and Current Requirements.
System O/P Power Power
Consumption Voltage Current
115 VAC 1.6 Amps to the Cabinet
CU0TD/RD-1 10 Watts 180 Watts 230 VAC .8 Amps to the Cabinet
115 VAC 2.7 Amps to the Cabinet
CU0TD/RD-2 30 Watts 300 Watts 230 VAC 1.4 Amps to the Cabinet
115 VAC 4.2 Amps to the Cabinet
CU0TD/RD-3 50 Watts 475 Watts 230 VAC 2.1 Amps to the Cabinet
CU0TD/RD-4 100 Watts 780 Watts 230 VAC 3.4 Amps to the Cabinet
CU0TD/RD-5 150 Watts 1000 Watts 230 VAC 4.3 Amps to the Cabinet
CU1TD/RD-1 250 Watts 1700 Watts 230 VAC 7.4 Amps to the Cabinet
CU1TD/RD-2 400 Watts 2400 Watts 230 VAC 10.4 Amps to the Cabinet
CU1TD/RD-3 750 Watts 4600 Watts 230 VAC 20 Amps to the Cabinet
CU2TD/RD 1400 Watts 8700 Watts 230 VAC 37.8 Amps to the Cabinet
CU3TD/RD 2100 Watts 11880 Watts 230 VAC 51.7 Amps to the Cabinet
CU4TD/RD 2500 Watts 14800 Watts 230 VAC 64.4 Amps to the Cabinet
NOTE: All values are approximate.
Input and Output Connections
The input and output connections to the system are made to the jacks mounted on the rear
panels of the CU0TD/RD-1 thru CU0TD/RD-5 systems, the drivers for the CU1TD/RD-1 and
high power systems, to the Watt amplifier drawers and to the Axciter Drawer if present in
your system. The CU0TD/RD-1 thru CU0TD/RD-5 systems and the drivers for the
CU1TD/RD-1 and higher power systems accept an On Channel RF signal (RD) or a SMPTE-
310 (TD) input and output a digital RF ON Channel signal. Refer to Figures 3 & 3A and to
Tables 2 & 2A that follow for the locations and information on the jacks and connectors. If
your system contains the Optional Internal GPS Kit, the output of the GPS Antenna
connects to the J5 TNC connector on the rear panel of the CXB drawer.
Figure 3: Rear View of Axciter Modulator Drawer
J33
J7
J2
J40
J12 J9
J27
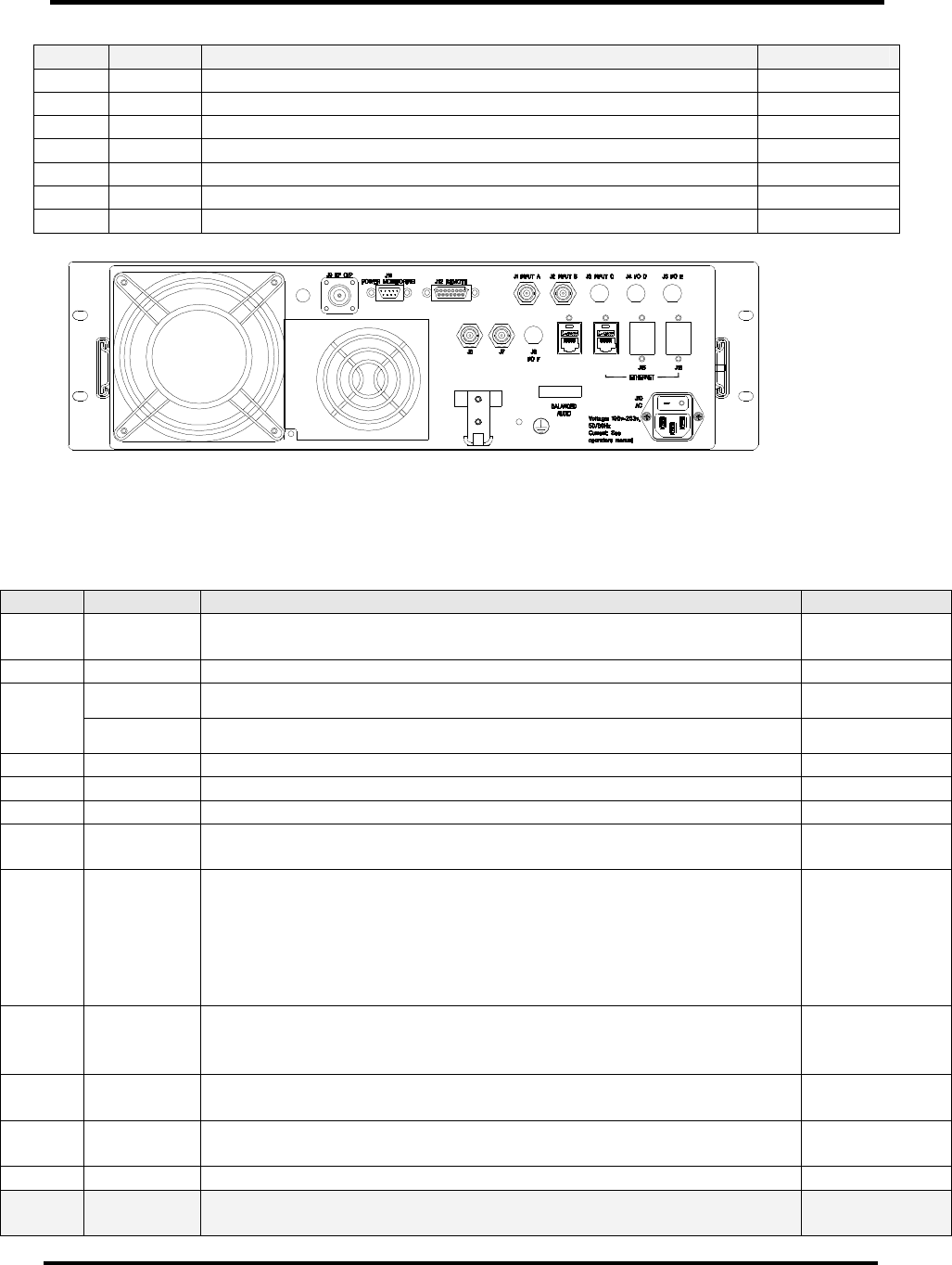
Innovator CU0TD-1/CU0RD-1 – CU4TD/CU4RD Unpacking, Installation &
ATSC Transmitter/Regenerative Translator Maintenance
Instruction Manual, Rev. 1 21
Table 2: Rear Chassis Connections for the Axciter Modulator Drawer
Port Type Function Impedance
J2 BNC IF Input (From Driver/Amplifier Assembly) 50Ω
J7 RJ-12 RF SW1 (To Axciter Relay) N/A
J9 BNC (Optional) 10MHz Reference Input 50Ω
J12 BNC 10MHz Output (To Driver/Amplifier Assembly) 50Ω
J27 BNC SMPTE 310 Input 75Ω
J33 BNC (Optional) ASI Input 75Ω
J40 BNC IF Output (To Driver/Amplifier Assembly) 50Ω
Figure 3A: Rear View CU0TD/RD-1 thru CU0TD/RD-5 and the driver for the CU1TD/RD-1 &
higher power systems
Table 2A: Connections for the CU0TD/RD-1 thru CU0TD/RD-5 and the driver for the
CU1TD/RD-1 & higher power systems
Port Type Function Impedance
J1 BNC Input A: On Channel RF Input (RD) –78 to –8 dBm or
SMPTE-310 Input (TD) 50 Ohms
J4 BNC SMPTE-310 Output (RD Only) Normally jumpered to J5 50 Ohms
BNC SMPTE-310 Input (RD Only) Normally jumpered to J4 or 50 Ohms
J5
TNC GPS Antenna Input (Only used with Internal GPS Kit) 75 Ohms
J6 BNC 10 MHz Input: Optional External 10 MHz Reference Input 50 Ohms
J7 BNC 1 PPS Input: Optional External 1 PPS Reference Input 50 Ohms
J9 N RF Output: On Channel RF Output 50 Ohms
J10 IEC AC Input: AC input connection to 85-264VAC Source and
On/Off circuit breaker N/A
J11 9 Pos
Male D
Power Monitoring: Interface to System and external amplifier
drawers, if present. Also provides an interlock for the Reject
Load (if used). If not used, in systems with no external
amplifier, a jumper from J11-6 to J11-9 needs to be in place.
Refer to Table 2B which follows for information on the
connections.
N/A
J12 15 Pos
Female D
Remote: Remote control and status indications. Refer to
Table 7A on pages 29 & 30 for information on the
connections.
N/A
J13 RJ-45 Serial: Provides communication to System and to external
amplifier drawers, if present. N/A
J14 RJ-45 Ethernet: Optional Ethernet connection. May not be present
in your drawer. N/A
J15
Front BNC RF Sample: Output Sample from Output Detector Board.
In a CU30, CU50, CU100 & CU125, the sample level at J15 is 50 Ohms
J1
J11
J12
J10
J6
J9
J
7
J
4
J13
J
5
J
2
J1
4
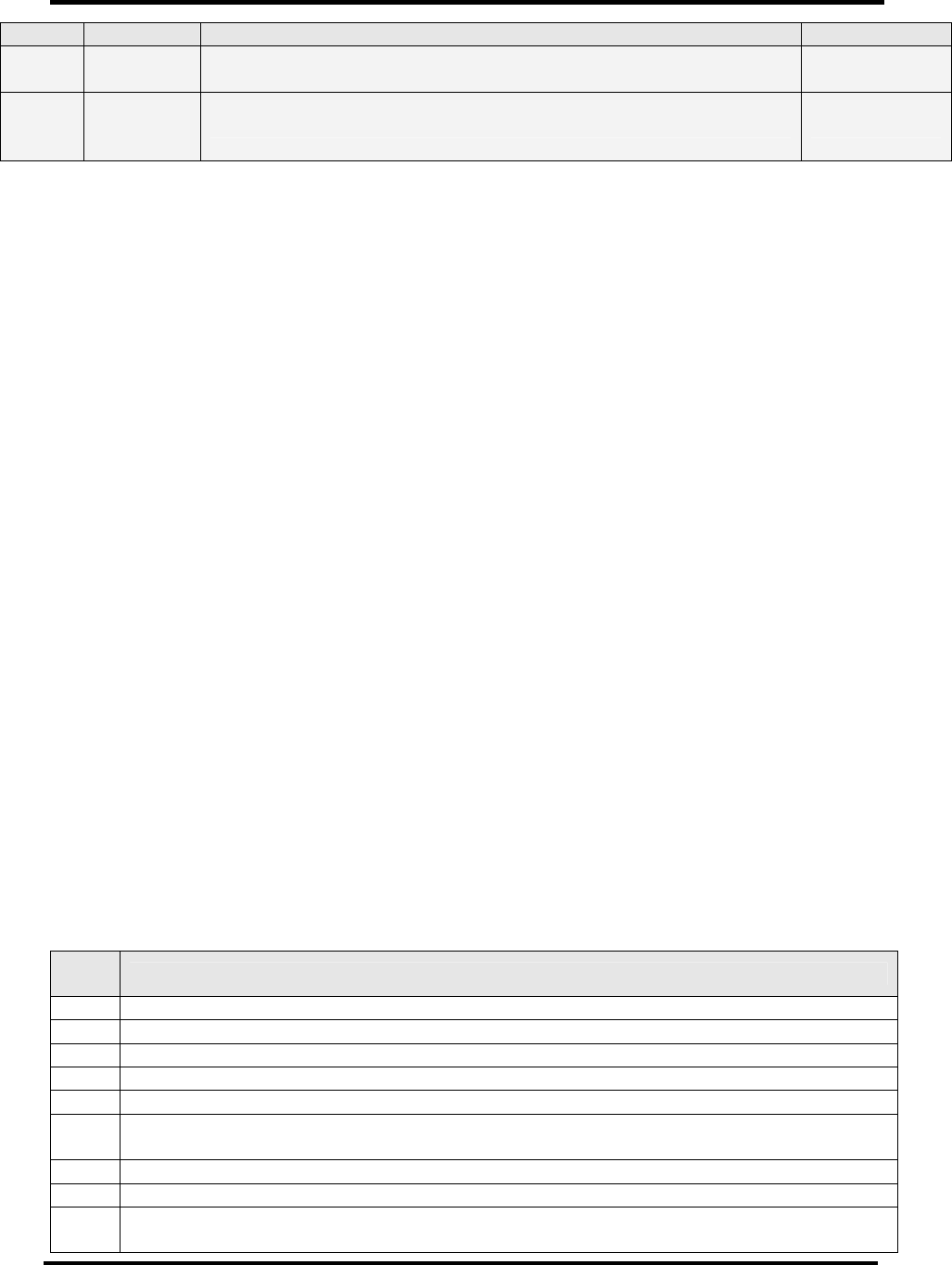
Innovator CU0TD-1/CU0RD-1 – CU4TD/CU4RD Unpacking, Installation &
ATSC Transmitter/Regenerative Translator Maintenance
Instruction Manual, Rev. 1 22
Port Type Function Impedance
Panel approximately 60dB down from the output power level of the
drawer.
J16
Front
Panel
9 Pos
Female D Serial: Used to load equalizer taps into the modulator. N/A
NOTES: 1) If your transmitter (TD) system contains an Optional ASI to S310 Converter,
connect the ASI output of the STL to the ASI in jack on the rear panel of the
converter. Connect the SMPTE-310 Output from the SMPTE 310 Out jack on the
rear panel of the converter module to the input jack J1 on the rear panel of the
CU0TD/RD-1 thru CU0TD/RD-5 drawer or the driver drawer for the CU1TD/RD-1
and higher power systems. 2) If your transmitter (TD) system contains an
Optional K-Tech receiver, connect the RF from the receive antenna or one output
of the splitter to the input jack J1 on the rear panel of the K-Tech receiver.
Connect the SMPTE-310 Output from the SMPTE 310 Out jack J2 on the rear
panel of the K-Tech receiver to the input jack J5 on the rear panel of the
CU0TD/RD-1 thru CU0TD/RD-5 or the driver for the CU1TD/RD-1 and higher
power systems. 3) If the system contains the optional K-Tech back up system,
the K-Tech receiver is bypassed by using the second output of the splitter that
connects to J1 on the rear panel of the CU0TD/RD-1 thru CU0TD/RD-5 or the
driver drawer and connecting a jumper from J4 to J5, after removing the cable
from the K-Tech receiver, on the rear panel of the CU0TD/RD-1 thru CU0TD/RD-5
or the driver drawer. This configuration uses the 8VSB demodulator board in the
CU0TD/RD-1 thru CU0TD/RD-5 or the driver drawer to produce the SEMTE-310
signal. 4) If the system contains an optional preamp it connects to the output of
the receive antenna and to J1 on the rear panel of the CU0TD/RD-1 thru
CU0TD/RD-5 drawer.
J11 Power Monitoring Connections
In systems with one or more external amplifiers, J11 is used to communicate the output
forward and reflected metering voltages back to the driver. J11 is connected directly to
the external amplifier when there is only one external amplifier and is connected through
the system metering module when multiple external amplifiers are used. In multiple
external amplifier systems there are thermal switches mounted on the reject loads of the
combiner, and the Reject load interlock is connected to the thermal switches and is used
to shut down the system if the reject load overheats. In systems with no external
amplifier, the only connection used is the Reject Load Interlock, which must be connected
to Supply Return using a jumper from J11-6 to J11-9.
Table 2B: J1 9 Pos Male “D” Connector
J11
Pin Function
1 +12VDC
2 System Forward Power
3 System Reflected Power
4 System Aural Power
5 Remote Spare Input
6 Reject Load Interlock. (If not used, in systems with no external amplifier, must
be jumpered to J11-9)
7 System Serial +
8 System Serial -
9 Supply Return (If Reject Load Interlock is not used, in systems with no external
amplifier, must be jumpered to J11-6)
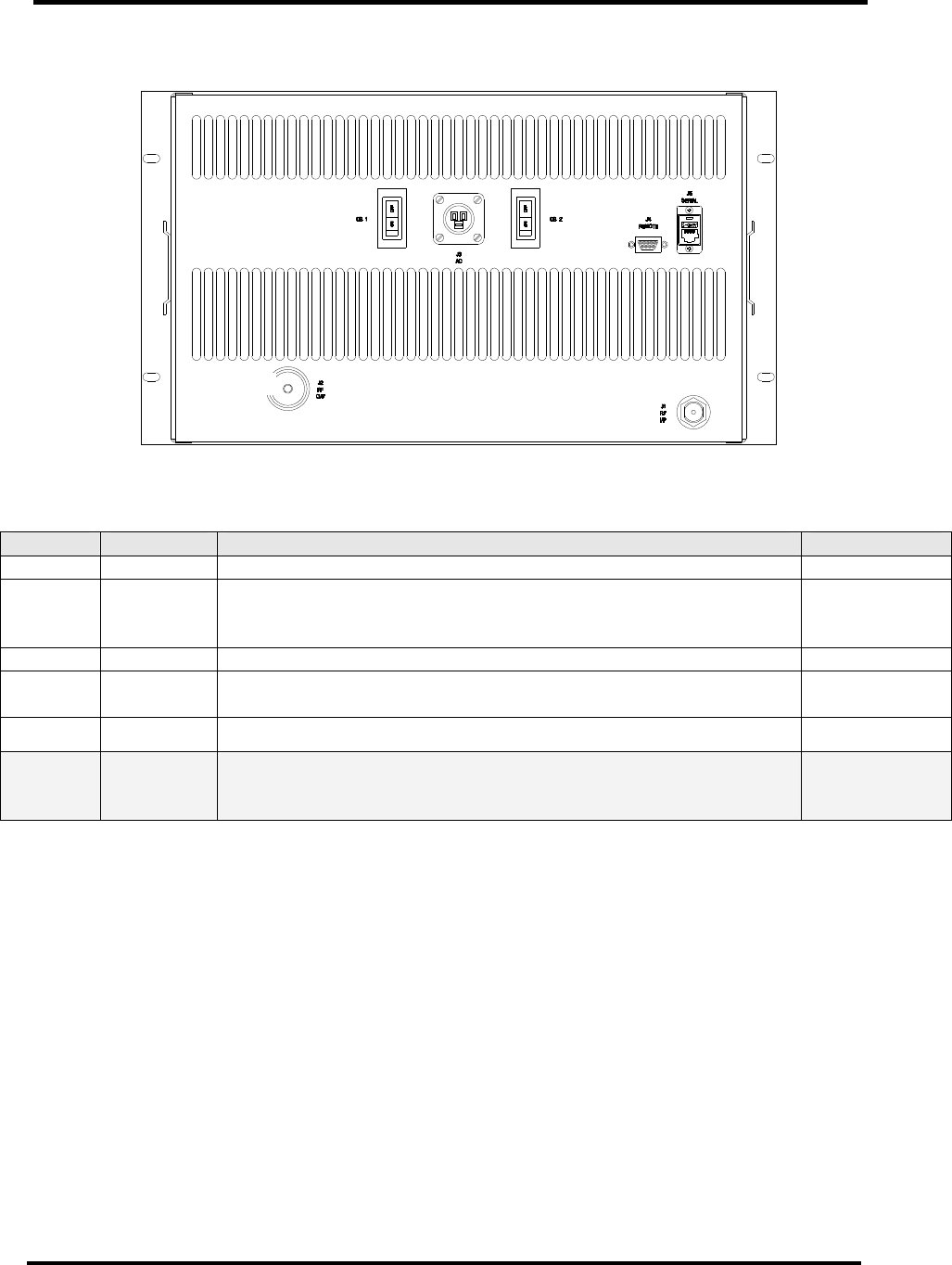
Innovator CU0TD-1/CU0RD-1 – CU4TD/CU4RD Unpacking, Installation &
ATSC Transmitter/Regenerative Translator Maintenance
Instruction Manual, Rev. 1 23
Figure 4: Rear View Amplifier Drawer. NOTE: Some amplifier drawers only has a CB1
circuit breaker.
Table 3: Connections for the Amplifier Drawer
Port Type Function Impedance
J1 N RF Input: On Channel RF from CU driver drawer 50Ω
J2
7/16”
(1.1cm)
Din
RF Output: On Channel RF Output 50Ω
J3 IEC AC Input: AC input connection to 230VAC Source N/A
J4 9 Pos D Remote: Amplifier Control Interface
(Connects to J11 on the exciter/driver drawer) N/A
J5 RJ-45 Serial data N/A
J8
Front
Panel
BNC
RF Sample: Output Sample from Combiner thru Control
Board. In a CU500, the sample level is approximately 70dB
down from the output power level of the drawer.
50Ω
Refer to Figures 3, 3A and 4, and Tables 2, 2A and 3 for detailed information on the jacks
and connectors. Connect the On Channel RF Input (RD), –78 to –8 dBm, or the SMPTE-
310 Input (TD), to the 50Ω BNC input jack J1, located on the rear panel of the CU5 thru
CU125 systems and the driver drawers for the CU250 and higher power systems. The
input to J1 can be from the ASI to S310 converter, the Axciter Drawer or any other source
of a SMPTE-310 signal.
If used, connect the external 10 MHz reference input to the 50Ω BNC 10 MHz input jack J6
located on the rear panel of the CU0TD/RD-1 thru CU0TD/RD-5 and the driver for the
CU1TD/RD-1 and higher power systems. If used, connect the external 1 PPS reference
input to the 50Ω BNC 1 PPS input jack J7 located on the rear panel of the CU0TD/RD-1
thru CU0TD/RD-5 and the driver for the CU1TD/RD-1 and higher power systems. If your
system contains the Optional Internal GPS Kit, the output of the GPS Antenna connects to
the J5 TNC connector on the rear panel of the CU0TD/RD-1 thru CU0TD/RD-5 and the
driver for the CU1TD/RD-1 and higher power systems. This kit supplies 10 MHz and 1 pps
references for use in the CU0TD/RD-1 thru CU0TD/RD-5 and the driver for the CU1TD/RD-
1 CXB drawer in higher power systems.
J
1
J
3
J
4
J
2
CB1
CB2
J5
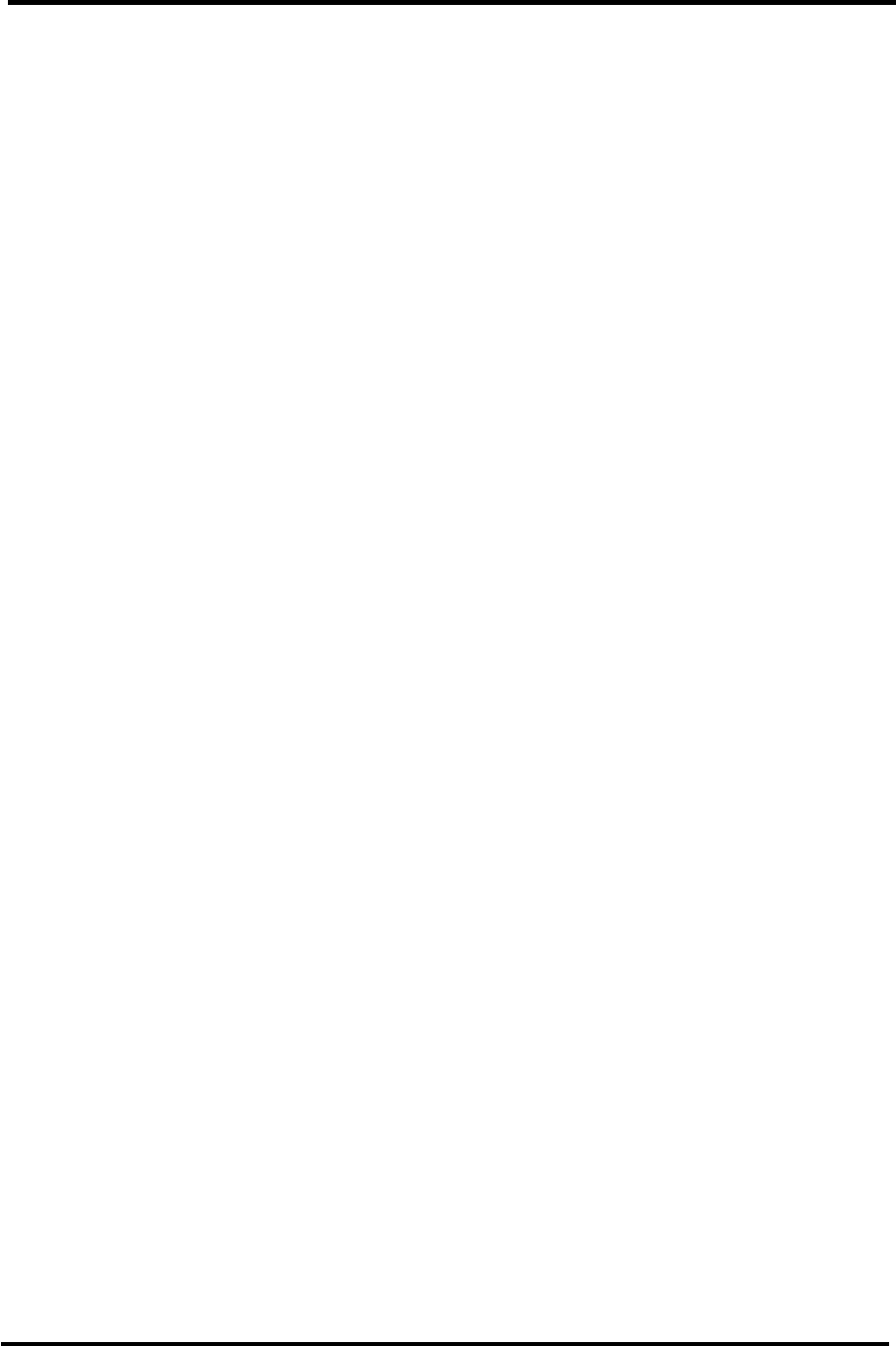
Innovator CU0TD-1/CU0RD-1 – CU4TD/CU4RD Unpacking, Installation &
ATSC Transmitter/Regenerative Translator Maintenance
Instruction Manual, Rev. 1 24
In Translator (RD) systems there is a SMPTE-310 loop-thru from the output of the
Demodulator Board at J4, mounted on the rear panel of the transmitter or driver drawer,
to the input to the Modulator Board at J5, mounted on the rear panel of the transmitter or
driver drawer. There is a jumper installed from J4 to J5. To feed SMPTE-310 directly to
the Modulator Board, remove the jumper and insert SMPTE-310 into J5. This is only used
in Translator (RD) systems not Transmitter (TD) systems.
The digital RF ON Channel output of the CU0TD/RD-1 thru CU0TD/RD-5 and the driver for
the CU1TD/RD-1 and higher power systems is at J9 the 50Ω “N” connector RF output jack
located on the rear panel. In CU0TD/RD-1 thru CU0TD/RD-5 systems, the output of the
drawer at J9 connects to the low pass, digital mask filter and then to the antenna for your
system. In CU1TD/RD-1 and higher power systems, the output of the driver drawer at J9
is connected to J1 the 50 Ohm “N” connector RF input jack located on the rear panel of
the amplifier drawer or to a splitter in multiple amplifier systems. In CU1TD/RD-1,
CU1TD/RD-2 or CU1TD/RD-3 systems, check that the system power metering interface
cable is connected from J11 the 9 position “D” connector located on the rear panel of the
driver drawer to J4 the 9 position “D” connector located on the rear panel of the amplifier
drawer. This cable provides the control, status and operating parameters of the amplifier
drawer to the driver drawer. In CU2TD/RD and higher power systems the output of the
driver drawer is split and connected to J1 the “N” type connector RF input jack on the
amplifier drawers. Check that the system power metering interface cable is connected
from J11 the 9 position “D” connector located on the rear panel of the driver drawer to J9
the 9 position “D” connector located on the System Metering Board. Also check that the
serial connection is cabled from the RJ-45 connector J13 on the driver drawer to the RJ-45
connector J1 on the system metering board. The system metering board provides serial
RJ-45 connections at J2 and J5 that are cabled to the RJ-45 serial port J5 on the rear
panel of the amplifier drawers. These cables provide the control, status and operating
parameters of the amplifier drawers to the driver drawer through the System Metering
Board.
The digital RF ON Channel output of the amplifier drawer is at J2 the 50Ω “7/16” (1.1cm)
Din connector RF output jack located on the rear panel that connects directly to the digital
mask filter, the low pass filter and then to the antenna for your system in single amplifier
systems. In multiple amplifier drawer systems the outputs of the drawers connect to a
combiner and then the digital mask filter, the low pass mask filter, the output coupler and
finally to the antenna for your system. The output coupler provides a forward and a
reflected power sample that are cabled to the System Metering Board at J8 reflected and
J3 forward. Also connected to the system metering board at J10-6 & 9, is the output of
the overtemperature switch mounted to the reject load that is used as the reject interlock
by the system. The samples and interlock are fed through J9 on the system metering
board to J11 on the driver drawer. This completes the connections of the system.
Maintenance
Innovator CX Series Transmitters are designed with components that require little or no
periodic maintenance except for the routine cleaning of the fans and the front panels of the
modules and the periodic check of general tightness of hardware.
It is recommended that periodically, the time interval depends on the amount of movement
the cabinet receives, all mounting hardware, holding drawer slides, shelving and mounting
plates inside the cabinet are checked for tightness. All screws and bolts that are accessible
should be tightened initially when the transmitter is received and periodically thereafter if
the transmitter is moved by vehicle. All coaxial connectors, hard-line connections and
hardware holding combiners, splitters, or any other mounted items should be checked and
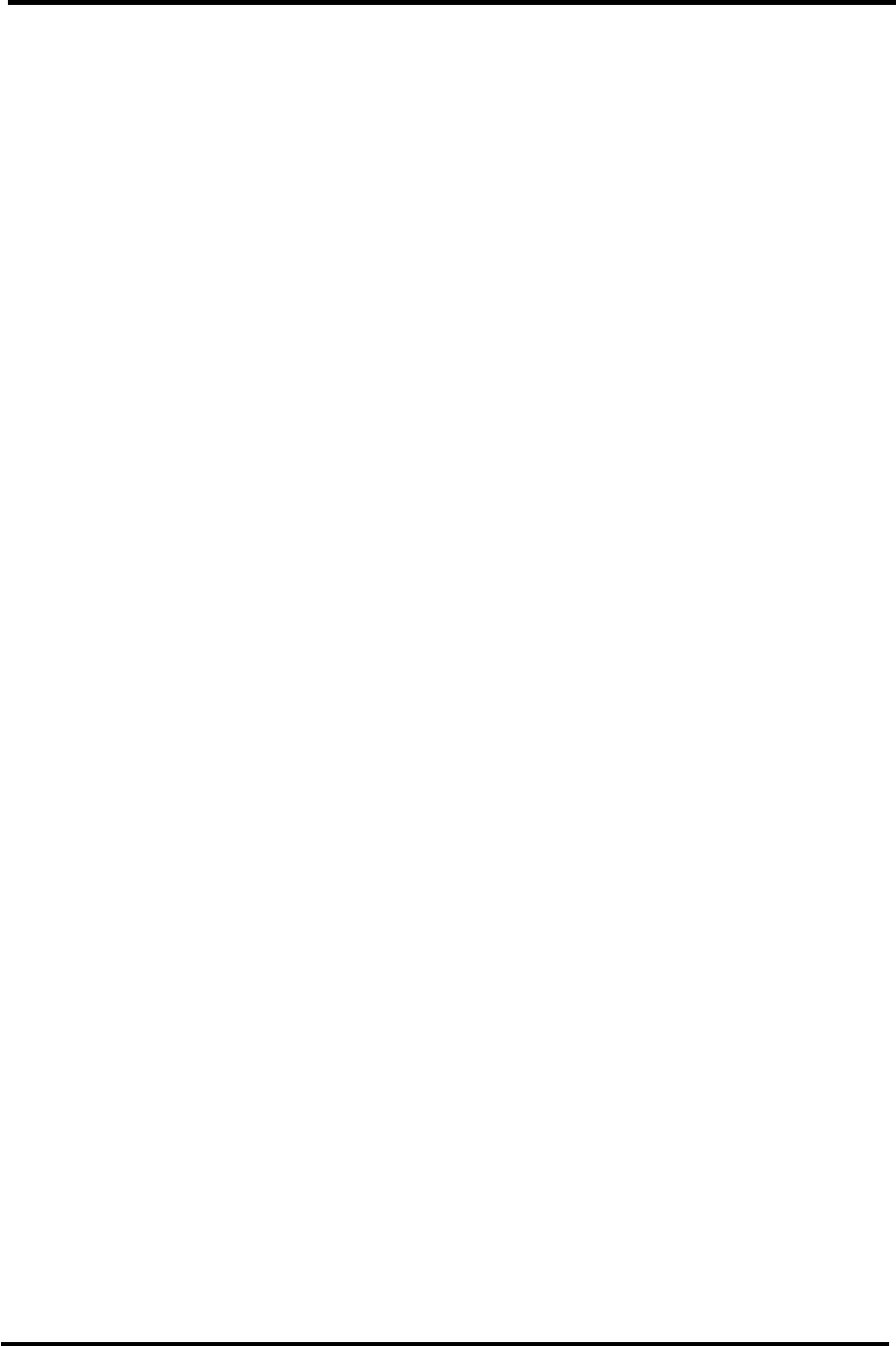
Innovator CU0TD-1/CU0RD-1 – CU4TD/CU4RD Unpacking, Installation &
ATSC Transmitter/Regenerative Translator Maintenance
Instruction Manual, Rev. 1 25
tightened. The amount of time between cleanings of the drawers and cabinets depends on
the conditions within the transmitter room. While the electronics have been designed to
function even if covered with dust, a heavy buildup of dust, dirt, or insects will affect the
cooling of the components. This could lead to a thermal shutdown or the premature failure
of the affected drawer. When the front panels of the drawers become dust covered, the
drawer should be pulled out and any accumulated foreign material should be removed.
NOTE: To remove the CX series transmitter from the cabinet, the input and output cables
must be removed from the rear of the transmitter before the drawer can be pulled out
completely from the cabinet.
A vacuum cleaner, utilizing a small, wand-type attachment, is an excellent way to suction
out any dirt from the drawer and cabinet. Alcohol and other cleaning agents should not be
used unless you are certain that the solvents will not damage components or the silk-
screened markings on the drawers and boards. Water-based cleaners can be used, but do
not saturate the components. The fans and heatsinks should be cleaned of all dust or dirt to
permit the free flow of air for cooling purposes. It is recommended that the operating
parameters of the transmitter be recorded from the LEDs and the LCD system metering on
the front panel of the drawer at least once a month to be used for comparison purposes in
case of a failure. It is suggested that this data be retained in a rugged folder or envelope
and stored near the transmitter.
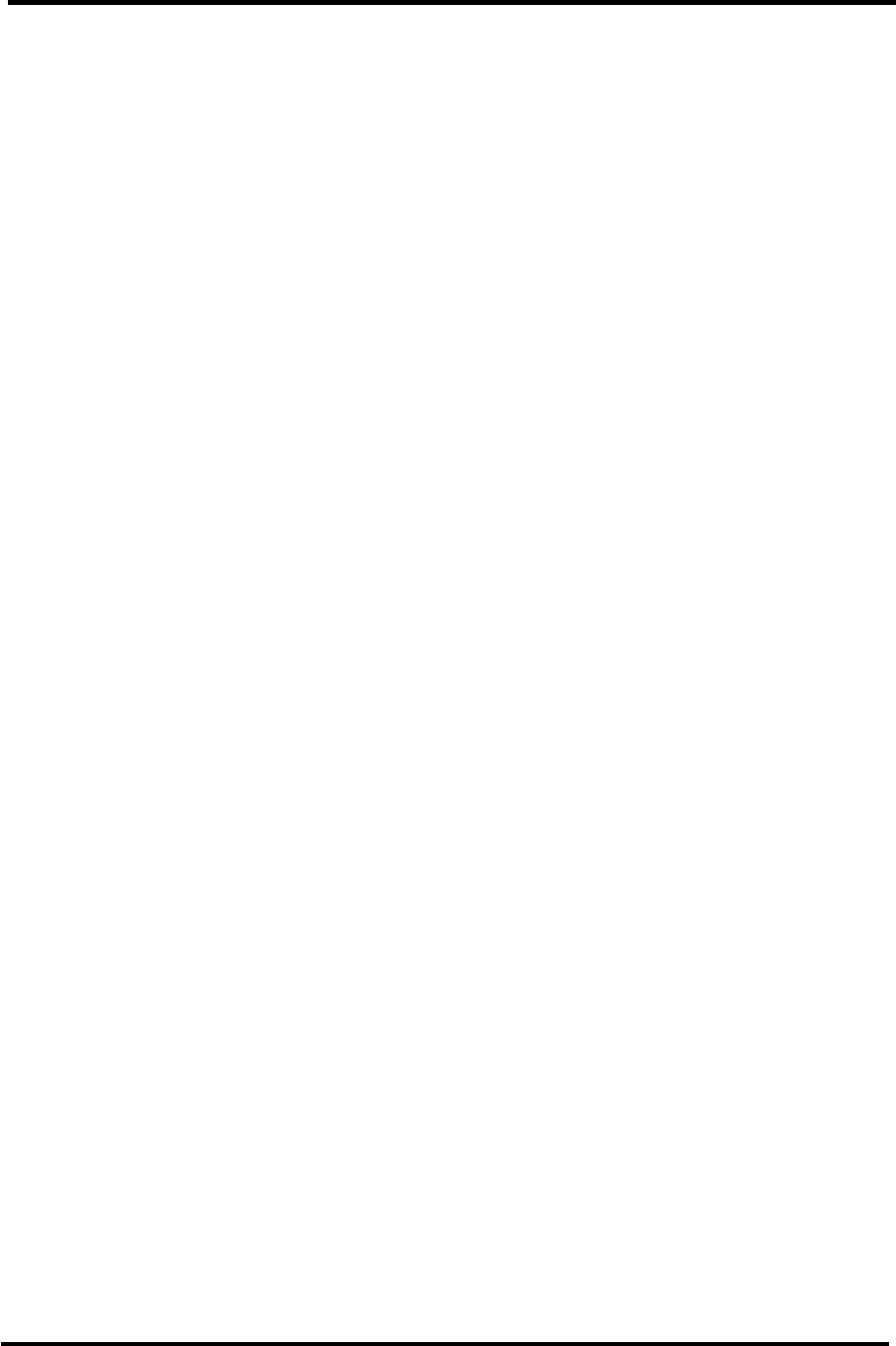
Innovator CU0TD-1/CU0RD-1 – CU4TD/CU4RD Unpacking, Installation &
ATSC Transmitter/Regenerative Translator Maintenance
Instruction Manual, Rev. 1 26
This page has intentionally been left blank.
