Bosch Automotive Diagnostics Equipment KT700VMI Vehicle Oscillograph User Manual KT700 VMI
Bosch Automotive Diagnostics Equipment (Shenzhen) Limited Vehicle Oscillograph KT700 VMI
KT700 VMI user manual
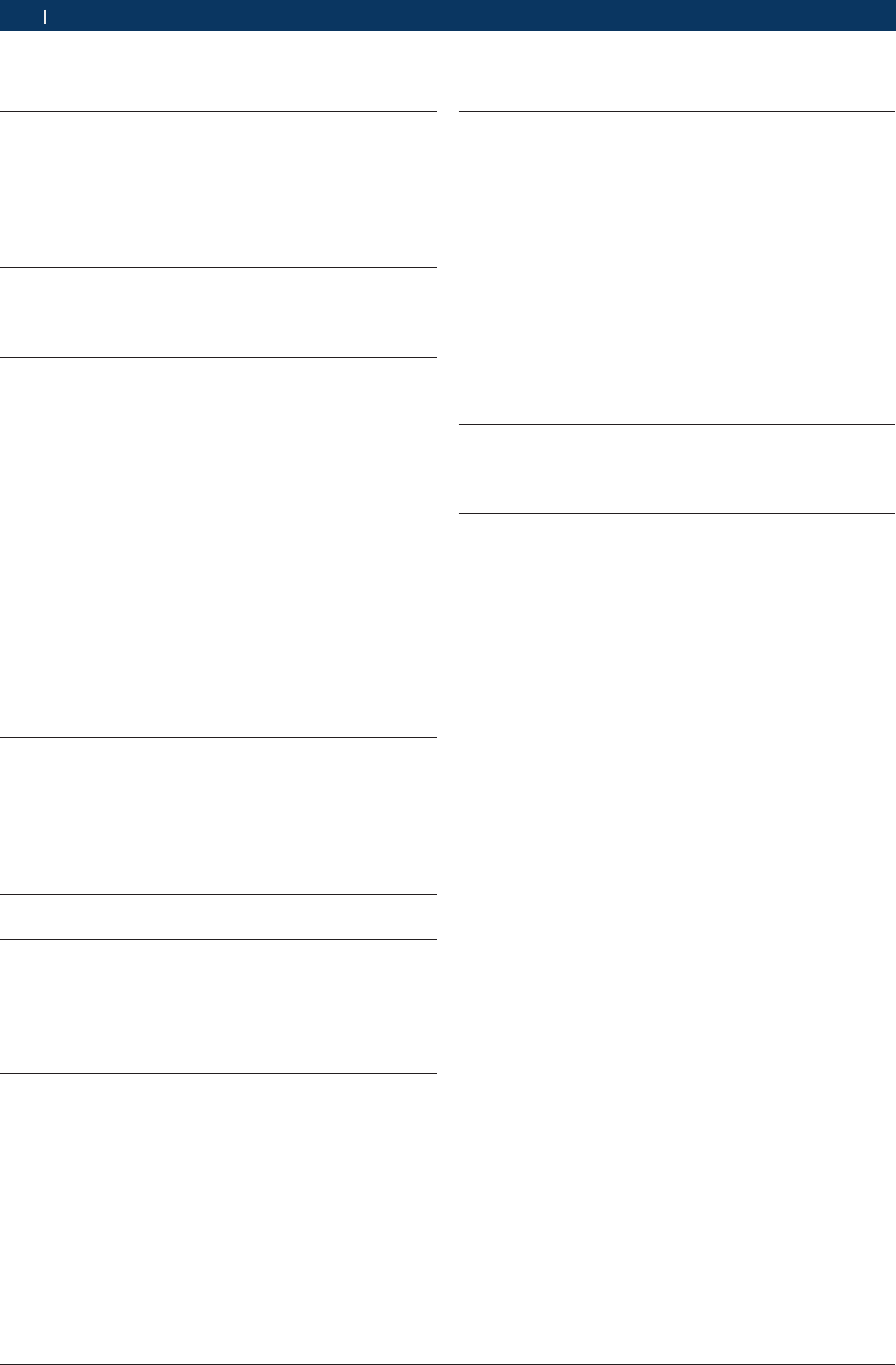
1 697 020 201 2013-05-24| Bosch Automotive Diagnostics Equipment (Shenzhen) Limited
16 | KT700 VMI | en
1. Symbols used 17
1.1 In the documentation 17
1.1.1 Warning notices -
Structure and meaning 17
1.1.2 Symbols in this documentation 17
1.2 On the product 17
2. Important notes 17
2.1 User group 17
2.3 Obligation of contractor 19
3. Safety instructions 20
3.1 Risk of electric shocks 20
3.1.1 Low voltages, high voltages 20
3.1.2 High voltages in hybrid vehicles and elec-
tric vehicles as well as their high-voltage
components 20
3.2 Danger of acid burning 21
3.3 Danger of injury, Danger of crushing 21
3.4 Danger of burning 22
3.5 Danger of fire, Danger of explosion 22
3.6 Danger of asphyxiation 22
3.7 Danger of tripping 22
3.8 Noise 22
3.9 FCC Warning 23
3.10 Satety Warning 23
3.11 Using notes 24
4. PC Software environment 24
4.1 Computer parameters 24
4.2 Installation guidance 24
4.2.1 VCI Software installation 24
4.3 USB driver installation 25
4.4 Software uninstall 25
5. Deliver scope 26
6. Introduction to VMI host 26
6.1 Host identifications 26
6.2 Connection terminal 26
6.3 Oscillograph terminal 27
6.4 Assistant function 27
7. Equipment connection 27
7.1 Measure connection 27
7.2 Selfcheck / Upgrade connection 28
8. Measure function 28
8.1 Power supply of host 28
8.2 Function button introduce 29
8.3 Parameters adjust 29
8.3.1 Period 29
8.3.2 Channels, amplitude and coupling 29
8.3.3 Trigger function 29
8.3.4 Negate routine 30
8.3.5 Adjust cursor 30
8.3.6 Waveform position 30
8.4 Sensor Measure 31
8.4.1 Manifold Absolute Pressure Sensor
(MAP) 31
9. Service and Maintenance 32
9.1 Cleaning 32
9.2 Maintenance 32
10. Technical Parameters 32
10.1 Host parameters 32
10.2 Oscillograph parameters 32
10.3 Multimeter parameters 32
10.4 Logic signal module parameters 32
Contents

1 697 020 201 2013-05-24| Bosch Automotive Diagnostics Equipment (Shenzhen) Limited
Symbols used | KT700 VMI | 17KT700 VMI | 17 | 17 en
1. Symbols used
1.1 In the documentation
1.1.1 Warning notices - Structure and meaning
Warning notices warn of dangers to the user or people in
the vicinity. Warning notices also indicate the consequen-
ces of the hazard as well as preventive action. Warning
notices have the following structure:
Warning
symbol
KEY WORD – Nature and source of hazard!
Consequences of hazard in the event of failu-
re to observe action and information given.
¶Hazard prevention action and information.
The key word indicates the likelihood of occurrence and
the severity of the hazard in the event of non-observance:
Key word Probability of
occurrence
Severity of danger if inst-
ructions not observed
DANGER Immediate impen-
ding danger
Death or severe injury
WARNING Possible impending
danger
Death or severe injury
CAUTION Possible dangerous
situation
Minor injury
1.1.2 Symbols in this documentation
Symbol Designation Explanation
!Attention Warns about possible property damage.
iInformation Practical hints and other
useful information.
1.
2.
Multi-step
operation
Instruction consisting of several steps.
eOne-step
operation
Instruction consisting of one step.
Intermediate
result
An instruction produces a visible inter-
mediate result.
"Final result There is a visible final result on com-
pletion of the instruction.
1.2 On the product
!Observe all warning notices on products and ensure
they remain legible.
2. Important notes
Before start up, connecting and opera-
ting Bosch products it is absolutely essenti-
al that the operating instructions/owner’s
manual and, in particular, the safety inst-
ructions are studied carefully. By doing so you can eli-
minate any uncertainties in handling Bosch products
and thus associated safety risks upfront; something
which is in the interests of your own safety and will ulti-
mately help avoid damage to the device. When a Bosch
product is handed over to another person, not only the
operating instructions but also the safety instructions
and information on its designated use must be handed
over to the person.
2.1 User group
The product may be used by skilled and instructed per-
sonnel only. Personnel scheduled to be trained, famili-
arized, instructed or to take part in a general training
course may only work with the product under the su-
pervision of an experienced person.
All work conducted on electrical and hydraulic de-
vices may be performed by persons with sufficient
knowledge and experience in the field of electrics and
hydraulics.
Children have to be supervised to ensure that they do
not play with the appliance.

1 697 020 201 2013-05-24| Bosch Automotive Diagnostics Equipment (Shenzhen) Limited
18 | KT700 VMI | Symbols useden
2.2 Agreement
By using the product you agree to the following regulations:
Declare
RRefer to packing list for detailed product configura-
tion;
RRefer to software for functions, pictures.
This product cannot use in:
Locations characterized by a separate power network,
in most cases supplied from a high- or medium-voltage
transformer, dedicated for the supply of installations
feeding manufacturing or similar plants with one or
more of the following conditions:
– frequent switching of heavy inductive or capacitive
loads;
– high currents and associated magnetic fields;
– presence of Industrial, Scientific and Medical (ISM)
apparatus (for example, welding machines).
The equipment complies with relevant require-
ments of Directive 2004/108/EC for Electromagnetic
compatibili¬ty (EMC) and Directive 2006/95/EC for Low
Voltage.
Copyright
Software and data are the property of Bosch or its
suppliers and protected against copying by copyright
laws, international agreements and other national legal
regulations. Copying or selling of data and software or
any part thereof is impermissible and punishable; in
the event of any infringements Bosch reserves the right
to proceed with criminal prosecution and to claim for
damages.
Liability
All data in this program is based - where possible - on
manufacturer and importer details. Bosch does not ac-
cept liability for the correctness and completeness of
software and data; liability for damage caused by faulty
software and data is ruled out. Whatever the event,
Bosch liability is restricted to the amount for which the
customer actually pays for this product. This disclaimer
of liability does not apply to damages caused by intent
or gross negligence on the part of Bosch.
Warranty
Any use of non-approved hardware and software will
result in a modification to our product and thus to exclu-
sion of any liability and warranty, even if the hardware or
software has in the meantime been removed or deleted.
