AquaCheck ACROVER OEM Data logger module and transceiver for Aquacheck soil moisture probes User Manual
AquaCheck (Pty) Ltd OEM Data logger module and transceiver for Aquacheck soil moisture probes Users Manual
Users Manual
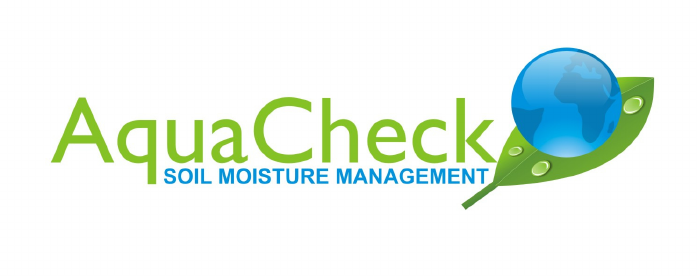
AquaCheck
AC-ROVER
User Guide for AquaCheck ROVER wireless OEM interface
Module
Version 2.01
12 Oct 2014
2
AquaCheck (Pty) Ltd
All rights reserved
Neither whole nor any part of the information contained in this publication
may be reproduced, transcribed or translated in any form, written or
electronic for any purpose whatsoever without prior written consent of
AquaCheck (Pty) Ltd.
This publication is intended only to assist the reader in the use of the
product. AquaCheck (Pty) Ltd shall not be liable for any loss or damage
arising from the use of any information contained in this publication, or any
error or omission in such information, or any incorrect use of the product.
“...then anyone who leaves behind him a written
manual, and likewise anyone who receives it, in
the belief that such writing will be clear and
certain, must be exceedingly simple-minded...”
Plato
(423-347 BC).
3
STATEMENT OF COMPLIANCY
ELECTRO-MAGNETIC COMPLIANCE
The AquaCheck AC-ROVER has been tested and found to comply with the limits
for this Class digital device, pursuant to the requirements of the CE rules. These
limits are designed to provide reasonable protection against harmful interference
in a residential installation. This equipment generates, uses and can radiate radio
frequency energy and, if not installed and used in accordance with the instruction
manual, may cause interference to other radio communications.
EMC APPROVALS
The AquaCheck AC-ROVER has been tested and found to comply with the
following EMC guidelines:
EMISSIONS:
ETSI EN 300 220-2 V2.4.1
47 CFR 15C - RSS 210
47 CFR 15C – 15.247 (a)(2), (b)(3), (d), (e)
47 CFR 15C – 15.31(e)
47 CFR 15B – 15.109 (Class B)
AS/NZ 4268 (2012)
IMMUNITY TESTING:
ETSI EN 301 489-3 V1.4.1 / ESTI EN 302 489-1 V1.9.2
Radiated Immunity - EN 61000-4-2
4
Table of Contents
CREDITS ...................................................................................................................................................... 5
OVERVIEW AND OPERATIONAL DESCRIPTION............................................................................. 5
LABELLING REQUIREMENTS............................................................................................................... 5
USERS MANUAL STATEMENT REQUIREMENTS............................................................................. 6
ANTENNA .................................................................................................................................................... 7
PHOTOS AND DRAWINGS OF THE ROVER MODULE .................................................................... 9
COMMUNICATIONS INTERFACE OPTIONS AND SETTINGS ....................................................... 9
COMMUNICATION INTERFACE......................................................................................................... 11
SDI
PROTOCOL
......................................................................................................................................... 11
A
QUA
C
HECK
D
ATA
A
PPLICATION
P
ROTOCOL
.......................................................................................... 11
Data Command (or DATA H Conmmand).......................................................................................... 12
DELETE Command ............................................................................................................................ 14
DATE Command ................................................................................................................................. 14
PING Command.................................................................................................................................. 15
PROBE LIST Command...................................................................................................................... 15
ERASEEE Command .......................................................................................................................... 17
STATUS Command ............................................................................................................................. 17
LOG INT Command............................................................................................................................ 17
CCTHR Command .............................................................................................................................. 18
CHANNEL Command ......................................................................................................................... 18
Digesting data..................................................................................................................................... 18
PRE INSTALLATION CONFIGURATION........................................................................................... 19
INSTALLING THE ROVER MODULE IN A RS300 MODEM ........................................................... 19
USING THE ROVER MODULE WITH OTHER 3
RD
PARTY EQUIPMENT ................................... 21
FIRMWARE UPGRADE .......................................................................................................................... 22
SPECIFICATIONS .................................................................................................................................... 24

5
Credits
AC-ROVER OEM module supports the Ranch Systems RSEXP command line protocol
over SPI making it "plug and play" compatible with Ranch Systems telemetry and other
OEM systems. The RSEXP protocol is referred to as “AquaCheck Data Application
Protocol” in this document. For more information about Ranch Systems, the RSEXP
protocol and their OEM telemetry programs, please visit www.ranchsystems.com
Overview and operational description
The AC-ROVER is a wireless interface that can establish a short range link to
AquaCheck Wireless soil moisture probes. This is intended as a “cable replacement”
option as well as a “node” or repeater that can service 10 probes.
The AC-ROVER is supplied as a bare board module that can be integrated into the
housing of any 3
rd
party equipment using UART, SPI or SDI communications.
Alternately it is available in a whether-proof enclosure with a serial SDI style
communication cable connection to any 3
rd
party equipment.
The AC-ROVER incorporates an ISM band low power transceiver in the 868 to 868.6
MHz (EU), 902 to 928 MHz (US and Canada) and 916 to 928 MHz (Australia, NZ)
bands. The module has an output power of 10mW maximum, employs GMSK (wide
band) modulation with a maximum packet length of 6.3 mSec and overall duty cycle less
than 1%. Range is approximately 300 meters.
