Advanced Radiotech ARCFLEXJX Industrial radio remote control systems User Manual Flex JX Manual 10122015 SGS
Advanced Radiotech Corporation Industrial radio remote control systems Flex JX Manual 10122015 SGS
Users Manual
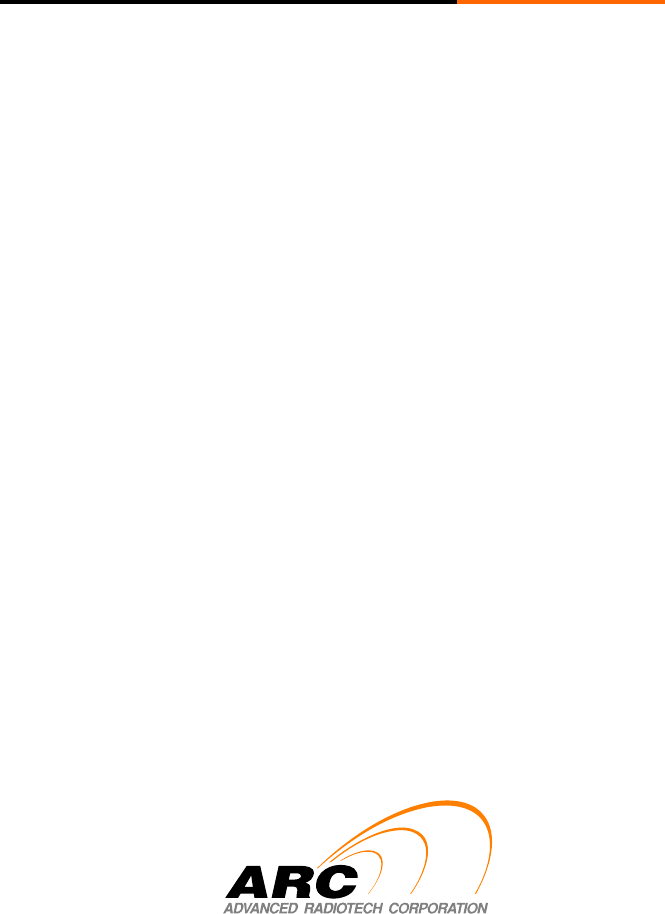
FLEX JX
User’s Manual
Page 1
Service Information
Your New Radio System
Thank you for your purchase of ARC Flex JX radio remote control system. Without a doubt, our Flex
JX system is the ultimate solution for providing precise, undeterred, and safe control of your material.
If your product ever needs modification or service, please contact our representative in your country
or at the following location:
World Headquarter:
Advanced Radiotech Corporation
288-1, Hsin Ya Road, Chien Chen District
Kaohsiung, Taiwan
Telephone:
+886 7 812 8112
Fax Number:
+886 7 812 8119
Website:
www.advanced-radiotech.com
e-mails:
info@advanced-radiotech.com
sales@advanced-radiotech.com
All rights reserved. This notice applies to all copyrighted materials included with this product, including,
but not limited to, this manual and software embodied within the product. This manual is intended for
the sole use of the person(s) to whom it was provided, and any unauthorized distribution of the
manual or dispersal of its contents is strictly forbidden. This manual may not be reproduced in whole
or in part by any means whatsoever without the expressed written permission of ARC.
Page 2
PRODUCT MANUAL SAFETY INFORMATION
Advanced Radiotech Corporation (ARC) offers a broad range of radio remote control product for
material handling applications. This manual has been prepared by ARC to provide information and
recommendations for the installation, use, operation and service of ARC’s material handling products
and systems (ARC Products). Anyone who uses, operates, maintains, services, installs or owns ARC
Products should know, understand, and follow the instructions and safety recommendations in this
manual for ARC Products.
The recommendations in this manual do not take precedence over any of the following requirements
relating to cranes, hoists lifting devices or other material handling equipment which use or include
ARC Products:
Instructions, manuals, and safety warnings of the manufacturers of the equipment where the
radio system is used.
Plant safety rules and procedures of the employers and the owners of facilities where the
ARC Products are being used.
Safety standards and practices for the industries in which ARC Products are used.
This manual does not include or address the specific instructions and safety warnings of these
manufacturers or any of the other requirements listed above. It is the responsibility of the owners,
users and operators of the ARC Products to know, understand and follow all of these requirements. It
is the responsibility of the employer to make its employees aware of all of the above listed
requirements and to make certain that all operators are properly trained. No one should use ARC
Products prior to becoming familiar with and being trained in these requirements and the
instructions and safety recommendations in this manual.
WARRANTY INFORMATION
For information on ARC’s product warranties, please contact ARC representative nearest to you or
visit www.advanced-radiotech.com.
FCC WARNINGS and CAUTIONS
NOTE: This equipment has been tested and found to comply with the limits for a Class B digital device, pursuant
to part 15 of the FCC Rules. These limits are designed to provide reasonable protection against harmful
interference in a residential installation. This equipment generates, uses and can radiate radio frequency energy
and, if not installed and used in accordance with the instructions, may cause harmful interference to radio
communications. However, there is no guarantee that interference will not occur in a particular installation. If this
equipment does cause harmful interference to radio or television reception, which can be determined by turning
the equipment off and on, the user is encouraged to try to correct the interference by one or more of the following
measures:
— Reorient or relocate the receiving antenna.
— Increase the separation between the equipment and receiver.
— Connect the equipment into an outlet on a circuit different from that to which the receiver is connected.
— Consult the dealer or an experienced radio/TV technician for help.
RADIO FREQUENCY INTERFERENCE STATEMENT
This device complies with Part 15 of the FCC rules. Operation is subject to the following two conditions:
1) this device may not cause harmful interference, and
2) this device must accept any interference received, including interference that may cause undesired
operation.
FCC Caution: Any change or modification not expressly approved by the party responsible for
compliance could void the user’s authority to operate this equipment.
Page 3
Table of Contents
Page
1. Introduction 5
2. Radio Controlled Safety 6
3. General System Information
3.1 Transmitter 11
3.2 Receiver
3.2.1 External Illustration 12
3.2.2 Internal Illustration 13
4. Function Settings
4.1 Transmitter
4.1.1 Programming Procedure 14
4.1.2 Transmitter Channel 15
4.1.3 Transmitter Type 15
4.1.4 Transmitter Inactivity Timer 16
4.1.5 Transmitter Output Power 16
4.1.6 Transmitter Infrared Mode 17
4.1.7 Transmitter Infrared ID 17
4.1.8 Transmitter Infrared START Function 18
4.1.9 Transmitter Tilt Function 18
4.1.10 SW1 Button Function 19
4.1.11 SW2 Button Function 19
4.1.12 SW3 Button Function 20
4.1.13 SW4 Button Function 20
4.1.14 SW5 Button Function 21
4.1.15 SW6 Button Function 21
4.1.16 SW7 Button Function 22
4.1.17 Save Function 22
4.1.18 I-Chip Installation 22
4.2 Receiver Unit
4.2.1 Programming Procedure 23
4.2.2 I-Chip Programming 24
4.2.3 Receiver Channel 24
4.2.4 Receiver Channel Scanning 25
4.2.5 Receiver Type 26
4.2.6 Main Relay Function 26
4.2.7 Function Relay #1 27
4.2.8 Function Relay #2 28
4.2.9 Joystick LX Acceleration and Deceleration Delay 29
4.2.10 Joystick LY Acceleration and Deceleration Delay 29
Page 4
4.2.11 Joystick RX Acceleration and Deceleration Delay 30
4.2.12 Joystick RY Acceleration and Deceleration Delay 30
4.2.13 SW1+SW2 Output Relays Function 31
4.2.14 SW1 Output Relay Function 32
4.2.15 SW2 Output Relay Function 33
4.2.16 SW3 Output Relay Function 34
4.2.17 SW4+SW5 Output Relays Function 35
4.2.18 SW4 Output Relay Function 36
4.2.19 SW5 Output Relay Function 37
4.2.20 SW6+SW7 Output Relays Function 38
4.2.21 SW6 Output Relay Function 39
4.2.22 SW7 Output Relay Function 40
4.2.23 Save Function 41
4.2.24 Voltage Settings 41
5. System Channels Table 42
6. Receiver Installation
6.1 Output Relay Contact Diagram 43
6.2 Pre-Installation Precautions 44
6.3 Step-By-Step Installation 44
6.4 System Testing 45
7. Operating Procedure
7.1 General Operating Procedure 46
7.2 Pitch & Catch Operating Procedure 47
7.3 Automatic Channel Scanning Operating Procedure 48
7.4 Battery Changing Instruction 48
8. Status & Warnings
8.1 Transmitter 49
8.2 Receiver
8.2.1 LED STATUS Indications 50
8.2.2 LED SQ Indications 50
8.2.3 LED POWER Indications 50
8.2.4 LED COM Indications 50
8.2.5 LCD Indications 51
9. Trouble Shooting Tips 52
10. System Specifications 53
11. EU Declaration of Conformity 54
Page 5
1. Introduction
The Flex JX radio remote control systems are designed for control of industrial equipment and
machinery such as overhead traveling cranes, jib cranes, gantry cranes, tower cranes and other
material handling equipment where wireless control is preferred.
Each Flex JX system consists of a transmitter belly box and receiver unit. Other standard-equipped
accessories include one rechargeable battery pack, one charging station, one each transmitter waist
and shoulder belt, one spare transmitter power key and user’s manual.
List of notable features include:
* 62 user-programmable channels – Advanced synthesized RF controls with 62 built-in
channels.
* Automatic channel scanning receiver – No more hassle of climbing up the crane to change
receiver channels. Transmitter channel can be changed directly on the transmitter via the LCD
panel.
* Transceiving RF modules – The Flex JX system is capable of two-way communication
between transmitter and receiver.
* LCD readout – All settings and system status information are displayed and executed via the
LCD panel on transmitter and in receiver.
* Goretex vent – The transmitter is equipped with special Goretex vent to guard against
water/vapor buildups inside transmitter enclosure.
* Transmitter tilt function – The transmitter is embedded with special tilt switch to guard against
accidental crane movements when the transmitter is dropped.
* Over one million unique serial numbers (20bit) – Each and every Flex JX system has its
own unique serial number; no repeats.
* Advanced controls – The Flex JX system utilizes dual advanced microprocessor controls with
32bit CRC and Hamming Code, which provide ultra-fast, safe, precise, and error-free encoding
and decoding.
* Unique I-Chip design – The I-Chip functions in a way that is very similar to SIM cards used
on mobile phones, with the ability to transfer system information and settings from one
transmitter to another without the hassle of resetting the spares.
* Fully sealed enclosures – The transmitter and receiver enclosures are IP66 rated.
* Infrared start/range limiting features – The Flex JX transmitter is standard-equipped with
infrared sensor for infrared start and infrared range limiting operation.
* Other features – Tandem operation, multi-receiver operation, random access operation, pitch
and catch operation, and many others.
* Full compliance – All systems are fully compliant with the FCC Part-15 Rules, European
Directives (Safety, EMC, R&TTE and Machinery), and Industry Canada Specifications (IC).
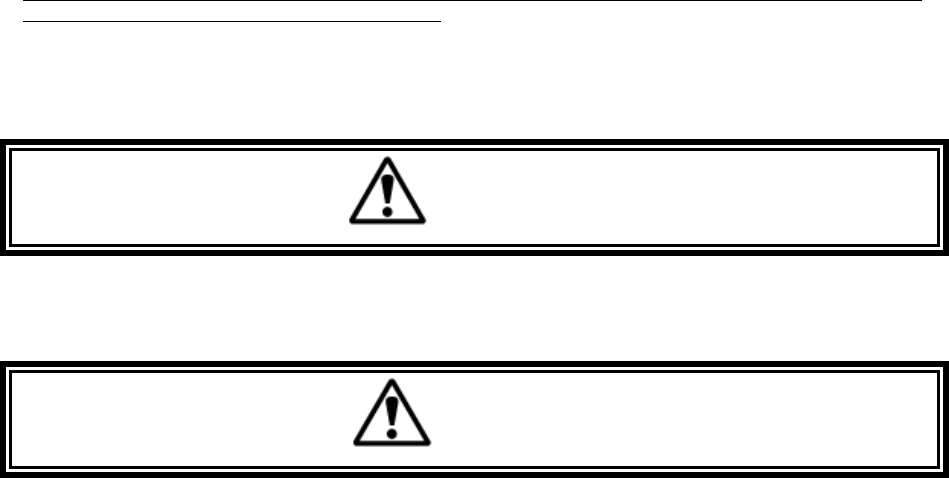
Page 6
2. Radio Controlled Safety
WARNINGS and CAUTIONS
Throughout this document WARNING and CAUTION statements have been deliberately placed to highlight items
critical to the protection of personnel and equipment.
WARNING – A warning highlights an essential operating or maintenance procedure, practice, etc. which if
not strictly observed, could result in injury or death of personnel, or long term physical hazards.
Warnings are highlighted as shown below:
WARNING
CAUTION – A caution highlights an essential operating or maintenance procedure, practice, etc. which if
not strictly observed, could result in damage to, or destruction of equipment, or loss of functional
effectiveness. Cautions are highlighted as shown below:
CAUTION
WARNINGS and CAUTIONS SHOULD NEVER BE DISREGARDED.
The safety rules in this section are not intended to replace any rules or regulations of any applicable local, state,
or federal governing organizations. Always follow your local lockout and tagout procedure when maintaining any
radio equipment. The following information is intended to be used in conjunction with other rules or regulations
already in existence. It is important to read all of the safety information contained in this section before installing
or operating the Radio Control System.
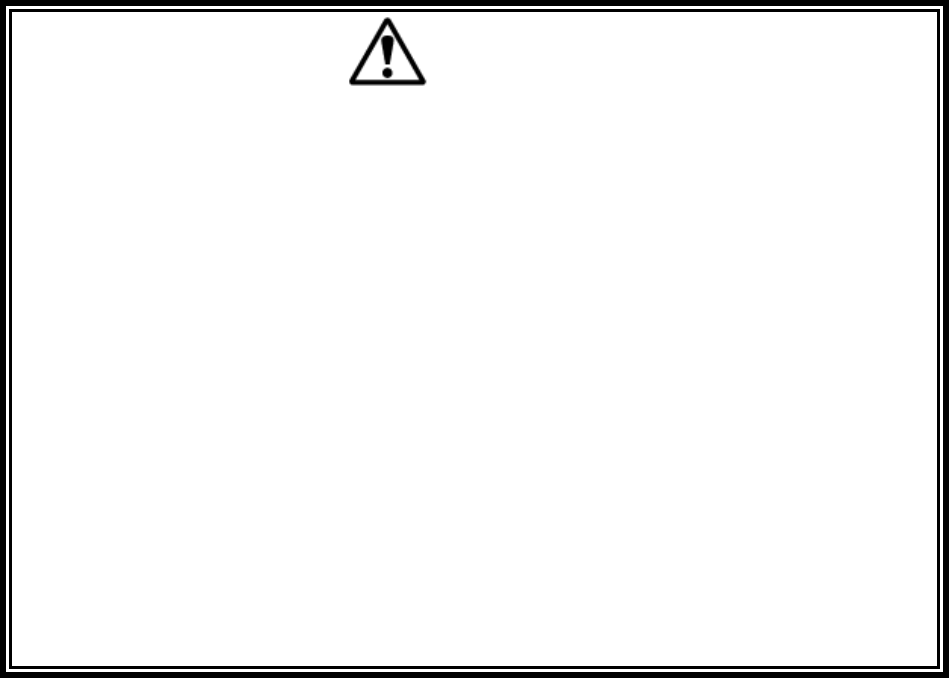
Page 7
2.1 CRITICAL INSTALLATION CONSIDERATIONS
WARNING
PRIOR TO INSTALLATION AND OPERATION OF THIS EQUIPMENT, READ AND DEVELOP AN
UNDERSTANDING OF THE CONTENTS OF THIS MANUAL AND THE OPERATION MANUAL OF THE
EQUIPMENT OR DEVICE TO WHICH THIS EQUIPMENT WILL BE INTERFACED. FAILURE TO FOLLOW
THIS WARNING COULD RESULT IN SERIOUS INJURY OR DEATH AND DAMAGE TO EQUIPMENT.
ALL EQUIPMENT MUST HAVE A MAINLINE CONTACTOR INSTALLED AND ALL TRACKED CRANES,
HOISTS, LIFTING DEVICES AND SIMILAR EQUIPMENT MUST HAVE A BRAKE INSTALLED. FAILURE TO
FOLLOW THIS WARNING COULD RESULT IN SERIOUS INJURY OR DEATH AND DAMAGE TO EQUIPMENT.
AN AUDIBLE AND/OR VISUAL WARNING MEANS MUST BE PROVIDED ON ALL REMOTE CONTROLLED
EQUIPMENT AS REQUIRED BY CODE, REGULATION, OR INDUSTRY STANDARD. THESE AUDIBLE
AND/OR VISUAL WARNING DEVICES MUST MEET ALL GOVERNMENTAL REQUIREMENTS. FAILURE TO
FOLLOW THIS WARNING COULD RESULT IN SERIOUS INJURY OR DEATH AND DAMAGE TO EQUIPMENT.
FOLLOW YOUR LOCAL LOCKOUT TAGOUT PROCEDURE BEFORE MAINTAINING ANY REMOTE
CONTROLLED EQUIPMENT. ALWAYS REMOVE ALL ELECTRICAL POWER FROM THE CRANE, HOIST,
LIFTING DEVICE OR SIMILAR EQUIPMENT BEFORE ATTEMPTING ANY INSTALLATION PROCEDURES.
DE-ENERGIZE AND TAGOUT ALL SOURCES OF ELECTRICAL POWER BEFORE TOUCH-TESTING ANY
EQUIPMENT. FAILURE TO FOLLOW THIS WARNING COULD RESULT IN SERIOUS INJURY OR DEATH AND
DAMAGE TO EQUIPMENT.
