UBS Axcera LHV100AT 100-Watt VHF High Band Transmitter User Manual Title Page
UBS-Axcera 100-Watt VHF High Band Transmitter Title Page
Compiled Users Manual
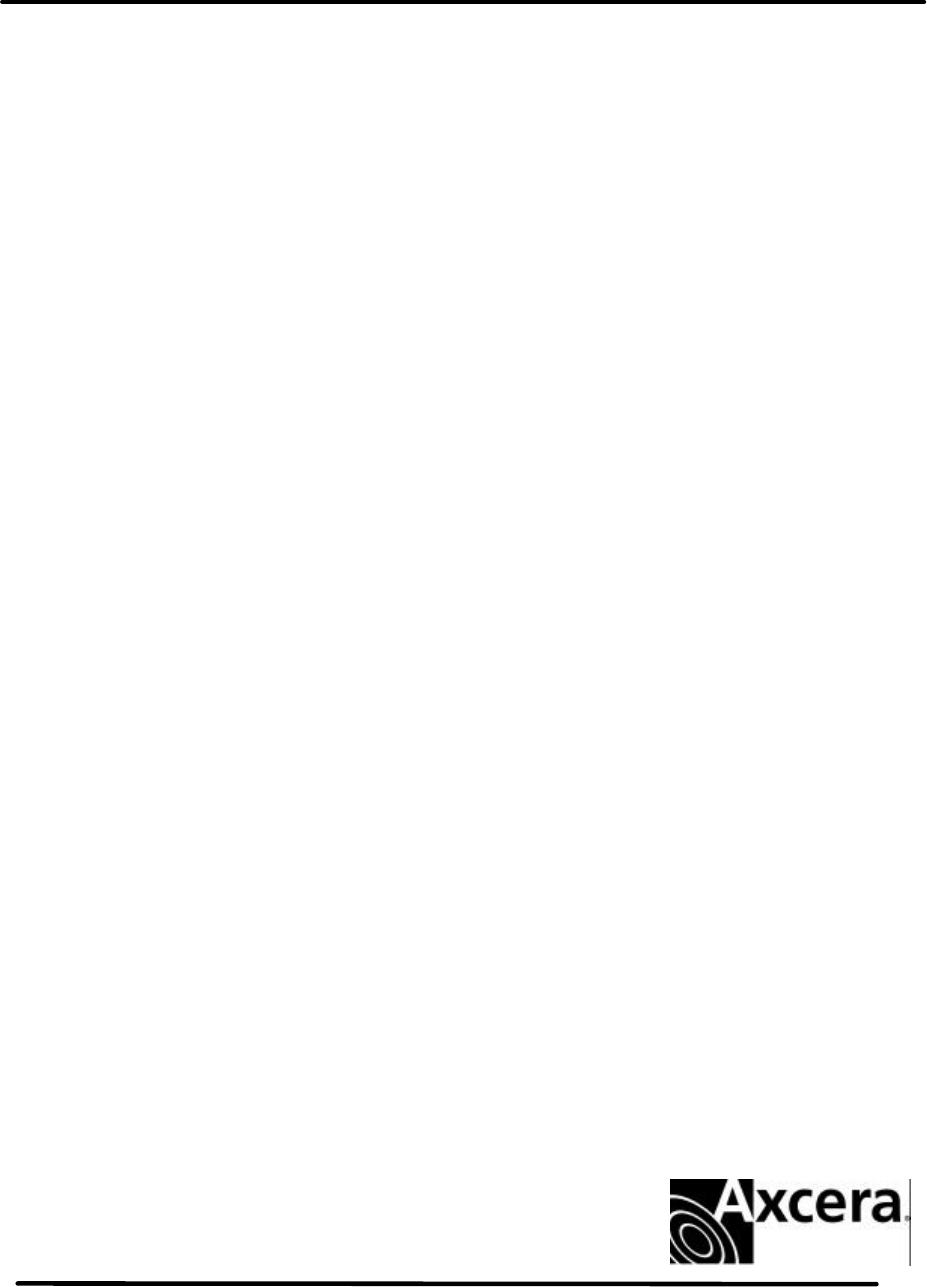
Instruction Manual
Innovator® HX Series
Analog VHF High Band
Transmitter
AXCERA
103 FREEDOM DRIVE • P.O. BOX 525 • LAWRENCE, PA 15055-0525 USA
(724) 873-8100 • FAX (724) 873-8105
www.axcera.com • service@axcera.com
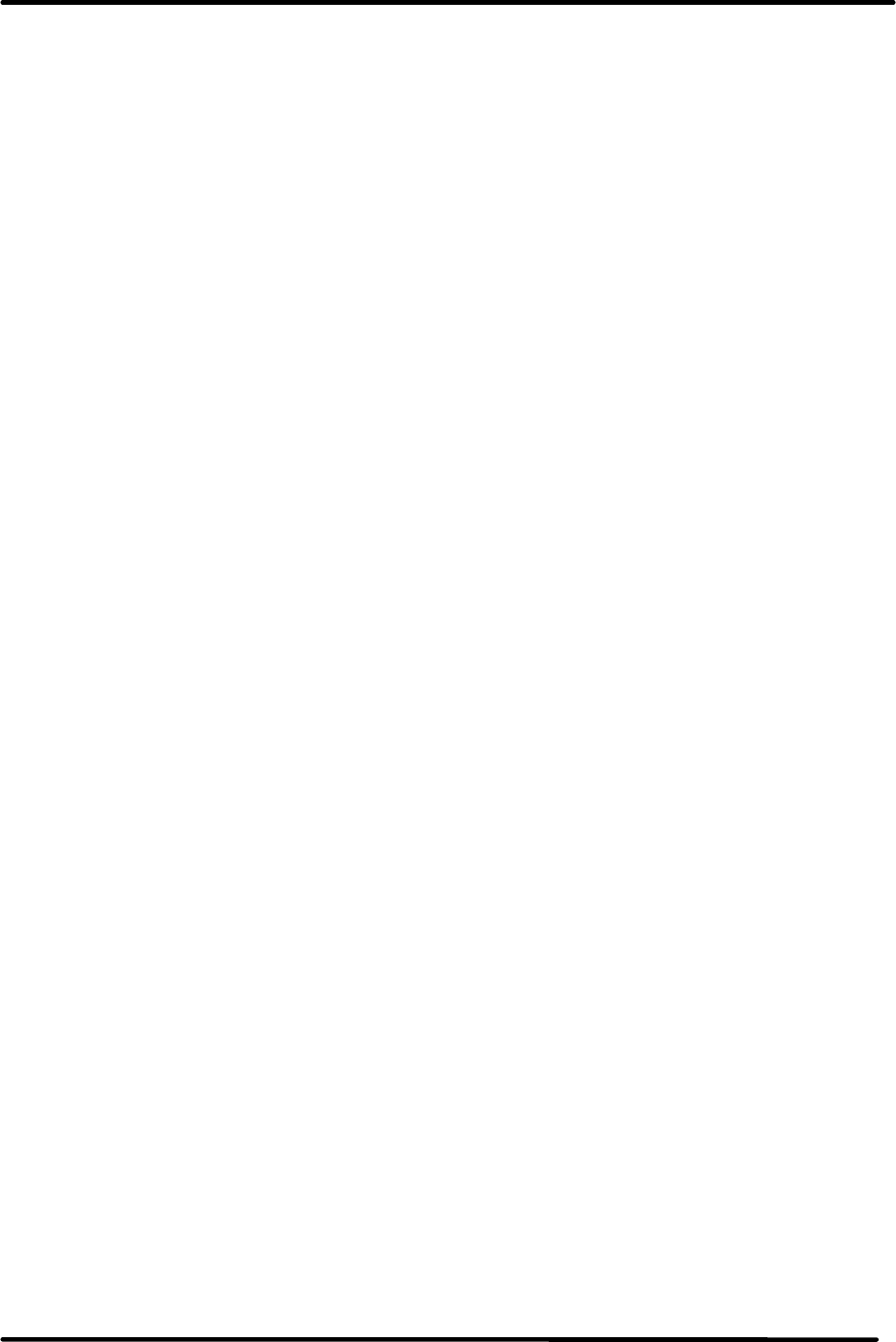
Innovator® HX Series Analog VHF Transmitter Table of Contents
HX Series, Rev. 0 i August 2, 2006
TABLE OF CONTENTS
CHAPTER 1 INTRODUCTION
SECTION PAGE
1.1 Manual Overview...................................................................................1-1
1.2 Assembly Designators............................................................................1-1
1.3 Safety..................................................................................................1-2
1.4 Contact Information...............................................................................1-2
1.5 Material Return Procedure ......................................................................1-2
1.6 Limited One-Year Warranty for Axcera Products........................................1-3
CHAPTER 2 SYSTEM DESCRIPTION AND REMOTE CONTROL CONNECTIONS
2.0 System Overview..................................................................................2-1
2.1 Exciter/Amplifier Chassis Assembly.........................................................2-1
2.1.1 Modulator Module.........................................................................2-2
2.1.2 IF Processor Module .....................................................................2-3
2.1.3 Upconverter Module......................................................................2-4
2.1.4 Control & Monitoring/Power Supply Module.....................................2-6
2.1.5 VHF Power Amplifier Module..........................................................2-7
2.1.5 VHF Power Amplifier Module..........................................................2-7
2.1.6 RF Output....................................................................................2-8
2.2 Control and Status.................................................................................2-8
2.2.1 Front Panel LCD Display Screens....................................................2-8
2.3 System Operation..................................................................................2-8
2.3.1 Principles of Operation..................................................................2-9
2.4 Maintenance .......................................................................................2-10
2.5 Customer Remote Connections....................................................... 2-11
CHAPTER 3 SITE CONSIDERATIONS, INSTALLATION AND SETUP PROCEDURES
3.1 Site Considerations................................................................................3-1
3.2 Unpacking & Installing the Transmitter ....................................................3-4
3.2.1 AC Input .....................................................................................3-5
3.3 Setup and Operation..............................................................................3-5
3.3.1 Input Connections........................................................................3-5
3.4 Initial Turn On.......................................................................................3-6
3.4.1 Exciter/Driver Front Panel LED Indicators........................................3-6
3.4.1.1 Modulator Module LEDs on Front Panel ..................................3-6
3.4.1.2 IF Processor Module LEDs on Front Panel...............................3-7
3.4.1.3 Upconverter Module LEDs on Front Panel...............................3-7
3.4.1.4 Controller Module LEDs on Front Panel ..................................3-7
3.4.1.5 Power Amplifier Module LEDs on Front Panel..........................3-7
3.4.2 Front Panel Screens for the Exciter/Amplifier Chassis Assembly.........3-7
3.4.3 Operation Procedure...................................................................3-15
CHAPTER 4 CIRCUIT DESCRIPTIONS
4.0 Exciter/Driver Chassis Assembly .............................................................4-1
4.1 Modulator Module..................................................................................4-1
4.1.1 Analog Modulator Board................................................................4-1
4.1.1.1 Mono, Balanced Audio Input.................................................4-1
4.1.1.2 Stereo, Composite Audio Input.............................................4-1
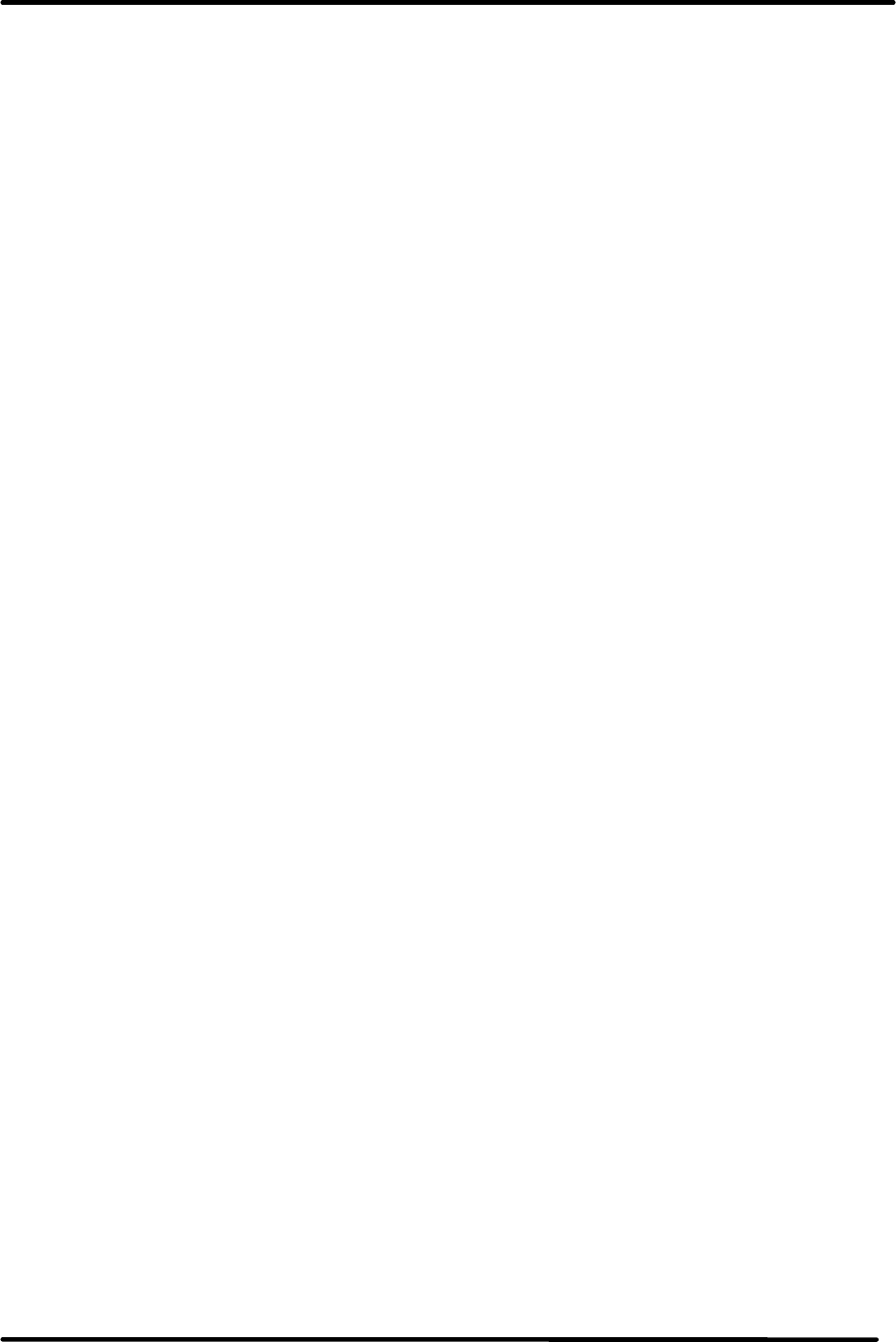
Innovator® HX Series Analog VHF Transmitter Table of Contents
HX Series, Rev. 0 ii August 2, 2006
TABLE OF CONTENTS (continued)
SECTION PAGE
4.1.1.3 SAP/PRO, Subcarrier Audio Input..........................................4-2
4.1.1.4 Audio Modulation of the 4.5 MHz VCO ..................................4-2
4.1.1.5 Phase Lock Loop (PLL) Circuit...............................................4-2
4.1.1.6 Main Video Signal Path (Part 1 of 2)......................................4-3
4.1.1.7 Delay Equalizer Circuits .......................................................4-3
4.1.1.8 Sync Tip Clamp Circuit.........................................................4-4
4.1.1.9 Main Video Signal Path (Part 2 of 2)......................................4-5
4.1.1.10 45.75 MHz Oven Oscillator Circuit .......................................4-5
4.1.1.11 Visual Modulator Circuit .....................................................4-6
4.1.1.12 Aural Modulator Circuit ......................................................4-6
4.1.1.13 Visual IF loop thru path......................................................4-6
4.1.1.14 Voltage Requirements........................................................4-7
4.2 IF Processor Module...............................................................................4-7
4.2.1 IF Processor Board .......................................................................4-7
4.2.1.1 Modulator Selected..............................................................4-7
4.2.1.2 External Modulated IF Selected.............................................4-7
4.2.1.3 Main IF Signal Path (Part 1 of 3)...........................................4-7
4.2.1.4 Input Level Detector Circuit..................................................4-8
4.2.1.5 Pin-Diode Attenuator Circuit.................................................4-9
4.2.1.6 Main IF Signal Path (Part 2 of 3).........................................4-10
4.2.1.7 Amplitude and Phase Pre-Correction Circuits........................4-10
4.2.1.8 Main IF Signal Path (Part 3 of 3).........................................4-11
4.2.1.9 ALC Circuit .......................................................................4-11
4.2.1.10 Fault Command...............................................................4-12
4.2.1.11 ±12 VDC needed to operate Board....................................4-13
4.3 Upconverter Module.............................................................................4-13
4.3.1 Downconverter Board .................................................................4-13
4.3.2 L-Band PLL Board.......................................................................4-13
4.3.3 First Conversion Board................................................................4-14
4.3.4 Upconverter Control Board ..........................................................4-14
4.4 Control Monitoring/Power Supply Module ...............................................4-15
4.4.1 Power Protection Board...............................................................4-15
4.4.1.1 +12 VDC Circuits ..............................................................4-15
4.4.1.2 -12 VDC Circuits ...............................................................4-16
4.4.2 Control Board ............................................................................4-16
4.4.2.1 Schematic Page 1..............................................................4-16
4.4.2.2 Schematic Page 2..............................................................4-17
4.4.2.3 Schematic Page 3..............................................................4-17
4.4.2.4 Schematic Page 4..............................................................4-17
4.4.2.5 Schematic Page 5..............................................................4-18
4.4.3 Switch Board .............................................................................4-18
4.4.4 Switching Power Supply Assembly................................................4-19
4.5 Power Amplifier Module .......................................................................4-19
4.5.1 25 Watt VHF Driver Pallet Assembly.............................................4-19
4.5.2 200 Watt VHF Amplifier Pallet Assembly .......................................4-19
4.5.3 Coupler Board Assembly .............................................................4-19
4.5.4 Amplifier Control Board...............................................................4-20
4.5.4.1 Schematic Page 1..............................................................4-20
4.5.4.2 Schematic Page 2..............................................................4-20
4.5.4.3 Current Monitoring Sections of the Board.............................4-21
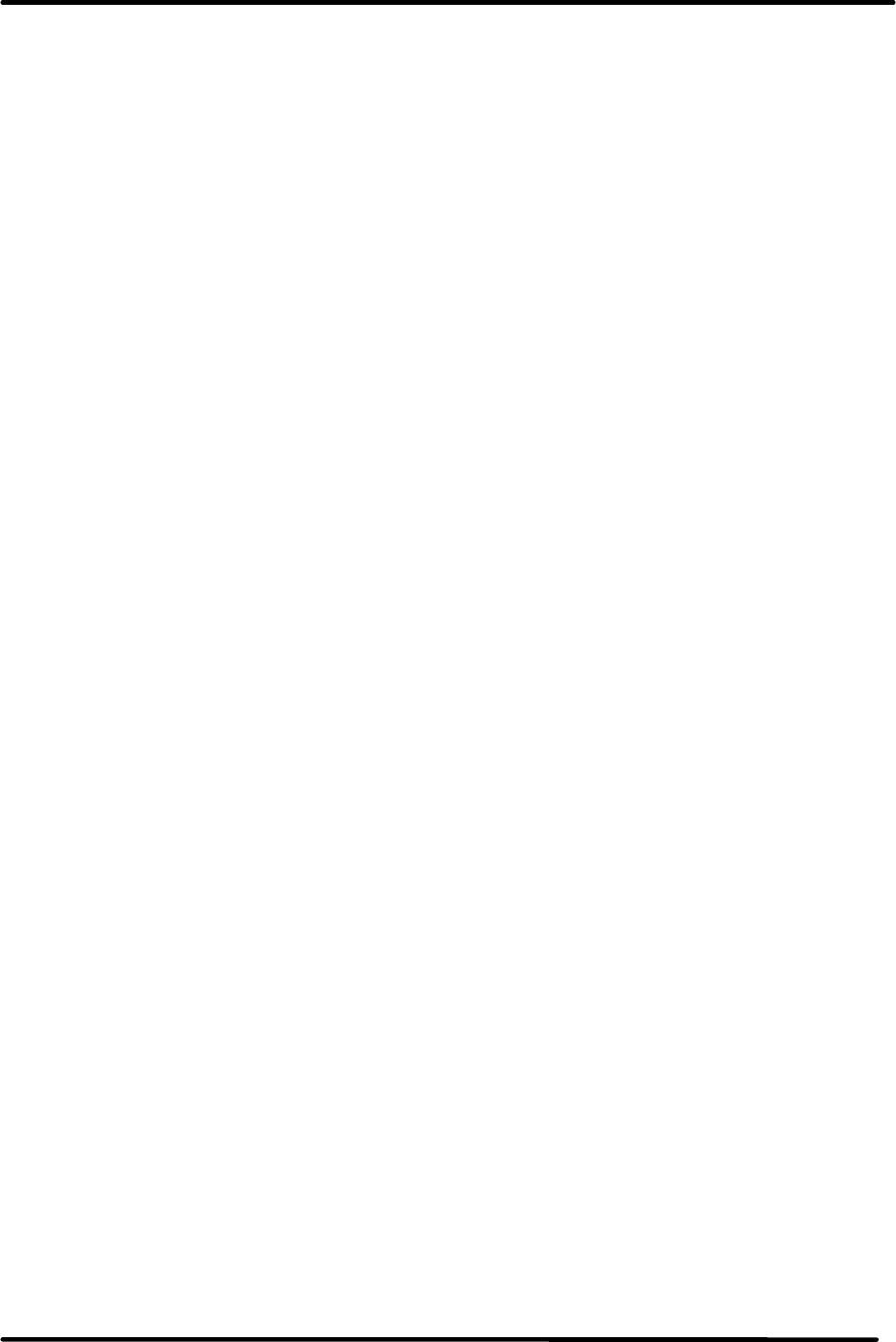
Innovator® HX Series Analog VHF Transmitter Table of Contents
HX Series, Rev. 0 iii August 2, 2006
TABLE OF CONTENTS (continued)
SECTION PAGE
4.6.4.4 Schematic Page 3 Aural, Visual. Aural Power Detectors .........4-21
4.6 Output Assemblies...............................................................................4-23
CHAPTER 5 DETAILED ALIGNMENT PROCEDURES
5.1 Module Replacement..............................................................................5-1
5.1.1 Initial Test Setup..........................................................................5-1
5.2 Innovator HX Series Exciter/Driver Chassis Assembly................................5-1
5.2.1 Modulator Module Assembly ..........................................................5-2
5.2.2 IF Processor Module Assembly.......................................................5-3
5.2.3 Upconverter Assembly..................................................................5-3
5.2.4 Setting up the Drive Level of the Transmitter Procedure...................5-3
5.3 Linearity Correction Adjustment..............................................................5-4
5.4 Differential Phase and ICPM Corrector Adjustment ....................................5-6
APPENDICES
APPENDICES
APPENDIX A HX SERIES VHF HIGH BAND TRANSMITTER
DRAWINGS
APPENDIX B SYSTEM SPECIFICATIONS
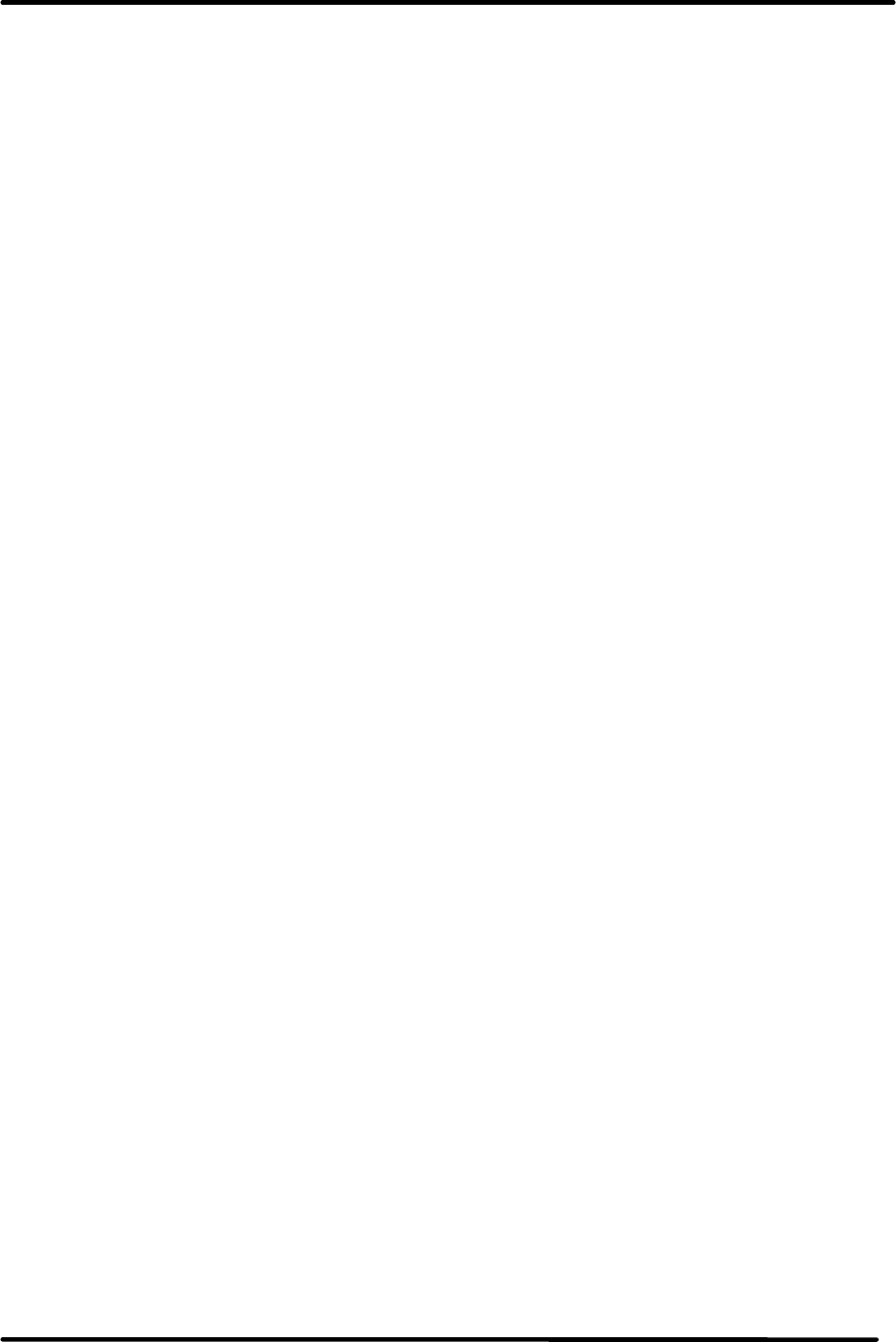
Innovator® HX Series Analog VHF Transmitter Table of Contents
HX Series, Rev. 0 iv August 2, 2006
LIST OF FIGURES
FIGURE PAGE
1-1 Brady Marker Identification Drawing.................................................1-1
2-1 Exciter/Driver Chassis Assembly Front View ......................................2-1
2-2 Exciter/Driver Chassis Assembly Rear View .....................................2-11
3-1 1 kW Minimum Ventilation Configuration...........................................3-4
3-2 Rear View exciter/driver chassis.......................................................3-5
5-1 Adjustments accessed through top of HX Exciter Chassis....................5-5
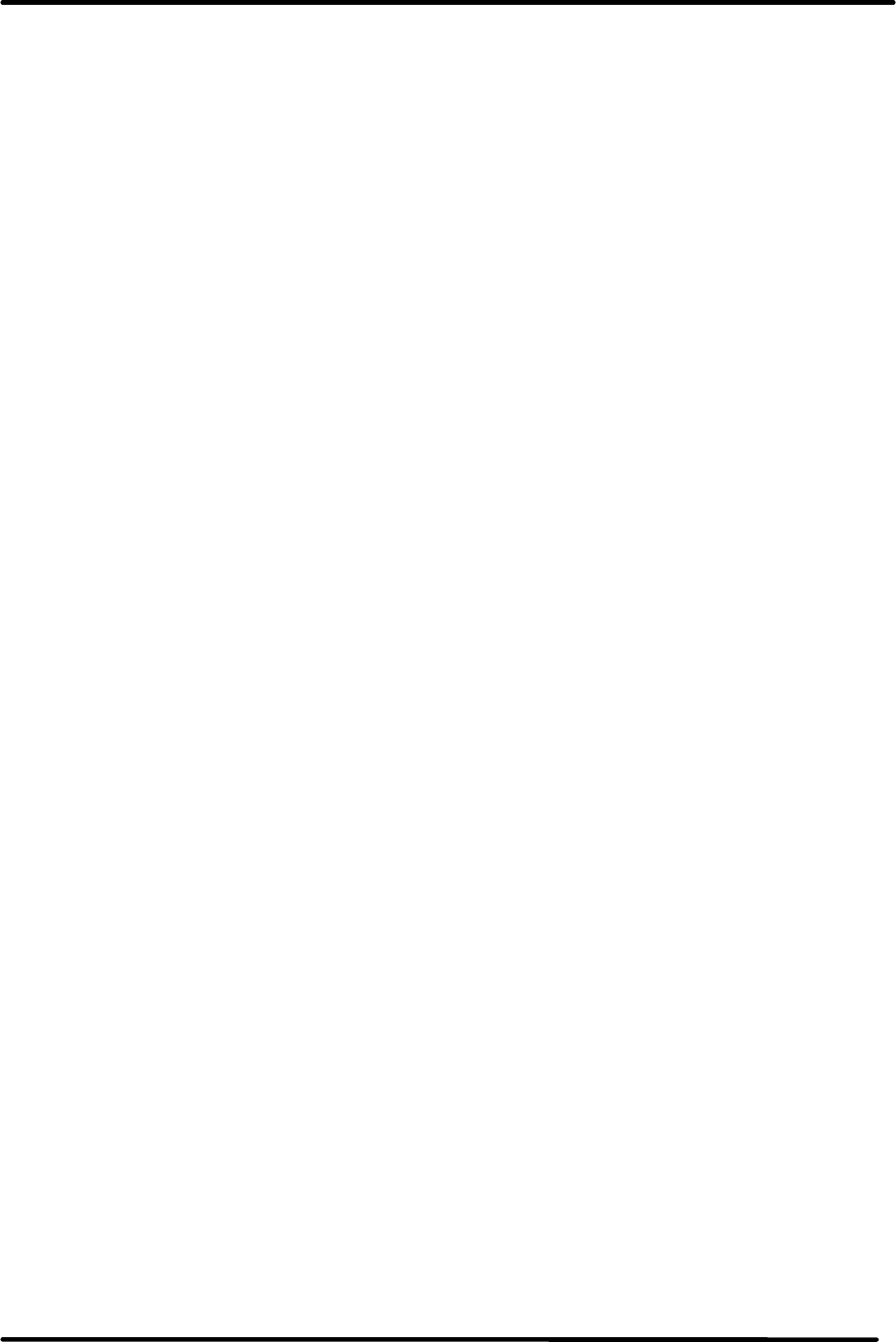
Innovator® HX Series Analog VHF Transmitter Table of Contents
HX Series, Rev. 0 v August 2, 2006
LIST OF TABLES
TABLE PAGE
2-1 HX Series Trays and Assemblies.......................................................2-1
2-2 Modulator Front Panel Switch...........................................................2-2
2-3 Modulator Front Panel Status Indicators............................................2-2
2-4 Modulator Front Panel Control Adjustments.......................................2-3
2-5 Modulator Front Panel Sample .........................................................2-3
2-6 IF Processor Front Panel Switch .......................................................2-4
2-7 IF Processor Front Panel Status Indicators ........................................2-4
2-8 IF Processor Front Panel Control Adjustments....................................2-4
2-9 IF Processor Front Panel Sample......................................................2-4
2-10 Upconverter Front Panel Switch .......................................................2-5
2-11 Upconverter Front Panel Status Indicators ........................................2-5
2-12 Upconverter Front Panel Control Adjustments....................................2-5
2-13 Upconverter Front Panel Samples.....................................................2-5
2-14 Controller/Power Supply Front Panel Display .....................................2-6
2-15 Controller/Power Supply Front Panel Status Indicators .......................2-6
2-16 Controller/Power Supply Front Panel Control Adjustments...................2-6
2-17 Power Amplifier Front Panel Status Indicators....................................2-8
2-18 Power Amplifier Front Panel Control Adjustments...............................2-8
2-19 Power Amplifier Front Panel Samples................................................2-8
2-20 HX Series Chassis Customer Remote Connections ................... 2-12
3-1 Rear Chassis Connections for HX Series Analog Transmitters ..............3-5
HX System Controller Menu Screens...................................................................3-8
3-2 Menu 01 Splash Screen #1..............................................................3-8
3-3 Menu 02 Splash Screen #2..............................................................3-8
3-4 Menu 10 Main Screen ..................................................................3-8
3-5 Menu 11 Error List Access Screen..................................................3-8
3-6 Menu 12 Transmitter Device Data Access Screen.............................3-9
3-7 Menu 13 Transmitter Configuration Access Screen...........................3-9
3-8 Menu 20 Error List Display Screen.................................................3-9
3-9 Menu 30 Transmitter Device Details Screen....................................3-9
3-10 Menu 30-1 System Details Screens..............................................3-10
3-11 Transmitter Device Parameters Detail Screens..............................3-10
3-12 Menu 40 Authorized Personnel Screen .........................................3-11
3-13 Menu 40-1 Transmitter Set Up: Power Control Screen ...................3-12
3-14 Menu 40-3 Transmitter Set Up: Model Select Screen .....................3-12
3-15 Menu 40-4 Transmitter Set Up: Upconverter Channel Select Screen 3-12
3-16 Menu 40-5 Transmitter Set Up: Serial Address Screen ...................3-12
3-17 Menu 40-6 Transmitter Set Up: Station ID Screen ...........................3-12
3-18 Menu 40-7 Transmitter Set Up: System Forward Power Cal. Screen...3-13
3-19 Menu 40-9 Transmitter Set Up: System Rfltd. Power Cal. Screen ......3-13
3-20 Menu 40-11 Transmitter Set Up: Modulated Output Cal. Screen ........3-13
3-21 Menu 40-12 Transmitter Set Up: Aural Deviation Screen ..................3-13
3-22 Menu 40-13 Transmitter Set Up: Min Fw Pwr Fault Threshold Screen.3-14
3-23 Menu 40-14 Transmitter Set Up: Refl Power Fault Threshold Screen 3-14
3-24 Menu 40-17 Transmitter Set Up: Auto Standby Control Screen .......3-14
3-25 Menu 40-18 Transmitter Set Up: Inner Loop Gain Control Screen....3-14
3-26 Menu 40-19 Transmitter Set Up: Remote Command Control Screen 3-57
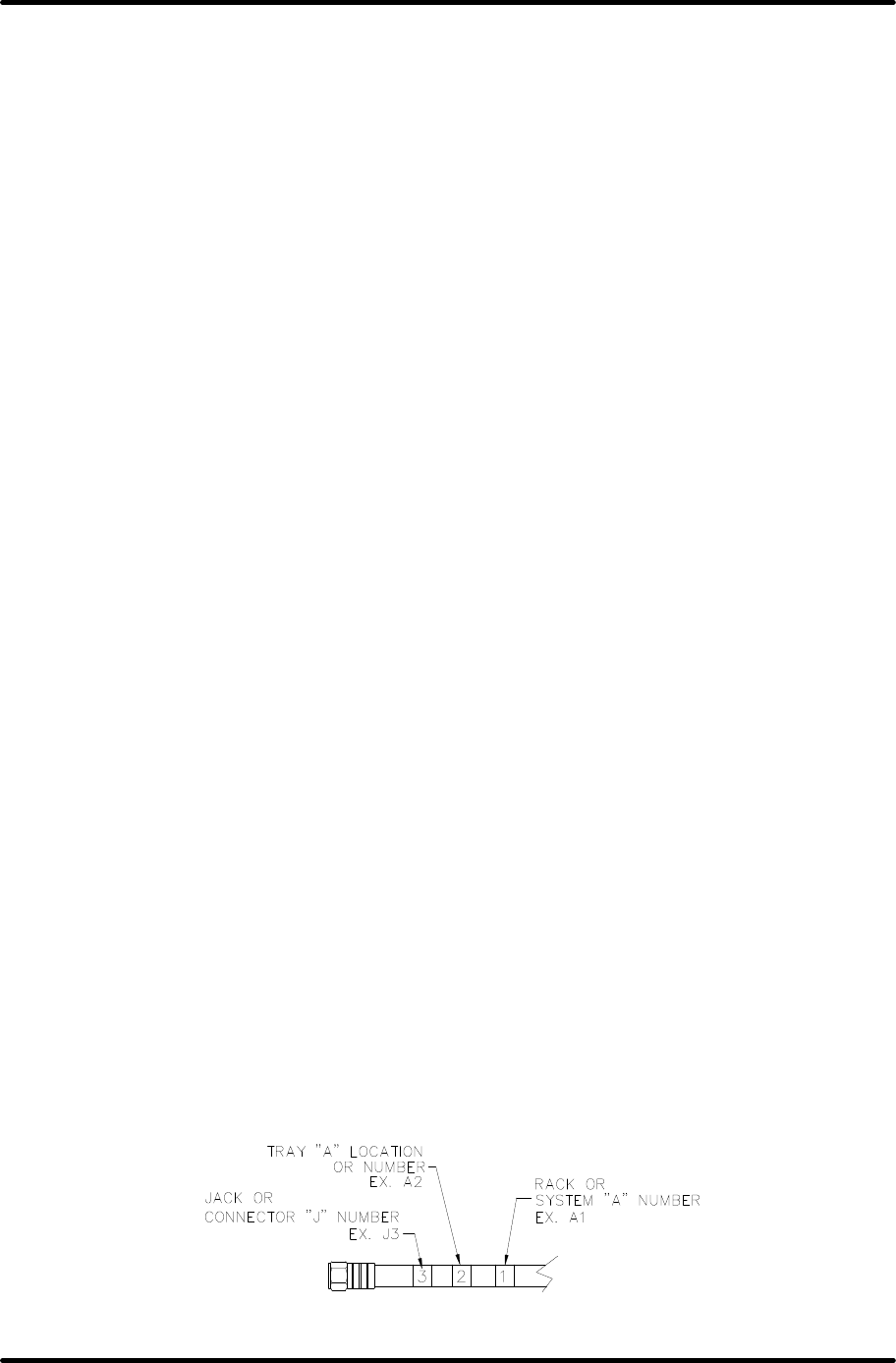
Innovator® HX Series Analog VHF Transmitter Chapter 1, Introduction
HX Series, Rev. 0 1-1
Chapter 1
Introduction
This manual provides information about
and documentation on the Innovator®
HX Series Analog VHF High Band
Transmitter.
It is important that any user of this
equipment read all of the instructions,
especially the safety information in this
chapter, before operating the
transmitter.
1.1 Manual Overview
This instruction manual is divided into
five chapters and the supporting
appendix. Chapter 1, Introduction,
contains information on safety, return
procedures, and warranties. Chapter 2
contains the system and assembly
descriptions. Chapter 3 describes the
installation and set up procedures and
the operation of the overall transmitter.
Chapter 4 contains the detailed circuit
descriptions of the boards and
subassemblies that are contained in the
transmitter. Chapter 5 describes the
alignment of the overall transmitter.
Appendix A contains the interconnects,
schematics and assembly drawings of the
system, trays, assemblies, subassemblies
and boards that make up the transmitter.
1.2 Assembly Designators
Axcera has assigned assembly numbers,
Ax designations such as A1, where
x=1,2,3…etc, to all assemblies, modules,
and boards in the system. These
designations are referenced in the text of
this manual and shown on the block
diagrams and interconnect drawings
provided in the appendices. The Block
Diagrams, Interconnects, Schematics,
Assembly Drawings and Parts Lists are
arranged in increasing numerical order in
the appendices. Section titles in the text
for assembly or module descriptions or
alignment procedures contain the
associated part number(s) and the
relevant appendix that contains the
drawings for that item.
The cables that connect between the
boards within a tray or assembly and
that connect between the trays, racks
and cabinets are labeled using Brady
markers.
Figure 1-1 is an example of a Brady
marked cable. There may be as few as
two or as many as four Markers on any
one cable. These Brady markers are
read starting furthest from the
connector. If there are four Brady
Markers, this marker is the transmitter
number such as transmitter 1 or
Transmitter 2. The next or the furthest
Brady Marker is the rack or cabinet
number on an interconnect cable or the
board number within a tray. The next
number on an interconnect cable is the
Tray location or number. The Brady
marker closest to the connector is the
Jack or Connector number on an
interconnect cable or the jack or
connector number on the board within a
tray.
Figure 1-1 Brady Marker Identification Drawing
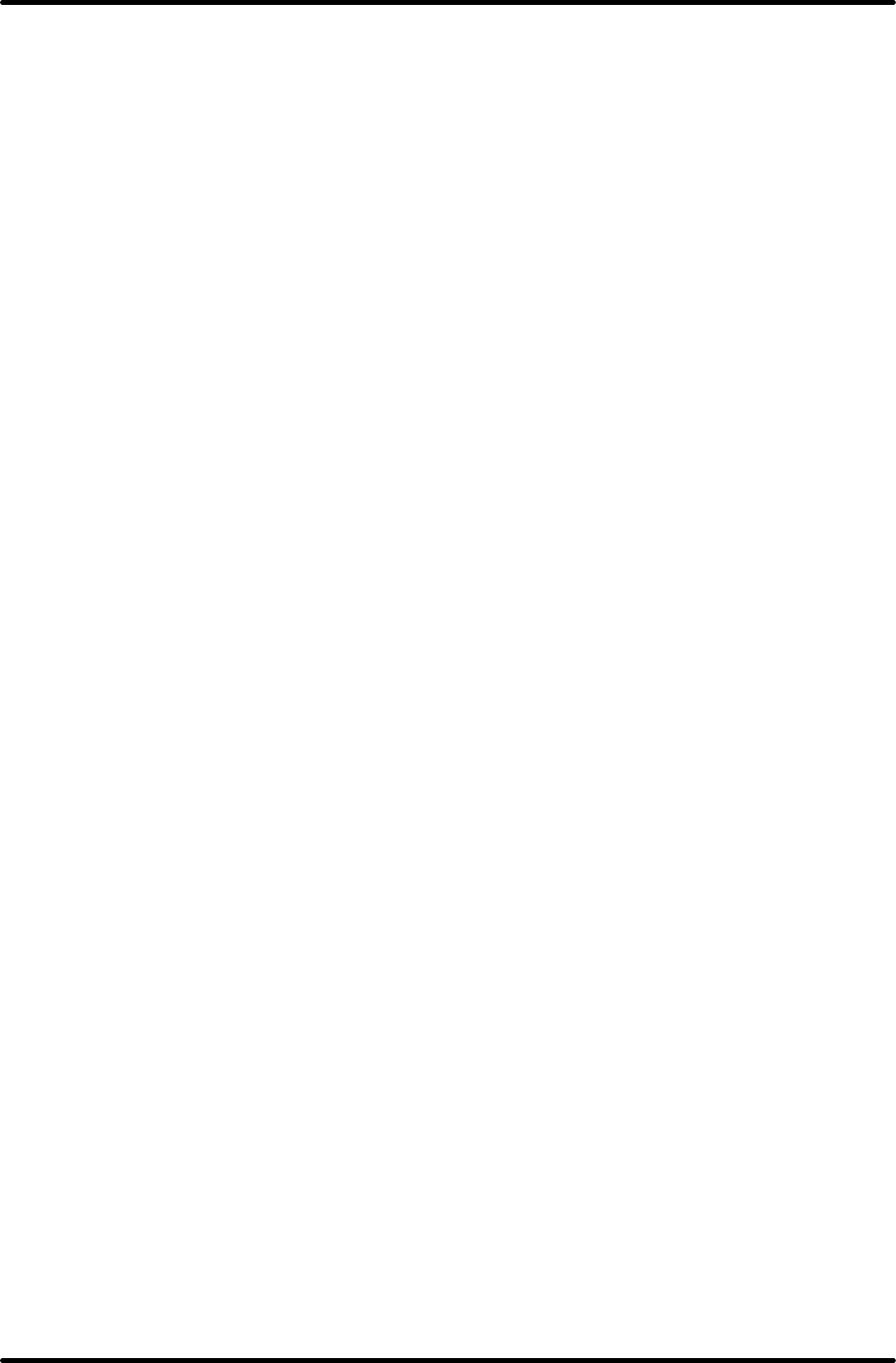
Innovator® HX Series Analog VHF Transmitter Chapter 1, Introduction
HX Series, Rev. 0 1-2
1.3 Safety
Products manufactured by Axcera are
designed to be easy to use and repair
while providing protection from electrical
and mechanical hazards. Listed
throughout the manual are notes,
cautions, and warnings concerning
possible safety hazards that may be
encountered while operating or servicing
the product. Please review these
warnings and familiarize yourself with the
operation and servicing procedures
before working on the product.
Read All Instructions – All of the
operating and safety instructions should
be read and understood before operating
this equipment.
Retain Manuals – The manuals for the
equipment should be retained at the site
in which the equipment is operating for
future reference. We provide two sets of
manuals for this purpose; one set can be
left at the office while one set can be
kept at the site.
Heed all Notes, Warnings, and
Cautions – All of the notes, warnings,
and cautions listed in this safety section
and throughout the manual must be
followed.
Follow Instructions – All of the
operating and use instructions for the
product should be followed.
Cleaning – Unplug or otherwise
disconnect all power from the equipment
before cleaning. Do not use liquid or
aerosol cleaners. Use a damp cloth for
cleaning.
Servicing – Do not attempt to service
this product yourself until becoming
familiar with the equipment. If in doubt,
refer all servicing questions to qualified
Axcera service personnel.
Replacement Parts – When
replacement parts are needed, be sure
that the parts have the same functional
and performance characteristics as the
original part. Unauthorized substitutions
may result in fire, electric shock, or other
hazards. Please contact the Axcera
Technical Service Department if you have
any questions regarding service or
replacement parts.
1.4 Contact Information
The Axcera Field Service Department can
be contacted by phone at (724) 873-
8100 or by fax at (724) 873-8105.
Before calling Axcera, please be prepared
to supply the Axcera technician with
answers to the following questions. This
will save time and help ensure the most
direct resolution to the problem.
1. What are the Customers’ Name
and call letters?
2. What are the model number and
type of transmitter?
3. Is the transmitter digital or
analog?
4. How long has the transmitter
been on the air? (Approximately
when was the transmitter
installed.)
5. What are the symptoms being
exhibited by the transmitter?
Include the current control/power
supply LCD readings and the
status of LEDs on the front
panels of the modules. If
possible, include the
control/power supply LCD
readings before the problem
occurred.
1.5 Material Return Procedure
To insure the efficient handling of
equipment or components that have been
returned for repair, Axcera requests that
each returned item be accompanied by a
Material Return Authorization Number
(MRA#).
An MRA# can be obtained from any
Axcera Service Engineer by contacting
the Axcera Technical Service Department
at (724) 873-8100 or by fax at (724)
873-8105. This procedure applies to all
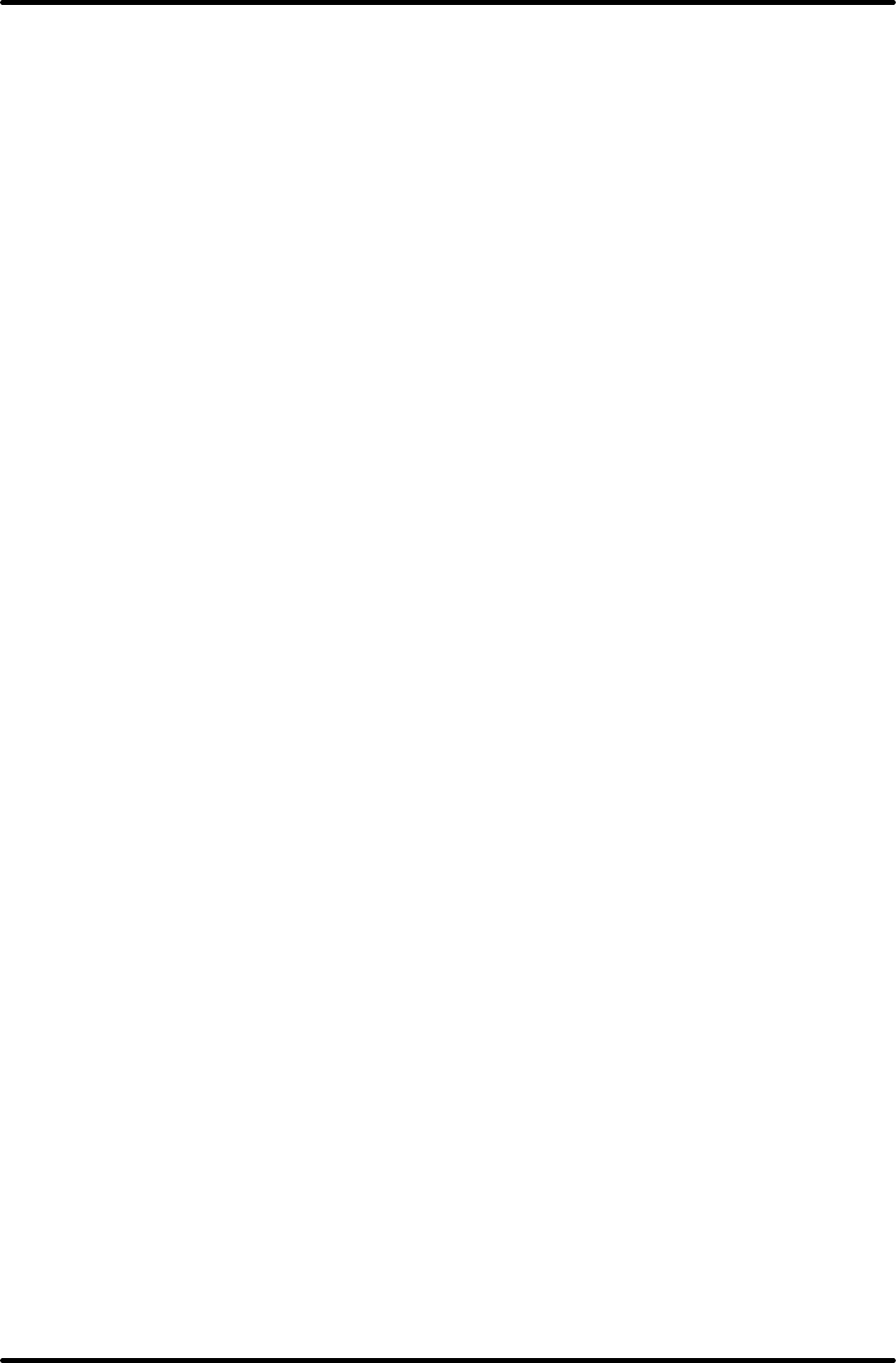
Innovator® HX Series Analog VHF Transmitter Chapter 1, Introduction
HX Series, Rev. 0 1-3
items sent to the Technical Service
Department regardless of whether the
item was originally manufactured by
Axcera.
When equipment is sent to the field on
loan, an MRA# is included with the unit.
The MRA# is intended to be used when
the unit is returned to Axcera. In
addition, all shipping material should be
retained for the return of the unit to
Axcera.
Replacement assemblies are also sent
with an MRA# to allow for the proper
routing of the exchanged hardware.
Failure to close out this type of MRA# will
normally result in the customer being
invoiced for the value of the loaner item
or the exchange assembly.
When shipping an item to Axcera, please
include the MRA# on the packing list and
on the Axcera-provided shipping
container. The packing slip should also
include contact information and a brief
description of why the unit is being
returned.
Please forward all MRA items to:
Axcera
Customer Service Department
103 Freedom Drive
P.O. Box 525
Lawrence, PA 15055-0525 USA
For more information, concerning this
procedure, call the Axcera Technical
Service Department.
Axcera can also be contacted through e-
mail at service@axcera.com and on the
Web at www.axcera.com.
1.6 Limited One-Year Warranty for
Axcera Products
Axcera warrants each new product that
it has manufactured and sold against
defects in material and workmanship
under normal use and service for a
period of one (1) year from the date of
shipment from Axcera's plant, when
operated in accordance with Axcera's
operating instructions. This warranty
shall not apply to tubes, fuses,
batteries, or bulbs.
Warranties are valid only when and if
(a) Axcera receives prompt written
notice of breach within the period of
warranty, (b) the defective product is
properly packed and returned by the
buyer (transportation and insurance
prepaid), and (c) Axcera determines, in
its sole judgment, that the product is
defective and not subject to any misuse,
neglect, improper installation,
negligence, accident, or (unless
authorized in writing by Axcera) repair
or alteration. Axcera's exclusive liability
for any personal and/or property
damage (including direct, consequential,
or incidental) caused by the breach of
any or all warranties, shall be limited to
the following: (a) repairing or replacing
(in Axcera's sole discretion) any
defective parts free of charge (F.O.B.
Axcera’s plant) and/or (b) crediting (in
Axcera's sole discretion) all or a portion
of the purchase price to the buyer.
Equipment furnished by Axcera, but not
bearing its trade name, shall bear no
warranties other than the special hours-
of-use or other warranties extended by
or enforceable against the manufacturer
at the time of delivery to the buyer.
NO WARRANTIES, WHETHER
STATUTORY, EXPRESSED, OR
IMPLIED, AND NO WARRANTIES OF
MERCHANTABILITY, FITNESS FOR
ANY PARTICULAR PURPOSE, OR
FREEDOM FROM INFRINGEMENT,
OR THE LIKE, OTHER THAN AS
SPECIFIED IN PATENT LIABILITY
ARTICLES, AND IN THIS ARTICLE,
SHALL APPLY TO THE EQUIPMENT
FURNISHED HEREUNDER.
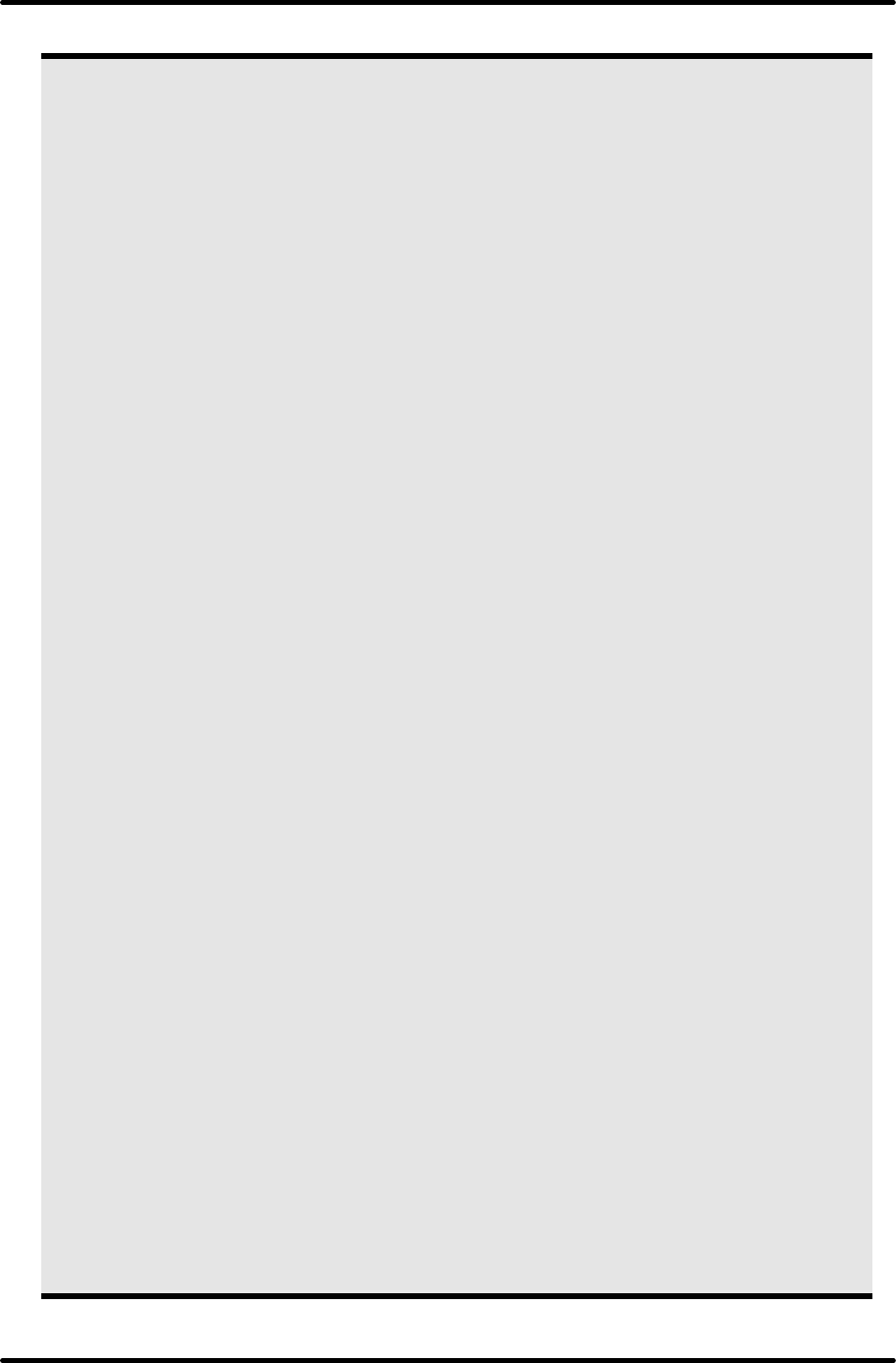
Innovator® HX Series Analog VHF Transmitter Chapter 1, Introduction
HX Series, Rev. 0 1-4
F WARNING!!!
