CARRIER Air Handler (indoor Blower&evap) Manual L0501315
User Manual: CARRIER CARRIER Air Handler (indoor blower&evap) Manual CARRIER Air Handler (indoor blower&evap) Owner's Manual, CARRIER Air Handler (indoor blower&evap) installation guides
Open the PDF directly: View PDF .
Page Count: 116 [warning: Documents this large are best viewed by clicking the View PDF Link!]

39MN,MW03-61
Indoor and Weathertight Outdoor
Air Handlers
Installation, Start-Up and
Service Instructions
CONTENTS
Page
INTRODUCTION ..................................... 1
SAFETY CONSIDERATIONS ......................... 2
UNIT AND COMPONENT IDENTIFICATION ........ 2-10
PRE-INSTALLATION ............................. 10-38
Inspection .......................................... 10
Rigging and Handling .............................. 10
Long-Term Storage ................................. 35
Service Clearance .................................. 35
Drain Positioning ................................... 35
Unit Suspension .................................... 35
Internal Vibration Isolation ......................... 35
External Vibration Isolation ......................... 36
Roof Curb .......................................... 36
Pier or Beam Mount ................................ 37
INSTALLATION .................................. 38-85
Indoor Unit/Section Connection .................... 38
Outdoor Unit ....................................... 39
Duct Connections .................................. 40
Panel Cutting ....................................... 42
Zone Damper Section .............................. 42
Face and Bypass Dampers ......................... 42
Mixing Box/Filter Mixing Box Damper Linkage ...... 45
Mixing Box Damper Actuators ...................... 45
Vertical Draw-Thru Units ............................ 47
Fan Sled Disassembly .............................. 48
Fan Sled Dimensions ............................... 49
Fan Motors and Drives ............................. 50
Motor Power Wiring ................................ 50
Sheaves ............................................ 50
V-Belts ............................................. 51
Outdoor Hoods and Louvers ....................... 52
Coil Connection Housing ........................... 52
Humidifier Installation .............................. 54
Assembly of Vertical Manifolds ..................... 58
Coil Installation ..................................... 59
Water and Steam Coil Piping
Recommendations ............................... 61
Coil Freeze-Up Protection .......................... 63
Refrigerant Piping, Direct-Expansion Coils ......... 64
Hot Gas Piping and Wiring ......................... 68
• INSTALL PIPING
Condensate Drain .................................. 69
Fan Motor Wiring Recommendations ............... 69
Motor Electrical Data ............................... 70
Fan Motor Starter ................................... 71
Disconnect ......................................... 71
VFD ................................................ 71
VFD with Bypass ................................... 72
VFD Configuration .................................. 78
VFD Modes ......................................... 78
Page
Electric Heaters .................................... 79
Energy Recovery Ventilation Sections .............. 84
• RECEIVING AND INSPECTION
• RIGGING AND STACKING
• ERV WHEEL MOTOR WIRING
START-UP ....................................... 85-87
Checklist ........................................... 85
Energy Recovery Wheel ............................ 87
SERVICE ....................................... 88-110
General ............................................ 88
Electric Heaters .................................... 88
Fan Motor Replacement ............................ 88
Energy Recovery Ventilation ....................... 88
• CLEANING
• CASSETTE REPLACEMENT
• ADJUSTING AIR SEALS
• SEGMENT INSTALLATION AND REPLACEMENT
• WHEEL DRIVE MOTOR AND PULLEY
REPLACEMENT
• SOLID BELT REPLACEMENT
• LINK BELT REPLACEMENT
• OTHER MAINTENANCE
Cleaning Unit Interior/Exterior ...................... 91
Coil Cleaning ....................................... 92
Winter Shutdown ................................... 92
Coil Removal ....................................... 93
Changing Coil Hand ................................ 94
Filters .............................................. 95
Magnehelic Gage Maintenance .................... 108
Fan Shaft Bearing Removal ....................... 108
Fan and Shaft Removal ............................ 108
Motor Location .................................... 109
Lubrication ........................................ 109
Motor and Drive Package Data .................... 109
Variable Frequency Drive .......................... 109
TROUBLESHOOTING .......................... 110-116
Steam Coil Performance Problems ................ 110
Steam Failure Modes .............................. 110
VFD Diagnostics .................................. 110
INTRODUCTION
The 39M series central staion air handlers me usually
installed with ductwork; they provide air conditioning at
nominal capacities of 1500 to 30,500 cfin. The 39M air handler
design allows hundreds of diffelent configuration possibilities.
Each unit is assembled to meet specific job requirements and
can be shipped in sections or as a single assembly. These
instructions describe how to install, start up, and service 39M
air handlel_.
Manufacturer reserves the right to discontinue, or change at any time, specifications or designs without notice and without incurring obligations.
PC 201 Catalog No, 533-952 Printed in U,S.A. Form 39M-6SI Pg 1 12-04 Replaces: 39M-5SI

SAFETY CONSIDERATIONS
39M air-handling equipment (see Fig. 1) is designed to
provide safe and reliable service when installed and operated
within design specifications. To avoid injury to personnel and
dmnage to equipment or property when operating this equip-
ment, use good judgment and follow safe practices as outlined
below.
NEVER enter an enclosed fan cabinet or reach into a unit
while the fan is running.
LOCK OPEN AND TAG the fan motor power disconnect
switch before working on a fan. Take fuses with you and
note removal on tag.
LOCK OPEN AND TAG the electric heat coil power dis-
connect switch before working on or near heateLs.
CHECK the assembly and component weights to be sure
that the rigging equipment can handle them safely.
Note also the centers of gravity and any specific rigging
instructions.
CHECK for adequate ventilation so that fumes will not
migrate through ductwork to occupied spaces when weld-
ing or cutting inside air-handling unit cabinet or plenum.
WHEN STEAM CLEANING COILS be sure that the area
is cle_u of personnel.
DO NOT lemove access panel fasteners until fan is com-
pletely stopped.
Pressme developed by a moving fan can cause excessive
force against the panel and toward personnel.
DO NOT work on dampeLs until their operators m'e
disconnected.
BE SURE that fans m'e properly grounded before working
on them.
SECURE fan drive sheave with a rope or strap before
working on a fan to ensure that rotor cannot freewheel.
DO NOT restole power to unit until all temporary walk-
ways inside components have been removed.
NEVER pressurize equipment in excess of specified test
pressures.
PROTECT adjacent flammable material when welding or
flame cutting. Have a fire extinguisher at hand and ready
for immediate use.
PREVENT unauthorized entry into the unit; leave safety
latches in place on access doors except during installation
or service procedures. After accessing a section, replace
and tighten the safety latch.
FIELD SUPPLIED MOTORS should be Underwriters'
Laboratories (UL) or Canadian Standmds Association
(CSA) approved.
FIELD WIRING must comply with Natiomfl Electric_fl
Code (NEC) and all local requirements.
DO NOT ground equipment to fan assembly when weld-
ing. Damage to fan bezu'ings could result.
UNIT AND COMPONENT IDENTIFICATION
The 39M air handler comes in two basic configurations;
horizontal and vertical. Using appropriate sections, it is possi-
ble to design many unit variations, including blow-thru units
and plenum fan units with multiple discharges. Fig. 2A-2H
show an exmnple of the model number used for 39M unit sec-
tions and components. Each unit's model number is listed on a
label affixed to the fan section. Section and major component
level part numbers are listed and affixed to each individual
component section.
For further information on unit and component identifica-
tion refer to Fig. 3A-3B and contact your Carrier representative
for the AHUBuilder® program. Refer to the 39M Product
Data cat,dog for more information on individual component
sections.
Fig. 1 -- Typical 39M Air Handler (Indoor Unit Shown)

39M N
39M-Air Handle I
N - Indoor Unit
W- Outdoor Unit
Unit Size
03
06
08
10
12
14
17
21
25
30
36
4O
50
61
03 000001 12 S
mX S
T f Shipping Option
S - Standard
Q- Quick Ship
X- Always
Unit Crating Option
S - Skid only
C-Protective cover skid
B- Export with protective cover
E - Export without protective cover
Shipping No. of Pieces
Example: 12 = 1 of 2
22=2of2
Odometer Number
Revision Level
Fig. 2A -- 39M Unit Nomenclature
28M0 - 1/2in. Chilled Water
28MH - 1/2in. Hot Water
Coil Position
H - Horizontal
V - Vertical
Rows
1 - 1Row
2 - 2Row
4 - 4 Row
6 - 8 Row
8 - 8 Row
O - 10 Row
Tubes In Face 12 -44 *
39M Unit
Size L M B S
28M0 V 6 20
T
B
L
M
S
03 20 14 12 N/A
06 20 14 12 12
08 22 16 14 12
10 22 16 14 12
12 28 22 20 14
14 28 24 20 14
17 30 24 22 16
21 38 32 28 18
25 38 32 28 18
30 38 32 28 18
36 44 36 30 24
40 24/24 44 36 24
50 28/28 44 36 28
61 34/34 28/28 44 34
Circuiting
H - Half Circuit
F - Full Circuit
D - Double Circuit
LEGEND
-- Bypass
-- Large
-- Medium
-- Small
D A 020 A R N X
-- -T
X - Always
Coating
N-Non-Coated
E - E-Coated
Hand
R - Righthand
L - Leffhand
Header Style
A - MPT Std
B - MPT-Non Ferrous
NOTE: If positions 7-8 are _>30,
then position 15 cannot = B.
Unit
Size DBTSt(in.)
03 020 21 065
06 034 25 074
08 040 30 092
10 052 36 096
12 052 40 096
14 059 50 104
17 065 61 104
Tube Wall and
Hairpin Type
1/2 in.O.D. Copper Tube
A- .016 Std. Hairpin
B - .025 Std. Hairpin
Fin Material
Fins Per Inch
Casing Material
A- AL 8 GALV.
D - AL 11 GALV.
F - AL 14 GALV.
G - AL 8 ST. STL.
K - AL 11 ST. STL.
M- AL 14 ST. STL.
N - CU 8ST. STL.
R - CU 11 ST. STL.
T - CU 14 ST. STL.
*Multiple values indicate that two coils must be ordered.
1-Distance between tube sheets.
Fig. 2B -- 28MC,28MH (1/2-in. Water Coil) Nomenclature

28MZ - IDT Steam
Coil Position
H - Horizontal
V - Vertical
Rows
1 - 1 Row
2 - 2 Row
28MZ H
Tubes In Face*
If position 11 = S
1in.
39M Unit
Size L M B S
03 08 05 05 N/A
06 08 05 05 05
08 09 06 05 05
10 09 06 05 05
12 11 09 08 05
14 11 10 08 05
17 12 10 09 06
21 15 13 11 07
25 15 13 11 07
30 15 13 11 07
36 18 15 12 10
40 10/10 18 15 10
50 12/11 18 15 11
61 14/14 12/11 18 14
If position 11 = T
5/8 in.
L M B S
16 10 10 N/A
16 10 10 10
18 12 11 10
18 12 11 10
22 18 16 10
22 20 16 10
24 20 19 12
30 26 22 14
30 26 22 14
30 26 22 14
36 30 24 20
20/20 36 30 20
24/22 36 30 22
28/28 24/22 36 28
Circuiting
F - Full
Fin Material
Fins Per Inch
Casing Material
B - AL 6 GALV.
E - AL 9GALV.
C - AL 12 GALV.
H - AL 6 ST. STL.
L - AL 9ST. STL.
J - AL 12 ST. STL.
P - CU 6 ST. STL.
S - CU 9ST. STL.
Q - CU 12 ST. STL.
26 FBT 074 A X N -
l-- Coil Revision
Coating
N - Non-Coated
E - E-Coated
X - Always
Header Style
A - MPT Std
Header Note:
Pos. 11 (Type 'S')
Supply = 2 1/2 in. MPT
Condensate = 2 1/2 in. MPT
Pos. 11 (Type 'T')
(1) Row 10-28TF = 2 in. MPT (Supply and Return)
29-40 = 2 1/2 in. MPT (Supply)
= 2 in. MPT (Return)
(2) Row 10-28TF = 2 t/2 in. MPT (Supply and Return)
29-40TF = 3 in. MPT (Supply)
= 2 1/2in. MPT (Return)
TF-Tubes in face
Unit
Size DBTSt (in.)
03 020
06 034
08 040
10 052
12 052
14 059
17 065
21 065
28 074
30 092
36 096
48 096
50 104
61 104
Tube Size and Copper Wall
S - 1 in. O.D.x. 030 Wall Outer Tube
5/8 in. O.D.x. 020 Wall Inner Tube
T - 5/8 in. O.D. x .035 Wall Outer Tube
3/8 in. O.D. x .020 Wall Inner Tube
LEGEND
B -- Bypass
L -- Large
M -- Medium
S -- Small
*Multiple values indicated that two coils must be ordered.
1-Distance between tube sheets.
Fig. 2C -- 28MZ (Steam Coil) Nomenclature
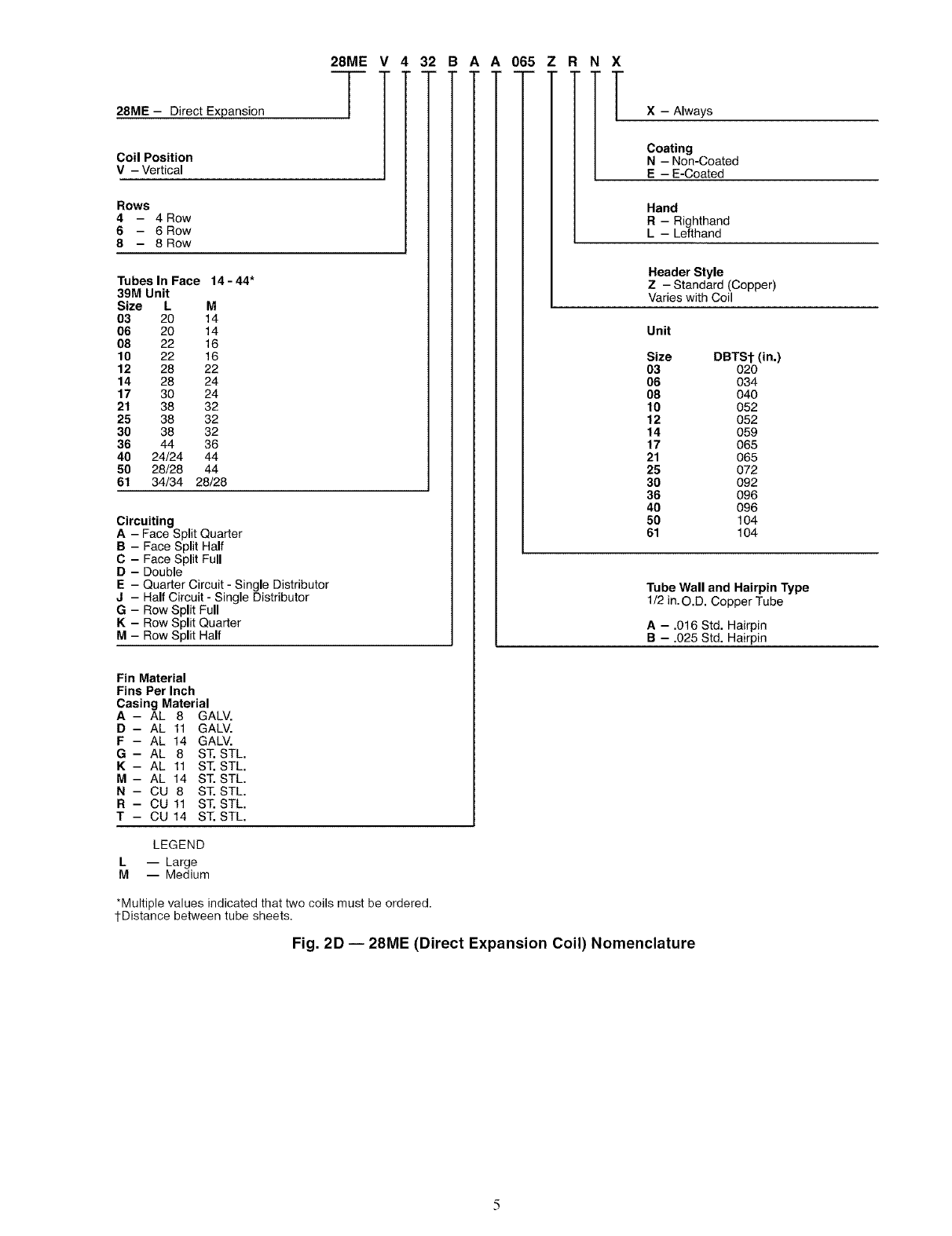
28ME - Direct Expansion
Coil Position
V - Vertical
Rows
4 - 4 Row
6 - 8 Row
8-8 Row
Tubes In Face 14 -44*
39M Unit
Size L M
03 20 14
06 20 14
08 22 16
10 22 16
12 28 22
14 28 24
17 30 24
21 38 32
25 38 32
30 38 32
36 44 36
40 24/24 44
50 28/28 44
61 34/34 28/28
Circuiting
A - Face Split Quarter
B - Face Split Half
C - Face Split Full
D - Double
E - Quarter Circuit - Single Distributor
J - Half Circuit - Single Distributor
G - Row Split Full
K - Row Split Quarter
M- Row Split Half
Fin Material
Fins Per Inch
Casing Material
A- AL 8GALV.
D - AL 11 GALV.
F - AL 14 GALV.
G - AL 8ST. STL.
K - AL 11 ST. STL.
M - AL 14 ST. STL.
N - CU 8ST. STL.
R - CU 11 ST. STL.
T - CU 14 ST. STL.
28ME V 4 32 B A A 065 ZRNX
-- lX - Always
Coating
N - Non-Coated
E - E-Coated
Hand
R - Righthand
L - Lefthand
Header Style
Z - Standard (Copper)
Varies with Coil
Unit
Size DBTSt(in.)
03 020
06 034
08 040
10 052
12 052
14 059
17 065
21 065
25 072
30 092
36 096
40 096
50 104
61 104
Tube Wall and Hairpin Type
1/2 in.O.D. Copper Tube
A - .016 Std. Hairpin
B - .025 Std. Hairpin
LEGEND
L-- Large
M -- Medium
*Multiple values indicated that two coils must be ordered.
1-Distance between tube sheets.
Fig. 2D -- 28ME (Direct Expansion Coil) Nomenclature

28MG - Integral Face and Bypass
Unit Size
Code Size
B03
C 06
D08
F10
G12
H14
J17
K21
L25
M 3O
N 36
p40
Q50
R61
28MG M
T
Coil Position
H - Horizontal
Coil Type
H - Hot water
S - Steam
Rows
1 -1row
2 - 2row
3 - 3 row
H S 2 04 G N H XX
1
m
lRevision Level
XX - Always
Tube Orientation
H- Horizontal
V - Vertical
Hand
R - Righthand
L - Lefthand
Actuator
Y - Yes
N - No
Casing Material
G - Galvanized
S - Stainless Steel
Fins per Inch
04 - 4
05- 5
06- 6
07- 7
08- 8
09- 9
10- 10
11- 11
12- 12
13- 13
14- 14
Fig. 2E -- 28MG (Integral Face and Bypass Coil) Nomenclature

28MKM
28MK- Humidifer
Unit Size
Code Size
B 03
C 06
DO8
F 10
G 12
H 14
J 17
K 21
L 25
M 30
N 36
P 40
Q50
R 61
R S XXXXXXXXXX -
-Revision Level
XXXXXXXXXX -Always
Frame Material
G - Galvanized (g90)
S- Stainless Steel
Hand
R - Righthand
L - Lefthand
Fig. 2F -- 28MK (Humidifier) Nomenclature

28MD V 4 30 F A C 092 A R N A
28MD - 5/8 in. Chilled Water /
28MJ - 5/8in. Hot Water 1
Coil Position
H - Horizontal
V - Vertical
Rows
1 - 1Row
2 - 2 Row
4 - 8 Row
6 - 6 Row
8 - 8 Row
Tubes In Face
10 -36
Circuiting
H - Half Circuit
F - Full Circuit
D- Double Circuit
Fin Material
Fins Per Inch
Casing Material
A- AL 8GALV.
C - AL 12 GALV.
F - AL 14 GALV.
G - AL 8 ST. STL.
J - AL 12 ST. STL.
M- AL 14 ST. STL.
N - CU 8 ST. STL.
Q- CU 12 ST. STL.
T - CU 14 ST. STL.
T,-Always
Coating
N - Non-Coated
E - E-Coated
Hand
R - Righthand
L - Lefthand
Header Style
A - MPT Standard
B- MPT-Non Ferrous
39M Unit DBTS* (in.)
Size
03 020
06 034
08 040
10 052
12 052
14 059
17 065
21 065
25 074
30 092
36 096
40 096
50 104
61 104
Tube Wall and Hairpin Type
5/8 in. O.D. Copper Tube
C - .020 Std. Hairpin
D- .035 Std. Hairpin
*Distance between tube sheets.
Fig. 2G -- 28MD,28MJ (5/8-in. Water Coil) Nomenclature

Fan Motor
MR- High Efficiency
MS- Premium Efficiency
Horsepower*
01 - 1/2 12- 25
02 - 3/4 13- 30
03 -114 - 40
04- 1 1/2 15- 50
05 - 2 16 - 60
06 - 3 17 - 75
07 - 5 18 -100
08 - 7 1/2 19 - 125
09- 10 20- 150
10- 15 21 - 200
11 - 20
93 MR 01 18 B A 02 0
mT
Voltage
02 -115/230-1-60
03 - 230-1-60
07 - 575-3-60
18 - 460-3-60
27 - 200/230/460-3-60
28 - 200/400-3-50
(190/380-3-50)
RPM Synchronous
B- 1800 60Hz
C - 3600 60 Hz
E -150050Hz
F - 3000 50 Hz
Type
A- Open Drip Proof
C - Totally Enclosed -Fan Cooled
*Not all horsepower values shown are applicable to 39M units.
1"F3 Box location may be substituted for either F1 or F2.
**F3 Mounting may only be available on ODP Motors.
Mounting numbers apply when facing Motor Shaft end.
03 S -
1'Revision Level
Fan Application
R - Return/Exhaust
S - Supply
Supplier Designation
Not Used
(Always 0)
Application Mounting
1-Fl1-
2-F21-
3 - F3**
Insulation Class
0-Vendors (Std.)
Frame
01 - 48 38- 365T
02- 56 39- 404T
25 - 143T 40 - 405T
26 - 145T 41 - 444T
27 - 182T 42 - 445T
28 - 184T 43 - 286TS
29 - 213T 44 - 324TS
30 - 215T 45 - 326TS
31 - 254T 46 - 364TS
32 - 245T 47 - 365TS
33 - 284T 48 - 405TS
34 - 286T 51 - 404TS
35 - 324T 52 - 444TS
36 - 326T 53 - 445TS
37 - 364T 54 - 284TS
F1 F2 F3
Fig. 2H -- Motor Nomenclature

_F Carrier
Model39MN08B0053Xl12SXS Serial 1504F26765
Odometer 0053X1 Size 008 Piece 1of 2
SLP 1 39MDSTD01DFPKFXJHH SLP 2 39MCSTDO1DGBXXXOHX SLP 339MHSTD01DPPXFXJBA
$LP 4 39MDSTDO1DJZZZXJBH 3WHSTD01DGHXFXGeF SLP 6
_LP 10 SLP 12
Tag
39M ! 594 i
A_Se_bJe0 _n LI_O_A PoaoMA5GOZ50C_
Fig. 3A -- Unit Nameplate Label
(Found on Each Component Section
Shipped Separately)
OCarrier
SLP# 39MHSTD01DGHXFXGBF
Odometer 0053X1
Fan
Motor
Drive
Coil 1
Coil 2
Serial 1504F26765
Size 008
28MCV614HAAO4OARNX
_OM ! 594A Assembled in U,S,A PN3OMA5C_Z5002
Fig. 3B -- Section Nameplate Label
(Each Component Section will have
a Section Nameplate Label)
PRE-INSTALLATION
Inspection -- Inspect the unit; file a claim with the ship-
ping company if the unit is &_maged, Check the packing list to
ensure that the correct items have been received and notify
your CatTier representative of any discrepancy,
Rigging and Handling -- To transfer the unit fiom the
shipping platform to the storage or installation site, refer to the
rigging label on the unit and these instructions,
You can use a forklift truck to move units or components
only if they have full skids, Lift fiom the heavy end of the
skid, Minimum recommended fork length is 48 inches,
Base units are shipped fully assembled, except when sec-
tions me separately ordered or when the unit height exceeds
108 in. or length exceeds 30 feet. All 39M units can be rigged
using the lifting brackets, as shown on the rigging label on the
unit.
Aero connect hitches or screws are provided at specified
sections to separate component sections:
1. Undo till fasteners (with red hex heads) on vertical and
horizontal (side and top) semns.
2. Remove the large through-bolts in adjacent lifting
brackets and smaller bolts that hold lifting brackets
togethet:
3. Lift the unit with slings and header bars, using
clevises and pins in the large round holes in the unit's
lifting brackets.
When the unit is in its final location, do not remove the caps
fiom the coil connections until the coil is ready for piping. Do
not remove grease fiom the fan shaft until the drive sheave is
ready for instalhttion.
Refer to Fig. 4 and 5 and Tables 1- 17 for component &tta.
10

39MN Indoor Unit Dimensions
39MN
UNIT
SIZE
O3
06
O8
10
12
14
17
21
25
3O
36
40
5O
61
UNIT CASING
H (in.) W (in.)
39 33
39 46
42 54
42 67
49 67
49 72
52 79
62 79
62 86
62 104
73 109
79 109
89 117
104 117
H
AWL
39MW Outdoor Unit Dimensions
39MN
UNIT
SIZE
O3
06
O8
10
12
14
17
21
25
3O
36
40
5O
61
NOTES:
UNIT CASING
H (in.) W (in.)
43 36
43 49
46 57
46 70
53 70
53 75
56 82
66 82
66 89
66 107
77 112
83 112
93 120
108 120
1. Weights and dimensions are approximate.
For more exact dimensions, consult with
your local Carrier Sales Engineer or select
your desired unit using AHUBuilder¢)
software.
2. All dimensions in inches unless otherwise
noted.
Fig. 4- Base Unit Dimensions
AWL
LEGEND
AWL -- Airway Length
HHeight
W -- Width
1!

Air Distribution Components
_Mixing box _2_ Mixing box
v(side inlet) _3_ Filter Mixing _Air mixer _Exhaust
box box
Plenum & Filtration Sections
@Plenum @Humidifier
section section (_) External bypass (_ Blow-thru
return section plenumsection
Exhaust
box (side
outlet)
(_) Internal face (_ Internal face
and bypass and bypass
heating coil
section
@External face
and bypass
damper section damper
section
(_ Vertical blow-thru discharge _Horizontal, flat
plenum section _filter section
(_) Horizontal, angle
filter section
Heat Transfer Sections
(_ Cooling coil
section with
drain pan
(_ Horizontal, bag/side loading (_) Vertical short bag/side _Horizontal, bag/front _Horizontal, blow-thru front
cartridge filter section loading cartridge filter -- loading cartridge section -- loading HEPA filter section
section
Extended length @Heating Extended @Extended length _Dual coil
cooling coil section coil section (_ length heating -- heating coil section section with
with drain pan coil section with drain pan drain pan
D
c
(_ Electric heat _Horizontal blow-thru _Cooling/Heating @Multizone
section -- coil section with -- blow-thru coil section damper section
drain pan with drain pan
Fan Motor Sections
A B
F E
Horizontal fan
with rear inlet
fan section
BYPASS
Blow-thru supply section
with rear inlet, diffuser and
external bypass return
(_) Vertical cooling
coil section with
drain pan
LEGEND
C-- Cooling
N -- Heating
Fan Configurations
@Draw-thru exhaust
fan section
A B
Available
ContlguraUons
_e
Blow-thru supply fan
section with rear inlet
and diffuser
be field-fabricated
Fan Section Access
Hinged Access on Both Sides
Hinged Door on Hand Side
Removable Panels
INLET _ X = Standard configuration
INLET
Vertical fan section
with bottom inlet @Plenum fan
Fig. 5 -- Component Drawings (Refer to Table 1)
Section Number
XXXXXX
XXXXXX
XXXXXX
12

Table 1 -- 39MN,MW Component Weights and Lengths
Refer to Fig. 5
1Mixing box
2Side inlet mixing box
3 Filter mixing box
4 Air mixer
5 Exhaust box
6
7
8
9
10
12
13
14
15
16
17
18
19
20
21
22
23
24
25
25
27
28
29
30
31
Nominal cfm at 500 fpm
Unit Size
H (in.)
Indoor
Outdoor
W(in,)
Indoor
Outdoor
AWL (in.)
(Indoor/Outdoor / Weight (Ih /
32_ 33_
34_ 35_ 36
Side outlet exhaust box
Integral face and bypass heating coil section
Internal face and bypass damper section
External face and bypass damper section
Plenum section -- 12 in.
Plenum section -- 24 in.
Plenum section -- 36 in.
Plenum section --48 in.
Humidifier section -- 24 in.
Humidifier section -- 36 in.
Humidifier section -- 48 in.
External bypass return section
Horizontal blow-thru discharge plenum section
FC
Vertical blow-thru discharge AF
_lenum section
Plenum Fan
Horizontal flat filter section
2in. or 4 in. side Ioadin_
Horizontal angle filter section
2in. or 4 in. side Ioadin_l
Horizontal bag/cartridge filter section, SL
6in. or 12 in. media with 2 in. pre-filter track
Horizontal bag/cartridge filter section, SL
15 in. or 30 in. media with 2 in. pre-filter track
Vertical bag/cartridge filter section, SL
6in. or 12 in. media with 2 in. pre-filter track
Horizontal bag/cartridge filter section, EL
Face loading media with or without header
Horizontal blow-thru HEPA filter section, FL
Cooling coil section with drain pan
Extended length cooling coil section with drain pan
Heating coil section
Extended length heating coil section and electric heat with remote
box
Extended length heating coil section with EBR
Dual coil section with drain pan
Low Amp (in.)
Electric heat section with (indoor /Outdoor / lib}
control box High Amp (in.)
(indoor /Outdoor) (Ib)
Horizontal blow thru coil with ducted discharge
Multizone/dual duct H (in,)
heating/cooling coil section AWL (in.)
Indoor /Outdoor / Weight lib/
MuIBzone damper section AWL
Number of Zones
Vertical coil section with drain pan
EC
AF
Fan sections
Downblast AF
Vertical FC/AF
37 Plenum fan section
LEGEND
AF -- Airfoil
AWL -- Aint_ayLength
EBR -- External Bypass Return
FC -- Forward Curved
FL -- Face Load
H-- Height
SL -- Side Lead
W-- Width
1500
03
33
36
18
270/370
21
300/410
36
320/450
18
170/270
18
160/260
21
300/410
48
250/400
18
130/230
18
140/--
12
120/210
24
170/280
36
210/340
48
250/400
24
247/360
36
287/410
48
327/470
18
140/--
24
170/280
24
150/--
42
210/--
25
150/--
12
190/280
24
230/340
24
230/340
42
300/440
33
300/--
48
320/470
48
320/470
24
170/280
42
230/370
12
120/210
24
170/280
36
200/--
36
210/340
24/30
180/300
36/42
180/320
30
200/320
42
250/--
24
480/590
42
550/690
42
550/690
42
560/--
48
600/770
SECTION DIMENSIONS lin,! AND WEIGHTS !lb)
3000 4000 5000
06
39
43
46
49
21
330/450
27
350/490
36
380/530
18
190/310
21
190/310
27
360/490
48
280/450
18
150/270
21
160/--
12
140/250
24
190/320
36
240/390
48
280/450
24
290/420
36
340/490
48
380/550
18
160/--
24
200/330
30
190/--
42
240/--
28
180/--
12
230/340
24
270/400
24
270/400
42
350/510
33
340/--
48
370/540
48
370/540
24
190/320
42
260/420
12
140/250
24
190/320
35
230/--
35
240/390
30135
240/390
35142
220/380
30
220/360
61
48
570/--
11
6
42
290/--
30
550/690
42
620/780
42
620/780
42
630/--
54
720/900
NOTES:
08 10
42 42
45 45
54 67
57 70
21 21
370/510 420/570
27 33
390/540 470/650
36 36
430/590 490/680
18 24
210/340 270/430
21 21
210/350 230/380
27 33
390/540 470/650
48 48
310/500 340/560
18 18
170/300 190/340
21 21
180/-- 190/--
12 12
150/270 170/300
24 24
210/350 230/390
36 36
260/420 280/470
48 48
310/500 340/550
24 24
330/470 370/530
36 36
380/540 420/610
48 48
430/620 480/700
18 18
170/-- 180/--
24 24
220/360 240/400
36 36
230/-- 260/--
36 36
250/-- 280/--
22 22
180/-- 200/--
12 12
260/380 300/430
24 24
310/450 350/510
24 24
310/450 350/510
42 42
390/570 440/540
36 36
380/-- 420/--
48 48
420/610 470/690
48 48
420/610 470/690
24 24
210/350 230/390
42 42
290/470 310/510
12 12
150/270 170/300
24 24
210/350 230/390
36 35
250/-- 270/--
36 35
260/420 280/470
30136 30136
280/440 320/510
42/48 42/48
290/480 340/560
30 30
250/400 270/440
64 64
48 48
620/-- 690/--
11 11
7 10
36 36
290/-- 320/--
36 36
640/800 700/890
36 36
640/800 700/890
42 42
570/550 740/940
36 36
660/-- 720/--
42 42
720/900 800/1000
6000
12
67
70
21
460/610
33
510/690
35
540/730
24
290/450
21
250/400
33
510/690
48
360/580
18
200/350
21
200/--
12
180/310
24
240/400
36
300/490
48
360/580
24
410/570
36
460/650
48
520/740
18
190/--
24
260/420
42
320/--
42
340/--
25
230/--
12
330/460
24
390/550
24
390/550
42
480/680
48
490/--
48
510/730
48
510/730
24
240/400
42
340/540
12
180/310
24
240/400
42
310/--
36
300/490
30136
350/540
42148
380/600
36
320/510
71
50
820/--
11
10
42
370/--
42
810/1010
42
810/1010
48
850/1070
42
840/--
48
940/1160
7OOO
14
72
75
24
520/590
39
580/780
36
570/770
24
300/470
24
250/450
39
580/780
48
380/510
18
210/360
24
220/--
12
190/330
24
250/420
36
310/510
48
380/610
24
420/590
36
490/690
48
550/780
24
220/--
24
270/440
46
360/--
48
380/--
25
240/--
12
340/480
24
400/570
24
400/570
42
500/710
48
520/--
48
540/770
48
540/770
24
250/420
42
350/560
12
190/330
24
250/420
42
320/--
36
310/510
30136
370/570
42148
400/530
36
330/530
71
50
850/--
11
10
48
420/--
48
910/1140
48
900/1130
54
940/1180
48
940/--
48
980/1210
8500
17
79
82
24
570/750
39
640/860
36
630/840
30
380/570
24
300/480
39
640/860
48
410/650
18
230/390
24
240/--
12
200/350
24
270/450
36
340/550
48
410/650
24
470/650
36
540/750
48
600/840
24
240/--
24
300/480
48
410/--
48
420/--
25
260/--
12
380/530
24
450/630
24
450/630
42
560/780
48
550/--
48
590/830
48
590/830
24
270/450
42
380/600
12
200/350
24
270/450
42
350/--
36
340/550
30135
410/620
42148
450/690
36
370/580
74
60
920/--
11
12
48
460/--
48
990/1230
48
990/1230
54
1030/1290
48
1030/--
48
1080/1320
1. Refer to the Aero Product Data Catalog for additional application information•
• Section weights do not include coils or motors• Refer to the product data catalog for additional
weights•
3. Section height is the same except as noted•
4. All bold numbers are inches, non-hold are pounds unless otherwise noted•
13

Table 1 -- 39MN,MW Component Weights and Lengths (cont)
Indoor
Refer to Fig. 5 Outdoor
1 Mixing box AWL (in.)
/IndooUOutdoor} Wei_lht lib}
2 Side inlet mixing box
3Filter mixing box
4Air mixer
5 Exhaust box
6 Side outlet exhaust box
7Integral face and bypass heating coil section
8Internal face and bypass damper section
9 External face and bypass damper section
Plenum section -- 12 in.
Plenum section -- 24 in.
10
Plenum section -- 36 in.
Plenum section -- 48 in.
Humidifier section -- 24 in,
11 Humidifier section -- 36 in,
Humidifier section --48 in,
12 External bypass return section
13 Horizontal b]ow-thru discharge plenum section
FC
14 Vertical blow-thru discharge AF
_lenum section
Plenum Far
15 Horizontal flat filter section
2in. or 4 in. side loading
16 Horizontal angle filter section
2in. or 4 in. side Ioadin_
Horizontal bag/cartridge filter section, SL
17 6 in. or 12 in. media with 2 in. pre-filter track
Horizontal bag/cartridge filter section, SL
15 in. or 30 in. media wBth 2 in. pre-filter track
18 Vertical bag/cartridge filter section, SL
0in. or 12 in. media with 2 in. pre-filter track
19 Horizontal bag/cartridge filter section, FL
Face loading media with or without header
20 Horizontal blow-thru HEPA filter section, FL
21 Cooling coil section with drain pan
22 Extended length cooling coil section with drain pan
23 Heating coil section
24 Extended length heating coil section and electric heat with remote
box
25 Extended length heating coil section with EBR
26 Dual coil section with drain pan
Low Amp AWL (in.',
27 Electric heat section with ndoo /Oudoo Wegh (b'
control box High Amp AWL (in.,
(indoor /Outdoor) Weight (Ib',
28 Horizontal blow thru coil with ducted discharge
Multizone/dua] duct H (in,)
AWL (in,)
29 heating/cooling coil section Indoor /Ou door / Wei{lh (Ib /
30 Multizone damper section AWL (in, I
Number of Zones
31 Vertical coil section with drain pan
FC
AF
32, 33, Fan sections
34_ 35_ 36 Downblast AF
Vertical FC/AF
37 Plenum fan section
LEGEND
AF -- Airfoil
AWL -- Airway Length
EBR -- External Bypass Return
FC Forward Curved
FL -- Face Load
H-- Height
SL -- Side Load
W-- Width
10,500
21
79
82
27
710/900
39
710/930
36
720 /930
30
430 /620
27
370 /560
39
710/930
48
450 /600
18
250/410
27
280 /--
12
220 /370
24
300 /480
36
380 /500
48
450 /690
24
530/710
35
600/810
48
680 /920
24
270 /--
30
380 /570
48
470 /--
48
480 /--
28
320 /--
12
430 /580
24
510/600
24
510/600
42
630 /850
60
630 /--
48
070/910
48
670/910
24
300 /480
48
450 /690
12
220 /370
24
300 /480
48
430 /--
36
380 /590
30135
470 /080
42148
530 /770
42
460 /080
90
72
1180/--
11
12
48
510/--
48
1100/1340
48
1100/1340
54
1150/1410
48
1160/--
54
1320 /1580
SECTION DIMENSIONS lin.! AND WEIGHTS !lb)
12,500 15,000 18,000
25
62
66
86
89
27
760 /960
45
830 /1080
36
760 /980
30
460 /060
27
390 /590
45
830 /1080
48
470 /720
18
270 /440
27
300 /--
12
230 /380
24
320/510
36
400 /020
48
470 /720
24
560 /750
36
640 /860
48
720 /970
24
280 /--
30
410/610
50
600 /--
60
610/--
28
340 /--
12
460/010
24
540 /730
24
540 /730
42
670/910
60
670 /--
48
710/960
48
710/960
24
320/510
48
480 /730
12
230 /380
24
320/510
48
450 /--
36
400 /620
30136
500 /720
42148
560/810
42
490 /730
90
30 36
62 73
66 77
104 109
107 112
27 36
870 /1090 1320 /1580
51 57
1050 /1350 1300 /1690
36 45
880 /1130 1260 /1550
36 36
600 /850 720 /080
27 36
440 /060 650 /010
51 57
1050 / 1350 1360 / 1690
48 48
530 /820 620 /920
18 18
300 /500 350 /550
27 33
330 /-- 450 /--
12 12
260 /-- 310 /490
24 24
350 /-- 410 /630
36 56
440 /690 510 /770
48 48
530 /820 620 /020
24 24
644 /860 770 /000
36 36
734 /990 570 /1130
48 48
824 /1120 070 /1270
24 24
310/-- 360/--
30 53
460 /690 590 /840
50 60
700 /-- 860 /--
60 60
700 /-- 850 /--
28 40
380 /-- 600 /--
12 12
530/710 630/810
24 24
620 /830 740 /960
24 24
620 /830 740 /960
42 42
700 /1030 900 /1180
60 72
760/-- 910/--
48 48
810 /11O0 960 /1260
48 48
810 /11O0 960 /1260
24 24
350 /560 410 /630
48 48
540 /830 630 /930
12 12
260 /440 310 /400
24 24
350 /560 410 /630
48 48
510/-- 600/--
36 36
440 /690 510 /770
30135 30 /42
580 /830 700 /980
42148 42 /54
660 /950 800 /1120
42 48
550 /820 740 /1040
90 101
20,000
40
79
83
109
112
39
1520/1700
57
1460/1700
48
1430/1730
42
870/1150
59
750/1020
57
1460/1790
48
650/950
18
380/580
53
470/--
12
320/500
24
430/650
36
540/800
48
650/950
24
820/1040
36
930/1190
48
1040/1340
27
420/--
33
630/880
60
920/--
66
990/--
40
050/--
12
680/860
24
790/1010
24
790/1010
42
960/1240
72
910/--
48
1020/1320
48
1020/1320
24
430/650
54
730/1050
12
320/500
24
430/650
54
700 /--
0
30142
740/1020
42/54
860/1180
54
840/1160
107
72
1250/--
11
13
60
630/--
60
1360/1650
60
1360/1650
66
1400/1700
60
1440/--
54
1400/1670
NOTES:
72
1430/--
11
16
60
722/--
60
1560/1890
60
1560/1890
56
1600/1950
60
1650/--
54
1610/1920
84
18401--
11
17
60
860/--
60
1840/2180
60
1840/2180
60
1750/2000
60
1950/--
65
2240/2600
90
2030/--
11
17
66
980/--
60
1960/2300
65
2120/2480
65
2010/2370
65
2250/--
72
2580/2960
25,000
50
117
120
42
1920/2220
63
1870/2240
51
1790/2120
42
1030/1330
42
930/1230
63
1870/2240
48
750/1070
18
440/650
39
630/--
12
370/560
24
490/730
35
020/900
48
750/1070
24
950/1190
35
1080/1360
48
1210/1530
30
520/--
36
790/1070
66
1200/--
72
1270/--
40
770/--
12
800/990
24
920/1160
24
920/1160
42
1120/1420
84
1090/--
48
1190/1510
48
1190/1510
24
490/730
60
930/1290
12
370/560
24
490/730
60
890/--
0
30142
880/1180
42154
1020/1360
60
1080/1440
119
102
2630/--
11
18
72
1240/--
65
2480/2860
72
2670/3070
72
2520/2020
72
2840/--
72
3040/3440
30,500
61
104
108
117
120
51
2650/2080
63
2140/2510
60
2390/2750
48
1330/1650
51
1270/1600
63
2140/2510
48
850/1170
18
490/700
45
810/--
12
420/610
24
550/790
36
700/980
48
850/1170
24
1090/1330
36
1230/1510
48
1380/1700
33
630/--
36
000/1180
66
1400/--
78
15801--
45
1000/--
12
910/1100
24
1060/1300
24
1060/1300
42
1270/1570
96
1210/--
48
1360/1680
48
1360/1680
24
550/790
72
1230/1630
12
420/010
24
550/700
72
1180/--
0
30142
1010/1310
42154
1180/1520
72
1420/1820
140
120
3500/--
11
18
78
1520/--
66
2830/3210
78
3270/3700
78
3080/3510
78
3500/--
78
3740/4170
. Refer to the Aero Product Data Catalog for additional application information•
• Section weights do not include coils or motors. Refer to the product data catalog for additional
weights•
3. Section height is the same except as noted•
4. All bold numbers are inches, non-bold are pounds unless otherwise noted•
14

Table 2A -- Physical Data -- Airfoil Fans (Supply, Return and Exhaust)
39M UNIT SIZE
WHEEL TYPE..SIZE
I3 06 08 10 12 14 17 21 25 30
AIl...Std All...Std AIhStd AIl...Std AlhStd AIl...Std AIl...Std All...Std AIl...Std AIl...Std
10 121/4 131/2 131/2 161/2 161/2 181/4 20 221/4 221/4
6.13 7.5 8.38 8.38 10.13 10.13 11.00 12.44 13.88 13.88
WHEEL DIAMETER (in.)
MIN INLET CONE DIAMETER (in.)
MAX SPEED (rpm)
Class I
Class II
FAN SHAFT DIAMETER (in.)
Class I
Class II
FAN WHEEL WEIGHT (Ib)
Class I
Class II
No. Fan Blades
MOTOR FRAME SIZE
Maximum (ODP/TEFC)
Minimum (ODP/TEFC)
MOTOR HP
Maximum
Minimum
1872
2442
115/16
23/16
73.0
73.0
9
324T
182T
4O
3
3gM UNIT SIZE Supply...StdWHEEL TYPE..SIZE
WHEEL DIAMETER (in.) 241/2
MIN INLET CONE DIAMETER (n.) 15/8
MAX SPEED (rpm)
Class I
Class II
FAN SHAFT DIAMETER (in.)
Class I
Class II
FAN WHEEL WEIGHT (Ib)
Class I 88
Class II 91
No. Fan Blades 18
MOTOR FRAME SIZE
36 40
Ret/Exh...Std Supply...Std Ret/Exh...Std
3O
1813/le
50
Supply...Std Ret/Exh...Std
33
209/16
27 27 30
1613/le 1613/le 1813/le
1700I 1202112o211055
2123 1910 1910 1715 1715 1568 1568 1378
27/16 27/lC 2Z/lc 211/16 211/16 23/16 23/lC 23/lC
11o411o4
106 106 148 145 176 176 233
18 18 18 18 18 18 18
0tl 0 tl 0t
184T 182T 184T 182T 213T 184T 213T 184T
i 18160 2o17812o
3 3 3 71/2 5 71/2 5
61
Supply...Stc Ret/Exh...Std
33 361/2
209/1G 231/8
Maximum (ODP/TEFC)
Minimum (ODP/TEFC)
MOTOR HP
Maximum 50
Minimum 5
LEGEND
ODP -- Open Dripproof
Ret/Exh -- Return Exhaust
TEFC -- Totally Enclosed Fan Cooled
NOTE: Data is for 50 Hz and 60 Hz motors.
15

Table 2B -- Physical Data -- Plenum Fans (Supply, Return and Exhaust)
3gM UNIT SIZE
WHEEL TYPE...SIZE
WHEEL DIAMETER (in.)
MIN INLET CONE DIAMETER (in,)
MAX SPEED (rpm)
Class I
Class II
FAN SHAFT DIAMETER (in,)
Class I
Class II
FAN WHEEL WEIGHT (Ib)
Class I
Class II
No. Fan Blades
MOTOR FRAME SIZE
Maximum (ODP/TEFC)
Minimum (ODP/TEFC)
MOTOR HP
Maximum
Minimum
I03 06 08 10 12 14 17 21 25
AlhStd AIl...Std AIL..Std AIl...Std AIl...Std AIl...Std AIl...Std AIL..Std AIL..Std
121/4 16 161/2 181/4 221/4 221/4 241/2 27 30
7.5 9.25 10.13 11.88 12.14 12.14 15.81 17.5 19.69
3O
AIl...Std
33
21.49
1202
1568
111/1G
111/16
135
135
12
286T
182T
30
3
39M UNIT SIZE
WHEEL TYPE._SIZE
WHEEL DIAMETER (in,)
MIN INLET CONE DIAMETER (in.)
MAX SPEED (rpm)
Class I
Class II
FAN SHAFT DIAMETER (in.)
Class I
36
AIl...Std
361/2
24
40
Supply...Std Ret/Exh...Std
361/2 401/4
24 265/8
50
Ret/Exh...Std
441/2
291/2
Supply...Std Supply...Std
401/4 441/2
265/8 291/2
1055 1055 955 I 955 865 I 865 808
1378 1378 1249 1249 1131 1131 1050
111/1G 111/16 115/1G I 115/16 23/16 I 23/16 211/16
Class II 111/1G 111/16 115/1G I 115/16 23/16 I 23/16 211/16
FAN WHEEL WEIGHT (Ib)
Class I 171 171 203 203 277 277 366
Class II 171 171 203 203 277 277 366
No. Fan Blades 12 12 12 12 12 12 12
MOTOR FRAME SIZE
Maximum (ODP/TEFC) 3247 324T 256713267 284713647 2867
Minimum (ODP/TEFC) 162T 184T 182T 213T 184T 213T 184T
MOTOR HP
Maximum 40 40 20 I 50 25 I 60 30
Minimum 3 5 3 I 71/2 5 I 71/2 6
LEGEND
ODP -- Open Dripproof
Ret/Exh -- Return Exhaust
TEFC -- Totally Enclosed Fan Cooled
NOTE: Data is for 50 Hz and 60 Hz motors.
61
Ret/Exh...Std
49
321/2
16

39M UNIT SIZE
WHEEL SIZE
WHEEL DIAMETER (in.)
MIN INLET CONE DIAMETER (in.)
MAX SPEED (rpm)
Class I
Class II
FAN SHAFT DIAMETER (in.)
Class I
Class II
Fan Shaft Weight (Ib) Class II
FAN WHEEL WEIGHT (Ib)
Class I
Class II
No. Fan Blades
MOTOR FRAME SIZE
Maximum (ODP/TEFC)
Minimum (ODP/TEFC)
MOTOR HP
Maximum
Minimum
Table 2C -- Physical Data -- Forward-Curved Fans (Supply)
I03 06 08 10 12 14 17 21
Std Std Std I Small Std Small Std Small Std I Small Std I Small Std Small
91/2 1OS/s 12s/8 ]1OS/8 15 12s/s 15 12s/s 18 ]15 18 ]15 20 15
7.81 8.81 10.38 8.81 12.12 10.38 12.62 10.38 15.5 12.62 15.5 12.62 16.25 12.62
1262
1639
111/16
111/16
12.8
16.2
16.9
51
184T 184T 213T1 213T ]213TI215T 1213T1 254T 1213T1 254T 1215T1 254T ]254TI284T
56 143T 143T 182T 145T 184T 145T 184T 145T 184T 182T 213T 182T 215T
25
10
39M UNIT SIZE
WHEEL SIZE
WHEEL DIAMETER (in.)
MIN INLET CONE DIAMETER (in.)
MAX SPEED (rpm)
Class I
Class II
FAN SHAFT DIAMETER (in.)
Class I
Class II
Fan Shaft Weight (Ib) Class II
FAN WHEEL WEIGHT (Ib)
Class I
Class II
No. Fan Blades
MOTOR FRAME SIZE
Maximum (ODP/=rEFC)
Minimum (ODP/TEFC)
MOTOR HP
Maximum
Minimum
LEGEND
ODP -- Open Dripproof
TEFC -- Totally Enclosed Fan Cooled
NOTE: Data is for 50 Hz and 60 Hz motors.
I 2i 30 36 40 50
Std Small Std Small Std Small Std Small Std Small
20 20 20 20 25 223/8 25 25 275/8 27s/s
1625 1625 1625 1625 215/16 181/16 215/16 215/16 2315/16 231_16
61
Std Small
301/4 275/8
263/8 2315/16
656
865
111/16
27/16
71,8
111.0
111.0
37
254T 284T ]256T ]286T ]256T ]286T ]284T ]286T ]286T ]324T ]324T ]326T
184T 215T 184T 215T 182T 254T 184T 254T 184T 254T 184T 256T
5O
2O
17