THE DIRECT OUTPUTS OF THIS PRODUCT ARE NOT DESIGNED TO INTERFACE DIRECTLY TO TWO
STATE SAFETY CRITICAL MAINTAINED FUNCTIONS, I.E., MAGNETS, VACUUM LIFTS, PUMPS,
EMERGENCY EQUIPMENT, ETC. A MECHANICALLY LOCKING INTERMEDIATE RELAY SYSTEM WITH
SEPARATE POWER CONSIDERATIONS MUST BE PROVIDED. FAILURE TO FOLLOW THIS WARNING
COULD RESULT IN SERIOUS INJURY OR DEATH OR DAMAGE TO EQUIPMENT.
2.2 GENERAL
Radio controlled material handling equipment operates in several directions. Cranes, hoists, lifting devices and
other material handling equipment can be large, and operate at high speeds. Quite frequently, the equipment is
operated in areas where people are working in close proximity to the material handling equipment. The operator
must exercise extreme caution at all times. Workers must constantly be alert to avoid accidents. The following
recommendations have been included to indicate how careful and thoughtful actions may prevent injuries,
damage to equipment, or even save a life.
2.3 PERSONS AUTHORIZED TO OPERATE RADIO
CONTROLLED CRANES
Only properly trained persons designated by management should be permitted to operate radio controlled
equipment.
Radio controlled cranes, hoists, lifting devices and other material handling equipment should not be operated by
any person who cannot read or understand signs, notices and operating instructions that pertain to the equipment.
Radio controlled equipment should not be operated by any person with insufficient eyesight or hearing or by any
person who may be suffering from a disorder or illness, is taking any medication that may cause loss of
equipment control, or is under the influence of alcohol or drugs.
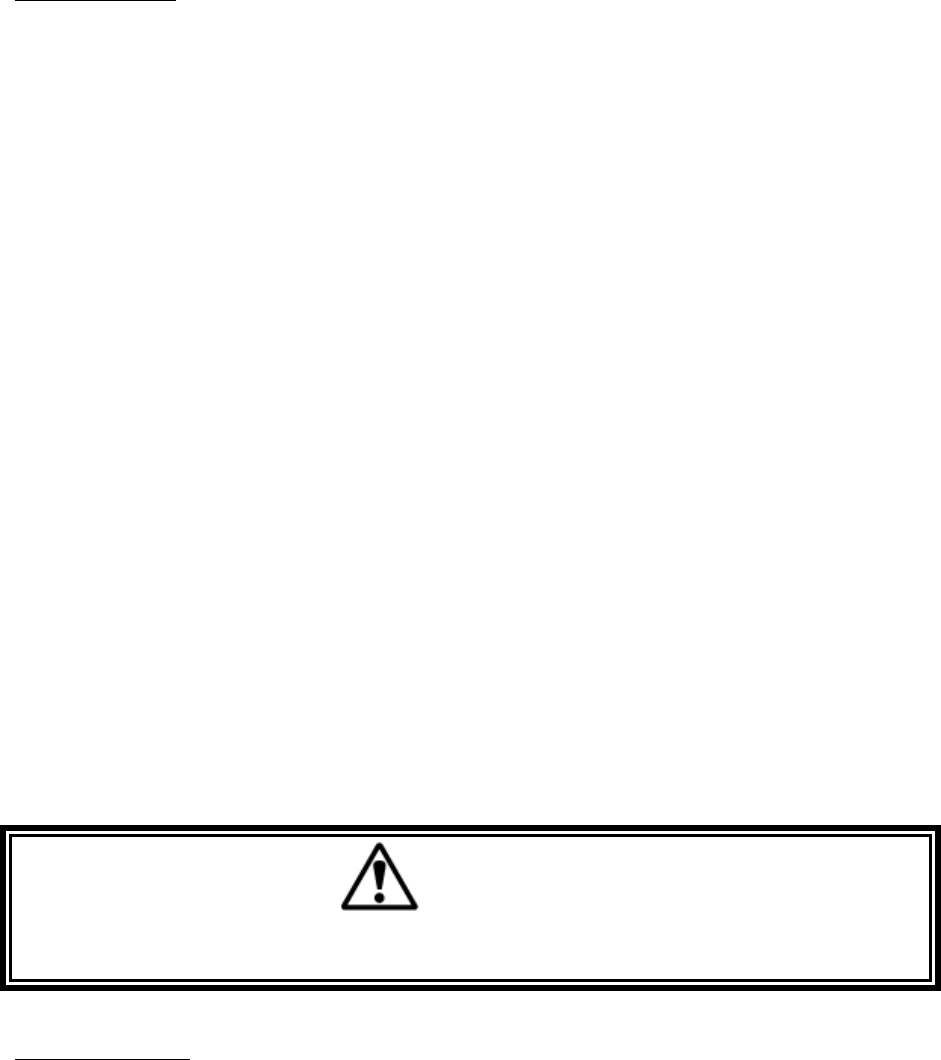
Page 8
2.4 SAFETY INFORMATION AND RECOMMENDED TRAINING
FOR RADIO CONTROLLED EQUIPMENT OPERATORS
Anyone being trained to operate radio controlled equipment should possess as a minimum the following
knowledge and skills before using the radio controlled equipment.
The operator should:
have knowledge of hazards pertaining to equipment operation
have knowledge of safety rules for radio controlled equipment
have the ability to judge distance of moving objects
know how to properly test prior to operation
be trained in the safe operation of the radio transmitter as it pertains to the crane, hoist, lifting device or
other material handling equipment being operated
have knowledge of the use of equipment warning lights and alarms
have knowledge of the proper storage space for a radio control transmitter when not in use
be trained in transferring a radio control transmitter to another person
be trained how and when to report unsafe or unusual operating conditions
test the transmitter emergency stop and all warning devices prior to operation; testing should be done on
each shift, without a load
be thoroughly trained and knowledgeable in proper and safe operation of the crane, hoist, lifting device, or
other material handling equipment that utilizes the radio control
know how to keep the operator and other people clear of lifted loads and to avoid “pinch” points
continuously watch and monitor status of lifted loads
know and follow cable and hook inspection procedures
know and follow the local lockout and tagout procedures when servicing radio controlled equipment
know and follow all applicable operating and maintenance manuals, safety procedures, regulatory
requirements, and industry standards and codes
WARNING
Keep away interference source to make sure performance integrate.
The operator shall not:
lift or move more than the rated load
operate the material handling equipment if the direction of travel or function engaged does not agree
with what is indicated on the controller
use the crane, hoist or lifting device to lift, support or transport people
lift or carry any loads over people
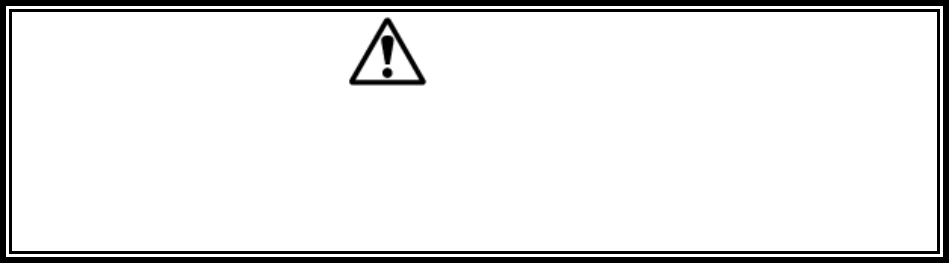
Page 9
operate the crane, hoist or lifting device unless all persons, including the operator, are and remain clear
of the supported load and any potential pinch points
operate a crane, hoist or lifting device when the device is not centered over the load
operate a crane, hoist or lifting device if the chain or wire rope is not seated properly in the sprockets,
drum or sheave
operate any damaged or malfunctioning crane, hoist, lifting device or other material handling equipment
change any settings or controls without authorization and proper training
remove or obscure any warning or safety labels or tags
leave any load unattended while lifted
leave power on the radio controlled equipment when the equipment is not in operation
operate any material handling equipment using a damaged controller because the unit may be unsafe
operate manual motions with other than manual power
operate radio controlled equipment when low battery indicator is on
WARNING
THE OPERATOR SHOULD NOT ATTEMPT TO REPAIR ANY RADIO CONTROLLER. IF ANY PRODUCT
PERFORMANCE OR SAFETY CONCERNS ARE OBSERVED, THE EQUIPMENT SHOULD IMMEDIATELY BE
TAKEN OUT OF SERVICE AND BE REPORTED TO THE SUPERVISOR. DAMAGED AND INOPERABLE
RADIO CONTROLLER EQUIPMENT SHOULD BE RETURNED TO MAGNETEK FOR EVALUATION AND
REPAIR. FAILURE TO FOLLOW THIS WARNING COULD RESULT IN SERIOUS INJURY OR DEATH AND
DAMAGE TO EQUIPMENT.
2.5 TRANSMITTER UNIT
Transmitter switches should never be mechanically blocked ON or OFF. When not in use, the operator should
turn the transmitter OFF. A secure storage space should be provided for the transmitter unit, and the transmitter
unit should always be placed there when not in use. This precaution will help prevent unauthorized people from
operating the material handling equipment.
Spare transmitters should be stored in a secure storage space and only removed from the storage space after the
current transmitter in use has been turned OFF, taken out of the service area and secured.
2.6 PRE-OPERATION TEST
At the start of each work shift, or when a new operator takes control of the crane, operators should do, as
a minimum, the following steps before making lifts with any crane or hoist:
Test all warning devices.
Test all direction and speed controls.
Test the transmitter emergency stop.
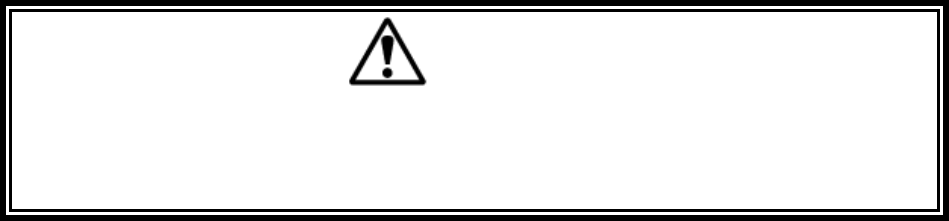
Page 10
2.7 BATTERIES
WARNING
KNOW AND FOLLOW PROPER BATTERY HANDLING, CHARGING AND DISPOSAL PROCEDURES.
IMPROPER BATTERY PROCEDURES CAN CAUSE BATTERIES TO EXPLODE OR DO OTHER SERIOUS
DAMAGE. FAILURE TO FOLLOW THIS WARNING COULD RESULT IN SERIOUS INJURY OR DEATH AND
DAMAGE TO EQUIPMENT.
2.8 BATTERY HANDLING
Use only battery packs provided by ARC for the specific product.
Do not dispose of a battery pack in fire; it may explode.
Do not attempt to open the battery pack.
Do not short circuit the battery.
Keep the battery pack environment cool during charging operation and storage (i.e., not in direct sunlight or close
to a heating source).
2.9 BATTERY CHARGING
For those transmitters equipped with battery chargers, please familiarize all users with the instructions of the
charger before attempting to use.
Do not attempt to charge non-rechargeable battery packs.
Avoid charging partially discharged rechargeable batteries to help prolong battery cycle life.
Avoid charging the battery pack for more than 24 hours at a time.
Do not charge batteries in a hazardous environment.
Do not short the charger unit.
Do not attempt to charge a damaged battery.
Use only ARC charger unit for the appropriate battery pack.
Do not attempt to use a battery pack that is leaking, swollen or corroded.
Charger units are not intended for outdoor use.
2.10 BATTERY DISPOSAL
Before disposing of battery packs consult local and governmental regulatory requirements for proper disposal
procedure.
2.11 SPECIFIC SYSTEM WARNINGS
Below are some specific operating safety tips that should be strictly followed when operating a Flex JX system:
1. Check the Status LCD on the transmitter for any signs of low battery power.
2. Check the Status LCD on the transmitter for any signs of irregularities.
3. Make sure the system is not set to the same channel as any other Flex systems in use within a
distance of 300 meters (900 feet).
4. Never operate equipment with two transmitters at the same time unless they are programmed to
do so.
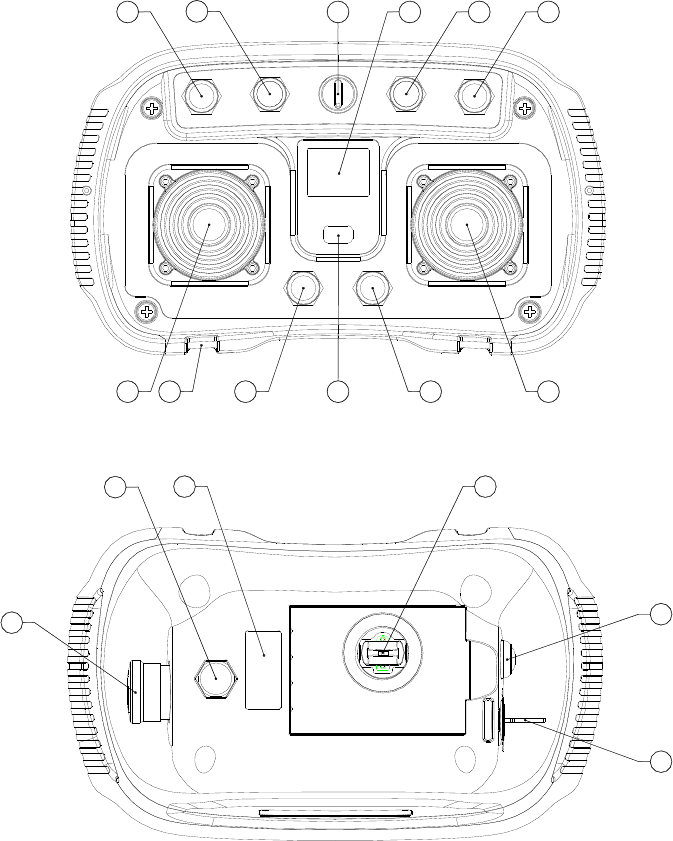
Page 11
23 4 5
1
611 7109
8
12
15
14 16
17
18
13
3. General System Information
3.1 Transmitter
1. SW1 button or switch 7. SW7 button 13. E-Stop button
2. SW2 button or switch 8. LCD screen 14. Goretex vent
3. SW3 button or switch 9. Left (L) joystick 15. System information
4. SW4 button or switch 10. Right (R) joystick 16. I-Chip port
5. SW5 button or switch 11. Infrared sensor 17. START button
6. SW6 button 12. Shoulder strap clip 18. Power key
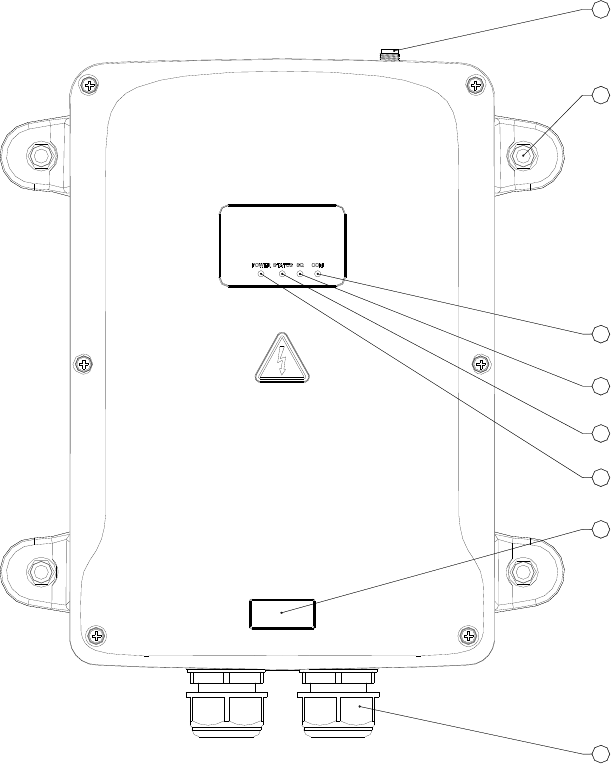
Page 12
1
2
6
7
8
5
4
3
3.2 Receiver
3.2.1 External Illustration
1. External antenna jack (optional) 5. Status LED display
2. Shock mount 6. Power LED display
3. COM LED display 7. System information
4. SQ LED display 8. Cord grip

Page 13
2
3
1
6
7
8
4
5
3.2.2 Internal Illustration
1. Power transformer 5. Receiving module
2. LCD display 6. AC line filter board
3. PS1 & PS2 programming buttons 7. Top relay board
4. Decoder module 8. Bottom relay board

Page 14
>S/N:
0000001
SW6 SW7
LCD
>S/N:
0000001 ABCDEF
>TYPE:
01
>CHANNEL
433.000
>FREQ:
NORMAL
>SW1FUNC>SW2FUNC
NORMAL
NORMAL
>SW3FUNC
NORMAL
>SW4FUNC
NORMAL
>SW5FUNC >SW6FUNC
NORMAL
>SW7FUNC
NORMAL YES NO
>SAVE?
GH
00M00S
>TIMER
+START
0.1mW
>RFpower
>IR MODE
OFF000
>IR_ID
OFF
>TILT >IRSfunc
IRS off
TimeOut
SETTING
MODE
4. Function Settings
4.1 Transmitter
4.1.1 Programming Procedure
How to enter transmitter programming mode:
1) Turn on the transmitter power switch.
2) Do not press the green START button.
3) Press both SW6 and SW7 buttons below the LCD screen at
the same time for up to 1 second to enter the Programming
Mode. Setting Mode screen will show up for a brief second
followed by the Serial Number screen (see below).
4) Serial number and frequency range can not be reprogrammed directly on the
transmitter so press SW7 button repeatedly until you see the Channel Setting
screen and so on.
5) Button functions:
SW6 button is the “Enter” or “Change” command.
SW7 button is the “Next” command.
