VEGA Grieshaber KG PS60XW2 VEGAPULS 64 Level Probing Radar User Manual R 02
VEGA Grieshaber KG VEGAPULS 64 Level Probing Radar Users Manual R 02
Users Manual R.02

Operating Instructions
Radar sensor for continuous level
measurement of liquids
VEGAPULS 64
4 … 20 mA/HART - two-wire
Document ID: 51141
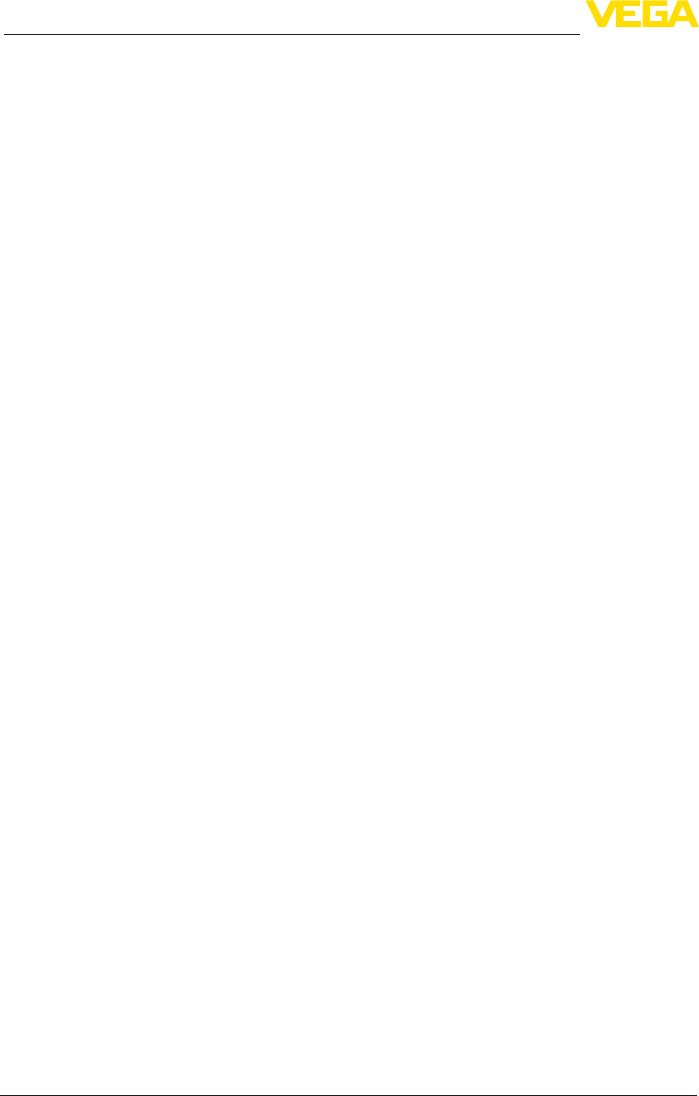
2
Contents
VEGAPULS 64 • 4 … 20 mA/HART - two-wire
51141-EN-160616
Contents
1 About this document
1.1 Function ........................................................................................................................... 4
1.2 Target group ..................................................................................................................... 4
1.3 Symbols used................................................................................................................... 4
2 For your safety
2.1 Authorised personnel ....................................................................................................... 5
2.2 Appropriate use ................................................................................................................ 5
2.3 Warning about incorrect use ............................................................................................. 5
2.4 General safety instructions ............................................................................................... 5
2.5 CE conformity ................................................................................................................... 6
2.6 NAMUR recommendations .............................................................................................. 6
2.7 Radio license for Europe .................................................................................................. 6
2.8 Radio license for USA ...................................................................................................... 7
2.9 Radio license for Canada ................................................................................................. 7
2.10 Environmental instructions ............................................................................................... 9
3 Product description
3.1 Conguration .................................................................................................................. 10
3.2 Principle of operation...................................................................................................... 11
3.3 Packaging, transport and storage ................................................................................... 12
3.4 Accessories and replacement parts ............................................................................... 12
4 Mounting
4.1 General instructions ....................................................................................................... 15
4.2 Mounting versions, plastic horn antenna ........................................................................ 15
4.3 Mounting preparations, mounting strap .......................................................................... 18
4.4 Mounting instructions ..................................................................................................... 19
4.5 Measurement setup - Flow ............................................................................................. 24
5 Connecting to power supply
5.1 Preparing the connection ............................................................................................... 26
5.2 Connecting ..................................................................................................................... 27
5.3 Wiring plan, single chamber housing.............................................................................. 29
5.4 Wiring plan, double chamber housing ............................................................................ 29
5.5 Double chamber housing Ex d ....................................................................................... 30
5.6 Double chamber housing with DISADAPT ..................................................................... 31
5.7 Wiring plan - version IP 66/IP 68, 1 bar ........................................................................... 32
5.8 Switch-on phase............................................................................................................. 32
6 Set up with the display and adjustment module
6.1 Insert display and adjustment module ............................................................................ 33
6.2 Adjustment system ......................................................................................................... 34
6.3 Measured value indication - Selection national language ............................................... 35
6.4 Parameter adjustment - Quick setup .............................................................................. 36
6.5 Parameter adjustment - Extended adjustment................................................................ 36
6.6 Saving the parameter adjustment data ........................................................................... 52
7 Setup with PACTware
7.1 Connect the PC .............................................................................................................. 54
7.2 Parameter adjustment .................................................................................................... 55
7.3 Saving the parameter adjustment data ........................................................................... 56

3
Contents
VEGAPULS 64 • 4 … 20 mA/HART - two-wire
51141-EN-160616
8 Set up with other systems
8.1 DD adjustment programs ............................................................................................... 57
8.2 Field Communicator 375, 475 ........................................................................................ 57
9 Diagnosis, asset management and service
9.1 Maintenance .................................................................................................................. 58
9.2 Measured value and event memory ............................................................................... 58
9.3 Asset Management function ........................................................................................... 59
9.4 Rectify faults ................................................................................................................... 63
9.5 Exchanging the electronics module ................................................................................ 66
9.6 Software update ............................................................................................................. 67
9.7 How to proceed if a repair is necessary .......................................................................... 67
10 Dismount
10.1 Dismounting steps.......................................................................................................... 68
10.2 Disposal ......................................................................................................................... 68
11 Supplement
11.1 Technical data ................................................................................................................ 69
11.2 Dimensions .................................................................................................................... 81
11.3 Industrial property rights ................................................................................................. 91
11.4 Trademark ...................................................................................................................... 91
Safety instructions for Ex areas
TakenoteoftheExspecicsafetyinstructionsforExapplications.
These instructions are attached as documents to each instrument
with Ex approval and are part of the operating instructions manual.
Editing status: 2016-03-23

4
1 About this document
VEGAPULS 64 • 4 … 20 mA/HART - two-wire
51141-EN-160616
1 About this document
1.1 Function
This operating instructions manual provides all the information you
need for mounting, connection and setup as well as important instruc-
tionsformaintenanceandfaultrectication.Pleasereadthisinforma-
tion before putting the instrument into operation and keep this manual
accessible in the immediate vicinity of the device.
1.2 Target group
This operating instructions manual is directed to trained specialist
personnel. The contents of this manual should be made available to
these personnel and put into practice by them.
1.3 Symbols used
Information, tip, note
This symbol indicates helpful additional information.
Caution: If this warning is ignored, faults or malfunctions can result.
Warning: If this warning is ignored, injury to persons and/or serious
damage to the instrument can result.
Danger: If this warning is ignored, serious injury to persons and/or
destruction of the instrument can result.
Ex applications
This symbol indicates special instructions for Ex applications.
•List
The dot set in front indicates a list with no implied sequence.
→Action
This arrow indicates a single action.
1 Sequence of actions
Numbers set in front indicate successive steps in a procedure.
Battery disposal
This symbol indicates special information about the disposal of bat-
teries and accumulators.

5
2 For your safety
VEGAPULS 64 • 4 … 20 mA/HART - two-wire
51141-EN-160616
2 For your safety
2.1 Authorised personnel
All operations described in this operating instructions manual must
be carried out only by trained specialist personnel authorised by the
plant operator.
During work on and with the device the required personal protective
equipment must always be worn.
2.2 Appropriate use
VEGAPULS 64 is a sensor for continuous level measurement.
Youcannddetailedinformationabouttheareaofapplicationin
chapter "Product description".
Operational reliability is ensured only if the instrument is properly
usedaccordingtothespecicationsintheoperatinginstructions
manual as well as possible supplementary instructions.
2.3 Warning about incorrect use
Inappropriate or incorrect use of the instrument can give rise to
application-specichazards,e.g.vesseloverllordamagetosystem
components through incorrect mounting or adjustment. Also the pro-
tectivecharacteristicsoftheinstrumentcanbeinuenced.
2.4 General safety instructions
This is a state-of-the-art instrument complying with all prevailing
regulations and guidelines. The instrument must only be operated in a
technicallyawlessandreliablecondition.Theoperatorisresponsible
for the trouble-free operation of the instrument.
During the entire duration of use, the user is obliged to determine the
compliance of the necessary occupational safety measures with the
current valid rules and regulations and also take note of new regula-
tions.
The safety instructions in this operating instructions manual, the na-
tional installation standards as well as the valid safety regulations and
accident prevention rules must be observed by the user.
For safety and warranty reasons, any invasive work on the device
beyond that described in the operating instructions manual may be
carried out only by personnel authorised by the manufacturer. Arbi-
traryconversionsormodicationsareexplicitlyforbidden.
The safety approval markings and safety tips on the device must also
be observed.
Depending on the instrument version, the emitting frequencies are in
the C, K or W band range. The low emitting frequencies are far below
the internationally approved limit values. When used correctly, the
device poses no danger to health.

6
2 For your safety
VEGAPULS 64 • 4 … 20 mA/HART - two-wire
51141-EN-160616
2.5 CE conformity
ThedevicefullsthelegalrequirementsoftheapplicableECguide-
lines.ByaxingtheCEmarking,weconrmsuccessfultestingofthe
product.
YoucanndtheCECerticateofConformityinthedownloadsection
of our homepage.
2.6 NAMUR recommendations
NAMUR is the automation technology user association in the process
industry in Germany. The published NAMUR recommendations are
acceptedasthestandardineldinstrumentation.
ThedevicefullstherequirementsofthefollowingNAMURrecom-
mendations:
•NE 21 – Electromagnetic compatibility of equipment
•NE 43 – Signal level for malfunction information from measuring
transducers
•NE53–Compatibilityofelddevicesanddisplay/adjustment
components
•NE107–Self-monitoringanddiagnosisofelddevices
For further information see www.namur.de.
2.7 Radio license for Europe
The instrument meets the legal requirements of the EU directive
1999/5/EC(R&TTED)andwastestedacc.totheharmonizedstand-
ards EN 302372-1/2 V1.2.1 (2011-02) (Tank Level Probing Radar)
and EN 302729-1/2 V1.1.2 (2011-05) (Level Probing Radar) and is
approved for use inside and outside of closed vessels.
For operation outside of closed vessels, the following conditions must
befullled:
•Theinstallationmustbecarriedoutbytrainedqualiedpersonnel
•The instrument must be stationary mounted and the antenna
directed vertically downward
•Operation of the instrument outside of closed vessels is only per-
mitted with thread G1½” with integrated horn antenna
•The mounting location must be at least 4 km away from radio
astronomy stations, unless special permission was granted by the
responsible national approval authority
•When installed within 4 to 40 km of a radio astronomy station,
the instrument must not be mounted higher than 15 m above the
ground
Youcanndalistoftherespectiveradioastronomystationsinchap-
ter "Supplement".
For operation inside of closed vessels, the following conditions must
befullled:
•The instrument must be permanently mounted on a closed vessel
made of metal, reinforced concrete, or comparable attenuating
materials

7
2 For your safety
VEGAPULS 64 • 4 … 20 mA/HART - two-wire
51141-EN-160616
•Flanges,processttingsandmountingaccessoriesmustensure
the microwave impermeability of the vessel and not let the radar
signal escape to the outside
•If necessary, existing viewing windows in the vessel must be
coated with a microwave impermeable material (e.g. electrically
conductive coating)
•Manholesandangesonthevesselmustbeclosedandsealedto
avoid penetration of the radar signal
•The instrument should be preferably mounted on top of the vessel
with antenna orientation downward
•The instrument must only be installed and maintained by appropri-
atelyqualiedsta
2.8 Radio license for USA
This approval is only valid for USA. Hence the following text is only
available in the English language.
This device complies with Part 15 of the FCC Rules. Operation is
subject to the following two conditions:
•This device may not cause interference, and
•This device must accept any interference, including interference
that may cause undesired operation of the device
This device is approved for unrestricted use only inside closed, sta-
tionary vessels made of metal, reinforced fiberglass or concrete.
For operation outside of closed vessels, the following conditions must
befullled:
•This device shall be installed and maintained to ensure a verti-
cally downward orientation of the transmit antenna's main beam.
Furthermore, the use of any mechanism that does not allow the
main beam of the transmitter to be mounted vertically downward is
prohibited.
•Operation of the instrument is only permitted with thread G1½"
with integrated horn antenna.
•Thisdeviceshallbeinstalledonlyatxedlocations.TheLPR
device shall not operate while being moved or while inside a mov-
ing container.
•Hand-held applications are prohibited.
•Marketing to residential consumers is prohibited.
Changesormodicationsnotexpresslyapprovedbythemanufac-
turer could void the user’s authority to operate this equipment.
2.9 Radio license for Canada
This approval is only valid for Canada. Hence the following texts are
only available in the English/French language.
This device complies with Industry Canada's license-exempt RSS
standard. Operation is subject to the following conditions:
•This device may not cause interference, and
•This device must accept any interference, including interference
that may cause undesired operation of the device

8
2 For your safety
VEGAPULS 64 • 4 … 20 mA/HART - two-wire
51141-EN-160616
This device has been approved for both closed containers and open-
air environments with the following limitations:
•ClosedContainers:Forinstallationsutilizingatiltduringinstalla-
tion: This device is limited to installation in a completely enclosed
container made of metal, reinforced fiberglass or concrete to
prevent RF emissions, which can otherwise interfere with
aeronautical navigation, the maximum approved tilt angel is 10°.
•Open Air Environment: For operation outside of closed vessels,
thefollowingconditionmustbefulfilled:Thisdeviceshallbe
installed and maintained to ensure a vertically downward orienta-
tion of the transmit antenna's main beam. Furthermore, the use of
any mechanism that does not allow the main beam of the
transmit-ter to be mounted vertically downward is prohibited.
•Operation of the instrument outside of closed vessels is only
permitted with G1½" with integrated horn antenna.
•The installation of the LPR/TLPR device shall be done by trained
installers, in strict compliance with the manufacturer's instructions.
•Thisdeviceshallbeinstalledonlyatfixedlocations.TheLPR
device shall not operate while being moved or while inside a mov-
ing container.
•Hand-held applications are prohibited.
•Marketing to residential consumers is prohibited.
•The use of this device is on a "no-interference, no-protection"
basis. That is, the user shall accept operations of high-powered
radar in the same frequency band which may interfere with or
damage this device.
•However, devices found to interfere with primary licensing opera-
tions will be required to be removed at the user's expense.
•The installer/user of this device shall ensure that it is at least 10
km from the Dominion Astrophysical Radio Observatory (DRAO)
near Penticton, British Columbia. The coordinates of the DRAO
arelatitude49°19′15″Nandlongitude119°37′12″W.Fordevices
not meeting this 10 km separation (e.g., those in the Okanagan
Valley, British Columbia,) the installer/user must coordinate with,
and obtain the written concurrence of, the Director of the DRAO
before the equipment can be installed or operated. The Director of
the DRAO may be contacted at 250-497-2300 (tel.)or
250-497-2355 (fax). (Alternatively, the Manager, Regulatory
Standards, Industry Canada, may be contacted.)
Le présent appareil est conforme aux CNR d’Industrie Canada ap-
plicables aux appareils radio exempts de licence. L’exploitation est
autorisée aux conditions suivantes:
•L’appareil ne doit pas produire de brouillage; et
•L’utilisateur de l’appareil doit accepter tout brouillage radioélect-
rique subi, même si le brouillage est susceptible d’en compromet-
tre le fonctionnement.
Cet appareil est homologué pour une utilisation dans les cuves fer-
mées et les environnements ouverts avec les restrictions suivantes :
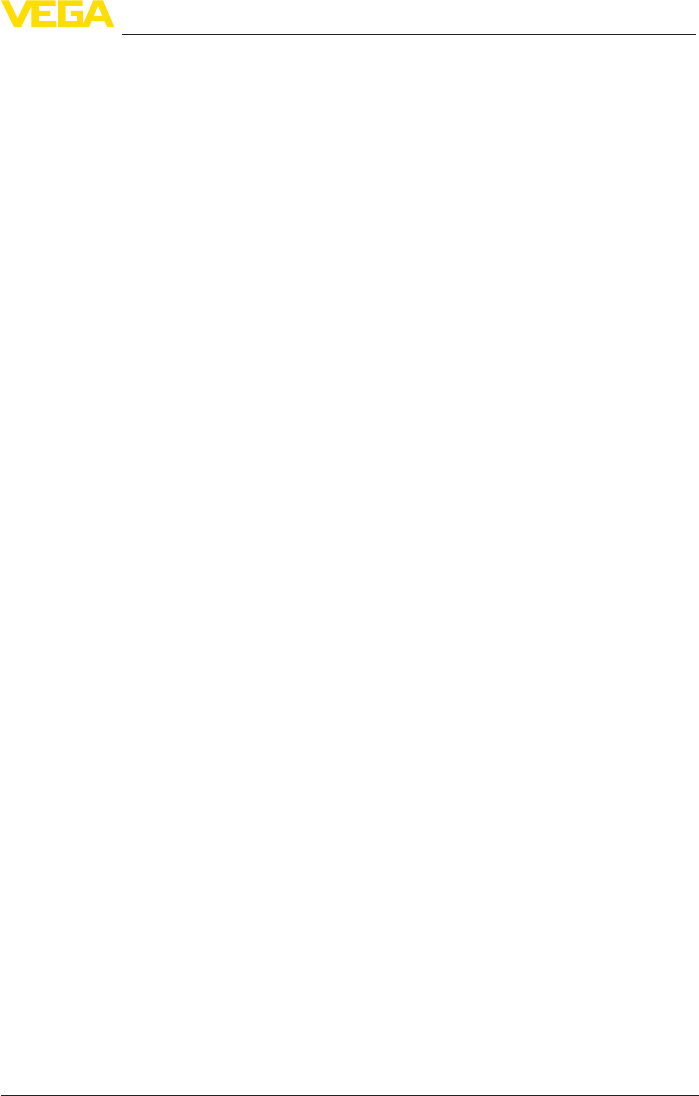
9
2 For your safety
VEGAPULS 64 • 4 … 20 mA/HART - two-wire
51141-EN-160616
• Cuves fermées : Pour les installations impliquant une inclinaison
lors de l'installation : cet appareil ne doit être installé que dans une
cuve totalement fermée en métal ou en béton, pour empêcher les
émissions RF susceptibles d'interférer avec la navigation aéronau-
tique. L'angle d'inclinaison maximum autorisé est de 10°.
• Environnement ouvert : Pour l'utilisation hors des cuves fermées,
la condition suivante doit être remplie : L'appareil doit être installé
et entretenu de manière à garantir une orientation verticale vers
le bas du faisceau principal de l’antenne émettrice. De plus,
l’utilisation de tout mécanisme ne permettant pas l’orientation ver-
ticale vers le bas du faisceau principal de l’émetteur est interdite
• Il est uniquement autorisé d'utiliser la version d'appareil avec le
letageG11/2"enenvironnementsouvertes.
• L’installationd’undispositifLPRouTLPRdoitêtreeectuéepar
desinstallateursqualiés,enpleineconformitéaveclesinstruc-
tions du fabricant.
• Cetappareilnedoitêtreinstalléqu'àdesemplacementsxes.
L’appareil LPR ne doit pas être utilisé pendant qu’il est en train
d’être déplacé ou se trouve dans un conteneur en mouvement.
• Les applications portables sont interdites.
• La vente à des particuliers est interdite
• Ce dispositif ne peut être exploité qu'en régime de non-brouillage
et de non-protection, c'est-à-dire que l'utilisateur doit accepter que
des radars de haute puissance de la même bande de fréquences
puissent brouiller ce dispositif ou même l'endommager. D'autre
part, les capteurs de niveau qui perturbent une exploitation autori-
sée par licence de fonctionnement principal doivent être enlevés
aux frais de leur utilisateur.
• La personne qui installe/utilise ce capteur de niveau doit s'assurer
qu'il se trouve à au moins 10 km de l'Observatoire fédéral de
radioastrophysique (OFR) de Penticton en Colombie-Britannique.
Lescoordonnéesdel'OFRsont:latitudeN49°19′15″,longitude
O119°37′12″.Lapersonnequiinstalle/utiliseundispositifne
pouvant respecter cette distance de 10km (p. ex. dans la vallée
de l'Okanagan [Colombie-Britannique]) doit se concerter avec le
directeurdel'OFRand’obtenirdesapartuneautorisationécrite
avant que l'équipement ne puisse être installé ou mis en marche.
Le directeur de l'OFR peut être contacté au 250-497-2300 (tél.) ou
au 250-497-2355 (fax). (Le Directeur des Normes réglementaires
d'Industrie Canada peut également être contacté).
2.10 Environmental instructions
Protection of the environment is one of our most important duties.
That is why we have introduced an environment management system
with the goal of continuously improving company environmental pro-
tection.Theenvironmentmanagementsystemiscertiedaccording
to DIN EN ISO 14001.
Pleasehelpusfullthisobligationbyobservingtheenvironmental
instructions in this manual:
• Chapter "Packaging, transport and storage"
• Chapter "Disposal"
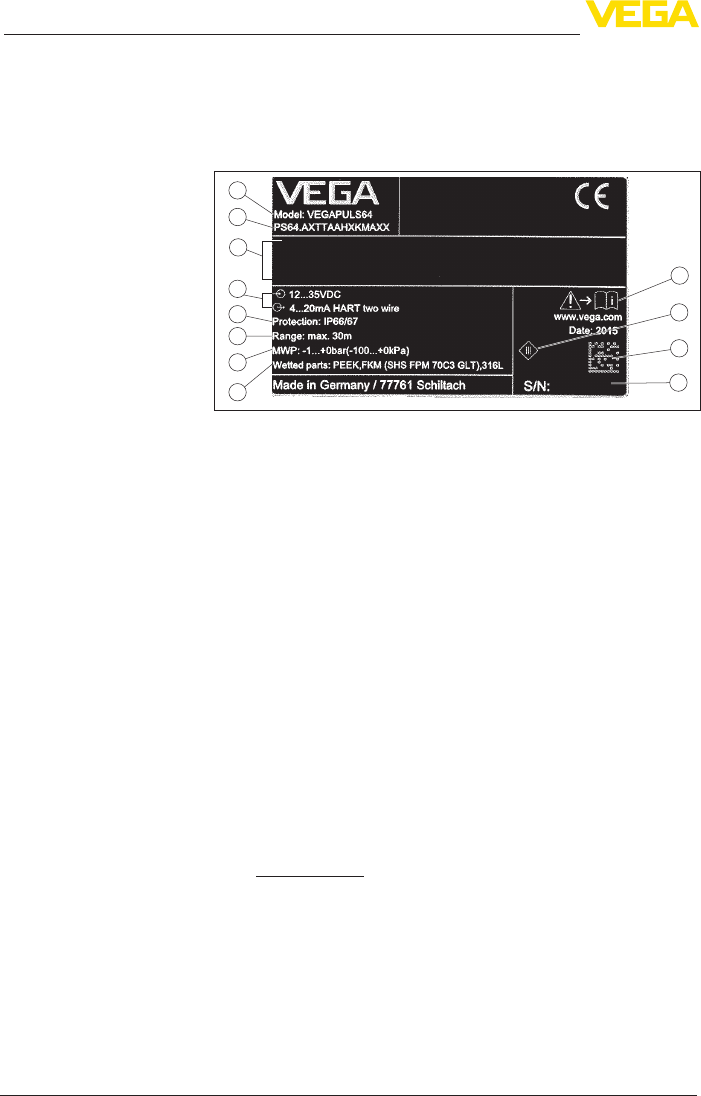
10
3 Product description
VEGAPULS 64 • 4 … 20 mA/HART - two-wire
51141-EN-160616
3 Product description
3.1 Conguration
Thetypelabelcontainsthemostimportantdataforidenticationand
use of the instrument:
2
1
12
11
10
9
5
6
4
3
7
8
Fig. 1: Layout of the type label (example)
1 Instrument type
2 Product code
3 License label
4 Power supply and signal output, electronics
5 Protection rating
6 Measuring range
7 Process and ambient temperature, process pressure
8 Material, wetted parts
9 Serial number of the instrument
10 Data-Matrix-Code for smartphone app
11 Symbol of the device protection class
12 Reminder to observe the instrument documentation
The type label contains the serial number of the instrument. With it
youcanndthefollowinginstrumentdataonourhomepage:
• Product code (HTML)
• Delivery date (HTML)
• Order-specicinstrumentfeatures(HTML)
• Operating instructions and quick setup guide at the time of ship-
ment (PDF)
• Order-specicsensordataforanelectronicsexchange(XML)
• Testcerticate(PDF)-optional
Go to www.vega.com "VEGA Tools" and "Instrument search". Enter
the serial number.
Alternatively, you can access the data via your smartphone:
• Download the smartphone app "VEGA Tools" from the "Apple App
Store" or the "Google Play Store"
• Scan the Data Matrix code on the type label of the instrument or
• Enter the serial number manually in the app
This operating instructions manual applies to the following instrument
versions:
Type label
Serial number - Instru-
ment search
Scope of this operating
instructions manual
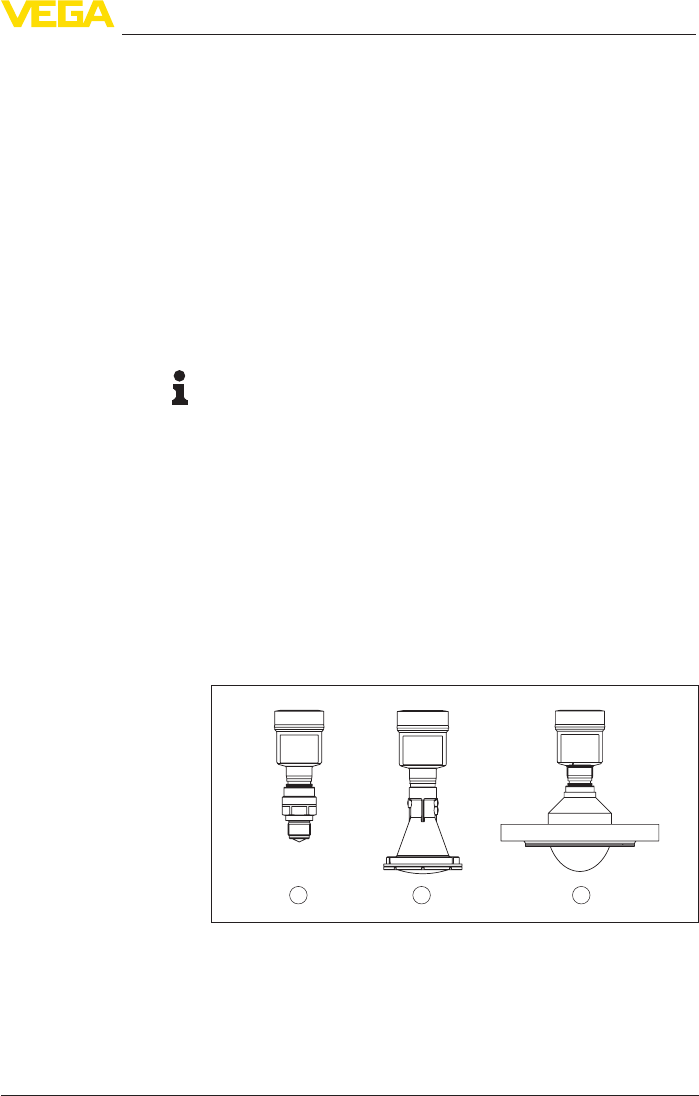
11
3 Product description
VEGAPULS 64 • 4 … 20 mA/HART - two-wire
51141-EN-160616
• Hardware version from 1.0.0
• Software version from 1.1.0
The scope of delivery encompasses:
• Radar sensor
• Optional accessory
• Documentation
– Quick setup guide VEGAPULS 64
– Instructions for optional instrument features
– Ex-specic"Safety instructions" (with Ex versions)
– Ifnecessary,furthercerticates
• DVD "Software", included therein
– PACTware/DTM Collection
– Driver software
Information:
In this operating instructions manual, the optional instrument features
are described. The respective scope of delivery results from the order
specication.
3.2 Principle of operation
VEGAPULS 64 is a radar sensor for continuous level measurement of
liquids.
Specialadvantagesresultfromthesmallprocessttingsforsmall
tanks and the very good focussing in applications in large tanks.
This is made possible by the sensor's functional principle: distance
measurement through frequency shifting with an especially small
beam angle.
Theinstrumentisavailablewithdierentantennasystemsandacces-
sories for virtually all applications and processes.
1 2 3
Fig. 2: Antenna systems VEGAPULS 64
1 Thread with integrated horn antenna
2 Plastic horn antenna
3 Flange with encapsulated antenna system
The instrument emits a continuous radar signal through its antenna.
This signal is frequency modulated in the form of a sawtooth wave.
Scope of delivery
Application area
Functional principle
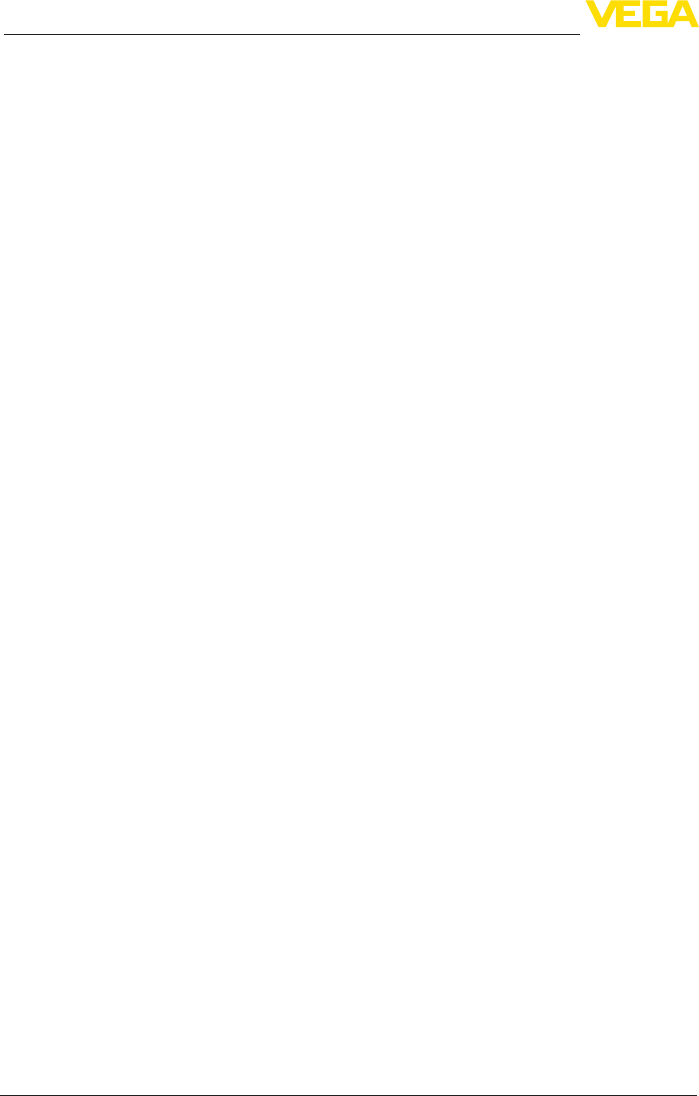
12
3 Product description
VEGAPULS 64 • 4 … 20 mA/HART - two-wire
51141-EN-160616
Theemittedsignalisreectedbythemediumandreceivedbythe
antenna as an echo.
The frequency of the received signal always deviates from the actual
emittingfrequency.Thefrequencydierenceisproportionaltothe
distanceandthustothellingheight.Thisdierenceiscalculated
viaspecialalgorithmsinthesensorelectronics.Thedeterminedll-
ing height is then converted into a corresponding output signal and
outputted as the measured value.
3.3 Packaging, transport and storage
Your instrument was protected by packaging during transport. Its
capacity to handle normal loads during transport is assured by a test
based on ISO 4180.
The packaging of standard instruments consists of environment-
friendly, recyclable cardboard. For special versions, PE foam or PE
foil is also used. Dispose of the packaging material via specialised
recycling companies.
Transport must be carried out in due consideration of the notes on the
transport packaging. Nonobservance of these instructions can cause
damage to the device.
The delivery must be checked for completeness and possible transit
damage immediately at receipt. Ascertained transit damage or con-
cealed defects must be appropriately dealt with.
Up to the time of installation, the packages must be left closed and
stored according to the orientation and storage markings on the
outside.
Unless otherwise indicated, the packages must be stored only under
the following conditions:
• Not in the open
• Dry and dust free
• Not exposed to corrosive media
• Protected against solar radiation
• Avoiding mechanical shock and vibration
• Storage and transport temperature see chapter "Supplement -
Technical data - Ambient conditions"
• Relative humidity 20 … 85 %
3.4 Accessories and replacement parts
The display and adjustment module PLICSCOM is used for measured
value indication, adjustment and diagnosis. It can be inserted into the
sensor and removed at any time.
Youcanndfurtherinformationintheoperatinginstructions"Display
and adjustment module PLICSCOM" (Document-ID 27835).
The interface adapter VEGACONNECT enables the connection of
communication-capable instruments to the USB interface of a PC. For
Packaging
Transport
Transport inspection
Storage
Storage and transport
temperature
PLICSCOM
VEGACONNECT
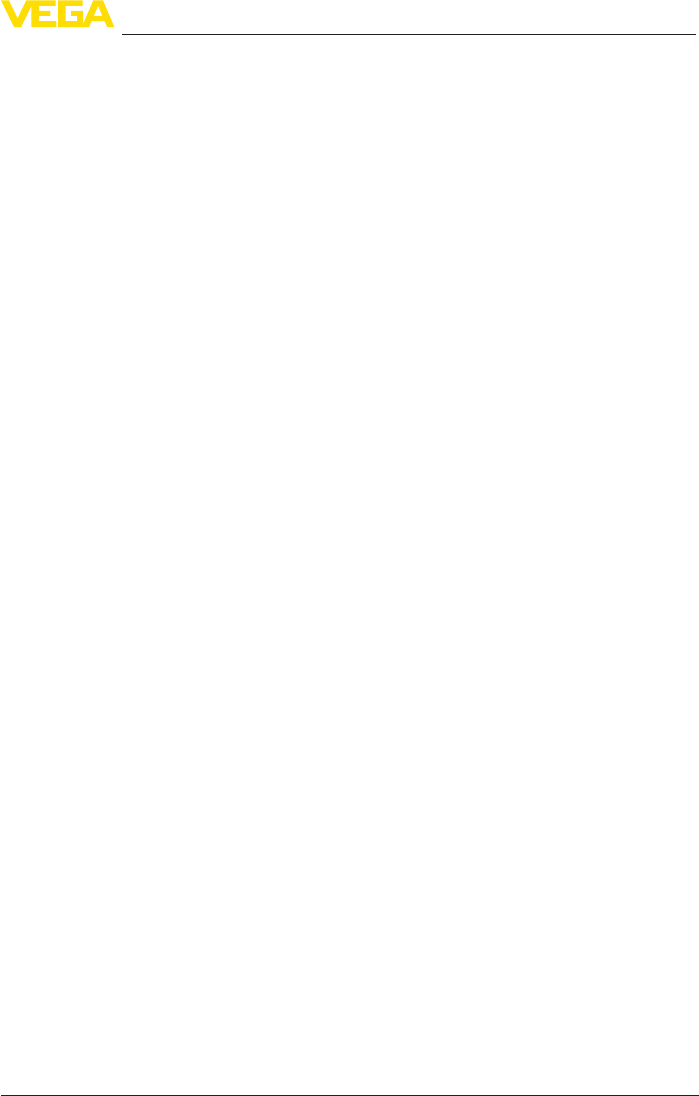
13
3 Product description
VEGAPULS 64 • 4 … 20 mA/HART - two-wire
51141-EN-160616
parameter adjustment of these instruments, the adjustment software
PACTware with VEGA-DTM is required.
Youcanndfurtherinformationintheoperatinginstructions"Interface
adapter VEGACONNECT" (Document-ID 32628).
The VEGADIS 81 is an external display and adjustment unit for VEGA
plics® sensors.
For sensors with double chamber housing the interface adapter
"DISADAPT" is also required for VEGADIS 81.
Youcanndfurtherinformationintheoperatinginstructions"VE-
GADIS 81" (Document-ID 43814).
The adapter "DISADAPT" is an accessory part for sensors with dou-
ble chamber housings. It enables the connection of VEGADIS 81 to
the sensor housing via an M12 x 1 plug.
Youcanndfurtherinformationinthesupplementaryinstructions
"Adapter DISADAPT" (Document-ID 45250).
VEGADIS 82 is suitable for measured value indication and adjustment
of sensors with HART protocol. It is looped into the 4 … 20 mA/HART
signal cable.
Youcanndfurtherinformationintheoperatinginstructions"VE-
GADIS 82" (Document-ID 45300).
PLICSMOBILE T61 is an external GSM/GPRS radio unit for transmis-
sion of measured values and for remote parameter adjustment of
plics® sensors. Adjustment is carried out via PACTware/DTM and the
integrated USB connection.
Youcanndfurtherinformationinthesupplementaryinstructions
"PLICSMOBILE T61" (Document-ID 37700).
The protective cover protects the sensor housing against soiling and
intense heat from solar radiation.
Youwillndadditionalinformationinthesupplementaryinstructions
manual "Protective cover" (Document-ID 34296).
Screwedangesareavailableindierentversionsaccordingtothe
following standards: DIN 2501, EN 1092-1, BS 10, ASME B 16.5,
JIS B 2210-1984, GOST 12821-80.
Youcanndadditionalinformationinthesupplementaryinstructions
manual "Flanges according to DIN-EN-ASME-JIS".
For mounting the instrument with plastic horn antenna to a socket,
twoangeversionsareavailable:thecombicompressionangeand
theadapterange
Youcanndadditionalinformationinchapter"Mounting" of this
operating instruction.
A mounting strap is available for mounting the instrument with plastic
horn antenna to the wall or ceiling.
VEGADIS 81
DISADAPT
VEGADIS 82
PLICSMOBILE T61
Protective cap
Flanges
Flanges with plastic horn
antenna
Mounting strap with plas-
tic horn antenna
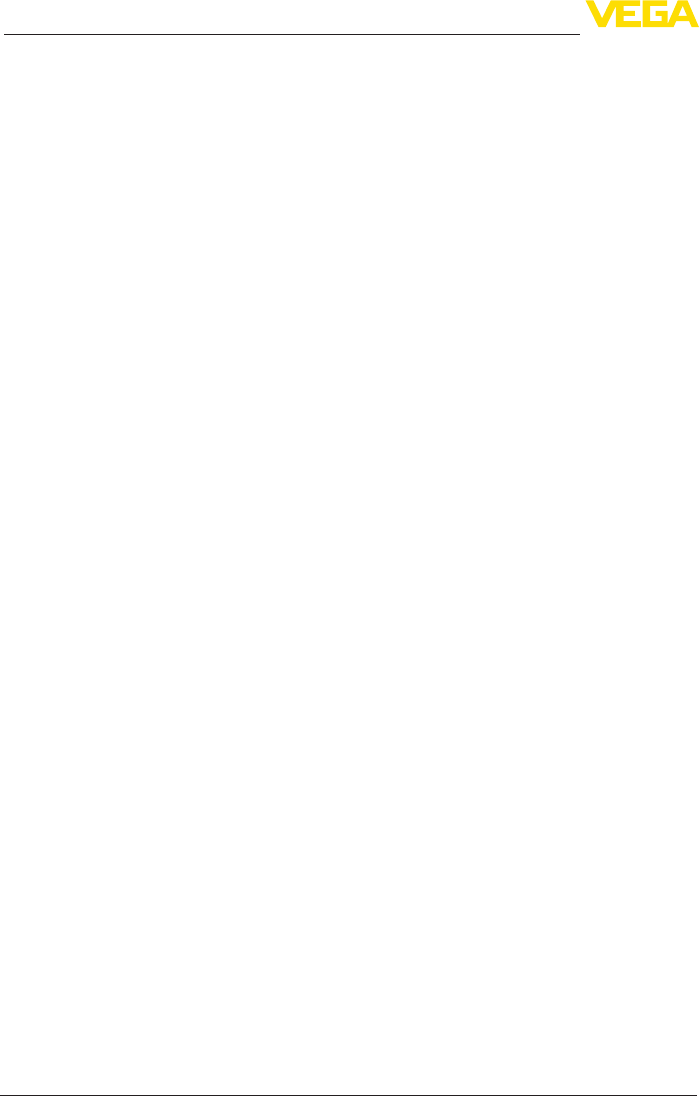
14
3 Product description
VEGAPULS 64 • 4 … 20 mA/HART - two-wire
51141-EN-160616
Youcanndadditionalinformationinchapter"Mounting" of this
operating instruction.
Electronics module "VEGAPULS series 60" is a replacement part for
radarsensorsofVEGAPULSseries60.Adierentversionisavailable
for each type of signal output.
Youcanndfurtherinformationintheoperatinginstructions"Elec-
tronics module VEGAPULS series 60" (Document-ID 36801).
Electronics module