Table 2D -- Physical Data -- Forward-Curved Fans (Return and Exhaust)
39M UNIT SIZE
WHEEL SIZE
WHEEL DIAMETER (in.)
MIN INLET CONE DIAMETER (in,)
MAX SPEED (rpm)
Class I
Class II
FAN SHAFT DIAMETER (in.)
Class I
Class II
Fan Shaft Weight (Ib) Class II
FAN WHEEL WEIGHT (Ib)
Class I
Class II
No. Fan Blades
MOTOR FRAME SIZE
Maximum (ODP/TEFC)
Minimum (ODPFrEFC)
MOTOR HP
Maximum
Minimum
I 03
Std
91/2
7.81
2132
2749
1!9
3,8
3,8
43
184T
86
06 08 10 12
Std Std Std Std
105& 12_s 15 15
8.81 10.38 12.62 12.62
1806 1533 1262 1262
2347 1986 1639 1639
1 13/16 I 13/16 I
1 13/16 13/16
4.2 7.7 8.7
5,8 10,0 16.2 16.2
5,8 10,4 16.9 16.9
48 43 51 51
184T 213T 213T 213T
56 56 143T 145T
3/4
1097
1378
13/16 13/16
13/16 13/16
8.7 14,9
213T
145T
71/2 t 71/211/2 11/2
14 17 21 25
Std Std Std Std
18 18 20 20
15.50 15.50 16.25 16.25
1097 952 952
1378 1237 1237
13/16 I 17/16 I 17/16
13/16 17/16 17/16
14.9 15.2 15.2
32.0 32.0 42.0 42.0
34.2 34.2 44.9 44.9
48 48 51 51
215T 254T I 254T
i
145T 145T 145T
182
39M UNIT SIZE
WHEEL SIZE
WHEEL DIAMETER (in,)
MIN INLET CONE DIAMETER (in,)
MAX SPEED (rpm)
Class I
Class II
FAN SHAFT DIAMETER (in,)
Class I
Class II
Fan Shaft Weight (Ib) Class II
FAN WHEEL WEIGHT (Ib)
Class I
Class II
No. Fan Blades
MOTOR FRAME SIZE
Maximum (ODP/TEFC)
Minimum (ODP/TEFC)
MOTOR HP
Maximum
Minimum
LEGEND
ODP -- Open Dripproof
TEFC -- Totally Enclosed Fan Cooled
30 36
Std Std I Small
20 25 I 223/8
16.25 215/16 181/16
960 _
1217
111/16 111/16 I 17/16 I
111/16 27/16 23/16
23.5 61.1 42.4
53,0 81 .O 63.0
53,0 81 .O 63.0
37 37 37
256T 256T 286T I
182T 182T 254T
20 20 30
3 3 15
40 50
Std Small Std I Small
25 25 275/8 I 27s/8
215/16 215/16 2315/16 2315/16
61
Std Small
301_ 275/8
263/8 231_16
751 _ 618 } 656
960 793 865
111/16 111/16 I 111/16 I 111/16 I
27/16 27/16 27/16 27/16
60.3 53.3 71.8 64,5
111/16 1_1/16
211/16 27/16
90.1 71.8
81.0 73.0 111.0 101.0 128.0 111.0
81.0 73.0 111.0 101.0 128.0 111.0
37 37 37 37 37 37
284T 286T 286T I 324T I 324T I 326T
184T 254T 184T 254T 184T I 256T
25 30 30 40 40 I 50
5 15 5 15 5 I 20
NOTE: Dataisfer50 Hzand 60 Hz motors.
18

Table 3- Coil Data
39M UNIT SIZE
1/2-in. CHILLED WATER/DIRECT EXPANSION
Large Face Area
Nominal Capacity (cfm) at 500 fpm
Lower Coil Height (in,)
Upper Coil Height (in,)
Length (in,)
Total Face Area (sq ft)
Medium Face Area
Nominal Capacity (cfm) at 500 fpm
Lower Coil Height (in,)
Upper Coil Height (in,)
Length (in,)
Total Face Area (sq ft)
Bypass Face Area (Internal Chilled Water
Only)
Nominal Capacity (cfm) at 500 fpm
Height (in,)
Length (in.)
Total Face Area (sq ft)
1/2-in. HOT WATER HEATING
Large Face Area
Nominal Capacity (cfm) at 700 fpm
Lower Coil Height (in.)
Upper Coil Height (in,)
Length (in,)
Total Face Area (sq ft)
Medium Face Area
Nominal Capacity (cfm) at 700 fpm
Lower Coil Height (in,)
Upper Coil Height (in,)
Length (in,)
Total Face Area (sq ft)
Small Face Area
Nominal Capacity (cfm) at 700 fpm
Height (in,)
Length (in,)
Total Face Area (sq ft)
Bypass Face Area (Internal)
Nominal Capacity (cfm) at 700 fpm
Height (in,)
Length (in,)
Total Face Area (sq ft)
5/8-in. STEAM HEATING
Large Face Area
Nominal Capacity (cfm) at 700 fpm
Lower Coil Height (in,)
Upper Coil Height (in,)
Length (in,)
Total Face Area (sq ft)
Medium Face Area
Nominal Capacity (cfm) at 700 fpm
Lower Coil Height (in,)
Upper Coil Height (in,)
Length (in.)
Total Face Area (sq ft)
Small Face Area
Nominal Capacity (cfm) at 700 fpm
Height (in.)
Length (in,)
Total Face Area (sq ft)
Bypass Face Area (Internal)
Nominal Capacity (cfm) at 700 fpm
Height (in,)
Length (in,)
Total Face Area (sq ft)
03 08 08 10 12 14 17 21 25 30 38 40 50 81
1,736 2,951 3,819 4,965 6,319 7,170 8,464 10,720 12,205 15,174 18,333 20,000 25,278 30,694
25 25 27.5 27.5 35 35 37.5 47.5 47.5 47.5 55 30 35 42.5
N/A N/A N/A N/A N/A N/A N/A N/A N/A N/A N/A 30 35 42.5
20 34 40 52 52 59 65 65 74 92 96 96 104 104
3.5 5.9 7.6 9.9 12.6 14.3 16.9 21.4 24.4 30.3 36.7 40.0 50.6 61.4
1,215 2,066 2,778 3,611 4,965 6,146 6,771 9,028 10,278 12,778 15,000 18,333 19,861 25,278
17.5 17.5 20 20 27.5 30 30 40 40 40 45 55 55 35
N/A N/A N/A N/A N/A N/A N/A N/A N/A N/A N/A N/A N/A 35
20 34 40 52 52 59 65 65 74 92 96 96 104 104
2.4 4.1 5.6 7.2 9.9 12.3 13.5 18.1 20.6 25.6 30.0 36.7 39.7 58.6
1,042 1,771 2,431 3,160 4,514 5,122 6,207 7,899 8,993 11,181 12,500 15,000 16,250 19,861
15 15 17.5 17.5 25 25 27.5 35 35 35 37.5 45 45 55
20 34 40 52 52 59 65 65 74 92 96 96 104 104
2.1 3.5 4.9 6.3 9.0 10.2 12.4 15.8 18.0 22.4 25.0 30.0 32.5 39.7
2,431 4,132 5,347 6,951 8,847 10,038 11,849 15,009 17,087 21,243 25,667 28,000 35,389 42,972
25 25 27.5 27.5 35 35 37.5 47.5 47.5 47.5 55 30 35 42.5
N/A N/A N/A N/A N/A N/A N/A N/A N/A N/A N/A 30 35 42.5
20 34 40 52 52 59 65 65 74 92 96 96 104 104
3.5 5.9 7.6 9.9 12.6 14.3 16.9 21.4 24.4 30.3 36.7 40.0 50.6 61.4
1,701 2,892 3,889 5,056 6,951 8,604 9,479 12,639 14,389 17,889 21,000 25,667 27,806 35,389
17.5 17.5 20 20 27.5 30 30 40 40 40 45 55 55 35
N/A N/A N/A N/A N/A N/A N/A N/A N/A N/A N/A N/A N/A 35
20 34 40 52 52 59 65 65 74 92 96 96 104 104
2.4 4.1 5.6 7.2 9.9 12.3 13.5 18.1 20.6 25.6 30.0 36.7 39.7 58.6
-- 2,479 2,917 3,792 4,424 5,019 6,319 7,109 8,094 10,063 14,000 14,000 17,694 21,486
-- 15 15 15 17.5 17.5 20 22.5 22.5 22.5 30 30 35 42.5
-- 34 40 52 52 59 65 65 74 92 96 96 104 104
-- 3.5 4.2 5.4 6.3 7.2 9.0 10.2 11.6 14.4 20.0 20.0 25.3 30.7
1,458 2,479 3,403 4,424 6,319 7,170 8,689 11,059 12,590 15,653 17,500 21,000 22,750 27,806
15 15 17.5 17.5 25 25 27.5 35 35 35 37.5 45 45 55
20 34 40 52 52 59 65 65 74 92 96 96 104 104
2.1 3.5 4.9 6.3 9.0 10.2 12.4 15.8 18.0 22.4 25.0 30.0 32.5 39.7
2,333 3,967 5,250 6,825 8,342 9,465 11,375 14,219 16,188 --
24 24 27 27 33 33 36 45 45 --
N/A N/A N/A N/A N/A N/A N/A N/A N/A --
20 34 40 52 52 59 65 65 74 --
3.3 5.7 7.5 9.8 11.9 13.5 16.3 20.3 23.1 --
1,458 2,479 3,500 4,550 6,825 8,604 9,479 12,323 14,029 --
15 15 18 18 27 30 30 39 39 --
N/A N/A N/A N/A N/A N/A N/A N/A N/A --
20 34 40 52 52 59 65 65 74 --
2.1 3.5 5.0 6.5 9.8 12.3 13.5 17.6 20.0 --
-- 2,479 2,917 3,792 3,792 4,302 5,688 6,635 7,554
-- 15 15 15 15 15 18 21 21
-- 34 40 52 52 59 65 65 74
-- 3.5 4.2 5.4 5.4 6.1 8.1 9.5 10.8
1,458 2,479 2,917 3,792 6,067 6,883 8,531 10,427 11,871
15 15 15 15 24 24 27 33 33
20 34 40 52 52 59 65 65 74
2.1 3.5 4.2 5.4 8.7 9.8 12.2 14.9 17.0
19

Table 3 -- Coil Data (cont)
39M UNIT SIZE
s&-In. CHILLED WATER
Large Face Area
Nominal Capacity (cfm) at 500 fpm
Lower Coil Height (in.)
Upper Coil Height (in.)
Length (in.)
Total Face Area (sq It)
Medium Face Area
Nominal Capacity (cfm) at 500 fpm
Lower Coil Height (in.)
Upper Coil Height (in.)
Length (in.)
Total Face Area (sq It)
Bypass Face Area (Internal Chilled Water Only)
Nominal Capacity (cfm) at 500 fpm
Height (in.)
Length (in.)
Total Face Area (sq It)
5&-In. HOT WATER HEATING
Large Face Area
Nominal Capacity (cfm) at 700 fpm
Lower Coil Height (in.)
Upper Coil Height (in.)
Length (in.)
Total Face Area (sq It)
Medium Face Area
Nominal Capacity (cfm) at 700 fpm
Lower Coil Height (in.)
Upper Coil Height (in.)
Length (in.)
Total Face Area (sq It)
Small Face Area
Nominal Capacity (cfm) at 700 fpm
Height (in.)
Length (in.)
Total Face Area (sq It)
Bypass Face Area (Internal)
Nominal Capacity (cfm) at 700 fpm
Height (in.)
Length (in.)
Total Face Area (sq It)
l-In. STEAM HEATING
Large Face Area
Nominal Capacity (cfm) at 700 fpm
Lower Coil Height (in.)
Upper Coil Height (in.)
Length (in.)
Total Face Area (sq It)
Medium Face Area
Nominal Capacity (cfm) at 700 fpm
Lower Coil Height (in.)
Upper Coil Height (in.)
Length (in.)
Total Face Area (sq It)
Small Face Area
Nominal Capacity (cfm) at 700 fpm
Height (in.)
Length (in.)
Total Face Area (sq It)
Bypass Face Area (Internal)
Nominal Capacity (cfm) at 700 fpm
Height (in.)
Length (in.)
Total Face Area (sq It)
5/_-In. HOT WATER IFB
Integral Face and Bypass
Nominal Capacity (cfm)
Coil Height (in.)
Length (in.)
Total Face Area (sq It)
s/_-In. STEAM IFB
Integral Face and Bypass
Nominal Capacity (cfm)
Coil Height (in.)
Length (in.)
Total Face Area (sq It)
LEGEND
IFB -- Integral Face and Bypass
03 08 08 10 12 14 17 21 28 30 38 40 50 81
1,667 2,833 3,750 4,875 5,958 6,760 8,125 10,156 11,563 14,375 18,000 20,000 24,917 30,333
24 24 27 27 33 33 36 45 45 45 54 30 36 42
N/A N/A N/A N/A N/A N/A N/A N/A N/A N/A N/A 30 33 42
20 34 40 52 52 59 65 65 74 92 96 96 104 104
3.3 5.7 7.5 9.8 11.9 13.5 16.3 20.3 23.1 28.8 36.0 40.0 49.8 60.7
1,042 1,771 2,500 3,250 4,875 6,146 6,771 8,802 10,021 12,458 15,000 18,000 19,500 24,917
15 15 18 18 27 30 30 39 39 39 45 54 54 36
N/A N/A N/A N/A N/A N/A N/A N/A N/A N/A N/A N/A N/A 33
20 34 40 52 52 59 65 65 74 92 96 96 104 104
2.1 3.5 5.0 6.5 9.8 12.3 13.5 17.6 20.0 24.9 30.0 36.0 39.0 49.8
1,042 1,771 2,083 2,708 4,333 4,917 6,094 7,448 8,479 10,542 12,000 15,000 16,250 19,500
15 15 15 15 24 24 27 33 33 33 36 45 45 54
20 34 40 52 52 59 65 65 74 92 96 96 104 104
2.1 3.5 4.2 5.4 8.7 9.8 12.2 14.9 17.0 21.1 24.0 30.0 32.5 39.0
2,333 3,967 5,250 6,825 8,342 9,465 11,375 14,219 16,188 20,125 25,200 28,000 34,883 42,467
24 24 27 27 33 33 36 45 45 45 54 30 36 42
N/A N/A N/A N/A N/A N/A N/A N/A N/A N/A N/A 30 33 42
20 34 40 52 52 59 65 65 74 92 96 96 104 104
3.3 5.7 7.5 9.8 11.9 13.5 16.3 20.3 23.1 28.8 36.0 40.0 49.8 60.7
1,458 2,479 3,500 4,550 6,825 8,604 9,479 12,323 14,029 17,442 21,000 25,200 27,300 34,883
15 15 18 18 27 30 30 39 39 39 45 54 54 36
N/A N/A N/A N/A N/A N/A N/A N/A N/A N/A N/A N/A N/A 33
20 34 40 52 52 59 65 65 74 92 96 96 104 104
2.1 3.5 5.0 6.5 9.8 12.3 13.5 17.6 20.0 24.9 30.0 36.0 39.0 49.8
-- 2,479 2,917 3,792 3,792 4,302 5,688 6,635 7,554 9,392 14,000 14,000 16,683 21,233
-- 15 15 15 15 15 18 21 21 21 30 30 33 42
-- 34 40 52 52 59 65 65 74 92 96 96 104 104
-- 3.5 4.2 5.4 5.4 6.1 8.1 9.5 10.8 13.4 20.0 20.0 23.8 30.3
1,458 2,479 2,917 3,792 6,067 6,883 8,531 10,427 11,871 14,758 16,800 21,000 22,750 27,300
15 15 15 15 24 24 27 33 33 33 36 45 45 54
20 34 40 52 52 59 65 65 74 92 96 96 104 104
2.1 3.5 4.2 5.4 8.7 9.8 12.2 14.9 17.0 21.1 24.0 30.0 32.5 39.0
2,333 3,967 5,250 6,825 8,342 9,465 11,375 14,219 16,188 20,125 25,200 28,000 34,883 42,467
24 24 27 27 33 33 36 45 45 45 54 30 36 42
N/A N/A N/A N/A N/A N/A N/A N/A N/A N/A N/A 30 33 42
20 34 40 52 52 59 65 65 74 92 96 96 104 104
3.3 5.7 7.5 9.8 11.9 13.5 16.3 20.3 23.1 28.8 36.0 40.0 49.8 60.7
1,458 2,479 3,500 4,550 6,825 8,604 9,479 12,323 14,029 17,442 21,000 25,200 27,300 34,883
15 15 18 18 27 30 30 39 39 39 45 54 54 36
N/A N/A N/A N/A N/A N/A N/A N/A N/A N/A N/A N/A N/A 33
20 34 40 52 52 59 65 65 74 92 96 96 104 104
2.1 3.5 5.0 6.5 9.8 12.3 13.5 17.6 20.0 24.9 30.0 36.0 39.0 49.8
-- 2,479 2,917 3,792 3,792 4,302 5,688 6,635 7,554 9,392 14,000 14,000 16,683 21,233
-- 15 15 15 15 15 18 21 21 21 30 30 33 42
-- 34 40 52 52 59 65 65 74 92 96 96 104 104
-- 3.5 4.2 5.4 5.4 6.1 8.1 9.5 10.8 13.4 20.0 20.0 23.8 30.3
1,458 2,479 2,917 3,792 6,067 6,883 8,531 10,427 11,871 14,758 16,800 21,000 22,750 27,300
15 15 15 15 24 24 27 33 33 33 36 45 45 54
20 34 40 52 52 59 65 65 74 92 96 96 104 104
2.1 3.5 4.2 5.4 8.7 9.8 12.2 14.9 17.0 21.1 24.0 30.0 32.5 39.0
-- 3,000 4,000 5,000 6,000 7,000 8,500 10,500 12,500 15,000 18,000 20,000 25,000 30,500
-- 22.9 30.6 30.6 30.6 30.6 24 33 33 33 45 51 60 75
-- 24 30 39 39 45 59.4 59.4 59.4 81.4 81.4 81.4 92.4 92.4
-- 3.3 5.7 7.4 7.4 8.5 9.2 12.6 12.6 17.6 24.1 27.3 36.7 45.8
-- 3,000 4,000 5,000 6,000 7,000 8,500 10,500 12,500 15,000 18,000 20,000 25,000 30,500
-- 22.88 30.56 30.56 30.56 30.56 24 33 33 33 45 51 60 75
-- 24 30 39 39 45 59.38 59.38 59.38 81.38 81.38 81.38 92.38 92.38
-- 3.3 5.7 7.4 7.4 8.5 9.2 12.6 12.6 17.6 24.1 27.3 36.7 45.8
20

Table 4- Direct-Expansion Circuiting Data
Medium Face Area Coils
39M UNIT SIZE
CIRCUITING TYPE
_.lrtlow (cfm) at 500 fpm
Total Face Area (sq It)
Tubes In Face
Tube Length (in.)
_1o. of Circuits -Total
d-Row Coil
Face Split Coils
No. of TXVs
Suction Connections (in. OD)
Distributor Connections (in. OD)
Distributor Nozzle Size*
Intertwined Row Split Coils
No. of TXVs
Suction Connections (in. OD)
Distributor Connections (in. OD)
Distributor Nozzle Size*
Single-Circuit Coils
No. of TXVs
Suction Connections (in. OD)
Distributor Connections (in. OD)
Distributor Nozzle Size
D-Row Coil
Face Split Coils
No. of TXVs
Suction Connections (in. OD)
Distributor Connections (in. OD)
Distributor Nozzle Size*
Intertwined Row Split Coils
No. of TXVs
Suction Connections (in. OD)
Distributor Connections (in. OD)
Distributor Nozzle Size*
Single-Circuit Coils
No. of TXVs
Suction Connections (in. OD)
Distributor Connections (in. OD)
Distributor Nozzle Size
D-Row Coil
Face Split Coils
No. of TXVs
Suction Connections (in. OD)
Distributor Connections (in. OD)
Distributor Nozzle Size*
Intertwined Row Split Coils
No. of TXVs
Suction Connections (in. OD)
Distributor Connections (in. OD)
Distributor Nozzle Size*
Single-Circuit Coils
No. of TXVs
Suction Connections (in. OD)
Distributor Connections (in. OD)
Distributor Nozzle Size
03 06 08 10 12 14
au_rterIN_lf IFu, Ouarteq Half IFu, OuarterIN_lfIFull auarted N_lfIFu, aoarterIN_lf IFu, OuarteqHalfIFull
2,066 2,778 4,965 6,146
4.1 5.6 9.9 12.3
144141137 _ 114 1611616 16 22 22 2412424
20 34 34 40 52 52 52 59 59
14 14 16 4 11 22 12 24
2
7/8
7/8
G-1.5
2
7/8
7/s
G-1.5
1,215
2.4
14 14
20 270
4
2
7/8
%
G-2.5/G-2
2
7/8
%
G-2.5/G-2
1
1%
%
G-6
1
7/8
7/s
G-2.5
22
7/s 7/8
7/8 7/8
G-1.5 G-2.5/G-2
2 2
7/8 7/8
7& %
G-1.5 G-2.5/G-2
1 1
7/8 11/8
7/s %
G-2.5 G-6
-- 2
__ 7/8
-- 7/8
-- G-2.5/G-2
-- 2
-- 7/8
-- 7/8
-- G-2.5/G-2 -- ---
1 1
7/8 11/8
7/s 7_
G-2.5 G-6
LEGEND
TXV -- Thermostatic Expansion Valve (Field Supplied)
_ 2 2
__ % %
-- % %
-- G-1.5 G-2._G-2
-- 2 2
-- % %
-- % %
-- G-1.5 G-2.5/G-2
-- 1 1
-- 7/8 1vs
-- % %
-- G-2.5 G-6
2 2
_ % %
_ % %
-- G-1.5 G-2.5/G-2
-- 2 2
-- % %
-- % %
-- G-1.5 G-2.5/G-2
-- 1 1
-- 7/8 1vs
-- % %
-- G-2.5 G-6
2 -- 2
1_/8 -- 7/8
% -- %
G-6 -- G-2.5/G-2
2
%
%
G-2.5/G-2
1
1vs
%
G-6
2
1V8
%
G-6
2
1V8
%
G-6
2 2 __ 2
7/8 7/8 __ 7/8
7/8 7/8 _ %
G-1.5 G-2.5 -- G-1.5
2 2 -- 2
7/8 7/8 __ 7/s
7/8 7/8 -- %
G-1.5 G-2.5 -- G-1.5
1 1 -- 1
7/_ 1V8 -- 7/8
7/8 7/8 -- ¼
G-2.5 G-8 -- G-2.5
2 2 2 2
7/8 7/8 1% 7/8
7/8 7/8 % %
G-1.5 G-2.5 G-8 G-1.5
2 2 -- 2
7/8 7/8 __ 7/s
% 7/8 __ 7/8
G-1.5 G-2.5 -- G-1.5
1 1 -- 1
7/8 1V8 -- 7/8
7/8 7/8 -- ¼
G-2.5 G-8 -- G-2.5
__ 2 2 --
-- 7/8 1% --
__ 7/s % --
-- G-2.5 G-8 --
-- 2 2 --
-- 7/8 1% --
__ 7/s % --
-- G-2.5 G-8 --
1
1v8
7/8
G-8
3,611
7.2
16 I 16 22
I
82 52 52
16 6
2 __ 2
¼ __ 7/8
% -- 7/s
G-2.5 -- G-2
2 -- 2
¼ -- 7/8
% -- 7/s
G-2.5 -- G-2
1 -- 1
1V8 -- 1Vs
¼ -- 7/s
G-8 -- G-4
2 2 2
7/8 1I/8 7/s
% 7& 7/s
G-2.5 G-8 G-2
2 -- 2
¼ -- 7/8
¼ _ 7&
G-2.5 -- G-2
1 -- 1
11/8 -- 11/8
¼ -- 7/s
G-8 -- G-4
2 2 --
7/8 11/8 __
¼ 7/8 --
G-2.5 G-8 --
22--
7/8 11/8 --
¼ 7/8 --
G-2.5 G-8 --
1
1V8
%
G-8
NOTE: Factory-supplied distributors have factor,
2
1%
¼
G-4/G-3
2
1%
¼
G-4/G-3
1
13/8
1%
E-12
2
1%
¼
G-4/G-3
2
1%
¼
G-4/G-3
1
13/8
1%
E-12
2
1%
¼
G-4/G-3
2
1%
%
G-4/G-3
2 2 2
13/8 _8 1_
1% U8 7/8
E-12 G-2 G-4
-- 2 2
-- 7/8 1 V8
-- 7/8 7/8
-- G-2 G-4
-- 1 1
-- 1% 13/8
-- 7/8 13/8
-- G-4 C-12
2 __ 2
18/8 __ 1 _/8
1V8 -- 7/8
E-12 -- G-4
2 -- 2
13/8 -- 1%
1% -- 7/8
E-12 -- G-4
1
1%
13/8
0-12
2 -- 2
13/8 __ 1%
1% -- 7/8
E-12 -- G-4
2 -- 2
13/8 -- 1%
1% -- 7&
E-12 -- G-4
2
13/8
13/8
C-12
2
13/8
13/8
C-12
2
13/8
13/8
C-12
2
13/8
13/8
C-12
2
13/8
13/8
C-12
1 1 --
13/8 1% --
1% 13/8 --
E-12 0-12 --
-selected nozzle sizes as shown. If neces-
sary, replace factory-supplied nozzles with field-supplied and installed nozzles. Consult
AHUBulIder@ software selection program for correct nozzle selection.
*When 2 nozzle sizes are listed, the smaller nozzle should be located on the upper
distributor.
21

Table 4 -- Direct-Expansion Circuiting Data (cont)
Medium Face Area Coils (cont)
39M UNIT SIZE
CIRCUITING TYPE
Airflow (cfm) at 500 tpm
Total Face Area (sq It)
Tubes In Face
Tube Length (in.)
No. of Circuits -Total
4-Row Coil
Face Split Coils
No. of TXVs
Suction Connections (In. OD)
17 21 25
Half I Full Half I Full IDouble Half I Full IDouble
6,771 9,028 10,276
13.5 18.1 20.6
24 24 32 32 32 32 32 I 32
65 65 65 65 65 72 72 I 7212 24 16 32 64 16 32 64
2 2 2 2 -- 2 2 --
11/8 13/8 11/s 15/8 __ 11/8 15/8 __
30 36 40 50 61
HalfIFuIIIDouble FulIIDouble FuIllDouble FuIIIDouble Full IDouble
12,778 15,000 18,333 19,861 25,278
25.6 30.0 36.7 39.7 56.6
"'l" "
92 92 92 96 96 60 60 104 104 104 104 104
16 32 64 36 72 44 88 44 88 28 28 56 56
Upper Lower Upper Lower
2 2 -- 2 -- 4 -- 4 -- 2 2
11/_ 15/8 -- 15/8 -- 1% -- 1% -- 15/8 15/8
Distributor Connections (In. OD) 7/8 13/8 7/8
Distributor Nozzle Size* G-4 C-12 G-8
Intertwined Row Split Coils
No. of TXVs 2 2 2
Suction Connections (In. OD) 11/8 13/8 11/s
Distributor Connections (In. OD) 7/8 13/8 7/8
Distributor Nozzle Size* G-4 C-12 G-8
Single-Circuit Coils
NO. of TXVs 1
Suction Connections (In. OD) 1%
Distributor Connections (In. OD) lS/8
Distributor Nozzle Size O-12
6-Row Coil
Face Split Coils
No. of TXVs 2 2 2
Suction Connections (in. OD) 11/8 13/8 11/s
Distributor Connections (In. OD) 7/8 13/8 7/8
Distributor Nozzle Size* G-4 C-12 G-8
Intertwined Row Split Coils
No. of TXVs 2 2 2
Suction Connections (In. OD) 11/8 13/8 11/s
Distributor Connections (In. OD) 7/o 13/8 7/8
Distributor Nozzle Size* G-4 C-12 G-8
Single-Circuit Coils
NO. of TXVs 1
Suction Connections (In. OD) 1%
Distributor Connections (In. OD) lS/o
Distributor Nozzle Size O-12
8-Row Coil
Face Split Coils
No. of TXVs 2 2 2
Suction Connections (in. OD) 1V8 13/8 1Vs
Distributor Connections (In. OD) 7/8 13/8 7/8
Distributor Nozzle Size* G-4 C-12 G-8
Intertwined Row Split Coils
No. of TXVs 2 2 --
Suction Connections (In. OD) 11/8 13/8 --
Distributor Connections (in. OD) 7/8 13/8 --
Distributor Nozzle Size* G-4 C-12 --
Single-Circuit Coils
NO. of TXVs 1
SucUon Connections (In. OD) 1%
Distributor Connections (In. OD) 1%
Distributor Nozzle Size C-12
13/8 _ 7/8 lS/a
C-17 G-6 C-17
2 -- 2 2
15/8 -- 1V8 15/8
13/o -- 7/8 1%
C-17 -- G-8 C-17
2 -- 2 2
15/8 -- 1V8 15/8
13/8 -- 7/8 lS/8
C-17 -- G-8 C-17
2 -- 2 2
15/8 -- 1V8 15/8
13/8 -- 7/8 1%
C-17 -- G-8 C-17
2 4 2 2
15/8 15/8 1V8 15/8
13/8 1% 7/8 lS/8
C-17 C-17 G-8 C-17
2 4 -- 2
15/8 15/8 -- 15/8
1% 1% -- 1%
C-17 C-17 -- C-17
-- %
-- G-8
-- 2
-- 7/8
-- G-8
-- 2
-- 1Ve
__ 7/8
-- G-8
-- 2
-- 1Ve
-- 7/8
-- G-8
4 2
15/8 1Ve
13/8 7/8
C-17 G-8
4 --
15/8 --
13/8 --
O-17 --
lS/a -- lS/8 -- 1V8 -- 1V8 -- lS/8
C-17 -- C-17 -- E-12 -- E-12 -- C-15
2 -- 2 -- 4 -- 4 -- 2
15/8 -- 15/8 -- 1% -- 13/8 -- 15/8
1% -- 1% -- 1Vo -- 1V8 -- 1%
C-17 -- C-17 -- E-12 -- E-12 -- C-15
2 -- 2 -- 4 -- 4 -- 2
15/8 __ 15/8 __ 13/8 __ lS/s __ 15/8
1% -- lS/8 -- 1V8 -- 1V8 -- lS/8
C-17 -- C-17 -- E-12 -- E-12 -- C-15
2 -- 2 -- 4 -- 4 -- 2
15/8 -- 15/8 -- 1% -- 13/8 -- 15/8
1% -- 1% -- 1V8 -- 1V8 -- 1%
C-17 -- C-17 -- E-12 -- E-12 -- C-15
24244848 2
15/8 15/8 15/8 15/8 13/8 13/8 13/8 13/8 15/8
1% 1% lS/8 lS/8 1V8 1V8 1V8 1V8 lS/8
C-17 C-17 C-17 C-17 E-12 E-12 E-12 E-12 C-15
24244848 2
15/8 15/8 15/8 15/8 1% 13/8 1% 1% 15/8
1% 1% 1% 1% 1V8 1V8 1V8 1V8 1%
C-17 C-17 C-17 C-17 E-12 E-12 E-12 E-12 C-15
1%
O-15
2
1%
13/o
C-15
2
1%
1%
O-15
2
1%
1%
O-15
2
1%
1%
O-15
2
1%
13/8
O-15
4 4
15/8 15/8
1% 1%
0-15 0-15
4 4
15/8 15/8
1% 1%
0-15 0-15
LEGEND
TXV- Thermostatic Expansion Valve (Field Supplied)
*When 2 nozzle sizes are listed, the smaller nozzle should be located on the upper
distributor.
NOTE: Factory-supplied distributors have factory-selected nozzle sizes as shown. If neces-
sary, replace factory=supplied nozzles with field-supplied and installed nozzles. Consult
AHUBullder® software selection program for correct nozzle selection.
22

Table 4-- Direct-Expansion Circuiting Data (cont)
Large Face Area Coil
39M UNIT SIZE
CIRCUITING TYPE
_.irflow (cfm) at 500 fpm
Total Face Area (sq it)
Tubes In Face
Tube Length (in.)
No. of Circuits _ Total
_-Row Coil
Face Split Coils
No. of TXVs
Suction Connections (in. OD)
Distributor Connections (in. OD)
Distributor Nozzle Size*
Intertwined Row Split Coils
No. of TXVs
Suction Connections (in. OD)
Distributor Connections (in. OD)
Distributor Nozzle Size*
Single-Circuit Coils
No. of TXVs
Suction Connections (in. OD)
Distributor Connections (in. OD)
Distributor Nozzle Size
_-Row Coil
Face Split Coils
No. of TXVs
Suction Connections (in. OD)
Distributor Connections (in. OD)
Distributor Nozzle Size*
Intertwined Row Split Coils
No. of TXVs
Suction Connections (in. OD)
Distributor Connections (in. OD)
Distributor Nozzle Size*
Single-Circuit Coils
No. of TXVs
Suction Connections (in. OD)
Distributor Connections (in. OD)
Distributor Nozzle Size
D-Row Coil
Face Split Coils
No. of TXVs
Suction Connections (in. OD)
Distributor Connections (in. OD)
Distributor Nozzle Size*
Intertwined Row Split Coils
No. of TXVs
Suction Connections (in. OD)
Distributor Connections (in. OD)
Distributor Nozzle Size*
Single-Circuit Coils
No. of TXVs
Suction Connections (in. OD)
Distributor Connections (in. OD)
Distributor Nozzle Size
03 06 08 10 12 14
auarterlNal11Fu"auarterlNalflFu" auarterl Nail IFu" euarterl Half IFull euarterINalflFull auarterINalflFull
1,736 2,951 3,619 6,319 7,170
3.5 5.9 7.6 12.6 14.3
20 20 20 34 34 34 40 40 40 62 62 62 59 59 69
4 10 20 4 10 20 6 11 22 6 14 28 7 14 28
2 2 --
7/8 1V8 --
% % --
G-1.5 G-3
2 2 --
7/8 lV8 --
% % --
G-1.5 G-3 --
1 1 --
11/8 13/8 --
7/8 1_/8 --
G-3 E-10 --
2 2 --
7/8 1_/8 --
% % --
G-1.5 G-3 --
2 2 --
7/8 1_/8 --
% % --
G-1.5 G-3 --
1 1 --
1_/s 1% --
7/8 lV8 --
G-3 E-10 --
-- 2 2
-- 11/8 13/8
-- 7/8 1V8
-- G-3 E-10
2 2 --
7/8 1V8 --
7/8 7& __
G-1.5 G-3 --
2 2 --
7/8 1V8 --
7& 7& __
G-1.5 G-3 --
1 1 --
1V8 13/8 --
7/8 1V8 --
G-3 E-10 --
2 2 --
7/8 1V8 --
7/8 7& __
G-1.5 G-3 --
2 2 --
7/8 1V8 --
7/8 7/8 __
G-1.5 G-3 --
1 1 --
1V8 13/8 --
7/8 1V8 --
G-3 E-10 --
-- 2 2
-- 1_/8 13/8
__ 7/8 1_/8
-- G-3 E-10
-- 2
-- 1%
-- 7/8
-- G-3
-- 1
-- 13/8
-- 1V8
-- E-10
2 2
1V8 13/8
7/8 1_/8
G-3 E-10
1
13/8
1V8
E-10
LEGEND
TXV -- Thermostatic Expansion Valve (Field Supplied)
*When 2 nozzle sizes are listed, the smaller nozzle should be located on the upper
distdbutor.
2 2 2
7/8 1_/8 -- _8
% % -- V8
G-2 G-4/G-3 -- G-2
2 2 -- 2
7/8 1_/8 -- V8
% % -- _8
G-2 G-4/G-3 -- G-2
1 1 -- 1
1_/8 13/8 -- 11/8
7/8 1_/8 -- q8
G-4 E-12 -- G-4
2 2 2 2
7/8 11/8 13/8 _8
7/8 7/8 11/8 _8
G-2 G-4/G-3 E-12 G-2
2 2 2 2
7/8 11/8 13/8 _8
7/8 7/8 11/8 q8
G-2 G-4/G-3 E-12 G-2
1 1 -- 1
1_/8 13/8 -- 11/8
7/8 1_/8 -- q8
G-4 E-12 -- G-4
-- 2 2 --
-- 11/8 13/8 --
-- 7/8 11/8 --
-- G-4/G-3 E-12 --
-- 2 2 --
-- 1% 13/8 --
-- 7/8 1V8 --
-- G-4/G-3 E-12 --
1
13/8
1V8
E-12
4,965
9.9
22 I 22 26
52 J 52 52
11 22 7
2 2
1%
¼
G-4/G-3
2
1%
¼
G-4/G-3
1
1%
1%
E-12
2 2 --
1V8 13/8 --
7/8 1V8 --
G-4/G-3 E-12 --
2 2 --
1V8 13/8 --
7/8 1% --
G-4/G-3 E-12 --
1 -- --
13/8 -- __
1% -- --
E-12 -- --
2 2 --
1V8 13/8 --
7/8 1V8 --
G-4/G-3 E-12 --
2 2 --
1V8 1% --
7/8 1% --
G-4/G-3 E-12 --
1 -- --
13/8 -- __
1% -- --
E-12 -- --
-- 7/8
__ 7/8
-- G-2.5/G-2
-- 2
-- 7/0
-- 7/8
-- G-2.5/G-2
-- 1
-- 1V8
-- 7/8
-- G-6
NOTE: Factory-supplied distributors have factor,
2 2 2
1% 1_/8 7/8
7/8 13/8 7/8
G-6 0-15 G-2.5/G-2
2 -- 2
1% -- 7/8
¼ __ 7&
G-6 -- G-2.5/G-2
1 -- 1
15/8 -- 1V8
13/8 -- 7/8
C-15 -- G-6
2 2 --
1% 15/8 --
¼ 13/8 --
G-6 0-15 --
2 2 --
1% 15/8 --
G-6 0-15 --
1 -- --
1-5/8 --
13/8 -- __
C-15 --
2 2
1% 15/8 --
¼ 13/8 --
G-6 0-15 --
2 2
1% 1% --
¼ 1% --
G-6 0-15 --
2
1%
%
G-6
2
1%
%
G-6
1
1%
13/8
0-15
2
1%
%
G-6
2
1%
%
G-6
1
1%
13/8
0-15
2
1%
%
G-6
2
1%
%
G-6
2
1%
1%
0-15
2
1%
1%
0-15
2
15/8
1%
0-15
2
1%
1%
0-15
2
1%
1%
0-15
1 -- -- 1 --
15/8 -- _ 15/8 --
1% -- -- 1% --
0-15 -- -- 0-15 --
-selected nozzle sizes as shown. If neces-
sary, replace factory-supplied nozzles with field-supplied and installed nozzles. Consult
AHUBulIdeI1_ software selection program for correct nozzle selection.
23

Table 4 -- Direct-Expansion Circuiting Data (cont)
Large Face Area Coil (cont)
39M UNIT SIZE
CIRCUITING TYPE
Airflow (cfm) at 500 tpm
Total Face Area (sq ft)
Tubes in Face
Tube Length (in,)
No. of Circuits - Total
&Row Coil
Face Split Coils
NO. of TXVs
Suction Connections (in, OD)
Distributor Connections (in. OD)
Distributor Nozzle Size *
Intertwined Row Split Coils
No. of TXVs
Suction Connections (in, OD)
Distributor Connections (in. OD)
Distributor Nozzle Size*
Single-Circuit Coils
No. of TXVs
Suction Connections (in, OD)
Distributor Connections (in. OD)
Distributor Nozzle Size
6-Row Cog
Face Split Coils
NO. of TXVs
Suction Connections (in, OD)
Distributor Connections (in, OD)
Distributor Nozzle Size*
Intertwined Now Split Coils
No. of TXVs
Suction Connections (in, OD)
Distributor Connections (in. OD)
Distributor Nozzle Size*
Single-Circuit Coils
NO, of TXVs
Suction Connections (in. OD)
Distributor Connections (in. OD)
Distributor Nozzle Size
8-Row Coil
Face Split Coils
NO. of TXVs
Suction Connections (in. OD)
Distributor Connections (in. OD)
Distributor Nozzle Size*
Intertwined Now Split Coils
No, of TXVs
Suction Connections (in. OD)
Distributor Connections (in. OD)
Distributor Nozzle Size*
Single-Circuit Cogs
No. of TXVs
Suction Connections (in. OD)
Distributor Connections (in. OD)
Distributor Nozzle Size
LEGEND
17
Half IFull IDouble
8,464
16.9
30 30 I 30
65 65 I65
15 30 60
7/8 13/8 --
G-8/G-6 C-1! --
7/8 13/8 _
G-8/G-6 C-1[
13/8
0-15
7/8 13/8 --
G-8/G-6 C-1!
7/8 13/8 --
G-81G-6 C-1! --
13/8
C-15
7/8 13/8 13/8
G-81G-6 C-1! C-15
7/8 13/8 13/8
G-81G-6 C-1! C-15
13/8
C-15
21
Half IFull IDoubl,
10,720
21.4
38
65 65 65
19 76
1Ve 13/8 --
E-IO/E-I _,-20 --
11/8 13/8 --
E-IOIE-I 2,-20
1118 13/8 --
E-IOIE-I 2,-20
11/6 13/8 --
E-IOIE-I 2,-20 --
11/8 13/8 13/8
E-IO/E-I _,-20 C-20
1Ve 13/8 13/e
E-IO/E-I _,-20 C-20
25
Half I Full IDoubie
12,205
24.4
38 38 I 38
72 72 I 72
19 38 76
11/8 1_/8 --
E-IO/E-8 C-2( --
1V_ 13/8 --
E-10/E-8 C-2(
1Va 13/8 --
E-IOIE-8 0-2(
1Va 13/8 --
E-IOIE-8 0-2( --
1Va 13/8 13/8
E-IOIE-8 0-2( 0-20
1Va 13/8 13&
E-IOIE-8 0-2( 0-20
TXV -- Thermostatic Expansion Valve (Field Supplied)
_When 2 nozzle sizes are li_ed, tbe smaller nozzle should be located on the upper di_ributor.
30 36
Half I FulllDouMe FulllDouble
15,174 18,333
30.3 36.7
3838138: 44
92 92 92 96 96
19 38 76 88
11/8 13/8 __ 11/8 --
E-IOIE-8 3-20 -- E-12 --
1118 13/s -- 11/8 __
E-IOIE-8 3-20 E-12
11/8 13/s -- 11/8 __
E-IOIE-8 3-20 E-12
1 U8 13/8 -- 1 V_ --
E-IOIE-8 3-2C -- E-12 --
11/8 13/8 13/8 11/8 11/8
E-IOIE-8 3-20 C-20 E-12 E-12
1 V8 13/s 13/8 1 l& 1 V8
E-IOIE-8 3-20 C-20 E-12 E-12
40
Full I Double
20,000
40.0
24 24 I 24 24
96 96 I 96 96
24 24 48 48
Upper Lowe Jppe_ Lower
13/8 13/8
C-12 C-12
13/8 13/8
C-12 C-12
13/8 13/8
C-12 C-12
13/8 13/8
C-12 C-12
13/8 13/8 13/8 13/8
C-12 C-12 C-12 C-12
13/8 13/8 13/8 13/8
C-12 C-12 C-12 C-12
5O
Full I Double
25,278
50.6
28 28 28 28
,o ,o4 lO2lO2
28
Upper Lowe JppeJ .owe[
13/8 13/8
-- --- C-15 C-15
13/8 13/8
C-15 C-15
13/8 13/8
C-15 C-15
13/B 13/8
-- --- C-15 C-15
13/8 13/8 13/8 13/8
C-15 C-15 C-15 C-15
13/_ 13/8 13/8 13/8
C-15 C-15 C-15 C-15
Full 611 DouMe
30,694
61.4
104 104 104
34 34 68 68
Upper Lowe dppe .owel
13/8 13/8
-- - -- C-17 C-17
13/8 13/8
C-17 C-17
13/8 13/8
C-17 C-17
13/8 13/8
-- - -- C-17 C-17
13/8 13/8 13/8 13/8
C-17 C-17 C-17 C-17
13/8 13/8 13/8 13/8
C-17 C-17 C-17 C-17
NOTE: Factory-supplied distributors have factory-selected nozzle sizes as shown, g necessary, replace
factory-supplied nozzles with fteld-supplied and installed nozzles. Consult AHUBuildet@ software selection
program for correct nozzle selection.
24

FACE
AREA
LARGE
MEDIUM
BYPASS
SMALL
ROWS
1,2
4
6,8,10
1,2
4
6,8,10
1,2
4
6,8,10
1,2
4
Table 5 -- 1/2-in. Water Coil Connection Sizes
CIRCUIT
TYPE
HAL_FULL
HAL_FULL
DOUBLE
HAL_FULL
DOUBLE
HAL_FULL
HAL_FULL
DOUBLE
HAL_FULL
DOUBLE
HAL_FULL
HAL_FULL
DOUBLE
HAL_FULL
DOUBLE
HAL_FULL
HAL_FULL
DOUBLE
3gM UNIT SIZE
0a10610811011211411712112s1301a61 4o Iso I61
Nozzle Size (in. MPT)
1.5 1.5 1.5 1.5 1.5 1.5 2.5 2.5 2.5 2.5 2.5 (2) 1.5 (2) 1.5 (2) 2.5
1.5 1.5 1.5 1.5 1.5 1.5 2.5 2.5 2.5 2.5 2.5 (2) 1.5 (2) 1.5 (2) 2.5
2.5 2.5 2.5 2.5 2.5 2.5 2.5 2.5 2.5 2.5 2.5 (2) 2.5 (2) 2.5 (2) 2.5
1.5 1.5 1.5 1.5 2.5 2.5 2.5 2.5 2.5 2.5 3 (2) 1.5 (2) 2.5 (2) 2.5
2.5 2.5 2.5 2.5 2.5 2.5 3 3 3 3 3 (2) 2.5 (2) 2.5 (2) 3
1.5 1.5 1.5 1.5 1.5 1.5 1.5 2.5 2.5 2.5 2.5 2.5 2.5 (2) 1.5
1.5 1.5 1.5 1.5 1.5 1.5 1.5 2.5 2.5 2.5 2.5 2.5 2.5 (2) 1.5
2.5 2.5 2.5 2.5 2.5 2.5 2.5 2.5 2.5 2.5 2.5 2.5 2.5 (2) 2.5
1.5 1.5 1.5 1.5 1.5 1.5 1.5 2.5 2.5 2.5 2.5 3 3 (2) 2.5
2.5 2.5 2.5 2.5 2.5 2.5 2.5 3 3 3 3 3 3 (2) 2.5
1.5 1.5 1.5 1.5 1.5 1.5 1.5 1.5 1.5 1.5 2.5 2.5 2.5 2.5
1.5 1.5 1.5 1.5 1.5 1.5 1.5 1.5 1.5 1.5 2.5 2.5 2.5 2.5
2.5 2.5 2.5 2.5 2.5 2.5 2.5 2.5 2.5 2.5 2.5 2.5 2.5 2.5
1.5 1.5 1.5 1.5 1.5 1.5 1.5 2.5 2.5 2.5 2.5 2.5 2.5 2.5
2.5 2.5 2.5 2.5 2.5 2.5 2.5 2.5 2.5 2.5 3 3 3 3
-- 1.5 1.5 1.5 1.5 1.5 1.5 1.5 1.5 1.5 1.5 1.5 1.5 2.5
-- 1.5 1.5 1.5 1.5 1.5 1.5 1.5 1.5 1.5 1.5 1.5 1.5 2.5
-- 2.5 2.5 2.5 2.5 2.5 2.5 2.5 2.5 2.5 2.5 2.5 2.5 2.5
FACE ROWS CIRCUIT
AREA TYPE
Table 6 -- 5/8-in. Water Coil Connection Sizes
3gM UNIT SIZE
Nozzle Size (in. MPT)
1HALF 1.5 1.5 1.5 1.5 1.5 1.5 1.5 2 2 2 2 (2) 1.5 (2) 1.5 (2) 1.5
HALF 1.5 1.5 1.5 1.5 1.5 1.5 1.5 2 2 2 2 (2) 1.5 (2) 1.5 (2) 2
2,4
LARGE FULL 2 2 2 2 2.5 2.5 2.5 2.5 2.5 2.5 2.5 (2) 2 (2) 2.5 (2) 2.5
FULL 2 2 2 2 2.5 2.5 2.5 3 3 3 3 (2) 2 (2) 2.5 (2) 2.5
6,8 DOUBLE 2.5 2.5 2.5 2.5 2.5 2.5 2.5 3 3 3 3 (2) 2.5 (2) 2.5 (2) 2.5
1HALF 1.5 1.5 1.5 1.5 1.5 1.5 1.5 2 2 2 2 2 2 (2) 1.5
HALF 1.5 1.5 1.5 1.5 1.5 1.5 1.5 2 2 2 2 2 2 (2) 1.5
2,4
MEDIUM FULL 1.5 1.5 2 2 2 2.5 2.5 2.5 2.5 2.5 2.5 2.5 2.5 (2) 2
FULL 1.5 1.5 2 2 2 2.5 2.5 2.5 2.5 2.5 3 3 3 (2) 2.5
6,8 DOUBLE 2.5 2.5 2.5 2.5 2.5 2.5 2.5 2.5 2.5 2.5 3 3 3 (2) 2.5
1 HALF 1.5 1.5 1.5 1.5 1.5 1.5 1.5 1.5 1.5 1.5 1.5 1.5 1.5 1.5
HALF 1.5 1.5 1.5 1.5 1.5 1.5 1.5 1.5 1.5 1.5 1.5 2 2 2
2,4
BYPASS FULL 1.5 1.5 1.5 1.5 2 2 2 2.5 2.5 2.5 2.5 2.5 2.5 2.5
FULL 1.5 1.5 1.5 1.5 2 2 2 2.5 2.5 2.5 2.5 3 3 3
6,8 DOUBLE 2.5 2.5 2.5 2.5 2.5 2.5 2.5 2.5 2.5 2.5 2.5 3 3 3
1 HALF -- 1.5 1.5 1.5 1.5 1.5 1.5 1.5 1.5 1.5 1.5 1.5 1.5 1.5
SMALL HALF -- 1.5 1.5 1.5 1.5 1.5 1.5 1.5 1.5 1.5 1.5 1.5 1.5 2
2FULL -- 1.5 1.5 1.5 1.5 1.5 2 2 2 2 2 2 2 2
Table 7 -- 1-in. Steam Coil Connection Sizes
3gM UNIT SIZE
FACE ROWS CONNECTION
AREA Nozzle Size (in. MPT)
ALL* ALL OUTLET 2.5 2.5 2.5 2.5 2.5 2.5 2.5 2.5 2.5 2.5 2.5 2.5 2.5
*Large face area sizes 40, 50 and 61 and medium face area size 61 units have 2 sets of steam coil connections.
2.5
2.5
25

ROWS FACE AREA
LARGE
MEDIUM
BYPASS
SMALL
LARGE
MEDIUM
BYPASS
SMALL
Table 8 -- 5/8-in. Steam Coil Connection Sizes
CONNECTION
INLET
OUTLET
INLET
OUTLET
INLET
OUTLET
INLET
OUTLET
39M UNIT SIZE
o31061osIto1121t41t712112s1301361 4o Iso I61
Nozzle Size (in. MPT)
2 2 2 2 2 2 2.5 2.5 2.5 2.5 (2) 2 (2) 2 (2) 2
2 2 2 2 2 2 2 2 2 2 (2) 2 (2) 2 (2) 2
2 2 2 2 2 2 2 2 2 2.5 2.5 2.5 (2) 2
2 2 2 2 2 2 2 2 2 2 2 2 (2) 2
2 2 2 2 2 2 2 2 2 2 2.5 2.5 2.5
2 2 2 2 2 2 2 2 2 2 2 2 2
2 2 2 2 2 2 2 2 2 2 2 2 2
2 2 2 2 2 2 2 2 2 2 2 2 2
2
2
2
2
2
2
2
2
INLET
OUTLET
INLET
OUTLET
INLET
OUTLET
INLET
OUTLET
2.5 2.5 2.5 2.5 2.5 2.5 2.5 3 3 3 3 (2) 2.5 (2) 2.5 (2) 2.5
2.5 2.5 2.5 2.5 2.5 2.5 2.5 2.5 2.5 2.5 2.5 (2) 2.5 (2) 2.5 (2) 2.5
2.5 2.5 2.5 2.5 2.5 2.5 2.5 2.5 2.5 2.5 3 3 3 (2) 2.5
2.5 2.5 2.5 2.5 2.5 2.5 2.5 2.5 2.5 2.5 2.5 2.5 2.5 (2) 2.5
2.5 2.5 2.5 2.5 2.5 2.5 2.5 2.5 2.5 2.5 2.5 3 3 3
2.5 2.5 2.5 2.5 2.5 2.5 2.5 2.5 2.5 2.5 2.5 2.5 2.5 2.5
2.5 2.5 2.5 2.5 2.5 2.5 2.5 2.5 2.5 2.5 2.5 2.5 2.5 2.5
2.5 2.5 2.5 2.5 2.5 2.5 2.5 2.5 2.5 2.5 2.5 2.5 2.5 2.5
ROWS
1
2
3
Table 9 -- Hot Water -- Integral Face and Bypass Coil Connection Sizes
39M UNIT SIZE
CONNECTION 03 I68 I08 I tO It2 I14 It7 I21I2SI30 I 36 I 40 I SOI 61
INLET
OUTLET
INLET
OUTLET
INLET
OUTLET
NozzleSize(in. MPT)
2.5 2.5 2.5 2.5 2.5 2 2 2 2 2 2 2 2
2.5 2.5 2.5 2.5 2.5 2 2 2 2 2 2 2 2
2.5 2.5 2.5 2.5 2.5 2 2 2 2.5 2.5 2.5 2.5 2.5
2.5 2.5 2.5 2.5 2.5 2 2 2 2.5 2.5 2.5 2.5 2.5
2.5 2.5 2.5 2.5 2.5 2 2 2 2.5 2.5 2.5 2.5 2.5
2.5 2.5 2.5 2.5 2.5 2 2 2 2.5 2.5 2.5 2.5 2.5
ROWS
1
2
3
Table 10 --Steam -- Integral Face and Bypass Coil Connection Sizes
39M UNIT SIZE
CONNECTION 03 I66 I08 I t0 112 114 I 17I 21I25I3OI 36 I 40 I SOI 61
INLET
OUTLET
INLET
OUTLET
INLET
OUTLET
NozzleSize(in. MPT)
2.5 2.5 2.5 2.5 2.5 2.5 2.5 2.5 2.5 2.5 2.5 3 3
2.5 2.5 2.5 2.5 2.5 2 2 2 2 2 2 2.5 2.5
2.5 2.5 2.5 2.5 2.5 3 3 3 3 3 3 3 3
2.5 2.5 2.5 2.5 2.5 2.5 2.5 2.5 2.5 2.5 2.5 2.5 2.5
2.5 2.5 2.5 2.5 2.5 3 3 3 3 3 3 3 3
2.5 2.5 2.5 2.5 2.5 2.5 2.5 2.5 2.5 2.5 2.5 2.5 2.5
ROWS
4
6
8
Table 11 -- Operating Charge (Approximate) -- Direct-Expansion Coil
CONNECTION
39M UNIT SIZE
o3Io8 108 I to It2 I t4 It7 121 I 2s 130 138 140 I so I6t
Refrigerant R-22 (Ib)
Large 1 3 4 4 5 6 7 9 11 13 16 18 22 27
Medium 1 2 3 3 4 5 6 7 8 10 12 13 17 20
Large 2 4 6 7 9 10 12 15 18 22 26 29 37 45
Medium 2 3 4 5 7 8 9 11 14 16 20 22 27 33
Large 3 6 8 10 12 15 18 22 26 31 37 42 52 63
Medium 2 5 6 8 9 11 13 16 20 23 28 31 39 48
26