Press and hold SW7 and then SW6 to go back to the previous main menu.
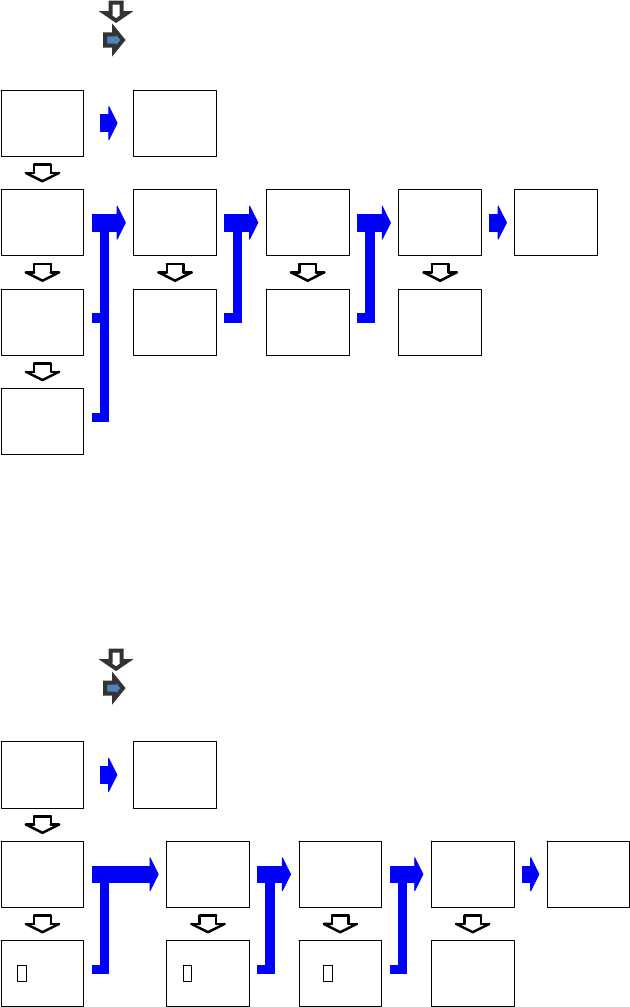
Page 15
>62
>CHANNEL
11>02
CHANNEL
>BACK
^
01
>CHANNEL
^
CHANNEL
^
^
CHANNEL
02
01 01
CHANNEL
CHANNEL
>01
CHANNEL
>01
CHANNEL
CHANNEL
01
CHANNEL
01
>TYPE:
ABCDEF
GH
+START
AC
F
F
>TYPE:
>TIMER
GH
TYPE:
^
00M00SABCDEF
E
C
>TYPE:
E
C
D A
^
D
>BACK
BF
TYPE:
D
E
TYPE:
^
TYPE:
B
BA ABCDEF
GH
H
TYPE:
^
GG
B to F
GHG
TYPE:
H
TYPE:
^
^
H
^
TYPE:TYPE:
GH
4.1.2 Transmitter Channel
SW6 button is the “Enter” or “Change” command.
SW7 button is the “Next” command.
When transmitter channel is changed make sure the receiver channel is also set to the newly
selected channel. Please refer to section 7.3 automatic channel scanning operating procedure
if the receiver is set to “scan all channels” (see section 4.2.4).
4.1.3 Transmitter Type
SW6 button is the “Enter” or “Change” command.
SW7 button is the “Next” command.
Transmitter Type is associated with functions such as tandem operation, random access
operation, multi-receiver operation, etc... Please do not alter the factory settings unless
authorized to do so.
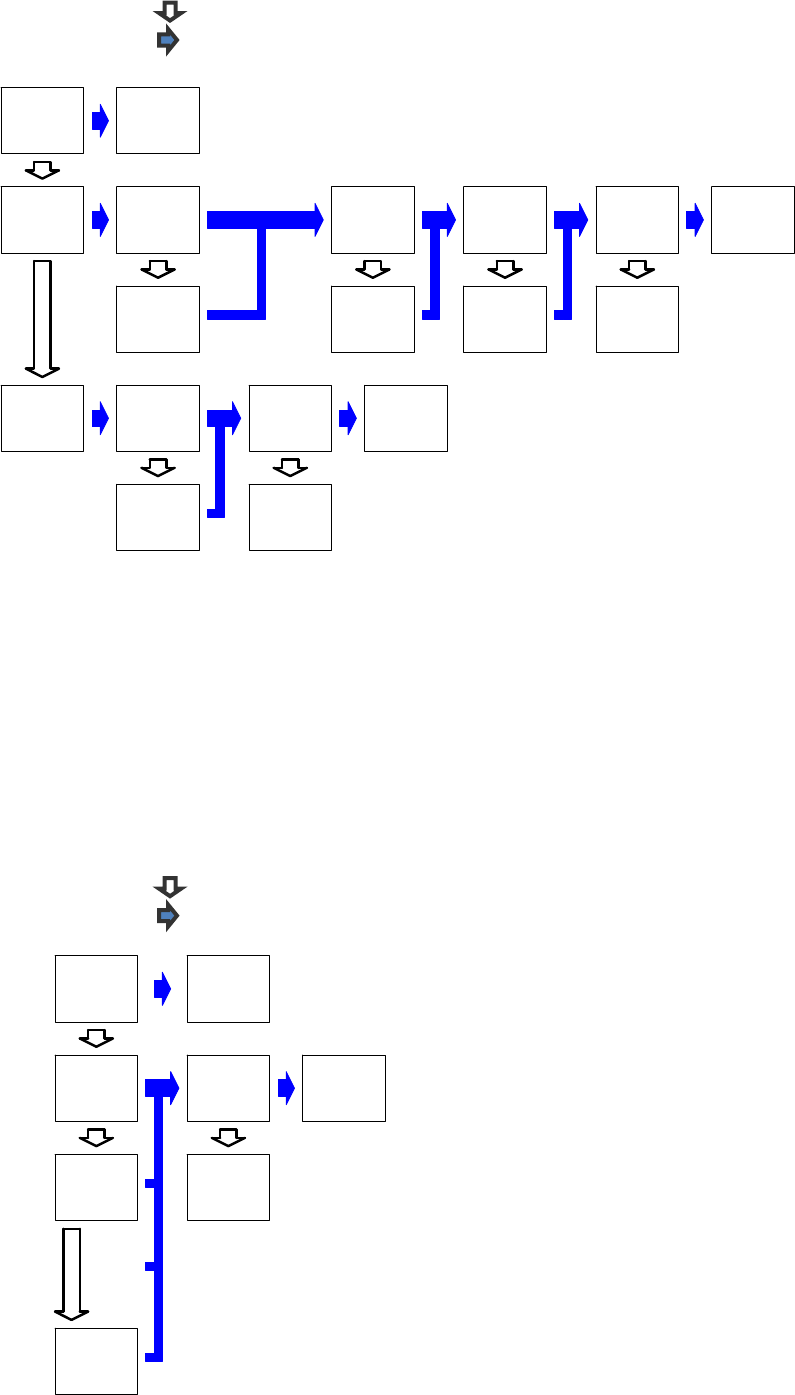
Page 16
TIMER
>00M00S 0
TIMER
^
TIMER
^^
0M00S
000MS0000MS0
^
TIMER
0S000M
>+START
TIMER
0S000M
TIMER
1
^
0M00S 0
TIMER
0
^
S10M
>BACK
TIMER
ON>ON
TIMER
TIMER
00M00S
0.1mW
>RFpower
00M00S
>TIMER
+START
+START
+START
>ON
TIMER
+START
ON
TIMER
>+START
TIMER
ON
>+ANY +START
>TIMER
ON
~
>+ANY
0S
>BACK
TIMER
00M
00M00S
>TIMER
0
+START
TIMER
>00M00S
+START
0.1mW
>RFpower >IR MODE
OFF
RFpower
>0.1mW
RFpower
>0.4mW
RFpower
0.1mW
>BACK
>0.1mW
RFpower
0.1mW
>RFpower
>02mW
>04mW
>08mW
>06mW
>10mW
RFpower
>01mW
4.1.4 Transmitter Inactivity Timer
SW6 button is the “Enter” or “Change” command.
SW7 button is the “Next” command.
Transmitter inactivity timer is for setting transmission cutoff time when the transmitter is not in
operation for a certain period of time. When set to 5 minutes (05M00S), the transmitter will
seize transmission at 5.0 minutes after last transmitter operation.
Select “ON” means the transmission is constantly on (inactivity timer disabled) until the e-stop
button is pressed or when the transmitter power is switched off.
Select “+START” means after 5 minutes of transmitter inactivity you must press the green
START button to continue operation. Select “+ANY” means after 5 minutes of transmitter
inactivity operate the joysticks, buttons or switches to continue operation.
4.1.5 Transmitter Output Power
SW6 button is the “Enter” or “Change” command.
SW7 button is the “Next” command.
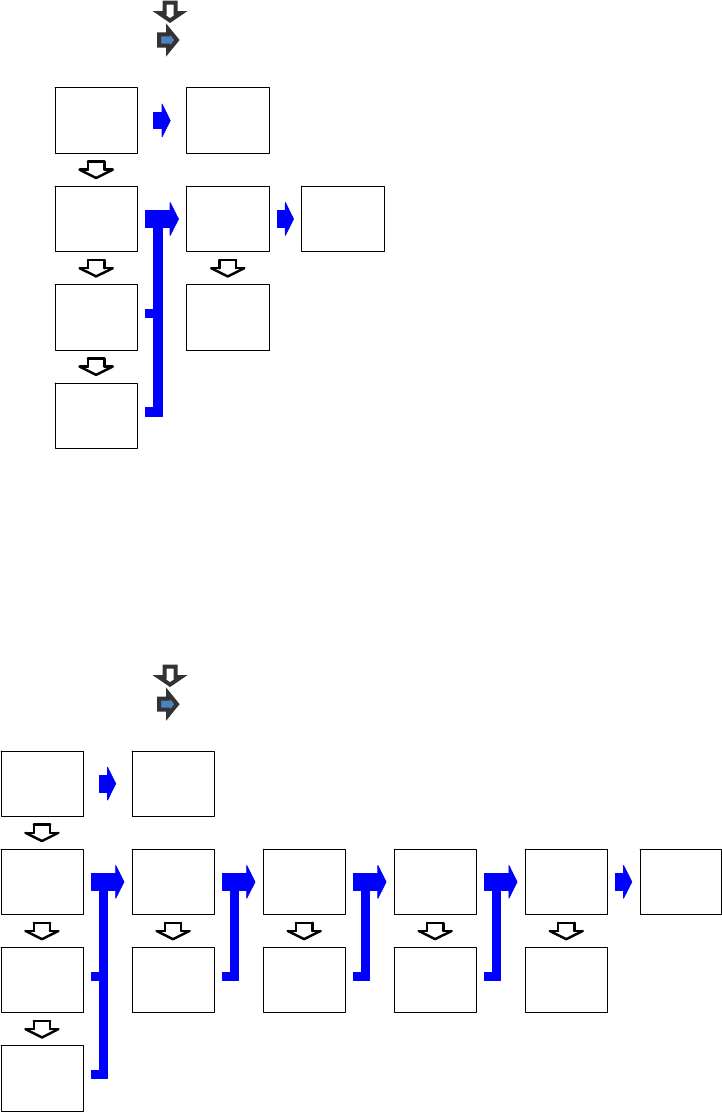
Page 17
OFF
>IR MODE
>BACK
>IR_ID
000
>OFF
IR MODE
IR MODE
>IRS
IR MODE
>IRL
IR MODE
OFF
IR MODE
>OFF
OFF
>IR MODE
000
>IR_ID
>000
IR_ID
IR_ID IR_ID IR_ID
IR_ID
IR_ID
>001
>255
000
^
100
^
000
^
IR_ID
010
^
IR_ID
000
^
^
001
IR_ID
000
>BACK
IR_ID
>IR_ID
000
>000
IR_ID
>IRSfunc
TimeOut
IRS off
4.1.6 Transmitter Infrared Mode
SW6 button is the “Enter” or “Change” command.
SW7 button is the “Next” command.
Select “OFF” to disable infrared function.
Select “IRS” to enable infrared START function.
Select “IRL” to enable infrared range limiting function.
4.1.7 Transmitter Infrared ID
SW6 button is the “Enter” or “Change” command.
SW7 button is the “Next” command.
Make sure the infrared module on crane is set to same ID code as the transmitter.
Select “000” disables the ID code function hence any types of infrared modules can be used.
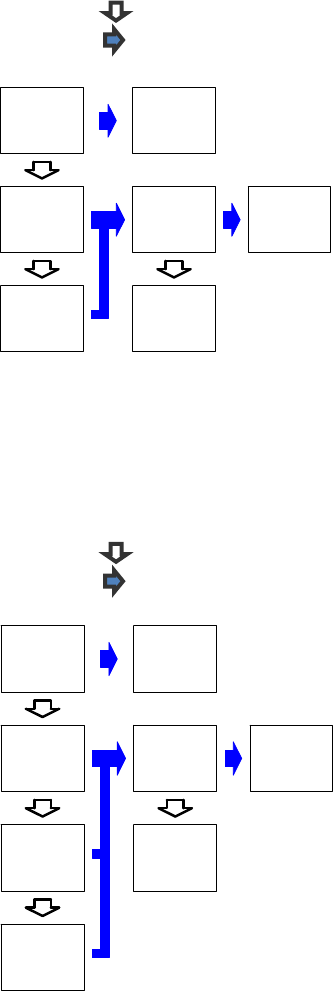
Page 18
>TILT
OFF
>SW1FUNC
NORMAL
>OFF
TILT
TILT
>0.5S
>1.0S
TILT
OFF
TILT
>BACK
OFF
>TILT
>OFF
TILT
>IRSfunc
TimeOut OFF
>TILT
IRS off
IRSfunc
TimeOut
>IRS off
TimeOut
IRSfunc
>IRS on
IRSfunc
TimeOut
>BACK
>IRSfunc
TimeOut
IRS off
IRSfunc
TimeOut
>IRS off
4.1.8 Transmitter Infrared START Function
SW6 button is the “Enter” or “Change” command.
SW7 button is the “Next” command.
Select “IRS ON” if infrared START is required after every transmitter timeout (see section 4.1.4).
Select “IRS OFF” if infrared START is not required after every transmitter timeout.
4.1.9 Transmitter Tilt Function
SW6 button is the “Enter” or “Change” command.
SW7 button is the “Next” command.
When TILT function is set to 0.5s (more sensitive) or 1.0s (less sensitive), the receiver mains
are disconnected (opened) when the transmitter is tilted for more than 35~40 degrees. Select
OFF disables the TILT function.
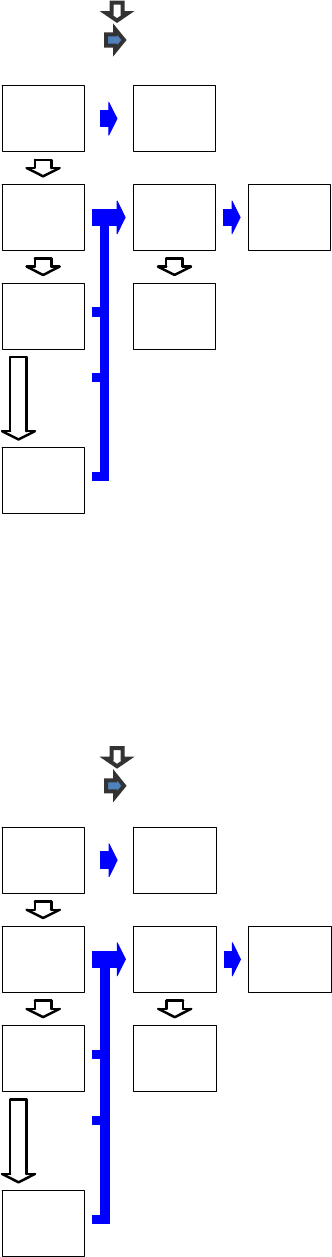
Page 19
>SW1FUNC
NORMAL
>SW2FUNC
NORMAL
>NORMAL
SW1FUNC
SW1FUNC
>TOGGLE
SW1FUNC
>BACK
NORMAL
NORMAL
>SW1FUNC
SW1FUNC
>NORMAL
SW1FUNC
>A->B
>0->A->B
>A->B->AB
>0->A->B->AB
>SW2FUNC
NORMAL
>SW3FUNC
NORMAL
>NORMAL
SW2FUNC
SW2FUNC
>TOGGLE
SW2FUNC
>BACK
NORMAL
NORMAL
>SW2FUNC
SW2FUNC
>NORMAL
SW2FUNC
>A->B
>0->A->B
>A->B->AB
>0->A->B->AB
4.1.10 SW1 Button Function
SW6 button is the “Enter” or “Change” command.
SW7 button is the “Next” command.
Select “NORMAL” the output relay becomes momentary contact.
Select “TOGGLE” the output relay becomes toggled contact.
Important note: If SW1 is equipped with a rocker switch then this SW1 button function and
SW1 output relay function in receiver (see section 4.2.14) must both set to “NORMAL”.
4.1.11 SW2 Button Function
SW6 button is the “Enter” or “Change” command.
SW7 button is the “Next” command.
Select “NORMAL” the output relay becomes momentary contact.
Select “TOGGLE” the output relay becomes toggled contact.
Important note: If SW2 is equipped with a rocker switch then this SW2 button function and
SW2 output relay function in receiver (see section 4.2.15) must both set to “NORMAL”.

Page 20
>SW3FUNC
>A->B
NORMAL
>0->A->B
>TOGGLE
SW3FUNC
NORMAL
>SW3FUNC
>NORMAL>NORMAL
SW3FUNC
NORMAL
NORMAL
>BACK
>0->A->B->AB
>SW4FUNC
SW3FUNCSW3FUNC
>A->B->AB
SW3FUNC
SW4FUNC SW4FUNCSW4FUNC
>0->A->B->AB
>SW5FUNC
SW4FUNC
NORMAL
>BACK
>A->B->AB
NORMAL
NORMAL
>0->A->B
>NORMAL
>SW4FUNC
>NORMAL
NORMAL>TOGGLE
>A->B
>SW4FUNC
SW4FUNC
4.1.12 SW3 Button Function
SW6 button is the “Enter” or “Change” command.