15
4 Mounting
VEGAPULS 64 • 4 … 20 mA/HART - two-wire
51141-EN-160616
4 Mounting
4.1 General instructions
Protect your instrument against moisture ingress through the following
measures:
• Use the recommended cable (see chapter "Connecting to power
supply")
• Tighten the cable gland
• Loop the connection cable downward in front of the cable gland
This applies particularly to:
• Outdoor mounting
• Installations in areas where high humidity is expected (e.g. through
cleaning processes)
• Installations on cooled or heated vessels
Make sure that all parts of the instrument exposed to the process are
suitable for the existing process conditions.
These are mainly:
• Active measuring component
• Processtting
• Process seal
Process conditions are particularly:
• Process pressure
• Process temperature
• Chemical properties of the medium
• Abrasionandmechanicalinuences
Youcannddetailedinformationontheprocessconditionsinchapter
"Technical data" as well as on the type label.
Metric threads
In the case of instrument housings with metric thread, the cable
glands are screwed in at the factory. They are sealed with plastic
plugs as transport protection.
You have to remove these plugs before electrical connection.
NPT thread
In the case of instrument housings with self-sealing NPT threads, it is
not possible to have the cable entries screwed in at the factory. The
free openings for the cable glands are therefore covered with red dust
protection caps as transport protection. The dust protection caps do
notprovidesucientprotectionagainstmoisture.
Prior to setup you have to replace these protective caps with ap-
proved cable glands or close the openings with suitable blind plugs.
4.2 Mounting versions, plastic horn antenna
The optional mounting strap allows simple mounting of the instrument
on a wall, ceiling or boom. Especially in the case of open vessels, this
Protection against mois-
ture
Suitability for the process
conditions
Cable glands
Mounting strap
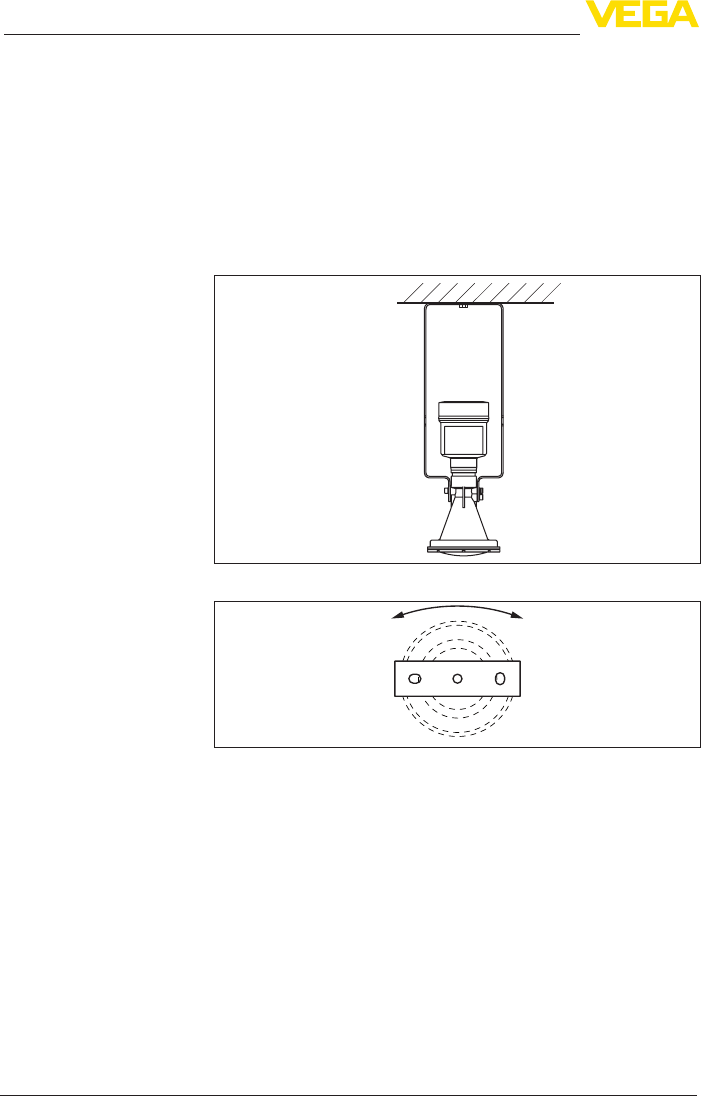
16
4 Mounting
VEGAPULS 64 • 4 … 20 mA/HART - two-wire
51141-EN-160616
isasimpleandeectivewaytoalignthesensortothesurfaceofthe
bulk solid material.
The following versions are available:
• Length 300 mm
• Length 170 mm
The instrument is normally mounted vertically with a bracket on the
ceiling.
This allows swivelling the sensor up to 180° for optimal orientation
and rotating for optimal connection.
Fig. 3: Ceiling mounting via the mounting strap with length 300 mm
Fig. 4: Rotating with ceil mounting
Asanalternativethestrapmountingiscarriedouthorizontallyor
obliquely.
Mounting strap - Ceiling
mounting
Mounting strap - Wall
mounting

17
4 Mounting
VEGAPULS 64 • 4 … 20 mA/HART - two-wire
51141-EN-160616
> 200 mm
(7.87")
Fig. 5: Wall mounting horizontally via the mounting strap with length 170 mm
Fig. 6: Wall mounting with inclined wall via the mounting strap with length
300 mm
Two versions are available for mounting the instrument on a socket:
• CombicompressionangettingtoDN80(ASME3"andJIS80)
• AdapterangefromDN100(ASME4"orJIS100)
Thecombicompressionangeissuitablefordierentangestand-
ards and can be used for simple applications. It comes unassembled
and not sealed against the radar sensor and can thus only be used
unpressurized.Itcanberetrottedoninstrumentswithsinglecham-
berhousing,retrottingtoadoublechamberhousingisnotpossible.
Flange
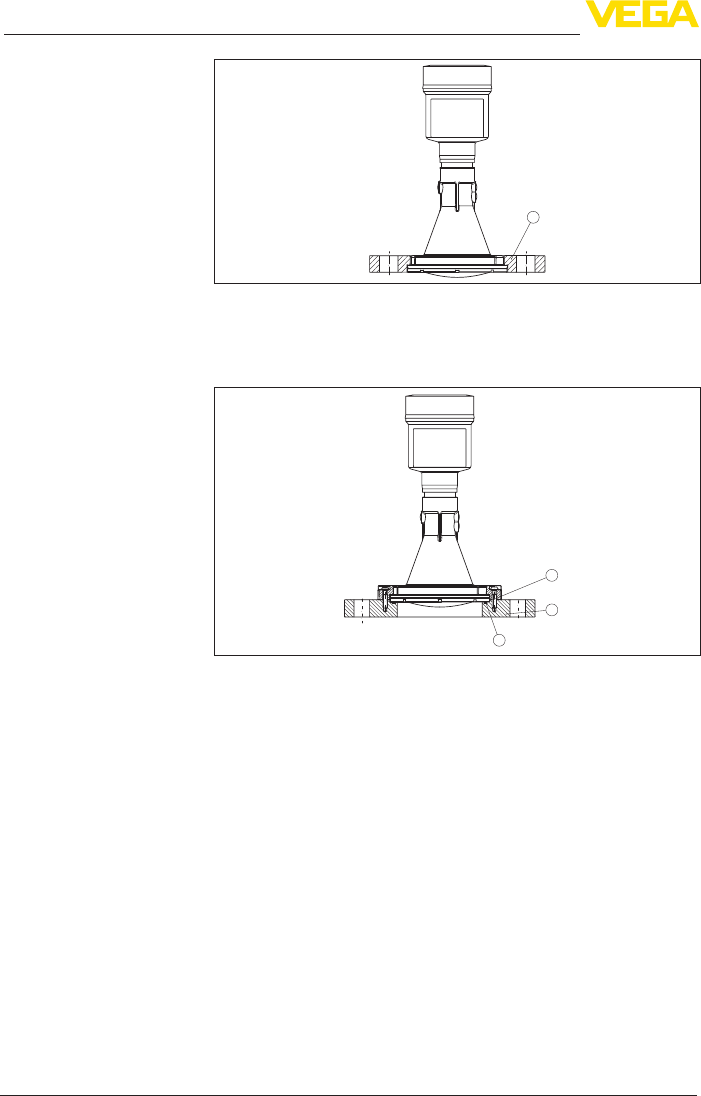
18
4 Mounting
VEGAPULS 64 • 4 … 20 mA/HART - two-wire
51141-EN-160616
1
Fig. 7: Combi compression ange
1 Combi compression ange
Theadapterangeisavailableindierentangesizes.Itisperma-
nently connected with the radar sensor and sealed.
3
1
2
Fig. 8: Adapter ange
1 Connection screw
2 Adapter ange
3 Process seal
Youcannddrawingsofthesemountingoptionsinchapter"Dimen-
sions".
4.3 Mounting preparations, mounting strap
The mounting strap is supplied unassembled (optionally) and must be
screwed to the sensor before setup with three hexagon socket screws
M5 x 10 and spring washers. Max. torque, see chapter "Technical
data".Requiredtools:Allenwrenchsize4.
Therearetwodierentvariantsofscrewingthestraptothesensor,
see following illustration:

19
4 Mounting
VEGAPULS 64 • 4 … 20 mA/HART - two-wire
51141-EN-160616
1 2
Fig. 9: Mounting strap for screwing to the sensor
1 For angle of inclination in steps
2 For angle of inclination, innitely variable
Depending on the selected variant, the sensor can be rotated in the
strap:
• Single chamber housing
– Angle of inclination in three steps 0°, 90° and 180°
– Angleofinclination180°,innitelyvariable
• Double chamber housing
– Angleofinclination90°,innitelyvariable
– Angle of inclination in two steps 0° and 90°
4.4 Mounting instructions
Radar sensors for level measurement emit electromagnetic waves.
Thepolarizationisthedirectionoftheelectricalcomponentofthese
waves.
Thepolarizationdirectionismarkedbyanoseonthehousing,see
following drawing:
1
Fig. 10: Position of the polarisation
1 Nose for marking the direction of polarisation
Information:
Whenthehousingisrotated,thedirectionofpolarizationchanges
andhencetheinuenceofthefalseechoonthemeasuredvalue.
Please keep this in mind when mounting or making changes later.
When mounting the sensor, keep a distance of at least 200 mm
(7.874 in) from the vessel wall. If the sensor is installed in the center
of dished or round vessel tops, multiple echoes can arise. However,
Polarisation
Installation position
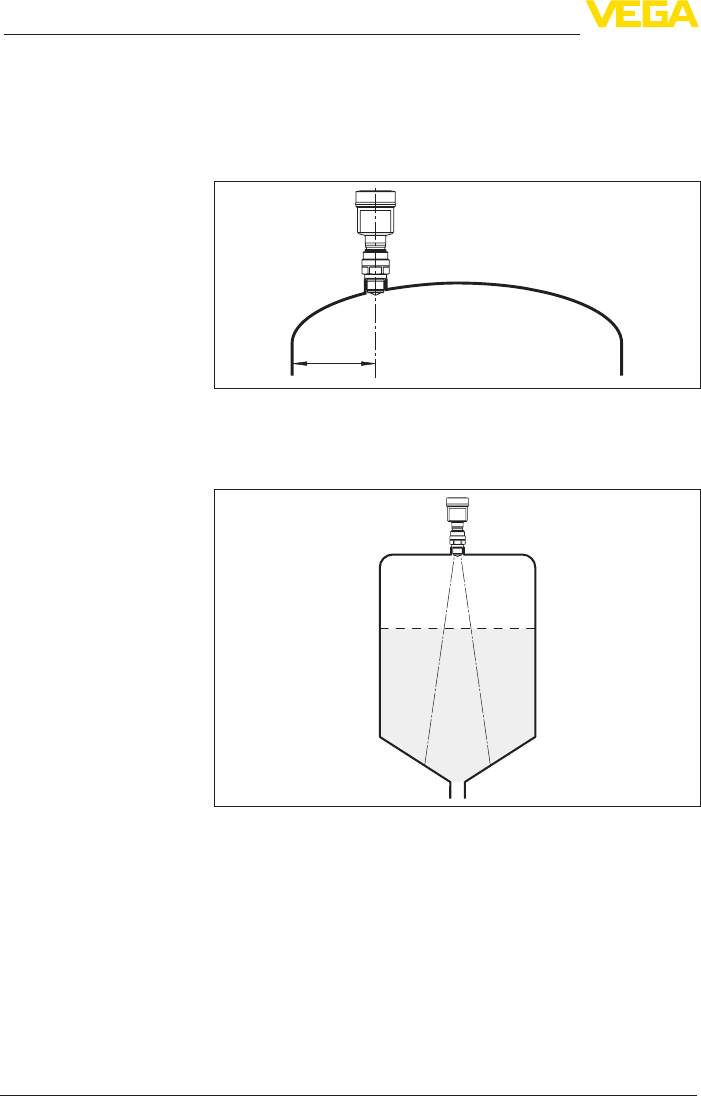
20
4 Mounting
VEGAPULS 64 • 4 … 20 mA/HART - two-wire
51141-EN-160616
these can be suppressed by an appropriate adjustment (see chapter
"Setup").
If you cannot maintain this distance, you should carry out a false
signal storage during setup. This applies particularly if buildup on the
vessel wall is expected. In such cases, we recommend repeating the
false signal storage at a later date with existing buildup.
> 200 mm
(7.87
")
Fig. 11: Mounting of the radar sensor on round vessel tops
In vessels with conical bottom it can be advantageous to mount the
sensor in the center of the vessel, as measurement is then possible
down to the lowest point of the vessel bottom.
Fig. 12: Mounting of the radar sensor on vessels with conical bottom
Donotmounttheinstrumentsinorabovethellingstream.Makesure
thatyoudetecttheproductsurface,nottheinowingproduct.
Inowingmedium
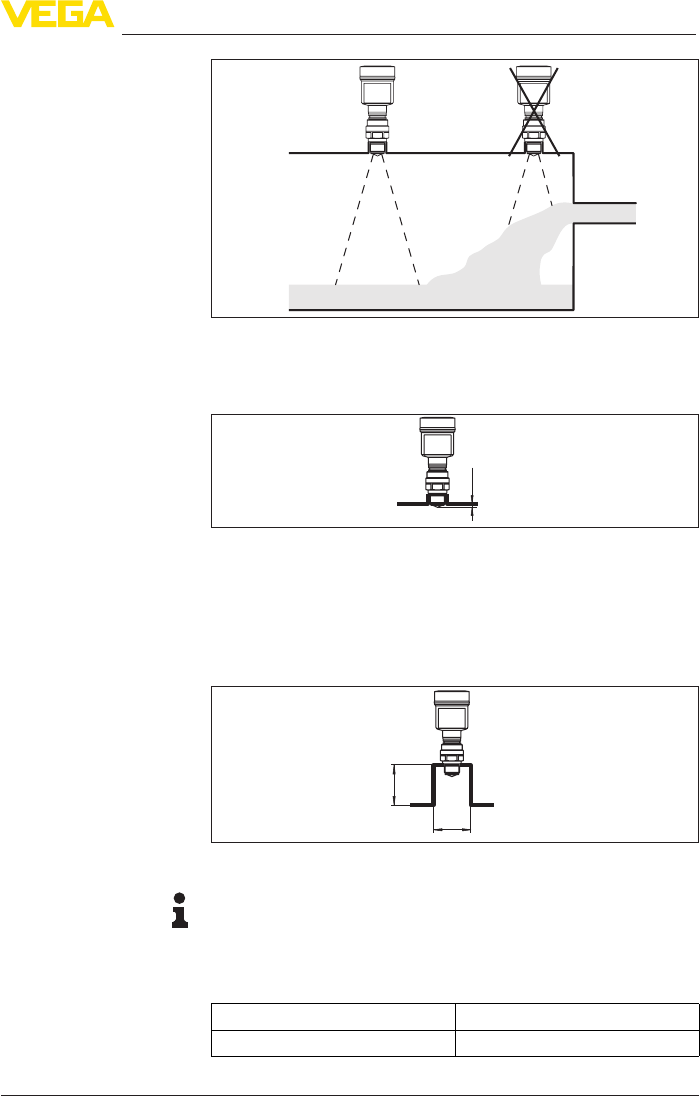
21
4 Mounting
VEGAPULS 64 • 4 … 20 mA/HART - two-wire
51141-EN-160616
Fig. 13: Mounting of the radar sensor with inowing medium
The socket piece should be dimensioned in such a way that the an-
tenna end protrudes at least 5 mm (0.2 in) out of the socket.
ca. 5 mm
Fig. 14: Recommended socket mounting
Ifthereectivepropertiesofthemediumaregood,youcanmount
VEGAPULS 64 on sockets which are higher than the length of the
antenna.Youwillndrecommendedvaluesforsocketheightsinthe
following illustration. The socket end should be smooth and burr-free,
if possible also rounded. After installation you must carry out a false
signal suppression.
d
h
Fig. 15: Deviating socket dimensions
Information:
When mounting on longer sockets, we recommend carrying out a
false signal suppression (see chapter "Parameter adjustment").
The below charts specify the max. socket length h depending on the
diameter d.
Socket diameter d Socket length h
40 mm ≤200mm
Socket with threaded
tting
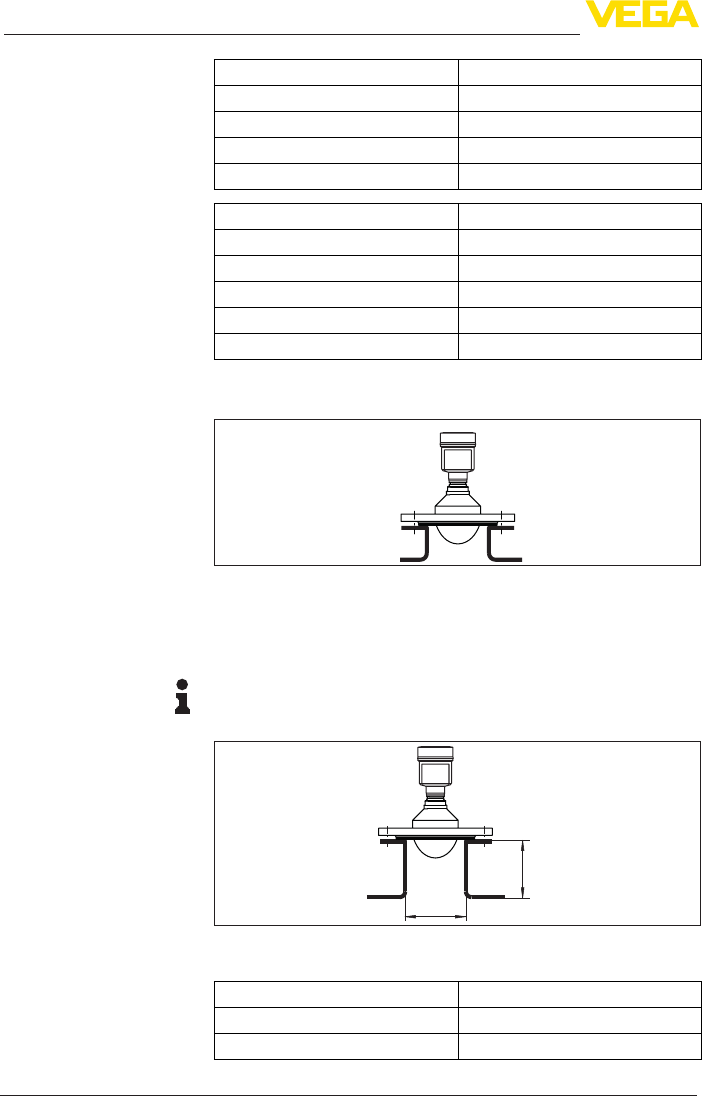
22
4 Mounting
VEGAPULS 64 • 4 … 20 mA/HART - two-wire
51141-EN-160616
Socket diameter d Socket length h
50 mm ≤250mm
80 mm ≤300mm
100 mm ≤400mm
150 mm ≤500mm
Socket diameter d Socket length h
1½" ≤7.9in
2" ≤9.9in
3" ≤11.8in
4" ≤15.8in
6" ≤19.7in
The mounting socket should be as short as possible and its end
rounded. This reduces false echoes from the vessel mounting socket.
Fig. 16: Recommended socket mounting
Ifthemediumhasgoodreectiveproperties,youcanalsomountthe
VEGAPULS 64 on longer sockets. Approximate socket heights are
shown in the following illustration.
Information:
When mounting on longer sockets, we recommend carrying out a
false signal suppression (see chapter "Parameter adjustment").
d
h
The below charts specify the max. pipe socket length h depending on
the diameter d.
Socket diameter d Socket length h
80 mm ≤200mm
100 mm ≤300mm
Socketwithangecon-
nection