Table 12 -- Coil Volume (Gal. Water)
39M
UNIT SIZE
CHILLED WATER
Large Face Area
4-Row
6-Row
8-Row
1O-Row
Medium Face Area
4-Row
6-Row
8-Row
1O-Row
Small Face Area
4-Row
Bypass Face Area
4-Row
6-Row
8-Row
1O-Row
HOT WATER
Large Face Area
1-Row
2-Row
Medium Face Area
1-Row
2-Row
Small Face Area
1-Row
2-Row
Bypass Face Area
1-Row
2-Row
Integral Bypass Face Area
1-Row
2-Row
3-Row
03 06 08 10 12 14 17 21 25 30 36 40 50 61
1.4 2.2 2.8 3.7 4.7 5.3 6.2 7.8 8.9 11.0 13.3 14.5 18.3 22.2
2.0 3.3 4.3 5.5 7.0 7.9 9.3 11.8 13.3 16.5 19.9 21.7 27.4 33.3
2.7 4.4 5.7 7.3 9.3 10.5 12.4 15.7 17.8 22.0 26.5 29.0 36.5 44.4
3.4 5.5 7.1 9.1 11.6 13.1 15.5 19.6 22.2 27.5 33.2 36.2 45.7 55.5
0.9 1.5 2,1 2.7 3.7 4.5 4.9 6.6 7.5 9.3 10.9 13.3 14.4 18.3
1.4 2.3 3.1 4.0 5.5 6.8 7.4 9.9 11.2 13.9 16.3 19.9 21.5 27.4
1.9 3.1 4,1 5.3 7,3 9.0 9.9 13.2 15.0 18.5 21.7 26.5 28.7 36.5
2.4 3.9 5.2 6.6 9.1 11.3 12.4 16.5 18.7 23.1 27.1 33.2 35.9 45.7
-- 1.3 1.5 2.0 2.3 2.6 3.3 3.7 4.2 5.2 7.2 7.2 9.1 11.1
0.8 1.3 1.8 2.3 3.3 3.8 4.5 5.8 6.5 8.1 9.0 10.9 11.7 14.4
1.2 2.0 2.7 3.5 5.0 5.6 6.8 8.7 9.8 12.2 13.6 16.3 17.6 21.5
1.6 2.7 3.6 4.7 6.6 7.5 9.1 11.5 13.1 16.2 18.1 21.7 23.5 28.7
2.0 3.3 4.5 5.8 8.3 9.4 11.3 14.4 16.4 20.3 22.6 27.1 29.4 35.9
0,3 0.6 0.7 0.9 1.2 1.3 1.5 2.0 2.2 2.7 3.3 3.6 4.6 5.5
0.7 1.1 1.4 1.8 2.3 2.6 3.1 3.9 4.4 5.5 6.6 7.2 9.1 11.1
02 0.4 0.5 0.7 0.9 1.1 1.2 1.6 1.9 2.3 2.7 3.3 3.6 4.6
0.5 0.8 1.0 1.3 1.8 2.3 2.5 3.3 3.7 4.6 5.4 6.6 7.2 9.1
-- 0.3 0.4 0.5 0.6 0.7 0.8 0.9 1.1 1.3 1.8 1.8 2.3 2.8
-- 0.7 0.8 1.0 1.2 1.3 1.6 1.9 2.1 2.6 3.6 3.6 4.6 5.5
0.2 0.3 0.5 0.6 0.8 0.9 1.1 1.4 1.6 2.0 2.3 2.7 2.9 3.6
0.4 0.7 0.9 1.2 1.7 1.9 2.3 2.9 3.3 4.1 4.5 5.4 5.9 7.2
-- 0.3 0.5 0.6 0.6 0.7 0.6 0.8 0.8 1.2 1.6 1.8 2.4 3.0
-- 0.6 0.9 1.2 1.2 1.4 1.2 1.7 1.7 2.3 3.2 3.6 4.8 5.9
-- 0.8 1.4 1.8 1.8 2.0 1.9 2.5 2.5 3.5 4.7 5.3 7.1 8.9
NOTE: One gallon of water weighs 8.33 lb.
27

Table 13 -- Dry Coil Weights (Ib)
COIL
TYPE
CHILLED
WATER OR
DIRECT
EXPANSION
HOT WATER
1-in, IDT STEAM
FACE AREA ROWS FPI
LARGE
MEDIUM
SMALL
BYPASS
LARGE
MEDIUM
SMALL
LEGEND
FPI -- Finperlnch
IDT -- Inner Distributing Tube
NOTES:
BYPASS
LARGE
MEDIUM
SMALL
BYPASS
39M UNIT SIZE
03 06 08 10 12 14 17 21 25 30 36 40 50 61
8 50 85 110 143 182 207 244 309 353 437 528 576 728 884
4 11 52 89 115 149 190 215 254 322 367 455 550 600 758 921
14 54 92 119 155 197 224 264 335 382 473 572 624 789 956
6 70 120 154 200 255 289 341 432 494 612 739 606 1019 1236
6 11 73 124 160 209 265 301 355 450 514 637 770 640 1062 1289
14 76 129 167 217 276 313 370 466 535 663 801 874 1104 1341
6 90 154 196 258 328 372 439 556 635 767 950 1037 1310 1591
8 11 94 160 206 268 341 387 457 579 661 819 990 1080 1365 1656
14 98 166 215 279 355 403 475 602 686 652 1030 1123 1420 1724
6 107 182 235 305 388 441 520 659 753 932 1126 1229 1553 1886
10 11 111 190 244 318 404 459 542 686 784 971 1173 1280 1618 1964
14 116 197 254 331 421 477 563 714 815 1010 1220 1331 1682 2043
8 35 60 80 104 143 177 195 260 296 366 432 528 572 726
4 11 36 62 83 108 149 184 203 271 308 383 450 550 596 758
14 38 64 87 113 155 192 211 282 321 399 468 572 620 789
8 49 83 112 146 200 246 273 364 414 515 605 739 801 1019
6 11 51 87 117 152 209 256 284 379 432 537 630 770 634 1062
14 53 90 121 158 217 266 296 394 449 556 655 601 668 1104
8 63 107 144 187 257 319 351 468 533 662 778 950 1030 1310
8 11 66 112 150 195 268 332 366 468 555 690 810 990 1073 1365
14 68 116 156 203 279 345 360 507 577 718 842 1030 1115 1420
8 75 127 171 222 305 378 416 555 631 785 922 1126 1220 1553
10 11 78 132 178 231 318 393 433 578 658 818 960 1173 1271 1618
14 81 136 185 240 330 409 451 601 684 850 998 1220 1322 1682
8 -- 51 60 78 91 103 130 146 167 207 288 288 364 442
4 11 -- 53 63 81 95 108 135 152 173 216 300 300 379 460
14 -- 55 65 85 99 112 141 158 180 224 312 312 394 479
8 30 51 70 91 130 148 179 228 259 322 360 432 468 572
4 11 31 53 73 95 135 154 186 237 270 335 375 450 488 596
14 33 55 76 99 141 160 194 246 281 349 390 468 507 620
8 42 71 98 127 182 207 250 319 363 461 504 605 655 801
6 11 44 74 102 133 190 215 261 332 378 470 525 630 683 834
14 46 77 106 138 197 224 271 345 393 488 546 655 710 868
8 54 92 126 164 234 266 322 410 466 580 648 778 842 1030
8 11 56 96 131 171 244 277 335 427 486 604 675 810 878 1073
14 59 99 137 177 254 288 349 444 505 628 702 842 913 1115
8 64 109 149 194 277 315 381 485 553 687 768 922 998 1220
10 11 67 113 156 202 289 328 397 506 576 716 800 960 1040 1271
14 69 118 162 210 300 341 413 526 599 744 832 998 1082 1322
8 17 28 37 48 61 69 81 103 118 146 176 192 243 295
1 11 17 30 38 50 63 72 85 107 122 152 183 200 253 307
14 18 31 40 52 66 75 88 112 127 158 191 208 263 319
8 23 40 51 67 85 96 114 144 165 204 246 269 340 413
2 11 24 41 53 70 88 100 118 150 171 212 257 280 354 430
14 25 43 56 72 92 104 123 156 178 221 267 291 368 447
8 12 20 27 35 48 59 65 87 99 123 144 176 191 243
1 11 12 21 28 36 50 61 68 90 103 128 150 183 199 253
14 13 21 29 38 52 64 70 94 107 133 156 191 207 263
8 16 28 37 49 67 83 91 121 138 172 202 246 267 340
2 11 17 29 39 51 70 86 95 126 144 179 210 257 278 354
14 18 30 40 53 72 89 99 131 150 186 218 267 289 368
8 -- 17 20 26 30 34 43 49 56 69 96 96 121 147
1 11 -- 18 21 27 32 36 45 51 58 72 100 100 126 153
14 -- 18 22 28 33 37 47 53 60 75 104 104 131 160
8 -- 24 28 36 42 48 61 68 78 97 134 134 170 206
2 11 -- 26 29 38 44 50 63 71 81 101 140 140 177 215
14 -- 26 30 39 46 52 66 74 84 105 146 146 184 223
8 10 17 23 30 43 49 60 76 86 107 120 144 156 191
1 11 10 18 24 32 45 51 62 79 90 112 125 150 163 199
14 11 18 26 33 47 63 65 82 94 116 130 156 169 207
8 14 24 33 42 61 69 83 106 121 150 168 202 218 267
2 11 15 26 34 44 63 72 87 111 126 157 176 210 228 278
14 15 26 35 46 66 75 90 116 131 163 182 218 237 289
6 23 40 51 67 86 96 114 144 165 204 246 269 340 413
9 24 41 53 70 88 100 118 150 171 212 267 280 354 430
12 25 43 56 72 92 104 123 156 178 221 267 291 368 447
6 16 28 37 49 67 83 91 121 138 172 202 246 267 340
9 17 29 39 51 70 86 95 126 144 179 210 257 278 354
1 12 18 30 40 53 72 89 99 131 150 186 218 267 289 368
6 -- 24 28 36 42 48 61 68 78 97 134 134 170 206
9 -- 26 29 38 44 50 63 71 81 101 140 140 177 215
12 -- 26 30 39 46 52 66 74 84 105 146 146 184 223
6 14 24 33 42 61 69 83 106 121 150 168 202 218 267
9 15 26 34 44 63 72 87 111 126 157 176 210 228 278
12 15 26 36 46 66 75 90 115 131 163 182 218 237 289
1. Weights shown include headers and are the sum of two coils where applicable.
2. Coils are full length.
3, Weights shown are for aluminum fin coils; for copper fin coils, multiply by 1.20.
4. Weights shown are for 1/2-in., .016 in. wall tubes; for 1/2-in., .025-in. wall tubes, multiply by 1.15.
5, Weights shown are for 1/2-in., .016-in. wall tubes; for s/8-in., .020-in. wall tubes, multiply by 1.15.
6. Weights shown are for 1/2-in., .016-in. wall tubes; for s/s-in., .035-in. wall tubes, multiply by 1.50.
28

Table 13 -- Dry Coil Weights (Ib) (cont)
COIL
TYPE
5/8-1N, IDT STEAM
HOT WATER
OR STEAM
FACE ROWS FPI
AREA
1
LARGE
2
1
MEDIUM
2
1
SMALL
2
1
BYPASS
2
1
INEGRAL
FAC E
AND 2
BYPASS
3
LEGEND
FPI -- Fin per Inch
IDT -- Inner Distributing Tube
NOTES:
39M UNIT SIZE
03 06 08 10 12 14 17 21 25 30 36 40 50 61
6 19 32 41 53 68 77 91 115 132 163 197 215 272 330
9 19 33 43 56 71 80 95 120 137 170 205 224 283 344
12 20 35 44 58 74 64 99 125 143 177 214 233 294 358
6 23 40 51 67 65 96 114 144 165 204 246 269 340 413
9 24 41 53 70 68 100 118 150 171 212 257 280 354 430
12 25 43 56 72 92 104 123 156 178 221 267 291 368 447
6 13 22 30 39 53 66 73 97 111 137 161 197 214 272
9 14 23 31 40 56 69 76 101 115 143 168 205 222 283
12 14 24 32 42 58 72 79 105 120 149 175 214 231 294
6 16 28 37 49 67 83 91 121 138 172 202 246 267 340
9 17 29 39 51 70 86 95 126 144 179 210 257 278 384
12 18 30 40 53 72 89 99 131 150 186 218 267 289 368
6 -- 19 22 29 34 39 49 55 62 77 108 108 136 165
9 -- 20 23 30 35 40 51 57 65 81 112 112 142 172
12 -- 21 24 32 37 42 53 59 67 84 116 116 147 179
6 -- 24 28 36 42 48 61 68 78 97 134 134 170 206
9 -- 25 29 38 44 50 63 71 81 101 140 140 177 215
12 -- 26 30 39 46 52 66 74 84 105 146 146 184 223
6 11 19 26 34 49 55 67 85 97 120 134 161 175 214
9 12 20 27 35 51 57 70 88 101 125 140 168 182 222
12 12 21 28 37 53 60 72 92 105 130 146 175 189 231
6 14 24 33 42 61 69 83 106 121 150 168 202 218 267
9 15 25 34 44 63 72 87 111 126 187 175 210 228 278
12 15 26 35 46 66 75 90 115 131 163 182 218 237 289
6 -- 146 207 216 216 231 507 567 567 723 828 880 1064 1210
9 -- 152 216 225 225 241 528 590 590 754 862 917 1108 1260
12 -- 158 225 234 234 251 550 615 615 785 898 955 1154 1313
6 -- 152 220 228 228 246 536 607 607 779 904 967 1180 1355
9 -- 158 229 238 238 256 559 633 633 811 1007 1007 1229 1411
12 -- 164 238 248 248 266 582 659 659 845 1049 1049 1280 1470
6 -- 158 231 241 241 259 585 668 668 863 1008 1081 1327 1532
9 -- 165 241 251 251 270 610 696 696 899 1050 1126 1382 1596
12 -- 172 251 261 261 281 635 725 725 936 1094 1173 1440 1662
1. Weights shown include headers and are the sum of two coils where applicable,
2. Coils are full length.
3. Weights shown are for aluminum fin coils; for copper fin coils, multiply by 1.20,
4. Weights shown are for 1/2-in., ,016 in, wall tubes; for 1/2-in., ,025-in, wall tubes, multiply by 1.15,
5. Weights shown are for 1/2-in., .016-in, wall tubes; for s/8-in., .020-in, wall tubes, multiply by 1.15.
6. Weights shown are for 1/2-in., ,016-in, wall tubes; for s/8-in., ,035-in, wall tubes, multiply by 1.50,
HP
E+
36
36
36
42
42
67
78
106
118
170
212
240
283
372
440
591
620
LEGEND
ODP
Table 14 -- Motor Weights (Ib)
200-230,460-3-60
E+3 E+
TEFC
E+3
20_400-3-50"
ODP TEFC ODP
E+
575-3-60
TEFC
E+/E+3
60/ 68
60/ 68
60/ 68
60/ 66
65/ 66
87
89/ 99
16 40 60 68 29 34 37
3/4 40 60 68 29 34 37
1 40 60 68 29 34 37
116 46 60 66 36 41 48
2 54 65 66 41 47 50
3 87 81 92 73 62 70
5 94 89 99 102 72 88
716 130 142 158 121 105 89 142/158
10 126 154 200 139 128 119 154/200
15 217 250 259 170 210 170 250/259
20 250 287 290 205 254 212 287/290
25 309 394 358 273 363 240 394/368
30 300 436 436 283 414 284 436/436
40 415 661 661 416t 470t 370 661/661
50 414 686 686 403t 527t 440 686/686
60 652** 790 799 545 790t 591 799
75 706** 840 850** 651t 884t 670 850
ODP -- Open Drip Proof
TEFC -- Totally Enclosed Fan Cooled
E+ -- High Efficiency
E+3 -- Premium Efficiency
*Both ODP and TEFC 50 Hz motors available in standard models
only.
1-Availability unconfirmed.
**460 volt only.
NOTE: Multiply motor weight by 0.10 to estimate drive weight.
29

Table 15- Forward-Curved Fan Drive Centerline Distances In Inches
39M UNIT
SIZE
03
REAR
MOUNT
MOTOR
03
SIDE
MOUNT
MOTOR
06
REAR
MOUNT
MOTOR
06
SIDE
MOUNT
MOTOR
O8
12
14
17
SUPPLY
Std
Std
Std
Std
Std
Small
Std
Small
Std
Small
Std
Small
Std
Small
LEGEND
BHF -- Bottom Horizontal Front
BHR -- Bottom Horizontal Rear
DBF -- Downblast Front
DBR -- Downblast Rear
RETURN/ MOTOR
EXHAUST FRAME
56
143T
N/A 145T
182T
164T
56
143T
Std 145T
162T
164T
56
143T
N/A 145T
162T
164T
56
143T
Std 145T
162T
164T
56
143T
145T
Std 162T
164T
213T
162T
N/A 164T
213T
143T
145T
Std 162T
164T
213T
164T
N/A 213T
215T
145T
162T
Std 164T
213T
164T
213T
N/A 215T
254T
145T
162T
Std 164T
213T
164T
213T
N/A 215T
254T
145T
162T
Std 184T
213T
215T
213T
N/A 215T
254T
THF -- Top Horizontal Front
THR -- Top Horizontal Rear
UBF -- Upblast Front
UBR -- Upblast Rear
BHF/BHR DBF/DBR THFFFHR UBF/UBR
Min Max Min Max Min Max Min Max
19.0 20,6 N/A N/A 17.6 19.4 15.5 17.2
19.0 20,6 N/A N/A 17.6 19.4 15.5 17.2
19.0 20,6 N/A N/A 17.6 19.4 15.5 17.2
18.6 20,3 N/A N/A 17.5 19.2 15.2 17.0
18.6 20.3 N/A N/A 17.5 19.2 15.2 17.0
8,0 8,4 5,7 6.3 5,5 6,0 7.4 7.9
8,0 8,4 5,7 6.3 5,5 6,0 7.4 7.9
8.0 8,4 5.7 6.3 5.5 6,0 7.4 7.9
7,0 7,4 4,7 5.4 4,5 5,1 6.4 7.0
7,0 7.4 4,7 5.4 4,5 5.1 6.4 7.0
18,9 20.4 N/A N/A 17.1 18.8 14.8 16.4
18.9 20,4 N/A N/A 17.1 18.8 14.8 16.4
18.9 20,4 N/A N/A 17.1 18.8 14.8 16.4
18.4 20,0 N/A N/A 16.9 18.6 14.4 16.1
18.4 20,0 N/A N/A 16.9 18.6 14.4 16.1
10.6 11.6 6.8 8.9 8,0 10.2 8.3 10.1
10.6 11,6 6.8 8.9 8,0 10.2 8.3 10.1
10.6 11,6 6.8 8.9 8.0 10.2 8.3 10.1
9.8 10.8 6.0 8.3 7.3 9,6 7.4 9.4
9,8 10.8 6.0 8.3 7,3 9,6 7.4 9.4
14,4 15.6 9.5 11.0 10.9 12.4 10.8 12.2
14,4 15,6 9.5 11.0 10.9 12.4 10.8 12.2
14,4 15,6 9.5 11.0 10.9 12.4 10.8 12.2
13.6 14,9 9.0 10.7 10.4 12.0 10.2 11.7
13,6 14,9 9.0 10.7 10.4 12.0 10.2 11.7
13.1 14,4 8.8 10.5 10.1 11.8 9.8 11.4
13,3 14.7 9.8 11.5 11.0 12.7 10.4 12.1
13,3 14,7 9.8 11.5 11.0 12.7 10.4 12.1
12,8 14.3 9.7 11.4 10.9 12.6 10.2 11.8
15,2 16,2 8.8 10.1 10.8 12.2 10.9 12.1
15,2 16,2 8.8 10.1 10.8 12.2 10.9 12.1
14.3 15.4 8.1 9.6 10.2 11.6 10.2 11.4
14.3 15,4 8.1 9.6 10.2 11.6 10.2 11.4
13.7 14.8 7.7 9.3 9,7 11.2 9.6 10.9
13.6 14,9 9.0 10.7 10.4 12.0 10.2 11.7
13.1 14,4 8.8 10.5 10.1 11.8 9.8 11.4
13.1 14,4 8.8 10.5 10.1 11.8 9.8 11.4
18.3 19,5 12.9 14.5 14.9 16.4 14.5 15.9
17.6 18.9 12.5 14.1 14.4 16.0 13.9 15.4
17.6 18,9 12.5 14.1 14.4 16.0 13.9 15.4
17.1 18.4 12.2 13.9 14.1 15.7 13.5 15.0
17.4 18,9 13.8 15.5 15.1 16.8 14.6 16.2
17.0 18,5 13.6 15.3 14.9 16.6 14.3 16.0
17.0 18,5 13.6 15.3 14.9 16.6 14.3 16.0
16.5 18,1 13.5 15.2 14.7 16.4 14.0 15.7
23.1 24,5 17.2 18.7 19.5 21.1 19.0 20.4
22.5 23,8 16.7 18.4 19.1 20.6 18.4 19.9
22.6 23,8 16.7 18.4 19.1 20.6 18.4 19.9
22.0 23,4 16.5 18.1 18.7 20.4 18.0 19.5
22.4 23.9 18.2 19.9 20.0 21.7 19.2 20.8
22.0 23,5 18.0 19.7 19.8 21.5 18.9 20.5
22.0 23.5 18.0 19.7 19.8 21.5 18.9 20.5
21.5 23,1 17.8 19.5 19.5 21.2 18.5 20.2
23.1 24,5 17.2 18.7 19.1 20.6 19.0 20.4
22.5 23.8 16.7 18.4 18.3 19.9 18.4 19.9
22.6 23,8 16.7 18.4 17.9 19.6 18.4 19.9
22.0 23.4 16.5 18.1 17.5 19.2 18.0 19.5
22.0 23.4 16.5 18.1 17.5 19.2 18.0 19.5
22.0 23,5 18.0 19.7 19.8 21.5 18.9 20.5
22.0 23,5 18.0 19.7 19.8 21.5 18.9 20.5
21.5 23,1 17.8 19.5 19.5 21.2 18.5 20.2
.30

Table 15- Forward-Curved Fan Drive Centerline Distances In Inches (cont)
39M UNIT
SIZE
21
25
3O
36
4O
5O
SUPPLY
Std
Small
Std
Small
Std
Small
Std
Small
Std
Small
Std
Small
Std
Small
RETURN/
EXHAUST
Std
N/A
Std
N/A
Std
N/A
Std
N/A
Std
N/A
Std
N/A
Std
N/A
MOTOR BHF/BHR DBF/DBR THF/THR UBF/UBR
FRAME Min Max Min Max Min Max Min Max
145T 24.7 26.0 14,6 16.4 17,4 19.1 18.6 20.0
182T 23.9 25.1 14.0 15,8 16.7 18,5 17.8 19.2
184T 23.9 25.1 14,0 15,8 16,7 18,5 17.8 19.2
213T 23.2 24.6 13,5 15,4 16,2 18,1 17.2 18.7
215T 23.2 24.6 13,5 15,4 16,2 18,1 17.2 18.7
254T 22.4 23.8 13.0 14,9 16.6 17,5 16.4 18.0
216T 19.9 21.3 15,6 17,3 17,4 19,0 16.6 18.2
254T 19.3 20.8 15,4 17,1 17,1 18,8 16.2 17.8
256T 19.3 20.8 15.4 17,1 17.1 18,8 16.2 17.8
284T 18.9 20.5 15,2 17.0 16,9 18.6 15.9 17.6
145T 32.4 34.1 24,1 26.2 27,4 29.5 26.6 28.5
182T 31.7 33.5 23,7 25,9 27,0 29,1 26.1 28.0
184T 31.7 33.5 23.7 25,9 27.0 29,1 26.1 28.0
213T 31.3 33.1 23.5 25,6 26.7 28,8 25.7 27.7
215T 31.3 33.1 23,5 25.6 26,7 28.8 25.7 27.7
254T 30.7 32.6 23,2 25,4 26,4 28,5 25.2 27.2
216T 31.3 33.1 23,5 25,6 26,7 28,8 25.7 27.7
254T 30.7 32.5 23,2 25.4 26,4 28.5 25.2 27.2
256T 30.7 32.6 23,2 25,4 26,4 28,5 25.2 27.2
284T 30.2 32.1 23,0 25,2 26,1 28,3 24.9 26.9
182T 31.7 33.5 23,7 25,9 27,0 29,1 26.6 28.5
184T 31.7 33.5 23,7 25.9 27,0 29.1 26.1 28.0
213T 31.3 33.1 23,5 25.6 26,7 28.8 26.1 28.0
215T 31.3 33.1 23,5 25,6 26,7 28,8 25.7 27.7
254T 30.7 32.6 23,2 25,4 26,4 28,5 25.7 27.7
256T 30.7 32.5 23,2 25.4 26,4 28.5 25.2 27.2
215T 31.3 33.1 23.5 25,6 26.7 28,8 25.7 27.7
254T 30.7 32.6 23,2 25,4 26,4 28,5 25.2 27.2
256T 30.7 32.6 23,2 25,4 26,4 28,5 25.2 27.2
284T 30.2 32.1 23.0 25,2 26.1 28,3 24.9 26.9
286T 30.2 32.1 23,0 25.2 26,1 28.3 24.9 26.9
182T 31.1 33.3 23,0 25,7 25,6 28,2 27.0 29.4
184T 31.1 33.3 23,0 25,7 25,6 28,2 27.0 29.4
213T 30.4 32.6 22,5 25.3 25,0 27.7 26.4 28.8
215T 30.4 32.6 22.5 25,3 25.0 27,7 26.4 28.8
254T 29.7 31.9 22,1 24.9 24,5 27.2 25.7 28.2
256T 29.7 31.9 22,1 24,9 24,5 27,2 25.7 28.2
254T 28.8 31.3 23.6 26,5 24.9 27,7 26.0 28.7
256T 28.8 31.3 23,6 26,5 24,9 27,7 26.0 28.7
284T 28.4 30.9 23.3 26,3 24.6 27,4 25.7 28.4
286T 28.4 30.9 23,3 26.3 24,6 27.4 25.7 28.4
184T 31.1 33.3 23,0 25.7 25,6 28.2 27.0 29.4
213T 30.4 32.6 22,5 25,3 25,0 27,7 26.4 28.8
215T 30.4 32.6 22,5 25.3 25,0 27.7 26.4 28.8
254T 29.7 31.9 22.1 24,9 24.5 27,2 25.7 28.2
256T 29.7 31.9 22,1 24.9 24,5 27.2 25.7 28.2
284T 29.2 31.5 21,8 24,7 24,1 26,9 25.3 27.8
254T 29.7 31.9 22,1 24,9 24,5 27,2 25.7 28.2
256T 29.7 31.9 22,1 24.9 24,5 27.2 25.7 28.2
284T 29.2 31.5 21,8 24,7 24,1 26,9 25.3 27.8
286T 29.2 31.5 21,8 24,7 24,1 26,9 25.3 27.8
184T 33.5 35.5 24,2 26,8 27,1 29,6 28.9 31.1
213T 32.7 34.8 23.7 26,3 26.5 29,1 28.2 30.5
215T 32.7 34.8 23,7 26.3 26,5 29.1 28.2 30.5
254T 31.9 34.1 23,2 25,9 26,0 28,5 27.5 29.8
256T 31.9 34.1 23,2 25,9 26,0 28,5 27.5 29.8
284T 31.4 33.6 22,8 25.6 25,5 28.2 27.0 29.4
286T 31.4 33.6 22.8 25,6 25.5 28,2 27.0 29.4
254T 31.9 34.1 23,2 25,9 26,0 28,5 27.5 29.8
256T 31.9 34.1 23,2 25,9 26,0 28,5 27.5 29.8
284T 31.4 33.6 22.8 25,6 25.5 28,2 27.0 29.4
286T 31.4 33.6 22,8 25.6 25,5 28.2 27.0 29.4
324T 30.7 32.9 22,4 25,2 25,0 27,7 26.3 28.8
213T 35.6 37.6 25,3 28,0 29,1 31,6 30.4 32.7
215T 35.6 37.6 25,3 28.0 29,1 31.6 30.4 32.7
254T 34.8 36.9 24.8 27,5 28.5 31,0 29.7 32.0
256T 34.8 36.9 24,8 27,5 28,5 31,0 29.7 32.0
284T 34.3 36.4 24,4 27,2 28,0 30,6 29.2 31.6
286T 34.3 36.4 24.4 27,2 28.0 30,6 29.2 31.6
324T 33.5 35.7 24,0 26.8 27,5 30.1 28.6 30.9
256T 34.0 36.3 25,8 28,6 28,5 31,2 29.8 32.2
284T 33.5 35.8 25,5 28,4 28,1 30,8 29.3 31.8
286T 33.5 35.8 25,5 28.4 28,1 30.8 29.3 31.8
324T 32.8 35.2 25.1 28,0 27.6 30,4 28.7 31.3
326T 32.8 35.2 25,1 28,0 27,6 30,4 28.7 31.3
LEGEND
BHF -- Bottom Horizontal Front THF -- Top Horizontal Front
BHR -- Bottom Horizontal Rear THR -- Top Horizontal Rear
DBF -- Downblast Front UBF -- Upblast Front
DBR -- Downblast Rear UBR -- Upblast Rear
31

Table 16 --Airfoil Fan Drive Centerline Distances In Inches
39M UNIT
SIZE
O3
O6
O8
12
14
17
21
25
SUPPLY
STD
STD
STD
STD
STD
STD
STD
STD
STD
LEGEND
BHF -- Bottom Horizontal Front
BHR -- Bottom Horizontal Rear
DBF -- Downblast Front
DBR -- Downblast Rear
RETURN/ MOTOR
EXHAUST FRAME
56
143T
STD 145T
182T
164T
56
143T
STD 145T
162T
164T
143T
145T
162T
STD 164T
213T
215T
145T
162T
164T
STD 213T
215T
254T
145T
162T
164T
STD 213T
215T
254T
145T
162T
164T
STD 213T
215T
254T
256T
145T
162T
164T
STD 213T
215T
254T
256T
145T
162T
164T
213T
STD 215T
254T
256T
284T
145T
162T
164T
213T
STD 215T
254T
256T
284T
286T
THF -- Top Horizontal Front
THR -- Top Horizontal Rear
UBF -- Upblast Front
UBR -- Upblast Rear
BHF/BHR DBF/DBR THFFFHR UBF/UBR
Min Max Min Max Min Max Min Max
16.3 17,6 14.0 15.5 15.0 16.5 14.8 16.2
16.3 17,6 14.0 15.5 15.0 16.5 14.8 16.2
16.3 17,6 14.0 15.5 15.0 16.5 14.8 16.2
15.8 17.2 13.6 15.1 14.6 16.2 14.3 15.8
15.8 17,2 13.6 15.1 14.6 16.2 14.3 15.8
19.5 20,3 15.0 15.5 17.3 18.2 19.1 19.9
19.5 20,3 15.0 15.5 17.3 18.2 19.1 19.9
19.5 20.3 15.0 15.5 17.3 18.2 19.1 19.9
19.0 19,8 14.5 15.0 17.0 18.0 18.6 19.4
19.0 19,8 14.5 15.0 17.0 18.0 18.6 19.4
11.1 12,4 8.5 9.8 8,2 9,5 10.3 11.6
11.1 12.4 8.5 9.8 8,2 9.5 10.3 11.6
10.0 11,5 7.6 9.1 7,2 8,7 9.3 10.8
lO.O 11,5 7.6 9.1 7.2 8,7 9.3 10.8
9,4 11 .O 7.0 8.6 6,7 8,3 8.6 10.2
9.4 11 .O 7.0 8.6 6.7 8,3 8.6 10.2
13.8 14,3 10.3 10.9 9,8 10.6 12.9 13.5
12.9 13,5 9.5 10.2 9.0 9,9 12.0 12.6
12.9 13,5 9.5 10.2 9,0 9,9 12.0 12.6
12.2 12,9 8.9 9.7 8.4 9,4 11.3 12.0
12.2 12,9 8.9 9.7 8,4 9,4 11.3 12.0
11.3 12.0 8.1 9.0 7,7 8.7 10.4 11.1
17.2 17,8 14.1 14.9 13.4 14.4 17.2 17.8
16.4 17.0 13.3 14.1 12.7 13.7 16.4 17.0
16.4 17,0 13.3 14.1 12.7 13.7 16.4 17.0
15.7 16.4 12.7 13.7 12.1 13.1 15.7 16.4
15.7 16,4 12.7 13.7 12.1 13.1 15.7 16.4
14.9 15,7 12.0 13.0 11.4 12.5 14.9 15.7
21.2 22,2 18.7 20.0 18.2 19.5 21.2 22.2
20.5 21,5 18.1 19.5 17.7 19.0 20.5 21.5
20.5 21,5 18.1 19.5 17.7 19.0 20.5 21.5
20.0 21,0 17.7 19.1 17.3 18.7 20.0 21.0
20.0 21,0 17.7 19.1 17.3 18.7 20.0 21.0
19.3 20.5 17.2 18.7 16.8 18.2 19.3 20.5
19.3 20,5 17.2 18.7 16.8 18.2 19.3 20.5
21.2 22,1 18.3 19.3 17.5 19.0 21.2 22.0
20.4 21,3 17.6 18.6 16.8 18.5 20.4 21.3
20.4 21,3 17.6 18.6 16.8 18.5 20.4 21.3
19.9 20,7 17.1 18.2 16.3 18.0 19.9 20.7
19.9 20,7 17.1 18.2 16.3 18.0 19.9 20.7
19.1 20.1 16.4 17.6 15.7 17.5 19.1 20.1
19.1 20,1 16.4 17.6 15.7 17.5 19.1 20.1
22.3 22,9 18.8 19.7 18.7 19.6 22.3 22.9
21.5 22.2 18.0 18.9 17.9 18.8 21.5 22.2
21.5 22,2 18.0 18.9 17.9 18.8 21.5 22.2
20.9 21,5 17.4 18.4 17.3 18.3 20.9 21.5
20.9 21,5 17.4 18.4 17.3 18.3 20.9 21.5
20.0 20,7 16.7 17.8 16.6 17.7 20.0 20.7
20.0 20,7 16.7 17.8 16.6 17.7 20.0 20.7
19.4 20.3 16.2 17.3 16.1 17.2 19.4 20.3
28.8 29.6 25.7 26.8 25.5 26.6 28.8 29.6
28.0 29,0 25.0 26.2 24.9 25.9 28.0 29.0
28.0 29,0 25.0 26.2 24.9 25.9 28.0 29.0
27.5 28.5 24.6 25.8 24.4 25.6 27.5 28.5
27.5 28,5 24.6 25.8 24.4 25.6 27.5 28.5
26.8 27,8 24.0 25.3 23.8 25.1 26.8 27.8
26.8 27.8 24.0 25.3 23.8 25.1 26.8 27.8
26.3 27.4 23.6 25.0 23.4 24.7 26.3 27.4
26.3 27,4 23.6 25.0 23.4 24.7 26.3 27.4
32

39M UNIT
SIZE
30 STD
STD
36
N/A
STD
40
N/A
STD
50
N/A
STD
61
N/A
SUPPLY
LEGEND
BHF -- Bottom Horizontal Front
BHR -- Bottom Horizontal Rear
DBF -- Downblast Front
DBR -- Downblast Rear
Table 16- Airfoil Fan Drive Centerline Distances In Inches (cont)
RETURN
EXHAUST
STD
N/A
STD
N/A
STD
N/A
STD
N/A
STD
MOTOR BHF/BHR DBF/DBR THFFrHR UBF/UBR
FRAME MIn Max MIn Max MIn Max MIn Max
182T 27.4 28.9 24.2 25.8 24.1 25.7 27.4 28.9
184T 27.4 28.9 24.2 25.8 24.1 25.7 27.4 28.9
213T 26.9 28.4 23.7 25.5 23.7 25.5 26.9 28.4
215T 26.9 28.4 23.7 25.5 23.7 25.5 26.9 28.4
254T 26.1 27.7 23.1 25.0 23.1 24.9 26.1 27.7
256T 26.1 27.7 23.1 25.0 23.1 24.9 26.1 27.7
284T 25.6 27.3 22.7 24.5 22.6 24.6 25.6 27.3
286T 25.6 27.3 22.7 24.5 22.6 24.6 25.6 27.3
324T 24.9 26.7 22.1 24.0 22.1 24.2 25.0 26.7
184T 26.0 27.3 20.2 22.9 20.2 22.0 24.3 25.7
213T 25.4 26.7 19.7 22.5 19.7 21.6 23.7 25.2
215T 25.4 26.7 19.7 22.5 19.7 21.6 23.7 25.2
254T 24.6 25.9 19.0 21.9 19.0 21.0 22.9 24.4
256T 24.6 25.9 19.0 21.9 19.0 21.0 22.9 24.4
284T 23.9 25.4 18.5 21.4 18.5 20.5 22.3 23.9
286T 23.9 25.4 18.5 21.4 18.5 20.5 22.3 23.9
324T 23.1 24.6 17.8 20.9 17.8 20.0 21.5 23.2
326T 23.1 24.6 17.8 20.9 17.8 20.0 21.5 23.2
182T 28.6 29.7 N/A N/A 22.2 23.9 27.0 28.1
184T 28.6 29.7 N/A N/A 22.2 23.9 27.0 28.1
213T 27.9 29.1 N/A N/A 21.6 23.4 26.4 28.5
215T 27.9 29.1 N/A N/A 21.6 23.4 26.4 28.5
254T 27.1 28.3 N/A N/A 20.9 22.7 25.5 27.7
184T 30.5 32.3 24.6 26.8 24.6 26.8 24.6 27.0
213T 29.9 31.7 24.1 26.3 24.1 26.3 24.1 26.5
215T 29.9 31.7 24.1 26.3 24.1 26.3 24.1 26.5
254T 29.1 31.0 23.5 25.8 23.5 25.8 23.5 25.9
256T 29.1 31.0 23.5 25.8 23.5 25.8 23.5 25.9
284T 28.5 30.4 23.0 25.3 23.0 25.3 23.0 25.1
286T 28.5 30.4 23.0 25.3 23.0 25.3 23.0 25.1
324T 27.7 29.7 22.4 28.8 22.4 24.8 22.4 25.0
326T 27.7 29.7 22.4 24.8 22.4 24.8 22.4 25.0
182T 30.9 32.1 N/A N/A 24.3 26.0 30.1 31.3
184T 30.9 32.1 N/A N/A 24.3 26.0 30.1 31.3
213T 30.3 31.4 N/A N/A 23.7 25.5 29.4 30.7
215T 30.3 31.4 N/A N/A 23.7 25.5 29.4 30.7
254T 29.4 30.6 N/A N/A 23.0 24.8 28.5 29.8
213T 32.9 34.5 24.5 27.0 27.0 29.1 32.1 33.8
215T 32.9 34.5 24.5 27.0 27.0 29.1 32.1 33.8
254T 32.1 33.8 24.0 26.4 26.3 28.5 31.3 33.0
256T 32.1 33.8 24.0 26.4 26.3 28.5 31.3 33.0
284T 31.5 33.2 23.6 26.1 25.8 28.1 30.7 32.4
286T 31.5 33.2 23.6 26.1 25.8 28.1 30.7 32.4
324T 30.7 32.5 23.0 25.6 25.2 27.5 29.9 31.8
326T 30.7 32.5 23.0 25.6 25.2 27.5 29.9 31.8
364T 30.4 31.8 22.5 25.2 24.6 27.0 29.2 31.1
184T 34.8 36.0 N/A N/A 27.3 29.0 33.9 35.1
213T 34.1 35.3 N/A N/A 26.7 28.4 33.3 34.5
215T 34.1 35.3 N/A N/A 26.7 28.4 33.3 34.5
254T 33.2 34.5 N/A N/A 25.9 27.7 32.4 33.7
256T 33.2 34.5 N/A N/A 25.9 27.7 32.4 33.7
213T 37.4 39.0 28.1 29.1 30.9 33.0 35.8 38.4
215T 37.4 39.0 28.1 29.1 30.9 33.0 35.8 38.4
254T 36.6 38.3 27.5 28.5 30.2 32.3 35.0 37.6
256T 36.6 38.3 27.5 28.5 30.2 32.3 35.0 37.6
284T 36.1 37.8 27.1 28.1 29.7 31.9 34.4 37.1
286T 36.1 37.8 27.1 28.1 29.7 31.9 34.4 37.1
324T 35.3 37.0 26.5 27.6 29.0 31.3 33.6 36.3
326T 35.3 37.0 26.5 27.6 29.0 31.3 33.6 36.3
364T 34.5 36.3 26.0 27.1 28.4 30.8 32.9 35.6
365T 34.5 36.3 26.0 27.1 28.4 30.8 32.9 35.6
184T 40.0 41.4 N/A N/A 31.0 33.2 38.3 39.5
213T 39.1 40.7 N/A N/A 30.3 32.7 37.4 38.6
215T 39.1 40.7 N/A N/A 30.3 32.7 37.4 38.6
254T 38.2 39.9 N/A N/A 29.5 33.0 36.5 37.8
256T 38.2 39.9 N/A N/A 29.5 33.0 36.5 37.8
THF -- Top Horizontal Front
THR -- Top Horizontal Rear
UBF -- Upblast Front
UBR -- Upblast Rear
33

39M UNIT
SIZE
03
06
08
10
12
14
17
25
Table 17 -- Plenum
SUPPLY
STD
STD
STD
STD
STD
STD
STD
STD
STD
RETURN/
EXHAUST
STD
STD
STD
STD
STD
STD
STD
STD
STD
Fan Drive Centerline Distances In Inches
MOTOR MIN MAX
FRAME
56 6.7 7.5
143T 6.7 7.5
145T 6.7 7.5
182T 5.5 6.5
184T 5.5 6.5
56 12.0 13.2
143T 12.0 13.2
145T 12.0 13.2
182T 11.3 12.6
184T 11.3 12.6
213T 10.9 12.2
56 21.2 22.4
143T 21.2 22.4
145T 21.2 22.4
182T 20.8 22.0
184T 20.8 22.0
213T 20.5 22.0
215T 20.5 22.0
143T 25.0 26.5
145T 25.0 26.5
182T 24.6 26.0
184T 24.6 26.0
213T 24.3 25.8
215T 24.3 25.8
254T 23.9 25.5
143T 28.1 29.6
145T 28.1 29.6
182T 27.6 29.1
184T 27.6 29.1
213T 27.3 28.8
215T 27.3 28.8
254T 26.8 28.5
145T 28.1 29.6
182T 27.6 29.1
184T 27.6 29.1
213T 27.3 28.8
215T 27.3 28.8
254T 26.8 28.5
256T 26.8 28.5
145T 31.3 32.8
182T 30.8 32.3
184T 30.8 32.3
213T 30.5 32.0
215T 30.5 32.0
254T 30.1 31.8
256T 30.1 31.8
145T 32.4 33.8
182T 31.9 33.4
184T 31.9 33.4
213T 31.6 33.1
215T 31.6 33.1
254T 31.2 32.9
256T 31.2 32.9
284T 30.9 32.6
145T 35.3 36.8
182T 34.8 36.3
184T 34.8 36.3
213T 34.4 36.0
215T 34.4 36.0
254T 34.0 35.6
256T 34.0 35.6
284T 33.6 35.3
39M UNIT
SIZE
30
36
40
50
SUPPLY
STD
STD
STD
RETURN/
EXHAUST
STD
STD
N/A
MOTOR
FRAME
182T
184T
213T
215T
254T
256T
284T
286T
182T
184T
213T
215T
254T
256T
284T
286T
324T
184T
213T
215T
254T
256T
284T
286T
324T
MIN MAX
38.1 39.6
38.1 39.6
37.8 39.4
37.8 39.4
37.3 39.0
37.3 39.0
37.0 36.7
37.0 38.7
42.8 47.2
42.8 47.2
42.5 46.9
42.5 46.9
42.0 46.5
42.0 46.5
41.7 46.2
41.7 46.2
41.2 45.8
42.9 47.2
42.5 46.9
42.5 46.9
42.0 46.5
42.0 46.5
41.7 46.2
41.7 46.2
41.3 45.8
N/A
STD
N/A
STD
N/A
STD
N/A
STD
N/A
STD
182T
184T
213T
215T
264T
266T
213T
215T
264T
266T
284T
286T
324T
326T
184T
213T
215T
254T
256T
284T
213T
215T
254T
256T
284T
286T
324T
326T
364T
184T
213T
215T
254T
256T
284T
286T
52.0
52.0
51.7
51.7
51.3
51.3
51.7
51.7
51.3
51.3
51.0
51.0
50.5
50.5
49.2
48.8
48.8
48.3
48.3
47.9
48.7
48.7
48.2
48.2
47.9
47.9
47.4
47.4
46.9
51.9
51.5
51.5
50,9
50.9
50,5
50.5
56.5
56.5
56.2
56.2
55.8
55.8
56.2
56.2
55.8
55.8
55.5
55.5
55.1
55.1
53.3
51.9
51.9
52.4
52.4
52.1
51.9
51.9
52.5
52.5
52.1
52.1
51.7
51.7
51.2
55.9
55.5
55.5
55.0
55.0
54.6
54.6
34

Long-Term Storage -- If stoting the unit before instal-
lation, observe the following precautions:
1. Tile storage site should be level, rigid, and flee of debtis. If
the site is in a heavy rain ;uea, set the unit off of the ground.
2. Do not stole the unit in a heavy traffic area or on a vibrat-
ing surface. Vibration can &Lmage stationary beatings.
3. Ensure that all coil connections have shipping caps in
place. Cover the entire unit with a waterproof t;upaulin or
plastic coverall; if the unit is stored on file ground, extend
the cover underneath the unit. Secme the cover with
tiedowns. Do not remove cover or coil end caps until unit
is ready for final installation.
4. Monthly -- Move the coverall, enter the fan section
through the access door or fan inlet, and slowly rotate the
fan and motor by hand. This operation prevents be;uing
corrosion by redisttibuting the bearing grease.
Service Clearance -- When planning the placement of
the unit, ensure adequate space for service access. Typical
service operations can require removing the coils and
filters and accessing the motor and &tmper linkage. Refer to
AHUBuilder® progrmn for recommended clearances.
Drain Positioning -- To prevent build-up of conden-
sate in file drain pan and ensure proper operation of the &ain
system, position the unit so that condensate is properly trapped.
Refer to the Condensate Drain section on page 69 in the Instal-
lation section.
Unit Suspension -- Unit suspension methods are shown
in Fig. 6. A field-supplied platfoml mount is recommended,
especially for larger unit sizes. An iniine twin-bemn mount is
also recommended. Units can also be supported by attaching
suspension rods to all of the lifting brackets on ;dl of the unit
sections that have more than 15 in. of airway length, or by
suspending the unit from cross-beams at the joint between each
unit component. Ensure that suspension rods are secured to
adequately support the unit and that the rods extend entirely
through their associated fasteners.
Internal Vibration Isolation -- Units equipped with
internal vibration isolation must be prepared as described in
this section before they tue inst_dled.
For applications that do not require internal fan isolation,
leave the holddown bracket screwed or bolted in place. Other-
wise, the combination of internal and external unit isolation
could lead to unwanted oscillation magnification.
REMOVING HOLDDOWN BOLTS, AIRFOIL, PLE-
NUM AND FORWARD-CURVED FANS -- Remove the
holddown bolts (Fig. 7) as follows:
1. Open the fan access dooc
2. Remove the bolts that fasten the fan sled to the holddown
bracket. (Fig. 7). Remove "S" shaped brackets.
3. Repeat Steps 1 and 2 on the opposite side of the fan
section. Fan sled assembly should float on isolator
springs when done.
ADJUSTING ISOLATOR SPRINGS -- Units with factory-
supplied motors and diives are preset to 13/16 -I- Us-in. clemance
between the base frame assembly and the bottom panels; field
adjustment of the isolator springs is not normally required.
When adjusting fan isolation components, DO NOT enter
or reach into the fan cabinet while fan is running. Serious
injury can result. Be sure to disconnect power and tag
controls before making adjustments.
LOCATE SUSPENSION RODS
SO THEY DO NOT INTERFERE
WITH ANY ACCESS DOOR/PANEL
(FIELD SUPPLIED)
MOUNT UNIT TO FIELD SUPPLIED
PLATFORM THROUGH
11/16-1N. DIAM HOLE PROVIDED IN
BASE RAIL. REMOVE LIFTING
BRACKETS AS REQUIRED.
CEILING -- RECOMMENDED
PLATFORM MOUNT
CEILING --ALTERNATE
CROSSBEAM MOUNT
CEILING -- RECOMMENDED
IN-LINE BEAM MOUNT
MOUNT UNIT TO FIELD SUPPLIED
BEAMS THROUGH
DIAM HOLE PROVIDED IN
BASE RAIL. REMOVE LIFTING
BRACKETS AS REQUIRED. CEILING -- ALTERNATE
LIFTING BRACKET MOUNT
Fig. 6 -- Unit Suspension
35
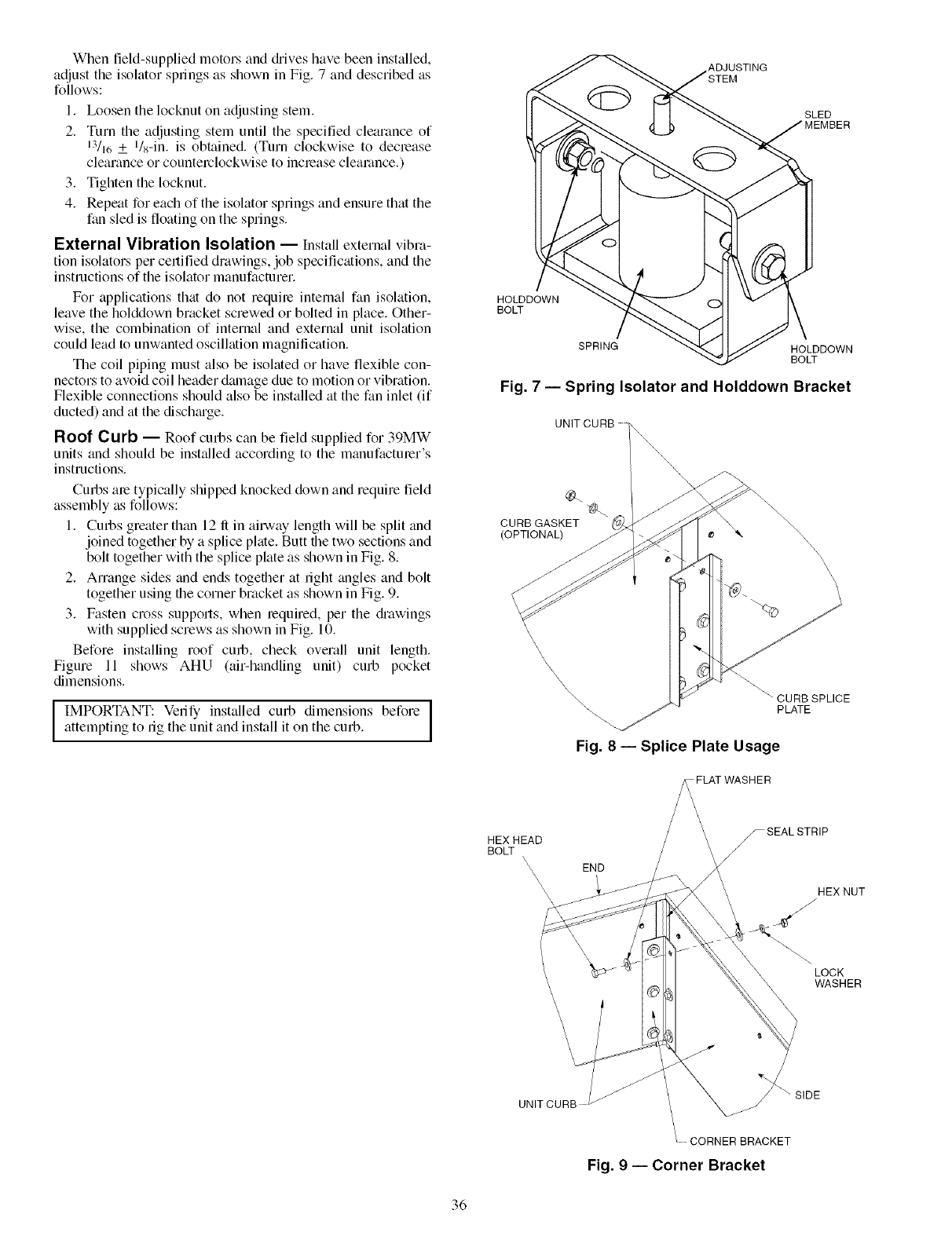
When field-supplied motors and &ives have been installed,
adjust the isolator spdngs as shown in Fig. 7 and described as
follows:
1. Ix_osen the locknut on adjusting stem.
2. Turn the adjusting stem until the specified clearance of
13/l<,+ l&-in, is obtained. (Turn clockwise to decrease
clearance or counterclockwise to increase clearance.)
3. Tighten the locknut.
4. Repeat for each of the isolator springs and ensure that the
fan sled is floating on the springs.
External Vibration Isolation -- Install external vibra-
tion isolators per certified drawings, job specifications, and the
instructions of the isolator manufacturer.
For applications that do not require internal fan isolation,
leave the holddown bracket screwed or bolted in place. Other-
wise, the combination of internal and external unit isolation
could lead to unwanted oscillation magnification.
The coil piping must also be isolated or have flexible con-
nectors to avoid coil header damage due to motion or vibration.
Flexible connections should also be installed at the fan inlet (if
ducted) and at the dischm'ge.
Roof Curb -- Roof curbs can be field supplied for 39MW
units and should be installed according to the manufacturer's
instructions.
Curbs am typically shipped knocked down and require field
assembly as follows:
1. Curbs greater than 12 ll in ailway length will be split and
joined together by a splice plate. Butt the two sections and
bolt together with the splice plate as shown in Fig. 8.
2. Arrange sides and ends together at right angles and bolt
together using the corner bracket as shown in Fig. 9.
3. Fasten cross supports, when required, per the diawings
with supplied screws as shown in Fig. 10.
Before installing roof curb, check overall unit length.
Figure 11 shows AHU (air-handling unit) curb pocket
dimensions.
IMPORTANT: Vedly installed curb dimensions before ]attempting to rig the unit and install it on the curb. I
_,DJUSTING
SLED
HOLDDOWN
BOLT
SPRING HOLDDOWN
BOLT
Fig. 7 -- Spring Isolator and Holddown Bracket
CURB GASKET
(OPTIONAL)
\\\\
\\\\,
\CURB SPLICE
PLATE
Fig. 8 -- Splice Plate Usage
- FLAT WASHER
HEX HEAD
BOLT
\\ \\\
END
SEAL STRIP
HEX NUT
J
\\\\
LOCK
WASHER
UNIT CURB
CORNER BRACKET
Fig. 9 -- Corner Bracket
36