SW7 button is the “Next” command.
Select “NORMAL” the output relay becomes momentary contact.
Select “TOGGLE” the output relay becomes toggled contact.
Important note: If SW3 is equipped with a rocker switch then this SW3 button function and
SW3 output relay function in receiver (see section 4.2.16) must both set to “NORMAL”.
4.1.13 SW4 Button Function
SW6 button is the “Enter” or “Change” command.
SW7 button is the “Next” command.
Select “NORMAL” the output relay becomes momentary contact.
Select “TOGGLE” the output relay becomes toggled contact.
Important note: If SW4 is equipped with a rocker switch then this SW4 button function and
SW4 output relay function in receiver (see section 4.2.18) must both set to “NORMAL”.
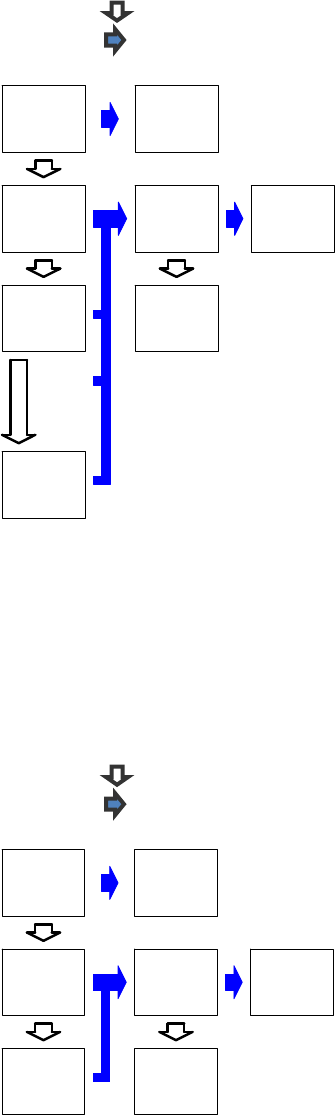
Page 21
>TOGGLE
>A->B
>SW6FUNC
>NORMAL
NORMAL
SW5FUNC
SW5FUNC
NORMAL
>NORMAL
>0->A->B
>A->B->AB
>0->A->B->AB
>SW5FUNC
NORMAL
SW5FUNC
NORMAL
SW5FUNC
>BACK
SW5FUNC
>SW5FUNC
>BACK
>SW7FUNC
>TOGGLE
>SW6FUNC
NORMAL
SW6FUNC
>SW6FUNC
NORMAL
NORMAL >NORMAL
SW6FUNC
NORMAL
>NORMAL
SW6FUNC
SW6FUNC
4.1.14 SW5 Button Function
SW6 button is the “Enter” or “Change” command.
SW7 button is the “Next” command.
Select “NORMAL” the output relay becomes momentary contact.
Select “TOGGLE” the output relay becomes toggled contact.
Important note: If SW5 is equipped with a rocker switch then this SW5 button function and
SW5 output relay function in receiver (see section 4.2.19) must both set to “NORMAL”.
4.1.15 SW6 Button Function
SW6 button is the “Enter” or “Change” command.
SW7 button is the “Next” command.
Select “NORMAL” the output relay becomes momentary contact.
Select “TOGGLE” the output relay becomes toggled contact.
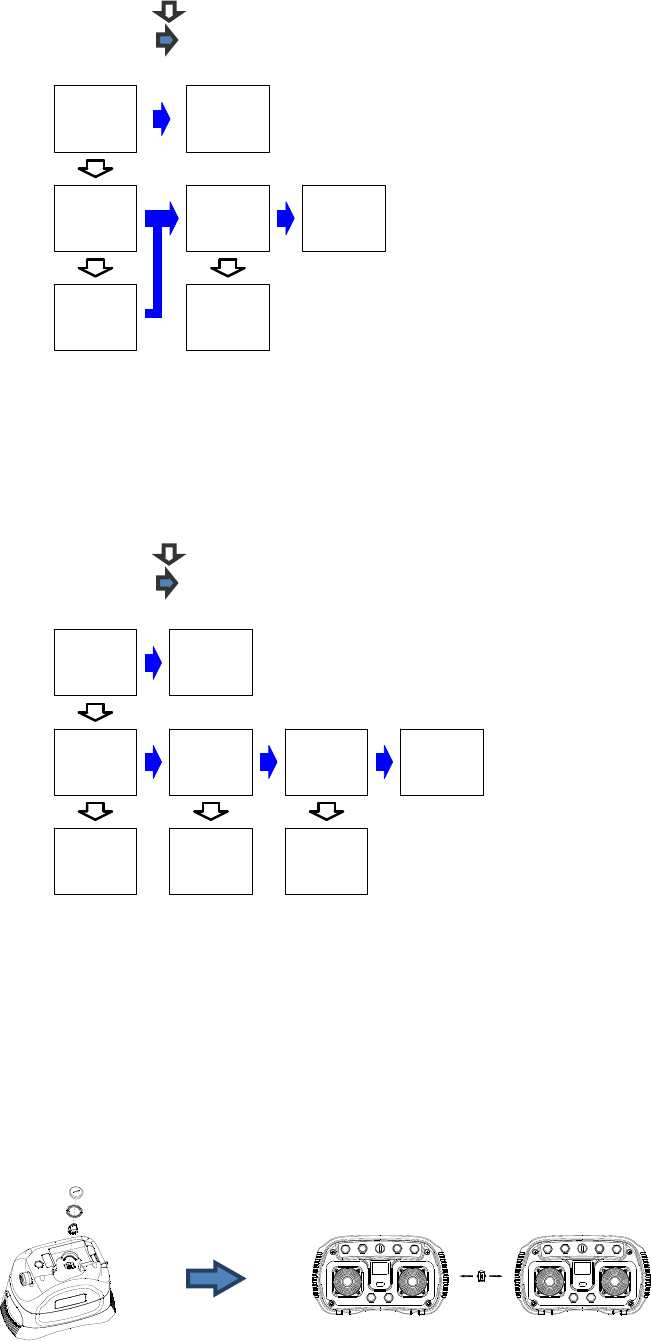
Page 22
>SAVE?
YES NO
>S/N:
0000001
YES NO
SAVE?
^
YES NO
^
SAVE? SAVE?
YES NO
>BACK
YES NO
SAVE?
^
>SAVE?
YES NO
PressSTART PressSTART
SW7FUNC
>TOGGLE
>SW7FUNC
>BACK
>SAVE?
NORMAL>NORMAL
SW7FUNC SW7FUNC
NORMAL
SW7FUNC
>NORMAL
>SW7FUNC
NORMAL YES NO
4.1.16 SW7 Button Function
SW6 button is the “Enter” or “Change” command.
SW7 button is the “Next” command.
Select “NORMAL” the output relay becomes momentary contact.
Select “TOGGLE” the output relay becomes toggled contact.
4.1.17 Save Function
SW6 button is the “Enter” or “Change” command.
SW7 button is the “Next” command.
When you see the “PressSTART” screen it means the information is saved or not saved.
The system will exit the programming mode after 5 minutes of inactivity (info not saved).
4.1.18 I-Chip Installation
Use a coin to unscrew the I-Chip cover by rotating it clockwise. The I-Chip is located
under the battery compartment (see below).

Page 23
PS1 PS2
>I-CHIP
COPY I/O
PROCEED
>S/N:
0000001 ABCDEFGH
>TYPE:
01
>CHANNEL
433.000
>FREQ:
ALL
>CH SCAN
>MAIN RLY
NORMALLV
>FUNCTION1>FUNCTION2
LV
>LX DELAY
ACC OFF
DEC OFF
ACC OFF
>LY DELAY
DEC OFF
ACC OFF
>RX DELAY
DEC OFF
ACC OFF
>RY DELAY
DEC OFF
>SW1&2 RLY
UNLOCK NORMAL
>SW1 RLY >SW2 RLY
NORMAL NORMAL
>SW3 RLY
UNLOCK
>SW4&5 RLY
NORMAL
>SW4 RLY
NORMAL
>SW5 RLY>SW6&7 RLY
UNLOCK
>SW6 RLY
NORMAL
>SW7 RLY
NORMALYES NO
>SAVE?
SETTING
MODE
>I-CHIP
COPY I/O
PROCEED
4.2 Receiver Unit
4.2.1 Programming Procedures
How to enter receiver programming mode:
1) Switch on the receiver power.
2) Press both PS1 and PS2 buttons below the LCD screen at
the same time for up to 1 second to enter the Programming
Mode. Setting Mode screen will show up for a brief second
followed by the I-Chip Copy I/O (see below).
3) Serial number and frequency range can not be reprogrammed directly on the
transmitter so press PS2 button repeatedly until you see the Channel Setting
screen and so on.
4) Button functions:
PS1 button is the “Enter” or “Change” command.
PS2 button is the “Next” command.
Press and hold PS2 and then PS1 to go back to the previous main menu.
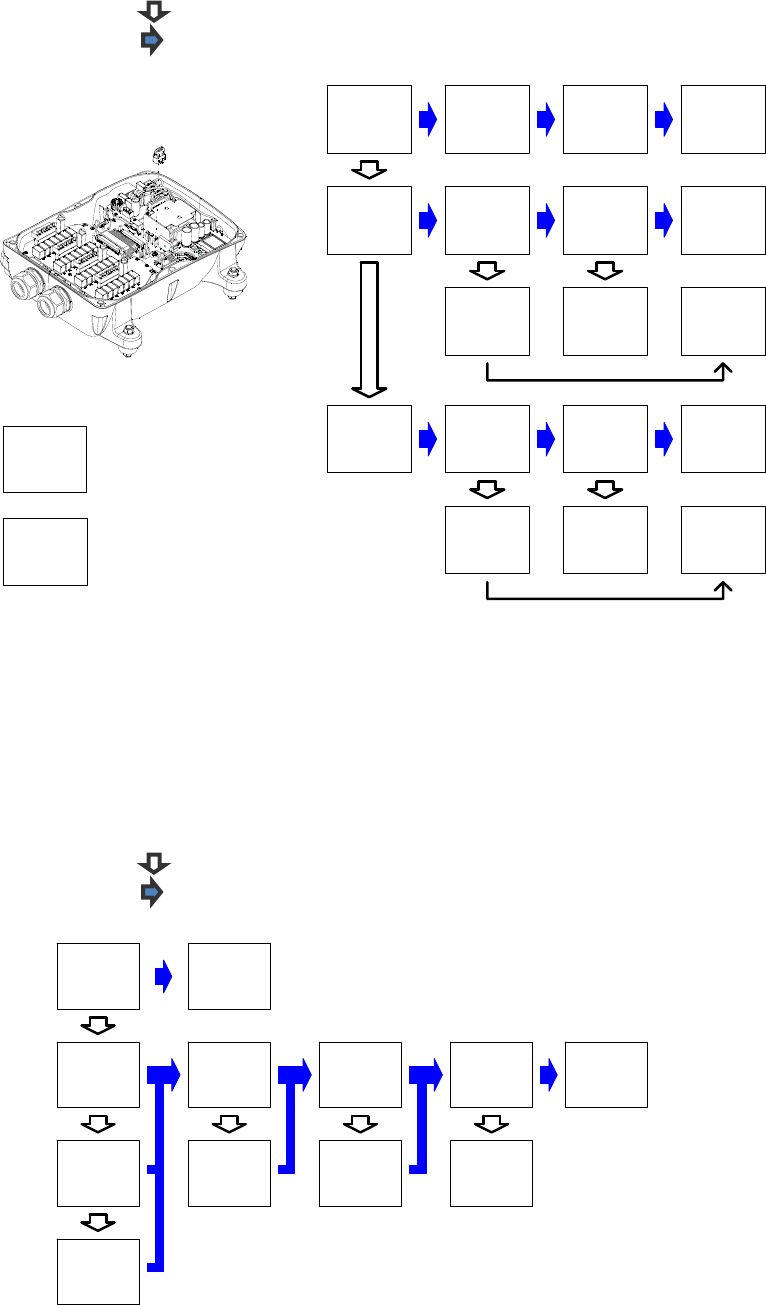
Page 24
^
01
CHANNEL
>01
CHANNEL
^
CHANNEL
>02 11
>BACK
CHANNELCHANNEL
0101
02
^
CHANNEL
CHANNEL
^
>CHANNEL
01
>CHANNEL
01
>01
CHANNEL
ALL
>CH SCAN
CHANNEL
>62
NOT
I-CHIP
MATCH
I-CHIP
NOT
CONNECT
>COPY IN
I-CHIP
PROCEED
COPY IN
I-CHIP
>PROCEED
COPY IN
I-CHIP
PROCEED
>BACK
COPY IN
I-CHIP
LOADING
>COPY OUT
I-CHIP
PROCEED
COPY OUT
I-CHIP
>PROCEED
COPY OUT
PROCEED
I-CHIP
>BACK
I-CHIP
LOADING
COPY OUT
>I-CHIP
COPY I/O
PROCEED
>I-CHIP
COPY I/O
>COPY IN
I-CHIP
PROCEED
>COPY OUT
I-CHIP
PROCEED
>I-CHIP
COPY I/O
PROCEED
>S/N:
0000001 01
>CHANNEL
433.000
>FREQ:
STATUS
STANDBY
STATUS
STANDBY
PROCEED
4.2.2 I-Chip Programming
PS1 button is the “Enter” or “Change” command.
PS2 button is the “Next” command.
Incorrect I-Chip type
I-Chip not installed correctly
Select “COPY IN” to transfer I-Chip information from transmitter to receiver.
Select “COPY OUT” to transfer I-Chip information from receiver to transmitter.
Select “Proceed” to begin transfer.
When transferring is completed the screen will display “STATUS STANDBY”.
4.2.3 Receiver Channel
PS1 button is the “Enter” or “Change” command.
PS2 button is the “Next” command.
When receiver channel is changed manually make sure the transmitter channel is also set to
the newly selected channel.
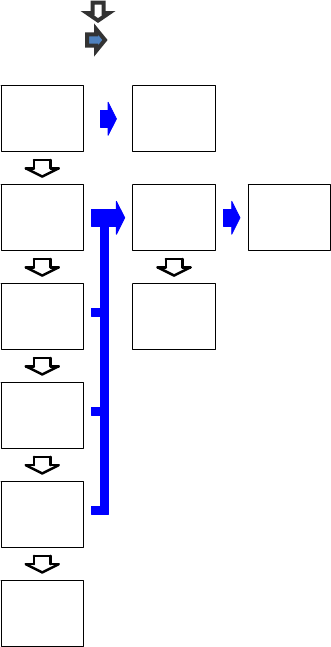
Page 25
CH SCAN
>ALL ALL
>BACK
>01
CH SCAN
>02
CH SCAN
>03
CH SCAN
>CH SCAN
ALL ABCDEFGH
>TYPE:
>CH SCAN
ALL
>ALL
CH SCAN
>ALL
CH SCAN CH SCAN
4.2.4 Receiver Channel Scanning
PS1 button is the “Enter” or “Change” command.
PS2 button is the “Next” command.
Select “01” the receiver only scans the channel set on section 4.2.3.
Select “02” the receiver scans the channel set on section 4.2.3 plus the next channel up (scans
channel N and channel N+1).
Select “03” the receiver scans the channel set on section 4.2.3 plus the next two channels up
(scans channel N, channel N+1 and channel N+2).
Select “ALL” the receiver scans all 62 channels.
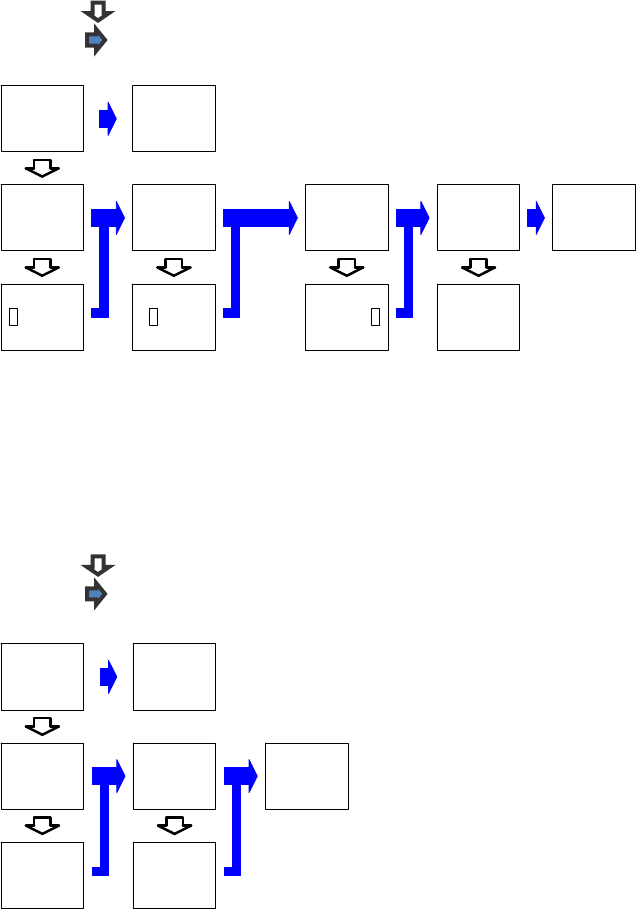
Page 26
TYPE: TYPE:
C
FF
H
B
TYPE:
GD
D
D
B
GBEF
^
CC
TYPE:
E
G
AA
D
HC
^
H
F
AH
^
^
EAG
B
E
^
FB
G
HC
H
TYPE:
DAC
ED
E
AG
B
^
F
TYPE: TYPE:
>BACK
ABCDEFGH
ABCDEFGH
>TYPE:
>TYPE:
ABCDEFGH
CFHD
TYPE:
^
BEAG
C to G
TYPE:
NORMAL
>MAIN RLY
>NORMAL NORMAL
>BACK
LV
>FUNCTION1
NORMAL
>MAIN RLY
MAIN RLY
MAIN RLY
>TEST
MAIN RLY
>NORMAL
MAIN RLY
>MAIN RLY
NORMAL
4.2.5 Receiver Type
PS1 button is the “Enter” or “Change” command.