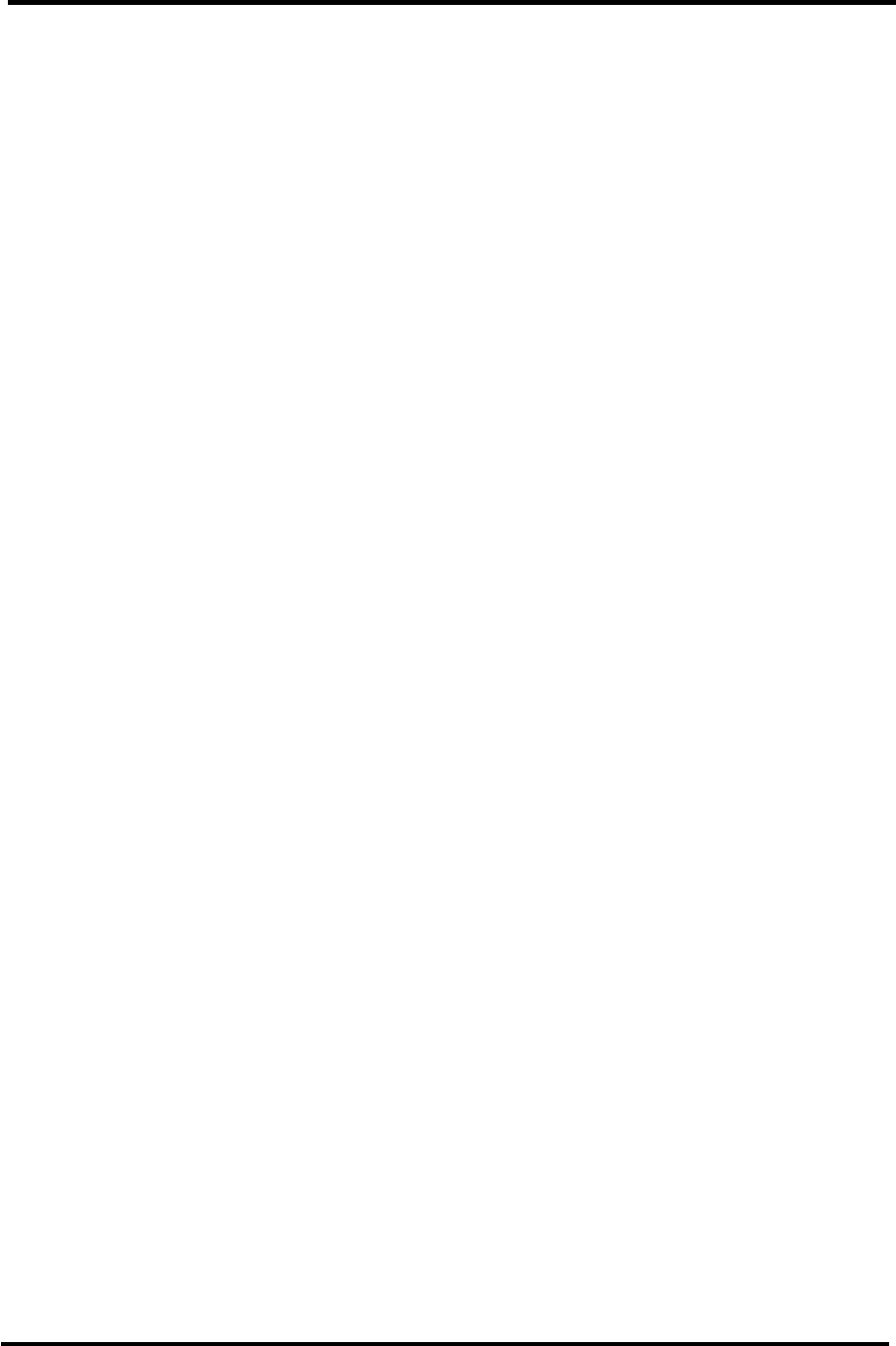
Innovator CU0TD-1/CU0RD-1 – CU4TD/CU4RD Initial On Site
ATSC Transmitter/Regenerative Translator Turn On Procedure
Instruction Manual, Rev. 1 27
Initial On Site Turn On Procedure
After the Innovator CX Series drawer or drawers are installed and all input, output and AC
connections are made, the system is ready for the initial on site turn on. Check that the
output of the CU0TD-1 thru CU0TD-5 drawer is connected to an appropriate rated load or to
the digital mask filter, low pass filter and the antenna for your system. If your system is a
CU1TD-1 or higher power system, check that the output of the amplifier drawer or the
combiner assembly is connected to an appropriate rated load or to the digital mask filter,
low pass filter and the antenna for your system. Check that the main AC power to the
System is ON. If your system contains an optional ASI to S310 converter module,
K-Tech receiver drawer or Axciter, check that they have AC connected to them and that
they are turned ON. NOTE: If your system is mounted in a cabinet and contains an Optional
UPS, check that the ON/OFF button, located on the left side of the top panel of the UPS is On.
The UPS is normally mounted behind the removable blank panel, located immediately above
the exciter/driver drawer, which is held in place by four #10 Phillips head screws.
If you have a CU0TD-1 thru CU0TD-5 system, push ON the switch located on the rear panel
of the drawer above the AC power jack. The large fan mounted on the rear panel of the
drawer should operate. If your system is a CU1TD/TD-1 or higher power system, switch ON
the ON/OFF circuit breaker(s), located on the rear panel of the amplifier drawer(s), mounted
on each side of the AC input power jack. The two fans mounted in the amplifier drawer
should operate. Place the system in Operate. The Operate/Standby LED and Status LEDs on
the CU0TD-1 thru CU0TD-5 should be Green indicating the system is in Operate and
performing normally. The Operate/Standby LED showing Amber indicates the System is in
Standby. The Status LED showing a blinking Red LED indicates an Event (Fault) is occurring
now. The Status LED showing Amber indicates that an Event (Fault) occurred since the last
time the Event (Fault) indications were reset.
If your system is CU1TD/RD-1 or higher power, the Enable LED and Status LEDs on the
Amplifier Drawer should be Green indicating the system is in Operate and performing
normally. The Enable LED showing Amber indicates the System is in Standby. The Status
LED should be Green indicating no Events (Faults) in the system. If the Operate/Standby LED
shows Amber it indicates that the System is in Standby. If the Status LED is blinking Red it
indicates an Event (Fault) is occurring now. If the Status LED shows Amber it indicates that
an Event (Fault) occurred since that last time the Event (Fault) indications were reset. The
output power is factory set according to customer request and does not need adjusted. If a
problem occurs, call Axcera field support at 724-873-8100 for information on modifying the
power level of the system.
NOTE: The RF System Interlock is provided on J12, a 15 position “D” connector, located on
the rear panel of the CU0TD-1 thru CU0TD-5 drawer. The RF System Interlock at
J12-5 provides the customer with a means of connecting the system to protection
circuits, for the loads, thermal switches, combiners, or the antenna, in the output of
your system, that will place the system in Standby if the protection circuit opens.
The Reject Load Interlock is provided at J11, a 9 position “D” connector. J11-6
provides the customer with a means of connecting the system to protection circuits,
for the reject load in multiple amplifier systems, which will place the system in
Standby if the protection circuit opens. If the interlocks are not used in your system,
a plug with a jumper from J12-5 to J12-15, ground, for RF system Interlock and
another plug with a jumper from J11-6 to J11-9, for Reject Load Interlock, need to
be connected. These jumpers provide the RF System and Reject Load Interlocks,
which allow the system to go to operate. Without the jumpers, the system will
remain in Standby.
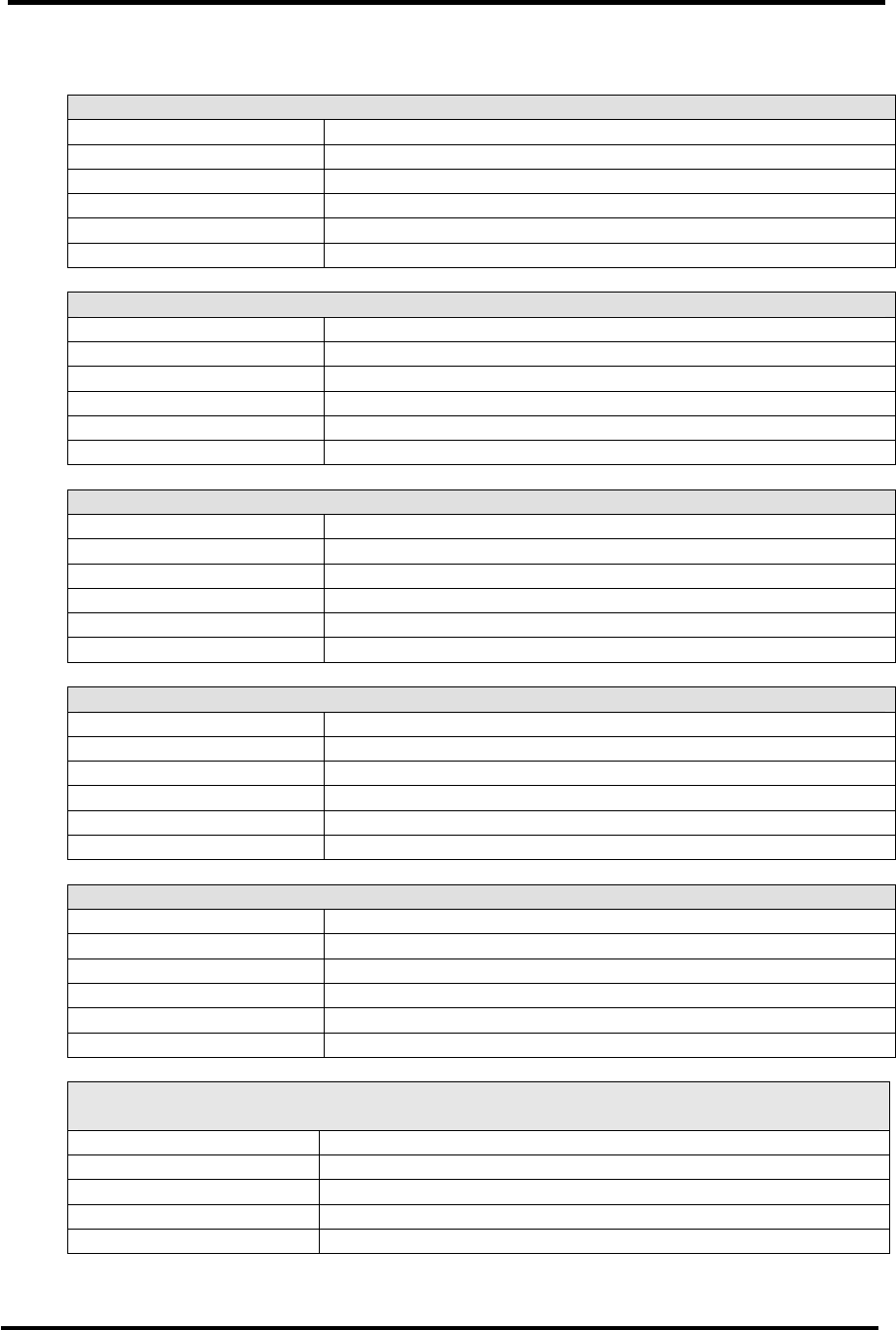
Innovator CU0TD-1/CU0RD-1 – CU4TD/CU4RD Initial On Site
ATSC Transmitter/Regenerative Translator Turn On Procedure
Instruction Manual, Rev. 1 28
Typical System Operating Parameters
Typical Operating Parameters for a CU0TD/RD-1
Parameter Typical Reading
Forward Power 100%
Reflected Power <5%
Power Supply Voltage +24 VDC
Heatsink Temperature 20º to 30º F/15º to 20º C above ambient temperature
Pin Attenuator Voltage 1 Volt to 5 Volts
Typical Operating Parameters for a CU0TD/RD-2
Parameter Typical Reading
Forward Power 100%
Reflected Power <5%
Power Supply Voltage +28 VDC
Heatsink Temperature 20º to 30º F/15º to 20º C above ambient temperature
Pin Attenuator Voltage 1 Volt to 5 Volts
Typical Operating Parameters for a CU0TD/RD-3
Parameter Typical Reading
Forward Power 100%
Reflected Power <5%
Power Supply Voltage +30 VDC
Heatsink Temperature 20º to 30º F/15º to 20º C above ambient temperature
Pin Attenuator Voltage 1 Volt to 5 Volts
Typical Operating Parameters for a CU0TD/RD-4 & as a Driver
Parameter Typical Reading
Forward Power 100%
Reflected Power <5%
Power Supply Voltage +42 VDC or 48 VDC w/888A devices
Heatsink Temperature 20º to 30º F/15º to 20º C above ambient temperature
Pin Attenuator Voltage 1 Volt to 5 Volts
Typical Operating Parameters for a CU0TD/RD-2 or -3 used as a Driver
Parameter Typical Reading
Forward Power 20-70% (Depending on output power level of system)
Reflected Power <3%
Power Supply Voltage +30 VDC
Heatsink Temperature 20º to 30º F/15º to 20º C above ambient temperature
Pin Attenuator Voltage 1 Volt to 5 Volts
Typical Operating Parameters for the external Amplifier Drawer(s)
in a C1TD/RD-1 or higher power System
Parameter Typical Reading
Forward Power 100%
Reflected Power <5%
Power Supply Voltage +42 VDC or 48 VDC w/888A devices
Heatsink Temperature 20º to 30º F/15º to 20º C above ambient temperature
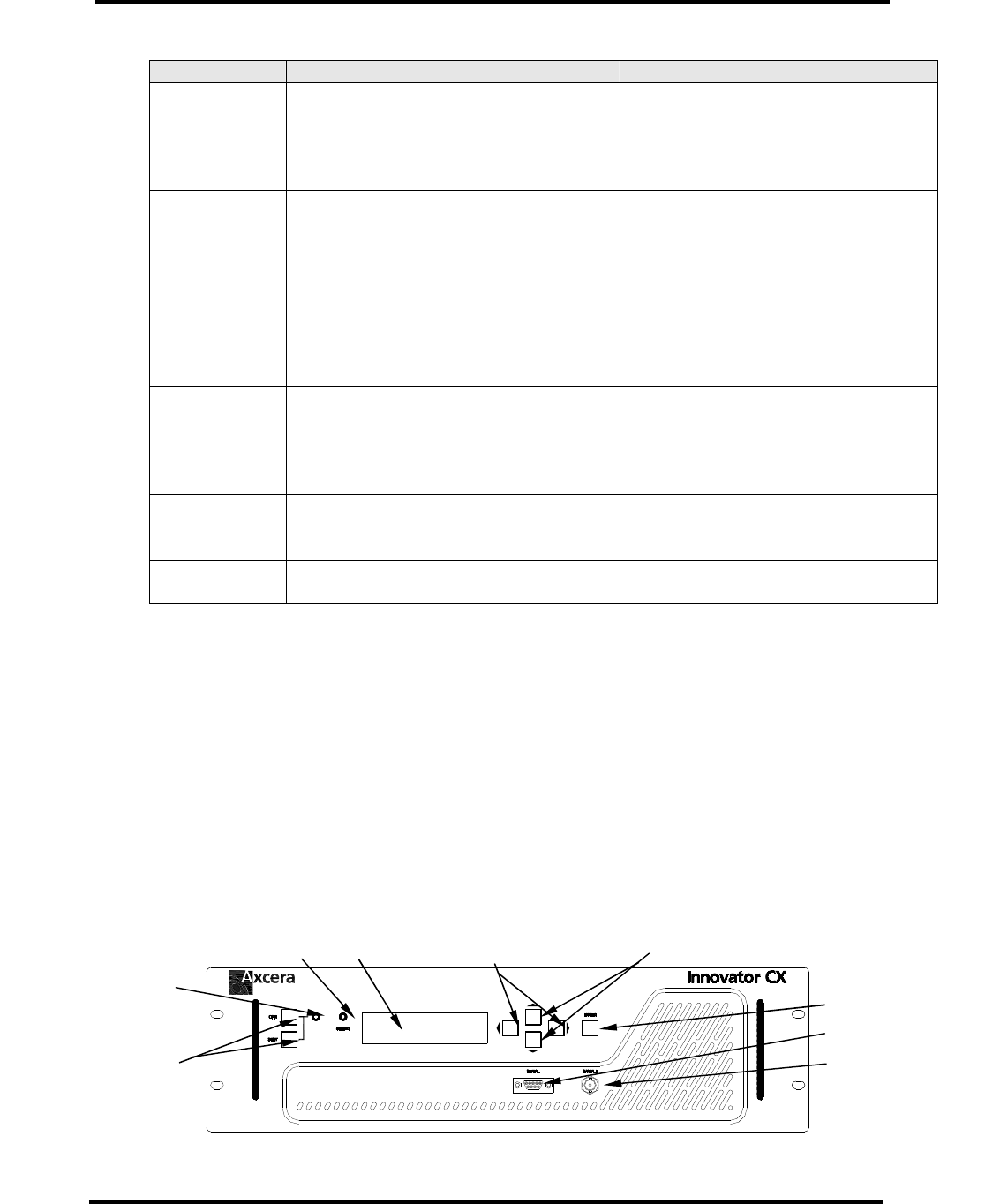
Innovator CU0TD-1/CU0RD-1 – CU4TD/CU4RD Initial On Site
ATSC Transmitter/Regenerative Translator Turn On Procedure
Instruction Manual, Rev. 1 29
Typical Problems, Indications and Causes in CU0TD/RD-2 or -3 Drawer
Problem Indication Cause
No power to
drawer
Operate/Standby and Enable LED
indicators and LCD display are Off
AC power cord not connected.
Main AC to System missing.
On/Off switch on back of drawer
Off. 10 Amp fuse (F1) blown*.
Power supply (A9) not operating
No Output
Signal
Front Panel Status LED is Amber
and blinking with no events, faults
indicated.
On the 8VSB Modulator S310
MPEG Input Selection Set Up
Screen, the Input is currently set
incorrectly to “from Internal
Source”. Set to “from External
Source”. (Not used with Axciter)
Loss of Input
Signal Loss of Input on Modulator Menu Loss of input signal.
(Not used with Axciter)
Loss of
Output
Signal
Amber Operate/Standby LED.
Blinking Red Status LED.
Any Event, Fault, which Mutes
the output. Including Input
Fault, VSWR Cutback, Overdrive,
Overtemperature and
Overvoltage.
Loss of 24V,
28V, 32V,
42V or 48V
Power Supply Fault on Power
Supply Menu
Power supply (A10) not
operating
Loss of ±12V
or 5V
Operate/Standby and Enable LED
indicators and LCD display are Off Power supply (A9) not operating
NOTE: *A spare 10 Amp fuse is provided in the blank fuse holder under the active
fuse.
If there is an Event (Fault) occurring in the system, the Status LED on the front panel will
flash RED as long as the Event (Fault) is present. In addition, the menu will jump to the
current Event (Fault) on the display and blink the Event (Fault) continuously, if the Jump to
Fault screen is set to Yes. When the Event (Fault) is corrected, the drawer will turn the
Status LED to AMBER to indicate that there was a Fault and the menu will still display the
Fault but it will not flash. This gives the user the knowledge that there was an Event (Fault)
and what type of Event (Fault) occurred. Before clearing the fault, check if there were other
Events (Faults) by stepping through the menus. To reset the indication of previous Events
(Faults) the user must push the Enter button with the Event (Fault) Reset Screen displayed.
This will reset all previous Events (Faults).
LCD Display and Front Panel LED Indicators
Figure 5: Front View CU0TD/RD-1 thru CU0TD/RD-5 systems and the driver for the
CU1TD-1 and higher power systems
Operate/Standby
Buttons
Status LED
Left/Right Buttons
LCD Display
Enter Button
Operate/Standby
LED
Up/Down Buttons
J11 Serial Port
J15 RF Sample
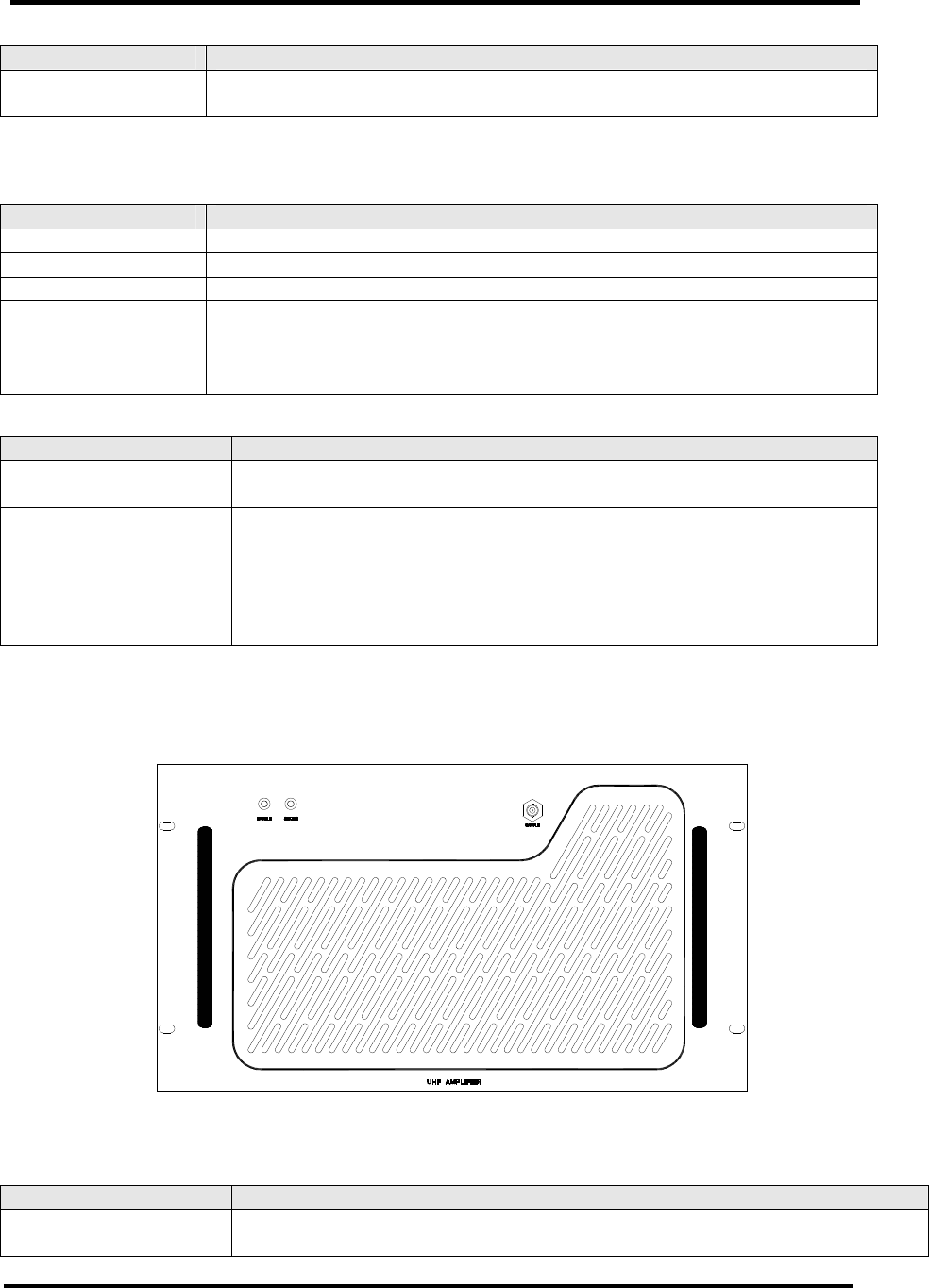
Innovator CU0TD-1/CU0RD-1 – CU4TD/CU4RD Initial On Site
ATSC Transmitter/Regenerative Translator Turn On Procedure
Instruction Manual, Rev. 1 30
Table 4: Innovator CX Series LCD Display
DISPLAY FUNCTION
LCD Provides a two line readout of the input received channel, internal
functions, status, and Fault (Event) conditions.
The front panel has seven pushbuttons, two for the control of the system, Operate & Standby,
and five for control of the displayed menus, Left, Right, Up, Down & Enter.
Table 5: Innovator CX Series Control Pushbuttons
PUSHBUTTON FUNCTION
OPR When pushed switches the system to Operate.
STBY When pushed switches the system to Standby.
ENTER Selects the changes made in the menus and submenus.
Up & Down Arrow Scrolls through the main menus and after entering the Main Menu
Steps through submenus of the main menu when they are present.
Left & Right Arrow Used to exit from main menus and submenus of the main menu
when they are present.
Table 6: Innovator CX Series Operate/Standby and Status Indicators
LED FUNCTION
OPERATE/STANDBY
(Green/Amber)
A Green LED indicates that the system is in Operate. An Amber
LED indicates that the system is in Standby.
STATUS
(Green/Red/
Amber)
A Green LED indicates that the system is functioning normally. A
flashing Red LED indicates an Event (Fault) is occurring at this
time. An Amber LED indicates an Event (Fault) occurred since
the last time the Event (Fault) indications were reset but the
system is now operating normally. Amber LED Blinking, with no
Events (Faults) indicates the MPEG input is set to Internal Source.
NOTE: J15 is a Front Panel BNC RF Sample Jack 50Ω that provides an RF output sample
from the output detector board in the drawer. In a CU0TD/RD-3, the sample level
at J15 is approximately 60dB down from the output power level of the drawer.
Figure 6: Front View Amplifier Drawer in CU1TD/RD and higher power systems
Table 7: Innovator Amplifier Drawer LED Indicators and Sample Jack
LED FUNCTION
ENABLE
(Green/Amber)
A Green LED indicates that the system is in Operate and operating
normally. An Amber LED indicates that the system is in Standby.
Enable LED
Status LED Sample
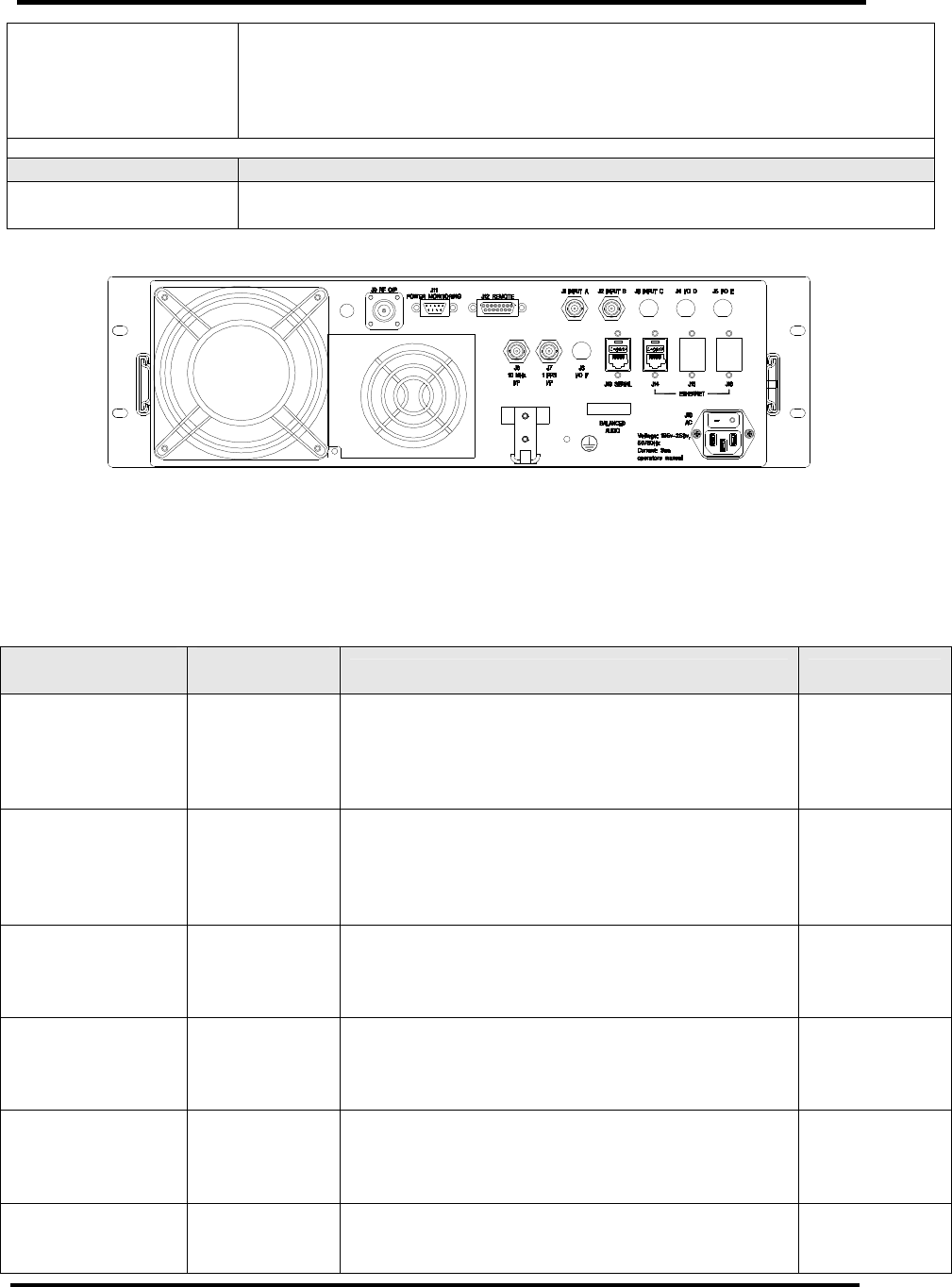
Innovator CU0TD-1/CU0RD-1 – CU4TD/CU4RD Initial On Site
ATSC Transmitter/Regenerative Translator Turn On Procedure
Instruction Manual, Rev. 1 31
STATUS
(Green/Red/
Amber)
A Green LED indicates that the system is functioning normally with no
faults. A flashing Red LED indicates an Event (Fault) is occurring at
this time. An Amber LED indicates an Event (Fault) occurred since the
last time the Event (Fault) indications were reset but the system is now
operating normally.
JACK FUNCTION
SAMPLE
J6
Typical sample value is 65dB down from the output power level of the
drawer. (500 Watts output power = -8dBm sample level)
System Remote Connections to J12
Figure 7: Rear View CU0TD/RD-1 thru CU0TD/RD-5 systems and the driver for the
CU1TD-1 and higher power systems
The remote connections for the Innovator CX Series system are made to the Remote 15 Pos
Female “D” connector Jack J12 located on the rear panel of the drawer. NOTE: In dual
exciter systems remote connections are made to the rear panels of the two drivers.
Table 7A: Remote Connections to J12, 15 Pos Female D Connector, for CX Series system
Remote Signal
Name
Pin
Designation Signal Type Description
System Operate J12-1
Discrete Open Collector Input - A pull down
to ground on this line indicates that the
System is to be placed into the operate
mode. Not Available in dual exciter systems.
(Low = Activate : Floating = No Change)
Command
System Standby J12-2
Discrete Open Collector Input - A pull down
to ground on this line indicates that the
System is to be placed into the standby
mode. Not Available in dual exciter systems.
(Low = Activate : Floating = No Change)
Command
Power Raise J12-3
Discrete Open Collector Input - A pull down
to ground on this line indicates that the
Power of the System is to be Raised.
(Low = Activate : Floating = No Change)
Command
Power Lower J12-4
Discrete Open Collector Input - A pull down
to ground on this line indicates that the
Power of the System is to be Lowered.
(Low = Activate : Floating = No Change)
Command
System Interlock J12-5
Discrete Open Collector Input - A pull down
to ground on this line indicates that the
Interlock is present. Normally jumpered to
J12-15. (Low = OK : Floating = Fault)
Set to
Modulation Type J12-6
Discrete Open Collector Input. - Sets the
Modulation type of the system.
(Low = Analog : Floating = Digital)
Command
J12
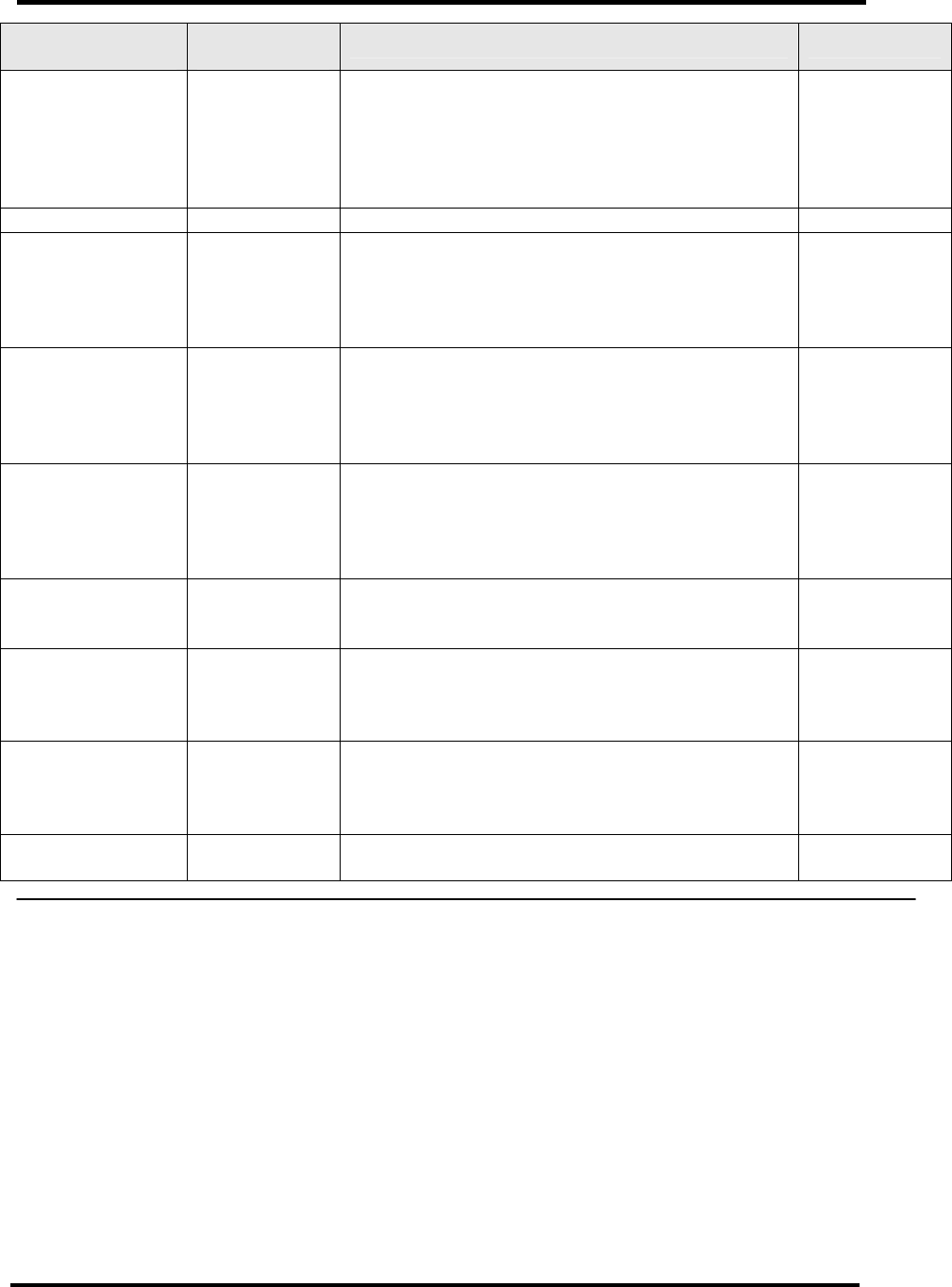
Innovator CU0TD-1/CU0RD-1 – CU4TD/CU4RD Initial On Site
ATSC Transmitter/Regenerative Translator Turn On Procedure
Instruction Manual, Rev. 1 32
Remote Signal
Name
Pin
Designation Signal Type Description
Set Channel
(Set Up 1 or Set
Up 2)
J12-7
Discrete Open Collector Input. – Selects one
of two possible Channel Setups of the
system. (Low = Set Up 2, CH 2 : Floating =
Set Up 1, CH 1) NOTE: The Set Up 1 & Set
Up 2 settings are displayed and changed in
the Upconverter Set Up Menus.
Command
Ground J12-8 Ground.
System Forward
Power Level J12-9
Analog Output - 0 to 4.0 V. - This is a
buffered loop through of the calibrated
“System Forward Power”. Indicates the
System Forward power.
Scale factor is 100 % = 2.0V.
Metering
System Aural
Power Level J12-10
Analog Output - 0 to 4.0 V. - This is a
buffered loop through of the calibrated
“System Aural Power”. Indicates the System
Aural power. Scale factor is
100 % = 2.0V. (Not used in Digital)
Metering
System Reflected
Power Level J12-11
Analog Output - 0 to 4.0 V. - This is a
buffered loop through of the calibrated
“System Reflected Power”. Indicates the
System Reflected power.
Scale factor is 25 % = 2.0V.
Metering
Report Input
Status J12-12
Discrete Open Collector Output. - Indicates if
input to system is Normal or Not.
(Low = OK : Floating = Fault)
Status
Report Fault
Status J12-13
Discrete Open Collector Output. - Indicates if
system is Operating Normally or has a Fault.
Not available in dual exciter systems.
(Low = OK : Floating = Fault)
Status
Report Operate
Status J12-14
Discrete Open Collector Output. – Indicates
whether system is in Operate or Standby. Not
available in dual exciter systems.
(Low = Operate : Floating = Standby)
Status
Ground J12-15 Ground. Not Available in dual exciter
systems. Normally jumpered to J12-5.
LCD Front Panel Screens
A LCD display, located on the front of the Innovator CXB Series systems, displays, on
screens, the current operating status of the system. When the drawer is powered On, the
LCD will initially display two splash screens. The first splash screen will be displayed for a
few seconds, then the second splash screen will be displayed for a few seconds and finally
the RF Power Display default screen will be displayed. See typical examples of the screens
below. NOTE: These screens are typical examples of an operating system, your systems
screens may be different. The RF Power Display default screen will be the screen displayed
if no buttons are pushed to access other screens. While viewing the RF Power Display
default screen, pushing the Left and Right arrow buttons together will also access the splash
screens. NOTE: In dual exciter systems, the On Air Exciter will display the operating
parameters of the system.
