ADC Telecommunications AKAD19 GSM Base Station User Manual
ADC Telecommunications Inc. GSM Base Station
User Manual

Installation and
Commissioning Guide
SW Release 7.2
July 2006
P/N 214323
UltraWAVE Micro BTS

ii UltraWAVE Micro BTS Installation and Commissioning Guide, Version B
Legal Rights
The material contained herein is proprietary, privileged, and confidential and
owned by Alvarion or its third party licensors. No disclosure thereof shall be made
to third parties without the express written permission of Alvarion Ltd.
This document applies to the Alvarion release of the GSM or CDMA product lines
and to all subsequent versions and releases of the hardware or software thereof
unless otherwise indicated in a new version or an update package for the current
edition dated November 2005.
Publications requests should be addressed to your local sales support office.
Alvarion Ltd. reserves the right to alter the equipment specifications and
descriptions in this publication without prior notice. No part of this publication
shall be deemed to be part of any contract or warranty unless specifically
incorporated by reference into such contract or warranty.
Use, duplication, or disclosure by the U.S. Government is subject to restrictions of
FAR 52.227-14 (g) (2) (6/87) and FAR 52.227-19 (6/87), or DFAR 252.227-7015
(b) (6/95) and DFAR 227.7202-3 (a).
The software described in this document is furnished under a license agreement.
The software may be used or copied only in accordance with the terms of the
agreement. It is a violation of Alvarion Ltd. proprietary rights to copy the software
on any medium except as specifically allowed in the license agreement. The
material contained herein is Alvarion proprietary, privileged, and confidential. No
disclosure thereof shall be made to third parties without the express written
permission of Alvarion.
The information contained in this manual is subject to change without notice.
Alvarion Ltd. shall not be liable for errors contained herein or for incidental or
consequential damages in connection with the furnishing, performance, or use of
this manual or equipment supplied with it.
Alvarion's products are patented by one or more of the following United States
Patents: No. 5,781,582, No. 5,682,403, No. 5,734,979, No. 5,734,699, No.
5,999,813, No. 5,953,651, No. 5,887,256, No. 5,577,029, No. 5,761,195, No.
5,842,138, No. 5,818,824, No. 5,957,464, No. 6,078,823, No. 6,070,071, No.
6,101,400, No. USP D 391,967, No. USP D 391,968, No. USP D 397,693.
Trademark Acknowledgment
Alvarion®, BreezeCOM®, WALKair®, WALKnet®, BreezeNET®, BreezeACCESS®,
BreezeMANAGE™, BreezeLINK®, BreezeConfig™, BreezeMAX™, AlvariSTAR™,
MGW™, eMGW™, WAVEXpress™, MicroXpress™, WAVEXchange™,
WAVEView™, GSM Network in a Box and TurboWAVE™ and/or other products
and/or services referenced here in are either registered trademarks, trademarks
or service marks of Alvarion Ltd. All other names are or may be the trademarks of
their respective owners.
©2006 Alvarion, Ltd. All Rights Reserved.
United States Federal Communications Commission Required User Information
Located on the equipment is a label that contains, among other information, the
FCC registration number. If requested, this information must be provided to the
telephone company.
The UltraWAVE BTS Series AUAC series complies with Part 22 of the FCC Rules.
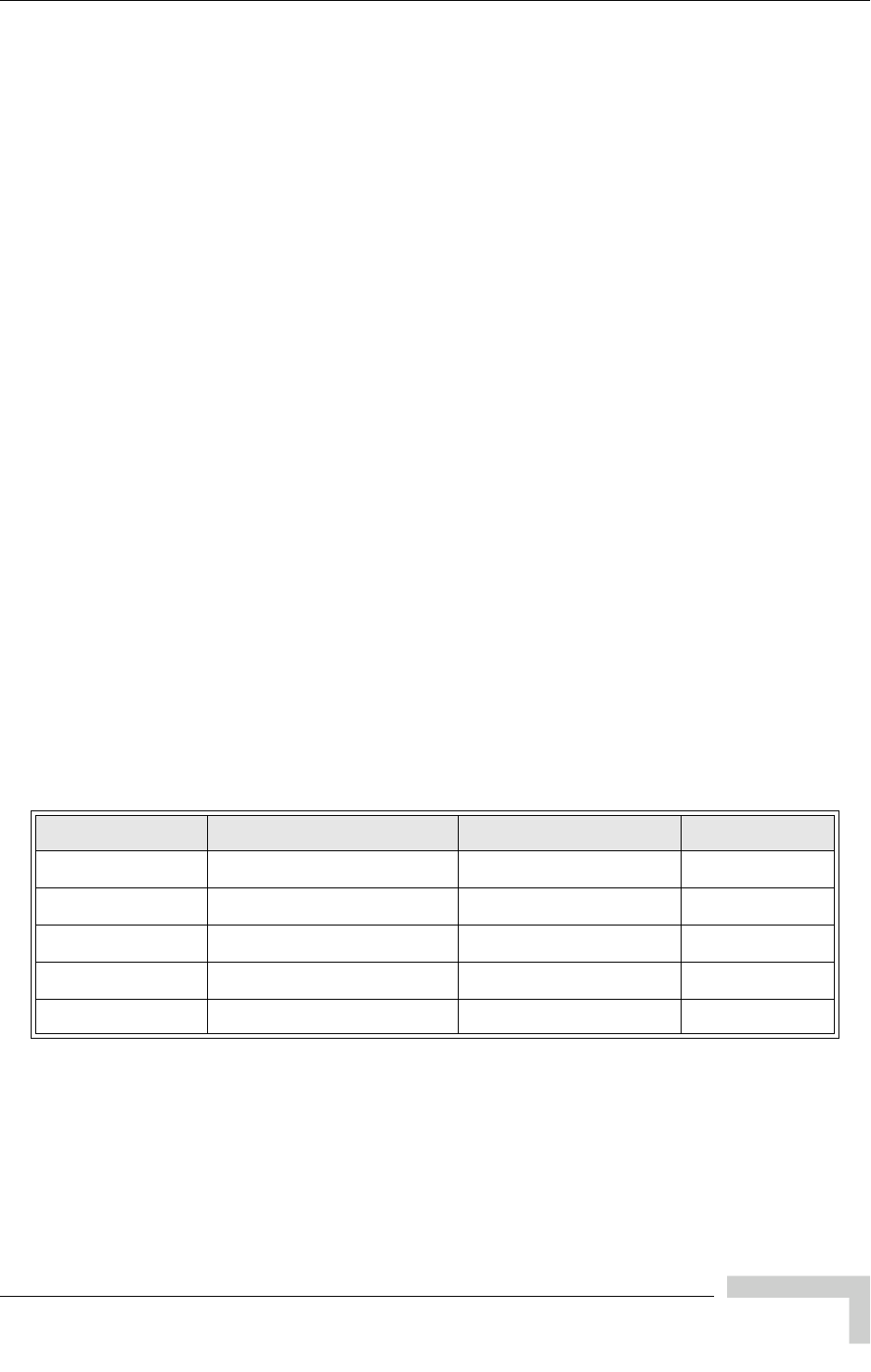
UltraWAVE Micro BTS Installation and Commissioning Guide, Version B iii
Legal Rights
The 1900 MHz WAVEXpress Series M50 complies with Part 24 of the FCC Rules.
The Breeze2000 BS Plus 800 MHz complies with Part 22 of the FCC Rules.
The Breeze2000 Pico BS Plus (800 MHz and 1900 MHz) comply with Part 22 and
Part 24 of the FCC Rules and UL 1950 safety certification.
This equipment cannot be used on the telephone company-provided coin service.
Connection to Party Line Service is subject to State Tariffs.
If this equipment causes harm to the telephone network, the telephone company
will notify you in advance that temporary discontinuance of service may be
required. If advance notice isn’t practical, the telephone company will notify the
customer as soon as possible. Also, you will be advised of your right to file a
complaint with the FCC if you believe it is necessary.
The telephone company may make changes in its facilities, equipment,
operations, of procedures that could affect the operation of the equipment. If this
happens, the telephone company will provide advance notice in order for you to
make the necessary modifications in order to maintain uninterrupted service.
If trouble is experienced with this equipment, please contact:
Alvarion, Inc.
2495 Leghorn Drive
Mountain View, CA 94043-1611 U.S.A.
If the trouble is causing harm to the telephone network, the telephone company
may request you to remove the equipment from the network until the problem is
resolved.
It is recommended that the customer install an AC surge arrester in the AC outlet
to which that device is connected. This is to avoid damaging the equipment
caused by local lightning strikes and other electrical surges.
This equipment uses the following USOC jacks and codes:
Note: This equipment has been tested and found to comply with the limits for a
Class A digital device, pursuant to Part 15 of the FCC Rules. These limits are
designed to provide reasonable protection against harmful interference when the
equipment is operated in a commercial environment. This equipment generates,
uses and can radiate radio frequency energy and, if not installed and used in
accordance with the instruction manual, may cause harmful interference to radio
communications. Operation of this equipment in a residential area is likely to
USOC Jacks and Codes
Model Name Facility Interface Code Service Order Code Jack Type
340122 04DU9-BN 6.ON RJ-48C
340122 04DU9-DN 6.ON RJ-48C
340122 04DU9-1KN 6.ON RJ-48C
340122 04DU9-1SN 6.ON RJ-48C
340122 04DU9-1ZN 6.ON RJ-48C
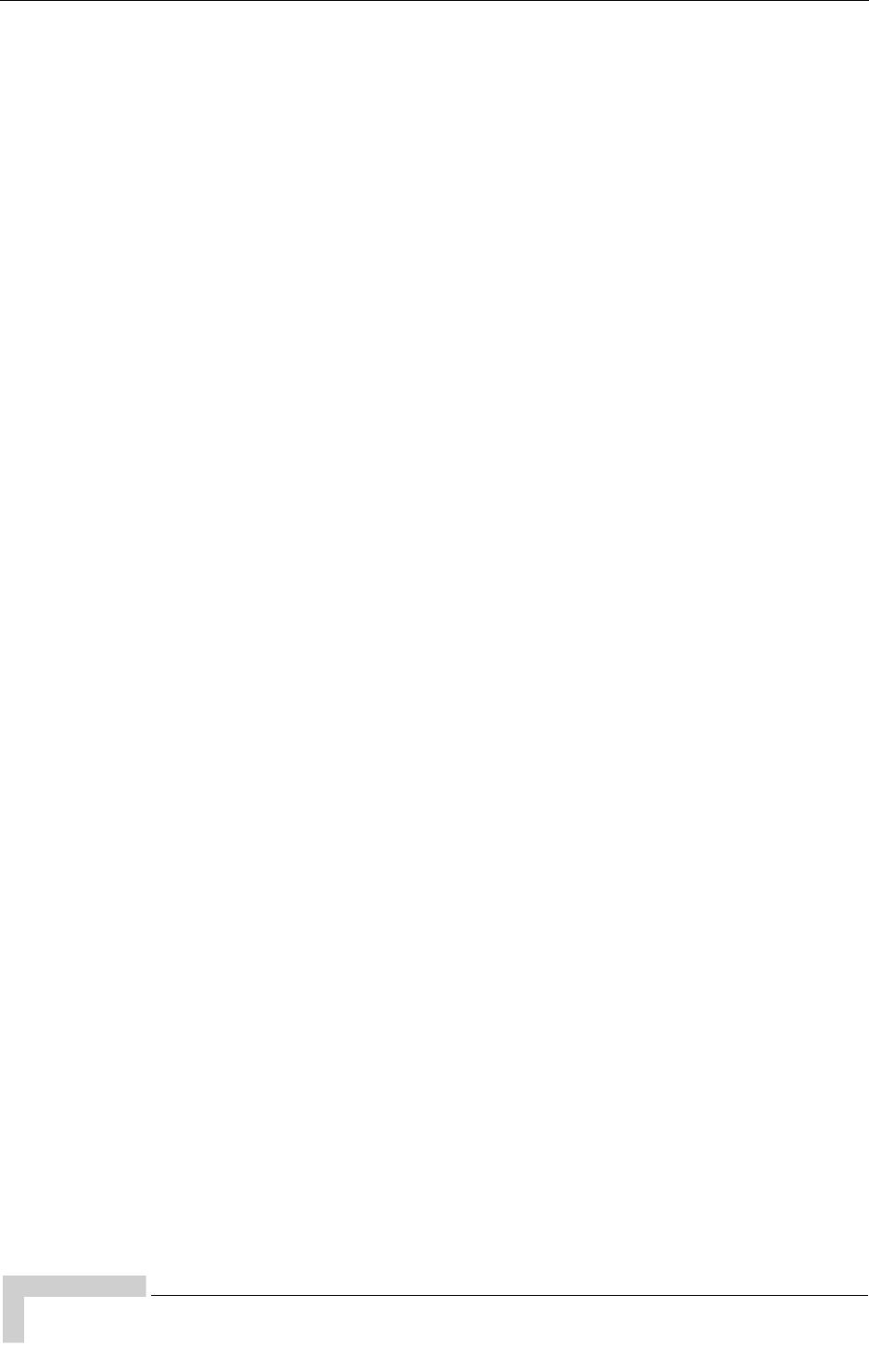
iv UltraWAVE Micro BTS Installation and Commissioning Guide, Version B
Legal Rights
cause harmful interference in which case the user will be required to correct the
interference at his own expense.
Changes of modifications not expressly approved by Alvarion can void the user’s
authority to operate the equipment. FCC and IC certification labels denoting the
product specific certification numbers may be found on the product.
Industry Canada Required User Information
CP-O1, Issue 8, Part 1, Section 14.1
NOTICE: The Industry Canada label identifies certified equipment. This
certification means that the equipment meets certain telecommunications
network protective, operational and safety requirements as prescribed in the
appropriate Terminal Equipment Technical Requirements document(s). The
Department does not guarantee the equipment will operate to the user’s
satisfaction.
Before installing this equipment, users should ensure that it is permissible to be
connected to the facilities of the local telecommunications company. The
equipment must also be installed using an acceptable method of connection. The
customer should be aware that compliance with the above conditions may not
prevent degradation of service in some situations.
Repairs to certified equipment should be coordinated by a representative
designated by the supplier. Any repairs or alterations made by the user to this
equipment, or equipment malfunctions, may give the telecommunications
company cause to request the user to disconnect the equipment.
Users should ensure for their own protection that the electrical ground
connections of the power utility, telephone lines and internal metallic water pipe
system, if present, are connected together. This precaution may be particularly
important in rural areas.
CAUTION: Users should not attempt to make such connections themselves, but
should contact the appropriate electric inspection authority, or electrician, as
appropriate.
The standard connecting arrangement (telephone jack type) for this equipment is
CA81A.
CP-01, Issue 8, Part 1, Section 14.2
NOTICE: The Ringer Equivalence Number (REN) assigned to each terminal device
provides an indication of the maximum number of terminals allowed to be
connected to a telephone interface. The termination of an interface may consist of
any combination of devices subject only to the requirement that the sum of the
Ringer Equivalence Numbers of all the devices does not exceed 5.
This Class A digital apparatus complies with Canadian ICES-003.
Cet appareil numerique de la classe A est conforme a la norme NMB-003 du
Canada.
This device complies with Industry Canada RSS-133 and SRSP-510 or RS132 &
SRPS-503.

Table of Contents
Preface . . . . . . . . . . . . . . . . . . . . . . . . . . . . . . . . . . . . . . . . . xi
Chapter 1 - Unpacking and Configuration Verification . . . . .1
1.1 Unpacking and Inspecting . . . . . . . . . . . . . . . . . . . . . . . . . . . . . . . . . . . . . . . . . . . .2
1.1.1 Unpacking the Cabinet . . . . . . . . . . . . . . . . . . . . . . . . . . . . . . . . . . . . . . . . .2
1.1.2 Opening the Cabinet Assembly . . . . . . . . . . . . . . . . . . . . . . . . . . . . . . . . . .6
1.1.3 Unpacking and Inspecting the Rack Assembly . . . . . . . . . . . . . . . . . . . . . .7
1.2 Electrostatic Discharge (ESD) . . . . . . . . . . . . . . . . . . . . . . . . . . . . . . . . . . . . . . . . .7
1.3 Inspecting Components and Recording Part Numbers . . . . . . . . . . . . . . . . . . . .8
1.3.1 Identifying the System Configuration . . . . . . . . . . . . . . . . . . . . . . . . . . . . . .9
1.3.2 Verifying System Labels . . . . . . . . . . . . . . . . . . . . . . . . . . . . . . . . . . . . . .11
1.4 Verifying and Documenting Cards and Modules . . . . . . . . . . . . . . . . . . . . . . . . .12
1.4.1 Required Equipment . . . . . . . . . . . . . . . . . . . . . . . . . . . . . . . . . . . . . . . . .12
1.4.2 Micro Subrack Assembly . . . . . . . . . . . . . . . . . . . . . . . . . . . . . . . . . . . . . .12
1.4.3 Slot Assignments . . . . . . . . . . . . . . . . . . . . . . . . . . . . . . . . . . . . . . . . . . . .13
1.4.4 Verification Procedure . . . . . . . . . . . . . . . . . . . . . . . . . . . . . . . . . . . . . . . .14
1.5 Verifying Cabling . . . . . . . . . . . . . . . . . . . . . . . . . . . . . . . . . . . . . . . . . . . . . . . . . .15
1.5.1 Verifying Internal Cabling . . . . . . . . . . . . . . . . . . . . . . . . . . . . . . . . . . . . . .15
1.5.2 Verifying Enclosure Cabling . . . . . . . . . . . . . . . . . . . . . . . . . . . . . . . . . . . .15
Chapter 2 - Installation . . . . . . . . . . . . . . . . . . . . . . . . . . . . .17
2.1 Analyzing Site Requirements . . . . . . . . . . . . . . . . . . . . . . . . . . . . . . . . . . . . . . . .18
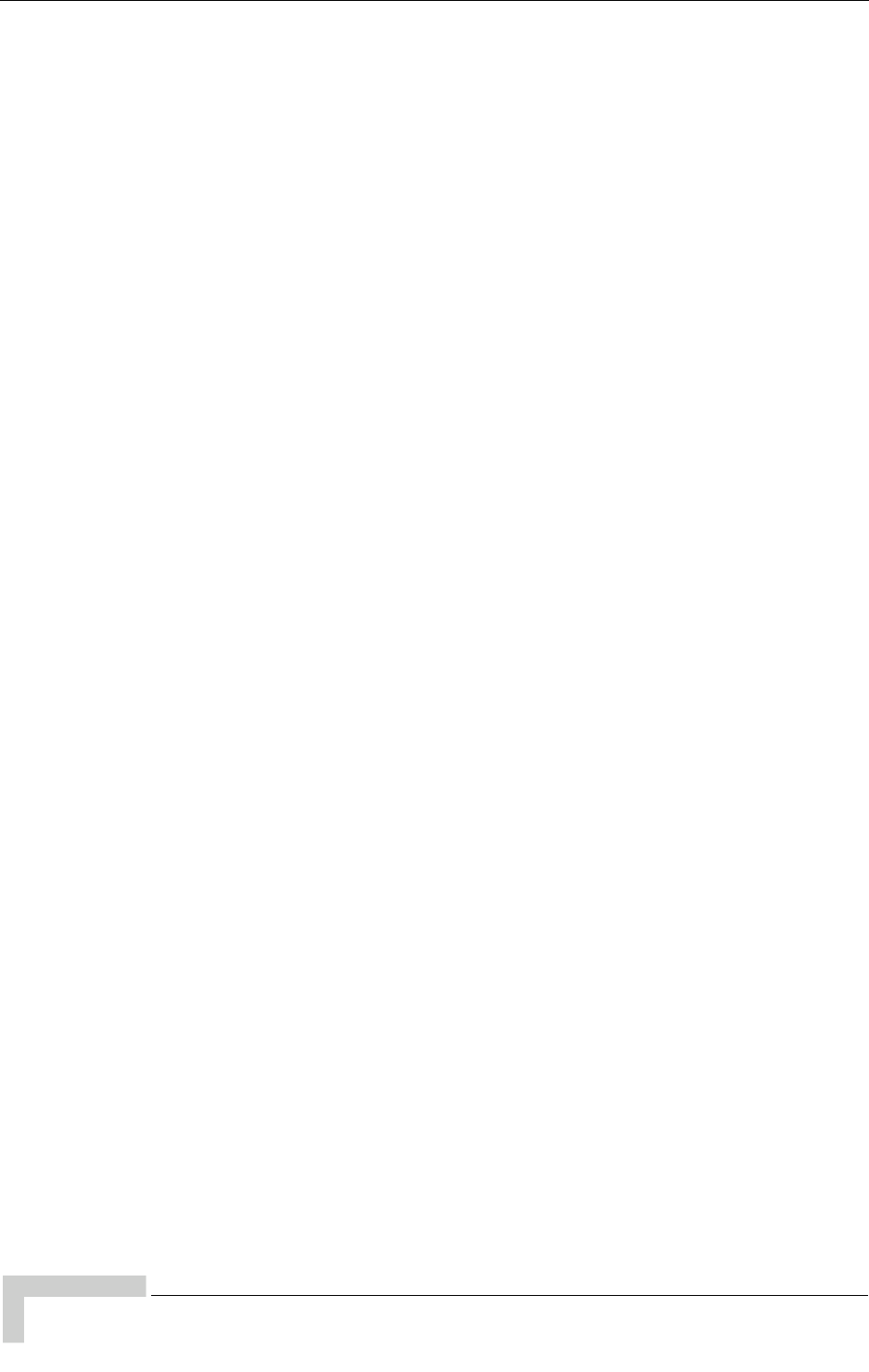
vi UltraWAVE Micro BTS Installation and Commissioning Guide, Version B
Table of Contents
2.1.1 Environmental Conditions . . . . . . . . . . . . . . . . . . . . . . . . . . . . . . . . . . . . . 18
2.1.2 Electrical Requirements . . . . . . . . . . . . . . . . . . . . . . . . . . . . . . . . . . . . . . 19
2.1.3 Chassis Requirements . . . . . . . . . . . . . . . . . . . . . . . . . . . . . . . . . . . . . . . 20
2.2 Mounting the Micro BTS Chassis . . . . . . . . . . . . . . . . . . . . . . . . . . . . . . . . . . . . 22
2.2.1 Rack Installation . . . . . . . . . . . . . . . . . . . . . . . . . . . . . . . . . . . . . . . . . . . . 23
2.2.2 Enclosure Mounting . . . . . . . . . . . . . . . . . . . . . . . . . . . . . . . . . . . . . . . . . 27
2.3 Configuring the E1 or T1 Trunk Card . . . . . . . . . . . . . . . . . . . . . . . . . . . . . . . . . 31
2.3.1 Configuring Ground Jumpers on 75 Ohm E1 Cards . . . . . . . . . . . . . . . . . 32
2.3.2 Configuring Cable Length DIP Switch Settings on T1 Cards . . . . . . . . . . 34
2.4 Connecting Ground Cables . . . . . . . . . . . . . . . . . . . . . . . . . . . . . . . . . . . . . . . . . 36
2.4.1 Connecting the Grounding Cable . . . . . . . . . . . . . . . . . . . . . . . . . . . . . . . 36
2.4.2 Grounding the Cabinet . . . . . . . . . . . . . . . . . . . . . . . . . . . . . . . . . . . . . . . 37
2.5 Connecting Power Supplies . . . . . . . . . . . . . . . . . . . . . . . . . . . . . . . . . . . . . . . . . 38
2.5.1 Connecting AC Power . . . . . . . . . . . . . . . . . . . . . . . . . . . . . . . . . . . . . . . 41
2.5.2 Connecting DC Power . . . . . . . . . . . . . . . . . . . . . . . . . . . . . . . . . . . . . . . 44
2.6 Connecting E1 or T1 Trunk Cables . . . . . . . . . . . . . . . . . . . . . . . . . . . . . . . . . . . 47
2.6.1 E1 Cables . . . . . . . . . . . . . . . . . . . . . . . . . . . . . . . . . . . . . . . . . . . . . . . . . 47
2.6.2 T1 Cables . . . . . . . . . . . . . . . . . . . . . . . . . . . . . . . . . . . . . . . . . . . . . . . . . 49
2.6.3 Connecting E1 or T1 Lines . . . . . . . . . . . . . . . . . . . . . . . . . . . . . . . . . . . . 50
2.6.4 Direct Cabling Between Multiple UltraWAVE or WAVEXpress Systems . 50
2.7 Connecting Antennas . . . . . . . . . . . . . . . . . . . . . . . . . . . . . . . . . . . . . . . . . . . . . . 52
2.7.1 Omni 1 TRX (O1) Configuration . . . . . . . . . . . . . . . . . . . . . . . . . . . . . . . . 54
2.7.2 Omni 2 TRX (O2) Configuration . . . . . . . . . . . . . . . . . . . . . . . . . . . . . . . . 54
2.7.3 Omni 3 TRX (O3) Configuration . . . . . . . . . . . . . . . . . . . . . . . . . . . . . . . . 55
2.7.4 Sectorized Three TRX (S111) Configuration . . . . . . . . . . . . . . . . . . . . . . 57
2.7.5 Three Sector Six TRX (S222) Configuration . . . . . . . . . . . . . . . . . . . . . . . 58
2.7.6 RF Radiation Hazard . . . . . . . . . . . . . . . . . . . . . . . . . . . . . . . . . . . . . . . . 58
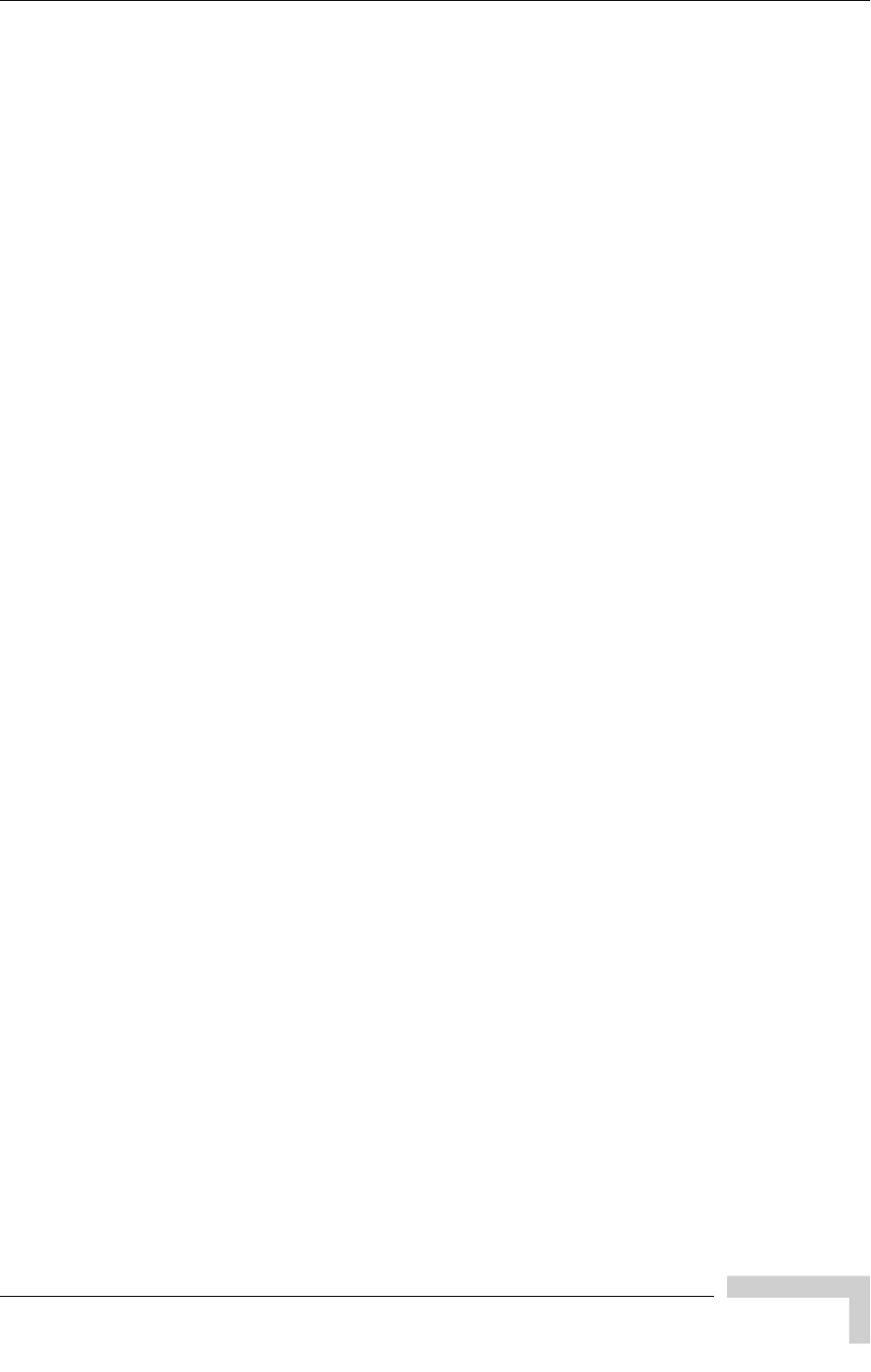
UltraWAVE Micro BTS Installation and Commissioning Guide, Version B vii
Table of Contents
2.8 Connecting External Alarms . . . . . . . . . . . . . . . . . . . . . . . . . . . . . . . . . . . . . . . . 60
2.9 Making a Serial Connection to the Processor Card . . . . . . . . . . . . . . . . . . . . . . 64
2.10 Network Connections . . . . . . . . . . . . . . . . . . . . . . . . . . . . . . . . . . . . . . . . . . . . . 65
2.11 Post Installation Cabling and Checks . . . . . . . . . . . . . . . . . . . . . . . . . . . . . . . . 66
2.11.1 Connecting the Chassis . . . . . . . . . . . . . . . . . . . . . . . . . . . . . . . . . . . . . 66
2.11.2 Verifying External Cabling . . . . . . . . . . . . . . . . . . . . . . . . . . . . . . . . . . . 66
Chapter 3 - Off-Line Commissioning . . . . . . . . . . . . . . . . . . 67
3.1 Pre Off-Line Commissioning . . . . . . . . . . . . . . . . . . . . . . . . . . . . . . . . . . . . . . . . 69
3.1.1 Visual Inspections . . . . . . . . . . . . . . . . . . . . . . . . . . . . . . . . . . . . . . . . . . . 69
3.2 Off-Line Commissioning of the Micro BTS . . . . . . . . . . . . . . . . . . . . . . . . . . . . . 71
3.2.1 Starting XWindows Using the Craft PC . . . . . . . . . . . . . . . . . . . . . . . . . . 71
3.2.2 Connecting the Craft PC to the ICP Processor Card . . . . . . . . . . . . . . . . 72
3.2.3 Setting Up a Serial Connection via the ICP Processor Card Serial Port . 73
3.2.4 Power-On LED Tests . . . . . . . . . . . . . . . . . . . . . . . . . . . . . . . . . . . . . . . . 76
3.2.5 Configuring Boot Parameters . . . . . . . . . . . . . . . . . . . . . . . . . . . . . . . . . . 79
3.2.6 Setting Up an Ethernet Connection to the ICP Processor Card
Ethernet Port . . . . . . . . . . . . . . . . . . . . . . . . . . . . . . . . . . . . . . . . . . 81
3.2.7 Verifying Telnet Communications with the Micro BTS over Ethernet . . . . 81
3.3 Software Verification using Craft PC . . . . . . . . . . . . . . . . . . . . . . . . . . . . . . . . . . 83
3.3.1 Verifying the Current Software Version and Patch Level . . . . . . . . . . . . . 83
3.3.2 Checking the Flash Version Number . . . . . . . . . . . . . . . . . . . . . . . . . . . . 84
3.3.3 Running E1 or T1 POST Diagnostics . . . . . . . . . . . . . . . . . . . . . . . . . . . . 85
3.3.4 Running TRX POST Diagnostics . . . . . . . . . . . . . . . . . . . . . . . . . . . . . . . 86
3.3.5 Reviewing POST Results . . . . . . . . . . . . . . . . . . . . . . . . . . . . . . . . . . . . . 88
3.3.6 Rebooting the Micro BTS after Running POST . . . . . . . . . . . . . . . . . . . . 89
3.3.7 Terminating Serial Communications with the Micro BTS . . . . . . . . . . . . . 89

viii UltraWAVE Micro BTS Installation and Commissioning Guide, Version B
Table of Contents
3.3.8 Exiting XWindows on the Craft PC . . . . . . . . . . . . . . . . . . . . . . . . . . . . . . 89
3.4 Upgrading the Micro BTS Software Version (Flash) . . . . . . . . . . . . . . . . . . . . . 90
3.5 Post Off-Line Commissioning . . . . . . . . . . . . . . . . . . . . . . . . . . . . . . . . . . . . . . . 92
3.5.1 Post Off-Line Commissioning Procedures at the Staging Area . . . . . . . . 92
3.5.2 Post Off-Line Commissioning Procedures On-Site . . . . . . . . . . . . . . . . . . 92
Chapter 4 - Off-Line Commissioning of a Daisy Chain . . . 107
4.1 Prerequisites to Daisy Chaining . . . . . . . . . . . . . . . . . . . . . . . . . . . . . . . . . . . . 108
4.2 Setting the Abis LAPD Signaling Timeslot . . . . . . . . . . . . . . . . . . . . . . . . . . . . 109
Chapter 5 - On-Line Commissioning . . . . . . . . . . . . . . . . . 111
5.1 Pre On-Line Commissioning Requirements . . . . . . . . . . . . . . . . . . . . . . . . . . . 113
5.2 On-Line Commissioning . . . . . . . . . . . . . . . . . . . . . . . . . . . . . . . . . . . . . . . . . . . 114
5.2.1 Unlocking the Abis Interface . . . . . . . . . . . . . . . . . . . . . . . . . . . . . . . . . . 116
5.2.2 Commissioning the Micro BTS . . . . . . . . . . . . . . . . . . . . . . . . . . . . . . . . 117
5.2.3 Recovery Tests . . . . . . . . . . . . . . . . . . . . . . . . . . . . . . . . . . . . . . . . . . . . 117
5.2.4 External Alarm Tests . . . . . . . . . . . . . . . . . . . . . . . . . . . . . . . . . . . . . . . 118
5.2.5 TCH Timeslot Tests . . . . . . . . . . . . . . . . . . . . . . . . . . . . . . . . . . . . . . . . 119
5.3 Antenna Cabling and Power Verification . . . . . . . . . . . . . . . . . . . . . . . . . . . . . 121
5.3.1 Setting up Power Measurements . . . . . . . . . . . . . . . . . . . . . . . . . . . . . . 121
5.3.2 Verifying TRX Output Power . . . . . . . . . . . . . . . . . . . . . . . . . . . . . . . . . . 122
5.3.3 Voltage Standing Wave Ratio (VSWR) Check . . . . . . . . . . . . . . . . . . . . 126
5.3.4 RX Signal Quality Measurements . . . . . . . . . . . . . . . . . . . . . . . . . . . . . . 127
5.4 Post On-Line Commissioning Procedures . . . . . . . . . . . . . . . . . . . . . . . . . . . . 129
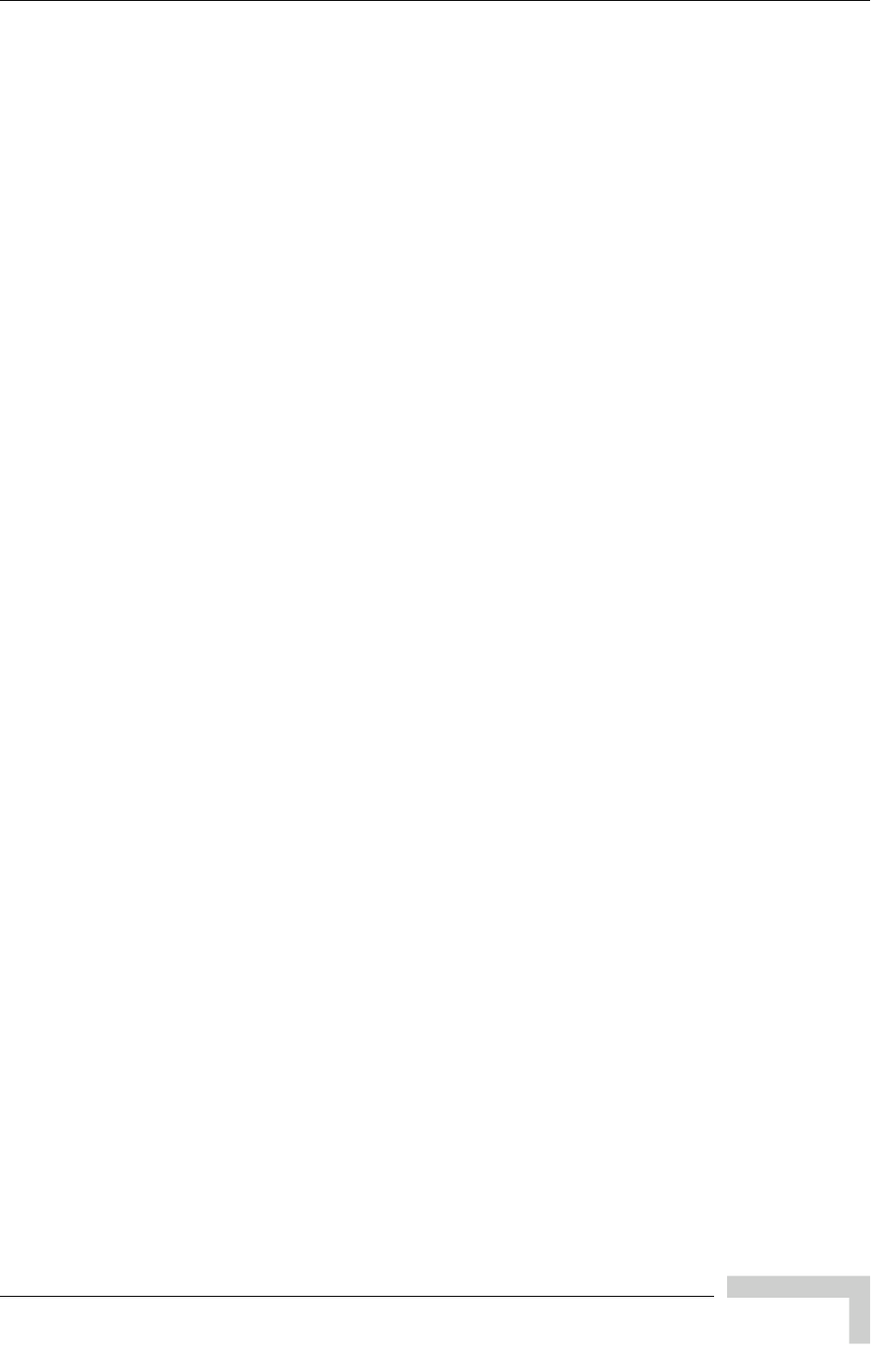
UltraWAVE Micro BTS Installation and Commissioning Guide, Version B ix
Table of Contents
Checklist 1 - Site Readiness Checklist . . . . . . . . . . . . . . . 129
Checklist 2 - Installation Checklist . . . . . . . . . . . . . . . . . . 131
Checklist 3 - Commissioning Checklist . . . . . . . . . . . . . . . 133
Index . . . . . . . . . . . . . . . . . . . . . . . . . . . . . . . . . . . . . . . . . 137

x UltraWAVE Micro BTS Installation and Commissioning Guide, Version B
Table of Contents
(this page intentionally left blank)
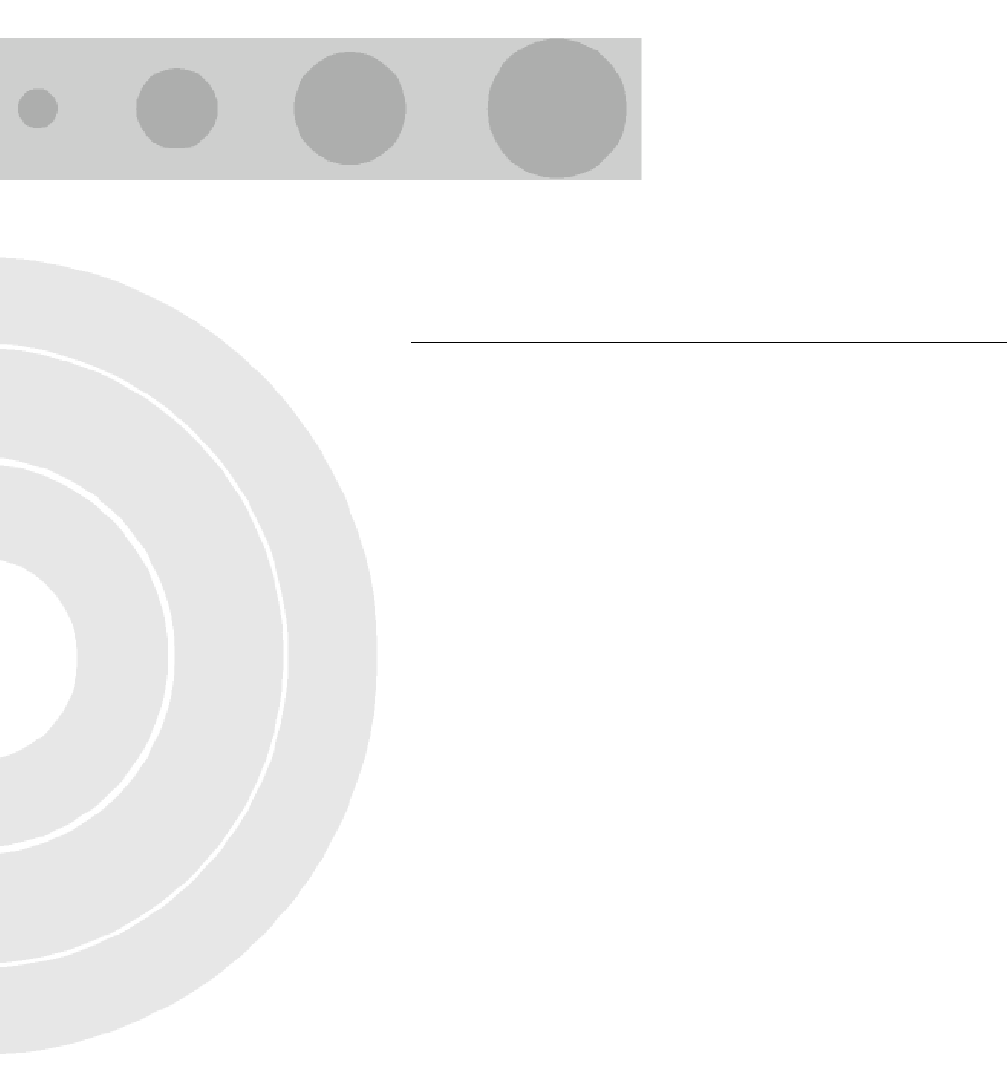
Preface
Welcome!
Welcome to the UltraWAVE Micro BTS Installation and Commissioning Guide. This
guide describes how to perform local installation and commissioning of the Micro
BTS at the customer’s site.
Assumptions, Purpose, and Audience
This document is intended for an Alvarion trained field service engineer (FSE) or
operator who performs local installation and commissioning at a customer site.
The FSE or operator should be equipped with the necessary tools for installation
and commissioning, and a basic understanding of the GSM cellular network. The
FSE or Operator should also be familiar with the use of Craft PC and procedures
conducted using the Craft PC.
Alvarion assumes that pre-installation project planning has occurred, and is
documented via a site survey report. This site survey should include items such as
the location of antennas, chassis, power connections and other interface accesses
and temperature control equipment.
Microwave Radio Radiation Warning
Although Alvarion products do not use microwave radio antennas, the equipment
is often mounted in the vicinity of microwave radio antennas. Under normal
operating conditions, microwave radio equipment complies with the limits for
human exposure to radio frequency (RF) fields adopted by the Federal
Communications Commission (FCC). All Alvarion microwave radio equipment is
designed so that under normal working conditions, microwave radiation directly
from the radio is negligible when compared with the permissible limit of
continuous daily exposure recommended in the United States by ANSI/IEEE
C95.1-1991 (R1997), Safety Levels with Respect to Human Exposure to Radio
Frequency Electromagnetic Fields, 3 kHz to 300 GHz.
Microwave signal levels that give rise to hazardous radiation levels can exist within
transmitter power amplifiers, associated RF multiplexers, and antenna systems.
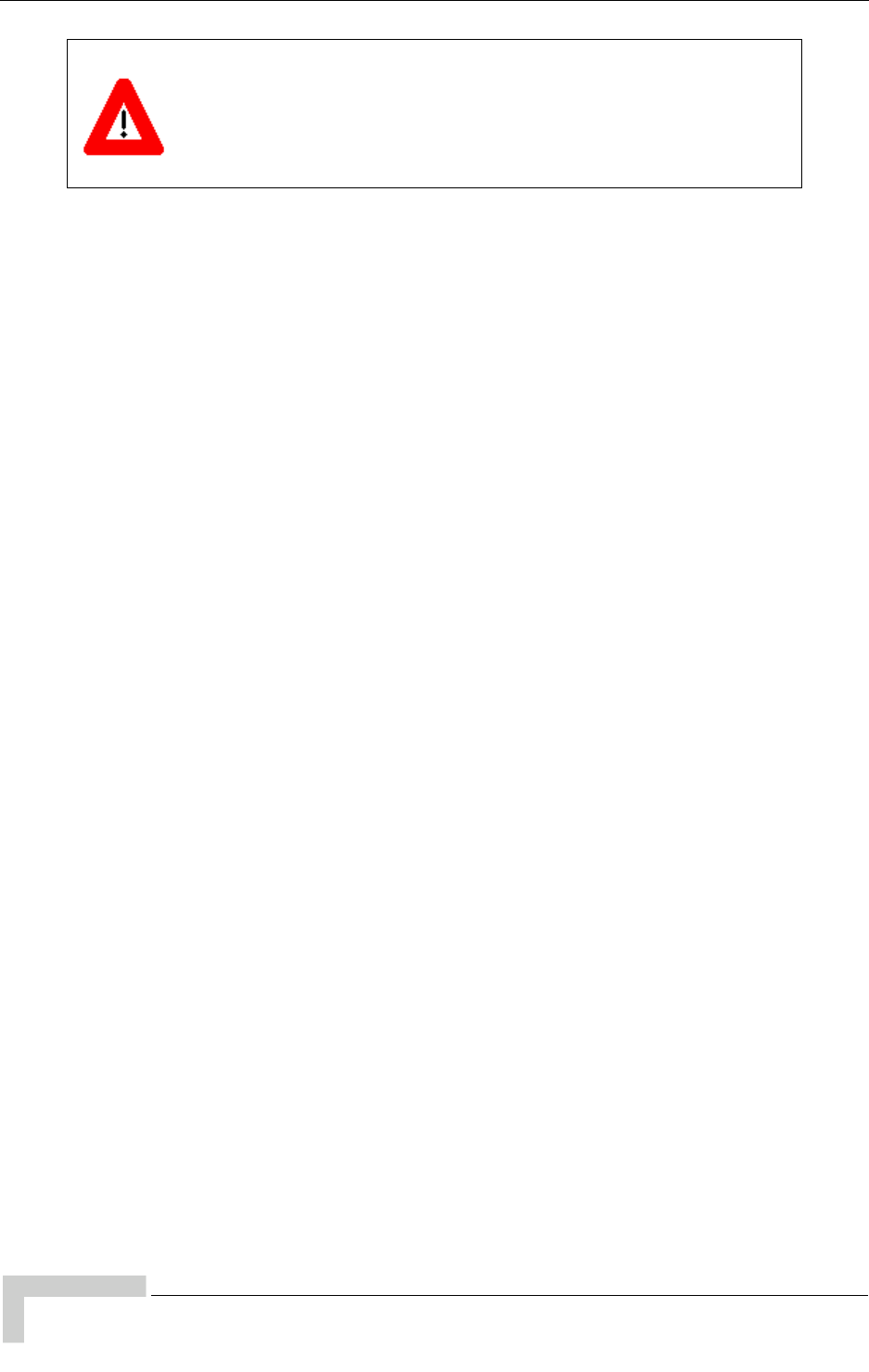
xii UltraWAVE Micro BTS Installation and Commissioning Guide, Version B
Preface
Related Documentation and Services
All manuals are available on a documentation CD-ROM in Adobe portable
document format or in an online format via our protected Internet site. To order
documentation, please contact Alvarion Sales department online at http://
www.alvarion.com.
Updates to this manual will be posted on the Alvarion Customer Service Website
at http://www.alvarion.com. Registered Alvarion customers can access the
Alvarion on-line information and support service, available 24 hours a day, seven
days a week. The Alvarion on-line service provides users with a wealth of
up-to-date information, with documents being added or updated each month.
Customer support services, such as technical support, RMAs, and training, are
described in the Customer Support Services document.
Warranties and Disclaimers
All Alvarion Ltd. (“Alvarion”) products purchased from Alvarion or through any of
Alvarion's authorized resellers are subject to the following warranty and product
liability terms and conditions.
Exclusive Warranty
(a) Alvarion warrants that the Product hardware it supplies and the tangible
media on which any software is installed, under normal use and conditions, will
be free from significant defects in materials and workmanship for a period of
fourteen (14) months from the date of shipment of a given Product to Purchaser
(the “Warranty Period”). Alvarion will, at its sole option and as Purchaser's sole
remedy, repair or replace any defective Product in accordance with Alvarion's
standard R&R procedure.
(b) With respect to the Firmware, Alvarion warrants the correct functionality
according to the attached documentation, for a period of fourteen (14) month from
invoice date (the “Warranty Period”). During the Warranty Period, Alvarion may
release to its Customers firmware updates, which include additional performance
improvements and/or bug fixes, upon availability (the “Warranty”). Bug fixes,
temporary patches and/or workarounds may be supplied as Firmware updates.
Never look into the open end of a waveguide or any other open RF
connection as eyes are particularly vulnerable to radiation. Do not
disconnect RF coaxial connectors, open microwave units, or break
down any microwave screening while the radio equipment is
operating.
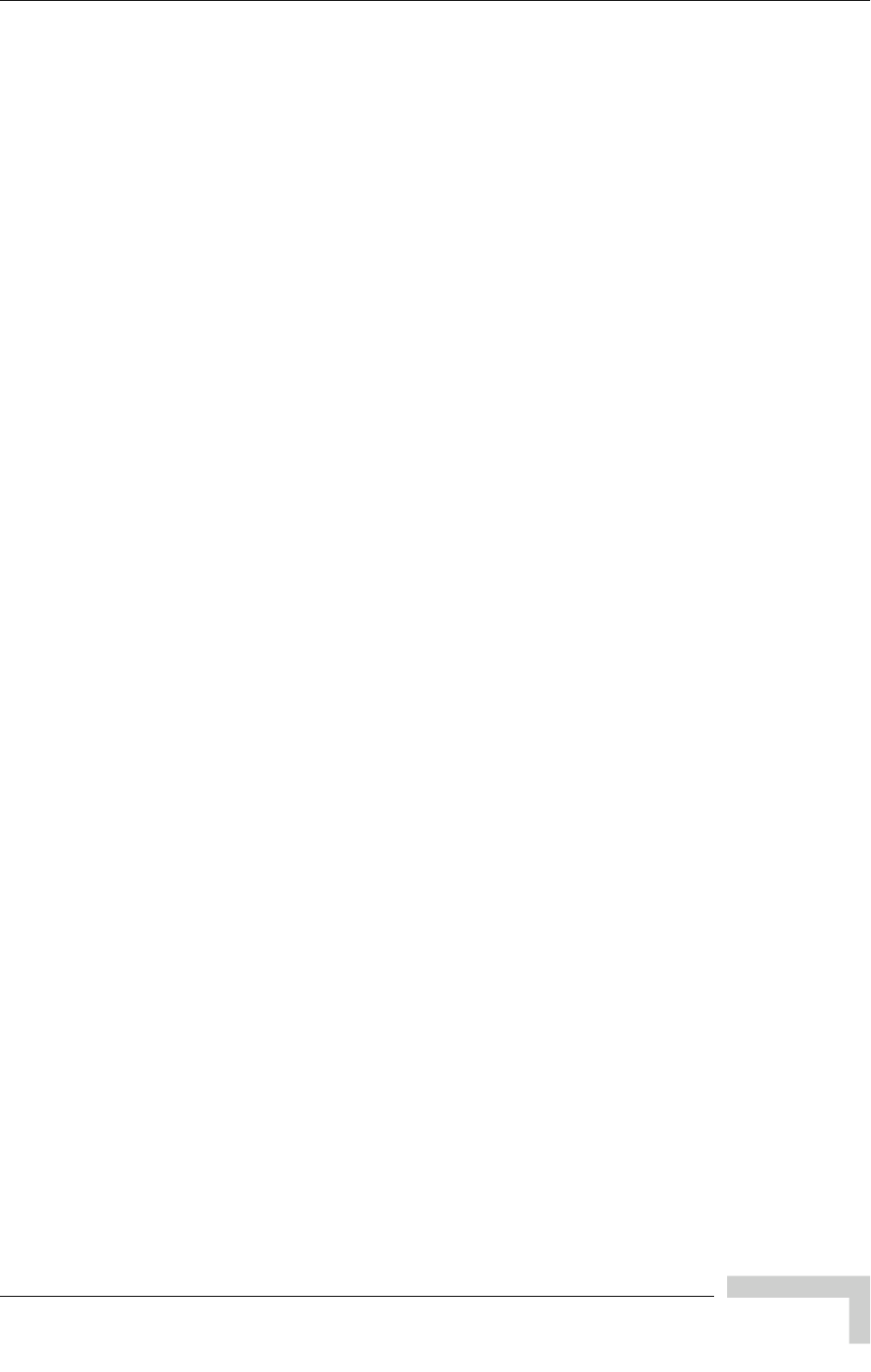
UltraWAVE Micro BTS Installation and Commissioning Guide, Version B xiii
Preface
Additional hardware, if required, to install or use Firmware updates must be
purchased by the Customer. Alvarion will be obligated to support solely the two (2)
most recent Software major releases.
ALVARION SHALL NOT BE LIABLE UNDER THIS WARRANTY IF ITS TESTING
AND EXAMINATION DISCLOSE THAT THE ALLEGED DEFECT IN THE PRODUCT
DOES NOT EXIST OR WAS CAUSED BY PURCHASER'S OR ANY THIRD
PERSON'S MISUSE, NEGLIGENCE, IMPROPER INSTALLATION OR IMPROPER
TESTING, UNAUTHORIZED ATTEMPTS TO REPAIR, OR ANY OTHER CAUSE
BEYOND THE RANGE OF THE INTENDED USE, OR BY ACCIDENT, FIRE,
LIGHTNING OR OTHER HAZARD.
Disclaimer
(a) The Software is sold on an “AS IS” basis. Alvarion, its affiliates or its licensors
MAKE NO WARRANTIES, WHATSOEVER, WHETHER EXPRESS OR IMPLIED,
WITH RESPECT TO THE SOFTWARE AND THE ACCOMPANYING
DOCUMENTATION. ALVARION SPECIFICALLY DISCLAIMS ALL IMPLIED
WARRANTIES OF MERCHANTABILITY AND FITNESS FOR A PARTICULAR
PURPOSE AND NON-INFRINGEMENT WITH RESPECT TO THE SOFTWARE.
UNITS OF PRODUCT (INCLUDING ALL THE SOFTWARE) DELIVERED TO
PURCHASER HEREUNDER ARE NOT FAULT-TOLERANT AND ARE NOT
DESIGNED, MANUFACTURED OR INTENDED FOR USE OR RESALE IN
APPLICATIONS WHERE THE FAILURE, MALFUNCTION OR INACCURACY OF
PRODUCTS CARRIES A RISK OF DEATH OR BODILY INJURY OR SEVERE
PHYSICAL OR ENVIRONMENTAL DAMAGE (“HIGH RISK ACTIVITIES”). HIGH
RISK ACTIVITIES MAY INCLUDE, BUT ARE NOT LIMITED TO, USE AS PART OF
ON-LINE CONTROL SYSTEMS IN HAZARDOUS ENVIRONMENTS REQUIRING
FAIL-SAFE PERFORMANCE, SUCH AS IN THE OPERATION OF NUCLEAR
FACILITIES, AIRCRAFT NAVIGATION OR COMMUNICATION SYSTEMS, AIR
TRAFFIC CONTROL, LIFE SUPPORT MACHINES, WEAPONS SYSTEMS OR
OTHER APPLICATIONS REPRESENTING A SIMILAR DEGREE OF POTENTIAL
HAZARD. ALVARION SPECIFICALLY DISCLAIMS ANY EXPRESS OR IMPLIED
WARRANTY OF FITNESS FOR HIGH RISK ACTIVITIES.
(b) PURCHASER'S SOLE REMEDY FOR BREACH OF THE EXPRESS
WARRANTIES ABOVE SHALL BE REPLACEMENT OR REFUND OF THE
PURCHASE PRICE AS SPECIFIED ABOVE, AT ALVARION'S OPTION. TO THE
FULLEST EXTENT ALLOWED BY LAW, THE WARRANTIES AND REMEDIES SET
FORTH IN THIS AGREEMENT ARE EXCLUSIVE AND IN LIEU OF ALL OTHER
WARRANTIES OR CONDITIONS, EXPRESS OR IMPLIED, EITHER IN FACT OR BY
OPERATION OF LAW, STATUTORY OR OTHERWISE, INCLUDING BUT NOT
LIMITED TO WARRANTIES, TERMS OR CONDITIONS OF MERCHANTABILITY,
FITNESS FOR A PARTICULAR PURPOSE, SATISFACTORY QUALITY,
CORRESPONDENCE WITH DESCRIPTION, NON-INFRINGEMENT, AND
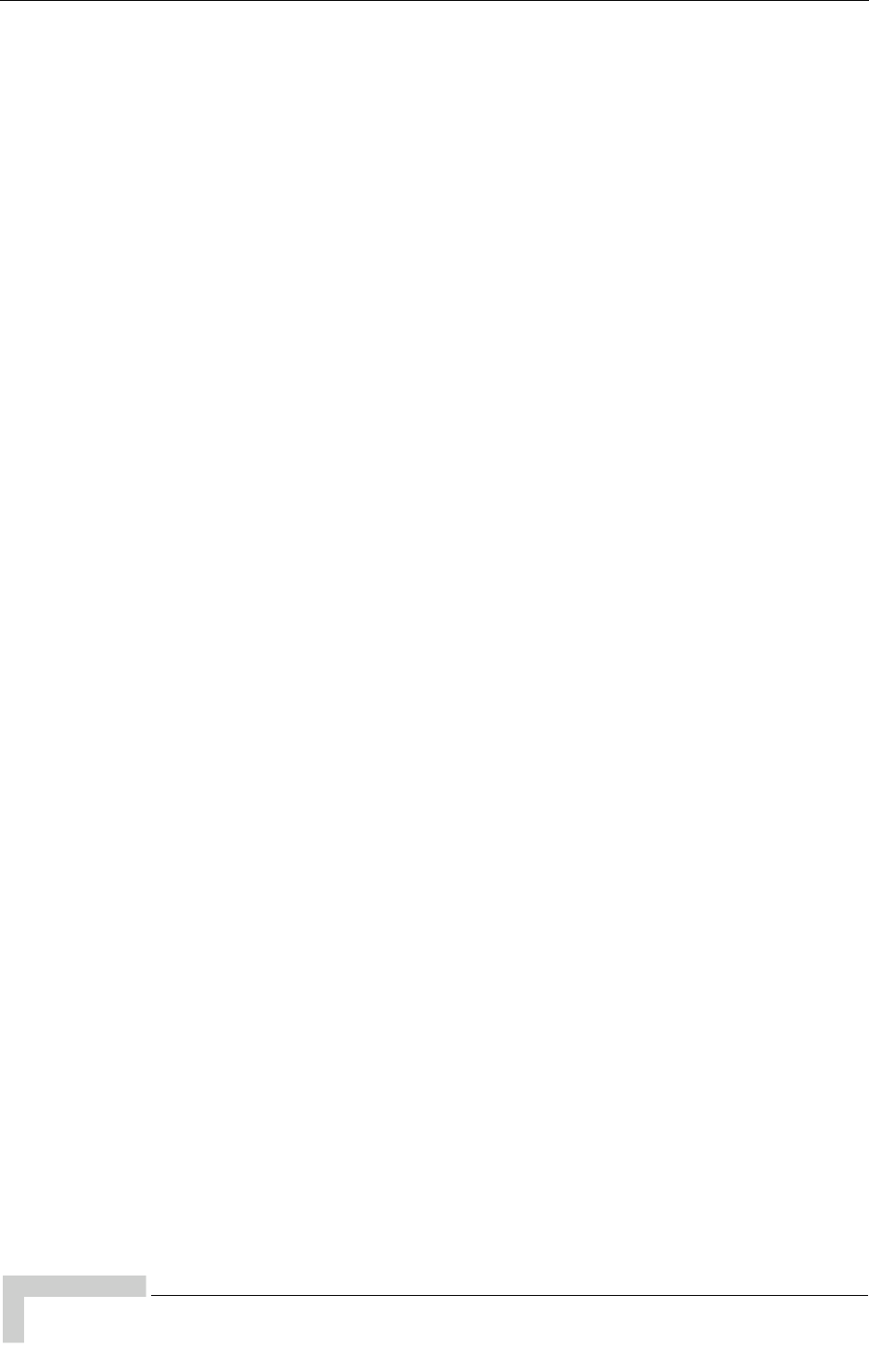
xiv UltraWAVE Micro BTS Installation and Commissioning Guide, Version B
Preface
ACCURACY OF INFORMATION GENERATED. ALL OF WHICH ARE EXPRESSLY
DISCLAIMED. ALVARION' WARRANTIES HEREIN RUN ONLY TO PURCHASER,
AND ARE NOT EXTENDED TO ANY THIRD PARTIES. ALVARION NEITHER
ASSUMES NOR AUTHORIZES ANY OTHER PERSON TO ASSUME FOR IT ANY
OTHER LIABILITY IN CONNECTION WITH THE SALE, INSTALLATION,
MAINTENANCE OR USE OF ITS PRODUCTS.
Limitation of Liability
(a) ALVARION SHALL NOT BE LIABLE TO THE PURCHASER OR TO ANY THIRD
PARTY, FOR ANY LOSS OF PROFITS, LOSS OF USE, INTERRUPTION OF
BUSINESS OR FOR ANY INDIRECT, SPECIAL, INCIDENTAL, PUNITIVE OR
CONSEQUENTIAL DAMAGES OF ANY KIND, WHETHER ARISING UNDER
BREACH OF CONTRACT, TORT (INCLUDING NEGLIGENCE), STRICT LIABILITY
OR OTHERWISE AND WHETHER BASED ON THIS AGREEMENT OR
OTHERWISE, EVEN IF ADVISED OF THE POSSIBILITY OF SUCH DAMAGES.
(b) TO THE EXTENT PERMITTED BY APPLICABLE LAW, IN NO EVENT SHALL
THE LIABILITY FOR DAMAGES HEREUNDER OF ALVARION OR ITS EMPLOYEES
OR AGENTS EXCEED THE PURCHASE PRICE PAID FOR THE PRODUCT BY
PURCHASER, NOR SHALL THE AGGREGATE LIABILITY FOR DAMAGES TO ALL
PARTIES REGARDING ANY PRODUCT EXCEED THE PURCHASE PRICE PAID
FOR THAT PRODUCT BY THAT PARTY (EXCEPT IN THE CASE OF A BREACH OF
A PARTY'S CONFIDENTIALITY OBLIGATIONS).
Important Notice
This user manual is delivered subject to the following conditions and restrictions:
This manual contains proprietary information belonging to Alvarion Ltd. Such
information is supplied solely for the purpose of assisting properly authorized
users of the respective Alvarion products.
No part of its contents may be used for any other purpose, disclosed to any
person or firm or reproduced by any means, electronic and mechanical,
without the express prior written permission of Alvarion Ltd.
The text and graphics are for the purpose of illustration and reference only.
The specifications on which they are based are subject to change without
notice.
The software described in this document is furnished under a license. The
software may be used or copied only in accordance with the terms of that
license.
Information in this document is subject to change without notice. Corporate
and individual names and data used in examples herein are fictitious unless
otherwise noted.