PS2 button is the “Next” command.
Receiver Type is associated with functions such as tandem operation, random access
operation, multi-receiver operation, etc… Please do not alter the factory settings unless
authorized to do so.
4.2.6 Main Relay Function
PS1 button is the “Enter” or “Change” command.
PS2 button is the “Next” command.
Select “NORMAL” for normal operation (receiver mains and all other outputs enabled).
Select “TEST” for system testing (receiver mains disabled and all other outputs enabled).
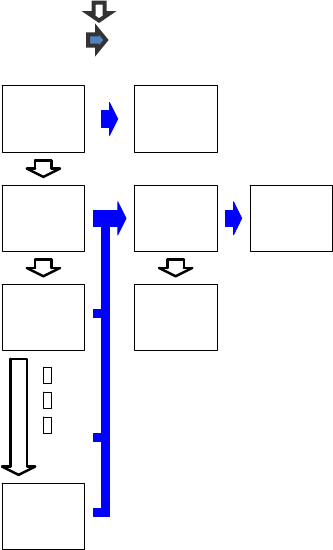
Page 27
FUNCTION1
>BACK
FUNCTION1
>S/P
FUNCTION1
>LV
>ID
LV
FUNCTION1
LV
>FUNCTION1
LV
>FUNCTION2
>FUNCTION1
LV
FUNCTION1
>LV
NORMAL>S
S TOGGLE>
S TOG&E>
>EXT
4.2.7 Function Relay #1
PS1 button is the “Enter” or “Change” command.
PS2 button is the “Next” command.
Select “LV” for receiver low voltage external warning output.
Select “ID” for receiver ID output (works simultaneously with all joystick motions and
interlocking momentary contacts).
Select “NORMAL” the output relay becomes momentary contact when START button is
pressed.
Select “TOGGLE” the output relay becomes toggled contact when START button is pressed.
Select “TOGGLE&E” the output relay becomes toggled contact affected by the e-stop
command (output relay opens when e-stop button is pressed).
Select “EXT” the output relay works simultaneously with the receiver mains.
Select “S/P” the output relay closes when the green START button is pressed and opens
only when transmitter power is switched off, not e-stop pressed.
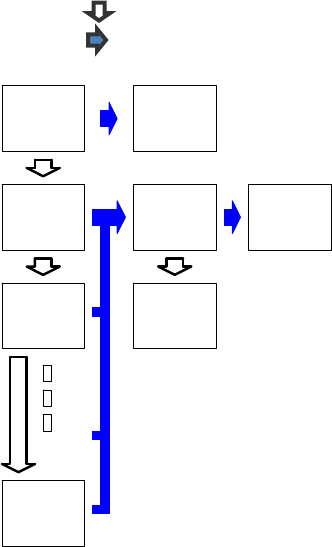
Page 28
>S/P
FUNCTION2
LV
FUNCTION2
FUNCTION2
>LV
>BACK
FUNCTION2
>ID
>FUNCTION2
LV
DEC OFF
ACC OFF
>LX DELAY
S
S
TOGGLE
>
>
>
TOG&E
S
>EXT
NORMAL
>FUNCTION2
LV
>LV
FUNCTION2
4.2.8 Function Relay #2
PS1 button is the “Enter” or “Change” command.
PS2 button is the “Next” command.
Select “LV” for receiver low voltage external warning output.
Select “ID” for receiver ID output (works simultaneously with all joystick motions and
interlocking momentary contacts).
Select “NORMAL” the output relay becomes momentary contact when START button is
pressed.
Select “TOGGLE” the output relay becomes toggled contact when START button is pressed.
Select “TOGGLE&E” the output relay becomes toggled contact affected by the e-stop
command (output relay opens when e-stop button is pressed).
Select “EXT” the output relay works simultaneously with the receiver mains.
Select “S/P” the output relay closes when the green START button is pressed and opens
only when transmitter power is switched off, not e-stop pressed.
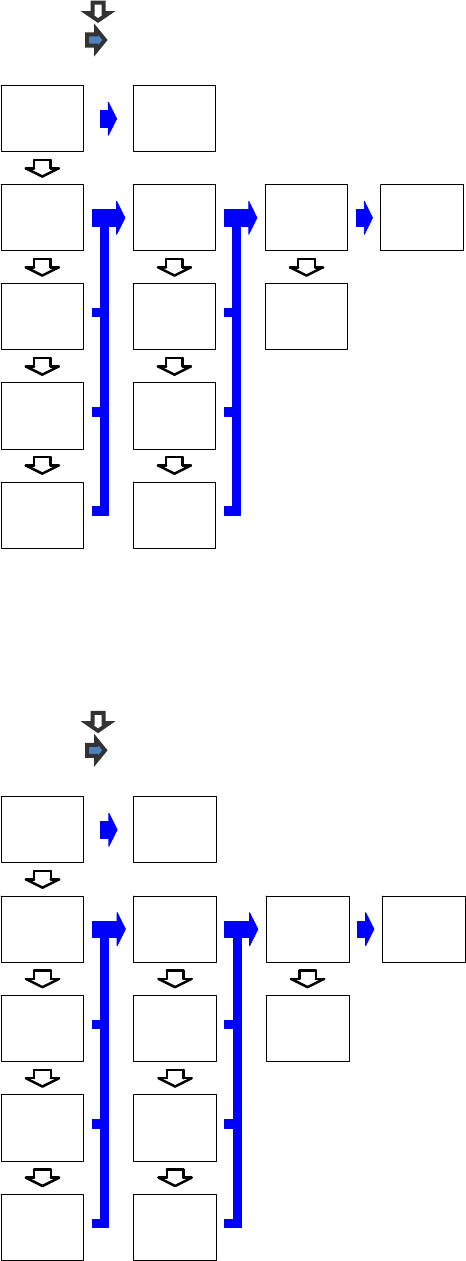
Page 29
LX DELAY
>ACC 1.0S
ACC OFF
LX DELAY
LX DELAY
DEC OFF
>ACC OFF
>DEC 1.0S
ACC OFF
ACC OFF
DEC OFF
LX DELAY
>BACK
>DEC OFF
>ACC 0.1S
LX DELAY
DEC OFF
DEC OFF
LX DELAY
>DEC 0.1S
LX DELAY
LX DELAY
LX DELAY
ACC OFF
DEC OFF
ACC OFF
>0.2S~0.9S
>0.2S~0.9S
ACC OFF
DEC OFF
>LX DELAY
DEC OFF
>LY DELAY
ACC OFF
LX DELAY
DEC OFF
>ACC OFF
>LX DELAY
DEC OFF
ACC OFF
DEC OFF
LY DELAY
LY DELAY
>BACK
ACC OFF>ACC OFF
LY DELAY
>0.2S~0.9S
LY DELAY
DEC OFF
DEC OFF
LY DELAY
LY DELAY
>DEC 1.0S
>ACC 1.0S
LY DELAY
>ACC 0.1S
ACC OFF
ACC OFF
LY DELAY
ACC OFF
>LY DELAY
DEC OFF
>RX DELAY
DEC OFF
DEC OFF
>ACC OFF
ACC OFF
ACC OFF
LY DELAY
>LY DELAY
DEC OFF
>DEC OFF
ACC OFF
>DEC 0.1S
>0.2S~0.9S
ACC OFF
DEC OFF
LY DELAY
DEC OFF
4.2.9 Joystick LX Acceleration and Deceleration Delay
PS1 button is the “Enter” or “Change” command.
PS2 button is the “Next” command.
Joystick LX is the left joystick X axis.
4.2.10 Joystick LY Acceleration and Deceleration Delay
PS1 button is the “Enter” or “Change” command.
PS2 button is the “Next” command.
Joystick LY is the left joystick Y axis.
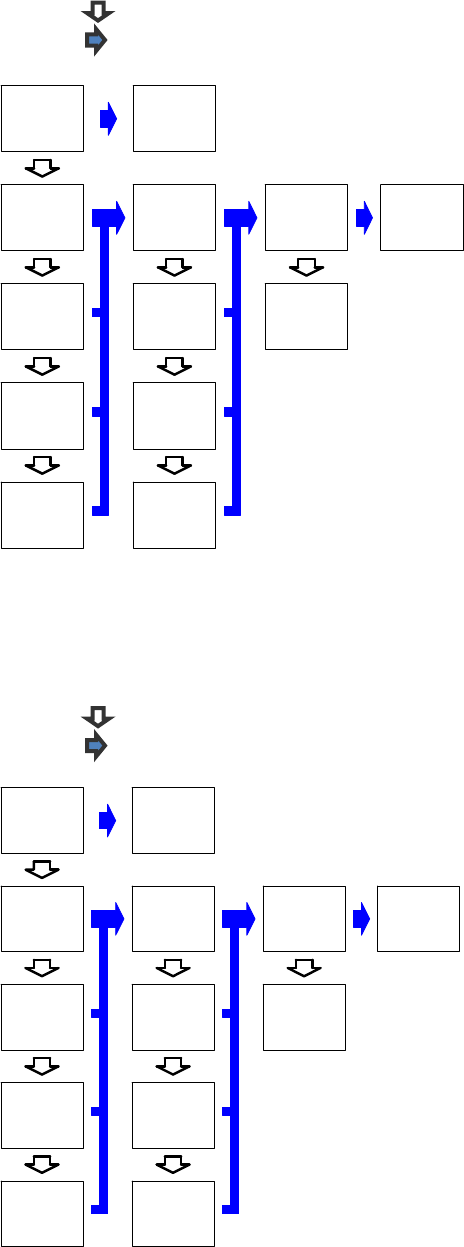
Page 30
DEC OFF
DEC OFF
DEC OFF
RX DELAY
>DEC OFF
>ACC OFF
ACC OFF
>0.2S~0.9S
RX DELAY
>RY DELAY
ACC OFF
>RX DELAY
DEC OFF
>RX DELAY
ACC OFF
>DEC 0.1S
ACC OFF
DEC OFF
>DEC 1.0S
>0.2S~0.9S
ACC OFF
RX DELAY
>ACC OFF
RX DELAY RX DELAY
DEC OFF
RX DELAY
>BACK
DEC OFF
>ACC 0.1S
DEC OFF
ACC OFF
DEC OFF
RX DELAY
>ACC 1.0S
RX DELAY
RX DELAY
RX DELAY
ACC OFF
ACC OFF
ACC OFFACC OFF
>DEC OFF
ACC OFF
RY DELAY
DEC OFF
ACC OFF
RY DELAY
>BACK
RY DELAY
>ACC 1.0S
RY DELAY
ACC OFF DEC OFF
>0.2S~0.9S
RY DELAY
DEC OFF
>ACC 0.1S
RY DELAY
RY DELAY
ACC OFF
RY DELAY
DEC OFF
RY DELAY
>DEC 1.0SDEC OFF
>ACC OFF
DEC OFF
>RY DELAY
>0.2S~0.9S
ACC OFF
>RY DELAY
>ACC OFF
DEC OFF
DEC OFF
>DEC 0.1S
RY DELAY
>SW1&2 RLY
UNLOCK
4.2.11 Joystick RX Acceleration and Deceleration Delay
PS1 button is the “Enter” or “Change” command.
PS2 button is the “Next” command.
Joystick RX is the right joystick X axis.
4.2.12 Joystick RY Acceleration and Deceleration Delay
PS1 button is the “Enter” or “Change” command.
PS2 button is the “Next” command.
Joystick RY is the right joystick Y axis.
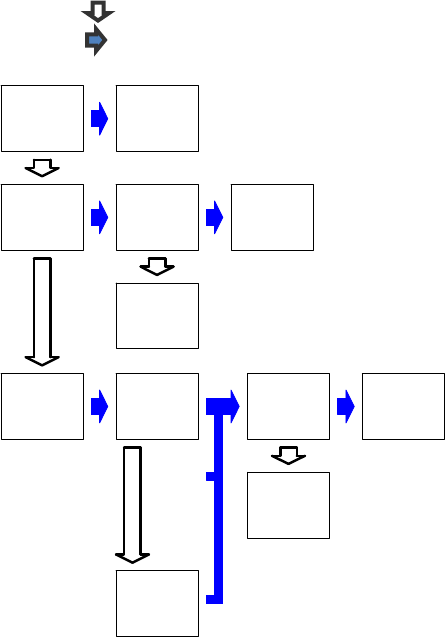
Page 31
>BACK
NORMAL
LOCK
SW1&2 RLY
NORMAL >BACK
>LOCK
SW1&2 RLYSW1&2 RLY LOCK
UNLOCK
SW1&2 RLY
>TOG/TOG&E
>UNLOCK
>NORMAL
SW1&2 RLY
LOCK
SW1&2 RLY
>SW1&2 RLY
UNLOCK NORMAL
>SW1 RLY
>UNLOCK
SW1&2 RLY
>SW1&2 RLY
UNLOCK
NORMAL
LOCK
>SW1&2 RLY
NORMAL
>LOCK
SW1&2 RLY
>ON/OFF
>MAGNET
>ON/OFF&E
>ON/OFF+S
>TOG/TOG
4.2.13 SW1+SW2 Output Relays Function
PS1 button is the “Enter” or “Change” command.
PS2 button is the “Next” command.
“UNLOCK” means both SW1 and SW2 output relays are not interlocked.
“LOCK” means both SW1 and SW2 output relays are interlocked.
When “UNLOCK” is selected proceed to SW1 and SW2 output relay function (see section
4.2.14 and 4.2.15)
When “LOCK” is selected proceed to the selections listed below and disregard section
4.2.14 and 4.2.15)
Select “NORMAL” both output relays become interlocking momentary contacts.
Select “TOG/TOG” both output relays become interlocking toggled contacts.
Select “TOG/TOG&E” both output relays become interlocking toggled contacts affected by
the e-stop command (output relay opens when e-stop button is pressed).
Select “ON/OFF” both output relays become interlocking On and Off contacts.
Select “ON/OFF+S” both output relays become interlocking On and Off contacts. Must press
the green START button along with the On or Off button to work.
Select “ON/OFF&E” both output relays become interlocking On and Off contacts affected by
the e-stop command (output relay opens when e-stop button is pressed).
Select “MAGNET” the two output relays become interlocking Magnet ON and OFF contacts.
Important note: When one of the above is selected make sure the same SW1 and SW2
button function on transmitter are both set to “NORMAL” (see section 4.1.10 and 4.1.11).
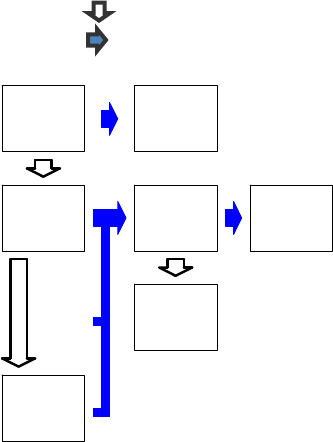
Page 32
>NORMAL
SW1 RLY SW1 RLY
NORMAL
>BACK
SW1 RLY
>STOP
>SW1 RLY
NORMAL NORMAL
>SW2 RLY
>TOGGLE
>TOGGLE&E
>NORMAL+S
>PITCH
>PITCH&E
>SW1 RLY
NORMAL
SW1 RLY
>NORMAL
4.2.14 SW1 Output Relay Function
PS1 button is the “Enter” or “Change” command.
PS2 button is the “Next” command.
Select “NORMAL” the output relay becomes momentary contact.
Select “NORMAL+S” the output relay becomes momentary contact. Must press the green
START button together to work.
Select “TOGGLE” the output relay becomes toggled contact.
Select “TOGGLE&E” the output relay becomes toggled contact affected by the e-stop
command (output relay opens when e-stop button is pressed).
Select “PITCH” SW1 button becomes the “Pitch” function in Pitch & Catch Operation.
Select “PITCH&E” SW1 button becomes the “Pitch” function in Pitch & Catch Operation.
When Pitch command is initiated the receiver mains are disconnected.
Select “STOP” SW1 button becomes an auxiliary e-stop function. Press to disconnect the
receiver mains and press START button to reconnect the receiver mains.
When select Pitch & Catch function make sure you set the spare transmitter to the next
channel up and the receiver channel scanning to “02” (see section 4.2.4).
Important note: When one of the above is selected make sure the same SW1 button
function on transmitter is set to “NORMAL” (see section 4.1.10).

Page 33
>SW2 RLY
>PITCH&E
SW2 RLY SW2 RLY
>PITCH
>NORMAL+S
SW2 RLY
>SW3 RLY
NORMAL
>TOGGLE&E
>TOGGLE
>NORMAL
NORMAL
>SW2 RLY
NORMAL
>BACK
NORMAL >NORMAL
>STOP
SW2 RLY
4.2.15 SW2 Output Relay Function
PS1 button is the “Enter” or “Change” command.
PS2 button is the “Next” command.
Select “NORMAL” the output relay becomes momentary contact.
Select “NORMAL+S” the output relay becomes momentary contact. Must press the green
START button together to work.
Select “TOGGLE” the output relay becomes toggled contact.
Select “TOGGLE&E” the output relay becomes toggled contact affected by the e-stop
command (output relay opens when e-stop button is pressed).
Select “PITCH” SW2 button becomes the “Pitch” function in Pitch & Catch Operation.
Select “PITCH&E” SW2 button becomes the “Pitch” function in Pitch & Catch Operation.
When Pitch command is initiated the receiver mains are disconnected.