No changes may be made to our products. Our products
may only be used in combination with original acces-
sories and original service parts. Failing to do so, will
render null and void all warranty claims.
This product may only be operated using Bosch appro-
ved operating systems. If the product is operated using
an operating system other than the approved one, then
our warranty obligation pursuant to our supply condi-
tions will be rendered null and void. Furthermore, we
will not be held liable for damage and consequential
damage incurred through the use of a non-approved
operating system.
Warning
Test on a known source within the rated voltage range
of the product, both before and after use to ensure unit
is in good working condition.
RNot to use the equipment for measurements on
mains circuits, not to use the equipment for measu-
rements on voltage exceed the voltage range descri-
be in the manual.
RNot to use the product for measurements within
other measurement categories, such as CAT II, CAT
III, CAT IV.
RAny parts of the device and its accessories are not
allowed to be changed or replaced, other than autho-
rized by the manufacturer of his agent
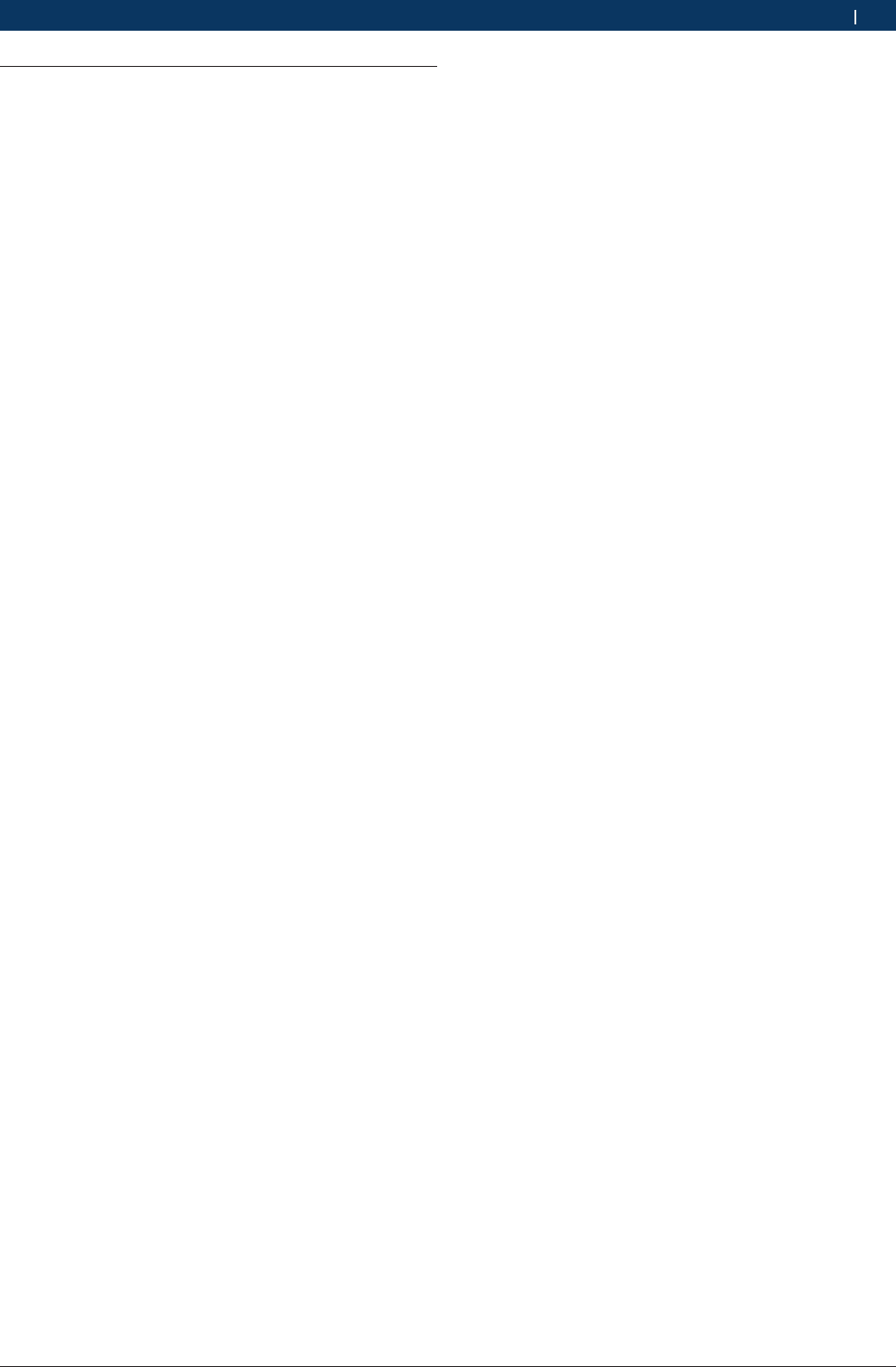
1 697 020 201 2013-05-24| Bosch Automotive Diagnostics Equipment (Shenzhen) Limited
Symbols used | KT700 VMI | 19KT700 VMI | 19 | 19 en
2.3 Obligation of contractor
The contractor is obliged to ensure that all measures
geared towards the prevention of accidents, industrial
diseases, labor-related health risks are taken and mea-
sures towards making the workplace fit for people to
work in are carried out.
Specifications for electrical systems (BGV A3)
Electrical engineering in Germany is subject to the ac-
cident prevention regulations of the trade association
"Electrical Plant and Equipment as under BGV A3 (previ-
ously VBG 4)". In all other countries, the applicable nati-
onal regulations acts or decrees are to be adhered to.
Basic rules
The contractor is bound to ensure that all electrical
equipment and operating material is set up, modified
and maintained by skilled electricians only or under
the guidance and supervision of a skilled electrician in
accordance with electrical engineering principles.
Furthermore, the contractor must ensure that all elec-
trical equipment and operating material is operated in
keeping with electrical engineering principles.
If a piece of electrical equipment or operating material
is found to be defective, i.e. it does not or no longer
complies with electrical engineering principles, the con-
tractor must ensure that the fault is rectified immedia-
tely and, in the event that imminent danger exists, also
ensure that the electrical equipment or the electrical
operating material is not used.
Tests (taking Germany as an example):
RThe contractor must ensure that all electrical sys-
tems and equipment are tested by a qualified electri-
cian or under the guidance of a qualified electrician
to ensure they are in proper working order:
$Before starting for the first time.
$After modification or repair before starting for the
first time.
$At given intervals. Set intervals such as to ensu-
re that faults that can be expected to occur are
determined in good time.
RThe test is to take the electrical engineering princip-
les relating hereto into account.
RUpon request of the trade association, a test manual
is to be maintained into which specific entries are
made.
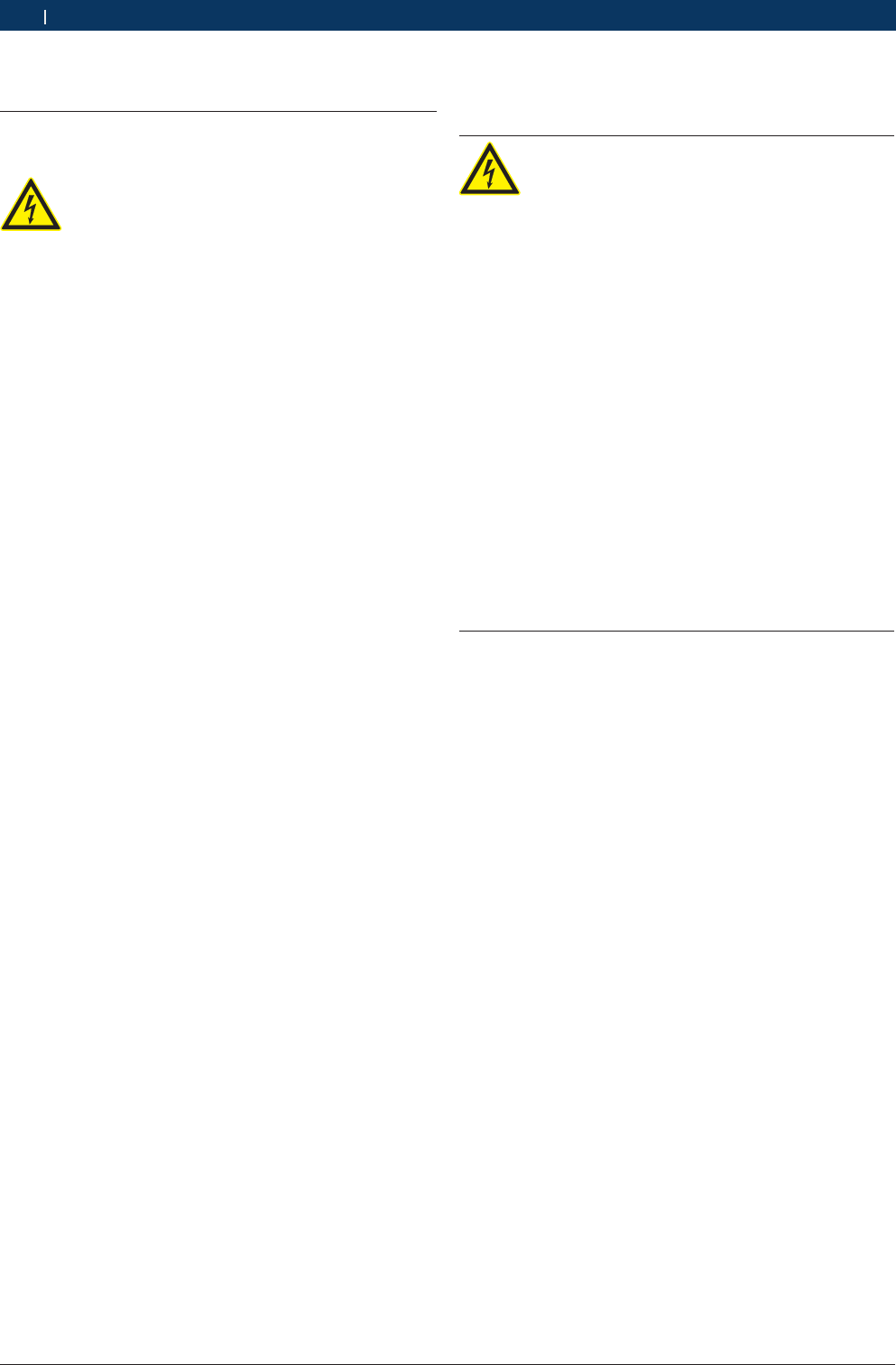
1 697 020 201 2013-05-24| Bosch Automotive Diagnostics Equipment (Shenzhen) Limited
20 | KT700 VMI | Safety instructionsen
3. Safety instructions
3.1 Risk of electric shocks
3.1.1 Low voltages, high voltages
Hazardous voltages occur in both the lighting
system and the electrical system of a motor
vehicle. If contact is made with live parts
(e.g. with the ignition coil), there is a risk of
electric shock from flashover voltages caused
by damaged insulation (e.g. ignition cables
which have been attacked by martens). These
apply to the secondary and primary sides of
the ignition system, the wiring harness with
connectors, lighting system (Litronic) as well
as connection to the vehicle.