Labelling Requirements
Any OEM (host manufacturer) using the AC-ROVER module must adhere to the
following labelling requirements:
if (1) the module’s certification numbers are not visible when installed in the host, or (2)
if the host is marketed so that end users do not have straightforward commonly used
methods for access to remove the module so that the certification numbers of the module
are visible; then a permanent label referring to the enclosed module must be placed on the
exterior of the finished enclosure. (other permanent methods of marking are also
acceptable, such as engraving). The following or similar text must be used; the FCC ID
and IC Certification numbers must be exactly reproduced.
Contains Transmitter Module FCC ID: YFF-ACROVER
Contains Transmitter Module IC: 8996A-ACROVER
Alternately, if the certification numbers of the module are visible or easily accessible by
the end user without the use of special tools, then the host OEM user manual must
6
contain clear instructions on how end users can find and/or access the module and view
the certification numbers.
Location of the ID label on the ROVER module is shown in Fig 1. The label is placed on
the cover screen of the radio.
Unless the OEM host is too small (approximately <4x4 inches), the final host must
include this statement on the exterior:
This device complies with Part 15 of the FCC Rules. Operation is subject to the
following two conditions: (1) this device may not cause harmful interference,
and (2) this device must accept any interference received, including interference
that may cause undesired operation.
Users Manual Statement Requirements
The following statements apply to this module. All of the following statements must be
included in the finished product’s users manual.
This device complies with part 15 of the FCC Rules and Industry Canada
licence-exempt RSS standard(s). Operation is subject to the following two
conditions:
1. This device may not cause harmful interference, and
2. this device must accept any interference received, including
interference that may cause undesired operation.
Le présent appareil est conforme aux CNR d'Industrie Canada applicables
aux appareils radio exempts de licence. L'exploitation est autorisée aux
deux conditions suivantes : (1) l'appareil ne doit pas produire de
brouillage, et (2) l'utilisateur de l'appareil doit accepter tout brouillage
radioélectrique subi, même si le brouillage est susceptible d'en
compromettre le fonctionnemen
Changes or modifications made to this equipment not expressly approved
by the party responsible for compliance could void the user's authority to
operate the equipment
This equipment has been tested and found to comply with the limits for a
Class B digital device, pursuant to part 15 of the FCC Rules. These limits
are designed to provide reasonable protection against harmful
interference in a residential installation. This equipment generates, uses
and can radiate radio frequency energy and, if not installed and used in
accordance with the instructions, may cause harmful interference to radio
communications. However, there is no guarantee that interference will not
7
occur in a particular installation. If this equipment does cause harmful
interference to radio or television reception, which can be determined by
turning the equipment off and on, the user is encouraged to try to correct
the interference by one or more of the following measures:
—Reorient or relocate the receiving antenna.
—Increase the separation between the equipment and receiver.
—Connect the equipment into an outlet on a circuit different from that to
which the receiver is connected.
—Consult the dealer or an experienced radio/TV technician for help.
This section needs to be contained only in the instruction manual for the main control
unit.
Antenna
If the OEM host employs an antenna connector which allows user access, then all of the
following statements apply and must be included in the finished product’s users manual.
If the OEM host employs a dedicated antenna (e.g. permanently attached) which does not
allow user access to change or modify the antenna, the following statements are not
required.
Under Industry Canada regulations, this radio transmitter may only
operate using an antenna of a type and maximum (or lesser) gain
approved for the transmitter by Industry Canada. To reduce potential radio
interference to other users, the antenna type and its gain should be so
chosen that the equivalent isotropically radiated power (e.i.r.p.) is not
more than that necessary for successful communication
This radio transmitter IC: 8996A ACROVER has been approved by
Industry Canada to operate with the antenna types listed below with the
maximum permissible gain and required antenna impedance for each
antenna type indicated. Antenna types not included in this list, having a
gain greater than the maximum gain indicated for that type, are strictly
prohibited for use with this device.
Conformément à la réglementation d'Industrie Canada, le présent
émetteur radio peut fonctionner avec une antenne d'un type et d'un gain
maximal (ou inférieur) approuvé pour l'émetteur par Industrie Canada.
Dans le but de réduire les risques de brouillage radioélectrique à
l'intention des autres utilisateurs, il faut choisir le type d'antenne et son
gain de sorte que la puissance isotrope rayonnée équivalente (p.i.r.e.) ne
dépasse pas l'intensité nécessaire à l'établissement d'une communication
satisfaisante.