UltraWAVE Micro BTS Installation and Commissioning Guide, Version B xv
Preface
Alvarion Ltd. reserves the right to alter the equipment specifications and
descriptions in this publication without prior notice. No part of this publica-
tion shall be deemed to be part of any contract or warranty unless specifically
incorporated by reference into such contract or warranty.
The information contained herein is merely descriptive in nature, and does not
constitute an offer for the sale of the product described herein.
Any changes or modifications of equipment, including opening of the equip-
ment not expressly approved by Alvarion Ltd. will void equipment warranty
and any repair thereafter shall be charged for. It could also void the user's
authority to operate the equipment.

xvi UltraWAVE Micro BTS Installation and Commissioning Guide, Version B
Preface
Conventions Used in This Manual
The following type and style conventions are used in this manual:
Conventions Used in This Manual
Convention Meaning
Body Text Used for regular body text
Bold Indicates a menu or button choice
Command Indicates computer generated text and prompts
User Input Indicates user input
<hostname> In command syntax, indicates user-specified command line
parameters
<variable> In body text, indicates user-specified command line parameters
[BRACKETS] Indicates a key on the keyboard or instrument
Provides relevant additional information
Provides important warning information that may affect operation
of or maybe a potential threat to the system
Used to tell the reader to STOP what they are doing and to read
important instructions that are vital to prevent equipment or
software damage
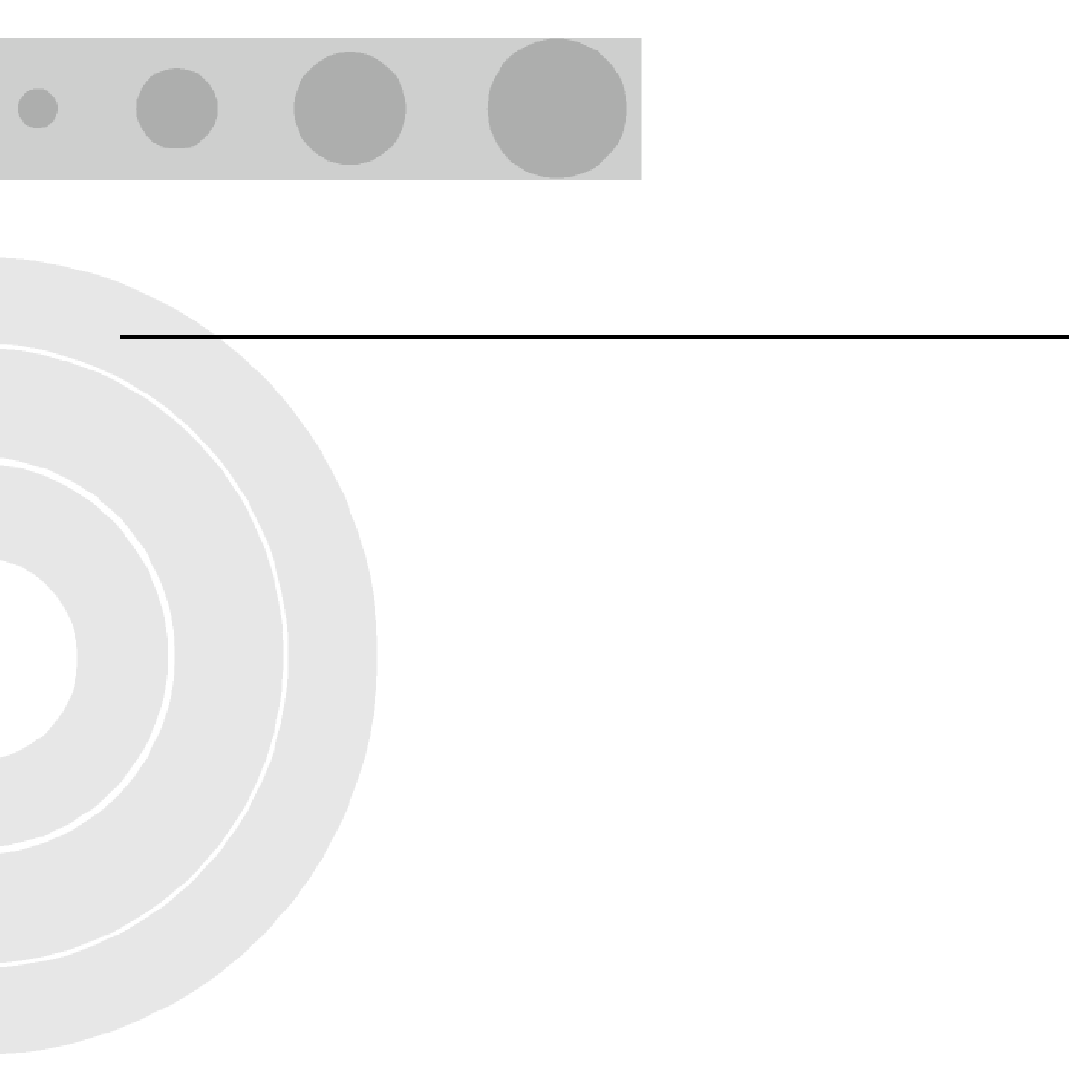
1
Chapter 1 - Unpacking and Configuration
Verification
In this Chapter:
“Unpacking and Inspecting” on page 2
“Electrostatic Discharge (ESD)” on page 7
“Inspecting Components and Recording Part Numbers” on page 8
“Verifying and Documenting Cards and Modules” on page 12
“Verifying Cabling” on page 15
This chapter provides instructions for opening the shipping container and
inspecting the contents. When you have completed the procedures in this chapter,
you will have confirmed that the hardware arrived undamaged and that everything
you ordered is present and configured correctly.

2 UltraWAVE Micro BTS Installation and Commissioning Guide, Version B
Chapter 1 - Unpacking and Configuration Verification
1.1 Unpacking and Inspecting
The UltraWAVE Micro BTS is packed with great care, and all containers are
inspected prior to shipment.
Micro BTS components that are shipped separately include:
Micro subrack assembly
Power supplies
Power supply subrack assembly
The Micro subrack assembly includes RF Module(s), processor card, E1 or T1
card, TRX card(s) and the clock module.
Upon receipt of these packages, immediately inspect the outside of the shipping
containers. If there is any visible damage, insist that a representative of the
carrier is present when unpacking the contents.
Carefully inspect the system as it is unpacked. If any damage, such as dents or
broken connections, is noticeable, immediately notify the carrier as well as
Alvarion Customer Service.
Store the shipping containers for future use. If the unit has to be returned for
upgrade or service, the specially designed shipping containers assure adequate
protection for the equipment. If for some reason the containers are not reusable or
if they are misplaced, please contact Alvarion to order new containers.
1.1.1 Unpacking the Cabinet
The UltraWAVE Micro BTS is shipped in a specially designed carton. The cabinet
should remain in the packaging until shipped to its final destination. Use this
procedure to unpack your cabinet.
1Move the cabinet to a level, well illuminated area.
2Cut all of the strapping on the outside of the shipping container. See
Figure 1-1.
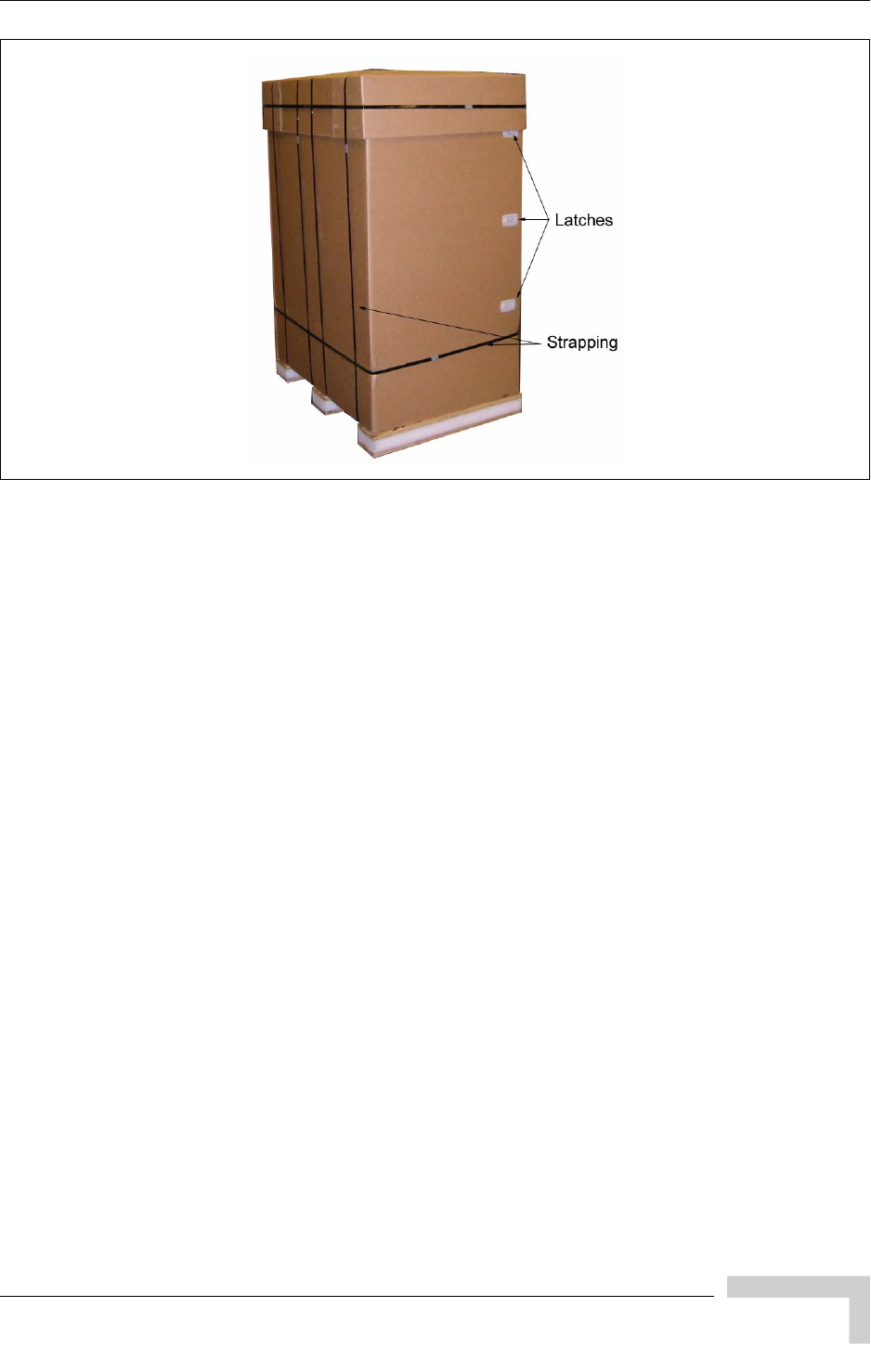
UltraWAVE Micro BTS Installation and Commissioning Guide, Version B 3
Unpacking and Inspecting
3Remove the cardboard top and set aside.
4Locate the plastic latches, shown in Figure 1-1. Pull on each latch to release
the cardboard side.
5Remove the cardboard enclosing the cabinet assembly.
6Carefully remove the two boxes from the top of the cabinet assembly. These
boxes contain the power supply units.
7Remove the insulating material from the top and sides of the cabinet.
8Cut the strapping which secures the cabinet to the pallet and remove the
protective plastic.
9Using an adjustable wrench, raise the rubber feet located at each corner on
the bottom of the cabinet. See Figure 1-2.
Figure 1-1: UltraWAVE Packaging

4 UltraWAVE Micro BTS Installation and Commissioning Guide, Version B
Chapter 1 - Unpacking and Configuration Verification
10 Remove the angled slope and ramps from the pallet. See Figure 1-3.
11 Attach ramps to pallet using loop and hook fasteners and slide the sloped
support underneath the ramps. See Figure 1-4.
Figure 1-2: Adjustable Feet
Figure 1-3: Pallet Accessories
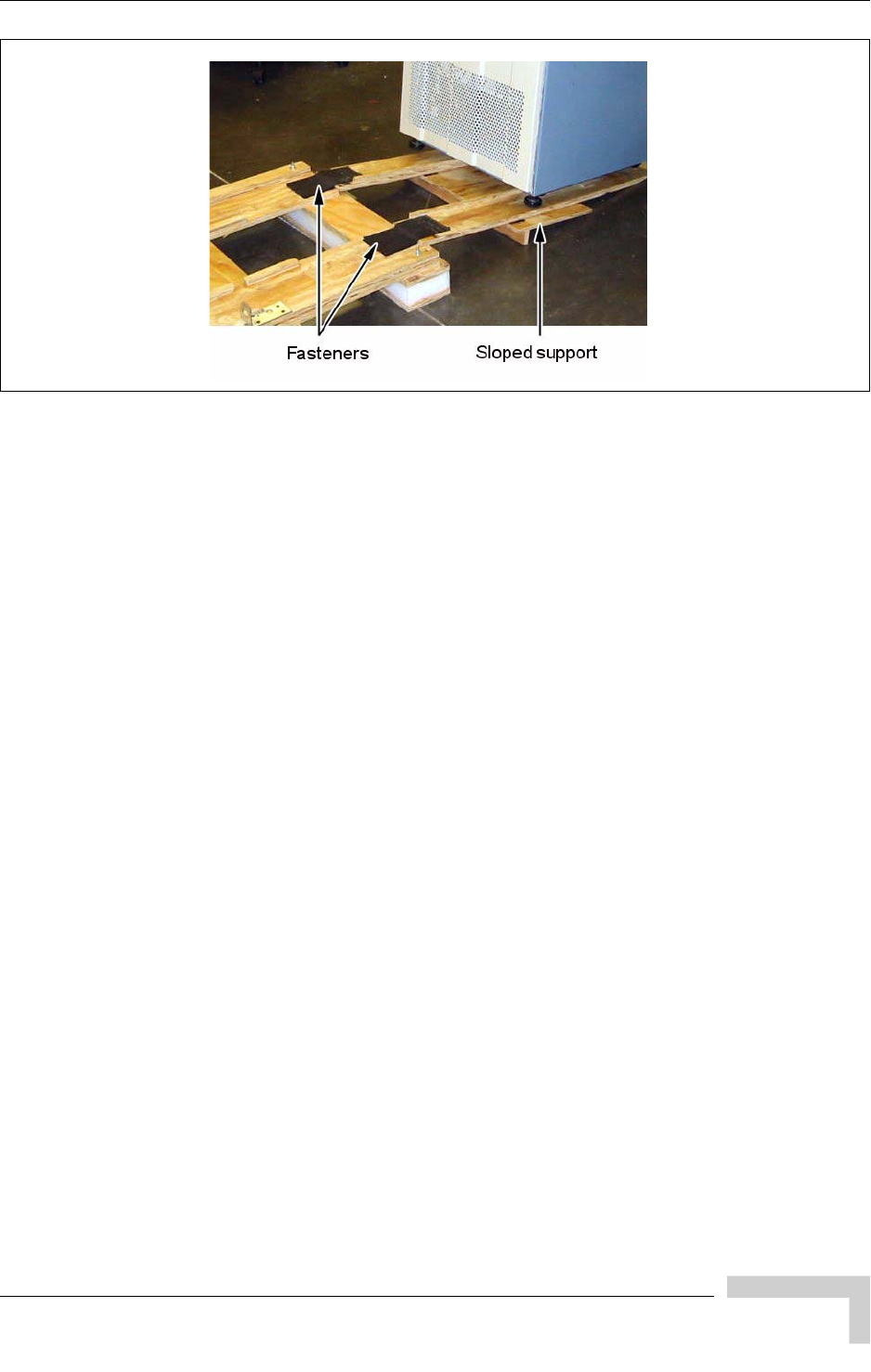
UltraWAVE Micro BTS Installation and Commissioning Guide, Version B 5
Unpacking and Inspecting
12 Carefully roll the cabinet down the ramps and off of the pallet.
13 Store all packaging material in a safe, dry location.
Figure 1-4: Pallet Ramps

6 UltraWAVE Micro BTS Installation and Commissioning Guide, Version B
Chapter 1 - Unpacking and Configuration Verification
1.1.2 Opening the Cabinet Assembly
The UltraWAVE Micro BTS is shipped pre-configured in a locking cabinet
assembly as shown in Figure 1-5.
Doors are provided for access to the front and rear of the internal assemblies. To
open the doors:
1Insert the key provided into the lock and turn to unlock.
2Depress the lock mechanism to release the door latch handle.
3Turn the door handle to unlatch and open the door.
4Carefully remove the packaging material from inside the cabinet.
Figure 1-5: Locking Cabinet
IW007302
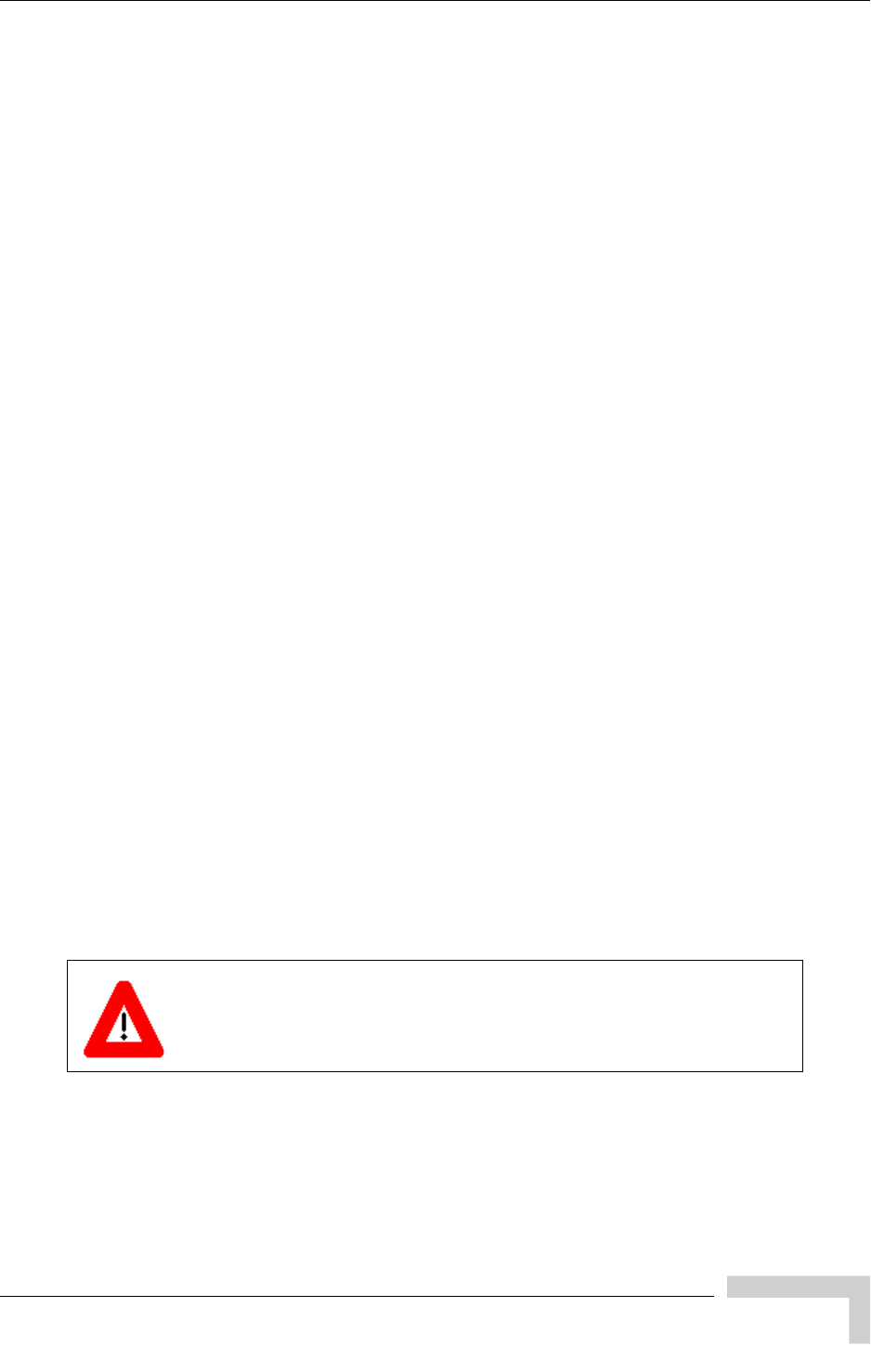
UltraWAVE Micro BTS Installation and Commissioning Guide, Version B 7
Electrostatic Discharge (ESD)
1.1.3 Unpacking and Inspecting the Rack Assembly
The Micro BTS may be shipped in a standard 19 inch rack assembly. Carefully
inspect the system as it is unpacked. Ensure that the required cabling is
included. If you notice any damage such as dents or broken connections,
immediately notify the carrier as well as Alvarion Customer Service.
Store the shipping containers for future use. If the unit has to be returned for
upgrade or service, the specially designed shipping containers assure adequate
protection of the equipment. If for some reason the shipping containers are not
reusable or if they are misplaced, please contact Alvarion to order new containers.
1.2 Electrostatic Discharge (ESD)
Electrostatic discharge is the movement of normally motionless electrical charges
which can destroy common electrical and electronic equipment.
Alvarion recommends that you use an anti-static wrist strap when handling
boards and components.
By using an anti-static wrist-strap, static electricity is constantly dispersed, via
the snug-fitting wrist-band, down the cable and to the grounded connection at the
other end, leaving hands free to work.
Use either the provided anti-static wrist-strap or an ESD mat.
Otherwise, touch the metal chassis to drain off any static electricity before
touching the cards.
Do not wear wool or polyester clothing.
Dry air can prevent dangerous charges from harmlessly dissipating. Alvarion
recommends a relative humidity of 50-60% when working on this equipment.
Handle the cards as little as possible and only by the edges.
Before starting any of the following procedures, the Field Service
Technician needs to ensure that anti-static precautions are taken.
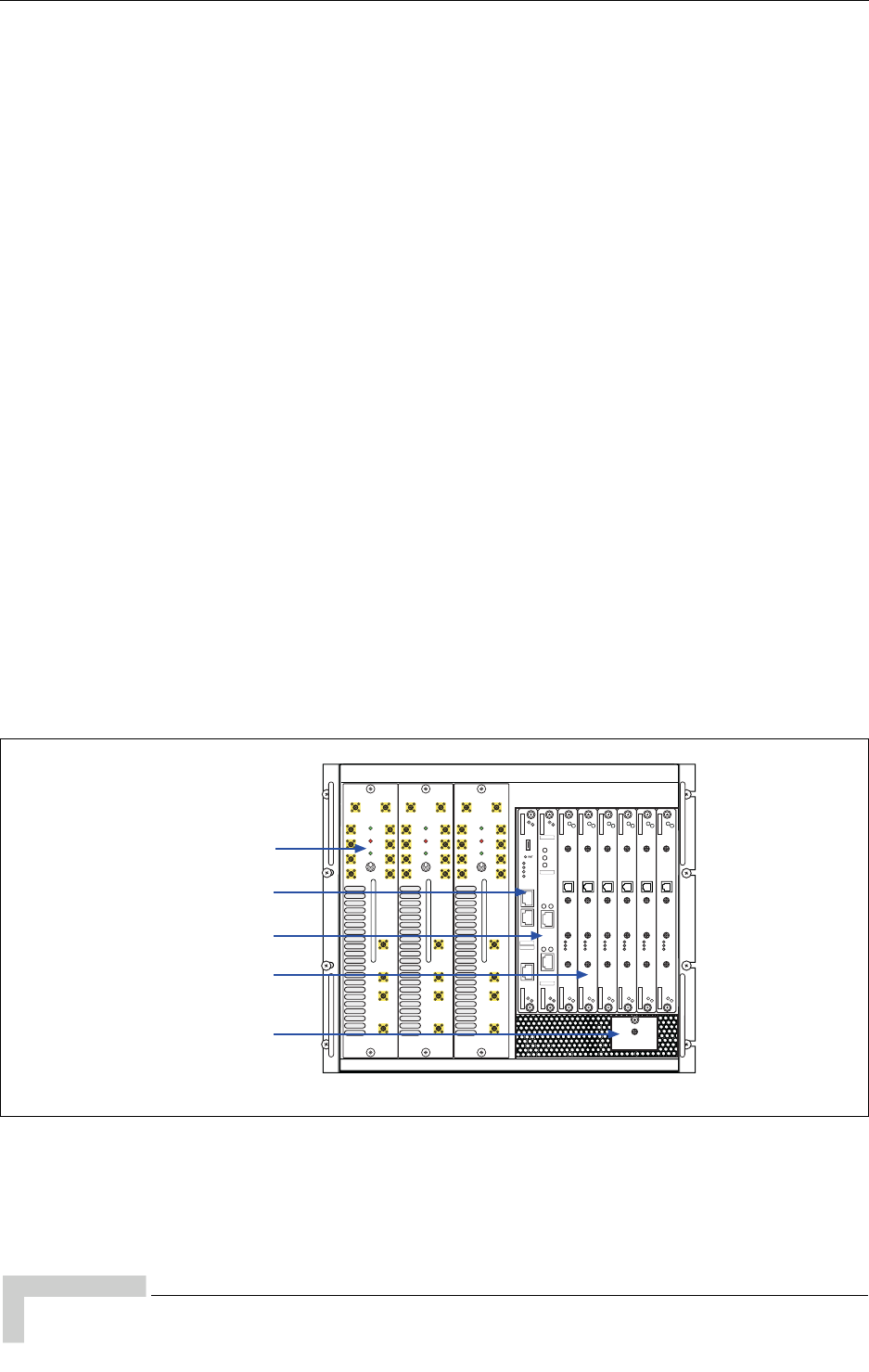
8 UltraWAVE Micro BTS Installation and Commissioning Guide, Version B
Chapter 1 - Unpacking and Configuration Verification
1.3 Inspecting Components and Recording
Part Numbers
The Micro BTS is shipped with all RF modules and cards installed in the Micro
subrack assembly as ordered by the customer. The Micro BTS components
include:
Micro subrack assembly
Processor card
E1 or T1 card
TRX cards
RF modules
Fan assemblies (located on the back of the chassis)
Clock module
Internal cabling
Blank panel(s)
Power supply modules and subrack assembly
Some of these components appear in Figure 1-6.
Figure 1-6: UltraWAVE Micro Subrack Assembly
RF Modules
Processor Card
E1 or T1 Trunk Card
TRX Cards
Clock Module
PA1
IN
ANT
DIV
ANT
MAIN
PWR
FLT
ON LINE
ON
OFF
RX1
RX2
RX3
RX4
TX1
DET
TX2
DET
PA2
IN
RX1
RX2
RX3
RX4
PA1
IN
ANT
DIV
ANT
MAIN
PWR
FLT
ON LINE
ON
OFF
RX1
RX2
RX3
RX4
TX1
DET
TX2
DET
PA2
IN
RX1
RX2
RX3
RX4
PA1
IN
ANT
DIV
ANT
MAIN
PWR
FLT
ON LINE
ON
OFF
RX1
RX2
RX3
RX4
TX1
DET
TX2
DET
PA2
IN
RX1
RX2
RX3
RX4
IW132601
PWR
DET
IN
ON LINE
FLT
RX-B
RX-A
13 MHZ
CLK
TX
OUT
PWR
DET
IN
ON LINE
FLT
RX-B
RX-A
13 MHZ
CLK
TX
OUT
PWR
DET
IN
ON LINE
FLT
RX-B
RX-A
13 MHZ
CLK
TX
OUT
PWR
DET
IN
ON LINE
FLT
RX-B
RX-A
13 MHZ
CLK
TX
OUT
PWR
DET
IN
ON LINE
FLT
RX-B
RX-A
13 MHZ
CLK
TX
OUT
PWR
DET
IN
ON LINE
FLT
RX-B
RX-A
13 MHZ
CLK
TX
OUT
ONLINE
PWR
FLT
SCN
CON
ENET
IIIIIIIIIIIIIIIIIIIIIIIII
P/N XXXXXX
IIIIIIIIIIIIIIIIIIIIIIIII
S/N XXXXXX
I2C
ON
LINE
FLT
PWR
PORT 1
12
PORT 0
12
ALARMS
ALARMS
IIIIIIIIIIIIIIIIIIIIIIIII
P/N XXXXXX
IIIIIIIIIIIIIIIIIIIIIIIII
S/N XXXXXX
120 OHM
01234567
ABC

UltraWAVE Micro BTS Installation and Commissioning Guide, Version B 9
Inspecting Components and Recording Part Numbers
1.3.1 Identifying the System Configuration
The UltraWAVE Micro BTS is available in a number of different configurations.
Micro BTS available configurations are listed in Table 1-1. Use this section to
verify the configuration of your UltraWAVE Micro BTS.
Locate the main configuration label on the exterior of your shipping container or
on the back of the Micro subrack assembly.
The main configuration label includes the following details:
Serial number (00xxxxxx).
P/N (xxxxxx).
Revision letter (X).
Model (example: AKAD) - denotes the type of Alvarion system, in this case an
UltraWAVE Micro BTS.
Factory configuration number.
Input Power (example: -48VDC, 10A).
Manufacturing date (month, date, year).
Figure 1-7: Configuration Label
MODEL: AKAD
MODEL NUMBER: AKADO21902512482B
SERIAL:
P/N:
REVISION:
INPUT POWER:
MFG DATE: JUL 11, 2006
-48VDC, 10A
00xxxxx
612872
B
IW192603
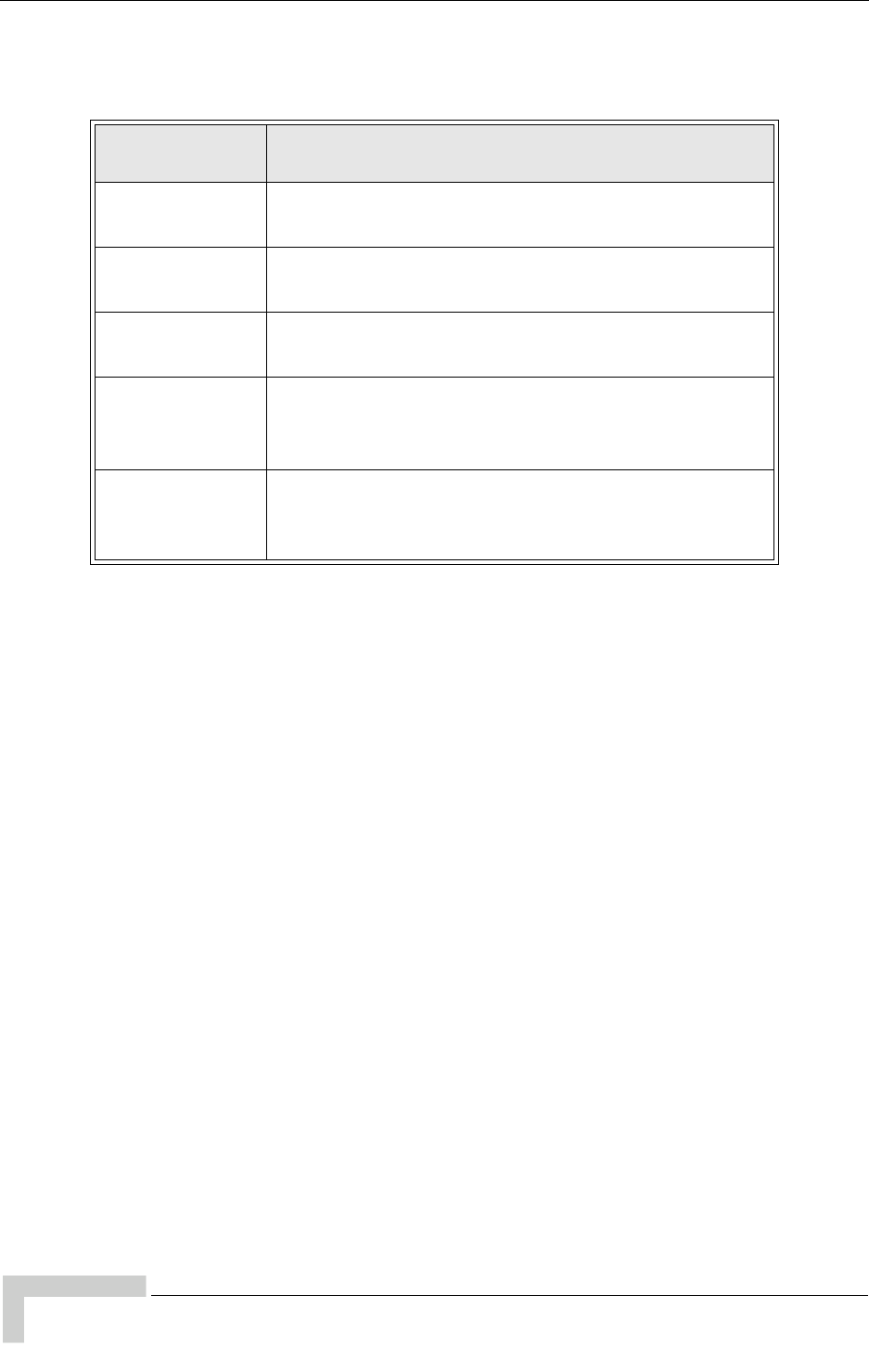
10 UltraWAVE Micro BTS Installation and Commissioning Guide, Version B
Chapter 1 - Unpacking and Configuration Verification
Table 1-1 lists Micro BTS configuration types and details.
Record your model and configuration details in Checklist 2 - Installation
Checklist.
Table 1-1: Configuration Type and Details
Configuration
Type Configuration Details
01 Omni single TRX (01); 15 Watt, 25 Watt, 40 Watt or
50 Watt, two antenna configuration
02 Omni two TRX (02); 15 Watt, 25 Watt, 40 Watt or
50 Watt, two antenna configuration
03 Omni three TRX (03); 15 Watt or 25 Watt, two
antenna configuration
S111
Three sector, one TRX per sector (S111); 15 Watt,
25 Watt, 40 Watt or 50 Watt, six antenna
configuration
S222
Three sector, two TRXs in one sector and one TRX in
the other two sectors (S222), 15 Watt, 25 Watt,
40 Watt or 50 Watt, six antenna configuration

UltraWAVE Micro BTS Installation and Commissioning Guide, Version B 11
Inspecting Components and Recording Part Numbers
1.3.2 Verifying System Labels
This procedure requires you to record each components’ part number, revision
number and serial number in Checklist 2 - Installation Checklist. The factory
places up to three configuration labels on the front of each Micro BTS card,
module and chassis to help identify the system’s configuration. These labels
identify the following:
Part number -- Part number identifies the type of component. All identical
components have the same part number. Part numbers use the format:
P/N NNNNNN
Revision or dash number -- Revision numbers record minor changes in design.
Revision numbers use the format:
-NNN
Serial number -- Each individual component has its own unique serial
number. Serial numbers use the format:
S/N NNNNNNNN
An example of the configuration labels appears in Figure 1-8.
Figure 1-8: Sample Configuration Labels
P/N 340127
-200
S/N 00719500
Part number
Dash or revision number
Serial number
Barcode identifier of
the part number
Barcode identifier of
the rev number
Barcode identifier of
the serial number
IE168405

12 UltraWAVE Micro BTS Installation and Commissioning Guide, Version B
Chapter 1 - Unpacking and Configuration Verification
1.4 Verifying and Documenting Cards and
Modules
The cabinet contains two subrack assemblies.
The Micro contains:
RF modules responsible for RF power amplification, duplexing and
combining when required
Processor Card, E1 or T1 trunk card, TRX cards, and clock module
The power supply consists of up to two power supply modules and a third slot
covered with a blank panel.
1.4.1 Required Equipment
To verify and record your system configuration, you need:
A copy of the Shipping Checklist. It is one of the papers inside the shipping
container.
A copy of Checklist 2 - Installation Checklist.
1.4.2 Micro Subrack Assembly
The Micro subrack assembly provides three RF slots, starting on the left with slot
A. Depending on your Micro BTS configuration, up to three slots will be required
for RF modules. These modules are shipped pre-installed and cabled from the
factory.
1Locate the configuration part and serial numbers on your RF modules.
Figure 1-8 illustrates a sample of these labels.
2Write down the part number, revision number and serial number in Checklist
2 - Installation Checklist.
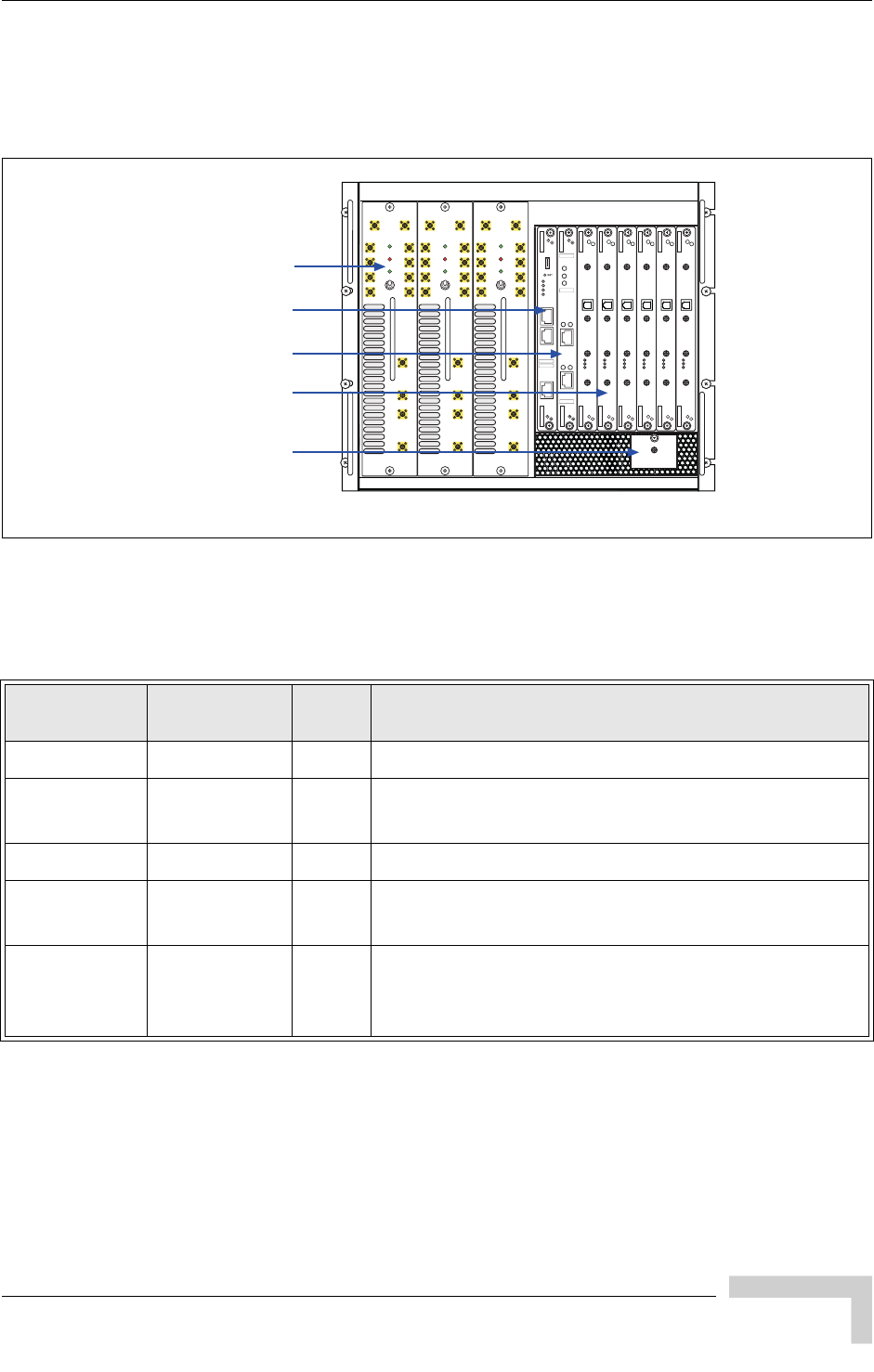
UltraWAVE Micro BTS Installation and Commissioning Guide, Version B 13
Verifying and Documenting Cards and Modules
1.4.3 Slot Assignments
Beside the RF slots, the Micro BTS chassis layout provides eight standard slots,
starting on the left with slot 0. See Figure 1-9.
Table 1-2 shows the Micro BTS slot assignments in the Micro subrack assembly.
The minimum configuration consists of a processor card in slot 0, one E1 or T1
card in slot 1, one TRX in slot 7, a clock module and an RF module in slot C. Any
unused slots must be covered by a blank panel.
Figure 1-9: Micro BTS Chassis Layout
Table 1-2: Micro BTS Slot Assignments
Card Slots Width
(slots) Function
RF Modules A, B, C 1 RF power amplification, duplexing and combining.
Processor
card 0 1 ICP processor card.
E1 or T1 1 1 Each E1 or T1 card provides 2 E1 or T1 lines.
TRX 2, 3, 4, 5, 6,
71 Each TRX manages 8 radio channels.
Clock
Module NA NA
The clock module is located directly underneath the
TRX cards, and provides synchronization for the
Air-interface and E1/ T1 modules.
RF Modules
Processor Card
E1 or T1 Trunk Card
TRX Cards
Clock Module
PA1
IN
ANT
DIV
ANT
MAIN
PWR
FLT
ON LINE
ON
OFF
RX1
RX2
RX3
RX4
TX1
DET
TX2
DET
PA2
IN
RX1
RX2
RX3
RX4
PA1
IN
ANT
DIV
ANT
MAIN
PWR
FLT
ON LINE
ON
OFF
RX1
RX2
RX3
RX4
TX1
DET
TX2
DET
PA2
IN
RX1
RX2
RX3
RX4
PA1
IN
ANT
DIV
ANT
MAIN
PWR
FLT
ON LINE
ON
OFF
RX1
RX2
RX3
RX4
TX1
DET
TX2
DET
PA2
IN
RX1
RX2
RX3
RX4
IW132601
PWR
DET
IN
ON LINE
FLT
RX-B
RX-A
13 MHZ
CLK
TX
OUT
PWR
DET
IN
ON LINE
FLT
RX-B
RX-A
13 MHZ
CLK
TX
OUT
PWR
DET
IN
ON LINE
FLT
RX-B
RX-A
13 MHZ
CLK
TX
OUT
PWR
DET
IN
ON LINE
FLT
RX-B
RX-A
13 MHZ
CLK
TX
OUT
PWR
DET
IN
ON LINE
FLT
RX-B
RX-A
13 MHZ
CLK
TX
OUT
PWR
DET
IN
ON LINE
FLT
RX-B
RX-A
13 MHZ
CLK
TX
OUT
ONLINE
PWR
FLT
SCN
CON
ENET
IIIIIIIIIIIIIIIIIIIIIIIII
P/N XXXXXX
IIIIIIIIIIIIIIIIIIIIIIIII
S/N XXXXXX
I2C
ON
LINE
FLT
PWR
PORT 1
12
PORT 0
12
ALARMS
ALARMS
IIIIIIIIIIIIIIIIIIIIIIIII
P/N XXXXXX
IIIIIIIIIIIIIIIIIIIIIIIII
S/N XXXXXX
120 OHM
01234567
ABC
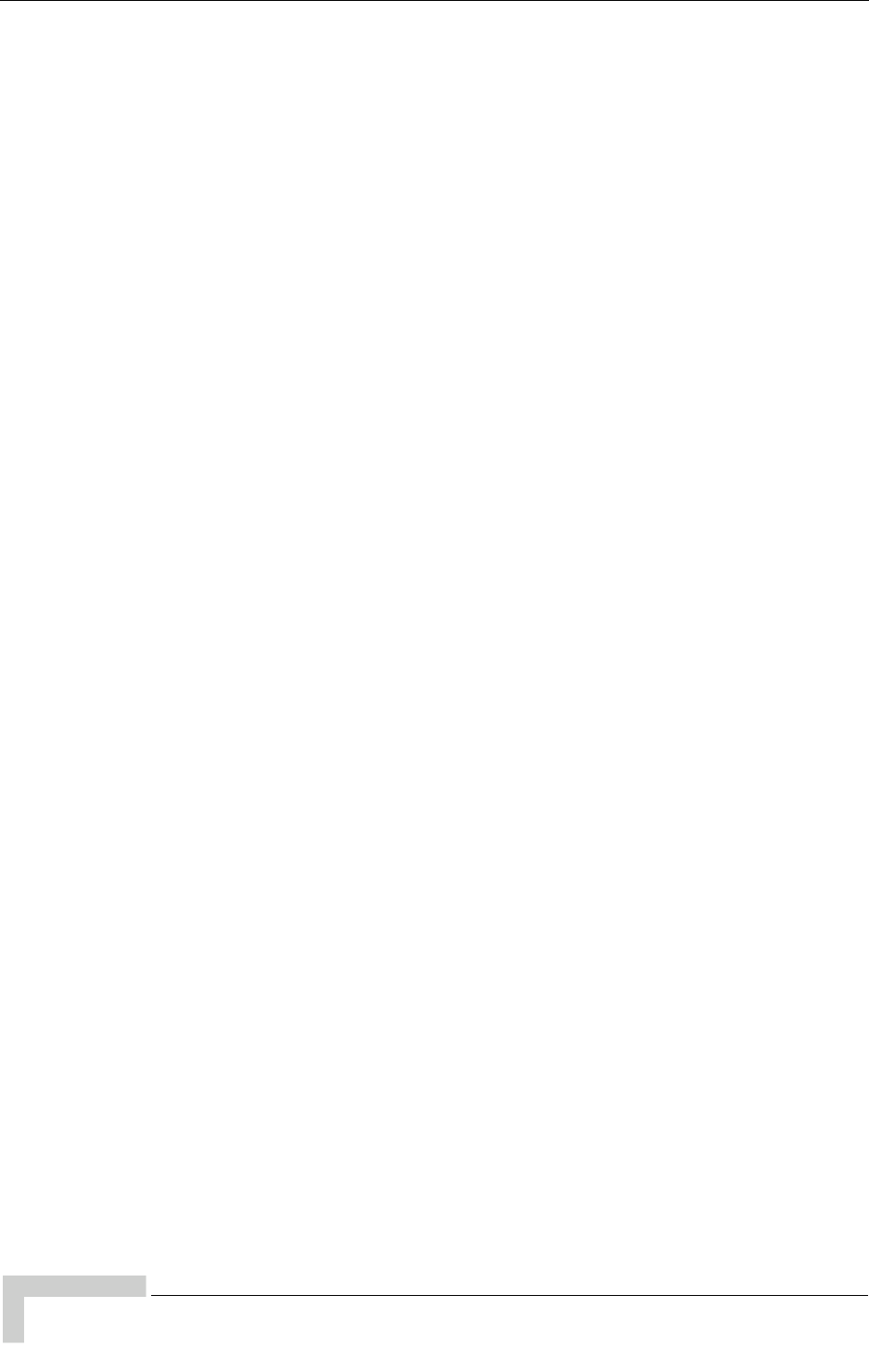
14 UltraWAVE Micro BTS Installation and Commissioning Guide, Version B
Chapter 1 - Unpacking and Configuration Verification
1.4.4 Verification Procedure
Use the following procedure to identify and record your system components.
Compare components against those listed in the shipping checklist. See
Figure 1-9 for Micro BTS chassis component locations.
1Verify that the subrack assembly has four fan assemblies on the power
amplifier side on the rear of the chassis and two fans on the VME bus cards
side on the rear of the chassis. Verify that the fans are securely fastened to the
chassis.
2Verify that the Micro BTS rack assembly contains an one or more RF modules
in slots A, B and/or C of the Micro rack assembly. Write down the part
number, revision number and serial number of each RF module in Checklist 2
- Installation Checklist.
3Verify that the chassis contains an ICP processor card in slot 0 of the Micro
subrack assembly. Write down the processor card part number, revision
number and serial number in Checklist 2 - Installation Checklist.
4Slot 1 of the Micro subrack assembly should contain an E1 or T1 card. From
the shipping checklist, write down the part number, revision number and
serial number of the E1 or T1 card in Checklist 2 - Installation Checklist.
5Slots 2 to 7 should contain one or more TRXs. Verify how many are required
from the shipping checklist, then verify that they are all there. Write down the
part number, revision number and serial number of each TRX card in Check-
list 2 - Installation Checklist.
6Check the shipping checklist and verify that the power supply subrack
assembly has one or two power supply modules and power supply fan assem-
blies. One or two power supply modules are required depending on your
configuration. Verify that a third slot and any other open slot is covered with a
blank panel.
For each power supply module, write down the part number, revision number
and serial number in Checklist 2 - Installation Checklist.
7Verify that all empty slots are covered by blank panels. These are necessary for
cooling, and to meet RF emission standards.
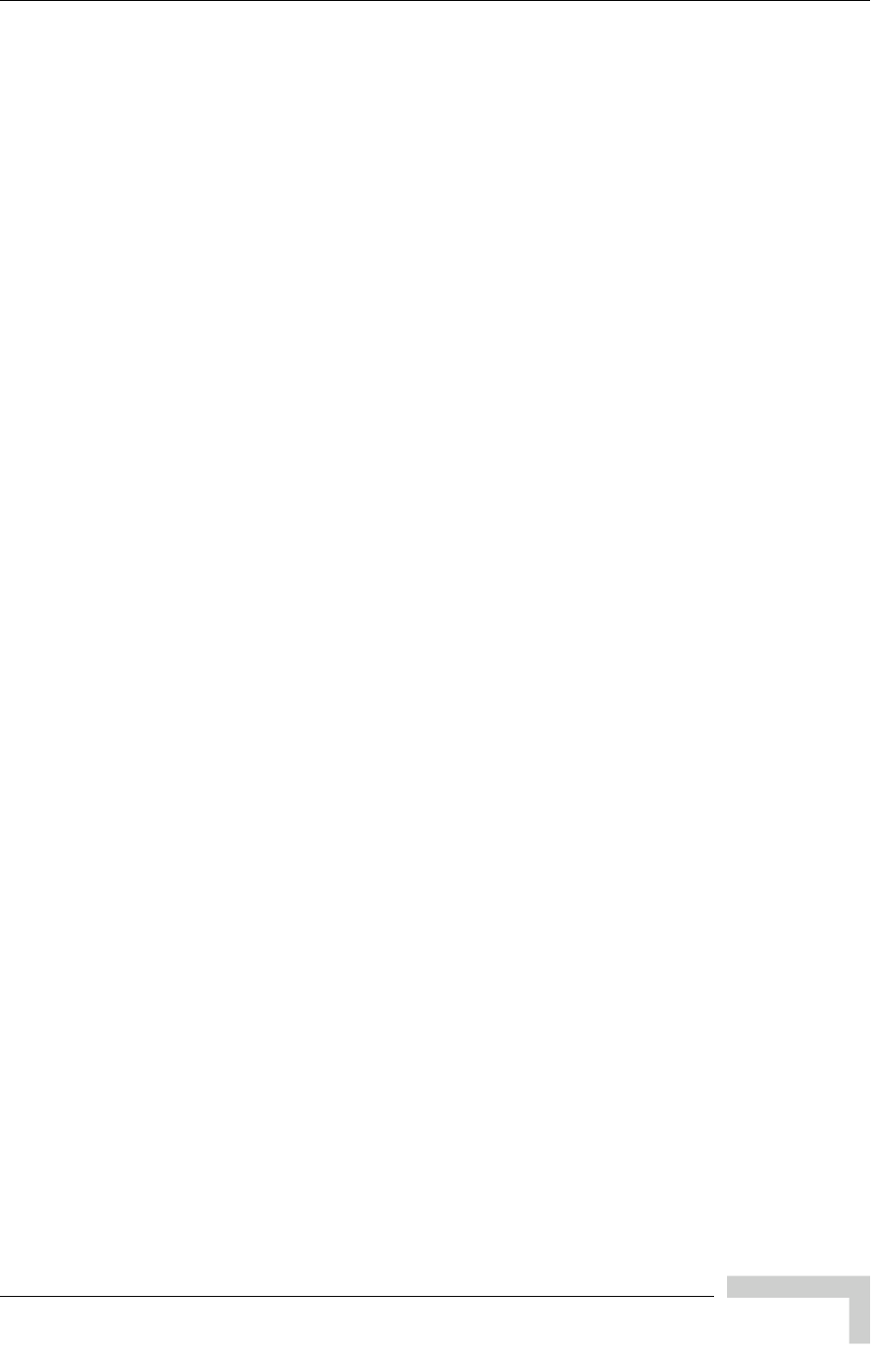
UltraWAVE Micro BTS Installation and Commissioning Guide, Version B 15
Verifying Cabling
1.5 Verifying Cabling
In this section, you inspect the internal cabling and verify that it is configured
correctly.
1.5.1 Verifying Internal Cabling
When the Micro BTS assembly and the power supply rack assembly are mounted
in the rack enclosure, all E1 or T1 interfaces are routed directly to the trunk cards
through a dust protector on the rack. The interface access area is mounted in the
rear recessed area of the rack enclosure. The internal cabling also connects the
power supply modules to the Micro subrack assembly and provides a plug on the
exterior of the cabinet for connection to the power source.
The internal cabling of the Micro BTS is included for the rack enclosure
configuration only, and is completed by the manufacturer. Due to its complexity,
it is not recommended for you to move or disconnect internal cabling.
1.5.2 Verifying Enclosure Cabling
When the Micro subrack assembly and power supply modules are mounted in the
rack enclosure, it is necessary to verify that the following cables are connected:
Alarm cable and I2C interface cable
Power supply cables
Ensure that:
The alarm cable is connected to the power supply subrack assembly and the
Micro assembly.
A USB style cable is connected from the I2C interface to the I2C connector on
the front of the ICP processor card.
The power supply subrack assembly power cables are connected to the Micro
subrack assembly. See Figure 1-10, Power Supply Cable 1 and Power Supply
Cable 2.
The external power supply cable (Input Power Supply) is connected to the
power supply subrack assembly.
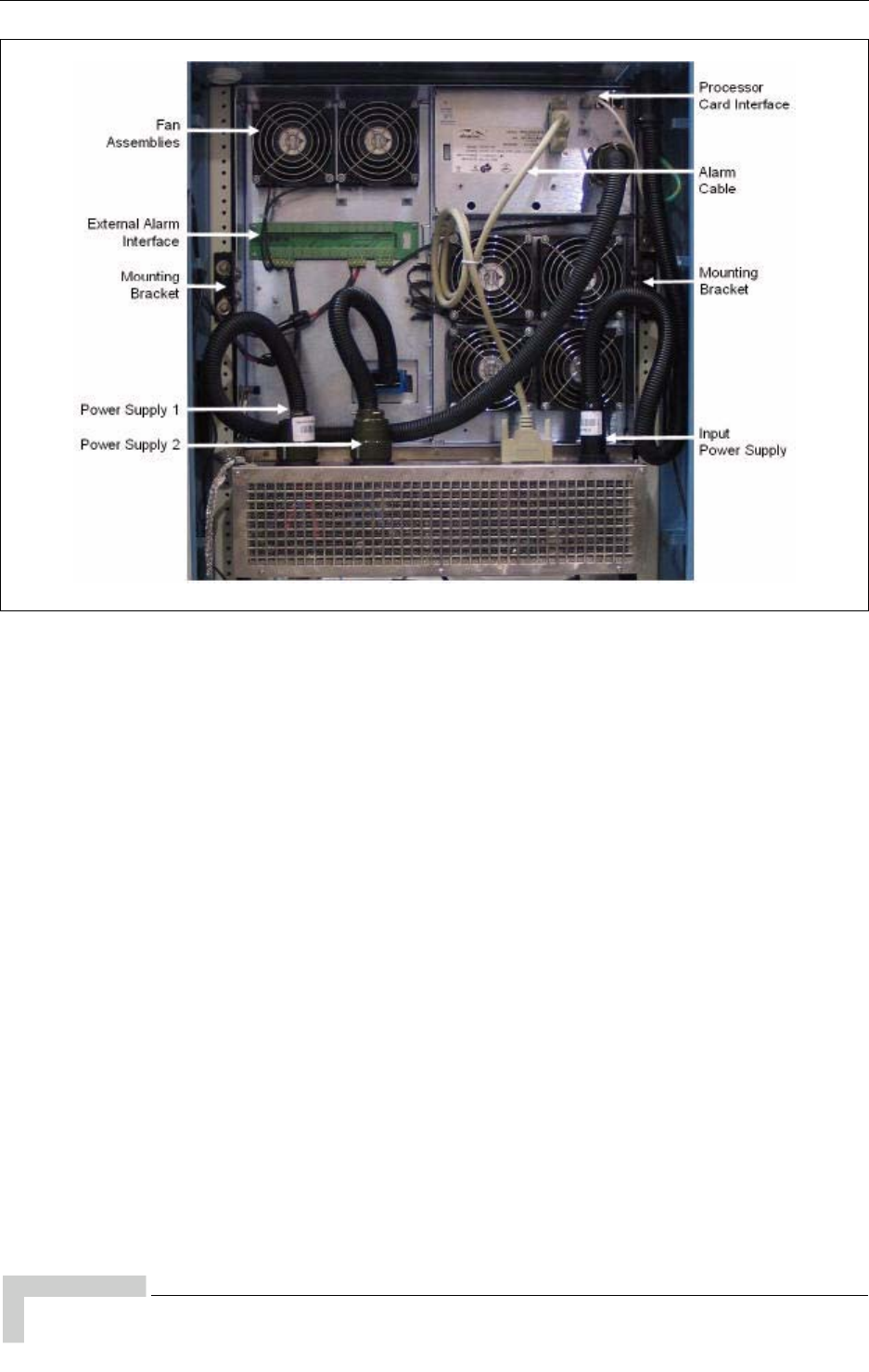
16 UltraWAVE Micro BTS Installation and Commissioning Guide, Version B
Chapter 1 - Unpacking and Configuration Verification
Figure 1-10 shows the location of the following components from the rear view of
the Micro subrack assembly and power supply assembly:
Fan Assemblies
External Alarm Interface
Mounting Brackets
Power Supply 1 cable for slots A through C
Power Supply 2 cable for slots 0 through 7
Processor Card Interface
The ICP processor card uses an I2C interface and connects physically with a
USB style cable between the processor card interface connector and the I2C
connector on the front of the ICP processor card.
Input Power Supply cable connection
Please proceed to Chapter 2 - Installation to install your Micro BTS.
Figure 1-10: Micro Subrack and Power Supply Assembly Rear View
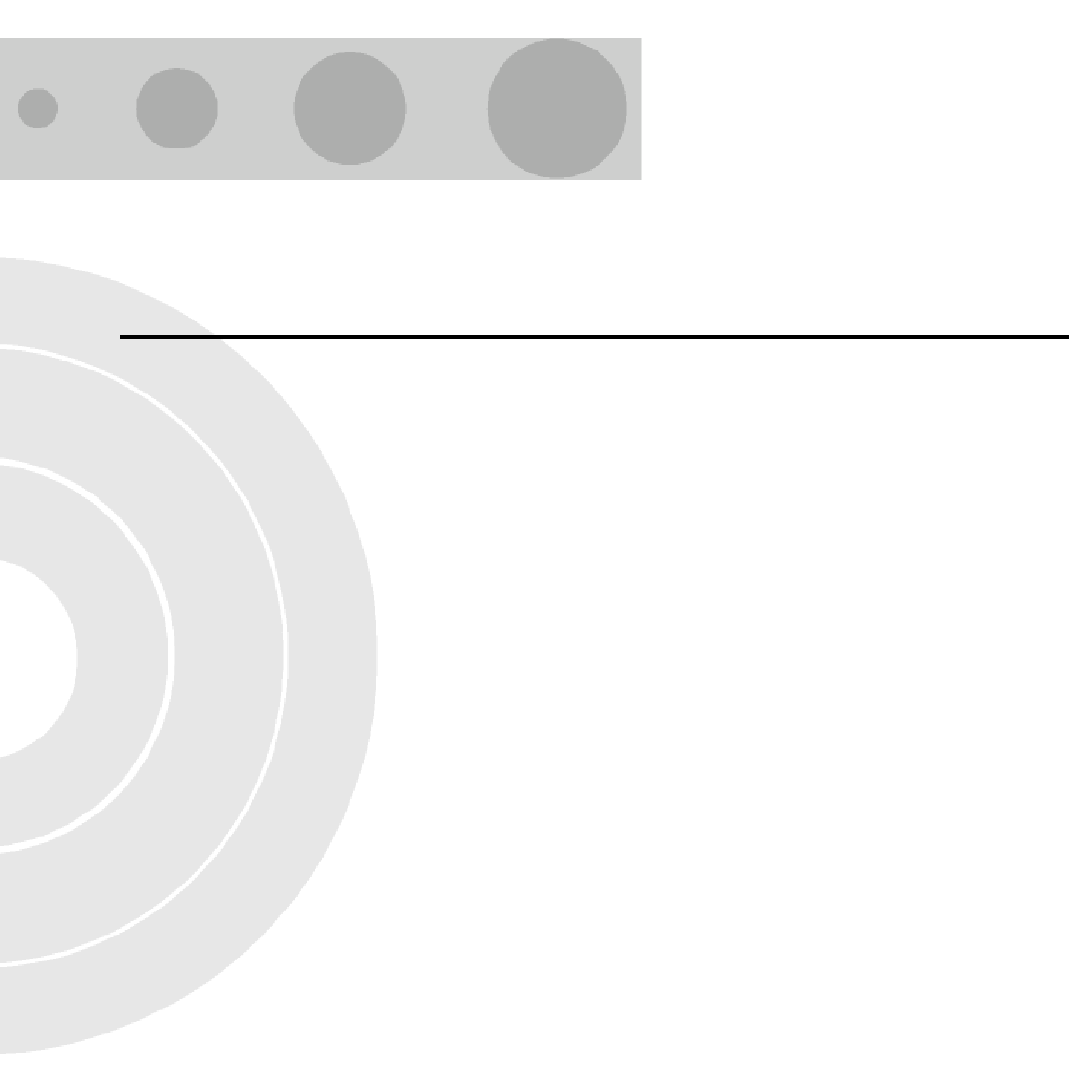
2
Chapter 2 - Installation
In this Chapter:
“Analyzing Site Requirements” on page 18
“Mounting the Micro BTS Chassis” on page 22
“Configuring the E1 or T1 Trunk Card” on page 31
“Connecting Ground Cables” on page 36
“Connecting Power Supplies” on page 38
“Connecting E1 or T1 Trunk Cables” on page 47
“Connecting Antennas” on page 52
“Connecting External Alarms” on page 60
“Making a Serial Connection to the Processor Card” on page 64
“Network Connections” on page 65
“Post Installation Cabling and Checks” on page 66
This chapter provides instructions for installing and configuring the Micro BTS
hardware.
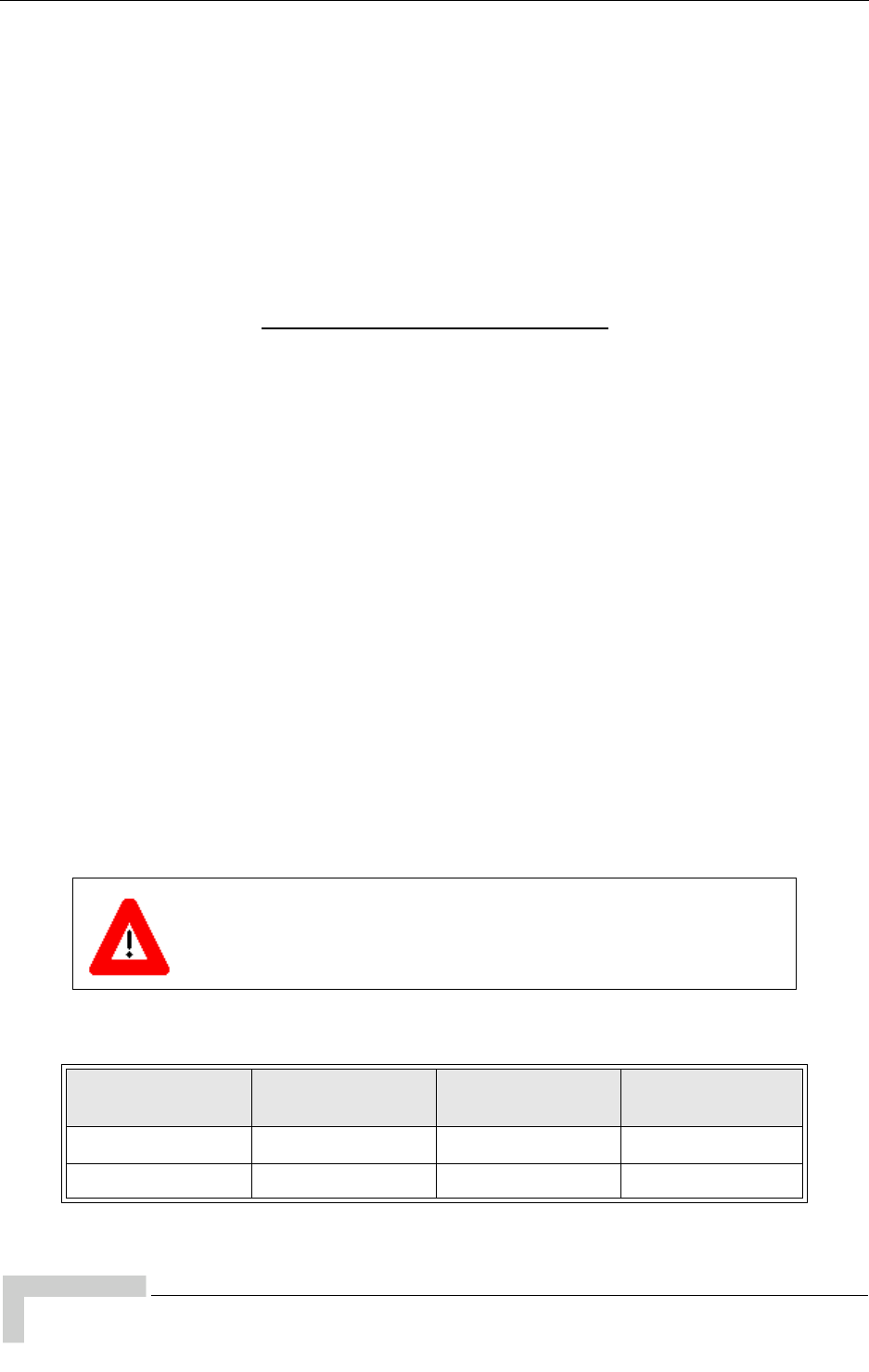
18 UltraWAVE Micro BTS Installation and Commissioning Guide, Version B
Chapter 2 - Installation
2.1 Analyzing Site Requirements
Before a site is chosen or equipment installed, a site survey must be carried out.
The site survey checklist assists the surveyor with the inspection and the
collection of site specific information such as environmental conditions, electrical
requirements, and mechanical requirements.
The site survey checklist must be completed before installation begins. The
necessary steps for site readiness are listed in Checklist 1 - Site Readiness
Checklist. The GSM Network Implementation Manual provides additional detailed
site requirements.
The site readiness checklist assists the field service engineer or operator to ensure
that the site is ready for equipment installation. It includes information about:
Environmental conditions
Electrical requirements
Chassis requirements
The site readiness checklist is located in Checklist 1 - Site Readiness Checklist. It
must be completed as part of the installation process.
2.1.1 Environmental Conditions
The Micro BTS is designed to operate indoors only. To facilitate long-term
operability and durability of the Micro BTS, observe specific environmental
constraints.
Before installing the Micro BTS, ensure that the operating environment maintains
a temperature and humidity within the ranges shown in Table 2-1.
Make sure the ambient temperature around the unit (which may
be higher than the room temperature) is within the specified limit
for the unit.
Table 2-1: Micro BTS Operating Environment
Scale Humidity
(non-condensing) Temperature
(Celsius) Temperature
(Fahrenheit)
Maximum 90% 55 degrees 131 degrees
Minimum 10% -5 degrees 23 degrees