23
4 Mounting
VEGAPULS 64 • 4 … 20 mA/HART - two-wire
51141-EN-160616
Socket diameter d Socket length h
150 mm ≤500mm
Socket diameter d Socket length h
3" ≤11.8in
4" ≤15.8in
6" ≤19.7in
In liquids, direct the sensor as perpendicular as possible to the prod-
uct surface to achieve optimum measurement results.
Fig. 18: Alignment in liquids
The mounting location of the radar sensor should be a place where no
otherequipmentorxturescrossthepathoftheradarsignals.
Vessel installations, such as e.g. ladders, limit switches, heating spi-
rals, struts, etc., can cause false echoes and impair the useful echo.
Make sure when planning your measuring point that the radar sensor
has a "clear view" to the measured product.
In case of existing vessel installations, a false echo storage should be
carried out during setup.
If large vessel installations such as struts or supports cause false
echoes, these can be attenuated through supplementary measures.
Small,inclinedsheetmetalbaesabovetheinstallationsscatterthe
radarsignalsandpreventdirectinterferingreections.
Fig. 19: Cover at, large-area proles with deectors
If there are agitators in the vessel, a false signal suppression should
be carried out with the agitators in motion. This ensures that the
interferingreectionsfromtheagitatorsaresavedwiththebladesin
dierentpositions.
Sensor orientation
Vessel installations
Agitators
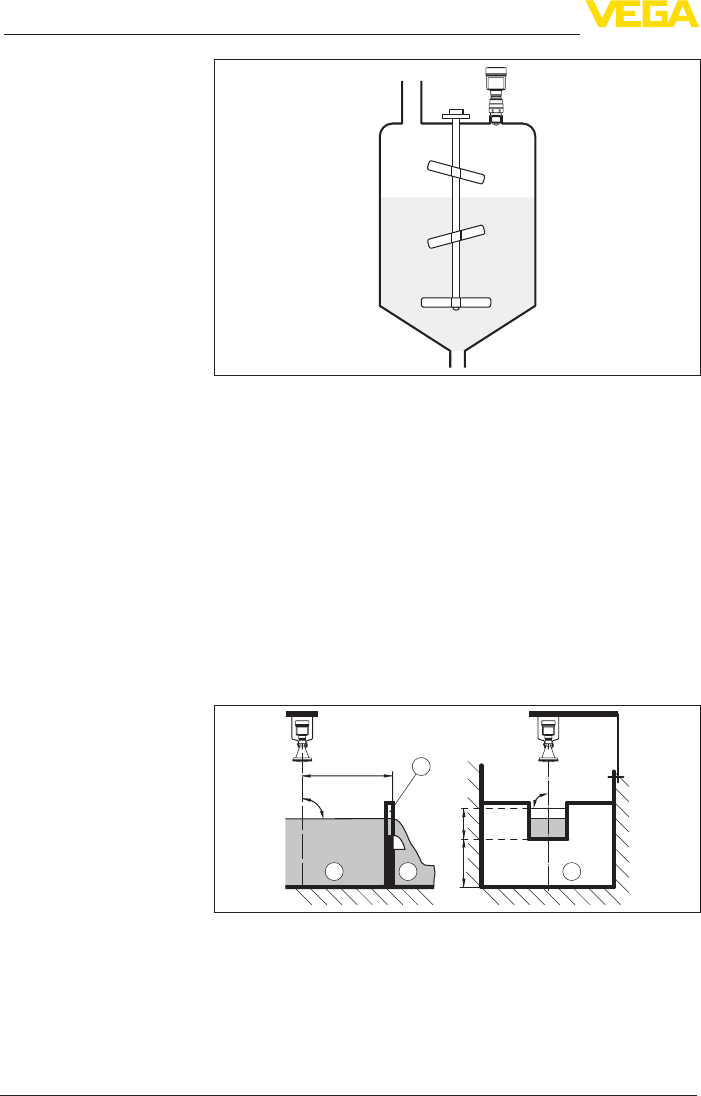
24
4 Mounting
VEGAPULS 64 • 4 … 20 mA/HART - two-wire
51141-EN-160616
Fig. 20: Agitators
Throughtheactionoflling,stirringandotherprocessesinthevessel,
compact foam can form on the product surface, damping the emitted
signals considerably.
If foam is causing measurement errors, the largest possible radar
antenna should be used.
As an alternative, sensors with guided microwave can be used. These
areunaectedbyfoamgenerationandarebestsuitedforsuchap-
plications.
4.5 Measurement setup - Flow
Theshortexamplesgiveyouintroductoryinformationonow
measurement.Detailedplanninginformationisavailablefromume
manufacturers and in special literature.
hmax
≥ 2 x hmax
90°
4
3 ... 4 hmax
90°
2 3
1
Fig. 21: Flow measurement with rectangular overfall: dmin. = min. distance of
the sensor (see chapter "Technical data"); hmax. = max. lling of the rectangular
spillway
1 Overow orice (side view)
2 Headwater
3 Tailwater
4 Overfall orice (view from tailwater)
In general, the following points must be observed:
Foam generation
Flow measurement with
rectangular overfall

25
4 Mounting
VEGAPULS 64 • 4 … 20 mA/HART - two-wire
51141-EN-160616
• Install the sensor on the headwater side
• Installationinthecentreoftheumeandverticaltotheliquid
surface
• Distancetotheoverfallorice
• Distanceoforiceopeningaboveground
• Min.distanceoftheoriceopeningtotailwater
• Min. distance of the sensor to max. storage level
2
3 ... 4 x hmax
90°
hmax
1
B
Fig. 22: Flow measurement with Khafagi-Venturi ume: hmax. = max. lling of the
ume; B = tightest constriction in the ume
1 Position sensor
2 Venturi ume
In general, the following points must be observed:
• Installation of the sensor at the inlet side
• Installationinthecentreoftheumeandverticaltotheliquid
surface
• DistancetotheVenturiume
• Min. distance of the sensor to max. storage level
Flow measurement with
KhafagiVenturiume
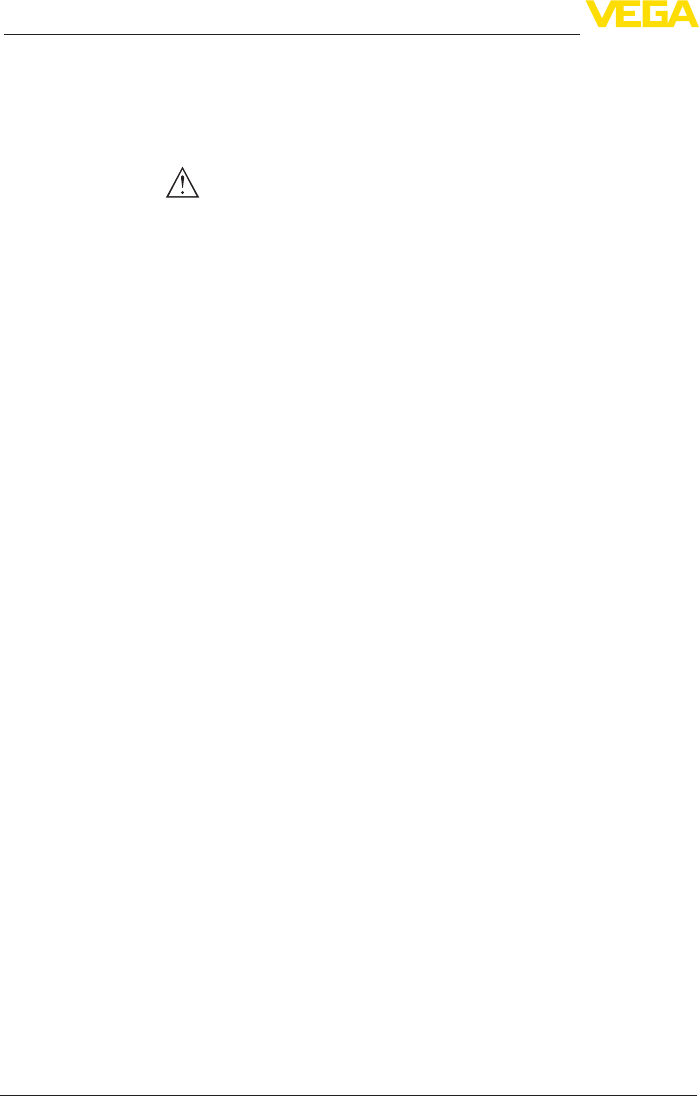
26
5 Connecting to power supply
VEGAPULS 64 • 4 … 20 mA/HART - two-wire
51141-EN-160616
5 Connecting to power supply
5.1 Preparing the connection
Always keep in mind the following safety instructions:
Warning:
Connect only in the complete absence of line voltage.
• The electrical connection must only be carried out by trained
personnel authorised by the plant operator.
• If overvoltage surges are expected, overvoltage arresters should
be installed.
Power supply and current signal are carried on the same two-wire
cable.Theoperatingvoltagecandierdependingontheinstrument
version.
Thedataforpowersupplyarespeciedinchapter"Technical data".
Provide a reliable separation between the supply circuit and the
mains circuits according to DIN EN 61140 VDE 0140-1.
Keepinmindthefollowingadditionalfactorsthatinuencetheoperat-
ing voltage:
• Lower output voltage of the power supply unit under nominal load
(e.g. with a sensor current of 20.5 mA or 22 mA in case of fault)
• Inuenceofadditionalinstrumentsinthecircuit(seeloadvaluesin
chapter "Technical data")
The instrument is connected with standard two-wire cable without
screen. If electromagnetic interference is expected which is above the
test values of EN 61326-1 for industrial areas, screened cable should
be used.
Screened cable generally necessary in HART multidrop mode.
Use cable with round cross section for instruments with housing and
cablegland.Toensurethesealeectofthecablegland(IPprotection
rating),ndoutwhichcableouterdiameterthecableglandissuitable
for.
Useacableglandttingthecablediameter.
Metric threads
In the case of instrument housings with metric thread, the cable
glands are screwed in at the factory. They are sealed with plastic
plugs as transport protection.
You have to remove these plugs before electrical connection.
NPT thread
In the case of instrument housings with self-sealing NPT threads, it is
not possible to have the cable entries screwed in at the factory. The
free openings for the cable glands are therefore covered with red dust
protection caps as transport protection.
Prior to setup you have to replace these protective caps with ap-
proved cable glands or close the openings with suitable blind plugs.
Safety instructions
Voltage supply
Connection cable
Cable glands

27
5 Connecting to power supply
VEGAPULS 64 • 4 … 20 mA/HART - two-wire
51141-EN-160616
With plastic housing, the NPT cable gland or the Conduit steel tube
must be screwed without grease into the threaded insert.
Max. torque for all housings, see chapter "Technical data".
If screened cable is required, the cable screen must be connected on
both ends to ground potential. In the sensor, the screen is connected
directly to the internal ground terminal. The ground terminal on the
outside of the housing must be connected to the ground potential (low
impedance).
In Ex systems, the grounding is carried out according to the installa-
tion regulations.
In electroplating and CCP systems (cathodic corrosion protection) it
mustbetakenintoaccountthatsignicantpotentialdierencesexist.
This can lead to unacceptably high currents in the cable screen if it is
grounded at both ends.
Information:
Themetallicpartsoftheinstrument(processtting,sensor,concen-
tric tube, etc.) are connected with the internal and external ground
terminal on the housing. This connection exists either directly via
the conductive metallic parts or, in case of instruments with external
electronics, via the screen of the special connection cable.
Youcanndspecicationsonthepotentialconnectionsinsidethe
instrument in chapter "Technical data".
5.2 Connecting
The voltage supply and signal output are connected via the spring-
loaded terminals in the housing.
Connection to the display and adjustment module or to the interface
adapter is carried out via contact pins in the housing.
Information:
The terminal block is pluggable and can be removed from the
electronics. To do this, lift the terminal block with a small screwdriver
and pull it out. When reinserting the terminal block, you should hear it
snap in.
Proceed as follows:
1. Unscrew the housing lid
2. If a display and adjustment module is installed, remove it by turn-
ing it slightly to the left.
3. Loosen compression nut of the cable gland and remove blind
plug
4. Remove approx. 10 cm (4 in) of the cable mantle, strip approx.
1 cm (0.4 in) of insulation from the ends of the individual wires
5. Insert the cable into the sensor through the cable entry
Cable screening and
grounding
Connection technology
Connection procedure
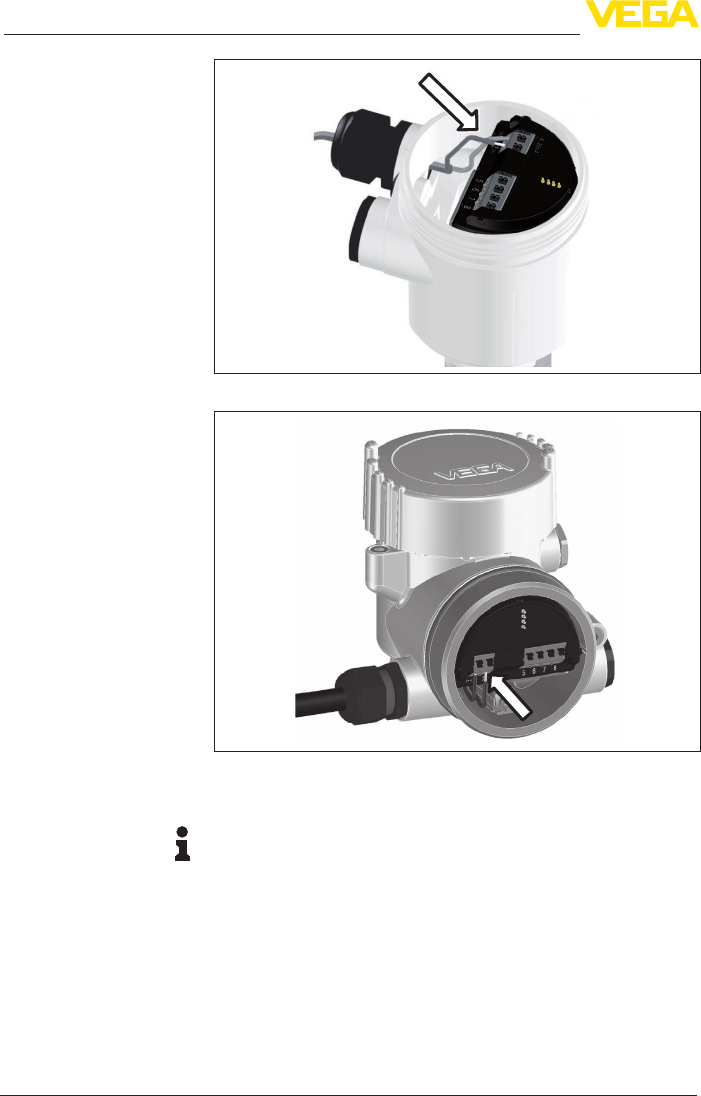
28
5 Connecting to power supply
VEGAPULS 64 • 4 … 20 mA/HART - two-wire
51141-EN-160616
Fig. 23: Connection steps 5 and 6 - Single chamber housing
Fig. 24: Connection steps 5 and 6 - Double chamber housing
6. Insert the wire ends into the terminals according to the wiring plan
Information:
Solidcoresaswellasexiblecoreswithwireendsleevesareinsert-
eddirectlyintotheterminalopenings.Incaseofexiblecoreswithout
end sleeves, press the terminal from above with a small screwdriver,
the terminal opening is then free. When the screwdriver is released,
the terminal closes again.
Youcanndfurtherinformationonthemax.wirecross-sectionunder
"Technical data - Electromechanical data"
7. Check the hold of the wires in the terminals by lightly pulling on
them
8. Connect the screen to the internal ground terminal, connect the
external ground terminal to potential equalisation

29
5 Connecting to power supply
VEGAPULS 64 • 4 … 20 mA/HART - two-wire
51141-EN-160616
9. Tighten the compression nut of the cable entry gland. The seal
ring must completely encircle the cable
10. Reinsert the display and adjustment module, if one was installed
11. Screw the housing lid back on
Theelectricalconnectionisnished.
5.3 Wiring plan, single chamber housing
The following illustration applies to the non-Ex as well as to the Ex-ia
version.
5
12
+
( ) (-)
678
4...20mA
2
3
4
1
Fig. 25: Electronics and terminal compartment, single chamber housing
1 Voltage supply, signal output
2 For display and adjustment module or interface adapter
3 For external display and adjustment unit
4 Ground terminal for connection of the cable screen
5.4 Wiring plan, double chamber housing
The following illustrations apply to the non-Ex as well as to the Ex-ia
version.
5678
4...20mA
12
+
( ) (-)
2
1 1
Fig. 26: Electronics compartment, double chamber housing
1 Internal connection to the terminal compartment
2 For display and adjustment module or interface adapter
Electronics and terminal
compartment
Electronics compartment

30
5 Connecting to power supply
VEGAPULS 64 • 4 … 20 mA/HART - two-wire
51141-EN-160616
5
12
+
( ) (-)
678
4...20mADisplay
2
3
4
1
Fig. 27: Terminal compartment, double chamber housing
1 Voltage supply, signal output
2 For display and adjustment module or interface adapter
3 For external display and adjustment unit
4 Ground terminal for connection of the cable screen
Information:
Parallel use of an external display and adjustment unit and a display
and adjustment module in the terminal compartment is not supported.
5.5 Double chamber housing Ex d
5678
4...20mA
2
12
+
( ) (-)
11
Fig. 28: Electronics compartment, double chamber housing Ex d
1 Internal connection to the terminal compartment
2 For display and adjustment module or interface adapter
Terminal compartment
Electronics compartment
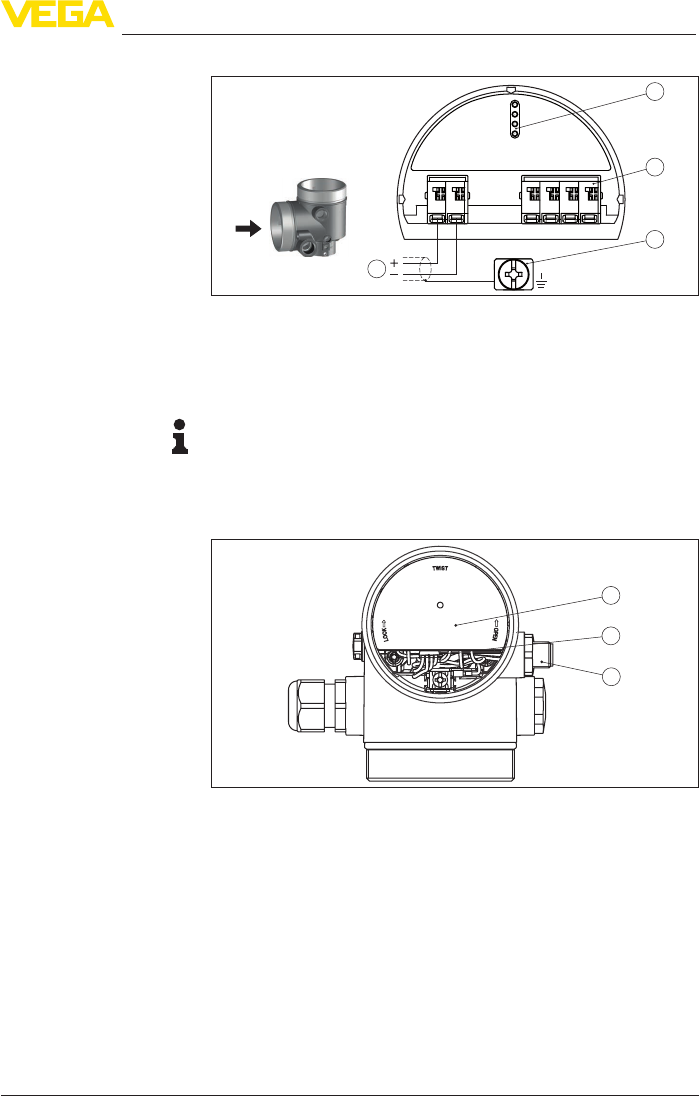
31
5 Connecting to power supply
VEGAPULS 64 • 4 … 20 mA/HART - two-wire
51141-EN-160616
5
12
+
( ) (-)
678
4...20mA
2
3
4
1
Fig. 29: Terminal compartment, double chamber housing
1 Voltage supply, signal output
2 For display and adjustment module or interface adapter
3 For external display and adjustment unit
4 Ground terminal for connection of the cable screen
Information:
Parallel use of an external display and adjustment unit and a display
and adjustment module in the terminal compartment is not supported.
5.6 Double chamber housing with DISADAPT
3
1
2
Fig. 30: View to the electronics compartment with DISADAPT for connection of
the external display and adjustment unit
1 DISADAPT
2 Internal plug connection
3 Plug connector M12 x 1
Terminal compartment
Electronics compartment
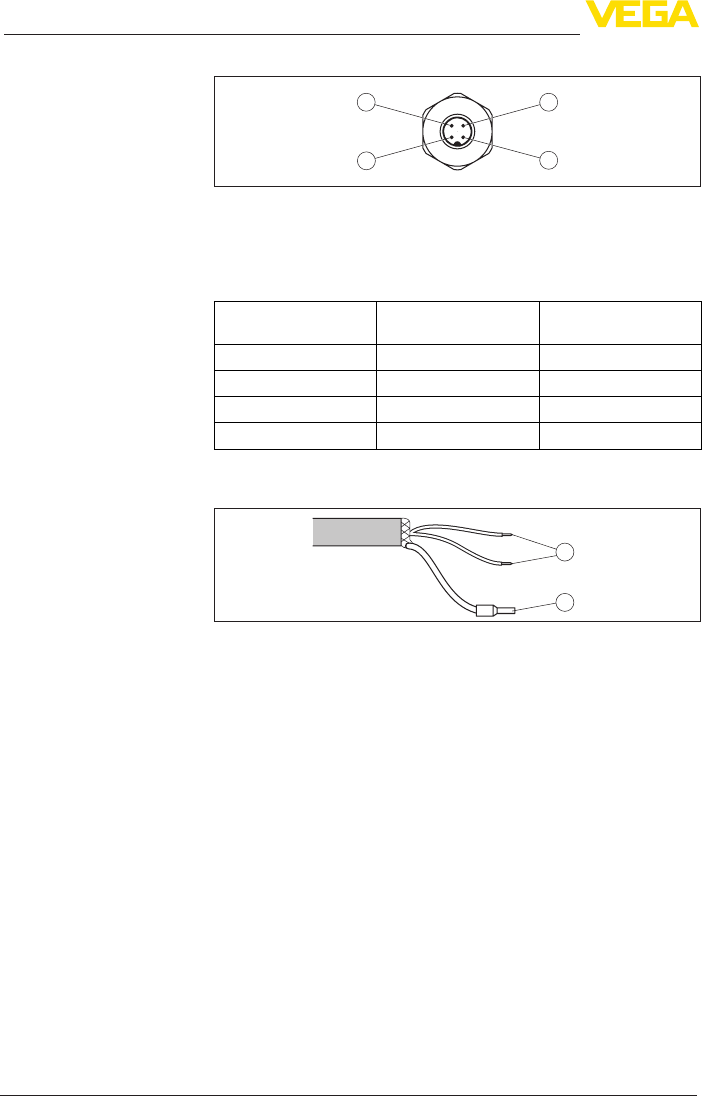
32
5 Connecting to power supply
VEGAPULS 64 • 4 … 20 mA/HART - two-wire
51141-EN-160616
34
12
Fig. 31: View to the plug connector M12 x 1
1 Pin 1
2 Pin 2
3 Pin 3
4 Pin 4
Contact pin Colour connection ca-
ble in the sensor
Terminal, electronics
module
Pin 1 Brown 5
Pin 2 White 6
Pin 3 Blue 7
Pin 4 Black 8
5.7 Wiring plan - version IP 66/IP 68, 1 bar
1
2
Fig. 32: Wire assignment in permanently connected connection cable
1 brown (+) and blue (-) to power supply or to the processing system
2 Shielding
5.8 Switch-on phase
After connecting the instrument to power supply or after a voltage
recurrence, the instrument carries out a self-check for approx. 30 s:
• Internal check of the electronics
• Indication of the status message "F 105 Determine measured
value" on the display or PC
• The output signal jumps to the set fault current
As soon as a plausible measured value is found, the corresponding
current is outputted to the signal cable. The value corresponds to the
actual level as well as the settings already carried out, e.g. factory
setting.
Assignment of the plug
connector
Wire assignment, con-
nection cable
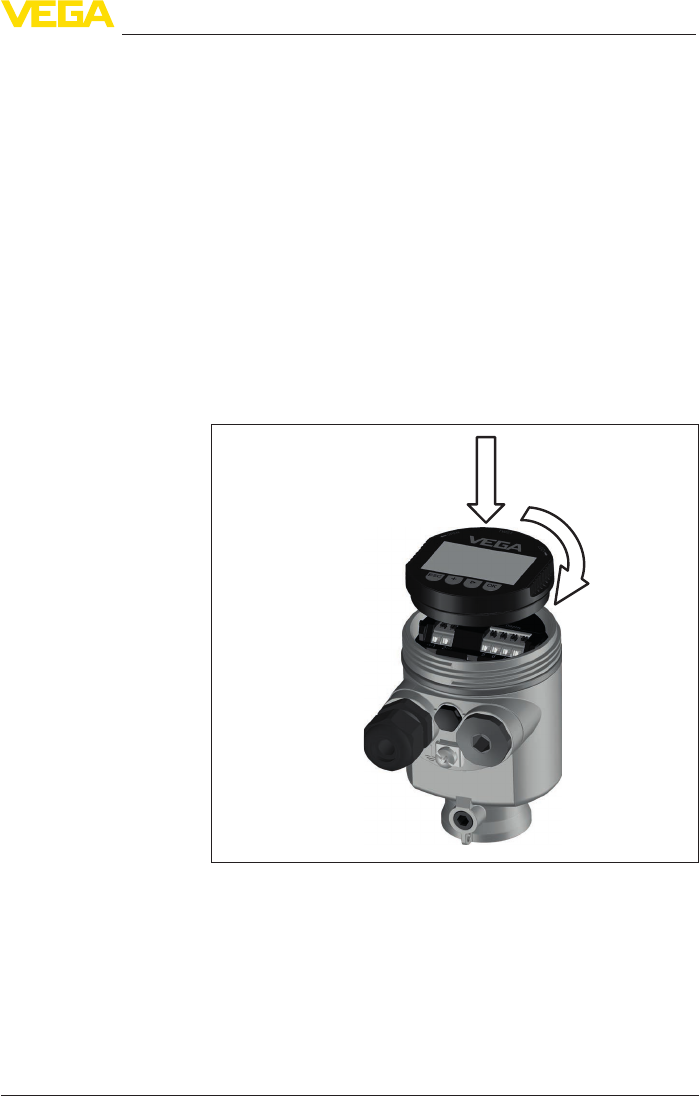
33
6 Set up with the display and adjustment module
VEGAPULS 64 • 4 … 20 mA/HART - two-wire
51141-EN-160616
6 Set up with the display and adjustment
module
6.1 Insert display and adjustment module
The display and adjustment module can be inserted into the sensor
andremovedagainatanytime.Youcanchooseanyoneoffourdier-
ent positions - each displaced by 90°. It is not necessary to interrupt
the power supply.
Proceed as follows:
1. Unscrew the housing lid
2. Place the display and adjustment module on the electronics in the
desired position and turn it to the right until it snaps in.
3. Screw housing lid with inspection window tightly back on
Disassembly is carried out in reverse order.
The display and adjustment module is powered by the sensor, an ad-
ditional connection is not necessary.
Fig. 33: Installing the display and adjustment module in the electronics compart-
ment of the single chamber housing
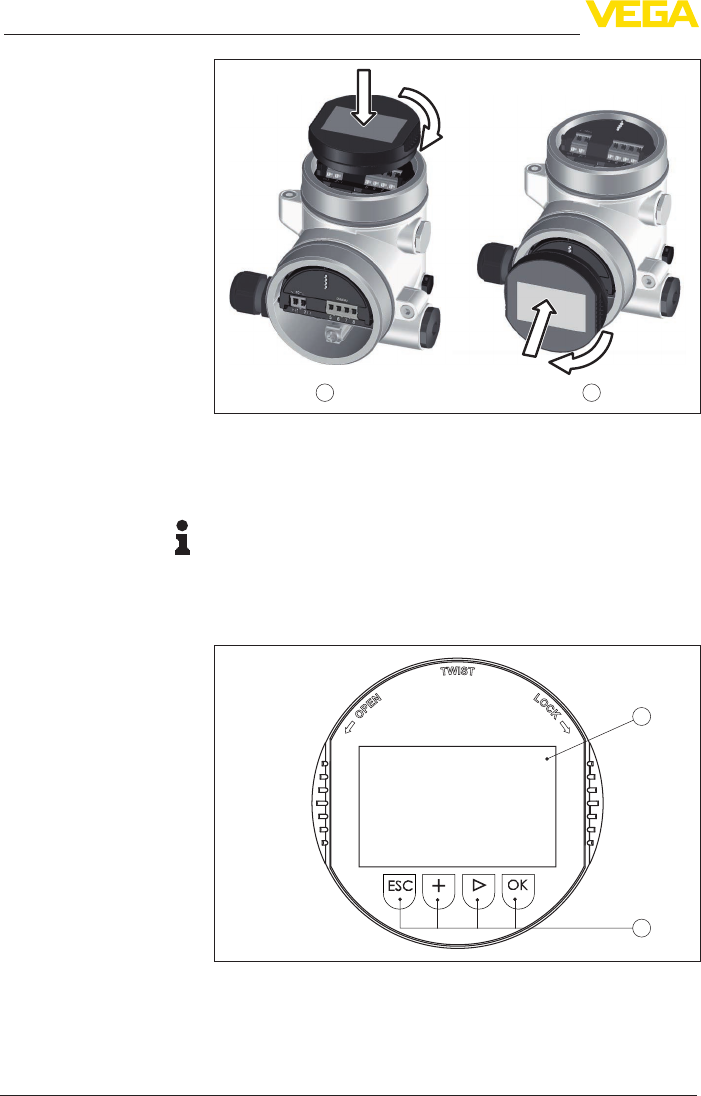
34
6 Set up with the display and adjustment module
VEGAPULS 64 • 4 … 20 mA/HART - two-wire
51141-EN-160616
1 2
Fig. 34: Installing the display and adjustment module in the double chamber
housing
1 In the electronics compartment
2 In the terminal compartment
Note:
Ifyouintendtoretrottheinstrumentwithadisplayandadjustment
module for continuous measured value indication, a higher lid with an
inspection glass is required.
6.2 Adjustment system
1
2
Fig. 35: Display and adjustment elements
1 LC display
2 Adjustment keys
• [OK] key:Key functions