\
UNIT CURB
\\
\\\\\\\\\\
CURB
CHANNEL
Fig. 10- Fasten Cross Supports
o4
Fig. 11 -- Curb Pocket Dimensions
(Size 03-30 Typical)
BUTT JOINTS, DO
Due to the pressure capabilities of the 39 sedes air handlers,
duct connections must be gasketed and screwed to the unit to
prevent leakage. No provisions have been made to attach the
ductwork to the curb. Fabricate inlet and discharge according
to the unit configuration. Dimensions for inlet and disch_uge
locations ale shown in diawings produced in AHUBuilder®
program.
The return and supply ducts must be supported indepen-
dently from the unit. Do not exert weight or downw_ud force on
the unit other than minimal force required to attach ductwoN.
Before the unit is installed, gasketing must be installed
between the curb and unit as shown in Fig. 12. This gasket
material is supplied by the curb manufacturel: If gasket is not
supplied with the curb, recommended field-supplied gasket
matedal is 1/2-in. thick by 2-in. wide closed cell neoprene.
When curb is installed, place gasket on curb without stretch-
ing or overlapping the material, which can cause gaps or leaks.
Butt _dljoints evenly and avoid creating gaps where water can
leak into the curb. Make sum semns in gasket matedal overlap
seams in the curb rail. See Fig. 12 for installation details.
After gasket is in place, rig unit into position as described in
Rigging and Handling section. Ix_cate unit on curb so it is
conectly oriented with respect to curb inlet and disch_uge
locations.
On curb installations, lower unit directly into place, ensur-
ing that the roof curb gasket does not shill or curl.
Pier or Beam Mount--As an _dternative to curb
mounting, units can also be mounted on I-bemns or piers. For
units mounted on I-beams, the beams must run the continuous
length of the unit. If seismic criteria apply, crosspieces must be
added between the beams according to seismic calculations.
For pier-mounted units, one pier must be installed in each
corner of the unit at the junction of the baserail comers. A
minimum of 4 piers can be used for size 03-61 units up to 8 II
long.
For each additional 8 II of length for size 03-61 units, inst_dl
one additional pier on each side of the unit underneath the
basemils. See Fig. 13 for a typical installation.
GASKET SEAM
RAIL SEAM
/
RAIL SEAM
WRONG METHOD
/
/GASKET SEAM
RIGHT METHOD
Fig. 12 -- Install Gasketing
37

BEAMMOUNT
PIERMOUNT*
(
7 r
*Minimum number of piers shown for pier-mounted unit. See
table on right for number of equally spaced piers required.
Foreach additional 8 ft of unit length, add 2 piers.
QUANTITY OF PIERS REQUIRED
UNIT LENGTH "L", FT
0-8 I9-16 17-24
4 I 6 8
Fig. 13 -- Pier or Beam Mounting
INSTALLATION
This section describes how to install 39M units, compo-
nents, and component p_uts. Units specified on a single order
are shipped with most components assembled in the specified
airflow direction. The assembled unit is attached to a single
shipping skid (30-ft maximum length). When an upper compo-
nent exceeds the 108-in. maximum height limit, it is shipped
out of its operating position on the unit skid or on a separate
skid. Some component paris also require assembly or adjust-
ment; see the section on each component type for specific
instructions.
Indoor Unit/Section Connection -- Indoor units _u'e
connected together using 2 different methods -- screws and
"T' latch cam latches. Refer to Fig. 14 and 15 for T-latch
assembly details. Connect units as follows:
1. Remove shipping plates from entering and leaving face
of sections. Replace 2 screws in baserail directly under
corner feet only. otherwise 2 inboard screws will not
allow a flush connection. See Fig. 16.
2. Rig and align units so that sides and tops are flush and
holes are aligned.
3. Fasten base rails together at the lifting brackets using
supplied h_udware.
4. Indoor units secured with "T" latches: Turn "T" latch
(indicated by red hex socket access) clockwise using a
5/16-in. hex wrench until latch fully engages. The latch
rotates 270 degrees. The first 90 degrees of rotation
positions the T-latch into a se;ding position on the fralne.
The second 180-degree rotation pulls the T-latch tight,
compressing the gasket which creates the frmne se_d.
Do not overtighten, damage to latch could occm: The latch
is not intended to pull units together over a distance. Latch
is designed for retention after units have been positioned
properly and only after base lails have been secured.
NOTE: [f T-latch becomes &_maged o1"inoperable, fasten sec-
tion frmnes using clearance and engagement holes located
below latch.
5. Units secured with screws: Remove side and top panels
flom unit by turning panel latches (indicated by black hex
socket access with arrow indicator). Fasten and secure
base rails.
NOTE: Upstream sections have a l-in. cle_uance hole on the
inner surface of the frame member to provide access to the
5/l(,-in. fastening screw hole.
38

6. Insertscrewthroughtheseholestoengagematinghole.
Followperimeterofunitandsecure.
7. Re-inst_fllpanelsandsecurepanellatches.Thepanel
latchincorporatescamactiononeachedge(topand
bottom)tosecurethepanel.SeeFig.17.Thepanellatch
assemblyhasa90degreerotationwitha clickdetent
featurethatdetentsat0and90degrees.Thearrowindica-
tor displays the latch position.
COMPONENT COMPONENT
SECTION A SECTION B
DETAIL A
Fig. 14 -- T-Latch Assembly
_ 'ENGAGEMENT
HOLE
Fig. 15 -- T-Latch Receptacle (End View)
DETAIL B
SEE FIG. 17
SIDE PANEL
I
Fig. 17- Panel Latch Assembly
NOTE: Panel latches have an indicator anow highlighted in
the face of the latch and that arrow must point tow_ud the panel
to assure that panel is fully secured. Ensure the latch arrow is
in its proper position prior to unit start-up.
Outdoor Unit -- Outdoor units are either shipped in one
piece or with minimal shipping splits. Refer to the shipping
split label attached to the unit.
DETAI L C
DETAIL B
FRAME MEMBER DETAIL
jSHIPPING
PLATE
Fig. 16 -- Section Frame Assembly
39

Duct Connections
MIXING BOX/INLET PLENUM/DISCHARGE PLE-
NUM --Attach the ductwork to the box fi'alne rails with
sheet metal screws as shown in Fig. 18. Ductwork should be
flanged out as close to the dmnper frmned opening as possible.
Screws with weatherproof washers and a bead of silicone
around the duct flange must be used for outdoor applications.
Do not remove the screws retaining the c_kLmperfi:Lme; the
dmnper will fall out.
MIXING BOX/INLET PLENUM (Bottom) -- Bottom damp-
er equipped air-handling units have tin insulated dmnper duct
connection sleeve fllat extends to the bottom of the basenill on
39MN indoor units and to the cm_o pocket on 39MW outdoor
units.
For indoor units, apply I/2 in. thick by 1 I/2 in. wide closed
cell neoprene gasketing or run a bead of silicone to the damper
duct flange. Flange the ductwork out no more than 11/4 in. and
screw file flanged ductwork to the &tmper duct flange under
the unit.
For curb mounted outdoor units, refer to the curb submitttd
drawings. Return ductwork may be flanged outward and
attached to the roof curb. Field-supplied stiffeners may be
required to properly support the long edges of the duct. Apply
1/2in. flfick by 11/2in. wide closed cell neoprene gasketing or
run a bead of silicone to the damper duct flange.
FAN DISCHARGE CONNECTIONS (Except Plenum
Fans)--Dischm'ge tfir ducts must be attached directly to the
discharge side of the unit. This applies to both indoor and
outdoor units! Use care when making turns and transitions in
ductwork to avoid excessive air fiiction. Duct elbows should
contain turning vanes. See Fig. 19.
Dnctwork connected to the fan discharge should run in a
straight line for at least 2.5 times the outlet diameter dimen-
sions and should not be reduced in cross-section. See Fig. 20.
Duct turns should be in file salne direction as fan rotation to
minimize any negative system effects.
Apply 1/2 in. thick by 11/2 in. wide closed cell neoprene
gasketing or run a bead of silicone mound the fan discharge.
Fltmge the ductwork out no more than 11/4 in. and screw the
flanged ductwork to the fan discharge.
BOTTOM RETURN FAN CONNECTIONS -- Return tfir
ducts must be attached directly to the return side of the unit.
This applies to both indoor and outdoor units! Use care
when making turns and transitions in ductwork to avoid exces-
sive tfir friction. Duct elbows should contain turning vanes. See
Fig. 19.
PLENUM FAN DUCT CONNECTIONS -- Plenum fans tue
designed for draw-thru or blow-thru operation. Draw-thru fan
sections have closed panels on _dl sides except for the fan inlet
side. On blow-thru fan sections, the panel on file end opposite
the inlet is omitted so that components such as coil or filter
sections can be added downstremn fiom the plenum fan.
DRAW-THRU PLENUM FAN DISCHARGE FABRICA-
TION -- Duct openings for draw-thru plenum fans must be
field fabricated. They should be located in the plenum fan sec-
tion according to the following guidelines:
• Locate discharge openings in side or top panels; the end
panel opposite the inlet will have a higher pressure drop
per the explanation in the 39M Product Data manual.
• Locate discharge openings on the side or top panels
between the fan wheel and end panel opposite the inlet.
Do not locate discharges in the direct path of airflow
flom the wheel.
•Avoid locating the discharge opening on the motor side
of the fan section. If a discharge on the motor side is
necessary, locate the opening near the top of the cabinet.
• Sizes 36-61 include intermediate frame members. When
cutting the discharge opening for the plenum fan, do not
cut through any intermediate frame membec
Typical duct locations are shown in Fig. 21.
Once the discharge locations are selected and cut, the
duct connections can be fabricated. Install field-supplied duct
flanges and frmning channels to smooth the airflow leaving the
discharge opening. Two of the channels should extend the
width or height of file cabinet to provide additional cabinet
support.
Fig. 18- Mixing Box Ductwork Attachment
NOTLESS
THAN
2-1/2
FAN DIA.
l,,.%1J
/
T______URNIN G
VANES
I
_--i
I I
I I _ AIRFLOW
I I
I I
NOTE: Make turns in the same direction as fan rotation.
Fig. 19- Recommended Discharge Duct
Arrangement When Turns are Required
NOT LESS THAN 2-1/2
FAN DIA.
SUPPLY DUCT
DUCT TRANSITION
30°
MAXIMUM
Fig. 20 -- Duct Connections
40

FIELD _SUPPLIED DUCTWOR t
J
/
A
_.A
UNIT OUTER CASING
FIELD FABRICATED ANGLES
FOR DUCTWORK CONNECTION FIELD FABRICATED SUPPORT CHANNELS
AS REQUIRED PER OPENING SIZE OR
LOCATION
INSULATION /' AIRFLOW
INTERNAL DOUBLE WALL PANEL
SECTION A-A
Fig. 21 -- Discharge Fabrication, Draw-Thru Plenum Fans
41

Panel Cutting -- The 39M unit's double-wall foam-filled
panels require speci_d attention when cutting and or penetrating.
1. Take ctu'e in planning before penetrating any panel with
electrical conduit, hydionic piping, sensor pickups or
wiring. Once these are routed through a panel, for _dl
practiced purposes, it becomes a fixed panel that is not
easily removed for service access.
2. In some cases it will be possible for smaller conduits
(l/2-in. or 3/4-in.) to enter the cabinet where individual
sections are joined togethel: Inspect the selected area
ctuefully to be certain that you do not encounter panel
kitches, "T-kitches," or section joining screws. Once the
conduit is in place, it must be securely sealed, watertight
and airtight, to prevent ANY infiltration.
Penetrations tu'e typic_dly located in one of the existing
"fixed" panels, such as the fan discharge panel, or the coil
connection panel to maximize the number of removable/
service panels. When it is necessary to penetrate the panel
for wiring or piping entry, make certain that the entry
point will not interfere with future component servicing,
block access doors, or obstruct airflow.
3. Drill a small pilot hole completely through the panel.
4. Use of a sharp hole saw or, if appropriate, a Unishea( r_'_
cutting tool or sheet metal nibbler to cut the hole or open-
ing from each side.
Do not use a cutting torah or open flmne on or near the fan.
Dmnage to the panel may occm:
5. Camlully remove the foam. The hole should be lined or
sleeved to confine the foam, and the penetration should
be sealed, both inside and out, to eliminate all possibility
of infiltration or leakage.
NOTE: Small quantities of locally available commerci;d
canned foam may be used, if necess;uy, to complete minor
repairs. Significant patching may justify ordering replacement
panels instead.
Zone Damper Section -- Refer to Fig. 22 and install
the section as follows:
1. Remove the screws holding the zone damper section to
the heating coil section and remove the lag screws hold-
ing the damper to the shipping skid.
2. Place the supplied I/4-in. thick x 1l/:-in, gley fomn gasket
around the perimeter of the cooling and heating coil section
discharges. Use two gasket strips on partition panels to ob-
tain double width.
3. Rig the zone damper section and lift it into position on
(vertical discharge) or next to (horizontal discharge) the
gasketed cooling and heating coil sections.
4. Fasten the &_mper section to the coil sections using the
supplied I14-14 x 314-in.sheet meted screws.
5. Install control shaft and bearing for each individual
zone after cutting linkage (for the job specific zone
application).
Control shaft extensions gue bagged and wrapped to the
inside of the zone dmnper blades. Additional field-
supplied shaft extensions may be ordered from local
Ruskin suppliek Dut no. 10-020569-00B.
6. Zones should be split for equal airflow through each
dampel:
Face and Bypass Dampers -- All face and bypass
damper sections are shipped fully asselnbledi Hat channels are
necessary for damper support. DO NOT remove (see Fig. 23).
Unit sizes 03-12 are built with a single damper assembly,
sizes 14-61 have two dmnper assemblies linked via a jackshaft.
Damper cmnkarms have 90 degrees of travel from fully open
to fully closed positions and are adjustable to suit conditions.
Refer to Fig. 24 and 25 for details.
Actuators must be mounted directly to the &_mper shaft.
Removed of crankarms is necessary for direct connection actua-
tor use. Refer to Table 18 for operating torque requirements.
FactoUduct colku's and damper assemblies are for attach-
ing ductwork only and must NOT be used to support the
duct's weight. Weight beguing deflection can increase
torque necessgu-yto operated dmnpers, or bind them pro_
venting aW movement.
ZONE DAMPER ASSEMBLY, ...... 7.---",
VERTICAL DISCHARGE --_--,-_..r,-----_ _._ ..... '1
POSITION _ '
COIL SECTION _
FAN SECTION __
DUCT WORK DUCT CLIP ZONE DIVIDER
"W" STRIP TO ATFACH
ZONE DUCTWORK-SEE
[ DETAIL
HOT/COLD DECK CUT BAR TO
PARTITION PANEL SEPARATE
ZONES
ZONE DAMPER ASSEMBLY
HORIZONTAL D SCHARGE
POSITION
ATTACH FOR
EACH ZONE
(RUSKIN PART NO. 10-020569-00B)
"W"STRIP
DETAIL
Fig. 22 -- Zone Damper Assembly Details (Horizontal Discharge Shown)
42

HAT CHANNEL
Fig. 23 -- Face and Bypass Section Detail
ZONE DAMPER DETAILS
39M UNIT SIZE DIMENSIONS(In.) OTY OF ZONES
AB C
06 28.50 41.50 12 S
08 28.50 49.50 12 7
10 28.50 62.50 12 10
12 34.50 62.50 15 10
14 34.50 67.50 15 10
17 34.50 74.50 15 12
21 40.50 74.50 18 12
25 40.50 81.50 18 13
30 40.50 99.50 18 16
36 52.50 104.50 24 17
40 52.50 104.50 24 17
50 56.50 112.50 26 18
61 68.50 112.50 32 18
OTY OF EXTENSION SHAFT KITS
4
4
6
6
6
7
7
8
10
10
10
12
12
FACE VIEW
7
q t pIZ BLANKOFF
PLATE
SECTION A-A
NOTE: All dimensions in inches unless otherwise noted,
AIR
FLOW
END VIEW
TOP VIEW
Fig. 24 -- Zone Damper Section Details
43

MIXINGBOX,EXHAUSTBOX,ANDEXTERNAL
BYPASSDAMPERDETAILS
UNIT SIZE
03
06
08
10
12
14
17
21
25
30
36
40
50
61
DETAIL (SECTIONS) JACKSHAFT DIAMETER (In.)
1 25.75 10.75 1/2
1 38.75 14 1/2
1 46.75 14 1/2
1 59.75 14 1
1 59.75 14 1
2 64.75 16.75 1
2 71.75 16.75 1
2 71.75 20 1
2 78.75 20 1
2 96.75 20 1
3 101.75 29 1
3 101.75 32 1
3 109.75 35 1
3 109.75 44 1
AAq
• ° • ° • *I _'
/
-u j!
A i
DETAIL 1
FACE VIEW
UNIT SIZE
03
06
08
10
12
14
17
21
25
30
36
40
50
61
SIDE DAMPER DETAILS
DETAIL (SECTIONS) JACKSHAFT DIAMETER (In.)
1 14 18 V2
1 20 26 V2
1 20 29 V2
1 26 29 1
1 26 36 1
1 32 36 1
2 32 39 1
2 32 49 1
2 38 49 1
2 44 49 1
2 50 60 1
2 50 66 1
2 56 76 1
3 56 91 1
A A
(j 2 ,
AJ-J
DETAIL 2
FACE VIEW
A _
!O.
i_ .I
--_d
_1..i
SECTION A-A
1/2-in, JACKSHAFT
PREMIUM DAMPER
[]" .... [] ,o..... []'
.I,_I..44"Iu .I,H,
. . 7_io
[] [] [] [] []
° ° _llP_°_'° °
DETAIL 3
FACE VIEW
1 1/2
--T
AIRFOIL
-BLADES
/TO OPEN
B AIRFOIL
C_ BLADES
°_ TO OPEN
BRA
SECTION A-A
1-in, JACKSHAFT
PREMIUM DAMPER
AIR
FLOW
I--5"'--1_ L
TO OPEN
/
% If
°_]
B
SECTION A-A SECTION A-A
1/2-in, JACKSHAFT 1-in, JACKSHAFT
STANDARD DAMPER STANDARD DAMPER
STANDARD
f BLADES
/TO OPEN
¢
RIGHT SIDE VIEW
NOTE: All dimensions in inches
unless otherwise noted.
Fig. 25 -- Mixing Box, Filter Mixing Box, Exhaust Box and External Bypass Damper Details
44

Mixing Box/Filter Mixing Box Damper Linkage
It is important to properly link the outdoor air and return air
dampel_. Failure to do so may cause mixing problems,
stratification, or coil freezing under some conditions, espe-
cially in combination type filter mixing boxes.
Refer to Fig. 26 for typical damper _m'angement and con-
necting rod position.
CONTROL DAMPERS -- Control dampers may be operat-
ed with pneumatic or electric actuators. These items should be
set up in accordance with the control manufactmers installation
instructions.
DAMPER LINKAGE ADJUSTMENT-- After the air-
handling unit has been powered, the dampers should be
checked to ensure they move freely and close tightly, adjust-
ment of the linkage may be required.
LINKAGE ADJUSTMENT
1. With the damper actuator unpowered and the damper
linkage disconnected, rotate the outdoor air dmnper so
that it is fully closed. Make sure the spring return actuator
has completed its stroke (with power disconnected this
will be achieved). The return air damper should be lidly
open at this point.
2. Tighten the actuator on the damper jackshaft, ensure all
linkage is connected, secure and moves freely.
3. With power applied to the actuatol: check for a complete
stroke and free movement in the dampers and damper
linkage.
Dampers and linkage must be checked prior to applying
powel: Make certain that there are no obstructions that
could interfere with the operation of the dampers.
NOTE: While adjusting linkage, one damper must be lidly
open and the other fully closed.
Top and rear dampers me shipped with both dampers in
closed position. Ix)osen the swivel on the interconnecting link-
age bar and fully open rear dmnper, leaving top dmnper closed.
Retighten the swivel.
Certain dmnper combinations require that dual actuators or
bellcrank linkages be field-provided when jack shafts are
90 degree opposed. This may occur when there is a combina-
tion of end dampers with either top or bottom dampers.
FIELD SUPPLIED AND INSTALLED ACTUATORS --
If one or two actuators are used, they must be mounted to the
outdoor-air damper jackshaft. To properly set the connecting
linkages, determine the rotation required to open the outdoor-
tdr dampel: Ensure the actuator spring return fully closes the
outdoor-air dampel:
If more than 2 actuators are used, they must be installed in
equal numbers on each jackshaft. To properly set these damp-
ers, determine the rotation required for each damper and mount
the actuatol_ so that the spring feature will open the return air
damper and close the outdoor-air dampel: Ix)ck each damper
actuator to the jackshaft. Remove any factory-supplied con-
necting linkage between the outdoor air and return-tdr damp-
ers. Failure to do so will damage the actuatol_. No additional
linkages are required for these applications.
Exhaust damper boxes me shipped with dampers in the
closed position.
All dmnper cmnkarms have 90 degrees travel from open to
closed. They may be adjusted to suit actuator location.
DO NOT mount damper actuators on the unit panels, actua-
tors me shaft mount only. See Table 18 for operating torque
requirements.
ZONE DAMPER LINKAGE (Fig. 22 and 24) -- Note that
damper control levers and a common operating bin are factoly
installed on upper end of damper shafts on top of zoning damp-
er assembly. To facilitate the installation of field-supplied
damper operators, the operating bar may be cut and the control
levers repositioned as follows:
Damper operation may be impaired if ductwork is
supported by the unit.
1. Check job prints to determine number and size of zones
required and damper operator locations.
2. Cut and remove portion of operating bar between zones
as required.
3. Inst_fll actuators on field-fabricated support brackets.
Connect actuator linkage to the center axle of intercon-
necting zones.
4. Adjust actuator for correct damper operation. Be sure
actuatol: linkage, and dampel_ operate fieely. See
Table 18 for operating torque requirements.
Mixing Box Damper Actuators-- The 39M mix-
ing boxes can be supplied with direct mounted dmnper actua-
tors. Refer to Fig. 27 for typical actuator mounting. Actuators
me also available for field installation. See Field Supplied and
Inst_flled Actuators section for more information. Refer to
Table 18 for damper operating torque.
To ensure torque is transmitted equally to both damper sec-
tions, actuator must be connected to the jackshaft that diives
the interconnecting linkage bin: Connection to any other shaft
is not lecommendedi
Table 18 -- Damper Operating Torque (Ib)
39M UNIT SIZE
COMPONENT 03 06 08 10 12 14 17 21 25 30 36 40 50 61
Zone Damper -- 4 4 4 5 5 5 5 5 5 7 7 8 10
Mixing orExhaustBox 13 26 32 41 41 53 58 70 77 94 143 158 187 235
Side MixingorExhaustBox 12 25 28 37 46 56 61 76 91 105 146 160 207 248
Airflow Measuring Damper 5 9 9 9 16 16 16 29 29 29 N/A N/A N/A N/A
Internal Face and Bypass 21 32 45 57 78 85 103 129 142 174 195 232 251 304
External Face and Bypass 29 44 59 76 96 104 126 161 176 217 282 312 390 470
NOTES:
1. Damper shaft moves 90 degrees from open to close.
2. Operating torques is shown for one damper. Multiply the value shown by the number of dampers for
total with one actuator.
45

DIRECT COUPLED
ACTUATOR
(SIDE MIXING BOX)
ACTUATOR AND
JACKSHAFT ARE
REPRESENTATIVE
ONLY (TYPICAL)
ONE ACTUATOR
ONLY WHEN USED
WITH LINKAGE -_
AIR
FLOW
TOP & REAR OR
SIDE & REAR
LINKAGE
ASY
TOP & BOTTOM OR
SIDE & SIDE
AIR
'_ LINKAGE
ASY
LOCATION
TYPICAL
ROTATIO
TO OPEN
ROTATI(
[.TO OPE
REAR & BOTTOM
.__.. LINKAGE
ASY
AIR
. >ROTAT'O
TO OPEN
AIR
ROTATION
TO OPEN
AIR
ROTATION
TO OPEN
REAR ONLY BOTTOM ONLY TOP ONLY
Fig. 26 -- Mixing Box/Filter Mixing Box, Typical Damper Arrangements (Size 14 Shown)
[ DIA JACKSHAFT
i-=-_r_ _ I BNLY
zr !
Fig. 27 -- Typical Mixing Box Actuator Mounting
46

Vertical Draw-Thru Units
NOTE: Size 21-61 vertical units that exceed the 108-in. maxi-
mum height or units with a vertical fan shipping split are
shipped with the fan out of its operating position, separate from
the vertical coil section. See Fig. 28A and 28B.
The unit is secured to a wooden skid with lag screws.
Remove screws before lifting the unit.
NOTE: Do not remove the fan holddown bolts until the section
is instaUed on the coil section.
1. For units with baserail, remove the 4 brackets securing
the top panel of file cooling section and reposition them to
the existing holes with the long flange in a vertical posi-
tion flush with the outer panel.
2. Attach the I/8-in. thick by 3/4-in. wide gray gasket
supplied with the unit to the top perimeter opening of the
vertical coil section.
3. For units with baseraU, attach joining collar (supplied
wifll unit) to top dischmge opening using hardware
included with unit.
4. Rig the fan section using the lilting brackets and place it
on top of the coil section.
NOTE: For units with basemil, the 4 brackets that were
repositioned emlier should be aligned with the appropriate
slots in the base rail of the fan section. Before setting the fan
section on the coil section, remove right and left side panels
from coil section.
5. For units without baserail, locate 1-in. tool clearance hole
in underside of top rail of coil section on each side.
6. Insert a pin or punch to assist alignment of corresponding
holes of fan section while lowering fan section, if needed.
7. Secure the fan and coil sections together using the sup-
plied I14x 314-in.long sheet metal screws. The securing
points will be on the bottom of each side and front top rail
of the coil section for units without baserail (Fig. 28B).
For units with baserail, securing points me located in the
side of the baserail (Fig. 28A).
NOTE: Do not remove the front panel of the coil section until
the side panels _uereinstalled. Secure brackets from top of coil
section to fan section base rail using 2 screws each.
VERTICAL FAN SECTION
"_BRACK[T
I)ETAIL Y
SCALE: {:4
ASSEMBLEDPOSITION
OF BRACKET SEE DEFA}L ys
WHENUNIT IS SN{PPgO
Ok ASSEMBLED STACK{D
_BASE RA{ ASS[MB Y
_JOINING COLLAR FOR
VERIICAL SUPPLY _AN
.......VERTICA{ COl/
SECT{ON
BE]AIL X
SCALE 1:4
ASSEMBLED_OSII}ON
OF BRACKEF
WHENVERIICAL FAN SECTION
IS SNIPPE_ SEPARATE
\_ BASE RAI{ ASSEmBlY
Fig. 28A -- Vertical Fan Installation with Baserail
47

REMOVE LIFTING BRACKETS AFTER
ASSEMBLING THE UPPER SECTION
TO THE LOWER SECTION
USE PLUG BUTTONS (BAG ASSEMBLY
39MA42000901 ) TO FILL SCREW
HOLES IN FRAME. _" /
PLACE GASKET ON LOWER SECTION
BEFORE SETTING UPPER SECTION
UNTO LOWER SECTION
USE 1/4-14 X 3/4 LG
SHEET METAL SCREWS
TO FASTEN UPPER
Fig. 28B -- Vertical Fan Installation without Baserail
Fan Sled Disassembly -- In some cases, it may be
necessary to remove the fan sled fiom the unit and break it
down into smaller components. See Tables 19-21 and Fig. 29
for maximum complete fan sled dimensions and housing only
dimensions.
To remove the fan sled:
1. Remove all of the panels from the fan section except for
the fan discharge panel.
2. Disconnect the vibration absorbent discharge seal by
unscrewing the seal channels fl'om the discharge of the
fan housing. Remove the fan discharge panel.
3. On larger units, the fan sled may be extremely heavy.
Remove file top and vertical frame members of the fan
section by removing the 4 screws from each frame to
corner piece connection.
4. If complete fan sled removal is required, unscrew bolts
holding the isolator base to the bottom of the unit.
5. Disassemble fan and fan housing in place and/or affix
appropriate rigging to remove tile required components
noting diagrammatically where each component is
attached. Components should be removed in the follow-
ing order:
a. Belts and sheaves
b. Motor
c. Fan shall
d. Fan wheel (forward curved fan wheels are
removed through the fan discharge opening, airfoil
wheels are removed through the side of the hous-
ing after removal of the drive side inlet volute)
e. Fan housing
NOTE: Install the preceding components in the reverse ordel:
48

Fan Sled Dimensions -- See Tables 19-21 and Fig. 29
for Fan Sled dimensions.
UNIT
SIZE
39M
03
06
08
10
12
14
17
21
25
30
36
40
5O
Table 19 -- Airfoil Fan Dimensions (in.)
ARRANGEMENT
FAN SLED ASSEMBLY FRAMED BLOWER
(See Fig. 29) WITHOUT SLED
Length Width Hei_lht Len_lth Width Hei_lht
All 35.5 23.5 28.8 18.6 21.0 21.9
All 36.5 33.5 28.7 22.4 24.0 26.8
All 29.8 45.5 31.8 24.6 26.3 29.3
All 29.8 58.5 31.8 24.6 26.3 29.3
All 35.8 58.5 38.8 29.6 30.3 36.0
All 41.8 63.5 38.8 29.6 30.3 36.0
All 41.8 70.5 41.8 32.5 33.8 39.6
All 41.7 72.0 51.8 35.9 36.5 43.6
All 53.8 77.5 51.8 39.5 39.8 48.1
All 53.8 95.5 51.8 39.5 39.8 48.1
Supply Std 56.3 100.5 62.8 43.8 43.3 52.8
Ret/Exh Std 56.3 100.5 62.8 47.8 48.5 58.1
Supply Std 62.3 100.5 68.8 47.8 48.5 58.1
Ret/Exh Std 62.3 100.5 68.8 52.9 53.0 64.9
Supply Std 68.3 108.5 78.8 52.9 53.0 64.9
Ret/Exh Std 68.3 108.5 78.8 57.9 57.5 71.0
Supply Std 74.3 108.5 93.8 57.9 57.5 71.0
Ret/Exh Std 74.3 108.5 93.8 65.9 62.8 78.8
NOTE: Different fan discharge positions have different dimensions.
The values shown are for the largest overall dimensions.
Table 21 -- Plenum Fan Dimensions (in.)
UNIT
SIZE
39M
03
06
08
10
12
14
17
21
25
30
36
40
5O
61
ARRANGEMENT
All
All
All
All
All
All
All
All
All
All
All
Supply Std
Ret/Exh Std
Supply Std
Ret/Exh Std
Supply Std
Ret/Exh Std
FAN SLED ASSEMBLY
(See Fig. 29)
Length Width Height
41 .O 26.4 23.7
42.5 36.0 26.2
24.8 46.5 29.1
26.3 53.3 31.3
30.1 58.3 36.7
30.1 58.3 36.7
32.6 62.5 40.1
38.3 66.3 41.4
42.3 70.3 45.4
41.0 75.8 48.9
48.9 91.4 54.4
48.9 91.4 54.4
48.9 91.4 58.3
57.4 99.4 58.4
57.4 99.4 64.0
57.4 99.4 64.0
57.4 99.4 70.0
Table 20 -- Forward Curve Fan Dimensions (in.)
UNIT
SIZE
39M
03
06
08
10
12
14
17
21
25
30
36
40
5O
61
FAN SLED ASSEMBLY FRAMED BLOWER
ARRANGEMENT (See Fig. 29) WITHOUT SLED
Length Width Height Length Width Height
All - Horizontal 17.5 26.0 20.2 16.7 15.1 16.7
All - Vertical 34.0 25.0 20.2 16.7 15.1 16.7
All - Horizontal 23.5 39.0 22.6 18.6 18.8 18.6
All-Vertical 34.0 25.0 22.1 18.6 18.8 18.6
Sup/Ret Std 28.5 47.0 25.1 21.6 23.9 21.6
Supply Small 28.5 47.0 20.6 18.6 18.8 18.6
Sup/Ret Std 28.5 60.0 29.0 25.5 27.9 25.5
Supply Small 28.5 60.0 23.6 21.6 23.9 21.6
Sup/Ret Std 34.5 60.0 30.2 25.5 27.9 25.5
Supply Small 34.5 60.0 25.8 21.6 22.9 21.6
Sup/Ret Std 40.5 65.0 35.1 30.4 32.5 30.4
Supply Small 40.5 65.0 30.2 25.5 27.9 25.5
Sup/Ret Std 40.5 72.0 35.1 30.4 32.5 30.4
Supply Small 40.5 72.0 30.2 25.5 27.9 25.5
Sup/Ret Std 40.5 72.0 42.7 38.0 33.3 38.0
Supply Small 40.5 72.0 30.2 25.5 27.9 25.5
Sup/Ret Std 52.5 79.0 43.2 38.0 33.3 38.0
Supply Small 52.5 79.0 43.2 38.0 30.3 38.0
Sup/Ret Std 52.5 97.0 43.2 38.0 37.3 38.0
Supply Small 52.5 97.0 43.2 38.0 35.3 38.0
Sup/Ret Std 53.8 100.5 62.8 46.8 43.5 46.8
Supply Small 53.8 100.5 62.8 41.5 39.8 41.5
Sup/Ret Std 53.8 100.5 68.8 46.8 43.5 46.8
Supply Small 53.8 100.5 68.8 46.8 38.5 46.8
Sup/Ret Std 58.3 108.5 78.8 51.5 52.3 51.5
Supply Small 58.3 108.5 78.8 51.5 46.8 51.5
Sup/Ret Std 56.8 108.5 93.8 55.5 54.3 55.5
Supply Small 56.8 108.5 93.8 51.5 52.3 51.5
Fig. 29 -- Fan Sled
49

Fan Motors and Drives -- When installing motors in
the field, locate the electrical junction box tow;ud file center of
the unit. This ammgement is required for correct belt tension.
Use the smallest mounting holes in the mounting base that will
accommodate the motor and provide minimum oveflmng.
Tighten the motor holddown bolts. Refer to Tables 2A-2D
for fan scroll inlet cone dimensions.
JUNCTION BOX CONDENSATE PREVENTION --
When air handlers ale installed outdoors in a high humidity
environment or indoors whele the apparatus room is used as a
fi'esh air plenum, precautions must be taken to prevent conden-
sation from forming inside the junction box of the internally
mounted motor.
Stan&ud installation practice is to mount the motor starter
or fused disconnect box adjacent to the air handler and enclose
the power wiring to the motor in flexible conduit.
The sheet metal housing of the disconnect switch or motor
strutter is not airtight (even when a box meeting NEMA
[National Electrical Manufacturel_ Association] IV stan&uds
is used). Thus, warm moist air can migrate through the flexible
conduit to the junction box on the motol: With the motor
located inside the unit, the motor temperature is that of the cool
supply air; thus, condensate can form inside the junction box
and, possibly, on the live terminal lugs.
To prevent the moist air from migrating through the conduit
to the motor, seal the power wires inside the flexible conduit at
the motor starter or fused disconnect (Fig. 30).
Use a nonconductive, non-hmdening sealant. Permagum
0nanufactuled by Schnee Morehead) or sealing compound,
thumb grade 0nanufactured by Calgon), tue acceptable materials.
SEAL AIRTIGHT FLEXIBLE CONDUIT
DUIT
FUSED DISCONNECT TYPICAL MOTORS
Fig. 30 -- Sealing Power Wires in Flexible Conduit
Motor Power Wiring--The fan section is provided
with a decal indicating the recommended location to drill or
punch hole(s) to accommodate an electrical conduit for the
fan-motor wiring. The decal is located on file motor side,
approximately 4-in. in fiom the side and 4-in. down fi_)m the
top of the corner above where the motor will be installed.
Where possible, the conduit should be installed in a panel
which will not be removed, such as the discharge panel.
MOTOR OVERLOAD PROTECTION -- Fan-motor start-
ers and overload protectors me field-supplied and installed. A
label on the fan motor indicates the correct size of the overload
protectors required to be installed in file motor startel:
Sheaves- Factory-supplied drives are pre-aligned and
tensioned, however. Carrier recommends checking the belt
tension and alignment before staffing the unit. Always check
the drive alignment after adjusting belt tension.
To install sheaves on the fan or motor shaft, remove any
rust-prevenfive coating on the shaft. Make sure the shaft is
clean and fi'ee of burrs. Add grease or lubricant to bore of
sheave before installing. Mount sheave on the shaft; to prevent
bearing damage, do not use excessive force (i.e., a hmnmer).
Place sheaves for minimum overhang (see Fig. 31).
Each factory-assembled fan, shaft, and chive sheave assem-
bly is precision aligned and balanced. If excessive unit vibra-
tion occm_ after field replacement of sheaves, the unit should
be rebalanced. To change the drive ratio, reselect and replace
the motor sheave, not the fan sheave.
FAN
SHAFT ,d
D_VE !
SHEAVE
EXCESSIVE
OVERHANG -
/SHAFT BEARING
DRIVEN SHEAVE
-'11 OVERHAHG
-_ MOTOR /
POOR INSTALLATION
MINIMUM
OVERHANG
/
MINIMUM
OVERHANG _- ,=
r--]
MOTOR 1
BETTER INSTALLATION
Fig. 31 -- Determining Sheave-Shaft Overhang
After 24 hours of unit operation, the &'ive belts may stretch.
Check the belt tension after 24 hours of operation and adjust if
necessary. Periodically check belt tension throughout the run-in
period, which is normally the initial 72 hours of operation.
ALIGNMENT -- Make sure that fan shafts and motor shafts
are pmallel and level. The most common causes of misalign-
ment are nonparallel shafts and improperly located sheaves.
Where shafts me not pmallel, belts on one side are drawn
tighter and pull more than their share of the load. As a result,
these belts wear out faster, requiring the entire set to be re-
placed before it has given maximum service. If misalignment is
in the sheave, belts enter and leave the grooves at an angle,
causing excessive belt and sheave weal:
1. Shaft alignment can be checked by measuring the
distance between the shafts at 3 or mole locations. If the
distances are equal, then the shafts ale parallel.
2. Sheave Alignment:
Fixed sheaves -- To check the location of the fixed
sheaves on the shafts, a straightedge or a piece of string
can be used. If the sheaves are properly aligned, the string
will touch them at the points indicated by the mTOWSin
Fig. 32.
Adjustable sheaves -- To check the location of adjustable
sheave on shaft, make sure that the centerlines of both
sheaves are in line and palallel with the beming suppofl
channel. See Fig. 32. Adjustable pitch drives me installed
on the motor shaft.
5O

Do not exceed maxilnum fan speed rpm with adjustable
sheave.
3. Rotate each sheave one-half revolution to determine
whether the sheave is wobbly or the diive shaft is bent.
Correct any misalignment.
4. With sheaves aligned, tighten cap screws evenly and
progressively.
NOTE: There should be a I/s-in. to l/4-in, gap between the
mating part hub and the bushing flange. If gap is closed, the
bushing is probably the wrong size.
5. With tapeMock bushed hubs, be sure the bushing bolts
are tightened evenly to prevent side-to-side pulley
wobble. Check by rotating sheaves and rechecking
sheave alignlnent. When substituting field-supplied
sheaves for factory-supplied sheaves, consider that fan
shaft sheave has been facto qbalanced with fan and shaft
as an assembly. For this reason, substitution of motor
sheave is preferable for final speed adjustment.
CENTER LINES
MUST COINCIDE
STRI NG LINES
MUST BE
PARALLEL
BEARING
SUPPORT
CHANNEL
LINES
MUST BE
PARALLEL
FIXED SHEAVE ADJUSTABLE
SHEAVE
Fig. 32 -- Sheave Alignment
V-Belts -- When inst_dling or replacing belts, always use a
complete set of new belts. Mixing old and new belts will result
in the premature wetu or breakage of the newer belts.
Refer to label on inside of fan access door for information
on factory-supplied diive.
1. Always adjust the motor position so that V-belts can be
installed without stretching over grooves. Forcing belts
can result in uneven stretching and a mismatched set of
belts.
2. Do not allow belt to bottom out in sheave.
3. Tighten belts by turning motor-adjusting jackscrews.
Turn each jackscrew an equal number of turns.
4. Equalize belt slack so that it is on the same side of belt for
_dl belts. Failure to do so may result in uneven belt
stretching.
5. Tension new drives at the maximum deflection force rec-
ommended (Fig. 33).
6. On current production, the correct tension information is
listed on the fan diive label. For older equipment or for
units with field-modified diives, use the deflection for-
mula given in the example below and the tension data
from Fig. 33.
EXAMPLE:
Given:
Belt Span 16 in.
Belt Cross-Section A, Super Belt
Small Sheave PD 5 in.
Deflection = Belt Span/64
Solution:
a. From Fig. 33 find that deflection force for type A,
super belt with 5-in. small sheave PD is 4 to 51/2 lb.
b. Deflection = 16/64
= l/4-in.
c. Increase or decrease belt tension until force required
for l/4-in, deflection is 5 lb.
Check belt tension at least twice during first oper-
ating day. Readjust as required to maintain belt
tension within the recommended range.
With correct belt tension, belts may slip and squeal momen-
tarily on strut-up. This slippage is notated and disappe_u's after
unit roaches operating speed. Excessive belt tension shortens
belt life and may cause bearing and shaft damage.
After run-in, set belt tension at lowest tension at which belts
will not slip during operation.
BELT
CROSS
SECTION
A
B
C
5V
SMALL
SHEAVE
PD RANGE
(in.)
3.0- 3.6
3.8- 4.8
5.0- 7.0
3.4- 4.2
4.4- 8.6
5.8- 8.6
7.0- 9.4
9.6-16.0
4.4- 6.7
7.1-10.9
11.8-16.0
12.5-17.0
8V 18.0-22.4
LEGEND
PD -- Pitch Diameter, inches
DEFLECTION FORCE (Ib)
Super Belts Notch Belts Steel Cable
Belts
Min Max Min Max Min Max
3 4% 37/8 51/2 31/4 4
31/2 5 41/2 61/4 33/4 43/4
4 5V2 5 67/8 4V4 51/4
481/2 83/4 8 41/2 81/2
51/8 71/8 61/2 91/8 83/4 71/4
63/8 83/4 73/8 101/8 7 83/4
111/4 143/8 133/4 177/8 111/4 14
141/8 181/2 151/4 201/4 141/4 173/4
-- -- 10 15 -- --
101/2 183/4 127/8 18a/4 -- --
13 191/2 15 22 -- --
27 401/2 ....
30 45 ....
Fig. 33 -- Fan Belt Tension Data
51

Outdoor Hoods and Louvers -- There are three op-
tions available: fixed rein intake hoods, intake louvers, and
collapsible exhaust box hoods. All hoods and louvers have an
intake screen to prevent unwanted ent Uof birds and debris.
The intake hoods have easily serviceable demisters via small
hinged doors. Intake louvers are a wind driven rain design that
will _dlow no more than .01 oz. per sq. fi of fiee area water
penetration at 1250 fpm. This is the maximum velocity
required by AMCA (Air Movement and Control Association)
511. Higher velocities tue possible without significant water
intrusion.
Fixed rear hoods (Fig. 34) and int_,e louvel_ (Fig. 35) ship
installed and should lequile no further assembly.
Collapsible exhaust box hoods ship covering the exhaust
outlet of the unit and require some basic assembly. Fasteners,
washers and gasket material for installation of the hood come
taped inside the exhaust section. Fig. 36 shows an exploded
view of the assembly in its shipping position. Fig. 37 shows
how the various parts assemble to form the hood and a view of
the completed assembly.
IMPORTANT: Hoods for power exhaust fans must be field ]
supplied based on local code requirements. I
UNIT
'_//_ _O/#"q/'_ _ SCREW TYPICAL
ENTIRE PERIPHERY
-- INTAKE HOOD
HOOD .... _GUTTER
ANGLE j J
PANEL
BRACKET MOUNT BELOW _ SCREW
HOOD BRACKET CAN BE
THROWN AWAY AFTER HOOD _PANEL
IS INSTALLED ON THE UNIT. "/"
Fig. 36 -- Collapsible Exhaust Box Hood
(Shipping Position)
SCREW _
HOOD_
GUTTER
_PANEL
OPEN DOORTO
REMOVE DEMISTERS
Fig. 34 -- Rear Intake Hood (Size 30 Shown)
GASKET
.125 THICK x 1.25 WIDE,
\\\\\\\\\\\\
LOUVER ASY \\ \..
SCREW
1/4-14 x 3/4 SNS
X
NOTE: All dimensions in inches unless otherwise noted.
Fig. 35 -- Louver Intake
WASHER
_'_SCREW
SCREEN TO BE
INSTALLED
I BETWEEN THE
t PANEL FLANGE
AND THE HOOD
FLANGE.
Fig. 37 -- Collapsible Exhaust Box Hood
(Assembly)
Coil Connection Housing (Outdoor Unit
Only) -- Coil connection housings are used to house piping
fi'om inside the building to its connections to the coil on the
unit. Piping must be insulated to building code standards or job
specifications (whichever is greater) for the area that the unit is
inst_flled to prevent excessive condensation within the housing
otherwise, water &tmage to floors below could result.
Install as follows:
1. Coil connection housing (CCH) will be shipped to the job
site on its own skid, separate from the air-handling unit as
shown in Fig. 38.
2. Before removing the coil connection housing from its
skid, remove panels and reposition shipping brackets/
lifting lugs as shown in Fig. 39.
3. Apply seal strip to roof as shown on the coil connection
housing roof gasketing detail in Fig. 40.
52

COIL CONNECTION
HOUSING \
SKID
Fig. 38 -- Coil Connection Housing
CCH END PANEL
REPOSITION SHIPPING
BRACKETS /LIFTING LUGS
TO FRAME AS SHOWN
4. Assemble seal strip to back side of the coil connection
housing frame as shown in Fig. 41 and 42.
5. Remove panel retainers from unit as shown in Fig. 43. If
file coil connection housing spans more than one section
DO NOT remove panel retainers that do not interfere
with the coil connection housing mounting.
Apply l/2-in, thick by 2-in. thick closed cell neoprene gas-
ket to the top of the CCH curb. Tile CCH will sit directly
on top of the curb.
6. Ensure that thele is a tight seal between the CCH and
AHU.
7. Secure the coil connection housing roof to air-handling
unit roof using the panel letainers and retainer screws as
shown in Fig. 44. Note that the view is fiom underneath
the roof. The retainers me rotated 180 degrees and hold
the coil connection housing roof to the side of the air-
handling unit. These _ue the same style retainers used to
hold the air-handling unit panel in place during shipment.
SEAL STRIP
1.50" WIDE X 0.375" THICK
APPLY TO TOP OF CCH FRAME
BEHIND CCH ROOF TO ROOF
OF AHU ROOF.
CCH ROOF_
CCH FRAME_
CCH FACE PANEL
SINGLE WALLVERSION SHOWN
CCH END PANEL
SINGLE WALL
VERSION SHOWN
CCH -- CoilConnection Housing
Fig. 39 -- Reposition to Upright and
Remove Panels
CCH ROOF
DO NOT DIS-ASSEMBLE ROOF
FROM CCH FRAME. ROOF SHOWN
THIS WAY FOR CLARITY
USE SCREWS FROM PANEL
RETAINERS TO MOUNT CCH
FRAME TO AHU FRAME.
LEGEND
AHU -- Air-Handling Unit
CCH -- Coil Connection Housing
0.75" WIDE X 0.125" THICK
APPLY TO OUTSIDE EDGE
OF CCH FRAME REAR
PERIMETER TO SEAL
AGAINST SIDE OF AHU.
Fig. 41 -- Detailed View of Seal Strip
SEAL STRIP
1.50" WIDE X 0.375" THICK
BEHIND CCH ROOF TO SEAL
AGAINST BOTTOM OF AHU ROOF
SEAL STRIP
0.75" WIDE X 0.125" THICK
USED TO SEAL BETWEEN
CCH ROOF AND AHU ROOF
SEAL STRIP
1.50" WIDE X 0.125" THICK
USED TO SEAL BETWEEN
CCH ROOF AND ROOF
CCH --Coil Connection Housing
Fig. 40 -- Apply Seal Strip
SEAL STRIP
USED TO SEAL BETWEEN
CCH AND AHU
LEGEND
AHU -- Air-Handling Unit
CCH -- CoiIConnection Housing
Fig. 42 -- Assembled Seal Strip
53

AHUPANEL_ \\
LEGEND
AHU -- Air-Handling Unit
Fig. 43 -- Remove Panel Retainers
CCHROOF_
_AHU ROOF
1/4 - 20 X 7/8 in.
LEGEND
AHU -- Air-Handling Unit
CCH -- Coil Connection Housing
Fig. 45 -- Secure Using Self-Drilling Screws
ROOF RETAINER CCH ROOF
_AHU ROOF
SEALING SCREW /
1/4-14 X 3/4 in.
LEGEND
AHU -- Air-Handling Unit
CCH -- Coil Connection Housing
Fig. 44 -- Secure the Coil Connection Roof
to the Air Handler Roof
8. Also secure the coil connection housing roof to air-
handling unit with self-&illing screws as shown in
Fig. 45. Remove screws from the air-handling unit roof if
they interfere with flush mounting of the coil connection
housing to air-handling unit roof. When file coil connec-
tion housing is located on the low side roof. cut the seal
strip at the slit and bend the tab in to create a better seal.
9. Remove shipping brackets and lifting lugs.
10. Reassemble panels. See Fig. 46 for view of assembled the
coil connection housing.
11. Seal any gaps between the main unit base rail and the cut
out in the CCH curb with tield-supplied flashing and
sealec
CCH CURB
CCHn _._::_AI. AHU
CCH CURB W-_W OD NAILER
SEAL GAPS BETWEEN CCH
CURB, AHU, & AHU CURB HU CURB
LEGEND
AHU -- Air-Handling Unit
CCH -- Coil Connection Housing
Fig. 46 -- Reassembled Coil Connection Housing
with Panels
Humidifier Installation
ASSEMBLE CONTROL VALVE ASSEMBLY (Fig. 47-
Fig. 50) -- V;flve kits m'e sold as separate items through your
loc_fl Creel representative (shipped unassembled).
54