Le présent émetteur radio IC: : 8996A ACROVER a été approuvé par
Industrie Canada pour fonctionner avec les types d'antenne énumérés ci-
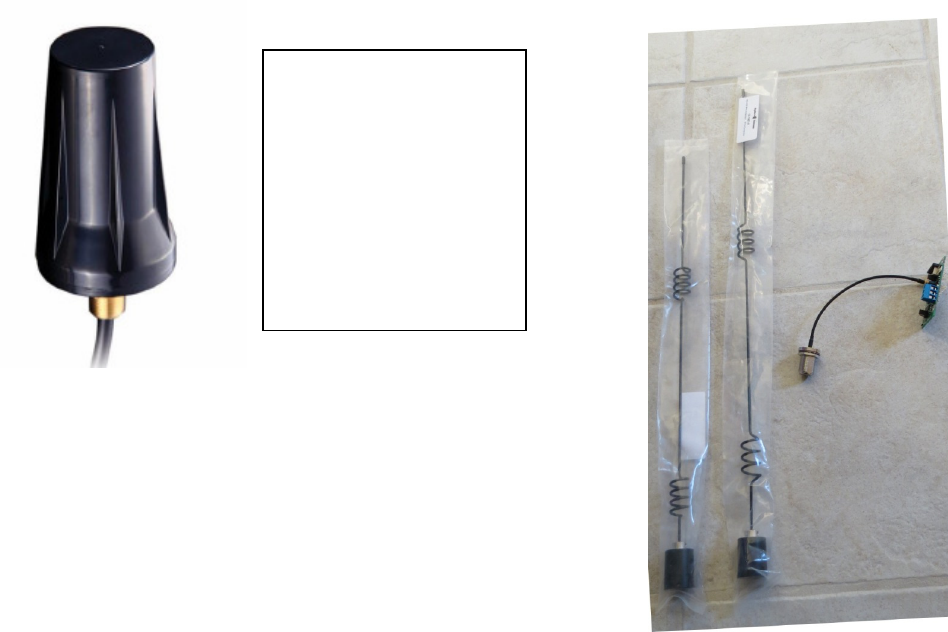
8
dessous et ayant un gain admissible maximal et l'impédance requise pour
chaque type d'antenne. Les types d'antenne non inclus dans cette liste, ou
dont le gain est supérieur au gain maximal indiqué, sont strictement
interdits pour l'exploitation de l'émetteur.
The AC-ROVER module must be used in conjunction with only the following antennas
• Approved antenna 1: Dual band antenna ANT-GSM-ST-SM-M5
• Approved antenna 2: Skywave 868 or 916 band antenna.
Both the dual band antenna and the Skywave
bulkhead have MMCX connector to attach to the ROVER
module.
Use only the antennas specified. Modifications to the
antenna tails, or use of alternate antennas is not permitted.
<- left is shown the dual
band antenna
Right is shown the
Skywave antennas for
868 or 916Mhz (Note
the Skywave has a
bulkhead connector) ->
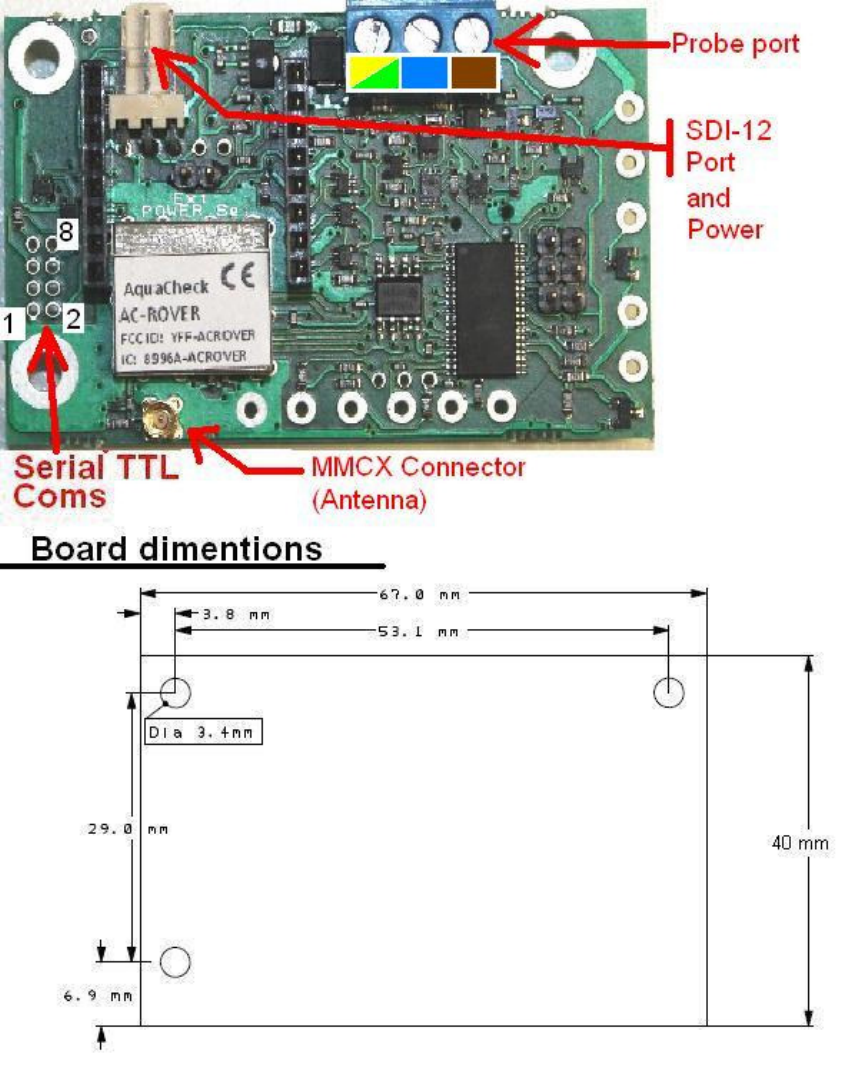
9
Photos and Drawings of the ROVER Module
OEM Rover Module – Fig1
Communications interface options and settings
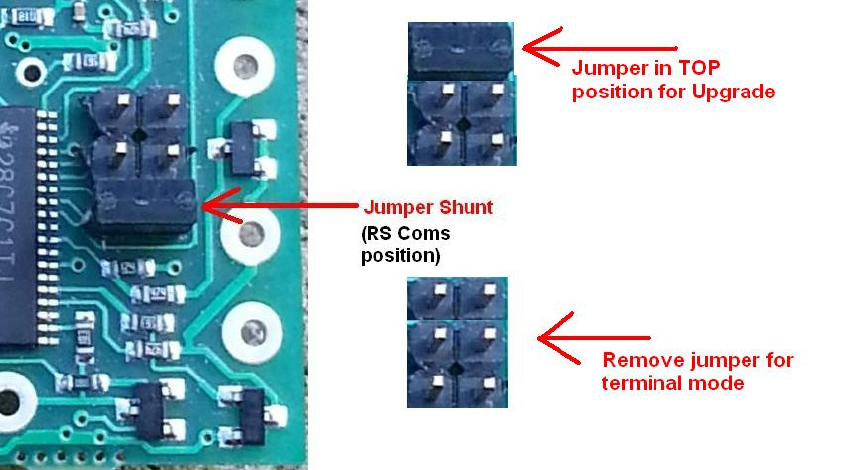
10
Jumper settings
Note: When the ROVER module is installed in the RS300 modem, the “Ext Power Sel”
jumper must be removed.