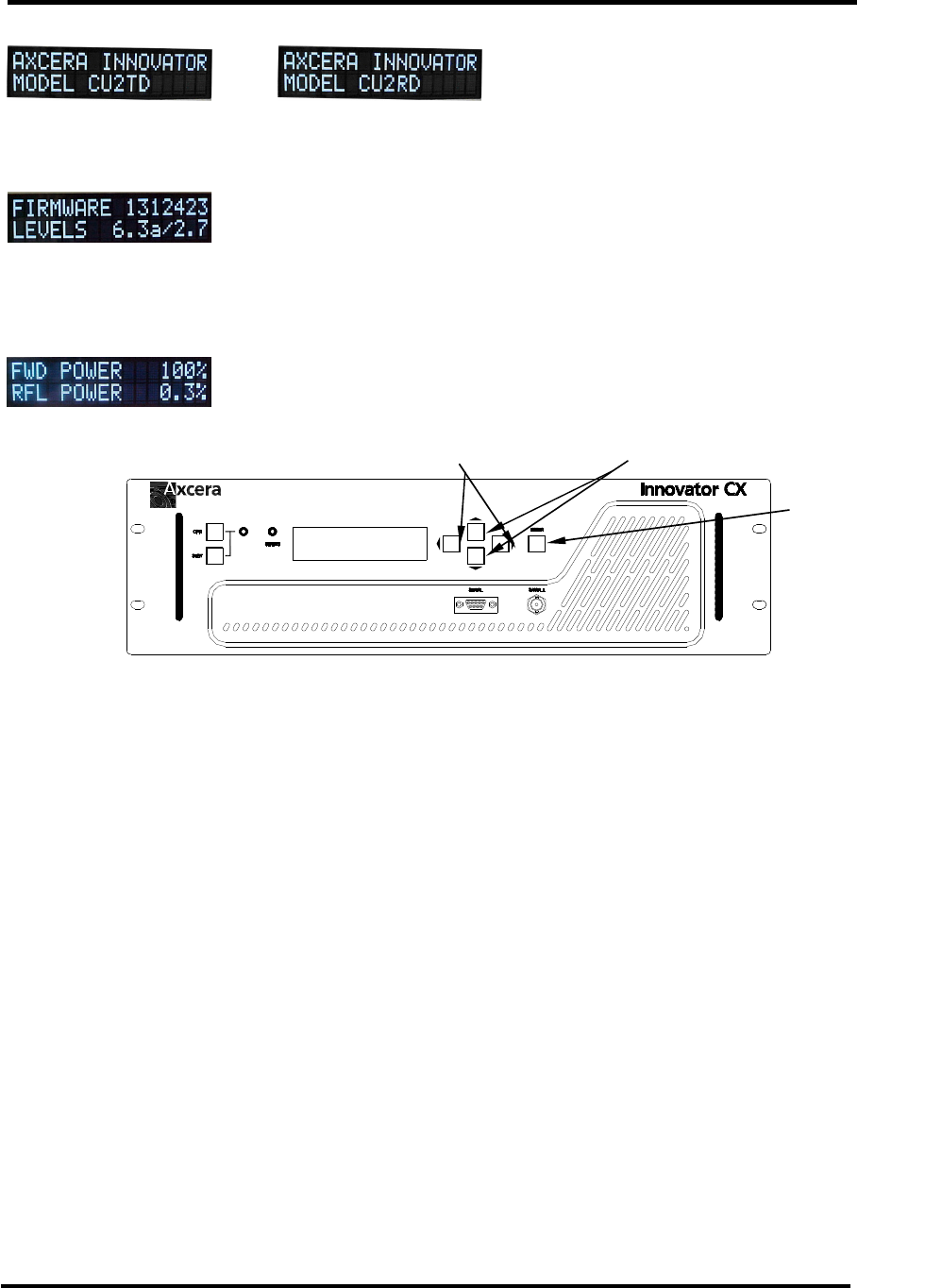
Innovator CU0TD-1/CU0RD-1 – CU4TD/CU4RD Initial On Site
ATSC Transmitter/Regenerative Translator Turn On Procedure
Instruction Manual, Rev. 1 33
Splash Screen Number 1
The first splash screen displayed indicates the manufacturer, type of transmitter and the
model number.
Splash Screen Number 2
The second splash screen indicates the Firmware and Version Numbers of the software used
in the system. The example shown is Firmware number 1312423: Version number 6.3/2.7.
The final screen is the RF Power default screen which indicates the Forward Power and
Reflected Power for the system.
The following screens are scrolled through using the buttons to the right of the display.
Pushing and releasing the Up & Down Arrows will scroll you through the Main Menus, which
are shown on the following pages aligned on the left side of the page. The Submenus of the
Main Menus are accessed by pushing and releasing the ENTER button. Once in the
Submenus, pushing and releasing the Up & Down Arrows will scroll you through the
submenus of the Submenus. The Submenus are shown on the following pages indented
under the Main Menus and the submenus of the Submenus are indented under the Submenu
in which they are contained. In the SET UP Menus, changes are made to the display by
Pushing and releasing the ENTER button which causes the item to be changed to blink, then
using the left and right arrow buttons to display the desired changed item, finally, pushing the
ENTER button will accept the changes made upon exit of the Set Up Menu.
NOTE: An example of accessing and changing an item using the Set Up Menus is as follows.
This procedure is to set the Off Air Receive Channel to the desired channel. Push
and release the DOWN Arrow button until the SYSTEM SET UP Main Menu is
displayed. Push and release the ENTER button. The Authorization Warning screen is
displayed. Push and release the ENTER button again and the ENTER BUTTON SETS
TO CHANGE MODE screen is displayed. Push and release the ENTER button again
and the first set up menu, which is the SET UP MENUS OF CHASSIS VALUES screen
is displayed. Push and release the DOWN Arrow button until the SET UP 8VSB
DEMODULATOR screen is displayed. Push and release the ENTER button to display
the submenus under the SET UP 8VSB DEMODULATOR menu. Push and release the
DOWN Arrow until the 8VSB DEMODULATOR USE OFF AIR CHxx is displayed. Push
and release the ENTER button and the XX, which indicates the Channel Number, will
blink. Push and release the UP or DOWN Arrow button until the desired new channel
number is displayed. Push and release the ENTER button, and the PUSH ENTER TO
ACCEPT CHANGES menu is displayed. Push and release the ENTER button again to
Left/Right Buttons
Ente
r Button
Up/Down Buttons
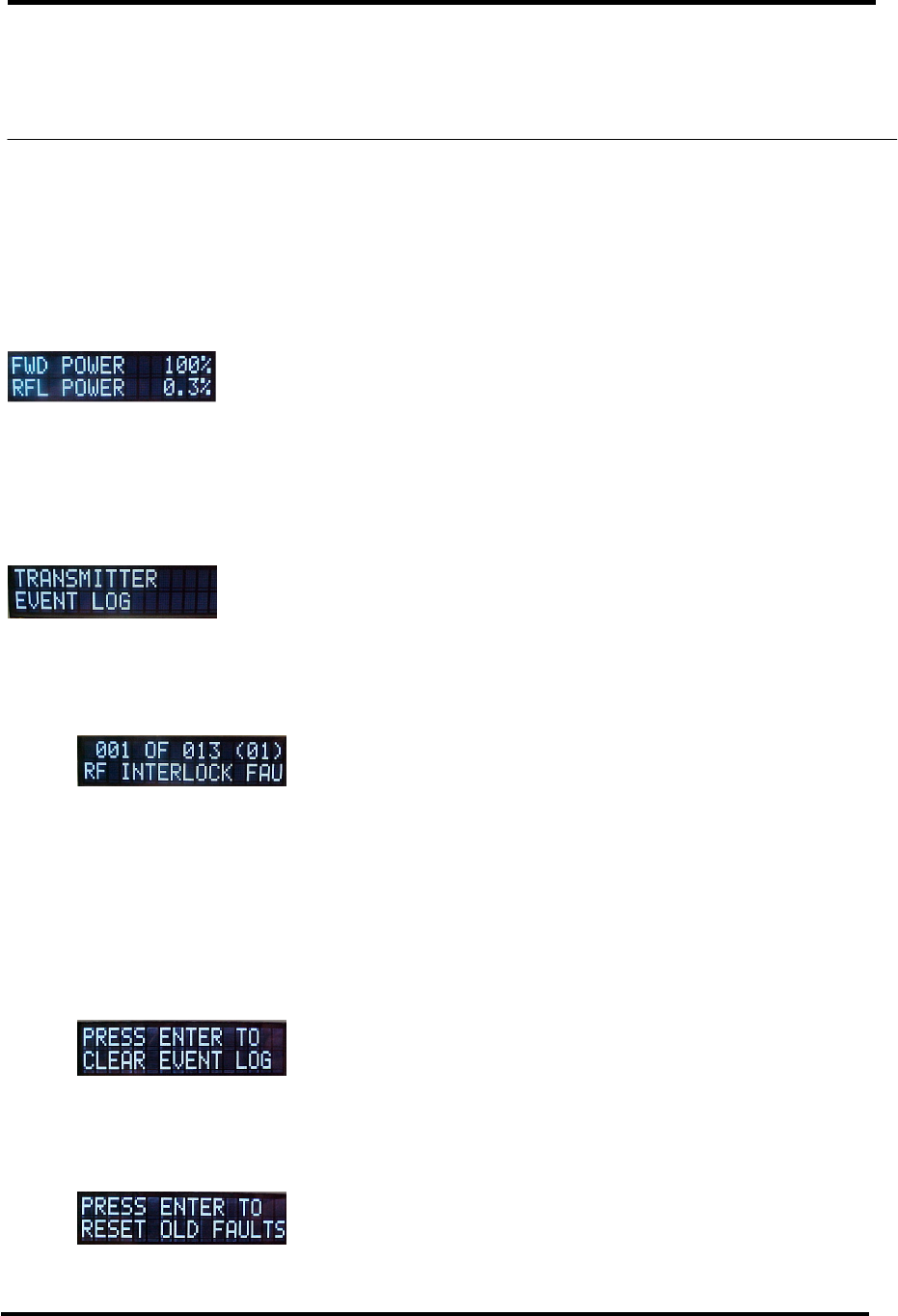
Innovator CU0TD-1/CU0RD-1 – CU4TD/CU4RD Initial On Site
ATSC Transmitter/Regenerative Translator Turn On Procedure
Instruction Manual, Rev. 1 34
accept the changes made. The channel is now changed. Push and release the LEFT
Arrow to exit to the SET UP 8VSB DEMODULATOR screen. Push and release the LEFT
Arrow again to exit to the SYSTEM SET UP Main Menu. Push and release the UP or
DOWN arrows to browse the main menus.
The following screens are typical of an operating system. The values indicated on the
screens in your system may vary from those shown below.
Operation Screens
NOTE: The following Operation screens provide operating information only. No adjustments
are available using these screens.
Table 8: Transmitter/Translator RF Power Screen (TD/RD)
This is the default screen that is displayed after the splash screens are displayed. This
screen provides an indication of the Forward Output Power of the system in terms of
Percent. (Typically 100%). The screen also provides an indication of the Reflected Power of
the system in terms of Percent. (Typically less than 5%). Push the DOWN Arrow to view
the next main menu, which is the Transmitter Event Log Main Menu.
Table 9: Transmitter/Translator Event Log Main Screen (TD/RD)
This is the Transmitter Event Log Main Screen. Push the ENTER button to access the Event
List submenu. Push the DOWN Arrow to view the next main menu, which is the Transmitter
Details Main Menu.
Table 9.1: Transmitter/Translator Event List Screen (TD/RD)
When events occur, they will be displayed on this screen. The Up and Down arrow
will page you through the different entries in the event log. The above screen
indicates the 001 event of 013 total events that have occurred in the Transmitter.
The number in the parenthesis on the top right, is this case 01, indicates the number
of times the displayed event has occurred. The bottom line scrolls to indicate the
event that occurred, in this case RF Interlock Fault, and the time the event occurred
after the prior event. Push the LEFT Key to exit to the Transmitter Event Log Main
Menu screen. Pushing the RIGHT Key will access the Event Reset Screen.
Table 9.2: Event Reset Screen (TD/RD)
This screen allows the resetting of the event log, after they are observed or
corrected. NOTE: Resetting the events on an amplifier may cause the transmitter to
momentarily mute.
Table 9.3: Event Reset Old Faults Screen (TD/RD)
This screen allows the resetting of old faults that are latched from the event log after
they are observed or corrected. The transmitter can be configured to latch faults as
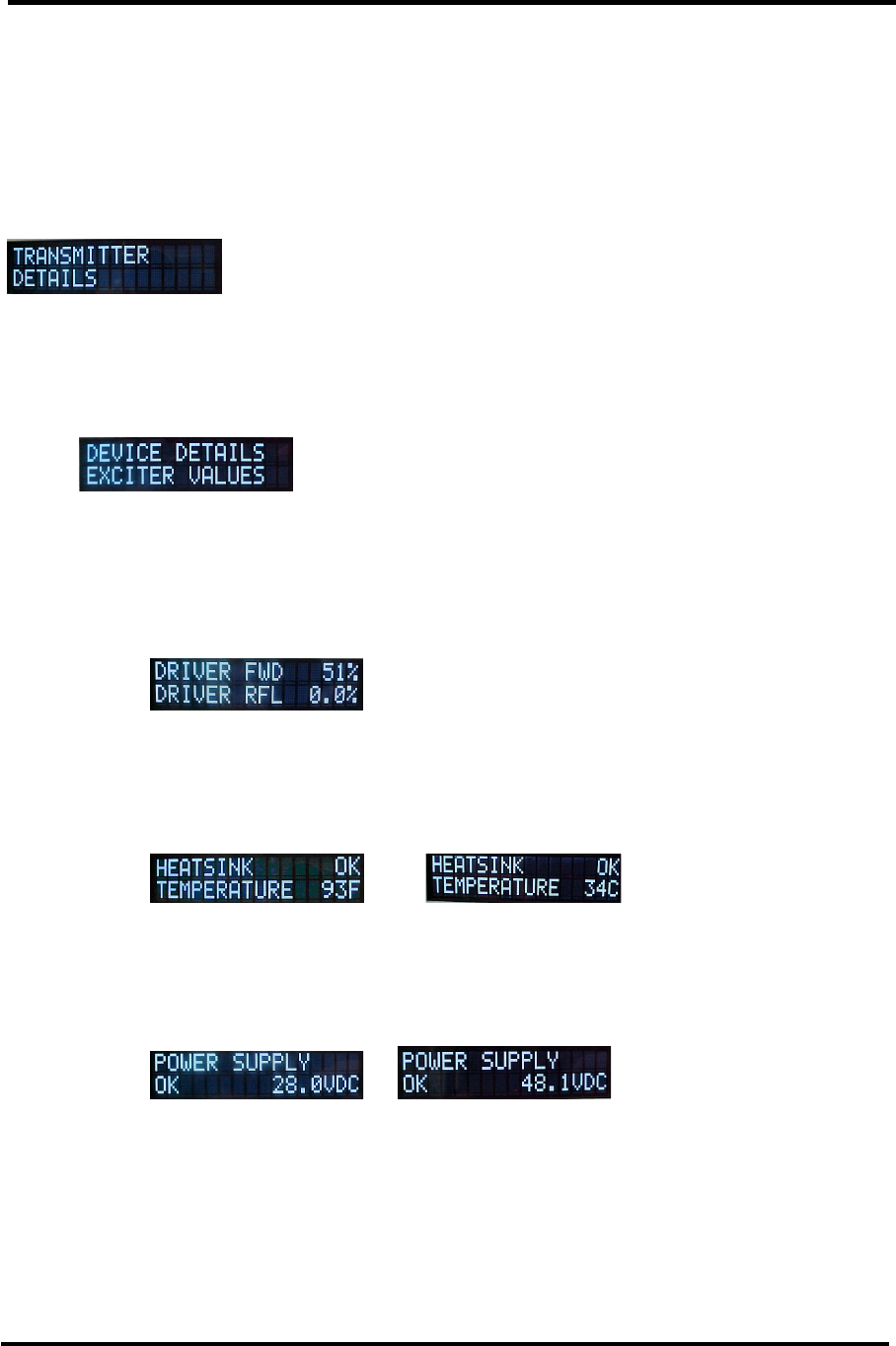
Innovator CU0TD-1/CU0RD-1 – CU4TD/CU4RD Initial On Site
ATSC Transmitter/Regenerative Translator Turn On Procedure
Instruction Manual, Rev. 1 35
detailed in Table 11.1.4. That means that if a fault occurs and then it clears, the
status of the parameter in the details screen will not blink indicating an active fault,
but it will still show fault indicating that previously this parameter was faulted.
Within the web pages, a latched fault is shown with an orange background while
faulted parameters are shown in red and good values are shown in green. Resetting
Old Faults will clear the latched fault and the display will show the value as OK or
with other text that indicates that it is not faulted.
Table 10: Transmitter/Translator Details Main Screen (TD/RD)
This is the System Details Main Screen. Push the ENTER button to access the Device Details
Chassis Values Main Sub Screen or push the DOWN Arrow to view the next main menu,
which is the System Set Up Main Menu.
Table 10.1: Transmitter/Translator Device Details Exciter Values Screen
(TD/RD)
This is the System Device Details Exciter Values Main Sub Screen. Push the ENTER
button to access the Device Details Exciter Values submenus or push the DOWN
Arrow to view the next main submenu, which is the 8VSB Demodulator Sub Menu.
(Not used with Axciter)
Table 10.1.1: Transmitter/Translator Driver Forward/Reflected Power Details
Screen (TD/RD)
This screen provides an indication of the Output Forward Power of the Driver
Drawer in terms of Percent, typically 20-70%. This screen also provides an
indication of the Reflected Output Power of the Driver Drawer in terms of
Percent, Typically less than 3%.
Table 10.1.2: Heatsink Temperature Details Screen (TD/RD)
This screen indicates the temperature of the amplifier heatsink assembly,
mounted in the system or driver drawer, in degrees Fahrenheit or Centigrade.
If the temperature is below the trip point, it will indicate OK. (Typically 20º to
30º F. or 15º to 20º C above ambient temperature)
Table 10.1.3: Power Supply Voltage Details Screen (TD/RD)
This screen indicates the power supply voltage in the system or driver drawer.
If the power supply voltage is below the trip point, it will indicate OK. The
fault limit is the nominal supply voltage as set in the Exciter Setup Screen
±10%. (Typically 24V for 3 Watt, 28V for a 30 Watt, 30V for 50 Watt, or
42/48V for 100/150 Watt Systems.)
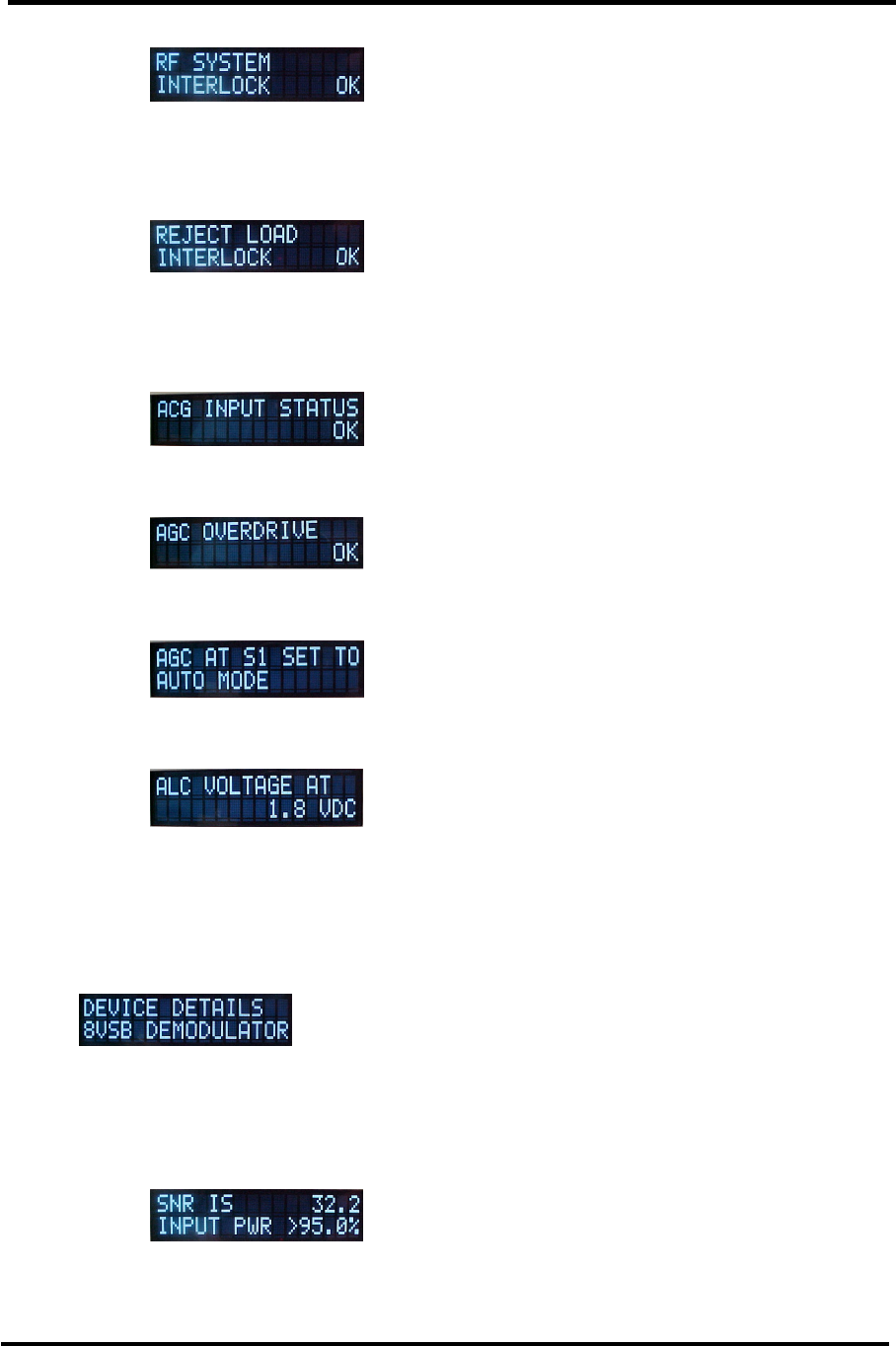
Innovator CU0TD-1/CU0RD-1 – CU4TD/CU4RD Initial On Site
ATSC Transmitter/Regenerative Translator Turn On Procedure
Instruction Manual, Rev. 1 36
Table 10.1.4: RF System Interlock Details Screen (TD/RD)
This screen indicates if the external RF system interlock is present in your
system. (Typically Present. Must be present or system will remain in
Standby.)
Table 10.1.5: Reject Load Interlock Details Screen (TD/RD)
This screen indicates if the external Reject Load interlock is present in your
system. (Typically Present. Must be present or system will remain in
Standby.)
Table 10.1.6: AGC Details Screen (TD/RD)
This menu indicates if the AGC circuit has an input.
Table 10.1.7: AGC Overdrive Details Screen (TD/RD)
This menu indicates if the AGC circuit is operating within its range.
Table 10.1.8: AGC Auto/Manual Details Screen (TD/RD)
This menu indicates if the AGC circuit is operating in Auto or Manual.
Table 10.1.9: ALC Voltage Level Details Screen (TD/RD)
This menu indicates the Auto ALC voltage setting. (Typically 1 to 5 V)
Pushing the Left Arrow will display the System Device Details Exciter Values
Main Sub Screen and then pushing the Down arrow will access the System
Device Details 8VSB Demodulator Main Sub Screen.
Table 10.2: Translator 8VSB Demodulator Details Screen (RD)
This is the System Device Details 8VSB Demodulator Main Sub Screen, if present in
the system. This screen is Not used with Axciter. Push the ENTER button to access
the Device 8VSB Demodulator submenus or push the DOWN Arrow to view the next
main menu, which is the Device Details 8VSB Modulator Main Sub Menu.
Table 10.2.1: System Input Details Screen (RD)
This screen provides the user information on the signal to noise ratio and
signal strength of the received signal. The signal to noise ratio is provided on
this menu to indicate to the user the quality of the receive signal. This
reading also assists the user in the positioning of the antenna. The signal
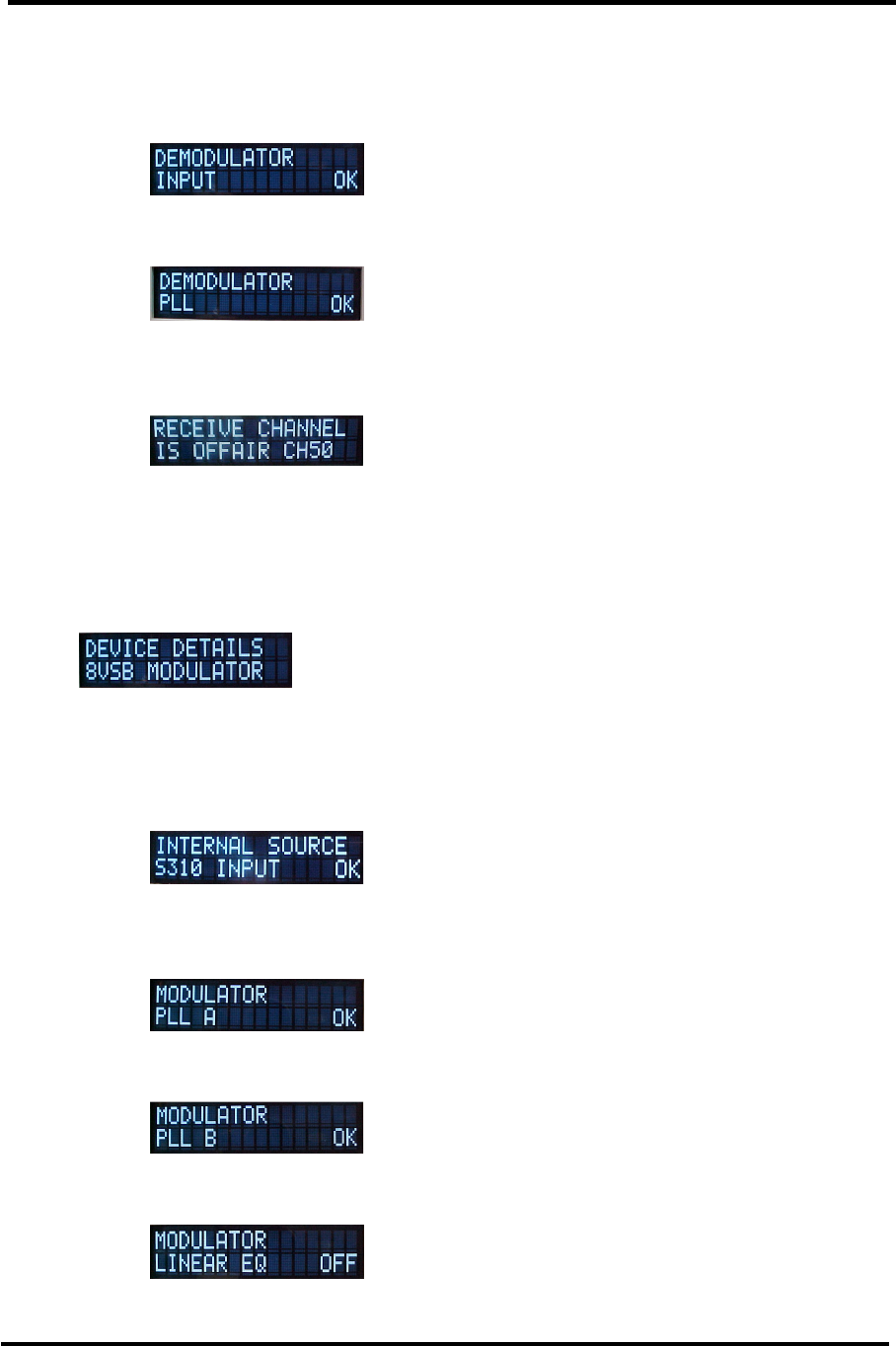
Innovator CU0TD-1/CU0RD-1 – CU4TD/CU4RD Initial On Site
ATSC Transmitter/Regenerative Translator Turn On Procedure
Instruction Manual, Rev. 1 37
strength ranges from 0 to 100% and typically should be above 40% for
reliable operation. The signal strength allows the user to optimize the
position of the receive antenna.
Table 10.2.2: Demodulator Details Screen (RD)
This menu indicates whether there is a signal present at the demodulator.
Table 10.2.3: Demodulator Phase Lock Loop Details Screen (RD)
This menu indicates whether the Phase Lock Loop is locked in the
demodulator.
Table 10.2.4: Receive Input Channel Details Screen (RD)
This menu indicates the input channel to the Demodulator circuit.
Pushing the Left Arrow will display the System Device Details 8VSB
Demodulator Values Main Sub Screen and then pushing the Down arrow will
access the System Device Details 8VSB Modulator Main Sub Screens.
Table 10.3: Transmitter/Translator 8VSB Modulator Details Screen (TD/RD)
This is the System Device Details 8VSB Modulator Main Sub Screen, not present with
Axciter. Push the ENTER button to access the Device 8VSB Modulator submenus or
push the DOWN Arrow to view the next main menu, which is the Device Details IF
Processor Main Sub Menu.
Table 10.3.1: Transmitter/Translator S310 Input Details Screen (TD/RD)
This menu indicates if the modulator has locked to the SMPTE-310 signal
coming from the demodulator.
Table 10.3.2: Modulator Phase Lock Loop A Details Screen (TD/RD)
This menu indicates if the Phase Lock Loop A in the modulator is locked.
Table 10.3.3: Modulator Phase Lock Loop B Details Screen (TD/RD)
This menu indicates if the Phase Lock Loop B in the modulator is locked.
Table 10.3.4: Modulator Linear Equalization Details Screen (TD/RD)
This menu indicates if the Linear Equalization is being used.
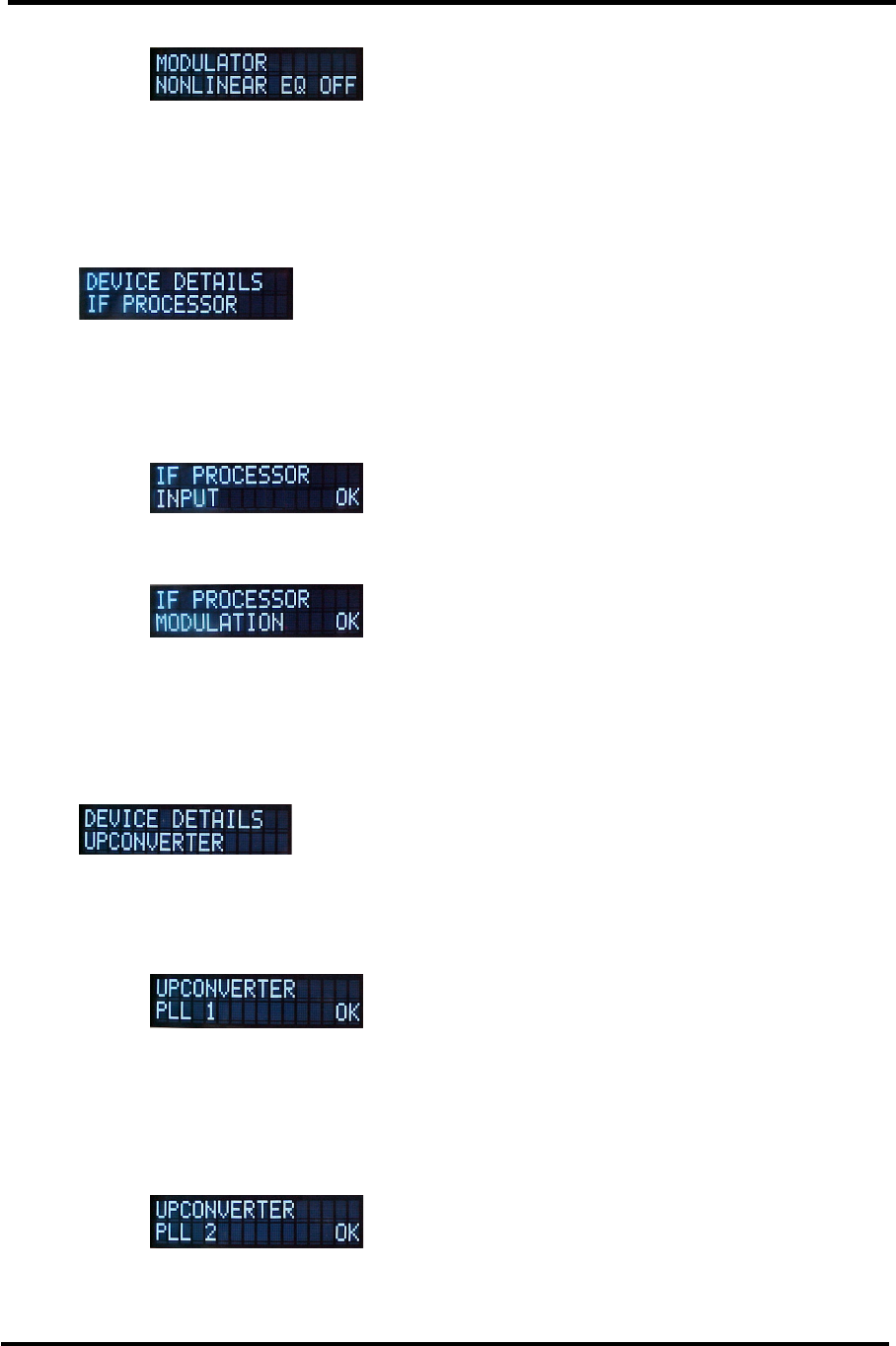
Innovator CU0TD-1/CU0RD-1 – CU4TD/CU4RD Initial On Site
ATSC Transmitter/Regenerative Translator Turn On Procedure
Instruction Manual, Rev. 1 38
Table 10.3.5: Modulator Non Linear Equalization Details Screen (TD/RD)
This menu indicates if the Non Linear Equalization is being used.
Pushing the Left Arrow will display the System Device Details 8VSB Modulator
Values Main Sub Screen and then pushing the Down arrow will access the
System Device Details IF Processor Main Sub Screen.
Table 10.4: Transmitter/Translator IF Processor Details Screen (TD/RD)
This is the System Device Details IF Processor Main Sub Screen, (if present, not used
with Axciter). Push the ENTER button to access the Device IF Processor submenus
or push the DOWN Arrow to view the next main menu, which is the Device Details
Upconverter Main Sub Menu.
Table 10.4.1: IF Processor Input Details Screen (TD/RD)
This menu indicates if there is an input signal to the IF Processor.
Table 10.4.2: IF Processor Modulation Present Details Screen (TD/RD)
This menu indicates if there is Modulation on the signal to the IF Processor.
Pushing the Left Arrow will display the System Device Details IF Processor
Values Main Sub Screen and then pushing the Down arrow will access the
System Device Details Upconverter Main Sub Screen.
Table 10.5: Upconverter Device Details Screen (TD/RD)
This is the System Device Details Upconverter Main Sub Screen. Push the ENTER
button to access the Device Upconverter submenus or push the DOWN Arrow to view
the next main menu, which is the Device Details Downconverter Main Sub Menu.
Table 10.5.1: Upconverter Phase Lock Loop 1 Details Screen (TD/RD)
This menu indicates if the Phase Lock Loop 1 in the upconverter is locked.
The LO1 oscillator operates at 1.008 GHz and is used to convert the pre-
corrected IF signal to 1044 MHz. The Red LED DS4, located on the
Upconverter board, will light if the PLL for the LO1 oscillator is not locked to
the on board 10 MHz VCXO and therefore will indicate a fault.
Table 10.5.2: Upconverter Phase Lock Loop 2 Details Screen (TD/RD)
This menu indicates if the Phase Lock Loop 2 in the upconverter is locked.
The second LO, LO2, consists of two VCOs, one operating from 1.1-1.5 GHz
and the second from 1.5-1.9 GHz, that are used to generate the second LO,
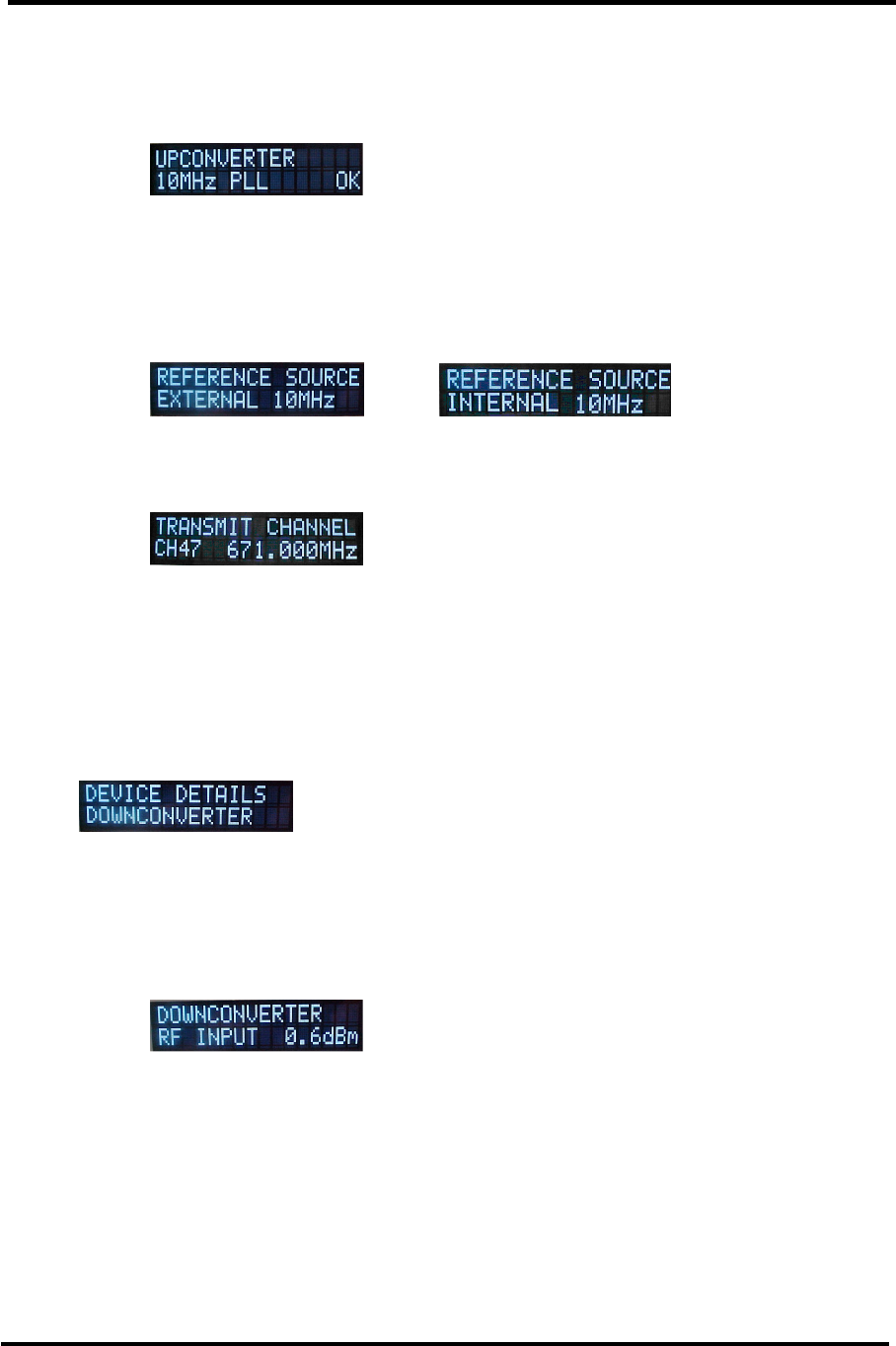
Innovator CU0TD-1/CU0RD-1 – CU4TD/CU4RD Initial On Site
ATSC Transmitter/Regenerative Translator Turn On Procedure
Instruction Manual, Rev. 1 39
which is the Channel Center Frequency + 1044 MHz. The Red LED DS2,
located on the upconverter board, will light if the PLL for the LO2 oscillator is
not locked and therefore will indicate a fault.