CAREL
PART NUMBER
599-02000CKIT
599-02002CKIT
599-02004CKIT
599-02006CKIT
599-02008CKIT
599-02010CKIT
599-02012CKIT
DESCRIPTION
1/2-in. valve size Cv= 0.4
1/2-in. valve size Cv= 0.63
1/2-in. valve sizes Cv= 1
1/2-in. valve sizes Cv= 1.6
1/2-in. valve sizes Cv= 2.5
1/2-in. valve sizes Cv= 4
3/4-in. valve size Cv= 6.3
Cv -- Flow Coefficient
COMPONENTS
(2) 1/2-in. MPT x
3-in. nipples
(2) 1/2-in. FPT x
1-in. MPT hex
bushings
1-in. union
1/2 in. or 3/4 in. valve body
1/2 in. or3/4 in. x 3 in. nipples (2) 1 in. union
1/2 in. or 3/4 in. FPT x 1 in. MPT hex bushing (2)
Fig. 47 -- 1/2-in. and 3/4-in. Valve Assemblies
55

CAREL PART NUMBER
599-02014CKIT
Cv -- Flow Coefficient
DESCRIPTION
1 in. valve size Cv=10 (2) 1 COMPONENTS
in. MPT x 3 in. nipples
1 in. union
1 in. union
1 in. x 3 in. nipple
Fig. 48 -- 1 in. Valve Assembly
CAREL PART NUMBER
590-03024KIT
590-03025KIT
Cv -- Flow Coefficient IDESCRIPTION
11/4-in. valve size Cv= 16
11/2-in. valve size Cv= 25
COMPONENTS
(2) 11/4-in. MPT x 3 in. nipples
(2) 11/4-in. FPT x 2 in. MPT hex bushings
2 in. union
1-1/4 in. or 1-1/2 in. valve body
1-1/4 in. or 1-1/2 in. x 3 in. nipples
2 in. union
1-1/4 in. FPT x 2 in. MPT hex bushings (2)
Fig. 49 -- 11/4-in. and 11/2-in. Valve Assemblies
CAREL PART NUMBER
590-03026KIT
Cv -- Flow Coefficient IDESCRIPTION
2 in. valve size Cv=40
COMPONENTS
(2) 2 in. MPT x 3 in. nipples
2 in. union
- v 2 in.unlon
Fig. 50 -- 2 in. Valve Assemblies
56

ASSEMBLE STRAINER AND TRAP ASSEMBLY AND
VALVE ASSEMBLY (Fig. 51 and 52) -- Strainer and trap
assemblies are sold as separate items through your local Carel
representative (shipped unassembled).
1 in. Strainer and Trap Assembly
CAREL COMPONENTS
PART NUMBER
US'I-r&SKIT1
DESCRIPTION
1 in. Steam trap
and strainer with
plumbing kit
1 in, Y-strainer
1 in, x 6 nipple
1 in, x 90 degree FPT elbow
1 in, x 3 in. nipple
1 in, FPT tee
3/4-in. x 1 in, hex bushing
2) 3/4-in, x 6 in, nipples
4-in. FPT union
a/4-in. 90 degree street elbow
a/4-in, float and thermostatic
trap
1 X 6 NIPPLE
1 Y-STAINER
X 90 '_FPT ELBOW
X 3 NIPPLE
HEX BUSHING
3/4 X 6 NIPPLES (2), UNION
THERMOSTATIC
STEAM TRAP
NOTE: All dimensions in inches.
Fig. 51 -- 1 in. Steam Trap and Strainer with
Plumbing Kit
2 in. Strainer and Trap Assembly
CAREL COMPONENTS
PART NUMBER
USTT&SKIT2
DESCRIPTION
2 in, Steam trap
and strainer with
plumbing kit
2 in. Y-strainer
2 in. x 6 nipple
2 in. x 90 degree FPT elbow
2 in. x 3 in, nipple
2 in. FPT tee
2 in. x s/4-in,hex bushing
(2) 3/4-in. x 6 in. nipples
3/4-in, FPT union
3/4-in, 90 degree street elbow
3/4-in. float and thermostatic
trap
2 X 90 FPT ELBOW 2 x 6 NIPPLE
2 Y-STAIN ER
2 x 3 NIPPLE
2 X 3/4 HEX
BUSHING
3/4 FPT UNION
_ 3/4 STREET ELBOW
FLOATAND
THERMOSTATIC STEAM
TRAP
NOTE: All dimensions in inches.
Fig. 53 -- 2 in. Steam Trap and Strainer with
Plumbing Kit
57

CONNECT CONTROL VALVE AND TRAP TO STEAM
SUPPLY AND MANIFOLD (Fig. 53 and 54)
STEAM IN
24 in. DROF
WATER
DRAIN
OUT
in. NPT
1/2 in. NPT
Fig. 53 -- Control Valve and Trap Connected to Supply and Manifold of Humidifier Sizes 03-14
(Size 14 Shown)
LIVE I1_
STEAM IN
WATER
DRAIN
OUT
2 in. NPT
Fig. 54 -- Control Valve and Trap Connected to Supply and Manifold of Humidifier Sizes 17-61
(Size 17 Shown)
Assembly of Vertical Manifolds -- Tile vertical dis-
tribution manifolds are inserted into the bottom feed header by
hand (slip fit) and then into file top header if any. See Fig. 55.
• Vertical slotted discharge manifolds must be installed
with the internal fishbone wick ends sloping up as in a
,,y,,
• Do not force the vertical manifolds into the headers
beyond the insulation.
• Do not use any lubricants. Manually reform the ends
slightly if necessary.
• Ensure discharge slots are perpendicular to the air flow.
• On top fed 17-61 sizes, run a bead of RTV silicone caulk
around the junction of the vertical manifolds and top
headec
INSERT
INSUL
Fig. 55 -- Vertical Manifold
58

Coil Installation
NOTE: If installing a replacement coil, refer to Coil Removal
section, page 93 for instructions on removing existing coil.
INSTALLATION OF SINGLE HEIGHT COILS (sizes 03- 36)
1. Lock open and tag all power supplies to unit fan motor
and electric heatel_ if present.
2. a. Identify the unit service panel latches and disen-
gage them (1/4 turn) with a 5h(-,-in. or 8-mm hex
wrench.
b. Remove service panel/coil connection panel and
the upstream service panel and set aside in a safe
place.
3. a. Remove the flat corner plug from each end piece of
the top rail.
b. Extract the Torx T25 screw visible within the
exposed cavity. (Do not mix these screws with
others; they are specific for this location. Set
screws aside for reinstallation of the top rail.)
c. Remove the top rail by pulling out fit a 45 degree
angle. Set top rail aside.
Do not handle the coil by the headers or connection
nipples, as irreparable damage might occur that is NOT
covered by WtuTanty. Protect the finned surface from
damage during all handling and shipping.
4. Slip the foam sealing sleeves on the connection nipples
before installing the coil.
5. The coil may now be hoisted in through the top opening,
or it may be slid in through either side, taking care to
avoid tipping or &opping the coil. Some lower stacked
unit sections may require slightly tipping the coil from the
vertical position in order to clear the upper frame rail and
seffl, which is not readily removed.
6. Loosely secure the coil at the top using the 3/s-in. dia]ne-
ter hoisting holes located in the side channel/tube sheet
juncture fit each end.
7. Install the first coil in the section. Access the upstream
face of the coil and install the screws holding the coil to
the mounting baffles around the entire perimetel: This
may require reaching through an opened damper assem-
bly or through the filter track after filters _ue removed.
8. Replace the top rail by reinstfdling the Torx T25 screws
and flat corner plugs.
9. Replace all service panels and engage all I/4-turn panel
latches.
INSTALLATION OF STACKED COILS (40, 50 and 61 )
IMPORTANT: The lengths of the coil supports and
intermediate pans and channels are designed to work
with Carrier coils. Substitution of other manufac-
turer's coils may require that custom mounting com-
ponents be field fabricated. Coil sections ordered
_'itkout coils _'ill come _4'ith tke refi, l_,nced parts in kit
NOTE: The length that the intermediate &'ain pan extends
downstremn from the coil face has been designed for use with
Cturier manufactured coils, and may prove insufficient for
other maker's coils.
10.
1. Ix)ck open and tag all power supplies to unit fan motor
and electric heaters if present.
2. a. Identify the unit service panel latches and disen-
gage them (1/4 turn) with a 5/l(-,-in. or 8-mm hex
wrench.
b. Remove service panel/coil connection panel and
the upstream service panel and set aside in a safe
place.
3. a. Remove the flat corner plug from each end piece of
the top rail.
b. Extract the Torx T25 screw visible within the
exposed cavity. (Do not mix these screws with
others; they are specific for this location. Set
screws aside for reinstallation of the top rail.)
c. Remove the top rail by pulling out fit a 45-degree
angle. Set top rail aside.
Do not handle the coil by the headers or connection
nipples, as irreparable damage might occur that is NOT
covered by warianty. Protect the finned surface from
&image during all handling and shipping.
4. Slip the foam sealing sleeves on the connection nipples
before installing the coil.
5. Before placing file coils inside the unit, apply the adhe-
sive backed gasket to the lower baffle, spanning the entire
unit, on the surface that will contact the coil (see Fig. 56).
6. a. Place the lower coil on the coil supports, sliding the
coil against the upstream baffle and aligning the
mounting holes so that the connection nipple will
extend approximately 3 in. outside the unit casing.
b. Place the heavy vertical angle (which is full height
of the finished coil bank) along the upstream right
and left side of the mounting baffles (see Fig. 56).
Install screws through this angle first and then into
the baffles, engaging the coil tube sheet mounting
holes and securing the coil within the unit.
c. Secure the lower side casing of the coil to the
lower horizontal baffle, sandwiching the gasket in
between.
7. For coil sections that do not have a &'ain pan within the
section, go to Step 10.
8. Secure the spacer (hat channel) to the top center of the
lower coil casing (see Fig. 57).
Do not penetrate through the coil casing into the fin pack.
Tube damage may occur.
Secure two spacers (hat channels) to each end of the
bottom of the upper coil casing before placing the coil in
position (refer to Fig. 56).
Place the intermediate condensate &ain pan on the lower
coil, centering the drain pan between the sides of the unit,
with the condensate outlet holes along the downstream
edge. (It may be helpful to temporarily secure the drain
pan by a strip of double-stick tape on the center hat
channel.)
59

BAFFLE, HEADER_
CHANNEL,
PAN, CONDENSATE_,
CENTERED WITHIN SECTION
BAFFLE, TOP
_ BAFFLE, HAIRPIN
ATTACHED TO COILS
BOTH SIDES
IMPORTANT: ADHESIVE GASKET MUST BE
APPLIED TO THE FULL LENGTH OF THE BOTTOM
THE COIL SIDE CASING AND THE BAFFLE.
SEE ILLUSTRATION BELOW.
APPLY FLUSH TO THIS EDGE_
GASKET, ADHESIV E--__
....BAFFLE, BOTTOM _/
_ BOTTOM BAFFLE
Fig. 56 -- Apply Gasket
11. Lift the upper coil (with spacer hat channels on the
bottom of each end) into place, aligning the upper coil
with the lower coil. When the upper coil is lowered into
place, it will deflect the intermediate condensate pan
downwmd on each end, providing for positive drainage.
12. Install factory-supplied screws around the ends and top of
the coil.
13. On the upstremn side of the stacked coils, attach the
center baffle (see Fig. 56), spanning the two coils with the
crease in the baffle away from the coils, centering it
between file side baffles, and aligning the baffle with the
holes in the coil casings.
14. Install the drain fittings into the pan. Route and secure the
hoses as shown in Fig. 58.
15. For sections that do not have a drain pan (heating only
sections):
a. After the lower coil has been secured in position,
fasten the three hat channel spacer supports to the top
of the coil.
CHANNEL, HAT ,\ ATTACH WITH 4 SCREWS
...... TO COIL CASING
\\\\
b. Place the upper coil into position directly above the
lower coil, resting on these hat channels.
16. Secure the uppermost coil frDm the upstream side, so that
the fastening screws provided pass through the vertical
angle and the baffles and engage the coil casing. See
Fig 56.
-_- DRAIN \\ CONDENSATE PAN
--GASKET
_HOSE
"ATTACHED TO COIL
J TUBE SHEET
Fig. 58 -- Install Drain Fittings
Fig. 57 -- Secure Spacer
6O

Water and Steam Coil Piping Recommendations
GENERAL -- Use straps around the coil casing or the lifting
holes (see Fig. 59) to lift and place file coil.
To prevent damage to the coil or coil headers: Do not use
the headers to lift file coil. Support the piping trod coil con-
nections independently. Do not use the coil connections to
support piping. When tightening coil connections, use a
backup wrench on the nozzles.
Piping practices ale outlined in the Carrier System Design
Manual, Pall 3, Piping Design.
WATER COILS- Typically, coils me piped by connecting
the supply at the bottom and the return at file top. See Fig. 59.
This is not always the case, especially if the coil hand has been
changed in the field. Coils must be piped for counterflow;
otherwise, a capacity reduction of 5% for each coil row will
result. To ensure counterllow, chilled water coils me piped so
that the coldest water meets file coldest air Hot water coils are
piped so that the warmest water meets the warmest all:
STEAM COILS -- Position the steam supply connection fit
the top of the coil, and the return (condensate) connection at the
bottom. The coil tubes must incline downwfuds toward
the return header connection for condensate di'ainage. See
Fig. 60-65.
LIFTING HOLES
(VENT_
(DRAIN)
HEADER ENDVIEW
Fig. 59 -- Coil Connections and Lifting Points
Figure 60 illustrates the normal piping components and the
suggested locations for high, medium, or low-pressure steam
coils. The low-pressure application (zero to 15 psig) can
dispense with the 1/4-in. petcock for continuous venting located
above the vacuum breaker (check valve).
Note the horizontal location of the 15-degree check valve,
and the orientation of the gate/pivot. This valve is intended to
relieve any vacuum forming in the condensate outlet of a
condensing steam coil, and to seal this port when steam
pressure is again supplied to the coil. It must not be installed in
tiny other position, and should not be used in the supply line.
For coils used in tempering service, or to preheat outside aik
install an immeLsion thermostat in the condensate line ahead of
the trap. This will shut down the supply fan and close the out-
door &tmper whenever the condensate falls to a predetermined
point, perhaps 120 E
NOTE: Do NOT use tin immersion thermostat to override a
duct thermostat and open the steam supply valve.
For vacuum return systems, the vacuum breaking check
valve would be piped into the condensate line between the trap
and the gate valve instead of open to the atmosphere.
Figure 61 illustrates the typical piping fit the end of every
steam supply main. Omitting this causes many field problems
and failed coils.
Figure 62 shows the typical field piping of multiple coils.
Use this only if the coils are the same size and have the same
pressure drop. If this is not the case, tin individual trap must be
provided for each coil.
Figure 63 shows a multiple coil arrangement applied to a
gravity return, including the open air relief to the atmosphere,
which DOES NOT replace the vacuum breakers.
Figure 64 illustrates the basic condensate lift piping.
Following the piping diagrams in Fig. 60-64, make all con-
nections while observing the following precautions:
• Install a drip line and trap on the pressure side of the
inlet control valve. Connect the drip line to the return
line downstream of the return line trap.
• To prevent scale or foreign matter from entering the con-
trol valve and coil, install a 3132-in. mesh strainer in the
steam supply line upstream from the control valve.
• Provide air vents for the coils to eliminate noncondens-
able gases.
• Select a control valve according to the steam load, not
the coils supply connection size. Do not use an oversized
control valve.
• Do not use bushings that reduce the size of the header
return connection. The return connection should be the
same size as the return line and reduced only fit the
downstream trap.
• To lift condensate above the coil return line into over-
head steam mains, or pressurized mains, install a pump
and receiver between the condensate trap and the
pressurized main. Do not try to lift condensate with
modulating or on-and-off steam control valves. Use only
15-degree check valves, as they open with a lower water
head. Do not use 45-degree or vertical-lift check valves.
• Use float and thermostatic traps. Select the trap size
according to the pressure difference between the steam
supply main and the return main.
• Load variations can be caused by uneven inlet air distri-
bution or temperature stratification.
• Drain condensate out of coils completely fit the end of
the heating season to prevent the formation of acid.
61

_-CONTROL VALVE (NOTE 5)
NOTE I -__ _- STRAINER
_" \_'_ /GATE VALVE
¼ iN. PET COCK "_ _,,_
UNIT FOR CONTINUOUS _STA_ STEAM SUPPLY
111
LWHEN END OF SUPPLY
". MAIN,SEE FIG. 61
MIN,
_-15 ° CHECK VALVE
FOR BREAKING VACUUM
IN, LINE
_'NOTEI
NOTE I-_
UNIT
UNIT
_ CONTROL VALVE
28_3)
.- STRAINER
7/ GATE VALVE
STEAM SUPPLY
_r'\REFER TO FIG, GI
WHEN DRIPPING
SUPPLY TO RETURN.
RMOSTATIC TRAP (½IN.)
GIRT LEG (61N.) "
15° CHECK VALVE -
FLOAT OR
BUCKET TRAP /
(NOTE 2) -j
VALVE
CONDENSATE
RETURN MAIN
NOTES:
1. Flange or union is located to facilitate coil removal.
2. Flash trap may be used if pressure differential between steam
and condensate return exceeds 5 psi.
3. When a bypass with control is required.
4. Dirt leg may be replaced with a strainer. If so, tee on drop can
be replaced by a reducing ell.
5. The petcock is not necessary with a bucket trap or any trap
which has provision for passing air. The great majority of high
or medium pressure returns end in hot wells or deaerators
which vent the air.
Fig. 60 -- Low, Medium or
High Pressure Coil Piping
FGATE
STEAM /VALVE
SUPPLY
TO UN
DIRT LEG
GLOBE VALVE /_ / "_
(PLUG TYPE) _ _i
DRIP
LINE=-_
CONDENSATE
RETURN
FROM
STEAM SUPPLY
MAIN
j--FLOAT BTHERMOSTATIC
/ TRAP
_--GATE VALVE
./-OPEN AIR RELIEF TO
_" ATMOSPHERE CLOSE
!TO UNIT. REQUIRED ON
LOW PRESSURE GRAVITY
RETURN SYSTEMS,
UNIT GATEVA VEI J
._-- CONDENSATE
JRETURN MAIN
NOTES:
1. A bypass is necessary around trap and valves when continu-
ous operation is necessary.
2. Bypass to be the same size as trap orifice but never less than
1/2inch.
Fig. 61 -- Dripping Steam Supply to
Condensate Return
NOTES:
OPEN AIR RELIEF
/T0 ATMOSPHERE
DIRT LEG ( 6IN.)-
15_ CHECK VALVE _/
FLOAT OR BUCKET -:
TRAP (NOTE 4) L_.
NOTE I!'_', /._
GATE VALVE _4co
NDENSATE
RETURN
1. Flange or union is located to facilitate coil removal.
2. When a bypass with control is required.
3. Flash trap can be used if pressure differential between supply and
condensate return exceeds 5 psi.
4. Coils with different pressure drops require individual traps. This is
often caused by varying air velocities across the coil bank.
5. Dirt leg may be replaced with a strainer. If so, tee on drop can be
replaced by a reducing ell.
6. The petcock is not necessary with a bucket trap or any trap which
has provision for passing air. The great majority of high pressure
return mains terminate in hot wells or deaerators which vent the air.
Fig. 62 -- Multiple Coil High Pressure Piping
UNIT
.... CONTROL VALVE
_j (NOTES 2 6 3)
'STRAINER
/ 15_CHECK VALVE STEAM SUPPLY
WHEN DRIPPING
SUPPLY TO RETURN.
STATIC TRAP (½IN.)
UNIT
/OPEN AIR RELIEF
TO ATMOSPHERE
DIRT LEG (6IN.)_
I5° C
FLOAT OR BUCKET
TRAP (NOTE 4) _/ '_
NOTE I'_CO
GATE VALVE
NDENSATE
RETURN
NOTES:
1. Flange or union is located to facilitate coil removal.
2. When control valve is omitted on multiple coils in parallel air flow.
3. When a bypass with control is required.
4. Coils with different pressure drops require individual traps. This is
often caused by varying air velocities across the coil bank.
Fig. 63 -- Multiple Coil Low Pressure
Piping Gravity Return
62

STEAM SUPPLY
Y
GATE VALVE_ _¢_OVERHEAD
_'_ CONDENSATE
RETURN
MAIN
UNiT
VALVE
12IN.
MIN.
( LOCATED BELOW COIL OUTLET)
DRAIN VALVE
(GATE,NOTE2
NOTES:
1. Flange or union is located to facilitate coil removal.
2. To prevent water hammer, drain coil before admitting steam.
3. Do not exceed one foot of lift between trap discharge and
return main for each pound of pressure differential.
4. Do not use this arrangement for units handling outside air.
Fig. 64 -- Condensate Lift to Overhead Return
Coil Freeze-Up Protection
WATER CO[LS -- If a chilled water coil is applied with out-
side air. provisions must be made to prevent coil fieeze-up.
Install a coil fieeze-up thermostat to shut down the system if
any air temperature below 36 F is encounteled entering the
water coil. Follow thermostat manufacturer's instructions.
When a water coil is applied downstremn of a direct-
expansion (DX) coil, a freeze-up thermostat must be installed
between the DX and water coil and electrically interlocked to
turn off the cooling to prevent fieeze-up of the water coil.
For outdoor-air application where intermittent chilled water
coil operation is possible, one of the following steps should be
taken:
• Install an auxiliary blower heater in cabinet to maintain
above-freezing temperature around coil while unit is
shut down.
• Drain coils and fill with an ethylene glycol solution suit-
able for the expected cold weather operation. Shut down
the system and drain coils. See Service section, Winter
Shutdown, page 92.
STEAM COILS -- When used for preheating outdoor air in
pressure or vacuum systems, an immersion thermostat to con-
trol outdoor-air damper and fan motor is recommended. This
control is actuated when steam supply fails or condensate tem-
perature drops below an established level, such as 120 to 150 IF.
A vacuum breaker should also be used to equalize coil pressure
with the atmosphere when stemn supply throttles close. Steam
should not be modulated when outdoor air is below 40 E
On low-pressure and vacuum steam-heating systems, the
thermostat may be replaced by a condensate drain with a ther-
mal element. This element opens and drains the coil when con-
densate temperature drops below 165 E Note that condensate
dndns are limited to 5 psig pressure.
INNER DISTRIBUTING TUBE STEAM COILS -- The
inner distributing tube (IDT) steam coil used in the Carrier
39M _fir-handling units has an inner tube pierced to facilitate
the distribution of the steam along the tube's length. The outer
tubes me expanded into plate fins. The completed assembly
includes the supply and condensate header and side casings
which are built to slant the fin/tube bundle back toward the
condensate header The slanting of the assembly ensures that
condensate will flow towmd the drains. This condensate must
be removed fllrough the mtum piping to prevent premature
fiulure of the coil. The fin/tube bundle is slanted vertically for
horizontal airflow coils, and hofizonttdly for vertical air-
flow coils.
IDT Steam Coil Piping -- The following piping guidelines
will contribute to eft]cient coil operation and long coil life:
1. Use full size coil outlets and return piping to the steam
trap. Do not bush return outlet to the coil. Run full size to
file trap, reduce tit the trap.
2. Use float and thermostatic (F & T) traps only for conden-
sate removal. Trap size selection should be based on the
difference in pressure between the steam supply main and
file condensate return main. It is good practice to select a
trap with 3 times the condensate rating of the coil to
which it is connected.
3. Use themlostatic traps for venting only.
4. Use only 1/2-in., 15-degree swing check valves installed
horizontally, piped open to atmosphere, and located tit
least 12 in. above die condensate outlet. Do not use
45-degree, vertictfl lift and ring check valves.
5. The supply valve must be sized for the maximum antici-
pated stemn load.
6. Do not drip stealn mains into coil sections. Drip them on
file pressure side of the control valve and trap them into
the return main beyond the trap for the coil.
7. Do not use a single trap for two or more coils installed in
series. Where two or more coils are installed in a single
bank, in parallel, the use of a single trap is permissible,
but only if the load on each coil is equal. Where loads in
file same coil bank vmy, best practice is to use a separate
trap for each coil.
Variation in load on different coils in the same bank may
be caused by sever_fl factors. Two of the most common
me uneven airflow distribution across file coil and stratifi-
cation of inlet air across the coil.
8. Do not try to lift condensate above the coil return into an
ovefllead main, or drain into a main under pressure with a
modulating or on/off steam control valves. A pump
and receiver should be installed between the coil conden-
sate traps and ovefllead mains and return mains under
pressure.
9. Use a strainer (3/32-in. mesh) on the steam supply side,
as shown in the piping diagrams, to avoid collection of
scale or other foreign matter in file inner tube distributing
orifices.
NOTE: IDT coils must be installed with the tubes draining
toward the header end of the coil. Carrier's IDT steam coils
are pitched toward the header end as installed in the unit.
10. Ensure the AHU is installed level to maintain the inherent
slope. Also ensure the unit is installed high enough to
tfllow the piping to be installed conectly, especially the
traps which require long drip legs.
11. Do not fail to provide all coils wifll the proper air vents to
eliminate noncondensable gasses.
12. Do not support steam piping fiom the coil units. Both
mains and coil sections should be supported sepmately.
IDT Steam Coil [nstallafion -- Refer to drawings to position
the coils properly with regard to the location of the supply and
return connections. Ensure that the IDT coil is pitched with the
tubes draining towmd the headel: Carrier's AHUs provide
proper coil pitch when the AHU is insttflled level.
Refer to schematic piping diagrams and piping connection
notes for the recommended piping methods.
63

Refrigerant Piping, Direct-Expansion Coils-
Direct-expansion (DX) coils me divided into 2 or4 splits depend-
ing upon file unit size and coil circuiting. Each split lequires its
own distributor nozzle, expansion valve, and suction piping. Suc-
tion connections ;ue on the air entering side when the coil is prop-
erly installed. Matching distributor connections for each coil split
m'e on file air leaving side. See unit label or certified drawing to
assme connection to matching suction and liquid connections.
NOTE: Distlibutor nozzles are factory selected trod installed
for adequate performance in many unit applications. For best
performance, use Carrier's AHUBuilderQ program to select
nozzle sizes for each unit and replace the factory-installed
nozzles as required. See file Thermostatic Expansion Valve
Piping section below for further details.
To prevent &_mage to file coil or coil headers: Do not use
the headers to lift the coil. Support the piping and coil con-
nections independently. Do not use the coil connections to
support piping. When tightening coil connections, use a
backup wlench on the stub outs.
Direct-expansion coils am shipped pressurized with diy ail:
Release pressure from each coil split through v_flves in pro-
tective caps before removing caps.
Do not leave piping open to the atmosphere unnecessarily.
Water and water vapor me detrimental to the refrigertmt
system. Until tile piping is complete, lecap the system and
charge with nitrogen at the end of each workday. Clean all
piping connections before soldering joints.
The lower split of face split coils should befirst-on, last-o_i
Row split coils utilize special intertwined circuits; either
split of these row split coils can befirst-on, last-q_i
SUCTION PIPING- Connect suction piping as shown in
Fig. 65 for face split coil or Fig. 66 for row split coil.
Suction line from coil connection to end of the 15-diameter-
long riser should be salne tube size as coil connection to ensure
proper refrigerant velocity.
Refer to Carrier System Design Manual, Part 3, and size
remaining suction line to compressor for a pressme diop equiv-
alent to 2.0 E This will provide a total suction line header
pressure diop equivalent to approximately 2.7 E Refer to
Fig. 67 for piping risels to the complessor.
To minimize the possibility of flooded starts and compres-
sor damage during prolonged light load operation, an accumu-
lator can be used in the suction line offirst-on, last-o_circuit.
Thefirst-on, last-o_ circuits shown in Fig. 65 and 66 assume
a single condensing unit. Note that in both figures the last-on,
Iil_t-off circuit is looped above the common return line to pre-
vent oil entrapment in the non-operating coil at partkfl load.
THERMOSTATIC EXPANSION VALVE PIPING -- Distrib-
utor nozzles me factory supplied. Thermostatic expansion
valves (TXVs) are field supplied. Be sure that correct nozzle is
installed in each distributor before installing expansion valve.
See Table 4 for factory-installed distributor nozzle sizes. Use
AHUBuilder program to select nozzles for best performance;
replacement nozzles must be field inst_dled.
Perform nozzle change-out procedure (if necessmy) as
follows:
1. Unsweat distributor cap and Schmder valve (see Fig. 68).
Cap is sweat on from facto Uwith 95.5 tin-antimony soft
solder
Do not overheat distributoc Overheating cap and distribu-
tor will hmden solder and make cap impossible to remove.
2. Clean off any remaining solder
3. Remove nozzle retaining ring with screwdriver or needle-
nosed pliers.
4. Remove nozzle from distributor by inserting 2 no. 6-32
threaded rods (at least 4-in. long) into the thleaded holes
provided in the nozzle. See Fig. 69.
5. Insert correct nozzle into distributor body.
6. Re-insert nozzle retainer ring into distributol:
COIL UNIT
CASING CASING
UPPER TXV
SPLIT SENSING
BULB
AIRFLOW
LOWER
SPLIT
EVAPORATOR
COIL
FIRST-ON, LAST-OFF
LEGEND
TXV -- Thermostatic Expansion Valve
Fig. 65 -- Face-Split Coil Suction-Line Piping
TXV SENSINGBULBS
AIRFLOW
15
DIAMS
MIN 15
DIAMS
MIN
EVAPORATOR COIL
10 DIAMS
COIL
CASING UNIT
31GHT
3LASS
FILTER
DRIER
(TYP)
FIRST-ON, LAST-OFF
LEGEND
TXV -- Thermostatic Expansion Valve
Fig. 66 -- Row-Split Coil Suction-Line Piping
64

I COMPRESSOR
PYL_ :Oo
ELBOWS
COMPRESSORABOVE COMPRESSORABOVE
SINGLERISER DOUBLERISER
Fig. 67 -- Suction-Line Riser Piping
DISTRIBUTOR /
DISCARD CAP
WITH TESTPORT
Fig. 68 -- Distributor and Cap
NOZZLE
RETAINER _\
RING \ \
\
\
SIMPLIFIED NOZZLE
REMOVAL
BODY TUBING
1
I
I
NO. 6-32 THREADED THREADED
PULLER HOLES PULLER RODS
Fig. 69 -- Nozzle Change-Out
Install expansion valve as follows:
1. Wrap wet cloths around valve body to plevent excesswe
heat from reaching diaphragm and internal palts. Do not
allow water to enter system. Disassemble expansion
valve before soldering, if accessible, for easy reassembly.
_Z_e9_5-5 tin-antimony soft soldel:
2. Solder expansion valve to distributoc
3. Solder expansion v_dve equalizer line to suction line and
locate control bulb on suction line as in Fig. 65 or66.
4. Insulate expansion valve body, diaphragm assembly, and
control bulb ;uea to prevent charge migration and exces-
sive condensation.
5. Inst¢dl filter drier ahead of expansion valve to ensure
satisfactory valve operation.
6. If hot gas bypass is required, see the following Hot Gas
Bypass section.
HOT GAS BYPASS--When low-load operation requires
use of hot gas bypass, hot gas must be introduced between
expansion v_dve and distributor
Install auxilituy hot gas bypass side connector (field-
supplied) in coil split that isfirst-on, last-qffi
NOTE: See Table 22 for auxiliary side connector sizes. Do
not attempt to use a valve that is smaller or larger than dis-
tributor size. Inserting a bushing at the outlet will defeat the
purpose of the internal nozzle tube extension.
Inst_dl the side connector as follows:
1. Remove distributor nozzle and letainer ring (area A) from
distributor and reinst;dl in inlet (area B) of side connectoc
See Fig. 70.
2. Solder field-supplied extension nipple to coupling on dis-
tributor, then to side connector outlet, using a silver solder
or equivalent with a melting point of 1300 to 1500E
Extension nipple should be as short as possible.
3. Solder expansion valve outlet to side connector using
95-5 tin-antimony soft solder, for easy removal.
4. If lequired, install field-supplied adapter bushing or
coupling to connector inlet before soldering to expansion
valve outlet.
SPECIAL PIPING WITH 4 SPLITS PER COIL
Manifolding for 2-Face Splits -- Refer to Fig. 71 and exter-
nally manifold as follows:
1. Connect the 4 expansion valves to the 4 distributors on
each coil and connect the 4 suction lines to the
15-diameter-long risers as outlined in previous piping
instructions.
2. Inst:dl common liquid line for upper face split to first
(upper) and second expansion valves. Also, install a com-
mon suction line flom suction lines attached to first
(upper) and second suction header connections.
3. Repeat step 2 for lower face split using third and fourth
distributor and suction connections.
Manifolding for2-RowSplits -- Refer to Fig. 72 and
externally manifold as outlined for the 2-face splits with the
following exceptions:
1. Manifold in pairs, the first and third coil connections for
one split.
2. Manifold the second and fourth pairs of coil connections
for the other split.
NOTE: Split section using first and third pairs of coil con-
nections should be fil_t-on, last-qffi
Hot Gas Bypass Connection with 4 Splits per Coil -- For
either face or row splits connect a hot gas bypass auxiliary side
connector to each distributor of coil split that is first-on,
last-qff_ Refer to installation instructions for Hot Gas Bypass.
SPECIAL PIPING FOR DOUBLE-CIRCUIT COILS --
All 8-row coils that are double circuited requile special piping
to manifold suction and liquid lines. See Tables 3 and 4 for
detailed coil data.
Manifolding for 2-Face Splits -- Refer to Fig. 71 for coils
with less than 34 tubes in face. Externally manifold as follows:
1. Coils with less than 34 tubes: Connect the 4 expansion
valves to the 4 distributors on each coil and connect the
4 suction lines to the 15-diameter-long riseLs as outlined
in previous piping instructions. Refer to Fig. 71.
65

2. [nstallcommonliquidlineforupperfacesplitto first
(upper)andsecondexpansionwdves.Also,installa
commonsuctionlinefromsuctionlinesattachedtofirst
(upper)andsecondsuctionheaderconnections.
3. RepeatStep2forlowerfacesplitusingthirdandfourth
distributorandsuctionconnections.
4. Forunitswithtwocoilsrepeatprocedmesof steps1,2
and3forsecondcoil.
Manifolding for 2-Row Splits -- Refer to Fig. 71 for coils
with less than 34 tubes in face. Externally manifold as outlined
for the 2-face splits with the following exceptions:
1. Manifold in pails, the filst and third coil connections for
one split.
2. Manifold file second and fourth pairs of coil connections
for the other split.
NOTE: Split section using first and third pairs of coil con-
nections should be first-on, last-oj/i
Hot Gas Bypass Connection for Double-Circuited Coils --
For either face or row splits connect a hot gas bypass auxilimy
side connector to each distributor of coil split that is first on,
last off. Refer to installation instructions for Hot Gas Bypass.
REINSTALL NOZZLE HERE
DISTRIBUTOR RETAINER
! 1
OUST I
\
RETAINER
RING
INLET
DISCARD CAP
SIDE WITH TESTPORT SIDE
CONNECTOR CONNECTOR
AREAA _ AREAB
Fig. 70 -- Distributor and Hot Gas Bypass Auxiliary Side Connector
TXV SENSING
BULBS
AIRFLOW
/,
/
SUCTION LINE /
FOR COIL CONNECTIONS
1 AND 2
/
/
SUCTION LINE
FOR COIL CONNECTIONS
3AND4
LEGEND
TXV -- Thermostatic Expansion Valve
TXV SENSING
1
Fig. 71 -- Face-Split Coil Manifolding (Typical)
SIGHT GLASS (TYP)
f
.__ SOLENOID VALVE (TYP)
/FILTER
DRIER
LIQUID LINE
_@_J FOR 1 AND 2
" TXV INSIDE CASING (TYP)
_DISTRIBUTOR (TYP)
FILTER
RIER
_LIQUID LINE
FOR 3 AN D 4
66

SPORLAN
TYPE
ASC-5-4
ASC-7-4
ASC-9-5
ASC-11-7
ASC-13-9
CARRIER
PART NO.
EA19BA504
EA19BA705
EA19BA905
Table 22 -- Auxiliary Side Connector (Hot Gas Bypass) Data
Inlet -- ODM Solder
%
7/8
11/s
1s/s
15/s
CONNECTION SIZES (in.)
Outlet -- ODF Solder Auxiliary -- ODF Solder
7/8 _/2
11/8 5/s
1s/8 7/s
15/8 11/s
USED WITH SPORLAN
DISTRIBUTOR TYPE
1620,1622
1112,1113
1115,1116
1117,1126
1125,1127,1143
SPORLAN
TYPE
ASC-5-4
ASC-7-4
ASC-9-5
ASC-11-7
ASC-13-9
DIMENSIONS (in.)
A
5/80DM
7/8 ODM
11/80DM
lS/8 ODM
15/80DM
LEGEND
BCD E F
5/80DF 1.88 0.95 1,25 1/2ODF
7/80DF 2.25 1.06 1,38 1/20DF
11/8ODF 2.81 1.47 1,62 5/8ODF
lS/80DF 3.53 1.89 2,19 7/80DF
15/8ODF 3.72 1.83 2,75 11/8ODF
ODF -- Outside Diameter, Female
ODM -- Outside Diameter, Male
OUTLET T
TO B
DISTRIBUTORJL --
HOTGAS
BYPASS
INLET
CONNECTION
NOZZLE
SIZE
J
G
E
C
A
t INLET
..... E×£°2'°NVA vE
E
AIRFLOW
\
SUCTION LINE
FOR COIL
CONNECTIONS
1 AND 3
/
SUCTION LINE
FOR COIL
CONNECTIONS
2AND4
LEGEND
TXV -- ThermostaticExpansionValve
TXV SENSING
BULBS
Fig. 72 -- Row-Split Coil Manifolding (Typical)
_ SIGHT GLASS (TYP)
-SOLENOID VALVE (TYP)
FILTER
DRIER
LIQUID LINE
J_ FOR 1 AND 3
FOR 2 AND 4
" TXV INSIDE CASING (TYP)
DISTRIBUTOR (TYP)
6?

Hot Gas Piping and Wiring
INSTALL PIPING (See Fig. 73)
Shut offall power to tfie unit and remove refiigerant charge
using an approved refrigelant recovely device before pro-
ceeding with inst;dlation.
1. [n applications where the air handler refrigerant distribu-
tor is not equipped with a side outlet connection, it is
recommended that a Spodan in-line auxiliary side
connector with standard distributor be used. Refer to the
installation instructions for the indoor fan coil to obtain
nozzle size and distributor connection size. Select the
auxilialy side connector based on this information. The
side connector must be installed on refrigerant circuit
no. 1 (fil3t stage of cooling) of the fan coil being used.
2. Install a field-supplied l/4-in. NPT to l/4-in, flare fitting on
the gage connection port of the compressor suction ser-
vice valve.
3. Sweat the pilot solenoid valve supplied in the hot gas ac-
cessary package directly to the hot gas bypass valve on
the 3/8-in.ODF external equalizer port.
4. Install field-supplied I/4-in.copper tube (flared with a nut
on each end) between the compressor suction valve and
the hot gas pilot solenoid valve.
5. Connect a field-supplied 5/8-in.OD copper tube between
the dischmge line process tube (hot gas stub) and a field-
supplied manu_d shutoff service v_flve,avoiding any traps
in piping.
6. Connect another field-supplied 5Is-in.OD copper tube be-
tween the manual shutoff valve outlet and the hot gas by-
pass valve inlet.
7. Connect a field-supplied 5/s-in. OD copper tube between
the leaving side of the hot gas bypass valve and the Sporlan
auxiliaqside connector (distributo>side connector).
8. Refer to Hot Gas Bypass installation instructions for
wiring information.
CONDENSING UNIT
1SUCTION
EXTERNAL ILINE
_'1_ _ EQUALIZER I
---I:L_ m -., .PORT
HOT GAS PI LOT \, HOT GAS I
SOLENOID VALVE \ I
BYPASS SHUT-OFF \\ I
SERVICE._ 5/8" TUBE I
VALVE
r_ TUBEI/4" P, DISCHARGE_ i/_
_I HOT GAS
IBYPASS
COMPRESSOR iLINE
_NDENSER __ j
EVAPORATOR COIL
EXTERNAL EQUALIZER
EVAPORATOR
CIRCUITI TXV
"l
I
I SOLENOID
IVALVE
I
LIQUID LINE
TO COMPRESSOR
SUCTION SERVICE VALVE SOLENOID PILOT VALVE
II
1/40D--_! r--_r._.-_ 318' sw EAT CONNECTION
I1 [L_ ::_1_-'--- BY PASS VALVE (5/8" OD CONN I
5--_ =_._
FIELD-SUPPLIED BYPASS LINE
SKETCH A
OUTLET
DISTRIBUTOR
FROM
TXV
AUXILIARY
SIDE CONNECTOR
AUXILIARY
{HOT GAS IN)
LEGEND
TXV -- Thermostatic Expansion Valve
*Pilot valve connects directly to bypass valve per sketch A.
Fig. 73 -- Hot Gas Bypass Piping
68

Condensate Drain -- Install a condensate-trapping di'ain
line at the units di'ain connection; use I q2-in, standard pipe. See
Fig. 74A and 74B for correct diain layout.
The lowest point of the di'ain pan is a minimum of 73/8-in.
higher than the bottom of the baserail.
When calculating trap depth on draw-thin or blow-thru ap-
plications, remember that it is not the total static pressure but
the upstream or downstream static resistance that is trapped
against. For instance, when c;dculating the trap depth for a
cooling coil condensate pan on the draw-thin side, trap against
the coil pressure drop in that coil section and any other pressure
drops upstream of it.
Example:
• Return duct -- 0.5 in. static
• Mixing box-- 0.4 in. static
• Filters-- 0.2 in. static
• Heating coil -- 0.2 in. static
• Cooling coil -- 1.2 in. static
• Fan-- 2.3 in. external static
If calculating the trap depth for the cooling coil, the total
trap static would be 2.5 in. plus 1 in. (Pl = negative static
pressure + 1 in.), as shown in Fig. 74A.
Traps on draw-thin units must store enough condensate to
prevent losing the drain seal at strut-up. The "minimum 1/2 Pl"
dimension ensures that enough condensate is stored.
To determine the trap dimensions for blow-thru units, lind
the coils maximum positive pressure (PI in Fig. 74B) and add
I/2 inch. This figure is normally the fan total static pressure
(Pl = fan toted static pressure).
NOTE: Trapping to 5 in. static pressure on blow-thru and 3 in.
static pressure on draw-thin units is possible with the stan&_rd
6 in. baserail.
For all units, provide condensate freeze-up protection as
required. On units with internal spring isolators, be sum the
unit is mounted to allow sufficient clearance for the required
drain trap depth.
Fig. 74A- Condensate Drain,
Draw-Thru Trapping
1/2 P1
MINIMUM
0.5"
MINIMUM
L
r
pl
Fig. 74B -- Condensate Drain,
Blow-Thru Trapping
Fan Motor Wiring Recommendations -- Motors
;u'e rated for use with variable frequency drives. Full load amp
(FLA) efficiency and power factoL's are listed in Tables 23A
and 23B. Refer to Fig. 75 for fan type and application.
TYPE
Forward-Curved(FC)
Side View
Airfoil (AF)
Side View
Plenum(PAF)
End View
CHARACTERISTICS APPLICATION
• Double-width, double-inlet (DWDI) construction.
• Best at low or medium pressure (approximately 0 to 5 in. wg).
• Horsepower increases continuously with increase in air quantity (overloads) as
static pressure decreases.
• Less expensive than AF fans.
• Runs at relatively low speed, typically 400 to 1200 rpm.
• Blades curve toward direction of rotation.
• Double-width, double-inlet (DWDI) construction.
• Best in high capacity and high-pressure applications (4 to 8 in. wg).
• Horsepower peaks at high capacities.
• Most expensive of centrifugal fans.
• Operates at high speeds, typically 1200 to 2800 rpm. About double the speed of
FC fan for similar air quantity.
• Blades have aerodynamic shape similar to airplane wing and are curved away
from direction of rotation.
• Single-width, single-inlet (SWSI) construction.
• Characteristics similar to DWDI airfoil fan.
• Blades have aerodynamic shape similar to airplane wing and are curved away
from direction of rotation. Fewer blades and wider blade spacing than AF fans.
For low to medium pressure
air-handling applications.
For medium to high air capacity
and pressure applications.
Best in applications with limited
space or multiple ducts.
Fig. 75 -- Fan Type and Application
69

Motor Electrical Data -- See Tables 23A and 23B for
Motor Electric;d Data.
Table 23A -- ODP 60 Hz Motor Data
HIGH EFFICIENCY
MOTOR FLA EFF. P.F.
HP 200v 230v 460v 575v (%) (%)
1/2 2.2 1.8 1.1 0.9 N/A N/A
3/4 2.6 2.5 1.3 1.0 N/A N/A
1 3.2 3.0 1.5 1.1 82.5 84
11/2 4.5 3.9 1.9 1.6 84.0 85.7
2 6.0 5.2 2.6 2.1 84.0 85.7
3 9.4 8.6 4.3 3.4 86.5 76.0
5 15.3 12.8 6.4 5.1 87.5 83.3
71/2 25.0 19.2 9.6 7.8 88.5 81.5
10 29.3 26.8 13.4 10.3 89.5 80.0
15 43.2 38.6 19.3 15.4 91.0 83.1
20 56.0 49.6 24.8 19.8 91.0 84.0
25 70.5 60.6 30.3 24.3 91.7 81.0
30 85.0 75.0 37.5 30.0 92.4 79.0
40 110.0 95.0 47.5 41.0 93.0 84.0
50 138.0 120.0 60.0 48.0 93.0 90.0
60 154.0 134.0 67.0 53.5 93.6 90.0
75 189.0 164.0 82.0 65.5 94.1 91.0
LEGEND
EFF. -- Efficiency
FLA -- Full Load Amps
ODP -- Open Dripproof
P.F. -- Power Factor
MOTOR
HP
1/2
3/4
1
1112
2
3
5
7112
10
15
20
25
30
40
50
60
75
PREMIUM EFFICIENCY
FLA EFF. P.F.
200v I 230v I 460v I575v (%) (%)
N/A N/A N/A
N/A N/A N/A
N/A N/A N/A
N/A N/A N/A
N/A N/A N/A
9.0 8.0 4.0 N/A 88.5 79.5
14.5 13.6 6.8 N/A 89.5 76.8
21.5 19.4 9.7 N/A 91.7 79.0
28.0 25.2 12.6 N/A 91.7 81.0
42.5 37.8 18.9 N/A 93.0 80.0
56.0 49.0 24.5 N/A 93.6 81.5
69.5 61.0 30.5 N/A 93.6 82.3
82.5 72.4 36.2 N/A 93.6 82.8
105.0 96.0 48.0 N/A 94.5 83.5
137.0 120.0 60.0 N/A 94.5 83.0
154.0 134.0 67.0 N/A 95.4 87.7
191.0 166.0 83.0 N/A 95.4 87.0
Table 23B -- TEFC 60 Hz Motor Data
HIGH EFFICIENCY
MOTOR FLA EFF. P.F.
HP 208v 230v 460v 575v (%) (%)
1/2 1.8 1.6 0.9 0.7 N/A N/A
3/4 2.4 2.4 1.2 0.8 N/A N/A
1 4.0 3.2 1.6 1.3 82.5 72.0
11/2 5.5 4.4 2.2 1.6 84.0 72.0
2 7.0 5.8 2.9 2.1 84.0 76.0
3 10.0 8.2 4.1 3.3 87.5 78.0
5 17.0 13.2 6.6 5.2 87.5 81.5
71/2 24.0 19.2 9.6 7.6 89.5 83.0
10 31.0 24.4 12.2 9.6 89.5 85.5
15 47.0 35.0 17.5 14.5 91.0 85.0
20 61.0 47.0 23.5 18.8 91.0 87.0
25 74.0 57.0 28.5 22.8 92.4 88.0
30 82.0 69.0 34.5 27.6 92.4 88.0
40 115.0 95.0 47.5 37.6 93.0 85.0
50 142,0 118.0 59.0 47.2 93.0 85.0
60 N/A 140.0 70.0 N/A 93.6 85.5
75 N/A 170.0 85.0 N/A 94.1 86.5
LEGEND
EFF. -- Efficiency
FLA -- Full Load Amps
P.R -- Power Factor
TEFC -- Totally Enclosed Fan Cooled
MOTOR
HP
1/2
3/4
1
1112
2
3
5
7112
10
15
2O
25
3O
4O
50
6O
75
PREMIUM EFFICIENCY
FLA EFF. P.F.
208v I 230v I 460v 1575v (%) (%)
N/A N/A N/A
N/A N/A N/A
4.0 3.0 1.5 1.2 84.5 72.0
5.5 4.2 2.1 N/A 85.5 72.0
7.0 5.6 2.8 2.2 86.5 77.5
10.0 8.2 4.1 3.3 88.5 78.0
17.0 13.0 6.5 5.2 88.5 84.5
24.0 19.2 9.6 7.6 90.2 81.5
31.0 24.0 12.0 9.6 90.2 85.0
47.0 35.0 17.5 14.0 91.7 86.0
61.0 47.0 23.5 18.8 92.4 87.0
74.0 57.0 28.5 22.8 93.0 88.0
82.0 69.0 34.5 27.6 93.0 88.0
115.0 90.0 45.0 37.0 94.1 88.5
147.0 115.0 57.5 46.0 9.41 86.4
N/A 140.0 70.0 56.0 94.1 89.0
N/A 172,0 86.0 69.0 95.4 86.0
70

Fan Motor Starter -- When starter is factory-installed, it
is wired to the motol: and fully tested before shipping. Before
proceeding, open the starter cover and fan section access door
to check for any &tmage.
WIRING
1. Select a suitable location for the field power supply
source; top is prefened.
2. Before drilling any hole, be sure the hole and any field-
supplied conduit fittings will not interfere with the door
or components inside the enclosme.
3. Drill the appropriate size hole and connect the field-
supplied conduit to the enclosure.
4. Refer to the wiring diagrmn supplied with the starter and
connect the line voltage power source to the line voltage
terminals (LI, L2, L3) as shown.
5. Refer to the factory-supplied voltage warning label and
verify that the power source is correct.
6. Connect the grounding wire to the grounding lug provid-
ed on the bottom of the starto:
NOTE: For remote control operation (AUTO position), fire/
smoke shutdown, or shutdown on coil freeze protection, a sec-
ond conduit should be used to connect these control functions.
IIMPORTANT: This starter is designed to stop the
equipment in both HAND and AUTO positions if
either a fire/smoke or coil freeze condition is detected.
7. Select a location at the bottom of the starter near the
control terminal block.
8. Before drilling any hole, be sure the hole and any field-
supplied conduit fittings will not interfere with the door
or components inside the enclosme.
9. Drill the appropriate size hole and connect the field-
supplied conduit to the enclosure.
10. If a smoke detector or remote fire shut down is provided
(field-supplied), remove the factory-supplied jumper
between terminals 1 and 2 in the starter Connect the
norm_dly closed, isolated &y contact from the smoke
detector or fire system to these terminals.
11. If a coil fieeze detection thermostat is provided, remove
the factory-supplied jumper between termimds 1 and 2 in
the stmtec Connect the normally closed contact from the
low temperatme thermostat to these terminals.
12. For remote st_ut/stop operation (when the HOA [hand/
auto/off] switch is placed in the AUTO position), connect
a field-supplied, normally open isolated dry contact
between terminals 3 and 4. This contact must be suitable
for at least 3 amps at 120 vac.
START-UP AND TEST -- Before applying power to the
starter, verify that the motor overload inside the starter is set to
the lhll load mnperage (FLA or RLA) specified on the motor
nameplate.
IMPORTANT: Many starters contain a multi-tap
control transformer. The line voltage tap on the control
transformer must be set in the field. For starters operat-
ing at 200/230-50 Hz, 208/230-60 Hz, or 380/400/
415-50 Hz, the line voltage tap on the control trans-
former must be set to the appropriate line input voltage.
1. Set the HOA switch on the front of the starter to the OFF
position.
2. Verify that the fan can freely rotate and remove any loose
items inside the fan section.
3. Close and secure the fan access door or panel and the
starter door coveg
4. Apply power to the stmter
5. Set the HOA switch in the HAND position and verify that
the fan operates.
For 3-phase motor:
Place the switch back in the OFF position and carefully
open the fan access dooc
Verify that the fan wheel is rotating in the proper dilection.
If it is not, remove power and reverse any two of the line
voltage connections at the starter termimds (LI, L2, L3).
6. With the fan operating and the starter in the HAND posi-
tion, verify that each safety or limit switch functions
properly.
7. Repeat Step 6 with the switch in the AUTO position and
the remote contact energized.
Disconnect- When disconnect is factory-inst_dled, it is
wired to the motol: and thlly tested befole shipped. Open the
disconnect cover and fan section access door to check for
&_mage before proceeding.
DISCONNECT WIRING
1. Connect the field line voltage power source to the top of
the disconnect (knockouts are provided).
2. Remove the knockouts as required to accommo&tte the
field-supplied conduit.
3. Refer to the wiring diagraln supplied with the unit and
connect the line voltage power source to the line voltage
terminals (LI, L2, L3) as shown.
4. Refer to the factory-supplied voltage w;uning label and
verify that the power source is correct.
5. Connect the ground wire to the grounding lug provided in
the disconnect.
START-UP AND TEST
1. Set the disconnect switch to the OFF position.
2. Verify that the fan can fi'eely rotate and remove any loose
items inside the fan section.
3. Close and secme the fan access door and the disconnect
door covel:
4. Apply powec
5. Set the disconnect switch to the ON position and verify
that the fan operates.
For 3-phase motor:
Place the switch back in the OFF position and carefully
open the fan access dool:
Verify that the fan wheel is rotating in the proper direction.
If it is not, remove power and reverse any two of the line
voltage connections at the starter termimds (LI, L2, L3).
NOTE: For lused type disconnects, blown luses MUST be
replaced with the stone type and size originally supplied.
VFD- When variable frequency diive (VFD) is factory-
installed, it is wired to the motor and frilly tested before ship-
ment. Drive programming is also done at the factory, including
electronic overload, which is programmed for the motor FLA.
Refer to Tables 24 and 25.
Open the VFD front cover and the fan section access door to
check for any &tmage before proceeding.
WIRING
1. Select a suitable location in the bottom of the VFD to
connect field-supplied power source.
2. Remove the appropriate size knockout using a suitable
knockout punch tool. Do NOT use a drill; metal shavings
will &tmage the chive.
3. Connect the field-supplied conduit to the VFD enclosure.
71