11
Communication interface
Communication to the ROVER module can be established via a comprehensive
command set that should address most of the needs to enable data transfer to various
OEM equipment vendors.
The command set is broken down into various levels – commands are only available via
the serial interface. Please refer to the chart detailing the JUMPER positions. The
JUMPER selection will determine the communication mode as well as the certain baud
rates.
SDI protocol
SDI-12 protocol is available on the AC-ROVER, however SDI has very limited
functions. Please contact AquaCheck for detail on how to implement the SDI interface
commands.
AquaCheck Data Application Protocol
The “AC-DAP” protocol is available on the UART, SDI and SPI communications
interface. This protocol provides a high level communication to the Rover. It is used to
retrieve logged data and manage user settings on the Rover. Since the Rover is able to log
data it would be advantageous to use this level of interfacing to retrieve data, set the
clock, and manage probe lists on the Rover module. Even if the SDI or MODBUS
protocols are chosen, this application protocol will need be used on a terminal emulator
(like “HyperTerminal”) to manage settings on the Rover. It would be advantageous if the
OEM supplier can implement a communication “pipe” via the upstream equipment (eg
via the internet) so the Rover can be managed remotely.
The data is exchanged in simple ASCII text format, so all communication over this
protocol is human readable. Every “Field” or “Line” is terminated with a carriage return-
line feed combination (in both directions). The Rover will terminate a sequence with the
caret character (>) without the CR-LF. Users should avoid sending data to the Rover
while it is busy with a reply and until the > is received. When the Rover sends data there
may be a maximum of 100ms delay between lines, if this time is exceeded the host may
assume and error and retry. There is about a one minute time limit between receiving
characters before the Rover will time-out, so typing commands to the Rover is possible.
The “enter” key will normally signal to the Rover that you have entered a complete
command.
Commands are non case-insensitive, but will always return text in upper case.
12
Data Command (or DATA H Command)
Syntax
DATA [<records>]
or DATA H [<records>]
Example: DATA 10
Description
Transmits a specified number of data records from the Rover module memory to the host.
The specified number of <records> will determine the number of DATA Records to be
returned. If less records than requested are available, only the number of available
records will be returned. If no number is supplied the Rover returns ONE record. The
DATA H command is only used for diagnostic purposes. The DAT H will return
previously DELETED data. The number of records requested at a time will need to be
optimized by the host, requesting say one record per digest will increase the time to load
the data. A larger number of records in the request may improve efficiency, but may also
lead to inefficiency should the host need to reload the data due to errors (eg checksum did
not work out)
The reply from the Rover as the following form:
<I-record>
{ <A0-record> }
{ <AD-record> }
{ <An-records> }
<EOF-record/checksum >
Each record is formatted as follows:
I-record:
Defines the reference time stamp for this data digest:
I,<reftimestamp>
Where:
<reftimestamp> is the absolute time in seconds since 00:00:00 on January 1st 1980. This
is the current clock time of the Rover’s internal clock.
A0-record:
Defines the information specific to the logged data record:
A0,<index>,<Serial Number>,<timestamp>,<volts>,<Analogue value>,<count1>,
<count2>
Where:
<index> is a number from 1 to 13 corresponding to the probe position in the list of probes
in the Rover. This can be used as an alternate unique identifier in combination with the
Host ID, rather than using the probes serial number.
<Serial Number> is the serial number of the probe.
13
<timestamp> is the absolute time (seconds since 00:00:00 on January 1st 1980) of the
data. Note: should the probe (or Rover) have suffered a reset (new installation, battery
change, etc.) this time will reflect a value that is unreasonably old. In this case the data
may be ignored.
<volts> the probe battery voltage at the time of the log.
<analogue value> is the data from the analogue input channel.
<count1>,<count2> are the rolling count values of the on module counter. The counter
values count 0-65535 then roll back to 0. Should an unreasonable difference occur
between logs, the counter may have suffered a reset and restarted at 0. In that case
substitute zero for the previous value when doing the difference calculation.
AD-record (DATA H command only):
This record is inserted for debugging purposes.
Ad,<text date>,<RSSI-R>,<RSSI-L>,<other debug info>
Where:
<d> is either D or d. lower case d indicates this record has been deleted (by a previous
data digest)
<text date> is the date in readable format YYYY/MM/DD HH:MM in 24-hour time
<RSSI-R> the RSSI (remote) value the probe experienced when the log was captured by
the Rover.
<RSSI-L> the RSSI (local) value the rover experienced from the probe. RSSI values are
in dBuV (dB Micro-volts). Reasonable values range from about -100 (weak signal) to
about -30 (very strong signal).
<other debug info> is diagnostic info to assist post analysis diagnostics. This record may
be ignored, or recorded where communication problems arise so as to assist in identifying
possible causes.