Safety measures:
¶Only connect to a properly grounded outlet.
¶Only the enclosed or a tested power supply cable is
to be used.
¶All extension cables must be fitted with shock-proof
contacts.
¶Any cables with damaged insulation must be repla-
ced.
¶First connect the lighting system and turn it on befo-
re connecting it to the vehicle.
¶Before switching on the ignition connect the (B-)
cable to engine ground or the battery (B–) terminal.
¶Always switch off the ignition before performing any
work on the electrical system of the vehicle. Inter-
vention includes, for instance, connection to the
vehicle, replacement of ignition system components,
removal of equipment (e. g. alternators), connection
of equipment to a test bench.
¶Wherever possible, tests and settings should always
be caried out with the ignition switched off and the
engine stationary.
¶If tests or settings are carried out with the ignition
switched on or the engine running, care must be
taken not to touch any live parts. This applies to all
connection cables and leads as well as to connec-
tions of equipment to test benches.
¶Test connections must always be made using sui-
table connectors (e.g. Bosch testing cable set or
vehicle-specific adapter cables).
¶Make sure that all test connections are properly
plugged in and secure.
¶Before disconnecting the (B-) cable from the engine
ground or battery (B–), switch off the ignition.
¶Never open the enclosures.
3.1.2 High voltages in hybrid vehicles and electric ve-
hicles as well as their high-voltage components
If high-voltage components or high-voltage
wires are inexpertly handled, there is a risk of
fatal injury from high voltages and the possib-
le transmission of current through the body.
¶Deenergization is only to be performed by
a qualified electrician, a qualified electri-
cian for specific tasks (hybrid) or a power
systems engineer.
¶Work on vehicles with high-voltage compo-
nents is only ever to be performed in a safe,
deenergized condition by persons with the
minimum qualification "Trained to perform
electrical work".
¶Even after deactivating the high-voltage
vehicle electrical system, the high-voltage
battery may still be live.
¶Operating condition cannot be established
from any running noise, as the electric ma-
chine is silent when stationary.
¶In gear positions "P" and "N" the engine or
electric motor may start spontaneously depen-
ding on the charge of the high-voltage battery.
Safety measures:
¶Never open or damage high-voltage batteries.
¶On accident vehicles, never touch high-voltage com-
ponents or exposed high-voltage wires before deacti-
vating the high-voltage vehicle electrical system.
¶Avoid contact with any high-voltage components
and high-voltage wires (orange sheathing) when in
operation.
¶Secure against unauthorized renewed start-up
(e.g. by means of a padlock).
¶Always wait at least 10 seconds after deactivating
the high-voltage system.
¶Visually inspect the high-voltage components and
high-voltage wires for damage. The power systems
engineer responsible should always be immediate-
ly notified of any irregularities, doubts or defects
found.
$High-voltage components must never exhibit signs
of external damage.
$The insulation of the high-voltage wiring must be
intact and undamaged.
$Watch out for any abnormal deformation of the
high-voltage wiring.
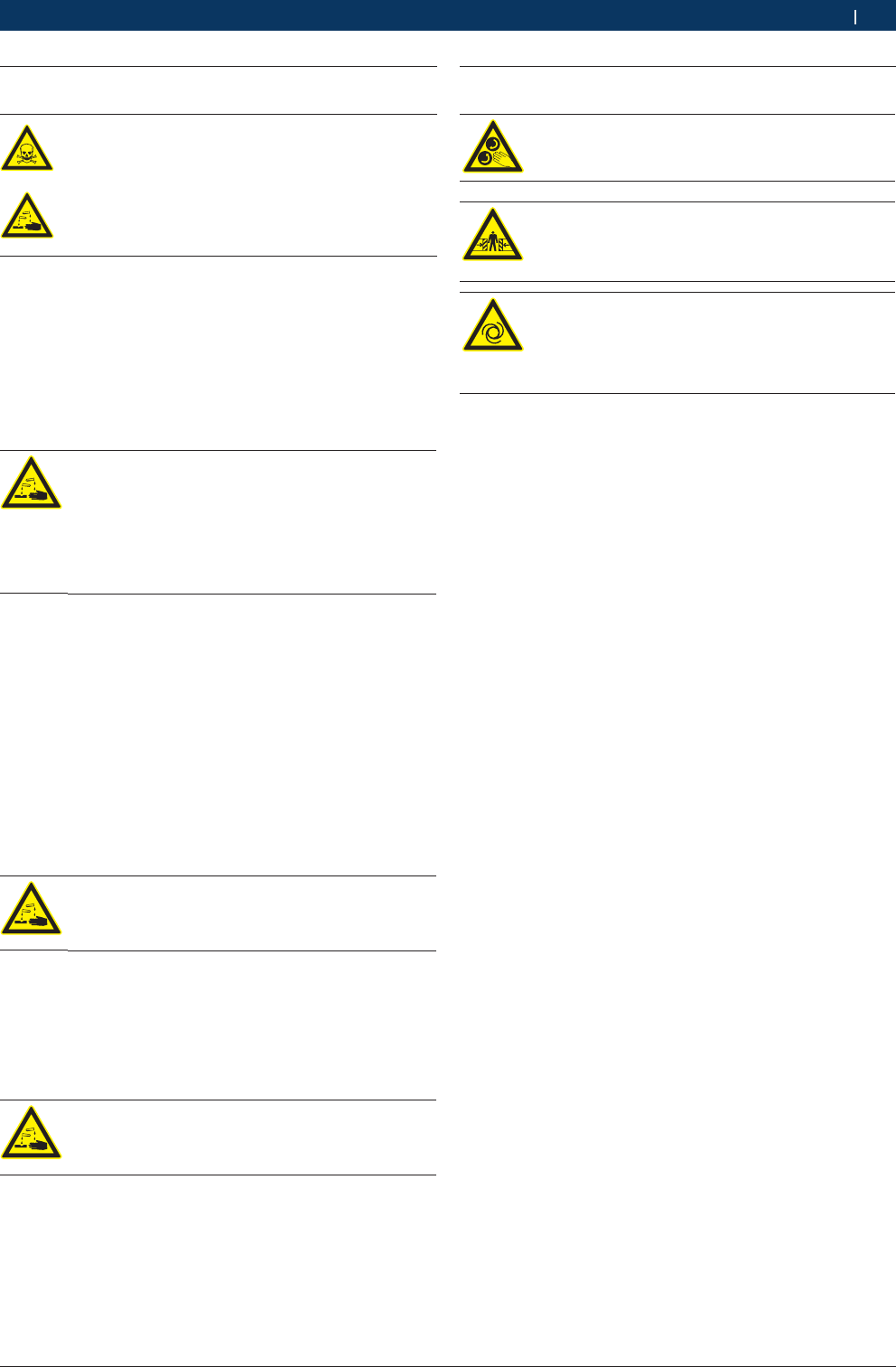
1 697 020 201 2013-05-24| Bosch Automotive Diagnostics Equipment (Shenzhen) Limited
Safety instructions | KT700 VMI | 21KT700 VMI | 21 | 21 en
3.2 Danger of acid burning
When exhaust gas measurements are taken,
the sampling hoses which are used release a
highly caustic gas (hydrogen fluoride) that can
cause acid burning in the respiratory system
when heated to temperatures in excess of
250 °C (482 °F) or in the event of fire.
Rules of conduct:
¶Consult a doctor immediately after inhaling!
¶Always wear gloves made of neoprene or PVC when
removing residues left after a fire.
¶Neutralize any residues left after a fire with a cal-
cium hydroxide solution. This produces non-toxic
calcium fluoride, which can be washed away.
Acids and alkalis can cause severe burning on
unprotected skin. Hydrogen fluoride in combi-
nation with moisture (water) forms hydroflu-
oric acid. The condensate, which accumulates
in the sampling hose and in the condensate
container likewise contains acid.
Rules of conduct:
¶When replacing the O2 measuring sensor, bear in
mind that it contains alkali.
¶When replacing the NO measuring sensor, bear in
mind that it contains acid.
¶Rinse any affected parts of the skin immediately in
water, then consult a doctor!
¶NO and O2 measuring sensors are hazardous waste
and must be disposed of separately. Your Bosch spe-
cialist equipper can dispose of sensors in the proper
manner.
If liquid crystal escapes from a damaged liquid
crystal display, it is imperative to avoid direct
skin contact, inhalation and swallowing.
Rules of conduct:
¶If you have inhaled or swallowed liquid crystal, con-
sult a doctor immediately!
¶Wash the skin and clothing thoroughly with soap and
water if it has come into contact with liquid crystal.
If fluid (electrolyte) escapes from batteries
and rechargeable batteries, avoid getting it on
your skin or in your eyes.
Rules of conduct:
¶If contact with skin or eyes happens nevertheless,
wash the affected parts immediately with clean wa-
ter and then consult a doctor.
3.3 Danger of injury, Danger of crushing
The vehicle has rotating and moving parts
that can injure fingers and arms.
If the vehicle is not prevented from rolling
away, there is a danger of people being crus-
hed against a workbench, for example.
There is the risk with electrically operated
fans in particular that the fan can start run-
ning unexpectedly even when the engine and
ignition are off.
Safety measures:
¶Take steps to prevent the vehicle from rolling away
while it is being tested. Select the park position if the
vehicle has an automatic transmission and apply the
handbrake or lock the wheels with chocks (wedges).
¶Operating staff must wear work clothes without
loose bands and loops.
¶Do not reach in any area with rotating or moving parts.
¶When working on or in the vicinity of electrically
driven fans, allow the engine to cool down first, then
disconnect the plug of the fan motor.