UltraWAVE Micro BTS Installation and Commissioning Guide, Version B 19
Analyzing Site Requirements
2.1.2 Electrical Requirements
The Micro BTS is specified to operate on either AC or DC power. Requirements for
the Micro BTS are dependent on the number of TRX cards supported.
Power Options
Main power supply options for the Micro BTS are:
110 VAC to 220 VAC auto-ranging, 30 A, 50-60 Hz
-40 VDC to -60 VDC (-48 VDC nominal), 40 A
Table 2-2 shows the estimated power requirements for the different TRX
configurations for the Micro BTS.
Table 2-3 shows Micro BTS Power Specifications.
Table 2-2: Estimated Power Requirements for TRX Configurations
Product
Configuration -48 VDC 110 VAC 220 VAC
One TRX 261 Watts 350 Watts 345 Watts
Two TRXs 531 Watts 700 Watts 690 Watts
Three TRXs 801 Watts 1050 Watts 1035 Watts
Four TRXs 1071 Watts 1400 Watts 1380 Watts
Six TRXs 1611 Watts 2100 Watts 2070 Watts
Table 2-3: Micro BTS Power Specifications
Power Requirements Specification
Micro BTS voltage range: 110 VAC 90 to 264 VAC
Micro BTS power protection: 110 VAC Dedicated 30 amp circuit breaker
Micro BTS voltage range: 220 VAC 90 to 264 VAC
Micro BTS power protection: 220 VAC Dedicated 15 Amp circuit breaker
Micro BTS DC voltage range: -48 VDC -40 to -60 VDC
Micro BTS DC power protection: -48 VDC Dedicated 40 Amp fuse/circuit breaker
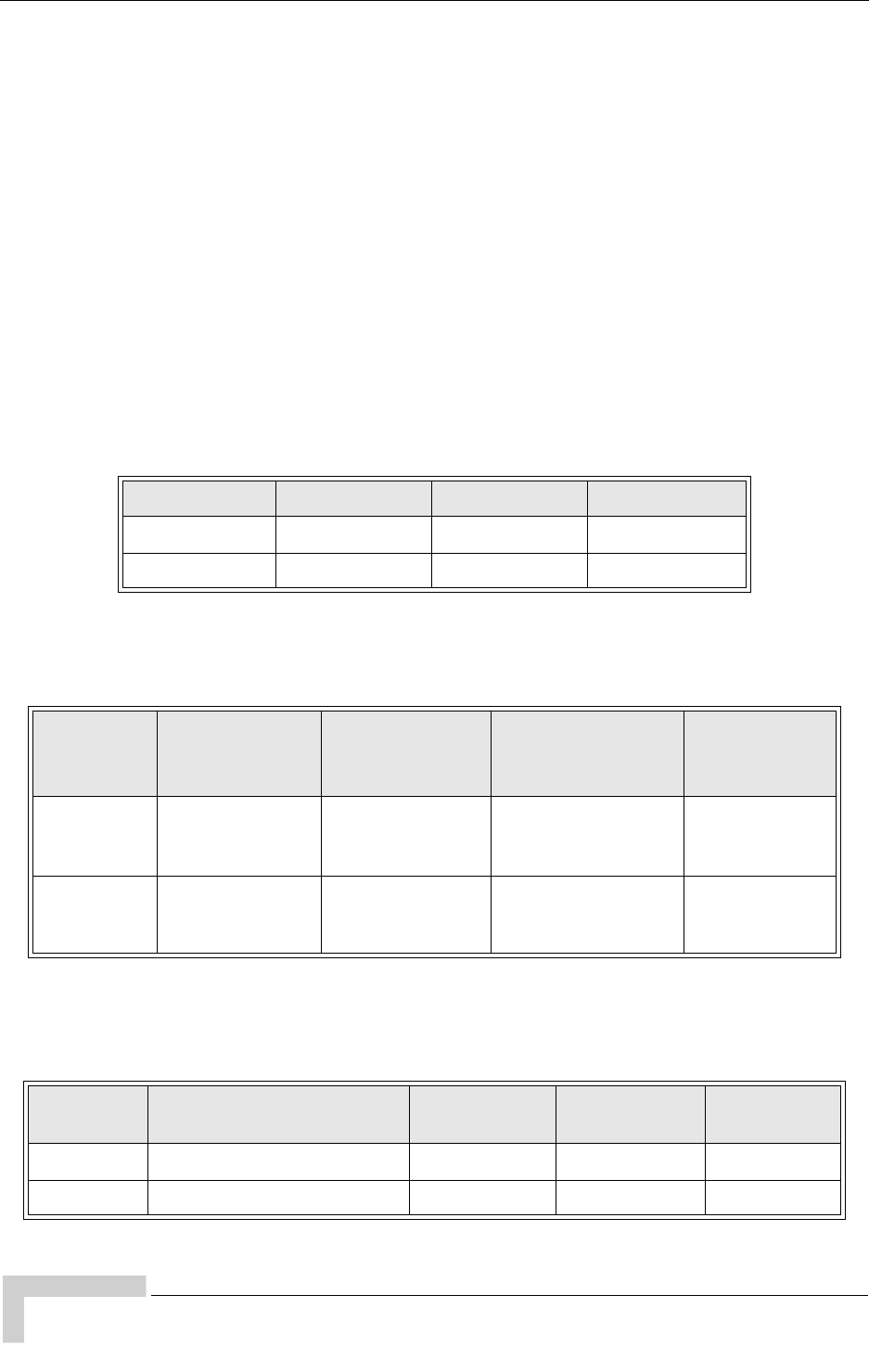
20 UltraWAVE Micro BTS Installation and Commissioning Guide, Version B
Chapter 2 - Installation
2.1.3 Chassis Requirements
Before installing the Micro BTS, ensure that adequate clearance space is allowed
around the unit. Enough clearance should be provided from the front and back of
the cabinet to fully open the doors. This requires at least 24 inches (61 cm) from
the front and rear doors. The minimum clearance required on either side of the
cabinet is 4.5 inches (11.4 cm) and the minimum clearance required below the
cabinet is 1.8 inches (4.59 cm). The mounting site should also have ample
clearance for the trunk and antenna cables to be attached to the connectors at the
top of the cabinet.
The Micro BTS should be installed away from salt spray and in an area where
there are minimal vibrations.
Table 2-4 lists the dimensions of the Micro BTS chassis.
Table 2-5 lists the weight and dimensions of the power supply rack.
Table 2-6 and Figure 2-1 provide the dimensions of the BTS cabinet. For detailed
cabinet dimensions, refer to Section 2.2.
Table 2-4: Micro BTS Chassis Dimensions
Scale Height Width Depth
Metric 39.93 cm 48.26 cm 43.82 cm
Imperial 15.72 inches 19.0 inches 17.25 inches
Table 2-5: Power Supply Rack Weight and Dimensions
Scale
Weight
(Maximum
Configuration)
Height Width Depth
Metric 23.8 kg
12.5 cm (AC)
13 cm (DC)
48.26 cm 51.44 cm
Imperial 52.35 lbs
5 inches (AC)
5.2 inches (DC)
19.0 inches 20.25 inches
Table 2-6: Micro BTS Cabinet Weight and Dimensions
Scale Weight
(Maximum Configuration) Height Width Depth
Metric 166 kg 105.1 cm 56.0 cm 64.77 cm
Imperial 365 lbs 41.38 inches 22.05 inches 25.5 inches
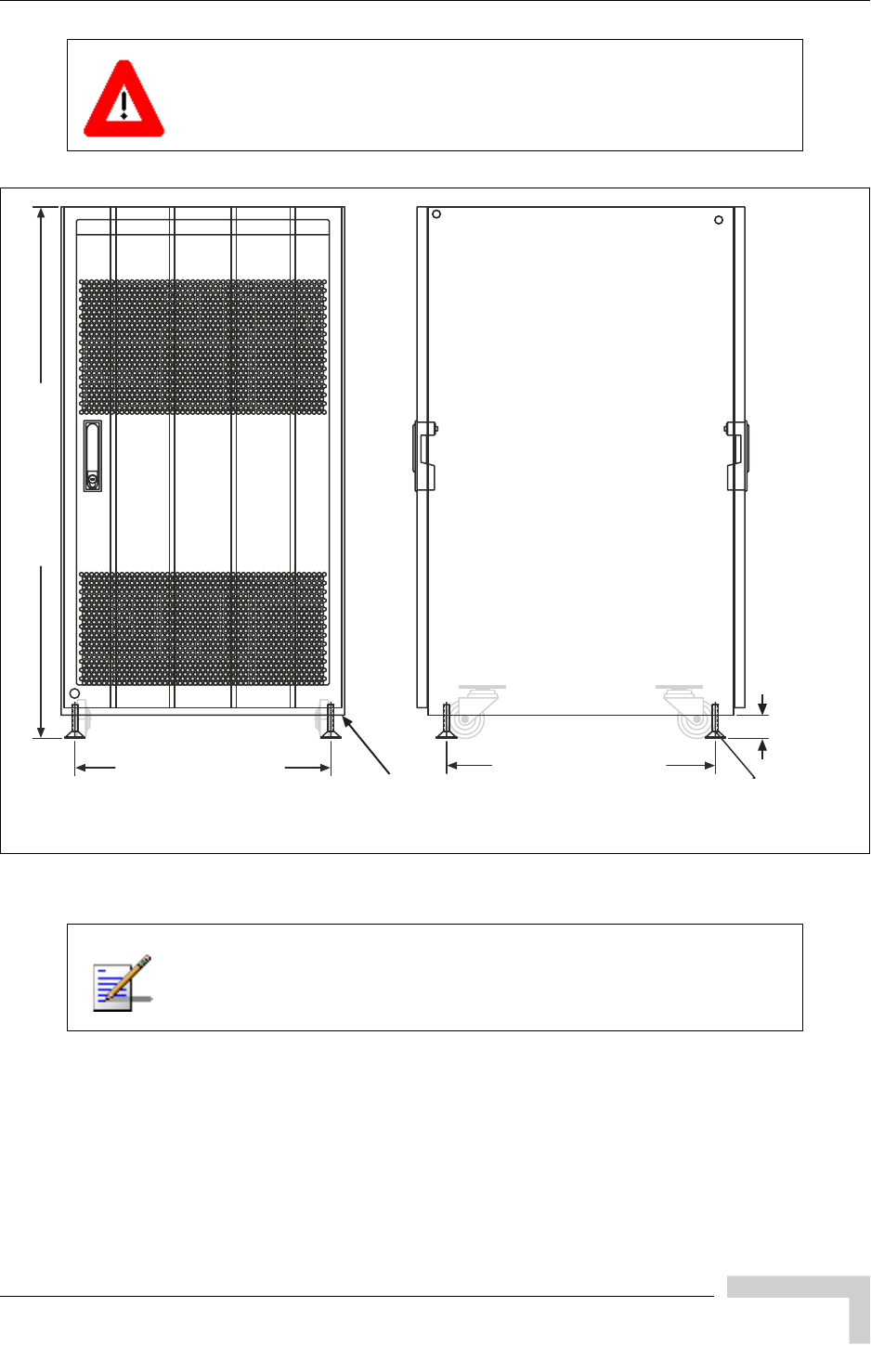
UltraWAVE Micro BTS Installation and Commissioning Guide, Version B 21
Analyzing Site Requirements
When fully loaded, two people are required to lift the chassis. (The
two man lift requirement applies to loads of over 80 kg.)
Figure 2-1: Cabinet Footing Dimensions
The steps for site readiness are listed in Checklist 1 - Site
Readiness Checklist.
WHEEL_SV
WHEEL_SV
WHEEL_FV
WHEEL_FV WHEEL_FV
DOOR_
DOOR_
FV
FV
CAB_F
CAB_F
V
V
RUBFE
RUBFE
ET
ET
RUBFE
RUBFE
ET
ET
CAB_S
CAB_S
V
V
DOOR_
DOOR_
SV
SV
DOOR_
DOOR_
SV
SV
RUBFE
RUBFE
ET
ET
RUBFE
RUBFE
ET
ET
20.925 in. [53.15 cm]
M12-1.75
(each corner)
1.808 in
[4.59 cm]
19.925 in. [50.61 cm]
41.375 in. [105.09 cm]
IW008301
M10 Tap Holes
(each corner)

22 UltraWAVE Micro BTS Installation and Commissioning Guide, Version B
Chapter 2 - Installation
2.2 Mounting the Micro BTS Chassis
The Micro BTS is offered in two different configurations:
19 inch (48.26 cm) rack assembly
Cabinet enclosure assembly
Upon ordering the Micro BTS, the desired type of mounting must be specified, as
a separate mounting kit is supplied for each option.
This section describes all the necessary steps for installing a Micro BTS. It is
divided into two subsections. These two sections are:
Rack installation. Section 2.2.1
Enclosure mounting. Section 2.2.2
Each of these sections contain complete instructions on how to install the Micro
BTS in different configurations. Please refer to the appropriate section.
Ensure that:
• The ambient temperature around the unit (which may be higher
than the room temperature) is within the limit specified for the
unit.
• There is sufficient airflow around the unit.
• The electrical circuits are not overloaded - consider the name
plate rating of all the connected equipment and make sure you
have over current protection.
• The equipment is properly grounded.
• No objects are placed on top of the unit.

UltraWAVE Micro BTS Installation and Commissioning Guide, Version B 23
Mounting the Micro BTS Chassis
2.2.1 Rack Installation
The Micro BTS may be ordered with or without a standard EIA 19 inch rack
enclosure as defined in EIA standard RS-310-D Racks, Panels and Associated
Equipment. If you ordered the rack enclosure, the Micro subrack assembly and
the power supply subrack assembly will be mounted inside the rack enclosure
with cable access to the outside of the enclosure.
The minimum clearance required above and below the chassis is 1.0" (2.54 cm)
and the minimum clearance required behind the chassis is 1.0" (2.54 cm). The
mounting site should also have ample clearance for the trunk cables to be
attached to the front panel connectors.
Required Materials
12 standard customer-provided rack mount screws
Optional Materials
One standard 19" (48.26 cm) rack mount shelf assembly
Required Tools
Rack mount screwdriver
Rack Mount Advisory
To prevent bodily injury when mounting or servicing this unit in a rack, you must
take special precautions to ensure that the system remains stable. The following
guidelines are provided to ensure your safety:
This unit should be mounted at the bottom of the rack if it is the only unit in
the rack.
When mounting this unit in a partially filled rack, load the rack from the
bottom to the top with the heaviest component at the bottom of the rack.
If the rack is provided with stabilizing devices, install the stabilizers before
mounting or servicing the unit in the rack.
Attention: Pour éviter toute blessure corporelle pendant les opérations de montage
ou de réparation de cette unité en casier, il convient de prendre des précautions
spéciales afin de maintenir la stabilité du système. Les directives ci-dessous sont
destinées à assurer la protection du personnel:
Si cette unité constitue la seule unité montée en casier, elle doit être placée
dans le bas.
Si cette unité est montée dans un casier partiellement rempli, charger le casier
de bas en haut en plaçant l'élément le plus lourd dans le bas.
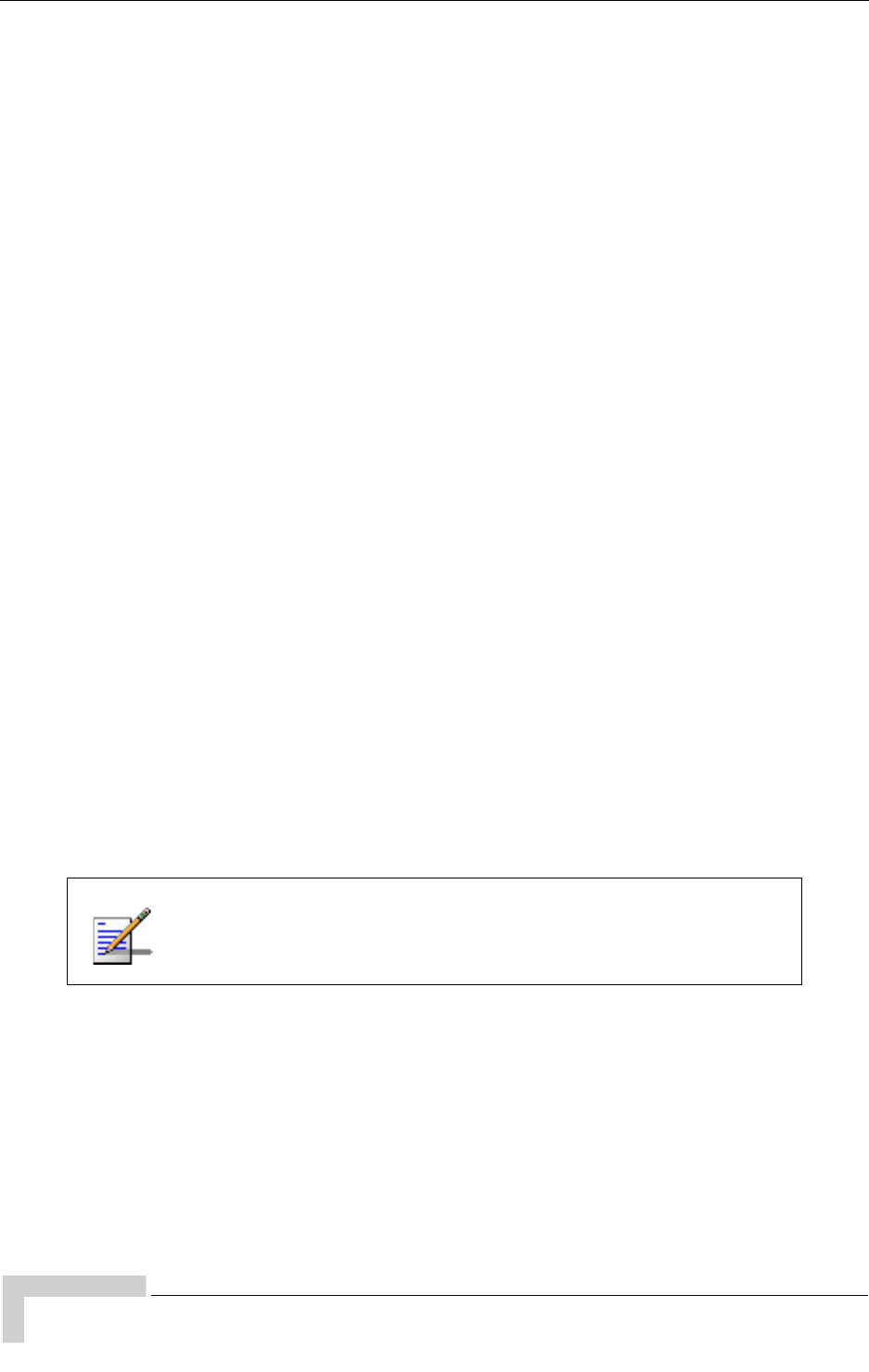
24 UltraWAVE Micro BTS Installation and Commissioning Guide, Version B
Chapter 2 - Installation
Si le casier est équipé de dispositifs stabilisateurs, installer les stabilisateurs
avant de monter ou de réparer l'unité en casier.
Warnung: Zur Vermeidung von Körperverletzung beim Anbringen oder Warten
dieser Einheit in einem Gestell müssen Sie besondere Vorkehrungen treffen, um
sicherzustellen, daß das System stabil bleibt. Die folgenden Richtlinien sollen zur
Gewährleistung Ihrer Sicherheit dienen:
Wenn diese Einheit die einzige im Gestell ist, sollte sie unten im Gestell ange-
bracht werden.
Bei Anbringung dieser Einheit in einem zum Teil gefüllten Gestell ist das
Gestell von unten nach oben zu laden, wobei das schwerste Bauteil unten im
Gestell anzubringen ist.
Wird das Gestell mit Stabilisierungszubehör geliefert, sind zuerst die Stabilisa-
toren zu installieren, bevor Sie die Einheit im Gestell anbringen oder sie
warten.
Installation Instructions
1Allocate nine rack units of space in your 19" rack for the Micro subrack
assembly and three rack units of space for the power supply subrack
assembly.
2The rack mount brackets have cutouts to accommodate the rack screws.
Using two people, carefully align the Micro subrack assembly with the rack
holes.
3Mount the Micro BTS subrack assembly in the rack using customer-provided
screws.
4Using the same procedure, align and mount the power supply subrack
assembly below the Micro BTS subrack assembly, as shown in Figure 2-2.
Optionally, you can mount a rack mount shelf assembly and use
the shelf to support the two rack assemblies. Both assemblies
must also be secured to the rack unit.

UltraWAVE Micro BTS Installation and Commissioning Guide, Version B 25
Mounting the Micro BTS Chassis
.
5Connect the alarm cable between the power supply subrack assembly and the
Micro subrack assembly. See Figure 2-3. Secure the cable by tightening the
phillips screws.
6Connect Power Supply Cable 1 and Power Supply Cable 2 between the power
supply subrack assembly and the Micro BTS subrack assembly. See
Figure 2-3. The connector to the Micro subrack assembly will snap into place,
while you must tighten the round quick disconnect connector by twisting the
connector housing.
Refer to Section 1.5 for more information on cabling and on verifying that cables
are connected correctly.
Figure 2-2: Attaching the Subrack Assemblies
Rack Screws
x8
IE027601
Rack Screws
x4
INPUT
OUTPUT
FAULT
OFF
ON
UNLOCK
INPUT
OUTPUT
FAULT
OFF
ON
UNLOCK
PA1
IN
ANT
DIV
ANT
MAIN
PWR
FLT
ON LINE
ON
OFF
RX1
RX2
RX3
RX4
TX1
DET
TX2
DET
PA2
IN
RX1
RX2
RX3
RX4
PA1
IN
ANT
DIV
ANT
MAIN
PWR
FLT
ON LINE
ON
OFF
RX1
RX2
RX3
RX4
TX1
DET
TX2
DET
PA2
IN
RX1
RX2
RX3
RX4
PA1
IN
ANT
DIV
ANT
MAIN
PWR
FLT
ON LINE
ON
OFF
RX1
RX2
RX3
RX4
TX1
DET
TX2
DET
PA2
IN
RX1
RX2
RX3
RX4
PWR
DET
IN
ON LINE
FLT
RX-B
RX-A
13 MHZ
CLK
TX
OUT
PWR
DET
IN
ON LINE
FLT
RX-B
RX-A
13 MHZ
CLK
TX
OUT
PWR
DET
IN
ON LINE
FLT
RX-B
RX-A
13 MHZ
CLK
TX
OUT
PWR
DET
IN
ON LINE
FLT
RX-B
RX-A
13 MHZ
CLK
TX
OUT
PWR
DET
IN
ON LINE
FLT
RX-B
RX-A
13 MHZ
CLK
TX
OUT
PWR
DET
IN
ON LINE
FLT
RX-B
RX-A
13 MHZ
CLK
TX
OUT
ONLINE
PWR
FLT
SCN
CON
ENET
IIIIIIIIIIIIIIIIIIIIIIIII
P/N XXXXXX
IIIIIIIIIIIIIIIIIIIIIIIII
S/N XXXXXX
I2C
ON
LINE
FLT
PWR
PORT 1
12
PORT 0
12
ALARMS
ALARMS
IIIIIIIIIIIIIIIIIIIIIIIII
P/N XXXXXX
IIIIIIIIIIIIIIIIIIIIIIIII
S/N XXXXXX
120 OHM
ABC
01234567
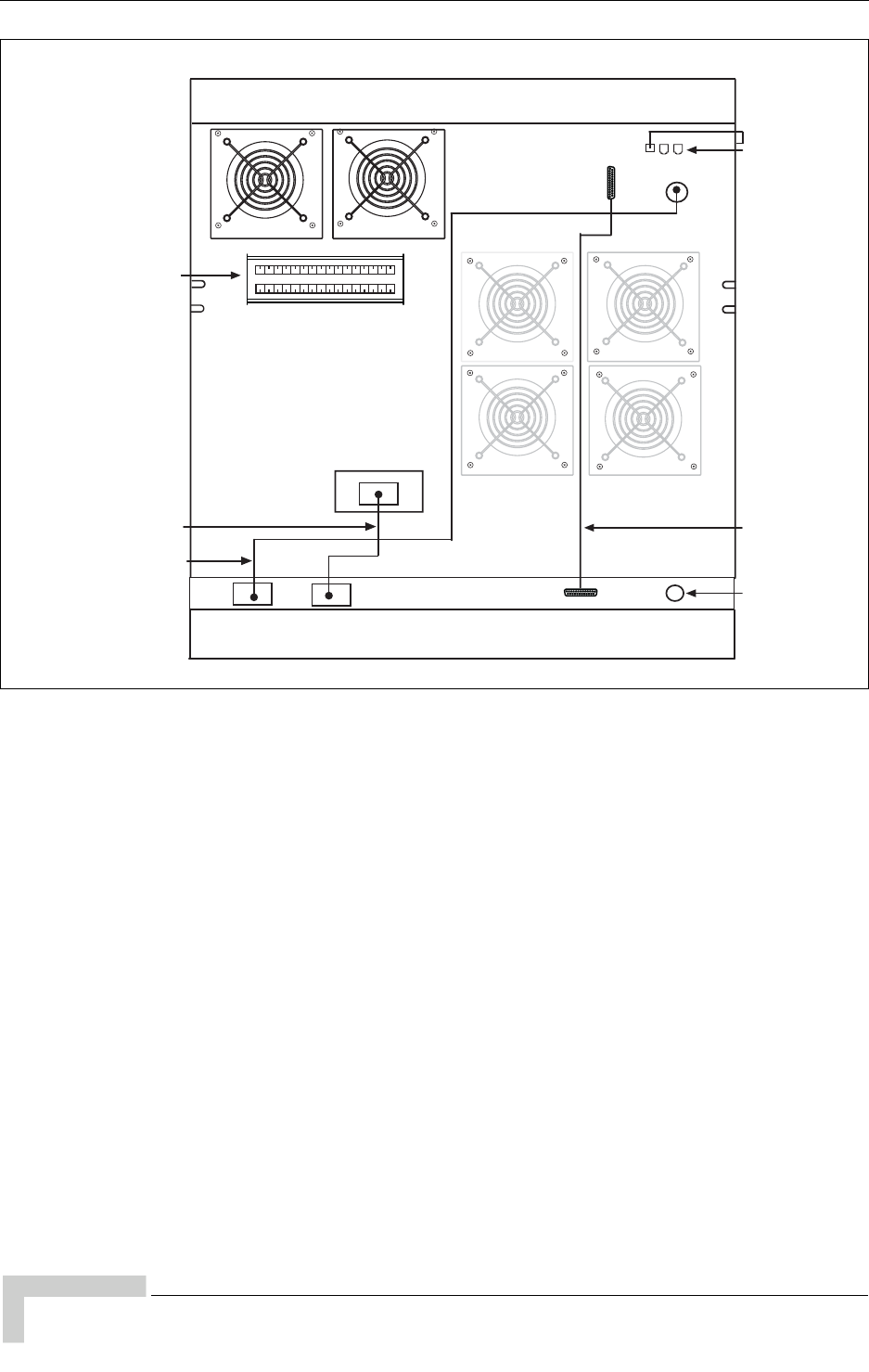
26 UltraWAVE Micro BTS Installation and Commissioning Guide, Version B
Chapter 2 - Installation
7You have completed the hardware installation. Proceed to Section 2.3 to
continue the Micro BTS configuration.
Figure 2-3: Power Cabling and Alarm Cabling
IW144601
EP1 EP2 EP3 EP4 EP5 EP6 EP7 EP8 EP9 EP10 EP11 EP12 EP13 EP14 EP15 EP16
EP17 EP18 EP19 EP20
Power Supply
Cable 2
USB Cable to
Processor Card
Input Power
Supply
Alarm Cable
Power Supply
Cable 1
External Alarm
Interface
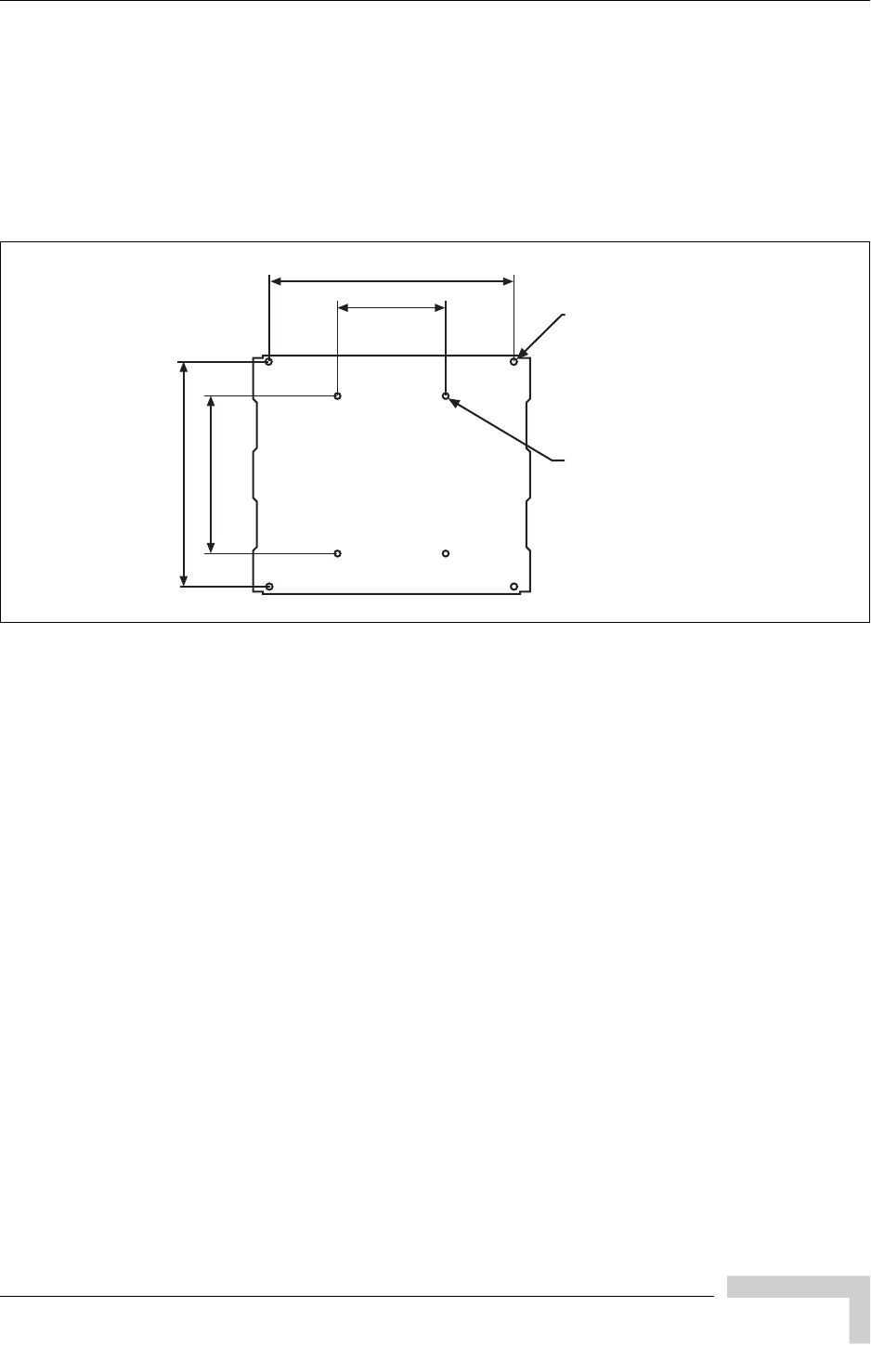
UltraWAVE Micro BTS Installation and Commissioning Guide, Version B 27
Mounting the Micro BTS Chassis
2.2.2 Enclosure Mounting
The Micro BTS chassis should be mounted on a concrete pad of sufficient density
to support the weight of the cabinet assembly. Alignment pins may be installed in
the concrete pad at the locations provided in Figure 2-4. The alignment pins
should be 0.5 inches (1.27 cm) in diameter and protrude from 4.1 inches to
4.4 inches (10.41 cm to 11.18 cm) from the concrete pad.
Enough clearance should be provided from the front and back of the cabinet to
fully open the doors. This requires at least 24 inches (61 cm) from the front and
rear doors. The minimum clearance required on either side of the cabinet is
4.5 inches (11.4 cm) and the minimum clearance required below the cabinet is
1.8 inches (4.59 cm). The mounting site should also have ample clearance for the
trunk and antenna cables to be attached to the connectors at the top of the
cabinet.
The required footprint for your cabinet installation must be at least 73.5 inches
(186.7 cm) by 31.5 inches (80 cm). Be sure there is sufficient airflow around the
unit.
Figure 2-4: Cabinet Footprint
Rubber feet
Mounting hole
M16-2 x4 places
20.898 in. [53.08 cm]
22.63 in. [57.48 cm]
Alignment holes
0.551 in. [1.40 cm]
10.00 in.
[25.40 cm]
14.567 in.
[37.00] cm
IW021301

28 UltraWAVE Micro BTS Installation and Commissioning Guide, Version B
Chapter 2 - Installation
The cabinet is mounted on casters and may be carefully moved from the
unpacking site to its final mounting location. The cabinet has four rubber feet
which will raise the cabinet off of the casters. The dimensions for the engagement
height of the rubber feet is shown in Figure 2-1. If you have alignment pins
mounted in your concrete pad, use the procedure in this section.
If you do not have the alignment pins, Figure 2-5 illustrates the location of eight
M10 tap holes which may be used for additional mounting studs, eye hooks or
angle brackets for securing the Micro BTS cabinet in its final location.
Figure 2-5: Cabinet Dimensions
• Make sure the ambient temperature around the unit (which
may be higher than the room temperature) is within the
specified limit.
• Make sure there is sufficient airflow around the unit.
• Make sure electrical circuits are not overloaded - consider the
nameplate rating of all the connected equipment, and make
sure you have over current protection.
• Make sure the equipment is properly grounded.
• Make sure no objects are placed on the top of the unit.
22.280 in.
[56.59 cm]
20.547 in.
[52.19 cm]
Tapped hole
M10-1.5 x4 places
19.780 in.
[50.24 cm]
40.904 in.
[103.90 cm]
0.868 in.
[2.21] cm
Cabinet (side)Cabinet (top)
Tapped hole
M10-1.5
x4 places
IW021302

UltraWAVE Micro BTS Installation and Commissioning Guide, Version B 29
Mounting the Micro BTS Chassis
Required Materials
Angle brackets
Four M10 machine screws and washers
Required Tools
15 mm open end wrench
Installation Instructions
1Move the cabinet into its final location. If using alignment pins to prevent
movement, move the cabinet into position over the pins.
2Lower each of the rubber feet until each reaches the concrete pad.
3Using the 15 mm open end wrench, lower each foot until the casters are raised
from the concrete floor, approximately 0.25 inches (0.65 cm).
4Remove the casters from the bottom of the cabinet.
5Lower the cabinet to within 4.1 inches to 4.4 inches (10.41 cm to 11.18 cm) of
the concrete pad. If you are using alignment pins, lower the cabinet until the
pins enter the alignment holes no more than 0.25 inches (0.6 cm). Do not
lower the cabinet too far over alignment pins as they may puncture internal
components.
6Secure locking nuts on foot studs.
7Secure the cabinet using customer-provided 10 mm studs.
Rack Mount Advisory
To prevent bodily injury when mounting or servicing this unit in a rack, you must
take special precautions to ensure that the system remains stable. The following
guidelines are provided to ensure your safety:
This unit should be mounted at the bottom of the rack if it is the only unit in
the rack.
When mounting this unit in a partially filled rack, load the rack from the
bottom to the top with the heaviest component at the bottom of the rack.
If the rack is provided with stabilizing devices, install the stabilizers before
mounting or servicing the unit in the rack.
You may use the additional M10 tap holes to secure the cabinet
as site-specific conditions allow.
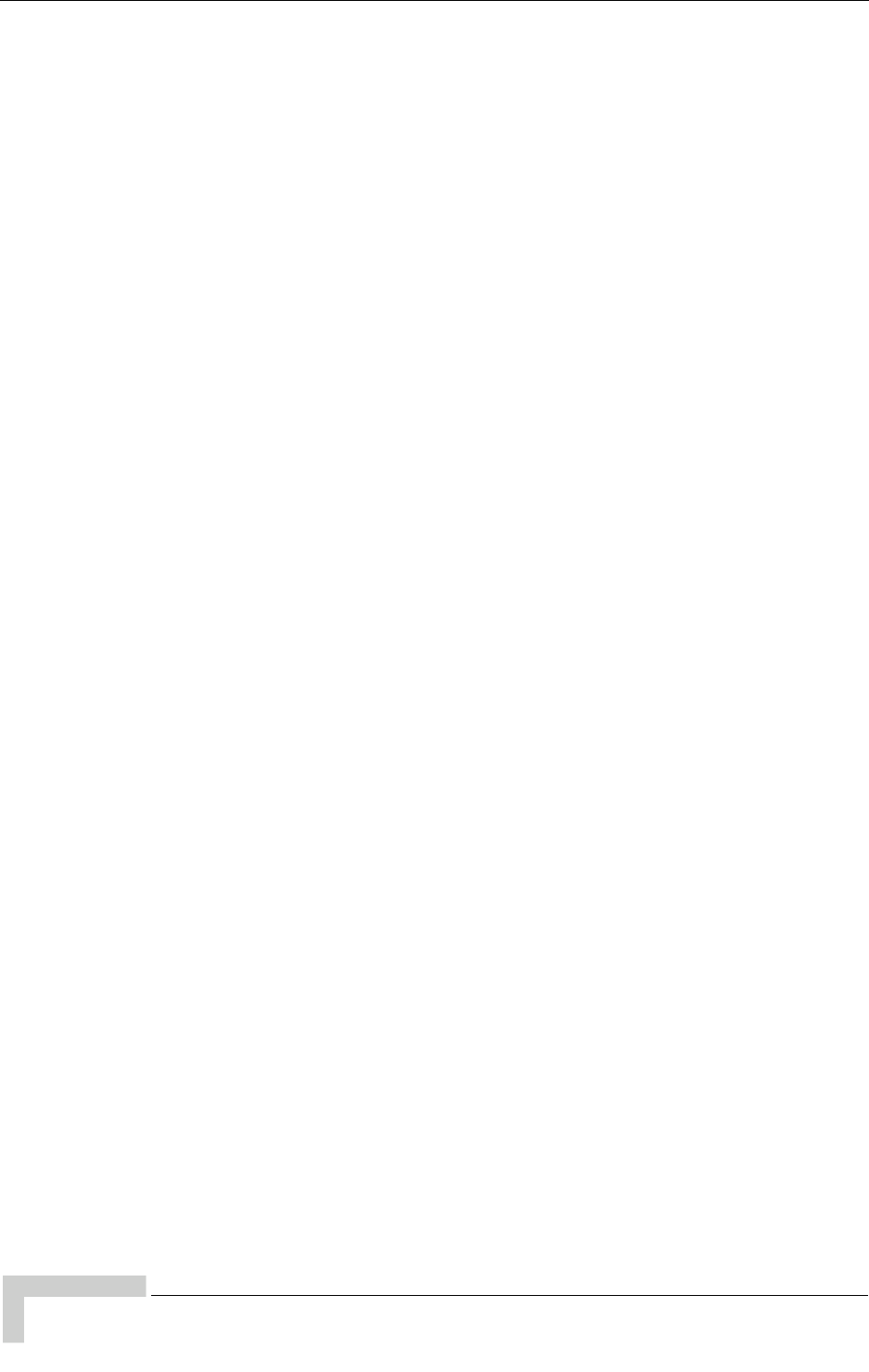
30 UltraWAVE Micro BTS Installation and Commissioning Guide, Version B
Chapter 2 - Installation
Attention: Pour éviter toute blessure corporelle pendant les opérations de montage
ou de réparation de cette unité en casier, il convient de prendre des précautions
spéciales afin de maintenir la stabilité du système. Les directives ci-dessous sont
destinées à assurer la protection du personnel:
Si cette unité constitue la seule unité montée en casier, elle doit être placée
dans le bas.
Si cette unité est montée dans un casier partiellement rempli, charger le casier
de bas en haut en plaçant l'élément le plus lourd dans le bas.
Si le casier est équipé de dispositifs stabilisateurs, installer les stabilisateurs
avant de monter ou de réparer l'unité en casier.
Warnung: Zur Vermeidung von Körperverletzung beim Anbringen oder Warten
dieser Einheit in einem Gestell müssen Sie besondere Vorkehrungen treffen, um
sicherzustellen, daß das System stabil bleibt. Die folgenden Richtlinien sollen zur
Gewährleistung Ihrer Sicherheit dienen:
Wenn diese Einheit die einzige im Gestell ist, sollte sie unten im Gestell ange-
bracht werden.
Bei Anbringung dieser Einheit in einem zum Teil gefüllten Gestell ist das
Gestell von unten nach oben zu laden, wobei das schwerste Bauteil unten im
Gestell anzubringen ist.
Wird das Gestell mit Stabilisierungszubehör geliefert, sind zuerst die Stabilisa-
toren zu installieren, bevor Sie die Einheit im Gestell anbringen oder sie
warten.

UltraWAVE Micro BTS Installation and Commissioning Guide, Version B 31
Configuring the E1 or T1 Trunk Card
2.3 Configuring the E1 or T1 Trunk Card
This section describes how to configure E1 or T1 trunk cards.
These procedures are designed for E1 or T1 cards that are shipped pre-configured
in a system. To configure E1 or T1 cards that are shipped as configured or
unconfigured replacements, refer to the GSM Field Maintenance Guide.
Your system is shipped from the manufacturer configured with the correct cards
for your site-specific application. These can be 75 Ohm E1, 120 Ohm E1 or
100 Ohm T1 cards. All cards are shipped with the appropriate connectors.
Table 2-7 lists the cards and the procedures that apply to each card type.
Cable runs of greater than 600 meters (1968 feet) are not
supported directly from the card. If you are attempting a longer
cable run between UltraWAVE chassis please contact Customer
Service to determine if you need a repeater for your application.
Table 2-7: Trunk Cards and Procedures
Label Description Operation
75 Ohm 75 Ohm E1 card
Set the ground to the Transmit or Receive
side using the jumpers. Refer to
Section 2.3.1.
120 Ohm 120 Ohm E1 card No configuration is required.
100 Ohm 100 Ohm T1 card
Configure the DIP switch based on cable
length to the DSX-1 demarcation point. Refer
to Section 2.3.2.
Note: No configuration is required unless
connecting to a DSX-1 demarcation point
greater than 133 feet.

32 UltraWAVE Micro BTS Installation and Commissioning Guide, Version B
Chapter 2 - Installation
2.3.1 Configuring Ground Jumpers on 75 Ohm
E1 Cards
To configure the ground jumpers on a 75 Ohm E1 card:
1Ensure that anti-static precautions are taken. Refer to Section 1.2 for
anti-static precautions.
2Make note of the orientation of the cables and disconnect them from the
selected card.
3Using a Phillips screwdriver, fully loosen the two captive screws located at the
top and bottom of the card.
4Remove the card by firmly pulling the two white tabs located at the top and
bottom of the card.
5See Figure 2-6 to locate jumpers P8 through P11.
6Set the signal grounding to the Transmit or Receive Side.
Jumpers P8, P9, P10 and P11 control the signal grounding. Placing the jumper
across Pins 1 and 2 sets the corresponding ground; otherwise the jumper
should be placed across Pins 2 and 3.
The following table shows the jumper assignments:
Alvarion recommends grounding the receive (RX) side on 75 Ohm cards.
7Place the card into the slot and slide in the card until it completely rests inside
the slot. Push the card firmly into place.
8Using a Phillips screwdriver, tighten the two captive screws.
Table 2-8: Ground Jumpers
Ground Selection Port Jumper Positions
Receive Side Port 0 P8 = 1 to 2 P9 = 2 to 3
Port 1 P10 = 2 and 3 P11 = 1 and 2
Transmit Side Port 0 P8 = 2 to 3 P9 = 1 to 2
Port 1 P10 = 1 and 2 P11 = 2 and 3
Only one side of the transmission link should be grounded. To
ensure that only the one side is grounded, you should check the
settings at the far end of the E1 transmission link when possible.
These settings should be identified by experienced personnel.
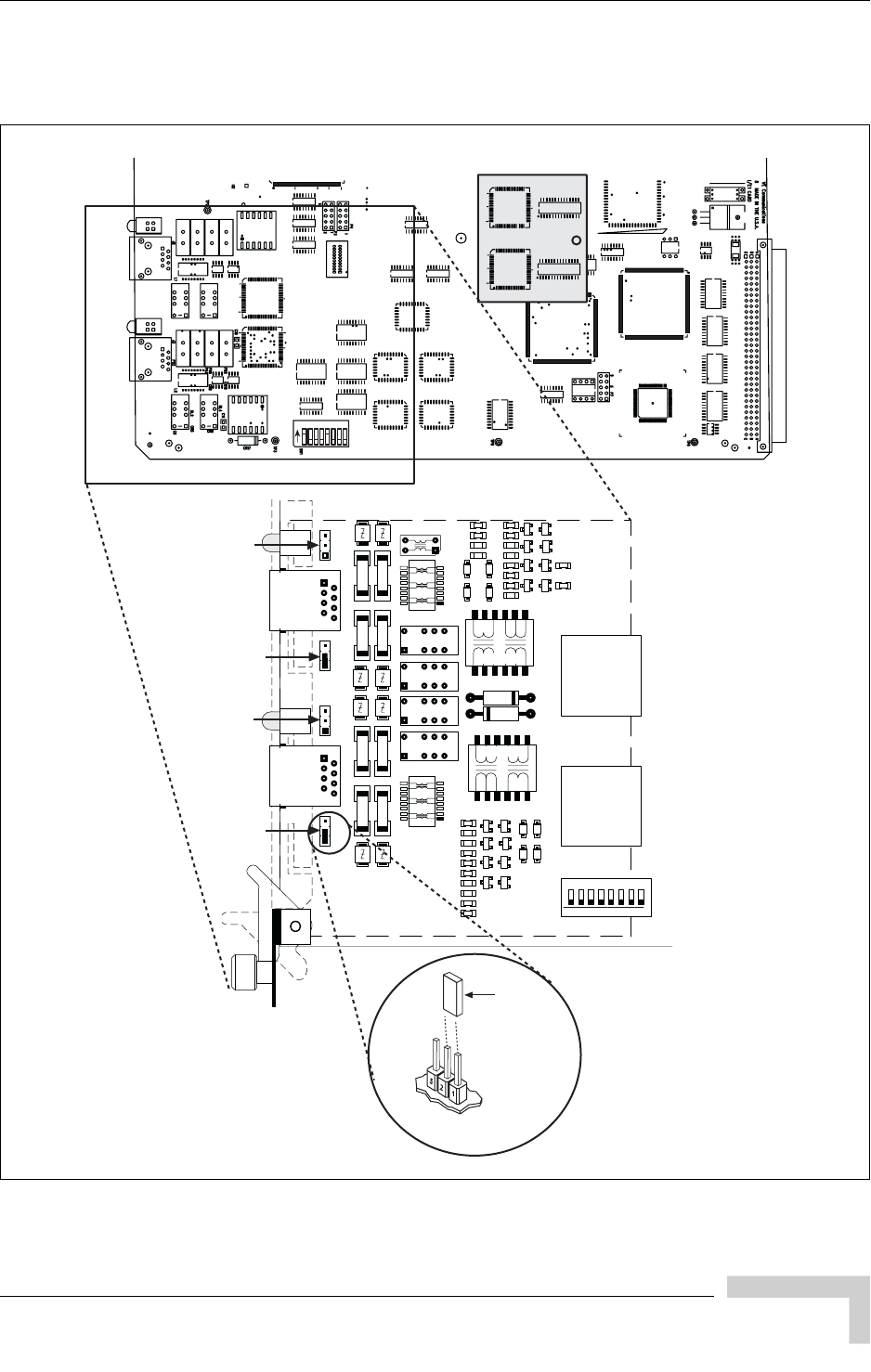
UltraWAVE Micro BTS Installation and Commissioning Guide, Version B 33
Configuring the E1 or T1 Trunk Card
9Reconnect all disconnected cables to their proper ports on the E1 card.
Figure 2-6 shows the location of the grounding jumpers.
Figure 2-6: Ground Jumpers (P8 through P11)
J7
ON 12 435678
IW068004
P8P11P10 P9
RJ45
1:2
1:1.36
PE68822
RJ45
FUSE
FUSE
FUSE
FUSE FUSE
FUSE
FUSE
FUSE
RELAY
NONC
+
RELAY
NONC
+
RELAY
NONC
+
RELAY
NONC
+
1:2
1:1.36
PE68822
555-
2940
555-
2940
BT-8370
21
61
41
80
1
T
X
RX
..... HOST .....
BT-8370
21
61
41
80
1
T
X
RX
..... HOST .....
Port 0
Port 1
TX
Ground
TX
Ground
Jumper
Item No.0015
Jumper Position 1,2
For P8-P11
RX
Ground
RX
Ground
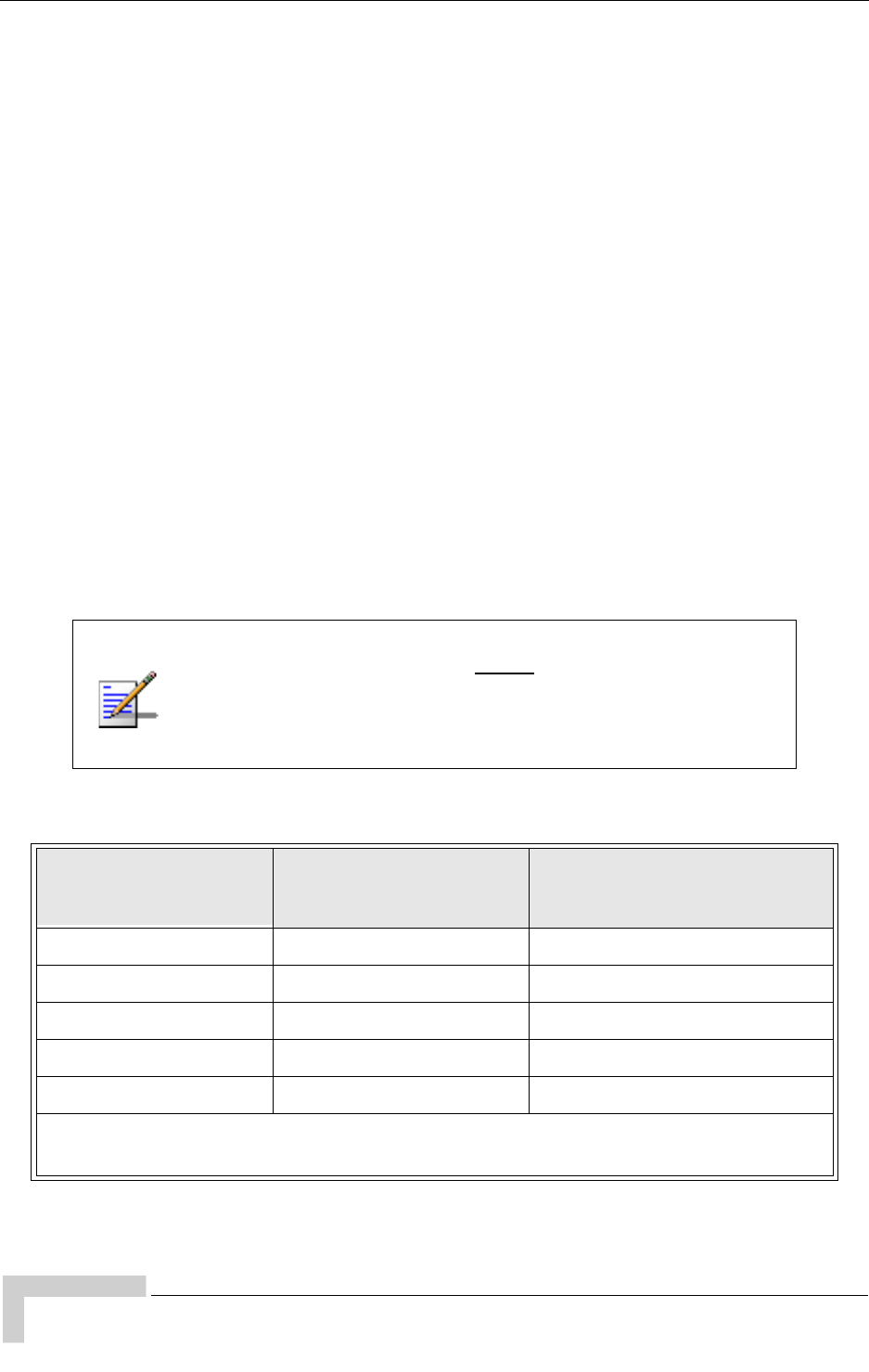
34 UltraWAVE Micro BTS Installation and Commissioning Guide, Version B
Chapter 2 - Installation
2.3.2 Configuring Cable Length DIP Switch Settings
on T1 Cards
To configure the DIP switch settings on a T1 card:
1Ensure that anti-static precautions are taken. Refer to Section 1.2 for
anti-static precautions.
2Make note of the orientation of the cables and disconnect them from the
selected card.
3Using a Phillips screwdriver, fully loosen the two captive screws located at the
top and bottom of the card.
4Remove the T1 card by firmly pulling the two white tabs located at the top and
bottom of the card.
5See Figure 2-7 to locate the DIP switch.
6On T1 cards, the DIP switch setting is determined by the cable distance from
the card to the DSX-1 demarcation point. The following table provides the
appropriate Port 0 and Port 1 DIP switch settings for DSX-1 demarcation
points located within various cable distance ranges.
In Table 2-9, the first setting (0-133 ft.) is the default and should
be used for all T1 applications unless connecting to a DSX-1
demarcation point beyond 133 ft. When connecting two chassis
you will always use the first setting regardless of distance (up to
600 m).
Table 2-9: T1 DIP Switch Settings
Port 0
Switch Setting
1-2-3-4
Port 1
Switch Setting
5-6-7-8
Cable distance from T1 Card to
DSX-1 Demarcation Point
Feet (Meters)
OFF-ON-ON-ON OFF-ON-ON-ON 0-133 (0-40.57)
OFF-OFF-ON-ON OFF-OFF-ON-ON 133-266 (40.57-81.13)
OFF-ON-OFF-ON OFF-ON-OFF-ON 266-399 (81.13-121.7)
OFF-OFF-OFF-ON OFF-OFF-OFF-ON 399-533 (121.7-162.57)
OFF-ON-ON-OFF OFF-ON-ON-OFF 533-655 (162.57-199.78)
Note: ON refers to the DIP switch pin being in the “UP” position and OFF refers to the
DIP switch pin being in the “DOWN” position. X = either ON or OFF.

UltraWAVE Micro BTS Installation and Commissioning Guide, Version B 35
Configuring the E1 or T1 Trunk Card
7Place the card into the slot and slide in the card until it completely rests inside
the slot. Push the card firmly into place.
8Using a Phillips screwdriver, tighten the two captive screws into the chassis
through the trunk card.
Figure 2-7 shows the location of the DIP switch.
Figure 2-7: Location of DIP Switch on a T1 Trunk Card
J6 J8
J7
ON 12 435678
J4 J9
ON 12 435678
IW180001

36 UltraWAVE Micro BTS Installation and Commissioning Guide, Version B
Chapter 2 - Installation
2.4 Connecting Ground Cables
Use this section to connect your earth ground and power cables to the Micro BTS
cabinet.
2.4.1 Connecting the Grounding Cable
The rack unit in which the Micro BTS subracks are being mounted should be
properly grounded to the site earth ground ring. You must attach a ground strap
to each subrack and to the rack unit or directly to the site ground ring.
1Locate the ground lugs on each subrack assembly. See Figure 2-8 for their
location.
2Remove the nut from each ground lug and connect a ground lead to each
subrack. Secure the nut tightly on each subrack assembly.
3Attach the ground cables to the properly grounded rack assembly or to the
closest earth ground bus.
Figure 2-8: Ground Lugs
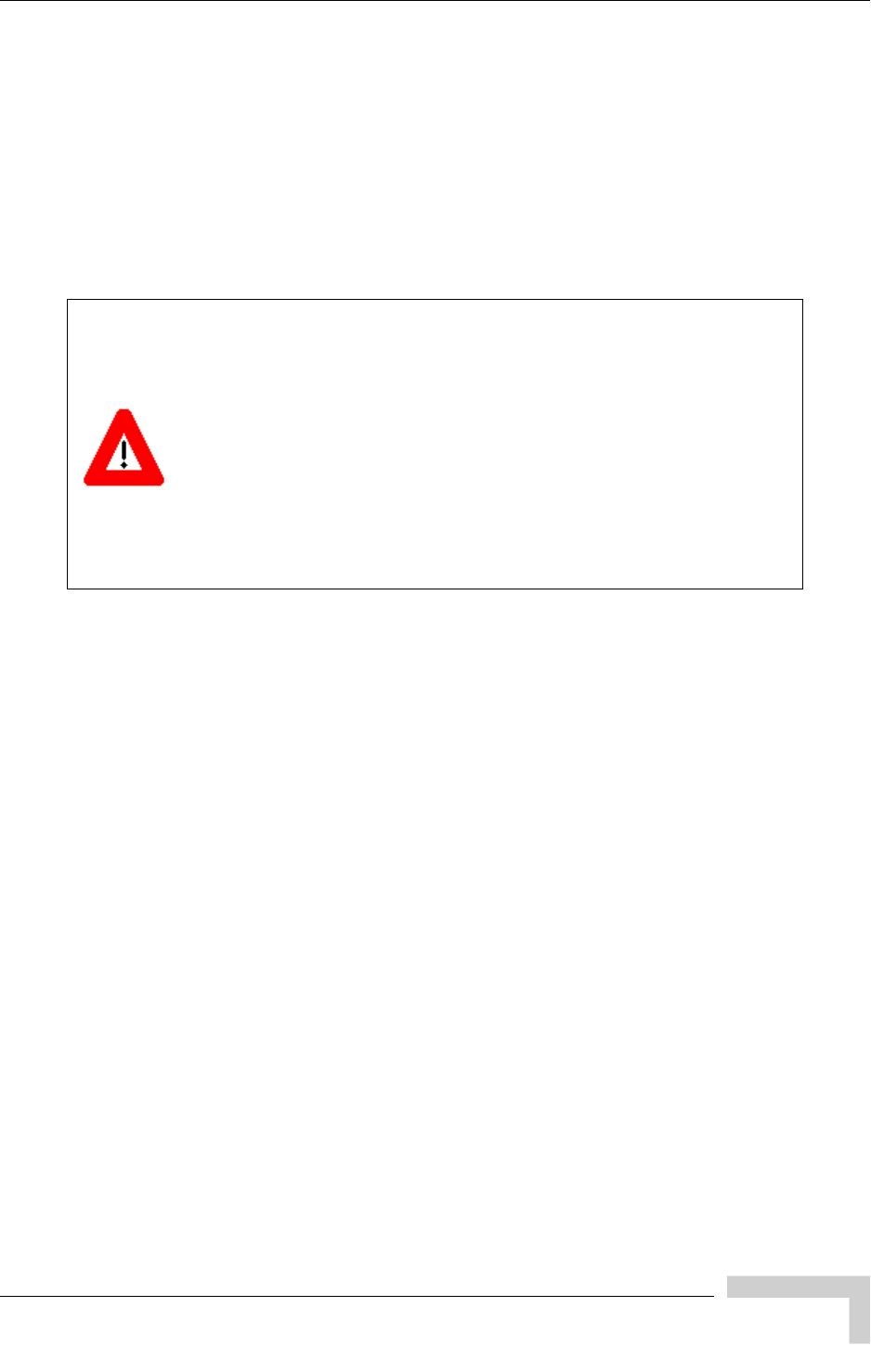
UltraWAVE Micro BTS Installation and Commissioning Guide, Version B 37
Connecting Ground Cables
2.4.2 Grounding the Cabinet
The subrack assemblies are grounded to the cabinet by the manufacturer. The
cabinet should be grounded to the site earth ground ring. Complete the following
to connect an earth ground to the chassis.
1Route a customer-supplied 10 AWG (2.5 mm) or larger copper wire to a
grounding lug inserted into one of the M10 tap holes shown in Figure 2-5.
2Connect the other end of the lead stud to the closest grounding bus.
Caution: Grounding circuit continuity is vital for safe operation of
machine. Never operate machine with grounding conductor
disconnected.
Attention: Un circuit de terre continu est essentiel en vue du
fonctionnement sécuritaire de l'appareil. Ne jamais metre
l'appareil en marche lorsque le cable de mise à la terre est
débranche.
Warnung: Achtung, Hoher Ableitstrom! Schutzleiteranschluß vor
dem Netzanschluß herstellen.
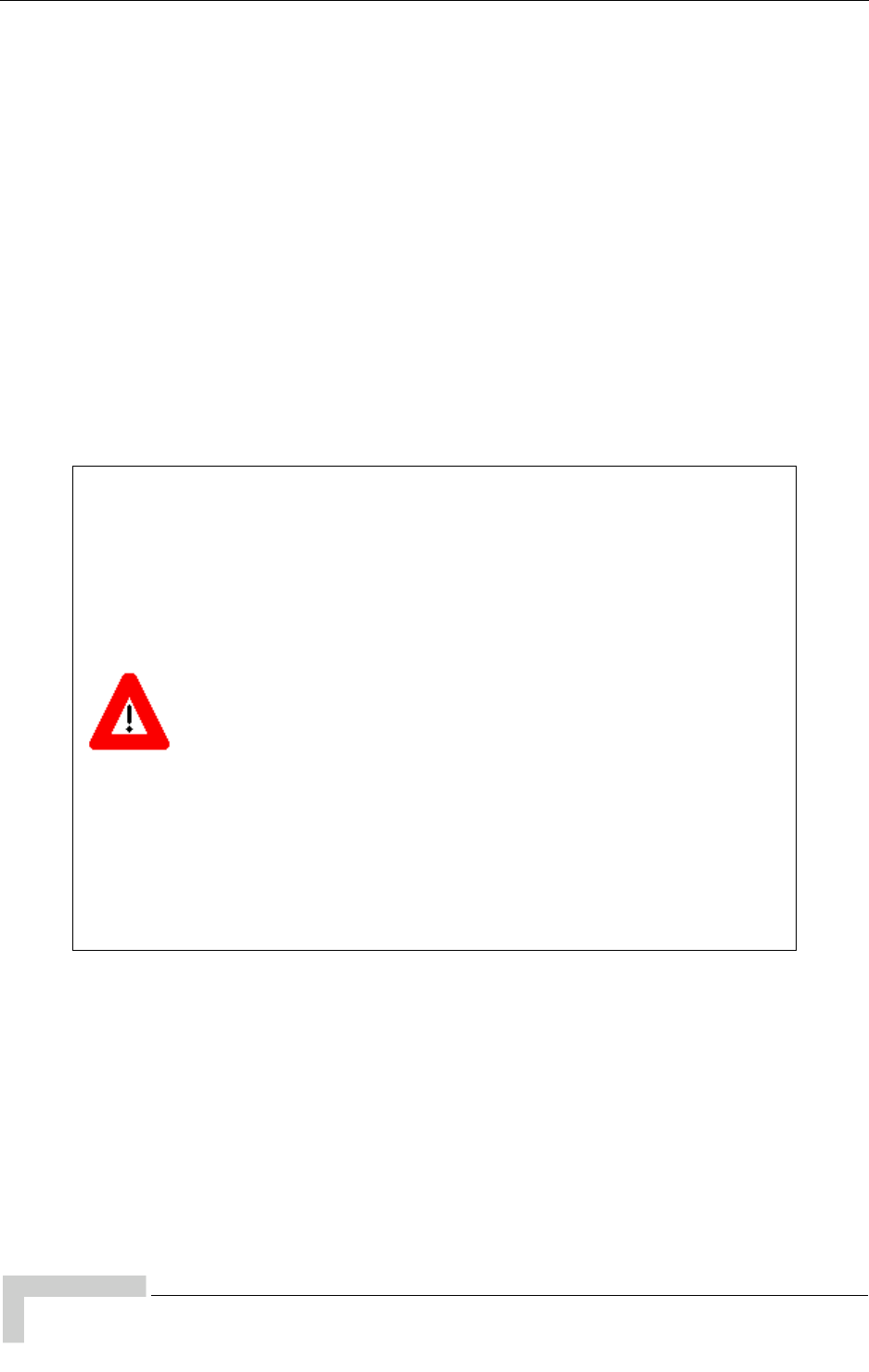
38 UltraWAVE Micro BTS Installation and Commissioning Guide, Version B
Chapter 2 - Installation
2.5 Connecting Power Supplies
In this section, you will connect the Micro BTS to your power source. Before
beginning it is necessary to first:
Identify your power configuration. This may be AC (110 V to 220 V, 30 A
50-60 Hz) or DC (-40 V to -60 V, 40 A).
Install your AC or DC power supplies.
When you have completed these tasks, refer to the appropriate subsection to
make either AC or DC power connections:
Connecting AC power. See Section 2.5.1
Connecting DC power. See Section 2.5.2
Identifying AC and DC Power Configurations
You can determine whether your system uses AC or DC power by checking the
main configuration label. The main configuration label is located on either the
exterior of your shipping container or on the rear of the Micro subrack assembly.
See Section 1.3.1 for the details included on the main configuration label. Use
Table 1-1 to identify your system power configuration.
Warning: This product relies on the building's installation for
short-circuit (over current) protection. Ensure that a fuse or
circuit breaker no larger than 110 VAC, 30 A; 220 VAC, 15 A; or
-48 VDC, 40 A is used on the phase conductors (all
current-carrying conductors).
Attention: Pour ce qui est de la protection contre les
courts-circuits (surtension), ce produit dépend de l'installation
électrique du local. Vérifier qu'un fusible ou qu'un disjoncteur de
110 VAC, 30 A alt., 220 VAC, 15 A alt., -48 VDC 40 A est utilisé
sur les conducteurs de phase (conducteurs de charge).
Warnung: Dieses Produkt ist darauf angewiesen, daß im
Gebäude ein Kurzschluß- bzw. Überstromschutz installiert ist.
Stellen Sie sicher, daß eine Sicherung oder ein Unterbrecher von
nicht mehr als 110 V Wechselstrom, 30 A; 220 V Wechselstrom,
15 A; oder -48 V Gleichstrom, 40 A an den Phasenleitern (allen
stromführenden Leitern) verwendet wird.
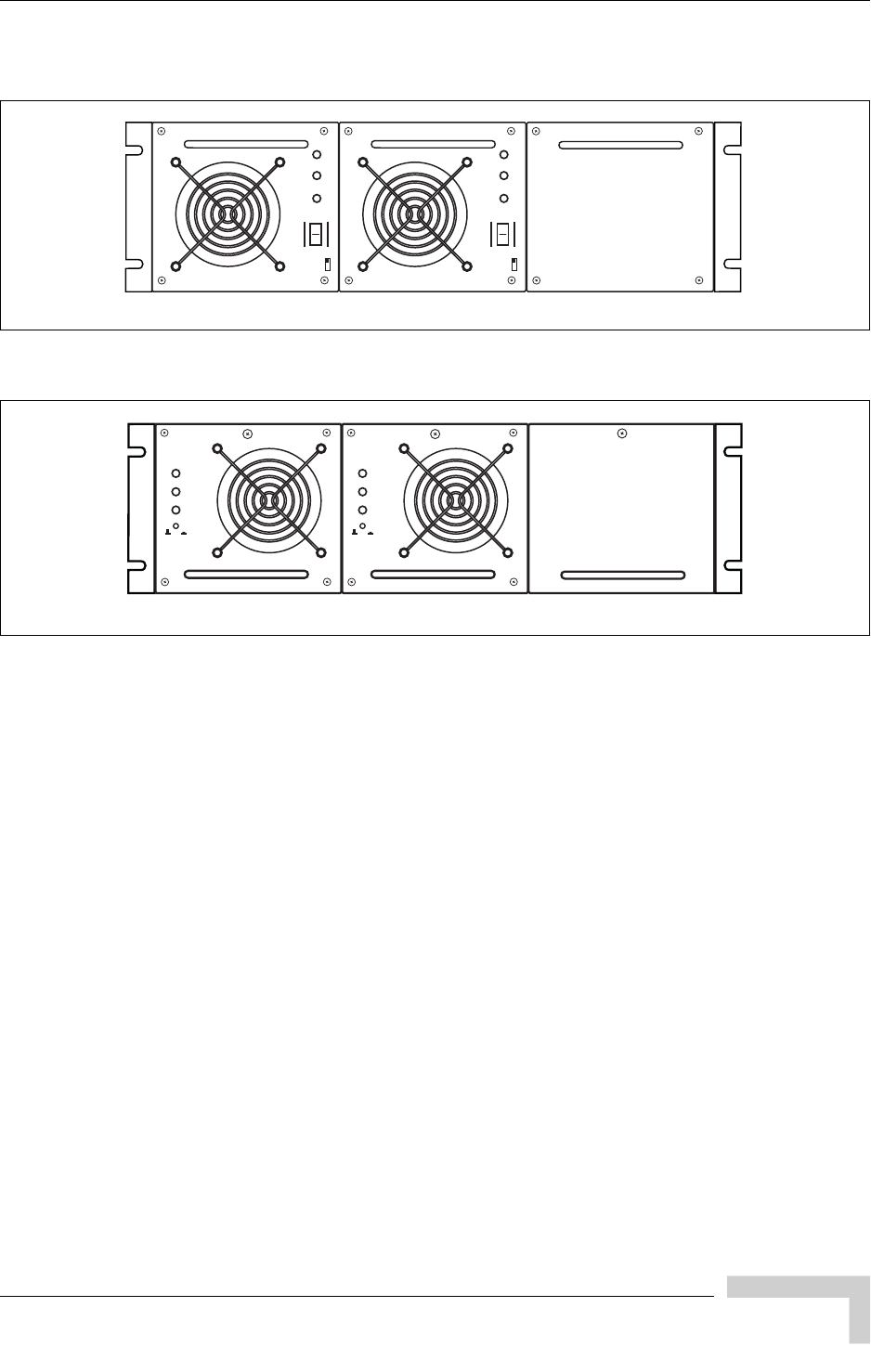
UltraWAVE Micro BTS Installation and Commissioning Guide, Version B 39
Connecting Power Supplies
Figure 2-9 displays the AC power supply modules. Figure 2-10 displays the DC
power supply modules.
Installing AC Power Supply Modules
The customer ordered configuration determines the number of power supply
modules included with the Micro BTS. The power supply modules must be
installed according to the following procedure:
1Remove the power supply module from the packaging.
2Insert the power supply module in the first empty slot at the front left of the
subrack assembly.
3Slide the power supply module into the chassis until it locks into place.
Figure 2-9: AC Power Supply Subrack Assembly
Figure 2-10: DC Power Supply Subrack Assembly
IW138601
INPUT
OUTPUT
FAULT
OFF
ON
UNLOCK
INPUT
OUTPUT
FAULT
OFF
ON
UNLOCK
IW138602
INPUT
OUTPUT
FAULT
OFF ON
INPUT
OUTPUT
FAULT
OFF ON