An-records:
These are the actual DATA records. The range of An (A1, A2, A3 etc.) depend on the
type of probe. A1 is reserved for Soil Moisture Values. A2 is reserved for
TEMPERATURE Values, and A3 for EC Values. Not all “A” values may be present in
the data record, the host should not be designed to expect all values. The An values will
however be in ascending sequence.
Any An-record has the following format:
An,<count>,<value1>,.......<value count>
Where count is the number of values following, and each value refers to the data
depending on the actual An record:
A1 are SOIL MOISTURE values. The first value is the uppermost sensor, and goes
downwards. To get a relative % value use the formula: Scaled value = (data value –
1600) / 320.
A2 are Temperature Values. The Temperature in Degrees C = (value/256) – 50.0.
A3 is reserved for future EC values.
EOF-record:
Defines the end of the data, and provide checksum protection.

14
EOF <checksum>
Where:
<checksum> is the simple (not CRC) decimal sum (32 bit) of all bytes in digest starting
with I record (ie. the "I") and ending with the last record before EOF record (including
the CR,LF before EOF).
Note: not all the An records will necessarily be present, for example if the data only
contains the analogue or counter info, then there would be no A1, A2 records. The host
must take this into account when digesting data. If the host is digesting data it is
recommended that record containing out of range or unexpected data be deleted, else
these record will prevent further data from being digested by the host.
DELETE Command
Syntax
DELETE
Description
Will delete the exact number of data records retrieved in previous data command. This
command must be issued by host when data digest has been received correctly (via data
command).
The Rover parses for the string “DELETED” as confirmation that command has
executed. Retrieving data from the rover involved alternate DATA and DELETE
commands. If two DATA commands are issued without a DELETE the Rover will resend
the same data. This would happen if the data record was not received properly by the host
the first time.
DATE Command
Syntax
DATE
DATE <seconds>
Description
Date without parameter will return the current date and time setting.
Date with parameter should update the expansion module on-board real-time clock. Note
that the date/time is specified as seconds since 00:00:00 on January 1st 1980. A value less
than 1/1/2010 will be ignored.
This command must be issued with current host time with poll session immediately
before data commands.
The host parses for the string “time is:” as confirmation that command has executed.
Example:
>date 1000000000
Time is: 1000000000 (2011/09/09 01:46:40)>
>date 1000000060
Time is: 1000000060 (2011/09/09 01:47:40)>

15
Notice how the last command moves clock forward 60 seconds relative to the previous
date command.
Note: the ROVER will not start calling probes or logging data if the date has not been set.
Note on setting the date: the date should be set on every data digest. Further the date
should not vary by more then +- 5 seconds from the target value each time it is set.
PING Command
(This is a management command and would not be used during ordinary operation)
Syntax
PING <index>
PING <serial number>
Description
The ping command will transmit in an attempt to wake the probe.
<index> is a number between 1 and 13, and will look up the probe serial number in the
probe list.
<serial number> will look for a probe matching that serial number.
The command may take as long as 40 seconds to complete.
Example
ping 2
PINGING..:00256>>>>>>>>>Found:256,19,10,02,07,11,3.62,-77.5,-82.0
Meaning after about 9 seconds the probe serial numbered 256 was found, the probe “type
ID” is 19, 10 sensors having 2 values each (moisture and temperature), CPU voltage of
3.62V, and signal strength of -77dBuV on the probe side and -82 on the Rover side. (See
the “AD” record above for more information about the RSSI).
NOTE: if the ROVER is in sync with the probes the PING command will not contact the
probe. Use the ping command before the probe is added to the probe list OR before the
date is set, else the probe may not respond.
PROBE LIST Command
(This is a management command and would not be used during ordinary operation)
Syntax
PROBE LIST <n>
or PROBE LIST <n> <Serial number> <Cx>
or PROBE LIST <n> <Serial number> <R> <Cx>
or PROBE LIST <n> <Serial number> <Sdi-Address>
Description
The probe list command queries or sets the serial number at the specified list index
<n> is a number between 1 and 13. (This is the index to the probe list table, it is also the
value returned in the A0 record “index”of the data command.)
16
Example(s)
PROBE LIST 1
Responds with the probe serial number at index 1
PROBE LIST 1:256,ON,10,00,00,-10.5,-138.0>
PROBE LIST 3
Responds with the serial at index 3 (in this case it is empty)
PROBE LIST 3:Empty>
Adding a probe (to slot 1 with serial number 123):
PROBE LIST 1 123
PROBE LIST 1 :123,ON….
Remove a probe from the list:
PROBE LIST 1 0
Responds with
PROBE LIST 1:Empty>
For adding a slave ROVER, use the suffix <R> after the serial number:
PROBE LIST 1 12345 R
This will indicate that that the slave is a ROVER instead of a probe
If the probe or slave rover is at the extreme edge of the range, one can optionally increase
the probes Rx gain by adding the C suffix with a value of 1 to 7.
PROBE LIST 1 5678 C3
or
PROBE LIST 1 5678 R C3
Values are C=1 (default) up to C=7 (most sensitive)
Note this MAY improve the sensing of the signal at the probe, BUT it may also increase
the power consumption due to the receiver triggering on background noise. Consult
AquaCheck for advice using this option.
For adding SDI-12 probes to the ROVER use the SDI address
PROBE LIST 1 1 0
Where the SDI address is 0. You can just use 1 as the serial number here, the ROVER
will update this on the first contact with the probe. The valid SDI address range is 1 to 9 –
do not use any other addresses.