Table 10.5.3: Upconverter 10 MHz Phase Lock Loop Details Screen (TD/RD)
This menu indicates if the 10 MHz Phase Lock Loop in the upconverter is
locked. When an external 10 MHz signal is applied to system, the internal
VCXO is locked to the external 10 MHz, otherwise, it is free-running. With no
external reference present, the PLL cannot function and is disconnected from
the internal 10 MHz oscillator and therefore will indicate a fault.
Table 10.5.4: Upconverter 10 MHz Details Screen (TD/RD)
This menu indicates if the 10 MHz reference used is generated internally or
provided by an external reference source.
Table 10.5.5: Upconverter System Channel Details Screen (TD/RD)
The upconverter transmit channel screen indicates the channel that the
upconverter is currently set and the center frequency of that channel.
Displayed above is CH: 47 that has a Center Frequency of 671MHz.
Pushing the Left Arrow will display the System Device Details Upconverter
Values Main Sub Screen and then pushing the Down arrow will access the
System Device Details Downconverter Main Sub Screen, if present.
Table 10.6: Downconverter Device Details Screen (TD/RD)
NOTE: This screen is only used with an Axciter.
This is the System Device Details Downconverter Main Sub Screen. Push the ENTER
button to access the Device Downconverter submenus or push the DOWN Arrow to
go to the External Amplifier Device Details Screen, if present, or back to the Device
Details Exciter Values screen.
Table 10.6.1: Downconverter RF Input Details Screen (TD/RD)
NOTE: This screen is only used with an Axciter.
The Downconverter RF Input details screen indicates that an RF input is
present to the downconverter and the level of the input.
This is the final Device Details Main Sub Menu. Push the LEFT Arrow twice to
go back the Main System Details Screen. Then push the DOWN Arrow to
access the System Set Up Main Menu.
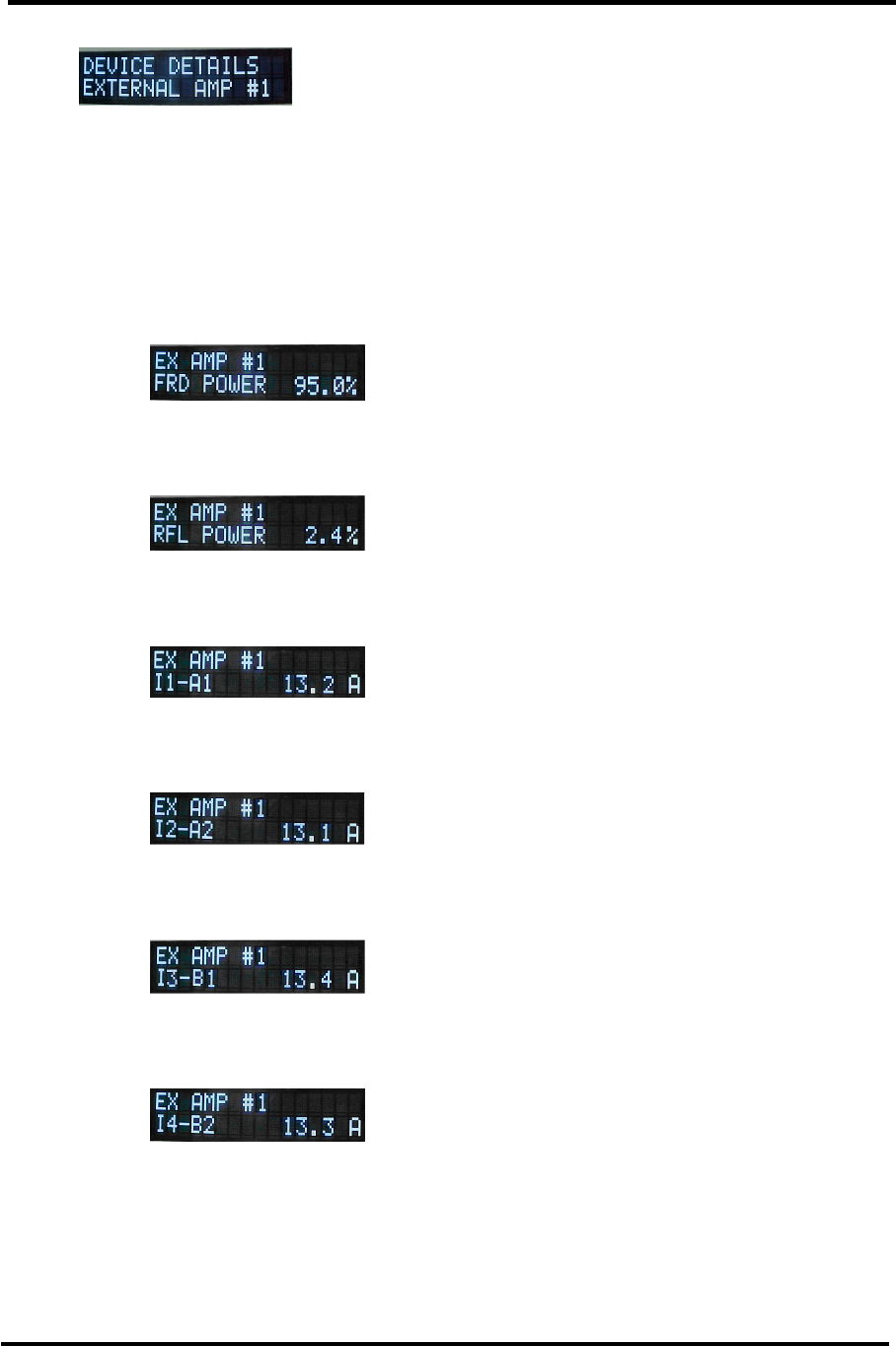
Innovator CU0TD-1/CU0RD-1 – CU4TD/CU4RD Initial On Site
ATSC Transmitter/Regenerative Translator Turn On Procedure
Instruction Manual, Rev. 1 40
Table 10.7: External Amplifier Device Details Screen (TD/RD)
This is the Transmitter Device Details External Amplifier Main Sub Screen. This is
the final Device Details Main Sub Menu. Push the ENTER button to access the Device
External Amplifier #1. Push the LEFT Arrow to go back the Main Device Details
Screen. Then push the DOWN Arrow to access the Transmitter Set Up Main Menu.
NOTE: Shown below are the External Amplifier #1 Details Screens. The
External Amplifier #2, #3 or #4 Details Screens are presented in the same
order if they are present in the system.
Table 10.7.1: External Amplifier #1 Forward Power Details Screen (TD/RD)
Indicates Output Power for external amplifier #1. NOTE: See the final test
data sheet for the typical value.
Table 10.7.2: External Amplifier #1 Reflected Power Details Screen (TD/RD)
Indicates Reflected Power for external amplifier #1. NOTE: See the final test
data sheet for the typical value.
Table 10.7.3: External Amplifier #1 I1-A1 Current Details Screen (TD/RD)
Indicates Current of the A1 device in the external amplifier #1. NOTE: See
the final test data sheet for the typical current value.
Table 10.7.4: External Amplifier#1 I2-A2 Current Details Screen (TD/RD)
Indicates Current of the A2 device in the external amplifier #1. NOTE: See
the final test data sheet for the typical current value.
Table 10.7.5: External Amplifier#1 I3-B1 Current Details Screen (TD/RD)
Indicates Current of the B1 device in the external amplifier #1. NOTE: See
the final test data sheet for the typical current value.
Table 10.7.6: External Amplifier#1 I4-B2 Current Details Screen (TD/RD)
Indicates Current of the B2 device in the external amplifier #1. NOTE: See
the final test data sheet for the typical current value.
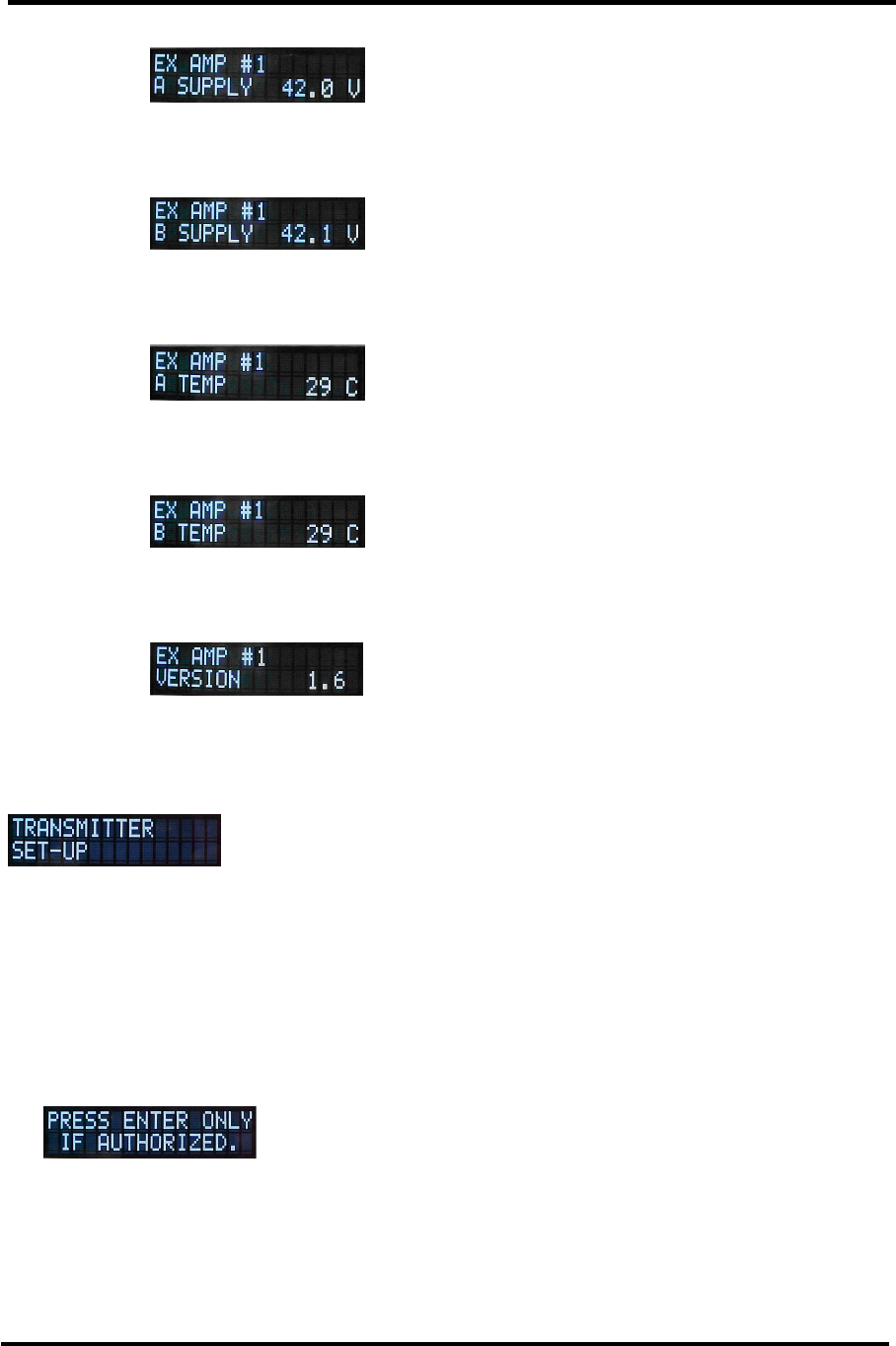
Innovator CU0TD-1/CU0RD-1 – CU4TD/CU4RD Initial On Site
ATSC Transmitter/Regenerative Translator Turn On Procedure
Instruction Manual, Rev. 1 41
Table 10.7.7: External Amplifier #1 A Power Supply Details Screen (TD/RD)
Indicates the voltage of the A power supply in the external amplifier #1.
NOTE: Typical voltage value is +42VDC or +48VDC w/888A devices.
Table 10.7.8: External Amplifier #1 B Power Supply Details Screen (TD/RD)
Indicates the voltage of the B power supply in the external amplifier #1.
NOTE: Typical voltage value is +42VDC nominal or +48VDC w/888A devices.
Table 10.7.9: External Amplifier #1 A Temperature Details Screen (TD/RD)
Indicates the temperature of the A heatsink in the external amplifier #1.
NOTE: Typical temperature for DVB = ≈20-30°C above ambient.
Table 10.7.10: External Amplifier#1 B Temperature Details Screen (TD/RD)
Indicates the temperature of the B heatsink in the external amplifier #1.
NOTE: Typical temperature for DVB = ≈20-30°C above ambient.
Table 10.7.11: External Amplifier #1 Code Version Details Screen (TD/RD)
Indicates the code version in the external amplifier #1.
Set Up Screens
Table 11: Transmitter/Translator Set Up Main Screen (TD/RD)
This is the System Set Up Main Screen. Push the ENTER button to access the Authorization
Warning Main Sub Screen or since this is the final Main Screen, pushing the DOWN Arrow
will take you back to the System RF Power Default Screen.
The Set Up item or parameter that can be changed on the displayed sub menu screen, is
indicated by pushing the ENTER button, which causes the changeable item to blink. The UP
or DOWN arrow will change the selection until the desired result is displayed. Pushing the
ENTER Button will accept the change.
Table 11A: Authorized Personnel Screen (TD/RD)
This screen of the system notifies an operator that they are only to proceed if they are
authorized to make changes to the system's operation. Changes made within the
following set-up screens can affect the system’s output power level, output frequency,
and the general behavior of the system. Please do not make changes within the
system's set-up screens unless you are familiar with the operation of the system.
Pressing the ENTER button will display the Enter Key Sets to Change screen.
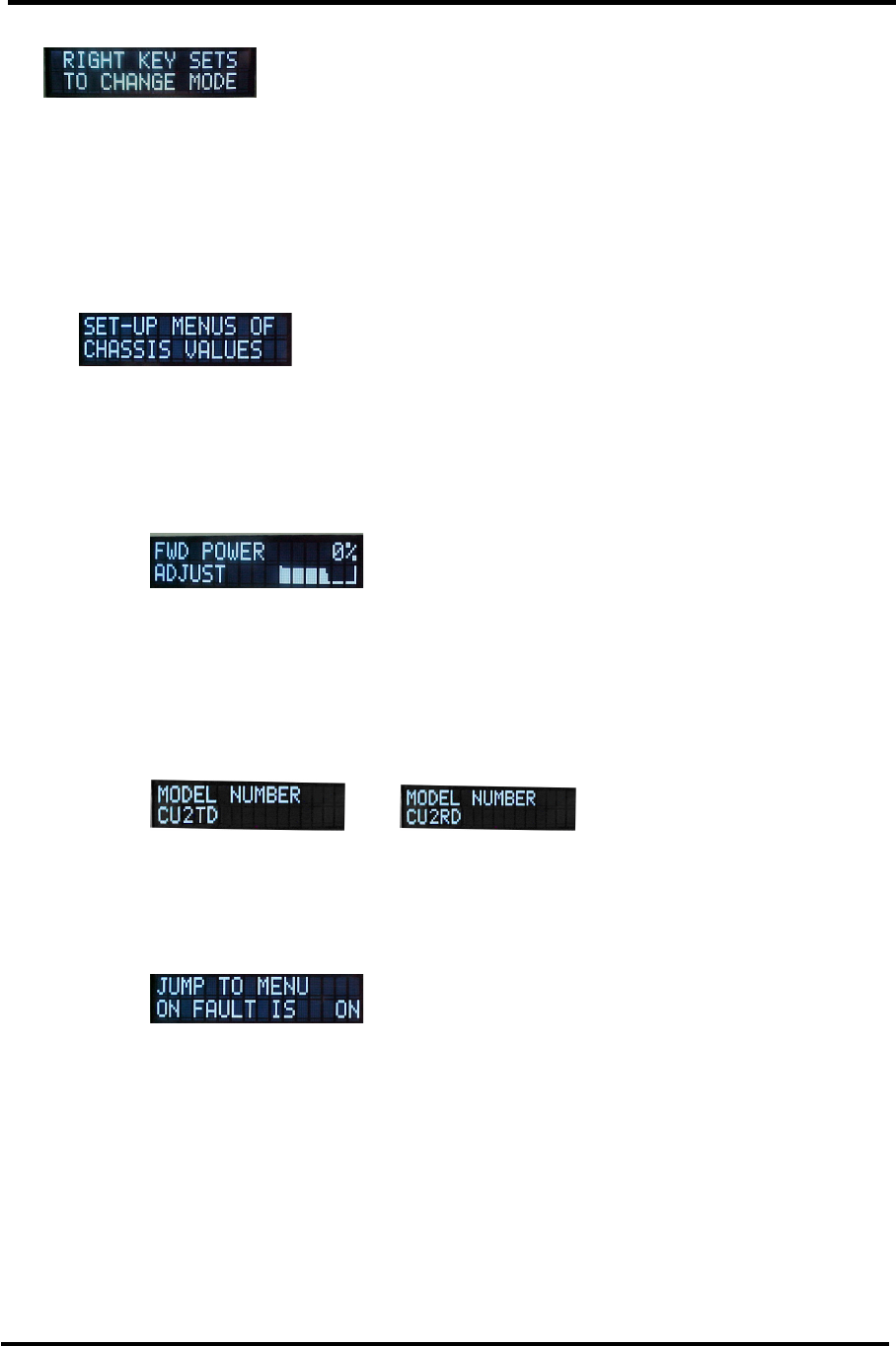
Innovator CU0TD-1/CU0RD-1 – CU4TD/CU4RD Initial On Site
ATSC Transmitter/Regenerative Translator Turn On Procedure
Instruction Manual, Rev. 1 42
Table 11B: Enter Key Sets to Change Mode Screen (TD/RD)
This screen informs the operator that to make changes, the Enter key or the Right key
must be pushed, which will cause the display that can be changed to blink. Use the up
or down key to change the display and the left or right key to move the blinking item on
the display. After changes are made in the Set Up Menus pushing the enter Key,
Button, will accept the changes made. With the Right Key Sets To Change Mode screen
displayed, pushing the ENTER button will access the first main submenu under the Set
Up main menu, which is the Chassis Values Set Up Menu.
Table 11.1: Chassis Values Main Set Up Menu Screen (TD/RD)
This is the System Set Up Chassis Values Main Sub Screen. Push the ENTER button
to access the Chassis Values submenus or push the DOWN Arrow to view the next
Set Up Main Sub Screen, which is the Set Up 8VSB Demodulator Main Sub Screen.
NOTE: Refer to the description in Table 11B for how to change the values on the
following set-up screens.
Table 11.1.1: Chassis Values Forward Power Set Up Screen (TD/RD)
Remote or front panel adjustment of the output power of the transmitter.
The bar graph indicates the range remaining in the adjustment.
NOTE: If the transmitter's output power is being adjusted through the web
page, the transmitter's forward power will be blinking on this screen. It will
remain blinking while the transmitter is adjusting to the desired target power
level.
Table 11.1.2: Chassis Values Model Number Set Up Screen (TD/RD)
This screen allows the set up of the Model Number of the
transmitter/regenerative translator. This causes the system to access the
proper parameters to be displayed on the LCD screens. NOTE: Do not
change this screen without first consulting with Axcera.
Table 11.1.3: Chassis Values Jump to Menu on Fault Set Up Screen (TD/RD)
The 'Jump To Menu' setting screen allows an operator to change how the
transmitter's display system works. When this value is set 'ON' and a new
fault occurs, the transmitter will automatically change the display screen to
show the new fault condition. When this value is set 'OFF', the display screen
does not change when a new fault is detected.
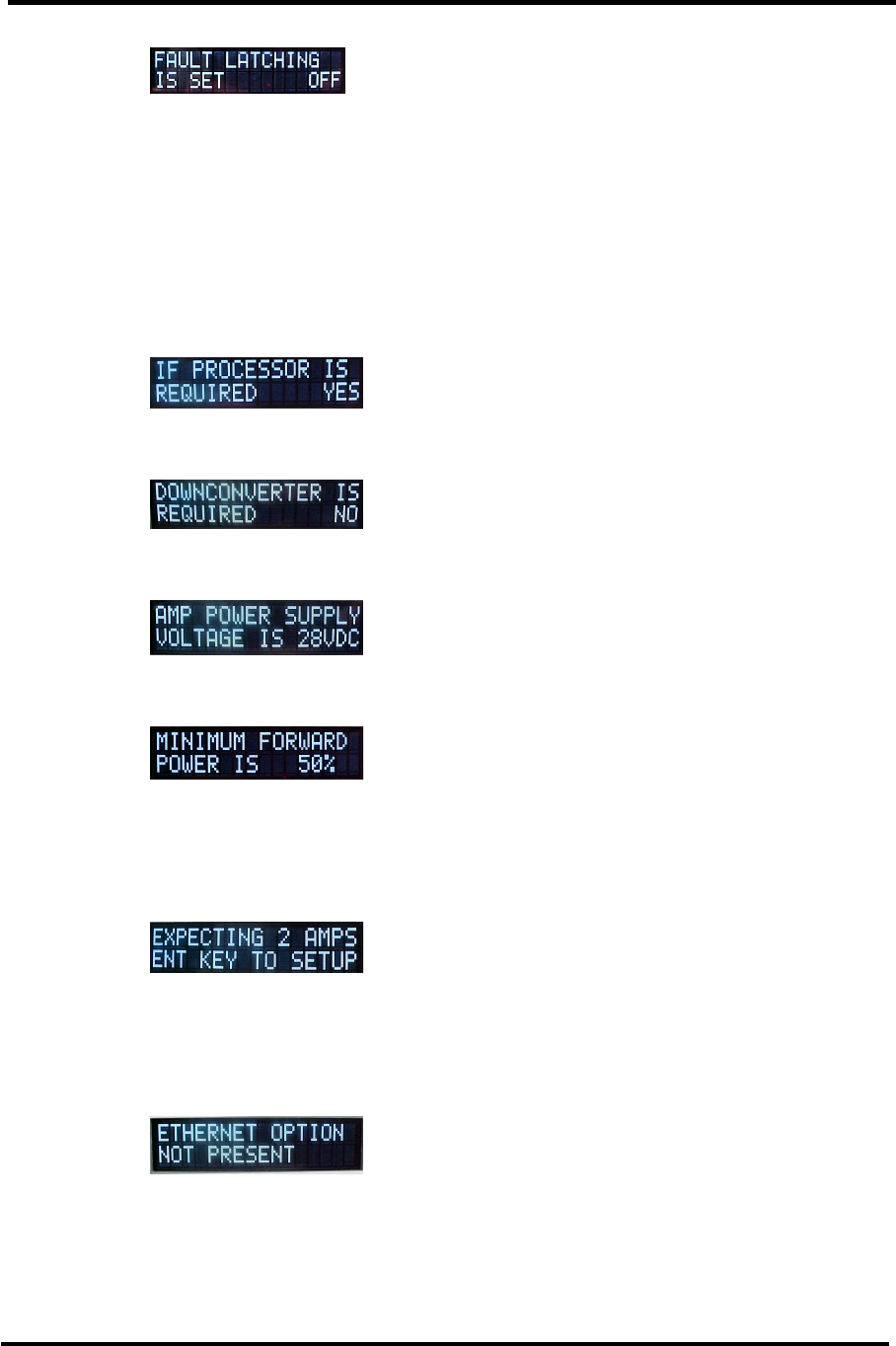
Innovator CU0TD-1/CU0RD-1 – CU4TD/CU4RD Initial On Site
ATSC Transmitter/Regenerative Translator Turn On Procedure
Instruction Manual, Rev. 1 43
Table 11.1.4: Chassis Values Latch On an Input Fault Set Up Screen (TD/RD)
This screen, by selecting ON, allows the user to select that the system will
latch the fault if it occurs, then if the problem is corrected the fault will still
register. Since latched faults are used to set the status LED color, when fault
latching is OFF, the status LED should only be green if there are no faults or
red if there are one or more active faults. When fault latching is ON, the
status LED will be amber if there are no current faults but a fault was
previously detected and is now a latched fault. A blinking amber status LED
indicates that there are no current faults or latched faults but that an internal
signal source is selected instead of an external source.
Table 11.1.5: Chassis Values IF Processor Selection Screen (TD/RD)
This screen allows the user to select that the system has an IF Processor.
Table 11.1.6: Chassis Values Downconverter Selection Screen (TD/RD)
This screen allows the user to select that the system has a Downconverter.
Table 11.1.7: Chassis Values Amplifier Power Supply Voltage Screen (TD/RD)
This screen allows the user to select the Power Supply Voltage.
Table 11.1.8: Chassis Values Forward Power Fault Adjust Screen (TD/RD)
This screen allows the operator to configure a forward power fault threshold
setting. When the exciter is enabled for at least a few seconds and the
system forward power is not greater than or equal to this setting, a fault is
indicated on the status LED and also on the remote fault indicator pin.
Table 11.1.9: Chassis Values number of Amplifiers in System Screen (TD/RD)
This screen indicates the number of external amplifier drawers in the system.
By selecting the enter key, the system will scan to find the number of
external amplifier drawers. NOTE: Do not change this screen without first
consulting with Axcera.
Table 11.1.10: Chassis Values Ethernet Option Set Up Screen (TD/RD)
Only displayed if Ethernet Controller is not present in your system.
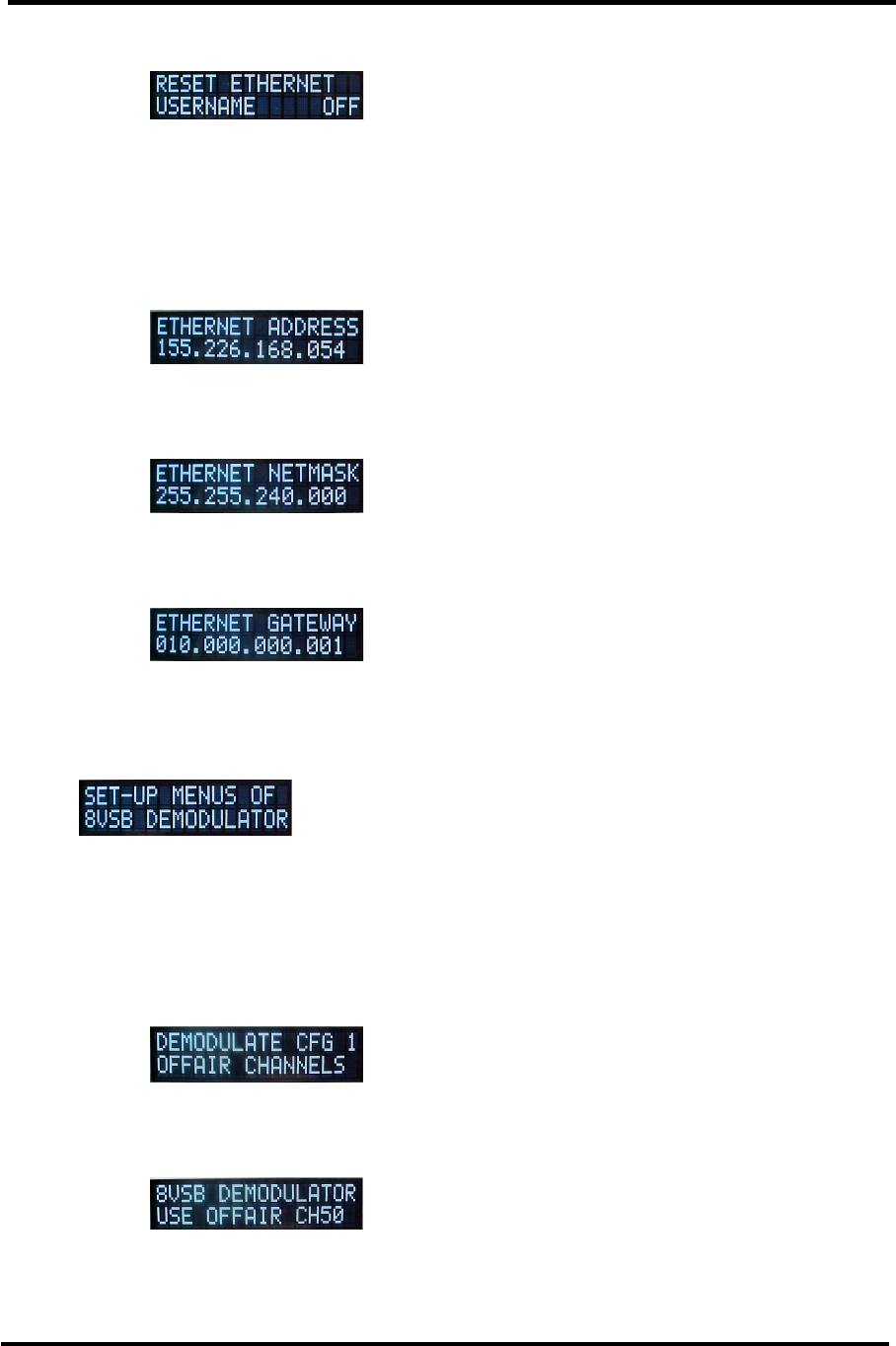
Innovator CU0TD-1/CU0RD-1 – CU4TD/CU4RD Initial On Site
ATSC Transmitter/Regenerative Translator Turn On Procedure
Instruction Manual, Rev. 1 44
Table 11.1.11: Chassis Values Reset Ethernet User Name Set Up Screen
(TD/RD)
When the optional Ethernet Controller is present, this screen is displayed. It
is used to reset the first username / password account of the Ethernet
controller. There are a total a five accounts available on the Web. If this
operation is selected, ON, and the change accepted, only the fist username /
password account file is replaced, with the user name set to ‘admin’ and the
password set to ‘axcera’.
Table 11.1.12: Chassis Values Ethernet Address Set Up Screen (TD/RD)
When the optional Ethernet Controller module is present, this screen is used
to view or change the Ethernet TCP Address of the controller.
Table 11.1.13: Chassis Values Ethernet Netmask Set Up Screen (TD/RD)
When the optional Ethernet Controller module is present, this screen is used
to view or change the TCP subnet mask of the Ethernet controller.
Table 11.1.14: Chassis Values Ethernet Gateway Set Up Screen (TD/RD)
When the optional Ethernet Controller module is present, this screen is used
to view or change the TCP gateway (router) address of the Ethernet
controller.
Table 11.2: 8VSB Demodulator Main Set Up Menu Screen (RD)
This is the System Set Up 8VSB Demodulator Main Sub Screen that is only present in
the Regenerative Translator mode. Push the ENTER button to access the Set Up
8VSB Demodulator submenus or push the DOWN Arrow to view the next Set Up Main
Sub Screen, which is the Set Up 8VSB Modulator Main Sub Screen. NOTE: Refer to
the description in Table 11B for how to change the values on the following set-up
screens.
Table 11.2.1: 8VSB Demodulator Channels Set Up Menu Screen (RD)
This screen allows selection of the channel plan which can be changed to
either Off Air or Cable.
Table 11.2.2: 8VSB Demodulator Channel Select Set Up Menu Screen (RD)
This screen allows selection of the channel, for the channel plan selected in
the previous screen.
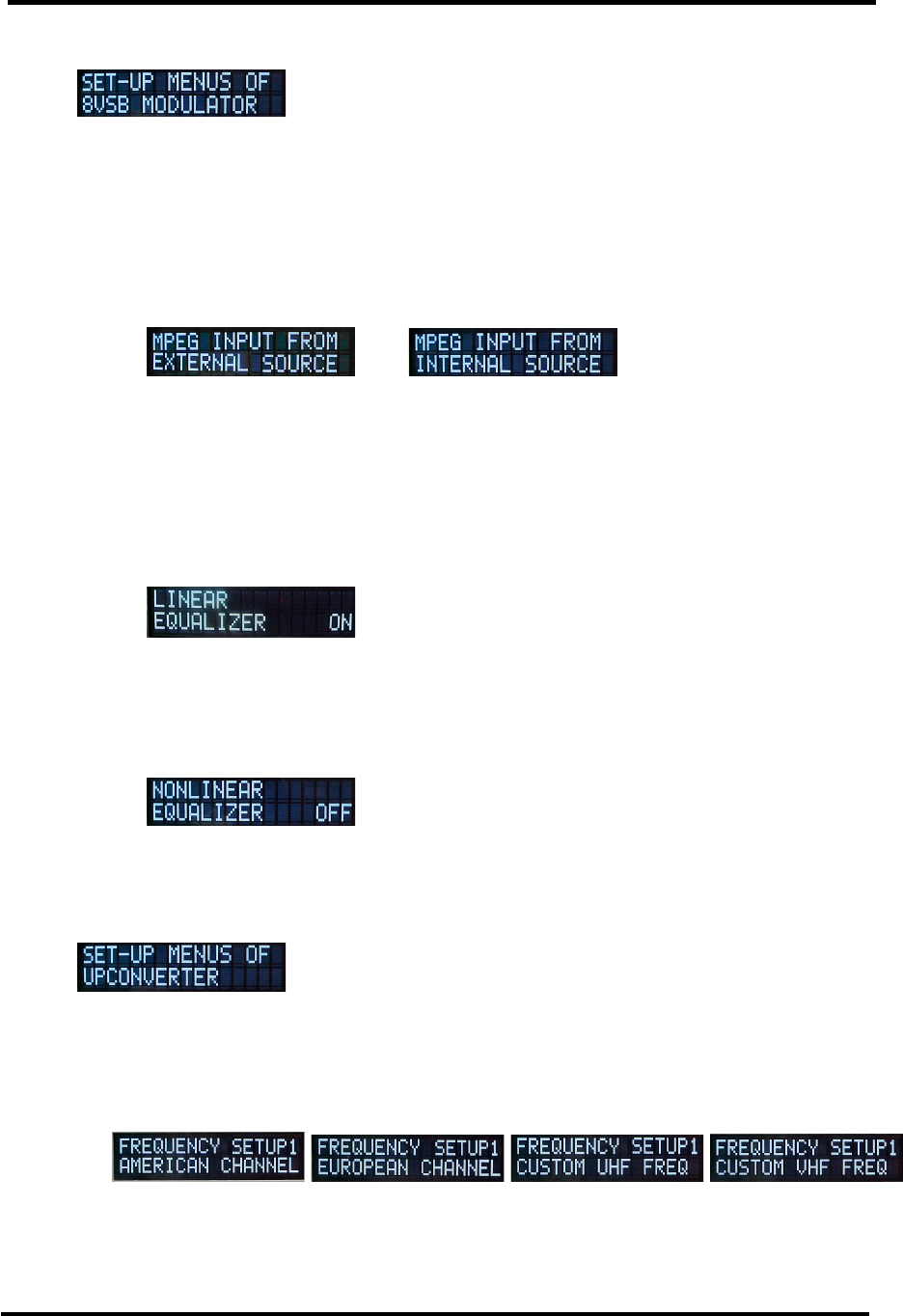
Innovator CU0TD-1/CU0RD-1 – CU4TD/CU4RD Initial On Site
ATSC Transmitter/Regenerative Translator Turn On Procedure
Instruction Manual, Rev. 1 45
Table 11.3: 8VSB Modulator Main Set Up Menu Screen (TD/RD)
(Not present with Axciter)
This is the System Set Up 8VSB Modulator Main Sub Screen. Push the ENTER button
to access the Set Up 8VSB Modulator submenus or push the DOWN Arrow to view
the next Set Up Main Sub Screen, which is the Set Up Upconverter Main Sub Screen.
NOTE: Refer to the description in Table 11B for how to change the values on the
following set-up screens.
Table 11.3.1: 8VSB Modulator MPEG Selection Set Up Screen (TD/RD)
This screen allows the user to select between an external and an internal
source in the 8 VSB modulator. During the installation of the system, an off
air signal may not be available to the modulator, therefore the user can set
the source to INTERNAL to generate an 8 VSB signal inside the drawer that
can be used for set up. Once the Receive Signal is available, the source must
be set to EXTERNAL. NOTE: The front panel Status LED will be Amber and
blinking, with no faults, events, if the MPEG input is set to Internal Source.
Table 11.3.2: 8VSB Modulator Linear Equalization Selection Screen (TD/RD)
This screen controls the operation of the linear equalizer. When set to ON,
the modulator applies linear correction to the IF output. When set to OFF, no
correction is applied to the IF.
Table 11.3.3: 8VSB Modulator Non Linear Equalization Selection Screen
(TD/RD)
This screen controls the operation of the non linear equalizer. When set to
ON, the modulator applies non linear correction to the IF output. When set to
OFF, no correction is applied to the IF.
Table 11.4: Upconverter Main Set Up Menu Screen (TD/RD)
This is the System Set Up Upconverter Main Sub Screen. Push the ENTER button to
access the Set Up Upconverter submenus. Push the LEFT Arrow to go back the Main
System Set Up Screen. NOTE: Refer to the description in Table 11B for how to
change the values on the following set-up screens.
Table 11.4.1: Upconverter Channel Type Selection Screen (TD/RD)
One of the above screens is displayed as the first screen on entering the
upconverter set up screens. It will indicate the Channel Type currently selected.