40 UltraWAVE Micro BTS Installation and Commissioning Guide, Version B
Chapter 2 - Installation
Installing DC Power Supply Modules
The customer ordered configuration determines the number of power supply
modules included with the Micro BTS. The power supply modules must be
installed according to the following procedure:
1Remove the power supply module from the packaging.
2Insert the power supply module in the first empty slot at the front left of the
subrack assembly.
3Slide the power supply module into the chassis.
4Twist the captive screws clockwise to secure the power supply module into
place. If you are connecting directly to the power supply subrack assembly,
Figure 2-11 shows the input power connector location.
Figure 2-11: Power Supply Subrack Connection

UltraWAVE Micro BTS Installation and Commissioning Guide, Version B 41
Connecting Power Supplies
2.5.1 Connecting AC Power
The Micro BTS is shipped from the factory with the internal cabling routed from
the AC power supply subrack assembly to a round quick disconnect connector on
the top rear of the cabinet.
The input power connector cable is supplied with the cabinet assemblies.
Figure 2-12 shows the AC input power connector which attaches to the cabinet
enclosure.
Connecting the AC Power Supply to the Cabinet
1Verify the ground connection you made in Section 2.4.1 is secure.
2Make sure that the power switch located on all power supply modules is in the
OFF position. See Figure 2-13 for the location of the power supply power
switches.
Figure 2-12: AC Input Power Connector and Cable
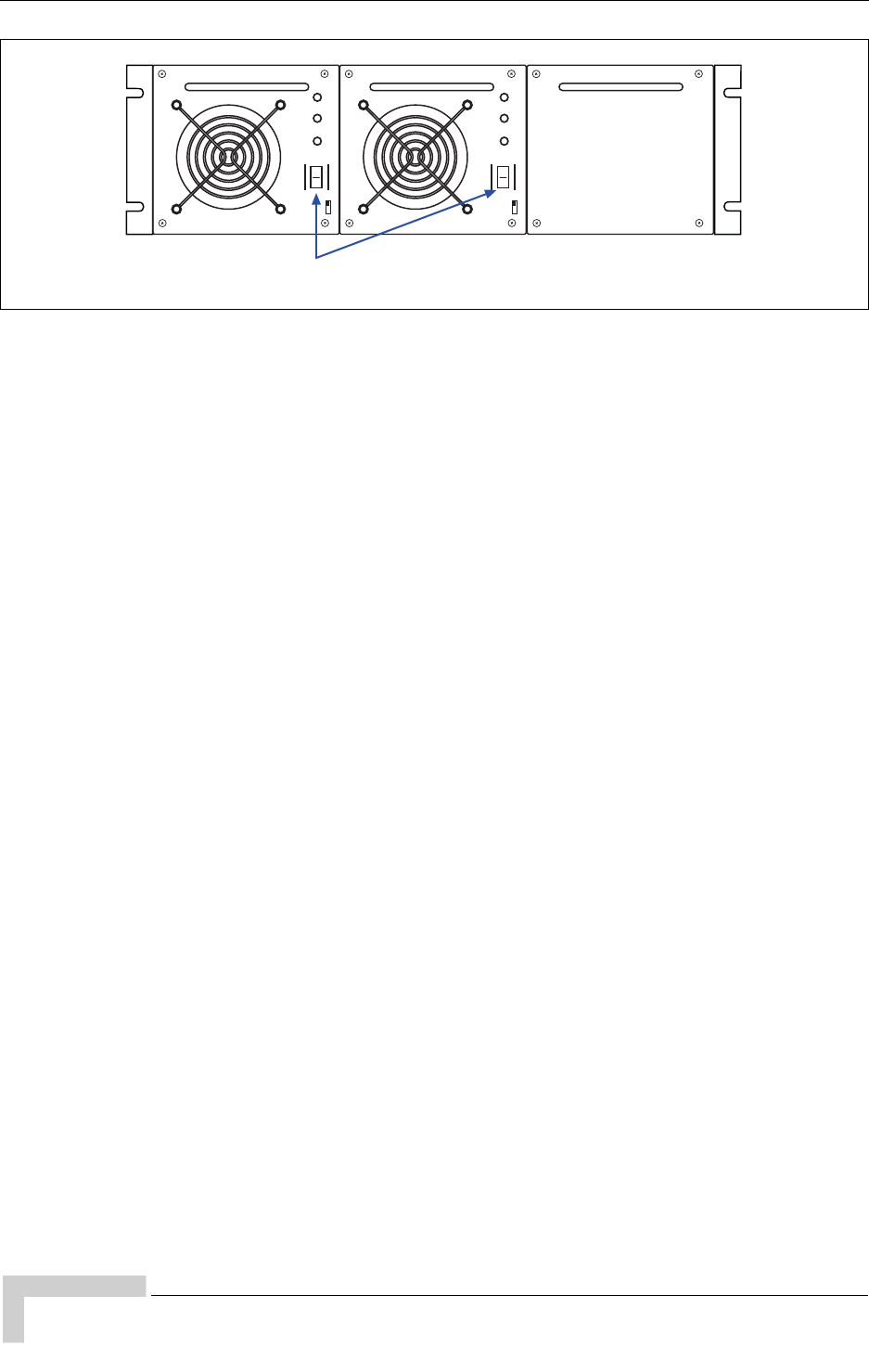
42 UltraWAVE Micro BTS Installation and Commissioning Guide, Version B
Chapter 2 - Installation
3Ensure the input power source is turned off and not supplying power to source
power connection.
4Plug the power cable into the electrical mains or connect the flat washers,
shown in Figure 2-12, directly to the input power source, as follows:
White is the neutral lead
Black is the line lead
Green is the ground lead
5Plug the round quick disconnect connector as illustrated in Figure 2-12 into
the power connection on the top of the cabinet as illustrated in Figure 2-14.
Secure the connector by twisting the connector sleeve until the lines on the
cable connector and chassis connector align.
If you have ordered the NIB as separate subrack assemblies, you will connect
the input power cable directly to the power supply subrack assembly, shown
in Figure 2-11.
6Do not apply power to the chassis at this time. Wait until you are
performing the off-line commissioning procedures in the next chapter.
Figure 2-13: AC Power Supply Module ON/OFF Switches
Power Switches
IW138603
INPUT
OUTPUT
FAULT
OFF
ON
UNLOCK
INPUT
OUTPUT
FAULT
OFF
ON
UNLOCK

UltraWAVE Micro BTS Installation and Commissioning Guide, Version B 43
Connecting Power Supplies
Figure 2-14: AC Power Supply Chassis Connection
Caution: The power supply cord is used as the main disconnect
device, ensure that the socket-outlet is located/installed near the
equipment and is easily accessible.
Attention: Le cordon d'alimentation est utilisé comme
interrupteur général. La prise de courant doit être située ou
installée à proximité du matériel et être facile d'accés.
Warnung: Das Netzkabel dient als Netzschalter. Stellen Sie
sicher, das die Steckdose einfach zugänglich ist.
The power supplies’ INPUT LEDs will illuminate and power
supply fans will start when connected to the power source. Do
not power on the cabinet at this time.

44 UltraWAVE Micro BTS Installation and Commissioning Guide, Version B
Chapter 2 - Installation
2.5.2 Connecting DC Power
The Micro BTS is shipped from the factory with the internal cabling routed from
the DC power supply subrack assembly to a round quick disconnect connector on
the top rear of the cabinet.
The input power connector cable is supplied with the cabinet assemblies. This
section explains how to assemble the input power connector and cable.
DC Input Power Connector Details
Figure 2-15 shows the DC quick disconnect power connector and cable.
The cable wires are connected to the input power supply as follows:
Black is connected to the -48 VDC supply.
Red is connected to the -48 VDC supply.
White is a return and typically connected to the cabinet ground.
Green is a return and typically connected to the cabinet ground.
Figure 2-15: DC Round Quick Disconnect Connector and Cable
Two wires carry -48 VDC and two wires must carry Return.
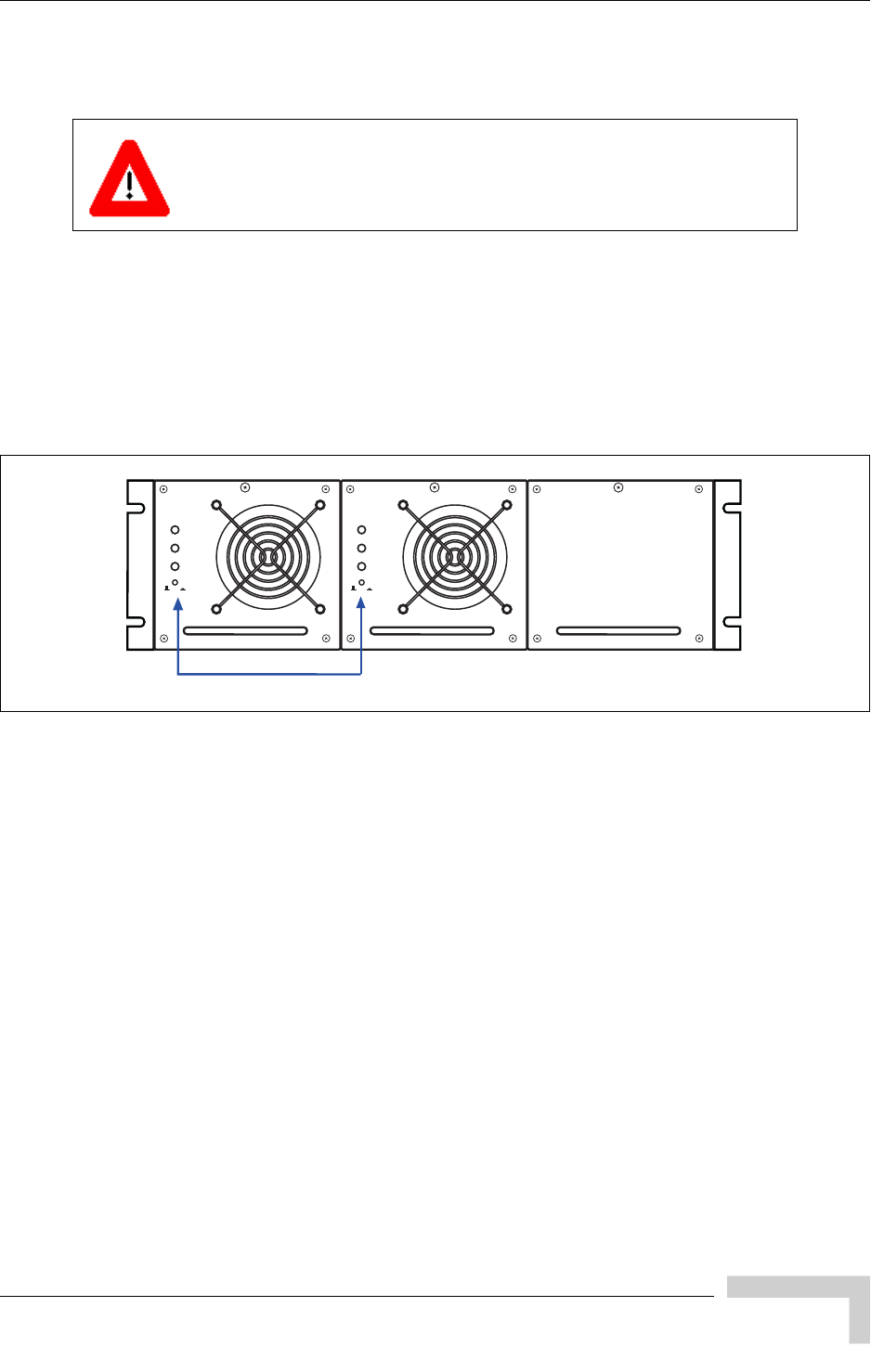
UltraWAVE Micro BTS Installation and Commissioning Guide, Version B 45
Connecting Power Supplies
Connecting the DC Power Supply to the Cabinet
Use the following procedure:
1Verify the ground connection you made in Section 2.4.1 is secure. The cabinet
is grounded through this connection. It is critical that this connection is made
properly.
2Make sure that the power button located on all power supply modules is in the
raised OFF position. See Figure 2-16 for the location of the power supply
power buttons.
3Verify the -48 VDC power source is off.
4The -48 VDC power cable has two wires for negative (-) connection and two
wires for return (+) connection. This spreads the current draw across two pins
of the round quick disconnect connector for each connection.
5Attach the two return (+) cables (white and green) to the positive side of your
-48 VDC power source or to ground if you are using a chassis ground for your
return.
6Attach the two negative (-) cables (black and red) to the negative side of your
-48 VDC power source.
7Plug the round quick disconnect connector as illustrated in Figure 2-15 into
the power connection on the top of the cabinet as illustrated in Figure 2-17.
Secure the connector by twisting the connector sleeve until the lines on the
cable connector and chassis connector align.
The power main must be a Safe Extra-Low Voltage (SELV),
-48 VDC supply as defined in IEC950 and EN60950.
Figure 2-16: DC Power Supply Module ON/OFF Switches
IW138604
Power Switches
INPUT
OUTPUT
FAULT
OFF ON
INPUT
OUTPUT
FAULT
OFF ON

46 UltraWAVE Micro BTS Installation and Commissioning Guide, Version B
Chapter 2 - Installation
8Do not apply power to the chassis at this time. Wait until you are
performing the off-line commissioning procedures in the next chapter.
Figure 2-17: Power Supply Connection
Caution: The power supply cord is used as the main disconnect
device, ensure that the socket-outlet is located/installed near the
equipment and is easily accessible.
Attention: Le cordon d'alimentation est utilisé comme
interrupteur général. La prise de courant doit être située ou
installée à proximité du matériel et être facile d'accés.
Warnung: Das Netzkabel dient als Netzschalter. Stellen Sie
sicher, das die Steckdose einfach zugänglich ist.
The power supplies’ INPUT LEDs will illuminate and power
supply fans will start when connected to the power source. Do
not power on the cabinet at this time.
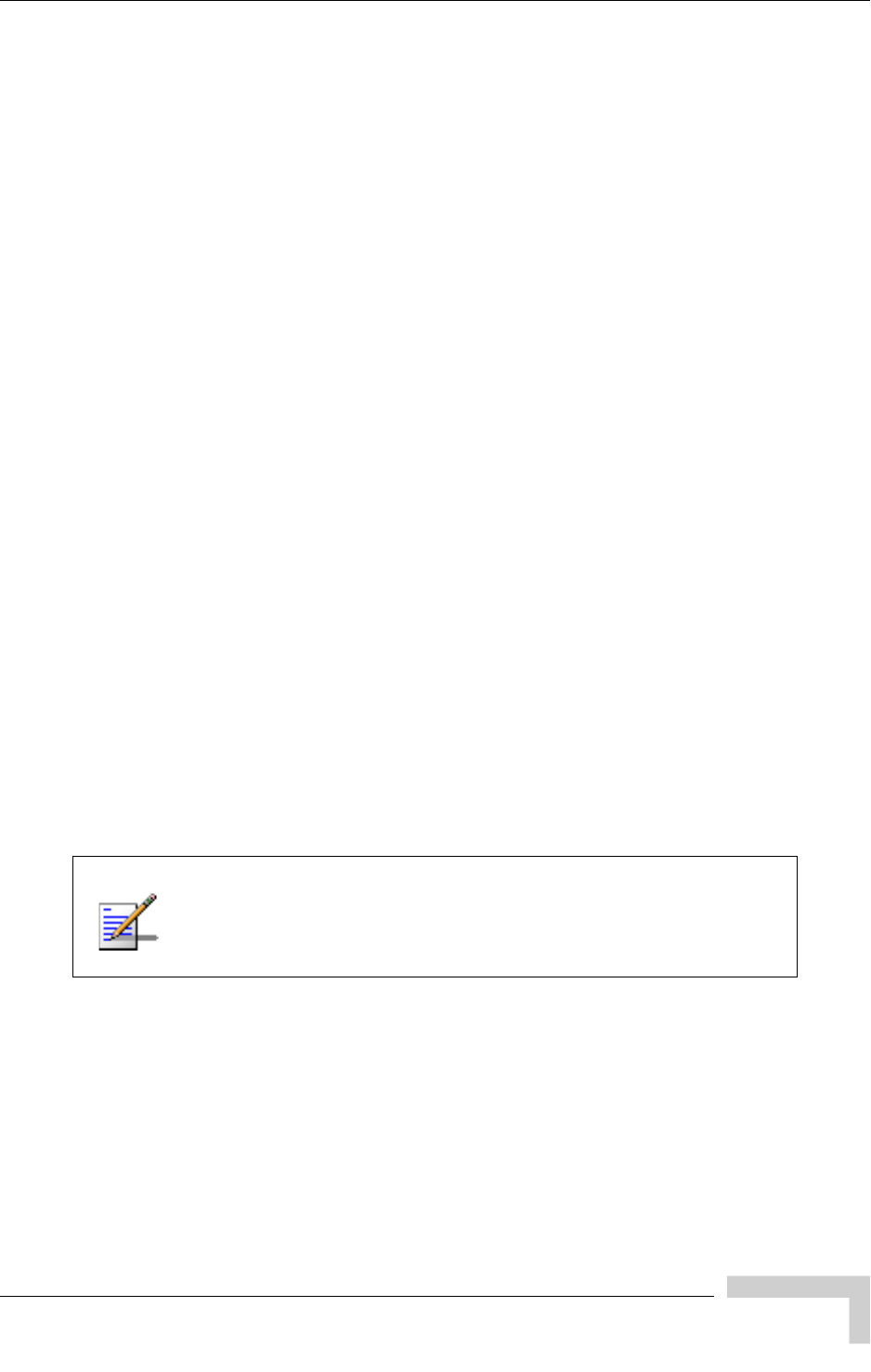
UltraWAVE Micro BTS Installation and Commissioning Guide, Version B 47
Connecting E1 or T1 Trunk Cables
2.6 Connecting E1 or T1 Trunk Cables
External trunk cabling depends on the configuration that the customer ordered
and the site-specific requirements. These cables will be supplied by the customer.
Failure to use electrically compliant T1 or E1 cables may cause transmission
errors. Please refer to the appropriate subsections to determine your cable
requirements.
The E1 or T1 trunk cables are routed directly to the E1 or T1 trunk card in the
Micro subrack assembly. All three types of signaling (E1 75 Ohm, E1 120 Ohm
and T1 100 Ohm) are terminated at the cabinet with RJ-48C port connectors.
2.6.1 E1 Cables
E1-75 Ohm
This is coaxial cable with a nominal impedance of 75 Ohm +/-5% at 1 MHz. The
maximum allowable cable distance depends directly on the insertion loss of the
cable at 1 MHz. In this mode, the E1 trunk card can accommodate up to 6 dB of
cable loss.
E1-120 Ohm
This cable is individually shielded twisted pair with a nominal impedance of
120 Ohm +/-5% at 1 MHz. The maximum allowable cable distance depends
directly on the insertion loss of the cable at 1 MHz. In this mode, the E1 trunk
card can accommodate up to 9 dB of cable loss.
Table 2-10 provides a description of cables required for installation and
connection to an E1 network, but not supplied with the Micro BTS.
Before connecting E1 lines to the Micro BTS, it is assumed that
the quality of the lines has been verified. It is recommended that
Bit Error Ratio (BER) tests are completed to ensure that the BER
is less than 10-8.
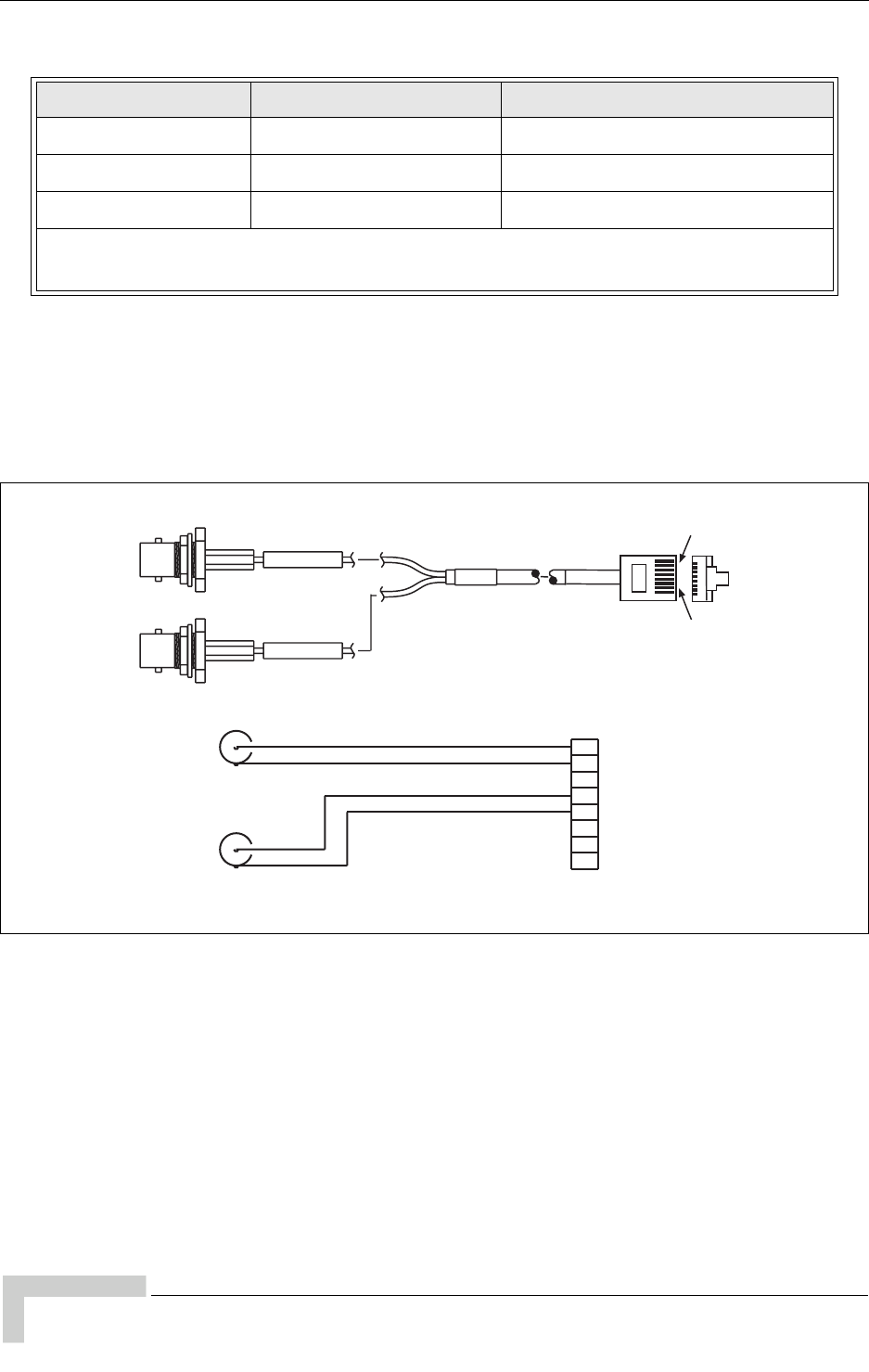
48 UltraWAVE Micro BTS Installation and Commissioning Guide, Version B
Chapter 2 - Installation
Conversion Cables
If you are connecting into an existing E1 network with standard BNC or DSUB
connectors, a conversion cable for either the 75 Ohm or 120 Ohm will be required.
To purchase these cables from Alvarion, contact your local sales support
representative.
Figure 2-18 illustrates the pinout for an RJ-48C to 75 Ohm BNC conversion cable.
Table 2-10: Customer-Supplied E1 Cabling
Cable Identity Cable Type Corresponding Cable Plug
E1, 120 Ohm Shielded, Twisted, 2-Pair RJ-48C Male
E1, 75 Ohm Coaxial RJ-48C Male
Antenna (external) Coaxial N-Type, Female
Note: The number of cables required depends on the ordered configuration of the
Micro BTS.
Figure 2-18: 75 Ohm BNC Conversion Cable
IW009302
8
ORANGE/WHITE
BLUE/WHITE
WHITE/ORANGE
WHITE/BLUE (R-TIP)
(R-RING)
(T-TIP)
(T-RING)
1
2
3
5
6
7
4
J2
J3
J1
J2
J3
RECEIVE
TRANSMIT
Pin 1
Pin 8
J1
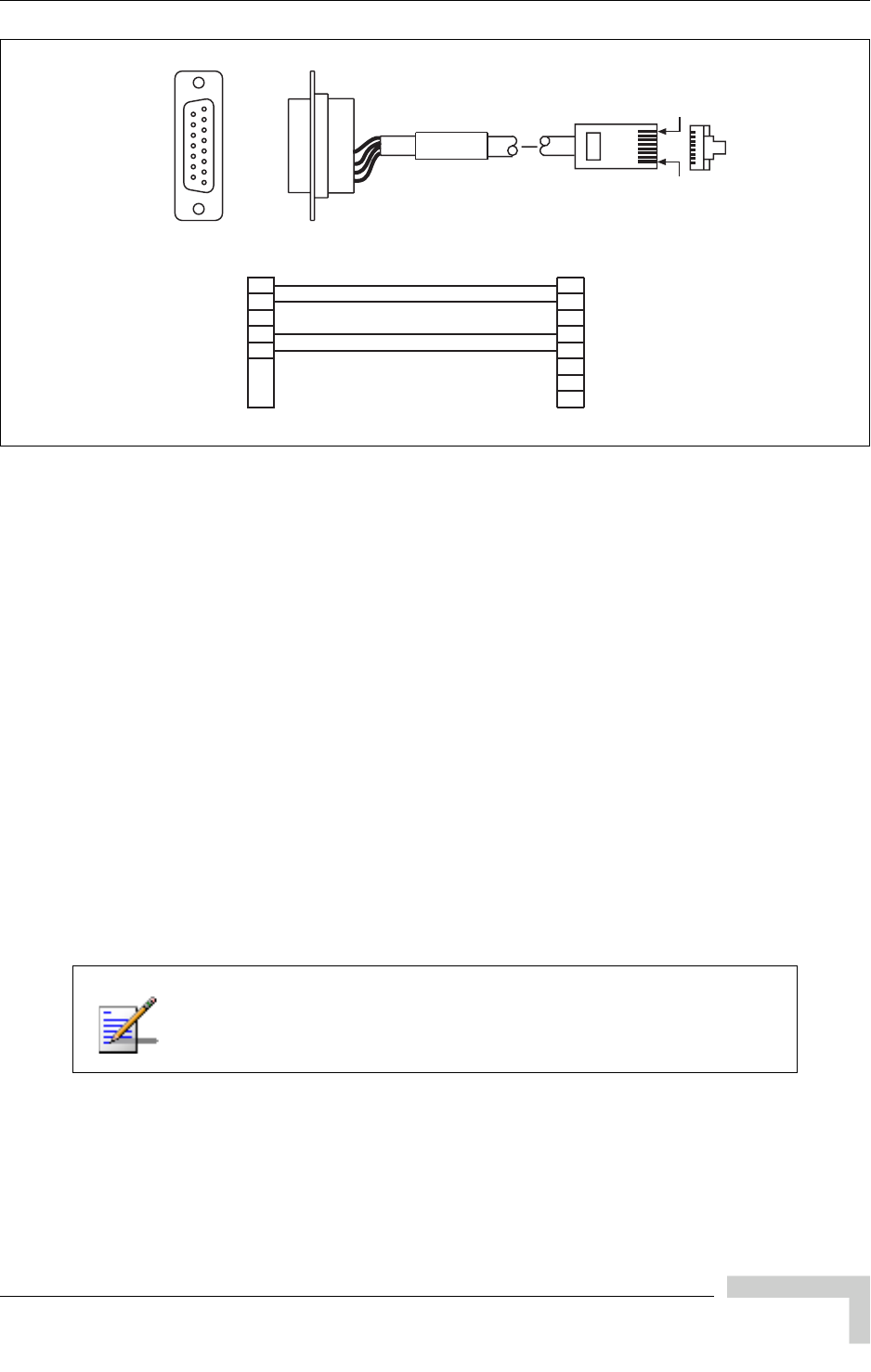
UltraWAVE Micro BTS Installation and Commissioning Guide, Version B 49
Connecting E1 or T1 Trunk Cables
Figure 2-19 illustrates the pinout for the RJ-48C to DSUB 120 Ohm conversion
cable.
2.6.2 T1 Cables
T1-100 Ohm
For T1 connections, the proper cable is an individually shielded twisted pair with
a nominal impedance of 100 Ohm +/-5% at 772 kHz. The maximum allowable
cable distance depends directly on the insertion loss of the cable at 772 kHz. The
T1 card can accommodate up to 9 dB of cable loss. When using 22 AWG ABAM
cable, 9 dB of loss is approximately 2000 feet. When using Belden type 9729 (with
a cable loss of 6 dB per 1000 feet at 772 kHz) the maximum cable distance is
approximately 1500 feet.
Table 2-11 provides a description of cables required for installation and
connection to a T1 network, but not supplied with the Micro BTS.
Figure 2-19: 120 Ohm Conversion Cable
Before connecting T1 lines to the Micro BTS, it is assumed that
the quality of the lines has been verified. It is recommended that
BER tests be completed to ensure that the BER is less than 10-8.
3
11
1
9
IW009303
8
ORANGE/WHITE
BLUE/WHITE
WHITE/ORANGE
WHITE/BLUE (R-TIP)
(R-RING)
(T-TIP)
(T-RING)
1
2
3
5
6
7
4
J2 J1
Pin 9
J1
J2
Pin 1
Pin 15 Pin 8
Pin 1
Pin 8
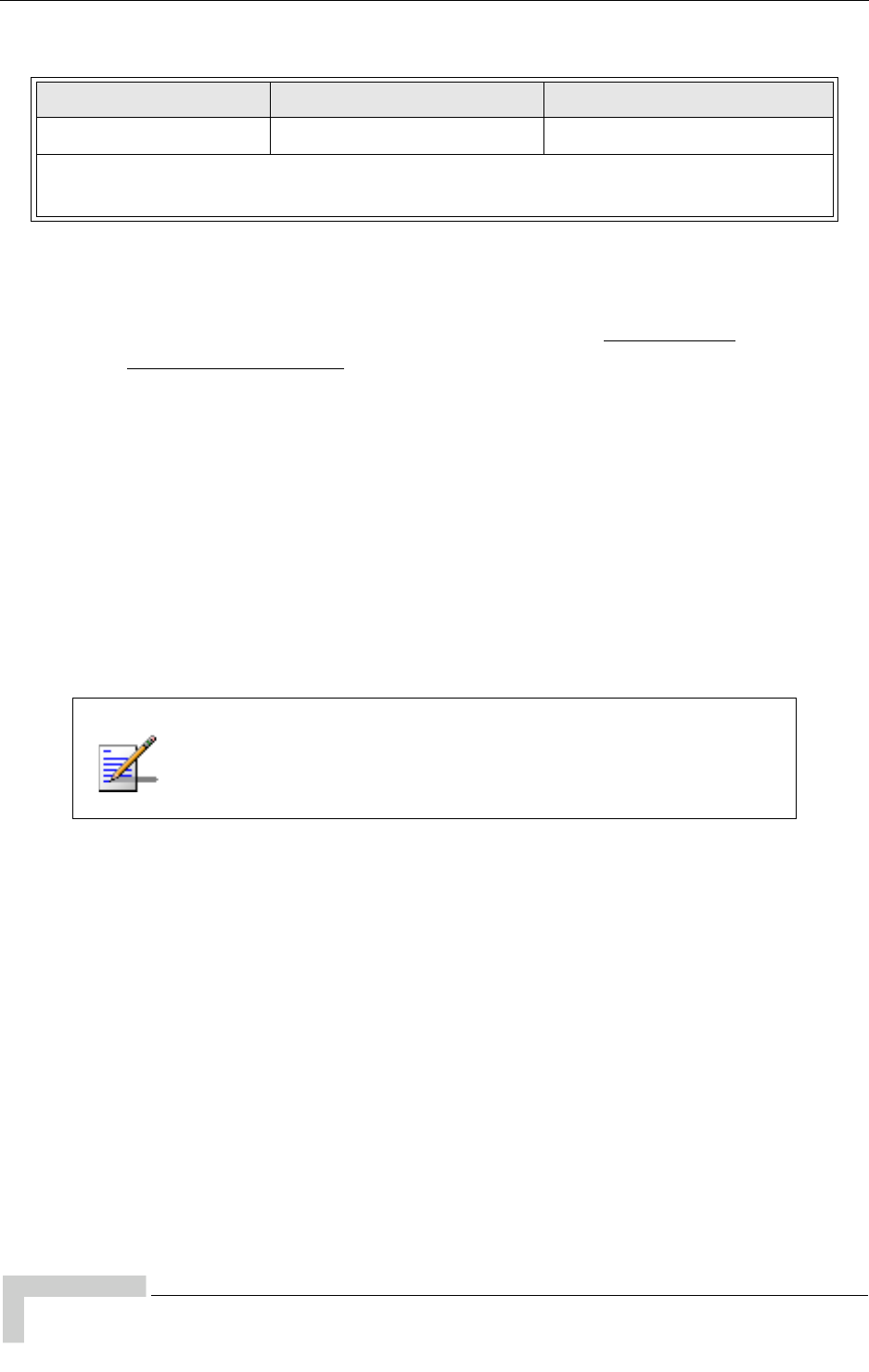
50 UltraWAVE Micro BTS Installation and Commissioning Guide, Version B
Chapter 2 - Installation
2.6.3 Connecting E1 or T1 Lines
All E1 or T1 cable routing should be installed per the site survey documentation
in conjunction with the information identified in the GSM Network
Implementation Manual.
Using the appropriate customer-supplied cables, connect the Abis interface E1
and/or T1 cables to the local E1 or T1 provider.
2.6.4 Direct Cabling Between Multiple UltraWAVE
or WAVEXpress Systems
This section provides information for cabling between Alvarion equipment. The
external cabling between your equipment will vary depending on the configuration
of the cable management assembly of each chassis. This could consist of any
combination of BNC, DSUB or RJ-48C connectors and either E1 or T1 signaling.
Table 2-11: Customer-Supplied T1 Cabling
Cable Identity Cable Type Corresponding Cable Plug
T1, 100 Ohm Shielded, Twisted, 2-Pair RJ-48C, Male
Note: The number of cables required depends on the ordered configuration of the
Micro BTS.
The direct cabling between systems requires crossover cables (Tx
to Rx, and Rx to Tx), instead of the straight-through cabling used
when connecting systems through a radio or telephone provider
network.
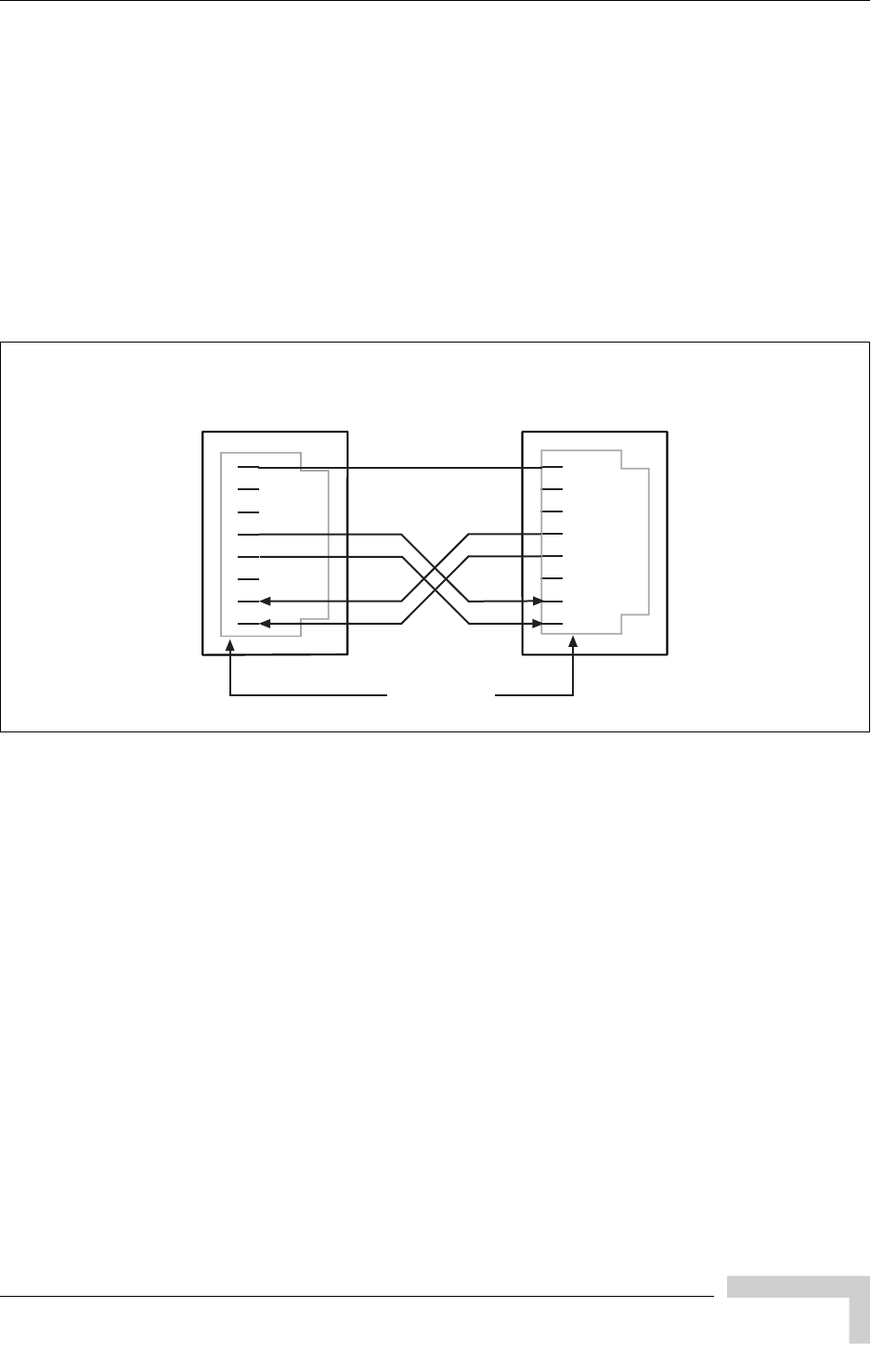
UltraWAVE Micro BTS Installation and Commissioning Guide, Version B 51
Connecting E1 or T1 Trunk Cables
Using Cross-Over RJ-48C Cables
When connecting a shielded twisted pair crossover cable between two UltraWAVE
or WAVEXpress systems, the routing of the pins needs to comply with the cable
mapping shown in Figure 2-20. The RJ-48C cable connector may be of the
conventional plastic body type with the shield and drain wires of the cable
connected to a pigtail to pin 8 (Signal Ground), which is internally grounded to the
card. However, a shielded cable plug may also be used, terminating the cable
shield to an integral metal shell of the RJ-48 jack which then makes an electrical
connection to the front panel when installed. Figure 2-20 provides the pin
assignments for the RJ-48C jacks.
To connect two systems using RJ-48C cables, connect a crossover cable (see
Figure 2-20) from port 1 of the first chassis to port 0 of the second chassis.
Figure 2-20: Cable Mapping of RJ-48C Crossover Cable
1
2
3
4
5
6
8
7
1
2
3
4
5
6
8
7
Pin 2: Receive Tip
Pin 5: Transmit Tip
Pin 1: Receive Ring
Pin 4: Transmit Ring
Pin 1: Receive Ring
Pin 2: Receive Tip
IW140401
Pin Numbers
PCB Signal
Ground
T1 or E1 Port
Connector
Pin 4: Transmit Ring
Pin 5: Transmit Tip
T1 or E1 Port
Connector
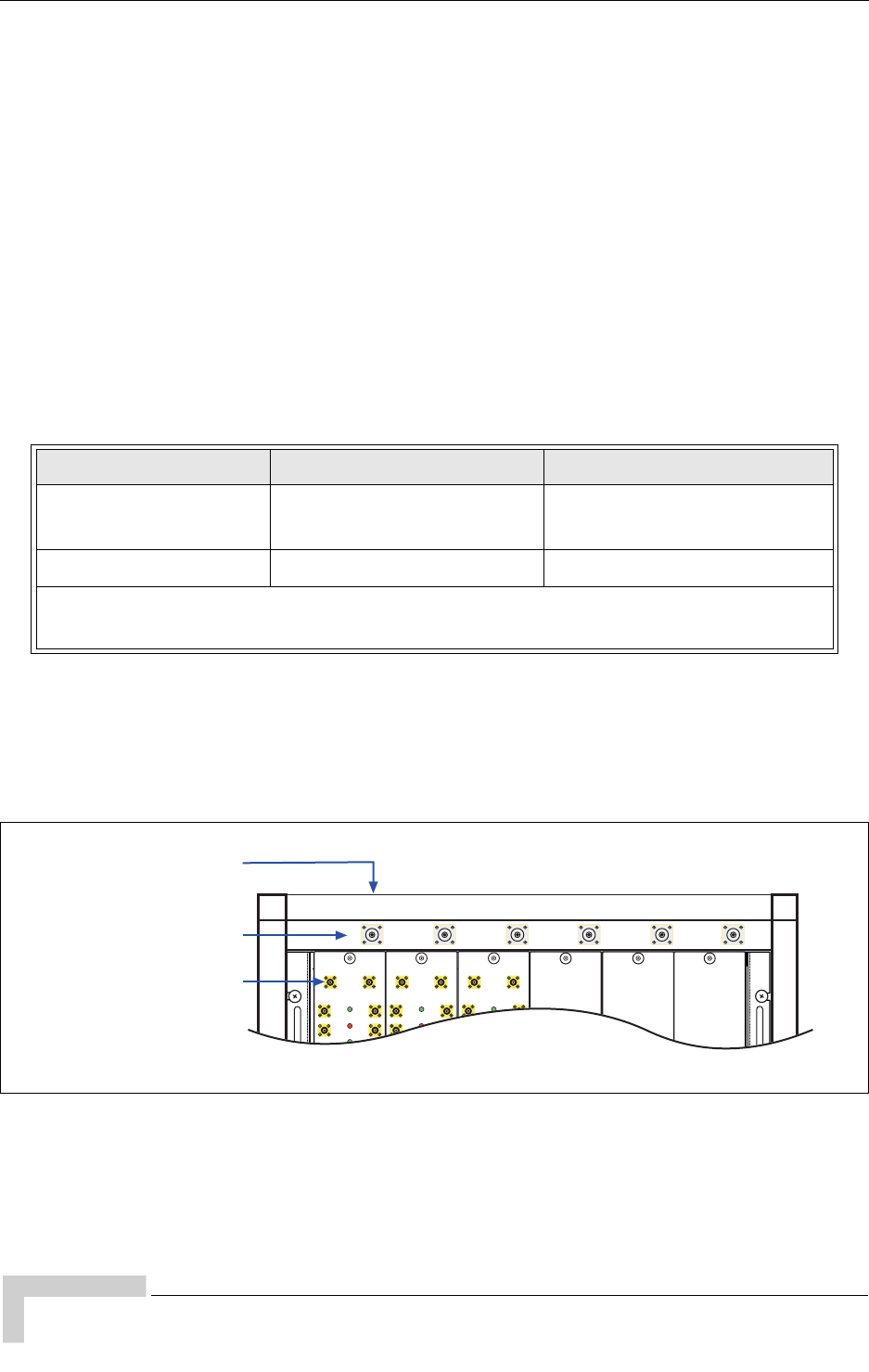
52 UltraWAVE Micro BTS Installation and Commissioning Guide, Version B
Chapter 2 - Installation
2.7 Connecting Antennas
The cabinet assembly provides external access to the male N-type connectors for
your external antennas. Your antenna cable should terminate with a 90° N-type
female connector or an N-type female to male elbow adapter may be used for a
more convenient connection to the cabinet. Insertion loss for the elbow type of
connector is typically between 0.1 and 0.2 dBm.
The antenna cabling for the Micro BTS can be configured in several ways
depending on a number of factors including the number of TRXs, number of
antennas and use of diversity. Your site specific configuration was determined
during the network planning stage of implementation.
In the subsequent sections, each RF configuration is detailed from the RF module
connector to the internal RF connector. Figure 2-21 illustrates the relationship
between the three connectors. The RF modules are connected to the internal RF
connectors at the factory and are pre-configured for your Micro BTS
configuration.
You will attach an elbow connector and your antenna cable to the external RF
connector associated with the internal RF connector shown in the appropriate
figure.
Table 2-12: Customer-Supplied Adapters and Cabling
Identity Cable Type Corresponding Cable Plug
Antenna cable
(external) Coaxial N-type, Female
Adapter (optional) 90 degree elbow N-type Female to N-type Male
Note: The number of cables required depends on the ordered configuration of the
Micro BTS.
Figure 2-21: Antenna Cabling for Standard BTS Configurations
Internal RF Connectors
(with port number)
RF Module Connectors
External RF Connectors
(Top of Cabinet)
ANT
DIV
ANT
MAIN
PWR
FLT
ON LINE
ON
OFF
RX1
RX2
RX3
RX4
RX1
RX2
RX3
RX4
ANT
DIV
ANT
MAIN
PWR
FLT
ON LINE
ON
OFF
RX1
RX2
RX3
RX4
RX1
RX2
RX3
RX4
ANT
DIV
ANT
MAIN
PWR
FLT
ON LINE
ON
OFF
RX1
RX2
RX3
RX4
RX1
RX2
RX3
RX4
01 23 54
IW009304
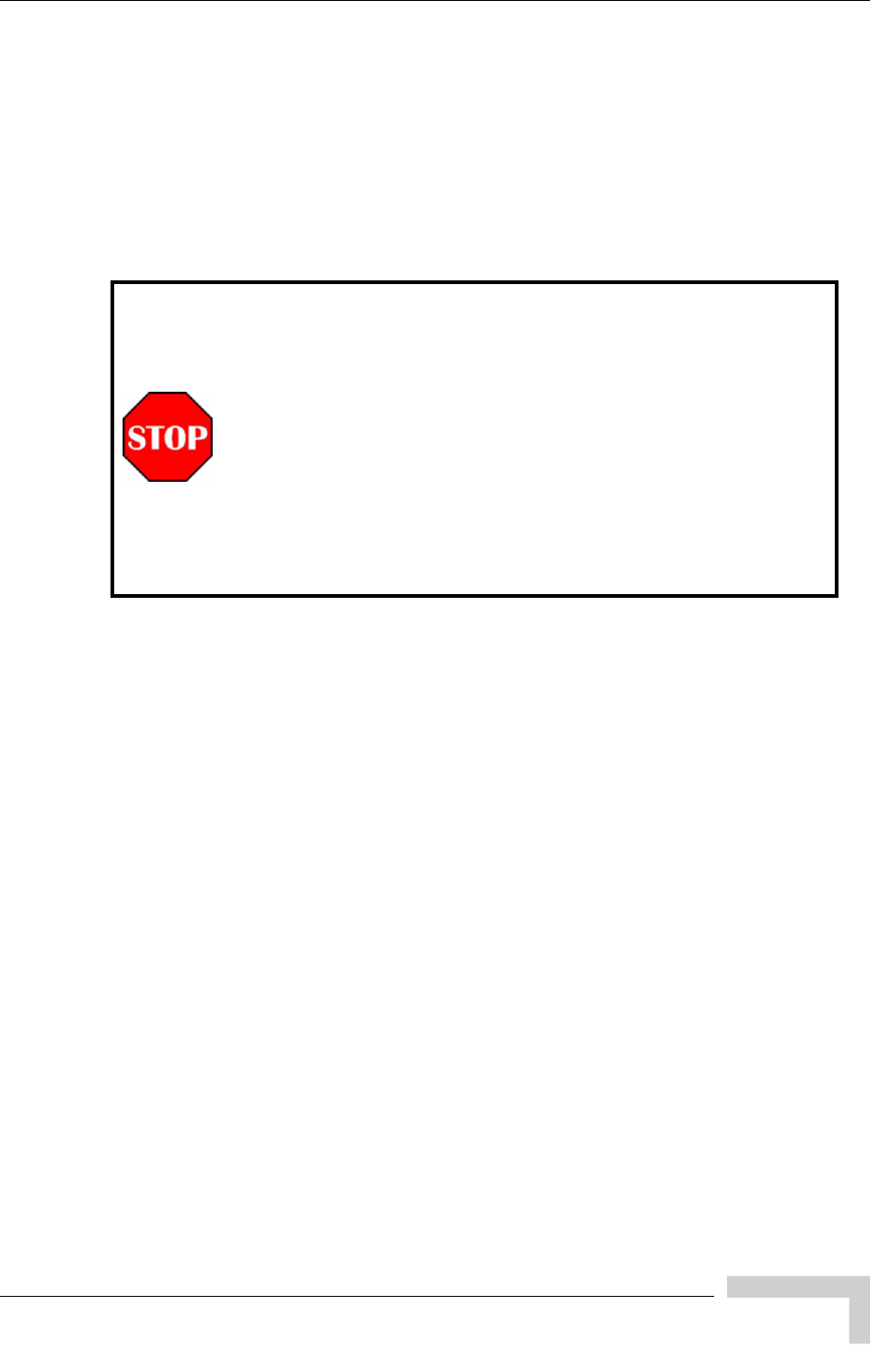
UltraWAVE Micro BTS Installation and Commissioning Guide, Version B 53
Connecting Antennas
The subsequent sections identify the cable routing for the different Micro BTS
antenna configurations that you identified in Chapter 1 - Unpacking and
Configuration Verification. You must install the antennas such that the general
population is kept at least 164 inches from the main beam of the antenna. For
more information on the RF radiation properties of the UltraWAVE, refer to
Section 2.7.6.
Proceed to the appropriate subsection to connect your site-specific antenna cable
configuration.
All RF cabling must be completed with the chassis powered off
and, preferably, with the power cable disconnected from the
cabinet.
Do not disconnect RF coaxial connectors on the Alvarion
equipment or antenna systems while the radio equipment is
operating. Never place any body part over or look into any RF
connector while the radio equipment is transmitting.
RF signal levels that give rise to hazardous radiation levels can
exist within the transmitter, power amplifiers, associated RF
multiplexers and antenna systems.

54 UltraWAVE Micro BTS Installation and Commissioning Guide, Version B
Chapter 2 - Installation
2.7.1 Omni 1 TRX (O1) Configuration
The Omni 1 TRX (01) configuration is available as a 15 Watt, 25 Watt, 40 Watt or
a 50 Watt, two antenna configuration. See Table 2-13.
For the 15 Watt, 25 Watt, 40 Watt, 50 Watt Omni 1 TRX (01) configurations,
connect your antennas as shown in Figure 2-22.
2.7.2 Omni 2 TRX (O2) Configuration
The Omni 2 TRX (02) configuration is available as a 15 Watt, 25 Watt, 40 Watt or
a 50 Watt, two antenna configuration. See Table 2-14.
Table 2-13: Omni 1 TRX (01) Configuration
Output Power Available Frequencies
15 W (42 dBm) 1800 MHz, 1900 MHz
25 W (44 dBm) 850 MHz, 900 MHz
40 W (46 dBm) 1800 MHz, 1900 MHz
50 W (47 dBm) 850 MHz, 900 MHz
/a
Figure 2-22: Antenna Cabling for O1 Configuration
Table 2-14: Omni 2 TRX (02) Configuration
Output Power Available Frequencies
15 W (42 dBm) 1800 MHz, 1900 MHz
25 W (44 dBm) 850 MHz, 900 MHz
40 W (46 dBm) 1800 MHz, 1900 MHz
50 W (47 dBm) 850 MHz, 900 MHz
RF modules
IW130601
ANT
DIV
ANT
MAIN
Internal RF connector
External RF connector
Antenna 1
Diversity
Antenna connection
1 2 3 4 50
Not UsedNot Used Not Used Not Used
Antenna 1
Main
ABC
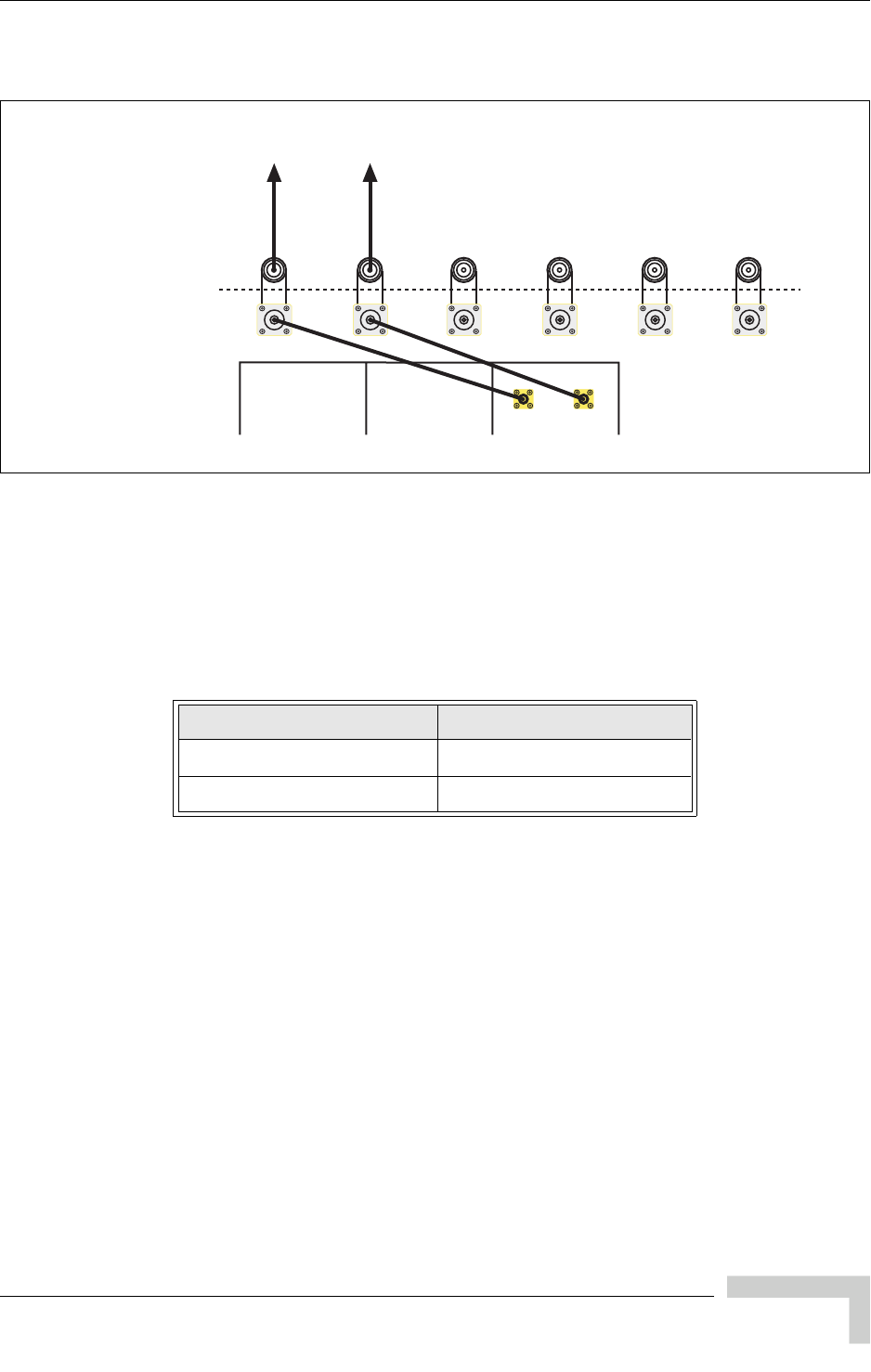
UltraWAVE Micro BTS Installation and Commissioning Guide, Version B 55
Connecting Antennas
For the 15 Watt, 25 Watt, 40 Watt and 50 Watt Omni 2 TRX (02) configurations,
connect your antennas as shown in Figure 2-23.
2.7.3 Omni 3 TRX (O3) Configuration
The Omni 3 TRX (03) configuration is available as a 15 Watt or a 25 Watt, two
antenna configuration. See Table 2-15.
For both the 15 Watt and 25 Watt Omni 3 TRX (03) configurations, connect your
antennas as shown in Figure 2-24.
Figure 2-23: Antenna Cabling for O2 Configuration
Table 2-15: Omni 3 TRX (03) Configuration
Power Output Available Frequencies
15 W (42 dBm) 1800 MHz, 1900 MHz
25 W (44 dBm) 850 MHz, 900 MHz
RF modules
IW130601
ANT
DIV
ANT
MAIN
Internal RF connector
External RF connector
Antenna 1
Diversity
Antenna connection
1 2 3 4 50
Not UsedNot Used Not Used Not Used
Antenna 1
Main
ABC
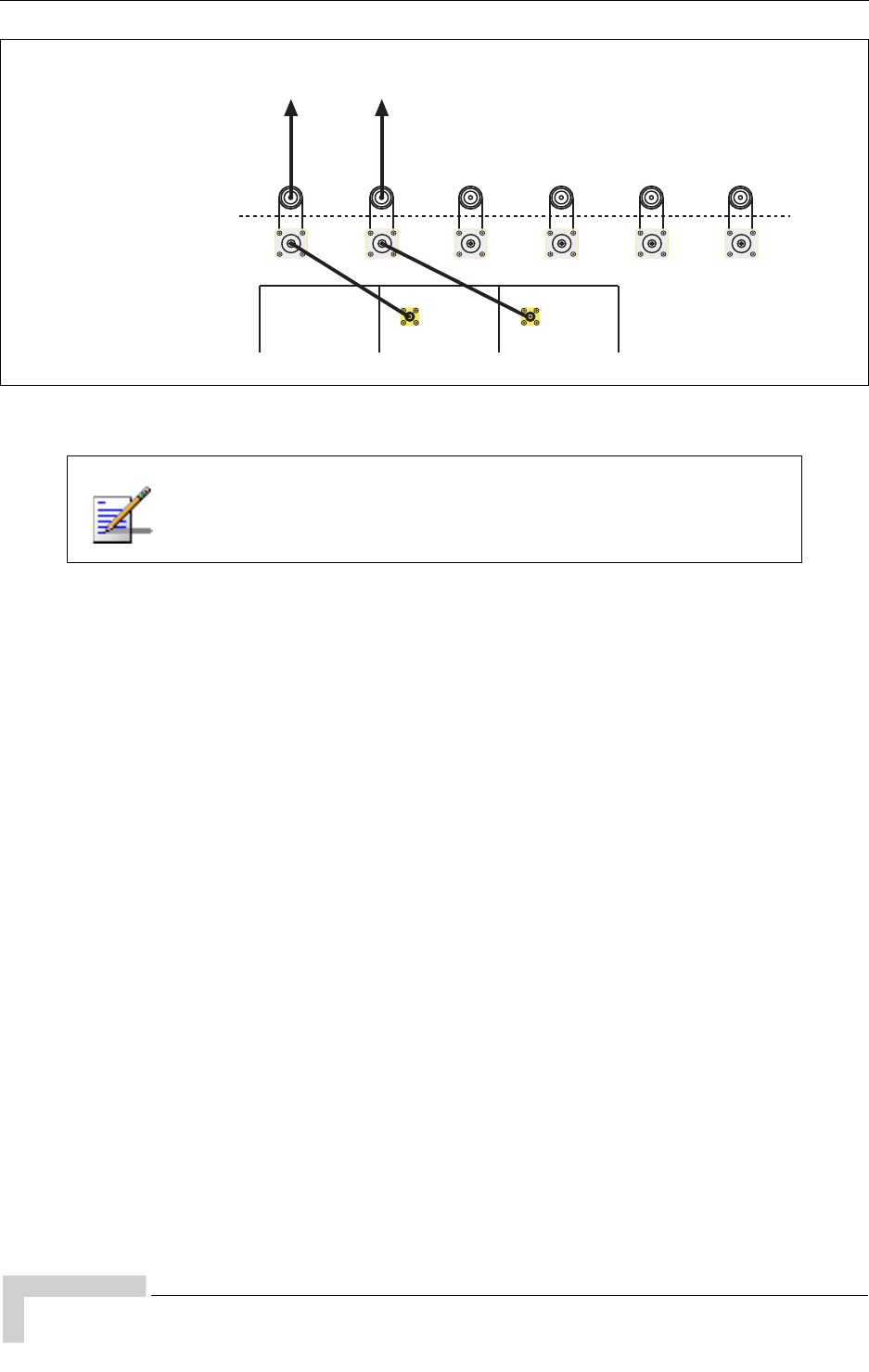
56 UltraWAVE Micro BTS Installation and Commissioning Guide, Version B
Chapter 2 - Installation
Figure 2-24: Antenna Cabling for O3 Configuration
For the Omni 3 TRX (03), a spatial diversity of 10 lambdas is
required between antennas.
ANT
RF modules
Internal RF connector
External RF connector
Antenna 1
Main
Antenna connection
1 2 3 4 50
Not UsedNot Used Not Used Not Used
Antenna 2
Main
ANT
IW130603
ABC