For adding Counter and analogue only logging, use the SDI option with address “A”
PROBE LIST 1 1 A
This should only be done if there is no SDI probe connected. All counter and analogue
values are logged with the first SDI-12 probe in the probe list, so it is not necessary to use
the “A” option if there are any SDI-12 probes connected.
17
NOTE FOR RS300 and other systems using the SPI interface to the ROVER: the SDI-12
options are no available in this mode since the port is occupied by the SPI
communication interface.
NOTE: when using a ROVER as a slave, please enter the slave ROVER serial number to
the master ROVER probe list. The slave ROVER must have its own probe list settings
according to the probes attached to it. DO NOT enter a probe serial number in both a
master and slave ROVER probe list, choose the one that is located appropriately closest
to the probe.
ERASEEE Command
(This is a management command and would not be used during ordinary operation)
Syntax
eraseEE (note the last 2 “E”’s must be in uppercase)
Description
Use this as a diagnostic or commissioning command only. This command wipes the log
memory clean. It takes a few seconds to complete and responds with the same
information as the status command
STATUS Command
(This is a management command and would not be used during ordinary operation)
Syntax
STATUS
Description
This command can be used to determine the current status of the probe list and the status
of the probe data
STATUS DATE,1,16,0,0,00,<some debug info….>,
01:1234,ON,RF
02:000256,ON,x1,x2,x3,other debug info
The first value after the DATE represents the number of logs in the memory, the balance
of the response if useful for debugging purposes only. The HOST should not use the
STATUS command to determine the amount of logs in the memory, it should only use
the “set time, data, delete” sequence of commands for normal operation.
LOG INT Command
(This is a management command and would not be used during ordinary operation)
Syntax
LOG INT <n>
Description
18
This command can be used to determine or set the interval that the system wakes up to
retrieve data from the probe. In the RS300 this should be set to the same as the “MESH”
interval.
CCTHR Command
(This is a management command and would not be used during ordinary operation)
Syntax
CCTHR <n>
Description
Sets the ROVER Rx sensitivity. Normally this should be left at default of 1. If any probes
connected to this ROVER have a “C” value other than default (see PROBE LIST), then
this rover should have the same value in this setting.
CHANNEL Command
(This is a management command and would not be used during ordinary operation)
Syntax
CHANNEL <n>
Description
Sets the RF channel. The following channels are available
• EU models the available channels are 1 to 10
• AU/NZ channels 168 to 254
• USA/Canada channels 100 to 254
Consult Aquacheck technical representative for help and advice on selecting an
appropriate channel.
Digesting data
The normal data digest sequence from the host would be
• DATE (set the clock)
• DATA x (get x number of data points)
• DELETE (delete the same data points
• DATA x …. (repeat the data/delete sequence until all the data is digested)
• done
The ROVER operates on a 15-minute cycle as follows:
• Minute 4 the ROVER collects SDI-12 data
• Minute 5 the ROVER collects probe data
• Minute 13 the ROVER collects slave ROVER data
19
Consequently it is preferred that the LOG INT be set at 15 minute multiples. Further it is
recommended that the host does a data digest between minute 14 and minute 17. Doing
regular data digest requests may interfere with the performance while the ROVER is
collecting data.
Pre installation CONFIGURATION
The Rover module needs to be configured prior to commissioning. These settings
include:
• Setting the correct channel
• Setting the logging frequency
• Adding Probes and slave ROVER’s in the probe list
• Clearing the log memory
It is advised to use a terminal emulator (like HyperTerminal) to manage the settings on
the ROVER module. Set the communications settings as follows:
• Bits per second 2400
• Data bits 8
• Parity None
• Stop bits 1
• Flow control None
In the “Ascii-Setup” (found in the “Settings” tab) select the option “send line ends with
line feeds”.
Connect a SDI to USB bridge to the SDI port of the ROVER module and supply the
module with power. (An “Upgrade kit” is available from AquaCheck, this kit supplies the
5V USB power to the SDI connector). Place a “Jumper Shunt” to the “Ext Power Sel”
pins to power the module. Remove the communications mode jumper.
Press “Enter” in the HyperTerminal program and you will get the “AC-NODE>” prompt.
Set the required settings on the ROVER module using the commands as given earlier in
this document.
Once you have set the channel and probe list you can “Ping” Probes and slave ROVER’s
(provided they are also setup and powered). To ping a probe in the probe list you can use
the command PING 2 – this will for example ping the probe in probe list position 2).