35
6 Set up with the display and adjustment module
VEGAPULS 64 • 4 … 20 mA/HART - two-wire
51141-EN-160616
– Move to the menu overview
– Conrmselectedmenu
– Edit parameter
– Save value
• [->] key:
– Change measured value presentation
– Select list entry
– Select menu items in the quick setup menu
– Select editing position
• [+] key:
– Change value of the parameter
• [ESC] key:
– Interrupt input
– Jump to next higher menu
The instrument is operated via the four keys of the display and adjust-
ment module. The individual menu items are shown on the LC display.
Youcanndthefunctionsoftheindividualkeysintheprevious
illustration.
When the [+] and [->] keys are pressed quickly, the edited value,
or the cursor, changes one value or position at a time. If the key is
pressed longer than 1 s, the value or position changes continuously.
When the [OK] and [ESC] keys are pressed simultaneously for more
than 5 s, the display returns to the main menu. The menu language is
then switched over to "English".
Approx. 60 minutes after the last pressing of a key, an automatic reset
tomeasuredvalueindicationistriggered.Anyvaluesnotconrmed
with [OK] will not be saved.
6.3 Measured value indication - Selection
national language
With the [->]keyyoumovebetweenthreedierentindicationmodes.
Intherstview,theselectedmeasuredvalueisdisplayedinlarge
digits.
In the second view, the selected measured value and a correspond-
ing bar graph presentation are displayed.
In the third view, the selected measured value as well as a second se-
lectable value, e.g. the temperature of the electronics, are displayed.
During the initial setup of an instrument shipped Ex works, use the
"OK" key to get to the menu "National language".
Adjustment system
Time functions
Measured value indica-
tion
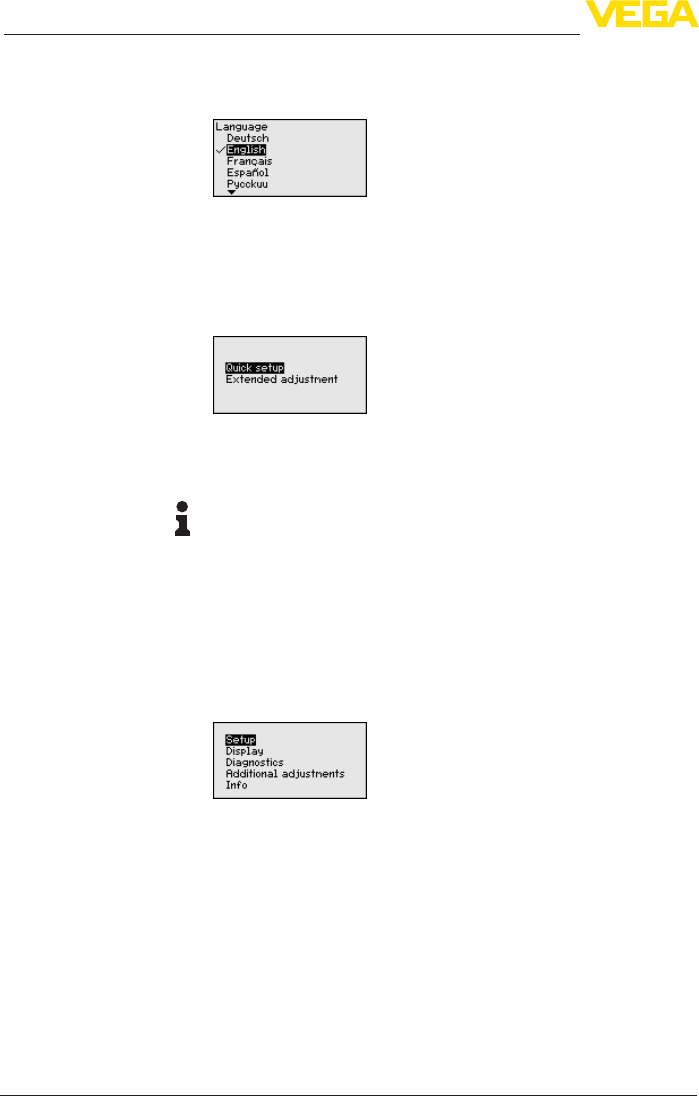
36
6 Set up with the display and adjustment module
VEGAPULS 64 • 4 … 20 mA/HART - two-wire
51141-EN-160616
This menu item is used to select the national language for further pa-
rameter adjustment. You can change the selection via the menu item
"Setup - Display, Menu language".
With the "OK" key you move to the main menu.
6.4 Parameter adjustment - Quick setup
To quickly and easily adapt the sensor to the application, select
the menu item "Quick setup" in the start graphic on the display and
adjustment module.
Select the individual steps with the [->] key.
After the last step, "Quick setup terminated successfully" is displayed
briey.
Information:
The echo curve of setup is stored automatically during the quick
setup.
The return to the measured value indication is carried out through the
[->] or [ESC] keys or automatically after 3 s
Youcannd"Extended adjustment" in the next sub-chapter.
6.5 Parameter adjustment - Extended adjustment
Themainmenuisdividedintovesectionswiththefollowingfunc-
tions:
Setup: Settings, e.g., for measurement loop name, units, application,
adjustment, signal output
Display: Settings, e.g., for language, measured value display, lighting
Diagnosis: Information, for example, on device status, peak value,
simulation, echo curve
Additional adjustments: Date/Time, reset, copy function, scaling,
currentoutput,falsesignalsuppression,linearization,HARTmode,
special parameters
Info: Instrument name, hardware and software version, calibration
date, instrument features
In the main menu item "Setup", the individual submenu items
should be selected one after the other and provided with the correct
Selection of national
language
Main menu

37
6 Set up with the display and adjustment module
VEGAPULS 64 • 4 … 20 mA/HART - two-wire
51141-EN-160616
parameters to ensure optimum adjustment of the measurement. The
procedure is described in the following.
Here you can assign a suitable measurement loop name. Push the
"OK" key to start the editing. With the "+" key you change the sign and
with the "->" key you jump to the next position.
You can enter names with max. 19 characters. The character set
comprises:
• Capital letters from A … Z
• Numbers from 0 … 9
• Special characters + - / _ blanks
In this menu item you select the distance unit and the temperature
unit.
For the distance units you can choose between m, in and ft and for
the temperature units °C, °F and K.
This menu item allows you to adapt the sensor to the measuring
conditions.
Medium
The following options are available:
Application
The following options are available:
The following features form the basis of the applications:
- Storage tank:
• Setup: large-volumed, upright cylindrical, spherical
• Productspeed:slowllingandemptying
Setup - Measurement
loop name
Setup - Units
Setup - Application

38
6 Set up with the display and adjustment module
VEGAPULS 64 • 4 … 20 mA/HART - two-wire
51141-EN-160616
• Process/measurement conditions:
– Condensation
– Smooth product surface
– High requirements on measurement accuracy
• Properties, sensor:
– Low sensitivity to sporadic false echoes
– Stable and reliable measured values through averaging
– High accuracy
– Short reaction time of the sensor not required
- Storage tank with product circulation:
• Setup: large-volumed, upright cylindrical, spherical
• Productspeed:slowllingandemptying
• Installations: small laterally mounted or large top mounted stirrer
• Process/measurement conditions:
– Relatively smooth product surface
– High requirements on measurement accuracy
– Condensation
– Slight foam generation
– Overllingpossible
• Properties, sensor:
– Low sensitivity to sporadic false echoes
– Stable and reliable measured values through averaging
– High accuracy, because not set for max. speed
– False signal suppression recommended
- Storage tank on ships (Cargo Tank):
• Productspeed:slowllingandemptying
• Vessel:
– Installations in the bottom section (bracers, heating spirals)
– High sockets 200 … 500 mm, also with large diameters
• Process/measurement conditions:
– Condensation, buildup by movement
– Max. requirement on measurement accuracy from 95 %
• Properties, sensor:
– Low sensitivity to sporadic false echoes
– Stable and reliable measured values through averaging
– High accuracy
– False signal suppression required
- Stirrer vessel (reactor):
• Setup:allvesselsizespossible
• Product speed:
– Fasttoslowllingpossible
– Vesselislledandemptiedveryoften
• Vessel:
– Socket available
– Large agitator blades of metal
– Vortex breakers, heating spirals
• Process/measurement conditions:
– Condensation, buildup by movement
– Strong spout generation
– Very agitated surface, foam generation

39
6 Set up with the display and adjustment module
VEGAPULS 64 • 4 … 20 mA/HART - two-wire
51141-EN-160616
• Properties, sensor:
– Higher measurement speed through less averaging
– Sporadic false echoes are suppressed
- Dosing vessel:
• Setup:allvesselsizespossible
• Product speed:
– Fastllingandemptying
– Vesselislledandemptiedveryoften
• Vessel: tight installation situation
• Process/measurement conditions:
– Condensation, buildup on the antenna
– Foam generation
• Properties, sensor:
– Measurementspeedoptimizedbyvirtuallynoaveraging
– Sporadic false echoes are suppressed
– False signal suppression recommended
- Plastic tank:
• Vessel:
– Instrumentxmountedorbuiltin
– Measurement through the vessel top, if appropriate to the
application
– With empty vessel, the measurement can go through the bot-
tom
• Process/measurement conditions:
– Condensation on the plastic ceiling
– In outdoor facilities, water and snow on vessel top possible
• Properties, sensor:
– False signals outside the vessel are not taken into consideration
– False signal suppression recommended
Operation of the device in plastic tanks is not approved for unre-
stricteduse.Therestrictionsfordierentapplicationscanbefoundin
chapters 2.7 to 2.9.
- Transportable plastic tank:
• Vessel:
– Materialandthicknessdierent
– Measurement through the vessel top
• Process/measurement conditions:
– Measured value jump with vessel change
• Properties, sensor:
– Quickadaptationtochangingreectionconditionsduetoves-
sel change
– False signal suppression required
The device shall not operate while being moved or while inside a
moving container.
Operation of the device in plastic tanks is not approved for unre-
stricteduse.Therestrictionsfordierentapplicationscanbefoundin
chapters 2.7 to 2.9.

40
6 Set up with the display and adjustment module
VEGAPULS 64 • 4 … 20 mA/HART - two-wire
51141-EN-160616
- Open water (gauge measurement):
• Rate of level change: slow level change
• Process/measurement conditions:
– Large distance from sensor to water surface
– Extreme damping of output signal due to wave generation
– Ice and condensation on the antenna possible
– Spiders and insects build nests in the antennas
– Floating material and animals sporadically appear on water
surface
• Properties, sensor:
– Stable and reliable measured values through frequent averag-
ing
– Insensitive in the close range
-Openume(owmeasurement):
• Rate of level change: slow level change
• Process/measurement conditions:
– Ice and condensation on the antenna possible
– Spiders and insects build nests in the antennas
– Smooth water surface
– Exact measurement result required
– Distance to the water surface normally relatively large
• Properties, sensor:
– Stable and reliable measured values through frequent averag-
ing
– Insensitive in the close range
- Rain water spillover (weir):
• Rate of level change: slow level change
• Process/measurement conditions:
– Ice and condensation on the antenna possible
– Spiders and insects build nests in the antennas
– Turbulent water surface
– Sensoroodingpossible
• Properties, sensor:
– Stable and reliable measured values through frequent averag-
ing
– Insensitive in the close range
- Demonstration:
• Adjustment for all applications which are not typically level meas-
urement
– Instrument demonstration
– Object recognition/monitoring (additional settings required)
• Properties, sensor:
– Sensor accepts all measured value changes within the measur-
ing range immediately
– High sensitivity to interference, because virtually no averaging
Vessel form
Apart from the medium and the application, the vessel form itself can
inuencethemeasurement.Toadaptthesensortothesemeasuring

41
6 Set up with the display and adjustment module
VEGAPULS 64 • 4 … 20 mA/HART - two-wire
51141-EN-160616
conditions,thismenuitemoersdierentoptionsforvesselbottom
and ceiling for certain applications.
Enter the requested parameters via the appropriate keys, save your
settings with [OK] and jump to the next menu item with the [ESC] and
the [->] key.
Vessel height/Measuring range
Through this selection the operating range of the sensor is adapted
to the vessel height, which considerably increases measurement
certaintyunderdierentbasicconditions.
The min. adjustment must be carried out independently of this.
Enter the requested parameters via the appropriate keys, save your
settings with [OK] and jump to the next menu item with the [ESC] and
the [->] key.
Caution:
Ifliquidswithdierentdielectricconstantsseparateinthevessel,for
example through condensation, the radar sensor can detect under
certain circumstances only the medium with the higher dielectric
constant. Keep in mind that layer interfaces can cause faulty meas-
urements.
If you want to measure the total height of both liquids reliably, please
contact our service department or use an instrument specially de-
signed for interface measurement.
Since the radar sensor is a distance measuring instrument, the
distance from the sensor to the product surface is measured. To
indicate the actual level, an allocation of the measured distance to the
percentage height must be carried out.
To perform the adjustment, enter the distance with full and empty ves-
sel, see the following example:
Setup - Adjustment

42
6 Set up with the display and adjustment module
VEGAPULS 64 • 4 … 20 mA/HART - two-wire
51141-EN-160616
100%
0%
0,5 m
(19.68
")
5 m
(196.9
")
2
1
3
Fig. 36: Parameter adjustment example min./max. adjustment
1 Min. level = max. measuring distance
2 Max. level = min. measuring distance
3 Reference plane
If these values are not known, an adjustment with the distances of e.g.
10%and90%ispossible.Startingpointforthesedistancespecica-
tionsisalwaysthesealingsurfaceofthethreadorange.Youcannd
specicationsonthereferenceplaneinchapter"Technical data". The
actual level is calculated on the basis of these settings.
The actual product level during this adjustment is not important,
because the min./max. adjustment is always carried out without
changing the product level. These settings can be made ahead of
time without the instrument having to be installed.
Proceed as follows:
1. Select with [->]themenuitemMax.adjustmentandconrmwith
[OK].
2. Prepare the percentage value for editing with [OK] and set the
cursor to the requested position with [->].
3. Set the requested percentage value with [+] and save with [OK].
The cursor jumps now to the distance value.
Setup - Max. adjustment

43
6 Set up with the display and adjustment module
VEGAPULS 64 • 4 … 20 mA/HART - two-wire
51141-EN-160616
4. For the full vessel, enter the distance value in m matching the
percentage value.
5. Save settings with [OK] and move with [ESC] and [->] to Min.
adjustment.
Proceed as follows:
1. Select with [->] the menu item "Min. adjustment"andconrmwith
[OK].
2. Edit the percentage value with [OK] and set the cursor to the
requested position with [->].
3. Set the requested percentage value with [+] and save with [OK].
The cursor jumps now to the distance value.
4. Enter the suitable distance value in m for the empty vessel (e.g.
distance from the sensor to the vessel bottom) corresponding to
the percentage value.
Todampprocess-dependentmeasuredvalueuctuations,setan
integration time of 0 … 999 s in this menu item.
The default setting is a damping of 0 s.
In the menu item "Current output mode" you determine the output
characteristics and reaction of the current output in case of failure.
The default setting is output characteristics 4 … 20 mA, failure mode
< 3.6 mA.
Setup - Min. adjustment
Setup - Damping
Setup - Current output
mode

44
6 Set up with the display and adjustment module
VEGAPULS 64 • 4 … 20 mA/HART - two-wire
51141-EN-160616
In the menu item "Current output Min./Max.", you determine the reac-
tion of the current output during operation.
The default setting is min. current 3.8 mA and max. current 20.5 mA.
In the menu item "Lock/unlock adjustment", you can protect the sen-
sorparametersagainstunauthorizedorinadvertentmodication.The
PIN is activated/deactivated permanently.
With active PIN, only the following adjustment functions are possible
without entering a PIN:
• Select menu items and show data
• Read data from the sensor into the display and adjustment mod-
ule.
Caution:
With active PIN, adjustment via PACTware/DTM as well as other
systems is also blocked.
This menu item enables the setting of the requested national lan-
guage.
The following languages are available:
• German
• English
• French
• Spanish
• Russian
• Italian
• Dutch
• Portuguese
• Japanese
• Chinese
• Polish
• Czech
• Turkish
In the delivery status, the VEGAPULS 64 is set to the ordered national
language.
Setup - Current output
Min./Max.
Lock/unlock setup - Ad-
justment
Display - Menu language
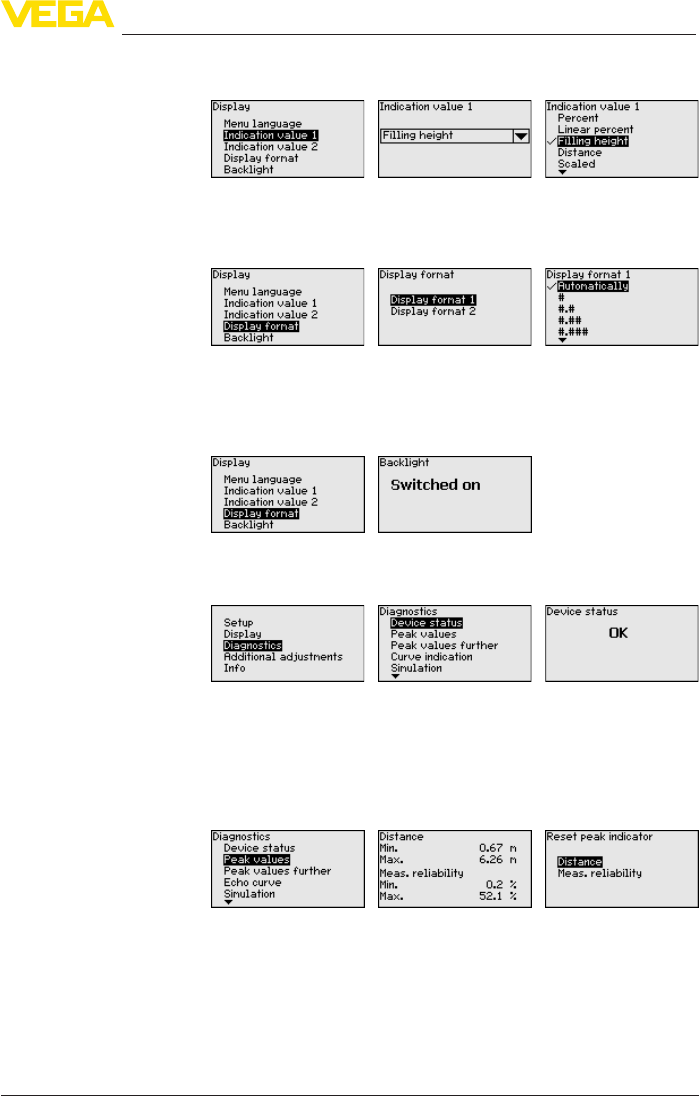
45
6 Set up with the display and adjustment module
VEGAPULS 64 • 4 … 20 mA/HART - two-wire
51141-EN-160616
Inthismenuitemyoucandenethewaymeasuredvaluesareindi-
cated on the display.
The default setting for the displayed value is "Distance".
Inthismenuitemyoudenethenumberofdecimalpositionswith
which the measured value is displayed.
The default setting for the display format is "Automatically".
The display and adjustment module has a backlight for the display. In
thismenuitemyoucanswitchthelightingonoro.Youcanndthe
required operating voltage in chapter "Technical data".
In delivery status, the lighting is switched on.
In this menu item, the device status is displayed.
The min. and max. measured value, the measurement certainty as
well as the min. and max. electronics temperature are stored in the
sensor. The values are displayed in menu item "Peak value" or "Fur-
ther peak values".
A reset menu is opened with the [OK] key in the respective peak
value window:
With the [OK] key in the reset menu, the peak values are reset to the
current measured value.
The "Echo curve" shows the signal strength of the echoes over the
measuring range in dB. The signal strength enables an evaluation of
the quality of the measurement.
Display - Displayed value
1 and 2
Display - Display format
Display - Backlight
Diagnostics - Device
status
Diagnosis - Peak value
Diagnoses - Curve indica-
tion

46
6 Set up with the display and adjustment module
VEGAPULS 64 • 4 … 20 mA/HART - two-wire
51141-EN-160616
Theselectedcurveiscontinuouslyupdated.Asubmenuwithzoom
functions is opened with the [OK] key:
• "X-Zoom":Zoomfunctionforthemeas.distance
• "Y-Zoom":1,2,5and10xsignalmagnicationin"dB"
• "Unzoom":Resetthepresentationtothenominalmeasuringrange
withoutmagnication
In this menu item you can simulate measured values via the current
output. This allows the signal path to be tested, e.g. through down-
stream indicating instruments or the input card of the control system.
Select the requested simulation variable and set the requested value.
Caution:
During simulation, the simulated value is outputted as 4 … 20 mA cur-
rent value and as digital HART signal. The status message within the
context of the asset management function is "Maintenance".
To deactivate the simulation, you have to push the [ESC] key and
conrmthemessage
with the [OK] key.
Information:
The sensor terminates the simulation automatically after 60 minutes.
The function "Setup" allows the echo curve to be saved at the time of
setup.
Information:
This is generally recommended, however, for use of the Asset
Management functions it is absolutely necessary. Saving should be
carried out with a very low level.
The function "Echo curve memory" allows up to ten individual echo
curves to be stored, for example to detect the measurement behav-
iourofthesensorindierentoperatingconditions.
Diagnosis - Simulation
Diagnostics - Echo curve
memory
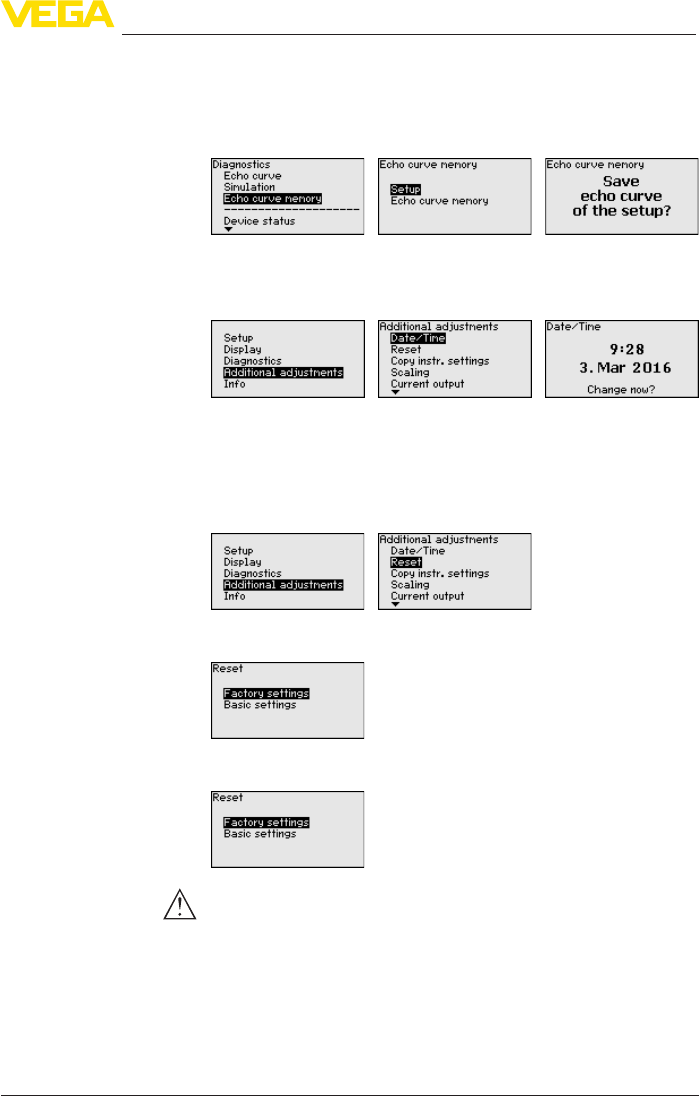
47
6 Set up with the display and adjustment module
VEGAPULS 64 • 4 … 20 mA/HART - two-wire
51141-EN-160616
With the adjustment software PACTware and the PC, the stored echo
curvescanbedisplayedwithhighresolutionandusedtorecognize
signal changes over time. In addition, the echo curve saved during
setup can also be displayed in the echo curve window and compared
with the current echo curve.
In this menu item, the internal clock of the sensor is set to the request-
ed time and time format. At the time of shipment from factory, the
instrument is set to CET (Central European Time).
During a reset, the parameter settings carried out by the user are
reset to the default values (see below table).
Proceed as follows:
1. Select with [->] under "Additional adjustments" the menu item
"Reset"andconrmwith[OK].
2. Conrmwith[OK] and select the requested reset function with
[->]
3. Conrmwith[OK], for approx. 5 s the message "Resetting" is
displayed, then the selection window appears.
Caution:
For the duration of the reset, the set trouble signal is outputted via the
current output. Within the context of the asset management function,
the message "Maintenance" is outputted.
The following reset functions are available:
Delivery status: Restores the parameter settings at the time of ship-
mentfromthefactory,incl.theorder-specicsettings.Anycreated
falsesignalsuppression,user-programmablelinearizationcurveas
Additional adjustments -
Date/Time
Additional adjustments
- Reset
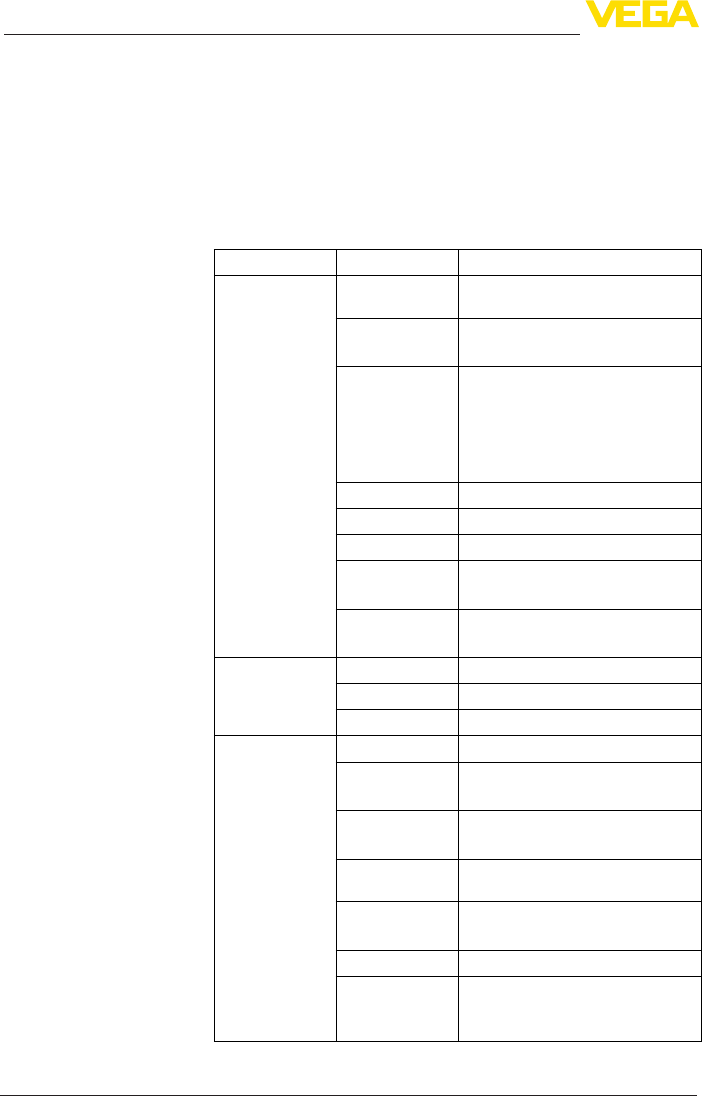
48
6 Set up with the display and adjustment module
VEGAPULS 64 • 4 … 20 mA/HART - two-wire
51141-EN-160616
well as measured value and echo curve memory is deleted. The event
andparametermodicationmemoriesremainunaected.
Basic settings: Resets the parameter settings, incl. special param-
eters, to the default values of the respective instrument. Any stored
false signal suppression or user programmable linearisation curve, as
well as the measured value memory, is deleted. Order-related settings
are not taken over into the current parameters after this reset.
The following table shows the scope of the reset function and the
default values of the instrument:
Menu Menu item Default value
Setup Measurement
loop name
Sensor
Units Distance in m
Temperature in °C
Application Medium: Water solution
Application: Storage tank
Vessel top: Dished form
Vessel bottom: Dished form
Vessel height/Measuring range: 30 m
Min. adjustment 30 m
Max. adjustment 0,000 m(d)
Damping 0.0 s
Current output
mode
Output characteristics: 4 … 20 mA
Failure mode: < 3.6 mA ▼
Current output
Min./Max.
Min. current: 3.8 mA
Max. current: 20.5 mA
Display Displayed value 1 Filling height
Displayed value 2 Electronics temperature
Backlight Switched on
Additional adjust-
ments
Date/Time Time format: 24 h
Scalingsize Volume
l
Scaling format 100.00 lin %, 100 l
0.00 lin %, 0 l
Current output 1
and2size
Lin %
Current output 1
and 2 adjustment
100.00 %, 100 l
0.00 %, 0 l
Linearization Linear
HART mode HART address: 0
Loop current mode: Analogue cur-
rent output
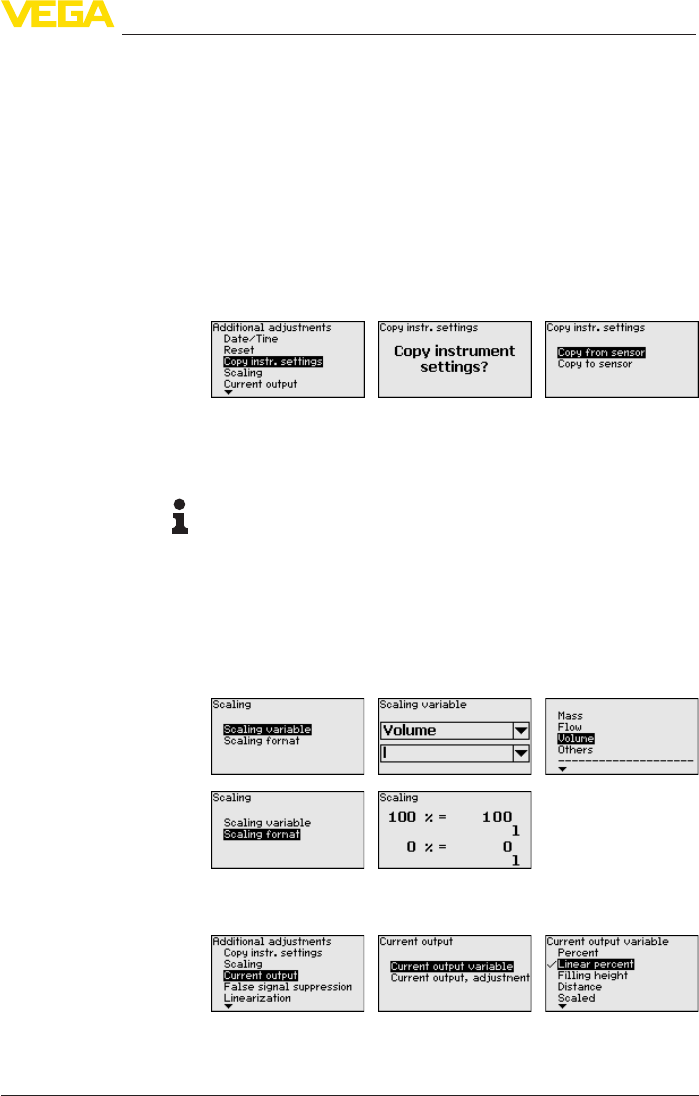
49
6 Set up with the display and adjustment module
VEGAPULS 64 • 4 … 20 mA/HART - two-wire
51141-EN-160616
The instrument settings are copied with this function. The following
functions are available:
Read from sensor: Read data from sensor and store into the display
and adjustment module
Write into sensor: Store data from the display and adjustment mod-
ule back into the sensor
The following data or settings for adjustment of the display and ad-
justment module are saved:
• All data of the menu "Setup" and "Display"
• The menu items "Reset, Date/Time" in the menu "Additional set-
tings"
• Theuser-programmablelinearizationcurve
The copied data are permanently saved in an EEPROM memory in
the display and adjustment module and remain there even in case of
power failure. From there, they can be written into one or more sen-
sors or kept as backup for a possible electronics exchange.
Note:
Before the data are saved in the sensor, a safety check is carried out
to determine if the data match the sensor. In the process the sensor
type of the source data as well as the target sensor are displayed. If
the data do not match, a fault message is outputted or the function is
blocked. The data are saved only after release.
In the menu item "Scaling"youdenethescalingvariableandthe
scaling format for the indication of the level measured value for 0 %
and 100 % on the display, for example as volume in l.
In menu item "Current output, variable" you specify which measured
variable the current output refers to.
In menu item "Current output, adjustment" you can assign a respec-
tive measured value to the current output.
Additional adjustments -
Copy instrument settings
Additional settings - Scal-
ing
Additional settings - Cur-
rent output (size)
Additional settings - Cur-
rent output (adjustment)