The display will not be blinking. Pushing the Down Button will display the
Upconverter Channel Selection Screen. NOTES: The Upconverter transmit
channel type should not be changed, unless the transmitter is being converted
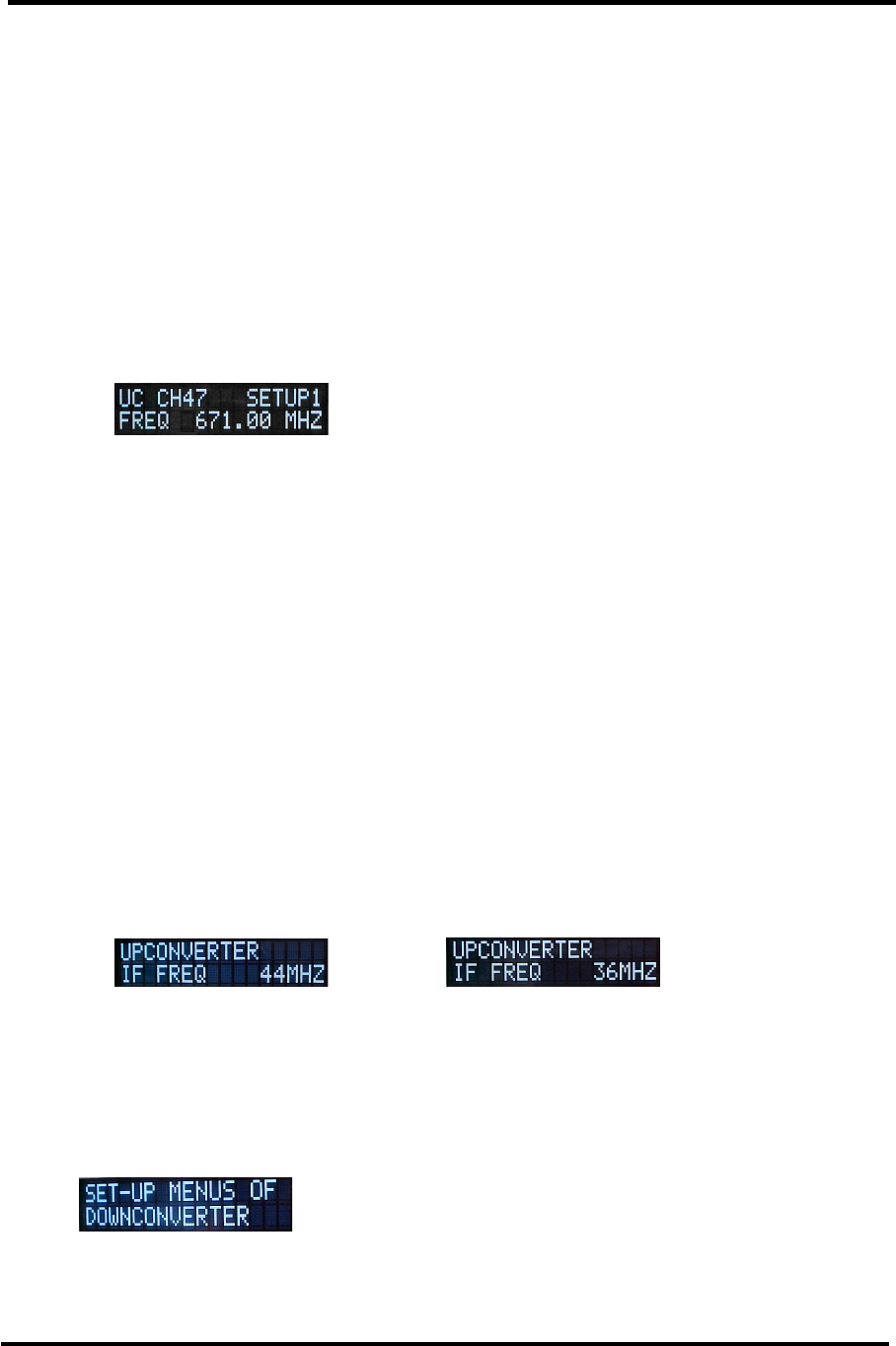
Innovator CU0TD-1/CU0RD-1 – CU4TD/CU4RD Initial On Site
ATSC Transmitter/Regenerative Translator Turn On Procedure
Instruction Manual, Rev. 1 46
from one channel to another. The SETUP 1 or SETUP 2 selection is controlled by
a Low, ground, for SETUP 2 or a High, open, for SETUP 1 at J12-7, on the
Remote Interface Jack J12 located on the rear panel of the Exciter/Driver Drawer.
Changes should only be made while the transmitter is in standby. Contact
Axcera Field Service before using this menu.
With a Channel or Custom Frequency screen displayed, the Channel type can be
set to the American Channel, European Channel, Custom UHF Frequency or
Custom VHF Frequency by first pushing the enter button. This will cause the
channel type to blink. Pushing the Up or Down Arrow Key will display each
Channel type screen in sequence. When the desired screen is displayed pushing
the Enter Button will cause the display to become steady. This displayed channel
type is now used in the following screen to configure the Upconverter PLL circuits.
Table 11.4.2: Upconverter Channel Selection Screen (TD/RD)
The above screen is displayed when the Down Arrow is pushed at the channel
type selection screen. It will indicate the Channel currently selected and the
center frequency of the selected channel. The display will not be blinking.
Pushing the Down Button will display the Upconverter IF Frequency Selection
Screen. NOTES: The Upconverter transmit channel should not be changed,
unless the transmitter is being converted from one channel to another. Changes
should only be made while the transmitter is in standby. Contact Axcera Field
Service before using this menu.
To change the Channel, the enter button must be pushed. This will cause the
Channel number to blink. Pushing the Up or Down Arrow Key will display each
Channel in sequence. To enter a custom Center Frequency, press the Right or
Left Key to select the value to change. The Up or Down Arrow will adjust the
value selected. When the desired Channel and Center Frequency are set,
pushing the Enter Button will cause the display to become steady. This displayed
Channel and corresponding Center frequency is now the upconverter output.
When exiting the set up menus a prompt will inform you that the Enter Key must
be pushed to accept the changes that were made.
Table 11.4.3: Upconverter IF Frequency Selection Screen
The transmit channel IF Frequency should not be changed, unless the transmitter
is being converted from one digital IF Frequency to another. The IF Frequency
can be changed to 36 MHz or 44 MHz by pushing the Up or Down Arrow. The
typical IF Frequency for an ATSC transmitter is 44 MHz. NOTES: Changes should
only be made while the transmitter is in standby. Contact Axcera Field Service
before using this menu.
Table 11.5:Downconverter Main Set Up Menu Screen
NOTE: This screen is only present when an Axciter is part of the system.
This is the System Set Up Downconverter Main Sub Screen. Push the ENTER button
to access the Set Up Downconverter submenu or push the LEFT Arrow to go back the

Innovator CU0TD-1/CU0RD-1 – CU4TD/CU4RD Initial On Site
ATSC Transmitter/Regenerative Translator Turn On Procedure
Instruction Manual, Rev. 1 47
Main Downconverter Set Up Screen. Push the LEFT Arrow again to go back the Main
System Set Up Screen.
Table 11.5.1: Downconverter RF Input Level Screen
This screen allows the operator to monitor the RF input level and to set the
desired input value.
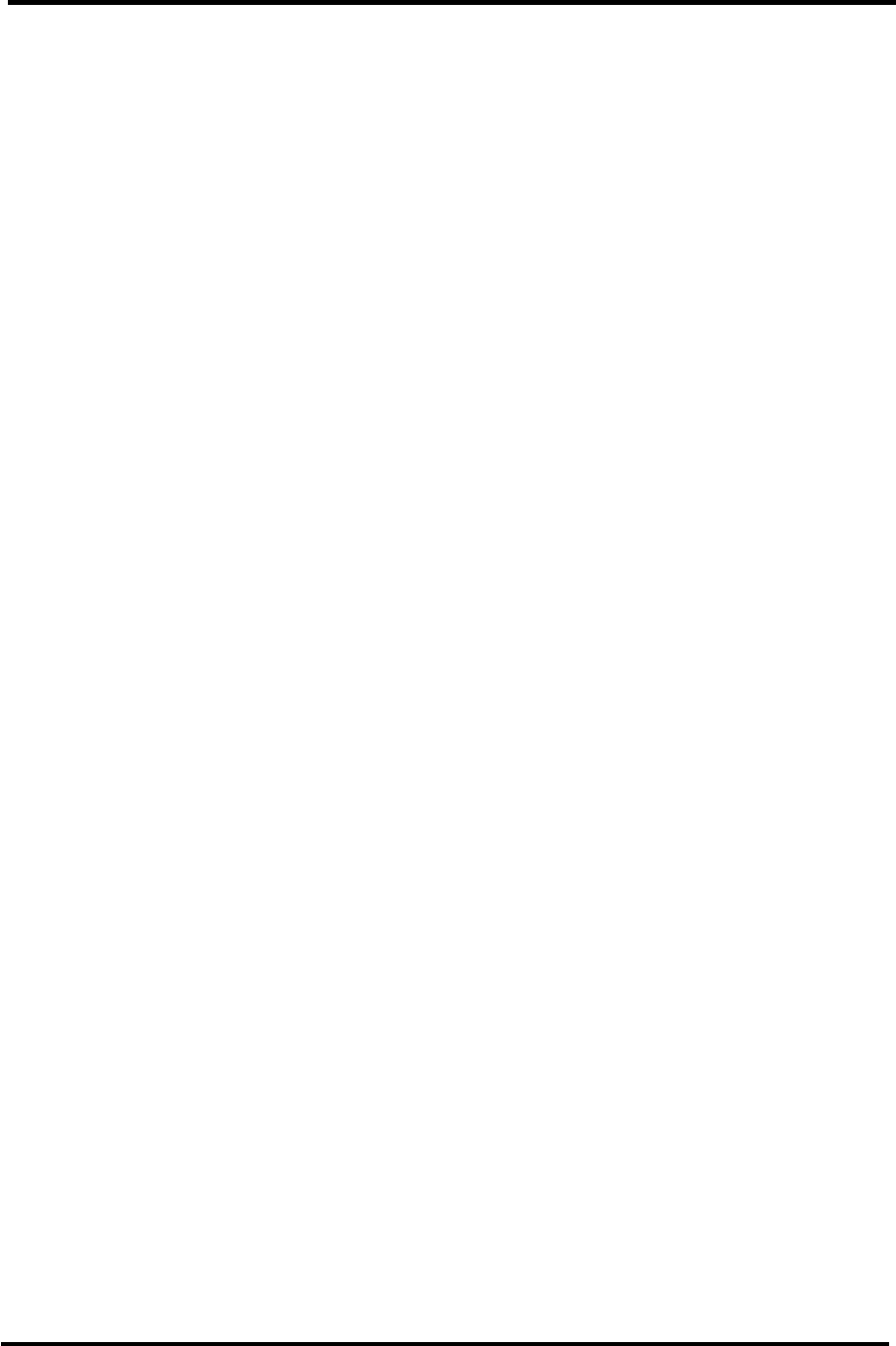
Innovator CU0TD-1/CU0RD-1 – CU4TD/CU4RD Initial On Site
ATSC Transmitter/Regenerative Translator Turn On Procedure
Instruction Manual, Rev. 1 48
This page has intentionally been left blank.
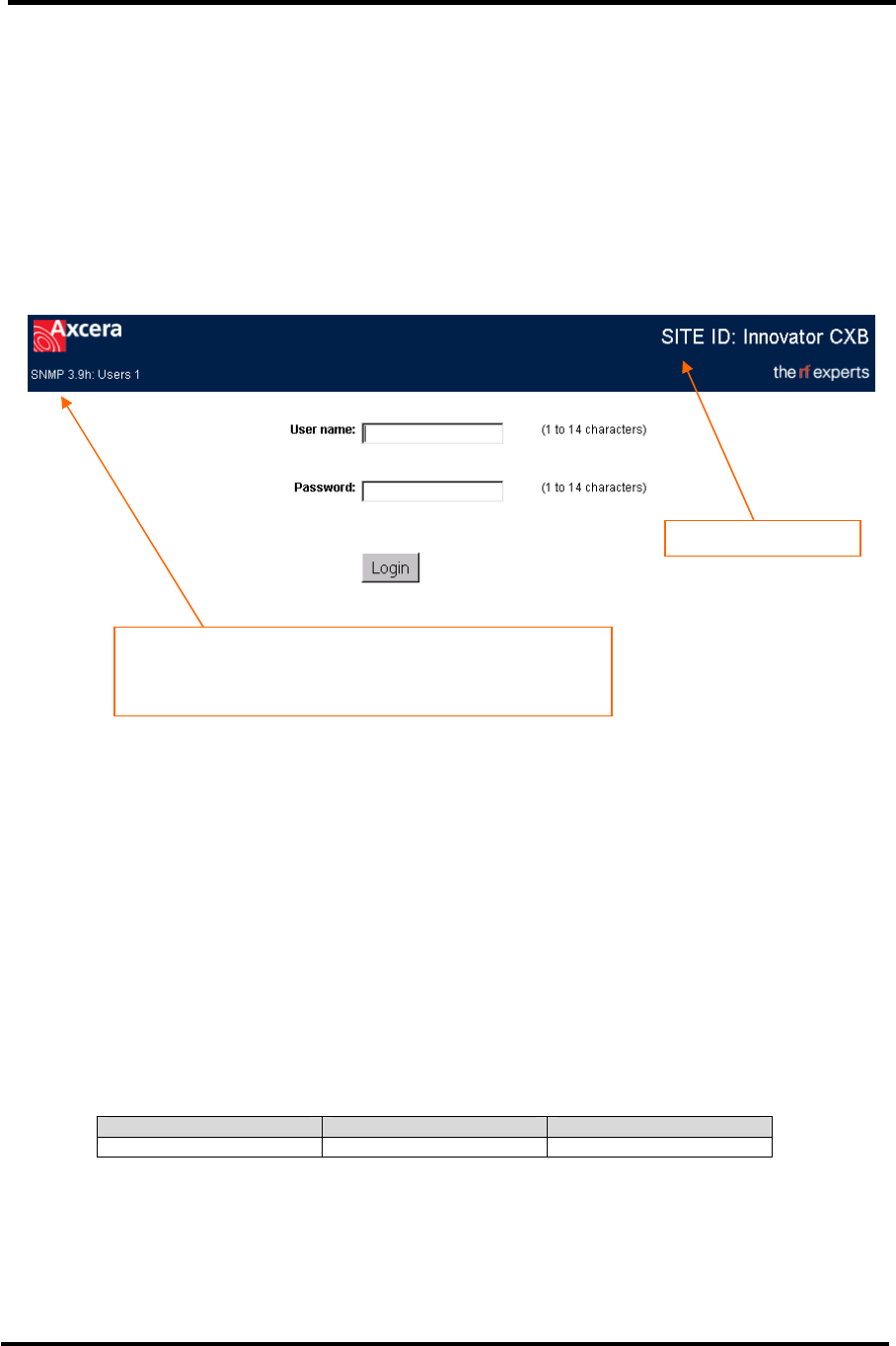
Innovator CU0TD-1/CU0RD-1 – CU4TD/CU4RD Web Ethernet
ATSC Transmitter/Regenerative Translator Interface Description
Instruction Manual, Rev. 1 49
(Optional) Innovator CXB Series Web Ethernet Interface Kit (1313100)
The Innovator CXB transmitter is available with two optional Ethernet interface
packages. Axcera part number (1313100) is the Axcera part number for an Ethernet
Interface kit that serves HTML web pages. Axcera part number (1313079) is an
Ethernet Interface kit that provides an SNMP interface to transmitter parameters and
also serves HTML web pages. Either option may be added to the Innovator CXB
transmitter if it was not originally installed at the factory. NOTE: Internet Explorer
Version 7 or higher is required.
Figure 8: Typical Ethernet User Log In Screen
Once a connection has been established, the web interface can be launched by entering
the IP address of the Innovator CXB Ethernet Controller as a URL in the browser of the
remote computer. A login screen will be displayed prompting for a user name and
password, which are case sensitive.
The controller has two levels of user access: Administrative and Read Only.
Administrators have full access to transmitter controls and controller configuration.
Read Only users can view all transmitter parameters and the event log entries but they
can not change the transmitter's state, clear faults, clear the event log or configure the
Ethernet parameters.
Five unique login accounts are available. The factory default user name and password
for account number one are:
User Name Password Access Level
admin axcera Administrator
The user name and password of account number one may be reset to factory default
values through a setup screen of the transmitter.
Indicates SNMP or GUI with package software version and
number of users currently on-line.
NOTE: Only 5 simultaneous on-lines users are allowed.
Unique Site ID value
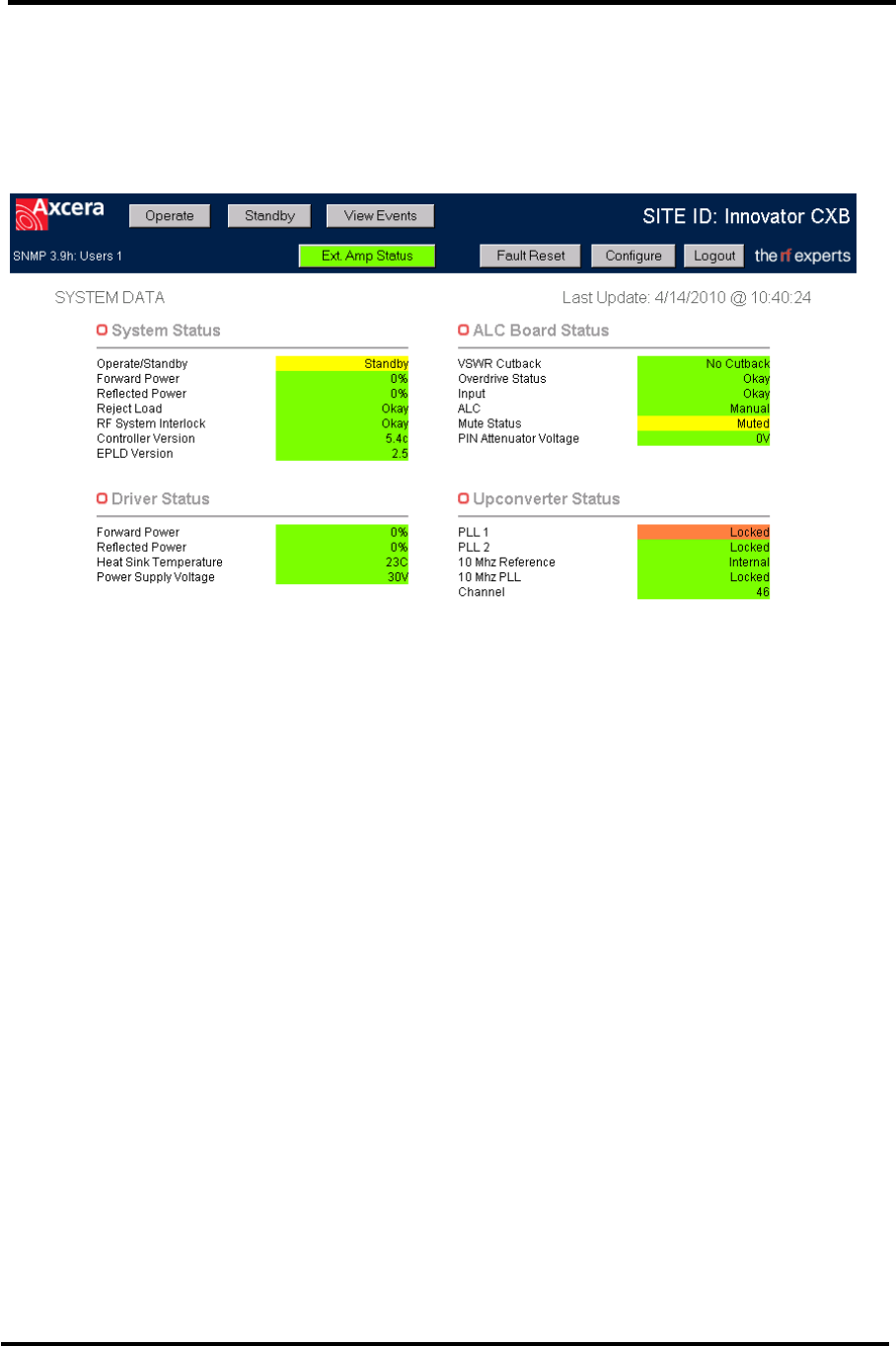
Innovator CU0TD-1/CU0RD-1 – CU4TD/CU4RD Web Ethernet
ATSC Transmitter/Regenerative Translator Interface Description
Instruction Manual, Rev. 1 50
After logging in, the main control/monitoring screen is displayed. Administrators have
the ability to change the transmitter's operate / standby state, and configure the
application. All users have the ability to view the transmitter's event log, and review
system parameters. Refer to Figure 9 for a sample main control/monitoring screen.
Figure 9: Typical Ethernet Main Control/Monitoring Screen
Color Key:
Green = Okay or Normal Operation
Yellow = Warning, But Not faulted
Red = Currently Active Fault
Orange = Old or Previously Latched Fault
If an item on screen is Orange, a latched fault is present. Activating the 'Fault Reset'
button will reset any latched faults, clears the transmitter's event log and causes the
parameter to display normally.
The date and time of the last message received by the web page browser is present to
assure connectivity. If the browser does not receive a new set of data from the Ethernet
Controller, it will show the last update field with a yellow background indicating a
connection problem is present.
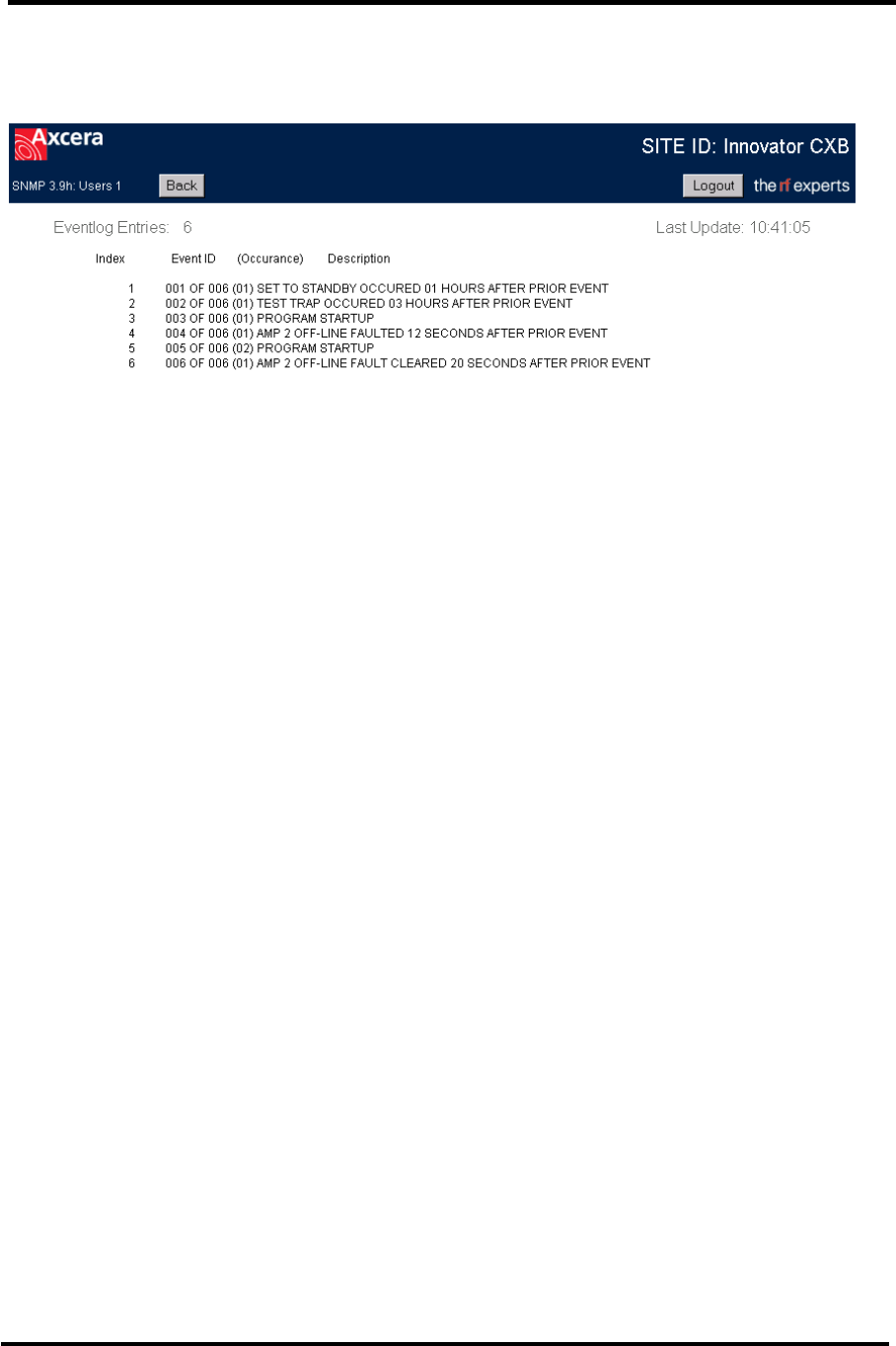
Innovator CU0TD-1/CU0RD-1 – CU4TD/CU4RD Web Ethernet
ATSC Transmitter/Regenerative Translator Interface Description
Instruction Manual, Rev. 1 51
Access to view the transmitter's event log is available by selecting the 'View Events'
button.
Figure 10: Typical Event Log Screen
This screen allows an operator to view events and to determine the time between
events. Events are logged in the order they are received. If more than 200 events are
detected, the transmitter's System Controller drops the oldest event to record the new
event. Transferring of events from the transmitter's System Controller and the Ethernet
Controller is scheduled so that device details are continuously monitored. Therefore the
event log screen may update a few seconds behind the transmitter display when the log
is full or changing quickly.
Each event record indicates the event number, the number of events, an occurrence
counter and text describing the event. The occurrence counter keeps track of the
number of times a specific event has occurred since the log was last cleared. Up to 99
occurrences are available for each event.
To view the next set of twenty events, activate the 'Next' button. If viewing events
higher in the log, the 'Previous' button allows you to return to prior events.
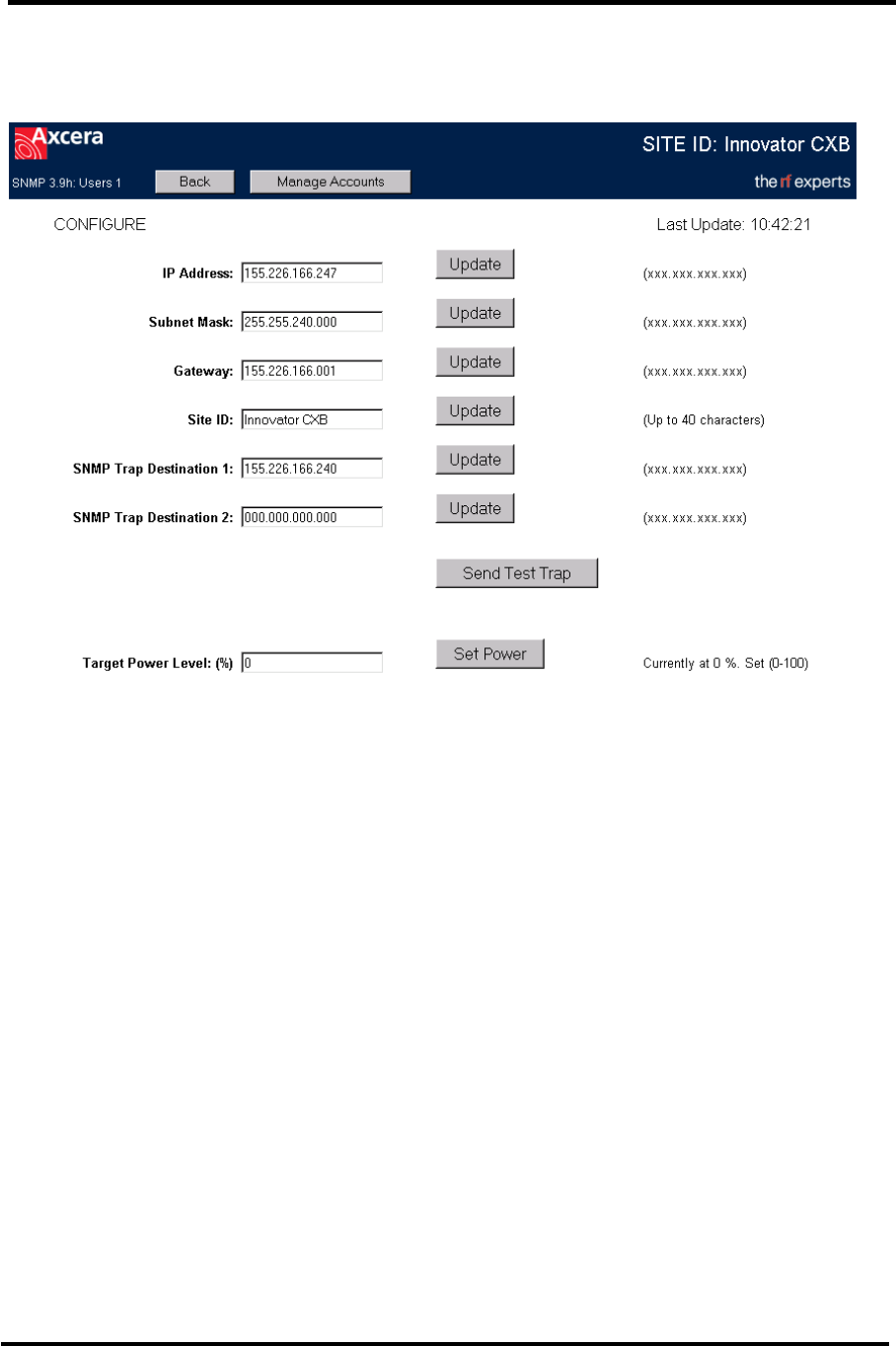
Innovator CU0TD-1/CU0RD-1 – CU4TD/CU4RD Web Ethernet
ATSC Transmitter/Regenerative Translator Interface Description
Instruction Manual, Rev. 1 52
From the main page, administrators may change the web interface settings or manage
user accounts by activating the ‘Configure’ button near the top of the screen.
Figure 11: Ethernet Configuration Screen
When entering a site ID, be sure to not use special characters except underscores,
dashes, and forward slashes. Changes to the transmitter's output power are available to
administrators when the transmitter is operating. Once changed, the menu defaults
back to the main display page and the systems forward power is noted as changing.
The screen above displays SNMP parameters and allows an operator to send a test trap.
If this system did not have SNMP enabled, then fields would not be populated and the
'Send Test Trap' button would not be present. New event log entries including an
activated test trap are automatically forwarded to SNMP agents specified to receive trap
messages. Trap messages do not need to be acknowledged by an agent.
The ability to reset a demodulator is only present in transmitters that have this
hardware and when the installed software versions allow for this feature. Resetting a
demodulator is only recommended if the tuner has lost input signal lock as this function
will take the transmitter off-air for a few seconds.
NOTE: The Innovator CXB controller does not use DHCP addresses – TCP/IP settings
must be fixed and entered manually. A crossover cable may be needed if connecting
directly from a computer to the Innovator CXB Transmitter.
To manage user accounts, click the ‘Manage Accounts’ button near the top of the
configure screen.
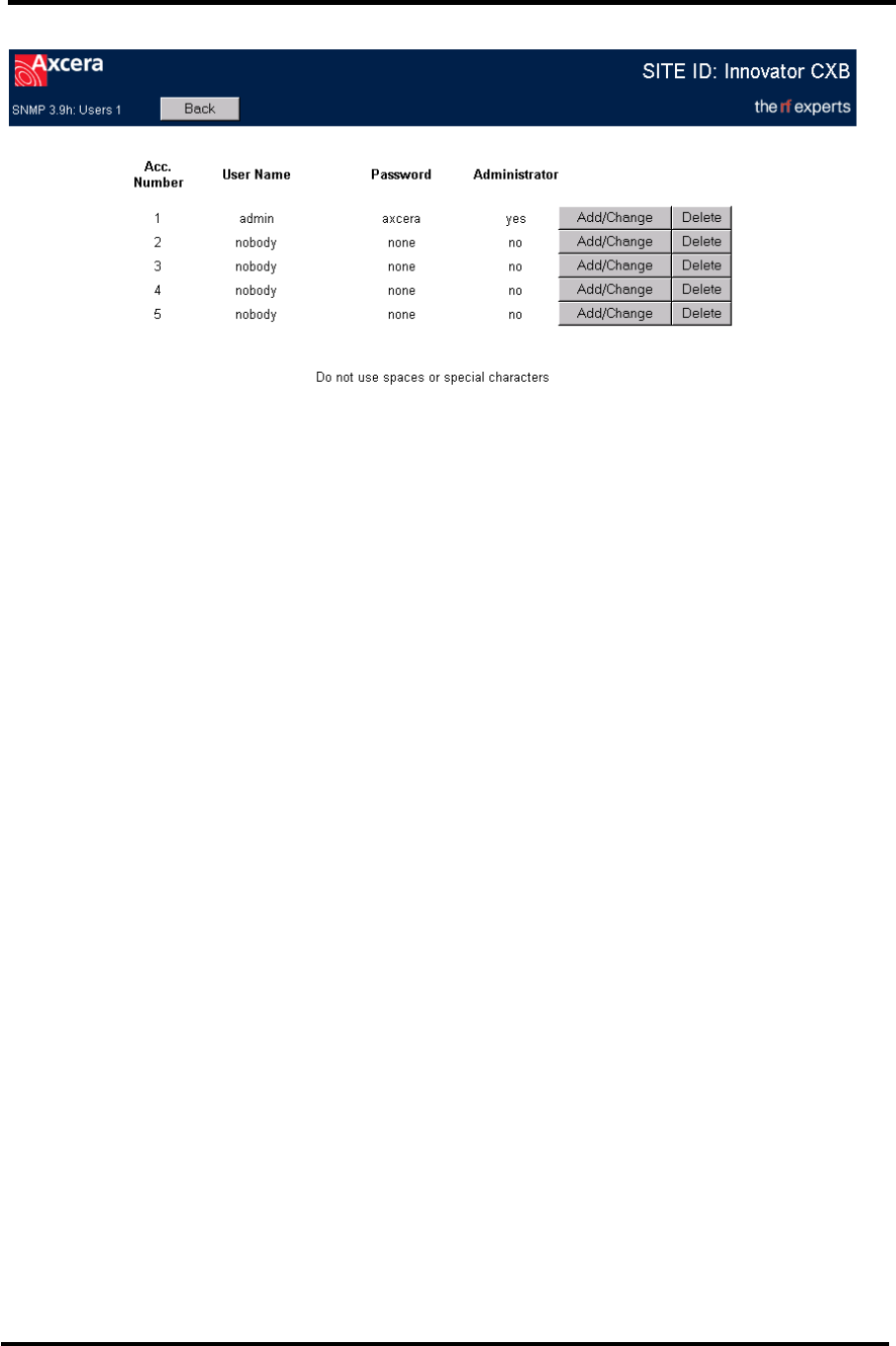
Innovator CU0TD-1/CU0RD-1 – CU4TD/CU4RD Web Ethernet
ATSC Transmitter/Regenerative Translator Interface Description
Instruction Manual, Rev. 1 53
Figure 12: Typical Manage Accounts Screen
The Innovator CXB Ethernet controller supports up to 5 different user accounts. To add or
change one of the accounts, click the Add/Change button in the row of the account you
want to modify, then enter the desired name, password, and administrator rights for the
user and click save.
NOTE: The transmitter's set up menus contain a Reset Ethernet User ID screen. This
screen allows a user to reset the first account User Name and Password. The
Yes or No selection can be changed by pushing the Up or Down Button. After
the selection has been made, the user needs to depress the right or left arrow
and then the display will ask “PUSH ENTER TO ACCEPT CHANGES”. If the
ENTER button is depressed, the change will be accepted. If any other button is
depressed, the change will not be made. If Yes is selected on the screen, and
accepted, the User name and Password will reset to the factory default of
admin / axcera.
Activate the 'Back' button to return to the main control/monitoring screen.
When you have completed using the web interface, please remember to log out via the
'logout' button at the top of the control/monitoring screen.
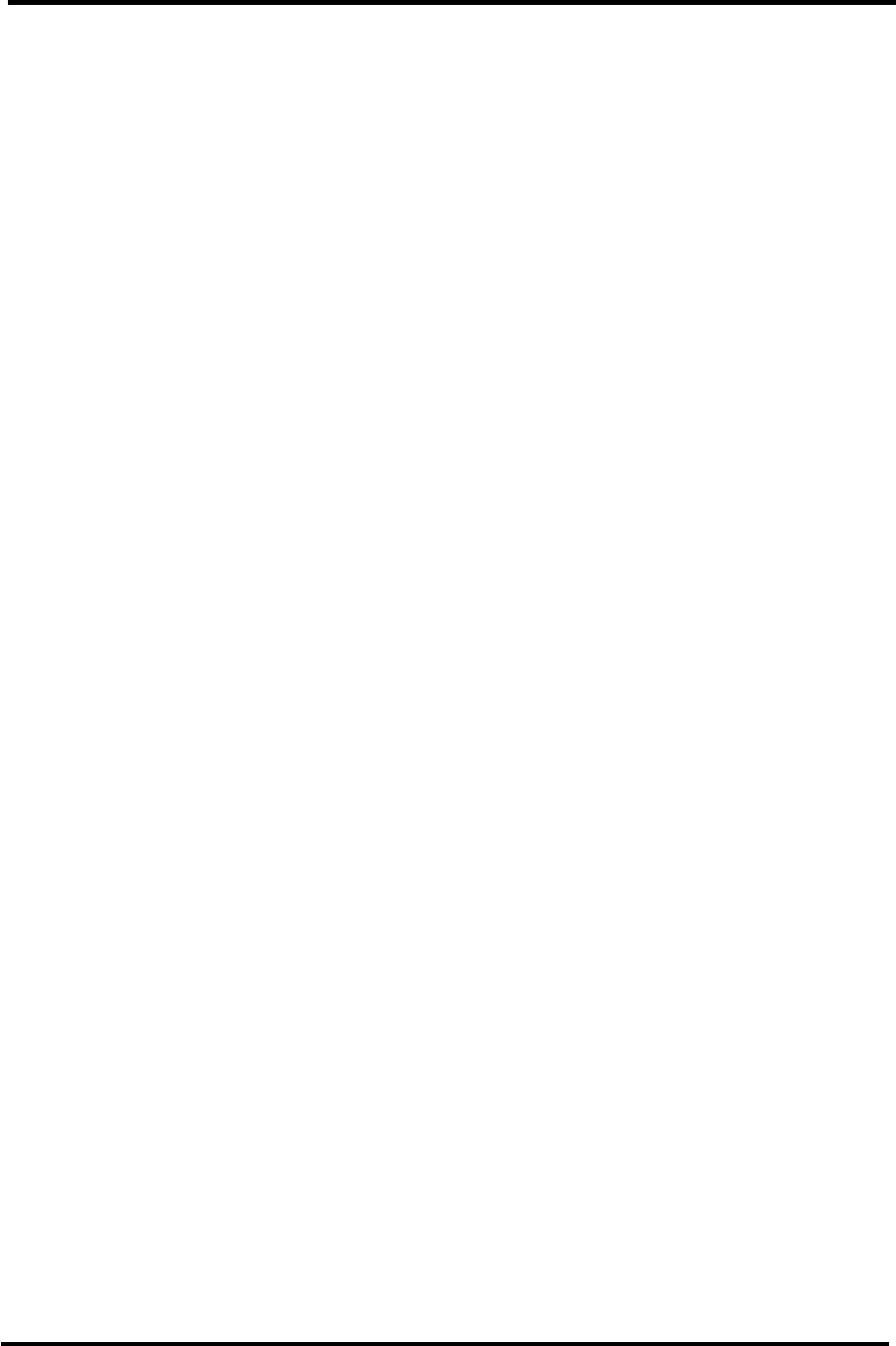
Innovator CU0TD-1/CU0RD-1 – CU4TD/CU4RD SNMP Ethernet
ATSC Transmitter/Regenerative Translator Interface Description
Instruction Manual, Rev. 1 54
(Optional) Innovator CXB Series SNMP Ethernet Interface (1313079)
NOTE: The Innovator CXB Series SNMP Ethernet Interface (1313079) includes the Web
Ethernet Interface described in the previous section of this manual. These interfaces
may not be part of your system. NOTE: Internet Explorer Version 7 or higher is
required.