UltraWAVE Micro BTS Installation and Commissioning Guide, Version B 57
Connecting Antennas
2.7.4 Sectorized Three TRX (S111) Configuration
The sectorized three TRX (S111) configuration is available as a 15 Watt, 25 Watt,
40 Watt or a 50 Watt six antenna configuration. See Figure 2-16.
This configuration has three sectors with one TRX per sector. For the 15 Watt,
25 Watt, 40 Watt and 50 Watt configurations, connect your antennas as shown in
Figure 2-25.
Table 2-16: Sectorized Three TRX (S11) Configuration Frequencies
Configurations Available Frequencies
15 W (42 dBm) 1800 MHz, 1900 MHz
25 W (44 dBm) 850 MHz, 900 MHz
40 W (46 dBm) 1800 MHz, 1900 MHz
50 W (47 dBm) 850 MHz, 900 MHz
Figure 2-25: Antenna Cabling for S111 Configuration
ANT
DIV
ANT
MAIN
ANT
DIV
ANT
MAIN
RF modules
Internal RF connector
External RF connector
Antenna 1
Diversity
Antenna connection
1 2 3 4 50
Antenna 1
Main
Antenna 2
Main
Antenna 2
Diversity
ANT
DIV
ANT
MAIN
Antenna 3
Main
Antenna 3
Diversity
IW130611
ABC
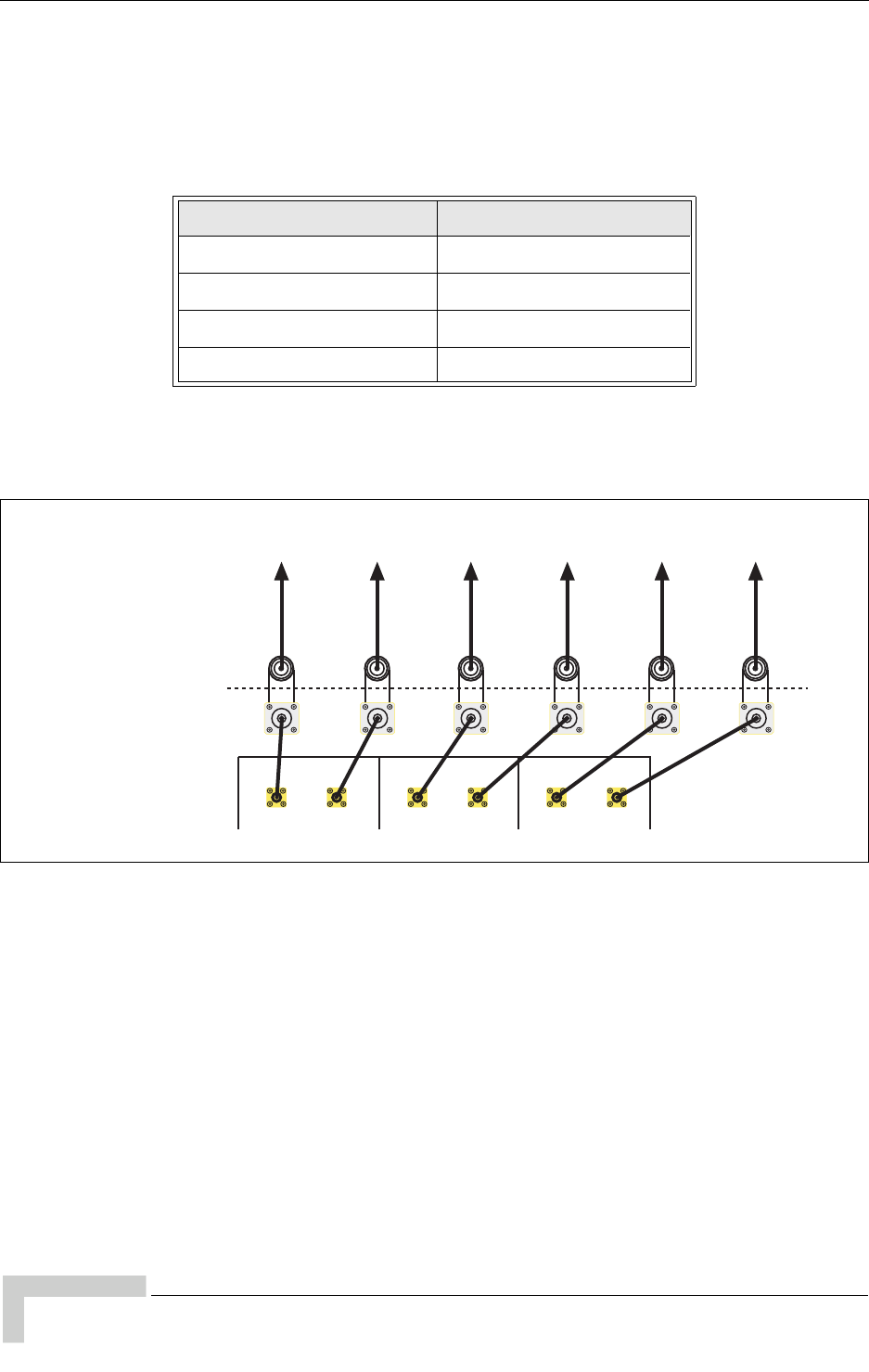
58 UltraWAVE Micro BTS Installation and Commissioning Guide, Version B
Chapter 2 - Installation
2.7.5 Three Sector Six TRX (S222) Configuration
The three sector, six TRX (S222) configuration is available as a 15 Watt, 25 Watt,
40 Watt or a 50 Watt, six antenna configuration. See Table 2-17.
This configuration has three sectors with two TRXs in one sector and one TRX in
the other two sectors. For the 15 Watt, 25 Watt, 40 Watt and 50 Watt S222
configurations, connect your antennas as shown in Figure 2-26.
2.7.6 RF Radiation Hazard
As of October 15, 1997, all products must address the issue of Human Exposure
to RF electromagnetic fields. Referring to OET Bulletin 65, RF radiation limits for
the 300 - 1500 MHz range are f / 300 mW/cm2 for occupational exposure, and f /
1500 mW/cm2 for general population exposure (where f is frequency in MHz). At
the 869 MHz cellular band these limits are 2.90 mW/cm2 for occupational
exposure, and 0.58 mW/cm2 for general population exposure.
The UltraWAVE base station may consist of up to six separate transceivers, with
each of the transmitters operating at a maximum output power of +47 dBm
Table 2-17: Three Sector Six TRX (S222) Configuration Frequencies
Configuration Available Frequencies
15 W (42 dBm) 1800 MHz, 1900 MHz
25 W (44 dBm) 850 MHz, 900 MHz
40 W (46 dBm) 1800 MHz, 1900 MHz
50 W (47 dBm) 850 MHz, 900 MHz
Figure 2-26: Antenna Cabling for S222 Configuration
ANT
DIV
ANT
MAIN
ANT
DIV
ANT
MAIN
RF modules
Internal RF connector
External RF connector
Antenna 1
Diversity
Antenna connection
1 2 3 4 50
Antenna 1
Main
Antenna 2
Main
Antenna 2
Diversity
ANT
DIV
ANT
MAIN
Antenna 3
Main
Antenna 3
Diversity
IW130611
ABC

UltraWAVE Micro BTS Installation and Commissioning Guide, Version B 59
Connecting Antennas
(50 W). The UltraWAVE base station transmitters operate in the U.S. cellular band
of 869 to 894 MHz.
As the UltraWAVE is intended to be operated in cellular service, each of its
transmitters is typically connected to a 65 - 120 degree sector antenna or omni
directional antenna. For the purpose of the MPE calculations, it will be assumed
that the UltraWAVE is fully equipped with six transceivers, and that two different
transmitters are used in each 120 degree sector. For the MPE calculations this
would be the worst case radiation levels as the equivalent RF power of +50 dBm
(100 Watt) would be transmitted into a 120 degree sector.
The typical gain of 65 - 120 degree sector antenna is in the range of +6 to +18 dBi.
However, there is the highest ERP limitation on the Part22 requirement which is
500 Watt (57 dBd).
The duty cycle of the transmitter is 100%. Assuming two transmitters are
operating into the same 120 degree sector, a maximum of +47 dBm of RF energy
would be transmitted into two antennas, with total EIRP=61 dBi would be the
worst case.
RF power density can be calculated with the equation: S = P * G / 4p R2, where
S = power density in mW/cm, P = power input to the antenna in mW, G = power
gain of the antenna, and R = distance to the center of radiation of the antenna in
cm. By rearranging this equation, the relationship between distance (R) and Power
Density (S) can be found.
Rearranging R = sqrt (PG/4pS), and solving for the maximum limits of
2.90 mW/cm2, and 0.58 mW/cm2 we have:
R(2.90 mW/cm2) = sqrt (1,260,000 mW/4p*2.90) = 186 cm, or 73 inches.
R(0.58 mW/cm2) = sqrt (1,260,000 mW/4p*0.58) = 416 cm, or 164 inches.
These results show that the general population RF exposure limits are not
exceeded as long as the general population is kept 164 inches from the feed point
of the antenna.
The propagation characteristics at 870 MHz dictate a line-of-sight type of RF path.
As such, typical installation locations are up on rooftops or masts to get above
ground level path obstructions. When the UltraWAVE antennas are installed in
this manner, the general population will be further than 164 inches from the
antenna, and RF exposure limits will be met.
1,260,000 mW is used to account for two 50,000 mW
transmitters operating into each 120 degree sector.
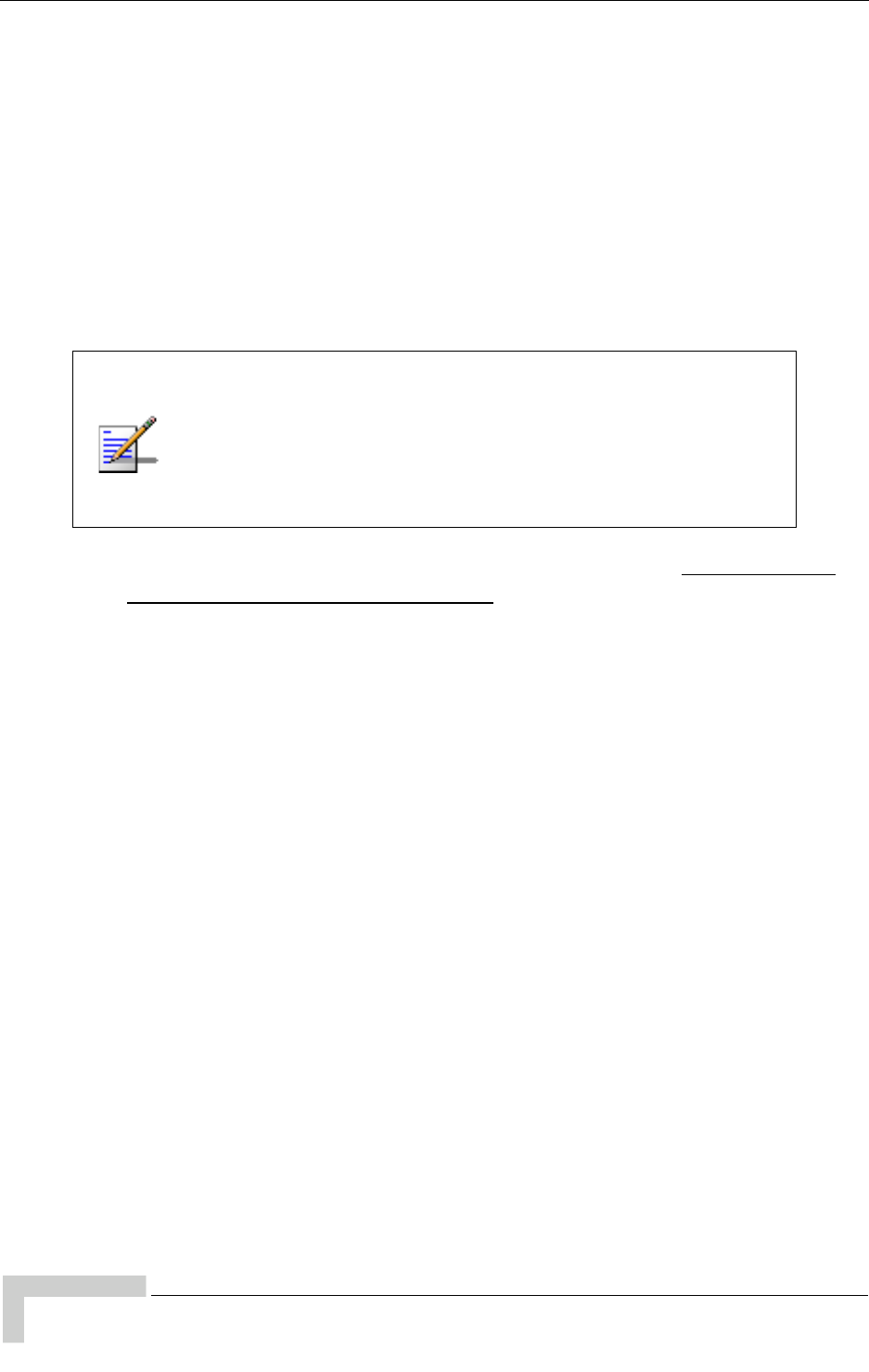
60 UltraWAVE Micro BTS Installation and Commissioning Guide, Version B
Chapter 2 - Installation
2.8 Connecting External Alarms
The OMC supports many alarms from the Micro BTS. The external alarms are
reflected at the OMC operator station, and may be used for site alarms, such as
open door, temperature and battery back-up alarms. These customer defined
alarms are sampled every two minutes by default and will report an alarm when
sent by the Micro BTS alarm controller.
Using the details provided in these sections, make your connections for external
alarm inputs.
The OMC operator can set the alarm text as described in the UltraVIEW OMC
Setup and System Administration Guide.
Identifying the Terminal Block
The alarms are processed on the alarm interface module located on the rear of the
Micro subrack assembly. The alarm interface module has connections for
incoming signals from external alarms and the power supplies and an outgoing
connection to the ICP processor card through a USB type cable. The interfaces are
shown in Figure 2-27.
If you are replacing an existing system which has external alarms
connected directly to the processor card, you may connect your
existing RJ-45 alarm cable directly into the ICP processor card
alarm connector. Optionally, you can re-route your existing
alarms to the UltraWAVE alarm terminal block or add additional
external alarms.
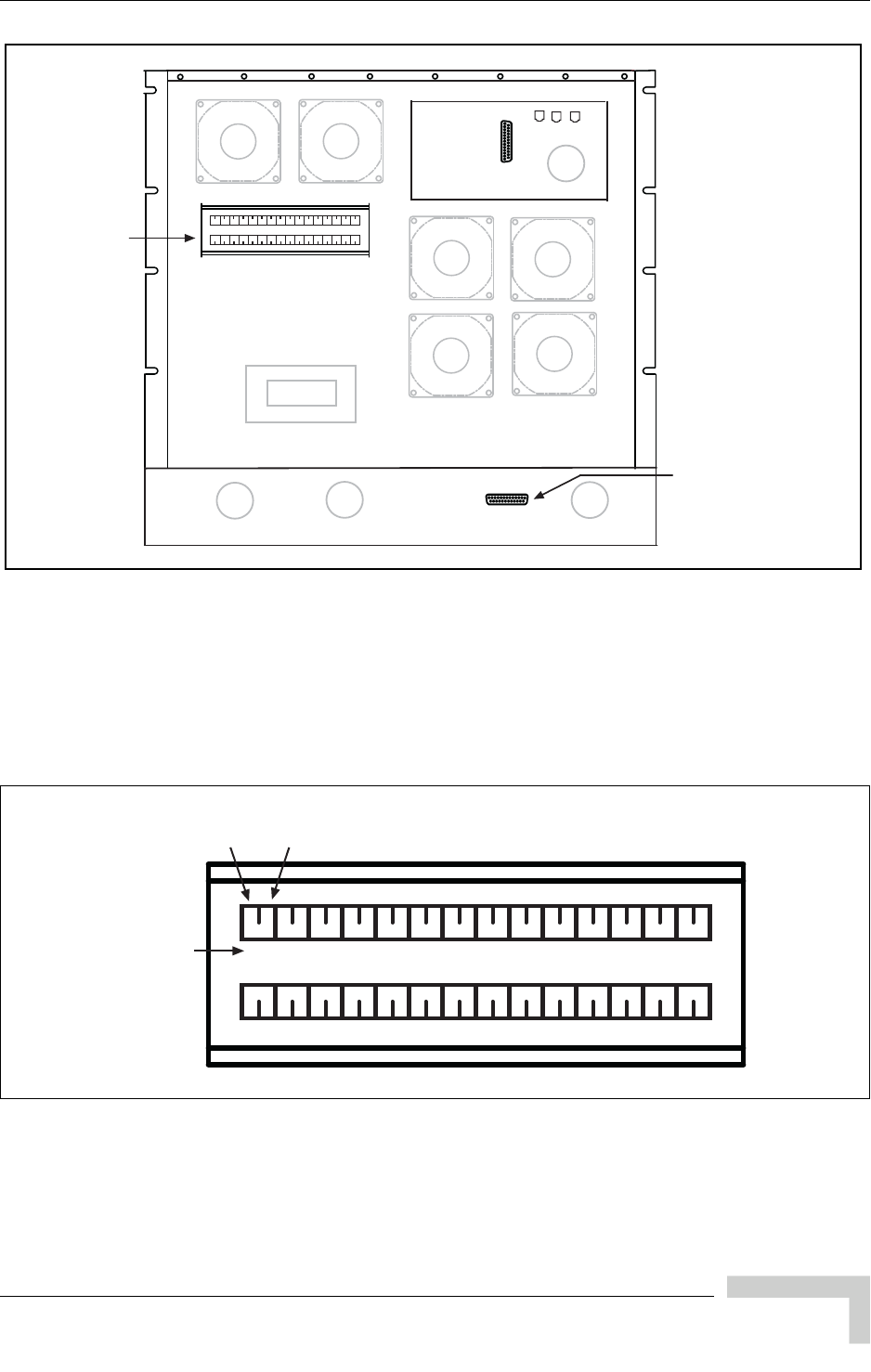
UltraWAVE Micro BTS Installation and Commissioning Guide, Version B 61
Connecting External Alarms
Figure 2-27: Alarm Interface Module
This terminal block provides a plug connection for up to 17 external alarms. The
plugs supplied with the Micro BTS provide an alarm loop for connection to a
normally open alarm mechanism. The plug identifiers correspond to the alarm
codes sent to the OMC. See Table 2-18 for Terminal Block pin assignments, and
see Figure 2-28 for external alarm terminal block details.
Figure 2-28: Customer-Defined External Alarm Connections
EP1 EP2 EP3 EP4 EP5 EP6 EP7 EP8 EP9 EP10 EP11 EP12 EP13 EP14 EP15 EP16
EP17 EP18 EP19 EP20
Power Supply
Alarm Interface
External Alarm
Interface
IW136601
EP1 EP2 EP3 EP4 EP5 EP6 EP7 EP8 EP9 EP10 EP11 EP12 EP13 EP14
EP15 EP16 EP17 EP18 EP19 EP20
Plug
Identifier
IW191604
Pin 1
(signal)
Pin 2
(ground)
FC1 FC2 FC3 TTL 27v VCC DR VCC
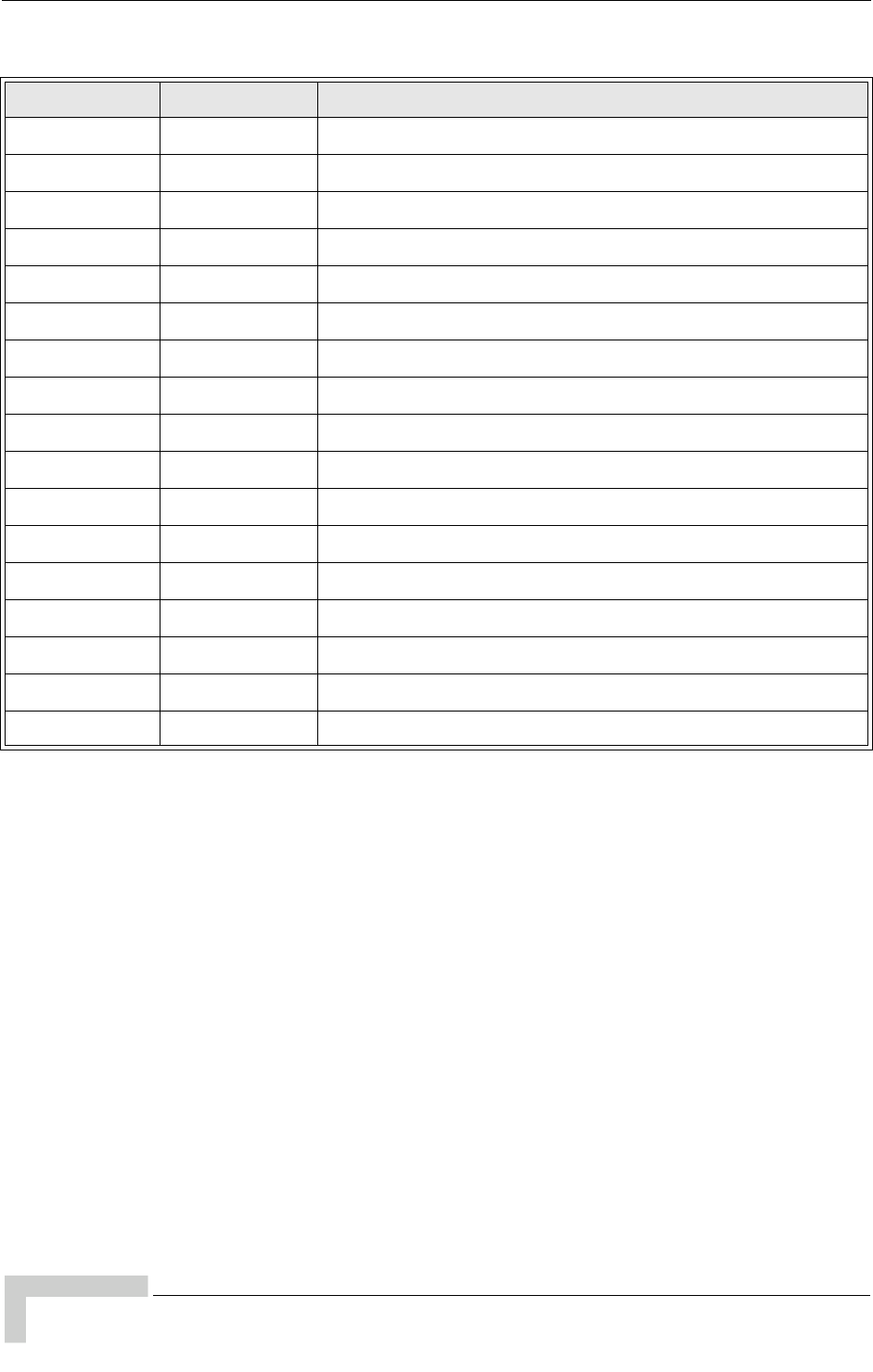
62 UltraWAVE Micro BTS Installation and Commissioning Guide, Version B
Chapter 2 - Installation
Table 2-18: External Alarm Terminal Block Pin Assignment
Plug Identifier Alarm Code Major Alarm Type
EP1 2326 Customer definable UltraWAVE External Alarm 1
EP2 2327 Customer definable UltraWAVE External Alarm 2
EP3 2328 Customer definable UltraWAVE External Alarm 3
EP4 2329 Customer definable UltraWAVE External Alarm 4
EP5 2330 Customer definable UltraWAVE External Alarm 5
EP6 2331 Customer definable UltraWAVE External Alarm 6
EP7 2332 Customer definable UltraWAVE External Alarm 7
EP8 2333 Customer definable UltraWAVE External Alarm 8
EP9 2334 Customer definable UltraWAVE External Alarm 9
EP10 2335 Customer definable UltraWAVE External Alarm 10
EP11 2336 Customer definable UltraWAVE External Alarm 11
EP12 2337 Customer definable UltraWAVE External Alarm 12
EP13 2338 Customer definable UltraWAVE External Alarm 13
EP14 2339 Customer definable UltraWAVE External Alarm 14
EP15 2340 Customer definable UltraWAVE External Alarm 15
EP16 2341 Customer definable UltraWAVE External Alarm 16
EP17 2342 Customer definable UltraWAVE External Alarm 17

UltraWAVE Micro BTS Installation and Commissioning Guide, Version B 63
Connecting External Alarms
To connect the external alarm contacts to the external alarm terminal block:
1Route the external alarm input cables from the external equipment through
the cable gland on the external interface to the external alarm terminal block.
2Using the details provided in Figure 2-29, connect the normally-open alarm
inputs from the external equipment to the external alarm plug.
3Connect the alarm plug to the terminal block. Note the plug identifier and
using Table 2-18 inform the OMC operator which alarm code corresponds to
the external alarm that you have just installed.
Only the EP1 through EP17 plugs shown in Figure 2-28 use the
signal and ground alarm input pins. DO NOT connect EP1
through EP17 plugs to FC, TTL, 27V, VCC or DR connection
pins, or you can cause serious damage to the system.
Figure 2-29: External Alarm Plug
Inputs from external alarms should be normally open. When the
external contacts close, the Micro BTS sends an alarm to the
OMC.
IW022302
Pin 1
(signal) Pin 2
(ground)
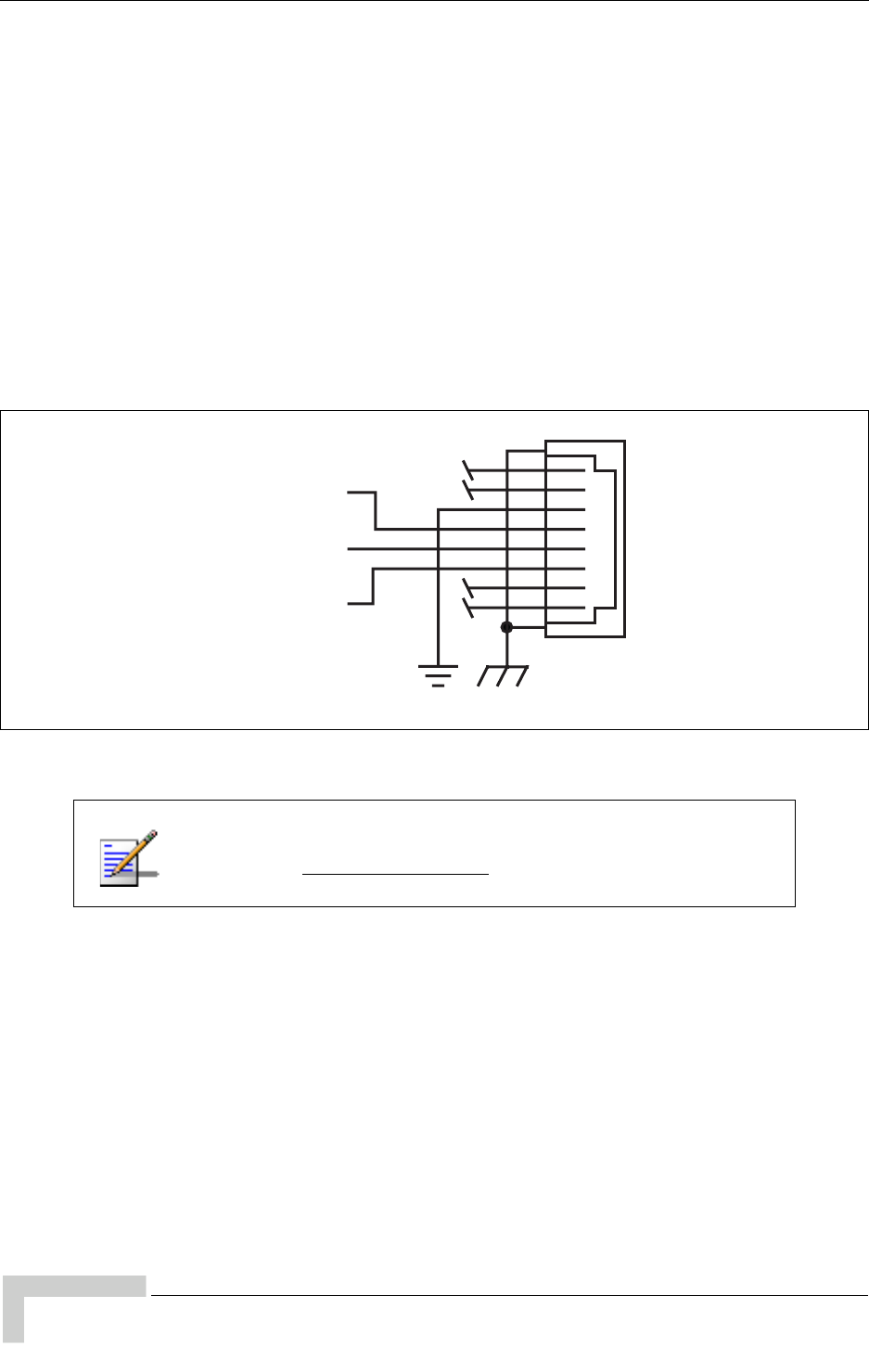
64 UltraWAVE Micro BTS Installation and Commissioning Guide, Version B
Chapter 2 - Installation
2.9 Making a Serial Connection to the
Processor Card
The serial connection is used to check the software version installed on the
processor card, verify boot parameters and monitor test results. An RJ-11 to
RJ-11 cable and an RJ-11 to DB-9 adapter is normally used to connect the Craft
PC to the ICP CON serial port. This hardware is supplied in the Craft PC
Accessories kit.
This adapter is not included with the Craft PC accessories kit.
See Figure 2-30 for the ICP CON serial port pin-out.
Figure 2-30: ICP Serial Pin-Out
For more information pertaining to pinouts and cables, please
refer to the GSM Craft PC Guide.
RJ-45
8
7
6
5
4
3
2
1
10
9
RS232 RXD
RS232 DCD
RS232 TXD
IW044302

UltraWAVE Micro BTS Installation and Commissioning Guide, Version B 65
Network Connections
2.10 Network Connections
External cabling is dependent upon the customer-ordered configuration and
site-specific requirements. These cables will be supplied by the customer. Failure
to use electrically compliant T1 or E1 cables may cause transmission errors.
Please refer to the appropriate subsections to determine your cable requirements.
Installing the Physical E1 or T1 Links
For the first E1 or T1 link between the Micro BTS and the BSC, connect Port 0 of
the Micro BTS E1 or T1 card in slot 1 to the BSC. For additional E1 or T1 links,
you can use any other port on any other Micro BTS (or BTS) E1 or T1 card. After
connecting the E1 or T1 link(s) between the Micro BTS and the BSC, connect the
BSC to the OMC.
Commissioning the E1 or T1 Links
The E1 or T1 links between the Micro BTS and the BSC are commissioned using
the W&G (Wandel & Goltermann) PA-25 multifunction communication analyzer,
or equivalent.
The E1 or T1 connections at the trunk cards and the BSC must
comply with the pin assignments detailed in Chapter 2 -
Installation. This chapter also explains the E1 or T1 trunk card
DIP switch, which must be set to reflect the E1 or T1 cable
characteristics.
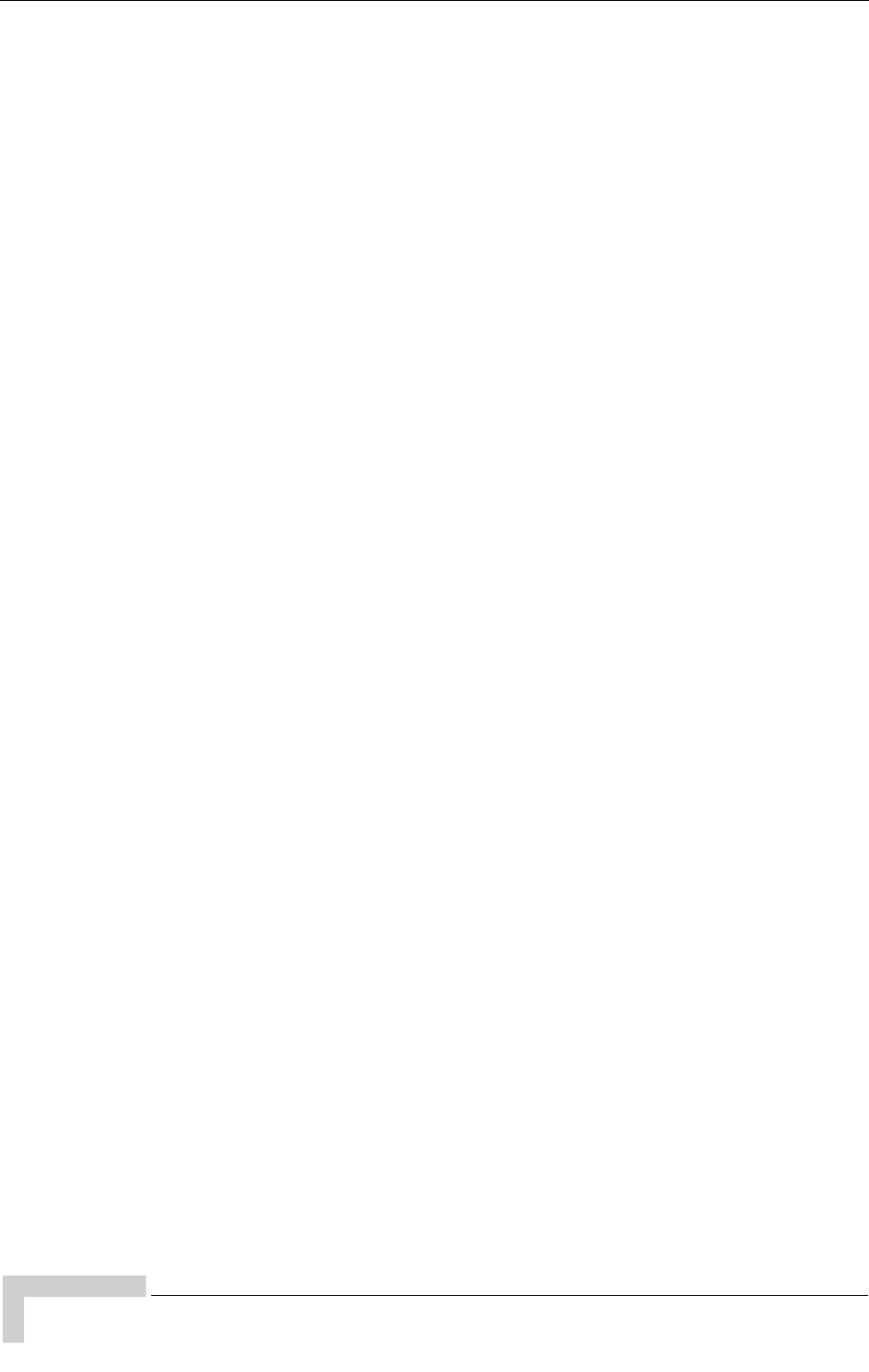
66 UltraWAVE Micro BTS Installation and Commissioning Guide, Version B
Chapter 2 - Installation
2.11 Post Installation Cabling and Checks
You should ensure that all internal and external cabling is correctly connected.
2.11.1 Connecting the Chassis
Before commissioning the equipment, ensure that:
The Abis interface E1 and/or T1 cables are routed to the telephone provider.
The DIP switch settings on the E1 or T1 trunk cards are set correctly and if
you are using the 75 Ohm E1 trunk card that the ground jumper is in the
correct position. Refer to Section 2.3 for E1 and/or T1 DIP switch settings.
The chassis power is turned off.
Antenna cables are connected to RF antenna port connectors as appropriate.
2.11.2 Verifying External Cabling
It is the operator's responsibility to verify that all inter-chassis E1 and/or T1
links are ordered, installed and certified by the telephone provider according to
ANSI T1.403 specifications before on-line commissioning is performed.
The operator should also perform end-to-end bit error ratio or Bit Error Rate
(BER) tests over a 20-minute period on the E1 and T1 Abis interface link(s),
and verify that the BER is 10-8 or better.
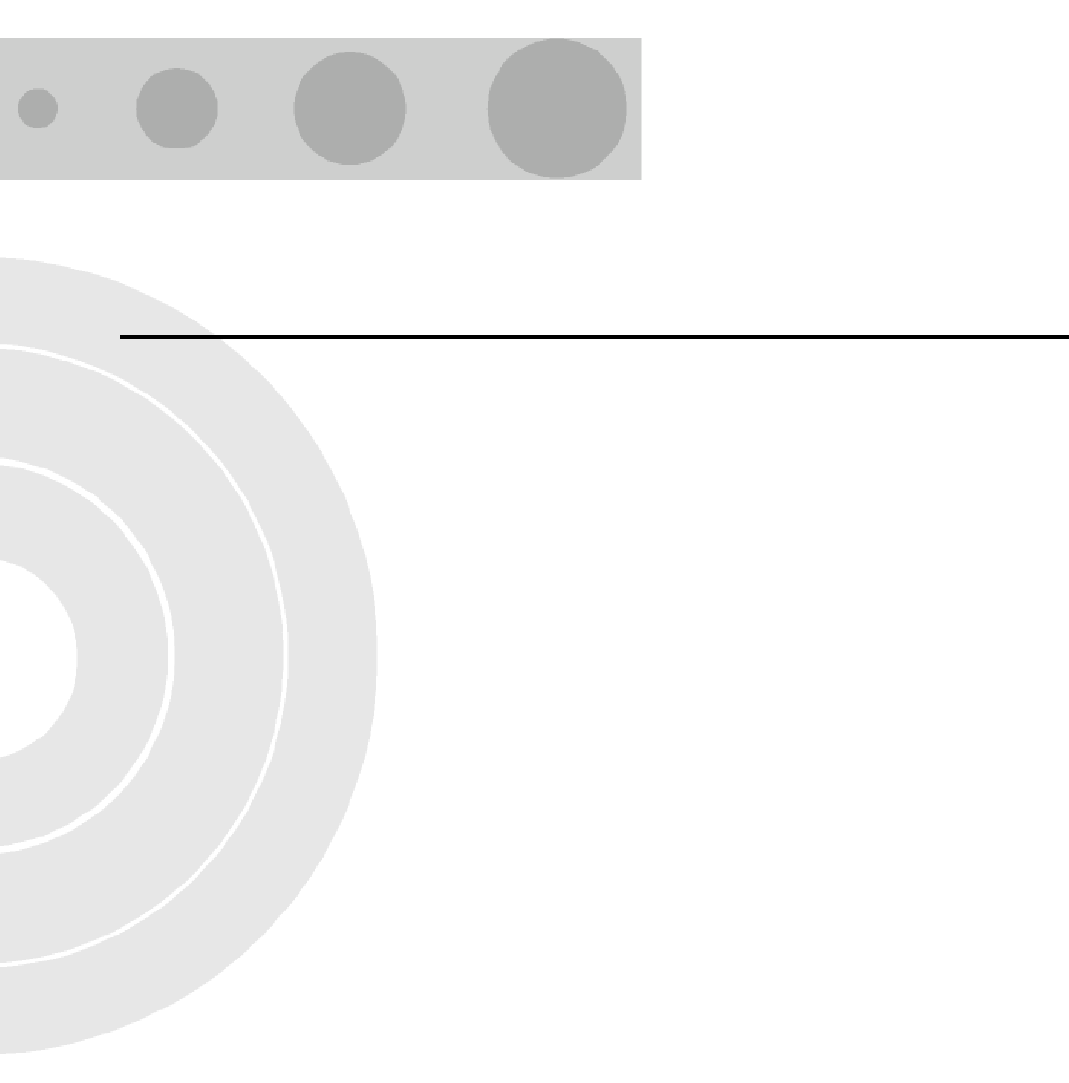
3
Chapter 3 - Off-Line Commissioning
In this Chapter:
“Pre Off-Line Commissioning” on page 69
“Off-Line Commissioning of the Micro BTS” on page 71
“Software Verification using Craft PC” on page 83
“Upgrading the Micro BTS Software Version (Flash)” on page 90
“Post Off-Line Commissioning” on page 92
The off-line commissioning process includes the following steps:
Pre off-line commissioning, where you ensure that the system is in an appro-
priate state. This includes:
Visual inspection
Compliance checks
Startup verification, where you verify that the system boots up correctly by
observing the LEDs on the front panel.
Craft PC tests, where you use the Craft PC to verify the software configuration
and run tests.
Post off-line commissioning, where you prepare the system for on-line
commissioning.
The rest of this chapter includes detailed instructions for these steps.

68 UltraWAVE Micro BTS Installation and Commissioning Guide, Version B
Chapter 3 - Off-Line Commissioning
Under normal operating conditions, Alvarion Communications
radio equipment complies with the limits for human exposure to
radio frequency (RF) fields adopted by the Federal
Communications Commission (FCC). All Alvarion
Communications, Inc. radio equipment is designed so that under
normal working conditions radio frequency radiation directly
from the radio is negligible when compared with the permissible
limit of continuous daily exposure recommended in the United
States of America by ANSI/IEEE C95.1-19991 (R1997), Safety
Levels with Respect to Human Exposure to RF Electromagnetic
Fields, 3 kHz to 300 GHz.
RF signal levels that give rise to hazardous radiation levels can
exist within the transmitter, power amplifiers, associated RF
multiplexers and antenna systems.
Do not disconnect RF coaxial connectors on the Alvarion
equipment or antenna systems while the radio equipment is
operating. Never place any body part over or look into any RF
connector while the radio equipment is transmitting.
The BSS software used in the UltraWAVE Micro BTS is highly
complex. Before proceeding, contact Customer Service to verify
that you have the latest available software. You must have the
correct software CD-ROM and know the current patch level for
your software version before commissioning the UltraWAVE
Micro BTS. Contact your Level 2 support representative for
additional assistance.
The off-line commissioning steps are listed in Checklist 3 -
Commissioning Checklist.
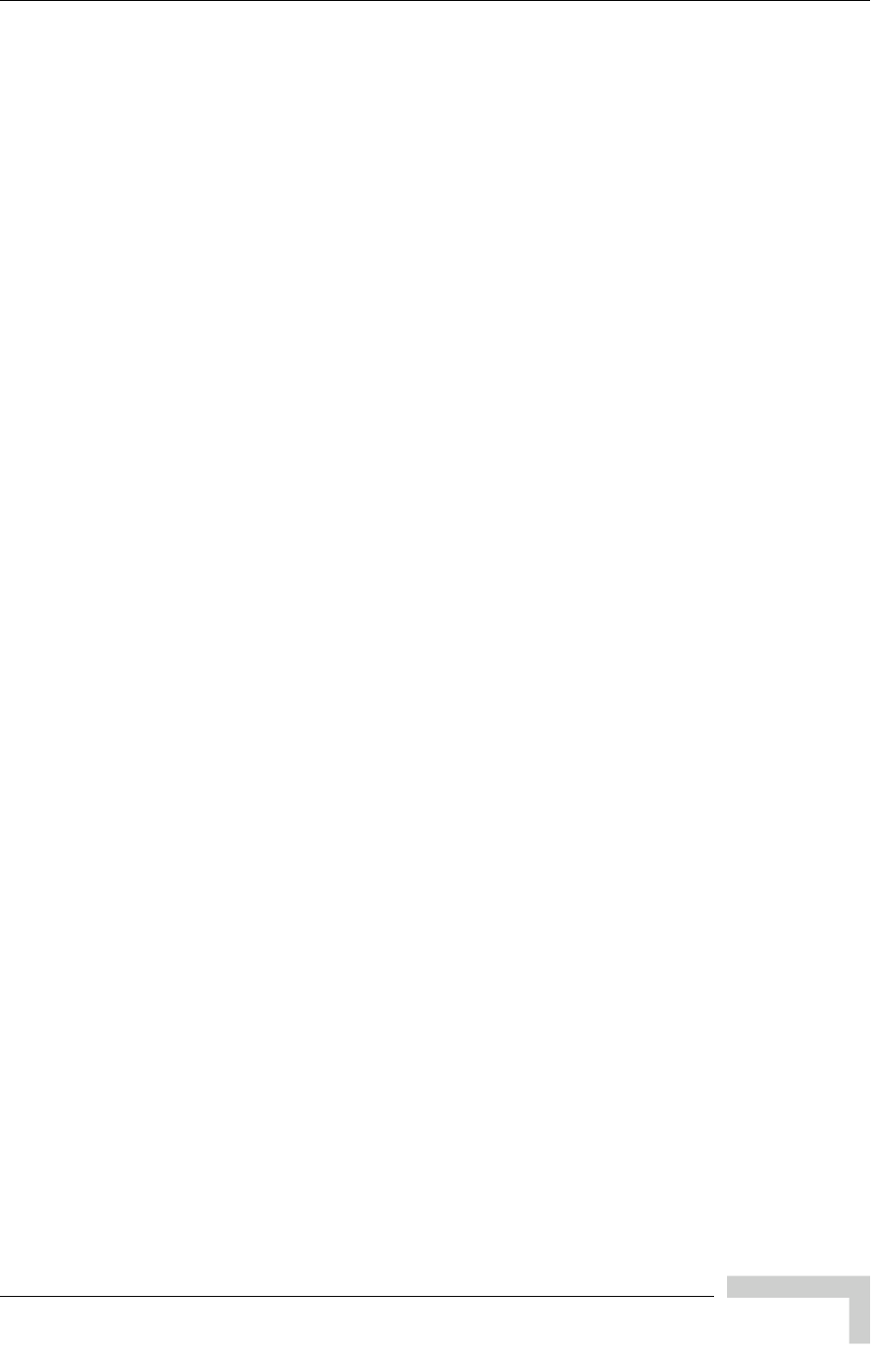
UltraWAVE Micro BTS Installation and Commissioning Guide, Version B 69
Pre Off-Line Commissioning
3.1 Pre Off-Line Commissioning
The following sections must be completed before doing the off-line commissioning.
The off-line commissioning of the Micro BTS must take place on-site after
installation. It is critical that all RF connections have been completed before
proceeding with the off-line commissioning.
3.1.1 Visual Inspections
Complete the following inspections to ensure that the system is ready for off-line
commissioning.
On-Site Visual Inspection
If you are doing your visual inspection on-site, check that:
The chassis has been securely installed at the appropriate site.
The chassis power supplies are OFF.
The chassis is connected to a suitable power source.
Power supply fans are running and INPUT LEDs are illuminated.
The chassis is correctly grounded.
All cables are available and secured in their correct positions.
All cards and modules are correctly seated and populated according to the
original purchase order.
E1 or T1 transmission cables are available and labeled.
RF transmission cables are connected to antennas.
Compliance and Power Checks
Cross-check with the site specific data to ensure that the Micro BTS is
correctly configured with all cards and modules.
Ensure that you have access to Checklist 2 - Installation Checklist and that all
serial numbers of all cards are listed there. This should have been completed
in Chapter 1 - Unpacking and Configuration Verification.
Verify that any test equipment to be used has a current calibration certificate.
Verify that the voltage for the installation site match those of the chassis
power supply modules (either 230 VAC, 110 VAC, or -48 VDC, as specified on
the front panel).

70 UltraWAVE Micro BTS Installation and Commissioning Guide, Version B
Chapter 3 - Off-Line Commissioning
Label and Disconnect Cables
1Verify that all E1 or T1 cables connected to the chassis are properly labeled.
2Disconnect all E1 or T1 cables from the top of the cabinet if there are any
cables connected.

UltraWAVE Micro BTS Installation and Commissioning Guide, Version B 71
Off-Line Commissioning of the Micro BTS
3.2 Off-Line Commissioning of the Micro
BTS
The verification procedures for off-line commissioning are run on the processor
card in the Micro BTS. Locate the processor card in the Micro BTS subrack
assembly as shown in Figure 3-1.
Figure 3-1: Micro BTS Subrack Assembly
3.2.1 Starting XWindows Using the Craft PC
In this chapter, you will use the Craft PC to verify the software configuration and
other aspects of the Micro BTS operation. This section describes how to start the
Craft PC and the Windows environment while subsequent sections will provide
connection, test and verification procedures.
1Login to your PC as the build user.
2With your left mouse button, double click the Craft PC icon on the desktop or
navigate through the Start menu -> Programs -> IWV Software -> Craft PC.
The following sections describe procedures performed using the
Craft PC. For more information pertaining to the use of the
Craft PC, please refer to the GSM Craft PC Guide. Note that all
commands in bold are those entered by the user.
RF Modules
Processor Card
E1 or T1 Trunk Card
TRX Cards
Clock Module
PA1
IN
ANT
DIV
ANT
MAIN
PWR
FLT
ON LINE
ON
OFF
RX1
RX2
RX3
RX4
TX1
DET
TX2
DET
PA2
IN
RX1
RX2
RX3
RX4
PA1
IN
ANT
DIV
ANT
MAIN
PWR
FLT
ON LINE
ON
OFF
RX1
RX2
RX3
RX4
TX1
DET
TX2
DET
PA2
IN
RX1
RX2
RX3
RX4
PA1
IN
ANT
DIV
ANT
MAIN
PWR
FLT
ON LINE
ON
OFF
RX1
RX2
RX3
RX4
TX1
DET
TX2
DET
PA2
IN
RX1
RX2
RX3
RX4
IW132601
PWR
DET
IN
ON LINE
FLT
RX-B
RX-A
13 MHZ
CLK
TX
OUT
PWR
DET
IN
ON LINE
FLT
RX-B
RX-A
13 MHZ
CLK
TX
OUT
PWR
DET
IN
ON LINE
FLT
RX-B
RX-A
13 MHZ
CLK
TX
OUT
PWR
DET
IN
ON LINE
FLT
RX-B
RX-A
13 MHZ
CLK
TX
OUT
PWR
DET
IN
ON LINE
FLT
RX-B
RX-A
13 MHZ
CLK
TX
OUT
PWR
DET
IN
ON LINE
FLT
RX-B
RX-A
13 MHZ
CLK
TX
OUT
ONLINE
PWR
FLT
SCN
CON
ENET
IIIIIIIIIIIIIIIIIIIIIIIII
P/N XXXXXX
IIIIIIIIIIIIIIIIIIIIIIIII
S/N XXXXXX
I2C
ON
LINE
FLT
PWR
PORT 1
12
PORT 0
12
ALARMS
ALARMS
IIIIIIIIIIIIIIIIIIIIIIIII
P/N XXXXXX
IIIIIIIIIIIIIIIIIIIIIIIII
S/N XXXXXX
120 OHM
01234567
ABC
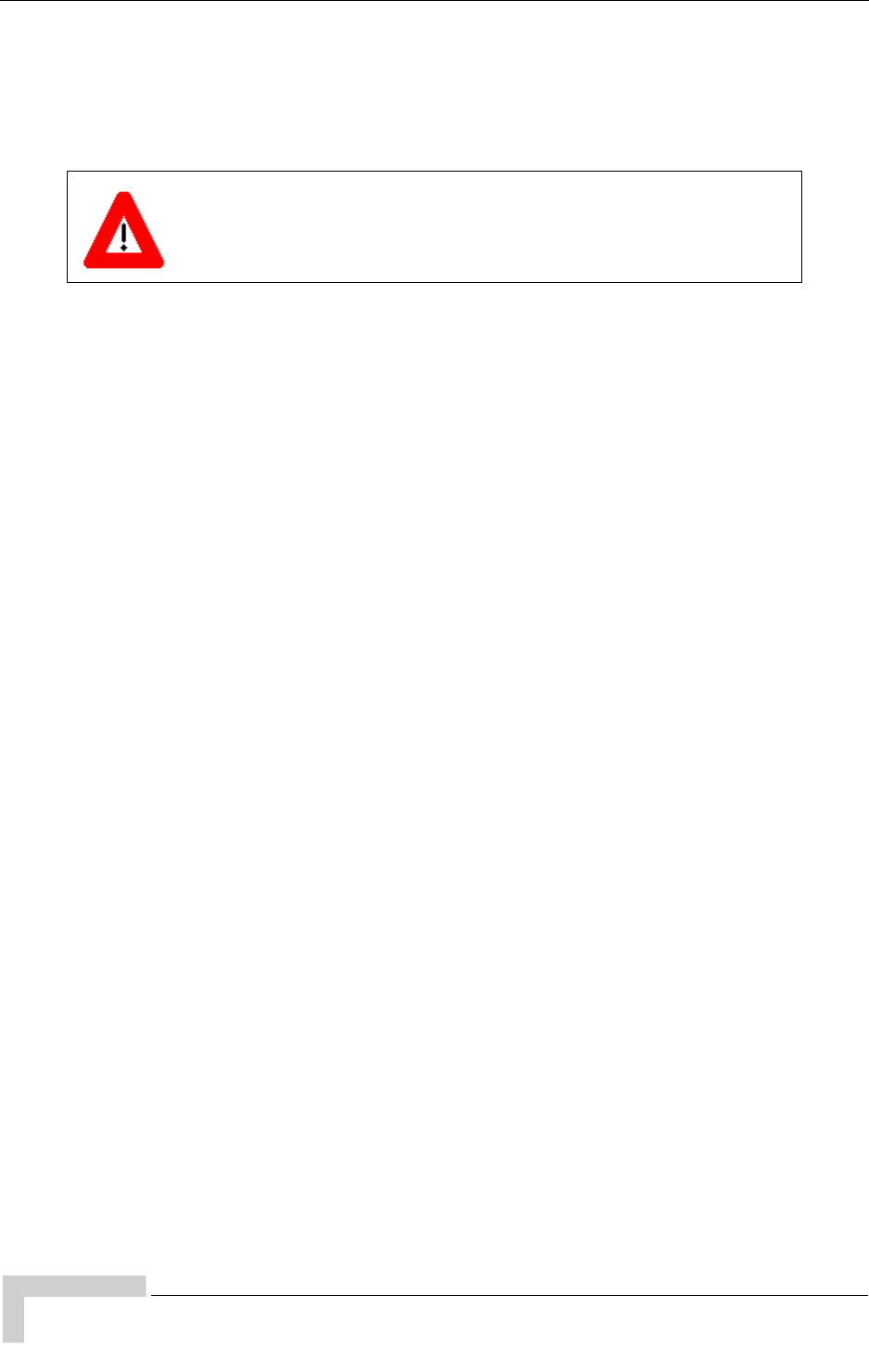
72 UltraWAVE Micro BTS Installation and Commissioning Guide, Version B
Chapter 3 - Off-Line Commissioning
If you get an error message, or if the XWindows environment does not allow
you to create new XWindows, stop the Craft PC environment by pressing
[ALT-F4] and restart the environment.
The XWindows environment now starts.
3.2.2 Connecting the Craft PC to the ICP Processor
Card
You will be making two connections from the Craft PC to the ICP processor card.
The first is a slow-speed serial connection used for checking the software version
installed on the card, verifying boot parameters and monitoring test results. The
second is a faster Ethernet connection used for opening telnet sessions with the
ICP. Telnet sessions are required for downloading software to the ICP. The serial
and Ethernet connections are both required to configure and test the Micro BTS.
Required Hardware
The following hardware is required to connect the Craft PC to the ICP processor
card through an Ethernet and serial connection. Note that this hardware is
supplied with the Craft PC:
One Windows 2000, NT or XP compatible Ethernet port
One 3 meter standard RJ-11 patch cable
One 3 meter standard Ethernet crossover cable
One RJ-11 to DB-9 adapter
Before starting, set the xterm window to its maximum width. This
prevents wordwrap.

UltraWAVE Micro BTS Installation and Commissioning Guide, Version B 73
Off-Line Commissioning of the Micro BTS
3.2.3 Setting Up a Serial Connection via the ICP
Processor Card Serial Port
1Connect one end of the RJ-11 patch cable to ICP processor card connector
labeled CON.
2Connect the opposite end of the RJ-11 patch cable to the DB-9 adapter and
connect the DB-9 adapter to the serial port on the back of the Craft PC, as
shown in the Figure 3-2.
Figure 3-2 shows a physical serial port connection between the Craft PC and the
ICP processor card.
Figure 3-2: Connecting the Craft PC to the ICP Serial Port
In order to establish a serial connection between the Craft PC
and the Micro BTS, there cannot be an existing telnet or rlogin
connection on the Micro BTS. In the case where a user using the
Craft PC tries to establish a connection locally and a user using
the OMC tries to establish a connection remotely, the remote
user has priority access to the Micro BTS over the local user.
IW043301
ON/LINE
PORT 1
12
PORT 0
12
ALARMS
FLT
PWR
ALARMS
Craft PC
computer
Serial Port
RJ-11 Patch Cable
RJ-11 to DB-9
Adapter
IIIIIIIIIIIIIIIIIIIIIIIII
P/N XXXXXX
ONLINE
PWR
FLT
SCN
RST
CON
ENET
IIIIIIIIIIIIIIIIIIIIIIIII
S/N XXXXXX
I2C

74 UltraWAVE Micro BTS Installation and Commissioning Guide, Version B
Chapter 3 - Off-Line Commissioning
1If not already done, connect the Craft PC to the Micro BTS as described in
Section 3.2.3, and start XWindows on the Craft PC as described in
Section 3.2.1.
2There are two methods to open a serial connection. You can use Hyper
Terminal or open the serial session in the Craft PC environment.
To use Hyper Terminal:
ALaunch the application by navigating: Start -> Programs ->
Accessories -> Communications -> Hyper Terminal
BEnter CraftPC for the connection name and select an icon. Then click the
OK button.
CThe Connect To dialog box displays. You select COM1 from the Connect
using drop-down list and click the OK button. If you know that your serial
port is configured on a different port, select that port from this drop-down
list.
DThe COM1 Properties dialog box displays. Set the following properties and
then click the OK button. See Figure 3-3.
Bits per second: 9600
Data bits: 8
Parity: None
Stop bits: 1
Flow control: None
The following section describes procedures performed using the
Craft PC. For more information pertaining to the use of the Craft
PC, please refer to the GSM Craft PC Guide.
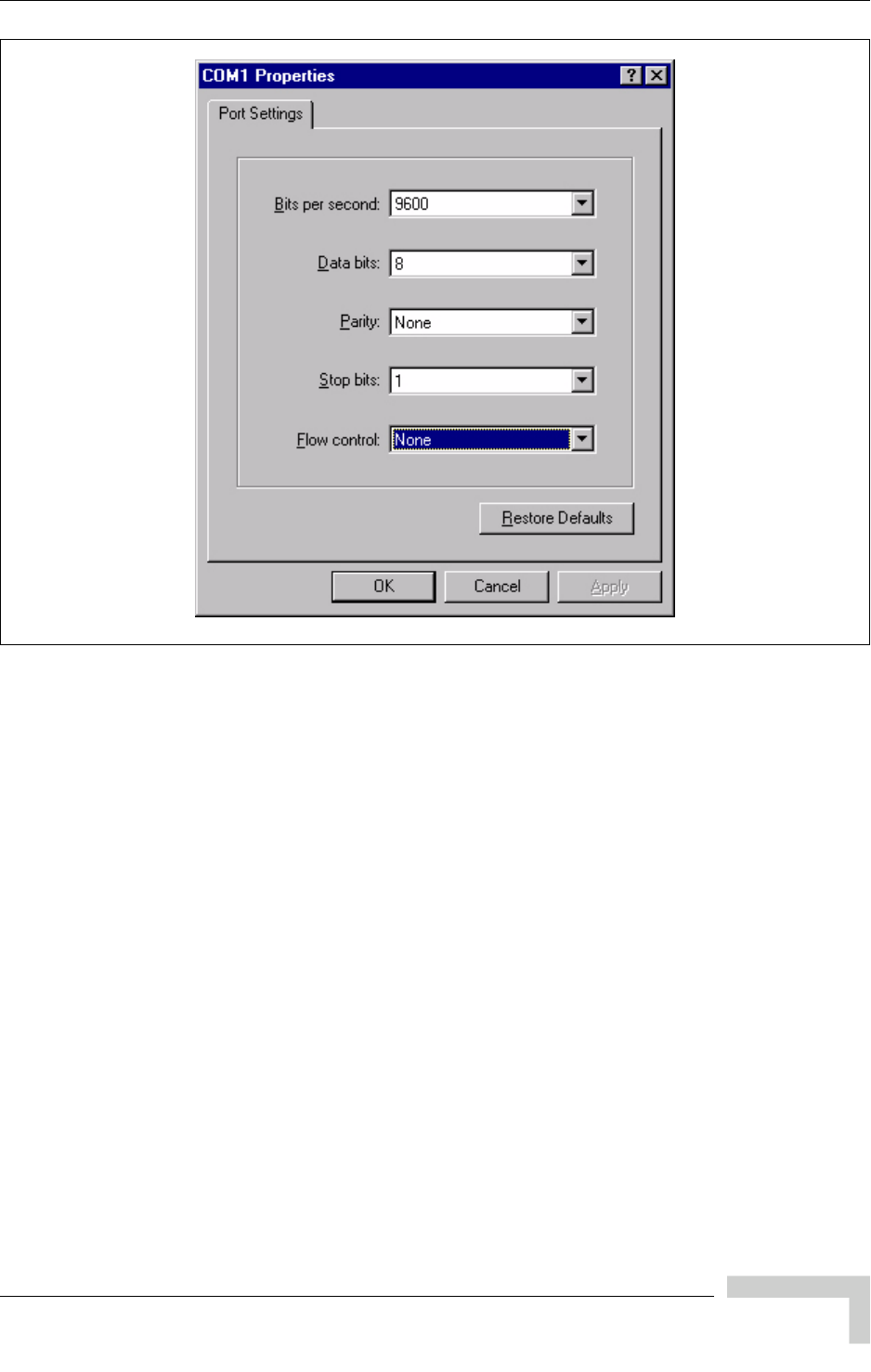
UltraWAVE Micro BTS Installation and Commissioning Guide, Version B 75
Off-Line Commissioning of the Micro BTS
ESelect OK to connect to the processor card. At this time, you will not see a
prompt. Proceed to Section 3.2.4 to power on the chassis.
If you do not have the Hyper Terminal application, you can open a serial
session in the Craft PC application. In an Xterm window, type:
build@craftpc:~> cu -l ttyS0 [ENTER]
Connected.
Figure 3-3: Serial Session Properties