¶Route cables at a suitable distance from rotating parts.
¶Secure the trolley against rolling away by setting the
brakes.
¶Do not place heavy objects on or lean on the sensor
holder.
¶Transport and operate the equipment only in ac-
cordance with the operating instructions.
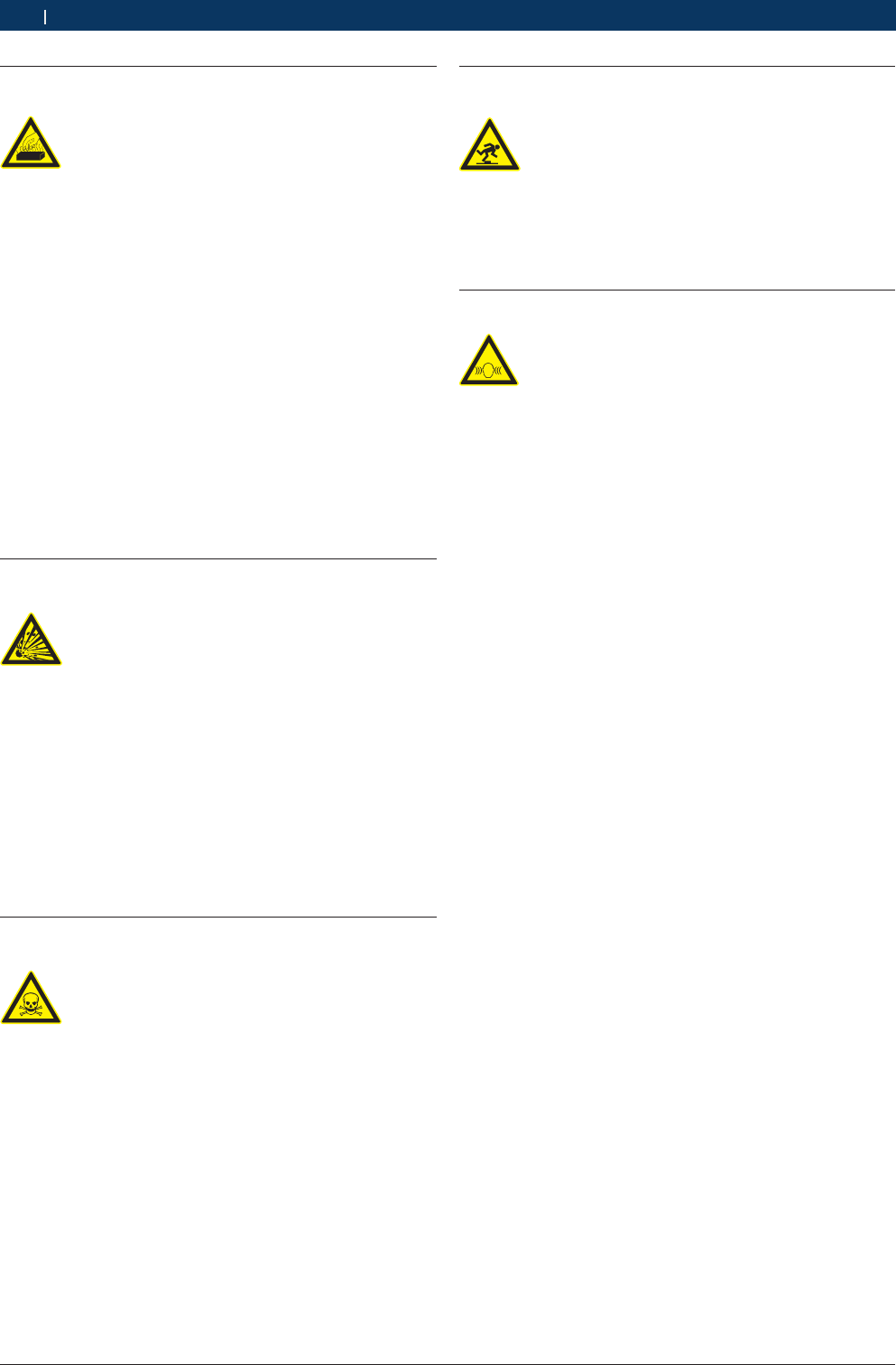
1 697 020 201 2013-05-24| Bosch Automotive Diagnostics Equipment (Shenzhen) Limited
22 | KT700 VMI | Safety instructionsen
3.4 Danger of burning
When working on a hot engine, there is a risk
of injury from burning if such components as
the exhaust gas manifold, the turbo-charger,
the Lambda sensor, etc. are touched or if
parts of the body come too close to them.
These components may be heated to tempe-
ratures of several hundred degrees Celsius.
Depending on the duration of the exhaust
gas measurements, the sampling probe of the
exhaust gas measuring instrument may also
become extremely hot.
Safety measures:
¶Always wear protective clothing, e.g. gloves.
¶Allow the engine to cool down first. This also applies
to auxiliary heating systems.
¶Keep connecting cables well away from all hot parts.
¶Do not leave the engine running any longer than
necessary for the test or setting.
3.5 Danger of fire, Danger of explosion
There is a risk of fire and explosion from fuels
and fuel vapors when work is performed on
the fuel system or on the mixture control
system.
Safety measures:
¶Switch off the ignition.
¶Allow the engine to cool down first.
¶Avoid naked flames and potential sources of sparks.
¶Do not smoke.
¶Collect any leaked fuel.
¶Always ensure effective ventilation and suction when
working in closed areas.
3.6 Danger of asphyxiation
Car exhaust fumes contain carbon monoxide
(CO) - a colorless, odorless gas. If inhaled,
carbon monoxide causes an oxygen deficien-
cy in the body. Extreme caution is therefore
essential when working in a pit, as some of
the components of the exhaust gas are heavier
than air and settle at the bottom of the pit.
Caution is also necessary when working on
LPG-driven vehicles.
Safety measures:
¶Always ensure effective ventilation and suction (es-
pecially when working in a pit).
¶Always switch on and connect the suction plant in a
closed area.
3.7 Danger of tripping
When conducting tests or making adjust-
ments, the sensor and connection cables
increase the risk of tripping.
Safety measures:
¶Route the connecting cables such that any risk of
tripping up is prevented.
3.8 Noise
Noise levels in excess of 70 dB(A) can oc-
cur when measurements are carried out on
a vehicle, especially at high engine speeds.
Damage to hearing may result if human beings
are exposed to noise at such levels over an
extended period of time.
Safety measures:
¶Noise protection facilities must be provided by the ow-
ner at all workplaces in the vicinity of the testing area.
¶Suitable personal noise protection facilities must be
used by the operator.

1 697 020 201 2013-05-24| Bosch Automotive Diagnostics Equipment (Shenzhen) Limited
Safety instructions | KT700 VMI | 23KT700 VMI | 23 | 23 en
3.9 FCC Warning
This device complies with Part 15 of the FCC Rules.
Operation is subject to the following two conditions:(1)
this device may not cause harmful intererence, and
(2) this device must accept any interference received,
including interference that may cause undesired opera-
tion.
Note: changes or modifications not expressly approved
by the party responsible for compliance could void the
user's authority to operate the equipment. This equip-
ment has been tested and found to comply with the
limits for a Class B digital device, pursuant to Part 15
of the FCC Rules. These limits are designed to provide
reasonable protection against harmful interference in
a residential installation. This equipment generates,
users and can radiate radio frequency energy and, if not
installed and used in accordance with the instructions,
may cause harmful interference to radio communica-
tions. However, there is no guarantee the interference
will not occur in a particular insatllation. If this equip-
ment does cause harmful interference to radio or televi-
sion reception, which can be determined by turning the
equipment off and on, the user is encouraged to try to
correct the interference by one or more of the following
measures:
RReorient or relocate the receiving antenna;
RIncrease the separation between the equipment and
receiver;
RConnect the equipment into an outlet on a circuit
different from that to which the receiver is connec-
ted;
RConsult the dealer or an experienced radio/TV tech-
nician for help.
3.10 Satety Warning
RInspection shall be carried out in good ventilation.
Connect the exhaust pipe to outside if there is no
enough ventilation;
RSmoking and open fire are prohibited in the inspec-
tion;
RThe battery liquid contains sulphuric acid that could
erode the skin. Avoid battery liquid from touching
the skin directly in operation, especially note that
the liquid shall not be splashed into eye;
RThe engine temperature is high when running. Avoid
touching the high-temperature parts, such as radia-
tor and exhaust pipe;
RPull manual brake before starting the engine. Block
the front wheels and place shift lever at P or neutral
gear to avoid accident when starting the engine;
RIf external batter is used as power supply, pay
attention to the electrode; use red alligator clip to
connect anode and black alligator clip to connect
cathode;
RKeep all the power cables, pens and tools away from
belt or other moving parts if using instrument in
engine compartment;
RDo not wear watch, ring and loose clothes in mainte-
nance for engine compartment;
RWear approved safety glasses in all inspection pro-
cesses;
ROnly the enclosed power adapter or power supply
cable can be used for supply connection;
RIf the equipment is used in a manner not specified
by the manufacturer, the protection provided by the
equipment may be impaired.

1 697 020 201 2013-05-24| Bosch Automotive Diagnostics Equipment (Shenzhen) Limited
24 | KT700 VMI | PC Software environmenten
3.11 Using notes
RThe instrument is precise electronic instrument, do
not drop it;
RThe instrument may respond slowly in first inspec-
tion. Please be patient. Do not operate the instru-
ment frequently;
RIf the program is interrupted or the display is disor-
dered after flashing. Shut off the power and switch it
on again for test;
REnsure that the instrument and the diagnosis retai-
ner are connected securely, otherwise the interrup-
ted signal will affect the test. ;
RHandle the instrument gently and put it in safe place
to avoid impact. Shut off the power when not using;
RAfter using put the accessories into the kit;
ROnline upgrade will be affected by local wire speed.
Please wait patiently if the loading is slow;
RCertain inspection and maintenance basis are requi-
red to operate the instrument, as well as electrical
control system of the inspected automobile.
4. PC Software environment
As VMI operates based on the computer, the VMI soft-
ware and relevant hardware driver software shall be
installed onto the computer first of all.