50
6 Set up with the display and adjustment module
VEGAPULS 64 • 4 … 20 mA/HART - two-wire
51141-EN-160616
Thefollowingcircumstancescauseinterferingreectionsandcan
inuencethemeasurement:
• High sockets
• Vessel internals such as struts
• Agitators
• Buildup or welded joints on vessel walls
Note:
A false signal suppression detects, marks and saves these false
signals so that they are no longer taken into account in the level
measurement.
This should be done with a low level so that all potential interfering
reectionscanbedetected.
Proceed as follows:
1. Select with [->] the menu item "False signal suppression" and
conrmwith[OK].
2. Conrmagainwith[OK].
3. Conrmagainwith[OK].
4. Conrmagainwith[OK] and enter the actual distance from the
sensor to the product surface.
5. All interfering signals in this section are detected by the sensor
andstoredafterconrmingwith[OK].
Note:
Check the distance to the product surface, because if an incorrect
(too large) value is entered, the existing level will be saved as a false
signal. The level would then no longer be detectable in this area.
If a false signal suppression has already been saved in the sensor,
the following menu window appears when selecting "False signal
suppression":
Additional adjustments -
False signal suppression

51
6 Set up with the display and adjustment module
VEGAPULS 64 • 4 … 20 mA/HART - two-wire
51141-EN-160616
Delete: An already created false signal suppression will be com-
pletely deleted. This is useful if the saved false signal suppression no
longer matches the metrological conditions in the vessel.
Extend: is used to extend an already created false signal suppres-
sion. This is useful if a false signal suppression was carried out with
too high a level and not all false signals could be detected. When
selecting "Extend", the distance to the product surface of the created
false signal suppression is displayed. This value can now be changed
and the false signal suppression can be extended to this range.
Alinearizationisnecessaryforallvesselsinwhichthevesselvolume
doesnotincreaselinearlywiththelevel.Correspondinglinearization
curves are preprogrammed for these vessels. They represent the
correlation between the level percentage and vessel volume. The
linearizationappliestothemeasuredvalueindicationandthecurrent
output.
In this menu item you specify the HART mode and enter the address
for multidrop mode.
In the mode "Fixed current output" up to 63 sensors can be operated
on one two-wire cable (Multidrop operation). An address between 0
and 63 must be assigned to each sensor.
If you select the function "Analogue current output", a 4 … 20 mA
signal is output in multidrop mode.
In the mode "Fixed current (4 mA)"axed4mAsignalisoutputinde-
pendently of the actual level.
The default setting is "Analogue current output" and the address "00".
In this menu item you gain access to the protected area where
you can enter special parameters. In exceptional cases, individual
parameterscanbemodiedinordertoadaptthesensortospecial
requirements.
Additional adjustments -
Linearization
Additional adjustments -
HART mode
Additional adjustments -
Special parameters
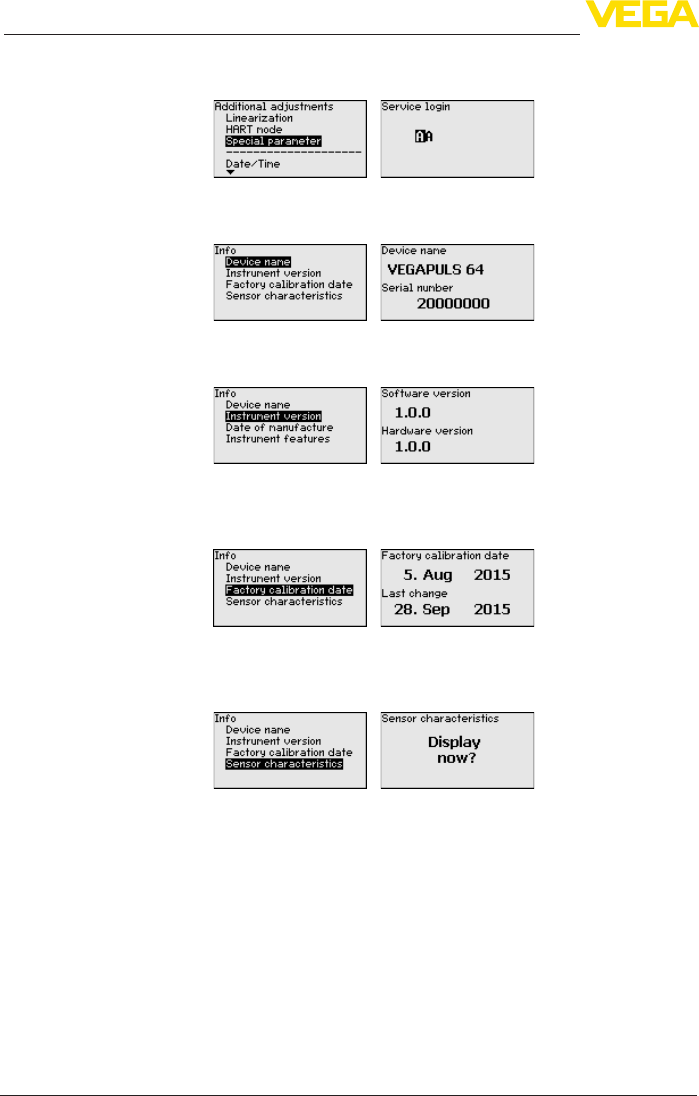
52
6 Set up with the display and adjustment module
VEGAPULS 64 • 4 … 20 mA/HART - two-wire
51141-EN-160616
Change the settings of the special parameters only after having con-
tactedourservicesta.
In this menu item, you can read out the instrument name and the
instrument serial number:
In this menu item, the hardware and software version of the sensor is
displayed.
In this menu item, the date of factory calibration of the sensor as well
as the date of the last change of sensor parameters are displayed via
the display and adjustment module or via the PC.
In this menu item, the features of the sensor such as approval, pro-
cesstting,seal,measuringrange,electronics,housingandothers
are displayed.
6.6 Saving the parameter adjustment data
We recommended noting the adjusted data, e.g. in this operating
instructions manual, and archiving them afterwards. They are thus
available for multiple use or service purposes.
If the instrument is equipped with a display and adjustment module,
the data in the sensor can be saved in the display and adjustment
module. The procedure is described in the menu "Additional adjust-
ments" in the menu item "Copy sensor data". The data remain there
permanently even if the sensor power supply fails.
The following data or settings for adjustment of the display and ad-
justment module are saved:
Info - Instrument name
Info - Instrument version
Info - Factory calibration
date
Info - Sensor character-
istics
Backup on paper
Backup in the display and
adjustment module
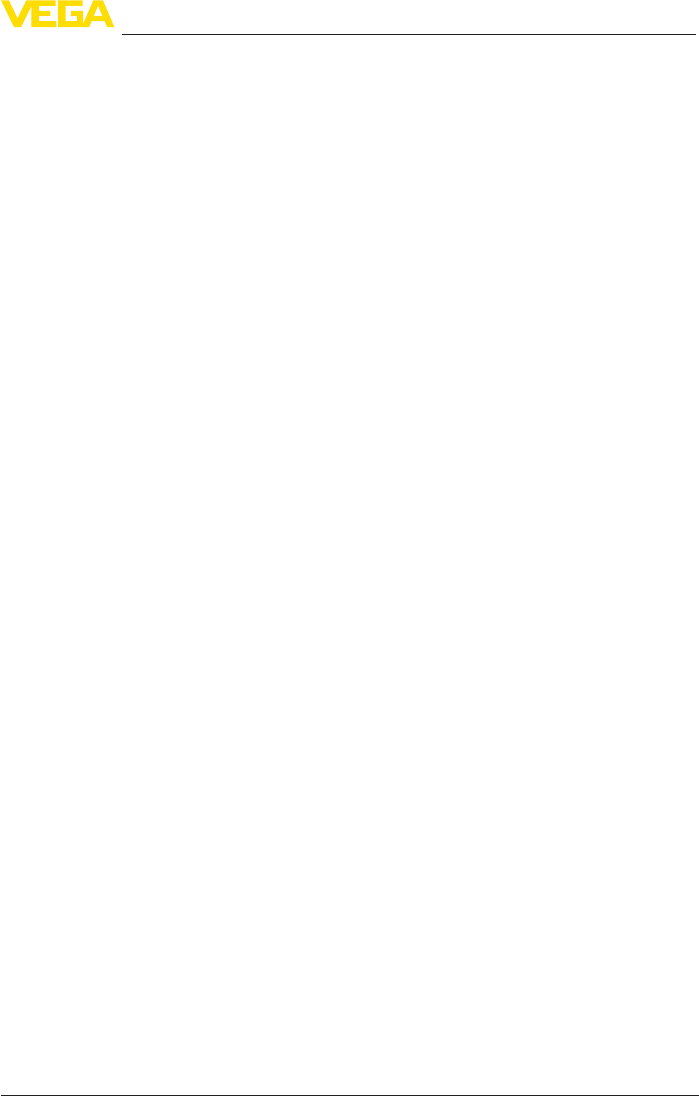
53
6 Set up with the display and adjustment module
VEGAPULS 64 • 4 … 20 mA/HART - two-wire
51141-EN-160616
• All data of the menu "Setup" and "Display"
• In the menu "Additional settings" the items "Sensor-specic units,
temperature unit and linearization"
• Thevaluesoftheuserprogrammablelinearizationcurve
The function can also be used to transfer settings from one instru-
ment to another instrument of the same type. If it is necessary to
exchange a sensor, the display and adjustment module is inserted
into the replacement instrument and the data are likewise written into
the sensor via the menu item "Copy sensor data".
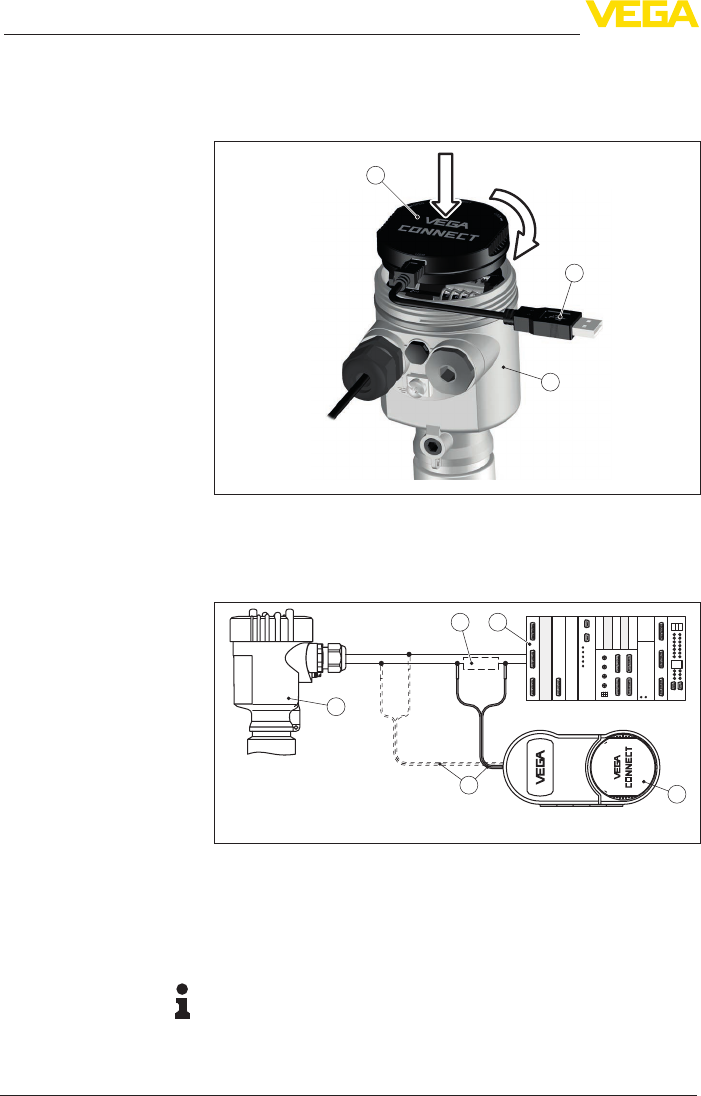
54
7 Setup with PACTware
VEGAPULS 64 • 4 … 20 mA/HART - two-wire
51141-EN-160616
7 Setup with PACTware
7.1 Connect the PC
3
1
2
Fig. 37: Connection of the PC directly to the sensor via the interface adapter
1 USB cable to the PC
2 Interface adapter VEGACONNECT
3 Sensor
1
5
2 4
3
OPEN
TWIST
USB
LOCK
Fig. 38: Connecting the PC via HART to the signal cable
1 Sensor
2 HART resistance 250 Ω (optional depending on evaluation)
3 Connection cable with 2 mm pins and terminals
4 Processing system/PLC/Voltage supply
5 Interface adapter, for example VEGACONNECT 4
Note:
With power supply units with integrated HART resistance (internal
resistanceapprox.250Ω),anadditionalexternalresistanceisnot
necessary. This applies, e.g. to the VEGA instruments VEGATRENN
149A, VEGAMET 381, VEGAMET 391. Common Ex separators are
Via the interface adapter
directly on the sensor
Via the interface adapter
and HART
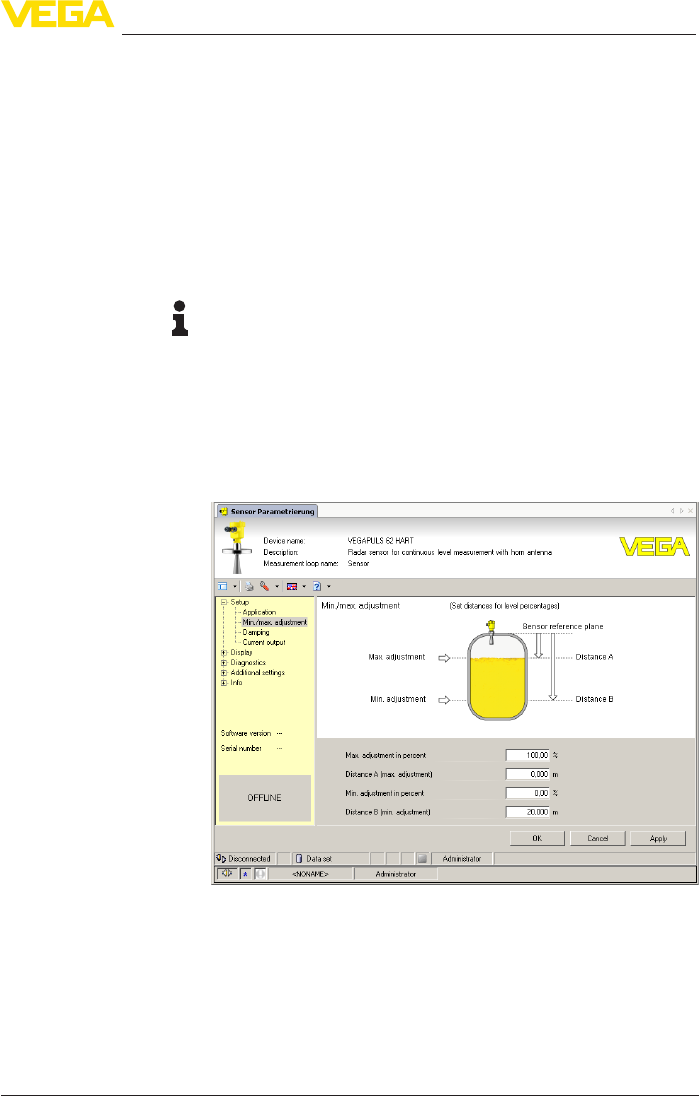
55
7 Setup with PACTware
VEGAPULS 64 • 4 … 20 mA/HART - two-wire
51141-EN-160616
alsousuallyequippedwithasucientcurrentlimitingresistance.In
such cases, the interface converter can be connected parallel to the
4 … 20 mA cable (dashed line in the previous illustration).
7.2 Parameter adjustment
For parameter adjustment of the instrument via a Windows PC, the
congurationsoftwarePACTwareandasuitableinstrumentdriver
(DTM) according to FDT standard are required. The latest PACTware
version as well as all available DTMs are compiled in a DTM Collec-
tion. The DTMs can also be integrated into other frame applications
according to FDT standard.
Note:
To ensure that all instrument functions are supported, you should
always use the latest DTM Collection. Furthermore, not all described
functionsareincludedinolderrmwareversions.Youcandownload
the latest instrument software from our homepage. A description of
the update procedure is also available in the Internet.
Further setup steps are described in the operating instructions manu-
al "DTM Collection/PACTware" attached to each DTM Collection and
which can also be downloaded from the Internet. Detailed descrip-
tions are available in the online help of PACTware and the DTMs.
Fig. 39: Example of a DTM view
All device DTMs are available as a free-of-charge standard version
and as a full version that must be purchased. In the standard version,
all functions for complete setup are already included. An assistant for
simpleprojectcongurationsimpliestheadjustmentconsiderably.
Saving/printing the project as well as import/export functions are also
part of the standard version.
Prerequisites
Standard/Full version
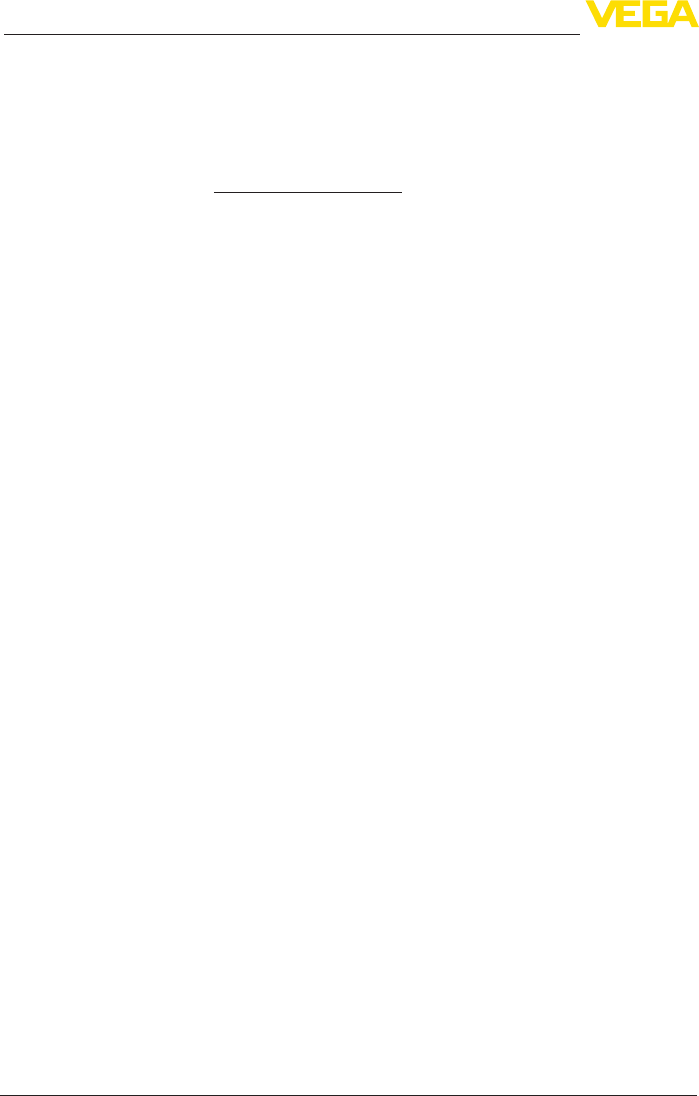
56
7 Setup with PACTware
VEGAPULS 64 • 4 … 20 mA/HART - two-wire
51141-EN-160616
In the full version there is also an extended print function for complete
project documentation as well as a save function for measured value
and echo curves. In addition, there is a tank calculation program as
well as a multiviewer for display and analysis of the saved measured
value and echo curves.
The standard version is available as a download under
www.vega.com/downloads and "Software". The full version is avail-
able on CD from the agency serving you.
7.3 Saving the parameter adjustment data
We recommend documenting or saving the parameter adjustment
data via PACTware. That way the data are available for multiple use or
service purposes.

57
8 Set up with other systems
VEGAPULS 64 • 4 … 20 mA/HART - two-wire
51141-EN-160616
8 Set up with other systems
8.1 DD adjustment programs
Device descriptions as Enhanced Device Description (EDD) are
available for DD adjustment programs such as, for example, AMS™
and PDM.
Thelescanbedownloadedatwww.vega.com/downloads under
"Software".
8.2 Field Communicator 375, 475
Device descriptions for the instrument are available as EDD for pa-
rameter adjustment with the Field Communicator 375 or 475.
For the integration of the EDD in the Field Communicator 375 or 475,
the software "Easy Upgrade Utility" is required which is available from
the manufacturer. This software is updated via the Internet and new
EDDs are automatically taken over into the device catalogue of this
software after they are released by the manufacturer. They can then
be transferred to a Field Communicator.

58
9 Diagnosis, asset management and service
VEGAPULS 64 • 4 … 20 mA/HART - two-wire
51141-EN-160616
9 Diagnosis, asset management and service
9.1 Maintenance
If the instrument is used correctly, no maintenance is required in
normal operation.
Insomeapplications,buildupontheantennasystemcaninuence
the measuring result. Depending on the sensor and application, take
measures to avoid heavy soiling of the antenna system. If necessary,
clean the antenna system in certain intervals.
9.2 Measured value and event memory
The instrument has several memories which are available for
diagnostic purposes. The data remain there even in case of voltage
interruption.
Up to 100,000 measured values can be stored in the sensor in a ring
memory. Each entry contains date/time as well as the respective
measured value. Storable values are for example:
• Distance
• Filling height
• Percentage value
• Lin. percent
• Scaled
• Current value
• Meas. certainty
• Electronics temperature
When the instrument is shipped, the measured value memory is
active and stores distance, measurement certainty and electronics
temperature every 3 minutes.
The requested values and recording conditions are set via a PC with
PACTware/DTM or the control system with EDD. Data are thus read
out and also reset.
Up to 500 events are automatically stored with a time stamp in the
sensor (non-deletable). Each entry contains date/time, event type,
event description and value. Event types are for example:
• Modicationofaparameter
• Switch-onandswitch-otimes
• Status messages (according to NE 107)
• Error messages (according to NE 107)
The data are read out via a PC with PACTware/DTM or the control
system with EDD.
The echo curves are stored with date and time and the corresponding
echo data. The memory is divided into two sections:
Echo curve of the setup: This is used as reference echo curve for
the measurement conditions during setup. Changes in the measure-
ment conditions during operation or buildup on the sensor can thus
berecognized.Theechocurveofthesetupisstoredvia:
Measured value memory
Event memory
Echo curve memory

59
9 Diagnosis, asset management and service
VEGAPULS 64 • 4 … 20 mA/HART - two-wire
51141-EN-160616
• PC with PACTware/DTM
• Control system with EDD
• Display and adjustment module
Further echo curves: Up to 10 echo curves can be stored in a ring
buerinthismemorysection.Furtherechocurvesarestoredvia:
• PC with PACTware/DTM
• Control system with EDD
9.3 Asset Management function
The instrument features self-monitoring and diagnostics according to
NE 107 and VDI/VDE 2650. In addition to the status messages in the
following tables, detailed error messages are available under menu
item "Diagnostics" via the display and adjustment module, PACTware/
DTM and EDD.
The status messages are divided into the following categories:
• Failure
• Function check
• Outofspecication
• Maintenance requirement
and explained by pictographs:
41 2 3
Fig. 40: Pictographs of the status messages
1 Failure - red
2 Out of specication - yellow
3 Function check - orange
4 Maintenance - blue
Failure: Due to a malfunction in the instrument, a failure message is
outputted.
This status message is always active. It cannot be deactivated by the
user.
Function check: The instrument is in operation, the measured value
is temporarily invalid (for example during simulation).
This status message is inactive by default. It can be activated by the
user via PACTware/DTM or EDD.
Outofspecication: The measured value is unstable because the
instrumentspecicationisexceeded(e.g.electronicstemperature).
This status message is inactive by default. It can be activated by the
user via PACTware/DTM or EDD.
Maintenance:Duetoexternalinuences,theinstrumentfunction
islimited.Themeasurementisaected,butthemeasuredvalueis
Status messages

60
9 Diagnosis, asset management and service
VEGAPULS 64 • 4 … 20 mA/HART - two-wire
51141-EN-160616
still valid. Plan in maintenance for the instrument because a failure is
expected in the near future (e.g. due to buildup).
This status message is inactive by default. It can be activated by the
user via PACTware/DTM or EDD.
The following table shows the error codes in the status message
"Failure"andgivesinformationonthereasonandrectication.Keep
in mind that some information is only valid with four-wire instruments.
Code
Text message
Cause Rectication DevSpec State in CMD
48
F013
no measured value avail-
able
– Sensor does not detect
an echo during opera-
tion
– Antenna system dirty or
defective
– Check or correct instal-
lation and/or parameter
adjustment
– Clean or exchange
process component or
antenna
Bit 0 of Byte 0…5
F017
Adjustment span too small
– Adjustment not within
specication
– Change adjustment
according to the limit
values(dierence
between min. and max.
≥10mm)
Bit 1 of Byte 0…5
F025
Errorinthelinearization
table
– Index markers are not
continuously rising, for
example illogical value
pairs
– Checklinearizationtable
– Delete table/Create new
Bit 2 of Byte 0…5
F036
No operable software
– Failed or interrupted
software update
– Repeat software update
– Check electronics
version
– Exchanging the elec-
tronics
– Send instrument for
repair
Bit 3 of Byte 0…5
F040
Error in the electronics
– Hardware defect – Exchanging the elec-
tronics
– Send instrument for
repair
Bit 4 of Byte 0…5
F080
General software error
– General software error – Disconnect operating
voltagebriey
Bit 5 of Byte 0…5
F105
Determine measured value
– The instrument is still
in the start phase, the
measured value could
not yet be determined
– Wait for the end of the
switch-on phase
– Duration depending on
the version and param-
eter adjustment up to
approximately 3 min.
Bit 6 of Byte 0…5
F113
Communication error
– EMC interference
– Transmission error with
the external communica-
tion with 4-wire power
supply unit
– RemoveEMCinuences
– Exchange 4-wire power
supply unit or electron-
ics
Bit 12 of Byte 0…5
Failure

61
9 Diagnosis, asset management and service
VEGAPULS 64 • 4 … 20 mA/HART - two-wire
51141-EN-160616
Code
Text message
Cause Rectication DevSpec State in CMD
48
F125
Impermissible electronics
temperature
– Temperature of the
electronics in the non-
speciedrange
– Check ambient tem-
perature
– Isolate electronics
– Use instrument with
higher temperature
range
Bit 7 of Byte 0…5
F260
Error in the calibration
– Error in the calibration
carried out in the factory
– Error in the EEPROM
– Exchanging the elec-
tronics
– Send instrument for
repair
Bit 8 of Byte 0…5
F261
Error in the instrument set-
tings
– Error during setup
– False signal suppression
faulty
– Error when carrying out
a reset
– Repeat setup
– Carry out a reset
Bit 9 of Byte 0…5
F264
Installation/Setup error
– Adjustment not within
the vessel height/meas-
uring range
– Max. measuring range
of the instrument not
sucient
– Check or correct instal-
lation and/or parameter
adjustment
– Use an instrument with
bigger measuring range
Bit 10 of Byte 0…5
F265
Measurement function dis-
turbed
– Sensor no longer carries
out a measurement
– Operating voltage too
low
– Check operating voltage
– Carry out a reset
– Disconnect operating
voltagebriey
Bit 11 of Byte 0…5
The following table shows the error codes and text messages in the
status message "Function check" and provides information on causes
as well as corrective measures.
Code
Text message
Cause Rectication DevSpec State in CMD
48
C700
Simulation active
– A simulation is active – Finish simulation
– Wait for the automatic
end after 60 mins.
"Simulation Active" in
"StandardizedStatus0"
The following table shows the error codes and text messages in the
status message "Out of specication" and provides information on
causes as well as corrective measures.
Code
Text message
Cause Rectication DevSpec State in CMD
48
S600
Impermissible electronics
temperature
– Temperature of the
electronics in the non-
speciedrange
– Check ambient tem-
perature
– Isolate electronics
– Use instrument with
higher temperature
range
Bit 8 of Byte 14…24
Function check
Outofspecication