× HIGH VOLTAGE Ø
DO NOT ATTEMPT TO REPAIR OR TROUBLESHOOT THIS EQUIPMENT UNLESS
YOU ARE FAMILIAR WITH ITS OPERATION AND EXPERIENCED IN
SERVICING HIGH VOLTAGE EQUIPMENT. LETHAL VOLTAGES ARE PRESENT
WHEN POWER IS APPLIED TO THIS SYSTEM. IF POSSIBLE, TURN OFF
POWER BEFORE MAKING ADJUSTMENTS TO THE SYSTEM.
« RADIO FREQUENCY RADIATION HAZARD «
MICROWAVE, RF AMPLIFIERS AND TUBES GENERATE HAZARDOUS RF
RADIATION THAT CAN CAUSE SEVERE INJURY INCLUDING CATARACTS,
WHICH CAN RESULT IN BLINDNESS. SOME CARDIAC PACEMAKERS MAY BE
AFFECTED BY THE RF ENERGY EMITTED BY RF AND MICROWAVE
AMPLIFIERS. NEVER OPERATE THE TRANSMITTER SYSTEM WITHOUT A
PROPERLY MATCHED RF ENERGY ABSORBING LOAD ATTACHED. KEEP
PERSONNEL AWAY FROM OPEN WAVEGUIDES AND ANTENNAS. NEVER
LOOK INTO AN OPEN WAVEGUIDE OR ANTENNA. MONITOR ALL PARTS OF
THE RF SYSTEM FOR RADIATION LEAKAGE AT REGULAR INTERVALS.
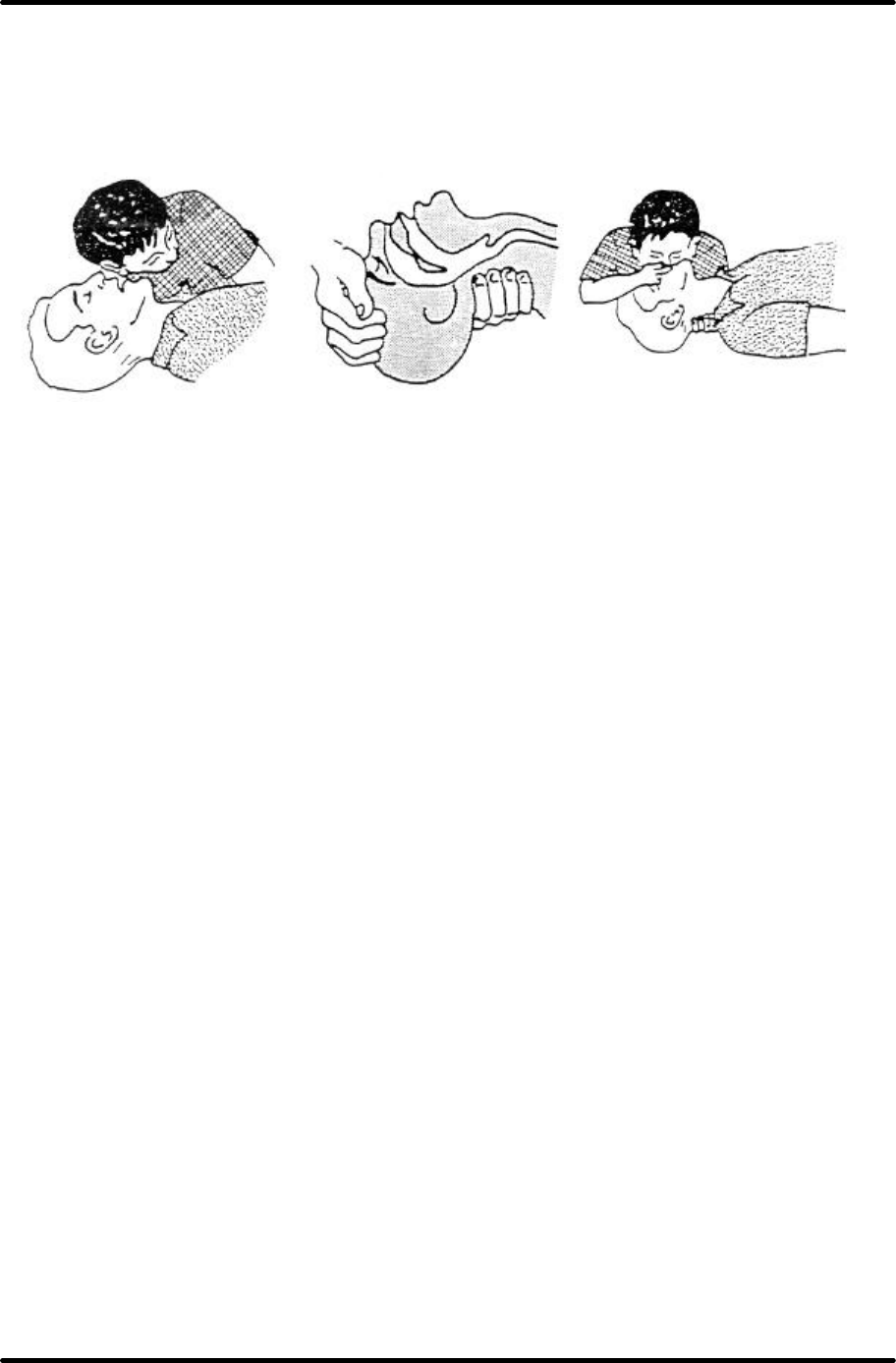
Innovator® HX Series Analog VHF Transmitter Chapter 1, Introduction
HX Series, Rev. 0 1-5
EMERGENCY FIRST AID INSTRUCTIONS
Personnel engaged in the installation, operation, or maintenance of this equipment are urged to become
familiar with the following rules both in theory and practice. It is the duty of all operating personnel to be
prepared to give adequate Emergency First Aid and thereby prevent avoidable loss of life.
RESCUE BREATHING
1. Find out if the person is
breathing.
You must find out if the person
has stopped breathing. If you
think he is not breathing, place
him flat on his back. Put your ear
close to his mouth and look at his
chest. If he is breathing you can
feel the air on your cheek. You
can see his chest move up and
down. If you do not feel the air
or see the chest move, he is not
breathing.
2. If he is not breathing, open
the airway by tilting his head
backwards.
Lift up his neck with one hand
and push down on his forehead
with the other. This opens the
airway. Sometimes doing this will
let the person breathe again by
himself.
3. If he is still not breathing,
begin rescue breathing.
-Keep his head tilted backward.
Pinch nose shut.
-Put your mouth tightly over his
mouth.
-Blow into his mouth once every
five seconds
-DO NOT STOP rescue breathing
until help arrives.
LOOSEN CLOTHING - KEEP
WARM
Do this when the victim is
breathing by himself or help is
available. Keep him as quiet as
possible and from becoming
chilled. Otherwise treat him for
shock.
BURNS
SKIN REDDENED: Apply ice cold water to burned
area to prevent burn from going deeper into skin
tissue. Cover area with a clean sheet or cloth to
keep away air. Consult a physician.
SKIN BLISTERED OR FLESH CHARRED: Apply
ice cold water to burned area to prevent burn from
going deeper into skin tissue.
Cover area with clean sheet or cloth to keep away
air. Treat victim for shock and take to hospital.
EXTENSIVE BURN - SKIN BROKEN: Cover area
with clean sheet or cloth to keep away air. Treat
victim for shock and take to hospital.
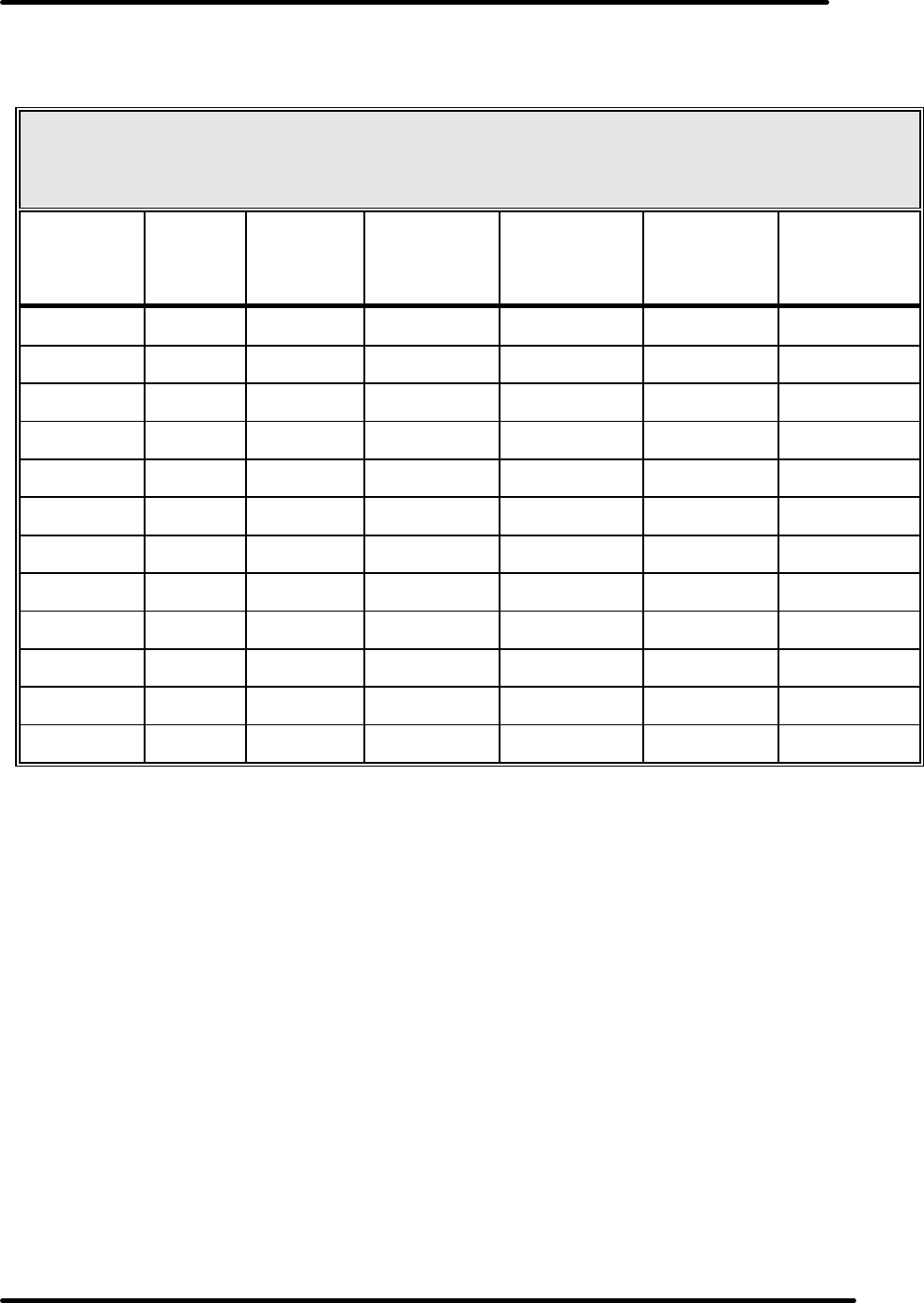
Innovator® HX Series Analog VHF Transmitter Chapter 1, Introduction
HX Series, Rev. 0 1-6
VHF TELEVISION CHANNEL FREQUENCIES
CHANNEL
FREQ
LIMIT
LOW
(MHz)
FREQ
LIMIT
HIGH
(MHz)
VISUAL
CARRIER
(Vc)
(MHz)
COLOR
CARRIER
(MHz)
AURAL
CARRIER
(MHz)
L.O. FREQ
45.75 + Vc
(MHz)
2 54.00 60.00 55.25 58.83 59.75 101
3 60.00 66.00 61.25 64.83 65.75 107
4 66.00 72.00 67.25 70.83 71.75 113
5 76.00 82.00 77.25 80.83 81.75 123
6 82.00 88.00 83.25 86.83 87.75 129
7 174.00 180.00 175.25 178.83 179.75 221
8 180.00 186.00 181.25 184.83 185.75 227
9 186.00 192.00 187.25 190.83 191.75 233
10 192.00 198.00 193.25 196.83 197.75 239
11 198.00 204.00 199.25 202.83 203.75 245
12 204.00 210.00 205.25 208.83 209.75 251
13 210.00 216.00 211.25 214.83 215.75 257
NOTE: Because of a possible FCC assigned offset, the carrier frequency may vary
from those given in the above table. Please check for the assigned carrier
frequency as written on the license.
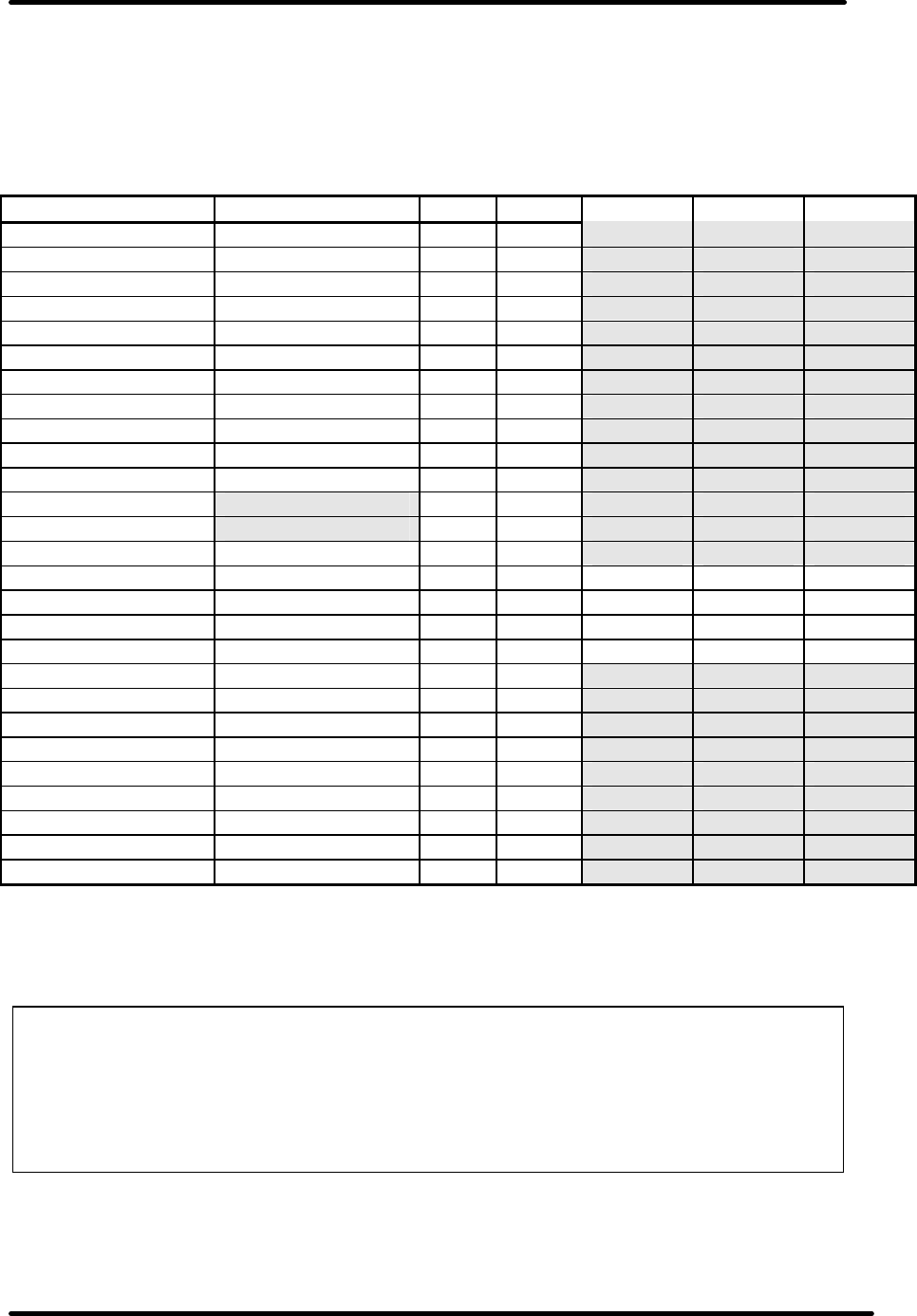
Innovator® HX Series Analog VHF Transmitter Chapter 1, Introduction
HX Series, Rev. 0 1-7
dBm, dBw, dBmV, dBµV, & VOLTAGE
EXPRESSED IN WATTS
50 Ohm System
WATTS PREFIX dBm dBw dBmV dBµV VOLTAGE
1,000,000,000,000 1 TERAWATT +150
+120
100,000,000,000 100 GIGAWATTS +140
+110
10,000,000,000 10 GIGAWATTS +130
+100
1,000,000,000 1 GIGAWATT +120
+ 99
100,000,000 100 MEGAWATTS +110
+ 80
10,000,000 10 MEGAWATTS +100
+ 70
1,000,000 1 MEGAWATT + 90 + 60
100,000
100 KILOWATTS + 80 + 50
10,000 10 KILOWATTS + 70 + 40
1,000 1 KILOWATT + 60 + 30
100 1 HECTROWATT + 50 + 20
50 + 47 + 17
20 + 43 + 13
10 1 DECAWATT + 40 + 10
1 1 WATT + 30 0 + 77 +137 7.07V
0.1 1 DECIWATT + 20 - 10 + 67 +127 2.24V
0.01 1 CENTIWATT + 10 - 20 + 57 +117 0.707V
0.001 1 MILLIWATT 0 - 30 + 47 +107 224mV
0.0001 100 MICROWATTS - 10 - 40
0.00001
10 MICROWATTS - 20 - 50
0.000001 1 MICROWATT - 30 - 60
0.0000001 100 NANOWATTS - 40 - 70
0.00000001 10 NANOWATTS - 50 - 80
0.000000001 1 NANOWATT - 60 - 90
0.0000000001 100 PICOWATTS - 70 -100
0.00000000001 10 PICOWATTS - 80 -110
0.000000000001 1 PICOWATT - 90 -120
TEMPERATURE CONVERSION
°F = 32 + [(9/5) °C]
°C = [(5/9) (°F - 32)]
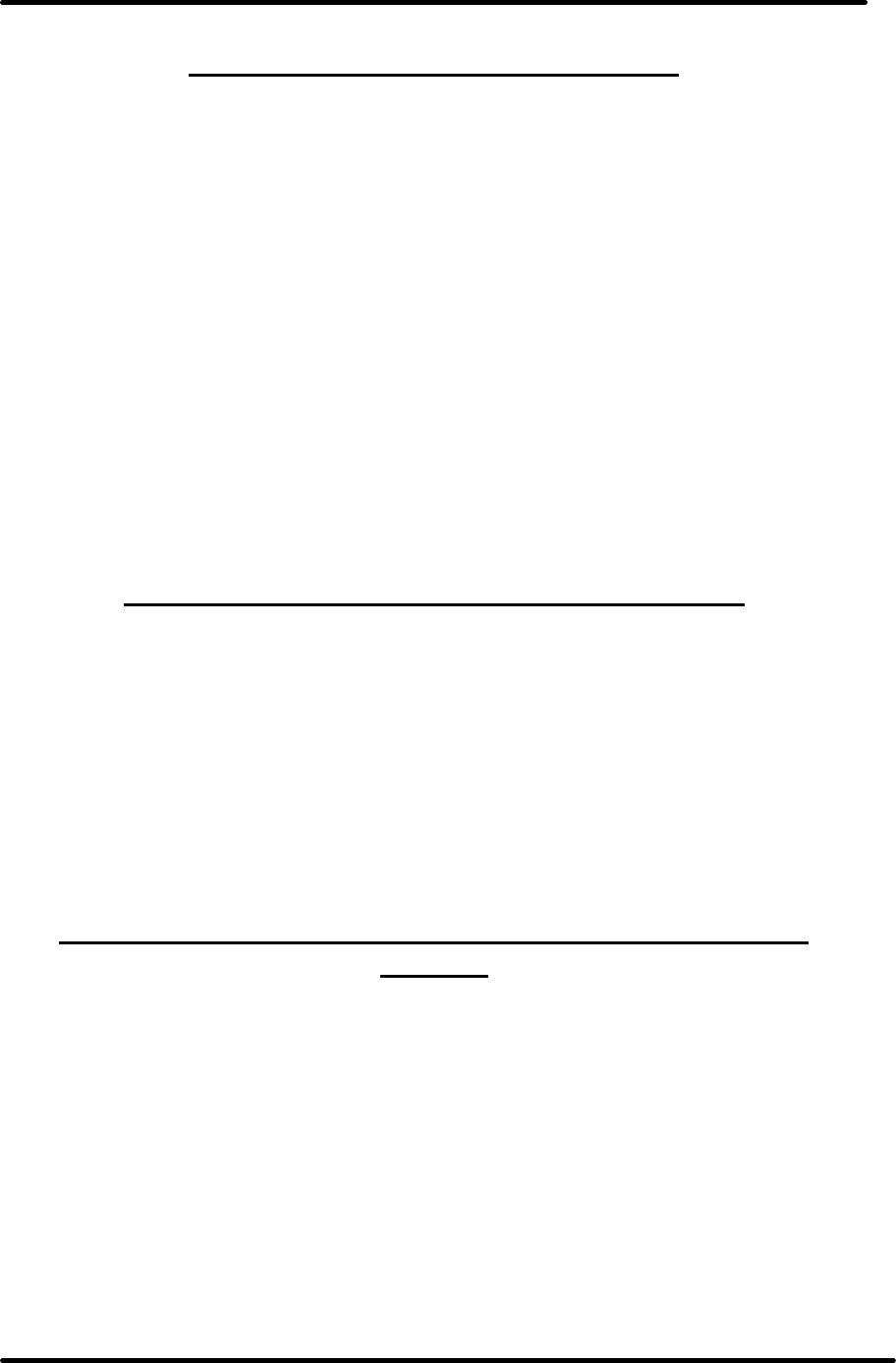
Innovator® HX Series Analog VHF Transmitter Chapter 1, Introduction
HX Series, Rev. 0 1-8
USEFUL CONVERSION FACTORS
TO CONVERT FROM TO MULTIPLY BY
mile (US statute) kilometer (km) 1.609347
inch (in) millimeter (mm) 25.4
inch (in) centimeter (cm) 2.54
inch (in) meter (m) 0.0254
foot (ft) meter (m) 0.3048
yard (yd) meter (m) 0.9144
mile per hour (mph) kilometer per hour(km/hr) 1.60934
mile per hour (mph) meter per second (m/s) 0.44704
pound (lb) kilogram (kg) 0.4535924
gallon (gal) liter 3.7854118
U.S. liquid
(One U.S. gallon equals 0.8327 Canadian gallon)
fluid ounce (fl oz) milliliters (ml) 29.57353
British Thermal Unit watt (W) 0.2930711
per hour (Btu/hr)
horsepower (hp) watt (W) 746
NOMENCLATURE OF FREQUENCY BANDS
FREQUENCY RANGE DESIGNATION
3 to 30 kHz VLF - Very Low Frequency
30 to 300 kHz LF - Low Frequency
300 to 3000 kHz MF - Medium Frequency
3 to 30 MHz HF - High Frequency
30 to 300 MHz VHF - Very High Frequency
300 to 3000 MHz UHF - Ultrahigh Frequency
3 to 30 GHz SHF - Superhigh Frequency
30 to 300 GHz EHF - Extremely High Frequency
LETTER DESIGNATIONS FOR UPPER FREQUENCY
BANDS
LETTER FREQ. BAND
L 1000 - 2000 MHz
S 2000 - 4000 MHz
C 4000 - 8000 MHz
X 8000 - 12000 MHz
Ku 12 - 18 GHz
K 18 - 27 GHz
Ka 27 - 40 GHz
V 40 - 75 GHz
W 75 - 110 GHz

Innovator® HX Series Analog VHF Transmitter Chapter 1, Introduction
HX Series, Rev. 0 1-9
RETURN LOSS VS. VSWR
1.001 1.01 1.1 2.0
VSWR
0
-
10
-
20
-
30
-
40
-
50
-
60
-
70
R
E
T
U
R
N
L
O
S
S
dB
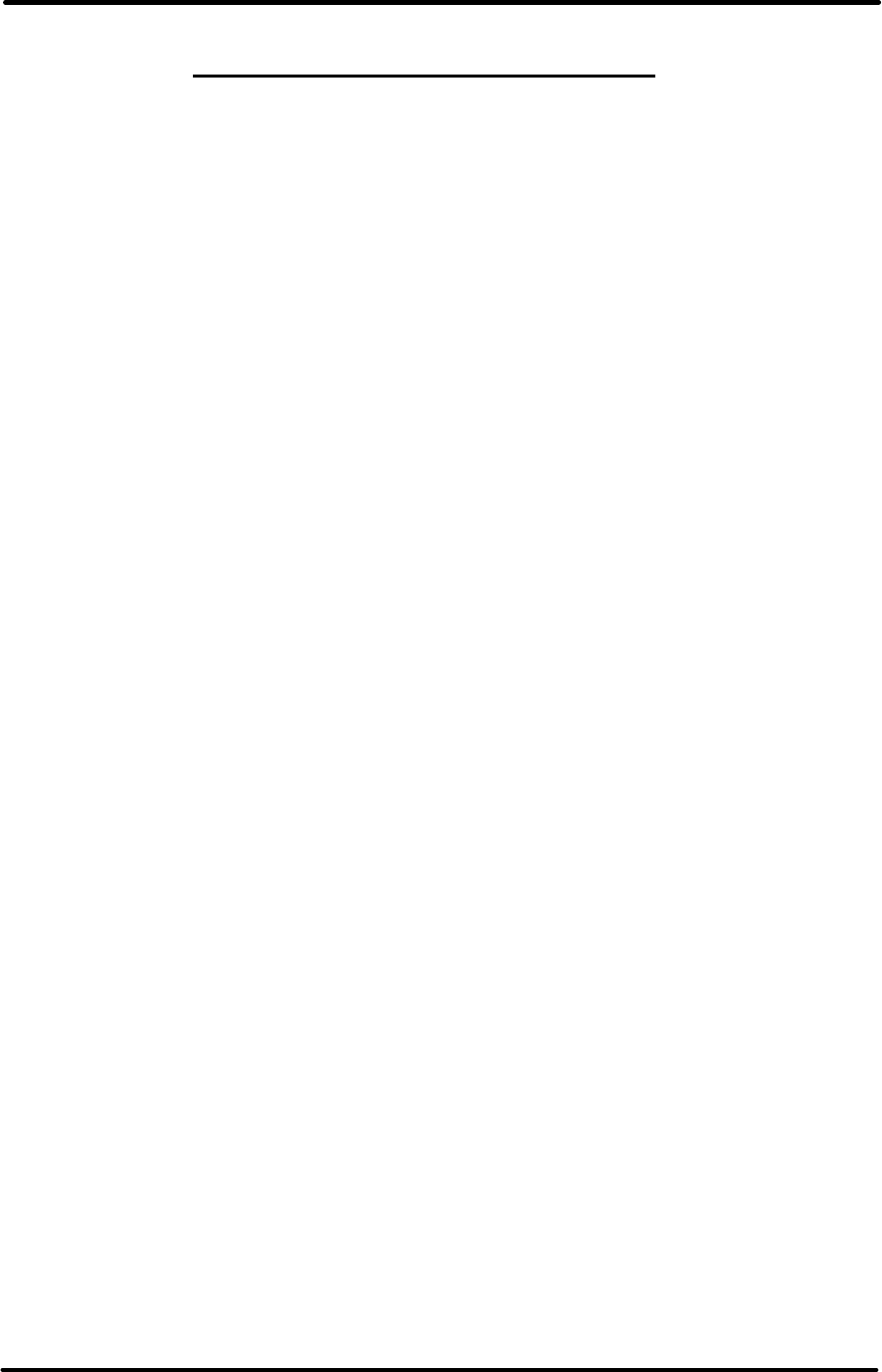
Innovator® HX Series Analog VHF Transmitter Chapter 1, Introduction
HX Series, Rev. 0 1-10
ABBREVIATIONS/ACRONYMS
AC Alternating Current
AFC Automatic Frequency Control
ALC Automatic Level Control
AM Amplitude modulation
AGC Automatic Gain Control
AWG American wire gauge
BER Bit Error Rate
BW Bandwidth
DC Direct Current
D/A Digital to analog
dB Decibel
dBm Decibel referenced to
1 milliwatt
dBmV Decibel referenced to
1 millivolt
dBw Decibel referenced to 1 watt
FEC Forward Error Correction
FM Frequency modulation
Hz Hertz
ICPM Incidental Carrier Phase
Modulation
I/P Input
LED Light emitting diode
LSB Lower Sideband
MPEG Motion Pictures Expert Group
O/P Output
PLL Phase Locked Loop
PCB Printed circuit board
QAM Quadrature Amplitude
Modulation
IF Intermediate Frequency
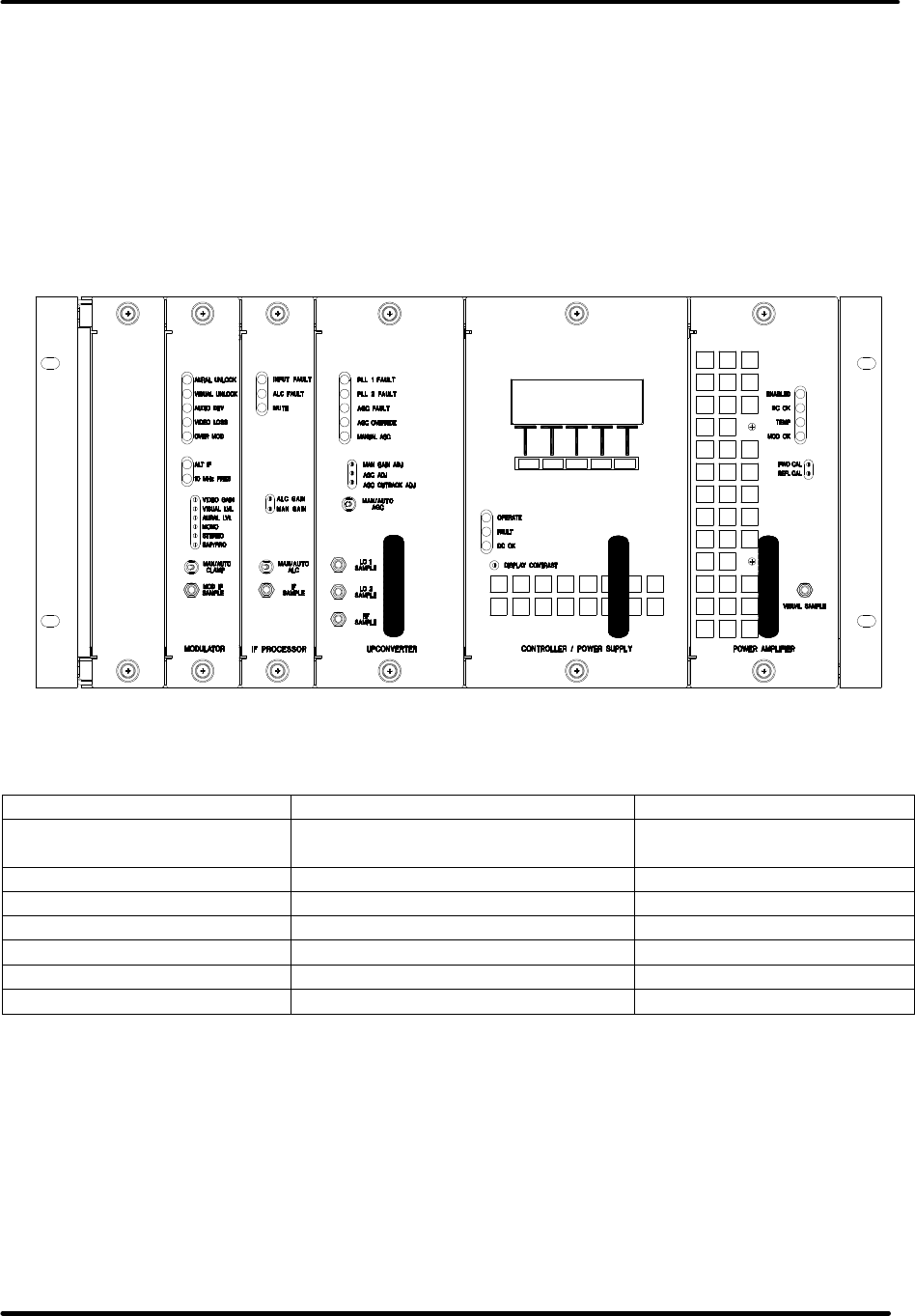
Innovator® HX Series Analog VHF Chapter 2, System Description
Transmitter and Remote Control Connections
HX Series, Rev. 0 2-1
Chapter 2
System Description and Remote Control Connections
2.0 System Overview
The Innovator® HX Series VHF
Transmitter is a complete internally
diplexed modular television transmitter.
It operates at a nominal output power of
100 watts analog.
The HX Series transmitter is made up of
the modules and assemblies as shown in
Figure 2-1 and listed in Table 2-1.
Figure 2-1: Transmitter Front View
Table 2-1: HX Series Trays and Assemblies
ASSEMBLY DESIGNATOR
TRAY/ASSEMBLY NAME PART NUMBER
Exciter Driver Chassis Assembly,
HX Series 1307715 (110 VAC)
A11 Backplane Board, Axciter 1307307
A2 Modulator Module 1305420
A3 IF Processor Module 1305421
A5 VHF/UHF Upconverter Module 1303829
A4 Control/Power Supply Module 1301936 (110 VAC)
A6 Power Amplifier Module 1305822
2.1 Exciter Amplifier Chassis
Assembly, (1307715/110VAC;
Appendix A)
All of the modules, except the power
amplifier module and the power supply
section of the Control & Monitoring/Power
Supply Module plug directly into the
Backplane Board, Axciter (1307307).
The backplane board provides module to
module interconnection as well as
interconnection to remote command and
control connectors. Refer to the
backplane board schematic drawing
(1307308), located in Appendix A, for the
exciter driver chassis assembly
connections.
A2
A3
A5
A4
A6
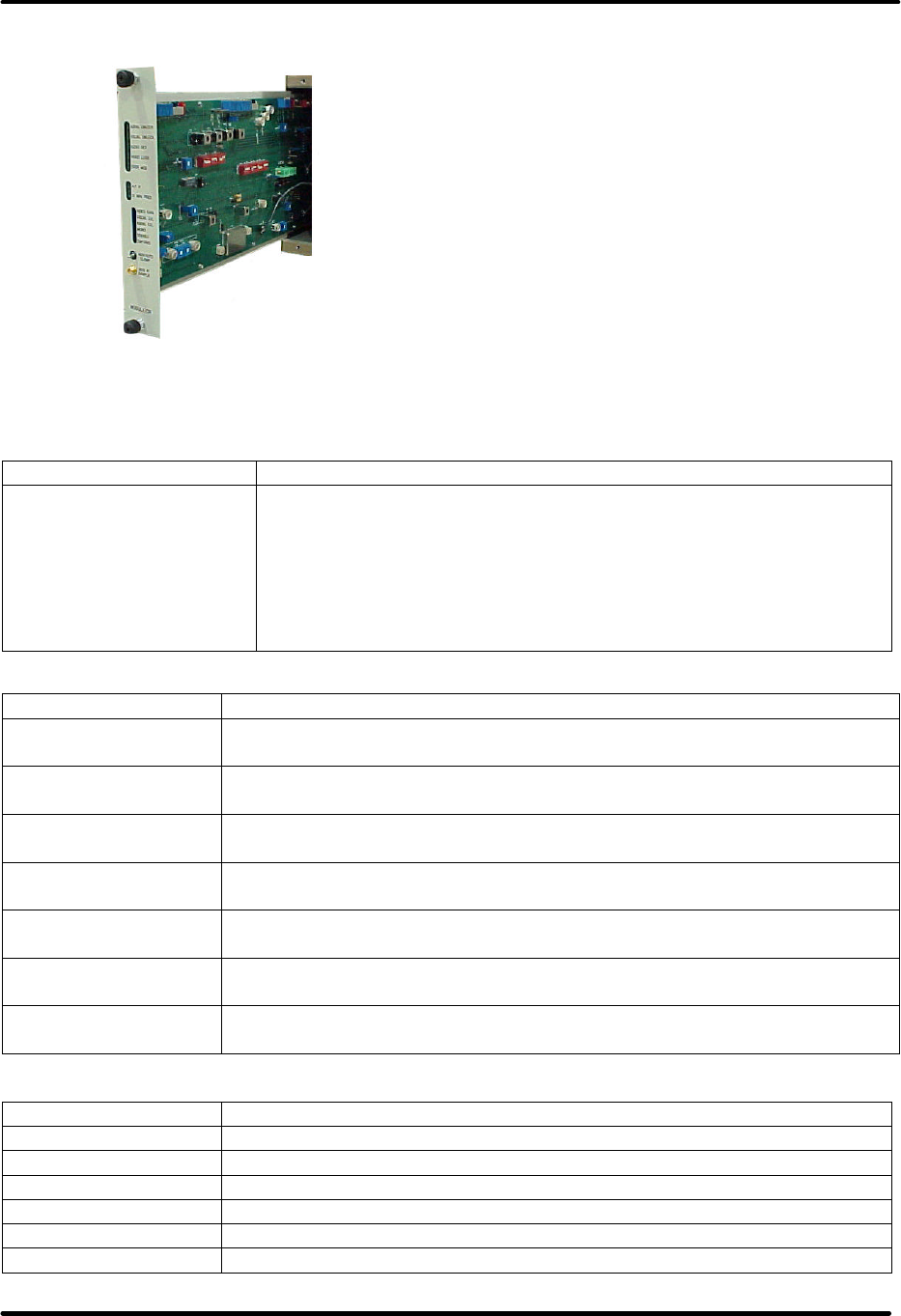
Innovator® HX Series Analog VHF Chapter 2, System Description
Transmitter and Remote Control Connections
HX Series, Rev. 0 2-2
2.1.1 (A2) Modulator Module
Assembly (1305420; Appendix A)
The (A2) Modulator Assembly contains
the Modulator Board (1304704). The
modulator is broadcast quality and
provides front panel access to control and
monitoring points. The video level is
controlled through a sync tip clamp and
sync and white clipping circuitry. The IF
oscillator is oven controlled and locked to
a 10 MHz reference for stability. The IF
signal is fed through a SAW filter for
precise sideband shaping. The Modulator
operates using the baseband audio and
video inputs to produce a diplexed,
modulated, and on-channel frequency
visual + aural IF output that is cabled to
the IF Processing Module.
Table 2-2. Modulator Front Panel Switch
SWITCH FUNCTION
MAN/AUTO CLAMP
SW1
When Manual Clamp is selected, the video level is set by the
Manual Bias Pot R67 located on the board. (NOTE: The pot is
factory set and needs no adjustment by the customer).
When Auto Clamp is selected, the video level control circuit
will automatically increase or decrease the video to maintain
the desired video level.
Table 2-3. Modulator Front Panel Status Indicators
LED FUNCTION
AUR UNLOCK
DS5 (Red) When lit it indicates that the 4.5 MHz VCO and the 10 MHz reference
are not PLL locked.
VIS UNLOCK
DS6 (Red) When lit it indicates that the 45.75 MHz VCXO and the 10 MHz
reference signal are not PLL locked.
AUDIO DEV
DS4 (Red) When lit it indicates the deviation level is more than ±80kHz
VIDEO LOSS
DS1 (Red) When lit it indicates the Video Input to the transmitter is lost.
OVER MOD
DS3 (Red) When lit it indicates the Video input level is too high.
ALT IF
DS7 (Green) When lit it indicates that external or alternate 4.5MHz is present.
10 MHz PRES
DS2 (Green) When lit it indicates that a 10MHz reference is present to the
transmitter.
Table 2-4. Modulator Front Panel Control Adjustments
POTENTIOMETERS
DESCRIPTION
Video Gain (R42) Adjusts the level of the output video.
Visual Level (R214) Adjusts the Visual IF level that combines with the Aural IF.
Aural Level (R243) Adjusts the Aural IF level that combines with the Visual IF.
MONO (R110) Adjusts the deviation level of the balanced audio input.
STEREO (R132) Adjusts the deviation level of the composite audio input.
SAP/PRO (R150) Adjusts the deviation level of the subcarrier audio input.
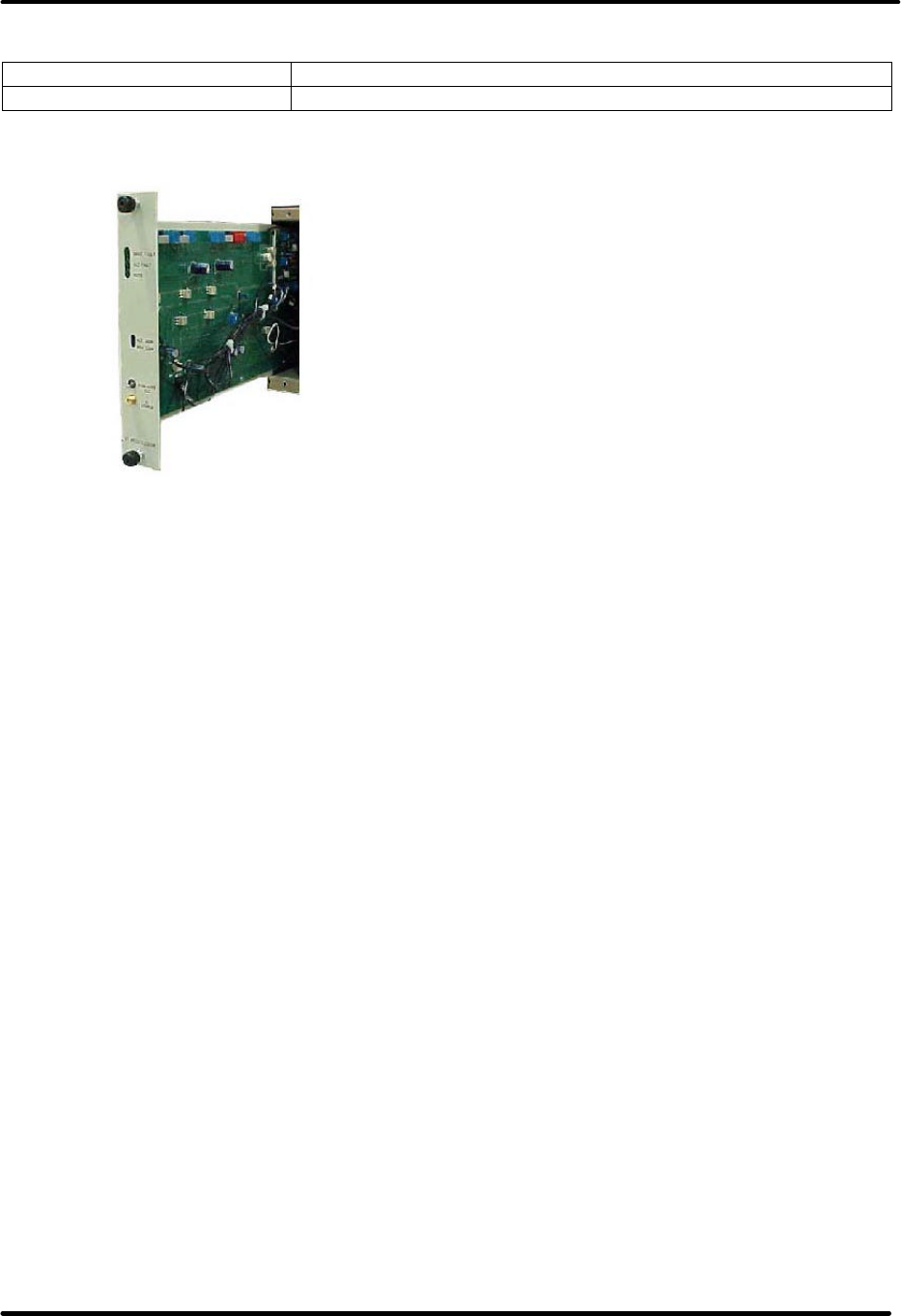
Innovator® HX Series Analog VHF Chapter 2, System Description
Transmitter and Remote Control Connections
HX Series, Rev. 0 2-3
Table 2-5. Modulator Front Panel Sample
SMA CONNECTOR DESCRIPTION
MOD IF SAMPLE (J10) Sample of the combined Aural IF and Visual IF signals.
2.1.2 (A3) IF Processor Module
Assembly (1305421; Appendix A)
The (A3) IF Processor Assembly contains
the IF Processor Board (1304687). The IF
Processor provides pre-correction to
ensure broadcast quality output signal.
The pre-correction consists of amplitude
linearity correction, Incidental Carrier
Phase Modulation (ICPM) correction and
frequency response correction.
The IF Processor module is configured
either for an analog or digital system.
Pin 13C of the IF Processor module is
grounded in analog systems and left not
connected in digital systems. An IF
Processor Interlock signal is used to
report the presence of the IF Processor
module to the Control Monitoring board.
If the IF Processor interlock signal is not
present, the HX Series Exciter Driver RF
output is Muted (turned off).
The Control & Monitoring/Power Supply
module uses the IF Processor module for
System output power control. Through
the front panel display or a remote
interface, an operator can set the RF
output power level of the transmitter.
The range of RF power adjustment is
between 0% (full off) and 105% (full
power plus). A front panel IF Processor
module potentiometer sets the upper
limit of RF power at 120%. The
system's Control Monitoring board
compares the RF Power Monitoring
module RF power level with the desired
level and uses the IF Power Control PWM
line to correct for errors.
The IF Processor module provides a
reference ALC voltage to the system's
Upconverter. When the ALC voltage
decreases, the Upconverter
automatically lowers the system output
power through the AGC circuits.
The IF Processor module has a front
panel switch to select Auto or Manual
ALC. When Manual ALC is selected, the
reference ALC voltage is set by a front
panel potentiometer. In this condition,
the RF power level control circuit is
removed from use. When the ALC select
switch is changed to Auto, the RF power
level control circuit will start at low
power and increase the RF output until
the desired output power is attained.
The IF Processor module Modulation
Present signal is monitored by the
Control Monitoring board. If the
modulation level is too low or non-
existent, a Modulation Present Fault is
reported to the Control Monitoring
board. When the controller detects this
fault, it can be set to Automatically Mute
the transmitter or if it is set to Manual
mode the transmitter will continue to
operate at 25% output.
The IF Processor module Input Signal
level is monitored by the Control
Monitoring board. If the signal level is
too low or non-existent, an Input Fault
is reported on the Control Monitoring
board. When the IF Processor board
detects an Input Signal Fault it
automatically Mutes the transmitter.
The system controller does not Mute on
an IF Processor Input Fault.
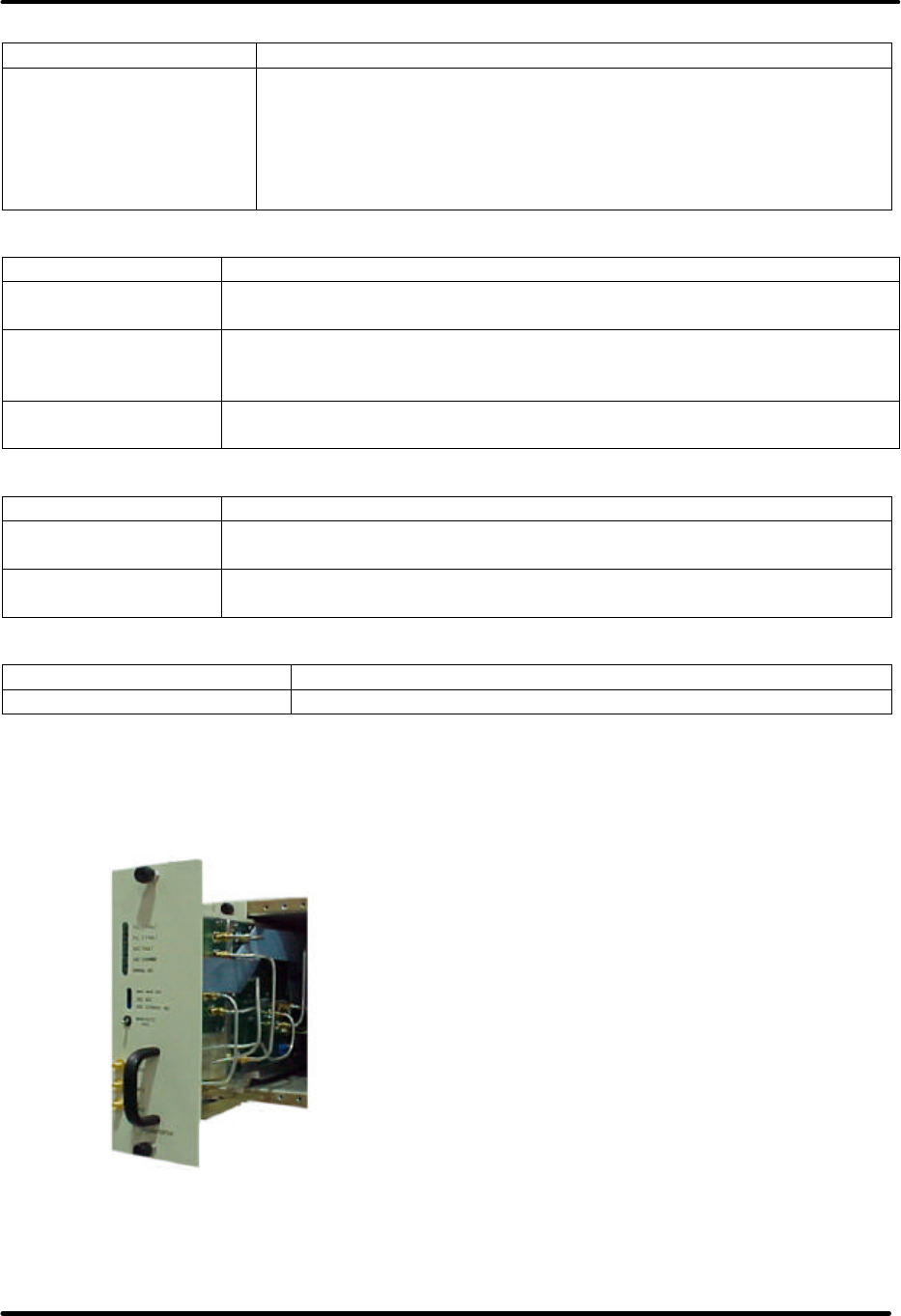
Innovator® HX Series Analog VHF Chapter 2, System Description
Transmitter and Remote Control Connections
HX Series, Rev. 0 2-4
Table 2-6. IF Processor Front Panel Switch
SWITCH FUNCTION
MAN/AUTO ALC
When Manual ALC is selected, the reference ALC voltage is set
by the ALC Gain front panel potentiometer.
When Auto ALC is selected, the IF level control circuit will
automatically increase the IF output until the desired output
power is attained.
Table 2-7. IF Processor Front Panel Status Indicators
LED FUNCTION
INPUT FAULT (Red) When lit it indicates that there is a loss of the IF Input signal to the
IF Processor. Transmitter can be set to Mute on an IF Input Fault.
ALC Fault (Red) When lit it indicates that the required gain to produce the desired
output power level has exceeded the operational range of the ALC
circuit. The LED will also be lit when ALC is in Manual.
MUTE (Red) When lit it indicates that the IF input signal is cut back but the
enable to the Power Supply is present and the +32 VDC remains on.
Table 2-8. IF Processor Front Panel Control Adjustments
POTENTIOMETERS
DESCRIPTION
ALC GAIN Adjusts the gain of the transmitter when the transmitter is in the
Auto ALC position.
MAN GAIN Adjusts the gain of the transmitter when the transmitter is in the
Manual ALC position.
Table 2-9. IF Processor Front Panel Sample
SMA CONNECTOR DESCRIPTION
IF SAMPLE Sample of the pre-corrected IF output of the IF Processor
2.1.3 (A5) VHF/UHF Upconverter
Module Assembly (1303829;
Appendix A)
The VHF/UHF Upconverter Module
Assembly contains (A1) a Downconverter
Board Assembly (1303834), (A3) a First
Conversion Board (1303838), (A2) a L-
Band PLL Board (1303846) and (A4) an
Upconverter Control Board (1304760).
A 44 MHz IF input @ 0 dBm level
connects to the upconverter through the
backplane board and is applied to a
mixer mounted on the first conversion
board. Also applied to the mixer is a
nominal 1 GHz LO1. The mixer converts
it to a nominal frequency centered at
1044 MHz. A filter selects the
appropriate conversion product, which is
then amplified to a level of
approximately –4 dBm. The frequency
of the first conversion LO1 can be
shifted by ± 10 kHz to generate channel
offsets of 10kHz. For +offsets the
frequency is 999.99 MHz and for –
offsets the frequency is 1000.01 MHz.
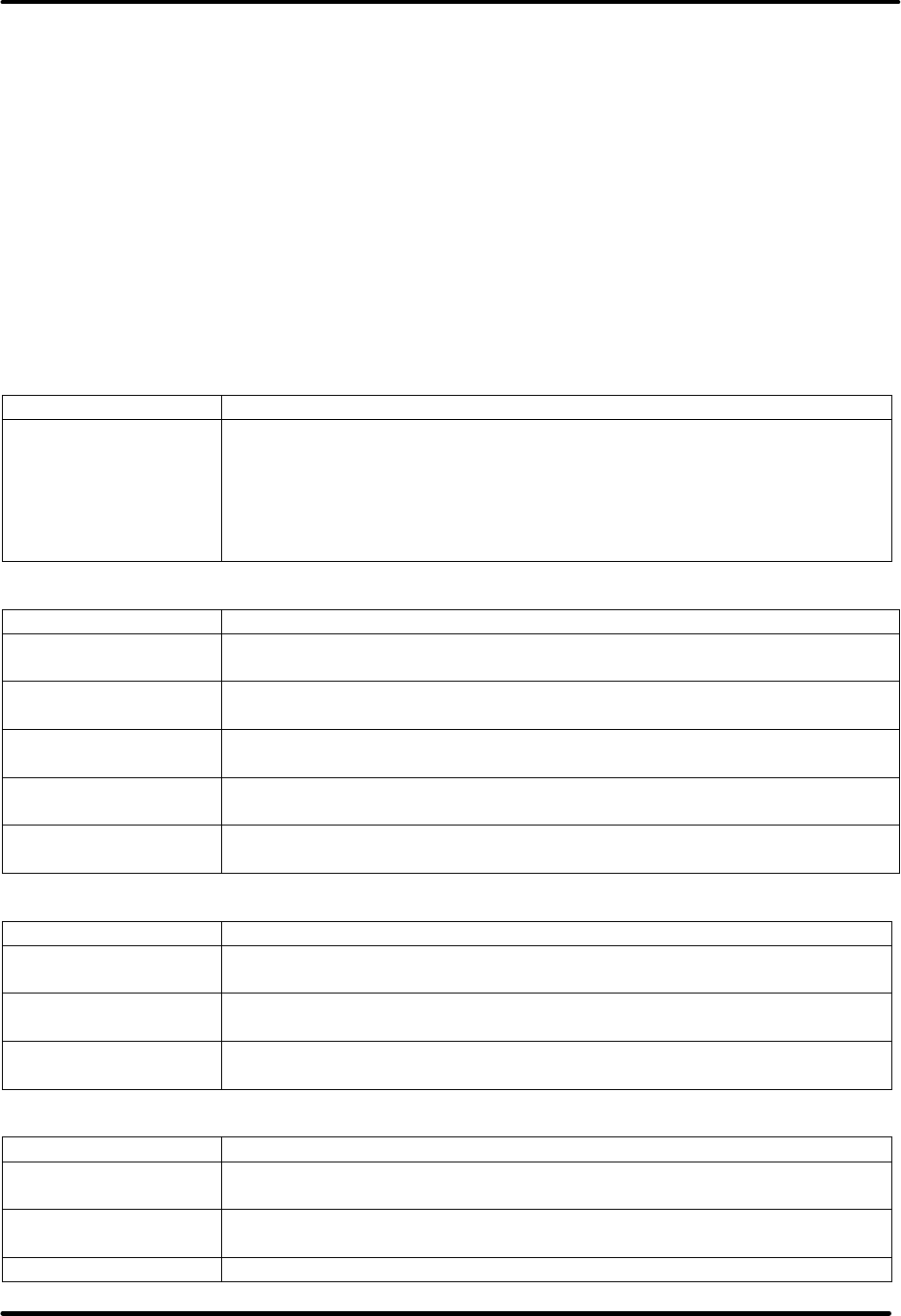
Innovator® HX Series Analog VHF Chapter 2, System Description
Transmitter and Remote Control Connections
HX Series, Rev. 0 2-5
This signal is applied to a second mixer
mounted on the downconverter board
that converts it back to a broadcast
channel (2-69) by an LO2 that operates
in 100kHz steps between 1.1-1.9 GHz
depending on the channel selected. The
LO2 frequency equals the Channel
center frequency plus the LO1 frequency
plus 44 MHz. (As an example CH9:
Center Frequency is 189.00 MHz and
LO1 is 1000.00 MHz therefore, LO2 is
189 + 1000 + 44, which equals 1233.00
MHz.)
The output of the mixer is applied to a
900 MHz Low pass filter to remove
unwanted conversion products. The
resulting signal is amplified and applied
to a Pin diode attenuator before it is
connected to the output of the
upconverter. This pin diode attenuator
adjusts the gain of the module and is
controlled by an Automatic Gain Control
circuit, which maintains a constant
power out of the upconverter, and also
the transmitter, that connects to the
power amplifier module.