4. Referto thewiringdiagramsuppliedwiththeVFD
connectthelinevoltagepowersourcetothelinevoltage
terlninals(U1,V1,W1)asshown.
5. Refertothefactory-suppliedvoltagewarninglabeland
verifythat the power source is correct.
6. Connect the ground wire to the grounding lug provided
on the bottom of the VFD.
7. Select another suitable location on the bottom of the VFD
to connect file field-supplied control wiling.
8. Ix_cate and use one of the unused knockouts on file VFD
housing and connect the control wiring conduit. Refer to
Fig. 76-79 for field control wiring connections.
NOTE: Ifa 0 to 10 or 2 to 10 vdc signal is used to control the
drive speed, refer to page 16 of the ABB ACH-550 manu_d
shipped with the &ive to reset the dipswitch to the voltage or
V position. Verify that the AI switch is set to the voltage
position. DO NOT reprogram the &ive.
START-UP AND TEST
1. Close and secure rite fan access door trod the VFD covel:
2. Apply power and allow &ive to initialize.
3. Press the HAND button and verify that rite drive operates
at 8Hz.
4. Press Up arrow to increase speed and Down turow to
decrease speed.
5. Press the Offbutton and verify that the fan stops.
6. Press the Auto button to operate the drive from the
Energy Management System (EMS) interface. Verify that
all VFD interface functions are working (start/stop, speed
controls, fire/smoke, shutdown, etc.) between the VFD
and the EMS.
Refer to Tables 24 and 25 for additional VFD information.
VFD With Bypass -- When the VFD and bypass m'e
factory-installed, they ;u'e wired to the motor and fully tested
before shipped. The VFD is programmed at the factory as
ordered, including electronic overload, which is progralnmed
for the motor FLA (full load amps) as supplied.
Open the bypass box cover and rite fan section access door
to check for any damage before proceeding.
WIRING
1. Select a suitable location in the bottom panel of the
bypass box to connect field-supplied power source.
2. Before drilling any hole, be sure the hole and any field-
supplied conduit fittings will not interfere with the door
or components inside the enclosure.
3. Drill the appropriate size hole and connect the field-
supplied conduit to the enclosure.
4. Refer to the wiring diagram supplied with rite bypass and
connect the line voltage power source to the line voltage
terlninals iLl, L2, L3) as shown.
5. Refer to the factory-supplied voltage warning label and
verify that the power source is correct.
6. Connect the ground wire to the grounding lug provided
on rite bottom of the Bypass box.
7. Refer to the VFD Steps 7 and 8 to connect VFD control
wiring.
START-UPAND TEST-- Before applying power to the
VFD Bypass and VFD, verify that the motor overload inside
the bypass has been set to the full load amperage (FLA or
RLA) as specified on the motor nameplate.
IMPORTANT: Some bypass assemblies (208/230-60,
200/230-50, 380/400/415-50) contain a multi-tap control
transformel: The line voltage tap on the control trans-
former must be adjusted to the appropriate line voltage.
I. Set rite switch on the front of rite bypass to rite OFF
position.
2. Verify that the fan freely rotates and remove and loose
items inside the fan section.
3. Close and secure the fan access door and the bypass and
VFD covers.
4. Apply pewee
5. Set the switch to rite LINE position and verify that the fan
operates.
For 3-phase motors:
Place the switch back in the OFF position and carefully
open the fan access dool:
Verify that the fan wheel is rotating in the proper direction.
If it is not, remover power and revel_e any two of the line
voltage connections in the bypass box (Ll, L2, L3). DO
NOT swap the motor leads; this will cause the fan to ro-
tate in the reverse direction when operating from the VFD.
6. Make sure the bypass cover is closed then apply power
7. Set the switch to the DRIVE position and verify that the
VFD operates.
8. Press the Hand button and verify that the fan operates.
9. Press the Auto button and verify that the drive operates
fi_m the EMS interface. Verify that all VFD interface l'unc-
tions between the VFD and the EMS system are working.
Table 24 -- VFD Data
80MI
MOTOR HP
PROGRAMMED SETTINGS
ABB PART MAX. CONTINUOUS MCCB
NO. ACH550-UH- OUTPUT AMPS FUSE AMPS RATED AMPS Overload Trip Ampe I Max. Output Ampe
4 pole /2 pole I 4 pole /2 pole
l&
3/4
1
1V2
2
3
5
7V2
10
15
20
25
30
40
LEGEND
208-230 Volt /3 Phase /60 Hz (Programmed to Operate at 208 volts)
04A6-2 4.6 10 15 1.8/ 1,7 3.0/ 2,2
04A6-2 4.6 10 15 2.6/ 2,5 3.2/ 3,0
04A6-2 4.6 10 15 3.5/ 3,2 3.8/ 3,8
06A6-2 6.6 10 15 5.2/ 4,2 5.8/ 5,8
07A5-2 7.5 10 15 6.7/ 5,9 7.2/ 7,0
012A-2 11,8 15 15 9.0/ 8,5 10.0/ 9,5
017A-2 16,7 25 25 14.5/ 13,6 16.7/ 16,0
024A-2 24.2 30 30 21.4/ 20,7 24.0/ 23,0
031A-2 30.8 40 40 27.4/ 27,4 30.8/ 3O,O
046A-2 46,2 60 60 40.5/ 40,5 46.2/ 43,0
059A-2 59,4 80 80 53.0/ 52,2 59.4/ 57,0
075A-2 74,8 100 100 67.0/ 66,0 74.0/ 71,0
088A-2 88,0 110 110 82.0/ 78,0 85.0/ 82,0
114A-2 114,0 150 150 92.0/107,0 114.0/110,0
MCCB -- Molded-Case Circuit Breaker
NOTE: Two-pole motors operate at a nominal 3600 rpm for 60 Hz and 3000 rpm for 50 Hz;
4-pole motors operate at a nominal 1800 rpm for 60 Hz and 1500 rpm for 50 Hz,
72

Table 24 -- VFD Data (cont)
I I I PROGRAMME iSETTINGS
39M ABB PART MAX. CONTINUOUS FUSE AMPS MCCB
MOTOR HP NO, ACH550-UH- OUTPUT AMPS RATED AMPS Overload Trip Amps Max. Output Amps
4 pole /2 pole 4 pole /2 pole
208-230 Volt /3 Phase /60 Hz (Programmed to Operate at 230 volts)
1
11/2
2
3
5
71/2
10
15
20
25
30
40
5O
6O
75
100
LEGEND
143A2143,200, 200,12 0/1300,1420J1300
60 178A-2 178 l l l T250 250 154.0/135.0 172.0/145.0
75 221A-2 221 300 300 186.0/166,0 221.0/172,0
460 Volt /3Phase /60 Hz (Programmed to Operate at 460 volts)
1/2 03A3-4 3.3 10 15 0.9/ 1.0 1.5/ 1.2
3/4 03A3-4 3.3 10 15 1.3/ 1.2 1.7/ 1.5
1 03A3-4 3.3 10 15 1.6/ 1.5 1.9/ 1.7
11/2 03A3-4 3.3 10 15 2.2/ 2.0 2.8/ 2.3
2 03A3-4 3.3 10 15 2.7/ 2.7 3.0/ 3.0
3 05A4-4 5.4 10 15 4.0/ 3.8 4.5/ 4.2
506A9-4 6.9 10 15 6.2/ 6,0 6.9/ 6,5
71/2 012A-4 11.9 15 15 9.0/ 8,8 10.0/ 9,5
10 015A-4 15.4 20 20 12.0/ 11.6 13,6/ 12.8
15 023A-4 23 30 30 17.6/ 16.5 19.3/ 19.0
20 031A-4 31 40 40 23.0/ 23.0 25,0/ 25.0
25 031A-4 31 40 40 29.0/ 28.0 31.0/ 30.0
30 038A-4 38 50 50 34.5/ 34.0 38.0/ 38.0
40 059A-4 59 80 80 46.0/ 44.0 48.0/ 50.0
50 072A-4 72 90 90 58.0/ 55.0 60.0/ 60.0
60 077A-4 77 100 100 73.0/ 68,0 77.0/ 72,0
75 096A-4 96 125 125 90.0/ 85.0 94.0/ 90.0
100 124A-4 124 175 175 118.0/110,0 124.0/114,0
200-230 Volt /3 Phase /50 Hz (Programmed to Operate at 200 volts)
1 04A6-2 4.6 10 15 3.3/ 3.3 3.9/ 3.9
11/2 06A6-2 6.6 10 15 4.9/ 4.9 5.8/ 5.8
2 07A5-2 7.5 10 15 6.3/ 6,3 7.1/ 7.1
3 012A-2 11.8 15 15 8.7/ 8,7 10.0/ 10,0
5 017A-2 16.7 25 25 14.0/ 14.0 16,7/ 16.7
71/2 024A-2 24.2 30 30 21.2/ 20.2 24.2/ 24.2
10 031A-2 30.8 40 40 27.2/ 27.4 30.8/ 30.8
15 046A-2 46.2 60 60 41.4/ 40.5 46,2/ 46.2
20 059A-2 59.4 80 80 53.4/ 49.0 59.4/ 56.0
25 075A-2 74.8 100 100 65.4/ 66.0 74.0/ 74.8
30 088A-2 88 110 110 78.0/ 78.0 86.0/ 86.0
40 114A-2 114 150 150 107.0/107,0 114.0/114,0
50 143A-2 143 200 200 135.0/135,0 135.0/135,0
60 178A-2 178 250 250 169.0/169.0 169.0/169.0
75 221A-2 221 300 300 210.0/210.0 210.0/210.0
380 Volts /3 Phase /50 Hz (Programmed to Operate at 400 volts)
03A3-4 3.3 10 15 1.7/ 1,7 2.3/ 2,3
03A3-4 3.3 10 15 2.5/ 2.5 3.3/ 3.3
04A1-4 4.1 10 15 3.2/ 3,2 3.8/ 3,6
05A4-4 5.4 10 15 4.5/ 4,5 5.4/ 5,3
08A8-4 8.8 15 15 7.0/ 7.0 8.5/ 8.0
012A-4 11.9 15 15 10.6/ 8,9 11.9/ 11,0
015A-4 15.4 20 20 13.6/ 11.6 15,4/ 14.6
023A-4 23 30 30 20.7/ 17.0 22.6/ 21.0
031A-4 31 40 40 26.7/ 24.5 29,3/ 29.0
038A-4 38 50 50 32.7/ 29.5 37,0/ 36.0
044A-4 44 60 60 39.0/ 39.0 44.0/ 44.0
059A-4 59 80 80 53.5/ 45.5 57.0/ 55.0
077A-4 77 100 100 67.5/ 67,5 70.0/ 70,0
096A-4 96 125 125 84.5/ 84,5 88.0/ 88,0
124A-4 124 175 175 105.0/105,0 105.0/105,0
157A-4 157 200 200 134.0/134,0 134.0/134,0
MCCB -- Molded-Case Circuit Breaker
NOTE: Two-pole motors operate at a nominal 3600 rpm for 60 Hz and 3000 rpm for 50 Hz;
4-pole motors operate at a nominal 1800 rpm for 60 Hz and 1500 rpm for 50 Hz.
73

Table 25 -- Air Handler Factory-Set Parameters
GROUP NUMBER PARAMETER NUMBER DESCRIPTION VALUE
9902 Application Macro Supply Fan
9904 Motor Control Mode Scalar
9905 Motor Nominal Voltage
99 9906 Motor Nominal Current t
9907 Motor Nominal Frequency 60 Hz or 50 Hz
9908 Motor Nominal Speed Nameplate rpm at Load
9909 Motor Nominal Power Nameplate Hp
1001 EXT1 Commands DI-1 Start /Stop
10 1002 EXT2 Commands (O) N/A
1003 Direction Forward
1104 REF1 Minimum 9.33 Hz at 60 Hz/7.78 Hz at 50 Hz
11 1105 REF1 Maximum 62.7 Hz at 60 Hz /52.2 Hz at 50 Hz
1201 Constant Speed Select DI-3
12 1202 Constant Speed Value Field Program (8 Hz - Motor Nominal Freq.)
1301 Minimum AI-1 0%
1302 Maximum AI-1 100%
1303 Filter AI-1 1 sec
13 1304 Minimum AI-2 0%
1305 Maximum AI-2 100%
1306 Filter AI-2 1 sec
1401 Relay Output 1 Started
14 1402 Relay Output 2 Run
1403 Relay Output 3 Fault (Inverted)
1601 Run Enable DI-2
16 1608 Start Enable 1 DI-4
1609 Start Enable 2 DI-5
2003 Maximum Current **
20 2007 Minimum Frequency 8 Hz
2008 Maximum Frequency 60 Hz /50 Hz
2101 Start Function FlyStart
21 2102 Stop Function Coast
2202 Accelerate Time 60 Seconds
22 2203 Decelerate Time 60 Seconds
2605 Volt/Freq Ratio Linear
26 2606 Switching Frequency 8 KHz
2607 Switching Frequency Control ON
3006 Motor Thermal Time 1050
3007 Motor Load Curve 105%
3008 Zero Speed Load 70%
3009 Break Point Frequency 35 Hz
30 3010 Stall Function Fault
3011 Stall Frequency 20 Hz
3012 Stall Time 20 sec
3017 Earth Fault Fault
3101 Number of Retries 2
3102 Trial Time 600 sec
3103 Delay Time 5 sec
3104 AR Overcurrent Enable
31 3105 AR Overvoltage Enable
3106 AR Undervoltage Enable
3107 AR AI< Minimum Disable
3108 AR External Fault (O) Disable
3415 Signal Parameter 3 SPEED
3416 Signal 3 Minimum O
3417 Signal 3 Maximum 30000
34 3418 Output 3 DSP Form O
3419 Output 3 DSP units rpm
3420 Output 3 Minimum O
3421 Output 3 Maximum 30000
4001 Gain 0.7
4002 Integration Time 30 sec
4005 Error Value Invert NO
4006 Units Volts
4007 Display Format x.xxx
40 401 O Setpoint Select Internal
4011 Internal Setpoint Field Program (O.Ov - lO.O v)
4012 Setpoint Minimum O.O v
4013 Setpoint Maximum 10.O v
4016 ACT 1 Input AI-2
4027 PID 1 Parameter Set SET 1
*Factory Programmed as follows: For 208-230v /60 Hz = 208,460v /60
tMotor Nameplate Amps. Factory programmed per Table 24. This value
**Maximum Output Amps -- Factory programmed per Table 24.
Hz =460,200-230v /50 Hz =200, 380 /50 Hz =400.
should always be compared to the actual motor nameplate value before start-up.
74

, ,.o° ,o°°**°°
Speed/ - - -4-20 ma //
IControl Signal _T - - -
Field-Supplied
Input Connections
Jumper E
N.O. Start /StopContact
_= = H. = ° .ll.,. °=_,_""_O=.H =... j, o.°..,,
_..._ c:V_._./&_.D..%C?.,._._t....
•:N,C. Low Limit Thermostat
i.......N.cA!i.g._e.Swi!_.!:......
AI-1 Cable Shield Ground
AI-t VFD SPEED Signal (+) 4-20 ma
AI-I VFD SPEED Signal (-) ground
24 Vdc
Ground -° DC Common
Digital Input Common
DI-1 Start/Stop
DI-2 Run Enable
DI-4 Start Enable 1
DI-5 Start Enable 2
NOTES:
1. All conductors are no. 18 AWG (American Wire Gage) minimum.
2. Install jumpers if fire/smoke detector, low limit thermostat, or high pressure switch are not required.
Fig. 76 -- Field-Supplied Control Wiring for VFD
Output
Adapter
corn
TB3
l -°,
2
3 ,..,
4 ...
5
6
7
8
9
10
Air Manager
:() Shielded Cable (_'!'_=!'" i
w°,_l_==*=mwH,*°,°,°mmmmm_**_°==_*m,,,°m*,_ I
r
I Jumper E
I
I
2
3
4
5
6
7
8
9
I0
11
--i7-
Jw==,=|_=m=,**J===°°°°,=°°,=°°°°,°,,,,,,=====°=°=, 13
I.. N.C,; F._ire_Det. Contact I"'7
15
--5-
18
AI-I Cable Shield Ground
AI-I VFD SPEED Signal (+) 4-20 ma
AI-I VFD SPEED Signal (-) ground
24 Vdc
Ground - DC Common
Digital Input Common
DI- l Start /Stop
DI-2 Run Enable
DI-4 Start Enable 1
DI-5 Start Enable 2
ABB VFD Drive
Air Manager Drive
Input Connections
NOTES:
1. All conductors are no. 18 AWG (American Wire Gage) minimum.
2. Install jumper wire if fire/smoke detector, is not required.
Fig. 77 -- Field Wiring the VFD to the AirManager TM Control
75

,....
?-;-
?;
II
I _ TB3
I I -T-
| I 2
I I :3
| 4
i _ --T-
I-- 6
i-._--7-
8
9
10
CC6400
Control Box
Shielded Cable
I Jumper E
I
iJ._,* ,.=...l............m= J= J J,m•Jllo°°o..°,,J=*,w,*,=
LN.C_ Fire/m..__m_Det. Con.tact .
CC6400 Drive
Input Connections
AI-1 Cable Shield Ground
AI-I VFD SPEED Signal (+) 4-20 ma
AI-I VFD SPEED Signal (-) ground
24 Vdc
Ground - DC Common
Digital Input Common
DI-I Start/Stop
DI-2 Run Enable
DI-4 Start Enable 1
DI-5 Start Enable 2
ABBVFD Drive
NOTES:
1. All conductors are no. 18 AWG (American Wire Gage) minimum.
2. Install jumper wire if fire/smoke detector, is not required.
Fig. 78 -- Field Wiring the VFD to the CC6400 Comfort Control
Field-Supplied
Input Connections
_,,=,,,,.,=l==m====_**_=======***==°°,,°.**J
:Jumper E
"_ N.O. Start /Stop Contact
............... o.--/o .................
1
2
3
4
5
d
7
8
9
10
11
-57-
_,..._,c:._!r_./&_bP.e.t,.C.'o".:_.%..--7Z-
N.C. Low Limit Thermostat
............... _ ................ 16
!......,N.-.c..._.t_ ._.Swi_.c..h....... --?7-
18
24 Vdc
Ground - DC Common
Digital Input Common
DI-I Start/Stop
DI-2 Run Enable
DI-3 Fixed Speed Enable
DI-4 Start Enable 1
DI-5 Start Enable 2
NOTES:
1. All conductors are no. 18 AWG (American Wire Gage) minimum.
2. Install jumpers if fire/smoke detector, low limit thermostat, or high pressure switch are not required.
3. Program desired speed setpoint in Hz using parameter 1202.
Fig. 79 -- Field Wiring for High Inertia/Low Horsepower Applications Using VFD as a Starter
76

VFD Configuration- The VFD keypad is shown in
Fig. 80. Tile flmction of SOFT KEYS 1 and 2 change depend-
ing on what is displayed on the screen. The function of SOFT
KEY 1 matches the word in the lower left-hand box on the
display screen. The function of SOFT KEY 2 matches the
word in the lower right-hand box on the display screen. If the
box is empty, then the SOFT KEY does not have a function on
that specific screen. The UP and DOWN keys am used to
navigate through the menus. The OFF key is used to turn off
the VFD. The AUTO key is used to change control of the drive
to automatic control. The HAND key is used to change control
of the drive to local (hand held) control. The HELP button is
used to access the help screens.
START UP WITH ASSISTANT-- The initial start-up has
been performed at the factory. To stm_ up the VFD with the
Stml-Up Assistant, perform the following procedure:
1. Select MENU (SOFT KEY 2). The Main menu will be
displayed.
2. Use the UP or DOWN keys to highlight ASSISTANTS
on the display screen find press ENTER (SOFT KEY 2).
3. Use the UP or DOWN keys to highlight Commission
Drive and press SEL (SOFT KEY 2).
4. The Stml-Up Assistant will display the parameters that
need to be configured. Select file desired values and press
SAVE (SOFT KEY 2) after every change. Tile process
will continue until all the parameters am set.
START UP BY CHANGING PARAMETSERS INDIVID-
UALLY -- Initial start-up is performed at the factory. To start
up the VFD with by changing individual parameters, perform
the following procedure:
1. Select MENU (SOFT KEY 2). The Main menu will be
displayed.
2. Use the UP or DOWN keys to highlight PARAMETERS
on the display screen and press ENTER (SOFT KEY 2).
3. Use the UP and DOWN keys to highlight the desired
parameter group and press SEL (SOFT KEY 2).
4. Use the UP or DOWN keys to highlight the desired
parameter and press EDIT (SOFT KEY 2).
5. Use the UP or DOWN keys to change the value of the
Du'ameteb:
6. Press SAVE (SOFT KEY 2) to store the modified vfflue.
Press CANCEL (SOFT KEY 1) to keep the previous
value. Any modifications that am not saved will not be
changed.
7. Choose another parameter or press EXIT (SOFT KEY 1)
to return to the listing of parameter groups. Continue until
all the Duameters have been configured and then press
EXIT (SOFT KEY 1) to return to the main menu.
STAJUS
LED
{GREEN WHEN
NORMA , IF FI ASH NG
RED, SEE
DIAGNOSTICS.)
SOFT
OFf
SOFT
KEY 2
HELP
(ALWAYS AVAILABLE)
Fig. 80 -- VFD Keypad
NOTE: The current parameter value appem.s above the high-
light parameter. To view the default pm'ameter value, press the
UP and DOWN keys simultaneously. To restore the default
factory settings, select the application macro "HVAC Default."
VFD Modes -- The VFD has several different modes for
configuring, operating, find diagnosing the VFD. The modes
ale:
• standard display mode-- shows drive status information
and operates the drive
• parameters mode-- edits parameter values individually
• start-up assistant mode -- guides the start up and
configuration
• changed parameters mode -- shows all changed
parameters
• drive parameter backup mode -- stores or uploads the
parameters
• clock set mode -- sets the time and date for the drive
• 1/O settings mode -- checks and edits the I/O settings
Standard Display Mode -- Use the standtud display mode to
read information on the diive status and operate the diive. To
reach the stan&trd display mode, press EXIT until the LCD dis-
play shows status information as described below. See Fig. 81.
MODE _ j4,._SET POINT
I ""=AUTO'_ . 15.8Hz'"- I
/30.0 Hz /
/3.7A /
|838 RPM /
Fig. 81 -- Standard Display Example
The top line of the LCD display shows the basic status
information of the diive. The HAND icon indicates that the
diive control is local from file control panel. The AUTO icon
indicates that the drive control is in remote control mode
flnough the I/O.
The anow icon indicates the drive and motor rotation status.
A rotating arrow (clockwise or counterclockwise) indicates
fllat the diive is running. A rotating blinking rerow indicates
flint the diive is running but not at set point. A stationary arrow
indicates that the diive is stopped. For Carrier air handler units,
the rotation is always forward.
Using parameter group 34, the middle of the LCD display
can be configured to display 3 pmameter values. The default
display shows parameters 0103 (OUTPUT FREQ) in Hz, 0104
(CURRENT) in amperes, and AII (Amflog Input 1) in revolu-
tions per minute.
The upper right hand corner shows the frequency set point
that the drive will maintain.
The bottom comers of the LCD display show the functions
currently assigned to the two soft keys. Tile lower middle
displays the current time (if configured to show the time).
The fib.st time the drive is powered up, it is in the OFF
mode. To switch to local hand-held control find control the
diive using the control pane, press the HAND or AUTO
buttons. Pressing the HAND button switches the drive to hand
control while keeping the drive running. Pressing the AUTO
button switches the diive to remote input control. The OFF
button stops the drive. To beturn to auto control, press the
AUTO button. To start the diive press the HAND or AUTO
button, to stop the drive press the OFF button.
To adjust the speed set point while in HAND mode, press
file UP or DOWN buttons (the reference changes immediate-
ly). The reference can be modified in the local control (HAND)
mode, and can be pfuameterized (using Group 11 reference
select) to also allow modification in the bemote control mode.
77

Parameters Mode -- The Parameters mode is used to change
the pm'ameters on the &ive. To change parameters, perform the
following procedure:
1. Select MENU (SOFT KEY 2). The Mtdn menu will be
displayed.
2. Use the UP or DOWN keys to highlight PARAMETERS
on the display screen and press ENTER (SOFT KEY 2).
3. Use the UP or DOWN keys to highlight the desired
p_u'ameter group and press SEL (SOFT KEY 2).
4. Use the UP or DOWN keys to highlight the desired
p_u'ametel_ and press EDIT (SOFT KEY 2).
5. Use the UP or DOWN keys to change the value of the
ptuameters.
6. Press SAVE (SOFT KEY 2) to store the modified value.
Press CANCEL (SOFT KEY 1) to keep the previous
v_due. Any modifications that are not saved will not be
changed.
7. Choose another parameter or press EXIT (SOFT KEY 1)
to return to the listing of pmameter groups. Continue until
all the parametelN have been configured and then press
EXIT (SOFT KEY 1) to return to file main menu.
NOTE: The current parmneter value appears above the high-
light pammetel: To view the default parmneter vMue, press the
UP and DOWN keys simultaneously. To restore the default
factory settings if a drive fails, download the pm'ameters to the
VFD from the control panel. Parameters can also be changed
individually.
Changed Parameters Mode -- The Changed ParametelN
mode is used to views and edit recently changed parametel_ on
the drive. To view the changed parametelN, perform the follow-
ing procedure:
1. Select MENU (SOFT KEY 2). The Main menu will be
displayed.
2. Use the UP or DOWN keys to highlight CHANGED
PAR on the display screen and press ENTER (SOFT
KEY 2). A list of the recently changed parameters will be
displayed.
3. Use file UP or DOWN keys to highlight the desired
p_u'ameter group and press EDIT (SOFT KEY 2) to
change the p_uameters if desired.
4. Press EXIT (SOFT KEYI ) to exit the Changed Parmne-
ters mode.
Drive Parameter Backup Mode -- The diive parameter back
up mode is used to store the drive parameters. The pammetel_
can be uploaded from a VFD to the removable control panel. If
a drive failure occurs, the control panel can then be transferred
to the new drive and the parameters downloaded into memory.
Each diive is custom progralnmed at the factory. The first
option is to download all parameters. This copies both applica-
tion and motor parameters to the drive from the control panel.
This is recommended to create a backup of the pm'ameters
group for the diive.
The second option downloads only the application parame-
ters to the di'ive. Parameters 9905, 9906, 9907, 9908, 9909,
1605, 1607, 5201, and group 51 ptuameters and internal motor
pm'ameters are not copied.
Upload All Parameters -- To upload and store _dl parametel_
to the control panel from the VFD, perform the following
procedure:
1. Select MENU (SOFT KEY 2). The Main menu will be
displayed.
2. Use the UP or DOWN keys to highlight PAR BACKUP
on the display screen and press ENTER (SOFT KEY 2).
3. Use the UP or DOWN keys to highlight UPLOAD TO
PANEL and press SEL (SOFT KEY 2).
4. The text "Copying Parmneters" will be displayed with a
progress indicator To stop the process, select ABORT
(SOFT KEY 1).
5. When the upload is complete, the text "Parameter upload
successlul" will be displayed.
6. The display will then return to the PAR BACKUP menu.
Select EXIT (SOFT KEY 1) to return to the main menu.
7. The control panel can now be disconnected from the
drive.
Download All Parameters -- To download all parameters
from the control panel to the VFD, perform the following
procedure:
1. Install the control panel with the conect parameters onto
the leplacement VFD.
2. Select MENU (SOFT KEY 2). The Main menu will be
displayed.
3. Use the UP or DOWN keys to highlight PAR BACKUP
on the display scleen and press ENTER (SOFT KEY 2).
4. Use the UP or DOWN keys to highlight DOWNLOAD
TO DRIVE ALL and press SEL (SOFT KEY 2).
5. The text "Restoring Parmneters" will be displayed with a
progress indicatol: To stop the plecess, select ABORT
(SOFT KEY 1).
6. When the download is complete, the text "Pmameter
download successful" will be displayed.
7. The display will then return to the PAR BACKUP menu.
Select EXIT (SOFT KEY 1) to return to the main menu.
8. The control panel can now be disconnected from the
drive.
Clock Set Mode -- The clock set mode is used for setting the
date and time for the internal clock of the VFD. In order to use
the timer functions of the VFD control, the internal clock must
be set. The date is used to determine week&tys and is visible in
the fault logs.
To set the clock, perform the following procedure:
1. Select MENU (SOFT KEY 2). The Main menu will be
displayed.
2. Use the UP or DOWN keys to highlight CLOCK SET on
the display screen and press ENTER (SOFT KEY 2). The
clock set pmameter list will be displayed.
3. Use the UP or DOWN keys to highlight CLOCK VISI-
BILITY and press SEL (SOFT KEY 2). This pm'ameter
is used to display or hide the clock on the screen. Use the
UP or DOWN keys to change the parameter setting. Pless
OK (SOFT KEY 2) to save the configuration and return
to the Clock Set menu.
4. Use the UP or DOWN keys to highlight SET TIME and
press SEL (SOFT KEY 2). Use the UP or DOWN keys to
change the hours and minutes. Press OK (SOFT KEY 2)
to save the configuration and return to the Clock Set
menu.
5. Use the UP or DOWN keys to highlight TIME FORMAT
and press SEL (SOFT KEY 2). Use the UP and DOWN
keys to change the parameter setting. Press OK (SOFT
KEY 2) to save the configuration and return to the Clock
Set menu.
6. Use the UP or DOWN keys to highlight SET DATE and
press SEL (SOFT KEY 2). Use the UP or DOWN keys to
change the day, month, and yem: Pless OK (SOFT KEY
2) to save the configuration and return to the Clock Set
menu.
78

7. UsetheUPorDOWNkeysto highlightDATEFOR-
MATandpressSEL(SOFTKEY2).UsetheUPor
DOWNkeystochangethep_uametersetting.PressOK
(SOFTKEY2)tosavetheconfigurationandreturntothe
ClockSetmenu.
8. PressEXIT(SOFTKEY1)twicetoreturntothemain
menu.
I/O Settings Mode -- The I/O Settings mode is used for view-
ing and editing the I/O settings.
To configure the I/O settings, perform the following
procedure:
1. Select MENU (SOFT KEY 2). The Main menu will be
displayed.
2. Use file UP or DOWN keys to highlight I/O SETHNGS
on the display screen and press ENTER (SOFT KEY 2).
The I/O Settings parameter list will be displayed.
3. Use the UP or DOWN keys to highlight the desired I/O
setting and press SEL (SOFT KEY 2).
4. Use the UP or DOWN keys to select file palameter to
view. Press OK (SOFT KEY 2).
5. Use the UP or DOWN keys to change the parameter set-
ting. Press SAVE (SOFT KEY 2) to save the configura-
tion. Press CANCEL (SOFT KEY 1) to keep file previ-
ous value. Any modifications that are not saved will not
be changed.
6. Press EXIT (SOFT KEY 1) twice to return to the main
menu.
Electric Heaters -- Electric heaters are facto]y installed.
If circumstances require field installation of an electric heater.
it can only be installed in a factory-supplied EHS (Electric
Heat section). Installation of electric heat in a section other than
an EHS section will void file UL listing of the product.
1. Identify ALL electrical power supplies serving the unit,
lock off and tag each before woNing on the unit.
2. Locate the electric heat section mounted on the unit and
remove the protective shipping cover
3. Identify file electric heater and verify the heater matches
the unit. Unit hand and heater hand must also agree.
4. Properly sized power wiring and control wiring entry
holes are provided in the upstrealn sidewall of the heater
control box.
A narrow, fixed upstream panel is provided for electricfd
power entUfrom the outside. Power may also enter the
unit from below, penetrating the floor of the unit. Careful-
fy seal all entries, weathertight where necessary. Control
wiring may enter the same way as electrical wiring.
Take future service requirements into account when
locating field power entUholes in the unit casing.
5. Sleeve these holes and seal around the conduit to preserve
the integrity of the casing. In some cases, it might be
preferable for the power to actufdfy enter the cabinet
through an adjacent section, or enter the control box from
another angle, which is acceptable.
6. If the original holes am not used, they must be appropri-
ately plugged.
7. Insert the electric heater into the section (the heater
element rack will be located along the leaving air side of
the section).
NOTE: If the heater must be hoisted into position, once the top
panel has been removed to a safe place, the horizontal top rail
may be removed by carefully removing the fiat corner plug
from the end corner pieces and extracting the screw visible
within the exposed cavity. (Do not mix these screws with
othel.s, as they me specific for this location.) The corners may
fllen be separated, lifting the rail and corner segments away
from the unit at approximately a 45 degree angle, taking cam
not to damage the double bulb seal.
8. The heater has lifting hook openings on each end. When
file heater is within 3 in. of its final position, reinstall the
crossrail, with the box-seal facing down, and panel seal
towmd the top.
9. Secure the heater to the section posts and mils with the
lurnished screws, drawing it the last 3/s in. into final
sealed position against the framework, by alternately
cross tightening the screws. The opposite end of the
heater rests on lateral spacel.s provided on the floor panel,
and is retained by a screw through an angle clip on the
last one or by tin upright corner flange.
10. Replace the top panel, and proceed to complete the
wiring in accord with all applicable codes and ordinances.
The wiring diagram is fastened inside the control box,
with a spare, loose copy provided as a convenience for
maintenance manual pmpmafion. Do not mix the wiring
diagrams, as they are specific for each unit.
11. Connect power and control wiring according to the
wiring diagram supplied (see Fig. 82 for typicfd wiring
details).
CONNECT POWER AND CONTROL WIRES -- Heater
wiring schematic is located on control box panel. Verify mini-
mum airflow requirement (minimum coil face velocity, fpm)
will be met, especially on applications where vguiable air vol-
ume is supplied.
Use copper power supply wires rated for 75 Cminimum.
On 250 v or greater applications, use 600 v rated wiring. Size
wires to carry 125% of current load on each set of terminals.
Use file following formulas as required:
Single-phase line cunent =
Three-phase line current =
(kW per set of termimds) (1000)
voltage
(kW per set of termimds) (1000)
(voltage) (1.73)
Note that if the heater is rated fit 50 kW (or morn) and is
controlled by a cycling device such as a multi-stage thermostat.
or a step controller, conductors may be sized fit 100% of load
mnperes (see Table 26) per NEC Section 424-22. Heater
construction and application information are based upon Space
Heating Standard UL No. 1096 and the requirements of
file NEC. Installer is responsible for observing locffl code
requirements.
Install a disconnect switch or main circuit breaker in
accordance with NEC and other applicable codes. Locate so
that it is easily accessible and within sight of heater control box
(per NEC Article 424-19 and 424-65).
Weatherproof junction boxes have no knockouts for wire
entrance. Provide knockouts for all wiring using field-supplied
grommets of correct size and type of conduit as required.
Where field-supplied thermostats are used, isolate circuits
to prevent possible interconnection of control circuit wiring.
Where field-supplied step controller is used, connect steps
to terminals as mmked on wiring schematic. When connecting
multi-stage heaters, wire stage no. 1 so that it is first stage on,
last stage off.
Provide suMcient clearance for convection cooling of heat-
ers wifll solid-state controllel.s. Provide at least 5-in. of free air
space above and below cooling fins extending from heater
terminal box. Be sure to connect interlock terminals FI and F2
to auxiliary contacts on fan starter
79

Each heater has 2 different types of factory-installed ther-
mal cutouts for over temperature protection; an automatic reset
thermal cutout for primaly protection and a manual reset ther-
mal cutout to protect against failure of the primary system.
Also provided is an airflow pressure differential switch to
plevent the heater from operating when file fan is not in opela-
tion or airflow is restricted or insufficient. The primary
automatic reset cutout is a bi-metal disk-type cutout. It is wired
into the control circuit which operates the magnetic disconnect-
ing contactors (the stone contactors which also switch on and
off the vtuious steps of file coil). The secondary manu_fl reset
cutout is a bi-met_fl disk-type cutout. This secondmy therm_fl
cutout is load cmrying and is inst_dled in each heater subcircuit.
The primmy and secondary overtempemture protection sys-
tems me independent of each other The secon&try system is
designed to protect agtfinst possible fifilure of the primmy sys-
tem to deenergize the heate_:
Subcircuits in the heaters are designed in complkmce with
pm'agmph 424-22 of the NEC. The coil is subdivided into
circuits that di'aw no more than 48 amps each and is fused for at
least 125% of the circuit rating.
Pilot tube is to be positioned so that the airflow switch is
actuated by a minimum negative pressure of 0.07 in. wg.
Refer to Table 27 for heater electric_fl data.
Table 26 -- Field Wiring for Incoming Conductors
Sized for 125% of Heater Load
WIRE SIZE
(AWG or
kcmil)
14
12
10
8
6
4
3
2
1
LOAD AMPS*
Copper
12
16
24
40
52
68
80
92
104
LEGEND
AWG -- American Wire Gage
kcmil -- Thousand Circular Mils
NEC -- National Electrical Code
WIRE SIZE LOAD AMPS*
(AWG or
kcmil) Copper
1/0 120
2/0 140
3/0 160
4/0 184
250 204
300 228
350 248
400 268
500 304
*Values are based on Table 310-16 of the NEC for 75 C insulated
copper wire. Not more than 3 conductors in a raceway.
NOTES:
1. Be sure to consider length of wiring run and possible voltage
drops when sizing wires.
2. Field power wiring -- Heaters are furnished with a terminal
block sized for incoming copper conductors with 75 C insulation
rated to carry at least 125% of the heater load. However, con-
ductors can be sized to carry 100% of the heater load if the
heater is rated at 50 kW or more, and the heater is controlled by
a cycling device such as a multi-stage thermostat, step control-
ler, or SCR (silicon control rectifier) power controller. Terminal
blocks and knockouts are sized to handle either 100% or 125%
conductors.
8O

oo 10 9.9
NOMINAL
39M HEATER NO. OF HEATER COIL TEMP
UNIT AREA CONTROL COIL FACE RISE Total
SIZE (sq ft) STEPS* kW VELOCITY (F) FLA
(fpm)
12 12,4
14 13.6
5 500
10 500
15 500
03 3 3 20 500
25 500
30 500
35 500
10 500
15 500
20 500
06 5.2 3 30 500
40 500
50 500
60 500
20 500
30 500
3 40 500
06 7.4 50 500
60 500
70 500
680 500
20 500
30 500
40 500
50 500
60 500
75 500
90 500
100 500
20 500
30 500
40 500
50 500
60 500
80 500
100 500
115 500
130 500
30 500
45 500
60 500
80 500
100 500
115 500
130 500
150 500
Ckt Ckt Ckt
11 14 17 1 20 12 15 1 20 6 8 1
21 28 35 1 35 24 30 1 35 12 15 1
32 42 52 1 60 36 45 1 50 18 23 1
43 56 69 2 70 48 60 2 70 24 30 1
53 69 87 2 90 60 75 2 80 30 38 1
64 83 104 2 110 72 90 2 100 36 45 1
75 97 122 3 125 84 105 2 110 42 53 1
12 28 35 1 35 24 30 1 35 12 15 1
18 42 52 1 60 36 45 1 50 18 23 1
25 56 69 2 70 48 60 2 70 24 30 1
37 83 104 2 110 72 90 2 100 36 45 1
49 111 139 3 150 96 120 3 125 48 60 2
61 139 174 3 175 120 151 3 175 60 75 2
Table 27 -- Electric Heater Data
208/3/60 VOLTS 240/3/60 VOLTS 480/3/60 VOLTS 600/3/60 VOLTS 380/3/50 VOLTS
No. Total No. Total No. Total No.
No. Total MCAt Sub MOCP MCAt Sub MOCP MCAt Sub MOCP MCAt Sub MOCP
MCAt Sub MOCP FLA FLA FLA FLA Ckt
Ckt
20 5 6 1
20 10 12 1
25 14 18 1
35 19 24 1
40 24 30 1
50 29 36 1
60 34 42 1
20 10 12 1
25 14 18 1
35 19 24 1
50 29 36 1
70 39 48 1
80 48 60 2
74 167 208 4 225 145 181 4 200 72 90 2 100 58 72 2
17 56 69 2 70 48 60 2 70 24 30 1 35 19 24 1
26 83 104 2 110 72 90 2 100 36 45 1 50 29 36 1
35 111 139 3 150 96 120 3 125 48 60 2 70 39 48 1
43 139 174 3 175 120 151 3 175 60 75 2 80 48 60 2
52 167 208 4 225 145 181 4 200 72 90 2 100 58 72 2
60 195 243 5 250 169 211 4 225 84 105 2 110 67 84 2
20 8 10 1 20
20 15 19 1 20
20 23 29 1 30
25 30 38 1 40
35 38 48 1 50
40 46 57 1 60
45 53 67 2 70
20 15 19 1 20
20 23 29 1 30
25 30 38 1 40
40 46 57 1 60
50 61 76 2 80
70 76 95 2 100
80 91 114 2 125
25 30 38 1 40
40 46 57 1 60
50 61 76 2 80
70 76 95 2 100
80 91 114 2 125
90 106 133 3 150
69 222 278 5 300 193 241 5 250 96 120 3 125 77 96 2 100 122 152 3 175
13 56 69 2 70 48 60 2 70 24 30 1 35 19 24 1 25 30 38 1 40
19 83 104 2 110 72 90 2 100 36 45 1 50 29 36 1 40 46 57 1 60
26 111 139 3 150 96 120 3 125 48 60 2 70 39 48 1 50 61 76 2 80
32 139 174 3 175 120 151 3 175 60 75 2 80 48 60 2 70 76 95 2 100
39 167 208 4 225 145 181 4 200 72 90 2 100 58 72 2 80 91 114 2 125
48 208 261 5 300 181 226 4 250 90 113 2 125 72 90 2 100 114 143 3 150
58 250 313 6 350 217 271 5 300 108 135 3 150 87 108 2 110 137 171 3 175
65 278 347 6 350 241 301 6 350 120 151 3 175 96 120 3 125 152 190 4 200
10 56 69 2 70 48 60 2 70 24 30 1 35 19 24 1 25 30 38 1 40
15 83 104 2 110 72 90 2 100 36 45 1 50 29 36 1 40 46 57 1 60
21 111 139 3 150 96 120 3 125 48 60 2 70 39 48 1 50 61 76 2 80
26 139 174 3 175 120 151 3 175 60 75 2 80 48 60 2 70 76 95 2 100
31 167 208 4 225 145 181 4 200 72 90 2 100 58 72 2 80 91 114 2 125
41 222 278 5 300 193 241 5 250 96 120 3 125 77 96 2 100 122 152 3 175
52 278 347 6 350 241 301 6 350 120 151 3 175 96 120 3 125 152 190 4 200
......... 138 173 3 175 111 138 3 150 175 219 4 225
......... 157 196 4 200 125 157 3 175 198 247 5 250
14 83 104 2 110 72 90 2 100 36 45 1 50 29 36 1 40 46 57 1 60
21 125 156 3 175 108 135 3 150 54 68 2 70 43 54 1 60 68 86 2 90
28 167 208 4 225 145 181 4 200 72 90 2 100 58 72 2 80 91 114 2 125
38 222 278 5 300 193 241 5 250 96 120 3 125 77 96 2 100 122 152 3 175
47 278 347 6 350 241 301 6 350 120 151 3 175 96 120 3 125 152 190 4 200
54 ........ 138 173 3 175 111 138 3 150 175 219 4 225
61 ........ 157 196 4 200 125 157 3 175 198 247 5 250
70 ........ 181 226 4 250 145 181 4 200 228 -- 5 300
LEGEND
ARI -- Air Conditioning and Refrigeration Institute FLA -- Full Load Amps MCA -- Minimum Circuit Amps
AWG -- American Wire Gage kW -- Kilowatts MOCP -- Maximum Overcurrent Protection
*Standard control steps are listed under the Control Step heading. "Free" additional steps of control are optionally available when the number of subcircuits exceeds the standard number of control steps.
I-MCA = 1.25 x FLA; for proper wire sizing, refer to Table 310-16 of the NEC (National Electrical Code).
NOTES:
1 Subcircuits are internal heater circuits of 48 amps or less.
2. Electric heat performance is not within the scope of ARI standard 430 certification.
3. To avoid damage due to overheating, minimum face velocity cannot fall below 350 fpm.
4. Heaters up to (and including) 60 kW have 3 control steps; beyond 60 kW, 6 steps are standard.

Table 27 -- Electric Heater Data (cont)
NOMINAL
39M HEATER NO. OF HEATER COIL TEMP
UNIT AREA CONTROL COIL FACE RISE Total
kW VELOCITY (F) FLASIZE (sq ft) STEPS*
3
17 16.6
6
21 21
6
Go
=_ 25 23.3
(fpm)
30 500
45 500
60 500
75 500
80 500
100 500
125 500
150 500
175 500
40 500
50 500
60 500
80 500
100 500
125 500
150 500
175 500
200 500
220 500
40 500
50 500
60 500
80 500
100 500
125 500
150 500
175 500
200 500
225 500
250 500
40 500
50 500
60 500
80 500
100 500
125 500
150 500
175 500
200 500
225 500
250 500
275 500
LEGEND
30 2g.3
208/3/60 VOLTS 240/3/60 VOLTS 480/3/60 VOLTS 600/3/60 VOLTS 380/3/50 VOLTS
No. Total No. Total No. Total No.
No. Total MCAt Sub MOCP MCAt Sub MOCP MCAt Sub MOCP MCAt Sub MOCP
MCAt Sub MOCP FLA FLA FLA FLA
Ckt Ckt Ckt Ckt Ckt
12 83 104 2 110 72 90 2 100 36 45 1 50 29 36 1 40 46 57 1 60
17 125 156 3 175 108 135 3 150 54 68 2 70 43 54 1 60 68 86 2 g0
23 167 208 4 225 145 181 4 200 72 g0 2 100 58 72 2 80 gl 114 2 125
29 208 261 5 300 181 226 4 250 90 113 2 125 72 90 2 100 114 143 3 150
31 222 278 5 300 103 241 5 250 96 120 3 125 77 96 2 100 122 152 3 175
38 278 347 6 350 241 301 6 350 120 151 3 175 g6 120 3 125 152 190 4 200
48 ........ 151 188 4 200 120 151 3 175 100 238 4 250
58 ........ 181 226 4 250 145 181 4 200 228 285 5 300
67 ........ 211 263 5 300 16g 211 4 225 266 333 6 350
12 111 13g 3 150 g6 120 3 125 48 60 2 70 3g 48 1 50 61 76 2 80
15 139 174 3 175 120 151 3 175 60 75 2 80 48 60 2 70 76 95 2 100
18 167 208 4 225 145 181 4 200 72 g0 2 100 58 72 2 80 gl 114 2 125
24 222 278 5 300 193 241 5 250 96 120 3 125 77 96 2 100 122 152 3 175
30 278 347 6 350 241 301 6 350 120 151 3 175 g6 120 3 125 152 190 4 200
38 ........ 151 188 4 200 120 151 3 175 100 238 4 250
46 ........ 181 226 4 250 145 181 4 200 228 285 5 300
53 ........ 211 263 5 300 169 211 4 225 266 333 6 350
61 ........ 241 301 6 350 193 241 5 250 304 380 7 400
67 ........ 265 331 6 350 212 265 5 300 335 418 7 450
11 111 13g 3 150 g6 120 3 125 48 60 2 70 3g 48 1 50 61 76 2 80
14 13g 174 3 175 120 151 3 175 60 75 2 80 48 60 2 70 76 g5 2 100
16 167 208 4 225 145 181 4 200 72 g0 2 100 58 72 2 80 gl 114 2 125
22 222 278 5 300 193 241 5 250 96 120 3 125 77 96 2 100 122 152 3 175
27 278 347 6 350 241 301 6 350 120 151 3 175 g6 120 3 125 152 190 4 200
34 ........ 151 188 4 200 120 151 3 175 190 238 4 250
41 ........ 181 226 4 250 145 181 4 200 228 285 5 300
48 ........ 211 263 5 300 169 211 4 225 266 333 6 350
55 ........ 241 301 6 350 193 241 5 250 304 380 7 400
62 ........ 271 339 6 350 217 271 5 300 ....
69 ........ 301 376 7 400 241 301 6 350 ....
g 111 13g 3 150 g6 120 3 125 48 60 2 70 3g 48 1 50 61 76 2 80
11 139 174 3 175 120 151 3 175 60 75 2 80 48 60 2 70 76 95 2 100
13 167 208 4 225 145 181 4 200 72 g0 2 100 58 72 2 80 gl 114 2 125
17 222 278 5 300 193 241 5 250 g6 120 3 125 77 g6 2 100 122 152 3 175
22 278 347 6 350 241 301 6 350 120 151 3 175 96 120 3 125 152 190 4 200
27 347 434 8 450 301 376 7 400 151 188 4 200 120 151 3 175 100 238 4 250
33 ........ 181 226 4 250 145 181 4 200 228 285 5 300
38 ........ 211 263 5 300 169 211 4 225 266 333 6 350
44 ........ 241 301 6 350 193 241 5 250 304 380 7 400
4g ........ 271 33g 6 350 217 271 5 300 ....
54 ........ 301 376 7 400 241 301 6 350 ....
60 ........ 331 414 7 450 265 331 6 350 ....
ARI -- Air Conditioning and Refrigeration Institute FLA -- Full Load Amps MCA -- Minimum Circuit Amps
AWG -- American Wire Gage kW -- Kilowatts MOCP -- Maximum Overcurrent Protection
*Standard control steps are listed under the Control Step heading. "Free" additional steps of control are optionally available when the number of subcircuits exceeds the standard number of control steps.
1-MCA = 1.25 x FLA; for proper wire sizing, refer to Table 310-16 of the NEC (National Electrical Code).
NOTES:
1. Subcircuits are internal heater circuits of 48 amps or less.
2. Electric heat performance is not within the scope of ARI standard 430 certification.
3. To avoid damage due to overheating, minimum face velocity cannot fall below 350 fpm.
4. Heaters up to (and including) 60 kW have 3 control steps; beyond 60 kW, 6 steps are standard.

oo
Table 27 -- Electric Heater Data (cont)
NOMINAL 208/3/60 VOLTS 240/3/60 VOLTS 480/3/60 VOLTS 600/3/60 VOLTS 380/3/50 VOLTS
39M HEATER NO. OF HEATER COIL TEMP
No. Total No. Total No. Total No. Total No.
UNIT AREA CONTROL COIL FACE RISE Total MCAt Sub MOCP MCAt Sub MOCP MCAt Sub MOCP MCAt Sub MOCP MCAt Sub MOCP
SIZE (sq _) STEPS* kW VELOCITY (F) FLA FLA FLA FLA FLA
(fpm) Ckt Ckt Ckt C_ Ckt
60 500 10 167 208 4 225 145 181 4 200 72 g0 2 100 58 72 2 80 gl 114 2 125
80 500 13 222 278 5 300 103 241 5 250 96 120 3 125 77 96 2 100 122 152 3 175
100 500 17 278 347 6 350 241 301 6 350 120 151 3 175 96 120 3 125 152 190 4 200
125 500 21 ........ 151 188 4 200 120 151 3 175 190 238 4 250
150 500 25 ........ 181 226 4 250 145 181 4 200 228 285 5 300
36 38 6 175 500 2g ........ 211 263 5 300 16g 211 4 225 266 333 6 350
200 500 34 ........ 241 301 6 350 193 241 5 250 304 380 7 400
225 500 38 ........ 271 33g 6 350 217 271 5 300 342 428 8 450
250 500 42 ........ 301 376 7 400 241 301 6 350 380 475 8 500
300 500 50 ........ 361 452 8 500 289 361 7 400 ....
350 500 59 ........ 421 527 9 600 337 421 8 450 ....
60 500 9 167 208 4 225 145 181 4 200 72 90 2 100 58 72 2 80 91 114 2 125
80 500 12 222 278 5 300 193 241 5 250 96 120 3 125 77 96 2 100 122 152 3 175
100 500 15 278 347 6 350 241 301 6 350 120 151 3 175 g6 120 3 125 152 190 4 200
125 500 lg ........ 151 188 4 200 120 151 3 175 190 238 4 250
150 500 23 ........ 181 226 4 250 145 181 4 200 228 285 5 300
40 41.g 6 175 500 27 ........ 211 263 5 300 16g 211 4 225 266 333 6 350
200 500 30 ........ 241 301 6 350 103 241 5 250 304 380 7 400
250 500 38 ........ 301 376 7 400 241 301 6 350 380 475 8 500
300 500 46 ........ 361 452 8 500 289 361 7 400 ....
350 500 53 ........ 421 527 9 600 337 421 8 450 ....
400 500 61 ........ 482 602 11 700 385 482 g 500 ....
60 500 7 167 208 4 225 145 181 4 200 72 90 2 100 58 72 2 80 91 114 2 125
80 500 10 222 278 5 300 193 241 5 250 g6 120 3 125 77 g6 2 100 122 152 3 175
100 500 12 278 347 6 350 241 301 6 350 120 151 3 175 96 120 3 125 152 190 4 200
125 500 15 ........ 151 188 4 200 120 151 3 175 100 238 4 250
150 500 18 ........ 181 226 4 250 145 181 4 200 228 285 5 300
175 500 21 ........ 211 263 5 300 169 211 4 225 266 333 6 350
50 52.6 6 200 500 24 ........ 241 301 6 350 193 241 5 250 304 380 7 400
250 500 30 ........ 301 376 7 400 241 301 6 350 380 475 8 500
300 500 36 ........ 361 452 8 500 289 361 7 400 ....
350 500 42 ........ 421 527 g 600 337 421 8 450 ....
400 500 49 ........ 482 602 11 700 385 482 9 500 ....
450 500 55 ............ 434 542 10 600 ....
500 500 61 ............ 482 602 11 700 ....
60 500 6 167 208 4 225 145 181 4 200 72 90 2 100 58 72 2 80 91 114 2 125
80 500 8 222 278 5 300 193 241 5 250 g6 120 3 125 77 g6 2 100 122 152 3 175
100 500 10 278 347 6 350 241 301 6 350 120 151 3 175 g6 120 3 125 152 190 4 200
125 500 13 ........ 151 188 4 200 120 151 3 175 100 238 4 250
150 500 15 ........ 181 226 4 250 145 181 4 200 228 285 5 300
175 500 18 ........ 211 263 5 300 169 211 4 225 266 333 6 350
61 63.1 6 200 500 20 ........ 241 301 6 350 103 241 5 250 304 380 7 400
250 500 25 ........ 301 376 7 400 241 301 6 350 380 475 8 500
300 500 30 ........ 361 452 8 500 289 361 7 400 ....
350 500 35 ........ 421 527 g 600 337 421 8 450 ....
400 500 40 ........ 482 602 11 700 385 482 g 500 ....
450 500 46 ............ 434 542 10 600 ....
500 500 51 ............ 482 602 11 700 ....
LEGEND
ARI -- Air Conditioning and Refrigeration Institute FLA -- Full Load Amps MCA -- Minimum Circuit Amps
AWG -- American Wire Gage kW -- Kilowatts MOCP -- Maximum Overcurrent Protection
*Standard control steps are listed under the Control Step heading. "Free" additional steps of control are optionally available when the number of subcircuits exceeds the standard number of control steps.
1-MCA = 1.25 x FLA; for proper wire sizing_ refer to Table 310-16 of the NEC (National Electrical Code).
NOTES:
1. Subcircuits are internal heater circuits of 48 amps or less.
2. Electric heat performance is not within the scope of ARI standard 430 certification.
3. To avoid damage due to overheating_ minimum face velocity cannot fall below 350 fpm.
4. Heaters up to (and including) 60 kW have 3 control steps; beyond 60 kW, 6 steps are standard.