Select “STOP” SW2 button becomes an auxiliary e-stop function. Press to disconnect the
receiver mains and press START button to reconnect the receiver mains.
When select Pitch & Catch function make sure you set the spare transmitter to the next
channel up and the receiver channel scanning to “02” (see section 4.2.4).
Important note: When one of the above is selected make sure the same SW2 button
function on transmitter is set to “NORMAL” (see section 4.1.11).
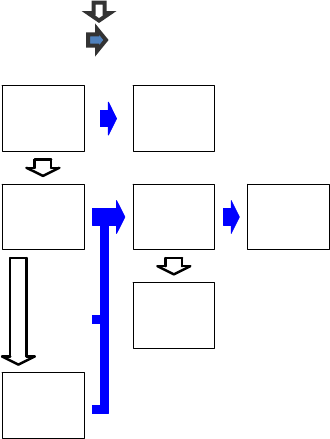
Page 34
>NORMAL >NORMAL
>TOGGLE&E
>NORMAL+S
>TOGGLE
>PITCH&E
>BACK
NORMAL
>SW3 RLY
>SW3 RLY
>STOP
SW3 RLY SW3 RLY
>SW4&5 RLY
NORMAL
NORMAL
SW3 RLY
NORMAL
>PITCH
SW3 RLY
4.2.16 SW3 Output Relay Function
PS1 button is the “Enter” or “Change” command.
PS2 button is the “Next” command.
Select “NORMAL” the output relay becomes momentary contact.
Select “NORMAL+S” the output relay becomes momentary contact. Must press the green
START button together to work.
Select “TOGGLE” the output relay becomes toggled contact.
Select “TOGGLE&E” the output relay becomes toggled contact affected by the e-stop
command (output relay opens when e-stop button is pressed).
Select “PITCH” SW3 button becomes the “Pitch” function in Pitch & Catch Operation.
Select “PITCH&E” SW3 button becomes the “Pitch” function in Pitch & Catch Operation.
When Pitch command is initiated the receiver mains are disconnected.
Select “STOP” SW3 button becomes an auxiliary e-stop function. Press to disconnect the
receiver mains and press START button to reconnect the receiver mains.
When select Pitch & Catch function make sure you set the spare transmitter to the next
channel up and the receiver channel scanning to “02” (see section 4.2.4).
Important note: When one of the above is selected make sure the same SW3 button
function on transmitter is set to “NORMAL” (see section 4.1.12).

Page 35
>SW4&5 RLY
SW4&5 RLY
LOCK
>LOCK
NORMAL
>UNLOCK
LOCK
SW4&5 RLY
>TOG/TOG
>ON/OFF+S NORMAL
UNLOCK
>SW4&5 RLY
>TOG/TOG&E
SW4&5 RLY
NORMAL
SW4&5 RLY
>NORMAL
>ON/OFF&E
SW4&5 RLY
>BACK
UNLOCK
LOCK
LOCK
NORMAL
>SW4&5 RLY
SW4&5 RLY
>MAGNET
>LOCK
>BACK
NORMALUNLOCK
SW4&5 RLY
>UNLOCK
>SW4 RLY
>ON/OFF
SW4&5 RLY
4.2.17 SW4+SW5 Output Relays Function
PS1 button is the “Enter” or “Change” command.
PS2 button is the “Next” command.
“UNLOCK” means both SW4 and SW5 output relays are not interlocked.
“LOCK” means both SW4 and SW5 output relays are interlocked.
When “UNLOCK” is selected proceed to SW4 and SW5 output relay function (see section
4.2.18 and 4.2.19)
When “LOCK” is selected proceed to the selections listed below and disregard section
4.2.18 and 4.2.19)
Select “NORMAL” both output relays become interlocking momentary contacts.
Select “TOG/TOG” both output relays become interlocking toggled contacts.
Select “TOG/TOG&E” both output relays become interlocking toggled contacts affected by
the e-stop command (output relay opens when e-stop button is pressed).
Select “ON/OFF” both output relays become interlocking On and Off contacts.
Select “ON/OFF+S” both output relays become interlocking On and Off contacts. Must press
the green START button along with the On or Off button to work.
Select “ON/OFF&E” both output relays become interlocking On and Off contacts affected by
the e-stop command (output relay opens when e-stop button is pressed).
Select “MAGNET” the two output relays become interlocking Magnet ON and OFF contacts.
Important note: When one of the above is selected make sure the same SW4 and SW5
button function on transmitter are both set to “NORMAL” (see section 4.1.13 and 4.1.14).
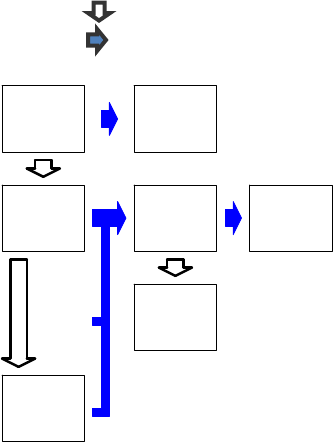
Page 36
SW4 RLY
>NORMAL+S
SW4 RLY
SW4 RLY
>BACK
NORMAL
NORMAL
>NORMAL
>TOGGLE&E
>STOP
>PITCH&E
>SW5 RLY
>PITCH
>SW4 RLY
>NORMAL
>SW4 RLY
NORMAL
SW4 RLY
>TOGGLE
NORMAL
4.2.18 SW4 Output Relay Function
PS1 button is the “Enter” or “Change” command.
PS2 button is the “Next” command.
Select “NORMAL” the output relay becomes momentary contact.
Select “NORMAL+S” the output relay becomes momentary contact. Must press the green
START button together to work.
Select “TOGGLE” the output relay becomes toggled contact.
Select “TOGGLE&E” the output relay becomes toggled contact affected by the e-stop
command (output relay opens when e-stop button is pressed).
Select “PITCH” SW4 button becomes the “Pitch” function in Pitch & Catch Operation.
Select “PITCH&E” SW4 button becomes the “Pitch” function in Pitch & Catch Operation.
When Pitch command is initiated the receiver mains are disconnected.
Select “STOP” SW4 button becomes an auxiliary e-stop function. Press to disconnect the
receiver mains and press START button to reconnect the receiver mains.
When select Pitch & Catch function make sure you set the spare transmitter to the next
channel up and the receiver channel scanning to “02” (see section 4.2.4).
Important note: When one of the above is selected make sure the same SW4 button
function on transmitter is set to “NORMAL” (see section 4.1.13).
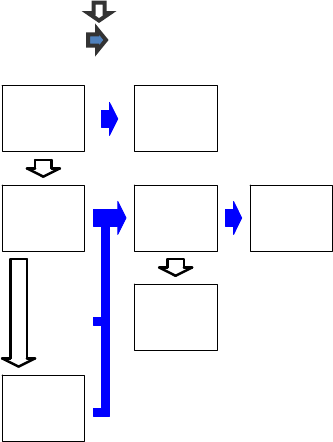
Page 37
>TOGGLE
SW5 RLY
>TOGGLE&E
SW5 RLY
>SW6&7 RLY
>SW5 RLY
NORMAL
>SW5 RLY
NORMAL
>NORMAL
>PITCH&E
SW5 RLY
>PITCH
NORMAL
>STOP
>NORMAL+S
SW5 RLY
NORMAL
>BACK
>NORMAL
4.2.19 SW5 Output Relay Function
PS1 button is the “Enter” or “Change” command.
PS2 button is the “Next” command.
Select “NORMAL” the output relay becomes momentary contact.
Select “NORMAL+S” the output relay becomes momentary contact. Must press the green
START button together to work.
Select “TOGGLE” the output relay becomes toggled contact.
Select “TOGGLE&E” the output relay becomes toggled contact affected by the e-stop
command (output relay opens when e-stop button is pressed).
Select “PITCH” SW5 button becomes the “Pitch” function in Pitch & Catch Operation.
Select “PITCH&E” SW5 button becomes the “Pitch” function in Pitch & Catch Operation.
When Pitch command is initiated the receiver mains are disconnected.
Select “STOP” SW5 button becomes an auxiliary e-stop function. Press to disconnect the
receiver mains and press START button to reconnect the receiver mains.
When select Pitch & Catch function make sure you set the spare transmitter to the next
channel up and the receiver channel scanning to “02” (see section 4.2.4).
Important note: When one of the above is selected make sure the same SW5 button
function on transmitter is set to “NORMAL” (see section 4.1.14).
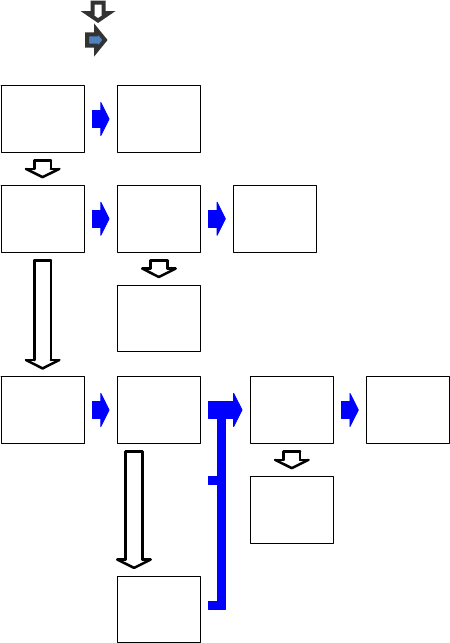
Page 38
LOCK
LOCK
SW6&7 RLY
>SW6&7 RLY
NORMAL
>SW6&7 RLY
LOCK SW6&7 RLY
>ON/OFF
NORMAL
UNLOCK
NORMAL
>ON/OFF+S
>SW6 RLY
>UNLOCK
UNLOCK
SW6&7 RLY
>NORMAL
>BACK
SW6&7 RLY
NORMAL
>BACK
>TOG/TOG
SW6&7 RLY
>SW6&7 RLY
SW6&7 RLY
UNLOCK
SW6&7 RLY
NORMAL
>LOCK
>ON/OFF&E
LOCK
>UNLOCK
>LOCK
>MAGNET
SW6&7 RLY
>TOG/TOG&E
4.2.20 SW6+SW7 Output Relays Function
PS1 button is the “Enter” or “Change” command.
PS2 button is the “Next” command.
“UNLOCK” means both SW6 and SW7 output relays are not interlocked.
“LOCK” means both SW6 and SW7 output relays are interlocked.
When “UNLOCK” is selected proceed to SW6 and SW7 output relay function (see section
4.2.21 and 4.2.22)
When “LOCK” is selected proceed to the selections listed below and disregard section
4.2.21 and 4.2.22)
Select “NORMAL” both output relays become interlocking momentary contacts.
Select “TOG/TOG” both output relays become interlocking toggled contacts.
Select “TOG/TOG&E” both output relays become interlocking toggled contacts affected by
the e-stop command (output relay opens when e-stop button is pressed).
Select “ON/OFF” both output relays become interlocking On and Off contacts.
Select “ON/OFF+S” both output relays become interlocking On and Off contacts. Must press
the green START button along with the On or Off button to work.
Select “ON/OFF&E” both output relays become interlocking On and Off contacts affected by
the e-stop command (output relay opens when e-stop button is pressed).
Select “MAGNET” the two output relays become interlocking Magnet ON and OFF contacts.
Important note: When one of the above is selected make sure the same SW6 and SW7
button function on transmitter are both set to “NORMAL” (see section 4.1.15 and 4.1.16).

Page 39
>SW6 RLY
NORMAL
>SW6 RLY
>NORMAL
>NORMAL+S
SW6 RLY
>NORMAL
>SW7 RLY
>TOGGLE&E
NORMAL
>TOGGLE
>PITCH NORMAL
SW6 RLY
>STOP
SW6 RLY
NORMAL
>PITCH&E
>BACK
SW6 RLY
4.2.21 SW6 Output Relay Function
PS1 button is the “Enter” or “Change” command.
PS2 button is the “Next” command.
Select “NORMAL” the output relay becomes momentary contact.
Select “NORMAL+S” the output relay becomes momentary contact. Must press the green
START button together to work.
Select “TOGGLE” the output relay becomes toggled contact.
Select “TOGGLE&E” the output relay becomes toggled contact affected by the e-stop
command (output relay opens when e-stop button is pressed).
Select “PITCH” SW6 button becomes the “Pitch” function in Pitch & Catch Operation.
Select “PITCH&E” SW6 button becomes the “Pitch” function in Pitch & Catch Operation.
When Pitch command is initiated the receiver mains are disconnected.
Select “STOP” SW6 button becomes an auxiliary e-stop function. Press to disconnect the
receiver mains and press START button to reconnect the receiver mains.
When select Pitch & Catch function make sure you set the spare transmitter to the next
channel up and the receiver channel scanning to “02” (see section 4.2.4).
Important note: When one of the above is selected make sure the same SW6 button
function on transmitter is set to “NORMAL” (see section 4.1.15).
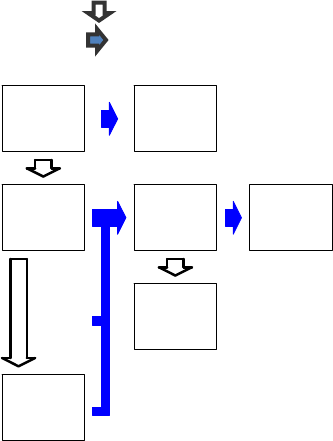
Page 40
>SW7 RLY
>PITCH&E
>PITCH
>BACK
SW7 RLY
NORMAL
NORMAL
>TOGGLE
SW7 RLYSW7 RLY
>NORMAL+S
>STOP
>TOGGLE&E
SW7 RLY
NORMAL
>NORMAL
>SW7 RLY
>NORMAL
>SAVE?
YES NO
4.2.22 SW7 Output Relay Function
PS1 button is the “Enter” or “Change” command.
PS2 button is the “Next” command.
Select “NORMAL” the output relay becomes momentary contact.
Select “NORMAL+S” the output relay becomes momentary contact. Must press the green
START button together to work.
Select “TOGGLE” the output relay becomes toggled contact.
Select “TOGGLE&E” the output relay becomes toggled contact affected by the e-stop
command (output relay opens when e-stop button is pressed).
Select “PITCH” SW7 button becomes the “Pitch” function in Pitch & Catch Operation.
Select “PITCH&E” SW7 button becomes the “Pitch” function in Pitch & Catch Operation.
When Pitch command is initiated the receiver mains are disconnected.
Select “STOP” SW7 button becomes an auxiliary e-stop function. Press to disconnect the
receiver mains and press START button to reconnect the receiver mains.
When select Pitch & Catch function make sure you set the spare transmitter to the next
channel up and the receiver channel scanning to “02” (see section 4.2.4).
Important note: When one of the above is selected make sure the same SW7 button
function on transmitter is set to “NORMAL” (see section 4.1.16).
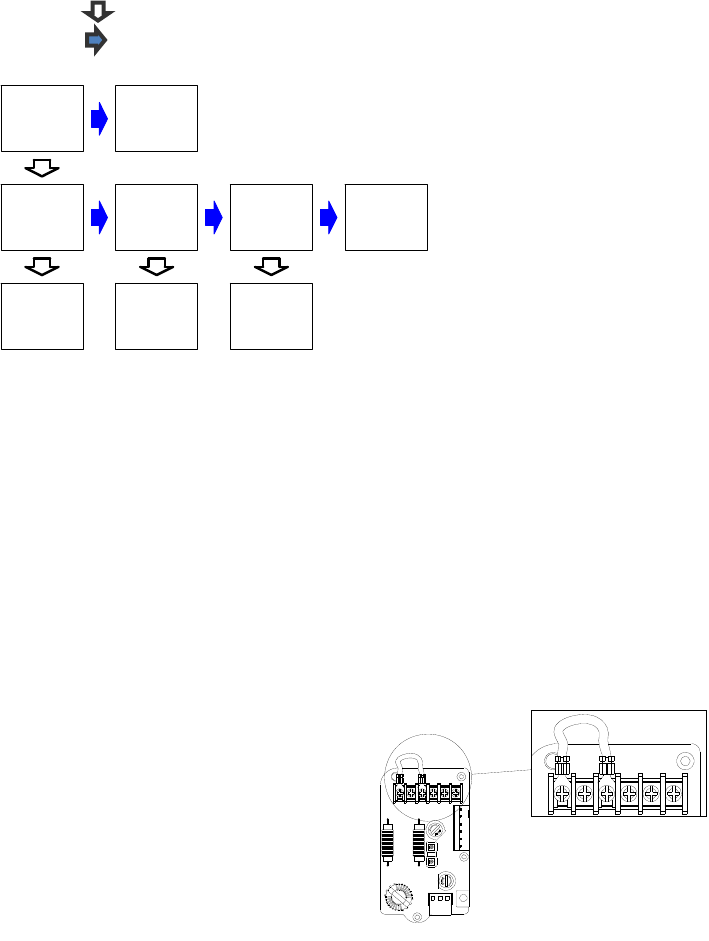
Page 41
COM 1234
^
YES NO
SAVE?
^
SAVE?
YES NO
SAVE?
YES NO
>BACK
>I-CHIP
COPY I/OYES NO
>SAVE?
YES NO
SAVE?
^
STATUS
STANDBY
STATUS
STANDBY YES NO
>SAVE?
PROCEED
4.2.23 Save Function
PS1 button is the “Enter” or “Change” command.
PS2 button is the “Next” command.
When you see the “STATUS STANDBY” screen it means the information is saved or not saved.
The system will exit the programming mode after 5 minutes of inactivity (info not saved).
4.2.24 Voltage Settings
Always check the voltage setting is correct for your application prior to installation.