Table 2-10. VHF/UHF Upconverter Front Panel Switch
SWITCH FUNCTION
MAN/AUTO AGC
(Left Manual, Right
AGC)
When Manual AGC is selected, the reference AGC voltage is set by
the AGC Manual Gain front panel potentiometer.
When Auto AGC is selected, the RF power level control circuit will
automatically increase the RF output until the desired output
power is attained.
Table 2-11. VHF/UHF Upconverter Front Panel Status Indicators
LED FUNCTION
PLL 1 Fault
(Red) When lit it indicates that the 1 GHz PLL is unlocked
PLL 2 Fault
(Red) When lit it indicates that the 1.1 –1.9 GHz PLL is unlocked
AGC Fault
(Red) When lit it indicates that the AGC is out of range.
AGC Override
(Red) When lit it indicates that the AGC is cutting back due to too much
drive to the driver module.
Man Gain
(Amber) When lit it indicates that the AGC is bypassed in Manual.
Table 2-12. VHF/UHF Upconverter Front Panel Control Adjustments
POTENTIOMETERS
DESCRIPTION
MAN GAIN ADJ Adjusts the gain of the upconverter and transmitter when in the
Manual AGC position.
AGC ADJ Adjusts the gain of the upconverter and transmitter when in the
Auto AGC position.
AGC CUTBACK ADJ
(AGC OVERRIDE) Adjusts the point at which the transmitter will cut back in power,
due to too much drive, when the Transmitter is in Auto AGC.
Table 2-13. VHF/UHF Upconverter Front Panel Samples
SMA CONNECTOR DESCRIPTION
LO1 SAMPLE Sample of the 1 GHz nominal LO1 signal in the Upconverter as
generated on the L-Band PLL Board.
LO2 SAMPLE Sample of the 1.1-1.9 GHz LO2 signal in the Upconverter as
generated on the First Conversion Board.
RF SAMPLE Sample of the On Channel RF Output of the Upconverter
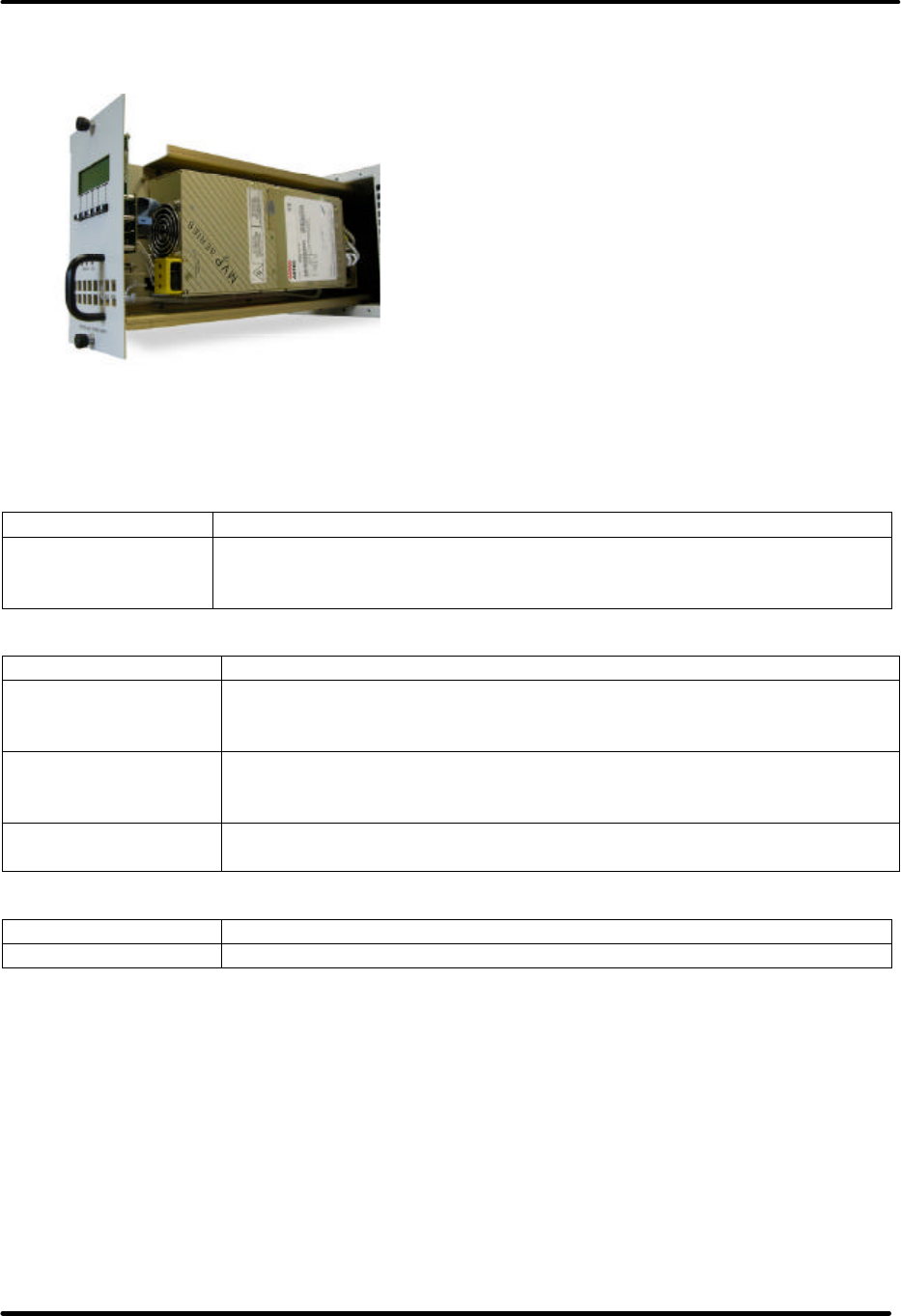
Innovator® HX Series Analog VHF Chapter 2, System Description
Transmitter and Remote Control Connections
HX Series, Rev. 0 2-6
2.1.4 (A4) Control/Power Supply
Module Assembly (1301936/110 VAC;
Appendix A)
The (A4) Control & Monitoring/Power
Supply Assembly is made up of a Control
Board (1302021), a Power Protection
Board (1302837) and a Switch Board
(1527-1406). The Assembly also
contains a switching power supply that
provides ±12 VDC to the rest of the
modules in the chassis and +32 VDC to
the Power Amplifier module.
The Assembly provides all transmitter
control and monitoring functions. The
Front panel LCD screens allow monitoring
of system parameters, including forward
and reflected power, transistor currents,
module temperatures and power supply
voltages. The LCD screens are detailed
in Chapter 3.
Table 2-14. Controller/Power Supply Display
DISPLAY FUNCTION
LCD A 4 x 20 display providing a four-line readout of the internal
functions, external inputs, and status. See Chapter 3,
Controller/Power Supply Display Screens, for a listing of displays.
Table 2-15. Controller/Power Supply Status Indicator
LED FUNCTION
OPERATE
(green)
When lit it indicates that the transmitter is in the Operate Mode. If
transmitter is Muted the Operate LED will stay lit, the transmitter
will remain in Operate, until the input signal is returned.
FAULT
(red or green)
Red indicates that a problem has occurred in the transmitter. The
transmitter will be Muted or placed in Standby until the problem is
corrected.
DC OK
( red or green ) Green indicates that the switchable fuse protected DC outputs that
connect to the modules in the transmitter are OK.
Table 2-16. Controller/Power Supply Control Adjustments
POTENTIOMETERS
DESCRIPTION
DISPLAY CONTRAST Adjusts the contrast of the display for desired viewing of screen.
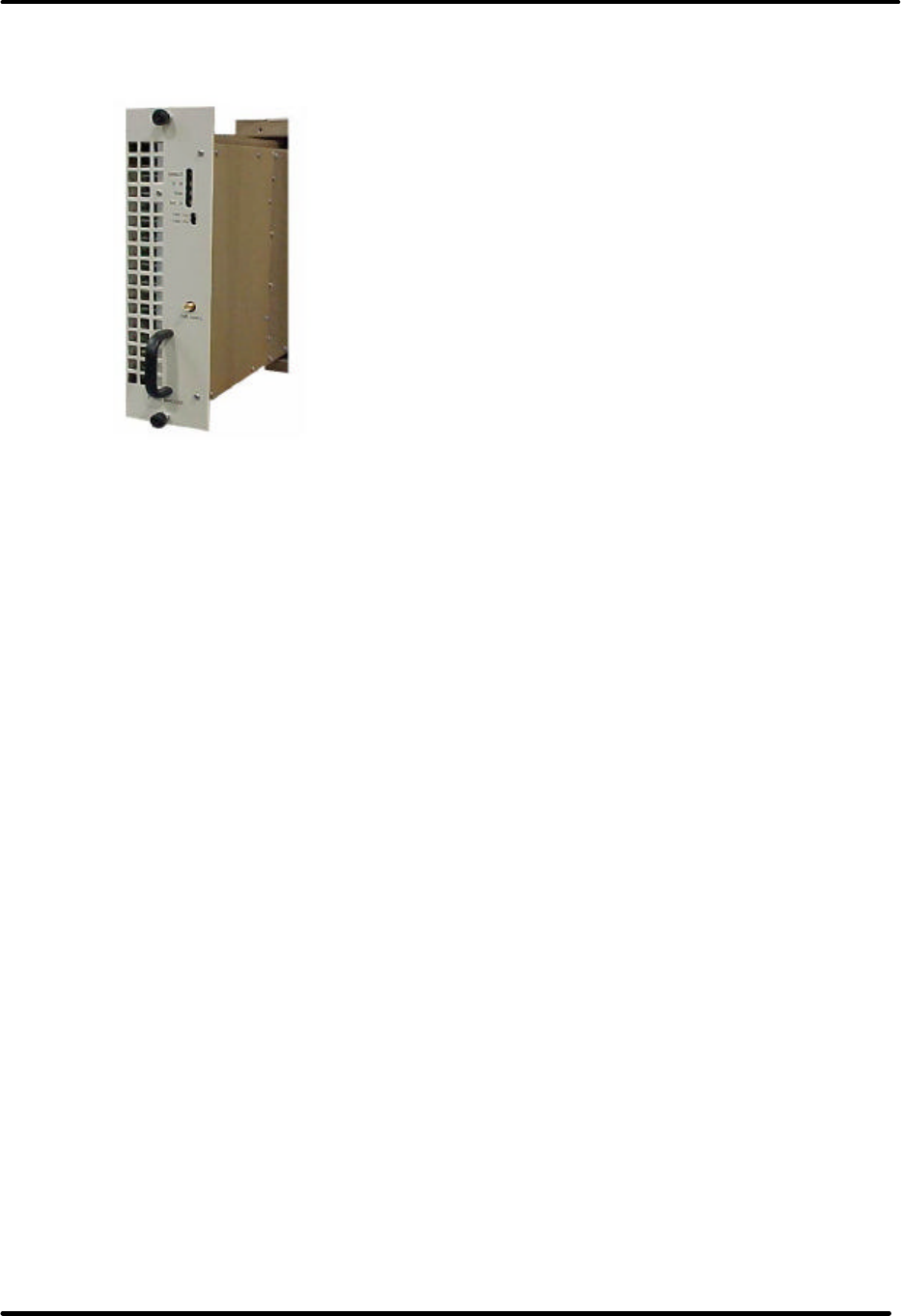
Innovator® HX Series Analog VHF Chapter 2, System Description
Transmitter and Remote Control Connections
HX Series, Rev. 0 2-7
2.1.5 (A6) VHF Power Amplifier
Module (1305822; Appendix A)
The (A6) Power Amplifier Module
Assembly is made up of a Coupler Board
Assembly (1211-1004), an Amplifier
Control Board (1303682), a Delta RF 25
Watt VHF Driver Assembly (1305820)
and a Delta RF 200 Watt VHF Amplifier
Assembly (1300167).
The Power Amplifier Module contains
Broadband LDMOS amplifiers that cover
the VHF High Band with no tuning
required. They amplify the RF to the
output power of the transmitter.
The Power Amplifier is used to amplify
the RF output of the Upconverter
module. A jumper cable, located on the
rear chassis, connects the RF output from
the LO/Upconverter at J23 to J24 the RF
input to the PA Assembly.
The Power Amplifier module contains an
amplifier control and monitoring board.
This board monitors the RF output
power, RF reflected power, the current
draw of amplifier sections, the supply
voltage, and the temperature of the PA
heat sink. The Control and monitoring
lines to the Power Amplifier module are
routed through the floating blind-mate
connector of the Control &
Monitoring/Power Supply module.
The RF power detector circuit outputs
vary with operating frequency. These
circuits must be calibrated at their
intended operating frequency. Front
panel adjustment potentiometers, R201
for Reflected Power and R202 for
Forward Power, are used for calibration.
The Aural power of the Power Amplifier
assembly is not reported by the system
Control Monitoring module. Additionally
the Visual power of the amplifier is
reported as Forward Power.
The Forward Power of the Power
Amplifier module is routed to the
Upconverter module as AGC #1. A
system over-drive condition is detected
when this value rises above 0.9 VDC.
When an over-drive condition is
detected, the Upconverter module
reduces its RF output level. For values
less than 0.9 VDC, the Upconverter uses
this voltage for automatic gain.
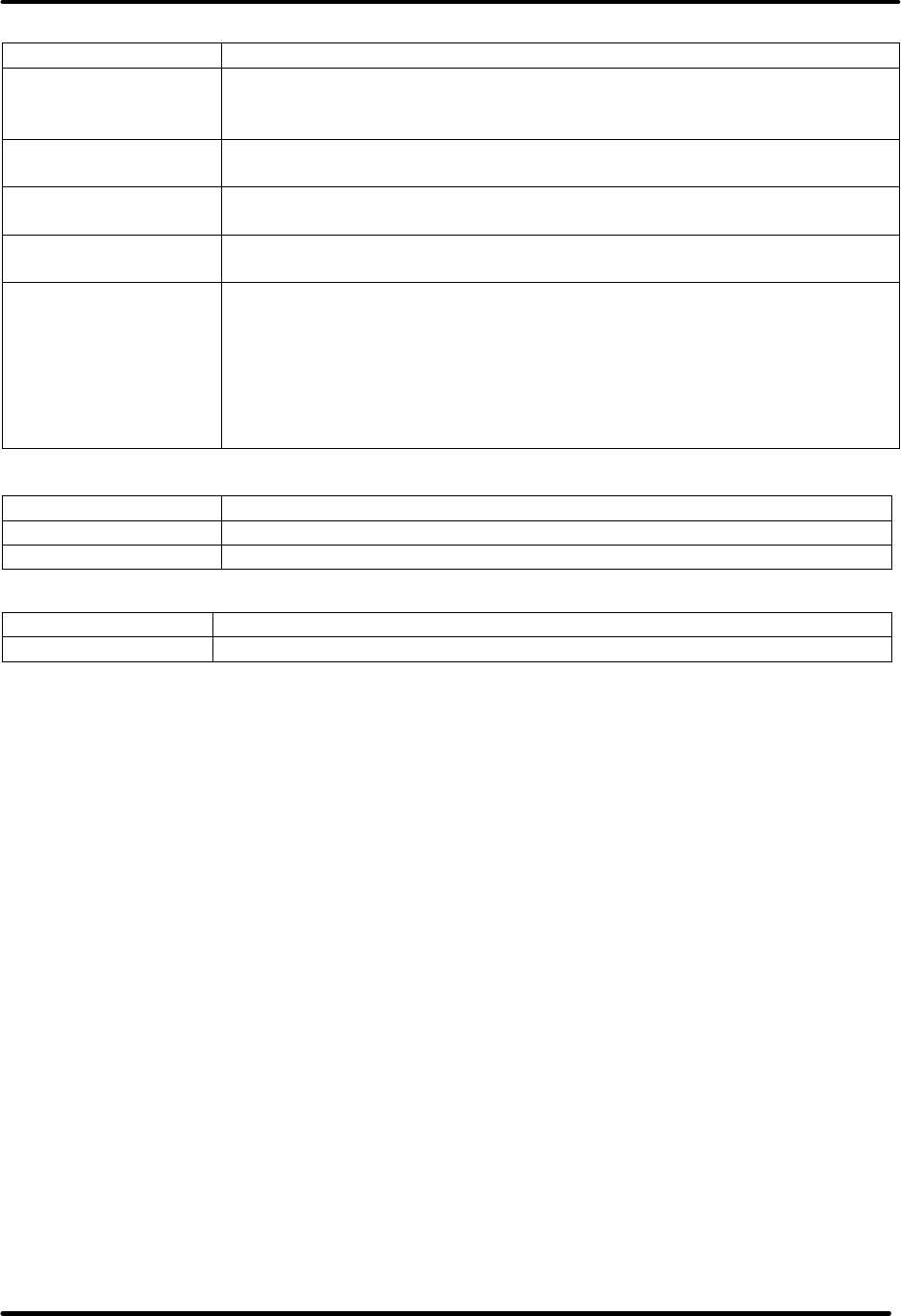
Innovator® HX Series Analog VHF Chapter 2, System Description
Transmitter and Remote Control Connections
HX Series, Rev. 0 2-8
Table 2-17. Power Amplifier Status Indicator
LED FUNCTION
ENABLED
(Green)
When lit Green, it indicates that the PA is in the Operate Mode. If a
Mute occurs, the PA will remain Enabled, until the input signal is
returned.
DC OK
(Green) When lit Green, it indicates that the fuse protected DC inputs to the
PA module are OK.
TEMP
(Green) When lit Green, it indicates that the temperature of the heatsink
assembly in the module is below 78°C.
MOD OK
(Green) When lit Green, it indicates that the PA Module is operating and has
no faults.
MOD OK
(Red)
If the Module OK LED is Red and blinking a fault is present.
1 Blink indicates Amplifier Current Fault.
2 Blinks indicate Temperature Fault.
3 Blinks indicate +32V Power Supply Over Voltage Fault.
4 Blinks indicate +32V Power Supply Under Voltage Fault.
5 Blinks indicate Reflected Power Fault.
6 Blinks indicate +12V or –12V Power Supply Fault.
Table 2-18. Power Amplifier Control Adjustments
POTENTIOMETERS
DESCRIPTION
FWD CAL Adjusts the gain of the Forward Power monitoring circuit
RFL CAL Adjusts the gain of the Reflected Power monitoring circuit
Table 2-19. Power Amplifier Sample
DISPLAY FUNCTION
VISUAL SAMPLE RF sample of the amplified signal being sent out the module on J25.
2.1.6 RF Output
The RF output from the power amplifier is
at the RF output jack, an “N” connector
J25, PA RF Output, of the chassis
assembly. This is the 100 Watt VHF
output of the transmitter that connects to
the bandpass filter for your system..
2.2 Control and Status
The control and status readings of the
chassis assembly are found by operating
the front panel display screen located on
the front of the control assembly.
Detailed information on the use of the
screens is found in chapter 3.
2.2.1 Front Panel Display Screens
A 4 x 20 display located on the front of
the Control & Monitoring/Power Supply
Module is used in the HX Series
transmitter for control of the operation
and display of the operating parameters
of the transmitter. Refer to Chapter 3
for descriptions of the screens.
2.3 System Operation
When the transmitter is in operate, as set
by the menu screen located on the
Control & Monitoring Module, the
following occurs. The IF Processor will be
enabled and the mute indicator on the
front panel will be extinguished. The
+32 VDC stage of the Power Supply in
the Control & Monitoring Module is
enabled, the operate indicator on the
front panel is lit and the DC OK on the
front panel will also be green. The
enable and DC OK indicators on the PA
Module will also be green.
When the transmitter is in standby, the
following occurs. The IF Processor will be
disabled; the mute indicator on the front
panel will be red. The +32 VDC stage of
the Power Supply in the Control &
Monitoring Module is disabled. The
operate indicator on the front panel will
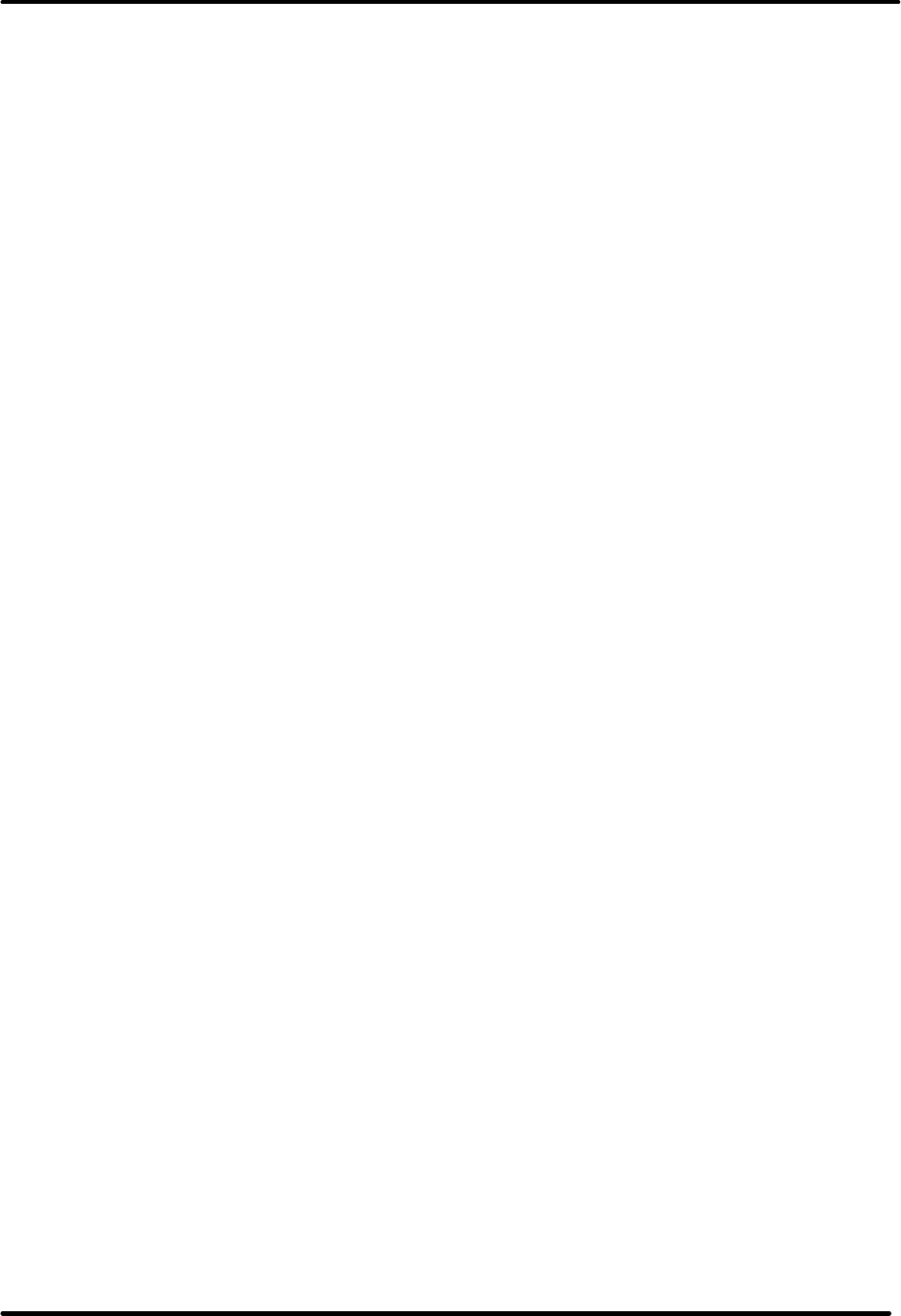
Innovator® HX Series Analog VHF Chapter 2, System Description
Transmitter and Remote Control Connections
HX Series, Rev. 0 2-9
be extinguished and the DC OK on the
front panel will remain green. The
enable indicator on the PA Module is
extinguished.
If the transmitter does not switch to
Operate when the operate menu is
switched to Operate, check that all faults
are cleared from the Fault Log and that
the remote control terminal block stand-
by signal is not active. Also check that
TB30-5 and TB30-17, on the remote
control terminal block are connected
together providing the needed
transmitter interlock.
The transmitter can be controlled by the
presence of a modulated input signal. If
the input signal to the transmitter is lost,
the transmitter automatically cutbacks
and the input fault indicator, located on
the IF Processor module lights. When the
video input signal returns, the
transmitter will automatically return to
full power and the input fault indicator
will be extinguished.
2.3.1 Principles of Operation
Operating Modes
This transmitter is either operating or in
the standby mode. The sections below
discuss the characteristics of each of
these modes.
Operate Mode
Operate mode is the normal mode for
the transmitter when it is providing RF
power output. To provide RF power to
the output, the transmitter must not be
in mute. Mute is a special case of the
operate mode where the +32 VDC
section of the power supply is enabled
but there is no RF output power from
the transmitter. This condition is the
result of a fault that causes the firmware
to hold the IF Processor module in a
mute state.
Operate Mode with Mute Condition
The transmitter will remain in the
operate mode but will be placed in mute
when the following fault conditions
exists in the transmitter.
• Upconverter is unlocked
• Upconverter module is not present
• IF Processor module is not present
• Modulator is in Aural/Visual Mute
Entering Operate Mode
Entering the operate mode can be
initiated a few different ways by the
transmitter control board. A list of the
actions that cause the operate mode to
be entered is given below:
• A low on the Remote Transmitter
Operate line.
• User selects "OPR" using switches
and menus of the front panel.
• Receipt of an “Operate CMD” over
the serial interface.
There are several faults or interlock
conditions that may exist in the
transmitter that will prevent the
transmitter from entering the operate
mode. These conditions are:
• Power Amplifier heat sink
temperature greater than 78°C.
• Transmitter is Muted due to
conditions listed above.
• Power Amplifier Interlock is high
indicating that the amplifier is not
installed.
Standby Mode
The standby mode in the transmitter
indicates that the output amplifier of the
transmitter is disabled.
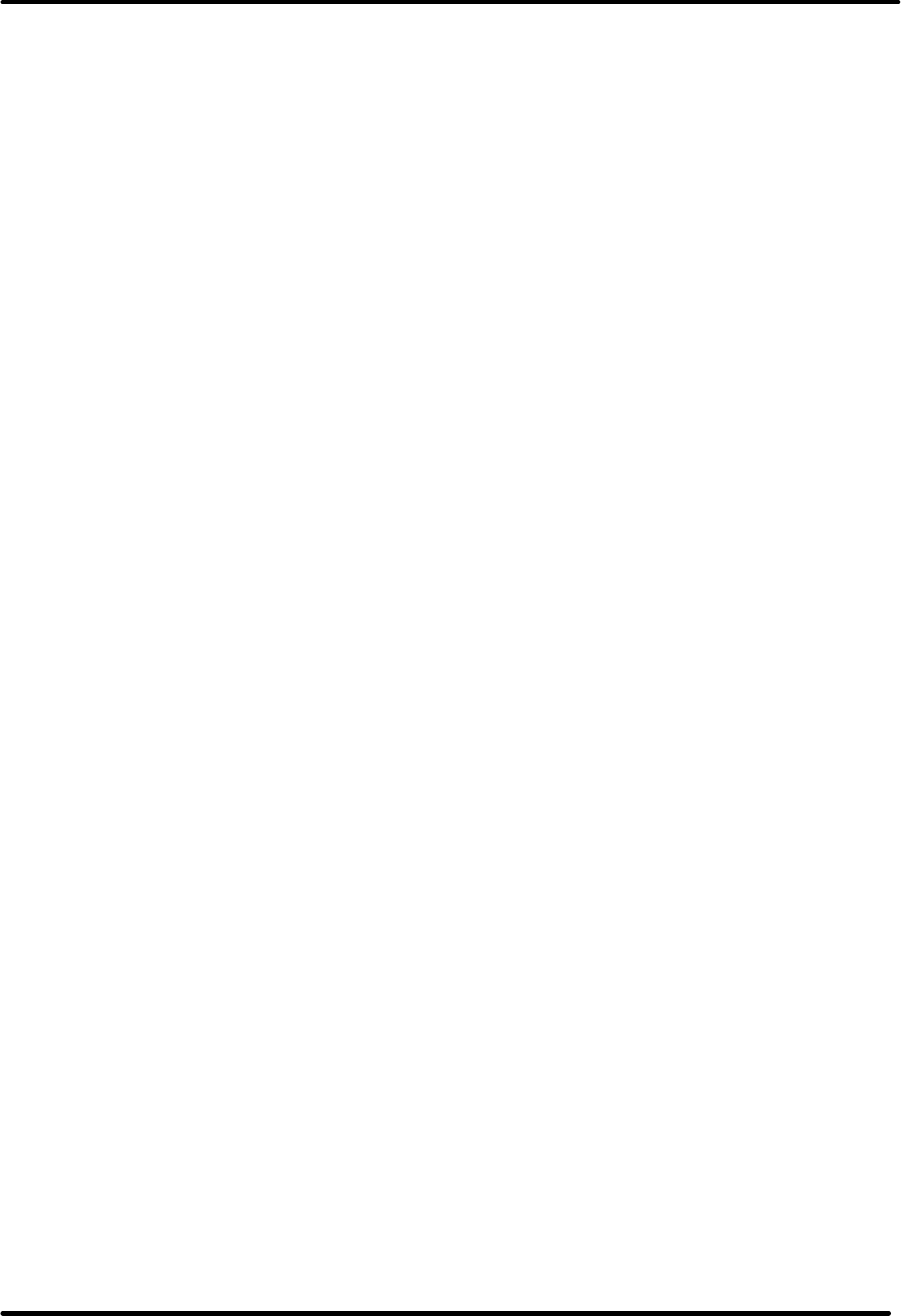
Innovator® HX Series Analog VHF Chapter 2, System Description
Transmitter and Remote Control Connections
HX Series, Rev. 0 2-10
Entering Standby Mode
Similar to the operate mode, the
standby mode is entered using various
means. These are:
• A low on the Remote Transmitter
Stand-By line.
• Depressing the “STB” key on
selected front panel menus.
• Receipt of a “Standby CMD” over the
serial interface.
Auto Standby Mode
The FCC requires that certain
transmitters automatically switch to
standby operation on loss of video input.
The HX Series exciter incorporates this
feature as a user configurable setting.
When Auto Stand-By on modulation loss
is selected in the set-up menus, the
transmitter temporarily switches to
standby after ten seconds of modulation
loss. When the modulated signal as
reported by the IF Processor module is
again present, the transmitter
automatically returns to Operate mode.
RF System Interlock
The RF System Interlock must be
provided through TB30-5. When this
interlock circuit is completed to ground
such as through a wire or an external
switch connected between TB30-5 and
TB30-17, the exciter/driver (transmitter)
is allowed to operate. If this circuit is
opened, the transmitter switches to a
Mute condition. This circuit may be
completed through coaxial relay
contacts and/or reject load contact
closures to assure the RF output system
is available to receive the transmitter's
RF output signal before it is allowed to
switch to operate.
Operating Frequency
The HX Series exciter driver controller is
designed to operate on VHF or UHF
frequencies. This transmitter is set for
the VHF channels. The VHF channel
center and + & - offset frequencies are
used to set the LO1 and LO2 frequencies
in the Upconverter Module. The exact
output frequency of the transmitter can
be set to one of the standard VHF
frequencies, or to a custom frequency
using the software channel set-up menu
on the Controller Module. NOTE: Refer
to the Channel Change Procedure found
in chapter 5 of this manual for additional
information. Since RF performance of
the transmitter requires different
hardware for different frequency bands,
not all frequency configurations are valid
for a specific transmitter. The Power
detectors in the transmitter are
frequency dependent, therefore
detectors of power amplifiers are
calibrated at their frequency of use. The
detectors for System RF monitoring are
also calibrated at the desired frequency
of use.
2.4 Maintenance
The Innovator HX Series transmitter is
designed with components that require
little or no periodic maintenance except
for the routine cleaning of the fans and
the front panels of the modules.
The amount of time between cleanings
depends on the conditions within the
transmitter room. While the electronics
have been designed to function even if
covered with dust, a heavy buildup of
dust, dirt, or insects will affect the
cooling of the components. This could
lead to a thermal shutdown or the
premature failure of the affected module.
When the front panels of the modules
become dust covered, the module should
be pulled out and any accumulated
foreign material should be removed.
NOTE: To remove the power amplifier
module, mounted in the exciter/driver
assembly, the input and output cables
must be removed from the rear of the
module and also a 6/32” x ½” Philips
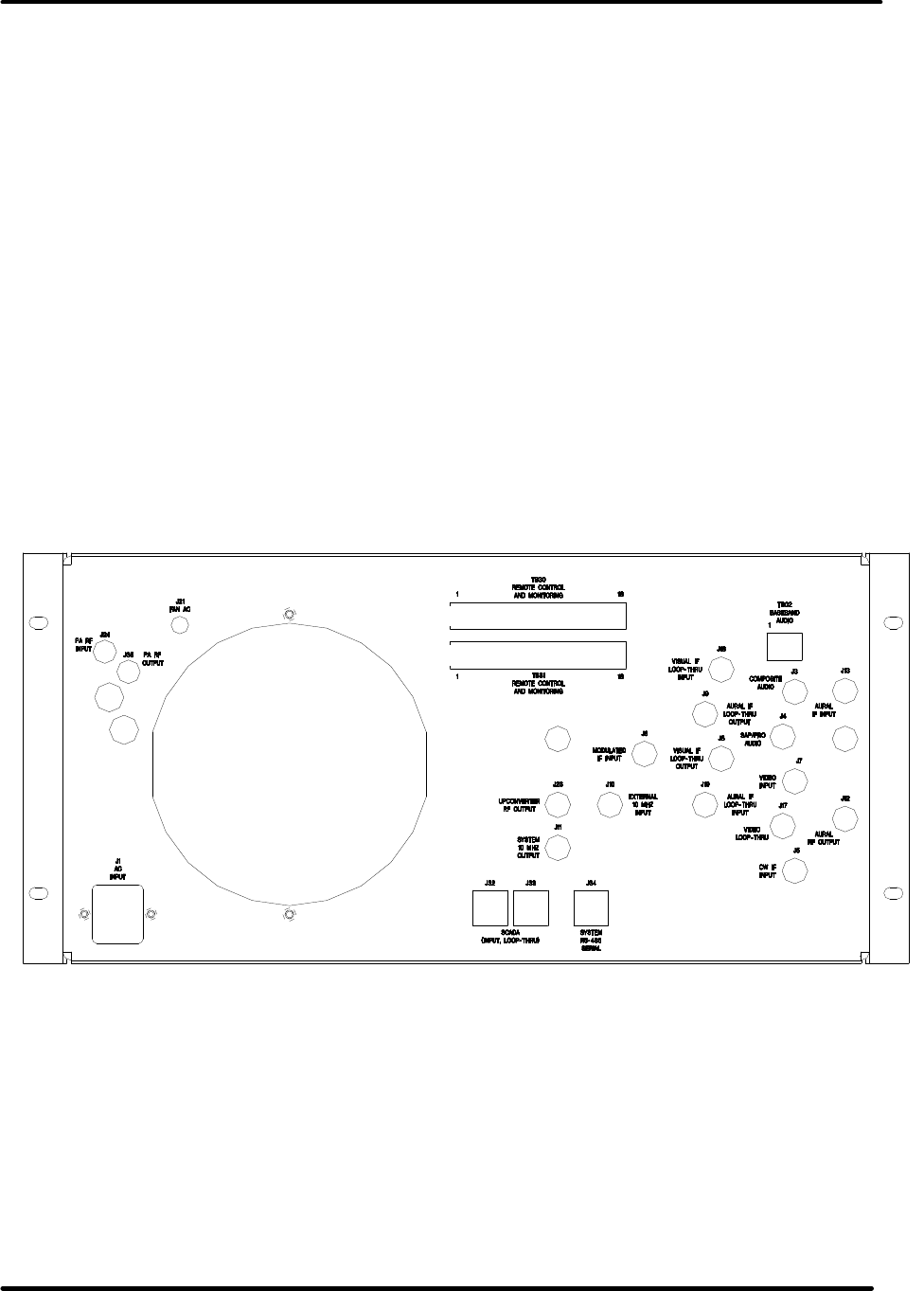
Innovator® HX Series Analog VHF Chapter 2, System Description
Transmitter and Remote Control Connections
HX Series, Rev. 0 2-11
screw, mounted between the two
connectors, needs to be removed before
the module will pull out. After removal of
the screw, which is used to hold the
module in place during shipping, it does
not need to be replaced.
A vacuum cleaner, utilizing a small,
wand-type attachment, is an excellent
way to suction out the dirt. Alcohol and
other cleaning agents should not be used
unless you are certain that the solvents
will not damage components or the silk-
screened markings on the modules and
boards. Water-based cleaners can be
used, but do not saturate the
components. The fans and heatsinks
should be cleaned of all dust or dirt to
permit the free flow of air for cooling
purposes.
It is recommended that the operating
parameters of the exciter driver and
transmitter be recorded from the LEDs on
the modules, the LCD system metering
on the control/monitoring module and
the GUI touch screen at least once a
month. It is suggested that this data be
retained in a rugged folder or envelope.
2.5 Customer Remote Connections
The remote monitoring and operation of
the transmitter is provided through jacks
TB30 and TB31 located on the rear of the
chassis assembly. If remote connections
are made to the transmitter, they must
be made through plugs TB30 and TB31
at positions noted on the transmitter
interconnect drawing and Table 2-20.
Figure 2-2. Exciter/Driver Chassis Assembly Rear View
TB30
TB31
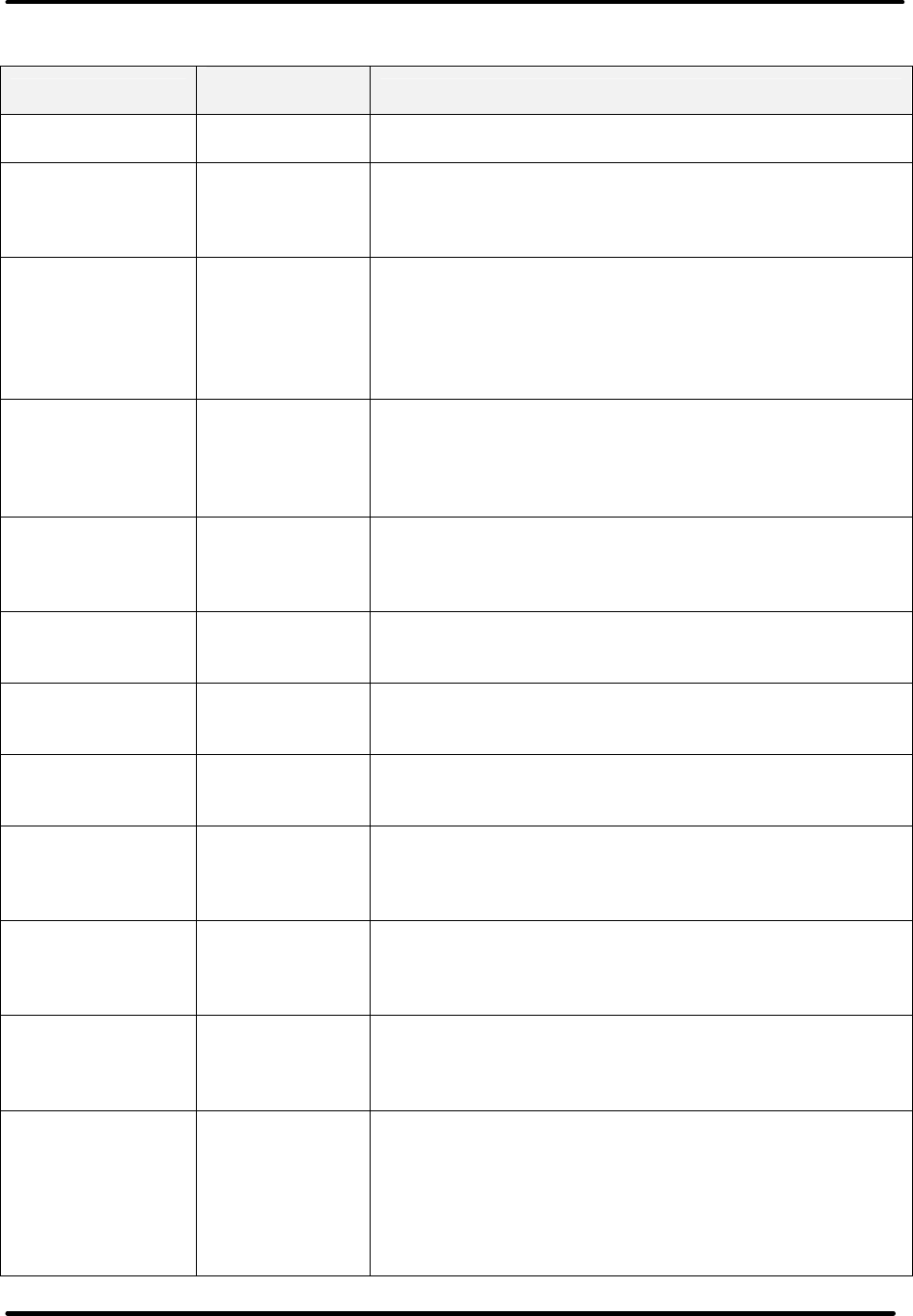
Innovator® HX Series Analog VHF Chapter 2, System Description
Transmitter and Remote Control Connections
HX Series, Rev. 0 2-12
Table 2-20: HX Series Chassis Assembly Hard Wired Remote Interface Connections to
TB30 or TB31, 18 pos. Terminal Blocks Located on the Rear of the Assembly
Signal Name Pin
Designations Signal Type/Description
RMT Transmitter
State TB30-1 Discrete Open Collector Output - A low indicates that
the transmitter is in the operate mode.
RMT Transmitter
Interlock TB30-2
Discrete Open Collector Output - A low indicated the
transmitter is OK or completes an interlock daisy
chain. When the transmitter is not faulted, the
interlock circuit is completed.
RMT Transmitter
Interlock Isolated
Return TB30-3
Ground - Configurable ground return which can be
either jumpered directly to ground or it can be the
“source” pin of a FET so that the transmitter
interlock can be daisy chained with other
transmitters. This signal does not directly interface
to the microcontroller.
RMT System
Interlock TB30-5
When this interlock circuit is completed to ground
such as through a jumper between TB30-5 and
TB30-17, the transmitter is allowed to operate. If
this circuit is opened, the transmitter switches to a
Mute condition.
RMT Set to
Operate
Transmitter TB30-6 Discrete Open Collector Input - A pull down to
ground on this line indicates that the transmitter is
to be placed into the operate mode.
RMT
Set to Stand-By
Transmitter TB30-7 Discrete Open Collector Input - A pull down to
ground on this line indicates that the transmitter is
to be placed into the standby mode.
RMT Power Raise TB30-8 Discrete Open Collector Input - A pull down to
ground on this line indicates that the transmitter
power is to be raised.
RMT Power Lower TB30-9 Discrete Open Collector Input - A pull down to
ground on this line indicates that the transmitter
power is to be lowered.
RMT
System Reflect
Power TB30-10
Analog Output (0 to 4.0 V). This is a buffered loop
through of the calibrated “System Reflected Power”
and indicates the transmitter's reflected output
power. The scale factor is 25% = 3.2V.
RMT System
Visual Power TB30-11
Analog Output (0 to 4.0 V). This is a buffered loop
through of the calibrated “System Visual Power ”.
Indicates the transmitter's Visual power. Scale factor
is 100% = 3.2V.
RMT System
Aural Power TB30-12
Analog Output (0 to 4.0 V). This is a buffered loop
through of the calibrated “System Aural Power ”.
Indicates the transmitter's Aural power. Scale factor
is 100% = 3.2V.
IF Processor
IF Signal Select TB31-3
Discrete Open Collector Input – By connecting a low
to this pin, the Modulator IF source is used by the IF
Processor module. When floating the IF from the
internal or external Receiver is used. (NOTE: The IF
Processor board must be configured for external
switching by placing jumper W11 on J29 between
pins 1 & 2).
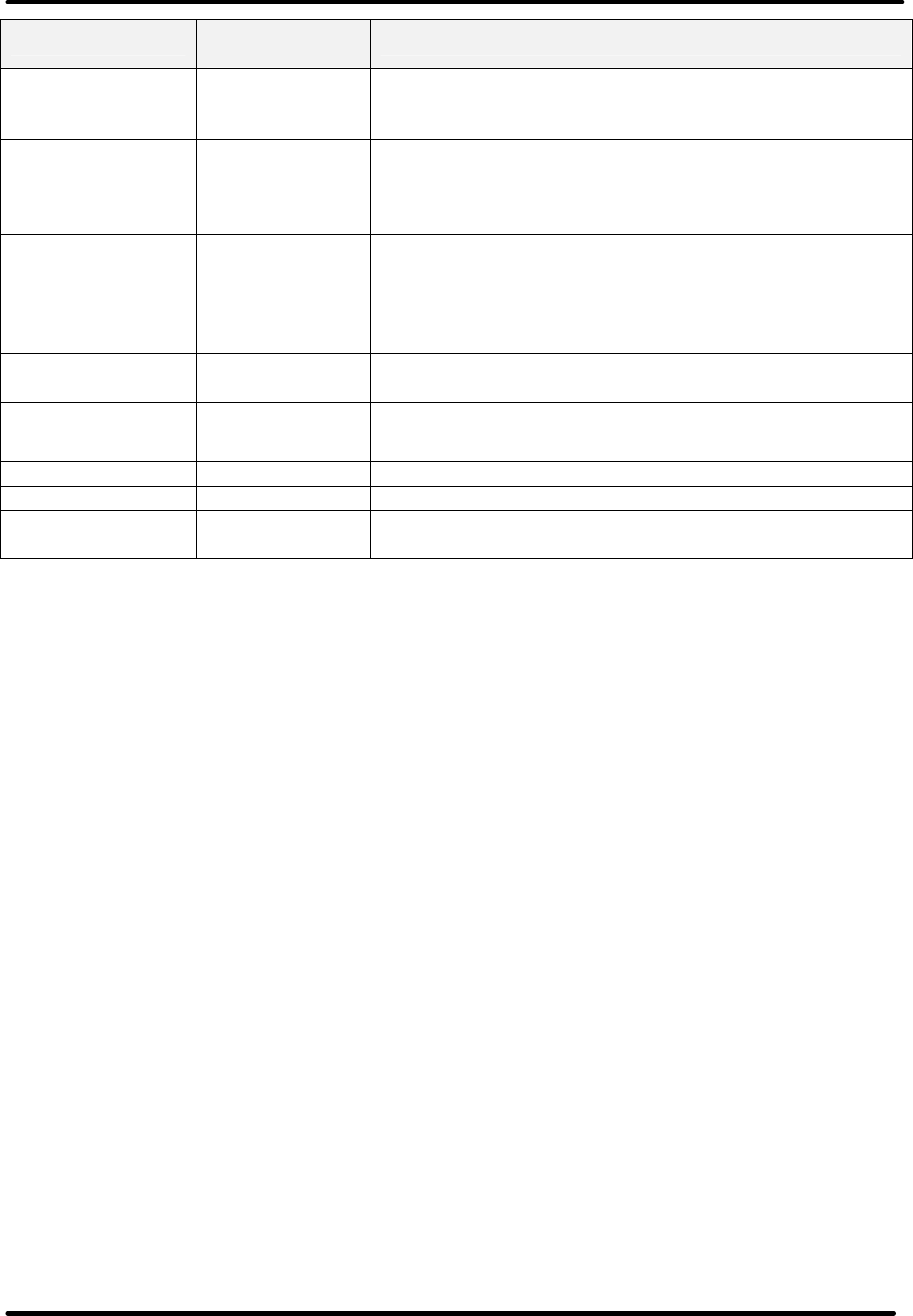
Innovator® HX Series Analog VHF Chapter 2, System Description
Transmitter and Remote Control Connections
HX Series, Rev. 0 2-13
Signal Name Pin
Designations Signal Type/Description
IF Processor
DLC Voltage TB31-4 Analog Output (0 to 5.00 V). This is the input of IF
Processor module for system RF output power
control.
System Reflect
Power TB31-13
Analog Input (0 to 1.00 V). This is the input of the
“System Visual Reflected Power ” indicating the
transmitter's reflected output power. The scale
factor is 25% = 0.80V.
System Visual
Power TB31-14
Analog Input (0 to 1.00 V). This is the input of the
“System Visual Power ” indicating the transmitter's
forward Visual output power. The scale factor is
100% = 0.80V.
*+12 VDC TB31-16 +12 VDC for external use w/ 2 Amp re-settable fuse
*-12 VDC TB31-18 -12 VDC for external use w/ 2 Amp re-settable fuse
RMT Ground TB31-1, 2, 6,
11, 12 & 17 Ground pins available through Remote
+12 VDC TB30-16 +12 VDC for external use w/ 2 Amp re-settable fuse
-12 VDC TB30-18 -12 VDC for external use w/ 2 Amp re-settable fuse
*RMT System
Interlock Rtn TB30-17 RMT System Interlock return.
* Indicates that these connections are used in the system and are not available for
remote use.
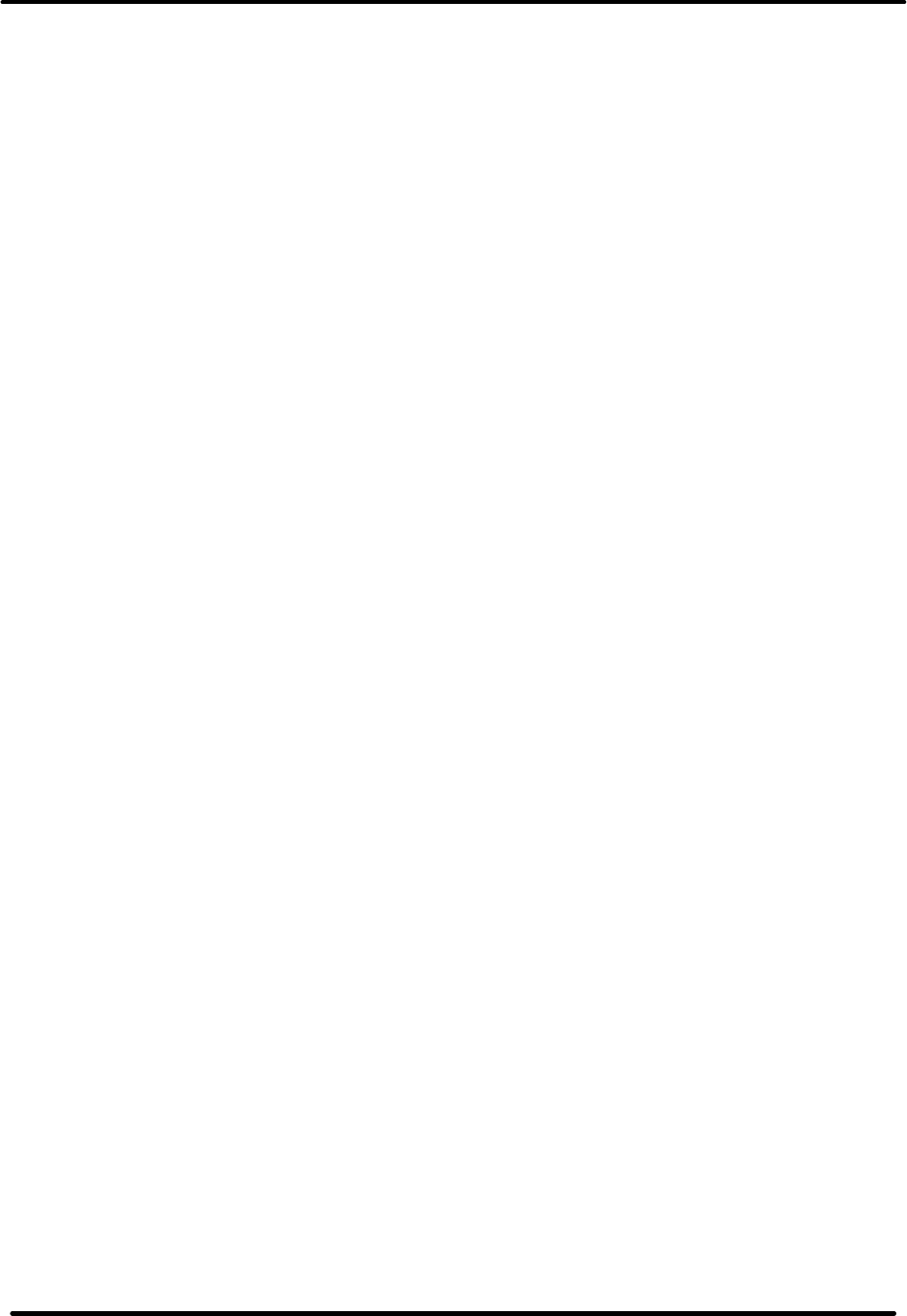
Innovator® HX Series Analog VHF Chapter 3, Site Considerations,
Transmitter Installation and Setup Procedures
HX Series, Rev. 0 3-1
Chapter 3
Site Considerations, Installation and Setup Procedures
3.1 Site Considerations
There are special considerations that need
to be taken into account before the
Innovator HX Series analog VHF
transmitter can be installed. For example,
if the installation is completed during cool
weather, a heat-related problem may not
surface for many months, suddenly
appearing during the heat of summer.
This section provides planning information
for the installation and set up of the
transmitter.
The transmitter is factory set for operation
using 110 VAC that connects to the AC
input jack J1, through the AC power cord,
located on the rear of the chassis
assembly.
The HX Series Analog transmitter is
designed and built to provide long life with
a minimum of maintenance. The
environment in which they are placed is
important and certain precautions must be
taken. The three greatest dangers to the
transmitter are heat, dirt, and moisture.
Heat is usually the greatest problem,
followed by dirt, and then moisture. Over-
temperature can cause heat-related
problems such as thermal runaway and
component failure. Each amplifier module
in the transmitter contains a thermal
interlock protection circuit that will shut
down that module until the temperature
drops to an acceptable level.
A suitable environment for the transmitter
can enhance the overall performance and
reliability of the transmitter and maximize
revenues by minimizing downtime. A
properly designed facility will have an
adequate supply of cool, clean air, free of
airborne particulates of any kind, and no
excessive humidity. An ideal environment
will require temperature in the range of
40° F to 70° F throughout the year,
reasonably low humidity, and a dust-free
room. It should be noted that this is rarely
if ever attainable in the real world.
However, the closer the environment is
to this design, the greater the operating
capacity of the transmitter.
The fans are designed and built into the
transmitter will remove the heat from
within the modules, but additional means
are required for removing this heat from
the building. To achieve this, a few issues
need to be resolved. The first step is to
determine the amount of heat to be
removed from the transmitter room.
There are generally three sources of heat
that must be considered. The first and
most obvious is the heat from the
transmitter itself.
This amount can be determined for a 100
Watt transmitter by subtracting the
average power to the antenna (69.5
watts) from the AC input power (675
watts) and taking this number in watts
(605.5) and then multiplying it by 3.41.
This gives a result of 2,065, the BTUs to
be removed every hour. 12,000 BTUs per
hour equals one ton. Therefore, a 1/4-
ton air conditioner will cool a 100W
transmitter.
The second source of heat is other
equipment in the same room. This
number is calculated in the same way as
the equation for BTUs. The third source
of heat is equally obvious but not as
simple to calculate. This is the heat
coming through the walls, roof, and
windows on a hot summer day. Unless
the underside is exposed, the floor is
usually not a problem. Determining this
number is usually best left up to a
qualified HVAC technician. There are far
too many variables to even estimate this
number without reviewing the detailed
drawings of the site that show all of the
construction details. The sum of these
three sources is the bulk of the heat that
must be removed. There may be other
sources of heat, such as personnel, and
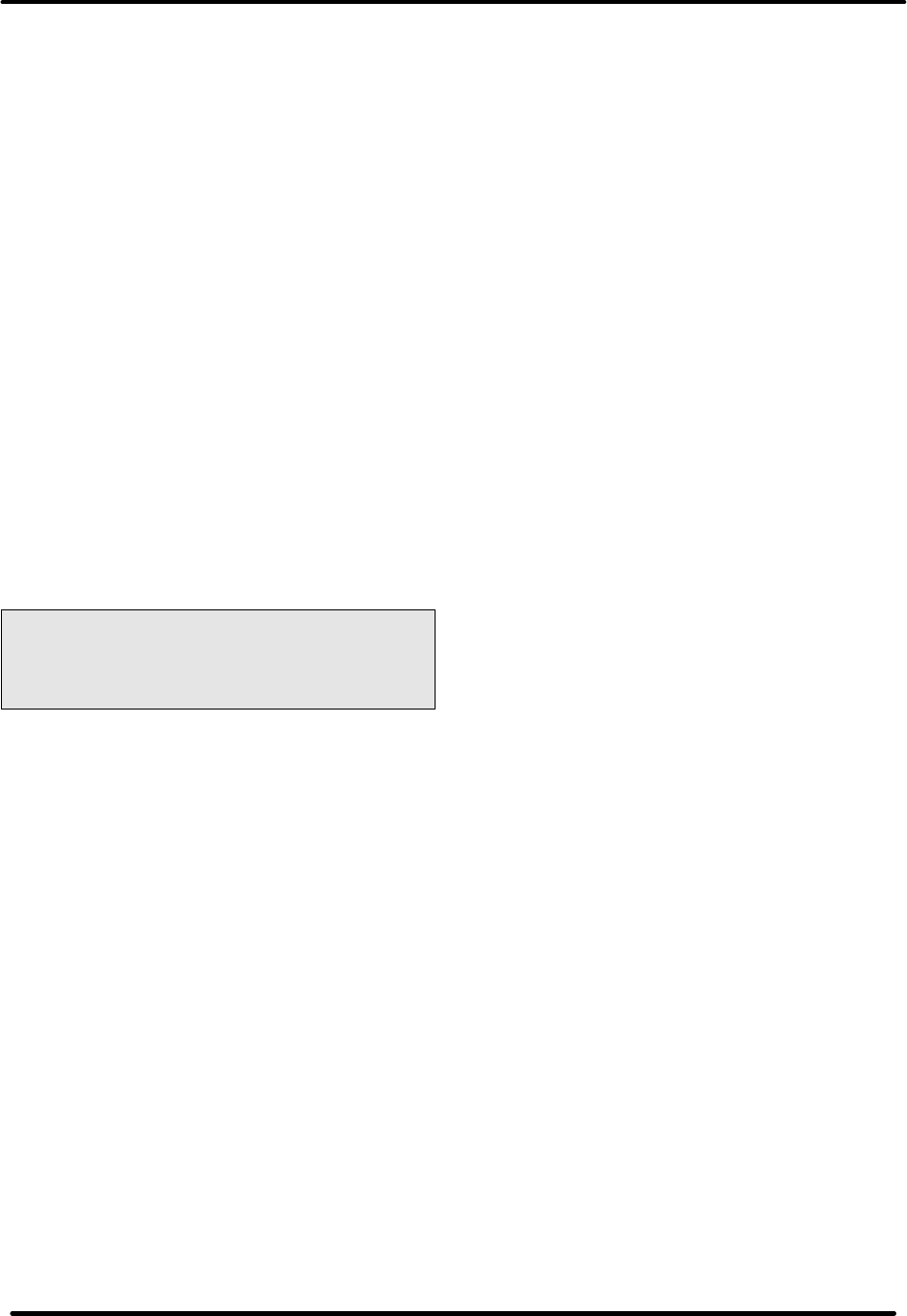
Innovator® HX Series Analog VHF Chapter 3, Site Considerations,
Transmitter Installation and Setup Procedures
HX Series, Rev. 0 3-2
all should be taken into account. Now
that the amount of heat that must be
removed is known, the next step is to
determine how to accomplish this. The
options are air conditioning, ventilation, or
a combination of the two. Air conditioning
is always the preferred method and is the
only way to create anything close to an
ideal environment.