62
9 Diagnosis, asset management and service
VEGAPULS 64 • 4 … 20 mA/HART - two-wire
51141-EN-160616
Code
Text message
Cause Rectication DevSpec State in CMD
48
S601
Overlling
– Danger of vessel
overlling
– Make sure that there is
nofurtherlling
– Check level in the vessel
Bit 9 of Byte 14…24
S603
Impermissible operating
voltage
– Operating voltage below
speciedrange
– Check electrical con-
nection
– If necessary, increase
operating voltage
Bit 11 of Byte 14…24
The following table shows the error codes and text messages in the
status message "Maintenance" and provides information on causes
as well as corrective measures.
Code
Text message
Cause Rectication DevSpec State in CMD
48
M500
Error with the reset deliv-
ery status
– With the reset to delivery
status, the data could
not be restored
– Repeat reset
– LoadXMLlewithsen-
sor data into the sensor
Bit 0 of Byte 14…24
M501
Error in the non-active lin-
earizationtable
– Hardware error
EEPROM
– Exchanging the elec-
tronics
– Send instrument for
repair
Bit 1 of Byte 14…24
M502
Error in the event memory
– Hardware error
EEPROM
– Exchanging the elec-
tronics
– Send instrument for
repair
Bit 2 of Byte 14…24
M503
Meas. reliability too low
– The echo/noise ratio
is too small for reliable
measurement
– Antenna dirty or defec-
tive
– Check installation and
process conditions
– Change polarisation
direction
– Use instrument with
higher sensitivity
– Clean the antenna
Bit 3 of Byte 14…24
M504
Error on an device inter-
face
– Hardware defect – Check connections
– Exchanging the elec-
tronics
– Send instrument for
repair
Bit 4 of Byte 14…24
M505
No echo available
– Sensor does not detect
an echo during opera-
tion
– Antenna dirty or defec-
tive
– Clean the antenna
– Use a more suitable
antenna/sensor
– Remove possible false
echoes
– Optimizesensorposition
and orientation
Bit 5 of Byte 14…24
M506
Installation/Setup error
– Error during setup – Check or correct instal-
lation and/or parameter
adjustment
Bit 6 of Byte 14…24
Maintenance

63
9 Diagnosis, asset management and service
VEGAPULS 64 • 4 … 20 mA/HART - two-wire
51141-EN-160616
Code
Text message
Cause Rectication DevSpec State in CMD
48
M507
Error in the instrument set-
tings
– Error during setup
– Error when carrying out
a reset
– False signal suppression
faulty
– Carry out reset and
repeat setup
Bit 7 of Byte 14…24
9.4 Rectify faults
The operator of the system is responsible for taking suitable meas-
ures to rectify faults.
Therstmeasuresare:
• Evaluation of fault messages, for example via the display and
adjustment module
• Checking the output signal
• Treatment of measurement errors
Further comprehensive diagnostics options are available with a PC
with PACTware and the suitable DTM. In many cases, the reasons can
bedeterminedinthiswayandfaultsrectied.
Connect a multimeter in the suitable measuring range according to
the wiring plan. The following table describes possible errors in the
current signal and helps to eliminate them:
Error Cause Rectication
4 … 20 mA signal not sta-
ble
– Fluctuations of the
measured variable
– Set damping appropriate to the instrument via the
display and adjustment module or PACTware/DTM
4 … 20 mA signal missing – Electrical connection
faulty
– Check connection according to chapter "Connection
steps" and if necessary, correct according to chapter
"Wiring plan"
– Voltage supply missing – Check cables for breaks; repair if necessary
– Operating voltage too
low or load resistance
too high
– Check, adapt if necessary
Current signal greater than
22 mA or less than 3.6 mA
– Electronics module in
the sensor defective
– Exchange the instrument or send it in for repair
The below tables show typical examples of application-related meas-
urementerrorswithliquids.Themeasurementerrorsaredierentiated
according to the following:
• Constant level
• Filling
• Emptying
The images in column "Error pattern" show the real level as a broken
line and the level displayed by the sensor as a continuous line.
Reaction when malfunc-
tion occurs
Procedure for fault recti-
cation
Check the 4 … 20 mA
signal
Treatment of measure-
ment errors with liquids

64
9 Diagnosis, asset management and service
VEGAPULS 64 • 4 … 20 mA/HART - two-wire
51141-EN-160616
1
2
Level
time
0
1 Real level
2 Level displayed by the sensor
Notes:
• Wherever the sensor displays a constant value, the reason could
also be the fault setting of the current output to "Hold value"
• If the level indication is too low, the reason could be a line resist-
ance that is too high
Measurement error with constant level
Fault description Error pattern Cause Rectication
1. Measured value
shows a too low or too
high level
Level
time
0
– Min./max. adjustment not
correct
– Adapt min./max. adjustment
– Incorrectlinearizationcurve – Adaptlinearizationcurve
– Installation in a bypass tube or
standpipe, hence running time
error (small measurement error
close to 100 %/large error close
to 0 %)
– Check parameter "Application"
with respect to vessel form,
adapt if necessary (bypass,
standpipe, diameter)
2. Measured value
jumps towards 0 %
Level
time
0
– Multiple echo (vessel top,
product surface) with amplitude
higher than the level echo
– Check parameter "Application",
especially vessel top, type of
medium, dished bottom, high
dielectric constant, and adapt if
necessary
3. Measured value
jumps towards 100 %
Level
time
0
– Due to the process, the ampli-
tude of the level echo sinks
– A false signal suppression was
not carried out
– Carry out a false signal sup-
pression
– Amplitude or position of a false
signal has changed (e.g. con-
densation, buildup); false signal
suppression no longer matches
actual conditions
– Determine the reason for the
changed false signals, carry out
false signal suppression, e.g.
with condensation
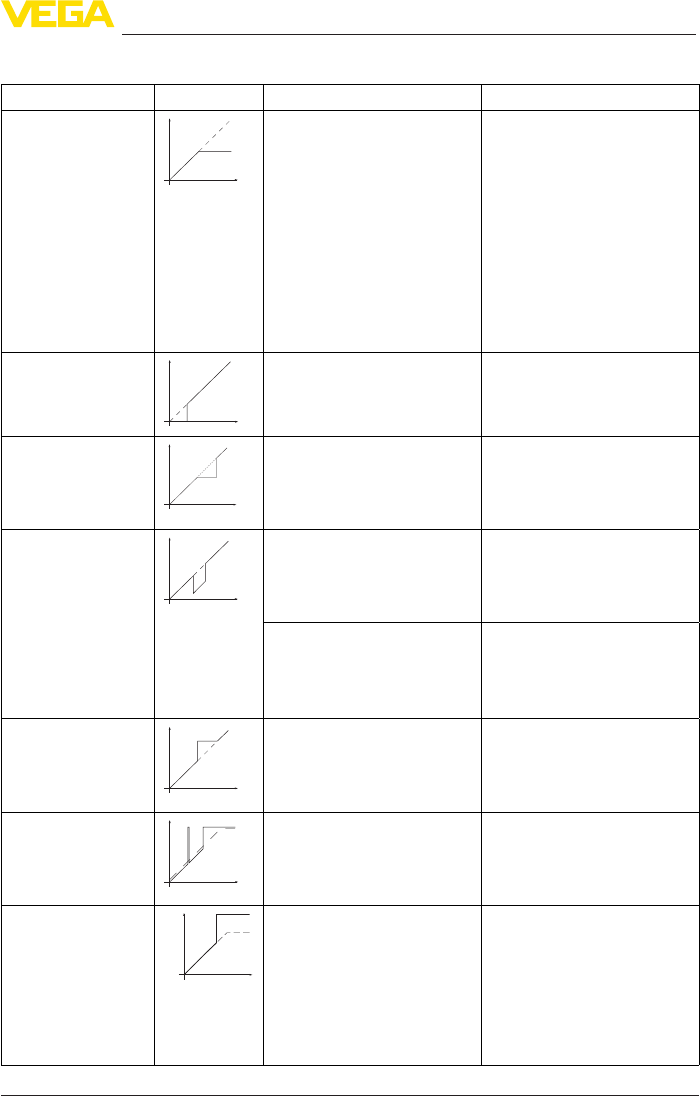
65
9 Diagnosis, asset management and service
VEGAPULS 64 • 4 … 20 mA/HART - two-wire
51141-EN-160616
Measurementerrorduringlling
Fault description Error pattern Cause Rectication
4. Measured value re-
mains unchanged
duringlling
Level
time
0
– False signals in the close range
too big or level echo too small
– Strong foam or spout genera-
tion
– Max. adjustment not correct
– Eliminate false signals in the
close range
– Check measurement situation:
Antenna must protrude out of
the socket, installations
– Remove contamination on the
antenna
– In case of interferences due to
installations in the close range:
Change polarisation direction
– Create a new false signal sup-
pression
– Adapt max. adjustment
5. Measured value re-
mains in the bottom
sectionduringlling
Level
time
0
– Echo from the tank bottom
larger than the level echo, for
example, with products with
εr < 2.5 oil-based, solvents
– Check parameters Medium,
Vessel height and Floor form,
adapt if necessary
6. Measured value re-
mains momentarily
unchangedduringll-
ing and then jumps to
the correct level
Level
time
0
– Turbulence on the product
surface,quicklling
– Check parameters, change if
necessary, e.g. in dosing ves-
sel, reactor
7. Measured value
jumps towards 0 %
duringlling
Level
time
0
– Amplitude of a multiple echo
(vessel top - product surface) is
larger than the level echo
– Check parameter "Application",
especially vessel top, type of
medium, dished bottom, high
dielectric constant, and adapt if
necessary
– The level echo cannot be distin-
guished from the false signal at
a false signal position (jumps to
multiple echo)
– In case of interferences due to
installations in the close range:
Change polarisation direction
– Chose a more suitable installa-
tion position
8. Measured value
jumps towards 100 %
duringlling
Level
time
0
– Due to strong turbulence and
foamgenerationduringlling,
the amplitude of the level echo
sinks. Measured value jumps to
false signal
– Carry out a false signal sup-
pression
9. Measured value
jumps sporadically to
100%duringlling
Level
time
0
– Varying condensation or con-
tamination on the antenna
– Carry out a false signal sup-
pression or increase false
signal suppression with con-
densation/contamination in the
close range by editing
10. Measured value
jumpsto≥100%or
0 m distance
Level
time
0
– Level echo is no longer
detected in the close range
due to foam generation or false
signals in the close range. The
sensorgoesintooverllprotec-
tion mode. The max. level (0 m
distance) as well as the status
message"Overllprotection"
are outputted.
– Check measuring site: Antenna
must protrude out of the socket
– Remove contamination on the
antenna
– Use a sensor with a more suit-
able antenna
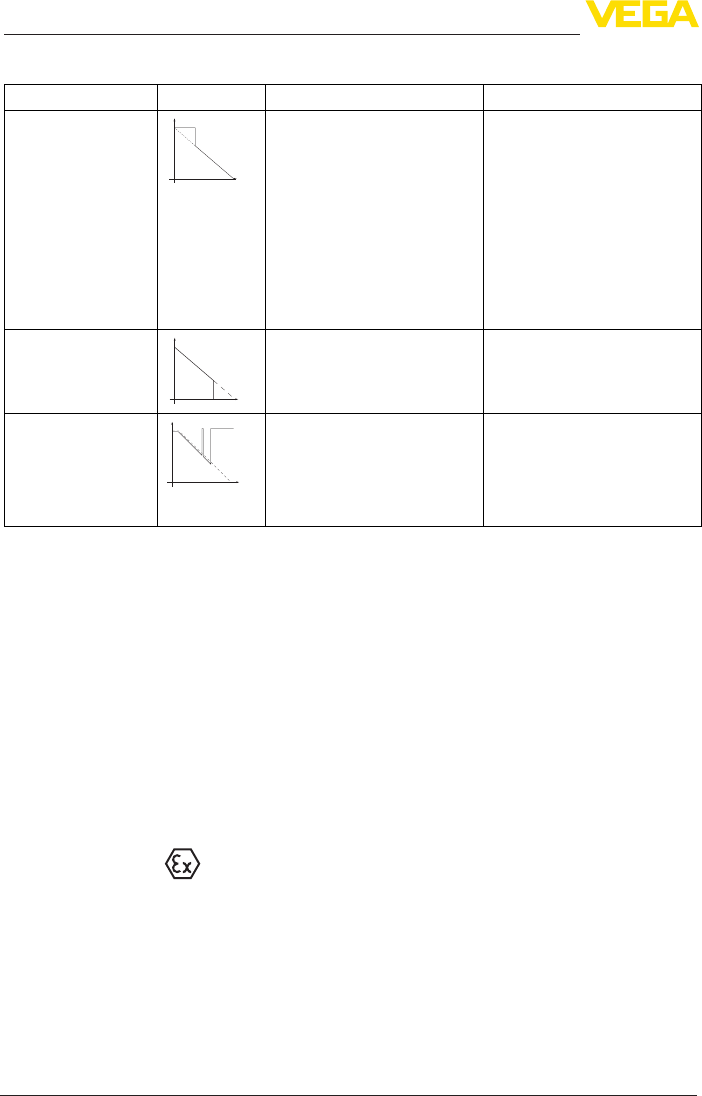
66
9 Diagnosis, asset management and service
VEGAPULS 64 • 4 … 20 mA/HART - two-wire
51141-EN-160616
Measurement error during emptying
Fault description Error pattern Cause Rectication
11. Measured value re-
mains unchanged in
the close range during
emptying
Level
time
0
– False signal larger than the
level echo
– Level echo too small
– Eliminate false signal in the
close range. Check: Antenna
must protrude from the socket
– Remove contamination on the
antenna
– In case of interferences due to
installations in the close range:
Change polarisation direction
– After eliminating the false sig-
nals, the false signal suppres-
sion must be deleted. Carry out
a new false signal suppression
12. Measured value
jumps towards 0 %
during emptying
Level
time
0
– Echo from the tank bottom
larger than the level echo, for
example, with products with
εr < 2.5 oil-based, solvents
– Check parameters Medium
type, Vessel height and Floor
form, adapt if necessary
13. Measured value
jumps sporadically to-
wards 100 % during
emptying
Level
time
0
– Varying condensation or con-
tamination on the antenna
– Carry out false signal suppres-
sion or increase false signal
suppression in the close range
by editing
– With bulk solids, use radar sen-
sor with purging air connection
Depending on the reason for the fault and the measures taken, the
steps described in chapter "Setup" must be carried out again or must
be checked for plausibility and completeness.
Should these measures not be successful, please call in urgent cases
the VEGA service hotline under the phone no. +49 1805 858550.
The hotline is also available outside normal working hours, seven
days a week around the clock.
Sinceweoerthisserviceworldwide,thesupportisprovidedin
English. The service itself is free of charge, the only costs involved are
the normal call charges.
9.5 Exchanging the electronics module
If the electronics module is defective, it can be replaced by the user.
In Ex applications, only instruments and electronics modules with ap-
propriate Ex approval may be used.
If there is no electronics module available on site, the electronics
module can be ordered through the agency serving you. The electron-
icsmodulesareadaptedtotherespectivesensoranddierinsignal
output or voltage supply.
The new electronics module must be loaded with the default settings
of the sensor. These are the options:
• In the factory
• Or on site by the user
Reaction after fault recti-
cation
24 hour service hotline
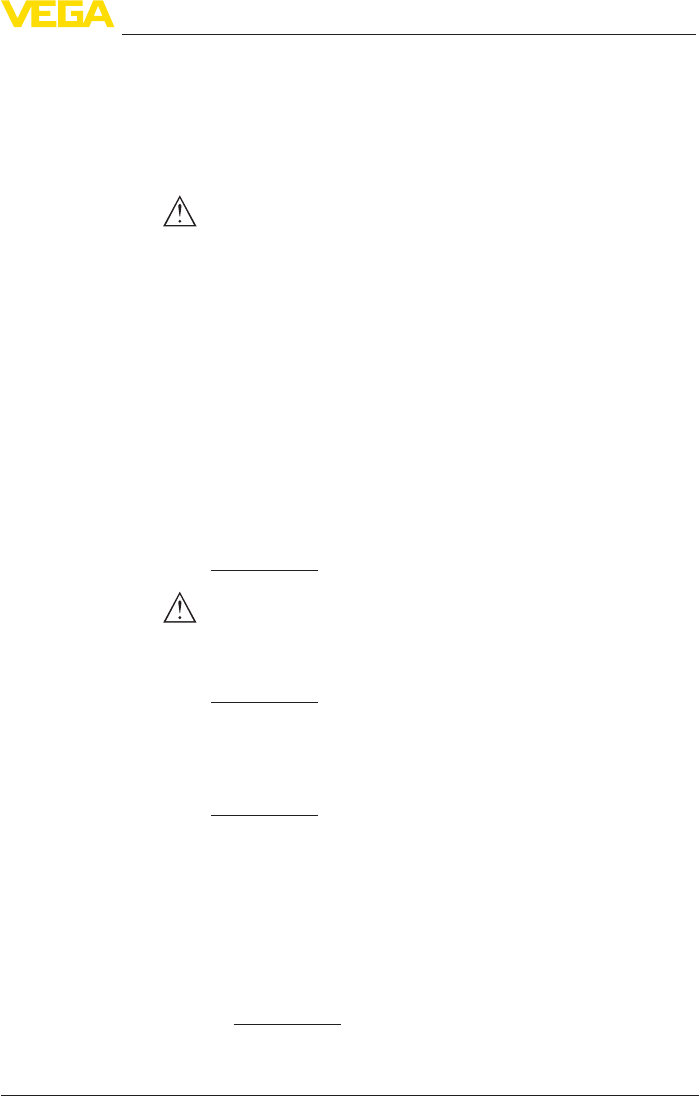
67
9 Diagnosis, asset management and service
VEGAPULS 64 • 4 … 20 mA/HART - two-wire
51141-EN-160616
In both cases, the serial number of the sensor is needed. The serial
numbers are stated on the type label of the instrument, on the inside
of the housing as well as on the delivery note.
Whenloadingonsite,rstofalltheorderdatamustbedownloaded
from the Internet (see operating instructions manual "Electronics
module").
Caution:
Alluser-specicsettingsmustbeenteredagain.Hence,youhaveto
carry out a new setup after the electronics exchange.
If you have stored the data of the parameter adjustment during the
rstsetupofthesensor,youcantransferthesetothereplacement
electronics module. A new setup is no more necessary.
9.6 Software update
The following components are required to update the instrument
software:
• Instrument
• Voltage supply
• Interface adapter VEGACONNECT
• PC with PACTware
• Currentinstrumentsoftwareasle
Youcanndthecurrentinstrumentsoftwareaswellasdetailed
information on the procedure in the download area of our homepage:
www.vega.com.
Caution:
Instruments with approvals can be bound to certain software versions.
Thereforemakesurethattheapprovalisstilleectiveafterasoftware
update is carried out.
Youcannddetailedinformationinthedownloadareaat
www.vega.com.
9.7 How to proceed if a repair is necessary
Youcanndaninstrumentreturnformaswellasdetailedinforma-
tion about the procedure in the download area of our homepage:
www.vega.com.
By doing this you help us carry out the repair quickly and without hav-
ing to call back for needed information.
If a repair is necessary, please proceed as follows:
• Printandlloutoneformperinstrument
• Clean the instrument and pack it damage-proof
• Attach the completed form and, if need be, also a safety data
sheet outside on the packaging
• Please contact the agency serving you to get the address for
thereturnshipment.Youcanndtheagencyonourhomepage
www.vega.com.

68
10 Dismount
VEGAPULS 64 • 4 … 20 mA/HART - two-wire
51141-EN-160616
10 Dismount
10.1 Dismounting steps
Warning:
Before dismounting, be aware of dangerous process conditions such
as e.g. pressure in the vessel or pipeline, high temperatures, cor-
rosive or toxic products etc.
Take note of chapters "Mounting" and "Connecting to power supply"
and carry out the listed steps in reverse order.
10.2 Disposal
The instrument consists of materials which can be recycled by spe-
cialised recycling companies. We use recyclable materials and have
designed the parts to be easily separable.
Correctdisposalavoidsnegativeeectsonhumansandtheenviron-
ment and ensures recycling of useful raw materials.
Materials: see chapter "Technical data"
If you have no way to dispose of the old instrument properly, please
contact us concerning return and disposal.
WEEE directive 2002/96/EG
This instrument is not subject to the WEEE directive 2002/96/EG and
the respective national laws. Pass the instrument directly on to a spe-
cialised recycling company and do not use the municipal collecting
points. These may be used only for privately used products according
to the WEEE directive.
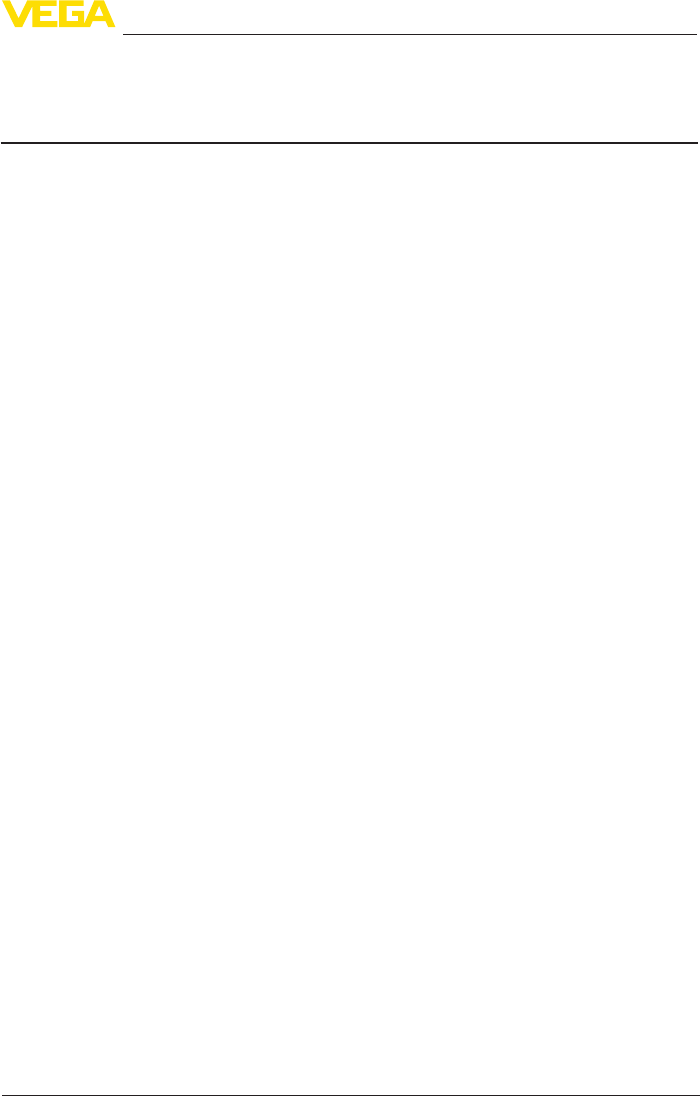
69
11 Supplement
VEGAPULS 64 • 4 … 20 mA/HART - two-wire
51141-EN-160616
11 Supplement
11.1 Technical data
Materials and weights
316L corresponds to 1.4404 or 1.4435
Materials, wetted parts with plastic horn antenna
Ʋ Adapterange PP-GF30 black
Ʋ Seal,adapterange FKM (COG VI500), EPDM (COG AP310)
ƲAntenna cone PBT-GF 30
ƲFocussing lense PP
Materials, wetted parts on thread with integrated antenna
Ʋ Processtting 316L
ƲAntenna PEEK
Ʋseal, antenna system FKM, FFKM
ƲProcess seal Klingersil C-4400
Materials,wettedpartsforangewithencapsulatedantennasystem
ƲFlange 316L
ƲFlange plating PTFE
ƲAntenna encapsulation PTFE
Material, wetted parts rinsing air connection
ƲRinsing air connection PP-GFK
ƲSeal FKM (COG VI500), EPDM (COG AP310)
Materials, non-wetted parts
Ʋ Compressionange PP-GF30 black
ƲMounting strap 316L
ƲFixing screws, mounting strap 316L
Ʋ Fixingscrews,adapterange 304
ƲPlastic housing plastic PBT (Polyester)
ƲAluminium die-casting housing Aluminium die-casting AlSi10Mg, powder-coated - basis:
Polyester
ƲStainless steel housing 316L
ƲCable gland PA, stainless steel, brass
ƲSealing, cable gland NBR
ƲBlind plug, cable gland PA
ƲSeal between housing and housing lid Silicone SI 850 R, NBR silicone-free
ƲInspection window in housing cover
(optional)
Polycarbonate
ƲGround terminal 316L
Processtting
ƲFlanges DIN from DN 80, ASME from 3"
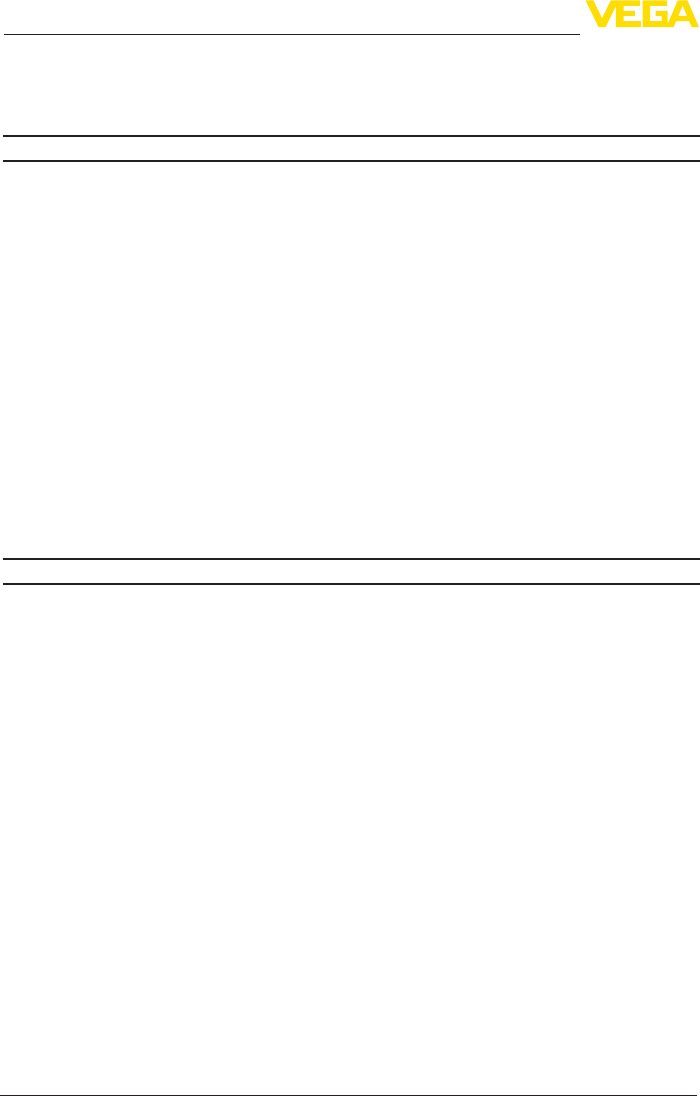
70
11 Supplement
VEGAPULS 64 • 4 … 20 mA/HART - two-wire
51141-EN-160616
Weights
ƲInstrument (depending on housing,
processttingandantenna)
approx. 2 … 17.2 kg (4.409 … 37.92 lbs)
Torques
Max. torques, threaded version
ƲG¾ 30 Nm (22.13 lbf ft)
ƲG1½ 200 Nm (147.5 lbf ft)
Max. torques, version plastic horn antenna
ƲMounting screws, mounting strap on
sensor housing
4 Nm (2.950 lbf ft)
Ʋ Flangescrews,compressionange
DN 80
5 Nm (3.689 lbf ft)
Ʋ Flangescrews,adapterangeDN100 7 Nm (5.163 lbf ft)
Torques,versionangewithencapsulatedantennasystem
Ʋ Requiredtorqueoftheangescrews 60 Nm (44.25 lbf ft)
ƲRecommended torque for tightening
theangescrews
60 … 100 Nm (44.25 … 73.76 lbf ft)
Max. torques for NPT cable glands and Conduit tubes
ƲPlastic housing 10 Nm (7.376 lbf ft)
ƲAluminium/Stainless steel housing 50 Nm (36.88 lbf ft)
Input variable
Measured variable The measured quantity is the distance between the end
of the sensor antenna and the product surface. The ref-
erence plane for the measurement is the sealing surface
onthehexagonorthelowersideoftheange.
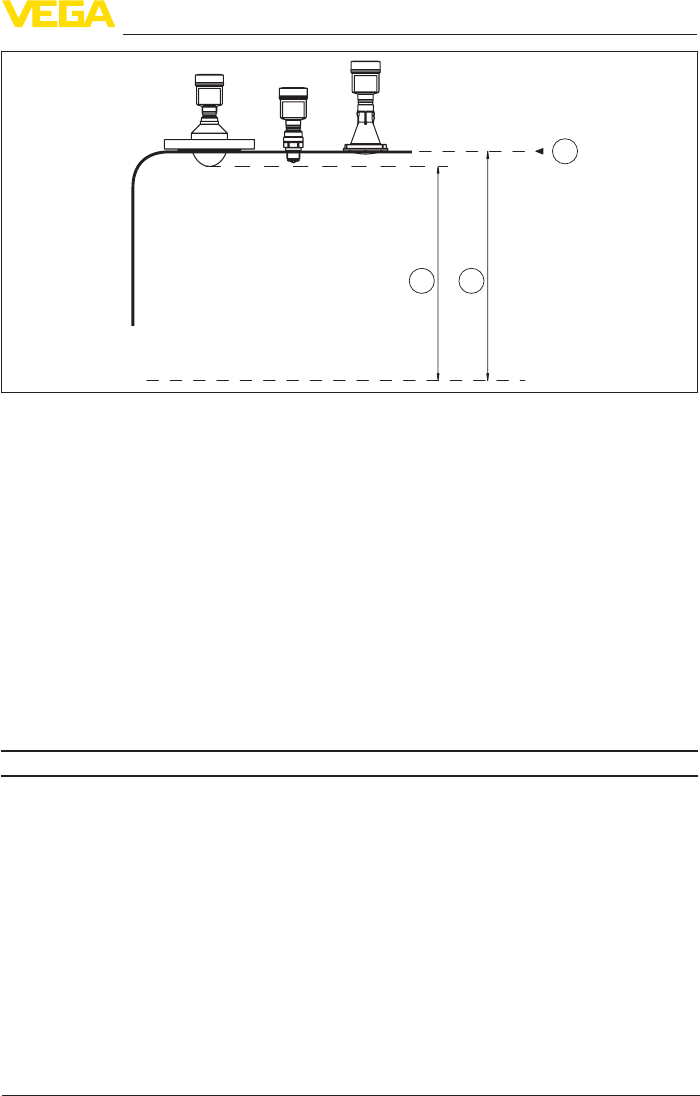
71
11 Supplement
VEGAPULS 64 • 4 … 20 mA/HART - two-wire
51141-EN-160616
2
1
3
Fig. 55: Data of the input variable
1 Reference plane
2 Measured variable, max. measuring range
3 Utilisable measuring range (depending on the antenna system)
Max. measuring range 30 m (98.43 ft)
Recommended measuring range (depending on the antenna system)
ƲPlastic horn antenna up to 30 m (98.43 ft)
ƲThread with integrated horn antenna
¾"
up to 10 m (32.81 ft)
ƲThread with integrated horn antenna
1½"
up to 20 m (65.62 ft)
ƲFlange DN 50, 2" with encapsulated
antenna system
up to 25 m (82.02 ft)
ƲFlange from DN 80, 3" with encapsu-
lated antenna system
up to 30 m (98.43 ft)
Output variable
Output signal 4 … 20 mA/HART
Range of the output signal 3.8 … 20.5 mA/HART (default setting)
Signal resolution 0.3 µA
Resolution, digital < 1 mm (0.039 in)
Failure signal current output (adjustable) mA-value unchanged 20.5 mA, 22 mA, < 3.6 mA
Max. output current 22 mA
Starting current ≤3.6mA;≤10mAfor5msafterswitchingon
Load see load diagram under Power supply
Damping (63 % of the input variable),
adjustable
0 … 999 s
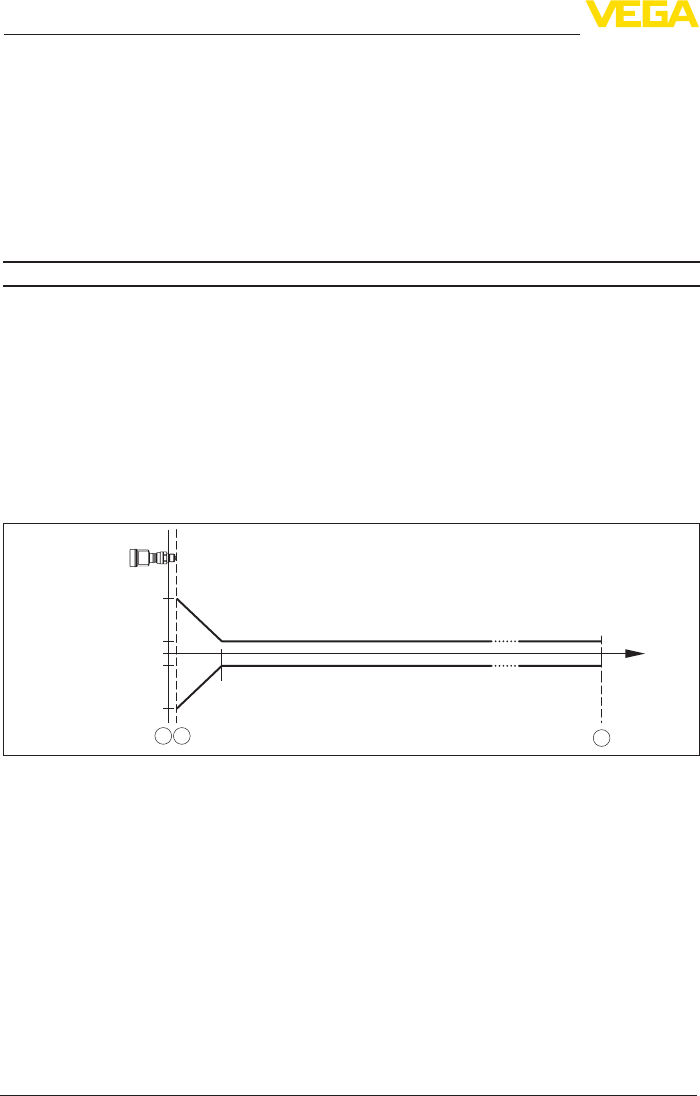
72
11 Supplement
VEGAPULS 64 • 4 … 20 mA/HART - two-wire
51141-EN-160616
HART output values according to HART 7.01)
ƲPV (Primary Value) Lin. percent
ƲSV (Secondary Value) Distance
ƲTV (Third Value) Meas. certainty
ƲQV (Fourth Value) Electronics temperature
FullledHARTspecication 7.0
Further information on Manufacturer ID,
Device ID, Device Revision
See website of HART Communication Foundation
Accuracy (according to DIN EN 60770-1)
Process reference conditions according to DIN EN 61298-1
ƲTemperature +18 … +30 °C (+64 … +86 °F)
ƲRelative humidity 45 … 75 %
ƲAir pressure 860 … 1060 mbar/86 … 106 kPa (12.5 … 15.4 psig)
Installation reference conditions
ƲMin. distance to internal installations > 200 mm (7.874 in)
Ʋ Reector Flatplatereector
Ʋ Falsereections Biggest false signal, 20 dB smaller than the useful signal
Deviation with liquids See following diagrams
0,25 m (0.8202 ft)
10 mm (0.3937 in)
- 10 mm (- 0.3937 in)
2 mm (0.079 in)
- 2 mm (- 0.079 in)
0
123
Fig. 56: Deviation under reference conditions - thread with integrated horn antenna
1 Reference plane
2 Antenna edge
3 Recommended measuring range
1) Default values can be assigned individually.