Position 1 → 110 ~ 120VAC
Position 2 → 220 ~ 240VAC
F1 ~ F8 Fuse @ 5.0 Amps
F9 ~ F10 Fuse @ 1.0 Amps
F11 ~ F14 Fuse @ 5.0 Amps

Page 42
5. System Channels Table
Channel Frequency Channel Frequency
01 433.000MHZ 32 433.775MHZ
02 433.025MHZ 33 433.800MHZ
03 433.050MHZ 34 433.825MHZ
04 433.075MHZ 35 433.850MHZ
05 433.100MHZ 36 433.875MHZ
06 433.125MHZ 37 433.900MHZ
07 433.150MHZ 38 433.925MHZ
08 433.175MHZ 39 433.950MHZ
09 433.200MHZ 40 433.975MHZ
10 433.225MHZ 41 434.000MHZ
11 433.250MHZ 42 434.025MHZ
12 433.275MHZ 43 434.050MHZ
13 433.300MHZ 44 434.075MHZ
14 433.325MHZ 45 434.100MHZ
15 433.350MHZ 46 434.125MHZ
16 433.375MHZ 47 434.150MHZ
17 433.400MHZ 48 434.175MHZ
18 433.425MHZ 49 434.200MHZ
19 433.450MHZ 50 434.225MHZ
20 433.475MHZ 51 434.250MHZ
21 433.500MHZ 52 434.275MHZ
22 433.525MHZ 53 434.300MHZ
23 433.550MHZ 54 434.325MHZ
24 433.575MHZ 55 434.350MHZ
25 433.600MHZ 56 434.375MHZ
26 433.625MHZ 57 434.400MHZ
27 433.650MHZ 58 434.425MHZ
28 433.675MHZ 59 434.450MHZ
29 433.700MHZ 60 434.475MHZ
30 433.725MHZ 61 434.500MHZ
31 433.750MHZ 62 434.525MHZ
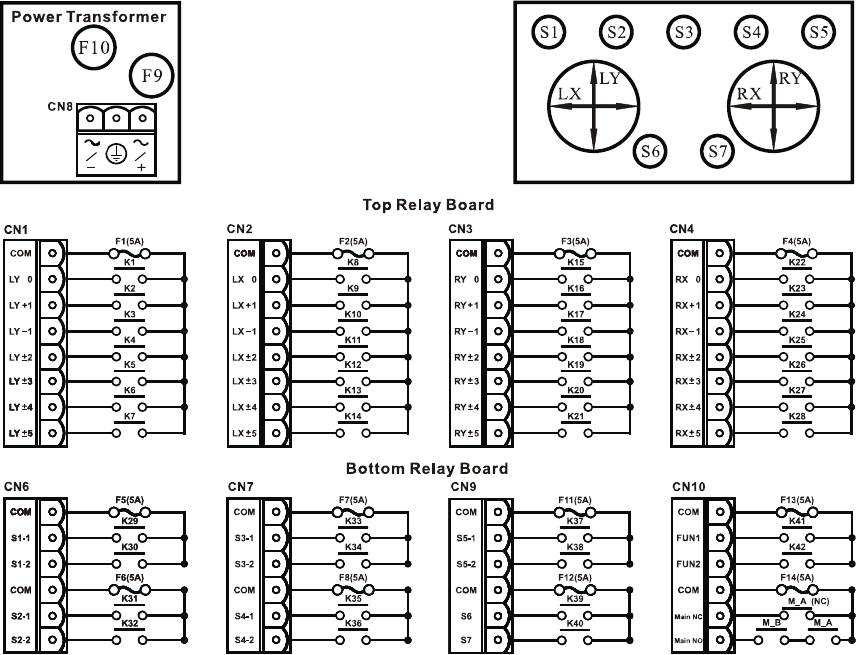
Page 43
6. Receiver Installation
6.1 Output Relay Contact Diagram
Please refer to section 4.2.24 for various input voltage settings.
Please refer to section 4.2.24 for all power fuse ratings.
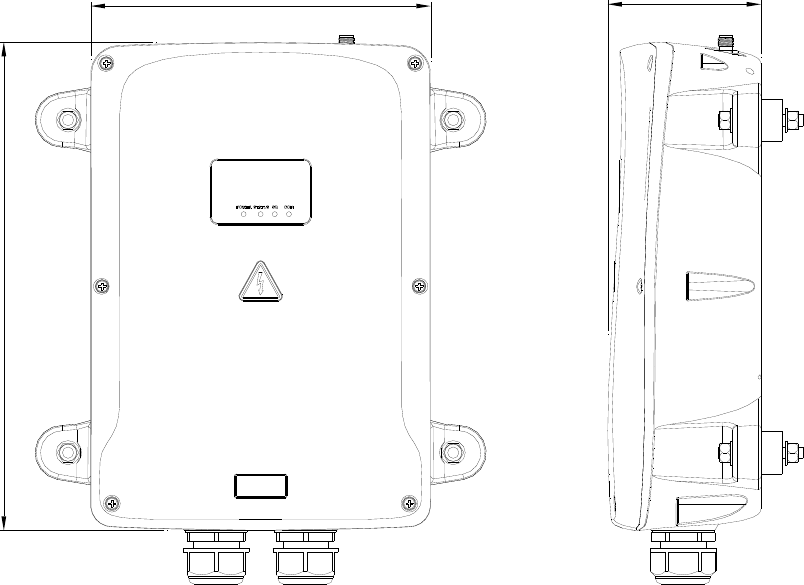
Page 44
240mm
345mm
108mm
6.2 Pre-Installation Precautions
1. Make sure the transmitter and receiver have identical serial number/ID codes and channels.
2. Make sure the receiver is not set to the same channel as any other systems in use in the
surrounding area.
3. Make sure that the crane or equipment is working properly prior to installation.
4. Make sure the power source to the receiver is set correctly.
5. Switch off the main power source to the crane or equipment prior to installation.
6.3 Step-By-Step Installation
1. For best reception the location of the receiver should be visible to the operator at all times.
2. The location selected should not be exposed to high levels of electric noise. Mounting
the receiver next to an unshielded variable frequency drive may cause minor
interference. Always locate the receiver as far away from the variable frequency drive
as possible.
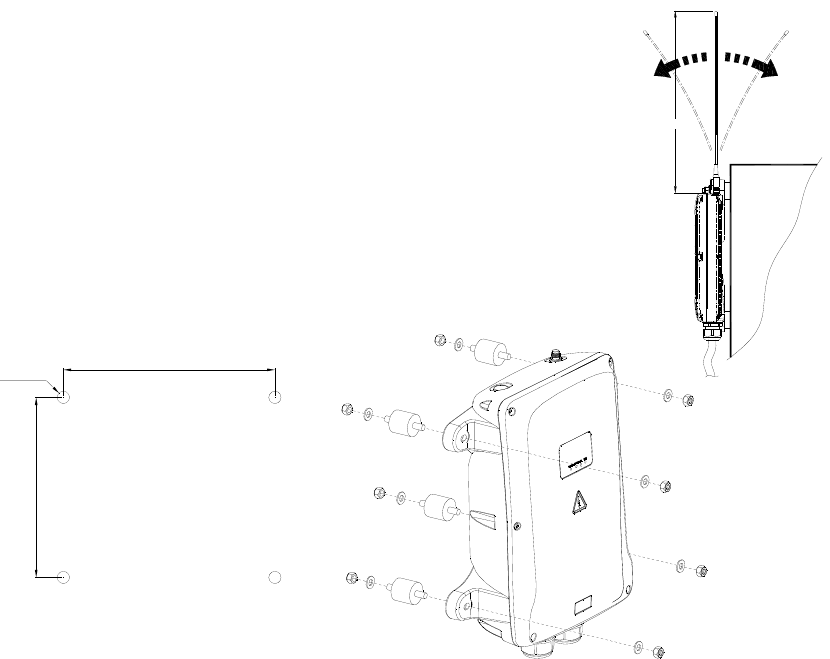
Page 45
432 mm
Control
Panel
276mm(10.87")
235mm(9.25")
8mm
3. Ensure the selected location has adequate space to accommodate
the receiver. If an external antenna is used, to avoid the possibility
of antenna damage always locate the receiver where the antenna is
free from any obstacles from all directions (refer to diagram at right).
4. For better reception, make sure the receiver is in an upright position.
5. Drill four holes (8mm in diameter) on the control panel or location
where the receiver is to be installed.
6. Make sure the bolts are tightened after installation.
7. For system wiring please refer to section 6.1.
6.4 System Testing
1. Turn on the power source to the receiver and test the MAIN relay output by pressing the red
emergency stop button and making sure that it properly opens and closes the mainline
disconnect contactor.
2. Test the operation of each function to ensure it corresponds to the transmitter direction
labels or the pendant it is replacing.
3. Test the limit switches (if any) to see if they are working properly.
4. If your new remote control is replacing an existing pendant, make sure it is completely
disconnected and placed in a safe location to prevent unwanted control commands.
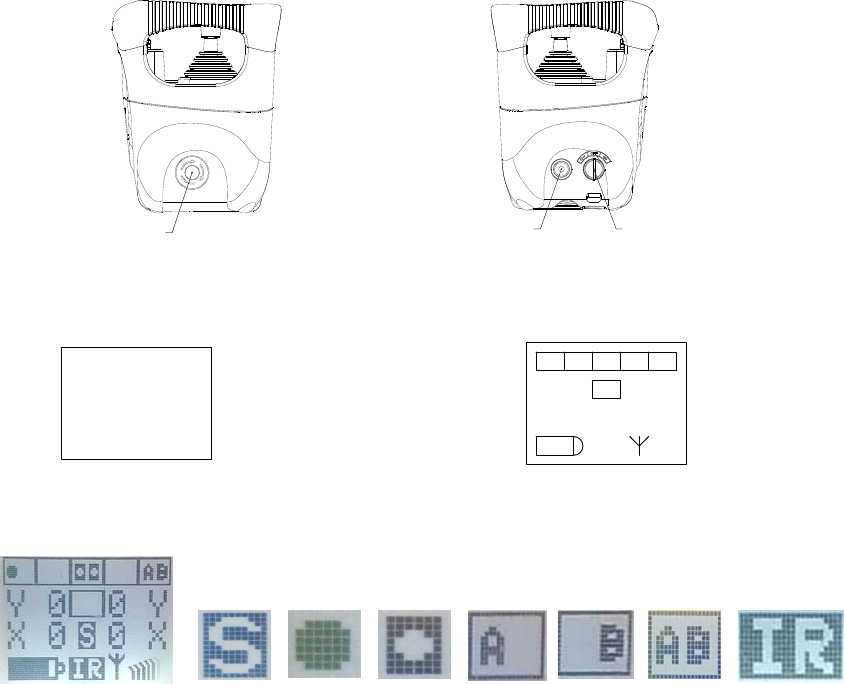
Page 46
E-STOP START POWER ON/OFF
Y 0
X 0
0 Y
0 X
PressSTART
7. Operating Procedure
7.1 General Operating Procedure
a. Reset the red emergency stop button located on the left hand side of the transmitter
by pulling it upward or rotating it clockwise.
b. Turn on the transmitter power by inserting the black-colored key into the keyswitch
slot located on the right hand side of the transmitter and rotate it clockwise to “On”
position.
c. After turning on the transmitter power the LCD screen will display “ PressSTART”.
Press the green START button next to the power keyswitch for up to one
(1) second to activate (connect) the receiver mains.
→ Press Start →
d. Available icons:
Main Screen Start Normal Toggle A B A+B Infrared
e. In case of an emergency, pressing the red e-stop button will immediately
disconnect the receiver mains (LCD turns off). Pull it upward or rotate the red
button clockwise to reset the e-stop button. Press the green START button for up
to one (1) second to reconnect the receiver mains when “ PressSTART”
reappears on the LCD screen.
f. After 5 minutes of inactivity the receiver mains are disconnected temporarily
(depends on transmitter inactivity timer set on section 4.1.4). Press the green
START button to reconnect the receiver mains and continue operation.
g. Turn off the transmitter power by rotating the power key counter-clockwise to “Off”
position; it will disconnect the transmitter power and the receiver mains altogether.
Turn it further counter-clockwise to release the key.
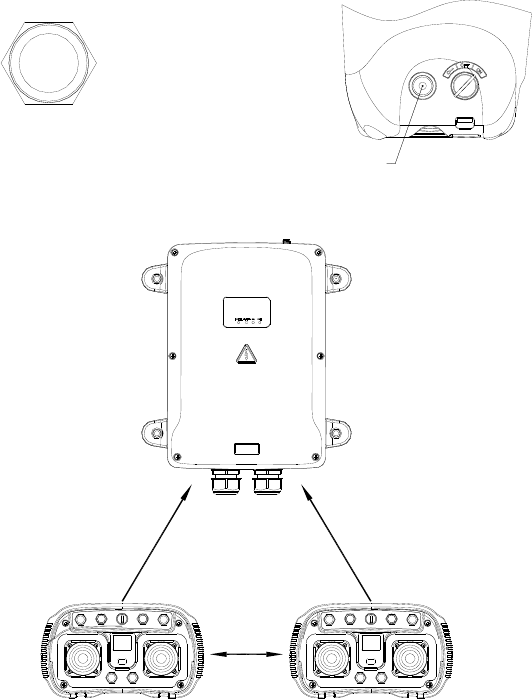
Page 47
CATCH
PITCH
Transmitter A Transmitter B
Receiver
7.2 Pitch & Catch Operating Procedure
In order for transmitter-B to take over the receiver, or vise versa, transmitter-A must press
the “Pitch” button on the transmitter for up to one (1) second. This will release
transmitter-A control of the receiver. Transmitter B then presses the green “Start/Catch”
button to gain control of the same receiver.
Transmitter A Transmitter B
press “Pitch press “Catch”
→
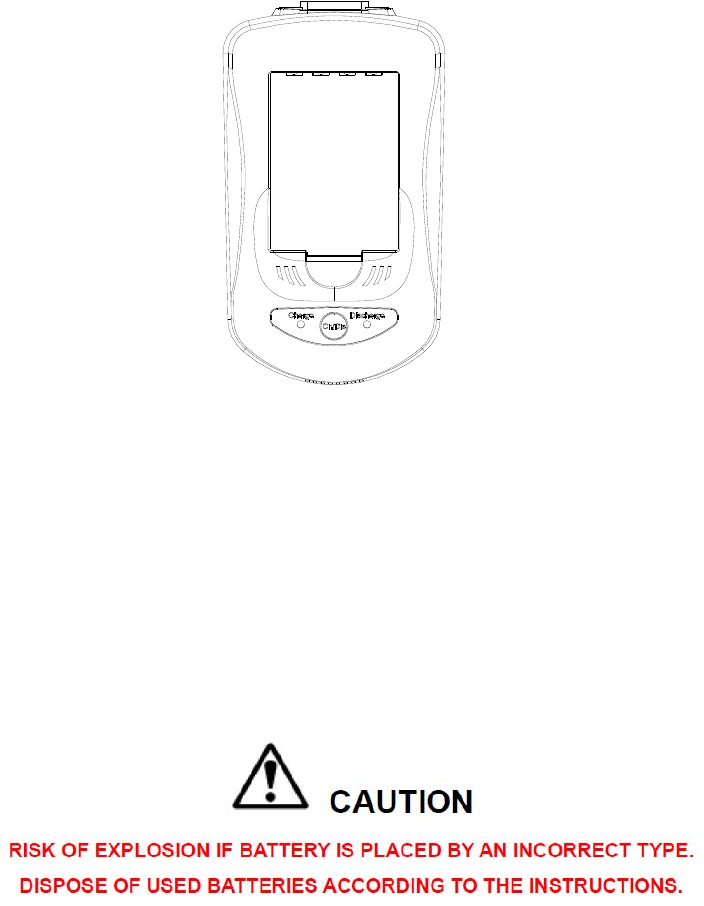
Page 48
7.3 Automatic Channel Scanning Operating Procedure
When transmitter channel is changed (see section 4.1.2) press the green START button
for up to 60 seconds to re-connect with the receiver unit. Make sure the receiver unit is
set to Scan “ALL” in the receiver channel scanning section 4.2.4.
7.4 Battery Charging Instruction
When battery pack is inserted it will automatically go into charging mode. Press the
Charge/Discharge button to switch from charging to discharging, or vise versa.
Power On → Charge LED blinks green 3 times.
Charging → Charge LED blinks green constantly.
Discharging → Discharge LED blinks red constantly.
Fully charged → Charge LED constant green.
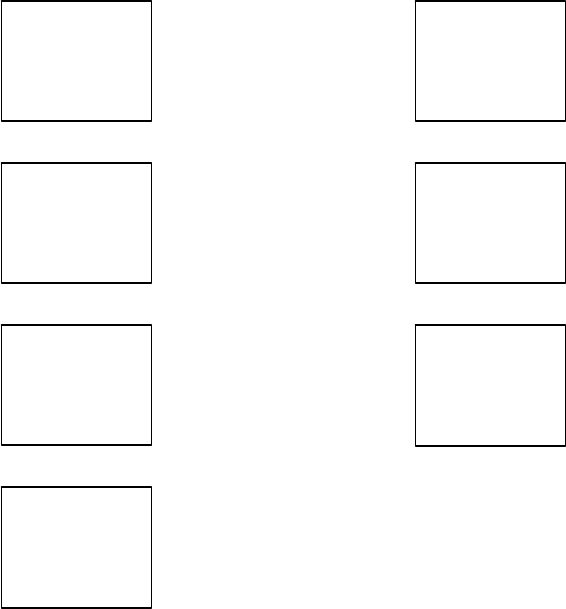
Page 49
xxxxxxxxxx
LYX xx RYX
JAMMED
TILTED!