Ventilation will work quite well if the
ambient air temperature is below 100° F,
or about 38° C, and the humidity is kept
at a reasonable level. In addition, the air
stream must be adequately filtered to
ensure that no airborne particulates of
any kind will be carried into the
transmitter. The combination of air
conditioning for summer and ventilation
during the cooler months is acceptable
when the proper cooling cannot be
obtained through the use of ventilation
alone and using air conditioning
throughout the year is not feasible.
Caution: The use of air conditioning
and ventilation simultaneously is not
recommended. This can cause
condensation in the transmitters.
The following precautions should be
observed regarding air conditioning
systems:
1. Air conditioners have an ARI nominal
cooling capacity rating. In selecting an
air conditioner, do not assume that
this number can be equated to the
requirements of the site. Make certain
that the contractor uses the actual
conditions that are to be maintained at
the site in determining the size of the
air conditioning unit. With the desired
conditioned room temperature under
80° F, the unit must be derated,
possibly by a substantial amount.
2. Do not have the air conditioner
blowing directly onto the transmitter.
Under certain conditions, condensation
may occur on, or worse in, the
transmitter.
3. Do not separate the front of the
transmitter from the back with the
thought of air conditioning only the
front of the unit. Cooling air is drawn
in at the front of all transmitters and
in the front and back of others. Any
attempt to separate the front of the
transmitter from the rear of the unit
will adversely affect the flow of
cooling air.
4. Interlocking the transmitter with the
air conditioner is recommended to
keep the transmitter from operating
without the necessary cooling.
5. The periodic cleaning of all filters is a
must.
When using ventilation alone, the
following general statements apply:
1. The blower, with attendant filters,
should be on the inlet, thereby
pressurizing the room and preventing
dirt from entering the transmitter.
2. The inlet and outlet vents should be
on the same side of the building,
preferably the leeward side. As a
result, the pressure differential
created by wind will be minimized.
Only the outlet vent may be released
through the roof.
3. The inlet and outlet vents should be
screened with 1/8-inch hardware
cloth (preferred) or galvanized
hardware cloth (acceptable).
4. Cooling air should enter the room as
low as practical but in no case higher
than four feet above the floor. The
inlet must be located where dirt,
leaves, snow, etc., will not be carried
in with the cooling air.
5. The exhaust should be located as
high as possible. Some ducting is
usually required to insure the
complete flushing of heated air with
no stagnant areas.
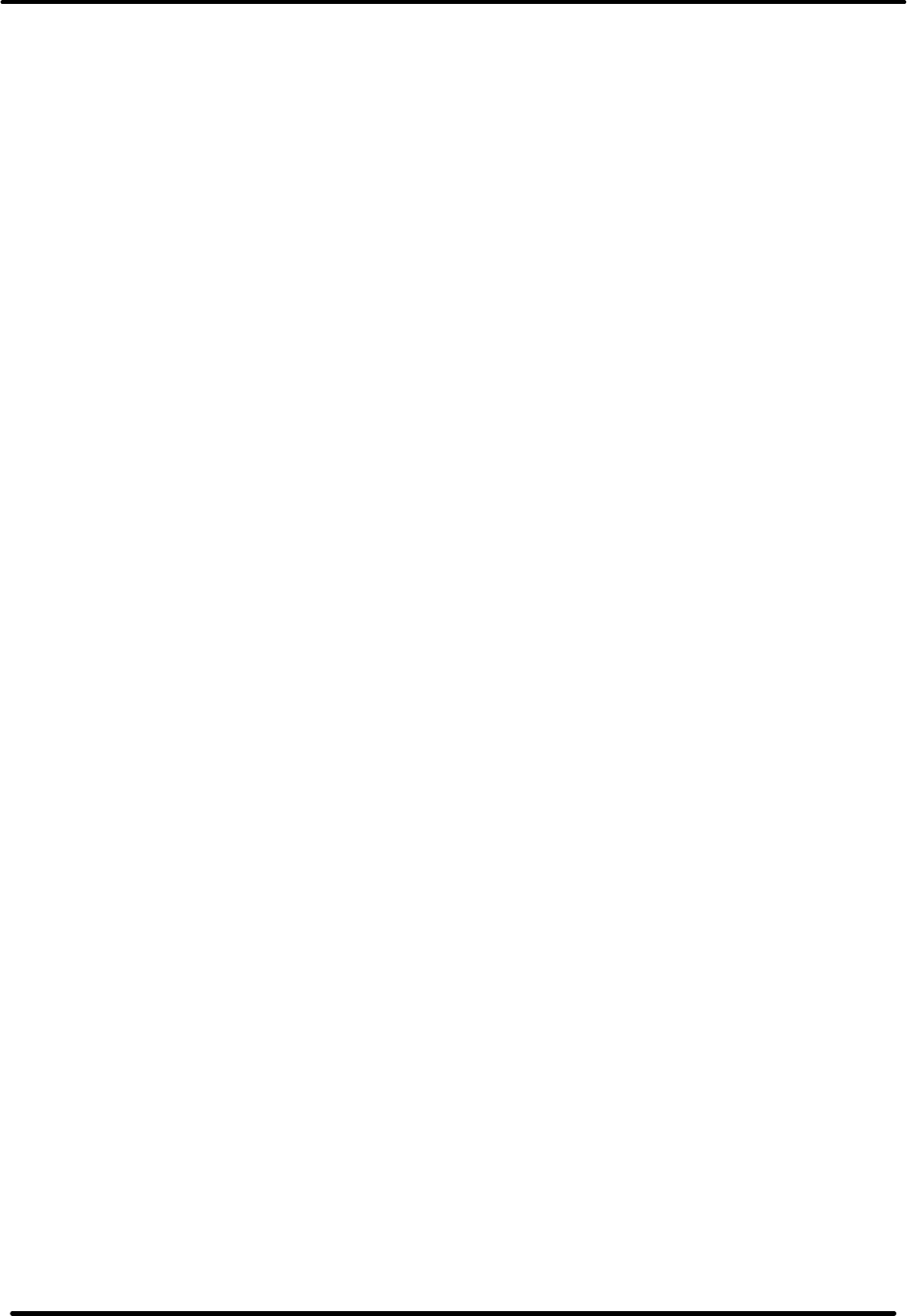
Innovator® HX Series Analog VHF Chapter 3, Site Considerations,
Transmitter Installation and Setup Procedures
HX Series, Rev. 0 3-3
6. The filter area must be large enough
to insure a maximum air velocity of
300 cubic feet per minute through the
filter. This is not a conservative
number but a never-exceed number.
In a dusty or remote location, this
number should be reduced to 150
CFM.
7. The inlet and outlet(s) must have
automatic dampers that close any time
the ventilation blower is off.
8. In those cases in which a transmitter
is regularly off for a portion of each
day, a temperature-differential sensor
that controls a small heater must be
installed. This sensor will monitor
inside and outside temperatures
simultaneously. If the inside
temperature falls to within 5° F of the
outside temperature, the heater will
come on. This will prevent
condensation when the ventilation
blower comes on and should be used
even in the summer.
9. A controlled air bypass system must
be installed to prevent the
temperature in the room from falling
below 40° F during transmitter
operation.
10. The blower should have two speeds,
which are thermostatically
controlled, and are interlocked with
the transmitter. The blower on high
speed must be capable of moving
the required volume of air into a half
inch of water pressure at the
required elevation. The free air
delivery method must not be used.
11. Regular maintenance of any filters
can not be overemphasized.
12. Above 4000 feet, for external
venting, the air vent on the cabinet
top must be increased to an 8-inch
diameter for a 1 kW transmitter and
to a 10 inch diameter for 5 kW and
6 kW transmitters. An equivalent
rectangular duct may be used but,
in all cases, the outlet must be
increased by 50% through the
outlet screen.
13. It is recommended that a site plan
be submitted to Axcera for
comments before installation
begins.
In calculating the blower requirements,
filter size, and exhaust size, if the total
load is known in watts, 2000 CFM into ½
inch of water will be required for each
5000 watts. If the load is known in BTUs,
2000 CFM into ½ inch of water will be
required for each 17,000 BTUs. The inlet
filter must be a minimum of seven
square feet, larger for dusty and remote
locations, for each 5000 watts or 17,000
BTUs. The exhaust must be at least four
square feet at the exhaust screen for
each 5000 watts or 17,000 BTUs.
The information presented in this section
is intended to serve only as a general
guide and may need to be modified for
unusually severe conditions. A
combination of air conditioning and
ventilation should not be difficult to
design (see Figure 3-1).
System interlocking and thermostat
settings should be reviewed with Axcera.
As with any equipment installation, it is
always good practice to consult the
manufacturer when questions arise.
Axcera can be contacted at (724) 873-
8100.
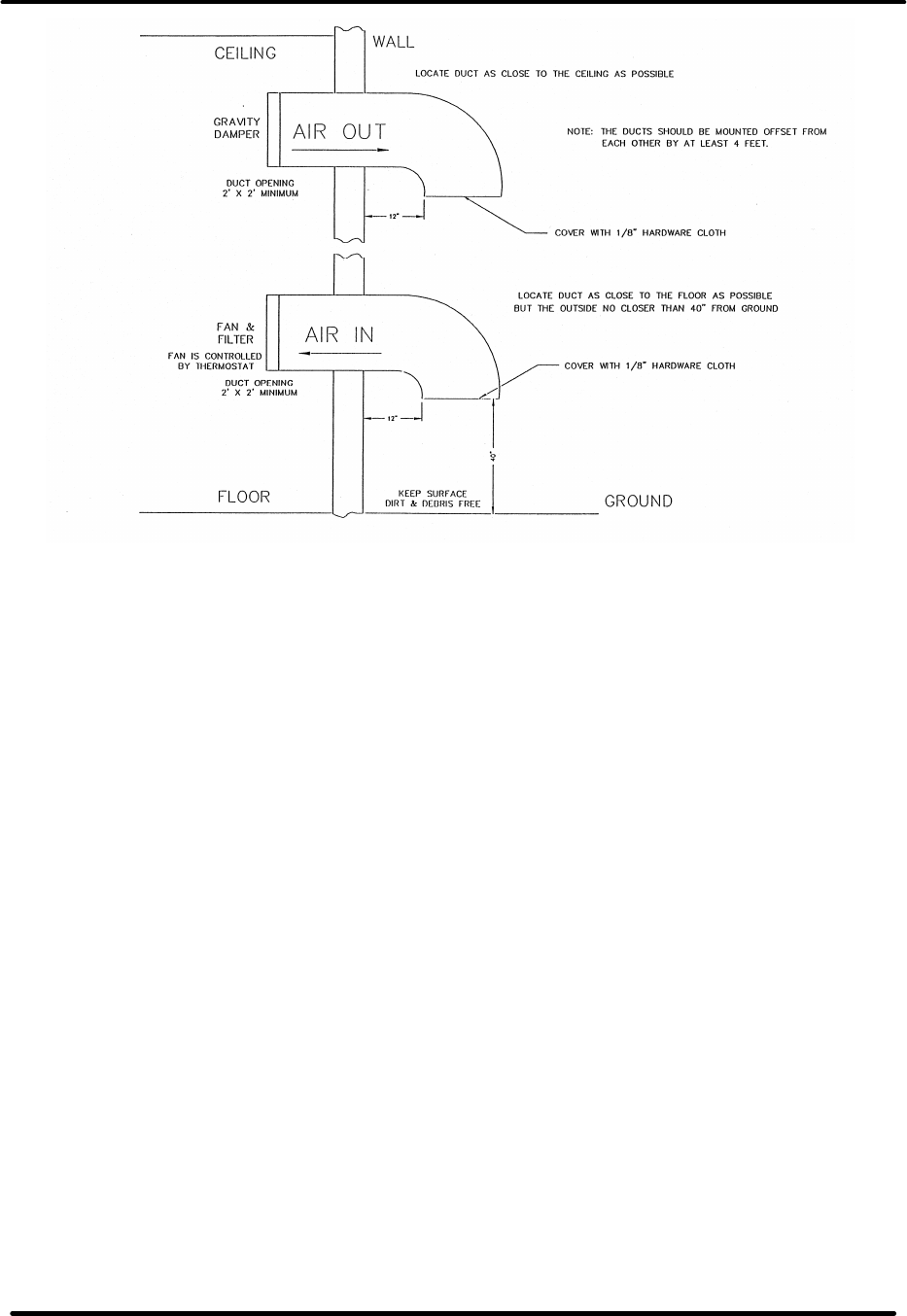
Innovator® HX Series Analog VHF Chapter 3, Site Considerations,
Transmitter Installation and Setup Procedures
HX Series, Rev. 0 3-4
Figure 3-1. 1 kW Minimum Ventilation Configuration
3.2 Unpacking and Installing the
Transmitter
Remove the transmitter and filter from
the shipping container. Remove the
plastic wrap and foam protection from
around the transmitter and filter.
Thoroughly inspect the chassis with
modules and all other materials upon their
arrival. Axcera certifies that upon leaving
our facility the equipment was undamaged
and in proper working order. The shipping
containers should be inspected for obvious
damage that indicates rough handling.
Check for dents and scratches or broken
connectors, switches, display, or
connectors. Any claims against in-transit
damage should be directed to the carrier.
Inform Axcera as to the extent of any
damage as soon as possible.
The chassis assembly and filter are made
to mount in a standard 19” rack. Two
tray slides are provided in the shipping
material to mount the chassis assembly
into a standard 19” rack. Follow the
instructions provided with the slides to
mount them into the cabinet. There are
two tray slide rails mounted on the sides
of the chassis assembly that fit the tray
slides just mounted in the rack. The tray
slides give the customer access to the
adjustments made through the top of the
chassis assembly. The front of the
chassis assembly and the front of the
filter have #10 mounting holes into
which screws can be inserted to hold the
chassis and filter in place.
The exciter/driver modules are mounted
to the chassis assembly with slides that
are on the top and the bottom of the
modules. There are two thumb screws
on the front panel that hold each of the
modules in place.
NOTE: To remove the power amplifier
module, mounted in the chassis
assembly, input and output cables must
be removed from the rear of the module
and also a 6/32” x ½” Philips screw,
mounted between the connectors, needs
to be removed before the module will pull
out. After removal of the screw, which is
used to hold the module in place during
shipping, it does not need to be replaced.
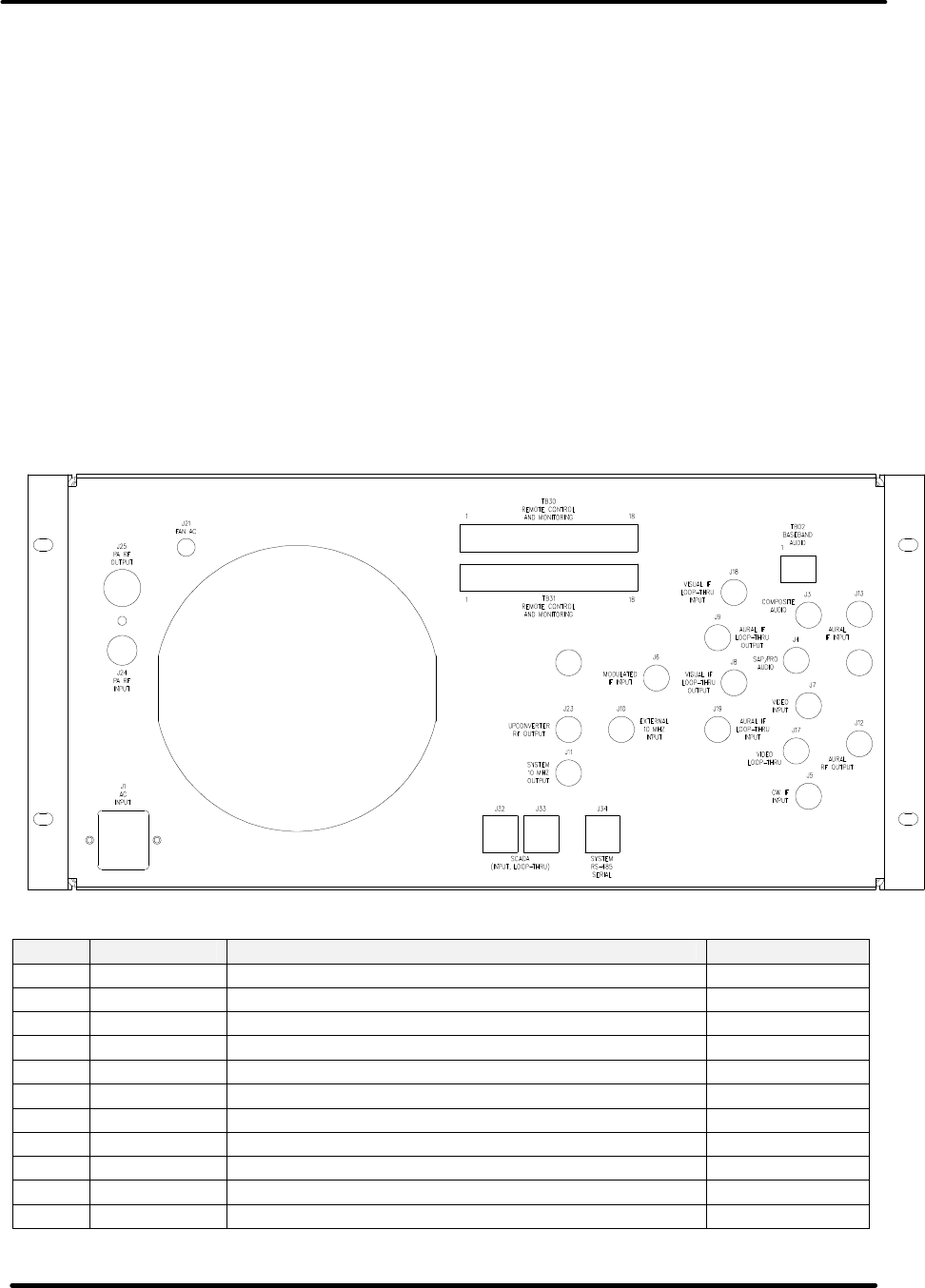
Innovator® HX Series Analog VHF Chapter 3, Site Considerations,
Transmitter Installation and Setup Procedures
HX Series, Rev. 0 3-5
3.2.1 AC Input
Once the chassis is mounted in the
equipment rack the AC can be connected
to the chassis.
Connect the AC power jack, found with
the shipping material, to J1 located on the
rear of the chassis assembly. Connect the
AC power plug to a 110 VAC/10 Amp
source.
This completes the unpacking and
installation of the HX Series VHF
transmitter. Refer to the setup and
operation procedures that follow before
applying power to the transmitter.
3.3 Setup and Operation
Initially, the transmitter should be turned
on with the RF output at the “N”
connector J25 terminated into a dummy
load or check that the output is
connected to the filter and the antenna
for your system.
3.3.1 Input Connections
The input connections to the transmitter
are to the rear of the Chassis Assembly.
Refer to the table and description that
follows for detailed information on the
input connections.
Figure 3-2: Rear View of HX Series Analog exciter/driver
Table 3-1: Rear Chassis Connections for the HX Series Analog Transmitter.
Port Type Function Impedance
J1 IEC AC Input N/A
TB02 Terminal Base Band Audio Input 600O
J3 BNC Composite Audio Input 75O
J4 BNC SAP/PRO Audio Input 50O
J5 BNC CW IF Input 50O
J6 BNC Modulated IF Input 50O
J7 BNC Video Input (Isolated) 75O
J8 BNC Visual IF Loop-thru Output (Jumpered to J18) 50O
J9 BNC Aural IF Loop-Thru Output (Jumpered to J19) 50O
J10 BNC External 10 MHz Reference Input 50O
J11 BNC System 10 MHz Reference Output 50O
J1
J24
J25
TB30
TB31
J32
J34
J33
J11
J10
J23
J6
J5
J19
J18
TB02
J13
J4
J7
J17
J8
J9
J12
J3
J15
SPARE
J14
SPARE
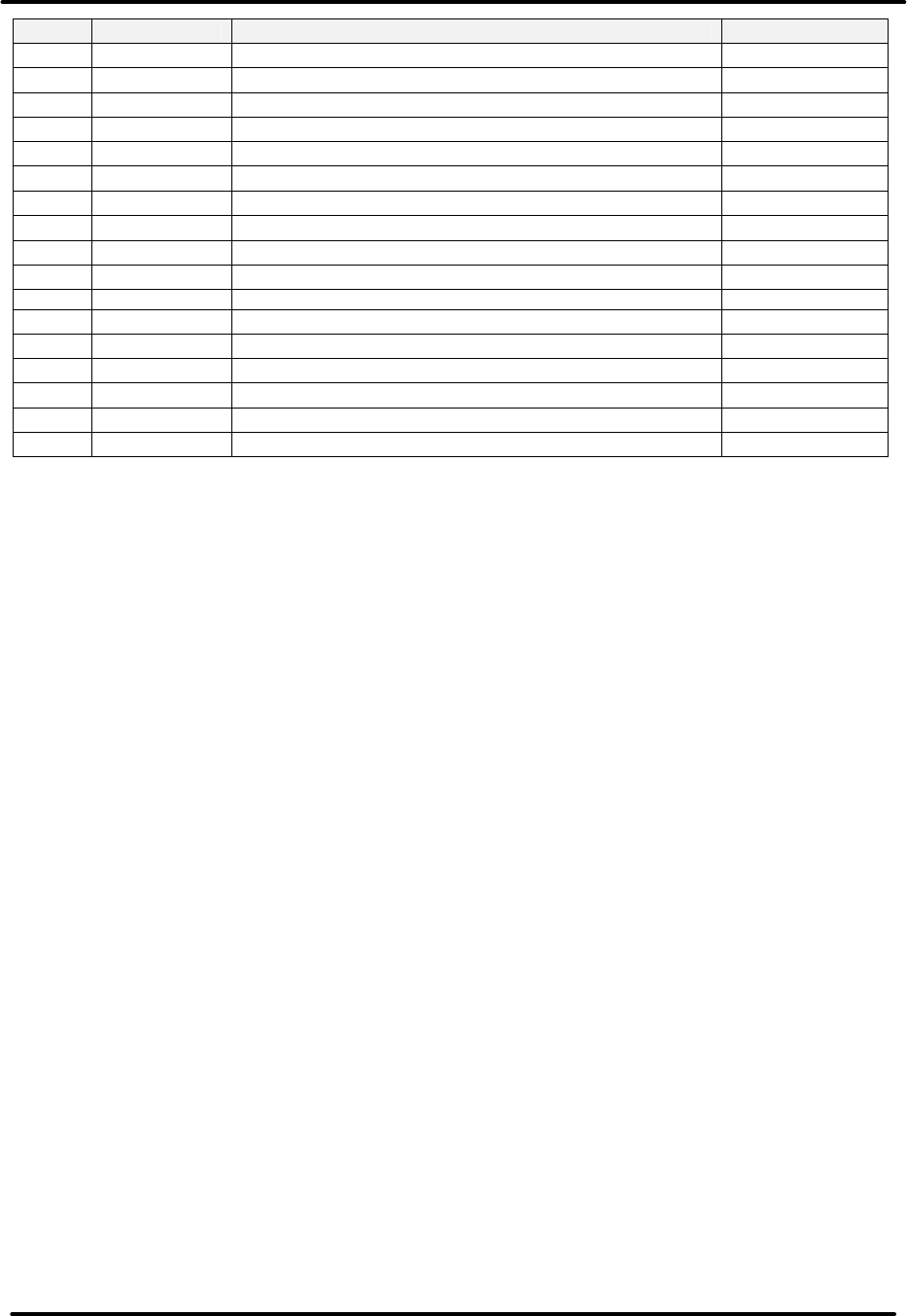
Innovator® HX Series Analog VHF Chapter 3, Site Considerations,
Transmitter Installation and Setup Procedures
HX Series, Rev. 0 3-6
Port Type Function Impedance
J14 BNC RF Spare 2 50O
J15 BNC RF Spare 1 50O
J17 BNC Video Loop-Thru (Isolated) 75O
J18 BNC Visual IF Loop-Thru Input (Jumpered to J8) 50O
J19 BNC Aural IF Loop-Thru Input (Jumpered to J9) 50O
J23 BNC Upconverter RF Output (Jumpered to J24) 50O
J24 BNC Power Amplifier RF Input 50O
J25 N Power Amplifier RF Output 50O
TB30 Termination
Remote Control & Monitoring N/A
TB31 Termination
Remote Control & Monitoring N/A
J32 RJ-45 SCADA (Input/Loop-Thru) CAT5
J33 RJ-45 SCADA (Input/Loop-Thru) CAT5
J34 RJ-45 System RS-485 Serial CAT5
3.4 Initial Turn On
Once the unit has been installed and all
connections have been made, the
process of turning on the equipment can
begin. First verify that AC power is
present and connected to the chassis
assembly. Verify all cables are properly
connected and are the correct type.
Once all of these things are completed,
the unit is ready to be turned on
following the procedures below.
Turn on the main AC power source that
supplies the AC to the chassis. Power is
now applied to the exciter/driver
assembly. If power is not applied check
that the on/off circuit breaker located
near the AC input Jack is switched On.
3.4.1 Exciter/Driver Front Panel LED
Indicators
Monitor the LCD display located on the
front of the control/monitoring module
as you proceed through this section.
When the transmitter is in the operate
mode, the STB menu appears. When in
the standby mode, the OPR menu
appears. Press the NXT key after each
menu to continue through the sequence.
3.4.1.1 Modulator Module LEDs on
Front Panel
Fault Indicators:
AURAL UNLOCK: This illuminates Red
when the Aural IF PLL is unlocked.
VISUAL UNLOCK: This illuminates RED
when the Visual IF PLL is unlocked.
AUDIO DEV: This indicator will
illuminate Red when the audio over-
deviates the aural carrier.
VIDEO LOSS: This indicates the loss of
Video to the modulator, when Red.
OVER MOD: This illuminates Red when
the video is over-modulated.
Status Indicators:
ALT IF CW: This indicates that there is
an external IF CW signal applied to the
Modulator
10MHz PRES: This indicates the
presence of a 10 MHz reference input.
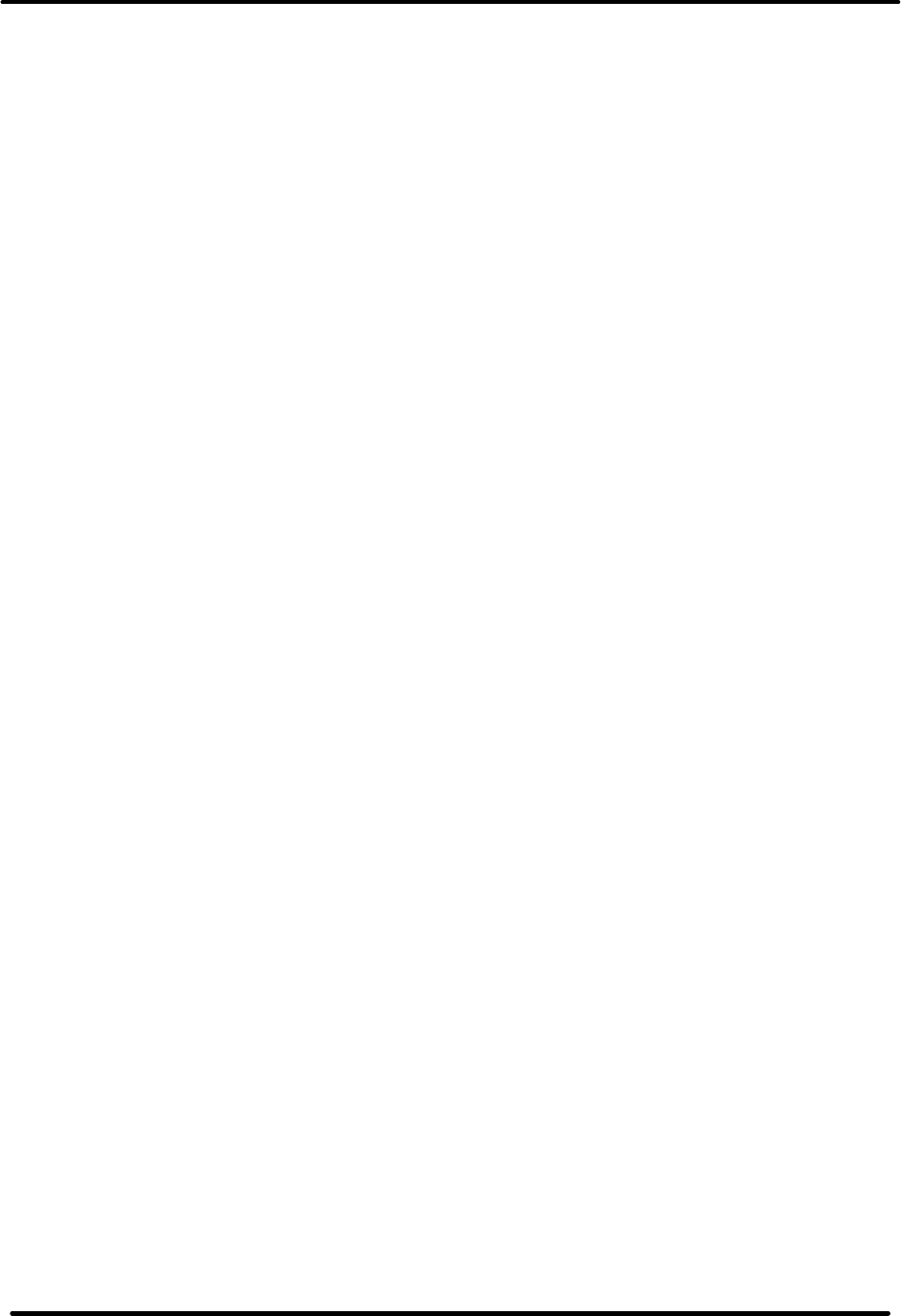
Innovator® HX Series Analog VHF Chapter 3, Site Considerations,
Transmitter Installation and Setup Procedures
HX Series, Rev. 0 3-7
3.4.1.2 IF Processor Module LEDs on
Front Panel
Fault Indicators:
INPUT FAULT: This illuminates Red if
the visual IF input to the module is
missing or low.
ALC FAULT: This illuminates RED when
the needed ALC value to maintain the
visual output level is beyond the range of
the circuitry.
MUTE: This indicator will illuminate Red
when the transmitter is muted.
3.4.1.3 Upconverter Module LEDs on
Front Panel
Fault Indicator:
PLL 1: This illuminates Red if the 1 GHz
PLL is unlocked.
PLL 2: This illuminates Red if the 1.0
GHz + LO PLL is unlocked.
AGC FAULT: NOT USED IN THIS
CONFIGURATION.
AGC OVERRIDE: This illuminates Red if
the drive to the PA module is too high.
MAN AGC: This illuminates Red if the
AGC is bypassed in Manual.
3.4.1.4 Controller Module LEDs on
Front Panel
Status Indicators:
OPERATE: This illuminates Green when
transmitter is in operate.
FAULT: This illuminates Red when a
fault has occurred in the transmitter.
DC OK: This illuminates Green when the
DC outputs that connect to the modules
in the exciter/driver assembly are
present.
3.4.1.5 Power Amplifier Module LEDs
on Front Panel
Status Indicators:
ENABLED: This illuminates Green when
the PA is in operate.
DC OK: This illuminates Green when the
DC inputs to the PA module are present.
TEMP: This illuminates Green when the
temperature of the heatsink in the PA is
below 78°C.
MOD OK: This illuminates Green when
the PA module is operating and has no
faults.
If the Module OK LED is Red and blinking
a fault is present. The meaning of the
blinking LED is as follows.
1 Blink: Indicates Amplifier Current
Fault.
2 Blinks: Indicate Temperature Fault.
3 Blinks: Indicate +32V Power Supply
Over Voltage Fault.
4 Blinks: Indicate +32V Power Supply
Under Voltage Fault.
5 Blinks: Indicate Reflected Power Fault.
6 Blinks: Indicate +12V or –12V Power
Supply Fault
3.4.2 Front Panel Screens on the
Exciter/Driver Chassis Display
A 4 x 20 display located on the front of
the Control & Monitoring/Power Supply
Module is used in the HX Series
exciter/driver for control of the operation
and display of the operating parameters.
Below are the display screens for the
system. The ↑ and ↓ arrows are special
characters used to navigate up or down
through the menu screens. Display text
flashes on discrete fault conditions for all
screens that display a fault condition.
When the transmitter is in operate mode,
the STB menu appears on the screen.
When the transmitter is in standby
mode, the OPR menu appears.
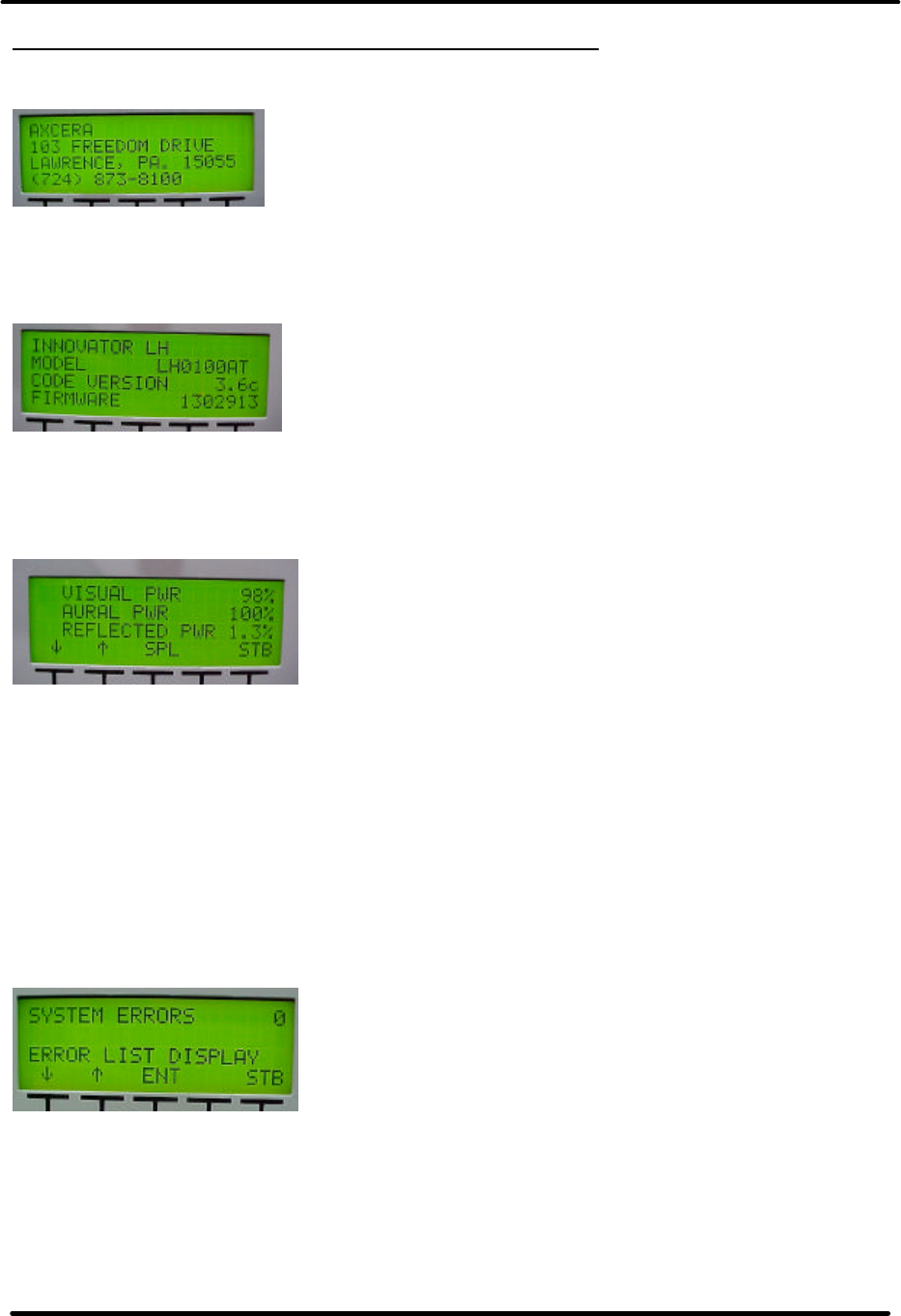
Innovator® HX Series Analog VHF Chapter 3, Site Considerations,
Transmitter Installation and Setup Procedures
HX Series, Rev. 0 3-8
Display Menu Screens for the HX Series Exciter/Driver
NOTE: The following screens are typical and vary with the system.
Table 3-2: Menu 01 - Splash Screen #1
This is the first of the two transmitter splash screens that is shown for the first few
seconds after reset or after pushing the SPL button on the Main Screen. Will
automatically switch to the second splash screen.
Table 3-3: Menu 02- Splash Screen #2
This is the second of the two transmitter splash screens. Will automatically switch to the
Main Screen. The Model Number, Code Version Number and Firmware Number for your
system are displayed on this screen. Make note of these two numbers when conferring
with Axcera on software problems.
Table 3-4: Menu 10 - Main Screen:
This is the default main screen of the transmitter. When the transmitter is in
operate, the 'STB' characters appear, allowing an operator to place the transmitter in
STANDBY, by pushing the right most button located under to display. When the
transmitter is in standby the 'STB' characters are replaced with 'OPR' and the forward
power values are displayed as OFF. An operator can change the transmitter from
STANDBY to OPERATE by pressing the right most button on the front panel display.
Pushing the SPL button will display the two splash screens.
If the ↓ key is activated the display changes to Menu 11, the System Error List Access
Screen. If the ↑ key is activated the display changes to Menu 13, the Transmitter
Configurations Access Screen.
Table 3-5: Menu 11 - Error List Access Screen
This screen of the transmitter shows the current number of errors, displayed in upper,
right of screen (0), and provides operator access to view Menu 20, the error list screens,
by pushing the ENT button. When ENT is pushed, Menu 20, the Error List Display Screen
is displayed. If the ↓ key is pushed the display changes to Menu 12, Table 3-6, the
Transmitter Device Data Access Screen. If the ↑ key is activated the display returns to
Menu 10, the Main Screen.
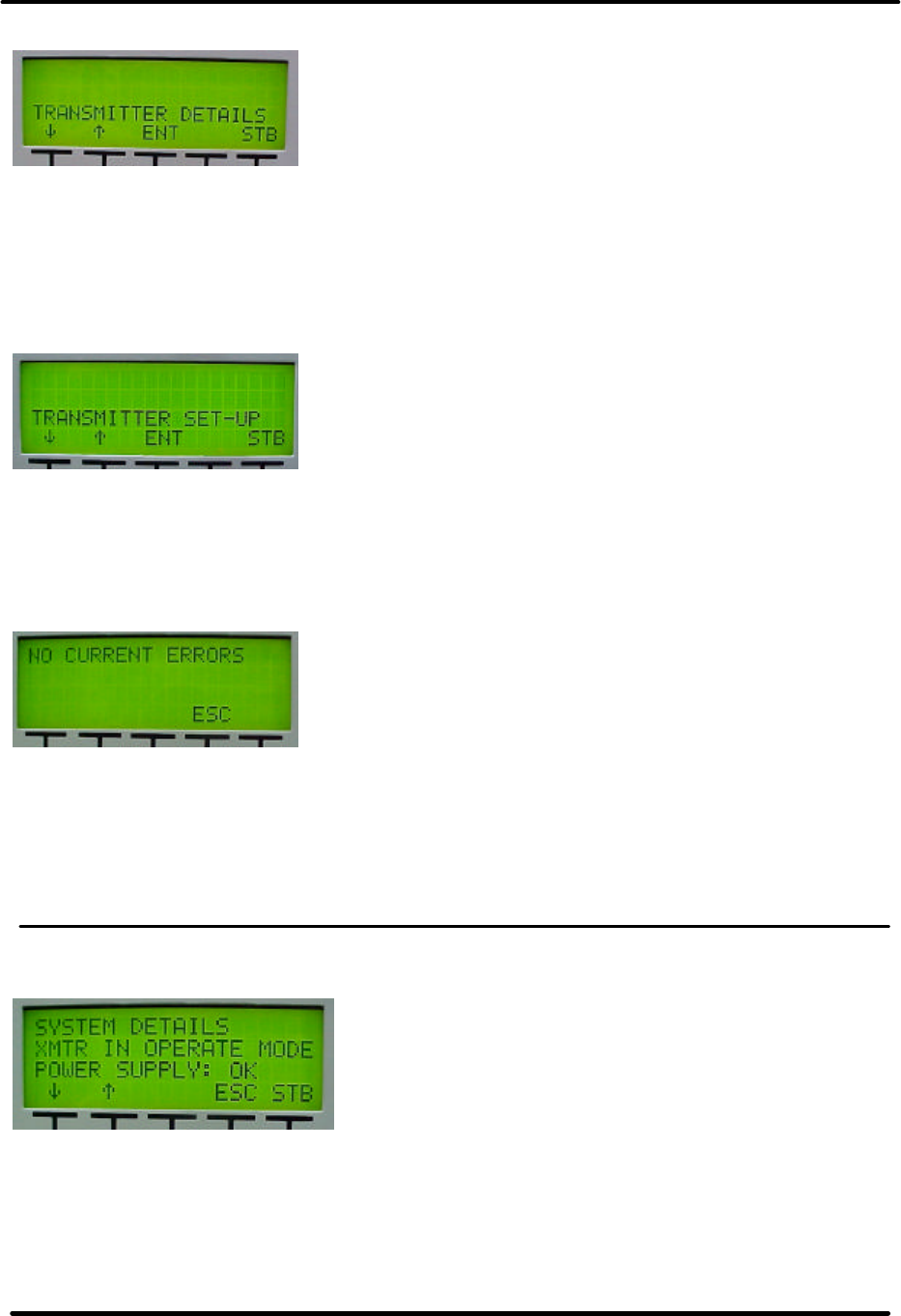
Innovator® HX Series Analog VHF Chapter 3, Site Considerations,
Transmitter Installation and Setup Procedures
HX Series, Rev. 0 3-9
Table 3-6: Menu 12 - Transmitter Device Data Access Screen
This screen of the transmitter allows access to various parameters of the transmitter
system. This is the entry point to Menu 30, the System Details Screens, by pausing the
ENT button. When the ENT button is pushed, Menu 30 is accessed. Go to Menu 30, Table
3-9 for set up details. Before pushing the ENT button: if the ↓ key is activated the
display changes to Menu 13, Transmitter Configurations Access Screen. If the ↑ key is
activated the display returns to Menu 11, the Error List Access Screen.
Table 3-7: Menu 13 - Transmitter Configuration Access Screen
This screen of the transmitter allows access to various software settings of the
transmitter system. If ENT is pushed, go to Menu 40, Table 3-13, the access to
transmitter configuration and set up. Before pushing the ENT button: if the ↓ key is
activated the display returns to Menu 10, Main Screen. If the ↑ key is activated the
display returns to Menu 12, the Transmitter Device Data Access Screen.
Table 3-8: Menu 20 - Error List Display Screen
This screen of the transmitter allows access to the system faults screens. Fault logging is stored in non-volatile
memory. The transmitter's operating state can not be changed using this screen. The
'CLR' switch is used to clear previously detected faults that are no longer active. The ↑
key and ↓ key allow an operator to scroll through the list of errors that have occurred.
The ESC button is used to leave this screen and return to Menu 11, Table 3-5, the Error
List Access Screen. NOTE: Shown is example of a typical screen.
Menu 30 is entered by selecting ENT at Menu 12, Table 3-6.
Table 3-9: Menu 30 - Transmitter Device Details Screen
This screen allows access to the transmitter parameters of installed devices. The system
is configured to know which devices are present. Current values for all installed devices
are shown. If a module is not installed, only a "MODULE NOT PRESENT" message will be
displayed. The first screen displayed is Menu 30-1, Table 3-10, the System Details
Screen.
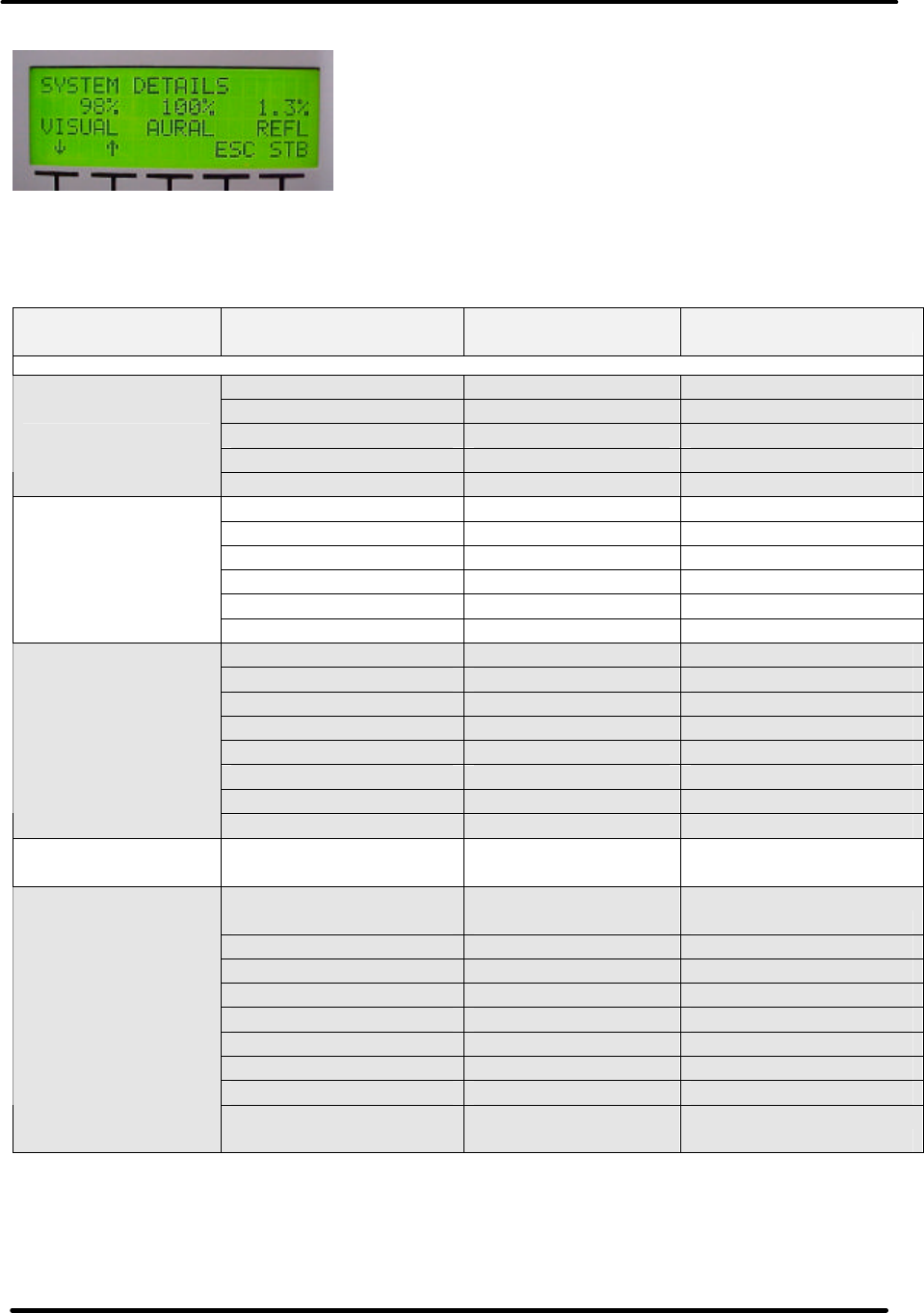
Innovator® HX Series Analog VHF Chapter 3, Site Considerations,
Transmitter Installation and Setup Procedures
HX Series, Rev. 0 3-10
Table 3-10: Menu 30-1 – System Details Screen
The ↓ and ↑ arrows allow you to scroll through the different parameters of each device as
shown in Table 3-11. Each System Component is a different screen. The proper IF
Processor and the Power Amplifier will be programmed for your system.
Table 3-11: Transmitter Device Parameters Detail Screens
System
Component Parameter Normal Faulted (Blinking)
PLL CIRCUIT LOCKED UNLOCKED
MOD DEPTH 0 – 100 IRE N/A
AURAL DEVIATION 0 - 125 kHz N/A
CW INPUT PRESENT NOT USED
Modulator Details
CALL SIGN NONE N/A
INPUT SIGNAL STATE OK FAULT
MODULATION OK FAULT
INPUT IF MODULATOR or J6 N/A
DLC CONTROL LOCK 0 - 5.00 V N/A
ALC LEVEL 0 - 5.00 V N/A
IF Processor
Details
ALC MODE AUTO or MANUAL N/A
AFC 1 LEVEL 0 – 5.00 V N/A
AFC 2 LEVEL 0 - 5.00 V N/A
CODE VERSION 1.8 N/A
PLL 1 CIRCUIT LOCKED FAULT
PLL 2 CIRCUIT LOCKED FAULT
AGC 1 LEVEL 0 - 5.00 V N/A
AGC 2 LEVEL 0 - 5.00 V N/A
Upconverter
Details
INT. 10 MHz IS USED N/A
System Control
Details SUPPLY ENABLED
FOR xxx HOURS N/A
POWER SUPPLY
STATE, 32V 32 VDC N/A
±12V SUPPLY OK or OFF FAULT
FORWARD POWER xxx% xxx%
REFLECTED POWER xxx% xxx%
AMP 1 CURRENT xx.xA xx.xA
AMP 2 CURRENT xx.xA xx.xA
TEMPERATURE xxC xxC
CODE VERSION 1.8 N/A
PA Details
PA HAS OPERATED
FOR xxx HOURS N/A
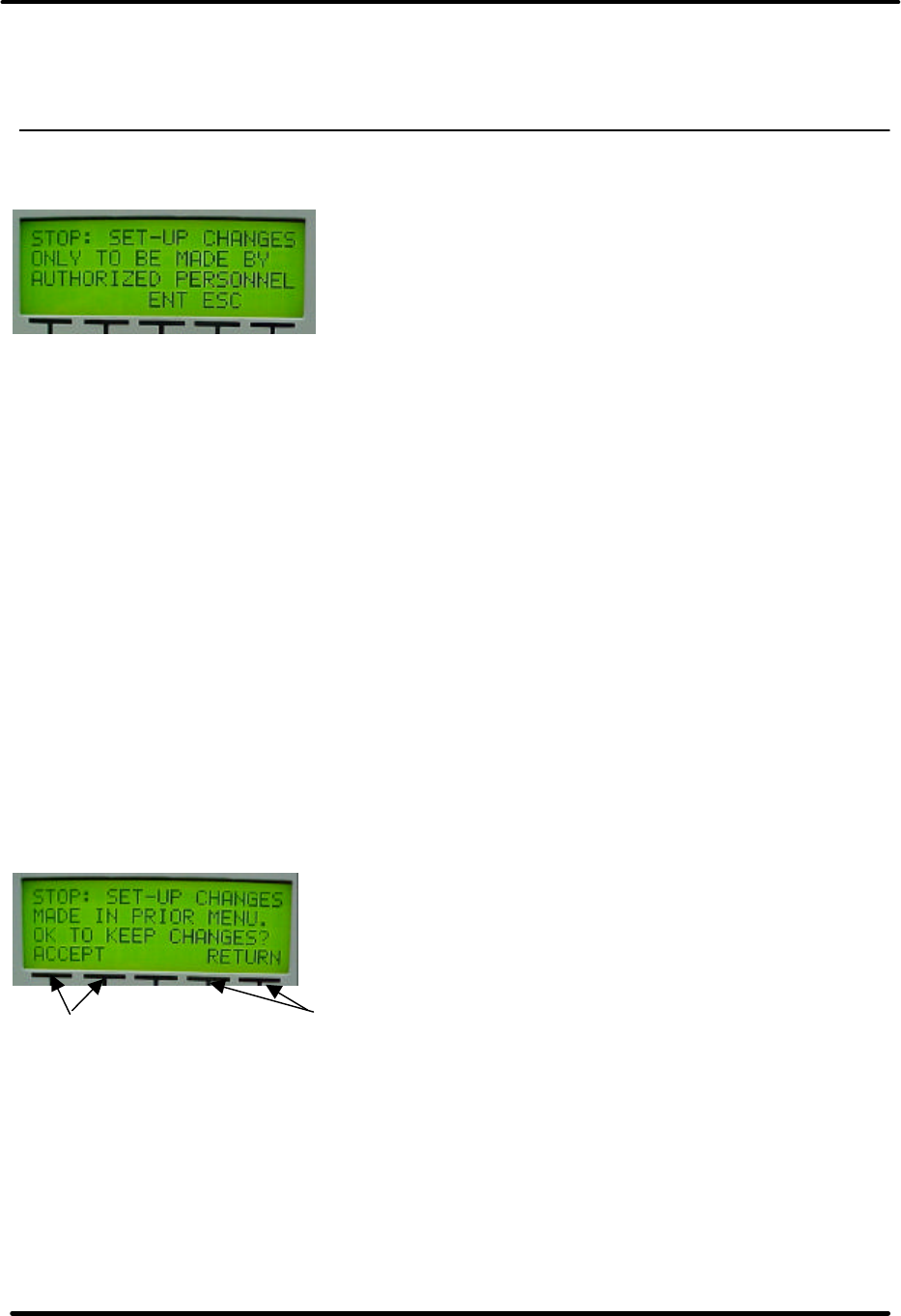
Innovator® HX Series Analog VHF Chapter 3, Site Considerations,
Transmitter Installation and Setup Procedures
HX Series, Rev. 0 3-11
Pushing the ↓ Down Arrow, after scrolling through all of the detail screens, will put you
back to Menu 30, Table 3-9. Push the ESC button to exit the Transmitter Device
Parameter Screens to Menu 12, Table 3-6, the Transmitter Device Parameter Access
Screen.
Menu 40 (Table 3-12) is entered by selecting ENT at Menu 13.
Table 3-12: Menu 40 - Authorized Personnel Screen
This screen of the transmitter notifies an operator that they are only to proceed if they
are authorized to make changes to the transmitter's operation. Changes made within the
following set-up screens can affect the transmitters output power level, output frequency,
and the general behavior of the transmitter. Please do not make changes within the
transmitter's set-up screens unless you are familiar with the operation of the transmitter.
This screen is implemented in transmitter software version 1.4 and above.
Pressing ENT will put you into the Transmitter Set Up Screens for Menu 40.
A safeguard is added to the Set Up Menus in software version 2.5 and above. If a change
is made to a screen within the Set Up Menus, when you go to the next menu, a new
screen asks if you accept the change or want to return to the previous menu to
reconsider the changes made.
To accept the changes, the two buttons located under ACCEPT must be pushed
simultaneously.
To return to the previous Menu to make corrections, the two buttons located under the
RETURN must be pushed simultaneously.
Upon returning to the previous Menu the correct input must be entered and the above
procedure repeated, this time accepting the changes
Accept or Return to previous Menu Screen
Pushing these two buttons Pushing these two buttons
Simultaneously will accept Simultaneously will return you
the change. to the previous Menu.
The Set Up Screens are shown in Table 3-13 Menu 40-1 through Table 3-26 Menu 40-19
that follow.