The Innovator CXB Ethernet Controller is available in a version that implements Simple
Network Management Protocol (SNMP). SNMP is a standardized method of transferring
information from one electronic device to another. SNMP is typically used to remotely
control and monitor several transmitter devices from a centralized network management
system (NMS). SNMP is a communication method between two applications and is not a
graphical user interface. Therefore, SNMP functionality is included along with web page
server functionality. SNMP is used to gather information or set control states but it
requires additional computer applications for operator monitoring and control.
The Innovator CXB Ethernet Controller implements SNMP version 2 (SNMP v2) using a
Management Information Base (MIB). The MIB file defines all SNMP parameters of the
transmitter, specifies the format of data, and orders the presentation of the parameters
using a hierarchical namespace containing object identifiers (OID). Each OID identifies a
variable that can be read, read and set, or only set via SNMP commands.
SNMP functionality also provides for alert messages that are issued from the Ethernet
Controller to one or two network computers. A SNMP trap message is sent only once
and is not acknowledged by the receiving device. The Ethernet Controller issues a trap
message when data is added to the transmitter Event log (either activation of a fault or
when a fault is cleared), or when the transmitter operate/standby status changes.
SNMP Configuration
The Ethernet Controller's TCP/IP Address, Subnet Mask, and Gateway must be
configured with static values that are valid within your network. Dynamic Host
Configuration Protocol (DHCP) is not implemented; however access to these
configuration parameters is available through the front panel setup menus of the
Innovator CXB.
The Innovator CXB's SNMP MIB allows up to two SNMP trap destinations. The trap
destination values can be set through WEB pages. The TCP/IP address of a trap
processing computer can also be configured through the SNMP parameters called
'site_trap_adr1' and 'site_trap_adr2'. To clear a previously configured trap destination
and cause the system not to issue traps to a specific address, set the value to
'000.000.000.000'.
Reading of SNMP values is done with the message's community access set to 'public'.
When setting SNMP values, a default community access level of 'private' is used. Future
implementations of the Ethernet SNMP agent may allow for the set community access
level to be defined through the device's web server.
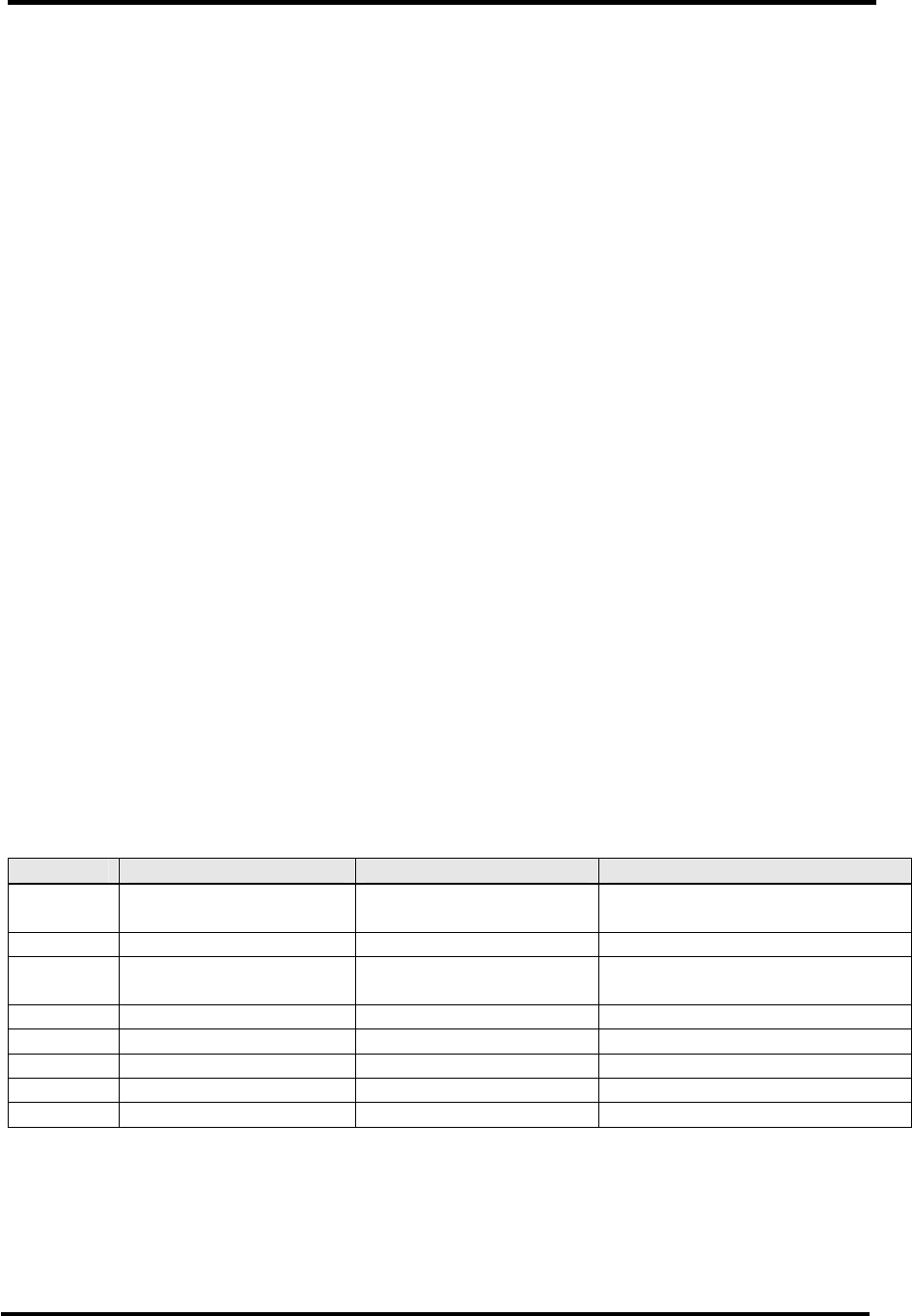
Innovator CU0TD-1/CU0RD-1 – CU4TD/CU4RD Board Descriptions
ATSC Transmitter/Regenerative Translator
Instruction Manual, Rev. 1 55
Circuit Descriptions of Boards in the CU0TD/RD-1 thru CU0TD/RD-5 Systems
(A1) 8 VSB Demodulator Board (1308275)
NOTE: Only used with RD operation except when the output of an external K-Tech
Receiver Drawer is used.
Overview
The 8 VSB demodulator assembly receives an off air 8 VSB signal on any VHF or UHF
channel and demodulates this to an MPEG-2 transport stream that is per the SMPTE-
310M standard. The input to the assembly is at an “F” style connector on the shielded
tuner and can be at a level of –8 to –78 dBm. The tuner (TU1) down converts the RF
channel to a 44 MHz IF signal. This signal is the input to the digital receiver chip U1.
The digital receiver chip subsequently decodes the IF and delivers an MPEG-2 transport
stream on a parallel data bus to a programmable logic array, U8. U8 clocks the
asynchronous MPEG data from the receiver chip and outputs a synchronous data stream
at a 19.39 MHz rate to buffer/driver U11. U11 subsequently drives the output at J13 to
a lower level that is AC coupled out of the board.
Microcontroller Functions
A microcontroller, U17, is provided on this assembly to supervise the operation of the
receiver chip and the tuner. In addition, the microcontroller also interfaces to the front
panel LCD display via connector J24 and pushbutton interface on J27. On power up, the
microcontroller sets the tuner to the last channel that was selected when the unit was
powered down. In addition, the microcontroller also configures the digital receiver to
operate as an 8 VSB receiver. The communication between all of the devices on this
board is via an I2C serial bus that is local to this board.
Jumper and DIP Switch Settings
This board can be used in various assemblies. When this assembly is installed in the
Innovator CXB product, the jumpers on J7 and J8 should be placed between pins 2 and 3
for normal operation. The DIP switch SW1 should be configured as indicated in Table
12.
Table 12: Innovator CX Receive /Demodulator/Transcoder Dip Switch SW1
Position
Function When Switch is Off When Switch is On
SW1-1 Tuner Type Original Tuner
(DTT765xx) Recent Tuner (DTT7680x)
SW1-2 Signal Strength Gain Gain = 8.0 Gain = 9.3
SW1-3 Special Channel Plan Normal Channels 2, 3, or 4 are offset
up 4 MHz
SW1-4 Reserved for Future
SW1-5 Reserved for Future
SW1-6 Reserved for Future
SW1-7 Reserved for Future
SW1-8 Operation Type Transcoder Operation Innovator CX/CXB Operation
NOTES: SW1-8 operation is available in software versions greater than or equal to 2.3
with hardware versions greater than or equal to D0, unless the board was factory
modified.
These switch positions are factory set for your system and should not be changed.
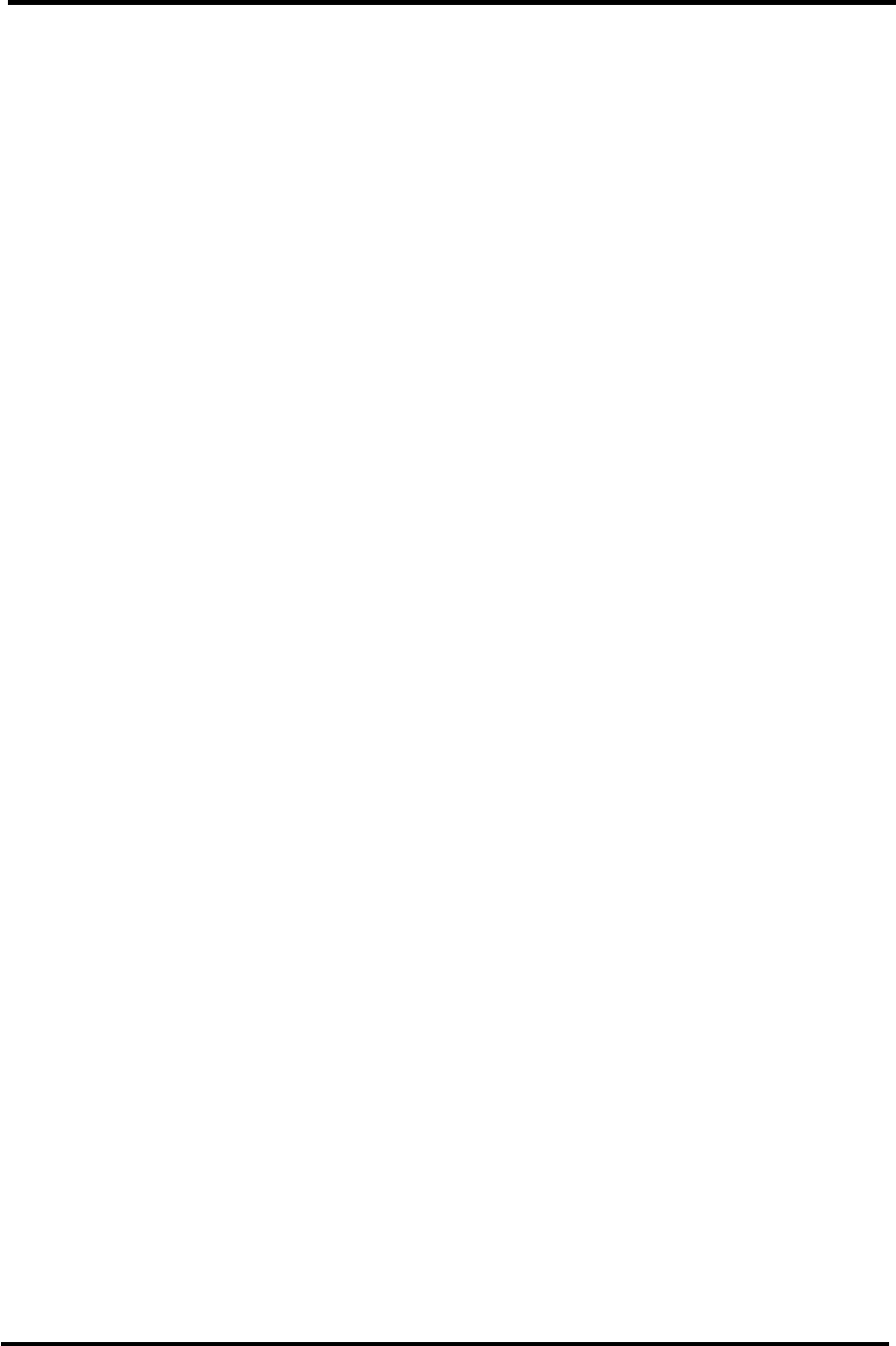
Innovator CU0TD-1/CU0RD-1 – CU4TD/CU4RD Board Descriptions
ATSC Transmitter/Regenerative Translator
Instruction Manual, Rev. 1 56
(A2) Digital Modulator (1316332)
SMPTE-310 or ASI input
The digital modulator board accepts a SMPTE-310 or ASI input at the SMA
connector J42 from the 8 VSB demodulator board in a RD system or directly from
the RF input jack on the rear panel of the drawer in a TD system. This input is
applied to a high speed window comparator U21 that adjusts the level to a low
voltage TTL signal to be used by the Altera FPGA, U3. The SMPTE-310 signal is
input to the FPGA to recover the clock and the data. A portion of the clock and
recovery circuit is performed by a high-speed comparator, U17, which functions
as an external delay circuit.
Channel Coder
The FPGA subsequently uses the SMPTE-310 clock and data as the input to the
channel coder contained inside the FPGA. The channel coder is a series of DSP
blocks defined by the ATSC standard for 8 VSB data transmission. These blocks
include the data randomizer, Reed Solomon Encoder, data interleaver, trellis
coder, and sync inserter.
The channel coder portion inside the FPGA generates the 8 distinct levels in an 8
VSB system. These levels are subsequently input to a linear equalizer that
provides for frequency response correction in the transmission path. The linear
equalizer is a 67 tap FIR filter that is loaded with tap values from the
microcontroller, U1, located on this board. The output of the linear equalizer is
then input to two pulse shaping filters, an in phase (I) and a quadrature (Q) filter
that are also located inside the FPGA. The pulse shaping filters are FIR filters
that have fixed tap values that are preset inside the FPGA. The output of the
pulse shaping filters is then applied to a Pre-Distortion Linearizer chip, U4, which
can be used to correct for nonlinearities in the data transmission path. The
output of the Pre-Distortion chip is gain scaled and output to a dual D/A
converter, which output a baseband I and Q analog signal.
Analog Output Section
The baseband I and Q signals from the D/A converter are applied to differential
analog filters that remove some of digital artifacts from the D/A conversion
process. The output of the I channel filter is then mixed with the pilot frequency,
46.69 MHz, using mixer U30. The output of the Q filter is mixed with the pilot
frequency that is phase shifted 90 degrees using mixer U34. The mixers are
current driven devices, therefore when the outputs of U30 and U34 are connected
together, they provide a combined output. This combined output is subsequently
input to a final differential output filter which provides the final RF output at the
SMA connector, J38. To maintain signal integrity, this RF output is connected to
the SMA connector J39 with a small semi-rigid cable assembly. The final RF
output then appears at J1-2B.
Pilot Frequency Generation
The on channel pilot, which is used in the mixing process, is generated from a
VCXO, U37 that is phase locked to a 10 MHz reference. The VCXO and the 10
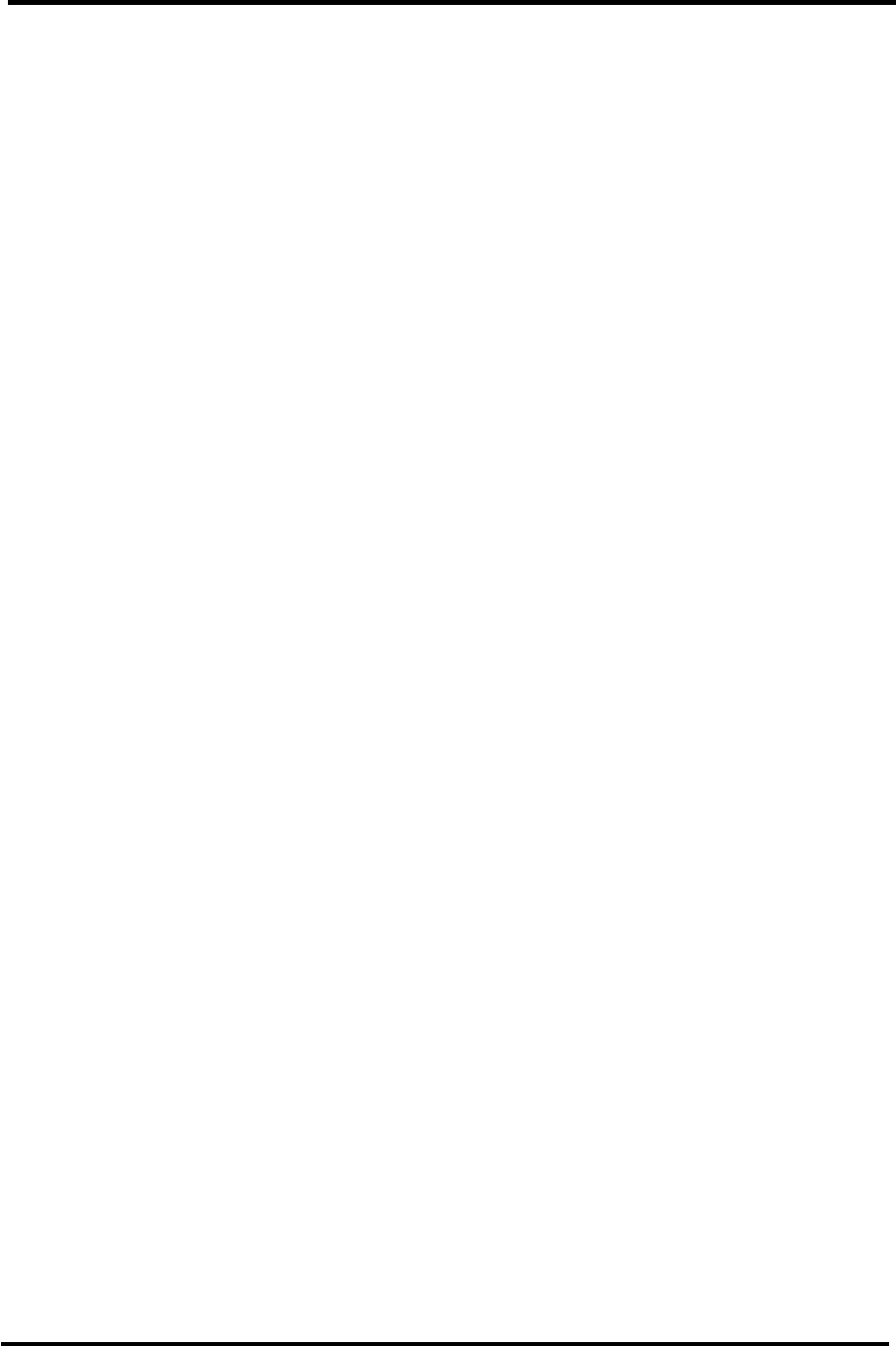
Innovator CU0TD-1/CU0RD-1 – CU4TD/CU4RD Board Descriptions
ATSC Transmitter/Regenerative Translator
Instruction Manual, Rev. 1 57
MHz are divided down to a common frequency, which is then compared internal
to the FPGA. The FPGA subsequently provides error signals to an analog phase
locked implemented with op amp stages U45-A, B and C. The output of these
compensation stages is used as the control voltage to the VCXO, U37. The
phase locked output of U37 is applied to an analog filter to remove harmonics of
the pilot and then input to the quadrature splitter Z1. The outputs of Z1 are used
as the inputs to the mixers in the analog output section.
Voltage Requirements
The ±12 VDC and +5VDC needed for operation of the board connect to J1 on the
Power Conditioner Board (1309404) which delays the +5VDC so that the ±12 VDC
to the 8 VSB Modulator Board is applied first. The voltage output of the power
conditioner board is at J2 that is jumpered to J30 on the 8 VSB modulator board.
The ±12 VDC connect to the 8 VSB modulator board at J30-1. The +12V SYS
connects to J18A, B & C and to regulator circuits. The +12V SYS is filtered by L2,
L3, C105 and C106 before it is applied to the rest of the board as +12VQ and
+12VI. The -12 VDC SYS connects to J19A, B & C and to regulator circuit. The -
12V SYS is filtered by L6, L7, C111 and C112 before it is applied to the rest of the
board as -12VI and –12VQ.
The +12V SYS also connects through the resistor R81 to provide +5V EXT to the
rest of the board, and to the regulators U23 that provides +3.3V to the rest of the
board and to U27 that provides +1.8V output. The +3.3V also connects to U24
that supplies +1.5V output. The +12V SYS connects to the regulator U25 and U26
to supply the +5VA output. The output of U25 also connects to U28, which
provides the +5V output to the rest of the board. +12V SYS is filtered by L4 and
C107 to provide the +12V output to the board. The –12V SYS also connects to the
regulator U22 that provides the –5V VA to the rest of the board. -12V SYS is
filtered by L5 and C108 to provide the -12V output to the board.
(A5) ALC Board, Innovator CX Series (1315006 or 1308570)
The ALC Board, Innovator CX Series, is used to control the RF drive power to the RF
amplifier chain in the CU0TD/RD-1 thru CU0TD/RD-5 systems. The board accepts an 8-
VSB RF input signal at a nominal input level of -3 dBm average power and amplifies it to
whatever drive level is necessary to drive the final RF amplifier in the drawer to full
power. The input signal to the board at J1 is split by U4, with one half of the signal
driving a PIN diode attenuator, DS1 and DS2, and the other half driving a detector, U13,
that is used to mute the PIN attenuator when there is no input signal. The output of the
PIN attenuator is sent to two cascaded amplifiers, U2 and U3, which are capable of
generating +10 dBm average power from the board at J2.
The PIN attenuator is driven by an ALC circuit or by a manual fixed voltage bias,
depending on the position of switch S1. When the switch is pointing to the left, looking
from the front of the drawer, the ALC circuit is enabled. When the switch is pointing to
the right, the ALC circuit is disabled and the PIN attenuator is controlled through the
Manual gain pot R62. When the switch is in either ALC or manual, the voltage in the
unused circuit is preset low by the circuitry connected to pins 4-6 on SW1. This allows
the RF power to ramp up slowly to full power when the switch changes positions. CR8,
C33 and associated components control the ramp up speed of the manual gain circuit.
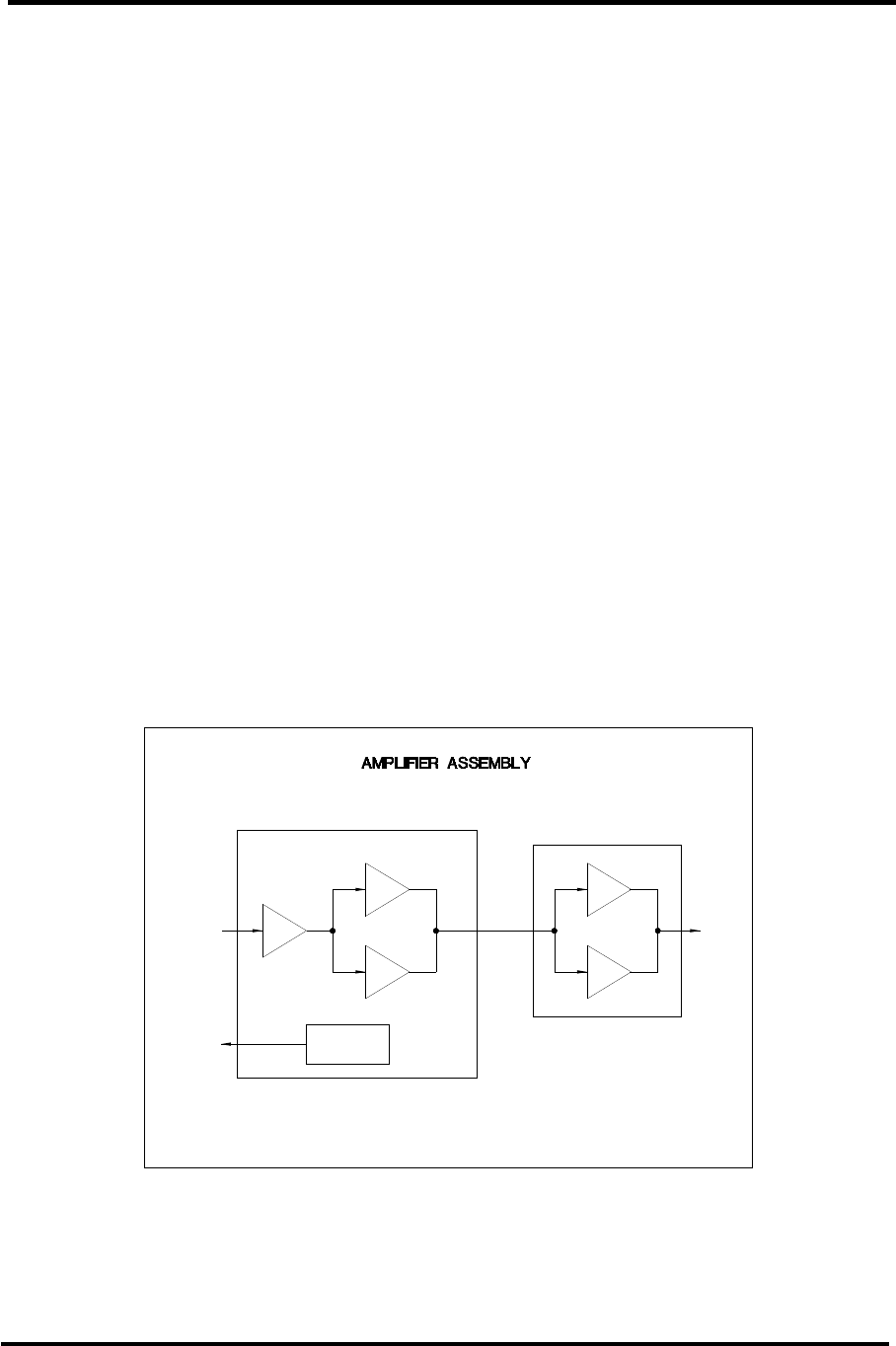
Innovator CU0TD-1/CU0RD-1 – CU4TD/CU4RD Board Descriptions
ATSC Transmitter/Regenerative Translator
Instruction Manual, Rev. 1 58
CR9, C42 and their associated circuits do the same thing for the ALC circuit. The
practical effect of this is to preset the RF drive power to near zero output power when
enabling and disabling the ALC, followed by a slow controlled ramp up of power.
The ALC circuit normally attempts to hold the drawer output power constant, but there
are four faults that can override this. These faults are Input Fault, VSWR Cutback Fault,
VSWR Shutdown Fault and Overdrive Fault.
The Input Fault is generated by comparator U7C and presets the PIN attenuator and ALC
circuit to maximum attenuation whenever the input signal drops below about -7 dBm.
Test point TP2 allows the user to measure the detected input voltage.
The VSWR cutback circuit is set so that the ALC circuit will start reducing RF drive once
the Reflected power reaches a level of about 6% and will keep reducing the drive to
maintain that level. The cutback is generated by U8A, U8B and their associated
components that diode-or the metering voltages. The forward power is scaled to
2V = 100 % and the reflected power is scaled to 2V = 25%. The Reflected metering
voltage is doubled again by U8B so that when the voltage of U8B exceeds the voltage at
the output of U8A, the reflected power takes over the ALC circuit. Once the U8B voltage
drops below the forward power at U8A, the forward power takes over again.
The VSWR shutdown circuit will shut the drawer down if the Reflected power increases to
15% or higher, which can happen if the drawer sees reflected power when the ALC is in
manual.
The Overdrive protection looks at a sample of the RF signal that is applied to J1 of the
board. The peak level of this signal is detected and can be measured on TP1. This
voltage is applied to a comparator with the threshold set by R38. If this threshold is
exceeded, the ALC circuit mutes then ramps up to try again. This circuit also works in
manual gain as well.
Heatsink
Temperature
Sensor
RF Input
+10 dBm
RF Output
+46 dBm
+32 dBm
NOTE: There are a number of different (A6) Amplifier Assemblies used in the multiple
CX transmitter and driver drawers. They are listed in the following sections. Use the
assembly that applies to your particular driver or transmitter or translator.
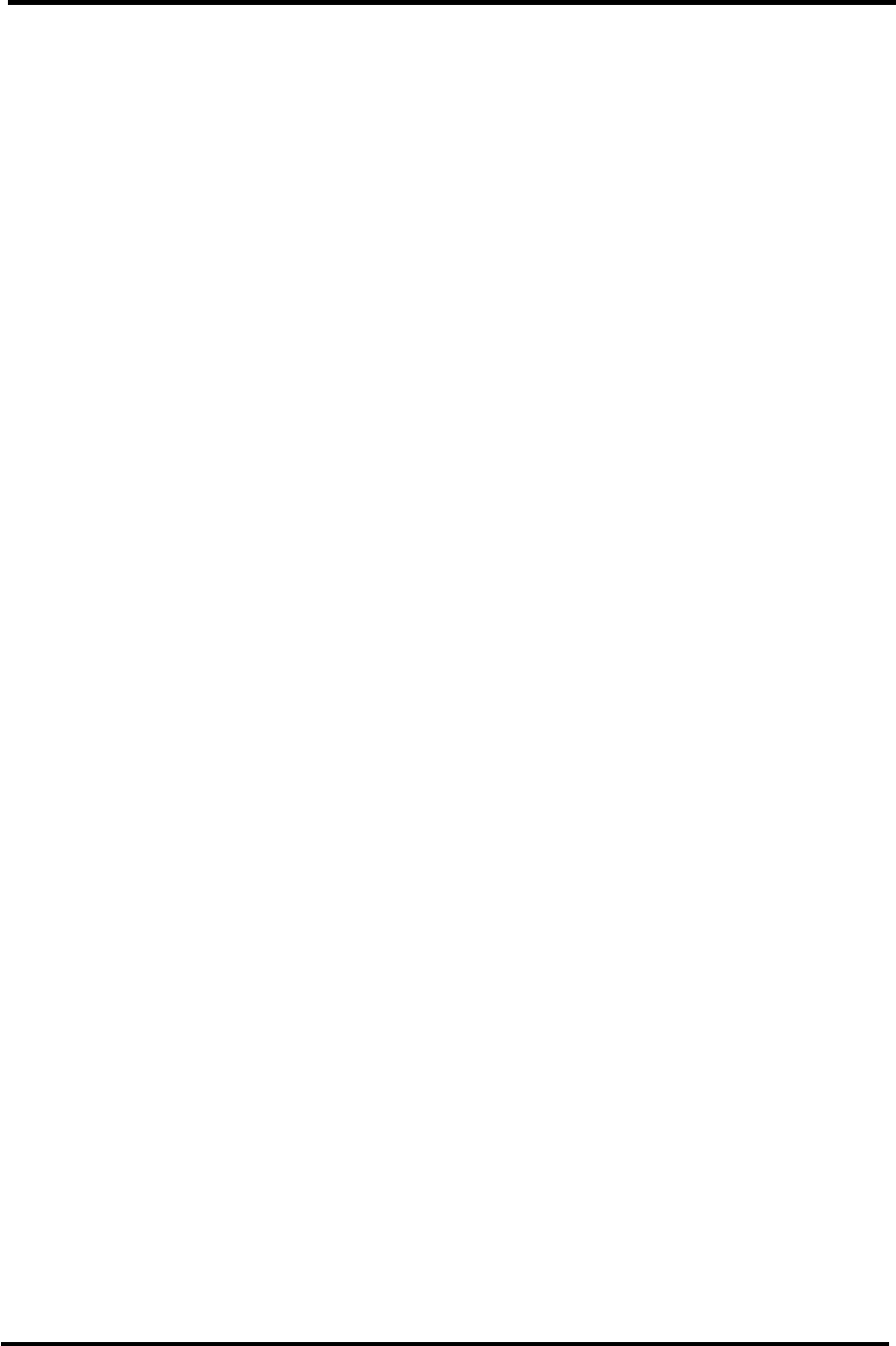
Innovator CU0TD-1/CU0RD-1 – CU4TD/CU4RD Board Descriptions
ATSC Transmitter/Regenerative Translator
Instruction Manual, Rev. 1 59
(A6) Amplifier Assembly (1309621) – Used in the CU0TD/RD-1
The (A6) Amplifier Assembly (1309621) is made up of (A6-A1) the 2 Stage UHF
Amplifier Board, 24V (1309608). The assembly has approximately 33 dB of gain.
(A6-A1) 2 Stage UHF Amplifier Board, 24V (1309608)
The 2 Stage UHF Amplifier Board, 24V (1309608) consists of a driver stage with a
gain of +14dB and two parallel connected final amplifier stages each with a gain
of +14dB. The working point settings for the 2 Stage Amplifier Board are factory
set using the potentiometers R32 for Q2, R15 for Q1, and R24 for Q3 and should
not be altered. The input RF connects to the first amplifier stage Q2. The output
is split by U2 and connected to the final amps. The final amplification circuit
consists of parallel-connected push-pull LDMOS amplifier circuits Q1 and Q3
operating in class AB each with approximately 14 dB of gain. The board uses a
power supply voltage of 24V. The RF transistors are operated at a voltage of 24V
generated by the voltage regulators U6 and U7 for Q2, U5 and U3 for Q3 and U1
and U3 for Q1, which provide a separate regulated voltage to each transistor. In
order to match the LDMOS impedance to the characteristic impedance of the
input and output sides, matching networks are located before and after the
amplifier circuits. The hybrid coupler U2 splits the input to the parallel amplifiers
and the hybrid coupler U4 combines the amplified outputs. The combined output
connects through a directional coupler to J1, the RF output jack of the board.
The directional coupler provides an RF sample at J3 that is used by an external
overdrive protection circuit located on (A5) the ALC Board. The RF output of the
board is 6W maximum 8-VSB. At this power level the board draws approximately
3.6A total from the power supply.
(A6) Amplifier Assembly (1315008 used w/External Axciter Drawer or 1312566
used in all other applications) – Used in the CU0TD/RD-2 and CU0TD/RD-3
The (A6) Amplifier Assembly (1312566 or 1315008) is made up of (A6-A1) the 2 Stage
UHF Amplifier Board (1308784) and (A6-A2) the RF Module Pallet, Philips, High Output
(1309580). The ALC Board (1308570 is used in the 1312566 Assembly & the 1315006
is used in the 1315008 Assembly) is also part of this assembly. The assembly has
approximately 36 dB of gain.
(A6-A1) 2 Stage UHF Amplifier Board (1308784)
The 2 Stage UHF Amplifier Board, (1308784) consists of a driver stage and a
parallel connected final amplifier stage which have a total gain of approximately
23 dB. The working point settings for the 2 Stage Amplifier Board are factory set
using the potentiometers R32 for Q2, R15 for Q1, and R24 for Q3 and should not
be altered. The input RF connects to the first amplifier stage U2, which has a
gain of approximately 14 dB. The output is split by U2 and connected to the final
amps. The final amplification circuit consists of parallel-connected push-pull
LDMOS amplifier circuits Q1 and Q3 operating in class AB each with
approximately 14 dB of gain. The board uses a power supply voltage of 28-32V.
The RF transistors are operated at a voltage of 24V generated by the voltage
regulators U1 for Q1, U5 for Q3 and U6 for Q2, which provide a separate
regulated voltage to each transistor. In order to match the LDMOS impedance to
the characteristic impedance of the input and output sides, matching networks
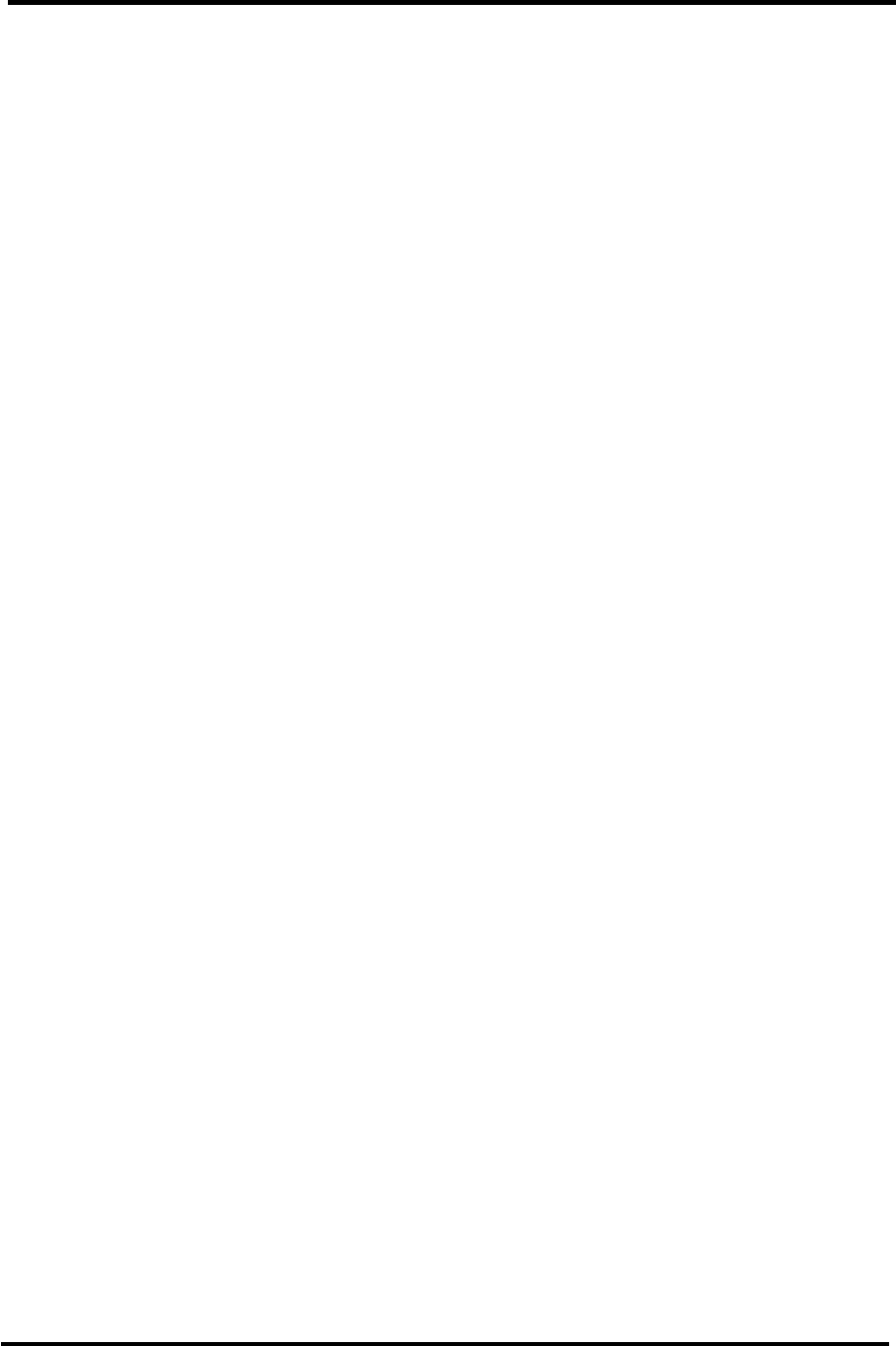
Innovator CU0TD-1/CU0RD-1 – CU4TD/CU4RD Board Descriptions
ATSC Transmitter/Regenerative Translator
Instruction Manual, Rev. 1 60
are located before and after the amplifier circuits. The hybrid coupler U2 splits
the input to the parallel amplifiers and the hybrid coupler U4 combines the
amplified outputs. The combined output connects through a directional coupler
to J1, the RF output jack of the board. The directional coupler provides an RF
sample at J3 that is used by an external overdrive protection circuit located on
(A5) the ALC Board. The RF output of the board is being used as a driver and
has a level of 3W maximum 8-VSB. At this power level the board draws
approximately 1.8A total from the power supply.