73
11 Supplement
VEGAPULS 64 • 4 … 20 mA/HART - two-wire
51141-EN-160616
0,25 m (0.8202 ft)
10 mm (0.3937 in)
- 10 mm (- 0.3937 in)
2 mm (0.079 in)
- 2 mm (- 0.079 in)
0
1 2 3
Fig. 57: Deviation under reference conditions - plastic horn antenna
1 Reference plane
2 Antenna edge
3 Recommended measuring range
0,25 m (0.8202 ft)
10 mm (0.3937 in)
- 10 mm (- 0.3937 in)
0
2 mm (0.079 in)
- 2 mm (- 0.079 in)
1
3
2
Fig. 58: Deviation under reference conditions - ange with encapsulated antenna system
1 Reference plane
2 Antenna edge
3 Recommended measuring range
Repeatability ≤±1mm
Deviation with bulk solids The values depend to a great extent on the application.
Bindingspecicationsarethusnotpossible.
Variablesinuencingmeasurementaccuracy
Specicationsapplytothedigitalmeasuredvalue
Temperature drift - Digital output ±3mm/10K,max.10mm
Specicationsapplyalsotothecurrentoutput
Temperature drift - Current output ±0.03%/10Krelatingtothe16mAspanmax.±0.3%
Deviation on the current output through analogue/digital conversion
ƲNon-Ex and Ex-ia version <±15µA
ƲEx-d-ia version <±40µA
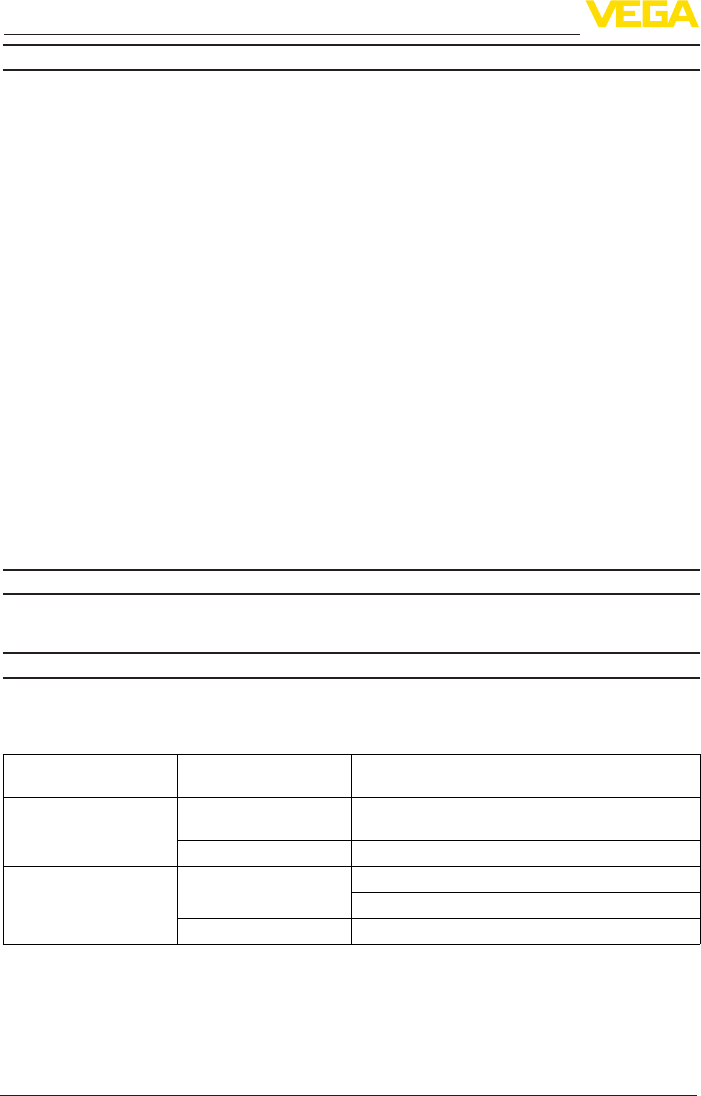
74
11 Supplement
VEGAPULS 64 • 4 … 20 mA/HART - two-wire
51141-EN-160616
Characteristics and performance data
Measuring frequency W-band(79GHztechnology)
Measuring cycle time approx.2) 700 ms
Step response time3) ≤3s
Beam angle4)
ƲPlastic horn antenna 3°
ƲThread ¾" with integrated horn
antenna
14°
ƲThread 1½" with integrated horn
antenna
7°
ƲFlange DN 50/2" with encapsulated
antenna system
6°
ƲFlange DN 80/3" with encapsulated
antenna system
3°
Ʋ Hygienicttings 6°
Emitted HF power (depending on the parameter adjustment)5)
ƲAverage spectral transmission power
density
-3dBm/MHzEIRP
ƲMax. spectral transmission power
density
+34dBm/50MHzEIRP
ƲMax. power density at a distance of
1 m
< 3 µW/cm²
Ambient conditions
Ambient, storage and transport tempera-
ture
-40 … +80 °C (-40 … +176 °F)
Process conditions
Fortheprocessconditions,pleasealsonotethespecicationsonthetypelabel.Thelowestvalue
always applies.
Process temperature
Antenna lens Seal Process temperature (measured on the process
tting)
PP FKM (SHS FPM 70C3
GLT)
-40 … +80 °C (-40 … +176 °F)
EPDM (COG AP310) -40 … +80 °C (-40 … +176 °F)
PEEK FKM (SHS FPM 70C3
GLT)
-40 … +130 °C (-40 … +266 °F)
-40 … +200 °C (-40 … +392 °F)
EPDM (COG AP302) -40 … +130 °C (-40 … +266 °F)
2) With operating voltage UB≥24VDC
3) Timespanafterasuddendistancechangefrom1mto5muntiltheoutputsignalreaches90%ofthenal
valueforthersttime(IEC61298-2).ValidwithoperatingvoltageUB≥24VDC
4) Outsidethespeciedbeamangle,theenergyleveloftheradarsignalis50%(-3dB)less.
5) EIRP: Equivalent Isotropic Radiated Power.

75
11 Supplement
VEGAPULS 64 • 4 … 20 mA/HART - two-wire
51141-EN-160616
Antenna lens Seal Process temperature (measured on the process
tting)
PTFE PTFE -40 … +130 °C (-40 … +266 °F)
-40 … +200 °C (-40 … +392 °F)
Ambient temperature - Process temperature
1
2
0 °C
(32 °F)
-40 °C
(-104 °F)
80 °C
(176 °F)
80 °C
(176 °F)
-40 °C
(-104 °F)
Fig. 59: Ambient temperature - Process temperature, plastic horn antenna
1 Ambient temperature
2 Process temperature
1
/
23
4
A
B
0°C / 32°F
-40°C / -40°F
80°C / 176°F
42°C / 108°F
50°C / 122°F
65°C / 149°F
130°C
266°F
100°C
212°F
50°C
122°F
80°C
176°F
-40°C
-40°F
Fig. 60: Ambient temperature - Process temperature, thread G¾ and G1½ with integrated horn antenna up to
+130 °C (+266 °F)
A Ambient temperature
B Process temperature
1 Aluminium housing
2 Plastic housing
3 Stainless steel housing, precision casting
4 Stainless steel housing, electropolished

76
11 Supplement
VEGAPULS 64 • 4 … 20 mA/HART - two-wire
51141-EN-160616
0°C / 32°F
-40°C / -40°F
80°C / 176°F
53°C / 127°F
56°C / 133°F
48°C / 118°F
64°C / 147°F
200°C
392°F
150°C
302°F
100°C
212°F
50°C
122°F
80°C
176°F
-40°C
-40°F
1
2
3
4
A
B
Fig. 61: Ambient temperature - Process temperature, thread G¾ and G1½ with integrated horn antenna up to
+200 °C (+392 °F)
A Ambient temperature
B Process temperature
1 Aluminium housing
2 Plastic housing
3 Stainless steel housing, precision casting
4 Stainless steel housing, electropolished
1
2/3
4
A
B
0°C / 32°F
-40°C / -40°F
80°C / 176°F
58°C / 136°F
62°C / 144°F
66°C / 151°F
130°C
266°F
100°C
212°F
50°C
122°F
80°C
176°F
-40°C
-40°F
Fig. 62: Ambient temperature - Process temperature, ange DN 50/2" and DN 80/3" with encapsulated antenna
system up to +130 °C (+266 °F)
A Ambient temperature
B Process temperature
1 Aluminium housing
2 Plastic housing
3 Stainless steel housing, precision casting
4 Stainless steel housing, electropolished
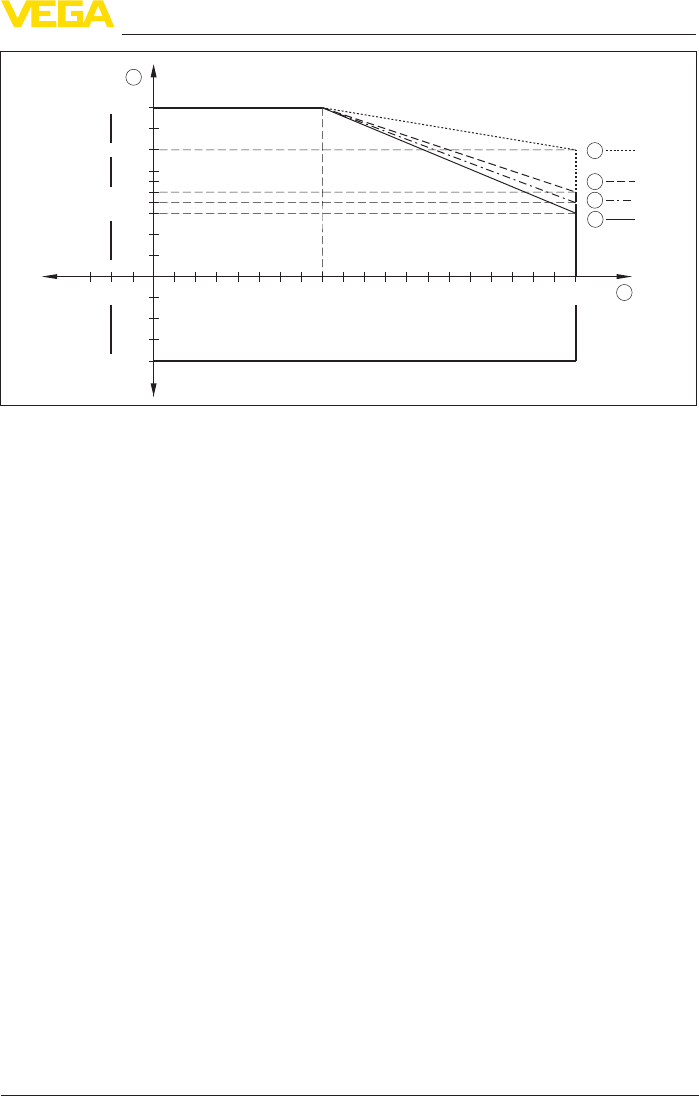
77
11 Supplement
VEGAPULS 64 • 4 … 20 mA/HART - two-wire
51141-EN-160616
0°C / 32°F
-40°C / -40°F
80°C / 176°F
57°C / 135°F
60°C / 140°F
52°C / 126°F
67°C / 159°F
200°C
392°F
150°C
302°F
100°C
212°F
50°C
122°F
80°C
176°F
-40°C
-40°F
1
2
3
4
A
B
Fig. 63: Ambient temperature - Process temperature, ange DN 50/2" and DN 80/3" with encapsulated antenna
system up to +200 °C (+392 °F)
A Ambient temperature
B Process temperature
1 Aluminium housing
2 Plastic housing
3 Stainless steel housing, precision casting
4 Stainless steel housing, electropolished
Vessel pressure
Vessel pressure
ƲPlastic horn antenna -1 … 2 bar (-100 … 200 kPa/-14.5 … 29.1 psig)
ƲPlastic horn antenna - Version with
adapterangefromDN100PPor
PP-GF 30
-1 … 1 bar (-100 … 100 kPa/-14.5 … 14.5 psig)
ƲThread with integrated horn antenna -1 … 20 bar (-100 … 2000 kPa/-14.5 … 290.1 psig)
ƲFlange with encapsulated antenna
system
-1 … 16 bar (-100 … 2000 kPa/-14.5 … 232.0 psig)
Vesselpressurerelatingtotheange
nominal pressure stage
see supplementary instructions manual "Flanges ac-
cording to DIN-EN-ASME-JIS"
Mechanial stresses
Vibration resistance - Plastic horn antenna
Ʋ Withadapterange 2gat5…200HzaccordingtoEN60068-2-6(vibration
with resonance)
Ʋwith mounting strap 1gat5…200HzaccordingtoEN60068-2-6(vibration
with resonance)
Vibration resistance - Thread with
integratedhornantenna,angewith
encapsulated antenna system
4gat5…200HzaccordingtoEN60068-2-6(vibration
with resonance)
Shock resistance 100 g, 6 ms according to EN 60068-2-27 (mechanical
shock)
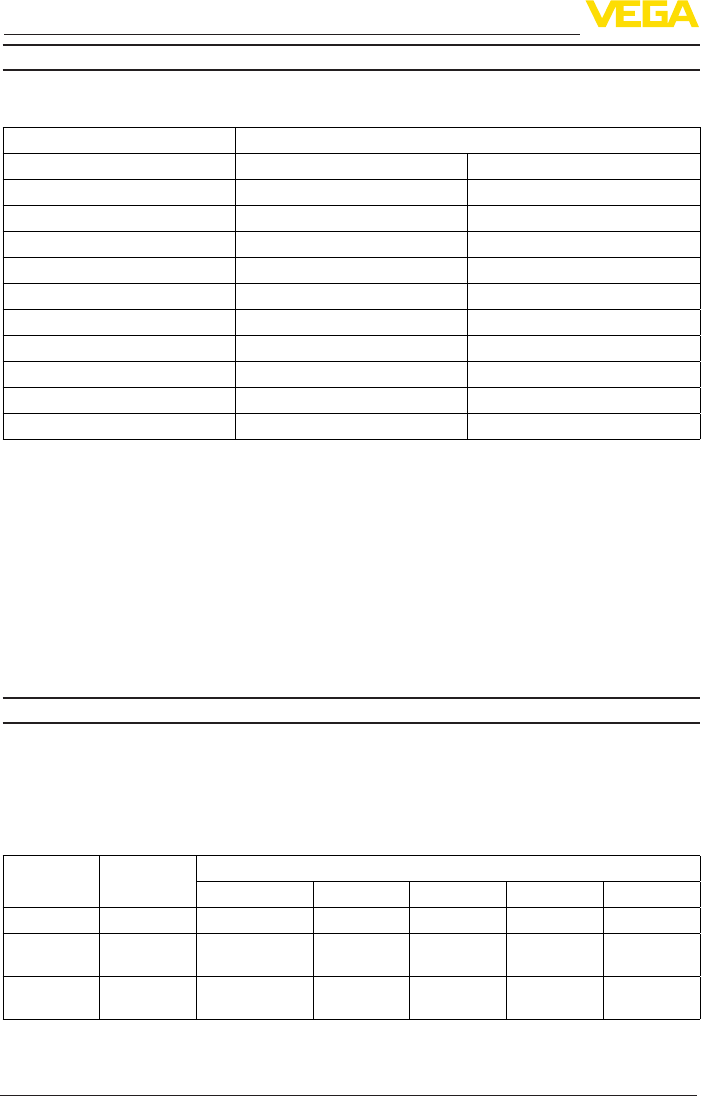
78
11 Supplement
VEGAPULS 64 • 4 … 20 mA/HART - two-wire
51141-EN-160616
Data on rinsing air connection
Max. permissible pressure 6 bar (87.02 psig)
Air volume, depending on pressure (recommended range)
Plastic horn antenna Air volume
Pressure Withoutreuxvalve Withreuxvalve
0.2 bar (2.9 psig) 3.3 m3/h -
0.4 bar (5.8 psig) 5 m3/h -
0.6 bar (8.7 psig) 6 m3/h 1 m3/h
0.8 bar (11.6 psig) - 2.1 m3/h
1 bar (14.5 psig) - 3 m3/h
1.2 bar (17.4 psig) - 3.5 m3/h
1.4 bar (20.3 psig) - 4.2 m3/h
1.6 bar (23.2 psig) - 4.4 m3/h
1.8 bar (20.3 psig) - 4.8 m3/h
2 bar (23.2 psig) - 5.1 m3/h
Connection
ƲThread G⅛
Reuxvalve-(optional,isabsolutelynecessaryforExapplications)
ƲMaterial 316Ti
ƲThread G⅛
ƲSeal FKM (SHS FPM 70C3 GLT), EPDM (COG AP310)
ƲFor connection G⅛
ƲOpening pressure 0.5 bar (7.25 psig)
ƲNominal pressure stage PN 250
Electromechanical data - version IP 66/IP 67 and IP 66/IP 68; 0.2 bar
Options of the cable entry
ƲCable entry M20 x 1.5, ½ NPT
ƲCable gland M20 x 1,5; ½ NPT (cable ø see below table)
ƲBlind plug M20 x 1.5; ½ NPT
ƲClosing cap ½ NPT
Material ca-
ble gland
Material seal
insert
Cable diameter
4.5 … 8.5 mm 5 … 9 mm 6 … 12 mm 7 … 12 mm 10 … 14 mm
PA NBR – ● ● –●
Brass, nickel-
plated
NBR ● ● ● – –
Stainless
steel
NBR –● ● –●
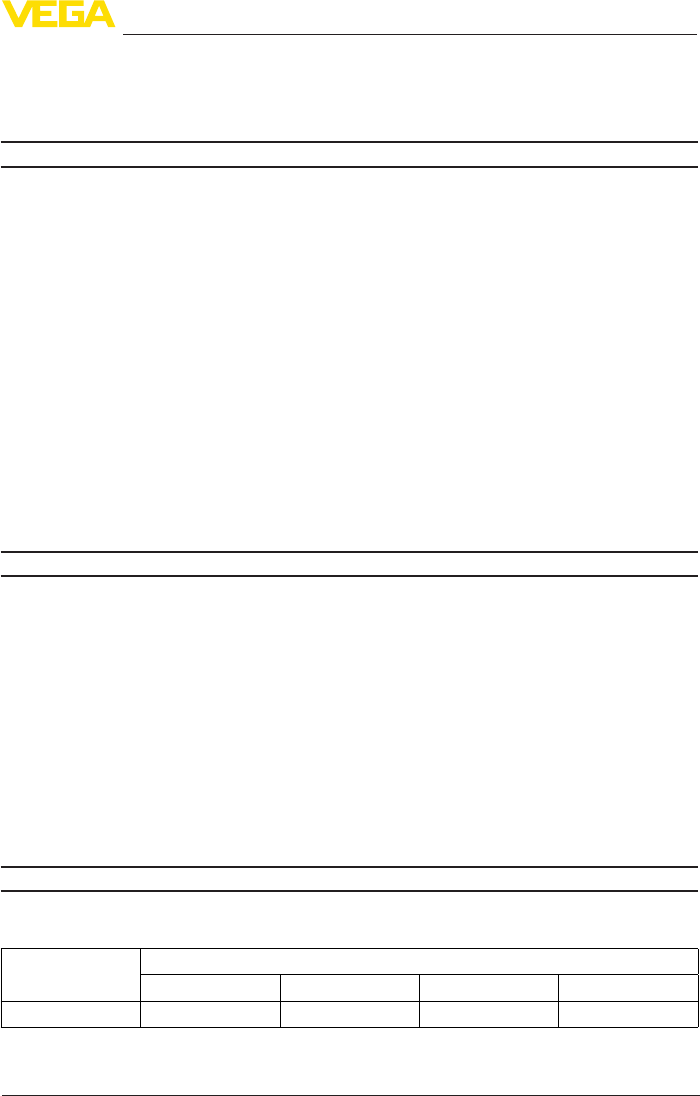
79
11 Supplement
VEGAPULS 64 • 4 … 20 mA/HART - two-wire
51141-EN-160616
Wire cross-section (spring-loaded terminals)
ƲMassive wire, stranded wire 0.2 … 2.5 mm² (AWG 24 … 14)
ƲStranded wire with end sleeve 0.2 … 1.5 mm² (AWG 24 … 16)
Electromechanical data - version IP 66/IP 68 (1 bar)
Options of the cable entry
ƲCable gland with integrated connec-
tion cable
M20 x 1.5 (cable: ø 5 … 9 mm)
ƲCable entry ½ NPT
ƲBlind plug M20 x 1.5; ½ NPT
Connection cable
ƲWire cross-section 0.5 mm² (AWG 20)
ƲWire resistance <0.036Ω/m
ƲTensile strength < 1200 N (270 lbf)
ƲStandard length 5 m (16.4 ft)
ƲMax. length 180 m (590.6 ft)
ƲMin. bending radius 25 mm (0.984 in) with 25 °C (77 °F)
ƲDiameter approx. 8 mm (0.315 in)
ƲColour - Non-Ex version Black
ƲColour - Ex-version Blue
Display and adjustment module
Display element Display with backlight
Measured value indication
ƲNumber of digits 5
Ʋ Sizeofdigits W x H = 7 x 13 mm
Adjustment elements 4 keys
Protection rating
Ʋunassembled IP 20
Ʋmounted in the housing without lid IP 40
Materials
ƲHousing ABS
ƲInspection window Polyester foil
Interface to the external display and adjustment unit
Data transmission Digital (I²C-Bus)
Connection cable Four-wire
Sensor version Conguration,connectioncable
Cable length max. Standard cable Special cable Screened
4 … 20 mA/HART 50 m ●–●
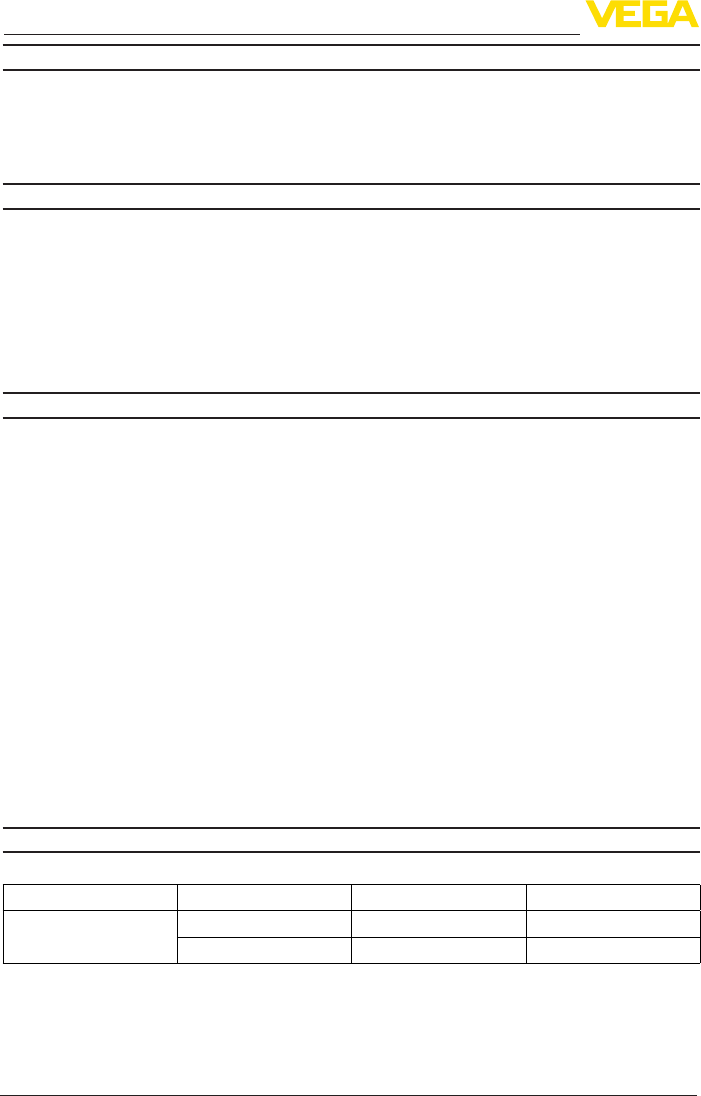
80
11 Supplement
VEGAPULS 64 • 4 … 20 mA/HART - two-wire
51141-EN-160616
Integrated clock
Date format Day.Month.Year
Time format 12 h/24 h
TimezoneExfactory CET
Rate deviation max. 10.5 min/year
Additional output parameter - Electronics temperature
Output of the temperature values
ƲAnalogue Via the current output
ƲDigital Via the digital output signal - depending on the electron-
ics version
Range -40 … +85 °C (-40 … +185 °F)
Resolution < 0.1 K
Accuracy ±3K
Voltage supply
Operating voltage UB
ƲNon-Ex instrument 12 … 35 V DC
ƲEx-d instrument 12 … 35 V DC
ƲEx ia instrument 12 … 30 V DC
Operating voltage UB - illuminated display and adjustment module
ƲNon-Ex instrument 18 … 35 V DC
ƲEx-d instrument 18 … 35 V DC
ƲEx ia instrument 18 … 30 V DC
Reverse voltage protection Integrated
Permissible residual ripple - Non-Ex, Ex-ia instrument
Ʋfor 12 V< UB < 18 V ≤0.7Ve(16…400Hz)
Ʋfor 18 V< UB < 35 V ≤1.0Ve(16…400Hz)
Load resistor
ƲCalculation (UB - Umin)/0.022 A
ƲExample - Non-Ex instrument with
UB= 24 V DC
(24V-12V)/0.022A=545Ω
Electrical protective measures
Protection rating
Housing material Version IP-protection class NEMA protection
Plastic Single chamber IP 66/IP 67 Type4X
Double chamber IP 66/IP 67 Type4X
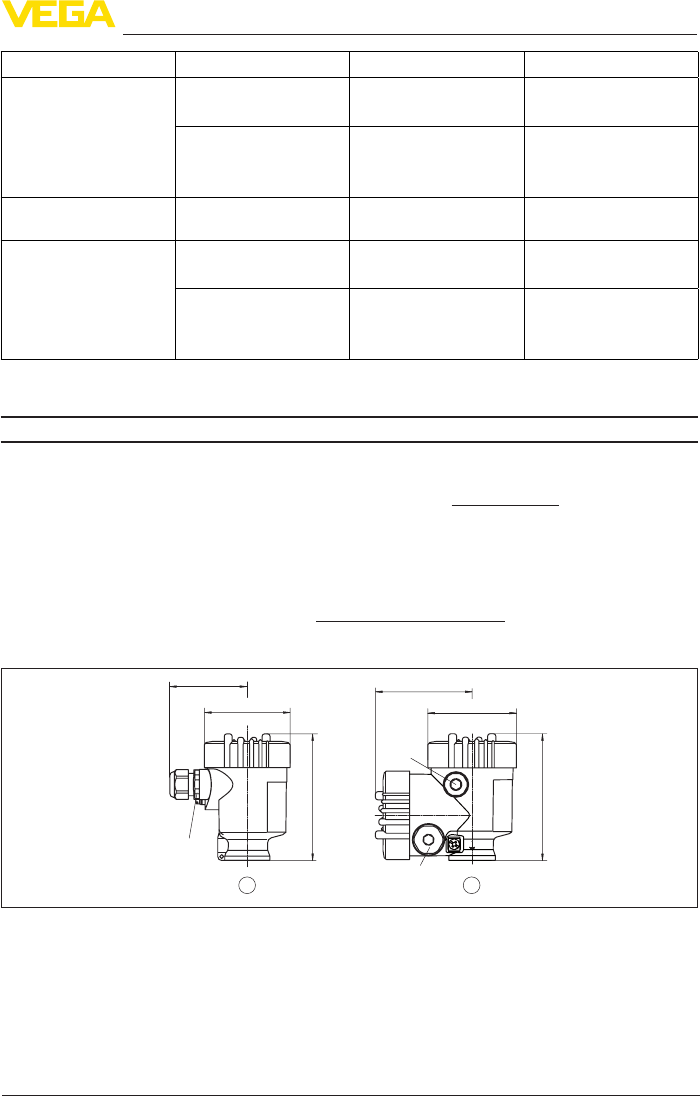
81
11 Supplement
VEGAPULS 64 • 4 … 20 mA/HART - two-wire
51141-EN-160616
Housing material Version IP-protection class NEMA protection
Aluminium Single chamber IP 66/IP 68 (0.2 bar)
IP 68 (1 bar)
Type 6P
Type 6P
Double chamber IP 66/IP 67
IP 66/IP 68 (0.2 bar)
IP 68 (1 bar)
Type4X
Type 6P
Type 6P
Stainless steel, electro-
polished
Single chamber IP 66/IP 68 (0.2 bar) Type 6P
Stainless steel, precision
casting
Single chamber IP 66/IP 68 (0.2 bar)
IP 68 (1 bar)
Type 6P
Type 6P
Double chamber IP 66/IP 67
IP 66/IP 68 (0.2 bar)
IP 68 (1 bar)
Type4X
Type 6P
Type 6P
Protection rating (IEC 61010-1) III
Approvals
Instrumentswithapprovalscanhavedierenttechnicalspecicationsdependingontheversion.
For that reason the associated approval documents of these instruments have to be carefully
noted. They are part of the delivery or can be downloaded under www.vega.com, "VEGA Tools"
and "Instrument search" as well as in the download area.
11.2 Dimensions
The following dimensional drawings represent only an extract of all possible versions. Detailed
dimensional drawings can be downloaded at www.vega.com/downloads under "Drawings".
Plastic housing
~ 69 mm
(2.72")
ø 79 mm
(3.11")
112 mm
(4.41")
M20x1,5/
½ NPT
~ 84 mm
(3.31")
M16x1,5
112 mm
(4.41")
M20x1,5/
½ NPT
12
ø 79 mm
(3.11")
Fig. 64: Housing versions with protection rating IP 66/IP 67 - with integrated display and adjustment module the
housing is 9 mm/0.35 in higher
1 Single chamber version
2 Double chamber version