Installing the ROVER Module in a RS300 modem
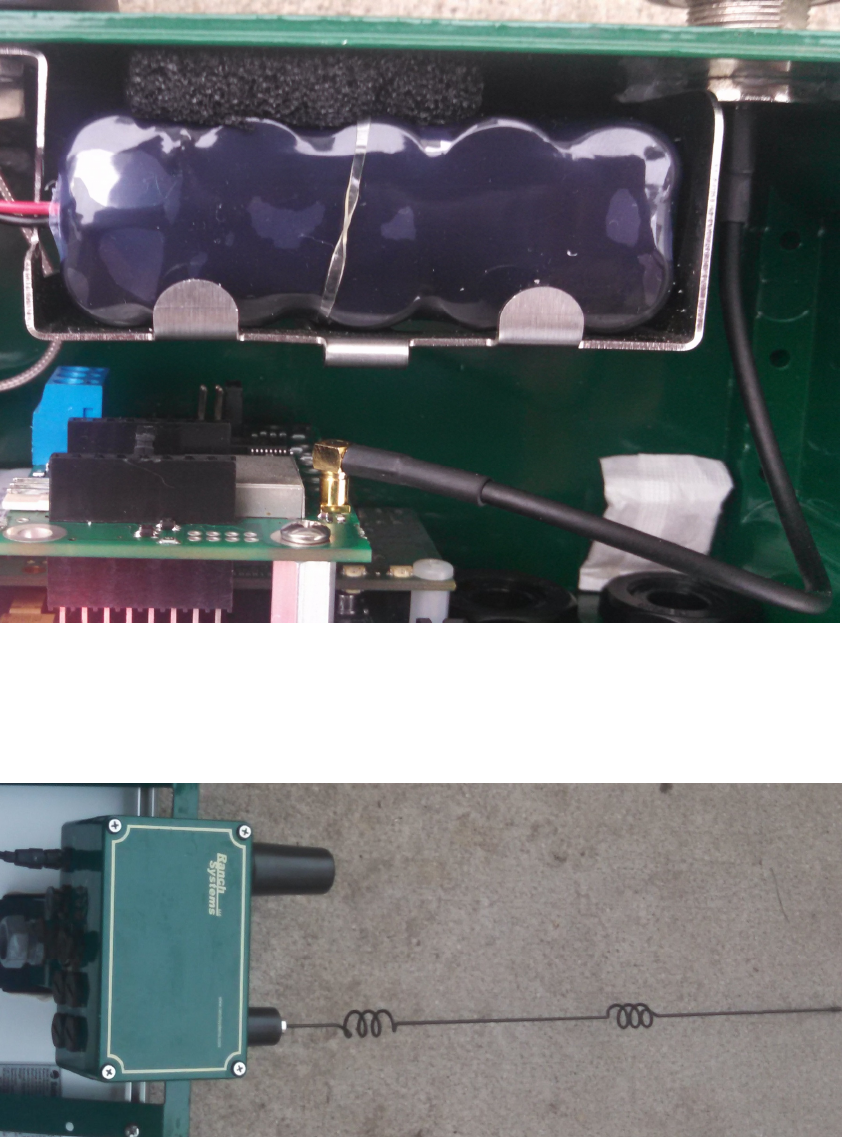
20
Please follow the instructions from Ranch-Systems in addition to this guide. Make sure
bulkhead connectors are water-proof according to Ranch-Systems specifications.
ROVER module is shown mounted above the cell modem in the RS300. Fit the bulkhead
connector as shown and attach the MMCX connector to the ROVER antenna connector.
Note the location of the shunt jumper for the communication mode, and remove the shunt
jumper for the “Ext Power Sel”.
Below is the RS300 modem with the “Skywave” antenna installed.
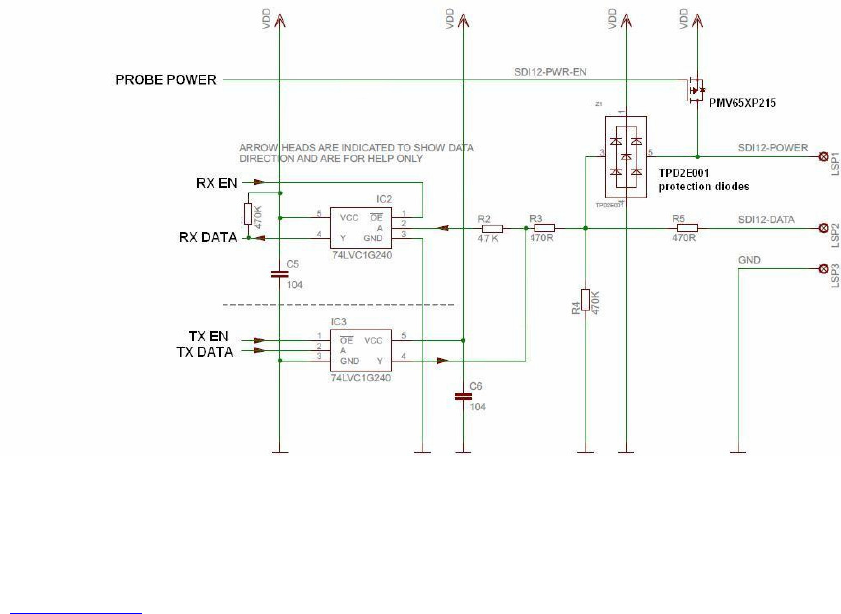
21
Using the ROVER module with OEM 3
rd
party equipment
When ordering the ROVER module for use in OEM equipment please consult an
AquaCheck representative for assistance about ordering the correct product. The module
is supplied in various configurations for use in OEM enclosures. The module can be
ordered with appropriate board-to-board connectors. Alternately the ROVER can be
ordered as a “stand alone” unit – where it is mounted in a weather-proof enclosure. A 3-
way cable can connect the ROVER to the host system.
SDI interface
When using the ROVER module with OEM equipment it is advised to use the SDI
communication port to manage the ROVER. The SDI port has built in ESD protection.
One can also drive the SDI port from a RS232 interface (consult AquaCheck for
appropriate circuit for connecting to RS232, for short cable runs less than 5m)
For reference this diagram shows a typical implementation for the SDI port. The exact
implementation may differ, this is shown for understanding of the SDI port electrical
implementation.
Use the SDI port to manage the ROVER data logger in the same way as described in the
“Configuration” section.
The ROVER is also equipped with a UART (TTL) style interface. This is intended as a
board-to-board interface and is not suitable in a stand alone mode (there is no ESD
protection on the UART interface).