76 UltraWAVE Micro BTS Installation and Commissioning Guide, Version B
Chapter 3 - Off-Line Commissioning
3.2.4 Power-On LED Tests
This section describes how to power-on the Micro BTS and verify that the cards in
the system come up properly by viewing the Light Emitting Diodes (LEDs) on the
front panel. The purpose of these tests is to verify that the LEDs come up in the
correct state, indicating that the system is operating normally.
When you power-on the Micro BTS, it automatically runs its power on self tests
(POST), downloads software to the E1 or T1 cards, and then attempts to bring up
the cards. While it is bringing up the cards and when it is finished, the LEDs
indicate the state of each card.
Use the following procedure to power on the chassis and verify the LEDs:
1Turn the power to the chassis on by simultaneously switching on two power
supplies. The power supply switches are shown in Figure 2-13 and
Figure 2-16. This will share the start up load across the power supplies.
2Verify that the front-panel LEDs flash in the sequence shown in Figure 3-4.
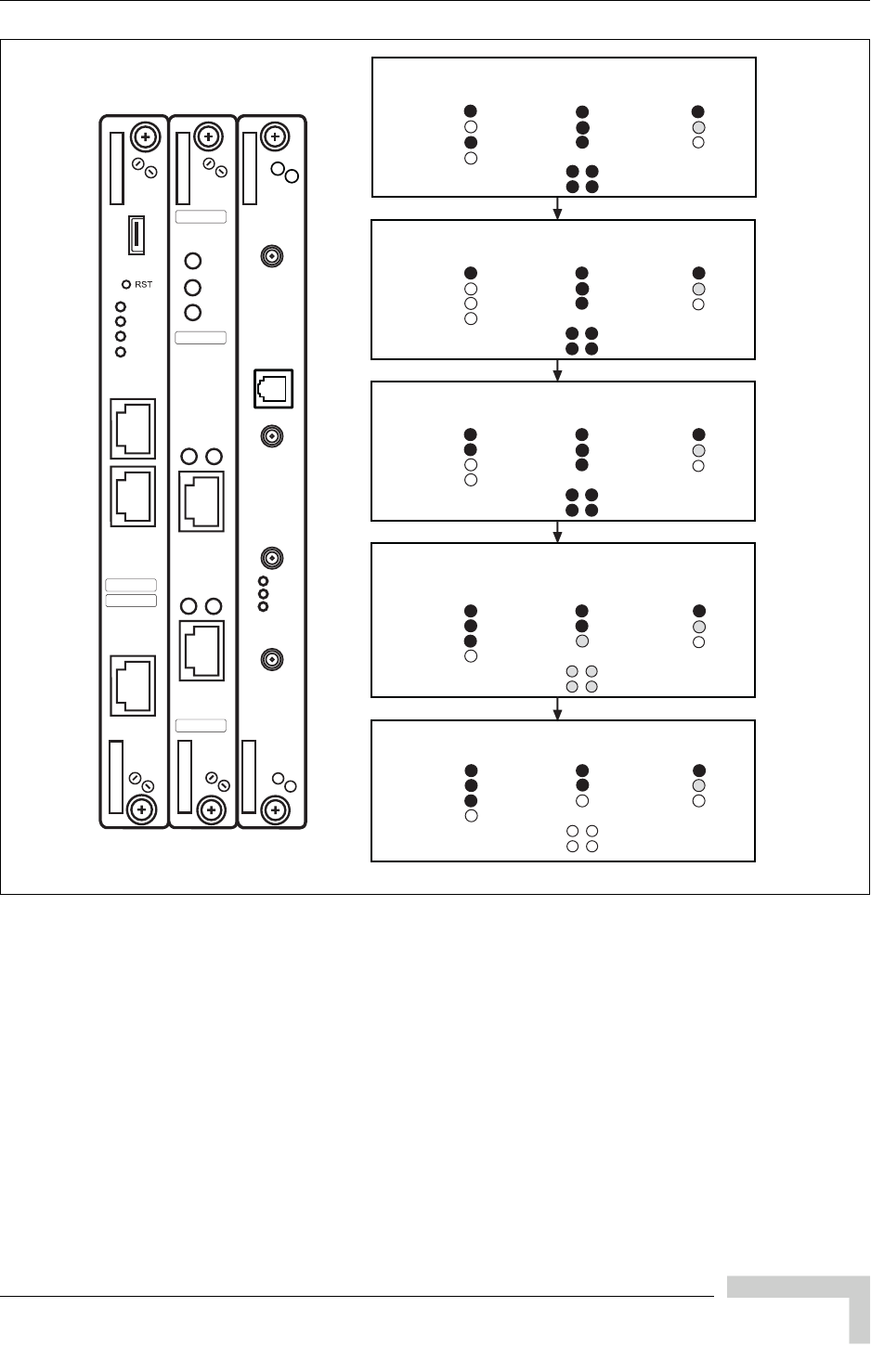
UltraWAVE Micro BTS Installation and Commissioning Guide, Version B 77
Off-Line Commissioning of the Micro BTS
Figure 3-4: LED Sequence During the Boot Process
ICP E1/T1 TRX
Power on BTS. Initial LED display is:
ICP E1/T1LEDs
SCN
PWR
ON LINE
FLT
PORT 0
PORT 1
OFF
ON
ON
N/A
N/A
N/A
ON
ON
ON
ON
ON
LED display after 50 seconds is:
ICP E1/T1LEDs
SCN
PWR
ON LINE
FLT
PORT 0
PORT 1
ON
N/A
OFF
N/A
N/A
ON
ON
ON
ON
ON
ICP code loads. LED display during download at 1:20:
ICP E1/T1LEDs
SCN
PWR
ON LINE
FLT
PORT 0
PORT 1
ON
ON
N/A
N/A
N/A
ON
ON
ON
ON
ON
OFF
ICP downloads code to E1 or T1 card. LED display
(at 2:45) during download is:
ICP E1/T1LEDs
SCN
PWR
ON LINE
FLT
PORT 0
PORT 1
ON
ON
N/A
N/A
N/A
ON
OFF
ON
IW022303
TRX
N/A
ON
N/A
N/A
TRX
N/A
ON
N/A
N/A
TRX
N/A
ON
N/A
N/A
TRX
N/A
ON
N/A
N/A
Final LED display at 3 minutes is:
ICP E1/T1LEDs
SCN
PWR
ON LINE
FLT
PORT 0
PORT 1
ON
ON
N/A
N/A
N/A
ON
OFF
OFF
OFF
ON
FLASH
TRX
N/A
ON
OFF
N/A
N/A
ON
OFF
OFF
OFF
OFF
ON
PWR
DET
IN
ON LINE
FLT
RX-B
RX-A
13 MHZ
CLK
TX
OUT
ON
LINE
FLT
PWR
PORT 1
12
PORT 0
12
ALARMS
ALARMS
IIIIIIIIIIIIIIIIIIIIIIIII
P/N XXXXXX
IIIIIIIIIIIIIIIIIIIIIIIII
S/N XXXXXX
120 OHM
ONLINE
PWR
FLT
SCN
CON
ENET
IIIIIIIIIIIIIIIIIIIIIIIII
P/N XXXXXX
IIIIIIIIIIIIIIIIIIIIIIIII
S/N XXXXXX
I2C
OFF
FLASH
OFF
FLASH
OFF
FLASH
OFF
FLASH
OFF
FLASH
FLASH
FLASH
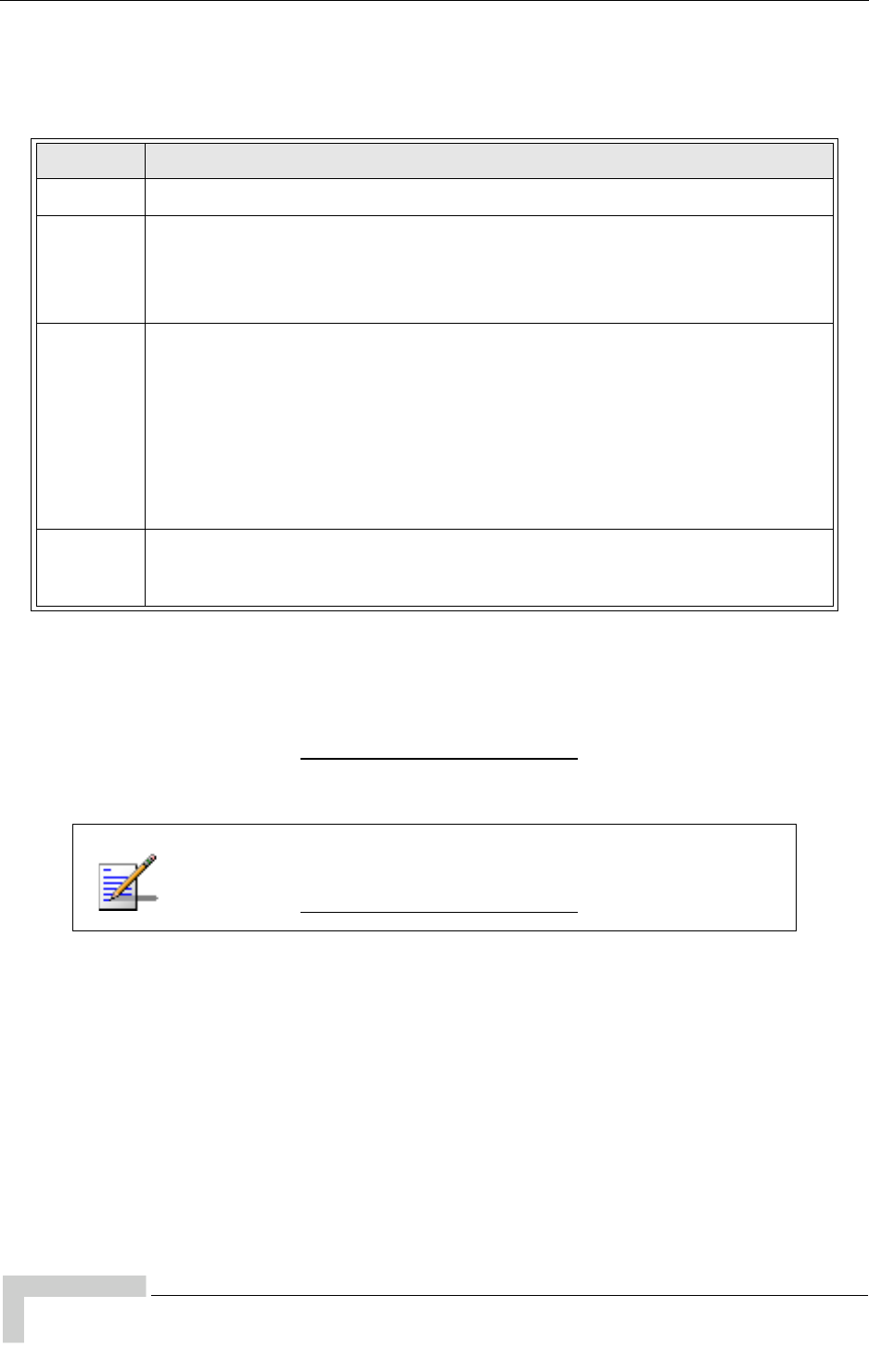
78 UltraWAVE Micro BTS Installation and Commissioning Guide, Version B
Chapter 3 - Off-Line Commissioning
3When the sequence is completed, verify that the LEDs appear as shown in
Table 3-1.
4If your LEDs appear as described above, you have completed the LED power
up tests.
5If your LEDs do not appear as described above, you can either:
Refer to the GSM Field Maintenance Guide for troubleshooting procedures
Contact Customer Service
6You can monitor the status of the boot process using the serial session opened
in Section 3.2.3.
Once the LEDs on the processor cards have reached their final online status,
press the [ENTER] key. The prompt now changes to the following:
bts->
Table 3-1: Normal LED Indications
LED Description
SCN Green LED, lit when processor card is operational.
PWR
Green LED, lit when card has power supplied.
The PWR LED of the ICP and E1 or T1 cards will be lit after all cards have
completed the boot-up process.
ON LINE
Green LED, lit when card is on-line, and card BOOT process has been
performed successfully.
The On-LINE LED of the ICP and E1 or T1 cards will be lit after all cards
have completed the boot-up process.
The TRX cards will not go on-line until they are unlocked by the OMC
operator.
FLT
Red LED, lit when card detects a fault or is not downloaded.
FLT LEDs will be lit on the TRX cards until their code is downloaded.
For more information about these unsuccessful power-up cases
and corrective actions to be taken upon unsuccessful power up,
refer to the GSM Field Maintenance Guide.
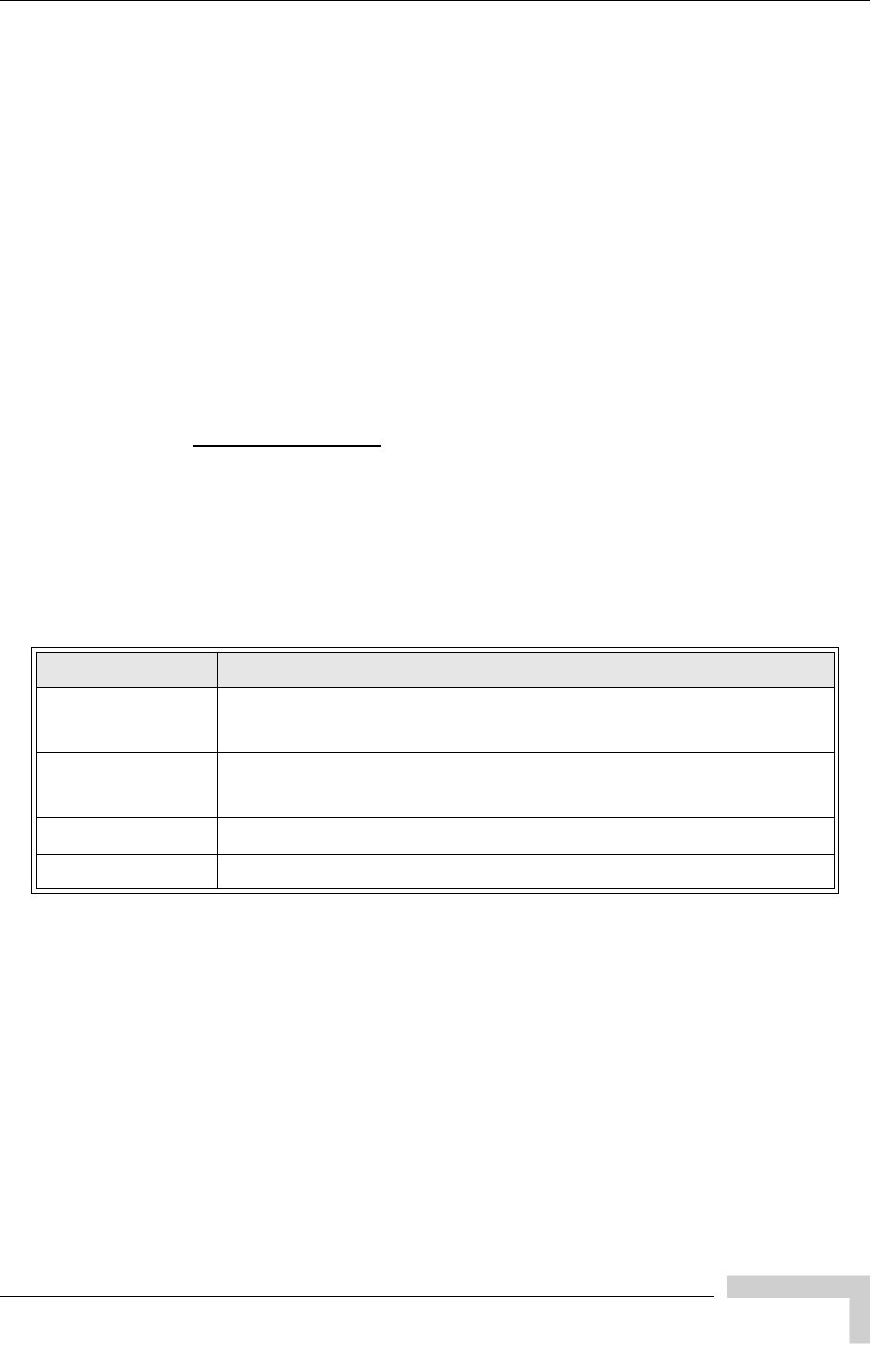
UltraWAVE Micro BTS Installation and Commissioning Guide, Version B 79
Off-Line Commissioning of the Micro BTS
3.2.5 Configuring Boot Parameters
In this section, you verify the boot parameters and change them if necessary.
There are two reasons to change boot parameters:
If they are configured incorrectly, you must set them to the values shown here.
If your system is connected to the Ethernet, you must set the IP address to
support the Craft PC IP address 172.16.80.43. To make a connection with the
Craft PC, set the processor card IP address to 172.16.80.42:fffff000.
After changing the boot parameters, the Micro BTS must be rebooted before the
changes take effect.
1If not already done, establish serial communications with the Micro BTS as
described in Section 3.2.3. If the Micro BTS starts rebooting endlessly, refer to
the GSM Craft PC Guide for corrective measures. If the Micro BTS boots
normally, type:
bts-> bootChange [ENTER]
2A list of boot parameters appears. Edit the parameter values using the
commands in Table 3-2.
Figure 3-5 shows the default bootChange parameters for the ICP processor card.
Table 3-2: Changing Boot Parameters
Command Action
[ENTER] Accepts the current parameter value and proceeds to the next
parameter.
. [ENTER] Erases the current parameter value and proceeds to the next
parameter.
- [ENTER] Returns to the previous parameter.
[CTRL][d] Aborts all changes and reverts to the current values.
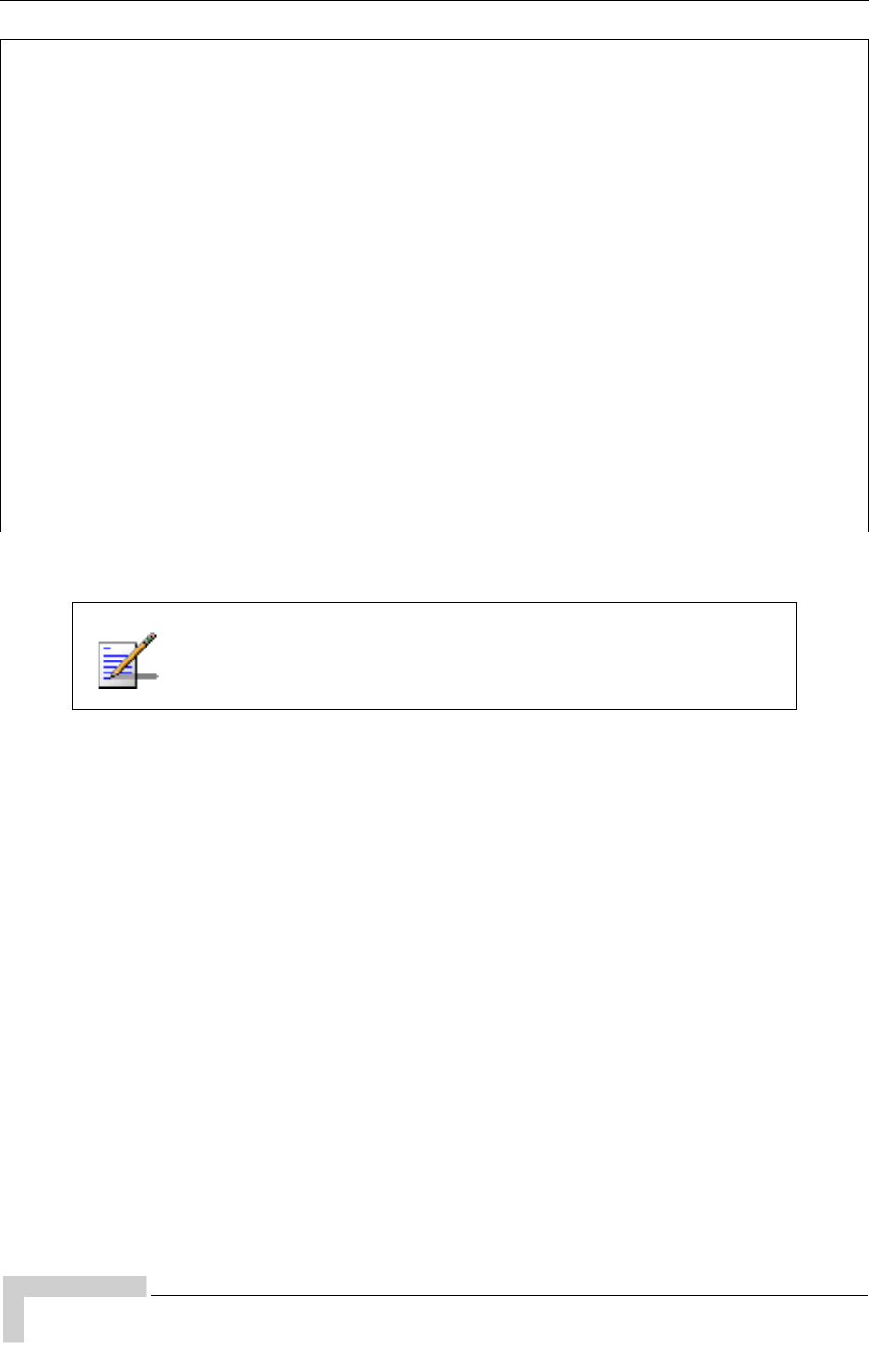
80 UltraWAVE Micro BTS Installation and Commissioning Guide, Version B
Chapter 3 - Off-Line Commissioning
3For the new parameters to take effect, reboot the Micro BTS by pressing the
key combination [CTRL][x].
'.' = clear field; '-' = go to previous field; ^D = quit
boot device : motfcc
processor number : 0
host name : craftpc
file name : /home/target/vxWorks
inet on ethernet (e) : 172.16.80.42:fffff000
inet on backplane (b):
host inet (h) : 172.16.80.43
gateway inet (g) :
user (u) : target
ftp password (pw) (blank = use rsh):
flags (f) : 0x0
target name (tn) : bts
startup script (s) : /home/target/bsxstart.ppc
other (o) : motfcc
value = 0 = 0x0
bts->
Figure 3-5: Boot Parameters for ICP Processor Card
You must edit the boot parameters to contain EXACT values, or
the equipment will not bootup properly.
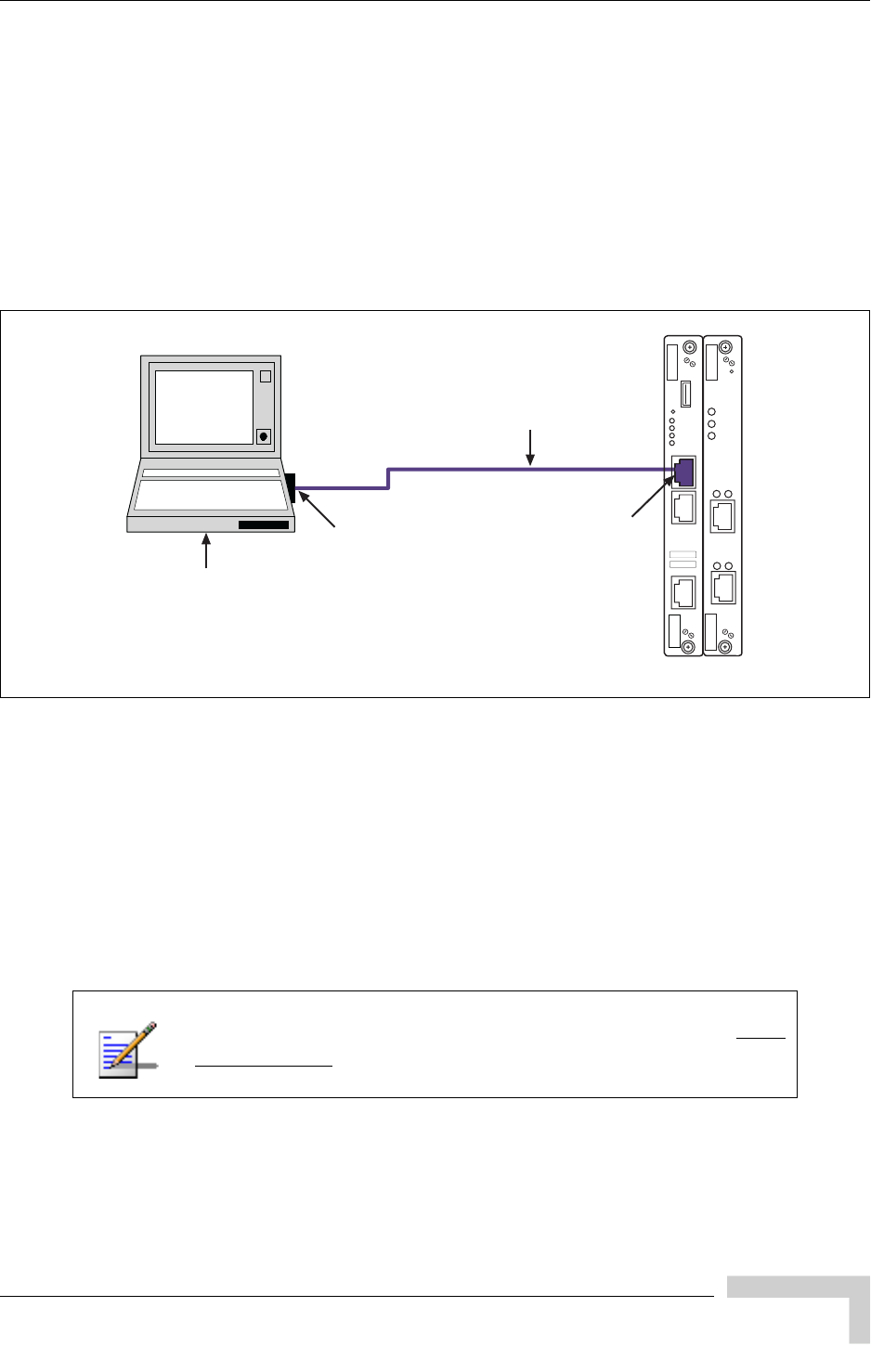
UltraWAVE Micro BTS Installation and Commissioning Guide, Version B 81
Off-Line Commissioning of the Micro BTS
3.2.6 Setting Up an Ethernet Connection to the ICP
Processor Card Ethernet Port
1Connect the Ethernet crossover cable to the ICP processor card Ethernet port
labeled ENET.
2Connect the other end of the cable to the Ethernet port on the Craft PC.
Figure 3-6 shows a typical Ethernet port connection between the Craft PC and the
ICP processor card.
3.2.7 Verifying Telnet Communications with the
Micro BTS over Ethernet
The Craft PC uses telnet communications across the Ethernet connection for code
downloads. Before performing any of the following procedures, ensure that you
can establish and terminate a telnet communications session as described in the
following procedures.
Figure 3-6: Connection to the Craft PC via the ICP Ethernet Port
For more information about the Craft PC, please refer to the GSM
Craft PC Guide.
IE069401
Ethernet
Port
RJ-45 Ethernet
Crossover cable
Craft PC
ON/LINE
PORT 1
12
PORT 0
12
ALARMS
FLT
PWR
ALARMS
IIIIIIIIIIIIIIIIIIIIIIIII
P/N XXXXXX
ONLINE
PWR
FLT
SCN
RST
CON
ENET
IIIIIIIIIIIIIIIIIIIIIIIII
S/N XXXXXX
PCMCIA Card Slot
or
Ethernet Port

82 UltraWAVE Micro BTS Installation and Commissioning Guide, Version B
Chapter 3 - Off-Line Commissioning
Establishing a Telnet Communications Session over Ethernet
1Start a new Xterm window in the Craft PC environment.
2Establish a telnet communications session by typing:
build@craftpc:-> telnet iwbox [ENTER]
3The Craft PC prompt now changes to bts->. This prompt verifies that the
telnet session can be established. If this is not the case, verify the Ethernet
wiring and retry.
Terminating a Telnet Communications Session over Ethernet
After verifying that a telnet communications session can be established, terminate
the telnet session as follows.
1Activate the Xterm window in which the telnet communications session was
established.
2To terminate the telnet session, type in the Xterm window containing the
telnet session:
bts-> logout [ENTER]
3The return message should read Connection closed by foreign host and
the prompt changes back to build@craftpc->. The telnet session has now
been terminated.
If the Craft PC hangs when attempting to establish a telnet
session, press the key combination [CTRL][c] to abort the failed
connection. Check the boot parameters and repeat the
connection procedures. Also verify that the Craft PC host table
contains the hostname of your equipment in reference to the
default IP address.
Once a telnet session has been established between the Craft PC
and the processor card, it must be terminated before the Craft PC
is powered off. Failure to do this will result in a hung
connection on the BSS system.

UltraWAVE Micro BTS Installation and Commissioning Guide, Version B 83
Software Verification using Craft PC
3.3 Software Verification using Craft PC
In this section, you use the Craft PC to verify the software configuration and other
aspects of the Micro BTS operation. It is assumed that you have:
Made the physical Craft PC connections to the processor card
An active serial session
3.3.1 Verifying the Current Software Version and
Patch Level
1If not already done, establish serial communications with the Micro BTS as
described in Section 3.2.3.
2After the bts-> prompt appears, verify the current software version and patch
level by typing:
bts-> iwversion [ENTER]
BTS code version: iw07_00.ZZZ
Release number: 7.0
ABIS version: 1.1
Packages Installed:
Encryption: A5/1
Patches Installed:
patch<#> <file directory> <patch size> <iw07_00.ZZZ>
The current software version is displayed, represented above by the parameter
iw07_00.ZZZ. This number should correspond to the software version detailed
in the release notes included with the CD-ROM. Keep this number for your
records.
3Verify under Patches Installed: that the most current patch is installed, if
applicable. Refer to the GSM Craft PC Guide for procedures to install required
patches. If you are unsure if you require software patches, contact your
Level 2 support representative for additional assistance.
The following section describes procedures performed using the
Craft PC. For more information about the Craft PC, refer to the
GSM Craft PC Guide.
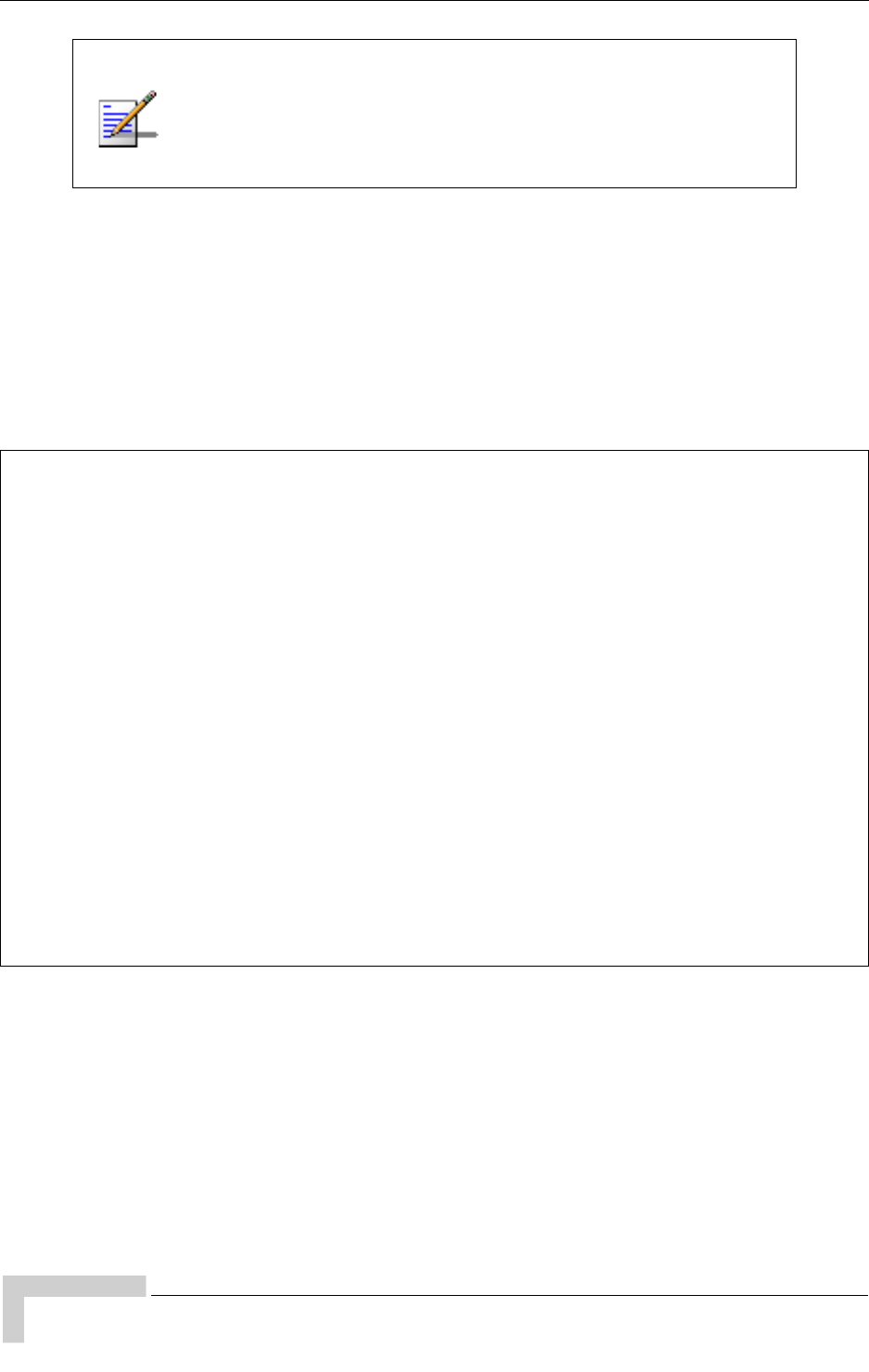
84 UltraWAVE Micro BTS Installation and Commissioning Guide, Version B
Chapter 3 - Off-Line Commissioning
3.3.2 Checking the Flash Version Number
In order to verify that the correct software build is loaded into flash memory, go to
your serial Xterm window and type:
bts-> printConfigBlocks [ENTER]
The screen displays information relating to the flash images. Figure 3-7 shows
Image 0, Image 1 and Image 2 from the ICP card configuration.
The ICP configuration states Current Image = N where N is either 0 or 1. The
flash version have lines in the format:
iw07_00.ZZZ
where iw07_00.ZZZ indicates the flash version.
If the displayed software version number does not coincide with
the software version being run on the network for which this
Micro BTS is going to be used, refer to Section 3.4 for
instructions on how to install a different software version on the
processor card.
**** Current Image = 1 ****
******** Image 0 *********
Image IW version : iw07_00.010
Image creation date: 04/15/02 13:44
Image crc : 1ff03d8d
******** Image 1 *********
Image IW version : iw7_00.012
Image creation date: 04/09/02 12:07
Image crc : e3b05e8c
******** Image 2 *********
Image IW version : iw07_00.010
Image creation date: 04/09/02 12:07
Image crc : e3b05e8c
Figure 3-7: Determining the Flash Version on an ICP Processor Card

UltraWAVE Micro BTS Installation and Commissioning Guide, Version B 85
Software Verification using Craft PC
The flash version number should be iw07_00.012 or higher for BTS TRX POST
diagnostics to be able to run. If it is not, the flash version number will have to be
changed and the Micro BTS rebooted.
3.3.3 Running E1 or T1 POST Diagnostics
1Disconnect all E1 and/or T1 lines from the BTS. This ensures that no Abis
connection exists. If an Abis connection does exist, the TRX POST might not
run properly.
2Wait until the bts-> prompt appears, and type:
bts-> reboot [ENTER]
This action reboots the Micro BTS. The VxWorks kernel is started, several E1
or T1 trunk card tests run sequentially, and the results of each test are listed
as PASSED/FAILED. Only if all seven tests passed successfully will the E1 or
T1 POST diagnostics be considered successful. The E1 or T1 POST results will
be displayed after the boot process has been completed.
Flash Image 2 is reserved for Alvarion Customer Service use
ONLY.
The coding for the E1 or T1 trunk card, its modules and scripts
generically refer to the E1 or T1 trunk card objects as “E1”,
whether the corresponding ports are configured as E1 or T1.
1 (e1diag) E1 CARD in SLOT 1: STARTING POST/OFFLINE Test
2 (e1diag) testsPtr 0xffb33ab4 testsPtr[0] 0x5
3 (e1diag) testsPtr 0xffb33ab4 testsPtr[0] 0x5 result 0x0 i 1
4 (e1diag) E1(1) TID01: Initialize Peripheral Registers: PASSED
5 (e1diag) testsPtr 0xffb33ab4 testsPtr[0] 0x5 result 0x0 i 2
6 (e1diag) E1(1) TID02: Peripheral Register Test: PASSED
7 (e1diag) testsPtr 0xffb33ab4 testsPtr[0] 0x5 result 0x0 i 3
8 (e1diag) E1(1) TID03: Framer Register Test: PASSED
9 (e1diag) testsPtr 0xffb33ab4 testsPtr[0] 0x5 result 0x0 i 4
10 (e1diag) E1(1) TID04: VME to CPU FIFO Flag Test: PASSED
11 (e1diag) testsPtr 0xffb33ab4 testsPtr[0] 0x5 result 0x0 i 5
12 (e1diag) E1(1) TID05: Initialize Time/Space sw Chip: PASSED
13 (e1diag) testsPtr 0xffb33ab4 testsPtr[0] 0x5 i 6
14 (e1diag) E1 CARD in SLOT 1: COMPLETED POST/OFFLINE Test: PASSED
Figure 3-8: E1 or T1 POST Results
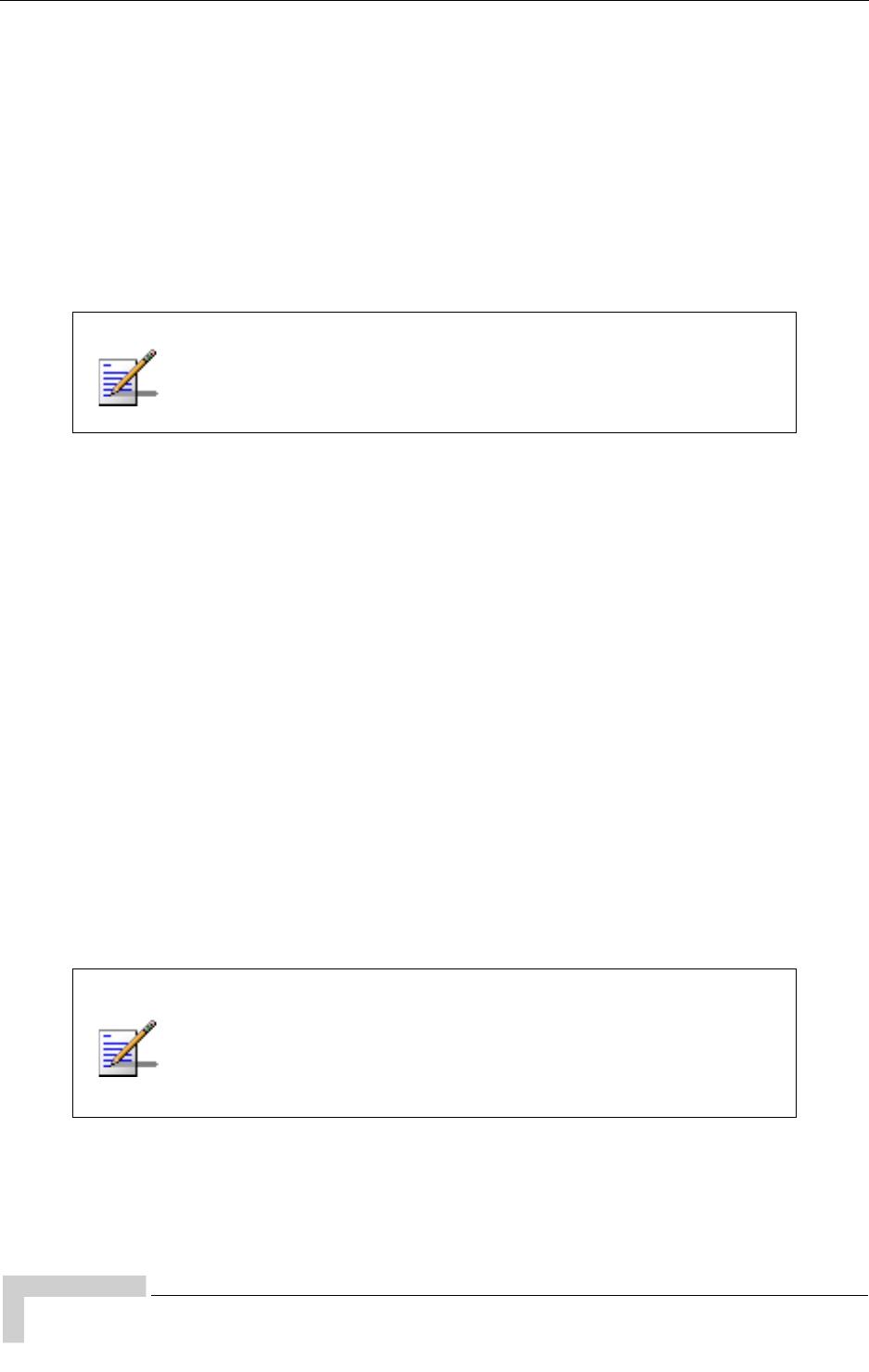
86 UltraWAVE Micro BTS Installation and Commissioning Guide, Version B
Chapter 3 - Off-Line Commissioning
3Figure 3-8 shows the E1 or T1 POST results that would appear if the E1 or T1
POST diagnostics ran successfully on the E1 or T1 trunk card in slot 1. The
format for each diagnostic line is:
[line number][action][E1 or T1 number][test number][test
description][test result]
In the case of an error, a FAILED message would appear following the test that
failed. In addition, the following message would be displayed in Line 8:
E1 CARD in SLOT 1: COMPLETED POST/OFFLINE Test: FAILED
3.3.4 Running TRX POST Diagnostics
This section explains how to use the Craft PC to run the TRX POST diagnostics on
the Micro BTS.
1Verify that you can establish and terminate a telnet communications session
as described in Section 3.2.7.
2Verify that you can establish a serial connection as described in Section 3.2.3.
3After the Micro BTS has booted up and the E1 or T1 POST has run during the
boot process, the TRX POST diagnostics can be initiated. Type:
bts-> runtrxpost [ENTER]
4A set of TRX POST diagnostic tests run sequentially over the Ethernet connec-
tion and the results of each test will be listed as PASSED/FAILED. Only if all
tests pass successfully will the TRX POST diagnostics be considered
successful. The TRX POST results will be displayed after the boot process has
been completed.
If an E1 or T1 trunk card fails the POST diagnostics, remove the
failed card and return it to Alvarion along with its test results file.
The defective card needs to be replaced with a new one, and
POST diagnostics should be run again on the new card.
The TRX ON LINE LED flashes continuously when TRX POST
diagnostics are being run and does not stop flashing until the
Micro BTS is rebooted. The flashing LED can be used as a
reminder to reboot the system after successfully completing the
TRX POST and other diagnostics.

UltraWAVE Micro BTS Installation and Commissioning Guide, Version B 87
Software Verification using Craft PC
The format for each diagnostic line is:
[line number][action][TRX number][test number][test description]
[test result]
For example:
14 (Diag) ISR(2) TF22: Test Basic op of VME/RTP FIFOs: PASSED
where:
Figure 3-9 shows the TRX POST results for a TRX in slot 2 of the Micro BTS and
shows that the TRX POST diagnostics ran successfully on the TRX card.
Table 3-3: Description of the TRX POST Results
Line Entry Description
14 Line number
Diag Diagnostic test being run
ISR(2) ISR TRX 2 is being tested
TF22 Test number
Test Basic op of VME/RTP FIFOs Test description
PASSED Indicates that the TRX passed this test
SerialNumber: 16 (txpostf) STARTING BTS FUNCTIONAL CODE...
a3 a8 0 0 1 0 20 4a
SerialNumber: a3 28 0 0 1 0 20 a0
SerialNumber: a3 2d 0 0 1 0 20 4b
SerialNumber: a3 50 1 0 1 0 20 54
SerialNumber: a3 95 0 0 1 0 20 ed
SerialNumber: a3 a9 0 0 1 0 20 7d
17 (Diag ) TRX CARD IN SLOT 2 : STARTING TRX POST OFFLINE Test
18 (Diag ) ISR(2) tf 5 Test VME Access ....................... PASSED
19 (Diag ) ISR(2) tf 12 Load FPGA (TDM) ....................... PASSED
20 (Diag ) ISR(2) tf 13 Load FPGA (RC) ........................ PASSED
21 (Diag ) ISR(2) tf 16 Load DSP (Coder) ...................... PASSED
22 (Diag ) ISR(2) tf 17 Load DSP (Equalizer) .................. PASSED
23 (Diag ) ISR(2) tf 18 Load DSP (Modulator) .................. PASSED
24 (Diag ) ISR(2) tf 19 Ping DSP (Coder) ...................... PASSED
25 (Diag ) ISR(2) tf 20 Ping DSP (Equalizer) .................. PASSED
26 (Diag ) ISR(2) tf 46 Ping DSP (Modulator) .................. PASSED
27 (Diag ) ISR(2) tf 22 DSP Diag Mode ON (Coder) .............. PASSED
28 (Diag ) ISR(2) tf 27 Test External RAM (Coder) ............. PASSED
29 (Diag ) ISR(2) tf 24 DSP Diag Mode ON (Equalizer) .......... PASSED
30 (Diag ) ISR(2) tf 28 Test External RAM (Equalizer) ......... PASSED
31 (Diag ) ISR(2) tf 47 Test Mdltr DSP Serial Bus loopback .... PASSED
32 (Diag ) ISR(2) tf 30 Test TDM Control Store RAM ............ PASSED
33 (Diag ) ISR(2) tf 34vvvvvvvvvvvvTest TDM Loop-back .................... PASSED
34 (Diag ) ISR(2) tf 36 Test RC to Equalizer Serial Bus ....... PASSED
35 (Diag ) ISR(2) tf 39 Test Coder to RC Serial Bus ........... PASSED
36 (Diag ) ISR(2) tf 40 Test Equalizer To Coder Serial Bus .... PASSED
37 (Diag ) ISR(2) tf 43 Test Tuner Register Read/Write ........ PASSED
lowChannel = 128, highChannel = 251
38 (Diag ) ISR(2) tf 41 Test Channel Synthesizers ............. PASSED
39 (Diag ) ISR(2) tf 48 Test Power Ramp External RAM .......... PASSED
40 (Diag ) ISR CARD IN SLOT 2 : COMPLETED POST OFFLINE Test : PASSED
Figure 3-9: TRX POST Results
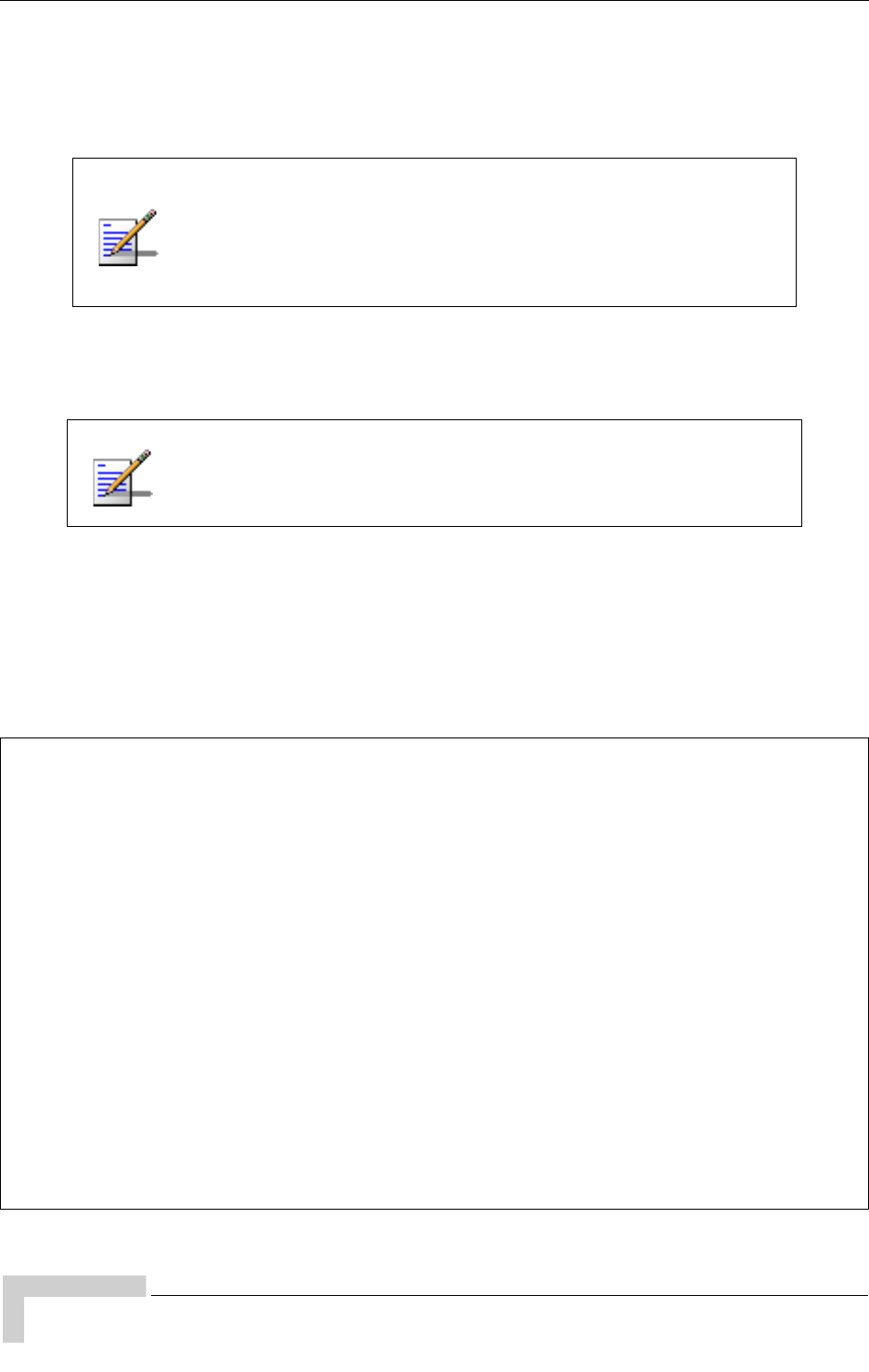
88 UltraWAVE Micro BTS Installation and Commissioning Guide, Version B
Chapter 3 - Off-Line Commissioning
3.3.5 Reviewing POST Results
This section explains how to review E1 or T1 POST and TRX POST diagnostics
results after POST has been completed on the Micro BTS.
1Turn on basic logging by typing:
bts-> log_none
2To display the most current E1 or T1 and TRX POST results after POST has
been completed, type:
bts-> postReportE1Trx [ENTER]
Figure 3-10 displays a summary of the E1 or T1 and TRX POST results that
will be displayed (note that some tests may not run).
The following procedure assumes that E1 or T1 and TRX POST
have just been completed on the selected Micro BTS and a serial
connection is still active between the Craft PC and the Micro
BTS. If this is not the case, reboot the Micro BTS and run POST
again.
This will result in extra output being displayed in the xterm,
subsequent commands entered may run into several lines as a
result of the extra logs.
bts:> postReportE1Trx
******************* E1 DIAGNOSTICS REPORT *******************
*************************************************************
Slot:1
E1(1)TID01: Initialize Peripheral Registers : PASS
E1(1)TID02: Peripheral Register Test : PASS
E1(1)TID03: Framer Register Test : PASS
E1(1)TID04: VME to CPU FIFO Flag Test : PASS
E1(1)TID05:Initialize Time/Space sw Chip : PASS
E1(1)TID06: Software Download Test : Not-Run
E1(1)TID07: Memory Test : Not-Run
E1(1)TID08: CPM download Test : Not-Run
E1(1)TID09: TRAU DSP Test : Not-Run
E1(1)TID10: Cross Connect Test : Not-Run
*************************************************************
******************* TRX DIAGNOSTICS REPORT ******************
*************************************************************
Slot 2
-------------------------------------------------------------
All Tests PASSED
*************************************************************
value=58=0x3a='=”
bts:>
Figure 3-10: Reviewing E1 or T1 and TRX POST Results
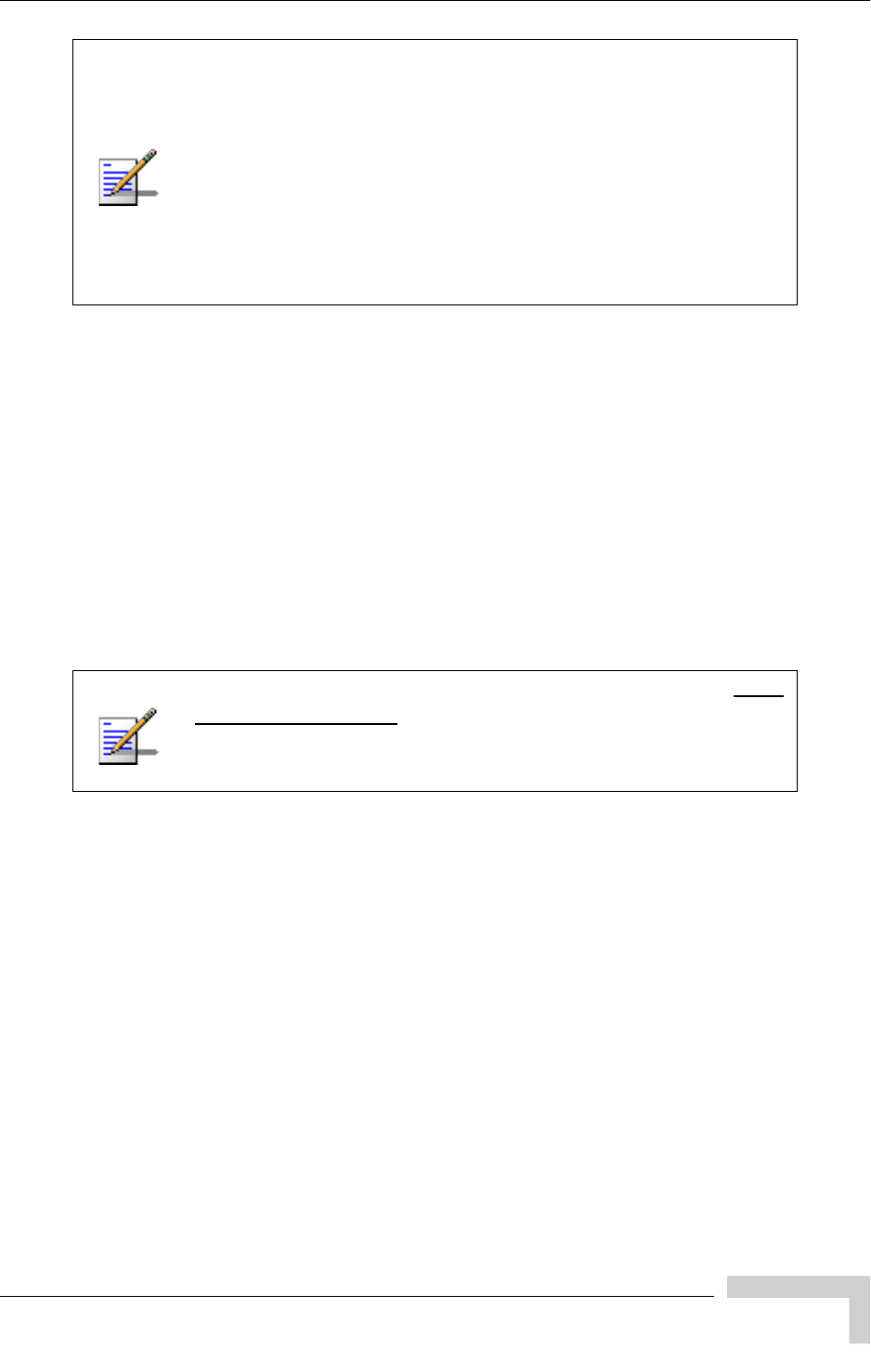
UltraWAVE Micro BTS Installation and Commissioning Guide, Version B 89
Software Verification using Craft PC
3.3.6 Rebooting the Micro BTS after Running POST
1In the serial communications window, type:
bts-> reboot [ENTER]
This action places the TRX in an on-line and operational state.
2Reconnect all E1 or T1 lines to the Micro BTS.
3.3.7 Terminating Serial Communications with the
Micro BTS
1To terminate the serial communications between the Craft PC and the BTS in
an xterm, type:
bts-> ~.
2After a few seconds the returned message should read Disconnected, and the
display will revert back to build@craftpc:-> prompt.
3Close the Hyper Terminal window if you are using Hyper Terminal for serial
communications.
3.3.8 Exiting XWindows on the Craft PC
This section explains how to close XWindows running the Windows 2000/XP
operating system on the Craft PC.
Left click the X in the upper right hand corner of your XWindows window.
There are five tests that are not run but show up in the results
section when the user manually retrieves the POST results.
These tests are not displayed when running POST by rebooting
the BTS. They are:
• T1(1) TID06: Software Download Test : Not-Run
• T1(1) TID07: Memory Test : Not-Run
• T1(1) TID08: CPM Download Test : Not-Run
• T1(1) TID09: TRAU DSP Test : Not-Run
• T1(1) TID10: Cross Connect Test : Not-Run
If you are going to perform the Racal tests described in the GSM
Radio Test Procedures at this time, ensure that you have
rebooted the chassis. Also, leave the Craft PC connected to the
ICP card and a serial communications session active.

90 UltraWAVE Micro BTS Installation and Commissioning Guide, Version B
Chapter 3 - Off-Line Commissioning
3.4 Upgrading the Micro BTS Software
Version (Flash)
Use this procedure if the procedures in Section 3.3.1 indicate that you need to
update your software version.
The Micro BTS stores its release software in Flash RAM. This section explains how
to upgrade the Micro BTS Flash boot image locally using the Craft PC.
1Power up the Craft PC and start the XWindows environment. For Craft PC
power-up procedures, refer to Section 3.2.2. For XWindows start-up
procedures, refer to Section 3.2.1.
2Verify that a telnet session can be established with the Micro BTS. In an Xterm
window, type:
build@craftpc:~> telnet iwbox [ENTER]
3If the Ethernet connection is setup correctly, then the Craft PC returns the
vxWorks bts-> prompt. If this is not the case, refer to Section 3.2.7 for setup
procedures.
4Once the Ethernet connection has been tested, terminate the telnet session by
typing:
bts-> logout [ENTER]
The Craft PC returns the build@craftpc:~> prompt.
5Establish a serial session with the Micro BTS. Refer to Section 3.2.3.
6Change the working directory to the directory containing the new software
version you wish to upgrade to the Micro BTS, type:
cd “/home/build/iw07_00.ZZZ/iwlib/platform/bspppc” [ENTER]
The iw07_00.ZZZ parameter represents the new software version you wish to
load on the Micro BTS.
In order to update the BTS Flash boot image locally using the
Craft PC, the Craft PC hard drive must contain the software
version (Flash boot image) to be installed.
If the required release is not installed on your Craft PC, use the
procedures in the GSM Craft PC Guide to install it.
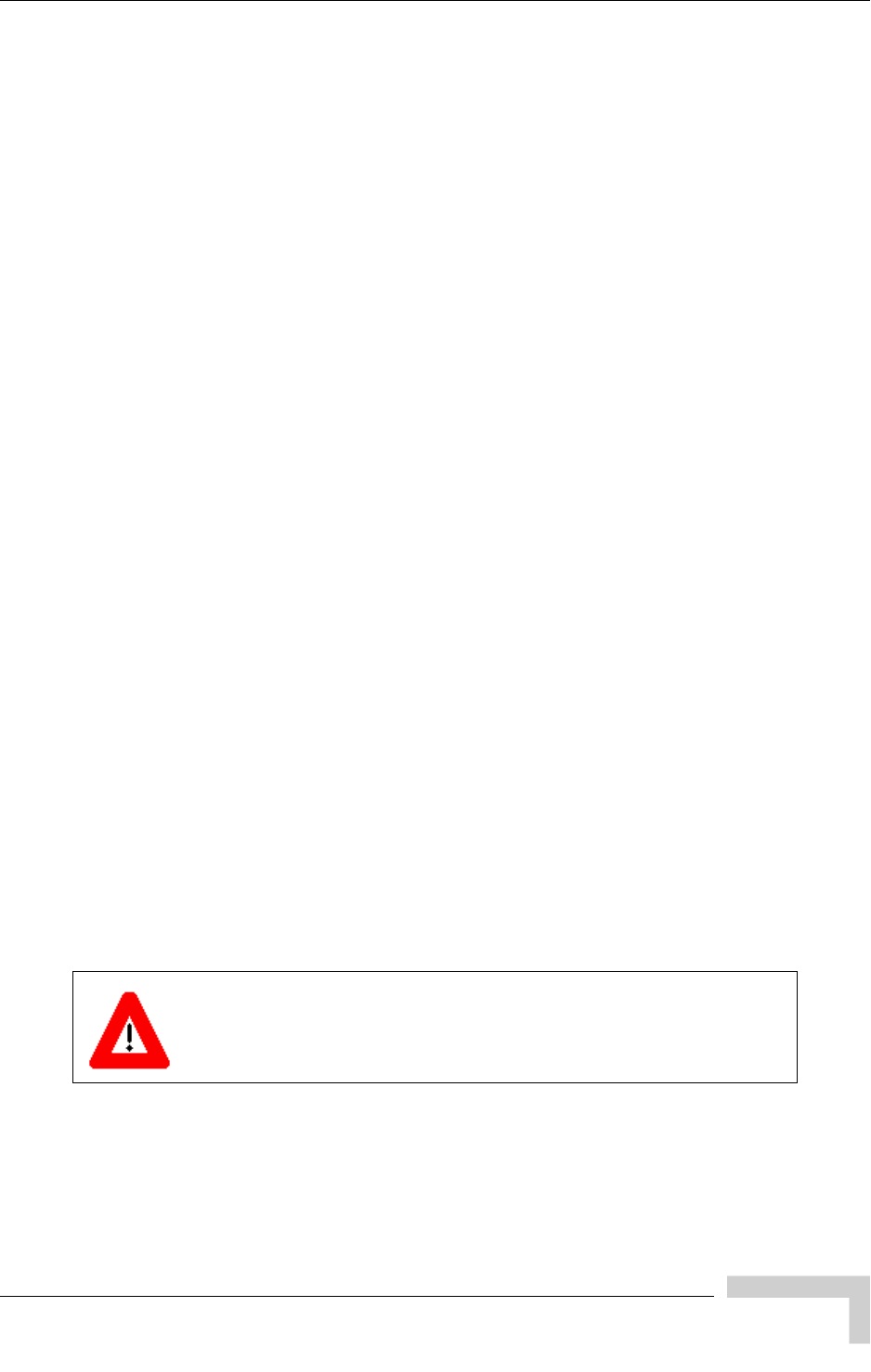
UltraWAVE Micro BTS Installation and Commissioning Guide, Version B 91
Upgrading the Micro BTS Software Version (Flash)
7To find out which Flash image in which the current software version resides,
type:
bts-> getCurrentImage [ENTER]
value = 0 = 0x0
8Make a note of the returned value, which might be either 0 or 1. This is the
active image in which the current Flash resides. The binary opposite of this
value will be used to load the new Flash in the following steps:
If Current Image Value is 0 (value = 0 = 0x0)
9Load the new Flash in the inactive image. At the bts-> prompt, type:
bts-> writeFlashImage “btsflash.bin”, 1 [ENTER]
10 This takes about one minute. When the bts-> prompt returns, set the
inactive image containing the new Flash as the active or current image, type:
bts-> setImageCurrent 1 [ENTER]
11 Reboot the Micro BTS for the new Flash image to take effect by pressing the
key combination [CTRL][x].
If Current Image Value is 1 (value = 1 = 0x1)
12 Load the new Flash in the inactive image. At the bts-> prompt, type:
bts-> writeFlashImage “btsflash.bin”, 0 [ENTER]
13 This takes about one minute. When the bts-> prompt returns, set the
inactive image containing the new Flash as the active or current image, type:
bts-> setImageCurrent 0 [ENTER]
14 Reboot the Micro BTS for the new Flash image to take effect by pressing the
key combination [CTRL][x].
The Flash boot image has been upgraded to the new software version and set as
the default.
Flash Image 2 is reserved for Alvarion Customer Service use
ONLY.
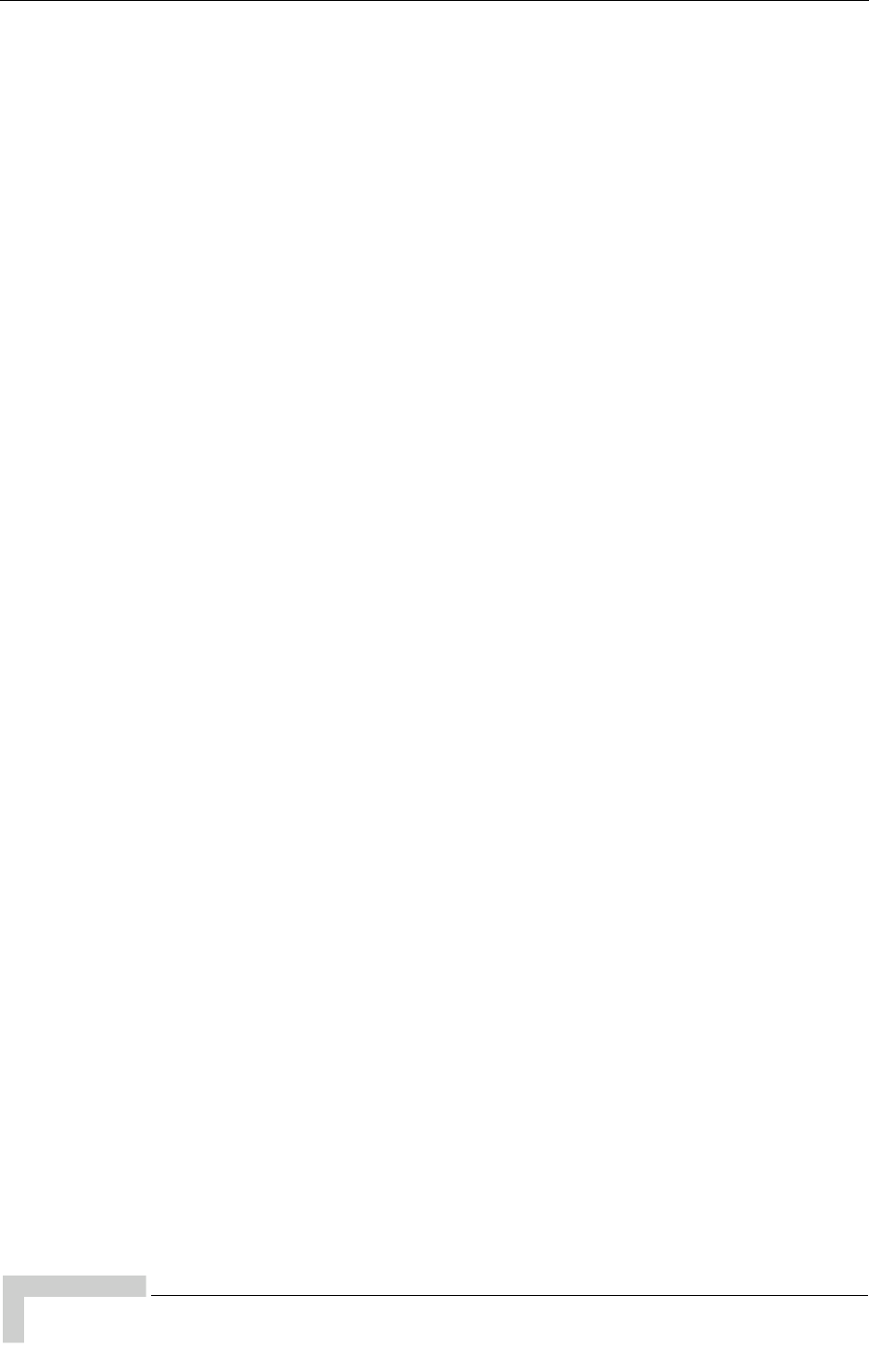
92 UltraWAVE Micro BTS Installation and Commissioning Guide, Version B
Chapter 3 - Off-Line Commissioning
3.5 Post Off-Line Commissioning
The following post off-line commissioning procedures are necessary to ensure that
the Micro BTS is ready for on-line commissioning. In the case of off-line
commissioning at a staging area, these procedures ensure that the Micro BTS is
ready for installation. In the case of off-line commissioning after on-site
installation, these procedures ensure that the Micro BTS is ready for on-line
commissioning.
3.5.1 Post Off-Line Commissioning Procedures at
the Staging Area
1Repack the Micro BTS in its original shipping containers and make sure that it
is shipped to the site where it will be installed.
2Once the Micro BTS is installed at its final site as described in Chapter 2 -
Installation, continue with the next section.
3.5.2 Post Off-Line Commissioning Procedures
On-Site
1Reconnect the E1 or T1 cables to the digital distribution frame.
2Power on the Micro BTS if it is not already on. Verify that all PWR and ON LINE
LEDs are green.
3Inform the OMC operator that the Micro BTS is ready for network
configuration.
4After the OMC operator has configured the Micro BTS, continue with on-line
commissioning tests in the next chapter.
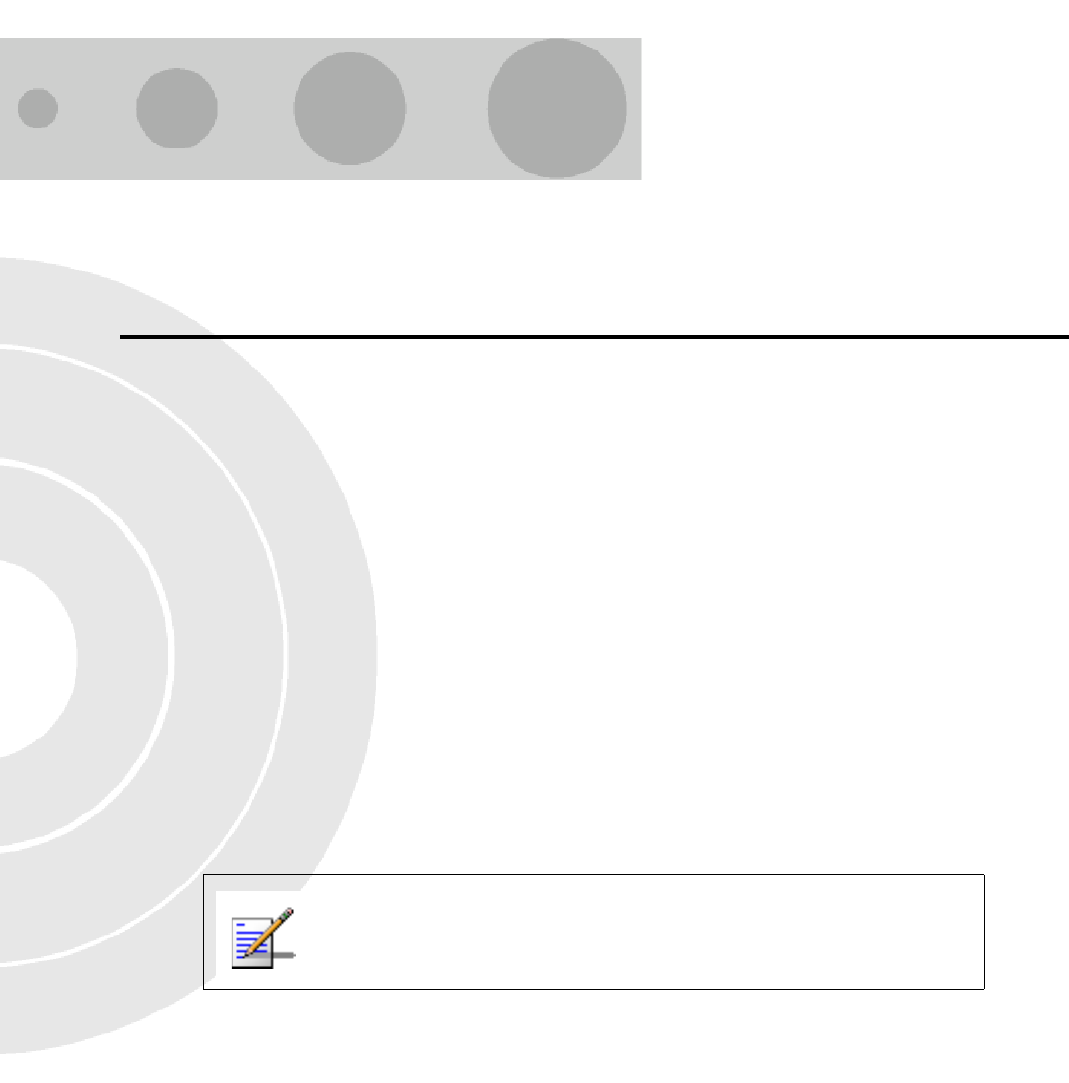
4
Chapter 4 - Off-Line Commissioning of a
Daisy Chain
In this Chapter:
“Prerequisites to Daisy Chaining” on page 108.
“Setting the Abis LAPD Signaling Timeslot” on page 109.
Up to five external Micro BTSs can be incorporated into a daisy chain connected to
a BSC. If this configuration is used, each Micro BTS must be installed separately,
and must have off-line commissioning procedures independently performed. Once
each Micro BTS is installed and commissioned, the Micro BTSs can be daisy
chained together.
If the power fails to one of the units or one of the units in a daisy
chain is rebooted, communication with the downstream units
will not be lost.
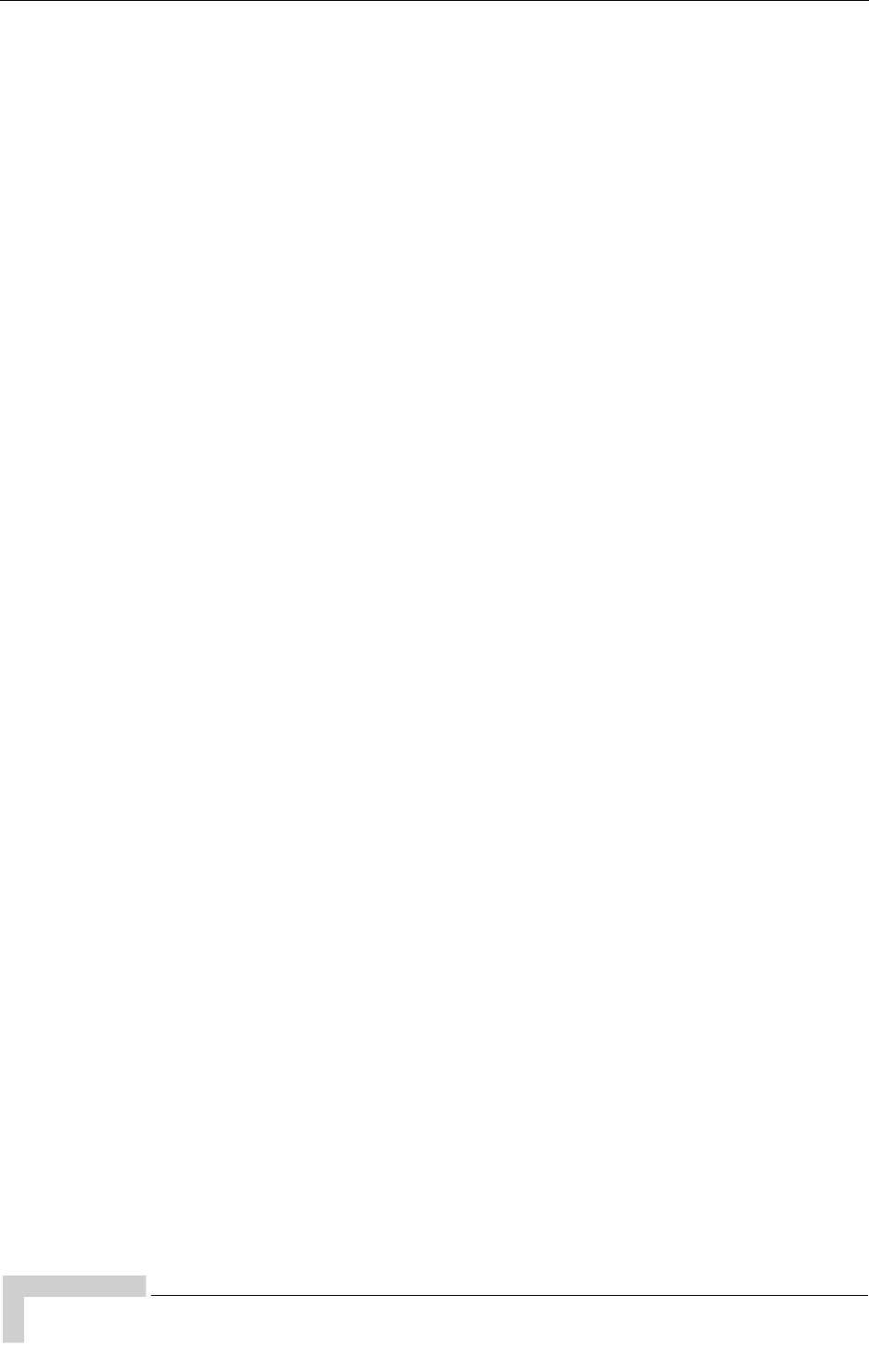
108 UltraWAVE Micro BTS Installation and Commissioning Guide, Version B
Chapter 4 - Off-Line Commissioning of a Daisy Chain
4.1 Prerequisites to Daisy Chaining
1Ensure that all Micro BTSs comprising the daisy chain are installed and
off-line commissioned.
Refer to Chapter 2 - Installation and Chapter 3 - Off-Line Commissioning for
instructions on how to install and off-line commission the Micro BTSs that are
part of the daisy chain.
2Ensure that the Abis Manager timeslot has been set for each Micro BTS in the
daisy chain as described in Section 4.2. Each Abis link within this daisy chain
MUST be allocated a unique Abis timeslot number.
3Turn the power to all units off.
4Using the instructions in Section 2.6.3, verify that all E1 and/or T1 lines are
in place and commissioned by the operator from the BSC to the first Micro
BTS, and between all successive Micro BTSs comprising the daisy chain.
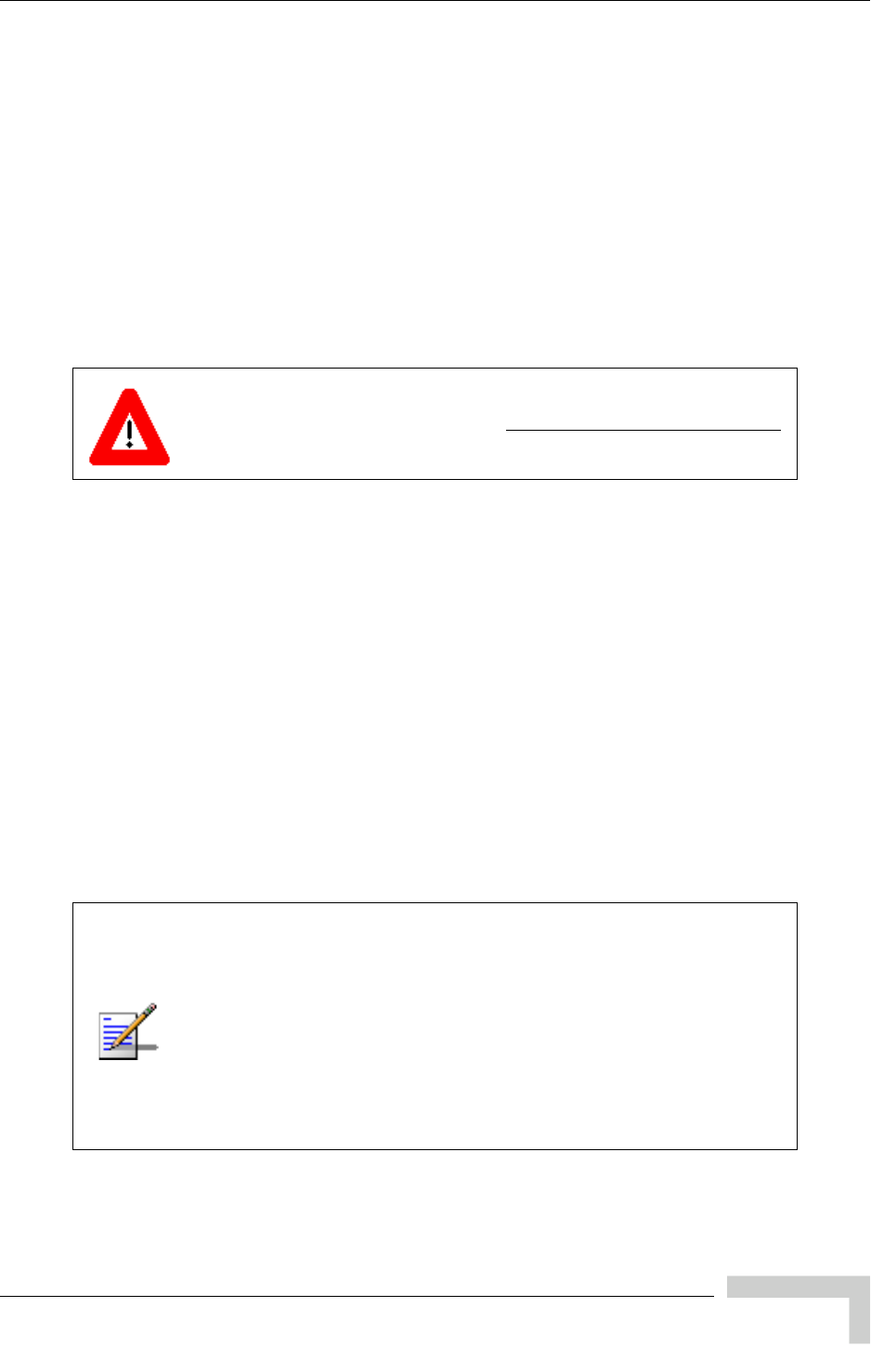
UltraWAVE Micro BTS Installation and Commissioning Guide, Version B 109
Setting the Abis LAPD Signaling Timeslot
4.2 Setting the Abis LAPD Signaling
Timeslot
This procedure sets the Abis LAPD timeslot between the MSC and each Micro
BTS. If the Abis timeslot is not set, it automatically defaults to 16.
This procedure is optional for a star configured Micro BTS, but is required for all
BTSs which will be used in a daisy chain. In this case, each Micro BTS must have
its Abis timeslot set to a unique number in the chain. This information will be
used by the OMC operator to configure the daisy chain.
1Ensure that the Craft PC is connected to the Micro BTS over a serial line, and
that a serial connection is established. Refer to Chapter 3 - Off-Line
Commissioning for instructions on how to do this.
2In an Xterm window, type:
bts-> getFlashE1Chan [ENTER]
This displays the timeslot reserved for the Abis LAPD signalling timeslot,
which is by default set to 16. To change this value, type:
bts-> setFlashE1Chan <number> [ENTER]
where <number> is the Abis LAPD signaling timeslot assigned to an
unassigned T1 channel between 1 and 24 or to an unassigned E1 channel
between 1 and 31.
This procedure must be performed after the Micro BTS is tested
using a Racal test set. Refer to the GSM Field Maintenance Guide
for further instructions.
The Abis signaling timeslot for each Micro BTS in the daisy chain
must be set to a different number. For example:
• Micro BTS 1 in the chain = Set timeslot 16 as the Abis timeslot
• Micro BTS 2 in the chain = Set timeslot 17 as the Abis timeslot
• Micro BTS 3 in the chain = Set timeslot 18 as the Abis timeslot
• Micro BTS 4 in the chain = Set timeslot 19 as the Abis timeslot
Make sure that this information is communicated to the OMC
operator.