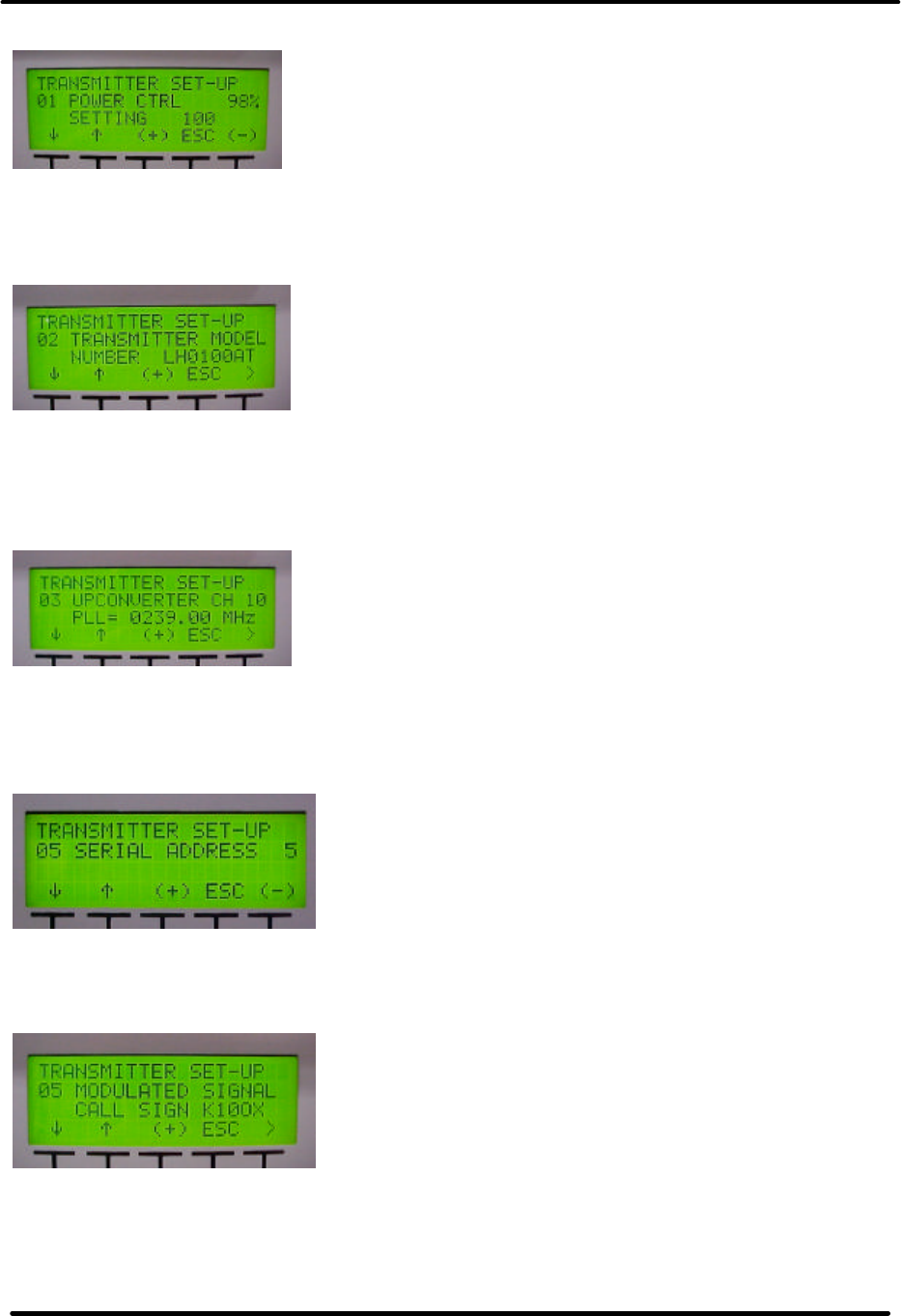
Innovator® HX Series Analog VHF Chapter 3, Site Considerations,
Transmitter Installation and Setup Procedures
HX Series, Rev. 0 3-12
Table 3-13: Menu 40-1 - Transmitter Set-up: Power Control Screen
This screen of the transmitter is the first of several that allows access to transmitter set-
up parameters. When + is selected, the Power will increase. When - is selected, the
Power will decrease.
Table 3-14: Menu 40-3 - Transmitter Set-up: Model Select Screen
This screen is used to specify which components are expected to be part of the system.
By specifying the model number, the transmitter control firmware knows which
components should be installed and it will be able to display faults for components that
are not properly responding to system commands.
Table 3-15: Menu 40-4 - Transmitter Set-up: Upconverter Channel Select Screen
The choices of this screen are to the standard UHF / VHF channels. The + and – buttons
change the desired channel of the transmitter. The PLL frequency is set for custom
Offsets within the upconverter frequency. Any change to the channel is immediately set
to the LO / Upconverter Frequency Synthesizer PLL circuit.
Table 3-16: Menu 40-5 - Transmitter Set-up: Serial Address Screen
This screen allows the user to set the serial address of the transmitter. The default
address is 5. This value and all other set-up parameters are stored in non-volatile
memory.
Table 3-17: Menu 40-6 - Transmitter Set-up: Station ID Screen
This screen allows the user to set the Station ID, Call Sign, in analog transmitters. If
blank characters are used for all five positions, then the Station ID feature is disabled.
Otherwise, the Station ID code is transmitted every 15 minutes. This value and all other
set-up parameters are stored in non-volatile memory. (NOTE: If an external Receiver
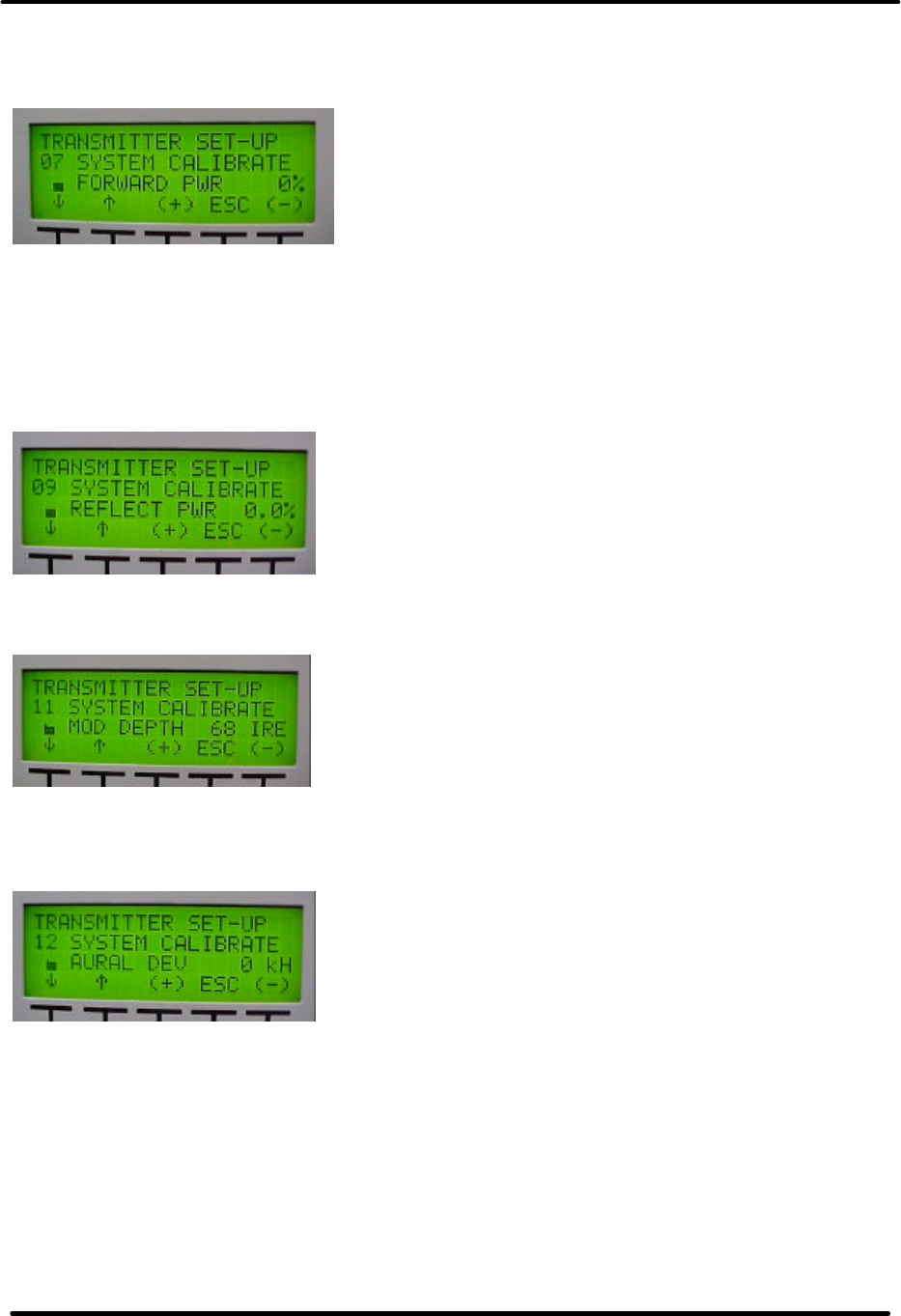
Innovator® HX Series Analog VHF Chapter 3, Site Considerations,
Transmitter Installation and Setup Procedures
HX Series, Rev. 0 3-13
Tray is used in your system, the HX Series Station ID is disabled. Therefore, the Station
ID must be set up in the external Receiver Tray.)
Table 3-18: Menu 40-7 - Transmitter Set-up: System Forward Power Calibration
This screen is used to adjust the calibration of the system's forward power. A symbol
placed under the '6' character is used to show major changes in the calibration value.
When the calibration value is at full value, the character will be full black. As the value
decreases, the character pixels are gradually turned off. The calibration value is a value
between 0 and 255 but the calibration value symbol only has 40 pixels. Therefore, small
changes in actual calibration value may not affect the symbol's appearance.
Table 3-19: Menu 40-9 - Transmitter Set-up: System Reflected Power Calibration
This screen is used to adjust the calibration of the system's reflected power. A calibration
value symbol is used for this screen as on the previous screens.
Table 3-20: Menu 40-11 - Transmitter Set-up: Modulated Output Calibration
This screen is used to adjust the calibration of the system's modulated output signal
detector. The calibration value symbol is again used to graphically represent the
modulated output signal detector's calibration value.
Table 3-21: Menu 40-12 - Transmitter Set-up: Aural Deviation Calibration
This screen adjusts the calibration of the system's aural deviation detector. The
calibration value symbol is again used to graphically represent the aural deviation
detector's calibration value.

Innovator® HX Series Analog VHF Chapter 3, Site Considerations,
Transmitter Installation and Setup Procedures
HX Series, Rev. 0 3-14
Table 3-22: Menu 40-13 - Transmitter Set-up: Forward Power Fault Threshold Screen
This screen is used to set the minimum forward power fault threshold. When the
transmitter is operating, it must operate above this value otherwise the system will shut
down with fault for 5 minutes. If after five minutes the fault is not fixed, the transmitter
will enable, measure power less than this value and again shut down for five minutes.
Table 3-23: Menu 40-14 - Transmitter Set-up: Reflected Power Fault Threshold
This screen sets the maximum reflected power fault threshold. When the transmitter is
operating, it must not operate above this value otherwise the system will slowly begin to
reduce the forward output power. If the system's reflected output power exceeds the
maximum reflected power threshold by five percent or more, the transmitter will shut
down with fault for 5 minutes. If after five minutes the fault is not fixed, the transmitter
will enable, measure power above this value plus five percent and again shut down for
five minutes. If the system's reflected output power exceeds the maximum reflected
power threshold due to some condition like the formation of ice on an antenna, the
transmitter reduces forward power to a level where the reflected power is less than this
threshold. The transmitter will automatically increase its output power to normal
operation when the cause of higher than normal reflected power is corrected.
Table 3-24: Menu 40-17 - Transmitter Set-up: Auto Stand-By Control
Certain HX transmitter locations are required to reduce to no output power on the loss of
video input. When a HX transmitter is configured for Auto Stand-By on Modulation Loss,
the transmitter will switch to stand-by, if a modulated input signal fault is detected by the
IF Processor module that lasts for more than ten seconds. Once the modulated input
signal fault is cleared, a transmitter in operate mode will return to normal operation. This
feature is implemented in transmitter software version 1.4 and above.
Table 3-25: Menu 40-18 - Transmitter Set-up: Inner Loop Gain Control
This screen is used to set up the Inner Loop Gain of the exciter/amplifier assembly. This
feature is implemented in transmitter software version 2.0 and above
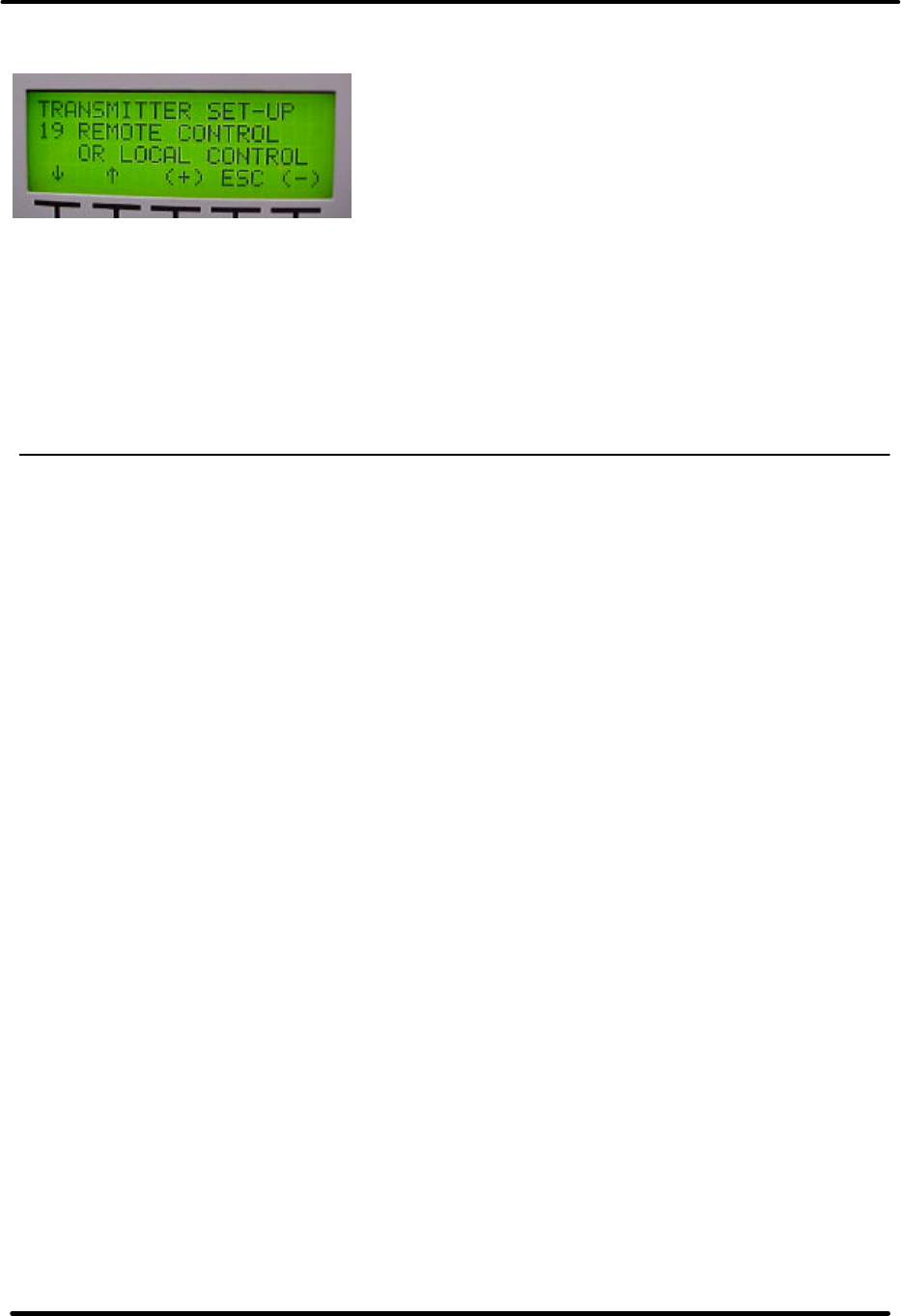
Innovator® HX Series Analog VHF Chapter 3, Site Considerations,
Transmitter Installation and Setup Procedures
HX Series, Rev. 0 3-15
Table 3-26: Menu 40-19 - Transmitter Set-up: Remote Commands Control
This screen is used to allow or deny the use of remote control commands. When
disabled, remote commands are not used. Remote commands are commands received
either through the rear terminal blocks or through serial messages.
Push the ESC button to exit the Transmitter Set up Screens to Menu 13, Table 3-7, and
the Transmitter Configuration Access Screen
This completes the description of the menu screens for the HX Series exciter/driver chassis
assembly.
3.4.3 Operation Procedure
If necessary, connect to the output of
the transmitter at the “N” connector
J25 to the external filter assembly.
Check that the RF output is 100% and
if needed adjust the ALC Gain adjust
pot on the front panel of the IF
Processor to attain 100% RF Output.
The power raise/lower settings, in the
menus, are only to be used for
temporary reductions in power.
The power set-back values do not
directly correspond to the output power
of the transmitter.
This completes the Installation, Set Up
and Turn On of the Transmitter.
If a problem occurred during the setup
and operation procedures, refer to
Chapter 5, Detailed Alignment
Procedures, of this manual for more
information.
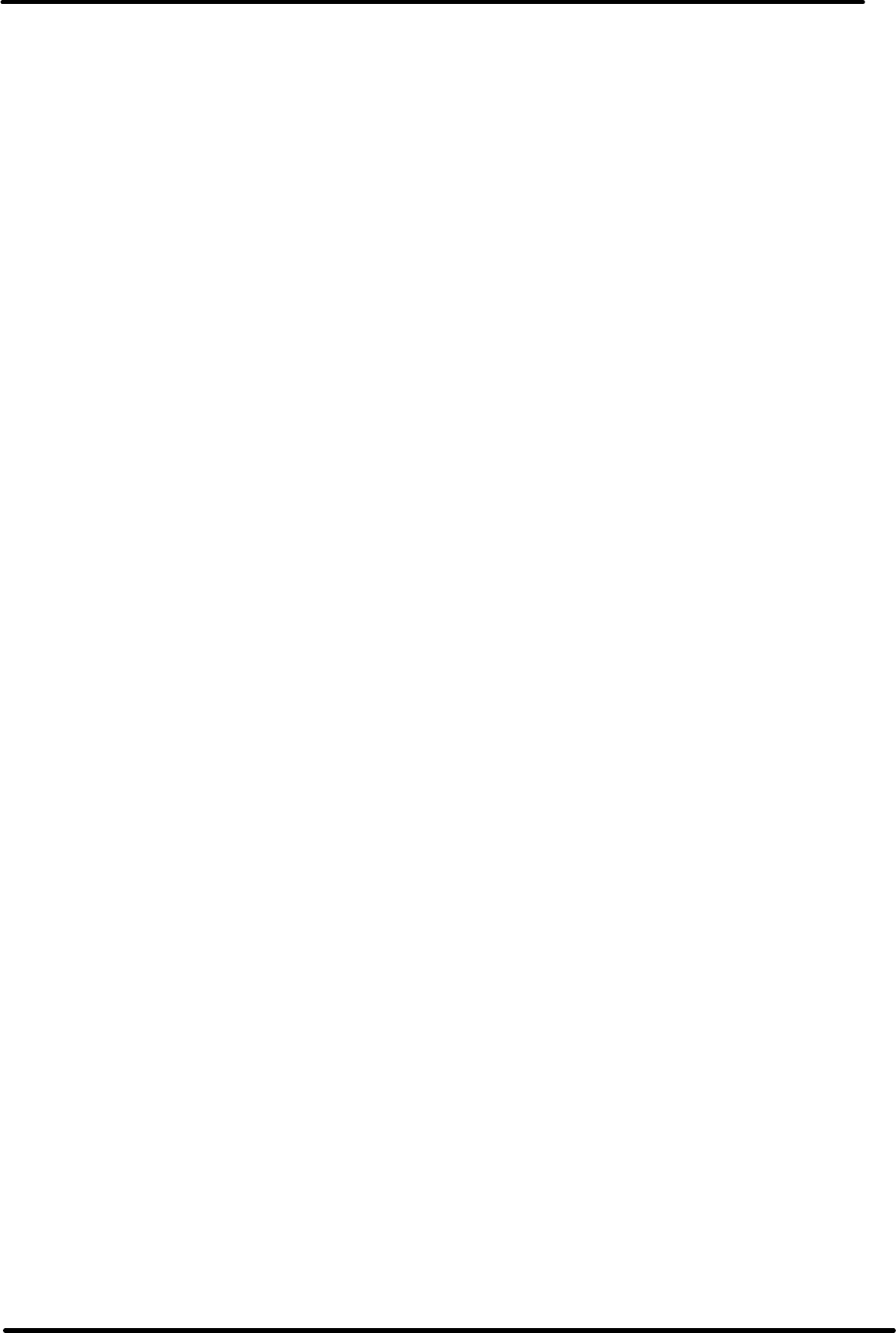
Innovator® HX Series Analog VHF Chapter 4, Circuit Descriptions,
Transmitter Control/Exciter Cabinet Assemblies
HX Series, Rev. 0 4-1
Chapter 4
Circuit Descriptions
4.0 (A2) Exciter/Driver Chassis
Assembly (1307715, 110 VAC;
Appendix A)
The Exciter/Driver Chassis Assembly
contains, as mounted in the assembly
from left to right, (A2) the Modulator
Module (1305420), (A3) the IF Processor
Module (1305421), (A5) the Upconverter
Module (1303829), (A4) the System
Controller/Power Supply Module
(1301936), and (A6) the Power Amplifier
Module (1308252).
4.1 (A2) Modulator Module, HX
Series (1305420; Appendix A)
Contains an Analog Modulator Board
(1304704).
4.1.1 Analog Modulator Board, HX
Series (1304704; Appendix A)
The board takes the audio and video
inputs and produces a modulated visual
IF and aural IF outputs. Refer to the
Schematic # 1304705 while following
this description.
Main Audio and Aural IF portion of
the board
The analog modulator board takes each
of the three possible audio inputs,
Balanced, Composite and/or Subcarrier
and provides a single audio output.
4.1.1.1 MONO, Balanced Audio Input
The first of the three possible baseband
inputs to the board is a 600Ω, balanced-
audio input (0 to +10 dBm) that enters
through Jack J41A, Pins 10A (+)A, 11A
(-)B and 12A (GND), on page 3 of the
schematic, “A” & “B”, and is buffered by
U11A and U11B, on page2 of the
schematic. Diodes CR9, CR10, CR12 and
CR13 protect the input to U11A and
U11B if an excessive signal level is
present on the input. The outputs of
U11A and U1B are applied to differential
amplifier U11C. U11C eliminates any
common mode signals (hum) on its input
leads. A pre-emphasis of 75 µs is
provided by R97, C44, and R98 and can
be eliminated by removing jumper W6 on
J22. The signal is then applied to
amplifier U11D whose gain is controlled
by jumper W12 on J23. Jumper W12 on
jack J23 is positioned according to the
input level of the audio signal (0 or +10
dBm). If the input level is approximately
0 dBm, the mini-jumper should be in the
high gain position between pins 1 and 2
of Jack J23. If the input level is
approximately +10 dBm, the mini-
jumper should be in low gain position
between pins 2 and 3 of Jack J23. The
balanced audio is then connected to
buffer amplifier U12A whose input level is
determined by the setting of the MONO,
balanced audio gain pot R110, accessed
through the front panel. The output of
the amplifier stage is wired to the
summing point at U13C, pin 9.
4.1.1.2 STEREO, Composite Audio
Input
The second possible audio input to the
board is the composite audio (stereo)
input that connects to the board at J41A
Pins 13A (-) and 14A (+), on page 3 of
the schematic, “R” & “S”.
NOTE: Refer to page 2 of the schematic.
For the transmitter to operate using the
composite audio input the Jumper W1 on
J4 must be between Pins 2 and 3, the
Jumper W2 on J6 must be between Pins
2 and 3 and the Jumper W4 on J5 must
be between Pins 1 and 2. These jumpers
connect the composite audio to the rest
of the board.
Jumper W14 on jack J26 provides a 75Ω
input impedance when the jumper is
between pins 1 and 2 and a high
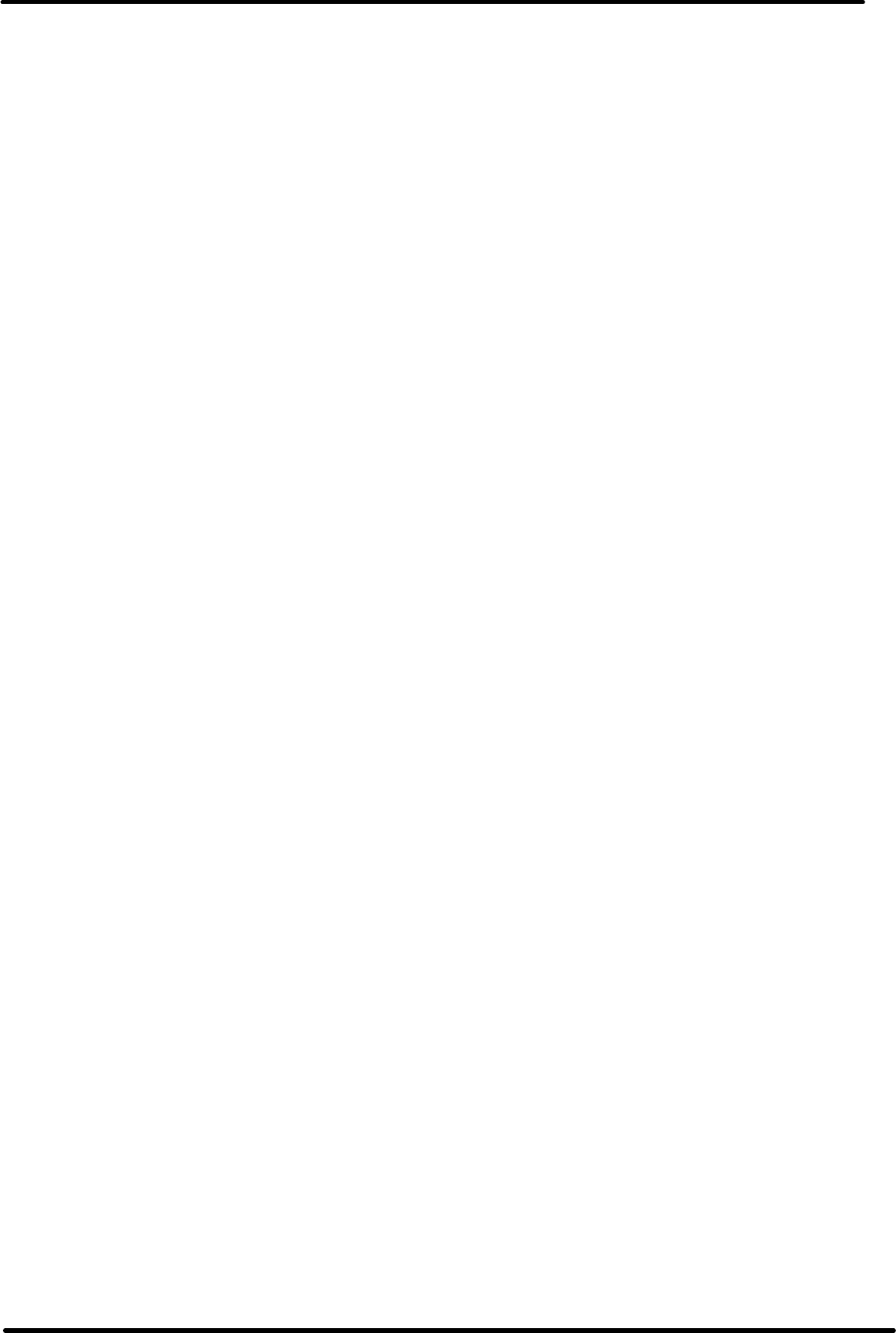
Innovator® HX Series Analog VHF Chapter 4, Circuit Descriptions,
Transmitter Control/Exciter Cabinet Assemblies
HX Series, Rev. 0 4-2
impedance when it is between pins 2 and
3. The Diodes CR17, CR18, CR20 and
CR21 protect the input stages of U14A
and U14B if an excessive signal level is
applied to the board. The outputs of
U14A and U14B are applied to the
differential amplifier U13A, which
eliminates common mode signals (hum)
on its input leads. The composite input
signal is then applied to the amplifier
U13B, whose gain is controlled by the
STEREO, composite audio gain pot R132,
accessed through the front panel. The
composite audio signal is then connected
to the summing point at U13C, pin 9.
4.1.1.3 SAP/PRO, Subcarrier Audio
Input
The third possible input to the board is
the SAP/PRO, SCA audio input at J41A
pin 16A(+) and 17A(-), on page 3 of the
schematic, “D”. On page 3 of the
schematic, the SCA input has an input
matching impedance of 75Ω that can be
eliminated by removing the jumper W15
from pins 1 and 2 on J28. The SCA input
is bandpass filtered by C73, C74, R145,
C78, C79, and R146 and is fed to the
buffer amplifier U13D. The amplified
signal is then applied though the
SAP/PRO, SCA gain pot R150, accessed
through the front panel, to the summing
point at pin 9 of U13C.
4.1.1.4 Audio Modulation of the
4.5 MHz VCO
On page 2 of the schematic, the Mono
balanced audio, or the Stereo composite
audio, or the SAP/PRO SCA buffered
audio signal, is fed to the common
junction of resistors R111, R130, and
R152 that connect to pin 9 of amplifier
U13C. The output audio signal at pin 8 of
U13C is typically .8 Vpk-pk at a ±25 kHz
deviation for Mono balanced audio or .8
Vpk-pk at ±75 kHz deviation for Stereo
composite audio as measured at the Test
Point TP1. This audio deviation signal is
applied to the circuits containing the 4.5
MHz aural VCO U16. A sample of the
aural deviation level is amplified,
detected by U15A and U15B, and
connected to J41A pin 5A on the board,
on page 3 of the schematic. This audio-
deviation level is connected to the front
panel LCD display on the Control/Power
Supply Assembly.
The audio from U13C is connected thru
C71, a frequency response adjustment,
to varactor diodes, CR24 to CR27, that
frequency modulate the audio signal onto
the generated 4.5 MHz signal. U16 is the
4.5 MHz VCO that generates the 4.5 MHz
continuous wave (CW) signal. The
output frequency of the 4.5 MHz signal is
maintained and controlled by the
correction voltage output of the U21 PLL
integrated circuit (IC), on page 3 of the
schematic, at “N”, that connects to the
varactor diodes. The audio modulated,
4.5 MHz signal is fed through the emitter
follower Q13 to the amplifiers U17A and
U17B. A sample of the audio modulated,
4.5 MHz is fed back to U21 the PLL
integrated circuit (IC), on page 3 of the
schematic, at “M”. The amplified output
of U17A is connected to a 4.5 MHz filter
and then to U17B. The output of U17B is
connected to the 4.5 MHz output sample
jack at J29 and through the Jumper W4
on J5 pins 1 & 2, “J”, to the I input of the
mixer Z1, on page 3.
4.1.1.5 Phase Lock Loop (PLL) Circuit
A sample of the signal from the 4.5 MHz
aural VCO at the output of Q13, “M”, is
applied to the PLL IC U21 at pin 1, the Fin
connection. In U21, the signal is divided
down to 50 kHz and is compared to a
50 kHz reference signal that is a divided-
down sample of the 45.75 MHz visual IF
signal. This 50 kHz sample is applied to
the oscillator-in connection at Pin 27 on
the PLL chip. These two 50 kHz signals
are compared in the IC and the fV, and
fR is applied to the differential amplifier
U18A. The output of U18A, “N”, is fed
back through CR28 and C85 to the 4.5
MHz VCO IC U16, which sets up a PLL
circuit. The 4.5 MHz VCO will maintain
the extremely accurate 4.5 MHz
separation between the visual and aural
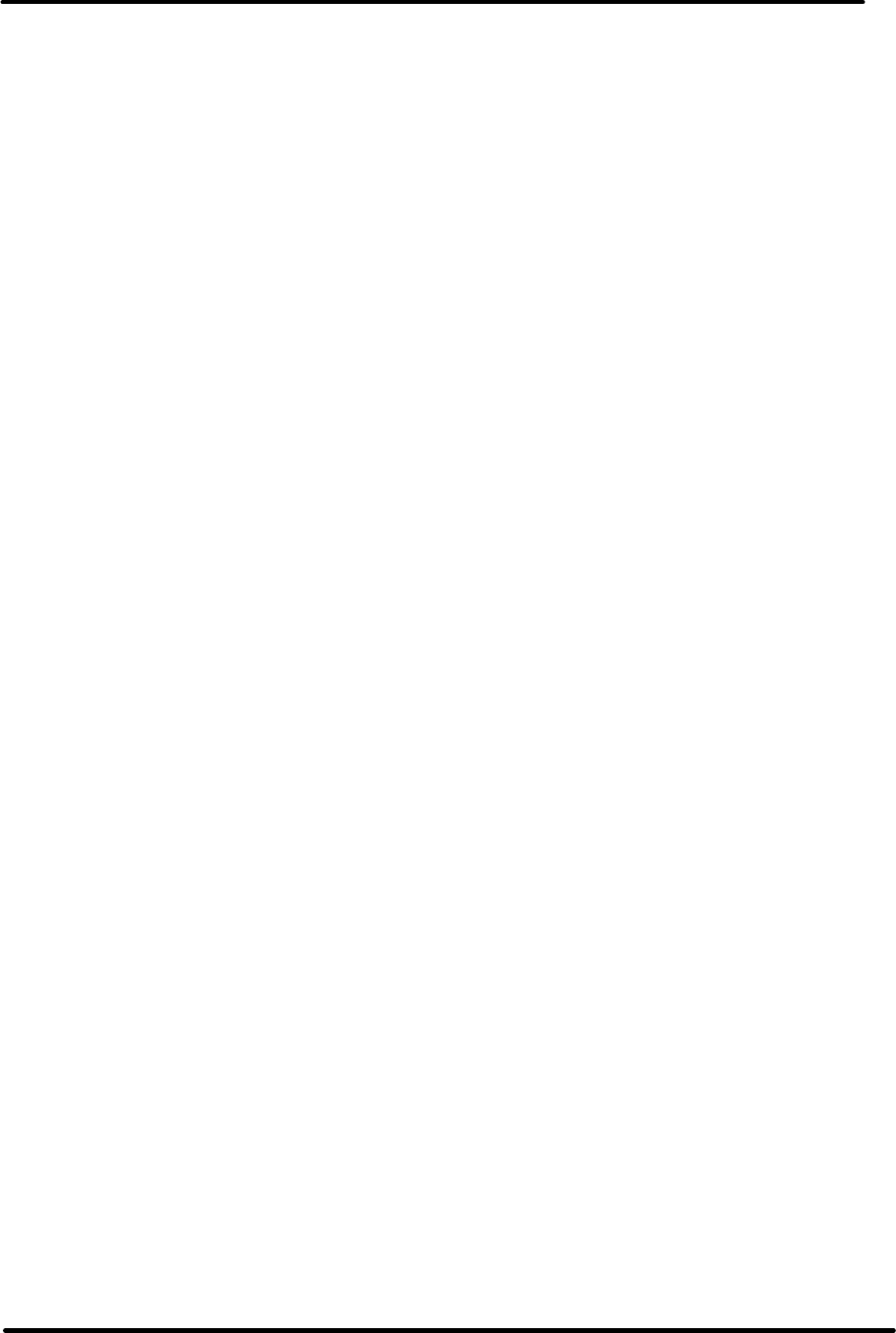
Innovator® HX Series Analog VHF Chapter 4, Circuit Descriptions,
Transmitter Control/Exciter Cabinet Assemblies
HX Series, Rev. 0 4-3
IF signals. Any change in frequency will
be corrected by the AFC error voltage.
The PLL chip U21 also contains an
internal lock detector that indicates the
status of the PLL circuit. When U21 is in
a "locked" state, pin 28 is high. If the
4.5 MHz VCO and the 45.75 MHz
oscillator become "unlocked," out of the
capture range of the PLL circuit, pin 28 of
U21 will go to a logic low and cause the
Aural Unlock LED DS5 to light red. The
Aural Unlock LED is viewed through the
front panel of the Assembly. An Aural
unlock, PLL Unlocked, output signal from
Q16 is also applied to jack J41B pin 1B.
Sync Tip Clamp and the Visual and
Aural Modulator portions of the
board
The sync tip clamp and modulator portion
of the board is made up of four circuits:
the main video circuit, the sync tip clamp
circuit, the visual modulator circuit and
the aural modulator circuit.
The clamp portion of the board maintains
a constant peak of sync level over
varying average picture levels (APL). The
modulator portion of the board contains
the circuitry that generates an
amplitude-modulated vestigial sideband
visual IF signal output that is made up of
the baseband video input signal (.5 to 1
Vpk-pk) modulated onto a 45.75 MHz IF
carrier frequency. The modulated visual
IF signal is amplified by U30 and
connected thru J17 and an external cable
assembly, W8, “WB” to J13 that connects
to J41C Pin 17C, the Visual IF Output of
the board. The modulated aural IF signal
is amplified by U27 and connected thru
J21 and an external cable assembly, W9,
“WC” to J18 that connects to J41C Pin
6C, the Aural IF Output of the board.
4.1.1.6 Main Video Signal Path
(Part 1 of 2)
The baseband video input connects to the
board at J41A pins 19A (-), “W”, and 20A
(+), “V”. The +, “V” and -, “W”, video
inputs are fed to Diodes CR1 to CR4, on
page 1 of the schematic, that form a
voltage-limiter network in which, if the
input voltages exceed the supply
voltages for U2B, the diodes conduct,
preventing damage to U2B. CR1 and CR3
conduct if the input voltage exceeds the
negative supply and CR2 and CR4
conduct if the input voltage exceeds the
positive supply voltage. The baseband
video input connects to the non-inverting
and inverting inputs of U2B, a differential
amplifier that minimizes any common-
mode problems that may be present on
the incoming signal
The video output of U2B is connected
through the Video Gain pot R42,
accessed through the front panel, to the
amplifier U2A. The output of U2A
connects to the delay equalizer circuits
4.1.1.7 Delay Equalizer Circuits
The delay equalizer circuits provide a
delay to the video signal, correction to
the frequency response, and
amplification of the video signal.
The video output of U2A is spit with a
sample connected to J7 for Pre Video
Delay signal testing. The other path is
wired to the first of four delay-equalizing
circuits that shape the video signal to the
FCC specification for delay equalization or
to the shape needed for the system. The
board has been factory-adjusted to this
FCC specification and should not be
readjusted without the proper
equipment.
Resistors R53, R63, R61, and R58, are
adjustable and accessed through the top
cover of the exciter/driver assembly.
They adjust the sharpness of the
response curve while inductors GD1,
GD2, GD3, and GD4 adjust the position
of the curve. The group delayed video
signal at the output of U3A is split with a
sample connected to J8 on the board that
can be used for testing purposes of the
Post Video Delay signal. The other
portion of the video signal connects
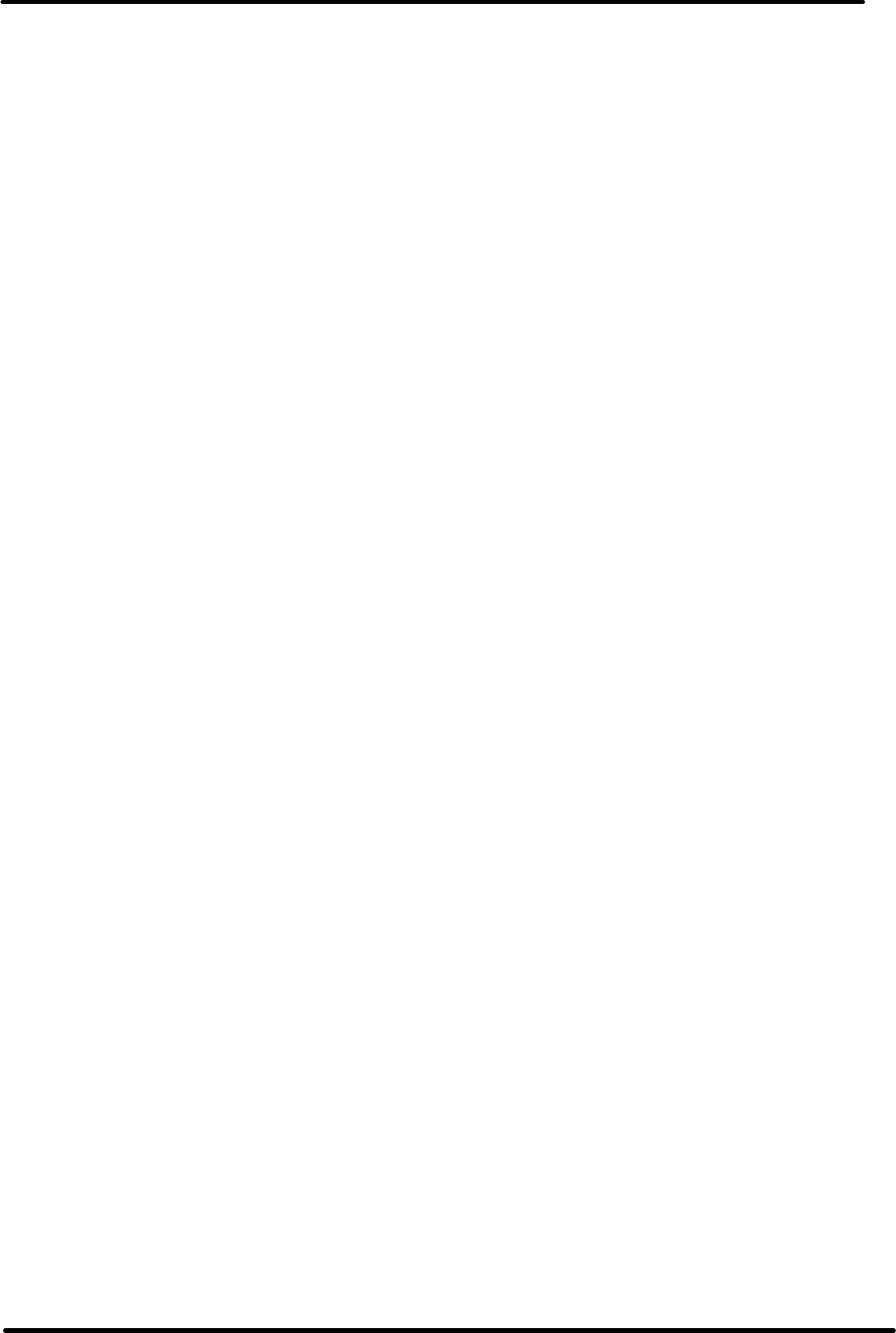
Innovator® HX Series Analog VHF Chapter 4, Circuit Descriptions,
Transmitter Control/Exciter Cabinet Assemblies
HX Series, Rev. 0 4-4
through the Jumper W5 on J9 pins 2 and
3. The delay-equalizing circuits can be
bypassed by placing the jumper W5 on
J9 between pins 1 and 2. The video at
VIN connects through SW13 or R325 a
0? resistor, on page 4 of the schematic,
to U35A and U35B. U35B is an inverting
amplifier that provides the inverted video
to the differential phase circuits. U35A is
an amplifier that provides the main video
to the differential phase circuits. The
Zener Diodes VR3 and VR4 offset the
in-phase main video signal by +3.9 VDC
and -3.9 VDC. A signal with no offset is
available at the junction of these Zener
diodes, Main Video. The three in-phase
video signals along with an inverted
video signal are applied to a Differential
Phase Corrector network. There are four
stages of Phase Correction, which are
combined at R355. The Color Subcarrier
Phase Shift is accomplished by summing
the inverted video signal with the main
video signal thru capacitors C205-C208.
Potentiometers R335-R337 & R333, are
adjustable and accessed through the top
cover of the exciter/driver assembly.
They set up the threshold points in the
video signal beyond which each Phase
Corrector section becomes effective.
Gating diodes CR43-CR46 can be
inverted, turned in the sockets in which
they are mounted, for an additional
degree of freedom in setting the correct
Differential Phase characteristic.
The output from the Differential Phase
Corrector circuit is connected to a buffer
amplifier IC U36A. The phase corrected
video output can be measured at TP6 on
the board. The phase corrected video, at
VOUT on page 4 of the schematic,
connects to a splitter, consisting of R44
and R62, on page 1 of the schematic.
The video is split with one part
connecting to a sync tip clamp circuit,
another part connecting to a video loss
detector circuit and the other part is the
main video output path that connects
through R44. The video input to the
video loss detector circuit is detected by
CR5 and connected to a comparator UC
U5A. If video is present Q5 will be off
and DS1 will be off. If video is lost Q5
will conduct and the Red Video Loss LED
DS1, located on the front panel, will be
on. A sample of the main video from
R44, at “P”, connects to U32 and U33, on
page 2 of the schematic, that provides a
zero adjust and a 1 Volt output level,
which connects at “T” to J41A pin 3A, on
page 3 of the schematic. This video level
is wired to the Control/Power Supply
assembly.
4.1.1.8 Sync Tip Clamp Circuit
The phase corrected video connects
through R62 to the automatic sync tip
clamp circuit that is made up of U6A, Q8,
U5C, and associated components. The
level at which the tip of sync is clamped
is -1.04 VDC as set by the voltage-
divider network, consisting of R77, R78,
R75, R76 and R80 connected to U6A. If
the video level changes, the sample
applied to U6A changes. The voltage
from the clamp circuit that is applied to
the summing circuit at the base of Q8 will
change; this will bring the sync tip level
back to -1.04 VDC. Q8 will be turned off
and on according to the peak of sync
voltage level that is applied to U6A. The
capacitors C35 and C24, in the output
circuit of Q8, will charge or discharge to
the new voltage level. This will bias U5C
more or less, through the front panel
MANUAL/AUTO CLAMP switch, SW1,
when it is in the Auto Clamp-On position,
between pins 2 and 3. In AUTO CLAMP,
U5C will increase or decrease its output,
as needed, to bring the peak of sync
back to the correct level. The voltage
level is applied through U5C to U2A. In
the Manual CLAMP position, SW1 in
manual position, between pins 1 and 2,
the adjustable resistor R67 provides the
manual clamp bias adjustment for the
video that connects to U5C. This level is
set at the factory and is not adjustable
by the customer. In Manual clamp the
peak of sync auto clamp circuit will not
automatically be clamped to the pre set
level.
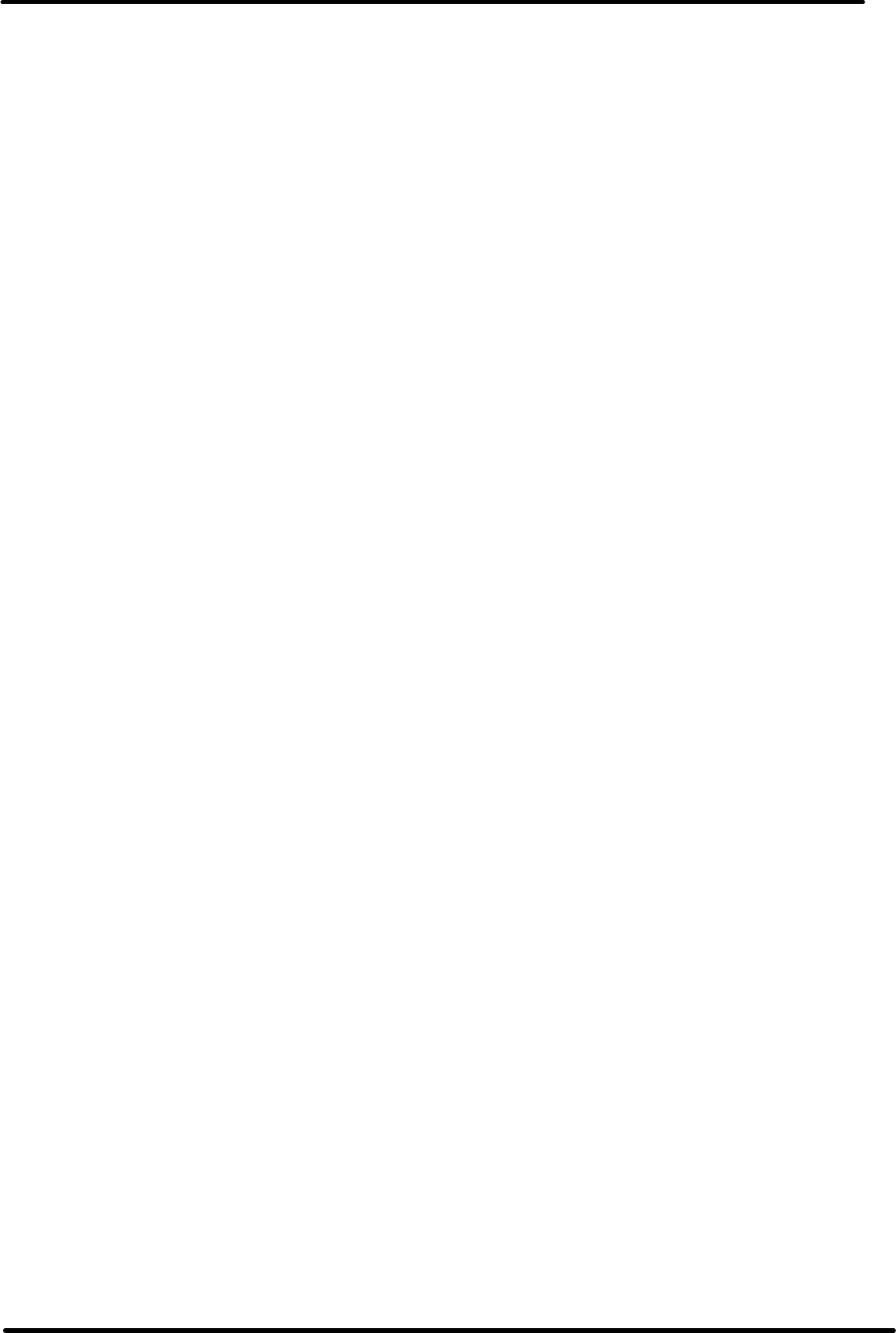
Innovator® HX Series Analog VHF Chapter 4, Circuit Descriptions,
Transmitter Control/Exciter Cabinet Assemblies
HX Series, Rev. 0 4-5
4.1.1.9 Main Video Signal Path
(Part 2 of 2)
A sample of the clamped video output
from the group delay circuitry through
R44 is connected through R322 to a
white clipper circuit consisting of Q1 and
associated circuitry. R322 adjusts the
level of the video to the clipper circuit.
The base voltage of Q1 is set by the
voltage divider network consisting of R1,
R9 and R5. R5 is adjustable and
accessed through the top cover of the
exciter/driver assembly and sets the level
of the white clipper circuit to prevent
video transients from over modulating
the video carrier.
At R322 another clamped video path
connects to a sync clip and sync-stretch
circuits that consist of Q2, Q3 and Q4.
The sync-stretch circuit contains R19,
which adjusts the Sync Stretch
Magnitude (amount), R11, which adjusts
the Sync Stretch Cut-In and R6, which
adjusts the Sync Clipping point. R11 and
R6 are accessed through the top cover of
the exciter/driver assembly. The sync-
stretch adjustments should not be used
to correct for output sync problems, but
it can be used for input video sync
problems. The output of the sync-stretch
circuit is amplified by U31A and
connected, “K”, to pin 5, the I input of
Mixer Z2, the Visual IF Mixer, found on
page 3 of the schematic.
4.1.1.10 45.75 MHz Oven Oscillator
Circuit
Refer to page 3 of the schematic. The
oven oscillator portion of the board
generates the visual IF CW signal at
45.75 MHz for NTSC system "M" usage.
The +12 VDC needed to operate the
oven is applied through jack J30 pin 1 on
the crystal oven HR1. The oven is preset
to operate at 60° C. The oven encloses
the 45.75 MHz crystal Y1 and stabilizes
the crystal temperature. The crystal is
the principal device that determines the
operating frequency and is the most
sensitive in terms of temperature
stability.
Crystal Y1 operates in an oscillator circuit
consisting of transistor Q24 and its
associated components. Feedback that is
provided by a voltage divider, consisting
of C173, L38 and R295, is fed to the base
of Q24 through C169. This circuitry
operates the crystal in a common-base
amplifier configuration using Q24. The
operating frequency of the oscillator is
maintained by a PLL circuit, which
consists of ICs U20 and U22 and
associated components, whose PLL
output connects to R293 in the crystal
circuit.
The oscillator circuit around Q24 has a
regulated voltage, +6.8 VDC, which is
produced from the +12 VDC by a
combination of dropping resistor R261,
diodes CR37 and CR38 and Zener diode
VR2. The output of the oscillator at the
collector of Q24 is capacitively coupled
through C165 to the base of Q23. The
small value of C165, 15 pF, prevents the
oscillator from being loaded down by
Q23. Q23 is operated as a common-
emitter amplifier stage whose bias is
provided through R259 from the +12
VDC line. The output of Q23, at its
collector, is connected to an emitter-
follower transistor stage, Q21. The
output of Q21 at its emitter is split. One
path connects to the input of the IC U20
in the PLL circuit. The other path is
through R270 to establish an
approximate 50O source impedance
through C166 to the Pin 1 contact of the
relay K2. The 45.75 MHz connects
through the closed contacts of K2 to a
splitter network consisting of L31 and
L32.
NOTE: The relay contacts for the
internally generated 45.75 MHz signal
will be closed unless an external IF
signal, such as the IF for offset and
precise frequency 45.74 or 45.76 MHz,
connects to the board.
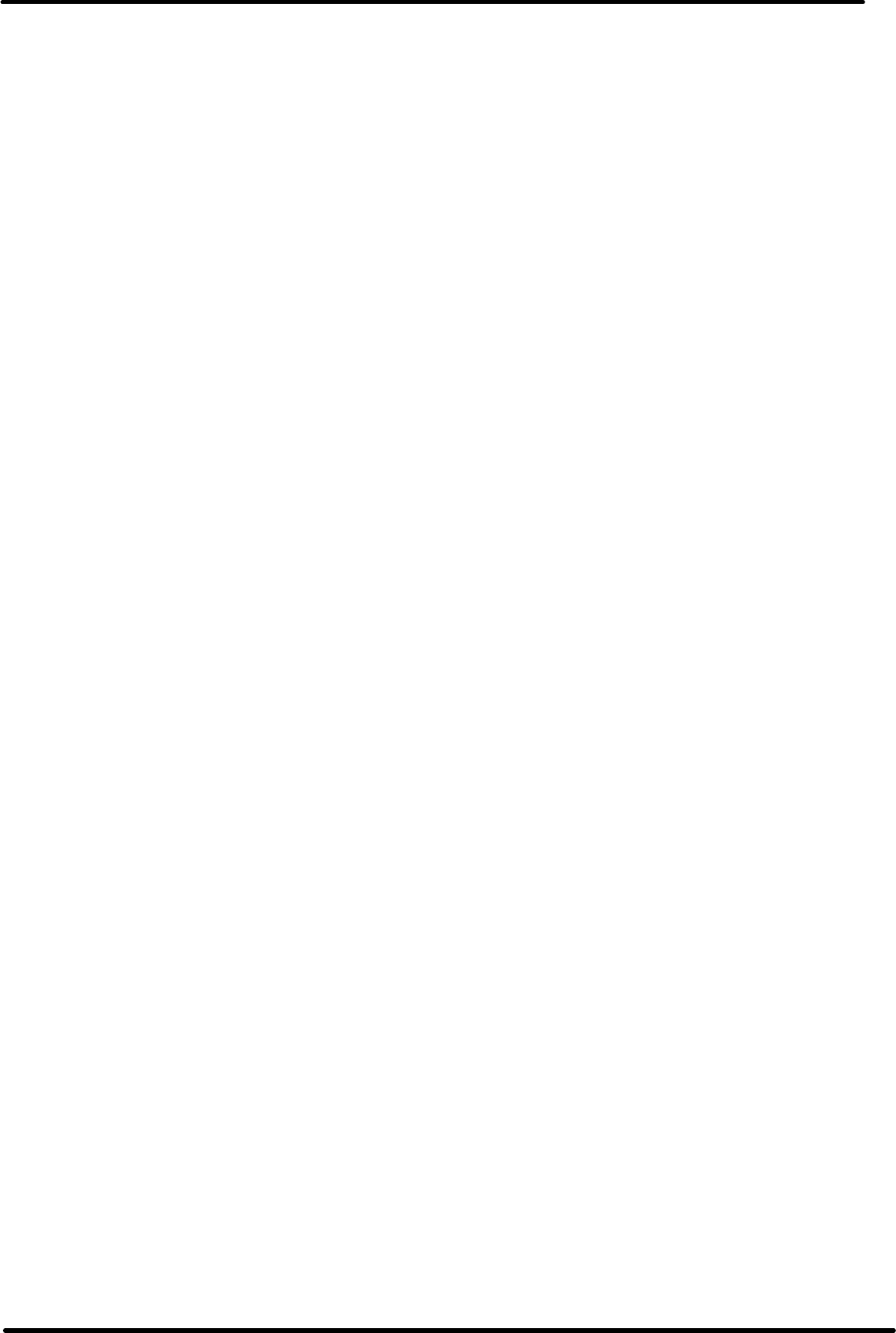
Innovator® HX Series Analog VHF Chapter 4, Circuit Descriptions,
Transmitter Control/Exciter Cabinet Assemblies
HX Series, Rev. 0 4-6
If Present, the external IF CW Input
connects at J41A pin 32A and is
connected to J19 and through the
external cable assembly W10 back to the
board at J20. The external IF CW input
is split on the board. One branch
connects through C157 to a buffer
amplifier Q20 to the K2 relay at pin 14.