4.1 Computer parameters
Configu-
ration
Parameter (Recommen-
ded)
Parameter (Minimum)
Main fre-
quency
CPU larger than 2G CPU larger than 1.5G
Memory Larger than 1G Larger than 512M
Free
space of
hard disc
Larger than 2G Larger than 1G
USB inter-
face
USB2.0 full speed or high
speed
USB2.0 full speed or
high speed
WLAN Wireless network card Wireless network card
LAN 10M/100M 10M/100M
Display re-
solution
Higher than 1280*800,
32-bit above color depth
1024*768, 16-bit above
color depth
OS WINDOWS XP /WIN-
DOWS 7
WINDOWS XP /WIN-
DOWS 7
4.2 Installation guidance
4.2.1 VCI Software installation
Installation Steps:
1. Get the installation file(KT700_Full_Setup_
V2.5.5.exe) from the CD disc furnished by Bosch Au-
tomotive Diagnostics Equipment (Shenzhen) Limited
or its official website;
2. Double click the file;
3. Click the “Next” button to get the interface display-
ing the user license protocol, which shall be carefully
read; if you accept all protocols, please click the
“Accept (I)” button;
4. Select the target folder for software installation
(disc C is the default file location); you can click the
“Browse” button to select the target folder, and the
program will automatically detect the corresponding
used and free spaces of target disc;
5. Click the “Installation” button, and the software will
be under installation; please wait for the installation
completion;
6. After installation, if you select the “Run KT700” and
click the “Finish” button, the installation completion
will be confirmed and the VMI software will be run;
if you only click the “Finish” button, the installation
completion will be confirmed but the VMI software
will not be run;
7. After installation, the shortcut will be displayed on
the computer desktop; just click the shortcut to run
the VMI software.
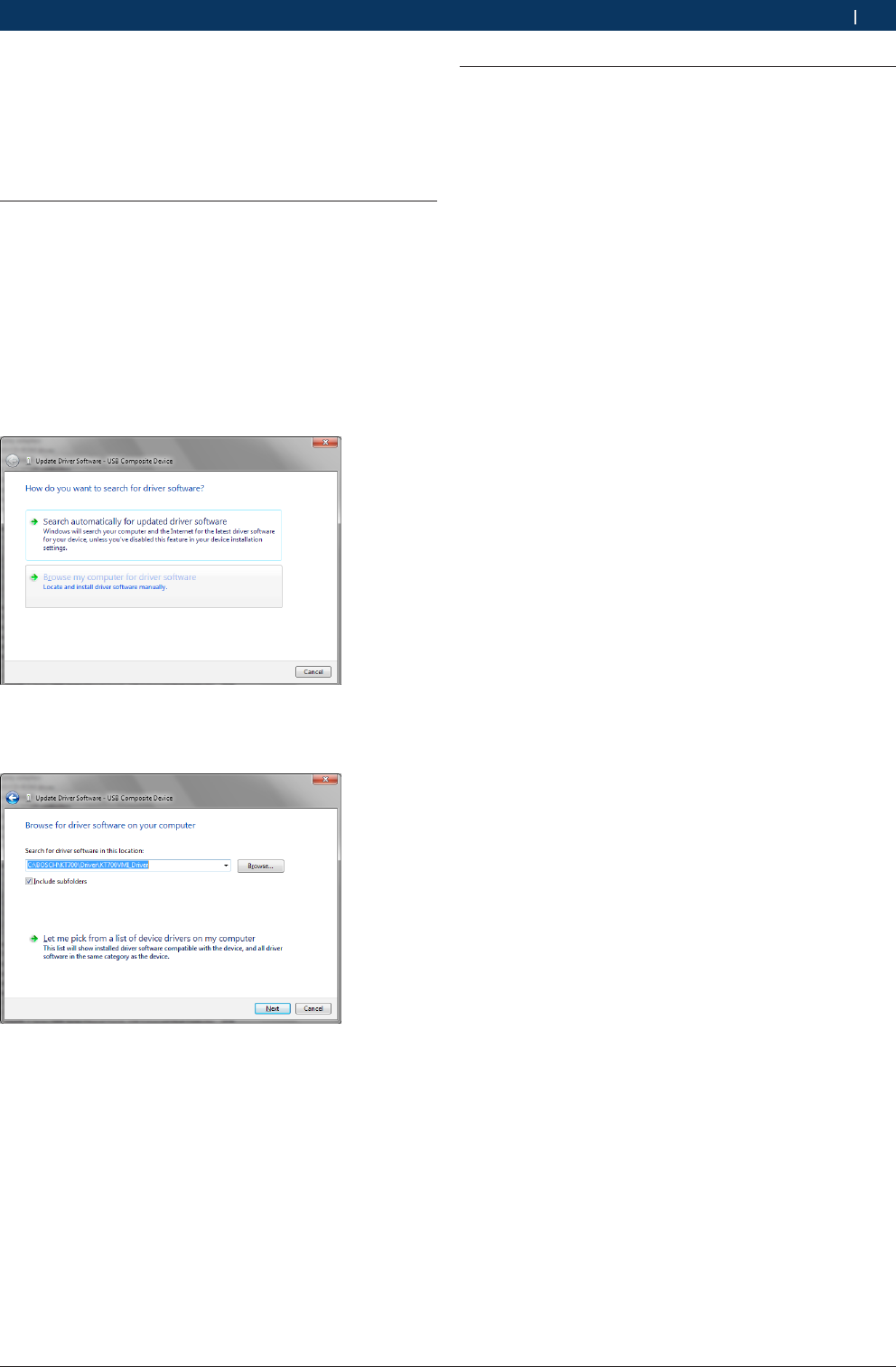
1 697 020 201 2013-05-24| Bosch Automotive Diagnostics Equipment (Shenzhen) Limited
PC Software environment | KT700 VMI | 25KT700 VMI | 25 | 25 en
iYou are adminiatrator when you insatll software;You
have access to write installed folders;
iPlease install the PDF reader to view more help files
conveniently.
4.3 USB driver installation
you must to manual install USB driver after VMI soft-
ware intallation.
Installation steps:
1. Select "Device Manager" in "Control Panel";
2. Select "RNDIS/Ethernet Gadget" in "Other Device";
3. Click right mouse button, select "Update Driver
Software ";
4. Select "Browse my computer for driver software";
5. Click "Browse" button, find the driver software in
install folder of BOSCH\KT700\Driver\KT700VMI_Dri-
ver .
6. Click "Next" button, wait for install successfully.
4.4 Software uninstall
After installing the software, KT700 folder will be
displayed under the program submenu of the “Start”
menu.
Directly click “Uninstall” to uninstall the software.
Please operate following the interface prompts till the
uninstall completion.
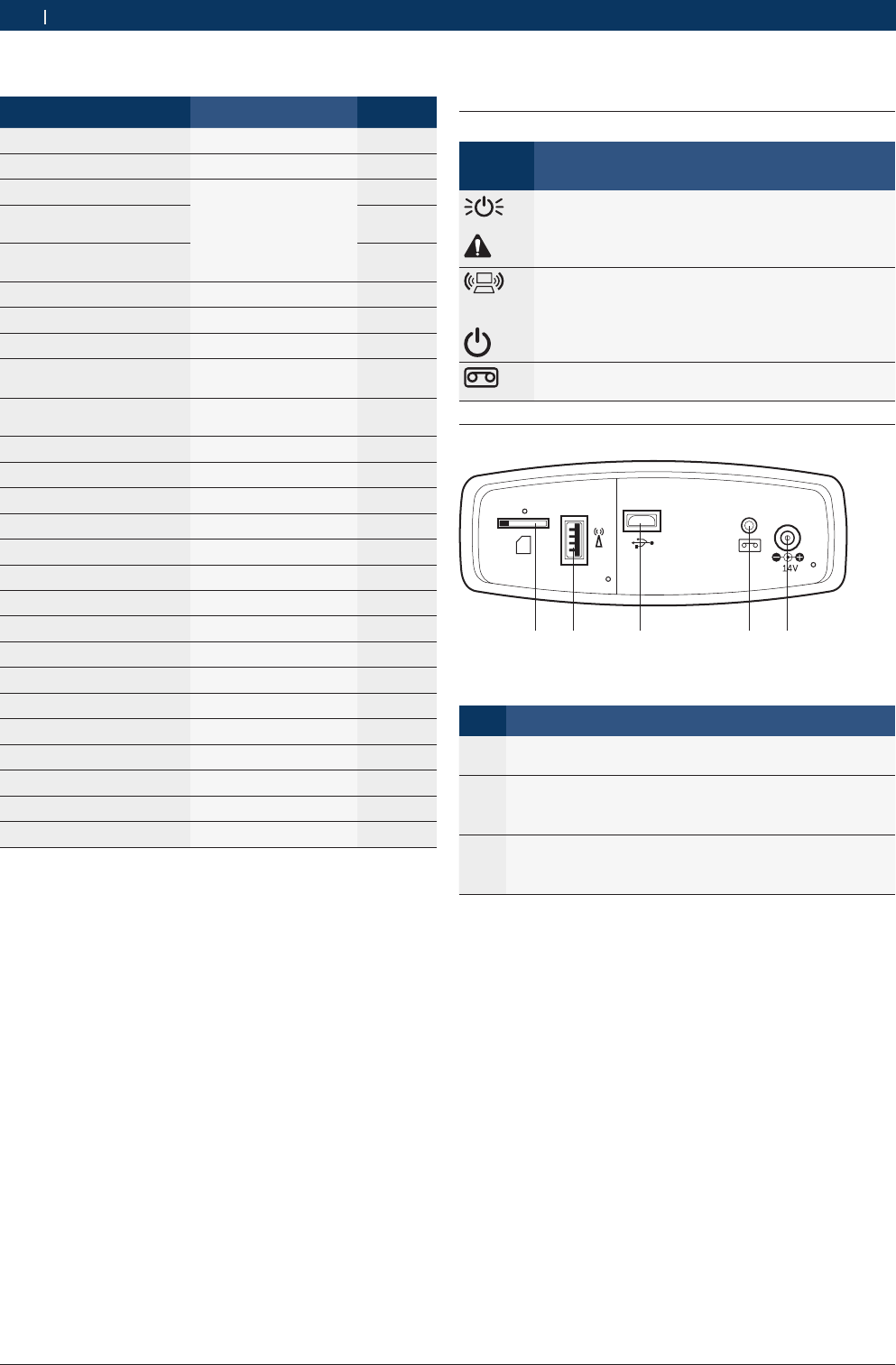
1 697 020 201 2013-05-24| Bosch Automotive Diagnostics Equipment (Shenzhen) Limited
26 | KT700 VMI | Deliver scopeen
5. Deliver scope
Name Part.No Amount
KT700 VMI device 1 697 020 073 1
VMI battery 1 697 020 132 1
Standard big box 1 697 020 196 1
KT700 VMI Standard big
instrument
1 697 020 079 1
KT700 VMI customer ma-
nual
1 697 020 201 1
USB communication cable 1 697 020 109 1
Record extention cable 1 697 020 225 1
14V power adapter 1 697 020 113 1
Power extension
cable(length<3m)
1 697 020 105 1
Cigarette igniter power
cable
1 697 020 107 1
Battery clip power cable 1 697 020 106 1
Red capacitive pickup 1 697 020 114 1
Gray capacitive pickup 1 697 020 115 1
Oscilloscope probe 1 697 020 116 2
Pierce probe(red) 1 697 020 117 1
Pierce probe(gray) 1 697 020 118 1
Pierce probe(black) 1 697 020 119 1
Cyl1 signal clip 1 697 020 120 1
Oscilloscope probe 1 697 020 121 2
Black alligator clip 1 697 020 125 1
Red alligator clip 1 697 020 124 1
KT700/780 SW DVD 1 697 020 178 1
Quality card 1 697 020 183 1
Anti-counterfeit label 1 697 020 232 1
Box barcode_blank 1 697 020 234 1
KT700 VMI Qucik start 1 697 020 256 1
Tab. 1: Deliver scope
6. Introduction to VMI host
6.1 Host identifications
Identifi-
cation
Description
The power indicator lamp, lighting in green to indi-
cate the normal power supply;
The malfunction indicator lamp, lighting in red to in-
dicate the VMI malfunction;
The computer communication indicator lamp, ligh-
ting in green to indicate the wired connection or in
yellow to indicate the wireless connection;
Power button;
The travel recorder button identification, used for
your convenient and rapid operation.