82
11 Supplement
VEGAPULS 64 • 4 … 20 mA/HART - two-wire
51141-EN-160616
Aluminium housing
21
ø 86 mm
(3.39")
~ 116 mm
(4.57")
116 mm
(4.57")
M20x1,5
M20x1,5/
½ NPT
~ 87 mm
(3.43")
M16x1,5
ø 86 mm
(3.39")
120 mm
(4.72")
M20x1,5/
½ NPT
Fig. 65: Housing versions with protection rating IP 66/IP 68 (0.2 bar) - with integrated display and adjustment
module the housing is 9 mm/0.35 in higher
1 Single chamber version
2 Double chamber version
Aluminium housing with protection rating IP 66/IP 68 (1 bar)
120 mm
(4.72")
~ 105 mm
(4.13")
116 mm
(4.57")
~ 150 mm
(5.91")
ø 86 mm
(3.39")
ø 86 mm
(3.39")
M20x1,5/
½ NPT
M16x1,5
2
M20x1,5
M20x1,5
1
Fig. 66: Housing version with protection rating IP 66/IP 68 (1 bar) - with integrated display and adjustment module
the housing is 9 mm/0.35 in higher
1 Single chamber version
2 Double chamber version
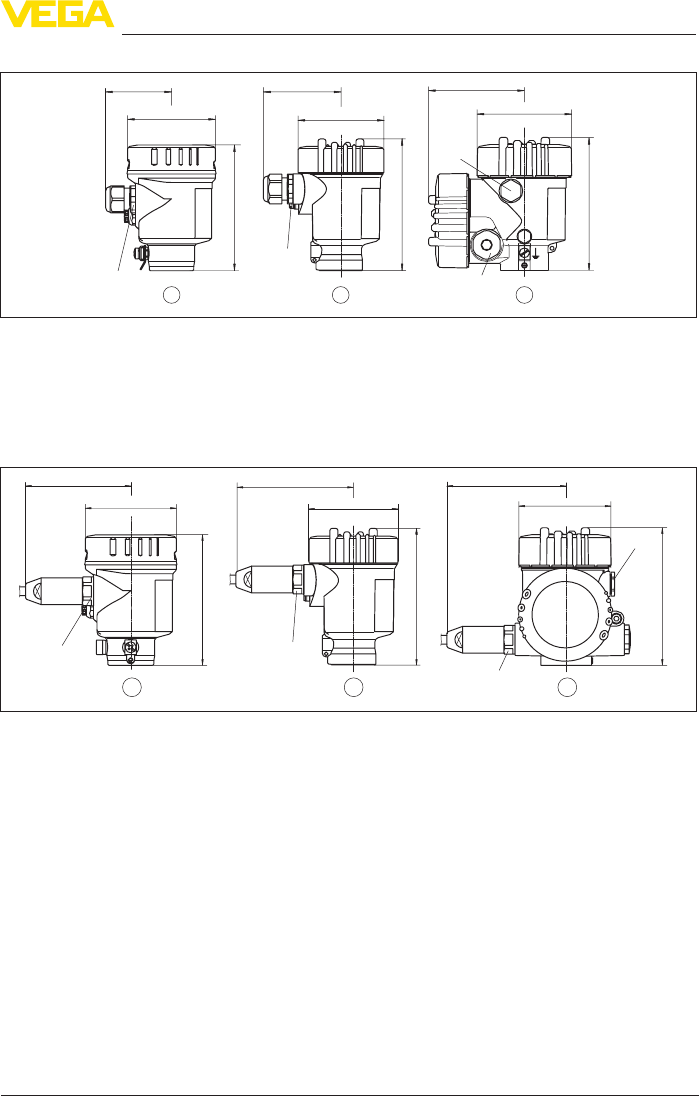
83
11 Supplement
VEGAPULS 64 • 4 … 20 mA/HART - two-wire
51141-EN-160616
Stainless steel housing
~ 69 mm
(2.72")
ø 79 mm
(3.11")
117 mm
(4.61")
M20x1,5/
½ NPT
~ 59 mm
(2.32")
ø 80 mm
(3.15")
112 mm
(4.41")
M20x1,5/
½ NPT
~ 87 mm
(3.43") ø 86 mm
(3.39")
120 mm
(4.72")
M20x1,5/
½ NPT
M16x1,5
321
Fig. 67: Housing versions with protection rating IP 66/IP 68 (0.2 bar) - with integrated display and adjustment
module the housing is 9 mm/0.35 in higher
1 Single chamber version, electropolished
2 Single chamber version, precision casting
3 Double chamber version, precision casting
Stainless steel housing with protection rating IP 66/IP 68, 1 bar
117 mm
(4.61")
~ 103 mm
(4.06") ø 79 mm
(3.11")
120 mm
(4.72")
~ 105 mm
(4.13") ø 86 mm
(3.39")
M20x1,5
M20x1,5/
½ NPT
M16x1,5
~ 93 mm
(3.66") ø 80 mm
(3.15")
112 mm
(4.41")
M20x1,5/
½ NPT
3
21
Fig. 68: Housing version with protection rating IP 66/IP 68 (1 bar) - with integrated display and adjustment module
the housing is 9 mm/0.35 in higher
1 Single chamber version, electropolished
2 Single chamber version, precision casting
3 Double chamber version, precision casting
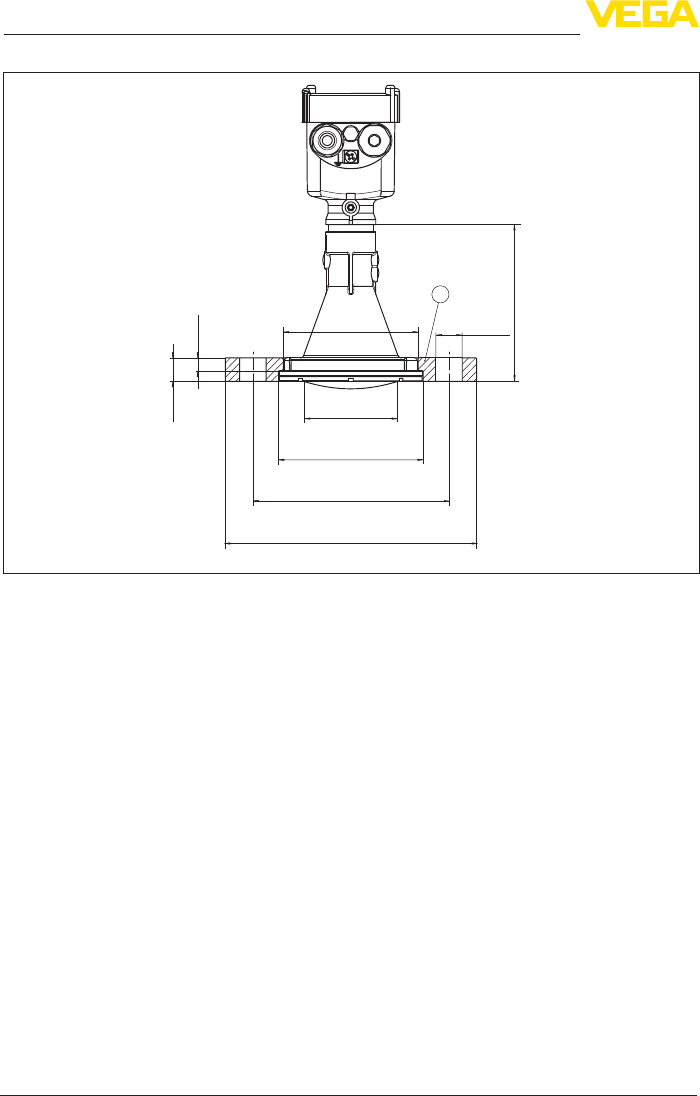
84
11 Supplement
VEGAPULS 64 • 4 … 20 mA/HART - two-wire
51141-EN-160616
VEGAPULS64,plastichornantennawithcompressionange
126 mm
(4.96")
10,5 mm
(0.41")
19 mm
(0.75")
ø 75 mm
(2.95")
ø 115 mm
(4.53")
ø 156 mm
(6.14")
ø 200 mm
(7.87")
ø 21 mm
(0.83")
ø 107 mm
(4.21")
1
Fig. 69: Radar sensor with compression ange
1 Compression ange

85
11 Supplement
VEGAPULS 64 • 4 … 20 mA/HART - two-wire
51141-EN-160616
VEGAPULS64,plastichornantennawithcompressionangeandrinsingconnection
126 mm
(4.96")
14,7 mm
(0.58")
10,5 mm
(0.41")
26,5 mm
(1.04")
19 mm
(0.75")
ø 75 mm
(2.95")
ø 156 mm
(6.14")
ø 200 mm
(7.87")
ø 21 mm
(0.83")
ø 107 mm
(4.21")
1
2
3
Fig. 70: Radar sensor with compression ange and rinsing connection
1 Compression ange
2 Reux valve
3 Rinsing connection
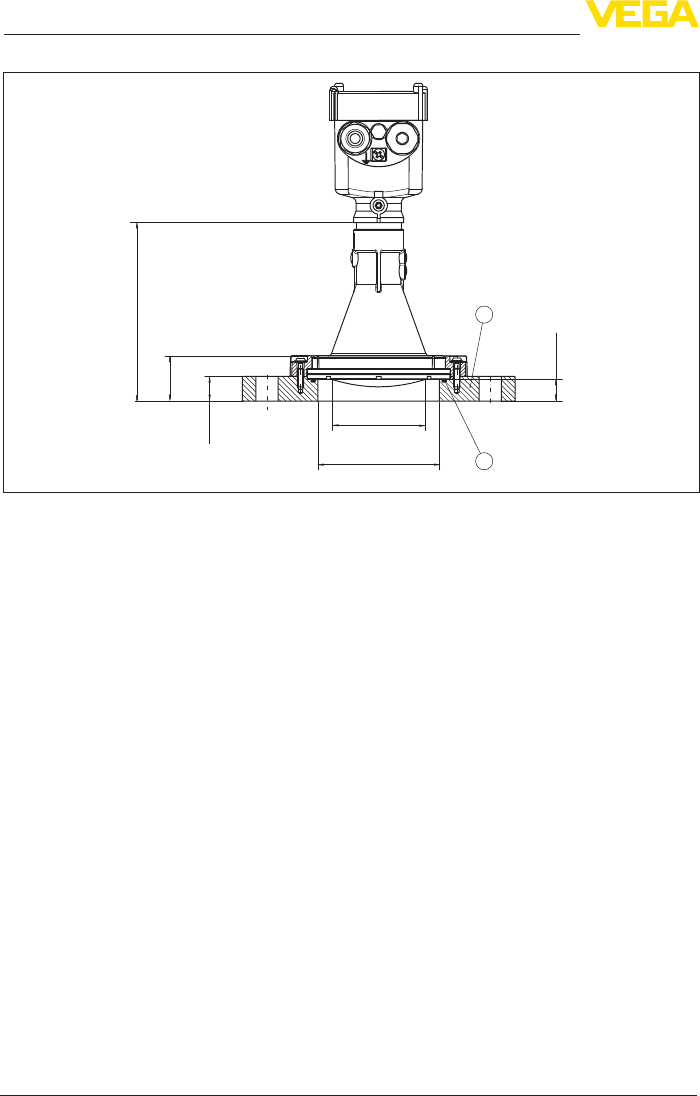
86
11 Supplement
VEGAPULS 64 • 4 … 20 mA/HART - two-wire
51141-EN-160616
VEGAPULS64,plastichornantennawithadapterange
2
1
144 mm
(5.67")
36,5 mm
(1.44")
20 mm
(0.79")
17,5 mm
(0.69")
ø 75 mm
(2.95")
ø 98 mm
(3.86")
Fig. 71: Radar sensor with adapter ange
1 Adapter ange
2 Process seal

87
11 Supplement
VEGAPULS 64 • 4 … 20 mA/HART - two-wire
51141-EN-160616
VEGAPULS64,plastichornantennamitadapterangeundrinsingconnection
3
21
170 mm
(6.69")
62,5 mm
(2.46")
20 mm
(0.79")
34,7 mm
(1.37")
ø 75 mm
(2.95")
ø 98 mm
(3.86")
Fig. 72: VEGAPULS 64, adapter ange and rinsing connection
1 Rinsing air connection
2 Reux valve
3 Adapter ange

88
11 Supplement
VEGAPULS 64 • 4 … 20 mA/HART - two-wire
51141-EN-160616
VEGAPULS 64, plastic horn antenna with mounting strap
125 mm
(4.92")
2,5 mm
(0.10")
ø 75 mm
(2.95")
ø 107 mm
(4.21")
ø 115 mm
(4.53")
300 mm
(11.81")
19 mm
(0.75")
98 mm
(3.86")
6 mm
(0.24")
8,5 mm
(0.34")
9 mm
(0.35")
85 mm
(3.35")
12 mm
(0.47")
9 mm
(0.35")
12 mm
(0.47")
170 mm
(6.69")
Fig. 73: VEGAPULS 64, plastic horn antenna, mounting strap in 170 or 300 mm length

89
11 Supplement
VEGAPULS 64 • 4 … 20 mA/HART - two-wire
51141-EN-160616
VEGAPULS 64, thread with integrated horn antenna
TA
25 mm
(0.98")
61 mm
(2.40")
ø 24 mm
(0.94")
SW 36 mm
(1.42")
G¾
TB
25 mm
(0.98")
61 mm
(2.40")
ø 24 mm
(0.94")
SW 36 mm
(1.42")
¾ NPT
G1 ½
101 mm
(3.98")
33 mm
(1.31")
ø 42,5 mm
(1.67")
ø 42,5 mm
(1.67")
1 ½ NPT
SW 55 mm
(2.17")
101 mm
(3.98")
33 mm
(1.31")
SW 55 mm
(2.17")
TC TD
Fig. 74: VEGAPULS 64, thread with integrated horn antenna
TA G¾ (DIN 3852-E)
TB ¾ NPT (ASME B1.20.1)
TC G1½ (DIN 3852-A)
TD 1½ NPT (ASME B1.20.1)

90
11 Supplement
VEGAPULS 64 • 4 … 20 mA/HART - two-wire
51141-EN-160616
VEGAPULS64,angewithencapsulatedantennasystemDN50
21
141 mm
(5.55")
89 mm
(3.50")
19 mm
(0.75")
ø45 mm
(1.77")
ø102 mm
(4.02")
19 mm
(0.75")
Fig. 75: VEGAPULS 64, encapsulated antenna system DN 50
1 Version up to 130 °C (266 °F)
2 Version up to 200 °C (392 °F)
VEGAPULS64,angewithencapsulatedantennasystemDN80
181 mm
(7.13")
129 mm
(5.08")
32 mm
(1.25")
ø75 mm
(2.95")
ø138 mm
(5.43")
32 mm
(1.25")
21
Fig. 76: VEGAPULS 64, encapsulated antenna system DN 80
1 Version up to 130 °C (266 °F)
2 Version up to 200 °C (392 °F)
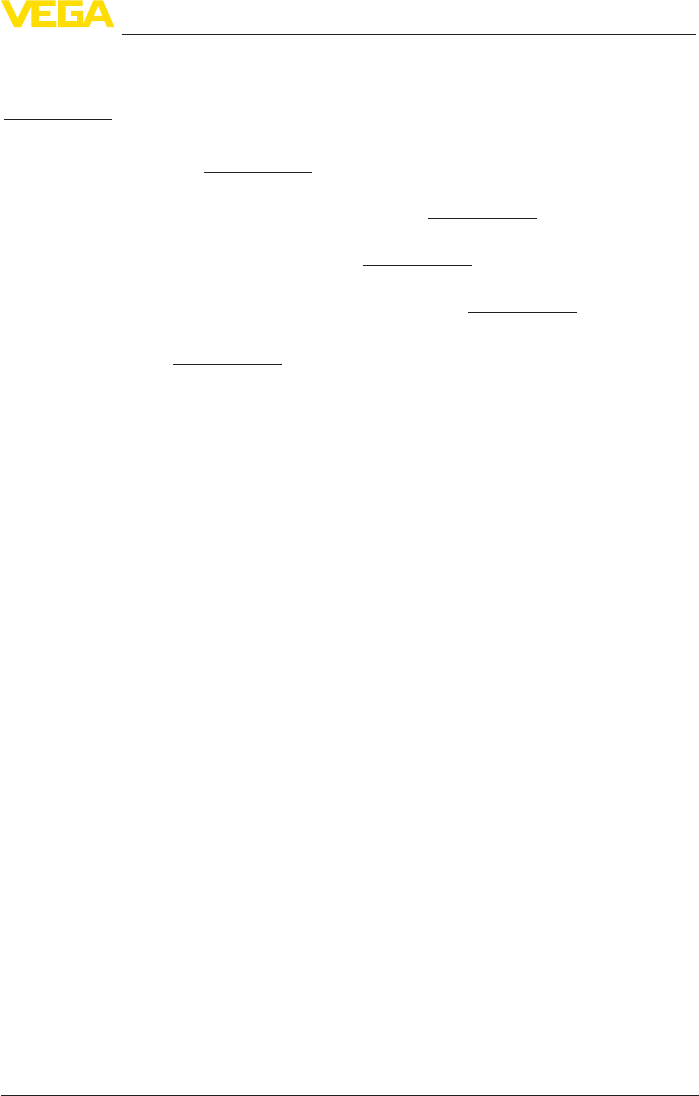
91
11 Supplement
VEGAPULS 64 • 4 … 20 mA/HART - two-wire
51141-EN-160616
11.3 Industrial property rights
VEGA product lines are global protected by industrial property rights. Further information see
www.vega.com.
VEGA Produktfamilien sind weltweit geschützt durch gewerbliche Schutzrechte.
Nähere Informationen unter www.vega.com.
Les lignes de produits VEGA sont globalement protégées par des droits de propriété intellec-
tuelle. Pour plus d'informations, on pourra se référer au site www.vega.com.
VEGA lineas de productos están protegidas por los derechos en el campo de la propiedad indus-
trial. Para mayor información revise la pagina web www.vega.com.
Линии продукции фирмы ВЕГА защищаются по всему миру правами на интеллектуальную
собственность. Дальнейшую информацию смотрите на сайте www.vega.com.
VEGA系列产品在全球享有知识产权保护。
进一步信息请参见网站<www.vega.com。
11.4 Trademark
All the brands as well as trade and company names used are property of their lawful proprietor/
originator.

92
INDEX
VEGAPULS 64 • 4 … 20 mA/HART - two-wire
51141-EN-160616
INDEX
A
Adjustment 42, 43
Agitator 23
C
Change the language 44
Check output signal 63
Connection 27
– Cable 26
Copy sensor settings 49
Current output
– Adjust 49
– Min./Max. 44
– Mode 43
D
Damping 43
Date/Time 47
Default values 48
Deviation 63
Display lighting 45
E
Echo curve
– Indication 45
– Memory 58
– Setup 46
EDD (Enhanced Device Description) 57
Electronics and terminal compartment 29
Error codes 61
Event memory 58
F
False signal suppression 50
Faultrectication63
Flow measurement 24, 25
Foam generation 24
Functional principle 11
G
Grounding 27
H
HART
– Address 51
– Resistor 54
I
Inowingmedium20
L
Linearization51
M
Main menu 36
Measured value memory 58
Measurement loop name 37
Mounting
– Flange 17
– Position 19
– Strap 15
Mounting socket 21, 22
N
NAMUR NE 107 59, 60, 62
O
Operation 35
– Lock 44
P
Peak value indicator 45
Polarisation 19
R
Repair 67
Reset 47
S
Sensor orientation 23
Sensor status 45
Service hotline 66
Set display parameters 45
Simulation 46
Special parameters 51
T
Type label 10
V
Vessel
– Form 40
– Height 41
Vessel installations 23

93
Notes
VEGAPULS 64 • 4 … 20 mA/HART - two-wire
51141-EN-160616

94
Notes
VEGAPULS 64 • 4 … 20 mA/HART - two-wire
51141-EN-160616
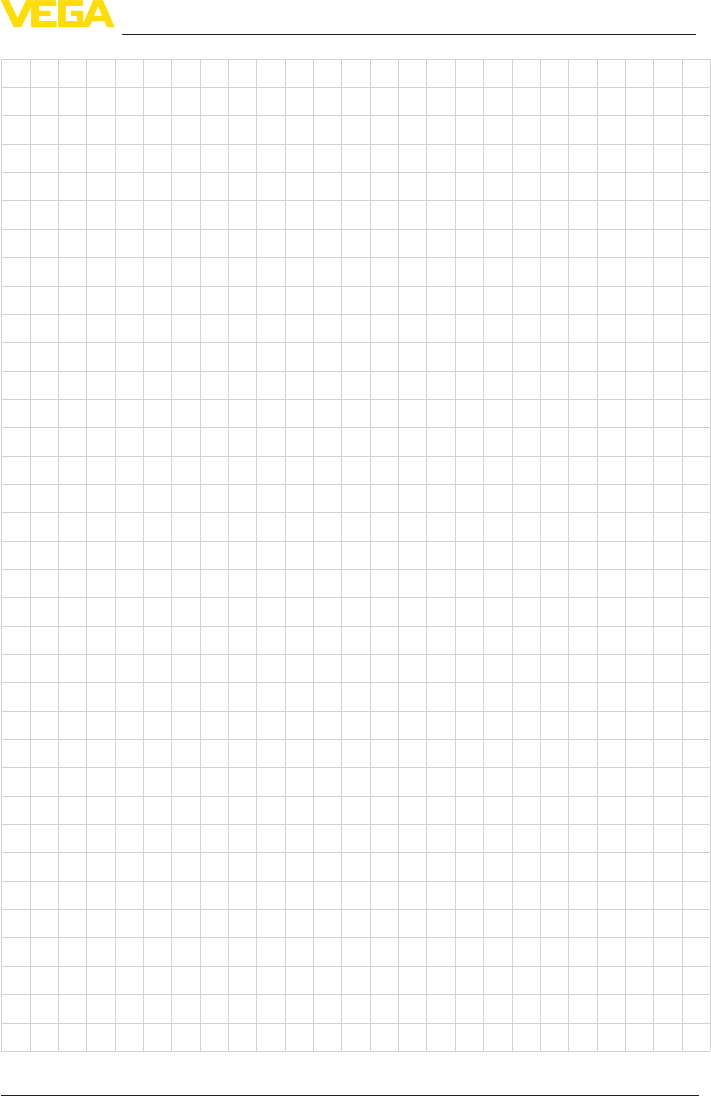
95
Notes
VEGAPULS 64 • 4 … 20 mA/HART - two-wire
51141-EN-160616
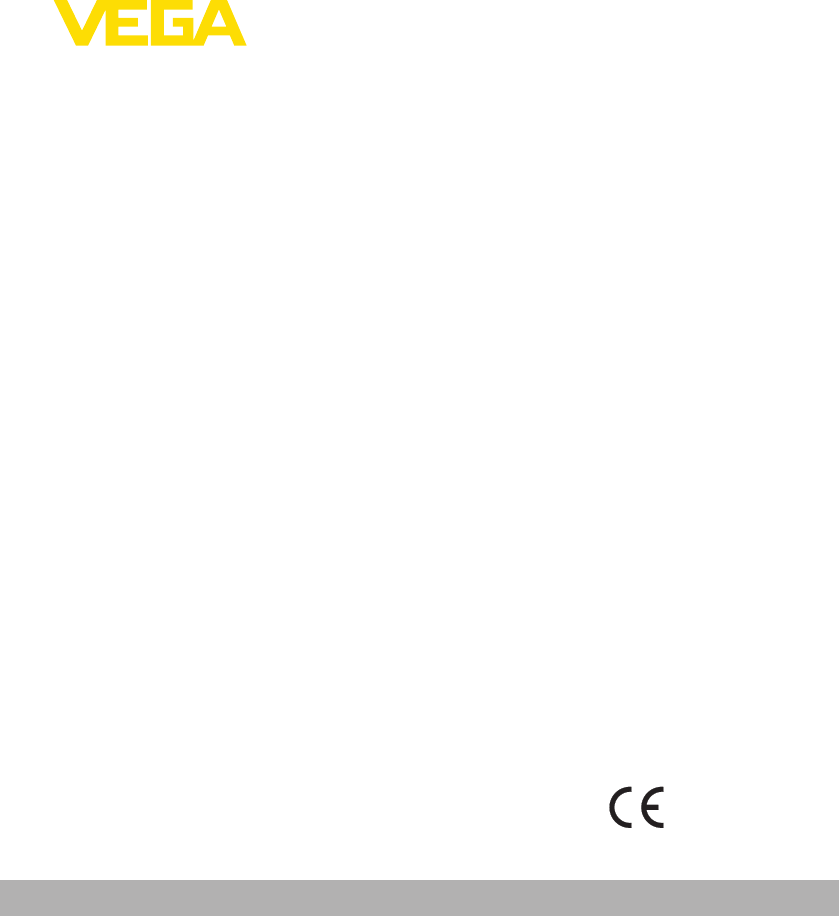
Printing date:
VEGA Grieshaber KG
Am Hohenstein 113
77761 Schiltach
Germany
51141-EN-160616
All statements concerning scope of delivery, application, practical use and operat-
ing conditions of the sensors and processing systems correspond to the information
available at the time of printing.
Subject to change without prior notice
© VEGA Grieshaber KG, Schiltach/Germany 2016
Phone +49 7836 50-0
Fax +49 7836 50-201
E-mail: info.de@vega.com
www.vega.com