(A6-A2) RF Module Pallet, Philips, High Output (1309580)
The RF Module Pallet, Philips, High Output, (1309580) is made from the RF
Module Pallet, High Output w/o Transistors (1309579). This broadband amplifier
is for the frequency range of 470 to 860 MHz. The amplifier is capable of
delivering a maximum output power of 100 Watts peak, with an amplification
factor of approximately 13 dB.
The amplification circuit consists of push-pull amplifier blocks V1 and V2,
connected in parallel, operating in class AB. In order to match the impedance of
the transistors to the characteristic impedance of the input and output sides,
matching networks are placed ahead and behind the amplifier blocks.
Transformers Z3 and Z4 at the input to V1 and V2 and Z5 and Z6 at the output
of V1 and V2 serve to balance the input and output signals. The paralleling
circuit is achieved using the 3-dB input coupler Z1 and the second part of Z1,
which is the 3-dB output coupler. The working point settings of the amplifier
circuits are factory implemented by means of the potentiometers R11 and R12
and should not be altered. The combined output of Z1 connects to the RF output
jack of the board at J2. The output of the amplifier assembly at J2 connects to J1
on (A7) the output detector board.
(A6) Amplifier Assembly w/878 devices (1312191) – Used in the CU0TD/RD-4
& CU0TD/RD-5
The (A6) Amplifier Assembly (1312191) is made up of (A6-A1) the 1 Watt Amplifier
Board (1310282), (A6-A2) the BL871 Single Stage Amplifier Board (1311041), and (A6-
A3) the Dual 878 Pallet Assembly (1313170 or 1310138). The ALC Board (1308570) is
also used with this assembly. The entire amplifier assembly has approximately 36 dB of
gain.
(A6-A1) 1 Watt UHF Amplifier Module (1310282)
This board is a broadband UHF amplifier capable of producing an output power in
excess of 1W Peak. It is normally operated at an average power of 100 mW 8VSB
or lower. It consists of two AH202 MMICs operating in parallel. The board is
powered by +12 VDC and has no adjustments. The board has a gain of
approximately 16 dB.
(A6-A2) BL871 Single Stage Amplifier Board (1311041)
This board consists of a single stage amplifier operating at +42 VDC. The board
has an overall gain of about 16 dB. The input to the board passes through a 3 dB
attenuator consisting of R11-R13, and then is applied to the gain stage, which
consists of a single LDMOS transistor Q1 operating in Class AB. The bias voltage
for the transistor is generated through the voltage regulator U1, and is adjusted
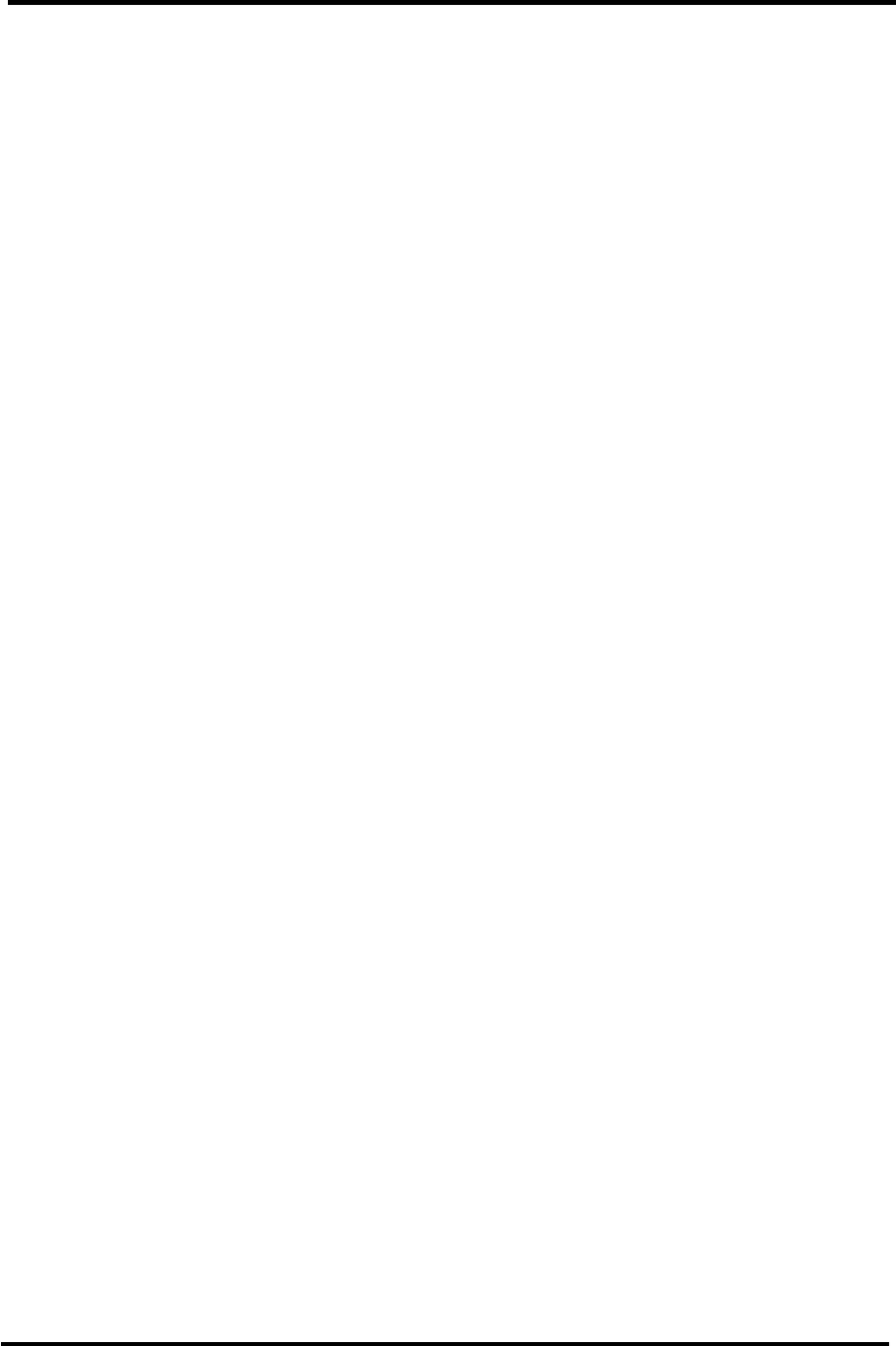
Innovator CU0TD-1/CU0RD-1 – CU4TD/CU4RD Board Descriptions
ATSC Transmitter/Regenerative Translator
Instruction Manual, Rev. 1 61
using pots R2 and R3. The Diode CR1 provides temperature compensation for the
transistor. The transistor will output over 20 Watts DVB, but is typically used in a
driver application at much lower output powers. The Directional Coupler U1
provides a 20 dB down sample of the RF output.
(A6-A3) Dual 878 Pallet Assembly (1313170 or 1310138)
This board is a LDMOS UHF power amplifier consisting of two power transistors
operating in parallel. The board operates on a power supply voltage of +42 VDC.
The voltage regulator U1 steps down the voltage to provide a bias voltage to
each transistor. The diodes CR1 and CR3 are used to temperature compensate
the bias voltage. As the RF transistors heat up, the diodes also heat up, causing
the voltage across them to drop, lowering the bias voltage to the RF transistors
so that it remains constant with device temperature.
The board has a gain of approximately 17 dB, and can operate at an output
power of 150 Watts average power DVB, 220 Watts average power ATSC, or 440
Watts Peak Sync plus sound in analog operation. The transistors are operated in
quadrature, with one transistor operating 90 degrees out of phase of the other,
which provides for a very good return loss across the UHF band on both the input
and output of the board.
(A6) Amplifier Assembly w/888A devices (1316132 used w/External Axciter
Drawer or 1315381 used in all other applications) – Used in the CU0TD/RD-4 &
CU0TD/RD-5
The (A6) Amplifier Assembly (1316132) is made up of (A6-A1) the 1 Watt Amplifier
Board (1315730), (A6-A2) the BL881 Single Stage Amplifier Board (1314882, (A6-A3)
the Dual 888A Pallet Assembly (1315347) and (A6-A5) a DC-DC Converter Board
(1315335). The ALC Board (The ALC Board (1308570 is used in the 1315381 Assembly
& the 1315006 is used in the 1316132 Assembly) is also used with this assembly. The
entire amplifier assembly has approximately 36 dB of gain.
(A6-A1) 1 Watt UHF Amplifier Module (1315730)
This board is normally operated at a power of 200 mW pk sync or lower. It
consists of two AH202 MMICs operating in parallel. The board is powered by +12
VDC and has no adjustments. The amplifier module has a gain of approximately
17 dB.
(A6-A2) BLF881 Single Stage Amplifier Board (1314882)
This board consists of a single stage amplifier operating at +48 VDC. The board
has an overall gain of about 16 dB. The input to the board passes through a 3 dB
attenuator consisting of R11-R13, and then is applied to the gain stage, which
consists of a single LDMOS transistor Q1 operating in Class AB. The bias voltage
for the transistor is generated through the voltage regulator U1, and is adjusted
using pots R2 and R3. The Diode CR1 provides temperature compensation for the
transistor. The transistor will output over 40 Watts pk sync, but is typically used
in a driver application at much lower output powers. The Directional Coupler U2
provides a 20 dB down sample of the RF output at the SMA Jack J4.
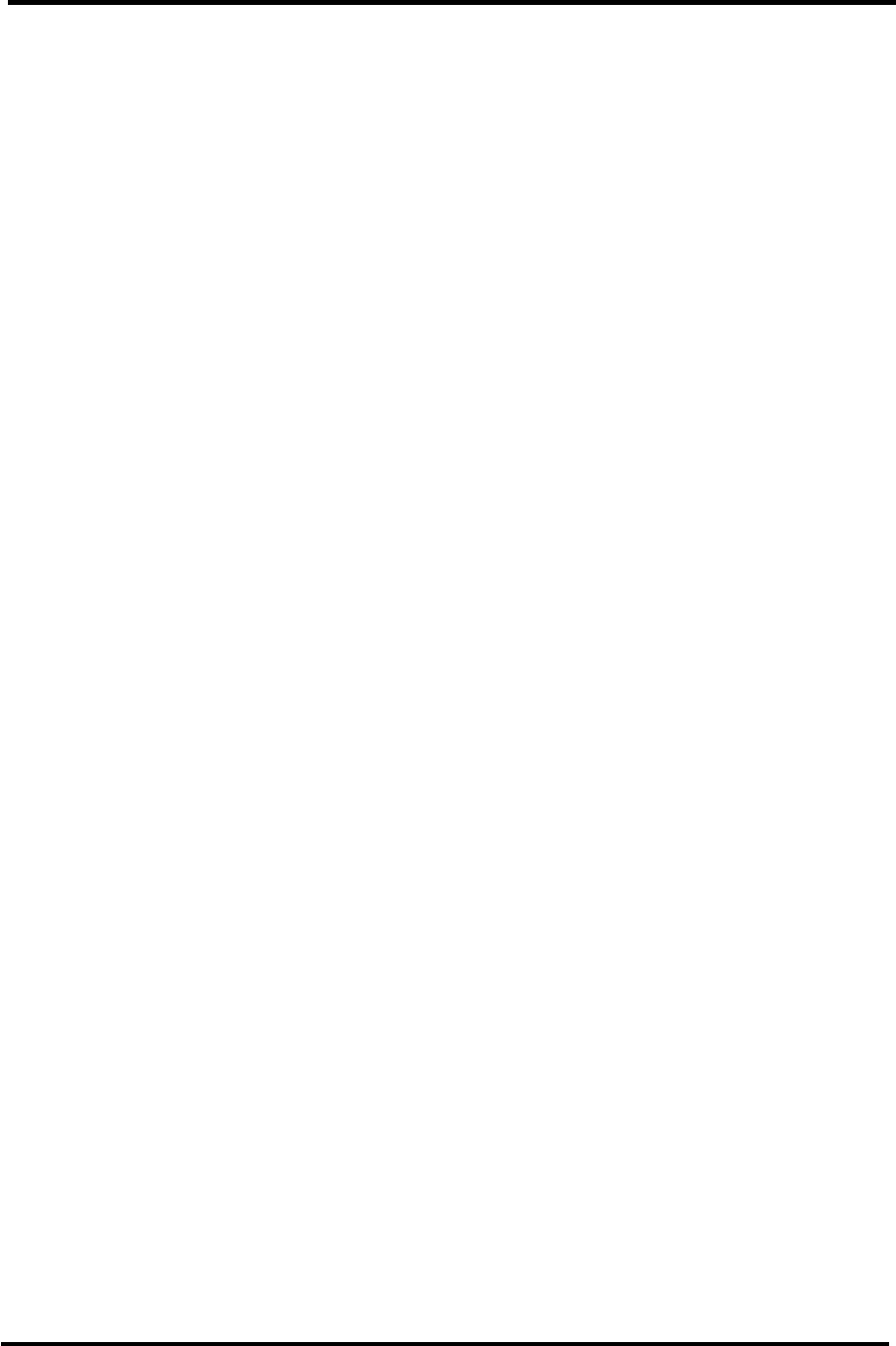
Innovator CU0TD-1/CU0RD-1 – CU4TD/CU4RD Board Descriptions
ATSC Transmitter/Regenerative Translator
Instruction Manual, Rev. 1 62
(A6-A3) Dual BLF888A Pallet Assembly (1315347)
This board is a UHF LDMOS power amplifier consisting of two pair of power
transistors operating in parallel. The board operates on a power supply voltage
of +48VDC. The voltage regulator U1 steps down the voltage to provide a bias
voltage to each pair of transistors. The diodes CR1 and CR3 are used to
temperature compensate the bias voltage that is applied to the Q1 and Q2 RF
transistor pairs. As the transistor pairs heat up, the diodes also heat up, causing
the voltage across them to drop, lowering the bias voltage to the RF transistors
so that the voltage remains constant with device temperature.
The board has a gain of approximately 18 dB. The RF input to the board is split
by HL1 and each output is connected through hybrid couplers to the Q1 and Q2
transistor pairs. The amplified outputs of the transistor pairs are connected
through hybrid couplers to the combiner HL2. The transistor pairs are operated
in quadrature, with one transistor pair operating 90° out of phase of the other,
which provides for a very good return loss across the UHF band on both the input
and output of the board.
(A6-A5) DC/DC Converter Board (1315335)
The DC/DC Converter Board provides the +12VDC needed to operate the 1 Watt
Amplifier board in the assembly. The DC/DC Converter Board acts as a switching
supply using U7 and the Q1 MOSFET. The switching voltage is applied to the
primary of the T1 Transformer. The AC output of the transformer is rectified by
CR1 and filtered before the +12 VDC is connected to the output of the board at
J3-3. A feedback path is provided through the other two coils of the transformer
which is fed to the IC U7 to maintain the oscillation.
(A7) Output Detector Board (1308685 or 1312207 in the CU0TD/RD-2 thru
CU0TD/RD-5)
The (1308685 and 1312207) output detector boards are identical in operation except the
(1312207) board can be used as either an average, for digital, or peak, for analog,
detector board using jumpers on J5 and J6. The (A7) Output Detector Board provides
forward (2V=100%) and reflected (2V=25%) power samples to the CU Control Board for
metering and monitoring purposes. R7 is the reflected power calibration pot and R23 is
the forward power calibration pot. A Forward power sample, -10 dBm, connects to J4 on
the board, which is cabled to the front panel sample jack of the drawer. The RF output
of the board, typically +46 dBm, is at J2, which is cabled to J9 the RF Output Jack of the
drawer.
(A8) Control Card, Innovator CX (1312543)
The Innovator CX control board provides the overall system control for the CXB system.
There are two main elements of the board, U7 and U9. U7 is a programmable logic
device that is loaded with firmware, which provides the overall system control. It
decides whether or not to allow the system to generate RF output power, and turns the
+32 VDC power supply on and off depending on whether or not it is receiving any faults,
either faults generated on board, or faults generated externally. The second major
component of the board is the microcontroller U9, which controls the front panel
indications and drives the display. The U9 microcontroller is not involved in the decision
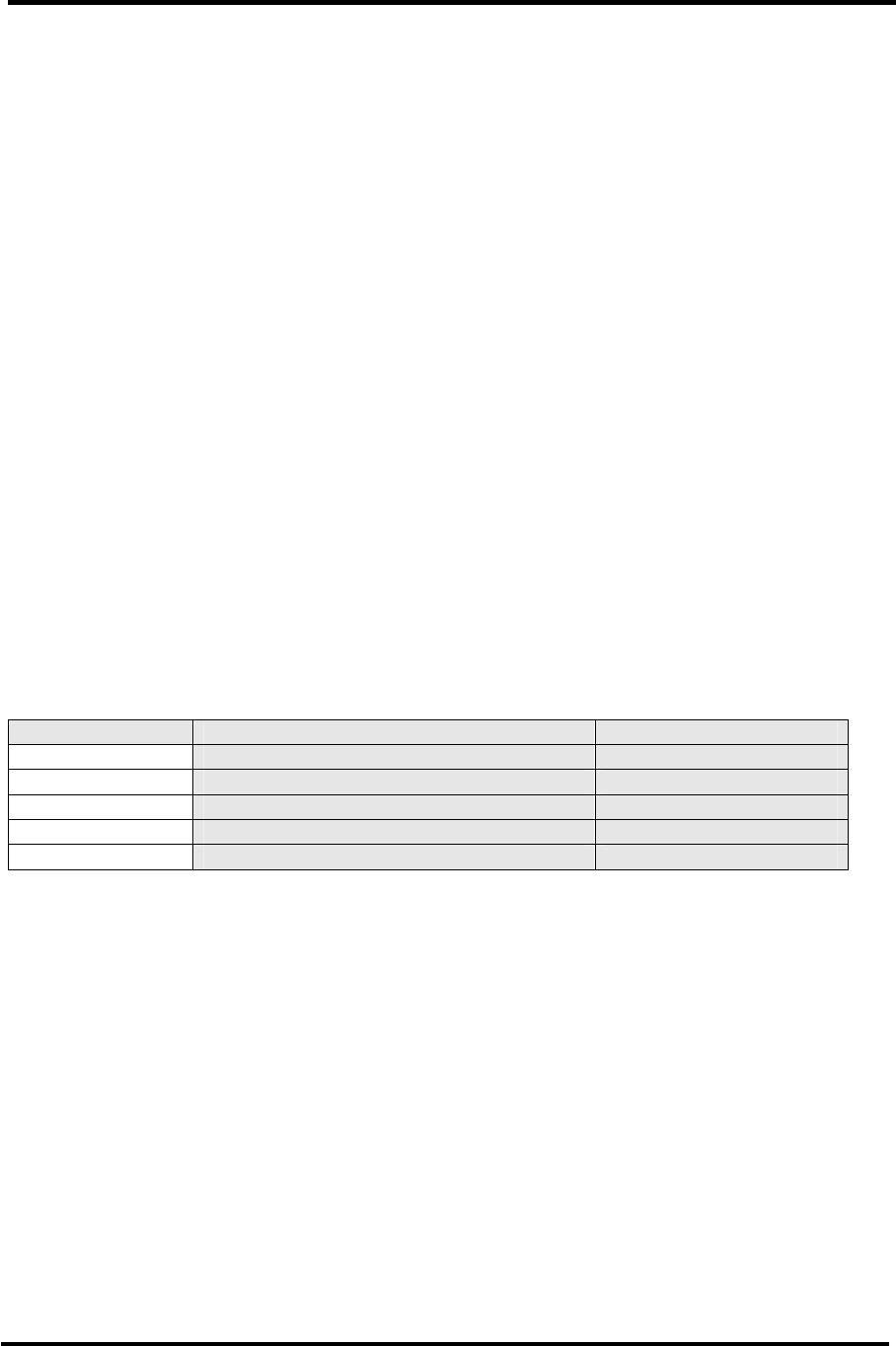
Innovator CU0TD-1/CU0RD-1 – CU4TD/CU4RD Board Descriptions
ATSC Transmitter/Regenerative Translator
Instruction Manual, Rev. 1 63
making process, U7 does that. Rather, it is layered on top of U7 and is the EPLD's
interface to the outside world. Information is passed between the microcontroller and
the EPLD. The microcontroller communicates information to and from the front panel
and sends the EPLD the information it needs to decide whether or not to allow the
system to turn on. The front panel viewable LEDs DS3 for Operate/Standby and DS4 for
Status indicate the current operating condition of the system are mounted on and
controlled by this board. The U9 microcontroller can also communicate, using the
Optional Ethernet Kit, with a daughter card that allows the user to view remote control
parameters via a web Ethernet interface.
The ±12 VDC and +5 VDC from the (A9) power supply and the +32 VDC from the (A10)
power supply are routed to the other boards in the drawer through this board. The +32
VDC power supply operates all the time, and connects the +32 VDC to the board at J19-
1, 2, & 3 with 5 common. Q13 on the control board is turned on and off to gate the +32
VDC, which connects through J19-6, 7 & 8, to the RF output stages.
The ±12 VDC and +5 VDC input voltages to this board is connected through J21 and
filtered before being connected to the rest of the board. +12 VDC connects through
J21-1, +5VDC through J21-2 & 3, and -12 VDC through J21-6. Common connections for
the input voltages are connected to J21-4 & 5. The ±12 VDC and +5 VDC are used on
this board and also routed to the other boards in the drawer through this board. The
+3.3 VDC for the microcontroller and programmable logic array, mounted on the board,
is provided by the voltage regulator IC U6 from the filtered +5 VDC input. The output of
U6 can be adjusted to +3.3 VDC using R120.
(A9 & A10) Power Supplies used in CU0TD/RD-1 thru CU0TD/RD-5 and Driver
for CU1TD/RD-1 & higher power
Table 13: Model Number with corresponding (A10) Voltages and AC Input Voltages
MODEL (A10) POWER SUPPLY VOLTAGE AC INPUT VOLTAGE
CU0TD/RD-1 +24VDC 115VAC or 230VAC
CU0TD/RD-2 +28VDC 115VAC or 230VAC
CU0TD/RD-3 +30VDC 115VAC or 230VAC
CU0TD/RD-4 +42VDC w/878A or +48VDC w/888A 230VAC
CU0TD/RD-5 +42VDC w/878A or +48VDC w/888A 230VAC
Voltages for the operation of the boards in the drawer are generated by (A9) a +5VDC
and ±12VDC power supply and (A10) a switching power supply which is a different
power supply providing a different voltage in each model. See the chart above. The
115VAC or 230VAC input to the CU0TD/RD-1 thru CU0TD/RD-3 drawer connects through
the AC power cord at J6, the power entry module located on the rear panel of the
drawer.
The CU0TD/RD-4 & CU0TD/RD-5 drawer only operates with 230VAC. An On/Off
10A/250VAC circuit breaker is part of the power entry module. With the circuit breaker
switched On, the (L) line input is wired to F1 a 10 Amp fuse for over current protection.
The AC lines are connected to terminal block TB1, which distributes the AC to (A9 and
A10) the two DC power supplies. There are two varistors, mounted on TB1, connected
from the line input to neutral and to ground for surge protection. The AC in the
CU0TD/RD-4 & CU0TD/RD-5 also connects to the (A11) fan mounted on the rear panel
of the drawer. The fan will run when AC is applied to the drawer and the circuit breaker
is switched On. The +5VDC and ±12VDC outputs of the (A9) power supply connects to
the terminal block (TB2) that distributes the DC to the boards in the drawer. Some of
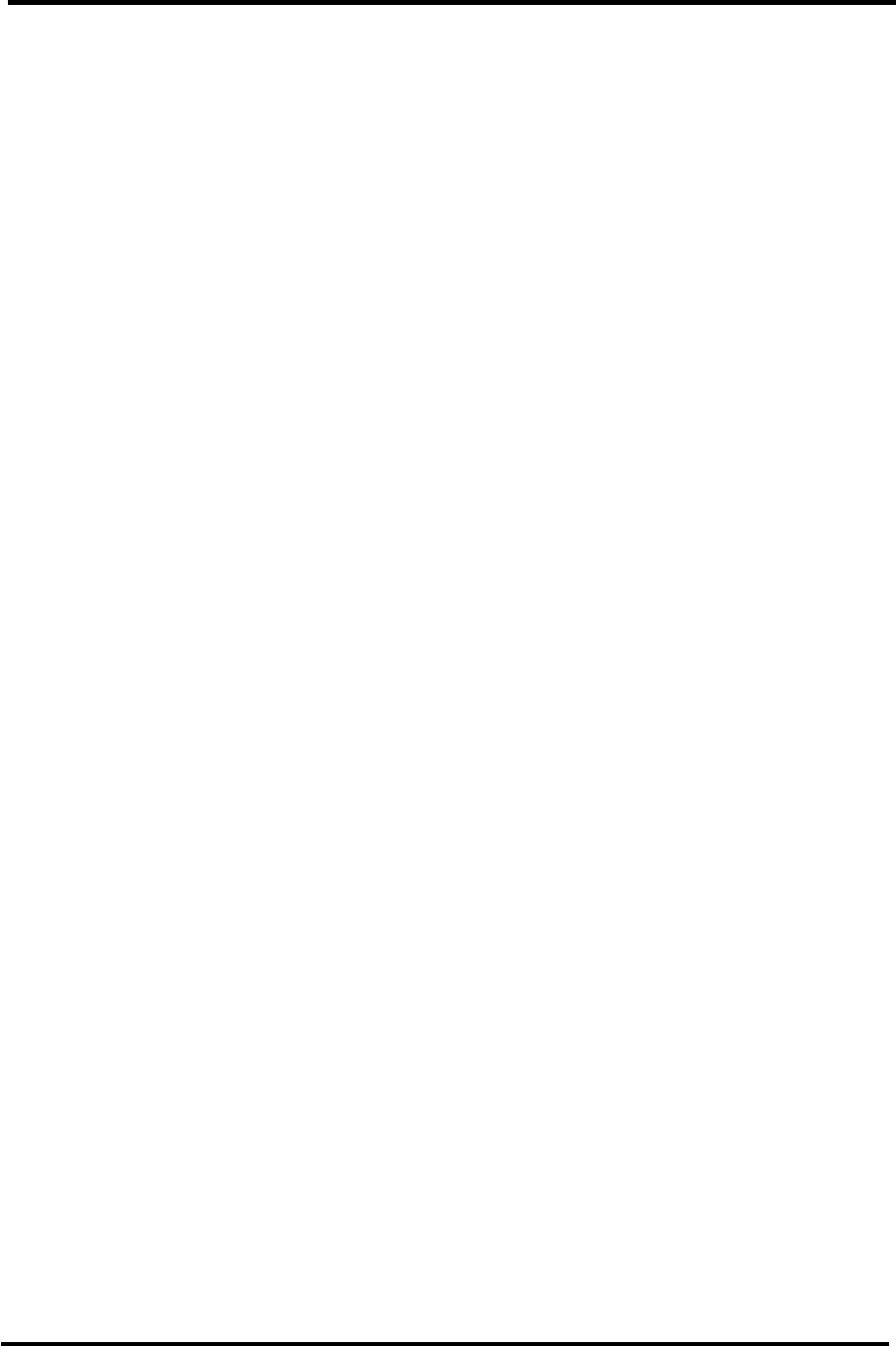
Innovator CU0TD-1/CU0RD-1 – CU4TD/CU4RD Board Descriptions
ATSC Transmitter/Regenerative Translator
Instruction Manual, Rev. 1 64
the +5VDC and ±12VDC outputs connect directly to the 8 VSB Demodulator and 8 VSB
Modulator boards while the other outputs connect through the CU Control Board to the
IF Precorrector, the Digital Upconverter, the ALC, the Amplifier Assembly and the Output
Detector Boards.
The +24/+28/+30/+42/+48VDC VDC outputs of the (A10) power supply connect to the
(A8) CU Control Board, which then supplies the switched +24/+28/+30/+42/+48VDC
VDC to the (A6) Amplifier Assembly. In CU0TD/RD-1 thru CU0TD/RD-3 drawers the DC
output of the (A10) power supply also connects to the (A11) fan mounted on the rear
panel, which will operate when AC is applied to the drawer, the On/Off circuit breaker is
On and the (A10) power supply is operating.
Circuit Description of External System Metering Board which is only used in
Transmitters with multiple external Amplifier Drawers
(A5) System Metering Board (1312666)
The function of the System Metering Board is to detect forward and reflected output power
samples and generate output voltages that are proportional to the power levels of the
sampled signals for use by the control monitoring assembly in the exciter/driver drawer.
There are two identical signal paths on the board: one for forward power and one for
reflected power. A sample of the forward output power, from the external (A11) output
coupler, enters the board at the SMA jack J3. The signal is filtered and connected to
resistors R5, R3 and R6 that form an input impedance-matching network to Pin 3 on U1.
The forward power signal is detected by the RF detector IC U1. The detected output at
pin 7 is split with one half connected to the forward average calibration pot R7, digital,
which adjusts the level of the signal connected to Pin 11 on U2. The other half of the split
is connected to the peak calibration pot R18, analog, which adjusts the level of the signal
connected to Pin 8 on U2. U2 is a Bilateral Switch IC whose output, digital or analog, is
controlled by the selection of the modulation type in the exciter/driver drawer. In this
BTC transmitter the average, digital, output connects to the amplifier IC U3A that is wired
to the SYS_FWD and RMT_FWD Power Metering Outputs. A reading of 2 VDC measured at
TP1 is equal to a 100% Forward Power reading on the meter. The SYS_FWD level
connects to J9 on the board that is cabled to J11 on the exciter/driver drawer for use in
the control monitoring assembly. The RMT_FWD level connects to J10 on the board for
use by remote control and monitoring.
A sample of the reflected output power, from the external (A11) output coupler, enters
the board at the SMA jack J8. The signal is filtered and connected to resistors R26, R22
and R27 that form an input impedance-matching network to Pin 3 on U6. The reflected
power signal is detected by the RF detector IC U6. The detected output at pin 7 is
connected to the reflected calibration pot R25, which adjusts the level of the signal
connected to the amplifier IC U3B that is wired to the SYS_RFLD and RMT_RFLD Power
Metering Outputs. A reading of 2 VDC measured at TP2 is equal to a 25% Reflected
Power reading on the meter. The SYS_RFLD level connects to J9 on the board that is
cabled to J11 on the exciter/driver drawer for use in the control monitoring assembly. The
RMT_RFLD level connects to J10 on the board for use by remote control and monitoring.
+12 VDC enters the board at J9-1, from the exciter/driver drawer and is connected
through a filter and isolation circuit consisting of C31, C14 and L5 before it is connected to
the regulator IC U5. U5 supplies the +5 VDC needed for operation of the ICs on the
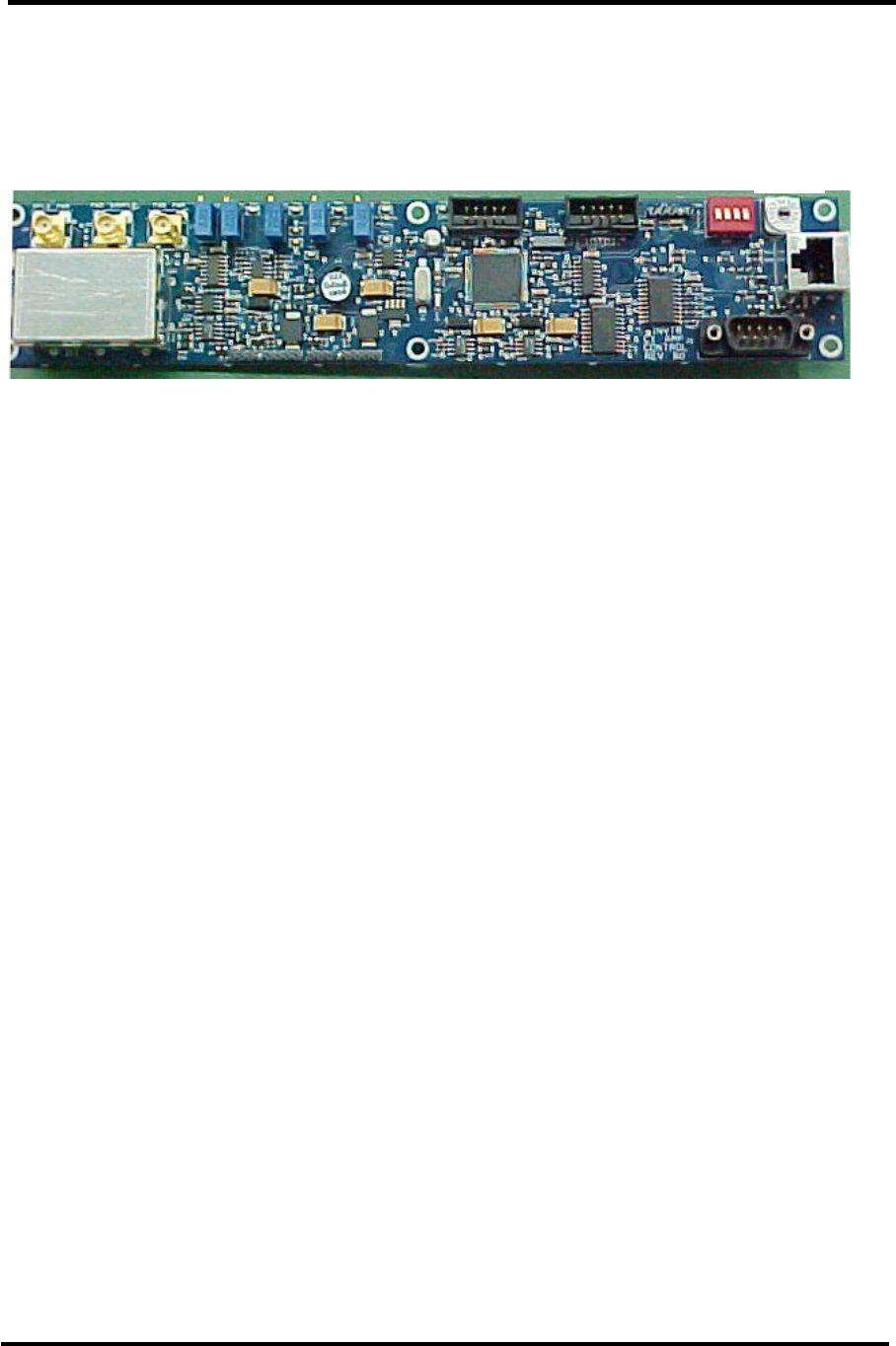
Innovator CU0TD-1/CU0RD-1 – CU4TD/CU4RD Board Descriptions
ATSC Transmitter/Regenerative Translator
Instruction Manual, Rev. 1 65
board. The +5 VDC is connected through a filter circuit consisting of C15, C19 and C21
before it is connected to the rest of the board.
Circuit Descriptions of Boards in the external ATSC Amplifier Drawers
(A7) Amplifier Control Board (1315011 or 1312260)
Amplifier Control Board
The Amplifier Control Board is mounted in the top front facing the rear of the Amplifier
Drawer as shown above.
The Amplifier Control Board uses a Programmable logic device, U12, to control the
amplifier drawer. It takes an enable signal from an external driver drawer, and turns
the power supplies on whenever the driver has told it to turn on, unless it detects faults
internal to the drawer. The board monitors the forward and reflected power, the
heatsink temperature, the pallet currents, and the power supply voltage and will
generate alarm signals if any of those parameters exceed safe limits. The amplifier
drawer has no front panel display other than a two LEDs, one for Status and one for
Enable. The board sends all its output information, including the forward and reflected
levels, back to the driver drawer, through J4, so the information can be displayed on
that drawer's LCD Display. The board will generate a Red Blinking Status LED if it
detects an alarm, fault, prompting the operator to look at the LCD display on the driver
drawer to see what fault has occurred.
A CUB transmitter System can have up to 4 external amplifier drawers and since they
are all the same, without differences in the wiring harness, there needs to be a way to
identify which amplifier drawer is which. The rotary switch SW1 is used to specify the
amplifier ID number which generates a unique serial address so that the individual
amplifier drawers will respond when polled for information.
The +5 VDC inputs to this board are routed through J4-8 and J5-8. The +5 VDC inputs
are diode Or connected so that either the +5VDC from the (A8) power supply or the
+5VDC from the (A9) power supply will operate the board. The +5VDC is split with one
output connected to U1 a voltage regulator IC, which provides +5V and +5V_ANALOG as
outputs. The +5 VDC is filtered before being connected to the rest of the board. The
other +5 VDC output is connected to the regulator IC U2 that supplies +3.3 V to the
microcontroller and programmable logic array.