110 UltraWAVE Micro BTS Installation and Commissioning Guide, Version B
Chapter 4 - Off-Line Commissioning of a Daisy Chain
3To double-check that the timeslot was changed, type again:
bts-> getFlashE1Chan [ENTER]
The new Abis signaling timeslot number should be displayed.
4If the Abis signaling timeslot was changed, the Micro BTS must be rebooted.
Type:
bts-> reboot [ENTER]
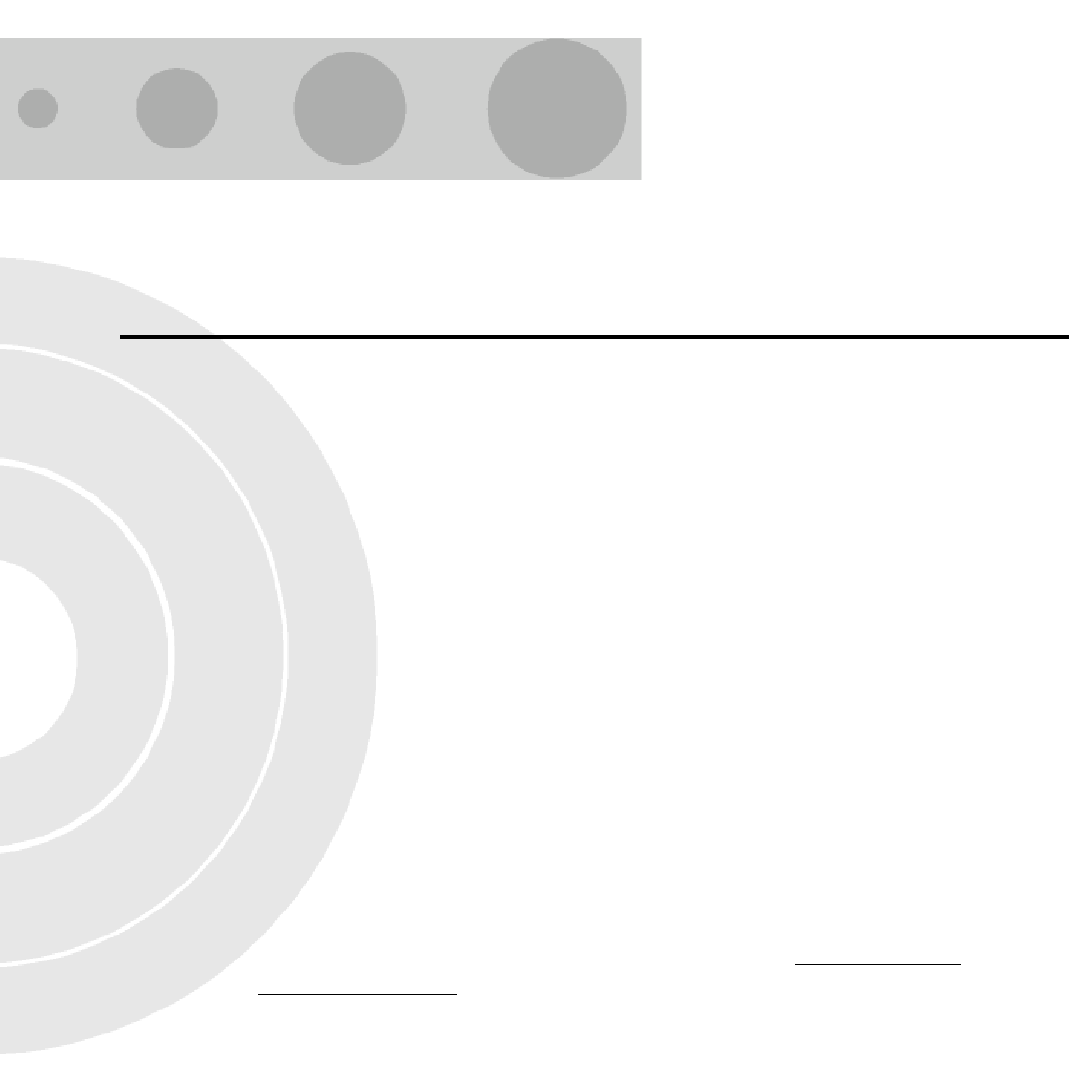
5
Chapter 5 - On-Line Commissioning
In this Chapter:
“Pre On-Line Commissioning Requirements” on page 113
“On-Line Commissioning” on page 114
“Antenna Cabling and Power Verification” on page 121
“Post On-Line Commissioning Procedures” on page 129
On-line commissioning takes place on-site after installation and off-line
commissioning. Its purpose is to verify that the equipment is operational and can
be integrated into the telecommunications network.
On-line commissioning requires the participation of two people; a field technician
who operates and tests the Micro BTS on-site and an OMC operator who remains
at the OMC console. These two must work together, performing the procedures in
this chapter in conjunction with the procedures in the UltraVIEW OMC
Configuration Guide.

112 UltraWAVE Micro BTS Installation and Commissioning Guide, Version B
Chapter 5 - On-Line Commissioning
Radio Frequency Radiation Warning
Under normal operating conditions, Alvarion radio equipment
complies with the limits for human exposure to radio frequency
(RF) fields adopted by the Federal Communications Commission
(FCC). All Alvarion, Inc. radio equipment is designed so that
under normal working conditions RF radiation directly from the
radio is negligible when compared with the permissible limit of
continuous daily exposure recommended in the United States of
America by ANSI/IEEE C95.1-19991 (R1997), Safety Levels with
Respect to Human Exposure to Radio Frequency Electromagnetic
Fields, 3 kHz to 300 GHz.
RF signal levels that give rise to hazardous radiation levels can
exist within the transmitter, power amplifiers, associated RF
multiplexers and antenna systems.
Do not disconnect RF coaxial connectors on the Alvarion
equipment or antenna systems while the radio equipment is
operating. Never place any body part over, or look into any RF
connector while the radio equipment is transmitting.
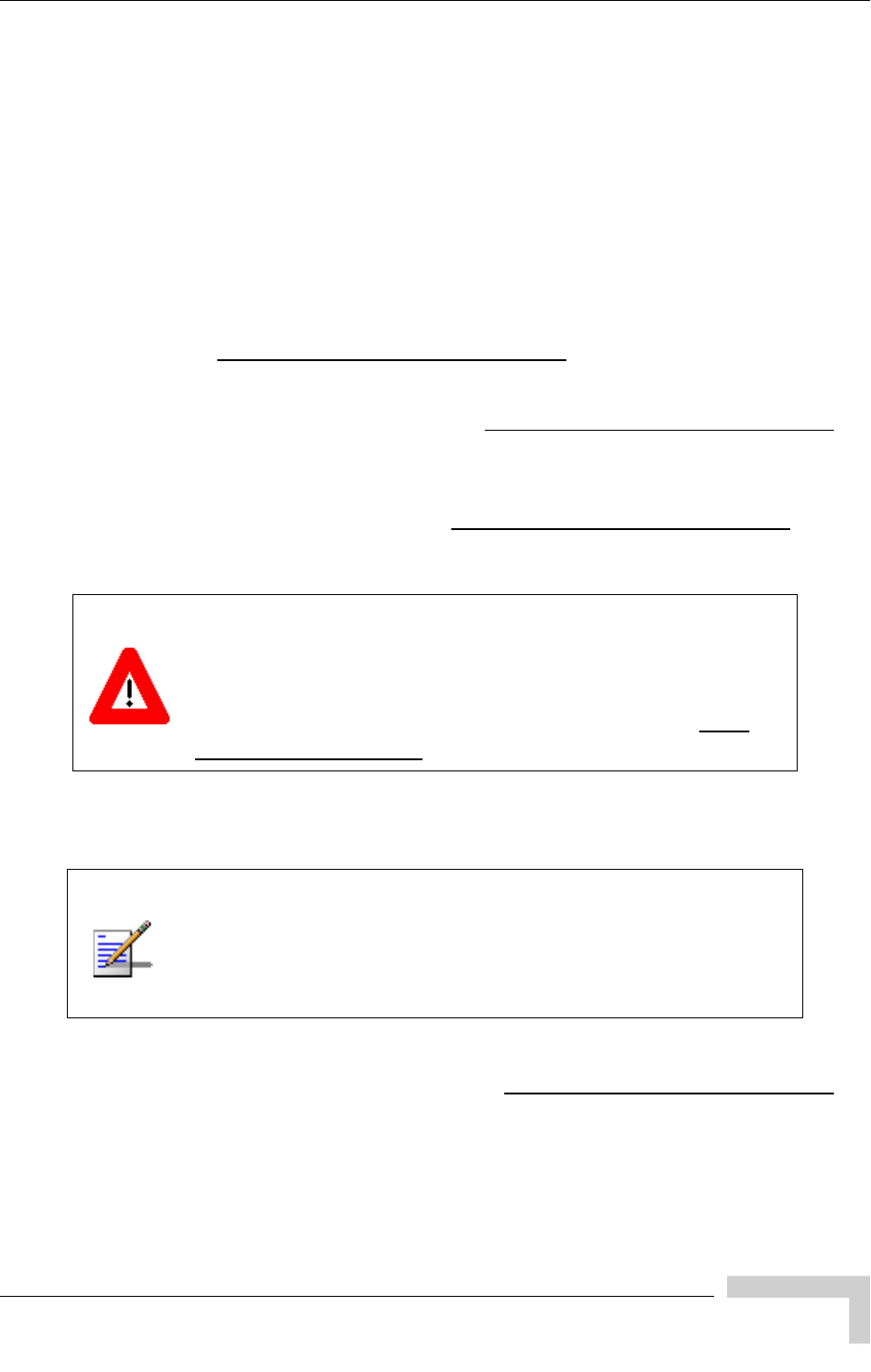
UltraWAVE Micro BTS Installation and Commissioning Guide, Version B 113
Pre On-Line Commissioning Requirements
5.1 Pre On-Line Commissioning
Requirements
Before on-line commissioning begins, the field technician or the OMC operator
must verify that:
The BSC, or Micro BTS, and the MSC are fully commissioned, in service and
connected to each other.
The OMC is in service and connected to the Micro BTS via the MSC as defined
in the GSM Network Implementation Manual.
The database questionnaire is completed, with all necessary Micro BTS
parameters listed, as defined in the GSM Network Implementation Manual.
The OMC operator has successfully created and configured the Micro BTS
object on the OMC and downloaded this information to the Micro BTS. Refer to
the procedures described in the UltraVIEW OMC Configuration Guide.
The RF frequencies are cleared to transmit.
The MSC-Micro BTS E1 or T1 link is properly certified. Note that the certifica-
tion should state length of testing and BER results.
The HLR subscriber data has been entered into the HLR using the Subscriber
Management GUI, as described in the GSM Subscriber Management Guide. In
particular, the HLR must be configured to support the SIM cards of the
mobiles used by the field technician.
Once the E1 or T1 link has been properly connected to the Micro
BTS E1 or T1 trunk card, both port alarm LEDs for the
connected port should turn off. If one or both LEDs remain
illuminated, an E1 or T1 link problem exists related to either a
faulty connector or the E1 or T1 link itself. Refer to the GSM
Field Maintenance Guide for additional information.
It is the operator's responsibility to verify that all Micro BTS E1 or
T1 Abis links are ordered, installed and certified by the local
telephone provider. Certification should include a bit error ratio/
rate test of at least 20 minutes on the Abis interface, with a BER of
10-8 or better.
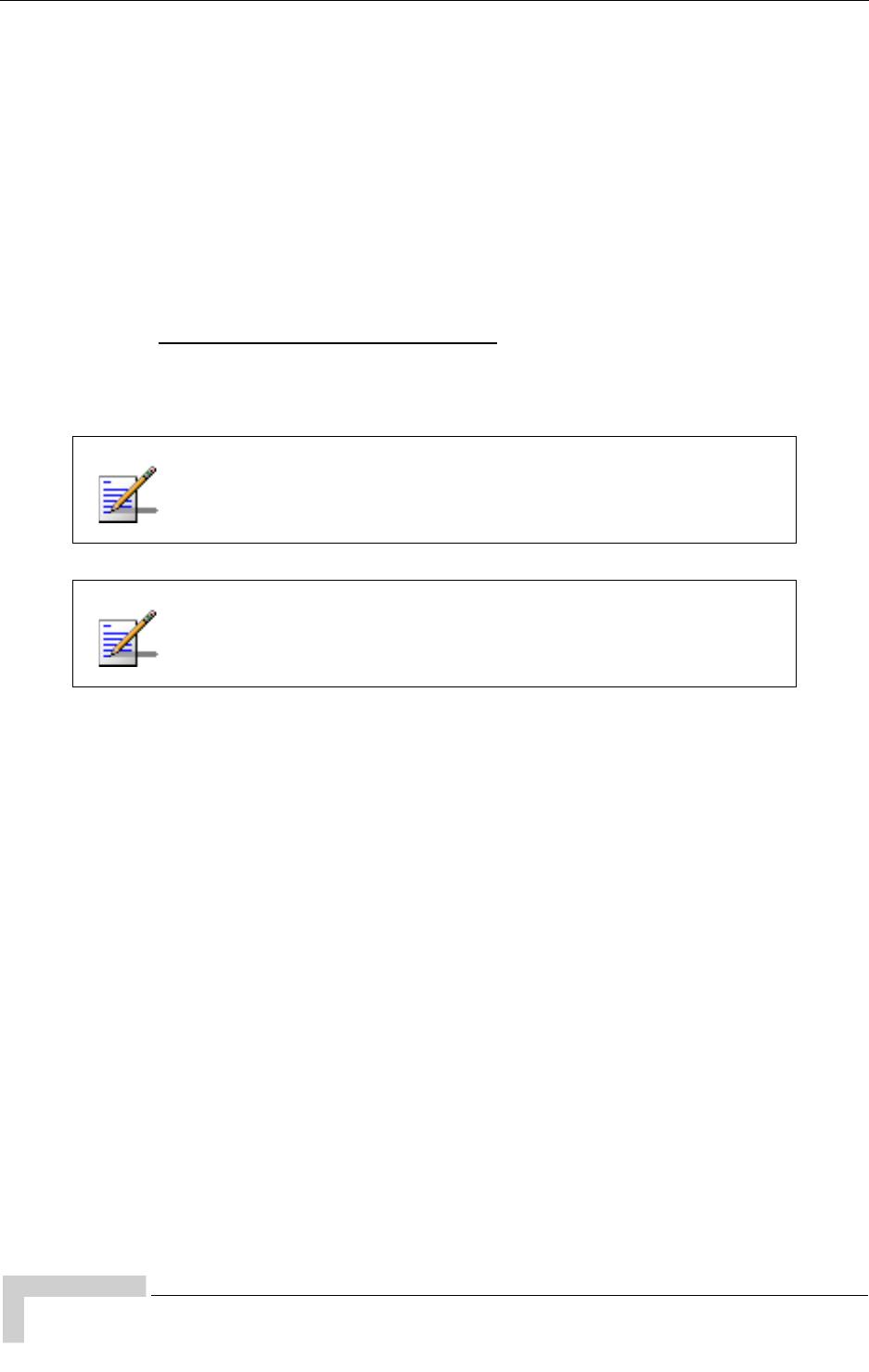
114 UltraWAVE Micro BTS Installation and Commissioning Guide, Version B
Chapter 5 - On-Line Commissioning
5.2 On-Line Commissioning
The network commissioning procedures must be performed at the OMC and at the
Micro BTS. This requires two persons working from two different documentation
sets:
A field technician who remains on-site. They must have a filled out copy of
Checklist 2 - Installation Checklist and a copy of this manual.
An OMC operator who remains at the OMC. They must have a copy of the
UltraVIEW OMC Configuration Guide.
The flow chart shown in Figure 5-1 provides a high-level view of the procedures.
The procedures in the following sections provide detailed, numbered steps.
Checklist 3 - Commissioning Checklist summarizes the steps for
on-line commissioning.
Before starting any of the following procedures, the field
technician needs to ensure that anti-static precautions are
taken. Refer to Section 1.2.
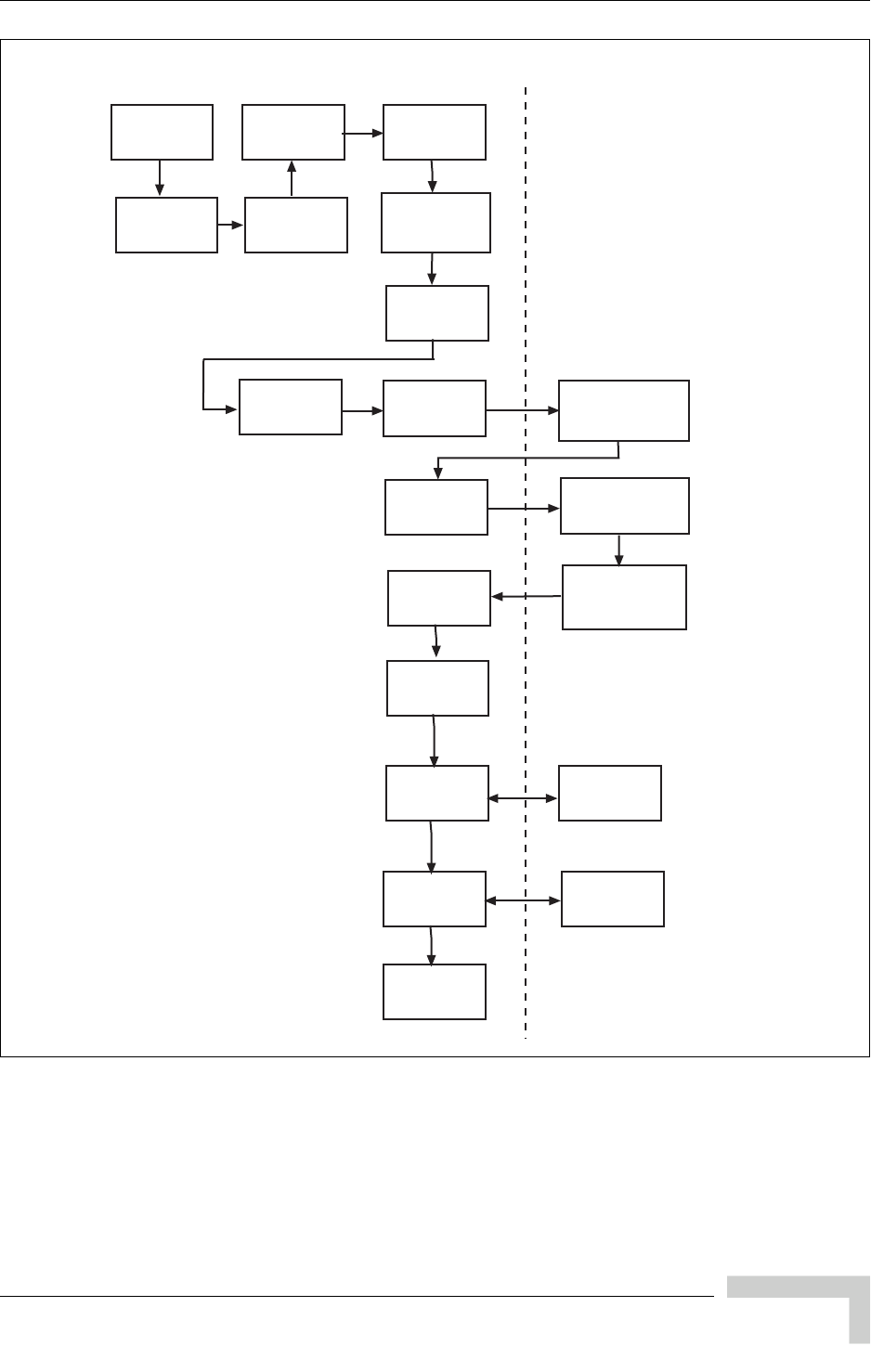
UltraWAVE Micro BTS Installation and Commissioning Guide, Version B 115
On-Line Commissioning
Figure 5-1: On-Line Commissioning Procedures
Unlock the Abis
Interface
Check state of
BTS
Verify
Database
Unlock the TRX
and RCARRIER Unlock the BTS
Open BTS alarm
and event list
views
Check state of
BTS
Lock E1/T1
ports
Check that
E1/T1 port
alarms clear
Step 1
Disconnect
Abis Link
Step 2
Reconnect
Abis Link
Check alarm
and event
detailed views
Check for
cleared events
and alarm in all
views
Check state of
BTS
Verify external
alarms
Step 4
Test external
alarms
Verify TRX
timeslots
Step 5
Use mobile to
verify timeslots
Lock the BTS
Procedures for
OMC Operator
IE101501
Procedures for BTS Field
Technician
Step 3
Check LEDs are
Green and Steady
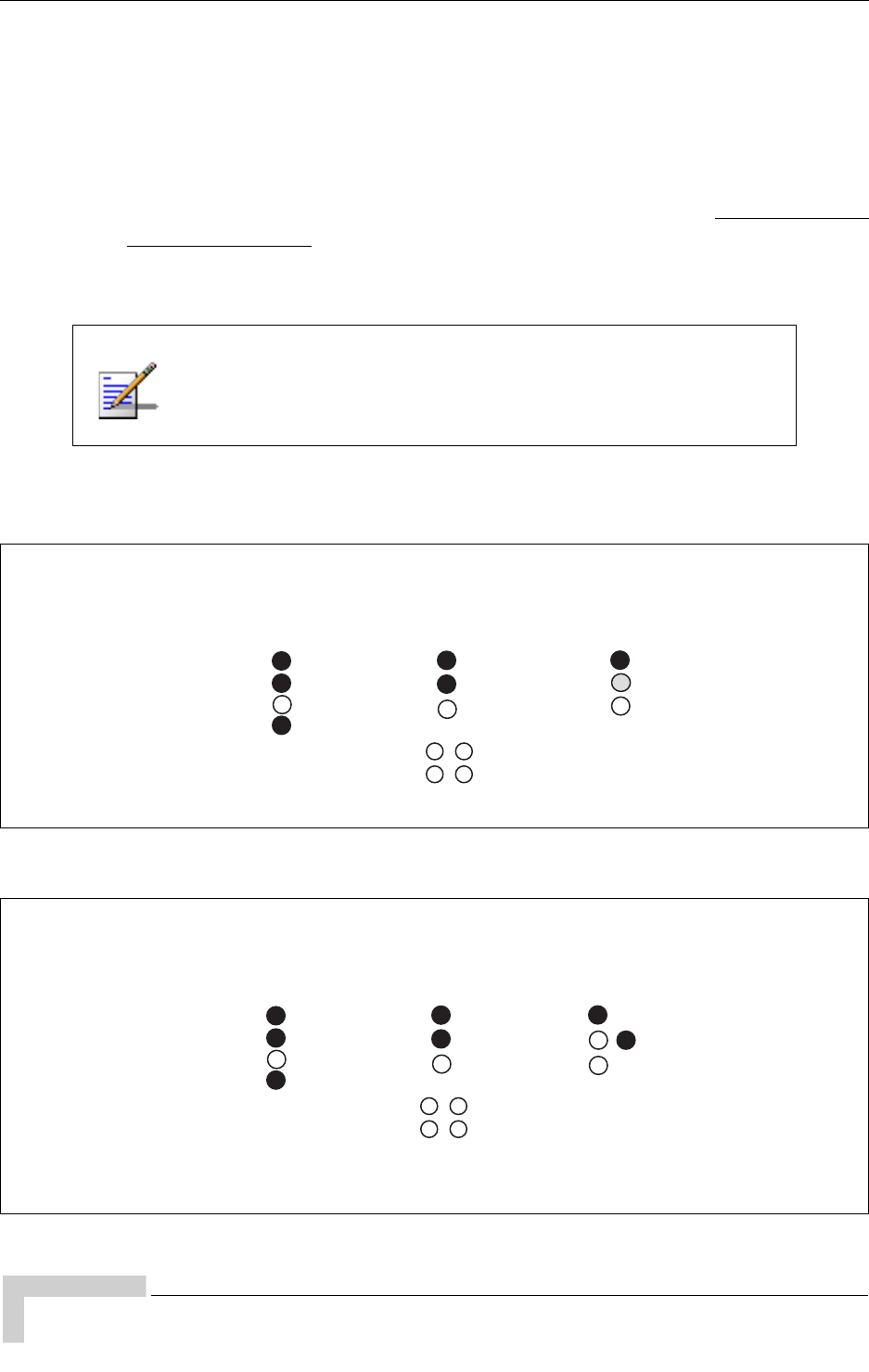
116 UltraWAVE Micro BTS Installation and Commissioning Guide, Version B
Chapter 5 - On-Line Commissioning
5.2.1 Unlocking the Abis Interface
The Abis interface between the BSC and BTS is established via a PPP link over E1
or T1 lines. Make the E1 or T1 connections to the provider and set up the Abis
signaling link to the OMC as described in Chapter 4 - Off-Line Commissioning of a
Daisy Chain. Once the Abis link is established it must be unlocked at the OMC to
allow the BSC to download the TRX code to the BTS. Refer to the UltraVIEW OMC
Configuration Guide for procedures to unlock the Abis. As the code downloads,
the TRXs run POST to verify their operation. This takes up to fifteen minutes
depending the number of TRXs in the system.
Figure 5-2 illustrates the LED display during the POST process and Figure 5-3
illustrates the final LED display.
For systems equipped with multiple TRXs, the TRXs download
their code and run POST simultaneously. If viewing the output in
a serial window, the POST messages will be mixed among
different TRXs while in progress.
Figure 5-2: LED Display During POST
Figure 5-3: Final LED Display
Abis connection to BSC completes TRX code download to each
card sequentially. LED display during POST is:
ICP E1/T1LEDs
SCN
PWR
ON LINE
FLT
PORT 0
PORT 1
ON
ON
N/A
N/A
N/A OFF
OFF
TRX 1-6
N/A
N/A
N/A
IE144501
ON ON
ON
OFF
FAST FLASH
ON
OFF OFF
Abis connection to BSC completes TRX code download to each
card sequentially. After 10 minutes, the final LED display is:
ICP E1/T1LEDs
SCN
PWR
ON LINE
FLT
PORT 0
PORT 1
ON
ON
N/A
N/A
N/A OFF
OFF
TRX 1-6
N/A
N/A
N/A
IE144502
ON ON
ON
OFF
ON
OFF OFF
/ON or OFF*
* Note: TRX ON LINE will display ON if it is unlocked, or OFF if it is locked (in the OMC database).
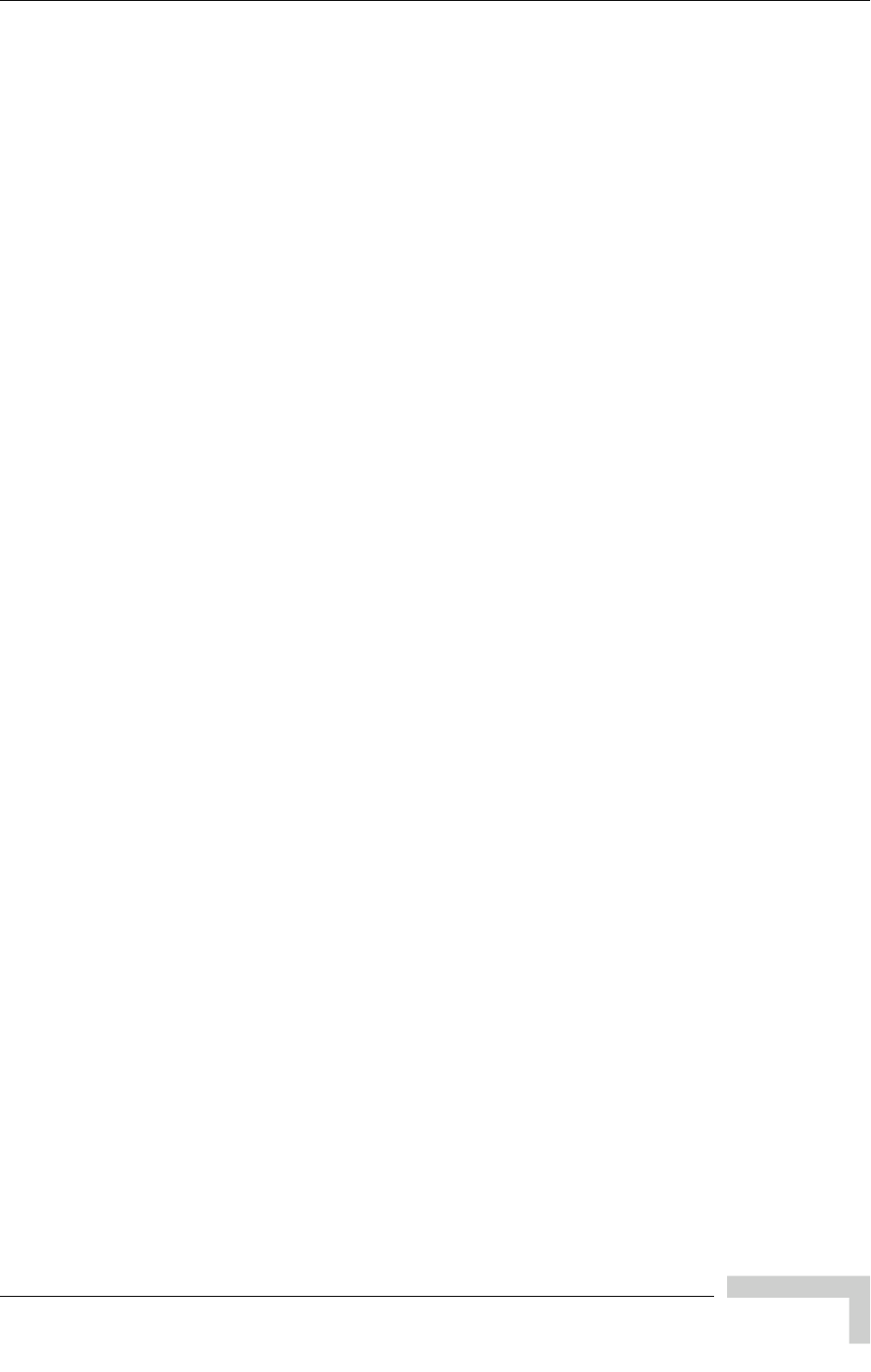
UltraWAVE Micro BTS Installation and Commissioning Guide, Version B 117
On-Line Commissioning
5.2.2 Commissioning the Micro BTS
Before disconnecting the E1 or T1 cables, the field technician must make sure
that the cable is labeled in a way that clearly identifies its origin (a particular E1
or T1 port on the Micro BTS, or a particular port of an E1 or T1 panel, etc.) and
destination (a particular E1 or T1 slot and port on the Micro BTS).
Provide the OMC operator with all part, revision and serial numbers for the
Micro BTS cards and modules. This information was gathered during the
physical installation and is available in Checklist 2 - Installation Checklist.
5.2.3 Recovery Tests
You should have the OMC operator lock the E1 or T1 ports and verify that the port
status changes to Locked, Enabled, Online. Then perform the following steps:
1At the Micro BTS, disconnect the physical OAM link cable. Monitor the LED
sequence of the Micro BTS as described in Chapter 3 - Off-Line
Commissioning.
2Coordinate with the OMC operator to ensure the proper alarms have appeared
on the OMC. Reconnect the physical OAM link cable to the Micro BTS E1 or T1
trunk card.
3Monitor the LED sequence of the Micro BTS as described in Chapter 3 -
Off-Line Commissioning.
4Test external alarms. See Section 5.2.4.
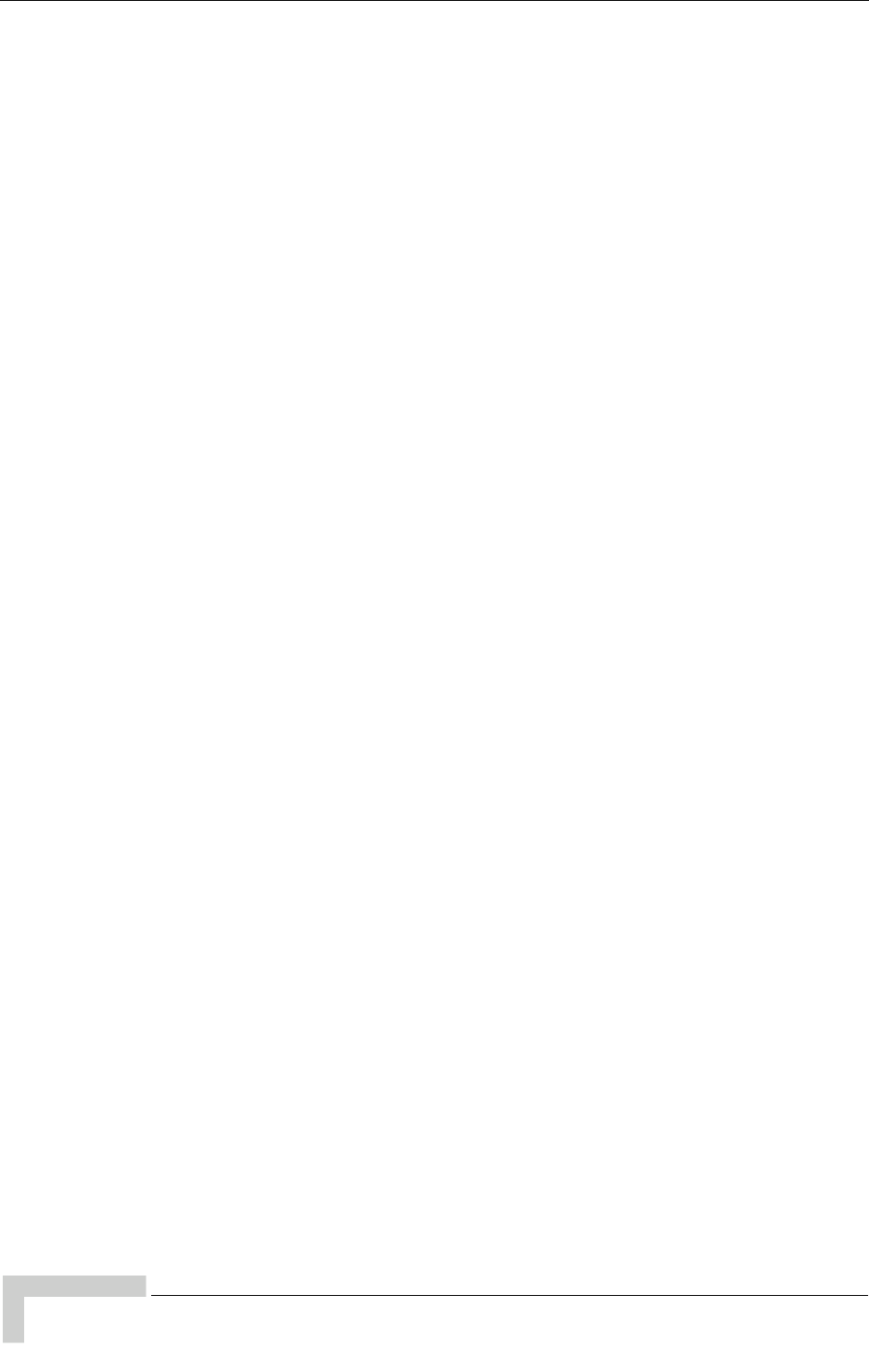
118 UltraWAVE Micro BTS Installation and Commissioning Guide, Version B
Chapter 5 - On-Line Commissioning
5.2.4 External Alarm Tests
1Test external alarms using the following procedures:
AOpen the door of the Micro BTS.
BAfter a delay, the OMC operator must observe an alarm event.
CClose the door.
DAfter a delay, the alarm state displayed at the OMC changes from open to
closed.
2For each external alarm that you connected in Section 2.8, verify that it is
propagated to the OMC.
AClose the alarm relay (i.e. trigger the first customer-defined alarm).
BAfter a delay, the OMC operator must observe an alarm event.
CClose the alarm relay by opening the alarm contact.
DAfter a delay, the alarm state displayed at the OMC changes from open to
closed.
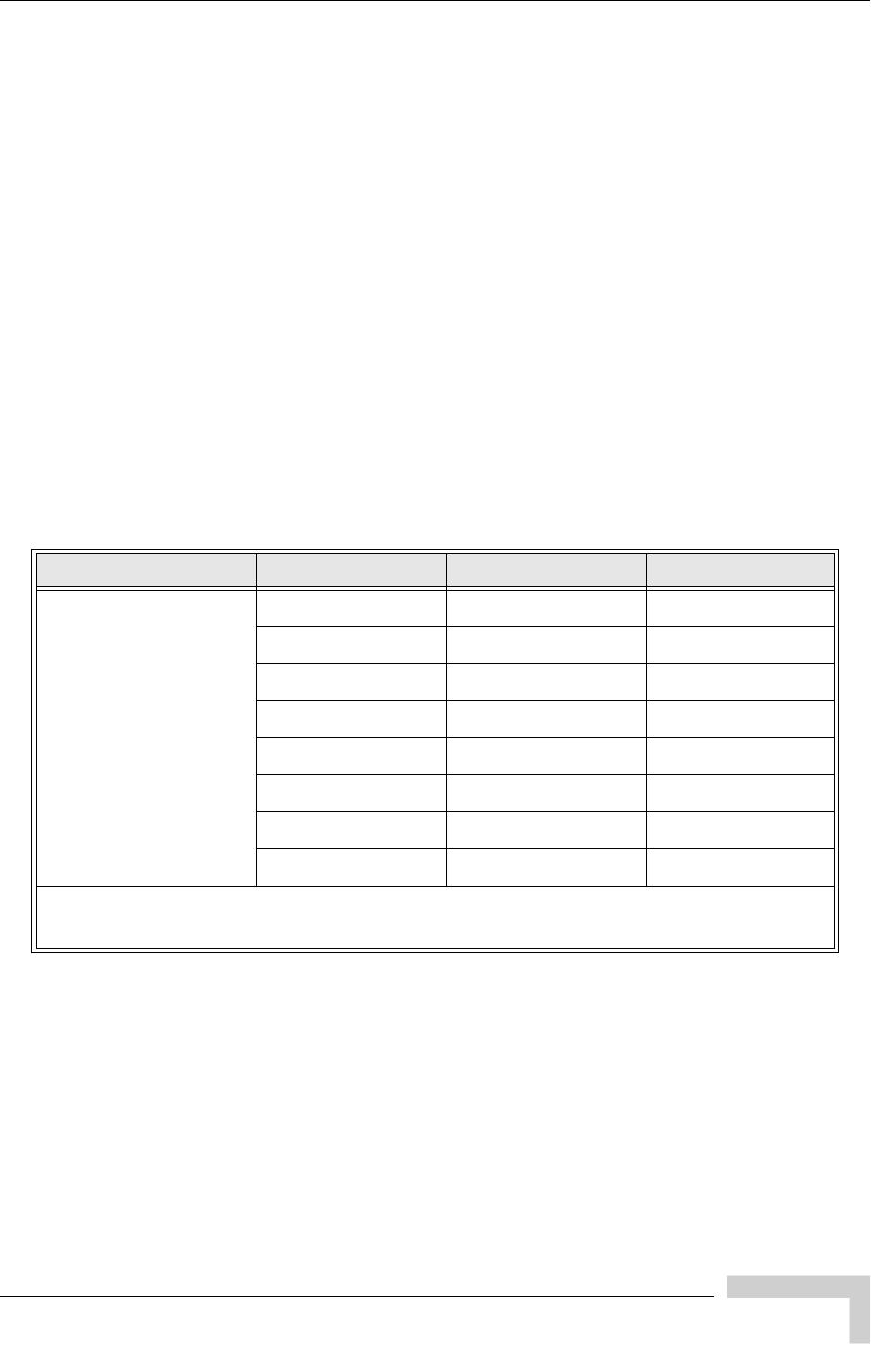
UltraWAVE Micro BTS Installation and Commissioning Guide, Version B 119
On-Line Commissioning
5.2.5 TCH Timeslot Tests
In this test, the OMC operator unlocks individual TCH timeslots and the field
technician places a mobile-to-mobile call over each timeslot using a mobile
handset in debug mode. Refer to the documentation provided by the module
handset manufacturer for the proper procedures.
For each timeslot, the commissioner should verify that:
The timeslot displayed on the handset corresponds to the timeslot
unlocked by the OMC operator.
A two-way call is completed successfully.
The call has good audio quality and power, and low interference.
The number of timeslots to be tested differs depending on whether you have
one, two or three TRXs. Table 5-1 provides the sequence for one TRX.
Table 5-2 provides the sequence for two or more TRXs.
Table 5-1: Timeslots Needing Testing in a One-TRX BTS
TRX Number Timeslot Number Channel Type Testing Necessary
First TRX 0 BCCH Combined No
1TCHYes
2TCHYes
3TCHYes
4TCHYes
5TCHYes
6TCHYes
7TCHYes
Note: To run an abbreviated version of this test, test any one of timeslots 0-3 and of
timeslots 4-7 on each TRX.
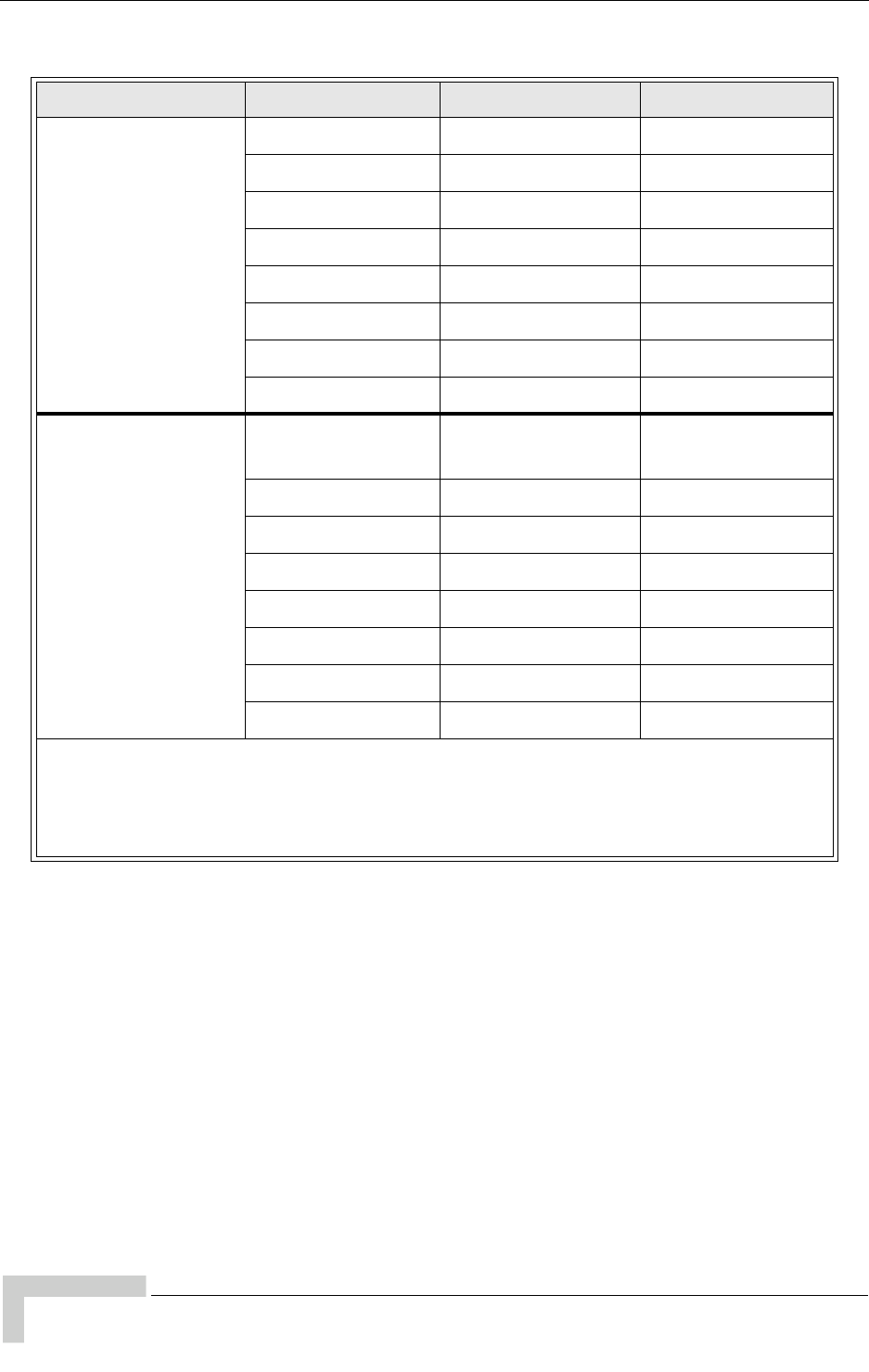
120 UltraWAVE Micro BTS Installation and Commissioning Guide, Version B
Chapter 5 - On-Line Commissioning
Table 5-2: Timeslots Needing Testing in BTS with More Than One TRX
TRX Number Timeslot Number Channel Type Testing Necessary
First TRX (Note) 0 BCCH No
1SDCCHNo
2TCHYes
3TCHYes
4TCHYes
5TCHYes
6TCHYes
7TCHYes
Second through
Sixth TRX (Note) 0TCHYes
1TCHYes
2TCHYes
3TCHYes
4TCHYes
5TCHYes
6TCHYes
7TCHYes
Note: The BCCH can be assigned to any TRX within the BTS. The label “First TRX”
applies to the TRX to which is assigned the BCCH. The OMC operator may determine
which physical TRX is the “First” or beacon TRX. All TCH timeslots on the second
through sixth TRX must be tested.