FANSTARTER_
FIELDWIRING
(BYCUSTOMER)
FIELD-SUPPLIEDI
&INSTALLED
STEPCONTROLLERS
CLASS1 TRANSFORMER
TRANSFORMERFUSING
_wooooooooo_
24 V AUTOMATIC
CUTOUT (S)
STAGE 1
AIRFLOW
SWITCH
STAGES 2-5 (NOT SHOWN) ARE THE SAME AS STAGES 1 & 6.
_.._ STAG E 6
A
THREE-PHASE .............................................. c_.o _ .
i FUSING PER CIRCUIT CONTROLLING MANUAL
i AS REQUIRED BY N E C CONTACTOR (S) CUTOUT(S) DELTA OR WYE
J CONNECTED
NOTE: All wiring must be copper and must conform to the NEC (National Electrical Code),
Fig. 82 -- Electrical Heater Wiring Schematic (Typical)
Energy Recovery Ventilation (ERV) Sections
The assembled sections will result in a unit center of grav-
ity (CG) higher than the horizontal centerline. Exercise
proper care when rigging, lifting and transpolling. Units
with a high CG will tip over more easily during installation
than those with a lower CG
RECEIVING AND INSPECTION -- Inspect the section for
freight damage upon receipt. Inspect the cassette that is mount-
ed inside the section. The cassette consists of a flmne, wheel
assembly and segments. Verify that the wheel turns freely by
hand (clockwise when viewed from the pulley side). Report
any damage immediately to the freight company.
RIGGING AND STACKING-- The ERV section sizes
03-17 me shipped lully assembled. These units can be stacked
and unstacked, as required, during installation by following the
same procedure as for lmger units described below.
NOTE: If an ERV section (size 08-17) does not fit through a
doorway, it may be taken apart by removing the top of the
section frmne. This will expose the ERV wheel; take plecau-
tions not to &_mage the wheel while moving the section. Once
the section is in place, put the top of the section flmne back on.
The ERV section sizes 21-30 are shipped unstacked due to
shipping height limitations. The lower sections me all assem-
bled on baserails and all fastened together on a single skid. The
upper sections me on a separate skid and fastened together (all
fasteners are T-kitches). Rigging and setting the lower sections
is the stone as for a standmd 39M indoor base unit. Refer to
Fig. 83.
The upper sections MUST be rigged and lifted one at a
time or injury or unit damage may occm:
Rigging and lifting upper sections:
1. Use the 4 lifting/holddown brackets (Fig. 84) holding the
row of sections to the skid, and/or a second set of brackets
shipped loose with the unit. For 12-in. airway length
sections, use the bracket shown in Fig. 85.
2. Separate each section one at a time (T-latches) and install
brackets at each corner using the screws provided. Be
carelul not to strip out the holes in the section frame. Lift
and set the section on top of the lower sections.
For sizes 21-30, upper sections should be stacked onto the
lower sections starting with the upper wheel section, and
then moving outward to each end of the unit.
3. Once the upper wheel section is in place and fastened
down to the lower section, subsequent sections should be
placed close to the side of the upper wheel section.
Lifting brackets may make it difl]cult to butt sections
tight together at this point.
With rigging still in place, but strap/chain tension
relieved, remove the 2 lifting brackets interfering with the
inst_dled section, then place tension back onto the rigging
to assist in sliding sections togethel: Fasten upper sections
together tightly first, then tighten screws downward into
the lower section frame.
Repeat this process for the remaining ERV sections.
84

RIGGING INFORMATION
CAUTION: Stacked units have a high CG (center of gravity).
Rig and lift carefully to prevent unit from tipping over.
For units 8 feet or longer, handle by crane only. _
Units under 8 feet long may be forked frorn _. _ _"
sides and ends in fork pockets (if provided) _ ._
in b ..... il ....... d ..... den skids _ _ |
when available _- _ _ _
p,aceb°forer+ngun.' '= ,, /
vertical lift at all lifting points, o& _/.._
Lifting angles greater than 15 _b L_
from vertical will damage unit. _
See view at right.
+gun,wgh,-.......herof,ft+g _. _ _'S_"
cables shown in table. Some units _ _/_
may have more lifting channels VERTICALU_ _,/
than the minimum number Of _ _4_ MAXIMUM
cables shown in the table at right. @ Unit Minimum # of lifting
length cables for each side
UptoSfL 3
8to 12ft. 3
12+ ft. 4
Fig. 83 -- Rigging Information
Fig. 84- Lifting/Holddown Brackets
Fig. 85- 12-in. Airway Bracket
ERV WHEEL MOTOR WIRING -- All ERV wheel motors
have stripped back power leads. For units with 3-phase wheel
motors, install and route the proper wire type and size directly
to the motor junction box provided.
For units with single-phase wheel motors connections must
be made in a separate, field-installed junction box. This
junction box must be installed in the ERV section close to the
motor.
Refer to Table 28 for motor electrical &tta.
Table 28 -- Electrical Requirements for
Energy Wheel Motor
MOTR
VOLTS-PHASE-Hz
115-1-50/60
200-230/460-3-60
200/400-3-50
575-3-60
3gM MOTOR MOTOR
UNIT SIZES HP AMPS (a)
03, 06 80 w 0.7
08, 10 1/6 1.03-1.04/0.52
12, 14, 17, 21 1/6 0.60-0.75/0.38
25, 30 1/4 2.3-2.5/1.2
06, 10 1/6 1.04/0.52
12, 14, 17, 21 1/6 0.80/0.40
25, 30 1/3 3.4/1.8
08, 10, 12,14 1/6 0.3
17, 21
25, 30 1/3 1.4
START-UP
Checklist- Remove all construction debris from unit
interior Verify that all &ains are free of debris. Prime all con-
densate traps.
FILTERS -- Inst;dl unit filters in all filter sections.
AIRFOIL AND FORWARD-CURVED FANS
1. Release the holddown that fastens the fan sled to the sec-
tion base on isolated units.
2. Check lubrication of fan, motor bearings, and linkages.
a. Note that bearings are shipped completely full of
grease for corrosion protection and may run warm
temponuily on start-up until excess grease has
discharged.
b. Hand operate all linkages, such as damper and
guide vanes, to check for freedom of movement.
3. Check tightness of bearing setscrews or locking coll_us
(Fig. 86). Also, check tightness of setscrews on fan
wheels and sheaves.
4. Check tightness of fan-shaft bearing mounting. See
Fig. 86.
5. Recheck sheave _dignment and belt tension. (Refer to
Fig. 32 and 33.)
6. Hand turn fan to make certain fan wheel does not rub in
housing.
7. Check fan speed with a strobe-type tachometer or use the
following formula:
Obtain the motor rpm from the fan motor nameplate and
read sheave pitch diameters marked on the fan and motor
pulleys, or approximate the pitch diameters by using the
pulley ODs.
Then:
Fan RPM =
Motor Rpm x Motor Sheave
Pitch Diameter (in.)
Fan Sheave Pitch Diameter (in.)
Example: Actual Approximate
Nameplate Motor
RPM = 1760 1760
Motor Sheave Pitch
Diameter = 8.9 9.0 (OD)
Fan Sheave Pitch 12.4 12.5 (OD)
Diameter =
1760 x 8.9 1760 x 9.0
Fan RPM = 12.4 12.5
= 1263 RPM = 1267 RPM
Refer to Tables 2A-2D for maximum allowable fan
speeds for fan wheels. Excessive fan speed may result in
condensate carryover from cooling coil or fan motor
overload and wheel failure.
85

SETSCREWS CAPSCREW
SQUEEZE-TYPE LOCKING COLLAR
ROLLER -- EXTENDED RACE, ONE OR BOTH SIDES
DRIVE PULLEY
NOMINAL TORQUE
SCREW SIZE (in.-Ib)
No. 6 9
No. 8 16
No. 10 30
1/4 70
5/16 140
3/6 216
TORQUE TABLE
TORQUE
CAPSCREW AND
SETSCREW
SIZE (No./in.)
10
1/4
5/16
3/6
7/16
1/2
%
3/4
HEX HEAD
ACROSS
FLATS(in.)
3/32
1/8
5/32
3/16
7/32
1/4
5/16
3/8
SQUARE HD
ACROSS
FLATS (in.)
1/2
BEARING HOLDDOWN BOLT TORQUE
BOLT SIZE (in.) TORQUE (ft-lb)
3/8 - 16 3O
1/2 - 13 63
6/8-11 100
3/4-10 165
Fig. 86 -- Fan, Shaft and Bearing Details
25 in.-Ib
60 in.-Ib
10 ft-lb
17 ft-lb
25 ft-lb
40 ft-lb
90 ft-lb
125 ftqb
8. Check direction of rotation (see Fig. 75). Anow on drive
side of fan housing indicates correct direction of rotation.
Drive ratios of l:l may cause excessive vibration. Avoid if
possible.
9. Check vibration. If excessive vibration occurs, check for
the following:
a. Variable sheave (if air balance of system has been
accomplished; replace sheave with fixed sheave for
continuous application).
b. Drive mis_dignment.
c. Mismatched, worn, or loose belts.
d. Wheel or sheaves loose on shaft.
e. Loose bearings.
f. Loose mounting bolts.
g. Motor out of b_flance.
h. Sheaves eccentric orout ofb_flance.
i. Vibration isolatol_ improperly adjusted.
j. Out-of-bahmce or corroded wheel (rebalance or
replace if necesstu-y).
k. Accumulation of materi_fl on wheel (remove excess
material).
PLENUM FANS -- Start-up procedures for plenum fans tue
similtu to those for airfoil or forward-curved fans described in
the preceding section. Also refer to the fan manufacturer's
Installation, Operation, and Maintenance instructions shipped
with the plenum fan section for ihrther details.
HUMIDIFIER INSTALLATION CHECKLIST -- Ensure:
1. Humidifier is properly assembled with all discharge slots
facing the proper direction. (Multipipe systems have the
vertical slots in line with the manifolds, 90 degrees to the
air flow.)
2. Humidifier headers are secured and level.
3. Humidifier upright discharge manifolds tue plumb.
4. Vtflve and trap assembly is properly assembled and con-
nected to the humidifier header.
5. P-trap is installed on discharge of each headel:
6. Stemn feed line is properly run, sloped and connected to
the valve and trap assembly inlet.
7. Controls are properly wired.
HUMIDIFIER START-UP
1. Slowly open the steam isolation valve from the steam
supply line. You should be able to hear steam running
through the valve. Wkdt a few minutes for the steam to
heat up the entire line to the humidifier and for all con-
densate to clear through the trap.
2. Verify that the stemn trap on the valve/trap assembly
of the humidifier is working properly -- condensate
discharge line should be hot.
86

3. Withairflowingin the duct or air handler, create a hu-
midification demand by increasing the humidity control
set point until it exceeds the actual humidity reading.
4. The valve on the humidifier should begin to open and
steam should enter the humidifier manifolds.
5. [nitially most of the steam will condense as it heats the
manifolds. Ensure that the P-traps on the manifolds are
clem and running to diain without leaking steam.
NOTE: On first stall-up, some steam may leak flom the
P-tlaps on the manifolds if they have not been primed
(filled with water).
6. Stemn should begin exiting the humidifier manifolds.
7. Return the humidity control set point to the desired level.
CO[LS
Water Coil -- Typical coil vents, drains, and lifting points are
shown in Fig. 59. Open the vent plug, partially turn on the
water supply until air is exhausted, and replace the vent plug.
Fully turn on the water supply.
Direct Expansion Coil -- Charge with refrigerant. Refer to
Condensing Unit instructions. Refrigerant operating charge is
shown in Table 11, page 26.
Steam Coil
1. Generate steam in the stemn main and open the supply
(gate) valve to the coil.
2. Thoroughly preheat file coil with steam before starling
fans, especi_dly when inlet air temperature is below
fleezing. If water hammer occurs, turn off fans until con-
densate trapped in coils is reduced by heat and steam
pressure.
3. Ensure continuous-vent petcock is open; also check oper-
ation of gate v_dves, control valve, and check valves.
4. After operating coil for 50 hom_, check strainer and
remove any foreign mattel: Check traps and drip lines for
conect condensate removal. Where necesstuy, increase
the pitch of lines to increase condensate di'ainage. (Re-
check operation after 50 hom_ and repeat if necessary.)
INTEGRAL FACE AND BYPASS COIL START-UP -- En-
sure that the damper operator allows the &tmpers to fully
close the face and reverses to fully close the bypass. Set the
thermostat so that the face opens and bypass closes when heat
is required.
On start-up, the steam or hot water supply will be lully ex-
panded prior to start of airflow. Allow time for 'all air to be
purged from the system and for the heating surface to lully
wm'm up in order to avoid heating lag.
Preheating a cold system will avoid excessive steam
condensate loading at the start of operation of a steam heating
system. It also protects steam and hot water units against
freezing up when subject to sub-freezing air temperatures.
After preheating, fully open the dampers for full-face exposure
(bypass closed). Start airflow. Set thermostat for desired air
temperature.
ELECTRIC HEATERS
1. Check tightness of _dlelectrical connections.
2. Remove heater circuit fuses.
3. Turn on power to activate transformel:
4. Stmt up base unit fans. Check airflow and switches. Refer
to base unit instructions as required.
5. Set thermostats so that heater contactors will operate.
6. Shut off unit power
7. Reinstall fuses.
8. Turn on unit power and heater powel:
Energy Recovery Wheel
Keep hands away from rotating wheel. Contact with rotat-
ing wheel can cause physic_d injury.
1. By hand, turn the wheel clockwise (as viewed from the
pulley side), to veril_ that the wheel turns freely through a
lhll 360-degree rotation.
2. Before applying power to the drive motol; confirm that
the wheel segments are fully engaged in the wheel frame
and that the segment rettdnel_ me completely fastened.
(,See Fig. 87).
3. With hands and objects away from moving parts, activate
the unit and confirm wheel rotation. The wheel rotates
clockwise (as viewed from the pulley side).
4. If the wheel has difl]culty starting, turn the power off and
inspect for excessive interference between the wheel
surface and each of the four (4) diameter seals. To correct,
loosen the diameter se:d adjusting screws and back
adjustable diameter seals away from the surface of the
wheel, apply power to conthm that file wheel is free to
rotate, then re-adjust and tighten the hub and diameter
seals according to the instructions in the Service section.
5. Stmt and stop the wheel sevend times to confirm seal ad-
justment and to confirm that the belt is tracking properly
on the wheel rim (approximately I/4-in. from outer edge
of rim).
ZEROING THE MAGNEHELIC GAGE BEFORE START-
UP -- While power is off, set the indicating pointer exactly on
the zero mark using the external zero adjust sclew on the cover
at the bottom. Note that the zero check or adjustment can only
be made while the high and low plessure taps are both open to
atmosphere.
ROTATE AWAY
FROM WHEEL RIM
SEGMENT
RETAINER.
CATCH
PUSH
TOWARD
CENTER
WHEEL RIM CENTER OF
WHEEL
Fig. 87 -- Segment Retainer
87

SERVICE
Electric shock haz_ud. Disconnect power before entering or
servicing.
More than one disconnect switch may be required to deen-
ergize the equipment.
General
I. Review Safety Considerations at beginning of these
instructions. Good safety habits are important tools when
performing service procedures.
2. To make speed measurements, use a strobe-style tachom-
eter or calculate per Step 7 of Start-Up, Checklist for
Airfoil and Forward-Curved Fans.
Electric Heaters -- At least once a year at start of oper-
ating season or whenever unit is serviced, check field and
factory-made electric_fl connections for tightness. Also periodi-
cally clean filteLs, fan, airways, ductwoN, grilles, and registers
as required. Differential air pressure switch is factory set
to open at 0.07 in. wg, close at 0.05 in. wg and requires no
adjustment.
Refer to the Troubleshooting section for more information.
Heater electrical data is shown in Table 27.
Fan Motor Replacement
I. Shut offlnotor powel:
2. Disconnect and tag power wires at motor termimfls.
3. Ix)osen motor brace-to-mounting-rail attaching bolts.
Ix)osen belt tensioning bolts to adjust the motor position
so V-belts can be removed without stretching over
grooves.
4. Mark belt as to position. Remove and set aside belts.
5. Remove motor to motor bracket holddown bolts.
6. Remove motor pulley and set aside.
7. Remove motol:
NOTE: It may be necessary to remove the end panel to
remove larger motors for some unit sizes.
8. Install new motol: Reassemble by reversing Steps 3-7. Be
sure to reinstall multiple belts in their origimfl positions.
Use a complete new set if required. Do not stretch belts
over sheaves. Review the sections on motor and sheave
installation, sheave alignment, and belt tensioning on
pages 50 and 51.
9. Reconnect motor leads, remove tags, and restore powec
Check fan for proper rotation as described in Start-Up,
Checklist.
Energy Recovery Ventilation -- Routine m_dntenance
of the Energy Recovery Cassettes includes inspection and clean-
ing. On occasion, a p_u't may need to be completely replaced.
IMPORTANT: This unit contains an Energy Recovery
Wheel heat transfer device. Proper service and mainte-
nance must be conducted as outlined below, or loss of
heat transfer and overall system performance will
occur,
1. Remove and clean or replace filters in adjoining
section to the ERV wheel every 6 months or sooner,
as required.
2. Remove and wash ERV wheel (or individual seg-
ments, if so equipped) every 6 months, or every
3 months max. for smoky or polluted environments.
See instructions for removal and cleaning details.
CLEANING- Periodic cleaning of the energy recovery
wheel will depend on operating schedule, climate and contami-
nants in the indoor air exhausted and the outdoor air supplied to
the building.
The wheel is "self-cleaning" with respect to din particles
due to its laminar flow characteristics. Smaller particles pass
through; larger particles land on the surface and are blown clear
as the flow direction is reversed. Any material that builds up on
the face of the wheel can be removed with a brash or vacuum.
All sizes can be vacuumed.
Cleaning the removable segments (size 08-30) or the entire
wheel (size 03-06) will remove oil-based aerosols that have
condensed on energy transfer surfaces.
To clean removable segments (size 08-30):
1. Access the wheel from the exhaust fan side. This may be
easiest fiom the adjoining section, depending on the type of
section installed. If it is necessary to access from the side of
the wheel section, remove side baffle as shown in Fig. 88.
This requires removing the screws (1) and (2) shown.
2. Unlock two segment retainers, one on each side of the
selected segment opening.
3. Use the tip of a flat screw diiver to pop the segment out of
the wheel. Repeat for each segment.
4. Brush foreign material from the face of the wheel. Wash
the segments (or sm_fll wheels) in a 5% solution of non-
acid based coil cleaner (such as Acti-Klean) or an alkaline
detergent and warm watel:
5. Soak the segments in the solution until grease and tar
deposits are loosened. (NOTE: some staining of the
desiccant may remain and is not htumful to performance.)
For better cletming action, rapidly run a finger across the
segment's surface to separate polymer strips.
6. Rinse dirty solution from segments and remove excess
water before reinstalling the segments in the wheel.
7. Replace the segments using the Segment Installation and
Replacement procedure on page 90.
To clean wheels (size 03-06) use the procedure and refer to
Fig. 89:
1. Remove the ERV section side access panel.
2. Remove wheel center partition holddown bracket (1).
3. Lift and Remove wheel center ptutition (2).
4. Remove the upper (3) and lower (4) wheel retainer
angles, being carelhl wheel does not tip and ftfll out.
5. Slide wheel cassette out of frame (toward main AHU),
and out the side of the unit (5).
6. Follow steps 2 through 4 of the cleaning procedure for re-
movable segments.
7. Reinstall the wheel into the section by reversing Steps 1-5.
Fig. 88 -- Remove Side Baffles
88

2. Rotate the wheel clockwise until two opposing spokes am
hidden behind the beating support beam.
3. Using a folded piece of paper as a feeler g_mge, position
file paper between the wheel surface find the diameter
seals.
4. Adjust the seals towards file wheel surface until a slight
fiiction on the feeler gauge (paper) is detected when the
gauge is moved along the length of the spoke.
5. Retighten the adjusting screws and recheck clem'ance
with the feeler gauge.
Fig. 89 -- Remove Wheel for Cleaning
(Sizes 03-06 Only)
CASSETTE REPLACEMENT
1. Inspect the replacement cassette for fieight damage upon
receipt. Inspect the cassette fi'ame, wheel assembly find
segments fGr damage and verify that the wheel turns
fieely by hand (clockwise when viewed from pulley
side). Report any &image immediately to the freight
company.
2. Handle ERV cassettes with care. Lift by file beming
support beam. Holes are provided on both sides of the
befuing support beams to facilitate rigging (Fig. 90).
3. Remove the ERV section side access panel.
4. Refer to Fig. 89. Remove wheel center partition hold-
down bracket (1).
5. Lift and Remove wheel center pmtition (2).
6. Remove the upper (3) and lower (4) wheel retfdner
angles, being carelhl wheel does not tip find fall out.
7. Slide wheel cassette out of frame (toward main AHU),
and out side of unit (5).
8. The new ERV section may be mounted in any orientation.
HoweveL make certain that the ,frame remains ,flat and
the bearing beams am not rocked as showll in Fig. 91.
9. TG ensure that the bemns are not racked, check that the
distance between the wheel rim find bearing beam is the
same at each end of the bearing beam, to within 1/4 of an
inch (dimension A and B in Fig. 91 ). Beming beam rack-
ing of as little as .040 inches (Dim Cin Fig. 91 ) will cause
the wheel to tilt 3/1_ in. fit the rim. Adjusting the diameter
seffls (Fig. 92) will compensate for up to 1/4 in. of racking.
NOTE: If racking is greater than 1/4 in., it must be correct-
ed to ensure that the drive belt will not disengage from the
wheel.
10. Wheel sections installed fit angles greater than 30 degrees
from vertical will require seal adjustment (Fig. 92).
Adjust the diameter seals to avoid excessive wheel diag.
A final check of seal adjustment is recommended for all
designs.
ADJUSTING AIR SEALS -- Four adjustable diameter seals
are provided on each cassette to minimize air transfer between
the counterflowing airstreams.
TG adjust diameter sefds:
1. Loosen the diameter sefd adjusting screws find back seals
away fi_m wheel surface (Fig. 92).
[]
/
HORIZONTAL -- VERTICAL
BEARING BEAM (2) BEARING BEAM (2)
Fig. 90 -- Lifting Hole Locations
\
_ FRAME
A _ BEARING BEAM _.
SHOWN RACKED "_,
/
, 1
I
i
,f--WHEEL !!i,
f
/BEAMS I I,
(2) , ,
i L
i
FLAT SURFACE "'_
BI.--
c
Fig. 91 -- Avoid Racking of Frame
FEELER
ADJUSTING SCREWS GAUGE
Fig. 92 -- Diameter Seal Adjustment
89

SEGMENT INSTALLATION AND REPLACEMENT --
Wheel segments are secured to the wheel franle by a segment
retainer, which pivots on the wheel rim and is held in pkice by
a segment retaining catch (Fig. 93).
To inst_dl wheel segments follow the steps below and refer
to Fig. 93.
1. Unlock two segment retainels, one on each side of the
selected segment opening.
2. With the embedded stiffener facing the motor side, insert
the nose of the segment between the hub pkites.
3. Holding segment by the two outer corners, press the
segment towards file center of the wheel and inwards
against the spoke flanges. If hand pressure does not fully
seat the segment, insert the flat tip of a screw &iver
between the wheel rim and the outer corners of the
segment and apply downwmd force while guiding the
segment into place.
4. Close and latch each segment retainer under the segment
retaining catch.
5. Slowly rotate the wheel 180 degrees. Install the second seg-
ment opposite the first for counterbalance. Rotate the two
inst_dled segments 90 degrees to balance file wheel while
the third segment is installed. Rotate the wheel 180 degrees
again to inst_fll the fourth segment opposite the third.
Repeat this sequence with the lemaining four segments.
WHEEL DRIVE MOTOR AND PULLEY REPLACEMENT
1. Disconnect power to the wheel drive motoc
2. Remove the belt from the pulley and position it tempo-
r;u'ily around the wheel rim.
3. Ix_osen the set screw in the wheel drive pulley using an
Allen wrench and remove file pulley from the motor drive
shaft.
4. While supporting the drive motor's weight in one hand,
loosen and remove the four mounting bolts.
5. Install the replacement motor using the hmdwme kit
supplied.
6. Install the pulley to the dimension shown in Fig. 94 and
secure the set screw to the drive shaft.
7. Stretch the belt over the pulley and engage it in the
groove.
8. Follow the start-up procedure on page 85.
SOLID BELT REPLACEMENT (Fig. 95)
1. Obtain access to the pulley side beming access plate.
Bearing access plates m'e not provided on 25 to 36-in.
cassettes. Remove the two bearing access pkite retaining
screws and the access pkite.
2. Using a hex wrench, loosen file set screw in the bearing
locking collm: Using a light hammer and &ift (in drift pin
hole), tap the collar in the direction of wheel rotation to
unlock the collm. Remove the collm:
3. Using a socket wrench with extension, remove the two
nuts that secure file bearing housing to the bearing
support beam. Slide the bearing from file shaft.
NOTE: Slight hand pressure against wheel rim will lift
the wheel's weight from the inner race of the bearing to
assist bearing removal and installation. If not removable
by hand, use a bearing pullel:
4. Using a wrench, remove the diameter seM retaining
screws (25 to 68-in. cassettes). Remove diameter seals
(25 to 68-in. cassettes) from the beming bemn.
5. Form a small loop of belt and pass it through the hole in
the bearing support beam. Grasp the belt at the wheel hub
and pull file entire belt down. Loop the trailing end of the
belt over the shaft (Fig. 95 shows the solid belt partially
through the opening).
6. Reinstall the bearing onto the wheel shaft, being careful
to engage the two locating pins into file holes in the bear-
ing support beam. Secure the bearing with the two self
locking nuts.
7. Install the belts around the wheel and pulley according to
the instructions provided with the belt.
8. Reinst_dl the diameter seals and tighten the retaining
screws (see page 89 for seal adjustment). Rotate the
wheel clockwise to determine that it rotates freely with
slight drag on the seals.
SEARING
Fig. 93 -- Segment Installation

9. Reinst;dl the bearing locking collm- Rotate the collm by
hand in the direction the wheel rotates (see label provided
on each cassette for wheel rotation). Dock the collar in
position by tapping the drift pin hole with a hammer and
drift. Secure in position by tightening the set screw.
10. Reinstall the bearing access covel:
11. Apply power to the wheel motor and ensure that the
wheel rotates freely without interference.
LINK BELT REPLACEMENT
Before performing service or maintenance operations on
unit, turn off main power switch to unit. Electrical shock
could cause personal injury.
1. Confirm the model number on the replacement belt kit
matches the model number on the energy recovery
cassette label.
2. Remove any remnant of old belt from cassette.
3. At location near pulley, attach the hook end of belt to
wheel rim with tape, making sure that nmrow side of "V"
belt is positioned against rim and link is covered by the
tape (see Fig. 96).
4. Rotate the wheel clockwise while feeding belt onto wheel
rim (be caleful not to twist belt) until taped end returns to
pulley location. Remove tape from wheel.
5. Link belt ends together with belt wrapped mound wheel
(Fig. 97).
6. Rotate wheel clockwise to position connector approxi-
mately 180 degrees fi_m pulley location.
7. At pulley location, insert the right angle belt retaining clip
ne_u spoke and between segment retainer latch and wheel
rim as shown in Fig. 98.
IMPORTANT: To avoid release of segment retainer
latch, do not insert retaining clip on other side of spoke.
8. Rotate wheel counterclockwise until belt retaining clip is
within a few inches of the wheel bearing beam (see
Fig. 99).
9. Lit) and remove the belt from the wheel rim between a
point opposite the pulley and belt retaining clip and
stretch over pulley (see Fig. 100).
10. Rotate wheel clockwise until the belt is fully stretched
onto pulley and wheel rim.
11. Remove belt retaining clip and rotate wheel by hand two
rotations while observing that belt is not twisted as it
enters pulley. Also ensure that belt is tracking midway
between outer edge of rim and seal plate, or in belt guide
channel where provided.
12. Apply power to cassette and observe belt tracking under
power.
OTHER MAINTENANCE
Wheel Drive Motor Bearings gue pro-lubricated and no further
lubrication is necessary.
The Wheel Drive Pulley is secured to the &ive motor shaft by
a combination of either a key or D-slot gradset screw, The set
screw is secured with removable locktite to prevent loosening.
Annually confirm that the set screw is secure,
The Wheel Drive Belt is a umthane stretch belt designed to
provide constant tension through the life of the belt. No adjust-
ment is required. Inspect the drive belt annu_flly for proper
tracking and tension. A properly tensioned belt will turn the
wheel immediately after power is applied with no visible
slippage during start-up.
Fig. 96 -- Belt Attached to Wheel Rim
Fig. 97- Belts Linked Together
SEGMENT RETAINER
LATCH
BELT RETAINING
CLIP
Fig. 98 -- Detail of Belt Retailing Clip
and Segment Retained Latch
Cleaning Unit Interior/Exterior -- Unit interior/exterior
panels should be wiped down using a dmnp soft cloth or sponge
with a mixture of waml water and a mild detergent. Avoid using
an abrasive cleanel; as &tmage to the paint could occur resulting
in rest and con'osion. Chemicals such as paint thinners can daln-
age the ptfinted panels and should be avoided.
Avoid washing unit electrical devices such as motors, start-
ers, electric heater control boxes, damper/valve actuators,
sensors, switches, relays, etc. as serious pel_onal injury or
&tmage to the device could result.
91

Fig. 99 -- Detail of Belt Retaining Clip Location
Fig. 100 -- Belt Removal
Coil Cleaning --Chilled water, hot water, steam, and
direct expansion coils must be cleaned regularly to m;fintain
peak performance. Dirty coils can contribute to loss of cooling
or heating capacity and efficiency, increased operating costs,
and compressor problems on direct expansion systems. Dirt,
grease, and other oils can also reduce the wettability of the coil
surfaces, which can result in moisture blow-off from cooling
coils and resulting water leakage problems. If the grime on the
surface of the coils becomes wet, which commonly occurs with
cooling coils, microbial growth (mold) can result, causing foul
odors trod health related indoor air quality problems.
Coils can become dirty over a period of time, especi;dly if
air filter maintenance is neglected. Coils should be inspected
regularly and cleaned when necessm-y. If coil fins become dirty.
pressure clean with hot water and detergent or a commercial
coil cleanel: Ensure to rinse coils thoroughly after cleaning
with chemical cleaners.
Follow all directions provided with the chemical cleaners to
avoid personal inju U, inju Uto others, and/or coil damage.
Chemical coil cleaners may contain corrosive or harmfiJl
agents.
1. Disconnect all electrical power to the ;fir-handling unit,
including any separate power supplies for unit mounted
controls (actuatol_, sensors, etc .... ).
2. Wear the appropriate protective clothing (eyewear.
gloves, etc....).
3. Ensure there is sufficient access to the coil.
4. Use a vacuum with a soft tip brush to remove any dust
and loose debris from both sides of the coil.
5. Clean the leaving airside of the coil first, then the entering
ail_ide, starting fi_)m the top of the coil and working
downwmd. Apply a mild non-fomning commercial coil
cleaner or detergent using a gmden type sprayel: Rinse coil
gently with clean wm'm water, avoiding high-pressure
sprays, which can cause dmnage to coil fins. Use a block-
off plate to prevent the water or chemical cleaner from
blowing through the coil and into a clean, @ section of
the unit. Confirm that the condensate diain line is fiee of
debris during and following the coil cleaning process.
Excess water from cleaning may result in flooding the unit
as well as causing &Lmage to the building if diain is
plugged. If coil section does not have a divin pan, it is
recommended that the coil be removed prior to cleaning.
6. Repeat steps 1 through 5 as necessary.
7. Allow the coil to dry thoroughly before placing the
system back into operation. A clean @ cloth may be
used to wipe down the interior panels before placing the
unit in operation.
8. Straighten any coil fins that may have been bent or dam-
aged during the cleaning process with a fin rake.
9. Replace all panels and parts that may have been removed
prior to cleaning and restore electrical power to the unit.
10. Use caution to assure that no contaminated materials con-
tact other meas of the unit or building. Properly dispose of
any polluted materi_ds and cleaning fluids.
Winter Shutdown -- It is recommended that auxilim'y
drain piping be added to coil piping if yearly winterizing of
coils is anticipated. This auxiliary piping should be located at
the highest and lowest point on the respective header connec-
tion for each coil.
ANTIFREEZE METHODS OF COIL PROTECTION
1. Close coil water supply and return valves.
2. Drain coil as follows:
Method I -- 'Break' flange of coupling at each header
location. Sepm'ate flange or coupling connection to facili-
tate coil di'aining.
Method II-- Open both v;dves to auxiliary drain piping.
3. After coil is di'ained, Method I, connect line with a
service valve and union from upper nozzle to an
antifreeze reservoir Connect a self-priming reversible
pump between the low header connection and the
reservoil: Method fl, make connection to auxilimy di'ain
valves.
4. Fill reservoir with any inhibited antifreeze acceptable to
code and undelwriter authority.
5. Open service valve and cimulate solution for 15 minutes;
then check its strength.
6. If solution is too weak, add more antifreeze until desired
strength is reached, then circulate solution through coil
for 15 minutes or until concentration is satisfactory.
7. Remove upper line from reservoir to reversible pump.
Drain coil to reservoir and then close service valve.
8. Break union and remove reservoir and its lines.
9. Leave coil flanges or coupling open and auxiliary diain
valves open until spring.
AIR-DRYING METHOD OF COIL PROTECTION (Unit
and coil must be level for this method.)
1. Close coil water supply and return main valves.
2. Drain coil as described in procedures for Antifreeze
Methods of Coil Protection, preceding.
3. Connect air supply or air blower to inlet header connec-
tion and close its drain connection.
92

4. Circulateairandcheckforair-drynessbyholdingmirror
in front of open vent in outlet header drain connection.
Min_or will fog if water is still present.
5. Allow coil to stand for a few minutes; repeat Step 4 until
coil is dry.
Coil Removal
NOTE: To reinstall coils, refer to Coil Installation section on
page 59.
REMOVAL OF SINGLE HEIGHT COILS (sizes 03-
36) -- The coils in horizontal coil sections may be removed
from the top of the unit or either end. Once the extern_fl panels
are removed from the unit, the horizontal upper coil section
frame members are easily removable from the frmnework, to
allow hoisting the coil up and out of the unit.
NOTE: Refer to Table 13 (DUCoil Weights) in the fi_ont of
this manual before attempting to remove a coil from the unit.
1. Lock open and tag all power supplies to unit fan motor
and electric heaters if present.
2. Identify the unit service panel latches and disengage them
(1/4 turn) with a 5/l_-in. or 8-ram hex wrench. Remove
service panel/coil connection panel and the upstremn
service panel and set aside in a safe place.
3. a. On horizontal coil sections without another unit
section stacked on top, remove the flat corner plug
from each end piece of the top rail.
b. Extract the Torx T25 screw visible within the
exposed cavity. (Do not mix these screws with
others; they are specific for this location. Set
screws aside for reinstallation of top rail.)
c. Remove the top rail by pulling out at a 45-degree
angle. Set top rail aside.
IMPORTANT: Properly support the coil to assure its
stability before continuing with this procedure.
4. Remove the fastening screws fiom the upstremn perime-
ter face of the coil that attach the coil to the coil baffles.
This may require reaching through an opened &lmper
assembly, reaching through a filter track after filters are
removed, or removing a coil immediately upstream.
Do not handle the coil by the headers or connection
nipples, as irrepgu'able damage might occur that is NOT
covered by wammty. Protect the finned surface fi'om
&image during all handling and shipping.
5. Slip the foam sealing sleeves off the connection nipples
before removing the coil and set the sleeves aside.
6. The coil may now be hoisted out through the top opening
or carefully slid out either side of the cabinet. Sections
where the top frame rail cannot be removed may require
slightly tipping of the coil from the vertical position, to
cle_u the upper frame rail and seal.
REMOVAL OF STACKED COILS (sizes 40, 50 and
61 )- The coils in horizontal coil sections may be removed
from the top of the unit or either end. Once the external panels
are removed from the unit, the horizontal upper coil section
fiame members are easily removable fiom the fialnework, to
allow hoisting the coil up and out of the unit.
1. Lock open, and tag all power supplies to unit fan motor
and electric heaters if present.
2. a. Identify the unit service panel latches and disen-
gage them (114turn) with a 5/ls-in. or 8-mm hex
wrench.
b. Remove service panel/coil connection panel and
the upstream service panel and set aside in a safe
place.
c. Remove the top rail by pulling out at a 45-degree
angle. Set top rail aside.
3. a. On horizontal coil sections without another unit
section stacked on top, remove the flat corner plug
from each end piece of the top rail.
b. Extract the Torx T25 screw visible within the
exposed cavity. (Do not mix these screws with
others; they are specific for this location. Set
screws aside for reinstallation of top rail.)
c. Remove the top rail by pulling out at a 45-degree
angle. Set top rail aside.
IMPORTANT: Properly support the coil to assure its staNDity before continuing with this procedure.
4. Remove the fastening screws of the uppermost coil from
the upstream side. Note that the fastening screws pass
through the vertical angle, baffles, and coil casing. See
Fig 101. Removal of the fastening screws may require
reaching through an opened &tmper assembly, reaching
through a filter track after filters are removed, or remov-
ing a coil immediately upstream.
Do not handle the coil by the headel.s or connection nip-
ples, as ineparable damage might occur that is NOT cov-
ered by warranty. Protect the finned surface from damage
during all handling and shipping.
5. Slip the foam sealing sleeves off the connection nipples
before removing the coil and set the sleeves aside.
6. The upper coil may now be hoisted out through the top
opening, or cguefully slid out either side of the cabinet.
Sections where the top frame nfil cannot be removed may
require slightly tipping of the coil fiom the vertical posi-
tion, to cle_u the upper frmne rail and se_d.
7. On the upstream side of the stacked coils, remove and
set aside the center baffle spanning the two coils (see
Fig. 101).
8. For sections that do not have a drain pan (heating only
sections), remove the three hat channel spacer supports
fastened to the top of the lower coil, and set aside.
9. For sections that do have a drain pan, remove the two hat
channel spacer supports from the bottom of the coil sec-
tion and set aside.
10. Remove the intemlediate condensate &ain pan.
11. Remove the spacer (hat channel) secured to the top center
of the lower coil casing (see Fig. 102) and set aside.
12. Remove the fastening screws of the lowermost coil from
the upstream side. Note that the fastening screws pass
through the vertical angle, baffles, and coil casing. See
Fig. 101. Removal of the fastening screws may require
reaching through an opened &tmper assembly, reaching
through a filter track after filters are removed, or remov-
ing a coil immediately upstream.
Do not handle the coil by the headers or connection nip-
ples, as irreparable damage might occur that is NOT cov-
ered by warranty. Protect the finned surface from damage
during all handling and shipping.
13. Slip the foam sealing sleeves off the connection nipples
before removing the coil and set the sleeves aside.
93

BAFFLE
BAFFLE, HEADER_ _- COIL FRAMES
CHANNEL, HAT_
\
PAN, CONDENSATE ......
CENTERED WITHIN SECTION
BAFFLE, HARPIN
ANGLE
BOTH SIDES
IMPORTANT: ADHESIVE GASKET MUST BE
APPLIED TO THE FULL LENGTH OF THE
BOTTOM BAFFLE MATING FLANGE TO
CREATE SEAL BETWEEN THE COIL SIDE
CASING AND THE BAFFLE. SEE
ILLUSTRATION BELOW,
BOTTOM
APPLY FLUSH TO THIS EDGE ........
GASKET, ADHESIVE .....
_OM BAFFLE
Fig. 101 -- Apply Gasket
14.
15.
Tile lower coil may now be hoisted out through the top
opening, or carefully slid out either side of the cabinet.
Inspect the adhesive backed gasket applied to the lower
baftle, spanning the entire unit, on the surface that
contacts the coil (see Fig. 101). If &imaged, remove the
remainder of the old gasket and replace.
Changing Coil Hand
NOTE: Electric heat coil hand cannot be changed.
NOTE: The coil cover panel is not pm't of the coil. Remove
cover panel fiom end of unit. New holes must be cut in coil
cover panel. Original holes must be plugged and insulated.
New side panels may be necessaly when changing coil hand.
NUFIN COILS -- The NuFin coil is airflow direction sensi-
tive, especially when used in dehumidifying applications.
Hy&onic versions are counterflow circuited for full gravity
draining when installed level.
Correct installation will result in file typical bottom inlet on
leaving air face _md top outlet on entering air face of coil, a
self-venting design. This will ensure cold air contact with cold
water, and warm air with hot watec
Coil repositioning for opposite hand application will com-
promise one or more of these characteristics. Howevek there
will be those situations where this may prove acceptable.
CHANNEL,
As a general rule, a change from counterflow circuiting to
parallel flow for sensible heating and cooling applications will
result in a 5% drop in net capacity per row of coil. In one and
two row heating coils, the actual drop may not be measurable,
thus of insignificant consequence.
It is important that the airflow direction of the NuFin coil be
adhered to when latent cooling is possible. Significant moisture
carryover fiom the face of the dehumidifying coil will result if
this rule is violated, even at very low face velocities. The stone
result is often experienced if after-mmket tin coatings are
applied.
Ira NuFin hydionic coil is installed with correct airflow, but
opposite piping hand, and counterflow is maintained, steps
must be taken to ensure that the coil is continuously vented,
and that the water velocity is maintained to prevent the coil
from air-binding.
Hot or cold areas of file coil face (or otherwise broad tem-
perature differences and stratification) me usually indications
that one or more circuits are air-locked internally. This can
result in coil freeze-up (a condition NOT covered by warranty).
Refiigemnt coils may be rotated for opposite hand applica-
tions, maintaining the proper airflow direction.
Do not reposition the distributor(s), they will perform equal-
ly well in upflow or downflow positions. When soldering
expansion valves to up-feed distributors, use the minimum
satisfactoly amount of solder to prevent dmnaging the valve or
plugging passages.
DIRECT EXPANSION COILS -- Rotate the coil in vertical
plane and reinstall. Distributor must be on downstremn side of
coil. (Refer to Fig. 103).
CHILLED WATER AND HOT WATER COILS -- These coils
can be rotated. If coil is rotated in vertical plane and reinstalled
with countertlow maintained, supply will be at the top of file coil
and return will be at the bottom. Ensure coil is continuously
vented and water velocity is maintained to prevent air binding.
Fig. 102 -- Secure Spacer
94

Chilled and hot water coils must not be rotated horizon-
t_dly. If coils are rotated horizontally, severe water blow-off
will result.
STEAM INNER DISTRIBUTING TUBE COILS -- Rotate
in horizontal plane and reinstall. See Fig. 103.
PIPING- Direct expansion, chilled watel; and hot water
coils should always be piped for counterflow. (Fluid should
enter the coil at the leaving-air side.) Steam coils must have the
condensate connection at bottom of coil.
To determine intervals for cleaning coils in contaminated air
operations, pressure taps should be inst_flled across the coils
and checked periodically. Abnormal air pressme diop will indi-
cate a need for cleaning the coils.
Annual maintenance should include:
1. Clean file line strainers.
2. Blow down the dirt leg.
3. Clean and check operation of steam traps.
4. Check operation of control v_dves.
5. Check the operation of check v_flves to prevent conden-
sate flowback.
6. Check operation of thermostatic air vents, if used. A float
and thermostatic trap will contain a thermostatic air vent.
When the bellows is raptured, it will fail closed.
7. Check operation of vacuum bre',_ers.
8. Check operation of the thermal protection devices used
for freeze-up protection.
9. Stemn or condensate should not be allowed to remain in
the coil during the off season.This will prevent the forma-
tion and build up of acids.
There me additional precautions and control strategies, as
found in various catalogues and in the ASHRAE Fundamentals
Handbook and in the Carrier System Design Guide -- Piping
Section, when the entering-;dr temperature to the coil falls be-
low 35 E These conditions occur when IDT coils me used for
pre-heat and/or face and bypass applications.
Freeze up protection:
1. Use a strainer in the supply line and the dirt leg ahead of
the trap.
2. Use a vacuum breaker in the return.
Fig. 103 -- Coil Rotation
3. Do not use overhead returns from the coil. A floodback
can occuE
4. An immersion themlostat to control outdoor-air dampers
and the fan motor is lecommended. This control is acti-
vated when the steam supply fails or the condensate
temperature drops below a predetermined temperature,
usu_dly 120 E
5. On low pressme and vacuum systems, the immersion
thermostat may be replaced by a condensate drain with a
thermal element. This element opens and drains the coil
when the condensate temperature &ops below 165 E
Note the thermal condensate drtdn is limited to 5 psig
pressure. At greater coil plessures they will not open.
In spite of the precautions listed above, a coil may still
fieeze up. An ovel.size capacity coil, at partial load, with a
modulating stealn control valve will occasionally freeze.
Freezing occurs in the 20 F to 35 F range of entering-air
temperatures. A better installation would be an undersize coil,
with an on/off control wtlve with thermostatic control in the
outside all: set at 35 F air temperature, installed downstream of
the fil.st coil; or setting the minimum stemn pressure at 5 psig.
Filters -- See Table 29 for filter data for flat filter section,
angle filter section, bag-cmtridge filter section, and filter mix-
ing box section. Filters are field supplied.
Air filtel.s should be inspected regularly and changed when
dirty. Filter life can vmy greatly from one unit to anothel: de-
pending upon the application and the mnount of contaminants
in the leturn and ventilation air entering the air handlel: Each
job should be evaluated and maintenance schedules established
accordingly. At a minimum, the filters should be changed at the
beginning of the cooling and heating seasons.
Although not a dilect part of the air handler, outdoor air inlet
screens and/or grilles that may be present should _dso be
checked regularly and cleaned as necessmy. They can easily
become plugged with debris, grease, or other contaminants,
depending upon their location.This reduces the availability of
ventilation air. which can contribute to indoor air quality
problems.
All filter sections use adjustable blank-off plates to close off
any airway area not filled with filter media. Check blank-off
plates to plevent unfiltered air from bypassing the filtel_.
Blank-off plates must be on door side of unit.
BAG-CARTRIDGE FILTERS -- Side loading bag-cartridge
filter section can use either bag or rigid filters, 6-in. to 30-in.
deep, with 7/s-in. headel: They will not accept headerless rigid
filters.
Face loading bag-c_utridge filter sections can use either bag
or rigid filters and tue loaded fi_)m the front of the section.
These sections use Purolator holding frames located at the
downstream edge of the filter section for prefilters and bag/
cartridge filters. Cartridge filtel.s without headers can extend
upstream of the holding frame by 24 inches. Cartridge and bag
filters with 7/u-in. header extend downstream of the filter
section with filter length limited only by the length of the
plenum following the filter section. Filter elements are retained
in fralnes by wire fastener clips. To replace filter elements,
remove clips, insert elements with bag or cartridge downstream
and reinstall clips. See Fig. 104.
See Fig. 105 for typical track for bag-cartridge filter section
used on di'aw-thru unit.
IN-TRACK BAFFLES- Filter sections are shipped with
adjustable in-track baftles. When installed properly as shown
in Fig. 106, the baffles close off empty space in the track pre-
venting air from bypassing the filtel.s. Remove the baffles to
install filter elements, and leplace the adjustable baffles aller
the filters tue in place. The adjustable baffles should be spread
ftu enough apart to ensure slight compression in the foam
gasket when closing the section door.
95

FLATANDANGLEFILTERS-- Flatfilterandanglefilter
sectionsaccommo&tte2-in.or4-in.thickfiilters.Thesectionas
shippedaccepts2-in.filters.Removeanglespacerineachtrack
toprovidethespacerequiredtoaccommodate4-in.filters.
HEPAFILTERS-ThePuro-Frame,HEPAholdingflame
will accommodate12-in.deepfiltel_.HEPAfiltersections
usedin blow-flnuapplicationsareloadedfiomthefiont,
m
GASKET'_,._ •
[
4¢
FILTER
RETAINING
CLIPS
Fig. 104 -- Puro-Frame Holding Frame and
Filter Retaining Clips
through the access door or removable panel. The HEPA filters
are retained in the fralne with retaining brackets. RTV sealant
should be used to seal between the filter frame and the filter
media's neoprene gasket to ensure a leaktight installation.
Refer to Fig. 107 for details. Downstream edge of fralne to
fiame and fi:tme to baffle shall be sealed with RTV sealant.
Filter arrangements are shown in Fig. 108-112.
3/4" x 3/4"
FOAM GASKET
FILTER
\\
ADJUSTABLEIN-TRACK
BAFFLE /
# 4;, -
N
Fig. 106 -- In-Track Baffle for Flat, Angle and
Sideloading Bag/Cartridge Filter Sections
Fig. 105 -- Track for Draw-Thru Bag Cartridge
Filter Section
12.625"
[ ...........
24.625"
i
HEPA
Height I Width I Height I Width
I 124 / "124%"
24" ] 12" ] 24_/8"]12_/_ "
FILTER RETAINING BRACKET
QTY. 4 SUPPLIED WITH EACH FRAME
INSTALL BY LATCHING OVER FRAME
TABS \\\
\
FRAME TABS
AIR FLOW
+
I
;-,' 8,0" -
FILTER HEPA
FRAMER_ FILTER
24" X 24"
RETAINING BRACKET
NOTES:
1. Filter sizes are 5/8-in. smaller than frame sizes.
2. 12-in. x 24-in. frame may be rotated for 24-in. x 12 in. arrangement.
3. Recommended RTV sealant: GE128.
Fig. 107- Puro-Frame, HEPA Holding Frame
96