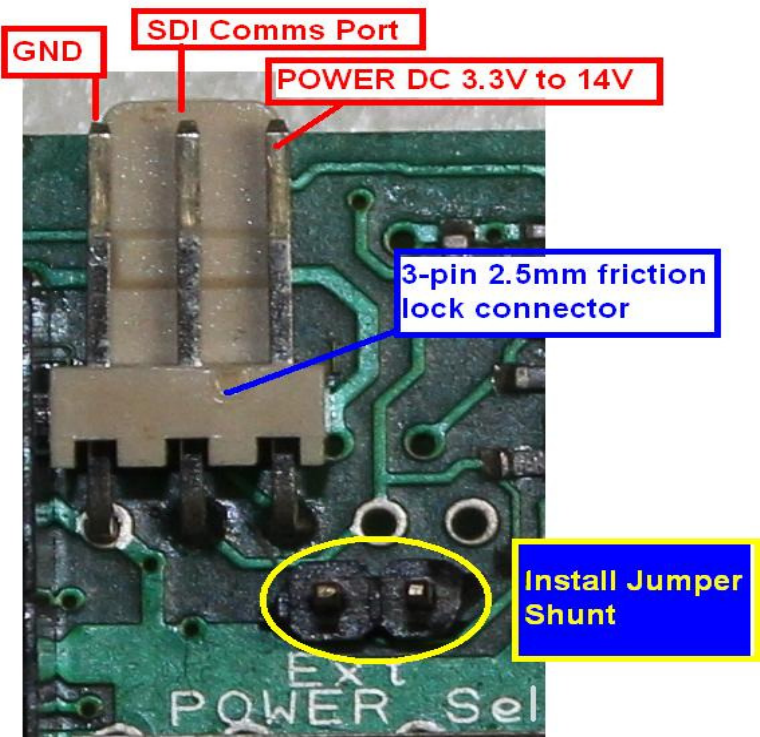
22
Diagram showing the SDI port. Note when using the SDI port the jumper shunt must be
installed. When the ROVER module is supplied potted in the weather-proof case, the
only interface available will be this SDI interface, and the power jumper will be
permanently enabled.
NOTE on the implementation of the SDI electrical interface:
SDI specification call for 12V supply and 5V data line levels. This is not “friendly” to
low power and low voltage systems. To this end AquaCheck implements the SDI
interface so as to work on 3.3V up to 14V. When power lower than 5V is applied – the
SDI data line “tracks” the supply voltage. For example if the supply voltage is 4V, then
the SDI data line will swing between 0V and 4V. For input voltages above 5V the SDI
data line will swing between 0V and 5V.
Firmware Upgrade

23
From time-to-time it may be required to upgrade the firmware to take advantage of new
feature that may be implemented. For upgrading the firmware – remove the module from
the equipment and set up a connection to the PC as described in the “Pre Installation
CONFIGURATION”. Follow the instructions for upgrading as supplied with the
firmware file, or as supplied or directed by your AquaCheck representative.
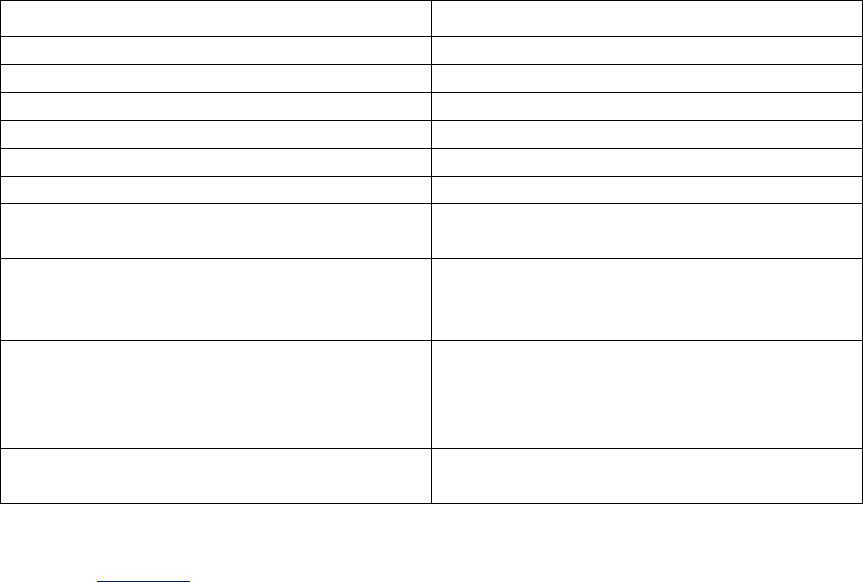
24
Specifications
Parameter
Value or Meaning
Supply Voltage SPI port (RS300) 3.0V to 3.3V
Supply Voltage SDI port 3.3V to 14V
SDI communication port ESD protection fitted
Baud rate SDI port 2400bd
Supply Current Active 23mA
Supply Current idle 0.01mA
RTC *2 Software – recommended to be set on
every cycle
Active times *1 SDI-12 Probes: Scans at 3 minute slot
Probes: Scans at 5 minute slot
Slave Rover: Scans at 13 minute slot
Active duration SDI-12 probes: about 10 seconds
Probes/Rovers: in sync about 4 seconds
Probes/Rovers: out of sync up to 40
seconds
NOTE: for correct function continuous
power must be supplied to the ROVER
*1 – the internal logger of the ROVER cycles around a 15minute interval. It is advised
that the “LOG INT” be set to 15, 30 or 60 minutes only. Further it is recommended that
the host collects data from the ROVER 14 to 17 minute time slot (ie -1 up to 2 minutes).
Continuous polling of the ROVER is not recommended, since the data for each time slot
will be available after the 13 minute slot.
*2 – the internal logger will not function until the date is set. To avoid the time going out
of sync with the host, it is recommended to set the clock on every data digest.
Last modified on 12 Oct 2014.