PressSTART
PressSTART
LOW
BATTERY
NOT
I-CHIP
MATCH
RF
NOT
CONNECT
I-CHIP
NOT
CONNECT
8. Status and Warnings
8.1 Transmitter
Battery low power Bad joystick internal contact or
contacts detected
Incorrect I-Chip version Transmitting module not installed
I-Chip not installed Transmitter not in upright position
system not error
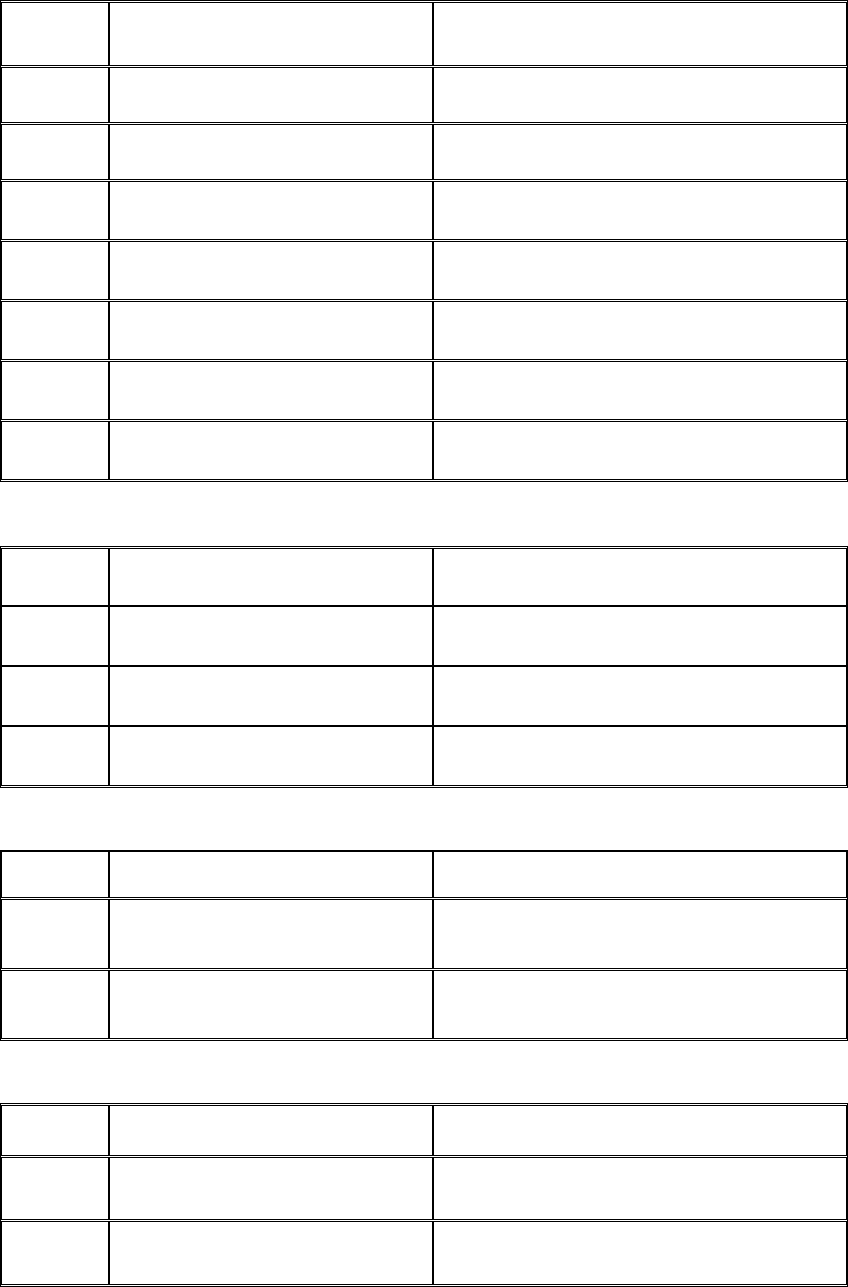
Page 50
8.2 Receiver
8.2.1 LED Status Indications
Type Display Type Indication
1 Fast green blinks Decoding in progress
2 Slow green blinks Decoding on standby
3 Fast red blinks Incorrect transmitter serial number and type
4 Two red blinks Receiver MAIN jammed or defective
5 Three red blinks Decoder module defective
6 Four red blinks + one green blink Receiving module defective
7 Constant red Receiver under-voltage, LV output relay
activated
8.2.2 LED SQ Indications
Type Display Type (Red) Indication
1 On Transmission received
2 Off No transmission
3 Blinks intermittently Other radio interference
8.2.3 LED POWER Indications
Type Display Type (Red) Indication
1 On Power to receiver
2 Off No power to receiver
8.2.4 LED COM Indications
Type Display Type (Red) Indication
1 On Power to relay Board
2 Off No power to relay board
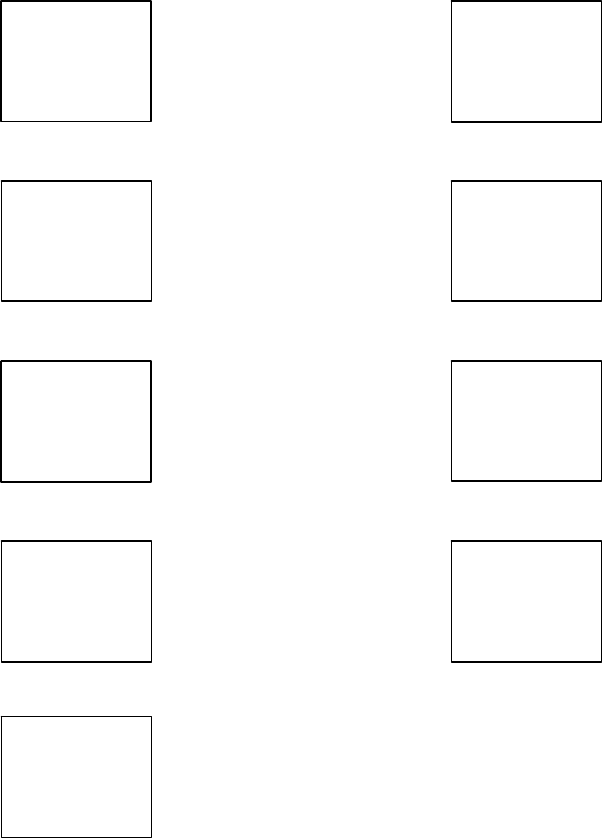
Page 51
STATUS
DEFECTIVE
DECODER
STATUS
MAIN
DEFECTIVE
LOW
STATUS
VOLTAGE
STATUS
RF1
DEFECTIVE
STATUS
STANDBY
DECODING
STATUS
STATUS
POS
INITIATED
STATUS
EMS
INITIATED
STATUS
INCORRECT
S/N
8.2.5 LCD Indications
Decoding in progress Decoder on standby
Transmitter power off Transmitter e-stop
command initiated
Receiver low input Incorrect serial number
voltage and type on transmitter
Decoder module defective Main relay defective
Receiving module defective
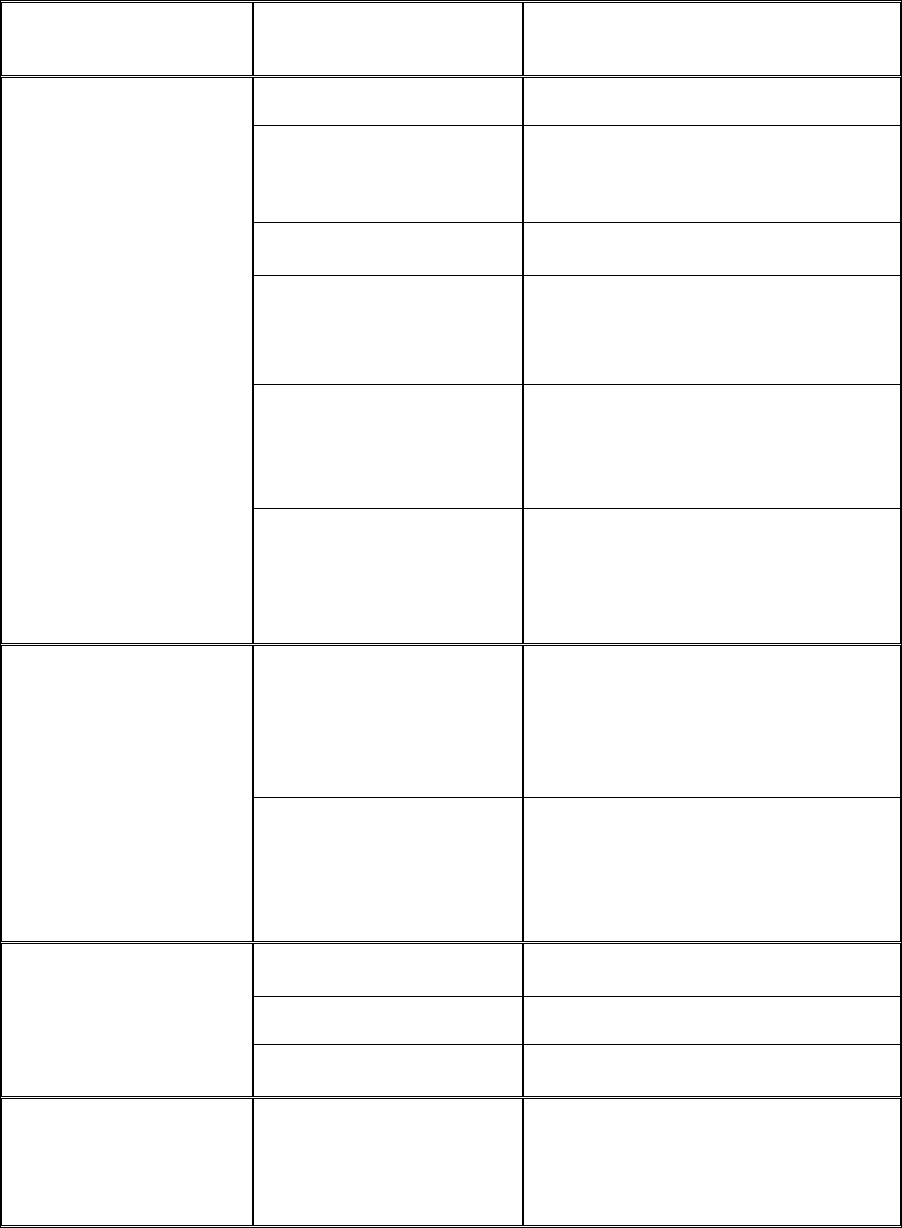
Page 52
9. Trouble Shooting Tips
Problems Possible Reasons Suggestions
Transmitter low battery Check the transmitter battery level.
Emergency stop button
activated prior to startup
Prior to turning on the transmitter power
make sure that the red emergency stop
button is elevated.
Improper startup procedure Redo the startup procedure.
Incorrect system channel Check and make sure the transmitter
and receiver are with same channel.
Incorrect system serial
number
Check and make sure the transmitter
and receiver are with same serial
number.
No response when
transmitter is in
operation
(Improper startup &
settings)
System out of range
Make sure the startup procedure is
initiated within 100 meters from the
receiver location.
Defective transmitting and
receiving module
Check the SQ display on the face of the
receiver unit. If it does not light up when
operating the transmitter then either the
transmitting or receiving module is
defective. Replace the transmitting
module first then the receiving module.
No response when
transmitter is in
operation
(Damaged hardware) Defective encoder
board or decoder module
If still no response after replacing the,
transmitting and receiving modules then
replace the transmitter encoder board. If
still doesn’t work then the decoder
module is defective.
Incorrect input voltage Make sure the source voltage is set
correctly.
Blown fuse Check for any blown fuse.
No AC power to the
receiver
Incorrect wiring Check input voltage connection.
Outputs do not
correspond to
transmitter
Incorrect output connection Check the system wiring again.
Page 53
10. System Specifications
Frequency Range : 433.000 MHz to 434.525 MHz
Channel Spacing : 25.0 KHz
Number of Channels : 62 channels
Modulation : Digital Frequency Modulation, 20bit
address, 32bit CRC Parity Check and
Hamming Code.
Encoder & Decoder : Microprocessor-controlled
Transmitting Range : >100 Meters / 300 Feet
Frequency Control : Synthesized PLL (Phase Lock Loop)
Receiver Type : Frequency Auto Scanning
Receiver Sensitivity : -116dBm
Antenna Impedance : 50 ohms
Responding Time : 50 Milliseconds (average)
Transmitting Power : 2.0mW
Enclosure Type : NEMA-4X
Enclosure Rating : IP-66
Output Contact Rating : 250V @ 8 Amps
Transmitter Operating Voltage : DC 6.0V
Receiver Power Consumption : 30 VA (max)
Receiver Supplied Voltage : 220-240VAC @ 50/60Hz
Charger Unit Power Consumption : 5.0 VA(max)
Charger Unit Supplied Voltage : 110~240VAC @ 50/60Hz
Operating Temperature : -25°C -- 50°C / -13°F -- 122°F
Transmitter Dimension : 247mm (L) x 145mm (W) x 180mm (H)
Receiver Dimension : 345mm (L) x 240mm (W) x 108mm (H)
Transmitter Weight : 1.80kg (include battery pack)
Receiver Weight : 3.65kg
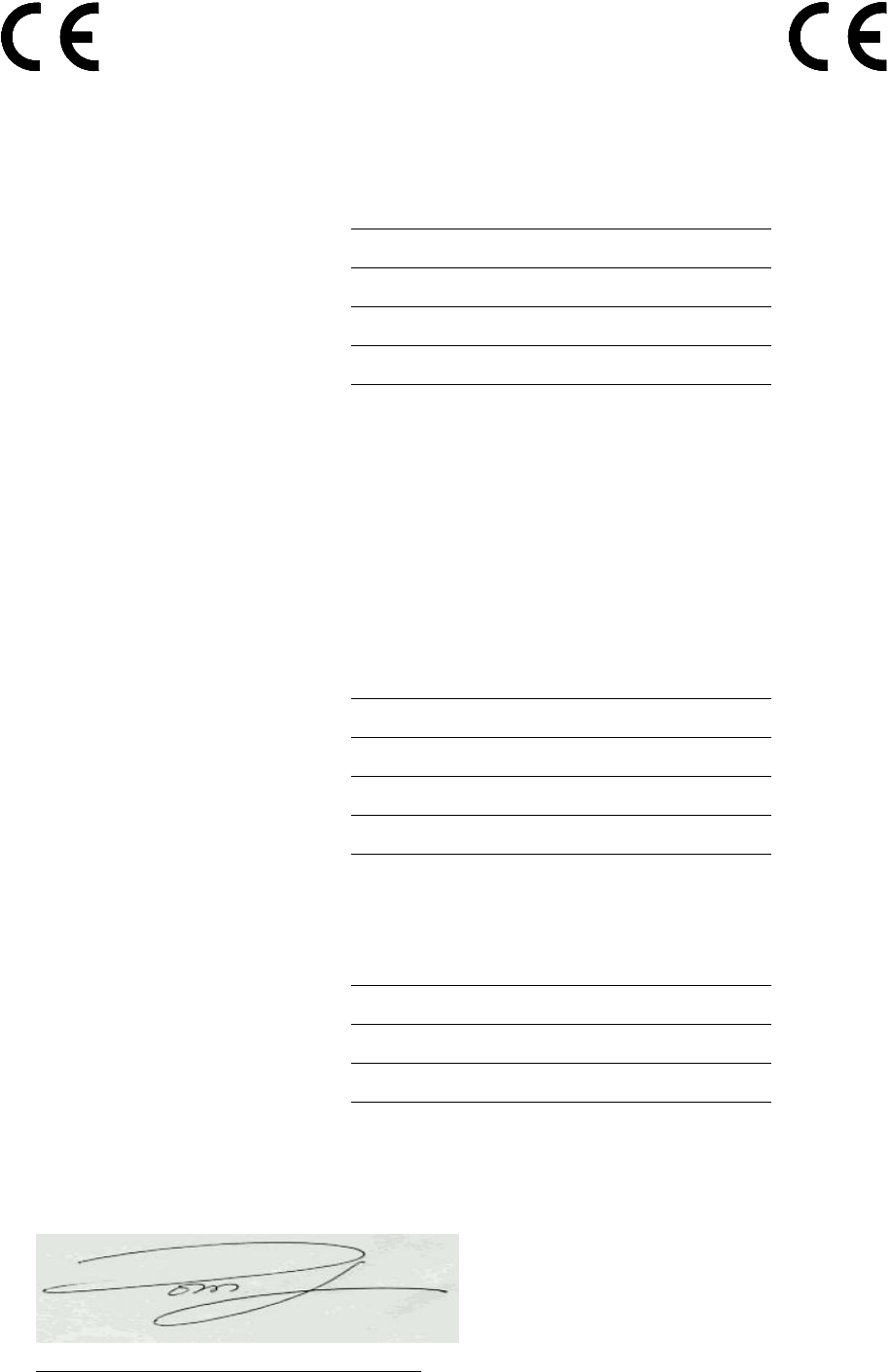
Page 54
EU Declaration of Conformity
(EMC, R&TTE, SAFETY & MACHINERY)
For the following equipment:
Product : Flex Series Radio Remote Control System
Multiple Listee Model No. : Flex JX
Manufacturer’s Name : Advanced Radiotech Corporation
Manufacturer’s Address : 1F, 288-1, Hsin Ya Road, Chien Chen District
Kaohsiung City, Taiwan
We herby declare, that all major safety requirements, concerning the CE Mark Directive
2006/42/EC and Low Voltage Directive 2006/95/EC, Electromagnetic Compatibility Directives
2004/108/EC, R&TTE Directive 1999/5/EC are fulfilled, as laid out in the guideline set down
by the member states of the EEC Commission.
The standards relevant for the evaluation of the electrical safety requirements are as follow:
EMC : EN 301 489-1 + EN 301 489-3
R&TTE : EN 300 220-2 V2.1.1
SAFETY : EN 60950:2006+A1+A11+A12
MACHINERY : EN 60204-32:2008, EN 13557:2003+A1:2008
EN ISO 13849-1:2008 (PL=d), EN 60529 (IP66)
Test reports issued by:
EMC : SGS
R&TTE : SGS
SAFETY : SGS
MACHINERY : SGS
Person responsible for marking this declaration:
Tom Jou / President
Name and signature of authorized person