UltraWAVE Micro BTS Installation and Commissioning Guide, Version B 121
Antenna Cabling and Power Verification
5.3 Antenna Cabling and Power Verification
Use the procedures in this section to verify the output power and antenna cabling.
After the hardware installation is complete, forward and reverse power needs
verification.
5.3.1 Setting up Power Measurements
After performing the BTS commissioning as described in the previous section, use
the following procedure to check the performance of an on-line Micro BTS without
using a Racal test procedure.
Required Test Equipment
Thruline RF Watt Meter (by Bird Electronics) or equivalent
Appropriate power sensors for watt meter according to frequency and output
power of the BTS under test
Calibrated RF cable for connection between equipment and watt meter
100 Watt, 30 dBm attenuator, if required
Two mobile telephones
Required Network Configuration
To perform satisfactory RF performance tests, the Micro BTS must be connected
to an operational BSC/MSC and OMC to enable call processing, as the SS7 must
be enabled for the BTS to transmit. Make sure you commission the Micro BTS as
described in the previous section before performing this procedure.
This procedure is NOT a substitute for the Racal tests. Please
refer to the GSM Radio Test Procedures to test the output power
of the BTS.
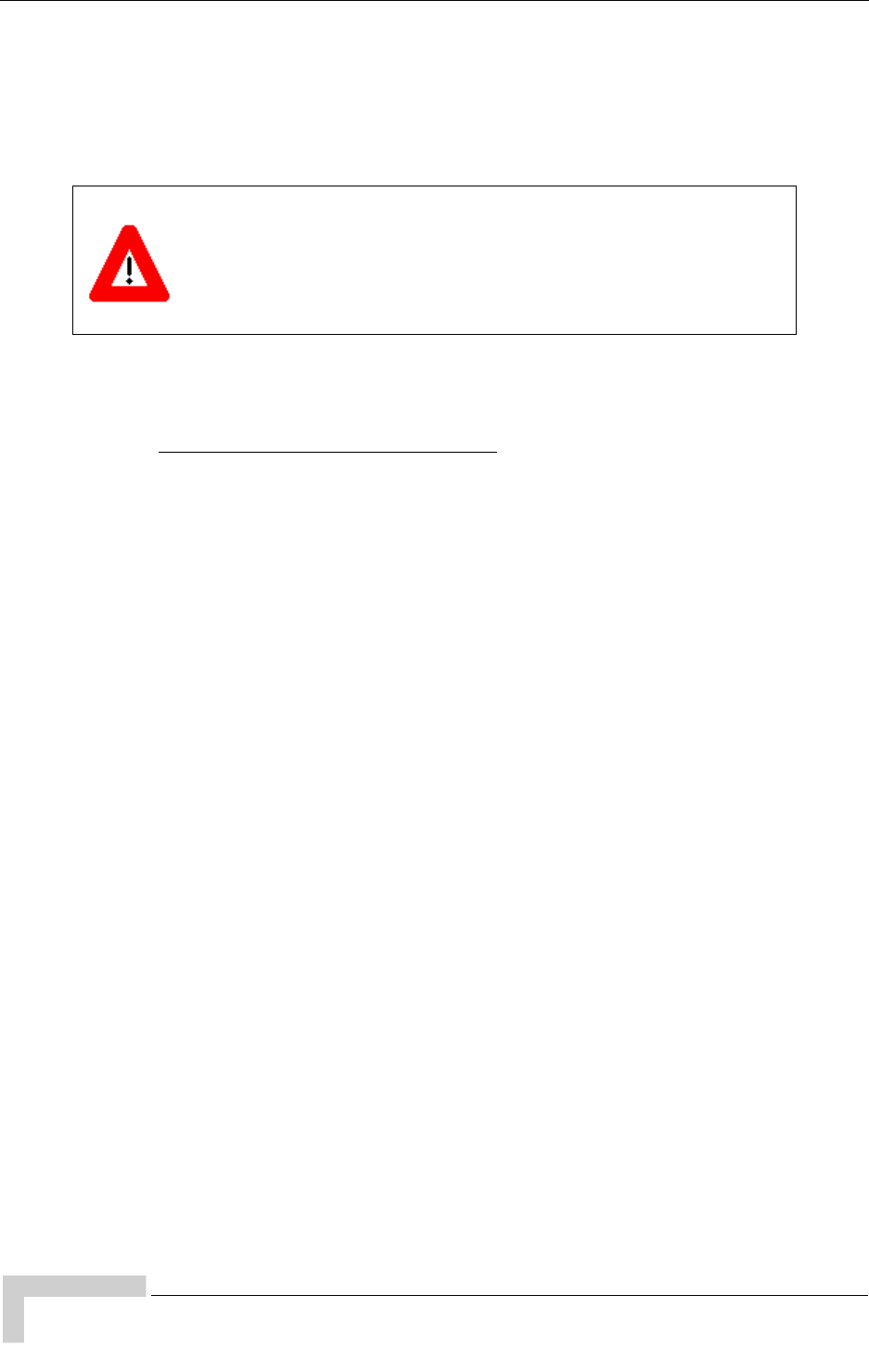
122 UltraWAVE Micro BTS Installation and Commissioning Guide, Version B
Chapter 5 - On-Line Commissioning
5.3.2 Verifying TRX Output Power
Starting with the first TRX, this procedure must be completed for each TRX in the
Micro BTS. The OMC operator will need to know what TRX is under test to enable
the BCCH on that specific TRX and lock all other TRXs.
Use the following procedure:
1At the OMC, make sure that the Micro BTS is in a locked state. Refer to the
UltraVIEW OMC Configuration Guide.
At the Micro BTS, check the TRX ONLINE LEDs are OFF. Do not disconnect
the RF connectors if the TRX is ONLINE!
2Determine the appropriate power sensor for your test. Power sensors are
specific for frequency (850 MHz, 900 MHz, 1800 MHz or 1900 MHz) and power
range.
For the forward power measurement, you should be using a 100 Watt, 50 Watt
or 25 Watt power sensor depending on the output power of equipment that
you are testing. The sensor rating must have a higher Watt rating than the RF
power output than you are testing, or an inline attenuator must be used to
bring the output power down to the range acceptable to your power sensor.
For the reflected power measurement, you should be using a 10 Watt or 5 Watt
power sensor.
3Disconnect the appropriate antenna cable from the equipment. This cable will
correspond to the TRX which you are testing. See Section 2.7 for additional RF
cabling information.
You must be an experienced RF field technician to perform these
procedures. Do not disconnect RF coaxial connectors on the
equipment or antenna systems while the radio equipment is
operating. Never place any body part over, or look into any RF
connector while the radio equipment is transmitting.
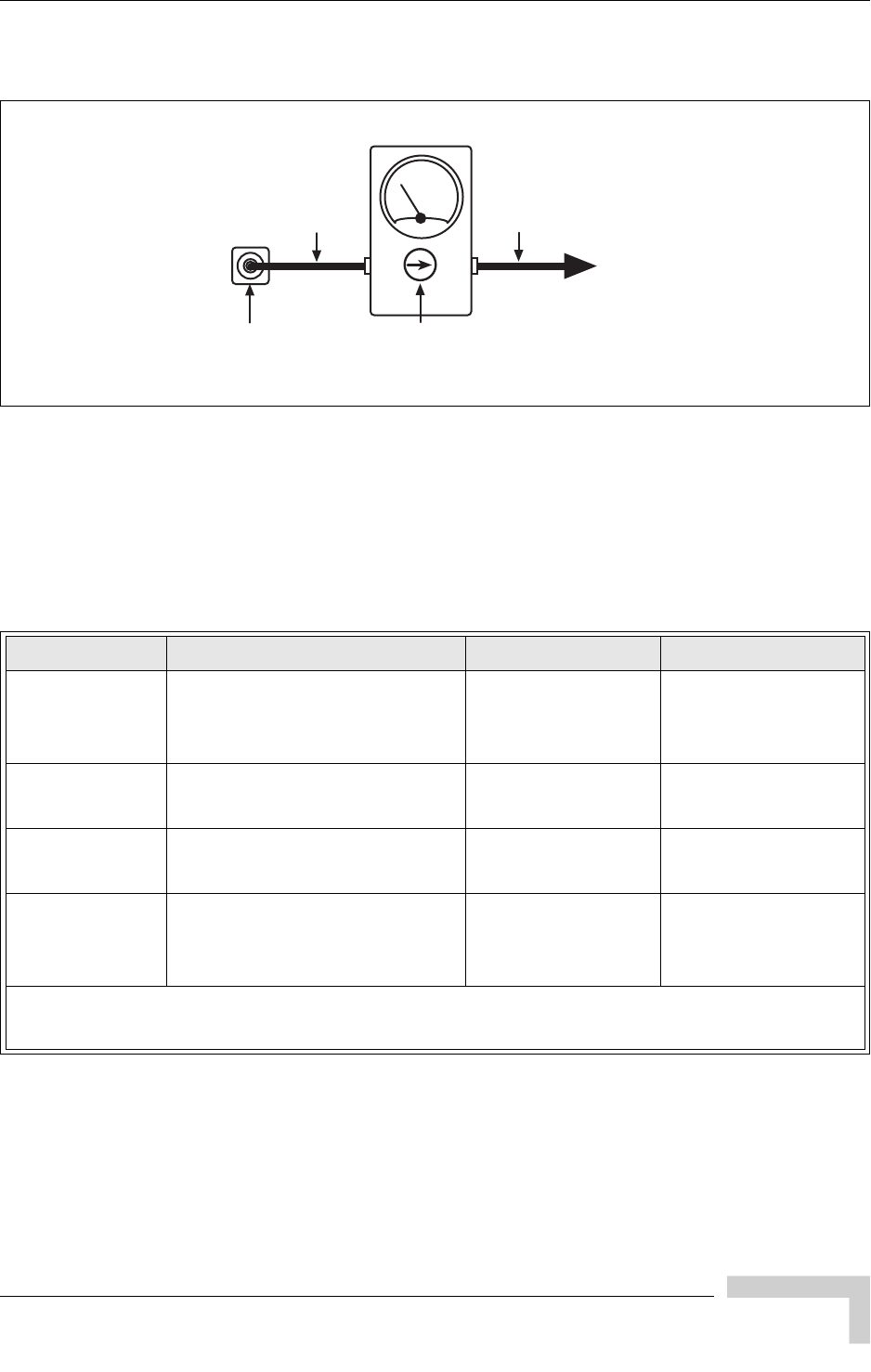
UltraWAVE Micro BTS Installation and Commissioning Guide, Version B 123
Antenna Cabling and Power Verification
4Connect the antenna cable from the TRX port that you are testing to the “out”
port of the RF watt meter. See Figure 5-4.
5Connect the RF cable between the Micro BTS RF output port (antenna
connector) and the RF watt meter, as shown in Figure 5-4. This is the recom-
mended method of testing forward and reflected power. Typical test cable loss
is listed in Table 5-3.
Figure 5-4: Direct RF Connection
Table 5-3: Typical Test Cable Loss
Cable Type Description Loss (900 MHz) Loss (1800 MHz)
LMR195 or
RG142
Outer diameter: 0.2 inch
Length: four feet
0.7 dB; add 0.1 dB
per foot if longer
than four feet
1.0 dB; add 0.17 dB
per foot if longer
than four feet
RG214 or RG8 Outer diameter: 0.4 inch
Length: four feet 0.5 dB 0.7 dB
LMR400 Outer diameter: 0.4 inch
Length: four feet 0.4 dB 0.5 dB
0.5 inch Heliax
Jumper
Hard corrugated copper outer
conductor; Outer diameter:
0.6 inch; Length: six feet
0.3 dB 0.4 dB
Note: It is strongly recommended NOT to use RG-58/U cable as a test cable because of its
poor RF performance.
RF Watt Meter
Equipment
Antenna
Connector IW136501
RF cable RF cable to Antenna
Power Sensor
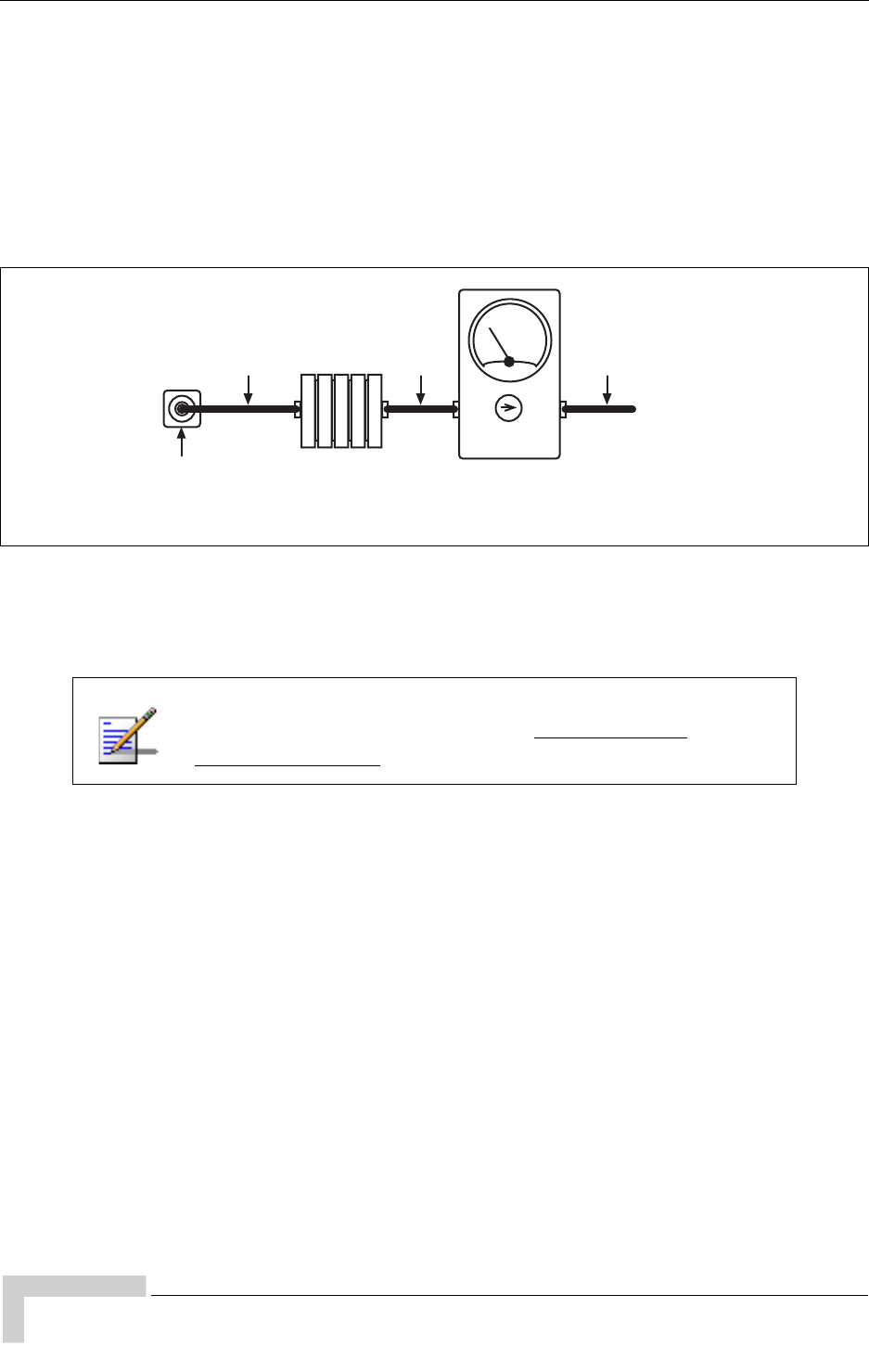
124 UltraWAVE Micro BTS Installation and Commissioning Guide, Version B
Chapter 5 - On-Line Commissioning
If you do not have a high power sensor, you need to reduce the output power
for the forward power measurement. Connect the appropriate attenuator
(50 Watt or more, 10-20 dB) inline between the Micro BTS RF output port and
the “in” port of the RF watt meter, as shown in Figure 5-5. You must figure the
power loss of both cables and the attenuator in this scenario. You cannot
measure the reflected power using this test setup. You must use the setup
without the attenuator, as shown in Figure 5-4, making sure the power sensor
direction arrow points toward the Micro BTS.
6Work with the OMC operator to ensure that the OMC is configured so that the
BCCH is on the TRX you are testing.
7To measure forward (output) power, the arrow on the power sensor should
point toward the antenna, as shown in Figure 5-4.
8At the OMC, change the TRX state to unlocked. The operator should be sure
that the output power for the TRX under test is set to “Static Power Control
Level 0” (full power). Note the ONLINE LED for the TRX under test turns green
at the Micro BTS site.
9In the serial session at the Micro BTS site, enter the following commands to
display the power control status for each TRX.
bts-> log_none
bts-> isr_debug_calb=1
Figure 5-5: Attenuated Power Connection
The procedure for BCCH configuration can be found in the
Network Configuration section of the UltraVIEW OMC
Configuration Guide.
RF Power Meter
Equipment
Antenna
Connector IW041304
RF cable
Attenuator
RF cable RF cable to Antenna
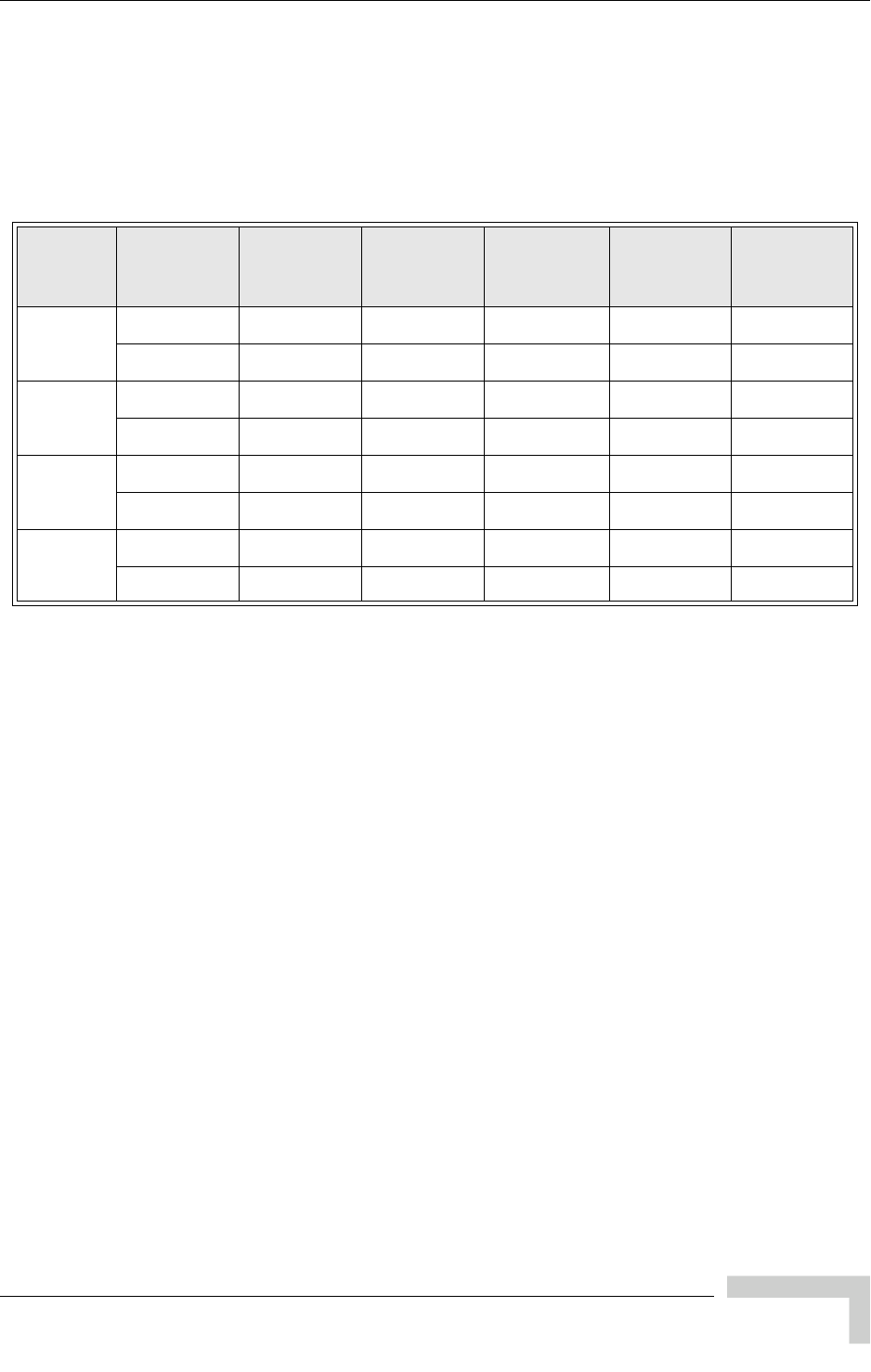
UltraWAVE Micro BTS Installation and Commissioning Guide, Version B 125
Antenna Cabling and Power Verification
10 Record the output power of the TRX on the power meter. This will be displayed
in either Watts or dBm. Your final reading should account for losses at the
cables and connectors, and if used the loss through the attenuator. Table 5-4
provides the allowable readings given a Thruline Watt Meter and the cable
losses referenced in Step 5.
11 To test the reflected power, remove the power sensor from the watt meter, and
put the 10 Watt or 5 Watt sensor into the meter with the arrow pointing
toward the equipment. It is not necessary to disconnect the meter or turn off
the Micro BTS power. You only need to exchange the power sensor and point it
in the direction of the Micro BTS.
If the measured reflected power is equal or less than 4% of the forward power
measured in the previous step, the installation is acceptable. If the
measurement is more than 4%, contact the responsible party for the antenna
and feeder installation. Section 5.3.3 provides more detail about the Voltage
Standing Wave Radio.
12 Complete these steps for each TRX in the Micro BTS.
If a TRX falls out of the above guideline margins, it is still within the operable
tolerance based on the GSM standard or 11.21 test requirement as long as the
power does not go beyond 25% of the maximum value or 20% less than the
minimum value.
For example, if the cable loss is 0.4 dB, the nominal power is 25 Watts and the
measured power is 16 Watts. It is out of the range of Table 5-4, but still
operable because it is above the 14.4 Watts which is the absolute minimum to
operate a Micro BTS according to the GSM standard. If a TRX falls below this
range, contact Customer Service.
Table 5-4: Allowable Power Meter Reading Range (Watts)
Nominal
Output
Power
Reading
Range 0.3 dB
Cable Loss 0.4 dB
Cable Loss 0.5 dB
Cable Loss 0.7 dB
Cable Loss 1.0 dB
Cable Loss
15 Watt Maximum181717 1615
Minimum111111 109
25 Watt Maximum292928 2725
Minimum191818 1716
40 Watt Maximum474645 4340
Minimum302928 2725
50 Watt Maximum595756 5450
Minimum373635 3432

126 UltraWAVE Micro BTS Installation and Commissioning Guide, Version B
Chapter 5 - On-Line Commissioning
5.3.3 Voltage Standing Wave Ratio (VSWR) Check
The antenna and feeder cable VSWR measurement should be performed before
the Micro BTS installation and commissioning by the team responsible for the
antenna installation using a VSWR meter. The required VSWR is 1.5 or less. It is
very important to confirm the antenna and feeder installation to ensure the Micro
BTS transmits its signal power to the air effectively.
The purpose of this check is to ensure the integrity of the antenna and the
antenna connection under the actual full power condition by determining whether
the reflected power reading is lower than the required value. The reflected power is
derived from the antenna and feeder VSWR. Table 5-5 shows the direct
relationship between VSWR and reflected power.
The recommended test approach is to use an in-line, forward/reflected power
meter (for example, Thruline Watt Meter by Bird Electronics or the NAS model by
Rohde and Scorers) inserted between the Micro BTS chassis and the antenna
cable. This approach validates that the antenna and cable are good. It also verifies
that the transmit power from the chassis is within tolerance limits. Record the
reflected power which should be less than 4% of the output power as measured in
Step 10.
If the measured reflected power is more than 4% of the forward power, it indicates
power installation of the antenna or a bad feeder cable. Contact the responsible
party for the antenna and feeder cable installation to have the problem fixed.
Table 5-5: VSWR and Reflected Power
VSWR Reflected Power (% of the Output Power)
1.2 0.8%
1.3 1.7%
1.4 2.8%
1.5 4.0%
1.6 5.3%
1.7 6.7%
2.0 11.1%
3.0 25.0%
4.0 36.0%
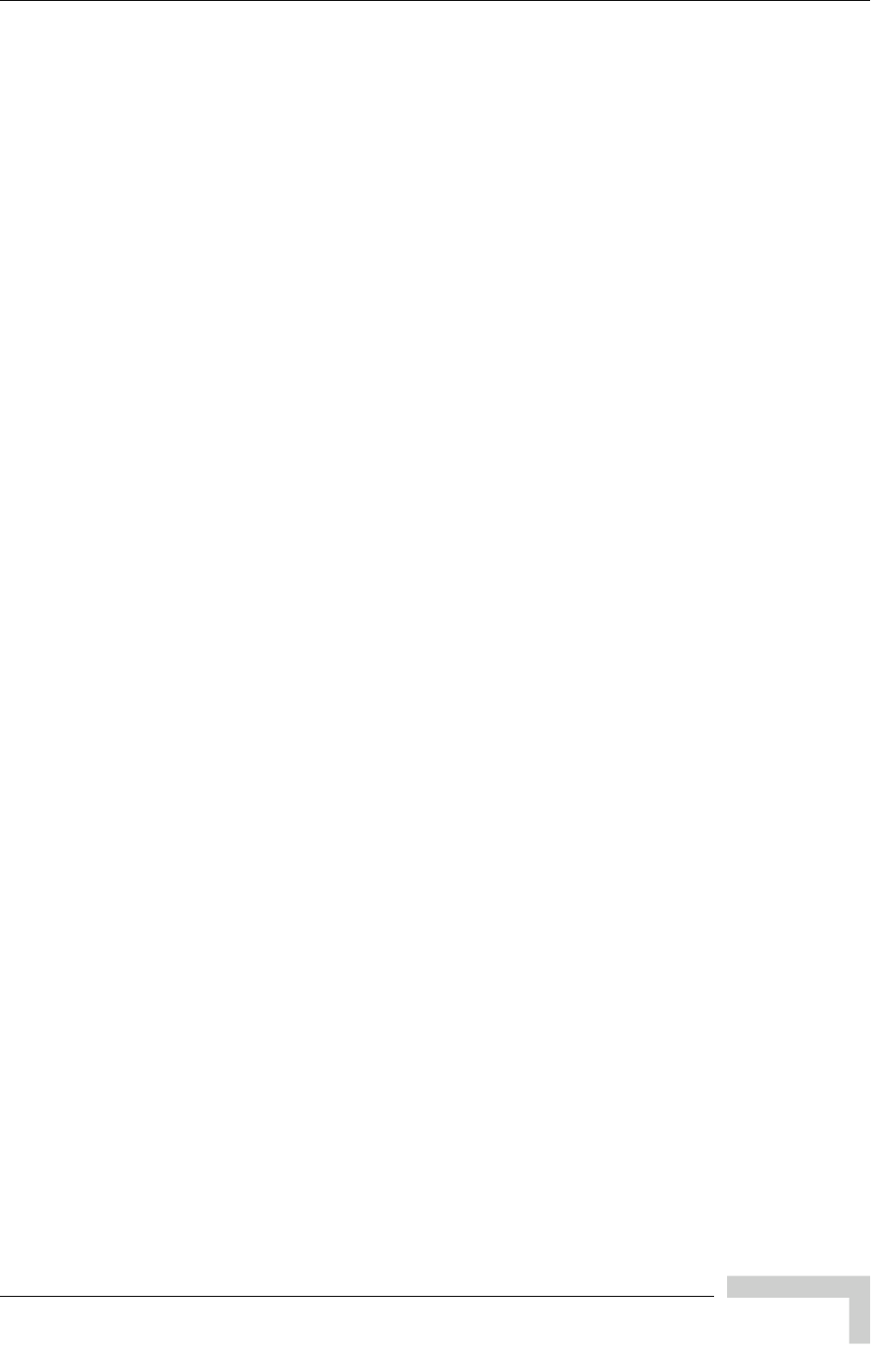
UltraWAVE Micro BTS Installation and Commissioning Guide, Version B 127
Antenna Cabling and Power Verification
5.3.4 RX Signal Quality Measurements
The objectives of this test are to verify the performance of the Receive path of the
Micro BTS and the operation of the RX module in the TRX. Before these tests can
take place, the Micro BTS must be returned to its original “on air” working state
with call processing possible.
1From an Xterm window on the OMC, telnet to the Micro BTS to be tested, or
alternatively connect directly to the Micro BTS with the Craft PC.
The field technician can also open a serial session directly with the Micro BTS,
and proceed to Step 4.
2From the iwbox prompt find the IP address of the Micro BTS by typing:
HD:iwbox-> ifShow “ppp” [ENTER]
A list of PPP connections will then be displayed. Look for the IP address of the
Micro BTS you will be testing. The last number of the 192.168.5.x address
relates to the BtsMgr number of the Micro BTS.
3From the iwbox prompt type the following to connect to the Micro BTS:
HD:iwbox-> rlogin “192.168.5.x” [ENTER]
If this is successful you will receive the bts-> prompt.
4From the Micro BTS prompt type the following to activate the RX RSSI and
quality data logging:
bts-> log_none [ENTER]
bts-> ho_log_on_bts [ENTER]
5Place a mobile to mobile call through the Micro BTS. The RSSI and Quality for
the call will be displayed, as illustrated in Figure 5-6.
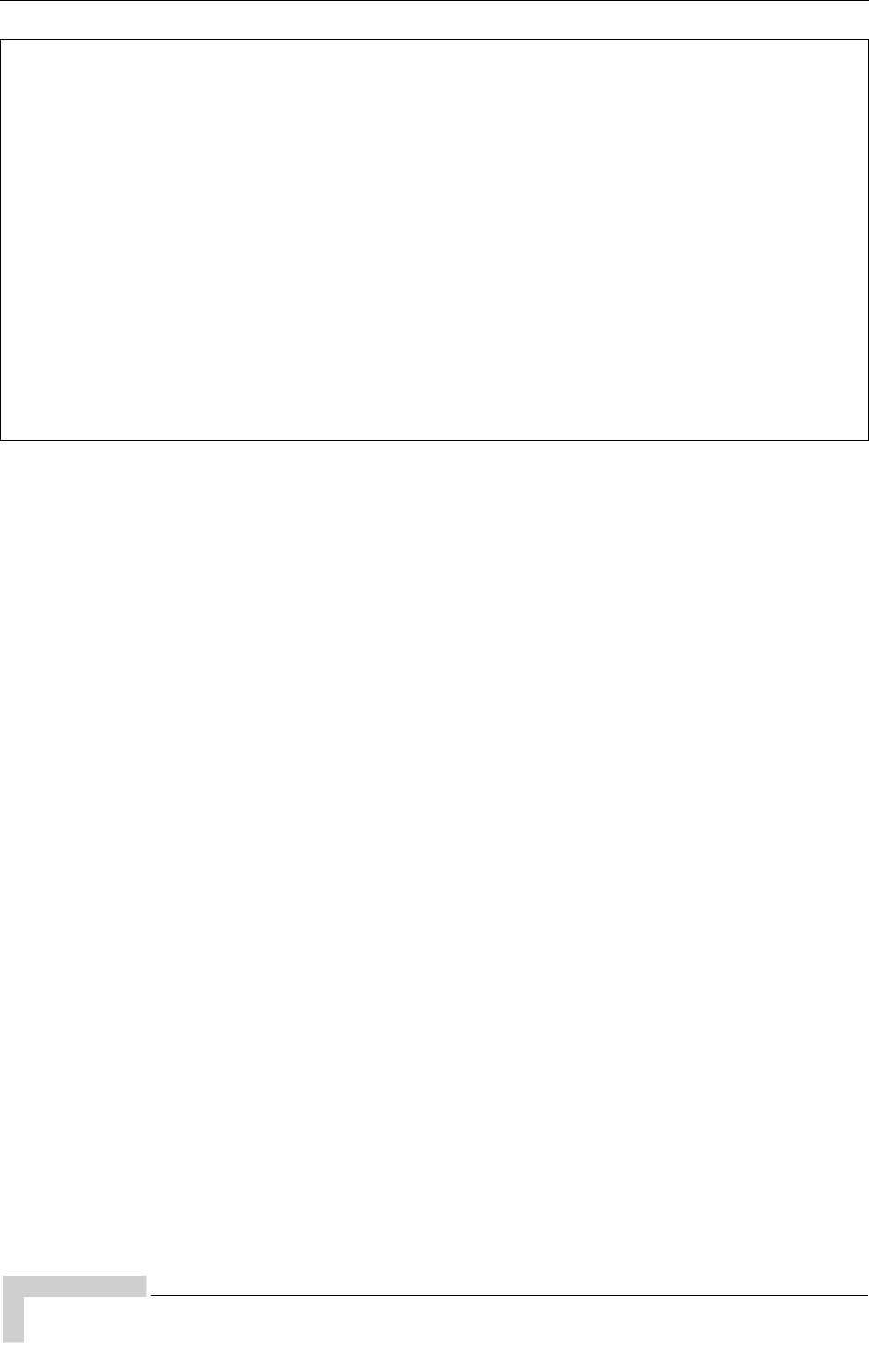
128 UltraWAVE Micro BTS Installation and Commissioning Guide, Version B
Chapter 5 - On-Line Commissioning
The sample log shows typical results for strong signals on both the uplink and
downlink where RSSI of 63 is the highest number. The quality should generally be
0 when the RSSI is above 40 (strong signal). If you have any 2 or higher numbers
in RX quality, you have some receiver problems and should contact Customer
Service.
210 (bts ) (4 0xe)UL:63/63 0/0 F AVG 63 0 DL:63/63 0/0 F AVG 63 0 NBR
211 (bts ) (4 0xe)UL:63/63 0/0 F AVG 63 0 DL:63/63 0/0 F AVG 63 0 NBR
212 (bts ) (4 0xe)UL:63/63 0/0 F AVG 63 0 DL:63/63 0/0 F AVG 63 0 NBR
213 (bts ) (4 0xe)UL:63/63 0/0 F AVG 63 0 DL:63/63 0/0 F AVG 63 0 NBR
214 (bts ) (4 0xe)UL:63/63 0/0 F AVG 63 0 DL:63/63 0/0 F AVG 63 0 NBR
215 (bts ) (4 0xa)UL:63/63 0/0 F AVG 61 0 DL:63/63 0/0 F AVG 63 0 NBR
216 (bts ) (4 0xe)UL:63/63 0/0 F AVG 63 0 DL:63/63 0/0 F AVG 63 0 NBR
217 (bts ) (4 0xa)UL:59/60 0/0 F AVG 62 0 DL:63/63 0/0 F AVG 63 0 NBR
218 (bts ) (4 0xe)UL:63/63 0/0 F AVG 63 0 DL:63/63 0/0 F AVG 63 0 NBR
Uplink RSSI/Quality Downlink RSSI/Quality
Figure 5-6: RSSI and Quality Log

UltraWAVE Micro BTS Installation and Commissioning Guide, Version B 129
Post On-Line Commissioning Procedures
5.4 Post On-Line Commissioning Procedures
1Leave the power to the OMC and Micro BTS on.
2Check that all E1, T1 and power cable connections between the MSC and
Micro BTS are tight.
3Close and lock the Micro BTS door.
4Inform the OMC operator that the Micro BTS is ready for integration testing
and connections to external BTSs.
5Ensure that the Micro BTS site is left in a tidy state.
This concludes the commissioning of the Micro BTS. The field technician can now
leave the Micro BTS site.
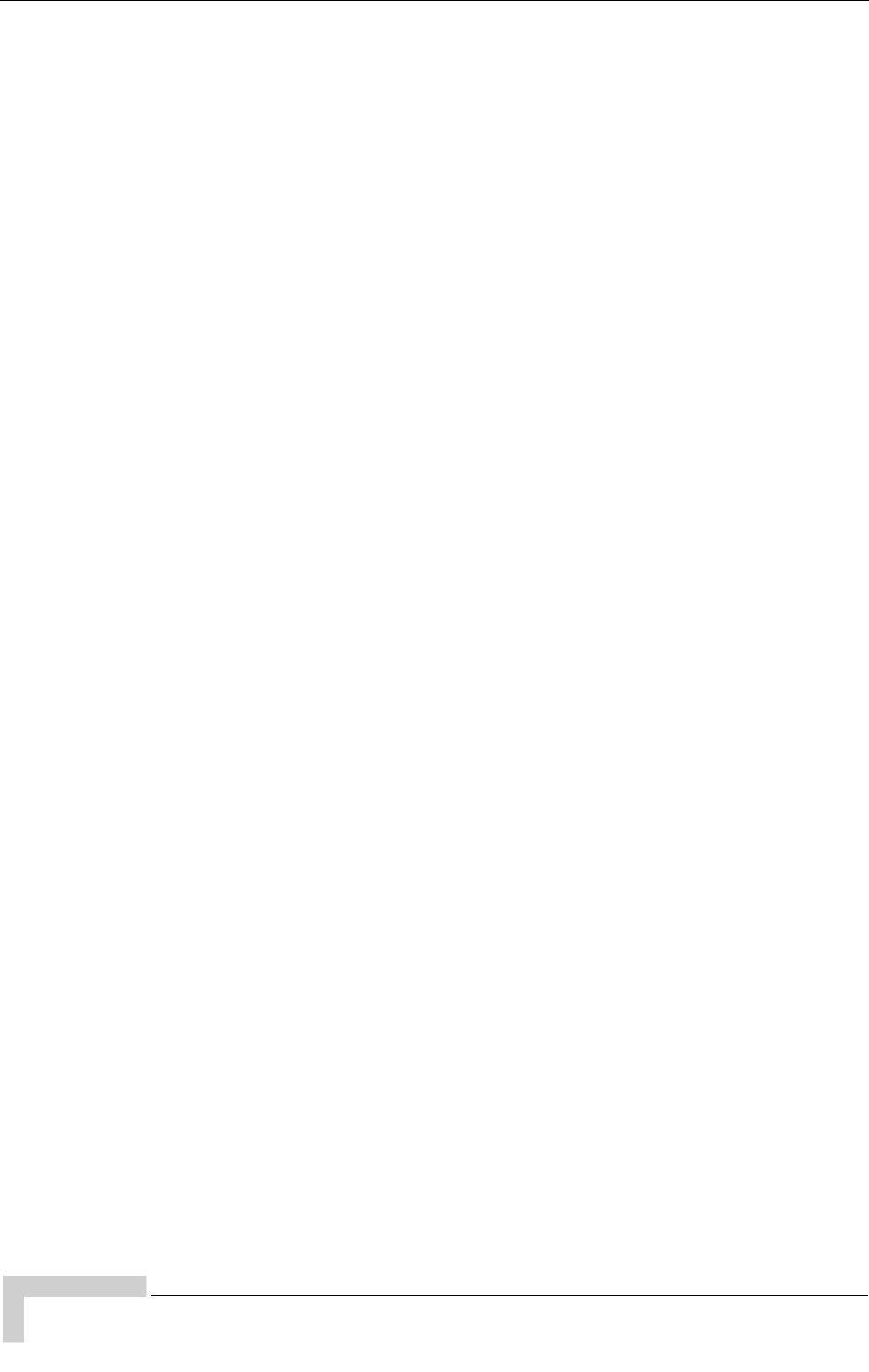
130 UltraWAVE Micro BTS Installation and Commissioning Guide, Version B
Chapter 5 - On-Line Commissioning
(this page intentionally left blank)
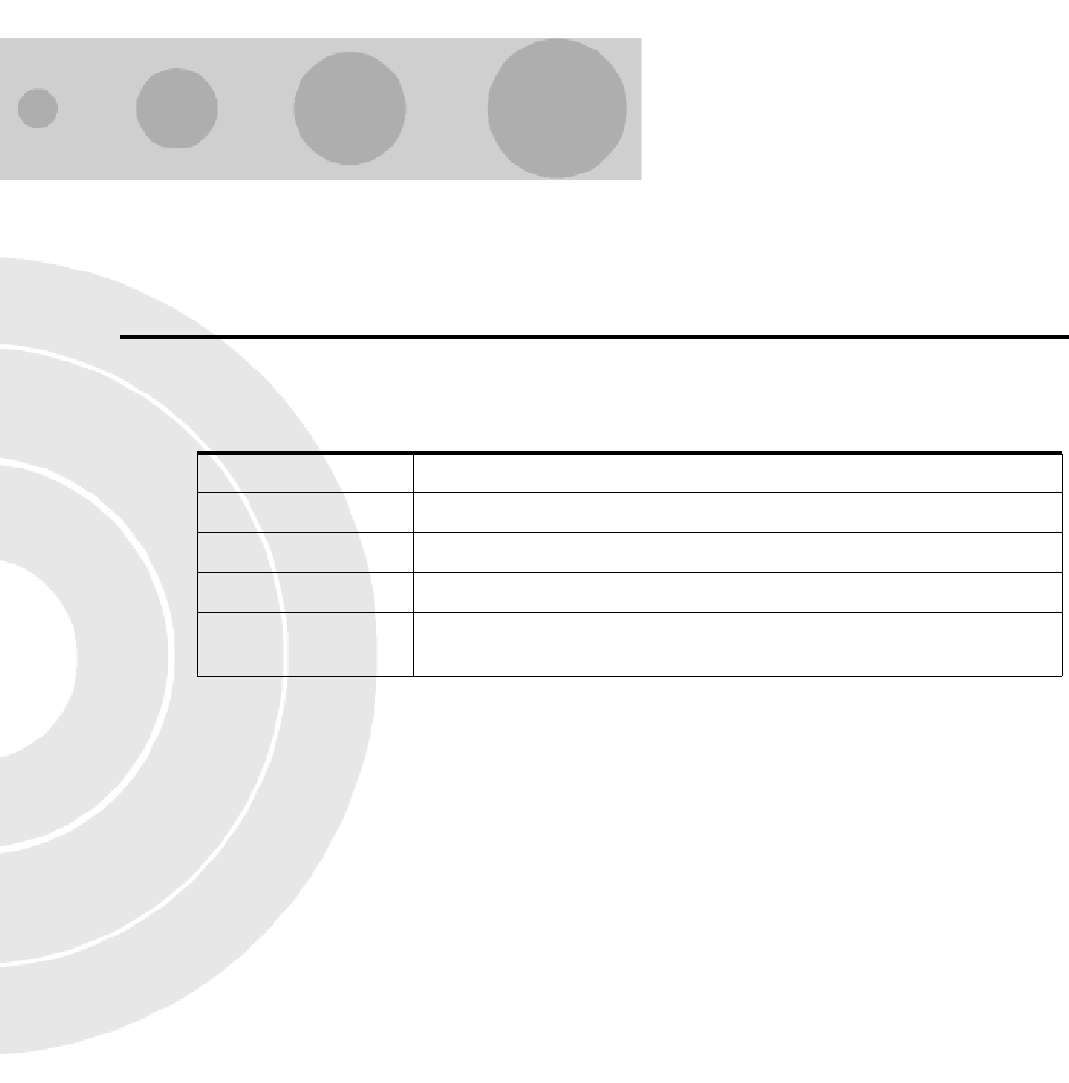
C1
Checklist 1 - Site Readiness Checklist
Environmental requirements
1 __ Ground and soil resistance measured.
2 __ Air conditioning available.
Electrical requirements
1 __ Site ground plate/ring installed and grounding rods connected.
2 __ Grounding bar installed on shelter/cabinet and bonded to site ground plate/ring.
3 __ Main feeder bend radius verified.
4 __ Power cable entry supports/conduits installed.
5 __ Main power cable installed and ready for connection.
6 __ Power utility meter installed and connected.
7 __ Main power supply available.
8 __ MCC & MNC frequencies assigned and confirmed.
9 __ Local electrician/power provider available.
Chassis requirements
1 __ Shelter/Cabinet anchored in position.
2 __ Foundation pad for shelter/cabinet constructed.
3 __ Backbone trunking equipment and installation material on site.
4 __ Shelter/Cabinet waterproofed.
5 __ PLMN/PSTN/E1/T1 lines installed (BER link measurements).
Table C1-1: Site Details
Site Name
IP Address
Micro BTS Name
MSC Name
Site/Access Phone
Number

130 UltraWAVE Micro BTS Installation and Commissioning Guide, Version B
Checklist 1 - Site Readiness Checklist
(this page intentionally left blank)
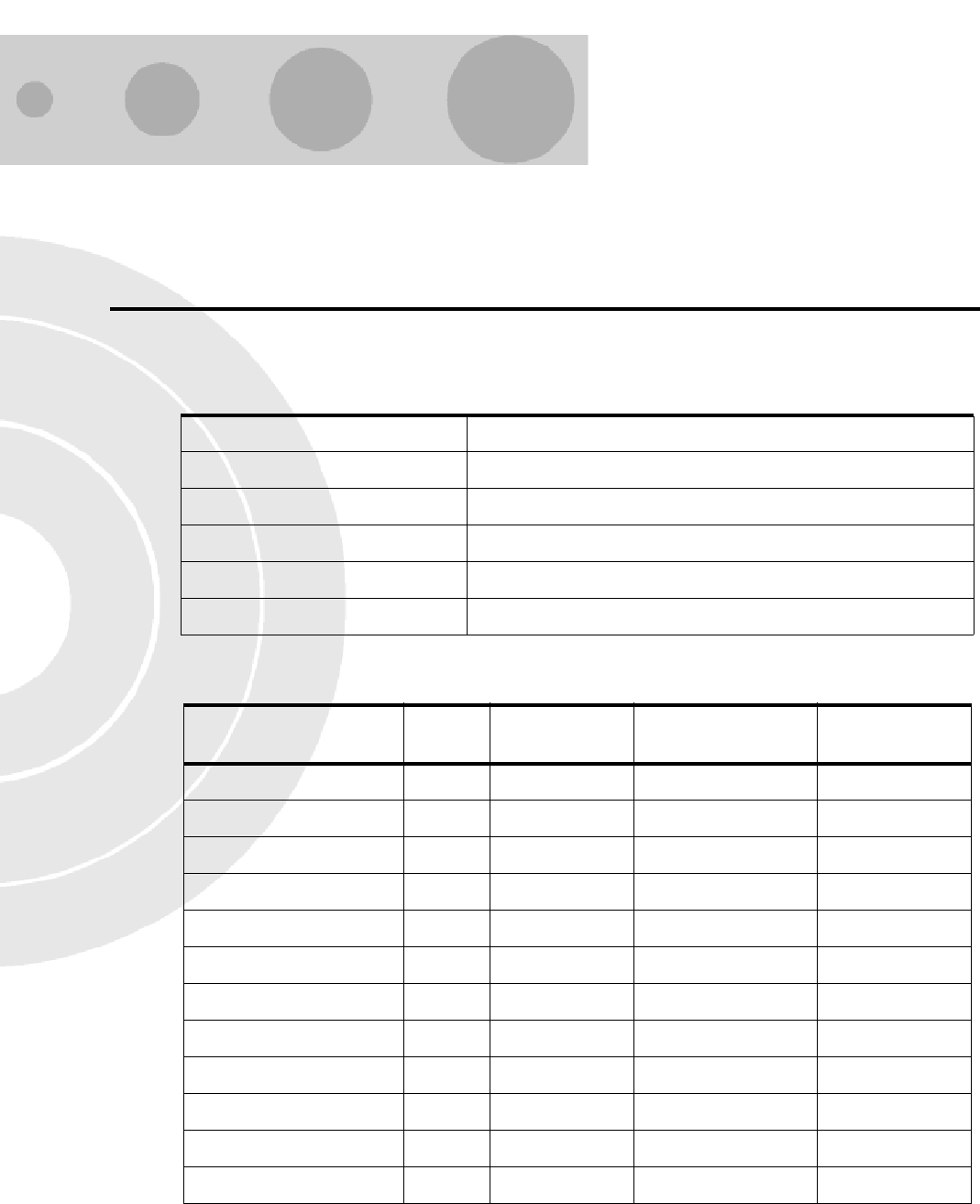
C2
Checklist 2 - Installation Checklist
Table C2-1: Site Details
Site Name
IP Address
IP Name (optional)
MSC Name
Micro BTS Name
Site/Access Phone Number
Table C2-2: Micro BTS Rack Assembly Equipment
Micro BTS Rack
Assembly Slot Part Number Revision Number Serial Number
RF Module A
RF Module B
RF Module C
ICP processor card 0
E1 or T1 Trunk card 1
TRX card 2
TRX card 3
TRX card 4
TRX card 5
TRX card 6
TRX card 7
Clock Module -
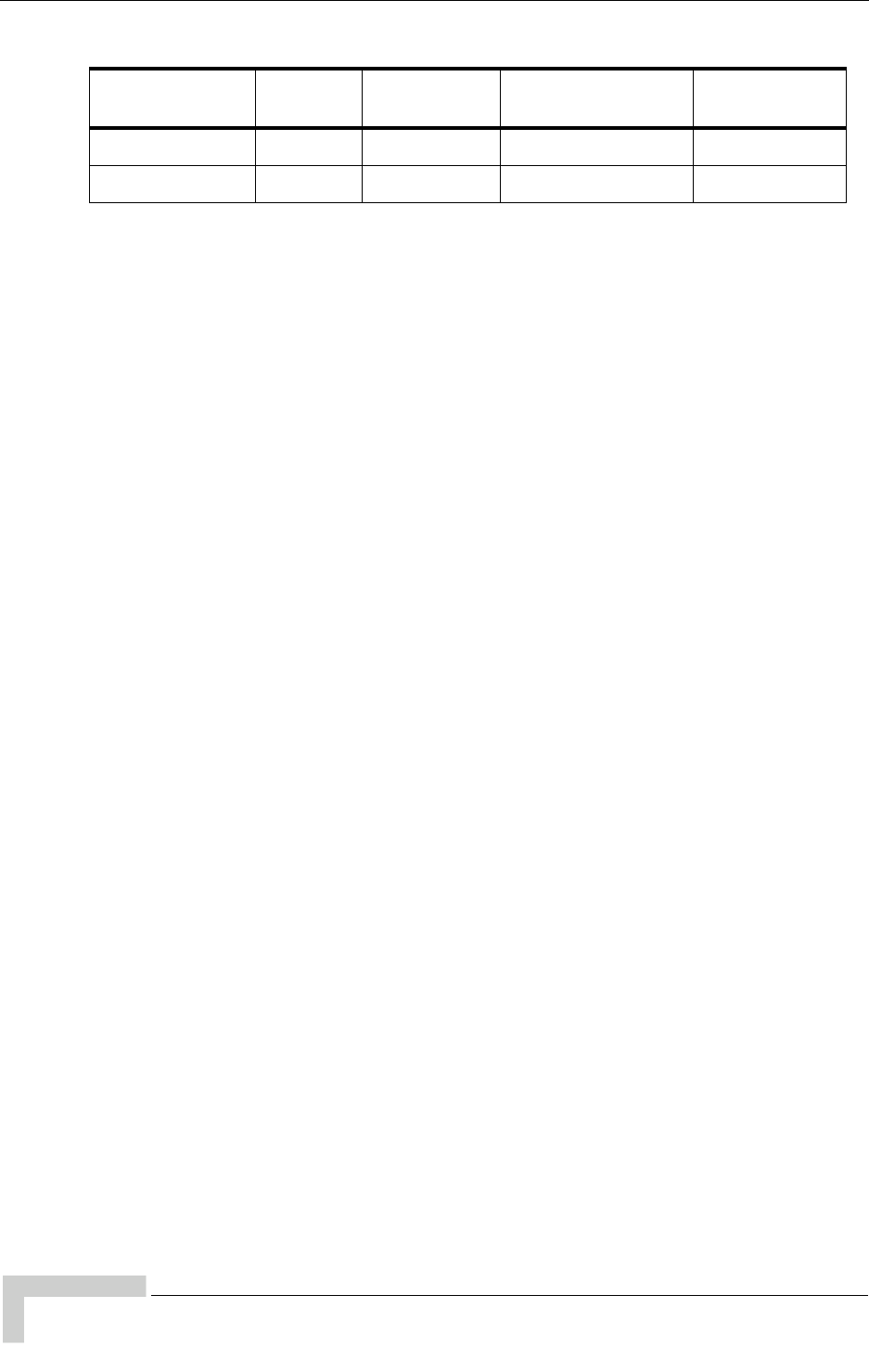
132 UltraWAVE Micro BTS Installation and Commissioning Guide, Version B
Checklist 2 - Installation Checklist
Unpacking the Micro BTS
1 __ Check for visible damage to shipping materials. Contact Alvarion Customer Ser-
vice if any visible damage is found.
2 __ All parts included per shipping invoice.
3 __ Cross check with site specific data to ensure Micro BTS is correctly configured
with all cards.
Mounting the Micro BTS on a Rack (if applicable)
1 __ Attach mounting brackets to chassis.
2 __ Mount chassis in rack.
3 __ Ground chassis.
4 __ Connect power supply: 110 VAC to 220 VAC, 30 A, 50-60 Hz or -40 VDC to
-60 VDC, 40 A.
Connecting the Micro BTS
1 __ Connect “A Interface” E1 or T1 trunk cables to local telephone provider demarca-
tion.
2 __ Configure E1 or T1 trunk card DIP switch settings.
3 __ Ensure power to BTS is off.
Verifying the MSC-Micro BTS Link
It is the operator’s responsibility to verify that all MSC-Micro BTS E1 or T1 links
are ordered, installed and certified by the local telephone facilities/operator.
Verify bit error rates on a nominal 20 minute soak test on the E1 or T1 A-interface
(end-to-end BER test to include E1or T1 trunk cables). The Micro BTS is now
ready for commissioning tests.
Table C2-3: Power Supply Subrack Equipment
Power Supply
Subrack Number Part Number Revision Number Serial Number
PS Module
PS Module
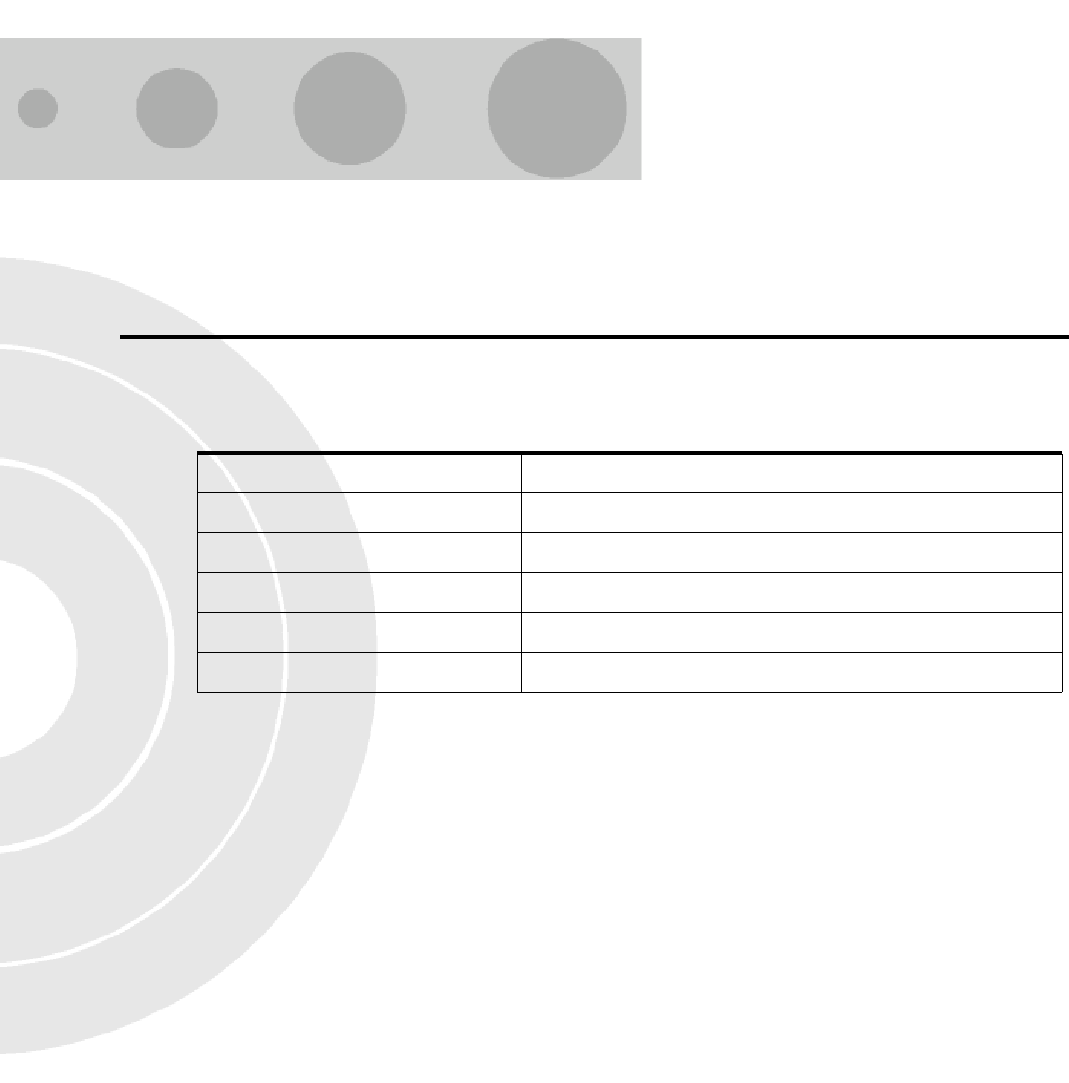
C3
Checklist 3 - Commissioning Checklist
Pre-Commissioning Visual Checks
1 __ Installation secure.
2 __ Power to the chassis is off.
3 __ The chassis is connected to a power source.
4 __ The chassis is grounded.
5 __ Equipment cables are labeled and secured.
6 __ Cards are seated securely.
7 __ Transmission cables are available and labeled.
Compliance Checks
1 __ Cross check with site-specific data to ensure the Micro BTS is correctly configured
with all cards.
2 __ Serial number of all cards are recorded.
3 __ Verify correct operating voltage supplied: AC (110 V to 220 V, 30 A, 50-60 Hz) or
DC (-40 V to -60 V, 40 A).
Powering On the Micro BTS
1 __ Disconnect all E1 and/or T1 cables from Micro BTS (if connected).
2 __ Turn power to the chassis on.
3 __ Verify all card power LEDs and processor and on-line LEDs are green.
Table C3-1: Site Details
Site Name
IP Address
IP Name (optional)
MSC Name
Micro BTS Name
Site/Access Phone Number

134 UltraWAVE Micro BTS Installation and Commissioning Guide, Version B
Checklist 3 - Commissioning Checklist
Micro BTS Off-Line Commissioning
1 __ Connect the Craft PC to the processor card using a serial and ethernet cable.
2 __ Establish a serial connection.
3 __ Check software version.
4 __ Start NMI.
5 __ Check the Micro BTS configuration database (refer to Steps 6 through 9 below).
6 __ Delete existing database files.
7 __ Verify that all E1 or T1 trunk cards are logically represented.
8 __ Check the serial numbers, revision numbers and part numbers of all E1 or T1
trunk cards.
9 __ Verify that DSP daughtercards are logically represented and tested.
POST Tests
1 __ Verify POST tests successfully passed.
2 __ Exit NMI. Disconnect Craft PC from the Micro BTS.
Connecting the BTS
1 __ Connect all E1 or T1 cables to the telephone provider demarcation at the MSC.
2 __ Connect all E1 or T1 cables to the telephone provider demarcation at the Micro
BTSs.
3 __ Inform Micro BTS operator (ready for on-line tests).
4 __ Leave power to Micro BTS on.
On-Line Commissioning
1 __ Micro BTS in service and connected to external Micro BTSs (if applicable).
2 __ BSC in service and connected to Micro BTS.
3 __ Micro BTS connected to MSC.
4 __ Database questionnaire completed with Micro BTS parameters defined.
5 __ OMC downloaded Micro BTS configuration with correct operational parameters.
6 __ Operator’s responsibility to verify all E1 or T1 links properly installed and certi-
fied by local telephone provider. Certification must rate Length of Testing and
BER results.
Verifying E1 or T1 Operation
1 __ Verify bit error rates on a nominal 20-minute soak test on the Abis interface to
remote Micro BTS(s) if applicable.
2 __ Verify bit error rates on a nominal 20-minute soak test on the A-interface.
Verifying Recovery
1 __ Unlock A-interface, A-Links and Micro BTS objects from Micro BTS.
2 __ Confirm A-interface re-establishes communications to MSC after E1 or T1 dis-
connects.
3 __ Confirm Abis interface re-establishes communications to remote Micro BTS(s)
after E1 or T1 disconnects.

UltraWAVE Micro BTS Installation and Commissioning Guide, Version B 135
Commissioning Checklist
Checking Clock Synchronization
1 __ Verify Micro BTS clock is free of error
Verifying the Database
1 __ Verify Micro BTS database matches Micro BTS physical configuration
Final Commissioning and On-Line Tests
1 __ Reconnect all E1 or T1 cables to telephone provider demarcation
2 __ Power off and then on the BTS locally. Verify that all LEDs are green
3 __ Inform Micro BTS operator that Micro BTS is ready for integration tests
4 __ Leave power to Micro BTS on
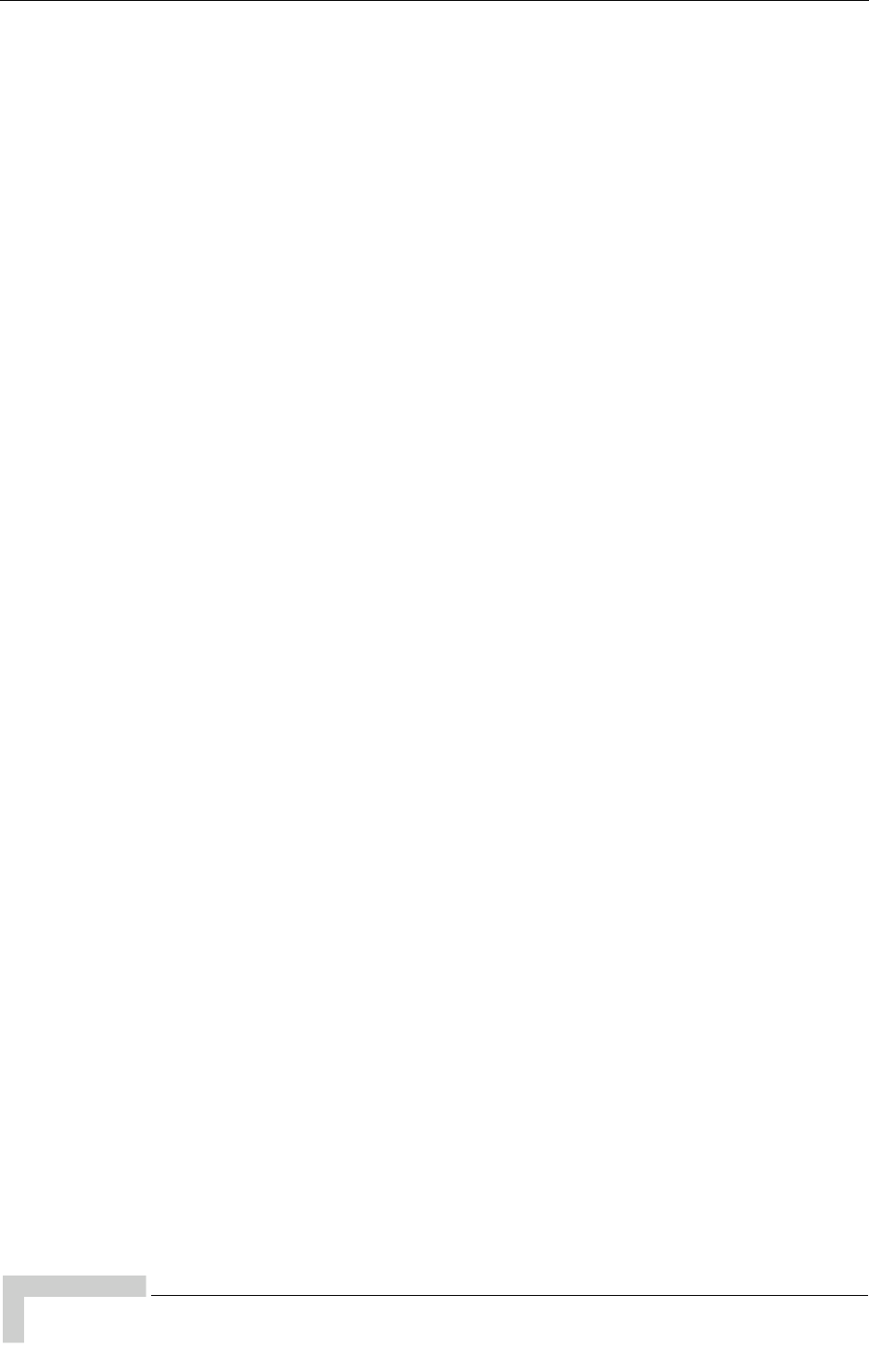
136 UltraWAVE Micro BTS Installation and Commissioning Guide, Version B
Checklist 3 - Commissioning Checklist
(this page intentionally left blank)
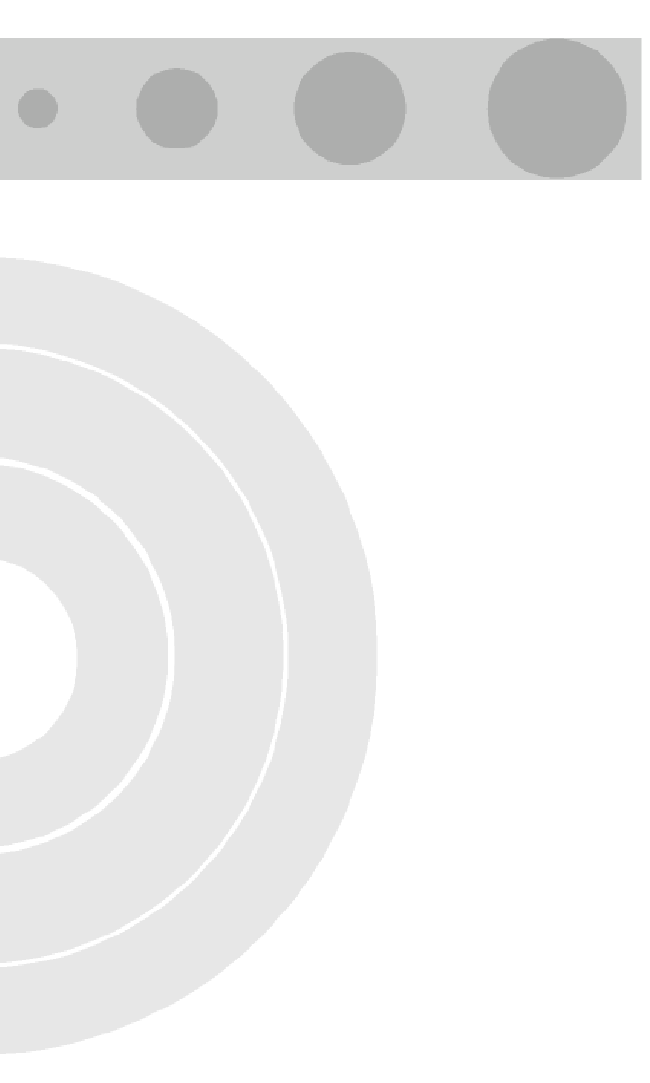
Index
A
AC
power supply 41
power switch 41
alarm
external 60
input connection 63
terminal block 60
antenna
connecting to the CMA 52
B
boot parameters
configuring for Craft PC 79
C
cabling
between multiple UltraWAVE or WAVEXpress systems 50
external 38, 65
serial 64
chassis mounting 22, 27
checklist
commissioning 133
installation 131
site readiness 129
commissioning
online 111
post off-line 92
commissioning checklist 133
configuration labels 11
configuring
boot parameters using Craft PC 79
E1 or T1 trunk card 31

138 UltraWAVE Micro BTS Installation and Commissioning Guide, Version B
Index
connecting
AC power 41
Craft PC
powering down 89
D
daisy chain off-line commissioning 107
daisy chain prerequisites 108
E
E1
configuring trunk card 31
connecting lines 50
E1 or T1 POST diagnostics 85
ethernet
verifying telnet communications 81
external alarms 60
external cabling 38
F
forward power 121
front panel LEDs 76
G
grounding cable 36
I
inspections
visual 69
installation 17
installation checklist 131
internal cabling 15
L
label
system configuration 9
LAPD signaling time slot 109
LEDs 76
M
measurements
forward and reverse power 121

UltraWAVE Micro BTS Installation and Commissioning Guide, Version B 139
Index
Micro BTS
serial communications with ICP processor card 73
mounting Micro BTS chassis 22
N
network integration 121
network integration procedures 114
O
off-line commissioning 67
daisy chain 107
on-line commissioning 111, 114
P
patch level verification 83
pinout
serial 64
post installation
cabling and checks 66
post off-line commissioning 92
post on-line commissioning procedures 129
POST results review 88
power supply
AC 41
connections 41
switch 41
power-on LED tests 76
pre on-line commissioning
requirements 113
prerequisites
network configuration 121
network integration 113, 121
prerequisites to daisy chaining 108
processor card
serial pinout 64
R
rebooting BTS after running POST 89
requirements
pre on-line commissioning 113
reverse power 121
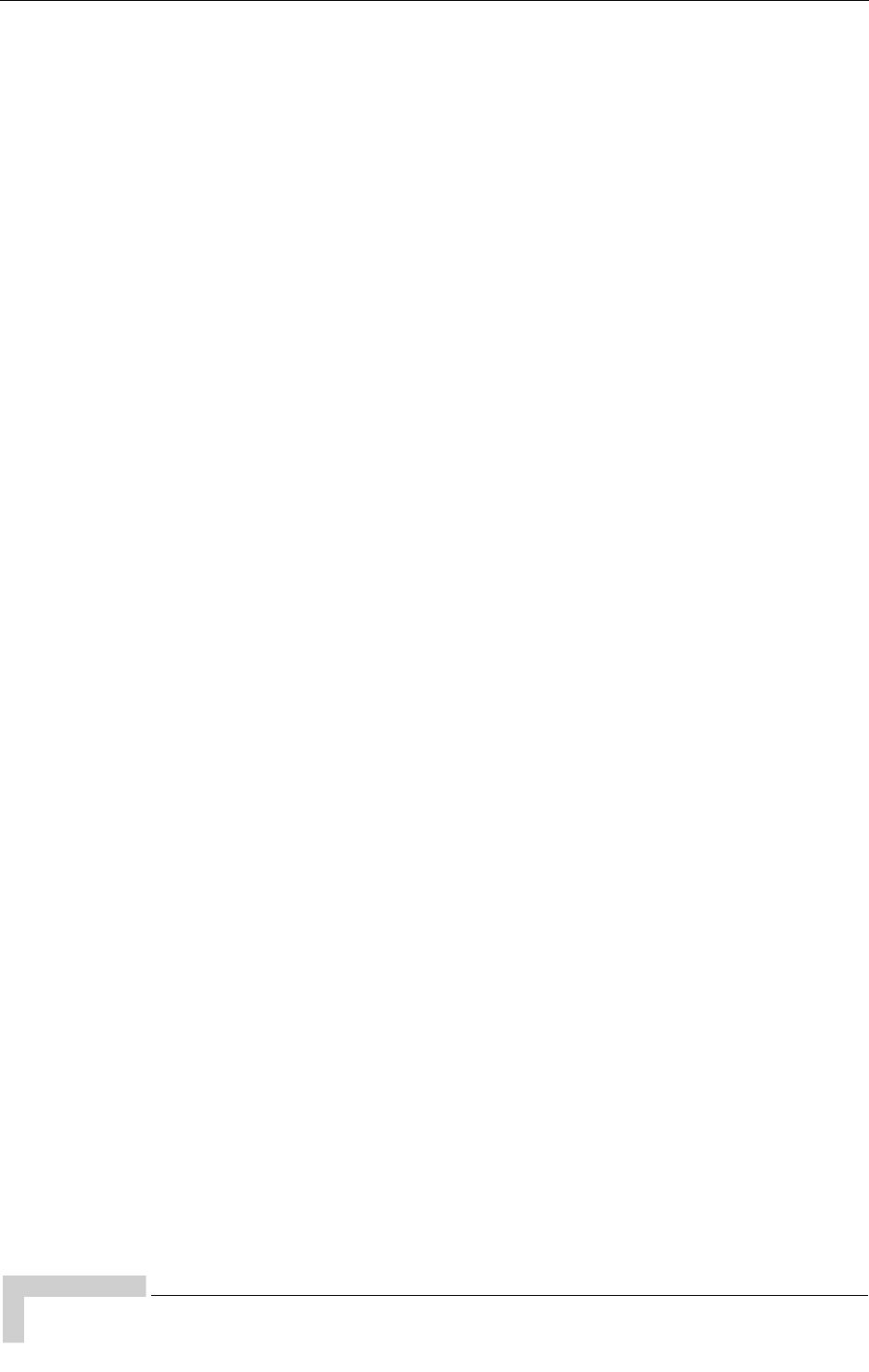
140 UltraWAVE Micro BTS Installation and Commissioning Guide, Version B
Index
reviewing POST results 88
S
serial communications
ICP processor card 73
terminating 89
serial port
pinout 64
setting Abis LAPD signaling timeslot 109
site readiness checklist 129
slot assignments 13
software
patch level 83
updating 90
verifying version 83
system
configuration 9
type of 9
T
T1
configuring trunk card 31
connecting lines 50
T1 or E1 POST diagnostics 85
telnet communications
establishing 82
terminating 82
terminating serial communications with BTS 89
TRX POST diagnostics 86
V
verifying
current software version and patch level 83
external cabling 66
internal cabling 15
telnet communications with Micro BTS over ethernet 81
verifying Micro BTS performance 121
Voltage Standing Wave Ratio (VSWR) check 126

Notes:
UltraWAVE Micro BTS Installation and Commissioning Guide, Version B 141