6.2 Connection terminal
1 2 3 4 5
Fig. 1: Connection terminal
No. Description
1 Trough of SD card, store measure data, the function
didn't used temporarily
2 Trough of wireless adapter, the function didn't used
temporarily
3 Micro USB
4 Data record interface, the function didn't used tempora-
rily
5 Power interface
Tab. 2: Connection terminal
iAvoid missing wireless adapter, please don't pull out.
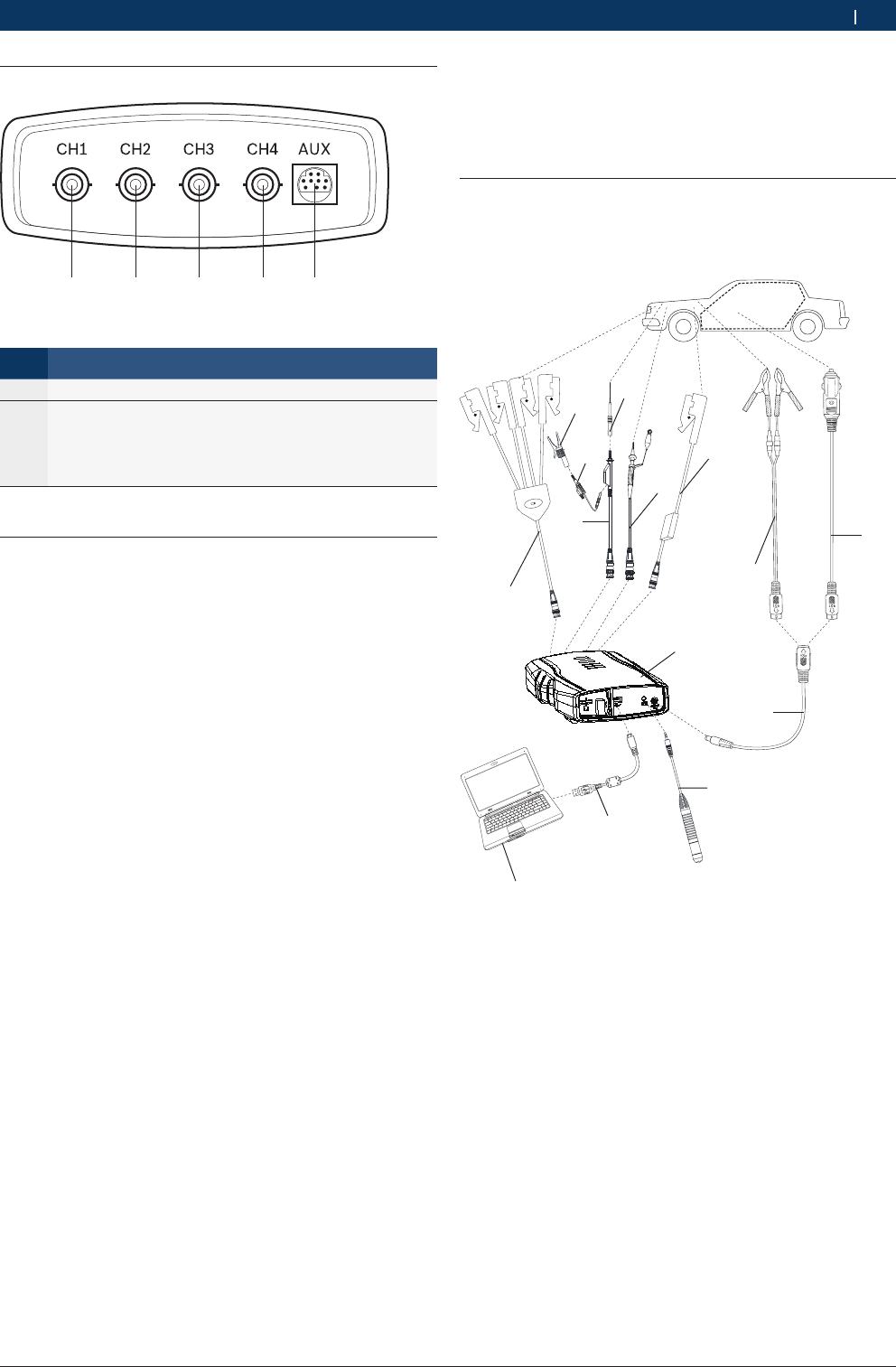
1 697 020 201 2013-05-24| Bosch Automotive Diagnostics Equipment (Shenzhen) Limited
Equipment connection | KT700 VMI | 27KT700 VMI | 27 | 27 en
6.3 Oscillograph terminal
1 2 3 4 5
Fig. 2: Oscillograph terminal
No. Description
1 CH1, Oscillographic channel 1, Logic channel 1
2 CH2, Oscillographic channel 2, Logic channel 2
3 CH3, Oscillographic channel 3, Logic channel 3
4CH4, Oscillographic channel 4, Logic channel 4
5 AUX, Assistant channel 5~8
Tab. 3: Oscillograph terminal
6.4 Assistant function
Hook: VMI device hung on the front of car cover in mea-
surement process, convenient measure.
Loading capacity: 5KG.
Battery: 2200mAh battery, the work time of battery is
at least 2 hours under USB communication.
7. Equipment connection
According to different functions, the connection modes
are: including measure connection, selfcheck connec-
tion and upgrade connection.
7.1 Measure connection
Before using the equipment, please ensure the normal
connection among the VMI, computer, and measure as-
sembly.
1
2
3
4
11
10
5
9
6
7
8
13
14
12
X1 X2 X4
Fig. 3: Measure connection
1 Cyl1 signal clip
2 Oscilloscope probe
3 Oscilloscope probe(Main)
4 Capacitive pickup(Red, Gray)
5 VMI device
6 Battery clip power cable
7 Cigarette igniter power cable
8 Power extension cable
9 Record extention cable
10 USB communication cable
11 Computer
12 Alligator clip(Red, Black)
13 Pierce probe(Red, Gray, Black)
14 Oscilloscope probe(Secondary)

1 697 020 201 2013-05-24| Bosch Automotive Diagnostics Equipment (Shenzhen) Limited
28 | KT700 VMI | Equipment connectionen
7.2 Selfcheck / Upgrade connection
1
2
3
4
Fig. 4: Selfcheck / Upgrade connection
1 14V power adapter
2 VMI device
3 USB communication cable
4 Computer
8. Measure function
Main display:
Fig. 5: Main display
No. Description
①The main function area, including vehicle diagnosis, ve-
hicle analyzer and service help;
②The system function area, including screenshot, play-
back, setting, help, feedback
③The display area for measure function, including oscillo-
scope function, recording, measure sensor, actuator, ig-
nition system, electronic system, communication system
and multimeter.
④The status column, including measure path , VMI connect
status, communication modes status, and battery status.
Tab. 4: Measure display
8.1 Power supply of host
There are 4 power supply modes for VMI host, you can
select according to your requirement:
RAC power supply: take out VMI standard configura-
tion power adapter in the instrument; Connect one
end to the power interface of the instrument and
another end to 100~240V AC socket;
RAutomobile battery cell power supply: take out VMI
standard configuration power extension lead and al-
ligator clip; connect one end to the power interface
of the instrument and another end to battery end;
RCigarette lighter power supply: take out VmI stan-
dard configuration power extension lead and cigaret-
te lighter; connect one end to power interface and
another end to cigarette lighter;
RVMI battery.