The other path is through C152 to the
amplifier U23A. The output of U23A is
split with one part connecting to Q26 that
shuts down the 45.75 MHz Oscillator.
Another path connects to Q25 that
conducts and lights the Red LED DS7,
Alternate IF, viewed on the front panel.
The final path connects through R268 to
Q22 that is biased on and energizes the
relay, K2. The external IF CW Input at
contact 14 now connects through the
closed contact to the splitter network
consisting of L31 and L32.
Either the internal or external CW IF from
the K2 relay is split with one path
through L31 to the amplifier U28 to the L
input of Z1 the Aural IF Mixer. The other
path is through L32 to the amplifier U29
to the L input of Z2 the Visual IF Mixer.
4.1.1.11 Visual Modulator Circuit
The video signal is heterodyned in mixer
Z2 with the visual IF CW signal (45.75
MHz). The visual IF CW signal from L32
of the splitter connects to U29, where it
is amplified and wired to pin 1, the L
input of mixer Z2. Adjustable capacitor
C168 and resistor R275 are set up to add
a small amount of incidental carrier
phase modulation (ICPM) correction to
the output of the mixer stage to
compensate for any non-linearities
generated by the mixer.
The modulated 45.75 MHz RF output of
the mixer Z2, at pin 4 the R output, is
amplified by U30 and is fed to J17
through W8, the external cable
assembly, “WB”, to J13 on the board.
J17 is the visual IF loop-through output
jack that is normally jumpered to J13 on
the board. On page 1 of the schematic,
the modulated visual IF through J13
connects to J41C pin 17C the Visual IF
Output of the board.
4.1.1.12 Aural Modulator Circuit
On page 3 of the schematic, the mixer Z1
heterodynes the aural-modulated 4.5
MHz signal with the 45.75 MHz IF CW
signal to produce the modulated 41.25-
MHz aural IF signal. The audio
modulated 4.5 MHz from the 4.5 MHz
VCO IC U16 connects, “J”, to the I input
at pin 5 of Z1. The visual IF CW signal
from L31 of the splitter connects to U28,
where it is amplified and wired to pin 1,
the L input of mixer Z1. The R output of
the mixer at pin 4 is fed to a bandpass
filter, consisting of L18-L21, L25-L28 and
C136, C137 and C142-144, that is tuned
to pass only the modulated 41.25-MHz
aural IF signal. The filtered 41.25 MHz is
fed to the amplifier U27. The amplified
41.25 MHz signal is connected by a
coaxial cable, W9, from J21, “WC”, to J18
on the board. On page 1 of the
schematic, the modulated 41.25 MHz
aural IF signal from J18 is connected to
J41C pin 6C, the Aural IF Output of the
board.
4.1.1.13 Visual IF loop thru path
The Visual IF connects back to the board
at J41C pin 3C, through a Visual IF
jumper cable connected to the rear
chassis of the exciter/driver. IF
processing equipment can be connected
in place of the jumper if needed. The
visual IF is connected to J12, through
jumper W7, “WA”, to J14. The visual IF
is amplified by U24 and filtered by FL1
with T1 and T2 providing isolation. The
filtered visual IF is amplified by U25 and
adjusted in level by R214 before it is
connected through L16 to the frequency
response correcting circuit. The
frequency response of the 45.75 MHz
Visual IF signal is set by R238 and R239
and associated components. The
corrected visual IF signal is amplified by
U26 and connected to a splitter matching
network consisting of T3 and T4. One
part of signal connects to J10, the visual
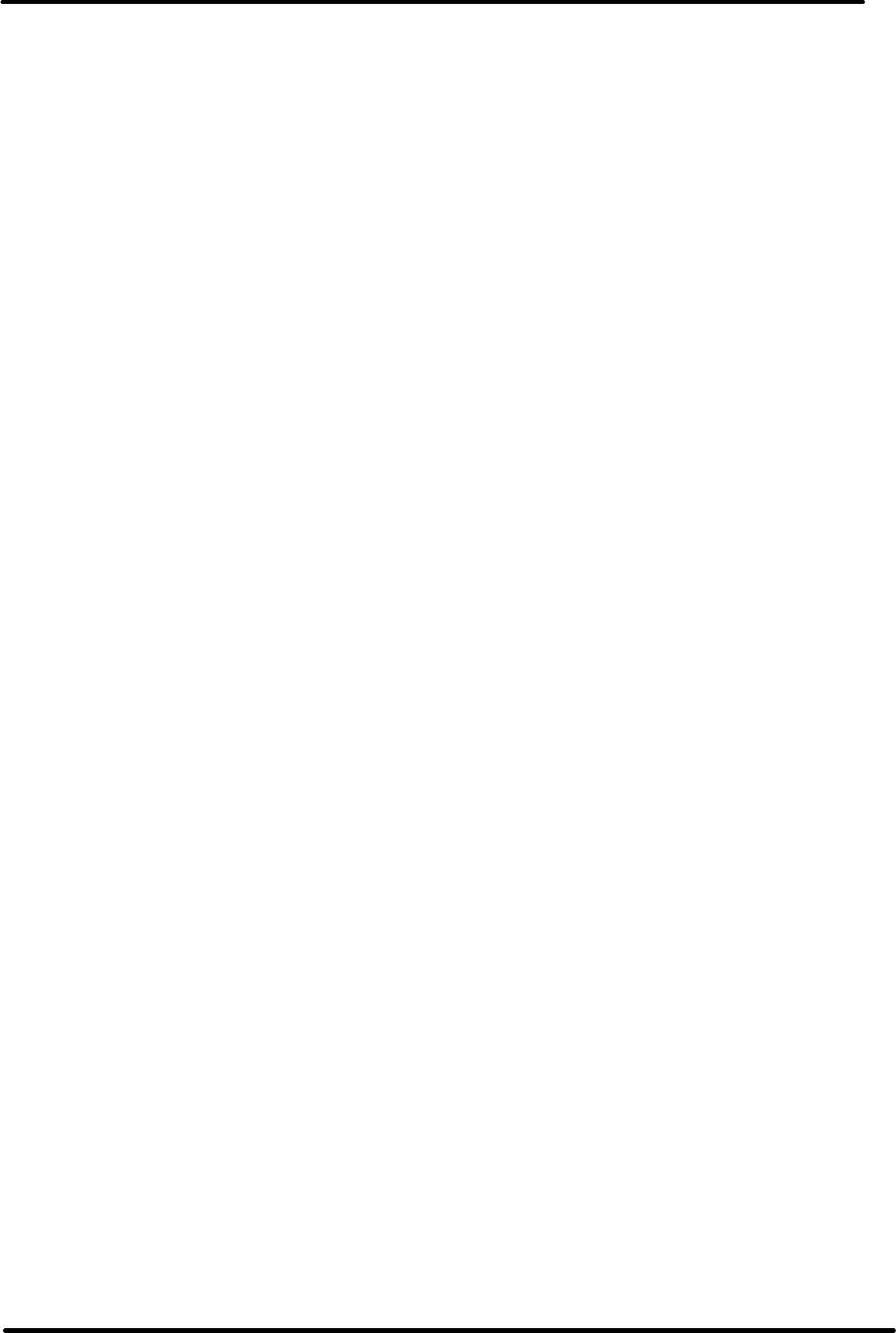
Innovator® HX Series Analog VHF Chapter 4, Circuit Descriptions,
Transmitter Control/Exciter Cabinet Assemblies
HX Series, Rev. 0 4-7
IF sample output jack, located on the
front panel. The other part, “G”,
connects to J41C pin 28C the Visual IF
Output of the board.
4.1.1.14 Voltage Requirements
The ±12 VDC needed for the operation of
the board enters through jack J41A pins
25A (+12 VDC_C4) and 26A (-12
VDC_C1), page 3 on schematic. The +12
VDC is filtered by L6, L7, and C27, on
page 1 of schematic, before it is
connected to the rest of the board. The
+12 VDC also connects to U7, a 5-volt
regulator IC, that provides +5 VDC to the
rest of the board.
The -12 VDC is filtered by L5, C16, and
C17, on page 1 of schematic, before it is
connected to the rest of the board.
4.2 (A3) IF Processor Module
Assembly (1305421; Appendix A)
The visual IF from the modulator enters
the module and the signal is pre-
corrected as needed for amplitude
linearity correction, Incidental Carrier
Phase Modulation (ICPM) correction and
frequency response correction.
The Module contains the IF Processor
board (1304687).
4.2.1 IF Processor Board (1304687;
Appendix A)
The automatic level control (ALC) portion
of the board provides the ALC and
amplitude linearity correction of the IF
signal. The ALC adjusts the level of the
IF signal that controls the output power
of the transmitter.
Refer to the schematic # 1304688 while
readings this description. The Visual IF
from the modulator enters the board at
J42B pin 32B, located on page 2 of the
schematic. If the (optional) receiver is
present, the Modulated IF input (-6 dBm)
from the receiver connects to the
modulated IF input jack J42C Pin 21C.
The modulator IF input, labeled J42-G,
connects to relay K3 and the receiver IF
input, labeled J42-D, connects to relay
K4, located on page 1 of the schematic.
The Modulator select enable/disable
jumper W11 on J29 controls whether the
Modulator Select command at J42 Pin
14C controls the operation of the relays.
With the jumper W11 on J29 between
pins 1 and 2, the external Modulator
Select command at J42C Pin 14C controls
the operation of the relays. With the
jumper W11 on J29 between pins 2 and
3, the Modulator input is selected all of
the time. NOTE: Modulator input is
normally selected all the time.
4.2.1.1 Modulator Selected
With the modulator selected, J42C-14C
low or the jumper W11 on J29 between
pins 2 and 3, the low shuts off Q12 and
causes Pin 8 on the relays to go high that
causes relays K3 and K4 to de-energize.
When K4 is de-energized, it connects the
receiver IF input at J42C-21C, if present,
to a 50O load. When K3 is de-energized,
it connects the modulator IF input at
J42B-32B to the rest of the board and
the Modulator Enable LED DS5 will be
illuminated.
4.2.1.2 External Modulated IF Selected
With the External Modulated IF selected,
J42C-14C high and jumper W11 on J29
between pins 1 and 2, this high turns on
Q12 and makes pin 8 on the relays Low
that causes the relays K3 and K4 to
energize. When K4 is energized, it
connects the receiver IF input at J42-
21C, if present, to the rest of the board.
When K3 is energized, it connects the
modulator IF input at J42B-32B to a 50O
load and the Modulator Enable LED DS5
will not be illuminated.
4.2.1.3 Main IF Signal Path (Part 1 of 3)
The selected Visual IF input (-6 dBm
average) signal, from the relays, is split,
with one half entering a bandpass filter
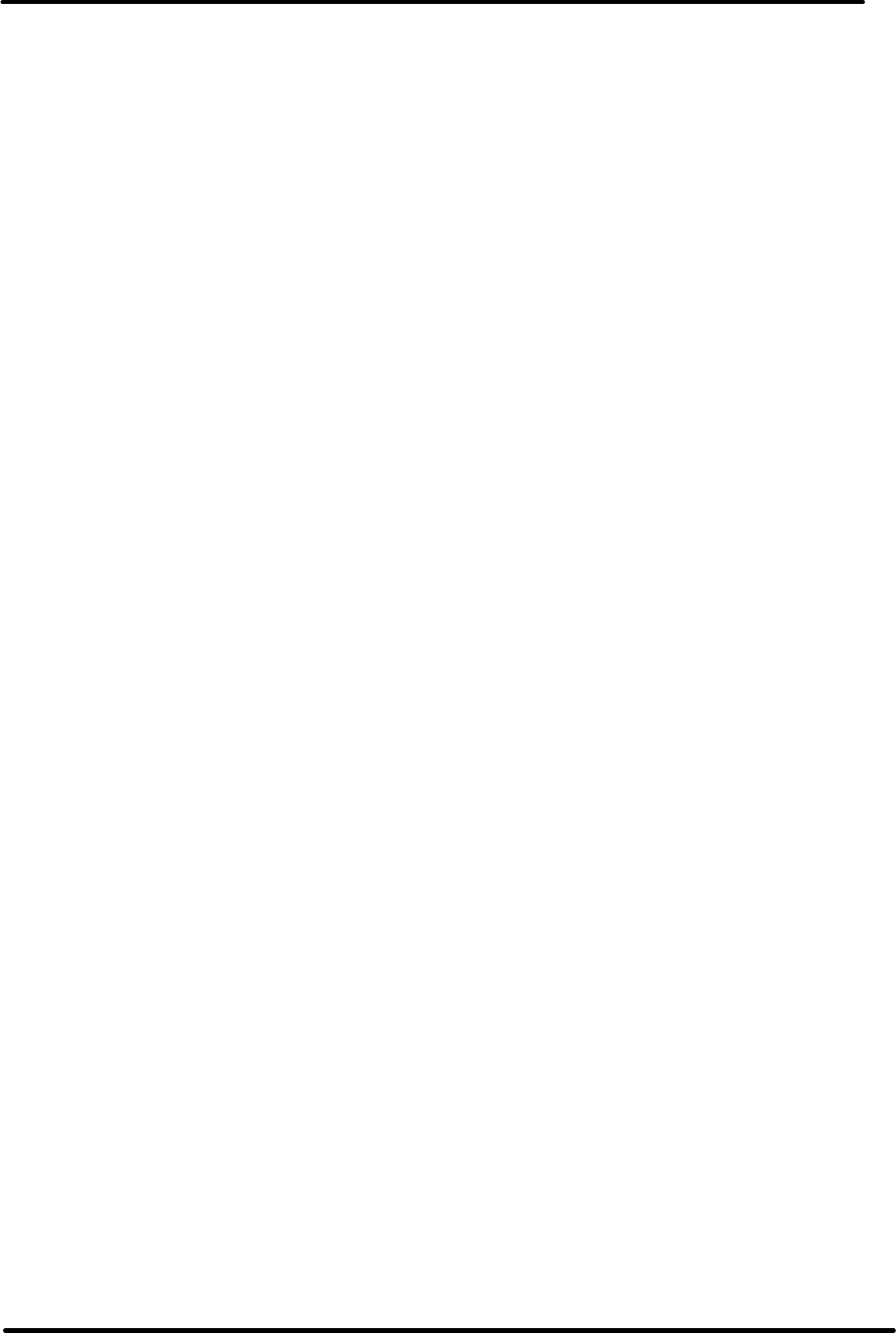
Innovator® HX Series Analog VHF Chapter 4, Circuit Descriptions,
Transmitter Control/Exciter Cabinet Assemblies
HX Series, Rev. 0 4-8
that consists of L3, L4, C4, L5, and L6.
This bandpass filter can be tuned with C4
and is substantially broader than the
visual IF signal bandwidth. It is used to
slightly steer the frequency response of
the IF to make up for any small
discrepancies in the frequency response
in the stages that precede this point.
The filter also serves the additional
function of rejecting unwanted
frequencies that may occur if the tray
cover is off and the tray is in a high RF
environment. (If this is the case, the
transmitter will have to be serviced with
the tray cover off in spite of the presence
of other RF signals). The filtered IF signal
is fed through a pi-type matching pad
consisting of R2, R3, and R4 to the pin-
diode attenuator circuit consisting of
CR1, CR2, and CR3.
4.2.1.4 Input Level Detector Circuit
The other part of the split IF input is
connected through L2 and C44 to U7. U7
is an IC amplifier that is the input to the
input level detector circuit. The amplified
IF is fed to T4, which is a step-up
transformer that feeds diode detector
CR14. The positive-going detected signal
is then low-pass filtered by C49, L18, and
C50. This allows only the positive peaks
to be applied through emitter follower
Q1. The signal is then connected to
detector CR15 to produce a peak voltage
that is applied to op-amp Pin 2 of U9A.
There is a test point at TP3, which is
accessed through the top cover of the
exciter/driver assembly, that provides a
voltage-reference check of the IF input
level. The detector serves the dual
function of providing a reference that
determines the input IF signal level to
the board and also it serves as an input
threshold detector.
The input threshold detector prevents the
automatic level control from reducing the
attenuation of the pin-diode attenuator to
minimum, the maximum signal output, if
the visual IF input to the board is
removed. The ALC, input loss cutback,
and the threshold detector circuits will
only operate when jumper W2 on jack J5
is in the Enabled position, between pins 2
and 3. Without the threshold detector,
and with the pin-diode attenuator at
minimum, the signal will overdrive the
stages following this board when the
input is restored.
As part of the threshold detector
operation, the minimum IF input level at
TP3 is fed through detector CR15 to op-
amp IC U9A, pin 2. The reference
voltage for the op-amp is determined by
the voltage divider that consists of R50
and R51, off the +12 VDC line. When
the detected input signal level at U9A,
pin 2, falls below this reference
threshold, approximately 10 dB below
the normal input level, the output of U9A
at pin 1 goes high, toward the +12 VDC
rail. This high is connected to the base
of Q2 that is forward biased and creates
a current path. This path runs from the
-12 VDC line, through red LED DS1, the
input level fault indicator, which lights,
resistor R54, and transistor Q2 to +12
VDC. The high from U9A also connects
through diode CR16 and R52, to U24D
pin 12, whose output at pin 14 goes high.
The high connects through the front
panel accessible ALC Gain pot R284 to
U24C Pin 9. This high causes U24C pin 8
to go low. A power raise/lower input
from the Control/Monitoring Module
connects to J42C pin 24C, labeled J42-F,
and is wired to Q14. This input will
increase or decrease the value of the low
applied to U24B and therefore increase or
decrease the power output of the
transmitter. The low connects to U24B
pin 5 whose output goes low. The low is
wired to U24A pin 2 whose output goes
high. The high, labeled A, is applied to
U10A, pin 2, on sheet 2 of the schematic,
whose output goes low. The low connects
through the switch SW1, if it is in the
auto gain position, labeled B, to the pin-
diode attenuator circuit, CR1, CR2 & CR3,
on sheet 1 of the schematic . The low
reverse biases them and cuts back the IF
level, therefore the output level, to 0.
When the input signal level increases
above the threshold level, the output
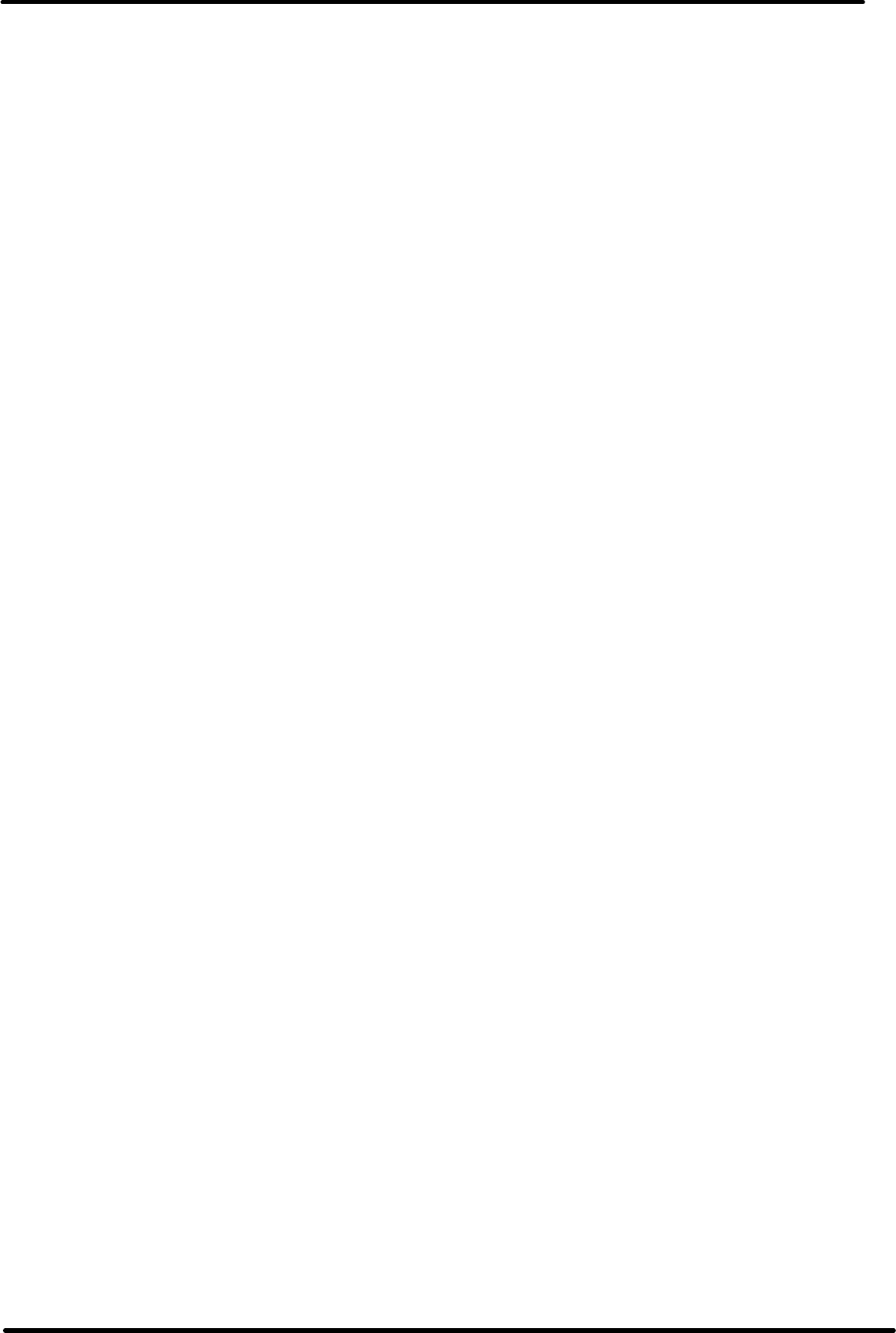
Innovator® HX Series Analog VHF Chapter 4, Circuit Descriptions,
Transmitter Control/Exciter Cabinet Assemblies
HX Series, Rev. 0 4-9
power will increase, as the input level
increases, until normal output power is
reached.
The IF input level at TP3, on page 1 of
the schematic, is also fed to a pulse
detector circuit, consisting of IC U8,
CR17, Q3, and associated components,
and then to a comparator circuit made up
of U9C and U9D. The reference voltage
for the comparators is determined by a
voltage divider consisting of R243, R65,
R66, and R130, off the -12 VDC line.
When the input signal level to the
detector at TP3 falls below this reference
threshold, which acts as a loss-of-signal
peak detector circuit, the output of U9C
and U9D goes towards the -12 VDC rail
and is split, with one part biasing on
transistor Q5. A current path is then
established from the +12 VDC line
through Q5, the resistors R69 and R137,
and the red LED DS3, Video Input loss
indicator, which is illuminated. When Q5
is on, it applies a high to the gate of Q6.
This causes it to conduct and apply a
modulation loss pull-down output,
labeled J42-A, to J42C, pin 7C, on page 2
of the schematic, which is applied to the
front panel display on the
Control/Monitor module.
The other low output of U9C and U9D is
connected through CR18, CR19 & CR20
to jack J5. Jumper W2 on J5, in the
Cutback Enable position, which is
between pins 2 and 3, connects the low
to the base of Q4 that is now forward-
biased. NOTE: If jumper W2 is in the
Disable position, between pins 1 and 2,
the auto cutback will not operate. With
Q4 biased on, a negative level
determined by the setting of cutback
level pot R71 is applied to U24D, pin 12.
The level is set at the factory to cut back
the output to approximately 25%. The
output of U24D at pin 14 goes low and is
applied through the power adjust pot to
U24C, pin 9, whose output goes low.
The low connects to U24B, pin 5, whose
output goes low. The low then connects
to U24A, pin 2, whose output goes high.
The high is applied to U10A, pin 2, whose
output goes low. The low connects
through the switch SW1, if it is in the
auto gain position, to the pin-diode
attenuator circuit, CR1, CR2 & CR3. The
low reverse biases them and cuts back
the level of the output to approximately
25%.
4.2.1.5 Pin-Diode Attenuator Circuit
The input IF signal is fed to a pin-diode
attenuator circuit that consists of CR1,
CR2 & CR3. Each of the pin diodes
contains a wide intrinsic region; this
makes the diodes function as voltage-
variable resistors at this intermediate
frequency. The value of the resistance is
controlled by the DC bias supplied to the
diode. The pin diodes are configured in a
pi-type attenuator configuration where
CR1 is the first shunt element, CR3 is the
series element, and CR2 is the second
shunt element. The control voltage,
which can be measured at TP1, originates
either from the ALC circuit when the
switch SW1 is in the ALC Auto position,
between pins 2 and 3, or from pot R87,
MAN GAIN, when SW1 is in the Manual
Gain position, between pins 1 and 2.
In the pin diode attenuator circuit,
changing the amount of current through
the diodes by forward biasing them
changes the IF output level of the board.
There are two extremes of attenuation
ranges for the pin-diode attenuators. In
the minimum attenuation case, the
voltage, measured at TP1, approaches
the +12 VDC line. There is a current path
created through R6, through series diode
CR3, and finally through R9 to ground.
This path forward biases CR3 and causes
it to act as a relatively low-value resistor.
In addition, the larger current flow
increases the voltage drop across R9 that
tends to turn off diodes CR1 and CR2 and
causes them to act as high-value
resistors. In this case, the shunt
elements act as a high resistance and the
series element acts as a low resistance to
represent the minimum loss condition of
the attenuator (maximum signal output).
The other extreme case occurs as the
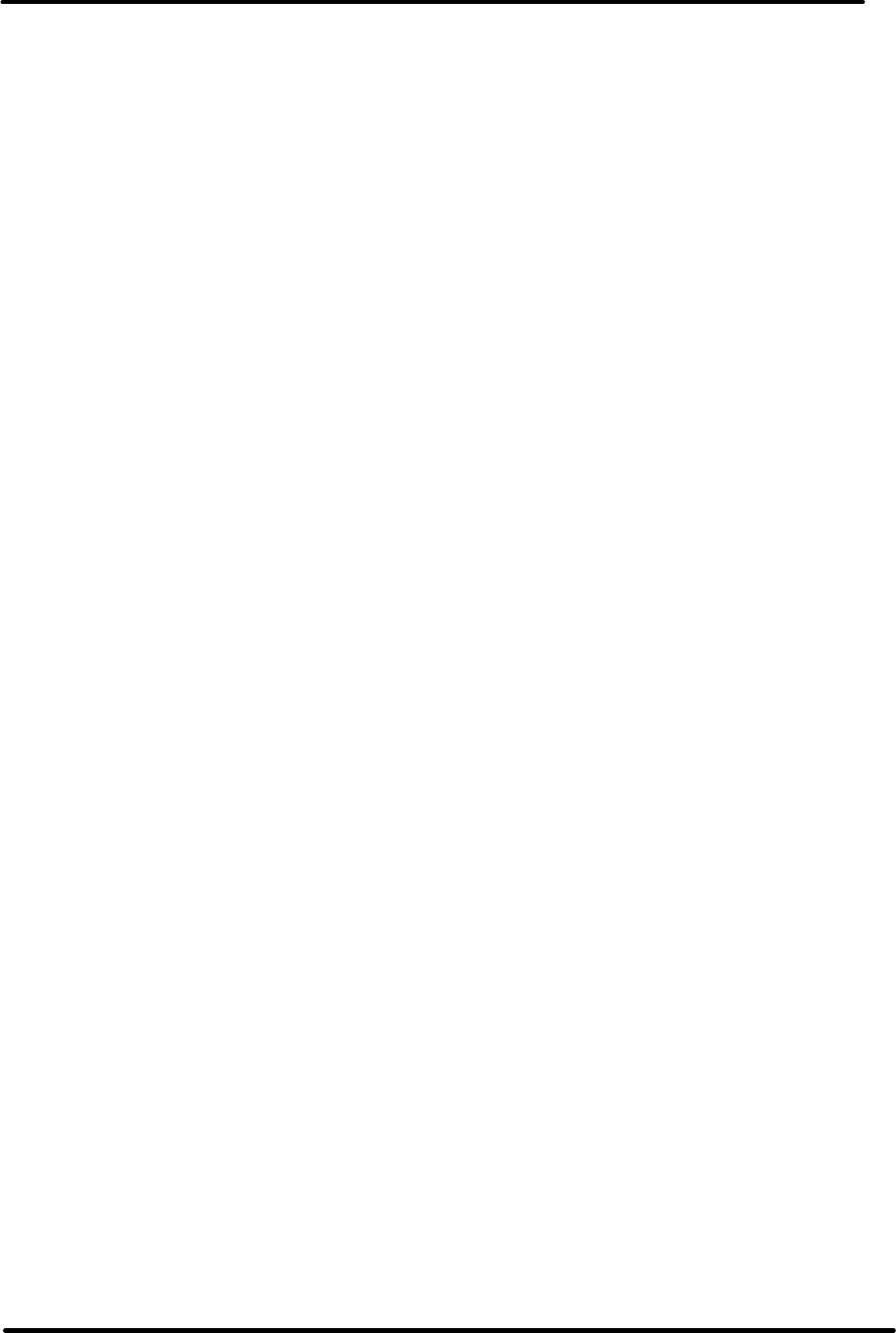
Innovator® HX Series Analog VHF Chapter 4, Circuit Descriptions,
Transmitter Control/Exciter Cabinet Assemblies
HX Series, Rev. 0 4-10
voltage at TP1 is reduced and goes
towards ground or even slightly negative.
This tends to turn off (reverse bias) diode
CR3, the series element, causing it to act
as a high-value resistor. An existing fixed
current path from the +12 VDC line, and
through R5, CR1, CR2, and R9, biases
series element CR3 off and shunt
elements, diodes CR1 and CR2, on,
causing them to act as relatively low-
value resistors. This represents the
maximum attenuation case of the pin
attenuator (minimum signal output). By
controlling the value of the voltage
applied to the pin diodes, the IF signal
level is maintained at the set level.
4.2.1.6 Main IF Signal Path (Part 2 of 3)
When the IF signal passes out of the pin-
diode attenuator through C11, it is
applied to the modular amplifier U1. This
device contains the biasing and
impedance-matching circuits that makes
it operate as a wide-band IF amplifier.
The output of U1 connects to J40 that is
jumpered through a cable to J41. The
J40 jack is available, as a sample of the
pre-corrected IF for troubleshooting
purposes and system setup. The IF signal
from J41 is connected to In-PHASE-OUT
on page 3 of the schematic, to the
transformer T9, which doubles the
voltage swing by means of a 1:4
impedance transformation. This is the
input to the amplitude and phase
correction circuits.
4.2.1.7 Amplitude and Phase
Pre-Correction Circuits
The linearity corrector circuits use six
stages of correction; three adjust for any
amplitude non-linearities and three for
phase non-linearities of the output signal.
Three of the stages are in the In Phase
Amplitude pre-correction path and three
stages are in the Quadrature Phase pre-
correction path. Each stage has a
variable threshold control adjustment,
R300, R211 and R216, in the In Phase
path, and R231, R308 and R 309 in the
Quadrature path, which determine the
point that the gain is changed in each of
the stages.
Two reference voltages are needed for
the operation of the corrector circuits.
The Zener diode VR3, through R261,
provides the +6.8 VDC reference. The
VREF is produced using the path through
R265 and the diodes CR30 and CR31.
They provide a .9 VDC reference, which
temperature compensates for the two
diodes in each corrector stage.
The first corrector stage in the In Phase
path operates as follows. The In Phase IF
signal is applied to transformer T9, which
doubles the voltage swing by means of a
1:4 impedance transformation. Resistors
R304 and R306 form an L-pad that
lowers the level of the signal. The input
signal level, when it reaches a set level,
causes the diodes CR35 and CR36 to turn
on, generating current flow that puts
them in parallel with the L-pad. When
the diodes are put in parallel with the
resistors, the attenuation through the
L-pad is lowered, causing signal stretch.
The signal is next applied to amplifier
U28 to compensate for the loss through
the L-pad. The breakpoint, or cut-in
point, for the first corrector is set by
controlling where CR35 and CR36 turn
on. This is accomplished by adjusting the
threshold cut-in resistor R300. R300
forms a voltage-divider network from
+6.8 VDC to ground. The voltage at the
wiper arm of R300 is buffered by the
unity-gain amplifier U27A. This reference
voltage is then applied to R301, R302,
and C185 through L54 to the CR35 diode.
C185 keeps the reference from sagging
during the vertical interval. The .9 VDC
reference voltage is applied to the unity-
gain amplifier U27B. The reference
voltage is then connected to diode CR36
through choke L55. The two chokes L54
and L55 form a high impedance for RF
that serves to isolate the op-amp ICs
from the IF.
After the signal is amplified by U28, it is
applied to the second corrector stage in
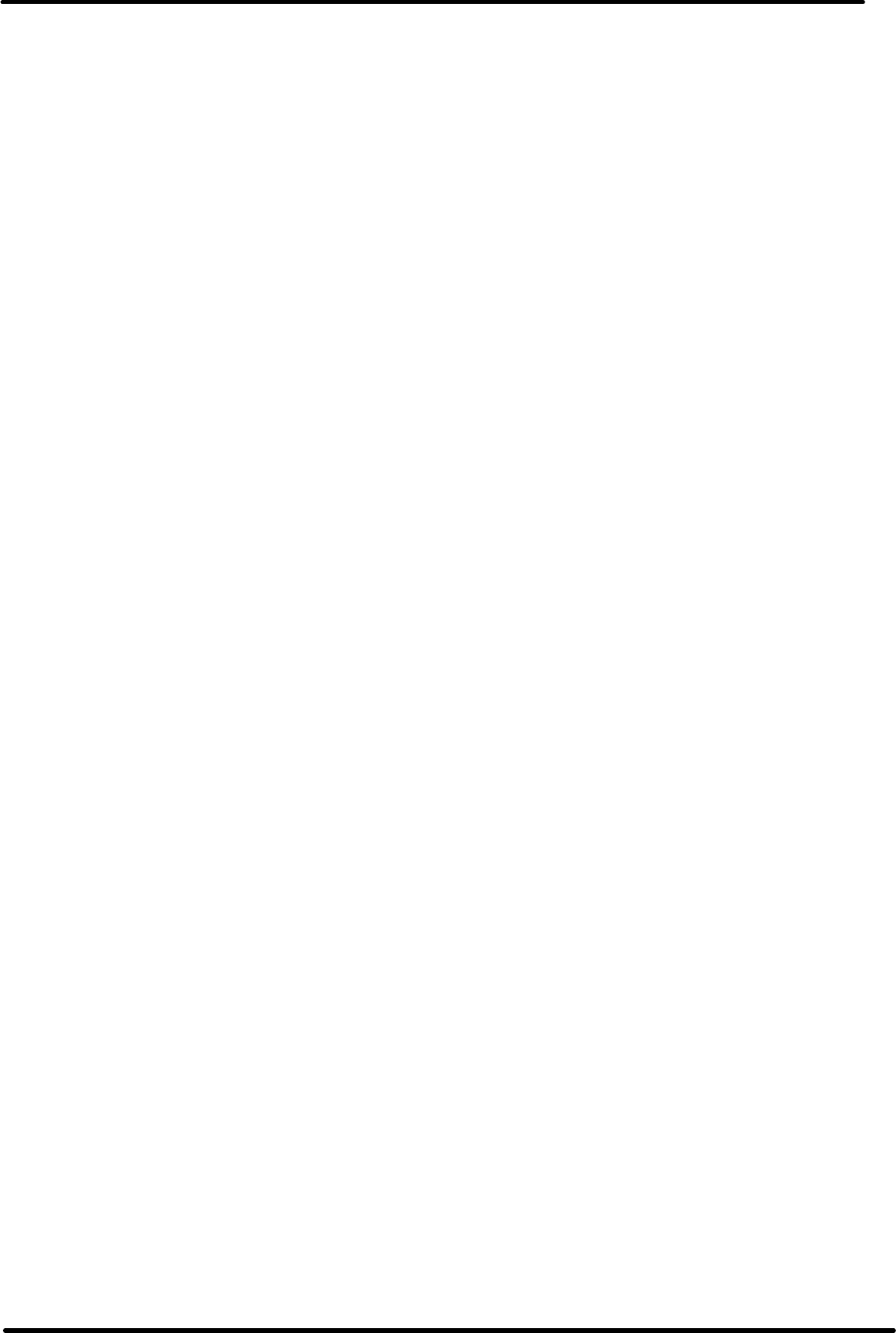
Innovator® HX Series Analog VHF Chapter 4, Circuit Descriptions,
Transmitter Control/Exciter Cabinet Assemblies
HX Series, Rev. 0 4-11
the In Phase path through T6. These
three correctors and the three corrector
stages in the Quadrature path operate in
the same fashion as the first. All six
corrector stages are independent and do
not interact with each other. The in
phase correctors can be disabled by
switching SW2 to the Disable position,
this moves all of the breakpoints past the
signal peaks so that they will have no
affect. The quadrature phase correctors
can be disabled by switching SW3 to the
Disable position, this moves all of the
breakpoints past the signal peaks so that
they will have no affect.
The pre-distorted IF signal in the In
Phase path, connects to an op amp U18
whose output level is controlled by R238.
R238 provides a means of balancing the
level of the amplitude pre-distorted IF
signal, IN-PHASE-IN, that connects to the
splitter/combiner Z1, located on page 1
of the schematic. There are two outputs
of Z1, at Port 1, that connects to J31,
Quadrature Output and at Port 2, In
Phase Output, which connects to J32.
The pre-distorted IF signal in the
Quadrature path at J31 is cabled to J34
that connects to a step up transformer T8
to the amp U20. The amplified output of
U20, QUAD-OUT, connects to a step up
transformer T10, located on page 3 of
the schematic. SW4 is switchable to
change the correction polarity as needed
in the quadrature path. The signal
connects to two corrector stages through
op-amp U31, QUAD-IN, to page 1 of the
schematic. The QUAD-IN is controlled by
the variable resistor R258 the provides a
means of balancing the level of the Quad
Phase pre-distorted IF signal that then
connects to the combiner Z2 at Port 2.
The In Phase signal connects to Port 1 of
Z2. The Amplitude and Phase pre-
distorted IF signals are combined by Z2
and connected to J37 that is jumpered to
J36 on the board. J37 can be used for
testing or monitoring purposes of the IF
signal after Amplitude and Phase pre-
distortion. The pre-distorted IF signal
connects through a resistor buffer
network, R239, R242 & R241, that
prevents loading of the combiner. The
output, labeled C, connects to L25 & L24
the input to the frequency response
circuitry located on page 2 of the
schematic.
4.2.1.8 Main IF Signal Path (Part 3 of 3)
On page 2 of the schematic, the IF
signal, labeled C, at the input to the
frequency-response corrector circuit, is
split using L24, L25 and R89. One path
is through L24, which is the main IF path
through the board. The main IF is fed
through a resistor network that controls
the level of the IF by adjusting the
resistance of R99, the output level
adjust. The IF signal is then applied to a
three-stage, frequency-response
corrector circuit that is adjusted as
needed.
The frequency-response corrector circuit
operates as follows. Variable resistors
R103, R106 and R274 are used to adjust
the depth and gain of the notches and
variable caps C71, C72 and C171 are
used to adjust the frequency position of
the notches. These are adjusted as
needed to compensate for frequency
response problems. The frequency-
response corrected IF is connected to J38
that is jumpered to J39 on the board.
J38 can be used for testing or monitoring
purposes of the IF signal after frequency
response pre-correction. The IF is next
amplified by U13 and U14. After
amplification, the IF is split with one path
connected to J42C pin 1C the IF output
to the Visual Upconverter Module. The
other path is fed through a divider
network to J35 a SMA IF Sample Jack,
located on the front panel, which
provides a sample of the corrected IF for
test purposes.
4.2.1.9 ALC Circuit
The other path of the corrected IF signal
at the input to the frequency response
corrector circuit is used in the ALC circuit.
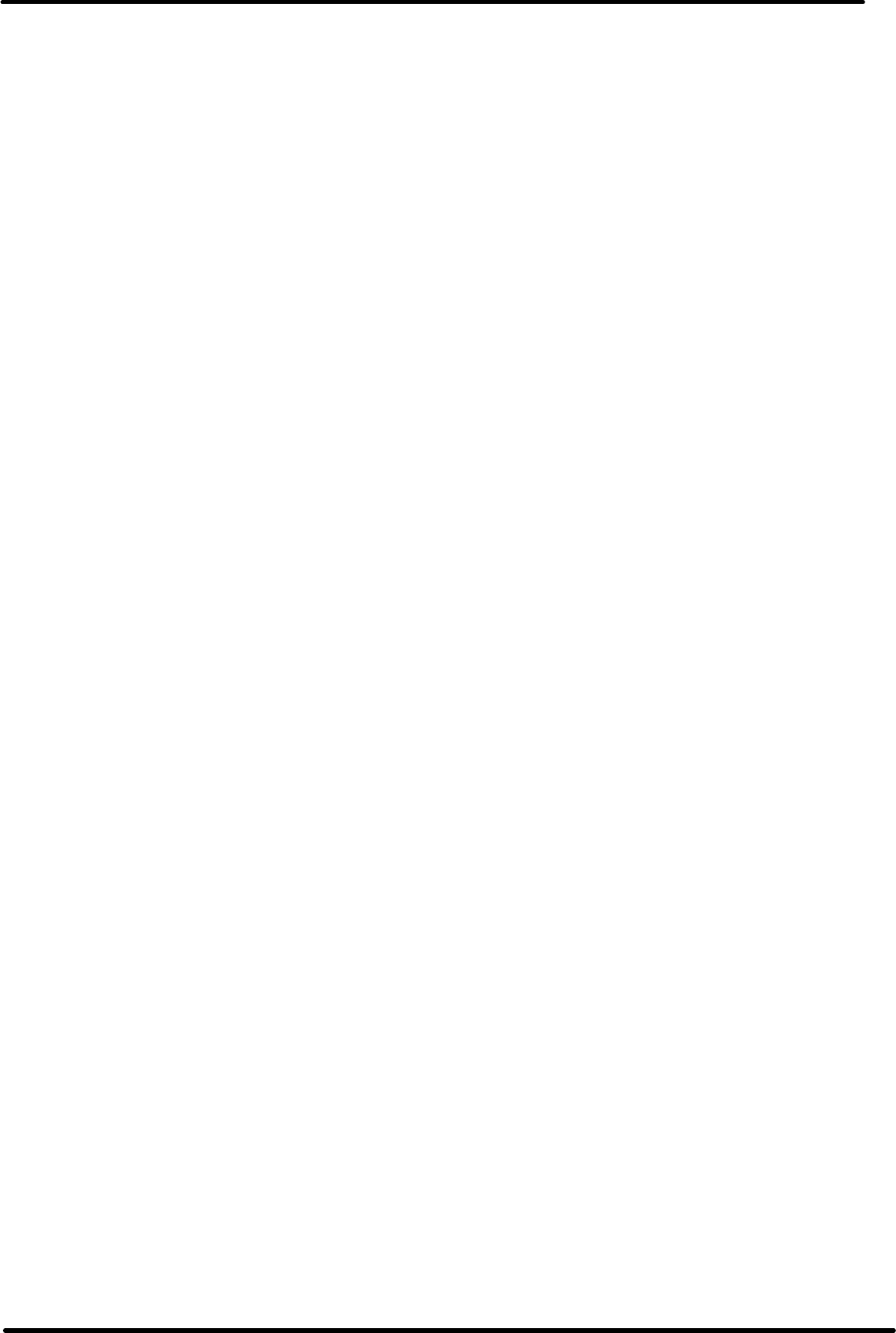
Innovator® HX Series Analog VHF Chapter 4, Circuit Descriptions,
Transmitter Control/Exciter Cabinet Assemblies
HX Series, Rev. 0 4-12
The IF through L25, of the L24 & L25
splitter connects to the op-amp U12. The
IF signal is applied through a resistor
divider network, R203-R205, to
transformer T5. T5 doubles the voltage
swing by means of a 1:4 impedance
transformation before it is connected to
the ALC detector circuit, consisting of
C70, CR23 and R91. The detected ALC
level output is amplified by U10B and
wired to U10A, pin 2, where it is summed
with the power control setting that
connects as A from page 1 of the
schematic, which is the output power
setting that is maintained by the ALC.
The output of U10A connects through
SW1, if it is in the auto gain position, to
the pin-diode attenuator circuit, CR1,
CR2 & CR3, located on page 1 of the
schematic. The high forward biases them
more or less, that increases or decreases
the IF level, therefore the output level,
opposite the input level. When the input
signal level increases, the forward bias
on the pin attenuator decreases,
therefore the output power will decrease,
which keeps the output power the same
as set by the customer.
An external power raise/lower switch can
be used by connecting it to TB30, at
TB30-8 power raise and TB30-9 power
lower, on the rear of the exciter/amplifier
chassis. The ALC voltage is set for
.8 VDC at TP4 with a 0 dBm output at
J42C pin 1C of the module. A sample of
the ALC at J42C pin 11C, is wired to the
Control Monitoring/Power Supply module
where it is used on the LCD display and
in the AGC circuits.
The ALC voltage, and the DC level
corresponding to the IF level after signal
correction, are fed to U10A pin 2, whose
output at pin 1 connects to the ALC pin-
diode attenuator circuit. If there is a loss
of gain somewhere in an IF circuit, the
output power of the transmitter will drop.
The ALC circuit senses this drop at U10A
and automatically decreases the loss
through the pin-diode attenuator circuit
therefore increasing its gain maintaining
the same output power level.
The ALC action starts with the ALC
detector level monitored at TP4. The
detector output at TP4 is nominally
+.8 VDC and is applied through resistor
R77 to a summing point at op-amp U10A
pin 2. The current available from the ALC
detector is offset, or complemented, by
current taken away from the summing
junction. In normal operation, U10A pin
2, is at 0 VDC when the loop is satisfied.
If the recovered or peak-detected IF
signal level at IF input to this board
should drop, which normally indicates
that the output power has decreased, the
null condition no longer occurs at U10A
pin 2. When the level drops, the output
of U10A pin 1, will go more positive. If
SW1 is in the Automatic position, it will
cause the ALC pin-diode attenuators CR1,
CR2, and CR3 to have less attenuation
and increase the IF level that will
compensate for the decrease in the
output power level. If the ALC cannot
increase the input level enough to satisfy
the ALC loop, due to the lack of range, an
ALC fault will occur. The fault is
generated because U10D pin 12,
increases above the trip point set by R84
and R83 until it conducts. This makes
U10D pin 14, high and causes the red
ALC Fault LED DS2, located on the front
panel, to light.
4.2.1.10 Fault Command
The board also has circuitry for an
external mute fault input at J42C pin
10C. This is a Mute command that
protects the circuits of high-gain output
amplifier devices against VSWR faults.
This action needs to occur faster than
just pulling the ALC reference down. Two
different mechanisms are employed: one
is a very fast-acting circuit to increase
the attenuation of the pin-diode
attenuator, CR1, CR2, and CR3, and the
second is the reference voltage being
pulled away from the ALC amplifier
device. An external Mute is a pull-down
applied to J42C pin 10C, which completes
a current path from the +12 VDC line
through R78 and R139, the LED DS4
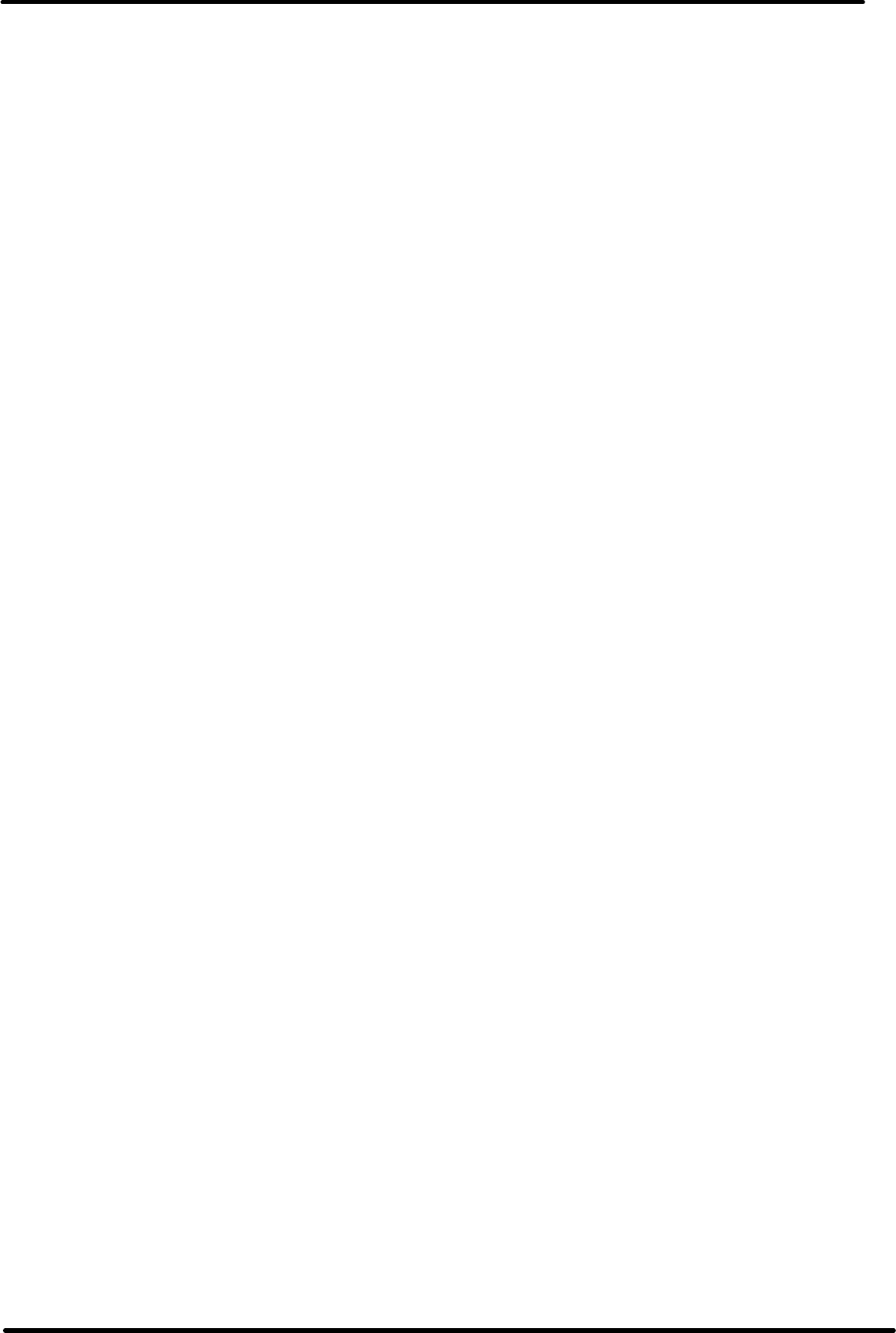
Innovator® HX Series Analog VHF Chapter 4, Circuit Descriptions,
Transmitter Control/Exciter Cabinet Assemblies
HX Series, Rev. 0 4-13
(Mute indicator), and the LED section of
opto-isolator U11. These actions turn on
the transistor section of U11 that applies
-12 VDC through CR21 to U10A pin 3,
and pulls down the reference voltage.
This is a fairly slow action controlled by
the low-pass filter function of R81 and
C61. When the transistor section of U11
is on, -12 VDC is also connected through
CR22 directly to the pin-diode attenuator
circuit. This establishes a very fast
muting action, by reverse biasing CR3.
This action occurs in the event of an
external VSWR fault.
4.2.1.11 ±12 VDC Needed to Operate the
Board
The ±12 VDC connects to the board at
jack J42C. The +12 VDC connects to
J42C pin 16C (J42-E) and is filtered (on
Page 1 of the schematic) by L30, L41,
and C80 before it is applied to the rest of
the board. The -12 VDC connects to
J42C pin 18C (J42-H) and is filtered (on
Page 1 of the schematic) by L31 and C81
before it is applied to the rest of the
board.
The +12 VDC is split by R261 and R265.
The +12 VDC output through R261 (on
Page 1 of the schematic) connects to the
Zener diode VR3, which generates the
+6.8 VDC output to the rest of the board.
The +12 VDC output through R265 (on
Page 1 of the schematic) connects to the
diodes CR30 and CR31, which provide a
.9 VDC reference output voltage, VREF,
which provides temperature
compensation for the two diodes in each
corrector stage.
4.3 (A5) VHF/UHF Upconverter
Module (1303829; Appendix A)
This module contains the Downconverter
Board Assembly, the First Conversion
Board, LX Series, L-Band PLL Board, LX
Series and the Upconverter Control
Board, LX Series. This module takes an
external IF and converts it to the final
RF output frequency using two internally
generated local oscillator frequencies.
4.3.1 (A1) Downconverter Board
Assembly (1303834; Appendix A)
This board converts a signal at an input
frequency of 1044 MHz to a broadcast
VHF or UHF TV channel.
The IF at 1044MHz is applied to the
board at J7, and is converted down to
VHF or UHF by the mixer IC U6. The LO
frequency is applied to the board at a
level of +20 dBm at J8. The output of
the mixer is applied to a 6 dB attenuator
and then to a 900 MHz Low Pass filter.
The filter is intended to remove any
unwanted conversion products. The
signal is next connected to the amplifier
U2, and then a pin diode attenuator
consisting of DS4, DS5 and their
associated components. The attenuator
sets the output level of the board and is
controlled either by a manual gain pot
R7, or an external AGC circuit. This
automatic or manual mode of operation
is controlled by the switch SW1. When
in manual mode, the LED DS6 is
illuminated.
The output of the pin attenuator is
applied to another amplifier U3 and
another low pass filter, before reaching
the final amplifier U1. The output of the
board is at J5 with a sample of the
output available at J6, which is 20 dB in
level below the signal at J5.
4.3.2 (A2) L-Band PLL Board
(1303846; Appendix A)
This board generates an LO at a
frequency of 1.1-1.9 GHz. The board
contains a PLL IC U6, which controls the
output frequency of a VCO. The PLL IC
divides the output of the VCO down to
100kHz, and compares it to a 100kHz
reference created by dividing down an
external 10 MHz reference that is
applied to the board at J1 pin 4. The IC
generates an error current that is
applied to U3 and its associated
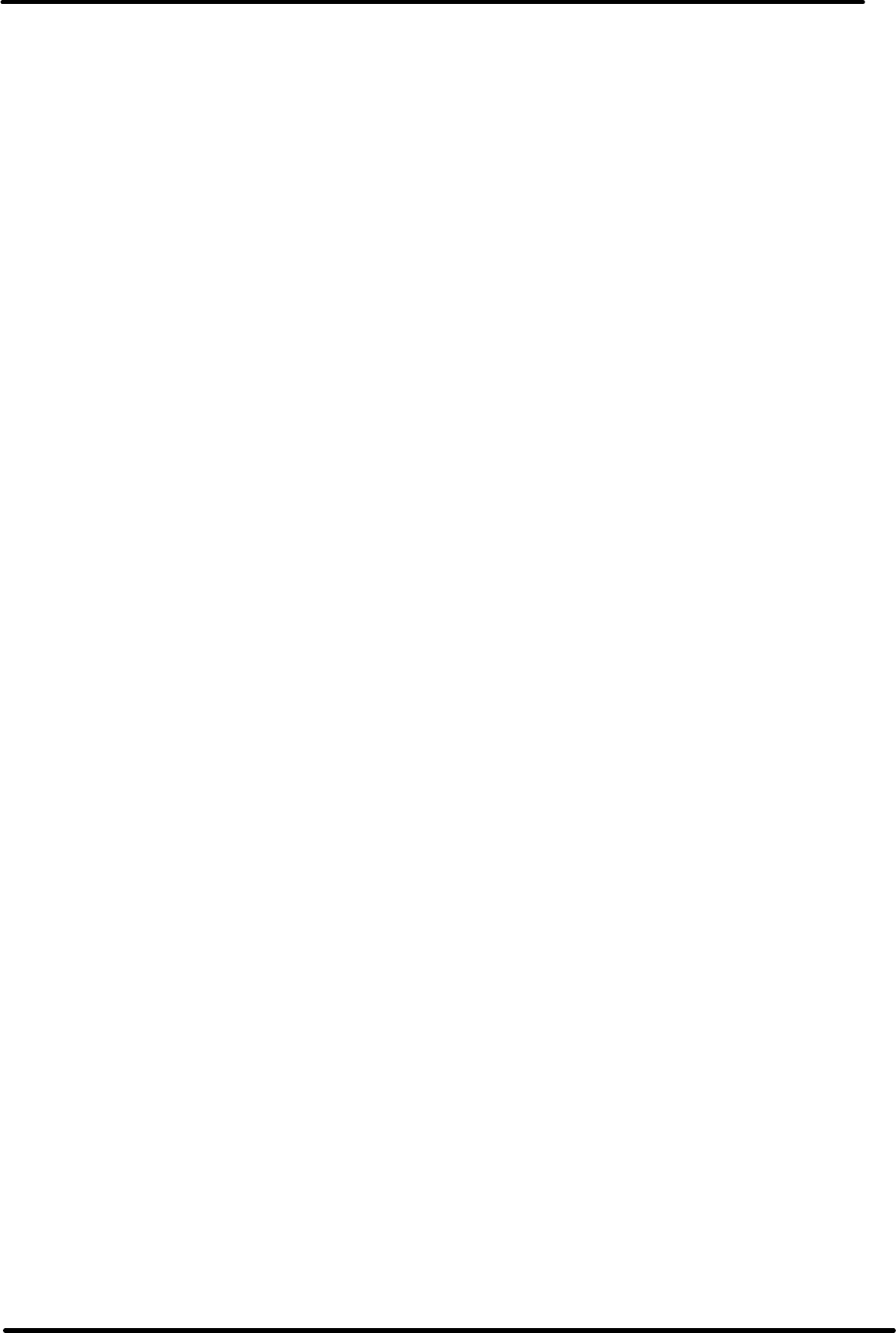
Innovator® HX Series Analog VHF Chapter 4, Circuit Descriptions,
Transmitter Control/Exciter Cabinet Assemblies
HX Series, Rev. 0 4-14
components to generate a bias voltage
for the VCO's AFC input.