Table 29 -- Filter Data
FILTER SIZE I 3gM UNIT SIZE
Fiat Filter Arrangement(2-in. or 4-in.)
03 06 08 10 12 14 17 21 25 30 36 40 50 61
16x20 6 3 ....... 14
16x25 3 .......... 14
20x20 -- 3 6 .......
20x24 .... 8 10 ....
20x25 1 2 -- 3 -- -- -- 6 -- -- 12 13 15 --
Face Area (sq ft) 3.5 6.9 8.3 10.4 13.3 15.0 16.7 20.8 26.7 33.3 41.7 45.1 52.1 70.0
Angle Filter Arrangement(2-in. or4-in.)
03 06 08 10 12 14 17 21 25 30 36 40 50 61
16x20 -- 4 -- 6 ........ 18 21
16x25 2 -- 4 -- -- -- 9 12 12 16 20 20 12 14
20x20 6 2 ........
20x24 -- 4 ........
20x25 ..........
Face Area (sq ft) 5.6 8.9 11.1 13.3 16.7 18.9 25.0 33.3 33.3 44.4 55.6 55.6 73.3 85.6
Filter Mixing Box Arrangement(2-in. or4-in.)
03 06 08 10 12 14 17 21 25 30 36 40 50 61
12x24 -- -- 12 .......
16x20 -- 4 -- 6 ........ 18 24
16x25 2 -- 4 .... 12 12 16 -- 24 12 16
20x20 6 2 ........
20x24 -- 4 ........
20x25 ...... 16 -- -- --
Face Area (sq ft) 5.6 8.9 11.1 13.3 16.7 18.9 24.0 33.3 33.3 44.4 55.5 66.7 73.3 97.8
Short Side Load Bag/Cartridge Filter Arrangement
03 06 08 10 12 14 17 21 25 30 36 40 50 61
12x24 -- 1 -- 1 3 3 3 -- -- -- 4 4 3 7
24x24 1 1 2 2 2 2 3 6 6 8 8 8 12 12
Face Area (sq ft) 4 6 8 10 14 14 18 24 24 32 40 40 54 62
Long Side Load Bag/Cartridge Filter Arrangement
03 06 08 10 12 14 17 21 25 30 36 40 50 61
12x24 -- 1 -- 1 3 3 3 -- -- -- 4 4 3 7
24x24 1 1 2 2 2 2 3 6 6 8 8 8 12 12
Face Area (sq ft) 4 6 8 10 14 14 18 24 24 32 40 40 54 62
Face Load Bag/Cartridge/HEPA Filter Arrangement
03 06 08 10 12 14 17 21 25 30 36 40 50 61
12x24 -- 1 -- 1 2 3 3 -- -- -- 4 4 3 7
24x24 1 1 2 2 2 2 3 6 6 8 8 8 12 12
Face Area (sq ft) 4 6 8 10 12 14 18 24 24 32 40 40 54 62
NOTES: 5.
1. Do not exceed filter manufacturer's velocity limits when select-
ing filters. 6.
2. There are two dedicated filter sections for 2 in. or 4 in. flat filters.
3. Angle filter or filter mixing box sections can be configured to 7.
accept either 2 in. or 4 in. filters.
4. Draw-thru bag/cartridge filter sections accept 2 in. pre-filters.
Filters must be a combination of bag filters in the sizes shown
or 6 in. or 12 in. deep rigid media with 7/8 in. header.
The draw-thru bag/cartridge filter section is designed for side
loading of filter media with a header for a 1 in. slide in track.
The blow-thru bag/cartridge/HEPA filter section is designed for
face loading of filters ONLY (no side loading).
The blow-thru filter section requires filter media with spring
clips, wire brackets, or retainers for use in a Puro-Frame hold-
ing frame.
97

2O
1125
Unit Size 03
Flat Filter Section
(1) 25x20
20 20
Unit Size 06
Flat Filter Section
(2) 25 x 20
16
Unit Size 08
Flat Filter Section
(3) 25 x 16
20 20 20
Unit Size 10
Flat Filter Section
(3) 25 x 2O
20 20 20
120 20 20
16
2O
20 20 20
2O
2O
Unit Size 12 Unit Size 14 Unit Size 17
Flat Filter Section Flat Filter Section Flat Filter Section
(6) 16 x 20 (3) 16 x 20, (3) 20 x 20 (6) 20 x 20
25 25 25 20 20 20 20
2O
2O
24
24
Unit Size 21
Flat Filter Section
(6) 20 x 25
20 20 20 20 20
Unit Size 25
Flat Filter Section
(8) 24 x 20
25 25 25 25
24
24
Unit Size 30
Flat Filter Section
(10) 24 x 20
Unit Size 36
Flat Filter Section
(12) 20 x 25
Shaded area represents filter section blankoff.
Fig. 108 -- Flat Filter Arrangement -- 2-in. or 4-in.
2O
2O
2O
98

25 25 25 25
2O
2O
25
2O 2O
Unit Size 40
Flat Filter Section
(8) 20 x 25, (5) 25 x 20
20 20 20
20 20 20 20 20
25
25
25
Unit Size 50
Flat Filter Section
(15) 25 x 20
16 16 16 16 16 16 16
2O
2O
25
25
Unit Size 61
Flat Filter Section
(14) 20 x 16, (14) 25 x 16
Fig. 108 -- Flat Filter Arrangement -- 2-in. or 4-in. (cont)
99

25 20 20
I 16
16
Unit Size 03 Unit Size 06
Angle Filter Section Angle Filter Section
(2) 16 x 25 (4) 16 x 20
20 20 20
I
Unit Size 12
Angle Filter Section
(6) 20 x 2O
2O
2O
25 25
16 16
16
Unit Size 14
Angle Filter Section
(4) 20 x 24, (2) 20 x 20
Unit Size 08
Angle Filter Section
(4) 16 x 25
24 24 20
25 25 25
16
16
16
16
Unit Size 21
Angle Filter Section
(12) 16 x 25
25 25 25 25
25 25
16
2O
2O
20 20 20
16
16
Unit Size 10
Angle Filter Section
(6) 16 x 20
25 25 25
Unit Size 17
Angle Filter Section
(9) 16 x 25
25
16
16
16
16
16
16
16
Unit Size 25
Angle Filter Section
(12) 16 x 25
16
25 25 25 25
16
16 16
16 16
16 16
Unit Size 30
Angle Filter Section
(16) 16 x 25
Unit Size 36 and 40
Shaded area represents filter section blankoff. Angle Filter Section
(20) 16 x 25
Fig. 109 -- Angle Filter Arrangement -- 2-in. or 4-in.
1O0
16

25 25 20 20 20
16
16
16
16
16
16
Unit Size 50
Angle Filter Section
(12) 16 x 25, (18) 16 x 20
25 25 20 20 20
16
16
16
16
16
16
16
Unit Size 61
Angle Filter Section
(14) 16 x 25, (21) 16 x 20
Fig. 109 -- Angle Filter Arrangement -- 2-in. or 4-in. (cont)
101

25
I 11
Unit Size 03
Filter Mixing Box Section
(2) 16 x 25
20 20
Unit Size 06
Filter Mixing Box Section
(4) 16 x 20
20 20 20
I2O
UnitSize12
Filter Mixing Box Section
(6) 20 x 2O
24 24 24
12
12
12
Unit Size 17
Filter Mixing Box Section
(12) 12 x 24
12
25 25
16
20 20 20
16
Unit Size 08
Filter Mixing Box Section
(4) 16 x 25
Unit Size 10
Filter Mixing Box Section
(6) 16x20
24 24 20
20
20
Unit Size 14
Filter Mixing Box Section
(4) 20 x 24, (2) 20 x 20
25 25 25
16
16
16
16
Unit Size 21
Filter Mixing Box Section
(12) 16 x 25
25 25 25 25 25 25 25
16
16
16
16
16
16
16
16
16
16
Unit Size 25 Unit Size 30
Filter Mixing Box Section Filter Mixing Box Section
(12) 16 x25 (16) 16 x25
Shaded area represents filter section blankoff.
Fig. 110 -- Filter Mixing Box Arrangement -- 2-in. or 4-in.
102

25 25 25 25 25 25 25 25
2O 16
2O 16
Unit Size 36
Filter Mixing Box Section
(16) 20 x 25
2O
2O
16
16
16
16
25 25 20 20
Unit Size 40
Filter Mixing Box Section
(24) 16 x 25
25 25 20 20
Unit Size 50
Filter Mixing Box Section
(12) 16 x 25, (18) 16 x 20
Unit Size 61
Filter Mixing Box Section
(16) 16 x 25, (24) 16 x 20
Fig. 110 -- Filter Mixing Box Arrangement- 2-in. or 4-in. (cont)
16
16
16
16
16
16
16
16
103

24
I
Unit Size 03
Bag/Cartridge
Pre-filter Section
(1)24 x 24
24 12
Unit Size 06
Bag/Cartridge
Pre-filter Section
(1) 24 x 24, (1) 24 x 12
24
24 24
Unit Size 08
Bag/Cartridge
Pre-filter Section
(2) 24 x 24
24
Unit Size 10
Bag/Cartridge
Pre-filter Section
(2) 24 x 24, (1) 24 x 12
24 12
24
12
Unit Size 12
Bag/Cartridge
Pre-filter Section
(3) 12 x 24, (2) 24 x 24
24
I12
24
12
Unit Size 14
Bag/Cartridge
Pre-filter Section
(3) 12 x 24, (2) 24 x 24
24 24
1[ 12
24
24 24 24 24 24 24
12
24
24
24
Unit Size 17
Bag/Cartridge
Pre-filter Section
(3) 12 x 24, (3) 24 x 24
Unit Size 21
Bag/Cartridge
Pre-filter Section
(6) 24 x 24
24 24 24 24 24 24 24
24
24
24
24
Unit Size 25
Bag/Cartridge
Pre-filter Section
(6) 24 x 24
Unit Size 30
Bag/Cartridge
Pre-filter Section
(8) 24 x 24
Shaded area represents filter section blankoff.
Fig. 111 --Side Load Bag/Cartridge Filter Arrangement
104

24 24 24 24
12
24
24
Unit Size 36 and 40
Bag/Cartridge Pre-filter Section
(4) 12 x 24, (8) 24 x 24
24 24 24 24 12
24
24
24
Unit Size 50
Bag/Cartridge Pre-filter Section
(12) 24 x 24, (3) 24 x 12
SUPPORT
BAFFLE_
12 24 24 24 24
12
24
24
24
Unit Size 60
Bag/Cartridge Pre-filter Section
(12) 24 x 24, (7) 24 x 12
Fig. 111 -- Side Load Bag/Cartridge Filter Arrangement (cont)
105

24
Unit Size 03
Bag/Cartridge/HEPA
Pre-filter Section
(1) 24 x 24
24 12
Unit Size 06
Bag/Cartridge/HEPA
Pre-filter Section
(1) 24 x 24, (1) 24 x 12
24
24 24
Unit Size 08
Bag/Cartridge/HEPA
Pre-filter Section
(2) 24 x 24
24
24
Unit Size 10
Bag/Cartridge/HEPA
Pre-filter Section
(2) 24 x 24, (1) 24 x 12
24 12
24
24 24
12
24
Support_ 12 24 24
12
24
Unit Size 12
Bag/Cartridge/HEPA
Pre-fiiter Section
(2) 12 x 24, (2) 24 x 24
Unit Size 14
Bag/Cartridge/HEPA
Pre-filter Section
(3) 12 x 24, (2) 24 x 24
24 24 24
Unit Size 17
Bag/Cartridge/HEPA
Pre-fiiter Section
(3) 12 x 24, (3) 24 x 24
12
24
24 24 24
Unit Size 21
Bag/Cartridge/HEPA
Pre-filter Section
(6) 24 x 24
24
24
24 24 24
24
24
24 24 24 24
24
24
Unit Size 25
Bag/Cartridge/HEPA
Pre-fiiter Section
(6) 24 x 24
Unit Size 30
Bag/Cartridge/HEPA
Pre-fiiter Section
(8) 24 x 24
Fig. 112- Face Load Bag/Cartridge/HEPA Filter Arrangement
106

24 24 24 24
12
24
24
Unit Size 36 and 40
Bag/Cartridge/HEPA
Pre-filter Section
(4) 12 x 24, (8) 24 x 24
24 24 24 24 12
24
24
24
Unit Size 50
Bag/Cartridge/HEPA
Pre-filter Section
(12) 24 x 24, (3) 24 x 12
12
SUPPORT
BAFFLE\
24 24 24 24
24
24
24
Unit Size 60
Bag/Cartridge/HEPA
Pre-filter Section
(12) 24 x 24, (7) 24 x 12
Fig. 112 -- Face Load Bag/Cartridge/HEPA Filter Arrangement (cont)
107

Magnehelic Gage Maintenance -- No lubrication or
periodic servicing is required. Keep case exterior and cover
clean. Occasionally disconnect pressure lines to vent both sides
of gage to atmosphere and le-zero.
CALIBRATION CHECK -- Select a second gage or
manometer of known accuracy and in an appropriate range.
Using short lengths of lubber or vinyl tubing, connect the high
pressme side of the Magnehelic gage and the test gage to two
legs of a tee. Very slowly apply pressure through the third leg.
Allow a few seconds for pressure to equalize, fluid to drain,
etc., and compare leadings. If accuracy unacceptable, gage
may be returned to factory for recalibration. To calibrate in the
field, use the following procedure.
7. Loosen bearing setsclews and locking collm, and remove
holddown bolts.
NOTE: To facilitate easy removal of setscrew fastened wheels,
sheaves, or bearings, remove the setscrew completely. Taking
care not to damage threads, insert a flat ended drift or punch,
tap lightly and carefully return the materi_fl displaced on the
shaft by the setscrew to its original place.
8. Remove bearing while observing the following
precautions:
a. Make certain fan shaft surface is not rough or scored.
If so, clean up surface with fine emery cloth.
b. Add a few drops ofoil after cleanup of shaft end.
If bezel binds when installing, lubricate threads sparingly
with light oil or molybdenum disulphide compound.
It should not be necesstuy to drive a new bearing onto
shaft, ff light tapping is needed, do not tap against outer
race.
Attempted field rep_ir may void your warranty. Recalibra-
tion or repair by the user is not recommended.
For best results, return gage to the factory. Ship prepaid to:
Dwyer Instruments, Inc.
Attn: Repair Dept.
102 Indiana Highway 212
Michigan City, IN 46360
Calibration:
1. With gage case, held firmly, loosen bezel, by turning
counterclockwise. To avoid &_mage, canvas strap wrench
or similar tool should be used.
2. Lift out plastic cover and "O" ring.
3. Remove scale sclews and scale assembly. Be ctueful not
to damage pointel:
4. The calibration is changed by moving the clamp. Ix_osen
the clamp screw(s) and move slightly towmd the helix if
gage is reading high; move away if gage is low. Tighten
clmnp sclew and install scale assembly.
5. Place cover and O-ring in position. Make sure the hex shaft
on inside of cover is properly engaged in zero adjust screw.
6. Secure cover in place by screwing bezel tightly. Note that
the alva under the cover is pressurized in operation and
therefore gage will leak if not properly tightened.
7. Zero gage and compare to test instrument. Make further
adjustments as necesstuy.
Fan Shaft Bearing Removal
1. Isolate the unit from the system by closing &unpers to
plevent "pin wheeling." Tie off the fan wheel to prevent
rotation.
2. Ix_ck open and tag electrical disconnect.
3. Enter through fan section access door or lemove panels as
required.
4. Ix_osen motor base to frame bolts. Adjust motor to
release belt tension and remove belts. Do not stwtch bel_
over sheaves. Damage to belts c_m result.
5. Remove bolts on bushing of fan shaft sheave, insert bolts
in jacking hole provided on bushing and slowly jack
bushing fi_m sheave. Remove bushing and sheave.
6. Ix_osen bearing holddown bolts, block shaft up.
9. Check fan shaft diameter at beming mount, ff worn by
more than 0.001-in. below nominal, shaft should be
replaced.
10. [nstall new bearing, tighten holddown bolts, and then
tighten bearing locking collm or setscrews.
11. Make ceflain fan wheel does not rub sides of fan housing
after installing new be_uings.
12. Recoat fan shaft with a rust inhibitor or grease.
13. Replace sheave and belts. Adjust and align as described
in Installation, Sheaves and V-Belts sections.
14. Replace access panels.
15. Restore electrical power
Fan and Shaft Removal -- On airfoil fans, the fan
wheel and shaft may be removed through inlet side of fan
housing. See Fig. 113. On plenum fans, remove side, top, or
end panel opposite inlet, wherever ductwork is not connected.
After removing panel, proceed as follows.
1. Remove drive belts as described in Fan Shaft Beming
Remov;d section above.
2. Block up fan wheel within housing to prevent diopping
when bearing bolts ale removed.
3. Loosen beming holddown bolts, block shaft up.
4. Loosen bearing setscrews and locking collm, and remove
holddown bolts. On forwmd-curved fans, remove cutoff
plate. Remove fan wheel through discharge opening.
NOTE: To facilitate easy removal of setscrew fastened wheels,
sheaves or bearings, remove the setscrew completely. Taking
care not to &_mage threads, insert a flat ended drift or punch,
tap lightly and carefully return the materi;d displaced on the
shaft by the setscrew to its original place.
5. Remove bearing support channels and inlet ring fiom one
side.
6. Remove fan shaft and fan wheel fi'om unit.
7. Remove fan shaft fi'om fan wheel.
8. Replace shaft and wheel into fan in the reverse order of
their removal.
9. Inspect bearings and if sel-¢iceable, replace on shall.
10. For airfoil and forward-curved fans, align fan wheel and
shaft assembly in fan scroll. Check cutoff location if
wheel failure damaged cutoff pkite. For plenum fan, align
wheel and shaft assembly per manufacturer's directions
supplied with fan.
108

J
Fig. 113 -- Fan Shaft and Bearing Removal
11. Tighten bearing holddown bolts, beating setscrews, and
shaft setscrews.
12. Field balancing of shaft and wheel is recommended.
IMPORTANT: Replacement shafts must have a diam-
eter tolerance at bearing mount of +.0000 in./-.001 in.
nominal. Carrier specified parts are recommended.
Motor Location -- The motor and motor base must be
moved to place the motor at the front or re;u of unit. The proper
location is the one that results in the longest &ive centerline
distance. The motor may need to be replaced since the conduit
box may need to be reversed: Tile conduit box (if not on top)
should always be under the fan shaft for maximum centerline
distance and motor adjustment.
INTERNALLY ISOLATED UNIT -- When fan discharge is
altered the motor is moved, then all isolators must be readjust-
ed to assure proper unit isolation.
Rebalancing of the unit is recommended.
Lubrication
MOTORS -- Lubricate in accor&mce with nameplate
attached to motor or with manufacturer's recommendations
included with motol:
BEARINGS
Fan Bearings -- Lubricate fan bearings every 3 months with
suitable betuing grease. Typic_d lubricants are given in
Table 30.
Porous Bronze Bearings -- These bearings are oil impregna-
ed. Annually lubricate with a few drops of non-detergent
SAE 20 oil.
Table 30 -- Lubrication Guide
GREASE RECOMMENDED
INTERVAL LUBRICANT
OPERATING
CONDITIONS
Clean
Dirty
BEARING
TEMPERATURES
(F)
32 to 120
120 to 150
150 to 200
32 to 150
6 to 10 months
1to 3 months
1 to 4 weeks
1 to 4 weeks
Shell Alvanina #2
Texaco Multifak #2
Mobil Mobilus #2
Motor and Drive Package Data -- Tables 2A-2D
give motor &_ta for forward-curved, airfoil, and plenum fans.
Variable Frequency Drive -- If installed in an appro-
priate environment, the VFD requires very little maintenance.
Table 31 lists the routine maintenance intervals recommended
by Carrier
Table 31 -- Maintenance Intervals
MAINTENANCE INTERVAL
Heat sink temperature check and Every 12 months (more often
if operating in a dusty envi-
cleaning ronment)
Main cooling fan replacement Every five years
Capacitor change (frame size R5 Every ten years
and R6)
HVAC Control panel battery change Every ten years
HEAT SINK -- The heat sink fins accumulate dust from the
cooling air. Since a dusty heat sink is less efficient at cooling
file drive, over temperature faults become more likely. In a nor-
mal environment check the heat sink annually, in a dusty
environment check more often.
Check the heat sink as follows (when necessary):
1. Remove power from drive.
2. Remove the cooling fan.
3. Blow clean compressed air (not humid) fiom bottom to
top and simultaneously use a vacuum cleaner at the air
outlet to trap the dust. If there is a risk of the dust entering
adjoining equipment, perform the cleaning in another
room.
4. Replace file cooling fan.
5. Restore powel:
MAIN FAN REPLACEMENT- Tile main cooling fan of
the VFD has a life span of about 60,000 operating hours at
maximum rated operating temperature and drive load. The
expected life span doubles for each 18 F drop in the fan
temperature (fan temperature is a function of ambient tempera-
turns and drive loads).
Fan failure can be predicted by the increasing noise from
fan bearings and the gradual rise in the heat sink temperature in
spite of heat sink cleaning, ff file drive is operated in a critical
part of a process, fan replacement is recommended once these
symptoms start appearing. Replacement fans are avtdlable
from C_u'riec
To replace the main fan for frame sizes RI through R4, per-
form the following (see Fig. 114):
1. Remove power from drive.
2. Remove drive covel:
3. For frame sizes RI and R2, press together the retaining
clips on the fan cover and lift. For frame sizes R3 and R4,
press in on the lever located on the left side of the fan
mount, and rotate the fan up and out.
4. Disconnect the fan cable.
5. Install file new fan by reversing Steps 2 to 4.
6. Restore powel:
To replace the main fan for frmne sizes R5 and R6, perform
file following (see Fig. 115):
1. Remove power from drive.
2. Remove the screws attaching file fan.
3. Disconnect the fan cable.
4. Install the fan in reveLse ordec
5. Restore powel:
CONTROL PANEL CLEANING- Use a soft damp cloth
to clean the control panel. Avoid harsh cleaners which could
scratch the display window.
BATTERY REPLACEMENT -- A batlery is only used in
assistant control panels that have the clock limction available
and enabled. The battery keeps the clock operating in memory
during power interruptions. Tile expected life for the battery is
greater than ten yeaLs. To remove the battery, use a coin to
rotate the battery holder on the back of file control panel.
Replace the battery with type CR2032.
109

Fig. 114- Main Fan Replacement
(Frame Sizes R1 - R4)
BOTTOM VIEW (R5)
Q
BOTTOM VIEW (R6)
_3
Fig. 115- Main Fan Replacement
(Frame Sizes R5 and R6)
TROUBLESHOOTING
Steam Coil Performance Problems -- Coil capac-
ity is nommlly not a probleln with stemn coils. Low capacity
can result from blocked or plugged air side surface, an tfir
bound coil, or a coil which is filled with condensate because of
a non-functioning steam trap. The CtuTier steam coils with the
1-in. OD outer tube have at least twice the condensate loading
capacity of a coil with 5/8-in. OD outer tubes.
Water hammer can &image the coil and cause leaks. It is
typically caused by improper piping of the stemn supply,
allowing condensate to enter the coil with the steam supply; or
by accumulation of condensate in the coil which can occur
with the coils operating tit partkd load without a vacuum break-
ing device.
Problems with temperature control can occur when a ther-
mostatic controller or stemn control valve is not functioning
properly. Temperature control problems will also occur when
the steam controls valve is oversized. Consider 1/3 to 2/3 Valve
arrangements for full range control.
Problems with "water logging" of the condensate tubes can
occur when a coil with over 6 foot tubes is selected tit high air
velocities, low steam pressures (below 5 psig) and high density
fin spacing (9 fins per inch or more). This high density fin
spacing, while producing high levels of heating capacity, also
promotes excessive condensate. Given the length of the
tubes and the low steam supply pressure, condensate can build
up faster than the drain system can cmry it away. Consider-
ations should be given for using two coils in series for this
application.
Steam Failure Modes -- The following failure modes
could take as little as a weekend to &image a coil, or much
longel:
Problems occur quickly in coils using low pressure steam
(<3 psig). Water hammer can develop inside the coil at the
header end because the steam has already condensed and the
low steam pressure does not adequately cletu it from the coil.
This condensate re-boils and starts up water hammer inside the
tubes. The action of this type of water hammeL which sounds
like crackling inside the coil, is many tiny bubbles impinging
on the inner and outer tubes. One result is the inner tube gets
work htudened and eventually shatters. Another result is the
eventual erosion of the outer tube causing pinhole leaks.
Coils which are not properly vented will eventually load up
wifll noncondensable gases. Coil performance (temperature
rise) drops off as file noncondensables act as insulation inside
the tubes.
The coils may also fill with condensate. The collapsing
steam causes a vacuum inside the coil when the supply valve
closes. The trapped condensate will then freeze causing the
tubes to rupture after it melts. The use of a vacuum breaker tit
the condensate discharge will aid in relieving the vacuum in the
coil and promote condensate drainage.
Refer to Tables 32-34 for 39M troubleshooting information.
Disconnect power and allow all rotating equipment to stop
before selwicing unit. Physically secure all fans before
performing unit service. Failure to do so may result in
serious personal injury or death.
Water coil performance (when piped in ptuallel flow), will
be reduced by approximately 5% for each coil row on coils
2 rows deep and deepo: Coils should always be piped with the
water inlet on the leaving air side of the coil, regardless of
water connection vertical position.
VFD Diagnostics- The &'ive detects enor situations
and reports them using:
• the green and red LEDs on the body of the drive (located
under the keypad)
• the status LED on the control panel
• the control panel display
• The Fault W\_rd and Alarm Word parameters bits
(parameters 0305 to 0309)
The form of the display depends on the severity of the errol:
The user can specify the severity for maW enors by directing
the drive to ignore the enor situation, report the situation as an
alarm, or report the situation as a fault.
llO

FAULTS (RED LED LIT)- The VFD signals that it has
detected a severe errok or fault, by:
• enabling the red LED on the drive (LED is either steady
or flashing)
• setting an appropriate bit in a Fault Word parameter
(0305 to 0307)
• overriding the control panel display with the display of a
fault code
• stopping the motor (if it was on)
• sets an appropriate bit in Fault Word parameter 0305 to
0307
The fault code on the control panel display is tempormy.
Pressing the MENU, ENTER, UP button or DOWN buttons
removes the fault message. The message reappefu's after a few
seconds if the control panel is not touched and the fault is still
active.
ALARMS (GREEN LED FLASHING)-- For less severe
errors, called akums, the diagnostic display is advisory. For
these situations, the drive is simply reporting that it had detect-
ed something unusual. In these situations, the drive:
• flashes the green LED on the drive (does not apply to
alarms that arise from control panel operation errors)
• sets an appropriate bit in an Alarm Word parameters
(0308 or 0309)
• overrides the control panel display with the display of an
alarm code and/or name
Alarm messages disappear from the control panel display
after a few seconds. The message returns periodically as long
as the alarm condition exists.
CORRECTING FAULTS -- The recommended corrective
fiction for faults is shown in the Fault Listing Table 35. The
VFD can also be reset to remove the fault. If fin external source
for a stmt command is selected find is active, the VFD may
start immediately after fault reset.
To reset a fault indicated by a flashing red LED, turn off the
power for 5 minutes. To reset a fault indicated by a red LED
(not flashing), press RESET from the control panel or turn off
the power for 5 minutes. Depending on the value of parameter
1604 (FAULT RESET SELECT), digital input or serial com-
munication could also be used to reset the diive. When the fault
has been corrected, the motor can be started.
HISTORY- For reference, the last throe fault codes am
stored into pmameters 0401, 0412, 0413. For the most recent
fault (identified by parameter 0401), the drive stores additional
&tta (in parameters 0402 through 0411) to aid in troubleshoot-
ing a problem. For example, a pfuameter 0404 stores the motor
speed fit the time of the fault. To clem" the fault history (all of
Group 04, Fault History parmneters), follow these steps:
1. In the control panel, Parameters mode, select parameter
0401.
2. Press EDIT.
3. Press the UP find DOWN button simultaneously.
4. Press SAVE.
CORRECTING ALARMS- To correct aimms, first deter-
mine if the Alarm requires any corrective action (fiction is not
fdways required). Use Table 36 to lind and addi'ess the root
cause of the problem.
Table 32 -- Magnehelic Gage Troubleshooting
SYMPTOM
Gage will not Indicate or is Sluggish.
Pointer Stuck-- Gage Cannot be Zeroed,
CAUSE
Duplicate pressure port is not plugged,
Diaphragm is ruptured due to excessive
_ressure.
Fittings or sensing lines are blocked, pinched,
or leaking.
Cover is loose or "0" ring is damaged or
missing.
Pressure sensor (static tips, Pitot tube, etc.) is
improperly located.
Ambient temperature is too low.
Metallic particles are clinging to the magnet
and interfering with helix movement.
Scale is touching pointer.
Spring/magnet assembly has shifted and is
touching helix.
Cover zero adjust shaft is broken or not
properly engaged in adjusting screw.
REMEDY
Plug duplicate pressure port.
Replace gage.
Repair lines and fittings.
Tighten cover and/or replace "0" ring.
Relocate pressure sensoK
For operation below 20 E order gage with
low temperature (LT) option.
Parts used in various sub-assemblies vary
from one range of gage to another, and use
of incorrect components may cause improper
operation. Gages needing repair should be
returned to:
Dwyer Instruments Inc.
Attn: Repair Dept.
102 Indiana Highway 212
Michigan City, IN 46360
III

SYMPTOM
Water is Spitting from the
Discharge Manifolds
Steam does not Discharge
from the Manifolds when
the Valve is Open
Steam Valve will not Open
Steam Valve will not Close
Steam Valve is Leaking
Humidity Exceeds Set Point
Humidity Remains Below
Set Point
Table 33 -- Humidifier Troubleshooting
CAUSE
Steam trap is not functioning properly.
The header P-traps are not draining,
The steam line has been taken from
the bottom of the steam source or is
not sloped properly.
The steam main is overloaded with water.
Vertical discharge manifolds are not plumb.
Horizontal headers are not level.
Vertical discharge manifolds are
installed upside down.
Check valve sizing to maximum
manifold capacity.
Valve is not open.
There is no steam available.
There is a change in steam pressure.
Steam is not visible.
Y-strainer may be clogged,
There is no power.
There is no control signal,
Control polarity has been reversed,
Actuator is not working,
There is high steam pressure.
Valve has been installed incorrectly.
There is no control signal,
Control polarity has been reversed,
Actuator is not working.
There is high steam pressure.
Valve has been installed incorrectly.
Control signal is not at full range,
Control polarity has been reversed,
Actuator is not working,
There is high steam pressure,
Control signal is not at full range,
There is no control signal.
The controller is out of calibration.
Humidity sensor is not installed properly.
Actuator is not working,
There is high steam pressure,
Boiler is not operating correctly.
Control signal is not at full range,
Control polarity has been reversed,
Controller is out of calibration,
Humidity sensor is not installed properly.
Actuator is not working,
There is high steam pressure,
Boiler is not operating correctly.
There is an airflow switch fault.
The high limit controller is not in
the correct location,
The humidifier is too small,
Condensate in unit The humidifier is too large,
There is a high limit controller fault,
Evaporation distance is too short.
Steam valve is leaking.
Steam leaks from P-traps The trap height is incorrect,
Valve sizing is incorrect.
There is excessively high steam pressure.
AHU -- Air-Handling Unit
REMEDY
Clean or replace non-functioning steam trap on the valve/trap assembly.
Clean and check that plumbing runs to gravity drain. Check that trap height
exceeds the static pressure of the duct/AHU, especially if it is under negative
_ressure.
Change line to take off from the top and check proper slopes.
Locate cause and correct problem.
Make manifolds plumb.
Make headers level.
Reinstall correctly.
Resize valve within manifold capacity.
Open valve.
Verify that steam is available.
Verify that the steam pressure has not changed. Excessively high pressure could
jam the valve.
Carefully place a mirror or metal object close to one of the steam discharge slots.
If it fogs, steam is discharging, but evaporating very quickly. This is not a problem.
DO NOT EVER PLACE YOUR HAND OVER OR NEAR THE STEAM DIS-
CHARGE SLOTS.
Clean or replace Y-strainer.
Verify and, if necessary, correct power or air pressure to the valve actuator.
Verify and, if necessary, correct control signal or pressure range to the valve
actuator.
Verify and, if necessary, correct control signal polarity to the valve actuator.
Remove actuator to verify that it is operational. Clean or replace jammed valve.
Verify that the steam pressure has not changed. Excessively high pressure could
jam the valve.
Verify proper valve orientation. Electric valves must face upward.
Verify and, if necessary, correct control signal to the valve actuator.
Verify and, if necessary, correct control signal polarity to the valve actuator.
Remove actuator to verify that it is operational. Clean or replace jammed valve.
Verify that the steam pressure has not changed. Excessively high pressure could
jam the valve.
Verify proper valve orientation. Electric valves must face upward.
Verify and, if necessary, correct full-range control signal to the valve actuator.
Verify and, if necessary, correct control signal polarity to the valve actuator.
Remove actuator and test to verify that it is operational. If not, clean or replace
jammed valve.
Verify that the steam pressure has not changed. Excessively high pressure could
am the valve.
Verify and, if necessary, correct compatibility of the full range control signal to the
valve actuator.
Verify and, if necessary, correct control signal polarity to the valve actuator.
Check and, if necessary, correct calibration of controller.
Ensure that humidity sensors are installed correctly and not located in drafts
(wall). If necessary, correct sensor installation.
Remove actuator and test to verify that it is operational. If not, clean or replace
jammed valve.
Verify that the steam pressure has not changed. Excessively high pressure could
jam the valve.
Verify stable boiler pressure. Wide swings in pressure could affect the humidity
controls.
Verify and, if necessary, correct compatibility of the full range control signal to the
valve actuator.
Verify and, if necessary, correct control signal polarity to the valve actuator.
Check and, if necessary, correct calibration of controller.
Ensure that humidity sensors are installed correctly and not located in drafts
(wall). If necessary, correct sensor installation.
Remove actuator and test to verify that it is operational. If not, clean or replace
jammed valve.
Verify that the steam pressure has not changed. Excessively high pressure could
jam the valve.
Verify stable boiler pressure. Wide swings in pressure could affect the humidity
controls.
Ensure that airflow switch is not fluttering. If necessary, correct fluttering airflow
switch.
Verify that high-limit controller is not located too close to steam discharge mani-
folds. If necessary, correct location of controller.
Humidifier is undersized. Check humidity load calculations.
Verify humidifier capacity versus air volume.
Verify that high limit controller is working. If necessary, correct problem.
Verify and, if necessary, correct evaporation distance to obstructions or elbows.
Verify steam valve is not leaking. If necessary, correct leaking steam valve.
Ensure that height of trap exceeds the static pressure of the duct/AHU, especially
if under negative pressure.
Check valve sizing to maximum manifold capacity. If necessary, resize valve
within manifold capacity.
Check that inlet steam pressure does not exceed humidifier capability.
112

Table 34 -- Troubleshooting
SYMPTOM CAUSE REMEDY
Motor Fails to Start Power line open Reset circuit breaker.
Improper wiring or loose connections Check wiring and connections.
Overload trip Check and reset overload,
Mechanical failure Inspect motor and drive for operation and/or damage,
Improper current supply Check rating plate against actual supply voltage, Contact
power provider for adjustments if needed,
Motor Stalls Open Phase Check line for open phase,
Overloaded motor Reduce motor load or replace with larger motor.
Low line voltage Check supply line, correct voltage,
Excessive Vibration Bearing/shaft misalignment Check and align bearing set screws,
Shipping blocks/spacers not removed Remove shipping blocks/spacers.
Excessive belt tension Adjust belt tension,
Drive misaligned Align drive.
Bearing(s) is Hot Grease not evenly distributed after lubrication Allow unit to cool down and restart,
Over-lubrication Clean and purge excess grease,
No lubricant Check bearings for damage and apply lubricant.
Misaligned bearing Check shaft level and reset alignment.
Motor Does Not Run at Low voltage at motor terminals Check supply voltage and correct voltage loss,
Full Speed Supply wiring to motor too small Rewire with properly sized wire,
Motor Overheats Overloaded motor Reduce motor load or replace with larger motor.
Motor fan is clogged, preventing motor cooling Clean motor fan.
Excessive Motor Noise Mounting bolts loose Tighten bolts,
Rigid coupling connectors Replace with flexible connectors,
Worn motor bearings Replace bearings and seals,
Fan rubbing on housing Adjust housing,
Motor Runs and Then Slows Partial supply voltage loss Check for loose/dirty connections.
Verify supply voltage,
Excessive Motor Bearing Wear High load due to over-tensioned drive Check belt tension and load.
Excessive overhung load caused by a small Replace with larger sheave,
diameter motor sheave
Loose Fan Belt Improper motor position
Worn sheaves
Worn or damaged belt
Drive Noise Sheave(s) not tight on fan/motor shaft(s)
Belts contacting guard(s)
Belts too loose or too tight
Belts and sheaves mismatched
Belts not length matched (multiple belt set-up)
Misaligned sheaves
Belts worn
Belts dirty or oily
Bearing Noise Defective bearing
Lack of lubrication
Loose bearing
Bearing misaligned
Foreign material/dirt inside bearing
Corrosion between bearing and shaft
High Velocity Air Noise Fan speed too high
Ductwork too restrictive
Low static pressure
Registers and grilles too restrictive
Rattling or Whistling Loose dampers, grilles, or splitters
Noise in Airstream Obstructed dampers or grilles
Sharp elbows in ductwork
Sudden expansion/contraction of ductwork
Turning vanes loose or not properly installed
CFM Lower than System Fan rotating backwards
Requirements Fan speed too slow
Duct system has more resistance than designed
Diffusers closed
High Current Draw Motor overload
(Motor) Low line voltage
Electric Heat Inoperative Electric heater manual reset tripped
Broken heating element
Electric heater fuses blown
Inoperative electric heating circuit contactor
Airflow switch interlock not closed
Heater Cycles Airflow marginally insufficient
Improper Temperature Intermittent power supply due to improper
Regulation installation
No Hot Water or Steam
Heat
Erratic thermostat operation due to improper
location or frequent resetting
Air system characteristics are not in accordance
with the job requirements
Defective hot water or steam valve actuator motor
Broken control linkage from actuator to valve assembly
Defective hot water or steam control valve
Adjust tension,
Replace sheaves.
Check sheave alignment and replace belt(s).
Tighten sheaves,
Adjust or tighten belt guard mounts.
Adjust belt tension.
Install proper belts.
Install matched belts.
Align sheaves.
Replace belts.
Replace belts.
Repair/replace bearing.
Lubricate bearing,
Adjust bearing support or bearing on shaft,
Align bearing properly.
Inspect and clean bearing.
Clean or replace bearing as required,
Check fan speed.
Increase duct size for proper air velocity.
Decrease fan speed to obtain proper pressure.
Replace with correctly sized registers and grilles,
Adjust as needed.
Remove obstruction(s),
Install larger radius elbows,
Install proper ductwork transitions.
Tighten or adjust as needed.
Reverse any two power leads to the fan motor,
Check fan RPM.
Enlarge ductwork to match system requirements.
Open diffusers.
Reduce system load or use larger motor,
Consult power company about increasing line
voltage,
Determine cause of cutout and reset switch,
Replace element,
Replace fuses,
Repair/replace as needed.
Check airflow sensing tube location and operation in
airstream. Repair/replace as needed,
Airflow switch may chatter and cycle heater circuits off
and on. Or, automatic reset may open and close, causing
a similar situation. Check unit airflow requirements and
clean the system,
Recheck installation procedure. Check contactor
operation and safety cutout switches, Refer to heater
wiring diagram,
Check thermostat installation instructions. Be certain
that the thermostat location is not subjected to adverse
temperature changes, such as those caused by opening
doors or windows. Check for thermostat tampering.
Check the supply-air fan is delivering adequate volume
and velocity. Check air system balance, Be certain that
heating coils are operating,
Repair/replace as needed.
Repair/replace as needed.
Repair/replace as needed.
113

Table 35 -- Fault Codes
FAULT CODE FAULT NAME IN PANEL DESCRIPTION AND RECOMMENDED CORRECTIVE ACTION
1 OVERCURRENT Output current is excessive. Check for excessive motor load, insufficient acceleration time
(parameters 2202 ACCELER TIME 1, default 30 seconds), or faulty motor, motor cables or
connections.
2 DC OVERVOLT Intermediate circuit DC voltage is excessive. Check for static or transient over voltages in
the input power supply, insufficient deceleration time (parameters 2203 DECELER TIME 1,
default 30 seconds), or undersized brake chopper (if present).
3DEV OVERTEMP Drive heat sink is overheated. Temperature is at or above 115 C (239 F). Check for fan fail-
ure, obstructions in the airflow, dirt or dust coating on the heat sink, excessive ambient
temperature, or excessive motor load.
4SHORT CIRC Fault current. Check for short-circuit in the motor cable(s) or motor or supply disturbances.
5 OVERLOAD Inverter overload condition. The drive output current exceeds the ratings.
6DC UNDERVOLT Intermediate circuit DC voltage is not sufficient. Check for missing phase in the input
power supply, blown fuse, or under voltage on main circuit.
7 All LOSS Analog input 1 loss. Analog input value is less than All FLT LIMIT (3021). Check source
and connection for analog input and parameter settings for AI 1 FLT LIMIT (3021) and 3001
AI<MIN FUNCTION.
8AI2 LOSS Analog input 2 loss. Analog input value is less than AI2 FLT LIMIT (3022). Check source
and connection for analog input and parameter settings for AI2 FLT LIMIT (3022) and 3001
AI<MIN FUNCTION.
9MOT OVERTEMP Motor is too hot, as estimated by the drive. Check for overloaded motor. Adjust the param-
eters used for the estimate (3005 through 3009). Check the temperature sensors and
Group 35 parameters.
10 PANEL LOSS Panel communication is lost and either drive is in local control mode (the control panel dis-
plays LOC), or drive is in remote control mode (REM) and is parameterized to accept start/
stop, direction or reference from the control panel. To correct, check the communication
lines and connections. Check parameter 3002 PANEL COMM ERROR, parameters in
Group 10: Command Inputs and Group 11: Reference Select (if drive operation is REM).
11 ID RUN FAIL The motor ID run was not completed successfully. Check motor connections.
12 MOTOR STALL Motor or process stall. Motor is operating in the stall region. Check for excessive load or
insufficient motor power. Check parameters 3010 through 3012.
13 RESERVED Not used.
14 EXT FAULT 1 Digital input defined to report first external fault is active. See parameter 3003 EXTERNAL
FAULT 1.
15 EXT FAULT 2 Digital input defined to report second external fault is active. See parameter 3004 EXTER-
NAL FAULT 1.
16 EARTH FAULT The load on the input power system is out of balance. Check for faults in the motor or
motor cable. Verify that motor cable does not exceed maximum specified length.
17 UNDERLOAD Motor load is lower than expected. Check for disconnected load, Check parameters 3013
UNDERLOAD FUNCTION through 3015 UNDERLOAD CURVE.
18 THERM FAIL Internal fault. The thermistor measuring the internal temperature of the drive is open or
shorted, Contact Carrier.
19 OPEX LINK Internal fault. A communication-related problem has been detected between the OMIO
and OINT boards. Contact Carrier.
20 OPEX PWR Internal fault. Low voltage condition detected on the OINT board. Contact Carrier.
21 CURR MEAS Internal fault. Current measurement is out of range. Contact Carrier.
22 SUPPLY PHASE Ripple voltage in the DC link is too high. Check for missing main phase or blown fuse.
23 RESERVED Not used,
24 OVERSPEED Motor speed is greater than 120% ef the larger (in magnitude) ef 2001 MINIMUM SPEED
or 2002 MAXIMUM SPEED parameters. Check parameter settings for 2001 and 2002.
Check adequacy of motor braking torque. Check applicability ef torque control. Check
brake chopper and resistor.
25 RESERVED Not used,
26 DRIVE ID Internal fault. Configuration block drive ID is not valid.
27 CONFIG FILE Internal configuration file has an error. Contact Carrier.
114

Table 35 -- Fault Codes (cont)
FAULT CODE FAULT NAME IN PANEL DESCRIPTION AND RECOMMENDED CORRECTIVE ACTION
28 SERIAL 1 ERR Field bus communication has timed out. Check fault setup (3018 COMM FAULT FUNC and
3019 COMM FAULT TIME). Check communication settings (Group 51 or 53 as appropriate).
Check for poor connections and/or noise on line.
29 EFB CON FILE Error in reading the configuration file for the field bus adapter.
30 FORCE TRIP Fault trip forced by the field bus. See the field bus reference literature.
31 EFB1 Fault code reserved for the EFB (Embedded Field Bus) protocol application. The meaning is
protocol dependent.
32 EFB2 Fault code reserved for the EFB protocol application. The meaning is protocol dependent.
33 EFB3 Fault code reserved for the EFB protocol application. The meaning is protocol dependent.
34 MOTOR PHASE Fault in the motor circuit. One of the motor phases is lost. Check for motor fault, motor cable
fault, thermal relay fault (if used), or internal fault.
35 OUTP WIRING Error in power wiring suspected. Check that input power wired to drive output. Check for
ground faults.
101-105 SYSTEM ERROR Error internal to the drive. Contact Carrier and report the error number.
201-206 SYSTEM ERROR Error internal to the drive. Contact Carrier and report the error number.
1000 PAR HZRPM Parameter values are inconsistent. Check for any of the following:
2001 MINIMUM SPEED > 2002 MAXIMUM SPEED
2007 MINIMUM FREQ > 2008 MAXIMUM FREQ
2001 MINIMUM SPEED /9908 MOTOR NOM SPEED is outside of the range: -128 to +128
2002 MAXIMUM SPEED /9908 MOTOR NOM SPEED is outside of the range: -128 to +128
2007 MINIMUM FREQ /9907 MOTOR NOM FREQ is outside ef the range: -128 te +128
2008 MAXIMUM FREQ /9907 MOTOR NOM FREQ is outside ef the range: -128 te +128
1001 PAR PFA REFNG Parameter values are inconsistent. Check that 2007 MINIMUM FREQ is negative, when
8123 PFA ENABLE is active.
1002 PAR PFA IOCNF Parameter values are inconsistent. The number of programmed PFA relays does not match
with Interlock configuration, when 8123 PFA ENABLE is active. Check consistency of RELAY
OUTPUT parameters 1401 through 1403, and 1410 through 1412. Check 8117 NR OF AUX
MOTORS, 8118 AUTOCHANGE INTERV, and 8120 INTERLOCKS.
1003 PAR AI SCALE Parameter values are inconsistent. Check that parameter 1301 AI MIN > 1302 AI 1 MAX and
that parameter 1304 AI 2 MIN > 1305 AI 2 MAX.
1004 PAR AO SCALE Parameter values are inconsistent. Check that parameter 1504 AO 1 MIN > 1505 AO 1 MAX
and that parameter 1510 AO 2 MIN > 1511 AO 2 MAX.
1005 PAR PCU 2 Parameter values for power control are inconsistent: Improper motor nominal kVA or motor
nominal power. Check the following parameters:
1.1 < (9906 MOTOR NOM CURR * 9905 MOTOR NOM VOLT * 1.73 /PN) < 2.6
Where: PN = 1000 * 9909 MOTOR NOM POWER (if units are kW) or PN = 746 * 9909
MOTOR NOM POWER (if units are HP, e.g., in US)
1006 PAR EXT RO Parameter values are inconsistent. Check the extension relay module for connection and
1410 through 1412 RELAY OUTPUTS 4 through 6 have non-zero values.
1007 PAR FBUS Parameter values are inconsistent. Check that a parameter is set for field bus control (e.g.
1001 EXT1 COMMANDS = 10 (COMM)), but 9802 COMM PROT SEL = 0.
1008 PAR PFA MODE Parameter values are inconsistent. The 9904 MOTOR CTRL MODE must be = 3 (SCALAR
SPEED), when 8123 PFA ENABLE is activated.
1009 PAR PCU 1 Parameter values for power control are inconsistent or improper motor nominal frequency or
speed. Check for both of the following:
1 < (60 * 9907 MOTOR NOM FREQ /9908 MOTOR NOM SPEED < 16 0.8 < 9908 MOTOR
NOM SPEED /(120 * 9907 MOTOR NOM FREQ /Motor poles) < 0.992
1010 OVERRIDE/PFA Override mode is enabled and PFA is activated at the same time. This cannot be done
CONFLICT because PFA interlocks cannot be observed in the override mode.
115

Table 36 -- Alarm Codes
ALARM CODE ALARM NAME IN PANEL DESCRIPTION AND RECOMMENDED CORRECTIVE ACTION
2001 I Reserved
2002 -- Reserved
2003 I Reserved
2004 DIR LOCK The change in direct being attempted is not allowed. Do not attempt to change the direction
of motor rotation, or Change parameter 1003 DIRECTION to allow direction change (if
reverse operation is safe).
2005 I/O COMM Field bus communication has timed out. Check fault setup (3018 COMM FAULT FUNC and
3019 COMM FAULT TIME). Check communication settings (Group 51 or 53 as appropriate).
Check for poor connections and/or noise on line.
2006 All LOSS Analog input 1 is lost, or value is less than the minimum setting. Check input source and con-
nections. Check the parameter that sets the minimum (3021) and the parameter that sets the
Alarm/Fault operation (3001).
2007 AI2 LOSS Analog input 2 is lost, or value is less than the minimum setting. Check input source and con-
nections. Check the parameter that sets the minimum (3022) and the parameter that sets the
Alarm/Fault operation (3001).
2008 PANEL LOSS Panel communication is lost and either the VFD is in local control mode (the control panel
displays HAND), or the VFD is in remote control mode (AUTO) and is parametrized to accept
start/stop, direction or reference from the control panel. To correct, check the communication
lines and connections, Parameter 3002 PANEL LOSS, and parameters in groups 10 COM-
MAND INPUTS and 11 REFERENCE SELECT (if drive operation is REM).
2009 I Reserved
2010 MOT OVERTEMP Motor is hot, based on either the VFD estimate or on temperature feedback. This alarm
warns that a Motor Overload fault trip may be near. Check for overloaded motor. Adjust the
)arameters used for the estimate (3005 through 3009). Check the temperature sensors and
Group 35 parameters.
2011 UNDERLOAD Motor load is lower than expected. This alarm warns that a Motor Underload fault trip may be
near. Check that the motor and drive ratings match (motor is NOT undersized for the drive).
Check the settings on parameters 3013 to 3015.
2012 MOTOR STALL Motor is operating in the stall region. This alarm warns that a Motor Stall fault trip may be
near.
2013" AUTORESET This alarm warns that the drive is about to perform an automatic fault reset, which may start
the motor. To control automatic reset, use parameter group 31 (AUTOMATIC RESET).
2014" AUTOCHANGE This alarm warns that the PFA autochange function is active. To control PFA, use parameter
group 81 (PFA) and the Pump Alternation macro.
2015 PFA INTERLOCK This alarm warns that the PFA interlocks are active, which means that the drive cannot start
any motor (when Autochange is used), or a speed regulated motor (when Autochange is not
used).
2016 I Reserved
2017* OFF BUTTON This alarm indicates that the OFF button has been pressed.
2018" PID SLEEP This alarm warns that the PID sleep function is active, which means that the motor could
accelerate when the PID sleep function ends. To control PID sleep, use parameters 4022
through 4026 or 4122 through 4126.
2019 ID RUN The VFD is performing an ID run.
2020 OVERRIDE Override mode is activated.
2021 START ENABLE 1 This alarm warns that the Start Enable 1 signal is missing. To control Start Enable 1 function,
MISSING use parameter 1608. To correct, check the digital input configuration and the communication
settings.
2022 START ENABLE 2 This alarm warns that the Start Enable 2 signal is missing. To control Start Enable 2 function,
MISSING use parameter 1609. To correct, check the digital input configuration and the communication
settings.
2023 EMERGENCY STOP Emergency stop is activated.
*This alarm is not indicated by a relay output, even when the relay output is configured to indicate alarm
conditions (parameter 1401 RELAY OUTPUT = 5 [ALARM] or 16 [FLT/ALARM]).
Copyright 2004 Carrier Corporation
Manufacturer reserves the right to discontinue, or change at any time, specifications or designs without notice and without incurring obligations.
PC 201 Catalog No. 533-952 Printed in U.S.A. Form 39M-6Sl Pg 116 12-04 Replaces: 39M-5Sl