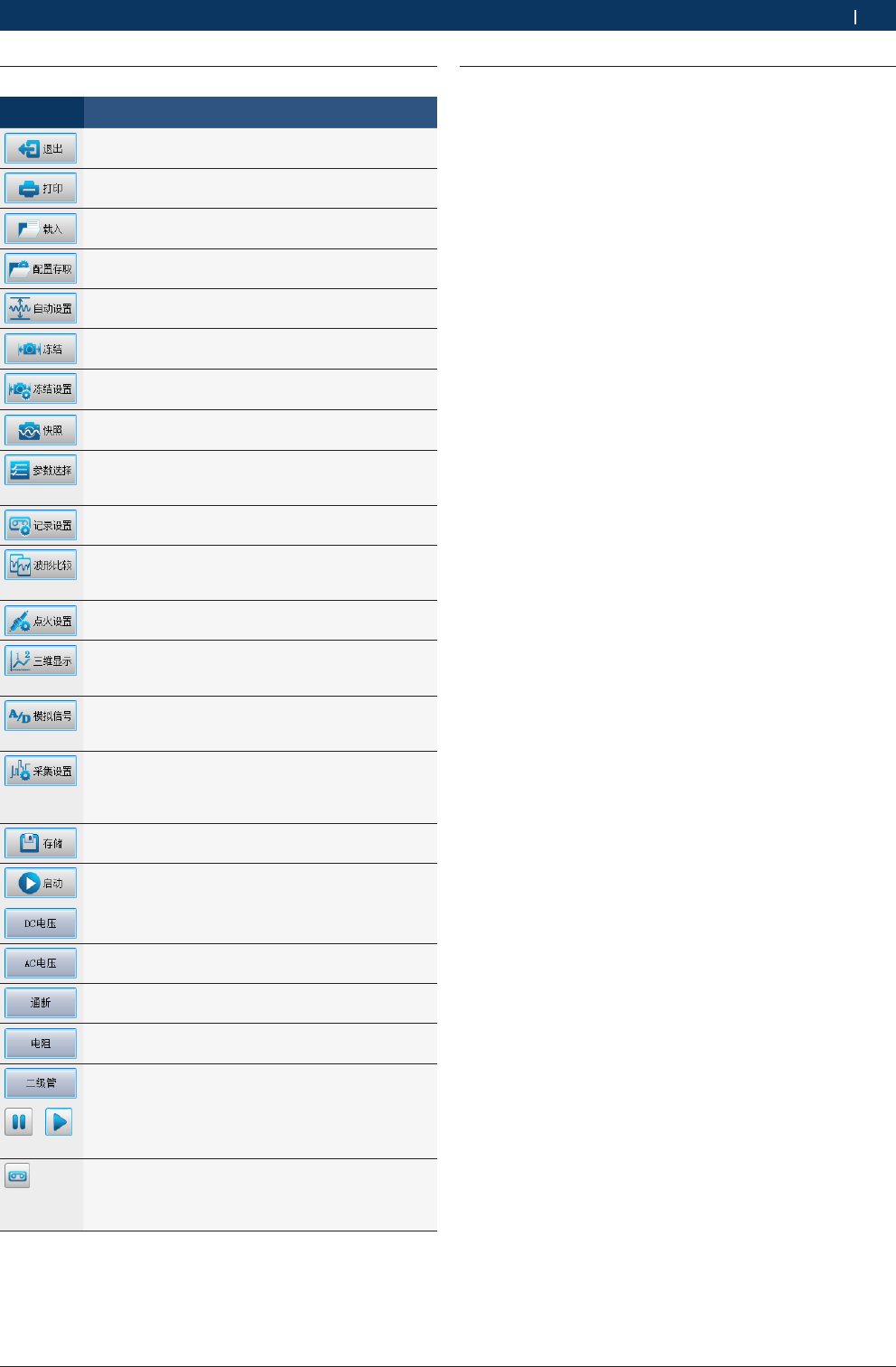
1 697 020 201 2013-05-24| Bosch Automotive Diagnostics Equipment (Shenzhen) Limited
Measure function | KT700 VMI | 29KT700 VMI | 29 | 29 en
8.2 Function button introduce
Button Description
Exit measure process
Work content, logo could be printed
Load previous data which saved before, and save
to point folder
Current parameter setting could be saving, and
configuration can be download
Amplitude parameters setting
Collected before and after the freezing point of the
waveform data, and save a file in a fixed format
Set freeze length and trigger position.
Length: 400~32K; Trigger position: length*100%
Capture current screen and save
Slect frequency, duty cycle, peak-to-peak, pulse
width, maximum, minimum, and average of current
acquisition waveform
Only Record display, setting trigger type and
length
Waveform comparison, reference wave form and
real-time waveform can be compared at same time.
Reference waveform display with dotted line.
Only Ignition display, setting ignition display mode,
precision,number of cylinder and ignition sequence
Ignition display mode, include 3D, longitudinal
wave, concatenation and signal cylinder. Default
is 3D.
Only communication system display, filter function,
signal change between simulation model and digtal
model, default is simulation model.
Only logical signal analysis display, include logi-
cal acquisition frequency, logical threshold pressu-
re, logical acquisiion length, logical channel, trigger
channel, trigger type, and trigger position
Only logical signal analysis display, save logical
wave
Only logical signal analysis display
Only multimeter display, measure DC pressure in
CH1 to CH4 channels
Only multimeter display, measure AC pressure in
CH4 channel
Only multimeter display, measure lead switching in
CH4 channel
Only multimeter display, measure resistance in
CH4 channel
Only multimeter display, measure diode in CH4
channel
Pause/Start button. Click pause button, display
didn't fresh, pasue change to start, click start but-
ton, continue collect.
Record button, record displayed waveform. Click
this button, start record; click again, stop record.
The function same as record button on main unit
and record extension cable.
Tab. 5: Function button introduce
8.3 Parameters adjust
8.3.1 Period
Adjust period of waveform, the high frequency will be
show one screen waveform everytime, the low frquency
will be show waveform by point scanning.
The time base. Use the sec/div control to set the
amount of time per division represented horizontally
across the screen.
High frequency: 1us~50ms
Low frequency: 100ms~50s
8.3.2 Channels, amplitude and coupling
Open channel and display waveform. CH1, CH2, CH3
and CH4 will display waveform at the same time. Red is
CH1, bule is CH2, green is CH3, brown is CH4.
Amplitude: The attenuation or amplification of the sig-
nal. Use the volts/div control to adjust the amplitude of
the signal to the desired measurement range.
Coupling: include AC, DC, and GND. The default is DC.
8.3.3 Trigger function
Trigger function will be enabled only when the frequen-
cy is less than 100ms/div can be selected by the user a
particular waveform events need to be concerned. The
user can be isolated from the waveform amplitude of
the need to care about a particular waveform, glitches,
setup and hold times and stable waveform display
through different trigger mode. Use repetitive waveform
can be shown in the waveform drawing area.
iTrigger function can only be used at high frequenci-
es.
10.3.3.1 Trigger position
Trigger position determines the length of viewable si-
gnal both preceding and following a grigger point. Va-
rying the trigger position allows you to capture what a
signal did before a trigger event.
¶You can set the trigger position through directly drag
the slider at the top of waveform drawing area.
10.3.3.2 Trigger channel
Use the trigger level to stabilize a repeating signal, or
to trigger on a single event. Trigger channel only be
selected by opened channels, and only used when the
frequency is less than 100ms/div.
iThere can be only one channel as the trigger chan-
nel.
iTrigger channel and trigger type should be binding.
iThe waveform will be bold display of trigger channel.
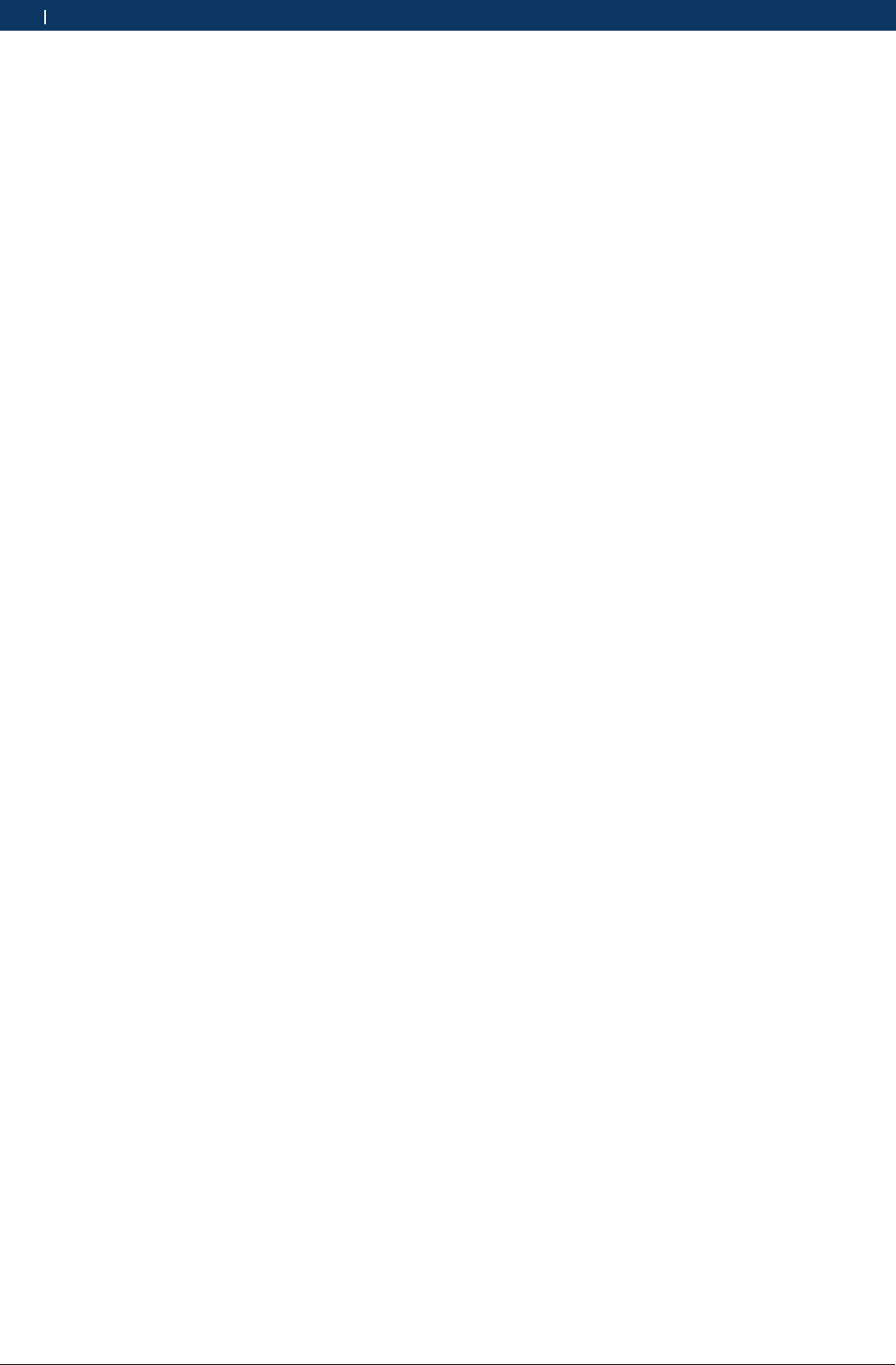
1 697 020 201 2013-05-24| Bosch Automotive Diagnostics Equipment (Shenzhen) Limited
30 | KT700 VMI | Measure functionen
10.3.3.3 Trigger level
The trigger level provide the basic trigger point defini-
tion, when inputed amplitude more than trigger level,
VMI will trigger.