There are two VCOs on the board, U4,
which operates at 1.1-1.3 GHz for VHF
channels, and U5, which operates at
1.5-1.9 GHz for UHF channels. The VCO
in use is selected by a signal applied to
J1 pin 20. This input enables the power
supply either U1 or U2 for the
appropriate VCO for the desired channel.
U7 is a power supply IC that generates
+5V for the PLL IC U6.
The output of each VCO is filtered by a
low pass filter to remove any harmonic
content and applied to a pin diode
switch consisting of CR1, CR2, and their
associated components. The selected
signal is amplified by U9 and U10, then
applied to a high pass filter and finally
amplified to a level of approximately
+21 dBm by U11. The output is
connected to a low pass filter to remove
any unwanted harmonic content and
leaves the board at J3 at a level of +20
dBm.
4.3.3 (A3) First Conversion Board
(1303838; Appendix A)
This board generates a 1 GHz LO signal
using the VCO U9, the PLL IC U12, and
the loop filter, C30-C33 and R49. The
PLL IC compares a divided down sample
of the VCO to a divided down sample of
the transmitter's system 10 MHz
reference.
The output of the VCO is amplified by
U10 and U11 and applied to a low pass
filter before being connected to an
image rejection mixer consisting of U1,
U2, U3 and U6. The 44 MHz IF input is
connected to the board at J2, and then
to the image rejection mixer. This mixer
converts the 44 MHz input to an output
frequency of 1044 MHz. The output of
the mixer is amplified by U4 and applied
to a band pass filter consisting of C2-C4
and some microstrip line sections. This
filter rejects any LO leakage at 1 GHz
and also any unwanted out of band
products. The output of the filter is
amplified by U5 and then filtered before
exiting the board at J1.
4.3.4 (A4) Upconverter Control
Board (1304760; Appendix A)
This board performs a variety of
functions, which include an interface
between the other boards in the
upconverter and the rest of the
transmitter. It also has a
microcontroller U8, which controls and
monitors the functions of the other
boards in the assembly.
The microcontroller communicates via
an RS-485 interface with the
transmitter's system control module. It
reports any faults and metering
information and receives channel
information, which it passes along to the
PLLs on the L-Band PLL Board and the
First Conversion Board.
The board also generates various
voltages used by the rest of the boards
in the upconverter. U9 converts the
+12V input to the board to +20V. U15
converts +12V to +5V for the on board
10 MHz crystal oscillator. U12 converts
+12V to +9V for the L-Band PLL board
and the First Conversion board. U13
and U14 generate +5V for the
microcontroller.
The board also selects whether the
internal or external 10 MHz reference
source will be used. There is an
onboard 10 MHz oscillator, U3, which is
used when no external 10 MHz source is
present. The Relay K1 is automatically
switched to the external 10 MHz
reference whenever it is present. The
LED DS1 illuminates whenever the
internal 10 MHz reference is used. The
diode detector CR1 detects the presence
of the 10 MHz external reference that
connects to U2, which compares the
detected level to a reference level and
switches the relay whenever the
reference is present. It also disables the
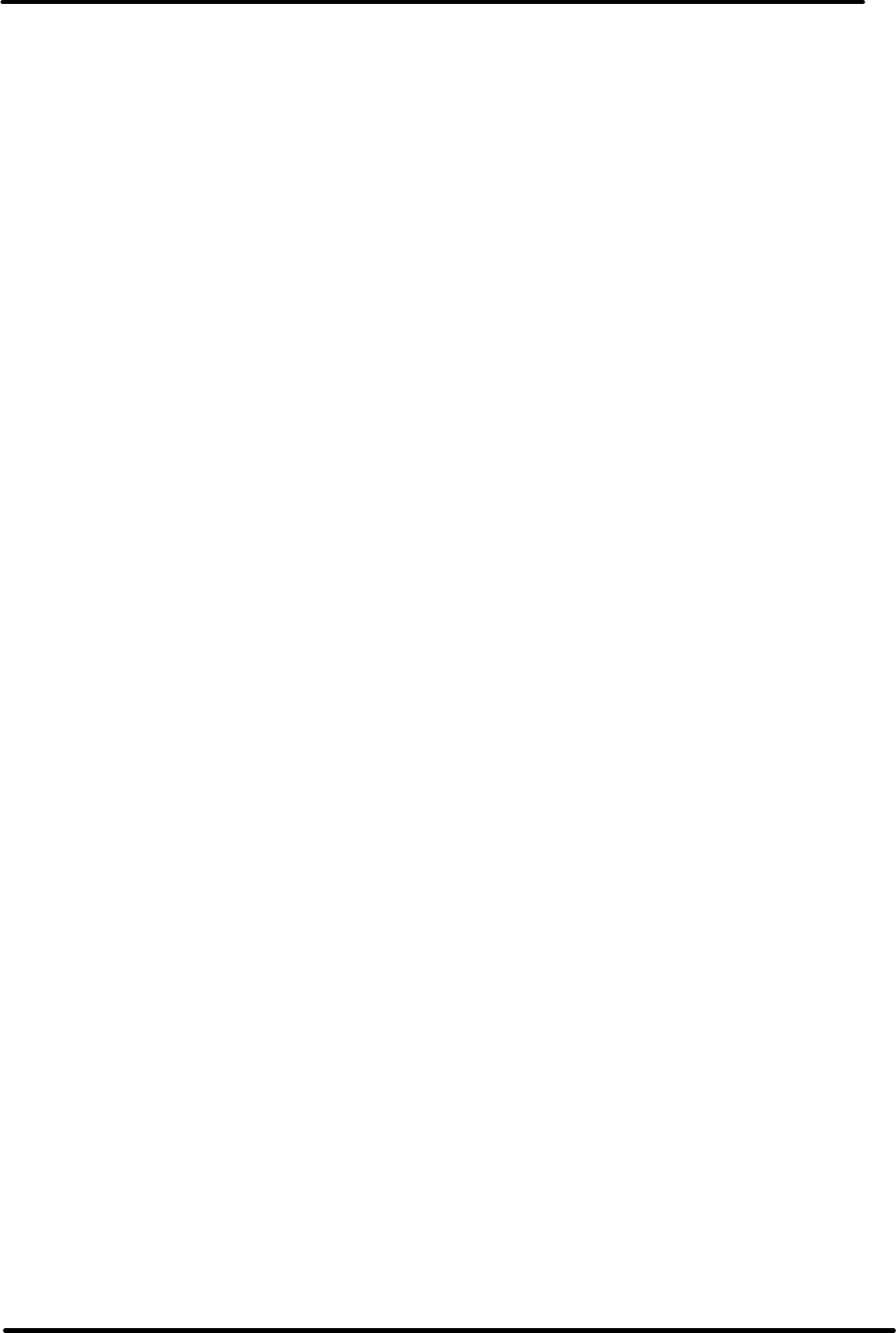
Innovator® HX Series Analog VHF Chapter 4, Circuit Descriptions,
Transmitter Control/Exciter Cabinet Assemblies
HX Series, Rev. 0 4-15
internal oscillator whenever the external
10 MHz reference is being used.
The output of the relay is split to drive
multiple outputs, some internal and
some external. The external outputs
leave the board at J1-22C and J1-31B
and are used by the external receiver
and modulator modules.
The board also contains AGC circuitry,
which controls a pin diode attenuator on
the Downconverter Board. There are
three references used by the AGC
circuit. The first is the AGC reference
#1, which comes from the transmitter's
driver module. The second is the AGC
reference #2, which is a diode ORed
sample of the output stages of the
transmitter. The IC U5 normalizes the
level of the AGC reference # 1 and sets
it at a level that is 0.2V less than the
level of AGC reference #2. The AGC
reference #1 and #2 are diode ORed
with only the highest reference used by
the AGC circuit.
The highest reference is compared to
the ALC reference, which originated on
the IF processor module, and the error
voltage generated by U4D and applied
to the external pin attenuator. The AGC
will try to maintain a constant ratio
between the ALC voltages and the
higher of the two AGC voltages. If
something in the output amplifier of the
transmitter fails, the AGC reference #1
voltage will take over and the power will
be regulated at the output of the driver.
4.4 (A4) Control Monitoring/Power
Supply Module, 110 VAC (1301936;
Appendix A)
The Control Monitoring/Power Supply
Module Assembly contains (A1) a Power
Protection Board (1302837), (A2) a 600
Watt Switching Power Supply, (A3) a
Control Board (1302021), (A4) a Switch
Board (1527-1406) and (A5) a LCD
Display.
AC Input to Innovator HX Exciter/Amplifier
Chassis Assembly
The AC input to the Exciter/Amplifier
Chassis Assembly is connected from J1,
part of a fused entry module, located on
the rear of the chassis assembly, to J50
on the Control Monitoring/Power Supply
Module. J50-10 is line #1 input, J50-8 is
earth ground and J50-9 is line #2 input.
The input AC connects to J1 on the Power
Protection Board where it is fuse
protected and connected back to J50, at
J50-11 AC Line #1 and J50-12 AC Line
#2, for distribution to the cooling Fan.
4.4.1 (A1) Power Protection Board
(1302837; Appendix A)
The input AC connects through J1 to two
10 Amp AC fuses F1 and F2. The AC
line #1 input connects from J1-1 to the
F1 fuse. The AC line #1 input after the
F1 fuse is split with one line connected
back to Jack J1 Pin 4, which becomes
the AC Line #1 to the power supply and
Fan. The other line of the split connects
to J4. The AC line #2 input connects
from J1-3 to the F2 fuse. The AC line
#2 input after the F2 fuse is split with
one line connected back to Jack J1 at Pin
5, which becomes the AC Line #2 to the
power supply and Fan. The other line of
the split connects to J2. J1-2 is the
earth ground input for the AC and
connects to J3.
Three 150 VAC MOVs are connected to
the 115 VAC input for protection. One
connects from each AC line to ground
and one connects across the two lines.
VR1 connects from J4 to J2, VR2
connects from J4 to J3 and VR3 connects
from J2 to J3.
4.4.1.1 +12 VDC Circuits
+12 VDC from the Switching Power
Supply Assembly connects to J6 on the
board. The +12 VDC is divided into four
separate circuits each with a 3 amp self
resetting fuse, PS3, PS4, PS5 and PS6.
The polyswitch resettable fuses may
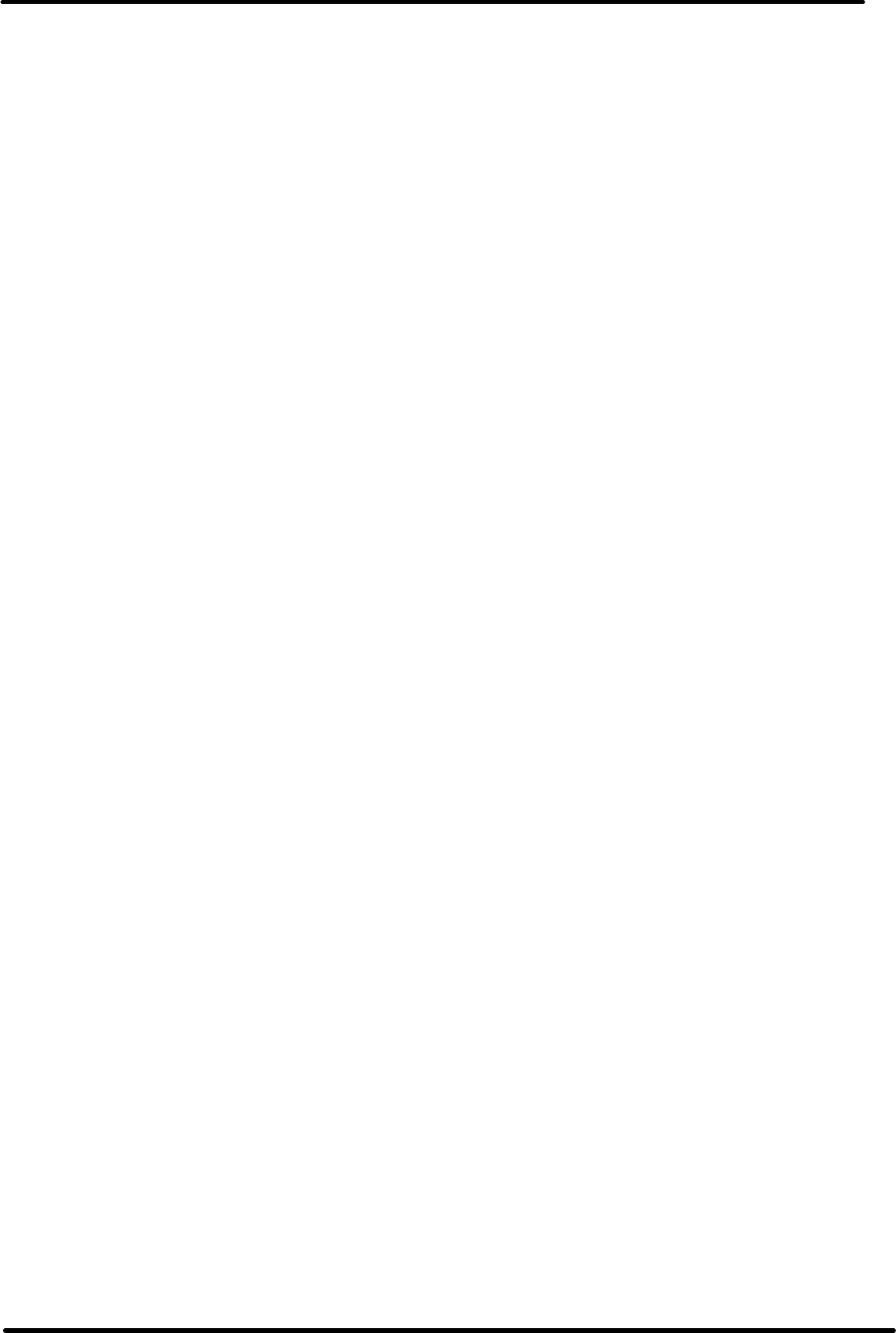
Innovator® HX Series Analog VHF Chapter 4, Circuit Descriptions,
Transmitter Control/Exciter Cabinet Assemblies
HX Series, Rev. 0 4-16
open on a current as low as 2.43 Amps
at 50°C, 3 Amps at 25°C or 3.3 Amps at
0°C. They definitely will open when the
current is 4.86 Amps at 50°C, 6 Amps
at 25°C or 6.6 Amps at 0°C.
PS3 protects the +12 VDC 2 Amp
circuits for the System Controller, the
Amplifier Controller and the Aural
Upconverter Slot through J62 pins 7, 8,
9 and 10. If this circuit is operational,
the Green LED DS3, mounted on the
board, will be lit.
PS4 protects the +12 VDC 2 Amp
circuits for the Modulator and the IF
Processor through J62 pins 13, 14, 15
and 16. If this circuit is operational, the
Green LED DS4, mounted on the board,
will be lit
PS5 protects the +12 VDC 2 Amp
circuits for the Upconverter through J62
pins 17, 18, 19 and 20. If this circuit is
operational, the Green LED DS5,
mounted on the board, will be lit
PS6 protects the +12 VDC 2 Amp
circuits for the Remote through J63 pins
17, 18, 19 and 20. If this circuit is
operational, the Green LED DS6,
mounted on the board, will be lit
4.4.1.2 -12 VDC Circuits
-12 VDC from the Switching Power
Supply Assembly connects to J5 on the
board. The -12 VDC is divided into two
separate circuits each with a 3 amp self
resetting fuse, PS1 and PS2.
PS1 protects the -12 VDC 2 Amp circuits
for the System through J63 pins 1, 2, 3
and 4. If this circuit is operational, the
Green LED DS1, mounted on the board,
will be lit
PS2 protects the -12 VDC 2 Amp circuits
for the Remote through J62 pins 1, 2, 3
and 4. If this circuit is operational, the
Green LED DS2, mounted on the board,
will be lit
The connections from J62 and J63 of the
Power Protection Board are wired to J62
and J63 on the Control Board.
4.4.2 (A3) Control Board (1302021;
Appendix A)
In this exciter/driver, control monitoring
functions and front panel operator
interfaces are found on the Control
Board. Front panel operator interfaces
are brought to the control board using a
26 position conductor ribbon cable that
plugs into J60. The control board
controls and monitors the Power Supply
and Power Amplifier module through a
16 position connector J61 and two 20
position connectors J62 & J63.
4.4.2.1 Schematic Page 1
U1 is an 8 bit RISC microcontroller that
is in circuit programmed or programmed
using the serial programming port J4 on
the board. When the microcontroller,
U1, is held in reset, low on pin 20, by
either the programming port or the
external watchdog IC (U2), a FET Q1
inverts the reset signal to a high that
connects to the control lines of U5, an
analog switch. The closed contacts of
U5 connects the serial programming
lines from J4 to U1. LED DS10 will be lit
when programming port J4 is enabled.
U2 is a watchdog IC, which holds the
microcontroller in reset, if the supply
voltage is less the 4.21 VDC; (1.25 VDC
< Pin 4 (IN) < Pin 2 (Vcc). The
watchdog momentarily resets the
microcontroller, if Pin 6 (ST) is not
clocked every second. A manual reset
switch S1 is provided but should not be
needed.
Diodes DS1 through DS8 are LEDs that
display the auto test results. A separate
test board is used to execute self test
routines. When the test board is
installed, Auto_Test_1 is held low and
Auto_Test_2 is allowed to float at 5
VDC. This is the signal to start the auto
test routines.
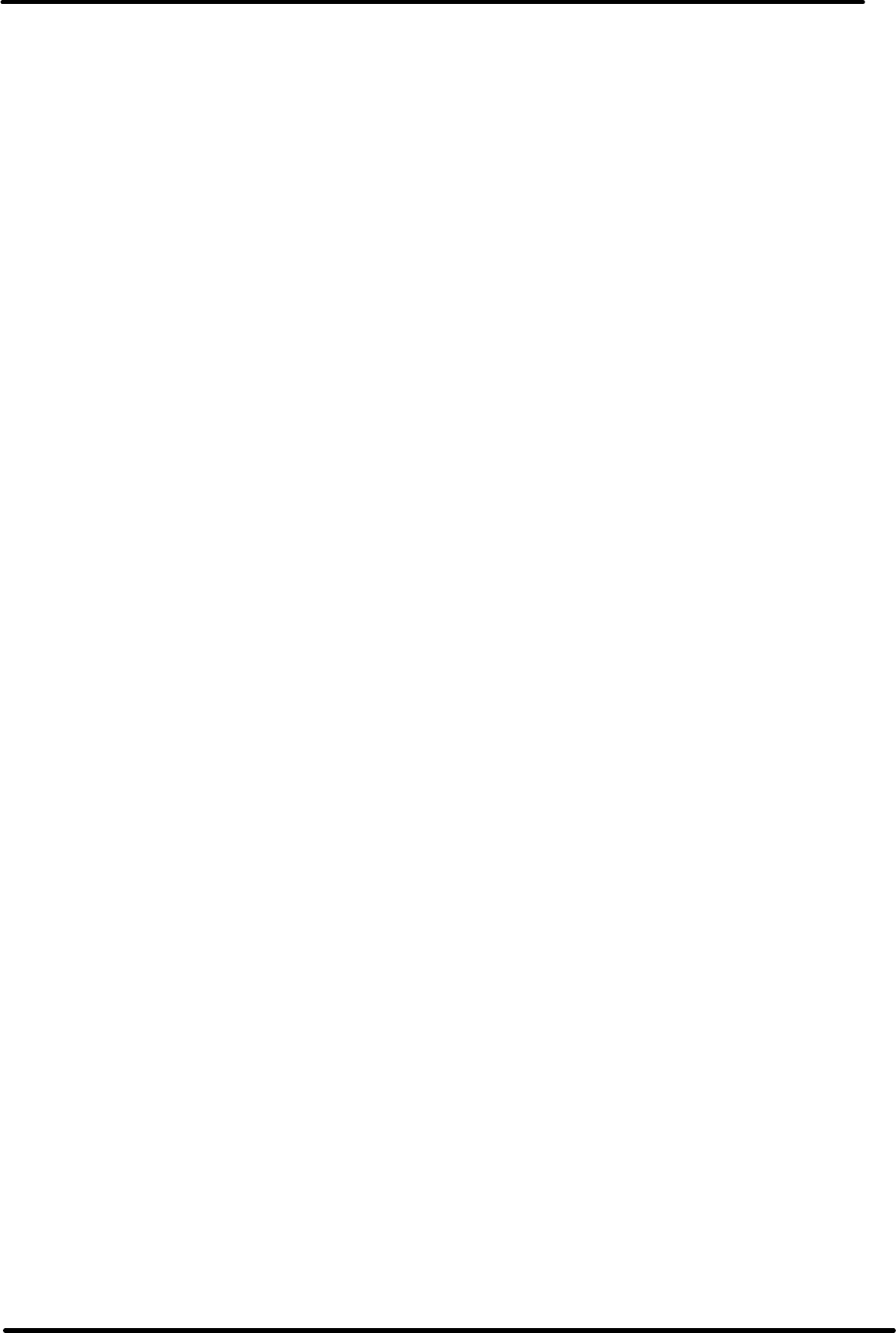
Innovator® HX Series Analog VHF Chapter 4, Circuit Descriptions,
Transmitter Control/Exciter Cabinet Assemblies
HX Series, Rev. 0 4-17
The ICs U3 and U4 are used to
selectively enable various input and
output ICs found on pages 2 & 3 of the
schematic.
U1 has two serial ports available. In this
application, one port is used to
communicate with transmitter system
components where U1 is the master of a
RS-485 serial bus. The other serial port
is used to provide serial data I/O where
U1 is not the master of the data port. A
dual RS-232 port driver IC and a RS-485
Port driver are also in the second serial
data I/O system. The serial ports are
wired such that serial data input can
come through one of the three serial
port channels. Data output is sent out
through each of the three serial port
channels.
Switch SW1, transmitter operation
select, is used to select either
transmitter operation or exciter/driver
operation. When the contacts of SW1
are closed, transmitter operation is
selected and the power monitoring lines
of the transmitter’s power amplifier are
routed to the system power monitoring
lines.
4.4.2.2 Schematic Page 2
U9 is a non-inverting transceiver IC that
provides 2 way asynchronous
communication between data busses.
The IC is used as an input buffer to
allow the microcontroller to monitor
various digital input values.
Digital output latch circuits are used to
control system devices. Remote output
circuits are implemented using open
drain FETs, Q13, Q14, Q16, and Q17,
with greater than 60 Volt drain to source
voltage ratings.
The remote digital inputs are diode
protected, using CR6, CR7, CR8 and CR9
with a 1 kO pull-up resistor, to +5 VDC.
If the remote input voltage is greater
than about 2 Volts or floating, the FET is
turned on and a logic low is applied to
the digital input buffer, U9. If the
remote input voltage is less than the
turn on threshold of the FET (about 2
VDC), a logic high is applied to the
digital input buffer, U9.
Four of the circuits on page two of the
schematic, which include Q2, Q9, Q19
and Q21, are auxiliary I/O connections
wired for future use. They are wired
similar to the remote digital inputs but
include a FET, Q5, Q12, Q20 and Q22,
for digital output operations. To operate
these signals as inputs, the associated
output FET must be turned off. The
FETs are controlled by U10 and U12,
analog input multiplexer ICs.
4.4.2.3 Schematic Page 3
U13, U14, U15, U16, U17 and U18 are 3
state non-inverting transceiver ICs that
provide 2 way asynchronous
communication between data busses.
The ICs are used as input buffers to
allow the microcontroller to monitor
various digital input values. The digital
inputs to the ICs utilize a 10 kO pull-up
resistor. The buffer IC, U18, used for
data transfer to the display is wired for
read and write control.
4.4.2.4 Schematic Page 4
U19 and U20 are digitally controlled
analog switches that provide samples
back to the microprocessor. Each
analog input is expected to be between
0 and 5 VDC. If a signal exceeds 5.1
VDC, a 5.1 Volt zener diode clamps the
signals voltage, to prevent damage to
the IC. Most signals are calibrated at
their source, however two dual serial
potentiometers ICs are used to calibrate
four signals, System Visual/Average
Power, System Aural Power, System
Reflected Power and the Spare AIN 1.
For these four circuits, the input value is
divided in half before it is applied to an
op-amp. The serial potentiometer is
used to adjust the output signal level to
between 80 and 120% of the input

Innovator® HX Series Analog VHF Chapter 4, Circuit Descriptions,
Transmitter Control/Exciter Cabinet Assemblies
HX Series, Rev. 0 4-18
signal level. Serial data, serial clock and
serial pot enables are supplied by the
microprocessor to the dual serial
potentiometer ICs. J62 and J63 are two
20 position connectors that provide the
+12 VDC and –12 VDC power through
the Power Protection Board. The ±12
VDC generated by the switching power
supply connects to J62 and J63 after
being fuse protected on the Power
Protection Board.
4.4.2.5 Schematic Page 5
There are three dual element,
red/green, common cathode LED
indicators, DC OK, Operate and Fault,
mounted on the front panel of the sled
assembly.
There are three, the fourth is a spare,
identical circuits that drive the front
panel mounted LED indicators. The
levels on the 1, 2, 3 and 4 LED Control
Lines, for both the red and green LEDs,
are generated by the IC U11 as
controlled by the DATABUS from the
microprocessor U1.
Each LED controller circuit consists of an
N-Channel MOSFET w/internal diode that
controls the base of an N-P-N transistor
in an emitter follower configuration. The
emitter of the transistor connects the
LED.
With the LED control line LOW, the
MOSFET is Off, which causes the base of
the transistor to increase towards +12
VDC, forward biasing the transistor.
With the transistor forward biased,
current will flow from ground through
the LED, the transistor and the current
limiting resistors in the collector to the
+12 VDC source. The effected LED will
light.
With the LED control line HIGH, the
MOSFET is On, which causes the base of
the transistor go toward ground
potential, reverse biasing the transistor.
With the transistor reverse biased, no
current through the transistor and LED,
therefore the effected LED will not light.
A third color, amber, can also be
generated by having both transistors
conducting, both control lines LOW. The
amber color is produced because the
current applied to the green element is
slightly greater than the red element.
This occurs because the current limiting
resistors have a smaller ohmage value
in the green circuit.
There are four voltage regulators, three
for +5 VDC, U26, U27 & U28, and one
for +7 VDC, U25, which are used to
power the Control Board. +12 VDC is
applied to U25 a +7 VDC regulator that
produces the +7 VDC, which is applied
to the LEDs mounted on the board. The
+7V is also connected to the input of
U26 a precision +5.0 Volt regulator.
The +5.0 VDC regulator output is used
to power the analog circuits and as the
microcontroller analog reference
voltage. Another two +5 Volt regulator
circuits U27, +5V, and U8, +5 Vserial,
are used for most other board circuits.
4.4.3 (A4) Switch Board (1527-1406;
Appendix A)
The switch board provides five front-
panel momentary contact switches for
user control and interface with the front-
panel LCD menu selections. The
switches, SW1 to SW5, complete the
circuit through connector J1 to
connector J2 that connects to J1 on (A5)
the 20 Character by 4 line LCD Display.
J1 on the switch board is also cabled to
the Control Board. When a switch is
closed, it connects a logic low to the
control board that supplies the
information from the selected source to
the display. By pushing the button
again, a different source is selected.
This occurs for each push button. Refer
to Chapter 3 for more information on the
Display Menu Screens.
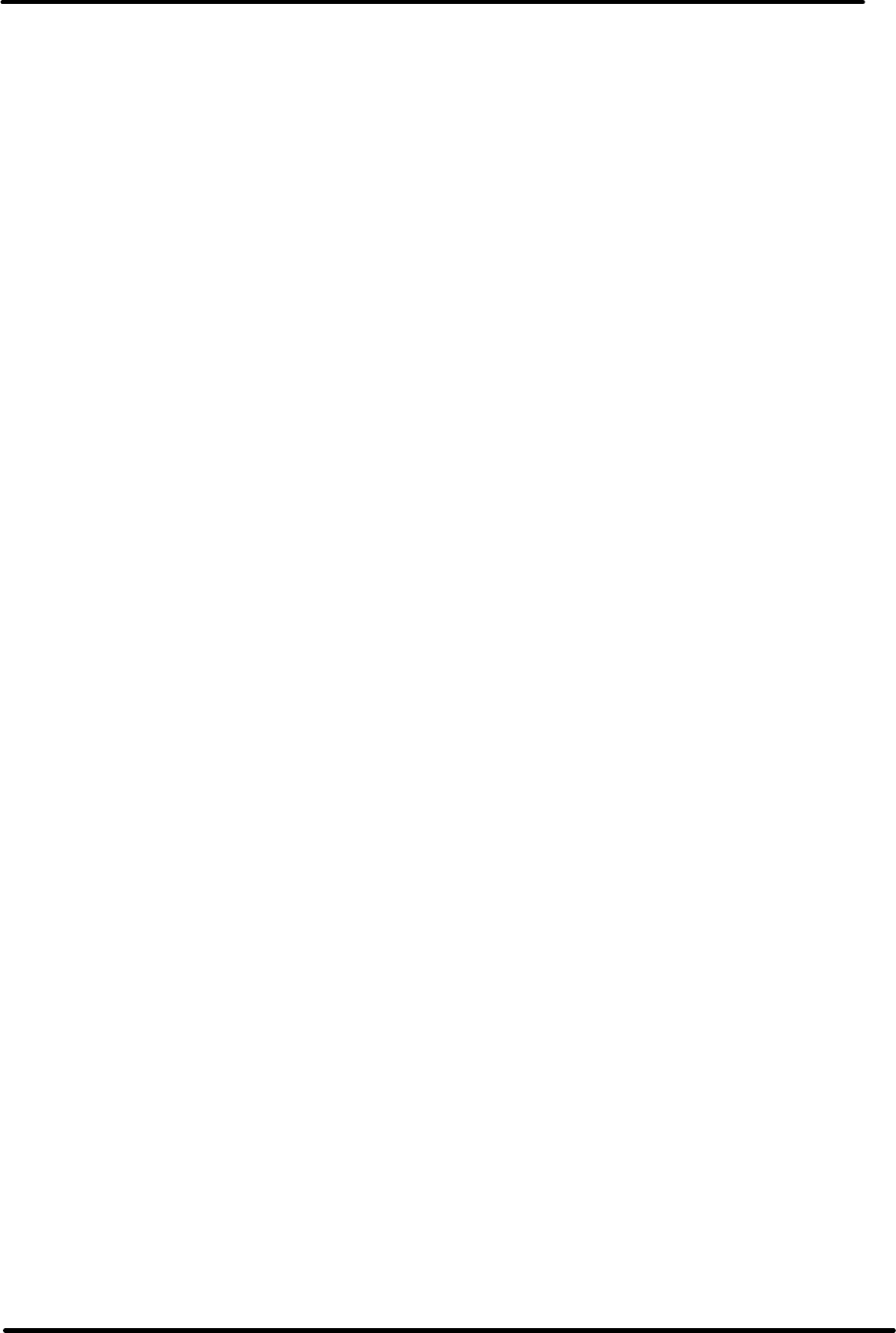
Innovator® HX Series Analog VHF Chapter 4, Circuit Descriptions,
Transmitter Control/Exciter Cabinet Assemblies
HX Series, Rev. 0 4-19
4.4.4 (A2) Switching Power Supply
Assembly
The power supply module contains a
switching power supply, an eight
position terminal block for distributing
the DC voltages, a three position
terminal block to which the AC Input
connects. Jack J1 connects to the
Control Board and supplies DC OK, at
J1-4 & 3, and AC OK, at J1-2 & 1, status
to the control board. A Power Supply
enable connects from the control board
to the power supply at V1-6 & 7. The
power supply is configured for three
output voltages +12V, -12V, at the 8
position terminal block, and a main
output power of +32 VDC at J50 pin A
(+) and J50 pin B (Rtn). The power
supply is power factor corrected to .98
for optimum efficiency and a decrease in
energy consumption. For safety
purposes all outputs are over voltage
and over current protected. This supply
accepts input voltages from 85 to 264
volts AC, but the power entry module,
for the exciter/amplifier chassis, must
be switched to the proper input voltage
setting, for the transmitter to operate.
4.5 (A4) VHF Power Amplifier Module
Assembly (1305822; Appendix A)
The Power Amplifier Module Assembly
contains (A5) an Amplifier Control Board
(1303682), a Coupler Board (1211-1004),
a 25 Watt VHF Driver Module (1305820),
and a 200 Watt Power Amplifier Assembly
(1300167).
The RF (-2 dBm) from the Upconverter
Module Assembly connects from the
Upconverter RF Output BNC Jack J23 to
the PA RF Input BNC Jack J24, located on
the rear of the exciter/amplifier chassis
assembly.
4.5.1 (A2) 25 Watt VHF Driver Pallet
(1305820; Appendix A)
The RF input at a level of -2 dBm
connects to the RF input jack on the (A2)
Driver Assembly Pallet. The pallet is an
assembly manufactured by Delta RF and
has a gain of approximately +30dB. The
Refer to the Delta RF data sheet (PA25-
VHF-H) located in Appendix A for more
information on the assembly. The RF
output (+32 dBm), connects to the RF
input jack on (A3) the 200 Watt power
amplifier assembly.
The +30 VDC bias voltage connects from
the amplifier control board at TB18 to the
feed thru capacitor FL2 on the module
assembly that is wired to the +Vdd input
on the 25 Watt VHF Amplifier Assembly.
4.5.2 (A3) 200 Watt VHF Amplifier
Assembly (1300167; Appendix A)
The RF input at a level of +32 dBm
connects to the RF input jack on the (A3)
200 Watt Amplifier Assembly Pallet. The
pallet is an assembly manufactured by
Delta RF and has a gain of approximately
+16dB. The Refer to the Delta RF data
sheet (P200-VHF-H) located in Appendix
A for more information on the assembly.
The RF output (+48.2 dBm) connects to
the coupler assembly at J1.
The +30 VDC bias voltage connects from
the amplifier control board at TB19 to the
feed thru capacitor FL1 on the module
assembly that is wired to the +Vdd input
on the 200 Watt VHF Amplifier Assembly.
4.5.3 (A4) Coupler Board Assembly
(1211-1004; Appendix A)
The coupler board assembly provides
forward and reflected power samples of
the output to (A5) the amplifier control
board where they connect to the
metering and overdrive protection
circuits in the system.
The RF input to the coupler assembly,
from the 200 Watt VHF Power Amplifier
module, connects to the SMA jack J1.
The RF is connected by a stripline track
to the SMA type connector RF Output
jack J2. A hybrid-coupler circuit picks off
a power sample that is connected to a
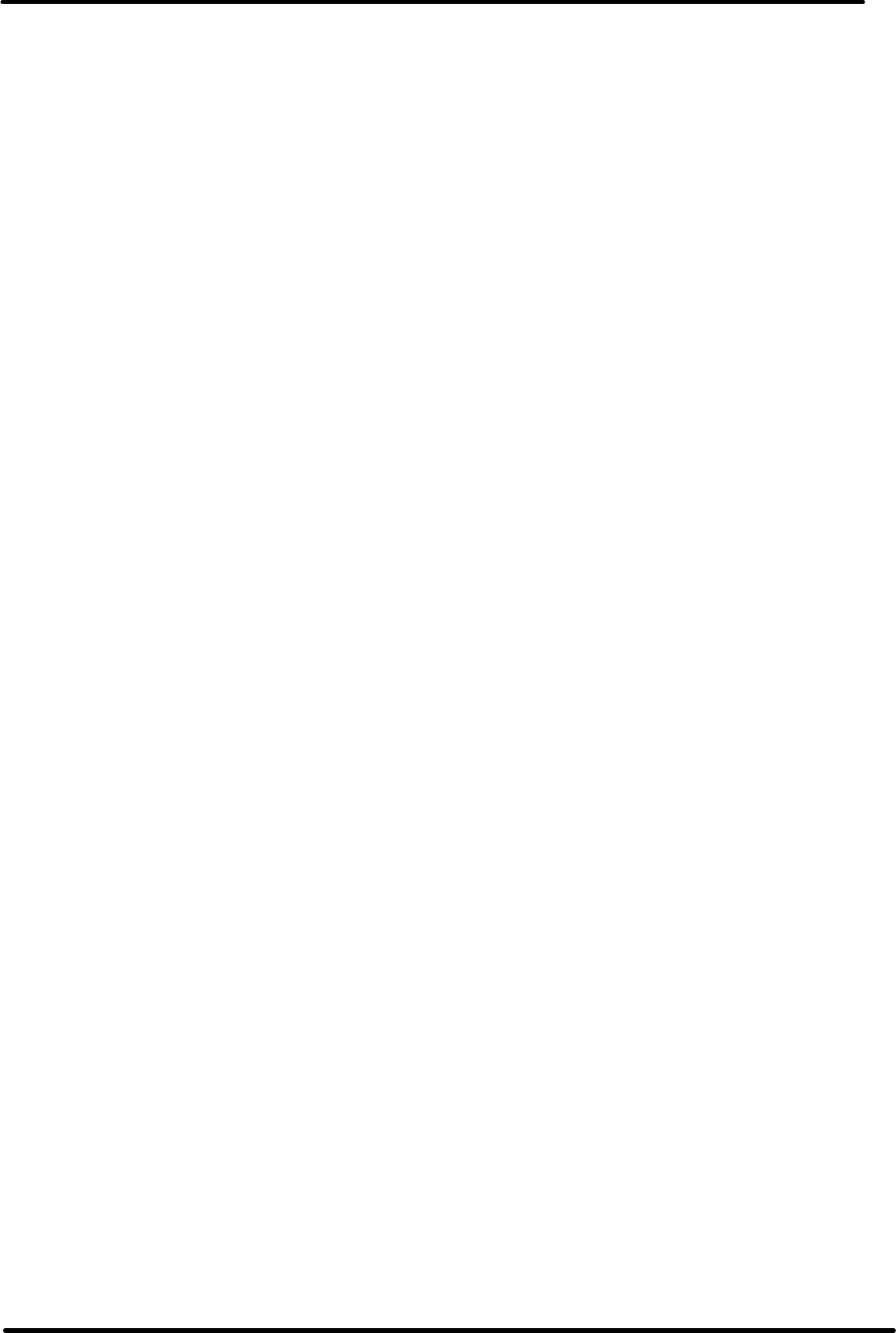
Innovator® HX Series Analog VHF Chapter 4, Circuit Descriptions,
Transmitter Control/Exciter Cabinet Assemblies
HX Series, Rev. 0 4-20
SMA type connector jack J3 as the
forward power sample. Another power
sample is taken from the coupler circuit
that is connected to the SMA type
connector jack J4 as the reflected power
sample.
4.5.4 (A5) Amplifier Control Board
(1303682; Appendix A)
The amplifier control board provides LED
fault and enable indications on the front
panel of the module and also performs
the following functions: overdrive
cutback, when the drive level reaches the
amount needed to attain 110% output
power; and overtemperature, VSWR, and
overdrive faults. The board provides
connections to the LCD Display for
monitoring the % Reflected Power, %
Output Power, and the power supply
voltage.
If the Module OK LED, located on the
front panel, is Red and blinking, a fault is
present. The meaning of the blinking
LED is as follows.
1 Blink: Indicates Amplifier Current
Fault.
2 Blinks: Indicate Temperature Fault.
3 Blinks: Indicate +32V Power Supply
Over Voltage Fault.
4 Blinks: Indicate +32V Power Supply
Under Voltage Fault.
5 Blinks: Indicate Reflected Power Fault.
6 Blinks: Indicate +12V or –12V Power
Supply Fault
4.5.4.1 Schematic Page 1
U4, located upper center of page, is an in
circuit microcontroller. The controller is
operated at the frequency of 3.6864 MHz
using crystal Y1. Programming of this
device is performed through the serial
programming port J2. U4 selects the
desired analog channel of U1 through the
settings of PA0-PA3. The outputs of Port
A must be set and not changed during an
analog input read of channels PA5-PA7.
PA4 of U4 is a processor operating LED
that monitors the ±12 VDC. PA5 is used
to monitor the +12VDC supply to the
board. PA6 is the selected channel of
analog switch U1. PA7 is connected to a
via, V10, for future access.
U6 is a serial to RS-485 driver IC. U7 is
a watchdog IC used to hold the
microprocessor in reset, if the supply
voltage is less than 4.21 VDC. U7
momentarily resets the microcontroller if
Pin 6 (!ST) is not clocked every second.
A manual reset switch is provided but
should not be needed.
In the Upper left corner, U3 is used to
determine where the amplifier control
board is located. The eight inputs come
from the main amp connector and are
used to set the SCADA address of the
controller. Pull-up resistors set a default
condition of logic high.
U5 below U3 is used for getting digital
input information of the board. Page two
has several monitoring circuits that
provide information on the amplifier’s
status. Many of these circuits
automatically shut down the amplifier if a
specific fault occurs.
U8 below U5 is used to control four board
mounted status LEDs. A FET is turned
On to shunt current away from the LED
to turn it Off. U9 below U8 is used to
enable different features within the
software. Actual use is to be determined.
4.5.4.2 Schematic Page 2
In the lower right corner are voltage
regulator circuits. U22 should allow for
0.14 amps of power using its 92 C/W
rating if Ta = 60°C max and Tj = 125°C
max 0.26 amps can be obtained from
U22 if the mounting pad is 0.5 square
inches. The controller will not need this
much current. U23 and U24 are low drop
out +5 VDC, voltage regulators with a
tolerance greater than or equal to 1%.
100mA of current is available from each
device but again the controller will not
need this much current.
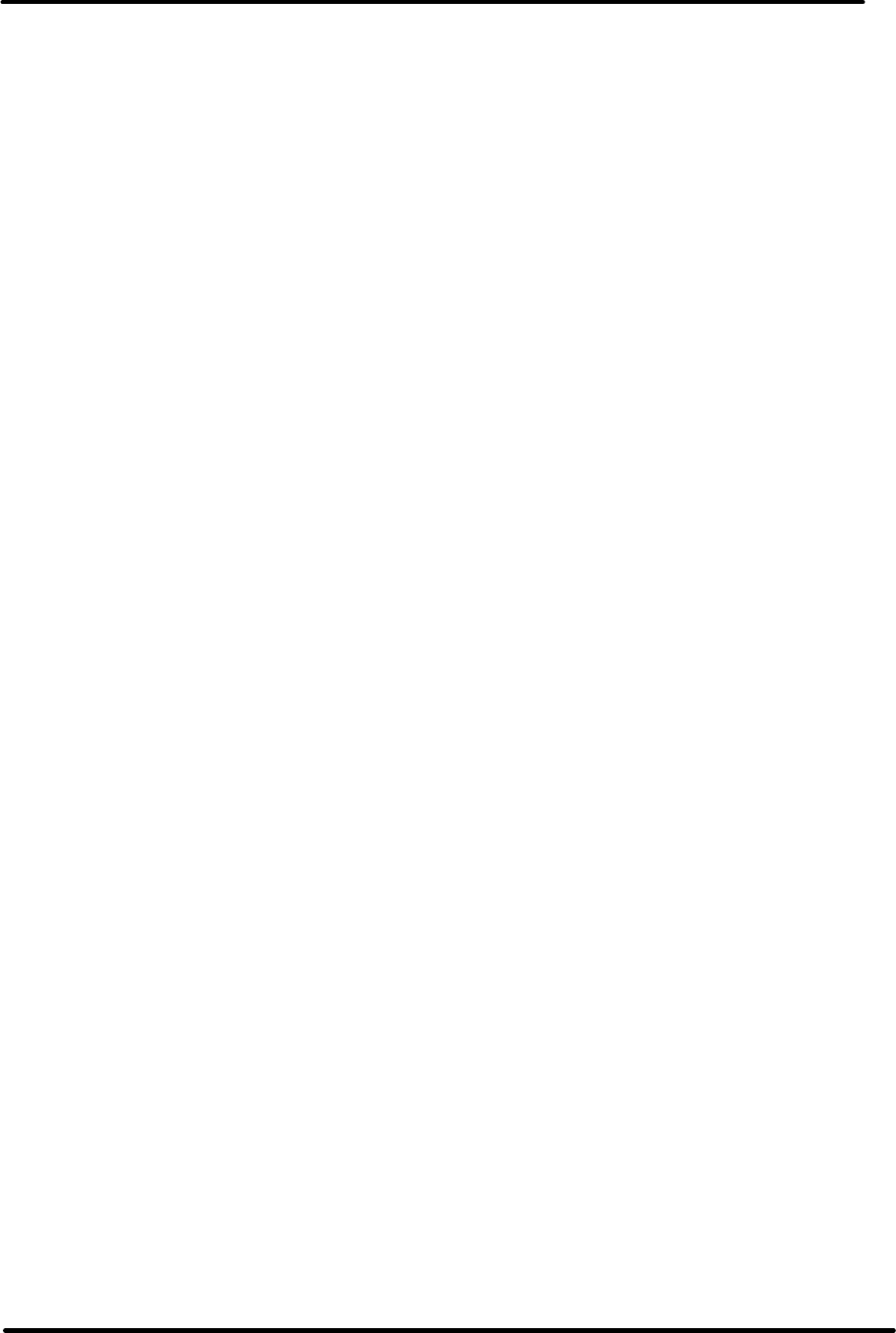
Innovator® HX Series Analog VHF Chapter 4, Circuit Descriptions,
Transmitter Control/Exciter Cabinet Assemblies
HX Series, Rev. 0 4-21
In the upper left section are circuits with
U12 and U13. U12 is used to generate a
regulated voltage that is about 5 volts
less than the +32 VDC supply,
approximately +26.25 VDC. When the
+32 VDC supply is enabled, the circuitry
around U13B is used to provide gate
voltage to Q10 that is 5 volts greater
than the source pin of this FET. The gate
of Q10 can be turned Off by any one of a
few different circuits. U10A is used to
turn Off the gate of Q10 in the event of
high current in amplifier #1. At 0.886
VDC the current to amplifier #1 should
be greater than 5 Amps. U11B is used to
turn off the Q10 FET, if high current is
detected in amplifier #2. U11A is used
to turn off the Q10 FET, if high current is
detected in amplifier #3. With 2.257
VDC at Pin 5 of U11B or Pin 3 of U11A,
the voltage output of current sense
amplifier U17 or U18 at high current shut
down should be greater than 15 Amps.
U14B is used to turn Off the gate of Q10
in the event of high power supply
voltage, approximately +35.4 VDC.
U14A is used to keep the FET disabled in
the event of low power supply voltage,
approximately +25.4 VDC.
4.5.4.3 Current monitoring sections of
the board.
The ICs U16, U17 and U18 along with
associated components set up the
current monitoring sections of the board.
R67, R68 and R69 are 0.01O/5W 1%
through hole resistors used for
monitoring the current through several
sections of the amplifier. The voltage
developed across these resistors are
amplified for current monitoring by U16,
U17 or U18. The LT1787HVCS8 precision
high side current sense IC amplifier
accepts a maximum voltage of 60 VDC.
The 43.2 kO resistor from pin 5 to
ground sets the gain of the amplifier to
about 17.28. This value is not set with
much accuracy since the manufacturer
internally matches the resistors of this
part but their actual resistance value is
not closely defined. A trimming resistor
is suggested to give a temperature
stability of –200 ppm/C, but instead the
microcontroller will determine the exact
gain of the circuit and use a correction
factor for measurements. Circuit loading
components are located in the lower
portion of each current monitoring circuit.
These components allow for short
duration high current loading of the
supply. By measuring the current
through the sense resistor with and
without the additional four 30.1 O 1%
resistors. For very short duration pulses,
a 1206 resistor can handle up to 60
watts. The processor requires 226 uSec
per conversion. A supply voltage of +32
VDC will pass 1.06 amps + 1% through
the load resistors.
A6 is a temperature sensor thermistor
that is used to monitor the temperature
of the module's heat sink. It connects
to J6 pins 1 & 2 on the board and is
wired to the comparator IC U10B. If the
temperature increases above 75°C the
output will go Low that is used as a
temperature fault output, which
generates a Fault alert at U15A and
disables Amplifier #1.
4.5.4.4 Schematic Page 3, Aural,
Visual/Average and Reflected power
detector sections of the board.
A Forward Power Sample enters the
board at SMA Jack J3 and is split. One
part connects to J4 on the board that is
cabled to J1, the SMA Forward Power
Sample Jack, located on the front panel
of the assembly. The other part of the
split forward power sample is detected by
CR17 and the DC level amplified by
U25A. The output of U25A at pin 1 is
split with one part connected to the Aural
Power sample, which is not used in a
digital transmitter. The other split output
connects to U265A that is part of the
Forward Average Power circuit. The
detected level is connected to L4 that is
part of an intercarrier notch filter circuit
that is tuned to eliminate the 4.5 MHz
aural intercarrier, if present. The
Average power sample is amplified by
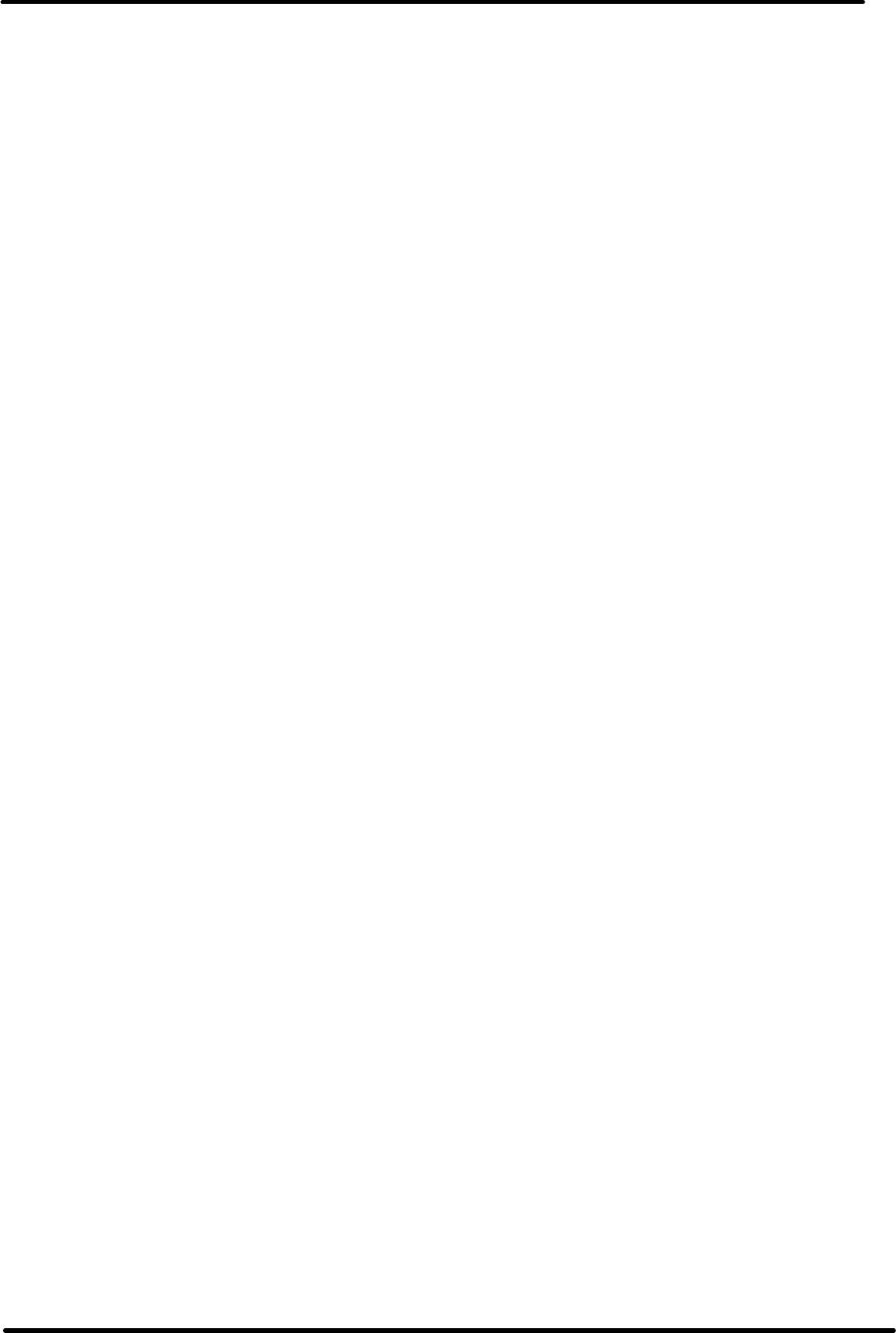
Innovator® HX Series Analog VHF Chapter 4, Circuit Descriptions,
Transmitter Control/Exciter Cabinet Assemblies
HX Series, Rev. 0 4-22
U26D and connected through the
average calibration pot R166 to U26C.
The output of U26C is connected to the
comparator IC U26B that has Aural Null
and Offset Null, if present in the system,
connected to the other input. The output
Average Forward power level connects to
J9 pin 2 of the board.
A Reflected Power Sample enters the
board at SMA Jack J5 and is detected by
CR20 and the DC level amplified by
U28B. The output of U28B at pin 7 is
connected through the reflected
calibration pot R163 to U28C. The
output is split with one part connected to
J9 pin 5, the Reflected Power Output
level of the board. The other part of the
split from U28C connects to the
comparator IC U28D that has a reference
level connected to the other input. If the
reflected level increases above the
reference level a low output is produced
and connected to the Reflected Power
Shutdown circuit at CR28. The low shuts
off Q14 causing pin 3 to go high that is
connected to the inverter U15C. The
output of U15C goes low producing a
Reflected Power Fault that is connected
to an output of the board, the Fault Alert
circuit and also shuts down Amplifier #1.
Gain of the power measurements is
completed through software. Only the
Aural Null and Offset Null need to be
done through front panel pots.
4.5.4.5 Schematic Page 3, Aural,
Visual/Digital and Reflected power
detector sections of the board.
A Visual/Digital Power Sample enters the
board at the SMA Jack J3 and is split.
One part connects to J4 on the board
that is the SMA Visual/Digital Power
Sample Jack, located on the front panel
of the assembly. NOTE: In this
configuration Jumper W3 on J12 is
connected between pins 2 & 3 that is for
a visual peak sample. The other part of
the split visual/forward power sample is
detected by CR35 and the DC level
amplified by U21A. The output of U21A
at pin 1 is connected to R202, the Visual
Power Calibration Adjustment. R202 sets
the level to the IC U27A, which amplifies
the visual power sample before it is split.
One visual power sample, Visual Power
connects back to U4 on Page 1. Another
visual power sample connects through
the jumper on J12 to a split point. A
sample of the visual power, Selected Frd
Power, connects back to U3 on Page 1.
The other visual power sample connects
to amp U27B whose output is level
detected by CR29, CR28 and CR30 and
back to Page 1, Visual Power Remote, at
J8-7 for remote use.
A Visual/Digital Reflected Power Sample
enters the board at the SMA Jack J5 and
is detected by CR31 and the DC level
amplified by U21B. The output of U21B
at pin 7 is connected through the visual
reflected calibration pot R203 to U25A.
The output is split with one part
connected to the Reflected Pwr V
connection on Page 1 of the schematic
that connects to U3. The other part of
the split from U25A connects to the
comparator IC U25B that has a reference
level connected to Pin 5. If the reflected
level increases above the reference level
a low Fault output is produced and
connected to the Reflected Power
Shutdown V circuit on Page 2 at CR14 &
CR15, which produces a Reflected Power
Fault V that is connected to an output of
the board, the Fault Alert circuit and also
shuts down the Amplifier.
An Aural Power Sample enters the board
at the SMA Jack J13 and is split. One
part connects to J14 on the board that is
the Aural Power Sample Jack, located on
the front panel of the assembly. The
other part of the split aural power sample
is detected by CR36 and the DC level
amplified by U28A. The output of U28A
at pin 1 is connected to R204, the Aural
Power Calibration Adjustment. R204 sets
the level to the IC U29A, which amplifies
the aural power sample before it is split.