(A10) Current Metering Board (1309130)
The current metering board measures the current into the RF output amplifier pallets
and supplies this value to the control board. In the single pallet amplifier drawer, there
are two sensing circuits which are used. In the multiple pallet amplifier drawer, there
are four sensing circuits which are used. Each circuit has two parallel .01Ω series
current sensing resistors and a differential input IC that supplies a voltage output that is
proportional to the current for metering purposes. The +42VDC from the (A8) power
SW1
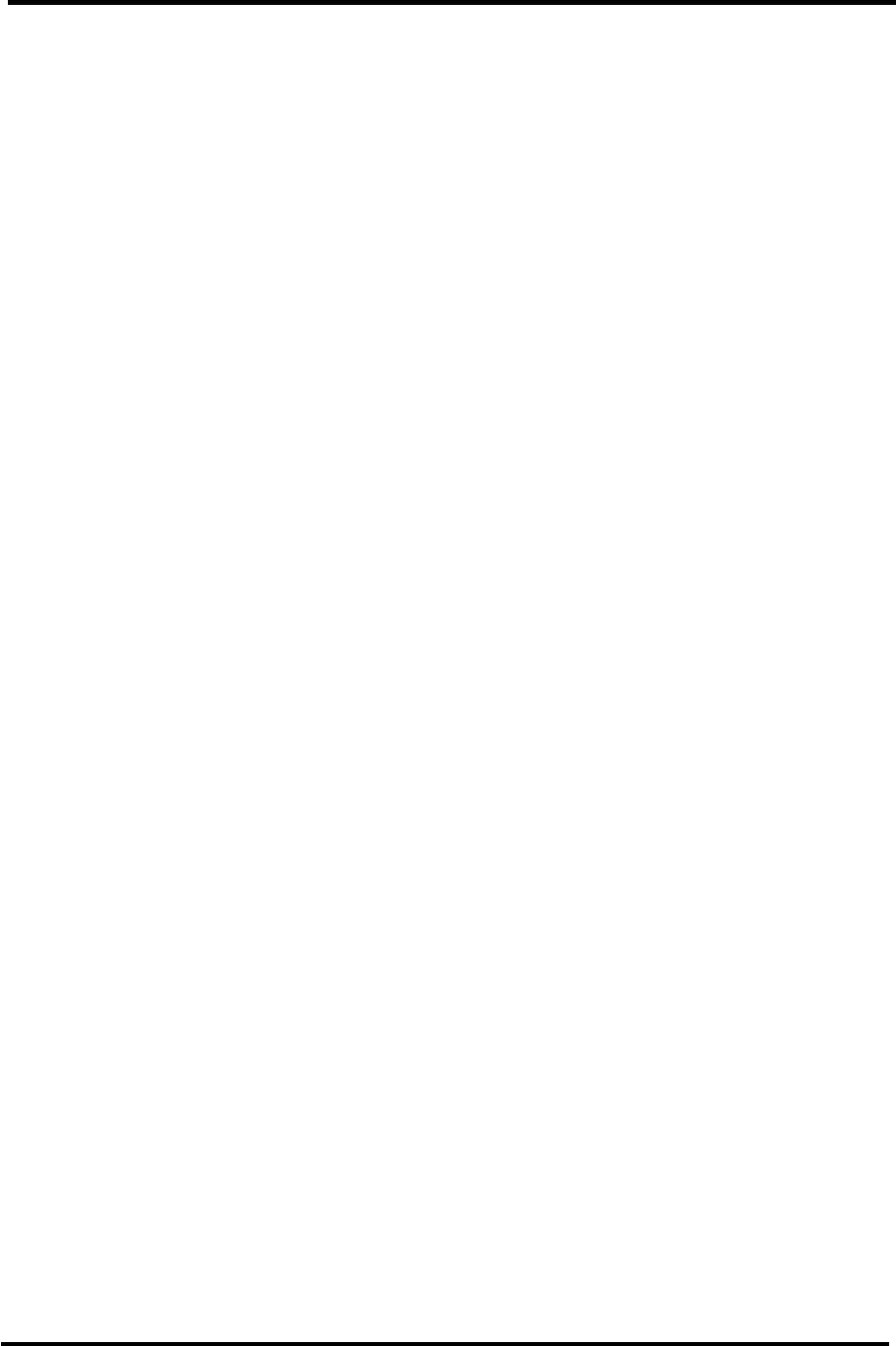
Innovator CU0TD-1/CU0RD-1 – CU4TD/CU4RD Board Descriptions
ATSC Transmitter/Regenerative Translator
Instruction Manual, Rev. 1 66
supply connects to TB2 and TB4 on the board. The +42VDC from the (A9) power supply
connects to TB8 and TB10 on the board. The +42VDC input at the TB2 input senses the
current to the (A1) 878 output amplifier pallet through TB1 on the board. The +42VDC
input at the TB4 input senses the current to the (A2) 878 output amplifier pallet through
TB3 on the board. The +42VDC input at the TB8 input senses the current to the (A3)
878 output amplifier pallet through TB7 on the board. The +42VDC input at the TB10
input senses the current to the (A4) 878 output amplifier pallet through TB9 on the
board.
The two or four sensing circuits are identical therefore only one will be described. For
the (A1) 878 amplifier pallet, the +42VDC from the (A8) switching power supply
connects to TB2. R1 and R2 are the parallel .01Ω current sensing resistors which
supplies the voltage values to the U1 current sense amplifier IC. R11 is a gain adjust,
which is adjusted to eliminate any rSense Error and to place the OpAmp output at 2.61V
for 40Amps sense as measured at TP3. The current sense output at J1-1 connects to
the (A7) control board for metering purposes.
(A5) 2 Way Splitter Board (1313158), in Amplifier Drawer w/two Dual 888A
Pallets
The 2 way splitter board takes the RF Input at J1 (≈12.5 Watts ATSC) on the board and
splits it into two equal outputs (≈5Watts ATSC) that connect to the inputs of the two
878 amplifier pallets at J1.
(A5) 4 Way Splitter Board (1308933), in multiple pallet amplifier drawer
The 4 way splitter board takes the RF Input at J1 (≈11Watts ATSC) on the board and
splits it into four equal outputs (≈4.75Watts ATSC) that connect to the inputs of the four
878 amplifier pallets at J1.
(A1-A4) 878A Amplifier Pallets (1314098, 1313170 or 1310138)
There are two 878 Amplifier Pallets mounted on the two pallet Amplifier Heatsink
Assembly and there are four 878A Amplifier Pallets mounted on the four pallet Amplifier
Heatsink Assembly. Each of the 878A pallets has approximately +16dB of gain for the
UHF frequency range of 470 to 860 MHz. The pallets operate Class AB and generate 150
Watts ATSC with an input of 4.75 Watts ATSC.
Or (A1-A2) Dual 888A Amplifier Pallets (1314173) Used in two pallet Amplifier
Drawer (CB005715)
There are two 888A Amplifier Pallets mounted on the two pallet Amplifier Heatsink
Assembly. Each of the 888A pallets has approximately +16dB of gain for the UHF
frequency range of 470 to 860 MHz. The pallets operate Class AB.
(A1-A4) 888A Amplifier Pallets (1315347) Used in three pallet Amplifier
Drawers
There are four 888A Amplifier Pallets mounted on the Amplifier Heatsink Assembly.
Each of the 888A pallets has approximately +15dB of gain for the UHF frequency range
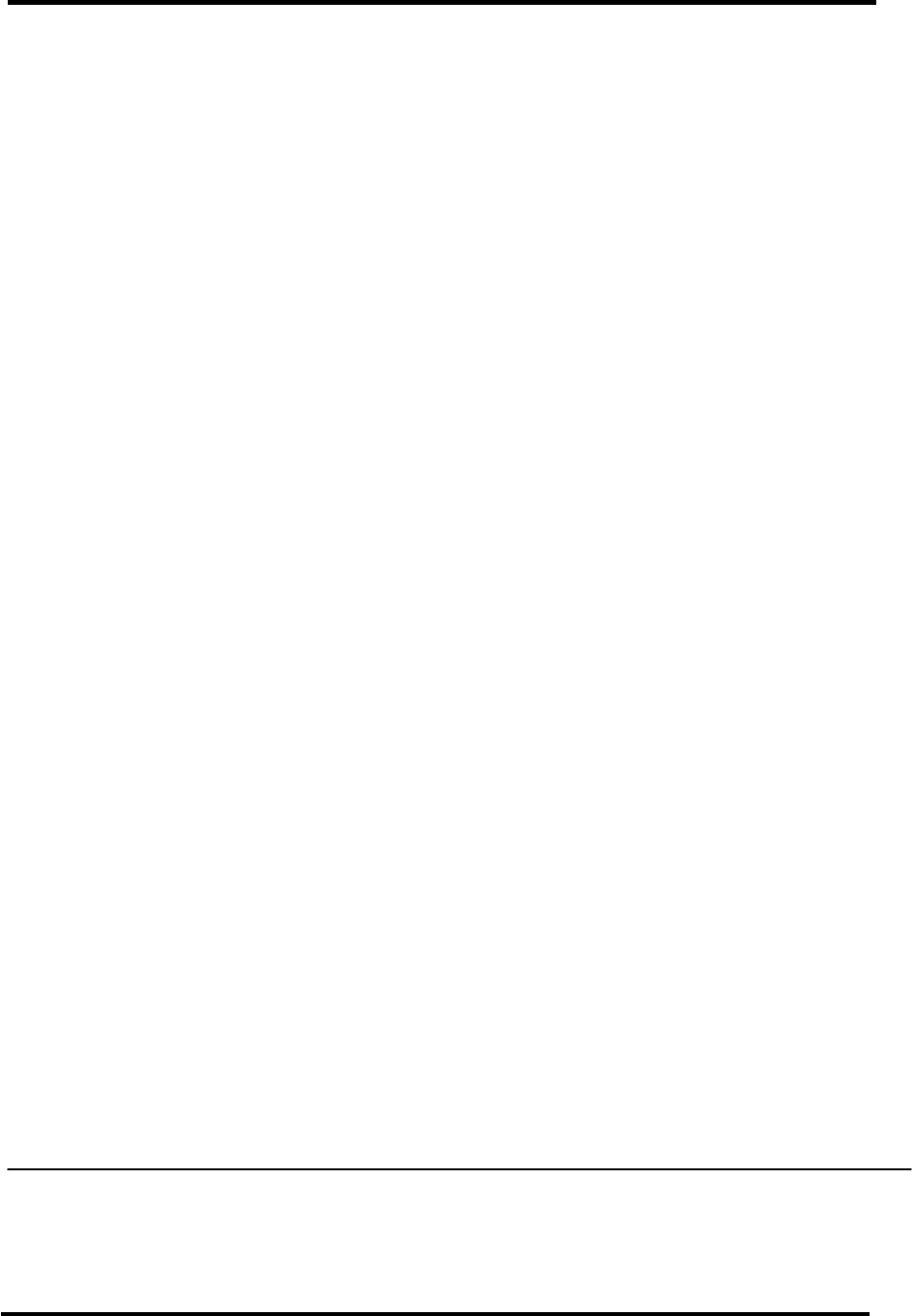
Innovator CU0TD-1/CU0RD-1 – CU4TD/CU4RD Board Descriptions
ATSC Transmitter/Regenerative Translator
Instruction Manual, Rev. 1 67
of 470 to 860 MHz. The pallets operate Class AB and generate approximately 230 Watts
ATSC with an input of 8 Watts ATSC.
(A6) 2 Way Combiner Board (1313155), in amplifier drawer w/two Dual 888A
Pallets
The 2 way combiner board takes the two RF Inputs at J4 & J5 (≈230Watts ATSC) on the
board and combines them to a single output (≈375Watts) at J1 that connects to J2 the
7/16” (1.1cm) Din RF output jack of the drawer.
(A6) 4 Way Combiner Board (1312368), in two pallet amplifier drawer
The 4 way combiner board takes the four RF Inputs at J4, J5, J6 & J7 (≈150Watts ATSC)
on the board and combines them to a single output (≈500Watts/600Watts) at J1 that
connects to J2 the 7/16” (1.1cm) Din RF output jack of the drawer.
(A8 & A9) One, two & three pallet Amplifier Drawer Power Supplies
The 230VAC, needed to operate the drawer, connects through the AC power cord at J3,
the power entry module located on the rear panel of the drawer. The AC lines are
connected to a terminal block TB1 to which the circuit breaker(s) connect. In a N+1 one
pallet amplifier drawer and all multiple pallet amplifier drawers, there are two On/Off
20A/250VAC circuit breakers that are mounted on the back panel of the drawer on either
side of J3 the AC input jack. With the circuit breakers switched On, the AC is distributed
to the two (A8 and A9) DC power supplies. In a standard one pallet amplifier drawer
one 20 Amp circuit breaker CB1 connects the AC to the (A8) DC power supply. TB1 has
three varistors (VR1-VR3) connected across the AC input lines for surge and over
voltage protection. The AC input from TB1 also connects to through 2 amp fuses to the
two fans (A11 & A12) mounted in the drawer. Both fans will run immediately when AC
is applied to the drawer.
The +5VDC for the operation of the amplifier control board in the drawer is generated by
the (A8 & A9) power supplies at J1-9 on each power supply. The +5VDC from the (A8)
power supply connects to J4-8 and the +5VDC from the (A9) power supply connects to
J5-8 on the control board. The +5VDC is produced when AC is connected to the drawer
and the CB1 and/or the CB2 circuit breakers are turned On. Either or both power
supplies provides the +5VDC for use by the control board.
The +48VDC needed by the amplifier modules on the heatsink assembly is generated by
the (A8 & A9) power supplies in the amplifier drawer. In a standard single pallet
amplifier drawer there is only the (A8) power supply. The power supplies will operate
when AC is connected to the drawer, the CB1 circuit breaker for the (A8) power supply
and the CB2 circuit breaker for the (A9) power supply, are turned On and a Low is
provided on the Inhibit Line that connects to J1-6 on the power supplies from the control
board. The CB1 circuit breaker supplies the AC to the (A8) power supply which provides
the +48VDC to the (A1) and (A2) 878 amplifier pallets. The CB2 circuit breaker supplies
the AC to the (A9) power supply which provides the +48VDC to the (A3) and (A4) 878A
amplifier pallets.
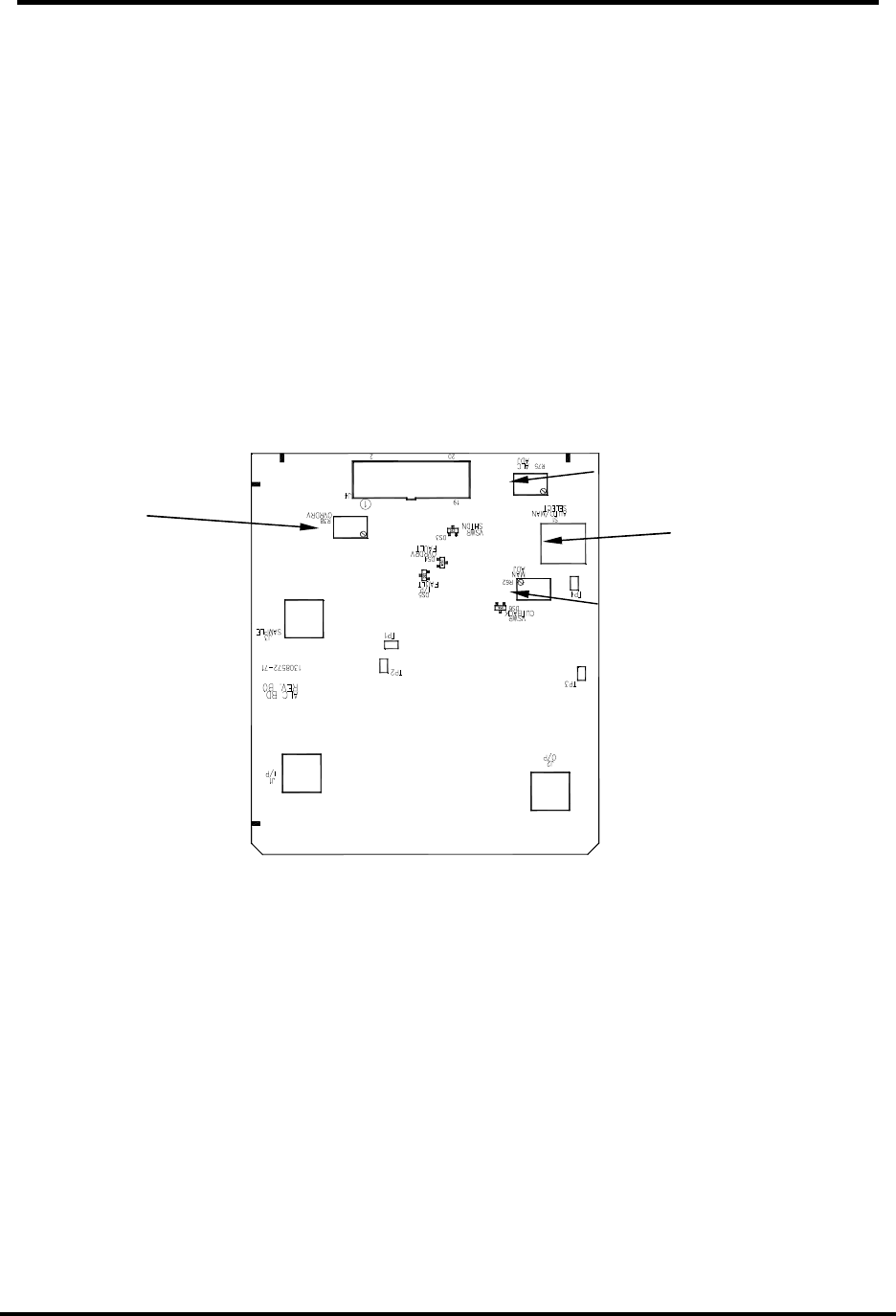
Innovator CU0TD-1/CU0RD-1 – CU4TD/CU4RD Appendix A: System &
ATSC Transmitter/Regenerative Translator Drawers Drawings and Parts List
Instruction Manual, Rev. 0 A-1
System Set Up Procedure
This system was aligned at the factory and should not require additional adjustments to
achieve normal operation.
This Innovator CX Series system is of a drawer design with multiple boards inside the
drawer. If a board fails, that board needs to be changed out with a replacement board. The
failed board can then be sent back to Axcera for repair. NOTE: Contact Axcera Customer
Service Department at 1-724-873-8100 or fax to 1-724-873-8105, before sending in any
board or module.
Refer to Figure 16. Check that the Auto/Man switch S1 on the ALC Board is in the
Automatic ALC position. (NOTE: The silkscreen is incorrect on Rev. A, B & C boards.
Auto position is with the bat to the left, toward J4.) Adjust R75 the ALC pot on the ALC
Board as needed to attain 100% output power. Switch to Manual Gain (Manual ALC) and
adjust the Manual Gain pot R62 for 100% output power. Switch the ALC Board back to
Automatic ALC.
Figure 16: (A5) ALC Board (1308570)
S1
AUTO/MAN
J4
R75
ALC ADJ
R62
MAN ADJ
R38
OVERDRIVE
THRESHOLD
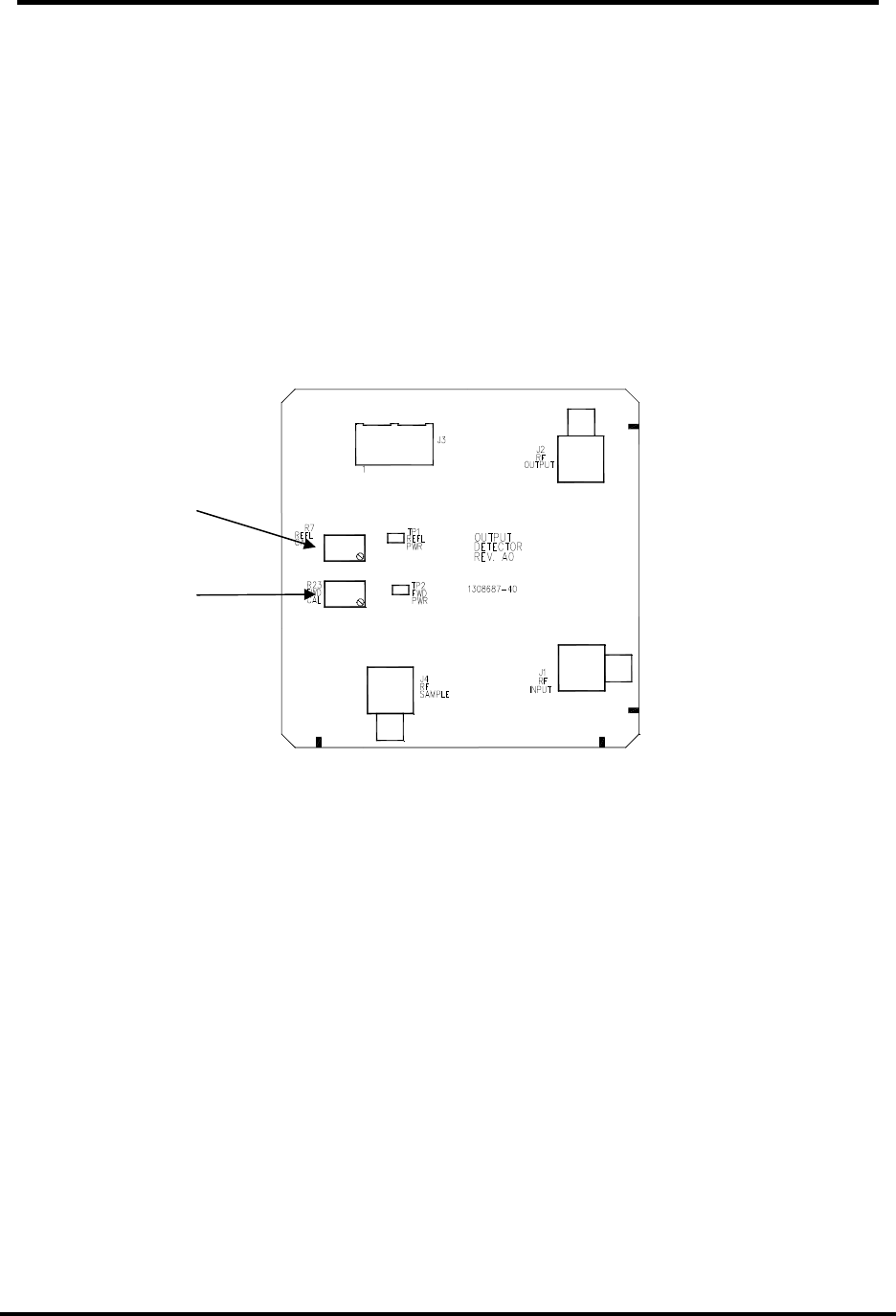
Innovator CU0TD-1/CU0RD-1 – CU4TD/CU4RD Appendix A: System &
ATSC Transmitter/Regenerative Translator Drawers Drawings and Parts List
Instruction Manual, Rev. 0 A-2
ALC Board Set-Up, Forward and Reflected Power Calibration for CU0TD/RD-1
thru CU0TD/RD-5 Systems
NOTE: If your system is a CU1TD/RD-1 or higher power with one or more external
amplifier drawers, refer to the next section for the forward and reflected power calibration
procedures.
Refer to Figure 16. Locate (A5) the ALC Board (1308570 & 1312207), preset the
Overdrive Threshold pot R38 full CW and set R62, Manual Adjust, and R75, ALC Adjust,
full CCW.
Switch S1 to Manual Gain, and increase the output power to 100% using R62. Calibrate
the system output power for 100% using R23, the Forward Calibration pot, on the Output
Detector Board. Refer to Figure 17.
Figure 17: (A7) Output Detector Board (1308685 & 1312207)
R23
FORWARD
CAL ADJ
R7
REFLECTED
CAL ADJ
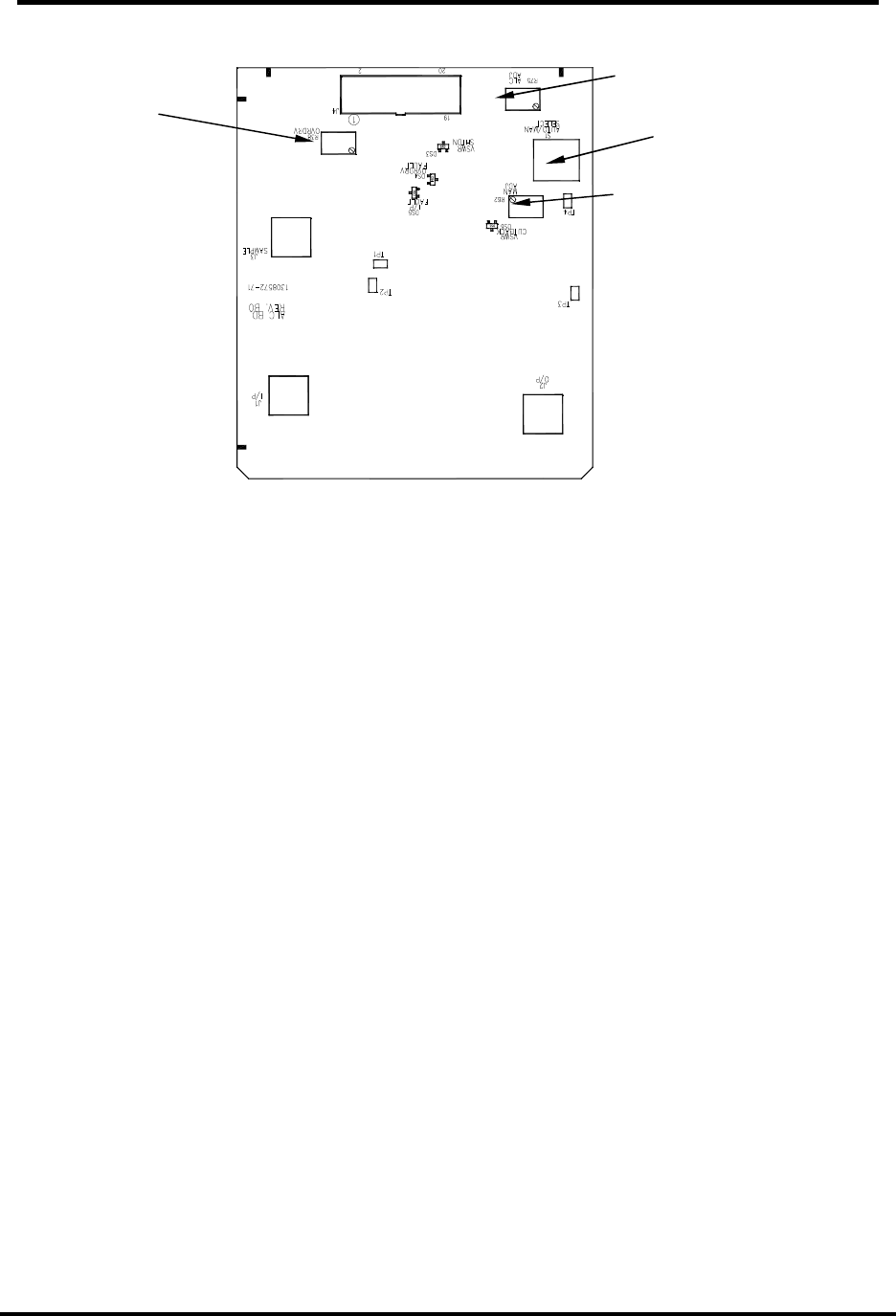
Innovator CU0TD-1/CU0RD-1 – CU4TD/CU4RD Appendix A: System &
ATSC Transmitter/Regenerative Translator Drawers Drawings and Parts List
Instruction Manual, Rev. 0 A-3
Figure 16A: (A5) ALC Board (1308570)
Refer to Figure 16A. Turn the output power down to 10% power with R62 on the ALC
Board. Remove the output RF connector from J2 on drawer and calibrate the reflected
power to 10%, using R7, the Reflected Calibration pot, on the Output Detector Board.
Refer to Figure 17. Re-connect the RF output connector to the drawer and increase the
power, in Manual gain using R62 on the ALC Board, to 115%. Adjust the Overdrive pot
R38 on the ALC Board, CCW until the overdrive threshold just trips and the Overdrive
Fault LED DS4 lights. Turn R38 slightly CW so that power comes back up and DS4 goes
out.
Switch S1 on the ALC Board to ALC. Turn the ALC Adjust pot R75 on the ALC Board until
the power is 100%. Switch S1 between ALC and Manual to verify smooth switching, with
minimal change in power. If necessary repeat the above procedure.
With the drawer in ALC, use the ALC Adjust pot, R75, to decrease the power to 10%.
Remove the RF output connector from the drawer. Verify that the VSWR Cutback LED,
DS6, comes on and the Reflected Power drops to approximately 6%. Reconnect the RF
output connector and increase the power back up to 100% using R75.
This completes the set up of the ALC board and the Forward and Reflected Power
Calibration.
Forward and Reflected Power Calibration of a CU1TD/RD-1 and Higher Power
Systems with one or more External Amplifier Drawers
NOTE: If your system is a CU0TD/RD-1 thru CU0TD/RD-5, refer to the previous section
for the forward and reflected power calibration procedures.
Connect a calibrated coupler and average reading power meter to the output of the DTV
mask filter. On the ALC Board (1308570), mounted in the Driver Drawer, set the Switch
S1, Auto/Manual ALC, to the Manual position. Refer to Figure 13A.
Adjust the Manual adjustment Pot, R62, for the desired output power level as indicated on
the average reading power meter. In the Amplifier Drawer, on the Amplifier Control Board
(1309822), refer to Figure 18; adjust the Forward Calibration Adjustment pot, R8, for a
R38
OVERDRIVE
THRESHOLD
S1
AUTO/MAN
R75
ALC ADJ
R62
MAN ADJ
J4
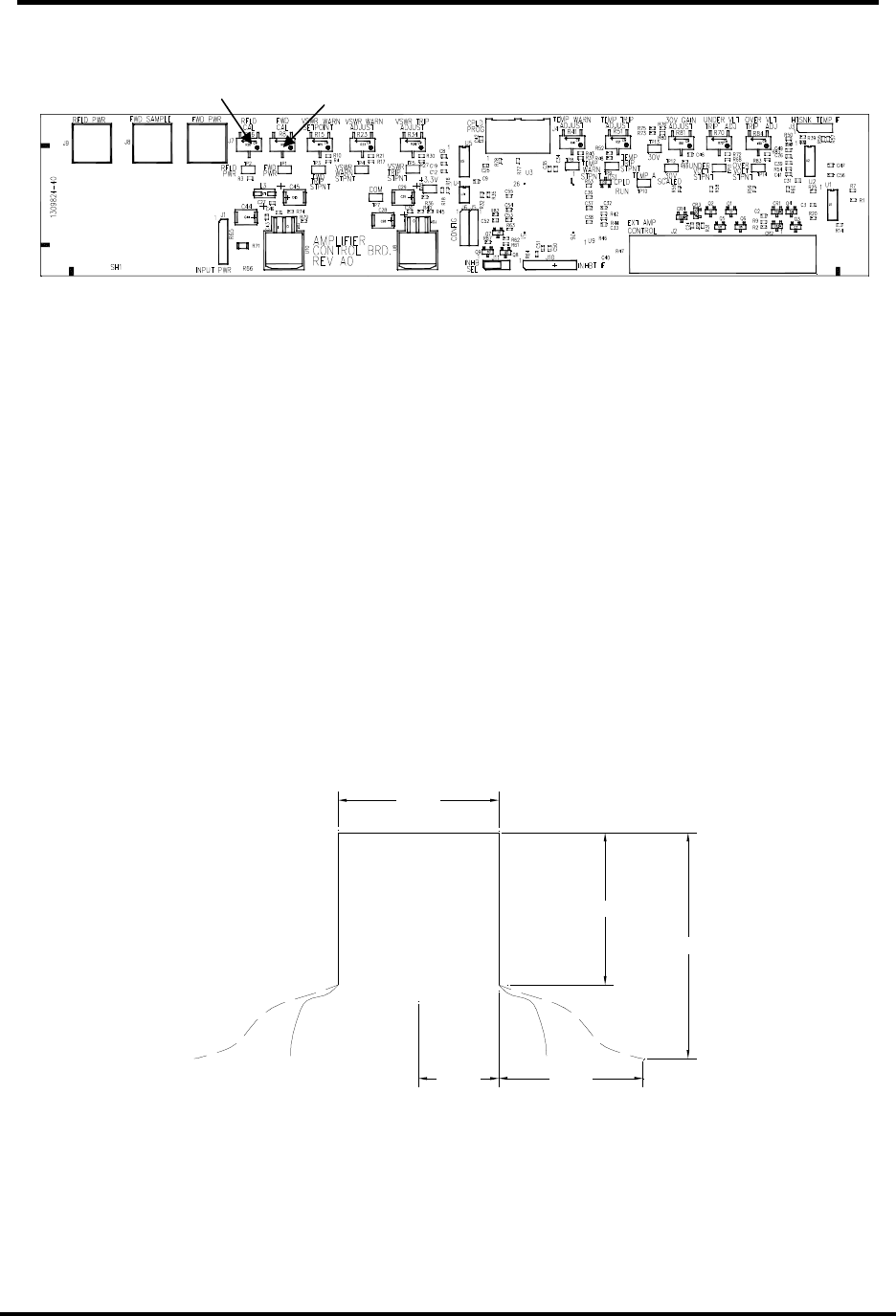
Innovator CU0TD-1/CU0RD-1 – CU4TD/CU4RD Appendix A: System &
ATSC Transmitter/Regenerative Translator Drawers Drawings and Parts List
Instruction Manual, Rev. 0 A-4
reading of 100% on the External Amplifier Forward Power screen of the LCD display
mounted on the Driver Drawer.
Figure 18: (A5) Amplifier Control Board (1309822)
On the ALC Board (1308570), mounted in the Driver Drawer, set the Switch S1,
Auto/Manual ALC, to the Auto position. Adjust the ALC adjustment Pot, R75, for a reading
of 100% on the External Amplifier Forward Power screen of the LCD display mounted on
the Driver Drawer. This completes the forward power set up and calibration adjustments.
On the ALC Board (1308570), mounted in the Driver Drawer, adjust the ALC adjustment
Pot, R75, for a reading of 10% on the External Amplifier Forward Power screen of the LCD
display mounted on the Driver Drawer. Disconnect the load or the antenna connected to
the system. In the Amplifier Drawer, on the Amplifier Control Board (1309822), adjust
the Reflected Calibration Adjustment pot, R26, for a reading of 10% on the External
Amplifier Reflected Forward Power screen of the LCD display mounted on the Driver
Drawer. Reconnect the load or the antenna to the system. Adjust the ALC adjustment
Pot, R75, for a reading of 100% on the External Amplifier Forward Power screen of the
LCD display mounted on the Driver Drawer. This completes the reflected power
calibration adjustment.
6 MHz
-35 dB
-110 dB
3 MHz 6 MHz
Figure 19: Typical 6 MHz Digital Spectrum
R8 FWD CAL ADJ R26 REFL CAL ADJ
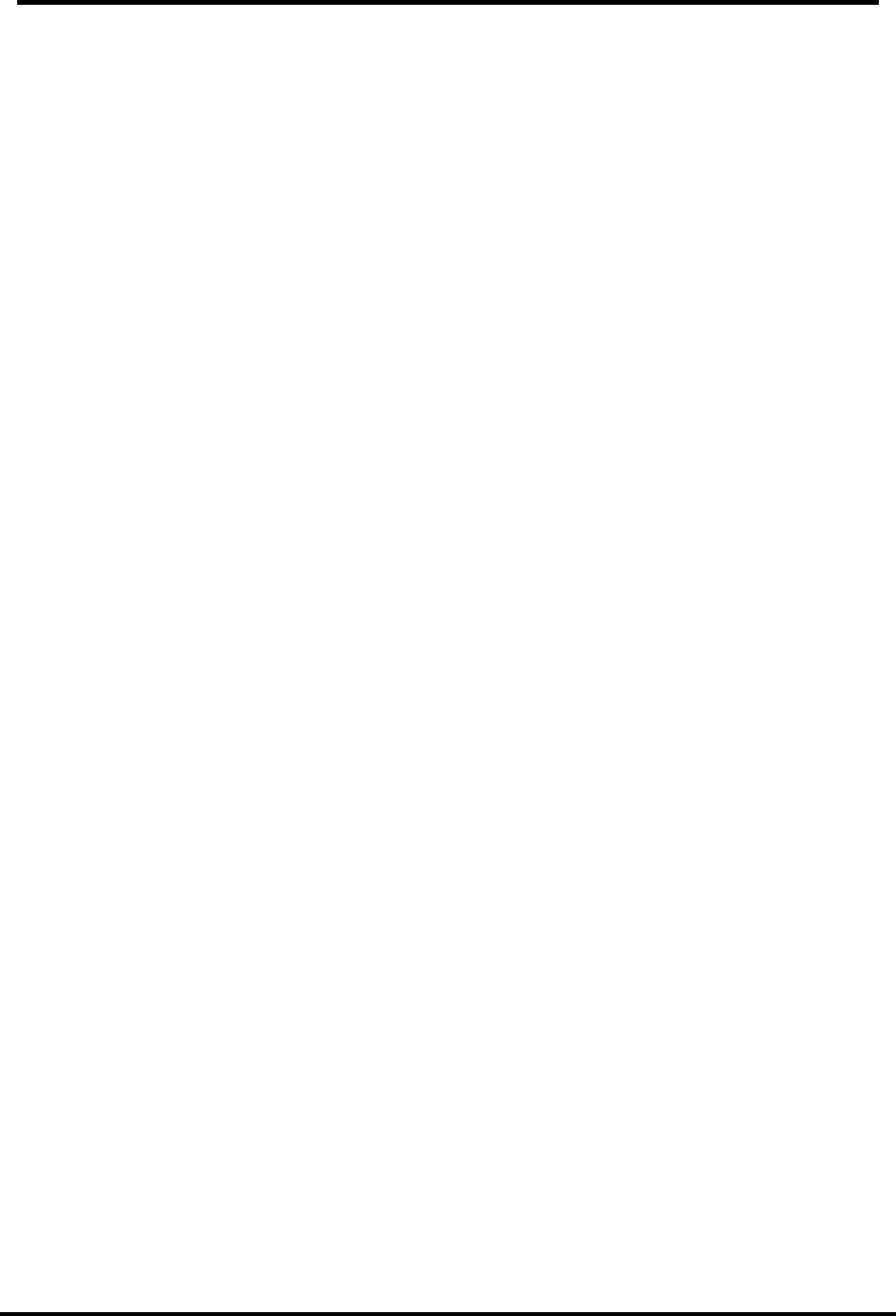
Innovator CU0TD-1/CU0RD-1 – CU4TD/CU4RD Appendix A: System &
ATSC Transmitter/Regenerative Translator Drawers Drawings and Parts List
Instruction Manual, Rev. 0 A-5
This page has been intentionally left blank.