¶You can set the grigger level through directly drag
the arrowhead on the right of waveform drawing
area.
10.3.3.4 Trigger type
There have 4 trigger type, as follow:
Level trigger: VMI will be user-set trigger level position
as a basic trigger point, when the rising edge amplitude
of the input waveform greater than the trigger level, VMI
will trigger waveform.
Rising edge of the trigger: VMI will trigger on the rising
edge of the input waveform.
Falling edge of the trigger: VMI will trigger on the falling
edge of the input waveform.
Automatic level trigger: VMI will automatically calculate
the trigger position, and trigger at position of the rising
edge greater than trigger level, and simultaneously up-
date trigger level position of VMI software.
8.3.4 Negate routine
Select the channel, the waveform will reverse display
based on waveform position. Default is off, check was
opened.
8.3.5 Adjust cursor
The cursor is to be measure the voltage amplitude and
period. Cursor measurement parameters to the current
channel as a reference.
Click the cursor with time and voltage, according to the
time(abscissa) move, according to the voltage(vertical
axis) move, and display the measurements between
cursors.
If you set the "parameters", software will automatically
calculate the amplitude, and displayed in the interface;
otherwise manual calculations.
8.3.6 Waveform position
The position of waveform display. Directly drag the
small arrow on the left of drawing area to change the
waveform display position.
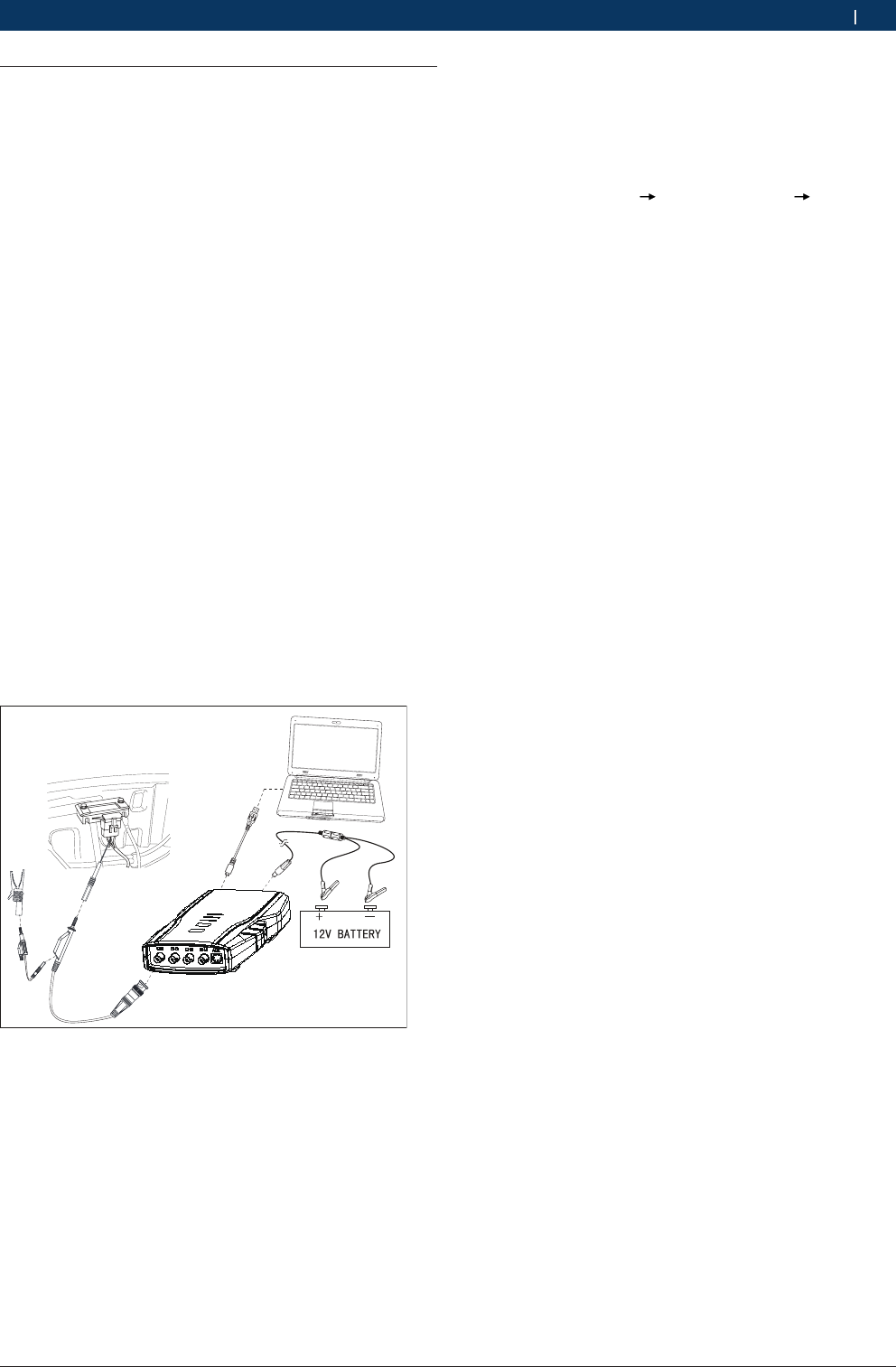
1 697 020 201 2013-05-24| Bosch Automotive Diagnostics Equipment (Shenzhen) Limited
Measure function | KT700 VMI | 31KT700 VMI | 31 | 31 en
8.4 Sensor Measure
8.4.1 Manifold Absolute Pressure Sensor (MAP)
Manifold absolute pressure sensor provides engine con-
trol unit (ECU) with engine load signal, which generally
is frequency-modulated square wave signal or voltage
level signal (depending on manufacturer) and is used to
change mixing ratio of fuel and other output value after
being processed by ECU.
When engine load increases, manifold pressure increa-
ses, or manifold pressure is low. Damaged MAP sensor
may affect air-fuel ratio when engine accelerates or
decelerates, and may affect ignition timing and other
computer output values.
Connecting Equipment
When connecting VMI to power extension cable for
power supply, choose power supply according to the
battery position of vehicle mode tested. All connec-
ting diagrams in this users manual take power supply
by battery clip power cable as example. Oscilloscope
probe(Main line) connect to Channel 1 (CH1 port), and
then put black alligator clip or black pierce probe in
oscilloscope probe(Secondary line) connect to the ne-
gative of battery or grounding, Put red pierce probe in
oscilloscope probe(Main line) into the trigger signal line
of manifold absolute pressure sensor (MAP).
Fig. 6: MAP connect
Measure conditions
RSwitch on automobile ignition switch, do not start
engine. Use manual vacuum pump to simulate vacu-
um and connect it to vacuum input port of manifold
absolute pressure sensor.
RMonitor signal from idle to acceleration with engine
running.
Measure steps
1. Connect equipment according to Fig 6, switch on
power supply;
2. Double click run KT700 software;
3. Communication connect ;
4. Click Auto analyzer
Sensor measure
MAP;
5. Waveform will be displayed on the screen depending
on measure conditions;
6. You can adjust X-deflection, amplitude, coupling,
negate routine, and cursor. If X-deflection at high
frequencies, you can also adjust the triger channel
and trigger mode;
7. You can also print measure data, loading waveform,
save or read config, automatic adjust amplitude,
freeze waveform, freeze setting, capture and wave-
form comparison;
8. If you want to read waveform on current display, you
can click "Pause" button,
9. You can click "Record" button to record a continuous
waveform.
Waveform Analysis
Generally, analog quantity output is common except
that the output of manifold absolute pressure sensor
in FORD is digital signal. Manifold pressure sensor of
analog quantity produces a voltage to ground signal
of about 0V in high degree of vacuum, and produces a
high voltage to ground signal in low degree of vacuum
(approaching atmospheric pressure). Refer to repair
manual since different manufacturers may have diffe-
rent indexes.
Digital MAP sensors are mounted on many FORD and
LINCOLN vehicles. Output waveform in digital quantity
should be pulse with amplitude value of 5V, at the same
time, shape is correct, waveform is steady, square angle
of rectangle is correct and rising edge is vertical. Fre-
quency and its corresponding degree of vacuum shall
comply with the values given in repair materials.

1 697 020 201 2013-05-24| Bosch Automotive Diagnostics Equipment (Shenzhen) Limited
32 | KT700 VMI | Service and Maintenanceen
9. Service and Maintenance
9.1 Cleaning
It is not recommended to clean the VMI host with the
corrosive detergent or any coarse cloth; only the soft
cloth and neutral detergent can be used.
9.2 Maintenance
RPlace the VMI in the flat and dry place with mode-
rate temperature and less dust when the VMI is not
used;
RDon’t place the VMI in the place with direct sunlight
or close to the heating device;
RDon’t place the VMI near the stove or in the place
where will be easily subjected to smoke erosion,
water entry, and oil splashing;
RDon’t disassemble the host without permission;
RIf the vehicle test is not performed for a long time,
please periodically run the VMI host to avoid being
affected with damp.
10. Technical Parameters
10.1 Host parameters
Item Index
Size 227*134*44(mm)
Host Weight Approximately 765g
External power supply 100V~240V/50~60Hz
Power ≤28W
Working temperature -10~45°C
Storage temperature -15~50°C
Relative humidity 10%~95%
Input voltage DC 7~32V
USB USB2.0 full speed
Key Recorder key
LED 4 LED indicator lamps indicating the
working status
Protection grade IP31
Battery(Optional) 2200mah
SD card ≤32GB
Hook Loading capacity: 5kg
Tab. 6: Host Parameters
10.2 Oscillograph parameters
Item Index
Sampling channels 4 channels
Bandwidth DC~2MHz
Sampling rate 40MS/s
Memory depth 64Kbyte/CH
Vertical scope 20mVDIV~20V/DIV
Level of collection 1uSec~50Sec/Div
Electric level reference With hardware adjustable(0~100%)
10.3 Multimeter parameters
Item Index
AC voltage ±33V
DC voltage ±70V
Diodes 0~2.0V
Resistance 0~60MΩ
Switching 0~60Ω
10.4 Logic signal module parameters
Item Index
Channel number 4CH independent, another 4 is BNC
channels
Input voltage 0~24V
Maximum frequency 1MHz
Reference adjusted value 4.096V