One aural power sample, Aural Power
connects back to U4 on Page 1. Another
aural power sample connects to amp
U29B whose output is level detected by
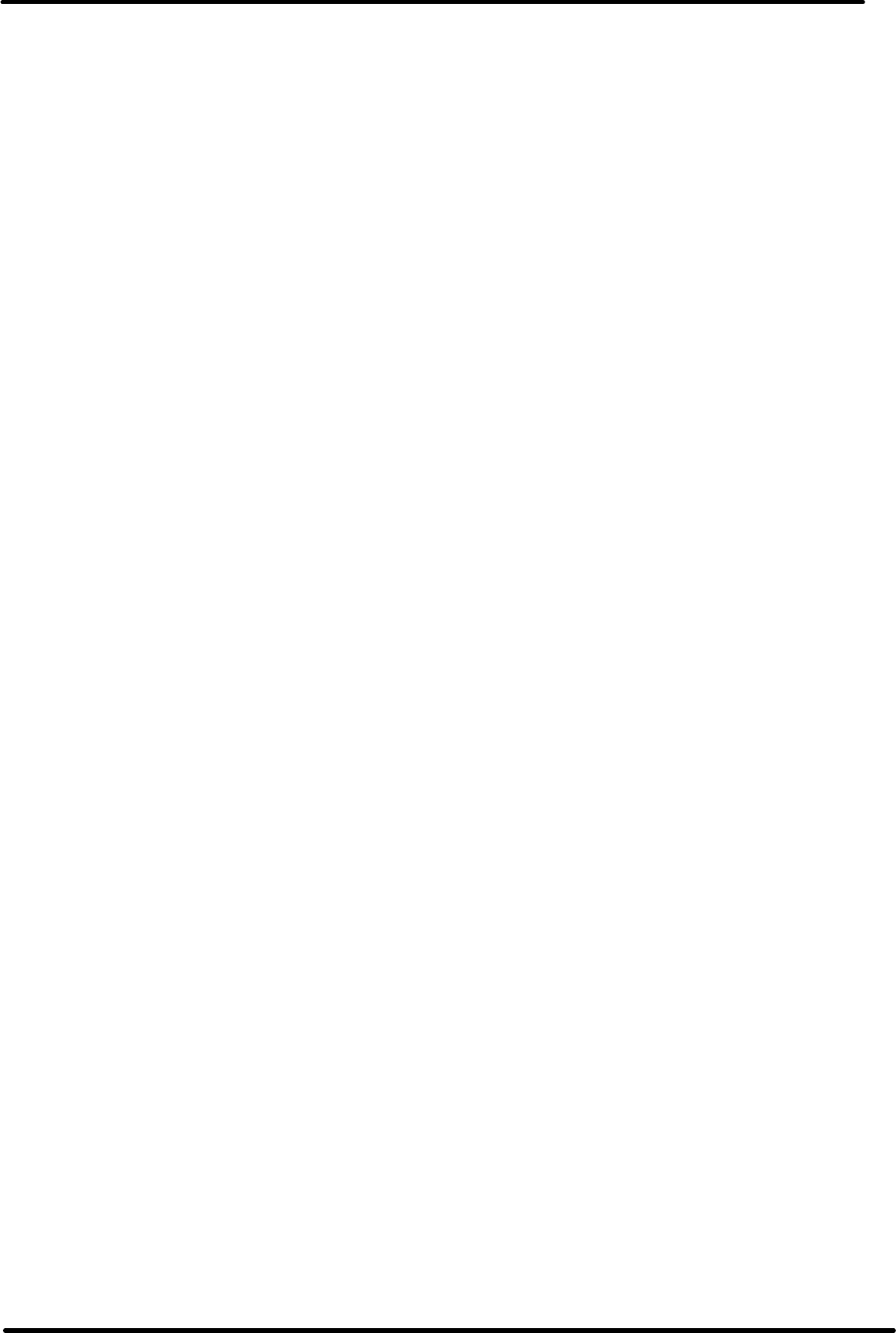
Innovator® HX Series Analog VHF Chapter 4, Circuit Descriptions,
Transmitter Control/Exciter Cabinet Assemblies
HX Series, Rev. 0 4-23
CR39, CR37 and CR40 and back to Page
1, Aural Power Remote, at J8-9 for
remote use.
An Aural Reflected Power Sample enters
the board at the SMA Jack J15 and is
detected by CR41 and the DC level
amplified by U28B. The output of U28B
at pin 7 is connected through the aural
reflected calibration pot R205 to U30A.
The output is split with one part
connected to the Reflected Pwr A
connection on Page 1 of the schematic
that connects to U3. The other part of
the split from U30A connects to the
comparator IC U30B that has a reference
level connected to Pin 5. If the reflected
level increases above the reference level
a low Fault output is produced and
connected to the Reflected Power
Shutdown A circuit on Page 2 at CR43 &
CR44, which produces a Reflected Power
Fault A that is connected to an output of
the board, the Fault Alert circuit and also
shuts down the Amplifier.
The Gain of the power measurements is
completed through software. Only the
Aural Null and Offset Null need to be
done through front panel pots.
This completes the description of the
Power Amplifier Module Assembly.
4.6 Output Assemblies
The RF output from the transmitter
power amplifier is at the RF output jack
(J25), an “N” connector labeled PA RF
Output, of the chassis assembly. The RF
is cabled thru RG-214 coaxial cable to
the RF input jack on the bandpass filter
assembly. The output of the bandpass
filter connects to the antenna for your
system.
This completes the description for the
entire HX transmitter.
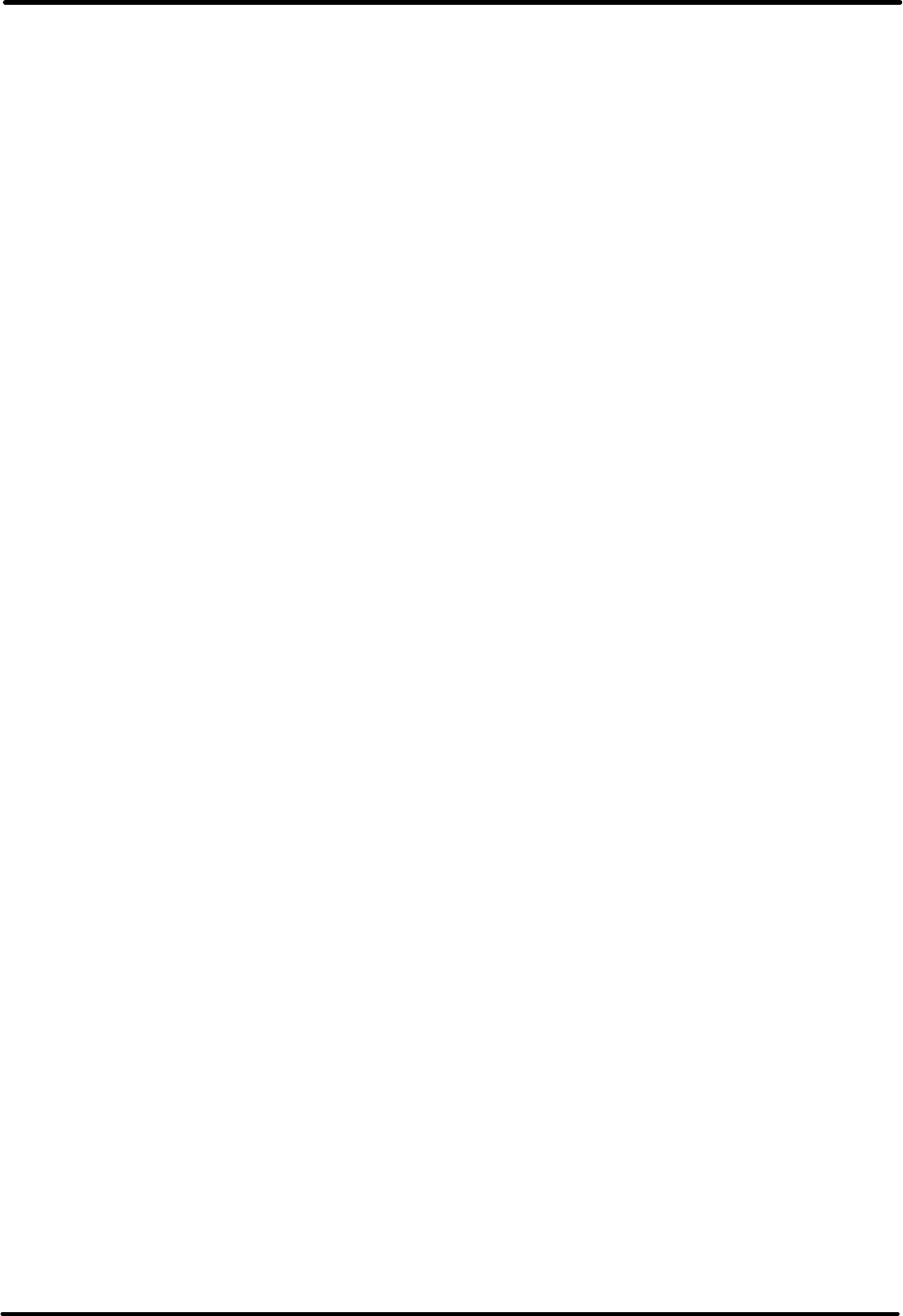
Innovator® HX Series Analog VHF Chapter 5,Detailed
Transmitter Alignment Procedures
HX Series, Rev. 0 5-1
Chapter 5
Detailed Alignment Procedures
This system was aligned at the factory
and should not require additional
adjustments to achieve normal operation.
This exciter/driver takes the baseband
audio and video inputs and converts
them to the desired VHF On Channel RF
Output.
The Innovator HX Series Exciter/Driver
assembly is of a Modular design and
when a Module fails that module needs to
be changed out with a replacement
module. The failed module can then be
sent back to Axcera for repair. Contact
Axcera Customer Service Department at
724-873-8100 or fax to 724-873-8105,
before sending in any module.
5.1 Module Replacement
Module replacement on the HX Series
products is a relatively simple process.
In the Exciter/Driver assembly, the
individual modules plug into a blind
mating connector located on the chassis.
To replace a module, refer to the
following procedure.
Loosen the two grip lock connectors,
located on the front panel, at the top
and bottom of the module,
counterclockwise until the module
releases.
NOTE: To remove the driver/power
amplifier module, mounted in the
exciter/driver assembly, the input and
output cables must be removed from the
rear of the module and also a 6/32” x ½”
Philips screw, mounted between the two
connectors, needs to be removed before
the module will pull out. After removal of
the screw, which is used to hold the
module in place during shipping, it does
not need to be replaced.
After removal of the failed module, slide
the replacement module in place and
make certain it connects to the blind
mate connector. Replace the two cables
on the rear of the PA chassis assembly.
If the replacement module does not
slide in easily, verify it is properly
aligned in the nylon tracks, located on
both the top and bottom of the module.
Note: Each Module has an assigned slot
and will not fit properly in the incorrect
slot. Do not try to place a Module in the
wrong slot as this may damage the slot
or the blind mate connectors.
5.1.1 Initial Test Set Up
Check that the RF output at the visual
combiner and the aural amplifier trays
are terminated into dummy loads of at
least the rated output of the each
system. While performing the alignment,
refer to the final Test Data Sheet for the
system and compare the final readings
from the factory with the readings on
each of the modules and trays. The
readings should be very similar. If a
reading is way off, the problem is likely
to be in that module.
Switch On the main AC for the system.
5.2 Innovator HX Series
Exciter/Driver Chassis Assembly
This system operates using the baseband
audio and video inputs.
On the LCD Display, located on the
Controller/Power Supply Module, in
Transmitter Set-Up, push the button to
switch the transmitter to Operate.
The check of and the setup of the Audio
and Video input levels are completed
using the LCD Display and the front panel
adjustments on the Modulator assembly.
The level of the RF output includes
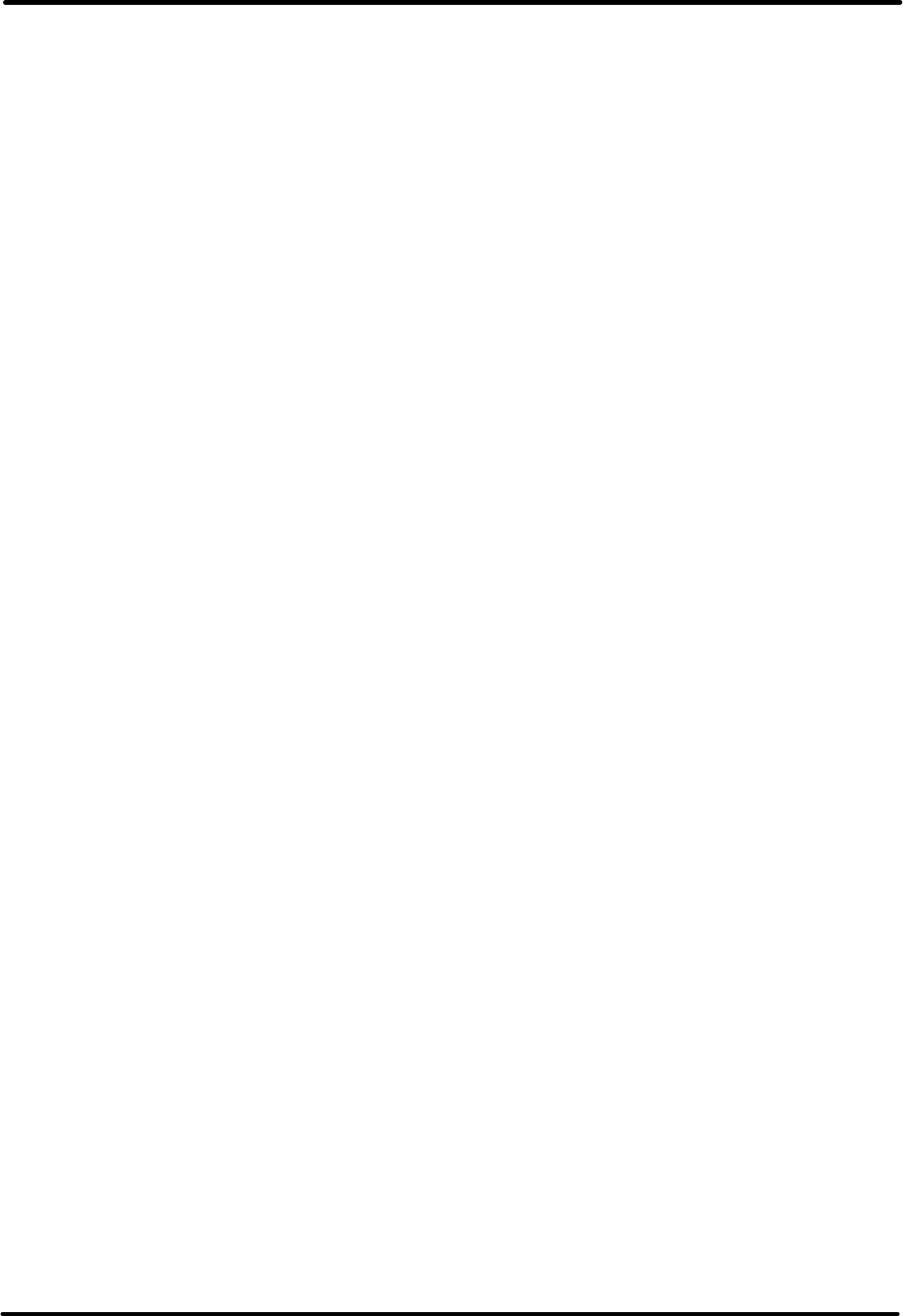
Innovator® HX Series Analog VHF Chapter 5,Detailed
Transmitter Alignment Procedures
HX Series, Rev. 0 5-2
adjustments of the drive level to the
Power Amplifier and the adjustment of
the linearity and phase predistortion to
compensate for any nonlinear response
of the Power Amplifier. The adjustments
are located on the front panel of the IF
Processor module.
5.2.1 Modulator Module Assembly
The Modulator Assembly has adjustments
for video levels and audio modulation
levels, and other related parameters.
Connect an NTSC baseband video test
signal input (1 Vpk-pk) to the transmitter
video input jack J7 on the rear of the
tray. Jacks J7 and J17 are loop-through
connected; the J17 jack can be used as a
video source for another transmitter.
Connect a baseband audio input (+10
dBm) to the balanced audio input
terminal block TB02-1 [+], TB02-2 [-],
and TB02-3 [ground] or, if
stereo/composite audio is provided,
connect it to BNC jack J3, the composite
audio input jack.
Verify that all LEDs located on the front
panel of the Modulator are Green. The
following details the meaning of each
LED:
AURAL UNLOCK (DS5) – Red Indicates
that 4.5 MHz Aural IF is unlocked from
the 45.75 MHz visual IF.
VISUAL UNLOCK (DS6) – Red Indicates
that the 45.75 MHz visual IF is unlocked
from the 10 MHz reference.
AUDIO OVER DEVIATION (DS4) – Red
Indicates that the input Audio level is too
high.
VIDEO LOSS (DS1) – Red Indicates that
the input Video level is too low.
OVER MODULATION (DS3) – Red
Indicates that the input Video level is too
high.
ALTERNATE IF (DS7) – Red Indicates
that an external 45.75 MHz IF is not
present to the modulator.
10 MHz PRESENT (DS2) – Red Indicates
that an external 10 MHz reference in not
present to the modulator.
Look at the front panel LCD meter on the
Control/Power Supply Module Assembly.
Set the LCD screen to the Modulator
Details video output level screen, the
screen indicates active video from 0 to 1
Vpk-pk. The normal video input level is 1
Vpk-pk on the front panel screen. If this
reading is not at the proper level, the
overall video level can be changed by
adjusting the VIDEO LEVEL control R42
on the front panel of the Modulator to the
1 Vpk-pk level on the front panel screen.
Switch the LCD display to the Modulator
Details screen that indicates the AUDIO
DEVIATION (modulation level) of the
signal from 0 to 100 kHz.
MONO SET UP: The modulator was
factory set for a ±25-kHz deviation with
a mono, balanced, audio input of +10
dBm. If the reading is not at the correct
level, adjust the MONO Audio Gain pot
R110, located on the front panel of the
modulator, as necessary, to attain the
±25-kHz deviation on the front panel
screen.
STEREO SET UP: The modulator was
factory set for a ±75-kHz deviation with
a stereo, composite, audio input of 1
Vpk-pk. If this reading is not correct,
adjust the STEREO Audio Gain pot R132,
located on the front panel of the
modulator, as necessary, for the ±75-
kHz deviation.
SECONDARY AUDIO SET UP: NOTE:
Remove any stereo or mono audio
modulation input to the transmitter
during the set up of the secondary audio.
The modulator was factory set for a ±15-
kHz deviation with a secondary audio
input of 1 Vpk-pk. If this reading is not
correct, adjust the SAP/PRO Audio Gain
pot R150, located on the front panel of
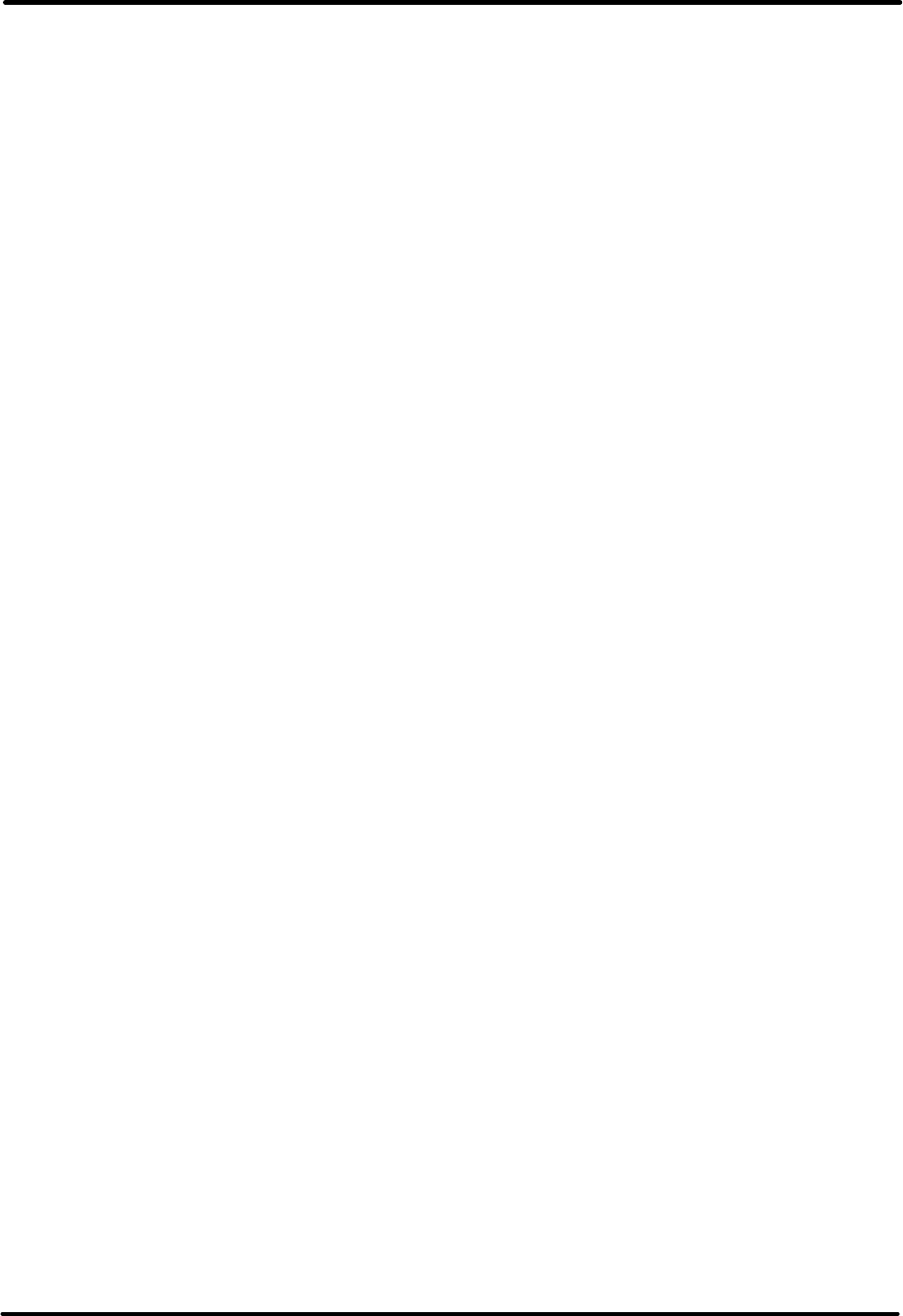
Innovator® HX Series Analog VHF Chapter 5,Detailed
Transmitter Alignment Procedures
HX Series, Rev. 0 5-3
the modulator, as necessary, for the
±15-kHz deviation.
5.2.2 IF Processor Module Assembly
Verify that all red LEDs located on the IF
Processor front panel are extinguished.
The following details the meaning of each
LED when illuminated:
• DS1 (input fault) – Indicates that
either abnormally low or no visual IF
is present at the input of the IF
Processor module.
• DS2 (ALC fault) – Indicates that the
ALC circuit is unable to maintain the
signal level requested by the ALC
reference. This is normally due to
excessive attenuation in the linearity
signal path or the IF phase corrector
signal path, or that switch SW1 is in
the Manual ALC Gain position.
• DS4 (Mute) – Indicates that a Mute
command is present to the system.
Switch the transmitter to Standby. The
ALC is muted when the transmitter is in
Standby.
5.2.3 Upconverter Module Assembly
Switch the transmitter to Operate. Verify
that all LEDs located on the front panel of
the visual Upconverter are Green. The
following details the meaning of each
LED:
PLL 1 Fault (DS1) - Displays the status
of the 1 GHz PLL, Green locked or Red
unlocked
PLL 2 Fault (DS2) - Displays status of
the 1.1-1.9 GHz PLL, Green locked or
Red unlocked
AGC Fault (DS7) – NOT USED IN THIS
CONFIGURATION.
AGC Override (DS3) - Displays status
of AGC cutback, either Green normal
drive level, no cutback, or Red cutback,
too much drive level to driver module.
Manual AGC (DS6) - Displays status of
the control of the AGC level, either
Green, in AGC, AGC Adj. using R6 or
Amber, in manual, Man Gain Adj. using
R7.
5.2.4 Setting Up the Drive Level of
the Transmitter Procedure
Setting the Manual AGC
Preset the front panel “MAN GAIN ADJ”
pot on the Upconverter full
Counterclockwise, and the MAN/AUTO
AGC Switch to the Left, Man. Turn the
transmitter to Operate, and slowly
adjust the Man Gain pot until the desired
% output power, as read on the LCD
display, has been reached. The Manual
AGC is now set. Normal operation of the
Transmitter is in the Auto AGC position.
Setting the Auto AGC
With the transmitter in Standby, preset
the AGC ADJ pot on the Upconverter full
Counterclockwise. Preset the AGC
Cutback Adj pot on the Upconverter full
Clockwise. Move the Man/Auto AGC
Switch on the Upconverter to the Right,
Auto. Switch the transmitter to
Operate and slowly adjust the AGC Adj
pot until the desired output power has
been reached.
Monitor the output of the transmitter
with a Spectrum Analyzer and turn the
power up 1 dB higher than the normal
desired output using the AGC Adj pot.
Enter the Transmitter Set-Up menu on
the LCD Control Panel and step through
the screens until the screen labeled
“Inner Loop Gain U/C” is reached. The
inner loop is adjustable from 0-255.
Use the + button to increase the Inner
Loop Gain until the power on the
spectrum analyzer just begins to
decrease. Use the – button to decrease
the inner loop gain by 10%. (If it begins
to affect power at setting 160, drop it
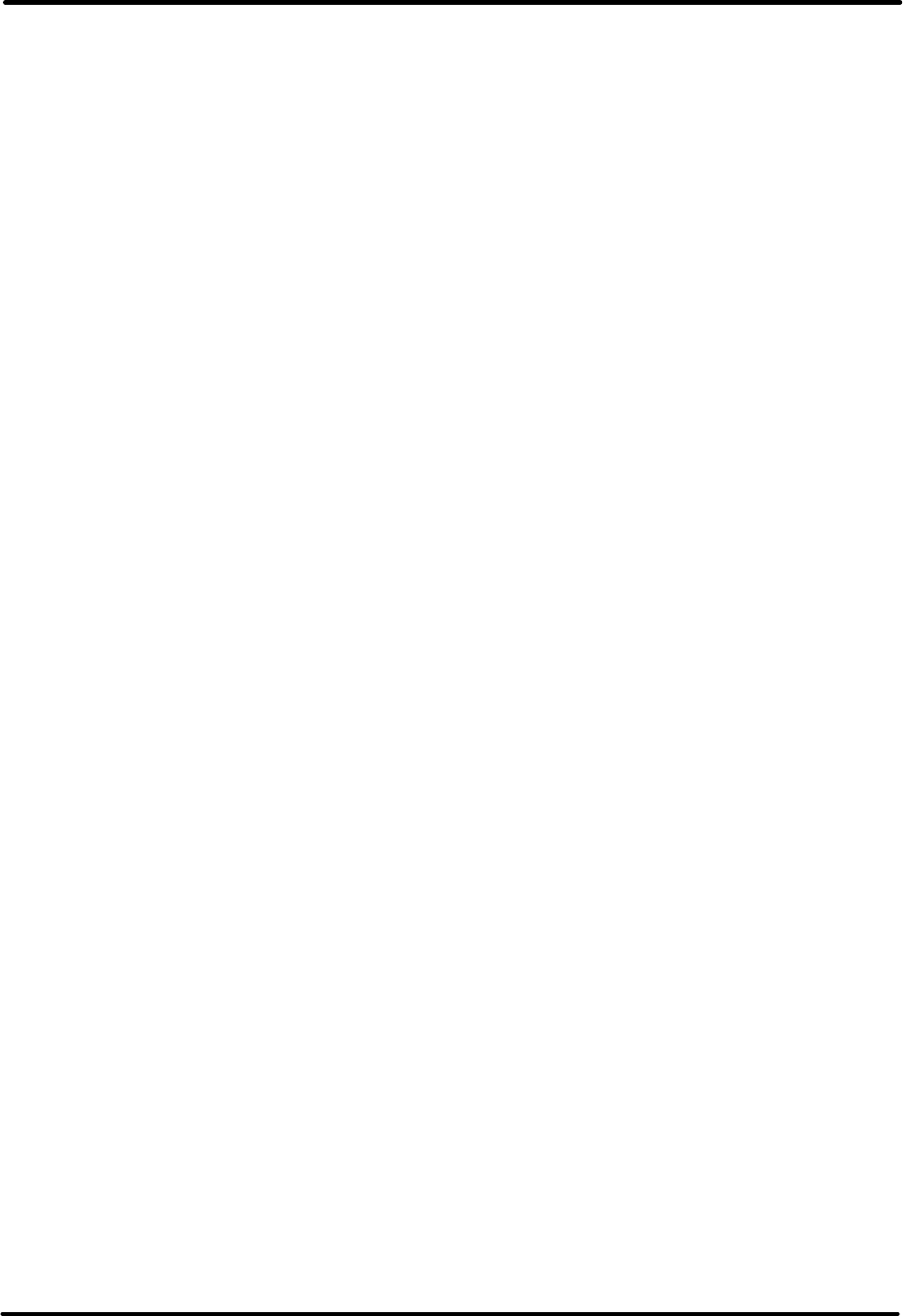
Innovator® HX Series Analog VHF Chapter 5,Detailed
Transmitter Alignment Procedures
HX Series, Rev. 0 5-4
back down to 160-16=144, if it affects
power at 100, drop it down by 10 to 90,
etc….). Slowly turn the AGC Cutback
Pot Counterclockwise until the AGC
Override light begins to flicker, and the
output power begins to drop. Turn the
pot Clockwise slightly, so the light just
goes out and the power stabilizes. Turn
the AGC pot down to get back to the
desired % output power level. The Auto
AGC is now set. Normal operation of the
Transmitter is in the Auto AGC position.
5.3 Linearity Corrector Adjustment
Refer to Figure 5-1, which shows the top
on the exciter chassis assembly and the
pots, switches and test points located on
the modulator and IF processor boards
that are accessed through the top cover.
The IF linearity correction function
consists of three non-linear cascaded
stages, each having adjustable threshold
or cut-in points. The threshold
adjustment determines at what IF signal
level the corresponding corrector stage
begins to increase gain. Using Figure 5-
1, locate the IN PHASE THRESHOLD
adjustments for the first through third
linearity corrector stages. Because the
stages are cascaded, the order of
correction is important. The first stage,
R294, should cut-in near white level, with
the cut-in point of the next stage, R295,
toward black and with the last stage,
R300, primarily stretching sync.
Check that ALC is set to +0.8 VDC on the
LCD display in the set up menu. The ALC
will operate to maintain the
corresponding peak power level following
the correctors. Therefore, the
adjustment procedure must be repeated
to achieve the correct differential gain
predistortion. A positive aspect of
linearity adjustment with the ALC
Enabled is that the control movements
will not affect peak power.
Start with the first linearity stage and
adjust R294 CW to stretch the signal
above the white region. Next, advance
the second Threshold Control R295 to
stretch the signal above the Black range.
Adjust the third Threshold Pot R300 to
stretch Sync. Go back through the white
through black and sync correctors to
touch up the effects of ALC level changes
during the adjustment.
If the Transmitter is being driven very
hard, it may not be possible to get
enough Sync Stretch while maintaining a
flat differential gain. In this case, some
Video Sync Stretch may be used from the
Modulator, R11, accessed through the
top cover of the exciter/driver chassis
assembly. The Video White Stretch
Circuit, R393, can be used to stretch the
Luminance portion of the Video Signal.
To adjust it, apply a 5 Step Staircase
Test Signal to the Transmitter and
monitor the Low Frequency Linearity.
Adjust R391 until the White portion of
Video begins to Stretch. Adjust R393 as
needed to control the amount of Stretch.
Switch the Waveform Monitor to look at
the full Video Signal. Adjust to the
proper Depth of Modulation using the
LCD screen set up depth of modulation
screen, located on the control monitoring
module. It may be necessary to repeat
the White Stretch and Depth of
Modulation adjustments a few times to
get both parameters correct at the same
time. If the Video Sync Stretch is used,
it will need to be readjusted as the Sync
Level has been slightly changed.
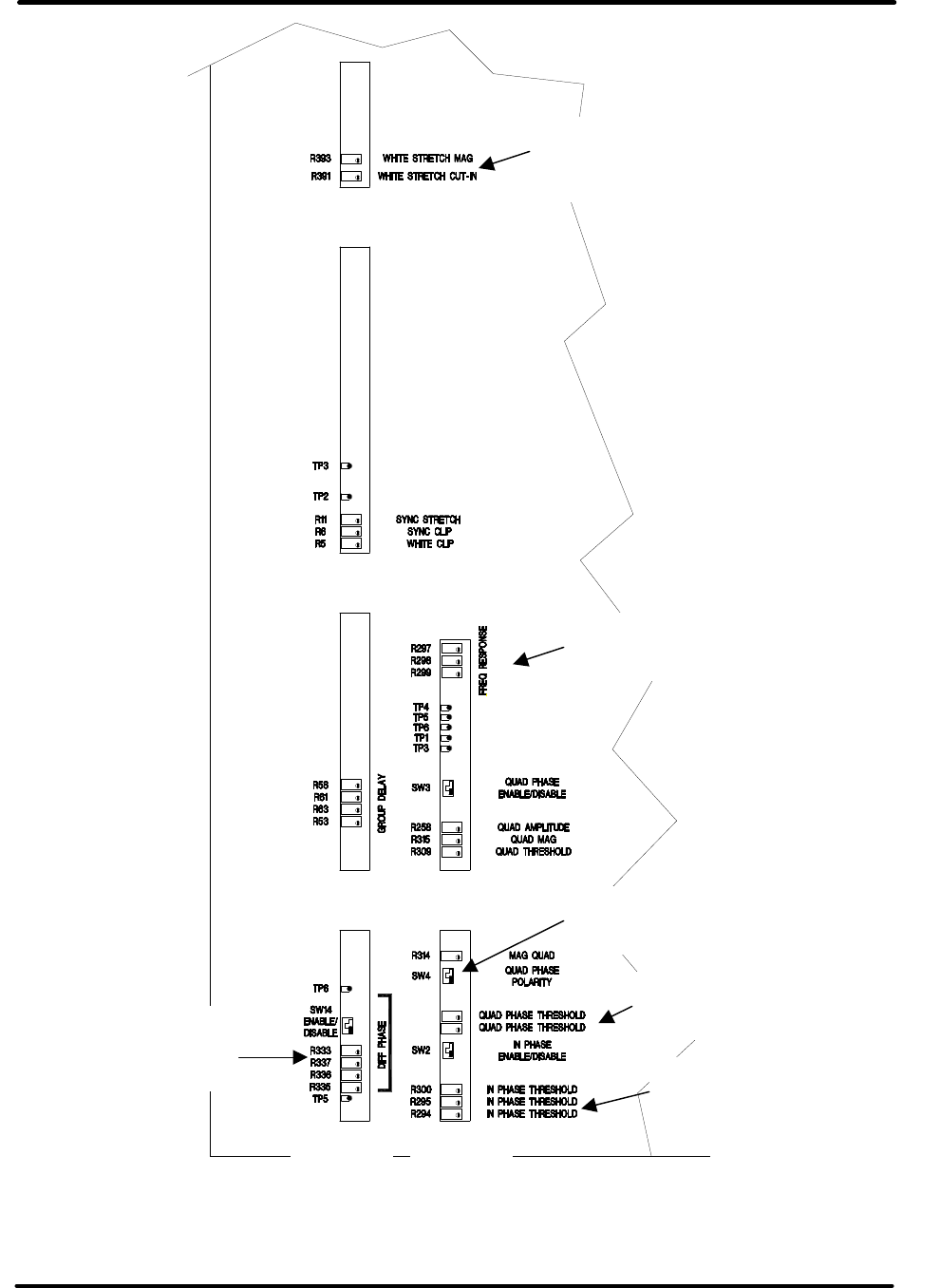
Innovator® HX Series Analog VHF Chapter 5,Detailed
Transmitter Alignment Procedures
HX Series, Rev. 0 5-5
Figure 5-1. Adjustments accessed through the top of the HX Exciter Chassis
Adjust for proper
Differential Gain and
Luminance Nonlinearity
Adjusts depth of
Preset Notches
Adjust to flip
correction direction
Adjust for ICPM and
Phase Distortions
Black Stretch affects
Differential Gain and
Differential Phase
Reversible diodes flip
the direction of
adjustment
Modulator
IF
Processor
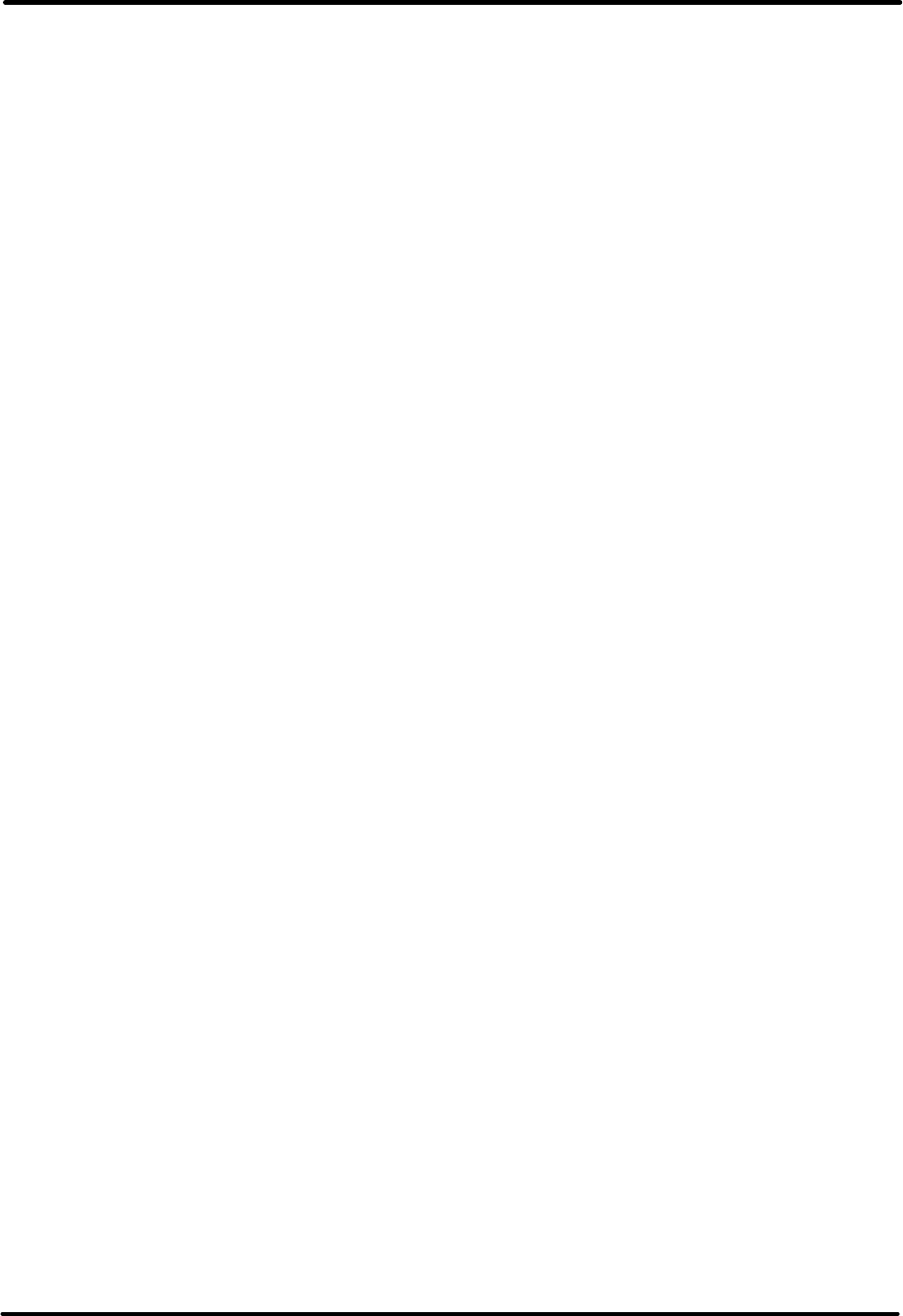
Innovator® HX Series Analog VHF Chapter 5,Detailed
Transmitter Alignment Procedures
HX Series, Rev. 0 5-6
5.4 Differential Phase and ICPM
Corrector Adjustment
The ICPM and phase distortions of the
Transmitter are adjusted with the quad
phase threshold and magnitude pots
accessed through the top cover of the
exciter/driver chassis. These pots are
adjusted to control the Video Signal
towards Sync, the point where the ICPM
is Inverted and the Video Signal towards
White. Switch SW4 sets up the quad
phase polarity of the adjustment that is
needed. SW3 enables or disables the
quad phase adjustment.
The last step in the set up procedure is to
correct whatever differential phase
remains after the ICPM correctors are
properly adjusted. Monitor the
differential phase of the Transmitter
Output and switch on the Video
Differential Phase Corrector Switch,
SW14 accessed through the top of the
exciter/driver chassis assembly. The
shape of the correction may be changed
by the adjustment of the differential
phase corrector pots R333, R335, R336
and R337. By reversing the diode
adjacent to each pot (each diode is
mounted in a plug socket), the direction
of adjustment can be changed. The
process of adjusting the pot and/or
reversing the diode will provide the
necessary phase correction.
This completes the set up and
adjustment of the transmitter. If a
problem occurred during alignment,
contact Axcera field service at (724) 873-
8100.
Appendix A
HX Series VHF High Band Transmitter
Drawings and Parts Lists
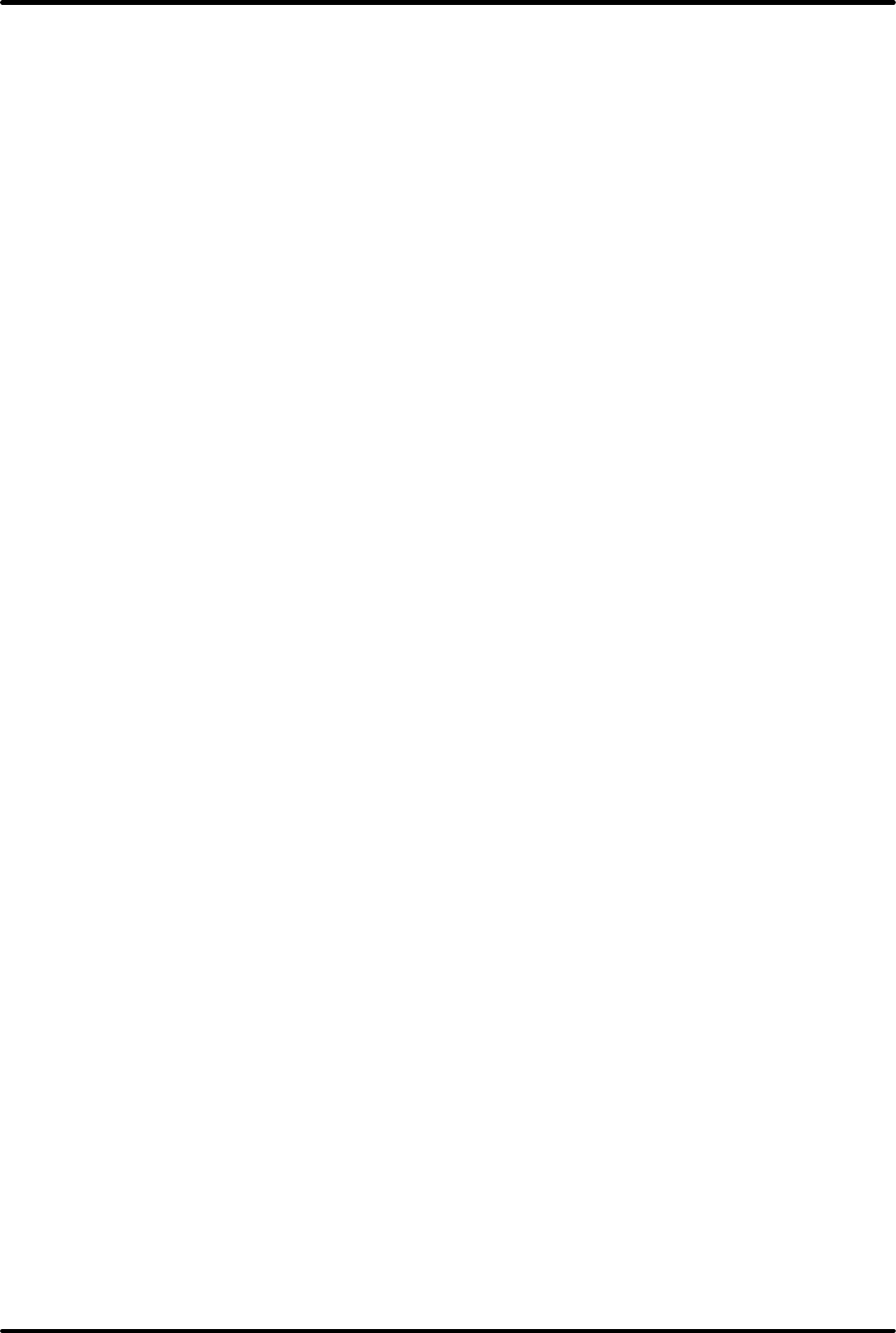
Innovator® HX Series Analog VHF Appendix A,
Transmitter Drawings and Parts Lists
HX Series, Rev. 0 A-1
Appendix A
Drawing List
HX Series VHF High Band Transmitter, Airwaves
Innovator HX Series Driver/Transmitter Block Diagram...........................1302139
Innovator HX Series Transmitter Interconnect........................................1303478
Exciter/Driver Chassis Assembly, 110 VAC, HX Series
Interconnect.......................................................................................1305554
Backplane Board, Axciter
Schematic..........................................................................................1307308
Modulator Assembly, VHF, HX SERIES
Analog Modulator Board, VHF, HX Series
Schematic..........................................................................................1304705
IF Processor Assembly, VHF, HX Series
IF Processor Board, VHF, HX Series
Schematic..........................................................................................1304688
Upconverter Assembly, VHF/UHF
Block Diagram....................................................................................1303830
Interconnect.......................................................................................1303831
Downconverter Board Assembly
Schematic..........................................................................................1303836
First Conversion Board
Schematic..........................................................................................1303840
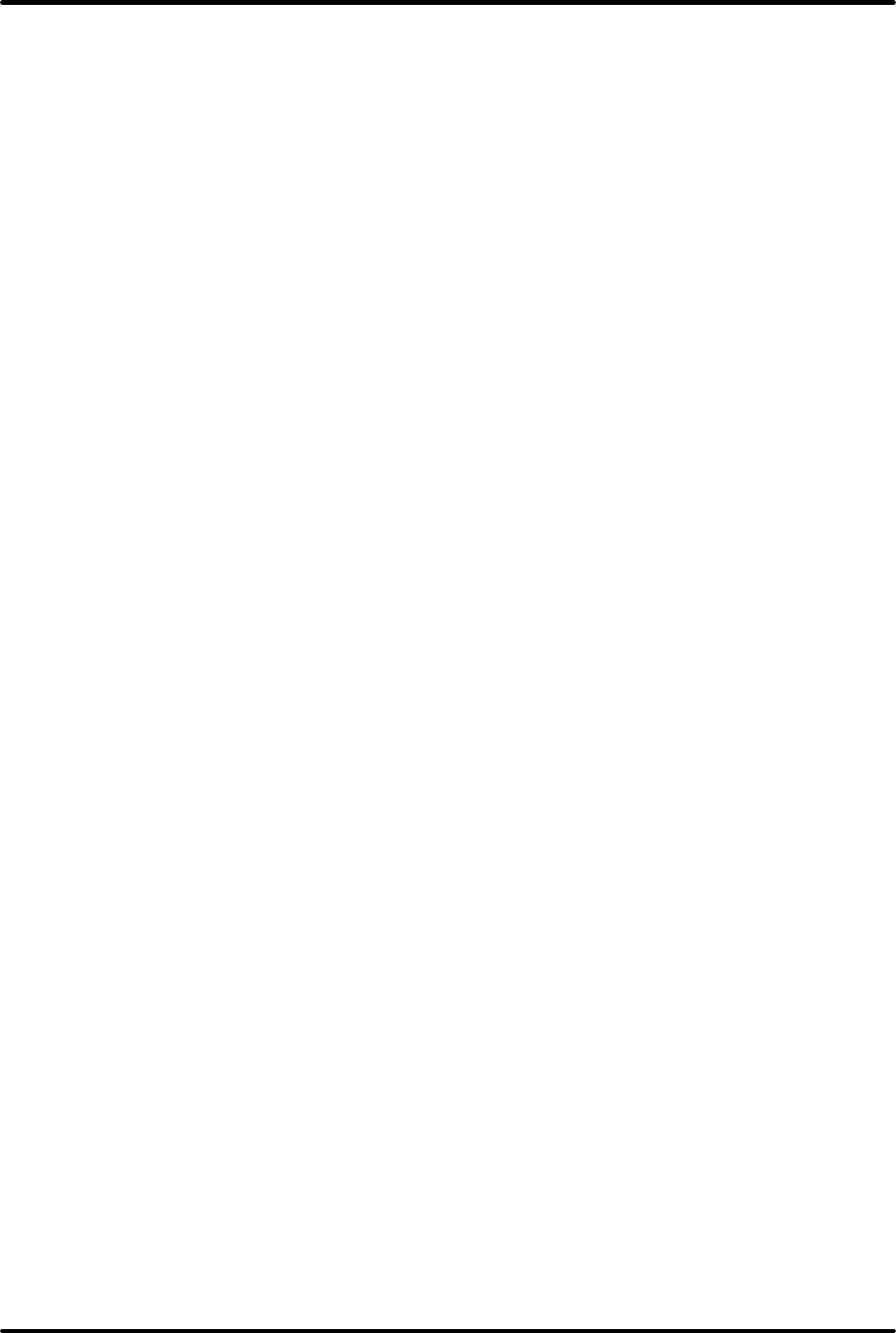
Innovator® HX Series Analog VHF Appendix A,
Transmitter Drawings and Parts Lists
HX Series, Rev. 0 A-2
L-Band PLL Board Assembly
Schematic..........................................................................................1303848
Upconverter Control Board
Schematic..........................................................................................1304761
Control/Power Supply Assembly, 110 VAC
Block Diagram....................................................................................1303889
Interconnect.......................................................................................1302062
Switch Board
Schematic.......................................................................................1527-3406
Control Board
Schematic..........................................................................................1302023
Power Protection Board
Schematic..........................................................................................1302839
Power Amplifier Assembly, VHF
Block Diagram....................................................................................1305824
Interconnect.......................................................................................1305823
Amplifier Control Board
Schematic..........................................................................................1303683
25 Watt VHF Driver Assembly (1305820)
Delta RF Data Sheet.......................................................................PA25-VHF-H
200 Watt VHF Amplifier Assembly (1300167)
Delta RF Data Sheet....................................................................... P200-VHF-H
Appendix B
SYSTEM SPECIFICATIONS
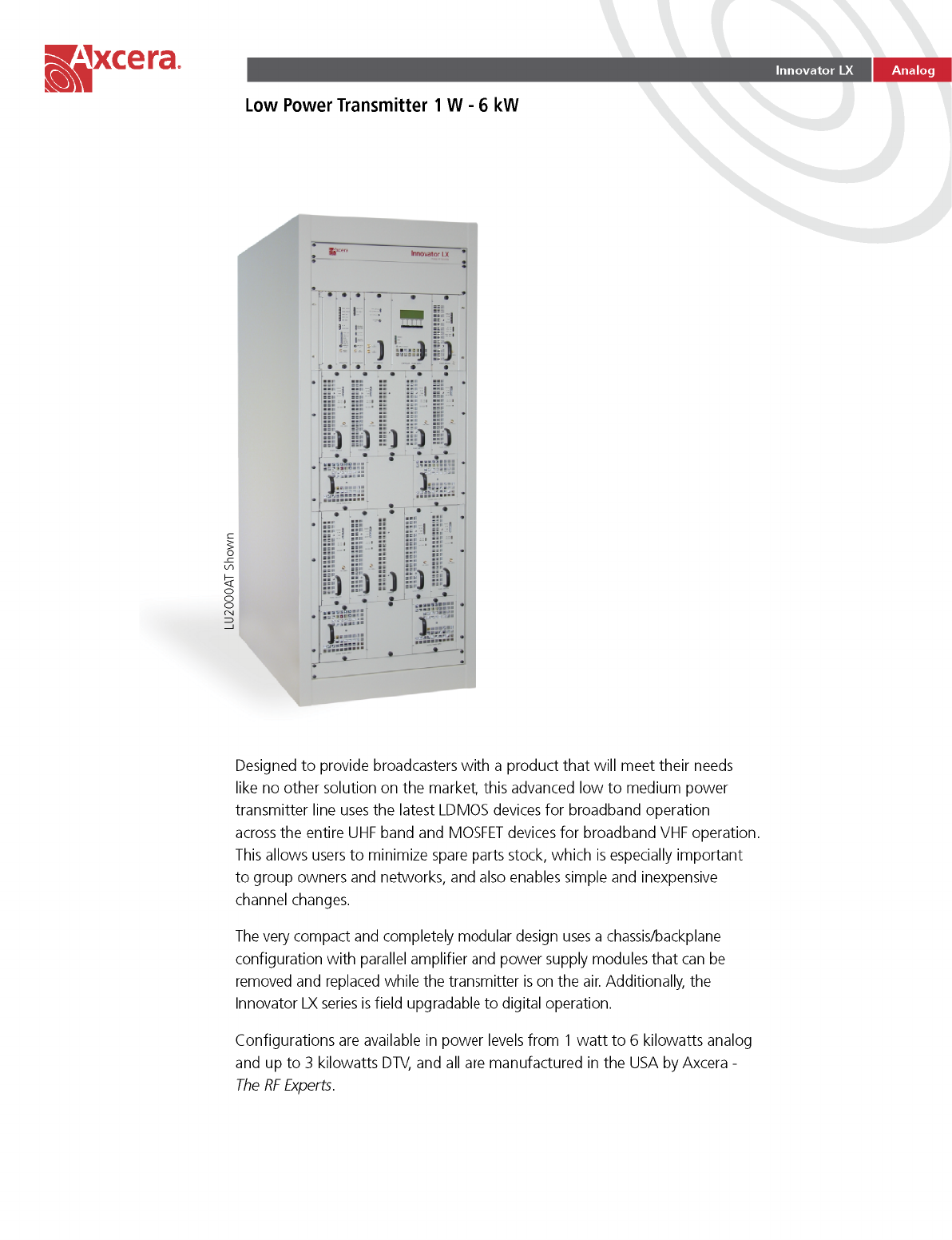
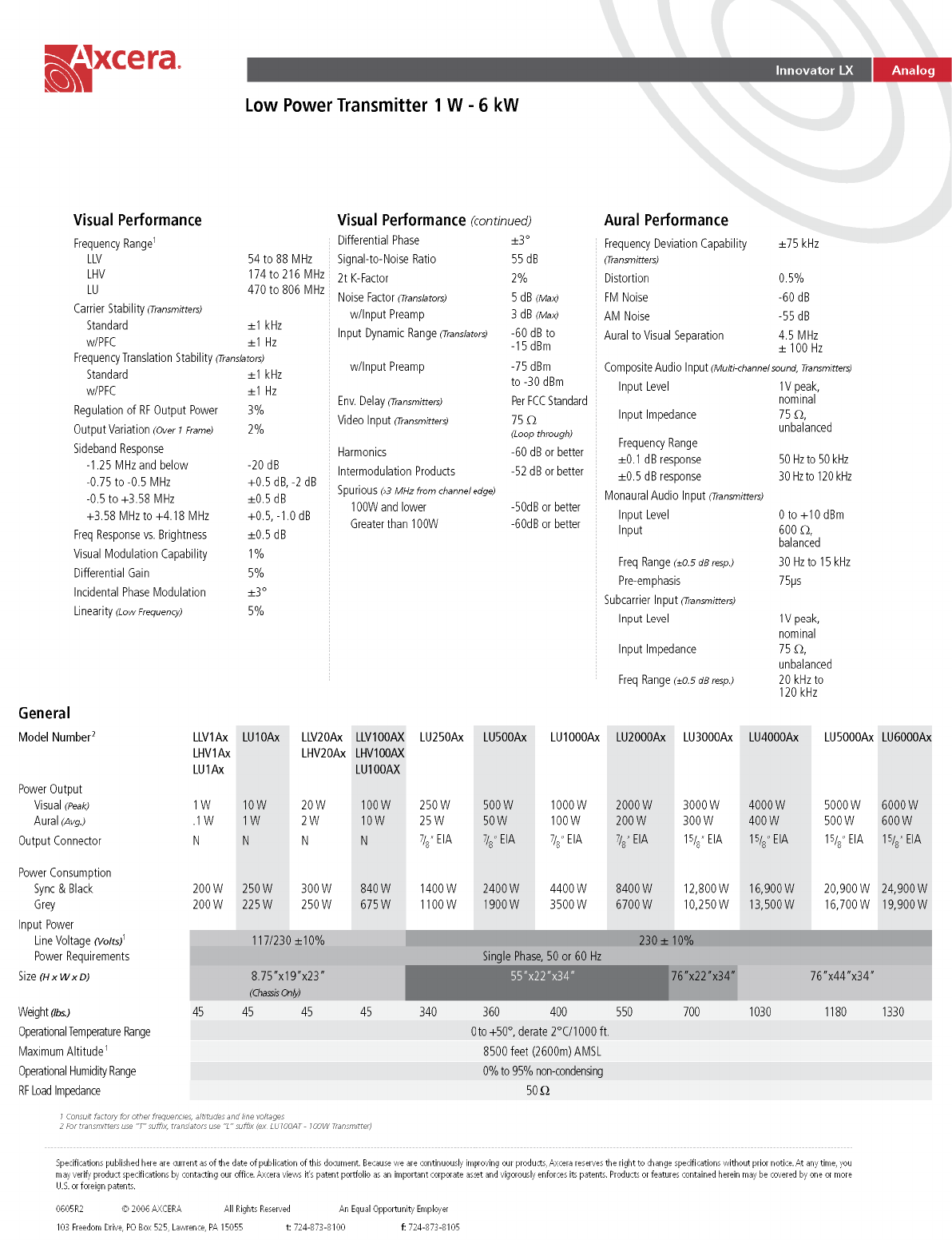